POWDER METALLURGY INTRODUCTION Powder metallurgy is the name
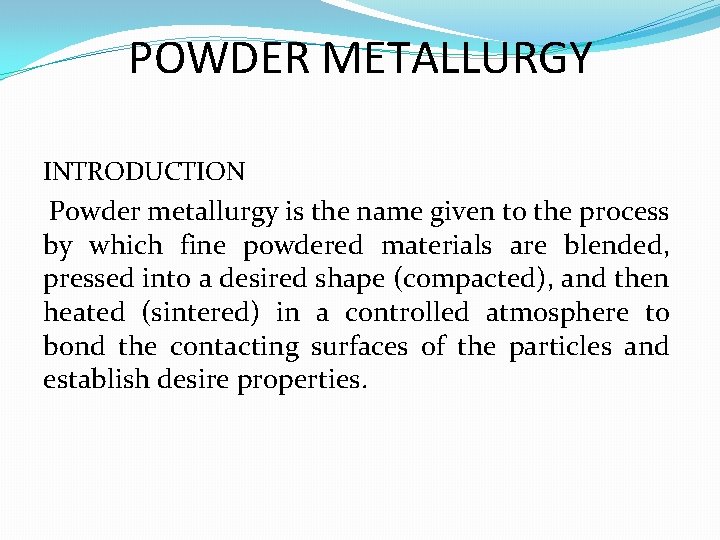
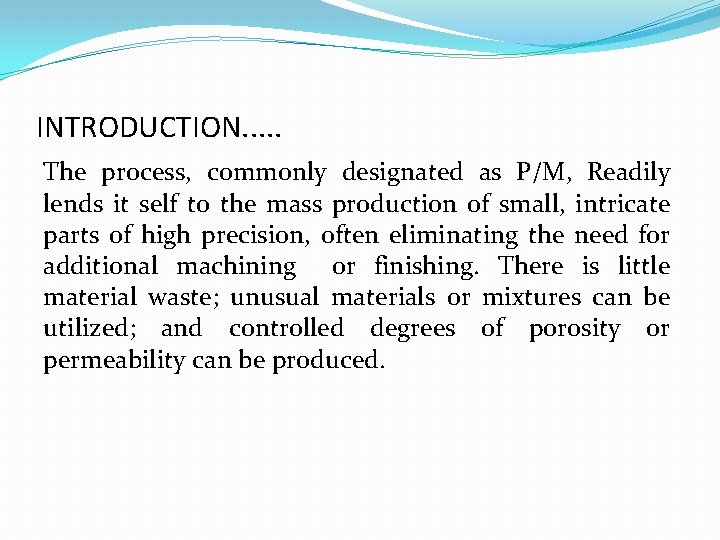
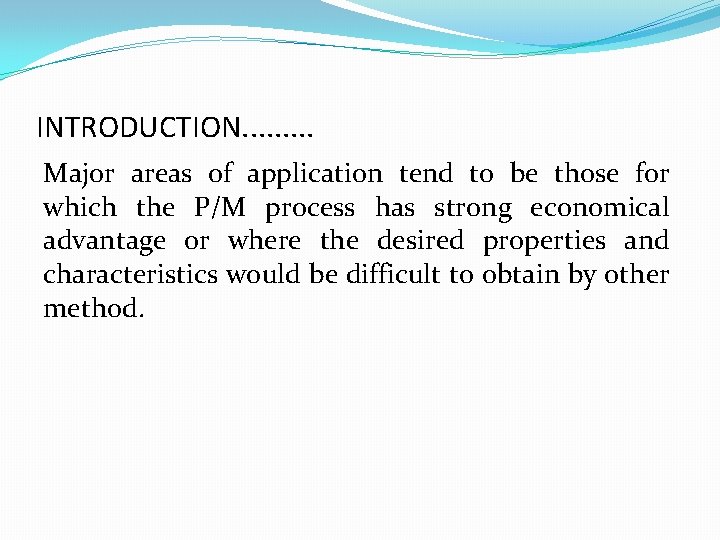

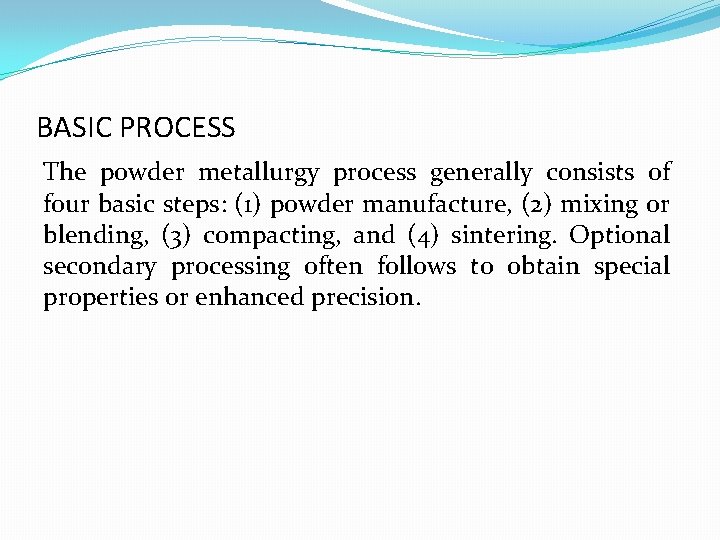
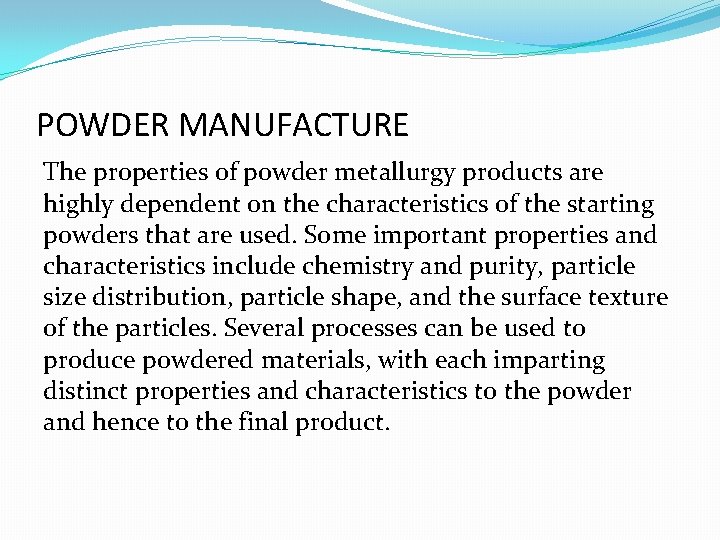
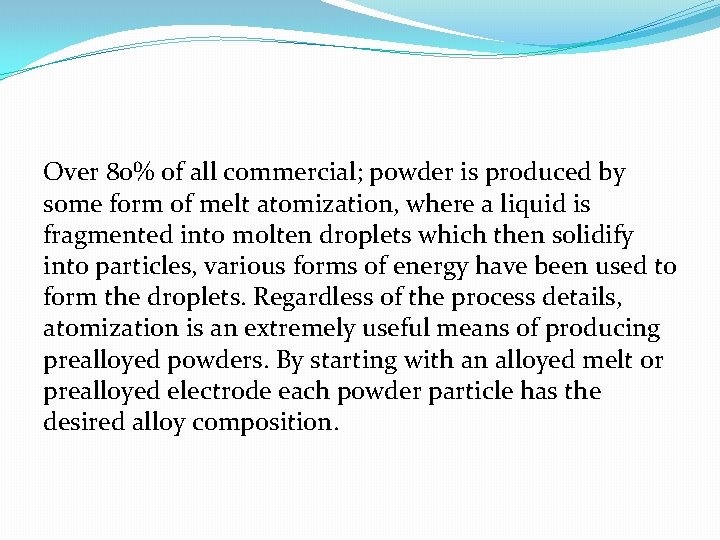
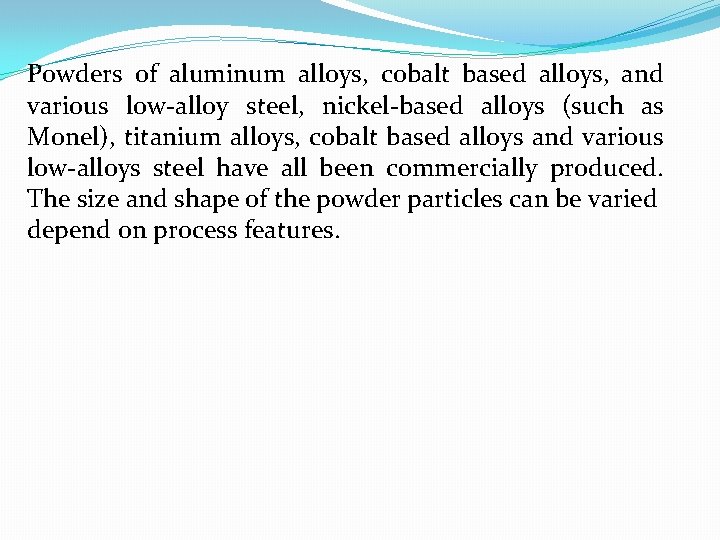
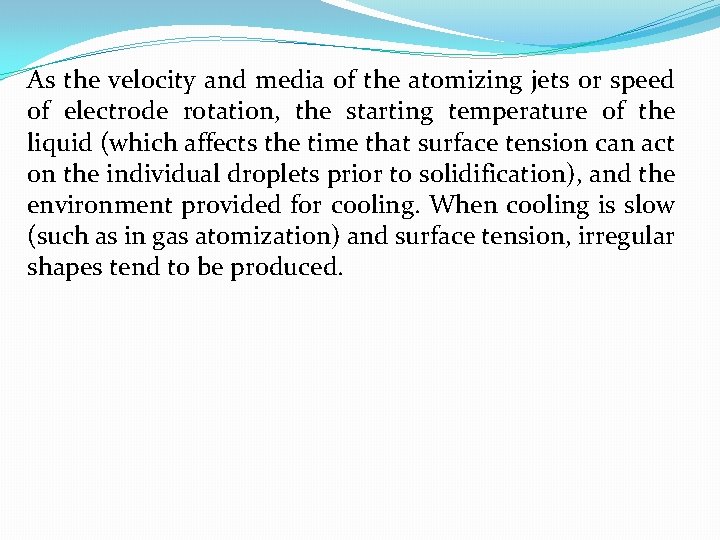
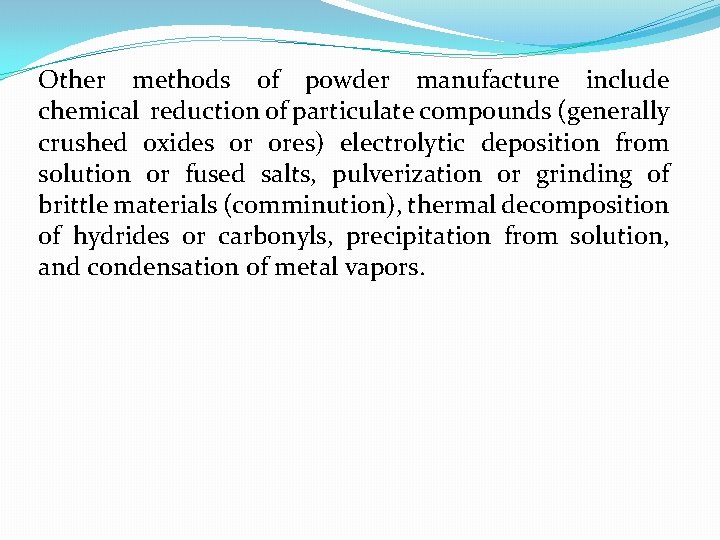
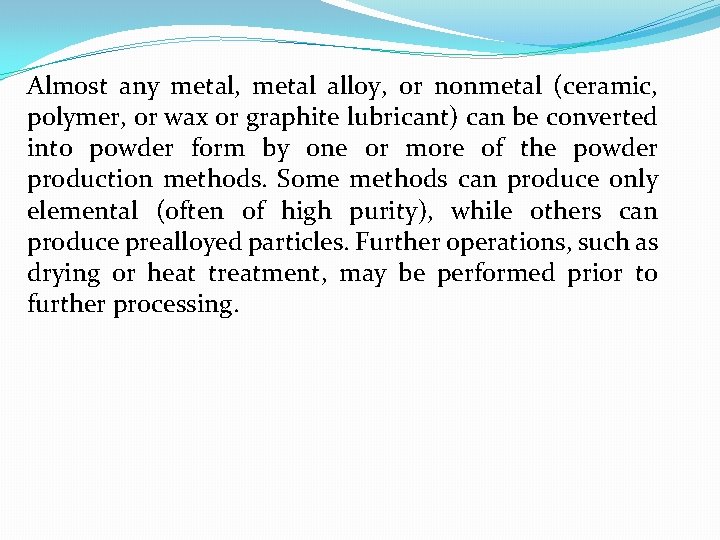
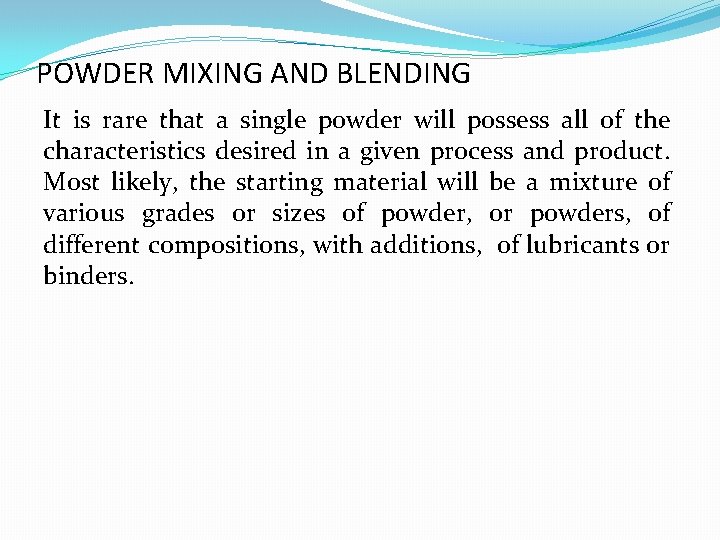
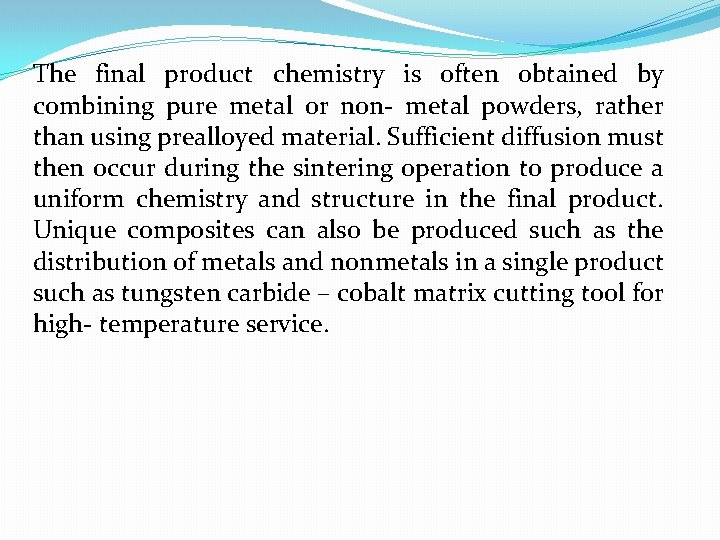
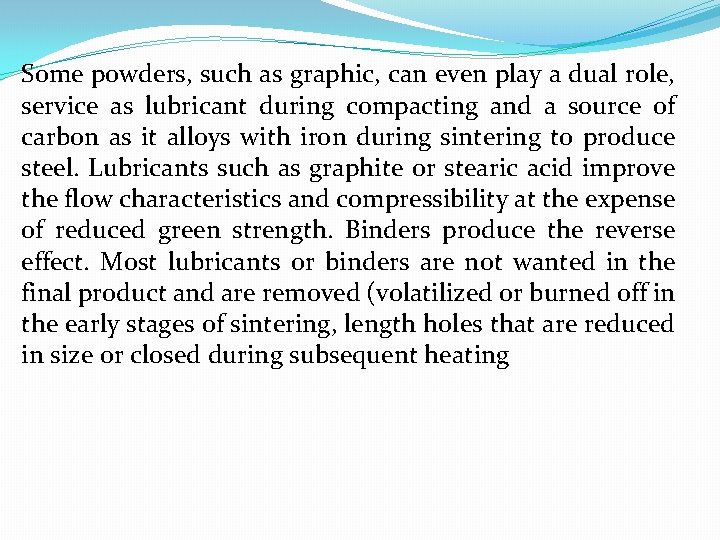
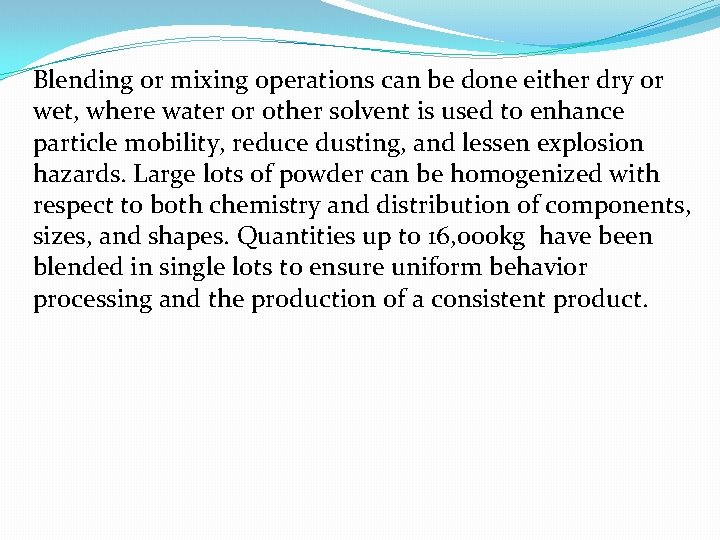
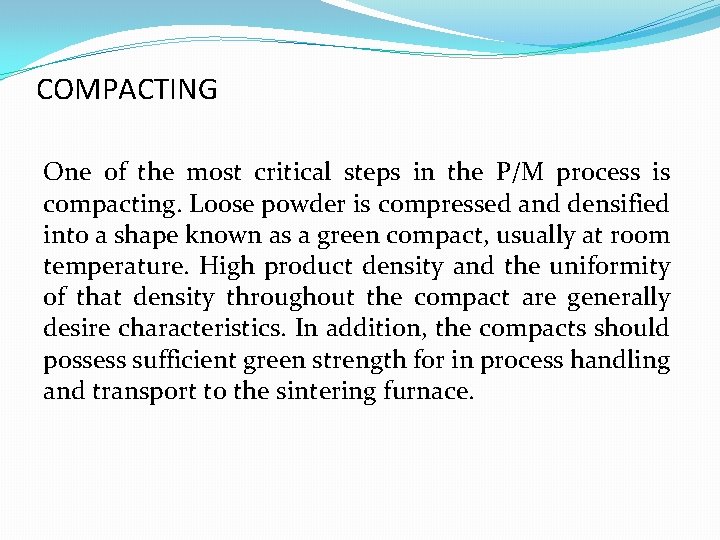
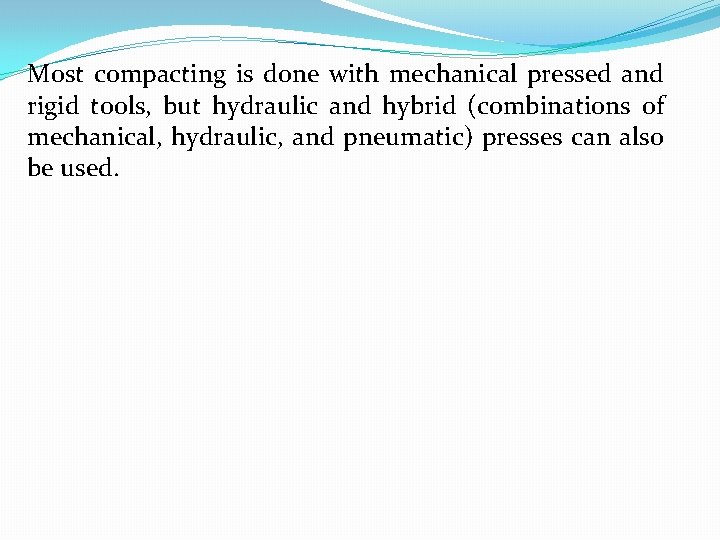
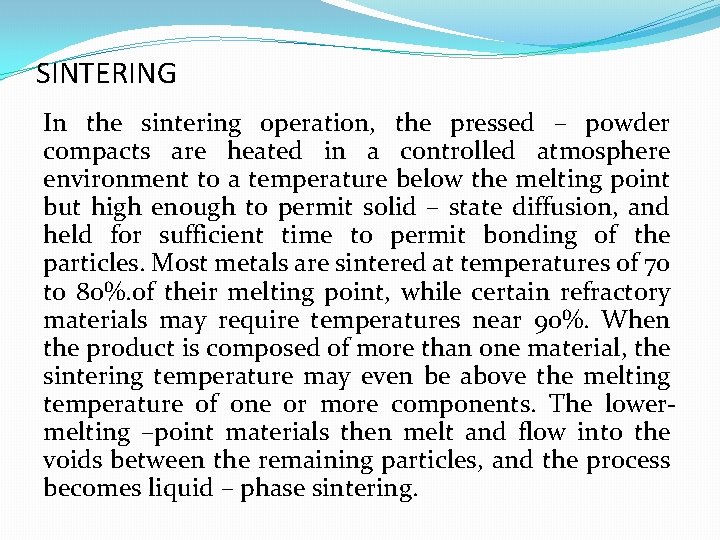
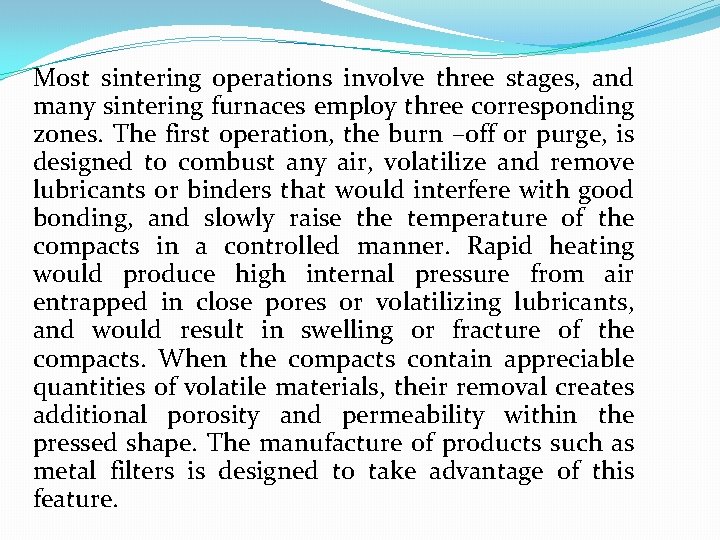
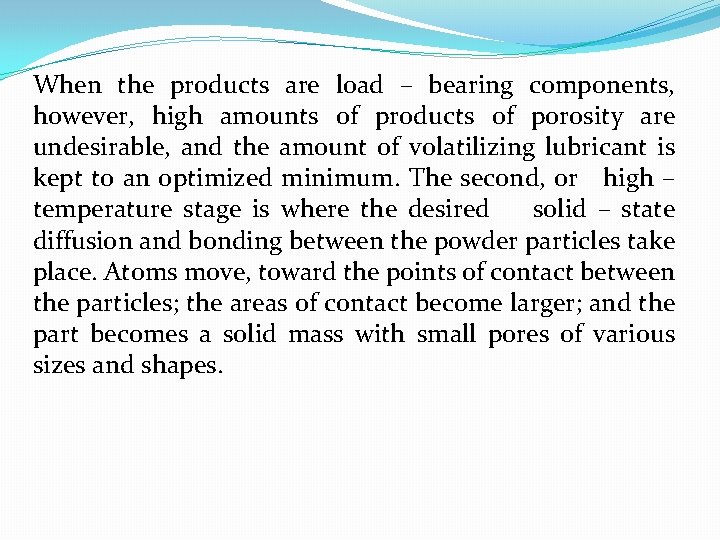
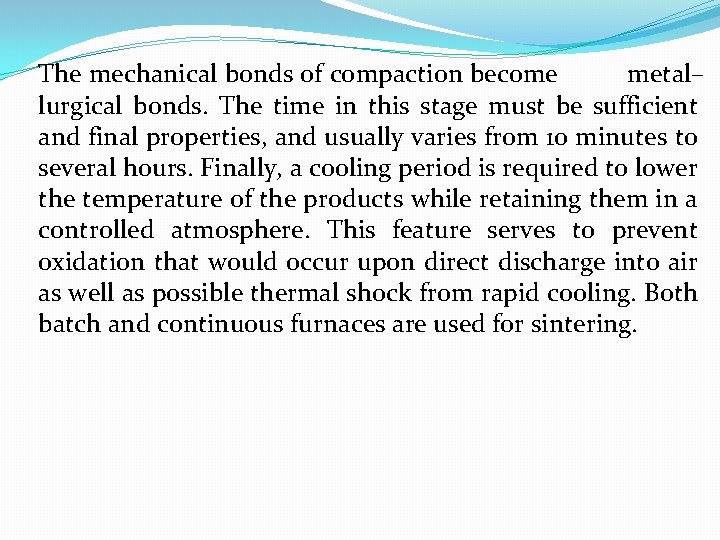
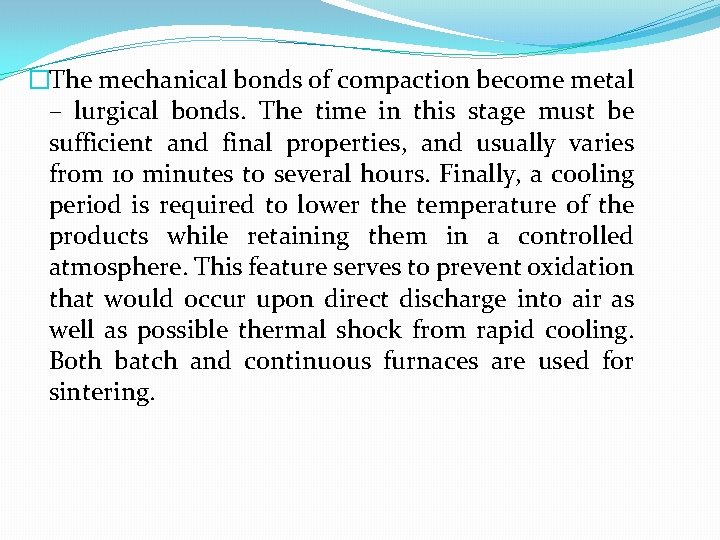
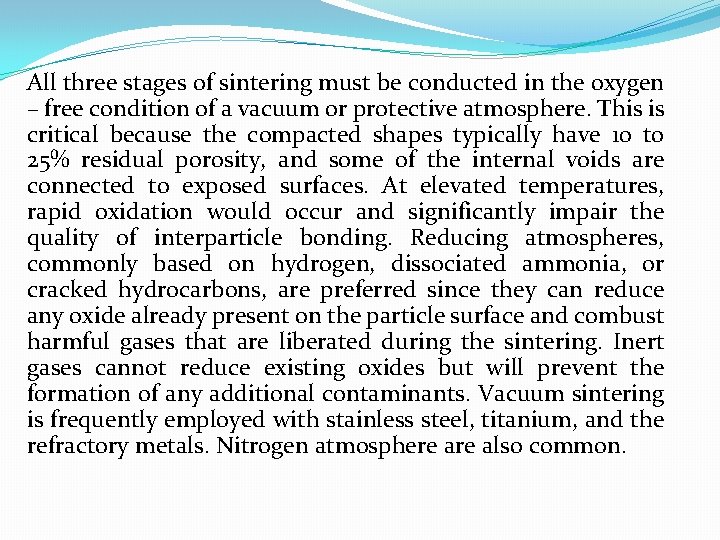
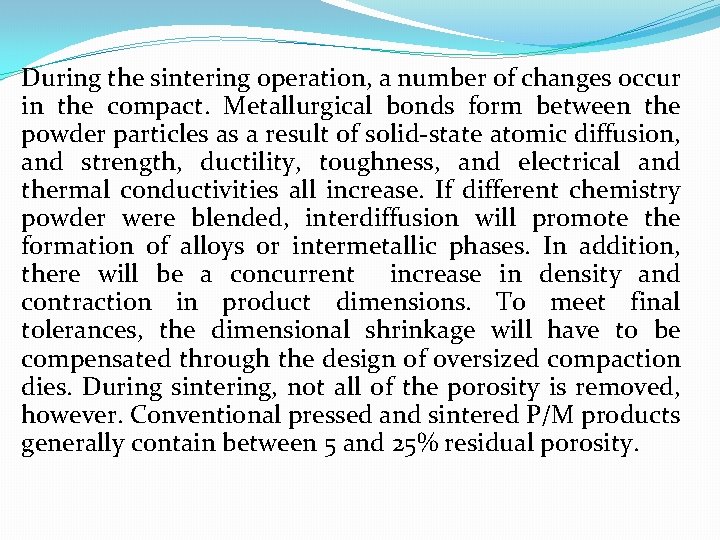
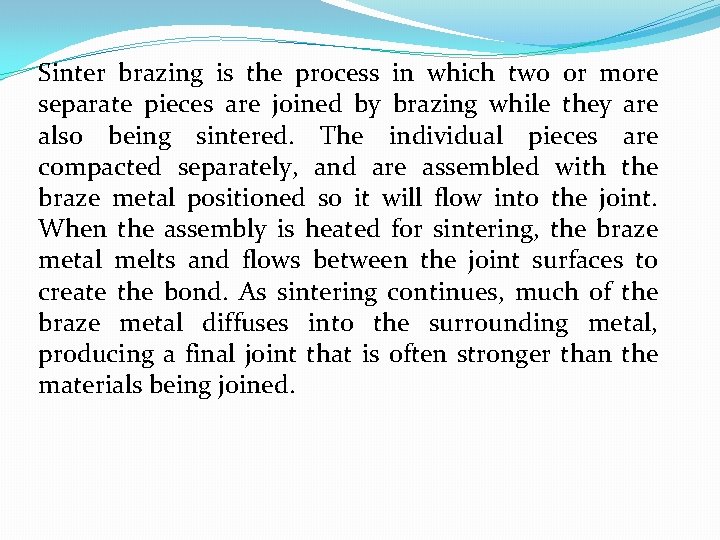
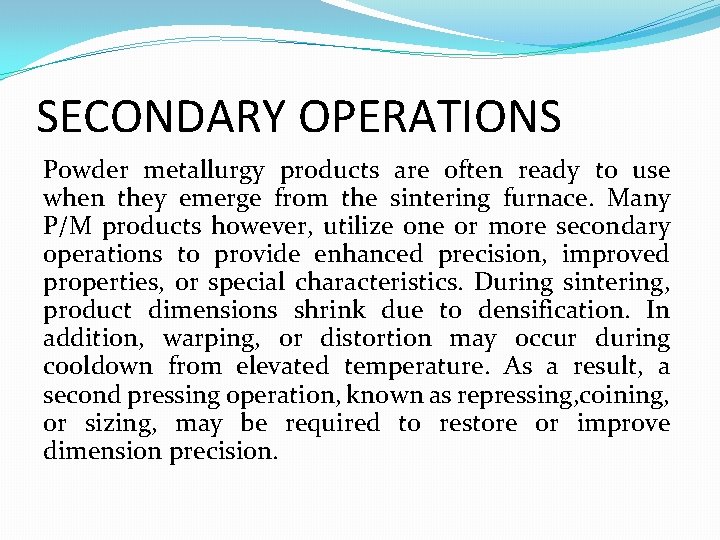
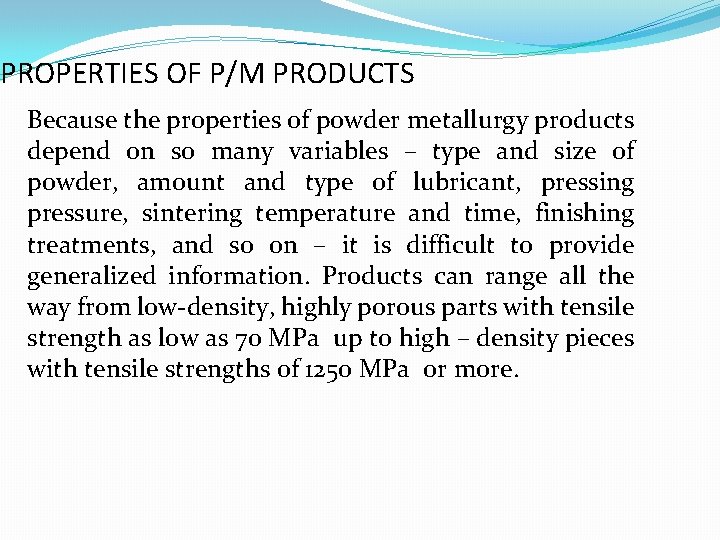
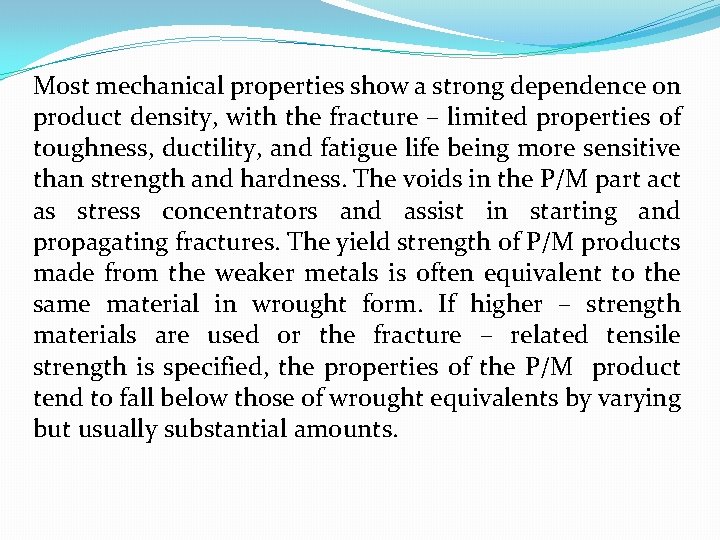

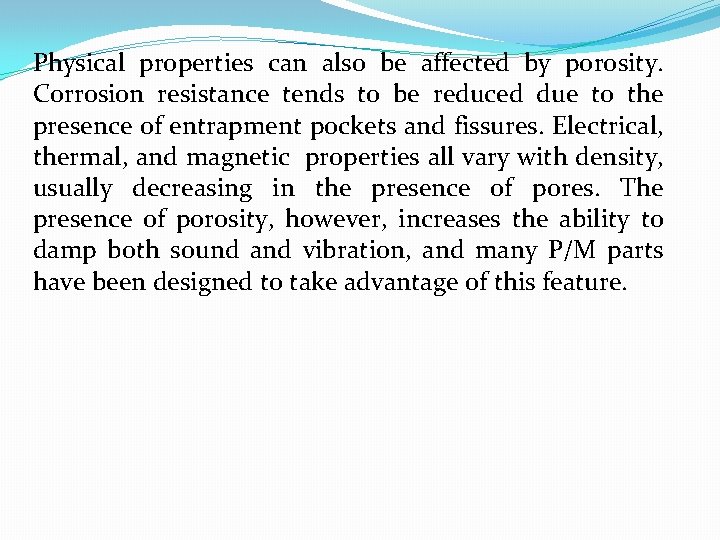
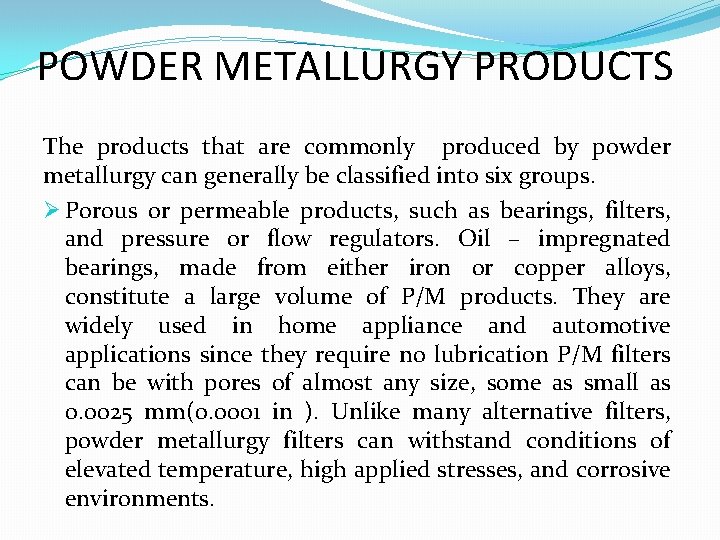
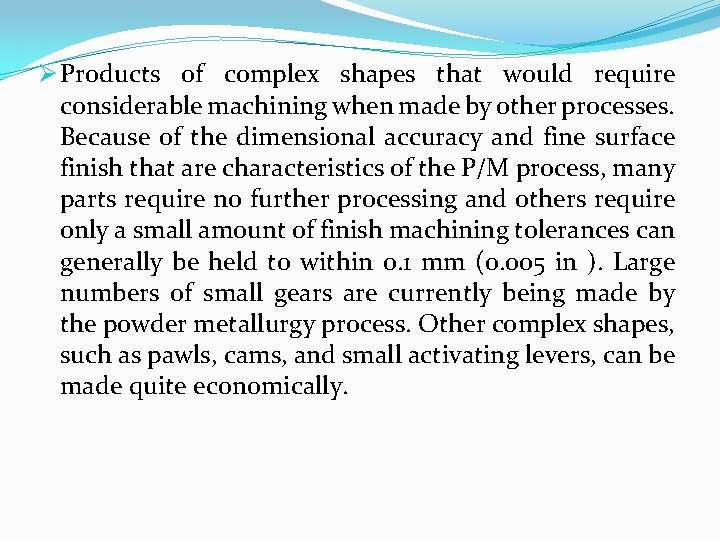
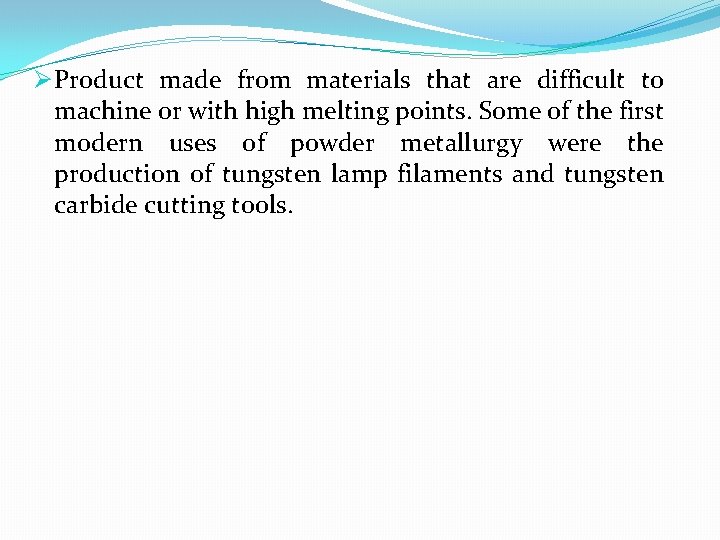
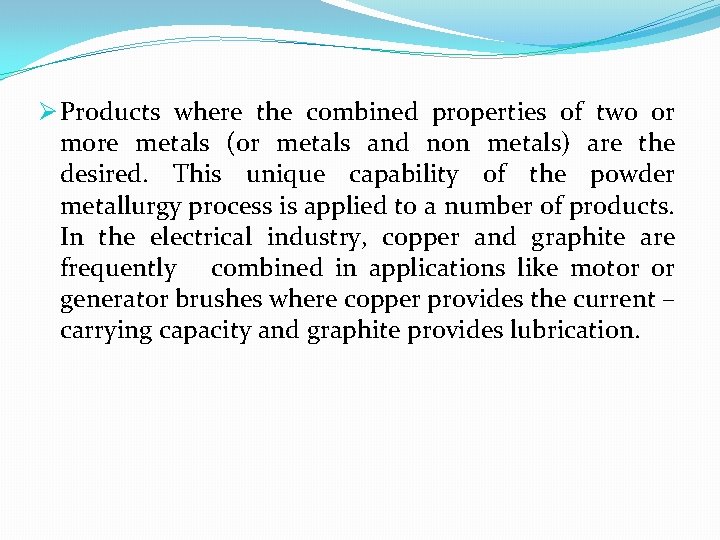
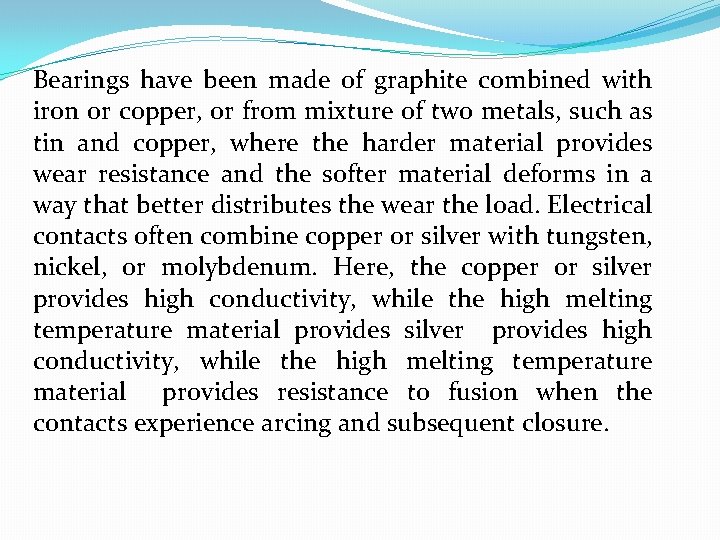
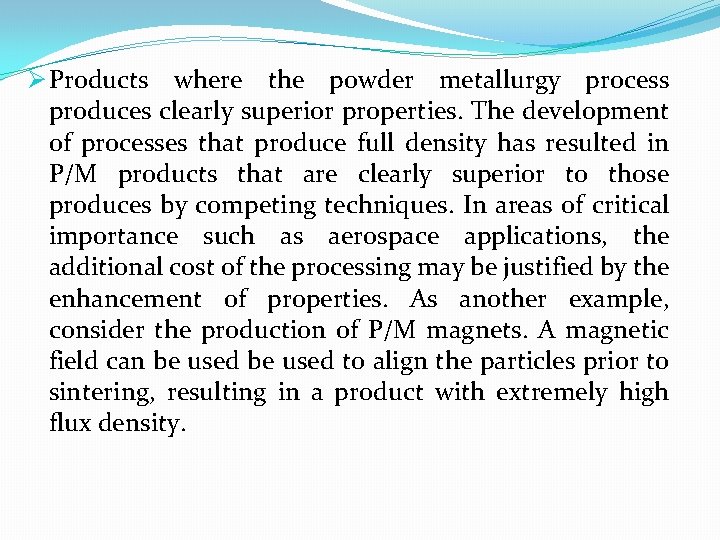
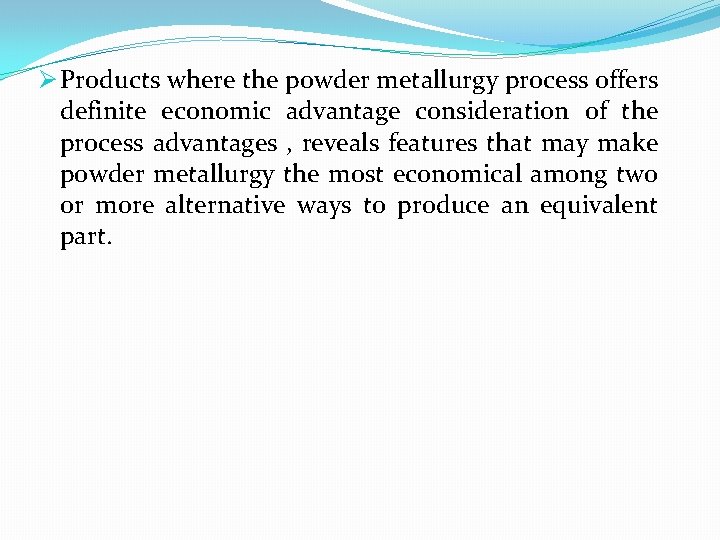
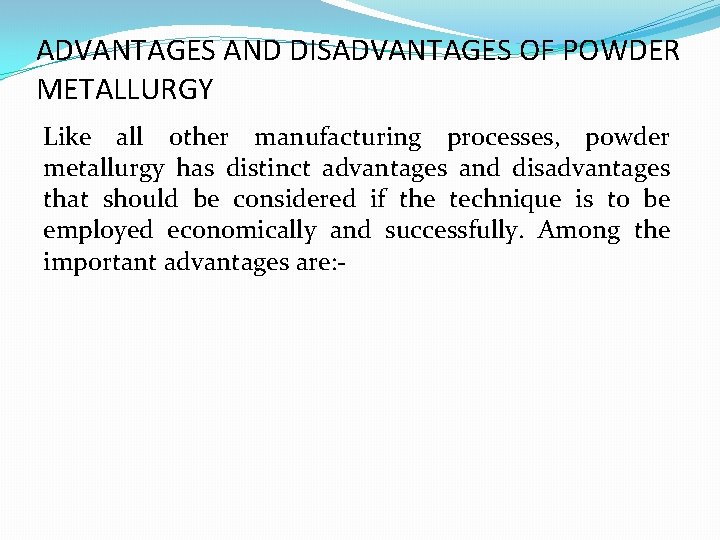
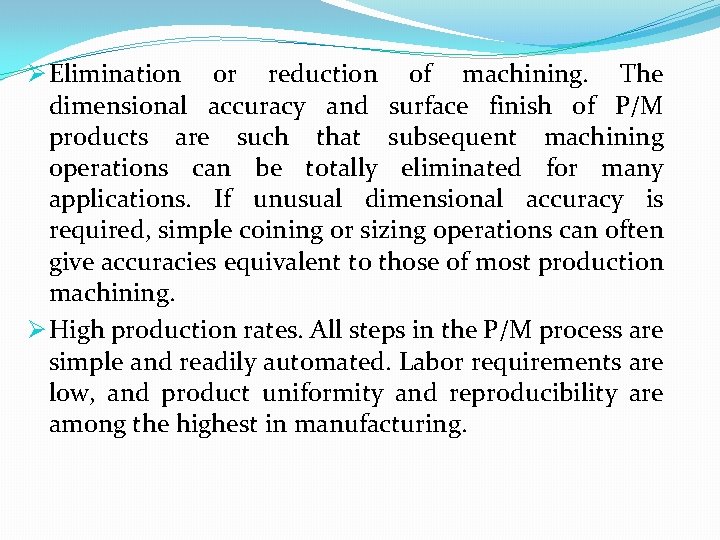
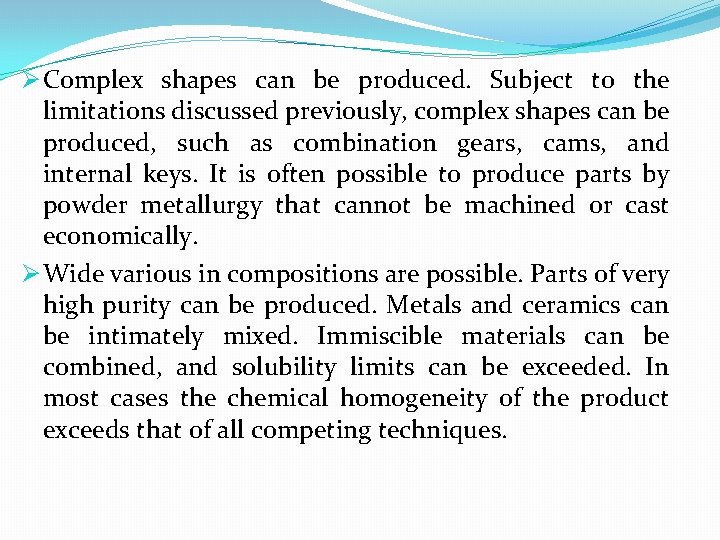
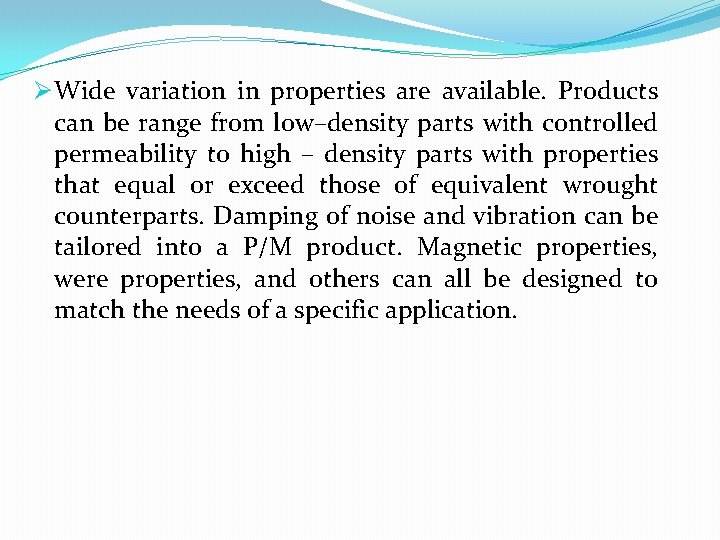
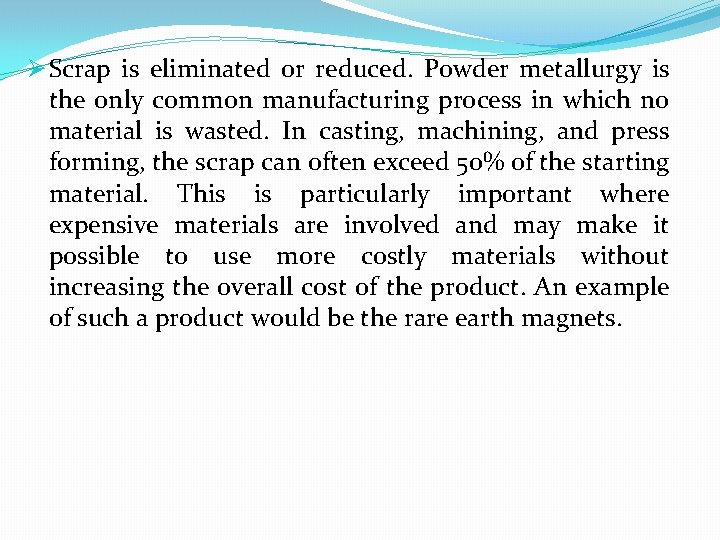
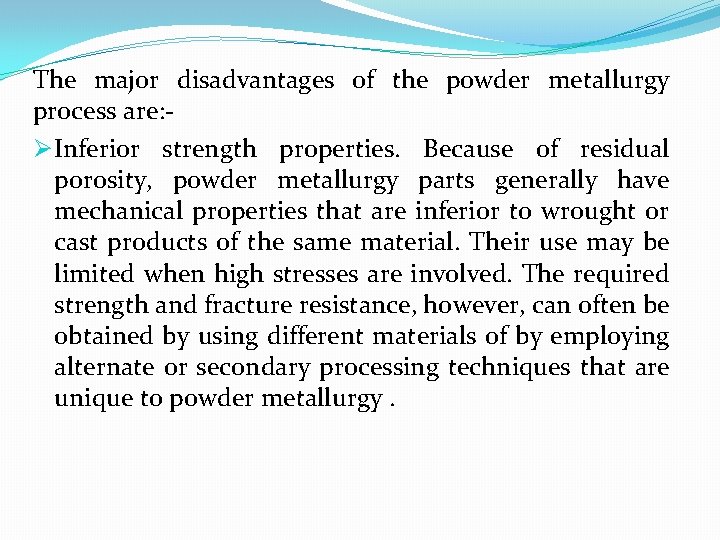
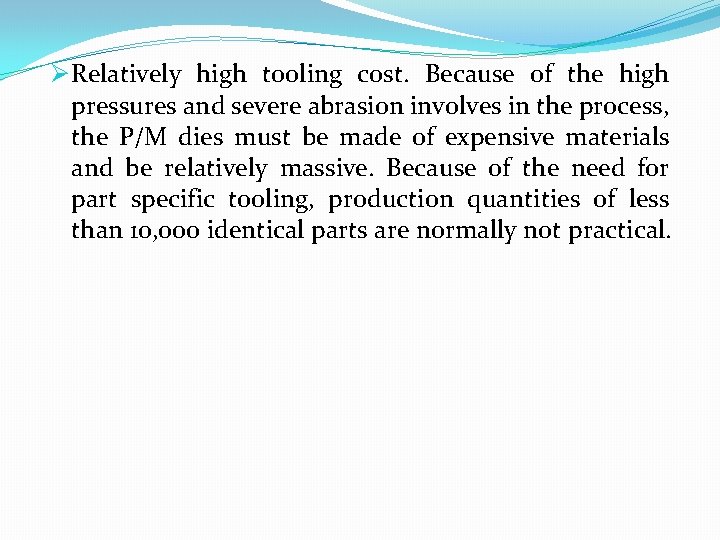
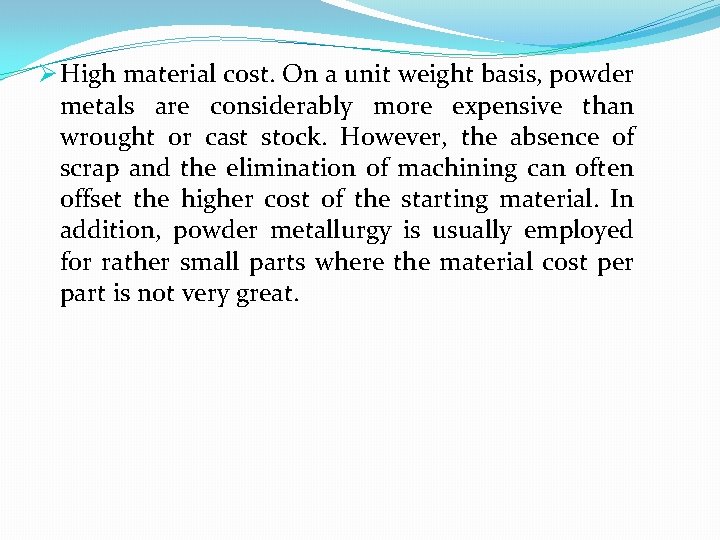
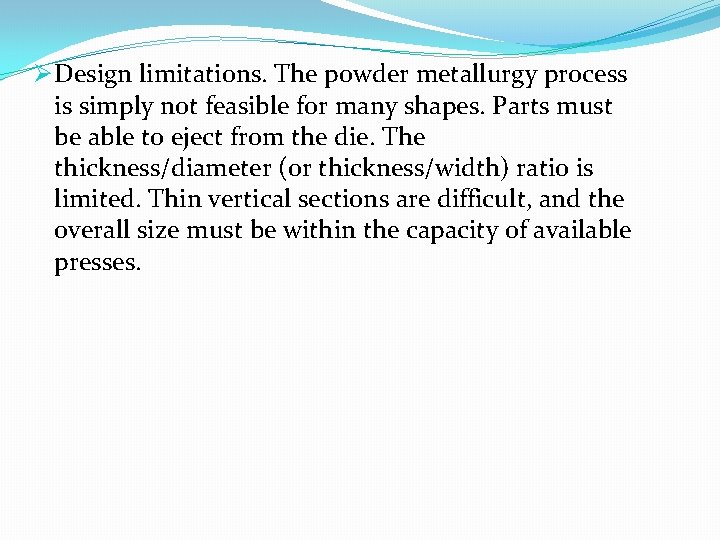
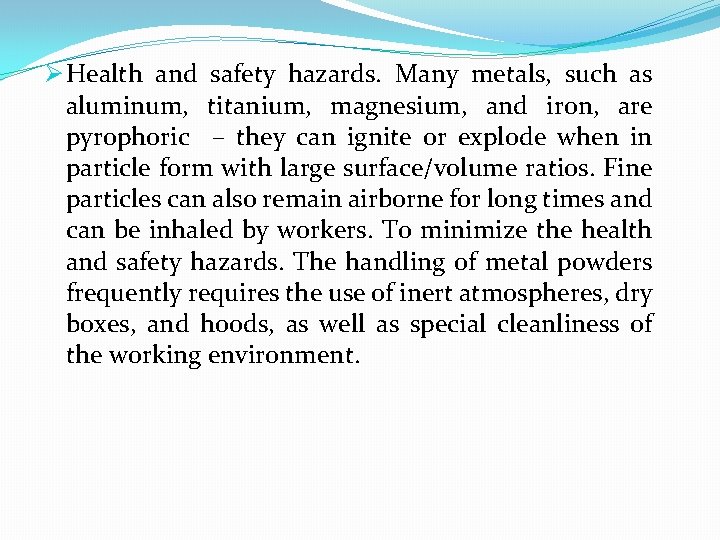
- Slides: 47
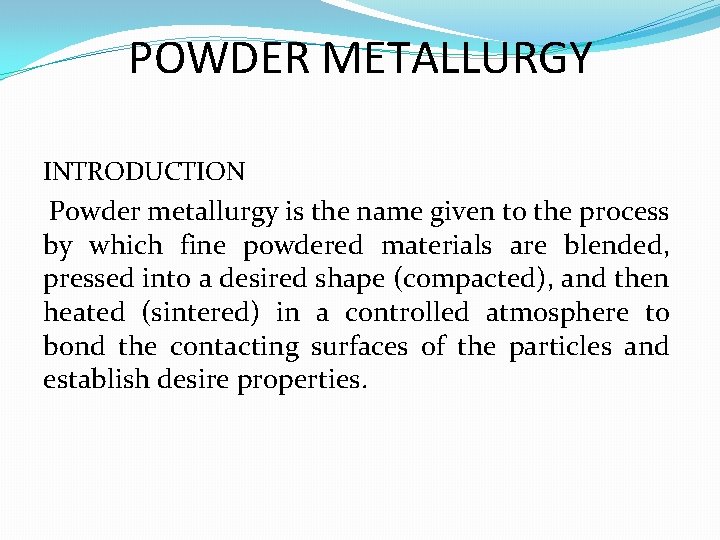
POWDER METALLURGY INTRODUCTION Powder metallurgy is the name given to the process by which fine powdered materials are blended, pressed into a desired shape (compacted), and then heated (sintered) in a controlled atmosphere to bond the contacting surfaces of the particles and establish desire properties.
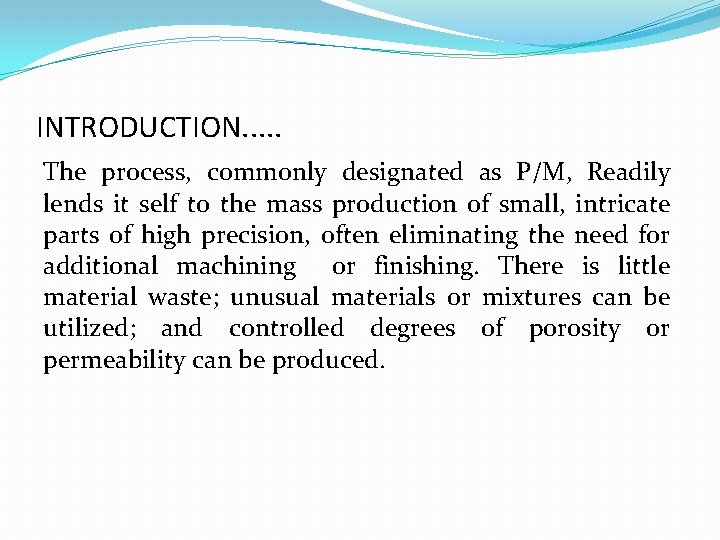
INTRODUCTION. . . The process, commonly designated as P/M, Readily lends it self to the mass production of small, intricate parts of high precision, often eliminating the need for additional machining or finishing. There is little material waste; unusual materials or mixtures can be utilized; and controlled degrees of porosity or permeability can be produced.
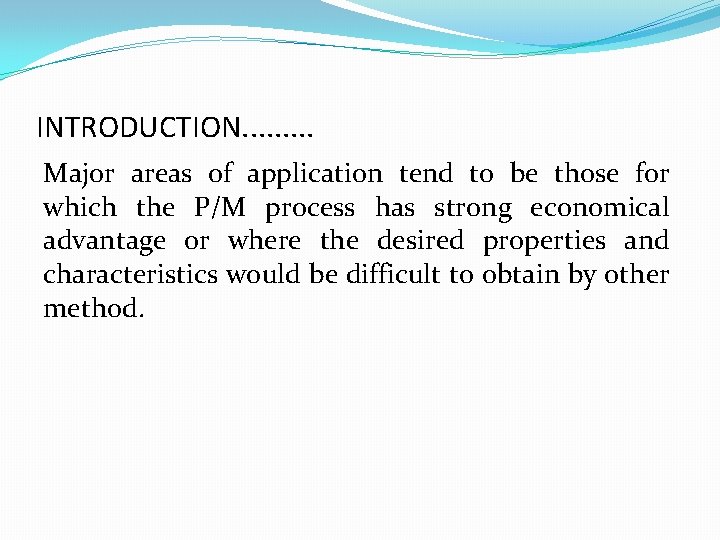
INTRODUCTION. . Major areas of application tend to be those for which the P/M process has strong economical advantage or where the desired properties and characteristics would be difficult to obtain by other method.

INTRODUCTION. . Because of its level of manufacturing maturity, powder metallurgy should actually be considered as a possible means of manufacture for any part where the geometry and production quality are appropriate.
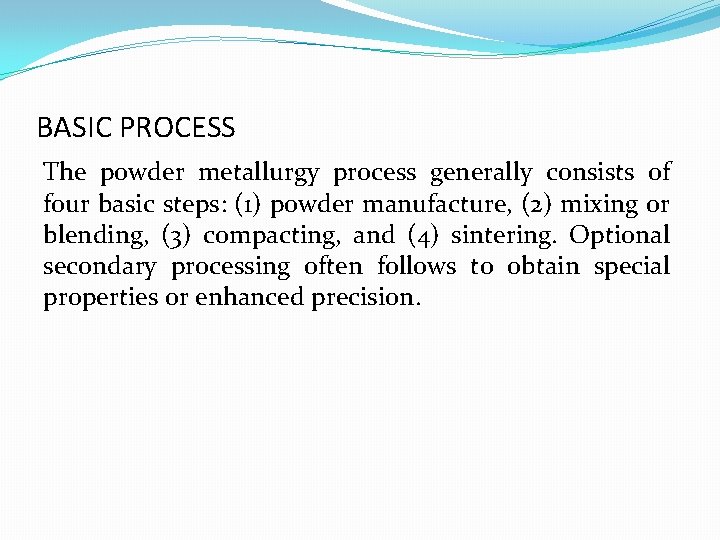
BASIC PROCESS The powder metallurgy process generally consists of four basic steps: (1) powder manufacture, (2) mixing or blending, (3) compacting, and (4) sintering. Optional secondary processing often follows to obtain special properties or enhanced precision.
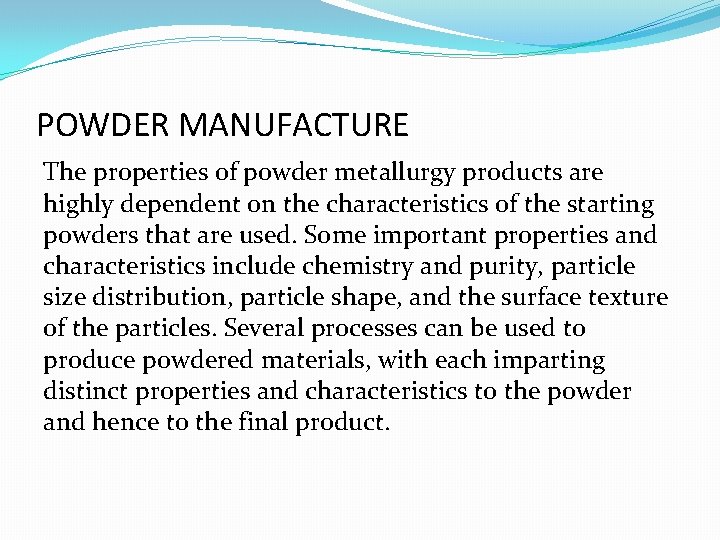
POWDER MANUFACTURE The properties of powder metallurgy products are highly dependent on the characteristics of the starting powders that are used. Some important properties and characteristics include chemistry and purity, particle size distribution, particle shape, and the surface texture of the particles. Several processes can be used to produce powdered materials, with each imparting distinct properties and characteristics to the powder and hence to the final product.
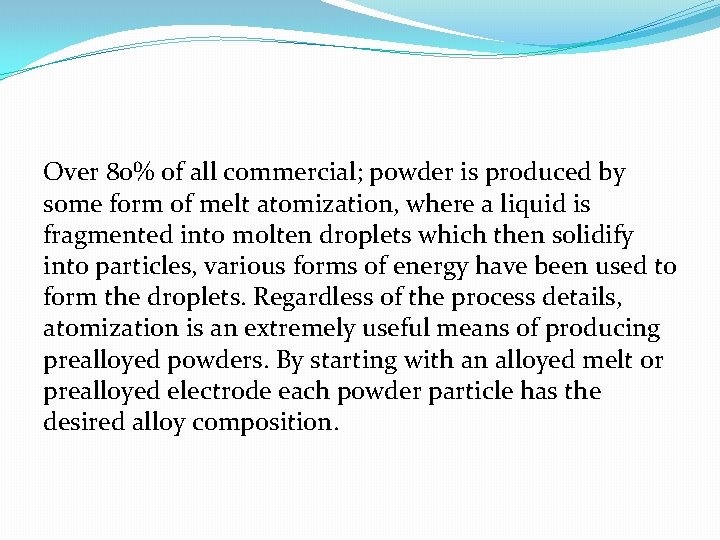
Over 80% of all commercial; powder is produced by some form of melt atomization, where a liquid is fragmented into molten droplets which then solidify into particles, various forms of energy have been used to form the droplets. Regardless of the process details, atomization is an extremely useful means of producing prealloyed powders. By starting with an alloyed melt or prealloyed electrode each powder particle has the desired alloy composition.
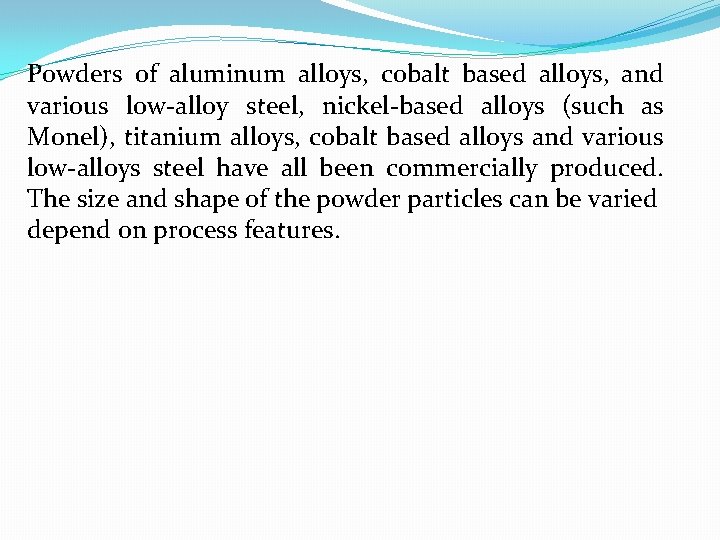
Powders of aluminum alloys, cobalt based alloys, and various low-alloy steel, nickel-based alloys (such as Monel), titanium alloys, cobalt based alloys and various low-alloys steel have all been commercially produced. The size and shape of the powder particles can be varied depend on process features.
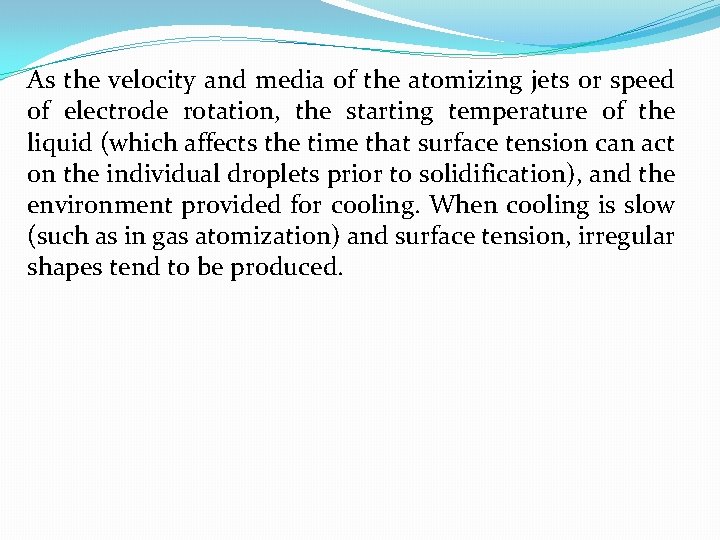
As the velocity and media of the atomizing jets or speed of electrode rotation, the starting temperature of the liquid (which affects the time that surface tension can act on the individual droplets prior to solidification), and the environment provided for cooling. When cooling is slow (such as in gas atomization) and surface tension, irregular shapes tend to be produced.
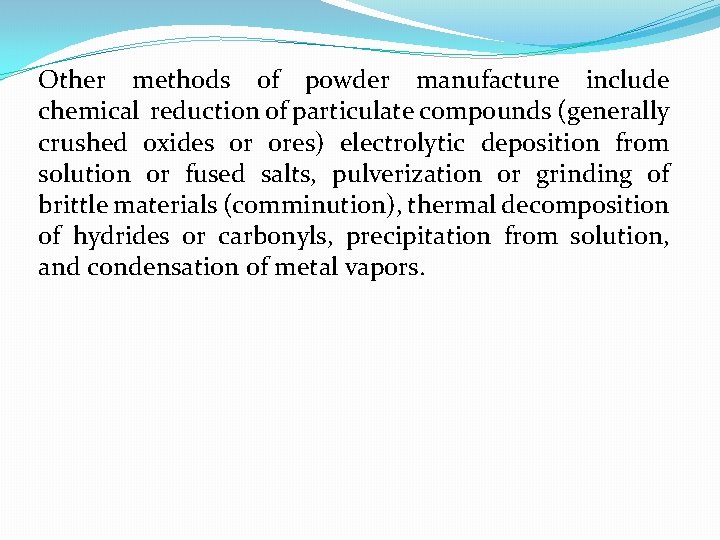
Other methods of powder manufacture include chemical reduction of particulate compounds (generally crushed oxides or ores) electrolytic deposition from solution or fused salts, pulverization or grinding of brittle materials (comminution), thermal decomposition of hydrides or carbonyls, precipitation from solution, and condensation of metal vapors.
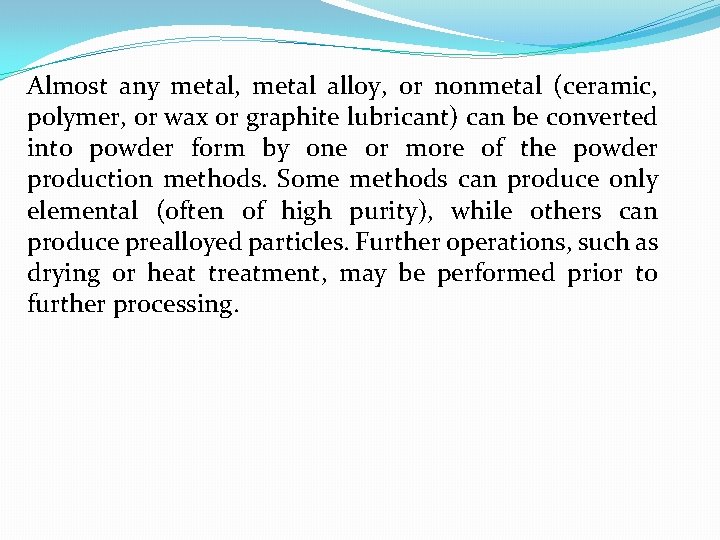
Almost any metal, metal alloy, or nonmetal (ceramic, polymer, or wax or graphite lubricant) can be converted into powder form by one or more of the powder production methods. Some methods can produce only elemental (often of high purity), while others can produce prealloyed particles. Further operations, such as drying or heat treatment, may be performed prior to further processing.
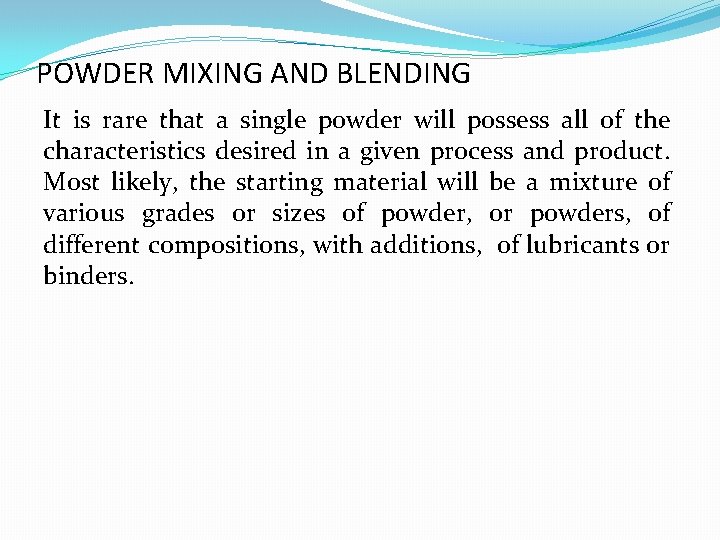
POWDER MIXING AND BLENDING It is rare that a single powder will possess all of the characteristics desired in a given process and product. Most likely, the starting material will be a mixture of various grades or sizes of powder, or powders, of different compositions, with additions, of lubricants or binders.
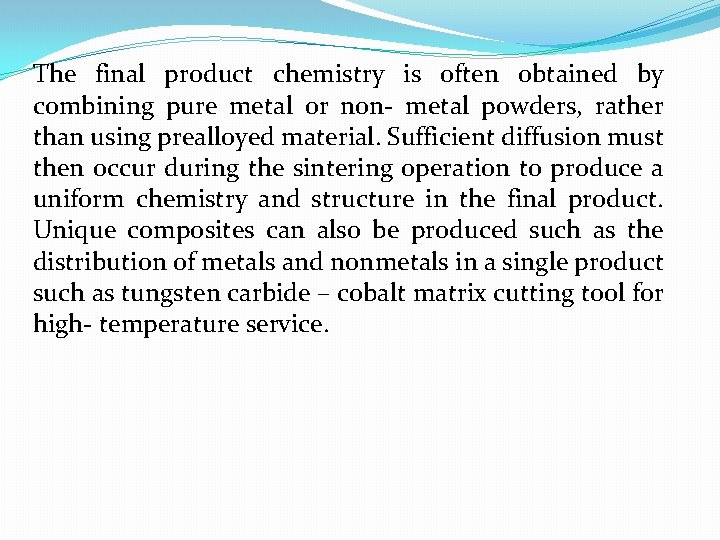
The final product chemistry is often obtained by combining pure metal or non- metal powders, rather than using prealloyed material. Sufficient diffusion must then occur during the sintering operation to produce a uniform chemistry and structure in the final product. Unique composites can also be produced such as the distribution of metals and nonmetals in a single product such as tungsten carbide – cobalt matrix cutting tool for high- temperature service.
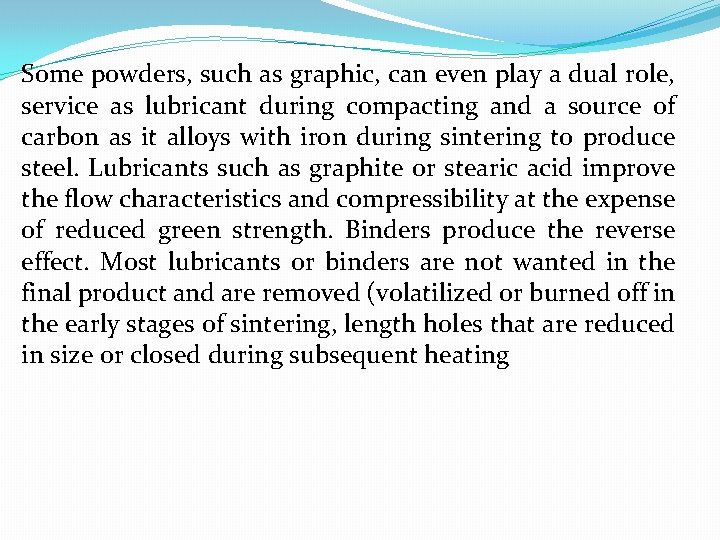
Some powders, such as graphic, can even play a dual role, service as lubricant during compacting and a source of carbon as it alloys with iron during sintering to produce steel. Lubricants such as graphite or stearic acid improve the flow characteristics and compressibility at the expense of reduced green strength. Binders produce the reverse effect. Most lubricants or binders are not wanted in the final product and are removed (volatilized or burned off in the early stages of sintering, length holes that are reduced in size or closed during subsequent heating
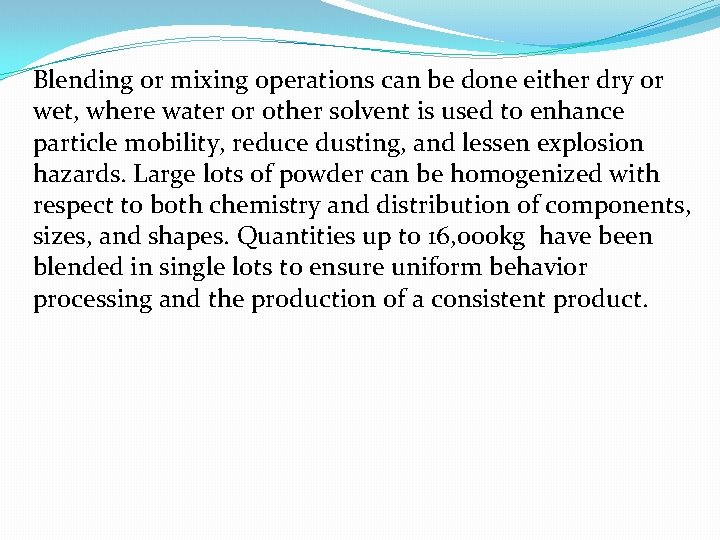
Blending or mixing operations can be done either dry or wet, where water or other solvent is used to enhance particle mobility, reduce dusting, and lessen explosion hazards. Large lots of powder can be homogenized with respect to both chemistry and distribution of components, sizes, and shapes. Quantities up to 16, 000 kg have been blended in single lots to ensure uniform behavior processing and the production of a consistent product.
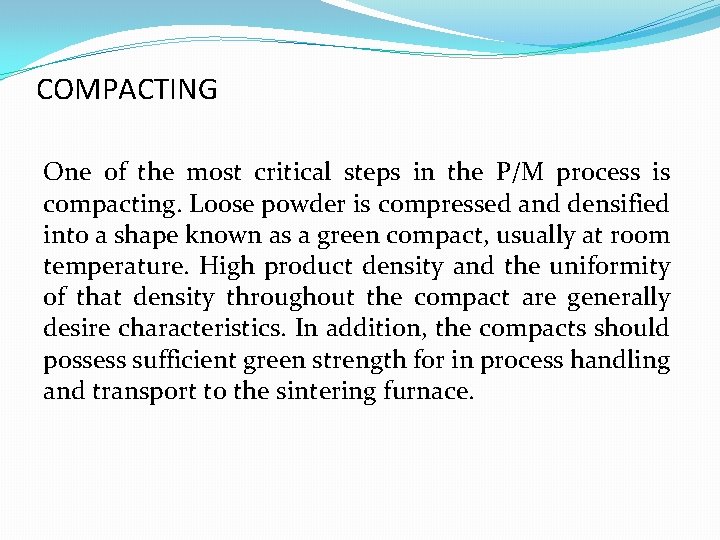
COMPACTING One of the most critical steps in the P/M process is compacting. Loose powder is compressed and densified into a shape known as a green compact, usually at room temperature. High product density and the uniformity of that density throughout the compact are generally desire characteristics. In addition, the compacts should possess sufficient green strength for in process handling and transport to the sintering furnace.
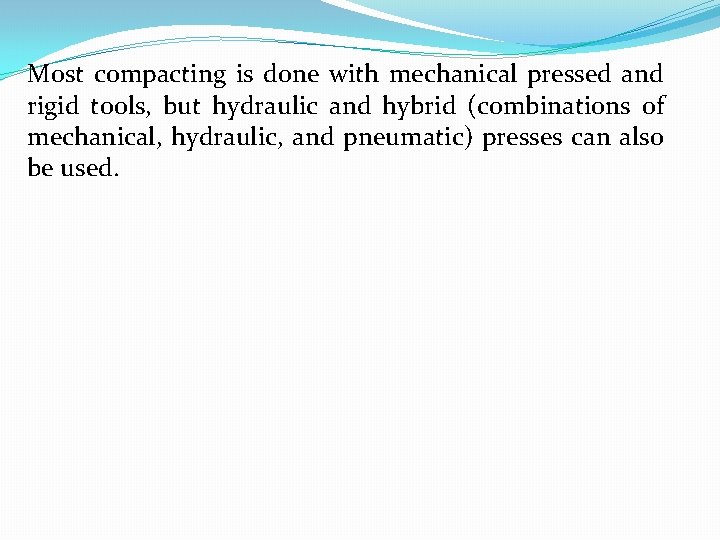
Most compacting is done with mechanical pressed and rigid tools, but hydraulic and hybrid (combinations of mechanical, hydraulic, and pneumatic) presses can also be used.
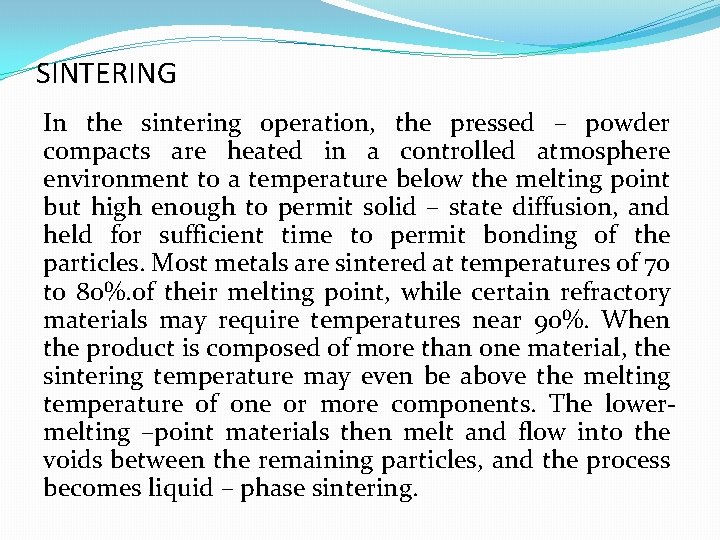
SINTERING In the sintering operation, the pressed – powder compacts are heated in a controlled atmosphere environment to a temperature below the melting point but high enough to permit solid – state diffusion, and held for sufficient time to permit bonding of the particles. Most metals are sintered at temperatures of 70 to 80%. of their melting point, while certain refractory materials may require temperatures near 90%. When the product is composed of more than one material, the sintering temperature may even be above the melting temperature of one or more components. The lowermelting –point materials then melt and flow into the voids between the remaining particles, and the process becomes liquid – phase sintering.
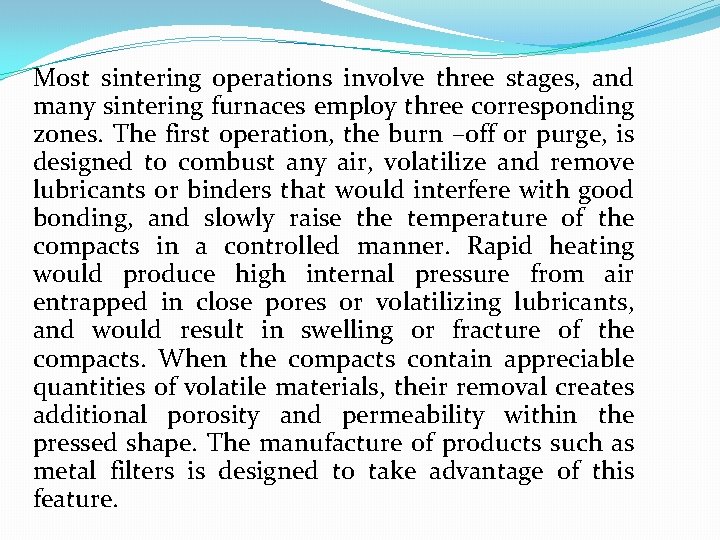
Most sintering operations involve three stages, and many sintering furnaces employ three corresponding zones. The first operation, the burn –off or purge, is designed to combust any air, volatilize and remove lubricants or binders that would interfere with good bonding, and slowly raise the temperature of the compacts in a controlled manner. Rapid heating would produce high internal pressure from air entrapped in close pores or volatilizing lubricants, and would result in swelling or fracture of the compacts. When the compacts contain appreciable quantities of volatile materials, their removal creates additional porosity and permeability within the pressed shape. The manufacture of products such as metal filters is designed to take advantage of this feature.
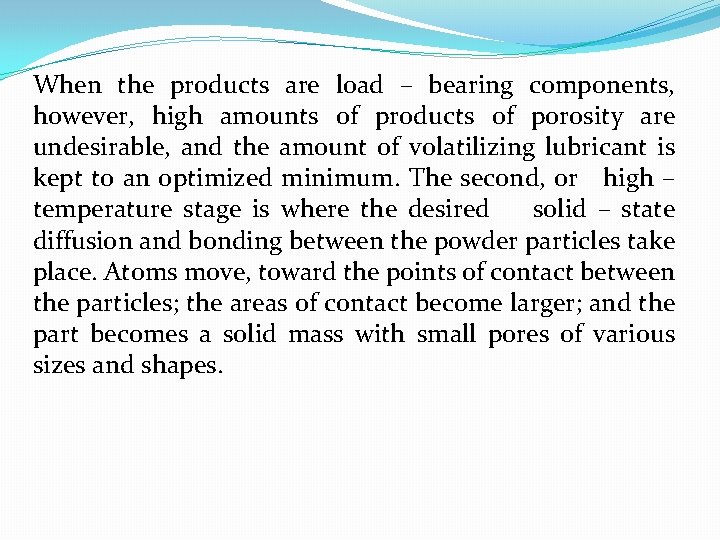
When the products are load – bearing components, however, high amounts of products of porosity are undesirable, and the amount of volatilizing lubricant is kept to an optimized minimum. The second, or high – temperature stage is where the desired solid – state diffusion and bonding between the powder particles take place. Atoms move, toward the points of contact between the particles; the areas of contact become larger; and the part becomes a solid mass with small pores of various sizes and shapes.
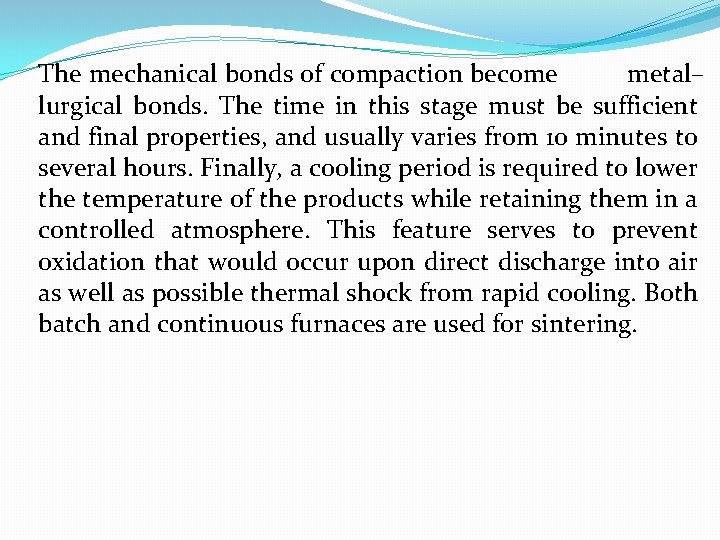
The mechanical bonds of compaction become metal– lurgical bonds. The time in this stage must be sufficient and final properties, and usually varies from 10 minutes to several hours. Finally, a cooling period is required to lower the temperature of the products while retaining them in a controlled atmosphere. This feature serves to prevent oxidation that would occur upon direct discharge into air as well as possible thermal shock from rapid cooling. Both batch and continuous furnaces are used for sintering.
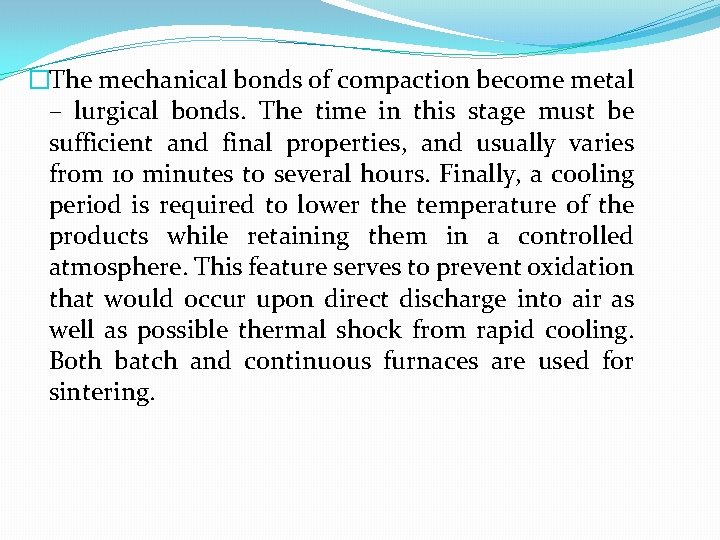
�The mechanical bonds of compaction become metal – lurgical bonds. The time in this stage must be sufficient and final properties, and usually varies from 10 minutes to several hours. Finally, a cooling period is required to lower the temperature of the products while retaining them in a controlled atmosphere. This feature serves to prevent oxidation that would occur upon direct discharge into air as well as possible thermal shock from rapid cooling. Both batch and continuous furnaces are used for sintering.
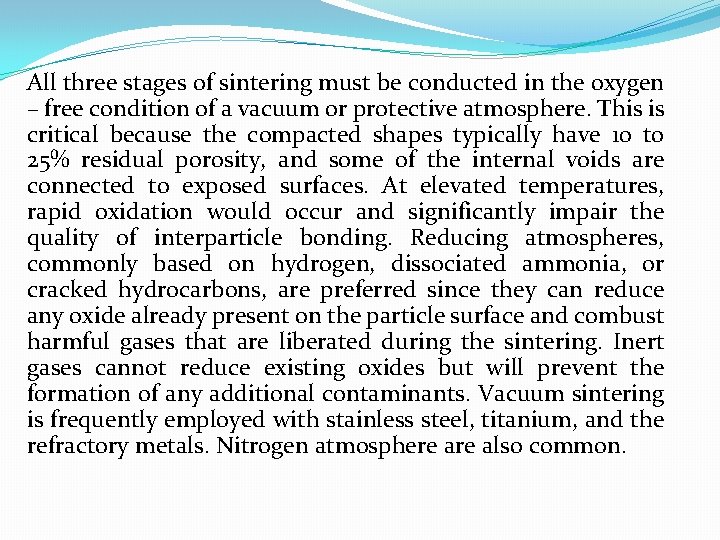
All three stages of sintering must be conducted in the oxygen – free condition of a vacuum or protective atmosphere. This is critical because the compacted shapes typically have 10 to 25% residual porosity, and some of the internal voids are connected to exposed surfaces. At elevated temperatures, rapid oxidation would occur and significantly impair the quality of interparticle bonding. Reducing atmospheres, commonly based on hydrogen, dissociated ammonia, or cracked hydrocarbons, are preferred since they can reduce any oxide already present on the particle surface and combust harmful gases that are liberated during the sintering. Inert gases cannot reduce existing oxides but will prevent the formation of any additional contaminants. Vacuum sintering is frequently employed with stainless steel, titanium, and the refractory metals. Nitrogen atmosphere also common.
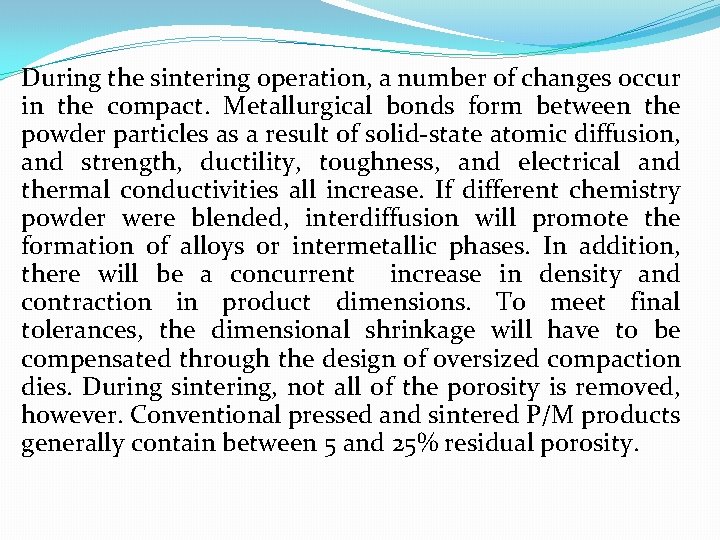
During the sintering operation, a number of changes occur in the compact. Metallurgical bonds form between the powder particles as a result of solid-state atomic diffusion, and strength, ductility, toughness, and electrical and thermal conductivities all increase. If different chemistry powder were blended, interdiffusion will promote the formation of alloys or intermetallic phases. In addition, there will be a concurrent increase in density and contraction in product dimensions. To meet final tolerances, the dimensional shrinkage will have to be compensated through the design of oversized compaction dies. During sintering, not all of the porosity is removed, however. Conventional pressed and sintered P/M products generally contain between 5 and 25% residual porosity.
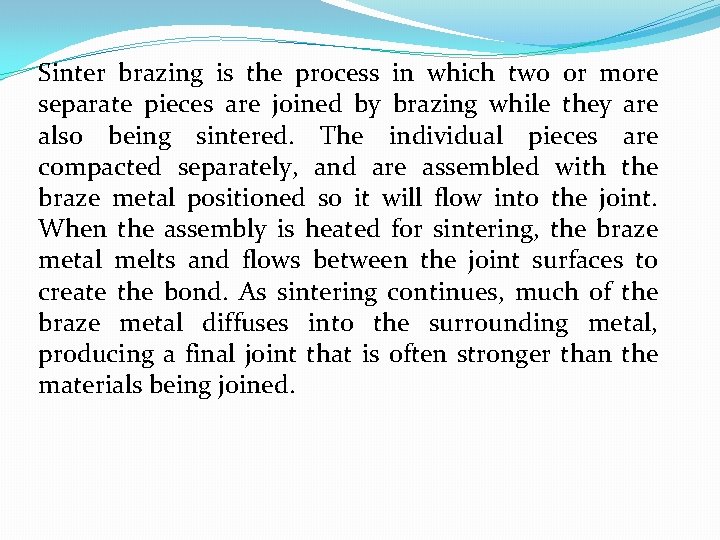
Sinter brazing is the process in which two or more separate pieces are joined by brazing while they are also being sintered. The individual pieces are compacted separately, and are assembled with the braze metal positioned so it will flow into the joint. When the assembly is heated for sintering, the braze metal melts and flows between the joint surfaces to create the bond. As sintering continues, much of the braze metal diffuses into the surrounding metal, producing a final joint that is often stronger than the materials being joined.
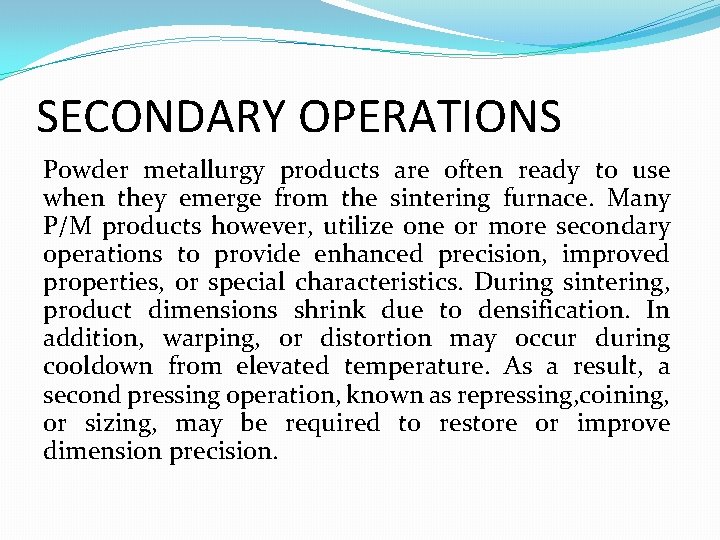
SECONDARY OPERATIONS Powder metallurgy products are often ready to use when they emerge from the sintering furnace. Many P/M products however, utilize one or more secondary operations to provide enhanced precision, improved properties, or special characteristics. During sintering, product dimensions shrink due to densification. In addition, warping, or distortion may occur during cooldown from elevated temperature. As a result, a second pressing operation, known as repressing, coining, or sizing, may be required to restore or improve dimension precision.
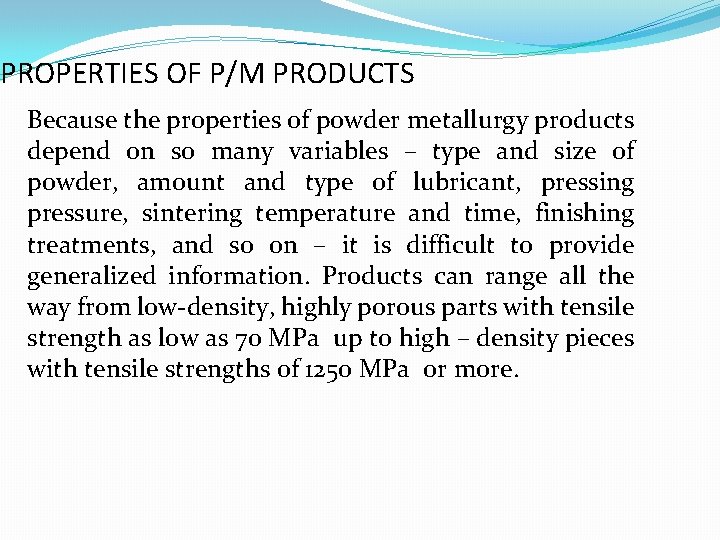
PROPERTIES OF P/M PRODUCTS Because the properties of powder metallurgy products depend on so many variables – type and size of powder, amount and type of lubricant, pressing pressure, sintering temperature and time, finishing treatments, and so on – it is difficult to provide generalized information. Products can range all the way from low-density, highly porous parts with tensile strength as low as 70 MPa up to high – density pieces with tensile strengths of 1250 MPa or more.
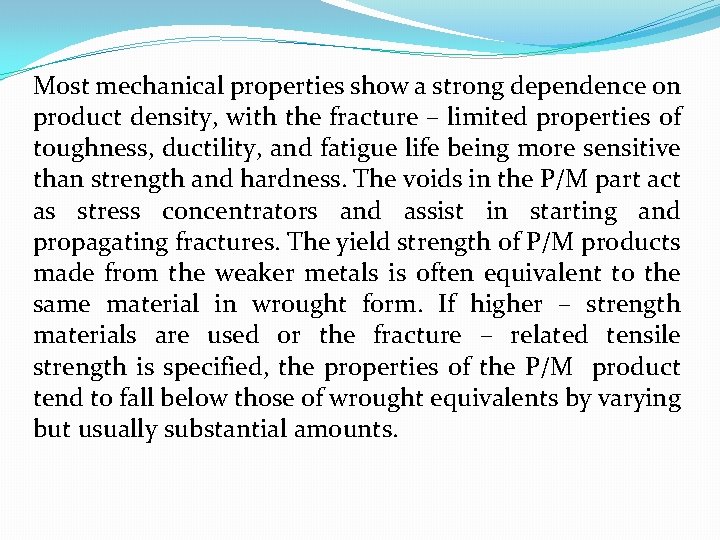
Most mechanical properties show a strong dependence on product density, with the fracture – limited properties of toughness, ductility, and fatigue life being more sensitive than strength and hardness. The voids in the P/M part act as stress concentrators and assist in starting and propagating fractures. The yield strength of P/M products made from the weaker metals is often equivalent to the same material in wrought form. If higher – strength materials are used or the fracture – related tensile strength is specified, the properties of the P/M product tend to fall below those of wrought equivalents by varying but usually substantial amounts.

When larger presses or processes such as P/M forging or hot isostatic pressing are used to produce higher density, the strength of P/M products a approaches that of the wrought material. If the processing results in full density with fine grain size, P/M parts can actually have properties that exceed their wrought or cast equivalents. Since the mechanical properties of powder metallurgy products are so dependent upon density, it is important that P/M products be designed and materials selected so that the final properties will be achieved with the anticipated amount of final porosity.
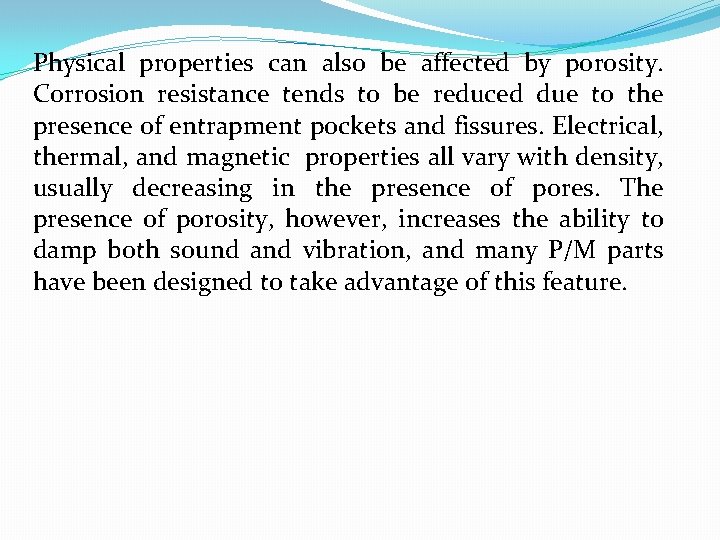
Physical properties can also be affected by porosity. Corrosion resistance tends to be reduced due to the presence of entrapment pockets and fissures. Electrical, thermal, and magnetic properties all vary with density, usually decreasing in the presence of pores. The presence of porosity, however, increases the ability to damp both sound and vibration, and many P/M parts have been designed to take advantage of this feature.
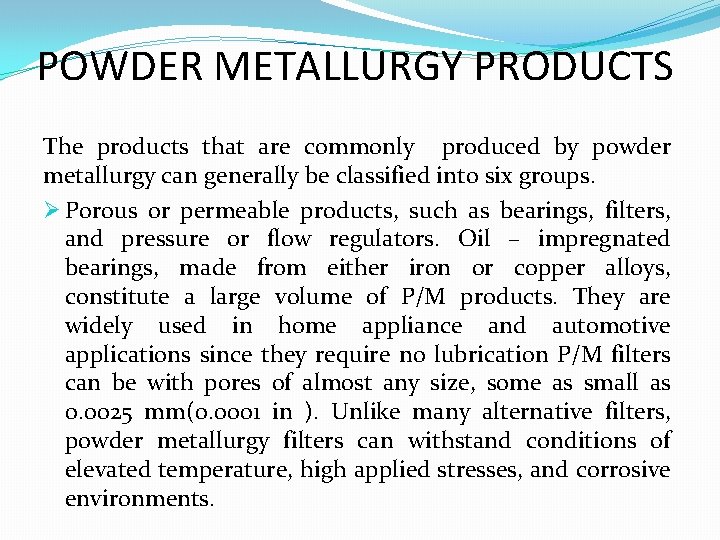
POWDER METALLURGY PRODUCTS The products that are commonly produced by powder metallurgy can generally be classified into six groups. Ø Porous or permeable products, such as bearings, filters, and pressure or flow regulators. Oil – impregnated bearings, made from either iron or copper alloys, constitute a large volume of P/M products. They are widely used in home appliance and automotive applications since they require no lubrication P/M filters can be with pores of almost any size, some as small as 0. 0025 mm(0. 0001 in ). Unlike many alternative filters, powder metallurgy filters can withstand conditions of elevated temperature, high applied stresses, and corrosive environments.
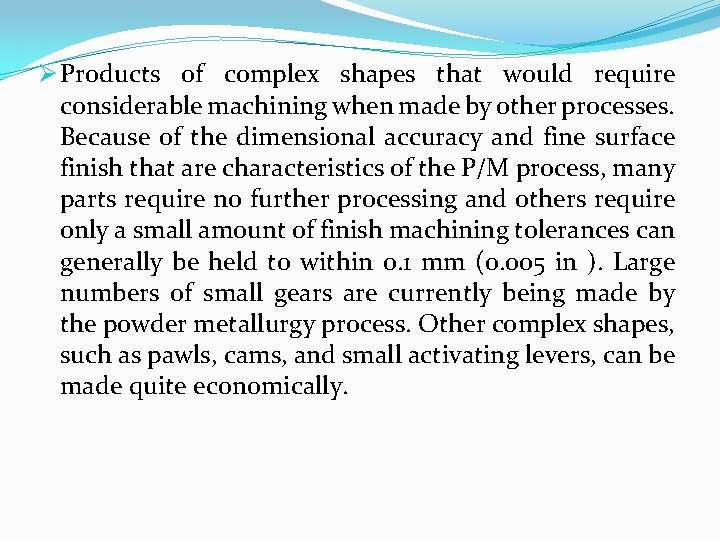
Ø Products of complex shapes that would require considerable machining when made by other processes. Because of the dimensional accuracy and fine surface finish that are characteristics of the P/M process, many parts require no further processing and others require only a small amount of finish machining tolerances can generally be held to within 0. 1 mm (0. 005 in ). Large numbers of small gears are currently being made by the powder metallurgy process. Other complex shapes, such as pawls, cams, and small activating levers, can be made quite economically.
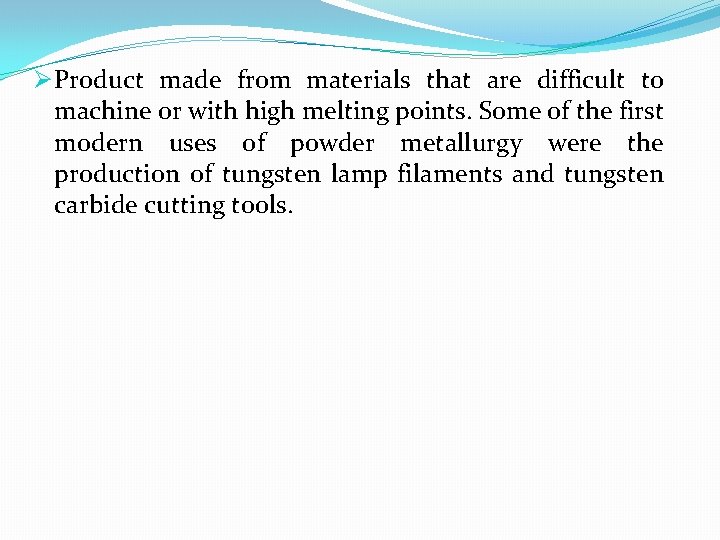
Ø Product made from materials that are difficult to machine or with high melting points. Some of the first modern uses of powder metallurgy were the production of tungsten lamp filaments and tungsten carbide cutting tools.
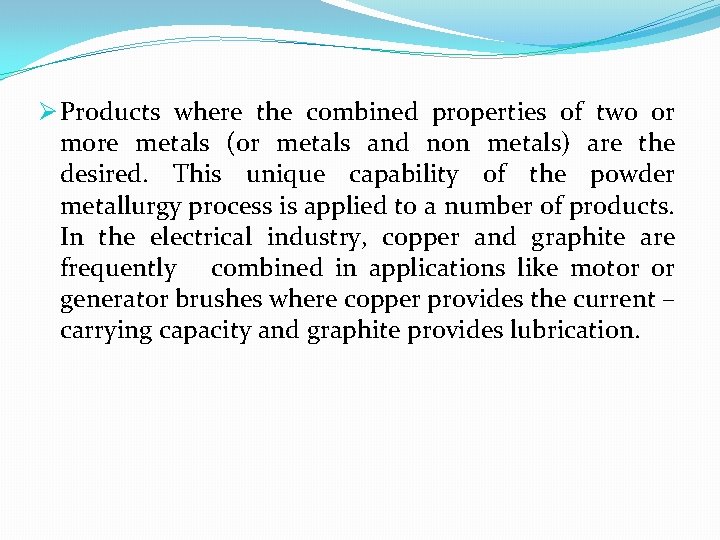
Ø Products where the combined properties of two or more metals (or metals and non metals) are the desired. This unique capability of the powder metallurgy process is applied to a number of products. In the electrical industry, copper and graphite are frequently combined in applications like motor or generator brushes where copper provides the current – carrying capacity and graphite provides lubrication.
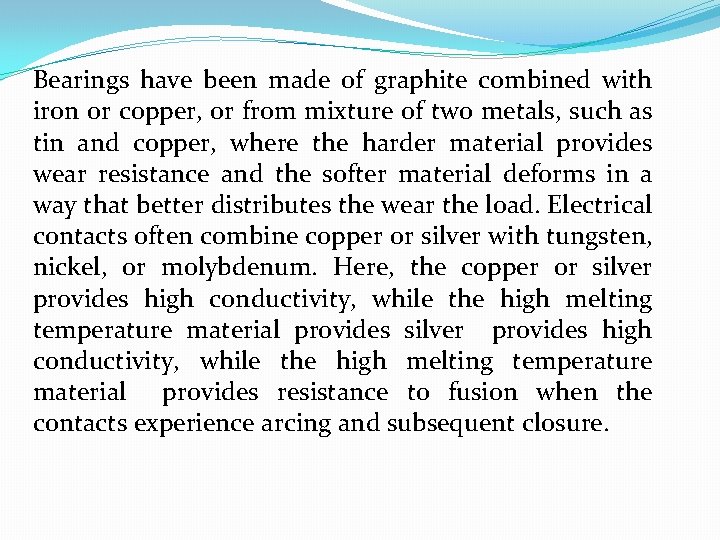
Bearings have been made of graphite combined with iron or copper, or from mixture of two metals, such as tin and copper, where the harder material provides wear resistance and the softer material deforms in a way that better distributes the wear the load. Electrical contacts often combine copper or silver with tungsten, nickel, or molybdenum. Here, the copper or silver provides high conductivity, while the high melting temperature material provides silver provides high conductivity, while the high melting temperature material provides resistance to fusion when the contacts experience arcing and subsequent closure.
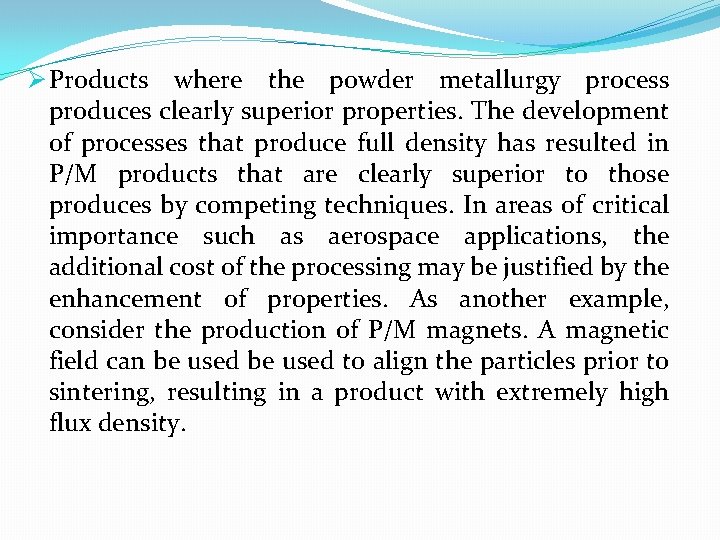
Ø Products where the powder metallurgy process produces clearly superior properties. The development of processes that produce full density has resulted in P/M products that are clearly superior to those produces by competing techniques. In areas of critical importance such as aerospace applications, the additional cost of the processing may be justified by the enhancement of properties. As another example, consider the production of P/M magnets. A magnetic field can be used to align the particles prior to sintering, resulting in a product with extremely high flux density.
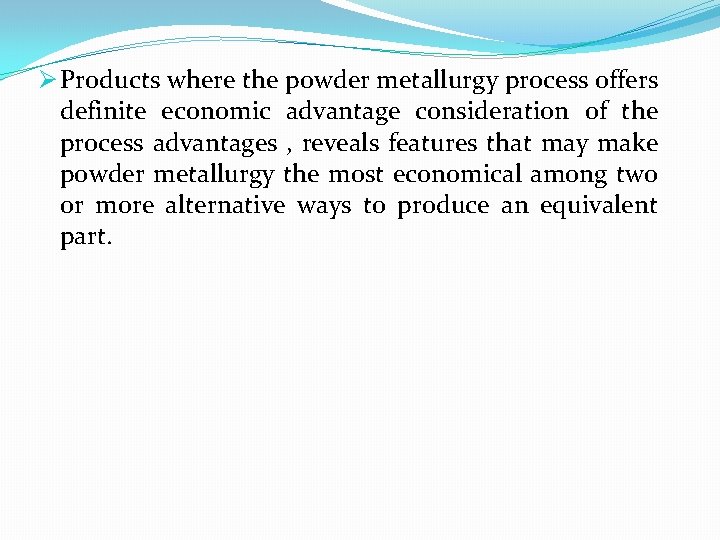
Ø Products where the powder metallurgy process offers definite economic advantage consideration of the process advantages , reveals features that may make powder metallurgy the most economical among two or more alternative ways to produce an equivalent part.
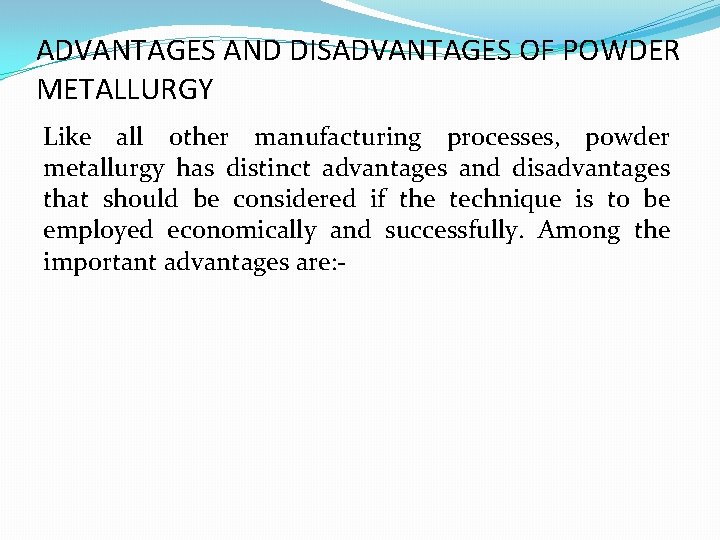
ADVANTAGES AND DISADVANTAGES OF POWDER METALLURGY Like all other manufacturing processes, powder metallurgy has distinct advantages and disadvantages that should be considered if the technique is to be employed economically and successfully. Among the important advantages are: -
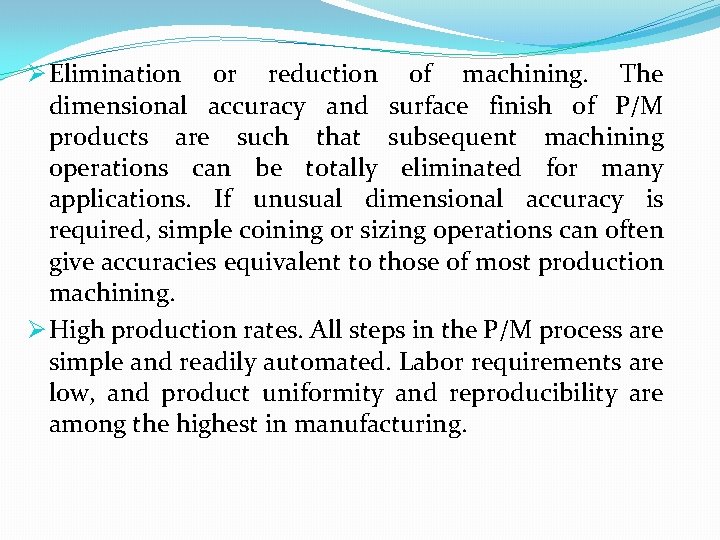
Ø Elimination or reduction of machining. The dimensional accuracy and surface finish of P/M products are such that subsequent machining operations can be totally eliminated for many applications. If unusual dimensional accuracy is required, simple coining or sizing operations can often give accuracies equivalent to those of most production machining. Ø High production rates. All steps in the P/M process are simple and readily automated. Labor requirements are low, and product uniformity and reproducibility are among the highest in manufacturing.
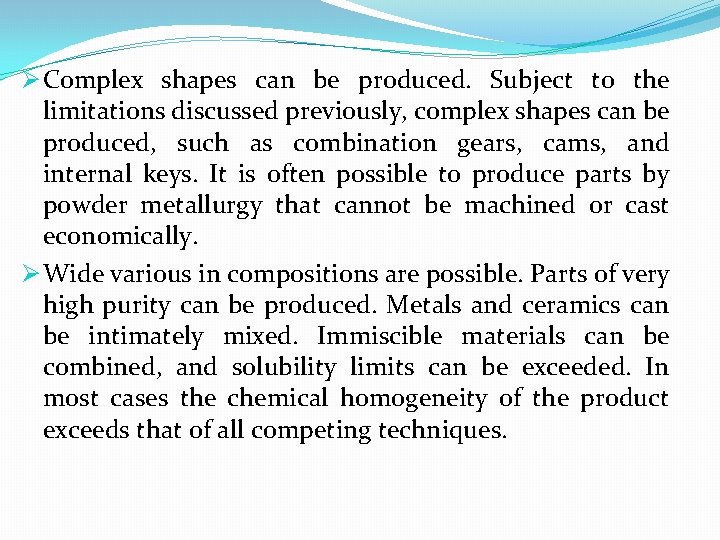
Ø Complex shapes can be produced. Subject to the limitations discussed previously, complex shapes can be produced, such as combination gears, cams, and internal keys. It is often possible to produce parts by powder metallurgy that cannot be machined or cast economically. Ø Wide various in compositions are possible. Parts of very high purity can be produced. Metals and ceramics can be intimately mixed. Immiscible materials can be combined, and solubility limits can be exceeded. In most cases the chemical homogeneity of the product exceeds that of all competing techniques.
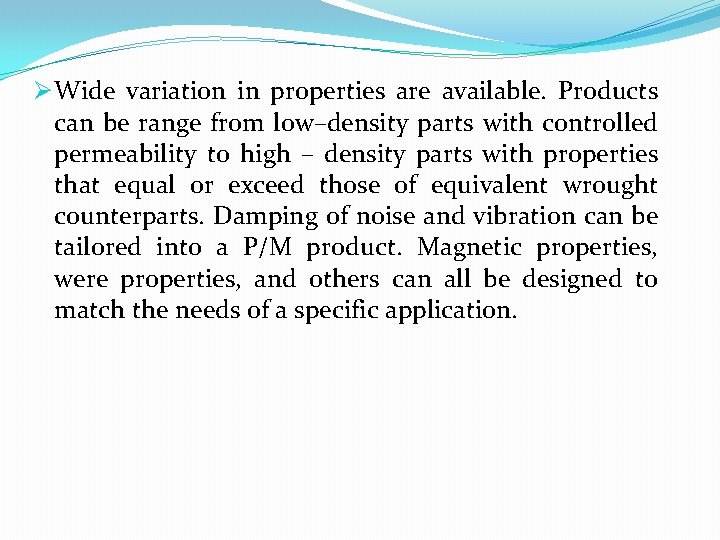
Ø Wide variation in properties are available. Products can be range from low–density parts with controlled permeability to high – density parts with properties that equal or exceed those of equivalent wrought counterparts. Damping of noise and vibration can be tailored into a P/M product. Magnetic properties, were properties, and others can all be designed to match the needs of a specific application.
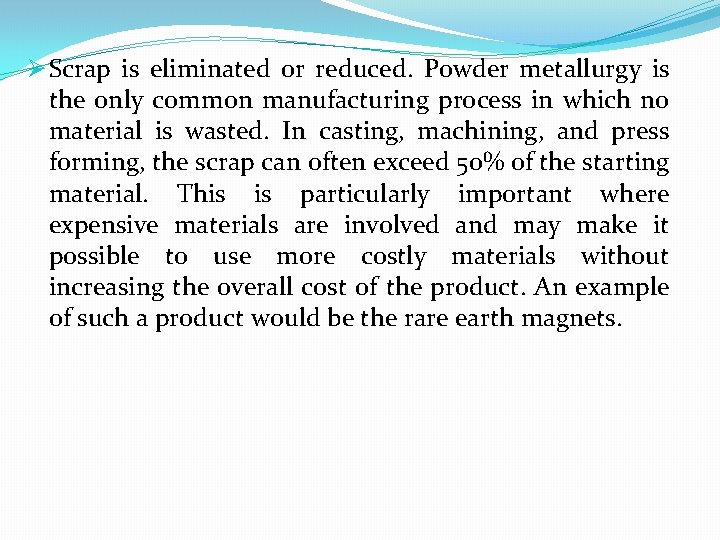
Ø Scrap is eliminated or reduced. Powder metallurgy is the only common manufacturing process in which no material is wasted. In casting, machining, and press forming, the scrap can often exceed 50% of the starting material. This is particularly important where expensive materials are involved and may make it possible to use more costly materials without increasing the overall cost of the product. An example of such a product would be the rare earth magnets.
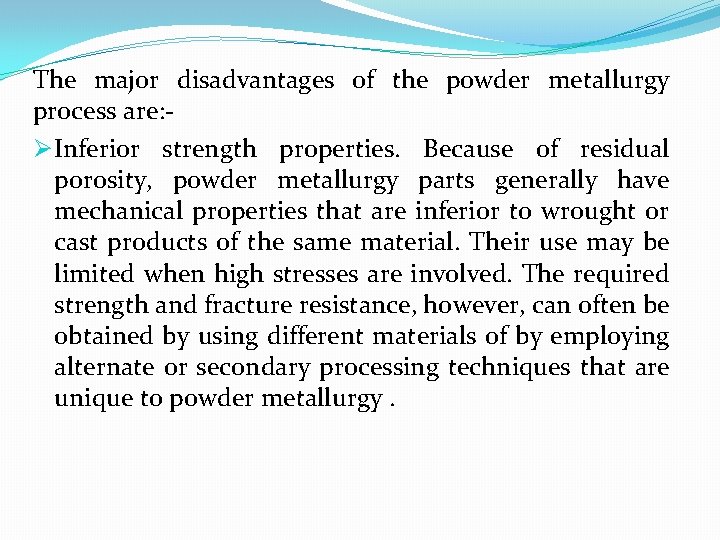
The major disadvantages of the powder metallurgy process are: Ø Inferior strength properties. Because of residual porosity, powder metallurgy parts generally have mechanical properties that are inferior to wrought or cast products of the same material. Their use may be limited when high stresses are involved. The required strength and fracture resistance, however, can often be obtained by using different materials of by employing alternate or secondary processing techniques that are unique to powder metallurgy.
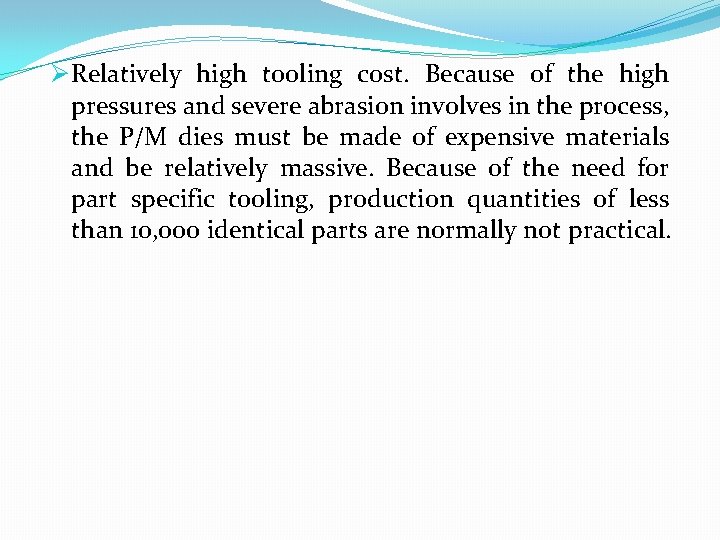
Ø Relatively high tooling cost. Because of the high pressures and severe abrasion involves in the process, the P/M dies must be made of expensive materials and be relatively massive. Because of the need for part specific tooling, production quantities of less than 10, 000 identical parts are normally not practical.
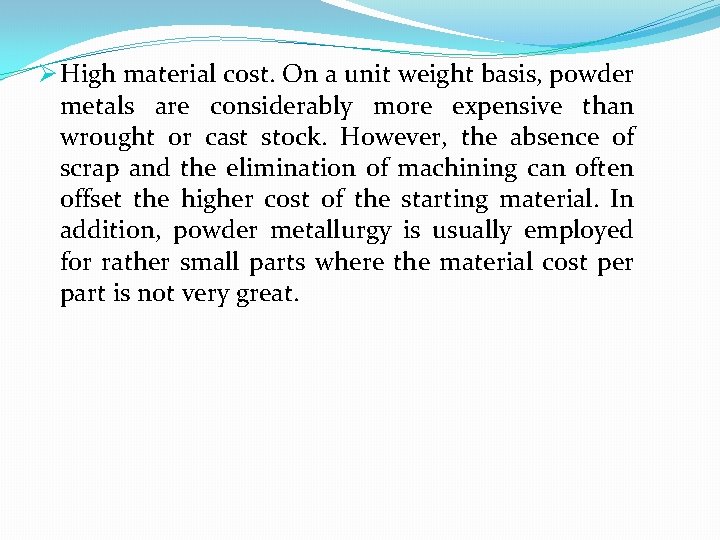
Ø High material cost. On a unit weight basis, powder metals are considerably more expensive than wrought or cast stock. However, the absence of scrap and the elimination of machining can often offset the higher cost of the starting material. In addition, powder metallurgy is usually employed for rather small parts where the material cost per part is not very great.
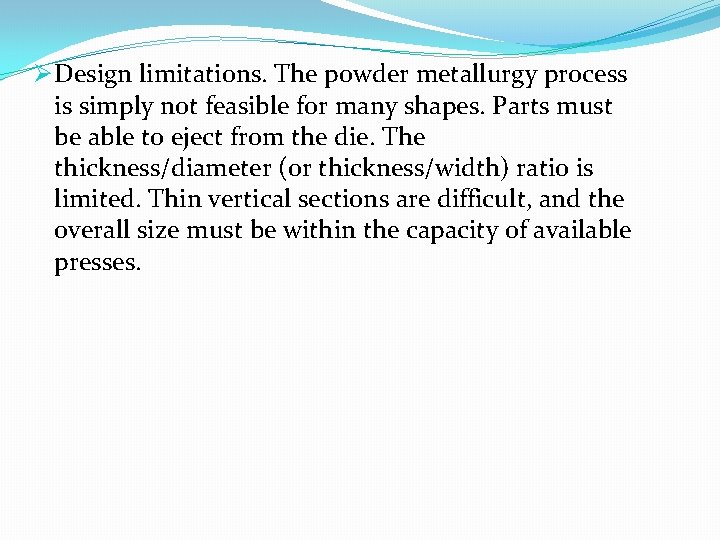
Ø Design limitations. The powder metallurgy process is simply not feasible for many shapes. Parts must be able to eject from the die. The thickness/diameter (or thickness/width) ratio is limited. Thin vertical sections are difficult, and the overall size must be within the capacity of available presses.
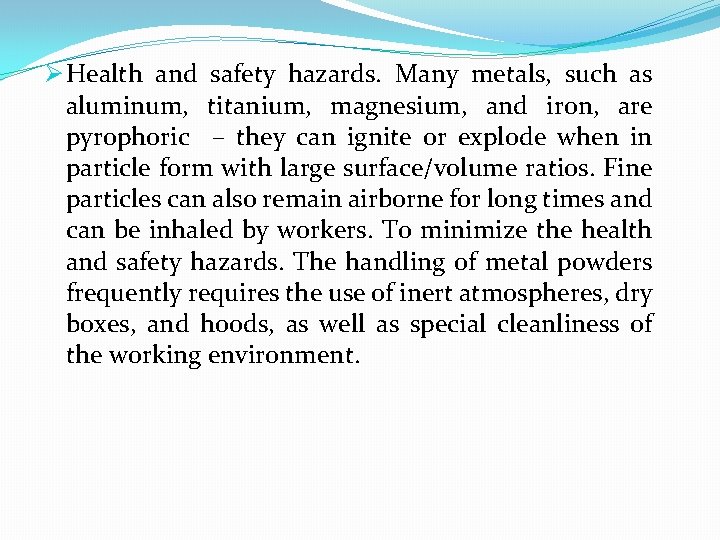
Ø Health and safety hazards. Many metals, such as aluminum, titanium, magnesium, and iron, are pyrophoric – they can ignite or explode when in particle form with large surface/volume ratios. Fine particles can also remain airborne for long times and can be inhaled by workers. To minimize the health and safety hazards. The handling of metal powders frequently requires the use of inert atmospheres, dry boxes, and hoods, as well as special cleanliness of the working environment.
Powder characterization in powder metallurgy
Powder metallurgy and metal ceramics
Powder metallurgy
Solid state reduction powder metallurgy
Metallurgy
University of chemical technology and metallurgy sofia
Metallurgy 2
Classification of powders in pharmaceutics
Advantages and disadvantages of powder dosage form
Divided powder example
Name a point that is collinear with the given points
Chemical equations review
Hát kết hợp bộ gõ cơ thể
Ng-html
Bổ thể
Tỉ lệ cơ thể trẻ em
Chó sói
Chụp phim tư thế worms-breton
Bài hát chúa yêu trần thế alleluia
Môn thể thao bắt đầu bằng chữ f
Thế nào là hệ số cao nhất
Các châu lục và đại dương trên thế giới
Công của trọng lực
Trời xanh đây là của chúng ta thể thơ
Mật thư anh em như thể tay chân
Phép trừ bù
Phản ứng thế ankan
Các châu lục và đại dương trên thế giới
Thơ thất ngôn tứ tuyệt đường luật
Quá trình desamine hóa có thể tạo ra
Một số thể thơ truyền thống
Cái miệng nó xinh thế
Vẽ hình chiếu vuông góc của vật thể sau
Biện pháp chống mỏi cơ
đặc điểm cơ thể của người tối cổ
Thứ tự các dấu thăng giáng ở hóa biểu
Vẽ hình chiếu đứng bằng cạnh của vật thể
Fecboak
Thẻ vin
đại từ thay thế
điện thế nghỉ
Tư thế ngồi viết
Diễn thế sinh thái là
Dot
Bảng số nguyên tố
Tư thế ngồi viết
Lời thề hippocrates
Thiếu nhi thế giới liên hoan