LAMINAO DE MADEIRAS Prof Setsuo Iwakiri UFPR DETF
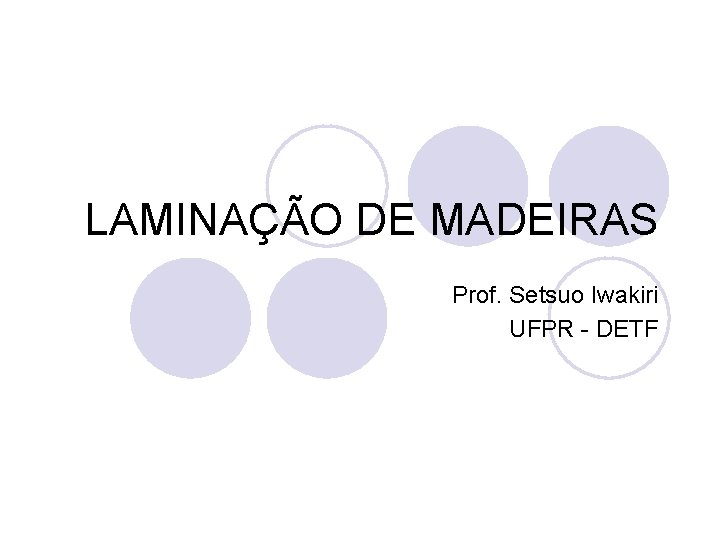
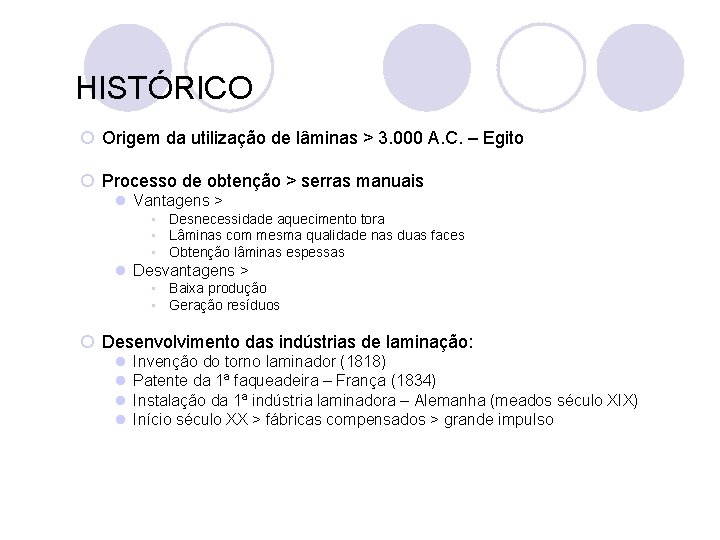
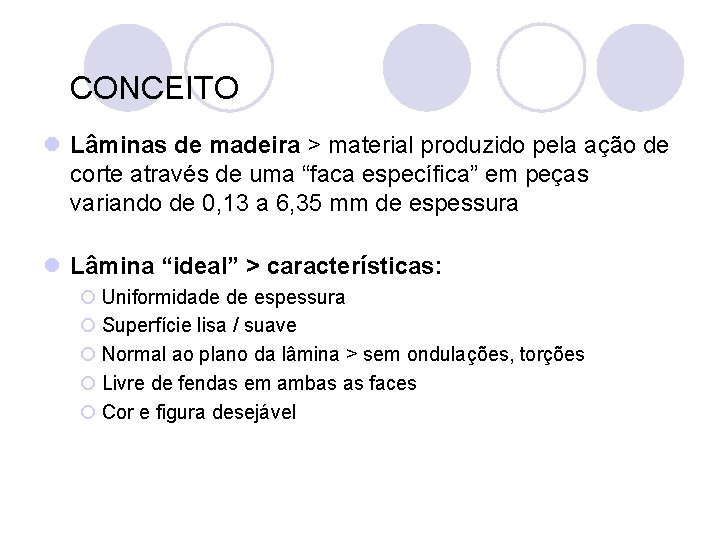
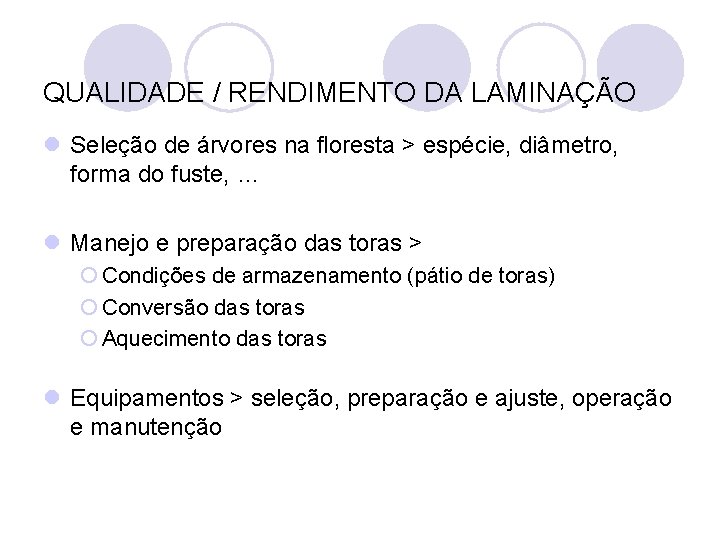
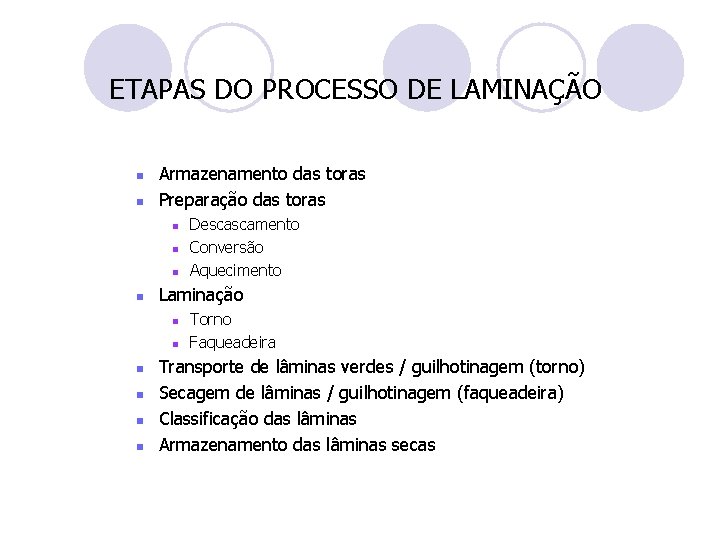
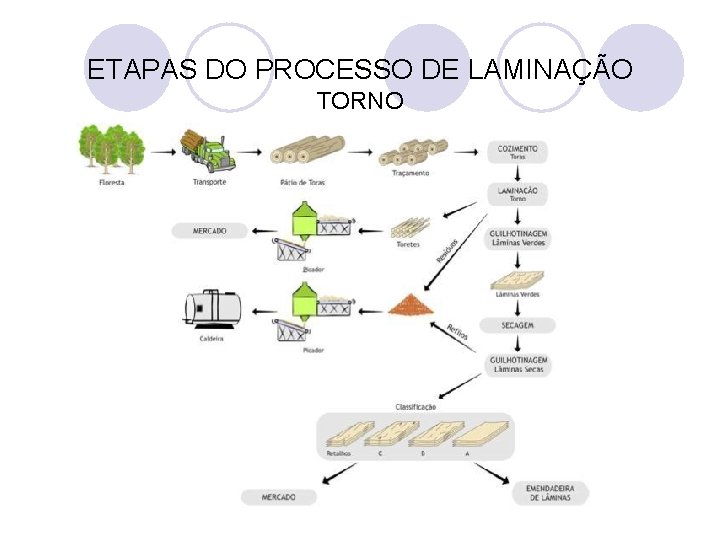
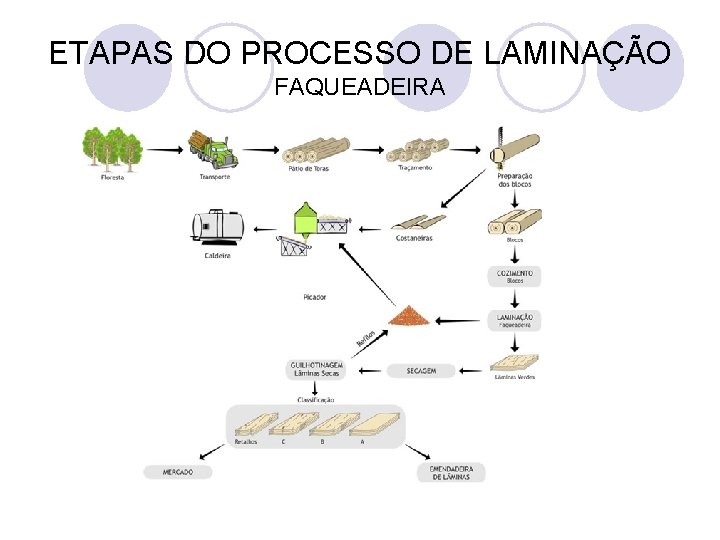
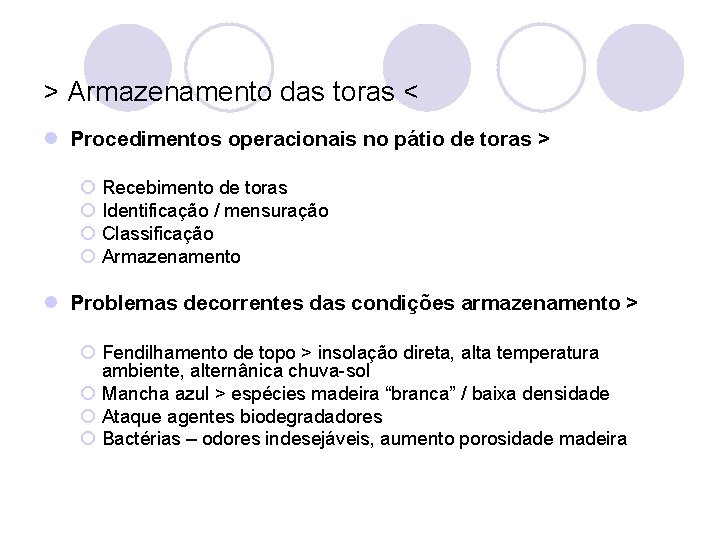
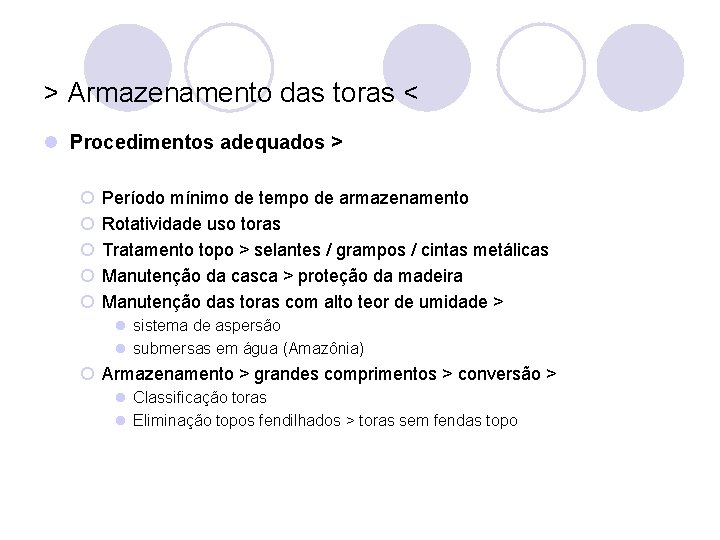
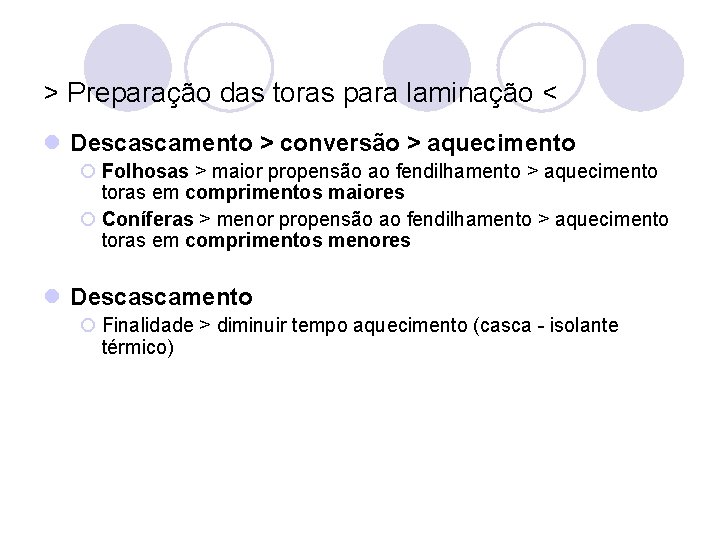
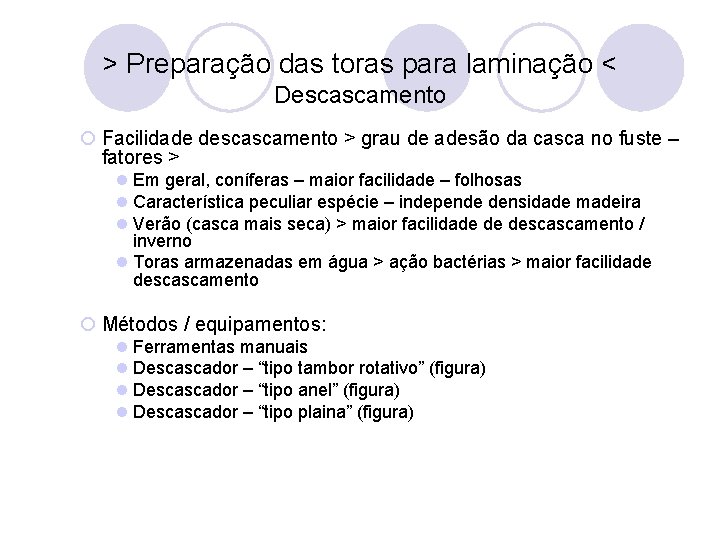
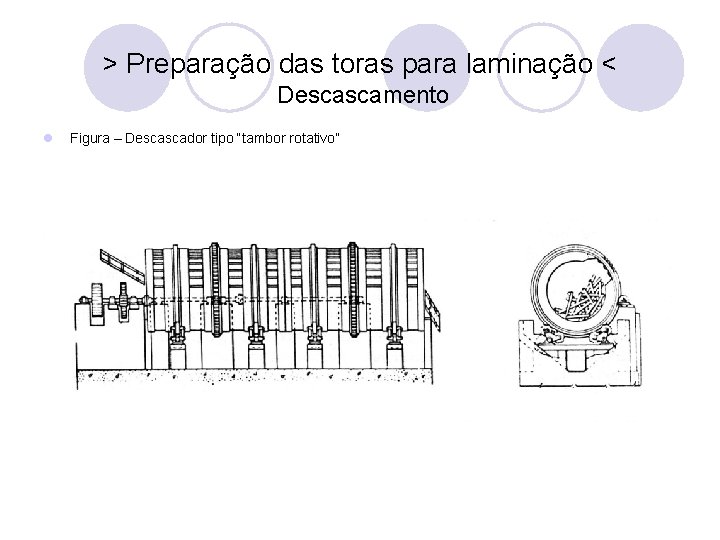
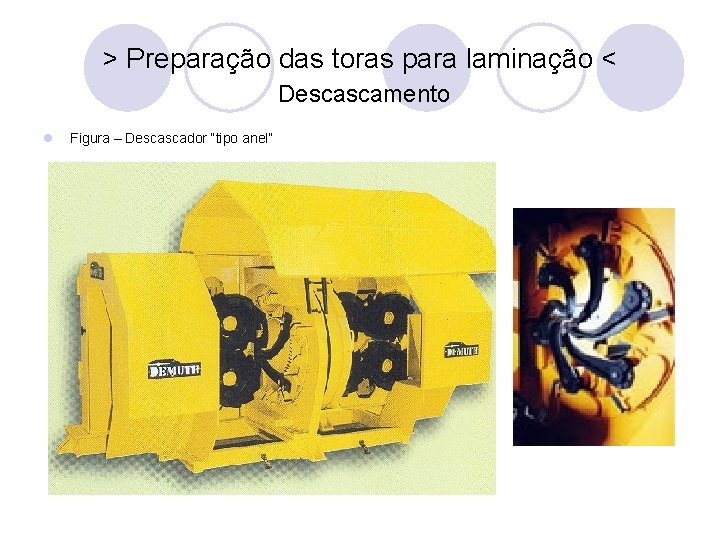
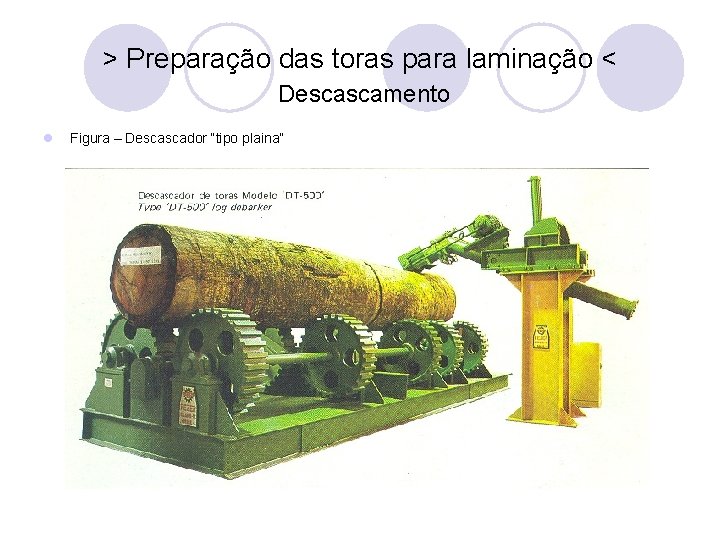
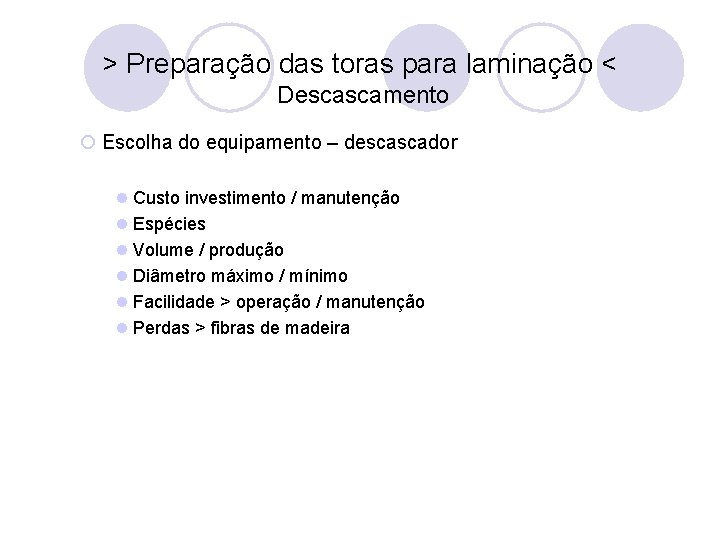

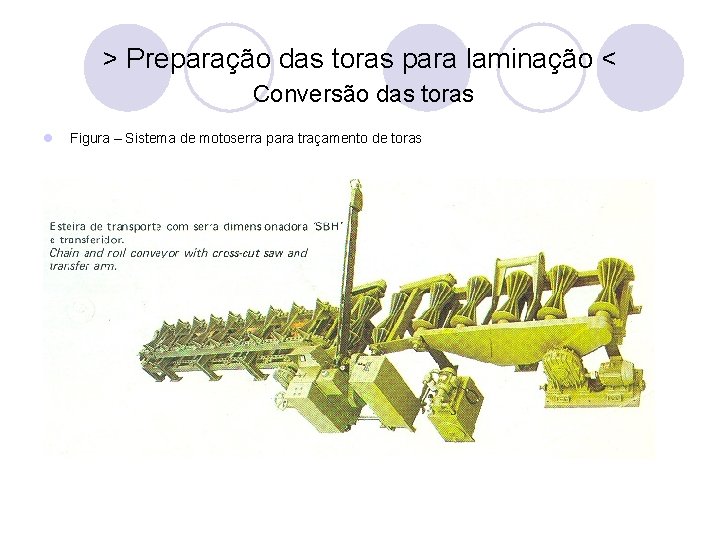
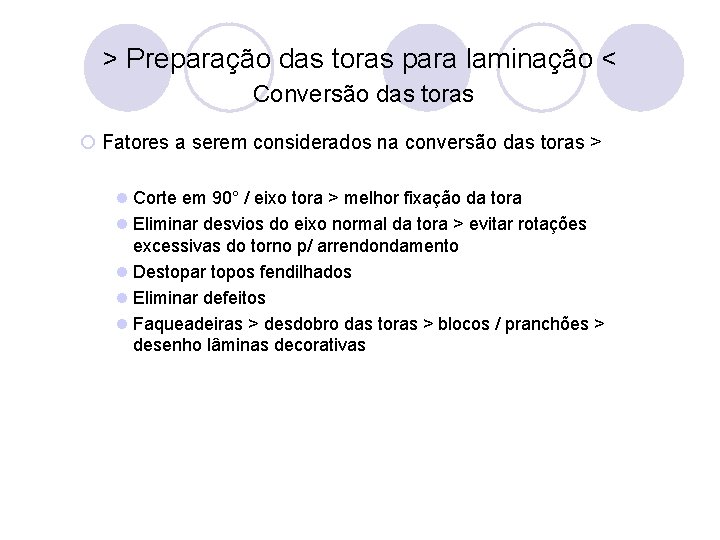
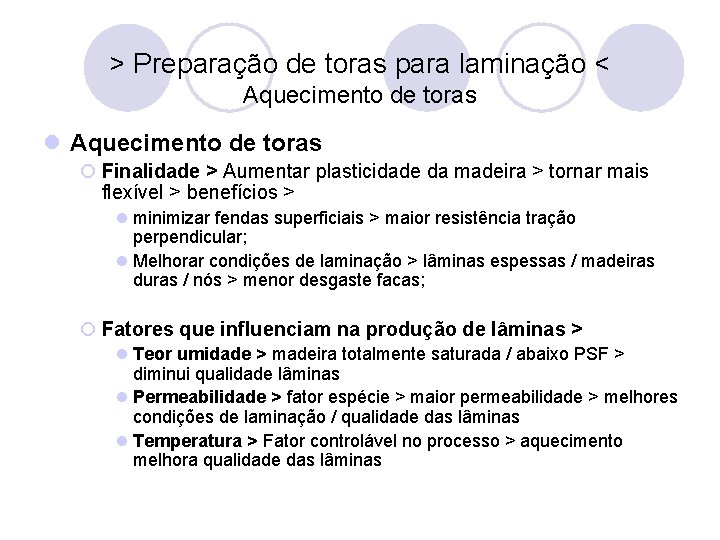
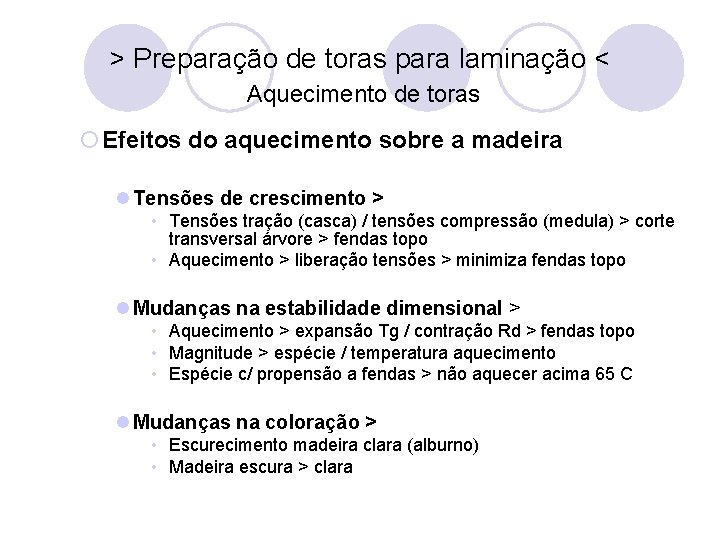
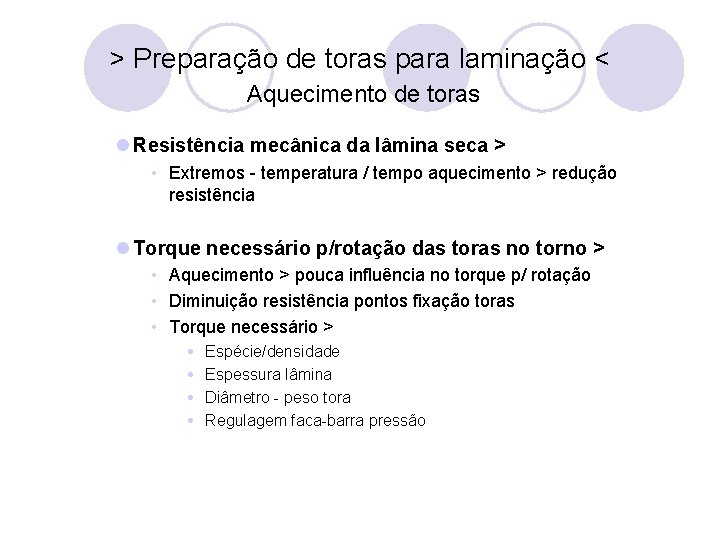
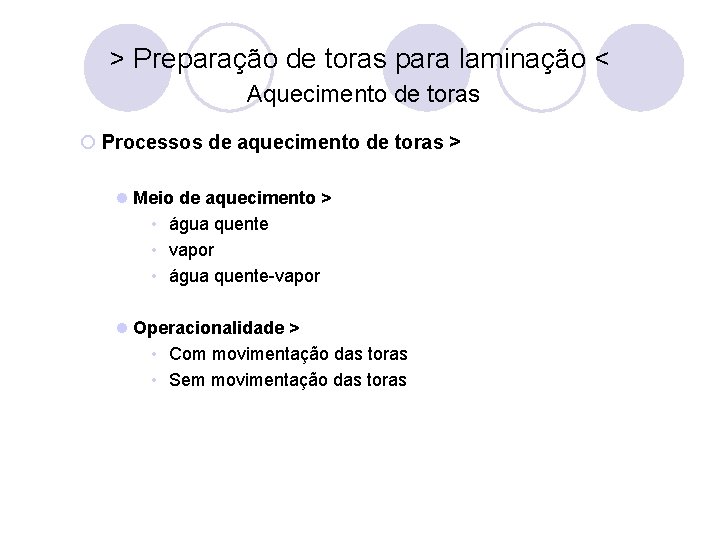
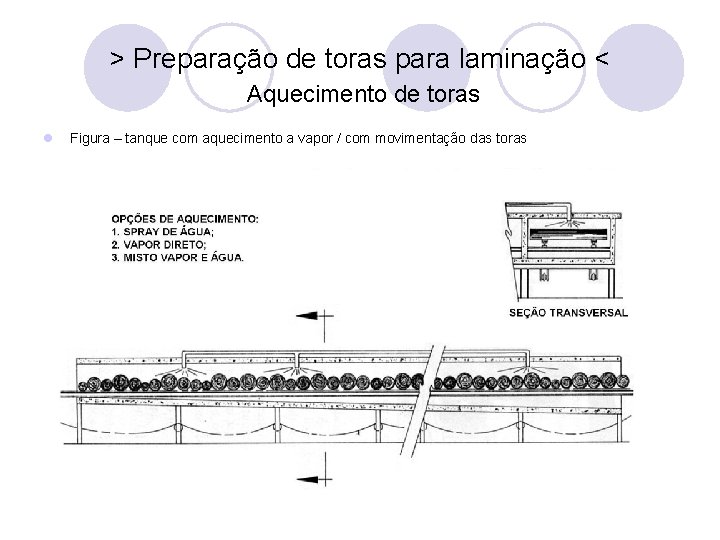
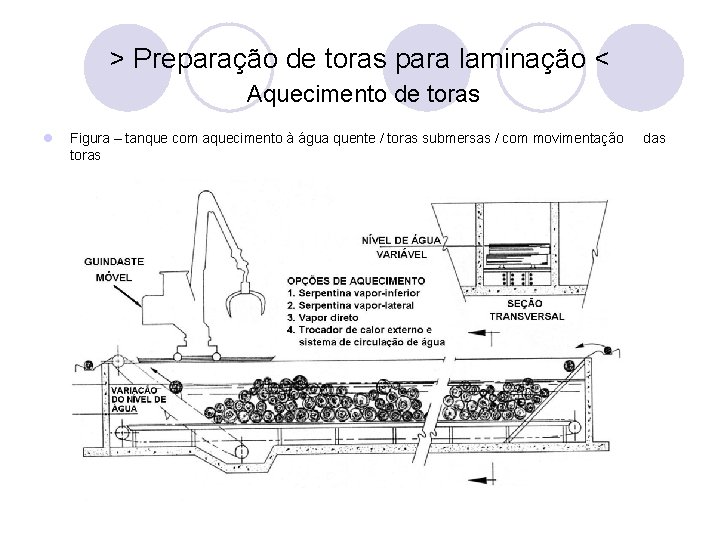
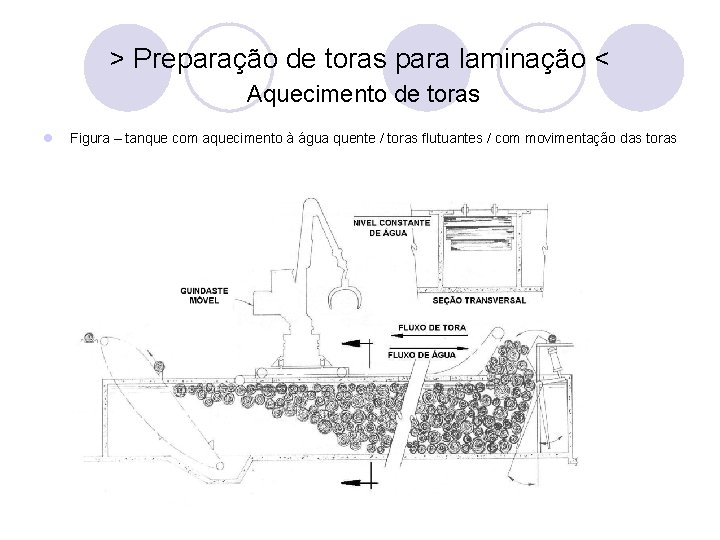
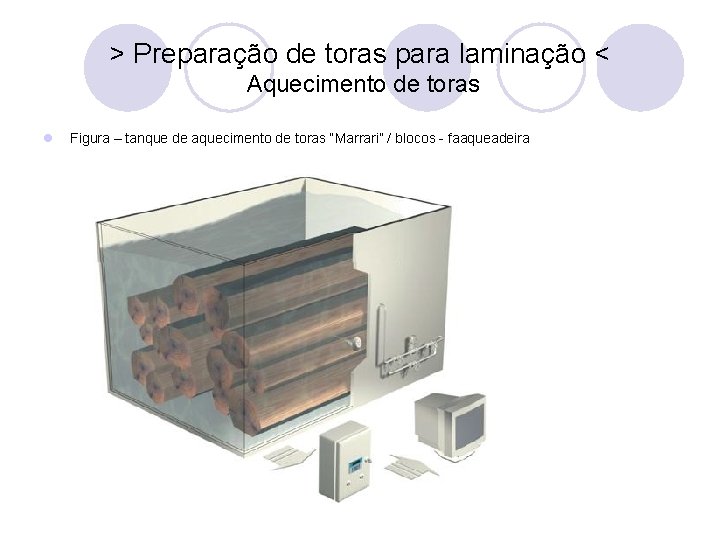
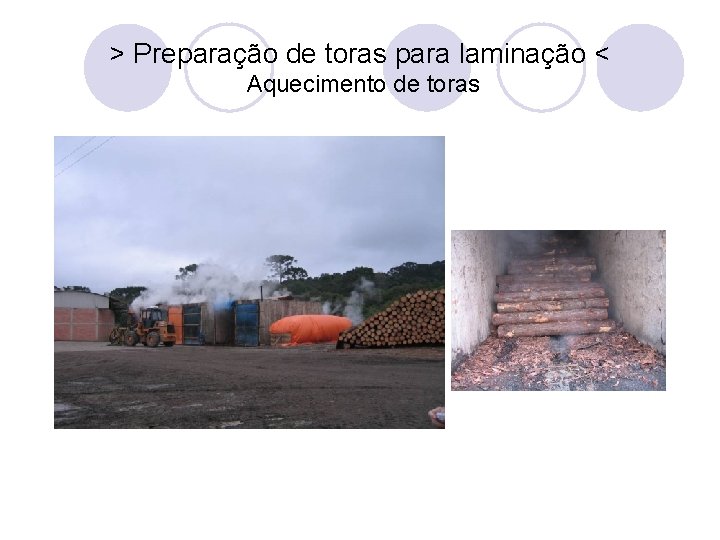
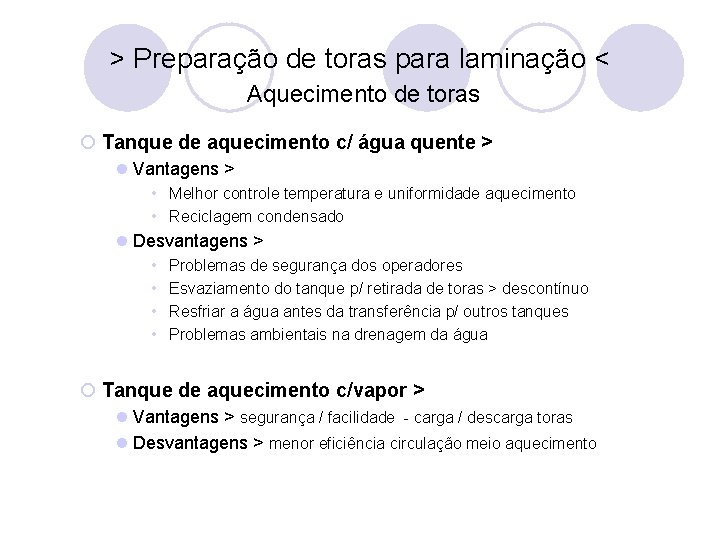
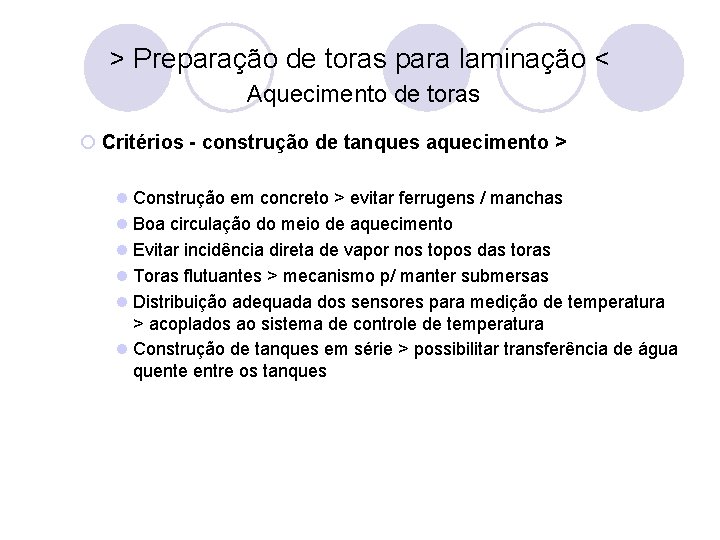
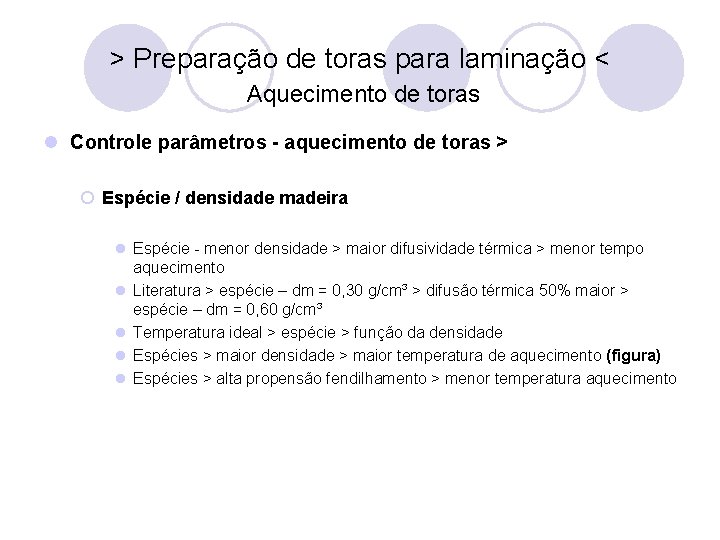
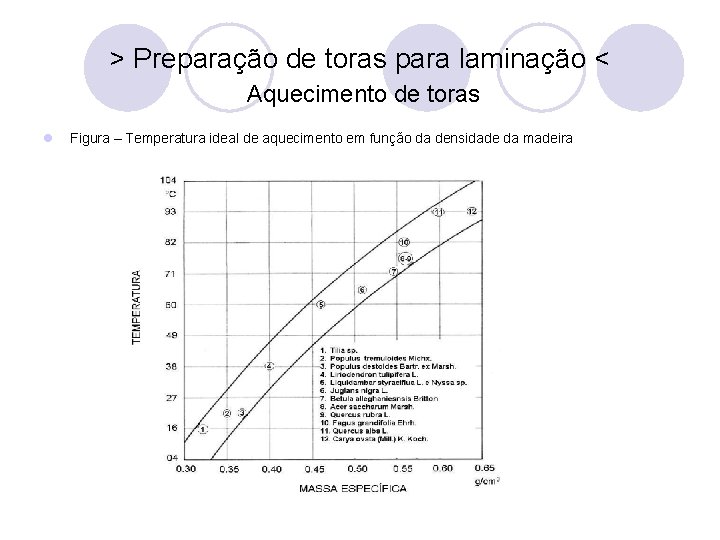
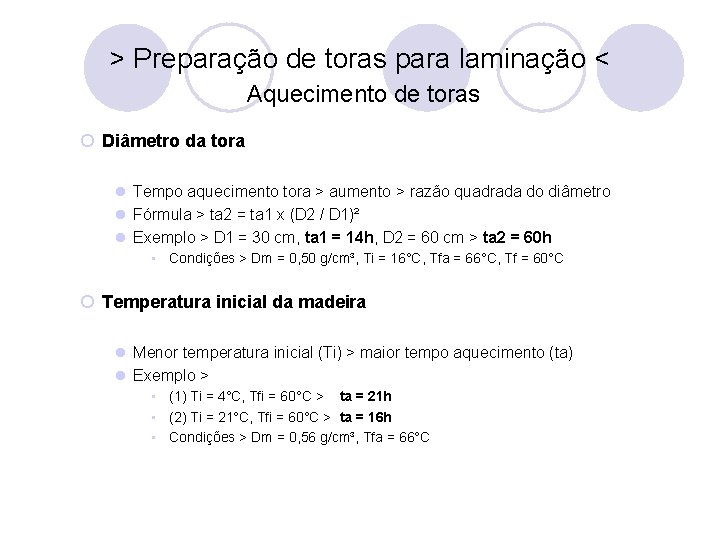
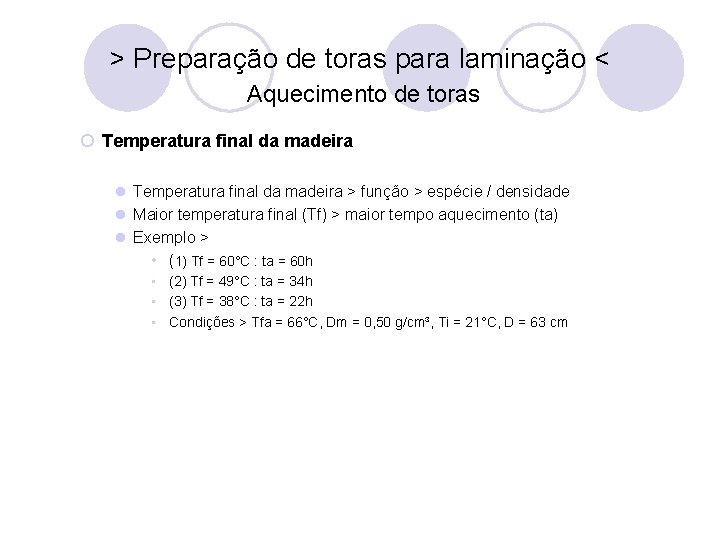
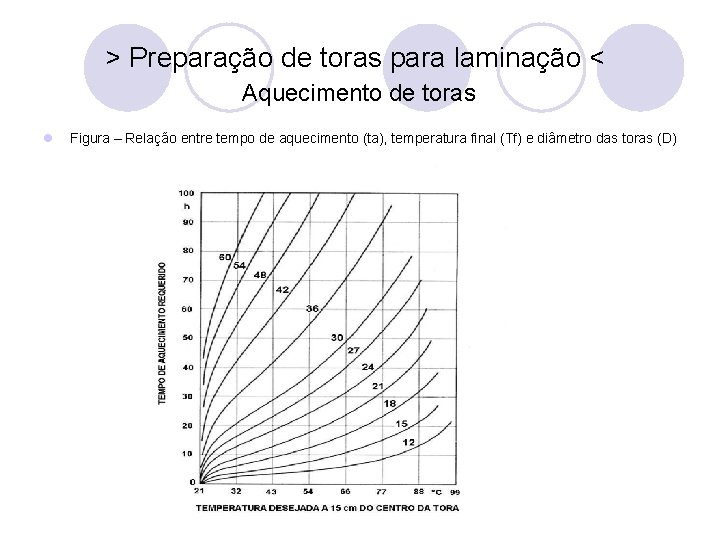
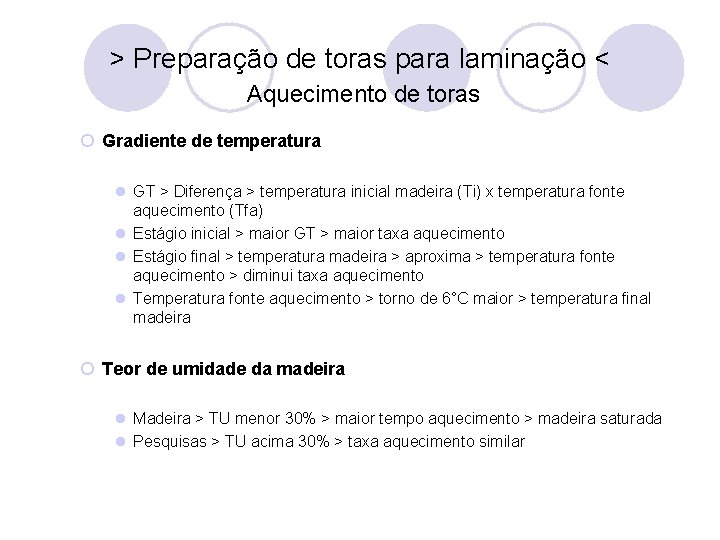
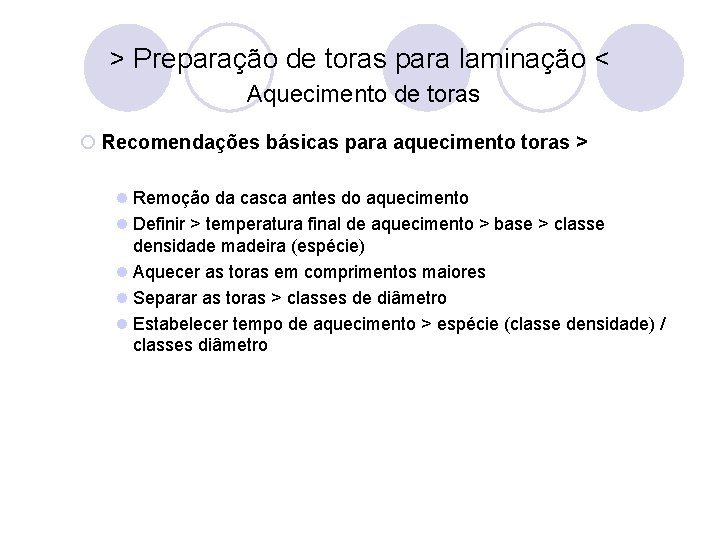
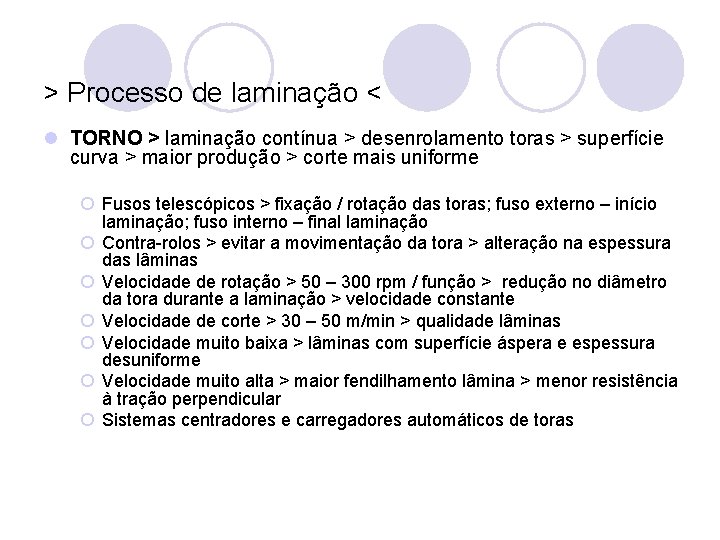
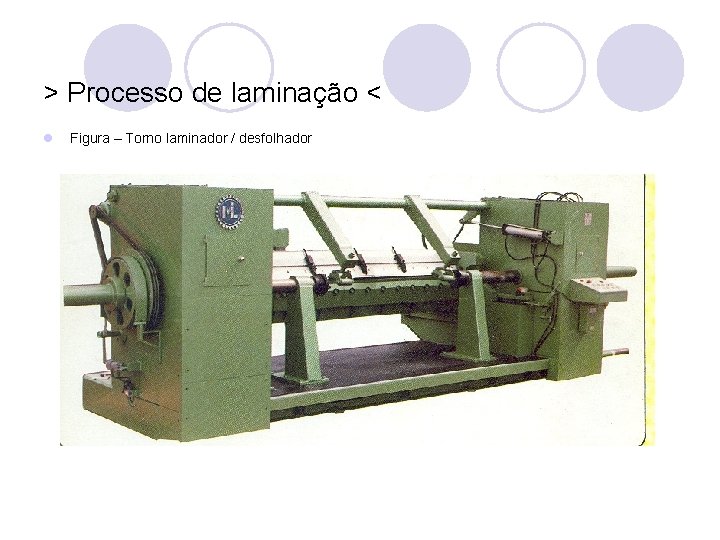
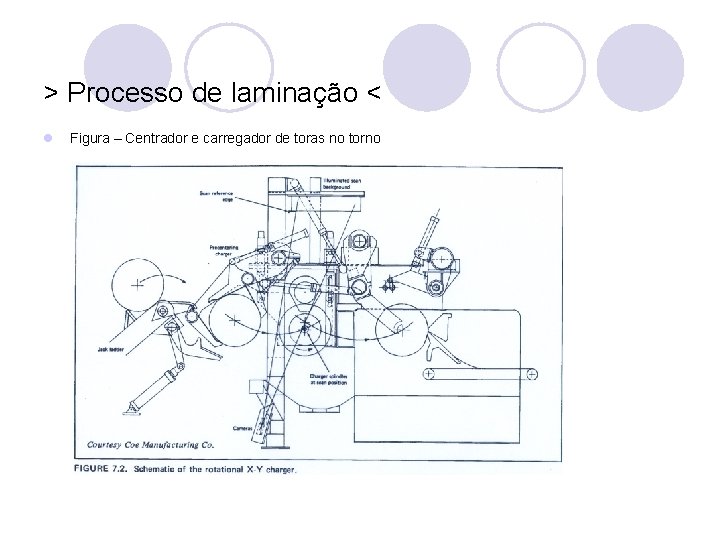
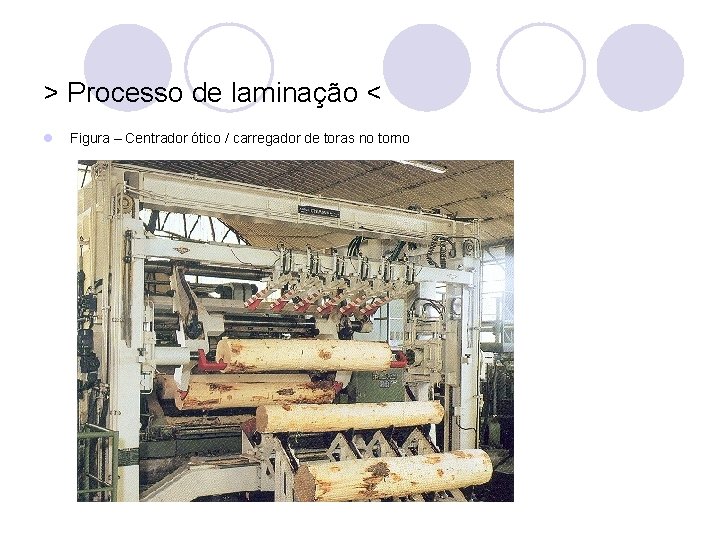
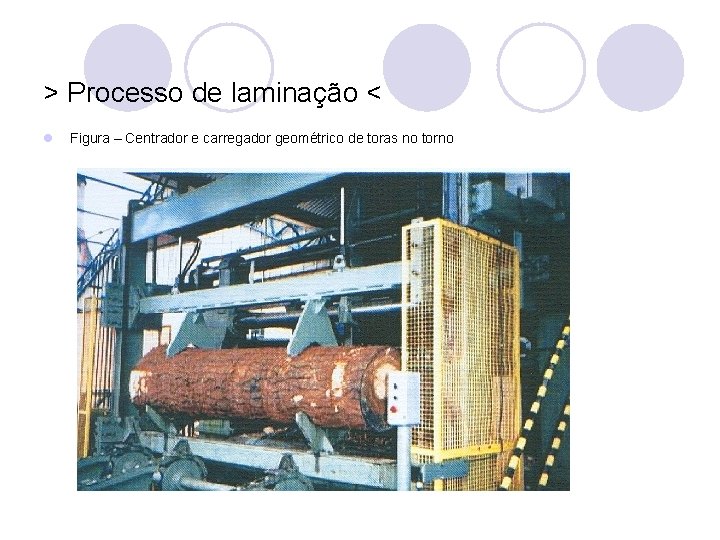
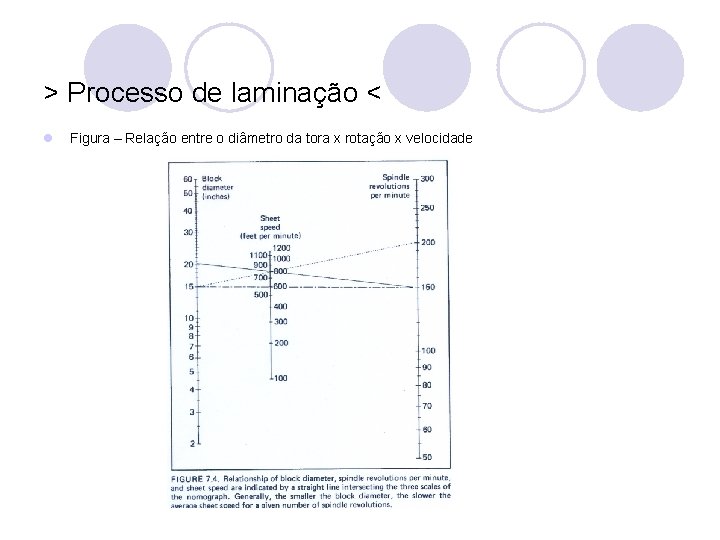
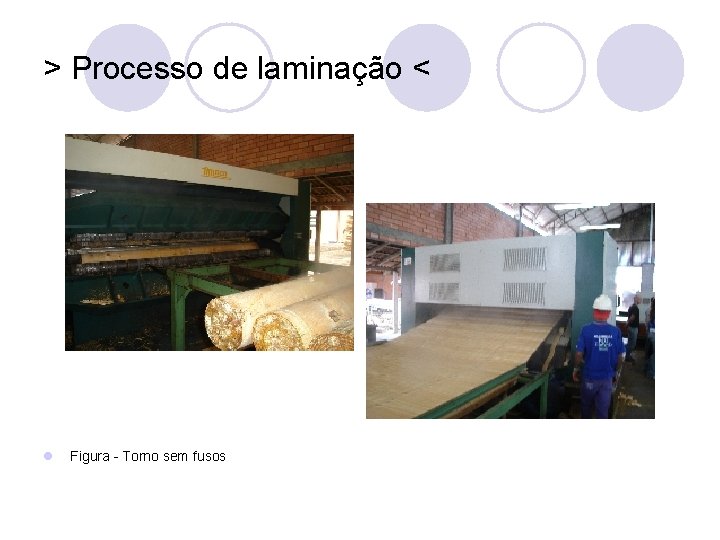
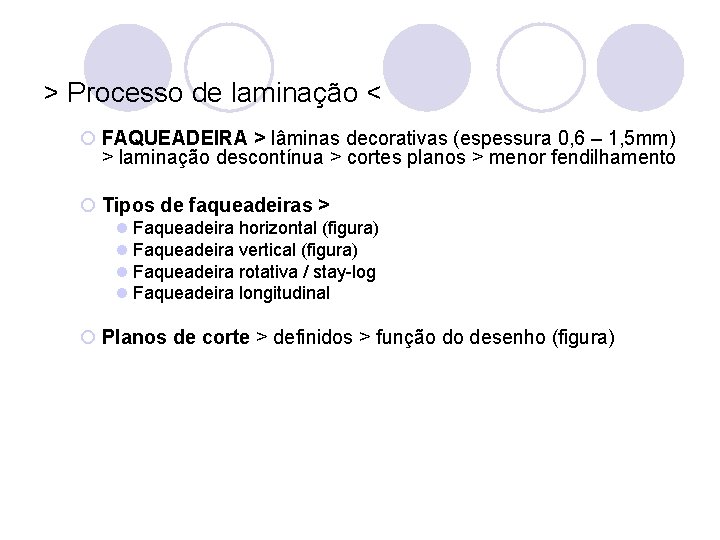
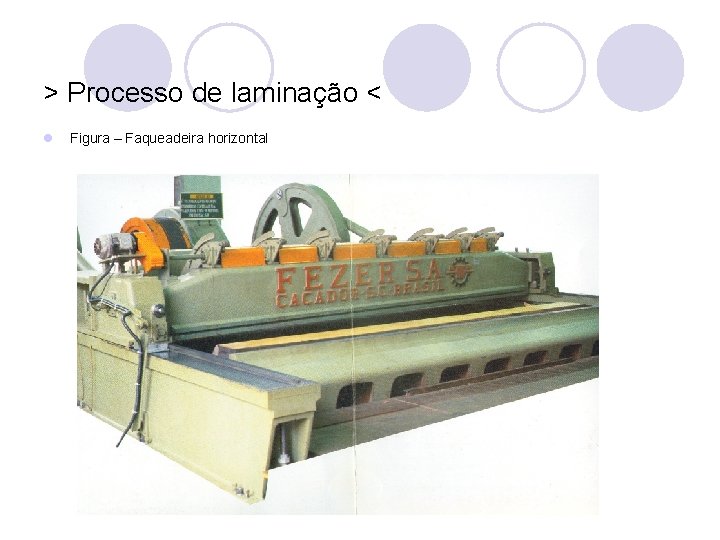
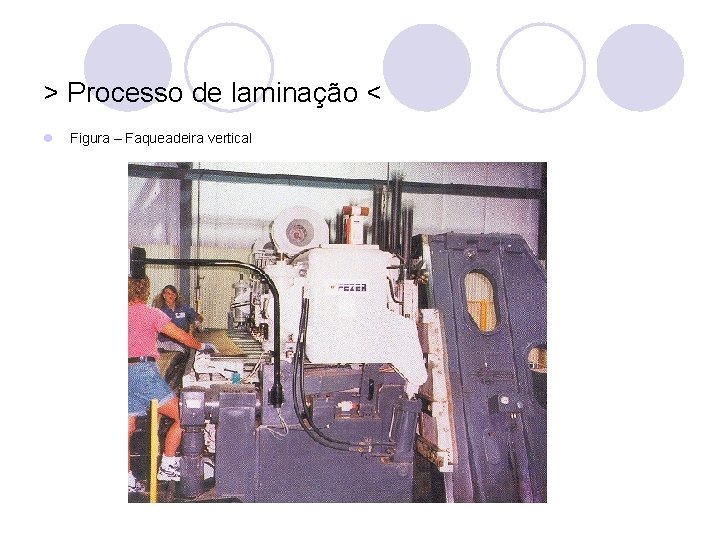
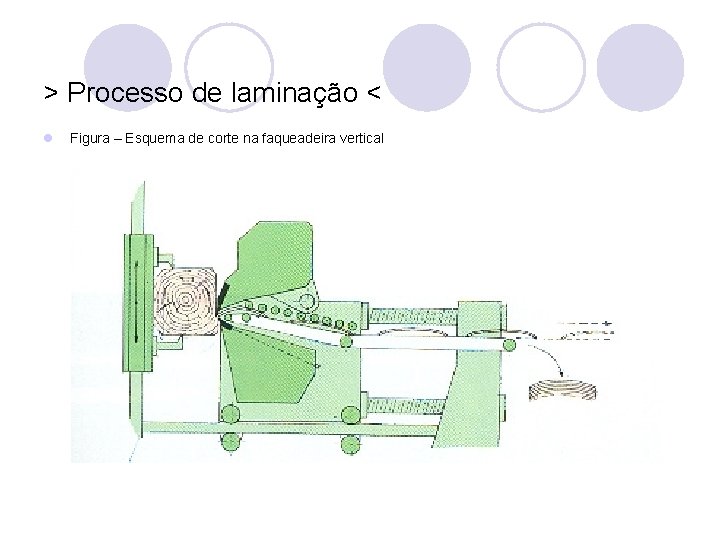
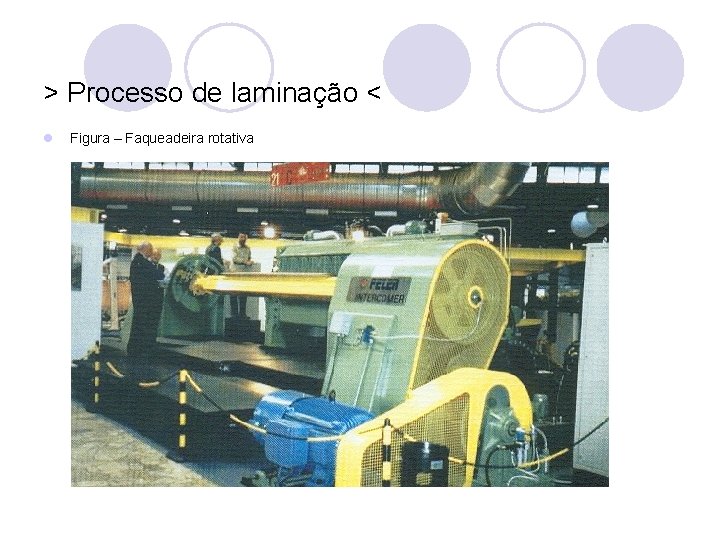
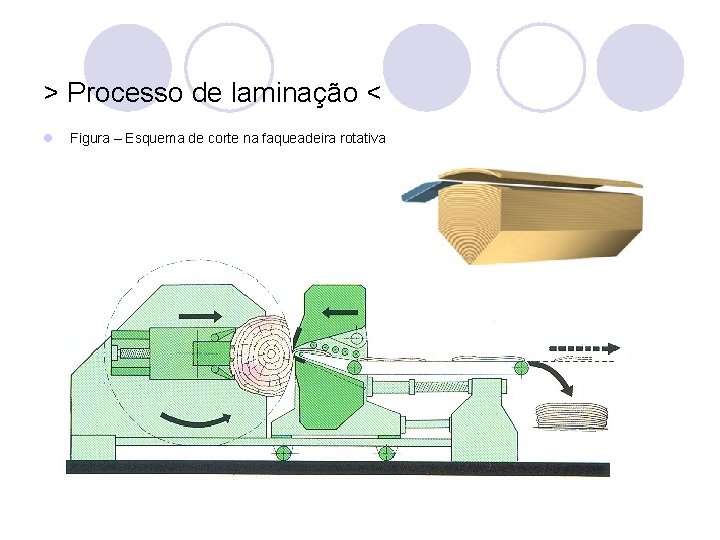
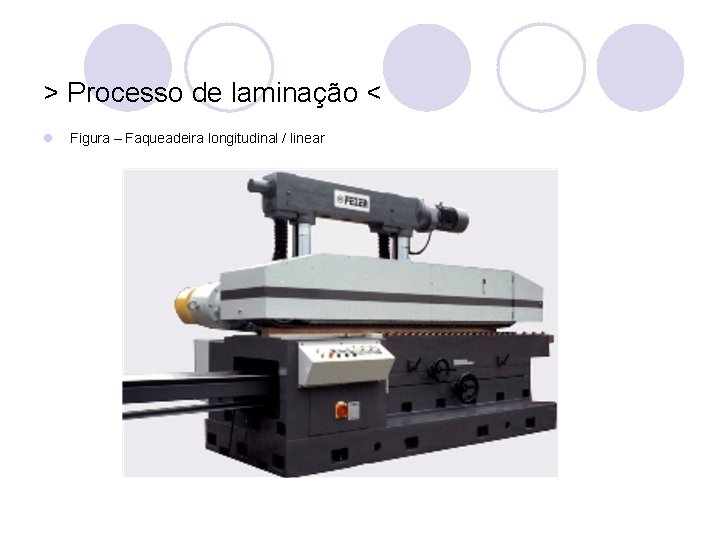
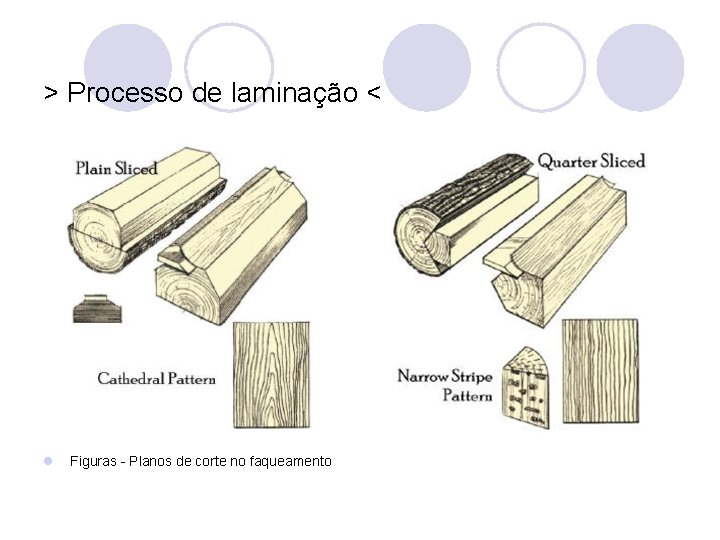
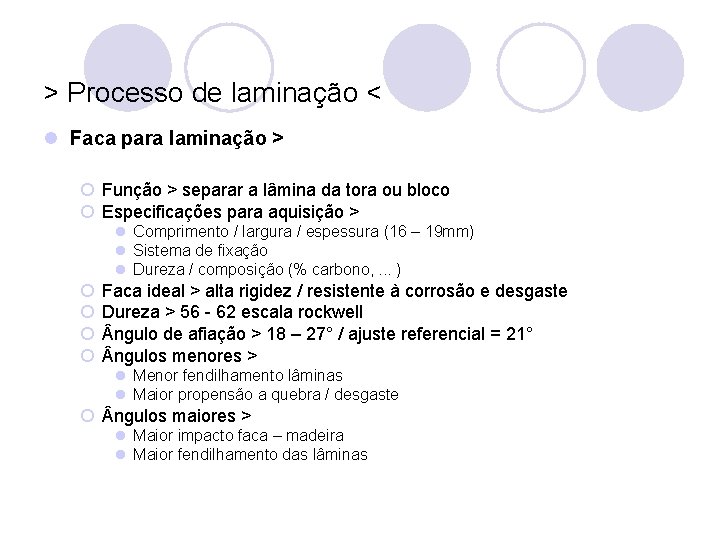

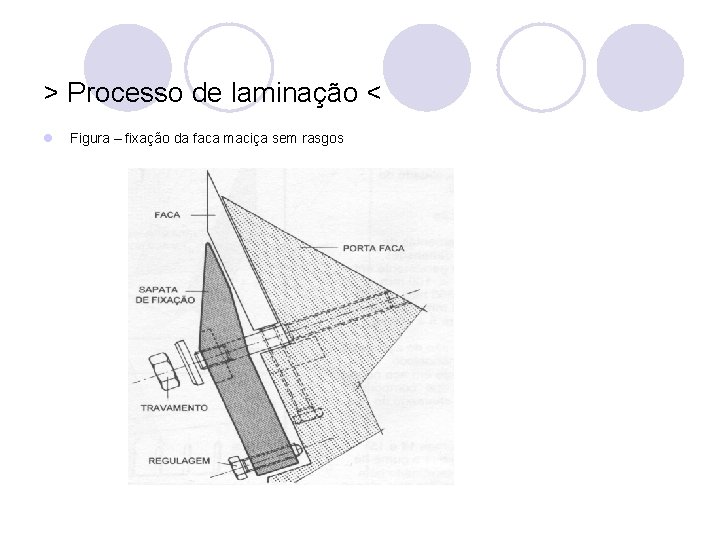
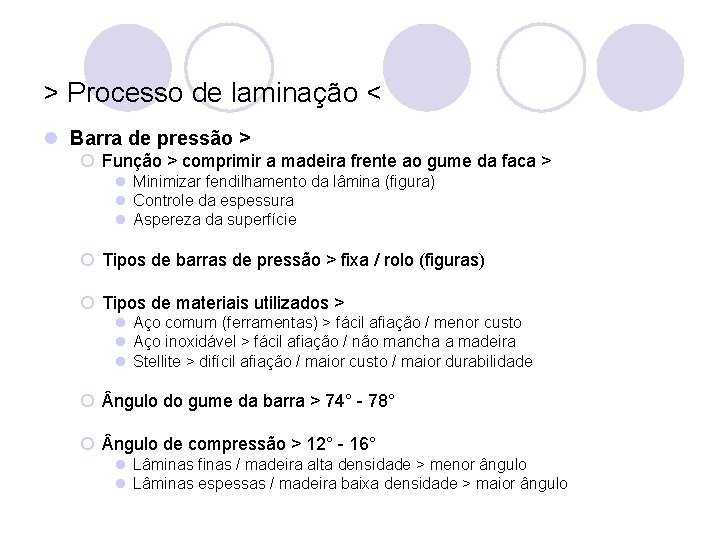
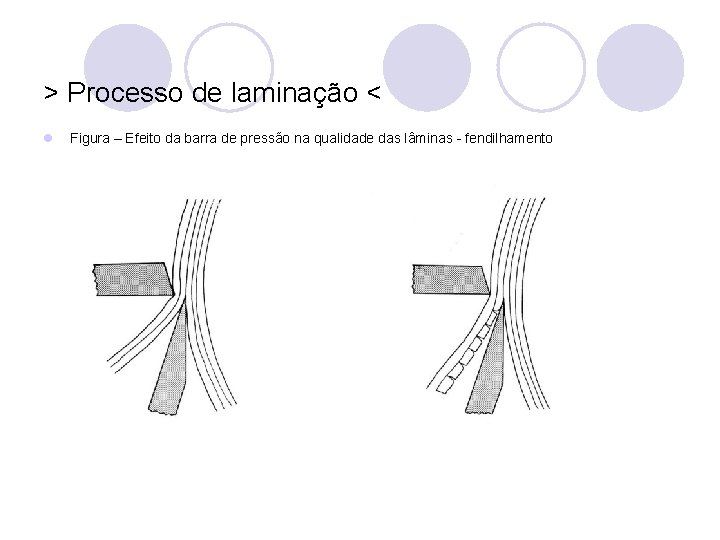
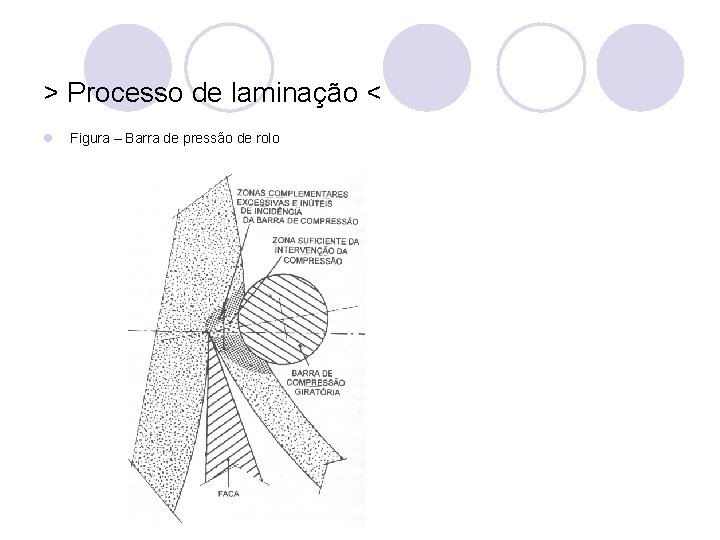
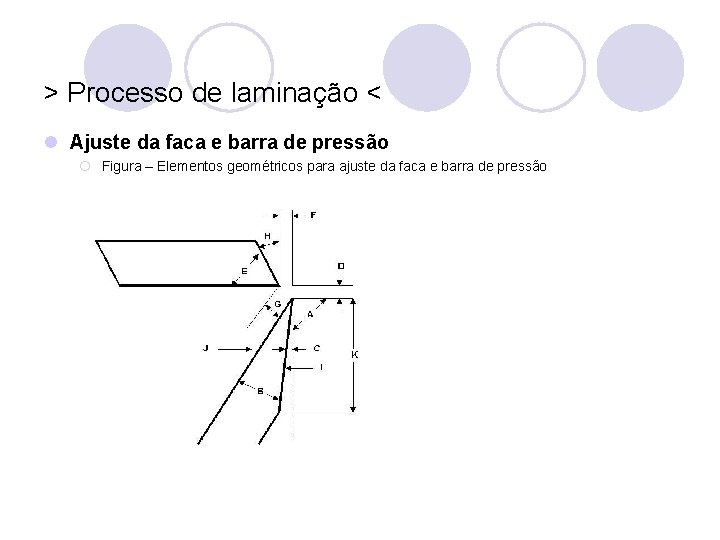
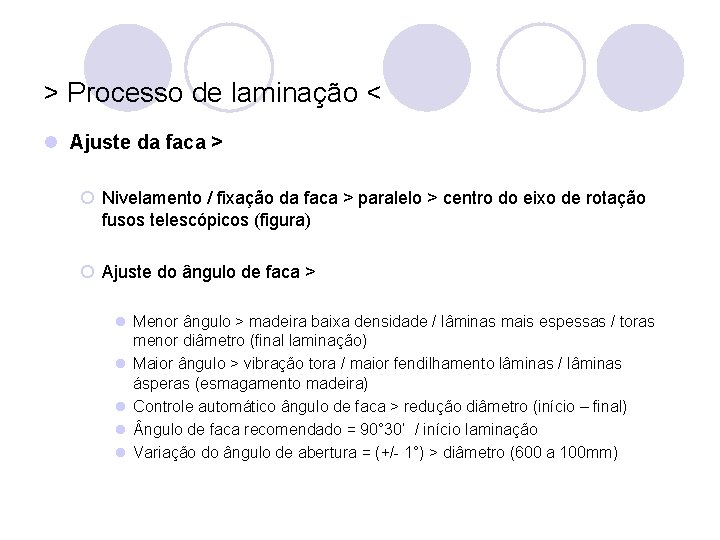
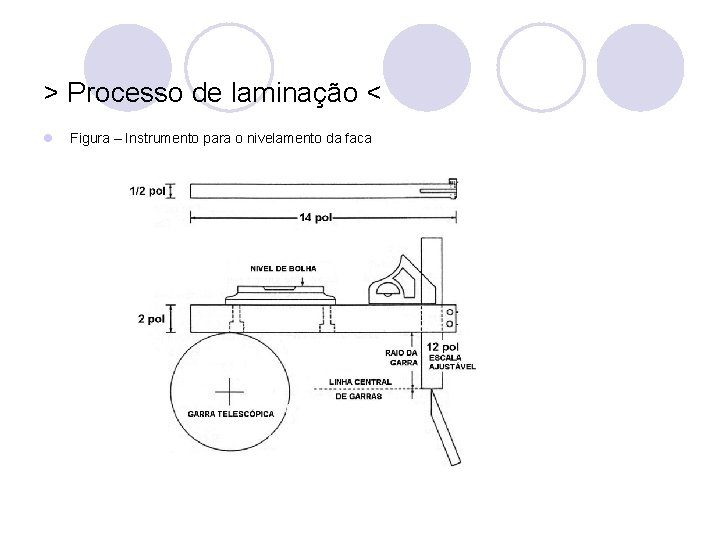
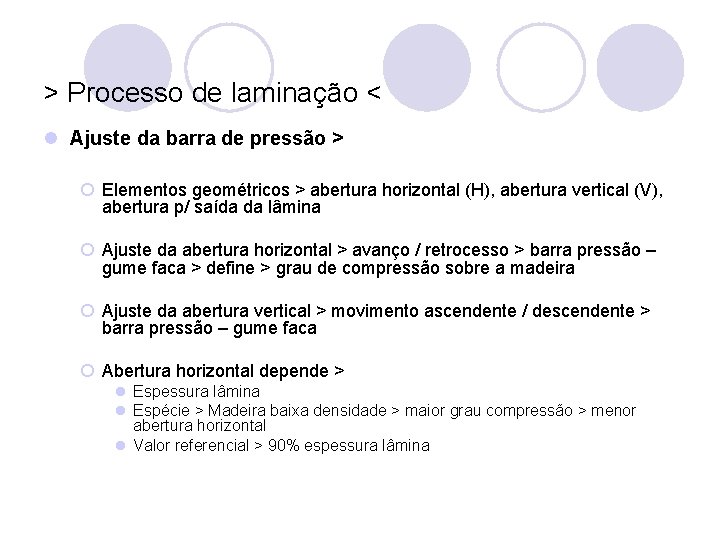
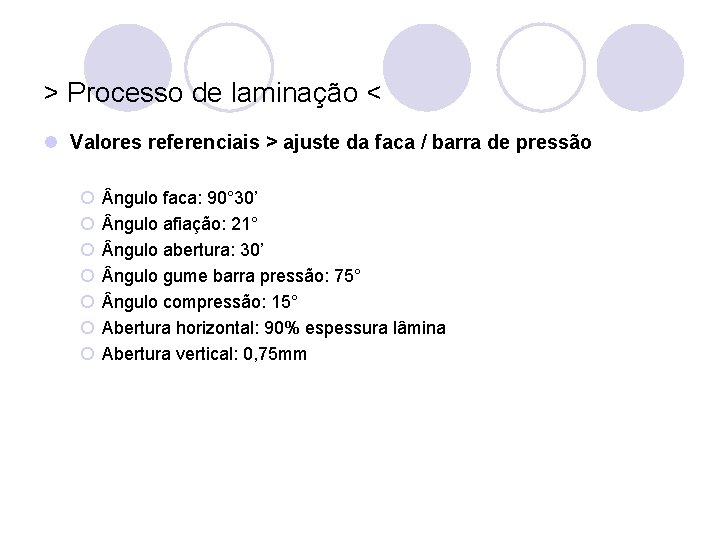
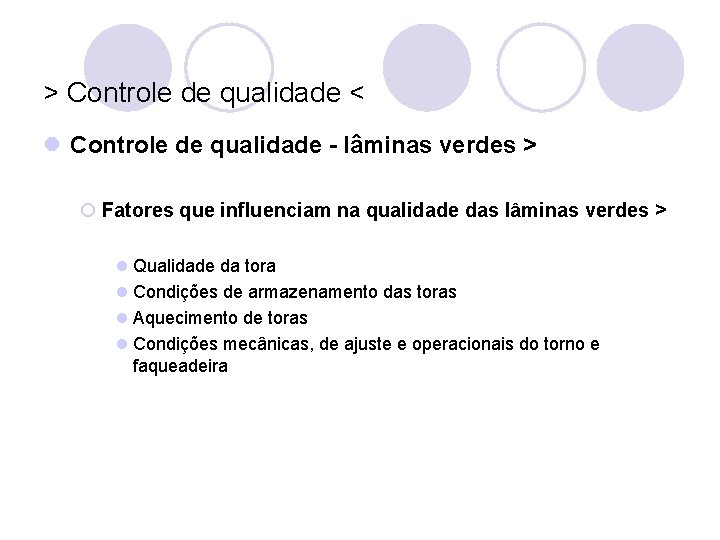
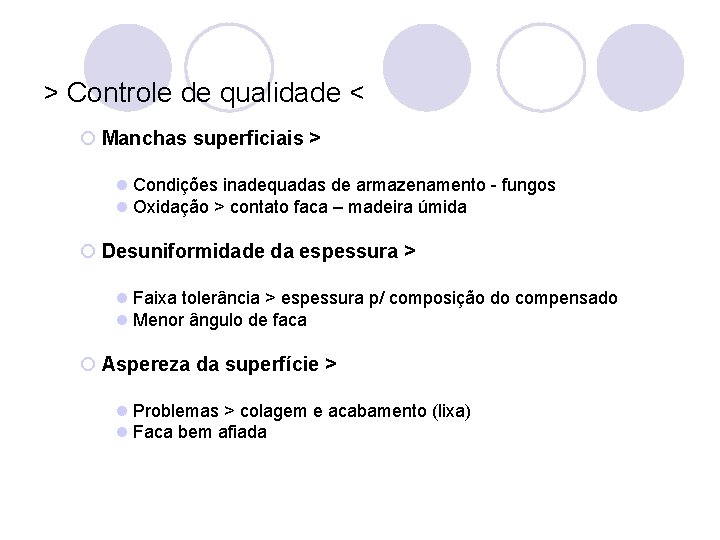
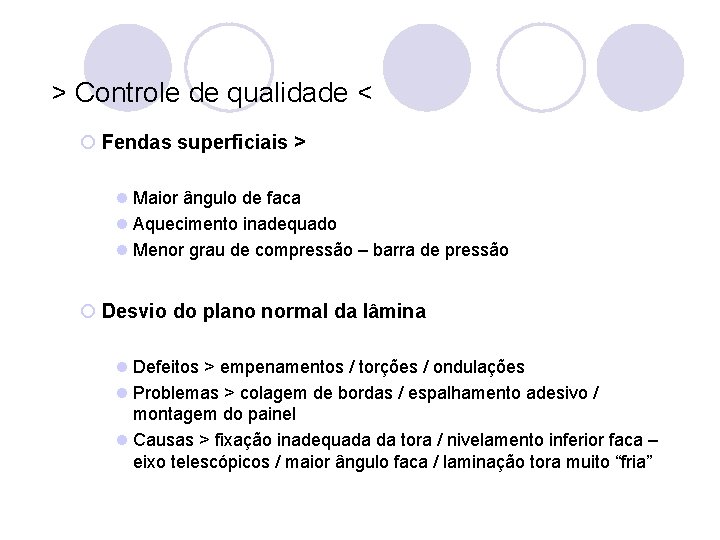
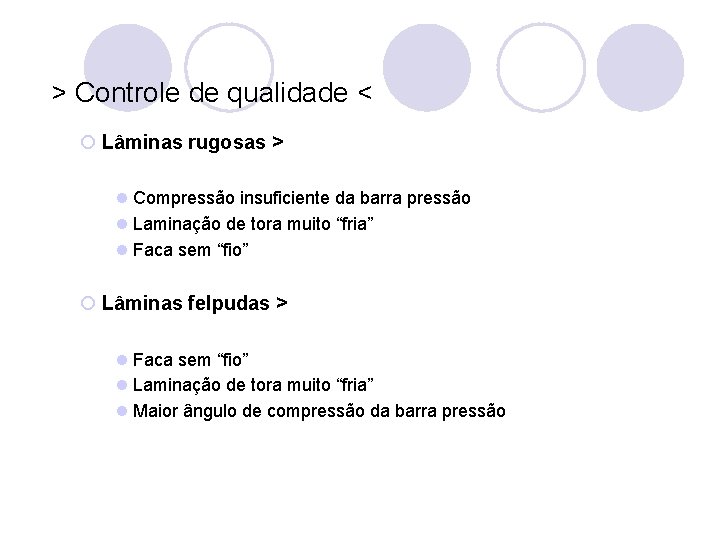
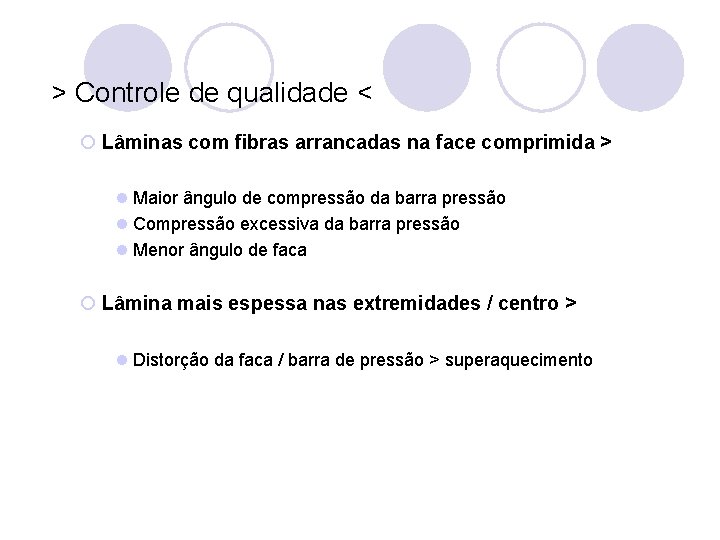
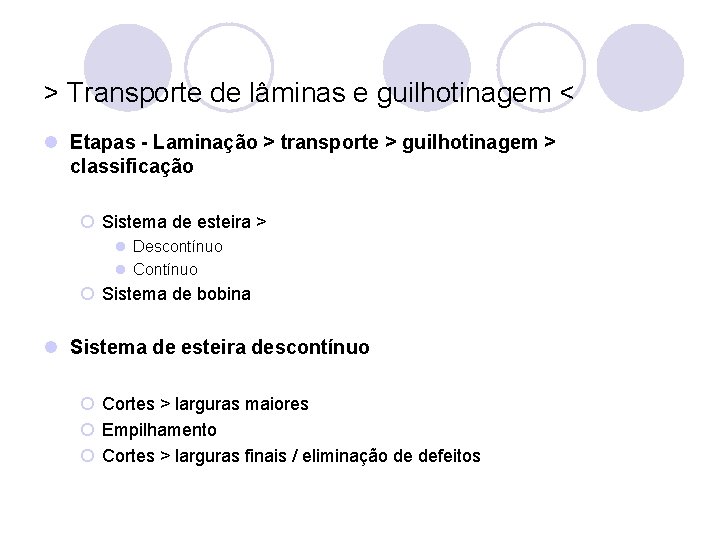
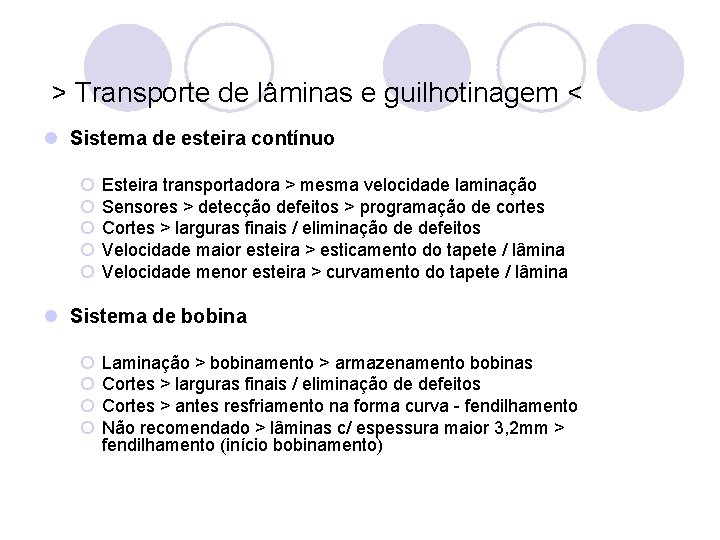
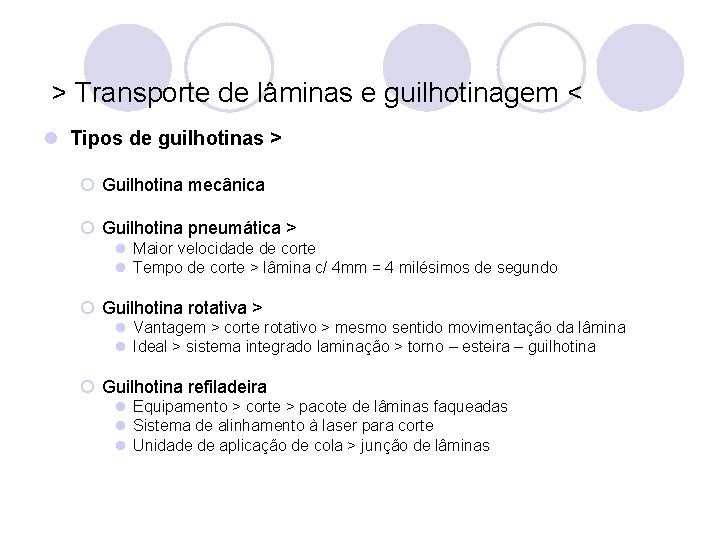
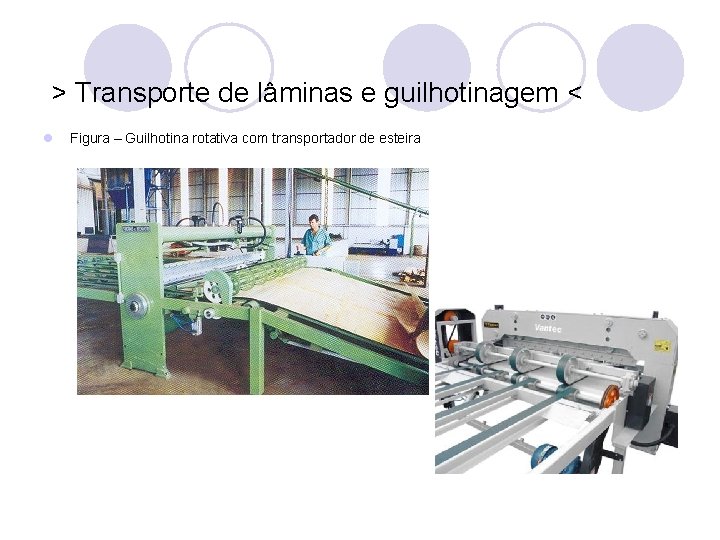
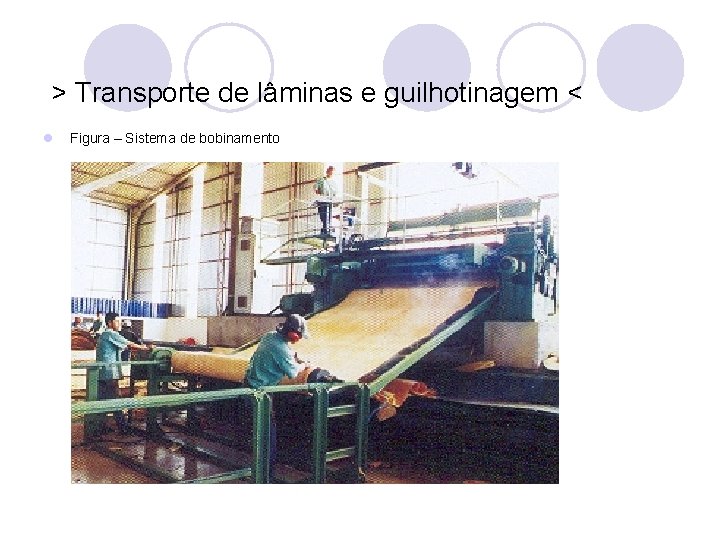
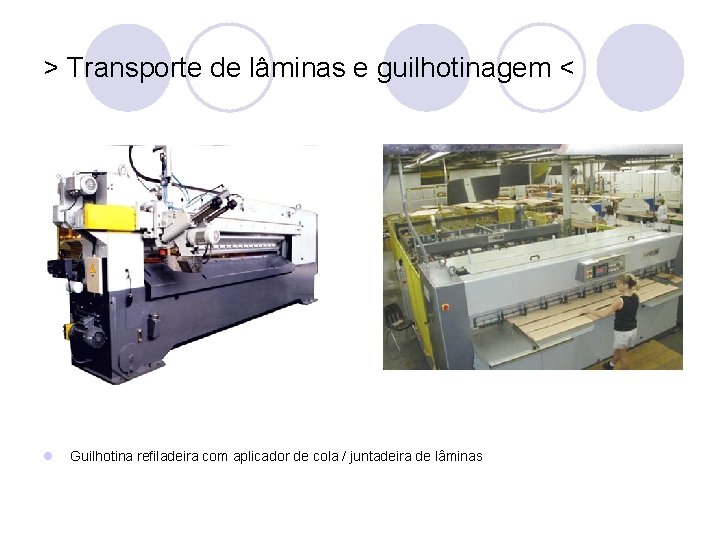
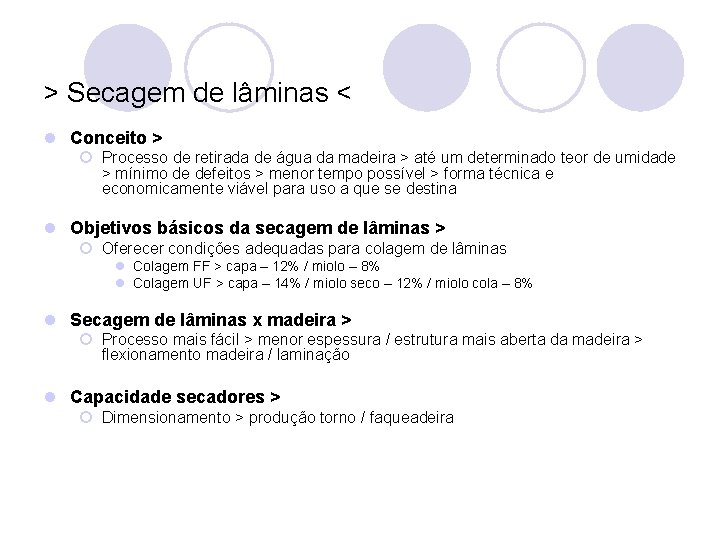
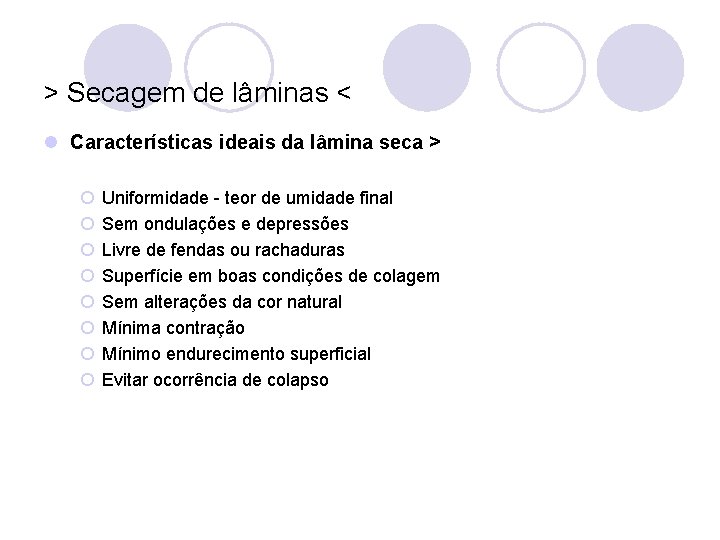
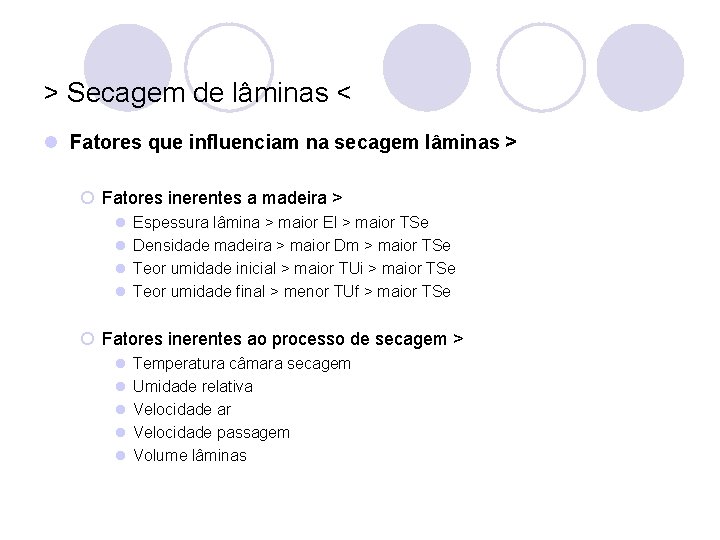
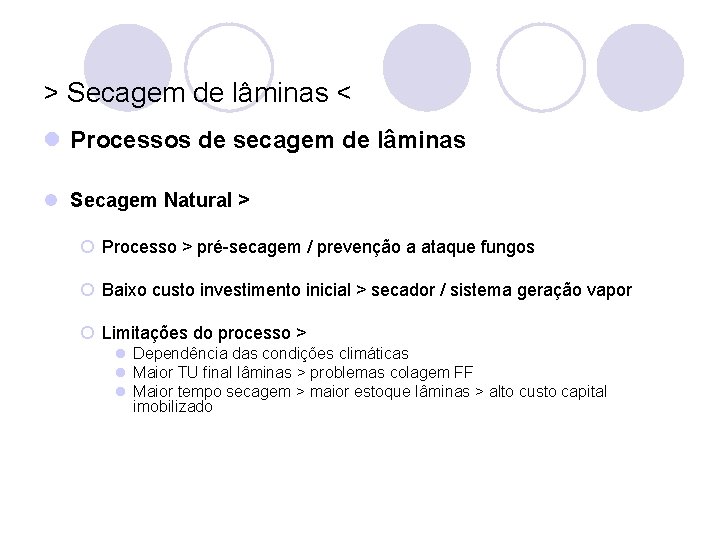
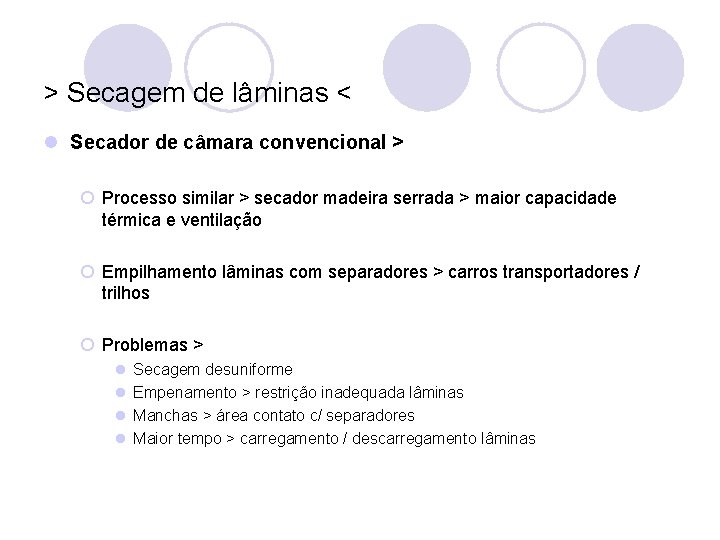
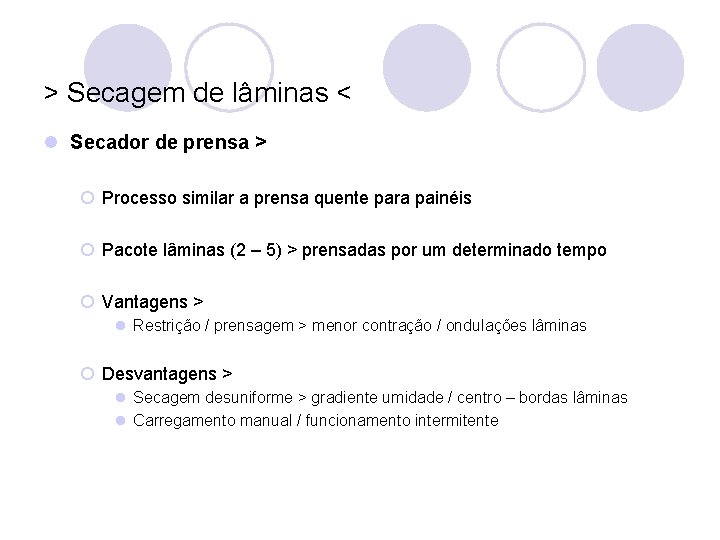
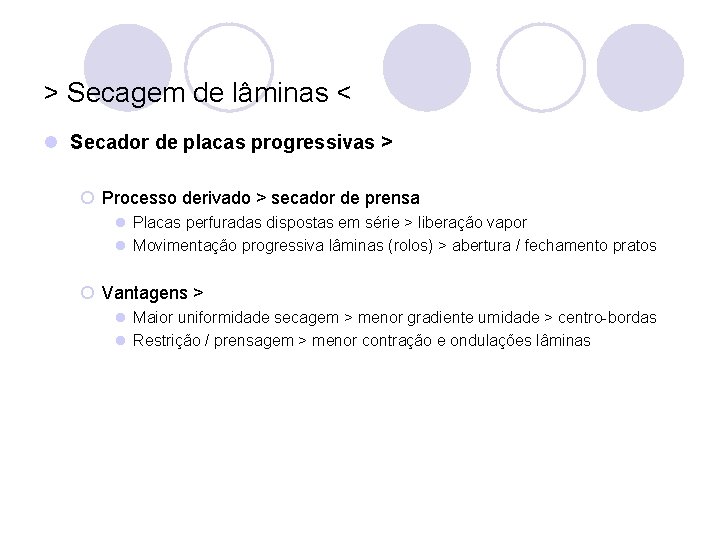
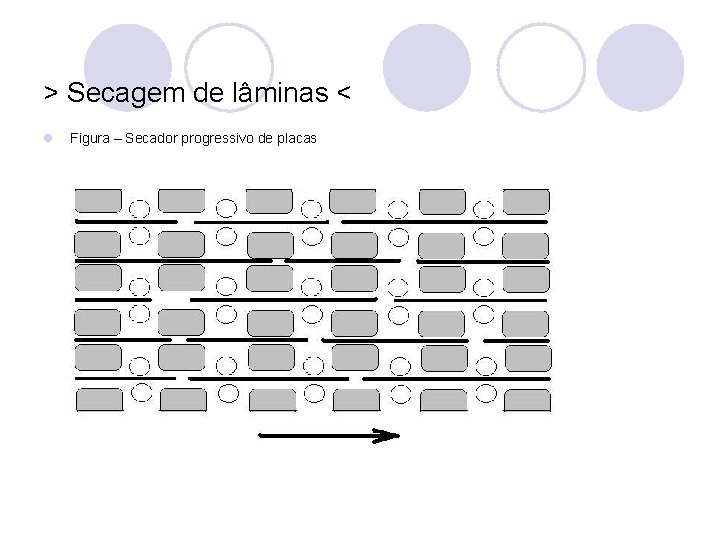
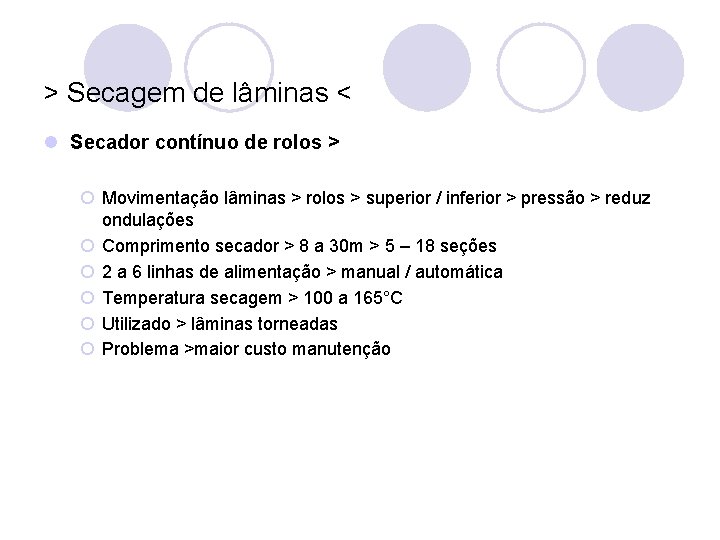
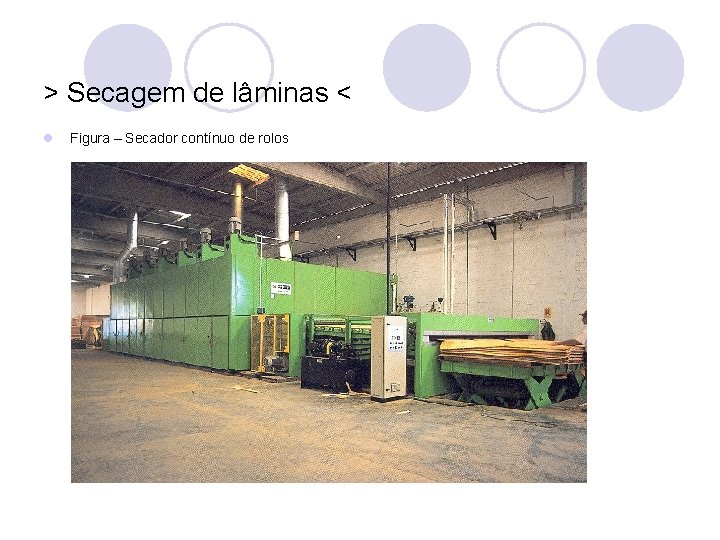
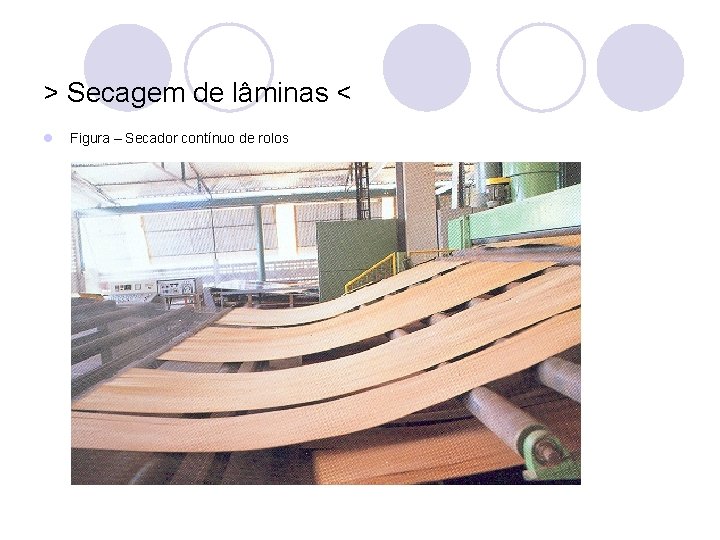
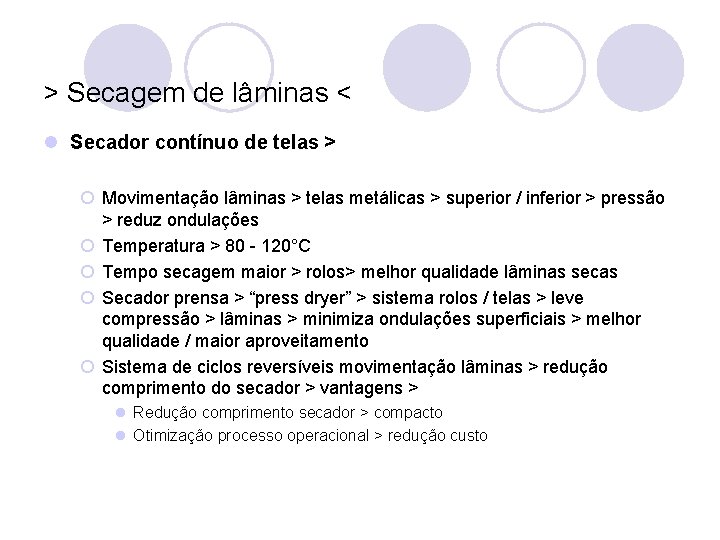
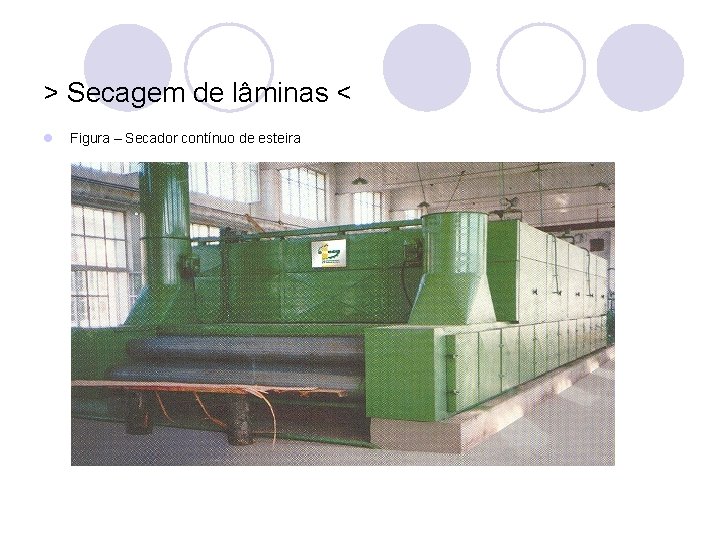
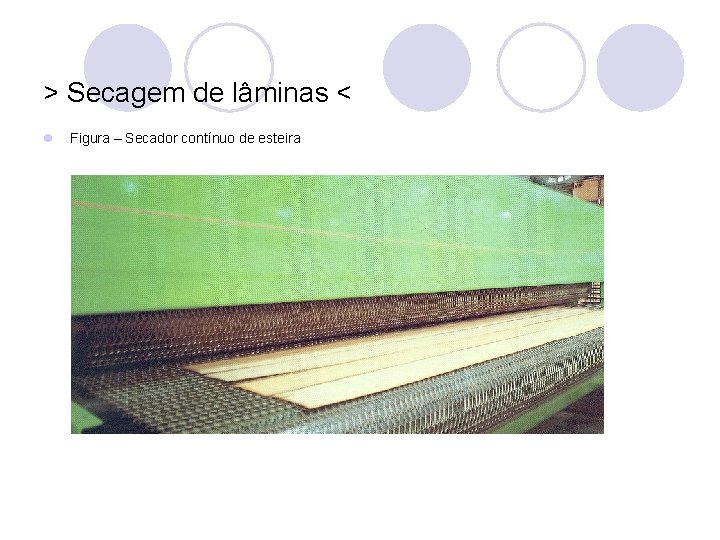
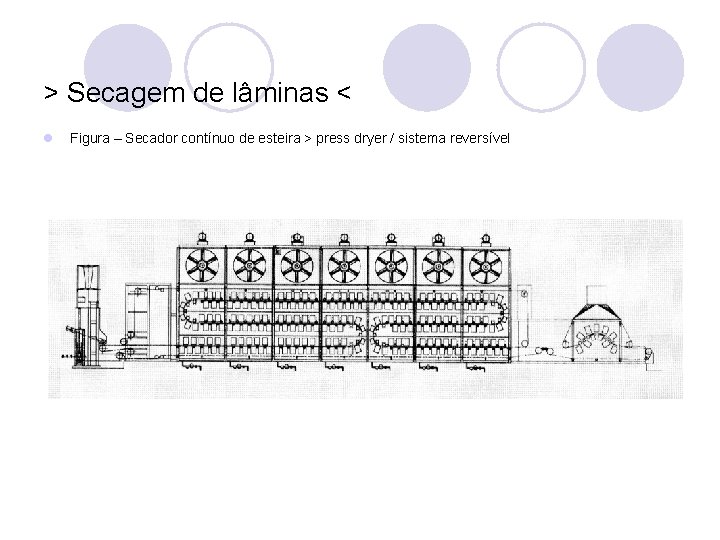
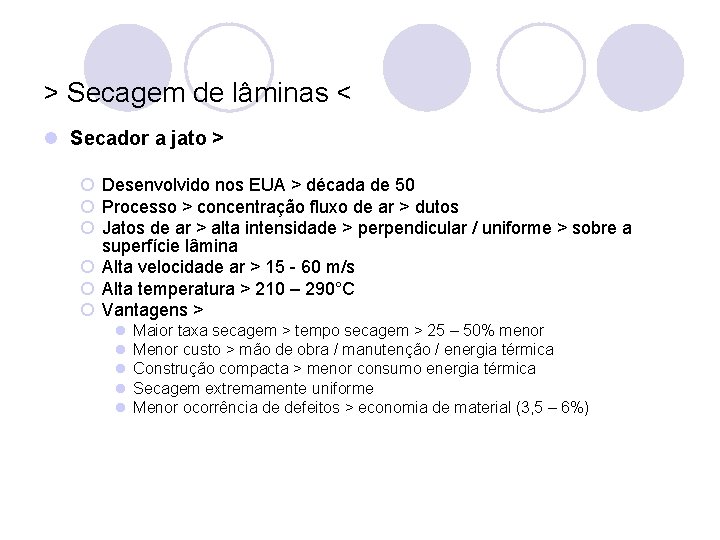
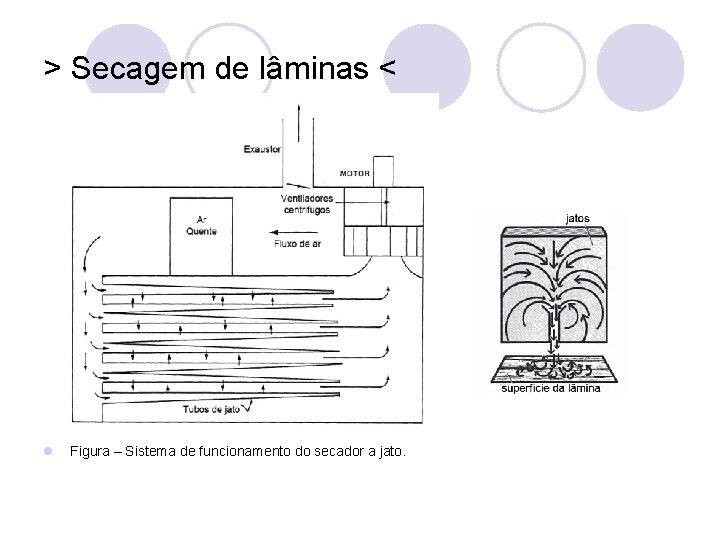
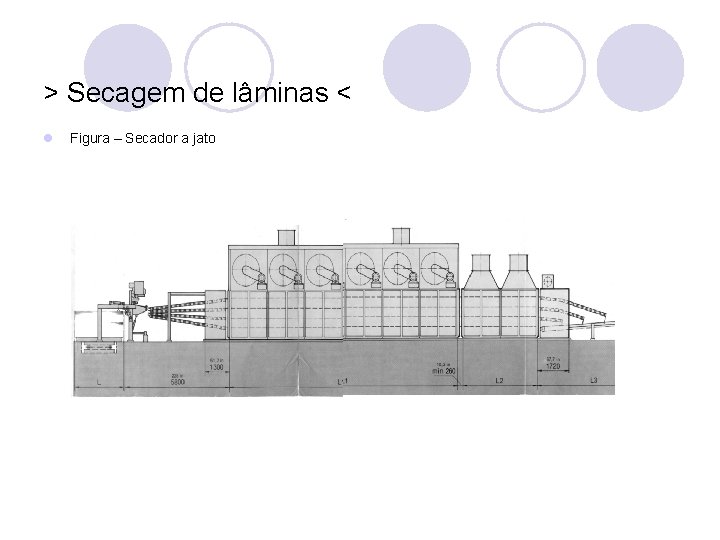
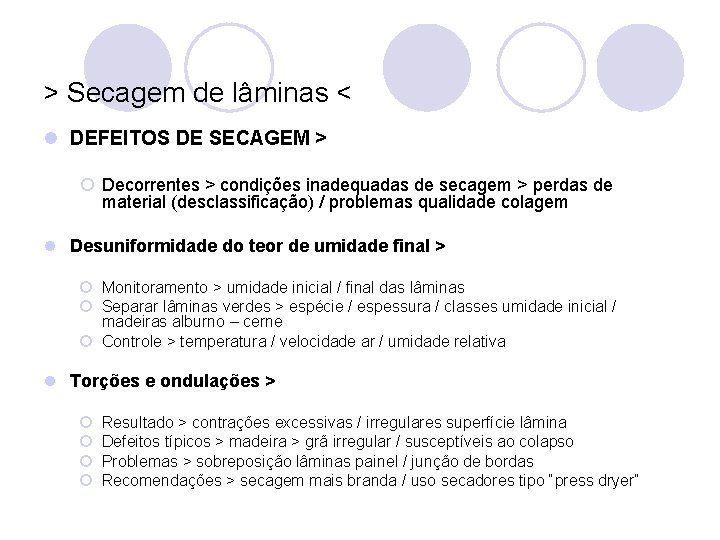
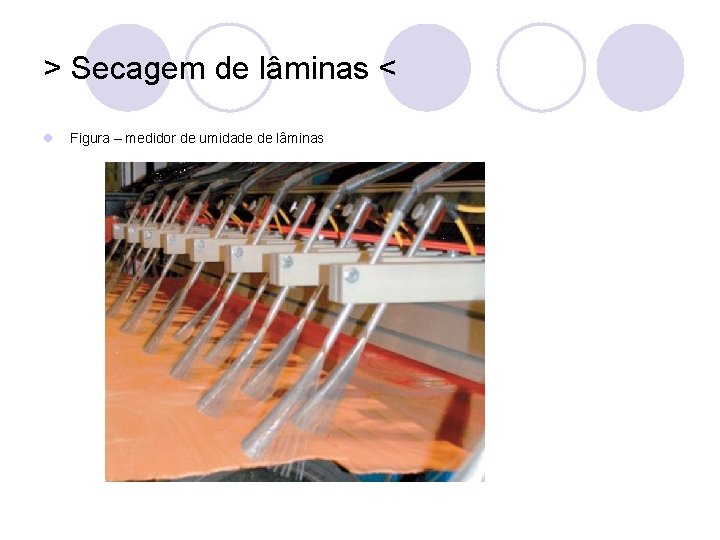
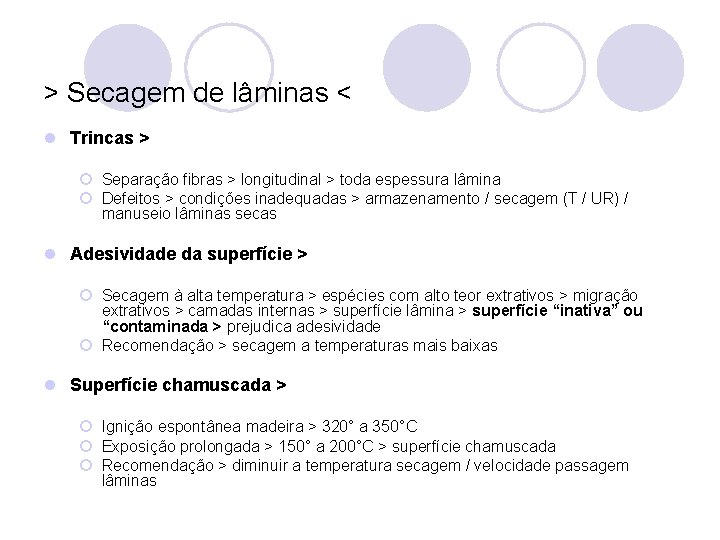
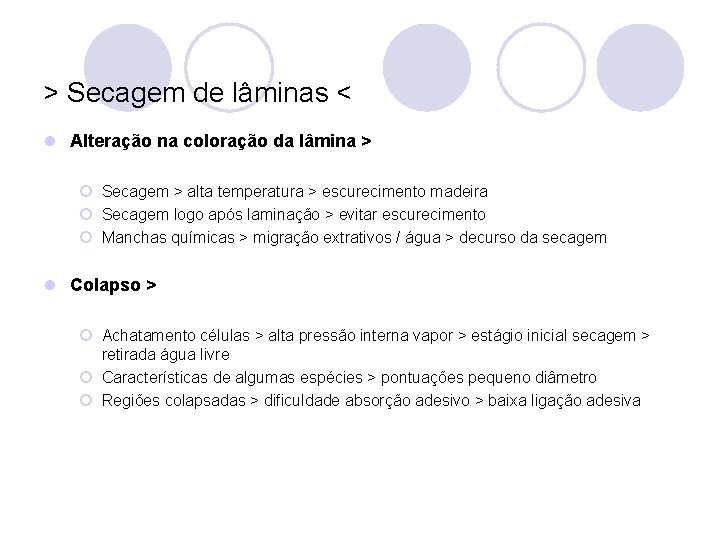
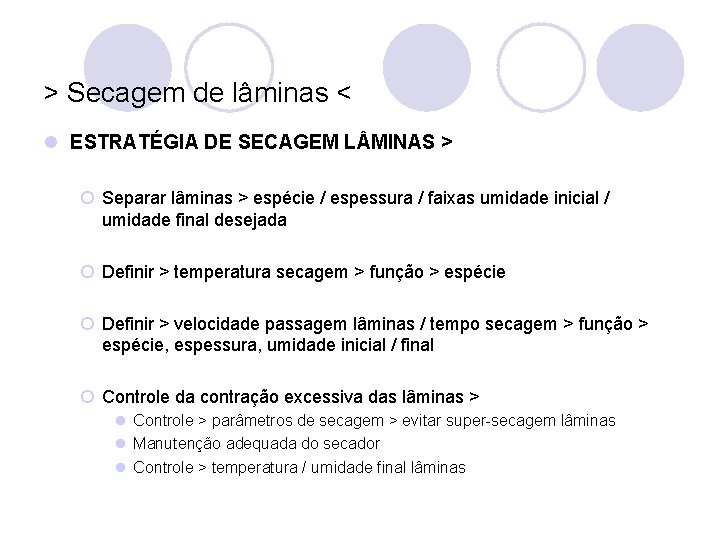
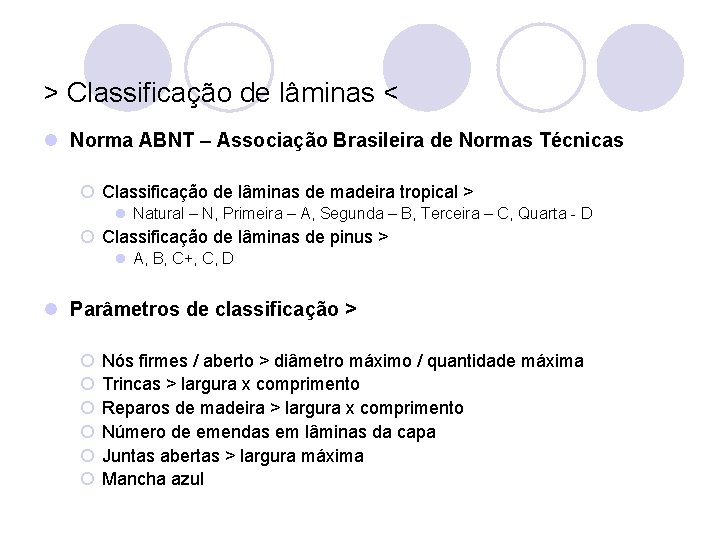
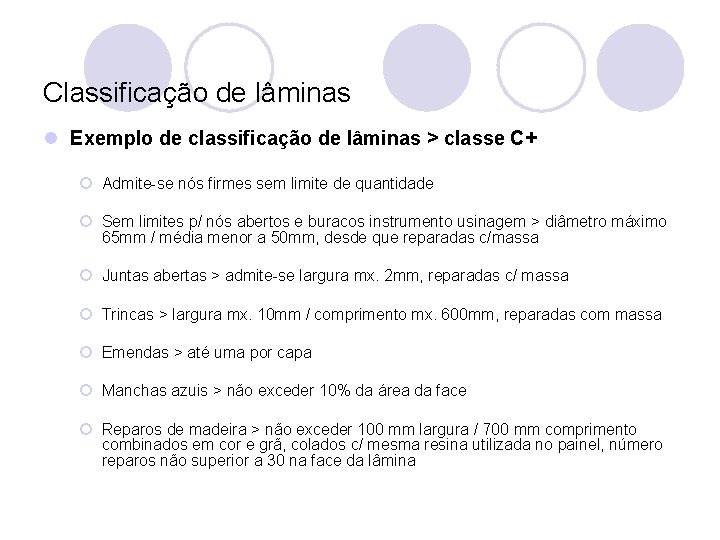
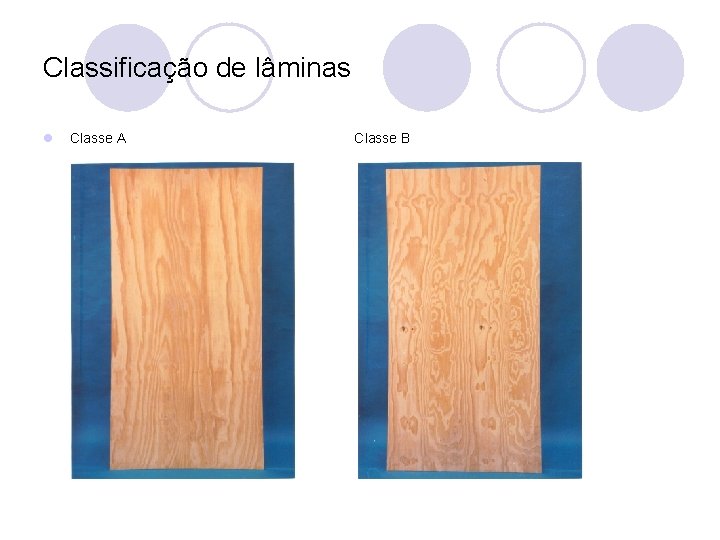
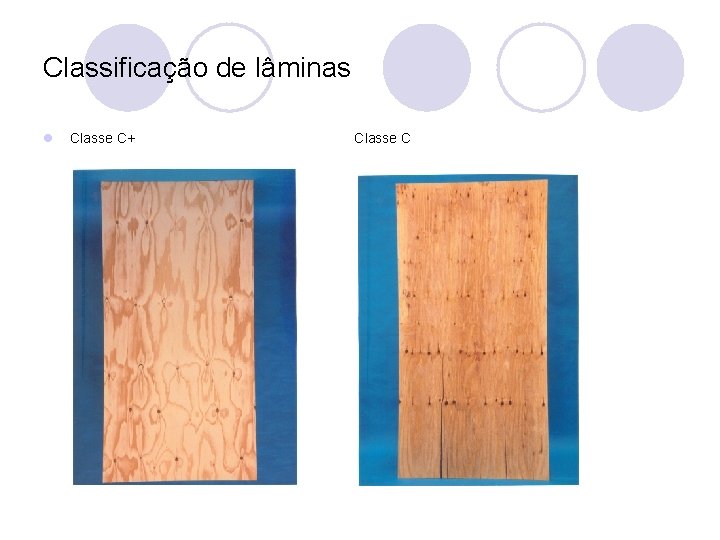
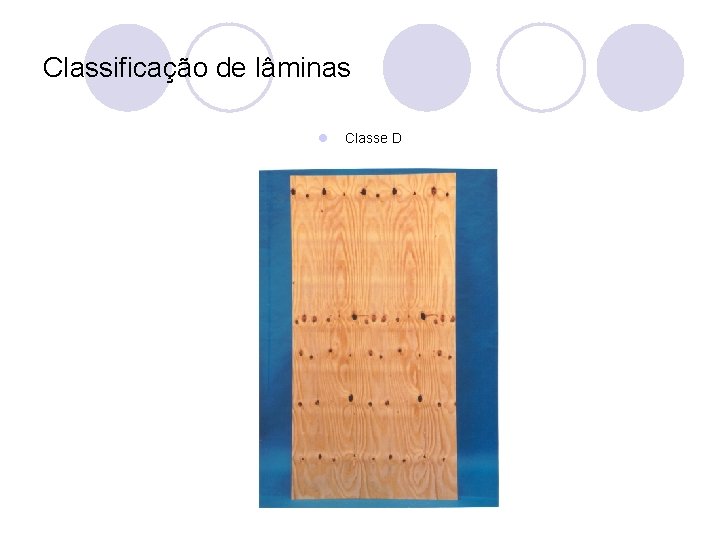
- Slides: 101
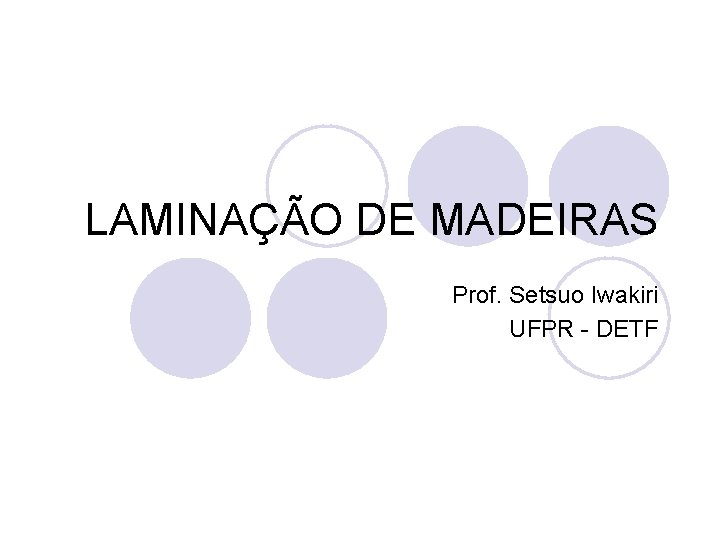
LAMINAÇÃO DE MADEIRAS Prof. Setsuo Iwakiri UFPR - DETF
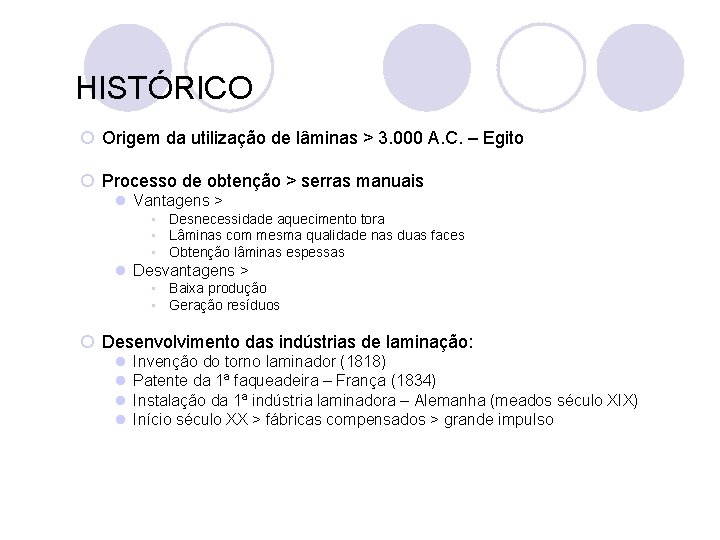
HISTÓRICO ¡ Origem da utilização de lâminas > 3. 000 A. C. – Egito ¡ Processo de obtenção > serras manuais l Vantagens > • Desnecessidade aquecimento tora • Lâminas com mesma qualidade nas duas faces • Obtenção lâminas espessas l Desvantagens > • Baixa produção • Geração resíduos ¡ Desenvolvimento das indústrias de laminação: l l Invenção do torno laminador (1818) Patente da 1ª faqueadeira – França (1834) Instalação da 1ª indústria laminadora – Alemanha (meados século XIX) Início século XX > fábricas compensados > grande impulso
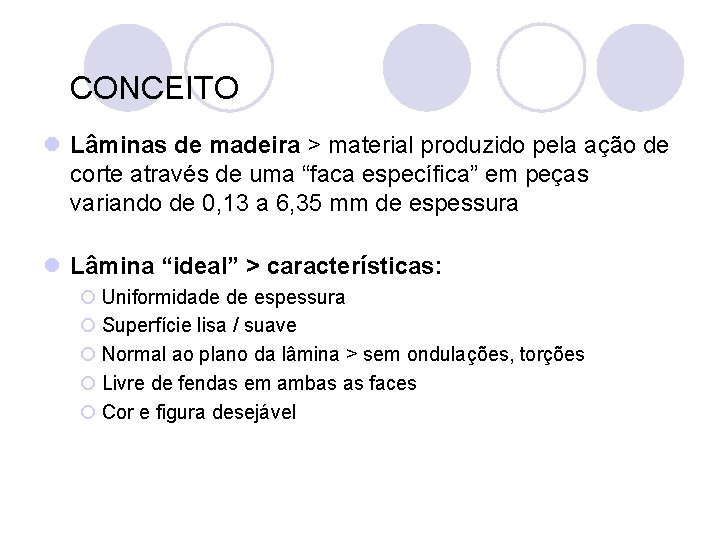
CONCEITO l Lâminas de madeira > material produzido pela ação de corte através de uma “faca específica” em peças variando de 0, 13 a 6, 35 mm de espessura l Lâmina “ideal” > características: ¡ Uniformidade de espessura ¡ Superfície lisa / suave ¡ Normal ao plano da lâmina > sem ondulações, torções ¡ Livre de fendas em ambas as faces ¡ Cor e figura desejável
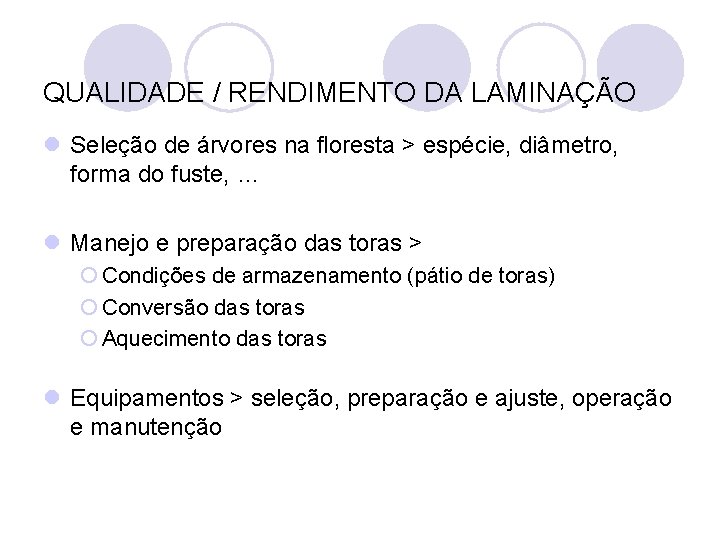
QUALIDADE / RENDIMENTO DA LAMINAÇÃO l Seleção de árvores na floresta > espécie, diâmetro, forma do fuste, … l Manejo e preparação das toras > ¡ Condições de armazenamento (pátio de toras) ¡ Conversão das toras ¡ Aquecimento das toras l Equipamentos > seleção, preparação e ajuste, operação e manutenção
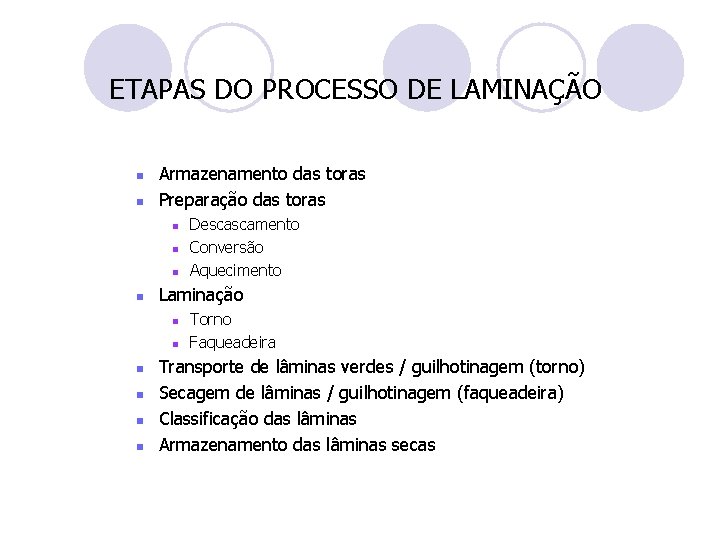
ETAPAS DO PROCESSO DE LAMINAÇÃO n n Armazenamento das toras Preparação das toras n n Laminação n n n Descascamento Conversão Aquecimento Torno Faqueadeira Transporte de lâminas verdes / guilhotinagem (torno) Secagem de lâminas / guilhotinagem (faqueadeira) Classificação das lâminas Armazenamento das lâminas secas
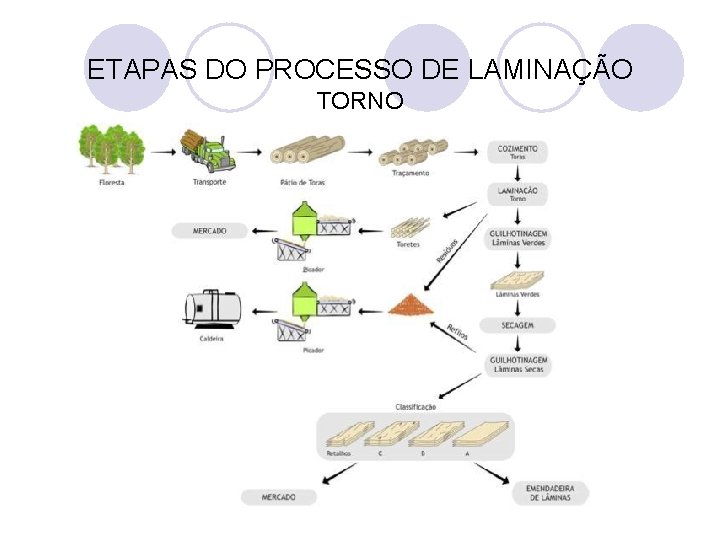
ETAPAS DO PROCESSO DE LAMINAÇÃO TORNO
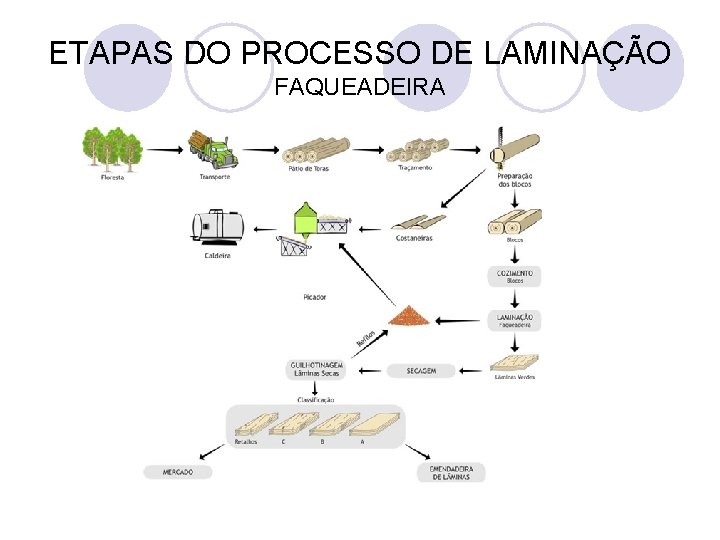
ETAPAS DO PROCESSO DE LAMINAÇÃO FAQUEADEIRA
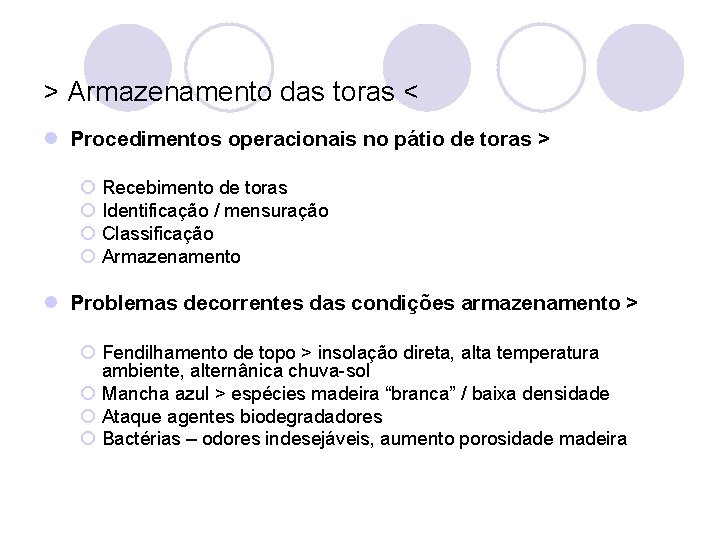
> Armazenamento das toras < l Procedimentos operacionais no pátio de toras > ¡ Recebimento de toras ¡ Identificação / mensuração ¡ Classificação ¡ Armazenamento l Problemas decorrentes das condições armazenamento > ¡ Fendilhamento de topo > insolação direta, alta temperatura ambiente, alternânica chuva-sol ¡ Mancha azul > espécies madeira “branca” / baixa densidade ¡ Ataque agentes biodegradadores ¡ Bactérias – odores indesejáveis, aumento porosidade madeira
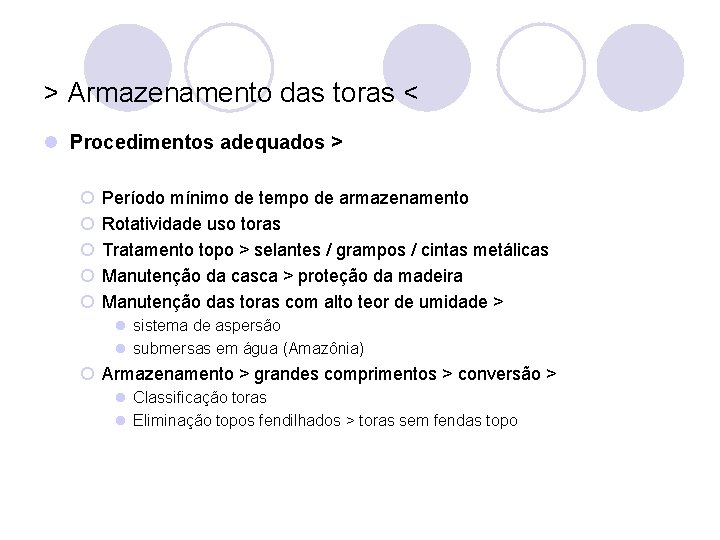
> Armazenamento das toras < l Procedimentos adequados > ¡ ¡ ¡ Período mínimo de tempo de armazenamento Rotatividade uso toras Tratamento topo > selantes / grampos / cintas metálicas Manutenção da casca > proteção da madeira Manutenção das toras com alto teor de umidade > l sistema de aspersão l submersas em água (Amazônia) ¡ Armazenamento > grandes comprimentos > conversão > l Classificação toras l Eliminação topos fendilhados > toras sem fendas topo
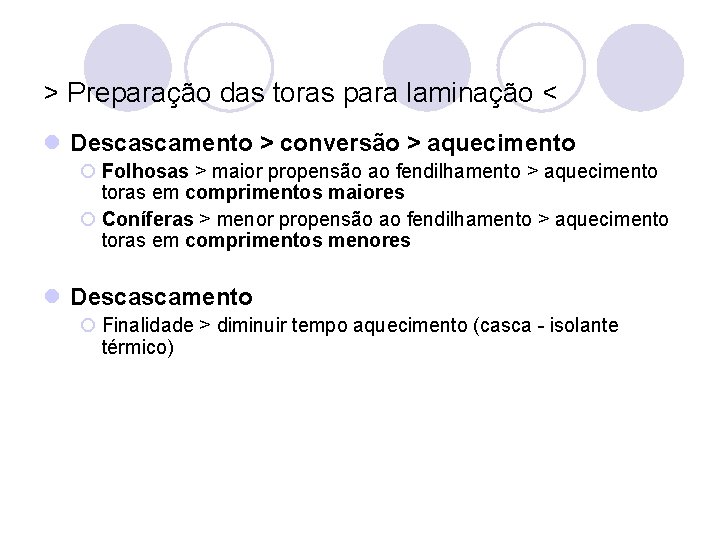
> Preparação das toras para laminação < l Descascamento > conversão > aquecimento ¡ Folhosas > maior propensão ao fendilhamento > aquecimento toras em comprimentos maiores ¡ Coníferas > menor propensão ao fendilhamento > aquecimento toras em comprimentos menores l Descascamento ¡ Finalidade > diminuir tempo aquecimento (casca - isolante térmico)
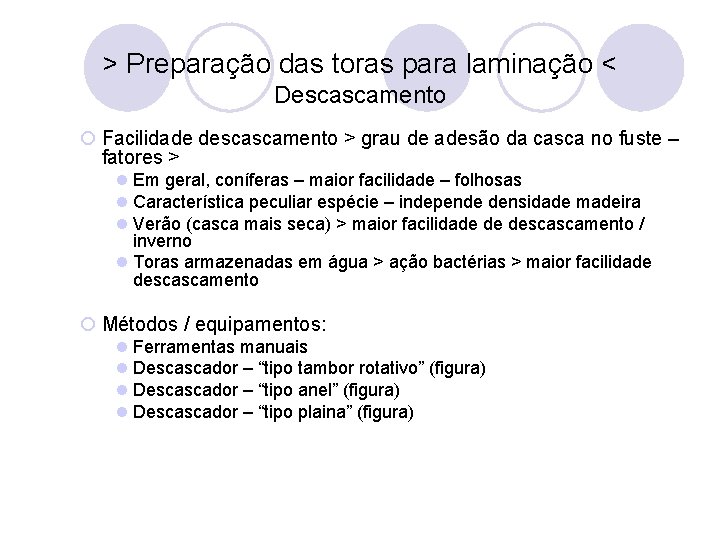
> Preparação das toras para laminação < Descascamento ¡ Facilidade descascamento > grau de adesão da casca no fuste – fatores > l Em geral, coníferas – maior facilidade – folhosas l Característica peculiar espécie – independe densidade madeira l Verão (casca mais seca) > maior facilidade de descascamento / inverno l Toras armazenadas em água > ação bactérias > maior facilidade descascamento ¡ Métodos / equipamentos: l Ferramentas manuais l Descascador – “tipo tambor rotativo” (figura) l Descascador – “tipo anel” (figura) l Descascador – “tipo plaina” (figura)
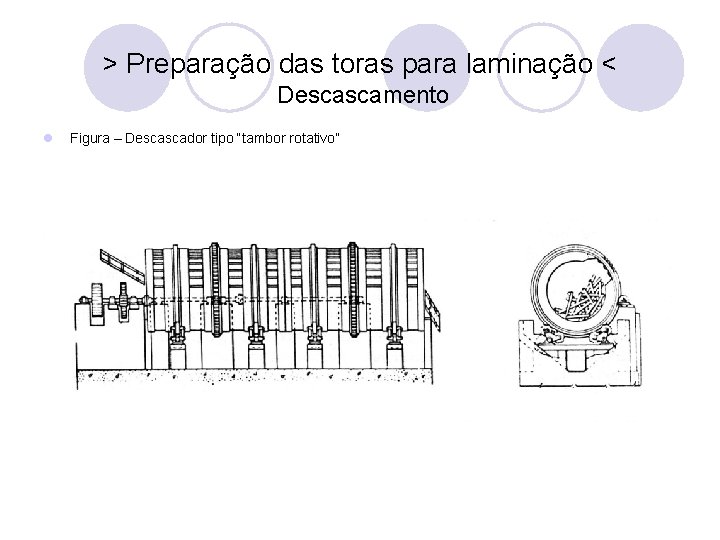
> Preparação das toras para laminação < Descascamento l Figura – Descascador tipo “tambor rotativo”
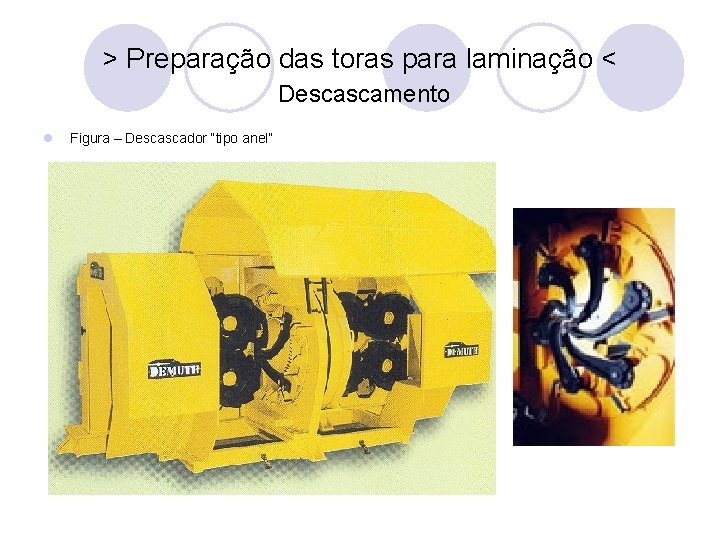
> Preparação das toras para laminação < Descascamento l Figura – Descascador “tipo anel”
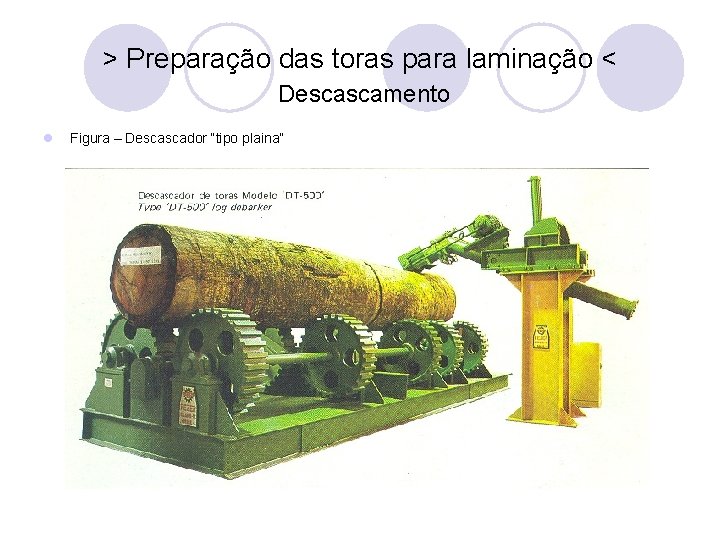
> Preparação das toras para laminação < Descascamento l Figura – Descascador “tipo plaina”
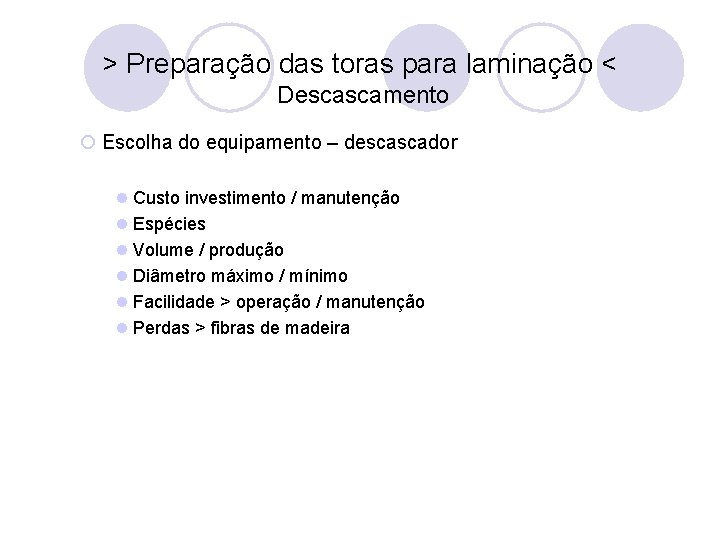
> Preparação das toras para laminação < Descascamento ¡ Escolha do equipamento – descascador l Custo investimento / manutenção l Espécies l Volume / produção l Diâmetro máximo / mínimo l Facilidade > operação / manutenção l Perdas > fibras de madeira

> Preparação das toras para laminação < Conversão das toras l Conversão das toras ¡ Traçamento das toras > comprimentos menores > função > l Dimensões dos compensados > • Lâminas compridas • Lâminas curtas ¡ Equipamentos > l Sistema de motosseras (figura) l Serra circular
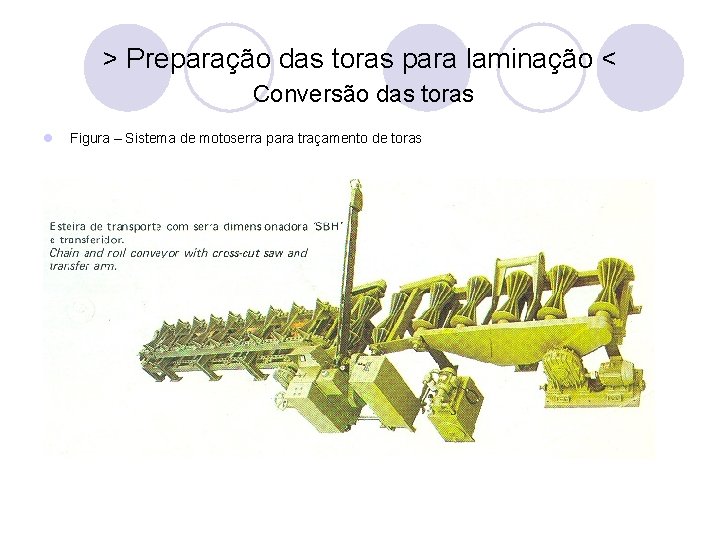
> Preparação das toras para laminação < Conversão das toras l Figura – Sistema de motoserra para traçamento de toras
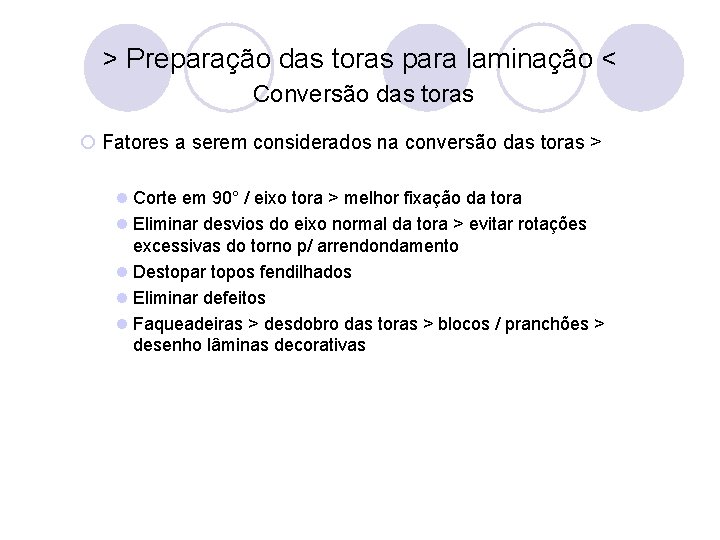
> Preparação das toras para laminação < Conversão das toras ¡ Fatores a serem considerados na conversão das toras > l Corte em 90° / eixo tora > melhor fixação da tora l Eliminar desvios do eixo normal da tora > evitar rotações excessivas do torno p/ arrendondamento l Destopar topos fendilhados l Eliminar defeitos l Faqueadeiras > desdobro das toras > blocos / pranchões > desenho lâminas decorativas
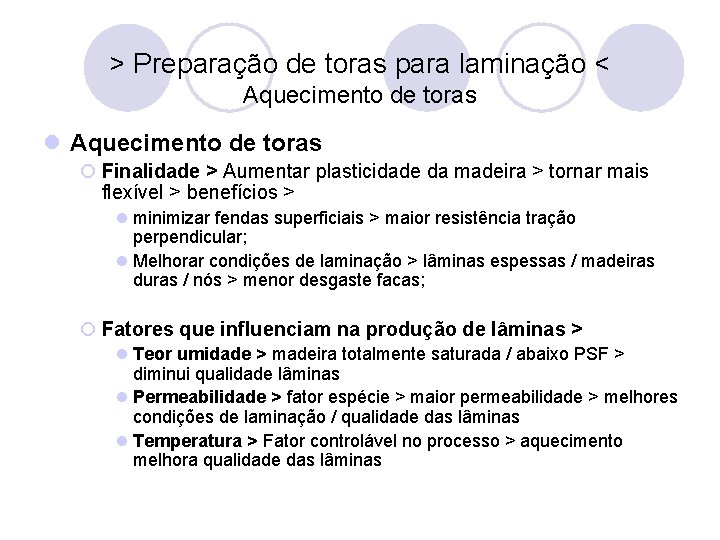
> Preparação de toras para laminação < Aquecimento de toras l Aquecimento de toras ¡ Finalidade > Aumentar plasticidade da madeira > tornar mais flexível > benefícios > l minimizar fendas superficiais > maior resistência tração perpendicular; l Melhorar condições de laminação > lâminas espessas / madeiras duras / nós > menor desgaste facas; ¡ Fatores que influenciam na produção de lâminas > l Teor umidade > madeira totalmente saturada / abaixo PSF > diminui qualidade lâminas l Permeabilidade > fator espécie > maior permeabilidade > melhores condições de laminação / qualidade das lâminas l Temperatura > Fator controlável no processo > aquecimento melhora qualidade das lâminas
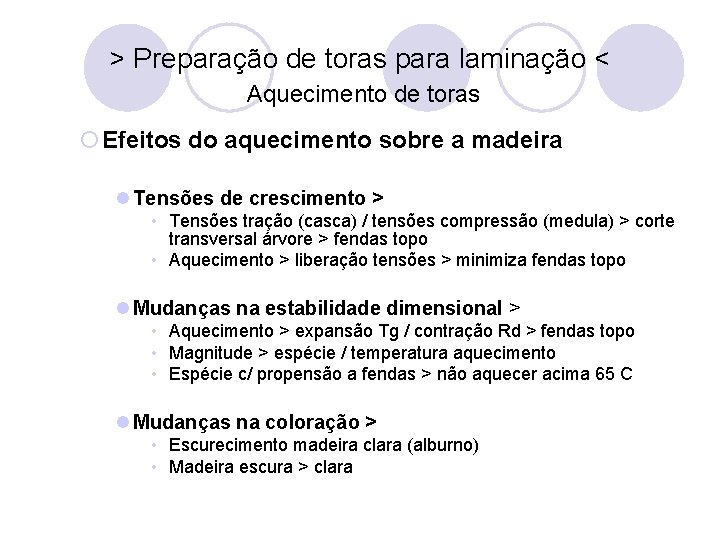
> Preparação de toras para laminação < Aquecimento de toras ¡Efeitos do aquecimento sobre a madeira l Tensões de crescimento > • Tensões tração (casca) / tensões compressão (medula) > corte transversal árvore > fendas topo • Aquecimento > liberação tensões > minimiza fendas topo l Mudanças na estabilidade dimensional > • Aquecimento > expansão Tg / contração Rd > fendas topo • Magnitude > espécie / temperatura aquecimento • Espécie c/ propensão a fendas > não aquecer acima 65 C l Mudanças na coloração > • Escurecimento madeira clara (alburno) • Madeira escura > clara
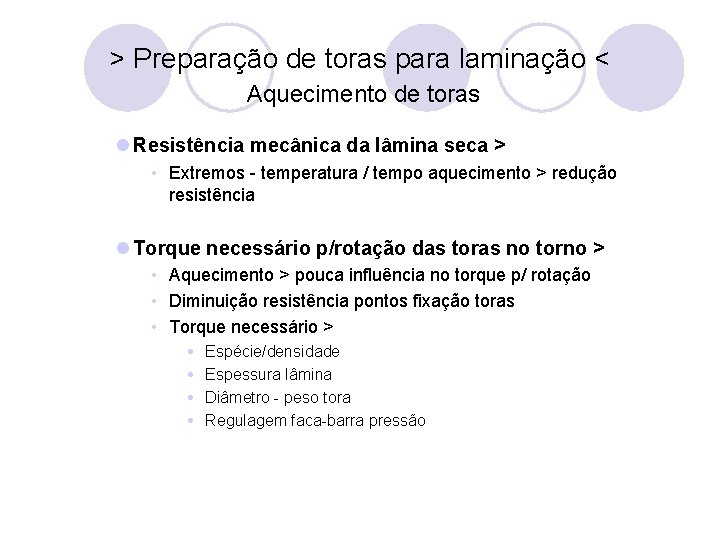
> Preparação de toras para laminação < Aquecimento de toras l Resistência mecânica da lâmina seca > • Extremos - temperatura / tempo aquecimento > redução resistência l Torque necessário p/rotação das toras no torno > • Aquecimento > pouca influência no torque p/ rotação • Diminuição resistência pontos fixação toras • Torque necessário > Espécie/densidade Espessura lâmina Diâmetro - peso tora Regulagem faca-barra pressão
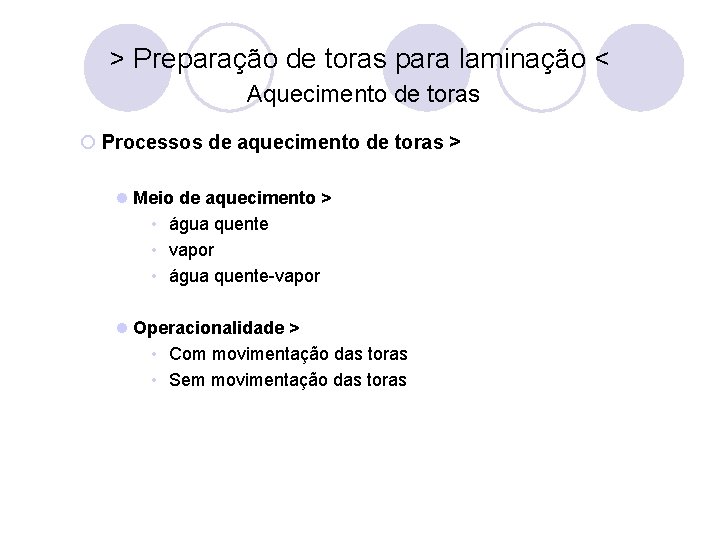
> Preparação de toras para laminação < Aquecimento de toras ¡ Processos de aquecimento de toras > l Meio de aquecimento > • água quente • vapor • água quente-vapor l Operacionalidade > • Com movimentação das toras • Sem movimentação das toras
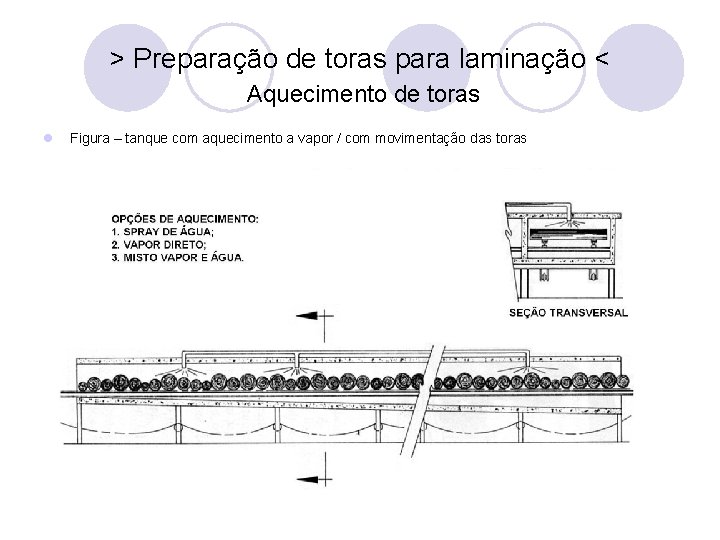
> Preparação de toras para laminação < Aquecimento de toras l Figura – tanque com aquecimento a vapor / com movimentação das toras
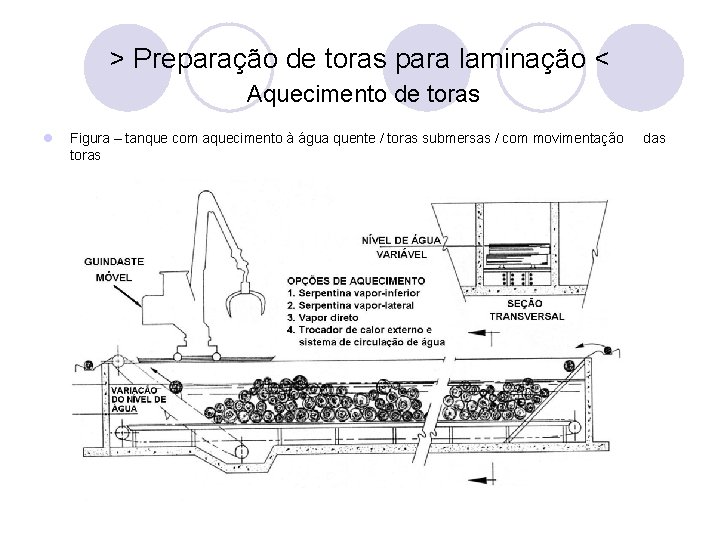
> Preparação de toras para laminação < Aquecimento de toras l Figura – tanque com aquecimento à água quente / toras submersas / com movimentação das toras
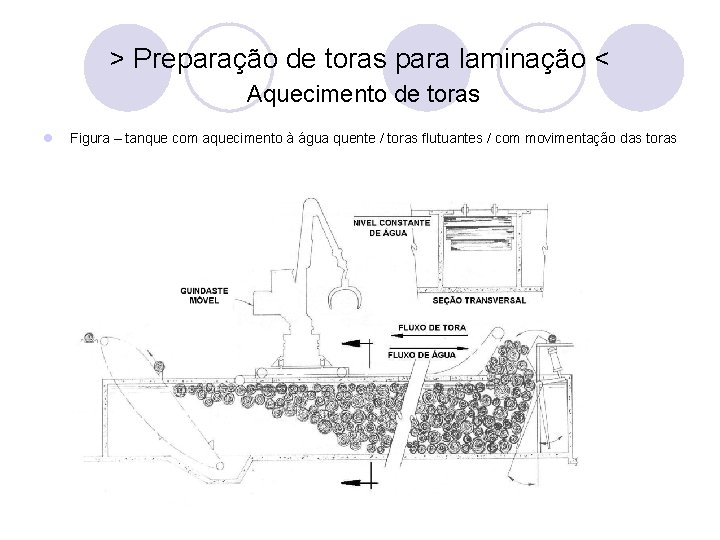
> Preparação de toras para laminação < Aquecimento de toras l Figura – tanque com aquecimento à água quente / toras flutuantes / com movimentação das toras
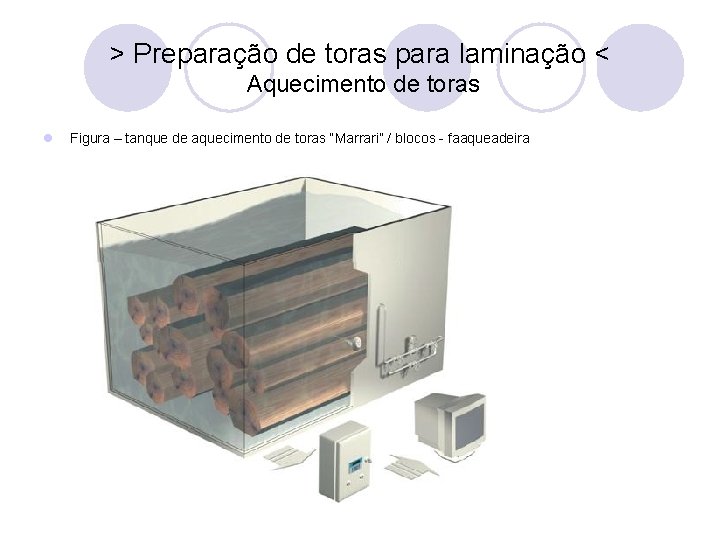
> Preparação de toras para laminação < Aquecimento de toras l Figura – tanque de aquecimento de toras “Marrari” / blocos - faaqueadeira
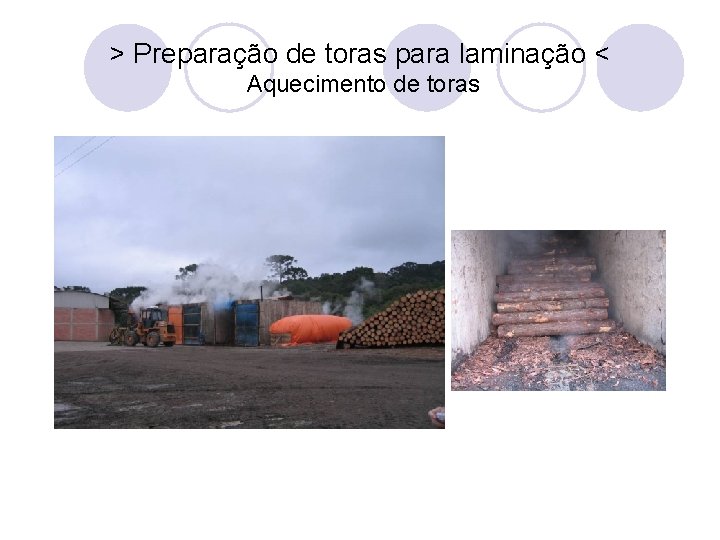
> Preparação de toras para laminação < Aquecimento de toras
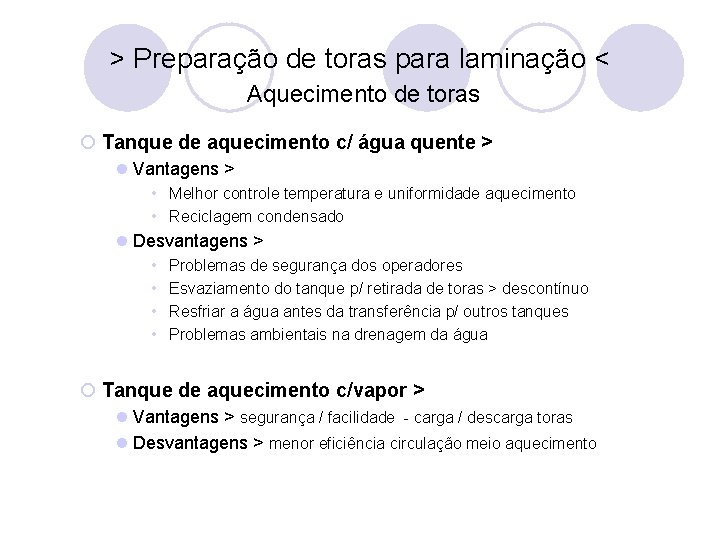
> Preparação de toras para laminação < Aquecimento de toras ¡ Tanque de aquecimento c/ água quente > l Vantagens > • Melhor controle temperatura e uniformidade aquecimento • Reciclagem condensado l Desvantagens > • • Problemas de segurança dos operadores Esvaziamento do tanque p/ retirada de toras > descontínuo Resfriar a água antes da transferência p/ outros tanques Problemas ambientais na drenagem da água ¡ Tanque de aquecimento c/vapor > l Vantagens > segurança / facilidade - carga / descarga toras l Desvantagens > menor eficiência circulação meio aquecimento
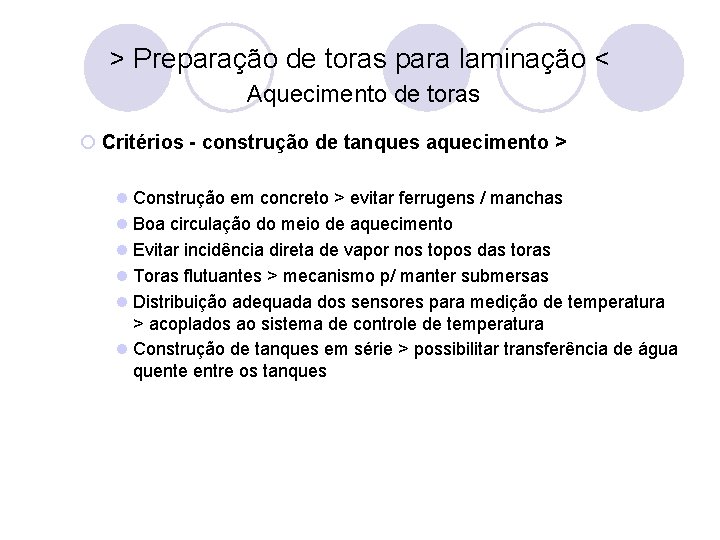
> Preparação de toras para laminação < Aquecimento de toras ¡ Critérios - construção de tanques aquecimento > l Construção em concreto > evitar ferrugens / manchas l Boa circulação do meio de aquecimento l Evitar incidência direta de vapor nos topos das toras l Toras flutuantes > mecanismo p/ manter submersas l Distribuição adequada dos sensores para medição de temperatura > acoplados ao sistema de controle de temperatura l Construção de tanques em série > possibilitar transferência de água quente entre os tanques
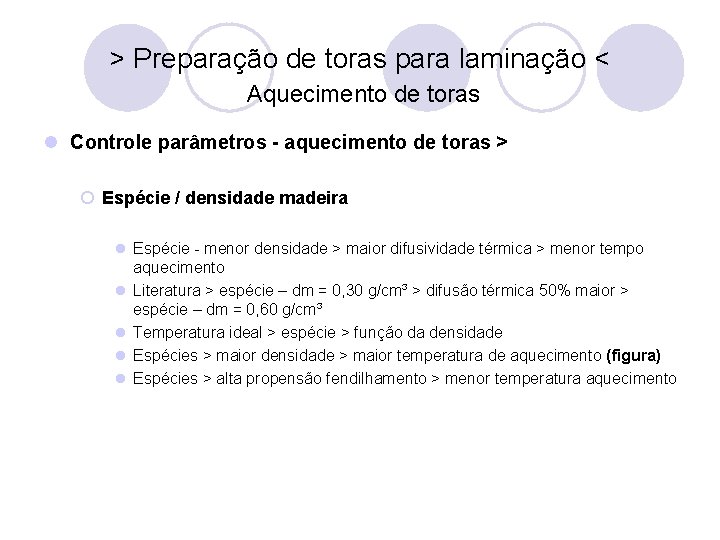
> Preparação de toras para laminação < Aquecimento de toras l Controle parâmetros - aquecimento de toras > ¡ Espécie / densidade madeira l Espécie - menor densidade > maior difusividade térmica > menor tempo aquecimento l Literatura > espécie – dm = 0, 30 g/cm³ > difusão térmica 50% maior > espécie – dm = 0, 60 g/cm³ l Temperatura ideal > espécie > função da densidade l Espécies > maior densidade > maior temperatura de aquecimento (figura) l Espécies > alta propensão fendilhamento > menor temperatura aquecimento
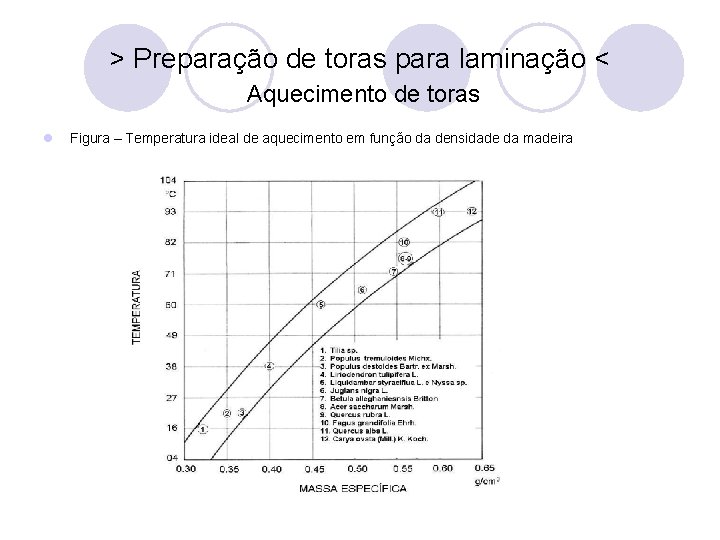
> Preparação de toras para laminação < Aquecimento de toras l Figura – Temperatura ideal de aquecimento em função da densidade da madeira
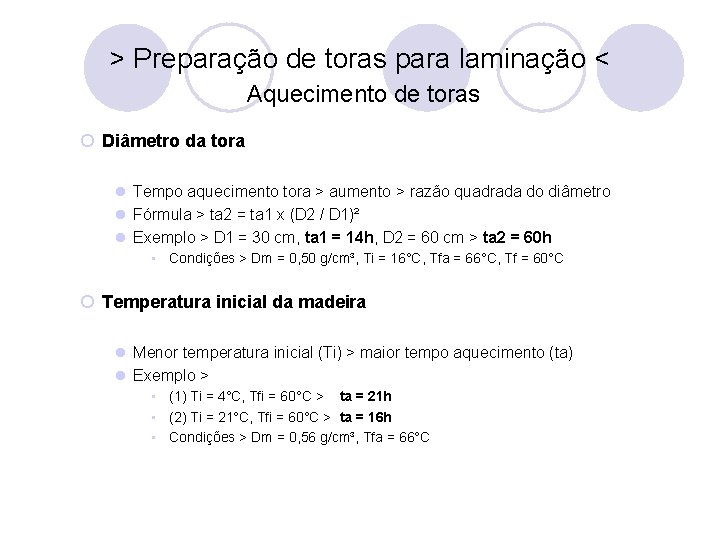
> Preparação de toras para laminação < Aquecimento de toras ¡ Diâmetro da tora l Tempo aquecimento tora > aumento > razão quadrada do diâmetro l Fórmula > ta 2 = ta 1 x (D 2 / D 1)² l Exemplo > D 1 = 30 cm, ta 1 = 14 h, D 2 = 60 cm > ta 2 = 60 h • Condições > Dm = 0, 50 g/cm³, Ti = 16°C, Tfa = 66°C, Tf = 60°C ¡ Temperatura inicial da madeira l Menor temperatura inicial (Ti) > maior tempo aquecimento (ta) l Exemplo > • (1) Ti = 4°C, Tfi = 60°C > ta = 21 h • (2) Ti = 21°C, Tfi = 60°C > ta = 16 h • Condições > Dm = 0, 56 g/cm³, Tfa = 66°C
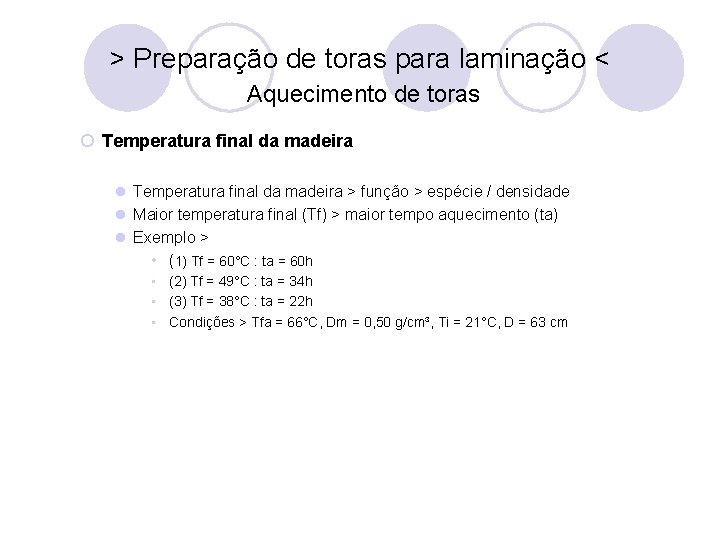
> Preparação de toras para laminação < Aquecimento de toras ¡ Temperatura final da madeira l Temperatura final da madeira > função > espécie / densidade l Maior temperatura final (Tf) > maior tempo aquecimento (ta) l Exemplo > • (1) Tf = 60°C : ta = 60 h • (2) Tf = 49°C : ta = 34 h • (3) Tf = 38°C : ta = 22 h • Condições > Tfa = 66°C, Dm = 0, 50 g/cm³, Ti = 21°C, D = 63 cm
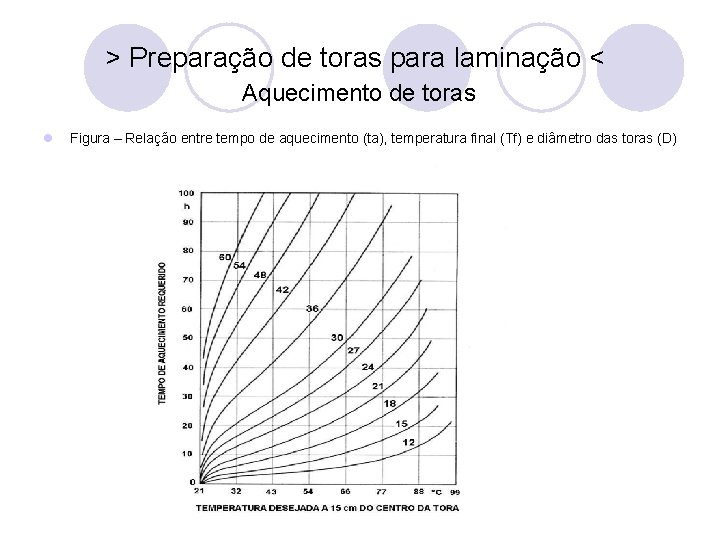
> Preparação de toras para laminação < Aquecimento de toras l Figura – Relação entre tempo de aquecimento (ta), temperatura final (Tf) e diâmetro das toras (D)
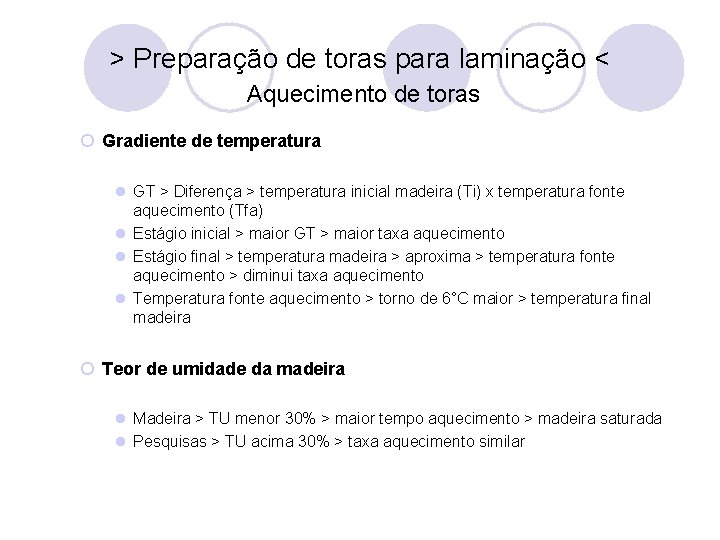
> Preparação de toras para laminação < Aquecimento de toras ¡ Gradiente de temperatura l GT > Diferença > temperatura inicial madeira (Ti) x temperatura fonte aquecimento (Tfa) l Estágio inicial > maior GT > maior taxa aquecimento l Estágio final > temperatura madeira > aproxima > temperatura fonte aquecimento > diminui taxa aquecimento l Temperatura fonte aquecimento > torno de 6°C maior > temperatura final madeira ¡ Teor de umidade da madeira l Madeira > TU menor 30% > maior tempo aquecimento > madeira saturada l Pesquisas > TU acima 30% > taxa aquecimento similar
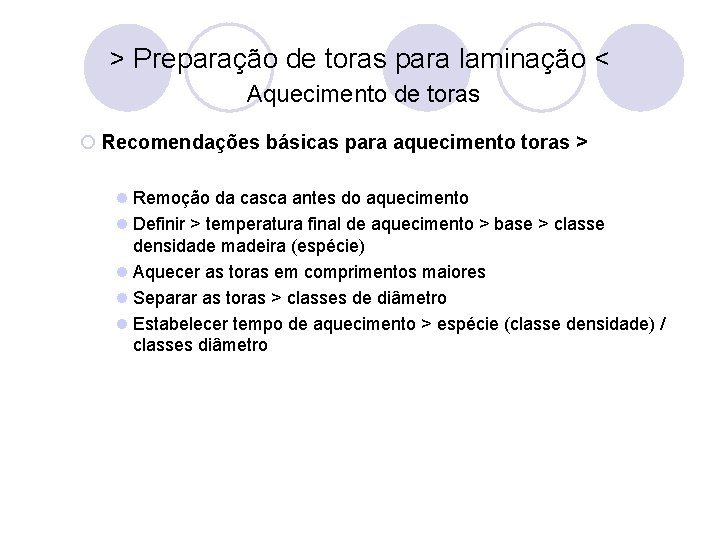
> Preparação de toras para laminação < Aquecimento de toras ¡ Recomendações básicas para aquecimento toras > l Remoção da casca antes do aquecimento l Definir > temperatura final de aquecimento > base > classe densidade madeira (espécie) l Aquecer as toras em comprimentos maiores l Separar as toras > classes de diâmetro l Estabelecer tempo de aquecimento > espécie (classe densidade) / classes diâmetro
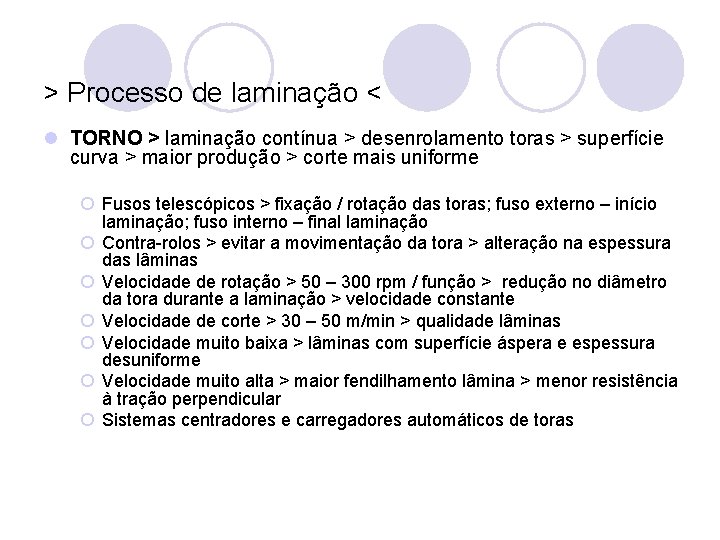
> Processo de laminação < l TORNO > laminação contínua > desenrolamento toras > superfície curva > maior produção > corte mais uniforme ¡ Fusos telescópicos > fixação / rotação das toras; fuso externo – início laminação; fuso interno – final laminação ¡ Contra-rolos > evitar a movimentação da tora > alteração na espessura das lâminas ¡ Velocidade de rotação > 50 – 300 rpm / função > redução no diâmetro da tora durante a laminação > velocidade constante ¡ Velocidade de corte > 30 – 50 m/min > qualidade lâminas ¡ Velocidade muito baixa > lâminas com superfície áspera e espessura desuniforme ¡ Velocidade muito alta > maior fendilhamento lâmina > menor resistência à tração perpendicular ¡ Sistemas centradores e carregadores automáticos de toras
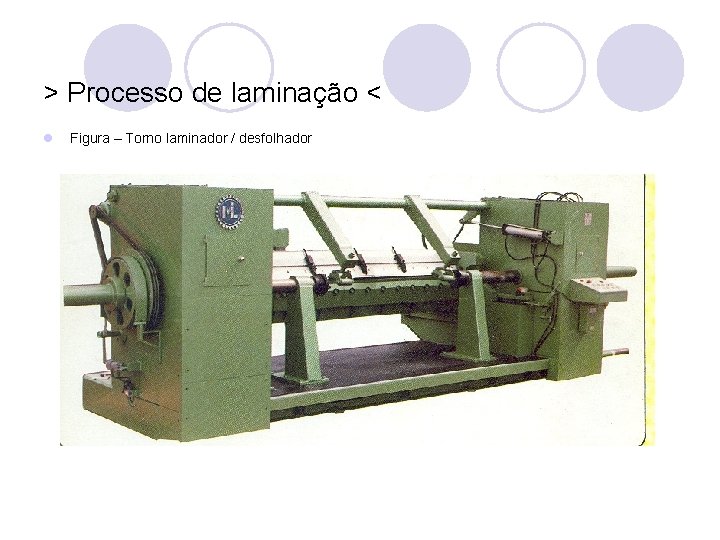
> Processo de laminação < l Figura – Torno laminador / desfolhador
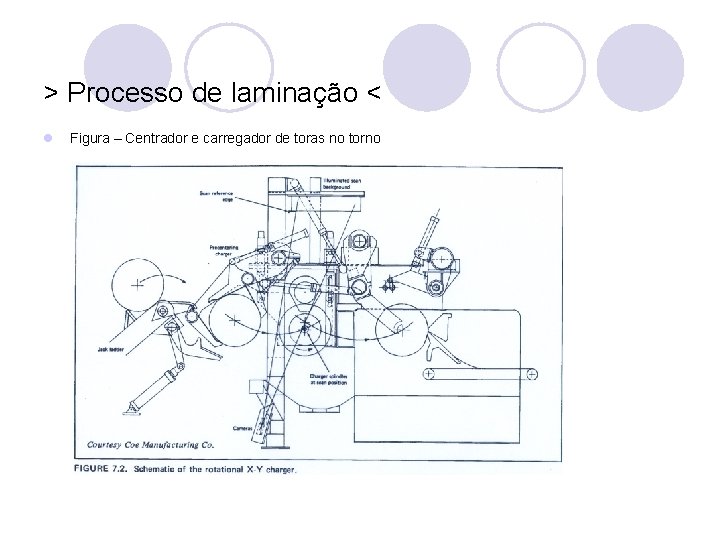
> Processo de laminação < l Figura – Centrador e carregador de toras no torno
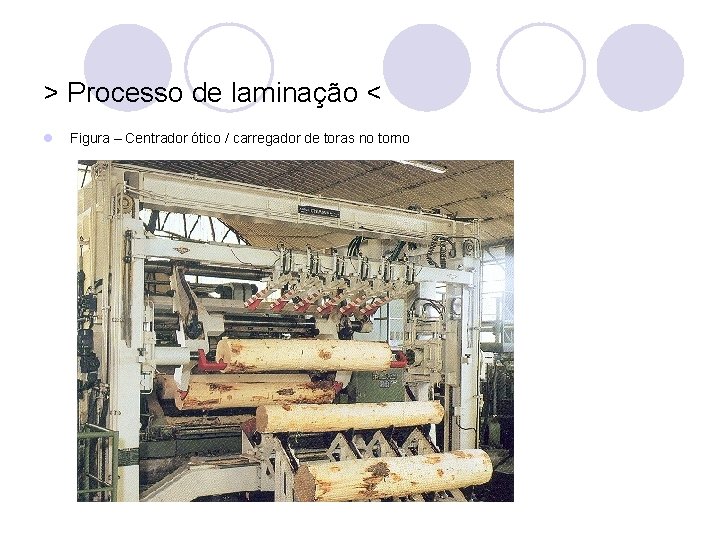
> Processo de laminação < l Figura – Centrador ótico / carregador de toras no torno
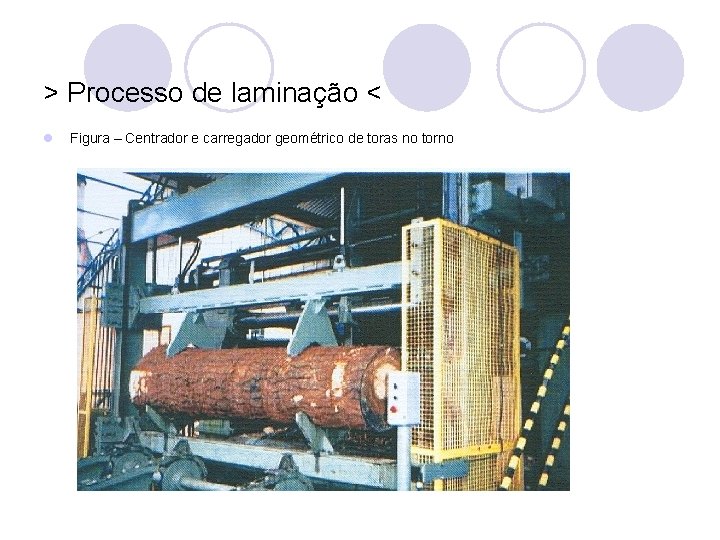
> Processo de laminação < l Figura – Centrador e carregador geométrico de toras no torno
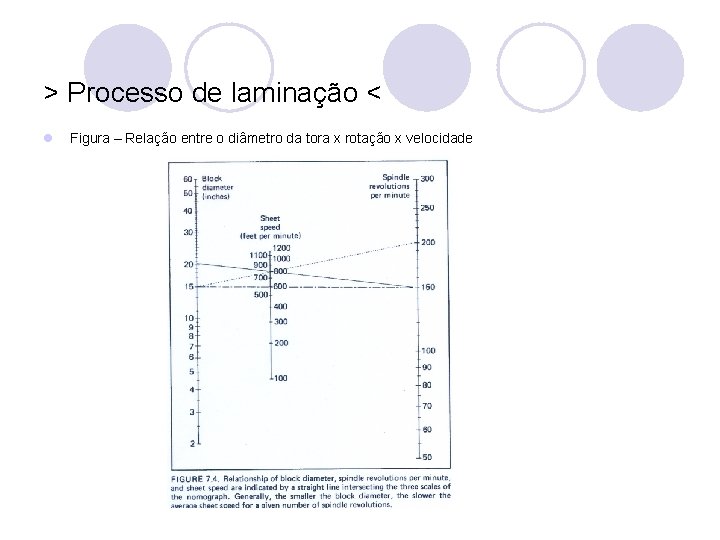
> Processo de laminação < l Figura – Relação entre o diâmetro da tora x rotação x velocidade
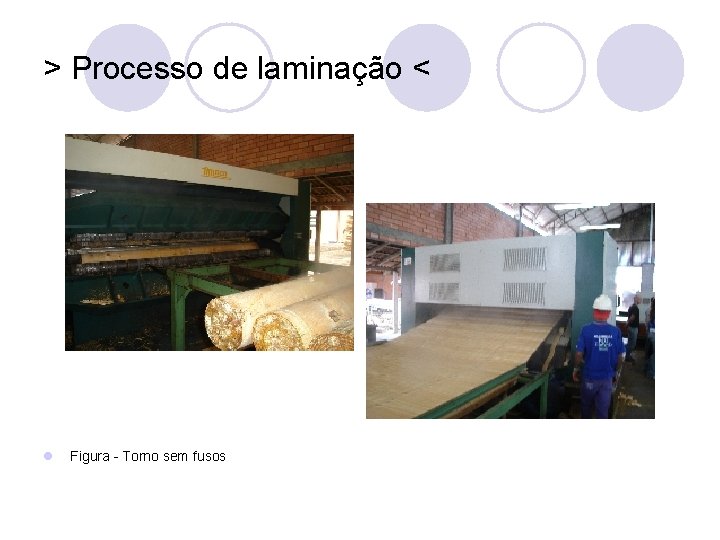
> Processo de laminação < l Figura - Torno sem fusos
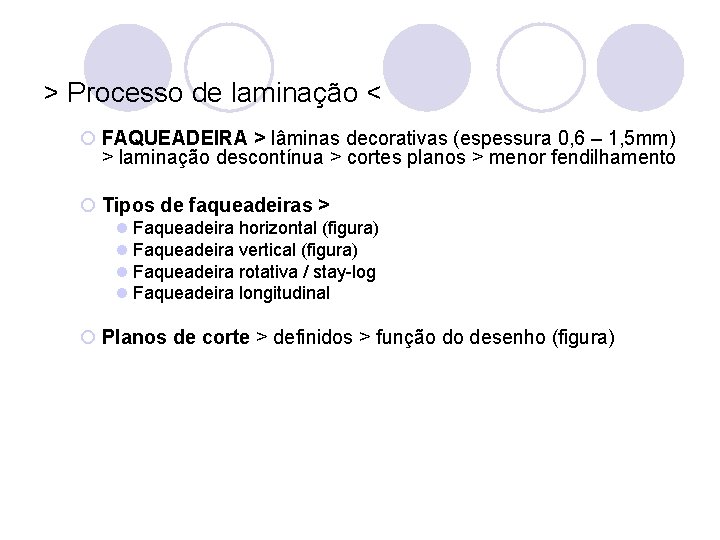
> Processo de laminação < ¡ FAQUEADEIRA > lâminas decorativas (espessura 0, 6 – 1, 5 mm) > laminação descontínua > cortes planos > menor fendilhamento ¡ Tipos de faqueadeiras > l Faqueadeira horizontal (figura) l Faqueadeira vertical (figura) l Faqueadeira rotativa / stay-log l Faqueadeira longitudinal ¡ Planos de corte > definidos > função do desenho (figura)
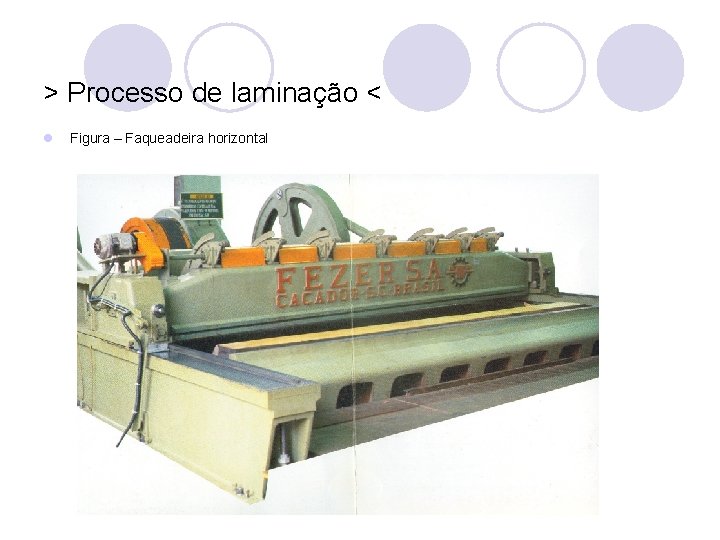
> Processo de laminação < l Figura – Faqueadeira horizontal
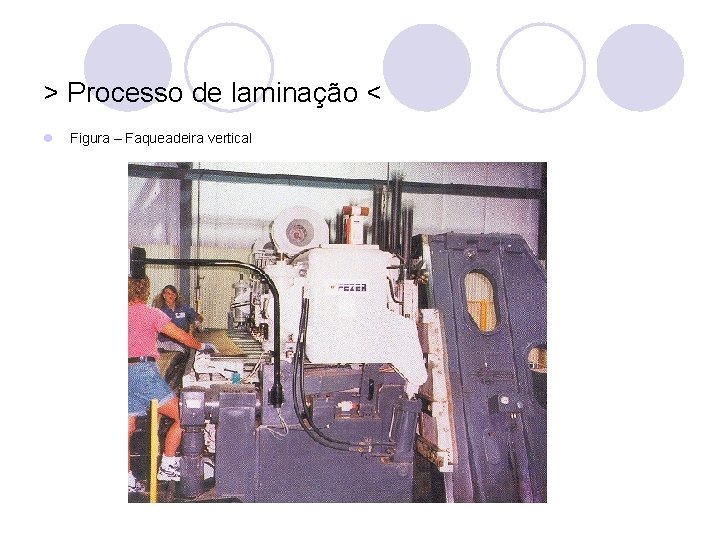
> Processo de laminação < l Figura – Faqueadeira vertical
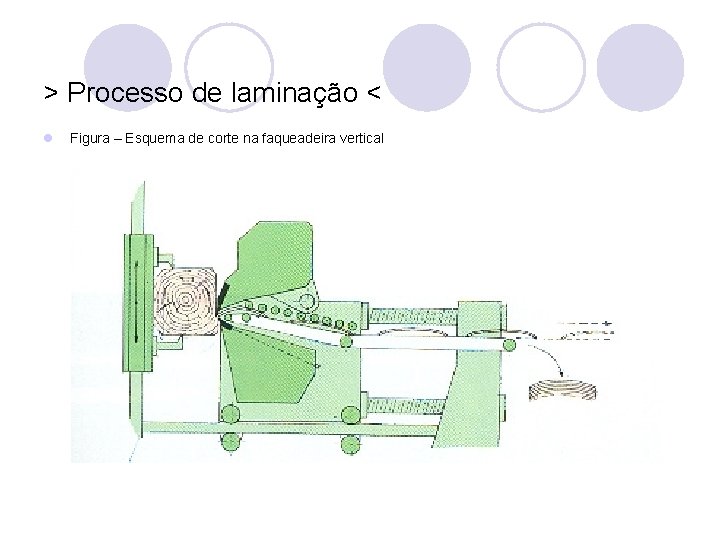
> Processo de laminação < l Figura – Esquema de corte na faqueadeira vertical
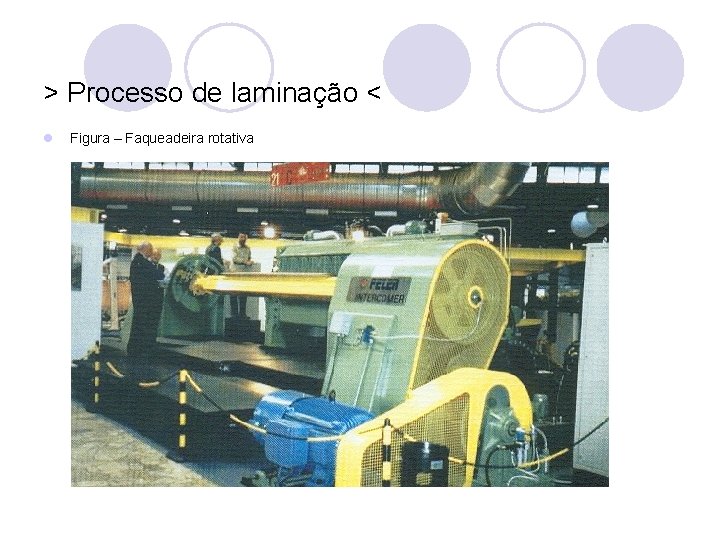
> Processo de laminação < l Figura – Faqueadeira rotativa
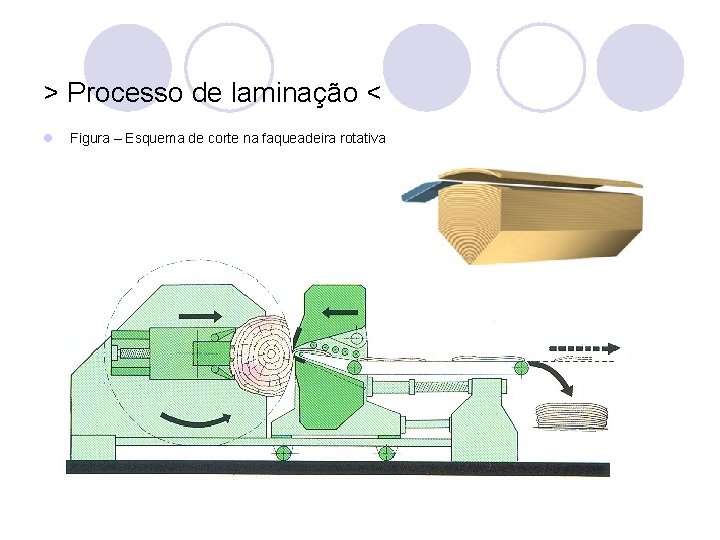
> Processo de laminação < l Figura – Esquema de corte na faqueadeira rotativa
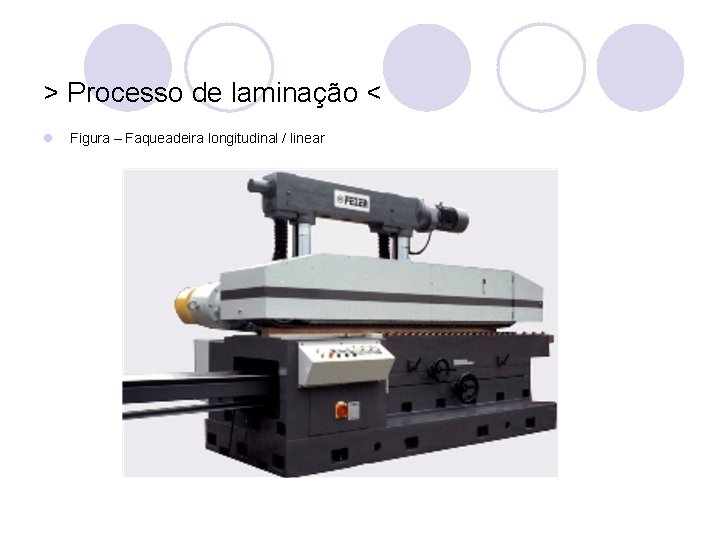
> Processo de laminação < l Figura – Faqueadeira longitudinal / linear
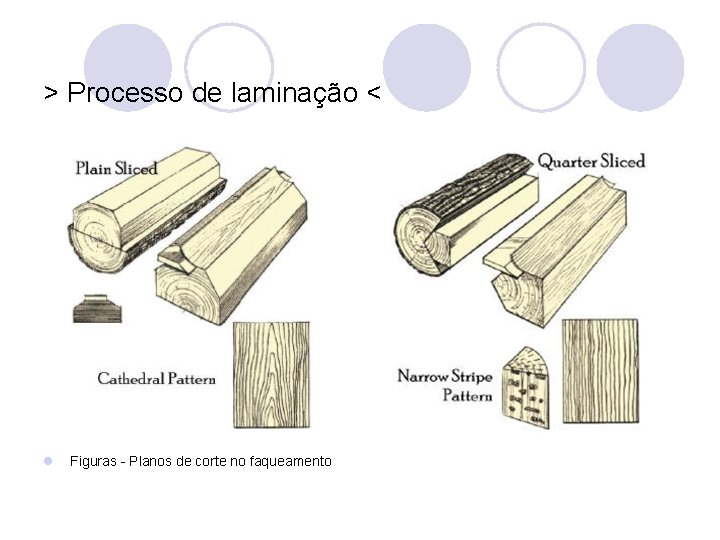
> Processo de laminação < l Figuras - Planos de corte no faqueamento
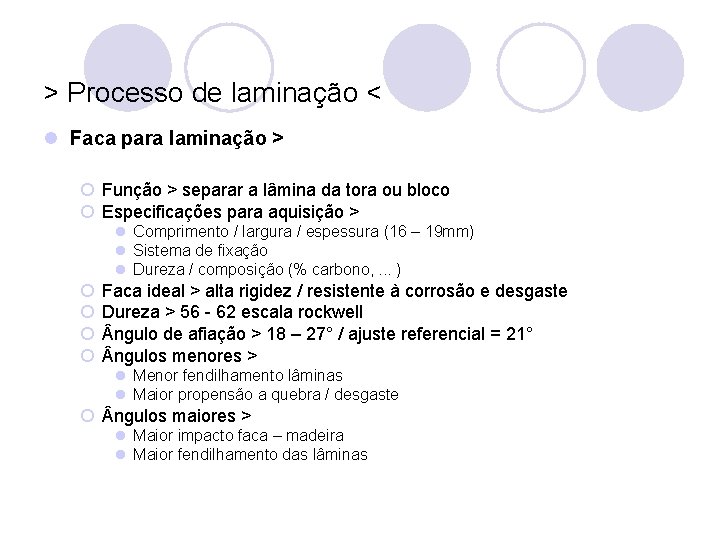
> Processo de laminação < l Faca para laminação > ¡ Função > separar a lâmina da tora ou bloco ¡ Especificações para aquisição > l Comprimento / largura / espessura (16 – 19 mm) l Sistema de fixação l Dureza / composição (% carbono, . . . ) ¡ ¡ Faca ideal > alta rigidez / resistente à corrosão e desgaste Dureza > 56 - 62 escala rockwell ngulo de afiação > 18 – 27° / ajuste referencial = 21° ngulos menores > l Menor fendilhamento lâminas l Maior propensão a quebra / desgaste ¡ ngulos maiores > l Maior impacto faca – madeira l Maior fendilhamento das lâminas

> Processo de laminação < l Figura – facas para laminação
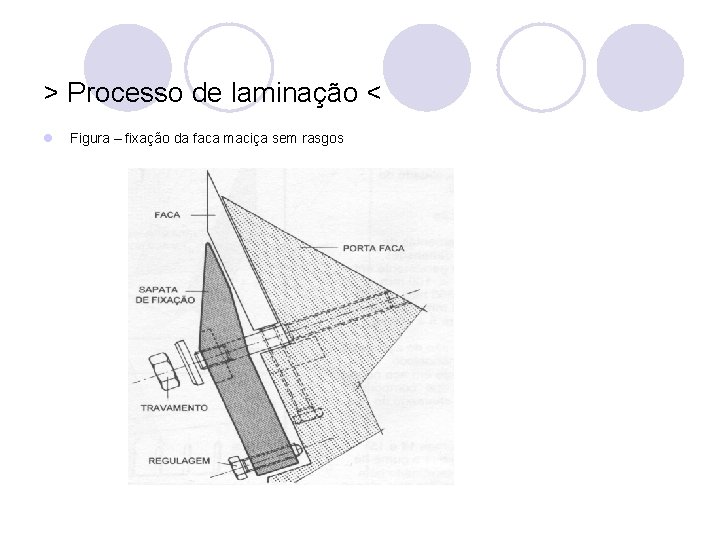
> Processo de laminação < l Figura – fixação da faca maciça sem rasgos
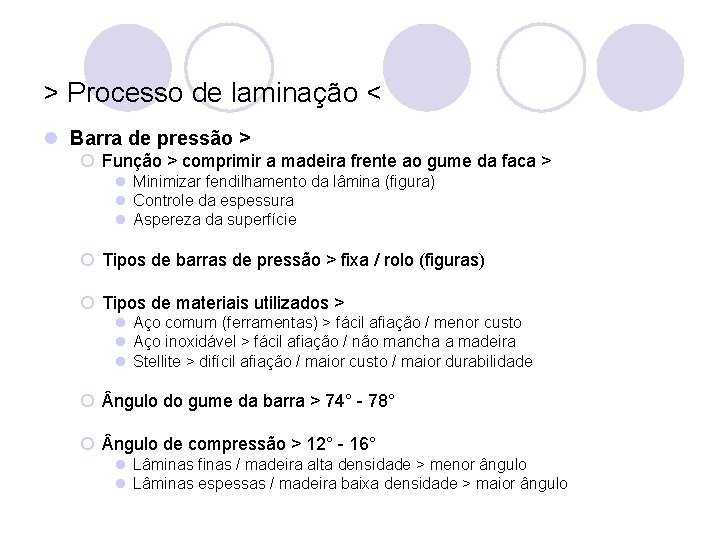
> Processo de laminação < l Barra de pressão > ¡ Função > comprimir a madeira frente ao gume da faca > l Minimizar fendilhamento da lâmina (figura) l Controle da espessura l Aspereza da superfície ¡ Tipos de barras de pressão > fixa / rolo (figuras) ¡ Tipos de materiais utilizados > l Aço comum (ferramentas) > fácil afiação / menor custo l Aço inoxidável > fácil afiação / não mancha a madeira l Stellite > difícil afiação / maior custo / maior durabilidade ¡ ngulo do gume da barra > 74° - 78° ¡ ngulo de compressão > 12° - 16° l Lâminas finas / madeira alta densidade > menor ângulo l Lâminas espessas / madeira baixa densidade > maior ângulo
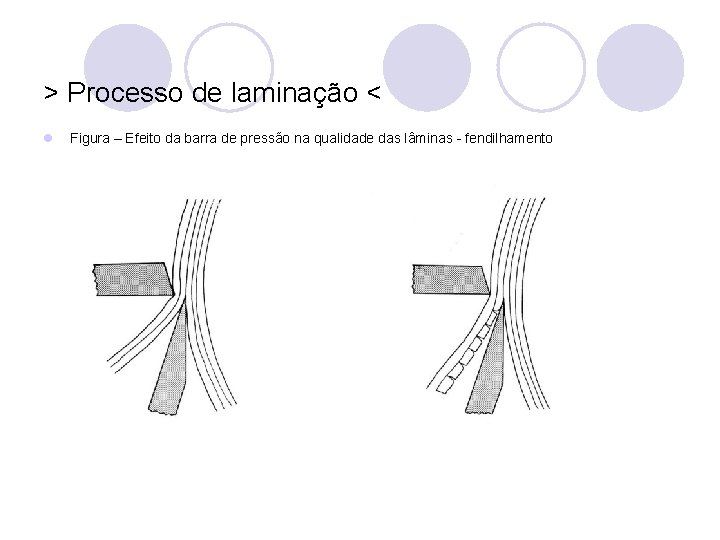
> Processo de laminação < l Figura – Efeito da barra de pressão na qualidade das lâminas - fendilhamento
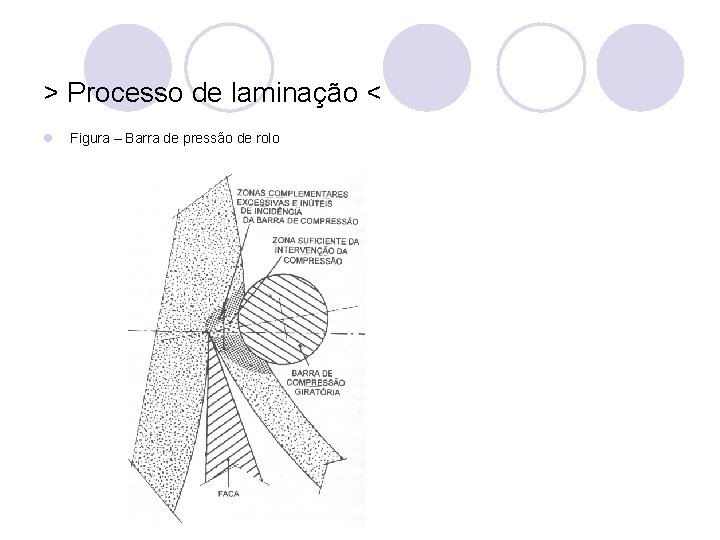
> Processo de laminação < l Figura – Barra de pressão de rolo
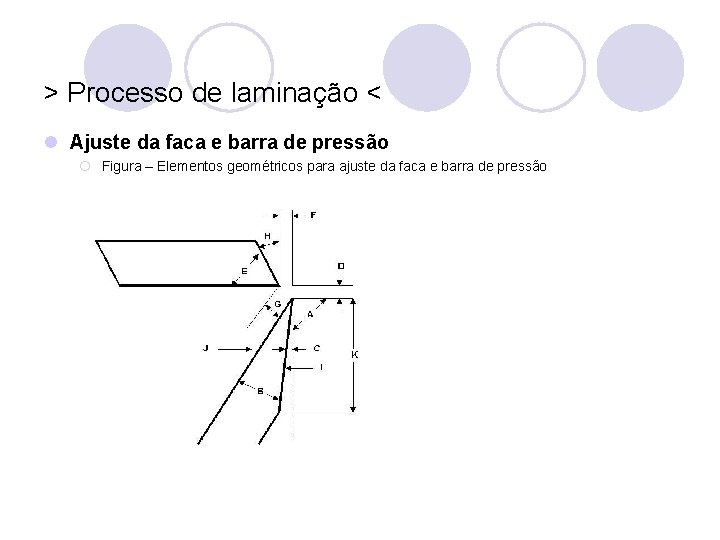
> Processo de laminação < l Ajuste da faca e barra de pressão ¡ Figura – Elementos geométricos para ajuste da faca e barra de pressão A ngulo de faca; B ngulo de afiação; C ngulo de abertura; D Abertura vertical; E ngulo de gume da barra de pressão; F Abertura horizontal; G Orifício de saída; H ngulo de compressão; I Superfície do gume da faca; J Dorso da faca; K Comprimento do gume.
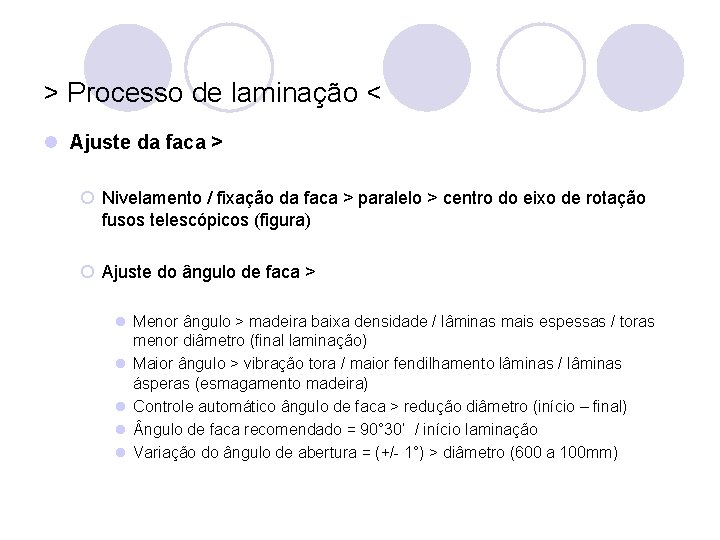
> Processo de laminação < l Ajuste da faca > ¡ Nivelamento / fixação da faca > paralelo > centro do eixo de rotação fusos telescópicos (figura) ¡ Ajuste do ângulo de faca > l Menor ângulo > madeira baixa densidade / lâminas mais espessas / toras menor diâmetro (final laminação) l Maior ângulo > vibração tora / maior fendilhamento lâminas / lâminas ásperas (esmagamento madeira) l Controle automático ângulo de faca > redução diâmetro (início – final) l ngulo de faca recomendado = 90° 30’ / início laminação l Variação do ângulo de abertura = (+/- 1°) > diâmetro (600 a 100 mm)
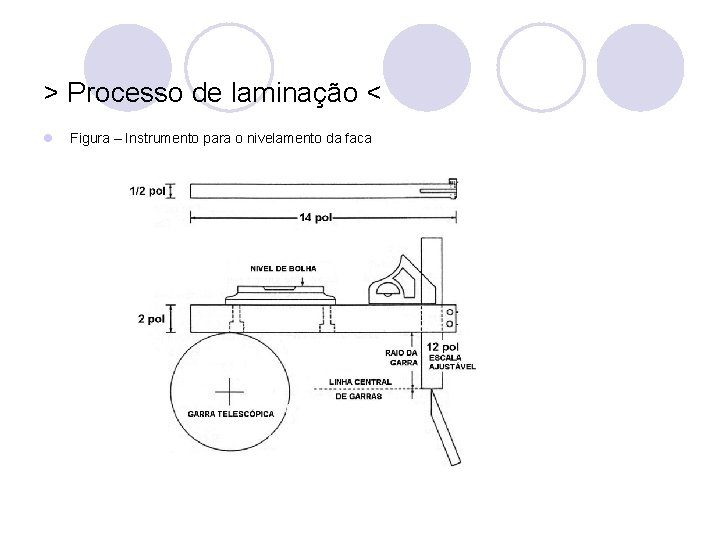
> Processo de laminação < l Figura – Instrumento para o nivelamento da faca
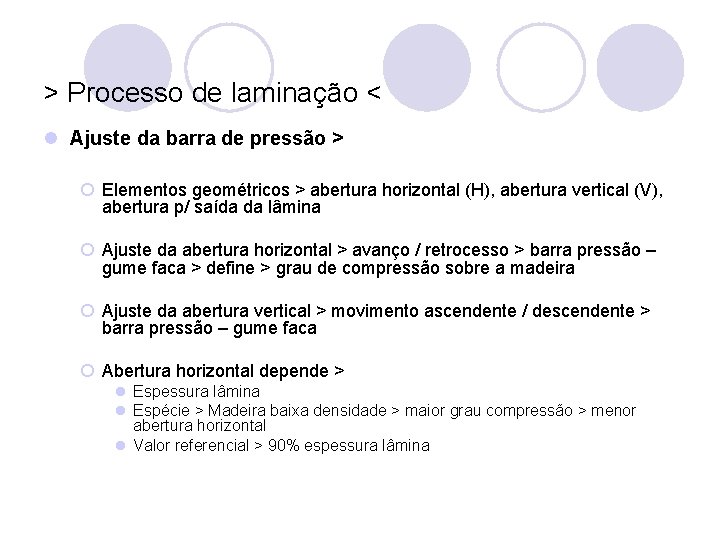
> Processo de laminação < l Ajuste da barra de pressão > ¡ Elementos geométricos > abertura horizontal (H), abertura vertical (V), abertura p/ saída da lâmina ¡ Ajuste da abertura horizontal > avanço / retrocesso > barra pressão – gume faca > define > grau de compressão sobre a madeira ¡ Ajuste da abertura vertical > movimento ascendente / descendente > barra pressão – gume faca ¡ Abertura horizontal depende > l Espessura lâmina l Espécie > Madeira baixa densidade > maior grau compressão > menor abertura horizontal l Valor referencial > 90% espessura lâmina
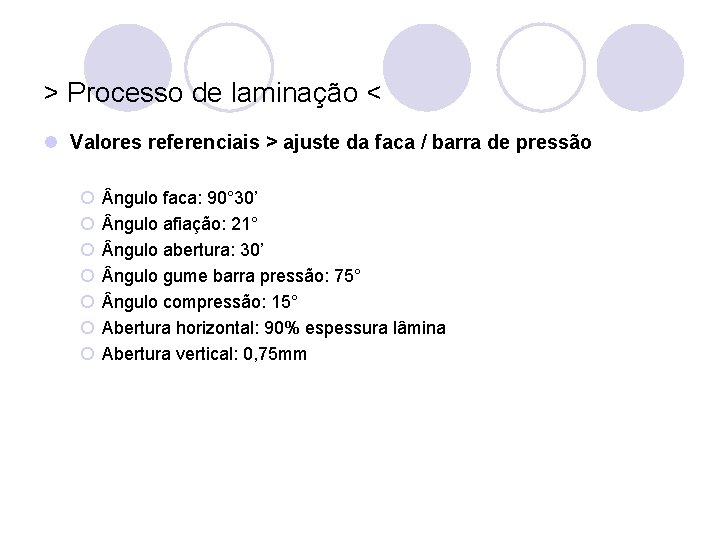
> Processo de laminação < l Valores referenciais > ajuste da faca / barra de pressão ¡ ¡ ¡ ¡ ngulo faca: 90° 30’ ngulo afiação: 21° ngulo abertura: 30’ ngulo gume barra pressão: 75° ngulo compressão: 15° Abertura horizontal: 90% espessura lâmina Abertura vertical: 0, 75 mm
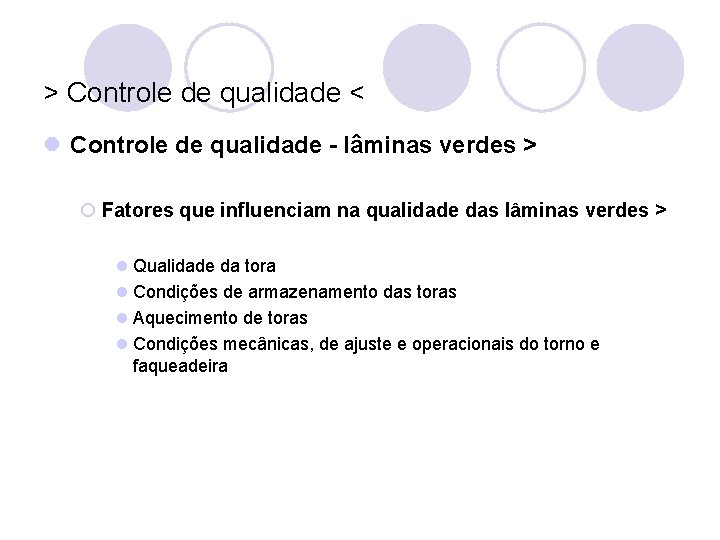
> Controle de qualidade < l Controle de qualidade - lâminas verdes > ¡ Fatores que influenciam na qualidade das lâminas verdes > l Qualidade da tora l Condições de armazenamento das toras l Aquecimento de toras l Condições mecânicas, de ajuste e operacionais do torno e faqueadeira
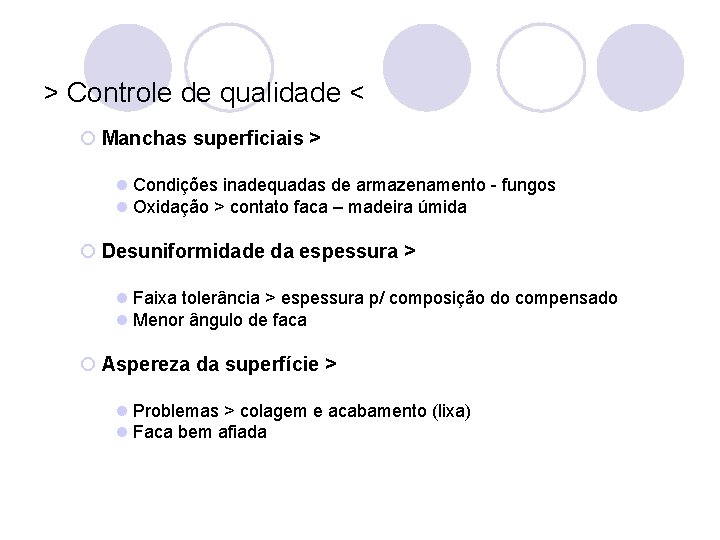
> Controle de qualidade < ¡ Manchas superficiais > l Condições inadequadas de armazenamento - fungos l Oxidação > contato faca – madeira úmida ¡ Desuniformidade da espessura > l Faixa tolerância > espessura p/ composição do compensado l Menor ângulo de faca ¡ Aspereza da superfície > l Problemas > colagem e acabamento (lixa) l Faca bem afiada
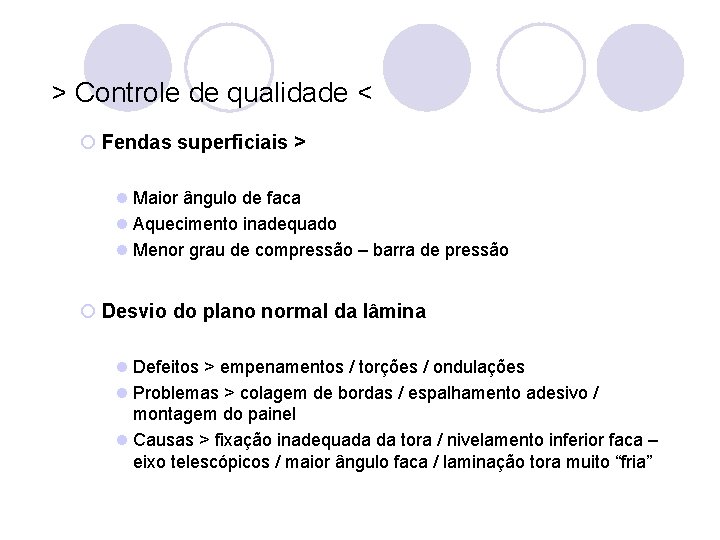
> Controle de qualidade < ¡ Fendas superficiais > l Maior ângulo de faca l Aquecimento inadequado l Menor grau de compressão – barra de pressão ¡ Desvio do plano normal da lâmina l Defeitos > empenamentos / torções / ondulações l Problemas > colagem de bordas / espalhamento adesivo / montagem do painel l Causas > fixação inadequada da tora / nivelamento inferior faca – eixo telescópicos / maior ângulo faca / laminação tora muito “fria”
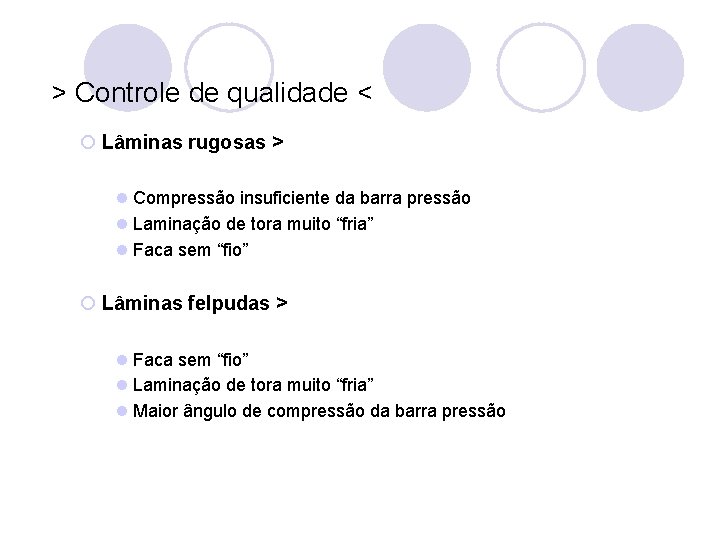
> Controle de qualidade < ¡ Lâminas rugosas > l Compressão insuficiente da barra pressão l Laminação de tora muito “fria” l Faca sem “fio” ¡ Lâminas felpudas > l Faca sem “fio” l Laminação de tora muito “fria” l Maior ângulo de compressão da barra pressão
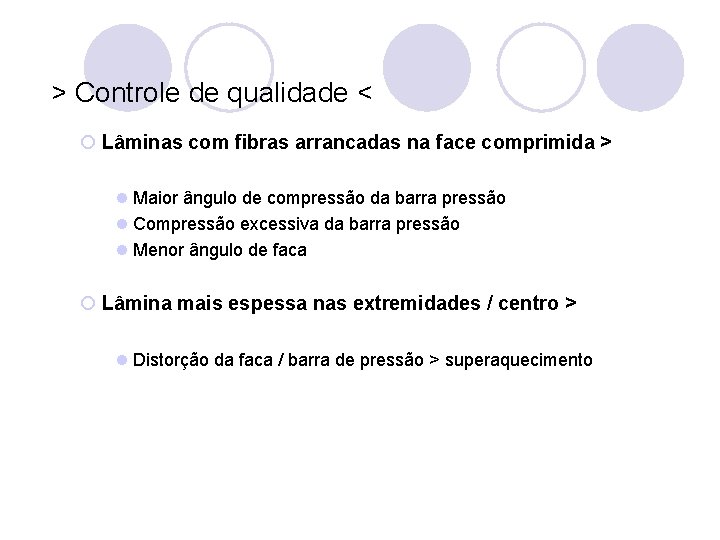
> Controle de qualidade < ¡ Lâminas com fibras arrancadas na face comprimida > l Maior ângulo de compressão da barra pressão l Compressão excessiva da barra pressão l Menor ângulo de faca ¡ Lâmina mais espessa nas extremidades / centro > l Distorção da faca / barra de pressão > superaquecimento
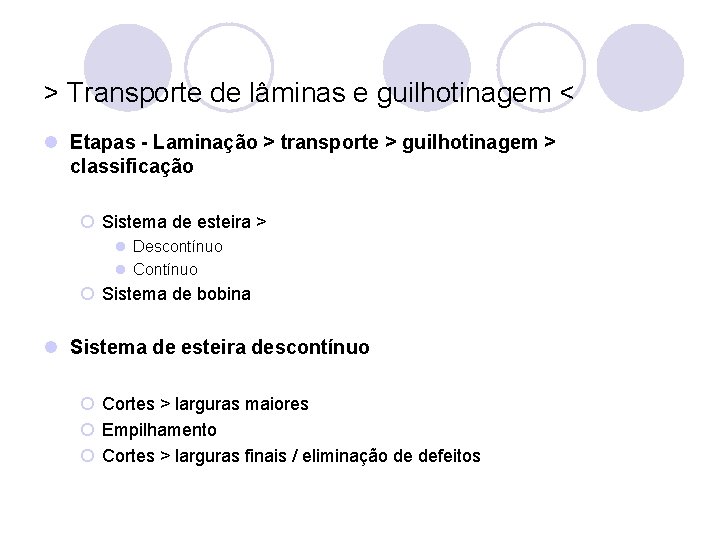
> Transporte de lâminas e guilhotinagem < l Etapas - Laminação > transporte > guilhotinagem > classificação ¡ Sistema de esteira > l Descontínuo l Contínuo ¡ Sistema de bobina l Sistema de esteira descontínuo ¡ Cortes > larguras maiores ¡ Empilhamento ¡ Cortes > larguras finais / eliminação de defeitos
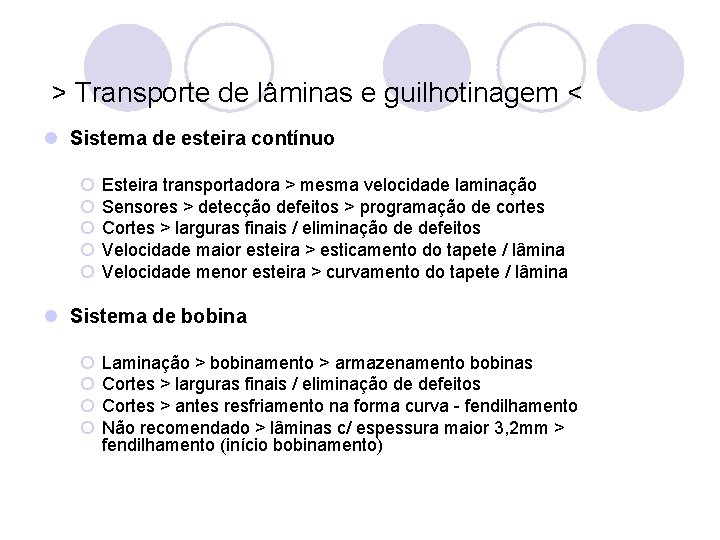
> Transporte de lâminas e guilhotinagem < l Sistema de esteira contínuo ¡ ¡ ¡ Esteira transportadora > mesma velocidade laminação Sensores > detecção defeitos > programação de cortes Cortes > larguras finais / eliminação de defeitos Velocidade maior esteira > esticamento do tapete / lâmina Velocidade menor esteira > curvamento do tapete / lâmina l Sistema de bobina ¡ ¡ Laminação > bobinamento > armazenamento bobinas Cortes > larguras finais / eliminação de defeitos Cortes > antes resfriamento na forma curva - fendilhamento Não recomendado > lâminas c/ espessura maior 3, 2 mm > fendilhamento (início bobinamento)
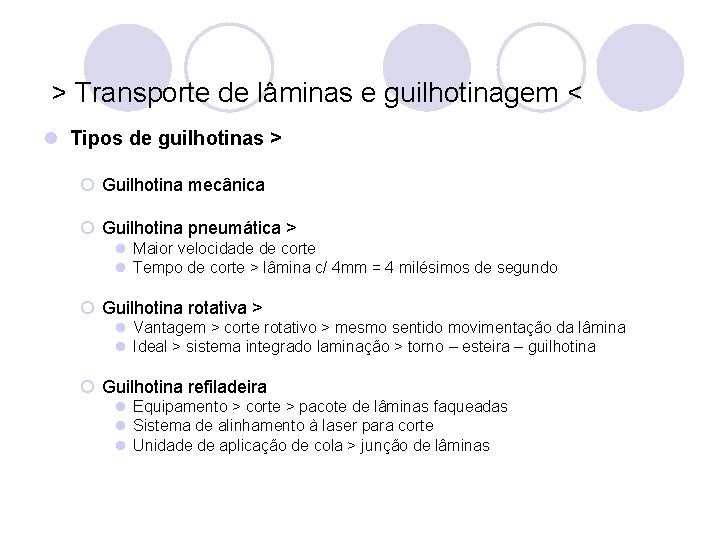
> Transporte de lâminas e guilhotinagem < l Tipos de guilhotinas > ¡ Guilhotina mecânica ¡ Guilhotina pneumática > l Maior velocidade de corte l Tempo de corte > lâmina c/ 4 mm = 4 milésimos de segundo ¡ Guilhotina rotativa > l Vantagem > corte rotativo > mesmo sentido movimentação da lâmina l Ideal > sistema integrado laminação > torno – esteira – guilhotina ¡ Guilhotina refiladeira l Equipamento > corte > pacote de lâminas faqueadas l Sistema de alinhamento à laser para corte l Unidade de aplicação de cola > junção de lâminas
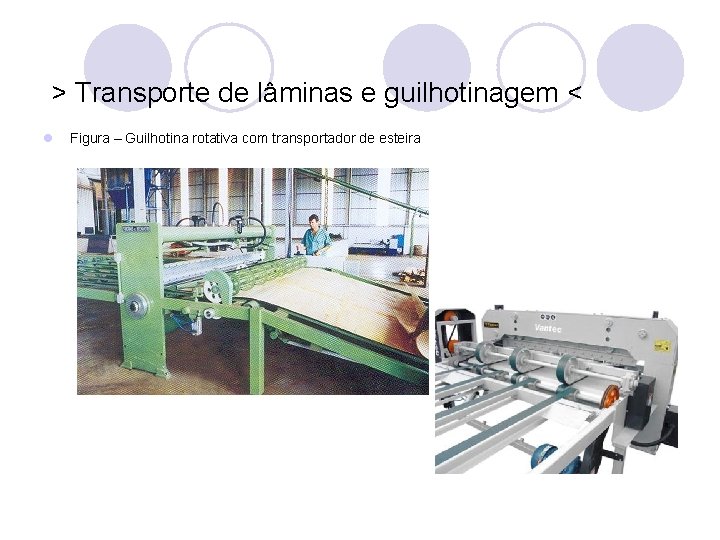
> Transporte de lâminas e guilhotinagem < l Figura – Guilhotina rotativa com transportador de esteira
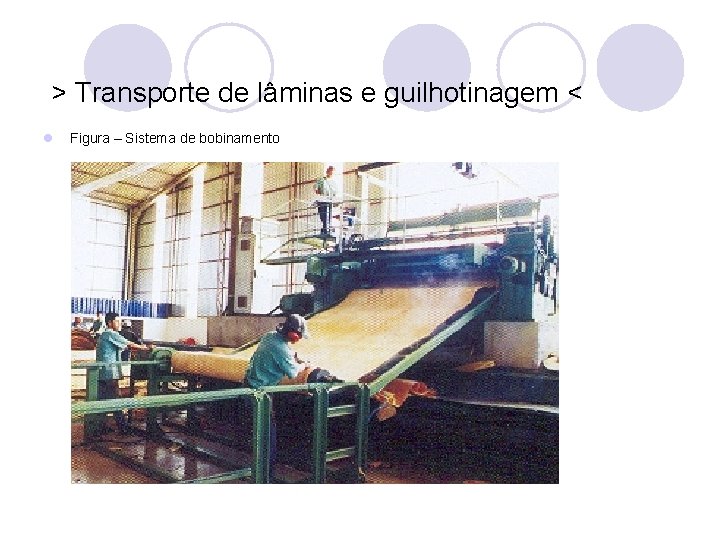
> Transporte de lâminas e guilhotinagem < l Figura – Sistema de bobinamento
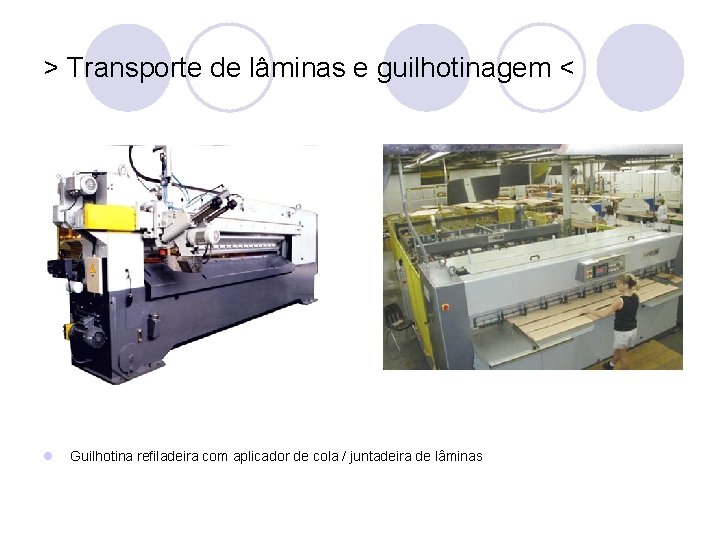
> Transporte de lâminas e guilhotinagem < l Guilhotina refiladeira com aplicador de cola / juntadeira de lâminas
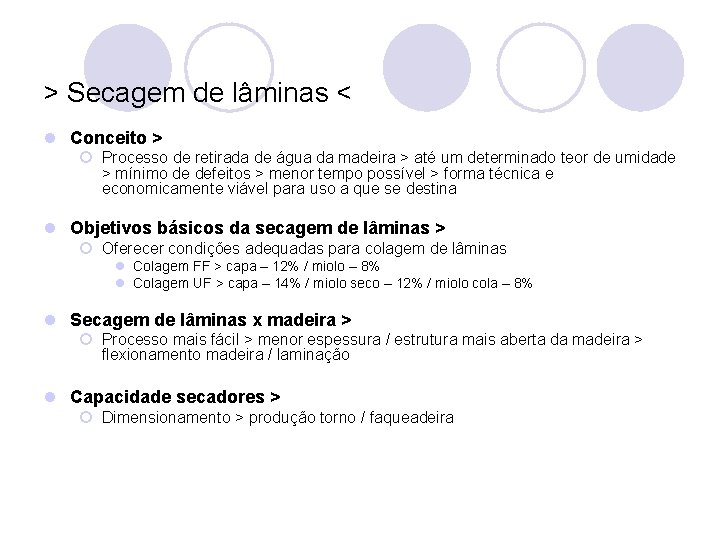
> Secagem de lâminas < l Conceito > ¡ Processo de retirada de água da madeira > até um determinado teor de umidade > mínimo de defeitos > menor tempo possível > forma técnica e economicamente viável para uso a que se destina l Objetivos básicos da secagem de lâminas > ¡ Oferecer condições adequadas para colagem de lâminas l Colagem FF > capa – 12% / miolo – 8% l Colagem UF > capa – 14% / miolo seco – 12% / miolo cola – 8% l Secagem de lâminas x madeira > ¡ Processo mais fácil > menor espessura / estrutura mais aberta da madeira > flexionamento madeira / laminação l Capacidade secadores > ¡ Dimensionamento > produção torno / faqueadeira
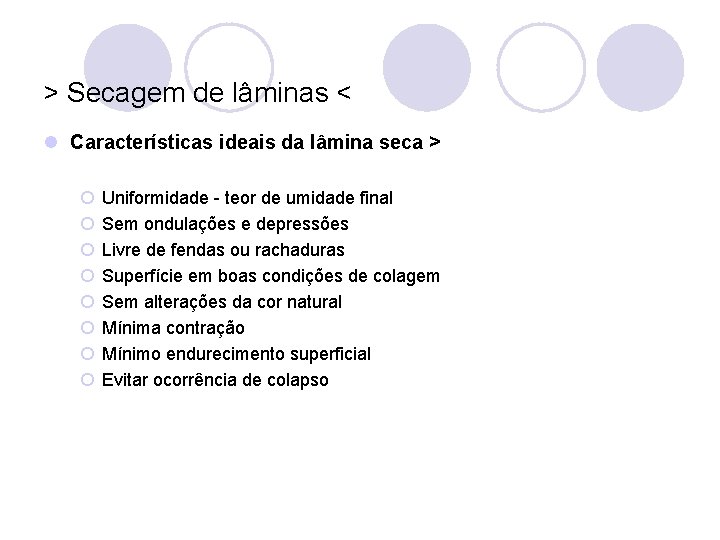
> Secagem de lâminas < l Características ideais da lâmina seca > ¡ ¡ ¡ ¡ Uniformidade - teor de umidade final Sem ondulações e depressões Livre de fendas ou rachaduras Superfície em boas condições de colagem Sem alterações da cor natural Mínima contração Mínimo endurecimento superficial Evitar ocorrência de colapso
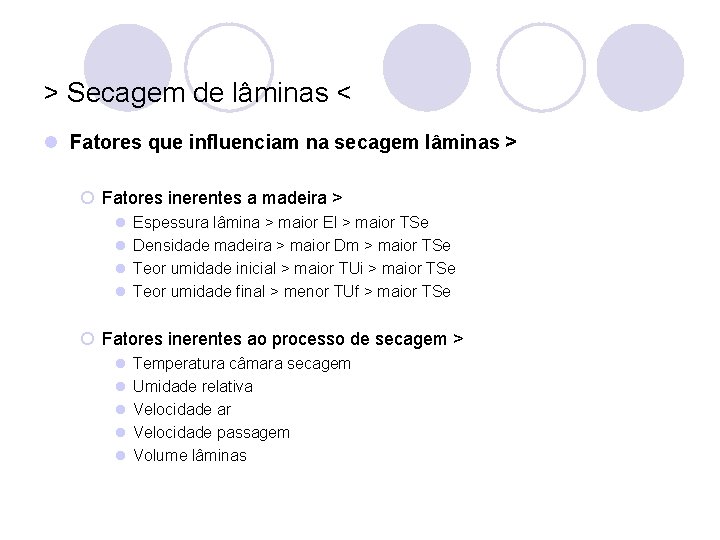
> Secagem de lâminas < l Fatores que influenciam na secagem lâminas > ¡ Fatores inerentes a madeira > l l Espessura lâmina > maior El > maior TSe Densidade madeira > maior Dm > maior TSe Teor umidade inicial > maior TUi > maior TSe Teor umidade final > menor TUf > maior TSe ¡ Fatores inerentes ao processo de secagem > l l l Temperatura câmara secagem Umidade relativa Velocidade ar Velocidade passagem Volume lâminas
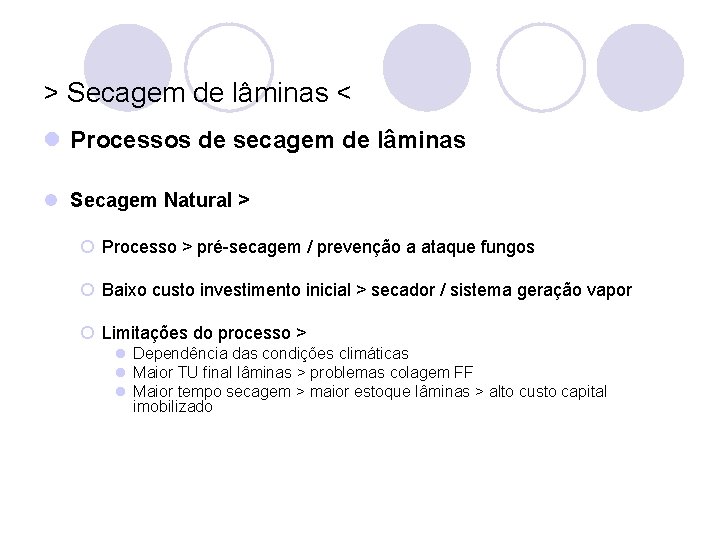
> Secagem de lâminas < l Processos de secagem de lâminas l Secagem Natural > ¡ Processo > pré-secagem / prevenção a ataque fungos ¡ Baixo custo investimento inicial > secador / sistema geração vapor ¡ Limitações do processo > l Dependência das condições climáticas l Maior TU final lâminas > problemas colagem FF l Maior tempo secagem > maior estoque lâminas > alto custo capital imobilizado
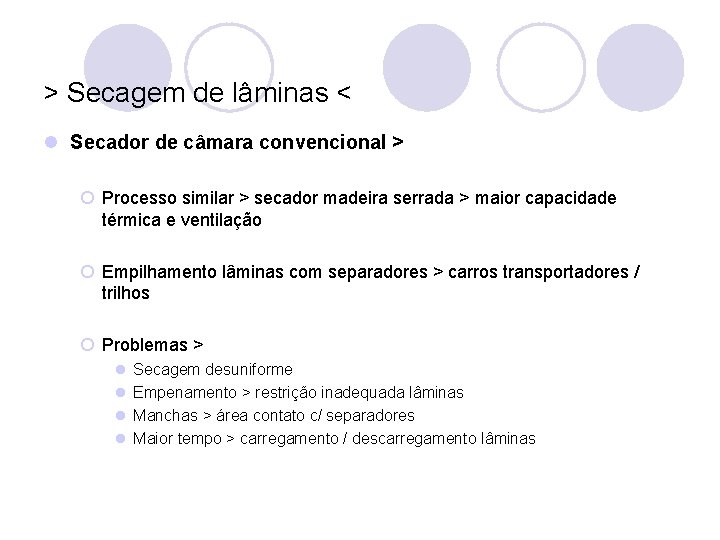
> Secagem de lâminas < l Secador de câmara convencional > ¡ Processo similar > secador madeira serrada > maior capacidade térmica e ventilação ¡ Empilhamento lâminas com separadores > carros transportadores / trilhos ¡ Problemas > l l Secagem desuniforme Empenamento > restrição inadequada lâminas Manchas > área contato c/ separadores Maior tempo > carregamento / descarregamento lâminas
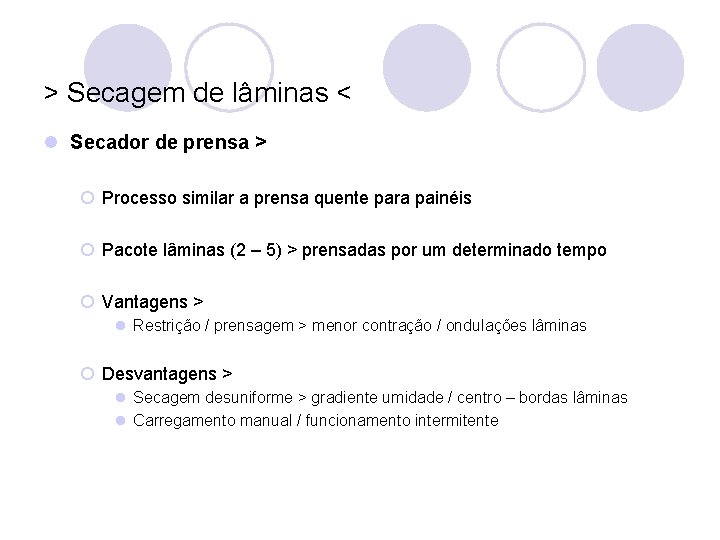
> Secagem de lâminas < l Secador de prensa > ¡ Processo similar a prensa quente para painéis ¡ Pacote lâminas (2 – 5) > prensadas por um determinado tempo ¡ Vantagens > l Restrição / prensagem > menor contração / ondulações lâminas ¡ Desvantagens > l Secagem desuniforme > gradiente umidade / centro – bordas lâminas l Carregamento manual / funcionamento intermitente
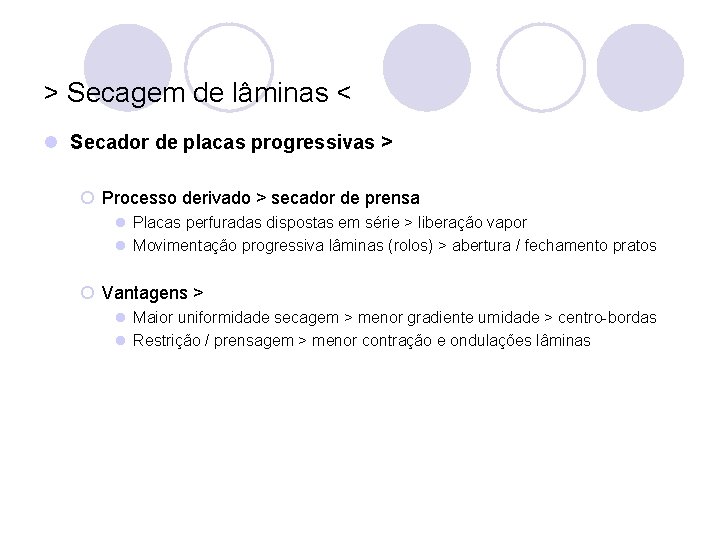
> Secagem de lâminas < l Secador de placas progressivas > ¡ Processo derivado > secador de prensa l Placas perfuradas dispostas em série > liberação vapor l Movimentação progressiva lâminas (rolos) > abertura / fechamento pratos ¡ Vantagens > l Maior uniformidade secagem > menor gradiente umidade > centro-bordas l Restrição / prensagem > menor contração e ondulações lâminas
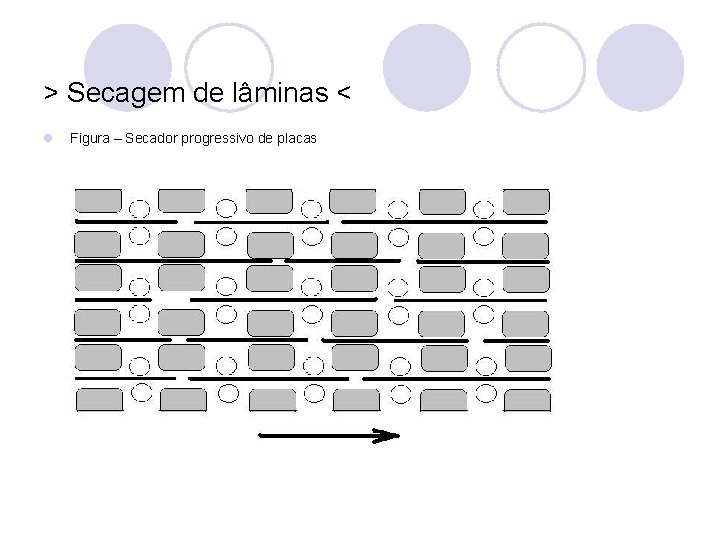
> Secagem de lâminas < l Figura – Secador progressivo de placas
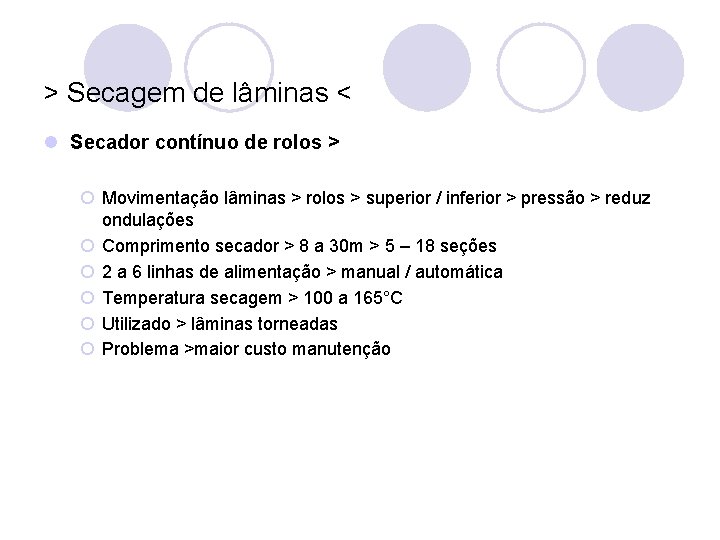
> Secagem de lâminas < l Secador contínuo de rolos > ¡ Movimentação lâminas > rolos > superior / inferior > pressão > reduz ondulações ¡ Comprimento secador > 8 a 30 m > 5 – 18 seções ¡ 2 a 6 linhas de alimentação > manual / automática ¡ Temperatura secagem > 100 a 165°C ¡ Utilizado > lâminas torneadas ¡ Problema >maior custo manutenção
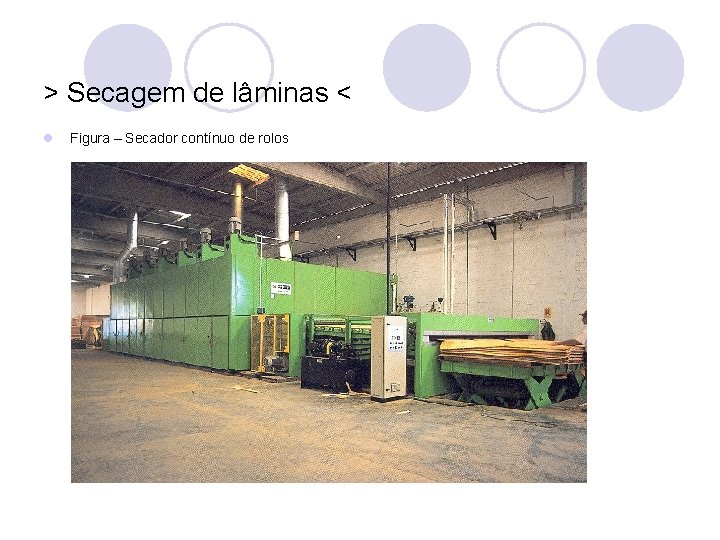
> Secagem de lâminas < l Figura – Secador contínuo de rolos
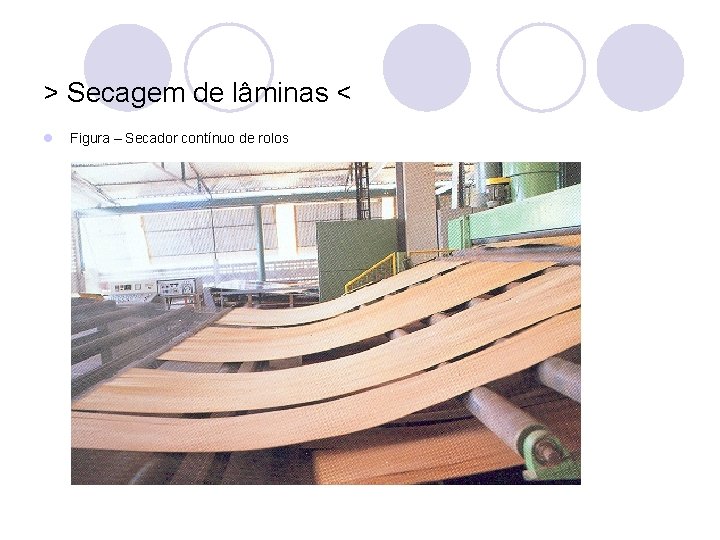
> Secagem de lâminas < l Figura – Secador contínuo de rolos
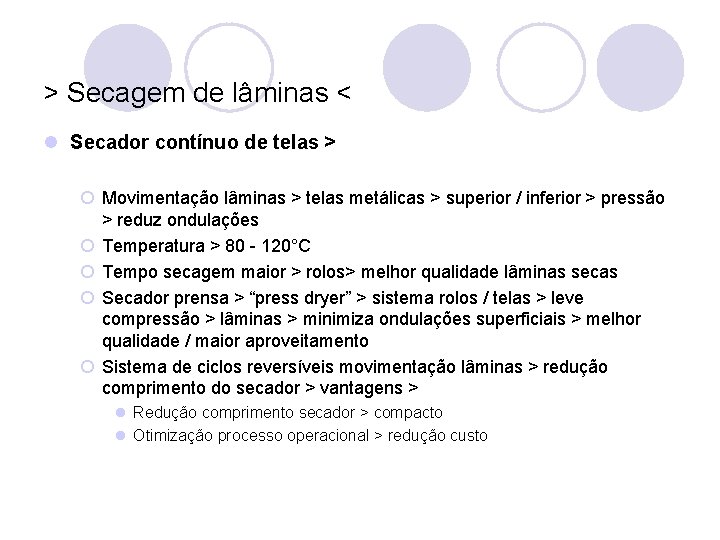
> Secagem de lâminas < l Secador contínuo de telas > ¡ Movimentação lâminas > telas metálicas > superior / inferior > pressão > reduz ondulações ¡ Temperatura > 80 - 120°C ¡ Tempo secagem maior > rolos> melhor qualidade lâminas secas ¡ Secador prensa > “press dryer” > sistema rolos / telas > leve compressão > lâminas > minimiza ondulações superficiais > melhor qualidade / maior aproveitamento ¡ Sistema de ciclos reversíveis movimentação lâminas > redução comprimento do secador > vantagens > l Redução comprimento secador > compacto l Otimização processo operacional > redução custo
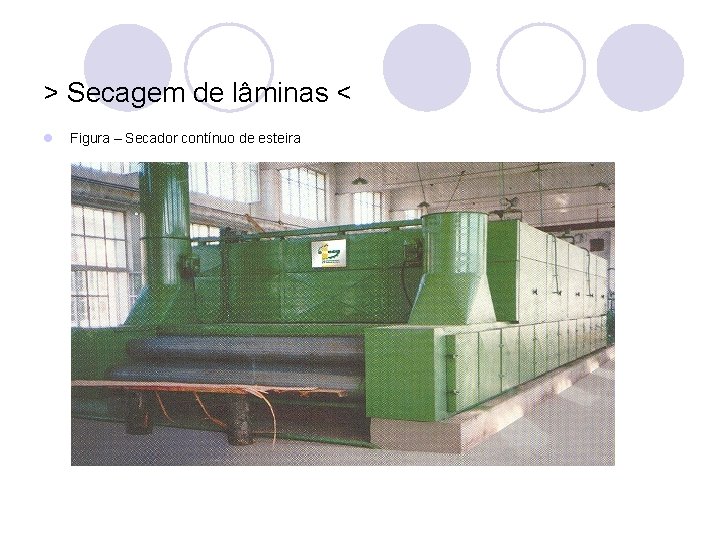
> Secagem de lâminas < l Figura – Secador contínuo de esteira
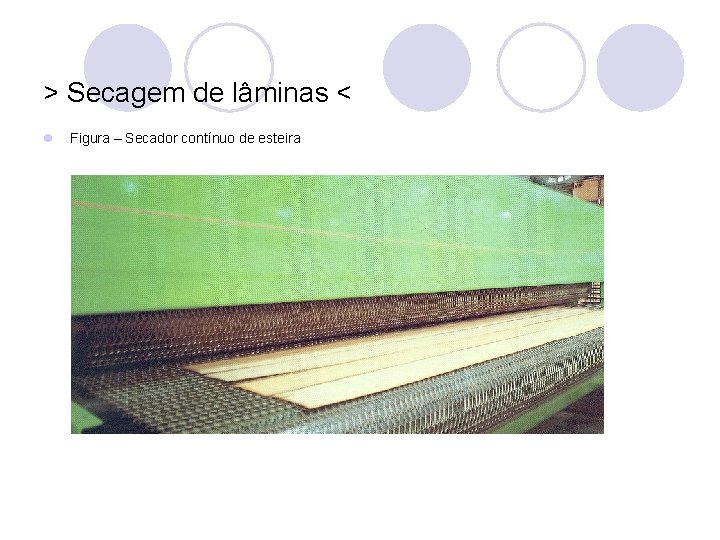
> Secagem de lâminas < l Figura – Secador contínuo de esteira
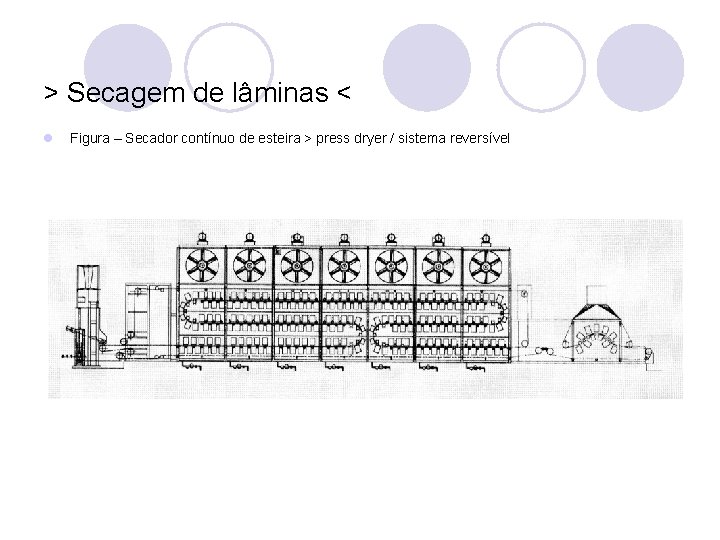
> Secagem de lâminas < l Figura – Secador contínuo de esteira > press dryer / sistema reversível
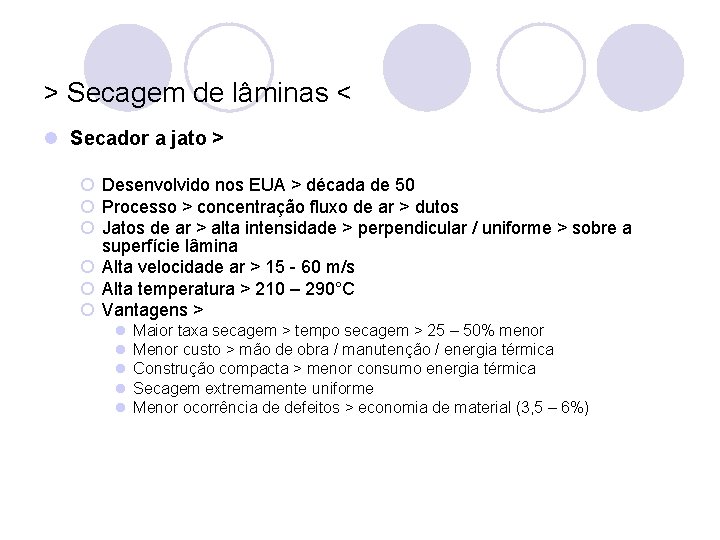
> Secagem de lâminas < l Secador a jato > ¡ Desenvolvido nos EUA > década de 50 ¡ Processo > concentração fluxo de ar > dutos ¡ Jatos de ar > alta intensidade > perpendicular / uniforme > sobre a superfície lâmina ¡ Alta velocidade ar > 15 - 60 m/s ¡ Alta temperatura > 210 – 290°C ¡ Vantagens > l l l Maior taxa secagem > tempo secagem > 25 – 50% menor Menor custo > mão de obra / manutenção / energia térmica Construção compacta > menor consumo energia térmica Secagem extremamente uniforme Menor ocorrência de defeitos > economia de material (3, 5 – 6%)
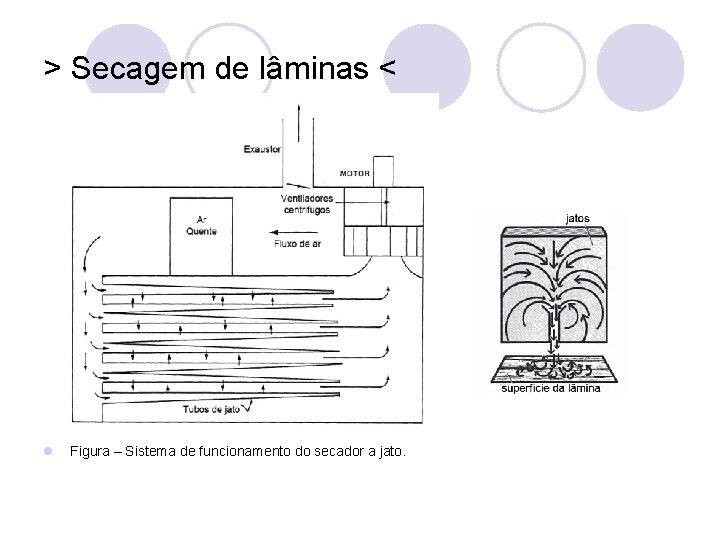
> Secagem de lâminas < l Figura – Sistema de funcionamento do secador a jato.
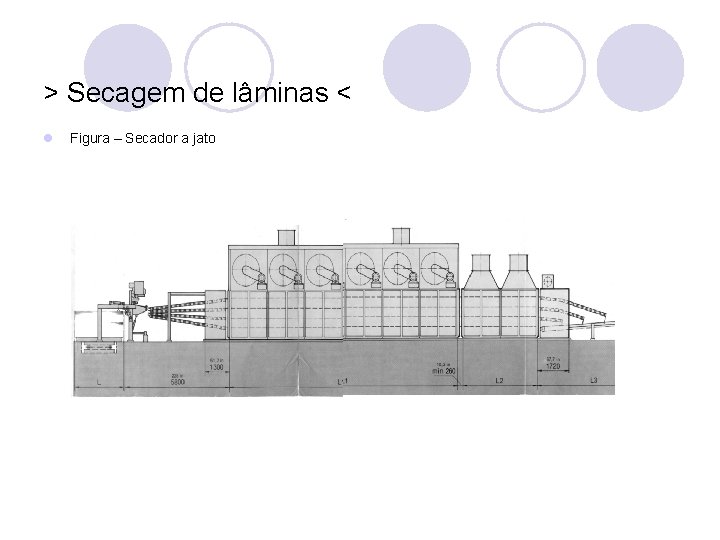
> Secagem de lâminas < l Figura – Secador a jato
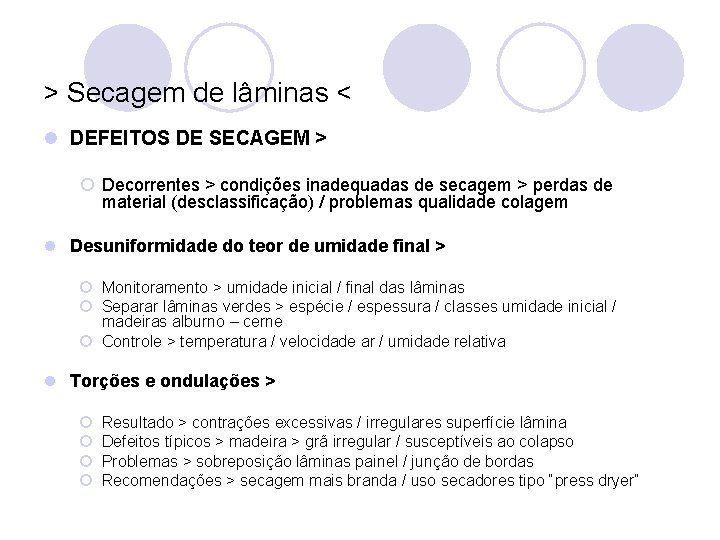
> Secagem de lâminas < l DEFEITOS DE SECAGEM > ¡ Decorrentes > condições inadequadas de secagem > perdas de material (desclassificação) / problemas qualidade colagem l Desuniformidade do teor de umidade final > ¡ Monitoramento > umidade inicial / final das lâminas ¡ Separar lâminas verdes > espécie / espessura / classes umidade inicial / madeiras alburno – cerne ¡ Controle > temperatura / velocidade ar / umidade relativa l Torções e ondulações > ¡ ¡ Resultado > contrações excessivas / irregulares superfície lâmina Defeitos típicos > madeira > grã irregular / susceptíveis ao colapso Problemas > sobreposição lâminas painel / junção de bordas Recomendações > secagem mais branda / uso secadores tipo “press dryer”
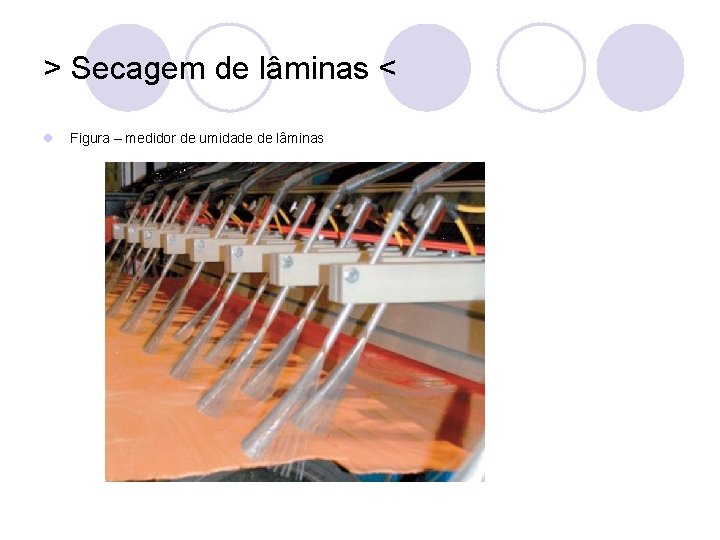
> Secagem de lâminas < l Figura – medidor de umidade de lâminas
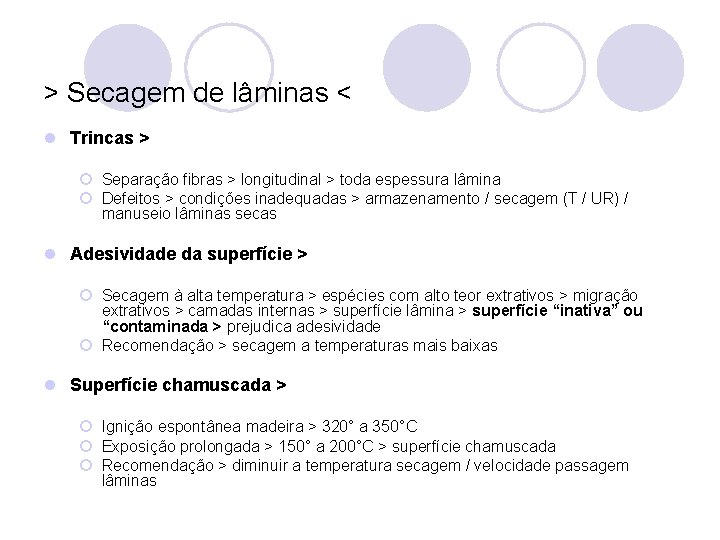
> Secagem de lâminas < l Trincas > ¡ Separação fibras > longitudinal > toda espessura lâmina ¡ Defeitos > condições inadequadas > armazenamento / secagem (T / UR) / manuseio lâminas secas l Adesividade da superfície > ¡ Secagem à alta temperatura > espécies com alto teor extrativos > migração extrativos > camadas internas > superfície lâmina > superfície “inativa” ou “contaminada > prejudica adesividade ¡ Recomendação > secagem a temperaturas mais baixas l Superfície chamuscada > ¡ Ignição espontânea madeira > 320° a 350°C ¡ Exposição prolongada > 150° a 200°C > superfície chamuscada ¡ Recomendação > diminuir a temperatura secagem / velocidade passagem lâminas
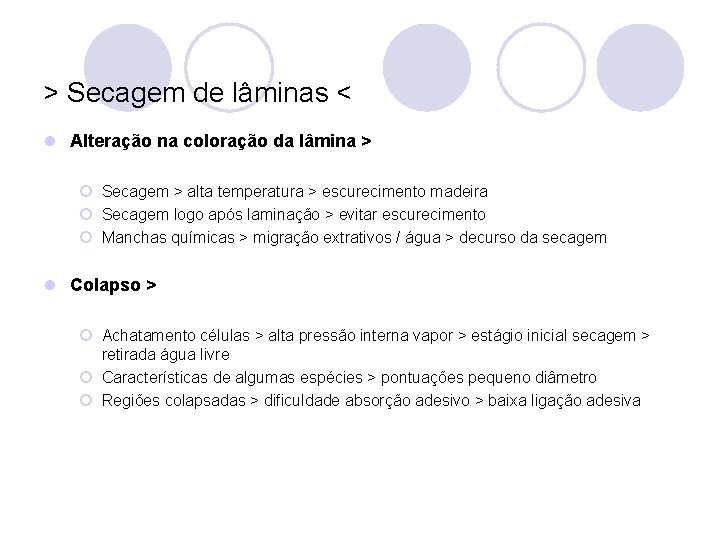
> Secagem de lâminas < l Alteração na coloração da lâmina > ¡ Secagem > alta temperatura > escurecimento madeira ¡ Secagem logo após laminação > evitar escurecimento ¡ Manchas químicas > migração extrativos / água > decurso da secagem l Colapso > ¡ Achatamento células > alta pressão interna vapor > estágio inicial secagem > retirada água livre ¡ Características de algumas espécies > pontuações pequeno diâmetro ¡ Regiões colapsadas > dificuldade absorção adesivo > baixa ligação adesiva
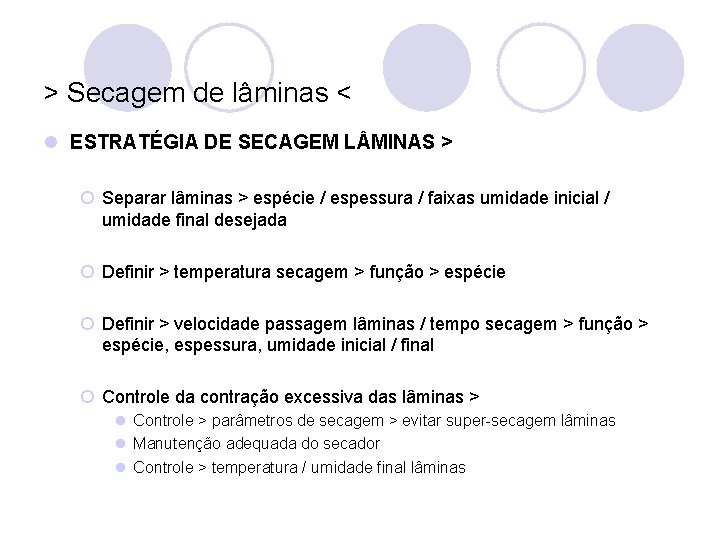
> Secagem de lâminas < l ESTRATÉGIA DE SECAGEM L MINAS > ¡ Separar lâminas > espécie / espessura / faixas umidade inicial / umidade final desejada ¡ Definir > temperatura secagem > função > espécie ¡ Definir > velocidade passagem lâminas / tempo secagem > função > espécie, espessura, umidade inicial / final ¡ Controle da contração excessiva das lâminas > l Controle > parâmetros de secagem > evitar super-secagem lâminas l Manutenção adequada do secador l Controle > temperatura / umidade final lâminas
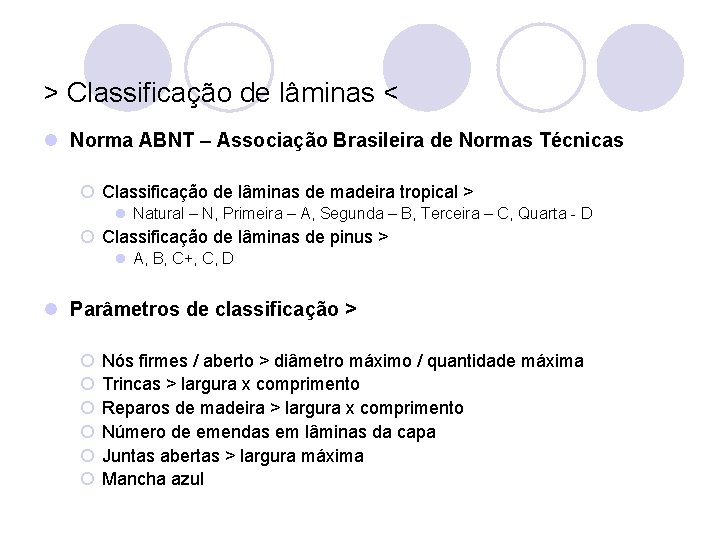
> Classificação de lâminas < l Norma ABNT – Associação Brasileira de Normas Técnicas ¡ Classificação de lâminas de madeira tropical > l Natural – N, Primeira – A, Segunda – B, Terceira – C, Quarta - D ¡ Classificação de lâminas de pinus > l A, B, C+, C, D l Parâmetros de classificação > ¡ ¡ ¡ Nós firmes / aberto > diâmetro máximo / quantidade máxima Trincas > largura x comprimento Reparos de madeira > largura x comprimento Número de emendas em lâminas da capa Juntas abertas > largura máxima Mancha azul
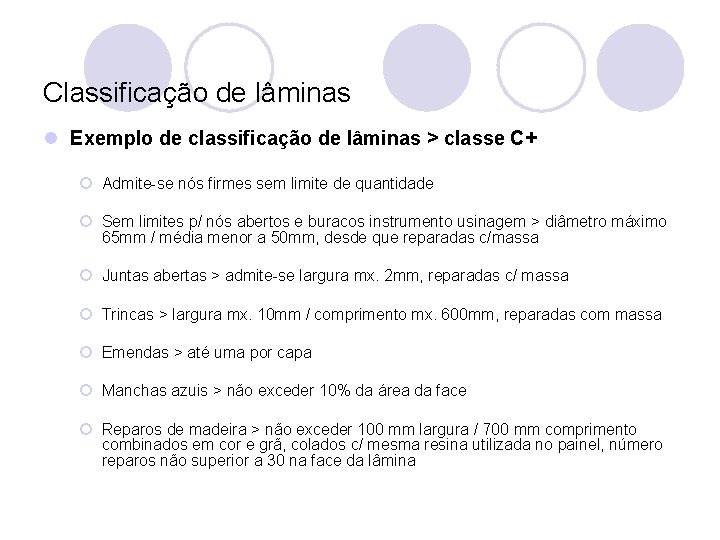
Classificação de lâminas l Exemplo de classificação de lâminas > classe C+ ¡ Admite-se nós firmes sem limite de quantidade ¡ Sem limites p/ nós abertos e buracos instrumento usinagem > diâmetro máximo 65 mm / média menor a 50 mm, desde que reparadas c/massa ¡ Juntas abertas > admite-se largura mx. 2 mm, reparadas c/ massa ¡ Trincas > largura mx. 10 mm / comprimento mx. 600 mm, reparadas com massa ¡ Emendas > até uma por capa ¡ Manchas azuis > não exceder 10% da área da face ¡ Reparos de madeira > não exceder 100 mm largura / 700 mm comprimento combinados em cor e grã, colados c/ mesma resina utilizada no painel, número reparos não superior a 30 na face da lâmina
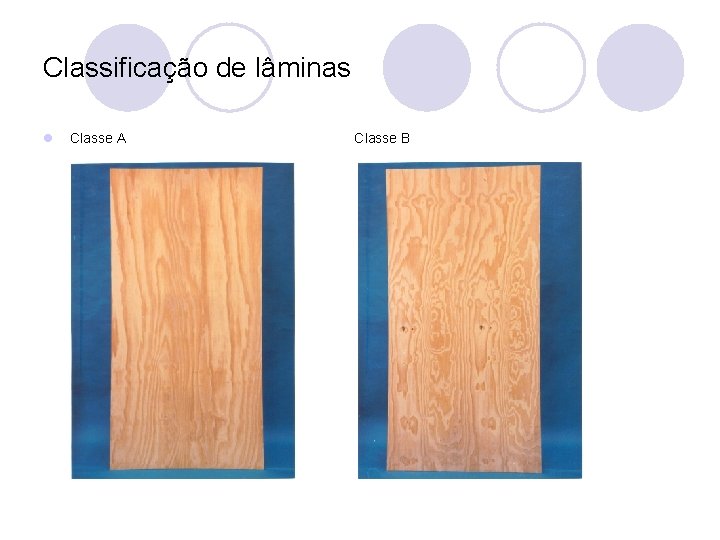
Classificação de lâminas l Classe A Classe B
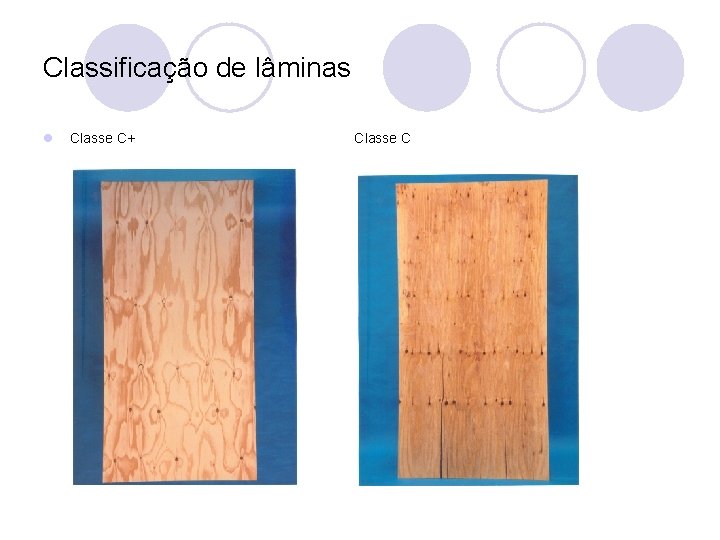
Classificação de lâminas l Classe C+ Classe C
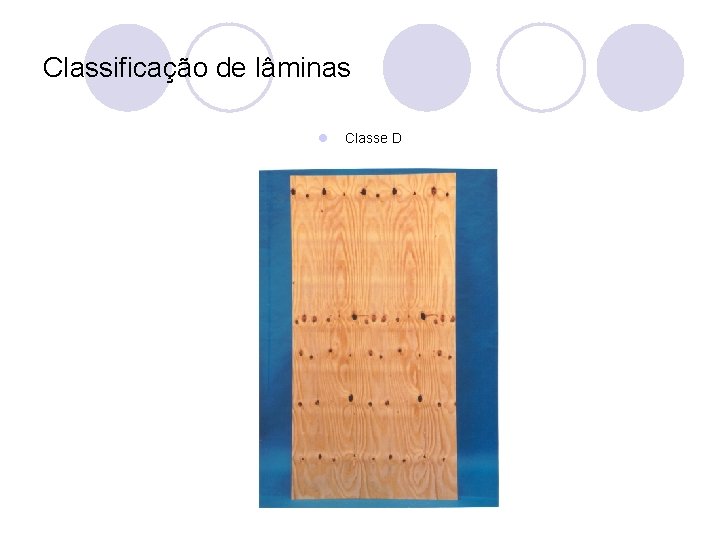
Classificação de lâminas l Classe D
Mil madeiras preciosas ltda
Detf
Laminao
Engenharia industrial madeireira ufpr
Demec ufpr
Zootecnia ufpr
Zona morta
Bisistema
Aparelho psiquico
Ufpr 2017 os processos industriais nao imitam a natureza
Bart selman rate my prof
Pangeneza
Prof kleiber
Samim
Sitotrofoblastik kabuk
Nader alaridah
Prof dr göksal keskin
The art of expressing one's thoughts in verse
Prof kuntoro fkm unair
Hello prof
Esterel prof
Prof. dr. mustafa serdar genç
Prof dr dr iris rengganis
Miyozit spesifik antikorlar
Kinestetik gaya belajar
Merton miller
Florian tschorsch tu berlin
Cua study abroad
Candda
Science prof online
Prof paul browne
Glomerülasyon nedir
Prof dr metin ingeç
Professor dr. gerd kirchhoff
Prof dr serkan yılmaz
Izricanje pogodbe mogućnosti i želje
Prof dr naz yeni
Learning without burden report was given by
Complex overt response example
Prof 2000
Conclusion for menstrual cycle
Prof dr ayça vitrinel
Prof.dr.saliha kırıcı
Prof.dr sait karakurt muayenehane
Prof dr emel ebru özçimen
Prof. dr. sc. ivana barković
Prof sandra lowe
Prof azamris
Angle congru allo prof
Prof.dr. ayhan demiriz
Prof ram meghe institute of technology and research
Prof.sse
Cretor
Prof. tahmina begum
Aptt karışım (mixing) testi
Milan miljevic
Pengertian wawasan nusantara menurut prof wan usman
"prof universidade paulista unip"
Professor atinga
Rachel lindner upb
Meneder
Prof bakdi
Cem yurtsev
Prof 2000
Prof. dr. nizamettin aydin
Prof dr petek askar
Prof dr nevzat yüksel
Subfebril ateş
Synergistik
Pozycja ortopnoe
Umi narimawati
Under supervision of prof
I prof 33
özofageal disfaji
Under supervision of prof
Dr baumeister
Corrado tamburino
Obsatar sinaga
Riadh habash rate my prof
Prof pedro marques
Prof dr gülay kınıklı
Pengertian pajak menurut dr rochmat soemitro
Yıldız akvardar
Modelo de nicolas copernico
Atrofi
Sadiye kayaarslan
Lehrstuhl gröpl
Blake poş kisti
Prof dr ali hossain
Prof dr mehmet kıyan
Prof eco
La mia prof
Randanan bandaso
Prof lorenz heidelberg
Definition of gtm
Prof. dr. cem ficicioglu
Anspruchsrechte
Exchange rate bnr
Esempi domande orale tfa sostegno
Gg prof
Primitivo lupoli
Dr. sadiq m. sait