CHAPTER 46 Engine Cooling Introduction Cooling systems play
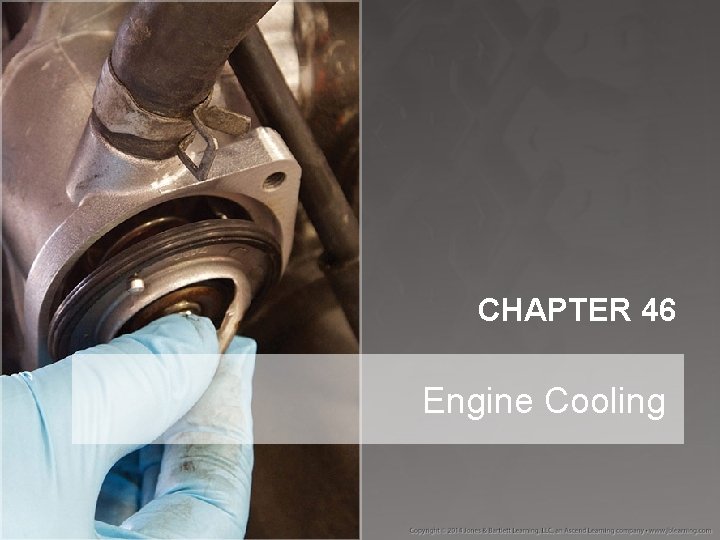
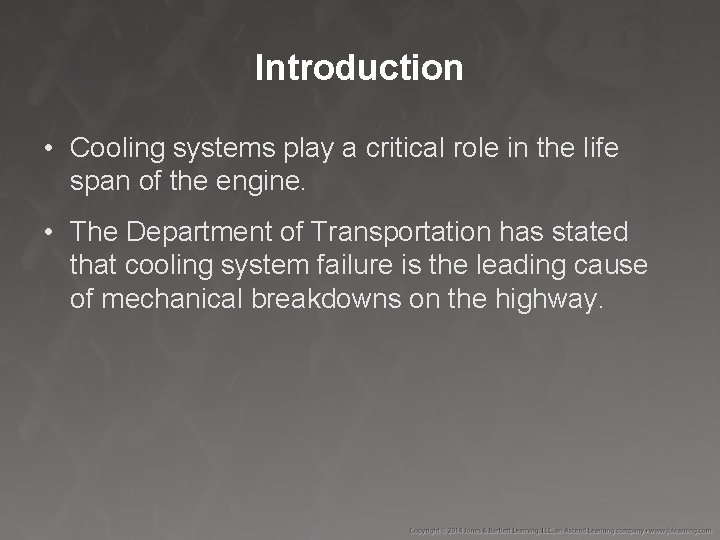
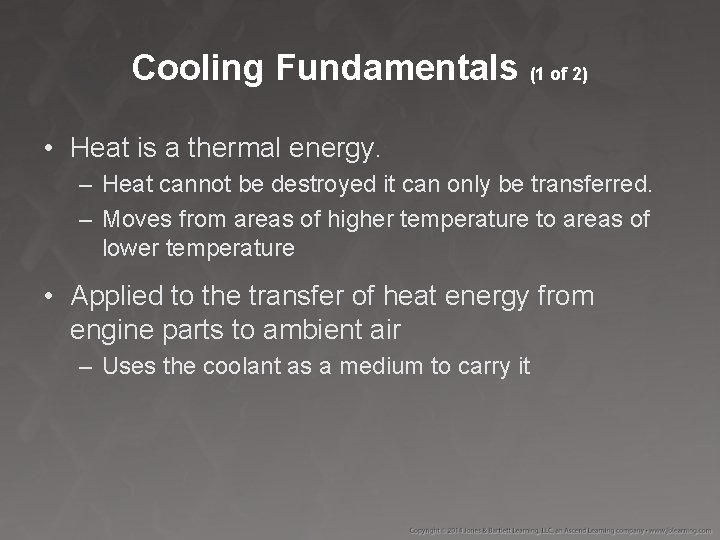
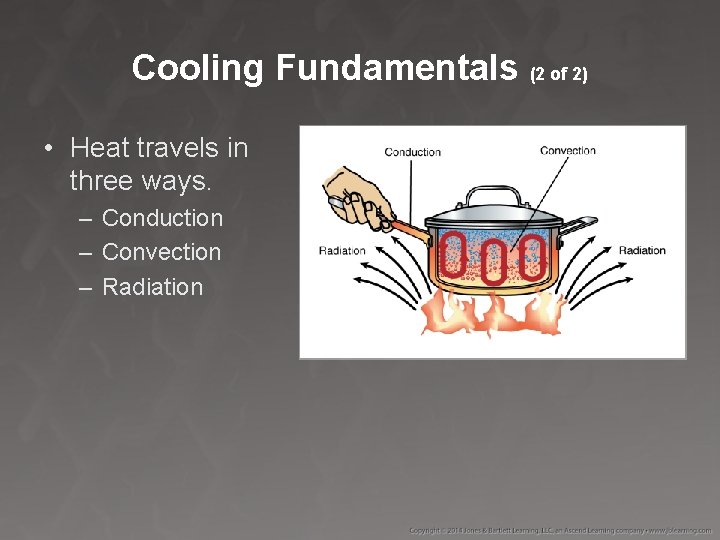
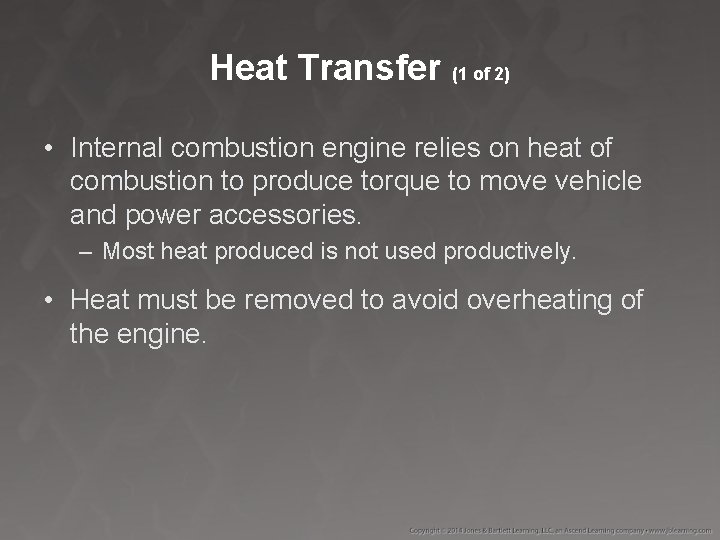
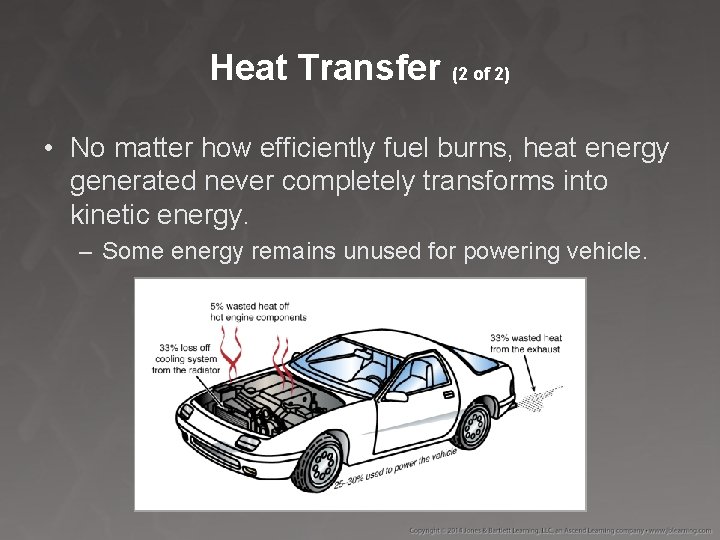
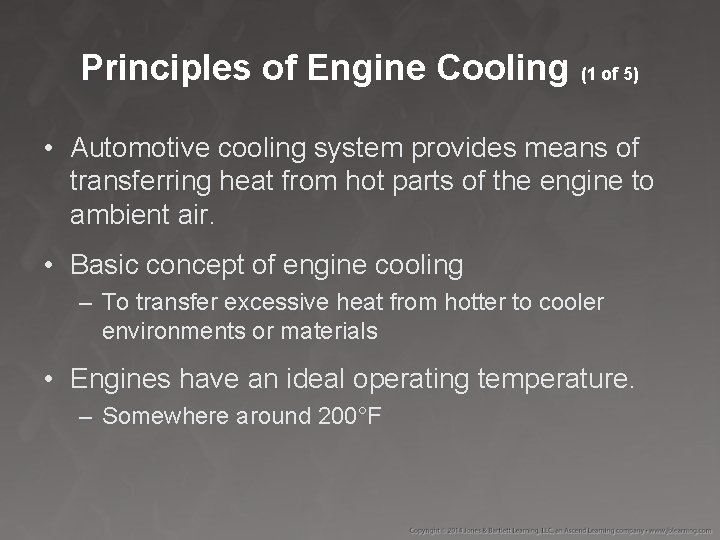
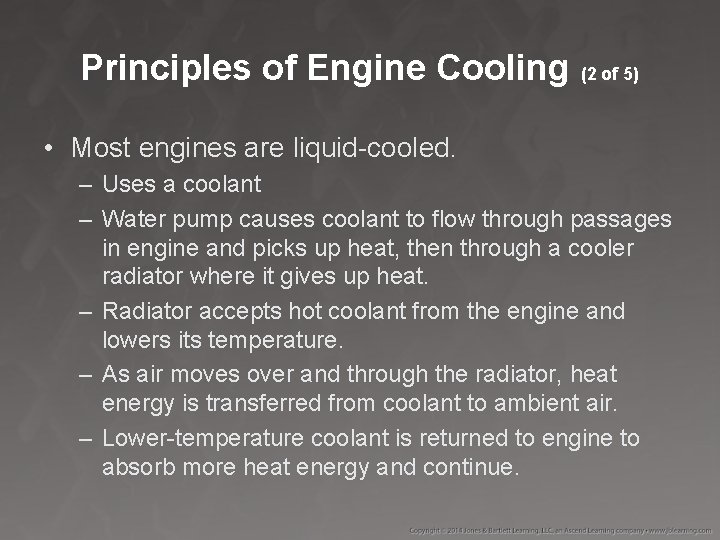
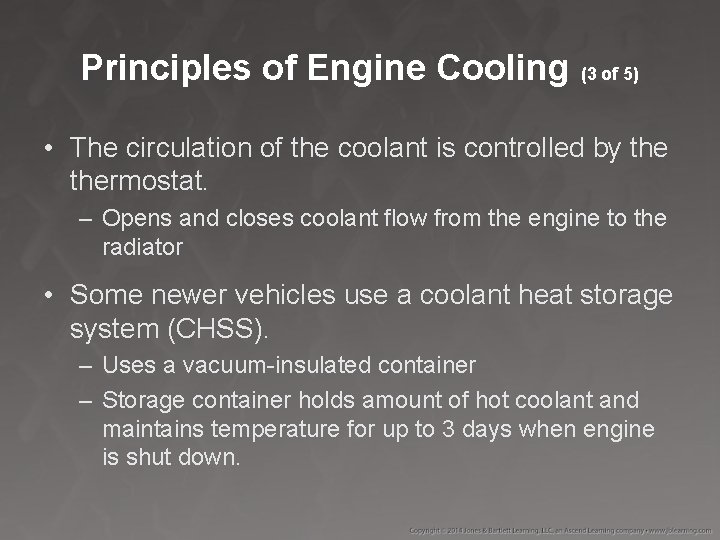
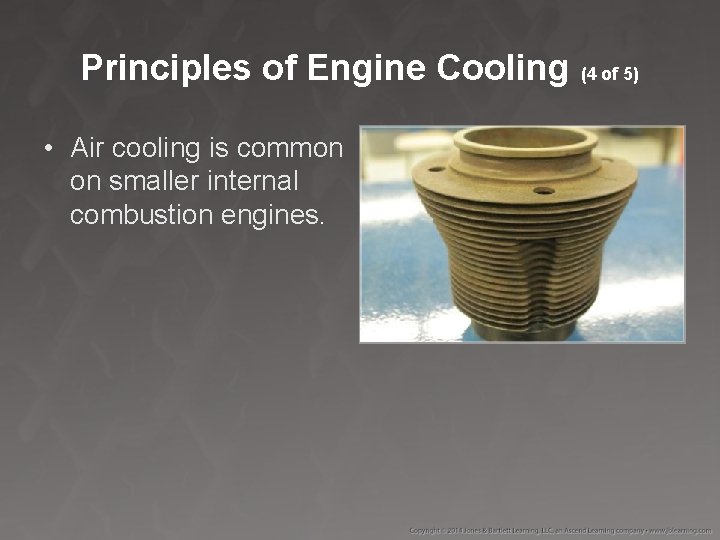
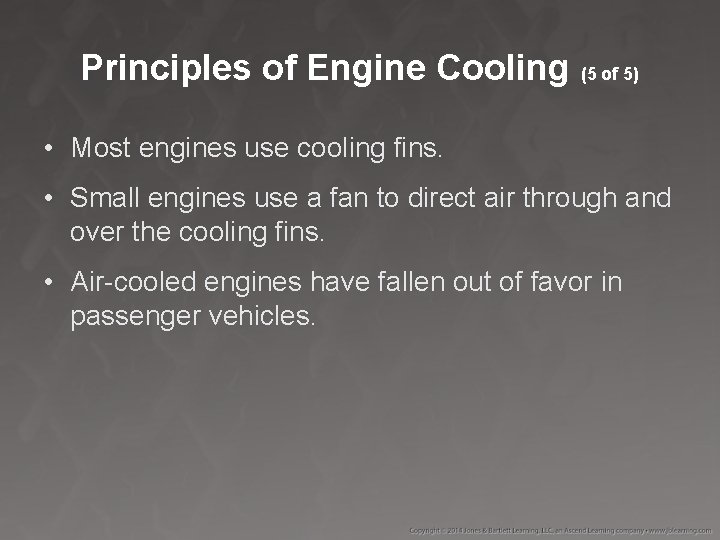
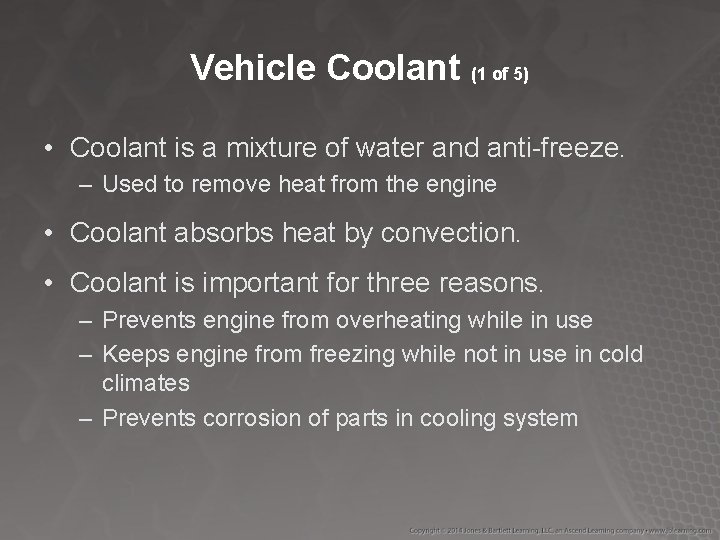
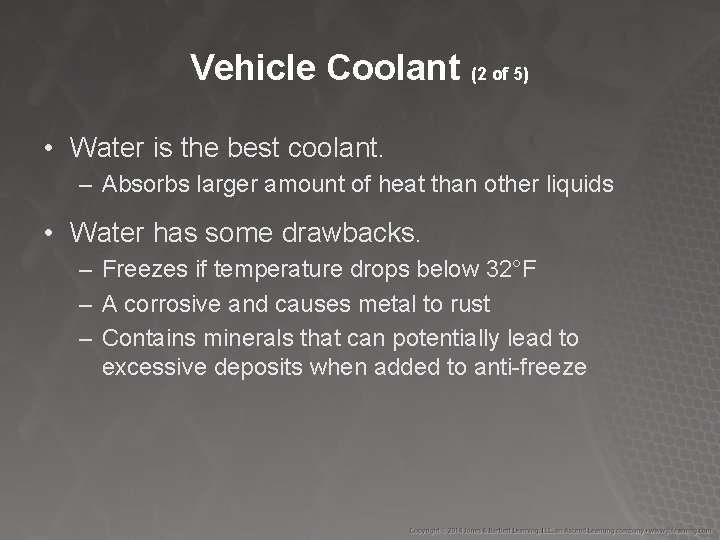
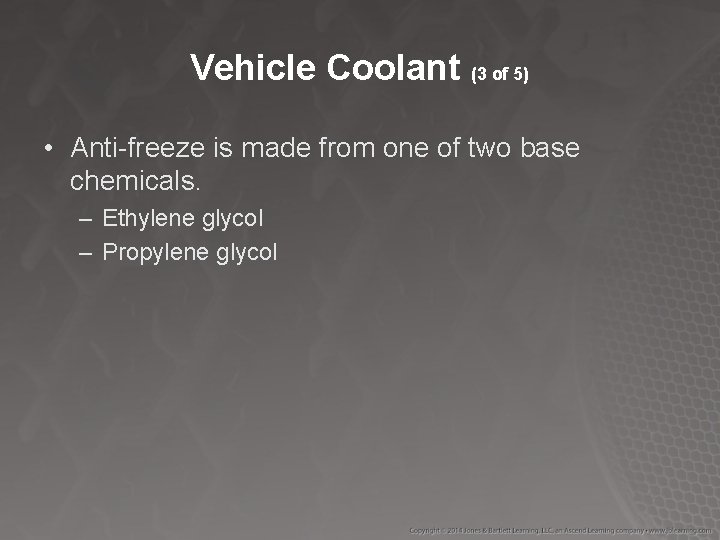
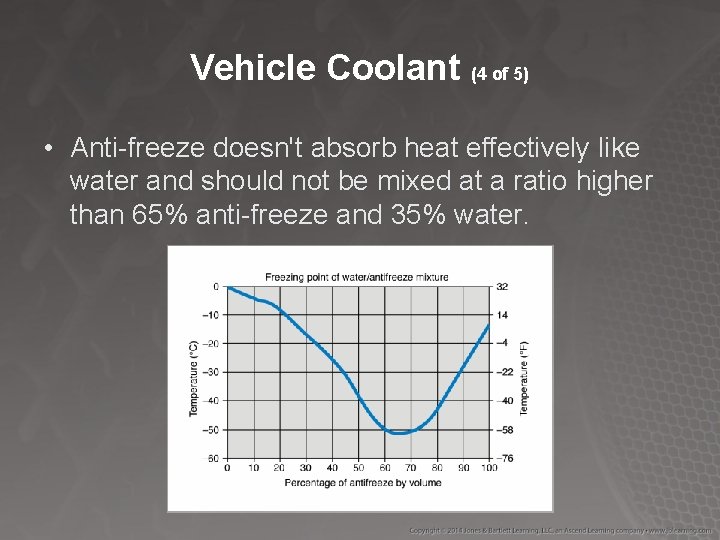
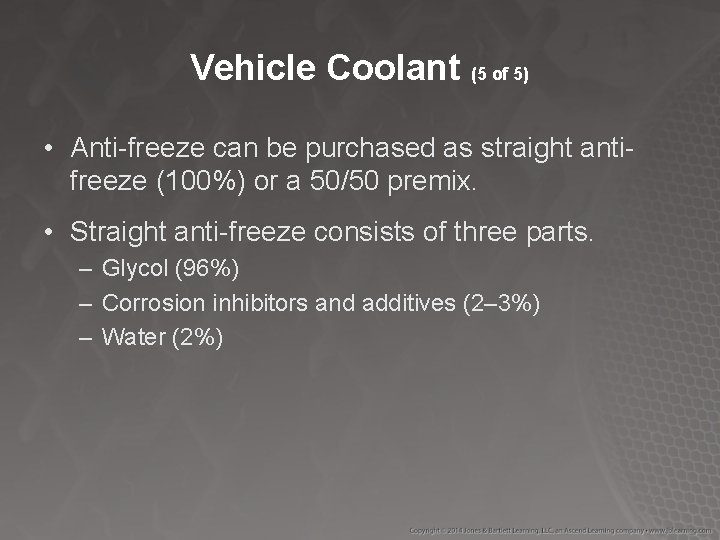
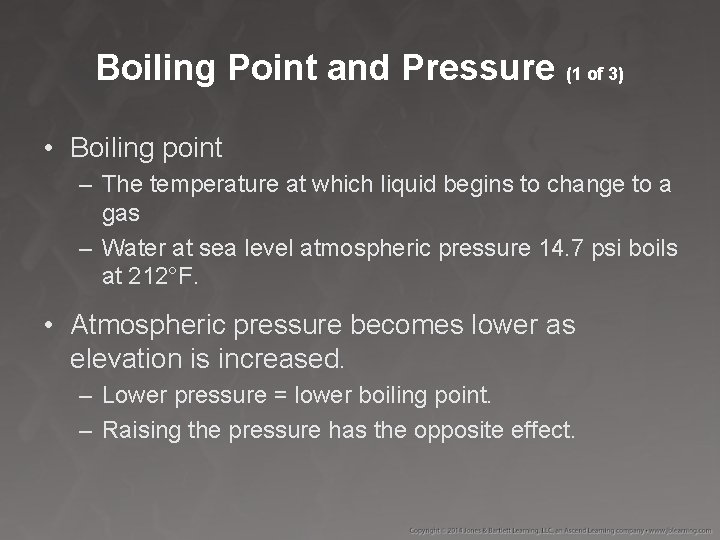
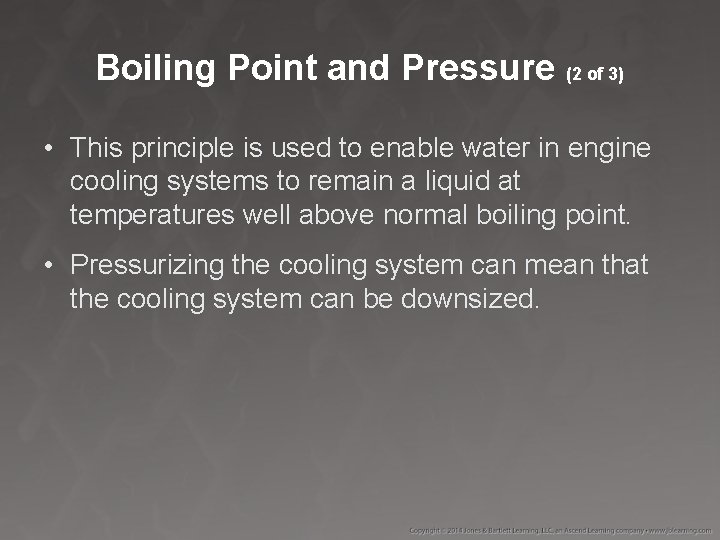
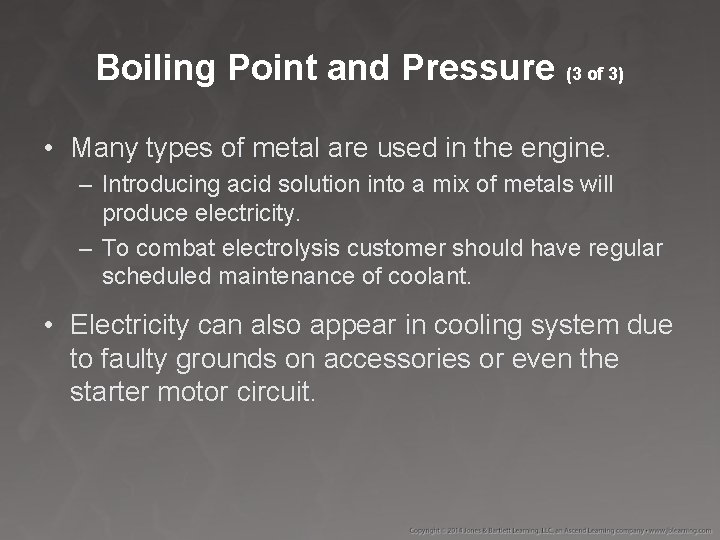
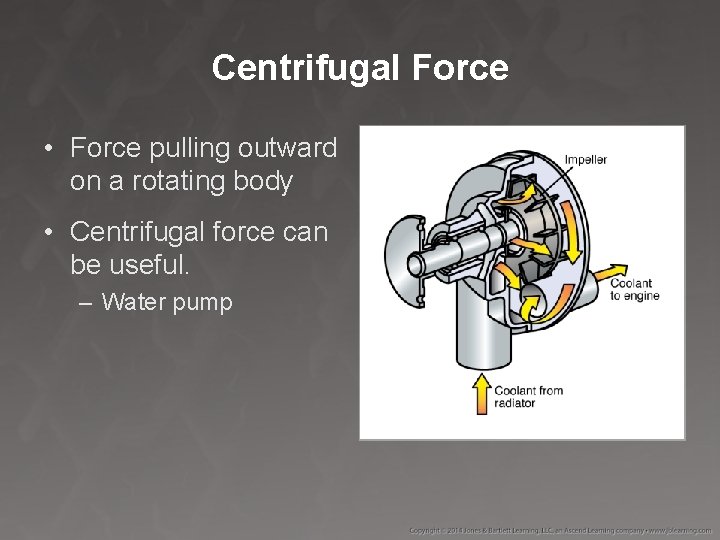
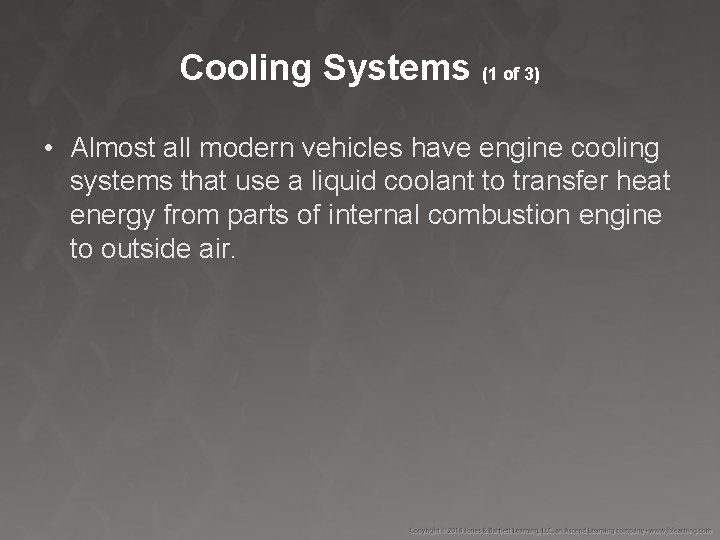
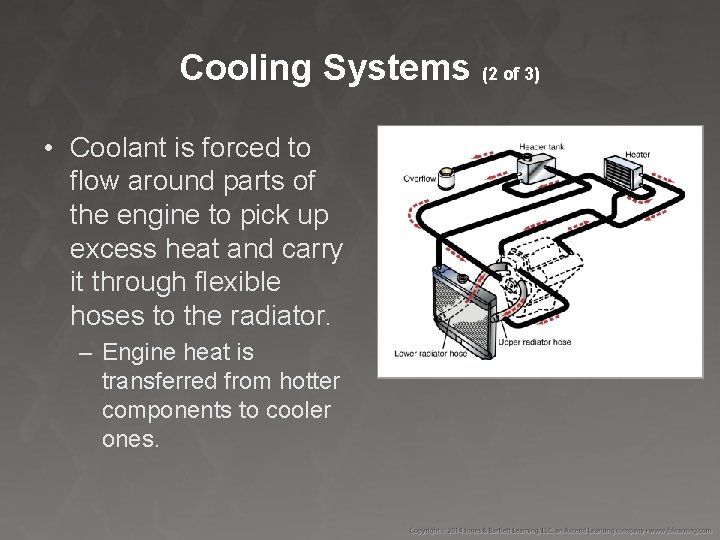
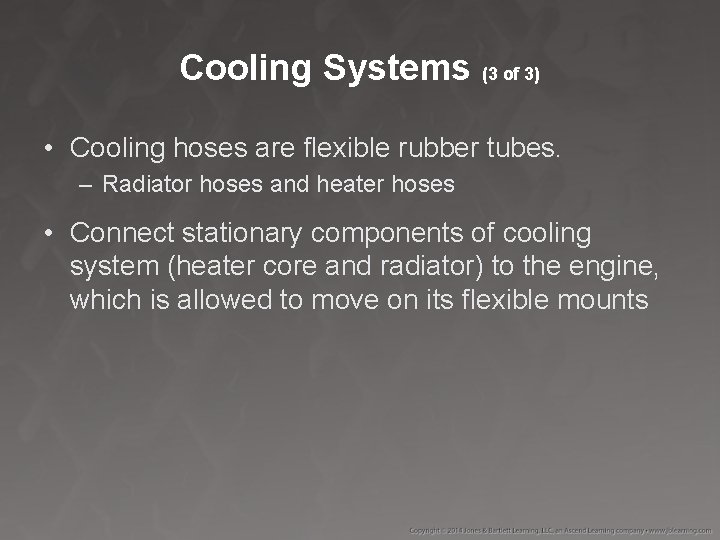

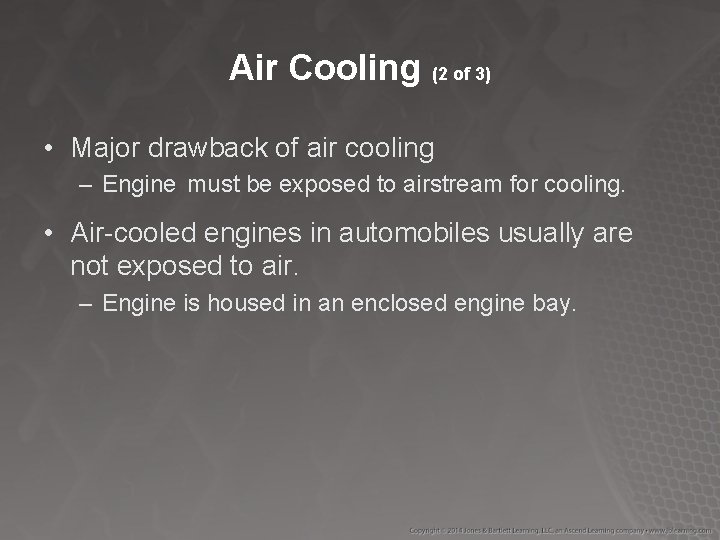
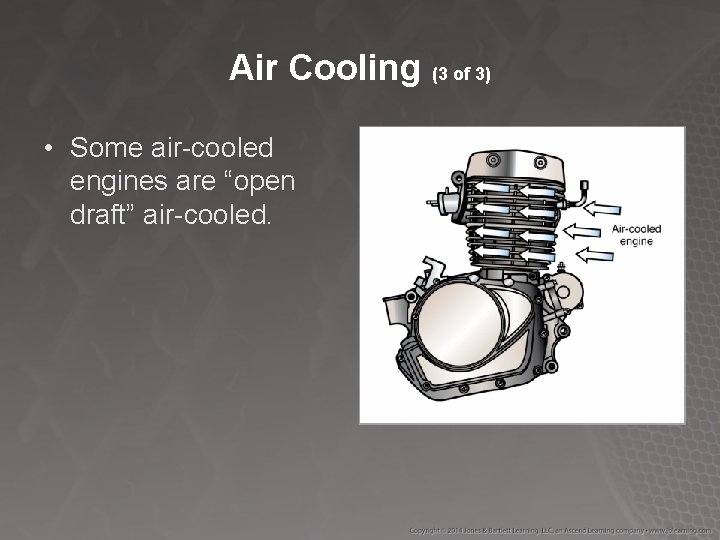
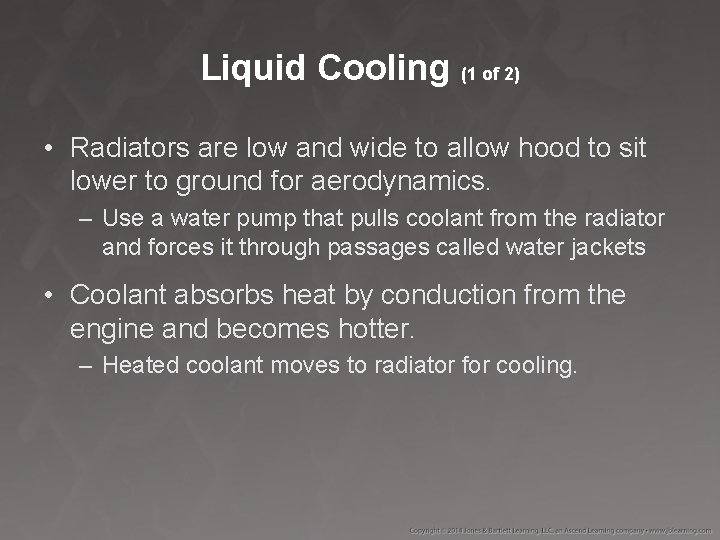
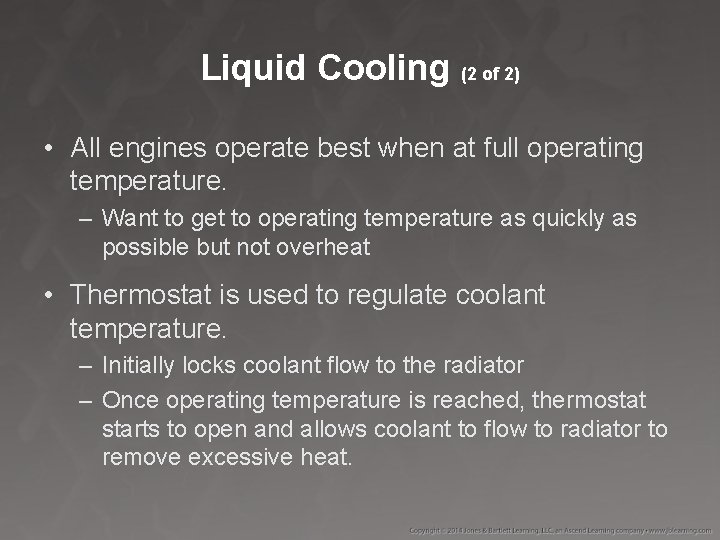
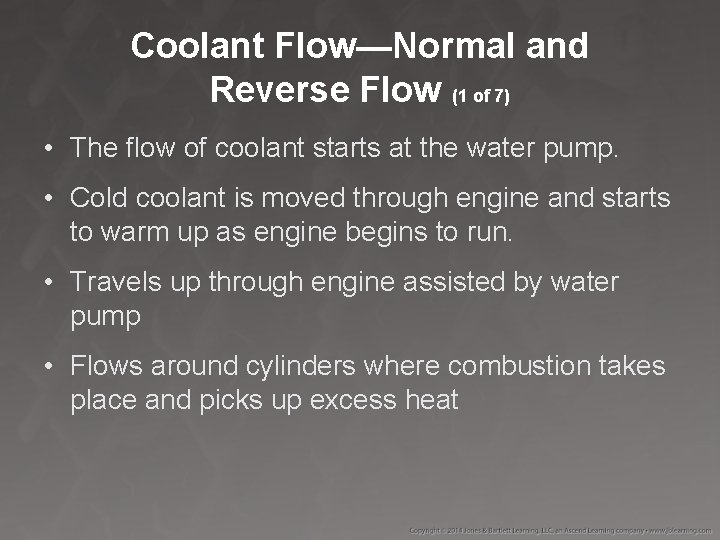
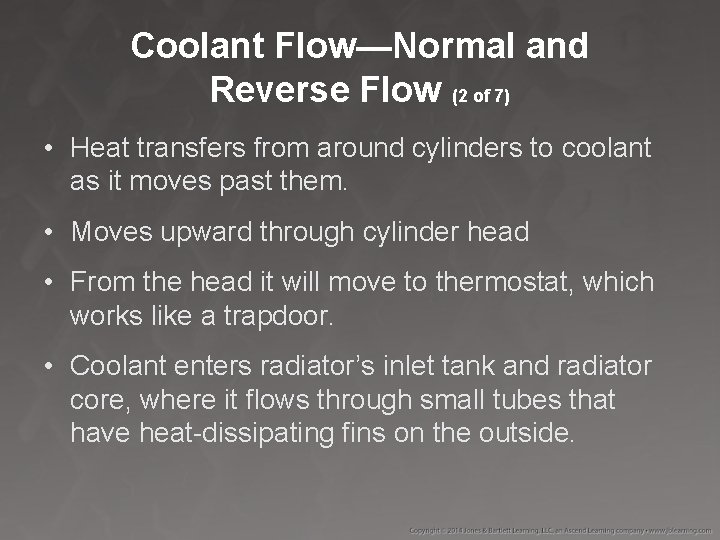
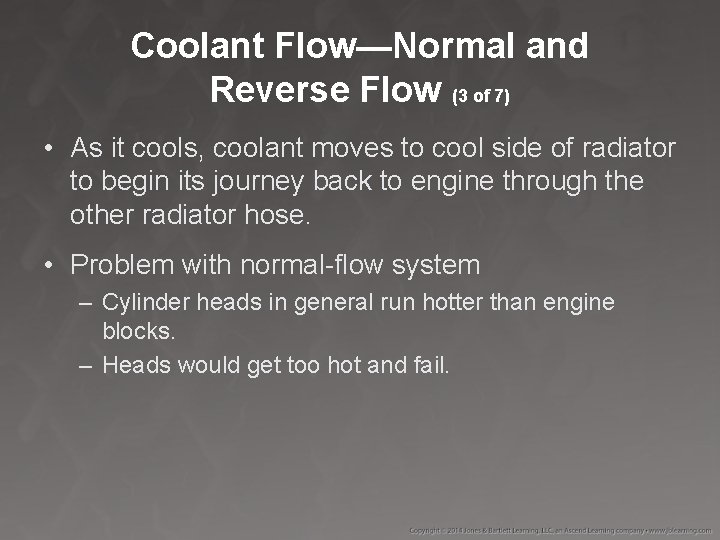
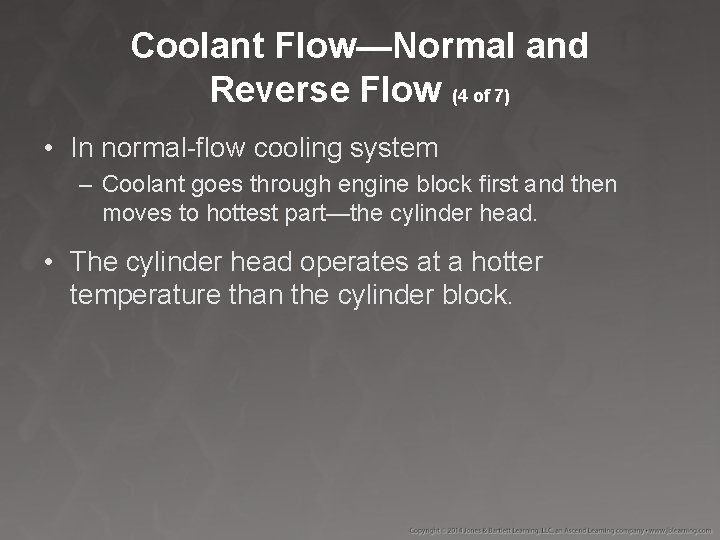
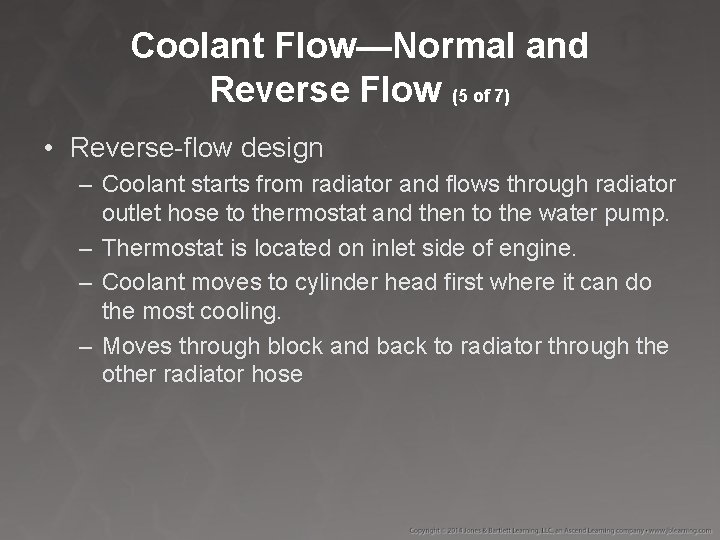
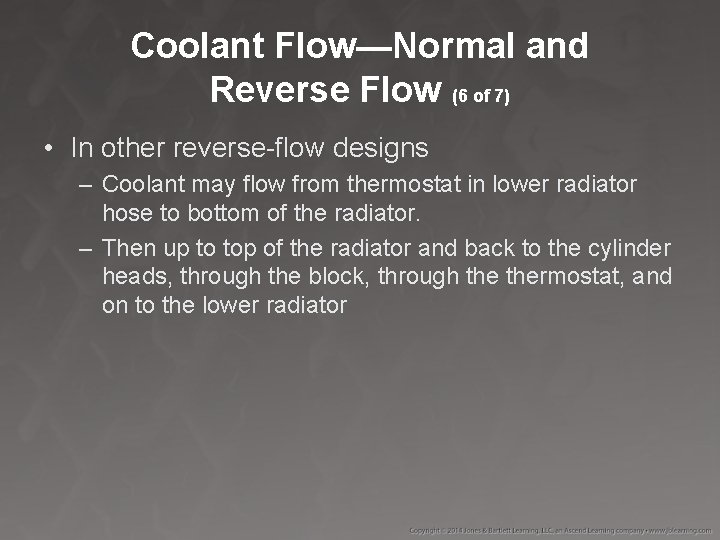
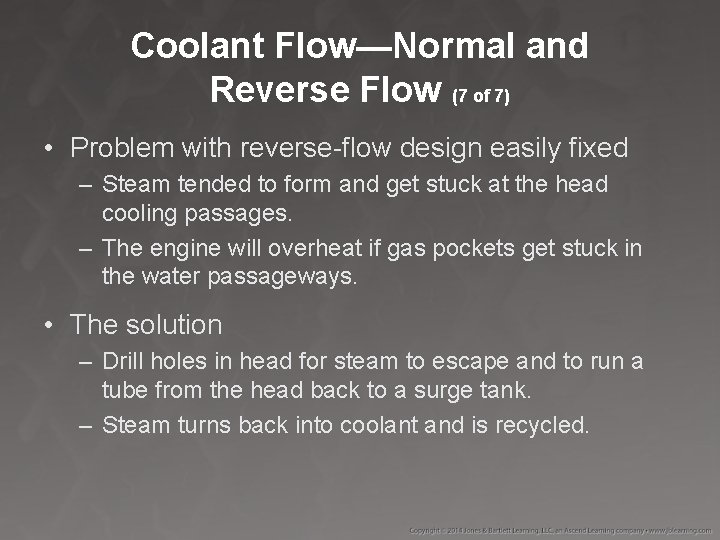
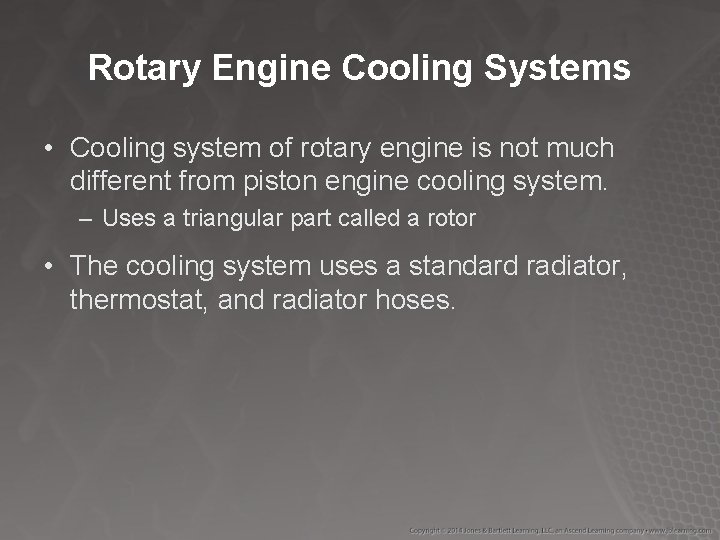
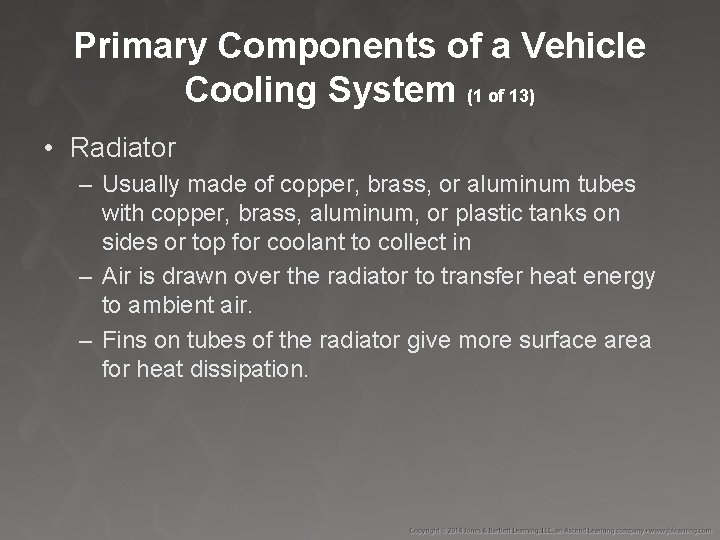
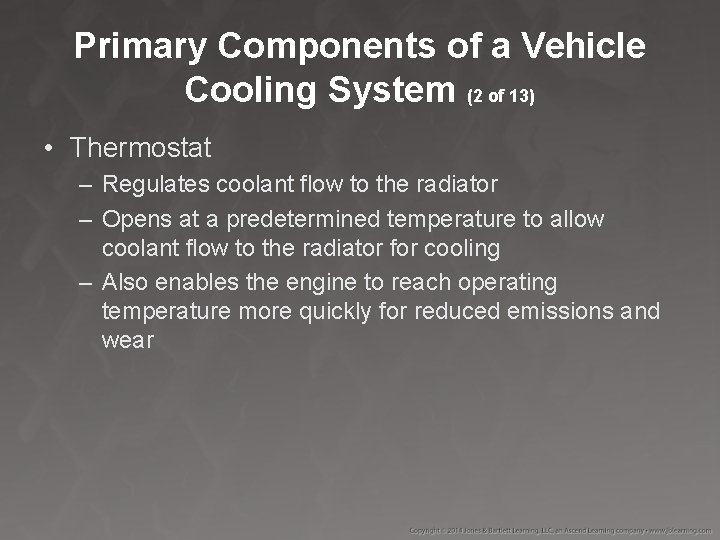
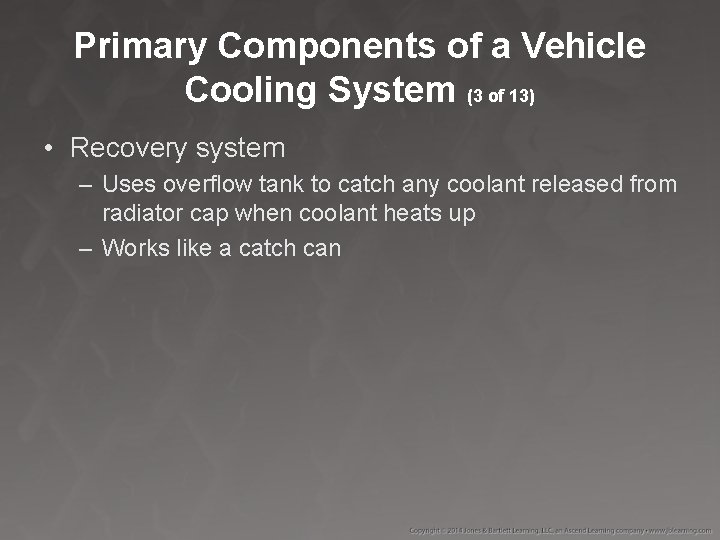
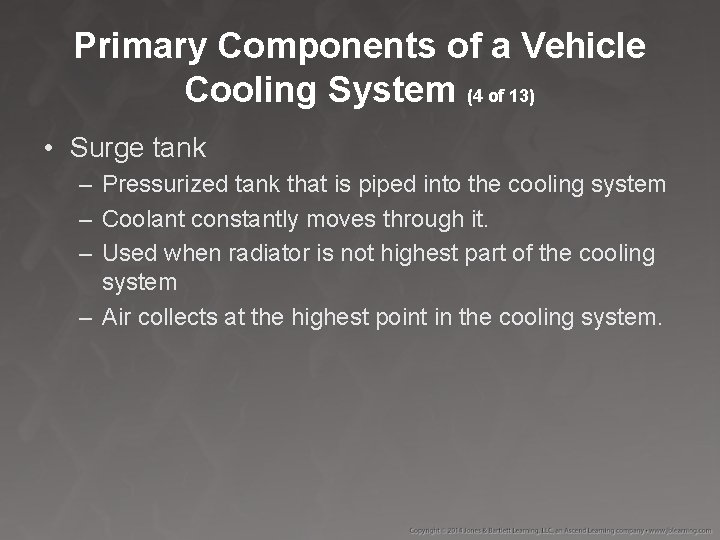
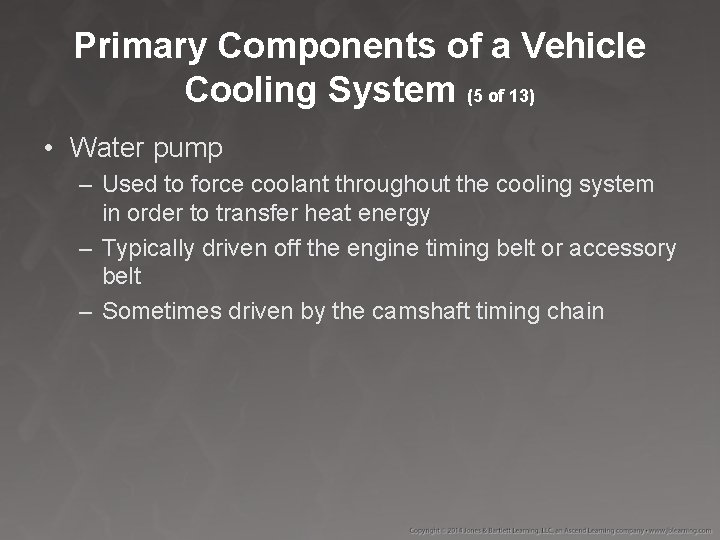
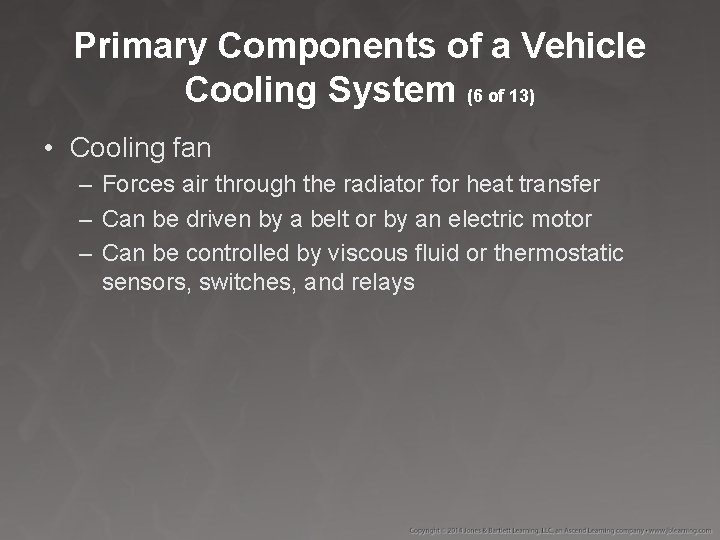
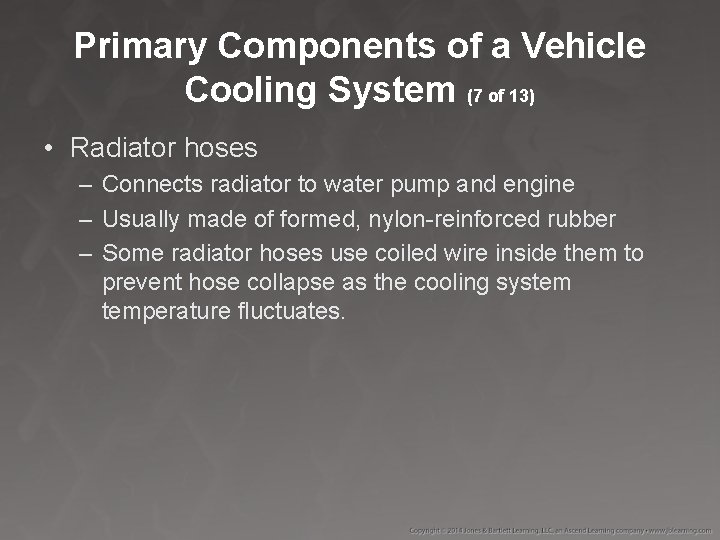
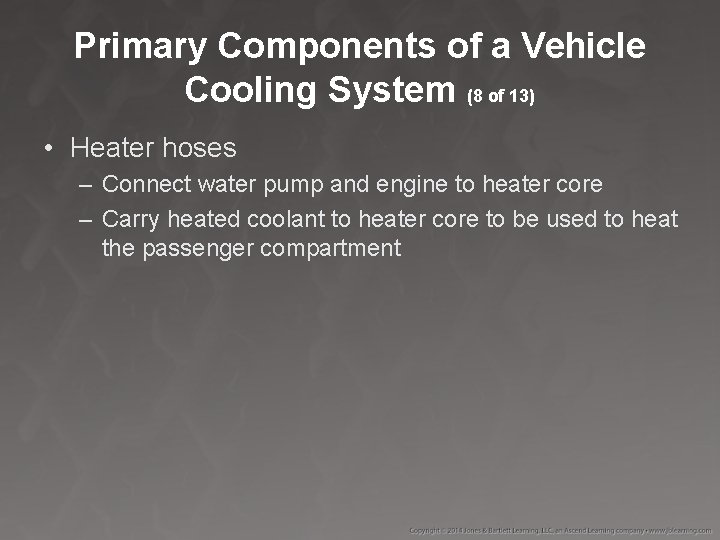
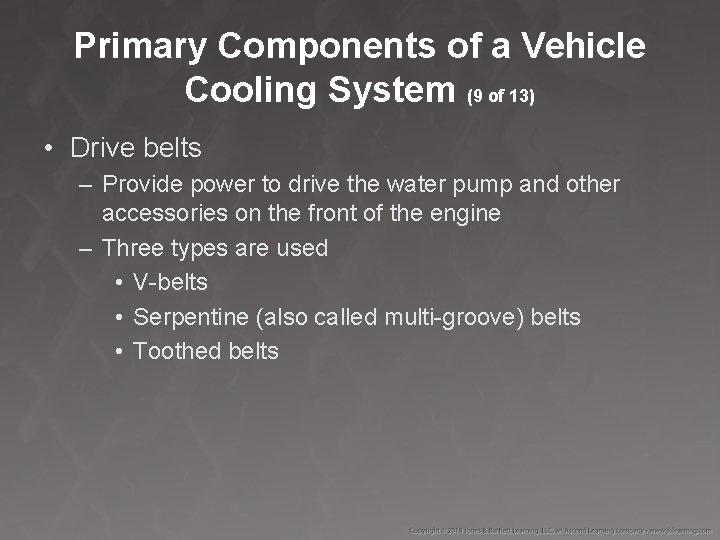
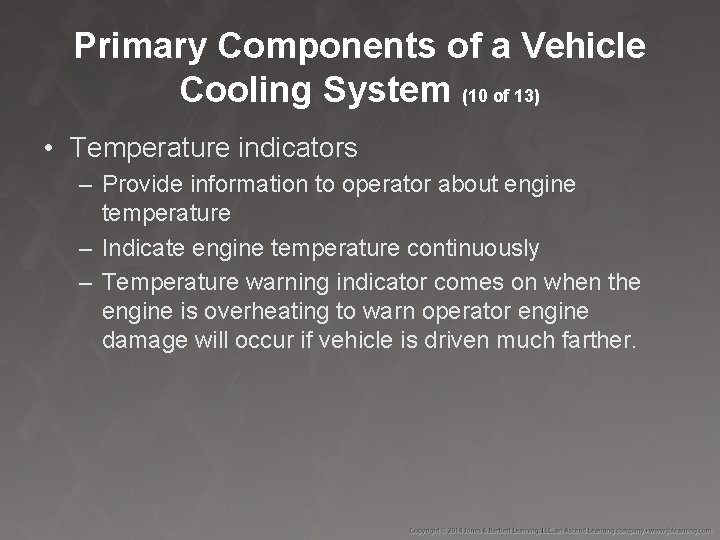
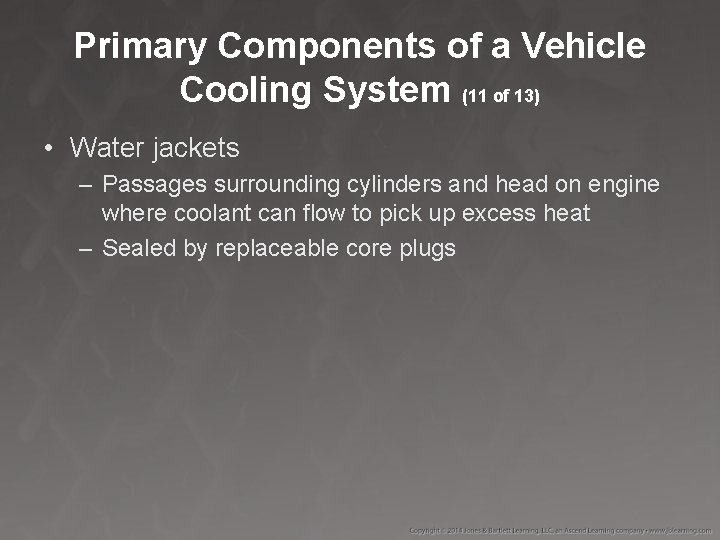
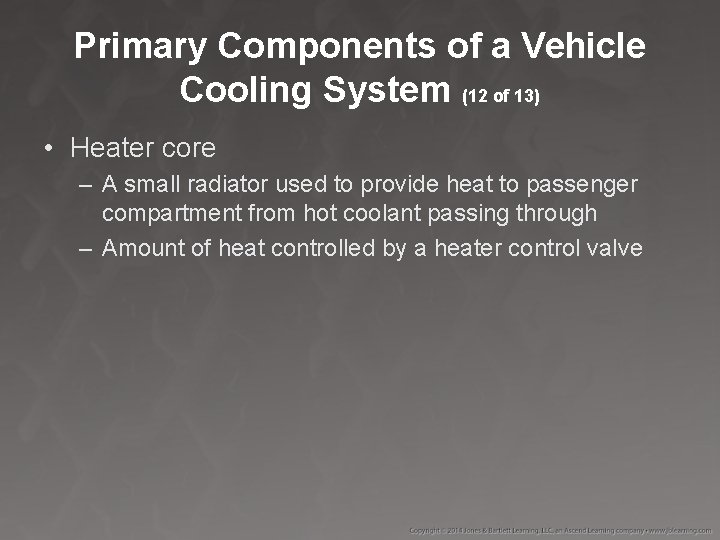
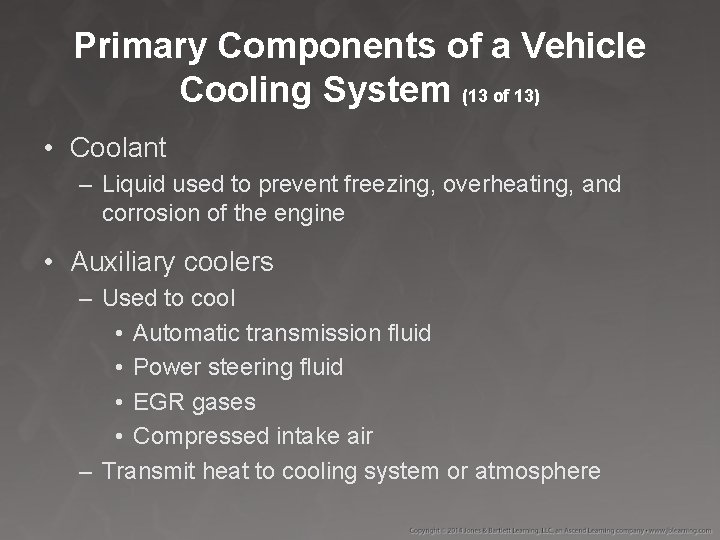
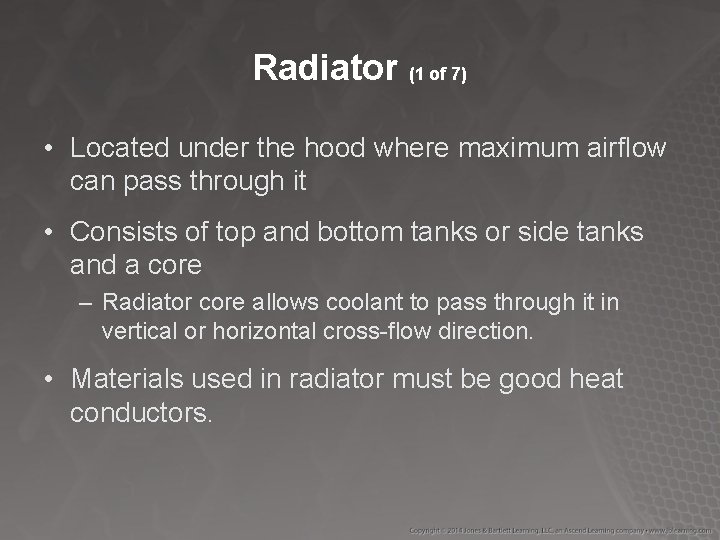
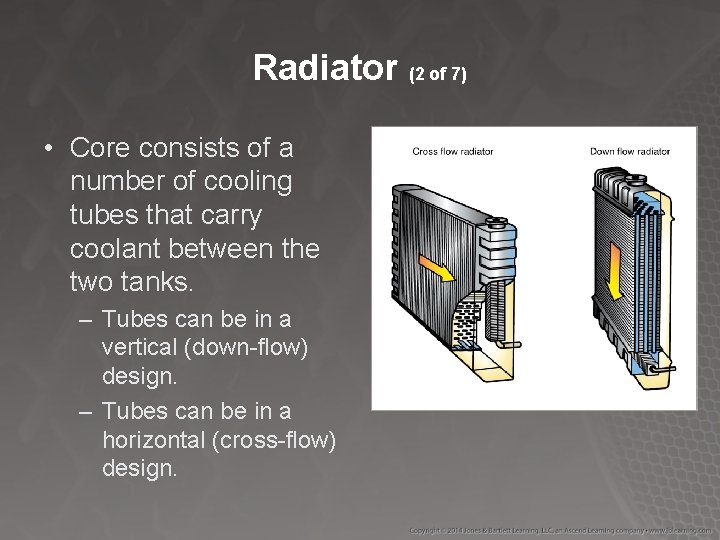
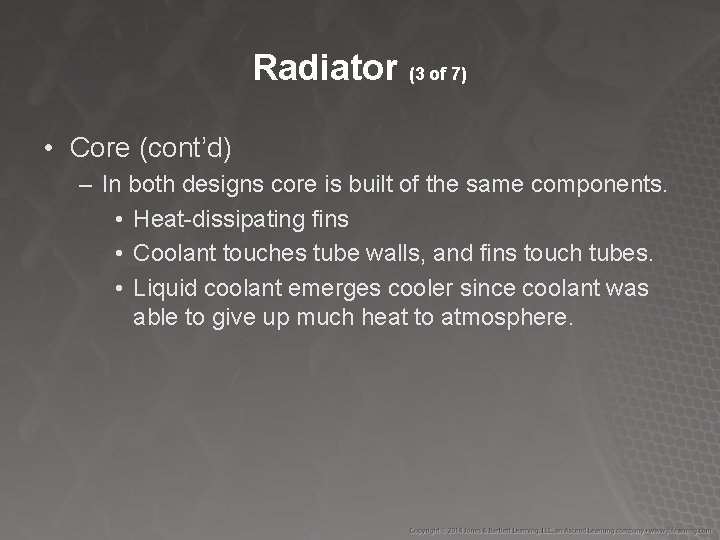
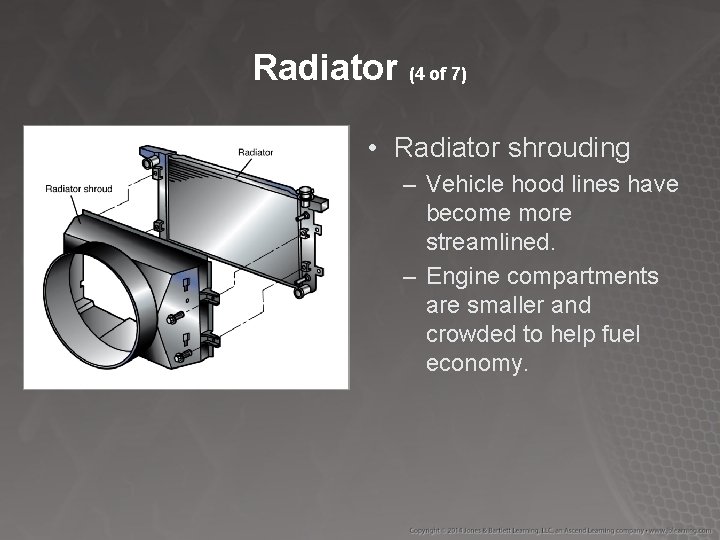
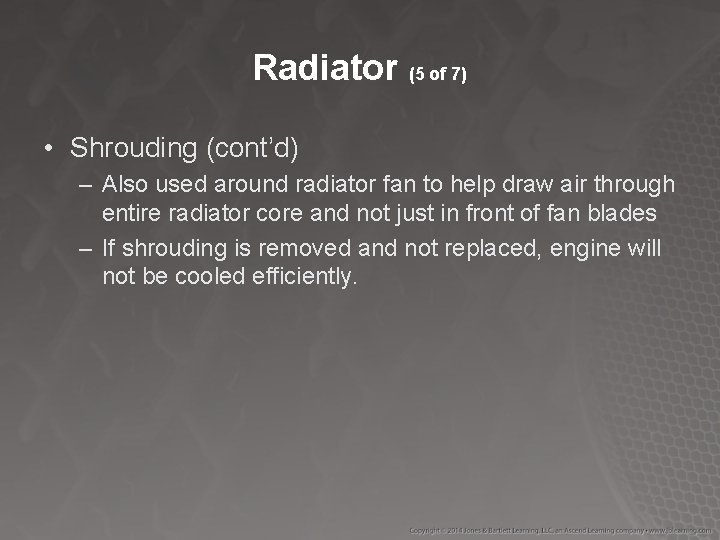
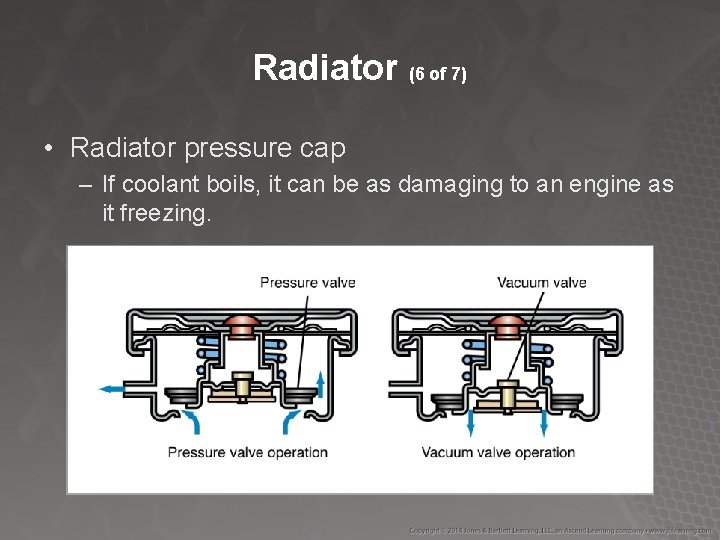
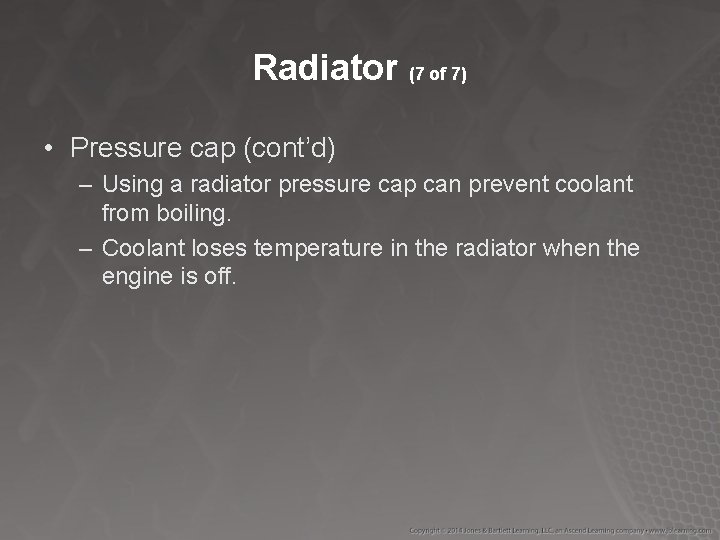
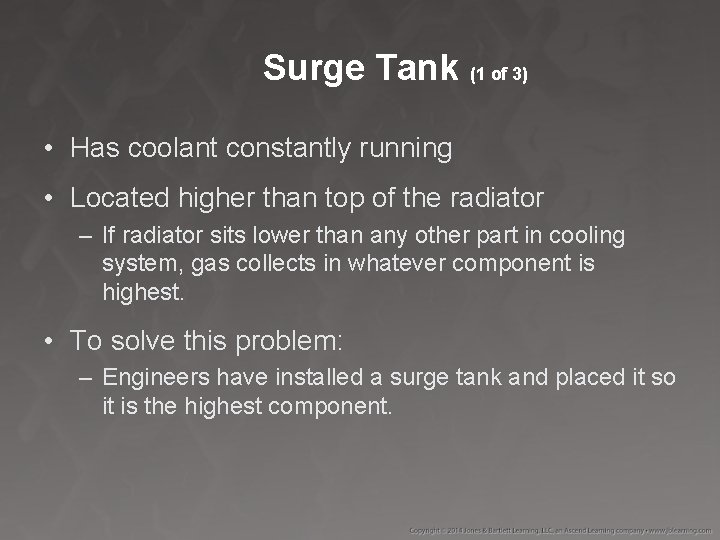
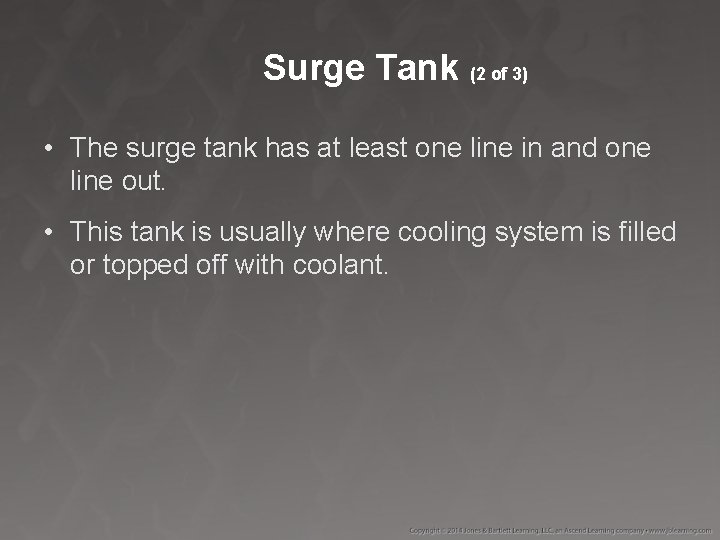
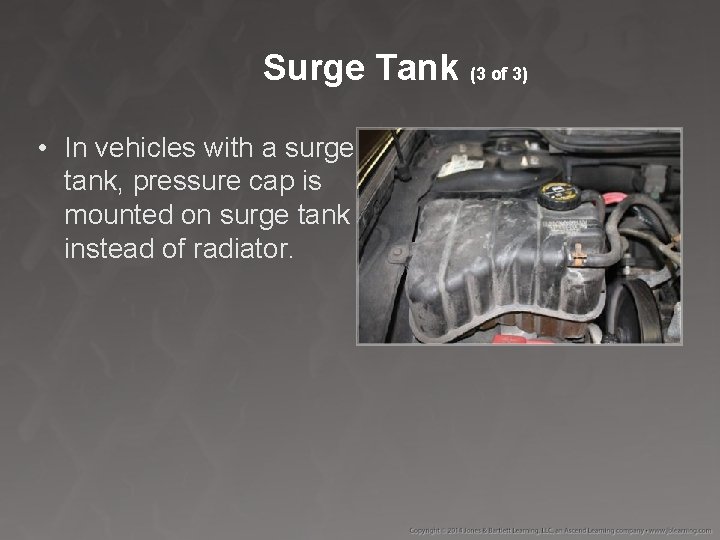
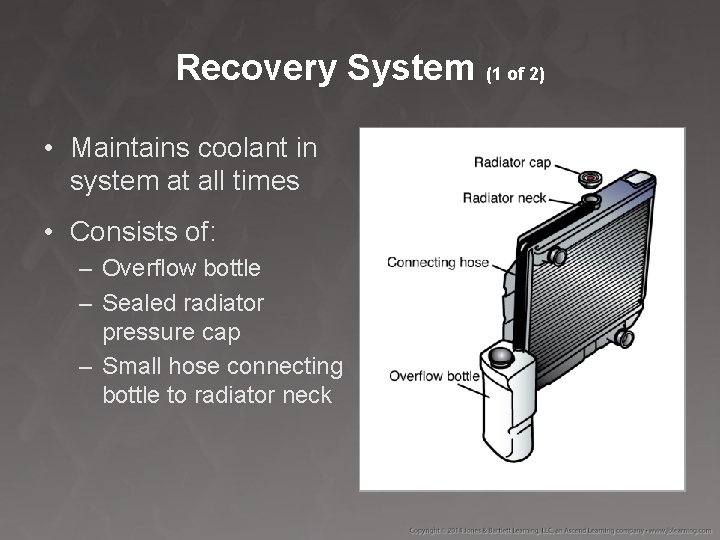
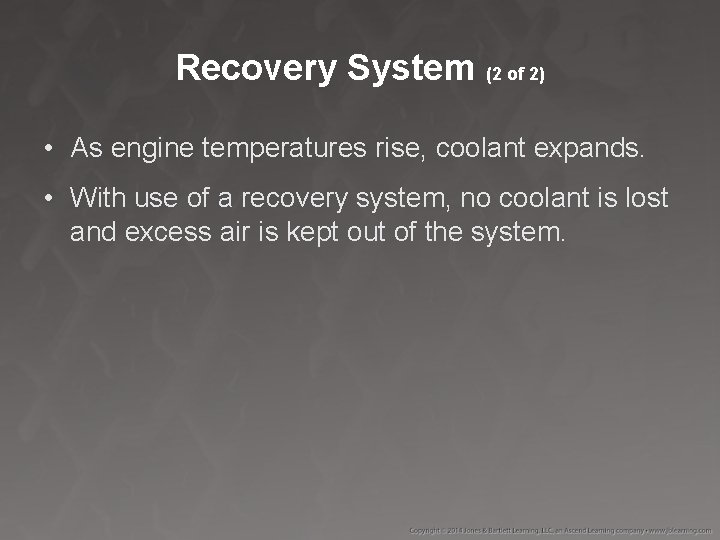
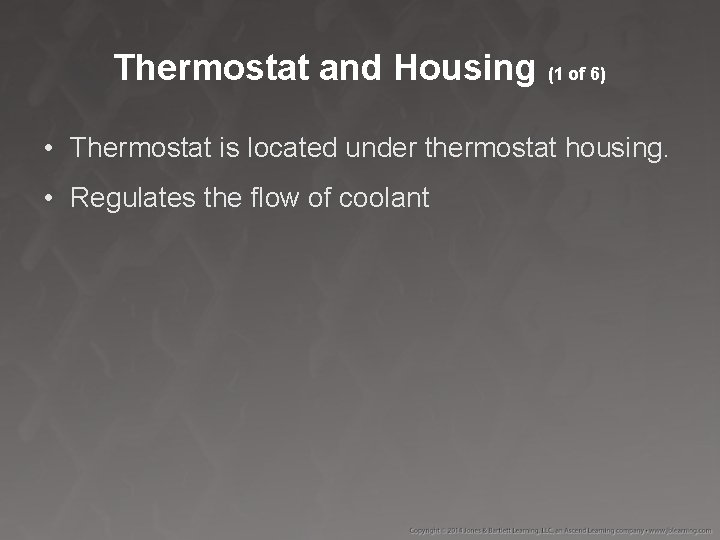
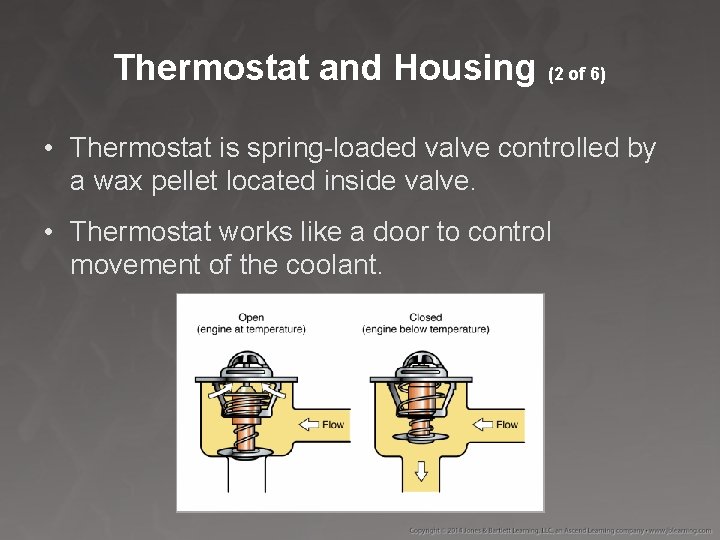
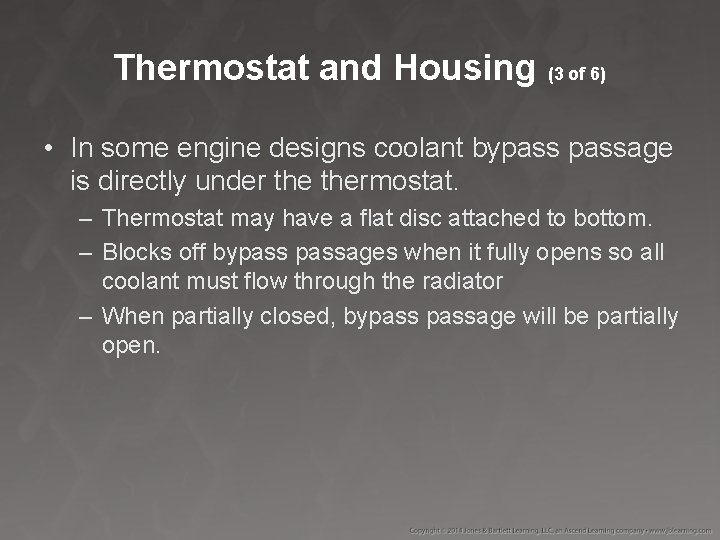
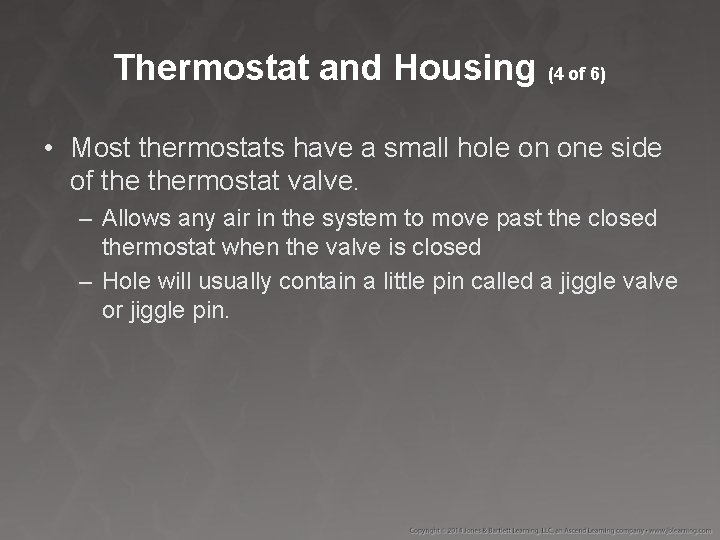
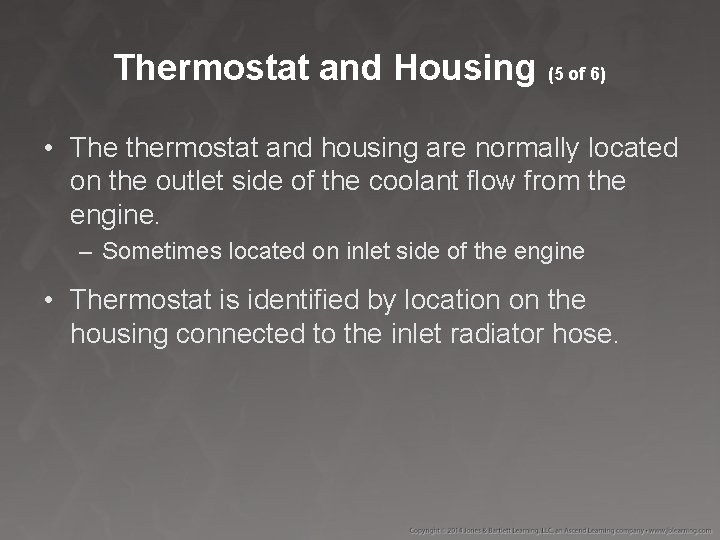
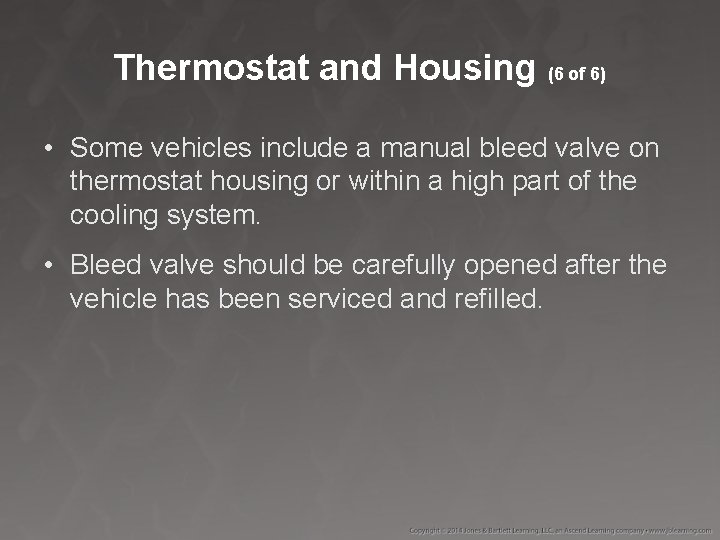
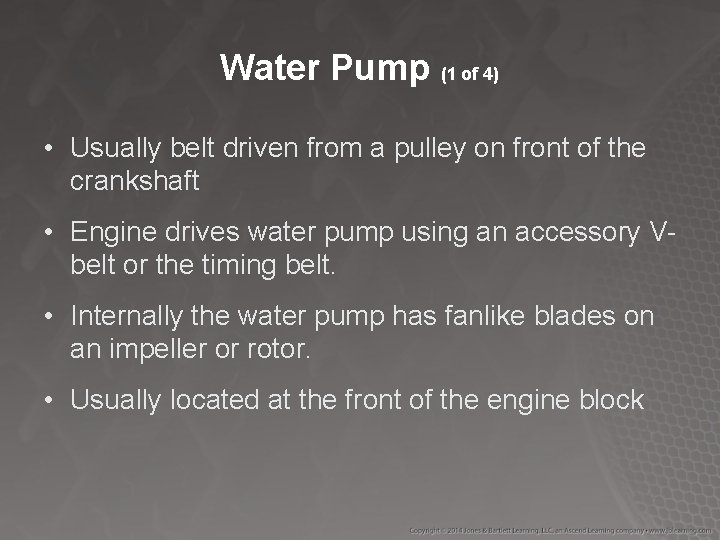
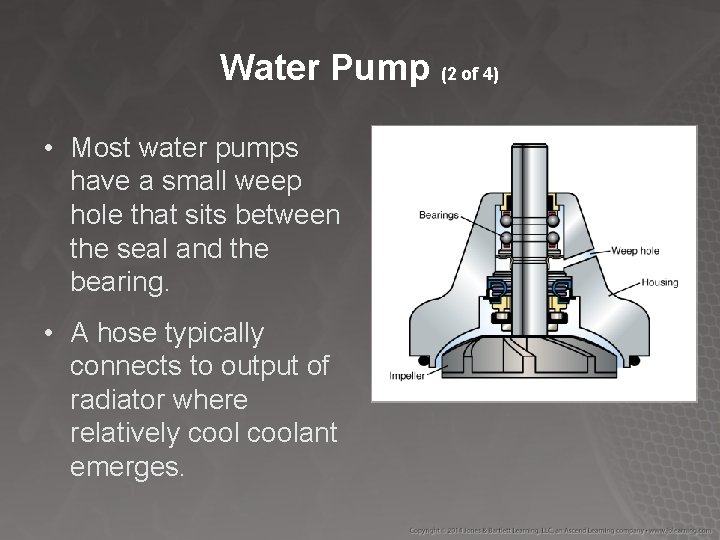
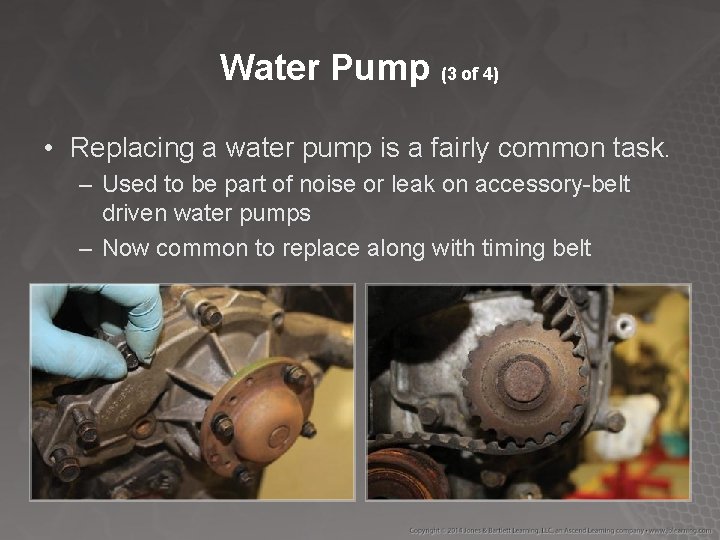
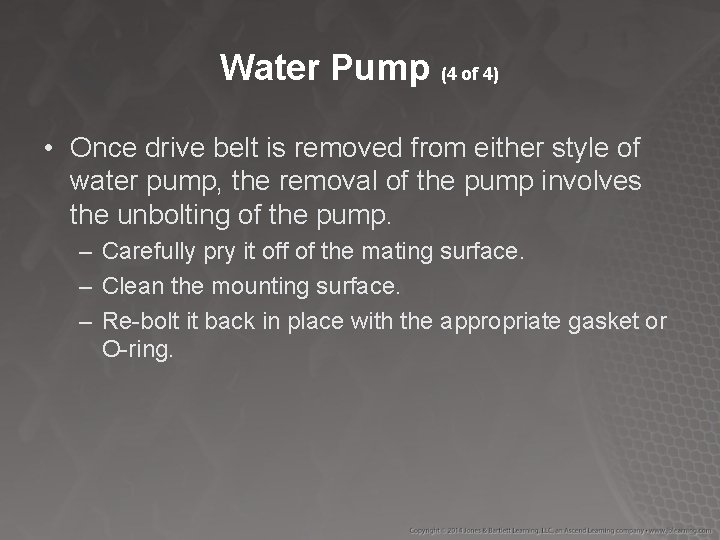
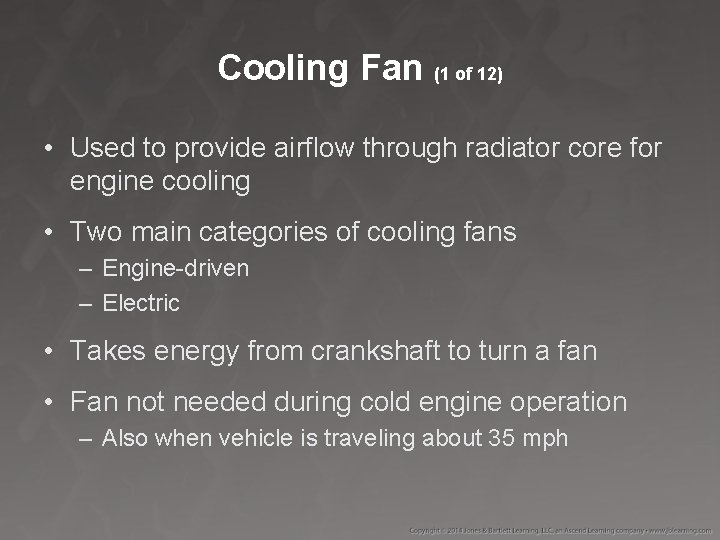
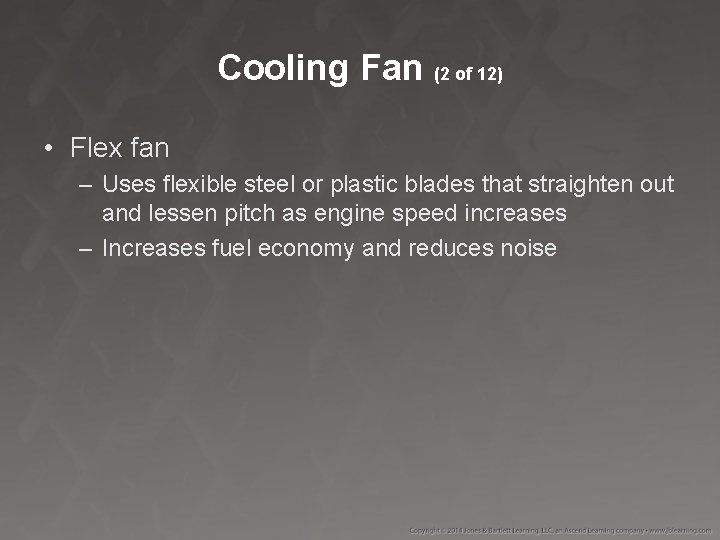
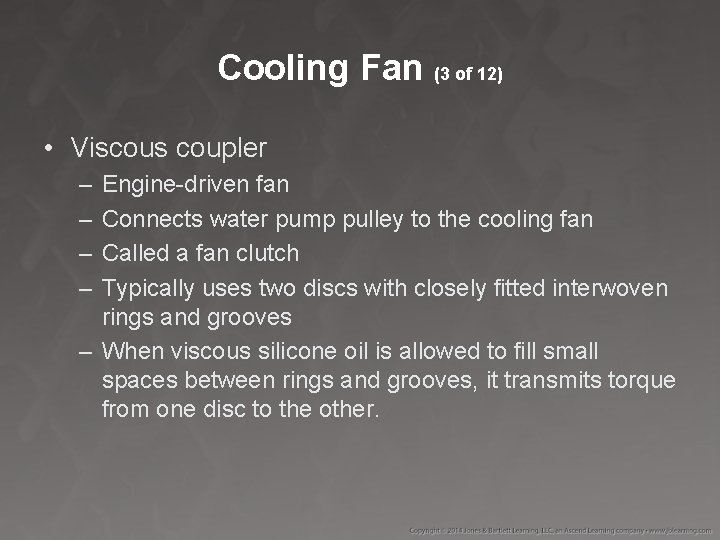
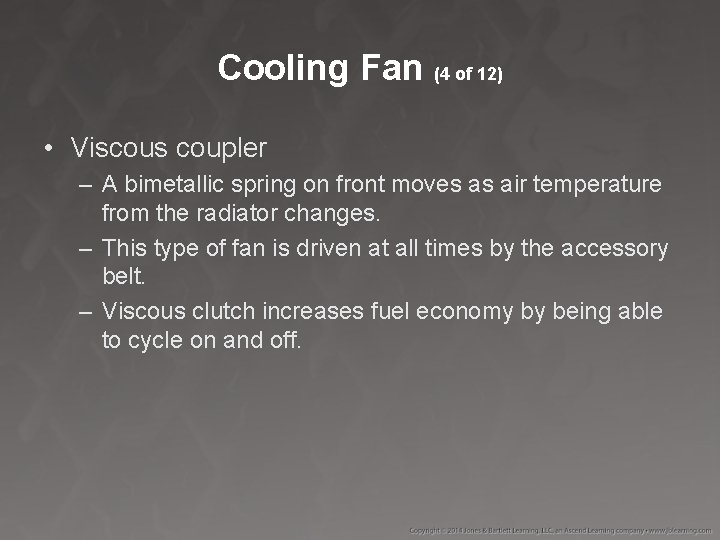
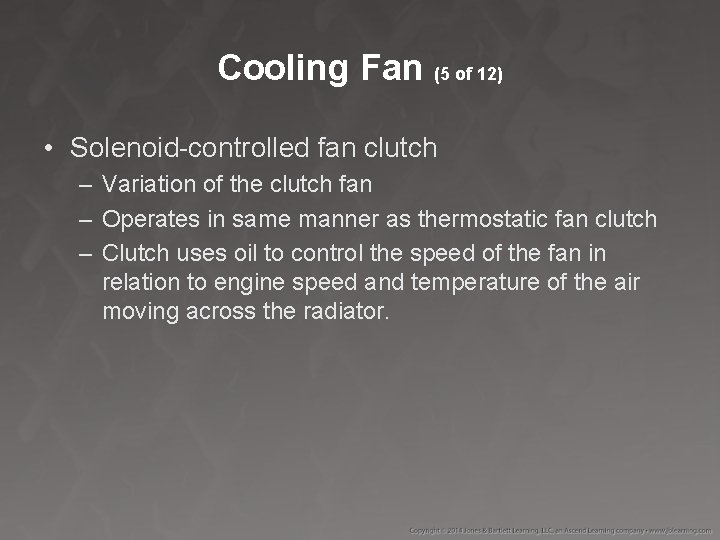
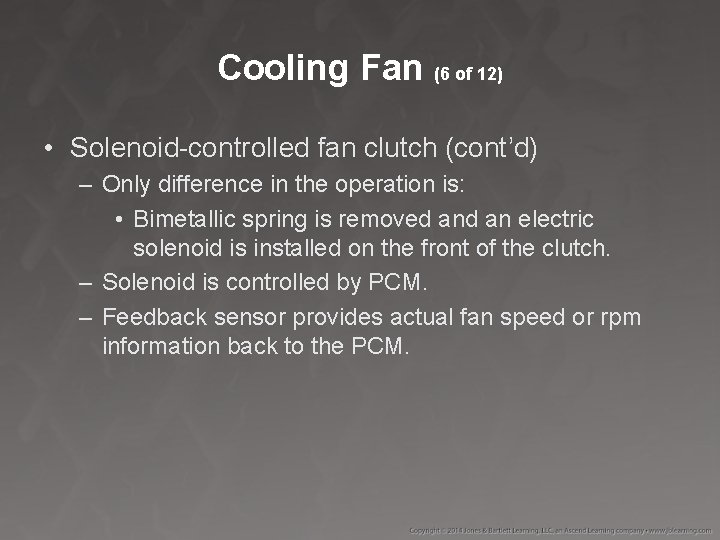
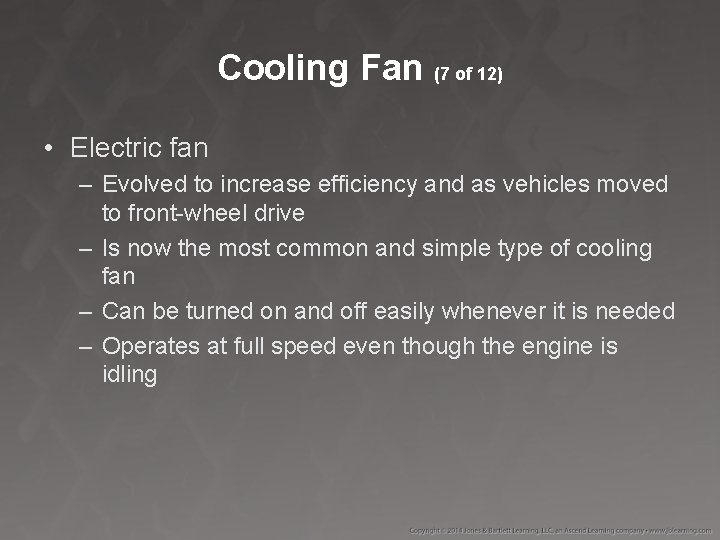
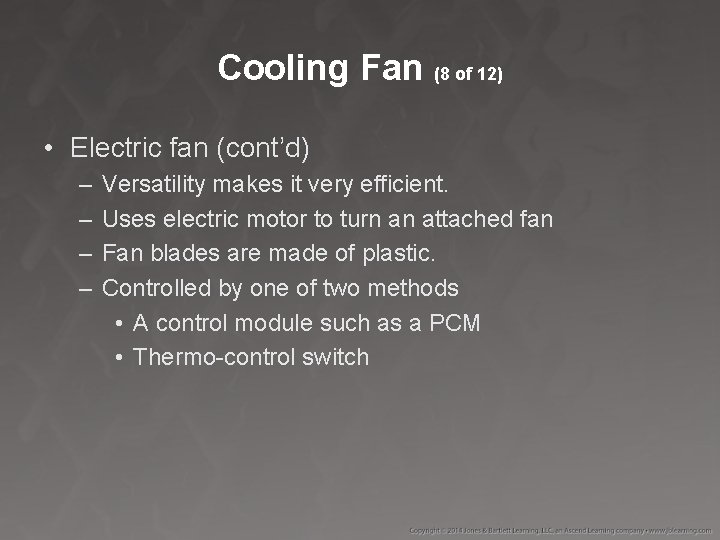
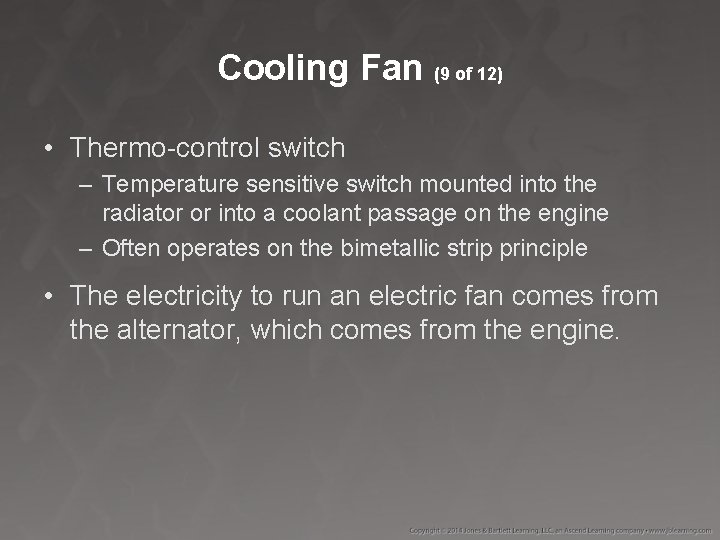
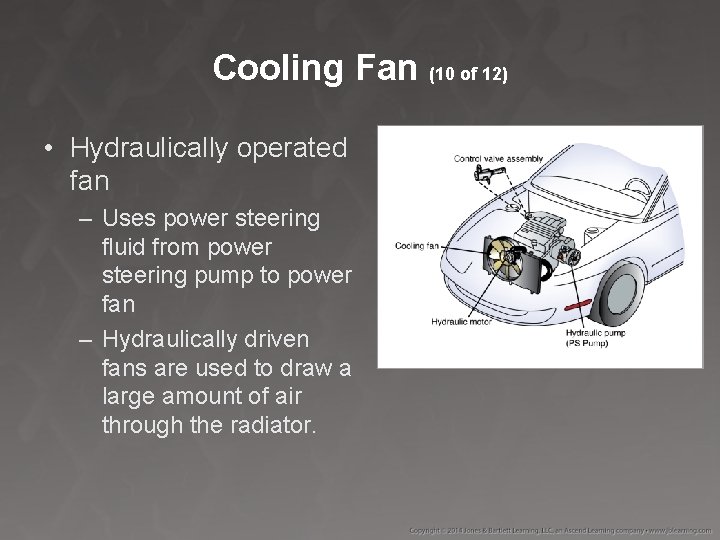
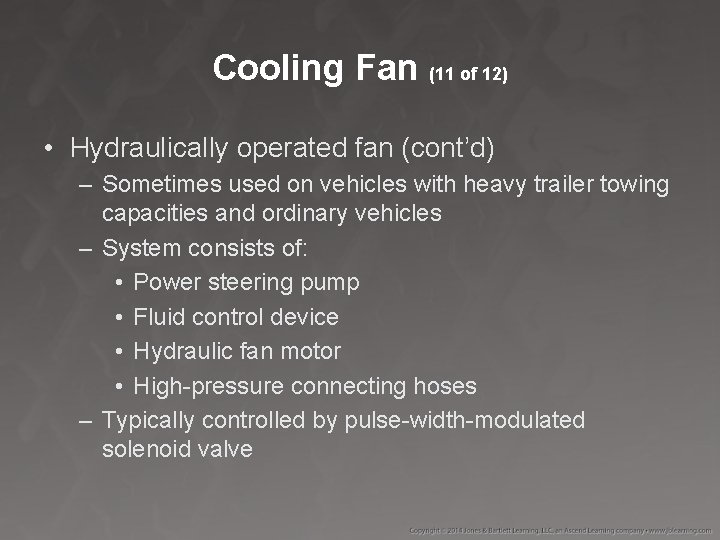
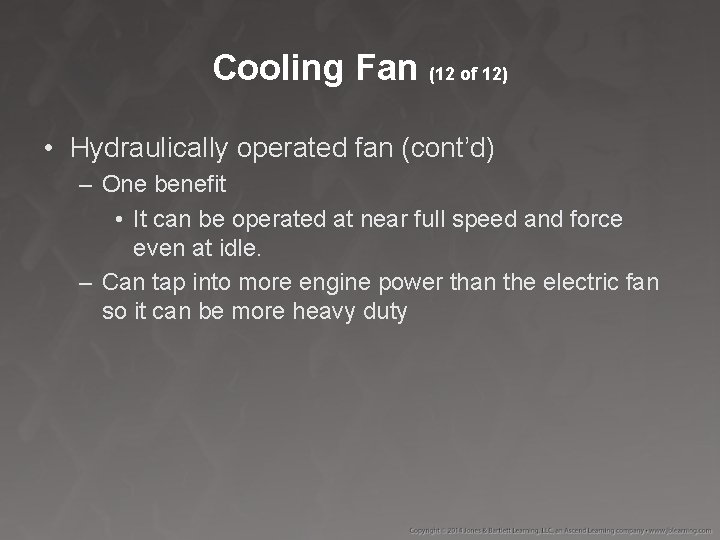
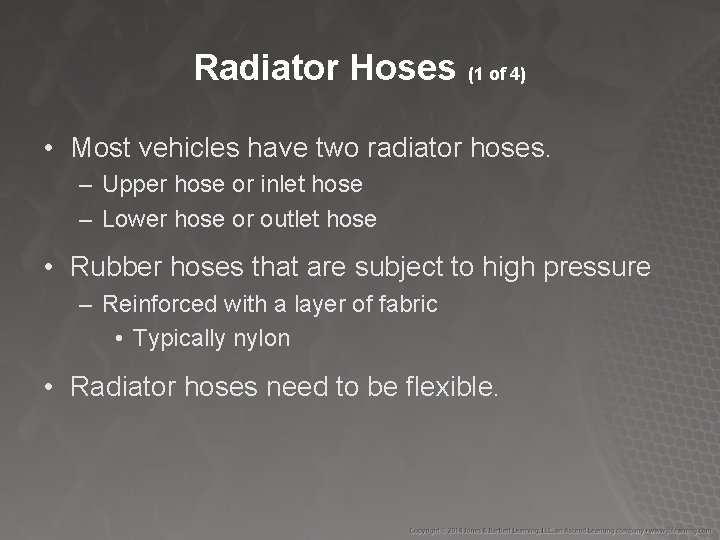
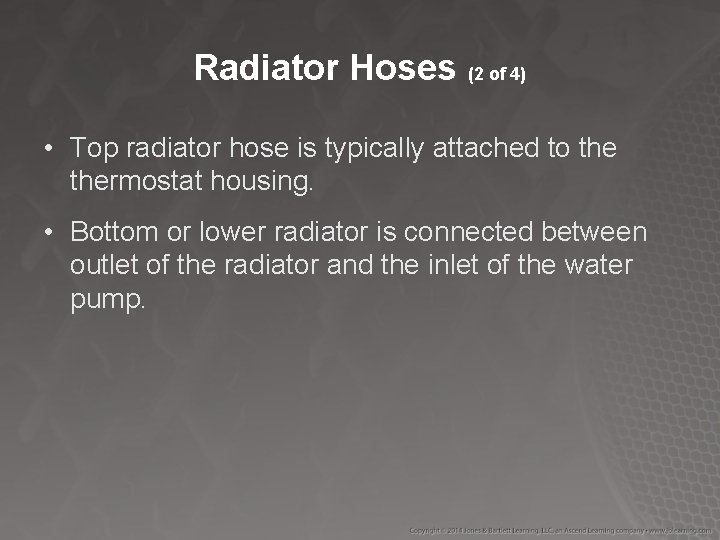
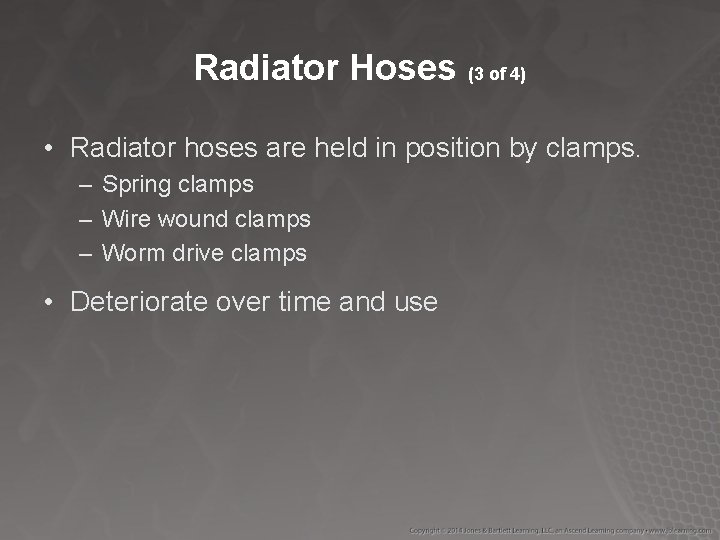
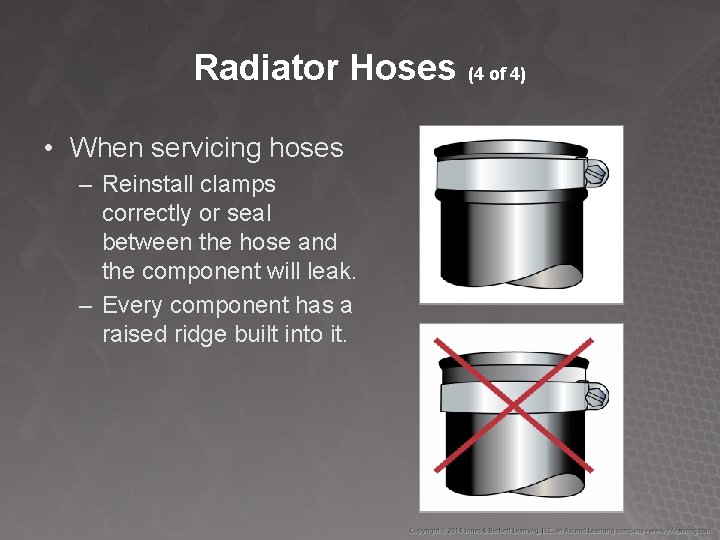
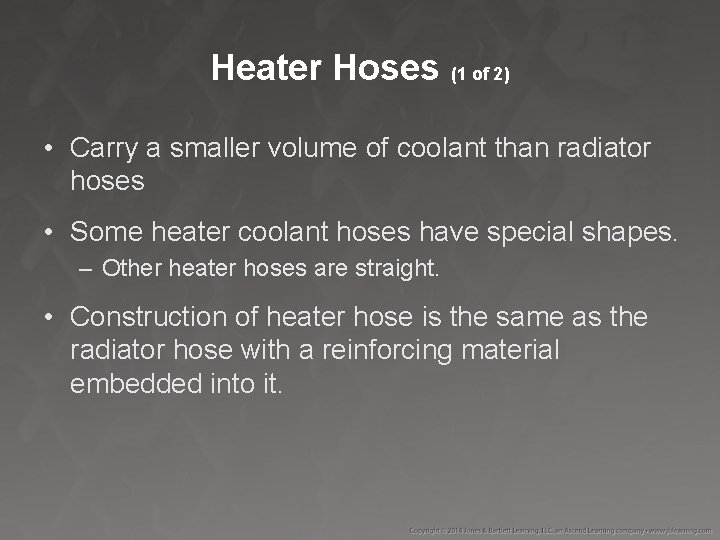
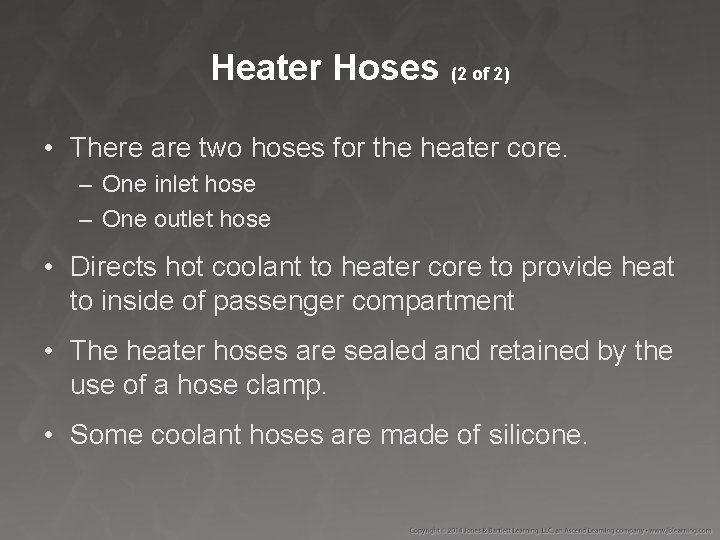
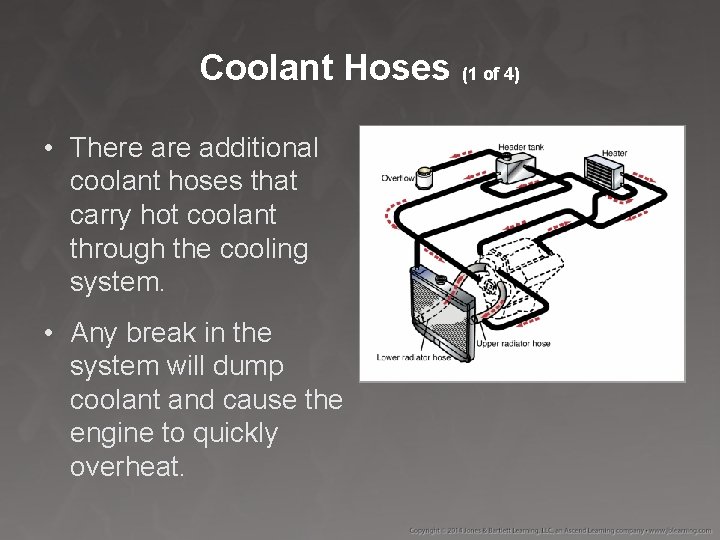
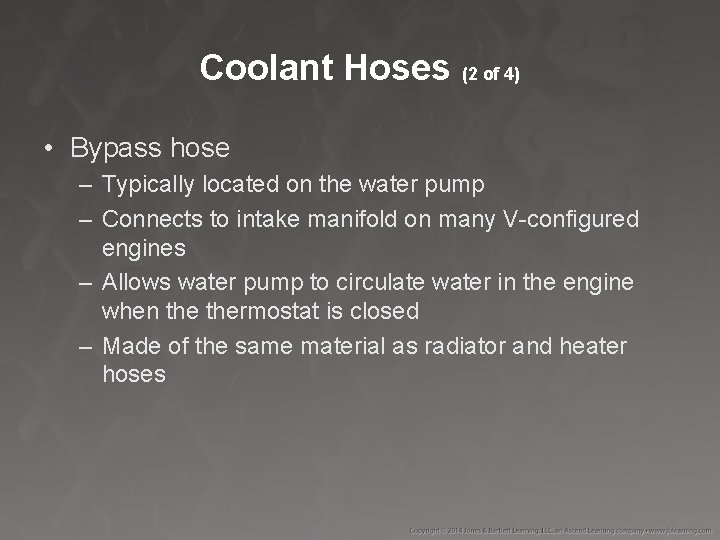
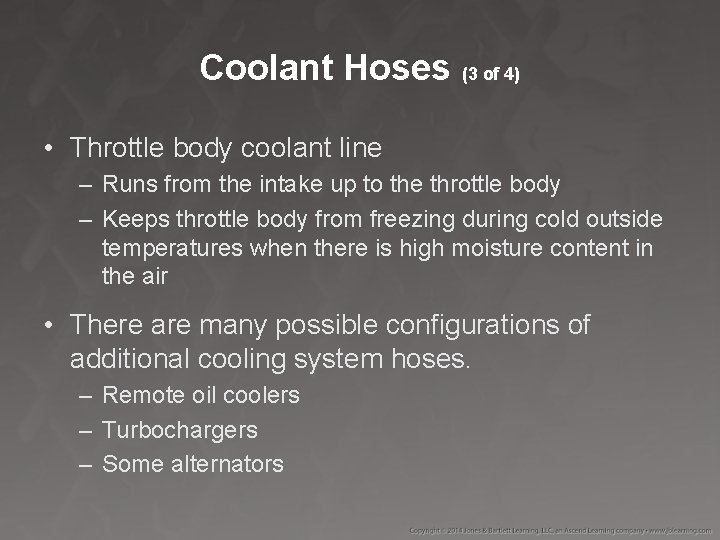
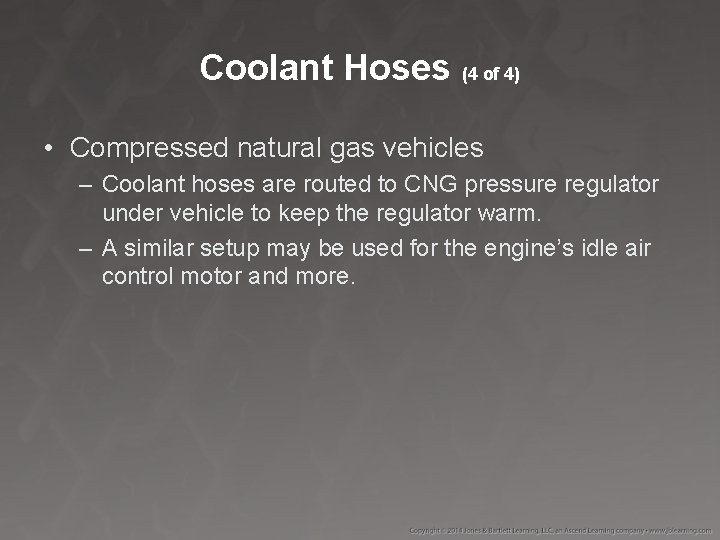
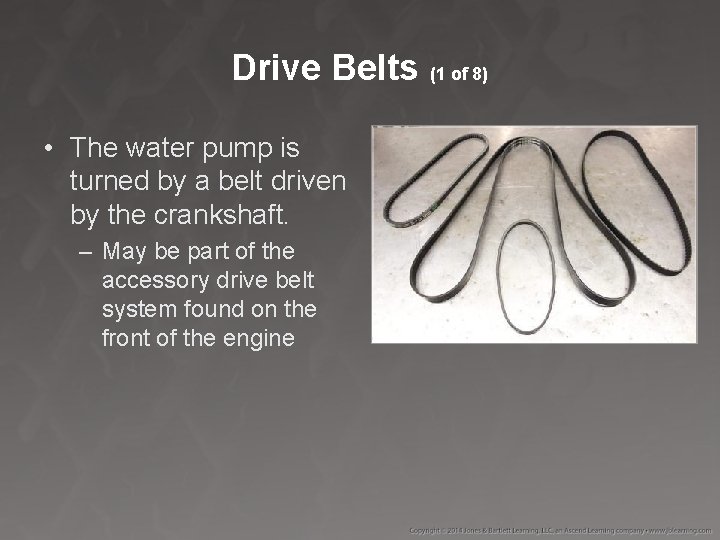
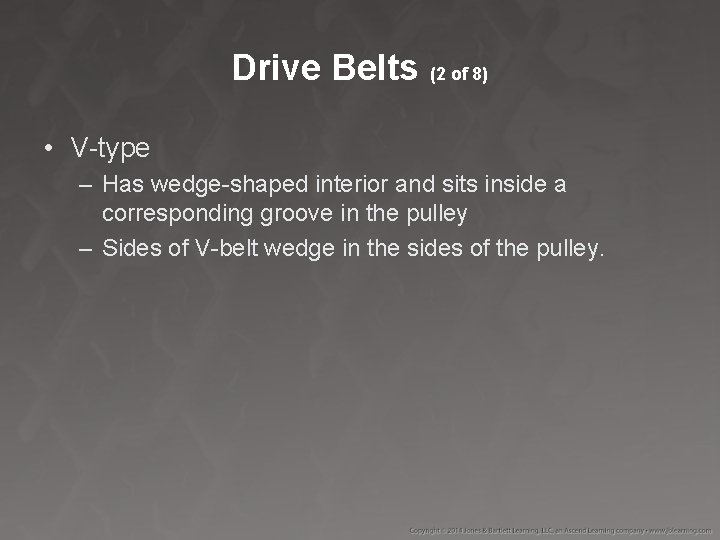
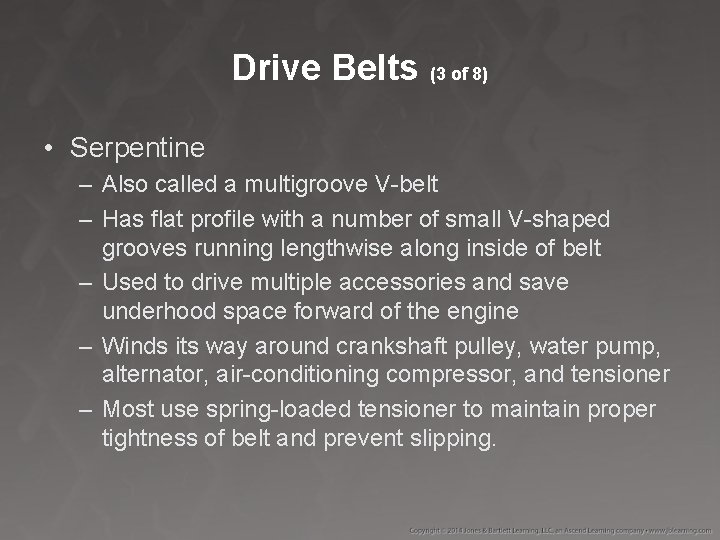
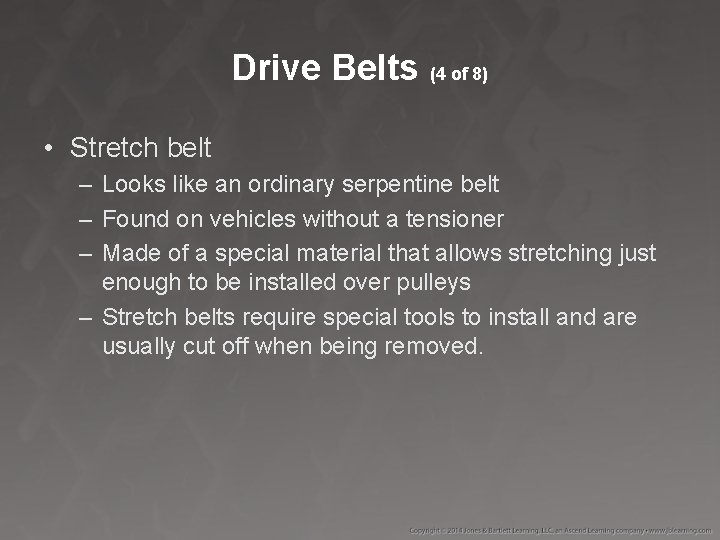
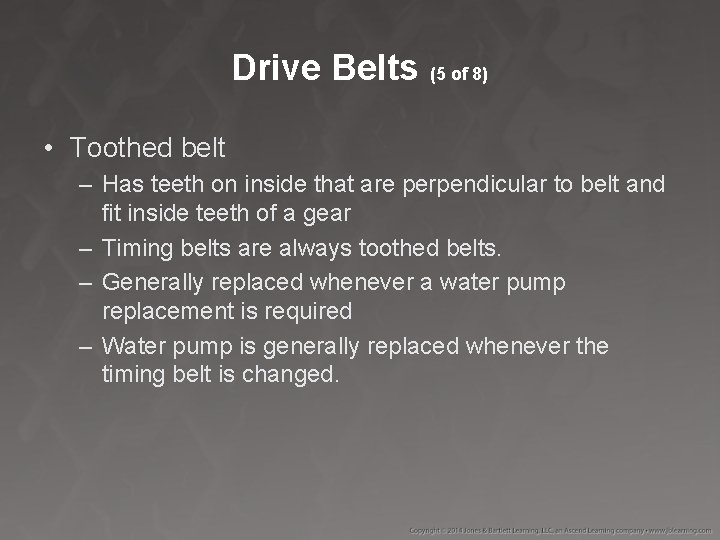
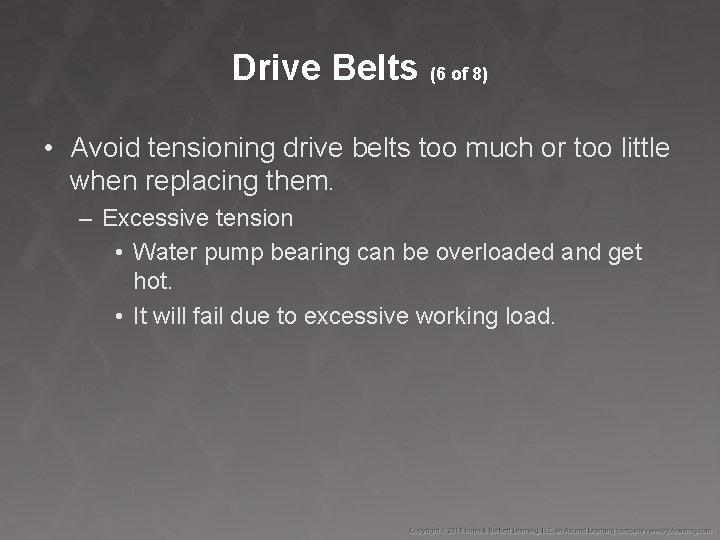
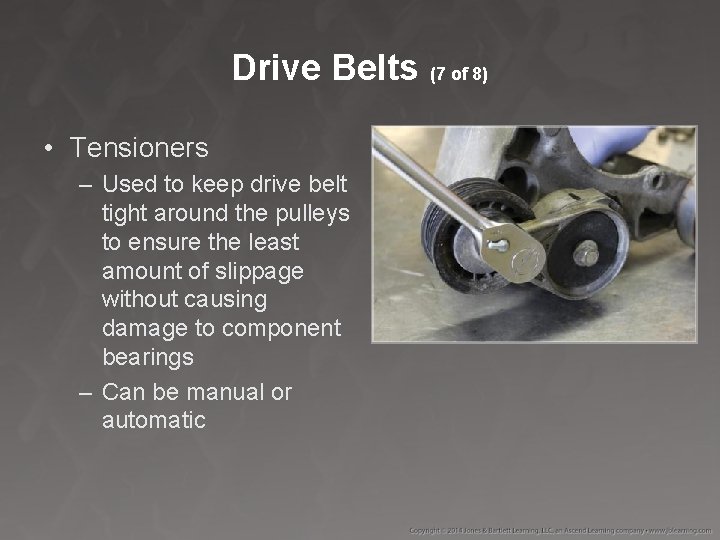
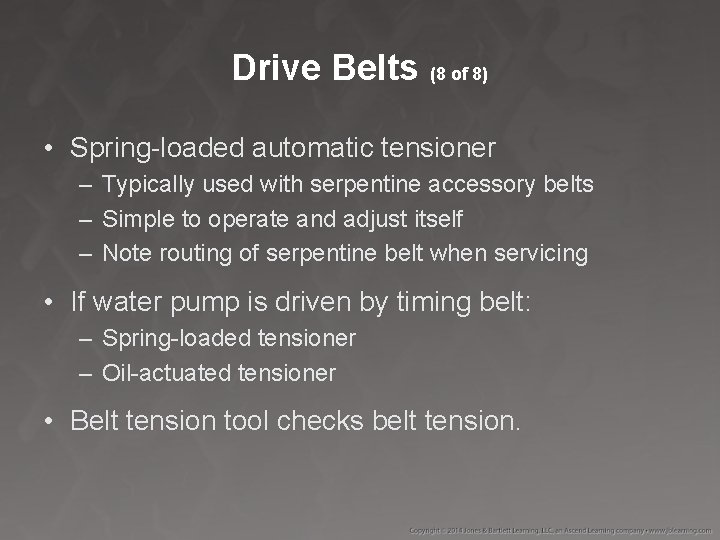
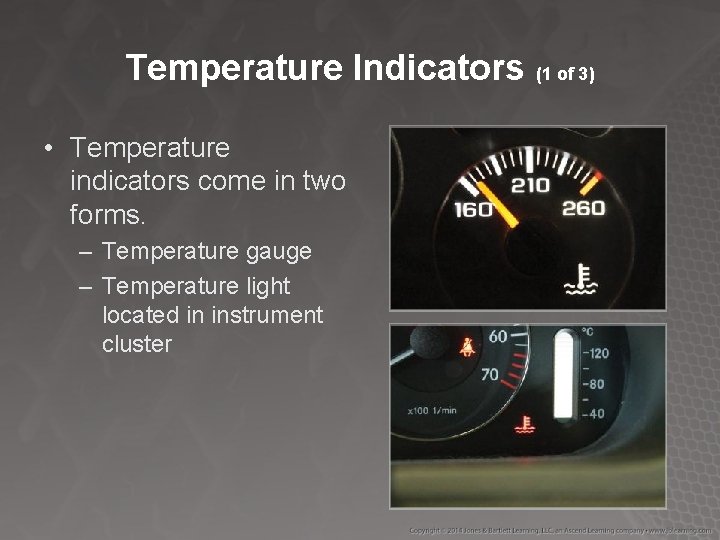
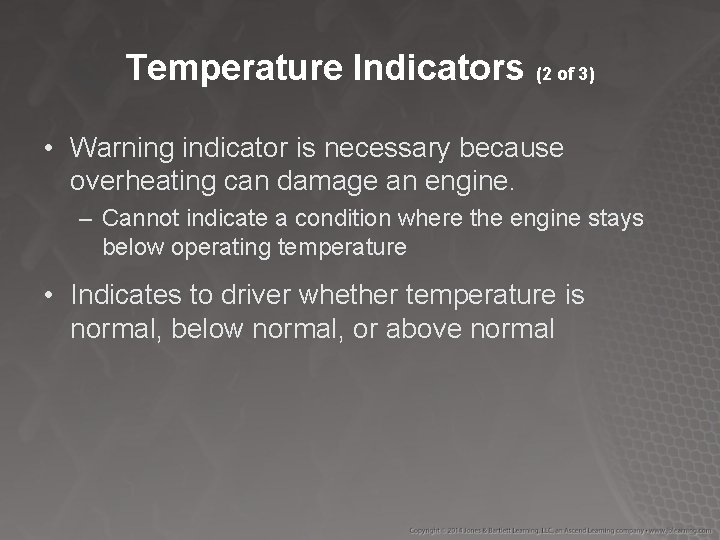
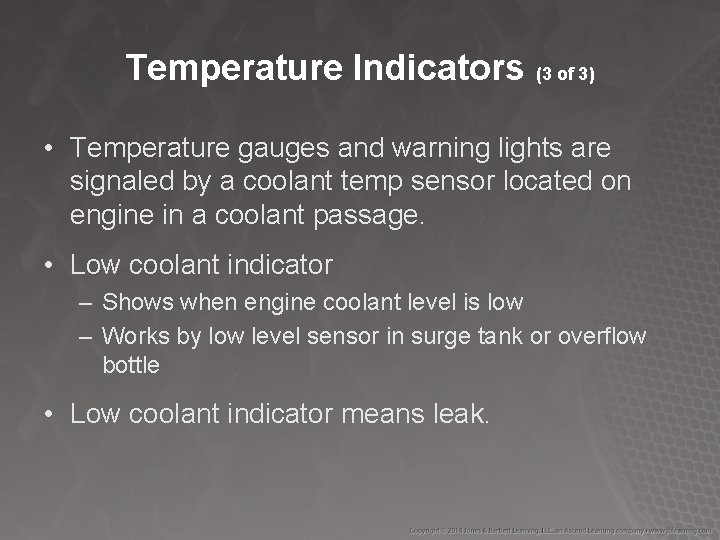
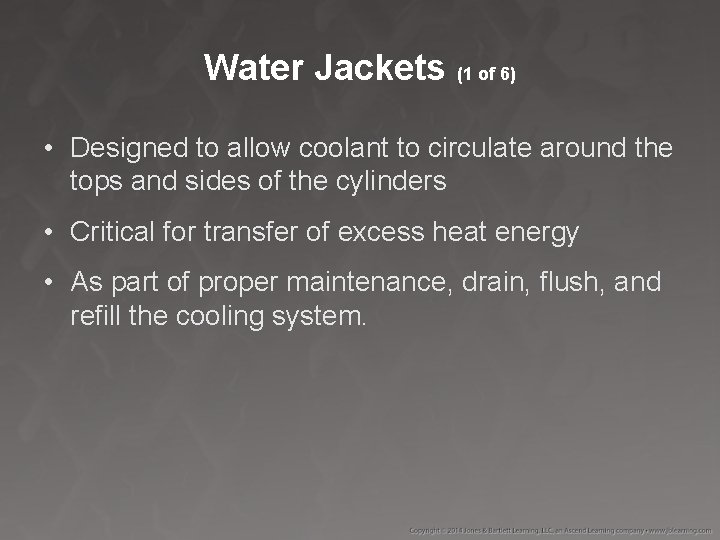
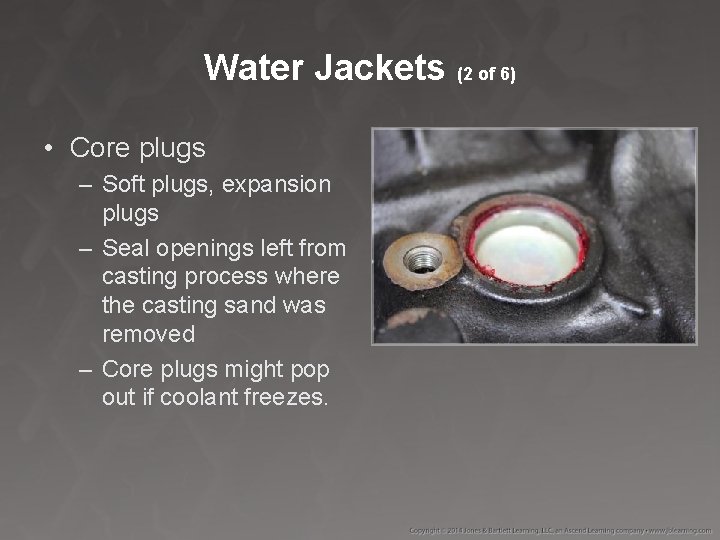
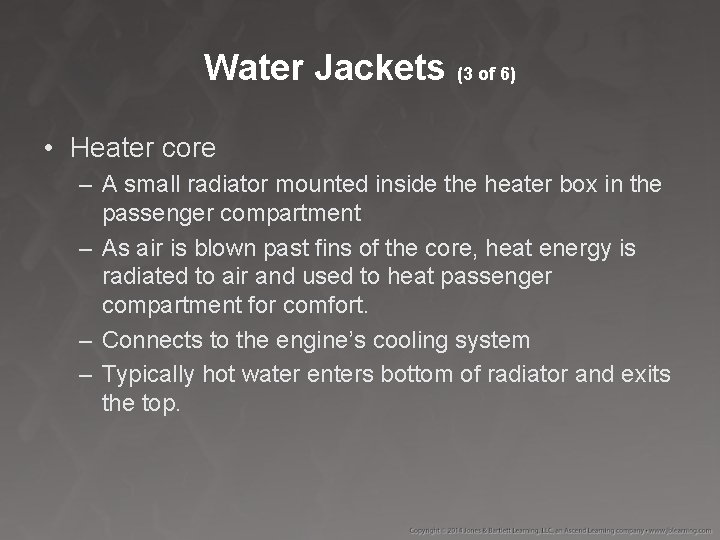
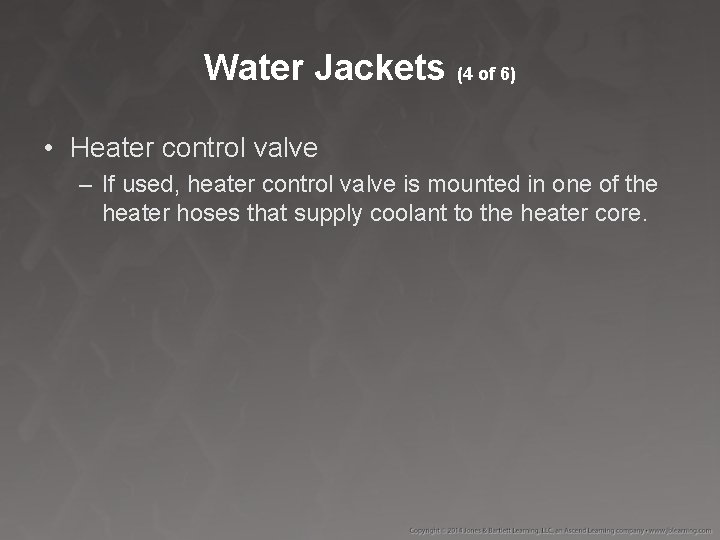
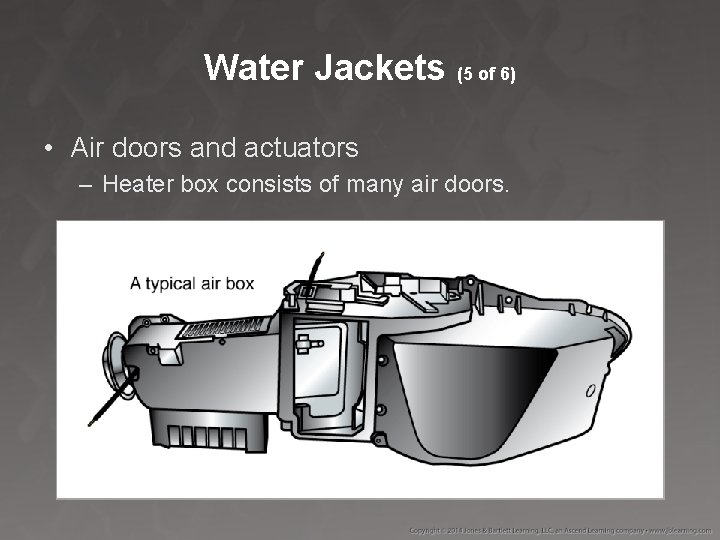
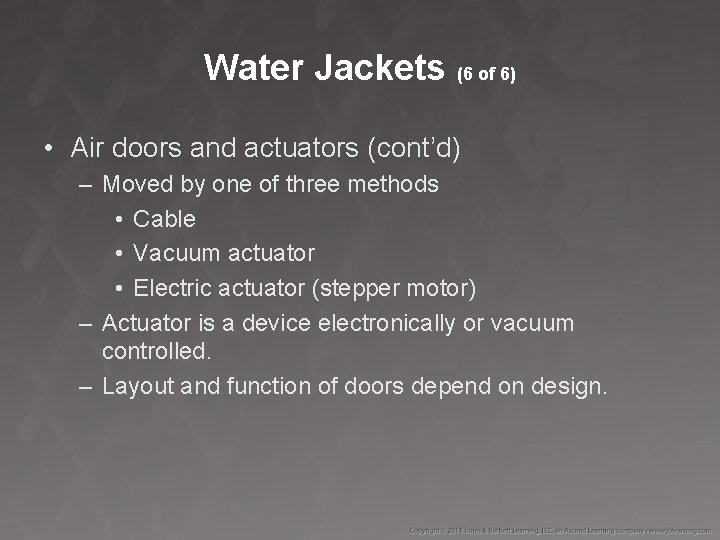
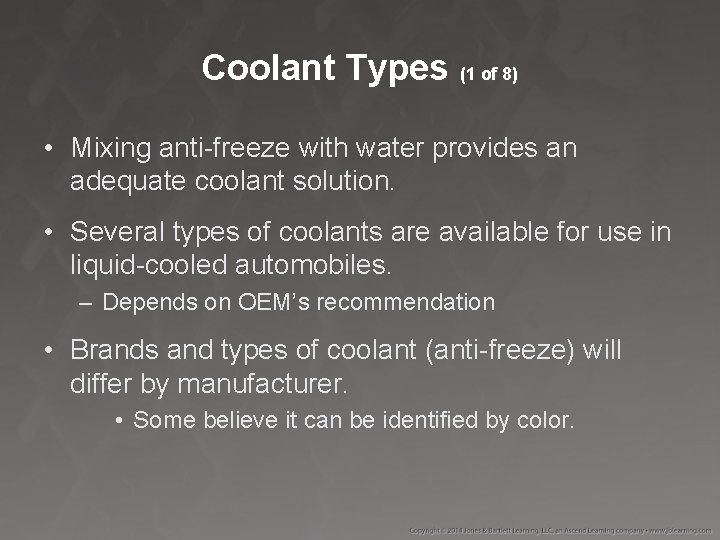
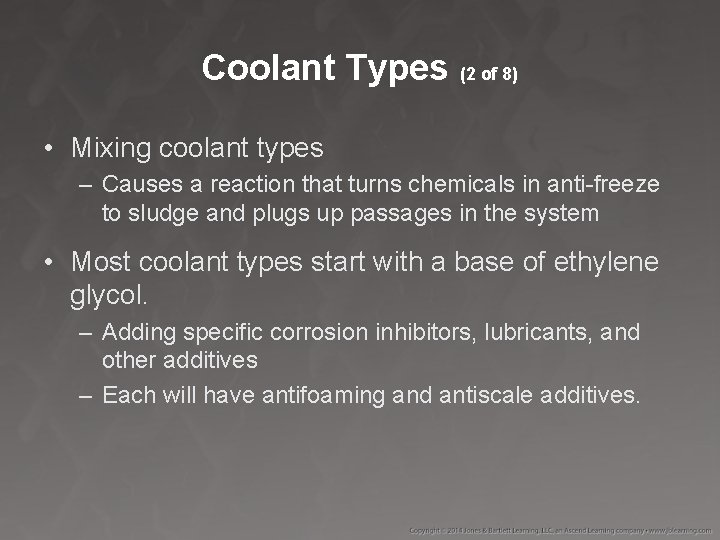
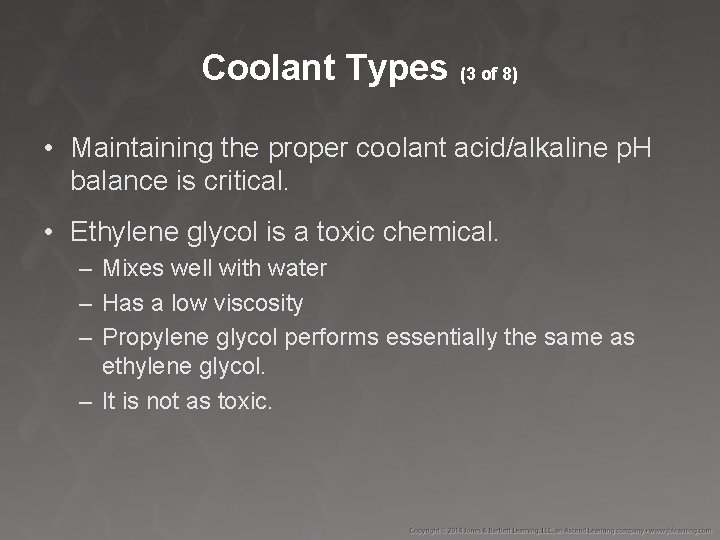
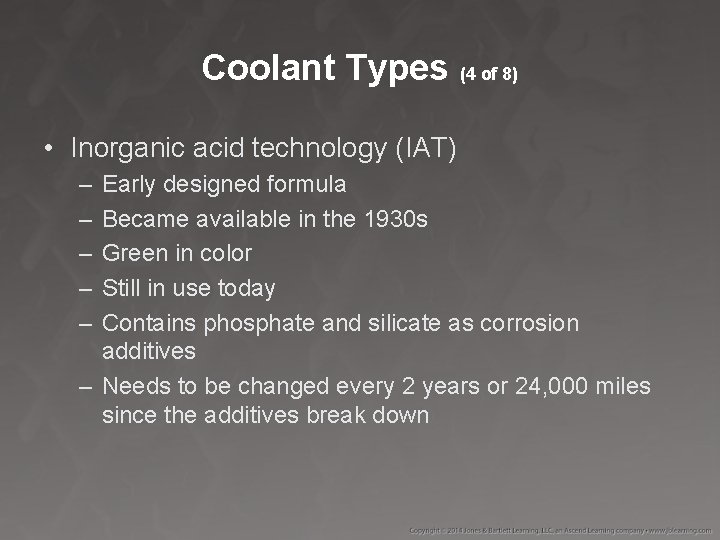
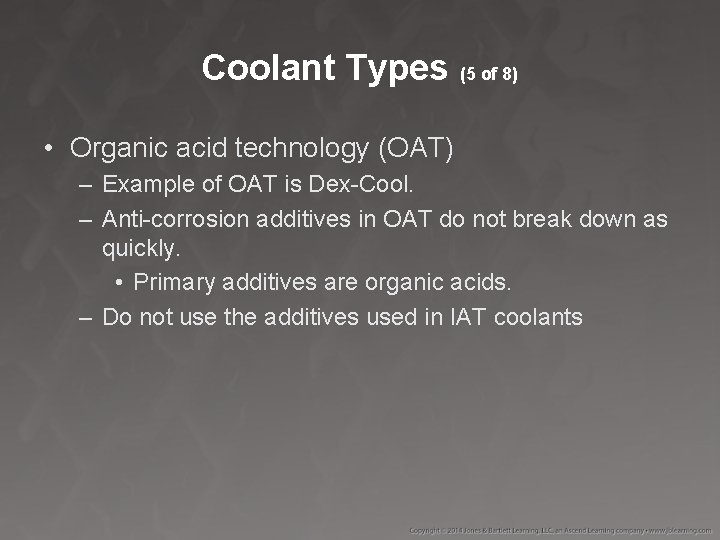
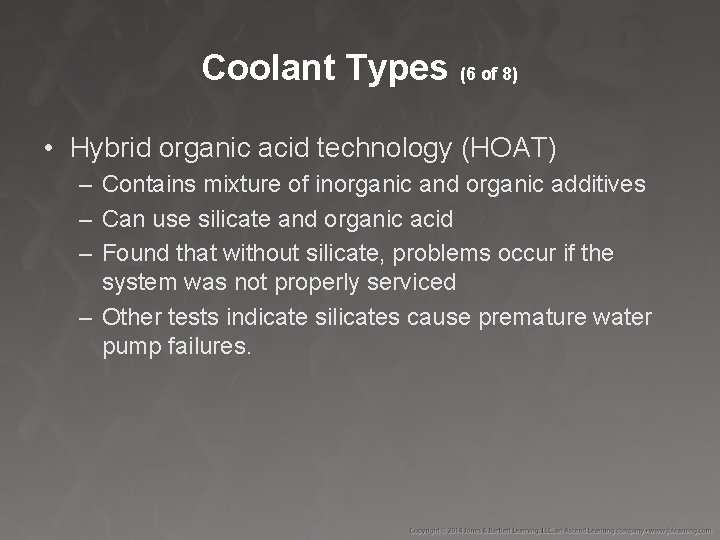
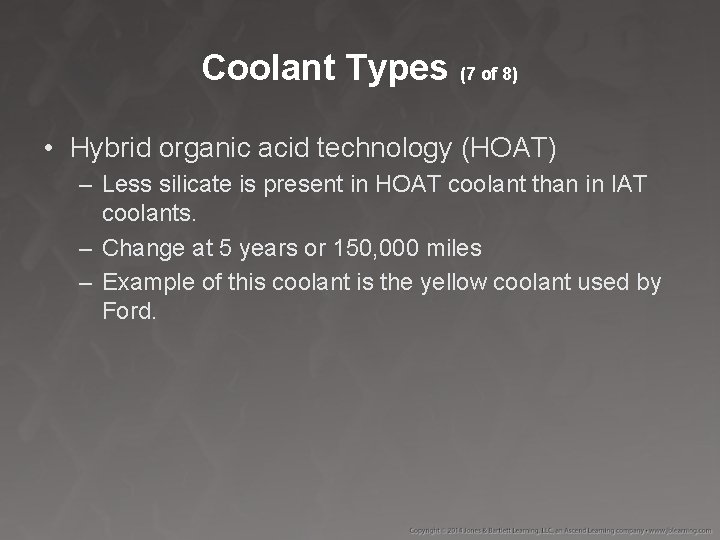
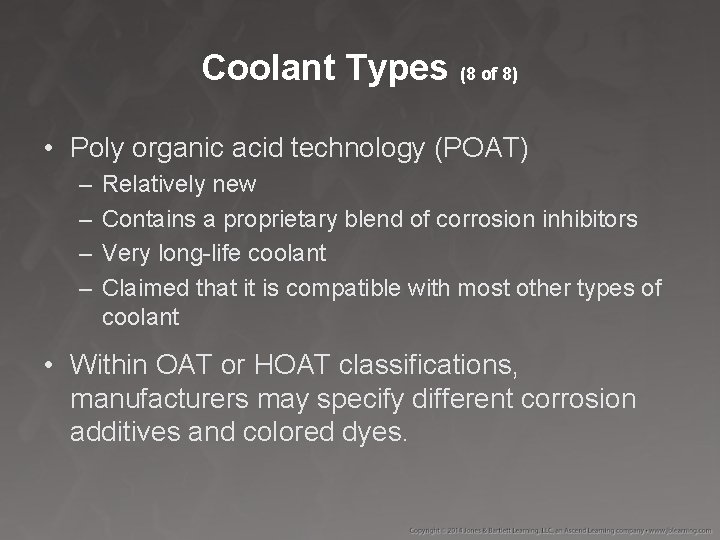
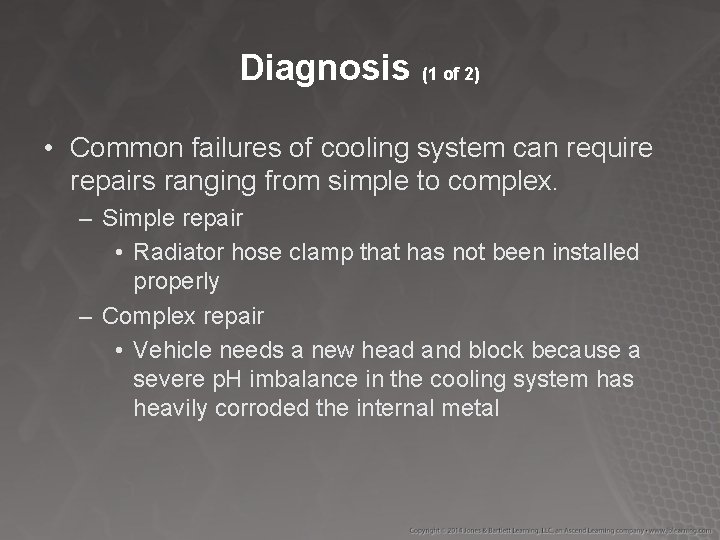
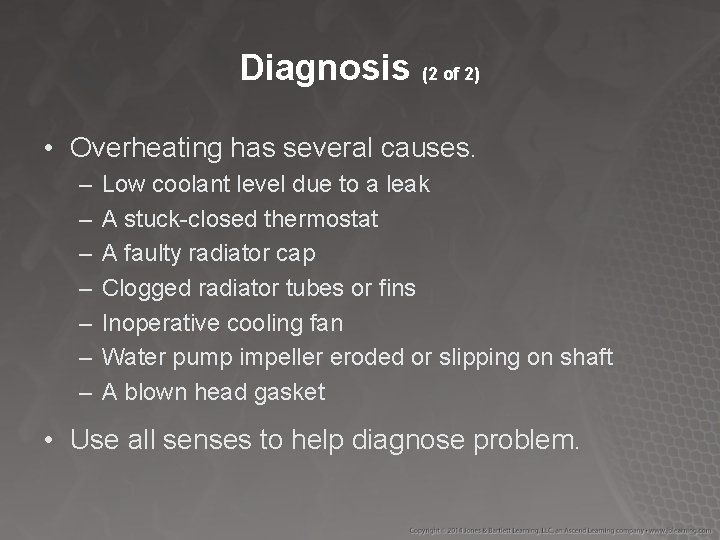
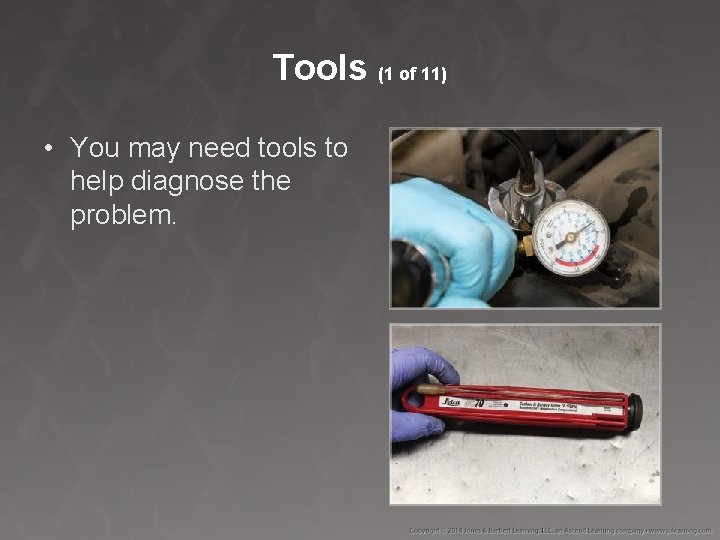
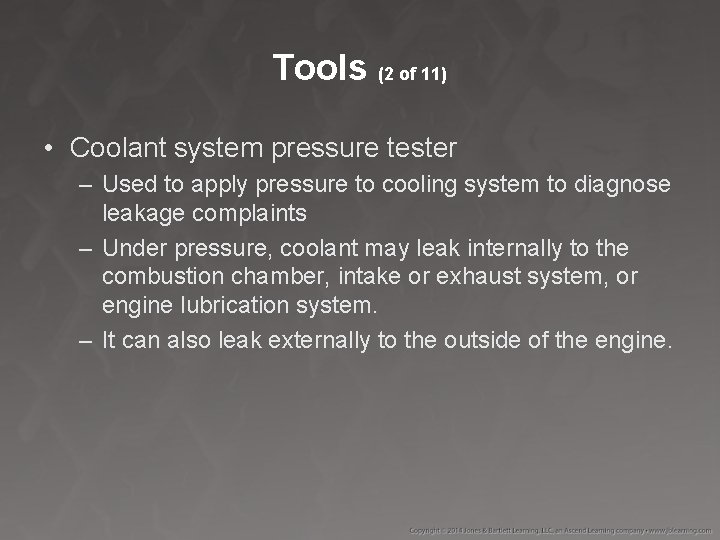
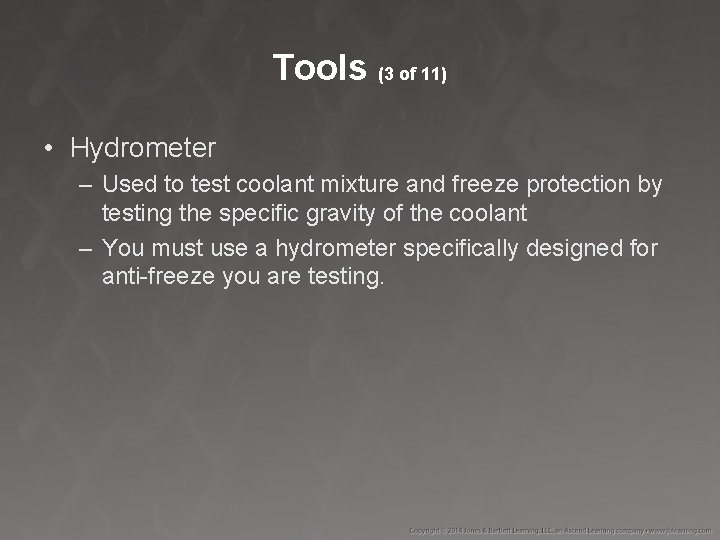
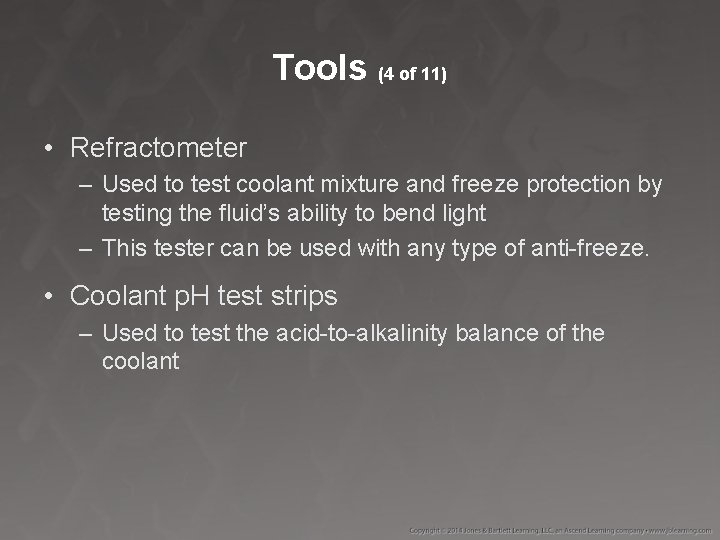
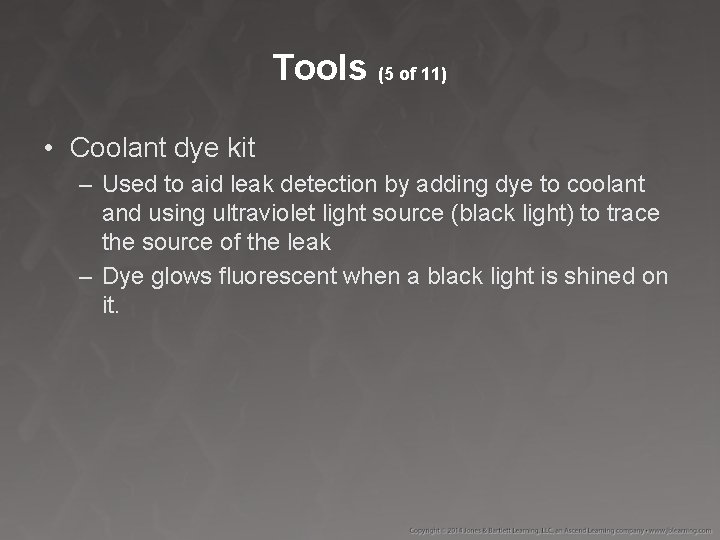
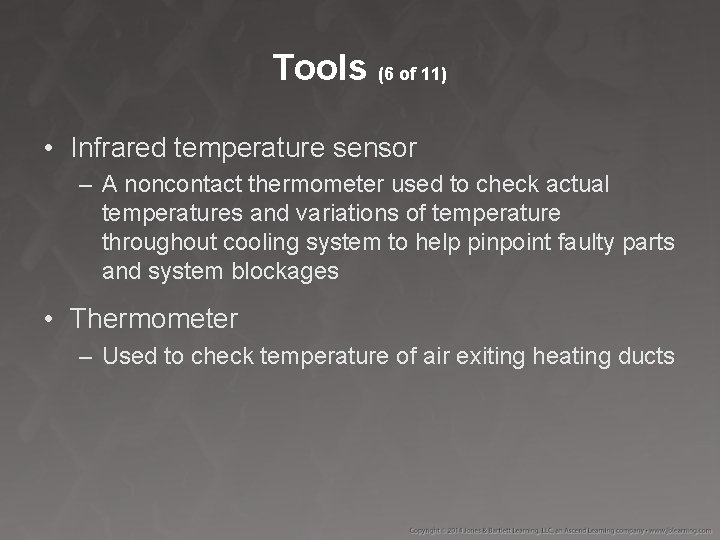
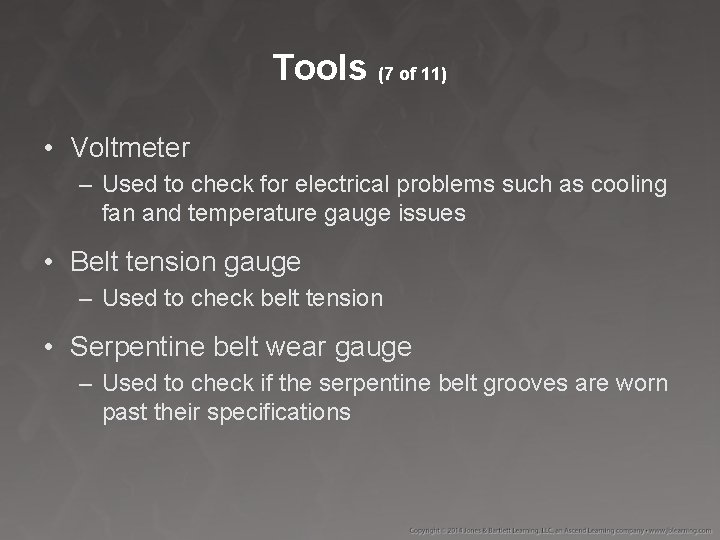
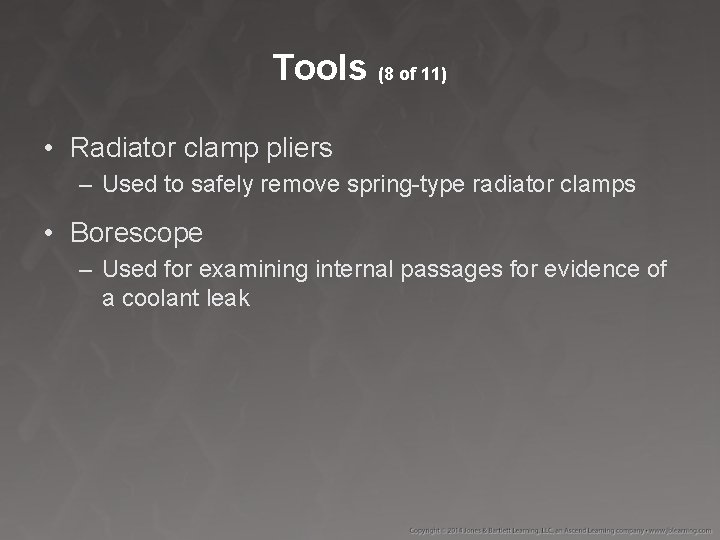
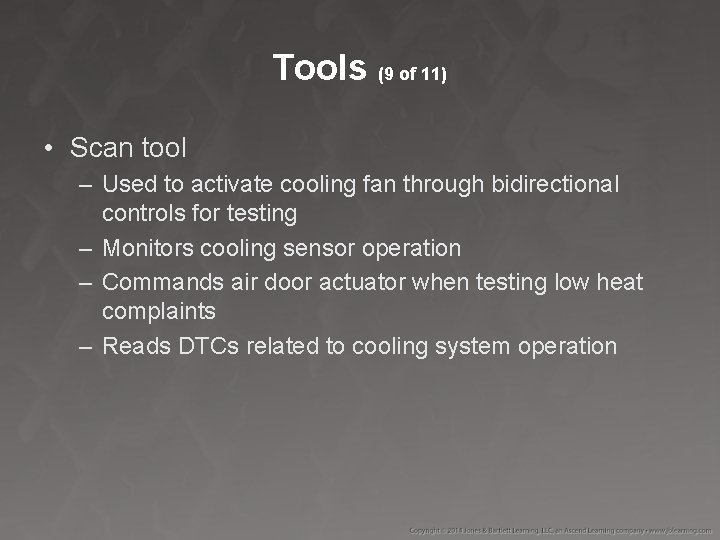
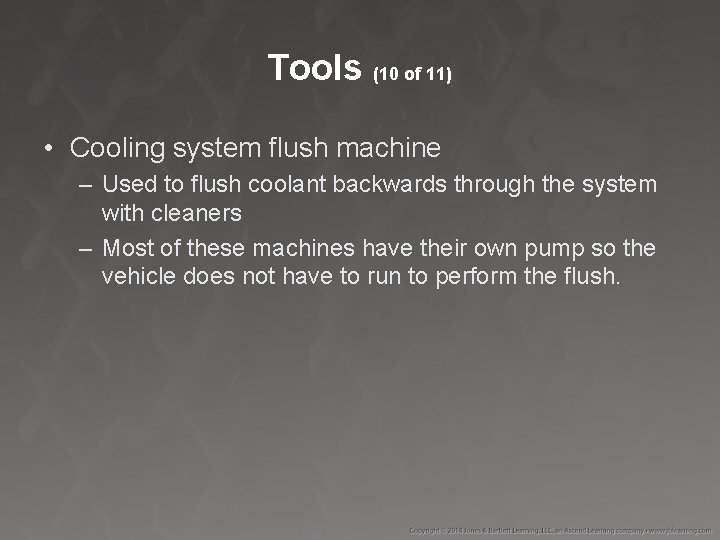
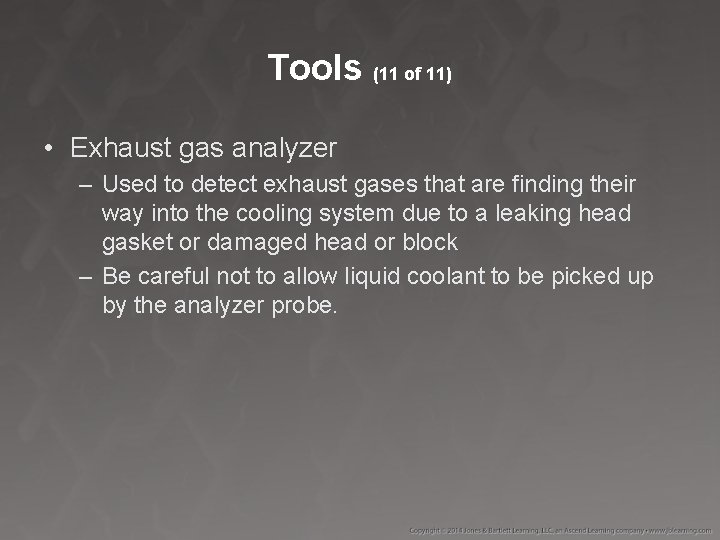
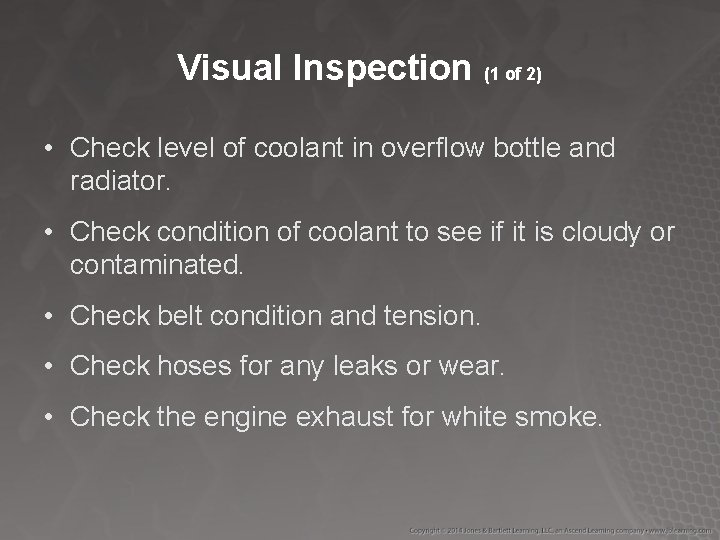
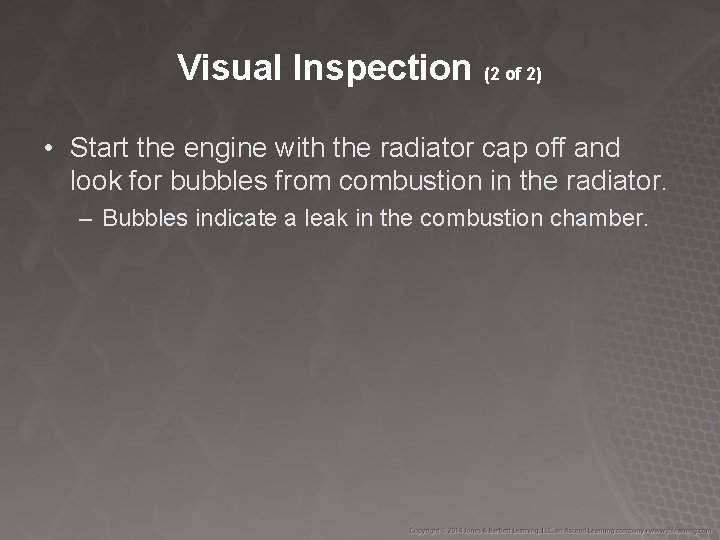
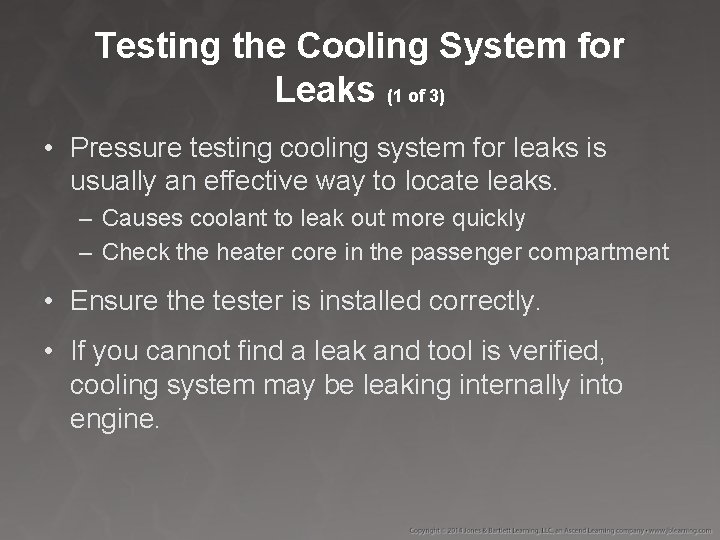


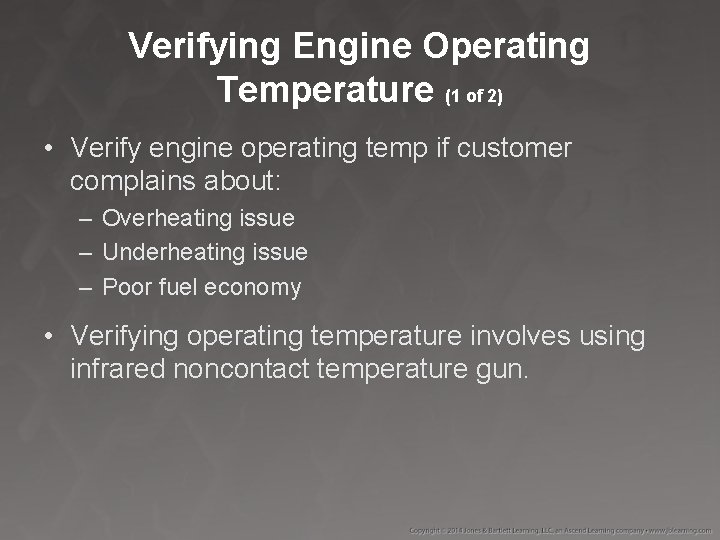
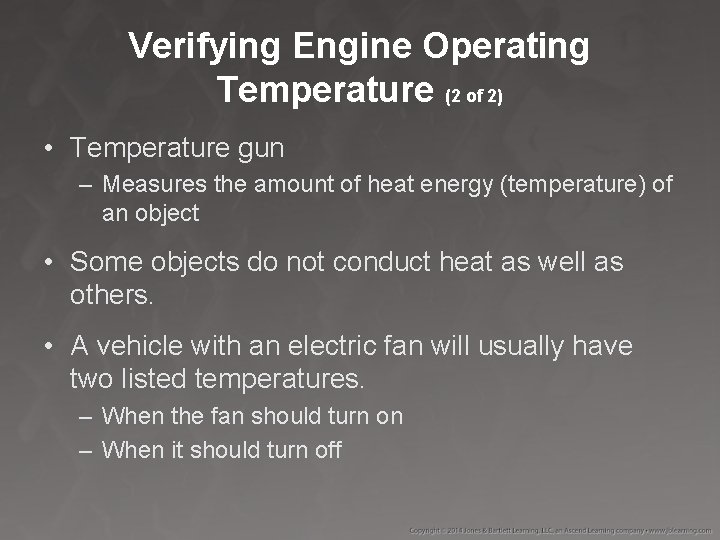
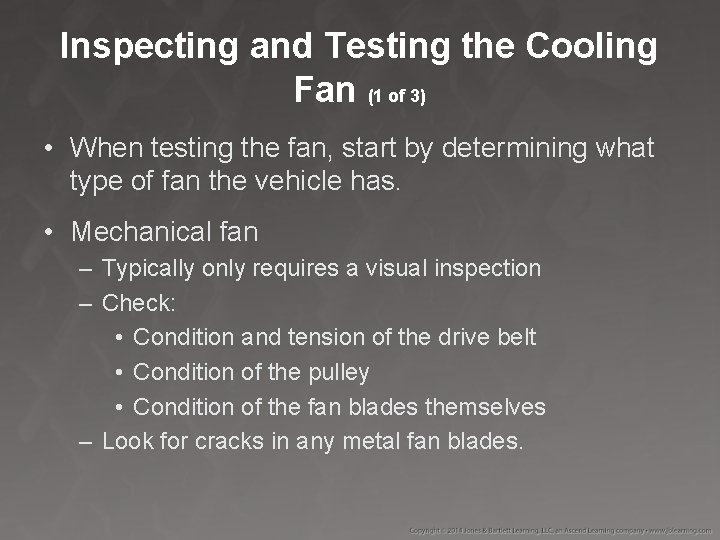

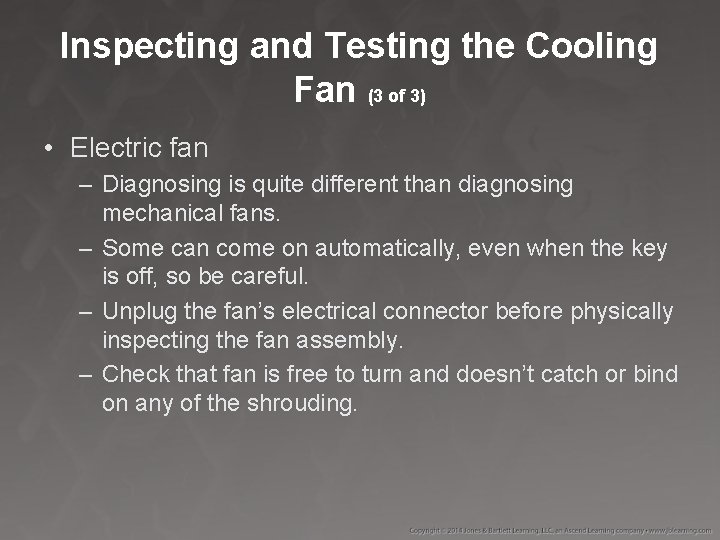
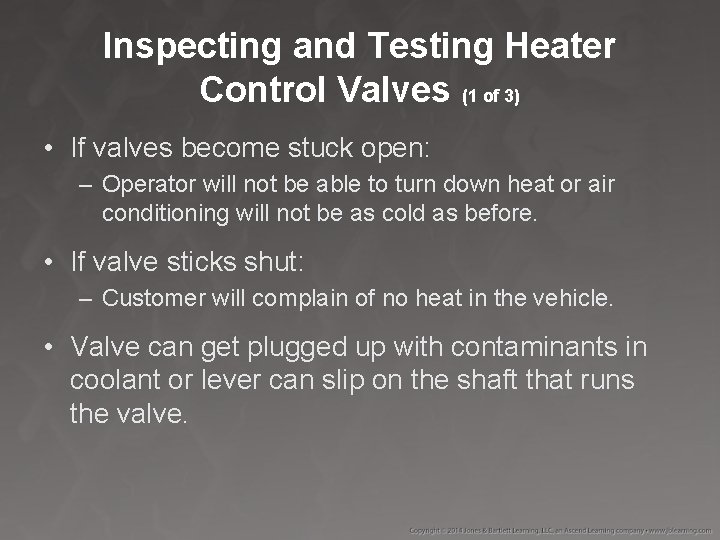
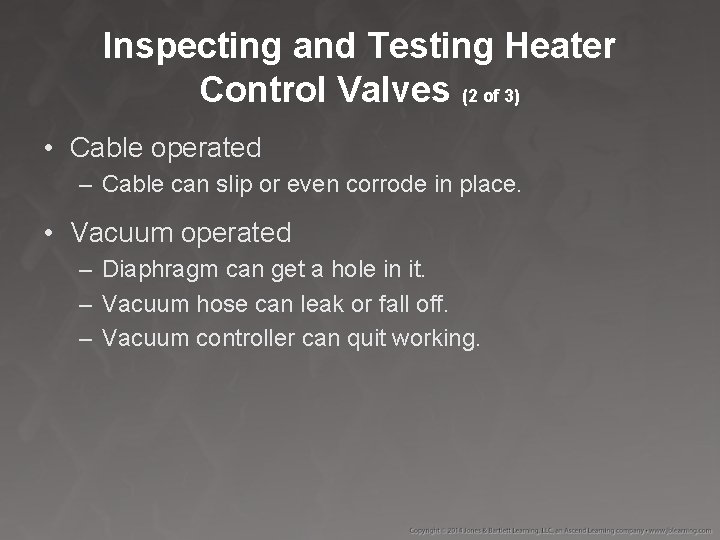
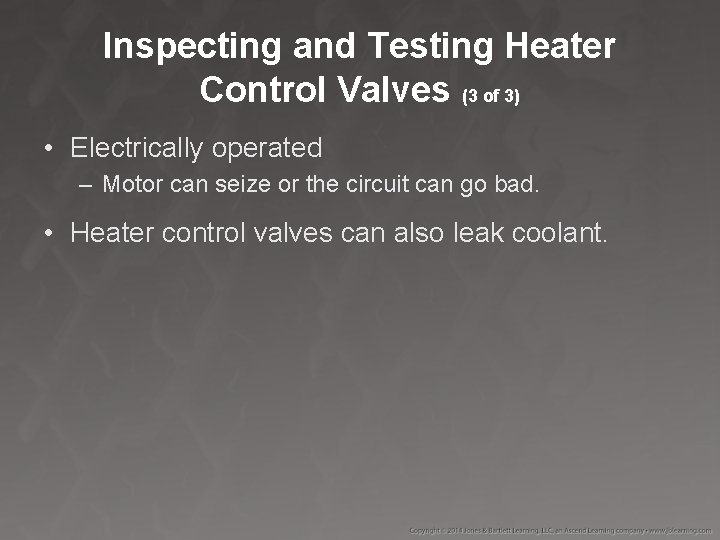
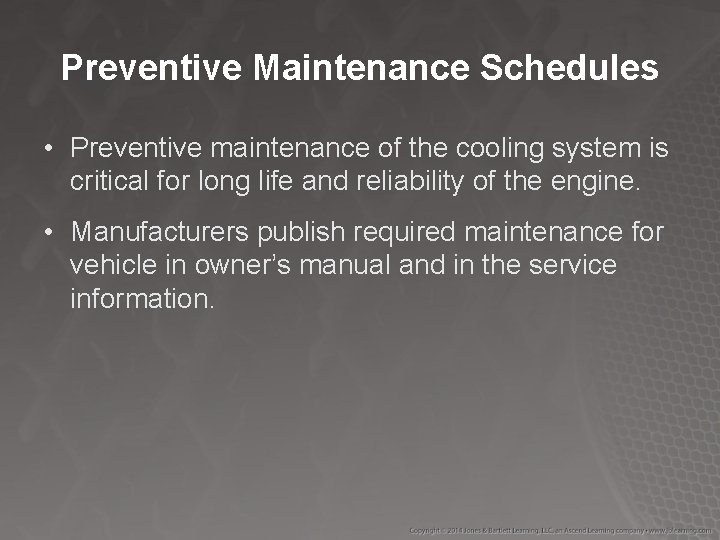
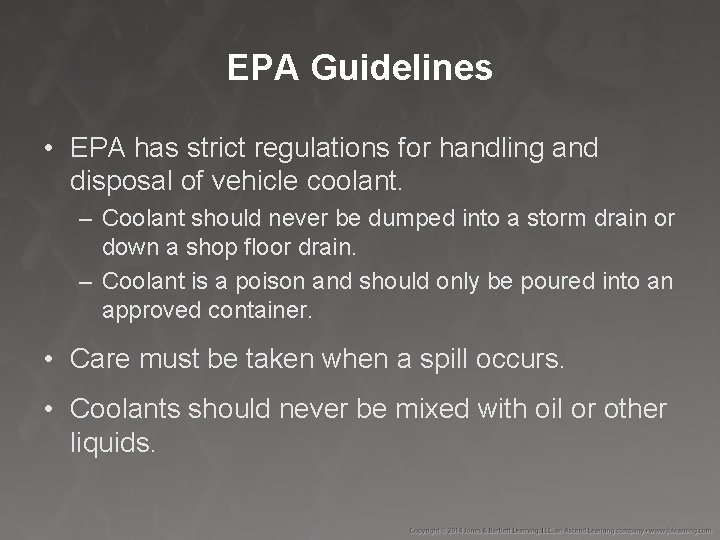
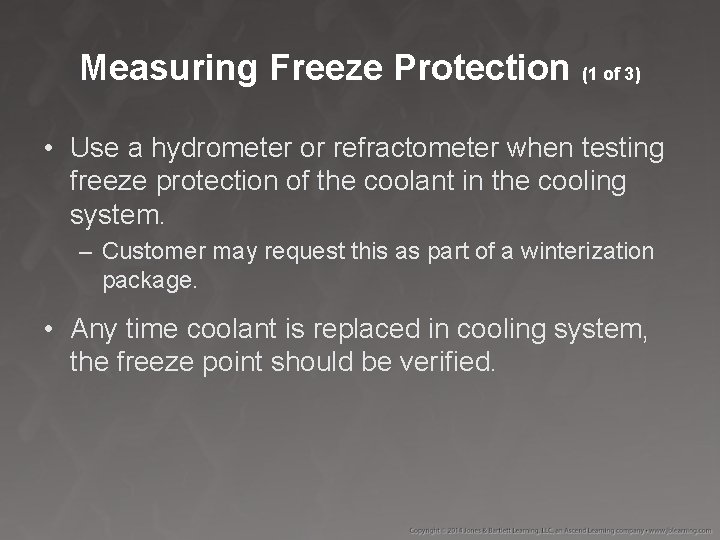
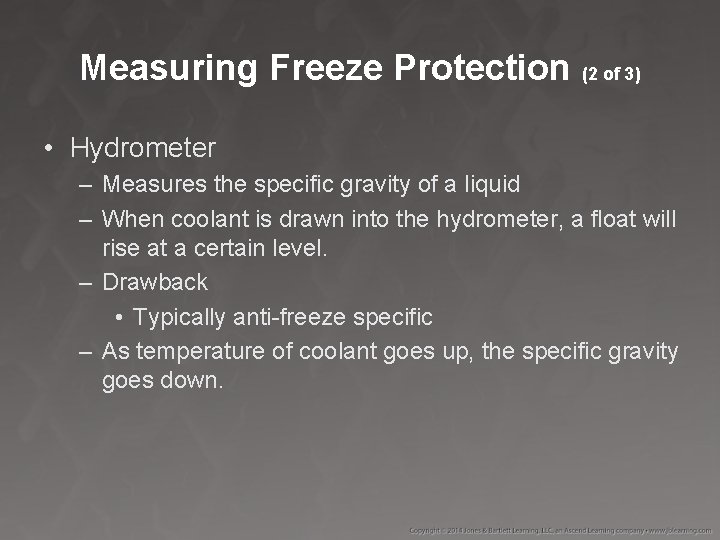
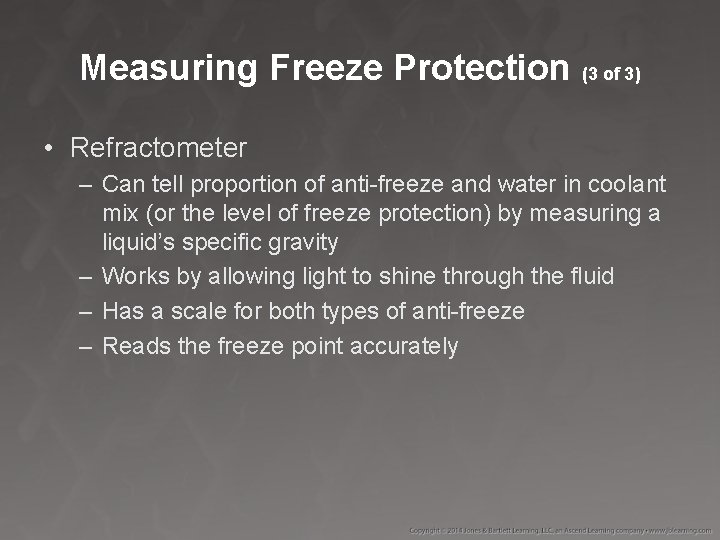
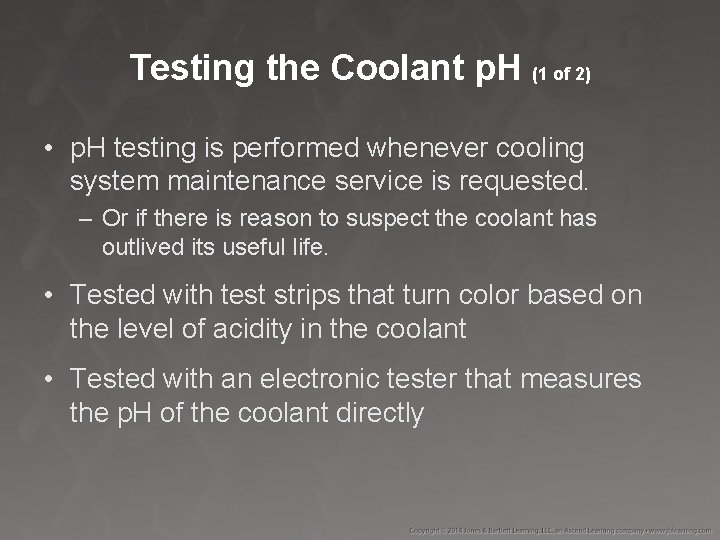
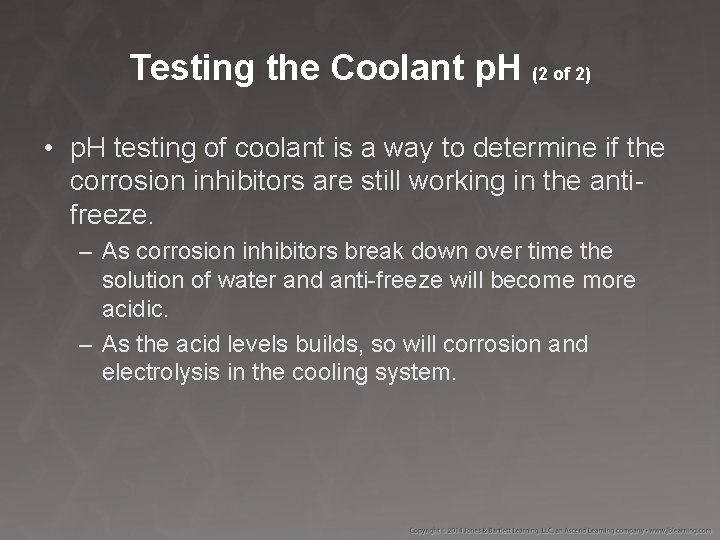
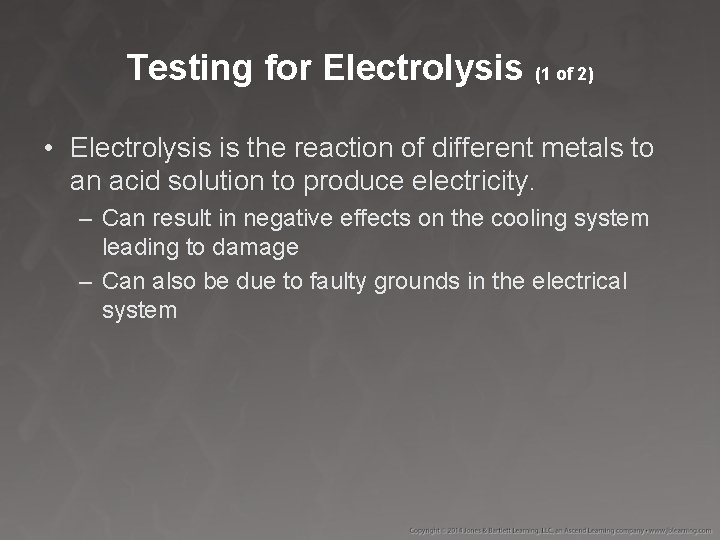
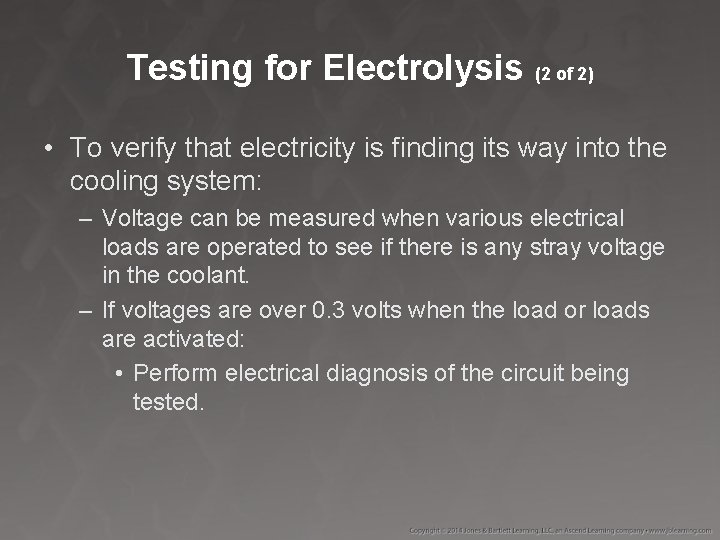
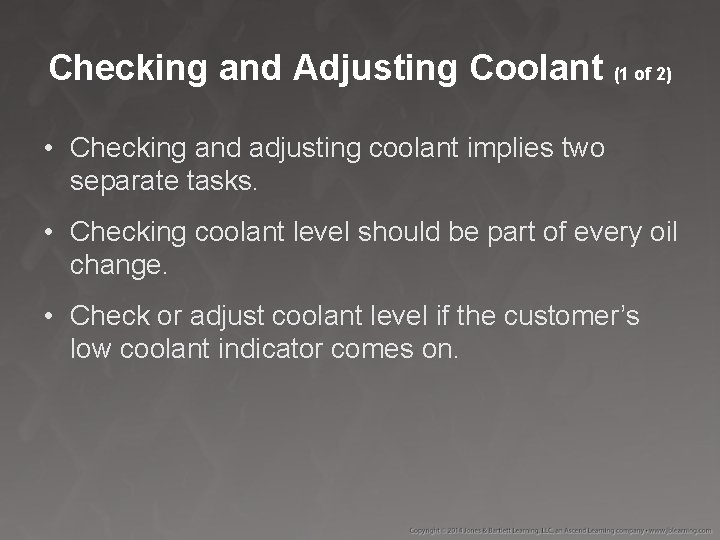
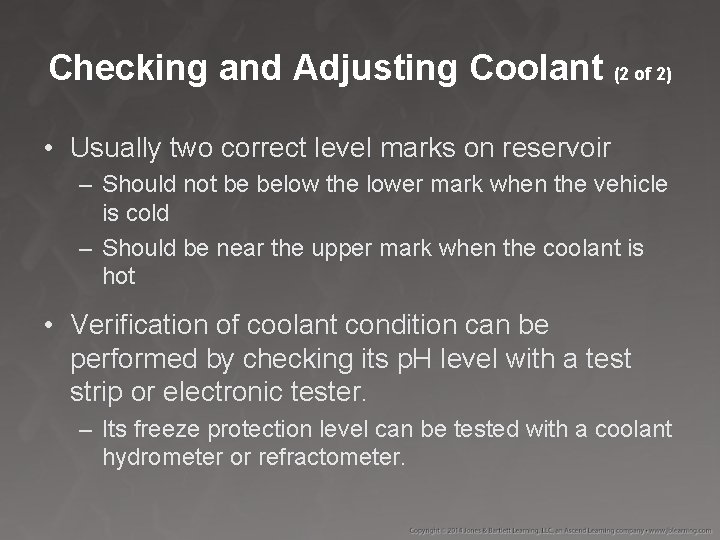
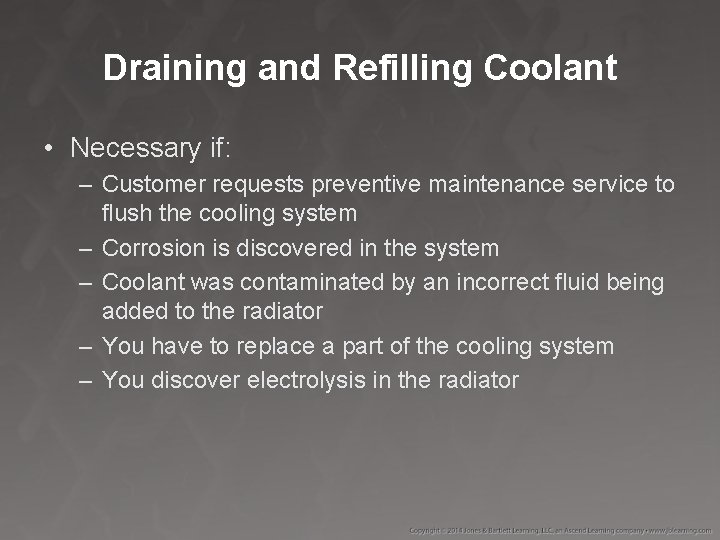
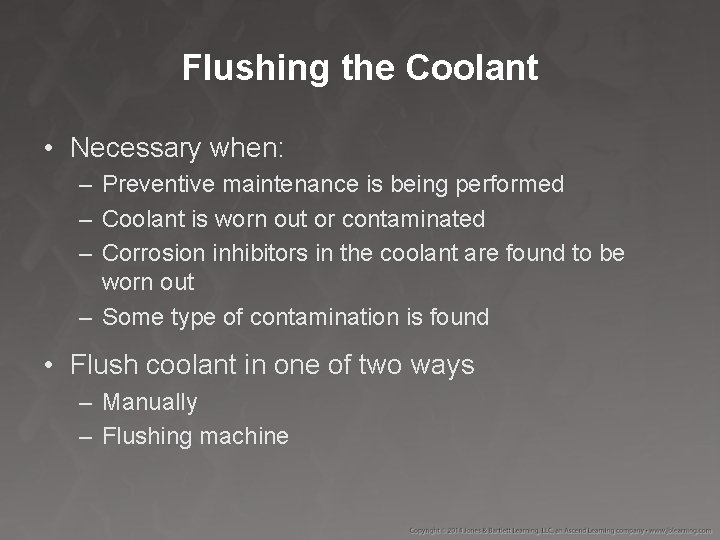
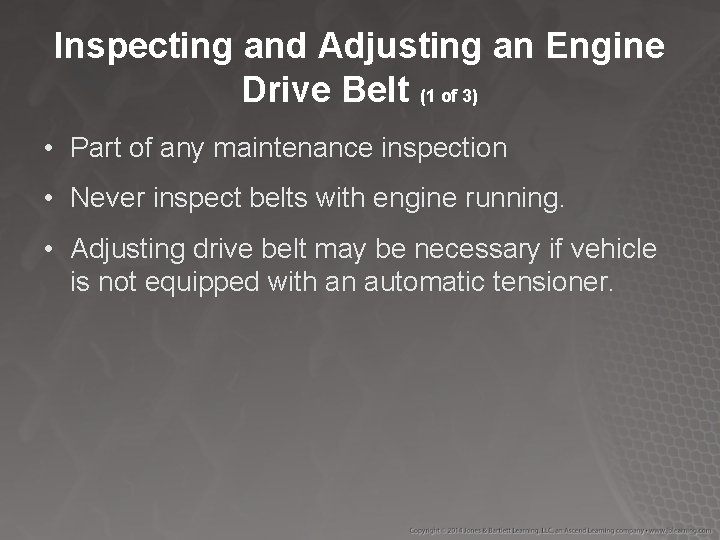
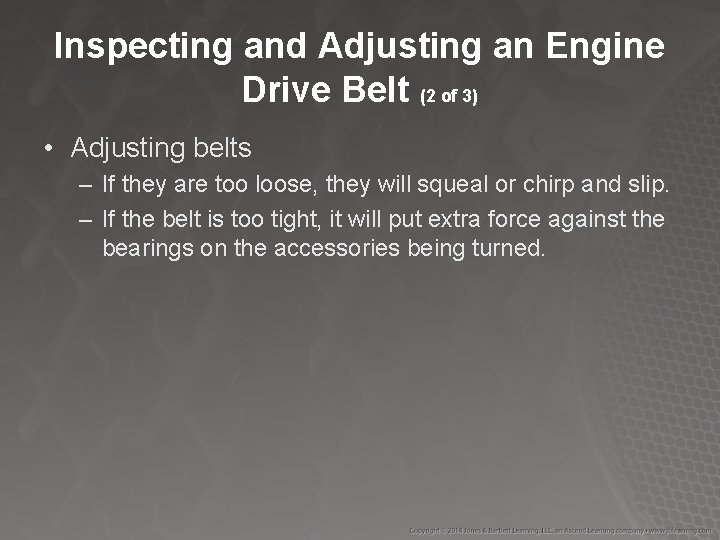
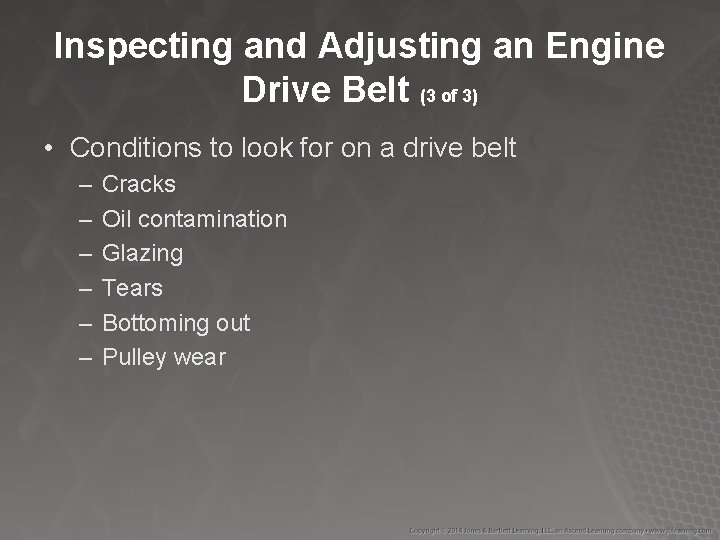
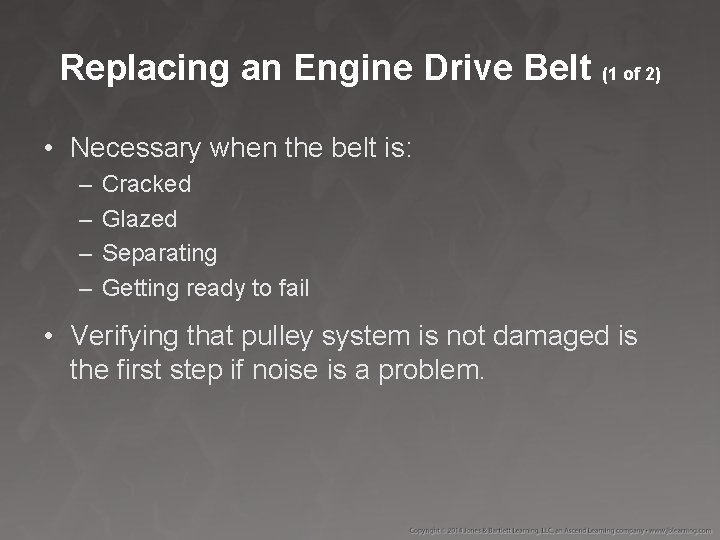
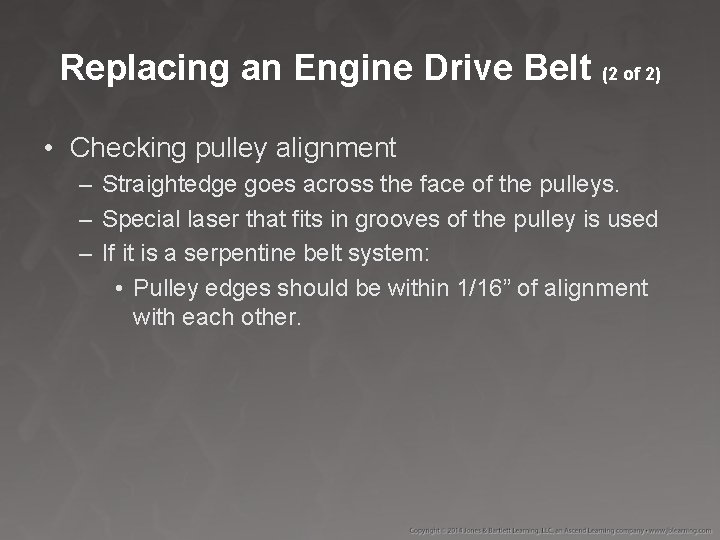
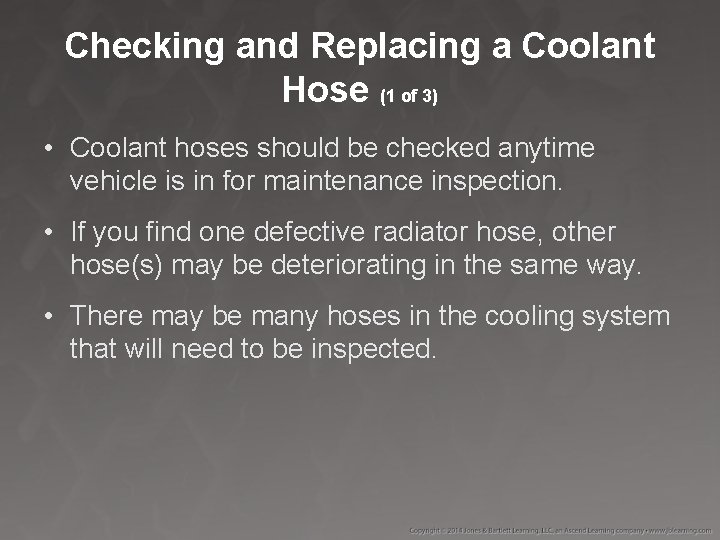
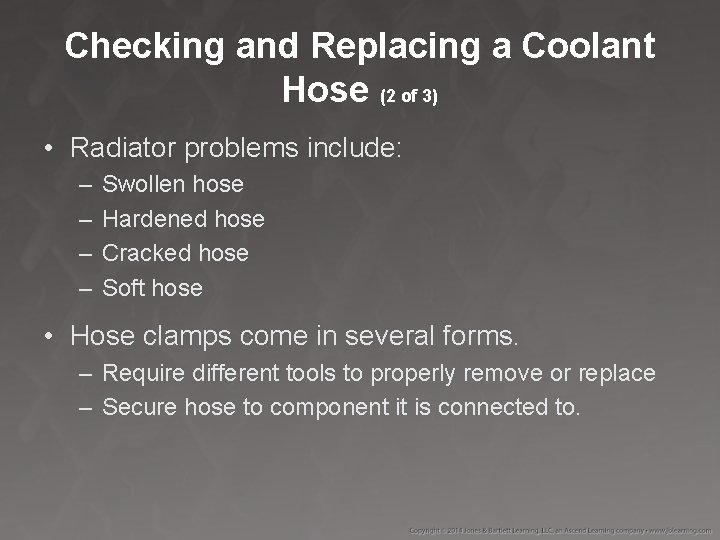
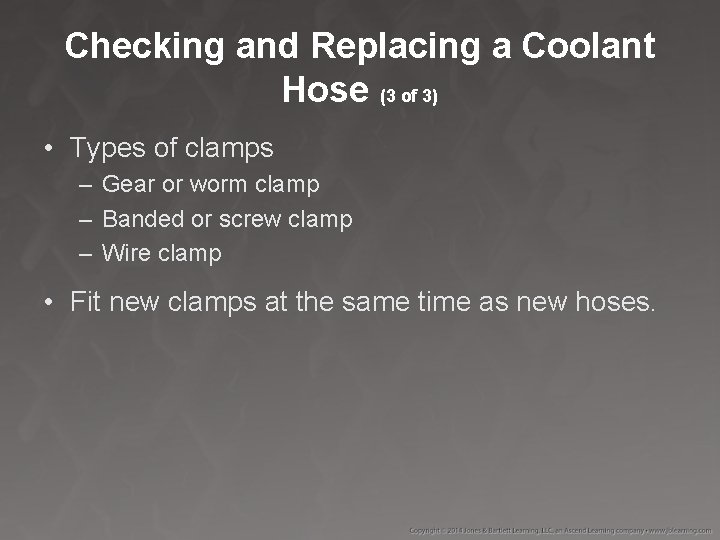
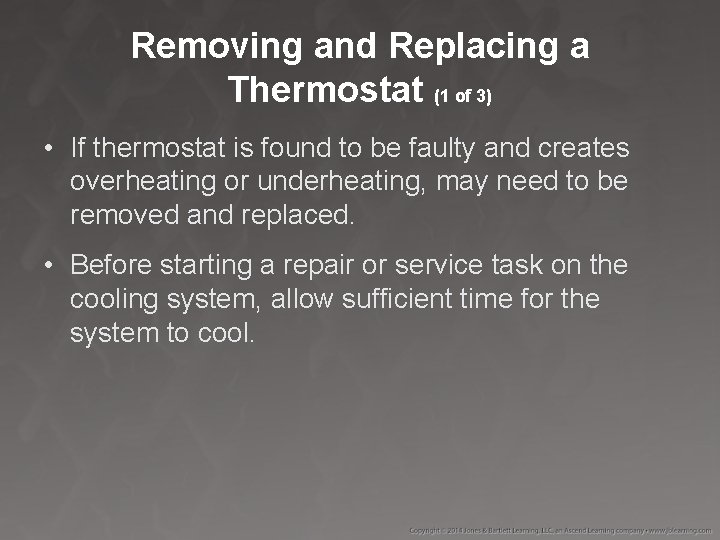
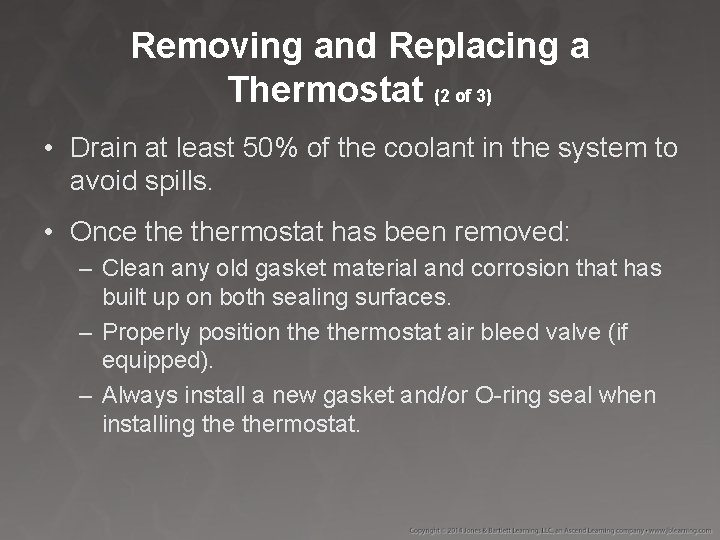
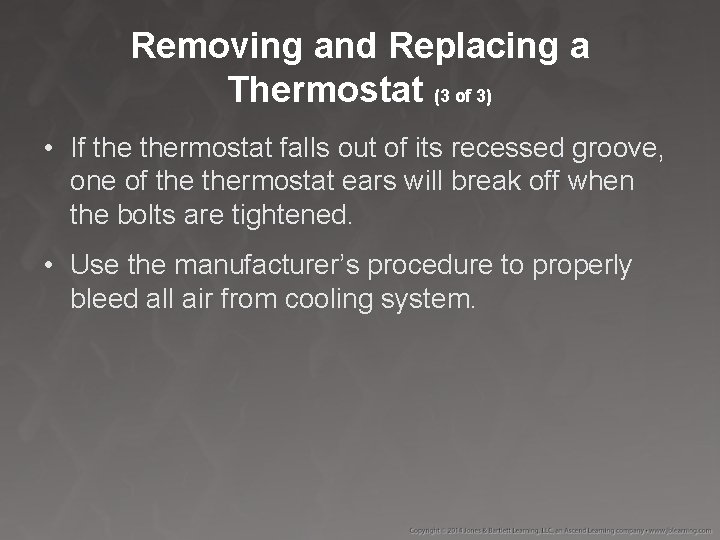
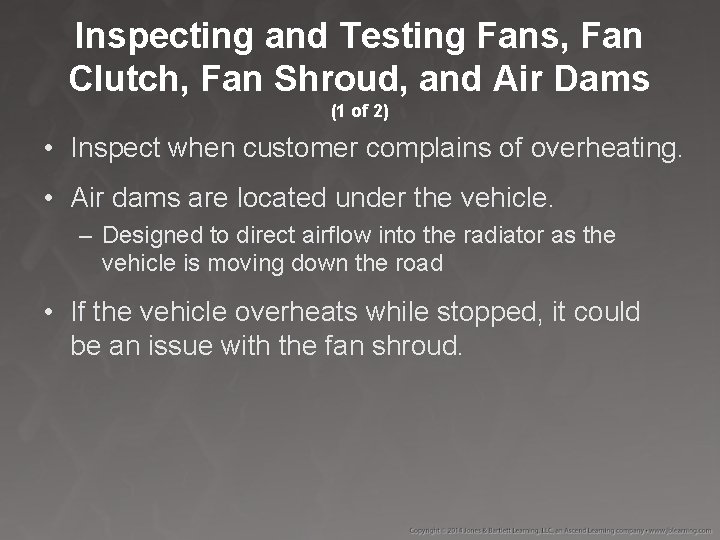
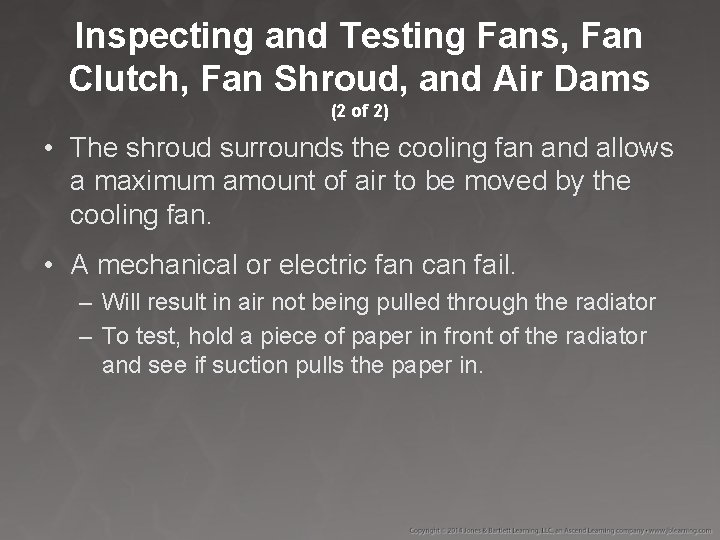
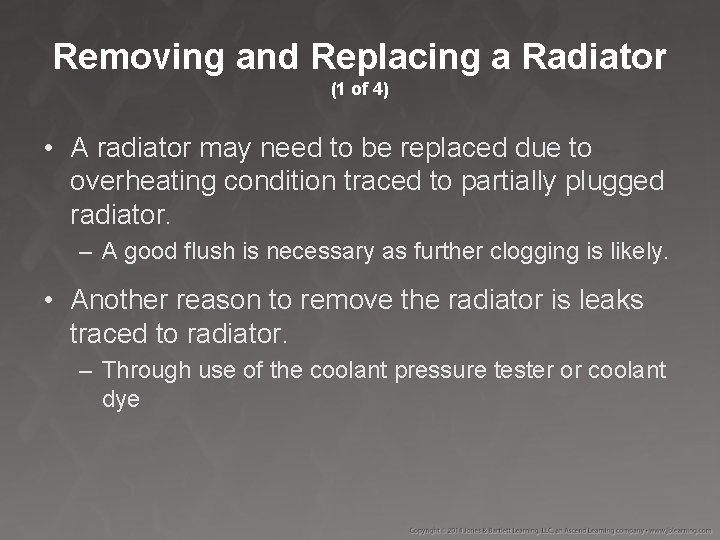
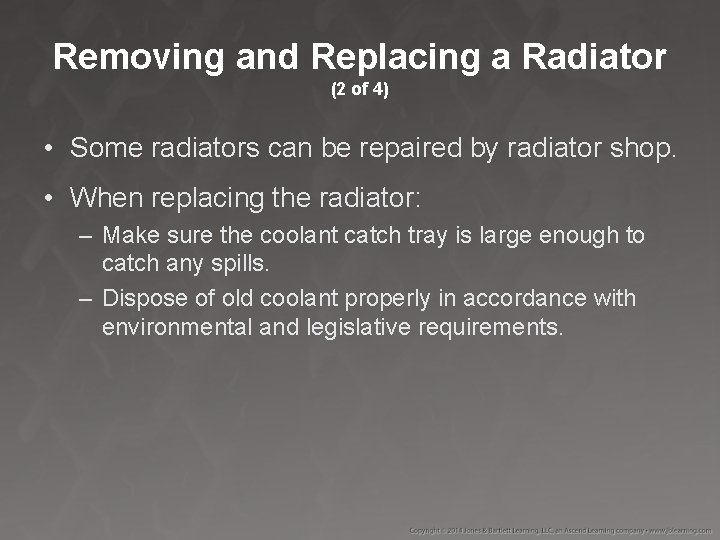
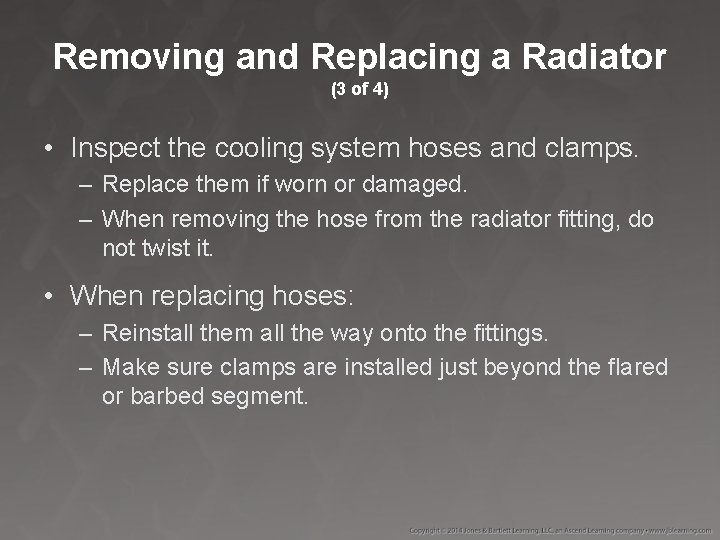
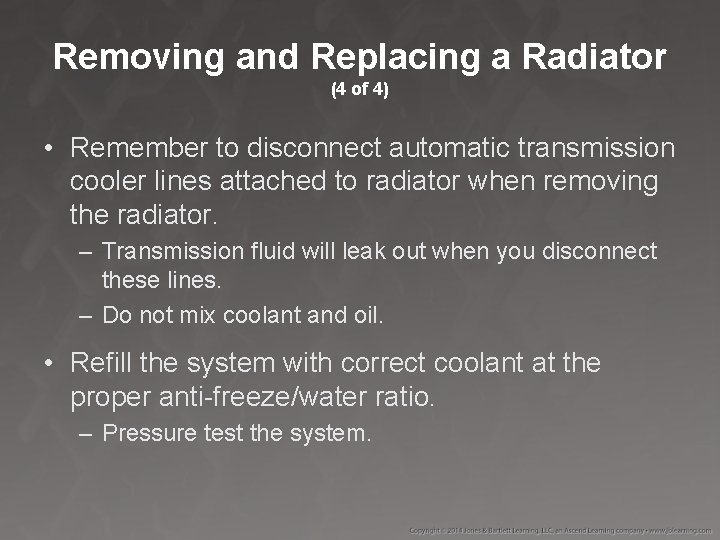
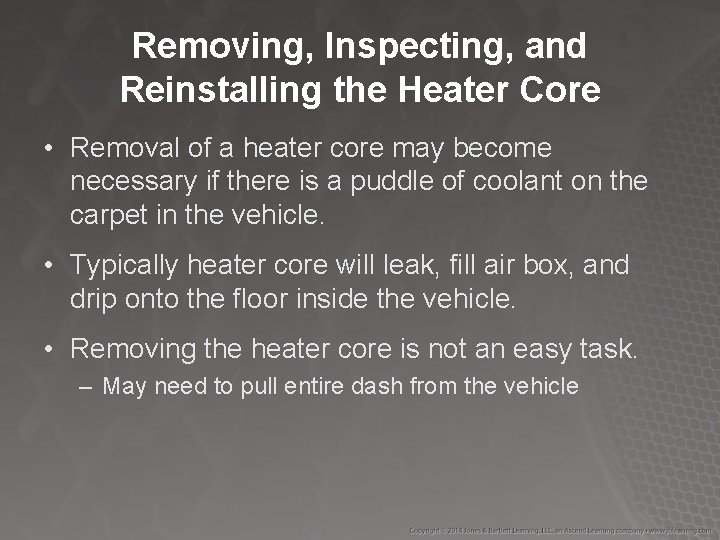
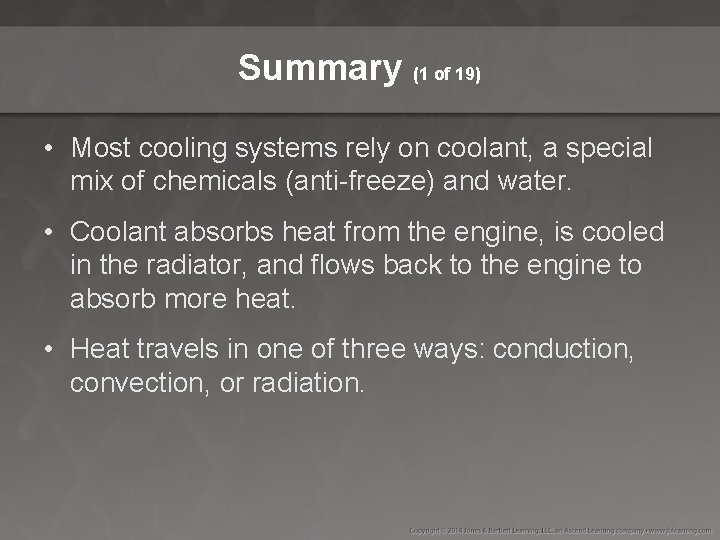
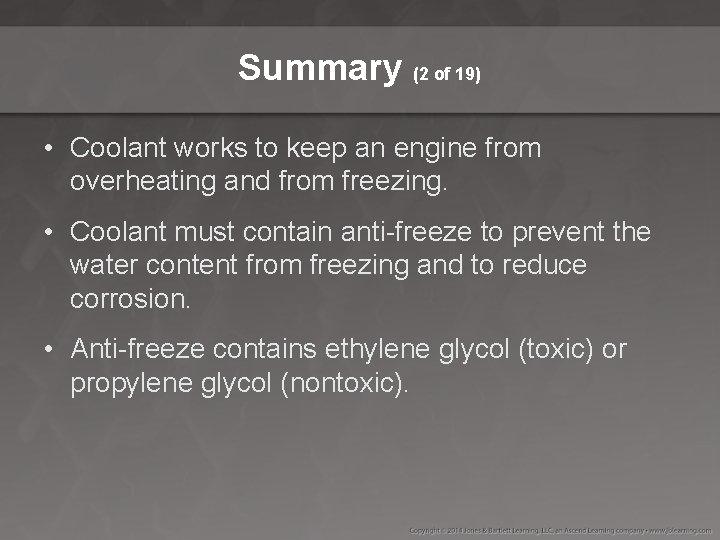
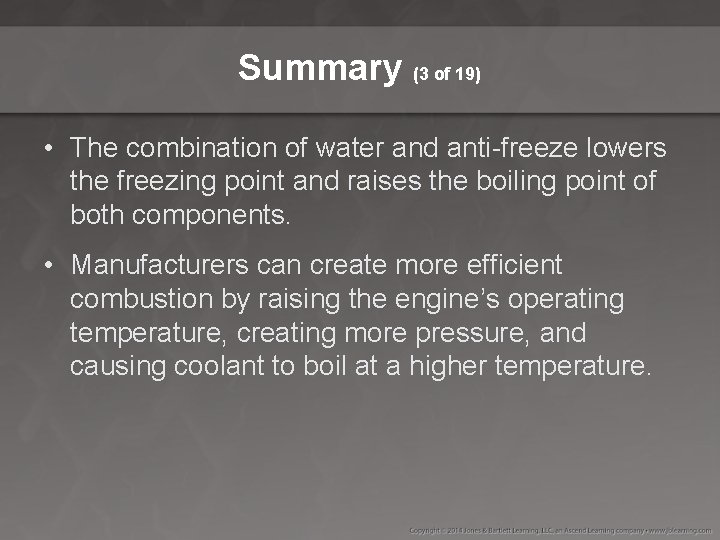
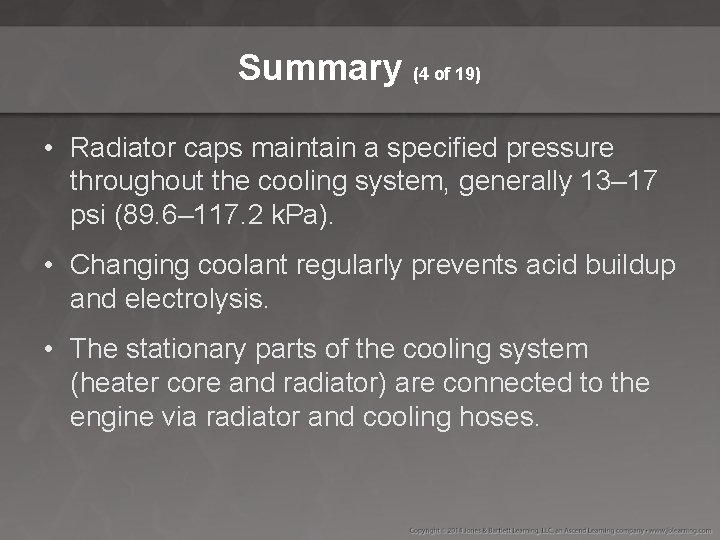
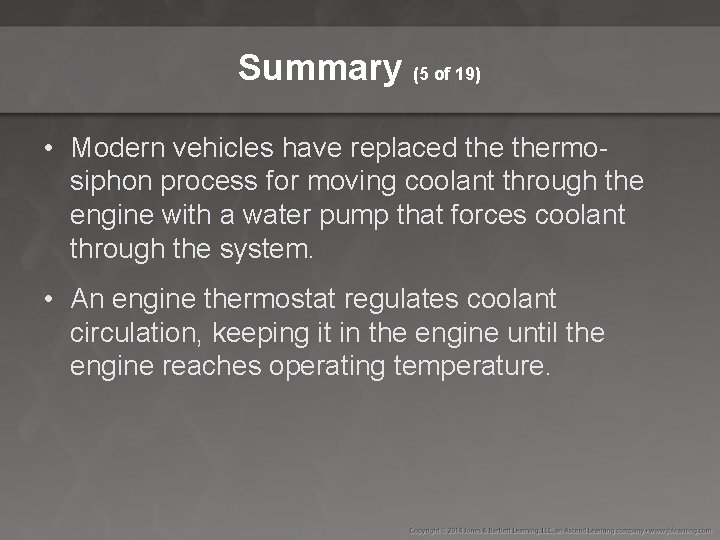
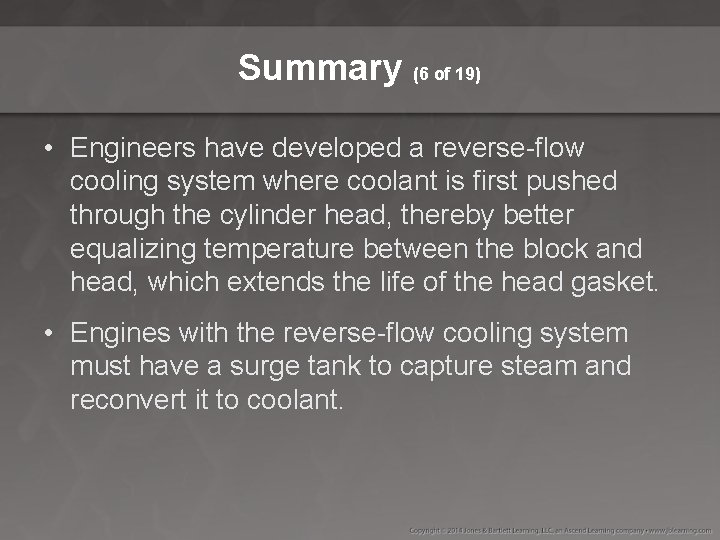
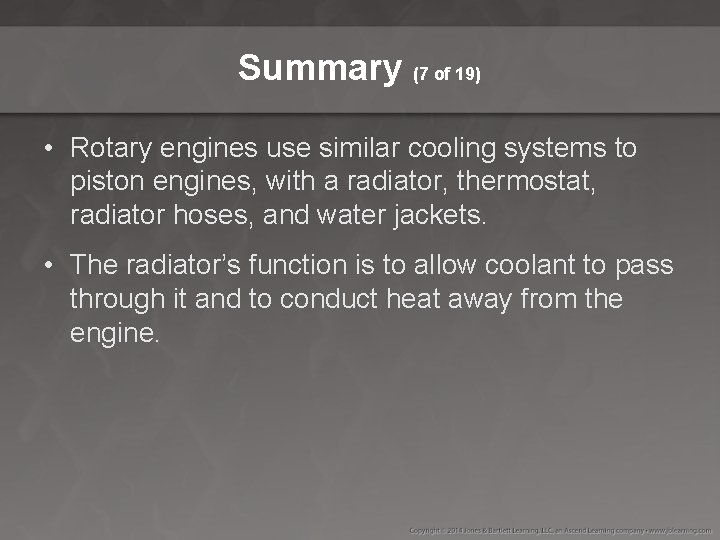
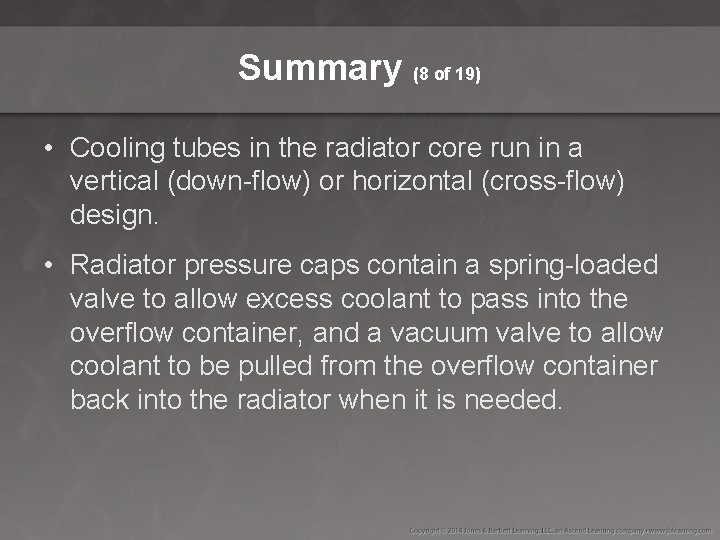
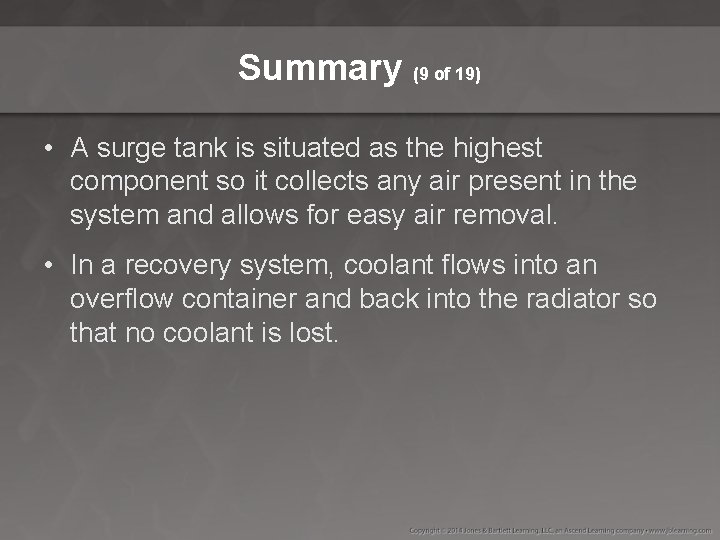
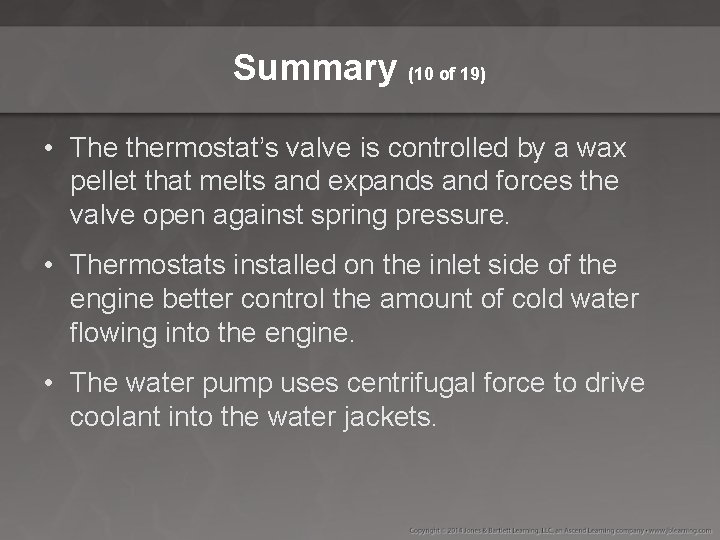
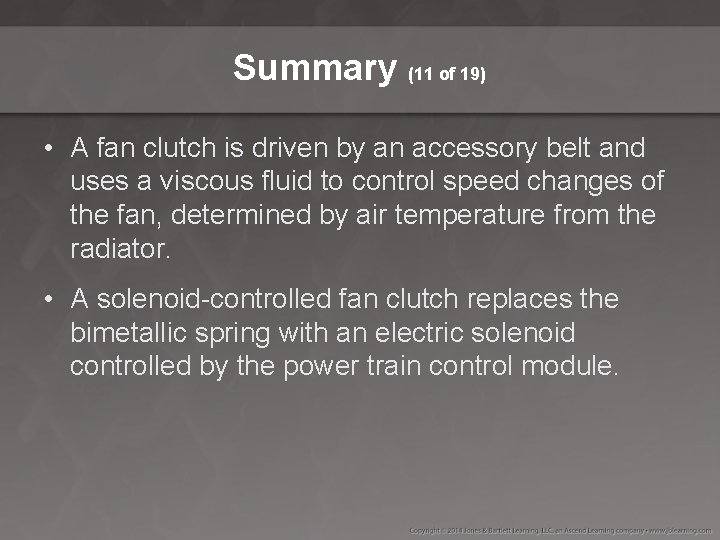
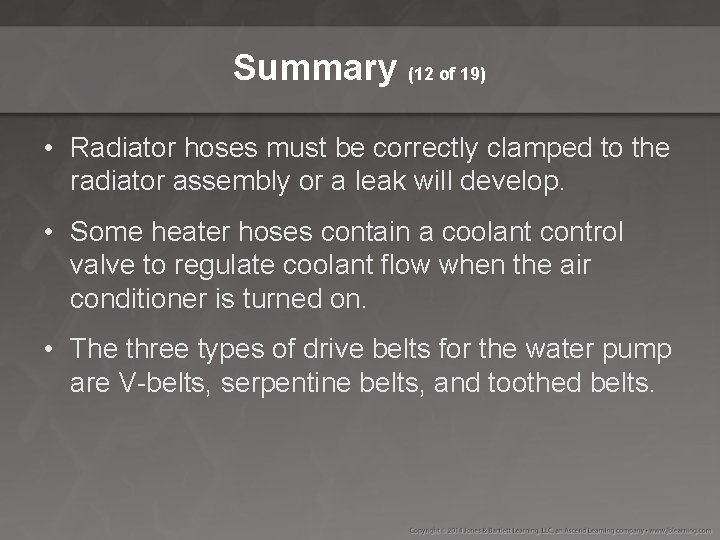
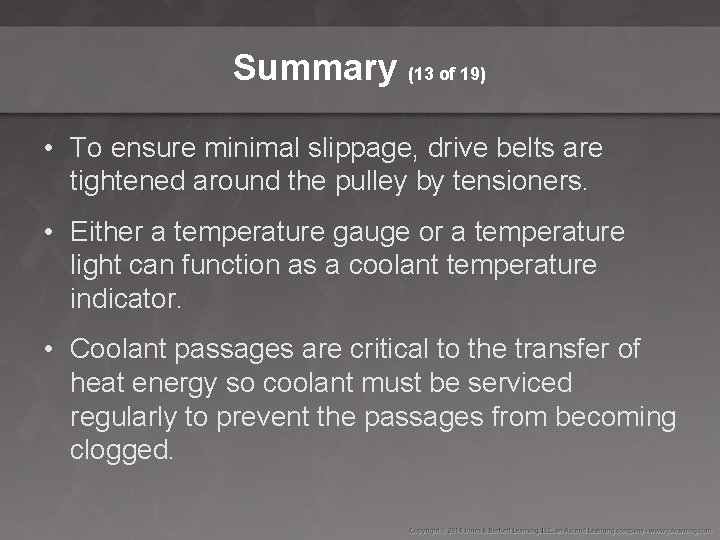
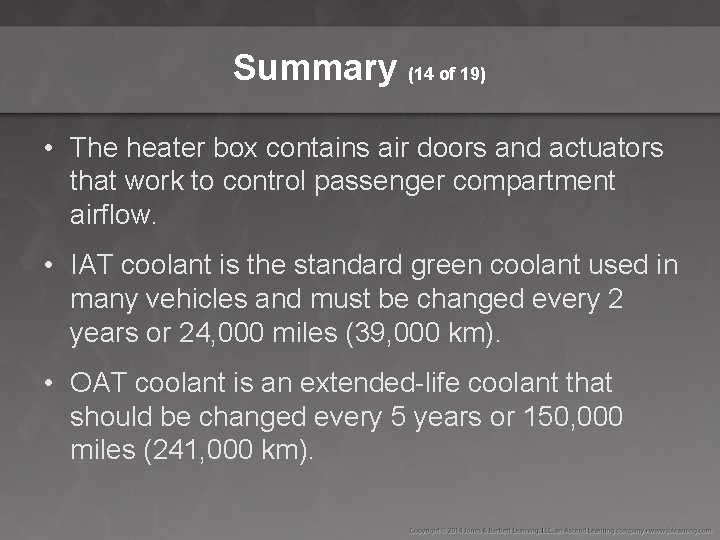
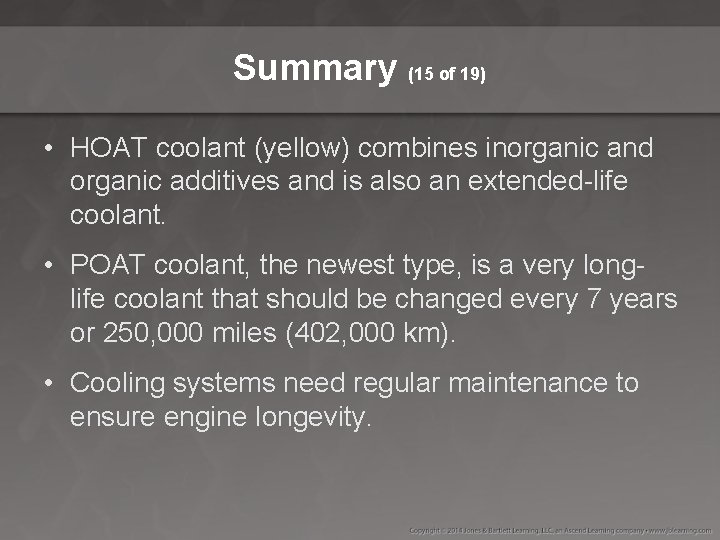
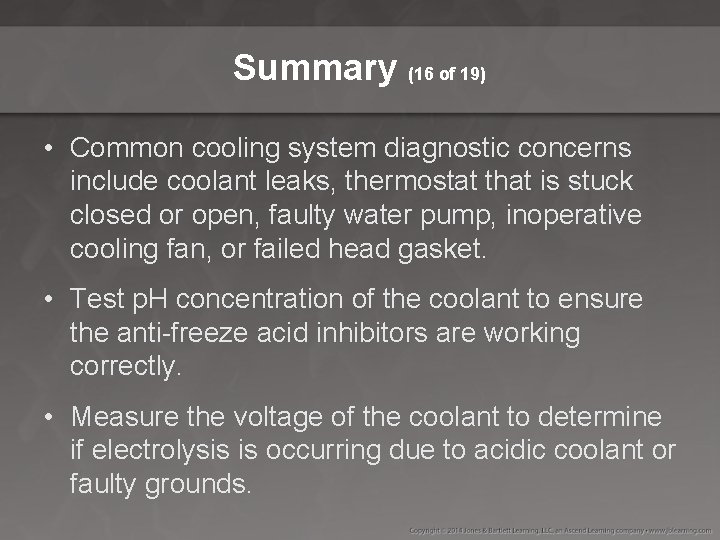
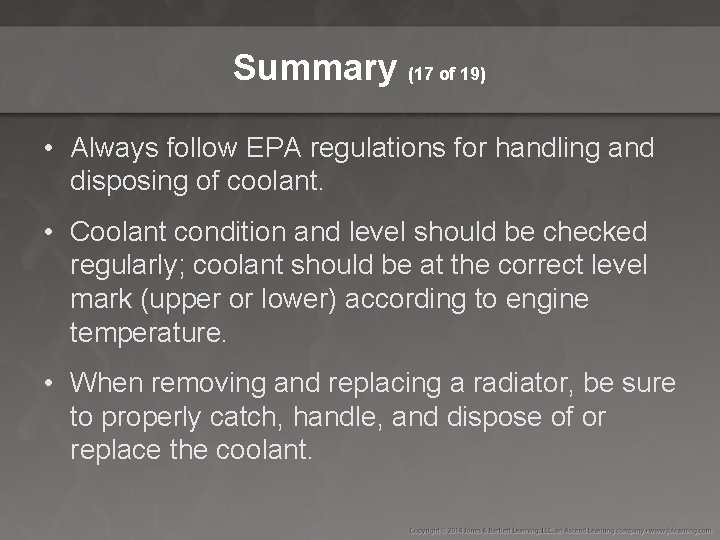
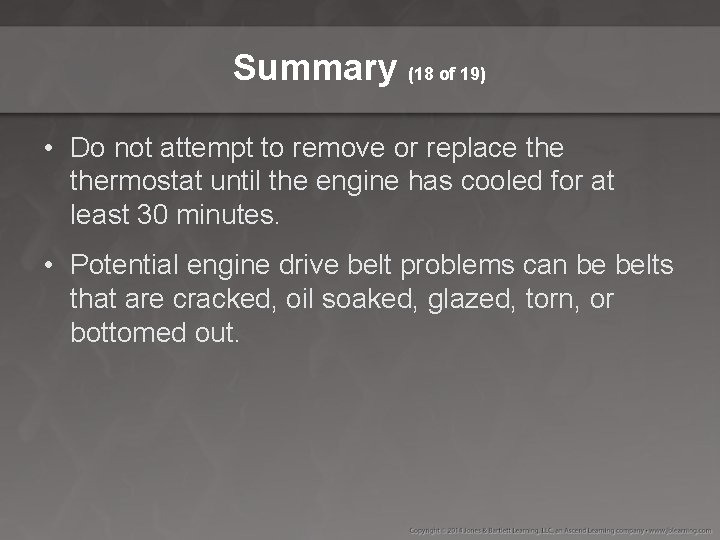
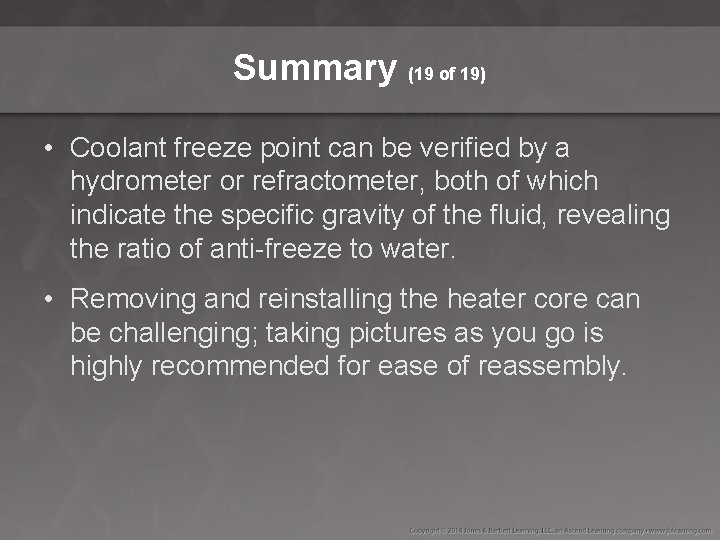
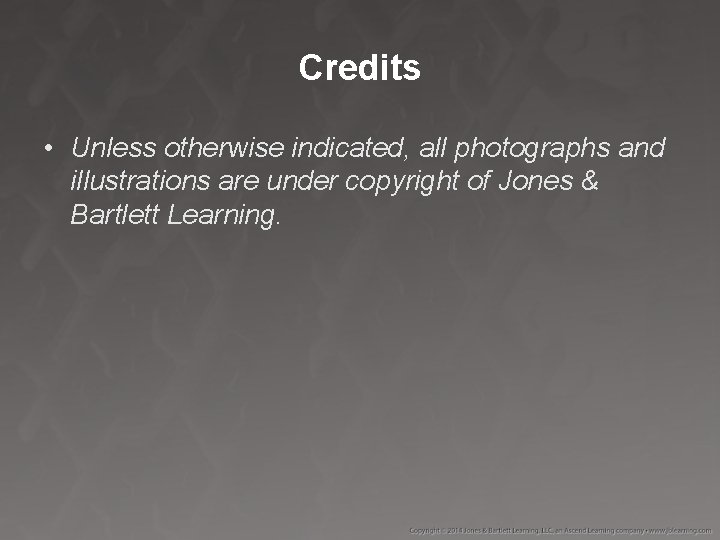
- Slides: 195
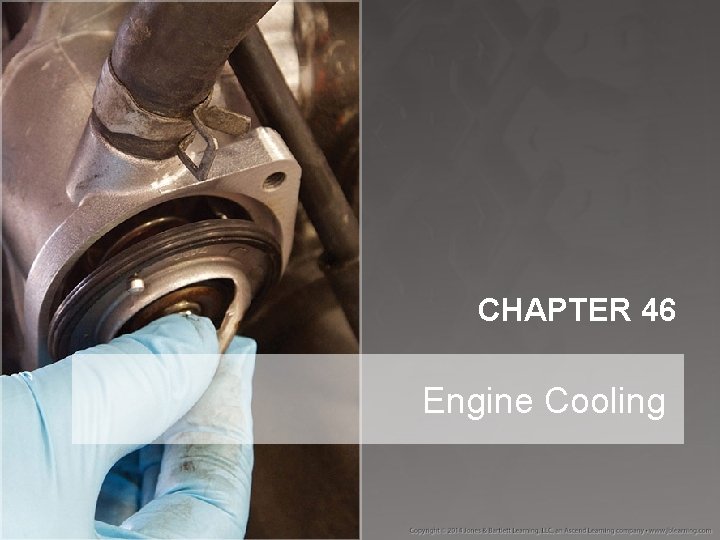
CHAPTER 46 Engine Cooling
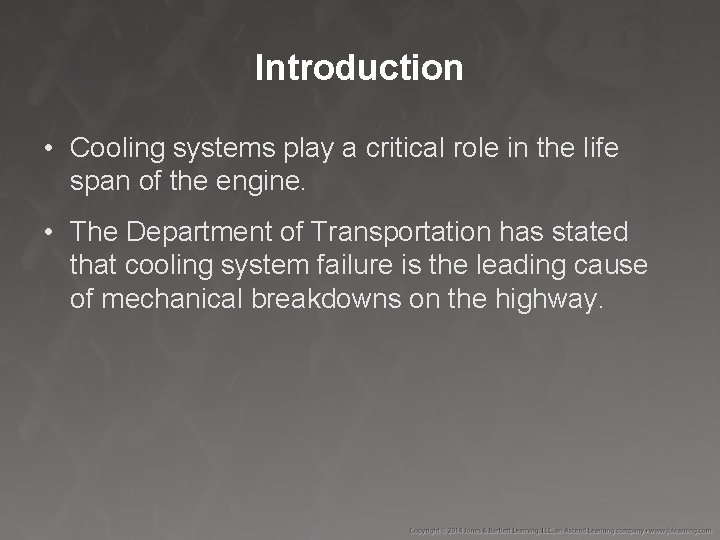
Introduction • Cooling systems play a critical role in the life span of the engine. • The Department of Transportation has stated that cooling system failure is the leading cause of mechanical breakdowns on the highway.
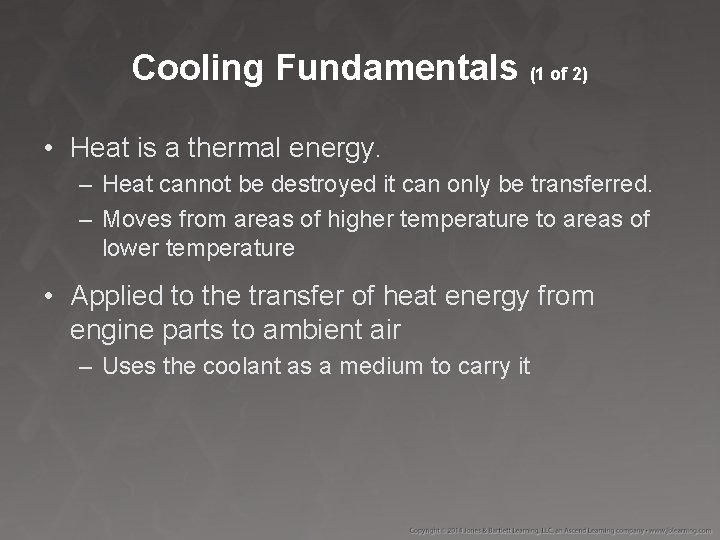
Cooling Fundamentals (1 of 2) • Heat is a thermal energy. – Heat cannot be destroyed it can only be transferred. – Moves from areas of higher temperature to areas of lower temperature • Applied to the transfer of heat energy from engine parts to ambient air – Uses the coolant as a medium to carry it
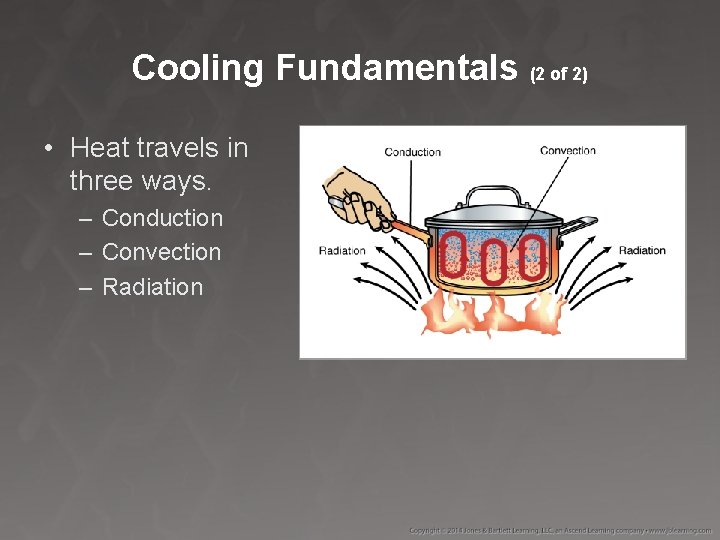
Cooling Fundamentals (2 of 2) • Heat travels in three ways. – Conduction – Convection – Radiation
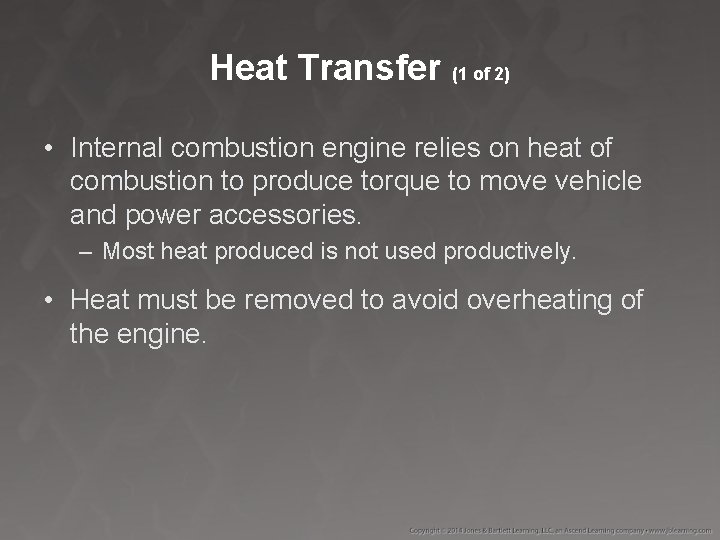
Heat Transfer (1 of 2) • Internal combustion engine relies on heat of combustion to produce torque to move vehicle and power accessories. – Most heat produced is not used productively. • Heat must be removed to avoid overheating of the engine.
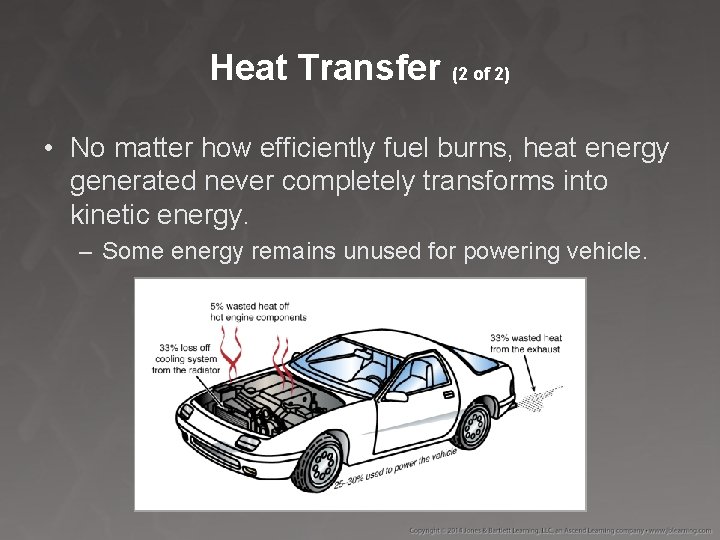
Heat Transfer (2 of 2) • No matter how efficiently fuel burns, heat energy generated never completely transforms into kinetic energy. – Some energy remains unused for powering vehicle.
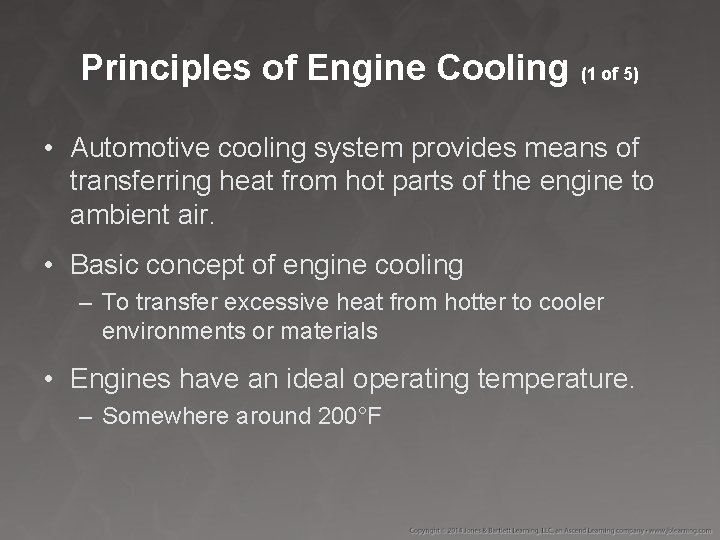
Principles of Engine Cooling (1 of 5) • Automotive cooling system provides means of transferring heat from hot parts of the engine to ambient air. • Basic concept of engine cooling – To transfer excessive heat from hotter to cooler environments or materials • Engines have an ideal operating temperature. – Somewhere around 200°F
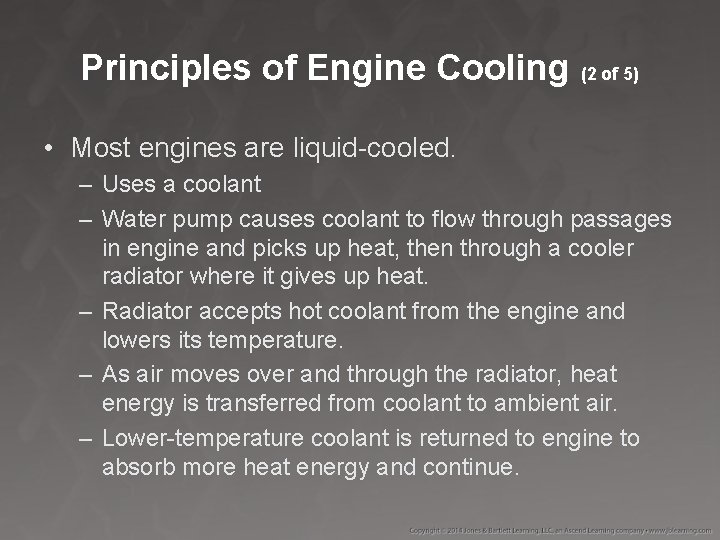
Principles of Engine Cooling (2 of 5) • Most engines are liquid-cooled. – Uses a coolant – Water pump causes coolant to flow through passages in engine and picks up heat, then through a cooler radiator where it gives up heat. – Radiator accepts hot coolant from the engine and lowers its temperature. – As air moves over and through the radiator, heat energy is transferred from coolant to ambient air. – Lower-temperature coolant is returned to engine to absorb more heat energy and continue.
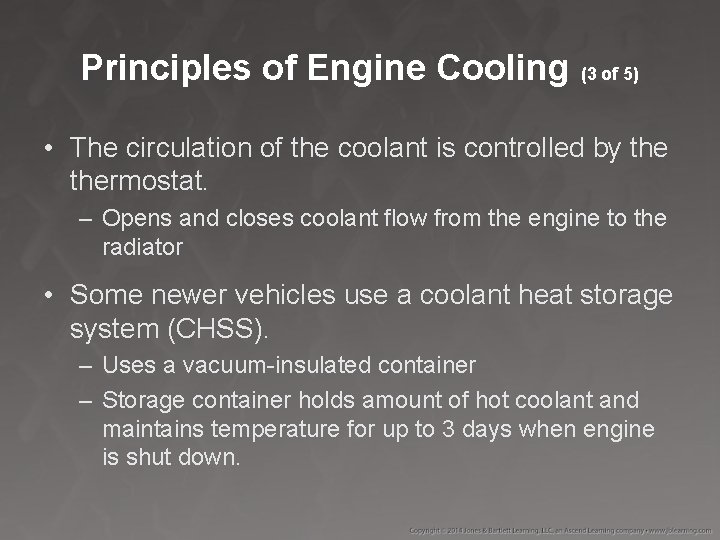
Principles of Engine Cooling (3 of 5) • The circulation of the coolant is controlled by thermostat. – Opens and closes coolant flow from the engine to the radiator • Some newer vehicles use a coolant heat storage system (CHSS). – Uses a vacuum-insulated container – Storage container holds amount of hot coolant and maintains temperature for up to 3 days when engine is shut down.
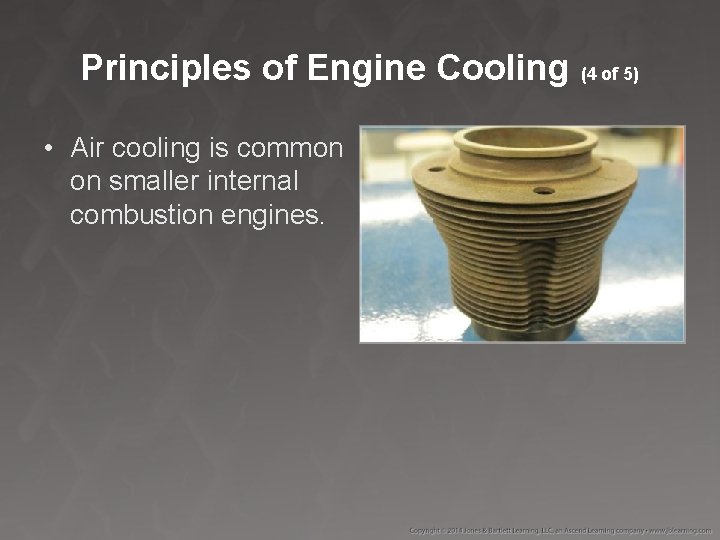
Principles of Engine Cooling (4 of 5) • Air cooling is common on smaller internal combustion engines.
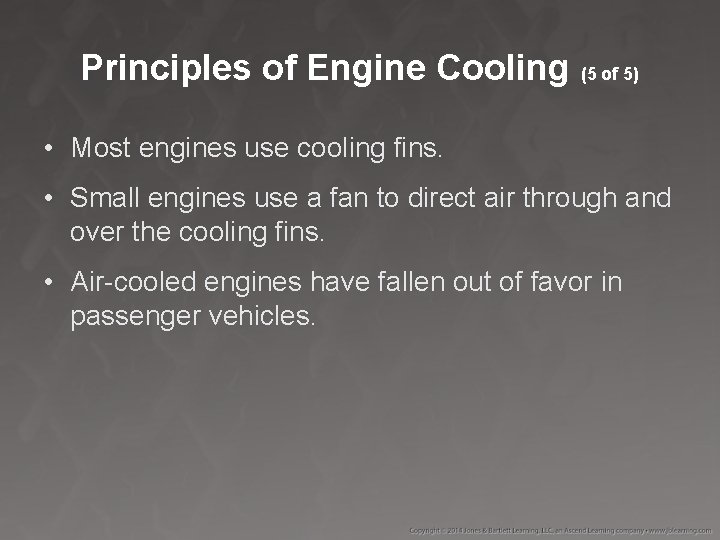
Principles of Engine Cooling (5 of 5) • Most engines use cooling fins. • Small engines use a fan to direct air through and over the cooling fins. • Air-cooled engines have fallen out of favor in passenger vehicles.
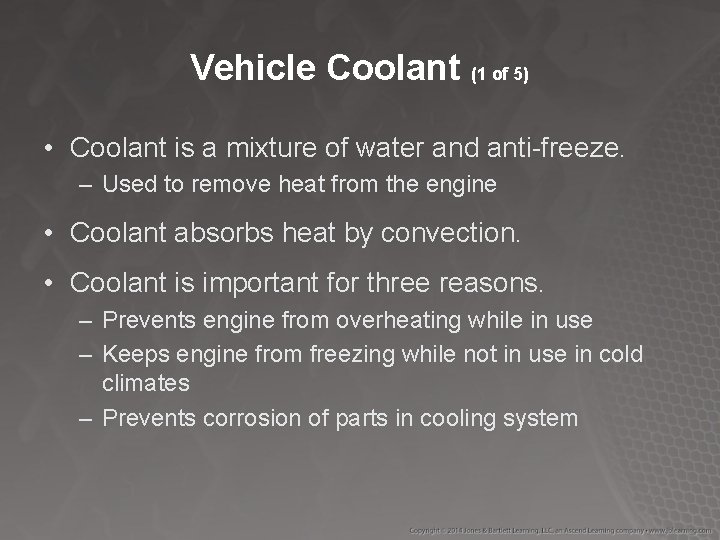
Vehicle Coolant (1 of 5) • Coolant is a mixture of water and anti-freeze. – Used to remove heat from the engine • Coolant absorbs heat by convection. • Coolant is important for three reasons. – Prevents engine from overheating while in use – Keeps engine from freezing while not in use in cold climates – Prevents corrosion of parts in cooling system
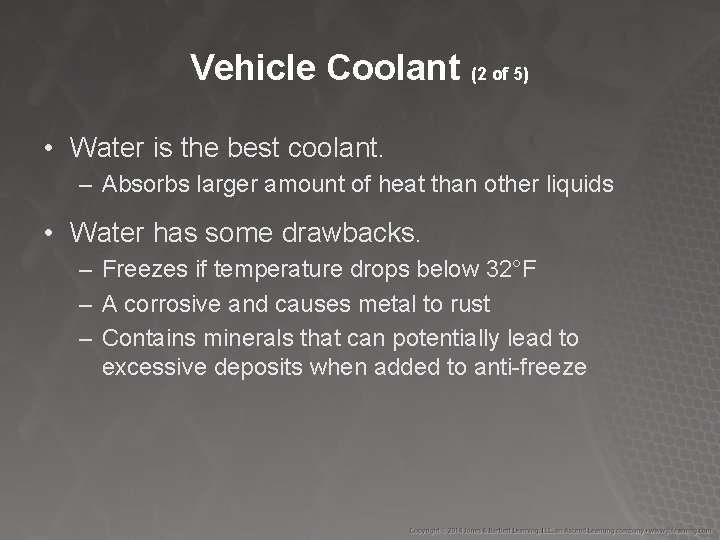
Vehicle Coolant (2 of 5) • Water is the best coolant. – Absorbs larger amount of heat than other liquids • Water has some drawbacks. – Freezes if temperature drops below 32°F – A corrosive and causes metal to rust – Contains minerals that can potentially lead to excessive deposits when added to anti-freeze
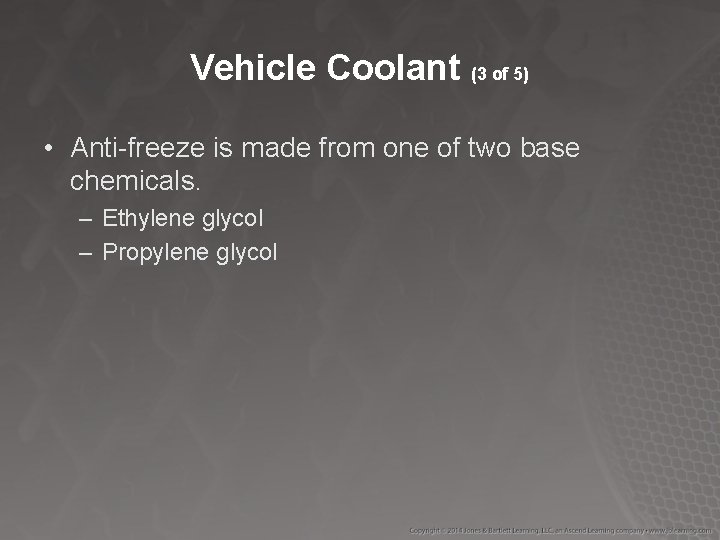
Vehicle Coolant (3 of 5) • Anti-freeze is made from one of two base chemicals. – Ethylene glycol – Propylene glycol
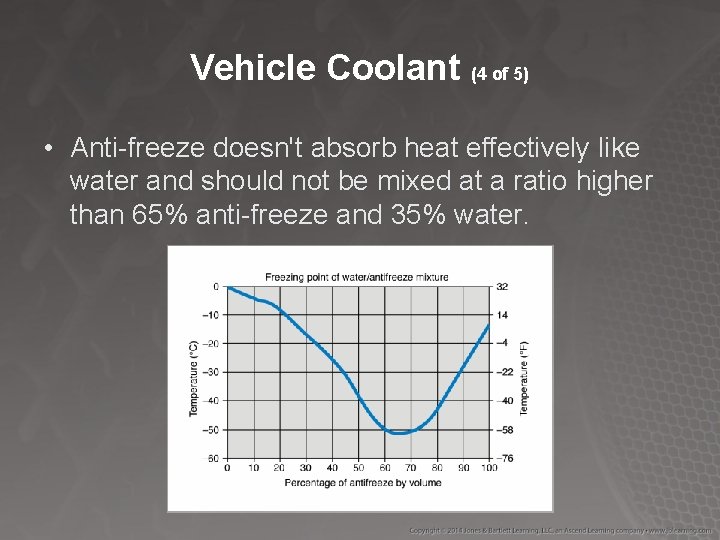
Vehicle Coolant (4 of 5) • Anti-freeze doesn't absorb heat effectively like water and should not be mixed at a ratio higher than 65% anti-freeze and 35% water.
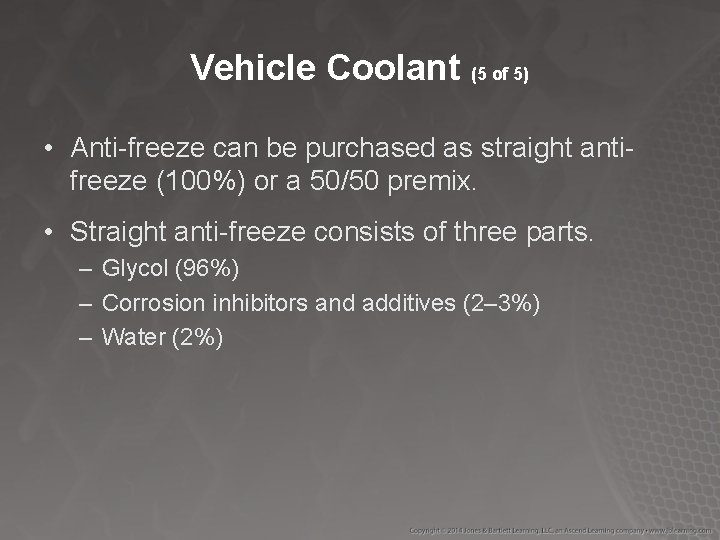
Vehicle Coolant (5 of 5) • Anti-freeze can be purchased as straight antifreeze (100%) or a 50/50 premix. • Straight anti-freeze consists of three parts. – Glycol (96%) – Corrosion inhibitors and additives (2– 3%) – Water (2%)
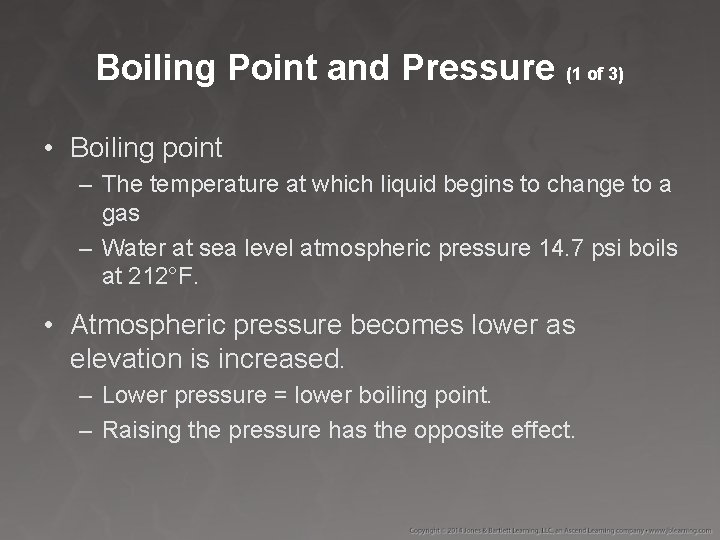
Boiling Point and Pressure (1 of 3) • Boiling point – The temperature at which liquid begins to change to a gas – Water at sea level atmospheric pressure 14. 7 psi boils at 212°F. • Atmospheric pressure becomes lower as elevation is increased. – Lower pressure = lower boiling point. – Raising the pressure has the opposite effect.
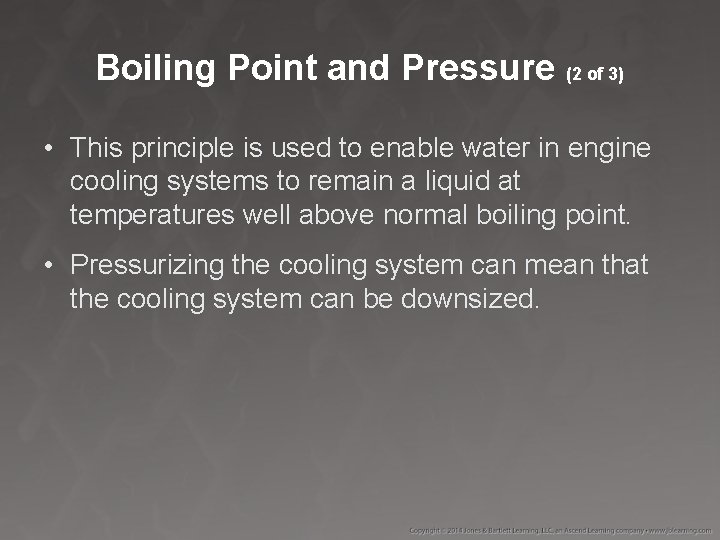
Boiling Point and Pressure (2 of 3) • This principle is used to enable water in engine cooling systems to remain a liquid at temperatures well above normal boiling point. • Pressurizing the cooling system can mean that the cooling system can be downsized.
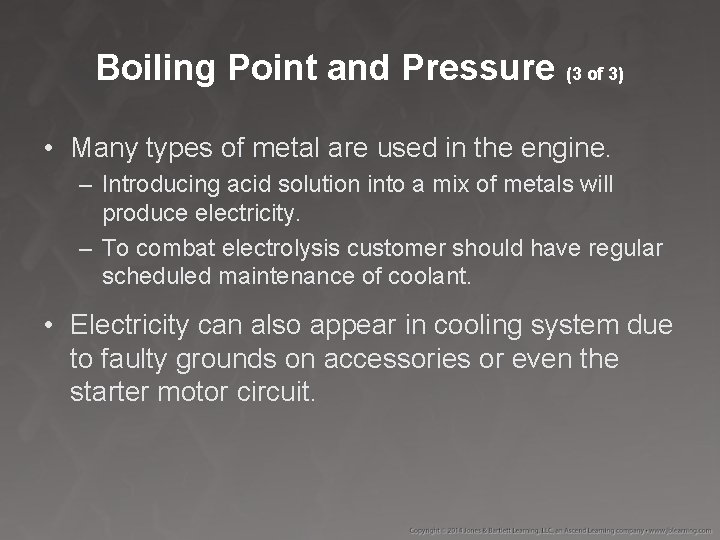
Boiling Point and Pressure (3 of 3) • Many types of metal are used in the engine. – Introducing acid solution into a mix of metals will produce electricity. – To combat electrolysis customer should have regular scheduled maintenance of coolant. • Electricity can also appear in cooling system due to faulty grounds on accessories or even the starter motor circuit.
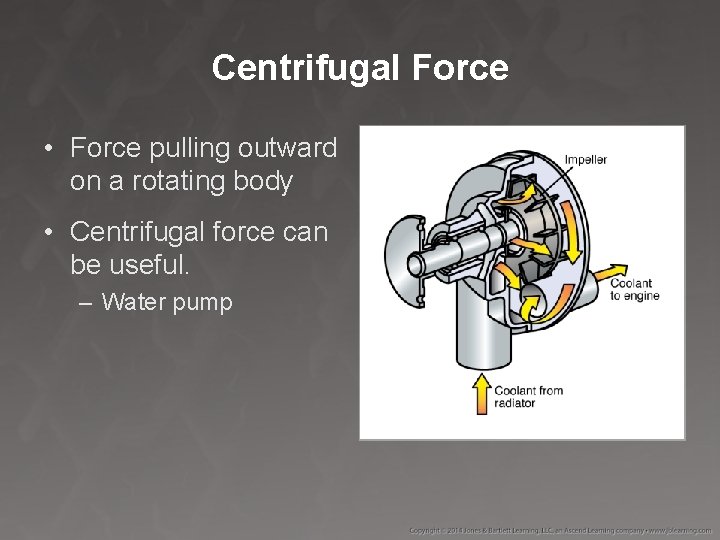
Centrifugal Force • Force pulling outward on a rotating body • Centrifugal force can be useful. – Water pump
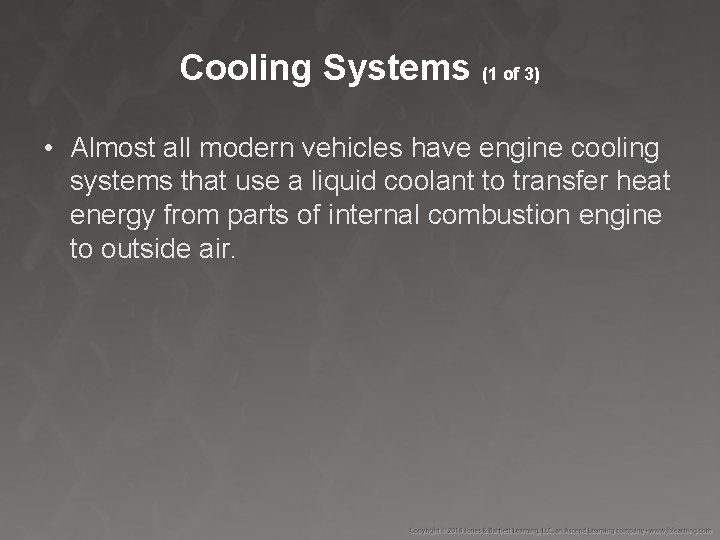
Cooling Systems (1 of 3) • Almost all modern vehicles have engine cooling systems that use a liquid coolant to transfer heat energy from parts of internal combustion engine to outside air.
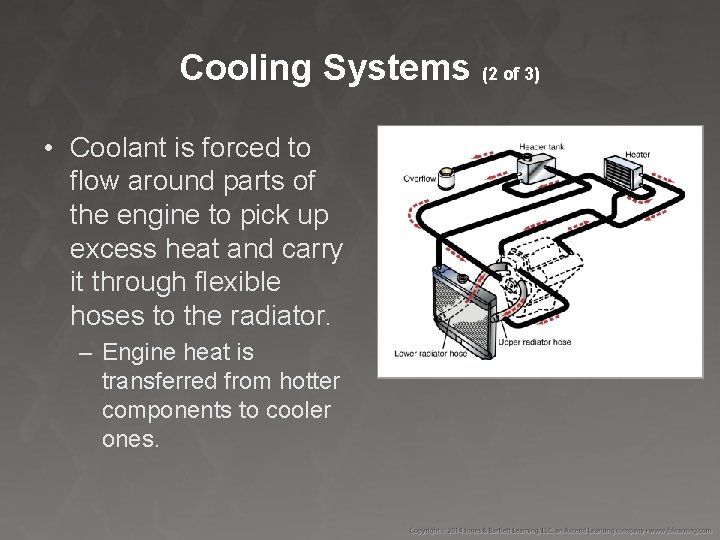
Cooling Systems (2 of 3) • Coolant is forced to flow around parts of the engine to pick up excess heat and carry it through flexible hoses to the radiator. – Engine heat is transferred from hotter components to cooler ones.
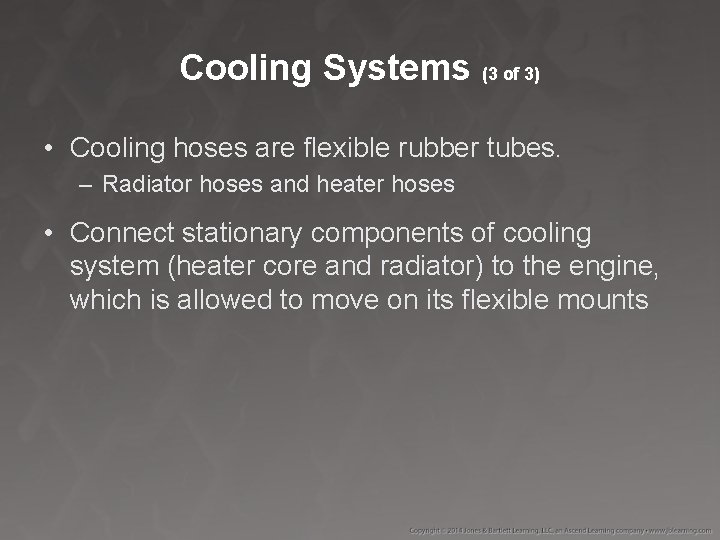
Cooling Systems (3 of 3) • Cooling hoses are flexible rubber tubes. – Radiator hoses and heater hoses • Connect stationary components of cooling system (heater core and radiator) to the engine, which is allowed to move on its flexible mounts

Air Cooling (1 of 3) • Common on smaller internal combustion engines and used in the past – Not ideal from emissions standpoint – Didn’t always provide sufficient cabin heat for passenger compartment • All automobiles are now water cooled. • Air cooling uses heat-dissipating fins on the engine cylinders and heads.
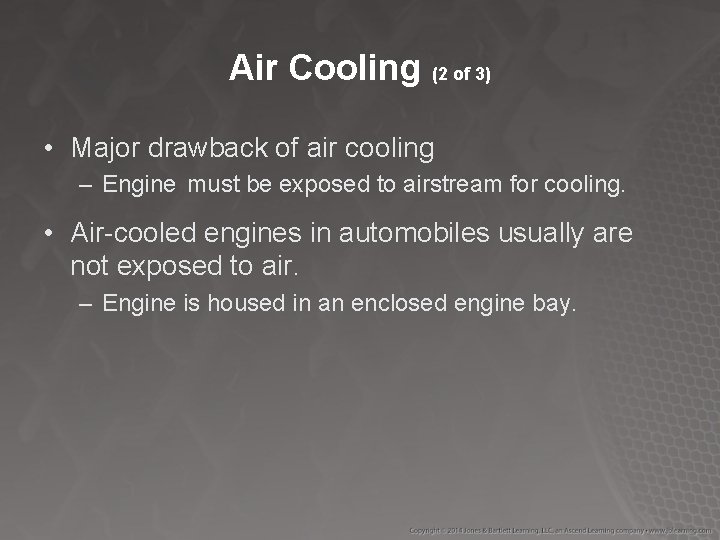
Air Cooling (2 of 3) • Major drawback of air cooling – Engine must be exposed to airstream for cooling. • Air-cooled engines in automobiles usually are not exposed to air. – Engine is housed in an enclosed engine bay.
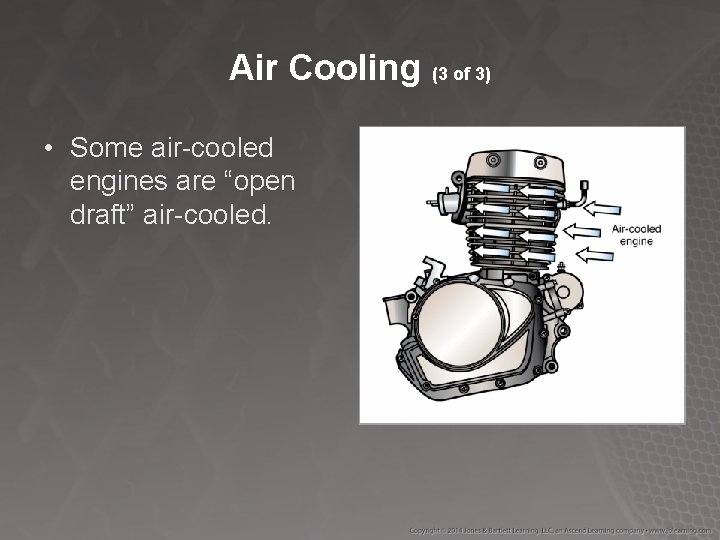
Air Cooling (3 of 3) • Some air-cooled engines are “open draft” air-cooled.
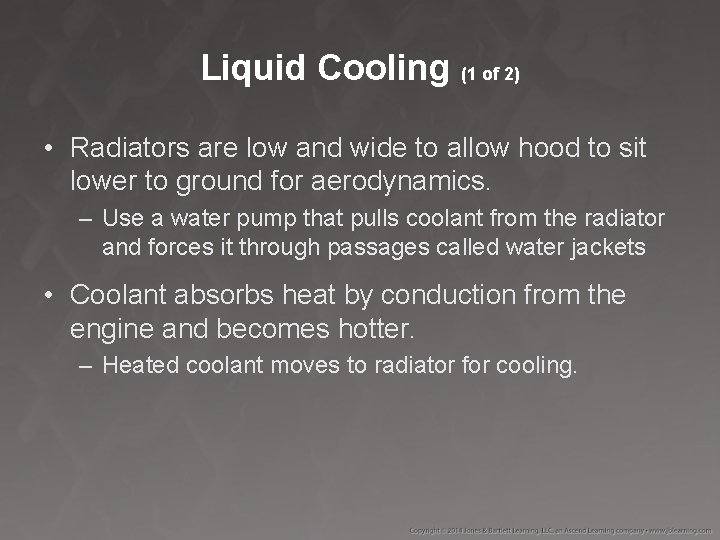
Liquid Cooling (1 of 2) • Radiators are low and wide to allow hood to sit lower to ground for aerodynamics. – Use a water pump that pulls coolant from the radiator and forces it through passages called water jackets • Coolant absorbs heat by conduction from the engine and becomes hotter. – Heated coolant moves to radiator for cooling.
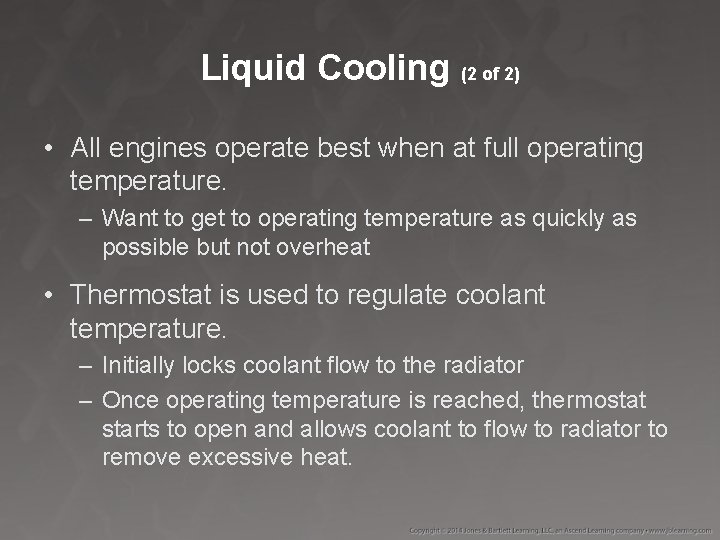
Liquid Cooling (2 of 2) • All engines operate best when at full operating temperature. – Want to get to operating temperature as quickly as possible but not overheat • Thermostat is used to regulate coolant temperature. – Initially locks coolant flow to the radiator – Once operating temperature is reached, thermostat starts to open and allows coolant to flow to radiator to remove excessive heat.
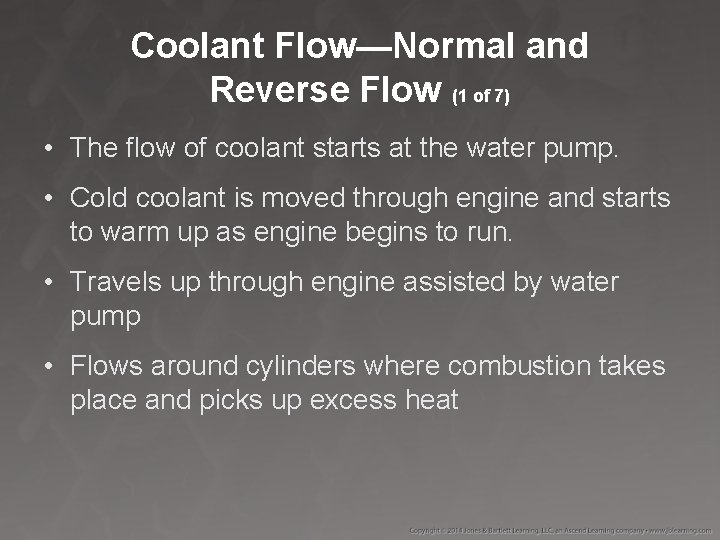
Coolant Flow—Normal and Reverse Flow (1 of 7) • The flow of coolant starts at the water pump. • Cold coolant is moved through engine and starts to warm up as engine begins to run. • Travels up through engine assisted by water pump • Flows around cylinders where combustion takes place and picks up excess heat
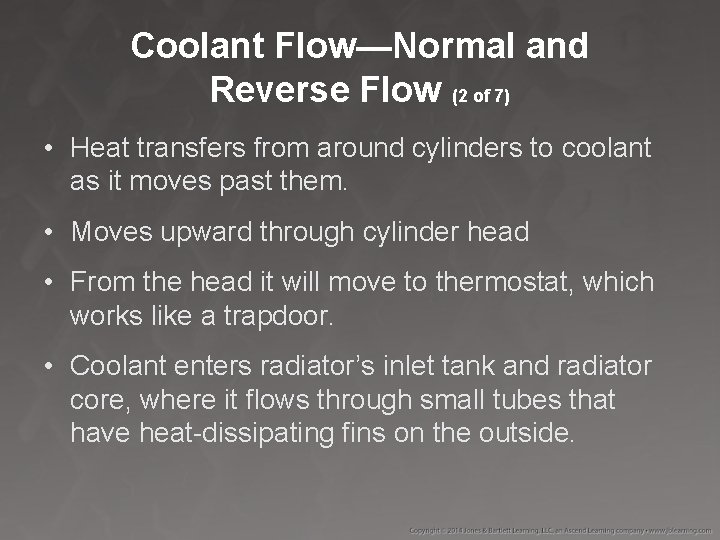
Coolant Flow—Normal and Reverse Flow (2 of 7) • Heat transfers from around cylinders to coolant as it moves past them. • Moves upward through cylinder head • From the head it will move to thermostat, which works like a trapdoor. • Coolant enters radiator’s inlet tank and radiator core, where it flows through small tubes that have heat-dissipating fins on the outside.
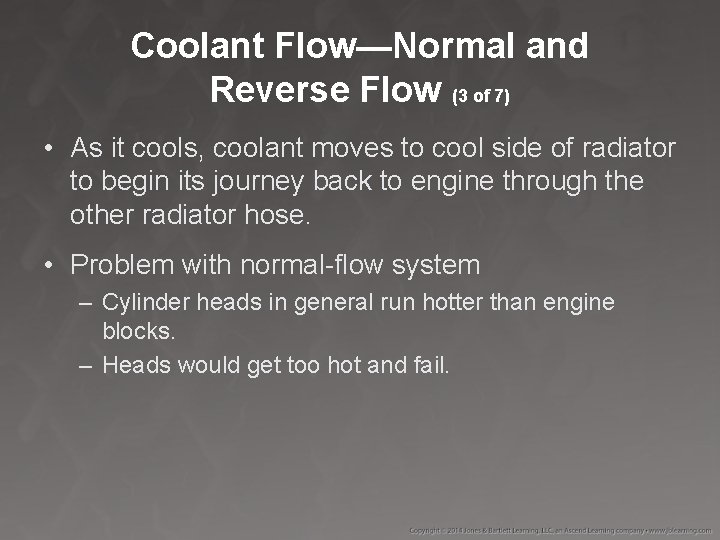
Coolant Flow—Normal and Reverse Flow (3 of 7) • As it cools, coolant moves to cool side of radiator to begin its journey back to engine through the other radiator hose. • Problem with normal-flow system – Cylinder heads in general run hotter than engine blocks. – Heads would get too hot and fail.
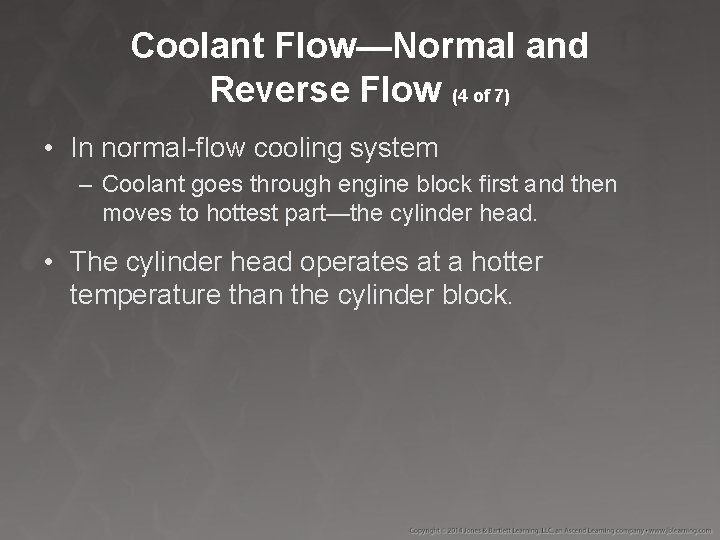
Coolant Flow—Normal and Reverse Flow (4 of 7) • In normal-flow cooling system – Coolant goes through engine block first and then moves to hottest part—the cylinder head. • The cylinder head operates at a hotter temperature than the cylinder block.
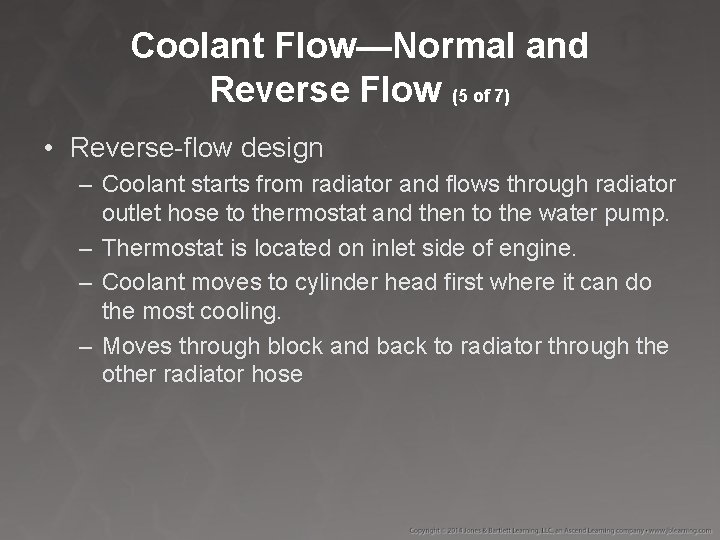
Coolant Flow—Normal and Reverse Flow (5 of 7) • Reverse-flow design – Coolant starts from radiator and flows through radiator outlet hose to thermostat and then to the water pump. – Thermostat is located on inlet side of engine. – Coolant moves to cylinder head first where it can do the most cooling. – Moves through block and back to radiator through the other radiator hose
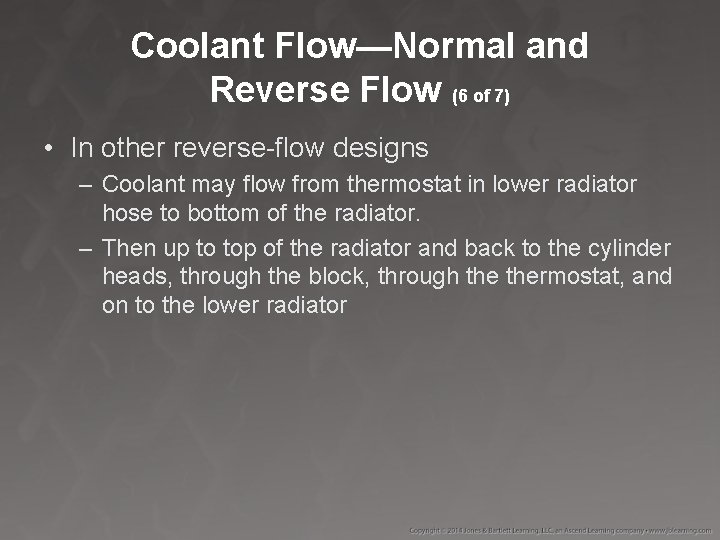
Coolant Flow—Normal and Reverse Flow (6 of 7) • In other reverse-flow designs – Coolant may flow from thermostat in lower radiator hose to bottom of the radiator. – Then up to top of the radiator and back to the cylinder heads, through the block, through thermostat, and on to the lower radiator
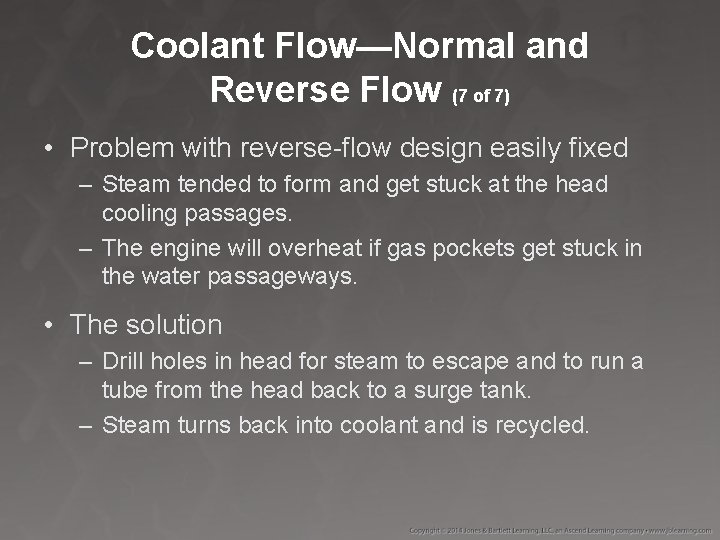
Coolant Flow—Normal and Reverse Flow (7 of 7) • Problem with reverse-flow design easily fixed – Steam tended to form and get stuck at the head cooling passages. – The engine will overheat if gas pockets get stuck in the water passageways. • The solution – Drill holes in head for steam to escape and to run a tube from the head back to a surge tank. – Steam turns back into coolant and is recycled.
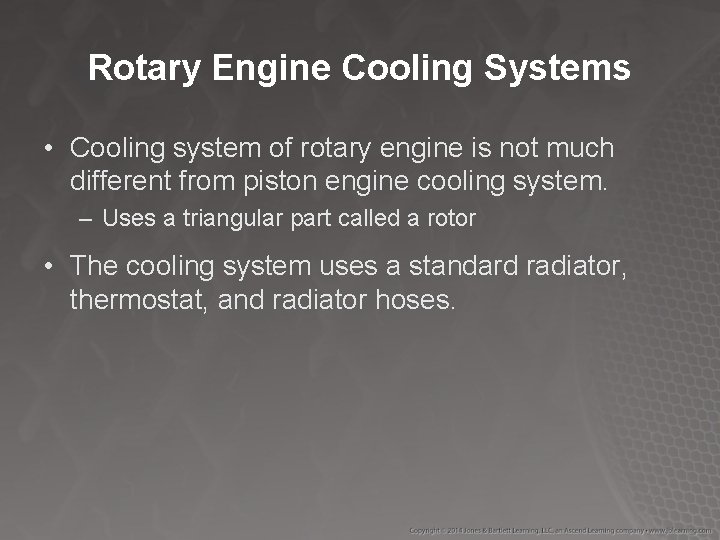
Rotary Engine Cooling Systems • Cooling system of rotary engine is not much different from piston engine cooling system. – Uses a triangular part called a rotor • The cooling system uses a standard radiator, thermostat, and radiator hoses.
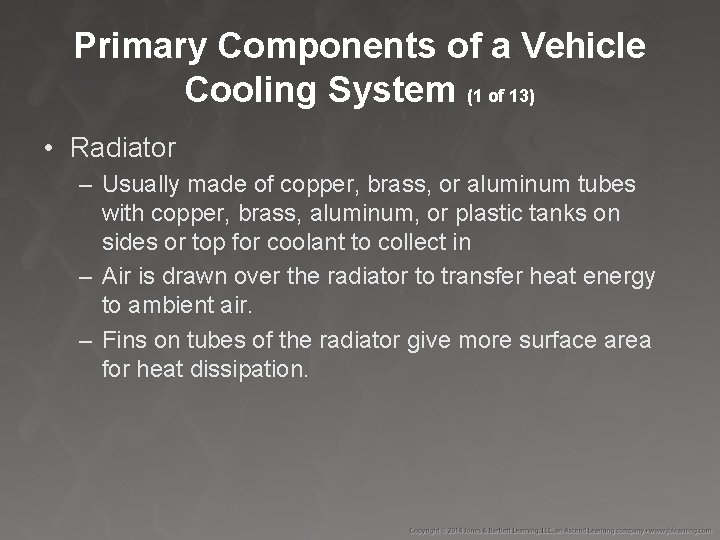
Primary Components of a Vehicle Cooling System (1 of 13) • Radiator – Usually made of copper, brass, or aluminum tubes with copper, brass, aluminum, or plastic tanks on sides or top for coolant to collect in – Air is drawn over the radiator to transfer heat energy to ambient air. – Fins on tubes of the radiator give more surface area for heat dissipation.
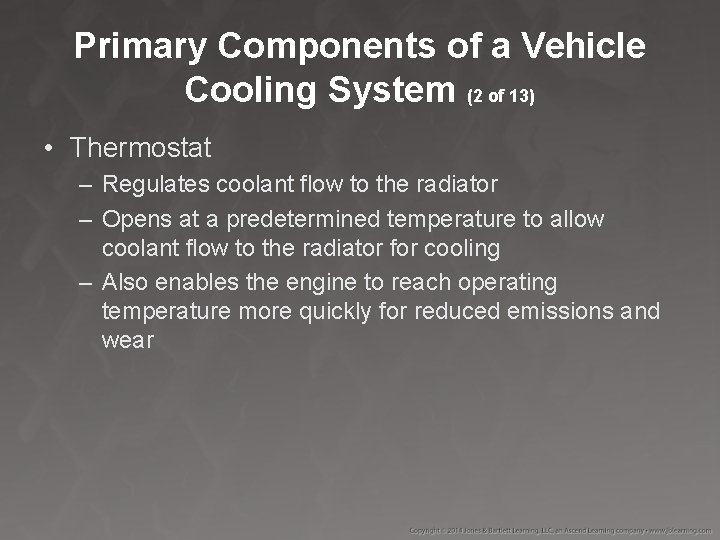
Primary Components of a Vehicle Cooling System (2 of 13) • Thermostat – Regulates coolant flow to the radiator – Opens at a predetermined temperature to allow coolant flow to the radiator for cooling – Also enables the engine to reach operating temperature more quickly for reduced emissions and wear
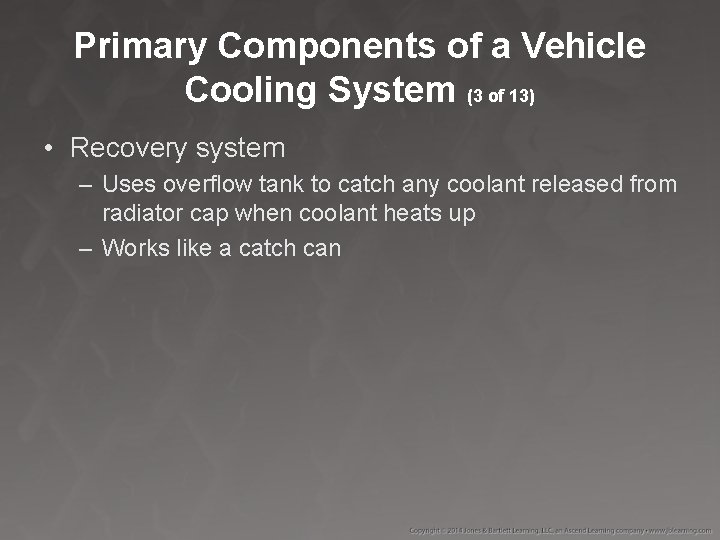
Primary Components of a Vehicle Cooling System (3 of 13) • Recovery system – Uses overflow tank to catch any coolant released from radiator cap when coolant heats up – Works like a catch can
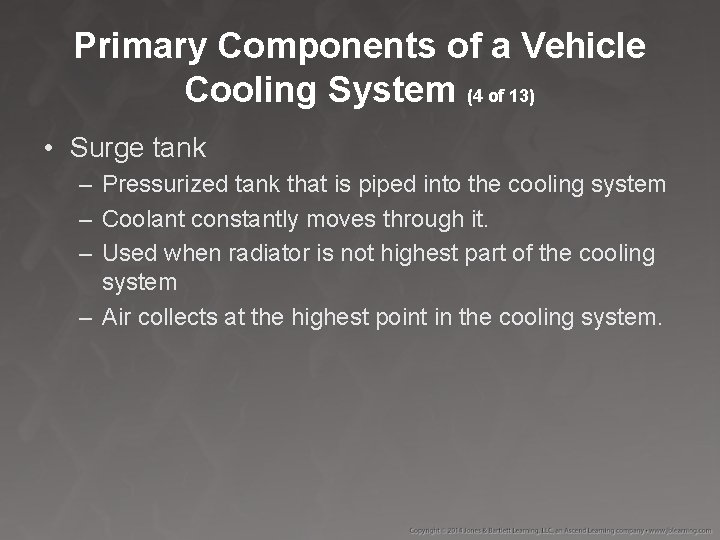
Primary Components of a Vehicle Cooling System (4 of 13) • Surge tank – Pressurized tank that is piped into the cooling system – Coolant constantly moves through it. – Used when radiator is not highest part of the cooling system – Air collects at the highest point in the cooling system.
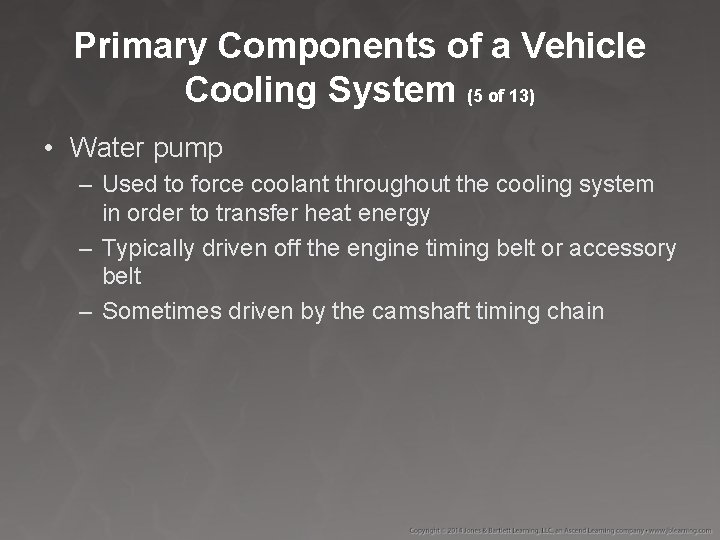
Primary Components of a Vehicle Cooling System (5 of 13) • Water pump – Used to force coolant throughout the cooling system in order to transfer heat energy – Typically driven off the engine timing belt or accessory belt – Sometimes driven by the camshaft timing chain
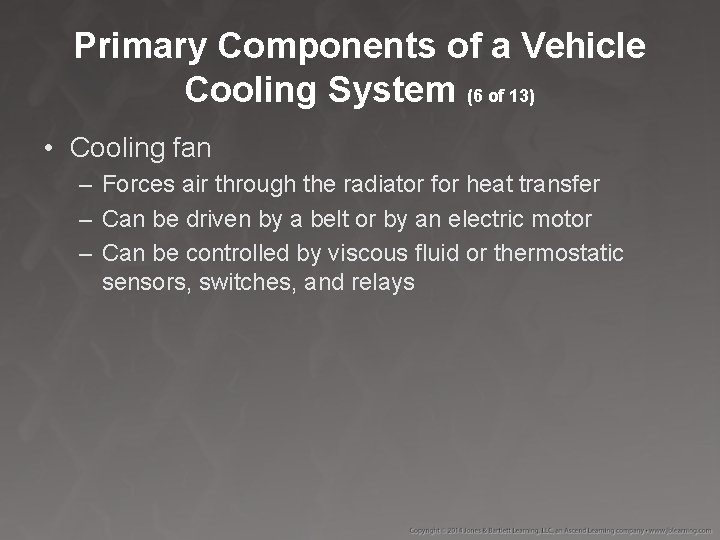
Primary Components of a Vehicle Cooling System (6 of 13) • Cooling fan – Forces air through the radiator for heat transfer – Can be driven by a belt or by an electric motor – Can be controlled by viscous fluid or thermostatic sensors, switches, and relays
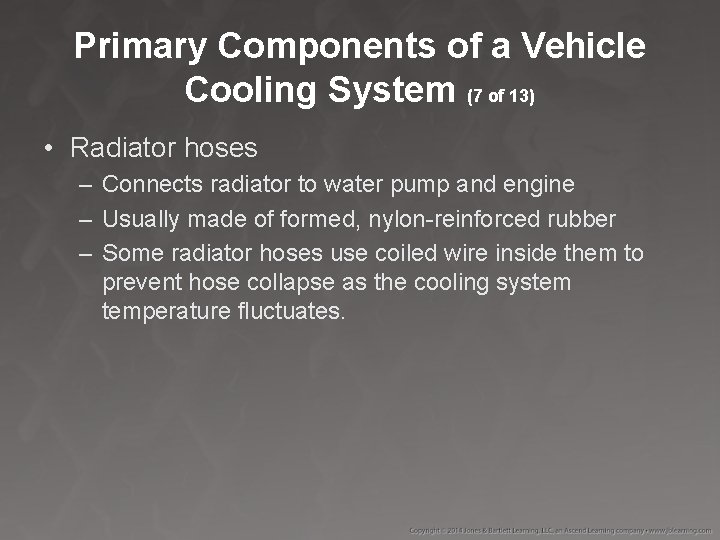
Primary Components of a Vehicle Cooling System (7 of 13) • Radiator hoses – Connects radiator to water pump and engine – Usually made of formed, nylon-reinforced rubber – Some radiator hoses use coiled wire inside them to prevent hose collapse as the cooling system temperature fluctuates.
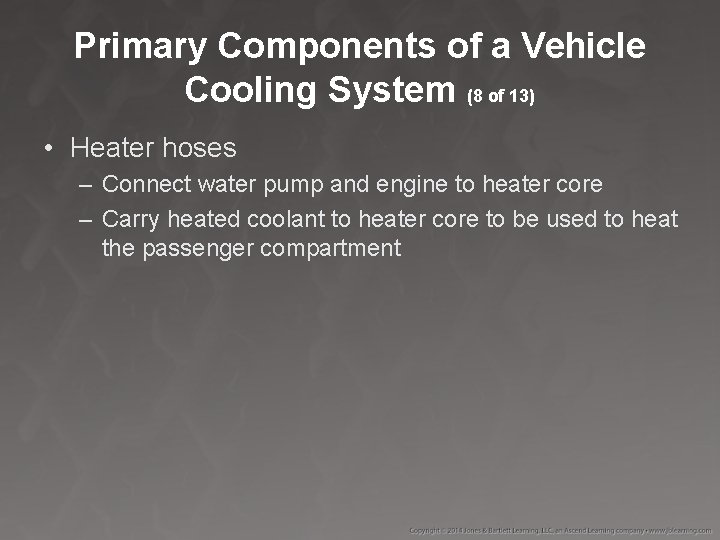
Primary Components of a Vehicle Cooling System (8 of 13) • Heater hoses – Connect water pump and engine to heater core – Carry heated coolant to heater core to be used to heat the passenger compartment
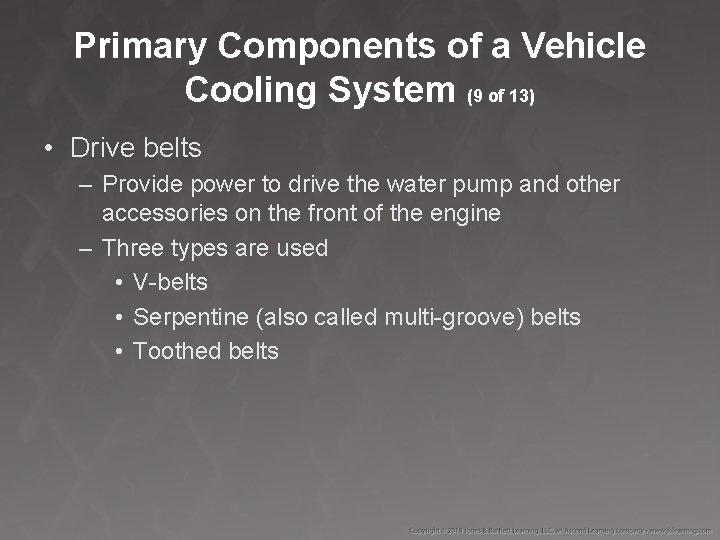
Primary Components of a Vehicle Cooling System (9 of 13) • Drive belts – Provide power to drive the water pump and other accessories on the front of the engine – Three types are used • V-belts • Serpentine (also called multi-groove) belts • Toothed belts
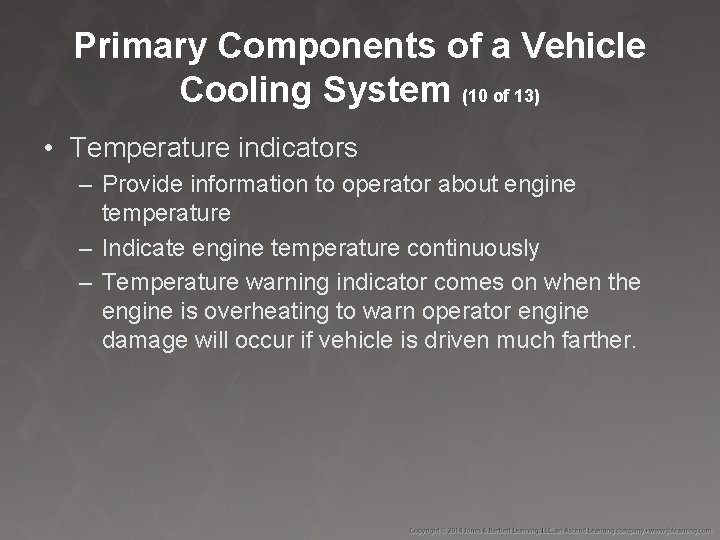
Primary Components of a Vehicle Cooling System (10 of 13) • Temperature indicators – Provide information to operator about engine temperature – Indicate engine temperature continuously – Temperature warning indicator comes on when the engine is overheating to warn operator engine damage will occur if vehicle is driven much farther.
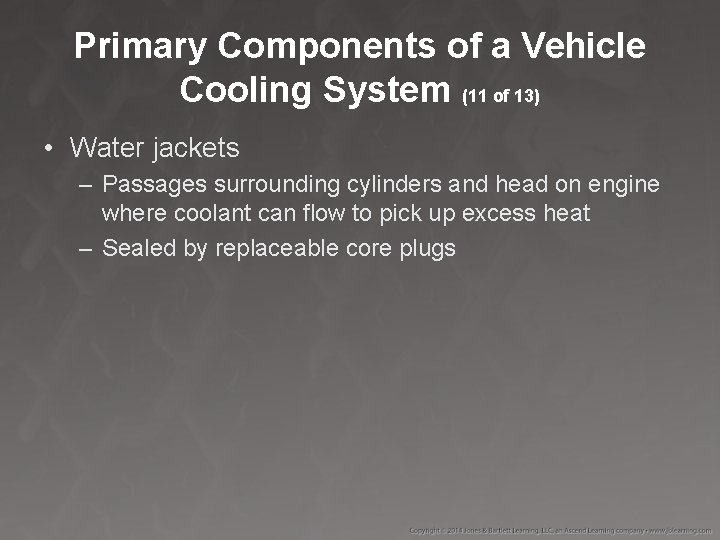
Primary Components of a Vehicle Cooling System (11 of 13) • Water jackets – Passages surrounding cylinders and head on engine where coolant can flow to pick up excess heat – Sealed by replaceable core plugs
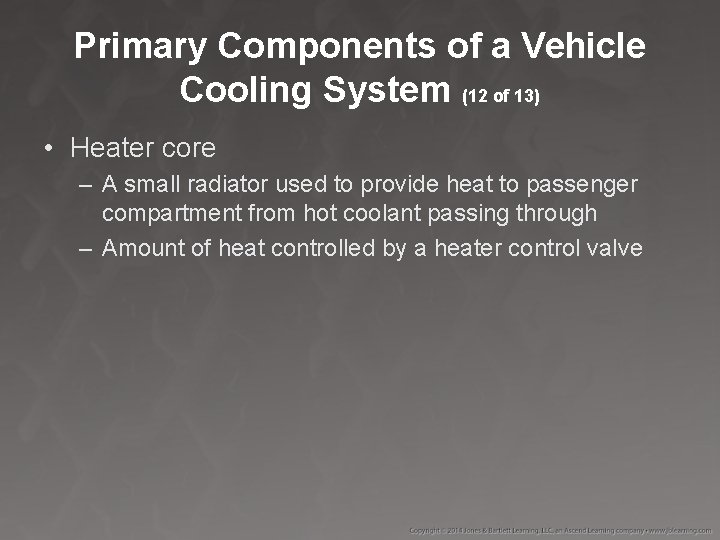
Primary Components of a Vehicle Cooling System (12 of 13) • Heater core – A small radiator used to provide heat to passenger compartment from hot coolant passing through – Amount of heat controlled by a heater control valve
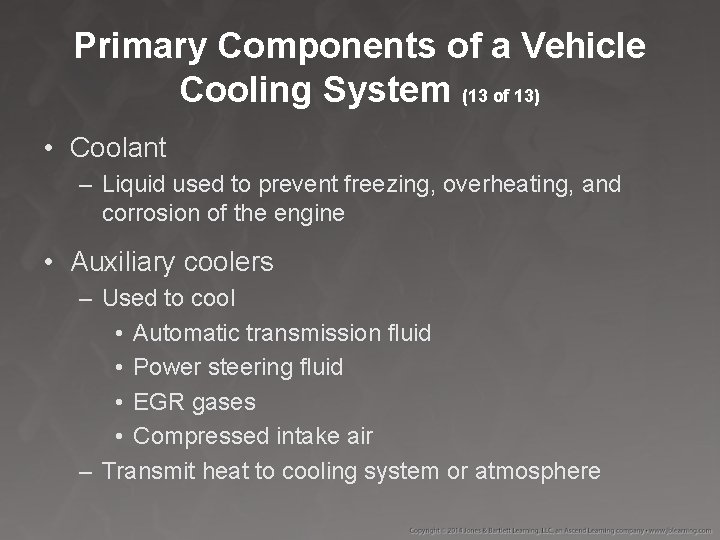
Primary Components of a Vehicle Cooling System (13 of 13) • Coolant – Liquid used to prevent freezing, overheating, and corrosion of the engine • Auxiliary coolers – Used to cool • Automatic transmission fluid • Power steering fluid • EGR gases • Compressed intake air – Transmit heat to cooling system or atmosphere
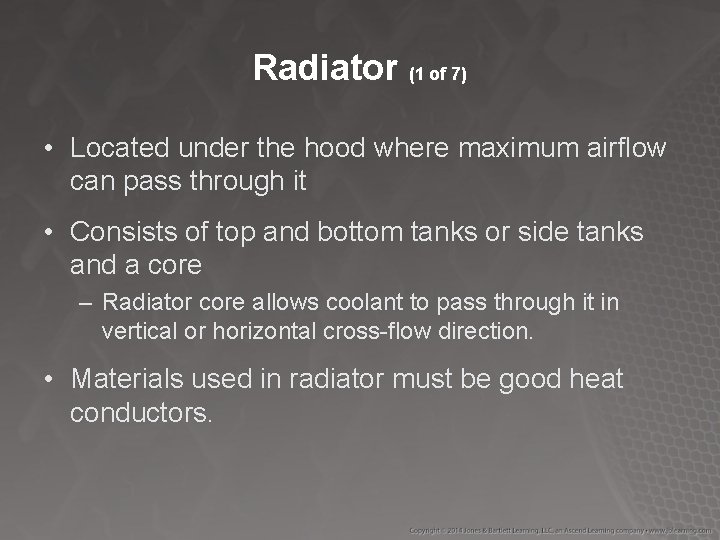
Radiator (1 of 7) • Located under the hood where maximum airflow can pass through it • Consists of top and bottom tanks or side tanks and a core – Radiator core allows coolant to pass through it in vertical or horizontal cross-flow direction. • Materials used in radiator must be good heat conductors.
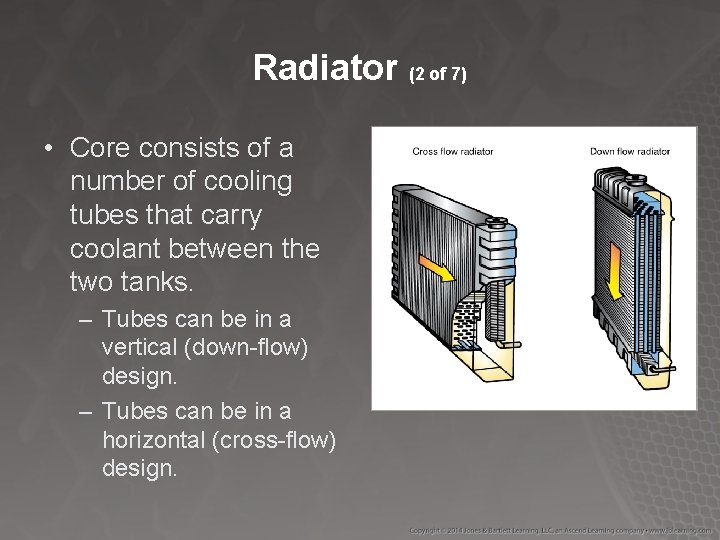
Radiator (2 of 7) • Core consists of a number of cooling tubes that carry coolant between the two tanks. – Tubes can be in a vertical (down-flow) design. – Tubes can be in a horizontal (cross-flow) design.
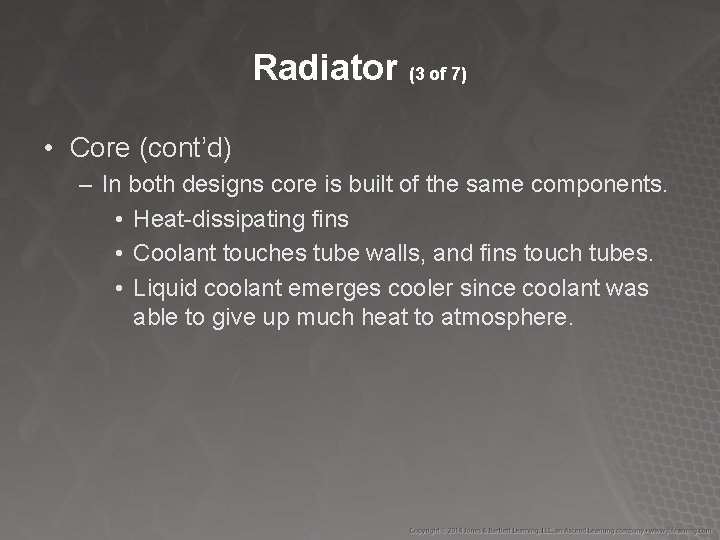
Radiator (3 of 7) • Core (cont’d) – In both designs core is built of the same components. • Heat-dissipating fins • Coolant touches tube walls, and fins touch tubes. • Liquid coolant emerges cooler since coolant was able to give up much heat to atmosphere.
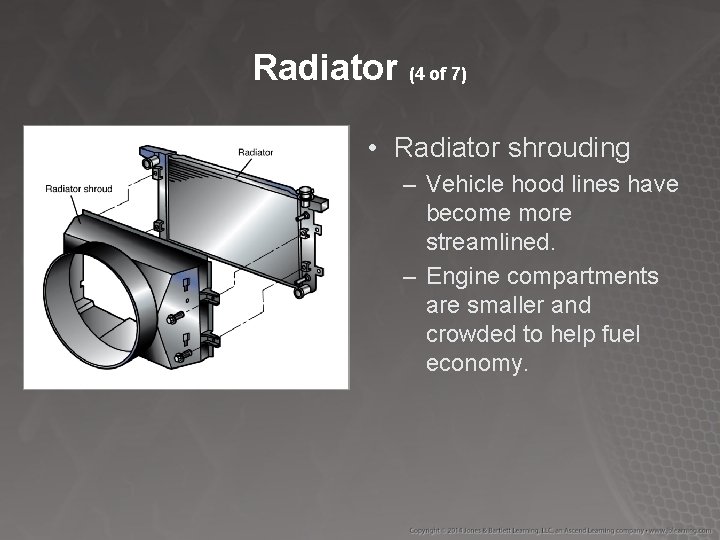
Radiator (4 of 7) • Radiator shrouding – Vehicle hood lines have become more streamlined. – Engine compartments are smaller and crowded to help fuel economy.
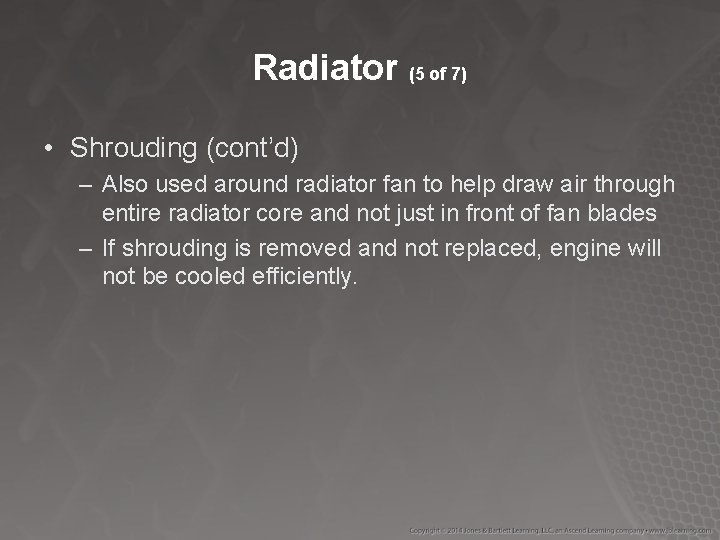
Radiator (5 of 7) • Shrouding (cont’d) – Also used around radiator fan to help draw air through entire radiator core and not just in front of fan blades – If shrouding is removed and not replaced, engine will not be cooled efficiently.
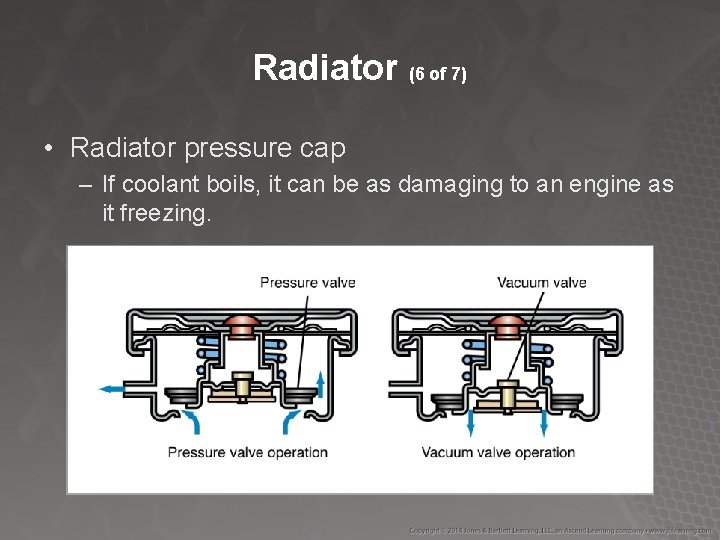
Radiator (6 of 7) • Radiator pressure cap – If coolant boils, it can be as damaging to an engine as it freezing.
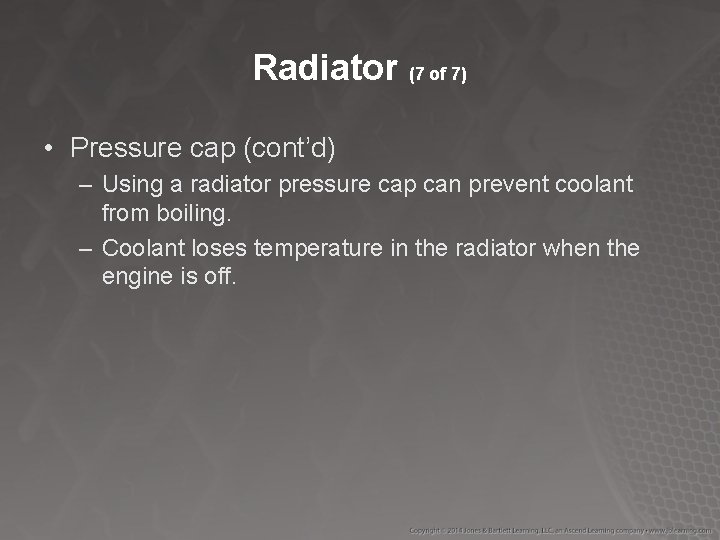
Radiator (7 of 7) • Pressure cap (cont’d) – Using a radiator pressure cap can prevent coolant from boiling. – Coolant loses temperature in the radiator when the engine is off.
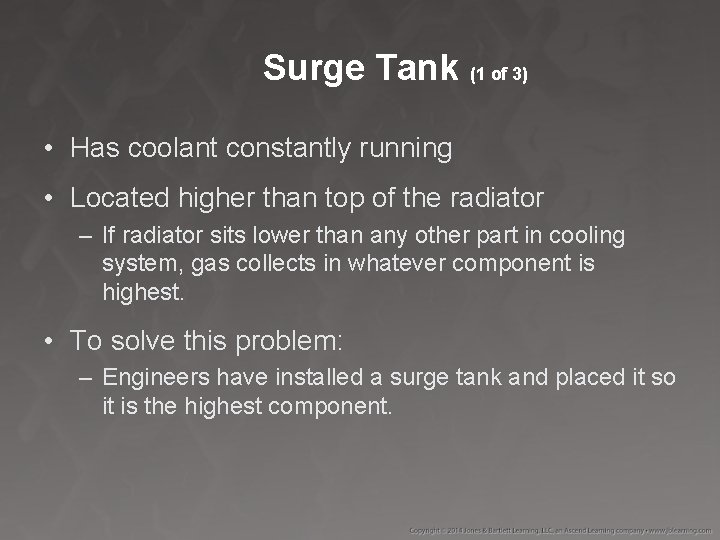
Surge Tank (1 of 3) • Has coolant constantly running • Located higher than top of the radiator – If radiator sits lower than any other part in cooling system, gas collects in whatever component is highest. • To solve this problem: – Engineers have installed a surge tank and placed it so it is the highest component.
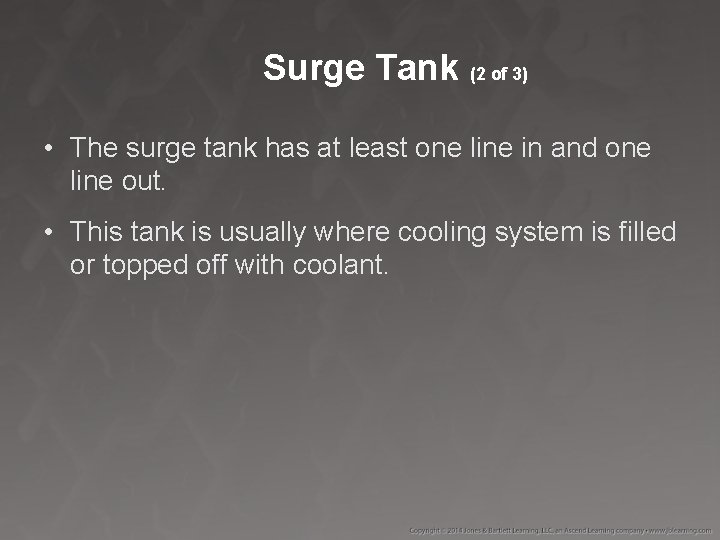
Surge Tank (2 of 3) • The surge tank has at least one line in and one line out. • This tank is usually where cooling system is filled or topped off with coolant.
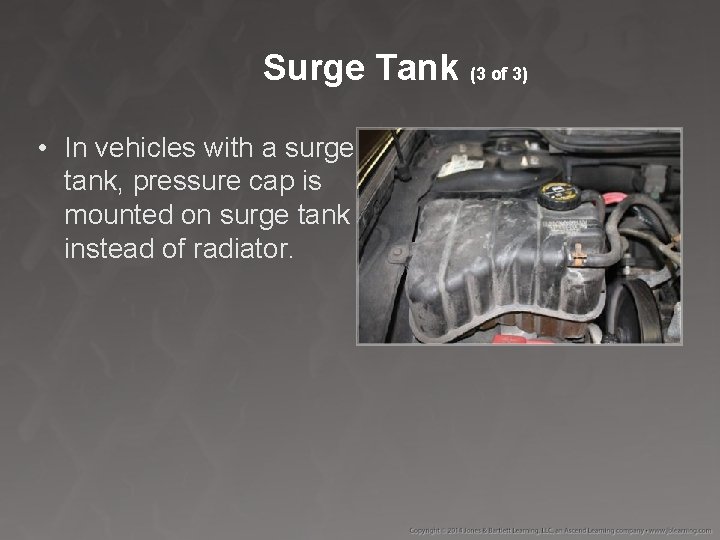
Surge Tank (3 of 3) • In vehicles with a surge tank, pressure cap is mounted on surge tank instead of radiator.
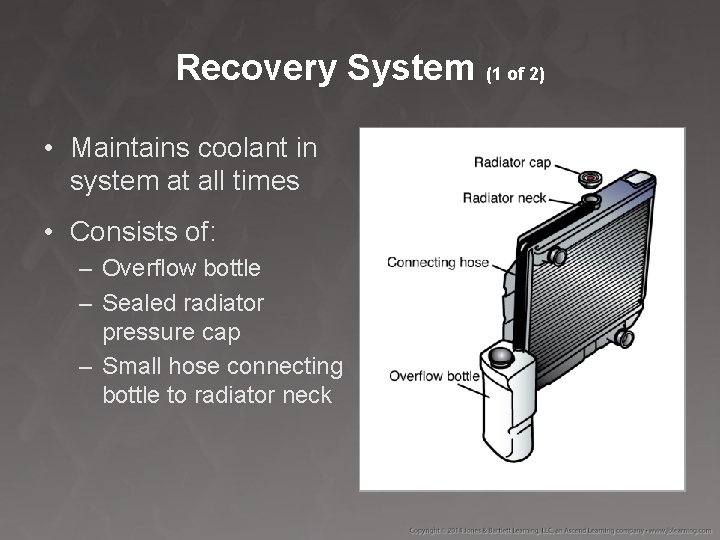
Recovery System (1 of 2) • Maintains coolant in system at all times • Consists of: – Overflow bottle – Sealed radiator pressure cap – Small hose connecting bottle to radiator neck
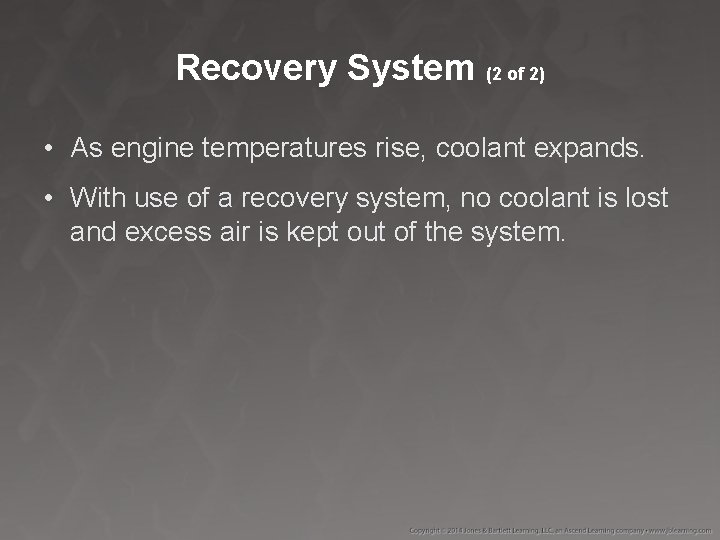
Recovery System (2 of 2) • As engine temperatures rise, coolant expands. • With use of a recovery system, no coolant is lost and excess air is kept out of the system.
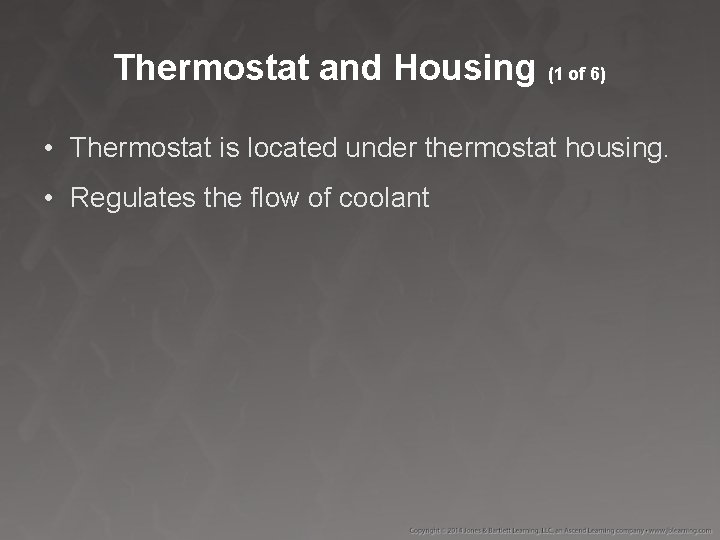
Thermostat and Housing (1 of 6) • Thermostat is located under thermostat housing. • Regulates the flow of coolant
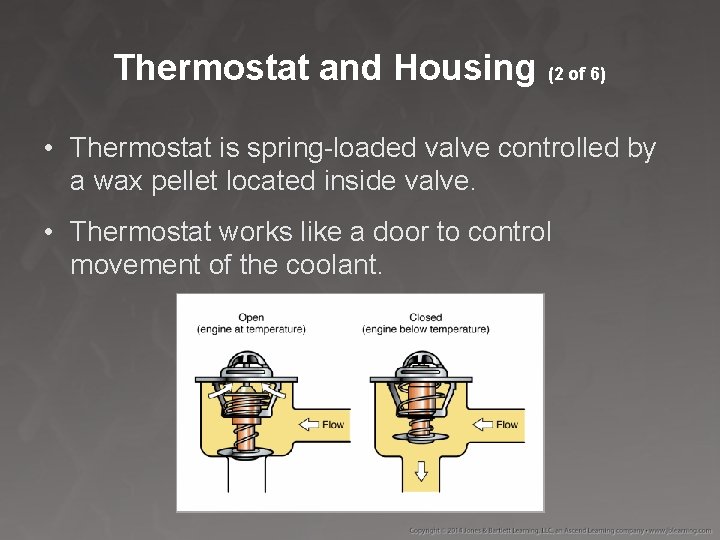
Thermostat and Housing (2 of 6) • Thermostat is spring-loaded valve controlled by a wax pellet located inside valve. • Thermostat works like a door to control movement of the coolant.
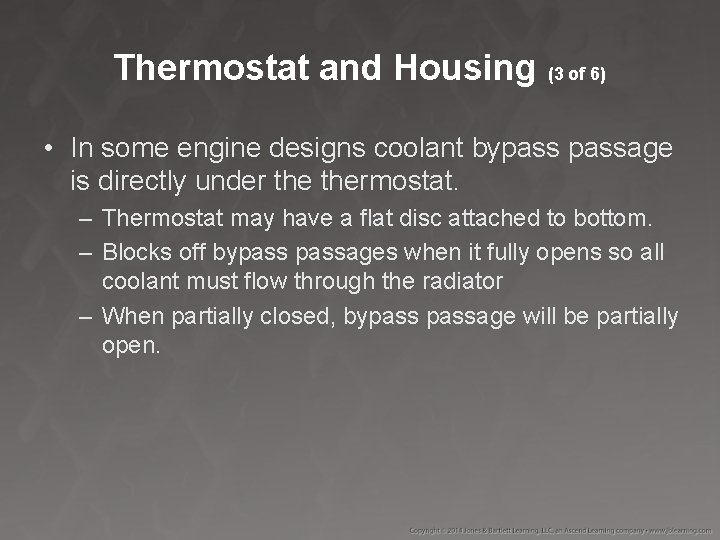
Thermostat and Housing (3 of 6) • In some engine designs coolant bypassage is directly under thermostat. – Thermostat may have a flat disc attached to bottom. – Blocks off bypassages when it fully opens so all coolant must flow through the radiator – When partially closed, bypassage will be partially open.
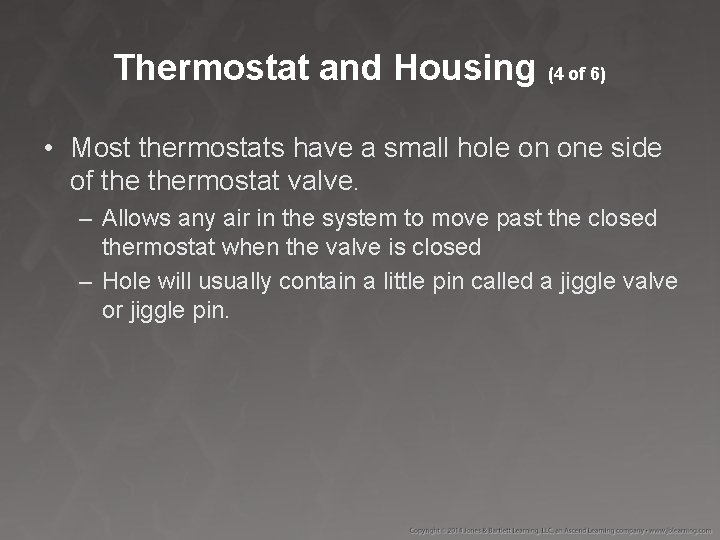
Thermostat and Housing (4 of 6) • Most thermostats have a small hole on one side of thermostat valve. – Allows any air in the system to move past the closed thermostat when the valve is closed – Hole will usually contain a little pin called a jiggle valve or jiggle pin.
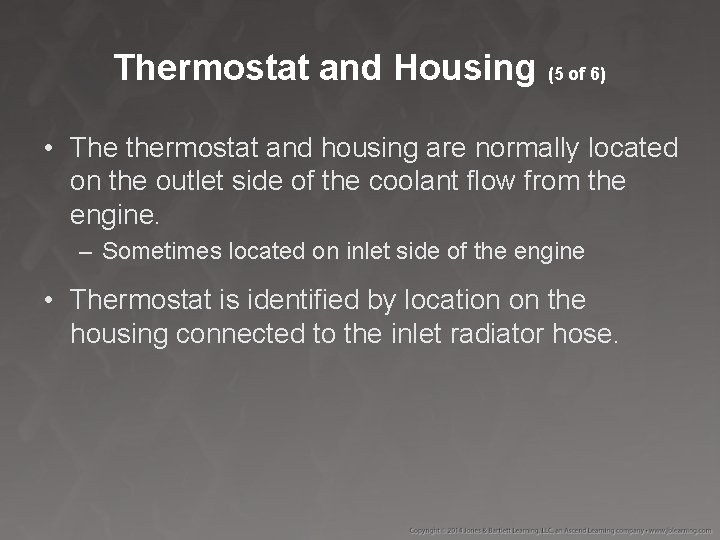
Thermostat and Housing (5 of 6) • The thermostat and housing are normally located on the outlet side of the coolant flow from the engine. – Sometimes located on inlet side of the engine • Thermostat is identified by location on the housing connected to the inlet radiator hose.
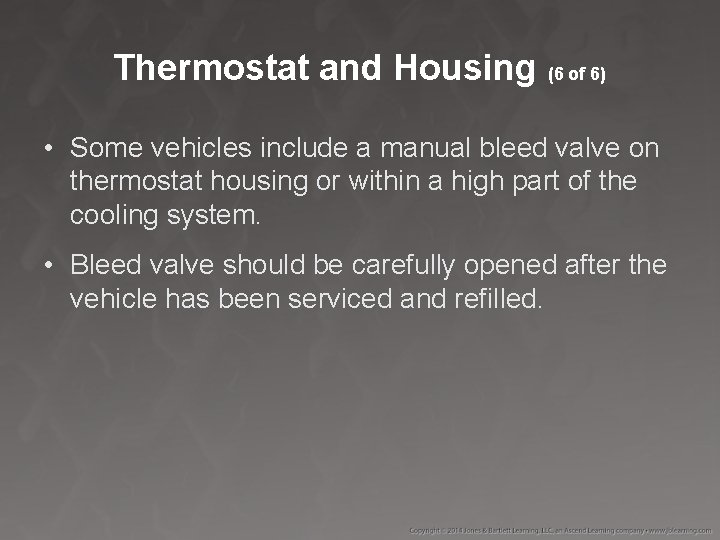
Thermostat and Housing (6 of 6) • Some vehicles include a manual bleed valve on thermostat housing or within a high part of the cooling system. • Bleed valve should be carefully opened after the vehicle has been serviced and refilled.
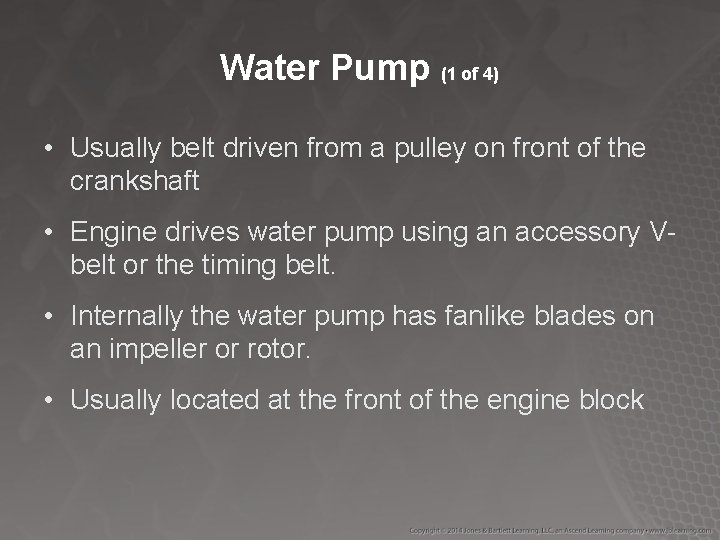
Water Pump (1 of 4) • Usually belt driven from a pulley on front of the crankshaft • Engine drives water pump using an accessory Vbelt or the timing belt. • Internally the water pump has fanlike blades on an impeller or rotor. • Usually located at the front of the engine block
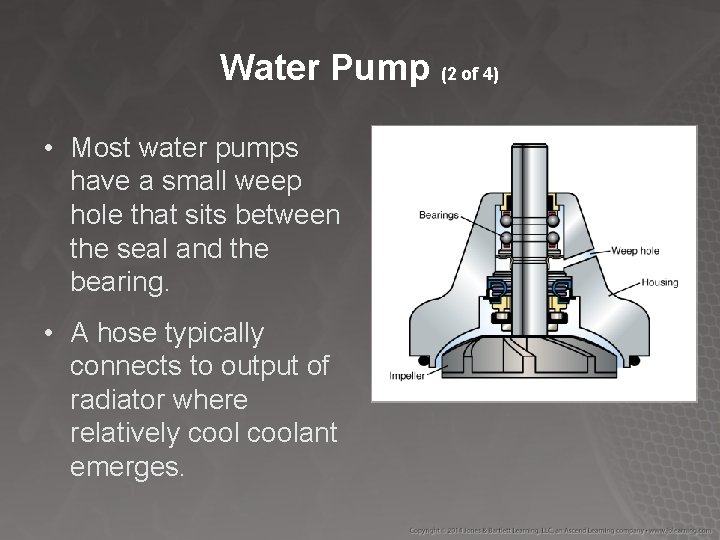
Water Pump (2 of 4) • Most water pumps have a small weep hole that sits between the seal and the bearing. • A hose typically connects to output of radiator where relatively coolant emerges.
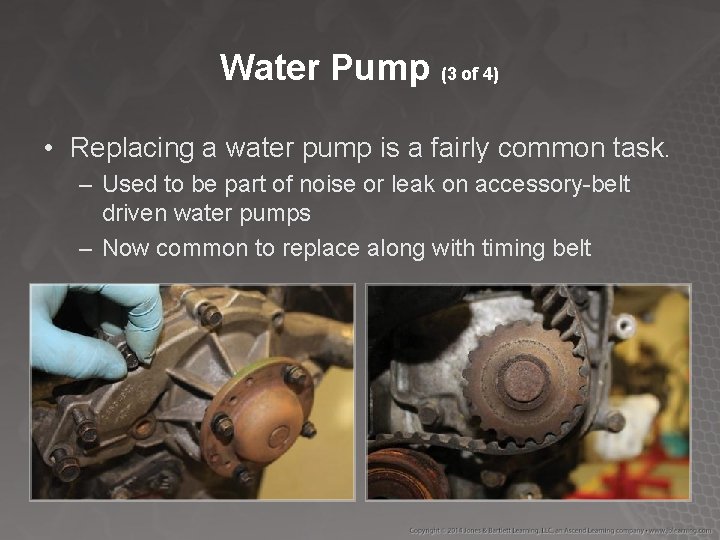
Water Pump (3 of 4) • Replacing a water pump is a fairly common task. – Used to be part of noise or leak on accessory-belt driven water pumps – Now common to replace along with timing belt
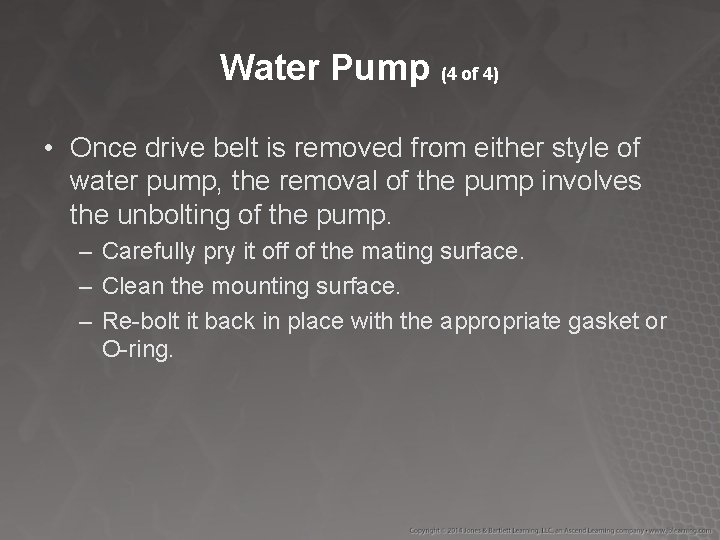
Water Pump (4 of 4) • Once drive belt is removed from either style of water pump, the removal of the pump involves the unbolting of the pump. – Carefully pry it off of the mating surface. – Clean the mounting surface. – Re-bolt it back in place with the appropriate gasket or O-ring.
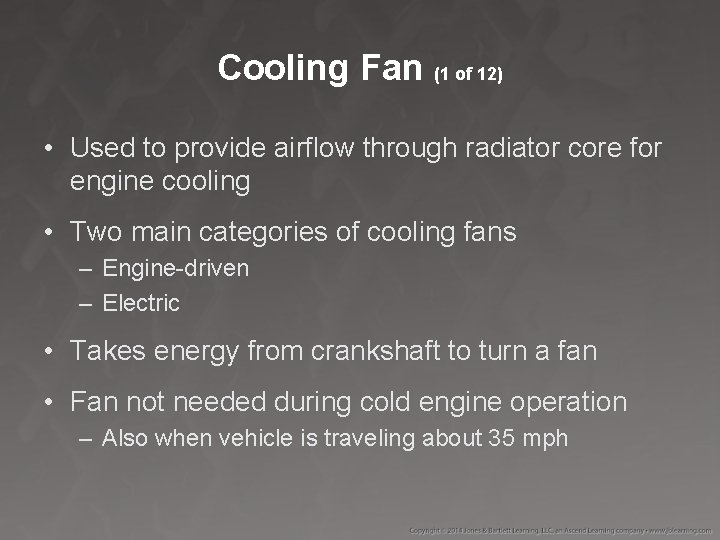
Cooling Fan (1 of 12) • Used to provide airflow through radiator core for engine cooling • Two main categories of cooling fans – Engine-driven – Electric • Takes energy from crankshaft to turn a fan • Fan not needed during cold engine operation – Also when vehicle is traveling about 35 mph
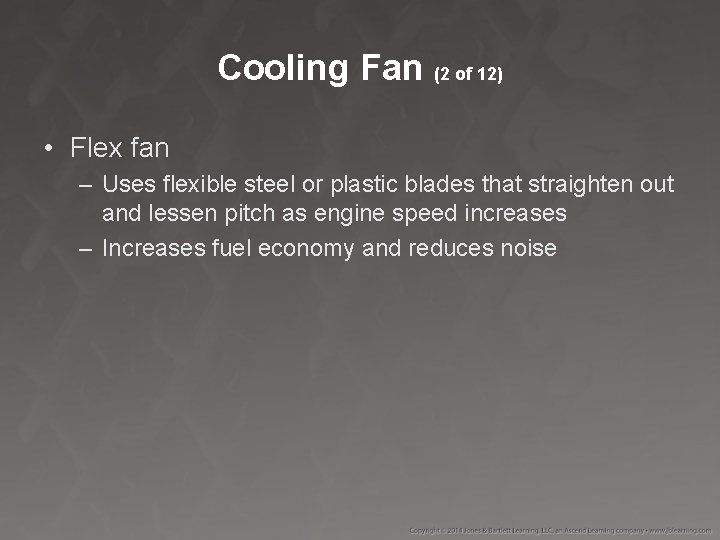
Cooling Fan (2 of 12) • Flex fan – Uses flexible steel or plastic blades that straighten out and lessen pitch as engine speed increases – Increases fuel economy and reduces noise
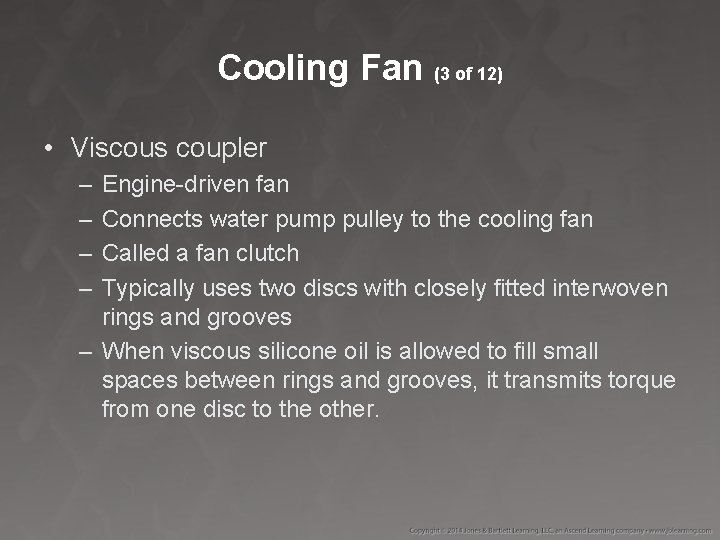
Cooling Fan (3 of 12) • Viscous coupler – – Engine-driven fan Connects water pump pulley to the cooling fan Called a fan clutch Typically uses two discs with closely fitted interwoven rings and grooves – When viscous silicone oil is allowed to fill small spaces between rings and grooves, it transmits torque from one disc to the other.
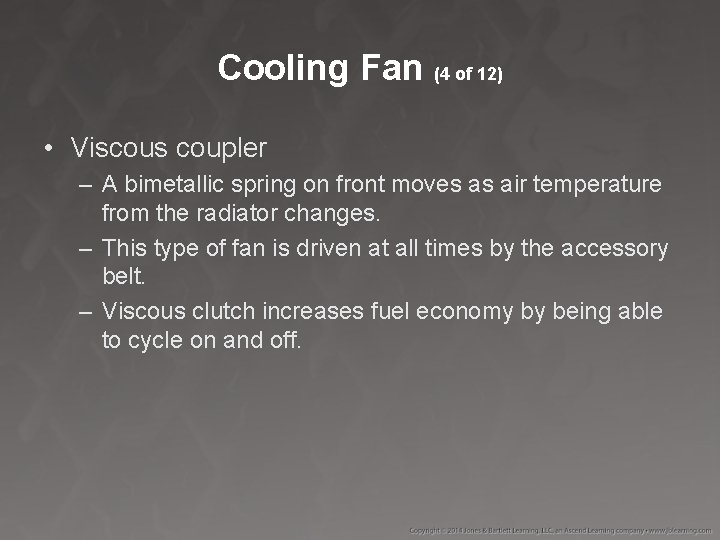
Cooling Fan (4 of 12) • Viscous coupler – A bimetallic spring on front moves as air temperature from the radiator changes. – This type of fan is driven at all times by the accessory belt. – Viscous clutch increases fuel economy by being able to cycle on and off.
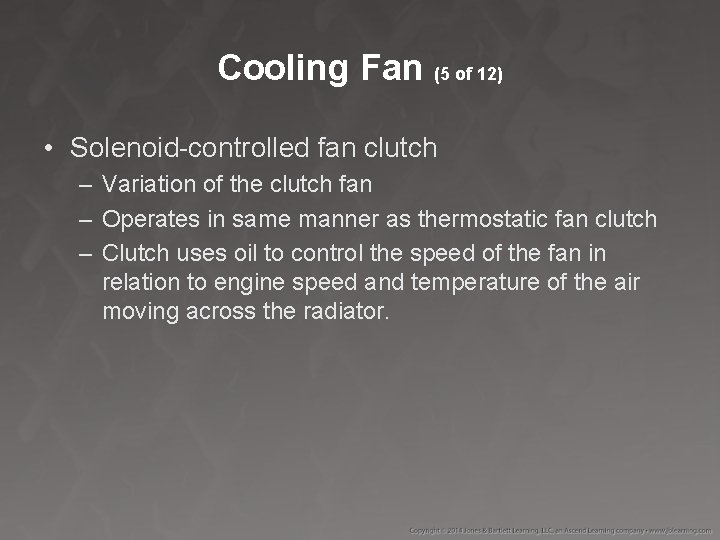
Cooling Fan (5 of 12) • Solenoid-controlled fan clutch – Variation of the clutch fan – Operates in same manner as thermostatic fan clutch – Clutch uses oil to control the speed of the fan in relation to engine speed and temperature of the air moving across the radiator.
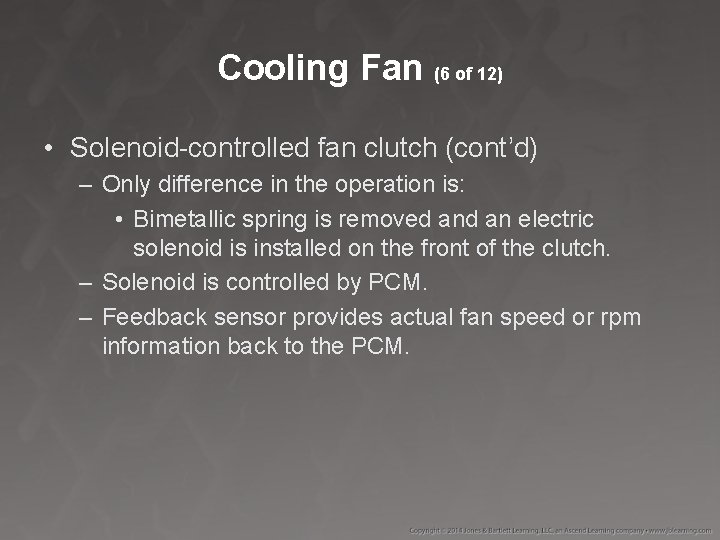
Cooling Fan (6 of 12) • Solenoid-controlled fan clutch (cont’d) – Only difference in the operation is: • Bimetallic spring is removed an electric solenoid is installed on the front of the clutch. – Solenoid is controlled by PCM. – Feedback sensor provides actual fan speed or rpm information back to the PCM.
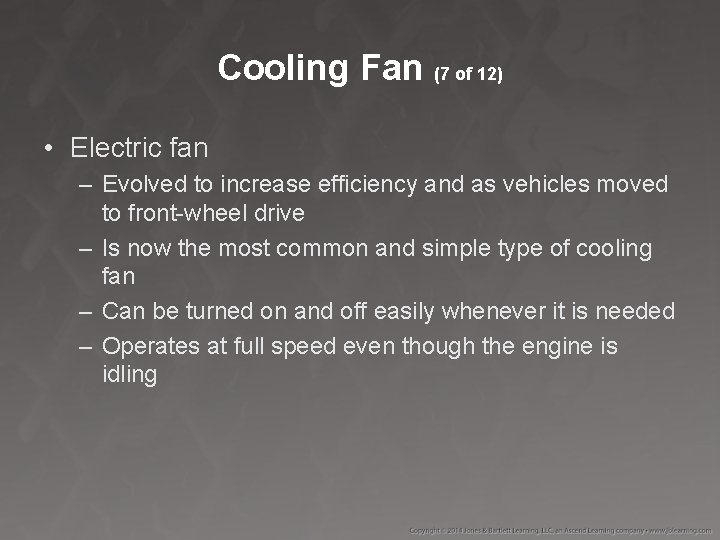
Cooling Fan (7 of 12) • Electric fan – Evolved to increase efficiency and as vehicles moved to front-wheel drive – Is now the most common and simple type of cooling fan – Can be turned on and off easily whenever it is needed – Operates at full speed even though the engine is idling
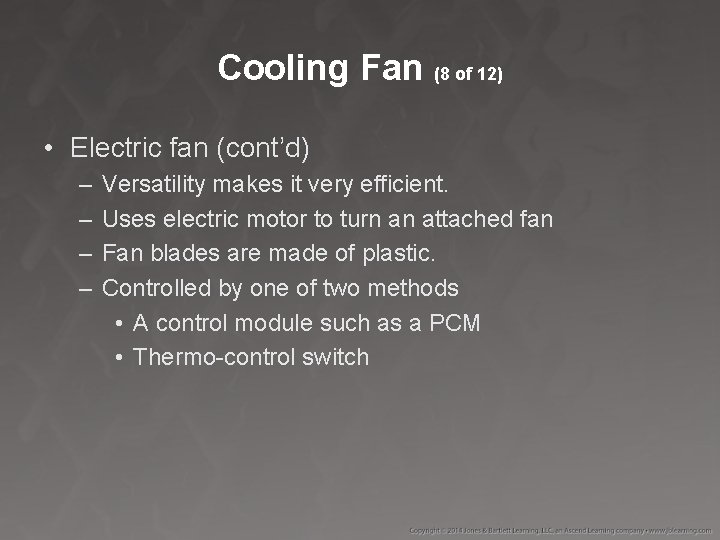
Cooling Fan (8 of 12) • Electric fan (cont’d) – – Versatility makes it very efficient. Uses electric motor to turn an attached fan Fan blades are made of plastic. Controlled by one of two methods • A control module such as a PCM • Thermo-control switch
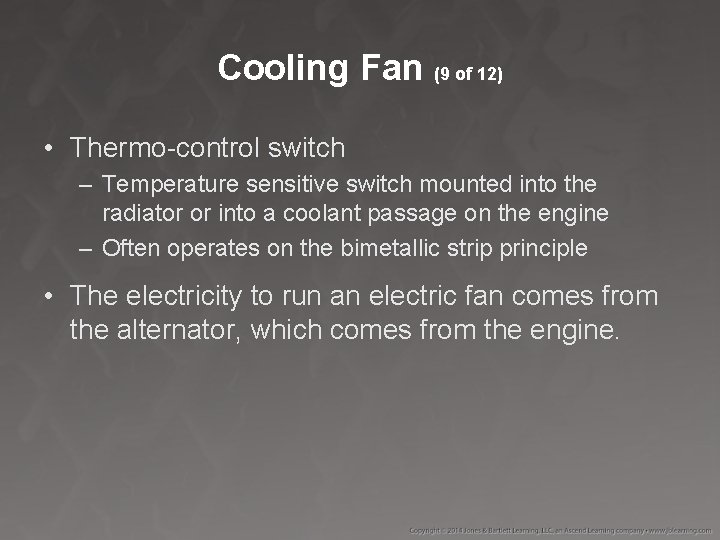
Cooling Fan (9 of 12) • Thermo-control switch – Temperature sensitive switch mounted into the radiator or into a coolant passage on the engine – Often operates on the bimetallic strip principle • The electricity to run an electric fan comes from the alternator, which comes from the engine.
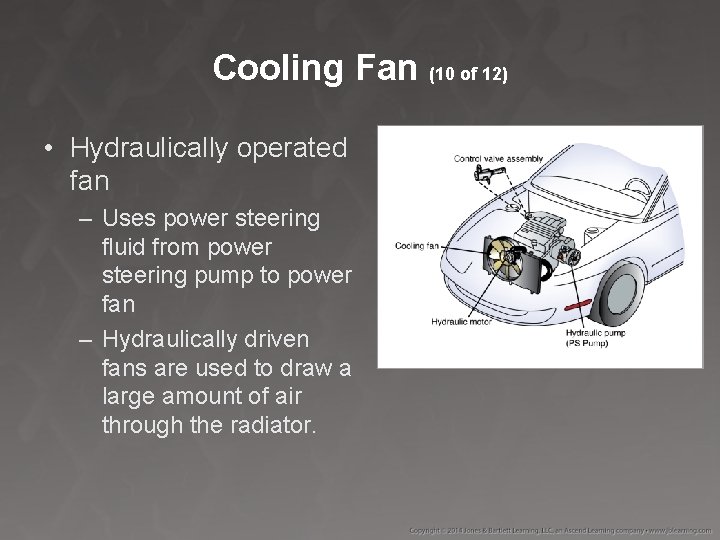
Cooling Fan (10 of 12) • Hydraulically operated fan – Uses power steering fluid from power steering pump to power fan – Hydraulically driven fans are used to draw a large amount of air through the radiator.
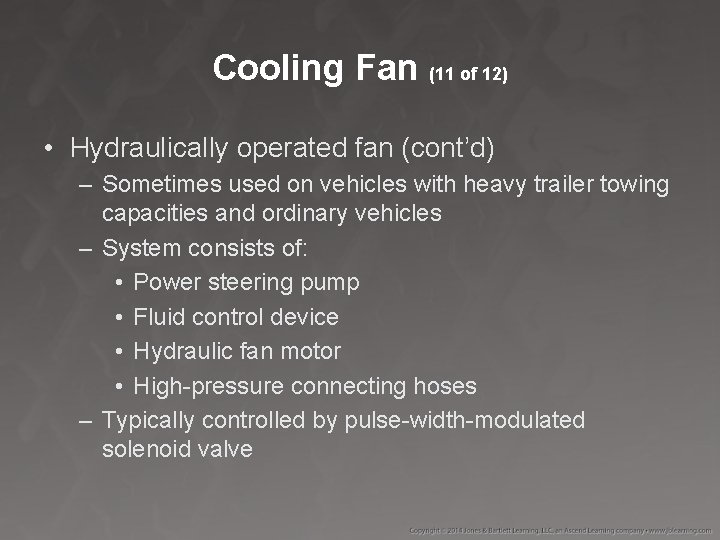
Cooling Fan (11 of 12) • Hydraulically operated fan (cont’d) – Sometimes used on vehicles with heavy trailer towing capacities and ordinary vehicles – System consists of: • Power steering pump • Fluid control device • Hydraulic fan motor • High-pressure connecting hoses – Typically controlled by pulse-width-modulated solenoid valve
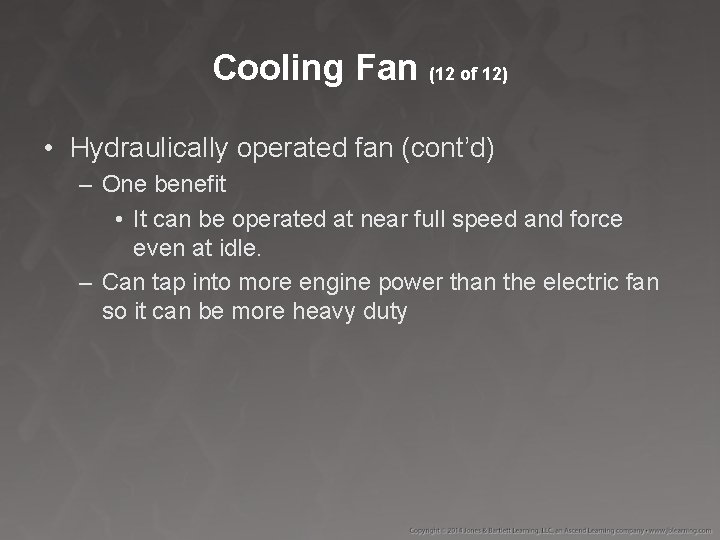
Cooling Fan (12 of 12) • Hydraulically operated fan (cont’d) – One benefit • It can be operated at near full speed and force even at idle. – Can tap into more engine power than the electric fan so it can be more heavy duty
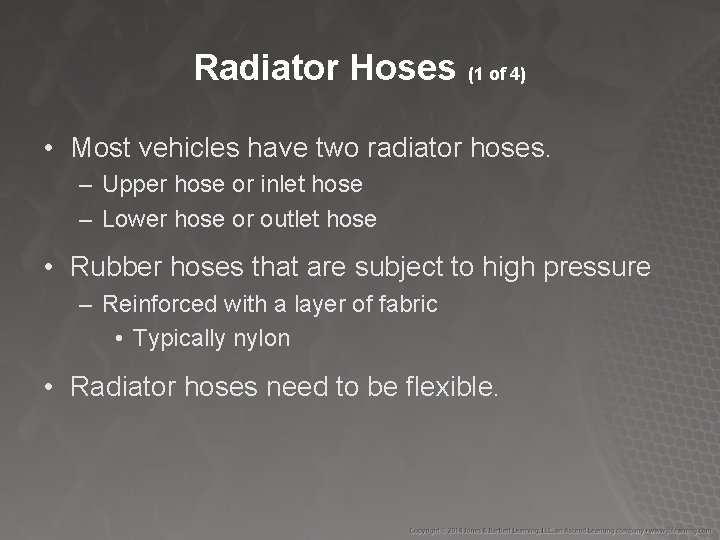
Radiator Hoses (1 of 4) • Most vehicles have two radiator hoses. – Upper hose or inlet hose – Lower hose or outlet hose • Rubber hoses that are subject to high pressure – Reinforced with a layer of fabric • Typically nylon • Radiator hoses need to be flexible.
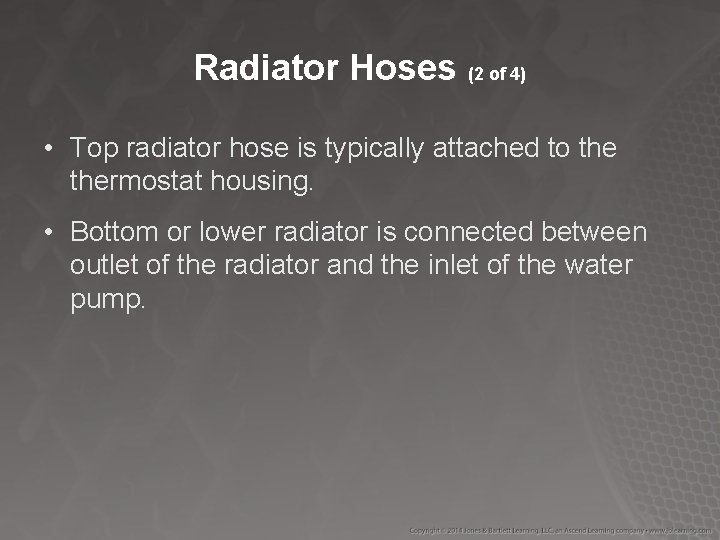
Radiator Hoses (2 of 4) • Top radiator hose is typically attached to thermostat housing. • Bottom or lower radiator is connected between outlet of the radiator and the inlet of the water pump.
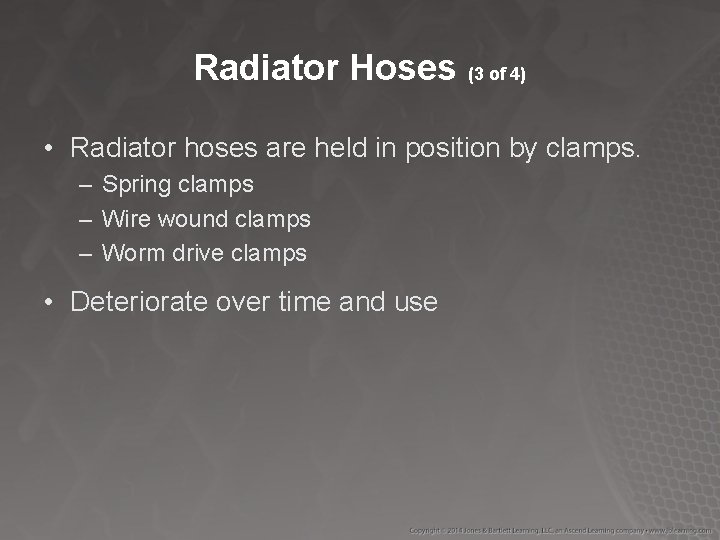
Radiator Hoses (3 of 4) • Radiator hoses are held in position by clamps. – Spring clamps – Wire wound clamps – Worm drive clamps • Deteriorate over time and use
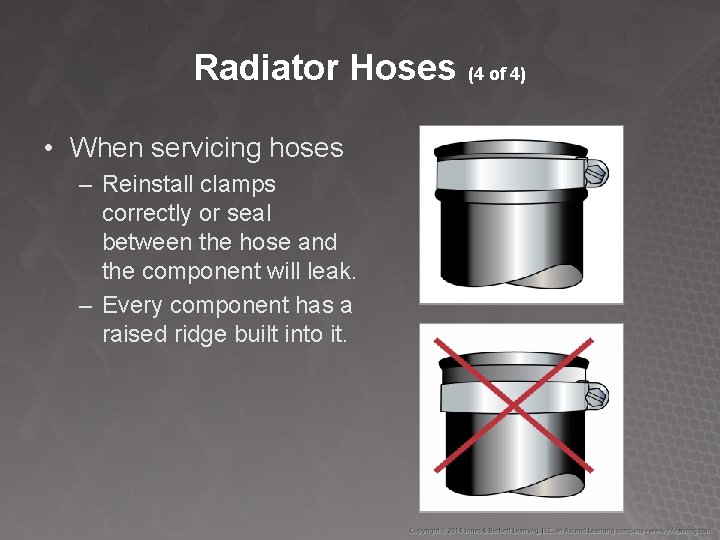
Radiator Hoses (4 of 4) • When servicing hoses – Reinstall clamps correctly or seal between the hose and the component will leak. – Every component has a raised ridge built into it.
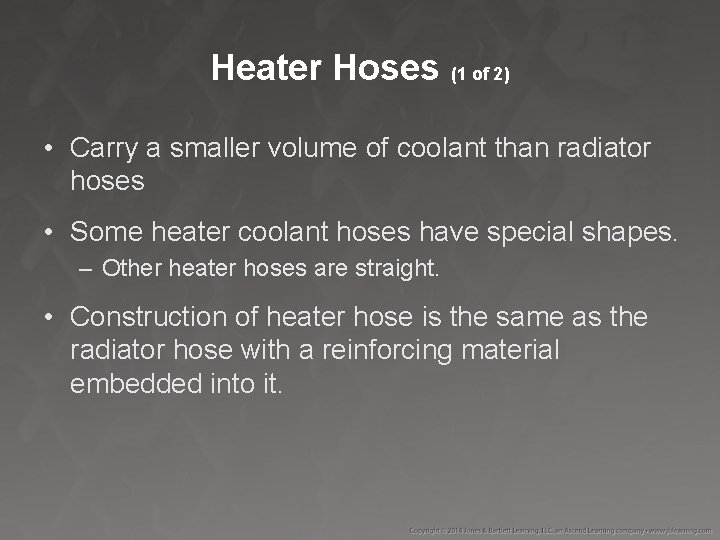
Heater Hoses (1 of 2) • Carry a smaller volume of coolant than radiator hoses • Some heater coolant hoses have special shapes. – Other heater hoses are straight. • Construction of heater hose is the same as the radiator hose with a reinforcing material embedded into it.
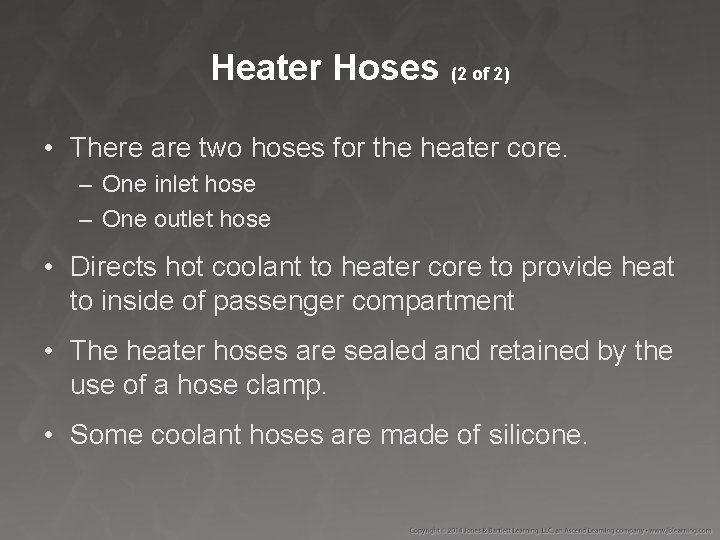
Heater Hoses (2 of 2) • There are two hoses for the heater core. – One inlet hose – One outlet hose • Directs hot coolant to heater core to provide heat to inside of passenger compartment • The heater hoses are sealed and retained by the use of a hose clamp. • Some coolant hoses are made of silicone.
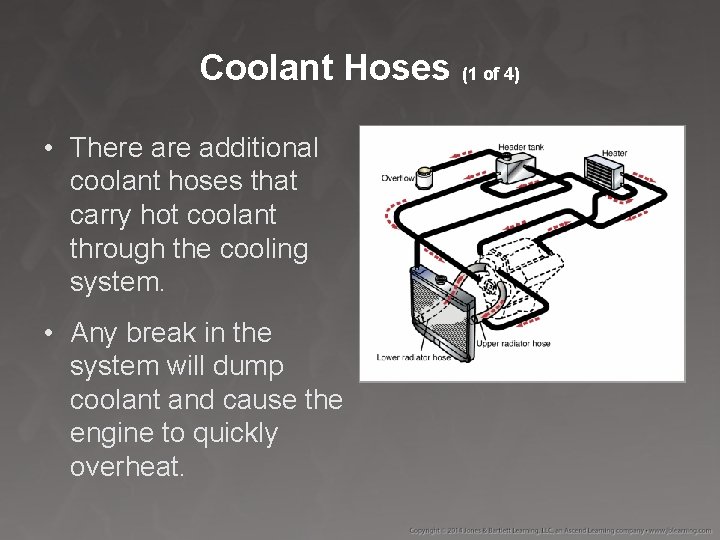
Coolant Hoses (1 of 4) • There additional coolant hoses that carry hot coolant through the cooling system. • Any break in the system will dump coolant and cause the engine to quickly overheat.
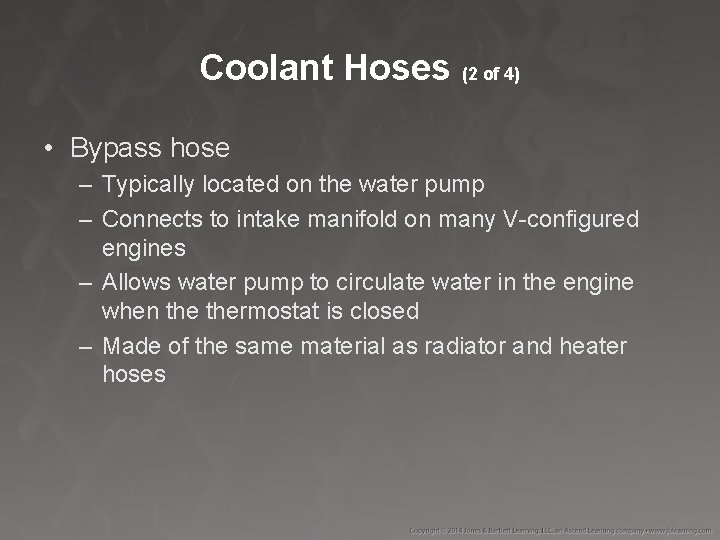
Coolant Hoses (2 of 4) • Bypass hose – Typically located on the water pump – Connects to intake manifold on many V-configured engines – Allows water pump to circulate water in the engine when thermostat is closed – Made of the same material as radiator and heater hoses
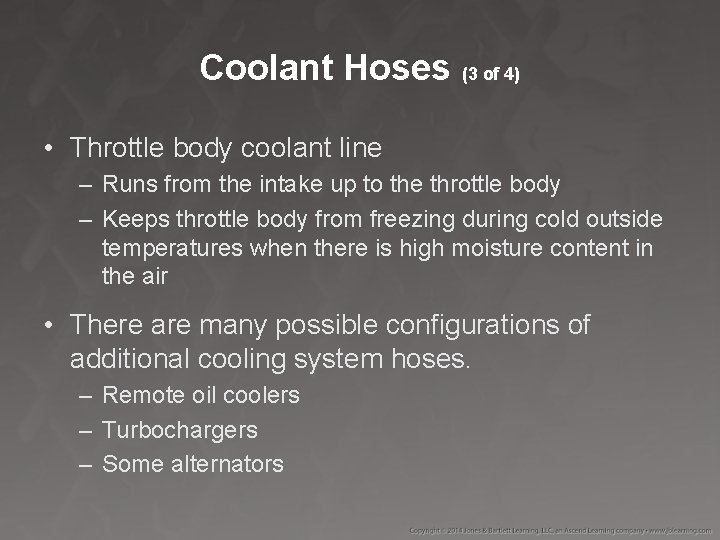
Coolant Hoses (3 of 4) • Throttle body coolant line – Runs from the intake up to the throttle body – Keeps throttle body from freezing during cold outside temperatures when there is high moisture content in the air • There are many possible configurations of additional cooling system hoses. – Remote oil coolers – Turbochargers – Some alternators
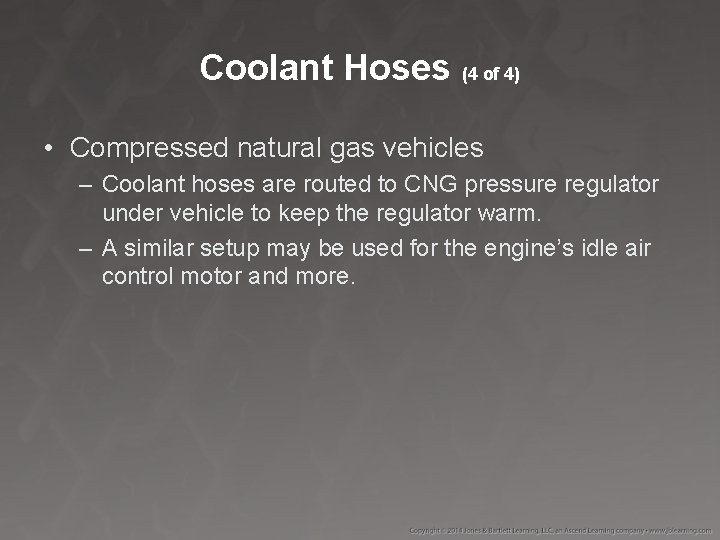
Coolant Hoses (4 of 4) • Compressed natural gas vehicles – Coolant hoses are routed to CNG pressure regulator under vehicle to keep the regulator warm. – A similar setup may be used for the engine’s idle air control motor and more.
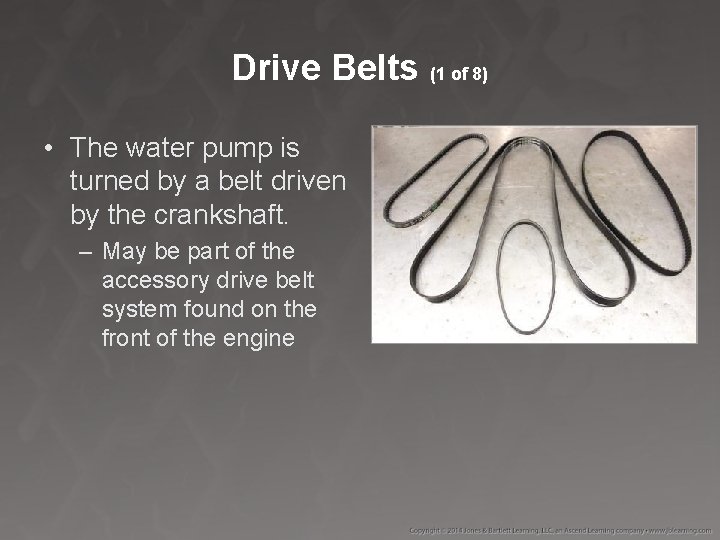
Drive Belts (1 of 8) • The water pump is turned by a belt driven by the crankshaft. – May be part of the accessory drive belt system found on the front of the engine
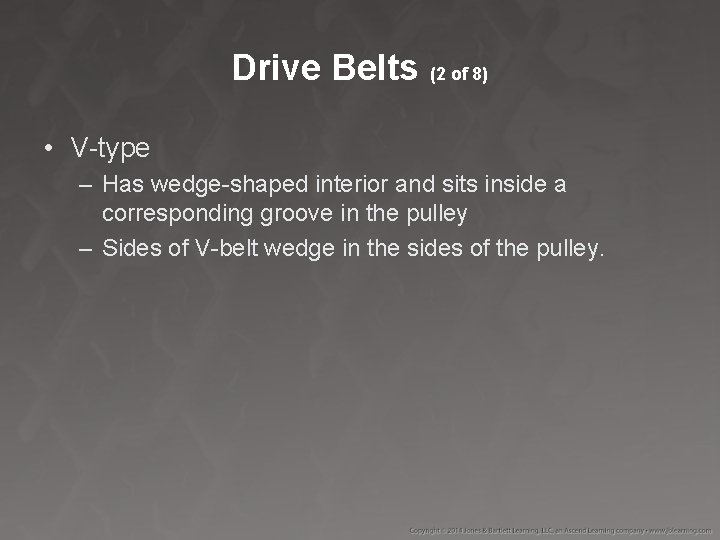
Drive Belts (2 of 8) • V-type – Has wedge-shaped interior and sits inside a corresponding groove in the pulley – Sides of V-belt wedge in the sides of the pulley.
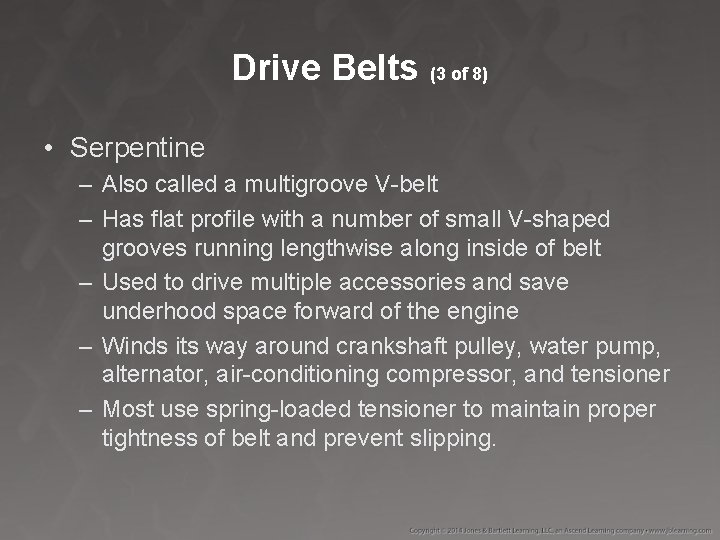
Drive Belts (3 of 8) • Serpentine – Also called a multigroove V-belt – Has flat profile with a number of small V-shaped grooves running lengthwise along inside of belt – Used to drive multiple accessories and save underhood space forward of the engine – Winds its way around crankshaft pulley, water pump, alternator, air-conditioning compressor, and tensioner – Most use spring-loaded tensioner to maintain proper tightness of belt and prevent slipping.
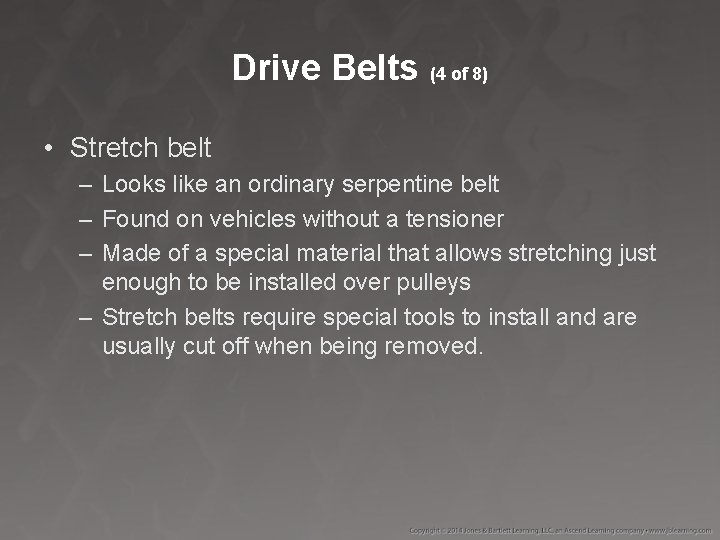
Drive Belts (4 of 8) • Stretch belt – Looks like an ordinary serpentine belt – Found on vehicles without a tensioner – Made of a special material that allows stretching just enough to be installed over pulleys – Stretch belts require special tools to install and are usually cut off when being removed.
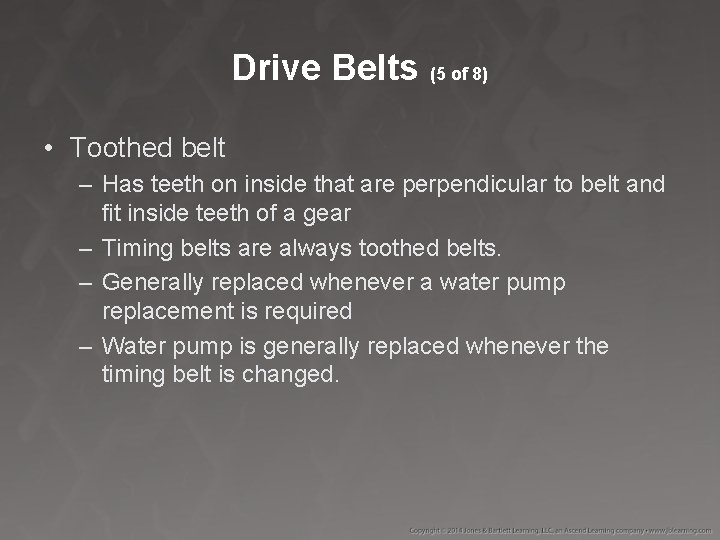
Drive Belts (5 of 8) • Toothed belt – Has teeth on inside that are perpendicular to belt and fit inside teeth of a gear – Timing belts are always toothed belts. – Generally replaced whenever a water pump replacement is required – Water pump is generally replaced whenever the timing belt is changed.
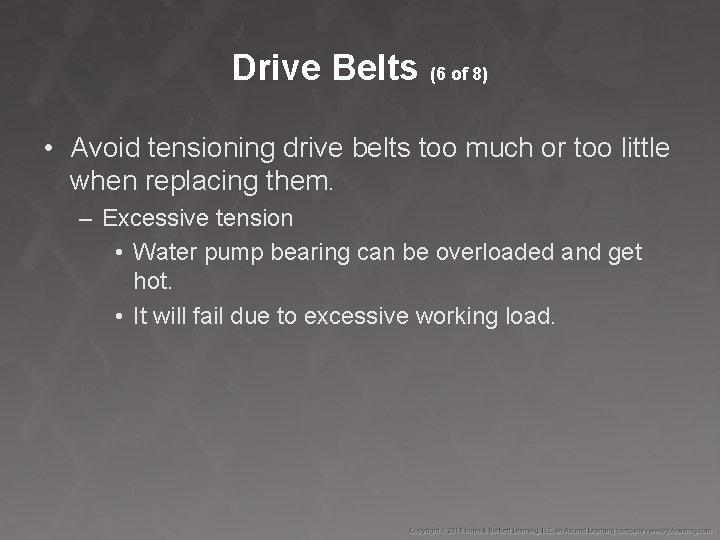
Drive Belts (6 of 8) • Avoid tensioning drive belts too much or too little when replacing them. – Excessive tension • Water pump bearing can be overloaded and get hot. • It will fail due to excessive working load.
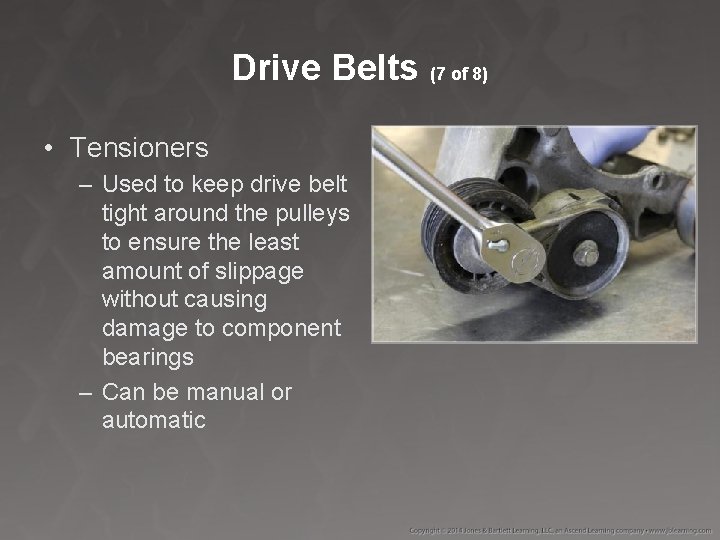
Drive Belts (7 of 8) • Tensioners – Used to keep drive belt tight around the pulleys to ensure the least amount of slippage without causing damage to component bearings – Can be manual or automatic
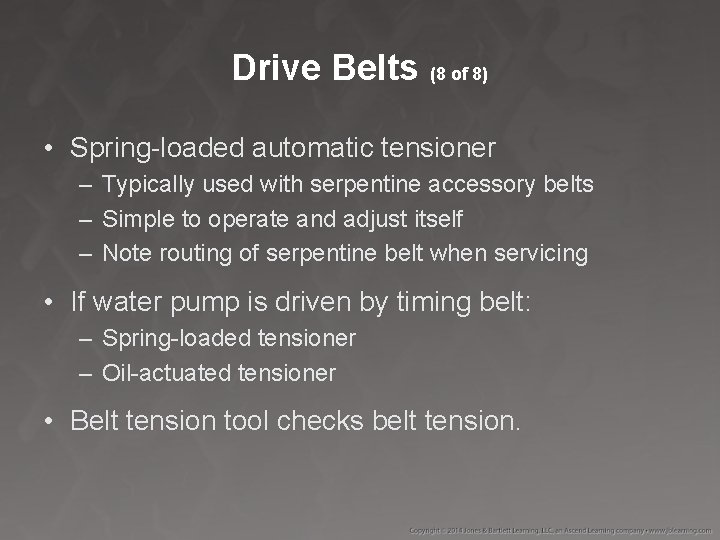
Drive Belts (8 of 8) • Spring-loaded automatic tensioner – Typically used with serpentine accessory belts – Simple to operate and adjust itself – Note routing of serpentine belt when servicing • If water pump is driven by timing belt: – Spring-loaded tensioner – Oil-actuated tensioner • Belt tension tool checks belt tension.
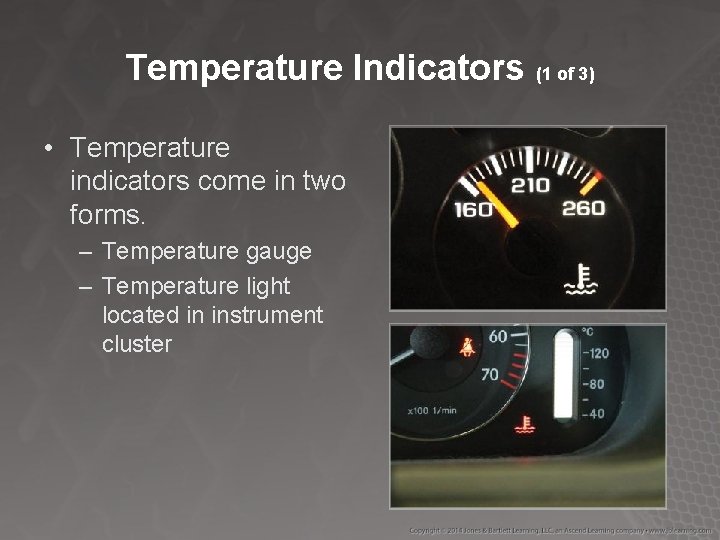
Temperature Indicators (1 of 3) • Temperature indicators come in two forms. – Temperature gauge – Temperature light located in instrument cluster
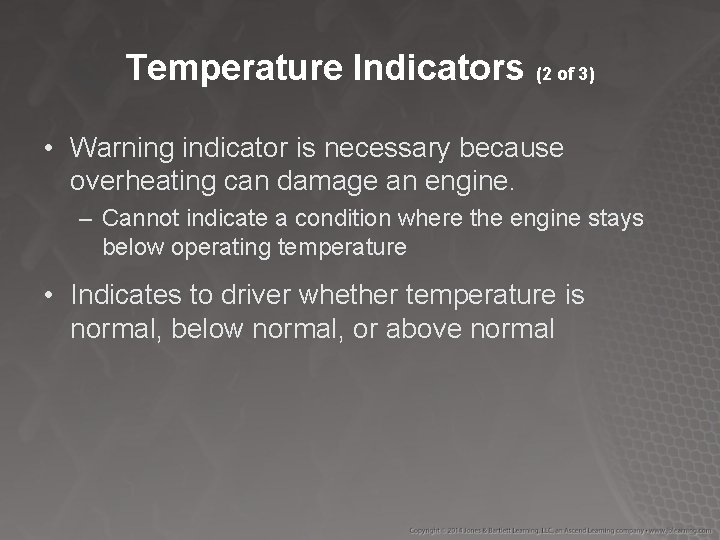
Temperature Indicators (2 of 3) • Warning indicator is necessary because overheating can damage an engine. – Cannot indicate a condition where the engine stays below operating temperature • Indicates to driver whether temperature is normal, below normal, or above normal
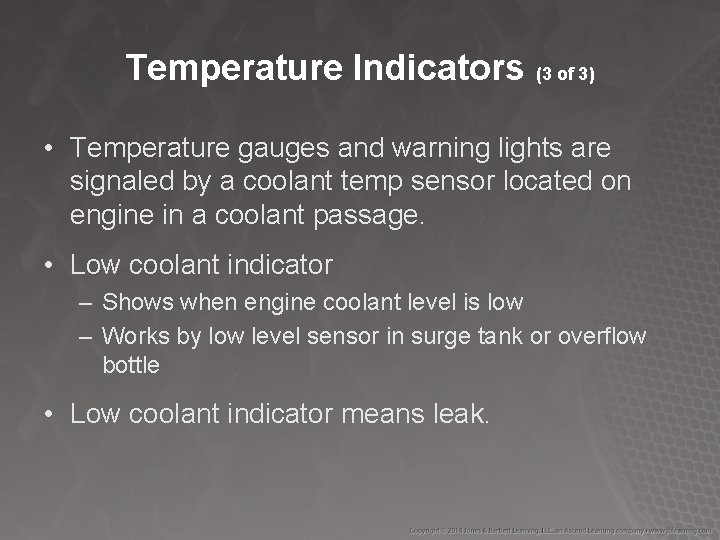
Temperature Indicators (3 of 3) • Temperature gauges and warning lights are signaled by a coolant temp sensor located on engine in a coolant passage. • Low coolant indicator – Shows when engine coolant level is low – Works by low level sensor in surge tank or overflow bottle • Low coolant indicator means leak.
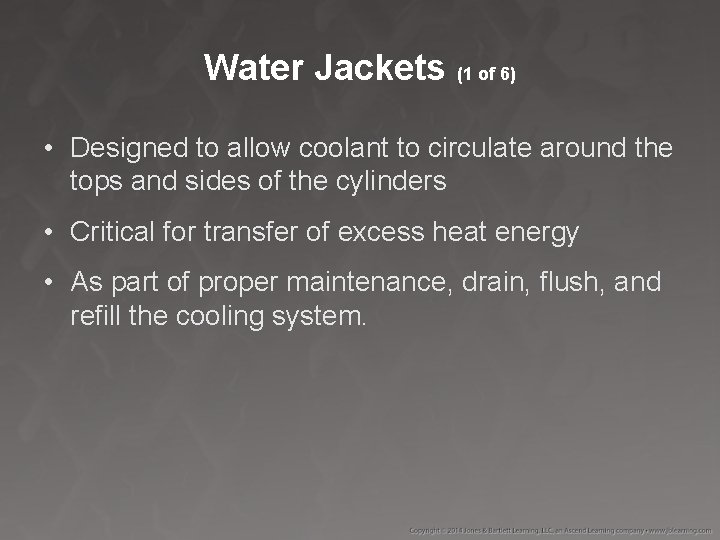
Water Jackets (1 of 6) • Designed to allow coolant to circulate around the tops and sides of the cylinders • Critical for transfer of excess heat energy • As part of proper maintenance, drain, flush, and refill the cooling system.
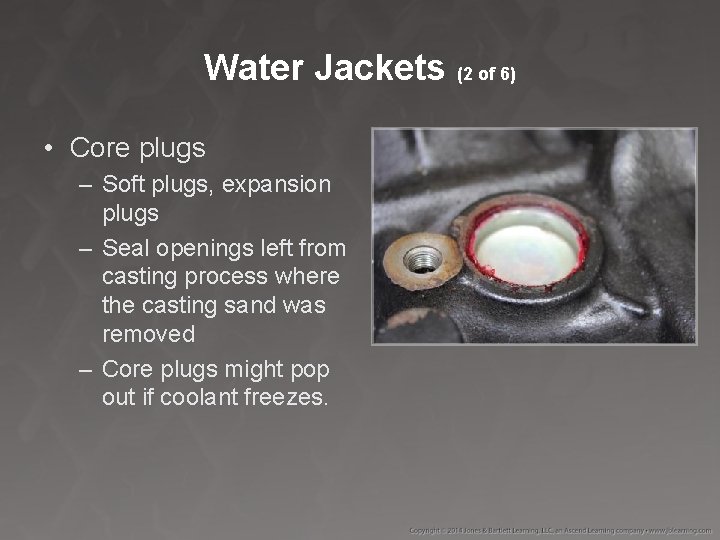
Water Jackets (2 of 6) • Core plugs – Soft plugs, expansion plugs – Seal openings left from casting process where the casting sand was removed – Core plugs might pop out if coolant freezes.
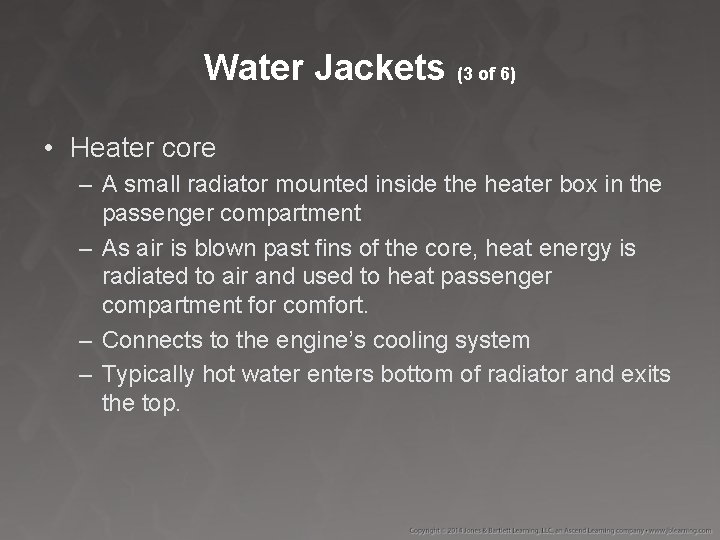
Water Jackets (3 of 6) • Heater core – A small radiator mounted inside the heater box in the passenger compartment – As air is blown past fins of the core, heat energy is radiated to air and used to heat passenger compartment for comfort. – Connects to the engine’s cooling system – Typically hot water enters bottom of radiator and exits the top.
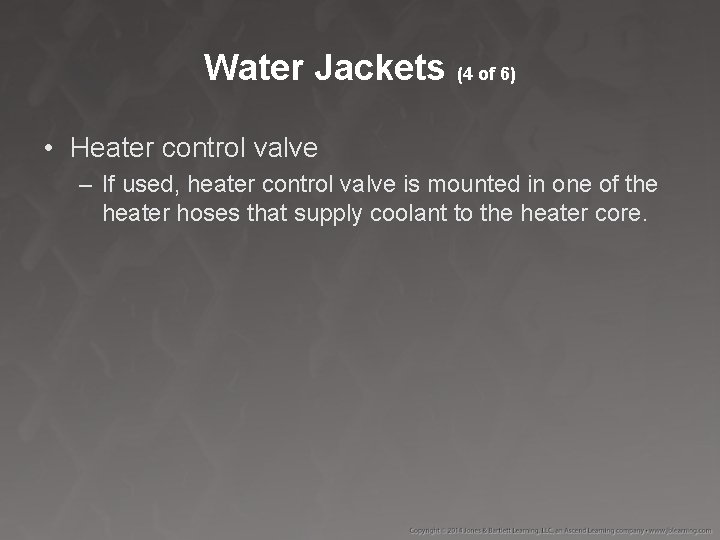
Water Jackets (4 of 6) • Heater control valve – If used, heater control valve is mounted in one of the heater hoses that supply coolant to the heater core.
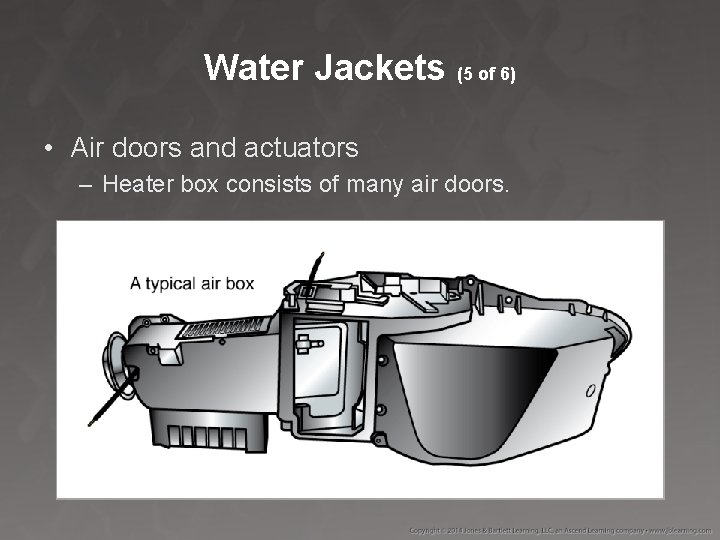
Water Jackets (5 of 6) • Air doors and actuators – Heater box consists of many air doors.
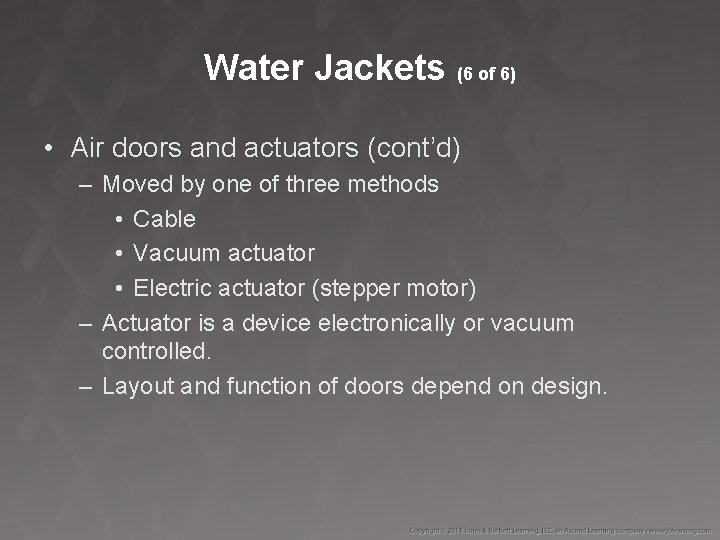
Water Jackets (6 of 6) • Air doors and actuators (cont’d) – Moved by one of three methods • Cable • Vacuum actuator • Electric actuator (stepper motor) – Actuator is a device electronically or vacuum controlled. – Layout and function of doors depend on design.
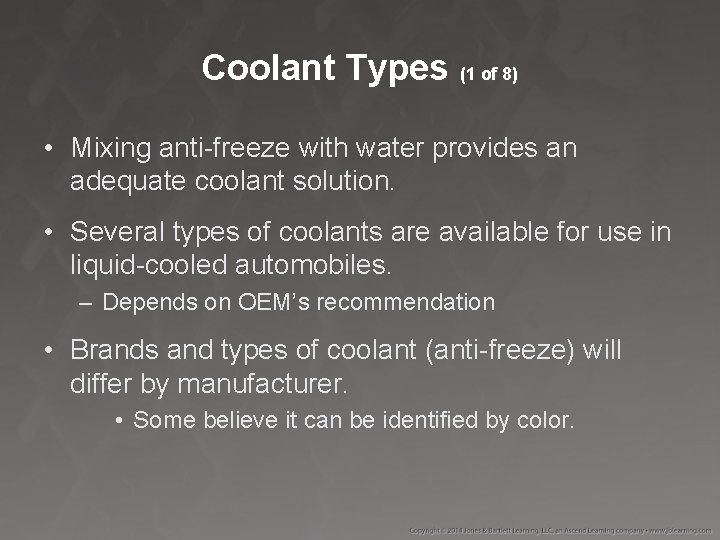
Coolant Types (1 of 8) • Mixing anti-freeze with water provides an adequate coolant solution. • Several types of coolants are available for use in liquid-cooled automobiles. – Depends on OEM’s recommendation • Brands and types of coolant (anti-freeze) will differ by manufacturer. • Some believe it can be identified by color.
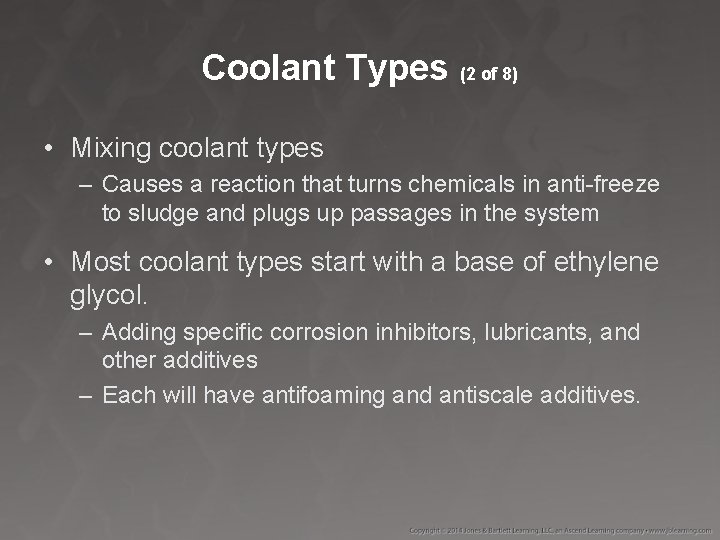
Coolant Types (2 of 8) • Mixing coolant types – Causes a reaction that turns chemicals in anti-freeze to sludge and plugs up passages in the system • Most coolant types start with a base of ethylene glycol. – Adding specific corrosion inhibitors, lubricants, and other additives – Each will have antifoaming and antiscale additives.
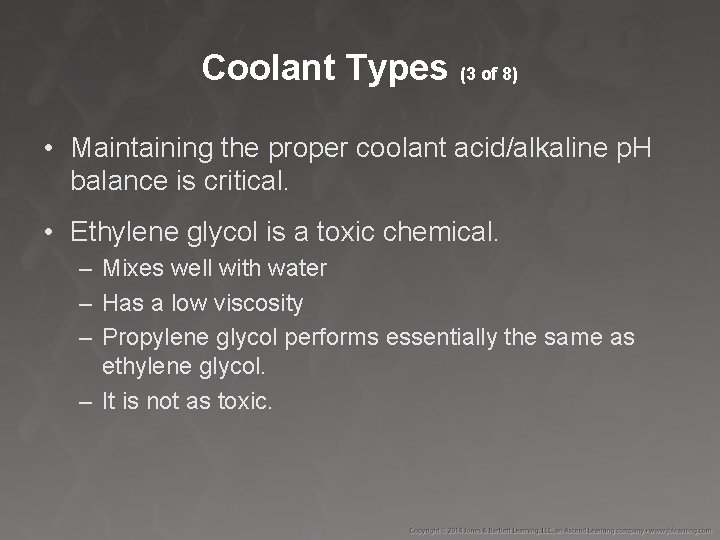
Coolant Types (3 of 8) • Maintaining the proper coolant acid/alkaline p. H balance is critical. • Ethylene glycol is a toxic chemical. – Mixes well with water – Has a low viscosity – Propylene glycol performs essentially the same as ethylene glycol. – It is not as toxic.
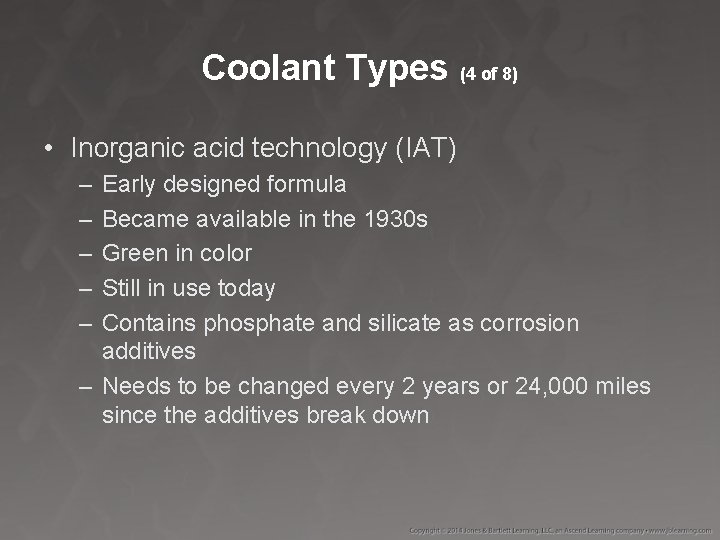
Coolant Types (4 of 8) • Inorganic acid technology (IAT) – – – Early designed formula Became available in the 1930 s Green in color Still in use today Contains phosphate and silicate as corrosion additives – Needs to be changed every 2 years or 24, 000 miles since the additives break down
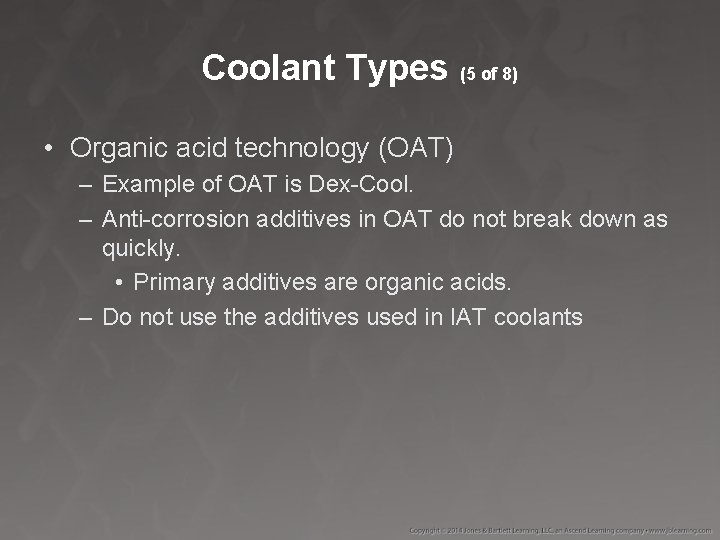
Coolant Types (5 of 8) • Organic acid technology (OAT) – Example of OAT is Dex-Cool. – Anti-corrosion additives in OAT do not break down as quickly. • Primary additives are organic acids. – Do not use the additives used in IAT coolants
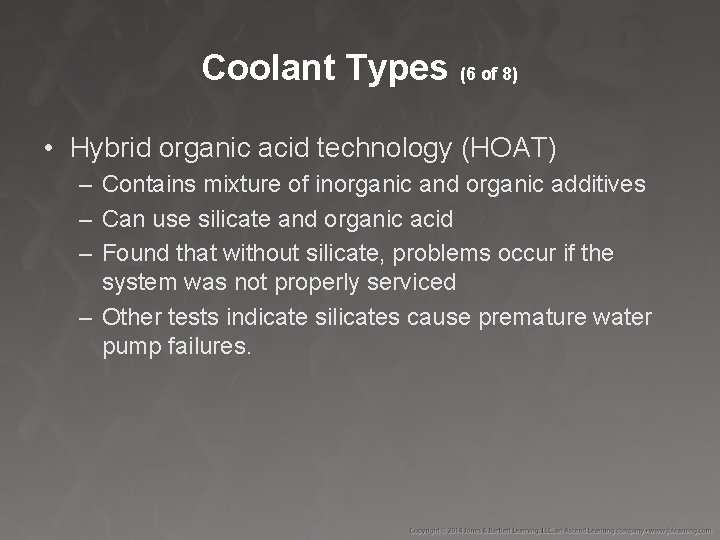
Coolant Types (6 of 8) • Hybrid organic acid technology (HOAT) – Contains mixture of inorganic and organic additives – Can use silicate and organic acid – Found that without silicate, problems occur if the system was not properly serviced – Other tests indicate silicates cause premature water pump failures.
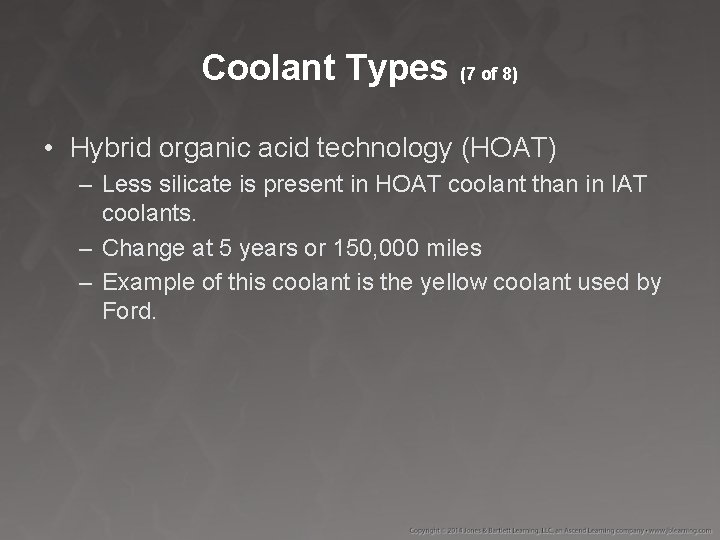
Coolant Types (7 of 8) • Hybrid organic acid technology (HOAT) – Less silicate is present in HOAT coolant than in IAT coolants. – Change at 5 years or 150, 000 miles – Example of this coolant is the yellow coolant used by Ford.
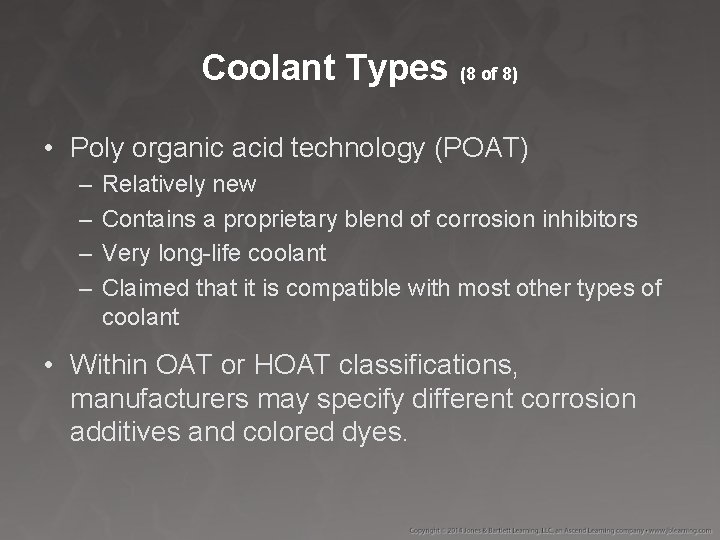
Coolant Types (8 of 8) • Poly organic acid technology (POAT) – – Relatively new Contains a proprietary blend of corrosion inhibitors Very long-life coolant Claimed that it is compatible with most other types of coolant • Within OAT or HOAT classifications, manufacturers may specify different corrosion additives and colored dyes.
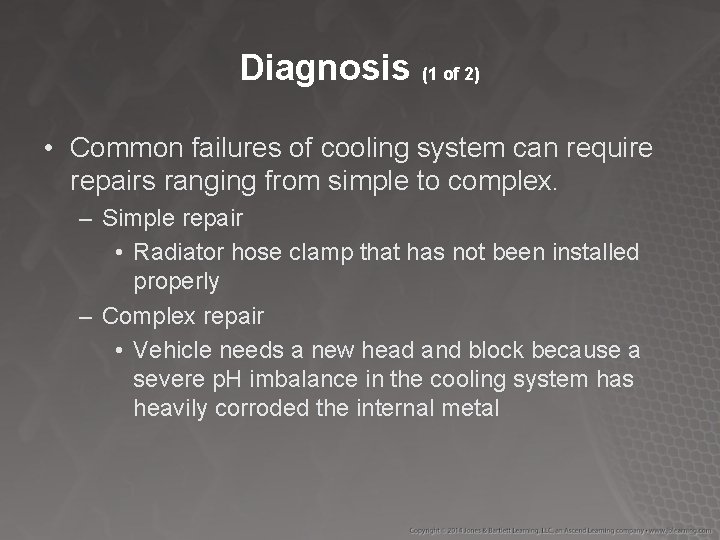
Diagnosis (1 of 2) • Common failures of cooling system can require repairs ranging from simple to complex. – Simple repair • Radiator hose clamp that has not been installed properly – Complex repair • Vehicle needs a new head and block because a severe p. H imbalance in the cooling system has heavily corroded the internal metal
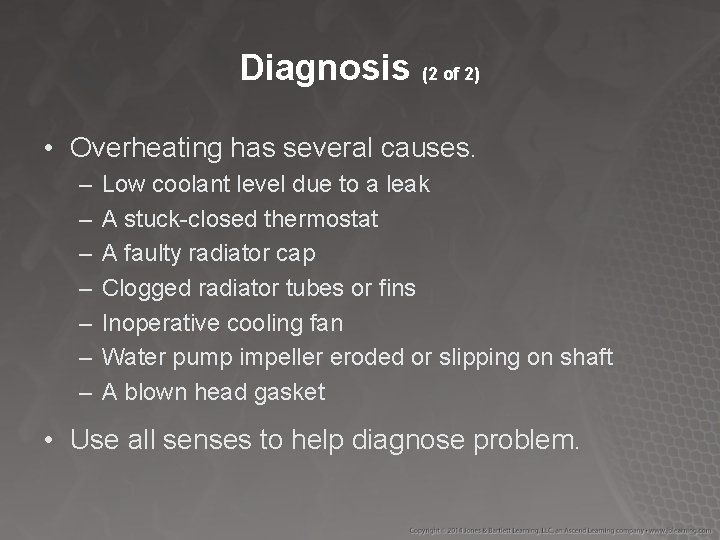
Diagnosis (2 of 2) • Overheating has several causes. – – – – Low coolant level due to a leak A stuck-closed thermostat A faulty radiator cap Clogged radiator tubes or fins Inoperative cooling fan Water pump impeller eroded or slipping on shaft A blown head gasket • Use all senses to help diagnose problem.
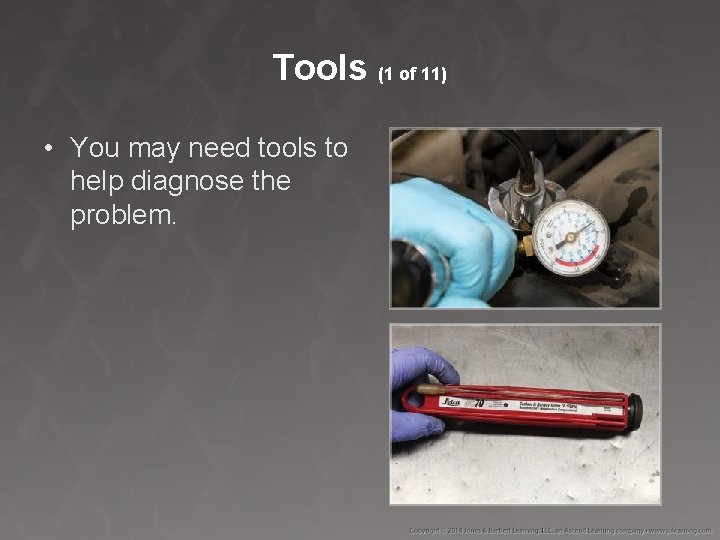
Tools (1 of 11) • You may need tools to help diagnose the problem.
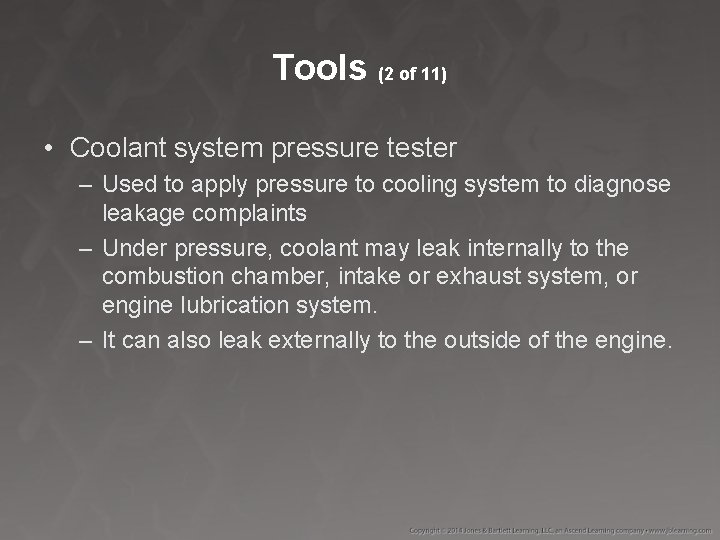
Tools (2 of 11) • Coolant system pressure tester – Used to apply pressure to cooling system to diagnose leakage complaints – Under pressure, coolant may leak internally to the combustion chamber, intake or exhaust system, or engine lubrication system. – It can also leak externally to the outside of the engine.
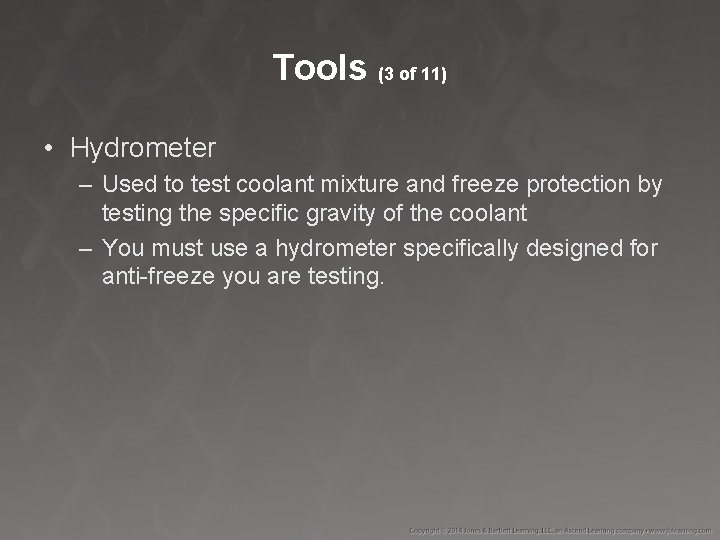
Tools (3 of 11) • Hydrometer – Used to test coolant mixture and freeze protection by testing the specific gravity of the coolant – You must use a hydrometer specifically designed for anti-freeze you are testing.
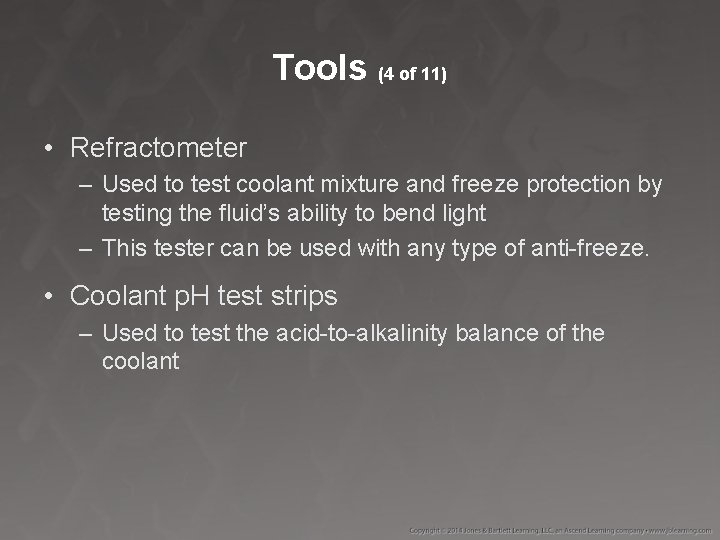
Tools (4 of 11) • Refractometer – Used to test coolant mixture and freeze protection by testing the fluid’s ability to bend light – This tester can be used with any type of anti-freeze. • Coolant p. H test strips – Used to test the acid-to-alkalinity balance of the coolant
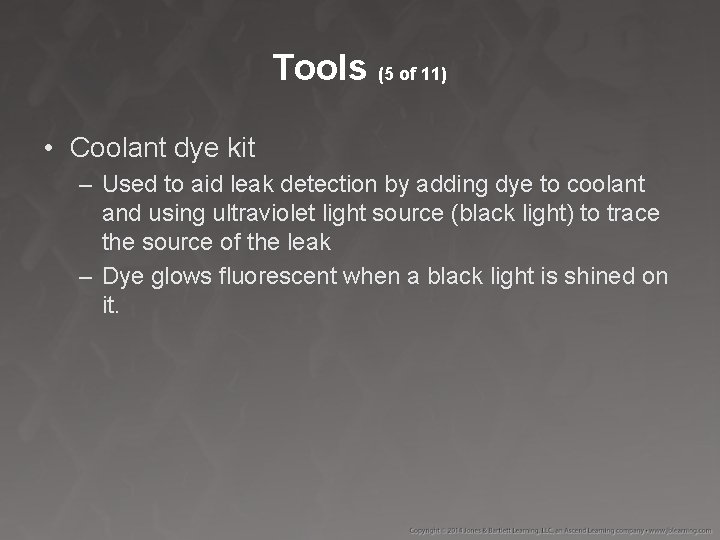
Tools (5 of 11) • Coolant dye kit – Used to aid leak detection by adding dye to coolant and using ultraviolet light source (black light) to trace the source of the leak – Dye glows fluorescent when a black light is shined on it.
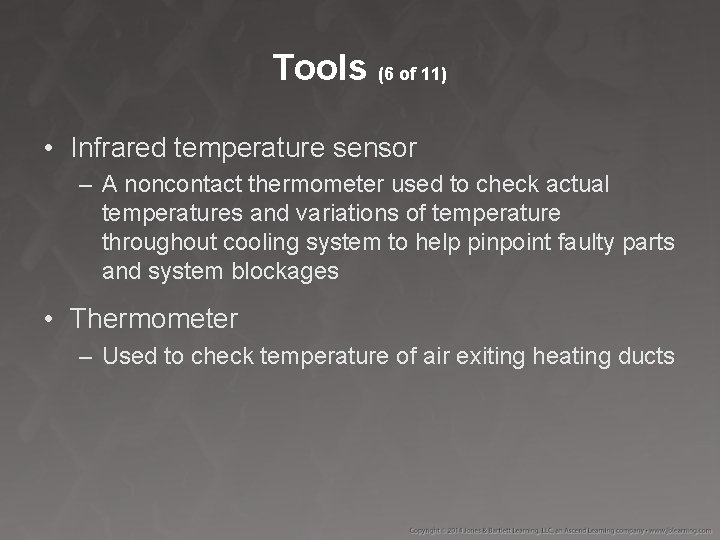
Tools (6 of 11) • Infrared temperature sensor – A noncontact thermometer used to check actual temperatures and variations of temperature throughout cooling system to help pinpoint faulty parts and system blockages • Thermometer – Used to check temperature of air exiting heating ducts
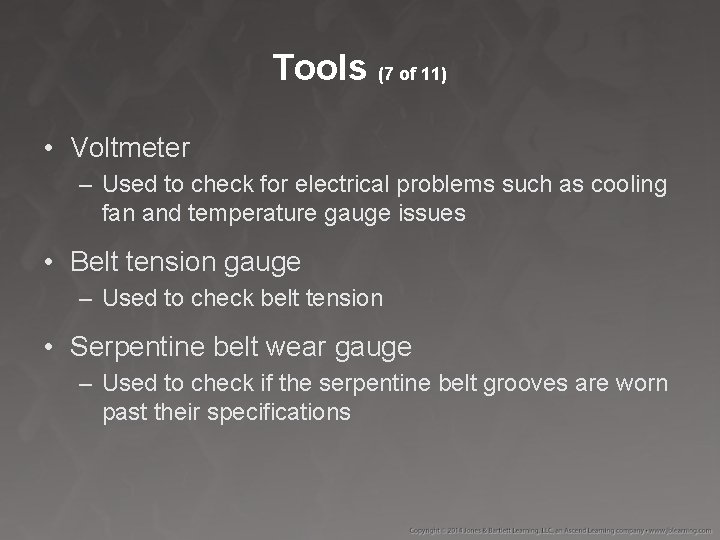
Tools (7 of 11) • Voltmeter – Used to check for electrical problems such as cooling fan and temperature gauge issues • Belt tension gauge – Used to check belt tension • Serpentine belt wear gauge – Used to check if the serpentine belt grooves are worn past their specifications
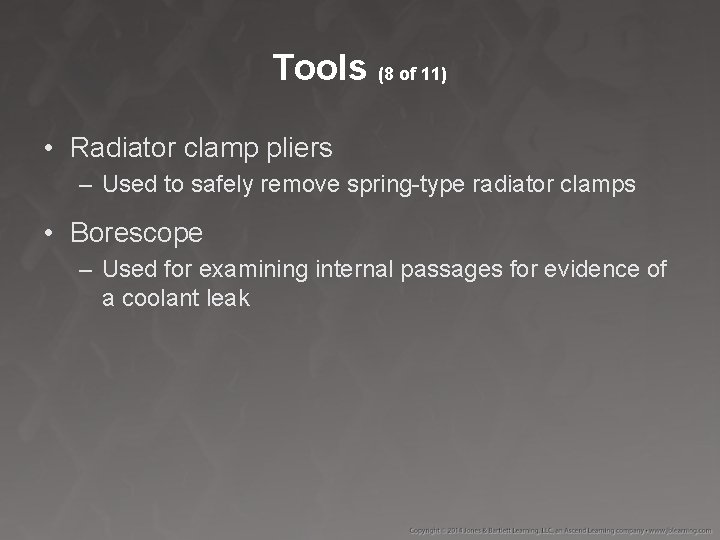
Tools (8 of 11) • Radiator clamp pliers – Used to safely remove spring-type radiator clamps • Borescope – Used for examining internal passages for evidence of a coolant leak
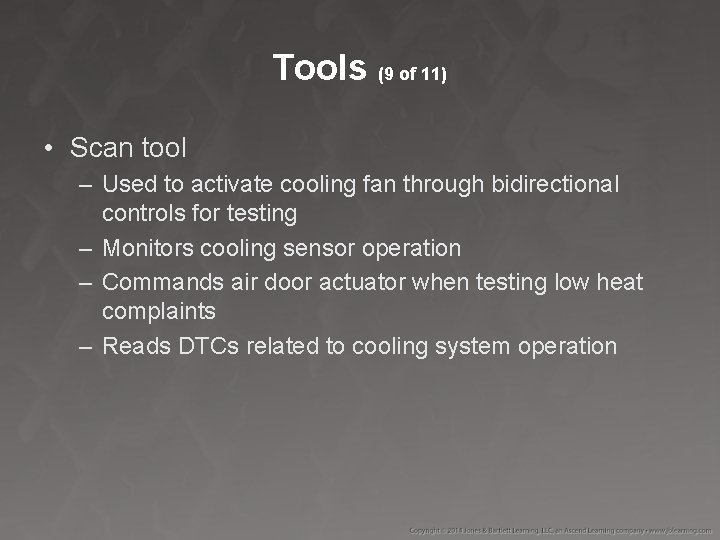
Tools (9 of 11) • Scan tool – Used to activate cooling fan through bidirectional controls for testing – Monitors cooling sensor operation – Commands air door actuator when testing low heat complaints – Reads DTCs related to cooling system operation
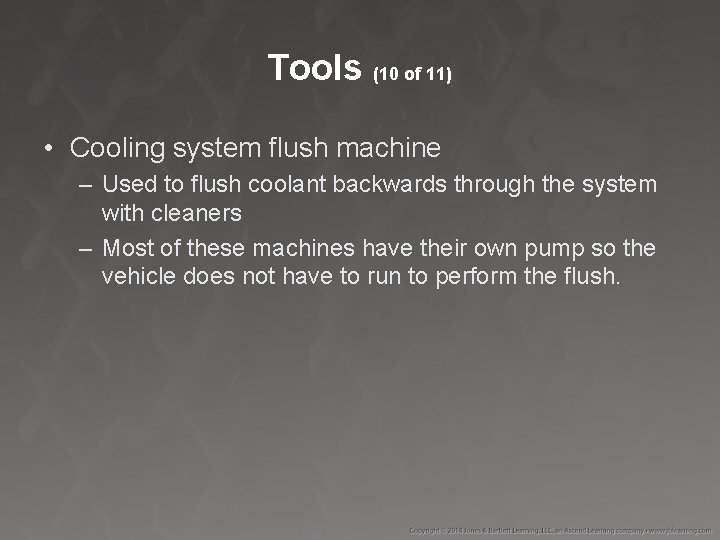
Tools (10 of 11) • Cooling system flush machine – Used to flush coolant backwards through the system with cleaners – Most of these machines have their own pump so the vehicle does not have to run to perform the flush.
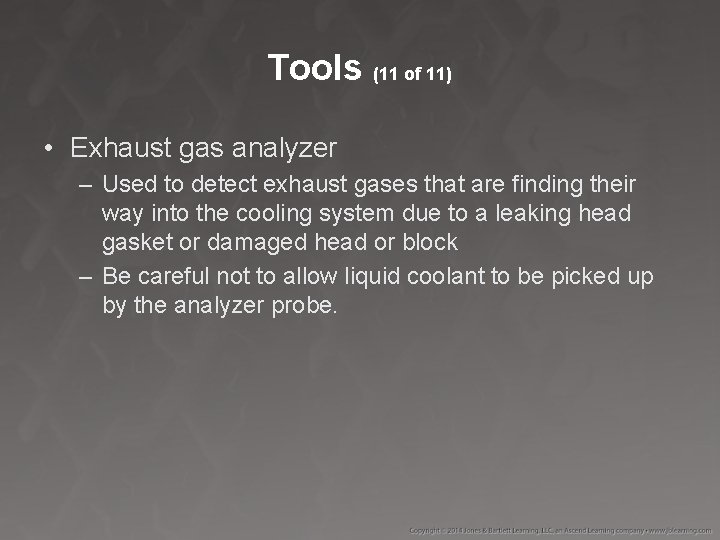
Tools (11 of 11) • Exhaust gas analyzer – Used to detect exhaust gases that are finding their way into the cooling system due to a leaking head gasket or damaged head or block – Be careful not to allow liquid coolant to be picked up by the analyzer probe.
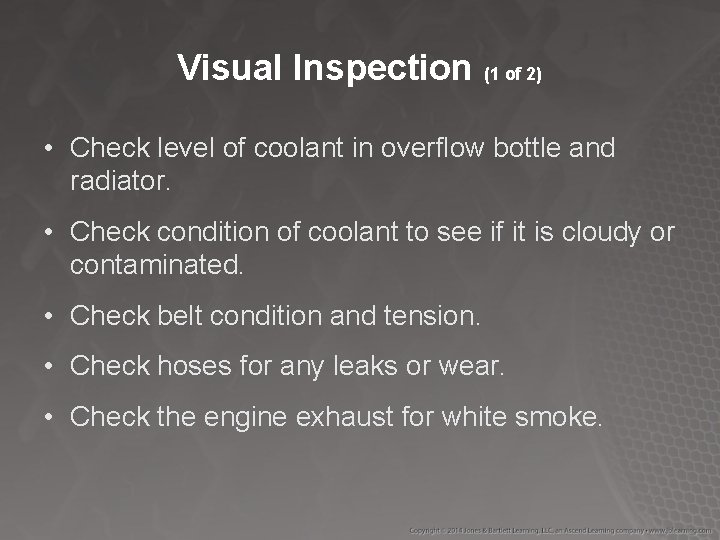
Visual Inspection (1 of 2) • Check level of coolant in overflow bottle and radiator. • Check condition of coolant to see if it is cloudy or contaminated. • Check belt condition and tension. • Check hoses for any leaks or wear. • Check the engine exhaust for white smoke.
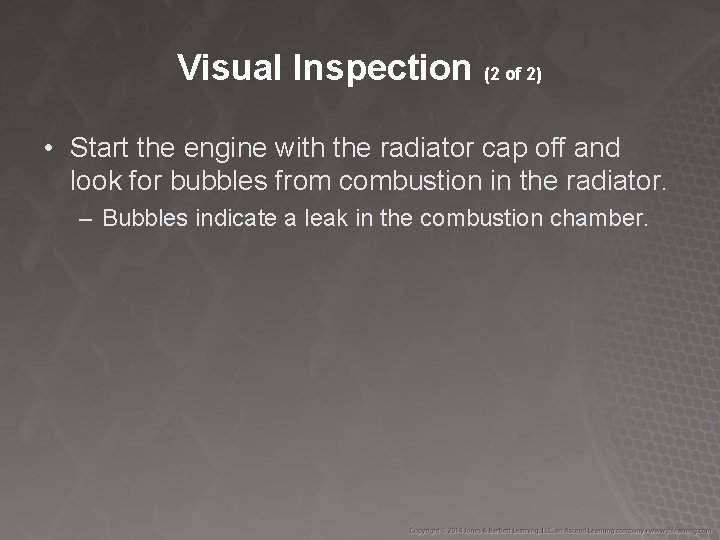
Visual Inspection (2 of 2) • Start the engine with the radiator cap off and look for bubbles from combustion in the radiator. – Bubbles indicate a leak in the combustion chamber.
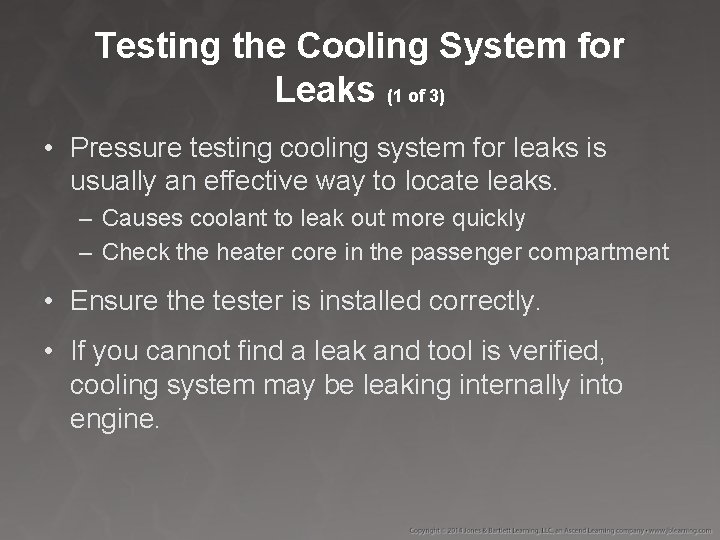
Testing the Cooling System for Leaks (1 of 3) • Pressure testing cooling system for leaks is usually an effective way to locate leaks. – Causes coolant to leak out more quickly – Check the heater core in the passenger compartment • Ensure the tester is installed correctly. • If you cannot find a leak and tool is verified, cooling system may be leaking internally into engine.

Testing the Cooling System for Leaks (2 of 3) • Check engine oil for evidence of coolant. • If coolant is not leaking into oil, it could be leaking into the cylinder. • Normally engine should be off when carrying out any visual inspection of system. – Possible that the leak only occurs when the engine is running

Testing the Cooling System for Leaks (3 of 3) • If you do have to run the engine after the tester has been installed and pressurized: – Watch pressure gauge. – Keep away from any rotating or hot parts. • Pressure test the radiator cap. • A pressure tester is normally used to test cooling system for both internal and external leaks.
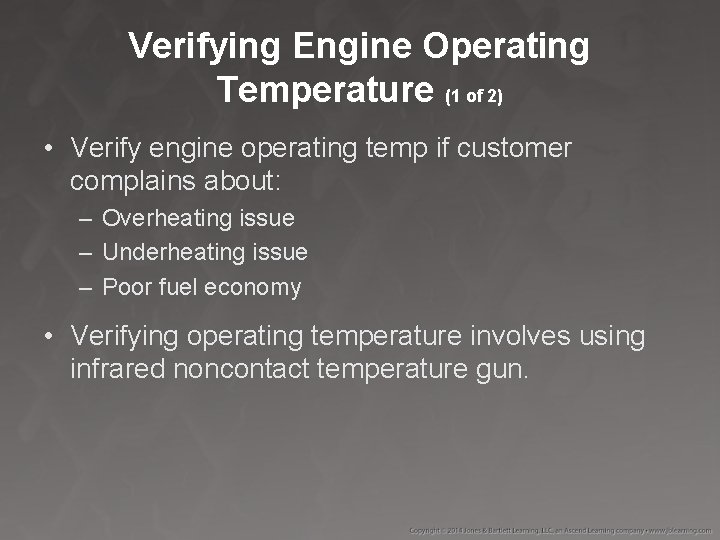
Verifying Engine Operating Temperature (1 of 2) • Verify engine operating temp if customer complains about: – Overheating issue – Underheating issue – Poor fuel economy • Verifying operating temperature involves using infrared noncontact temperature gun.
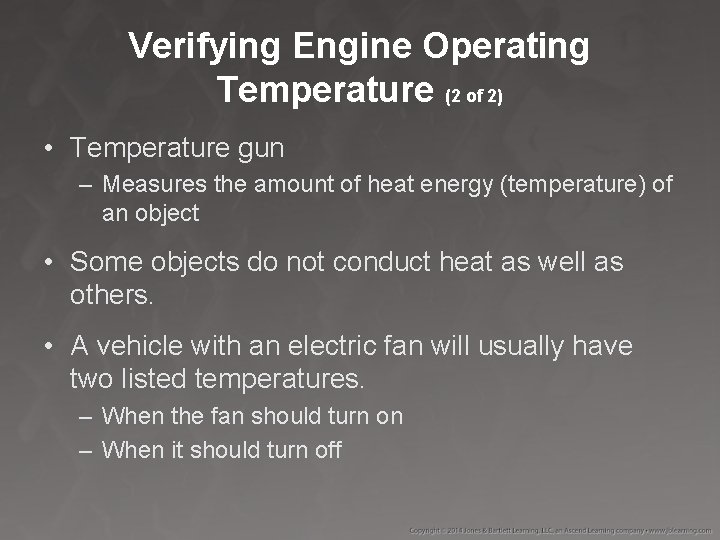
Verifying Engine Operating Temperature (2 of 2) • Temperature gun – Measures the amount of heat energy (temperature) of an object • Some objects do not conduct heat as well as others. • A vehicle with an electric fan will usually have two listed temperatures. – When the fan should turn on – When it should turn off
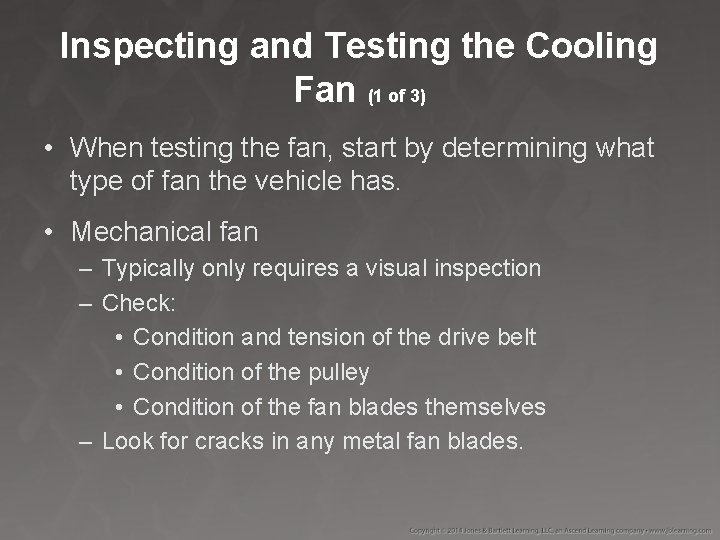
Inspecting and Testing the Cooling Fan (1 of 3) • When testing the fan, start by determining what type of fan the vehicle has. • Mechanical fan – Typically only requires a visual inspection – Check: • Condition and tension of the drive belt • Condition of the pulley • Condition of the fan blades themselves – Look for cracks in any metal fan blades.

Inspecting and Testing the Cooling Fan (2 of 3) • Clutch fan – Inspected in the same way as mechanical fan – Clutch also needs to be inspected. – With the engine off, the bearings in the fan clutch can be tested. – Some manufacturers specify placing cardboard in front of the radiator to block most of it.
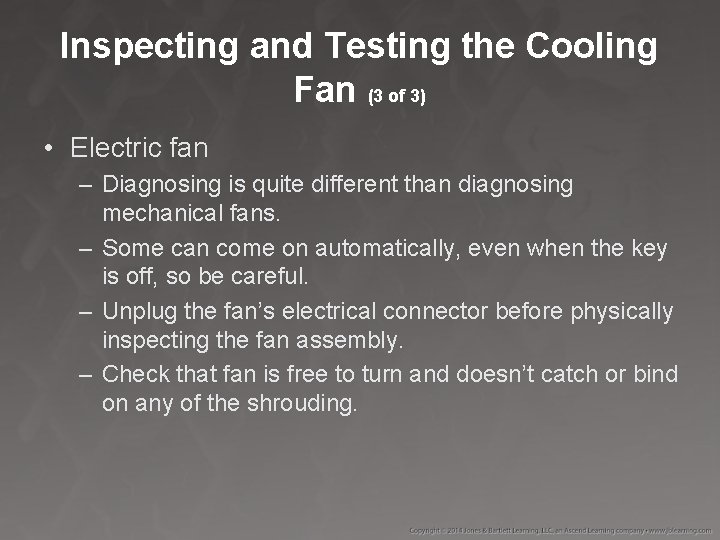
Inspecting and Testing the Cooling Fan (3 of 3) • Electric fan – Diagnosing is quite different than diagnosing mechanical fans. – Some can come on automatically, even when the key is off, so be careful. – Unplug the fan’s electrical connector before physically inspecting the fan assembly. – Check that fan is free to turn and doesn’t catch or bind on any of the shrouding.
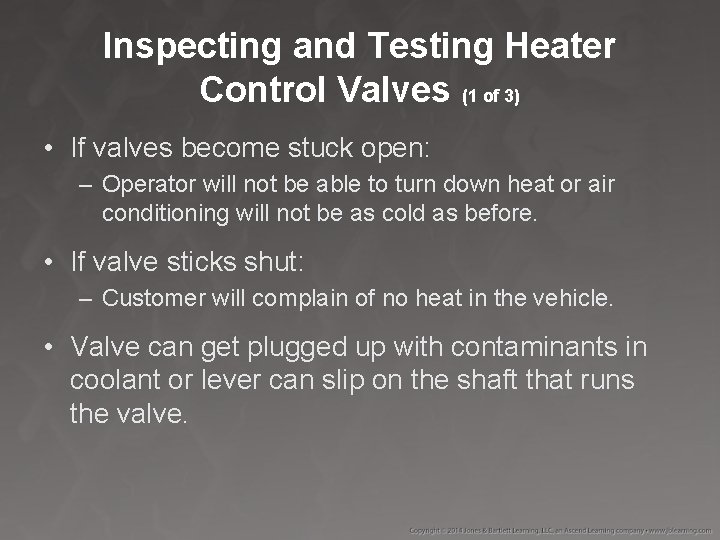
Inspecting and Testing Heater Control Valves (1 of 3) • If valves become stuck open: – Operator will not be able to turn down heat or air conditioning will not be as cold as before. • If valve sticks shut: – Customer will complain of no heat in the vehicle. • Valve can get plugged up with contaminants in coolant or lever can slip on the shaft that runs the valve.
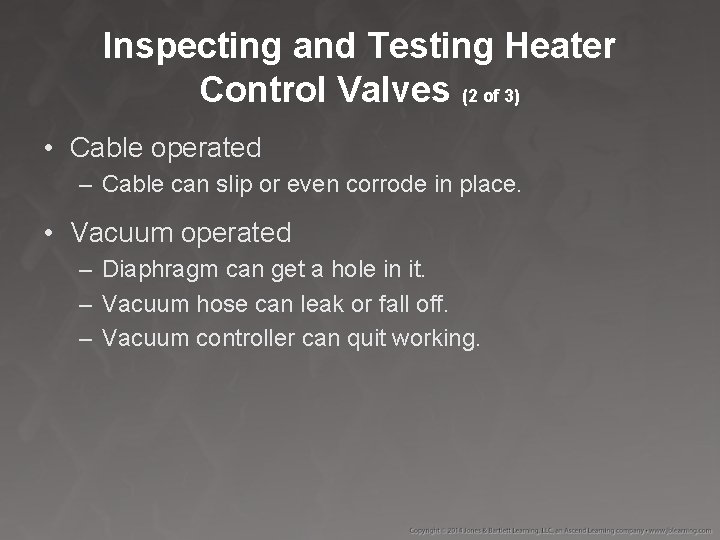
Inspecting and Testing Heater Control Valves (2 of 3) • Cable operated – Cable can slip or even corrode in place. • Vacuum operated – Diaphragm can get a hole in it. – Vacuum hose can leak or fall off. – Vacuum controller can quit working.
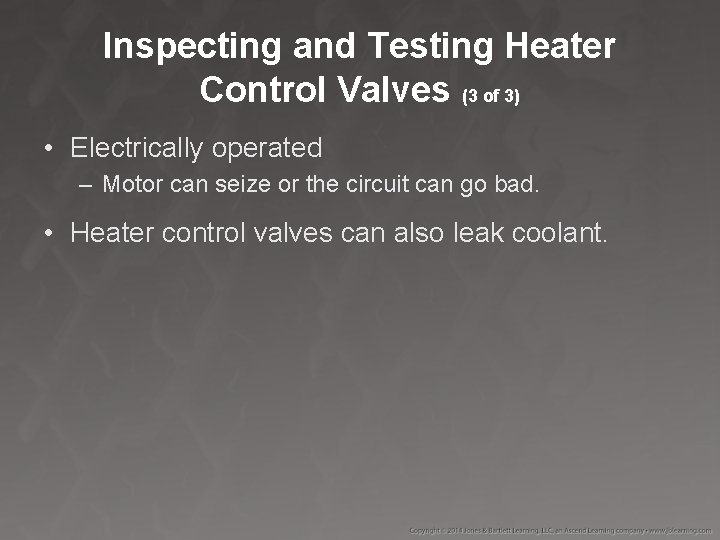
Inspecting and Testing Heater Control Valves (3 of 3) • Electrically operated – Motor can seize or the circuit can go bad. • Heater control valves can also leak coolant.
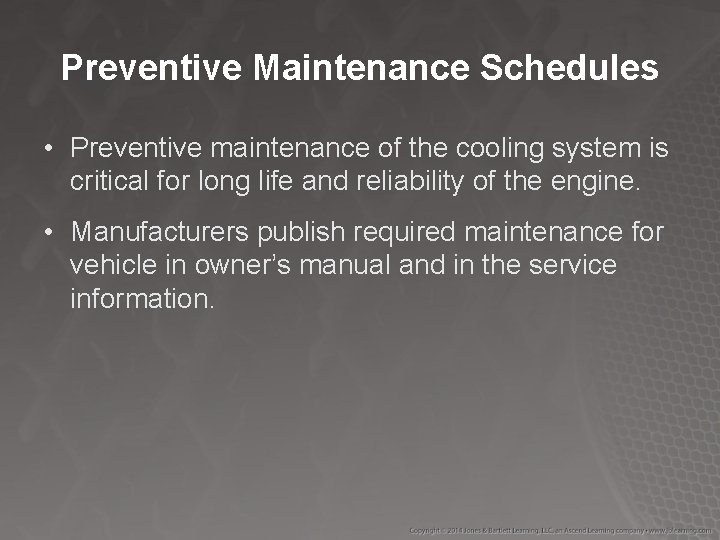
Preventive Maintenance Schedules • Preventive maintenance of the cooling system is critical for long life and reliability of the engine. • Manufacturers publish required maintenance for vehicle in owner’s manual and in the service information.
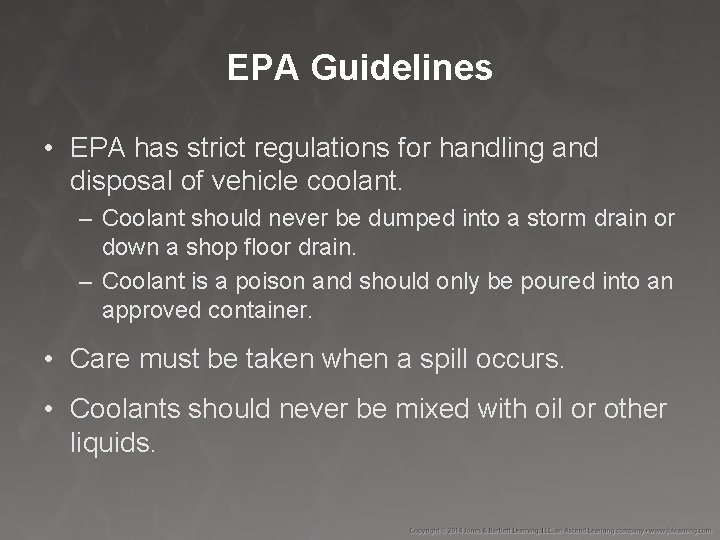
EPA Guidelines • EPA has strict regulations for handling and disposal of vehicle coolant. – Coolant should never be dumped into a storm drain or down a shop floor drain. – Coolant is a poison and should only be poured into an approved container. • Care must be taken when a spill occurs. • Coolants should never be mixed with oil or other liquids.
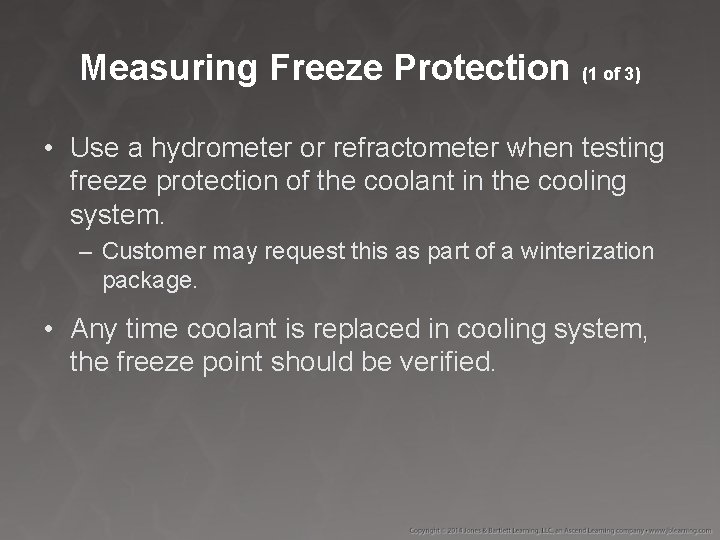
Measuring Freeze Protection (1 of 3) • Use a hydrometer or refractometer when testing freeze protection of the coolant in the cooling system. – Customer may request this as part of a winterization package. • Any time coolant is replaced in cooling system, the freeze point should be verified.
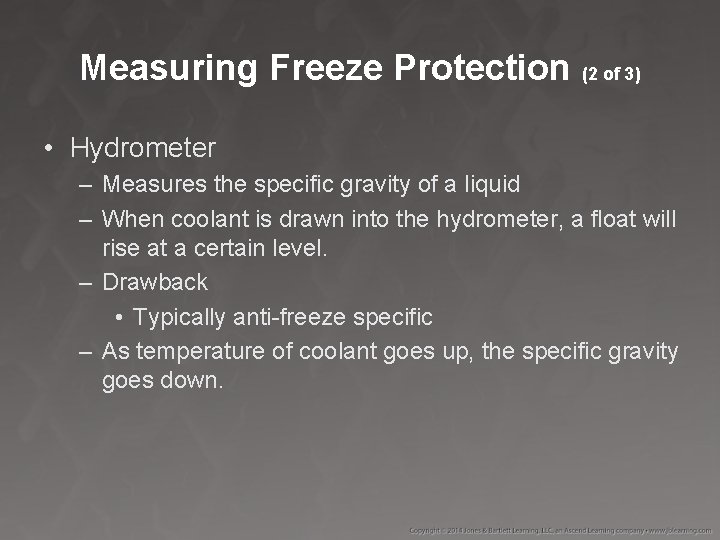
Measuring Freeze Protection (2 of 3) • Hydrometer – Measures the specific gravity of a liquid – When coolant is drawn into the hydrometer, a float will rise at a certain level. – Drawback • Typically anti-freeze specific – As temperature of coolant goes up, the specific gravity goes down.
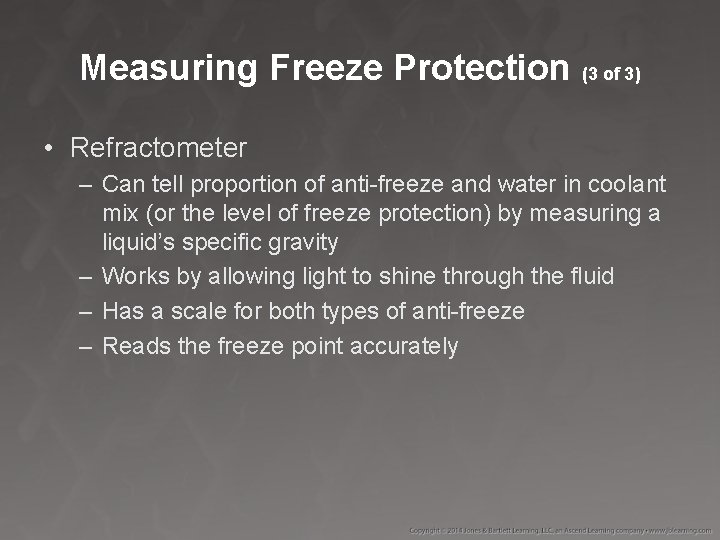
Measuring Freeze Protection (3 of 3) • Refractometer – Can tell proportion of anti-freeze and water in coolant mix (or the level of freeze protection) by measuring a liquid’s specific gravity – Works by allowing light to shine through the fluid – Has a scale for both types of anti-freeze – Reads the freeze point accurately
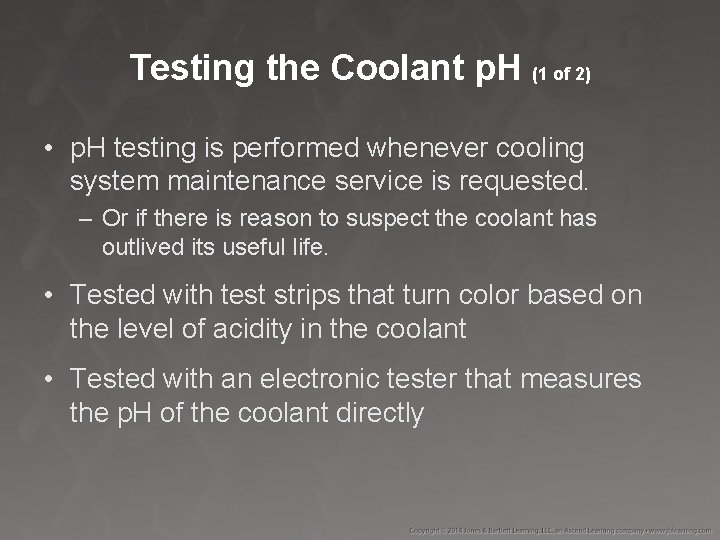
Testing the Coolant p. H (1 of 2) • p. H testing is performed whenever cooling system maintenance service is requested. – Or if there is reason to suspect the coolant has outlived its useful life. • Tested with test strips that turn color based on the level of acidity in the coolant • Tested with an electronic tester that measures the p. H of the coolant directly
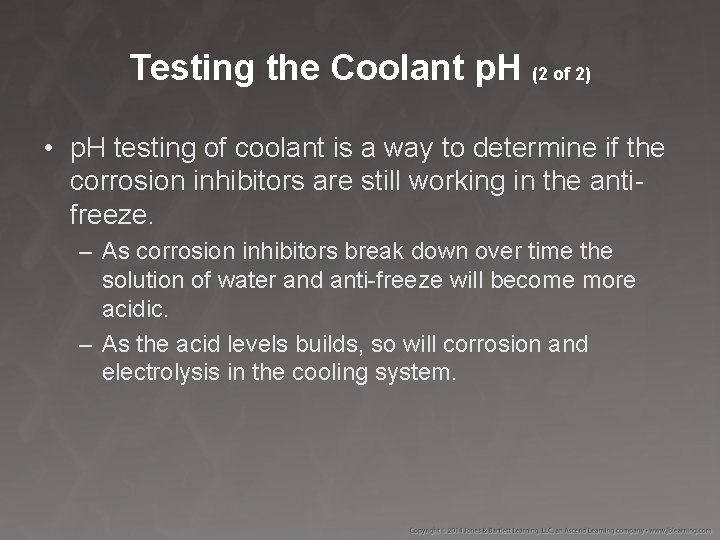
Testing the Coolant p. H (2 of 2) • p. H testing of coolant is a way to determine if the corrosion inhibitors are still working in the antifreeze. – As corrosion inhibitors break down over time the solution of water and anti-freeze will become more acidic. – As the acid levels builds, so will corrosion and electrolysis in the cooling system.
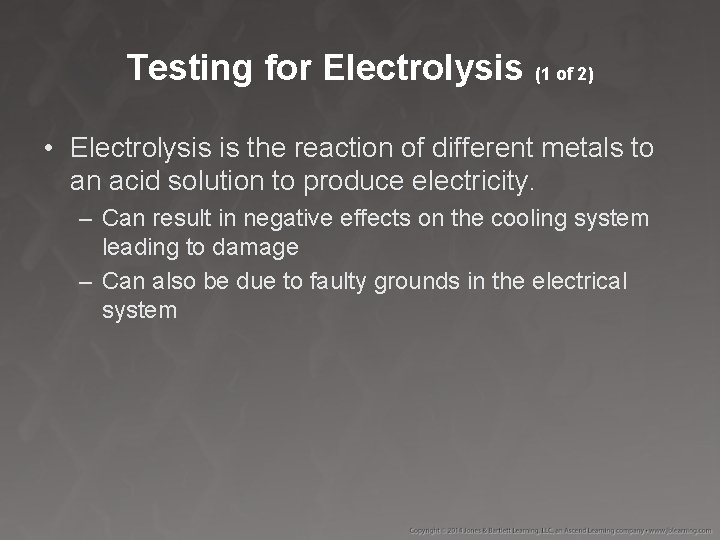
Testing for Electrolysis (1 of 2) • Electrolysis is the reaction of different metals to an acid solution to produce electricity. – Can result in negative effects on the cooling system leading to damage – Can also be due to faulty grounds in the electrical system
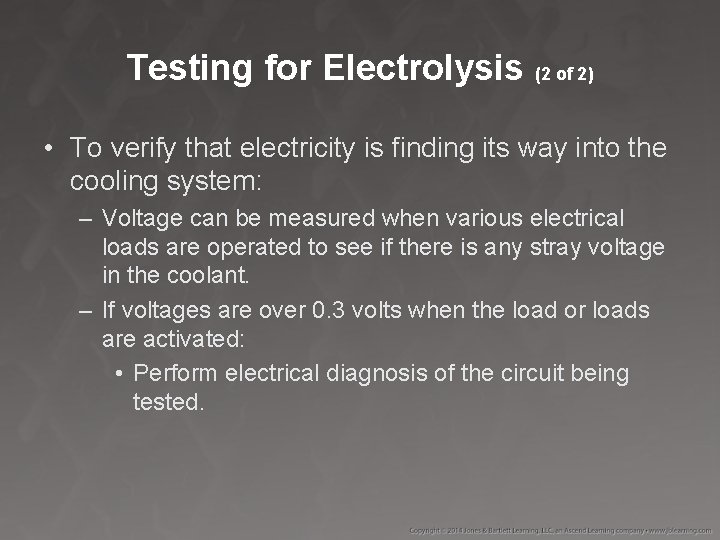
Testing for Electrolysis (2 of 2) • To verify that electricity is finding its way into the cooling system: – Voltage can be measured when various electrical loads are operated to see if there is any stray voltage in the coolant. – If voltages are over 0. 3 volts when the load or loads are activated: • Perform electrical diagnosis of the circuit being tested.
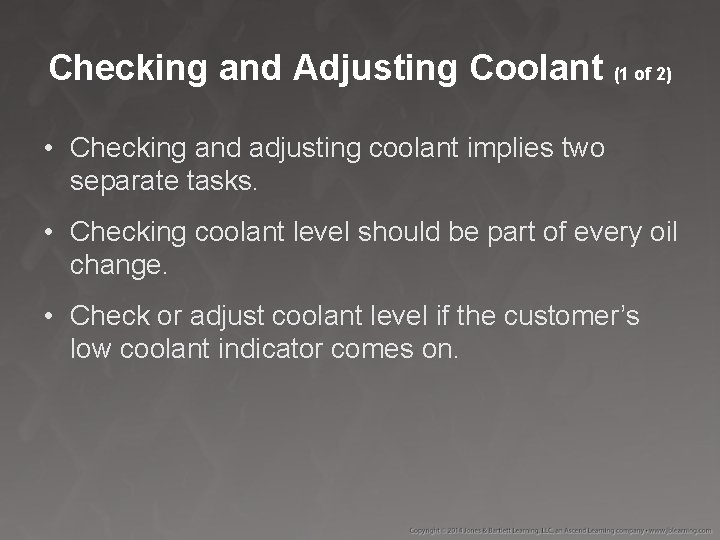
Checking and Adjusting Coolant (1 of 2) • Checking and adjusting coolant implies two separate tasks. • Checking coolant level should be part of every oil change. • Check or adjust coolant level if the customer’s low coolant indicator comes on.
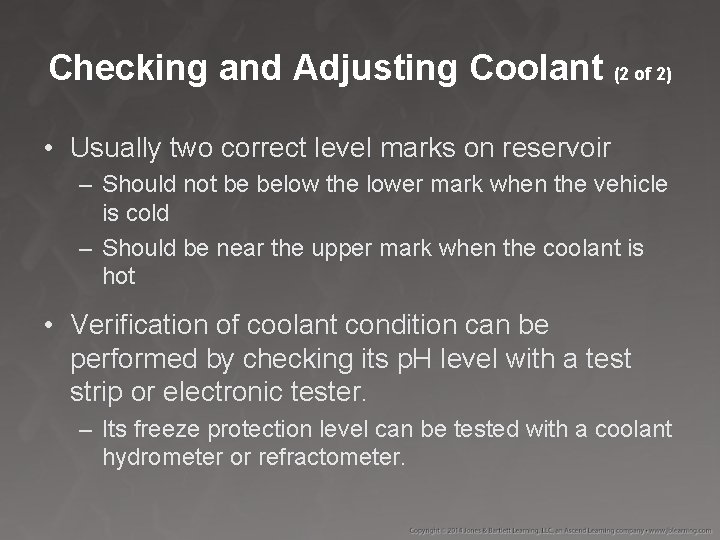
Checking and Adjusting Coolant (2 of 2) • Usually two correct level marks on reservoir – Should not be below the lower mark when the vehicle is cold – Should be near the upper mark when the coolant is hot • Verification of coolant condition can be performed by checking its p. H level with a test strip or electronic tester. – Its freeze protection level can be tested with a coolant hydrometer or refractometer.
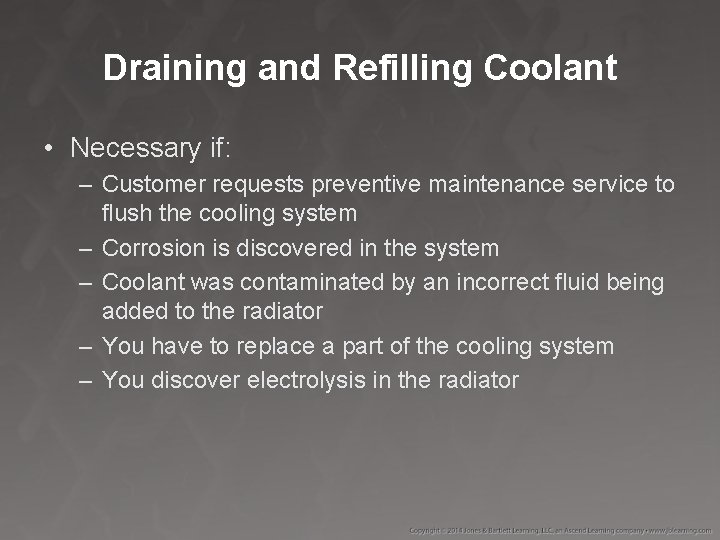
Draining and Refilling Coolant • Necessary if: – Customer requests preventive maintenance service to flush the cooling system – Corrosion is discovered in the system – Coolant was contaminated by an incorrect fluid being added to the radiator – You have to replace a part of the cooling system – You discover electrolysis in the radiator
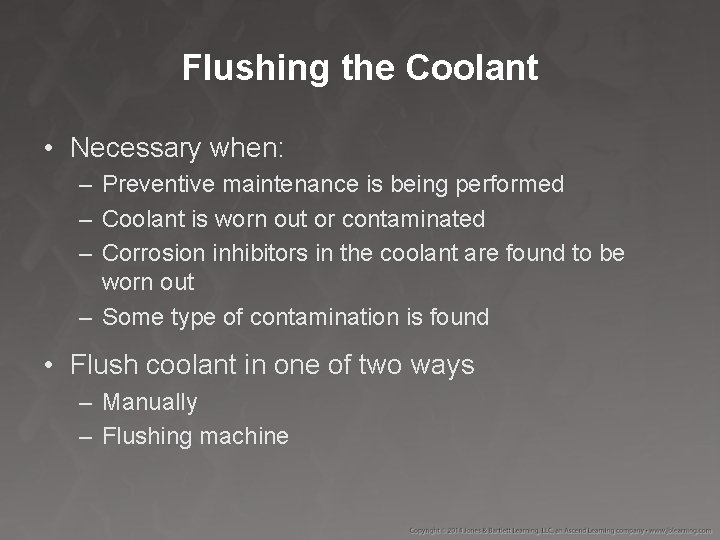
Flushing the Coolant • Necessary when: – Preventive maintenance is being performed – Coolant is worn out or contaminated – Corrosion inhibitors in the coolant are found to be worn out – Some type of contamination is found • Flush coolant in one of two ways – Manually – Flushing machine
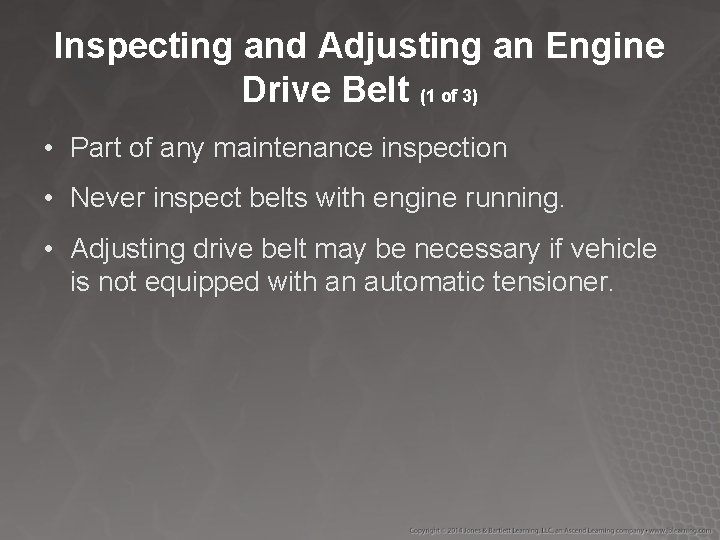
Inspecting and Adjusting an Engine Drive Belt (1 of 3) • Part of any maintenance inspection • Never inspect belts with engine running. • Adjusting drive belt may be necessary if vehicle is not equipped with an automatic tensioner.
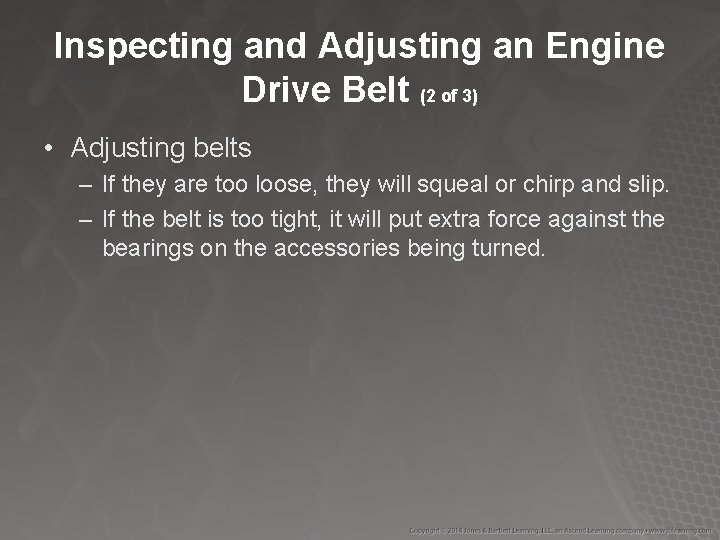
Inspecting and Adjusting an Engine Drive Belt (2 of 3) • Adjusting belts – If they are too loose, they will squeal or chirp and slip. – If the belt is too tight, it will put extra force against the bearings on the accessories being turned.
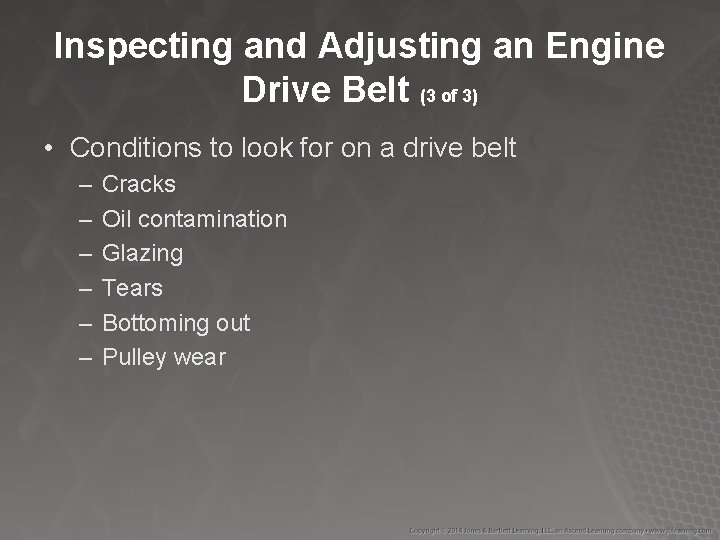
Inspecting and Adjusting an Engine Drive Belt (3 of 3) • Conditions to look for on a drive belt – – – Cracks Oil contamination Glazing Tears Bottoming out Pulley wear
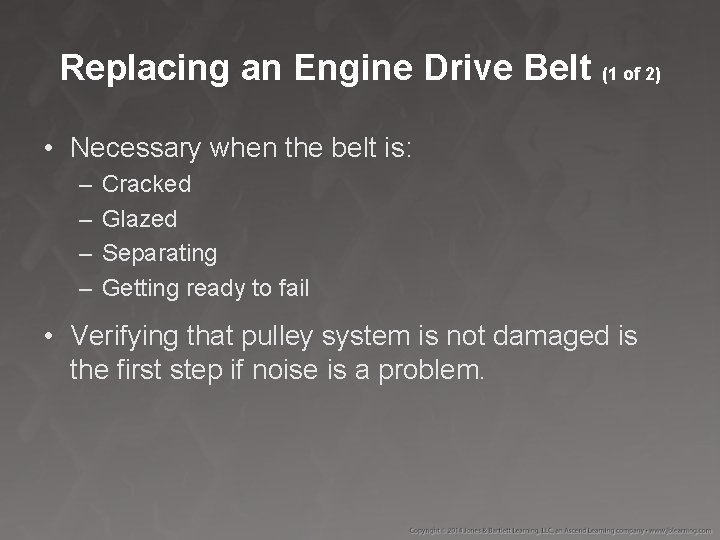
Replacing an Engine Drive Belt (1 of 2) • Necessary when the belt is: – – Cracked Glazed Separating Getting ready to fail • Verifying that pulley system is not damaged is the first step if noise is a problem.
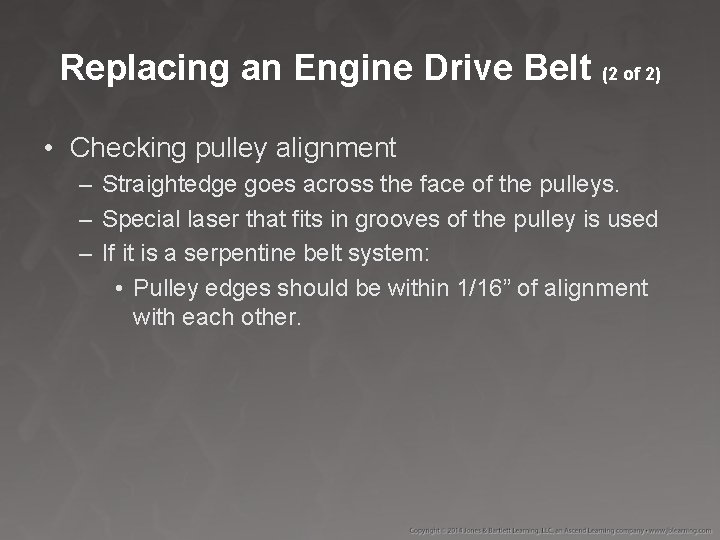
Replacing an Engine Drive Belt (2 of 2) • Checking pulley alignment – Straightedge goes across the face of the pulleys. – Special laser that fits in grooves of the pulley is used – If it is a serpentine belt system: • Pulley edges should be within 1/16” of alignment with each other.
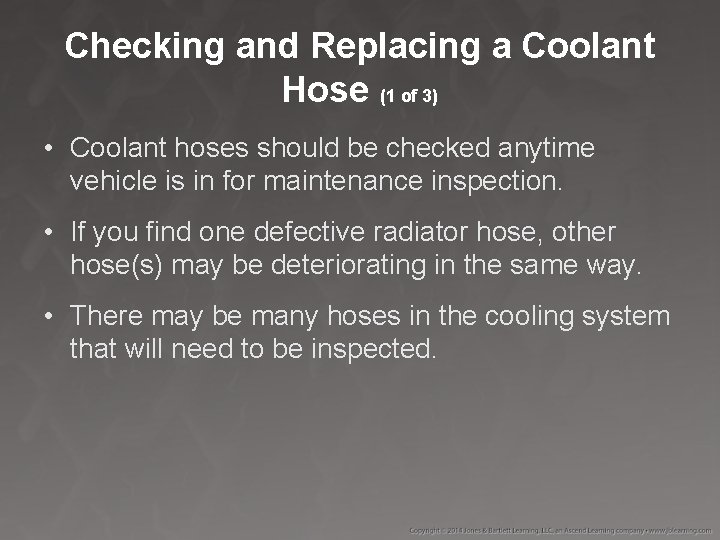
Checking and Replacing a Coolant Hose (1 of 3) • Coolant hoses should be checked anytime vehicle is in for maintenance inspection. • If you find one defective radiator hose, other hose(s) may be deteriorating in the same way. • There may be many hoses in the cooling system that will need to be inspected.
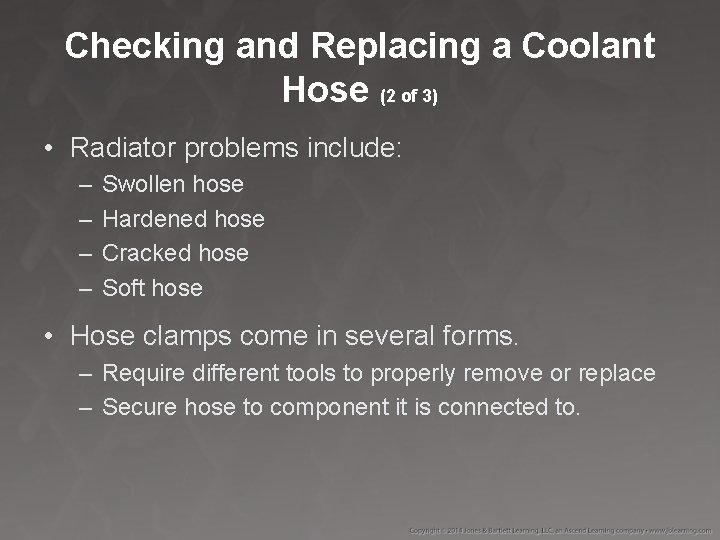
Checking and Replacing a Coolant Hose (2 of 3) • Radiator problems include: – – Swollen hose Hardened hose Cracked hose Soft hose • Hose clamps come in several forms. – Require different tools to properly remove or replace – Secure hose to component it is connected to.
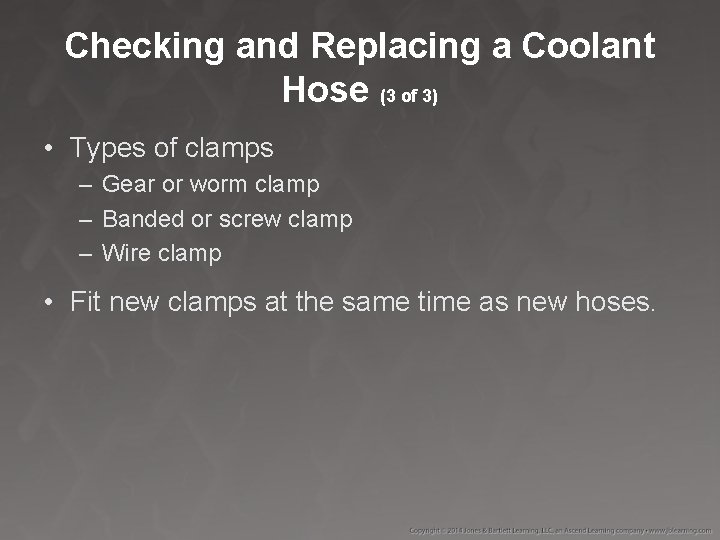
Checking and Replacing a Coolant Hose (3 of 3) • Types of clamps – Gear or worm clamp – Banded or screw clamp – Wire clamp • Fit new clamps at the same time as new hoses.
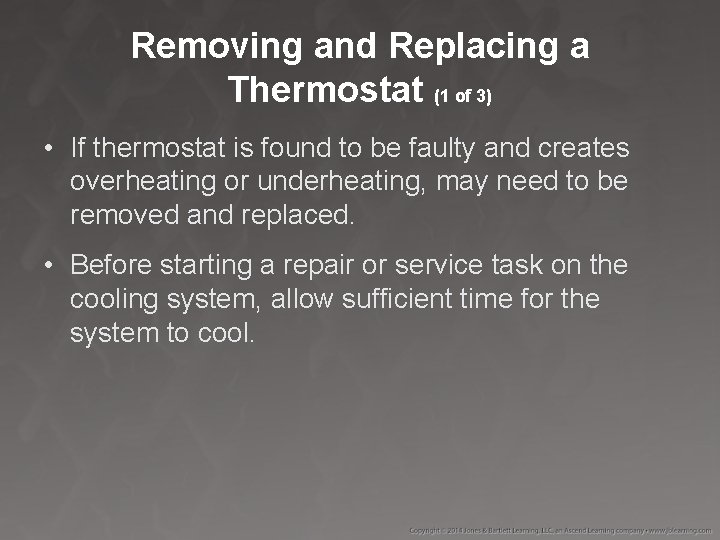
Removing and Replacing a Thermostat (1 of 3) • If thermostat is found to be faulty and creates overheating or underheating, may need to be removed and replaced. • Before starting a repair or service task on the cooling system, allow sufficient time for the system to cool.
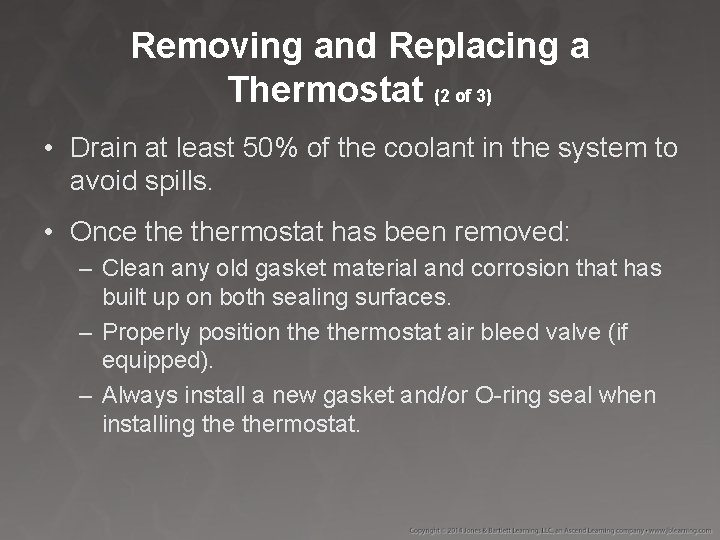
Removing and Replacing a Thermostat (2 of 3) • Drain at least 50% of the coolant in the system to avoid spills. • Once thermostat has been removed: – Clean any old gasket material and corrosion that has built up on both sealing surfaces. – Properly position thermostat air bleed valve (if equipped). – Always install a new gasket and/or O-ring seal when installing thermostat.
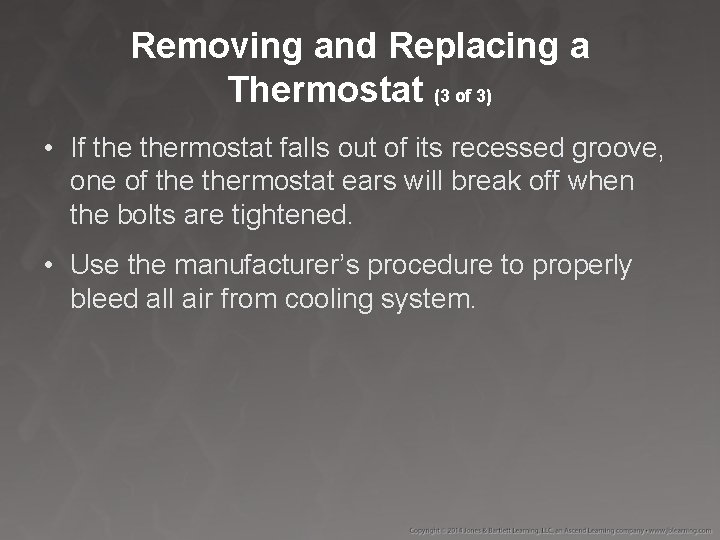
Removing and Replacing a Thermostat (3 of 3) • If thermostat falls out of its recessed groove, one of thermostat ears will break off when the bolts are tightened. • Use the manufacturer’s procedure to properly bleed all air from cooling system.
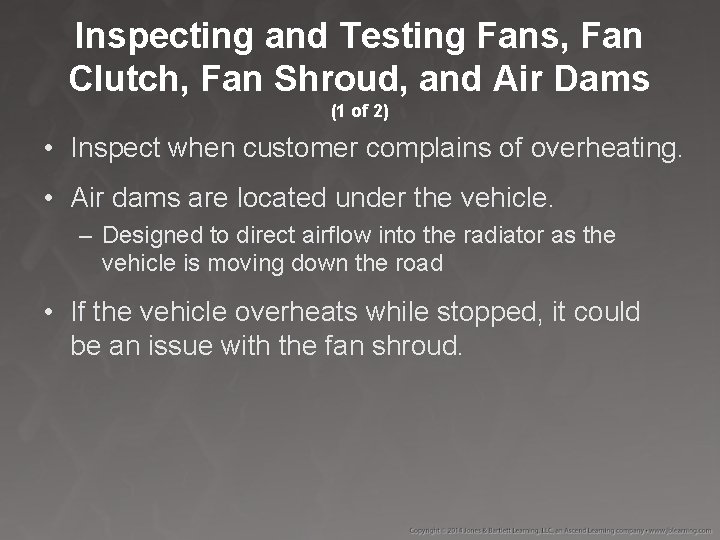
Inspecting and Testing Fans, Fan Clutch, Fan Shroud, and Air Dams (1 of 2) • Inspect when customer complains of overheating. • Air dams are located under the vehicle. – Designed to direct airflow into the radiator as the vehicle is moving down the road • If the vehicle overheats while stopped, it could be an issue with the fan shroud.
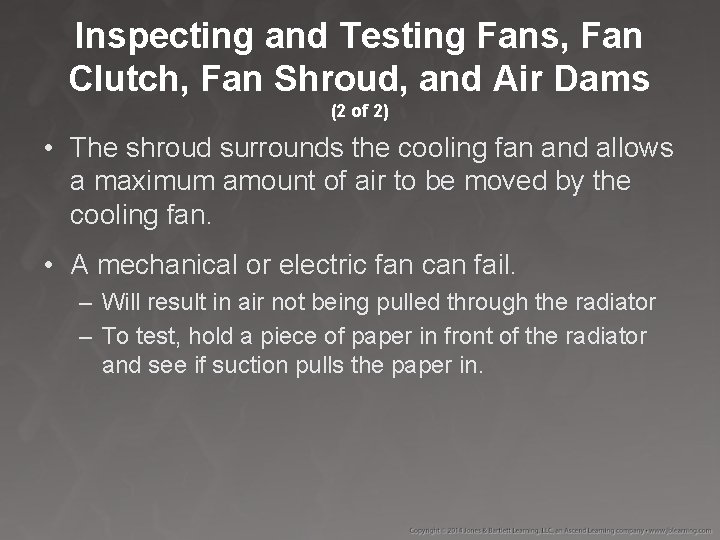
Inspecting and Testing Fans, Fan Clutch, Fan Shroud, and Air Dams (2 of 2) • The shroud surrounds the cooling fan and allows a maximum amount of air to be moved by the cooling fan. • A mechanical or electric fan can fail. – Will result in air not being pulled through the radiator – To test, hold a piece of paper in front of the radiator and see if suction pulls the paper in.
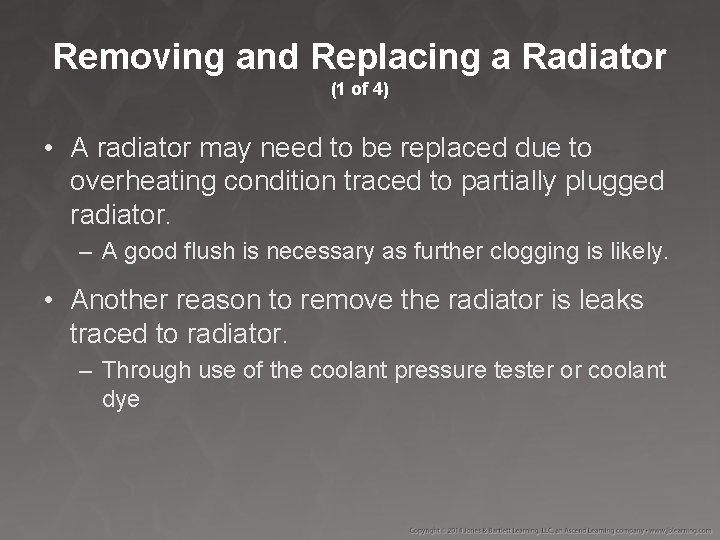
Removing and Replacing a Radiator (1 of 4) • A radiator may need to be replaced due to overheating condition traced to partially plugged radiator. – A good flush is necessary as further clogging is likely. • Another reason to remove the radiator is leaks traced to radiator. – Through use of the coolant pressure tester or coolant dye
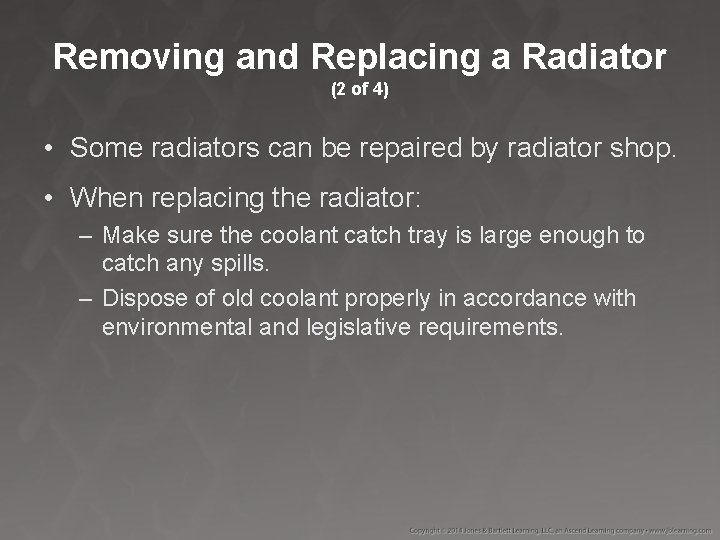
Removing and Replacing a Radiator (2 of 4) • Some radiators can be repaired by radiator shop. • When replacing the radiator: – Make sure the coolant catch tray is large enough to catch any spills. – Dispose of old coolant properly in accordance with environmental and legislative requirements.
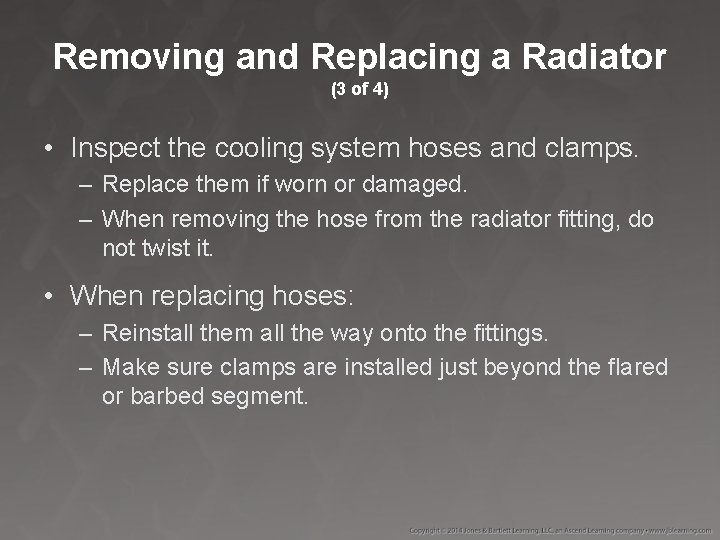
Removing and Replacing a Radiator (3 of 4) • Inspect the cooling system hoses and clamps. – Replace them if worn or damaged. – When removing the hose from the radiator fitting, do not twist it. • When replacing hoses: – Reinstall them all the way onto the fittings. – Make sure clamps are installed just beyond the flared or barbed segment.
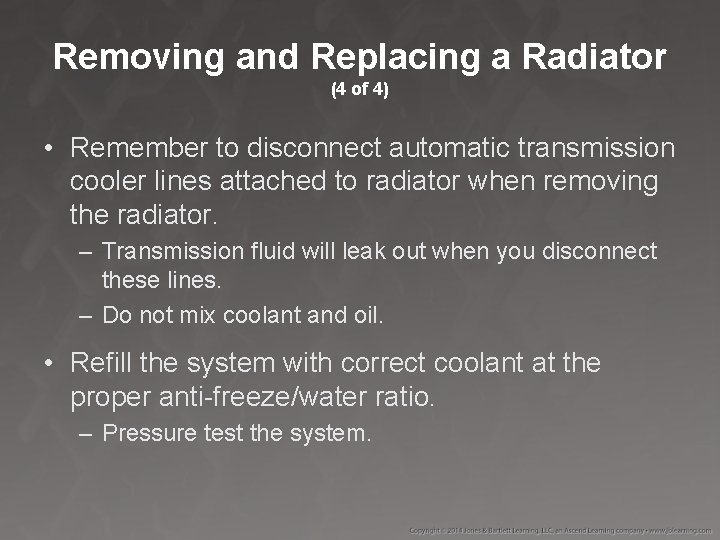
Removing and Replacing a Radiator (4 of 4) • Remember to disconnect automatic transmission cooler lines attached to radiator when removing the radiator. – Transmission fluid will leak out when you disconnect these lines. – Do not mix coolant and oil. • Refill the system with correct coolant at the proper anti-freeze/water ratio. – Pressure test the system.
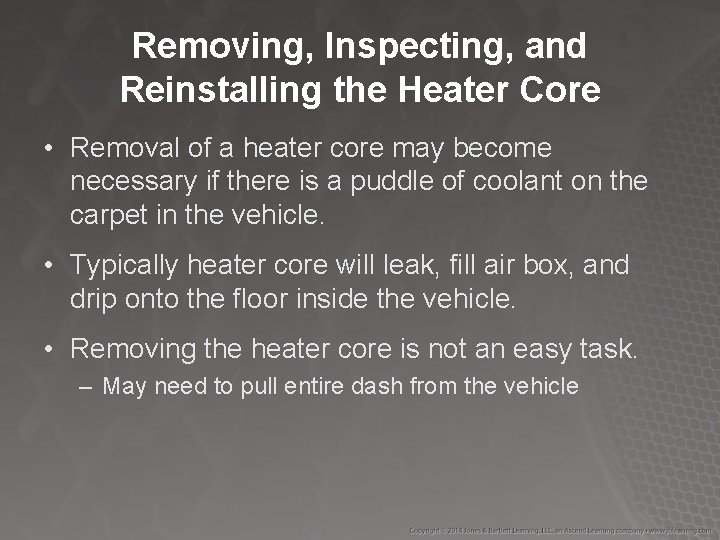
Removing, Inspecting, and Reinstalling the Heater Core • Removal of a heater core may become necessary if there is a puddle of coolant on the carpet in the vehicle. • Typically heater core will leak, fill air box, and drip onto the floor inside the vehicle. • Removing the heater core is not an easy task. – May need to pull entire dash from the vehicle
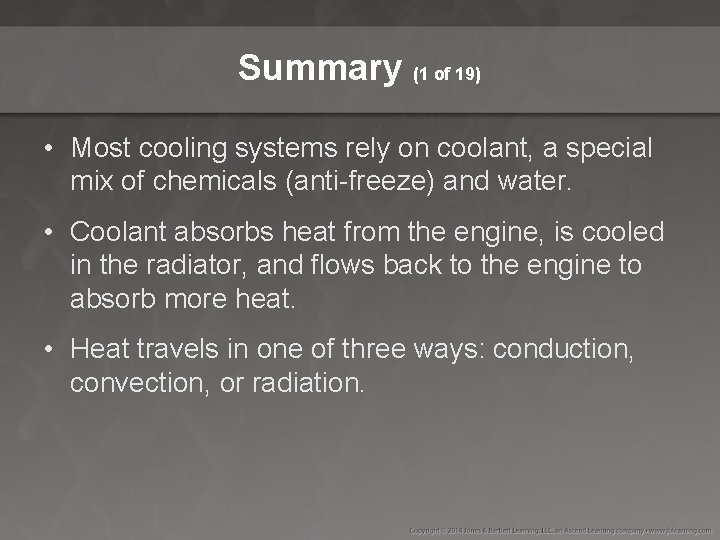
Summary (1 of 19) • Most cooling systems rely on coolant, a special mix of chemicals (anti-freeze) and water. • Coolant absorbs heat from the engine, is cooled in the radiator, and flows back to the engine to absorb more heat. • Heat travels in one of three ways: conduction, convection, or radiation.
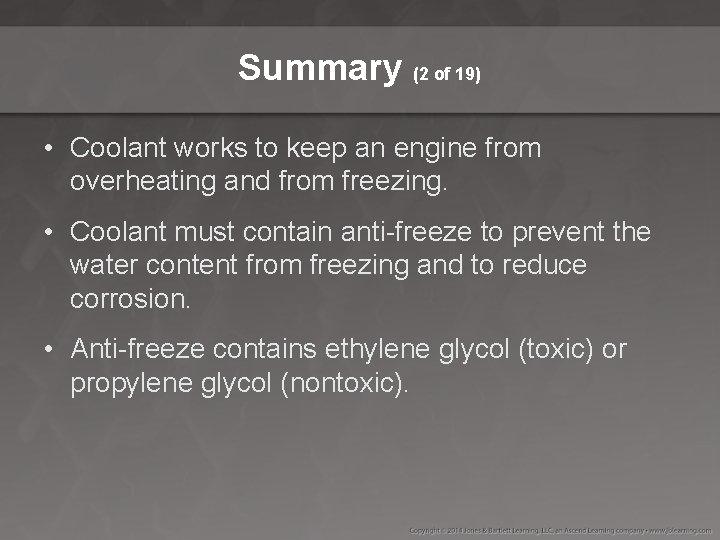
Summary (2 of 19) • Coolant works to keep an engine from overheating and from freezing. • Coolant must contain anti-freeze to prevent the water content from freezing and to reduce corrosion. • Anti-freeze contains ethylene glycol (toxic) or propylene glycol (nontoxic).
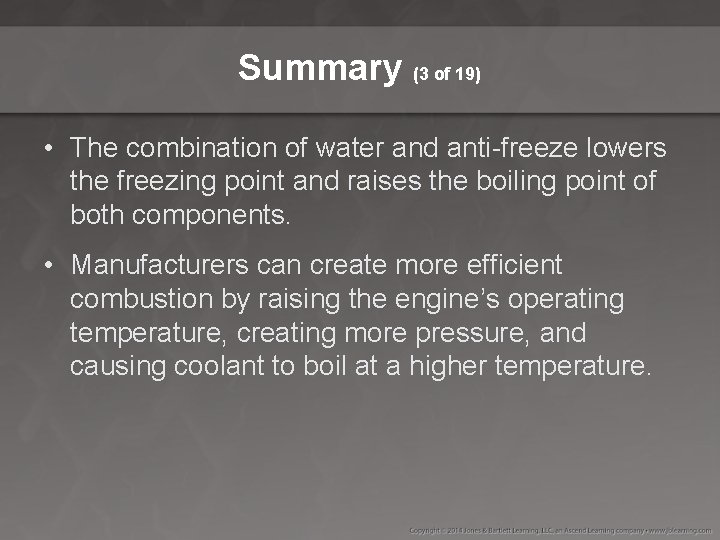
Summary (3 of 19) • The combination of water and anti-freeze lowers the freezing point and raises the boiling point of both components. • Manufacturers can create more efficient combustion by raising the engine’s operating temperature, creating more pressure, and causing coolant to boil at a higher temperature.
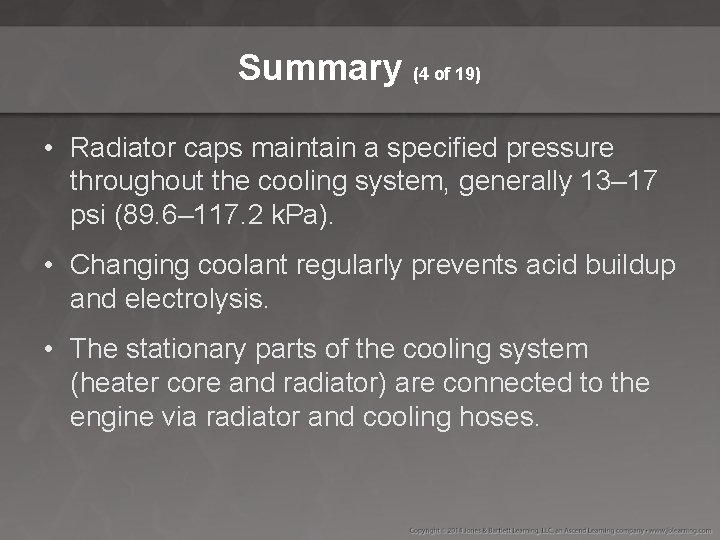
Summary (4 of 19) • Radiator caps maintain a specified pressure throughout the cooling system, generally 13– 17 psi (89. 6– 117. 2 k. Pa). • Changing coolant regularly prevents acid buildup and electrolysis. • The stationary parts of the cooling system (heater core and radiator) are connected to the engine via radiator and cooling hoses.
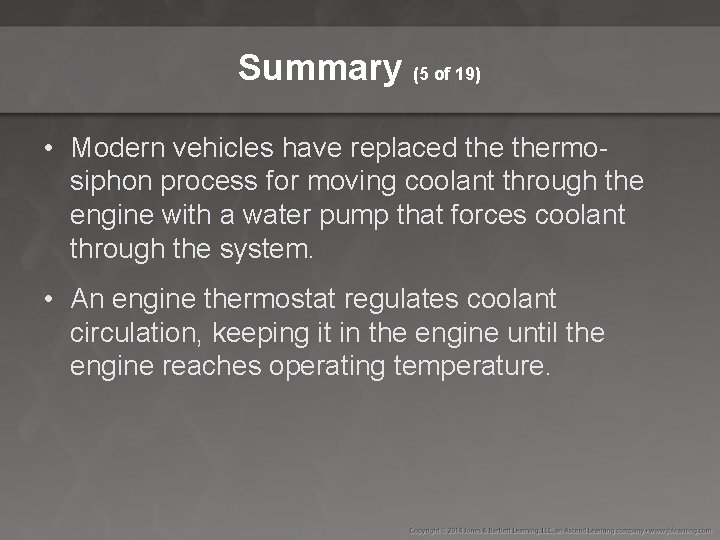
Summary (5 of 19) • Modern vehicles have replaced thermosiphon process for moving coolant through the engine with a water pump that forces coolant through the system. • An engine thermostat regulates coolant circulation, keeping it in the engine until the engine reaches operating temperature.
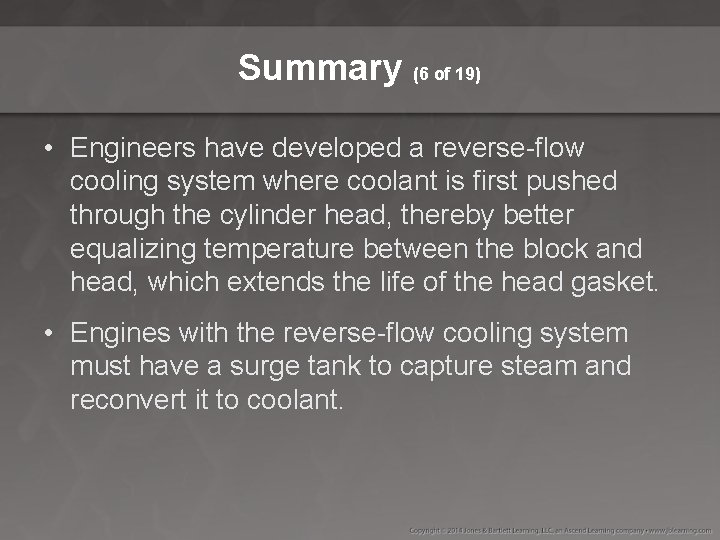
Summary (6 of 19) • Engineers have developed a reverse-flow cooling system where coolant is first pushed through the cylinder head, thereby better equalizing temperature between the block and head, which extends the life of the head gasket. • Engines with the reverse-flow cooling system must have a surge tank to capture steam and reconvert it to coolant.
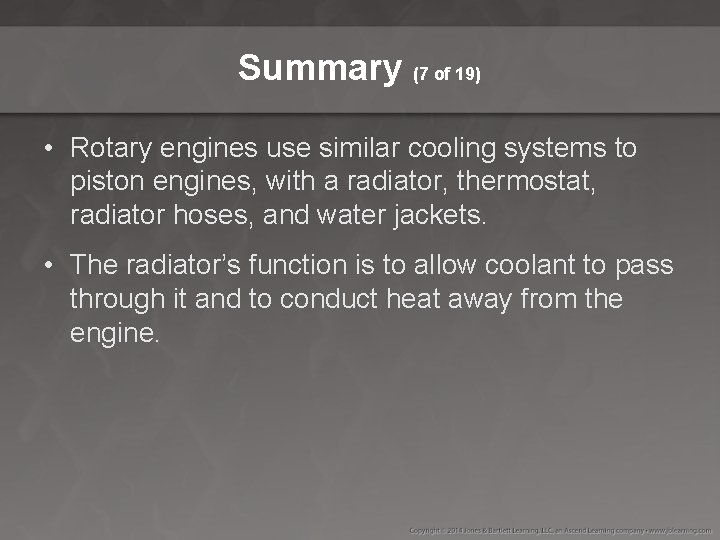
Summary (7 of 19) • Rotary engines use similar cooling systems to piston engines, with a radiator, thermostat, radiator hoses, and water jackets. • The radiator’s function is to allow coolant to pass through it and to conduct heat away from the engine.
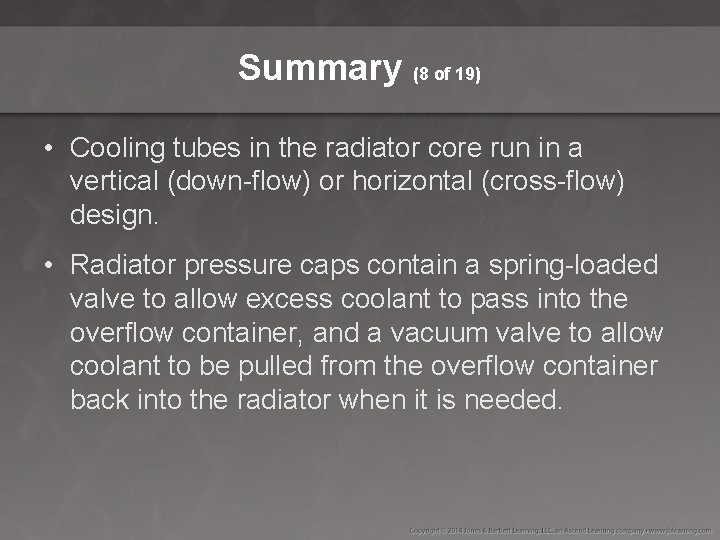
Summary (8 of 19) • Cooling tubes in the radiator core run in a vertical (down-flow) or horizontal (cross-flow) design. • Radiator pressure caps contain a spring-loaded valve to allow excess coolant to pass into the overflow container, and a vacuum valve to allow coolant to be pulled from the overflow container back into the radiator when it is needed.
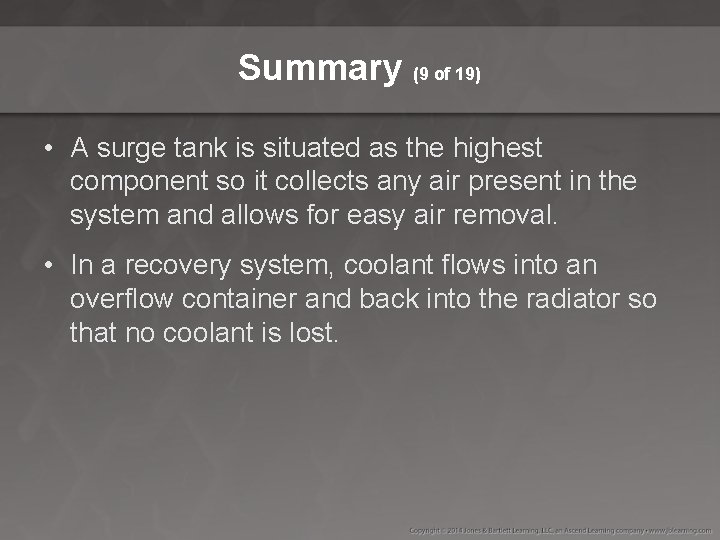
Summary (9 of 19) • A surge tank is situated as the highest component so it collects any air present in the system and allows for easy air removal. • In a recovery system, coolant flows into an overflow container and back into the radiator so that no coolant is lost.
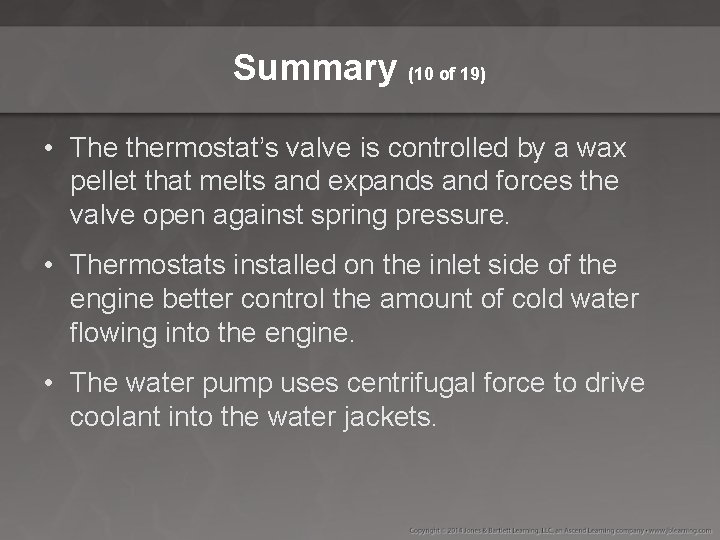
Summary (10 of 19) • The thermostat’s valve is controlled by a wax pellet that melts and expands and forces the valve open against spring pressure. • Thermostats installed on the inlet side of the engine better control the amount of cold water flowing into the engine. • The water pump uses centrifugal force to drive coolant into the water jackets.
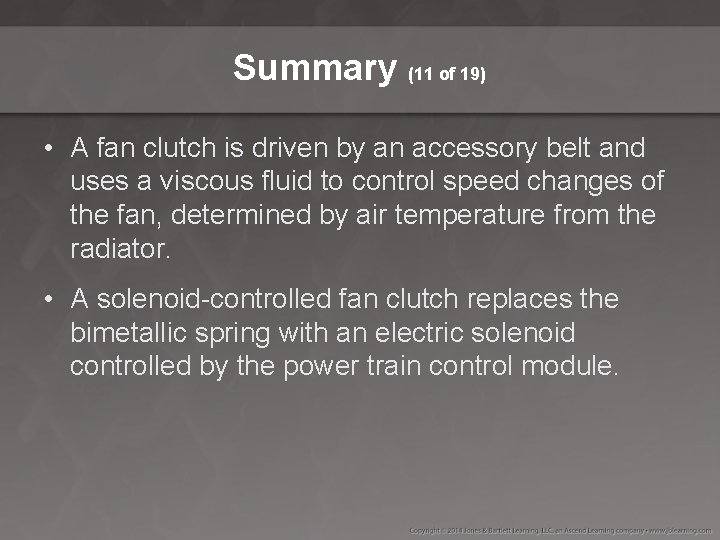
Summary (11 of 19) • A fan clutch is driven by an accessory belt and uses a viscous fluid to control speed changes of the fan, determined by air temperature from the radiator. • A solenoid-controlled fan clutch replaces the bimetallic spring with an electric solenoid controlled by the power train control module.
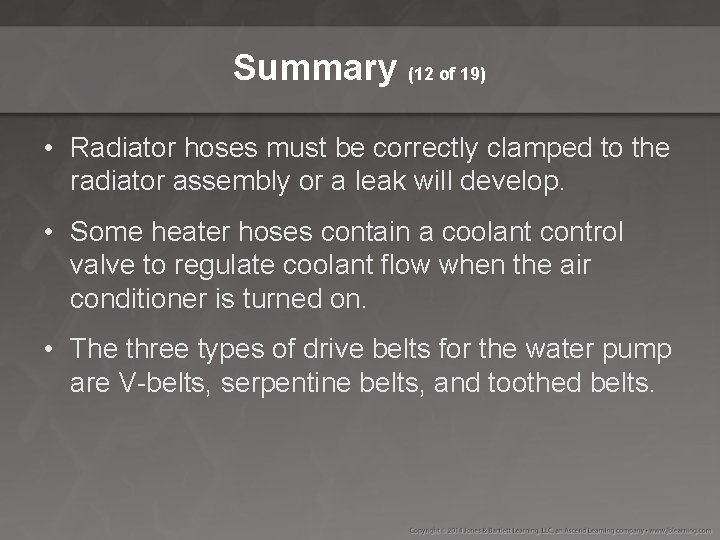
Summary (12 of 19) • Radiator hoses must be correctly clamped to the radiator assembly or a leak will develop. • Some heater hoses contain a coolant control valve to regulate coolant flow when the air conditioner is turned on. • The three types of drive belts for the water pump are V-belts, serpentine belts, and toothed belts.
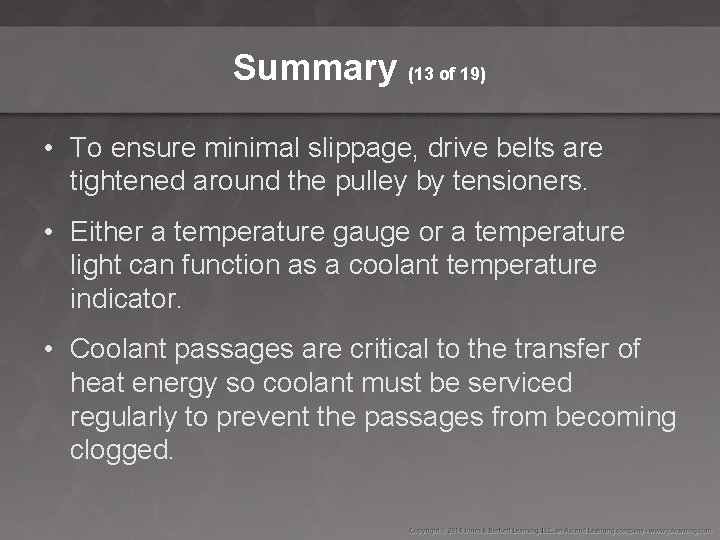
Summary (13 of 19) • To ensure minimal slippage, drive belts are tightened around the pulley by tensioners. • Either a temperature gauge or a temperature light can function as a coolant temperature indicator. • Coolant passages are critical to the transfer of heat energy so coolant must be serviced regularly to prevent the passages from becoming clogged.
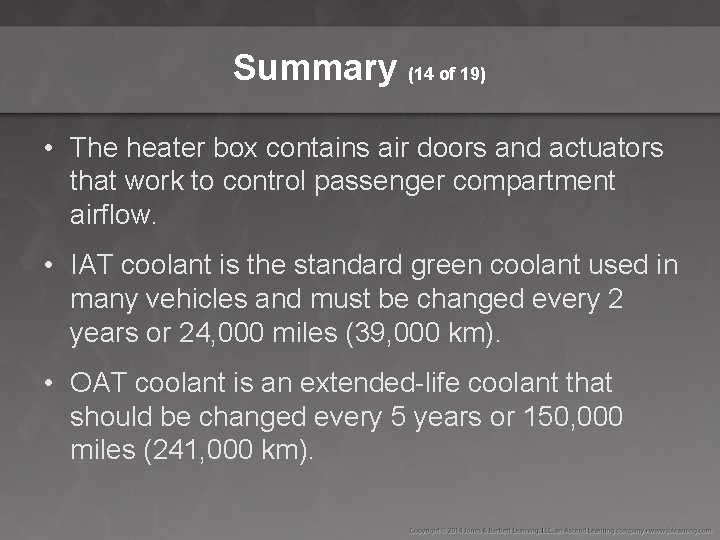
Summary (14 of 19) • The heater box contains air doors and actuators that work to control passenger compartment airflow. • IAT coolant is the standard green coolant used in many vehicles and must be changed every 2 years or 24, 000 miles (39, 000 km). • OAT coolant is an extended-life coolant that should be changed every 5 years or 150, 000 miles (241, 000 km).
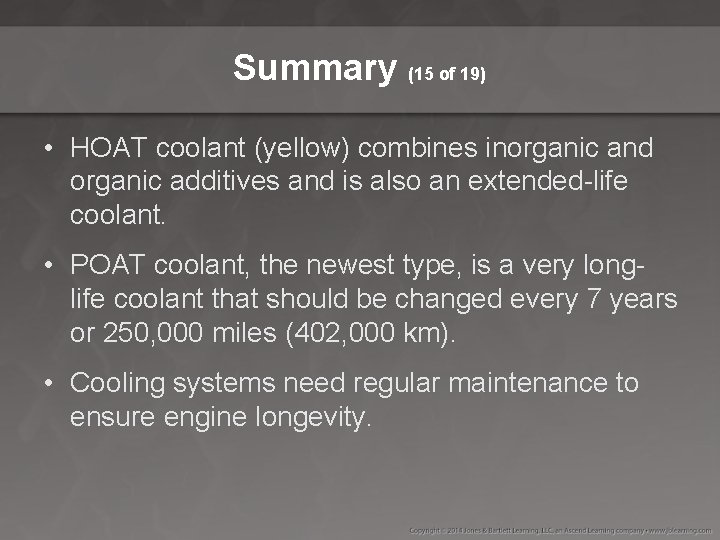
Summary (15 of 19) • HOAT coolant (yellow) combines inorganic and organic additives and is also an extended-life coolant. • POAT coolant, the newest type, is a very longlife coolant that should be changed every 7 years or 250, 000 miles (402, 000 km). • Cooling systems need regular maintenance to ensure engine longevity.
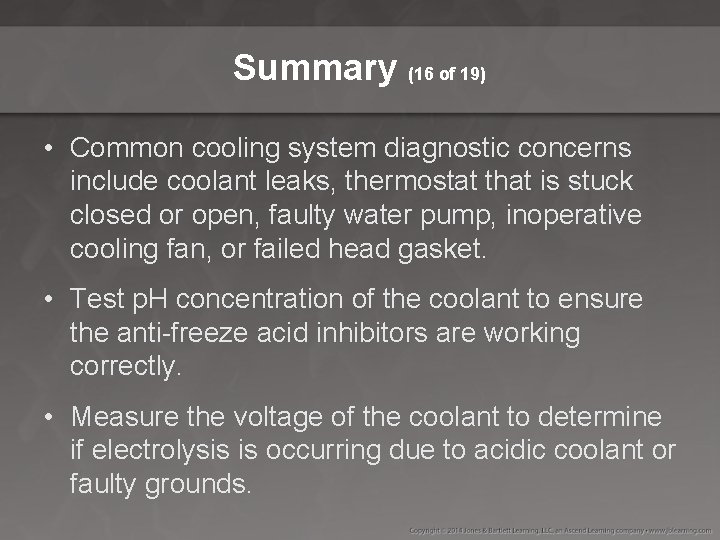
Summary (16 of 19) • Common cooling system diagnostic concerns include coolant leaks, thermostat that is stuck closed or open, faulty water pump, inoperative cooling fan, or failed head gasket. • Test p. H concentration of the coolant to ensure the anti-freeze acid inhibitors are working correctly. • Measure the voltage of the coolant to determine if electrolysis is occurring due to acidic coolant or faulty grounds.
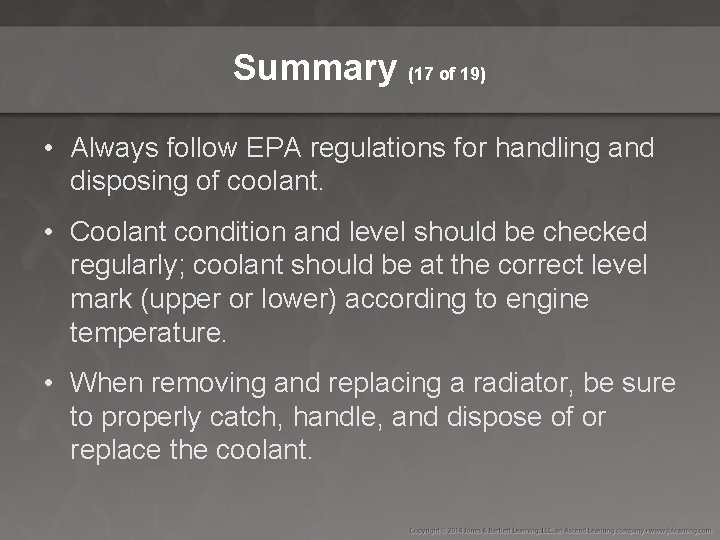
Summary (17 of 19) • Always follow EPA regulations for handling and disposing of coolant. • Coolant condition and level should be checked regularly; coolant should be at the correct level mark (upper or lower) according to engine temperature. • When removing and replacing a radiator, be sure to properly catch, handle, and dispose of or replace the coolant.
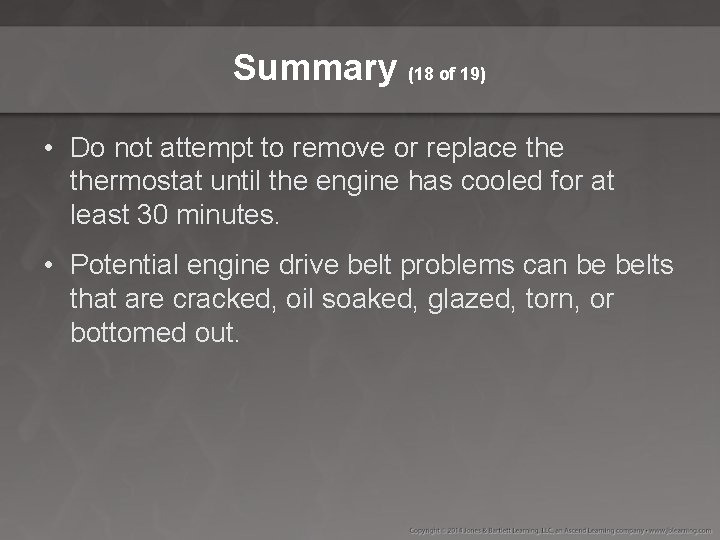
Summary (18 of 19) • Do not attempt to remove or replace thermostat until the engine has cooled for at least 30 minutes. • Potential engine drive belt problems can be belts that are cracked, oil soaked, glazed, torn, or bottomed out.
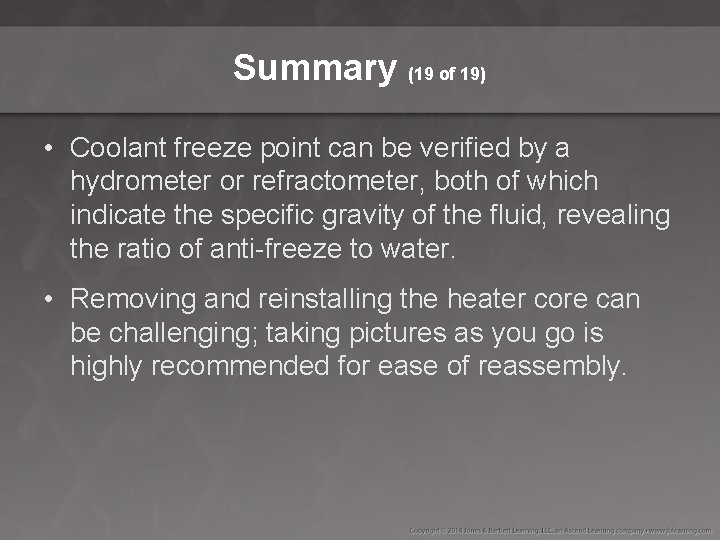
Summary (19 of 19) • Coolant freeze point can be verified by a hydrometer or refractometer, both of which indicate the specific gravity of the fluid, revealing the ratio of anti-freeze to water. • Removing and reinstalling the heater core can be challenging; taking pictures as you go is highly recommended for ease of reassembly.
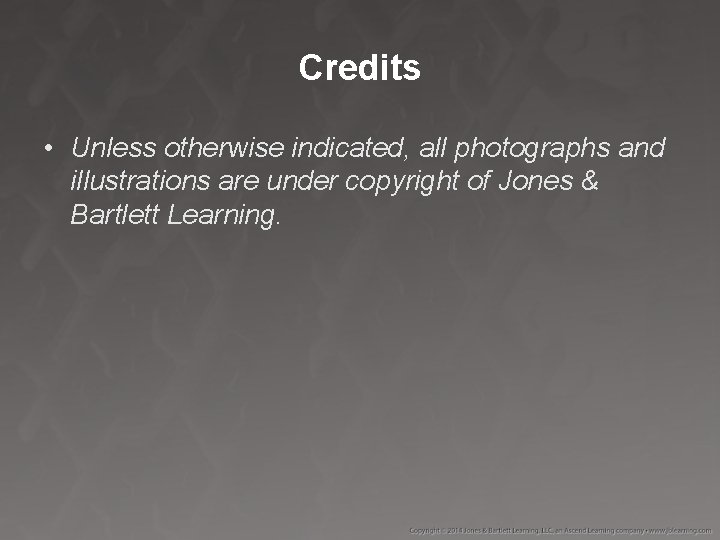
Credits • Unless otherwise indicated, all photographs and illustrations are under copyright of Jones & Bartlett Learning.
Lubrication of couling systems
Components of water cooling system
Engine cooling system
Chapter 30 engine starting systems
Internal combustion vs external combustion
Ebullient cooling systems
Advanced cooling systems inc
I've got a friend we like to play we play together
Play random play basketball
Play by play
Hamlet
5 engine systems
Chapter 3 lesson 1 introduction to global systems
Introduction to ems systems chapter 1
Introduction to google app engine
Definition of play
Introduction to role play
Introduction of role play
Engine operation chapter 3 test 1
Chapter 5 two-cycle and four-cycle engines answers
Decision support systems and intelligent systems
Engineering elegant systems: theory of systems engineering
Embedded systems vs cyber physical systems
Elegant systems
System analysis and design
Introduction to recommender systems
Markus zanker
Introduction to operating systems
Systems applications and products
Introduction to radar systems
Introduction of health care delivery system
Introduction to information systems 6th edition
Introduction to erp systems
Content database software
Introduction to information systems 6th edition
Introduction to multimedia systems
Introduction to information systems 3rd edition
Introduction to management information systems 5th edition
Pxdes expert system
Introduction to signals and systems
Introduction to business information systems
Introduction to accounting information systems
An introduction to database systems
Introduction to global systems
Hvac basics fundamentals ppt
Introduction to manufacturing systems
Introduction to embedded systems lee seshia solution manual
Introduction to electrical power systems
Erp system options and selection methods
Operating system
Sic/xe programming examples
Introduction to digital control system
101101-100111
Cit593
Introduction to low voltage systems
Introduction to information systems 3rd edition
Introduction to analog and digital control systems
15-213 introduction to computer systems
Medconsulting
Introduction to information systems 3rd edition
15-213 introduction to computer systems
The case of the cooling corpse answers
Liz owns stock in nar heating/cooling and cilla shipping
Cooling load calculation software
410a suction pressure chart
Electronic cooling methods
Final assembly
Immersion cooling case
Ocp liquid cooling
Cooling load calculation example
Lan closet
Introduction of refrigeration system
His cart might be a flower bed
Latent heat of fusion
Definition heat exchanger
Vessel cooling
What is k in newtons law of cooling
Close control unit air conditioning
Unequal heating and cooling erosion
Ess cooling system
Ess cooling
The act of cooling tea
Cooling curve worksheet answers
Double roof for cooling
Air conditioner cooling capacity
Adiabatic cooling
Heat transfer function
Dyno cooling fan
Solar cooling system
Frazier heating and cooling
Housing cooling chart
Physical behavior of matter heating and cooling curves
Air washer psychrometric process
Factors affecting rate of cooling
Perancangan cooling tower
Chapter 18 moisture clouds and precipitation
Thou hast described a hot friend cooling.
Young heat exchangers
Heat pipes for electronics cooling applications
Free cooling
Formula student cooling system
Cenozoic cooling
Latent loads in radiant cooling
Thermo bello
Free cooling
Cooling tower water treatment training
Sensible cooling on psychrometric chart
H&c heating and cooling
Dump cooling
Oni cooling system
Cooling system diagnostic
Latent heat of fusion
Physical behavior of matter heating and cooling curves
Terra cooling
Reverse brayton cycle
Jon snow golden ratio
Champion cooling company is locating a warehouse
Heating cooling curve equations
Heating curve
Devcco
Bello heating and cooling
Cooling curve of impure substance
Bmdas
Dump cooling
Once-through cooling
Characteristic radiation
Status cooling
Kale heating and cooling
Cable cooling system
National cooling action plant
Convection tube cooling in greenhouse
Encon fan
Cooling rate
Thermosyphon cooling system design
Cryoprecipitate
Roman cooling system
Spx cooling technologies olathe ks
What are 3 acceptable methods for thawing food
Corpse
Self cooling can
Reziator
Sideband cooling
Que es status cooling
Laura cooling
Cooling
Energy process cooling
Heating and cooling curves
Future of outdoor cooling
Geothermal cooling tuscarora
Smart car cooling system
Cooling toer
The case of the cooling corpse
Sieb plumbing and heating
Heating and cooling physics
Dtm cooling system
Essay structure introduction
Chapter 28 human systems and homeostasis
Signals and systems oppenheim solutions chapter 5
Chapter 15 river systems answers
System chapter 1
Chapter 11 lubrication systems answer key
Chapter 10 ignition systems
Chapter 13 federal and state court systems
Chapter 2 economic systems and decision making
Section 38-1 food and nutrition
Chapter 8 securing information systems
Chapter 8 securing information systems
Chapter 7 accounting information systems
Chapter 7 accounting information systems
Spot welded matrix band
Chapter 39 endocrine and reproductive systems
Chapter 36 skeletal muscular and integumentary systems
Chapter 36 section 1 reproductive systems
Chapter 33 circulatory and respiratory systems
Chapter 2 economic systems answer key
Chapter 2 economic systems and decision making
Water and aqueous systems chapter 15 answers
Chapter 15 water and aqueous systems answer key
The number of tankers needed for a fire will depend on the
Chapter 14 the skeletal muscular and nervous systems
Dfd chapter 13
Chapter 10 ignition systems
What is the musical classification of shank
Chapter 24 the immune and lymphatic systems and cancer
Managing global systems chapter 15
Chapter 15 water and aqueous systems
System of nonlinear inequalities
Securing information systems
Classification of bases in dentistry
Energy analysis of closed systems
Endorse a check to someone else
Cash control systems
Fundamental of information system
Food safety management systems servsafe chapter 8 notes
Chapter 2 economic systems and decision making answer key
Earth's environmental systems chapter 3