Session 3 LRFD Theory for Geotechnical Design Topic
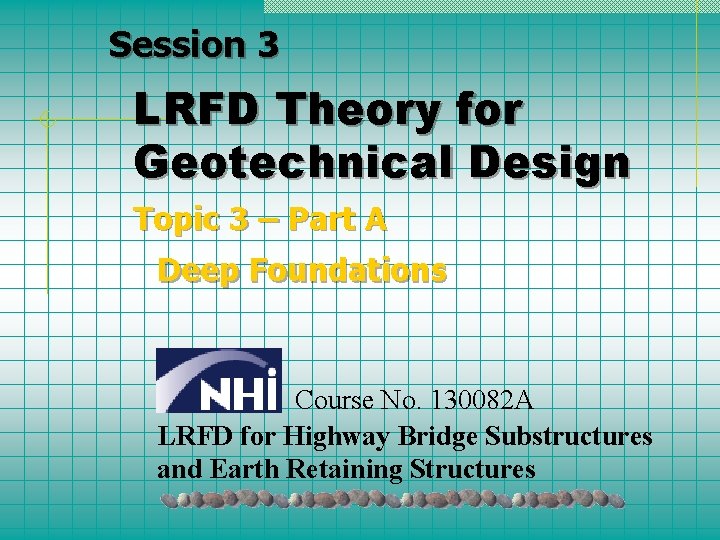
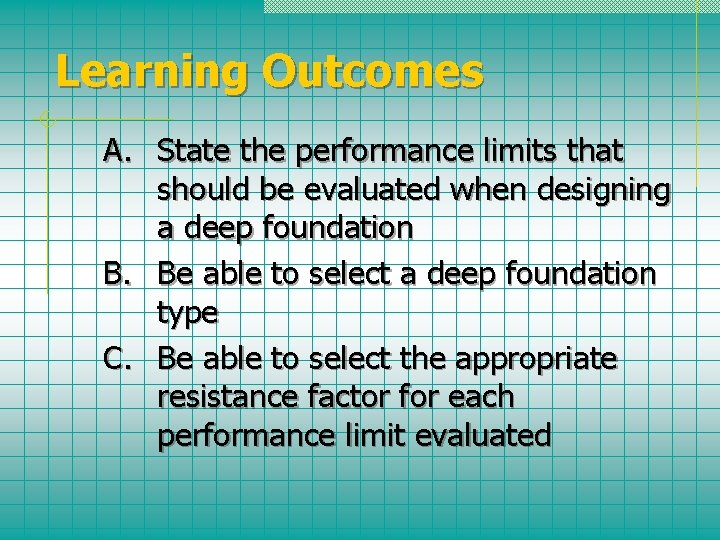
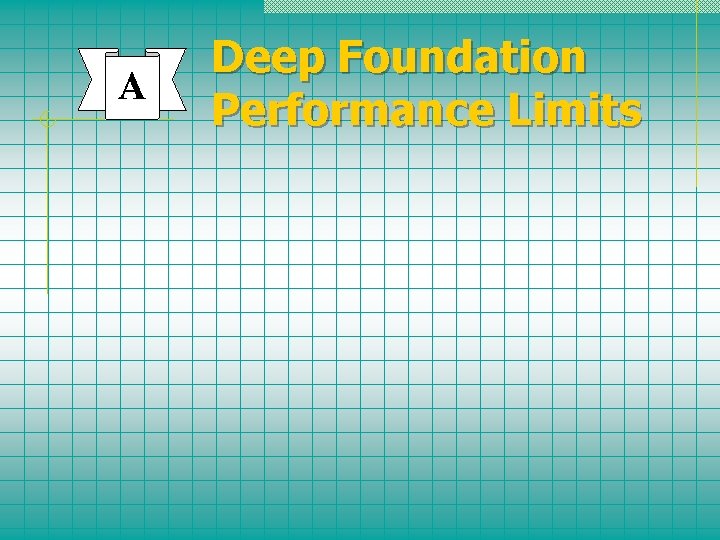
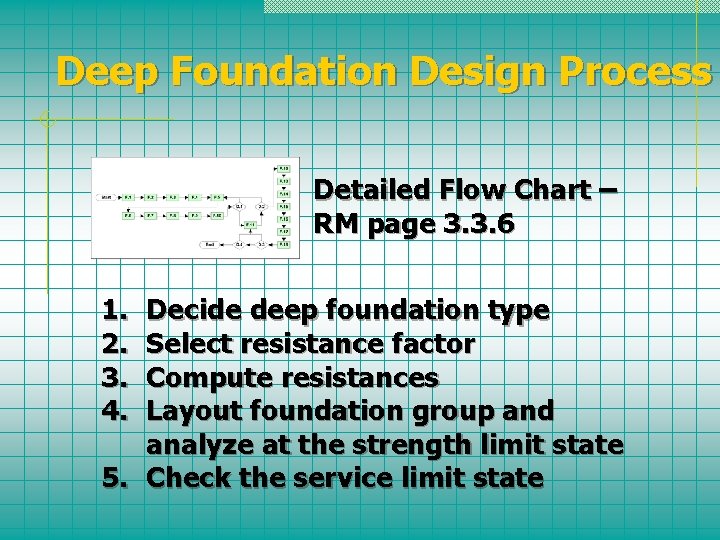
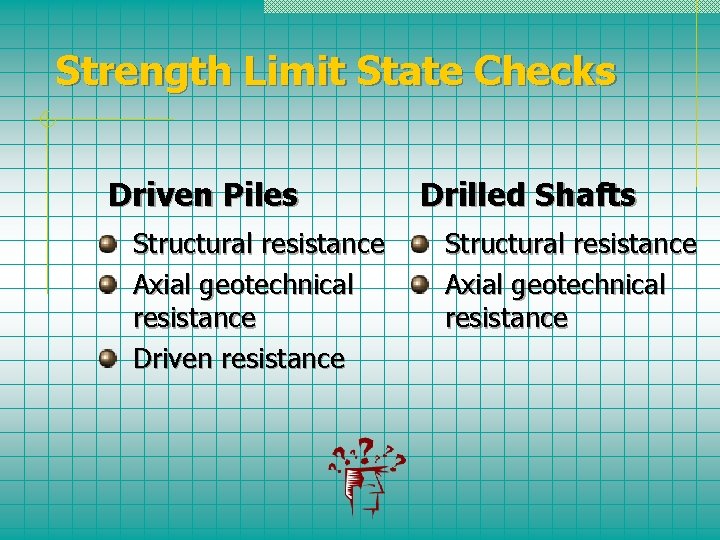
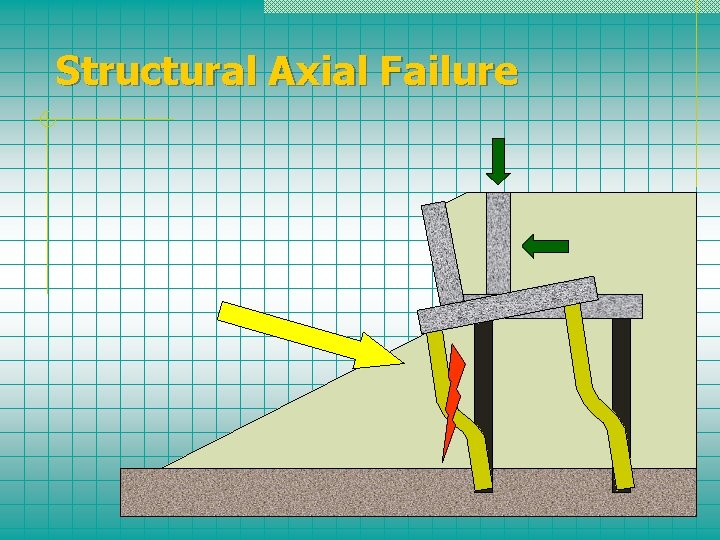
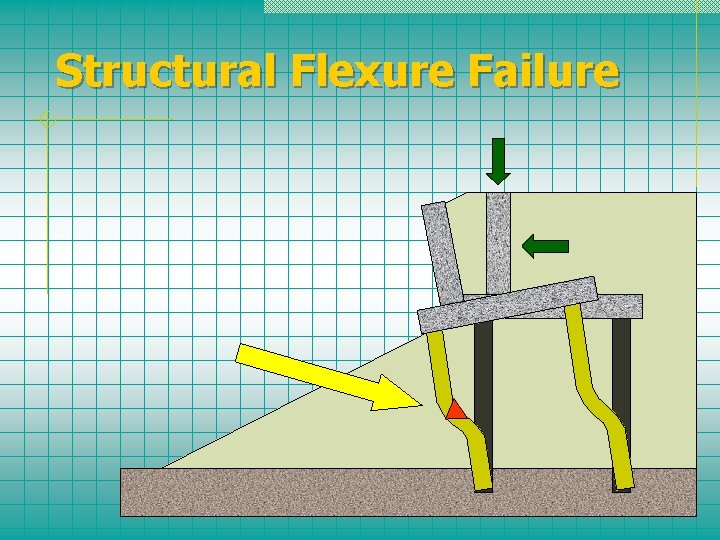
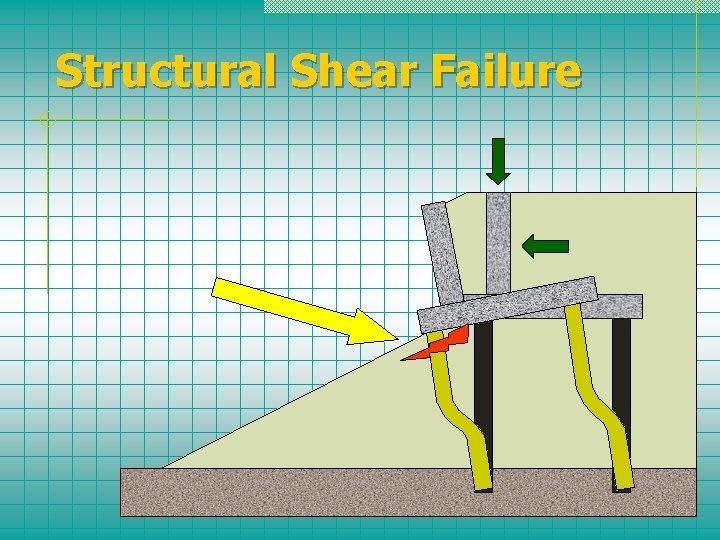
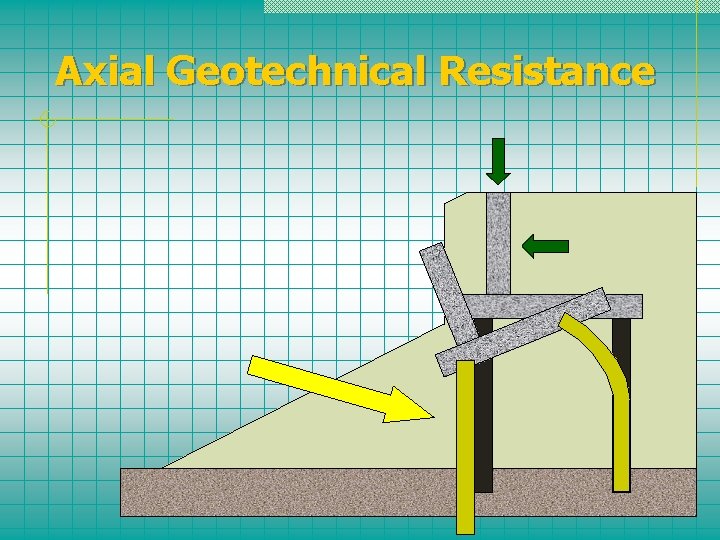
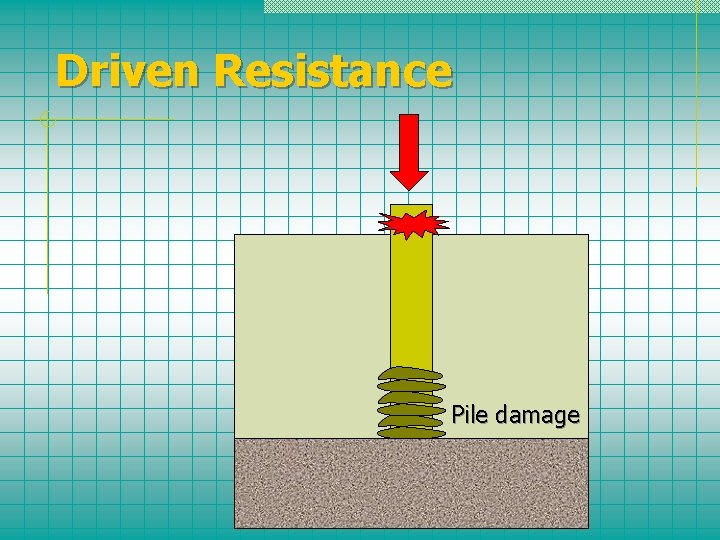
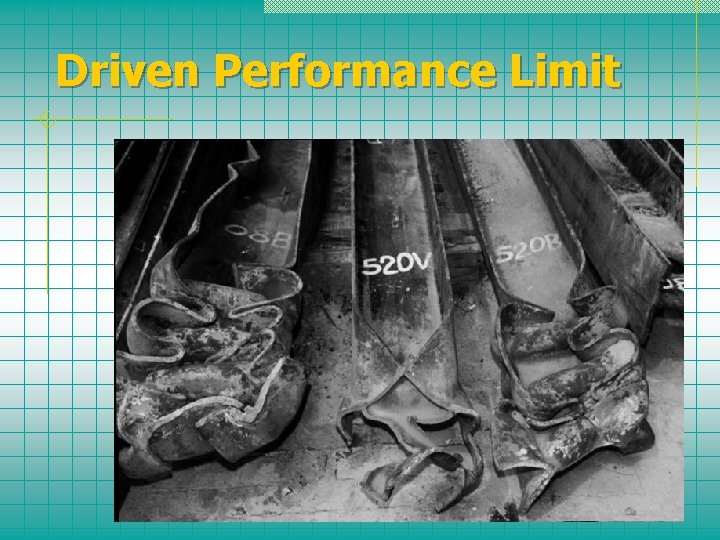
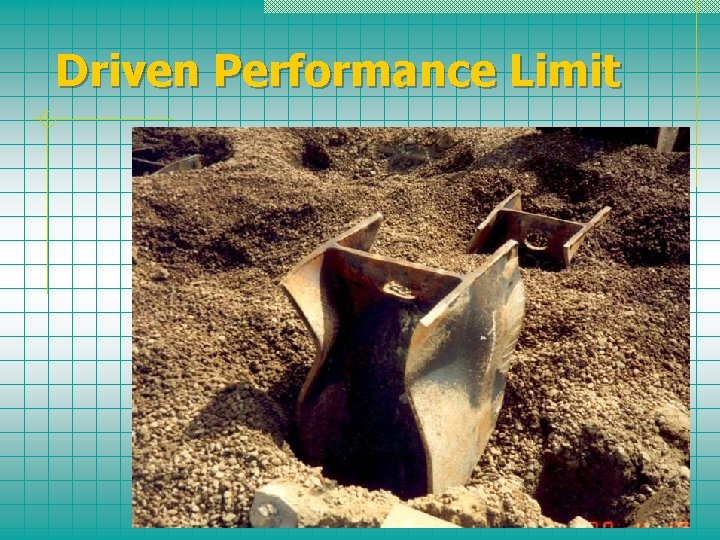
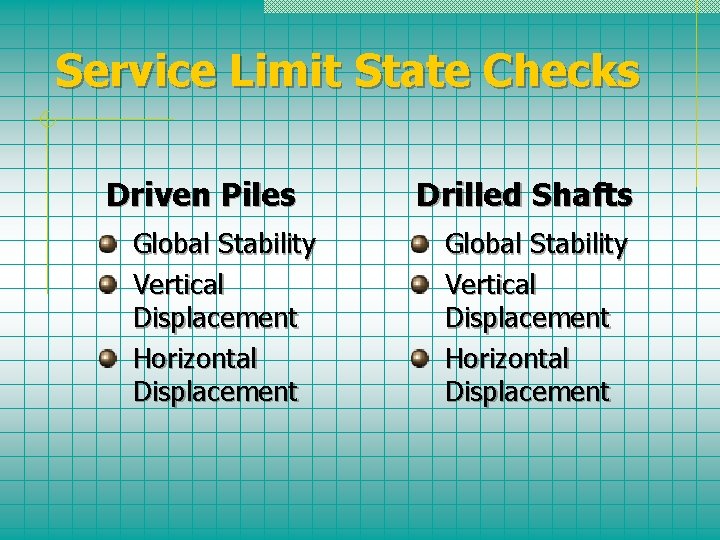
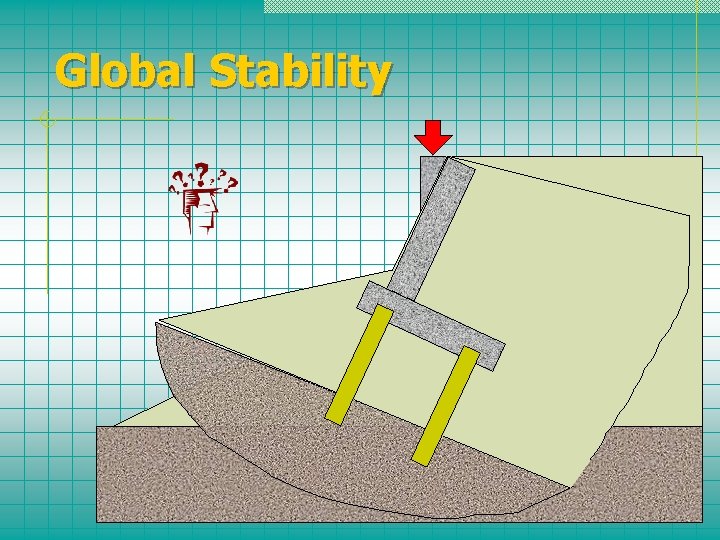
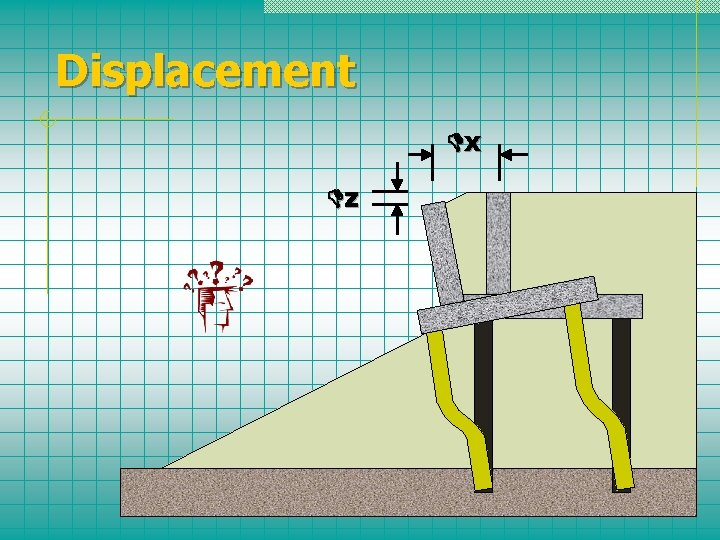
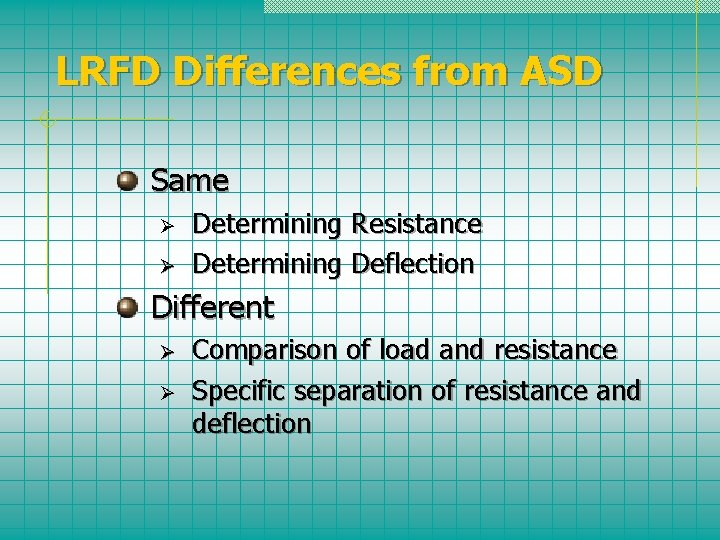
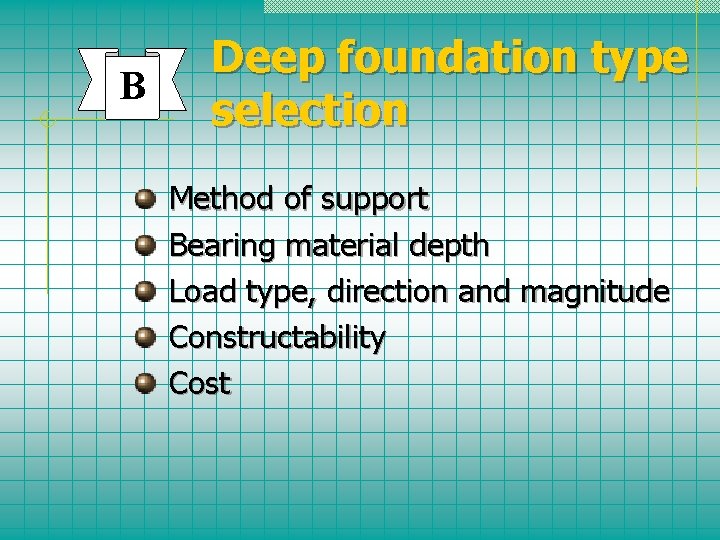
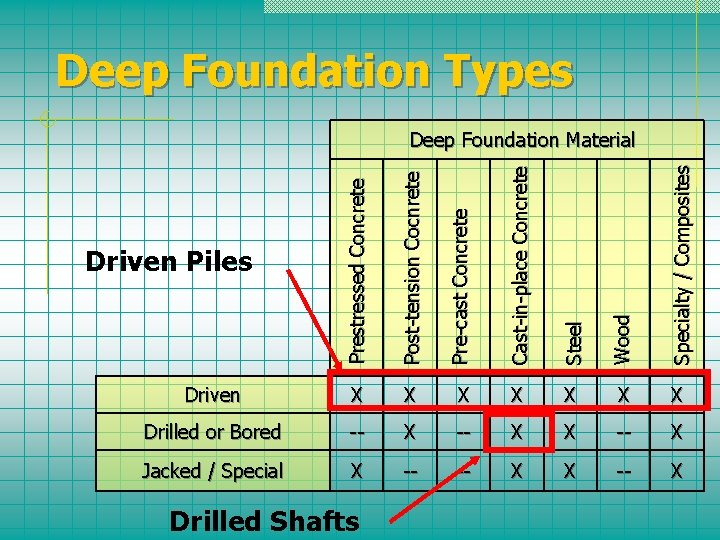
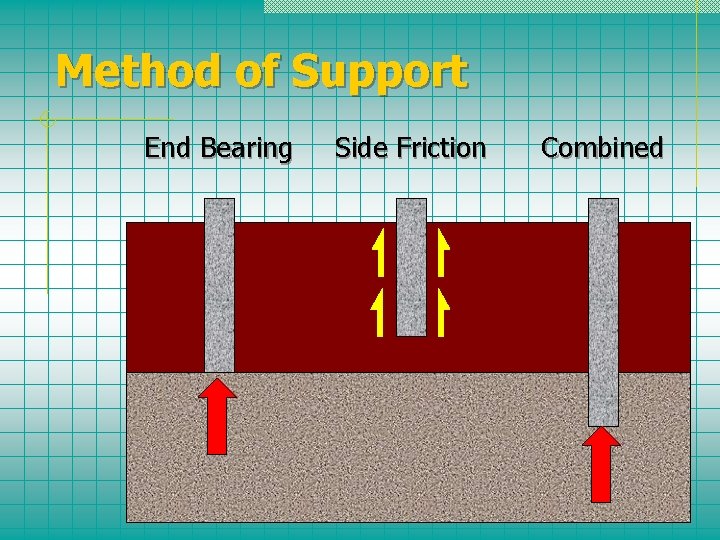
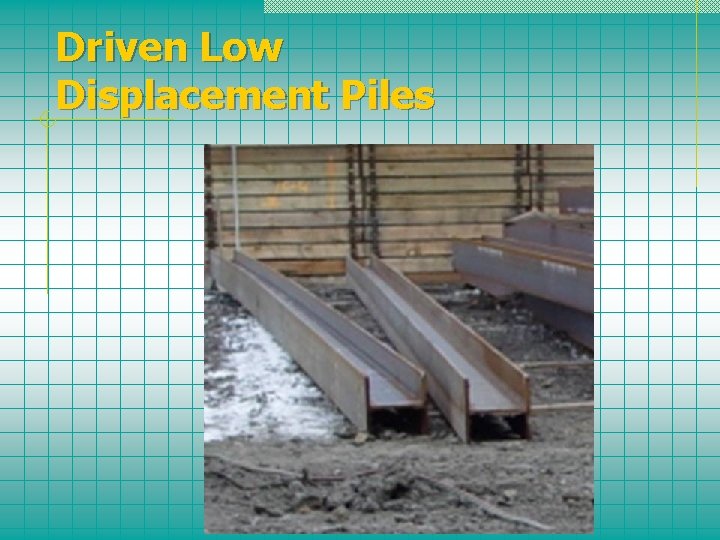
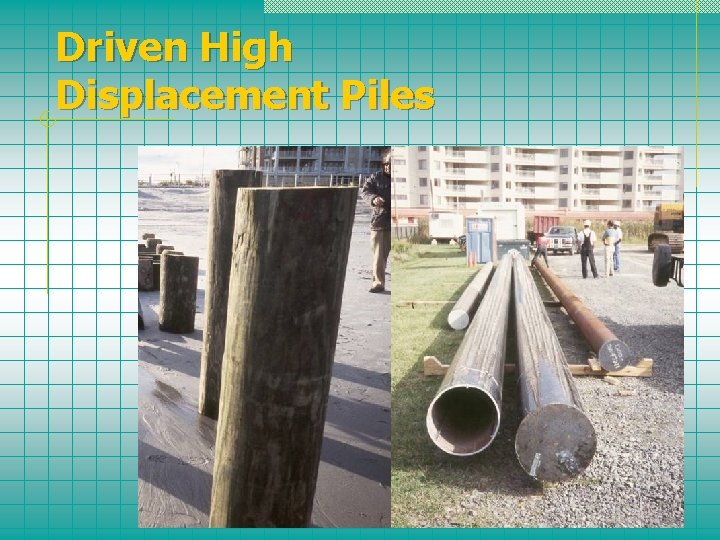
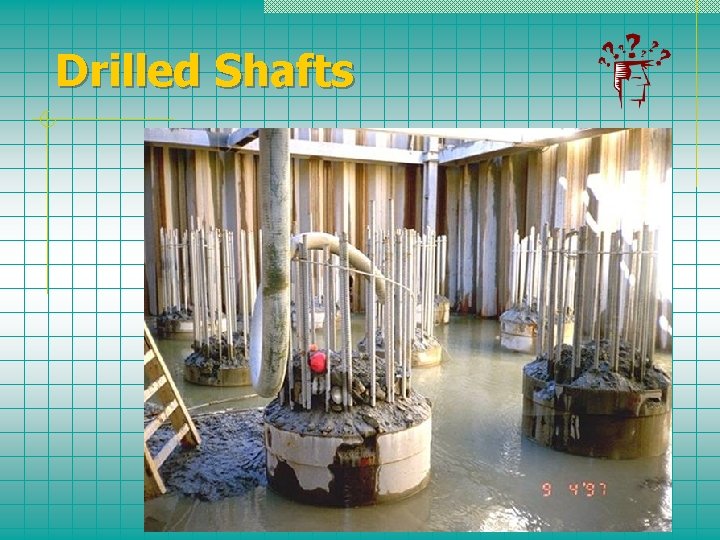
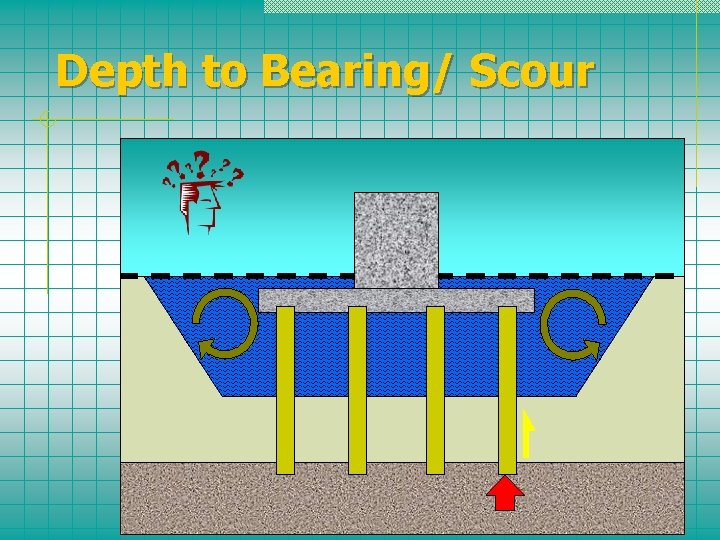
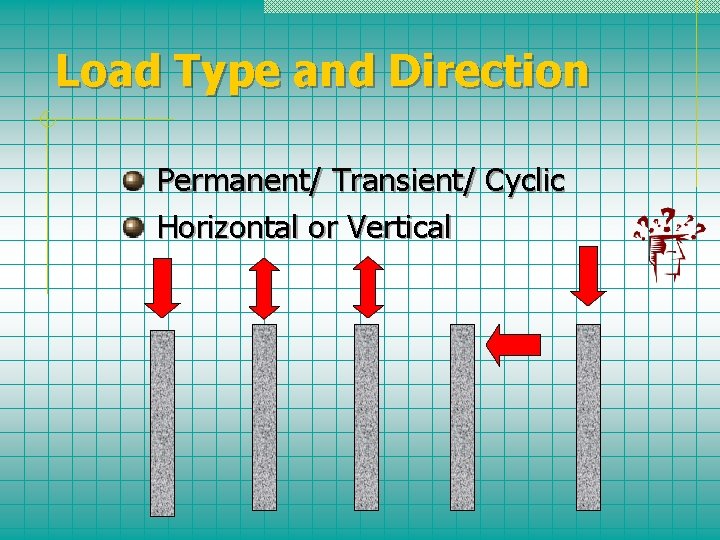
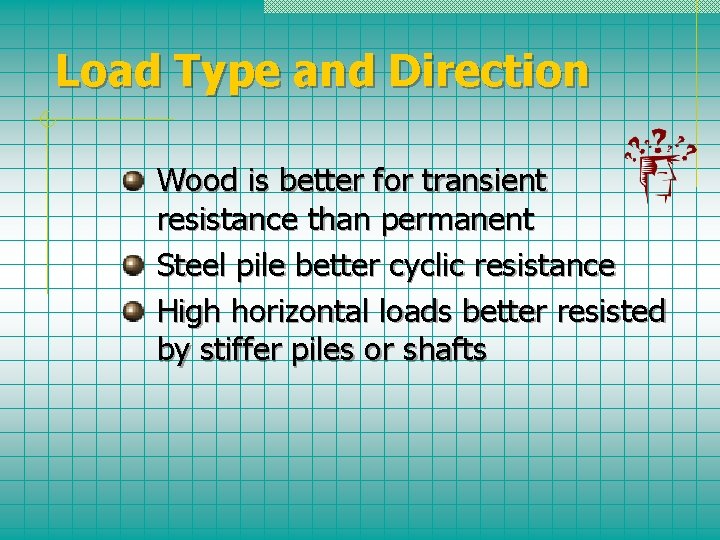
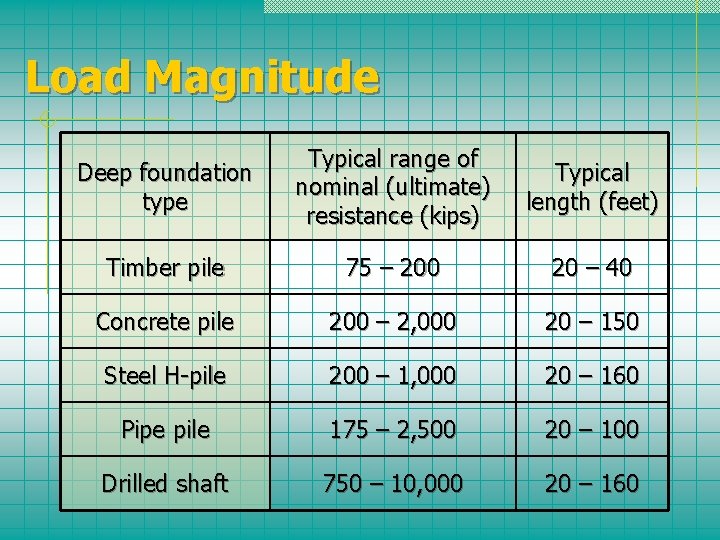
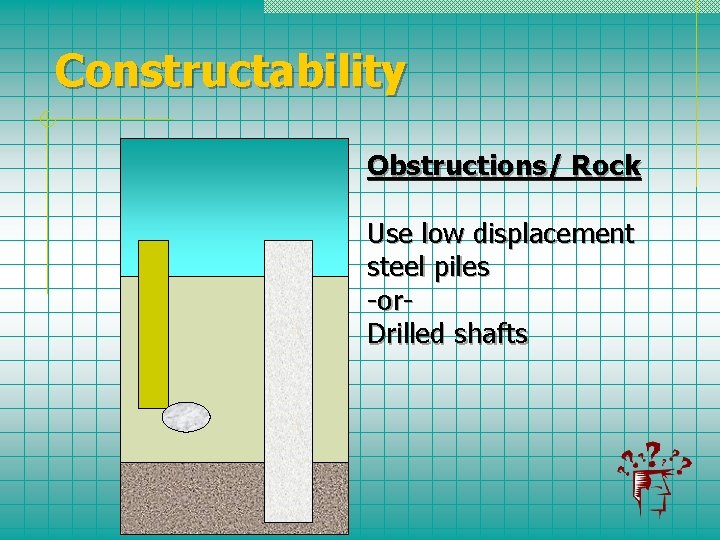
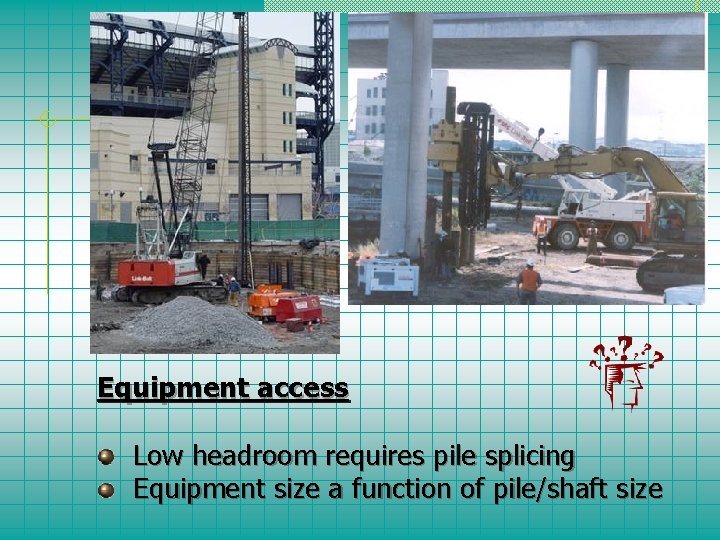
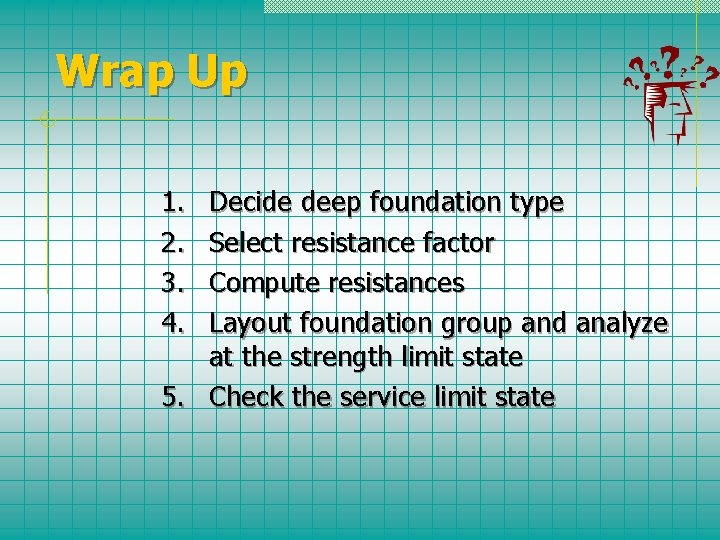
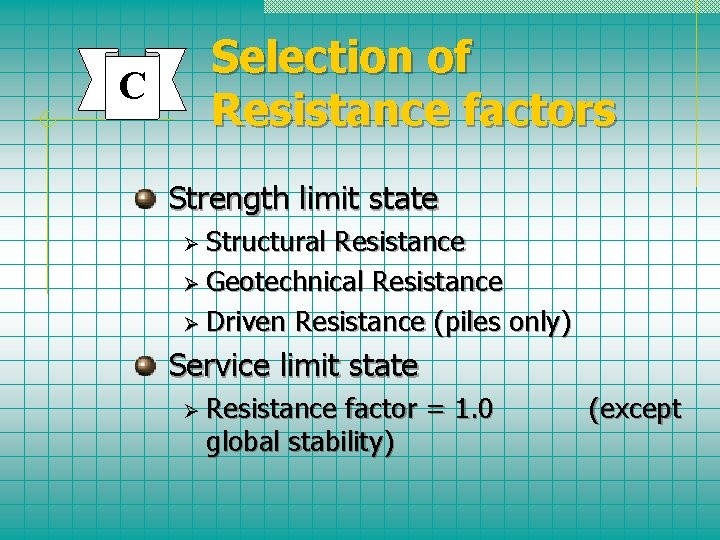
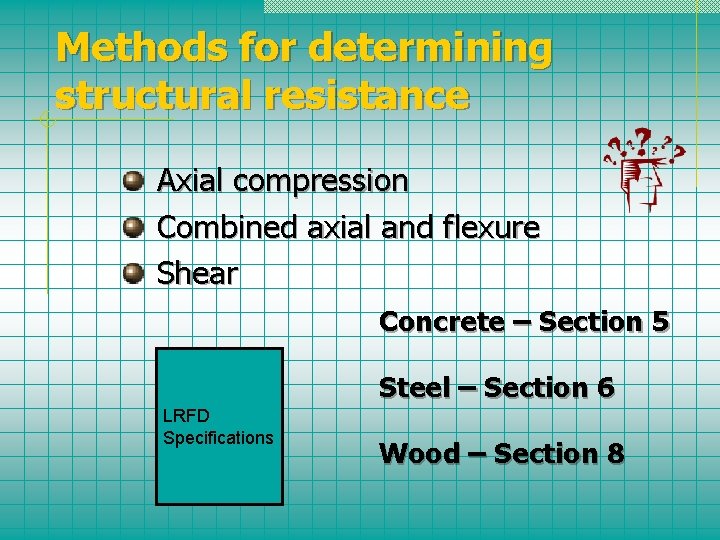
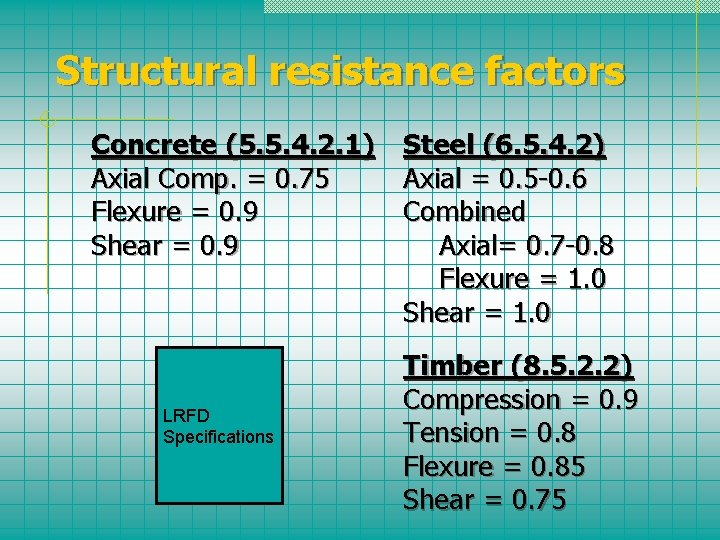
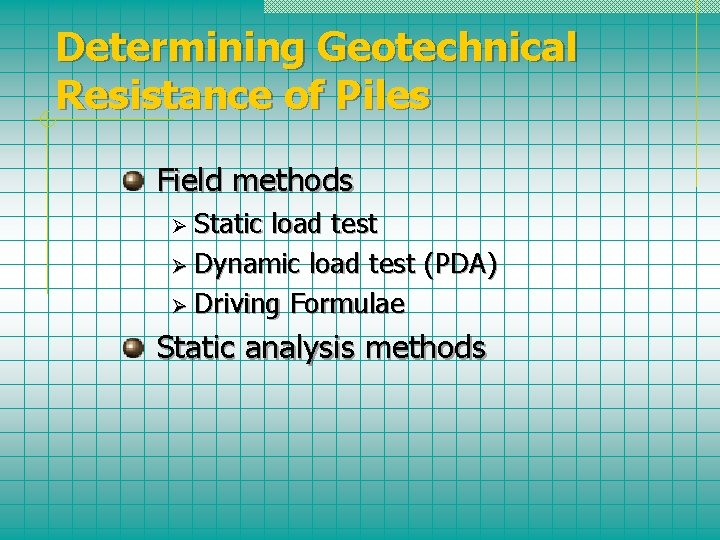
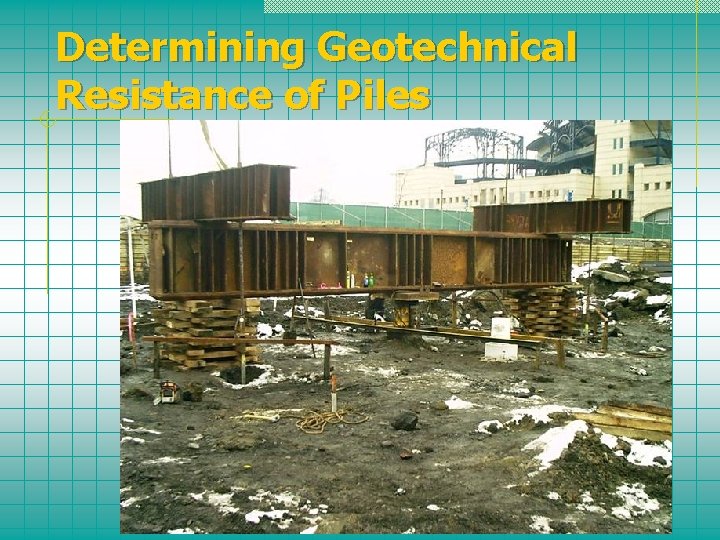
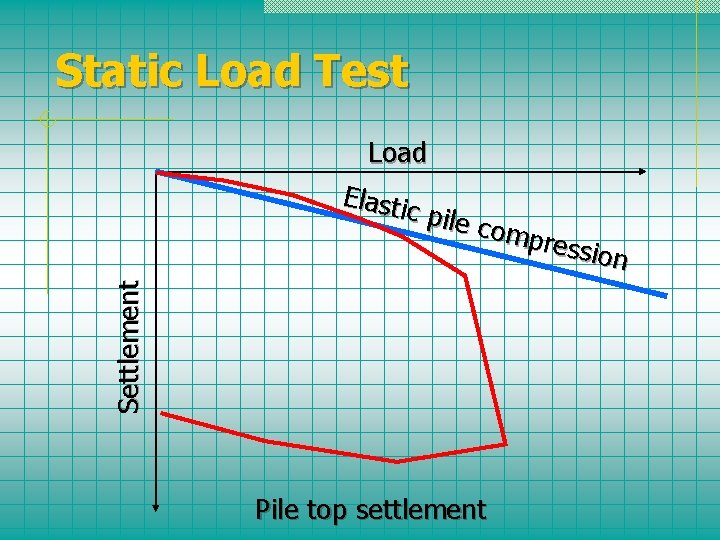
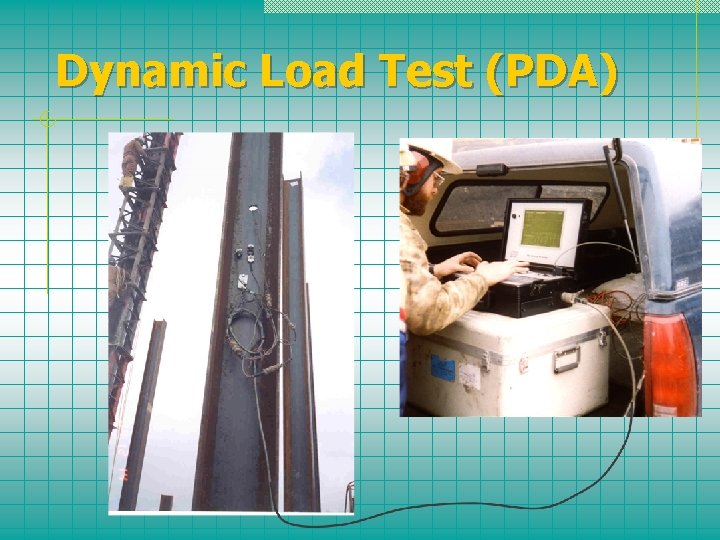
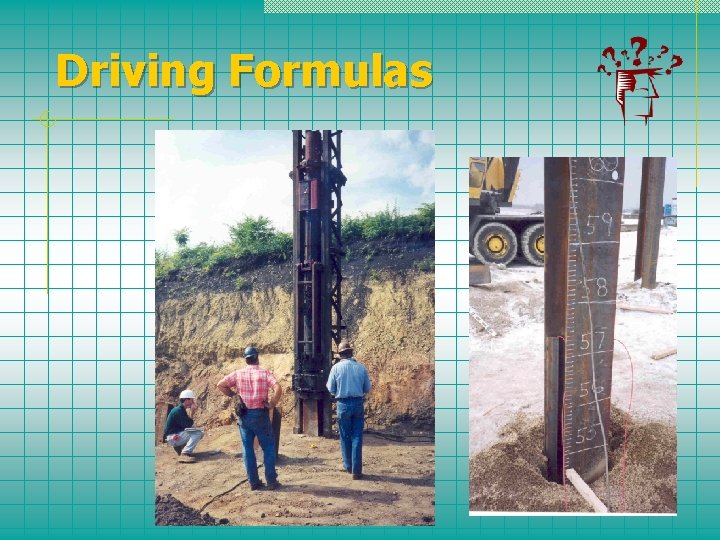
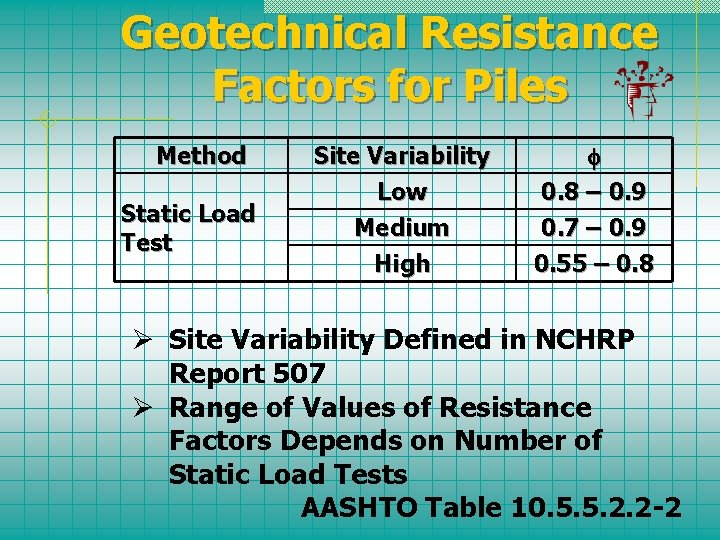
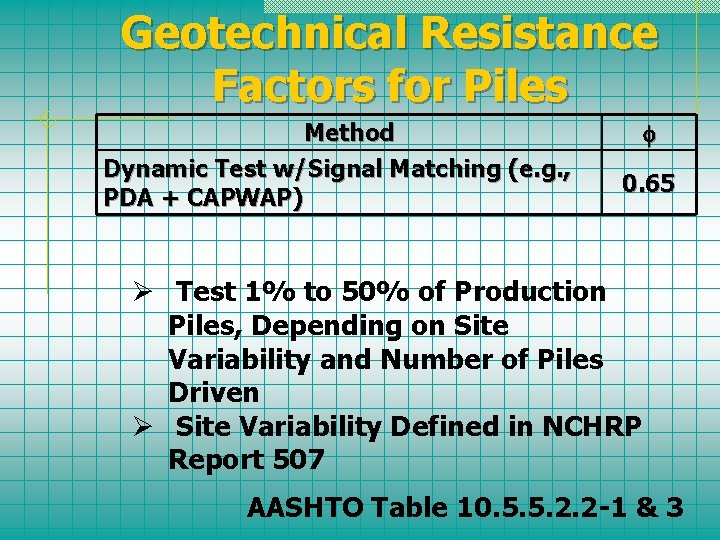
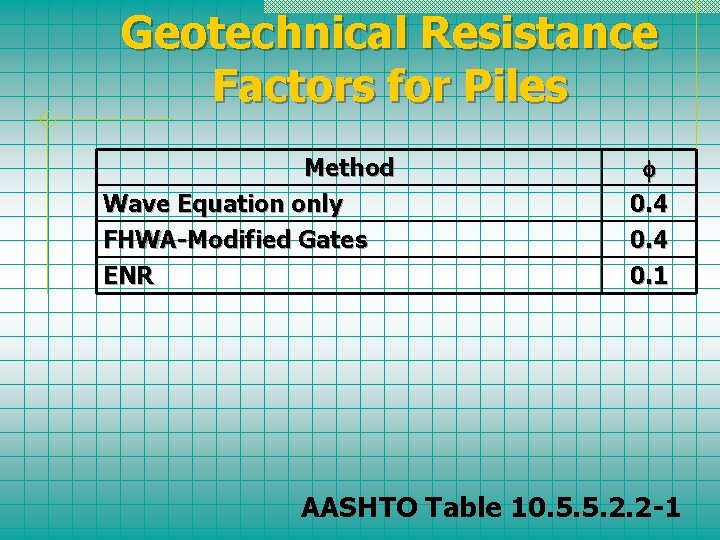
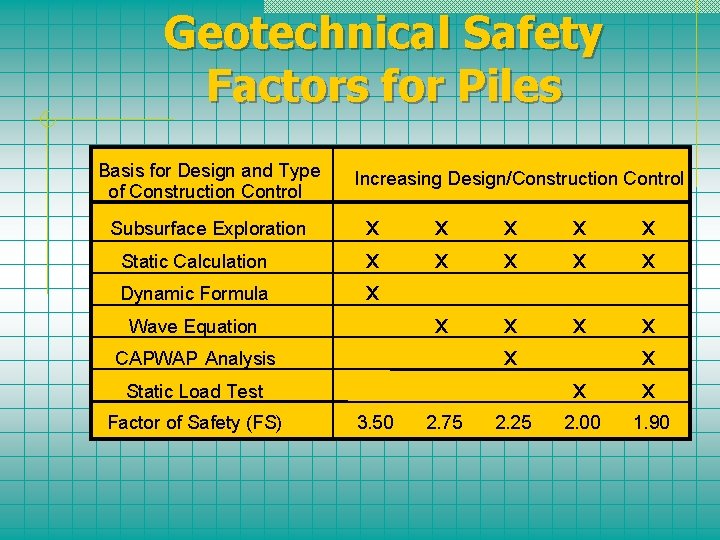
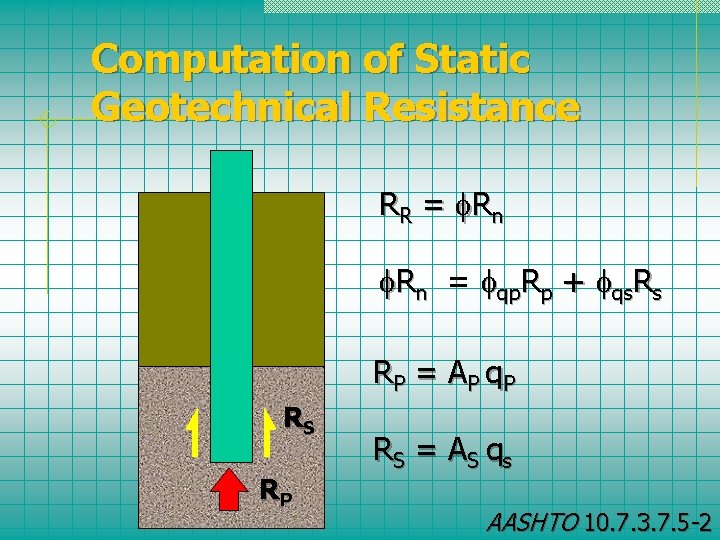
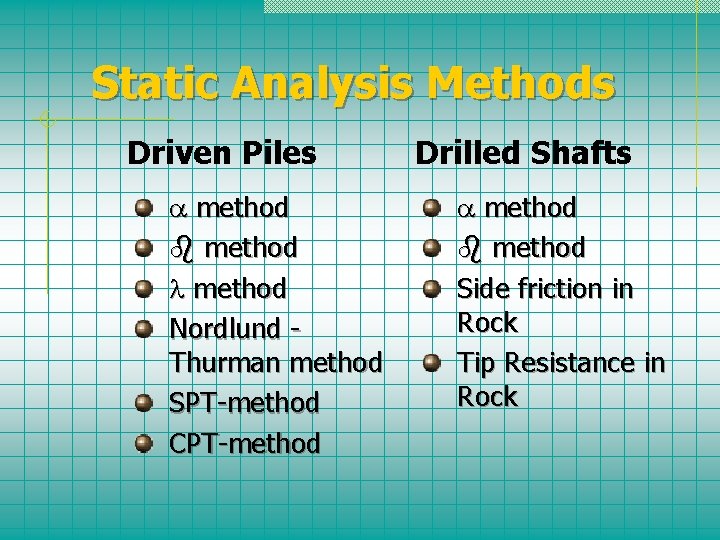
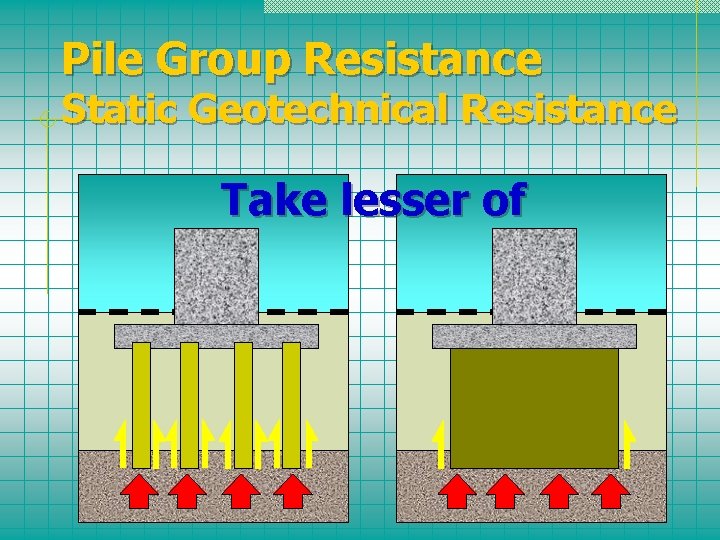
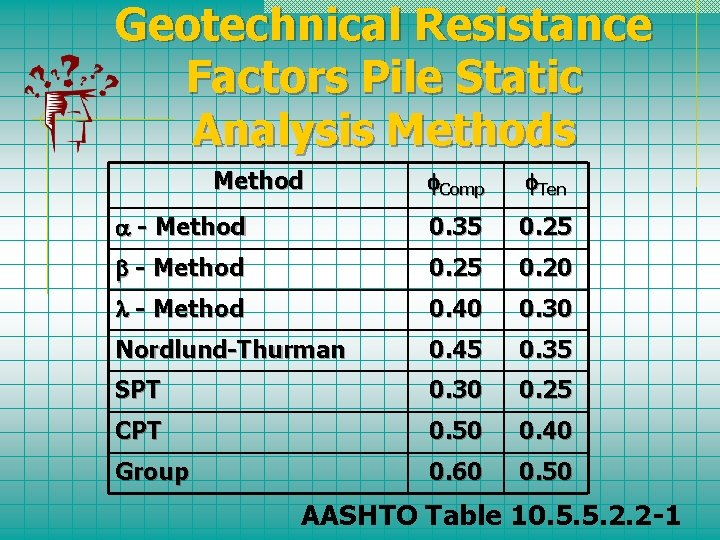
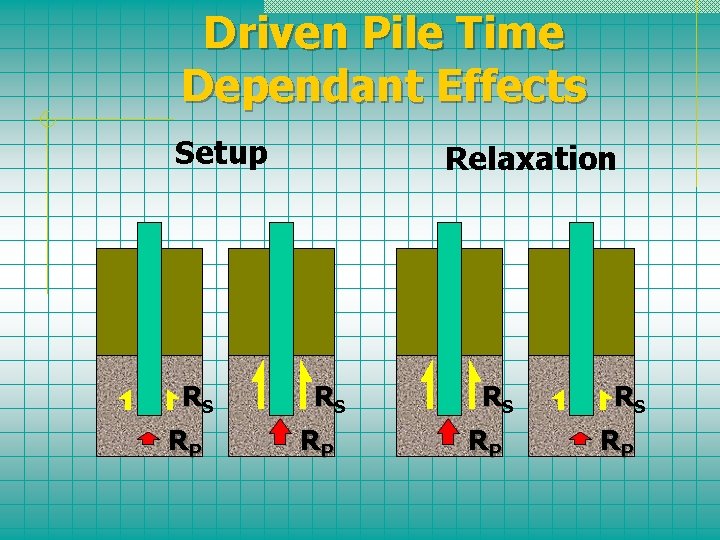
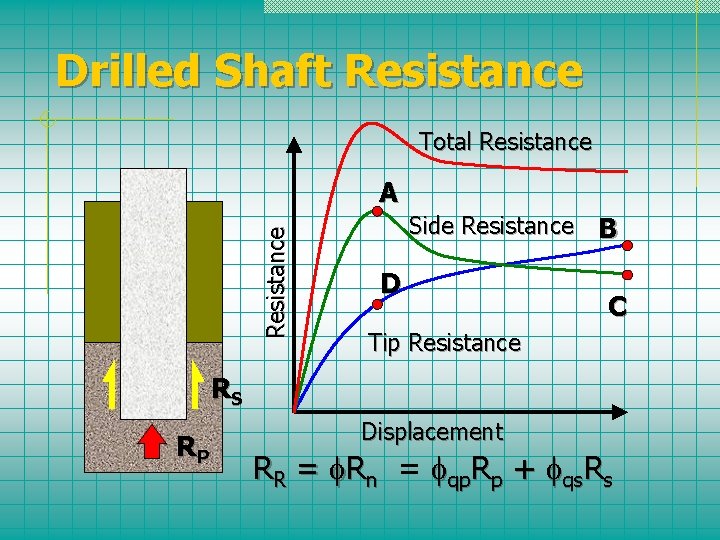
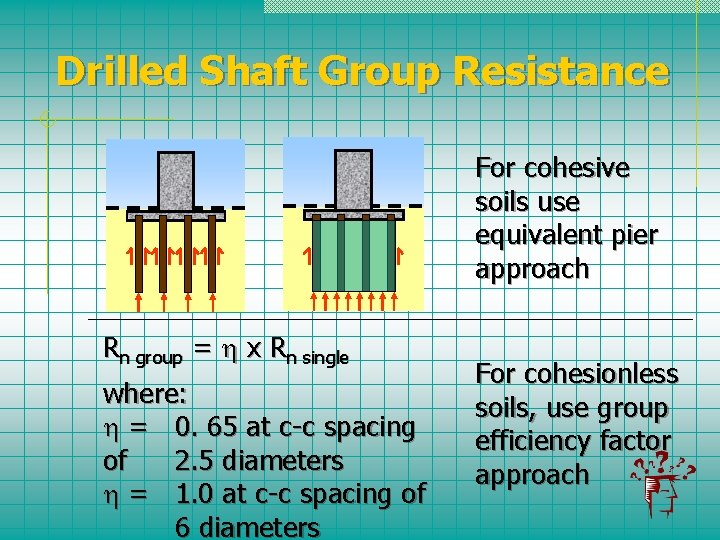
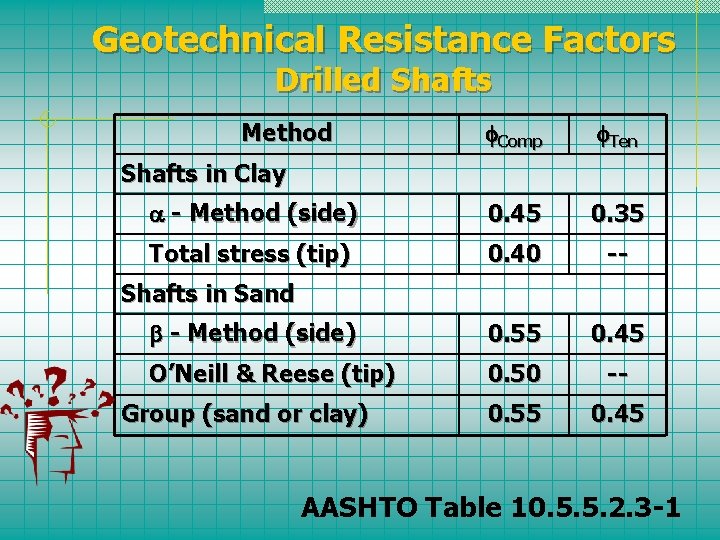
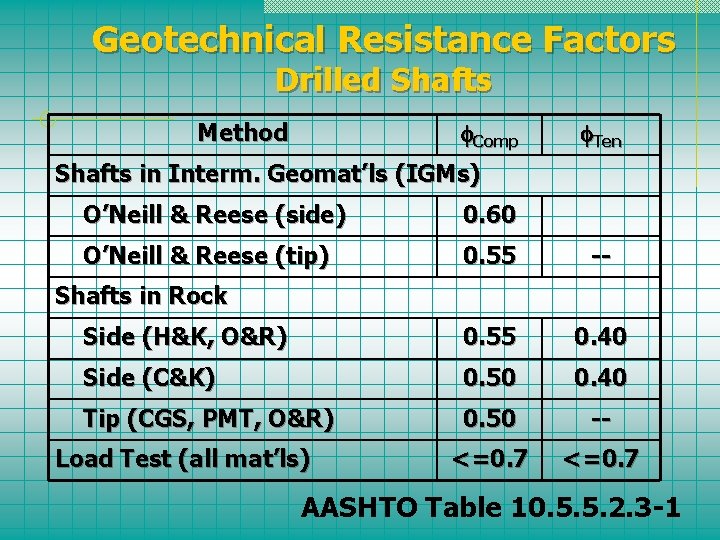
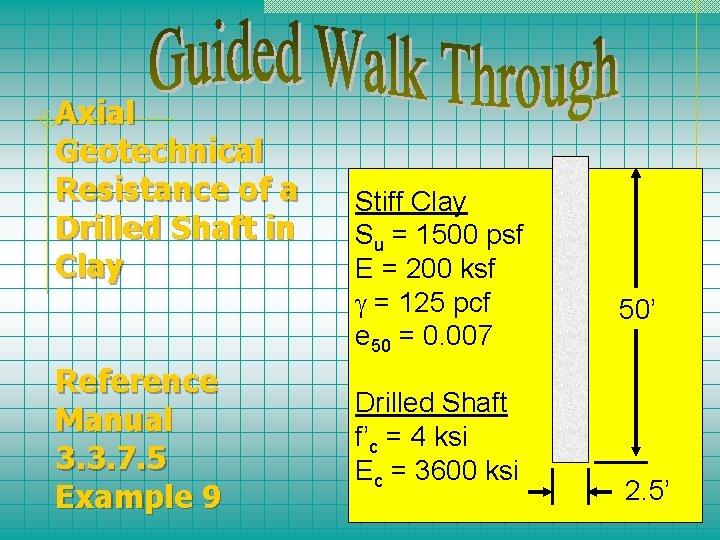
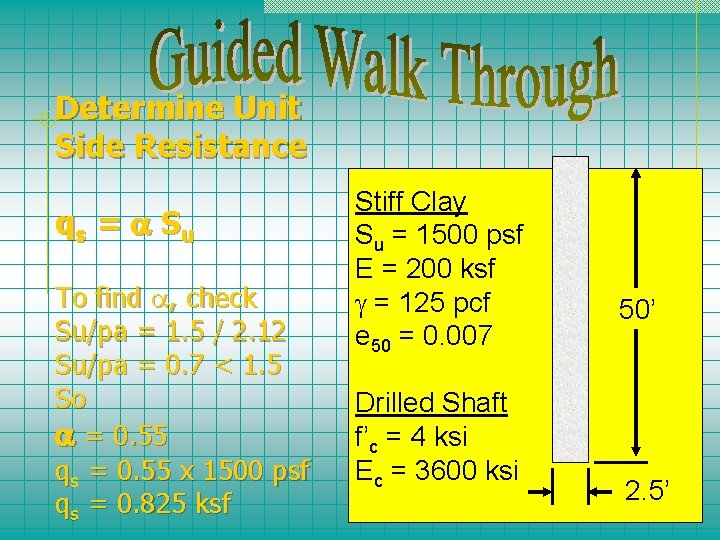
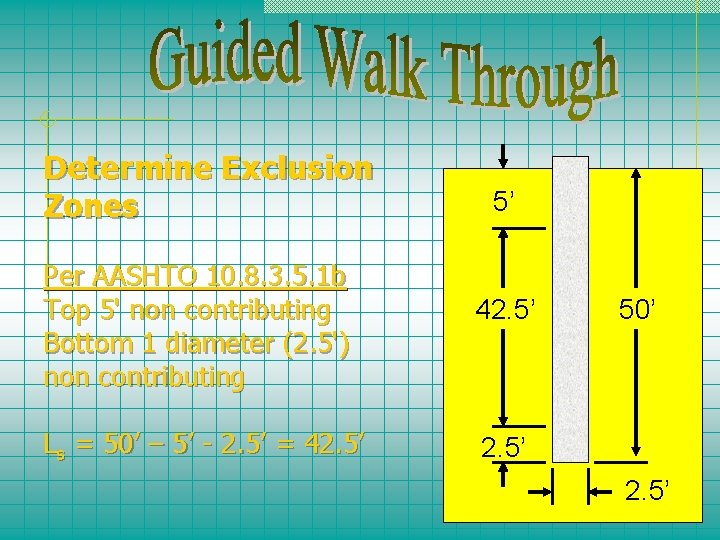
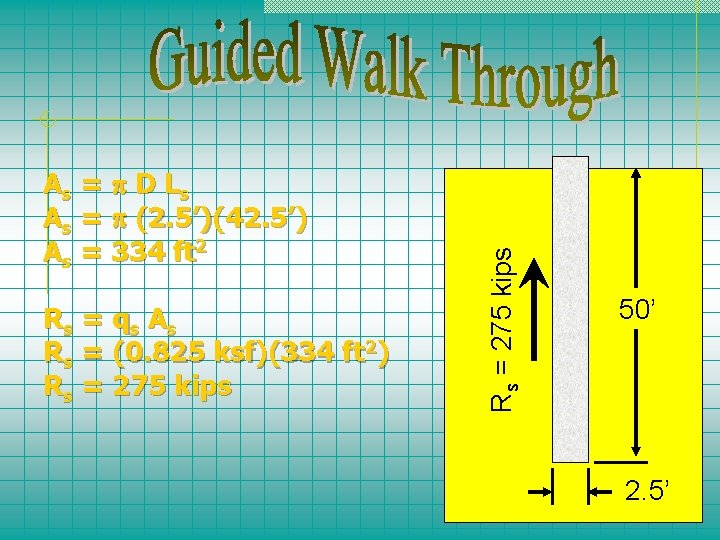
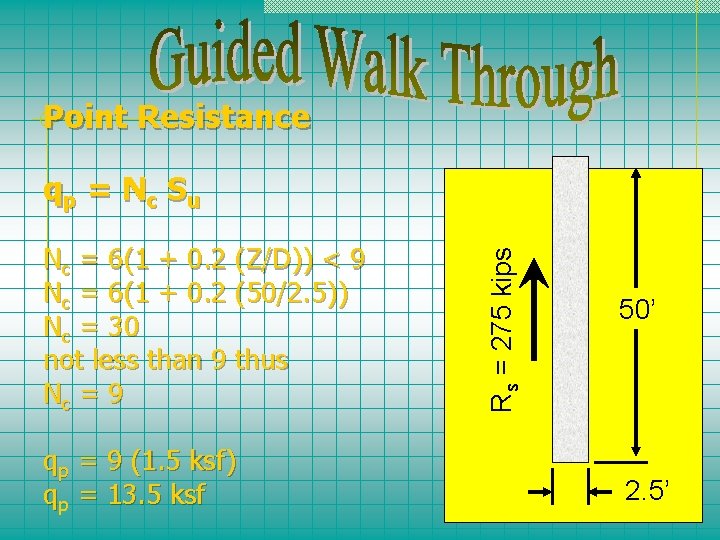
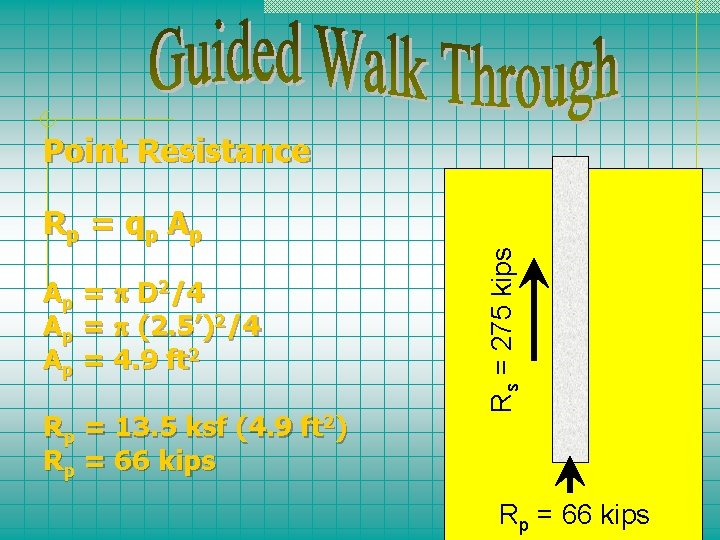
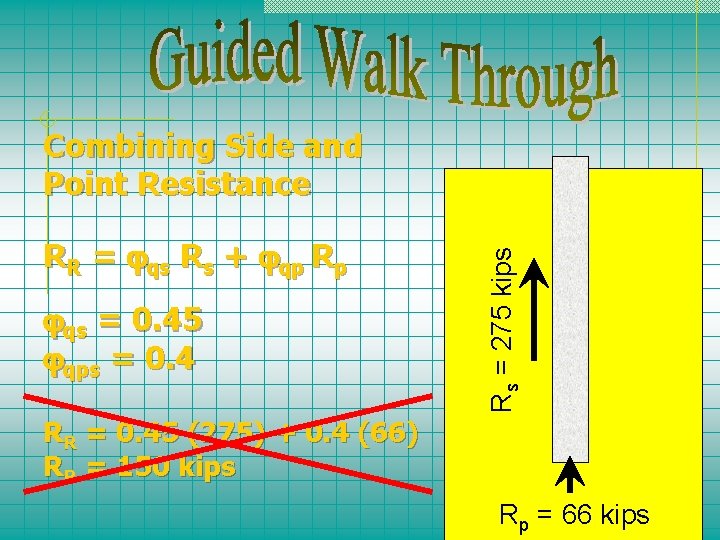
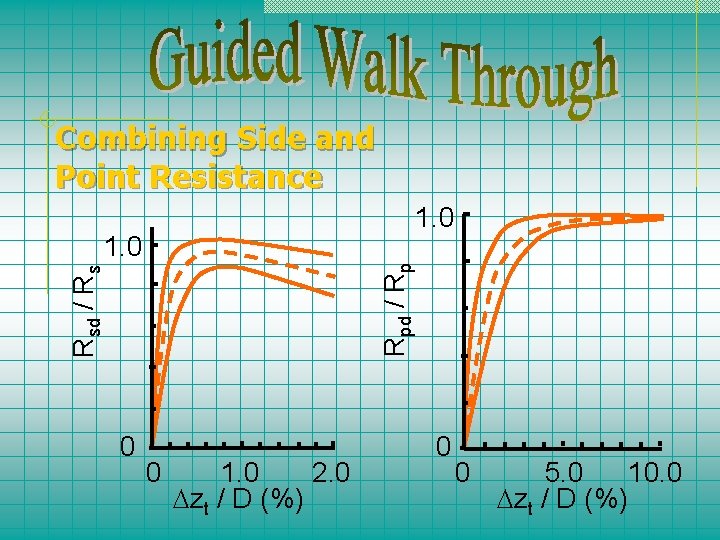
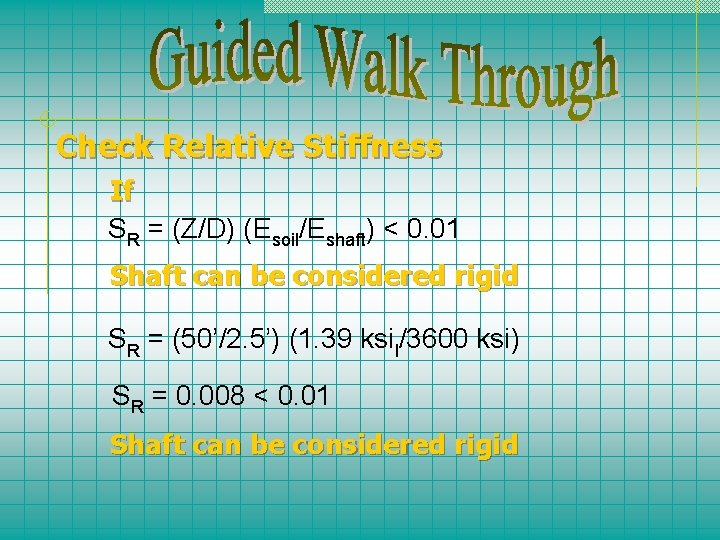
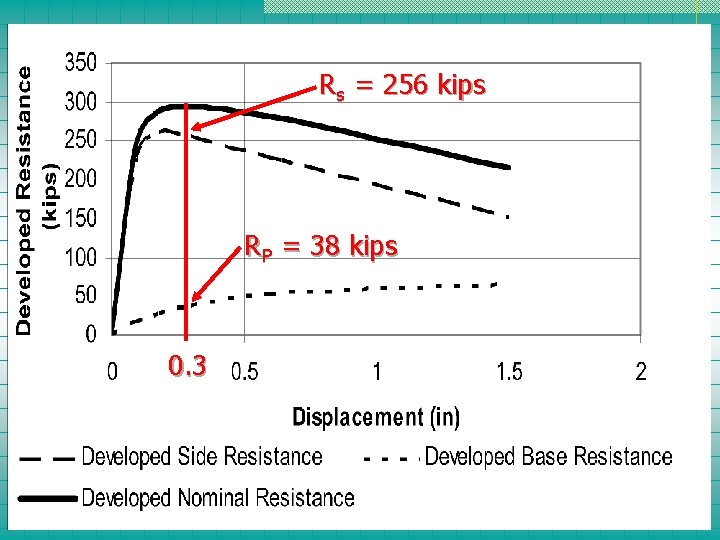
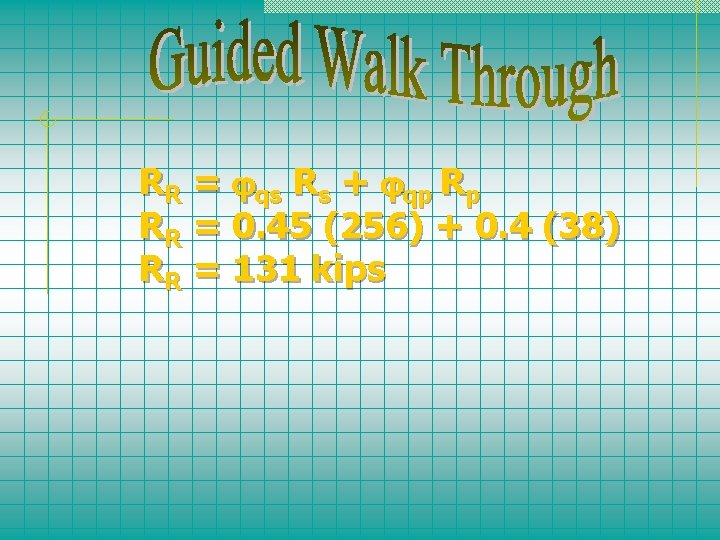
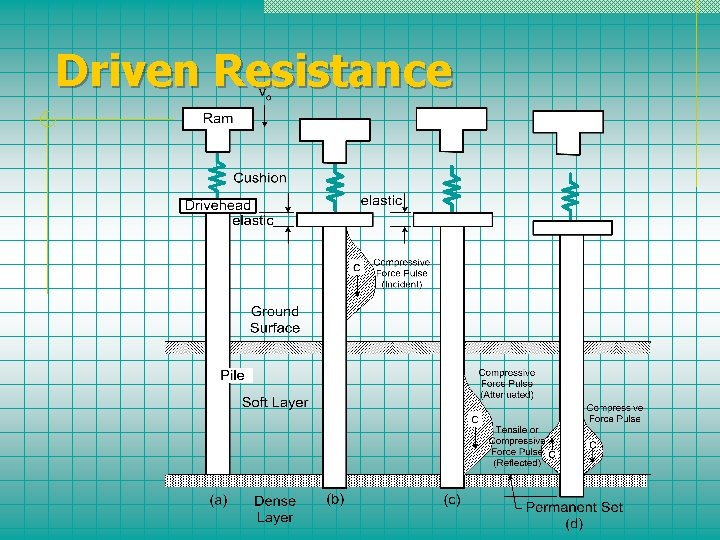
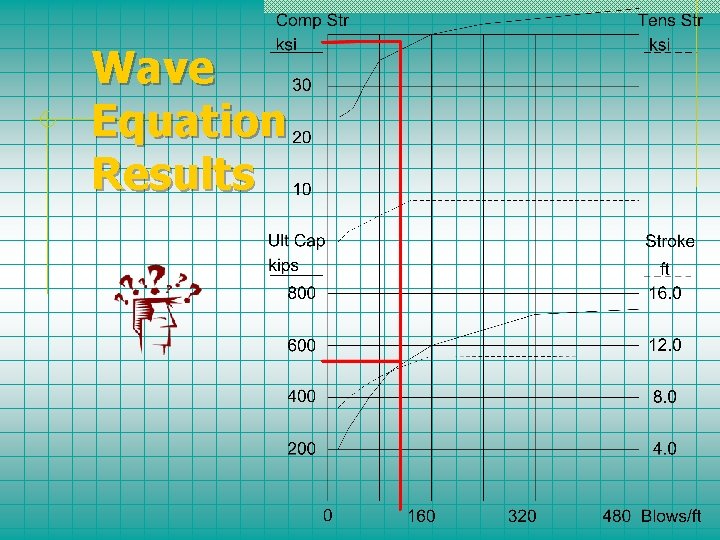
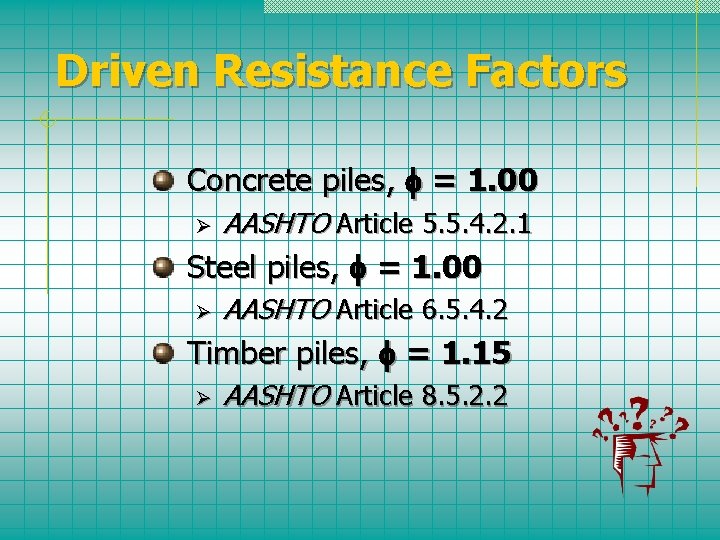

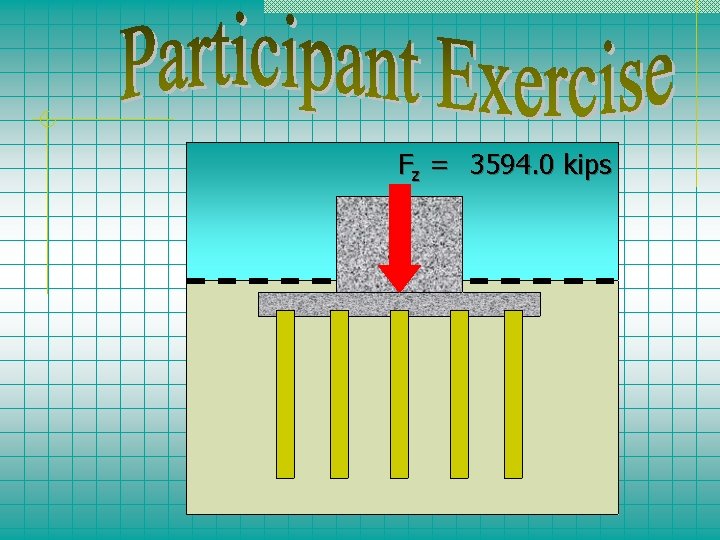
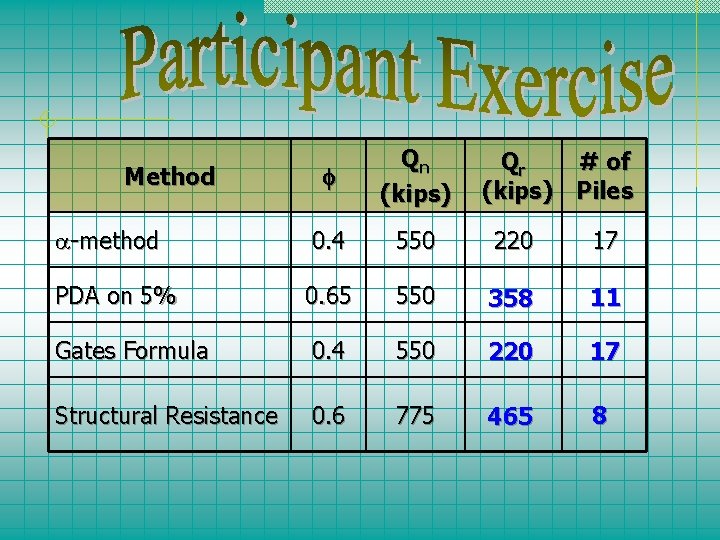
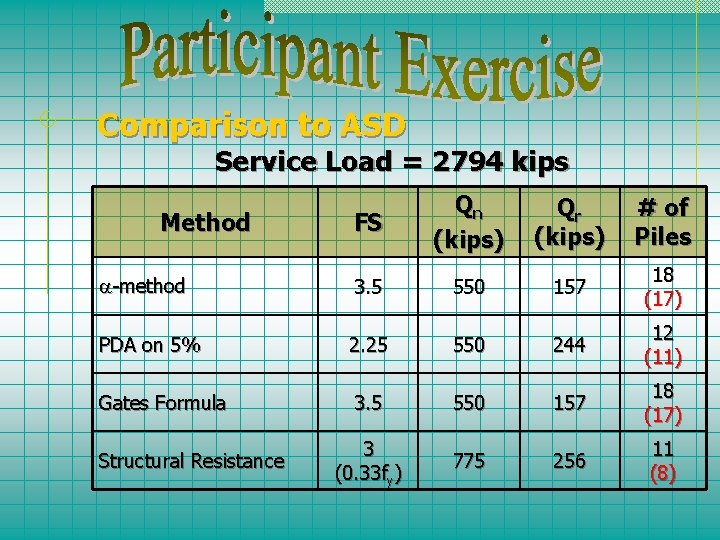
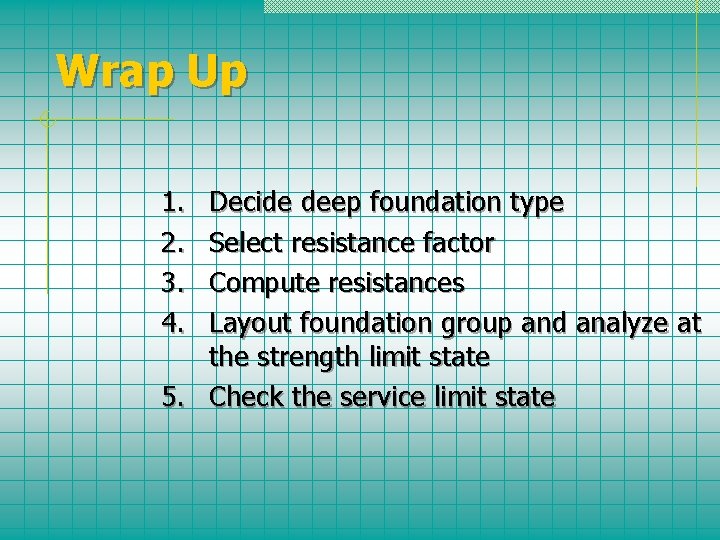

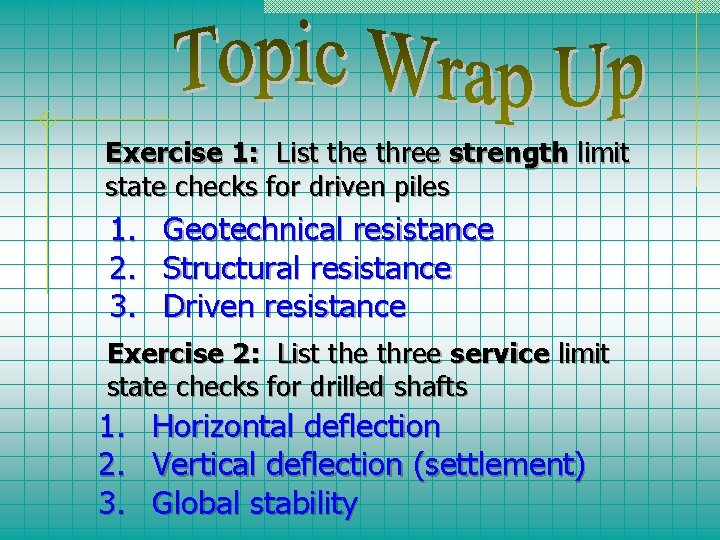
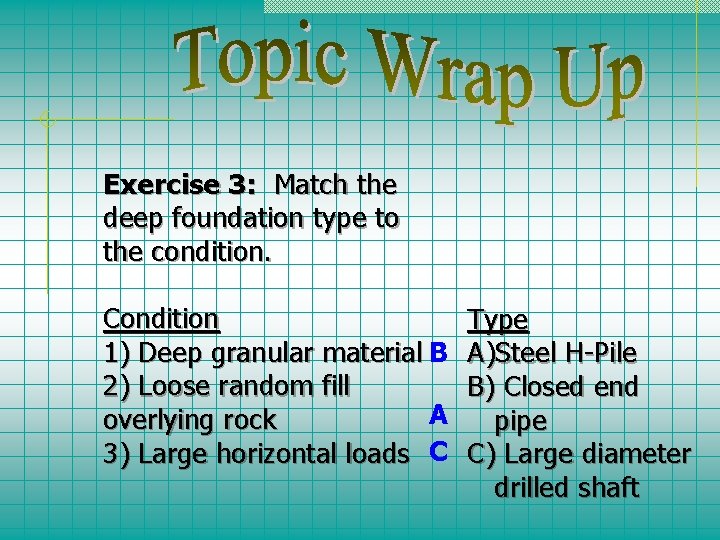
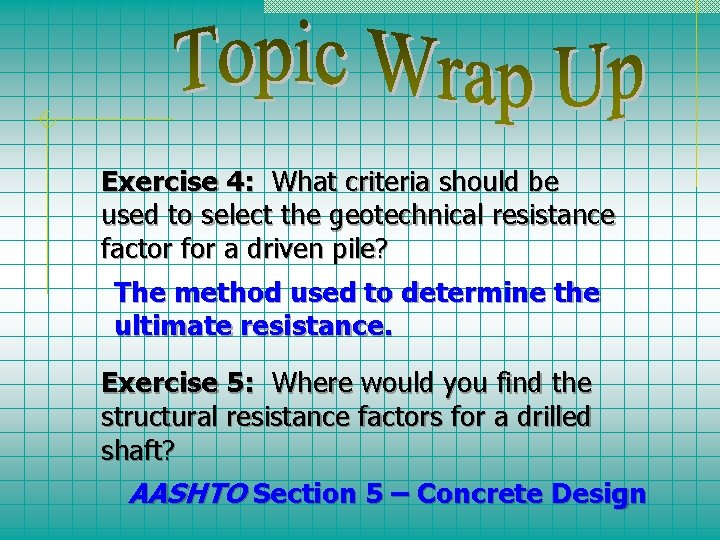
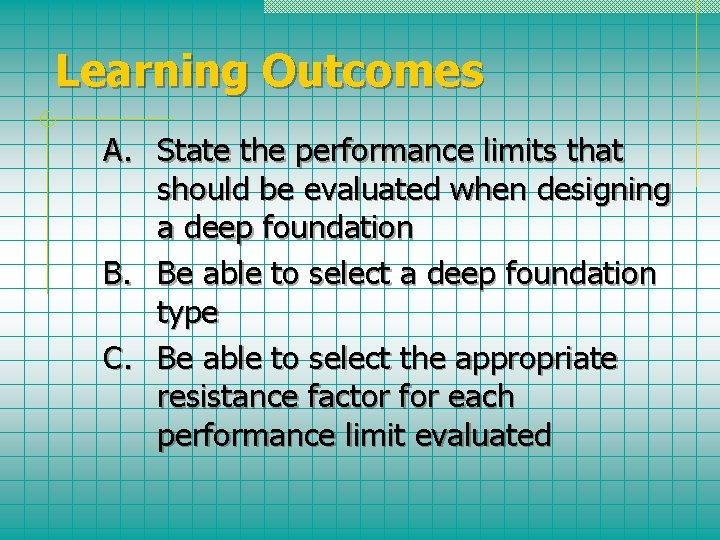
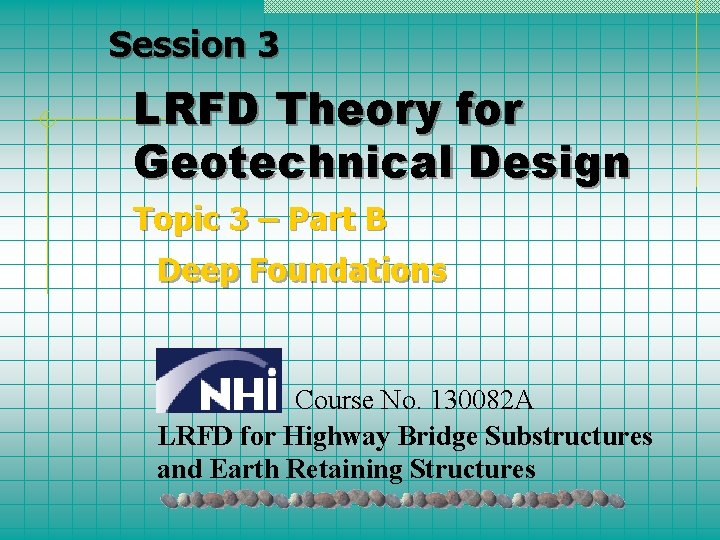
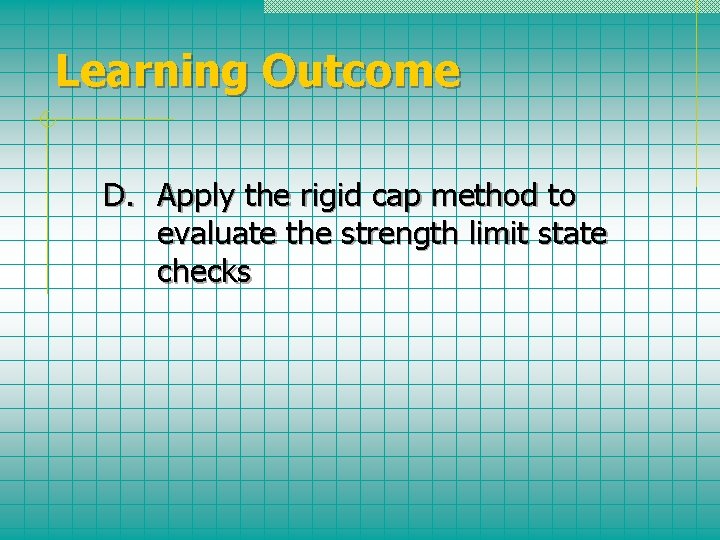
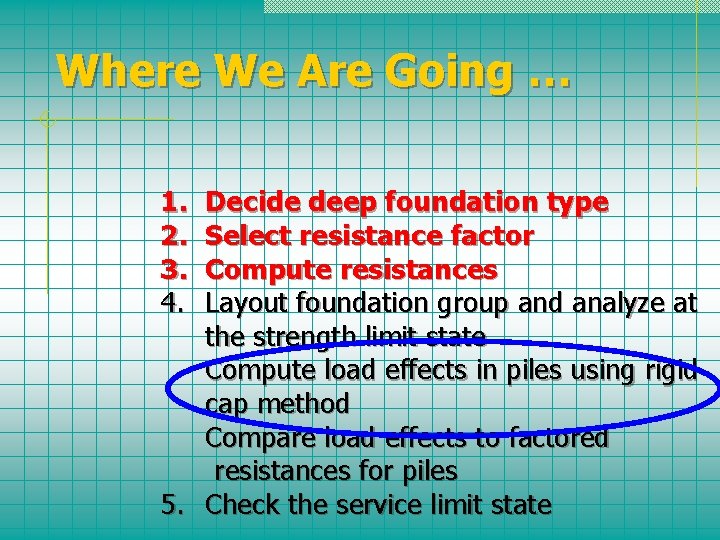
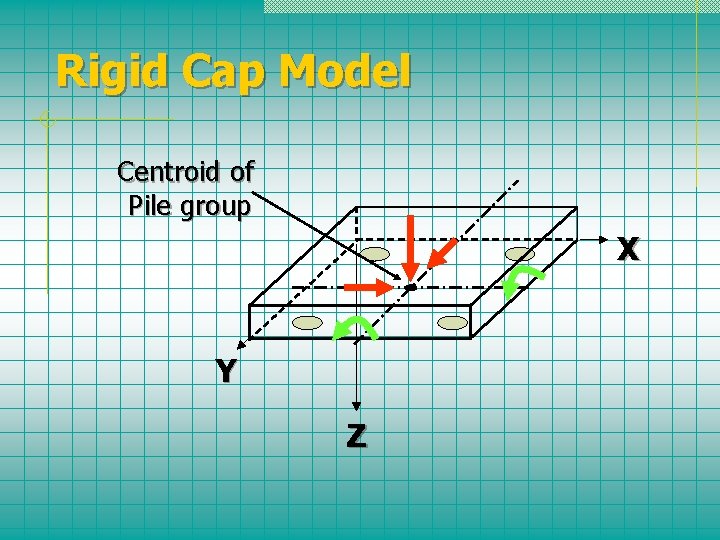
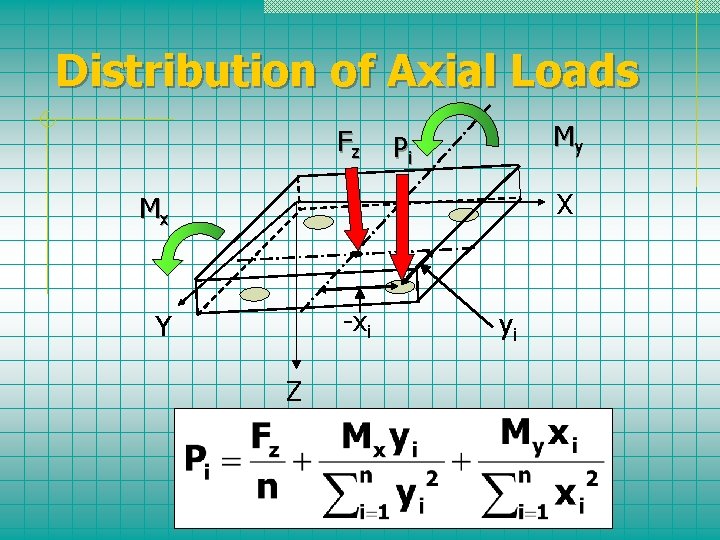
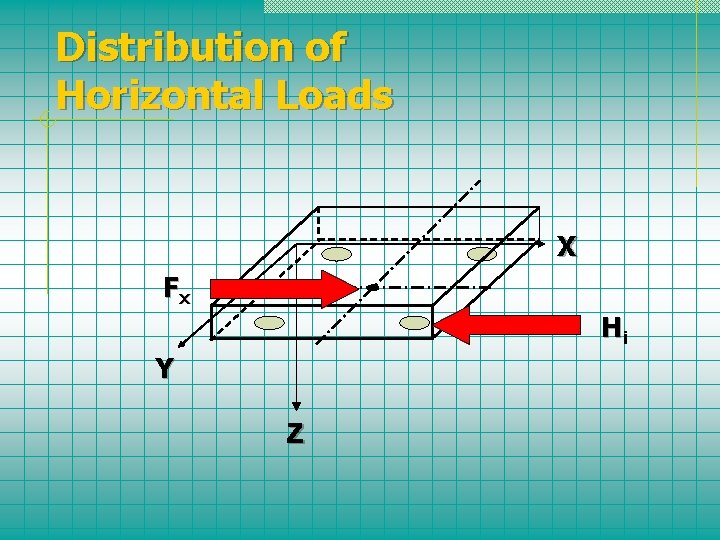
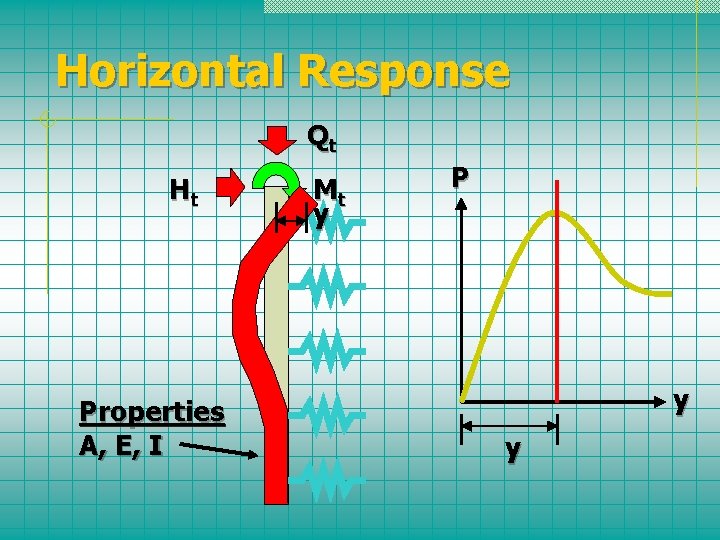
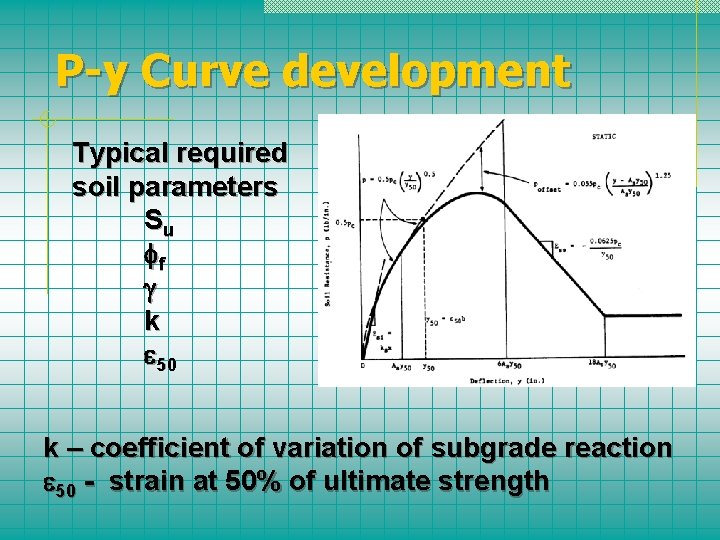
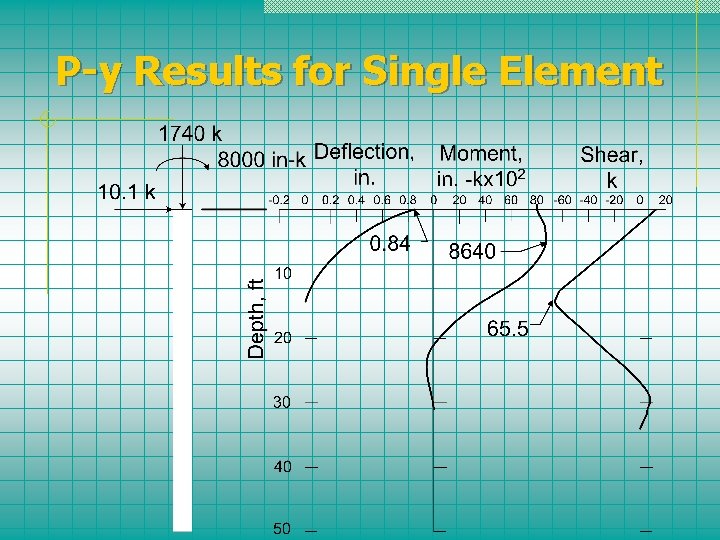
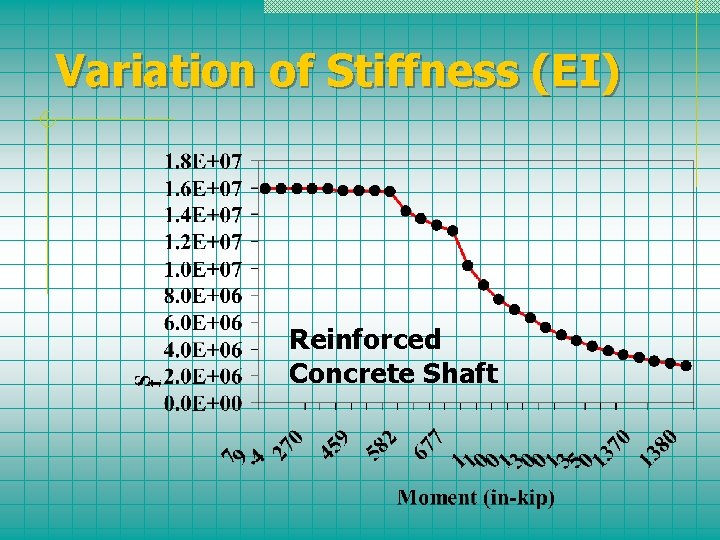
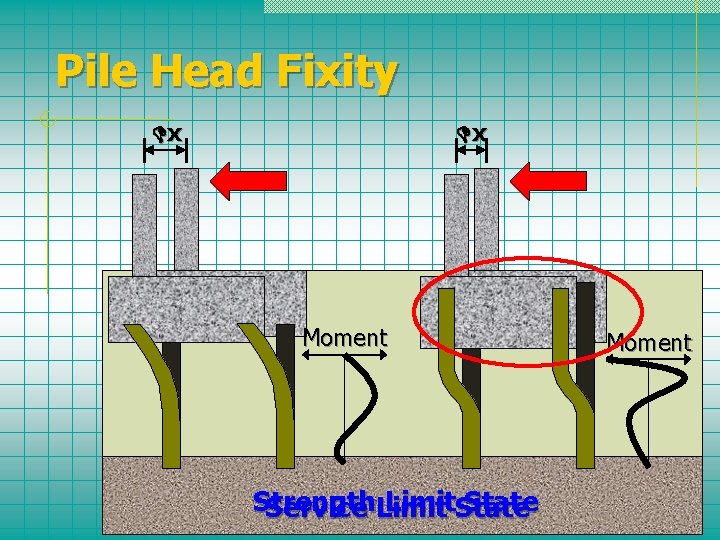
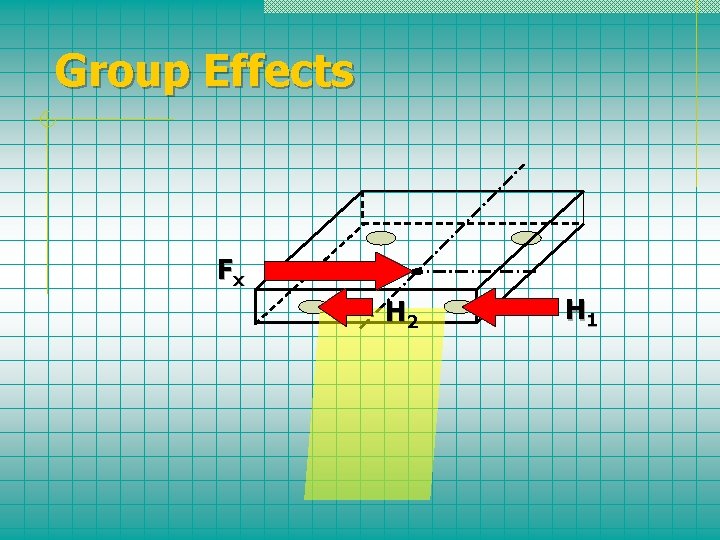
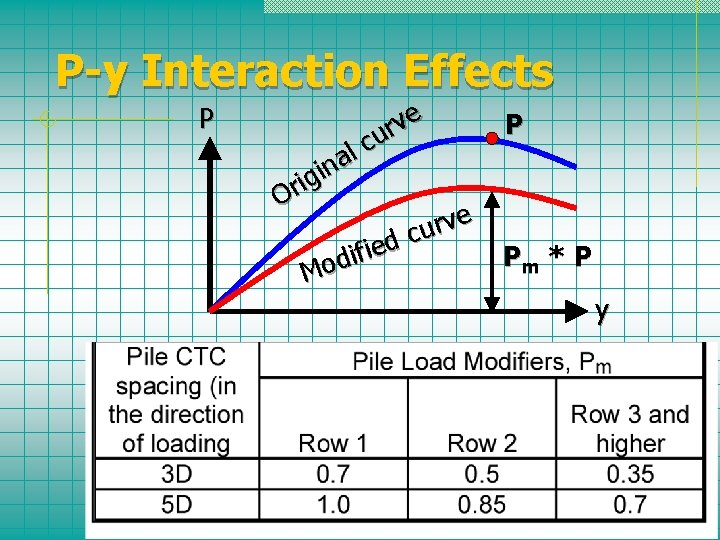
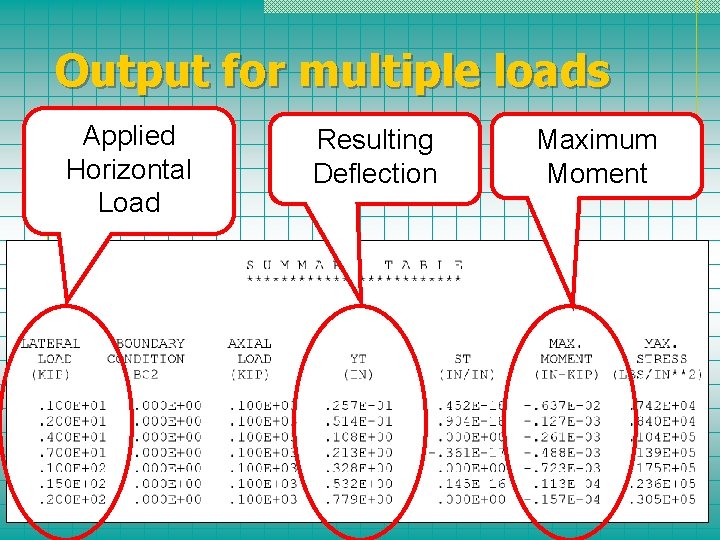
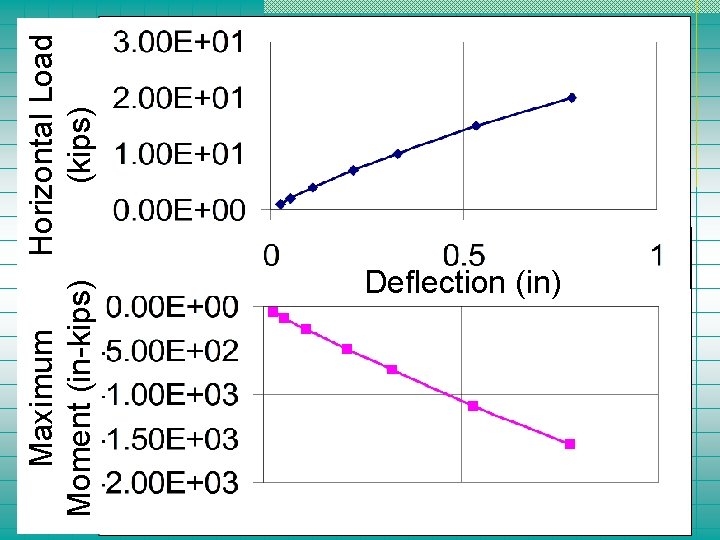
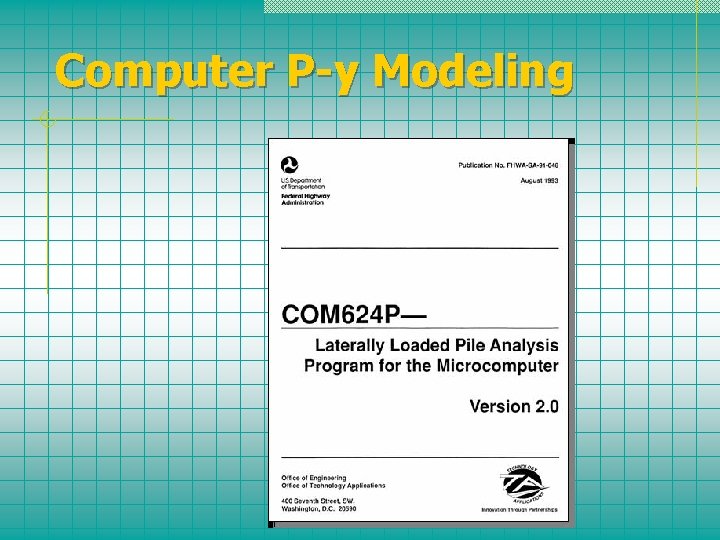
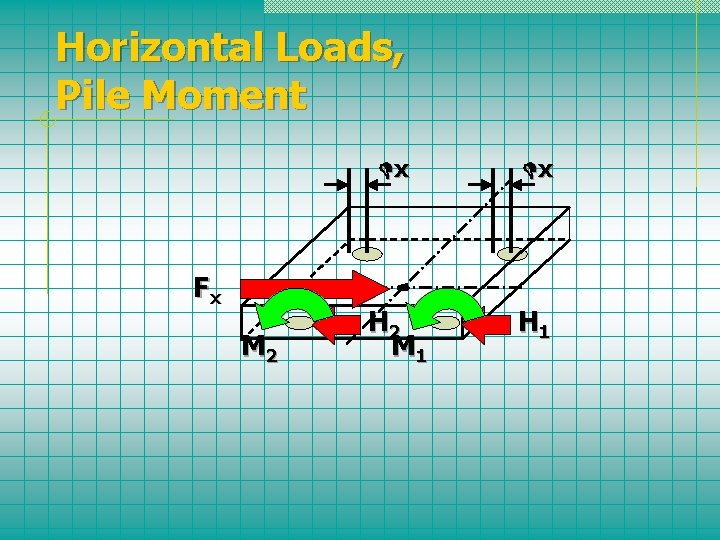
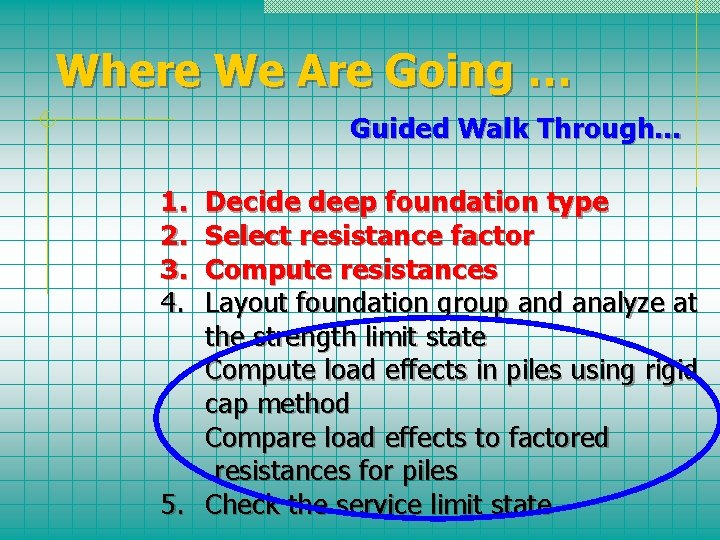
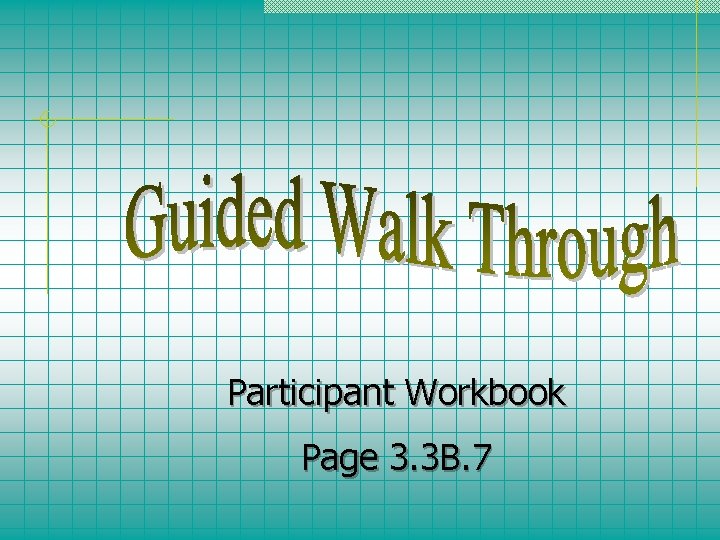
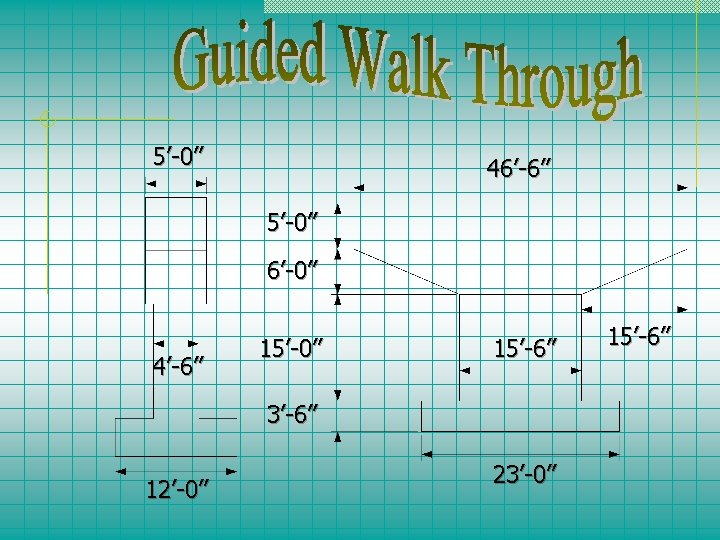
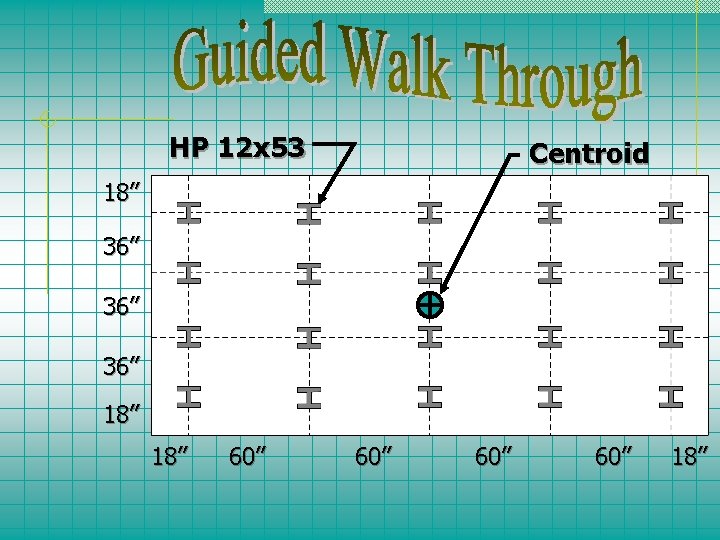
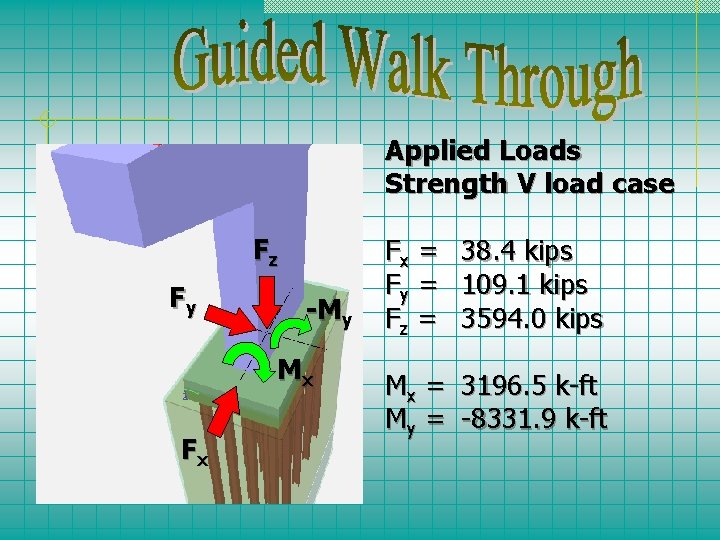
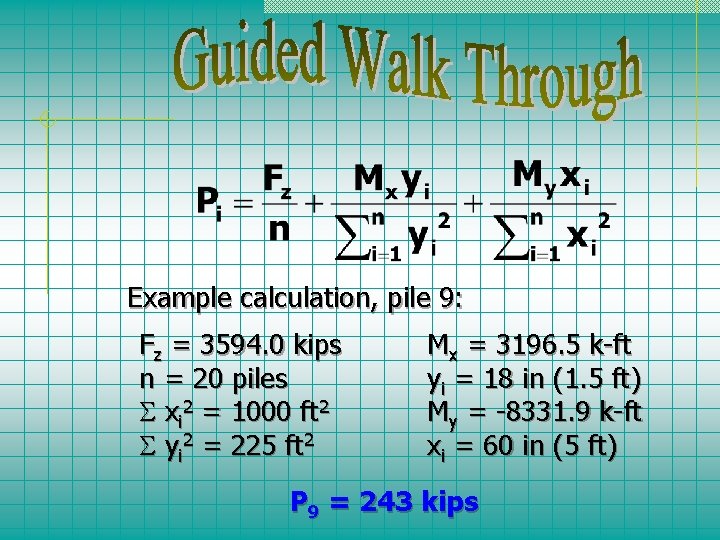
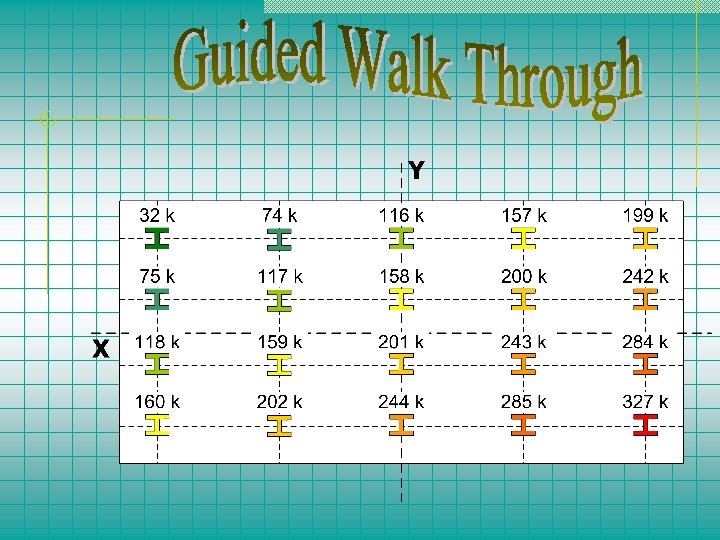
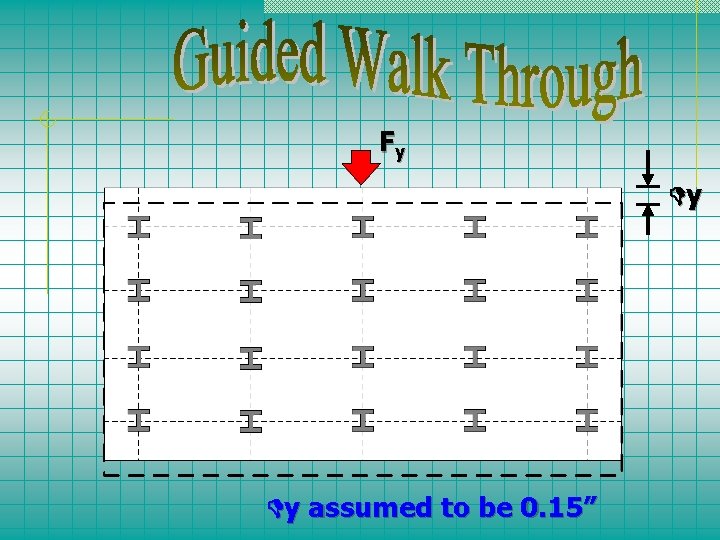
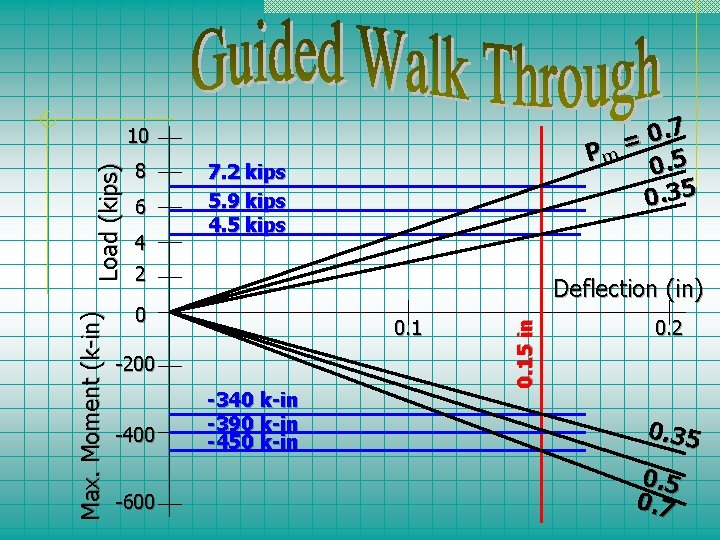
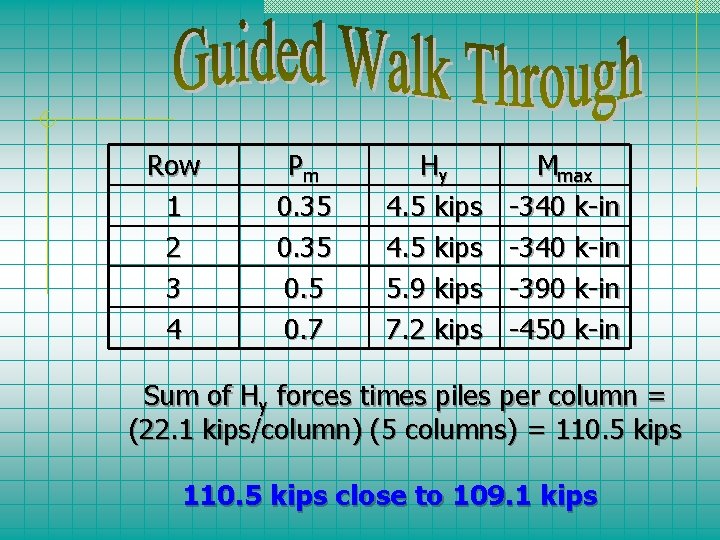
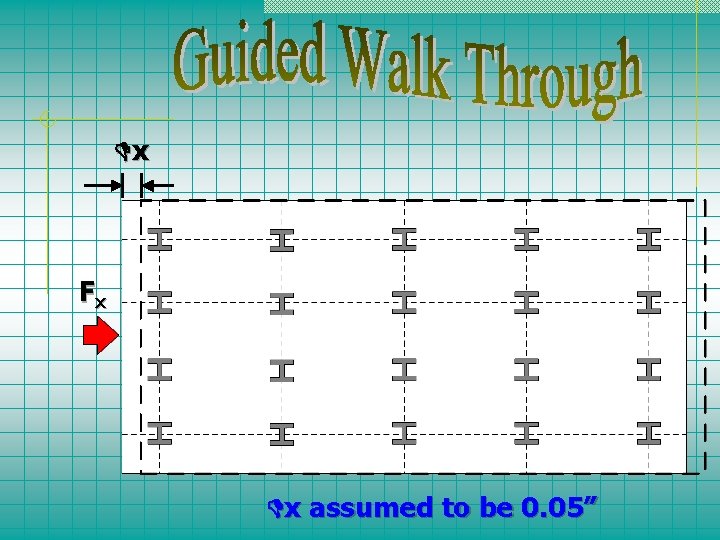
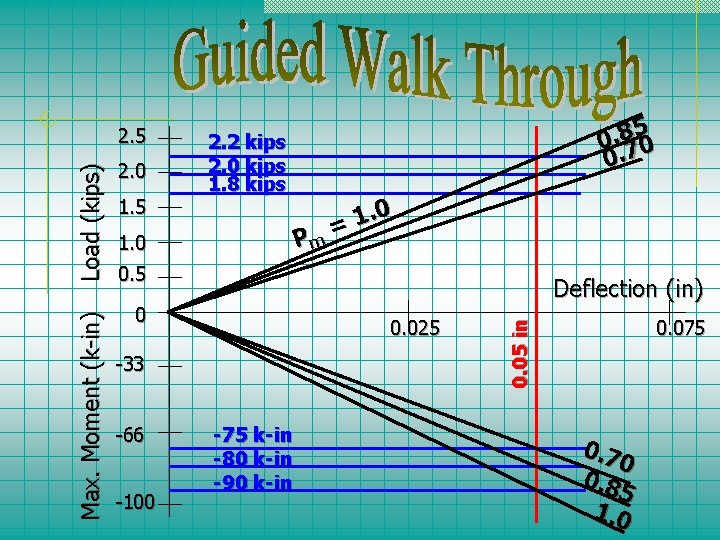
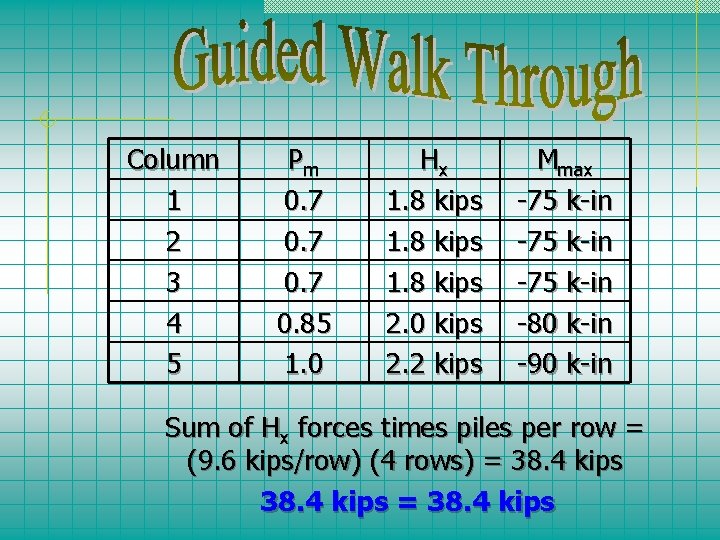
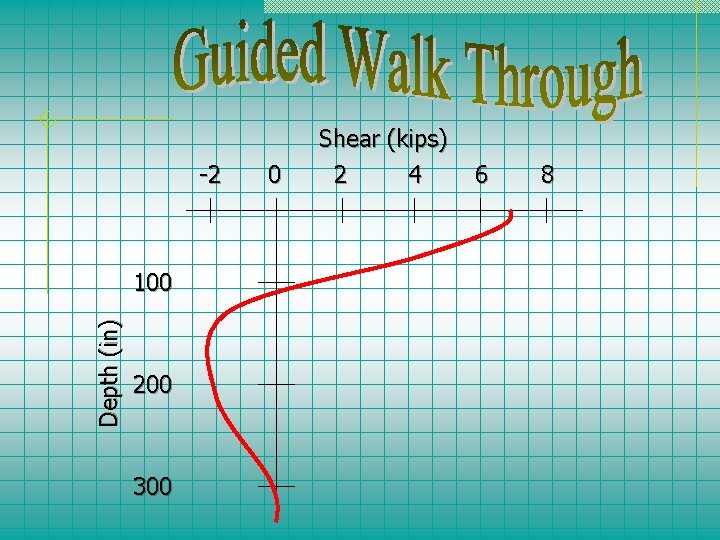
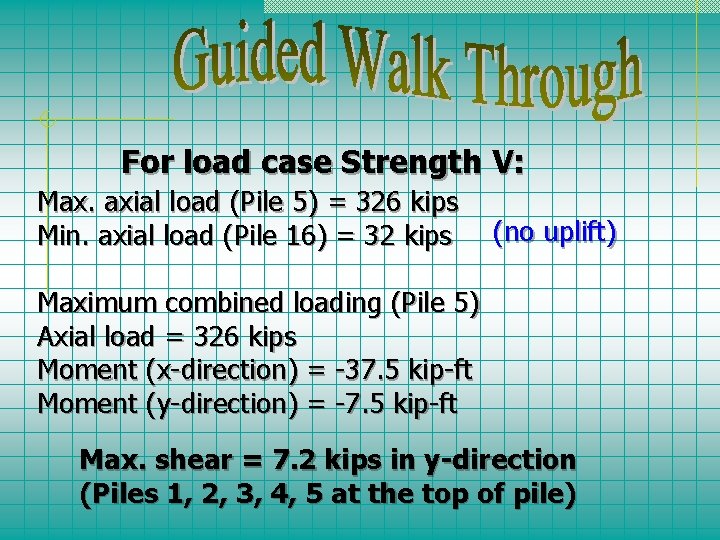
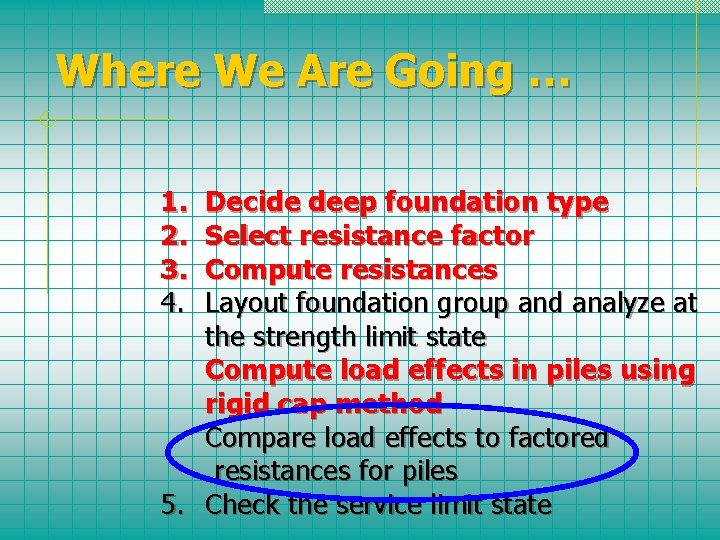
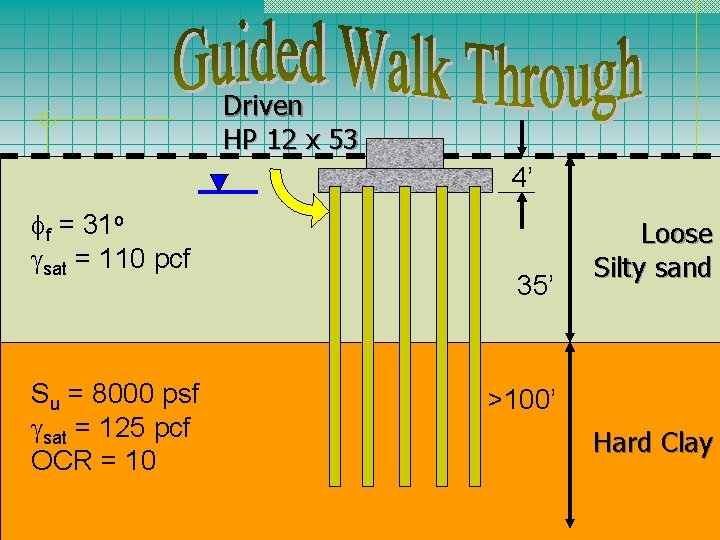
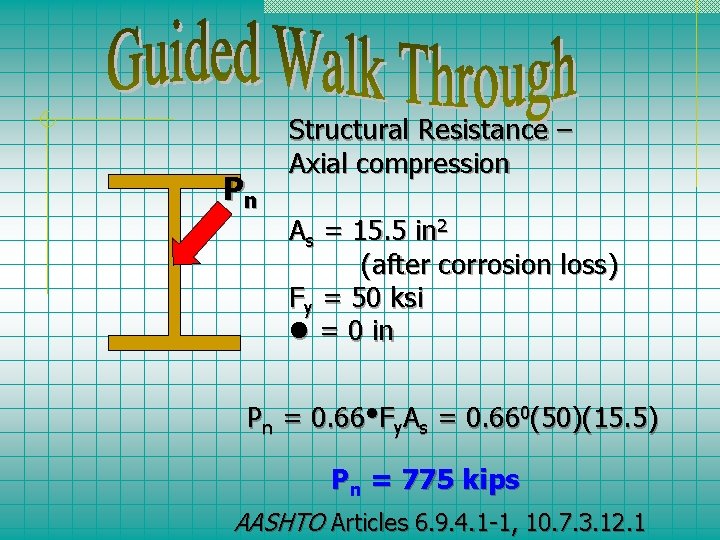
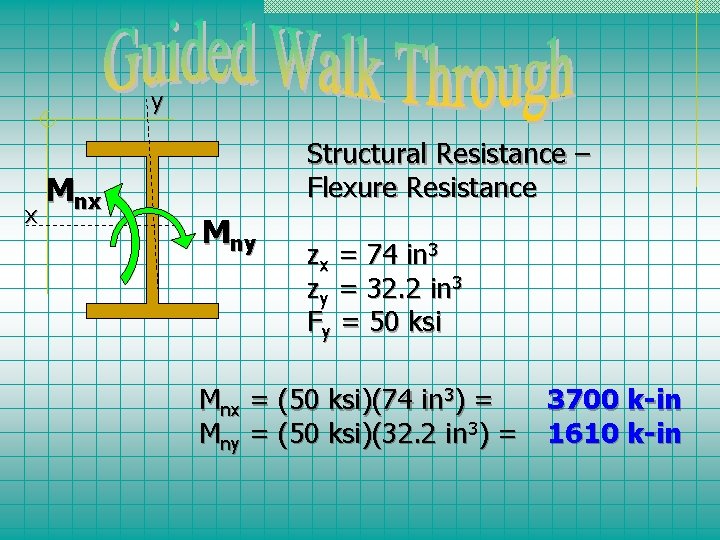
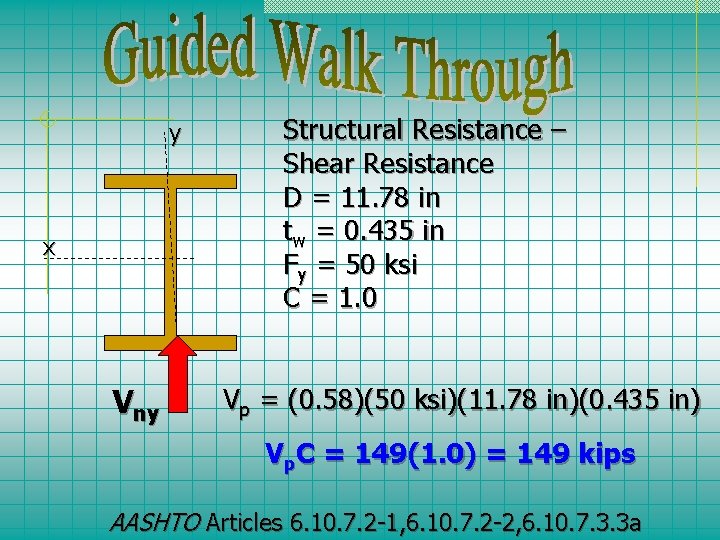
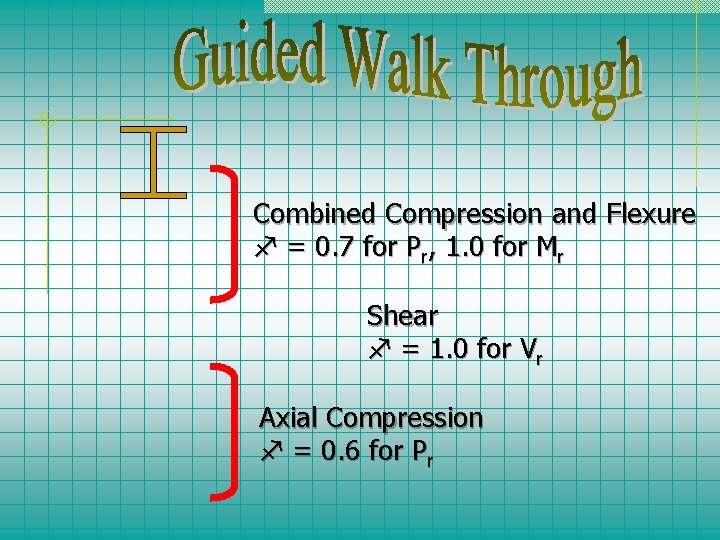
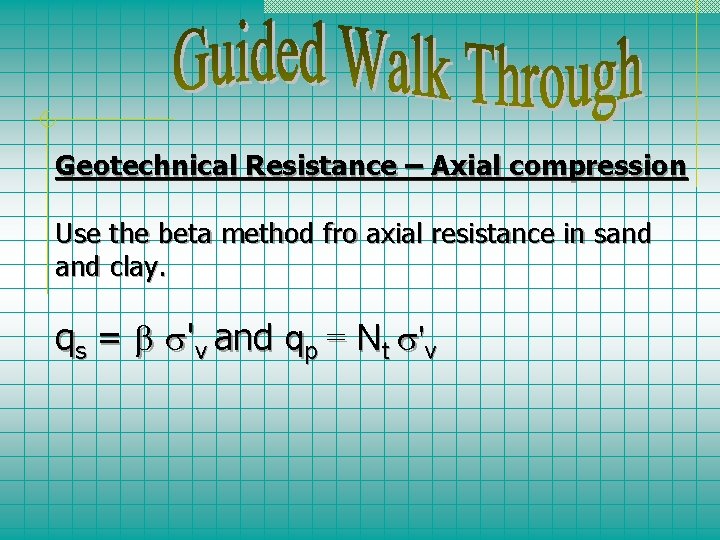
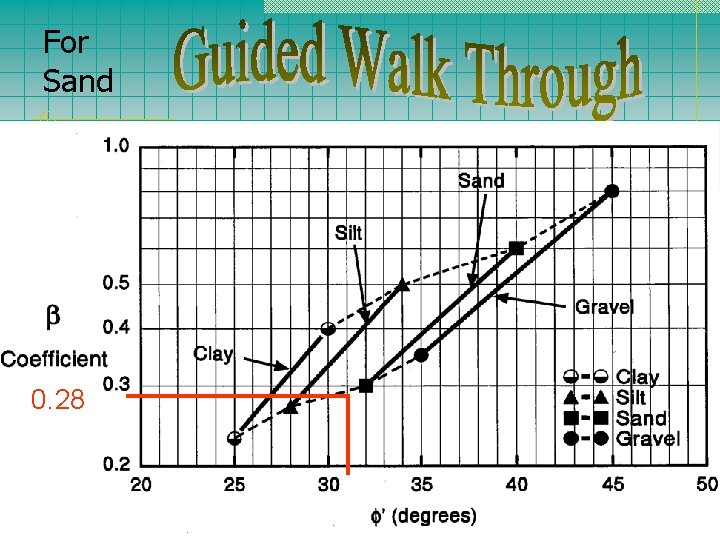
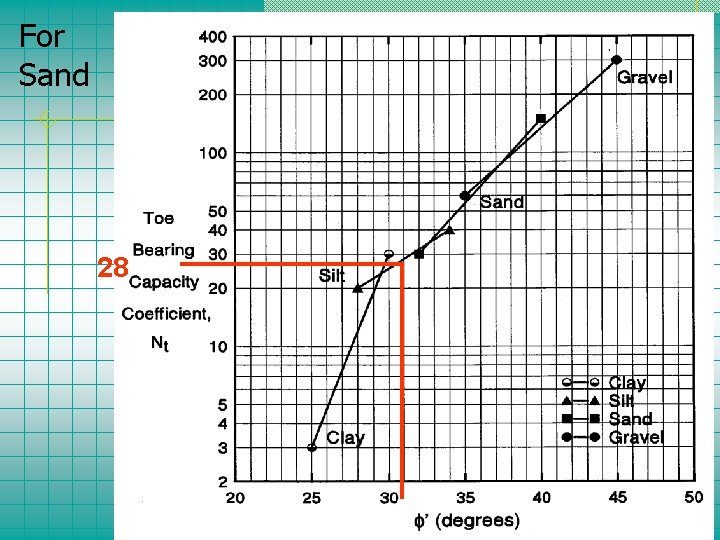
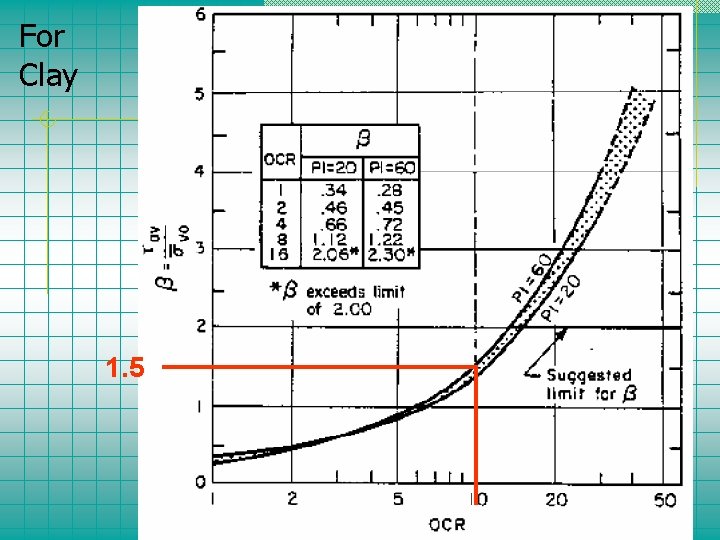
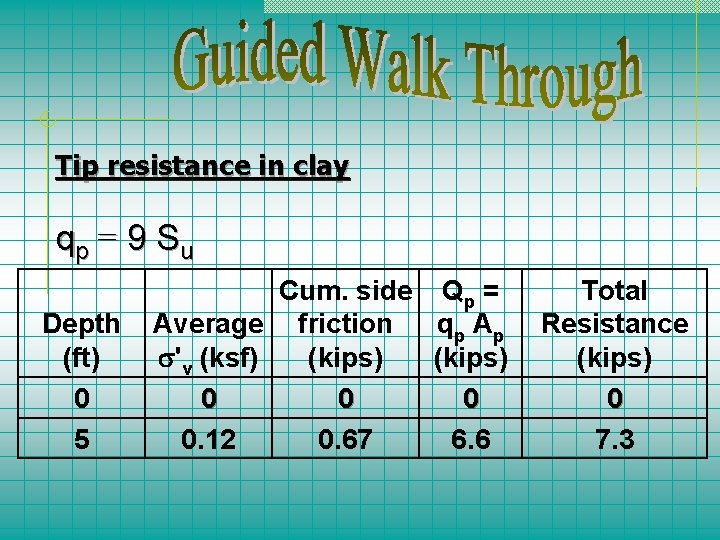
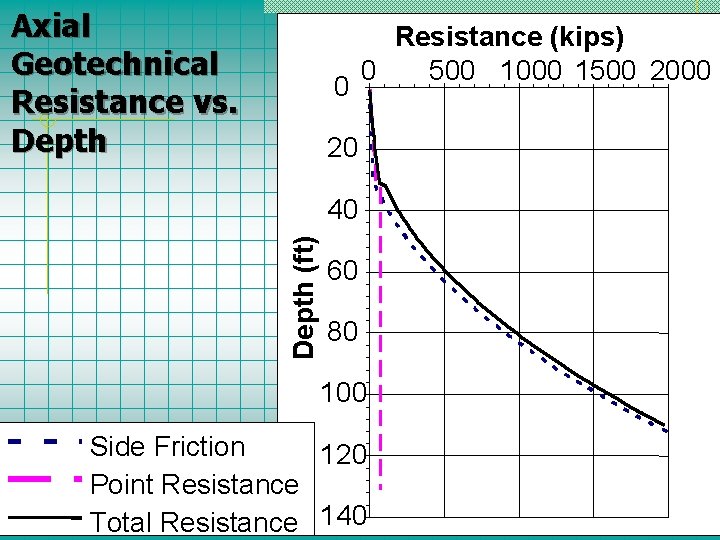
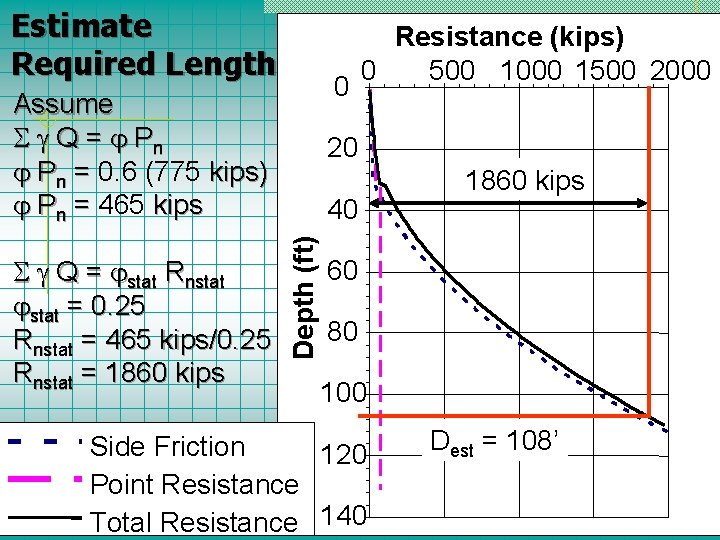
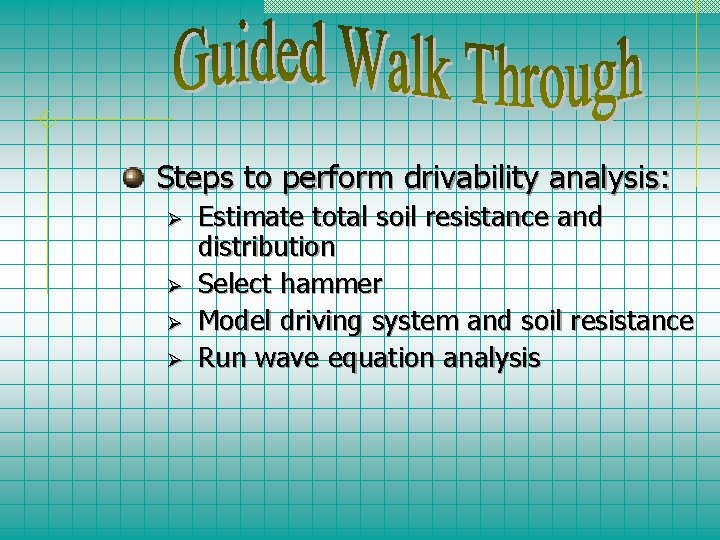
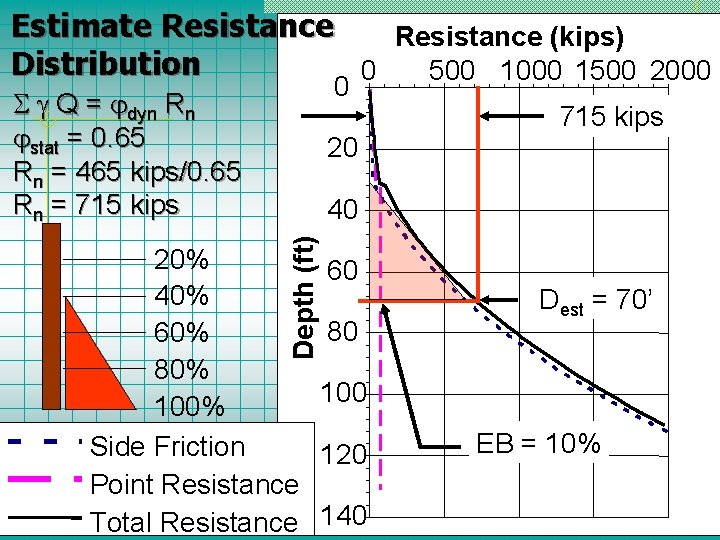
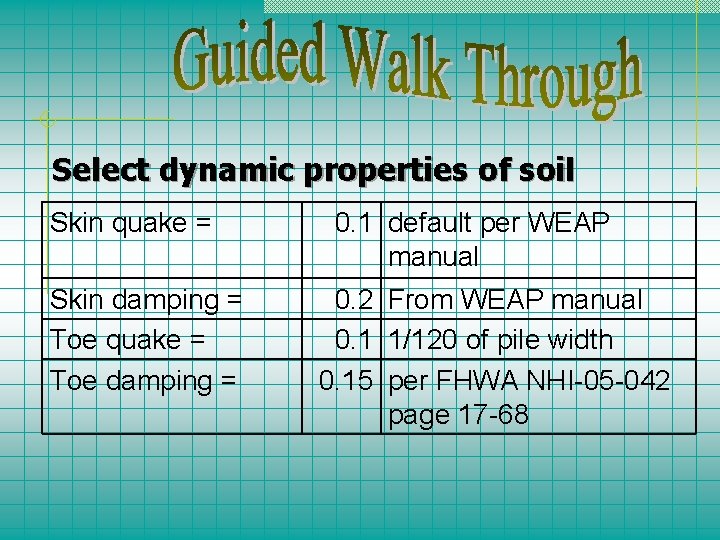
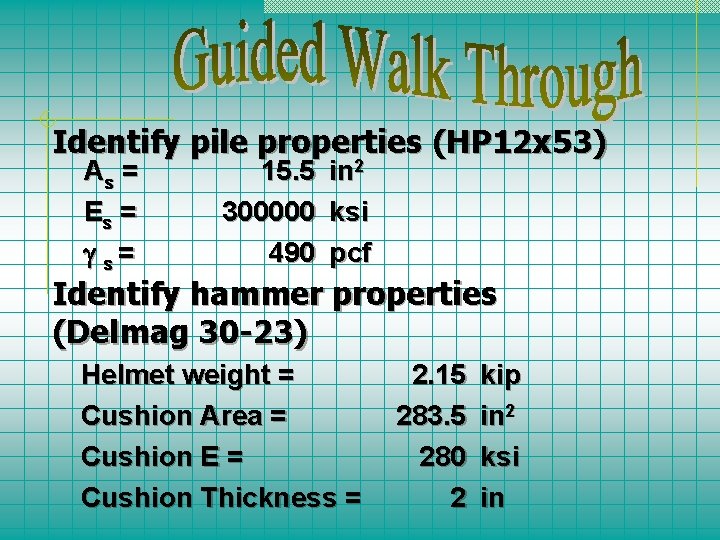
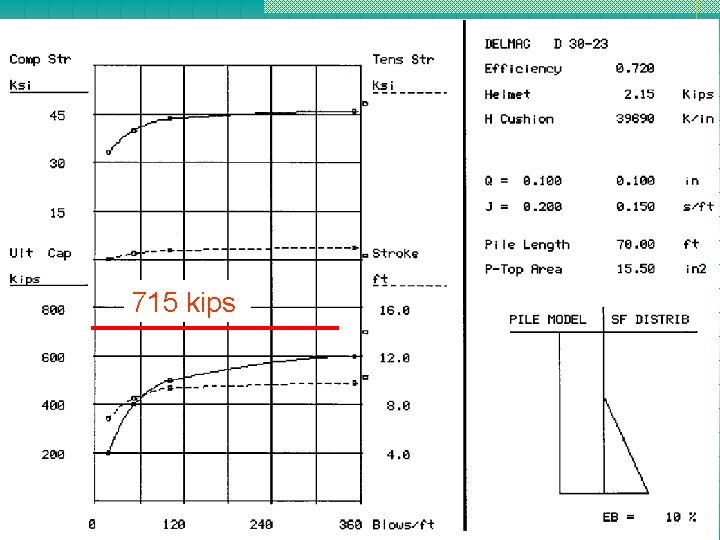
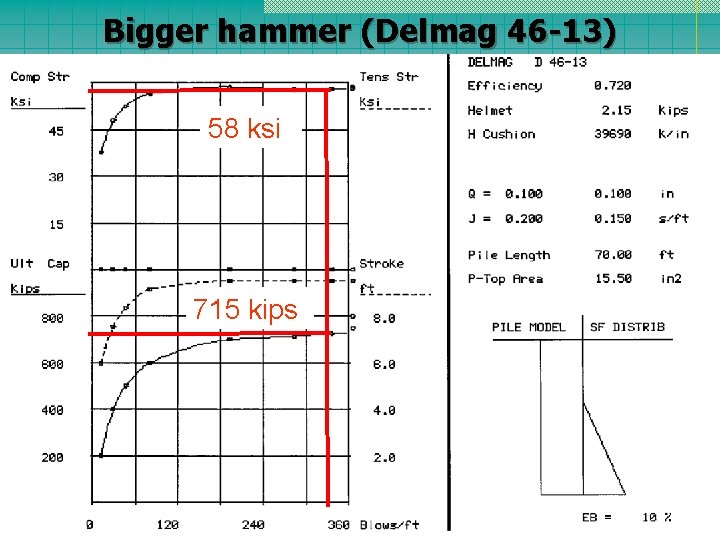
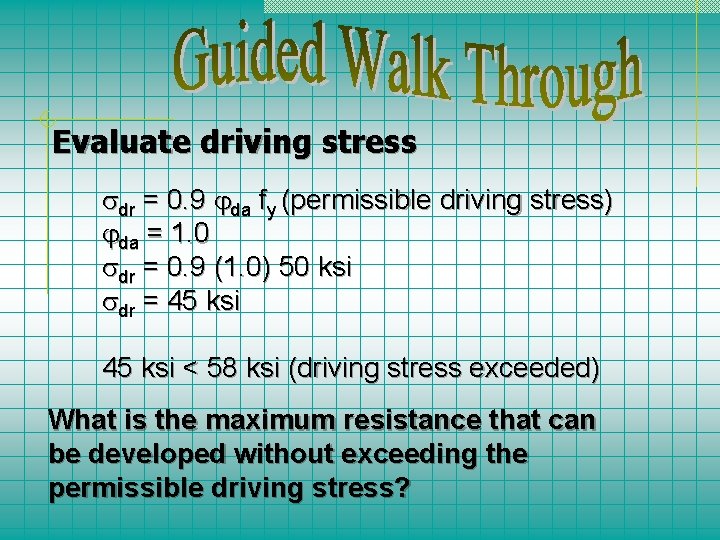
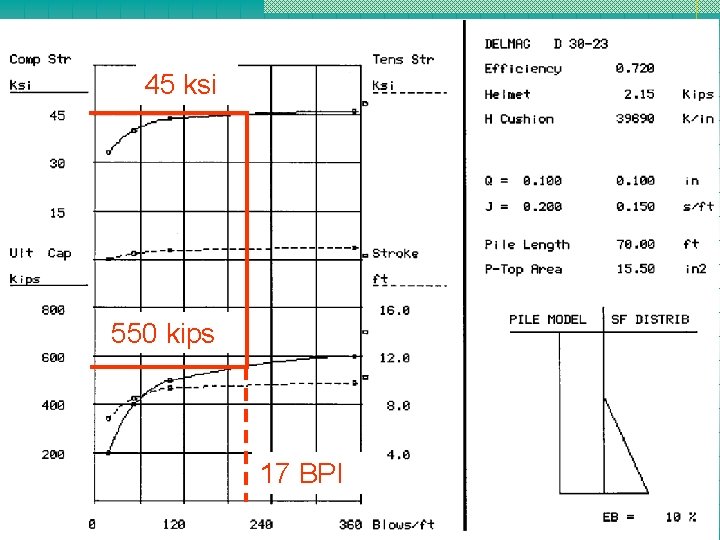
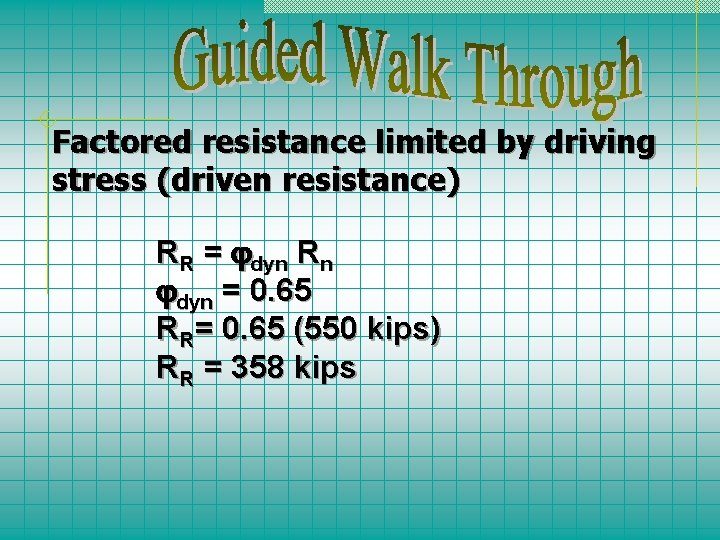
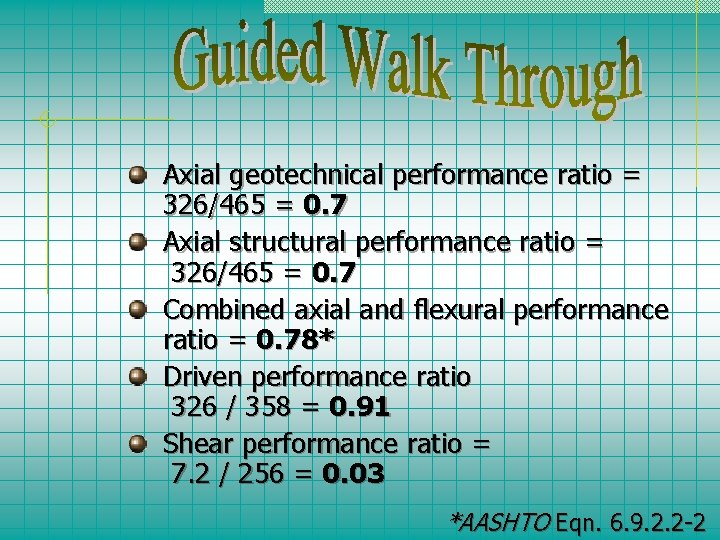
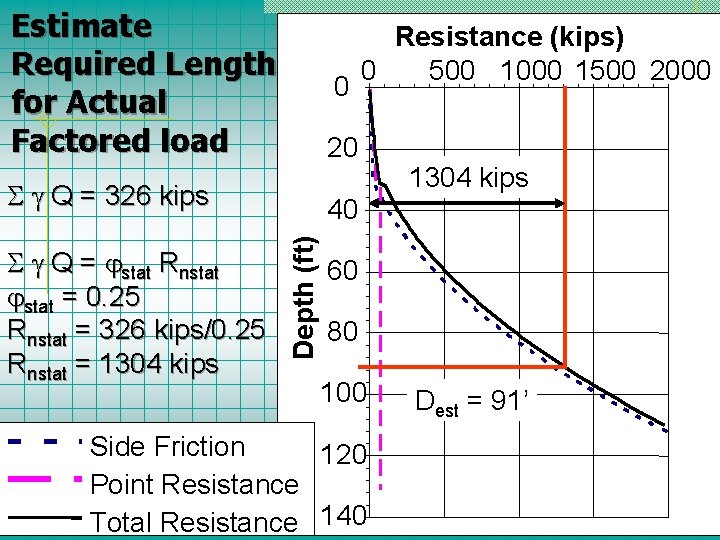
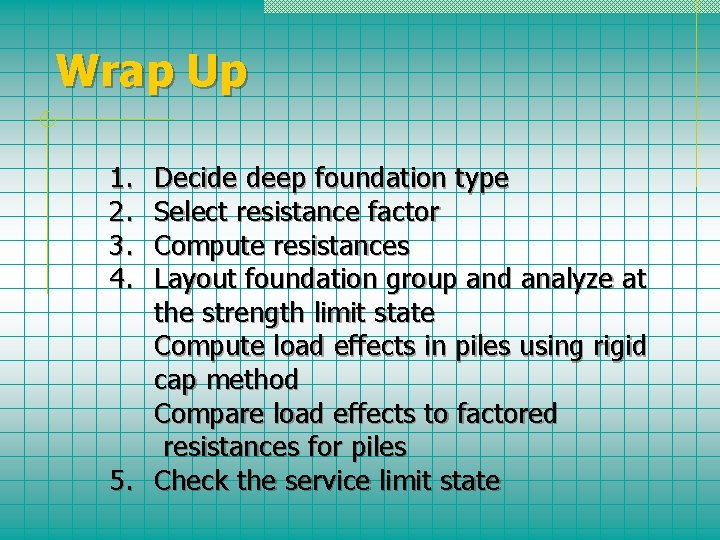
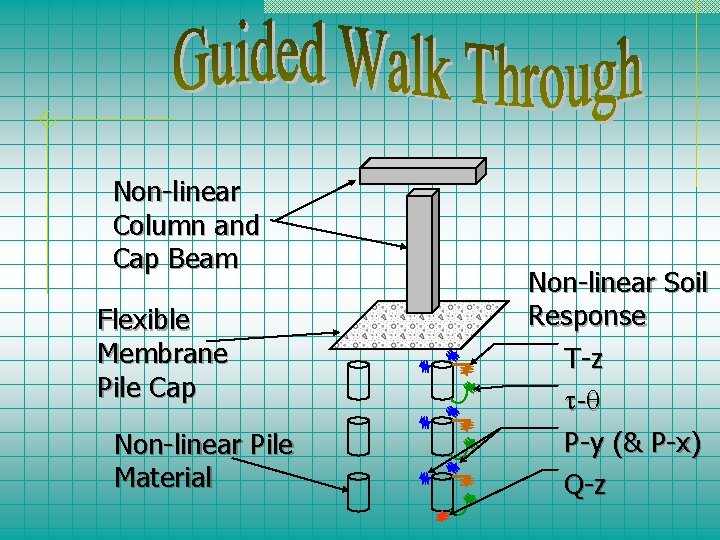
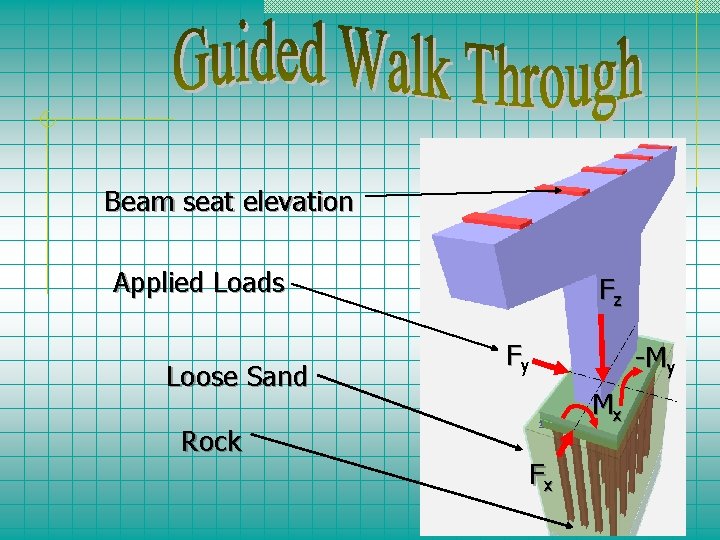

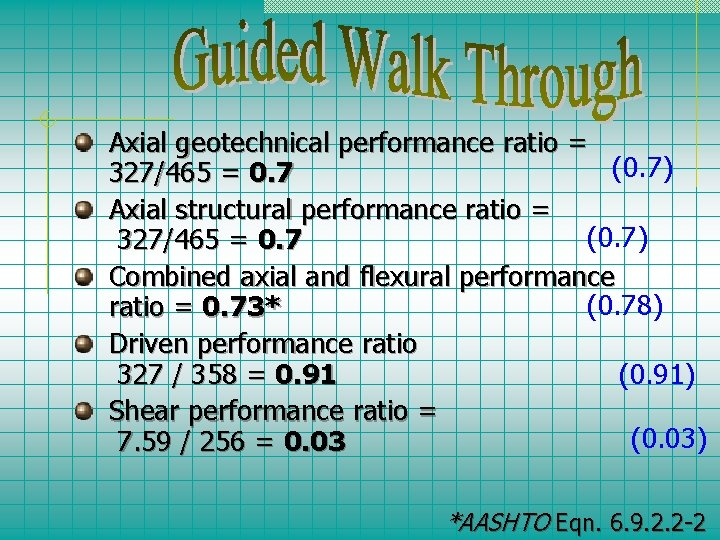
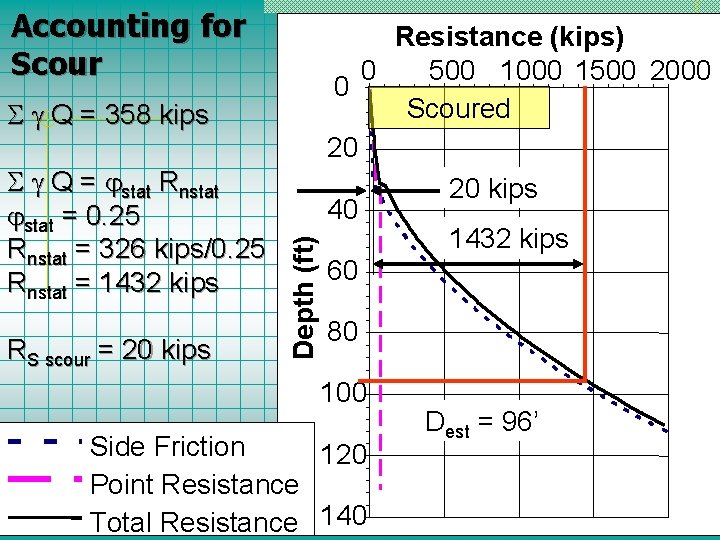
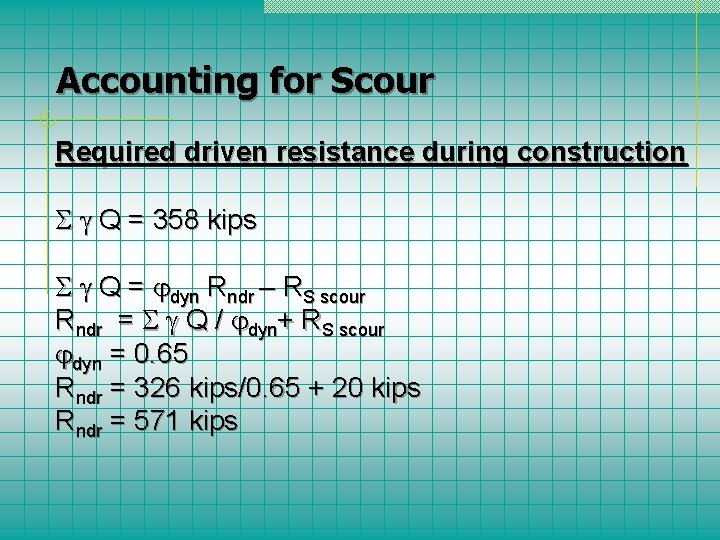
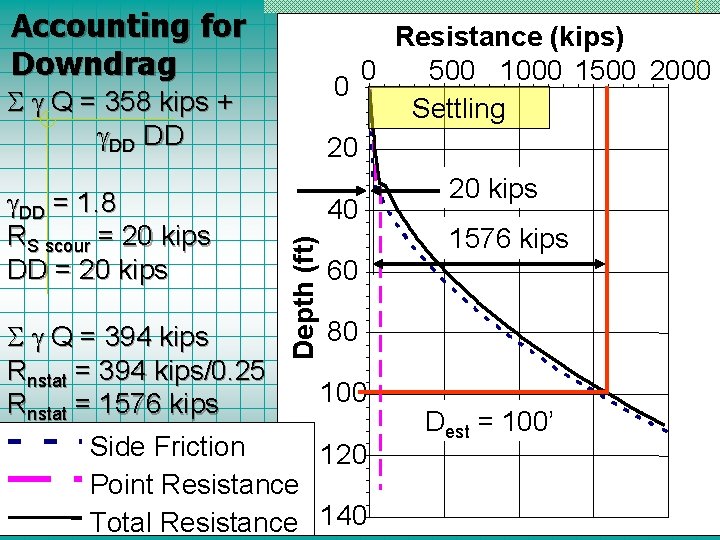
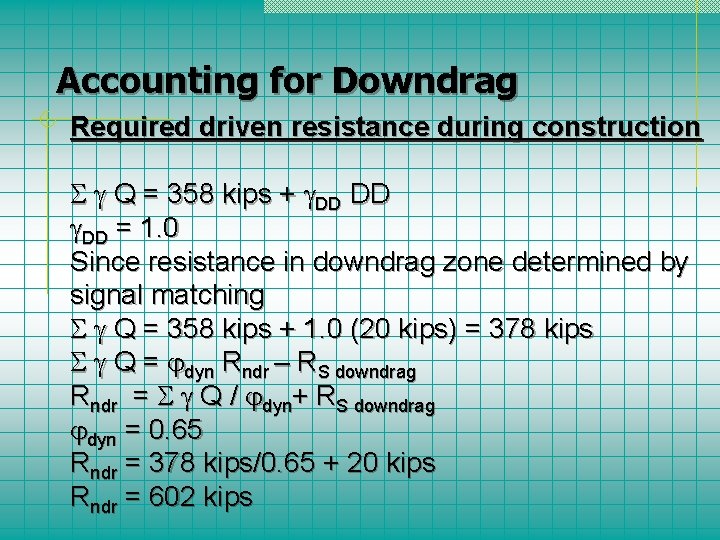
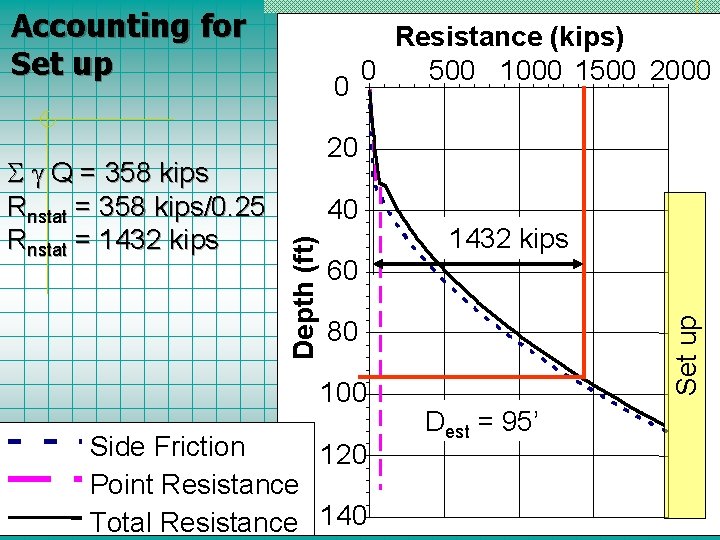
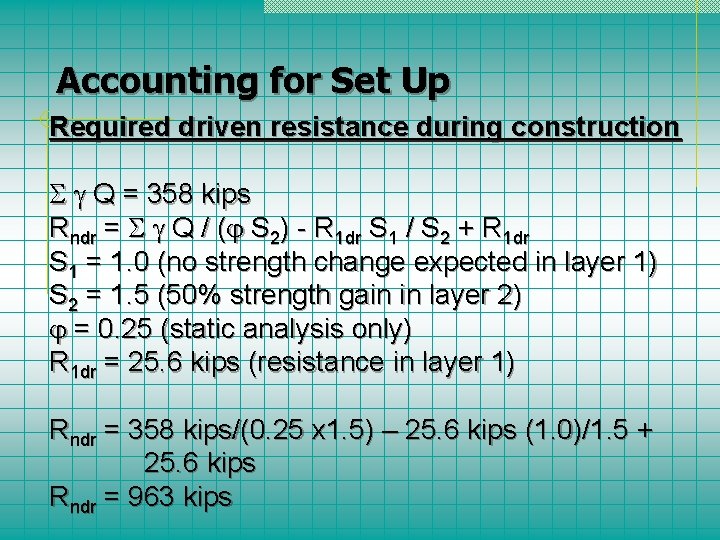
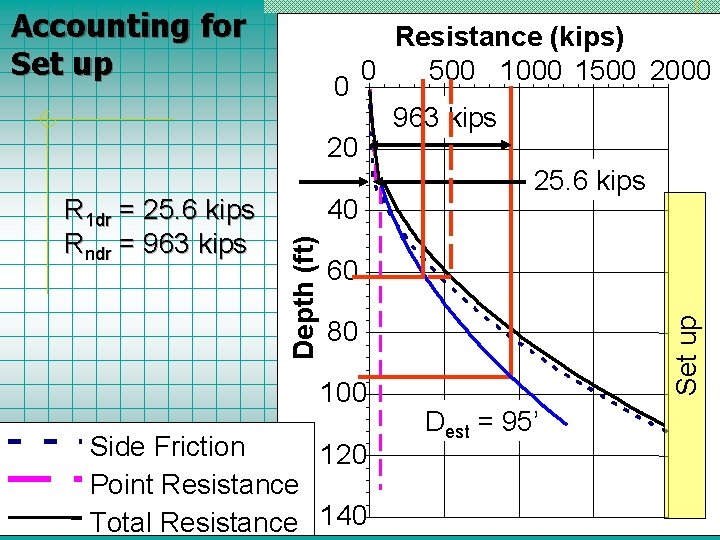
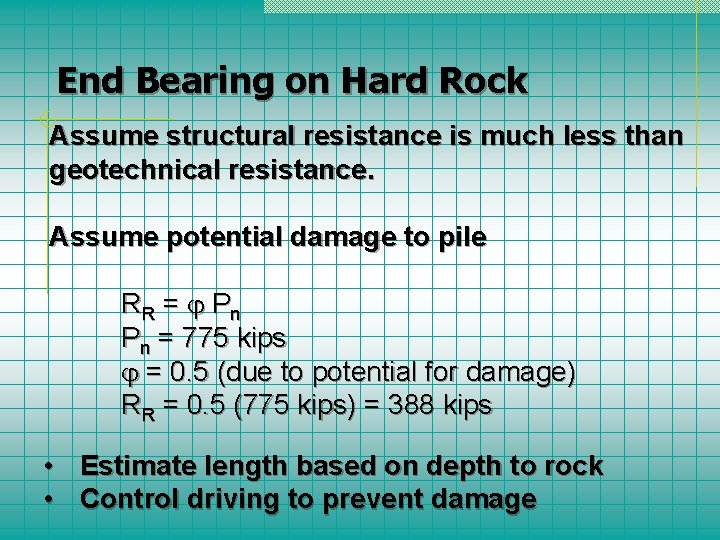
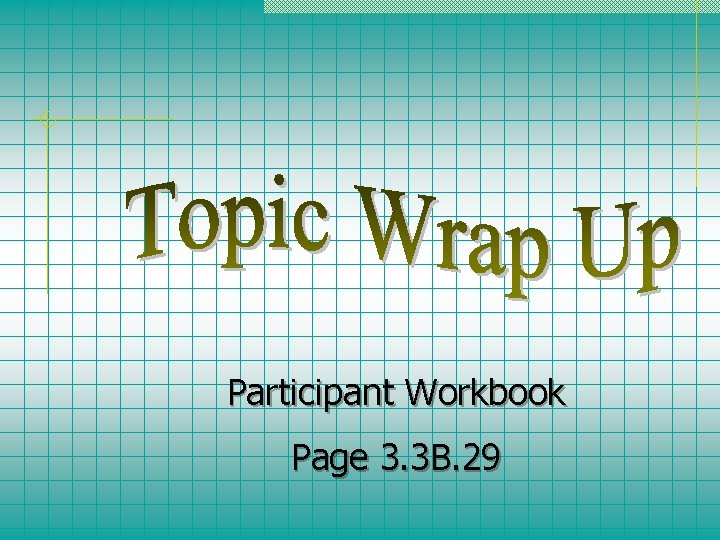
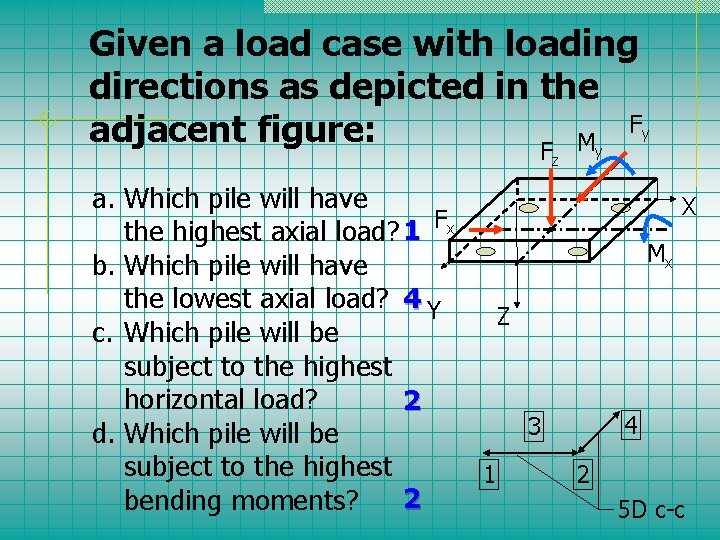
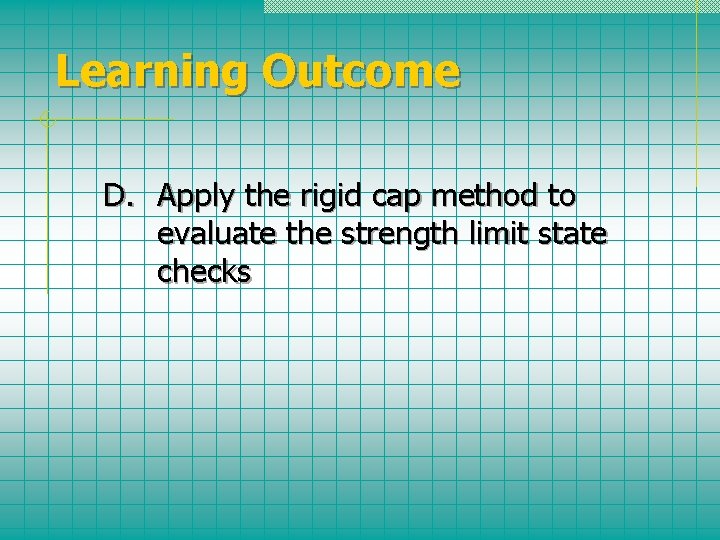
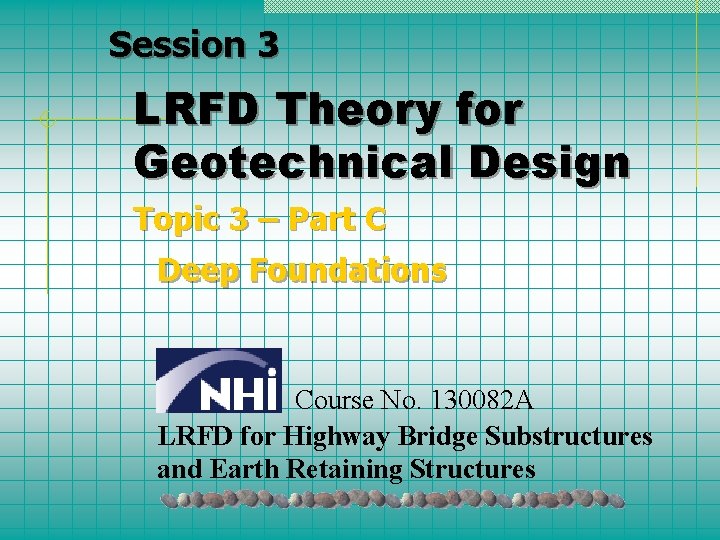
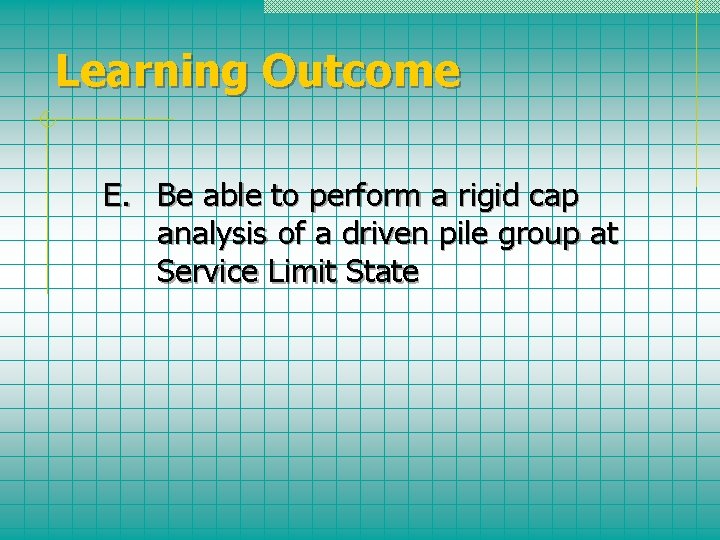
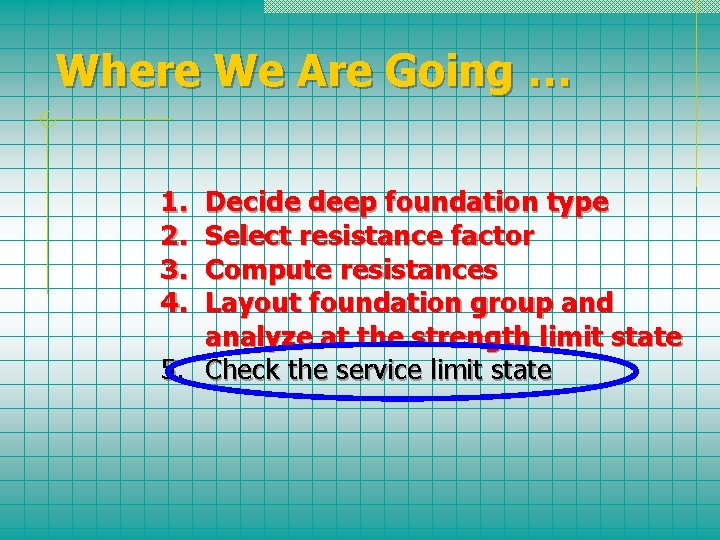
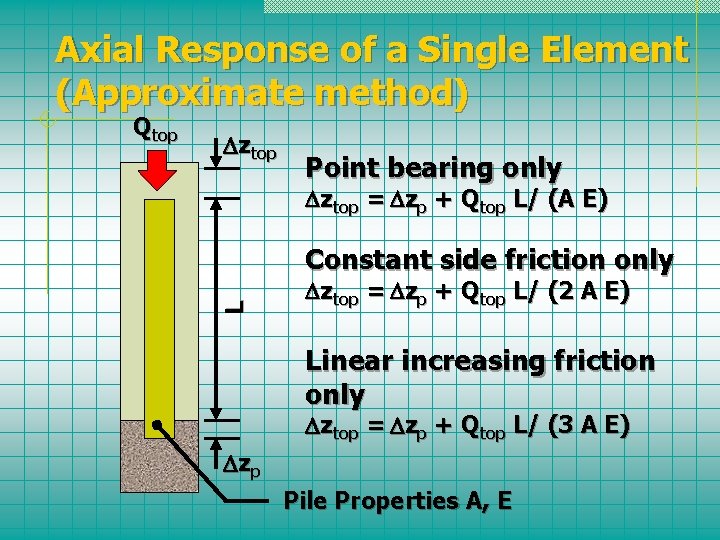
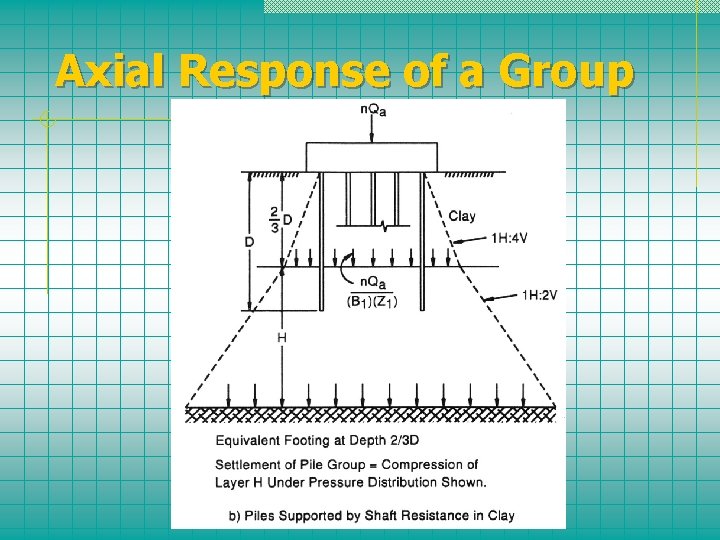
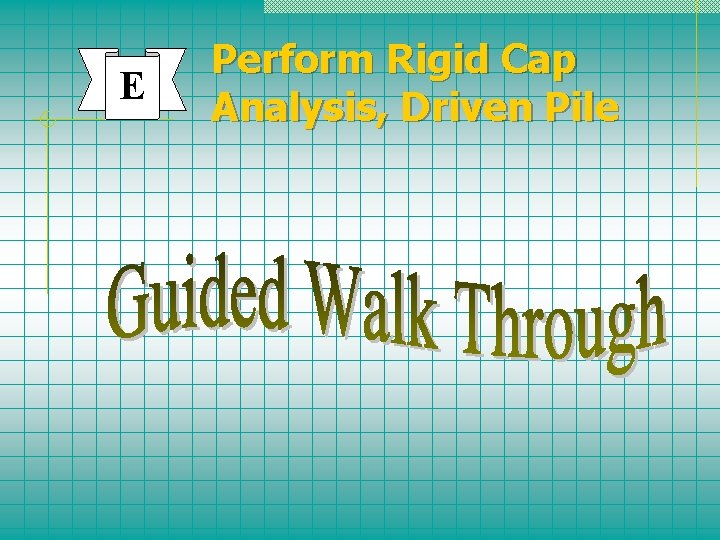
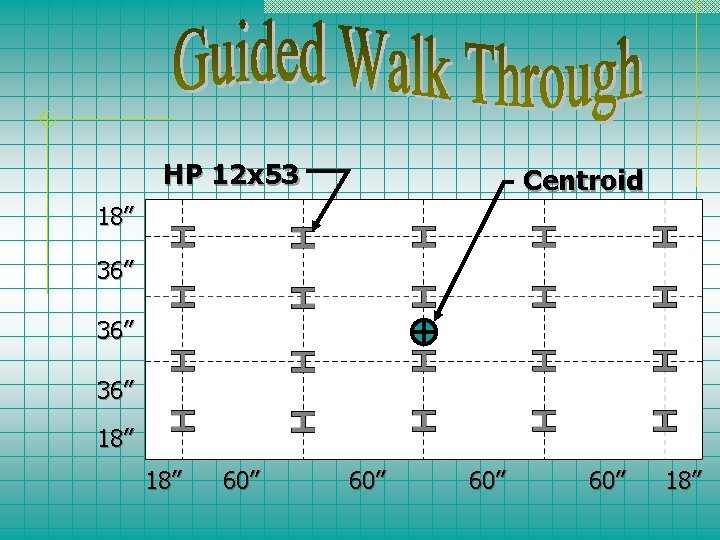
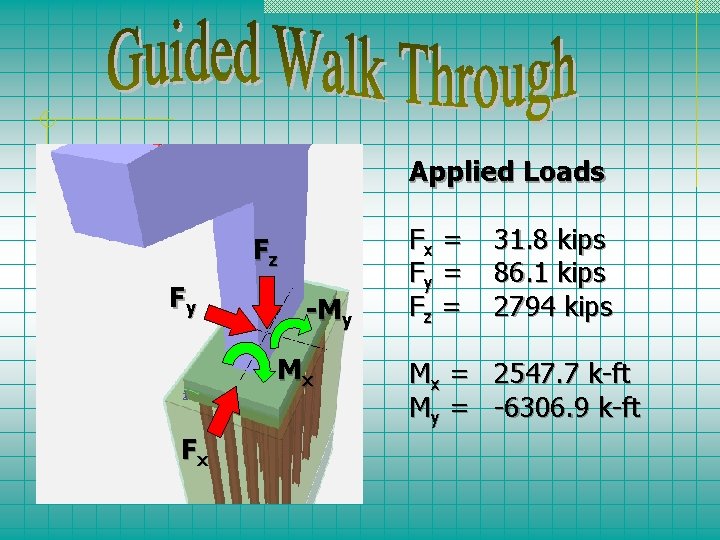
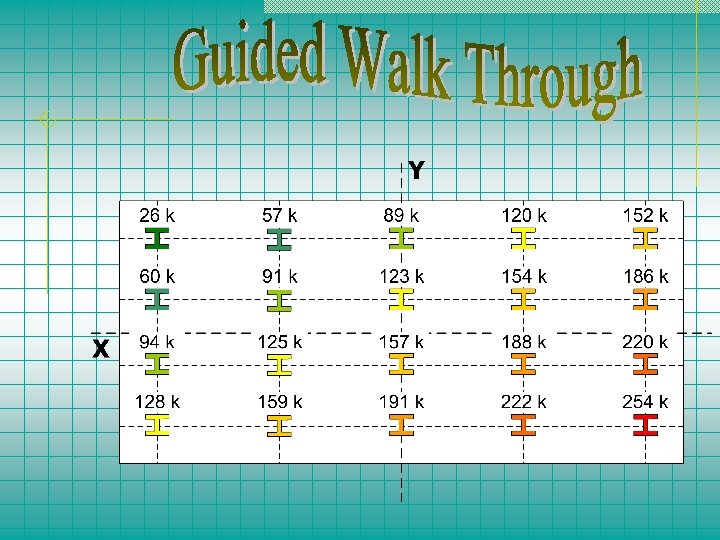
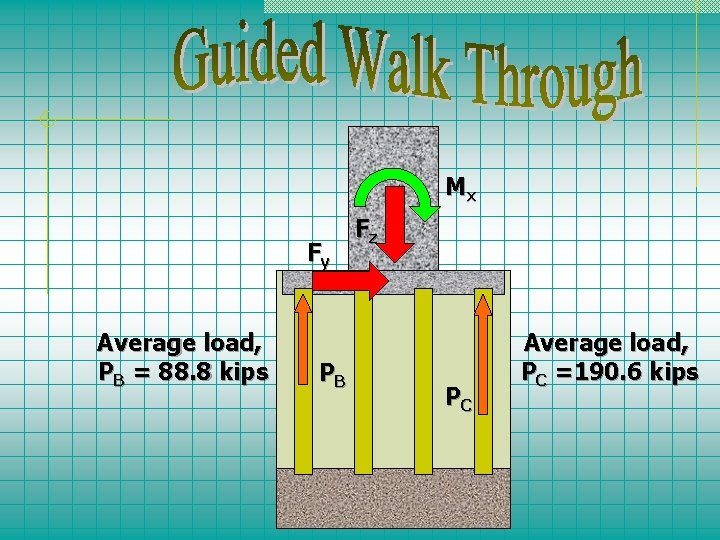
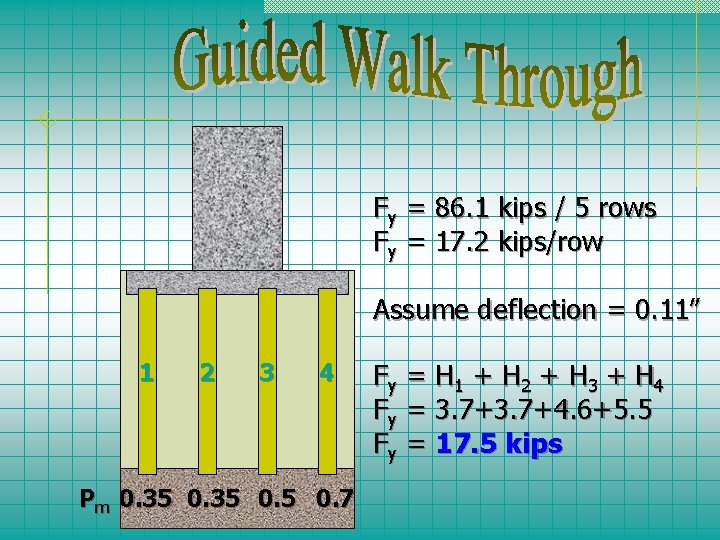
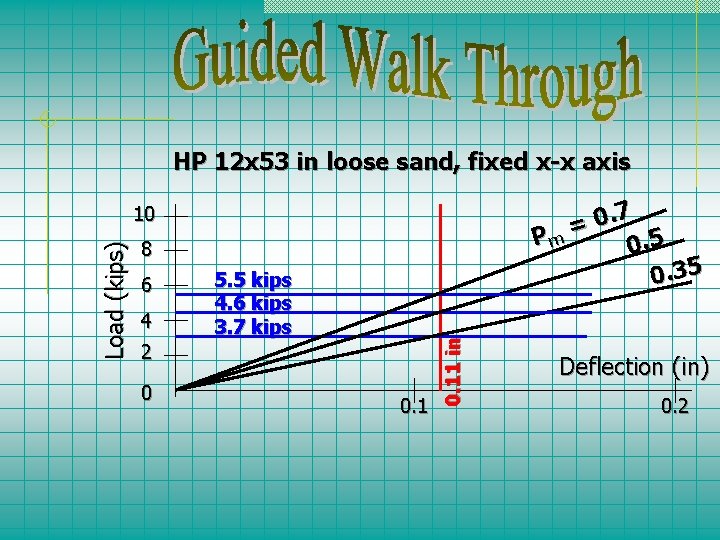
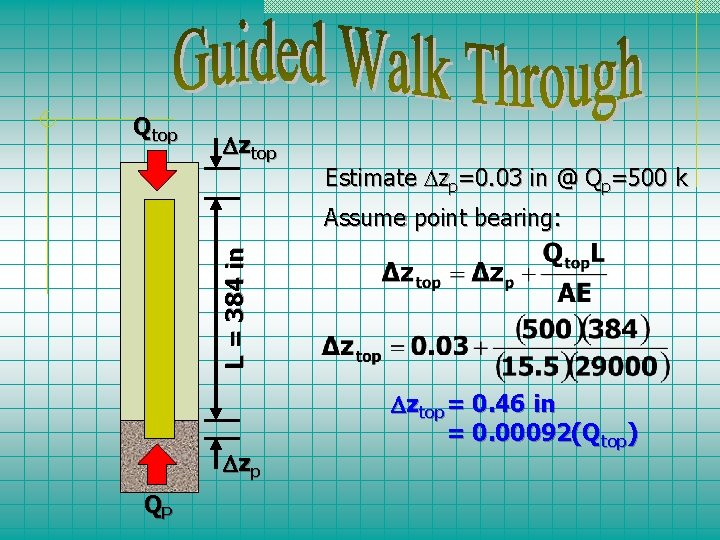
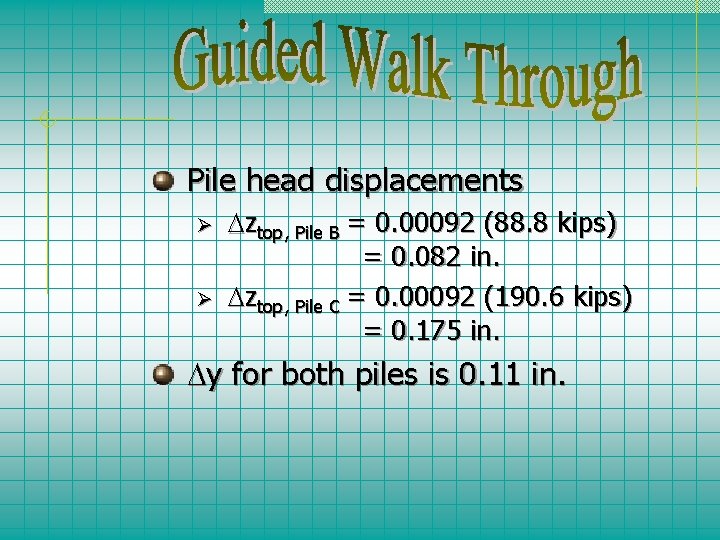

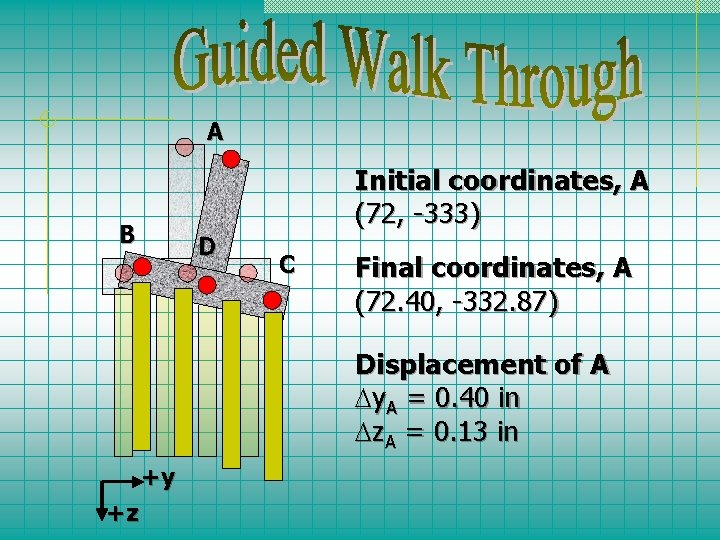
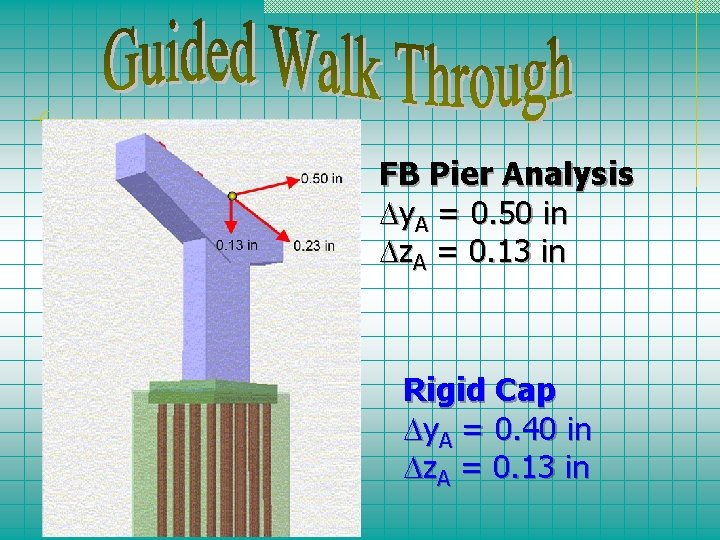
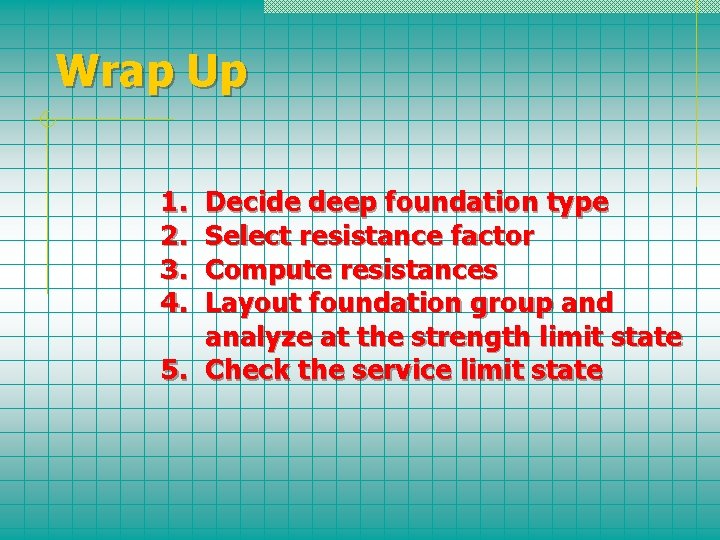
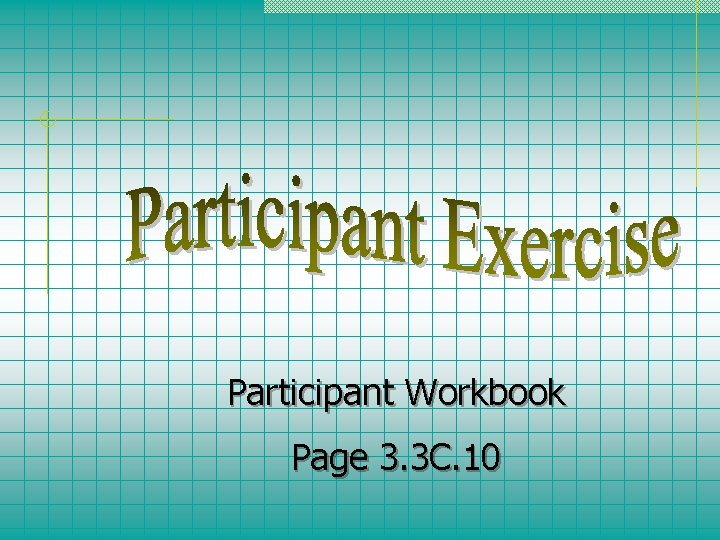
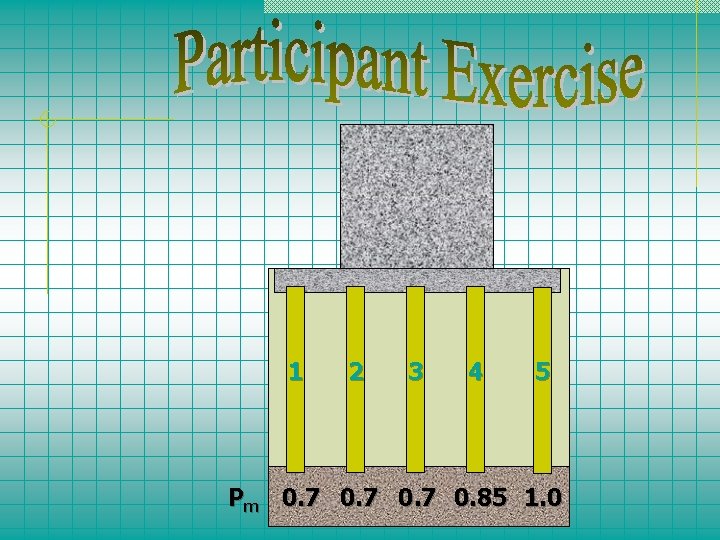
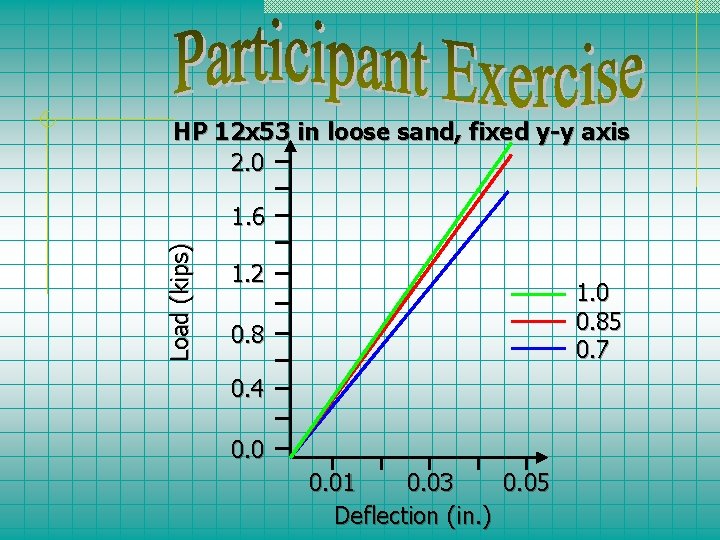
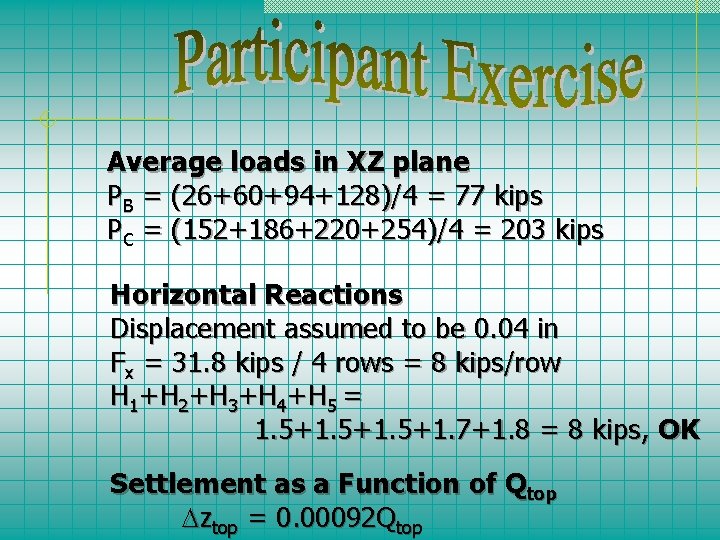
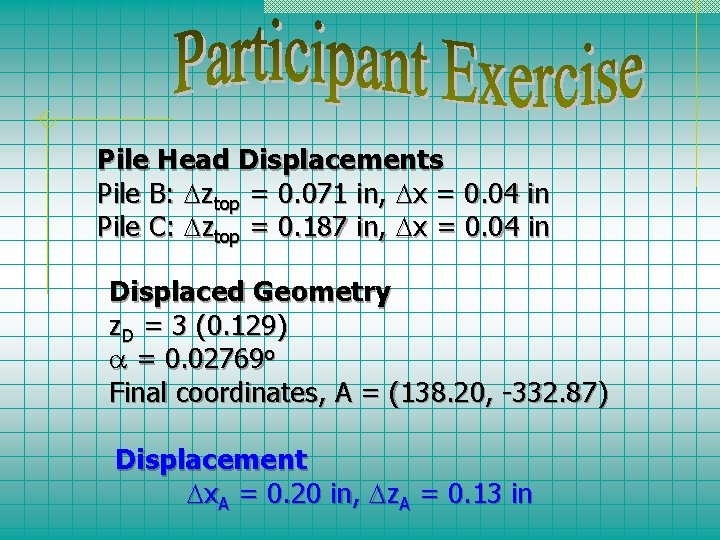
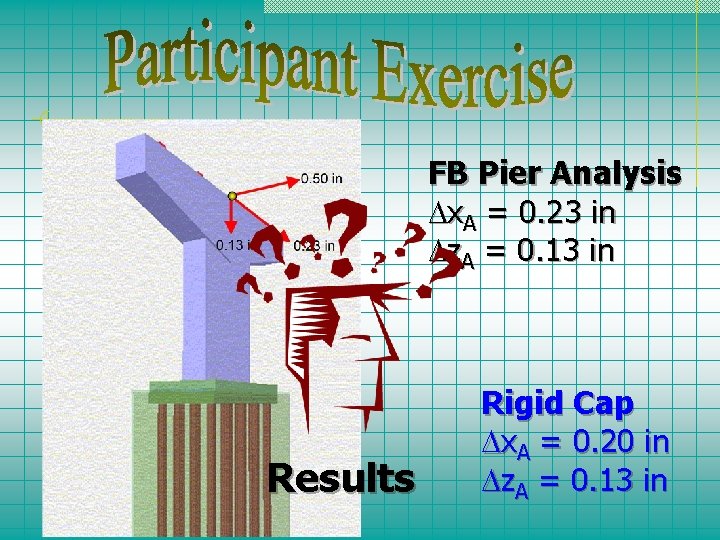
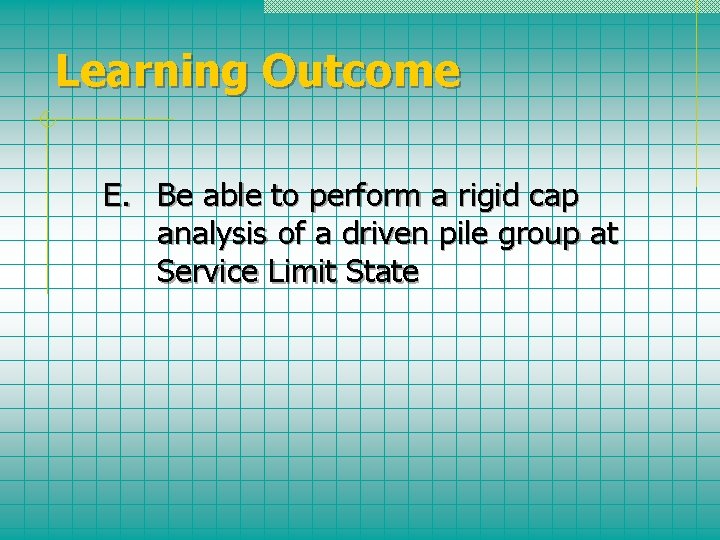
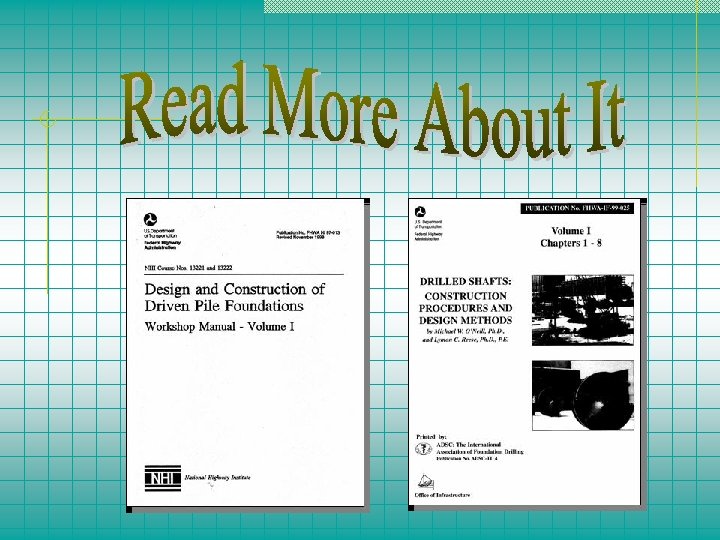
- Slides: 172
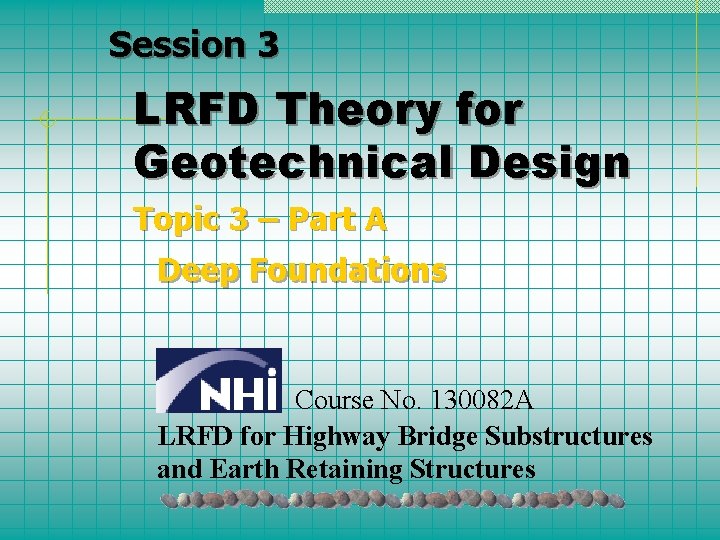
Session 3 LRFD Theory for Geotechnical Design Topic 3 – Part A Deep Foundations Course No. 130082 A LRFD for Highway Bridge Substructures and Earth Retaining Structures
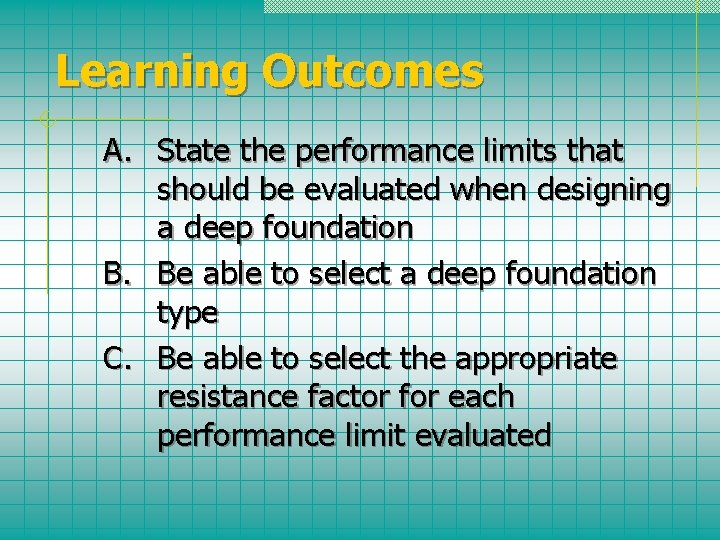
Learning Outcomes A. State the performance limits that should be evaluated when designing a deep foundation B. Be able to select a deep foundation type C. Be able to select the appropriate resistance factor for each performance limit evaluated
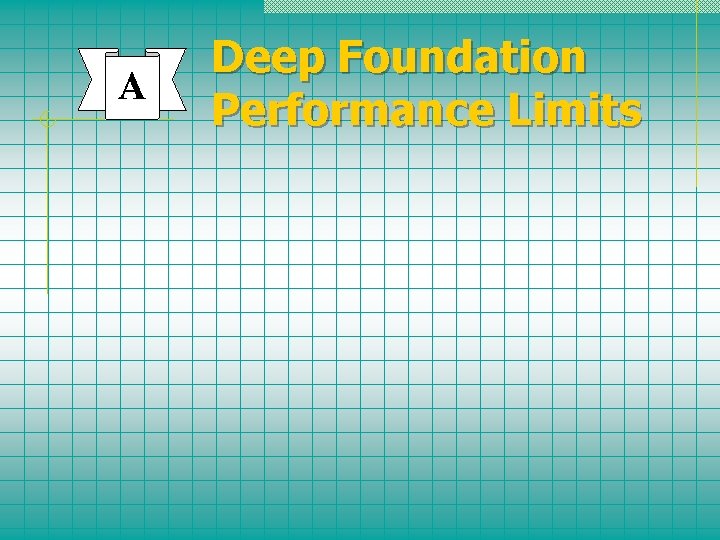
A Deep Foundation Performance Limits
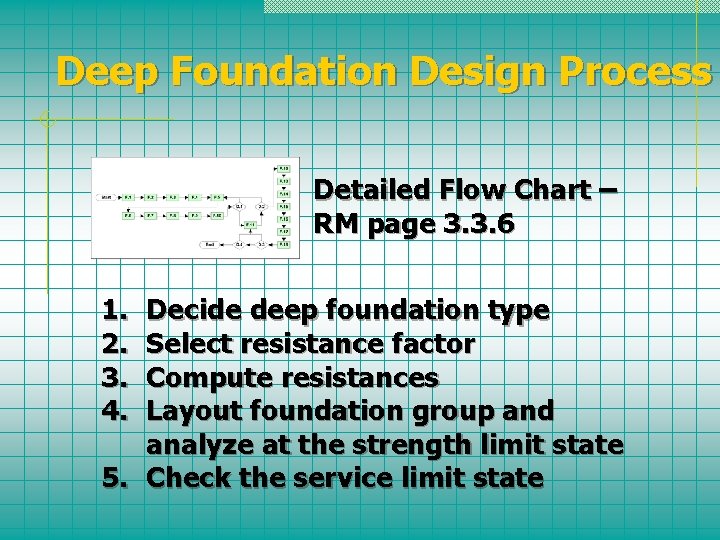
Deep Foundation Design Process Detailed Flow Chart – RM page 3. 3. 6 1. 2. 3. 4. Decide deep foundation type Select resistance factor Compute resistances Layout foundation group and analyze at the strength limit state 5. Check the service limit state
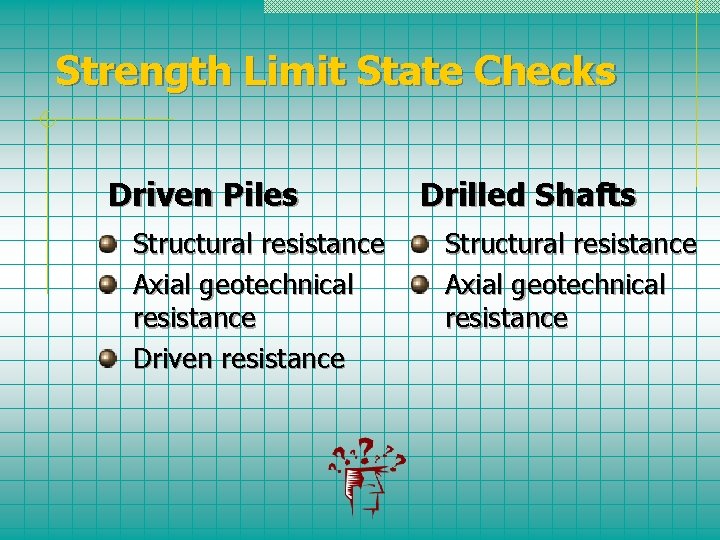
Strength Limit State Checks Driven Piles Structural resistance Axial geotechnical resistance Driven resistance Drilled Shafts Structural resistance Axial geotechnical resistance
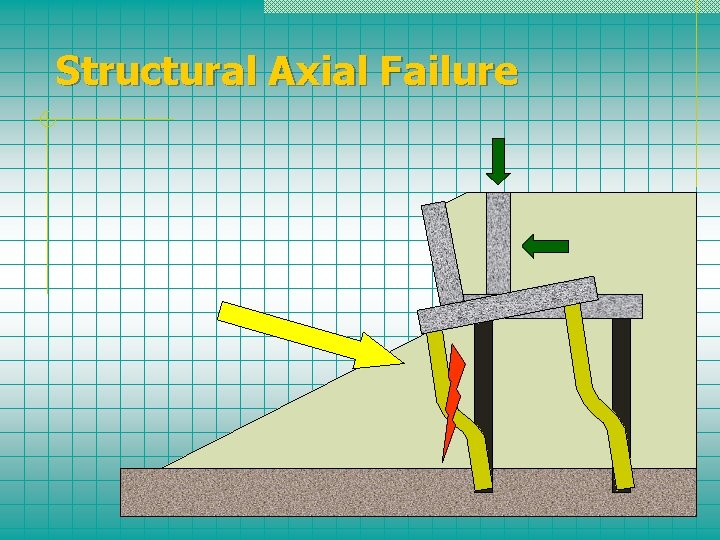
Structural Axial Failure
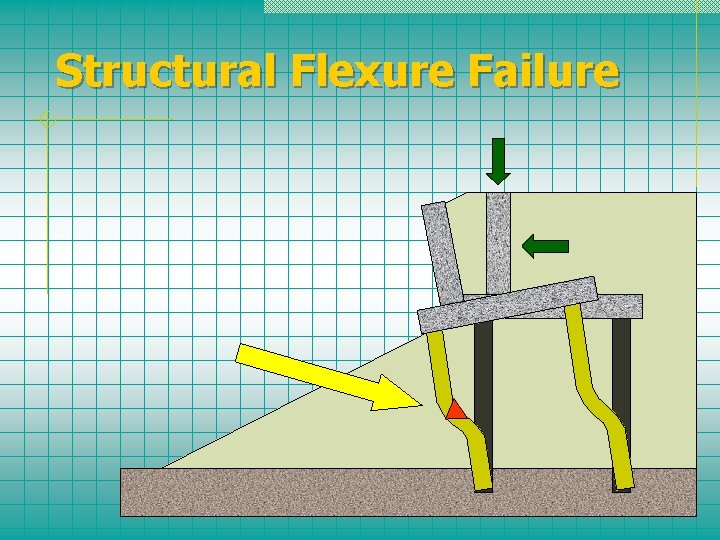
Structural Flexure Failure
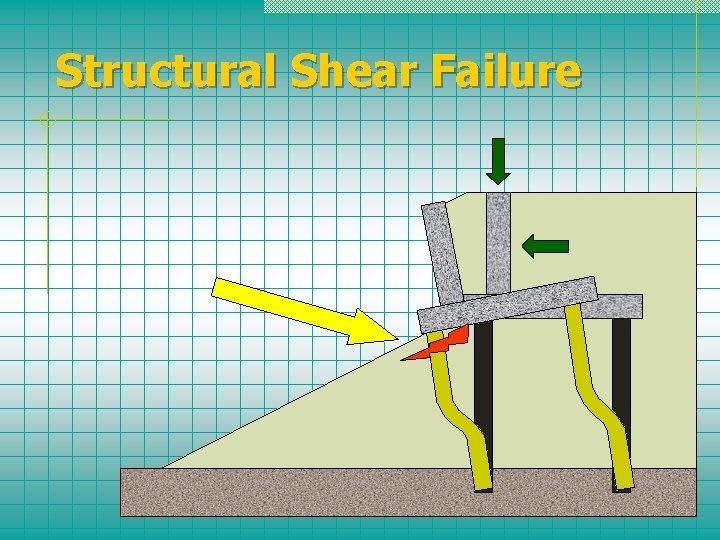
Structural Shear Failure
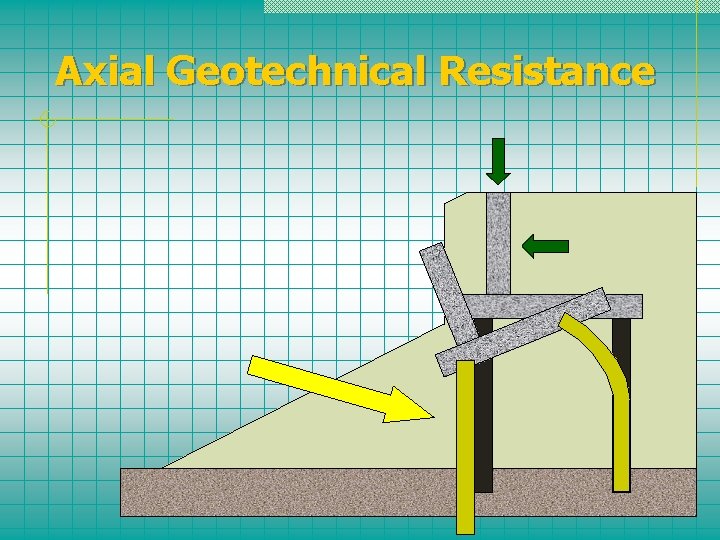
Axial Geotechnical Resistance
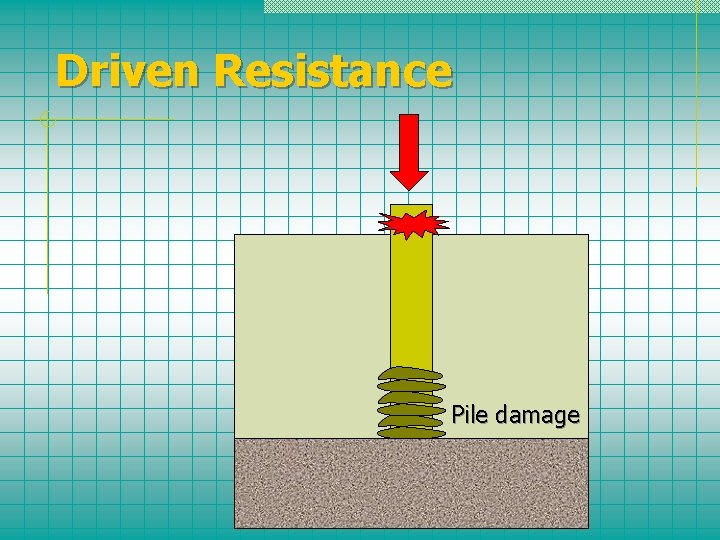
Driven Resistance Pile damage
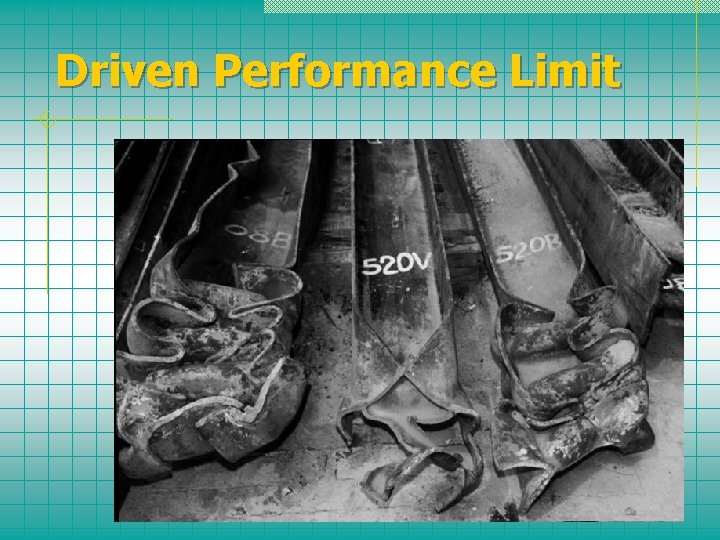
Driven Performance Limit
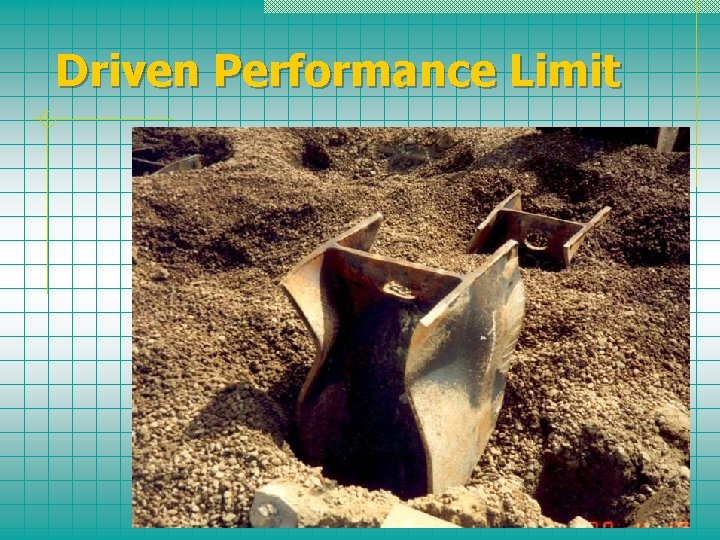
Driven Performance Limit
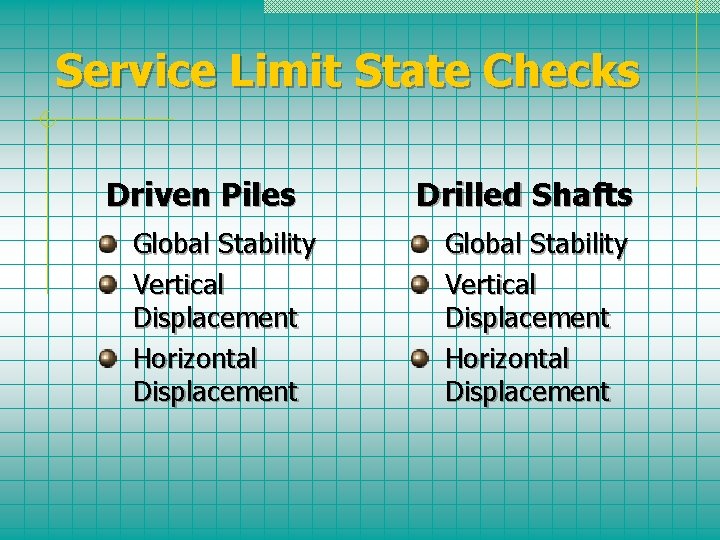
Service Limit State Checks Driven Piles Global Stability Vertical Displacement Horizontal Displacement Drilled Shafts Global Stability Vertical Displacement Horizontal Displacement
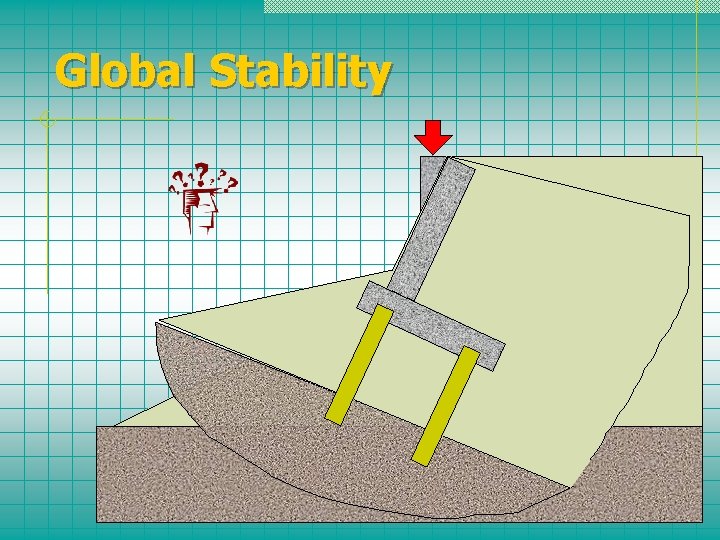
Global Stability
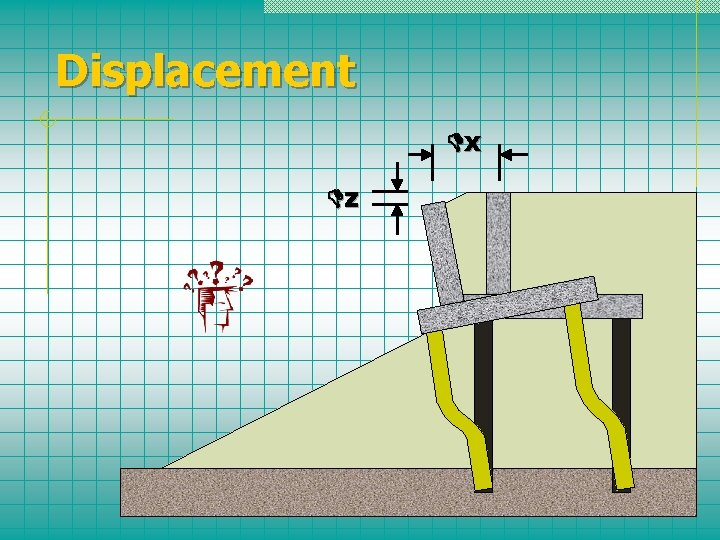
Displacement Dx Dz
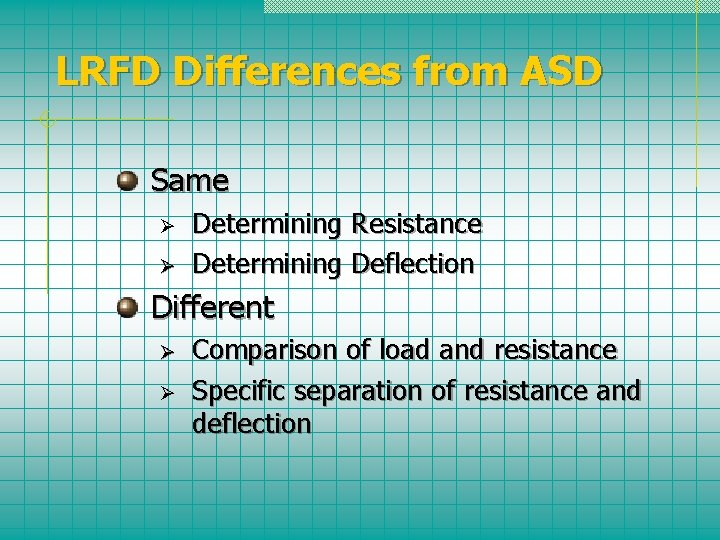
LRFD Differences from ASD Same Ø Ø Determining Resistance Determining Deflection Different Ø Ø Comparison of load and resistance Specific separation of resistance and deflection
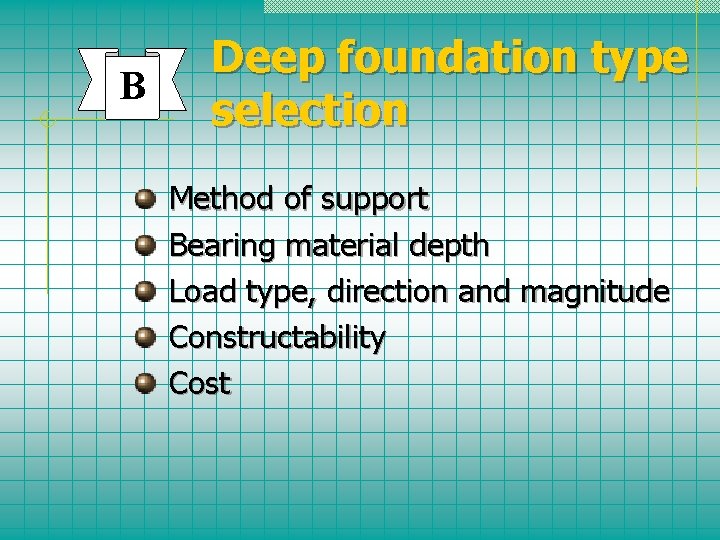
B Deep foundation type selection Method of support Bearing material depth Load type, direction and magnitude Constructability Cost
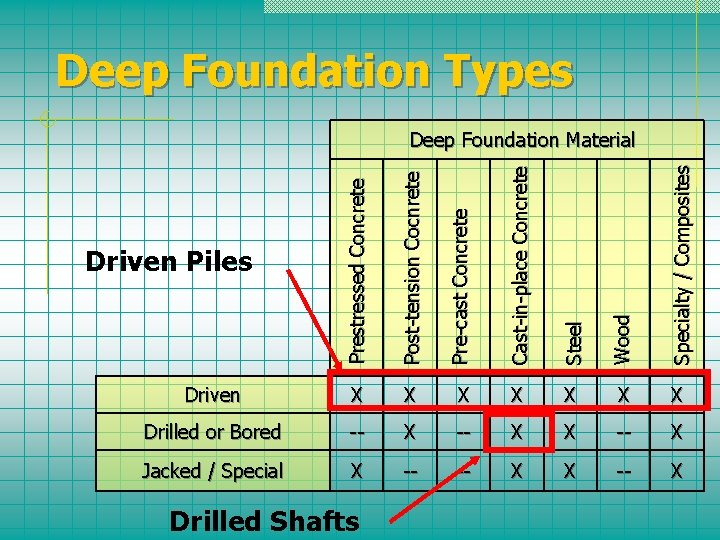
Deep Foundation Types Prestressed Concrete Post-tension Cocnrete Pre-cast Concrete Cast-in-place Concrete Steel Wood Specialty / Composites Deep Foundation Material Driven X X X X Drilled or Bored -- X X -- X Jacked / Special X -- -- X X -- X Driven Piles Drilled Shafts
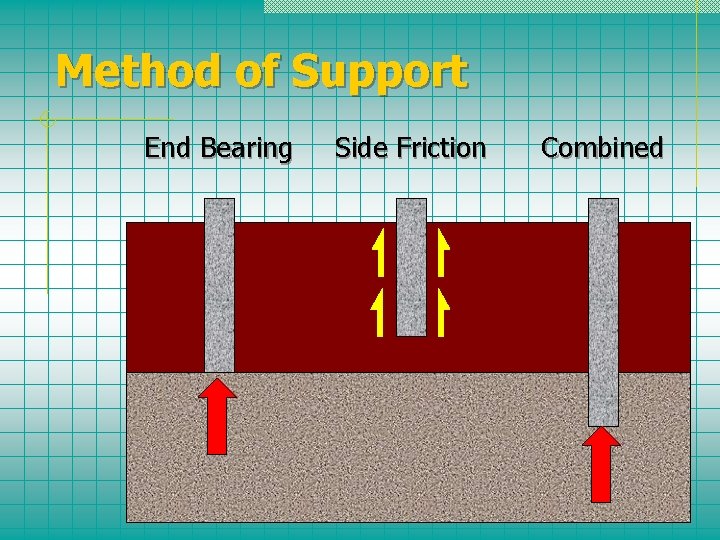
Method of Support End Bearing Side Friction Combined
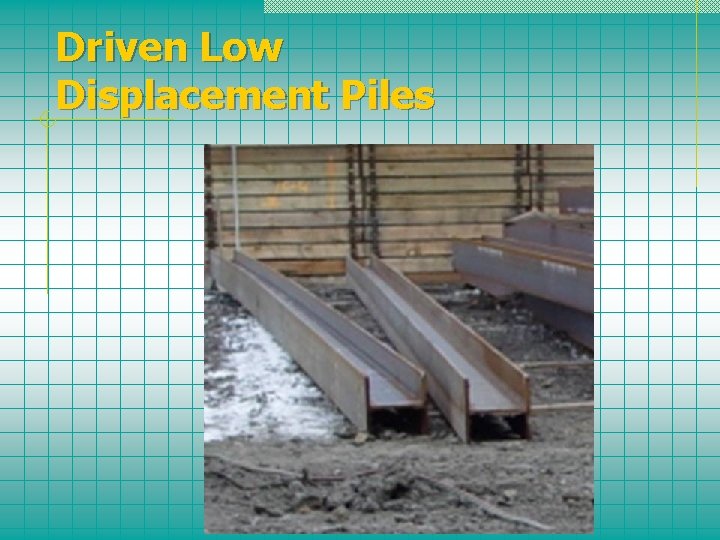
Driven Low Displacement Piles
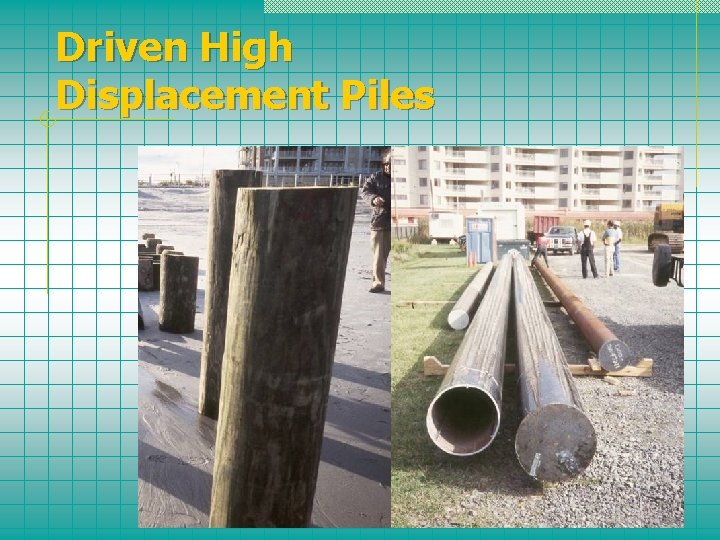
Driven High Displacement Piles
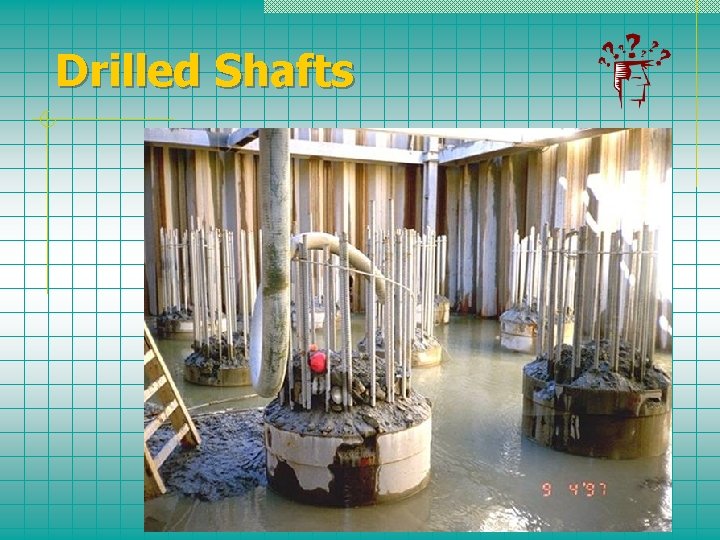
Drilled Shafts
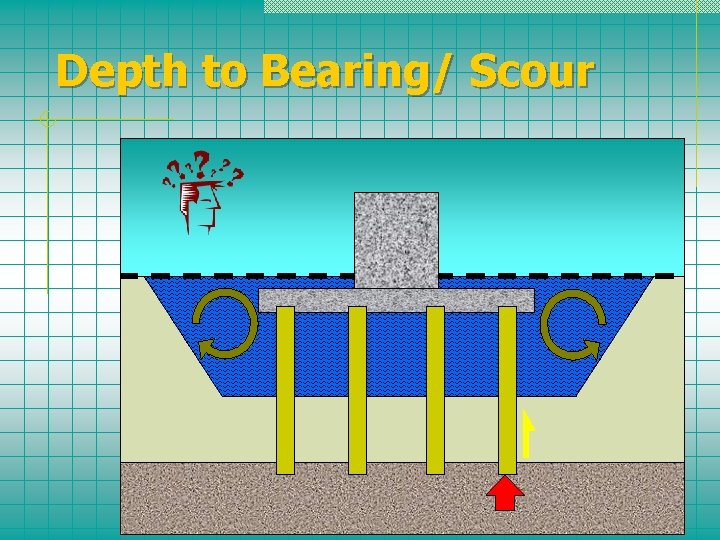
Depth to Bearing/ Scour
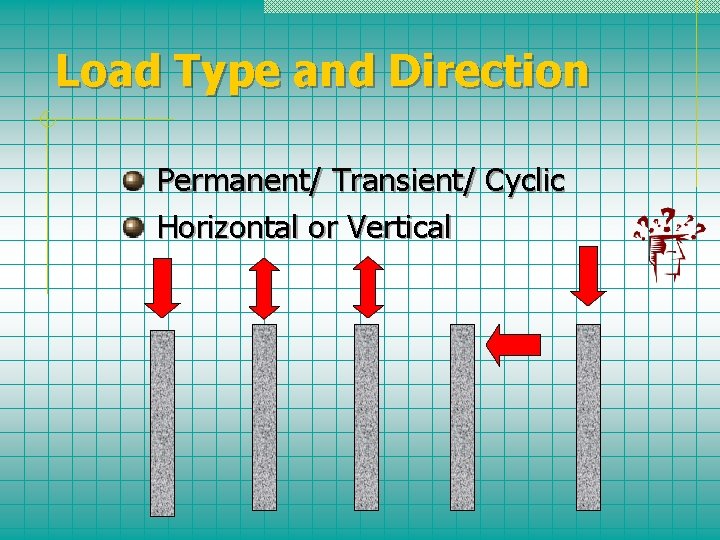
Load Type and Direction Permanent/ Transient/ Cyclic Horizontal or Vertical
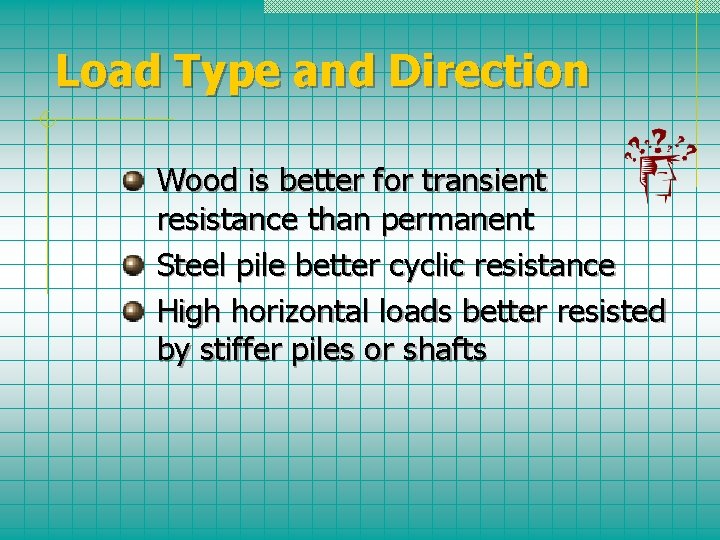
Load Type and Direction Wood is better for transient resistance than permanent Steel pile better cyclic resistance High horizontal loads better resisted by stiffer piles or shafts
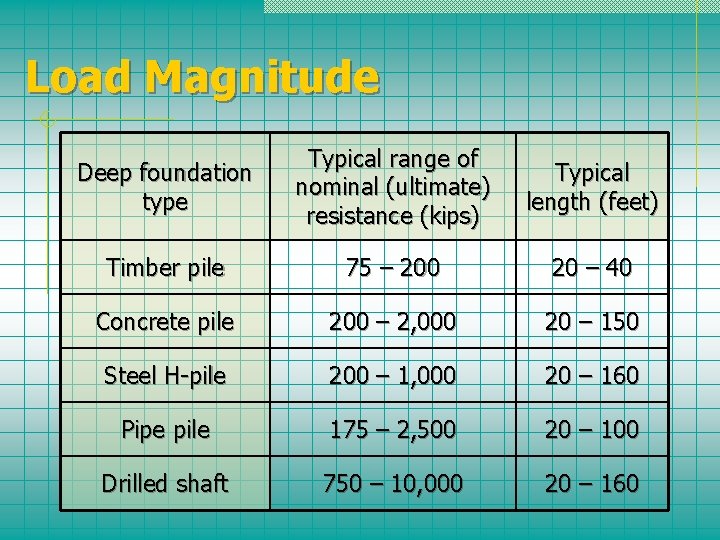
Load Magnitude Deep foundation type Typical range of nominal (ultimate) resistance (kips) Typical length (feet) Timber pile 75 – 200 20 – 40 Concrete pile 200 – 2, 000 20 – 150 Steel H-pile 200 – 1, 000 20 – 160 Pipe pile 175 – 2, 500 20 – 100 Drilled shaft 750 – 10, 000 20 – 160
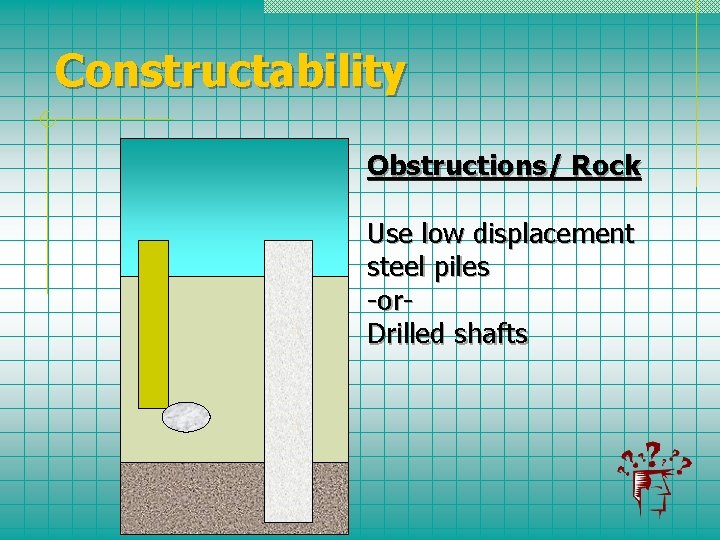
Constructability Obstructions/ Rock Use low displacement steel piles -or. Drilled shafts
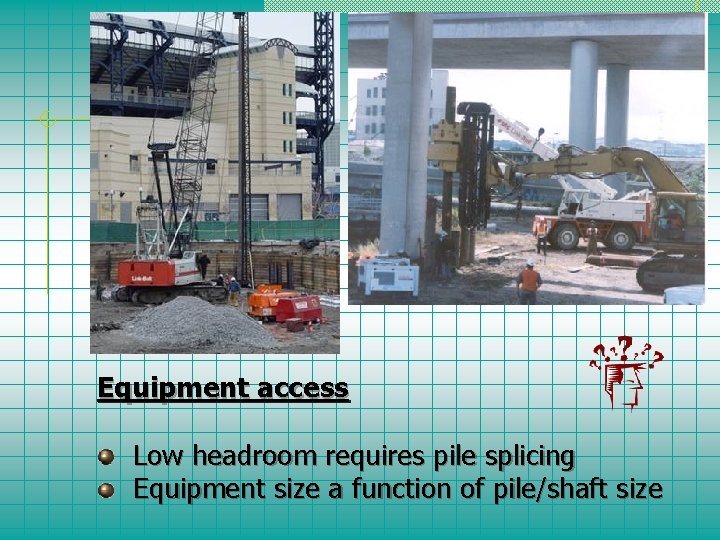
Equipment access Low headroom requires pile splicing Equipment size a function of pile/shaft size
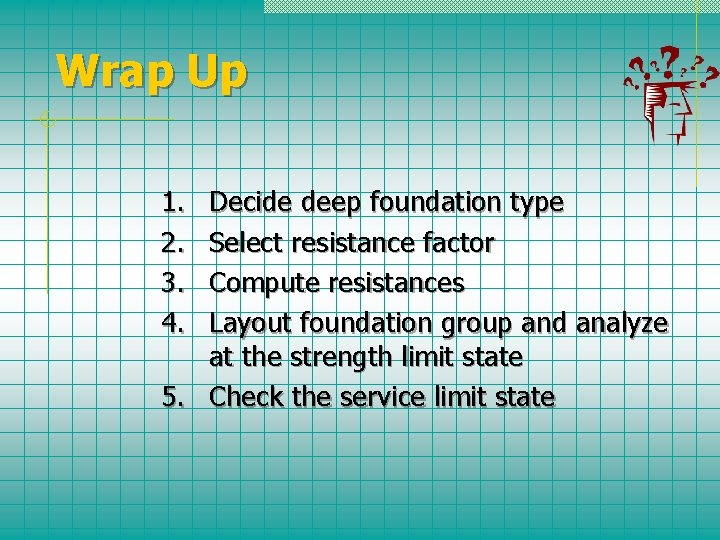
Wrap Up 1. 2. 3. 4. Decide deep foundation type Select resistance factor Compute resistances Layout foundation group and analyze at the strength limit state 5. Check the service limit state
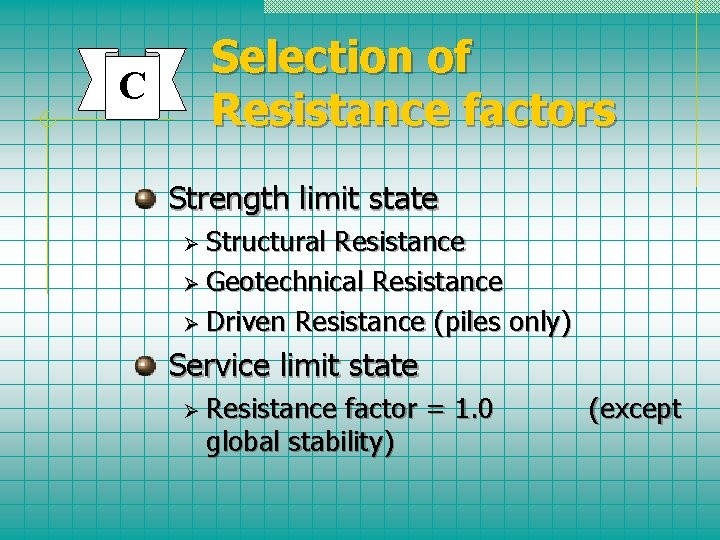
C Selection of Resistance factors Strength limit state Ø Structural Resistance Ø Geotechnical Resistance Ø Driven Resistance (piles only) Service limit state Ø Resistance factor = 1. 0 global stability) (except
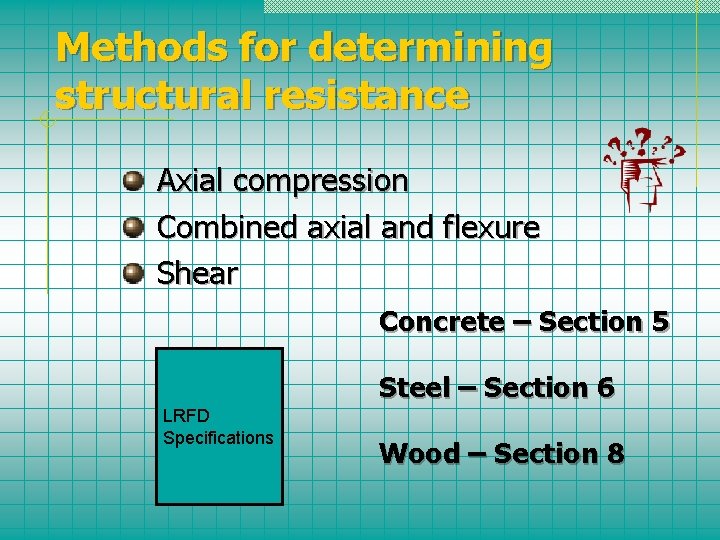
Methods for determining structural resistance Axial compression Combined axial and flexure Shear Concrete – Section 5 Steel – Section 6 LRFD Specifications Wood – Section 8
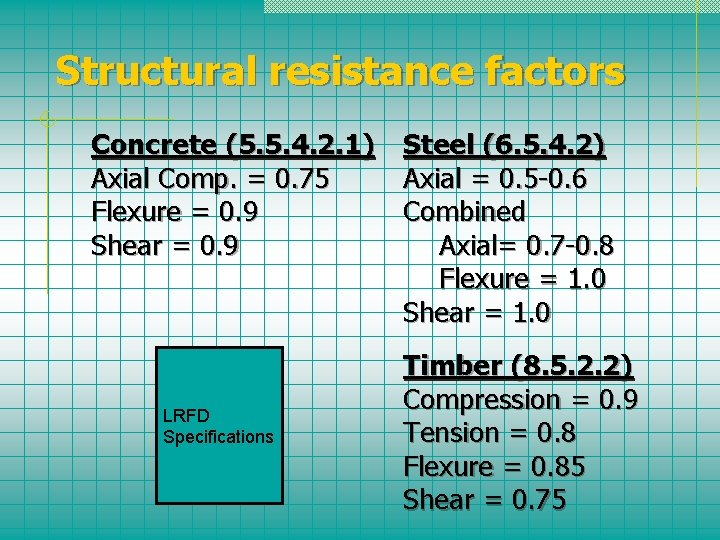
Structural resistance factors Concrete (5. 5. 4. 2. 1) Steel (6. 5. 4. 2) Axial Comp. = 0. 75 Axial = 0. 5 -0. 6 Flexure = 0. 9 Combined Shear = 0. 9 Axial= 0. 7 -0. 8 Flexure = 1. 0 Shear = 1. 0 LRFD Specifications Timber (8. 5. 2. 2) Compression = 0. 9 Tension = 0. 8 Flexure = 0. 85 Shear = 0. 75
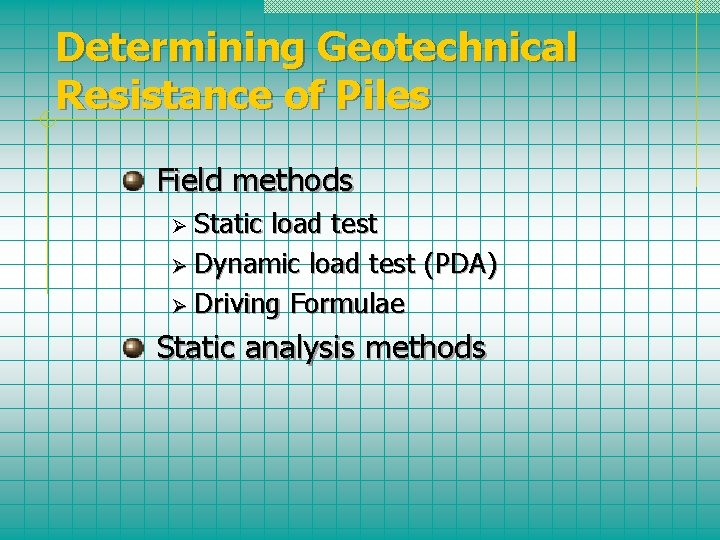
Determining Geotechnical Resistance of Piles Field methods Ø Static load test Ø Dynamic load test (PDA) Ø Driving Formulae Static analysis methods
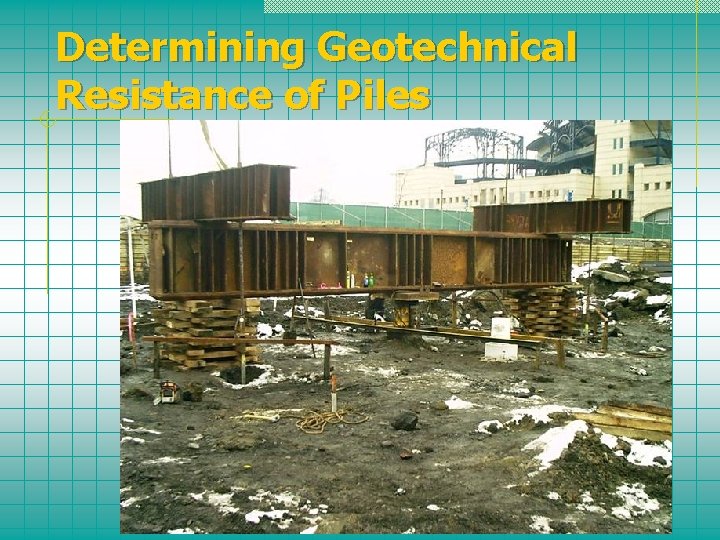
Determining Geotechnical Resistance of Piles
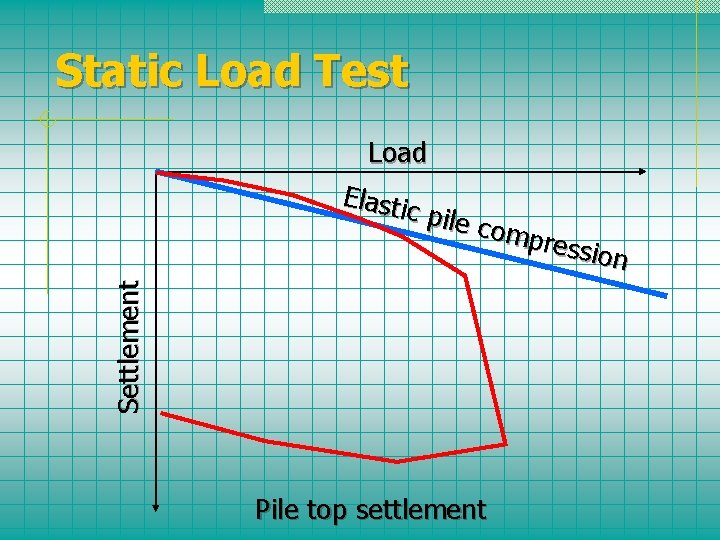
Static Load Test Load comp ressio n Settlement Elasti c pile Pile top settlement
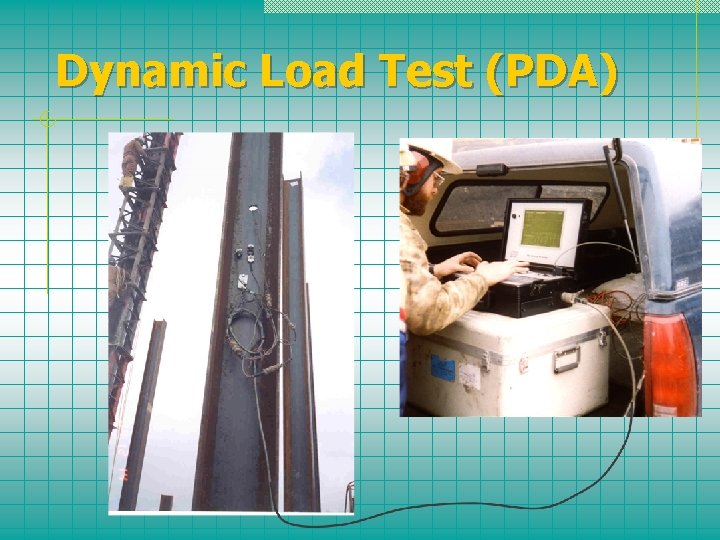
Dynamic Load Test (PDA)
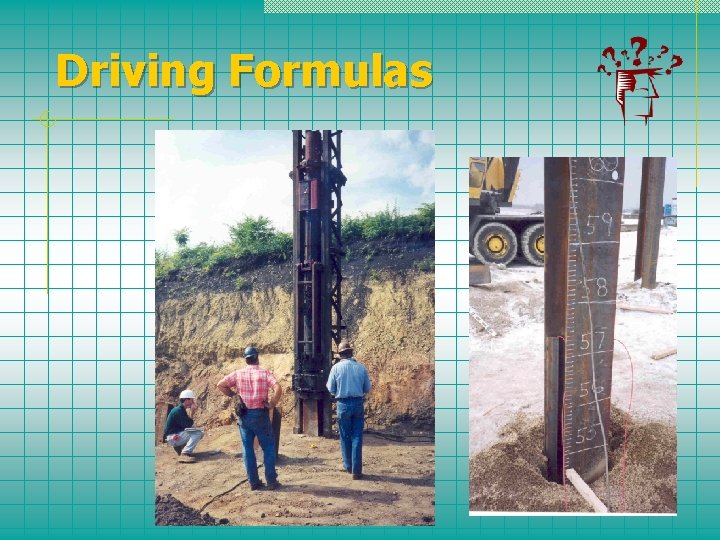
Driving Formulas
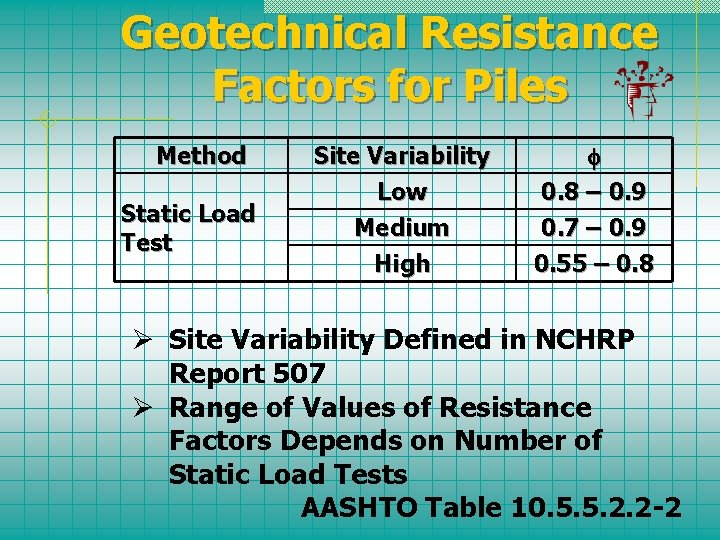
Geotechnical Resistance Factors for Piles Method Static Load Test Site Variability Low Medium High 0. 8 – 0. 9 0. 7 – 0. 9 0. 55 – 0. 8 Ø Site Variability Defined in NCHRP Report 507 Ø Range of Values of Resistance Factors Depends on Number of Static Load Tests AASHTO Table 10. 5. 5. 2. 2 -2
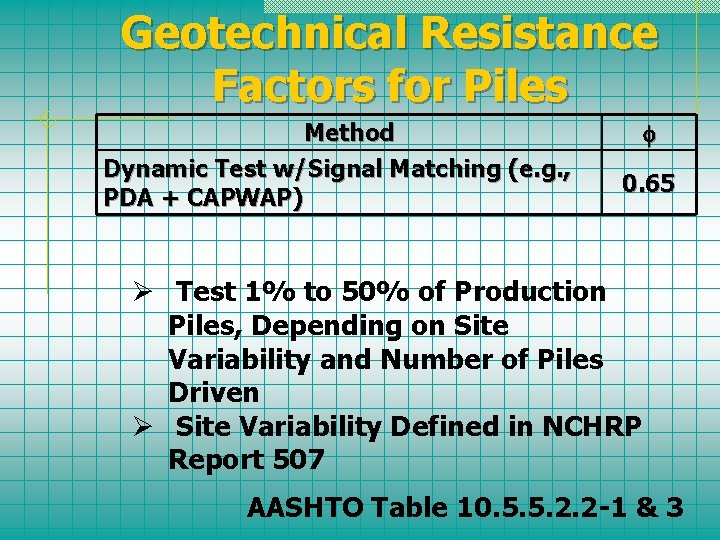
Geotechnical Resistance Factors for Piles Method Dynamic Test w/Signal Matching (e. g. , PDA + CAPWAP) 0. 65 Ø Test 1% to 50% of Production Piles, Depending on Site Variability and Number of Piles Driven Ø Site Variability Defined in NCHRP Report 507 AASHTO Table 10. 5. 5. 2. 2 -1 & 3
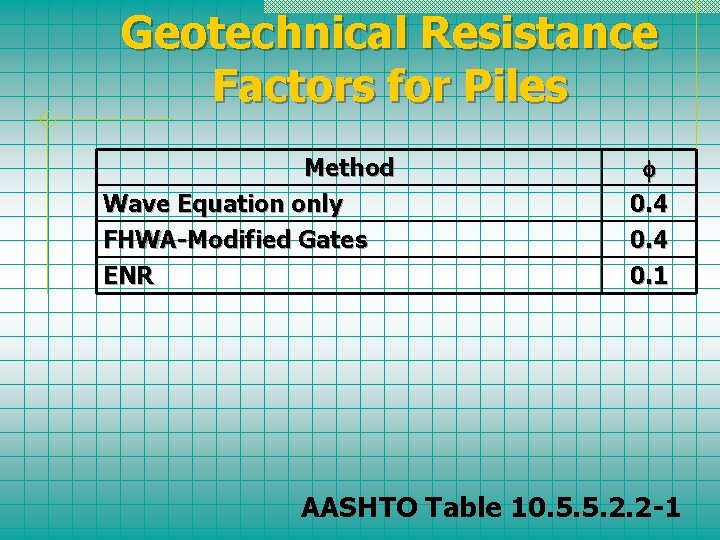
Geotechnical Resistance Factors for Piles Method Wave Equation only FHWA-Modified Gates ENR 0. 4 0. 1 AASHTO Table 10. 5. 5. 2. 2 -1
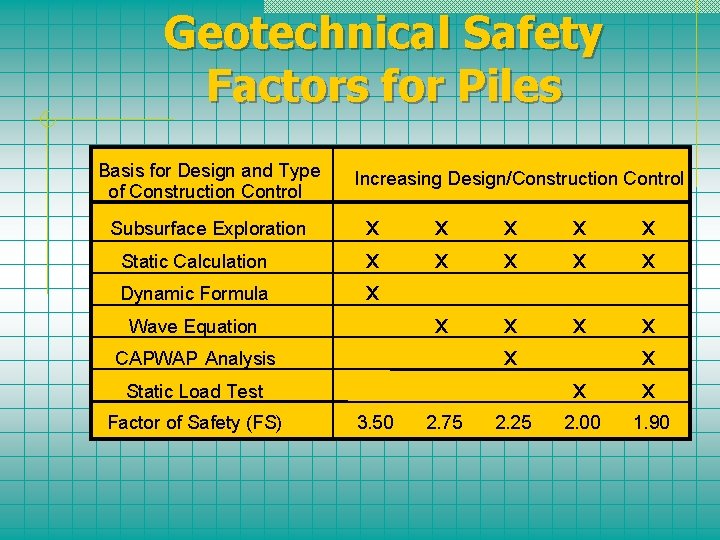
Geotechnical Safety Factors for Piles Basis for Design and Type of Construction Control Increasing Design/Construction Control X X X Static Calculation X X X Dynamic Formula X X X Subsurface Exploration Wave Equation X CAPWAP Analysis Static Load Test Factor of Safety (FS) 3. 50 2. 75 2. 25 X X X 2. 00 1. 90
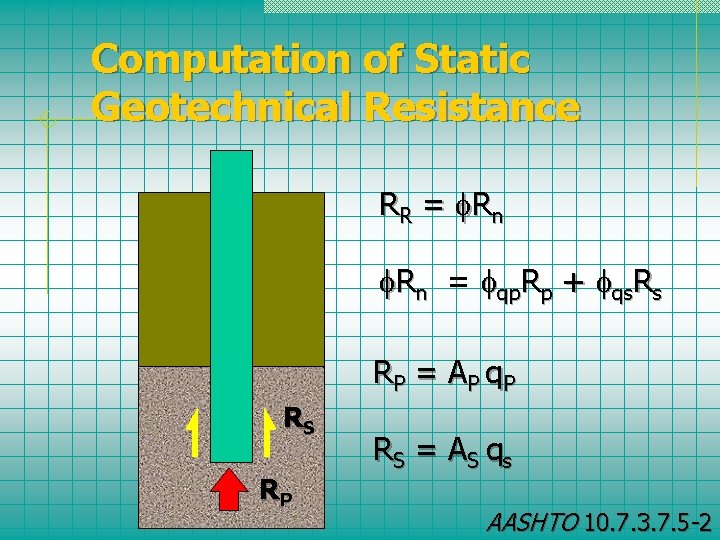
Computation of Static Geotechnical Resistance RR = Rn Rn = qp. Rp + qs. Rs RP = A P q. P RS RP RS = A S qs AASHTO 10. 7. 3. 7. 5 -2
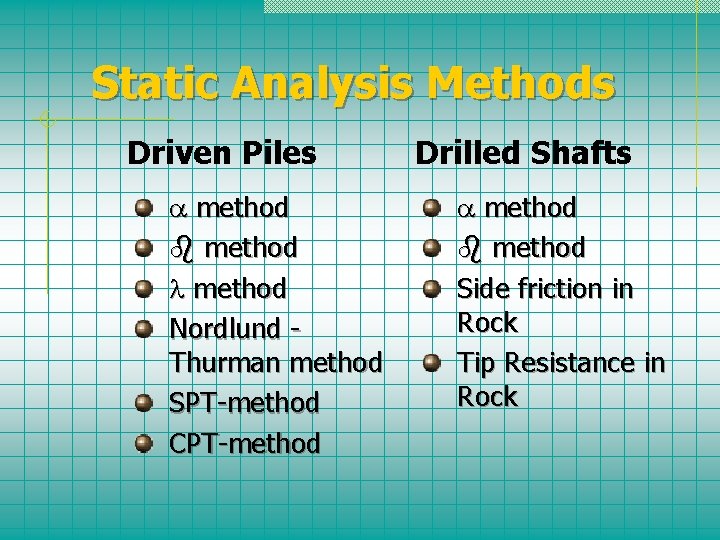
Static Analysis Methods Driven Piles method b method l method Nordlund Thurman method SPT-method CPT-method Drilled Shafts method b method Side friction in Rock Tip Resistance in Rock
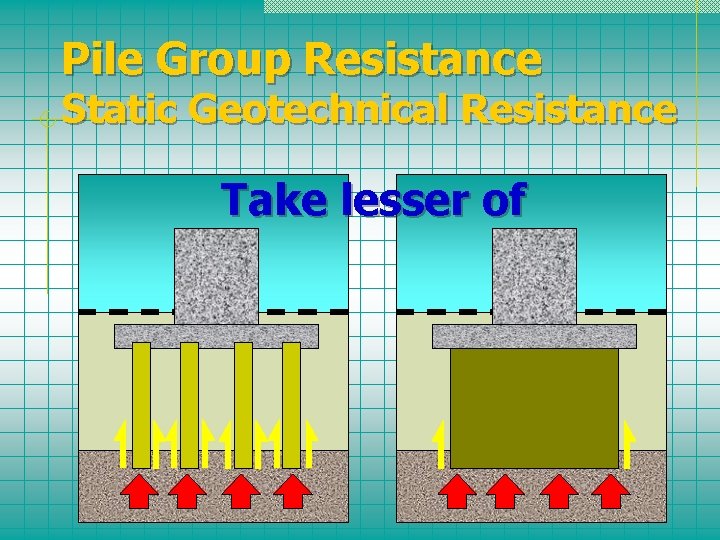
Pile Group Resistance Static Geotechnical Resistance Take lesser of
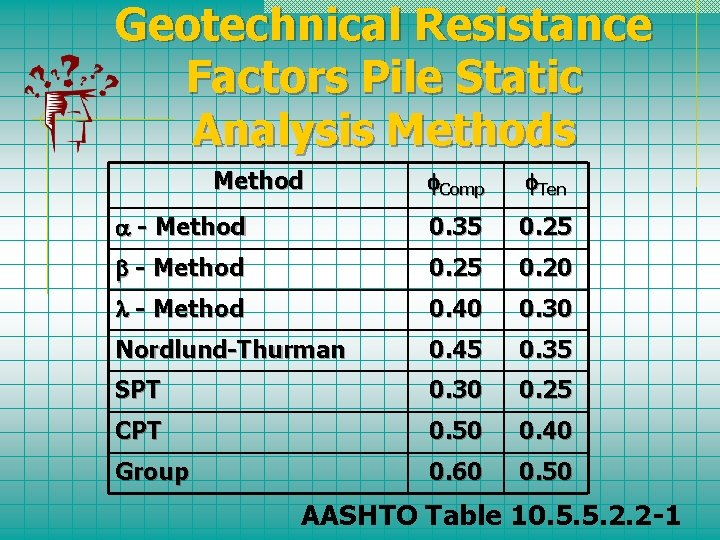
Geotechnical Resistance Factors Pile Static Analysis Methods Comp Ten - Method 0. 35 0. 25 - Method 0. 25 0. 20 - Method 0. 40 0. 30 Nordlund-Thurman 0. 45 0. 35 SPT 0. 30 0. 25 CPT 0. 50 0. 40 Group 0. 60 0. 50 Method AASHTO Table 10. 5. 5. 2. 2 -1
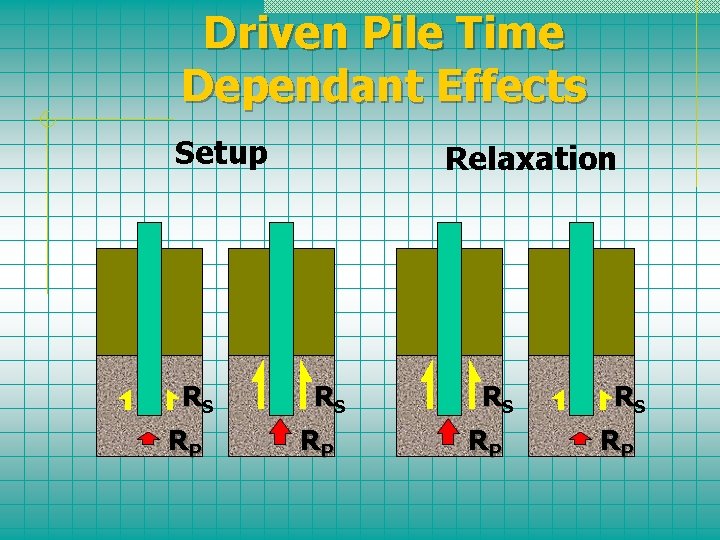
Driven Pile Time Dependant Effects Setup RS RP Relaxation RS RP
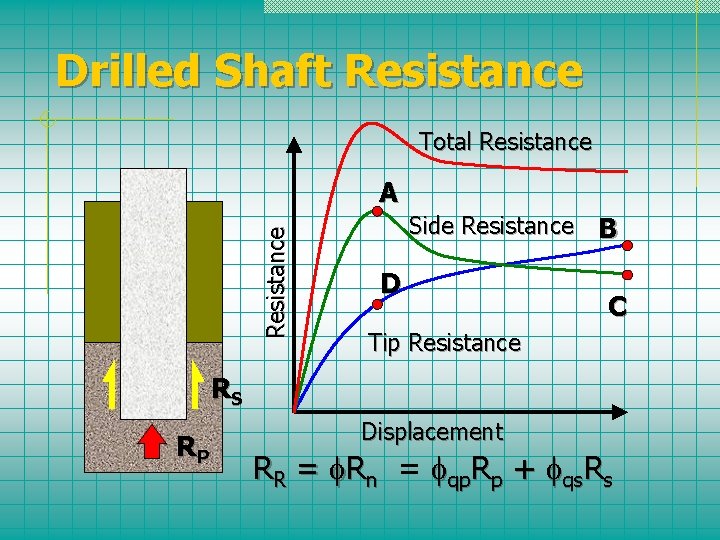
Drilled Shaft Resistance Total Resistance A Side Resistance B D C Tip Resistance RS RP Displacement RR = Rn = qp. Rp + qs. Rs
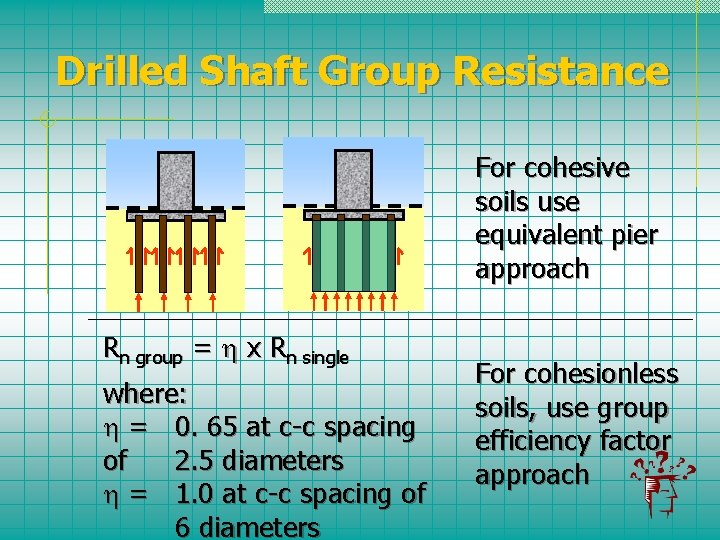
Drilled Shaft Group Resistance For cohesive soils use equivalent pier approach Rn group = h x Rn single where: h = 0. 65 at c-c spacing of 2. 5 diameters h = 1. 0 at c-c spacing of 6 diameters For cohesionless soils, use group efficiency factor approach
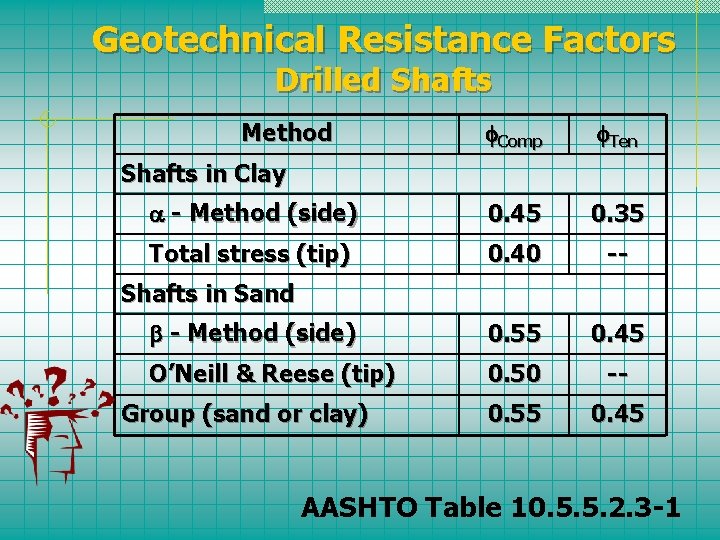
Geotechnical Resistance Factors Drilled Shafts Comp Ten - Method (side) 0. 45 0. 35 Total stress (tip) 0. 40 -- - Method (side) 0. 55 0. 45 O’Neill & Reese (tip) 0. 50 -- 0. 55 0. 45 Method Shafts in Clay Shafts in Sand Group (sand or clay) AASHTO Table 10. 5. 5. 2. 3 -1
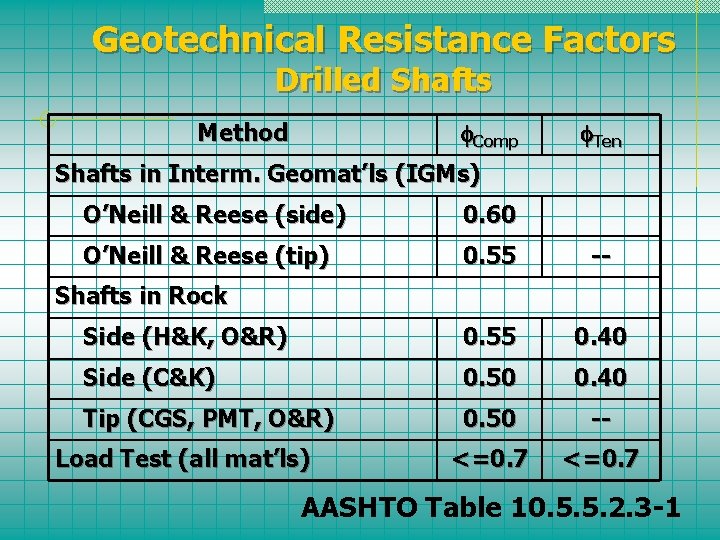
Geotechnical Resistance Factors Drilled Shafts Comp Method Ten Shafts in Interm. Geomat’ls (IGMs) O’Neill & Reese (side) 0. 60 O’Neill & Reese (tip) 0. 55 -- Side (H&K, O&R) 0. 55 0. 40 Side (C&K) 0. 50 0. 40 Tip (CGS, PMT, O&R) 0. 50 -- <=0. 7 Shafts in Rock Load Test (all mat’ls) AASHTO Table 10. 5. 5. 2. 3 -1
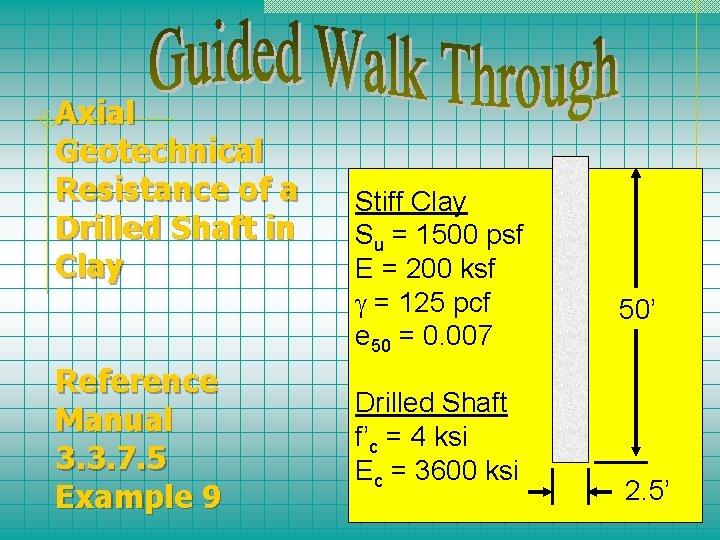
Axial Geotechnical Resistance of a Drilled Shaft in Clay Reference Manual 3. 3. 7. 5 Example 9 Stiff Clay Su = 1500 psf E = 200 ksf = 125 pcf e 50 = 0. 007 Drilled Shaft f’c = 4 ksi Ec = 3600 ksi 50’ 2. 5’
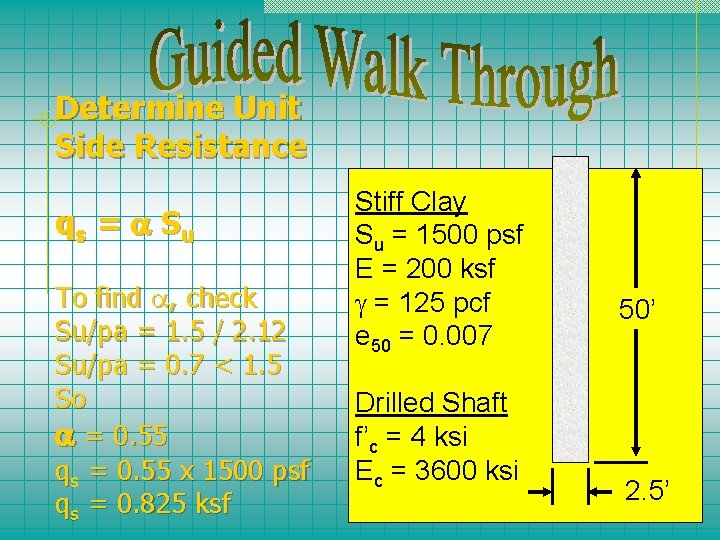
Determine Unit Side Resistance qs = S u To find , check Su/pa = 1. 5 / 2. 12 Su/pa = 0. 7 < 1. 5 So = 0. 55 qs = 0. 55 x 1500 psf qs = 0. 825 ksf Stiff Clay Su = 1500 psf E = 200 ksf = 125 pcf e 50 = 0. 007 Drilled Shaft f’c = 4 ksi Ec = 3600 ksi 50’ 2. 5’
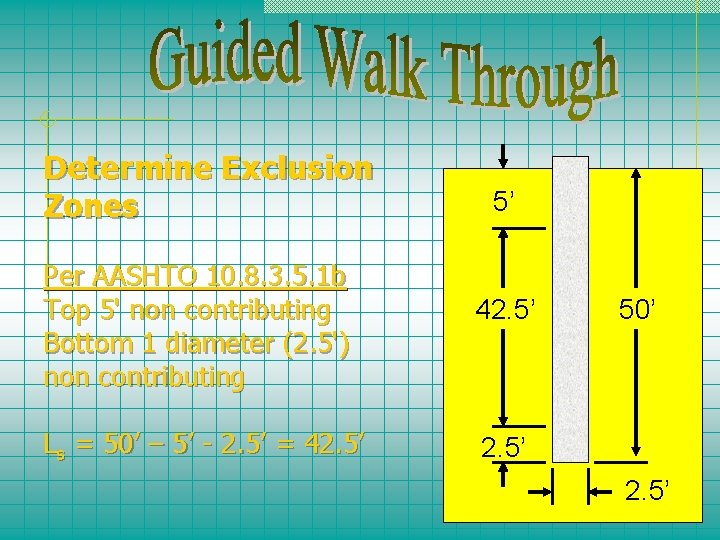
Determine Exclusion Zones Per AASHTO 10. 8. 3. 5. 1 b Top 5' non contributing Bottom 1 diameter (2. 5') non contributing Ls = 50’ – 5’ - 2. 5’ = 42. 5’ 5’ 42. 5’ 50’ 2. 5’
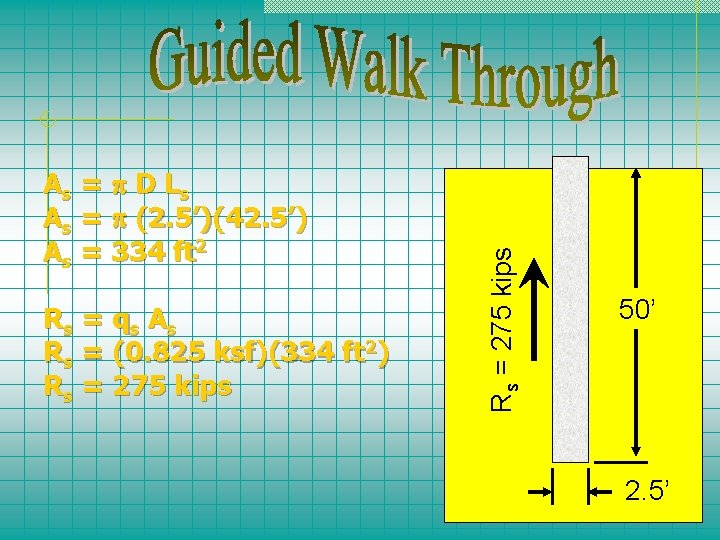
Rs = q s A s Rs = (0. 825 ksf)(334 ft 2) Rs = 275 kips As = D L s As = (2. 5’)(42. 5’) As = 334 ft 2 50’ 2. 5’
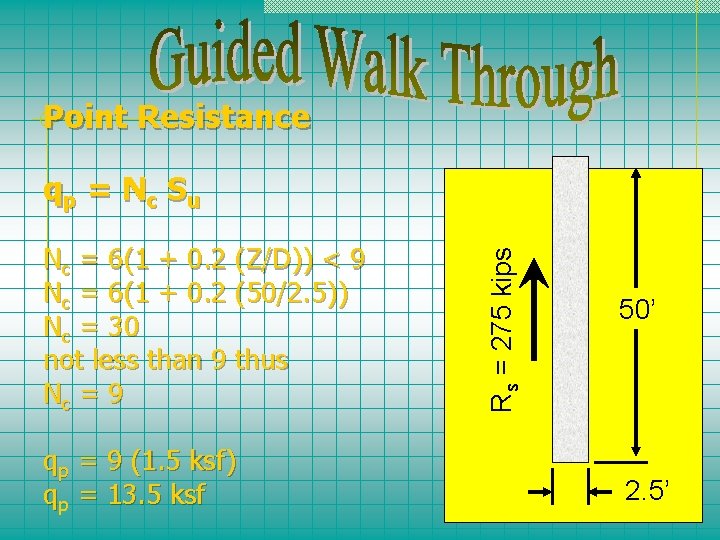
Point Resistance Nc = 6(1 + 0. 2 (Z/D)) < 9 Nc = 6(1 + 0. 2 (50/2. 5)) Nc = 30 not less than 9 thus Nc = 9 qp = 9 (1. 5 ksf) qp = 13. 5 ksf Rs = 275 kips qp = Nc S u 50’ 2. 5’
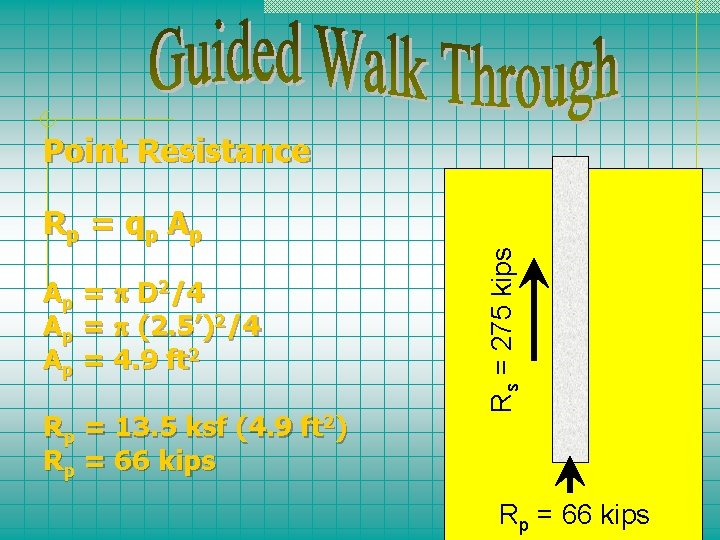
Rp = q p Ap = D 2/4 Ap = (2. 5’)2/4 Ap = 4. 9 ft 2 Rp = 13. 5 ksf (4. 9 ft 2) Rp = 66 kips Rs = 275 kips Point Resistance Rp = 66 kips
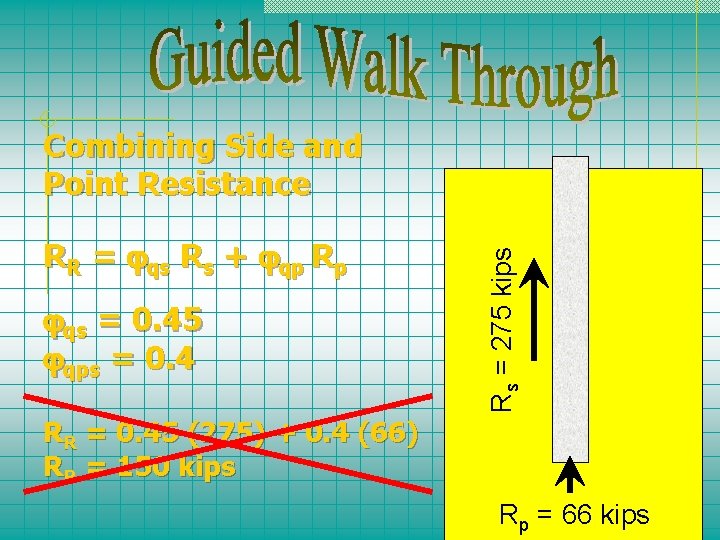
RR = qs Rs + qp Rp qs = 0. 45 qps = 0. 4 Rs = 275 kips Combining Side and Point Resistance RR = 0. 45 (275) + 0. 4 (66) RR = 150 kips Rp = 66 kips
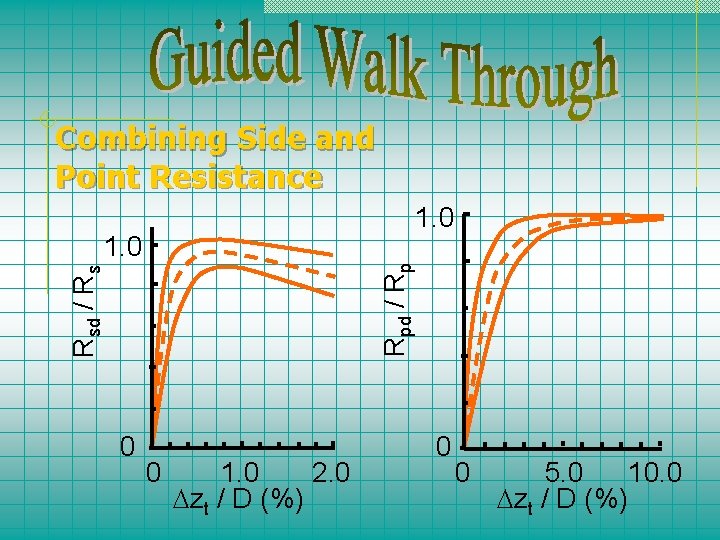
Combining Side and Point Resistance 1. 0 Rsd / Rs Rpd / Rp 1. 0 0 0 1. 0 2. 0 zt / D (%) 0 0 5. 0 10. 0 zt / D (%)
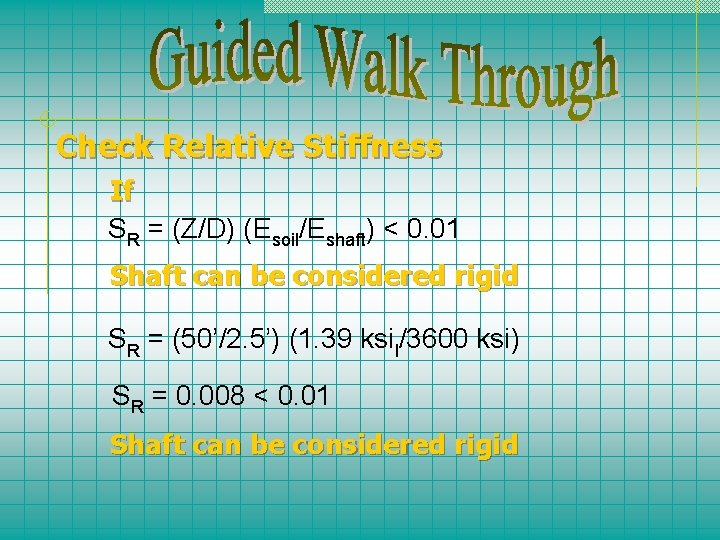
Check Relative Stiffness If SR = (Z/D) (Esoil/Eshaft) < 0. 01 Shaft can be considered rigid SR = (50’/2. 5’) (1. 39 ksil/3600 ksi) SR = 0. 008 < 0. 01 Shaft can be considered rigid
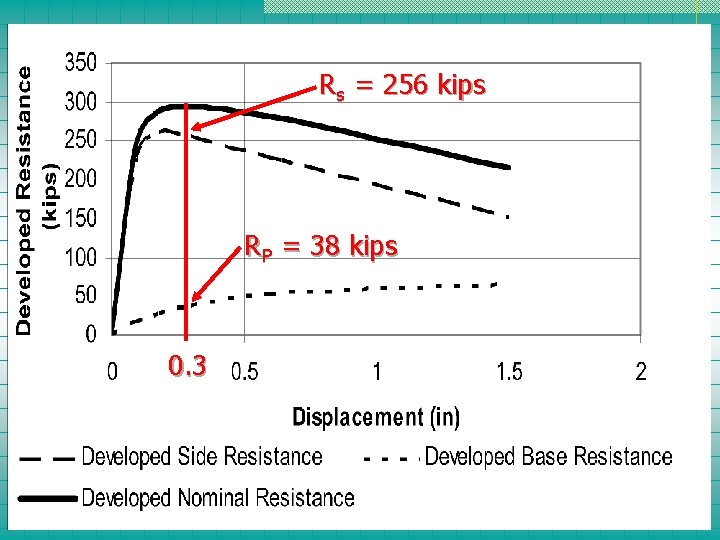
Rs = 256 kips RP = 38 kips 0. 3
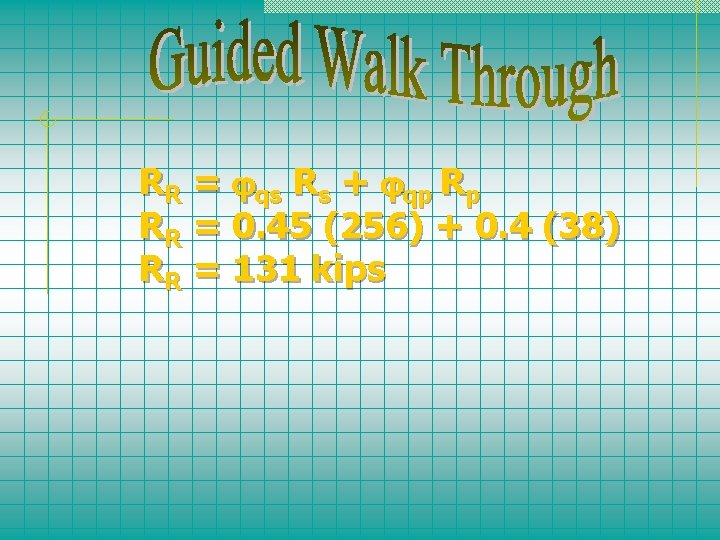
RR = qs Rs + qp Rp RR = 0. 45 (256) + 0. 4 (38) RR = 131 kips
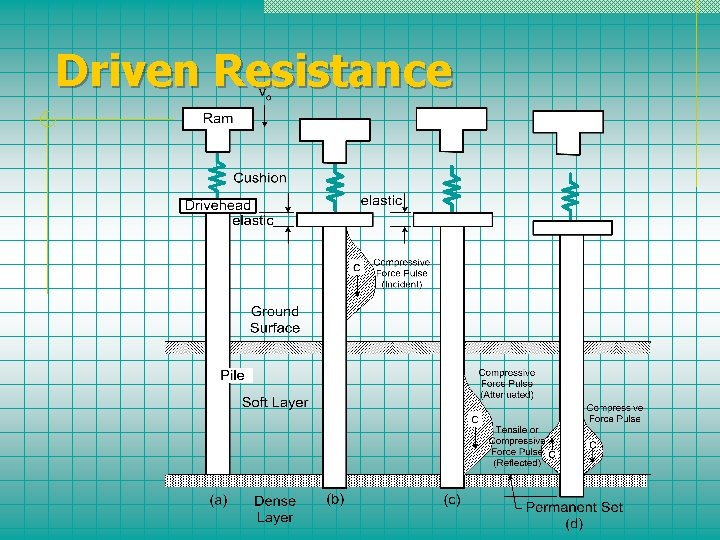
Driven Resistance
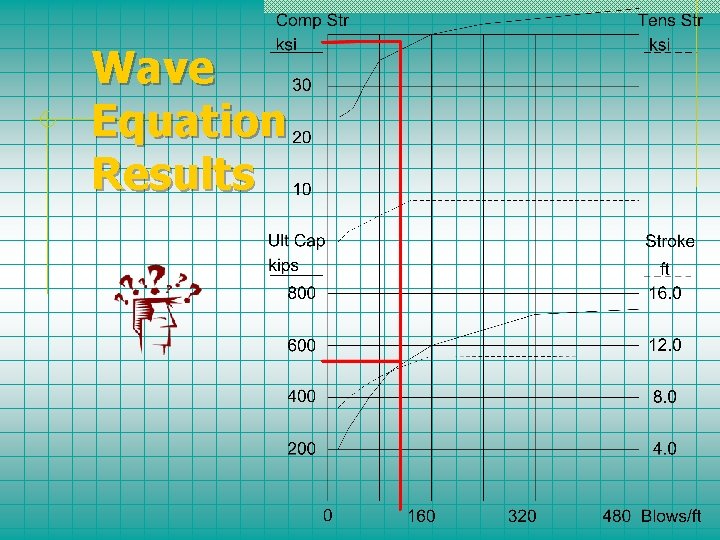
Wave Equation Results
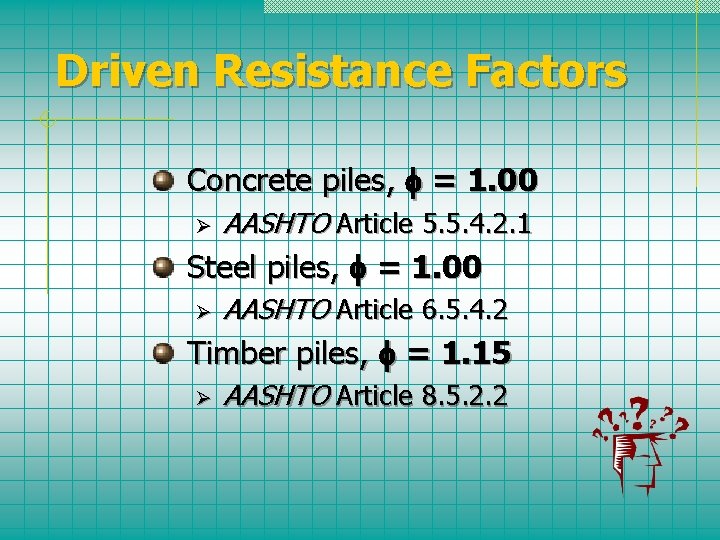
Driven Resistance Factors Concrete piles, = 1. 00 Ø AASHTO Article 5. 5. 4. 2. 1 Steel piles, = 1. 00 Ø AASHTO Article 6. 5. 4. 2 Timber piles, = 1. 15 Ø AASHTO Article 8. 5. 2. 2

Participant Workbook Page 3. 3 A. 22
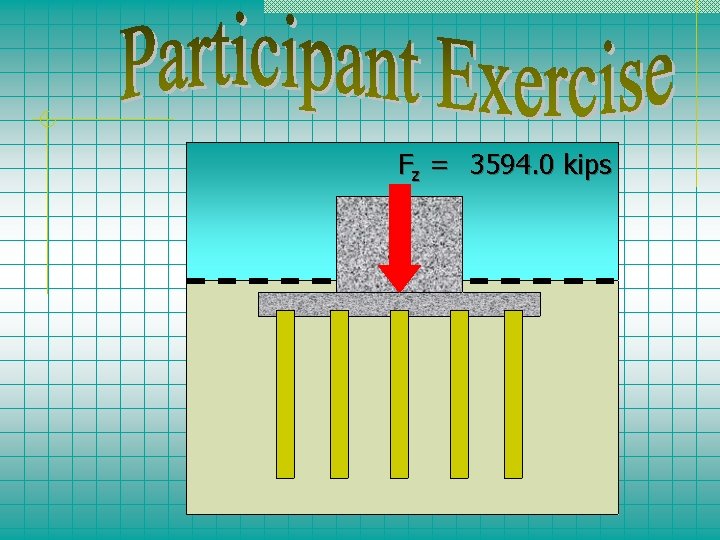
Fz = 3594. 0 kips
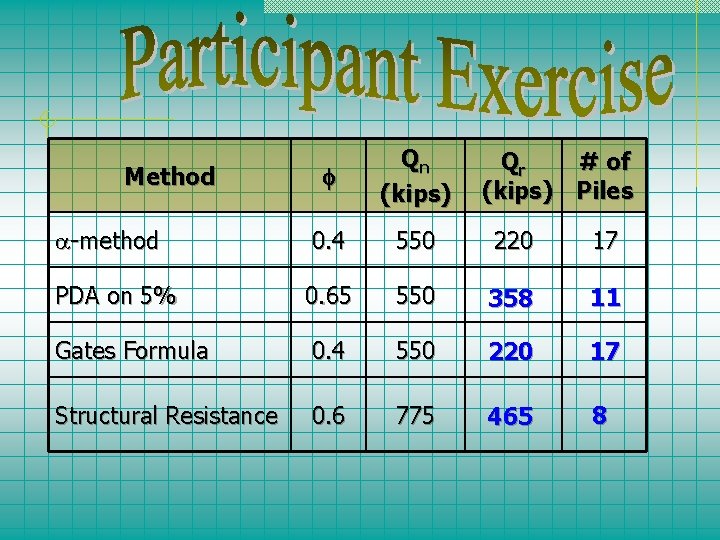
Qn (kips) -method 0. 4 550 220 17 PDA on 5% 0. 65 550 358 11 Gates Formula 0. 4 550 220 17 Structural Resistance 0. 6 775 465 8 Method Qr # of (kips) Piles
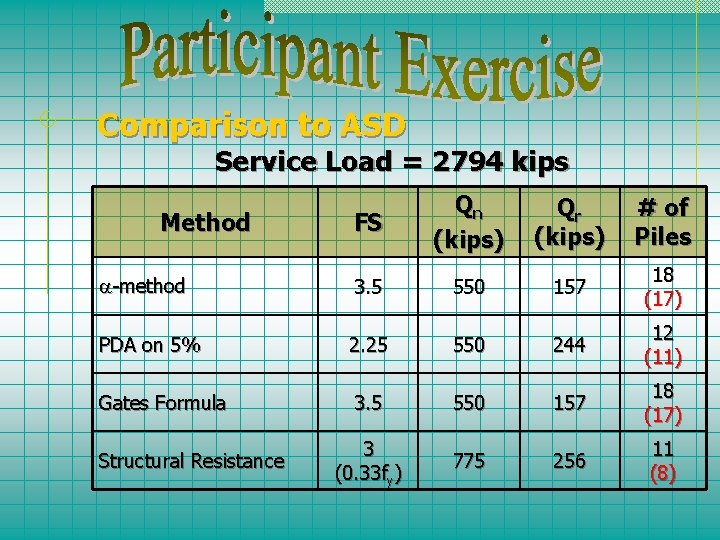
Comparison to ASD Service Load = 2794 kips FS Qn (kips) Qr (kips) # of Piles -method 3. 5 550 157 18 (17) PDA on 5% 2. 25 550 244 12 (11) Gates Formula 3. 5 550 157 18 (17) 3 (0. 33 fy) 775 256 11 (8) Method Structural Resistance
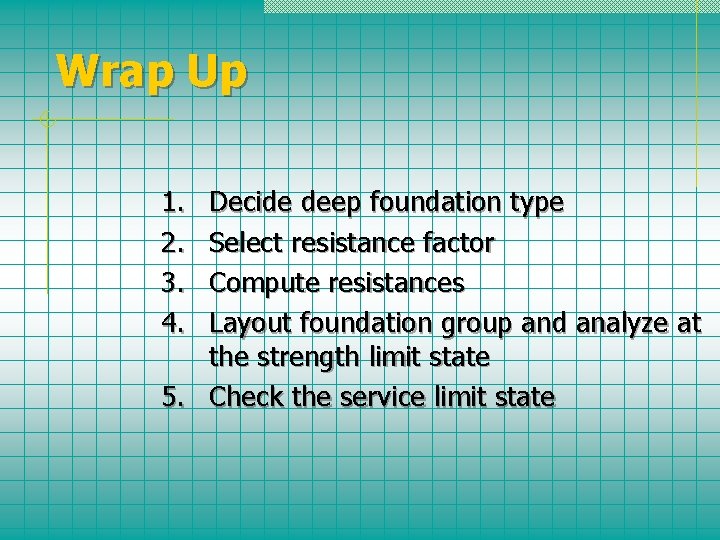
Wrap Up 1. 2. 3. 4. Decide deep foundation type Select resistance factor Compute resistances Layout foundation group and analyze at the strength limit state 5. Check the service limit state

Participant Workbook Page 3. 3 A. 25
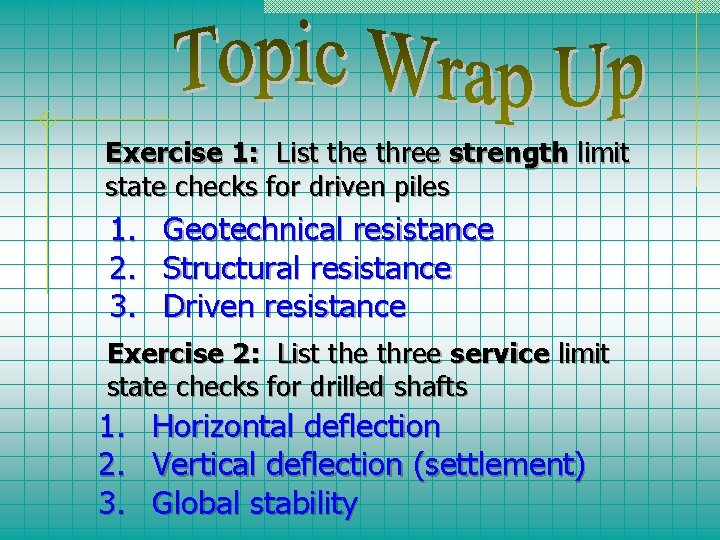
Exercise 1: List the three strength limit state checks for driven piles 1. 2. 3. Geotechnical resistance Structural resistance Driven resistance Exercise 2: List the three service limit state checks for drilled shafts 1. 2. 3. Horizontal deflection Vertical deflection (settlement) Global stability
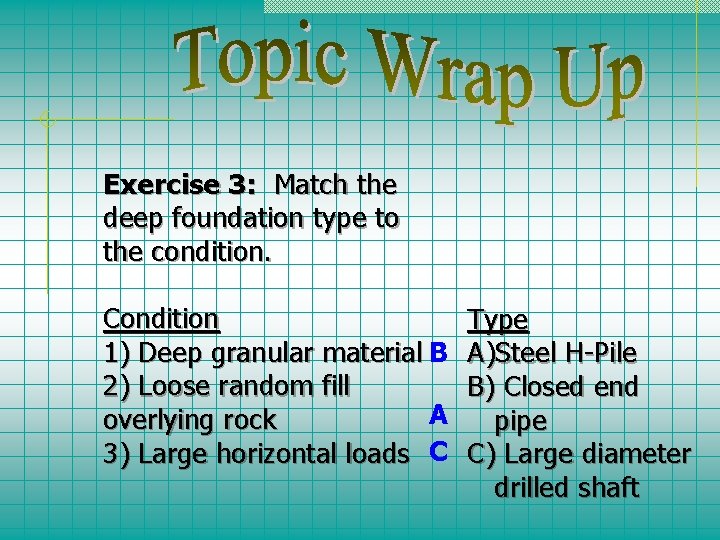
Exercise 3: Match the deep foundation type to the condition. Condition 1) Deep granular material B 2) Loose random fill A overlying rock 3) Large horizontal loads C Type A)Steel H-Pile B) Closed end pipe C) Large diameter drilled shaft
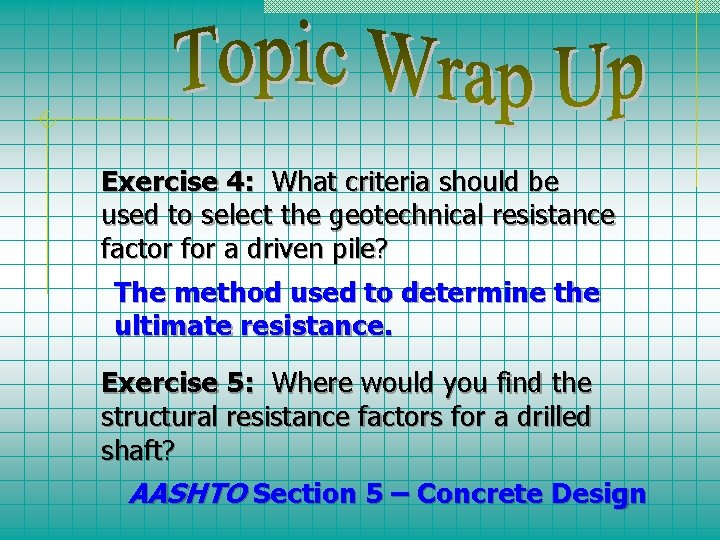
Exercise 4: What criteria should be used to select the geotechnical resistance factor for a driven pile? The method used to determine the ultimate resistance. Exercise 5: Where would you find the structural resistance factors for a drilled shaft? AASHTO Section 5 – Concrete Design
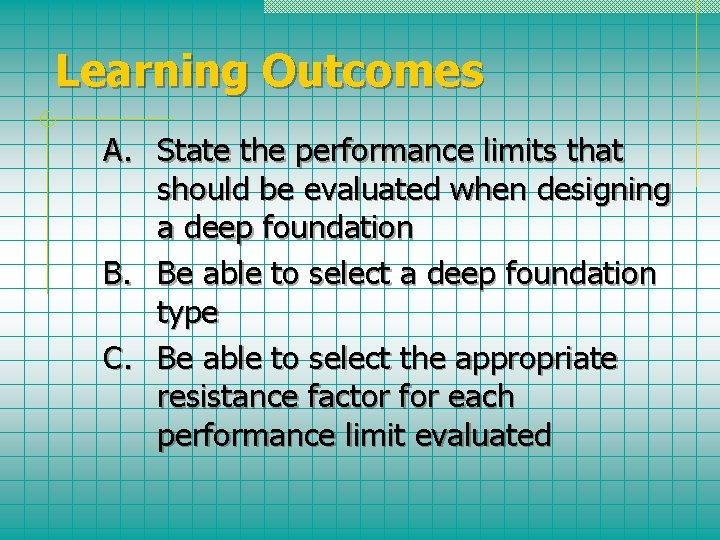
Learning Outcomes A. State the performance limits that should be evaluated when designing a deep foundation B. Be able to select a deep foundation type C. Be able to select the appropriate resistance factor for each performance limit evaluated
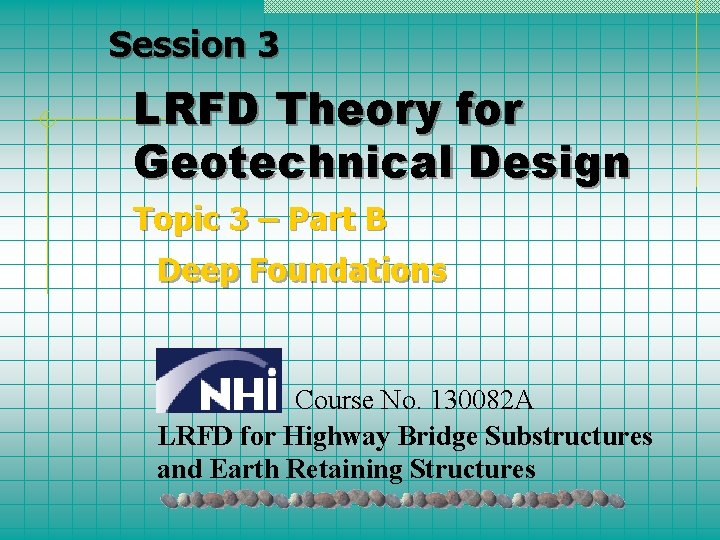
Session 3 LRFD Theory for Geotechnical Design Topic 3 – Part B Deep Foundations Course No. 130082 A LRFD for Highway Bridge Substructures and Earth Retaining Structures
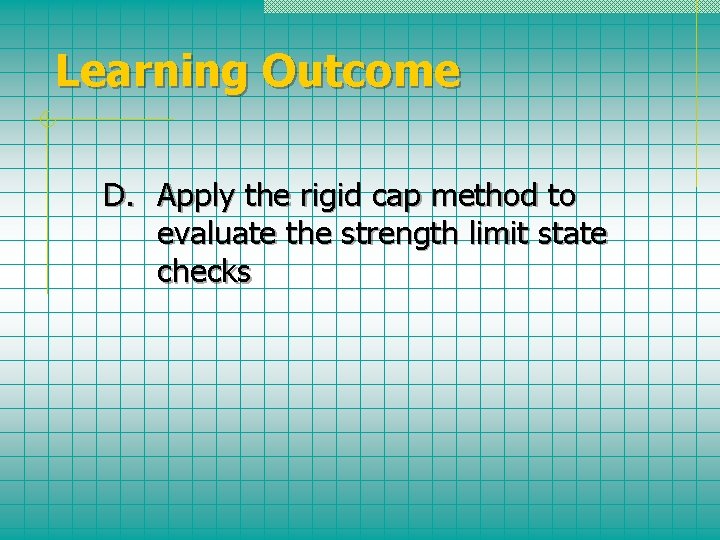
Learning Outcome D. Apply the rigid cap method to evaluate the strength limit state checks
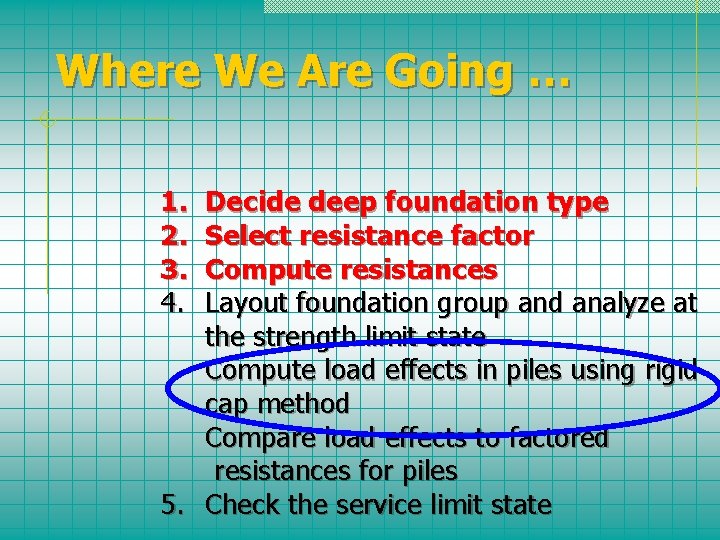
Where We Are Going … 1. 2. 3. 4. Decide deep foundation type Select resistance factor Compute resistances Layout foundation group and analyze at the strength limit state Compute load effects in piles using rigid cap method Compare load effects to factored resistances for piles 5. Check the service limit state
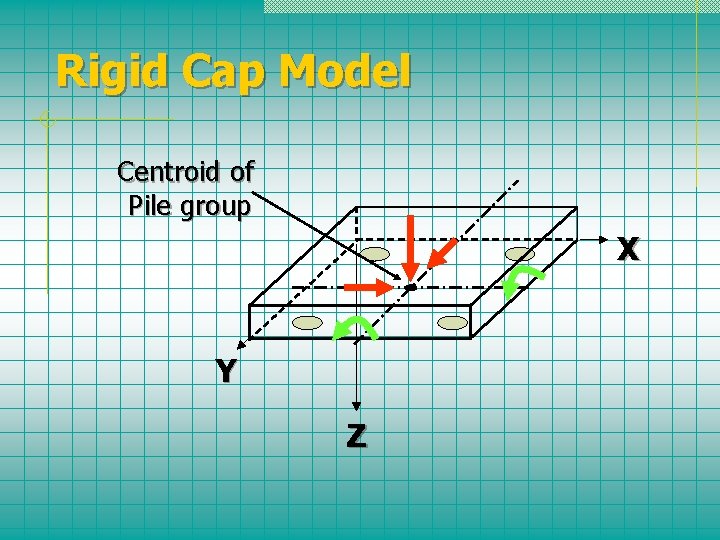
Rigid Cap Model Centroid of Pile group X Y Z
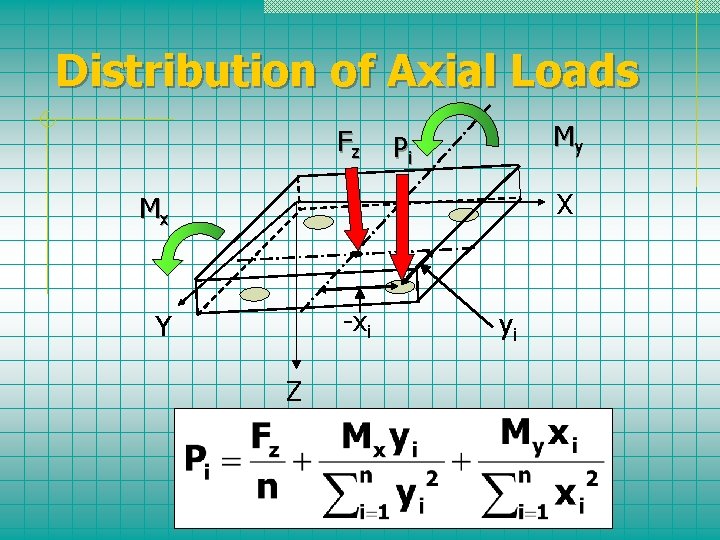
Distribution of Axial Loads Fz My Pi X Mx -xi Y Z yi
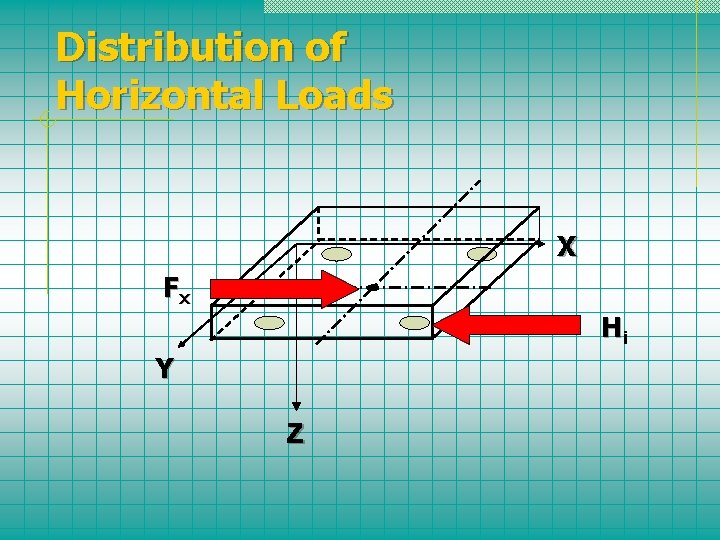
Distribution of Horizontal Loads X Fx Hi Y Z
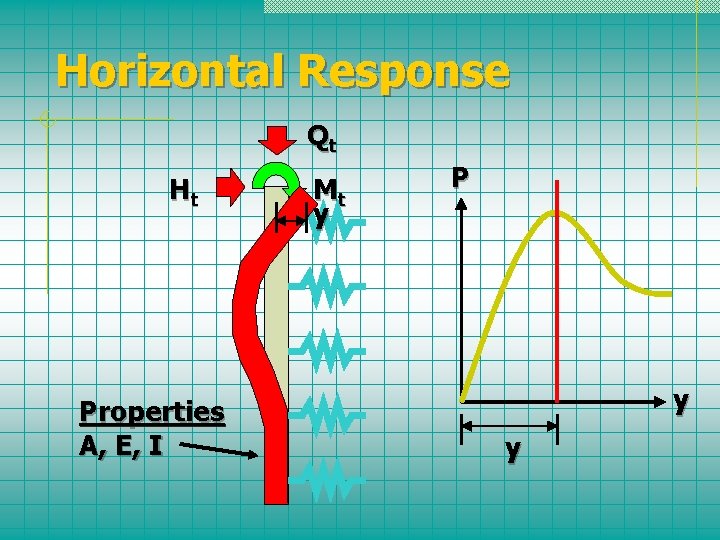
Horizontal Response Qt Ht Properties A, E, I Mt y P y y
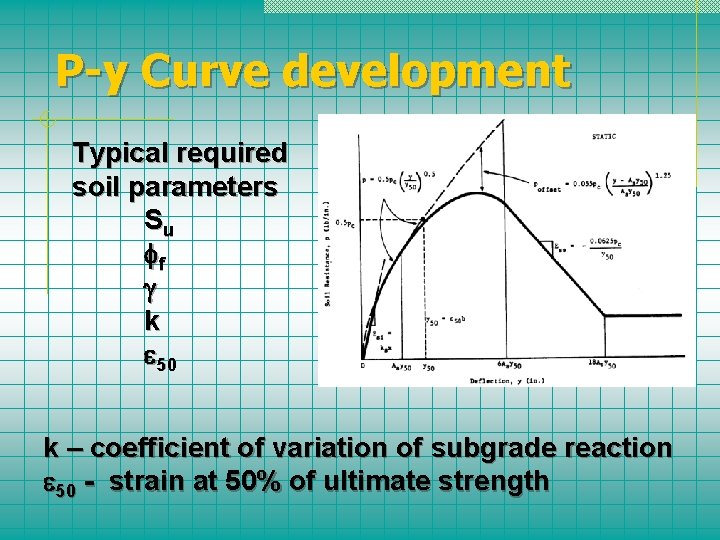
P-y Curve development Typical required soil parameters Su f k 50 k – coefficient of variation of subgrade reaction 50 - strain at 50% of ultimate strength
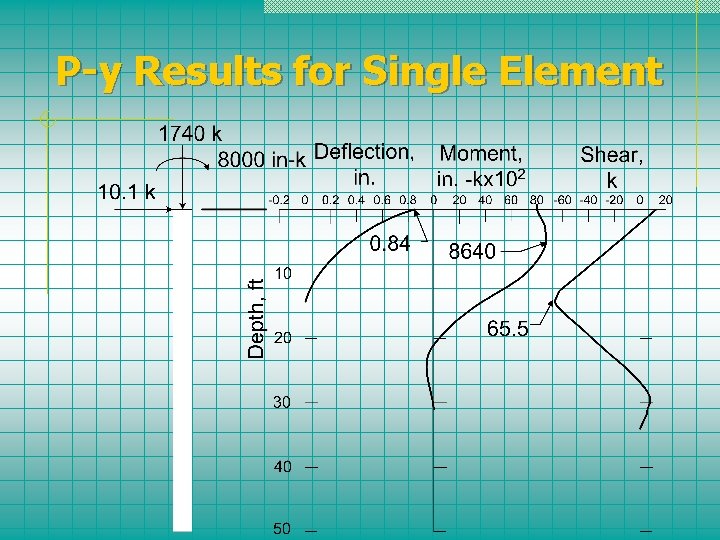
P-y Results for Single Element
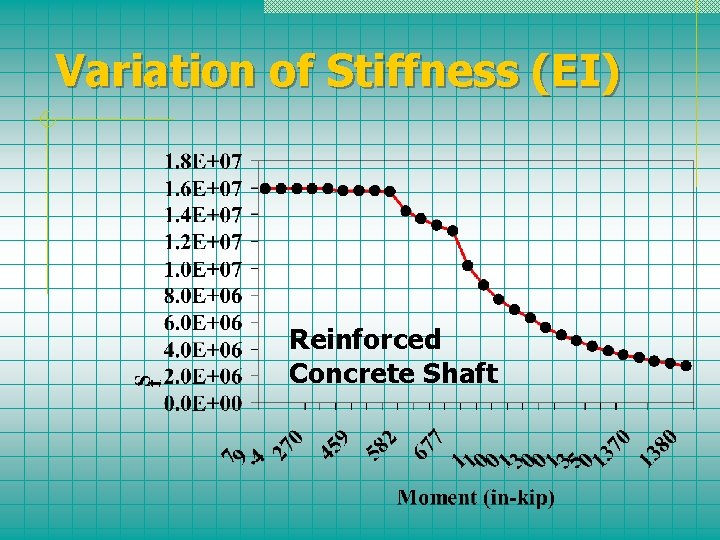
Variation of Stiffness (EI) Reinforced Concrete Shaft
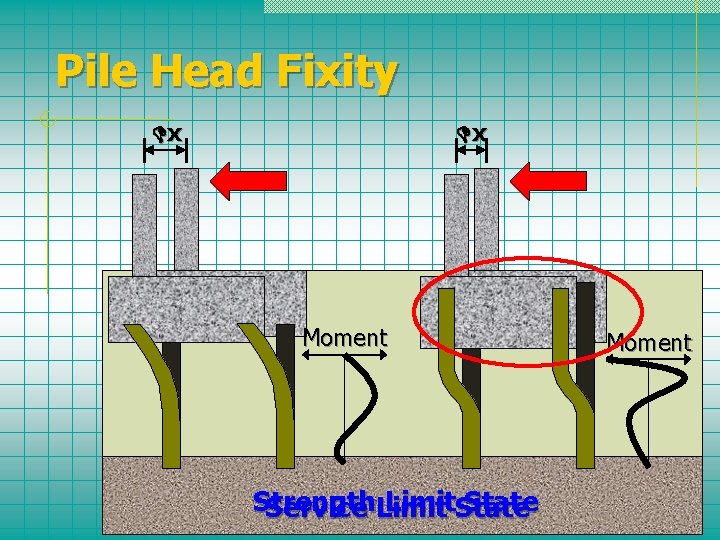
Pile Head Fixity Dx Dx Moment Strength Limit. State Service Limit Moment
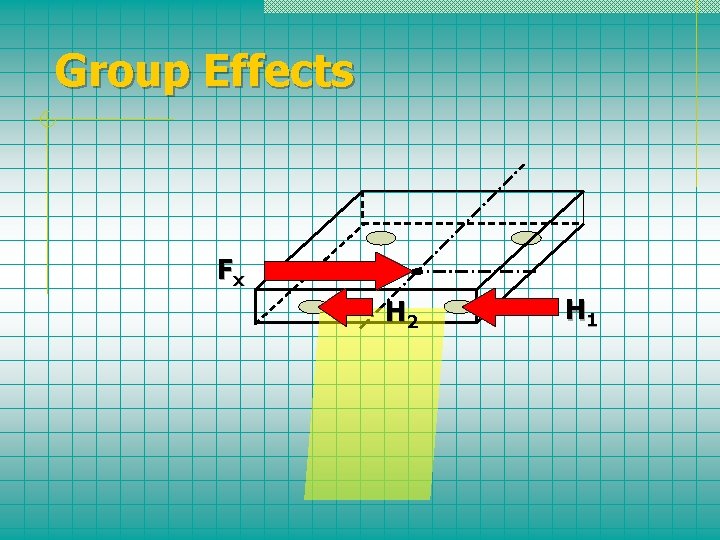
Group Effects Fx H 2 H 1
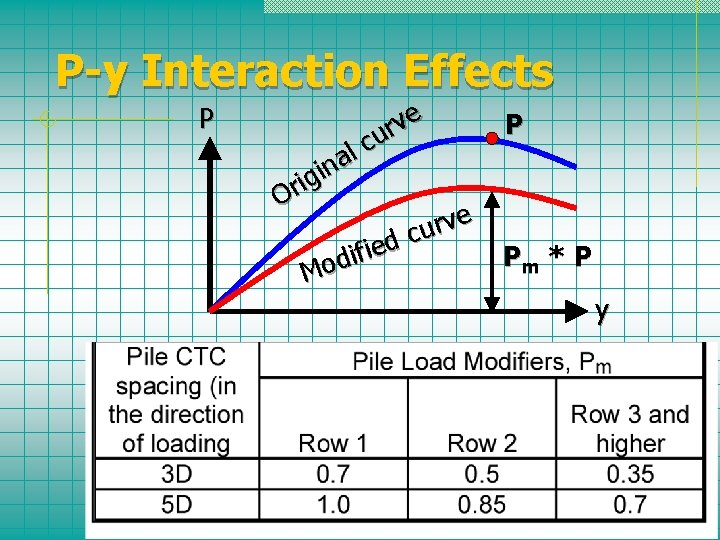
P-y Interaction Effects P e v r u c l a n ir gi O e v r u c d ie f i d Mo P Pm * P y
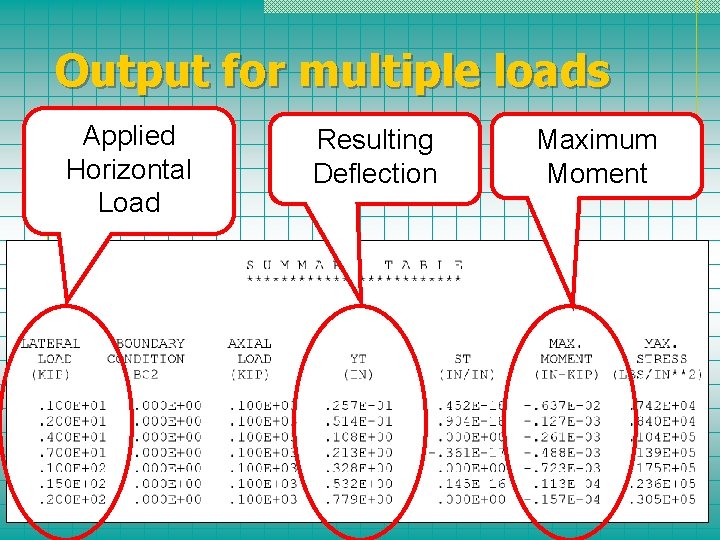
Output for multiple loads Applied Horizontal Load Resulting Deflection Maximum Moment
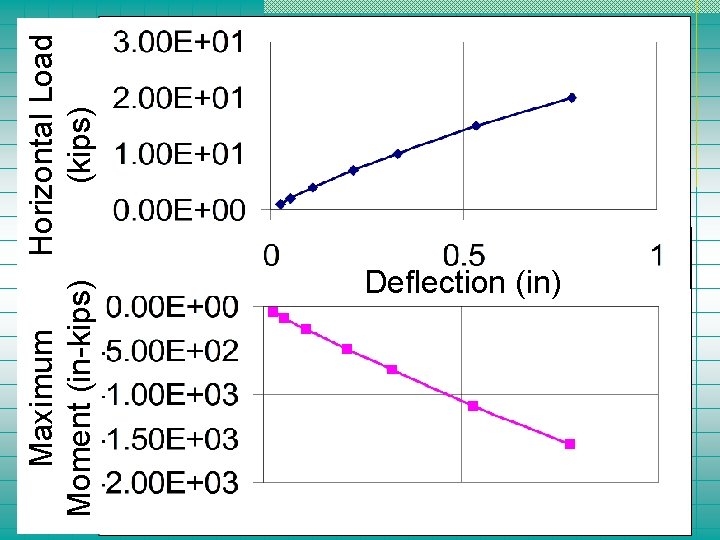
Horizontal Load Maximum (kips) Moment (in-kips) Deflection (in)
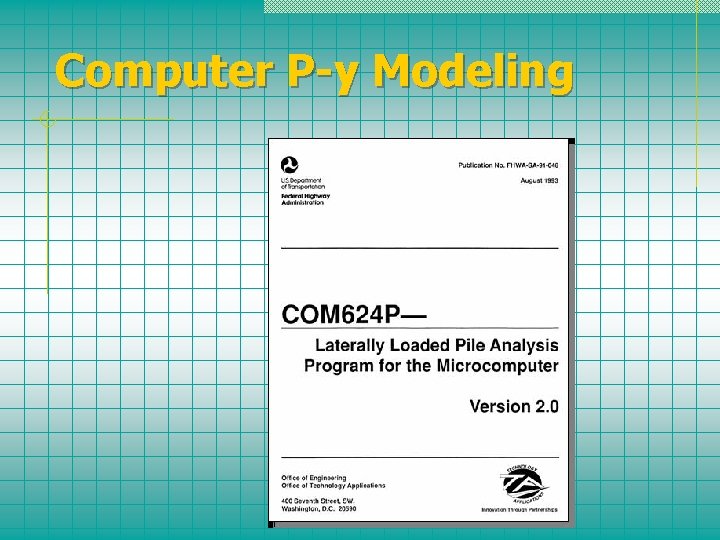
Computer P-y Modeling
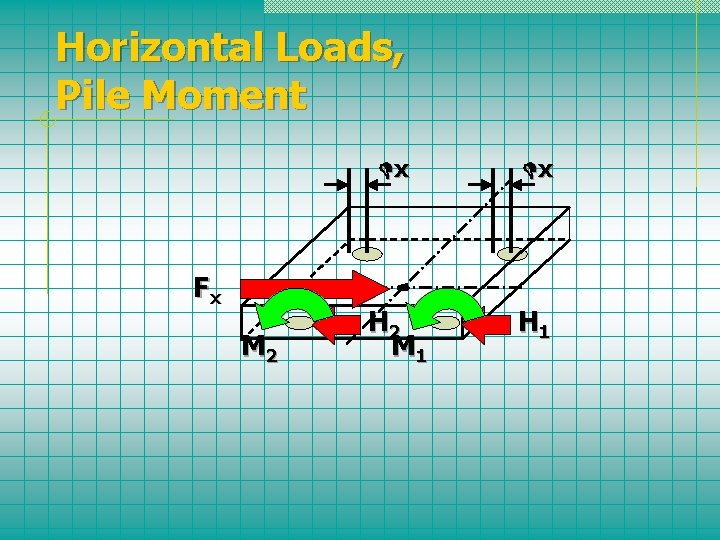
Horizontal Loads, Pile Moment Fx M 2 Dx Dx H 2 M 1 H 1
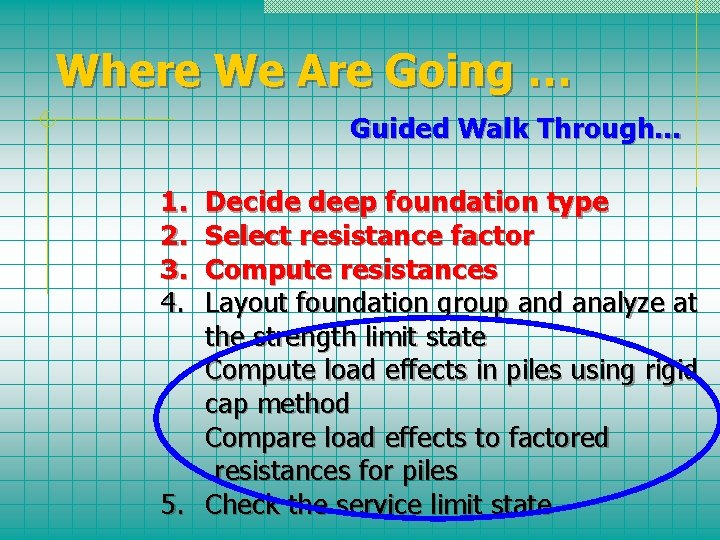
Where We Are Going … Guided Walk Through… 1. 2. 3. 4. Decide deep foundation type Select resistance factor Compute resistances Layout foundation group and analyze at the strength limit state Compute load effects in piles using rigid cap method Compare load effects to factored resistances for piles 5. Check the service limit state
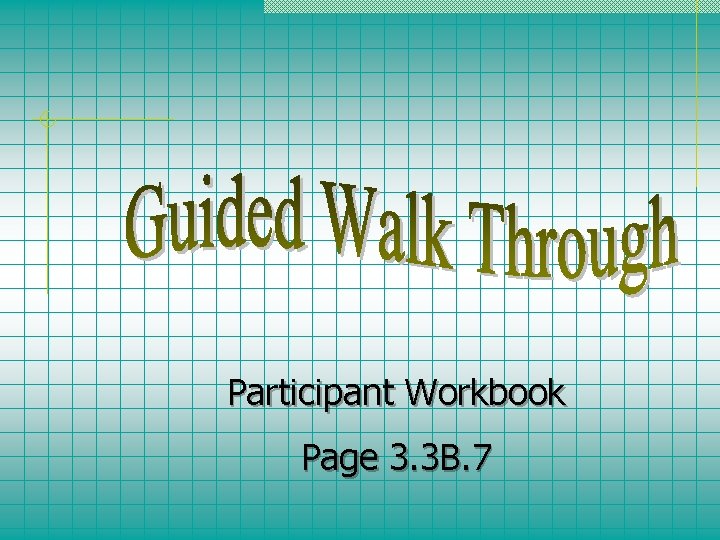
Participant Workbook Page 3. 3 B. 7
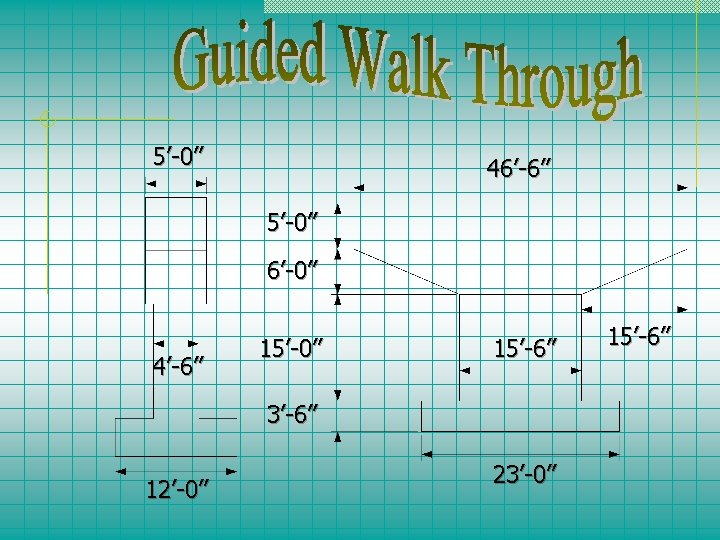
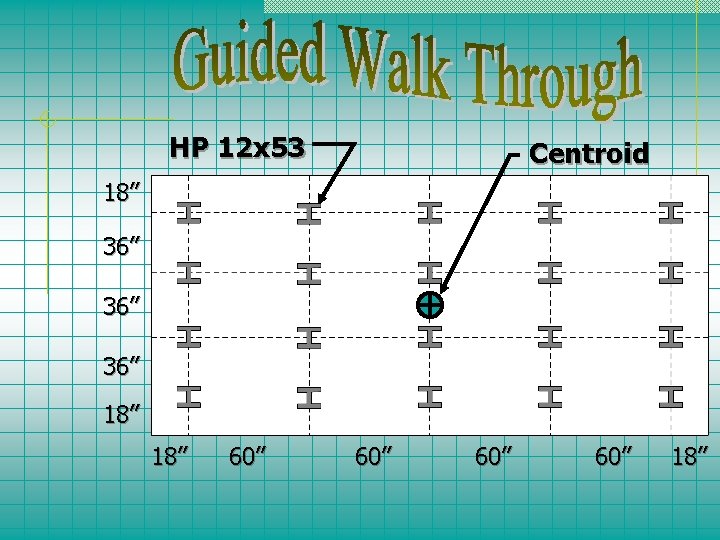
HP 12 x 53 Centroid 18” 36” 36” 18” 60” 60” 18”
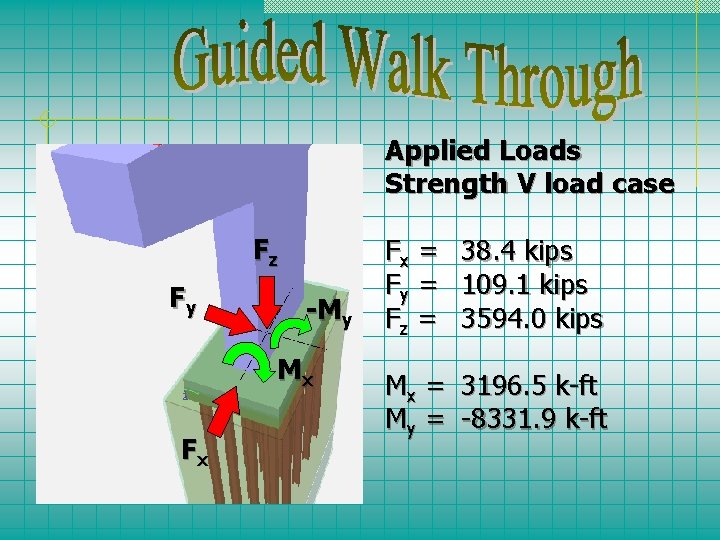
Applied Loads Strength V load case Fz Fy -My Mx Fx Fx = Fy = Fz = 38. 4 kips 109. 1 kips 3594. 0 kips Mx = 3196. 5 k-ft My = -8331. 9 k-ft
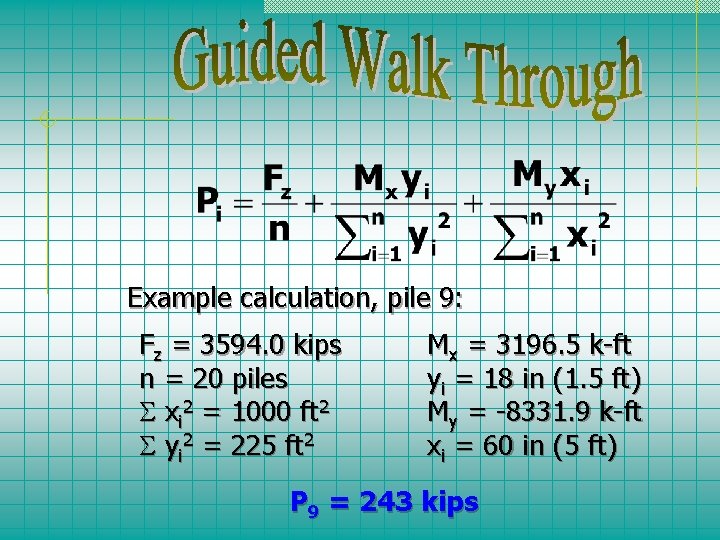
Example calculation, pile 9: Fz = 3594. 0 kips n = 20 piles xi 2 = 1000 ft 2 yi 2 = 225 ft 2 Mx = 3196. 5 k-ft yi = 18 in (1. 5 ft) My = -8331. 9 k-ft xi = 60 in (5 ft) P 9 = 243 kips
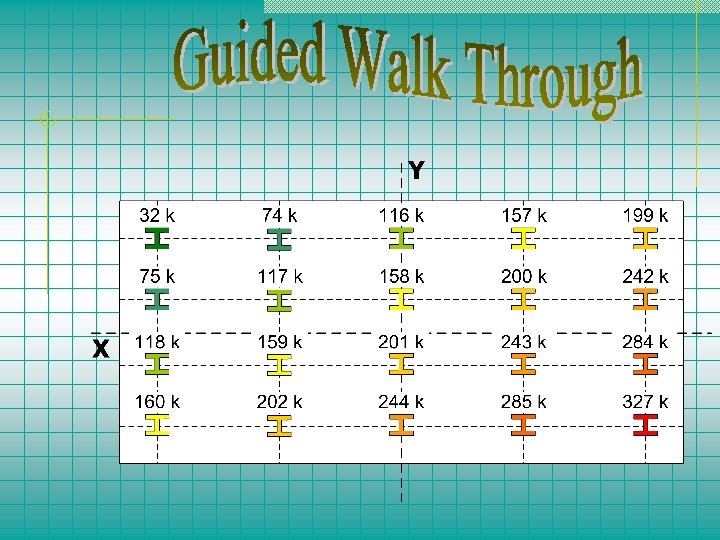
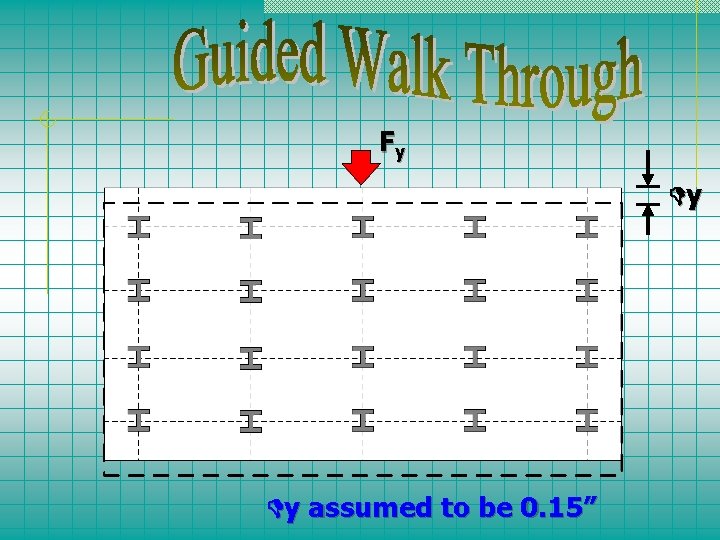
Fy Dy Dy assumed to be 0. 15”
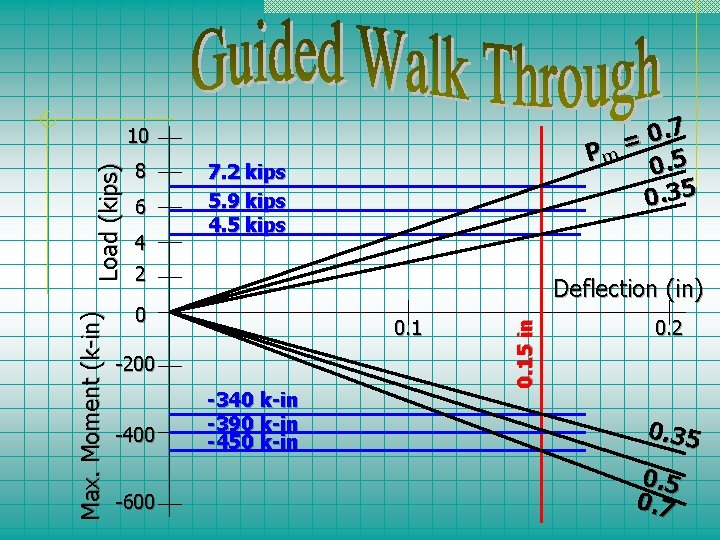
0. 7 = Pm 0. 5 0. 35 8 6 4 7. 2 kips 5. 9 kips 4. 5 kips 2 Deflection (in) 0 0. 1 -200 -400 -600 -340 k-in -390 k-in -450 k-in 0. 15 in Max. Moment (k-in) Load (kips) 10 0. 2 0. 35 0. 7
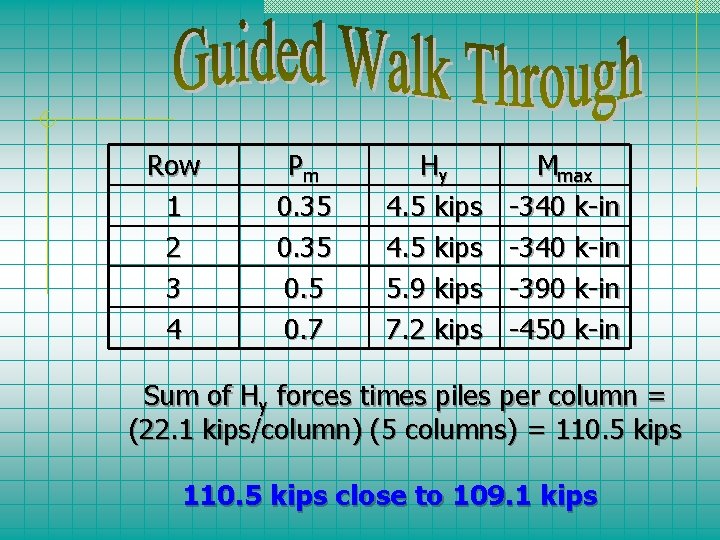
Row 1 2 3 4 Pm 0. 35 0. 7 Hy 4. 5 kips 5. 9 kips 7. 2 kips Mmax -340 k-in -390 k-in -450 k-in Sum of Hy forces times piles per column = (22. 1 kips/column) (5 columns) = 110. 5 kips close to 109. 1 kips
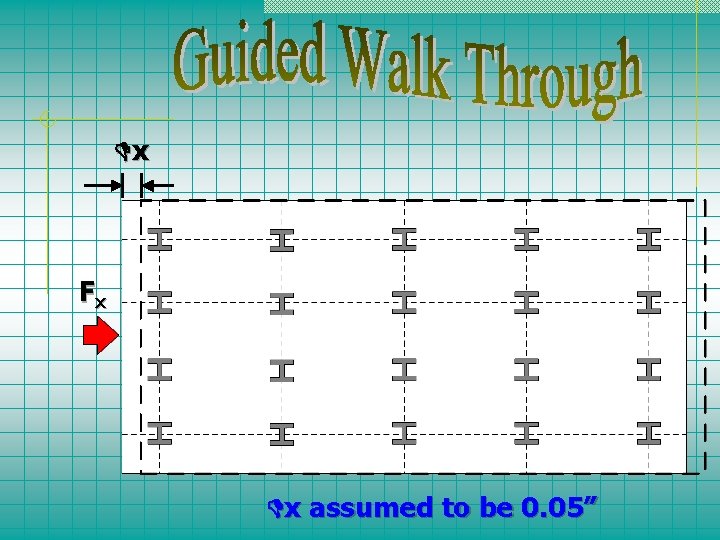
Dx Fx Dx assumed to be 0. 05”
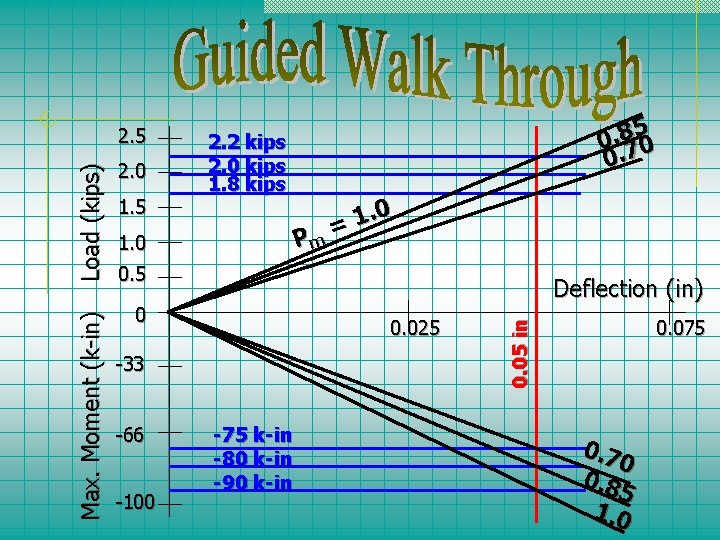
2. 0 1. 5 5 0. 870 0. 2. 2 kips 2. 0 kips 1. 8 kips Pm 1. 0 1 = 0. 5 Deflection (in) 0 0. 025 -33 -66 -100 -75 k-in -80 k-in -90 k-in 0. 075 0. 05 in Max. Moment (k-in) Load (kips) 2. 5 0. 7 0 0. 8 5 1. 0
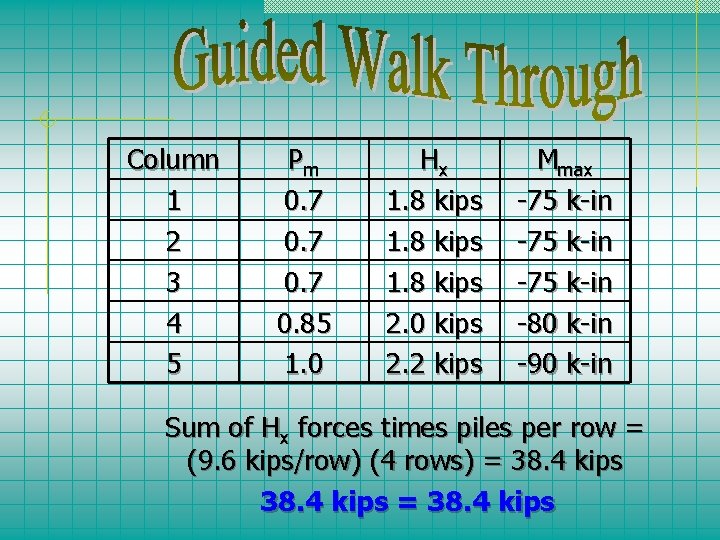
Column 1 2 3 4 5 Pm 0. 7 0. 85 1. 0 Hx 1. 8 kips 2. 0 kips 2. 2 kips Mmax -75 k-in -80 k-in -90 k-in Sum of Hx forces times piles per row = (9. 6 kips/row) (4 rows) = 38. 4 kips
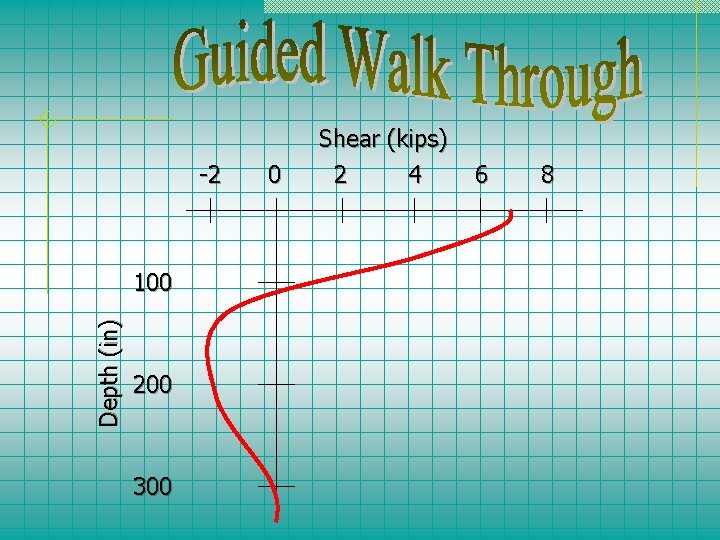
-2 Depth (in) 100 200 300 0 Shear (kips) 2 4 6 8
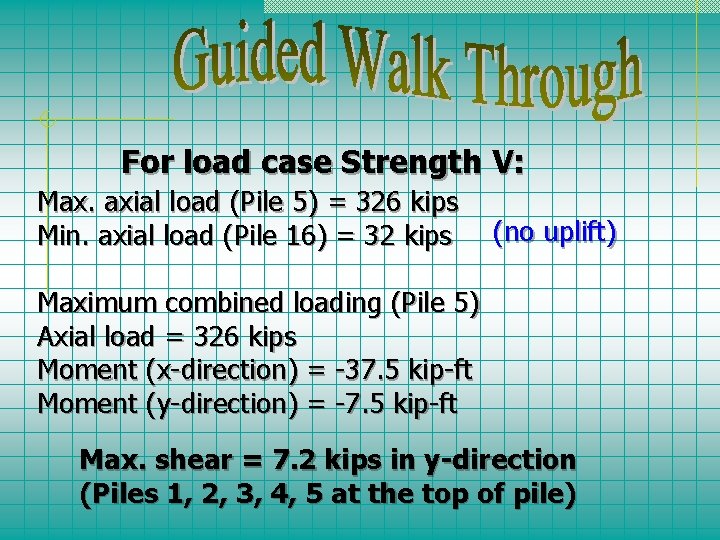
For load case Strength V: Max. axial load (Pile 5) = 326 kips Min. axial load (Pile 16) = 32 kips (no uplift) Maximum combined loading (Pile 5) Axial load = 326 kips Moment (x-direction) = -37. 5 kip-ft Moment (y-direction) = -7. 5 kip-ft Max. shear = 7. 2 kips in y-direction (Piles 1, 2, 3, 4, 5 at the top of pile)
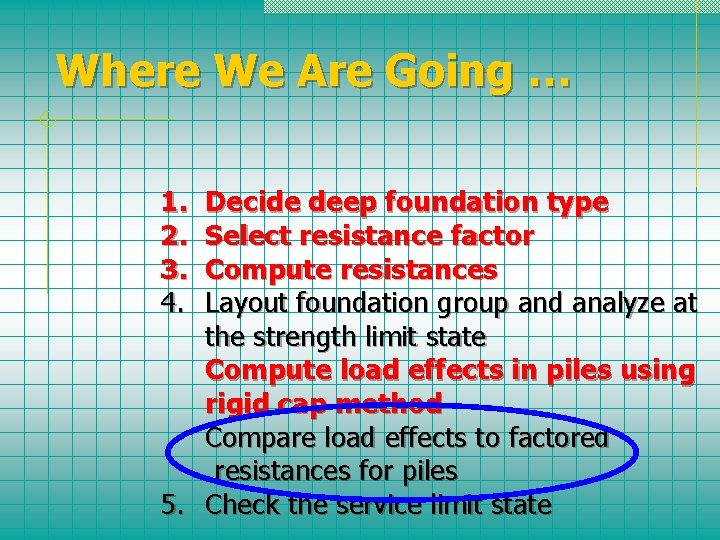
Where We Are Going … 1. 2. 3. 4. Decide deep foundation type Select resistance factor Compute resistances Layout foundation group and analyze at the strength limit state Compute load effects in piles using rigid cap method Compare load effects to factored resistances for piles 5. Check the service limit state
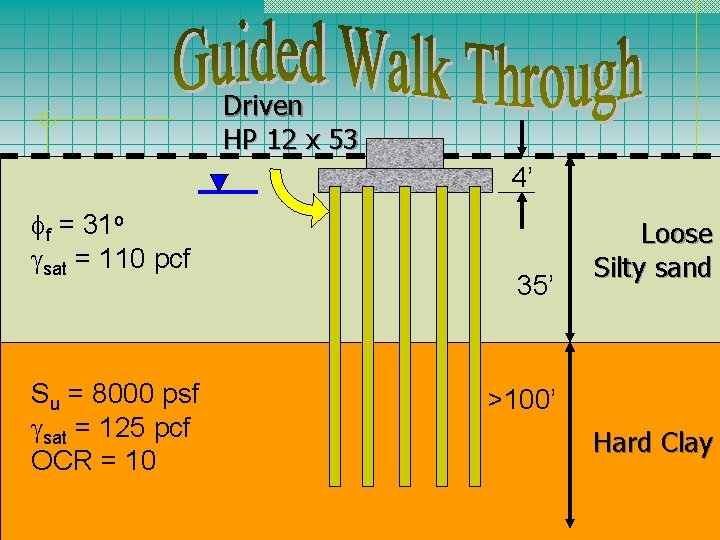
Driven HP 12 x 53 4’ f = 31 o sat = 110 pcf Su = 8000 psf sat = 125 pcf OCR = 10 35’ Loose Silty sand >100’ Hard Clay
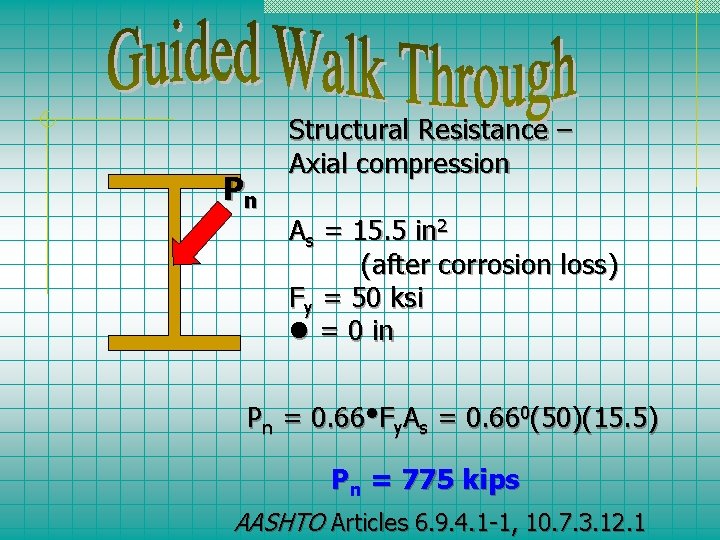
Pn Structural Resistance – Axial compression As = 15. 5 in 2 (after corrosion loss) Fy = 50 ksi l = 0 in Pn = 0. 66 l. Fy. As = 0. 660(50)(15. 5) Pn = 775 kips AASHTO Articles 6. 9. 4. 1 -1, 10. 7. 3. 12. 1
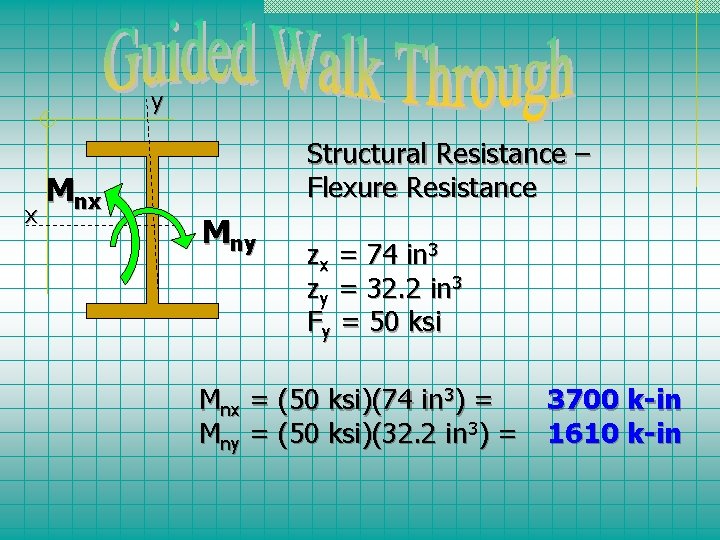
y x Mnx Structural Resistance – Flexure Resistance Mny zx = 74 in 3 zy = 32. 2 in 3 Fy = 50 ksi Mnx = (50 ksi)(74 in 3) = Mny = (50 ksi)(32. 2 in 3) = 3700 k-in 1610 k-in
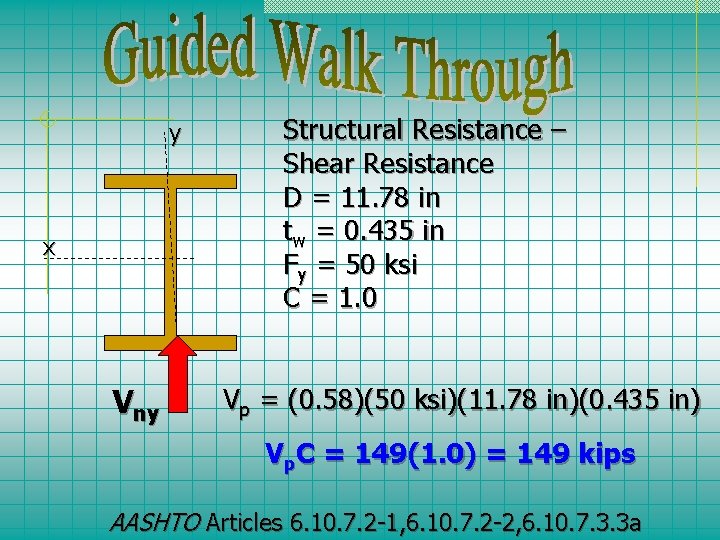
y x Vny Structural Resistance – Shear Resistance D = 11. 78 in tw = 0. 435 in Fy = 50 ksi C = 1. 0 Vp = (0. 58)(50 ksi)(11. 78 in)(0. 435 in) Vp. C = 149(1. 0) = 149 kips AASHTO Articles 6. 10. 7. 2 -1, 6. 10. 7. 2 -2, 6. 10. 7. 3. 3 a
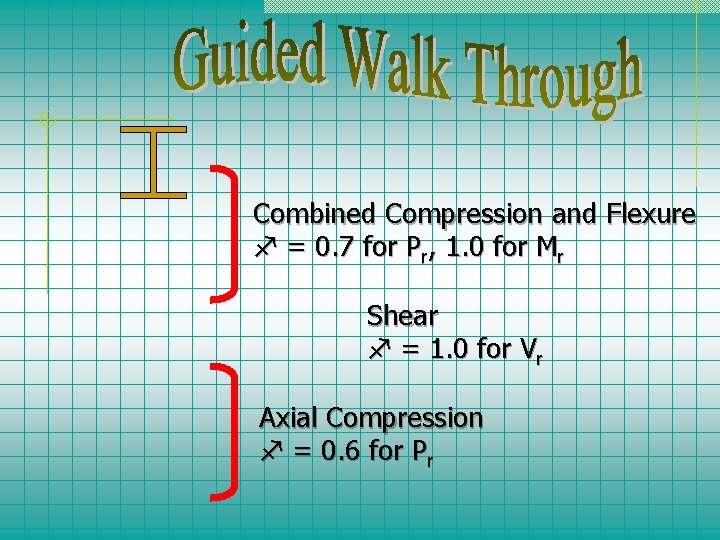
Combined Compression and Flexure f = 0. 7 for Pr, 1. 0 for Mr Shear f = 1. 0 for Vr Axial Compression f = 0. 6 for Pr
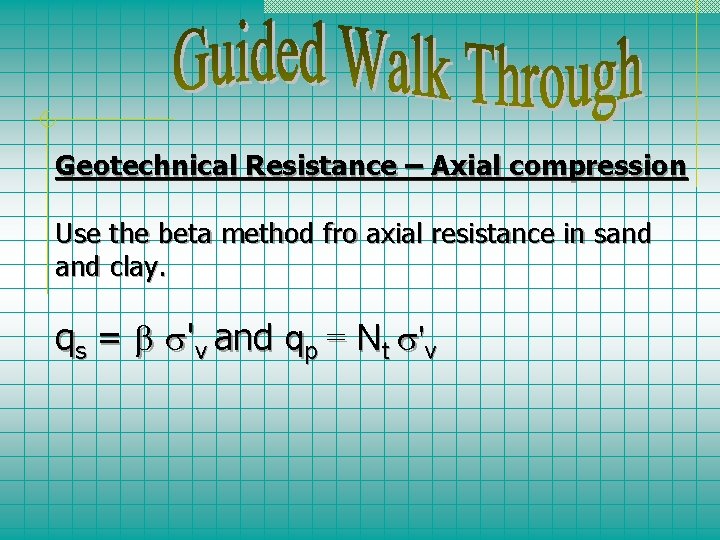
Geotechnical Resistance – Axial compression Use the beta method fro axial resistance in sand clay. qs = 'v and qp = Nt 'v
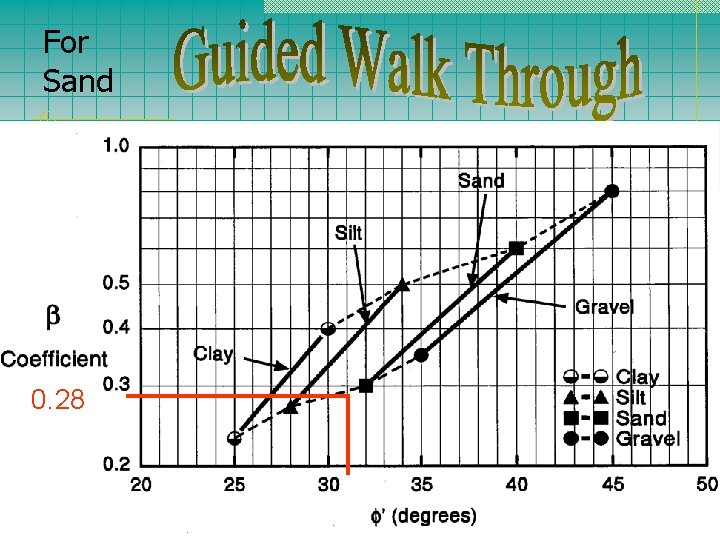
For Sand 0. 28
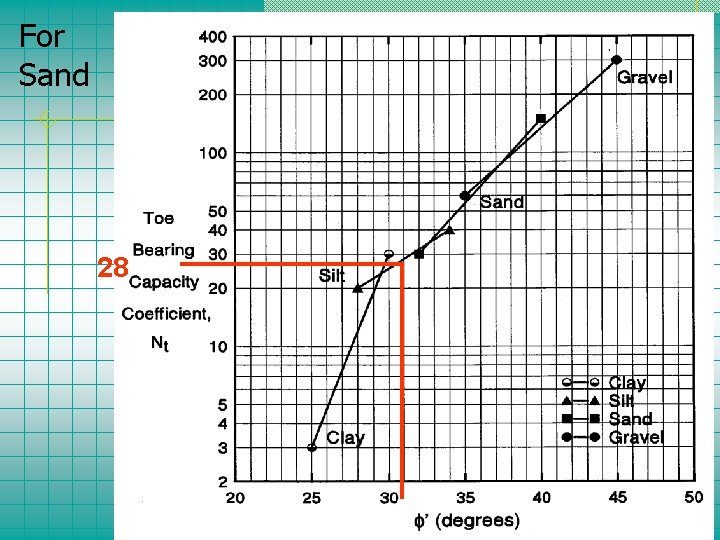
For Sand 28
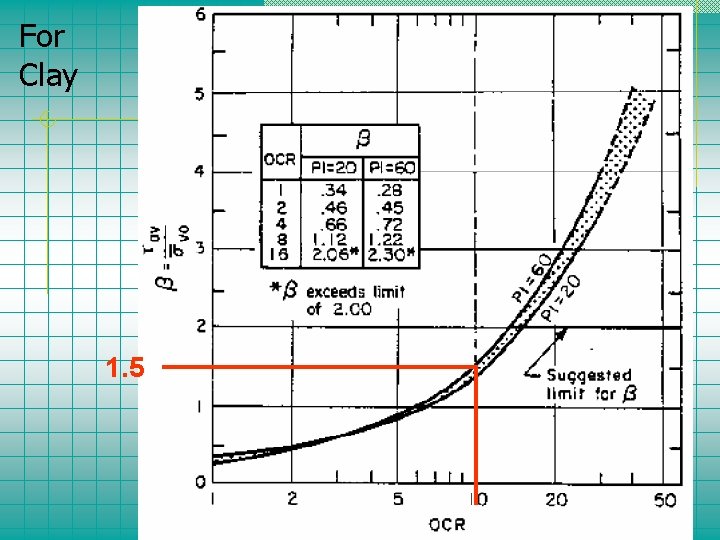
For Clay 1. 5
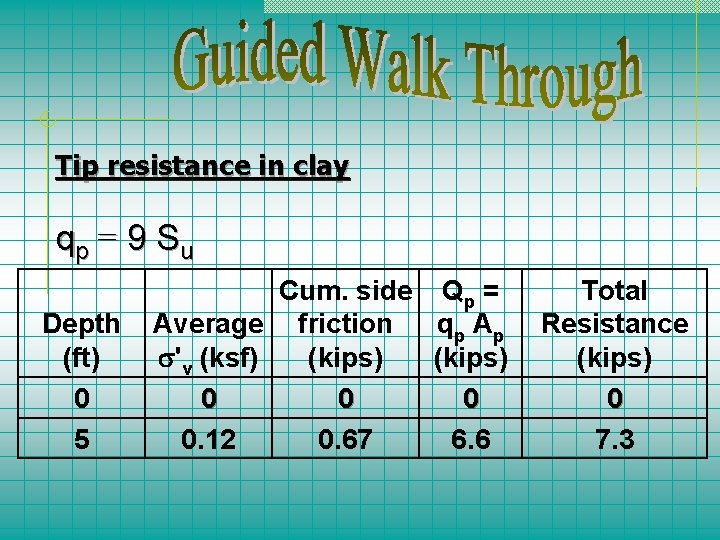
Tip resistance in clay qp = 9 S u Depth (ft) 0 5 Cum. side Qp = q p Ap Average friction s'v (ksf) (kips) 0 0. 12 0. 67 6. 6 Total Resistance (kips) 0 7. 3
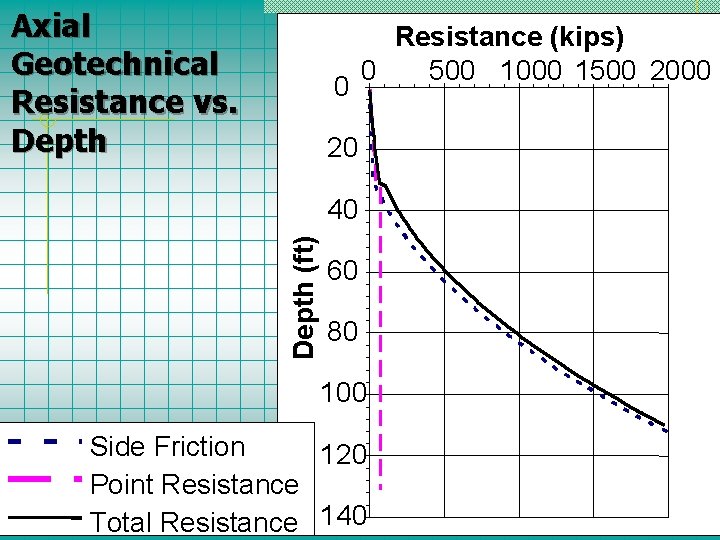
Axial Geotechnical Resistance vs. Depth 0 Resistance (kips) 0 500 1000 1500 20 Depth (ft) 40 60 80 100 Side Friction 120 Point Resistance Total Resistance 140
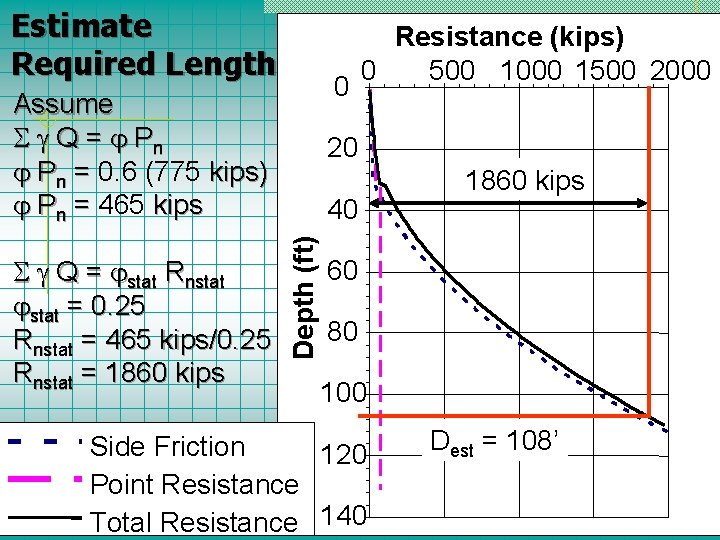
Estimate Required Length 0 Assume Q = Pn = 0. 6 (775 kips) Pn = 465 kips 20 40 Depth (ft) Q = stat Rnstat = 0. 25 Rnstat = 465 kips/0. 25 Rnstat = 1860 kips Resistance (kips) 0 500 1000 1500 2000 1860 kips 60 80 100 Side Friction 120 Point Resistance Total Resistance 140 Dest = 108’
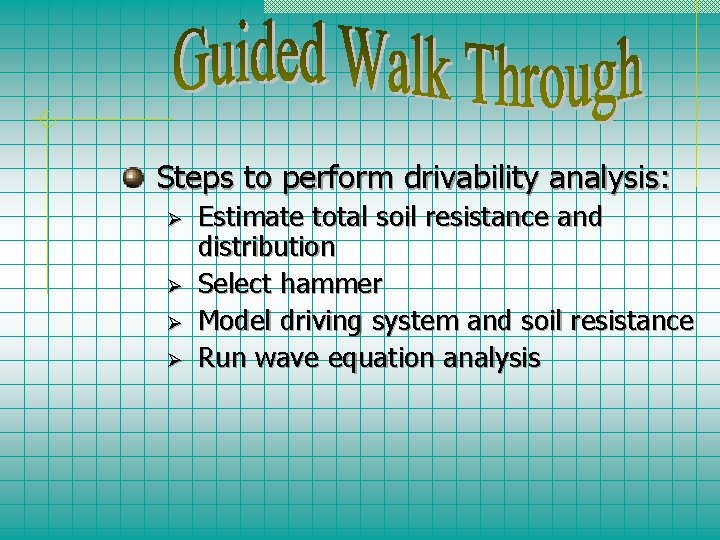
Steps to perform drivability analysis: Ø Ø Estimate total soil resistance and distribution Select hammer Model driving system and soil resistance Run wave equation analysis
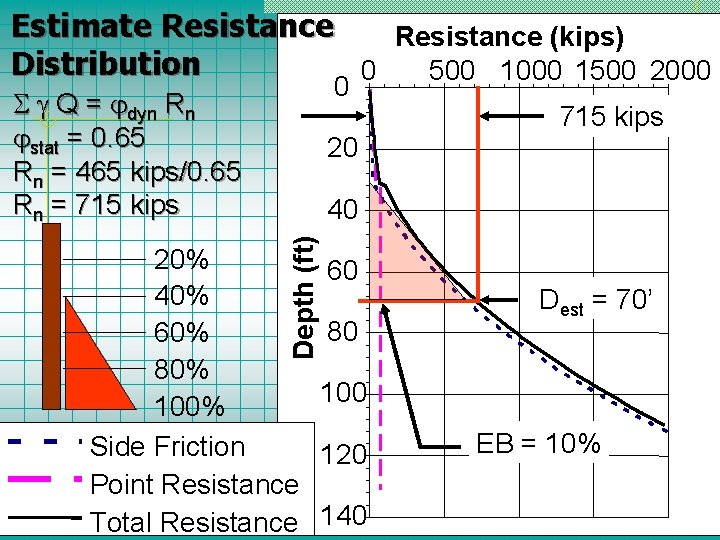
Estimate Resistance (kips) Distribution 0 500 1000 1500 2000 0 Q = dyn Rn stat = 0. 65 Rn = 465 kips/0. 65 Rn = 715 kips 20 Depth (ft) 40 20% 40% 60% 80% 100% Side Friction Point Resistance Total Resistance 60 80 Dest = 70’ 100 120 140 EB = 10%
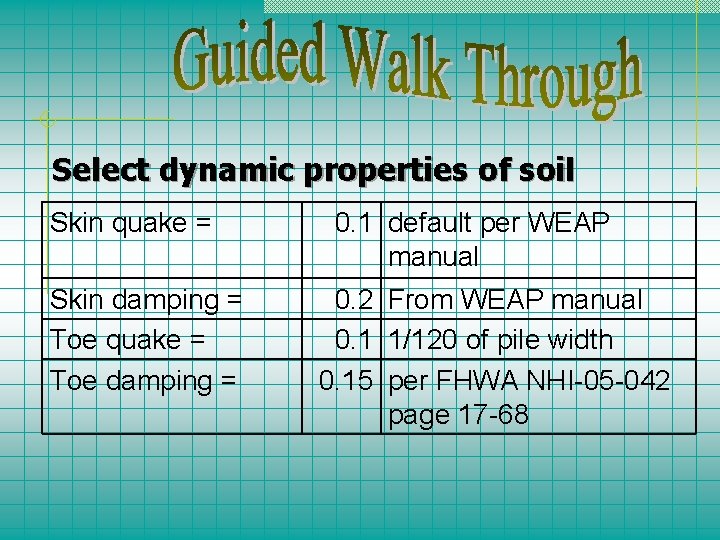
Select dynamic properties of soil Skin quake = Skin damping = Toe quake = Toe damping = 0. 1 default per WEAP manual 0. 2 From WEAP manual 0. 1 1/120 of pile width 0. 15 per FHWA NHI-05 -042 page 17 -68
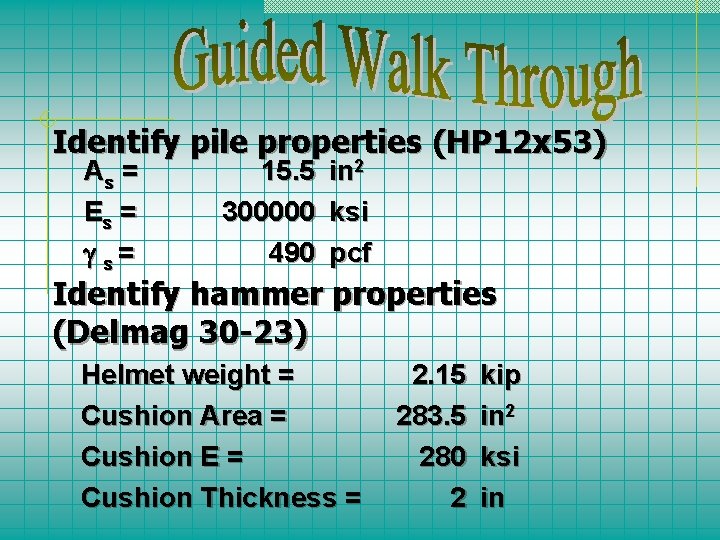
Identify pile properties (HP 12 x 53) As = Es = s= 15. 5 in 2 300000 ksi 490 pcf Identify hammer properties (Delmag 30 -23) Helmet weight = Cushion Area = Cushion E = Cushion Thickness = 2. 15 283. 5 280 2 kip in 2 ksi in
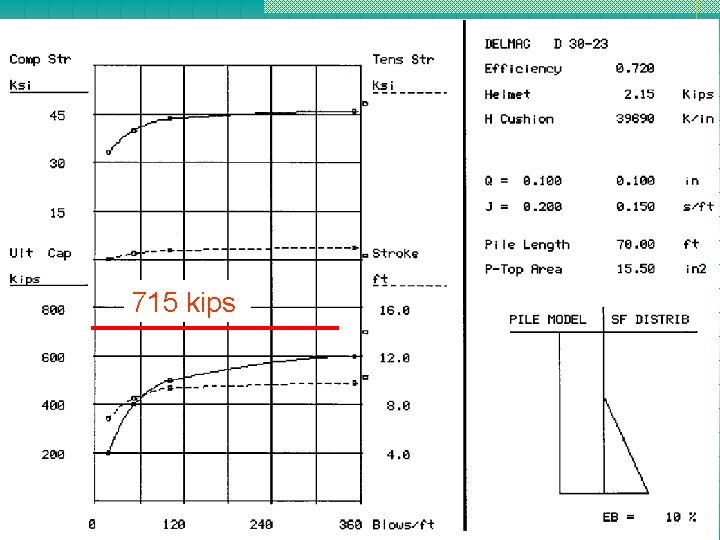
715 kips
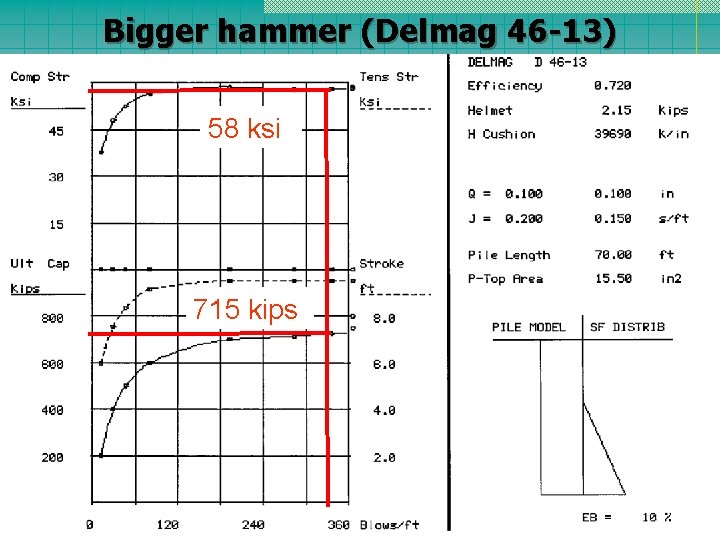
Bigger hammer (Delmag 46 -13) 58 ksi 715 kips
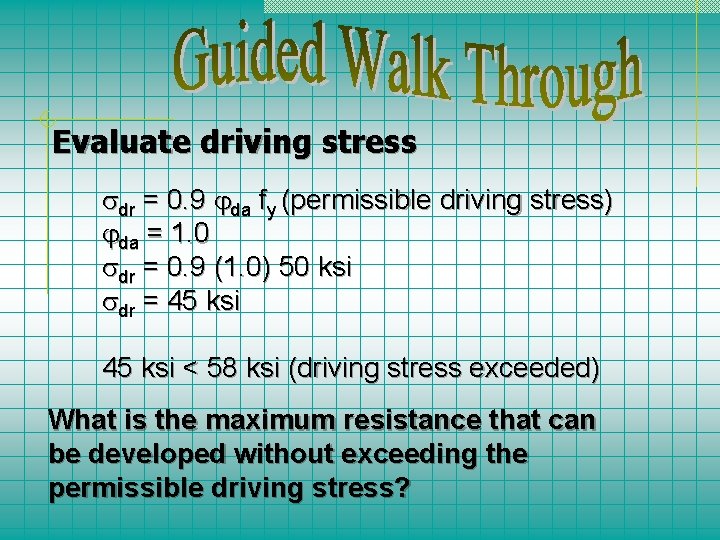
Evaluate driving stress dr = 0. 9 da fy (permissible driving stress) da = 1. 0 dr = 0. 9 (1. 0) 50 ksi dr = 45 ksi < 58 ksi (driving stress exceeded) What is the maximum resistance that can be developed without exceeding the permissible driving stress?
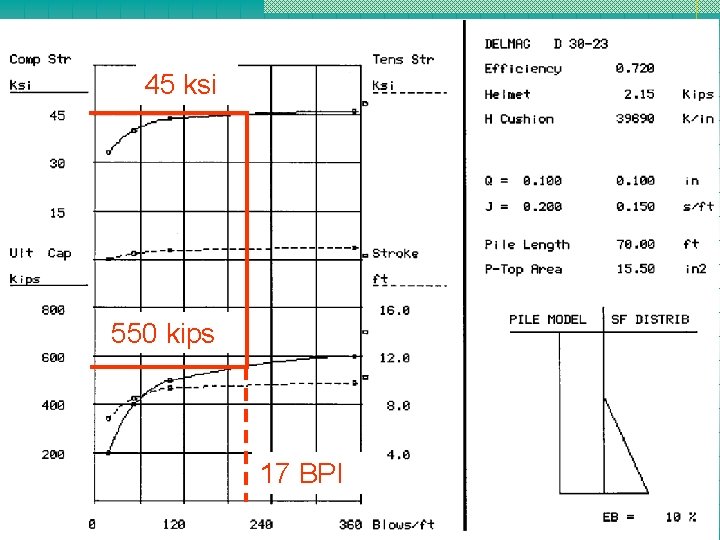
45 ksi 550 kips 17 BPI
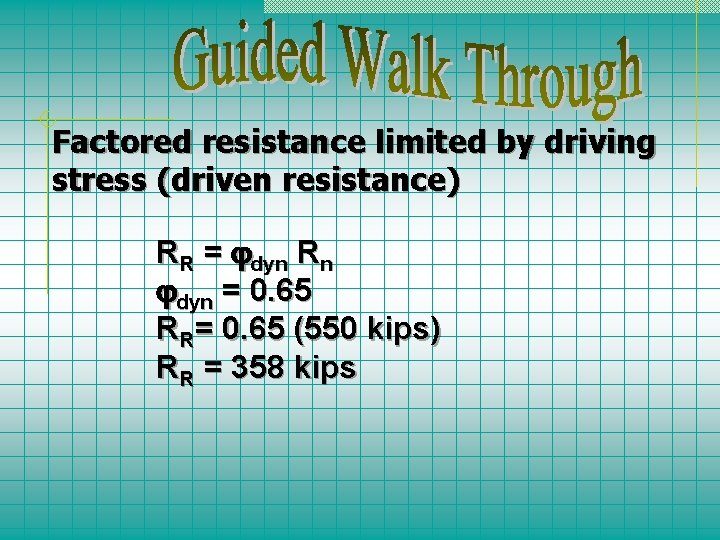
Factored resistance limited by driving stress (driven resistance) RR = dyn Rn dyn = 0. 65 RR= 0. 65 (550 kips) RR = 358 kips
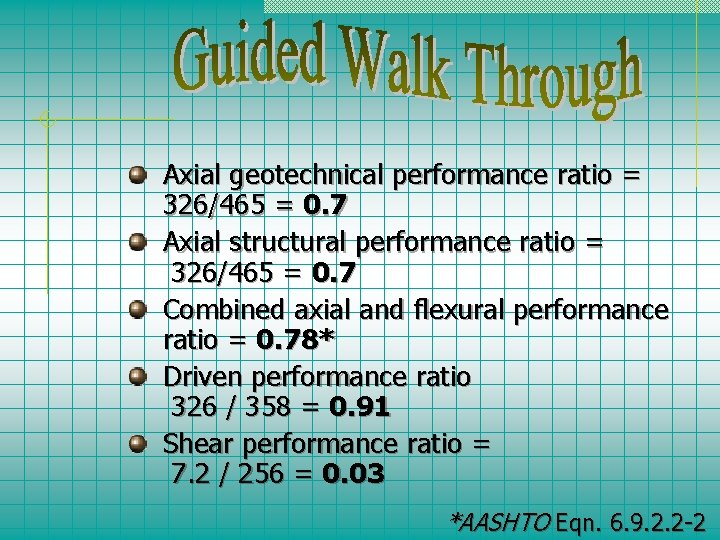
Axial geotechnical performance ratio = 326/465 = 0. 7 Axial structural performance ratio = 326/465 = 0. 7 Combined axial and flexural performance ratio = 0. 78* Driven performance ratio 326 / 358 = 0. 91 Shear performance ratio = 7. 2 / 256 = 0. 03 *AASHTO Eqn. 6. 9. 2. 2 -2
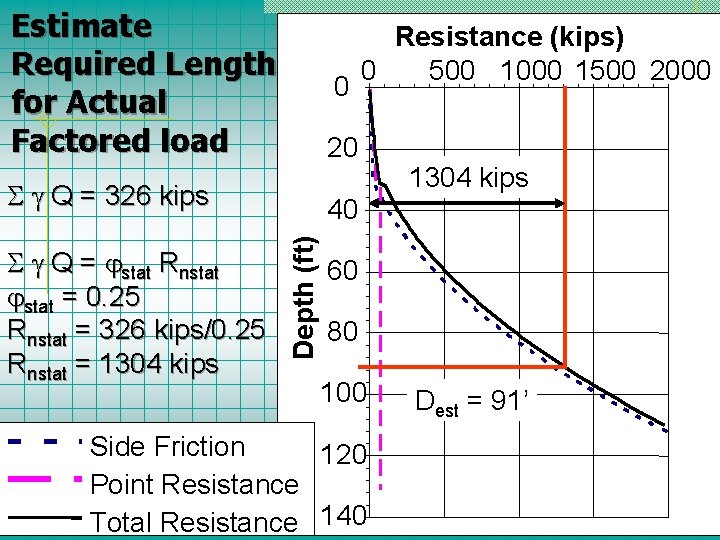
Estimate Required Length for Actual Factored load 0 20 Q = 326 kips 1304 kips 40 Depth (ft) Q = stat Rnstat = 0. 25 Rnstat = 326 kips/0. 25 Rnstat = 1304 kips Resistance (kips) 0 500 1000 1500 2000 60 80 100 Side Friction 120 Point Resistance Total Resistance 140 Dest = 91’
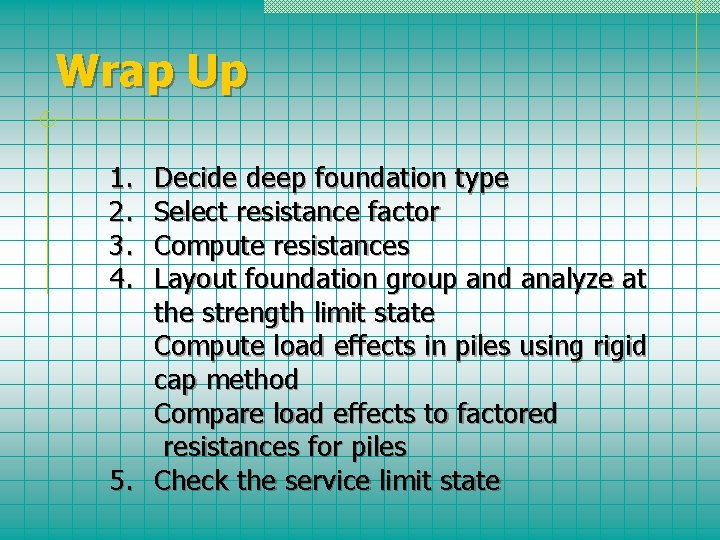
Wrap Up 1. 2. 3. 4. Decide deep foundation type Select resistance factor Compute resistances Layout foundation group and analyze at the strength limit state Compute load effects in piles using rigid cap method Compare load effects to factored resistances for piles 5. Check the service limit state
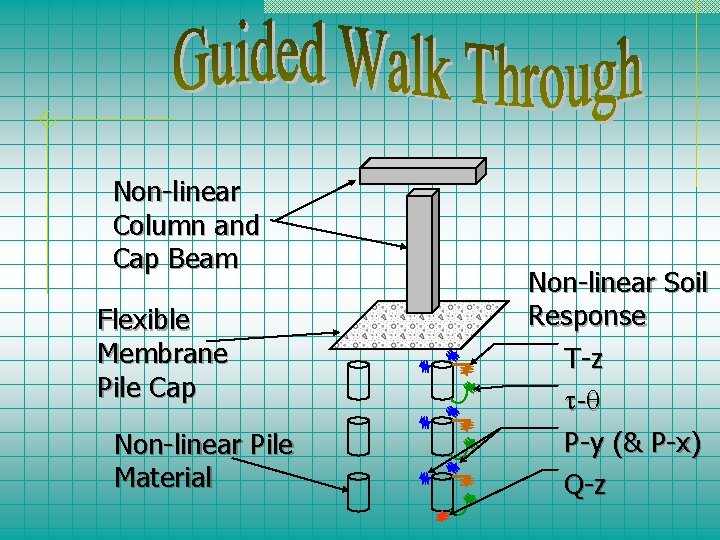
Non-linear Column and Cap Beam Flexible Membrane Pile Cap Non-linear Pile Material Non-linear Soil Response T-z - P-y (& P-x) Q-z
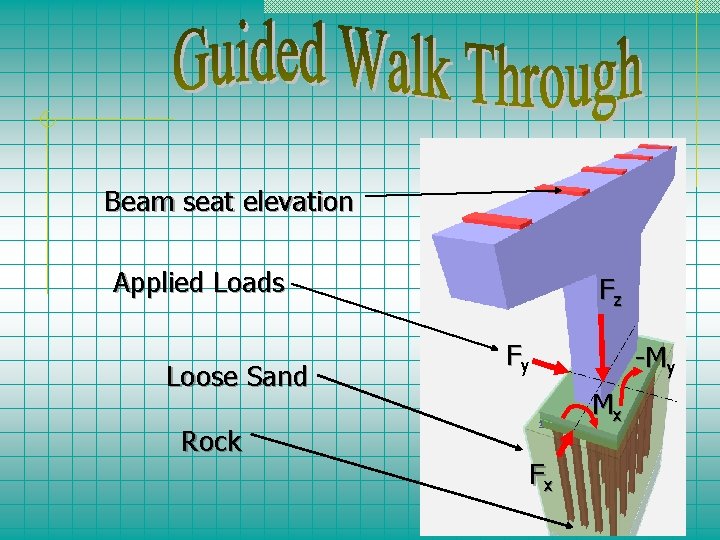
Beam seat elevation Applied Loads Loose Sand Rock Fz Fy -My Mx Fx

Axial Results Shear Results Moment Results Pile 5 Pile 16 Rigid Cap Results Shear = 7. 2 kips Max. Axial = 327 k-in kips Moment = - 37. 5 Min. Axial = 32 kips
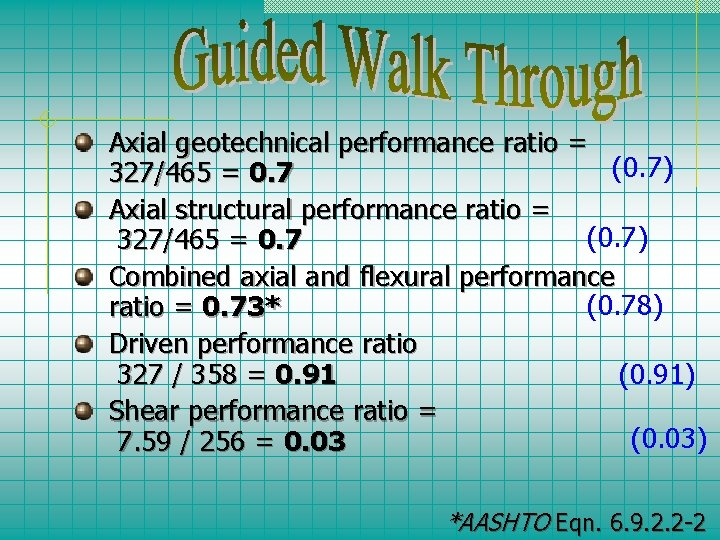
Axial geotechnical performance ratio = (0. 7) 327/465 = 0. 7 Axial structural performance ratio = (0. 7) 327/465 = 0. 7 Combined axial and flexural performance (0. 78) ratio = 0. 73* Driven performance ratio 327 / 358 = 0. 91 (0. 91) Shear performance ratio = (0. 03) 7. 59 / 256 = 0. 03 *AASHTO Eqn. 6. 9. 2. 2 -2
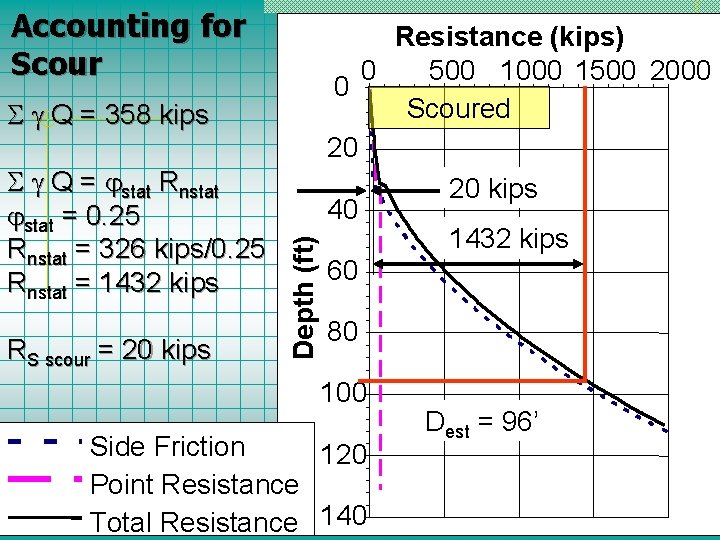
Accounting for Scour Q = stat Rnstat = 0. 25 Rnstat = 326 kips/0. 25 Rnstat = 1432 kips RS scour = 20 kips Depth (ft) Q = 358 kips Resistance (kips) 0 500 1000 1500 2000 0 Scoured 20 20 kips 40 1432 kips 60 80 100 Side Friction 120 Point Resistance Total Resistance 140 Dest = 96’
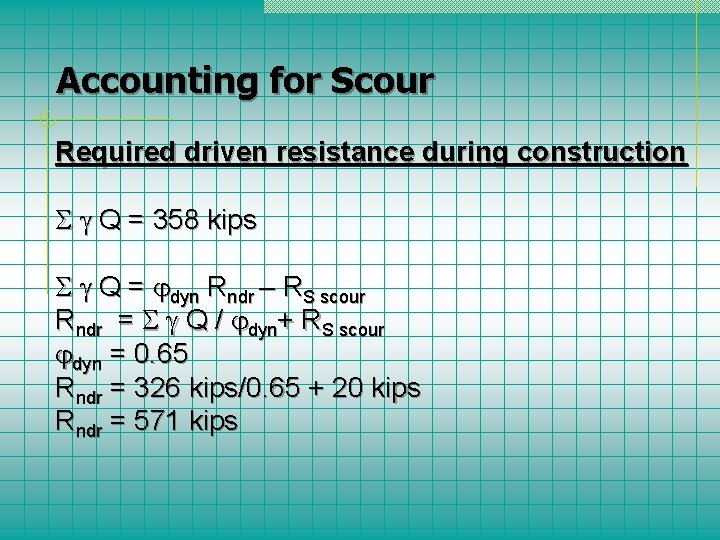
Accounting for Scour Required driven resistance during construction Q = 358 kips Q = dyn Rndr – RS scour Rndr = Q / dyn+ RS scour dyn = 0. 65 Rndr = 326 kips/0. 65 + 20 kips Rndr = 571 kips
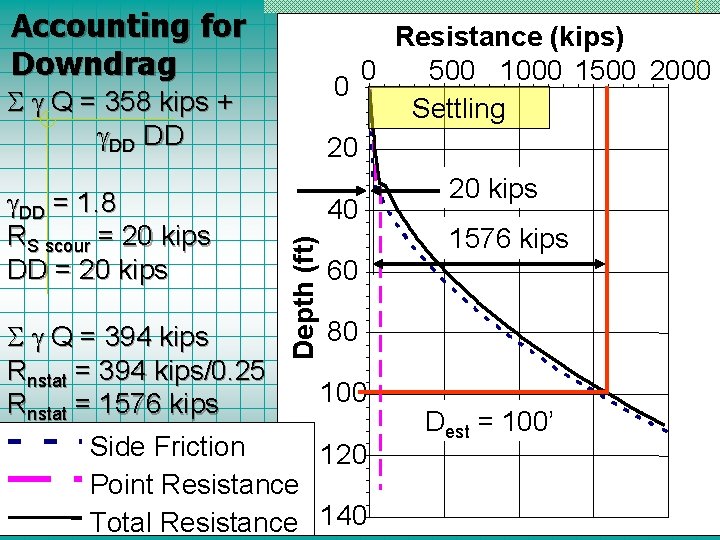
Accounting for Downdrag DD = 1. 8 RS scour = 20 kips DD = 20 kips Depth (ft) Q = 358 kips + DD DD Q = 394 kips Rnstat = 394 kips/0. 25 Rnstat = 1576 kips Side Friction Point Resistance Total Resistance (kips) 0 500 1000 1500 2000 0 Settling 20 20 kips 40 1576 kips 60 80 100 120 140 Dest = 100’
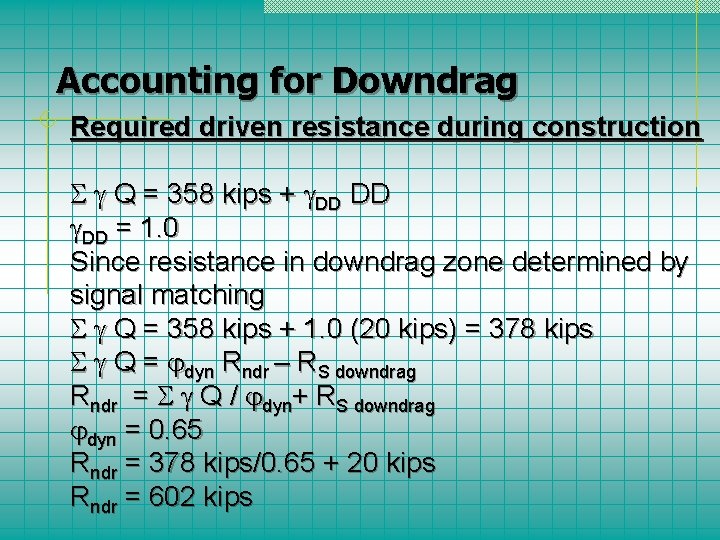
Accounting for Downdrag Required driven resistance during construction Q = 358 kips + DD DD DD = 1. 0 Since resistance in downdrag zone determined by signal matching Q = 358 kips + 1. 0 (20 kips) = 378 kips Q = dyn Rndr – RS downdrag Rndr = Q / dyn+ RS downdrag dyn = 0. 65 Rndr = 378 kips/0. 65 + 20 kips Rndr = 602 kips
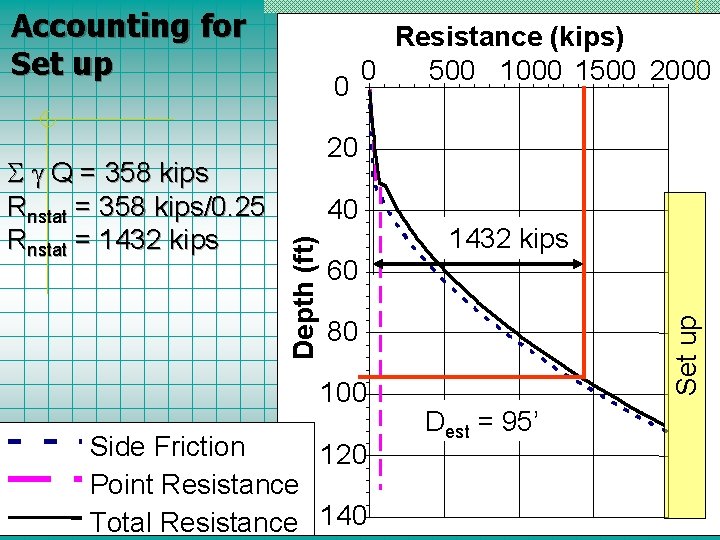
Accounting for Set up 20 40 1432 kips 60 Set up Depth (ft) Q = 358 kips Rnstat = 358 kips/0. 25 Rnstat = 1432 kips 0 Resistance (kips) 0 500 1000 1500 2000 80 100 Side Friction 120 Point Resistance Total Resistance 140 Dest = 95’
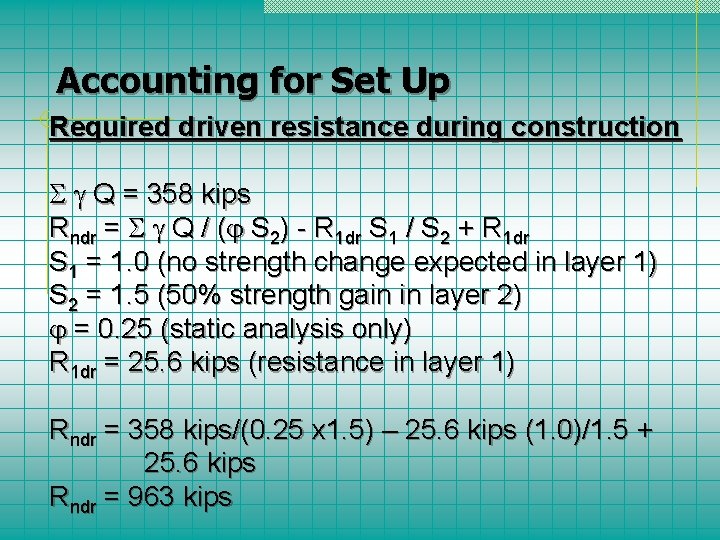
Accounting for Set Up Required driven resistance during construction Q = 358 kips Rndr = Q / ( S 2) - R 1 dr S 1 / S 2 + R 1 dr S 1 = 1. 0 (no strength change expected in layer 1) S 2 = 1. 5 (50% strength gain in layer 2) = 0. 25 (static analysis only) R 1 dr = 25. 6 kips (resistance in layer 1) Rndr = 358 kips/(0. 25 x 1. 5) – 25. 6 kips (1. 0)/1. 5 + 25. 6 kips Rndr = 963 kips
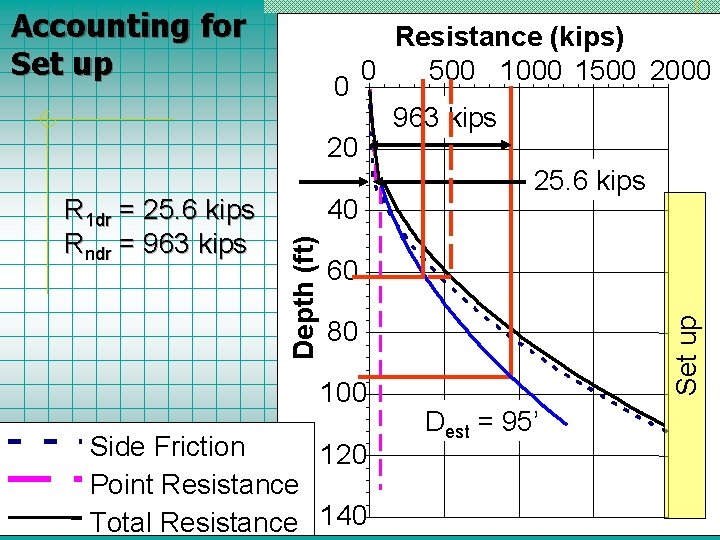
0 Resistance (kips) 0 500 1000 1500 20 40 Depth (ft) R 1 dr = 25. 6 kips Rndr = 963 kips 25. 6 kips 60 Set up Accounting for Set up 80 100 Side Friction 120 Point Resistance Total Resistance 140 Dest = 95’
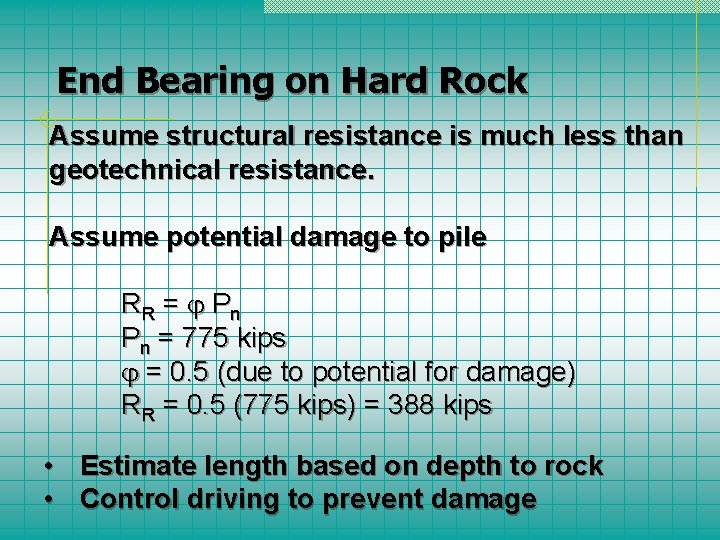
End Bearing on Hard Rock Assume structural resistance is much less than geotechnical resistance. Assume potential damage to pile RR = P n Pn = 775 kips = 0. 5 (due to potential for damage) RR = 0. 5 (775 kips) = 388 kips • Estimate length based on depth to rock • Control driving to prevent damage
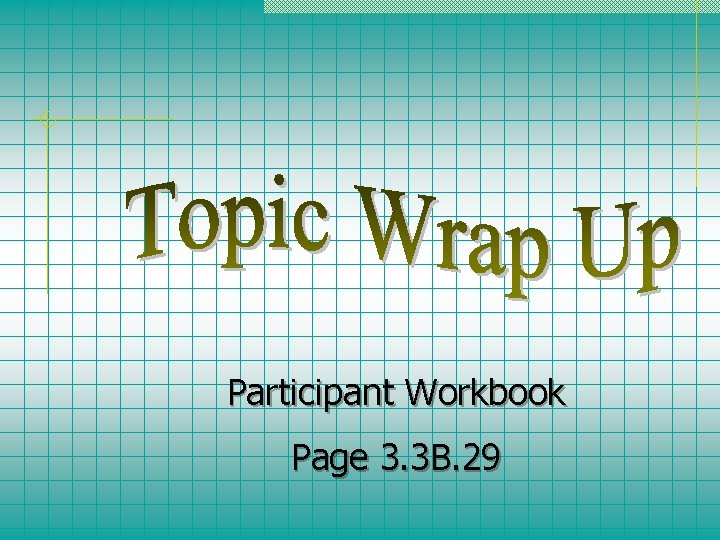
Participant Workbook Page 3. 3 B. 29
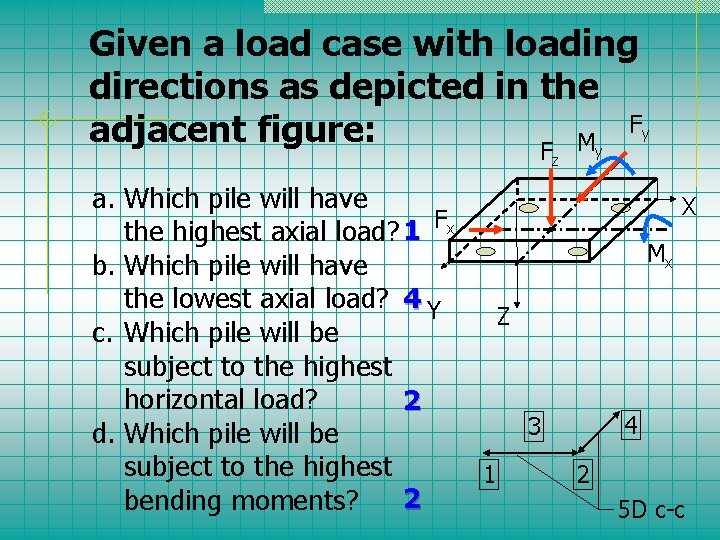
Given a load case with loading directions as depicted in the Fy adjacent figure: My Fz a. Which pile will have the highest axial load? 1 Fx b. Which pile will have the lowest axial load? 4 Y Z c. Which pile will be subject to the highest horizontal load? 2 3 d. Which pile will be subject to the highest 1 2 bending moments? X Mx 4 2 5 D c-c
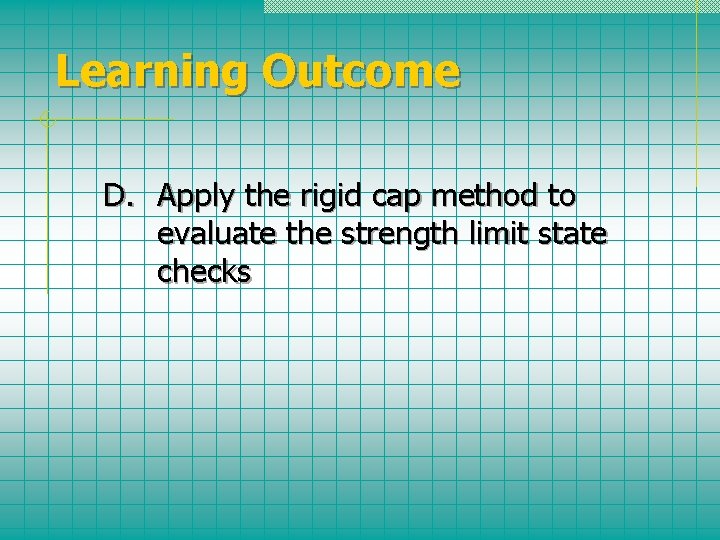
Learning Outcome D. Apply the rigid cap method to evaluate the strength limit state checks
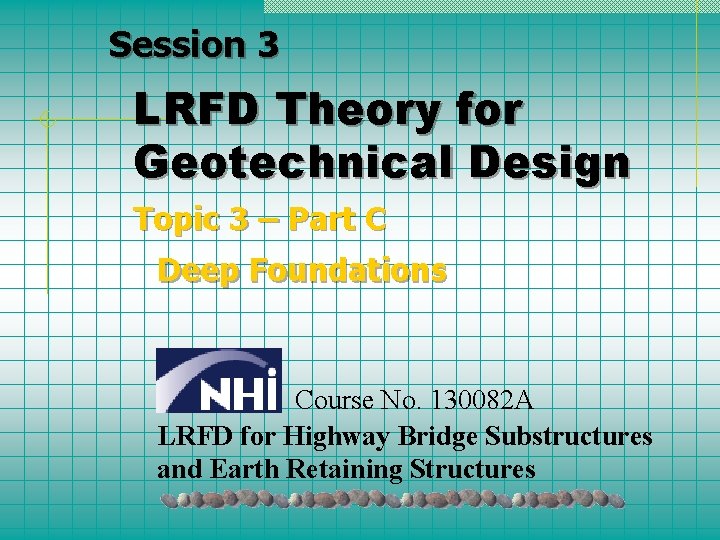
Session 3 LRFD Theory for Geotechnical Design Topic 3 – Part C Deep Foundations Course No. 130082 A LRFD for Highway Bridge Substructures and Earth Retaining Structures
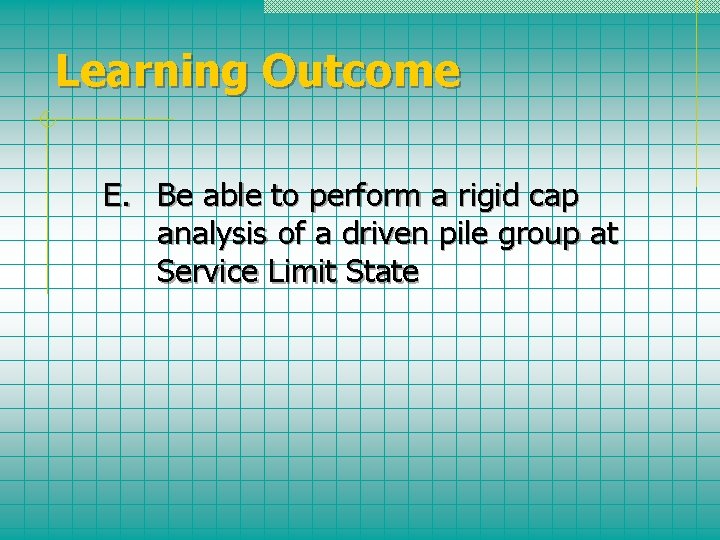
Learning Outcome E. Be able to perform a rigid cap analysis of a driven pile group at Service Limit State
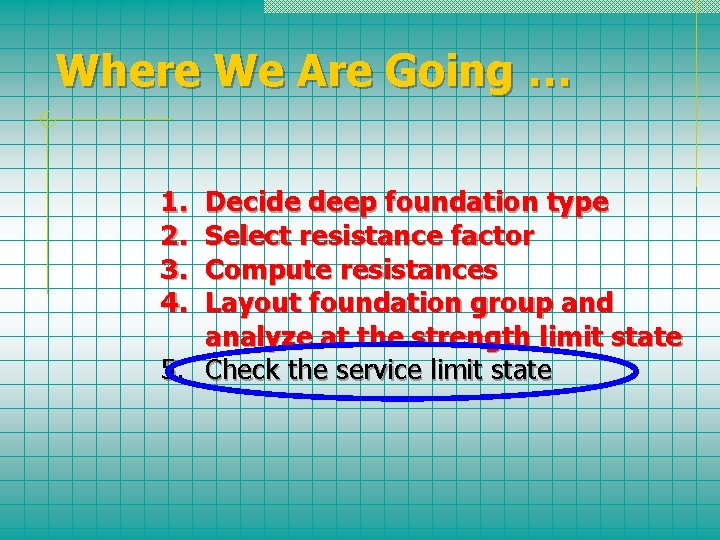
Where We Are Going … 1. 2. 3. 4. Decide deep foundation type Select resistance factor Compute resistances Layout foundation group and analyze at the strength limit state 5. Check the service limit state
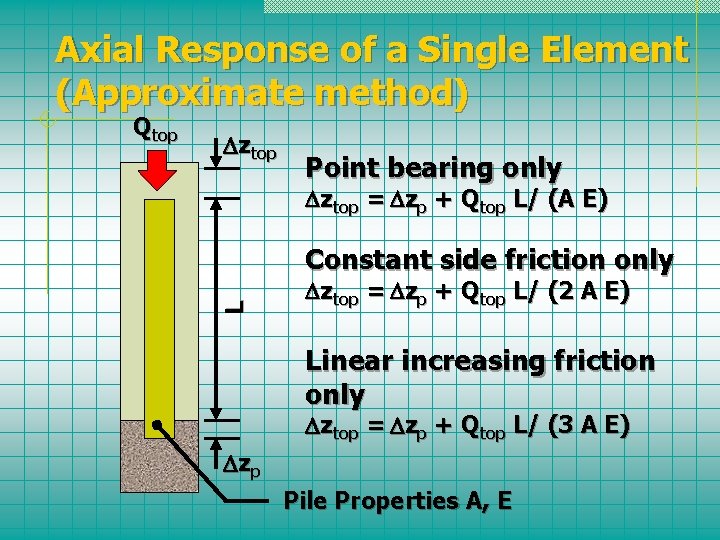
Axial Response of a Single Element (Approximate method) Dztop Point bearing only Dztop = Dzp + Qtop L/ (A E) Constant side friction only L Qtop Dztop = Dzp + Qtop L/ (2 A E) Linear increasing friction only Dztop = Dzp + Qtop L/ (3 A E) Dzp Pile Properties A, E
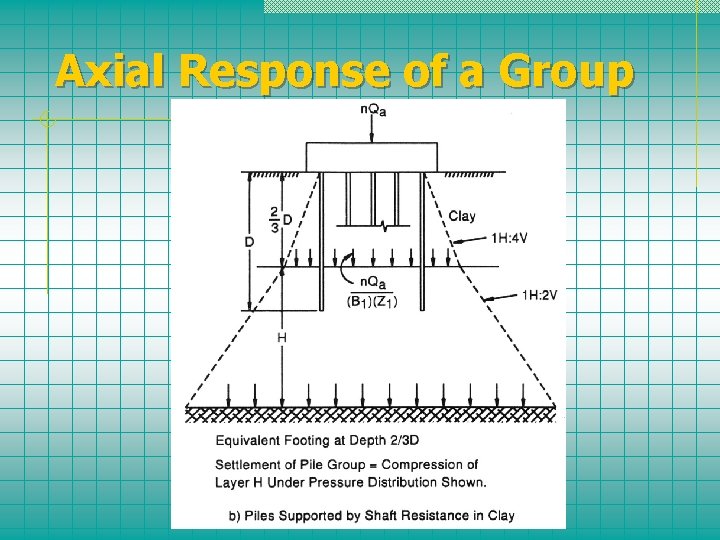
Axial Response of a Group
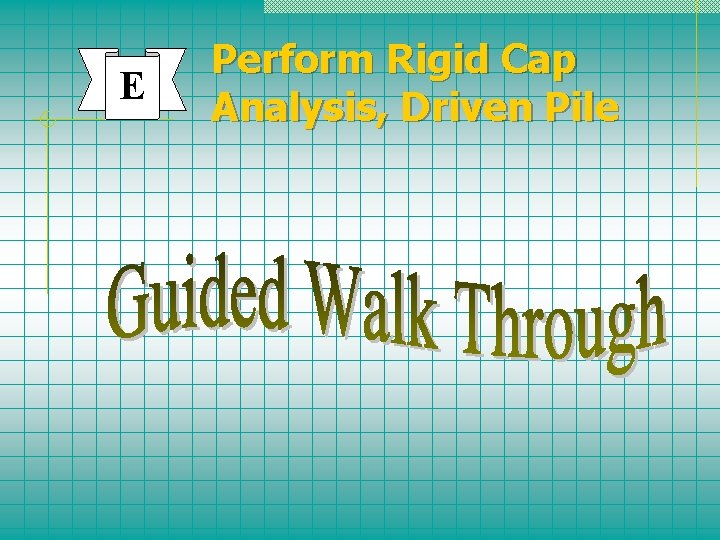
E Perform Rigid Cap Analysis, Driven Pile
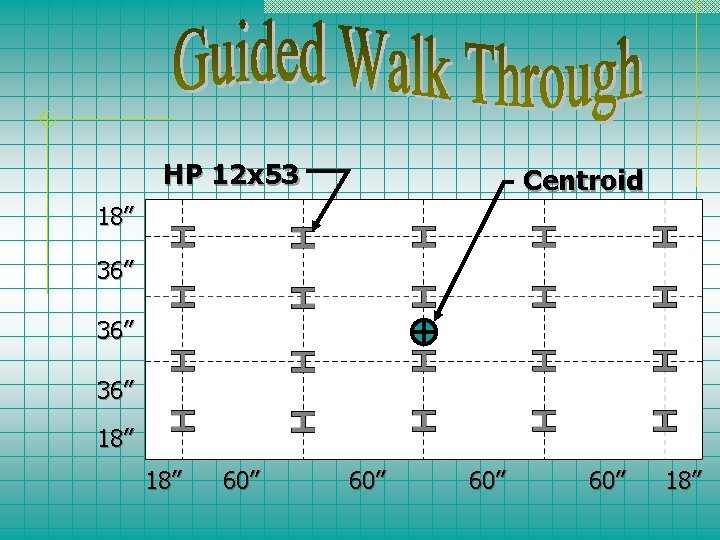
HP 12 x 53 Centroid 18” 36” 36” 18” 60” 60” 18”
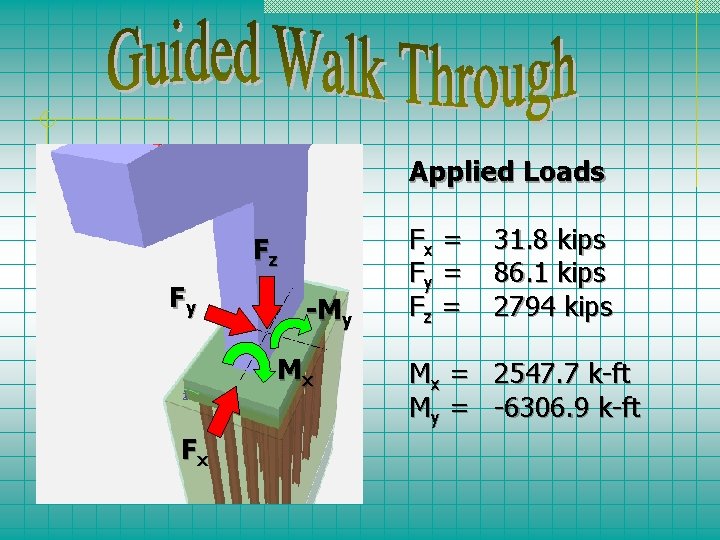
Applied Loads Fz Fy -My Mx Fx Fx = Fy = Fz = 31. 8 kips 86. 1 kips 2794 kips Mx = 2547. 7 k-ft My = -6306. 9 k-ft
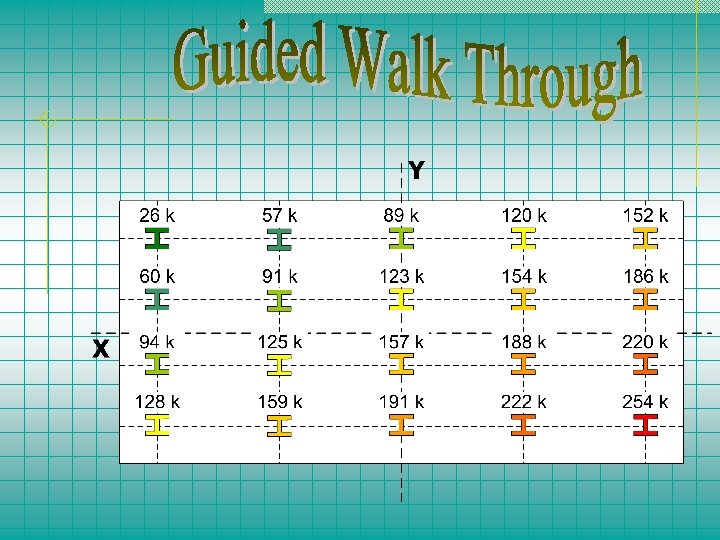
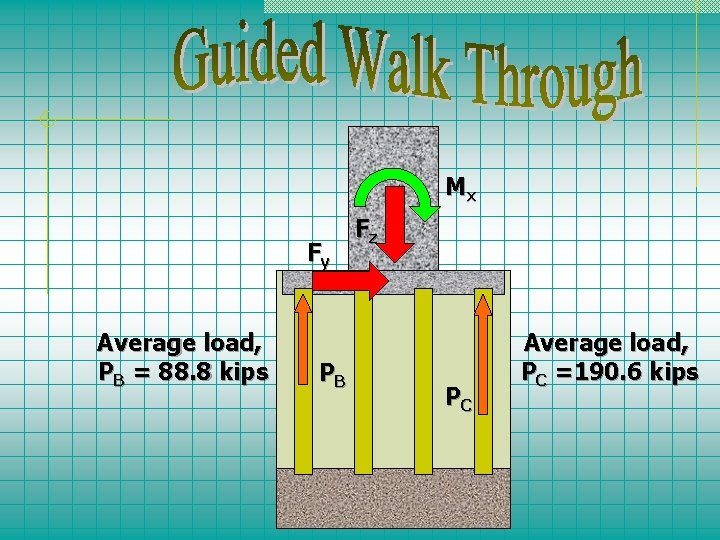
Mx Fy Average load, PB = 88. 8 kips PB Fz PC Average load, PC =190. 6 kips
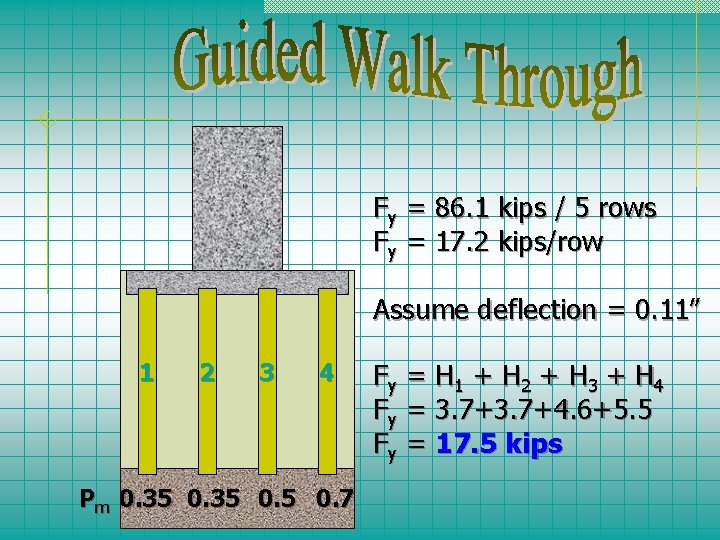
Fy = 86. 1 kips / 5 rows Fy = 17. 2 kips/row Assume deflection = 0. 11” 1 2 3 4 Pm 0. 35 0. 7 Fy = H 1 + H 2 + H 3 + H 4 Fy = 3. 7+4. 6+5. 5 Fy = 17. 5 kips
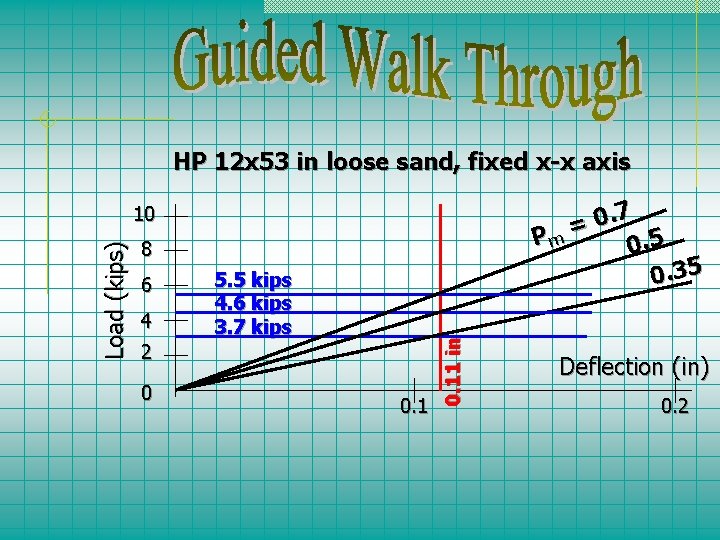
HP 12 x 53 in loose sand, fixed x-x axis 0. 7 = Pm 0. 5 0. 35 8 6 4 5. 5 kips 4. 6 kips 3. 7 kips 2 0 0. 11 in Load (kips) 10 Deflection (in) 0. 2
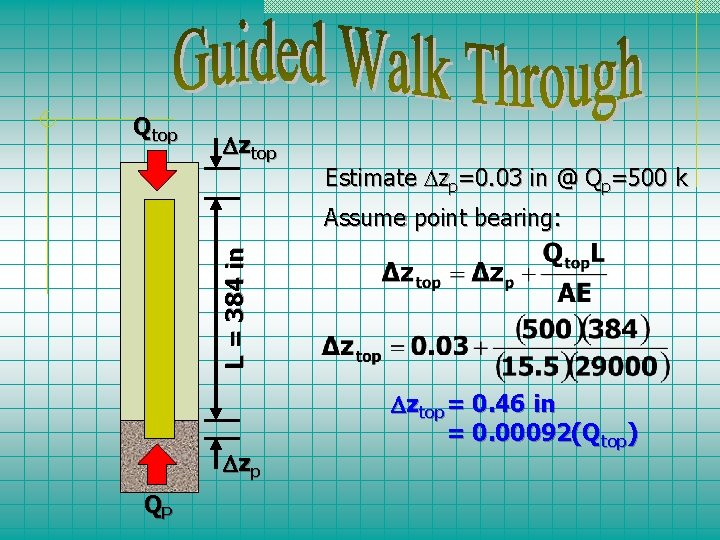
Qtop Dztop Estimate zp=0. 03 in @ Qp=500 k L = 384 in Assume point bearing: Dzp QP Dztop = 0. 46 in = 0. 00092(Qtop)
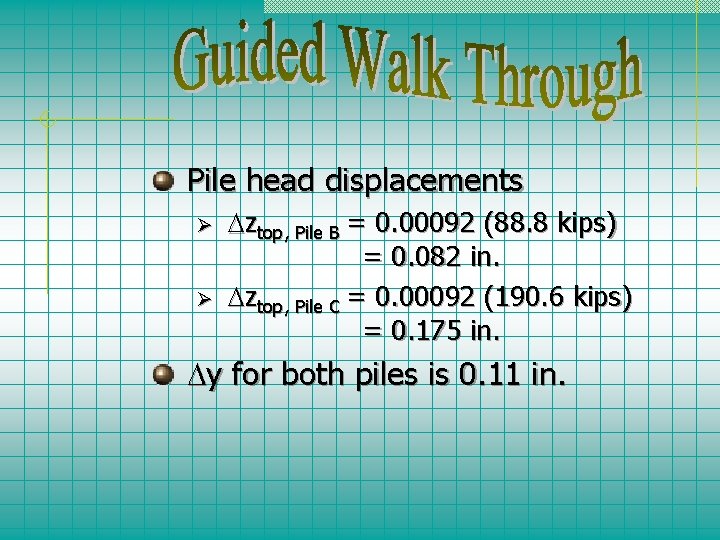
Pile head displacements Ø Ø ztop, Pile B = 0. 00092 (88. 8 kips) = 0. 082 in. ztop, Pile C = 0. 00092 (190. 6 kips) = 0. 175 in. y for both piles is 0. 11 in.

A B D +y +z C Given coordinates: A = (72 , -333) B = (18. 11 , ztop, Pile B) C = (126. 11 , ztop, Pile C) D = (72. 11 , z. D) 1. 2. 3. Find z. D by similar triangles Find of line BC Use trigonometry to find: y. A , z A
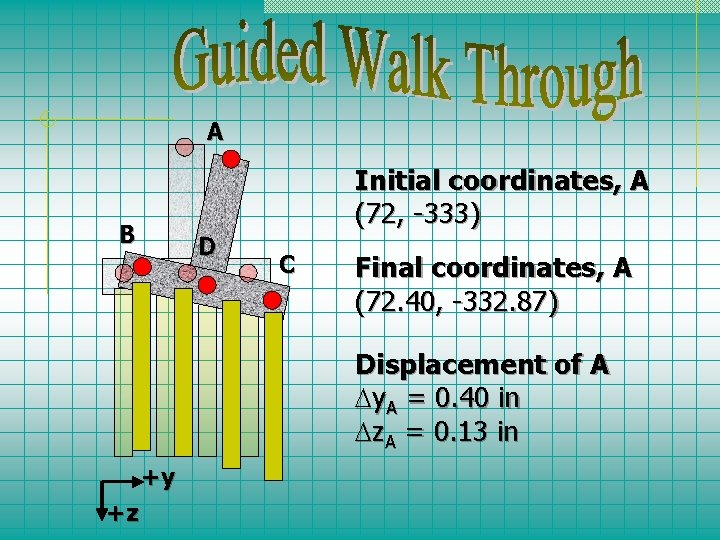
A Initial coordinates, A (72, -333) B D C Final coordinates, A (72. 40, -332. 87) Displacement of A y. A = 0. 40 in z. A = 0. 13 in +y +z
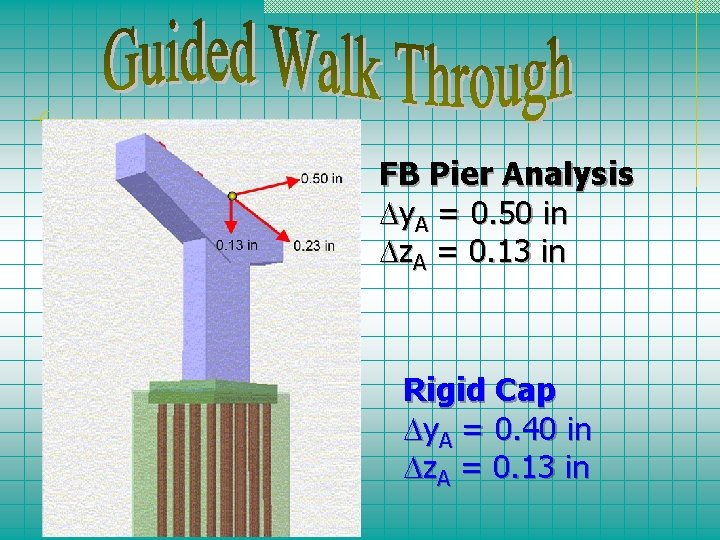
FB Pier Analysis y. A = 0. 50 in z. A = 0. 13 in Rigid Cap y. A = 0. 40 in z. A = 0. 13 in
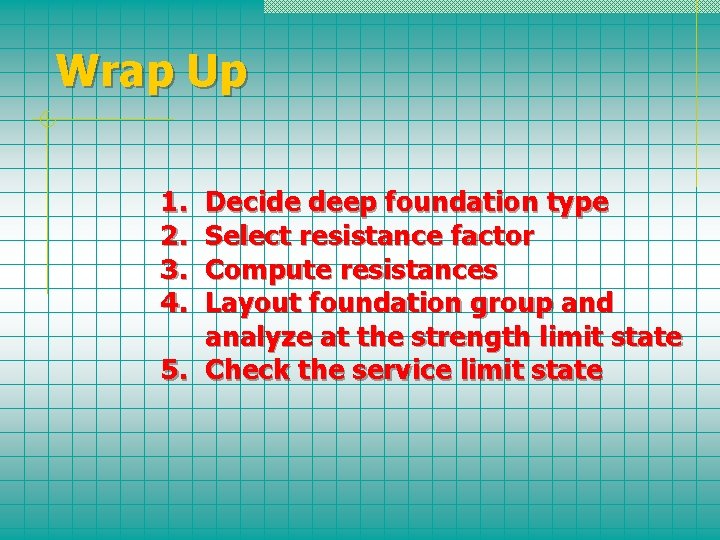
Wrap Up 1. 2. 3. 4. Decide deep foundation type Select resistance factor Compute resistances Layout foundation group and analyze at the strength limit state 5. Check the service limit state
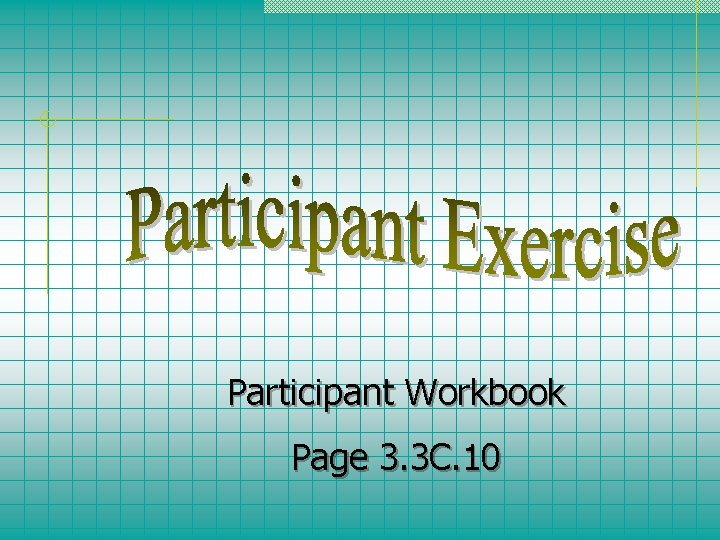
Participant Workbook Page 3. 3 C. 10
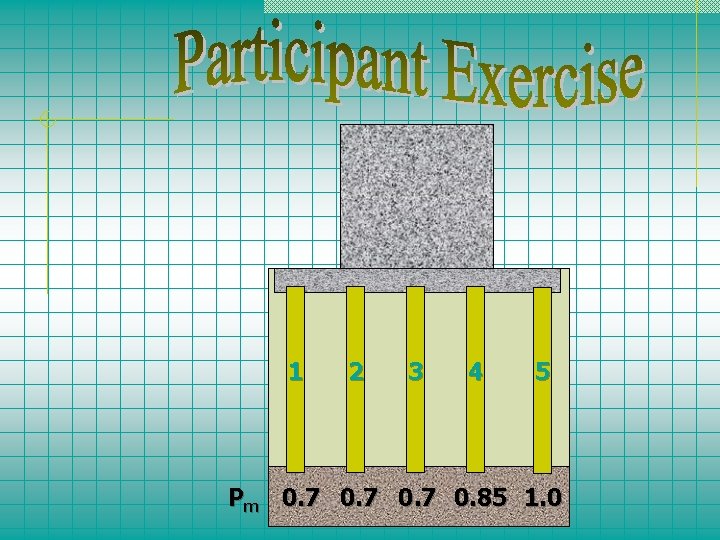
1 2 3 4 5 Pm 0. 7 0. 85 1. 0
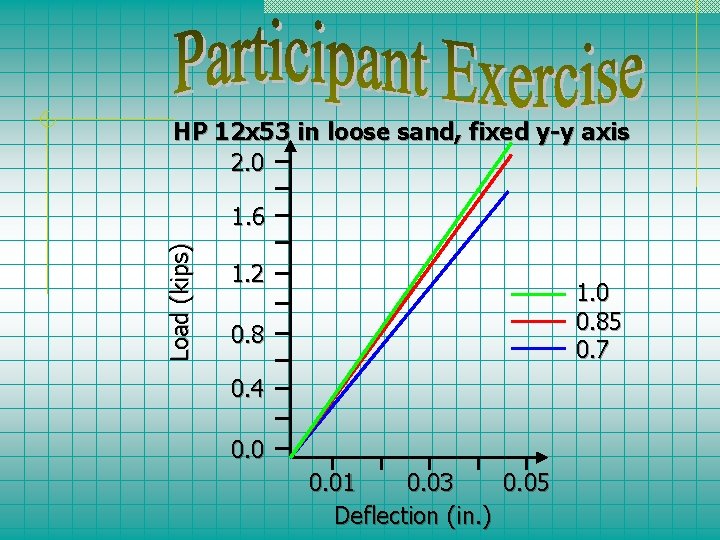
HP 12 x 53 in loose sand, fixed y-y axis 2. 0 Load (kips) 1. 6 1. 2 1. 0 0. 85 0. 7 0. 8 0. 4 0. 01 0. 05 0. 03 Deflection (in. )
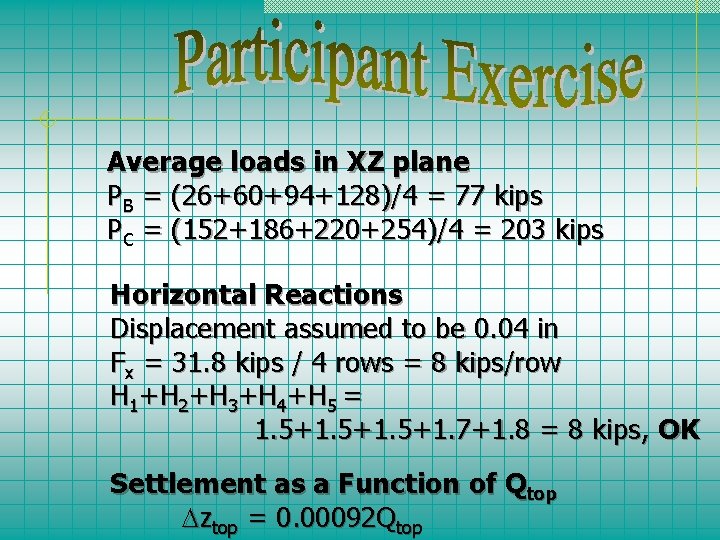
Average loads in XZ plane PB = (26+60+94+128)/4 = 77 kips PC = (152+186+220+254)/4 = 203 kips Horizontal Reactions Displacement assumed to be 0. 04 in Fx = 31. 8 kips / 4 rows = 8 kips/row H 1+H 2+H 3+H 4+H 5 = 1. 5+1. 7+1. 8 = 8 kips, OK Settlement as a Function of Qtop ztop = 0. 00092 Qtop
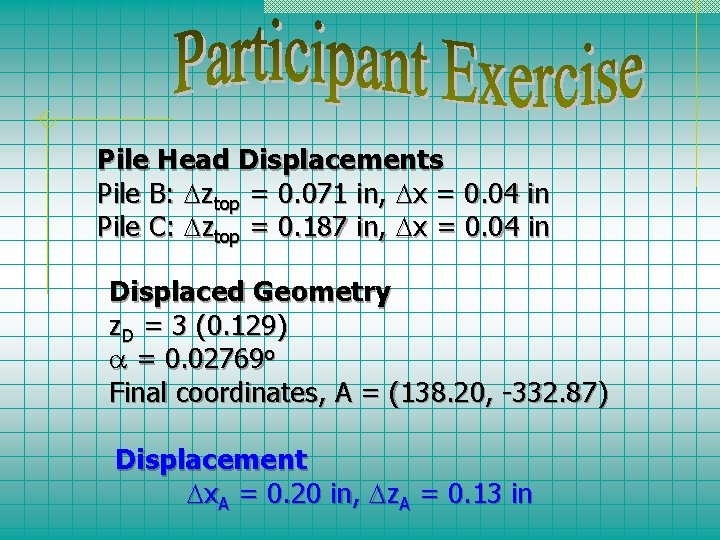
Pile Head Displacements Pile B: ztop = 0. 071 in, x = 0. 04 in Pile C: ztop = 0. 187 in, x = 0. 04 in Displaced Geometry z. D = 3 (0. 129) = 0. 02769 o Final coordinates, A = (138. 20, -332. 87) Displacement x. A = 0. 20 in, z. A = 0. 13 in
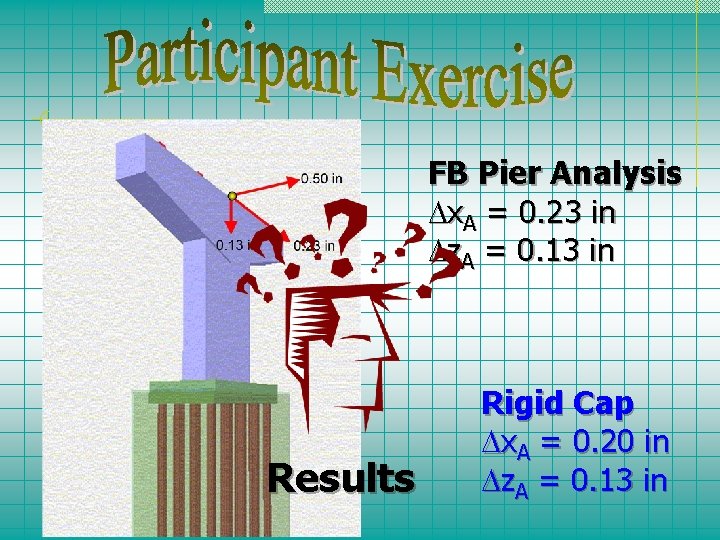
FB Pier Analysis x. A = 0. 23 in z. A = 0. 13 in Results Rigid Cap x. A = 0. 20 in z. A = 0. 13 in
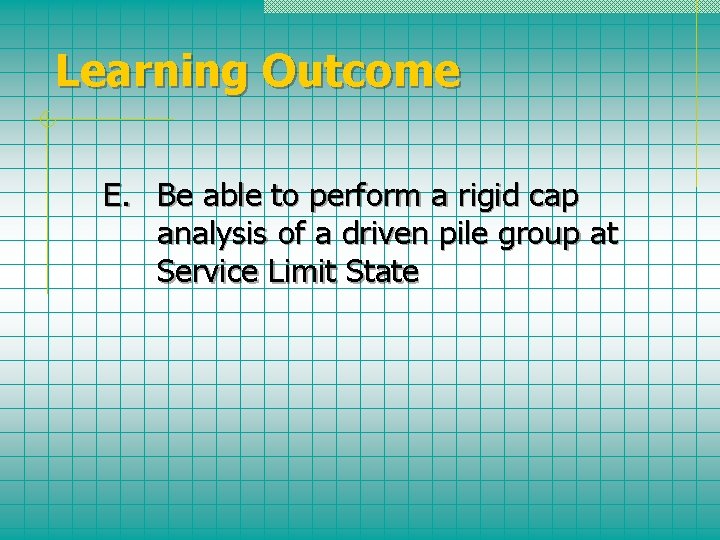
Learning Outcome E. Be able to perform a rigid cap analysis of a driven pile group at Service Limit State
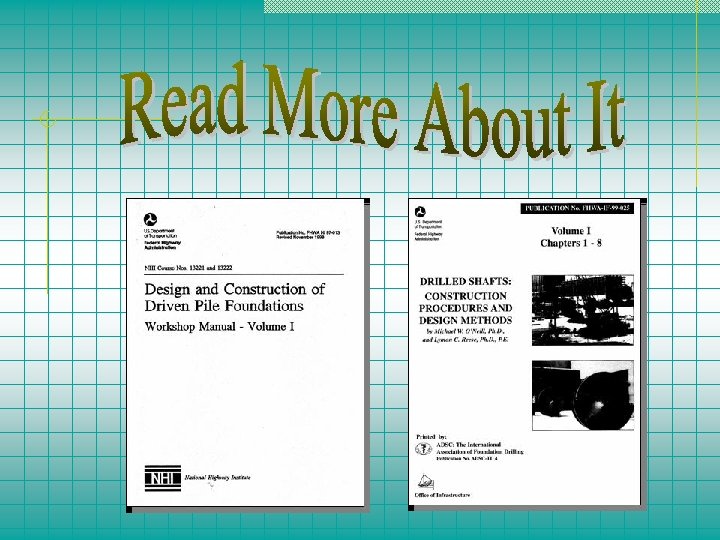
Lrfd
Lrfd
Trabes armadas
Lrfd
Lrfd
Load and resistance factor design
Gsoe9220
Applied geotechnical engineering
How to draw mohr's circle for triaxial test
Geotechnical data management
Geotechnical data management
Consistency limits in geotechnical engineering
Geotechnical
Geotechnical earthquake engineering kramer
Finite element method in geotechnical engineering
Master of construction management swinburne
Lac session on ict
What is a clincher sentence
Topic down
Training session design
Microsoft architecture design session
Kontinuitetshantering i praktiken
Typiska novell drag
Nationell inriktning för artificiell intelligens
Ekologiskt fotavtryck
Varför kallas perioden 1918-1939 för mellankrigstiden
En lathund för arbete med kontinuitetshantering
Underlag för särskild löneskatt på pensionskostnader
Vilotidsbok
Sura för anatom
Vad är densitet
Datorkunskap för nybörjare
Stig kerman
Mall debattartikel
För och nackdelar med firo
Nyckelkompetenser för livslångt lärande
Påbyggnader för flakfordon
Kraft per area
Offentlig förvaltning
Jag har nigit för nymånens skära text
Presentera för publik crossboss
Jiddisch
Bat mitza
Klassificeringsstruktur för kommunala verksamheter
Luftstrupen för medicinare
Bästa kameran för astrofoto
Centrum för kunskap och säkerhet
Programskede byggprocessen
Mat för idrottare
Verktyg för automatisering av utbetalningar
Rutin för avvikelsehantering
Smärtskolan kunskap för livet
Ministerstyre för och nackdelar
Tack för att ni har lyssnat
Referat mall
Redogör för vad psykologi är
Matematisk modellering eksempel
Atmosfr
Borra hål för knoppar
Vilken grundregel finns det för tronföljden i sverige?
Beräkna standardavvikelse
Tack för att ni har lyssnat
Rita perspektiv
Verksamhetsanalys exempel
Tobinskatten för och nackdelar
Toppslätskivling dos
Gibbs reflekterande cykel
Egg för emanuel
Elektronik för barn
Plagg i gamla rom
Strategi för svensk viltförvaltning
Kung som dog 1611
Ellika andolf
Romarriket tidslinje
Tack för att ni lyssnade
Vilket tal pekar pilen på
Dikt rimma
Inköpsprocessen steg för steg
Rådet för byggkompetens
Etik och ledarskap etisk kod för chefer
Aktiv exspektans
Myndigheten för delaktighet
Trög för kemist
Sju principer för tillitsbaserad styrning
Läkarutlåtande för livränta
Karttecken tät skog
Geometriska former i förskolan
Texter för hinduer tantra
Meios steg för steg
Bris för vuxna
Jätte råtta
Topic design for project
Session 0 windows
Welcome to the new session
Session
Skill 18: anticipate the topics
Team norming session
Session title examples
Session name
Asp.net session management
Stateful session bean life cycle
Multi product profit volume chart
Eis portal principal per session
Ergonomics session
Practical session definition
Multipicand
General.php?seccion=
Pdp staff
Mentorship kickoff meeting
How do you conduct a jad session
Poster imrad
Ece 329
Ece 310
Breakout session questions
Facilitate learning session
Stateful session bean life cycle
Listening session template
Ece 120 uiuc
Aba notes examples
Session protocol data unit
Differential reinforcment
Functions of session layer
Meditech suspend session icon
Alpha session 7
Active session history
Asp net session state
Meaningful prayer before meeting
Meeting will begin shortly
This session will be recorded
Training session outline
Name of the session
Instagram session cookie
Session 7
Server.servlet.session.persistent
Sip session timer
Practical session meaning
5g pdu session
Network osi
Session 1 research simulation task
Baker session agile
Coaching session agenda
Pals debriefing session
Word 2016 session 2 post assessment
Webex event breakout rooms
Interchage keys
Cbt session structure
Brown paper workshop
Asp session object
Active session history
Gate aon test
Cosmos db cap theorem
Harriet josephine terry
Alpha course session 7
Alpha session 2
Welcome to the training session
Uw absn
First cbt session structure
Space cube session
Session initialisation protocol
3270 session
Stateful session bean example
Understanding rigid transformations and their properties
Servlet technology is used to create web application mcq
Balabit review
How to make session plan
How to introduce yourself in training session
An exercise session has three stages
Nexthink library
Nexthink demo
Message session relay protocol
Corey snyder uiuc
Hkn review session
Afternoon session