Chapter 1 Introduction to Statistical Quality Control 6
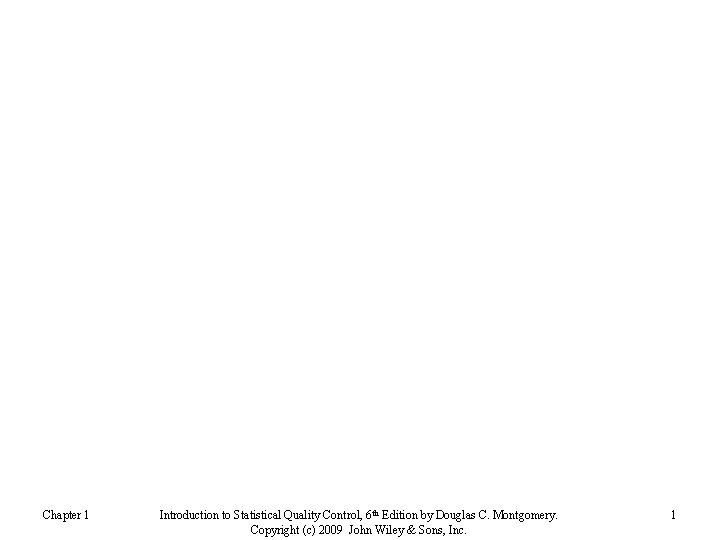
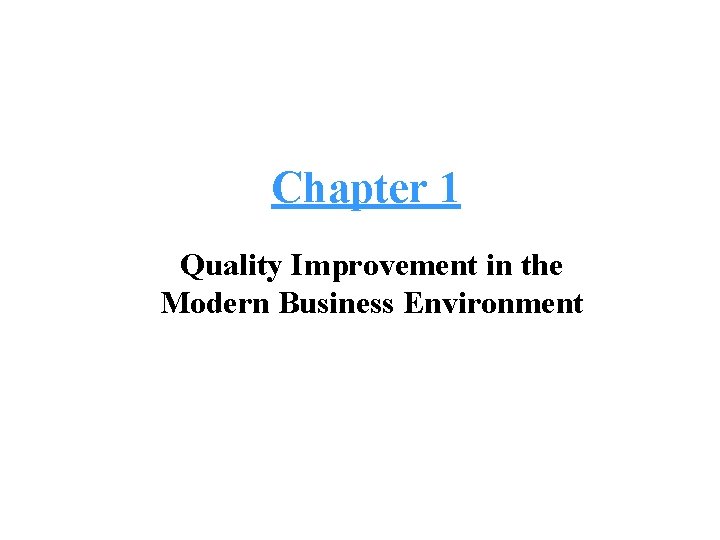
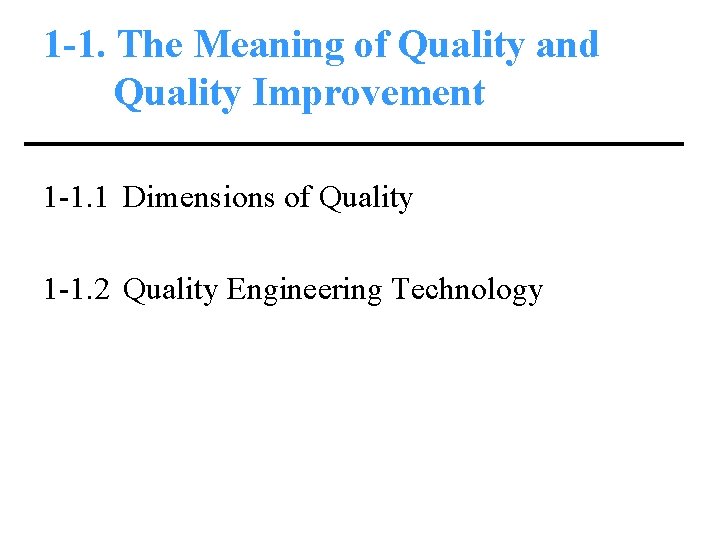
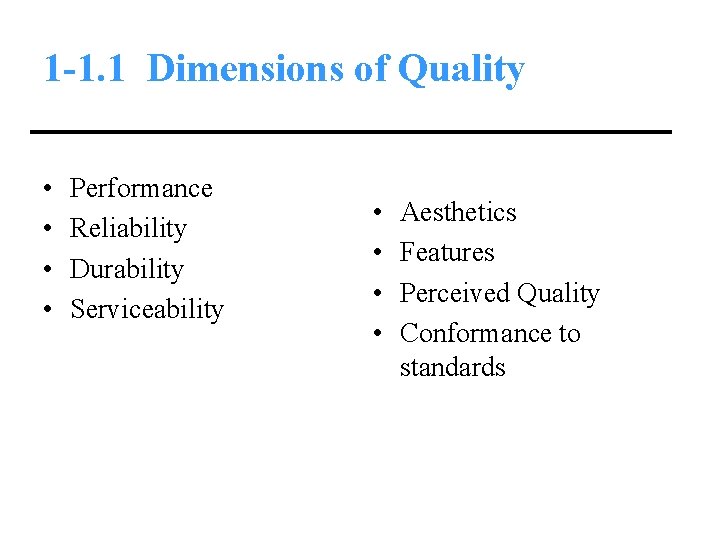
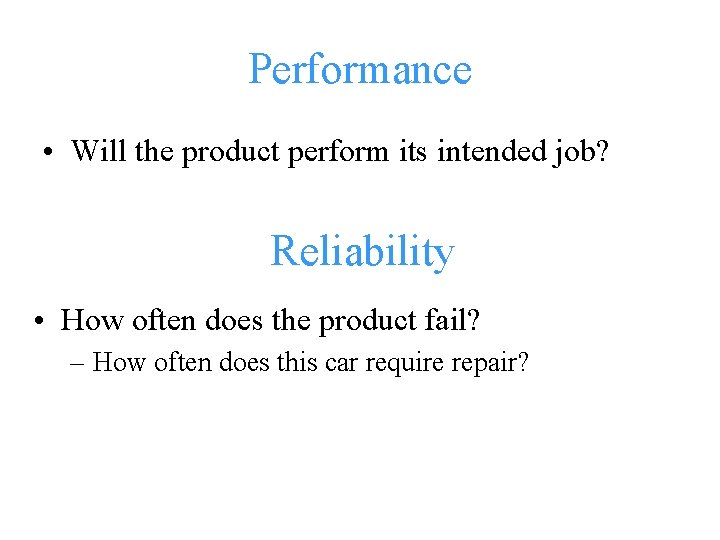
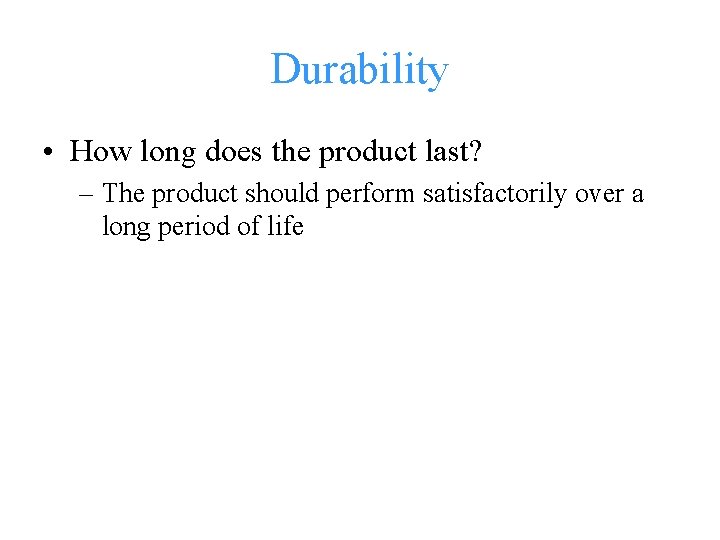
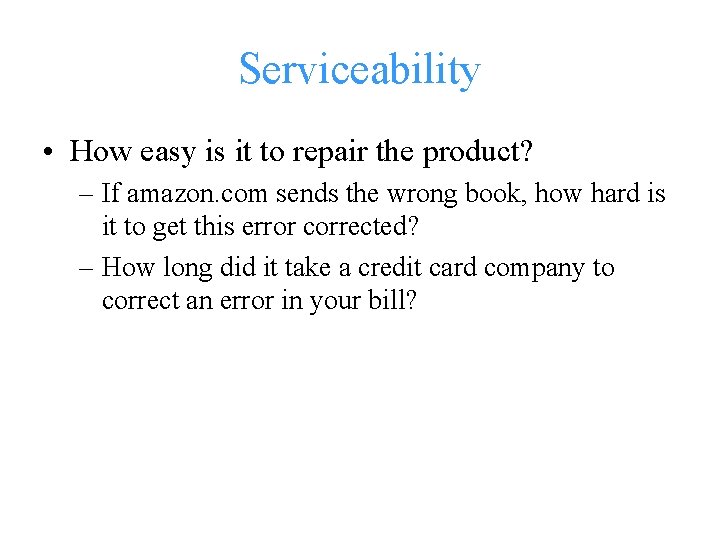

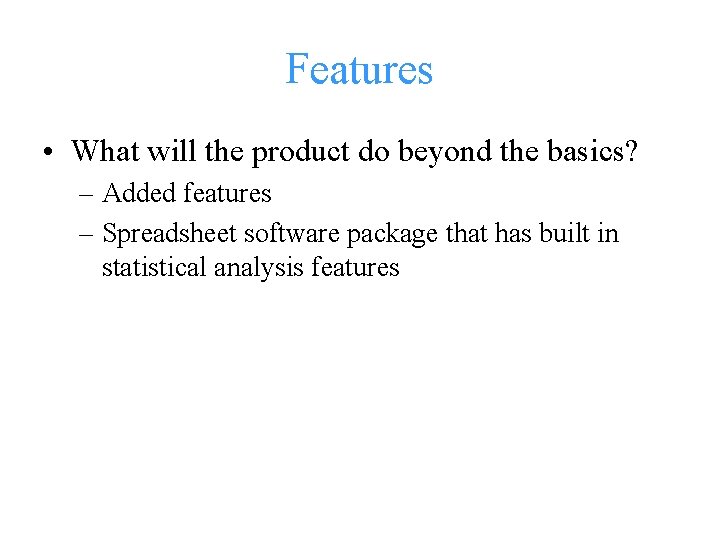
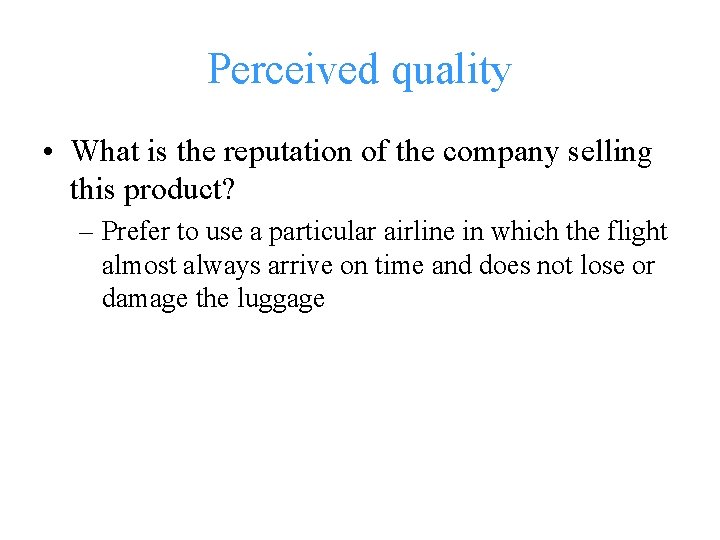
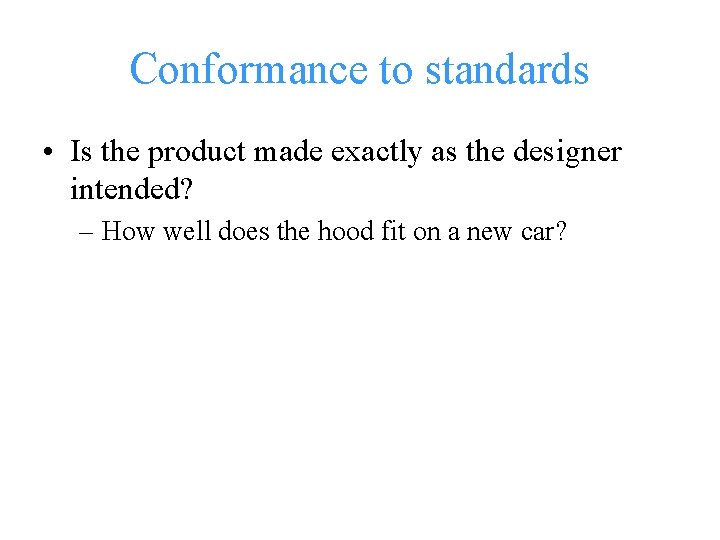
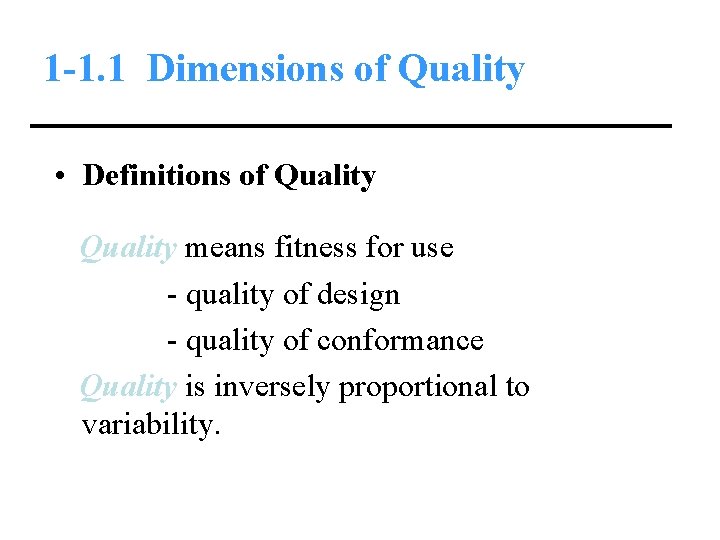
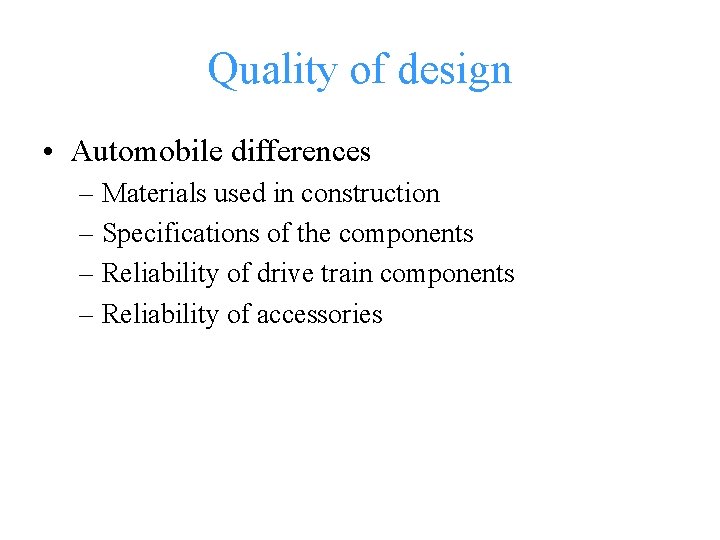
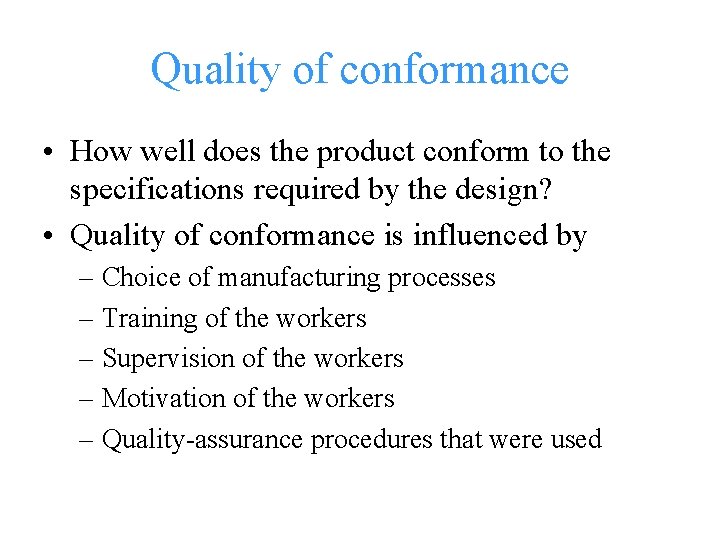
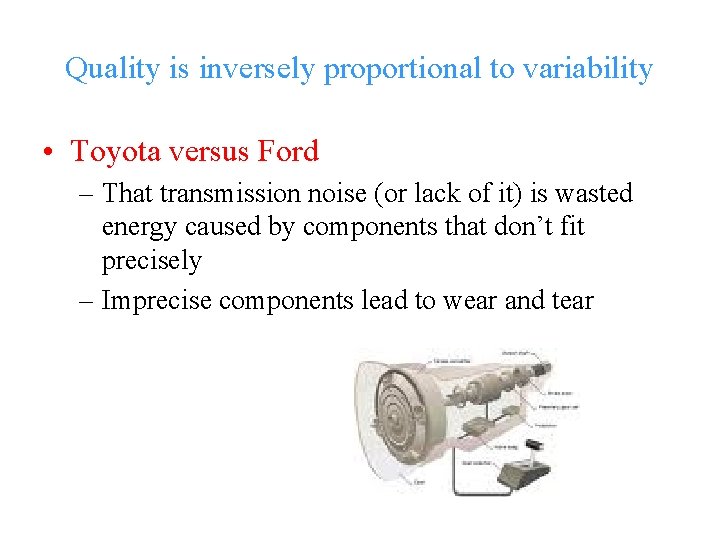
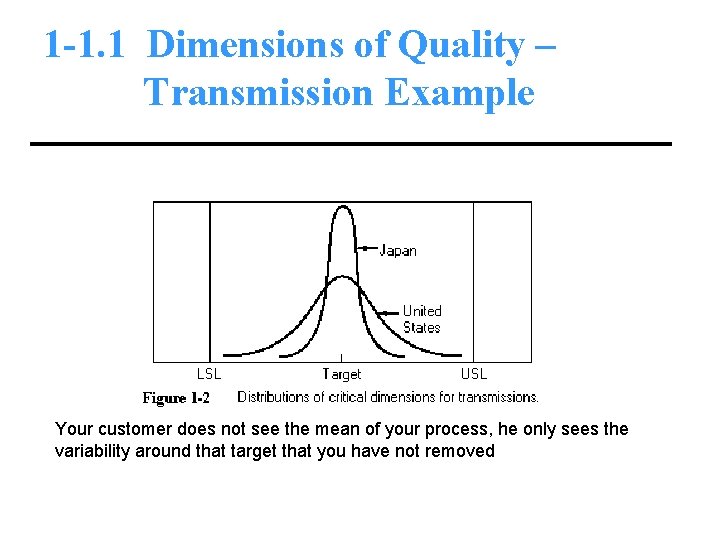
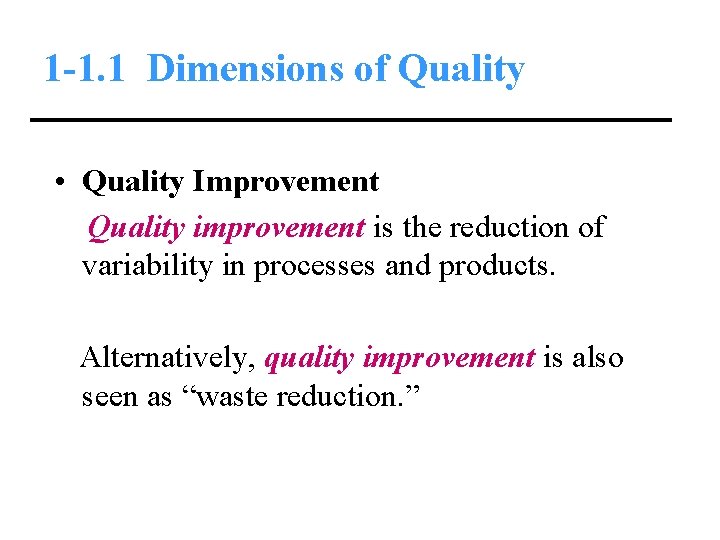
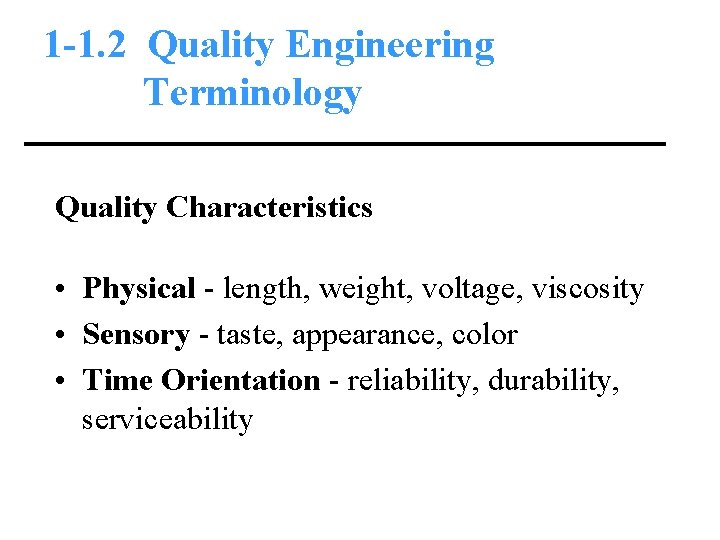
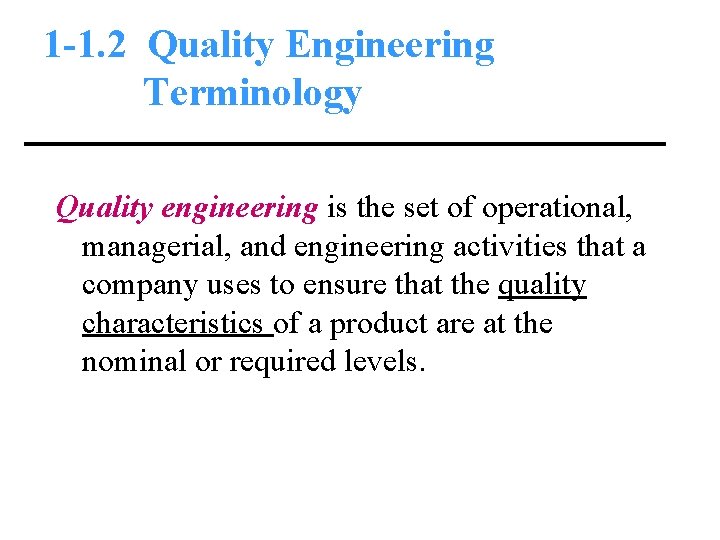
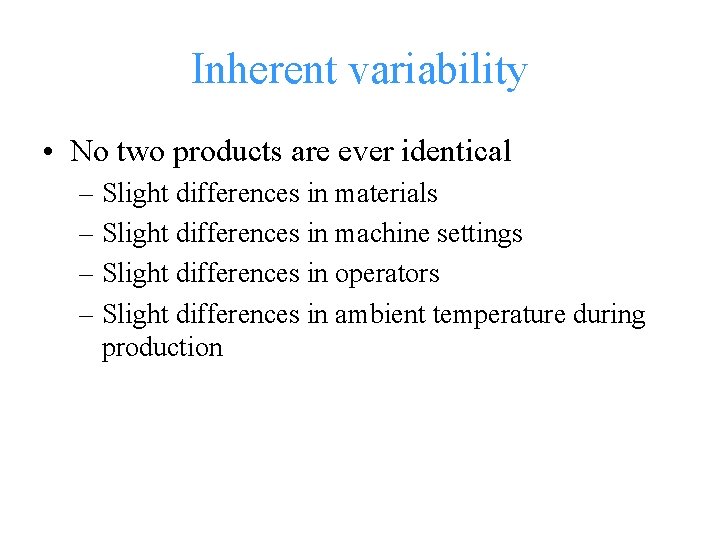
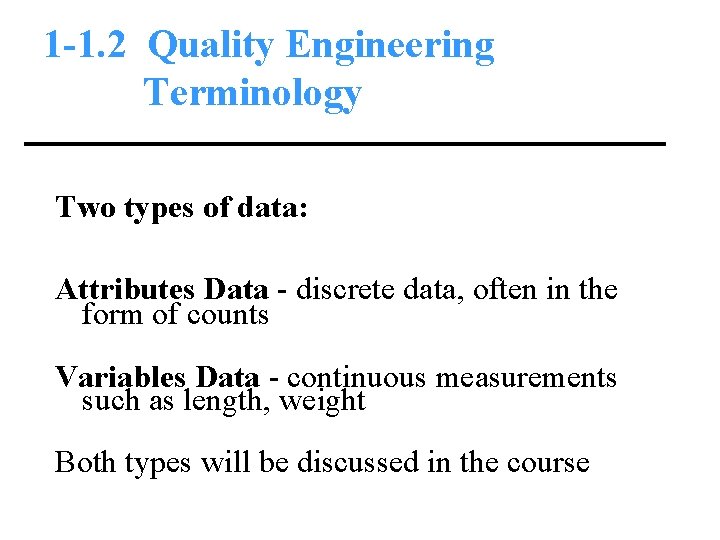
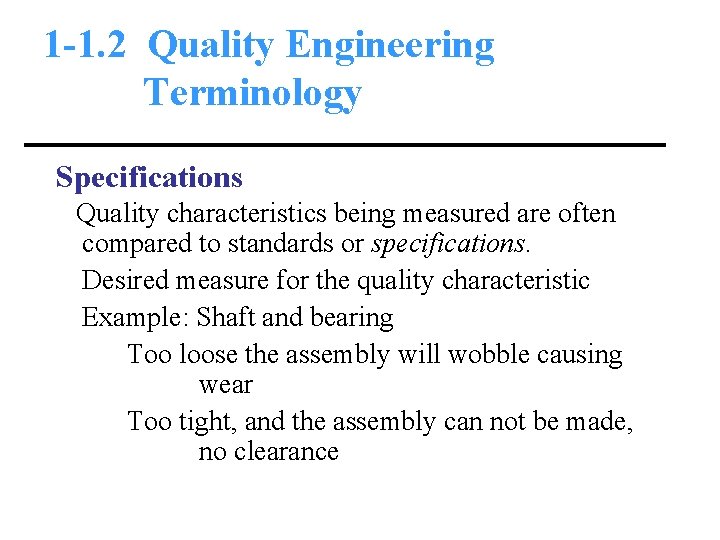
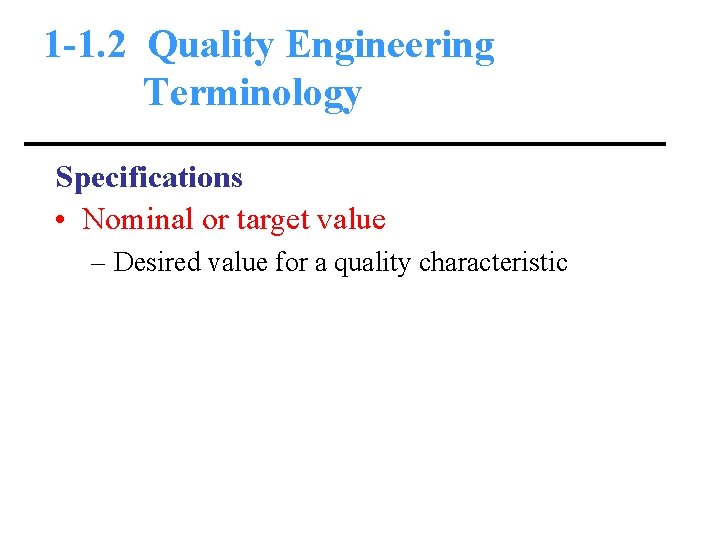
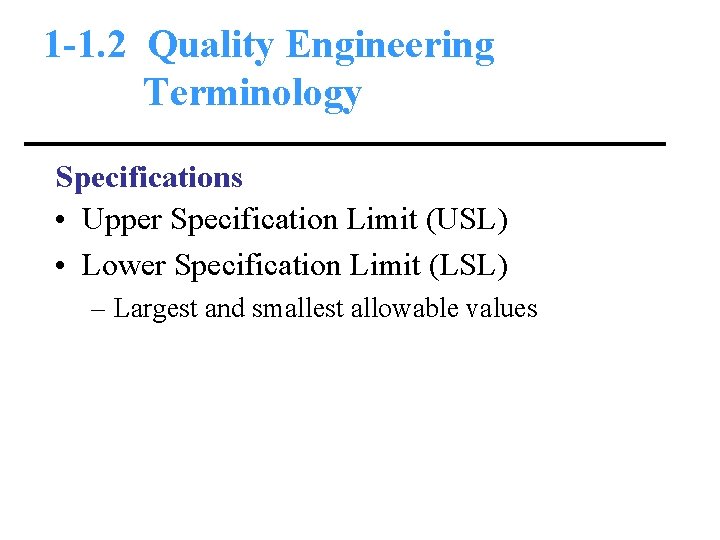
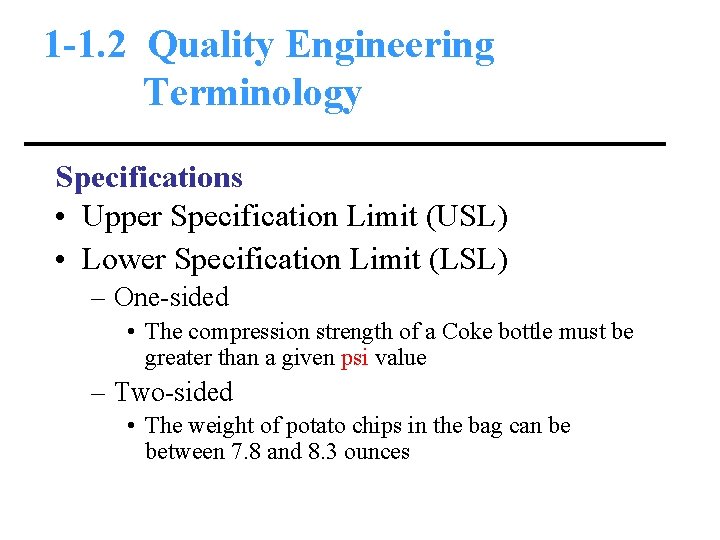
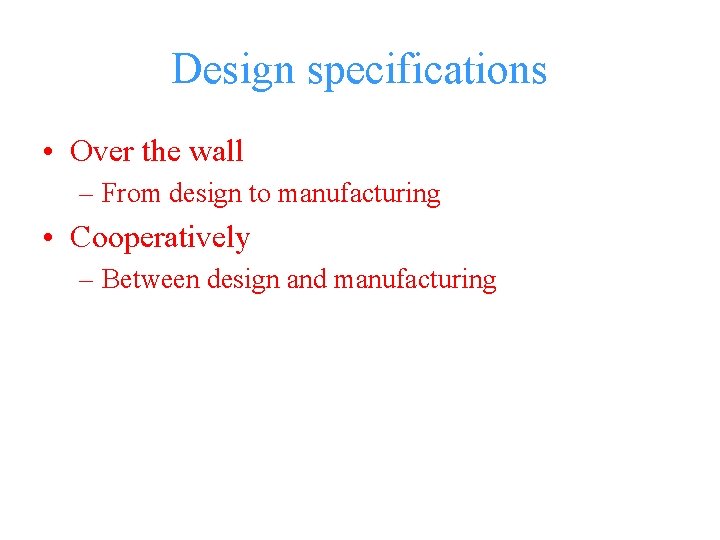
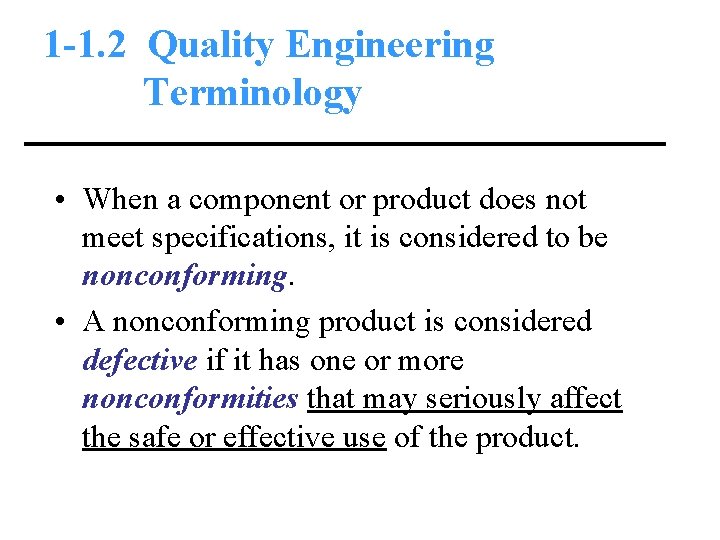
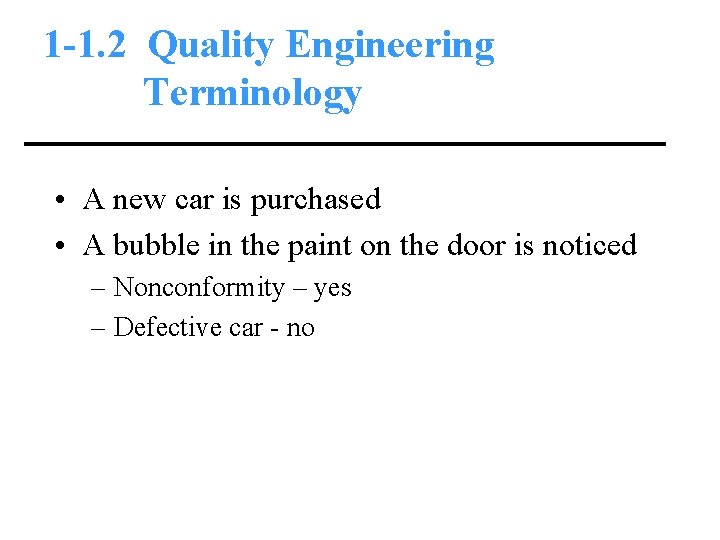
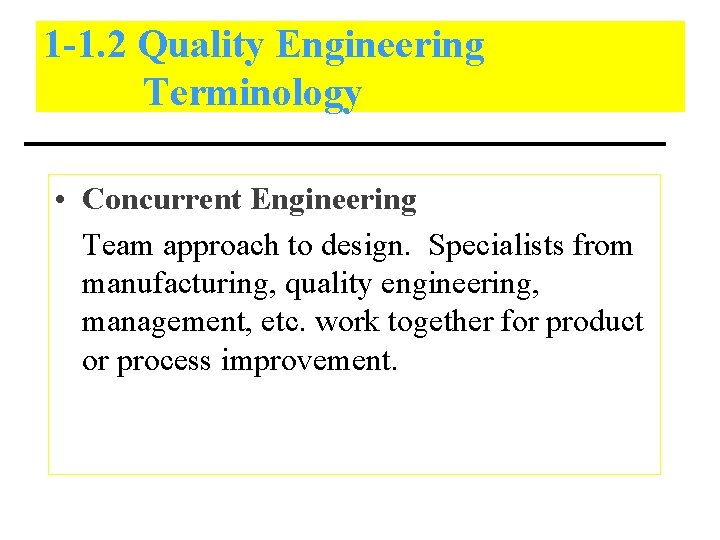
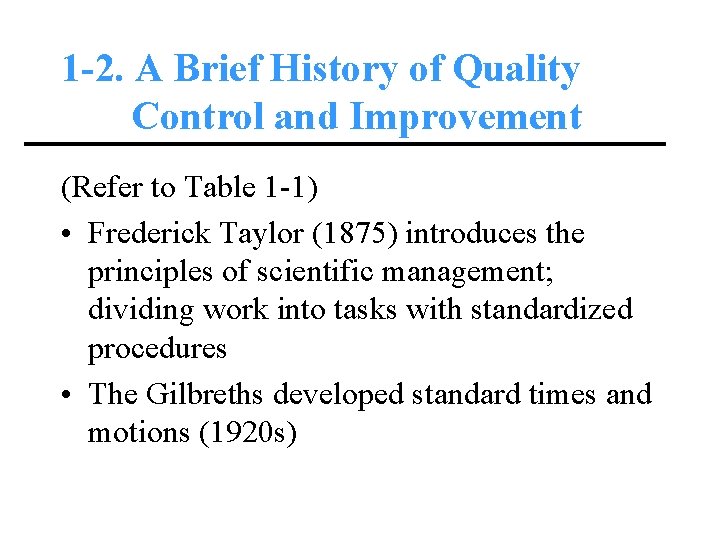

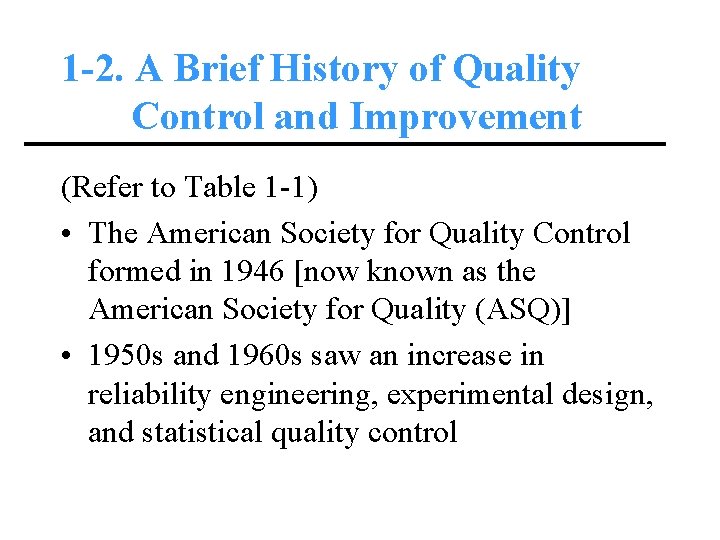
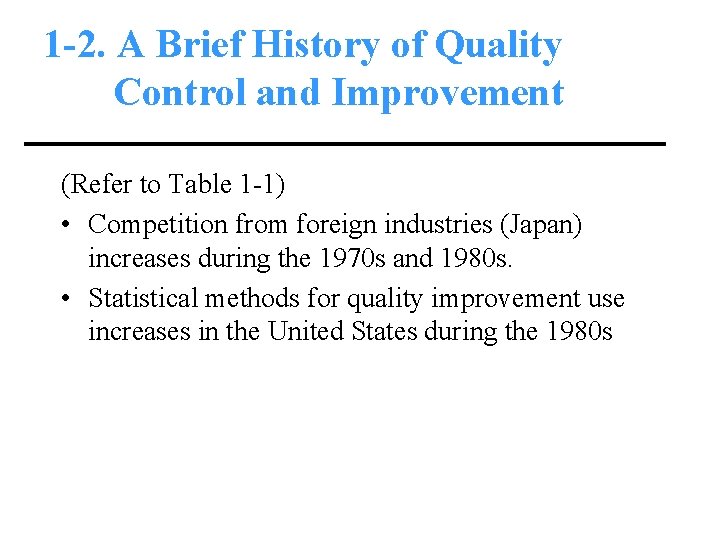
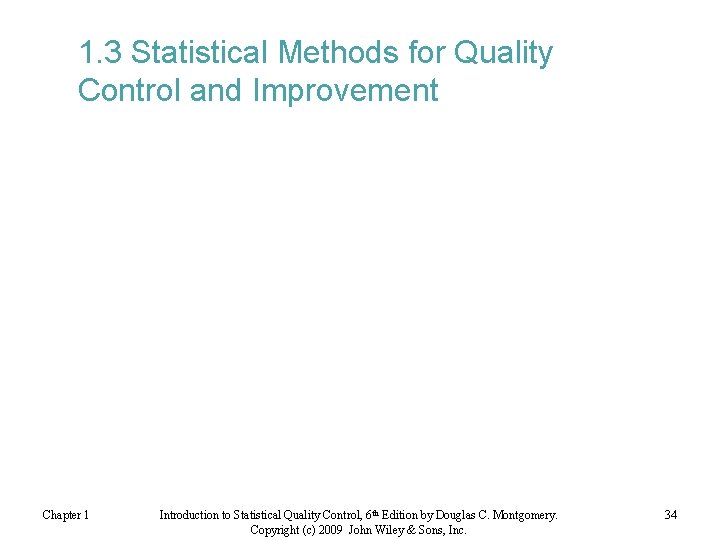
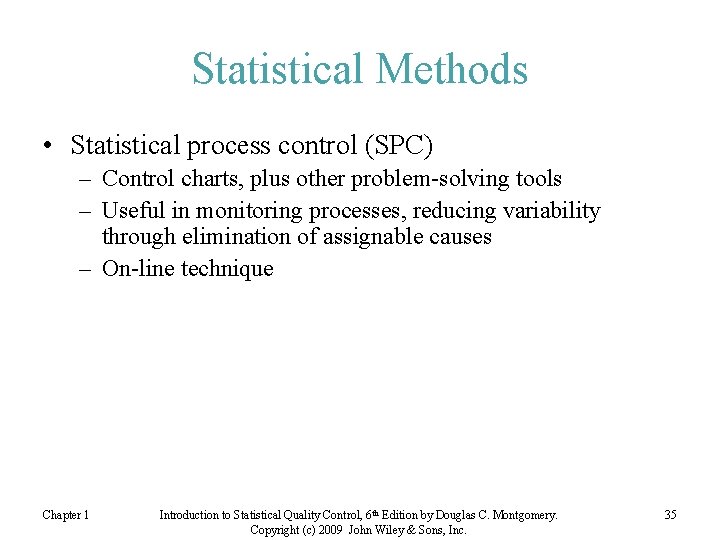
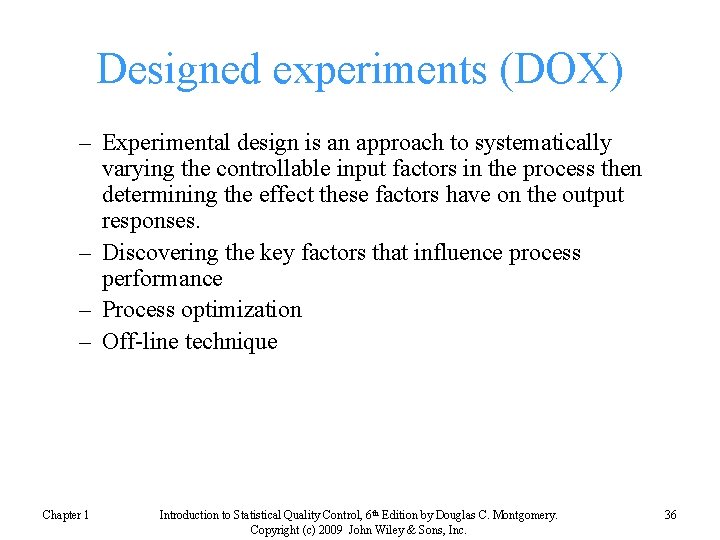
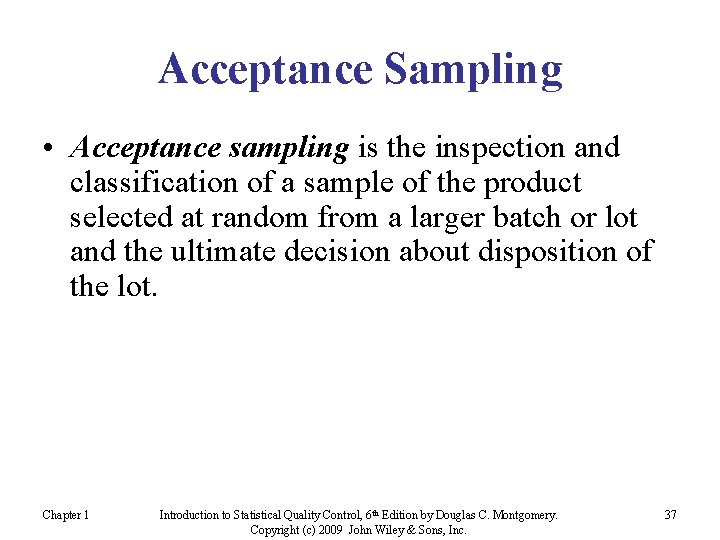

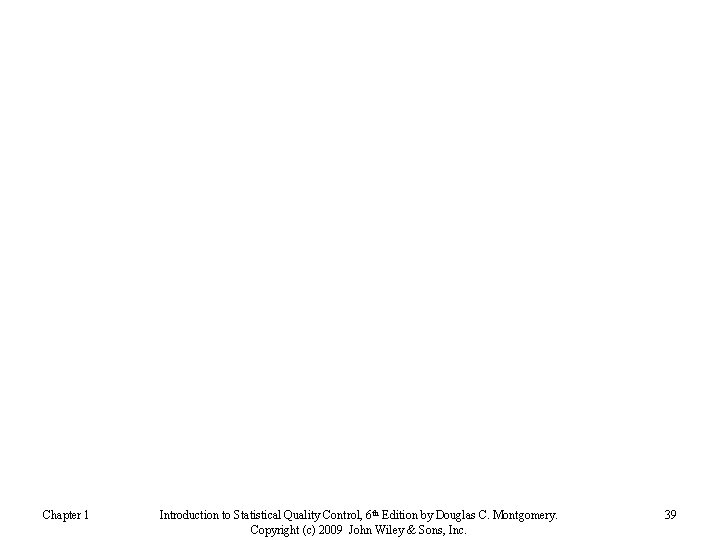
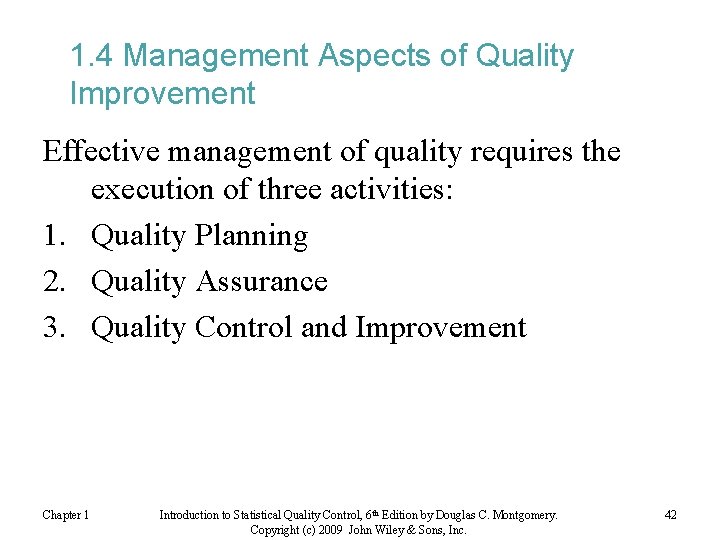
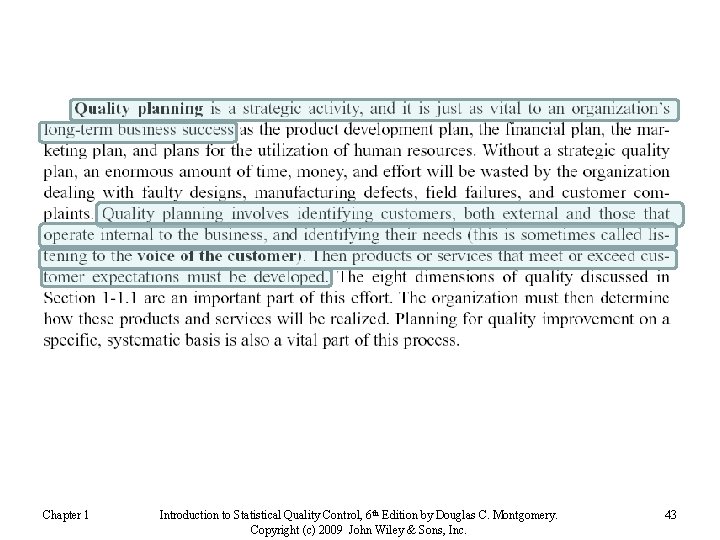
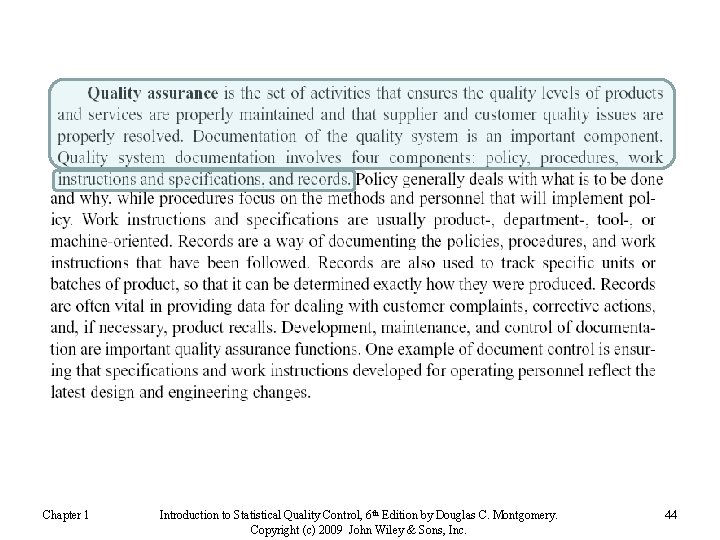
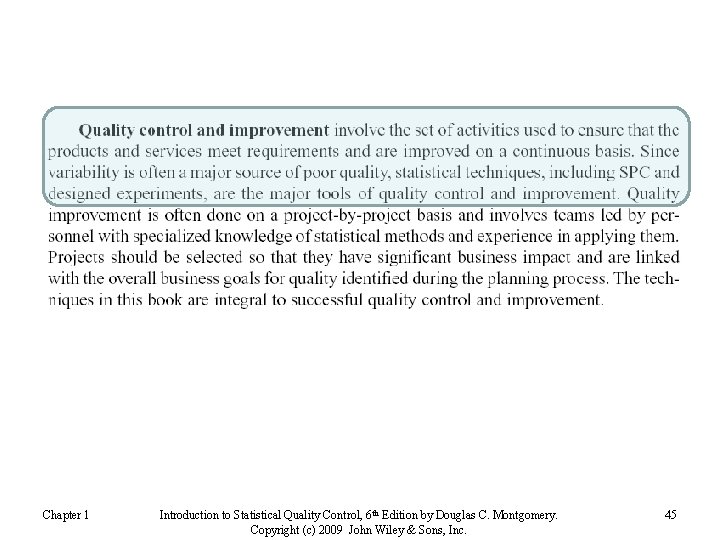
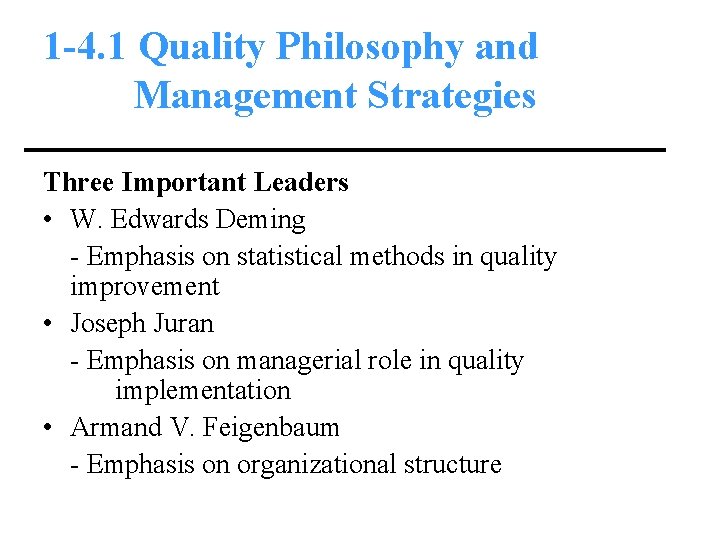
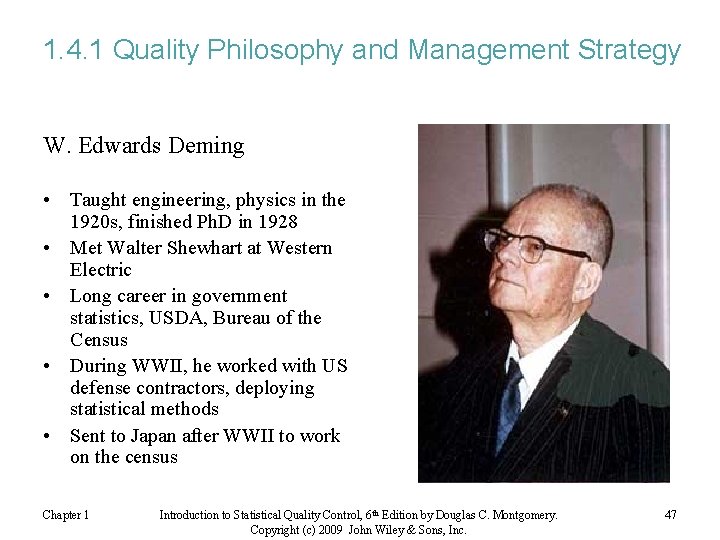

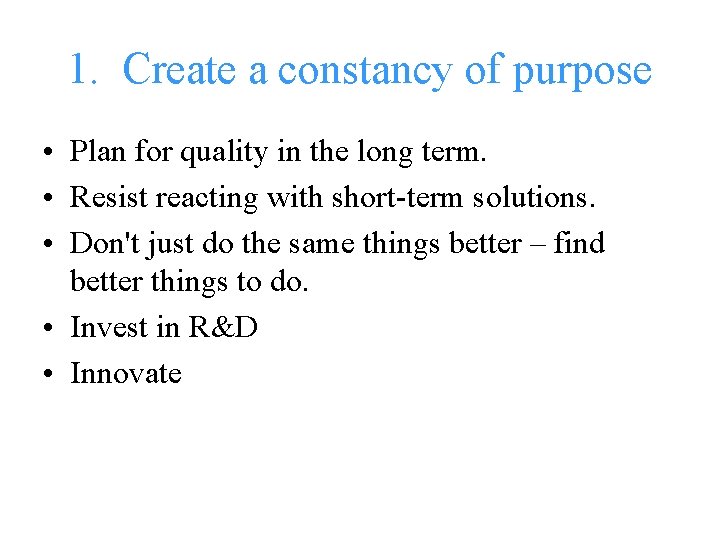
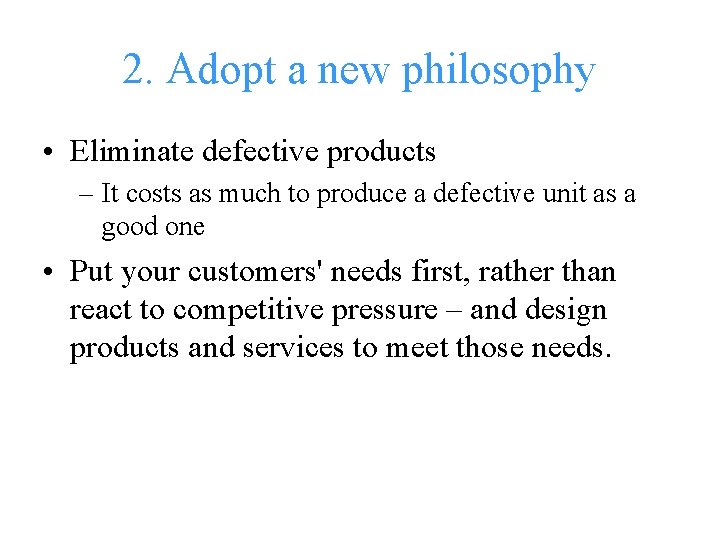
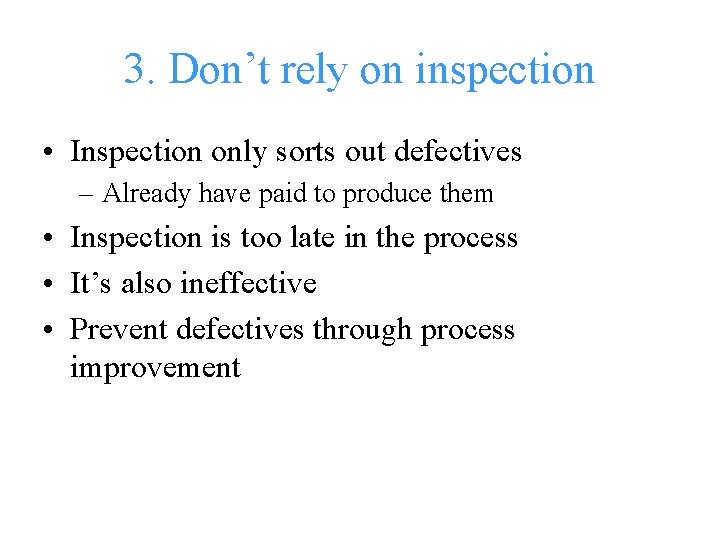
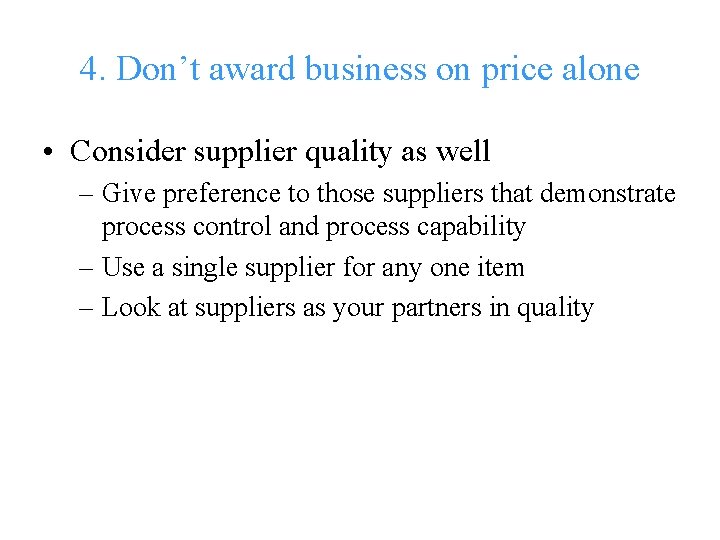
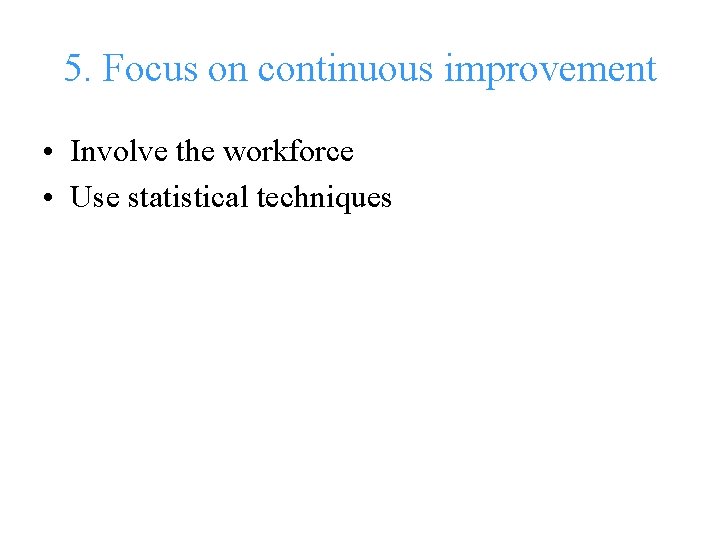
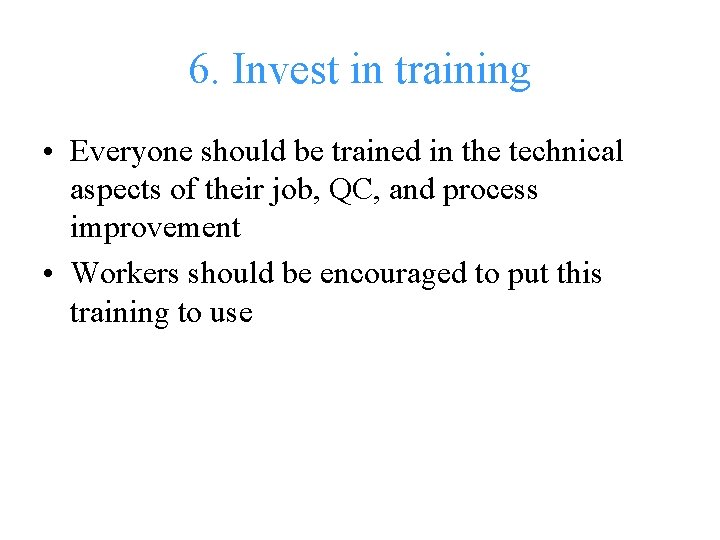
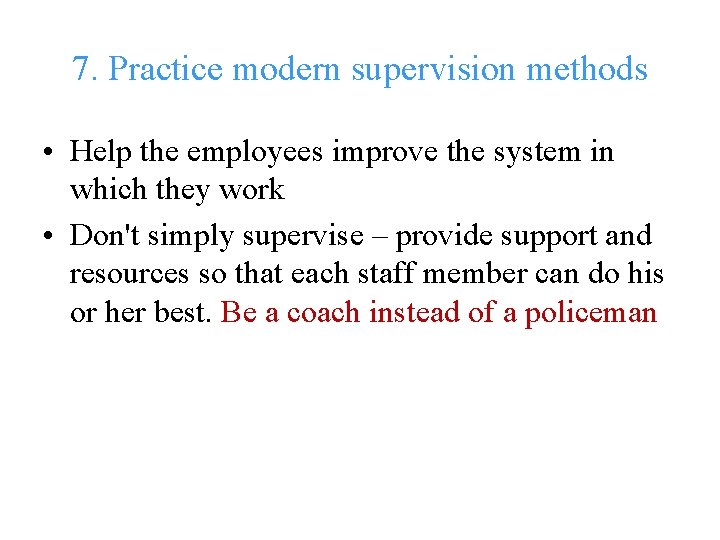
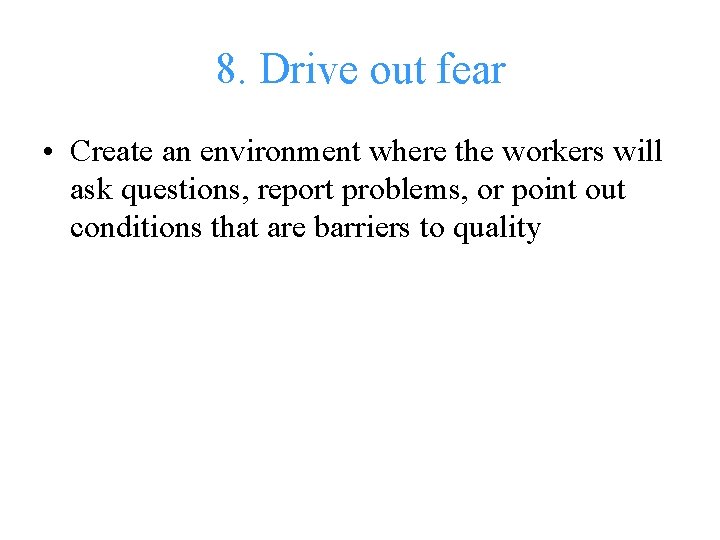
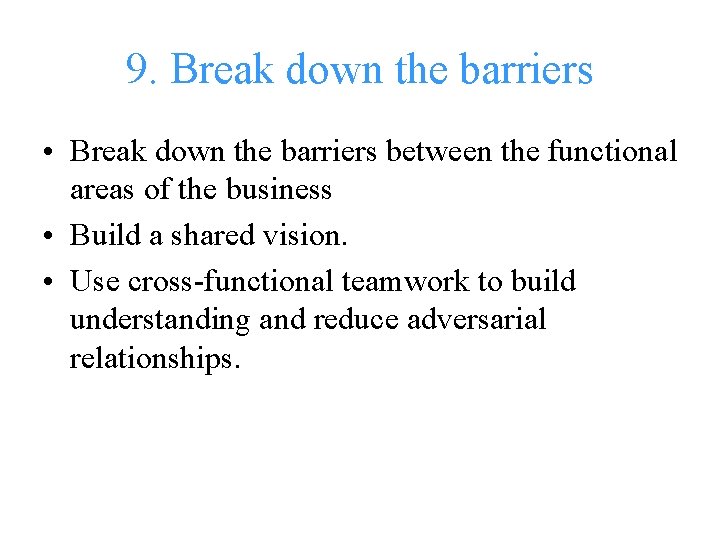
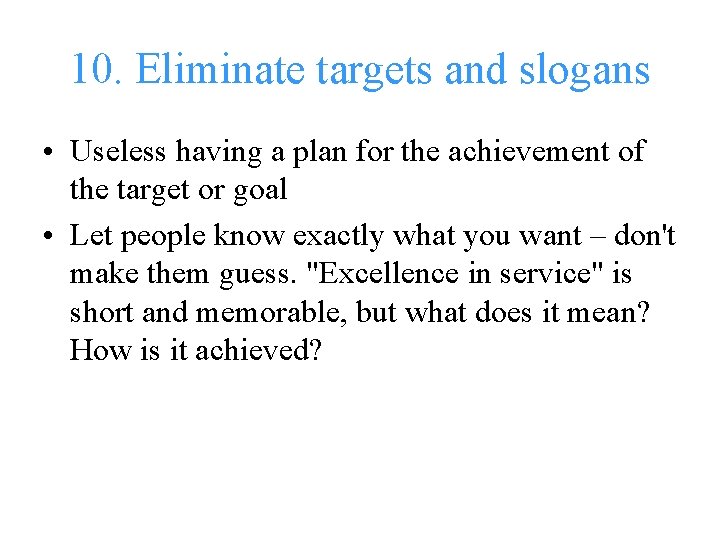
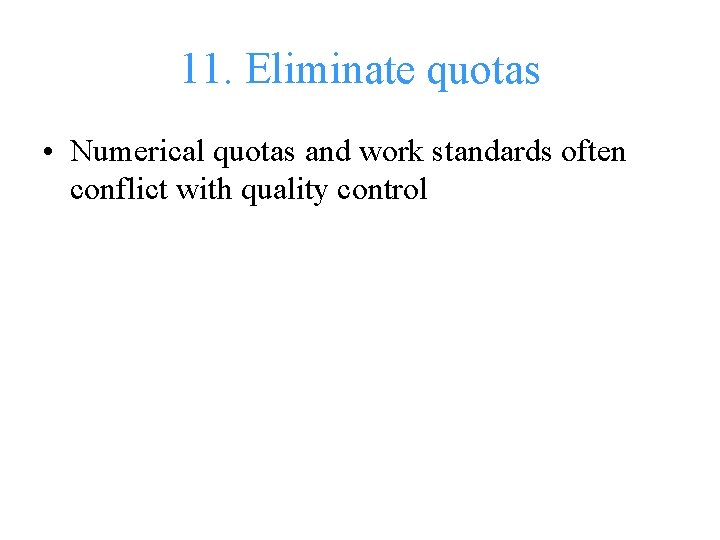
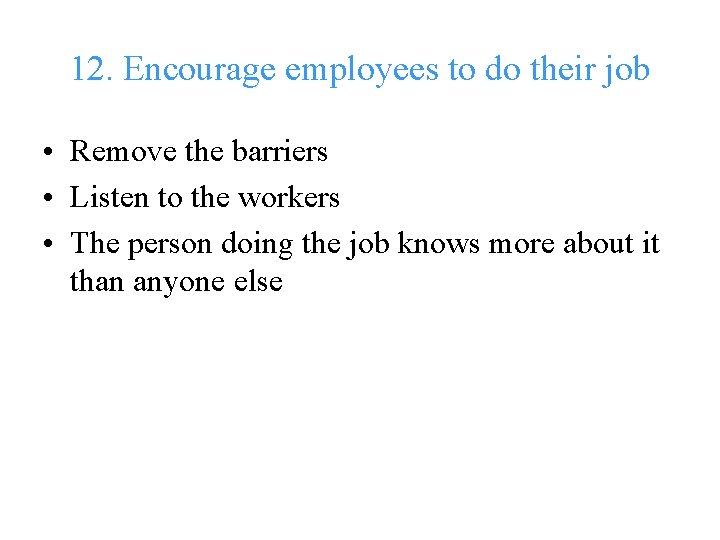
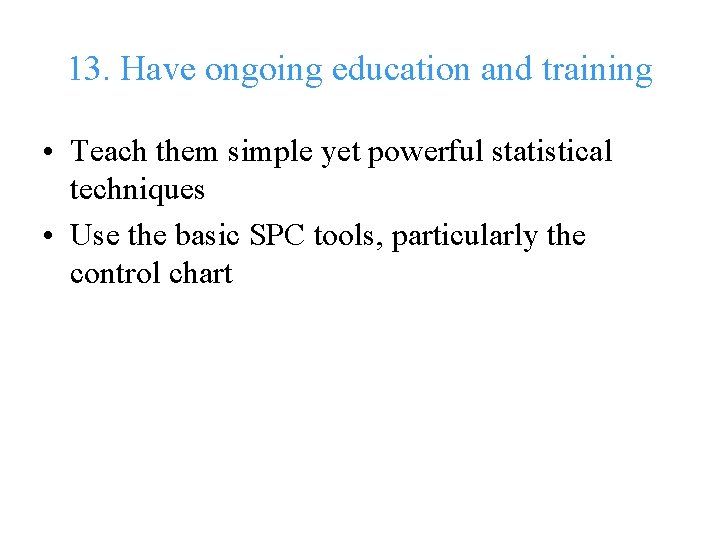
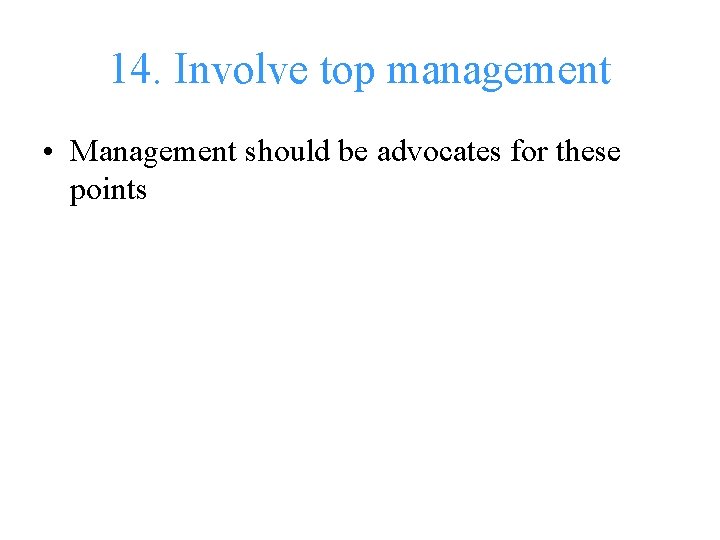
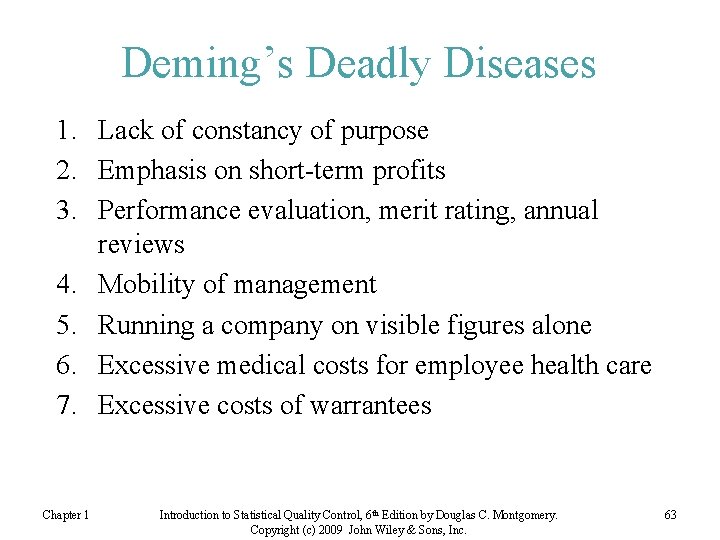
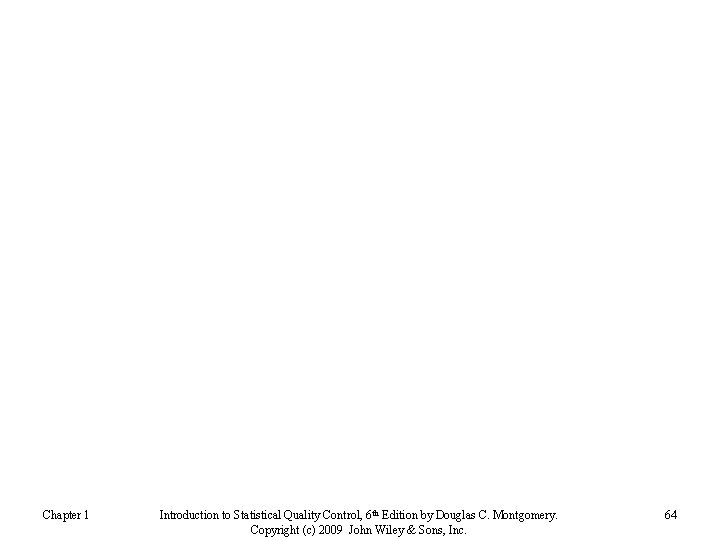
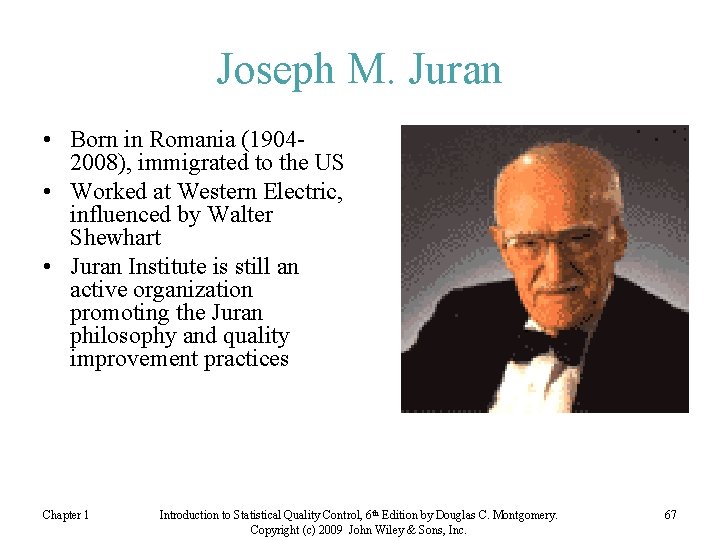
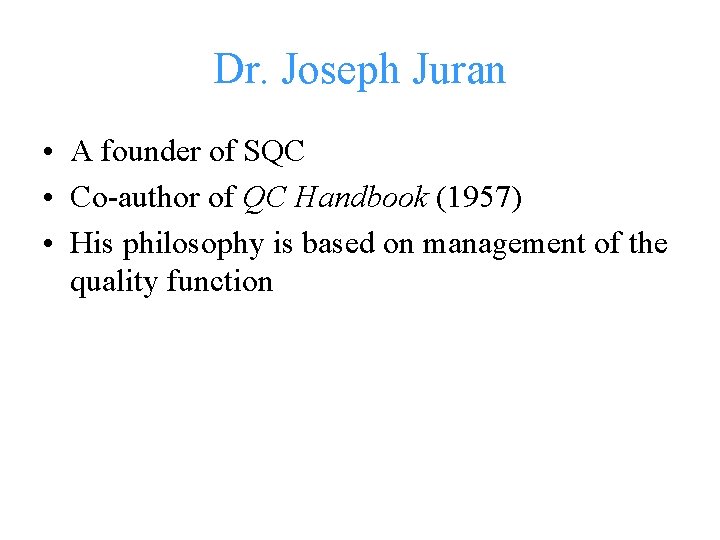
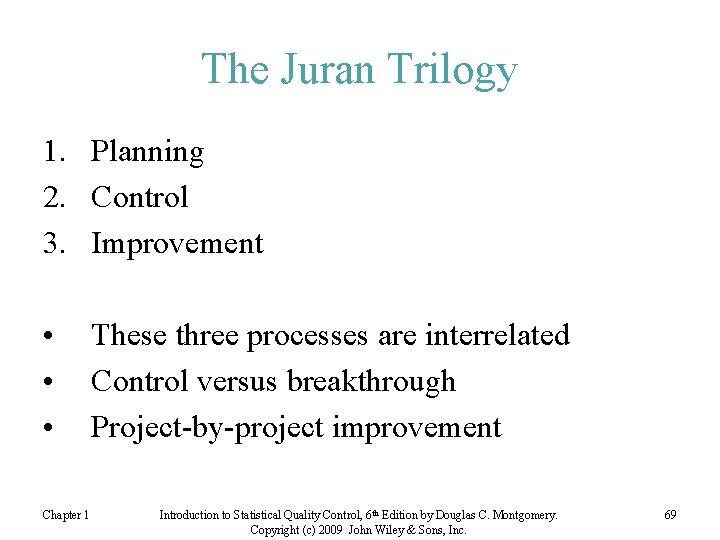
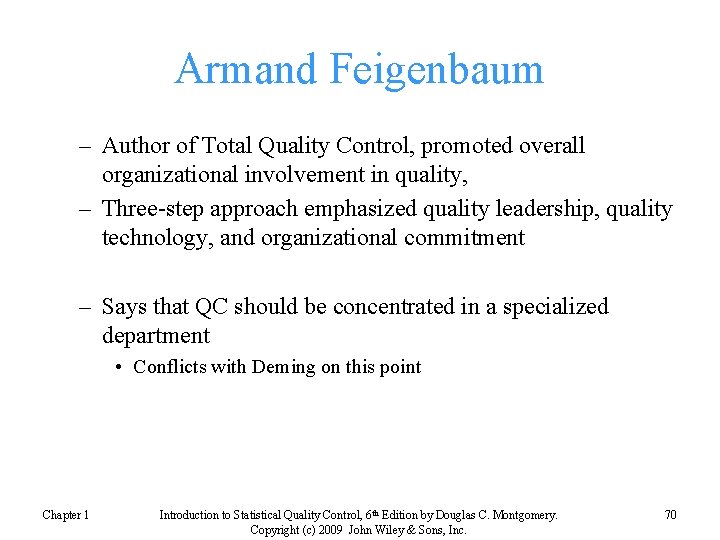
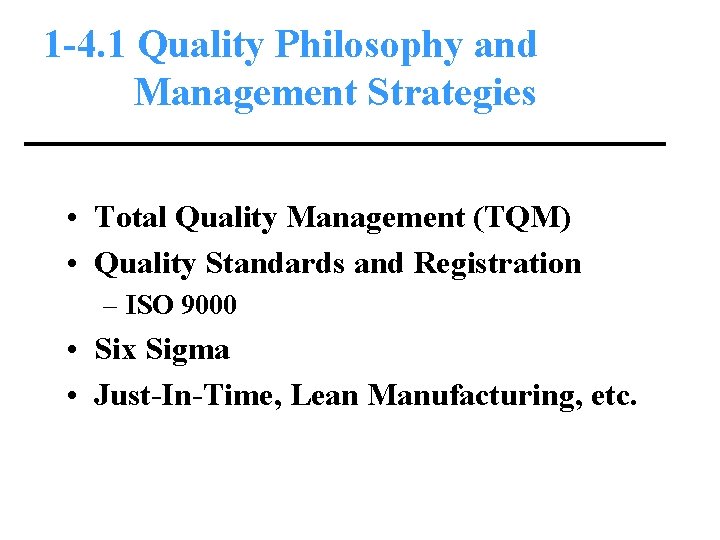
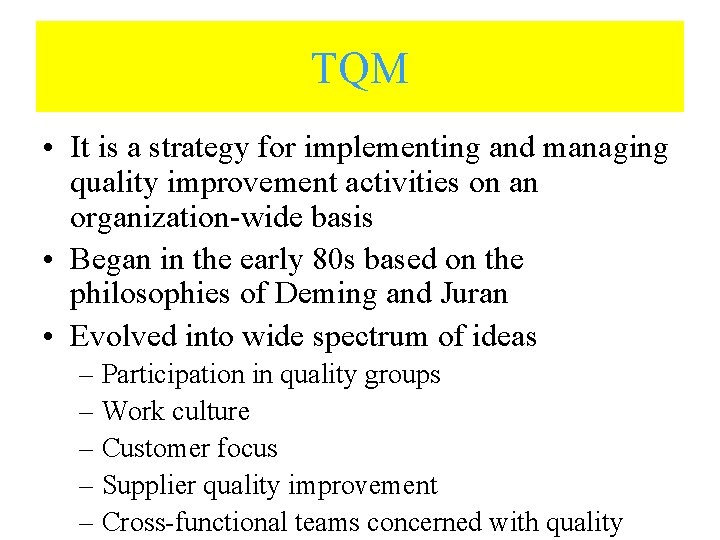
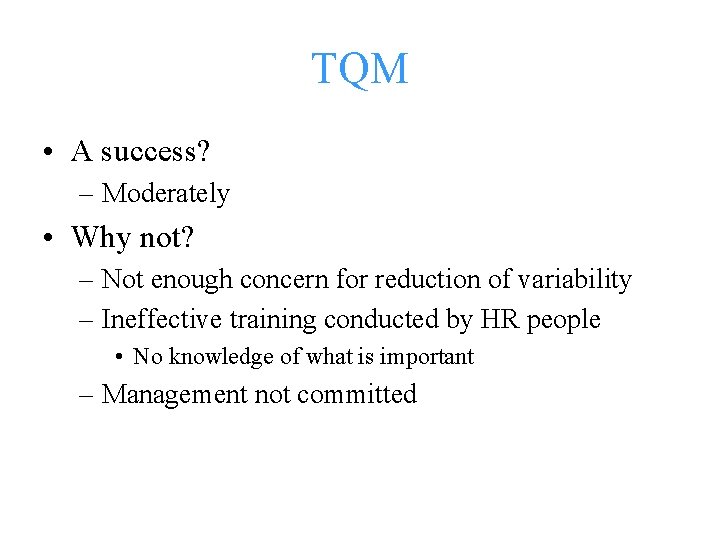
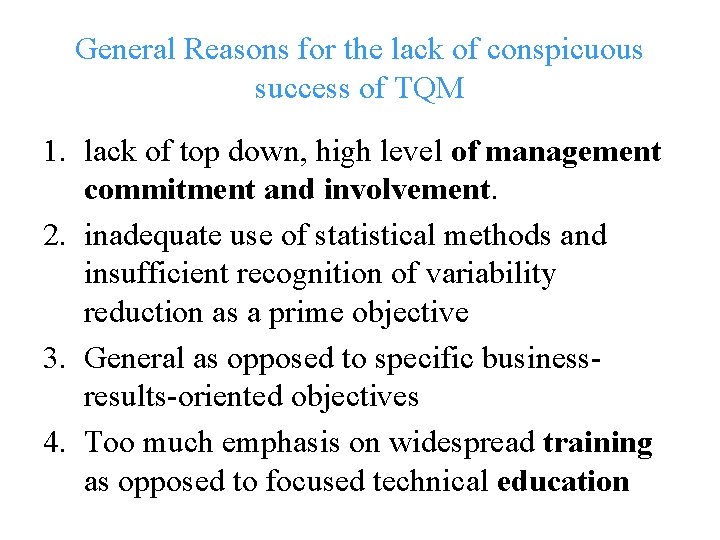
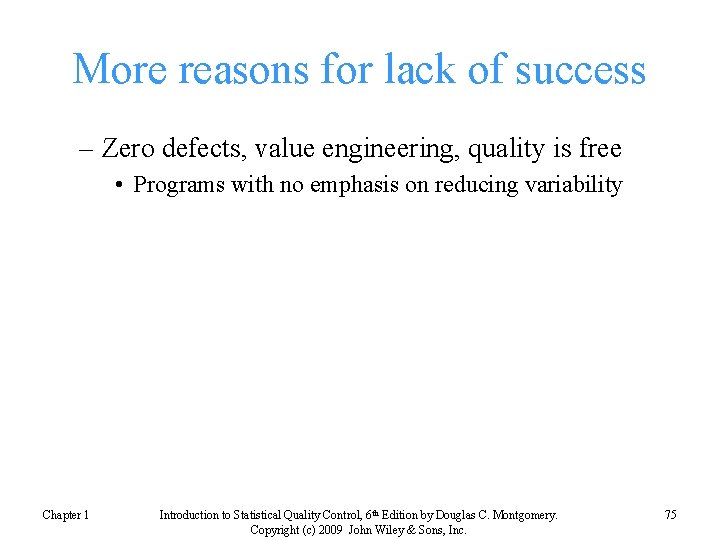
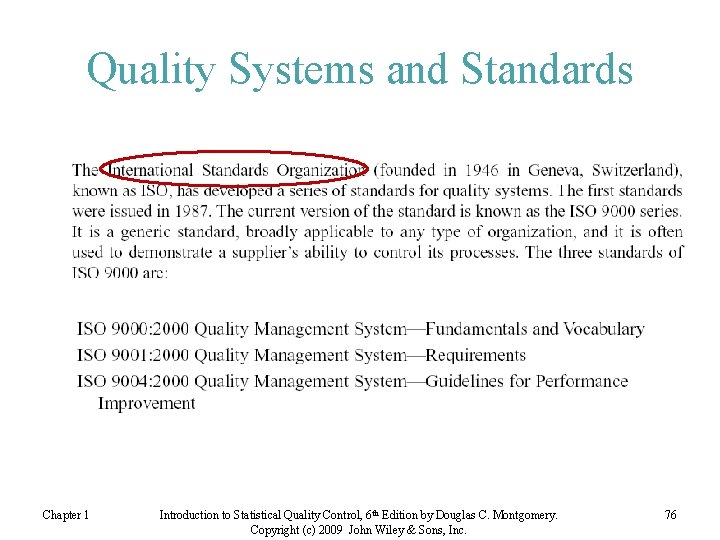
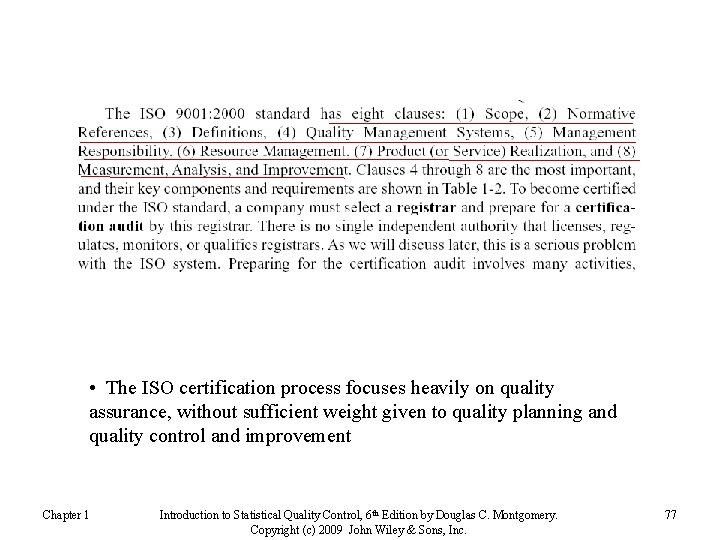
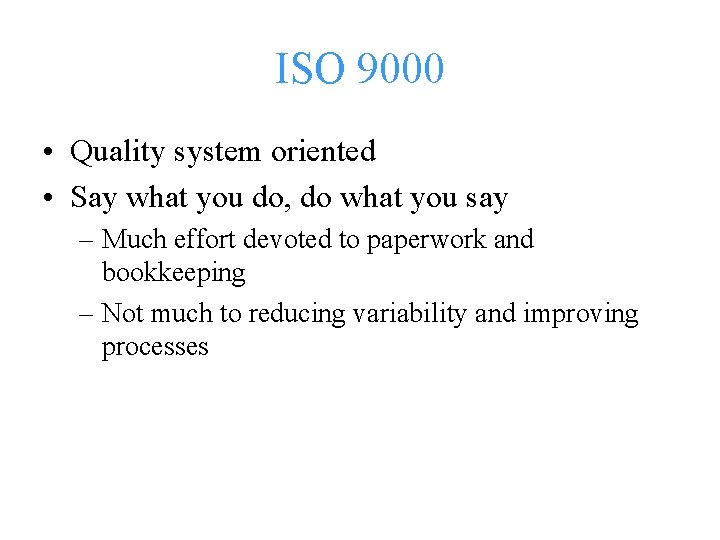
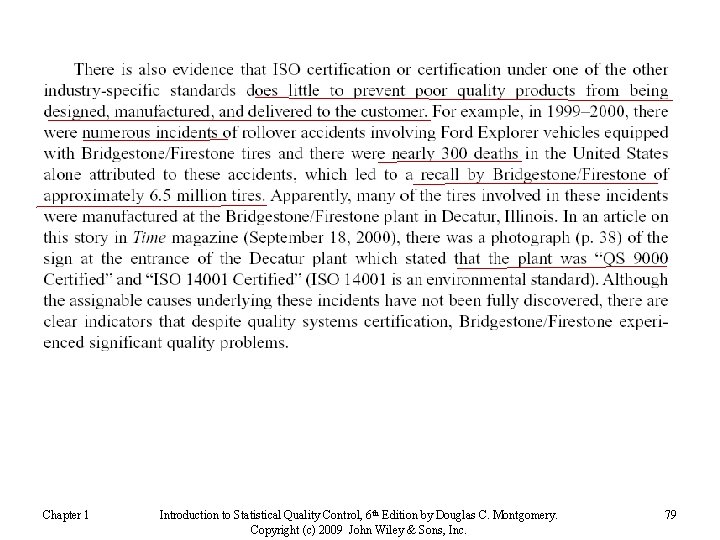
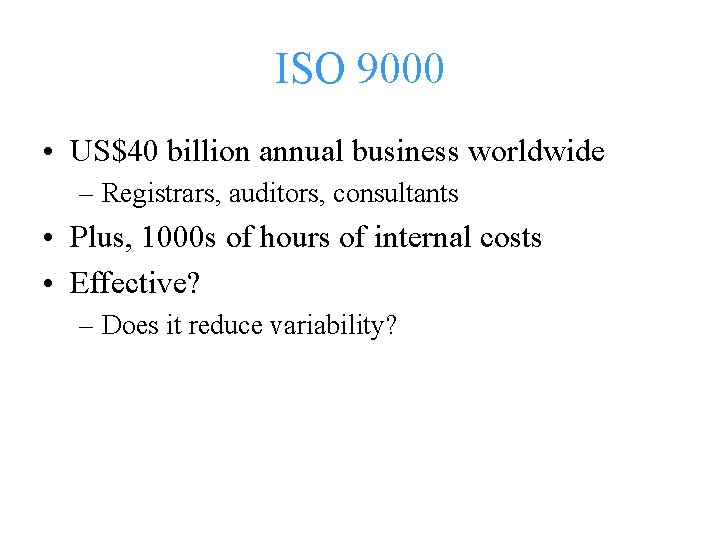
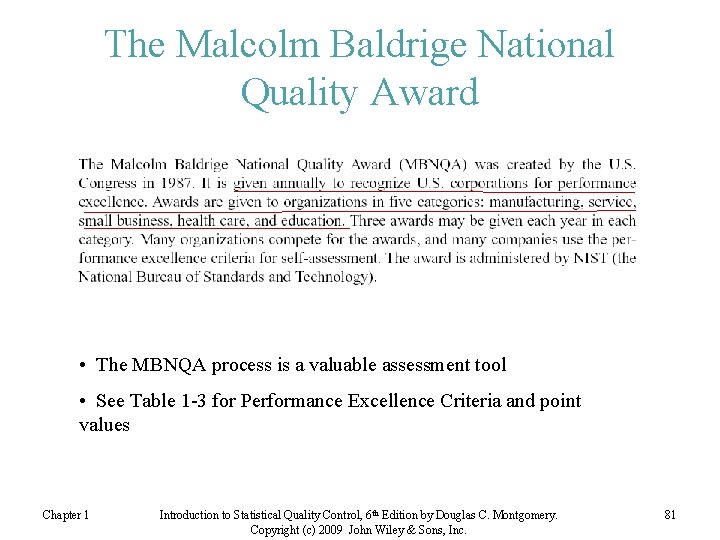
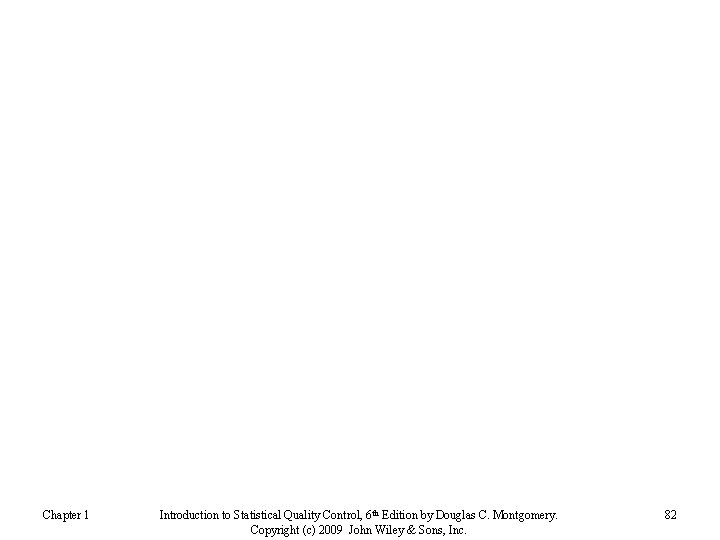
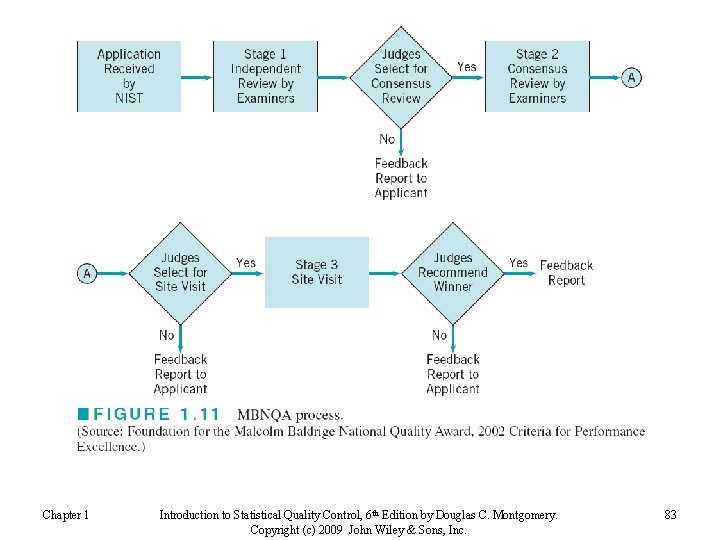
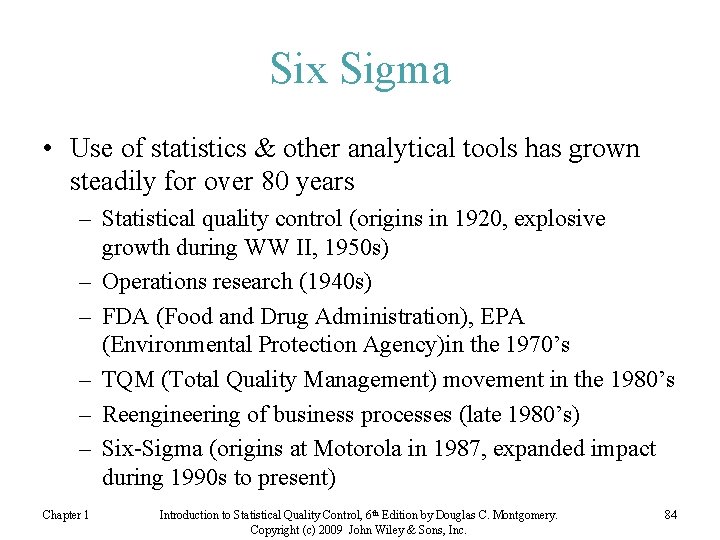
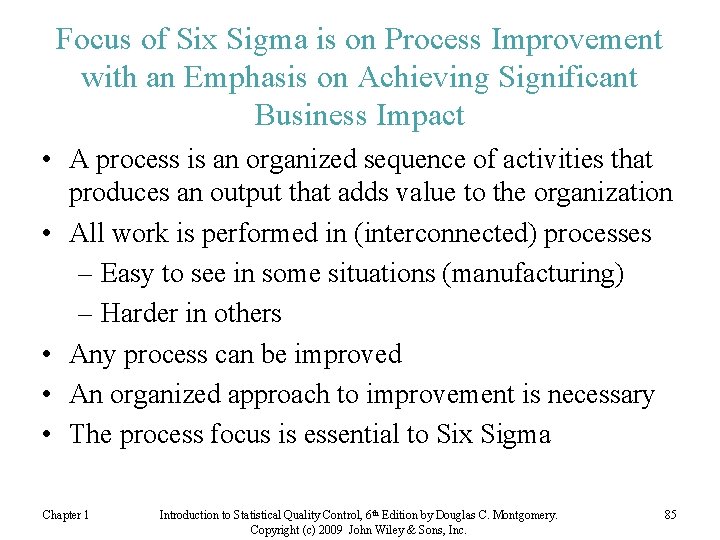
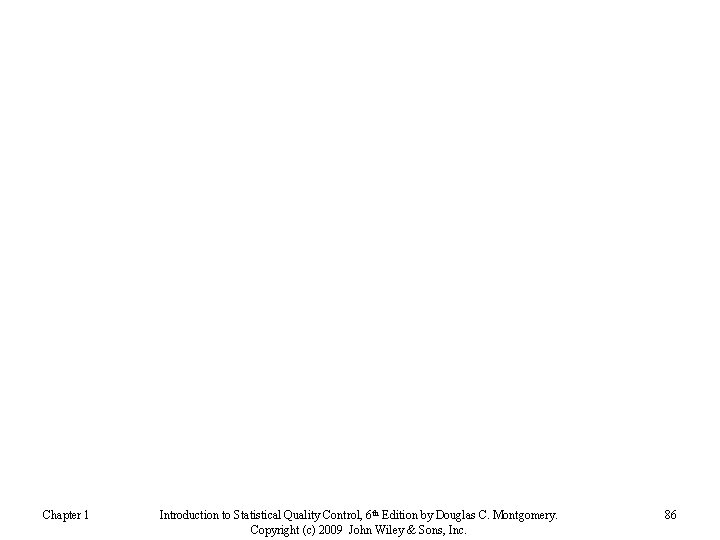
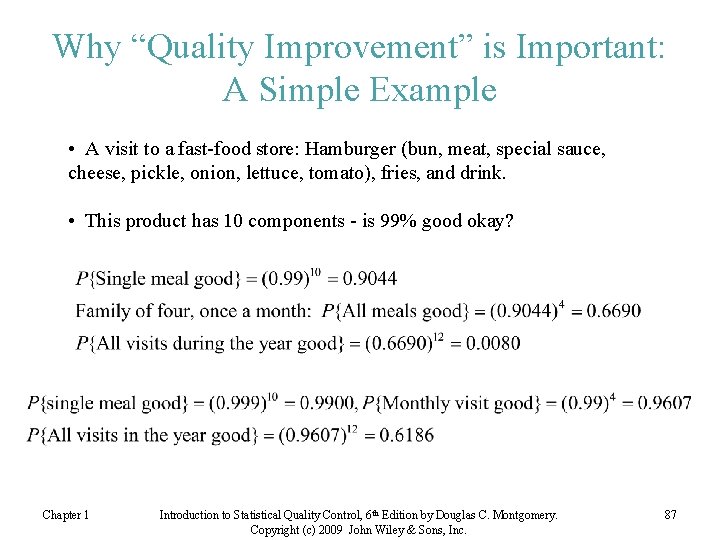
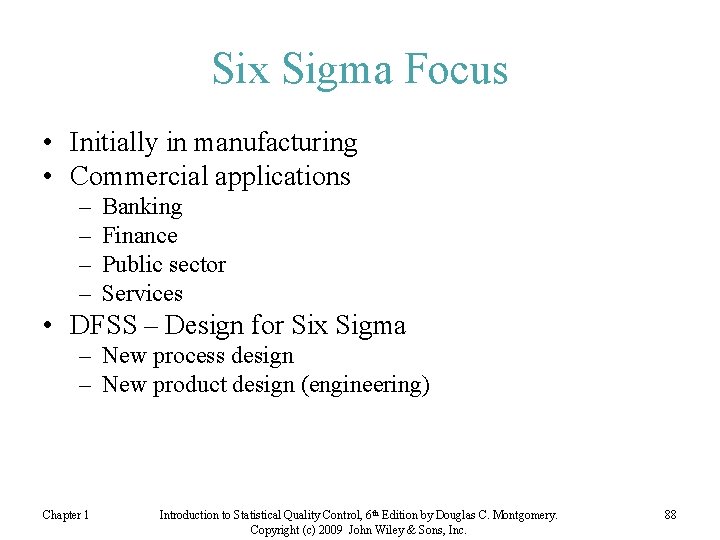
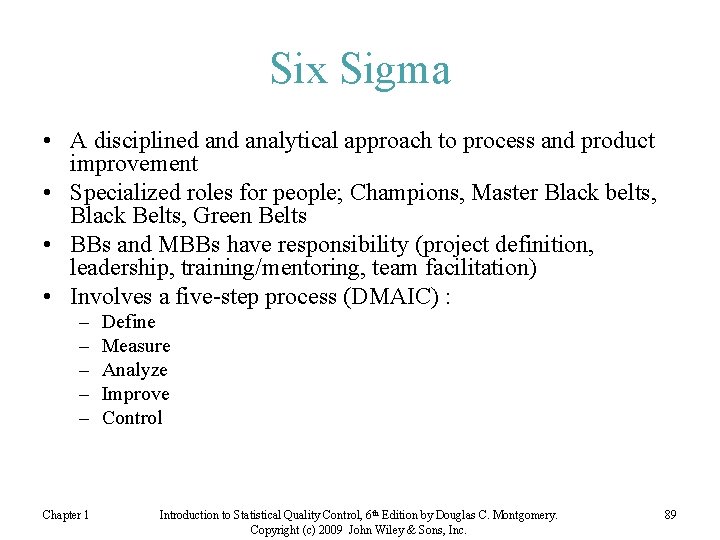
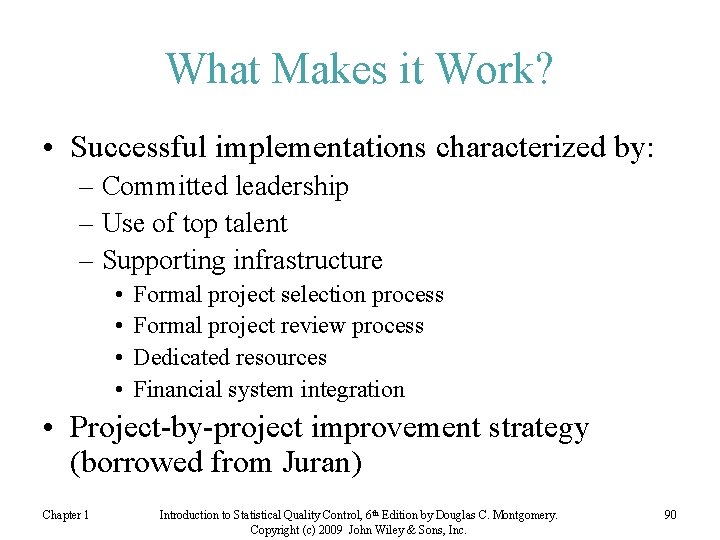
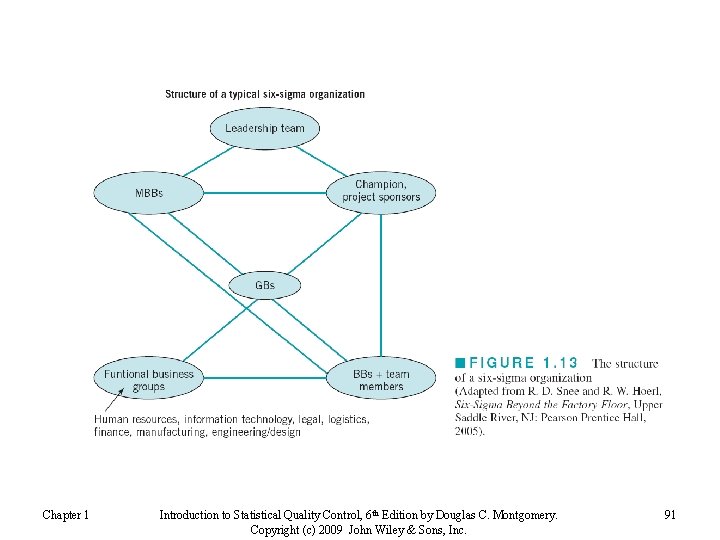
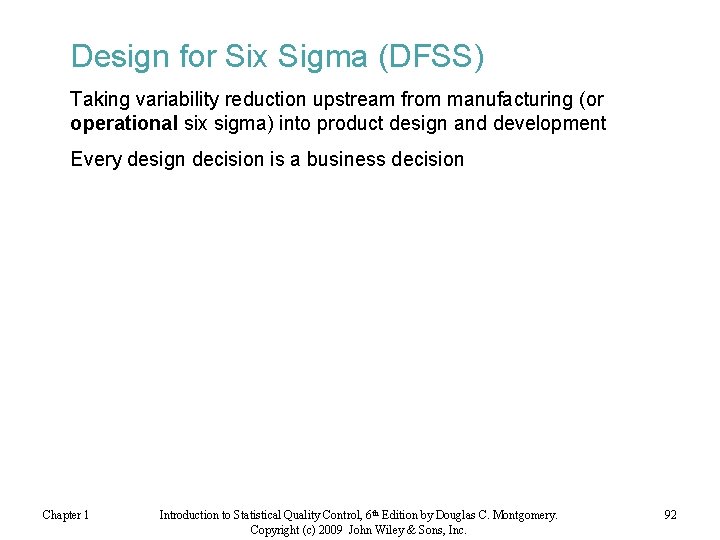
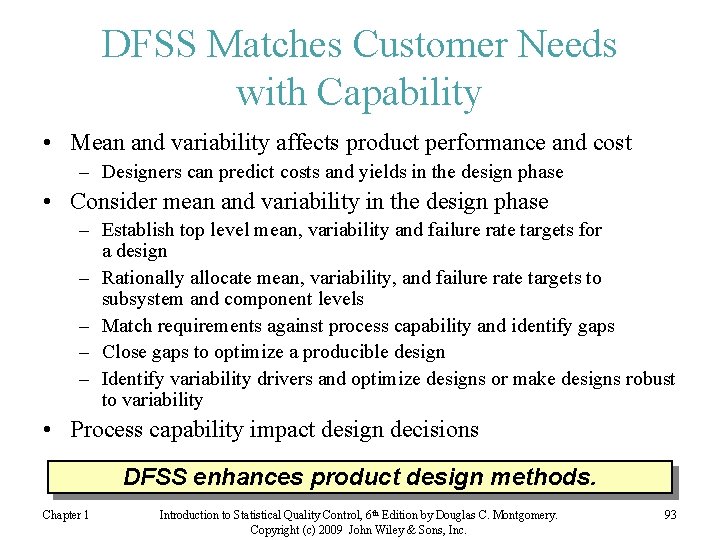
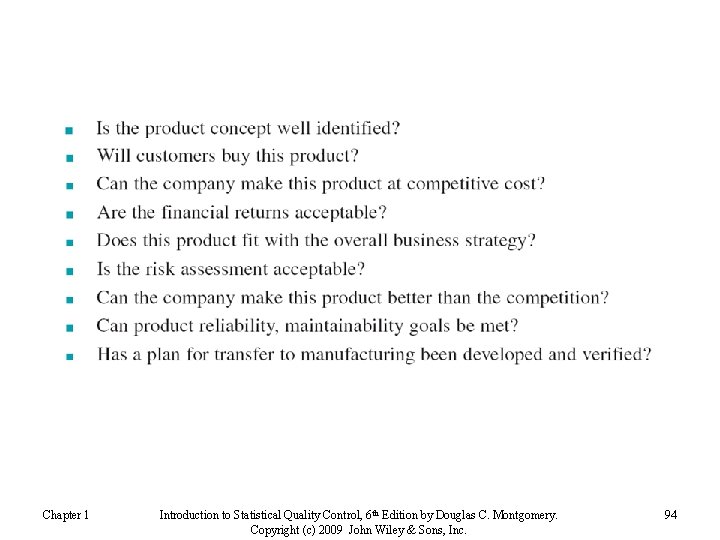
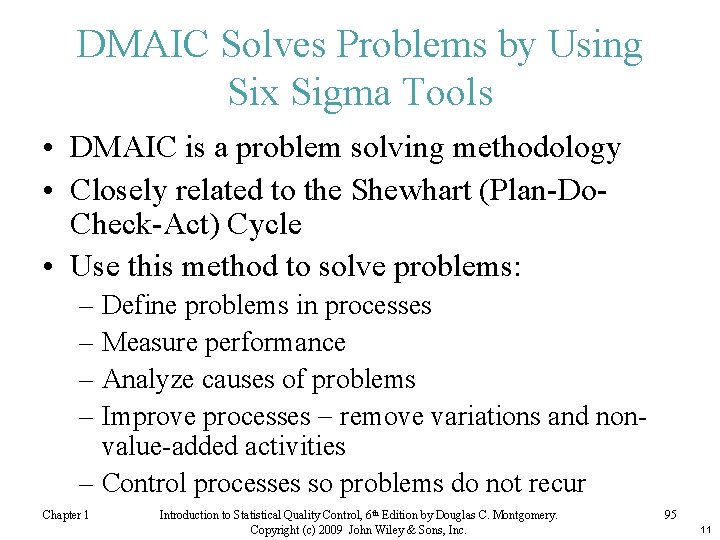
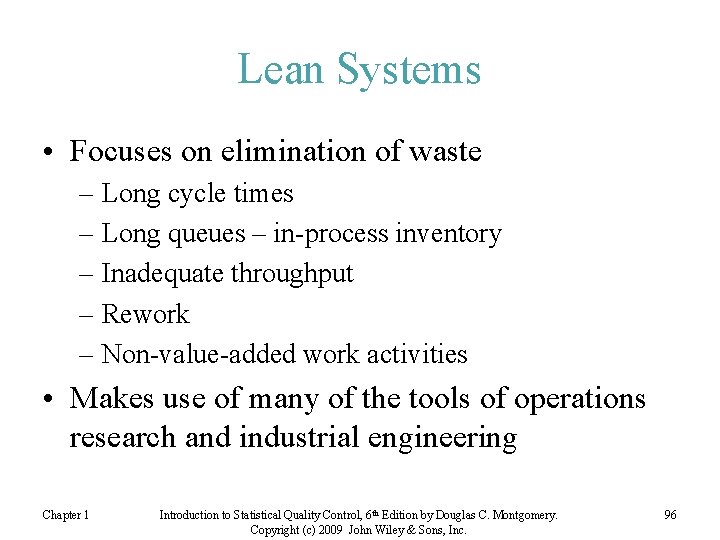
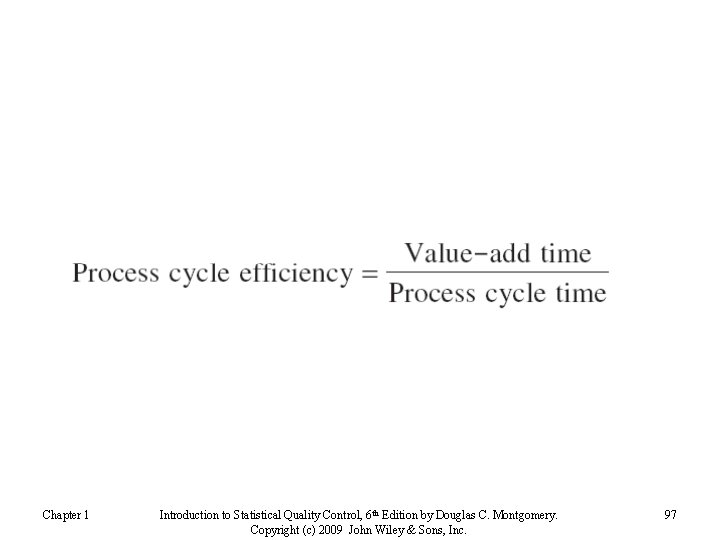
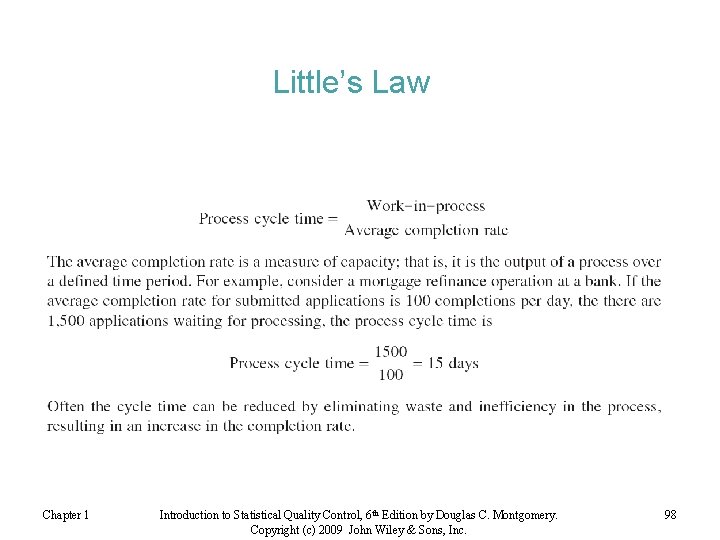
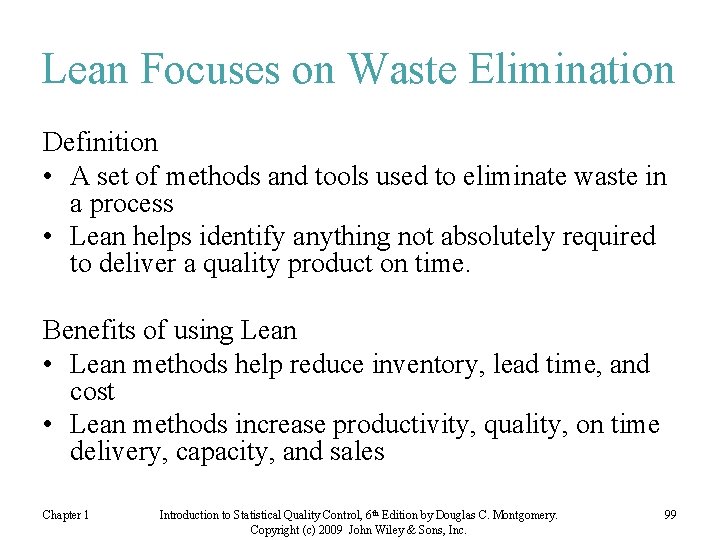
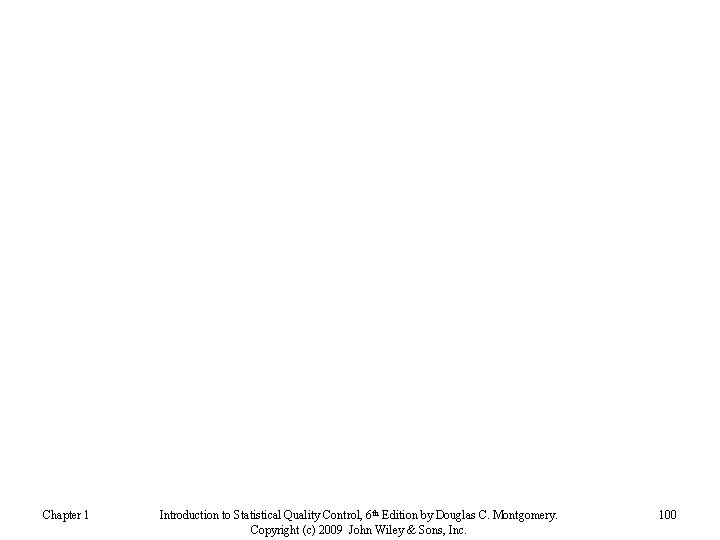
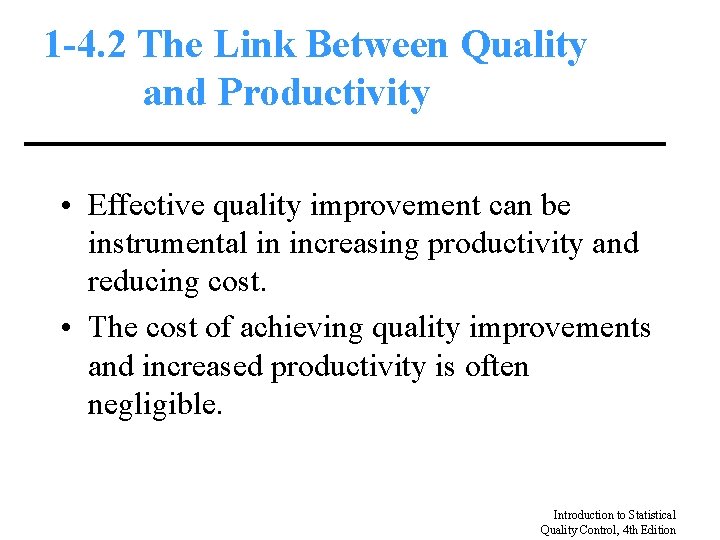
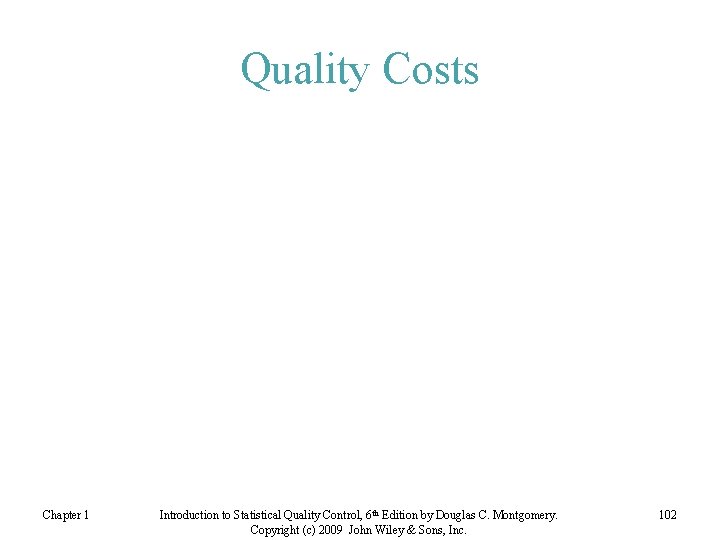
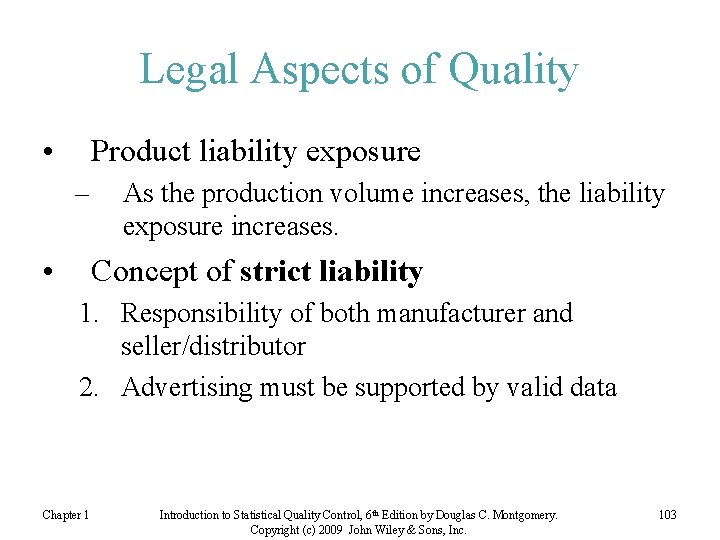
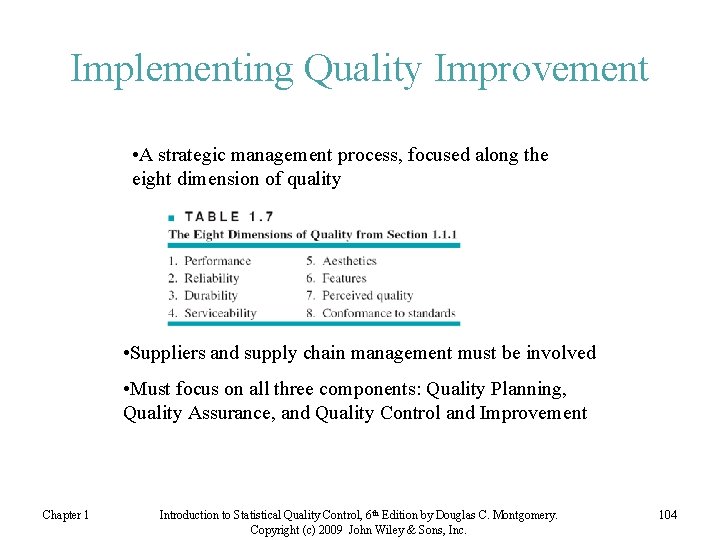
- Slides: 100
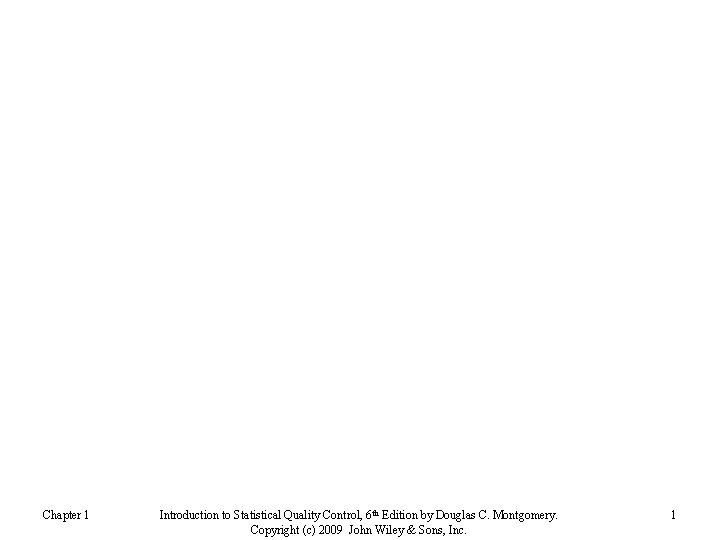
Chapter 1 Introduction to Statistical Quality Control, 6 th Edition by Douglas C. Montgomery. Copyright (c) 2009 John Wiley & Sons, Inc. 1
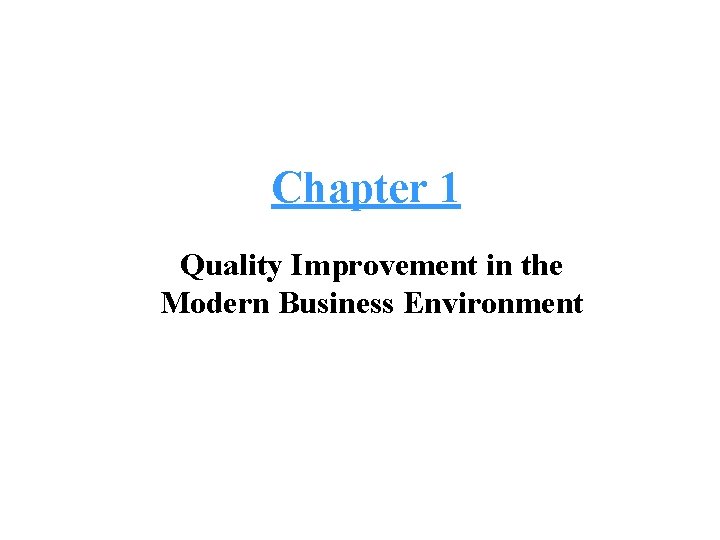
Chapter 1 Quality Improvement in the Modern Business Environment
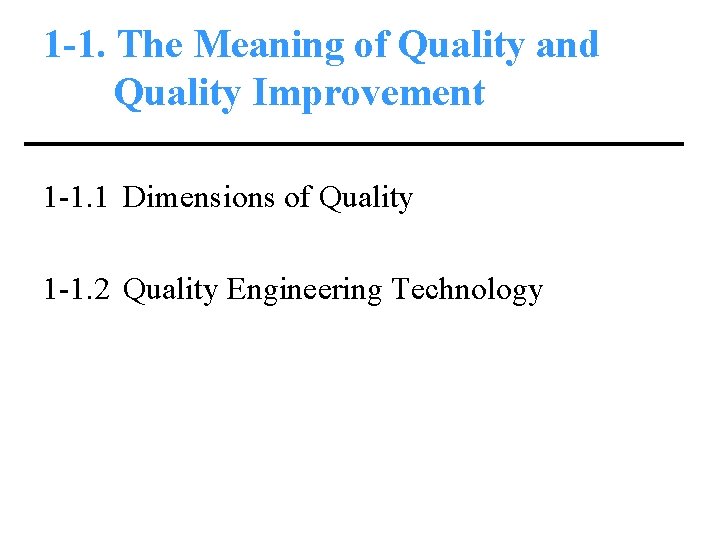
1 -1. The Meaning of Quality and Quality Improvement 1 -1. 1 Dimensions of Quality 1 -1. 2 Quality Engineering Technology
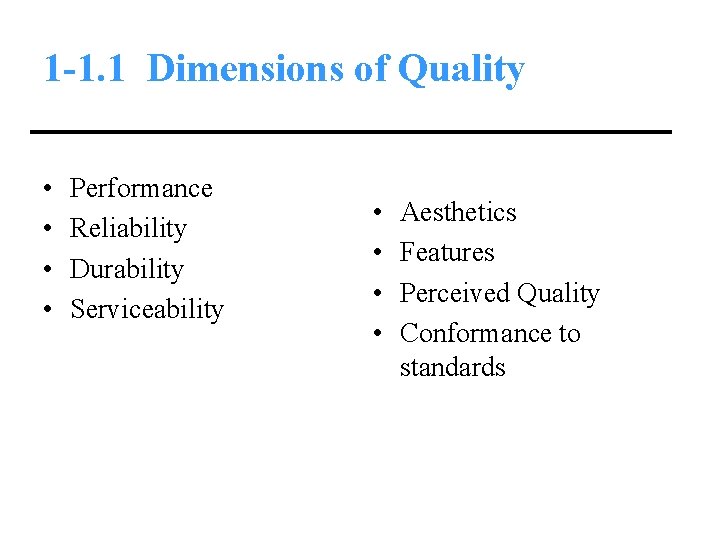
1 -1. 1 Dimensions of Quality • • Performance Reliability Durability Serviceability • • Aesthetics Features Perceived Quality Conformance to standards
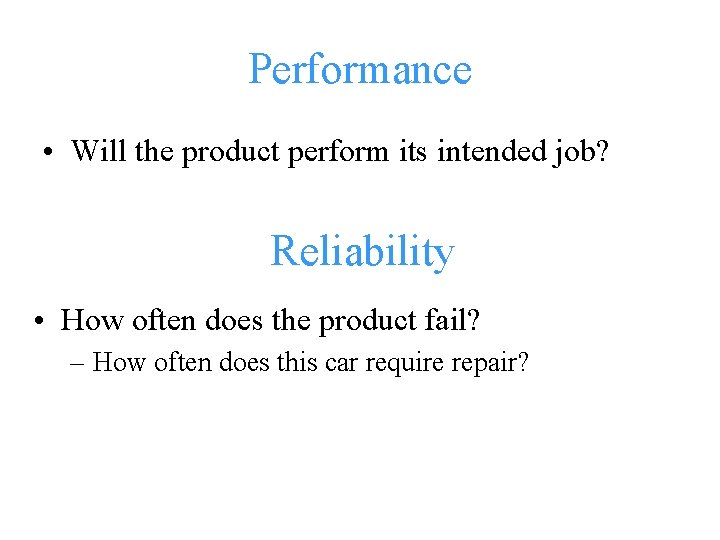
Performance • Will the product perform its intended job? Reliability • How often does the product fail? – How often does this car require repair?
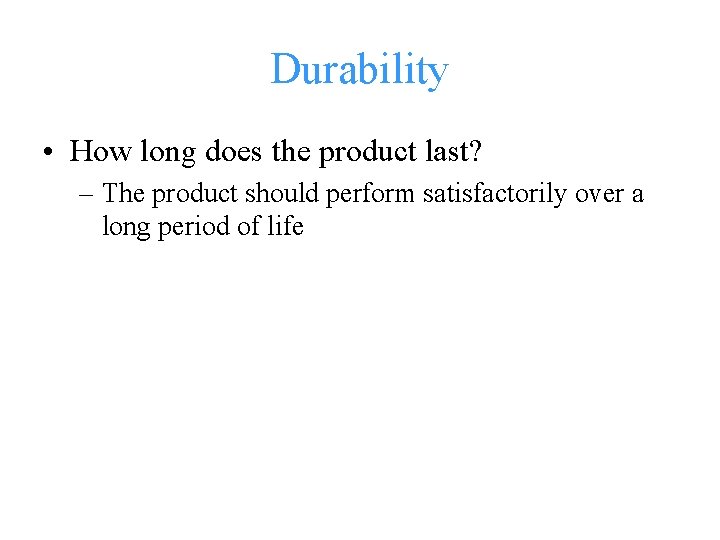
Durability • How long does the product last? – The product should perform satisfactorily over a long period of life
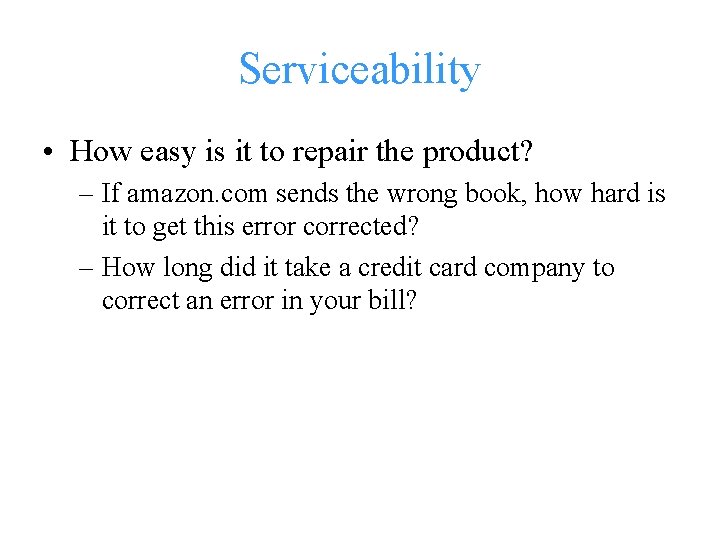
Serviceability • How easy is it to repair the product? – If amazon. com sends the wrong book, how hard is it to get this error corrected? – How long did it take a credit card company to correct an error in your bill?

Aesthetics • What does the product look like? – Do you like the box in which Shoes are packaged?
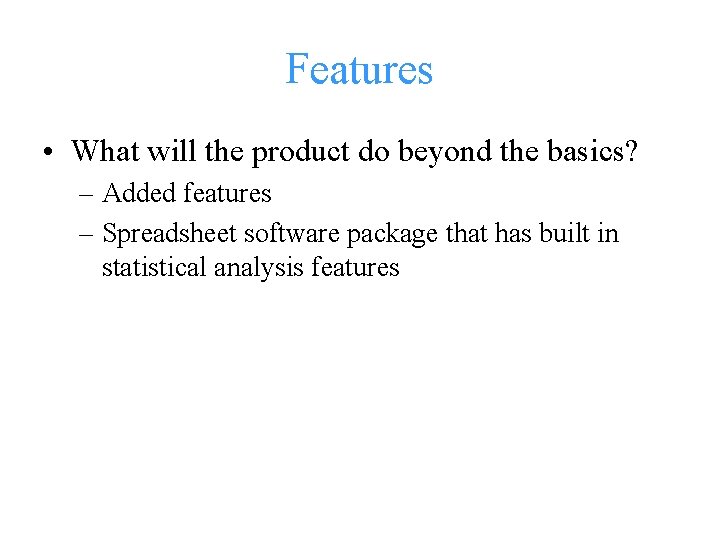
Features • What will the product do beyond the basics? – Added features – Spreadsheet software package that has built in statistical analysis features
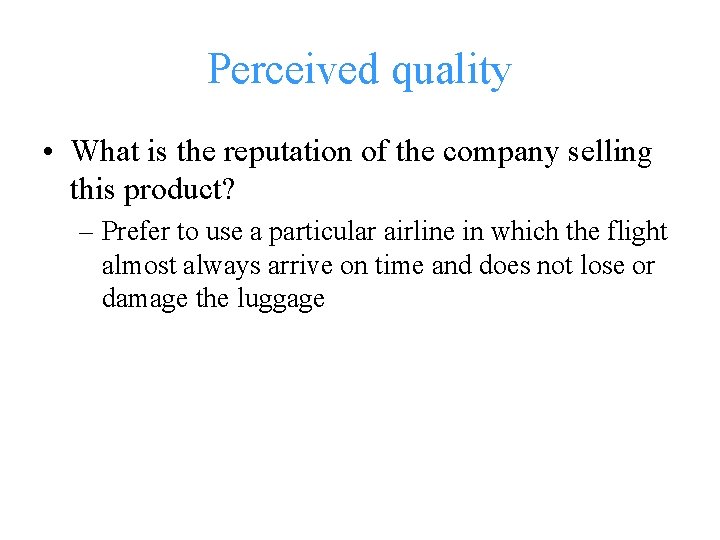
Perceived quality • What is the reputation of the company selling this product? – Prefer to use a particular airline in which the flight almost always arrive on time and does not lose or damage the luggage
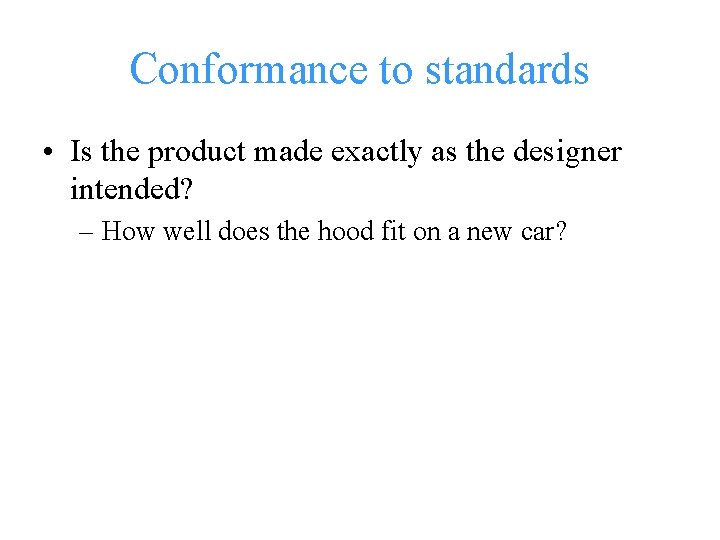
Conformance to standards • Is the product made exactly as the designer intended? – How well does the hood fit on a new car?
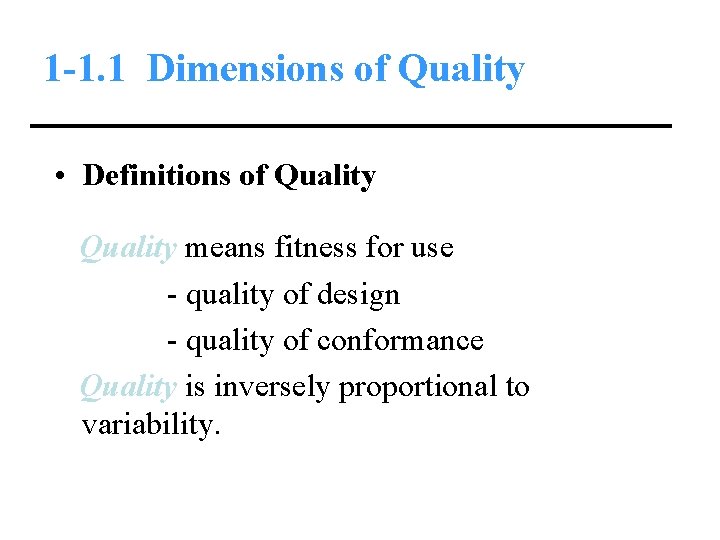
1 -1. 1 Dimensions of Quality • Definitions of Quality means fitness for use - quality of design - quality of conformance Quality is inversely proportional to variability.
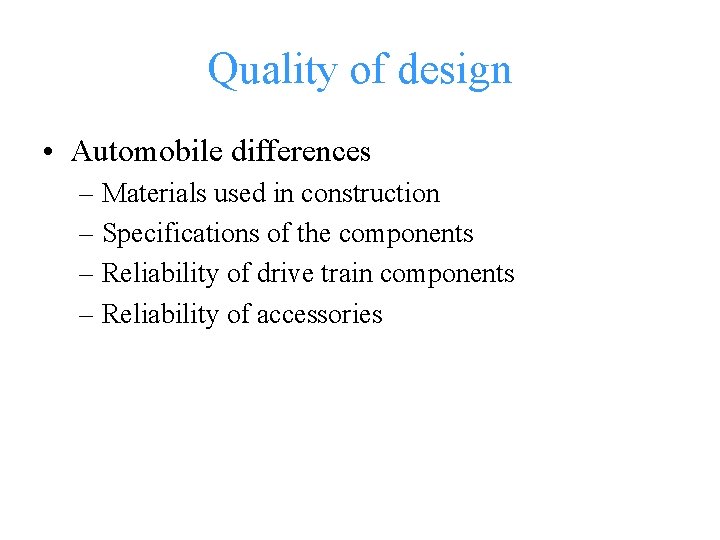
Quality of design • Automobile differences – Materials used in construction – Specifications of the components – Reliability of drive train components – Reliability of accessories
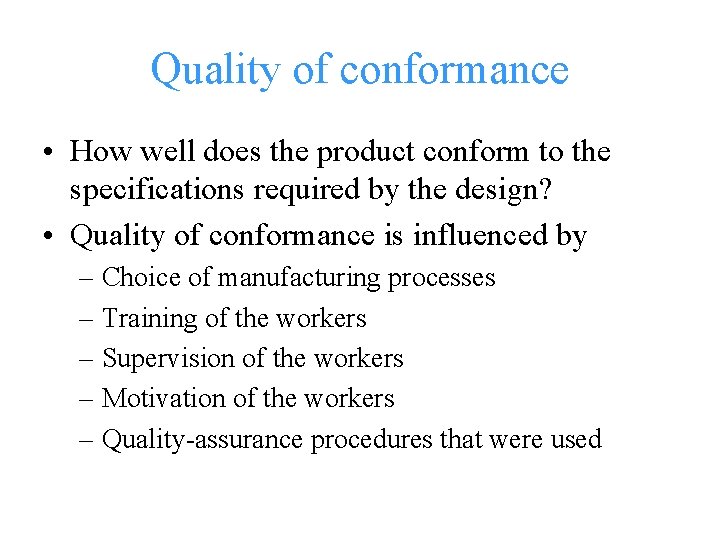
Quality of conformance • How well does the product conform to the specifications required by the design? • Quality of conformance is influenced by – Choice of manufacturing processes – Training of the workers – Supervision of the workers – Motivation of the workers – Quality-assurance procedures that were used
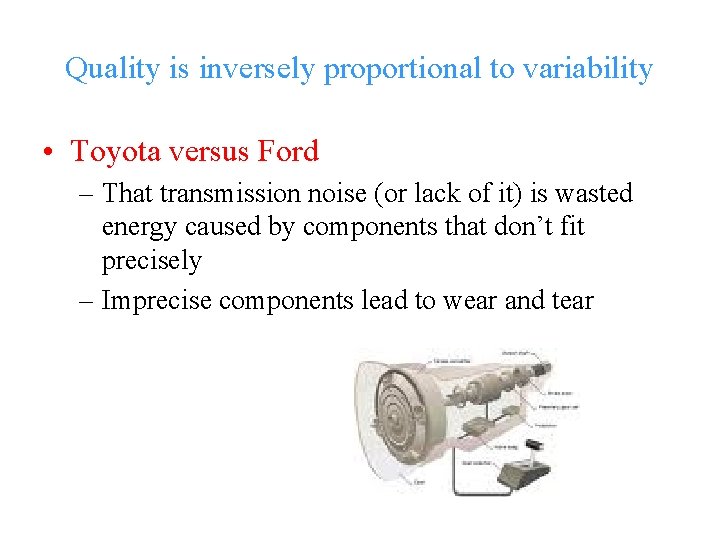
Quality is inversely proportional to variability • Toyota versus Ford – That transmission noise (or lack of it) is wasted energy caused by components that don’t fit precisely – Imprecise components lead to wear and tear
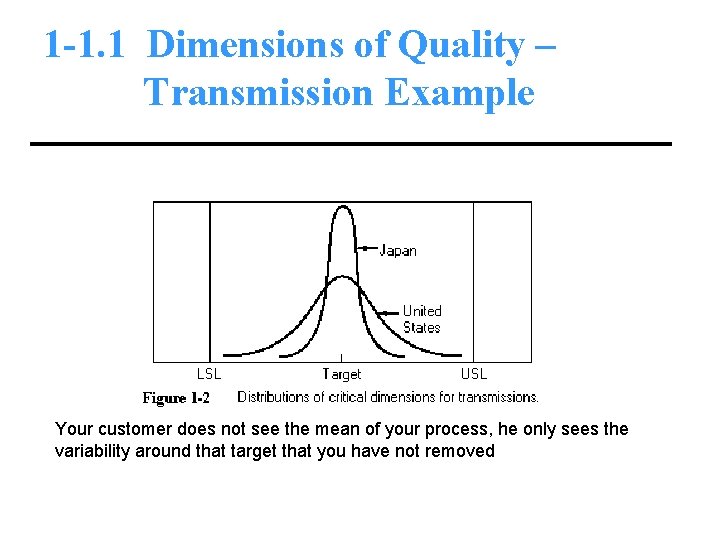
1 -1. 1 Dimensions of Quality – Transmission Example Your customer does not see the mean of your process, he only sees the variability around that target that you have not removed
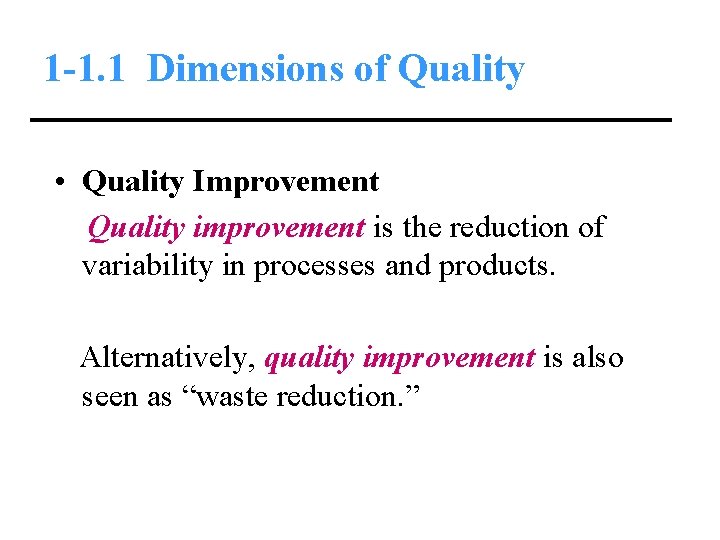
1 -1. 1 Dimensions of Quality • Quality Improvement Quality improvement is the reduction of variability in processes and products. Alternatively, quality improvement is also seen as “waste reduction. ”
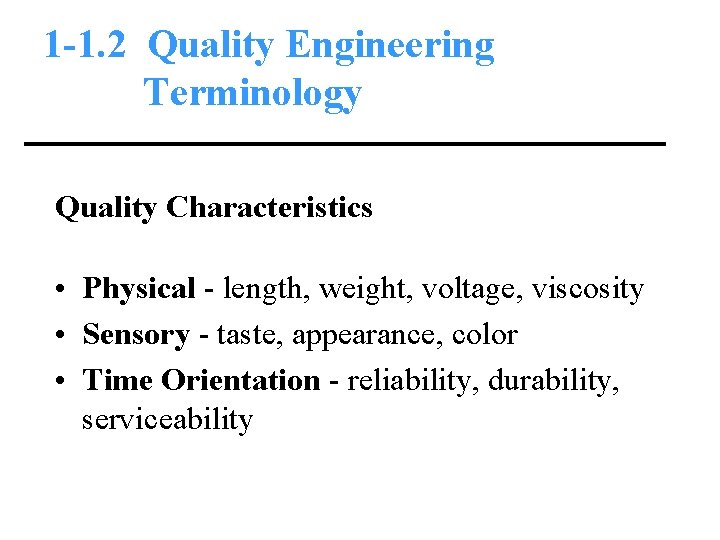
1 -1. 2 Quality Engineering Terminology Quality Characteristics • Physical - length, weight, voltage, viscosity • Sensory - taste, appearance, color • Time Orientation - reliability, durability, serviceability
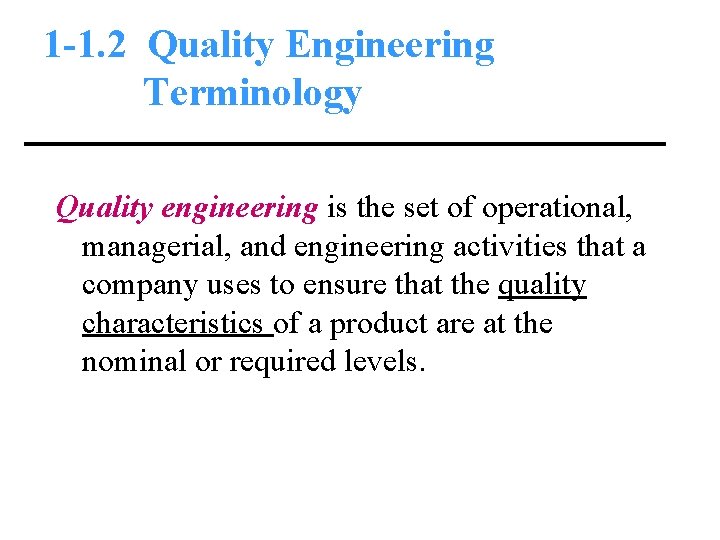
1 -1. 2 Quality Engineering Terminology Quality engineering is the set of operational, managerial, and engineering activities that a company uses to ensure that the quality characteristics of a product are at the nominal or required levels.
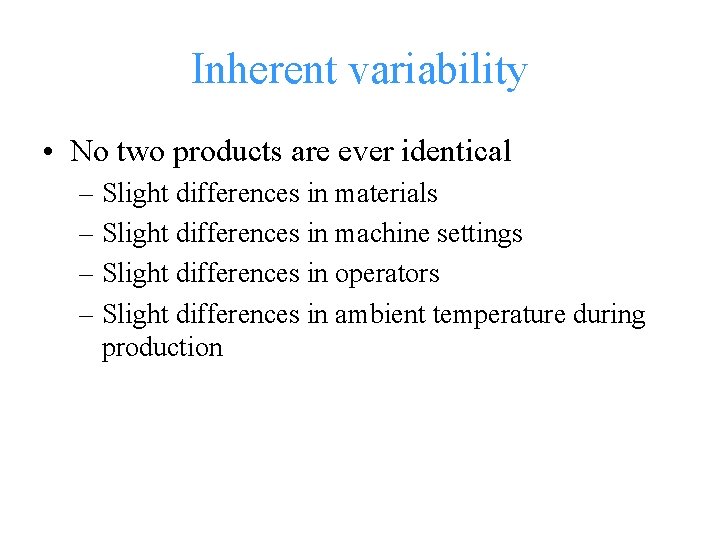
Inherent variability • No two products are ever identical – Slight differences in materials – Slight differences in machine settings – Slight differences in operators – Slight differences in ambient temperature during production
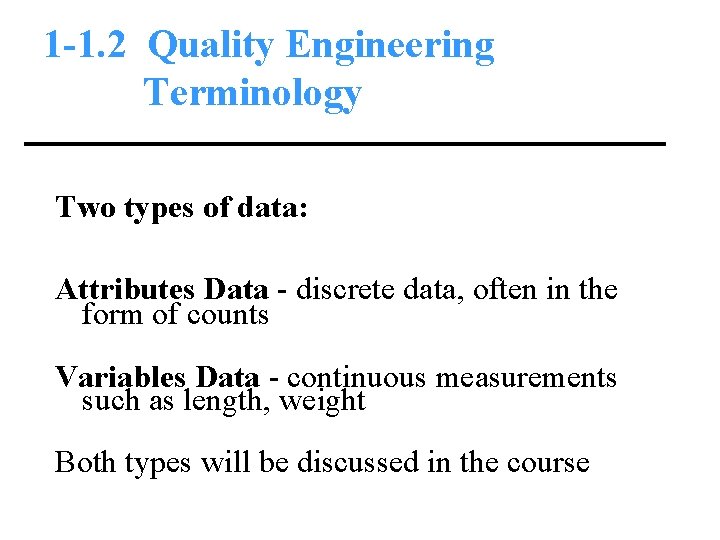
1 -1. 2 Quality Engineering Terminology Two types of data: Attributes Data - discrete data, often in the form of counts Variables Data - continuous measurements such as length, weight Both types will be discussed in the course
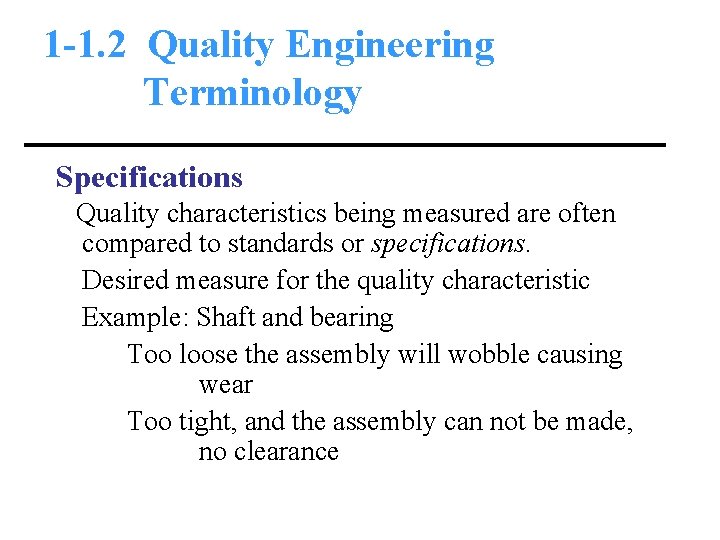
1 -1. 2 Quality Engineering Terminology Specifications Quality characteristics being measured are often compared to standards or specifications. Desired measure for the quality characteristic Example: Shaft and bearing Too loose the assembly will wobble causing wear Too tight, and the assembly can not be made, no clearance
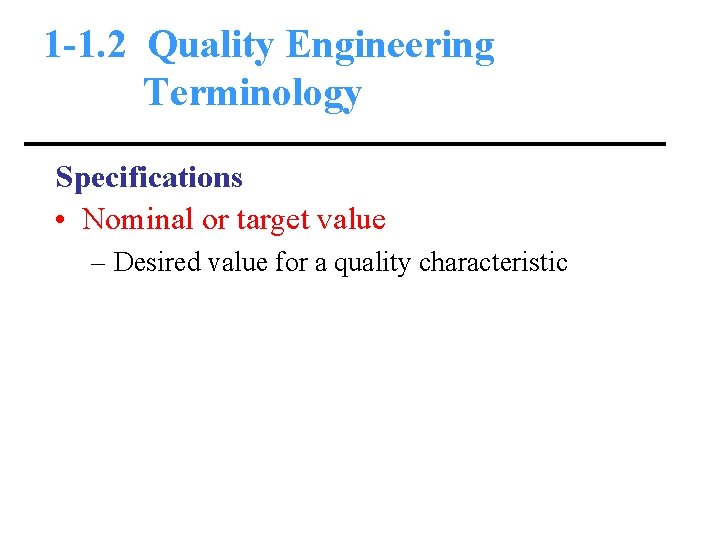
1 -1. 2 Quality Engineering Terminology Specifications • Nominal or target value – Desired value for a quality characteristic
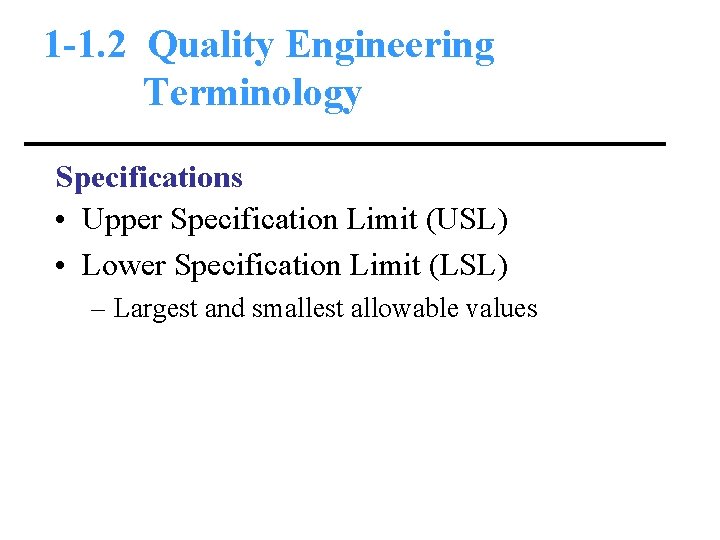
1 -1. 2 Quality Engineering Terminology Specifications • Upper Specification Limit (USL) • Lower Specification Limit (LSL) – Largest and smallest allowable values
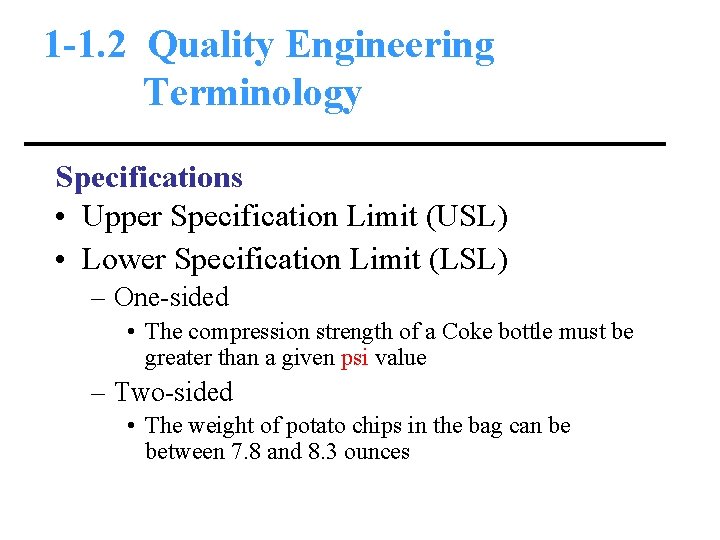
1 -1. 2 Quality Engineering Terminology Specifications • Upper Specification Limit (USL) • Lower Specification Limit (LSL) – One-sided • The compression strength of a Coke bottle must be greater than a given psi value – Two-sided • The weight of potato chips in the bag can be between 7. 8 and 8. 3 ounces
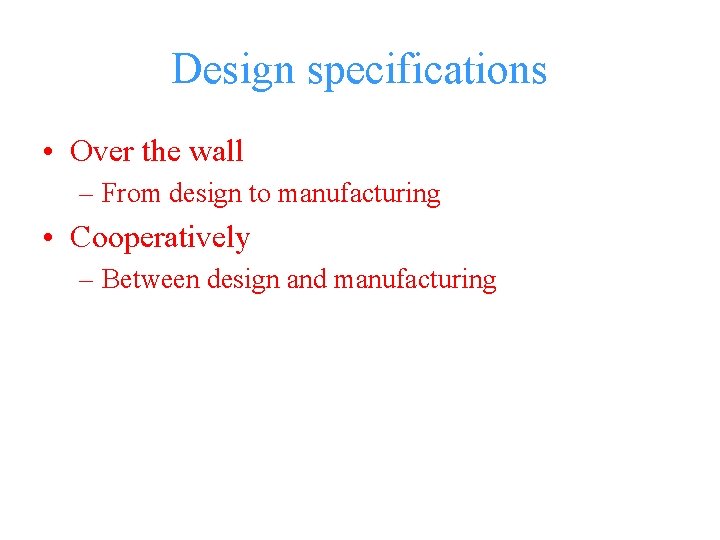
Design specifications • Over the wall – From design to manufacturing • Cooperatively – Between design and manufacturing
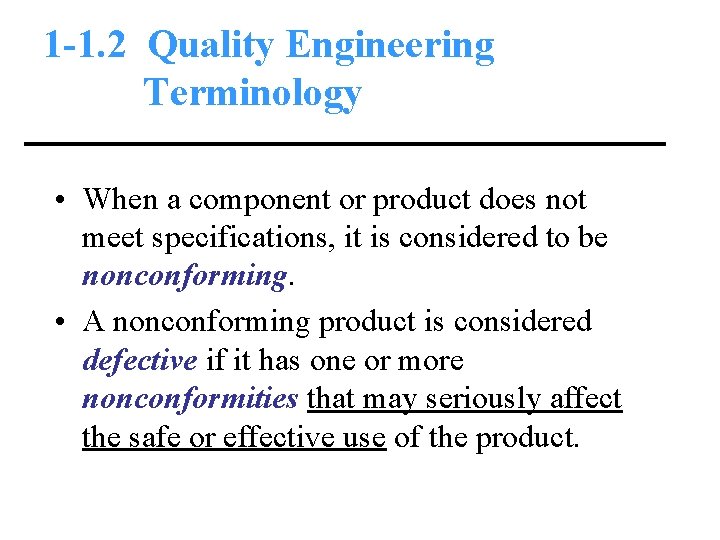
1 -1. 2 Quality Engineering Terminology • When a component or product does not meet specifications, it is considered to be nonconforming. • A nonconforming product is considered defective if it has one or more nonconformities that may seriously affect the safe or effective use of the product.
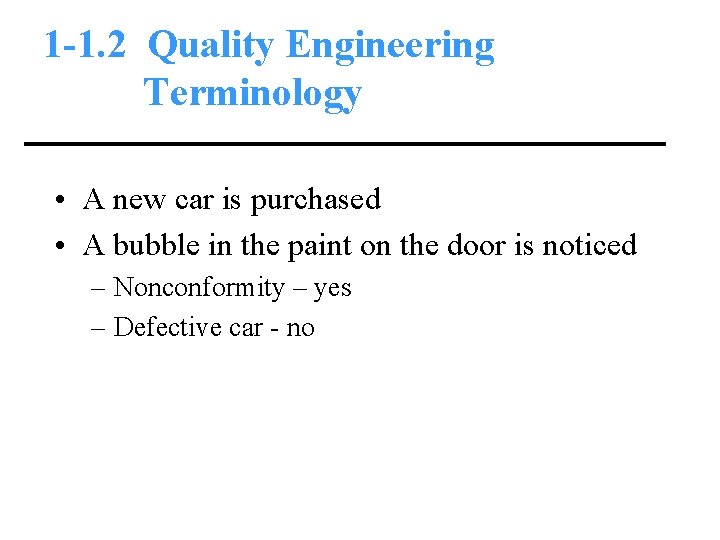
1 -1. 2 Quality Engineering Terminology • A new car is purchased • A bubble in the paint on the door is noticed – Nonconformity – yes – Defective car - no
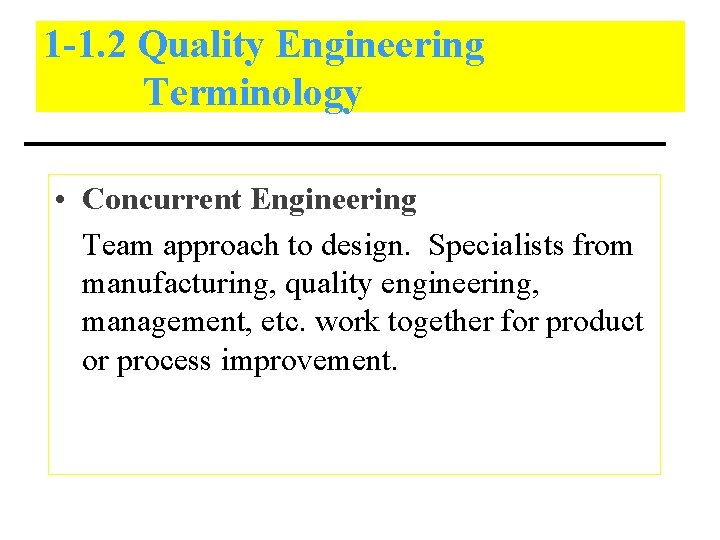
1 -1. 2 Quality Engineering Terminology • Concurrent Engineering Team approach to design. Specialists from manufacturing, quality engineering, management, etc. work together for product or process improvement.
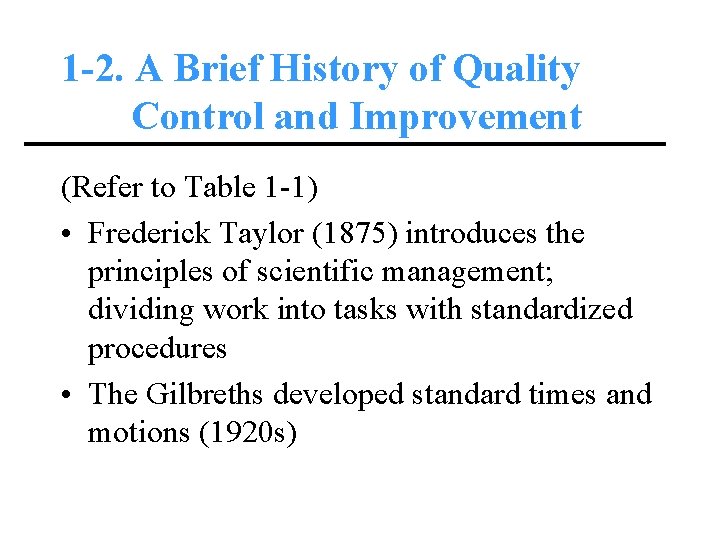
1 -2. A Brief History of Quality Control and Improvement (Refer to Table 1 -1) • Frederick Taylor (1875) introduces the principles of scientific management; dividing work into tasks with standardized procedures • The Gilbreths developed standard times and motions (1920 s)

1 -2. A Brief History of Quality Control and Improvement (Refer to Table 1 -1) • Walter Shewhart (1924) introduced statistical control chart concepts and QC begins • Dodge and Romig (1928), Bell Labs, develop acceptance sampling as an alternate to 100% inspection • During WW II the shells didn’t fit the howitzers leading to development of MIL-STDs
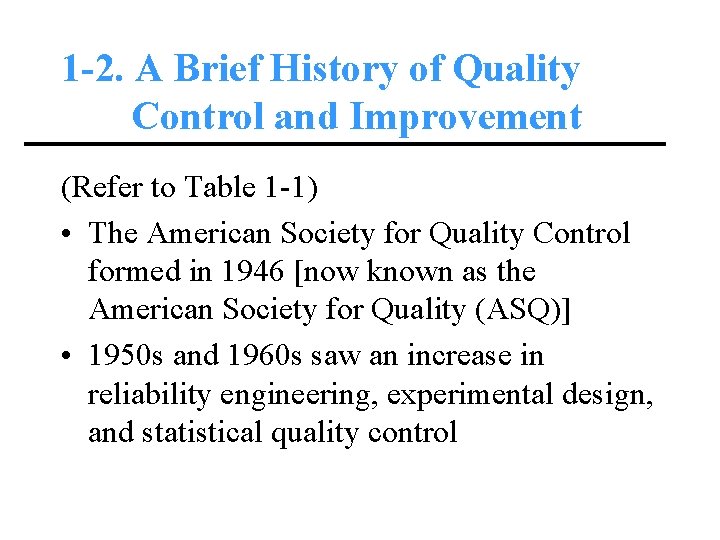
1 -2. A Brief History of Quality Control and Improvement (Refer to Table 1 -1) • The American Society for Quality Control formed in 1946 [now known as the American Society for Quality (ASQ)] • 1950 s and 1960 s saw an increase in reliability engineering, experimental design, and statistical quality control
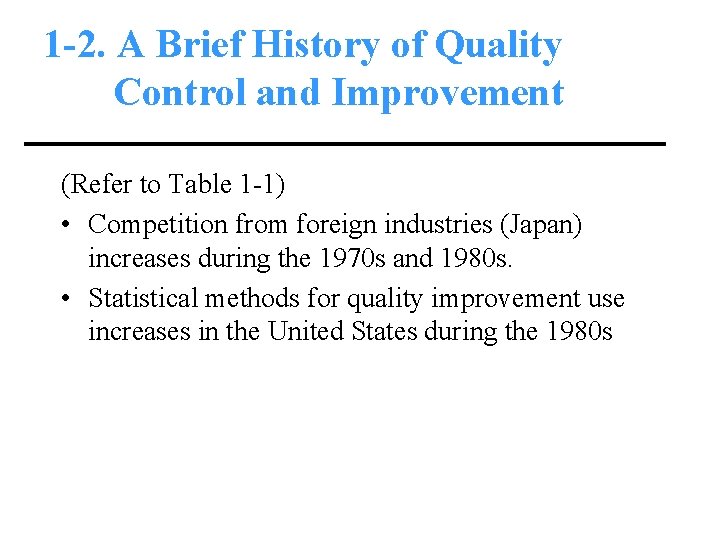
1 -2. A Brief History of Quality Control and Improvement (Refer to Table 1 -1) • Competition from foreign industries (Japan) increases during the 1970 s and 1980 s. • Statistical methods for quality improvement use increases in the United States during the 1980 s
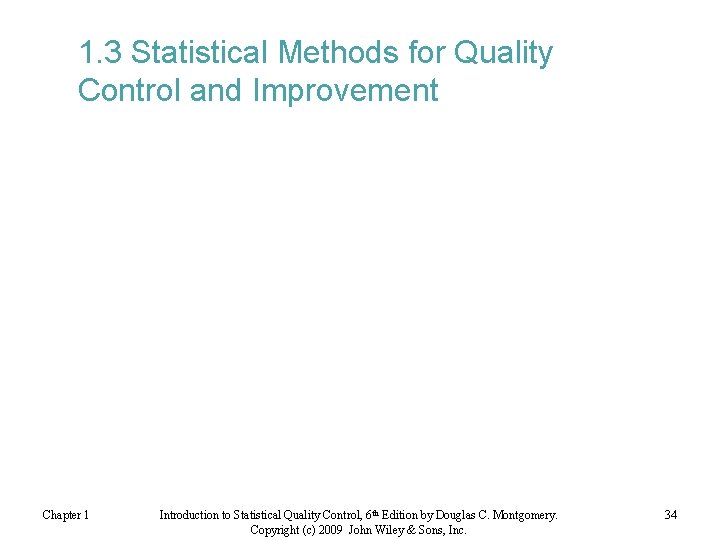
1. 3 Statistical Methods for Quality Control and Improvement Chapter 1 Introduction to Statistical Quality Control, 6 th Edition by Douglas C. Montgomery. Copyright (c) 2009 John Wiley & Sons, Inc. 34
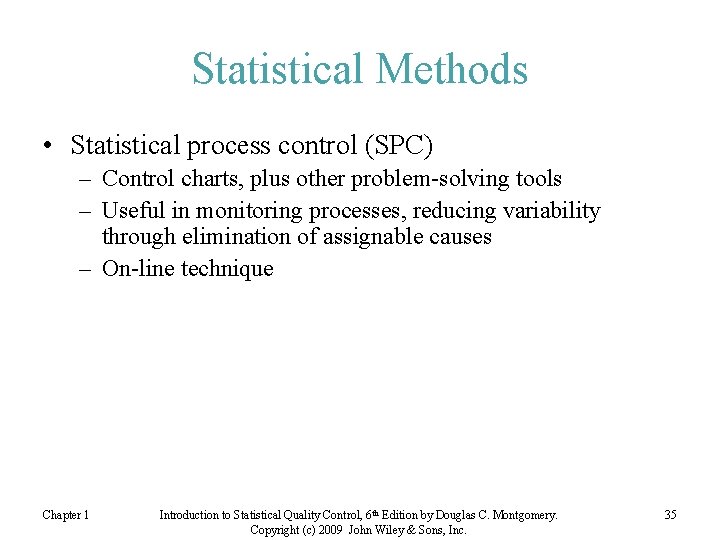
Statistical Methods • Statistical process control (SPC) – Control charts, plus other problem-solving tools – Useful in monitoring processes, reducing variability through elimination of assignable causes – On-line technique Chapter 1 Introduction to Statistical Quality Control, 6 th Edition by Douglas C. Montgomery. Copyright (c) 2009 John Wiley & Sons, Inc. 35
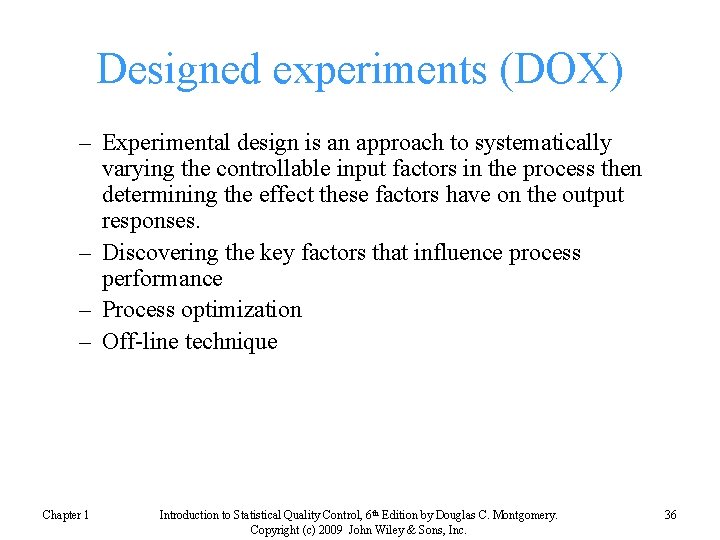
Designed experiments (DOX) – Experimental design is an approach to systematically varying the controllable input factors in the process then determining the effect these factors have on the output responses. – Discovering the key factors that influence process performance – Process optimization – Off-line technique Chapter 1 Introduction to Statistical Quality Control, 6 th Edition by Douglas C. Montgomery. Copyright (c) 2009 John Wiley & Sons, Inc. 36
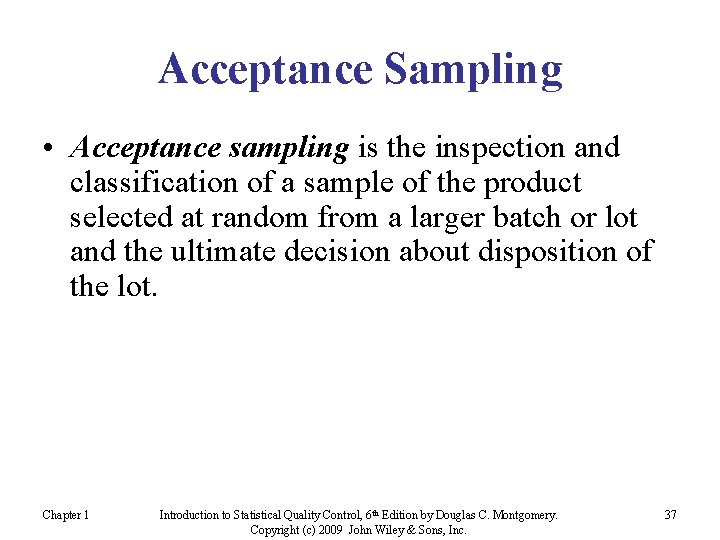
Acceptance Sampling • Acceptance sampling is the inspection and classification of a sample of the product selected at random from a larger batch or lot and the ultimate decision about disposition of the lot. Chapter 1 Introduction to Statistical Quality Control, 6 th Edition by Douglas C. Montgomery. Copyright (c) 2009 John Wiley & Sons, Inc. 37

Walter A. Shewart (1891 -1967) • Trained in engineering and physics • Long career at Bell Labs • Developed the first control chart about 1924 Chapter 1 Introduction to Statistical Quality Control, 6 th Edition by Douglas C. Montgomery. Copyright (c) 2009 John Wiley & Sons, Inc. 38
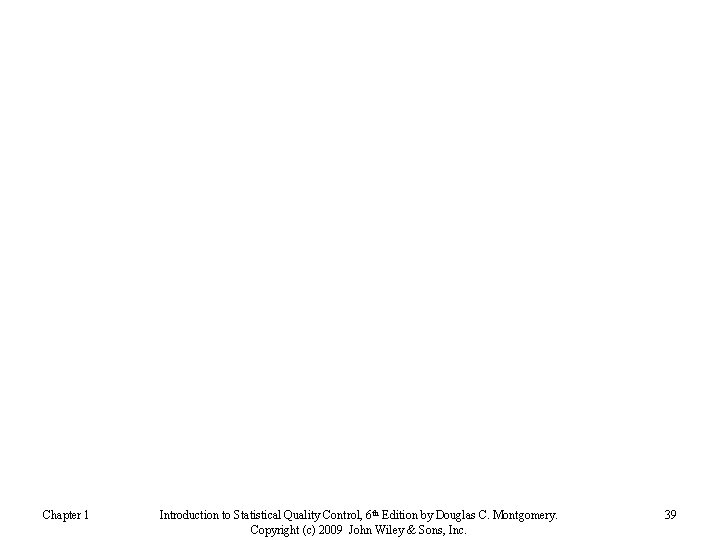
Chapter 1 Introduction to Statistical Quality Control, 6 th Edition by Douglas C. Montgomery. Copyright (c) 2009 John Wiley & Sons, Inc. 39
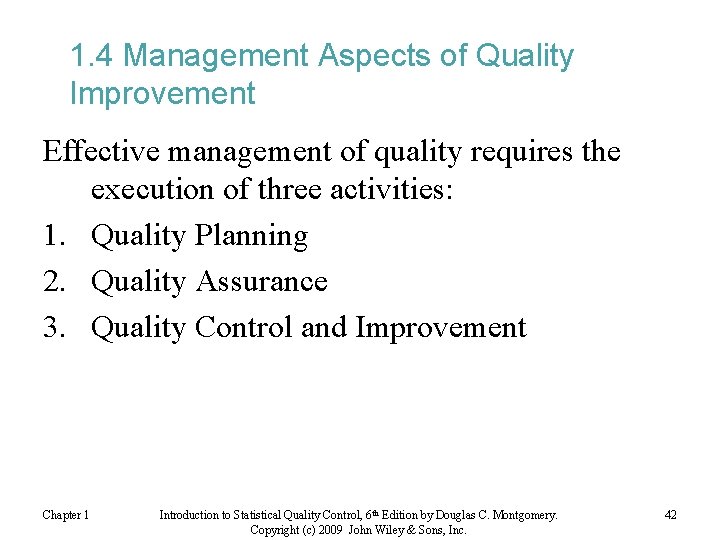
1. 4 Management Aspects of Quality Improvement Effective management of quality requires the execution of three activities: 1. Quality Planning 2. Quality Assurance 3. Quality Control and Improvement Chapter 1 Introduction to Statistical Quality Control, 6 th Edition by Douglas C. Montgomery. Copyright (c) 2009 John Wiley & Sons, Inc. 42
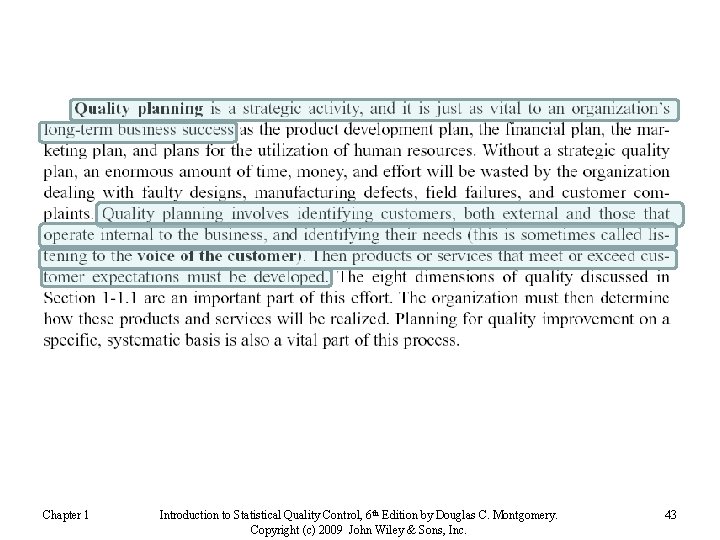
Chapter 1 Introduction to Statistical Quality Control, 6 th Edition by Douglas C. Montgomery. Copyright (c) 2009 John Wiley & Sons, Inc. 43
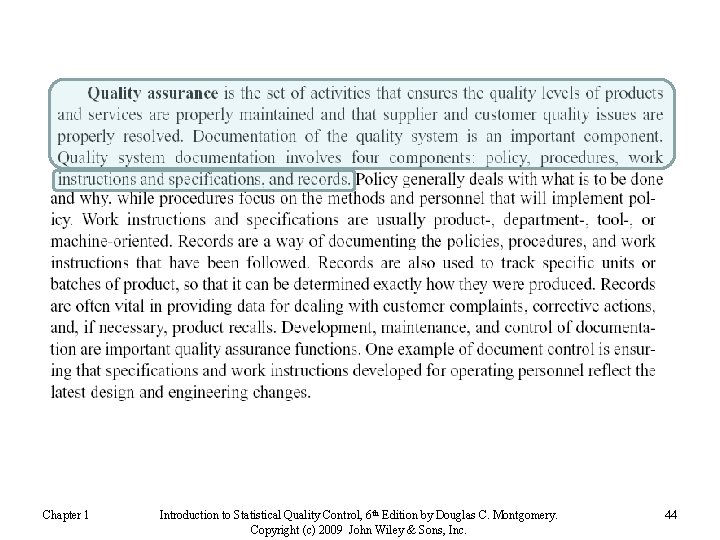
Chapter 1 Introduction to Statistical Quality Control, 6 th Edition by Douglas C. Montgomery. Copyright (c) 2009 John Wiley & Sons, Inc. 44
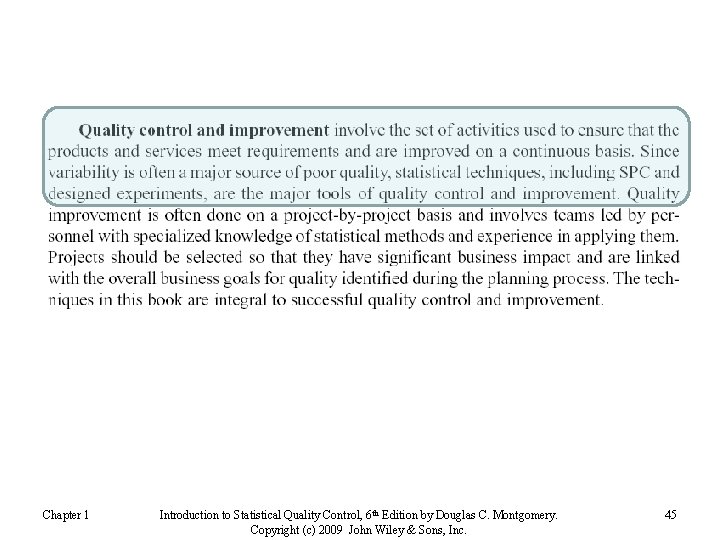
Chapter 1 Introduction to Statistical Quality Control, 6 th Edition by Douglas C. Montgomery. Copyright (c) 2009 John Wiley & Sons, Inc. 45
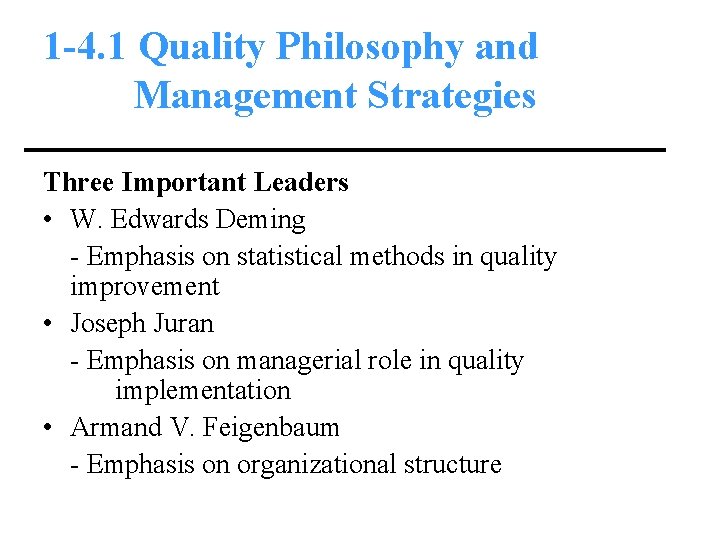
1 -4. 1 Quality Philosophy and Management Strategies Three Important Leaders • W. Edwards Deming - Emphasis on statistical methods in quality improvement • Joseph Juran - Emphasis on managerial role in quality implementation • Armand V. Feigenbaum - Emphasis on organizational structure
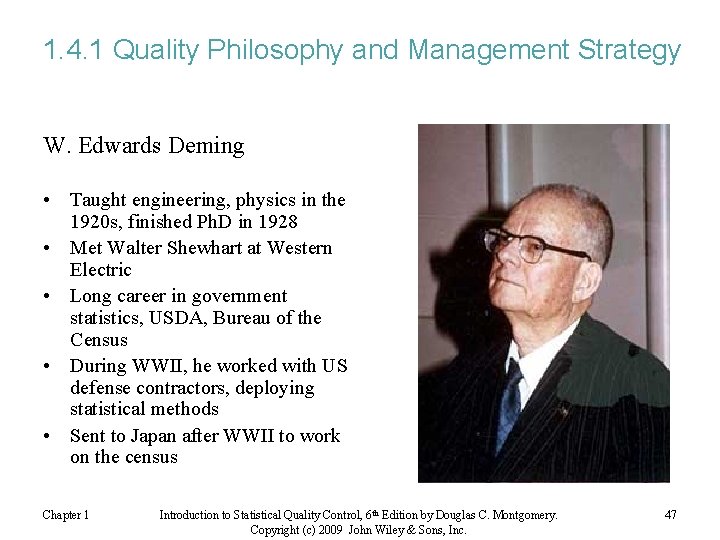
1. 4. 1 Quality Philosophy and Management Strategy W. Edwards Deming • Taught engineering, physics in the 1920 s, finished Ph. D in 1928 • Met Walter Shewhart at Western Electric • Long career in government statistics, USDA, Bureau of the Census • During WWII, he worked with US defense contractors, deploying statistical methods • Sent to Japan after WWII to work on the census Chapter 1 Introduction to Statistical Quality Control, 6 th Edition by Douglas C. Montgomery. Copyright (c) 2009 John Wiley & Sons, Inc. 47

Chapter 1 Introduction to Statistical Quality Control, 6 th Edition by Douglas C. Montgomery. Copyright (c) 2009 John Wiley & Sons, Inc. 48
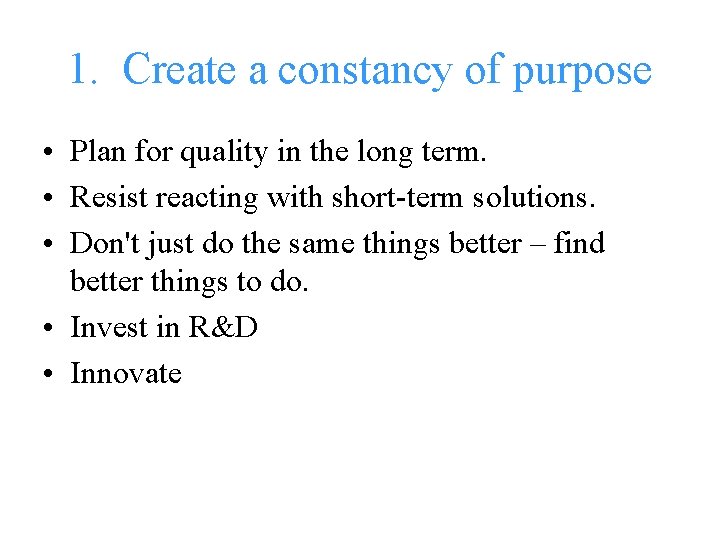
1. Create a constancy of purpose • Plan for quality in the long term. • Resist reacting with short-term solutions. • Don't just do the same things better – find better things to do. • Invest in R&D • Innovate
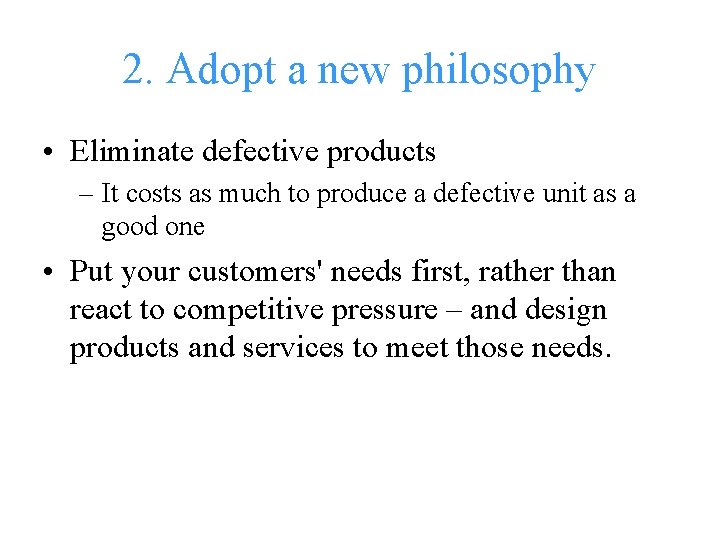
2. Adopt a new philosophy • Eliminate defective products – It costs as much to produce a defective unit as a good one • Put your customers' needs first, rather than react to competitive pressure – and design products and services to meet those needs.
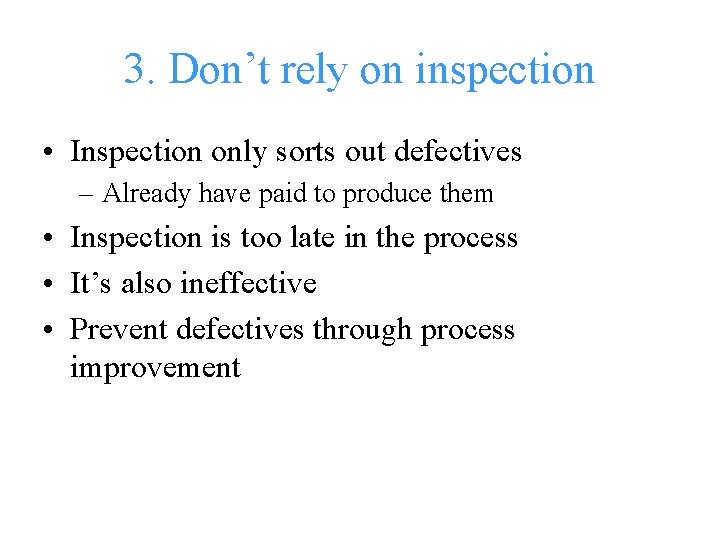
3. Don’t rely on inspection • Inspection only sorts out defectives – Already have paid to produce them • Inspection is too late in the process • It’s also ineffective • Prevent defectives through process improvement
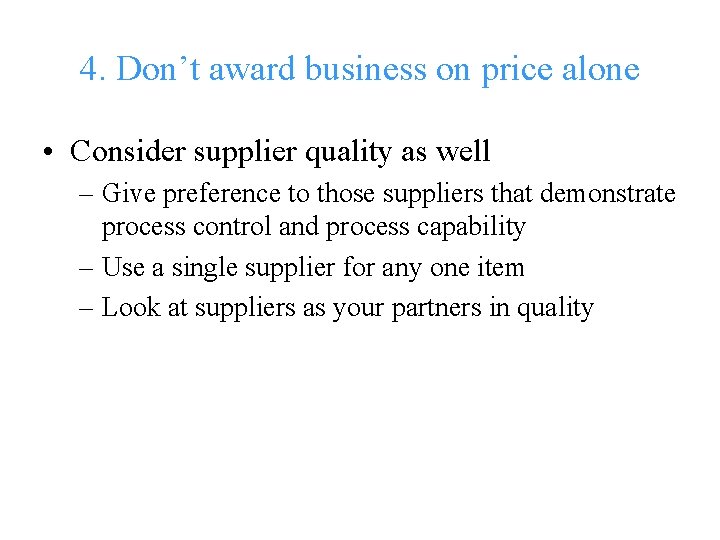
4. Don’t award business on price alone • Consider supplier quality as well – Give preference to those suppliers that demonstrate process control and process capability – Use a single supplier for any one item – Look at suppliers as your partners in quality
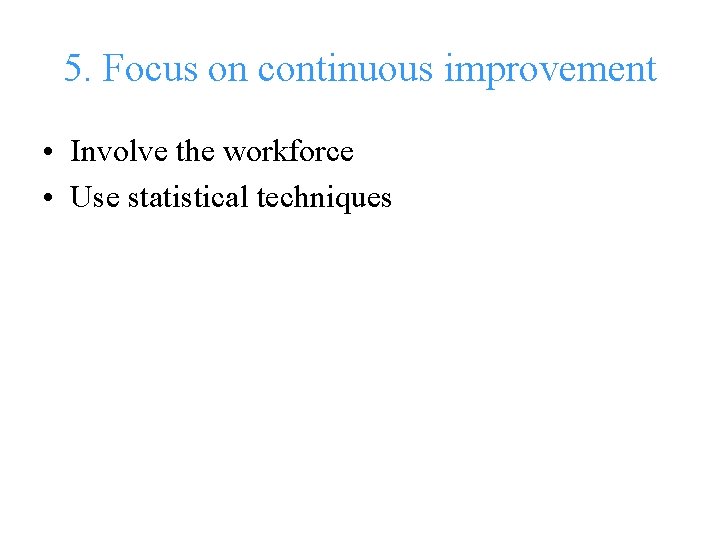
5. Focus on continuous improvement • Involve the workforce • Use statistical techniques
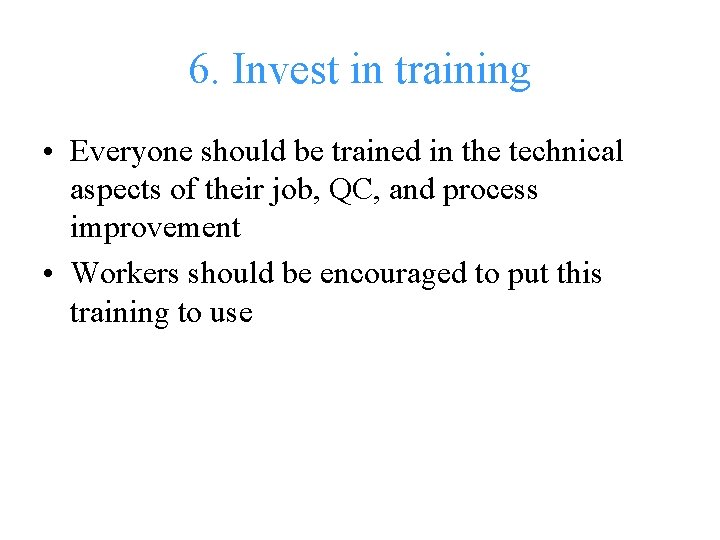
6. Invest in training • Everyone should be trained in the technical aspects of their job, QC, and process improvement • Workers should be encouraged to put this training to use
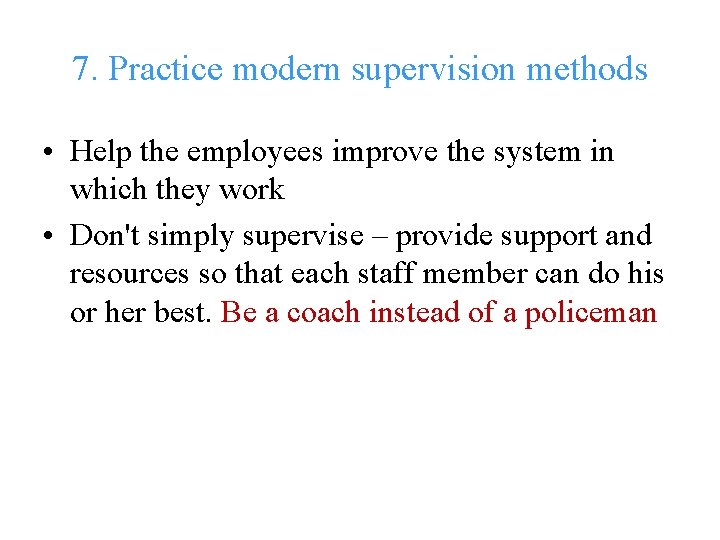
7. Practice modern supervision methods • Help the employees improve the system in which they work • Don't simply supervise – provide support and resources so that each staff member can do his or her best. Be a coach instead of a policeman
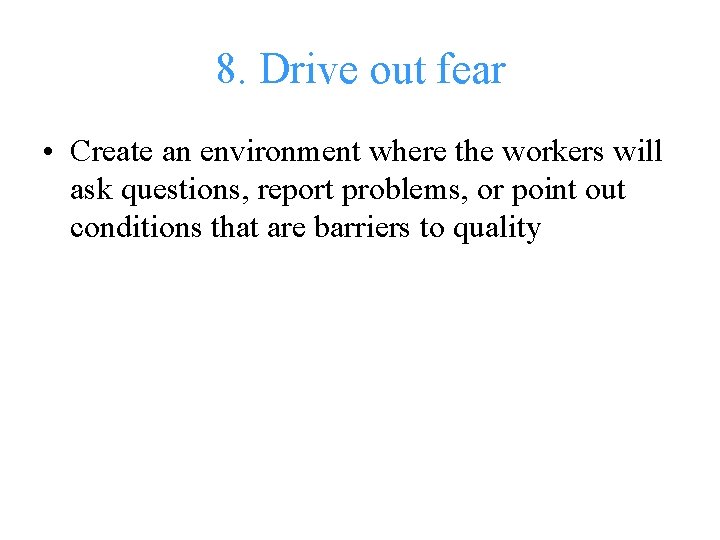
8. Drive out fear • Create an environment where the workers will ask questions, report problems, or point out conditions that are barriers to quality
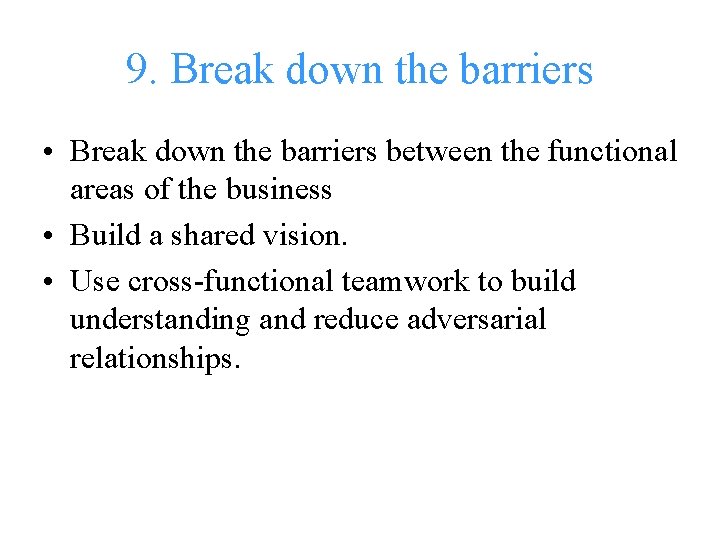
9. Break down the barriers • Break down the barriers between the functional areas of the business • Build a shared vision. • Use cross-functional teamwork to build understanding and reduce adversarial relationships.
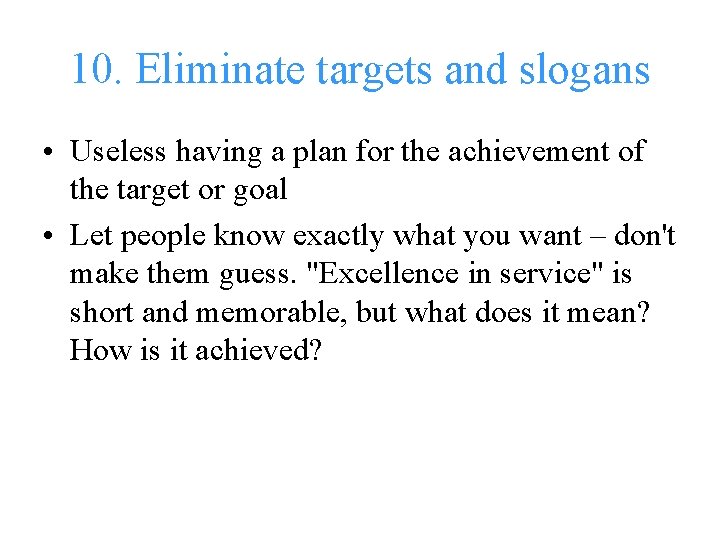
10. Eliminate targets and slogans • Useless having a plan for the achievement of the target or goal • Let people know exactly what you want – don't make them guess. "Excellence in service" is short and memorable, but what does it mean? How is it achieved?
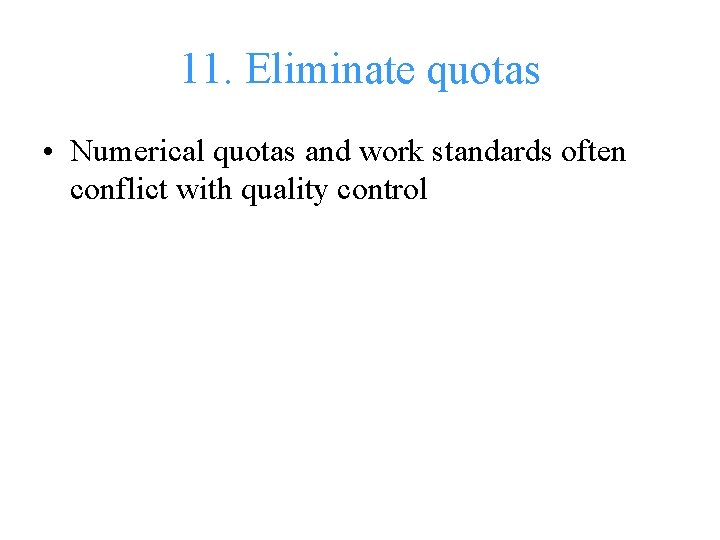
11. Eliminate quotas • Numerical quotas and work standards often conflict with quality control
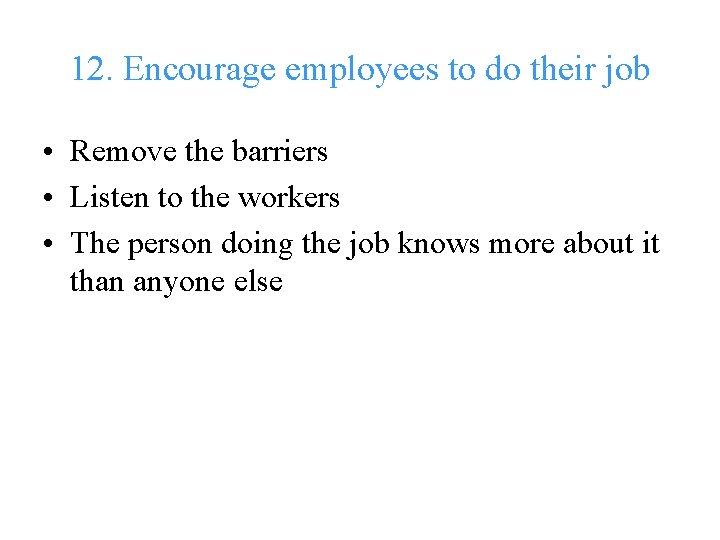
12. Encourage employees to do their job • Remove the barriers • Listen to the workers • The person doing the job knows more about it than anyone else
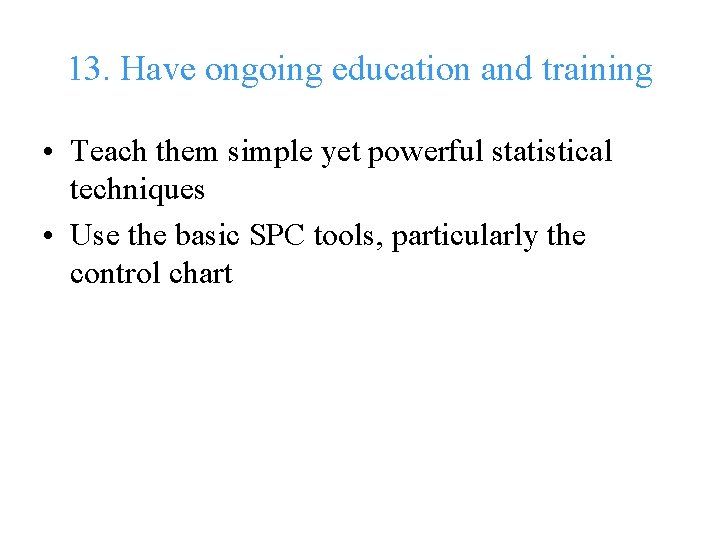
13. Have ongoing education and training • Teach them simple yet powerful statistical techniques • Use the basic SPC tools, particularly the control chart
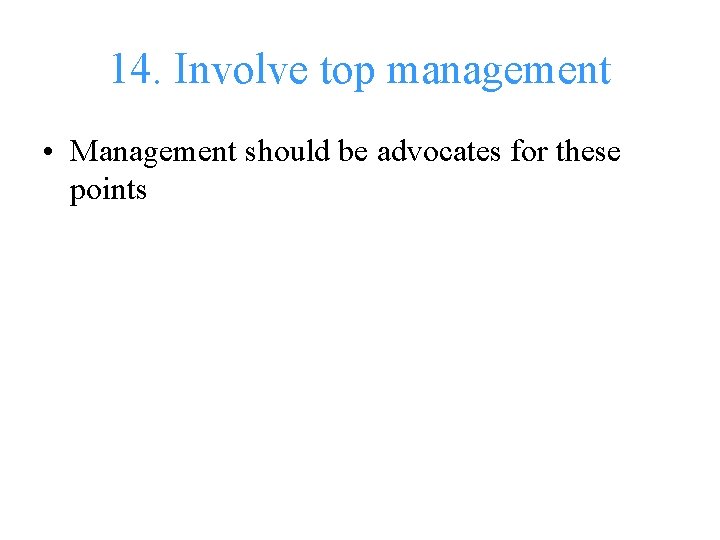
14. Involve top management • Management should be advocates for these points
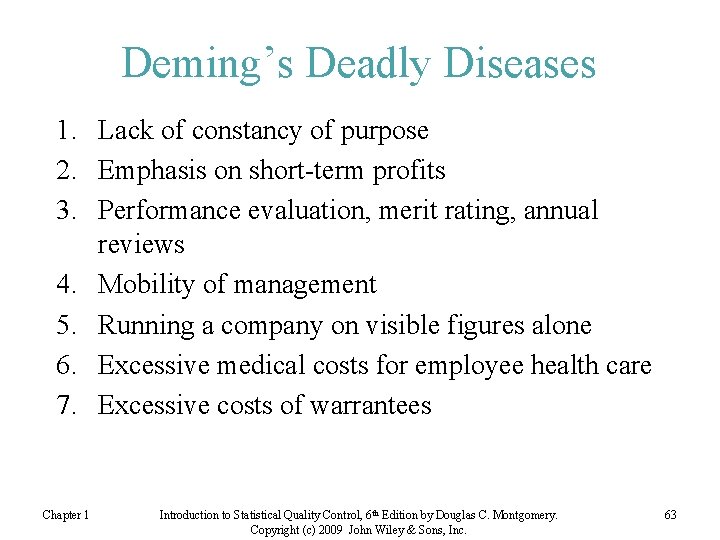
Deming’s Deadly Diseases 1. Lack of constancy of purpose 2. Emphasis on short-term profits 3. Performance evaluation, merit rating, annual reviews 4. Mobility of management 5. Running a company on visible figures alone 6. Excessive medical costs for employee health care 7. Excessive costs of warrantees Chapter 1 Introduction to Statistical Quality Control, 6 th Edition by Douglas C. Montgomery. Copyright (c) 2009 John Wiley & Sons, Inc. 63
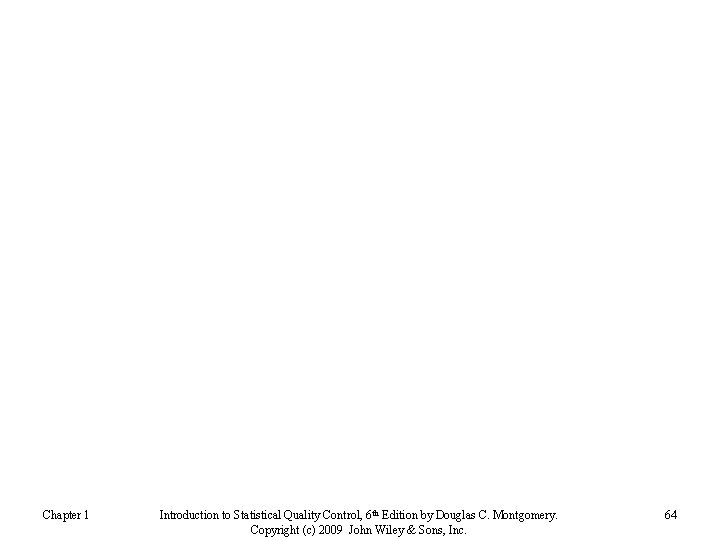
Chapter 1 Introduction to Statistical Quality Control, 6 th Edition by Douglas C. Montgomery. Copyright (c) 2009 John Wiley & Sons, Inc. 64
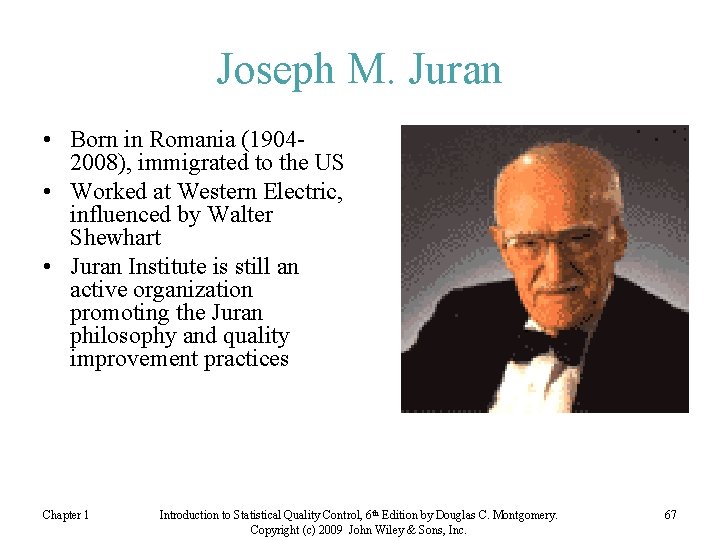
Joseph M. Juran • Born in Romania (19042008), immigrated to the US • Worked at Western Electric, influenced by Walter Shewhart • Juran Institute is still an active organization promoting the Juran philosophy and quality improvement practices Chapter 1 Introduction to Statistical Quality Control, 6 th Edition by Douglas C. Montgomery. Copyright (c) 2009 John Wiley & Sons, Inc. 67
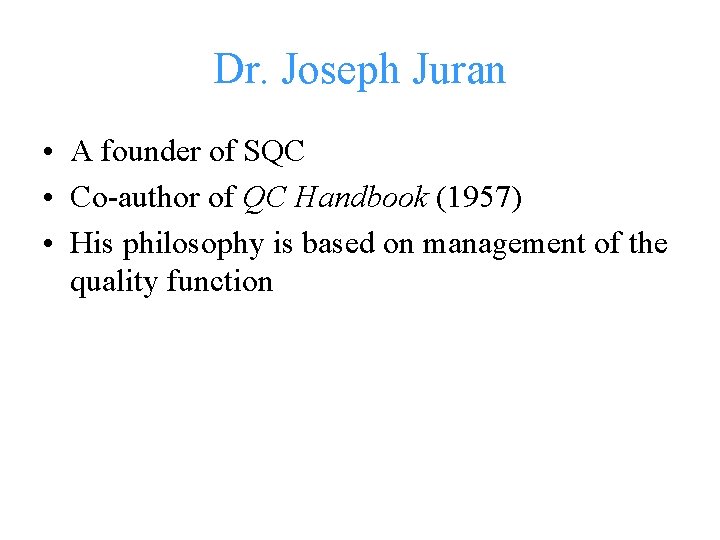
Dr. Joseph Juran • A founder of SQC • Co-author of QC Handbook (1957) • His philosophy is based on management of the quality function
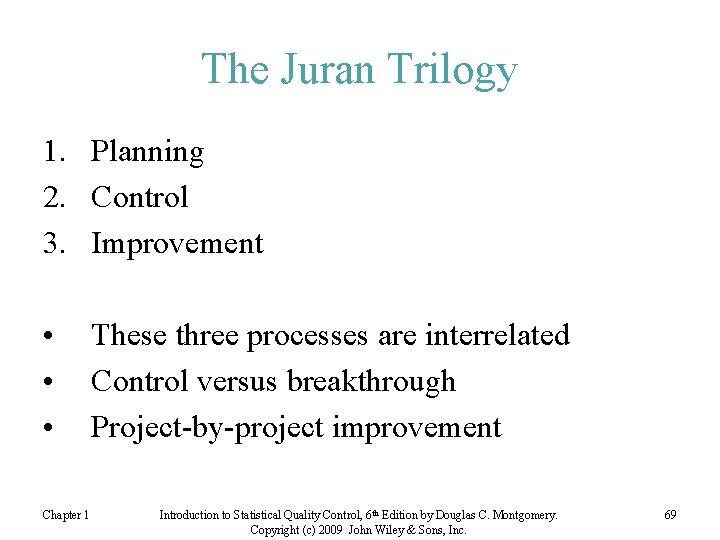
The Juran Trilogy 1. Planning 2. Control 3. Improvement • • • Chapter 1 These three processes are interrelated Control versus breakthrough Project-by-project improvement Introduction to Statistical Quality Control, 6 th Edition by Douglas C. Montgomery. Copyright (c) 2009 John Wiley & Sons, Inc. 69
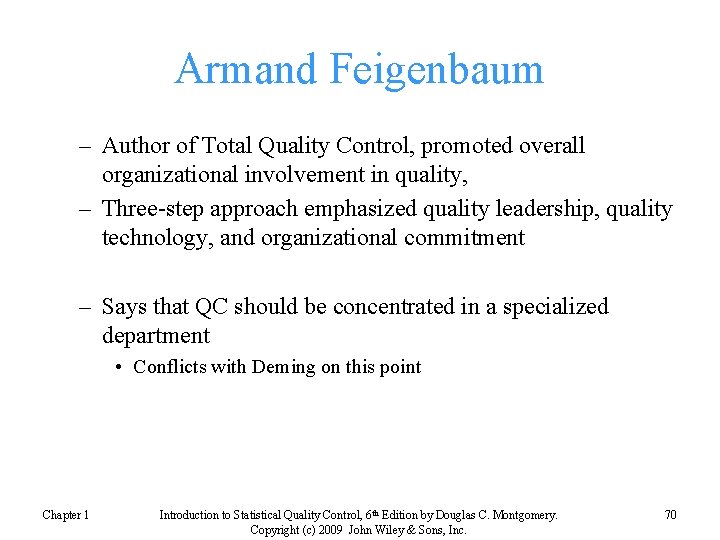
Armand Feigenbaum – Author of Total Quality Control, promoted overall organizational involvement in quality, – Three-step approach emphasized quality leadership, quality technology, and organizational commitment – Says that QC should be concentrated in a specialized department • Conflicts with Deming on this point Chapter 1 Introduction to Statistical Quality Control, 6 th Edition by Douglas C. Montgomery. Copyright (c) 2009 John Wiley & Sons, Inc. 70
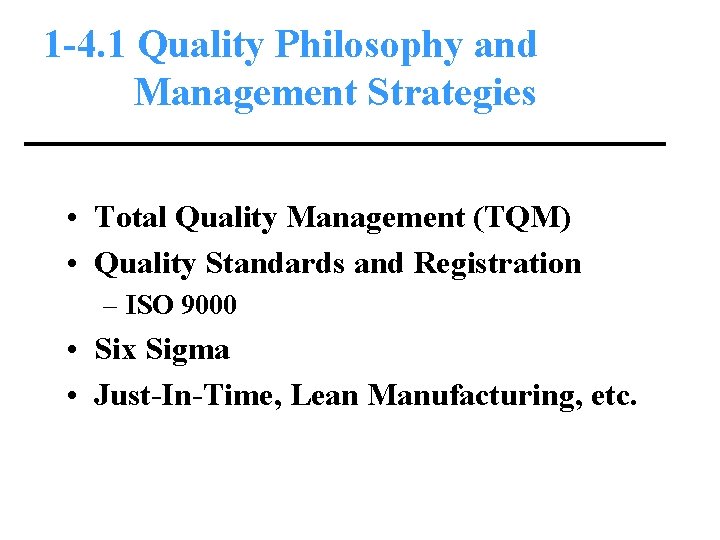
1 -4. 1 Quality Philosophy and Management Strategies • Total Quality Management (TQM) • Quality Standards and Registration – ISO 9000 • Six Sigma • Just-In-Time, Lean Manufacturing, etc.
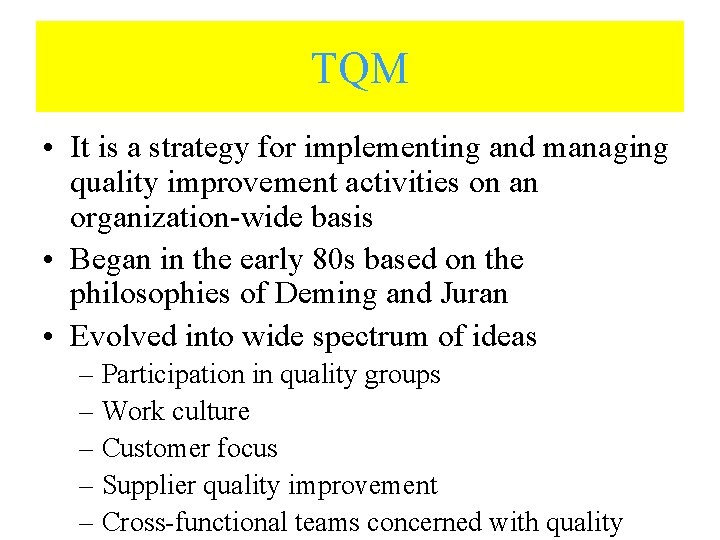
TQM • It is a strategy for implementing and managing quality improvement activities on an organization-wide basis • Began in the early 80 s based on the philosophies of Deming and Juran • Evolved into wide spectrum of ideas – Participation in quality groups – Work culture – Customer focus – Supplier quality improvement – Cross-functional teams concerned with quality
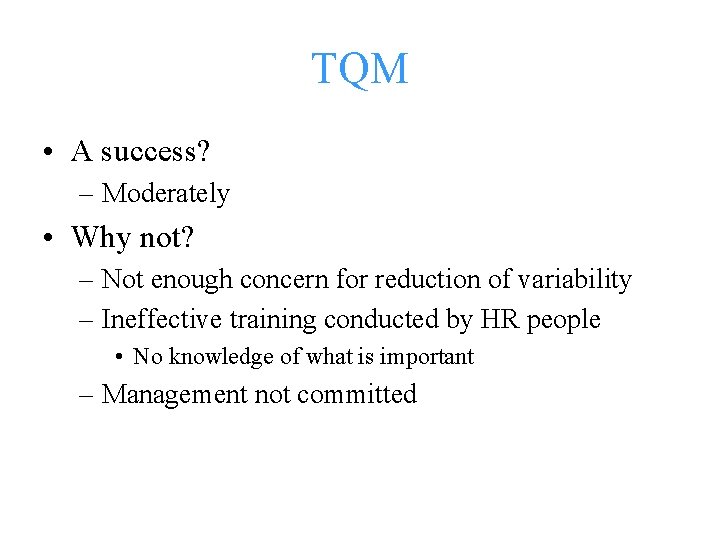
TQM • A success? – Moderately • Why not? – Not enough concern for reduction of variability – Ineffective training conducted by HR people • No knowledge of what is important – Management not committed
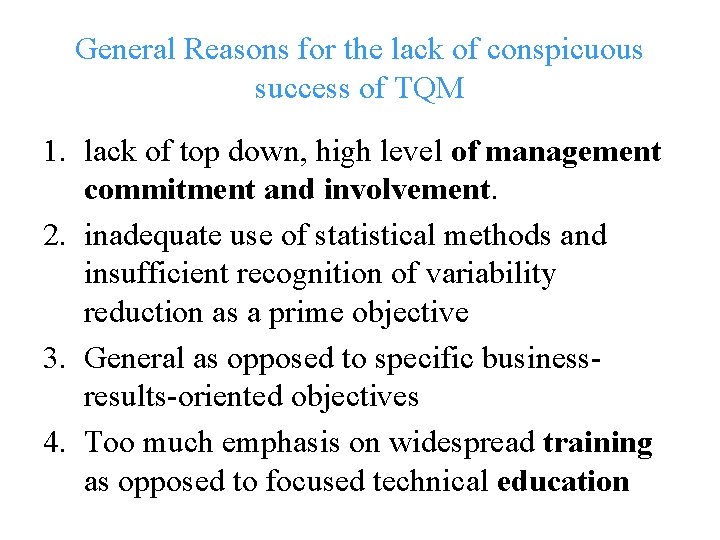
General Reasons for the lack of conspicuous success of TQM 1. lack of top down, high level of management commitment and involvement. 2. inadequate use of statistical methods and insufficient recognition of variability reduction as a prime objective 3. General as opposed to specific business- results-oriented objectives 4. Too much emphasis on widespread training as opposed to focused technical education
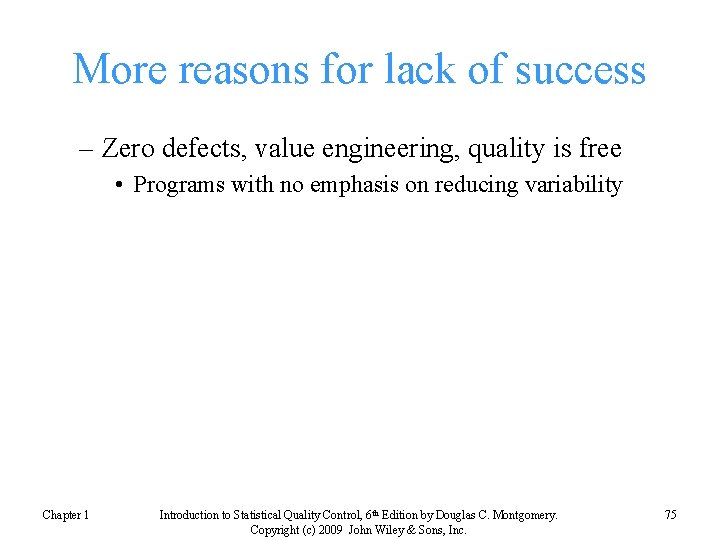
More reasons for lack of success – Zero defects, value engineering, quality is free • Programs with no emphasis on reducing variability Chapter 1 Introduction to Statistical Quality Control, 6 th Edition by Douglas C. Montgomery. Copyright (c) 2009 John Wiley & Sons, Inc. 75
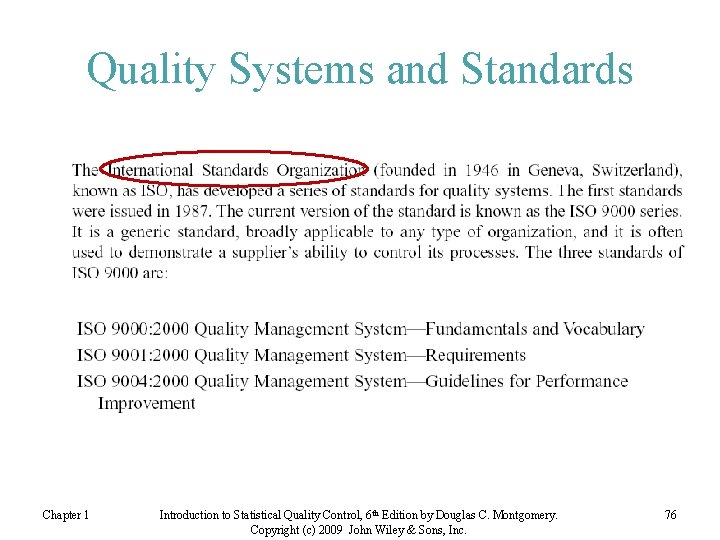
Quality Systems and Standards Chapter 1 Introduction to Statistical Quality Control, 6 th Edition by Douglas C. Montgomery. Copyright (c) 2009 John Wiley & Sons, Inc. 76
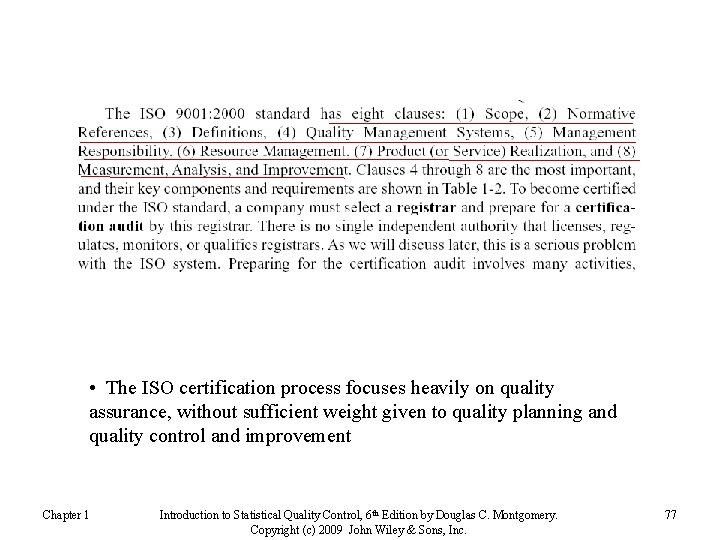
• The ISO certification process focuses heavily on quality assurance, without sufficient weight given to quality planning and quality control and improvement Chapter 1 Introduction to Statistical Quality Control, 6 th Edition by Douglas C. Montgomery. Copyright (c) 2009 John Wiley & Sons, Inc. 77
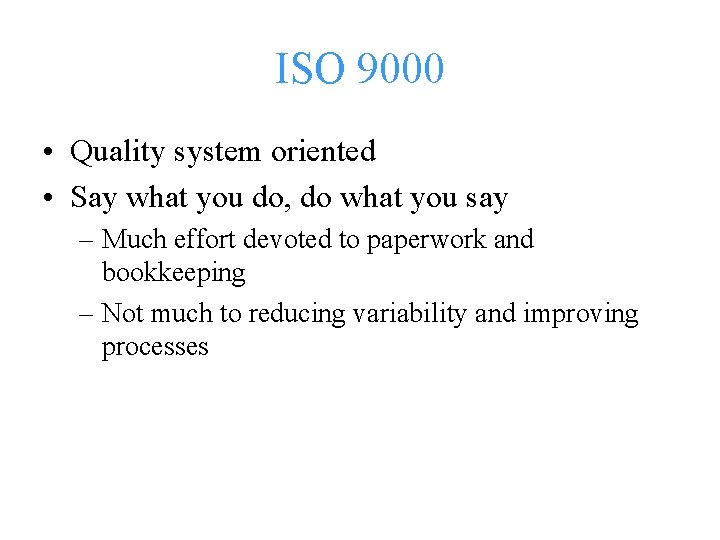
ISO 9000 • Quality system oriented • Say what you do, do what you say – Much effort devoted to paperwork and bookkeeping – Not much to reducing variability and improving processes
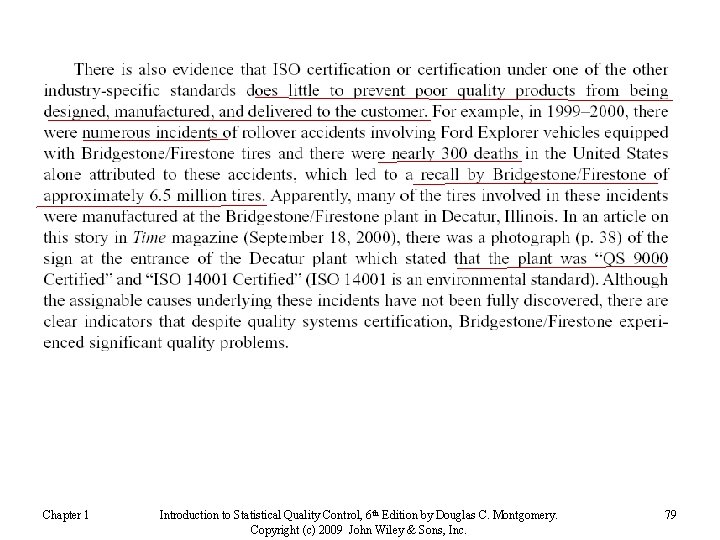
Chapter 1 Introduction to Statistical Quality Control, 6 th Edition by Douglas C. Montgomery. Copyright (c) 2009 John Wiley & Sons, Inc. 79
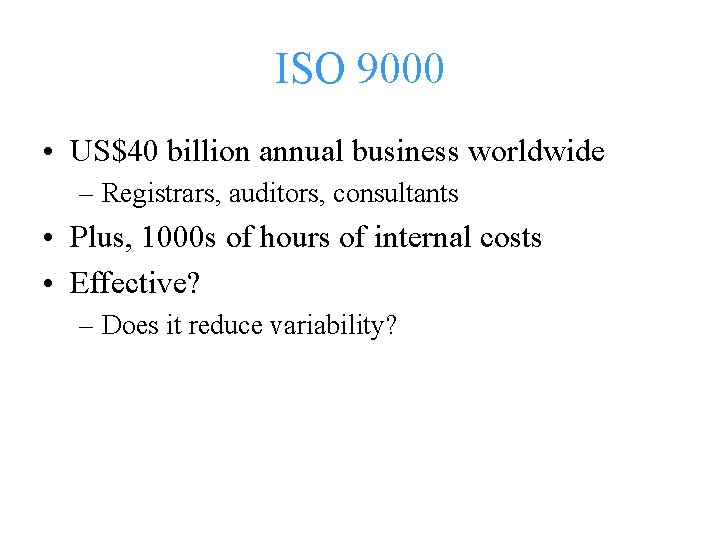
ISO 9000 • US$40 billion annual business worldwide – Registrars, auditors, consultants • Plus, 1000 s of hours of internal costs • Effective? – Does it reduce variability?
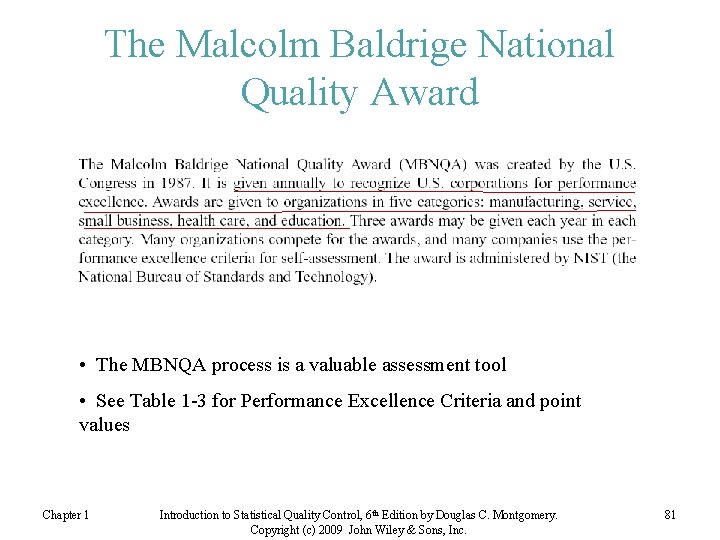
The Malcolm Baldrige National Quality Award • The MBNQA process is a valuable assessment tool • See Table 1 -3 for Performance Excellence Criteria and point values Chapter 1 Introduction to Statistical Quality Control, 6 th Edition by Douglas C. Montgomery. Copyright (c) 2009 John Wiley & Sons, Inc. 81
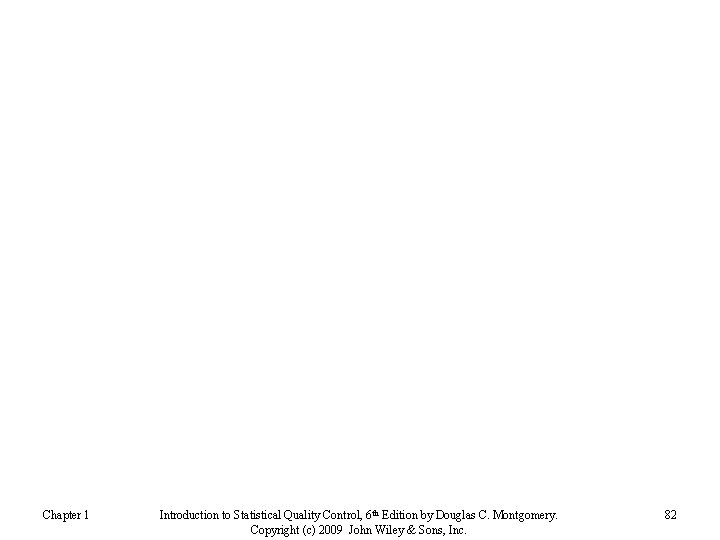
Chapter 1 Introduction to Statistical Quality Control, 6 th Edition by Douglas C. Montgomery. Copyright (c) 2009 John Wiley & Sons, Inc. 82
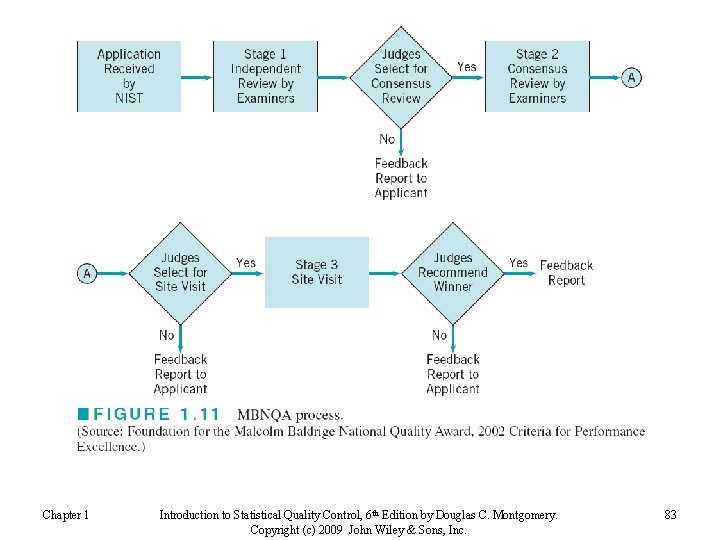
Chapter 1 Introduction to Statistical Quality Control, 6 th Edition by Douglas C. Montgomery. Copyright (c) 2009 John Wiley & Sons, Inc. 83
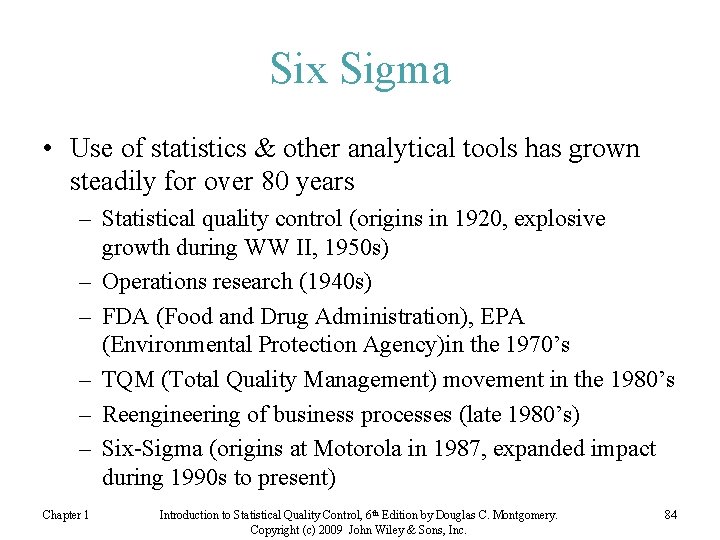
Six Sigma • Use of statistics & other analytical tools has grown steadily for over 80 years – Statistical quality control (origins in 1920, explosive growth during WW II, 1950 s) – Operations research (1940 s) – FDA (Food and Drug Administration), EPA (Environmental Protection Agency)in the 1970’s – TQM (Total Quality Management) movement in the 1980’s – Reengineering of business processes (late 1980’s) – Six-Sigma (origins at Motorola in 1987, expanded impact during 1990 s to present) Chapter 1 Introduction to Statistical Quality Control, 6 th Edition by Douglas C. Montgomery. Copyright (c) 2009 John Wiley & Sons, Inc. 84
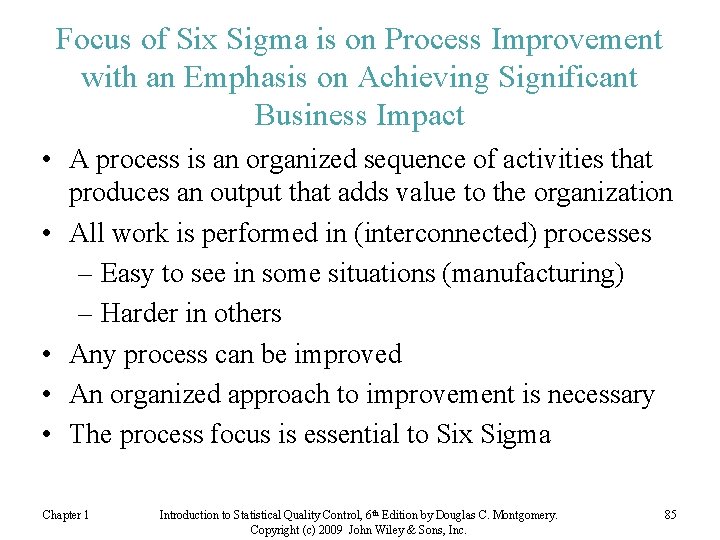
Focus of Six Sigma is on Process Improvement with an Emphasis on Achieving Significant Business Impact • A process is an organized sequence of activities that produces an output that adds value to the organization • All work is performed in (interconnected) processes – Easy to see in some situations (manufacturing) – Harder in others • Any process can be improved • An organized approach to improvement is necessary • The process focus is essential to Six Sigma Chapter 1 Introduction to Statistical Quality Control, 6 th Edition by Douglas C. Montgomery. Copyright (c) 2009 John Wiley & Sons, Inc. 85
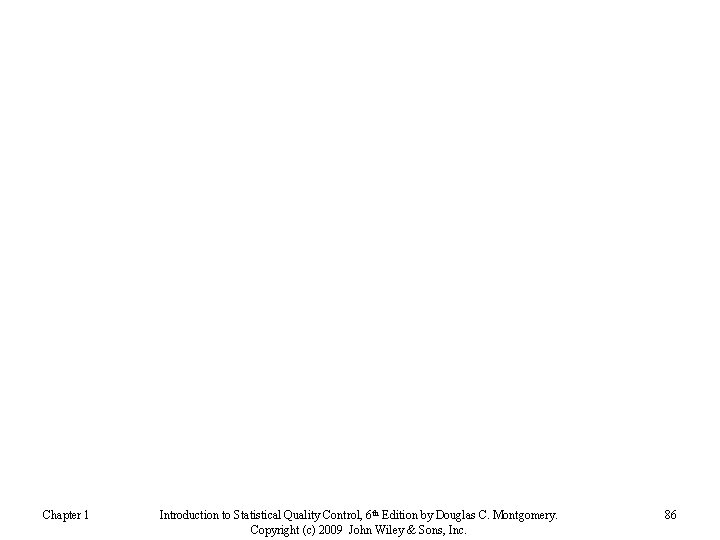
Chapter 1 Introduction to Statistical Quality Control, 6 th Edition by Douglas C. Montgomery. Copyright (c) 2009 John Wiley & Sons, Inc. 86
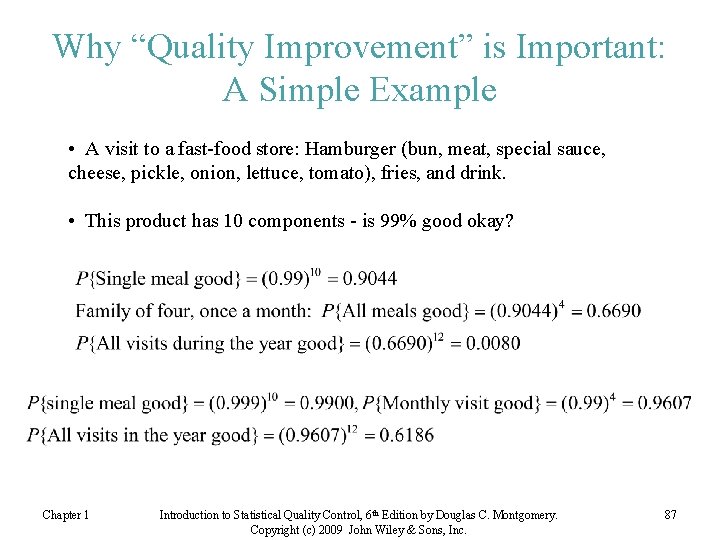
Why “Quality Improvement” is Important: A Simple Example • A visit to a fast-food store: Hamburger (bun, meat, special sauce, cheese, pickle, onion, lettuce, tomato), fries, and drink. • This product has 10 components - is 99% good okay? Chapter 1 Introduction to Statistical Quality Control, 6 th Edition by Douglas C. Montgomery. Copyright (c) 2009 John Wiley & Sons, Inc. 87
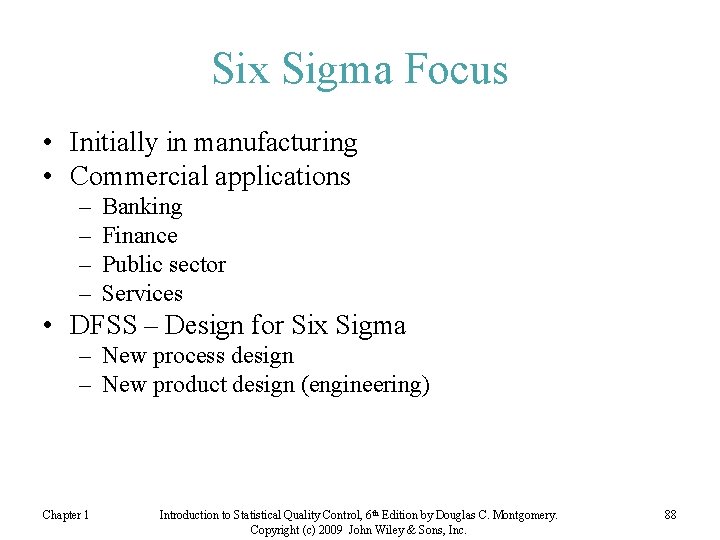
Six Sigma Focus • Initially in manufacturing • Commercial applications – – Banking Finance Public sector Services • DFSS – Design for Six Sigma – New process design – New product design (engineering) Chapter 1 Introduction to Statistical Quality Control, 6 th Edition by Douglas C. Montgomery. Copyright (c) 2009 John Wiley & Sons, Inc. 88
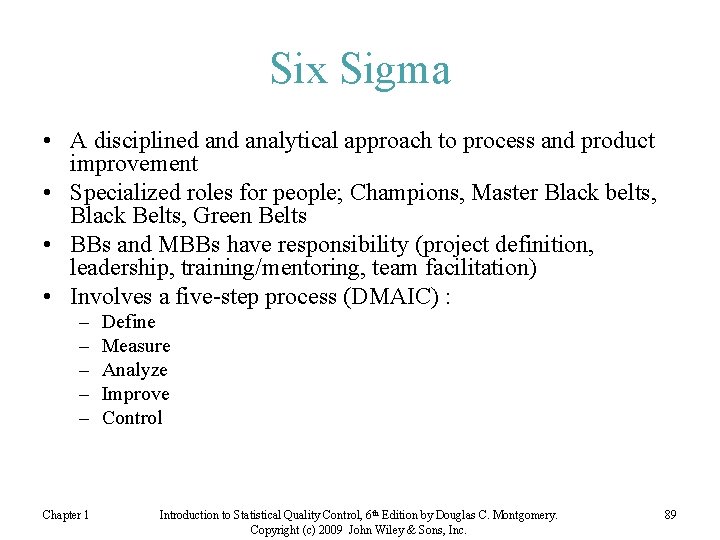
Six Sigma • A disciplined analytical approach to process and product improvement • Specialized roles for people; Champions, Master Black belts, Black Belts, Green Belts • BBs and MBBs have responsibility (project definition, leadership, training/mentoring, team facilitation) • Involves a five-step process (DMAIC) : – – – Chapter 1 Define Measure Analyze Improve Control Introduction to Statistical Quality Control, 6 th Edition by Douglas C. Montgomery. Copyright (c) 2009 John Wiley & Sons, Inc. 89
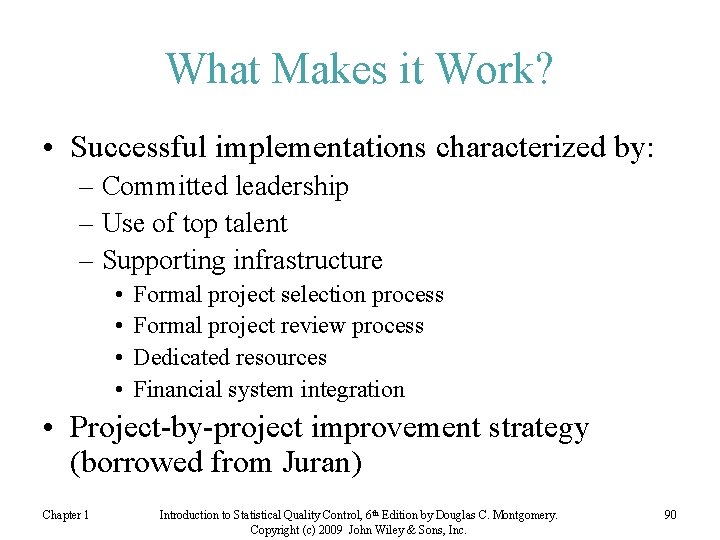
What Makes it Work? • Successful implementations characterized by: – Committed leadership – Use of top talent – Supporting infrastructure • • Formal project selection process Formal project review process Dedicated resources Financial system integration • Project-by-project improvement strategy (borrowed from Juran) Chapter 1 Introduction to Statistical Quality Control, 6 th Edition by Douglas C. Montgomery. Copyright (c) 2009 John Wiley & Sons, Inc. 90
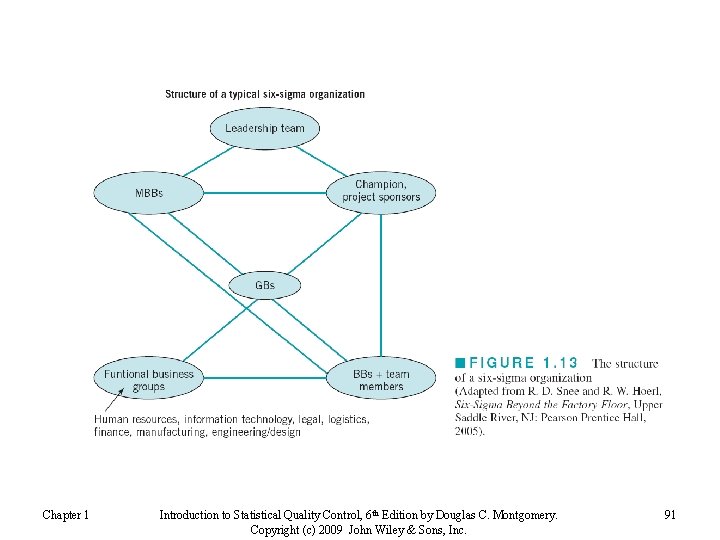
Chapter 1 Introduction to Statistical Quality Control, 6 th Edition by Douglas C. Montgomery. Copyright (c) 2009 John Wiley & Sons, Inc. 91
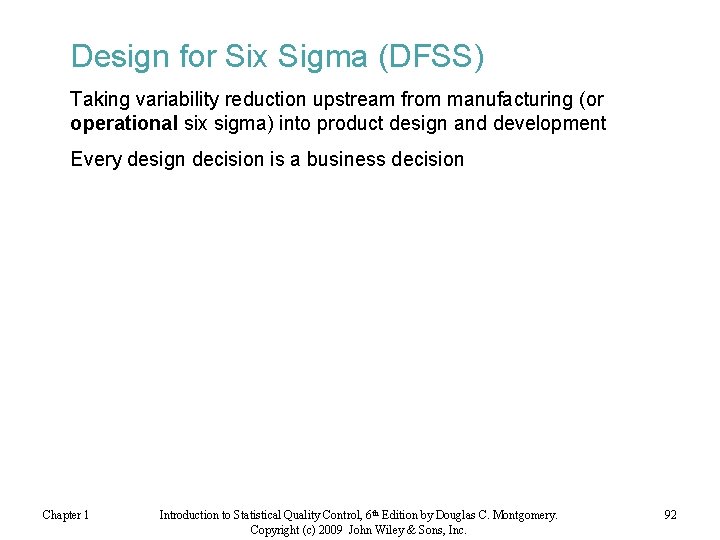
Design for Six Sigma (DFSS) Taking variability reduction upstream from manufacturing (or operational six sigma) into product design and development Every design decision is a business decision Chapter 1 Introduction to Statistical Quality Control, 6 th Edition by Douglas C. Montgomery. Copyright (c) 2009 John Wiley & Sons, Inc. 92
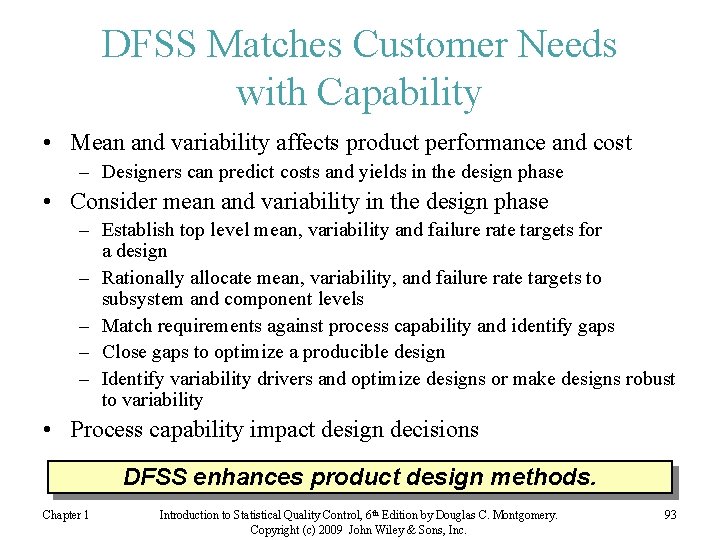
DFSS Matches Customer Needs with Capability • Mean and variability affects product performance and cost – Designers can predict costs and yields in the design phase • Consider mean and variability in the design phase – Establish top level mean, variability and failure rate targets for a design – Rationally allocate mean, variability, and failure rate targets to subsystem and component levels – Match requirements against process capability and identify gaps – Close gaps to optimize a producible design – Identify variability drivers and optimize designs or make designs robust to variability • Process capability impact design decisions DFSS enhances product design methods. Chapter 1 Introduction to Statistical Quality Control, 6 th Edition by Douglas C. Montgomery. Copyright (c) 2009 John Wiley & Sons, Inc. 93
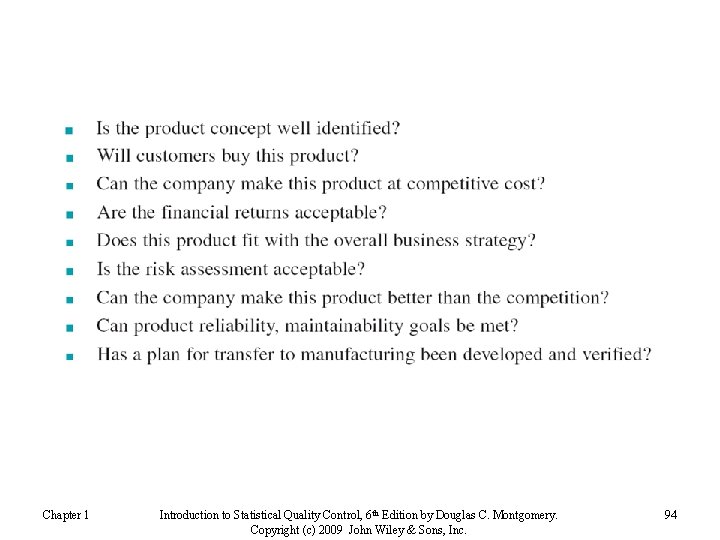
Chapter 1 Introduction to Statistical Quality Control, 6 th Edition by Douglas C. Montgomery. Copyright (c) 2009 John Wiley & Sons, Inc. 94
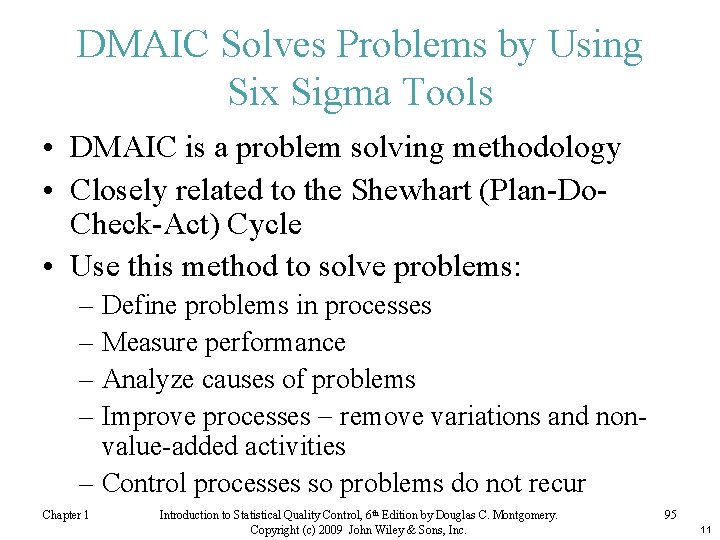
DMAIC Solves Problems by Using Six Sigma Tools • DMAIC is a problem solving methodology • Closely related to the Shewhart (Plan-Do. Check-Act) Cycle • Use this method to solve problems: – Define problems in processes – Measure performance – Analyze causes of problems – Improve processes remove variations and nonvalue-added activities – Control processes so problems do not recur Chapter 1 Introduction to Statistical Quality Control, 6 th Edition by Douglas C. Montgomery. Copyright (c) 2009 John Wiley & Sons, Inc. 95 11
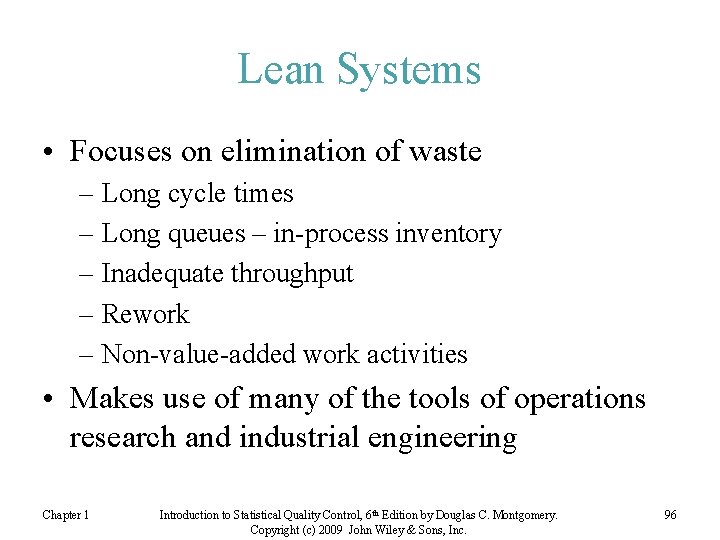
Lean Systems • Focuses on elimination of waste – Long cycle times – Long queues – in-process inventory – Inadequate throughput – Rework – Non-value-added work activities • Makes use of many of the tools of operations research and industrial engineering Chapter 1 Introduction to Statistical Quality Control, 6 th Edition by Douglas C. Montgomery. Copyright (c) 2009 John Wiley & Sons, Inc. 96
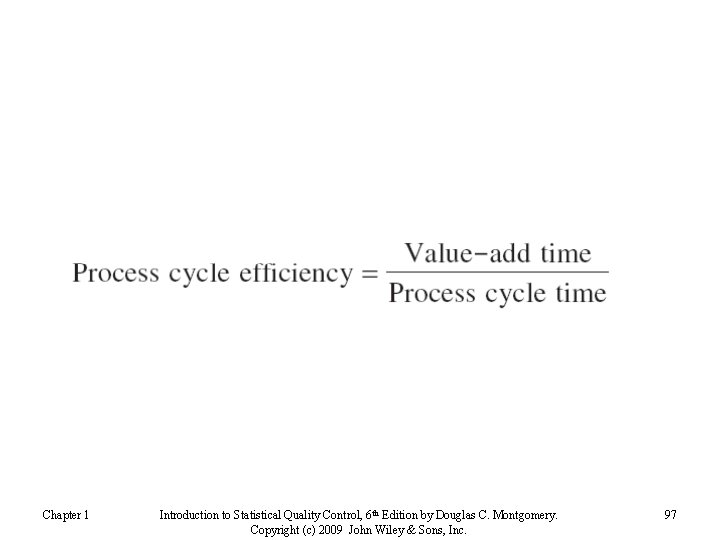
Chapter 1 Introduction to Statistical Quality Control, 6 th Edition by Douglas C. Montgomery. Copyright (c) 2009 John Wiley & Sons, Inc. 97
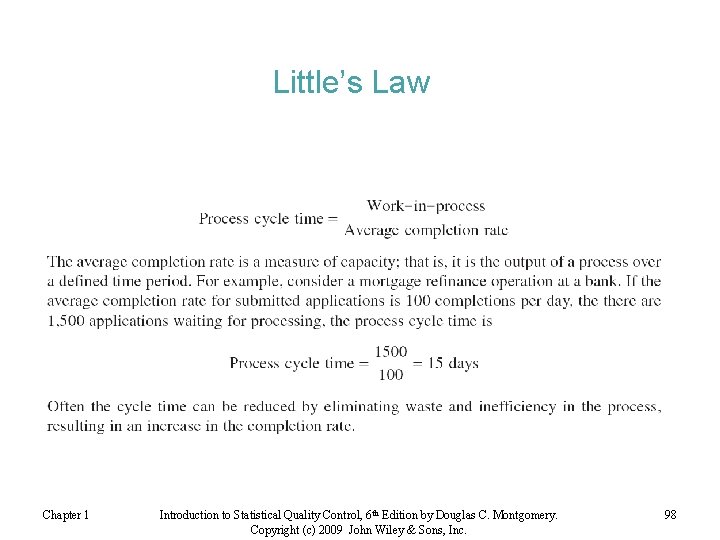
Little’s Law Chapter 1 Introduction to Statistical Quality Control, 6 th Edition by Douglas C. Montgomery. Copyright (c) 2009 John Wiley & Sons, Inc. 98
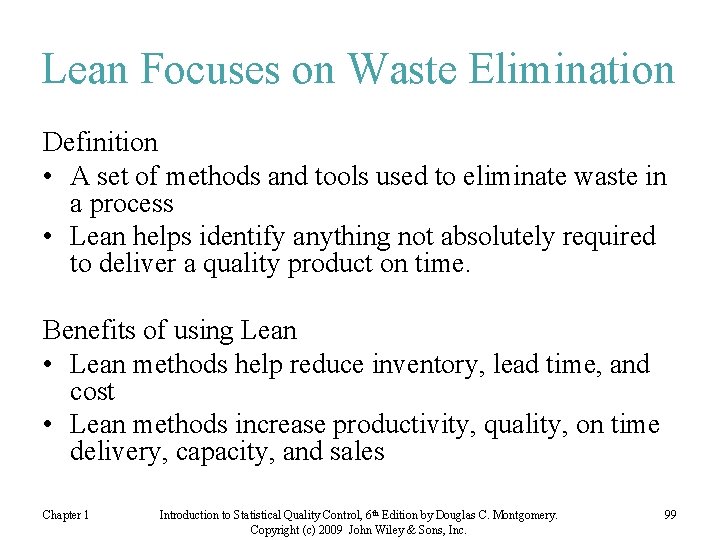
Lean Focuses on Waste Elimination Definition • A set of methods and tools used to eliminate waste in a process • Lean helps identify anything not absolutely required to deliver a quality product on time. Benefits of using Lean • Lean methods help reduce inventory, lead time, and cost • Lean methods increase productivity, quality, on time delivery, capacity, and sales Chapter 1 Introduction to Statistical Quality Control, 6 th Edition by Douglas C. Montgomery. Copyright (c) 2009 John Wiley & Sons, Inc. 99
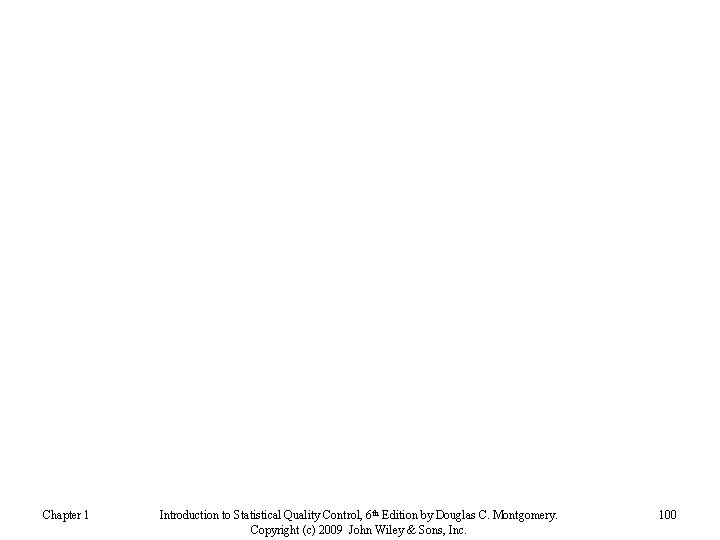
Chapter 1 Introduction to Statistical Quality Control, 6 th Edition by Douglas C. Montgomery. Copyright (c) 2009 John Wiley & Sons, Inc. 100
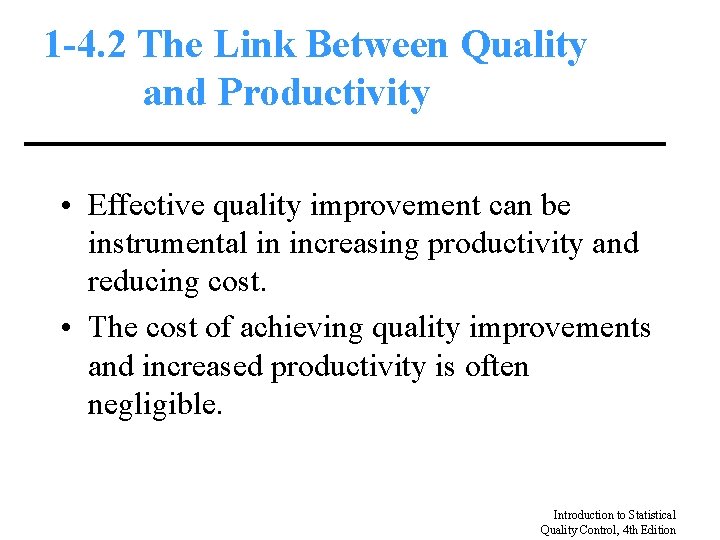
1 -4. 2 The Link Between Quality and Productivity • Effective quality improvement can be instrumental in increasing productivity and reducing cost. • The cost of achieving quality improvements and increased productivity is often negligible. Introduction to Statistical Quality Control, 4 th Edition
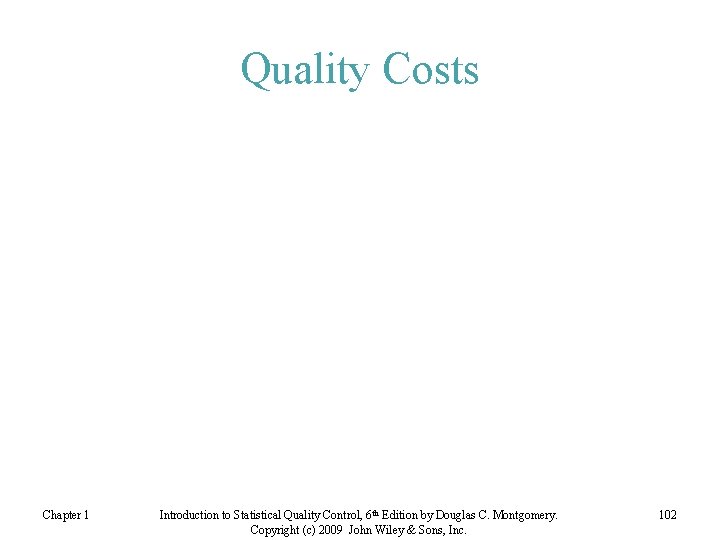
Quality Costs Chapter 1 Introduction to Statistical Quality Control, 6 th Edition by Douglas C. Montgomery. Copyright (c) 2009 John Wiley & Sons, Inc. 102
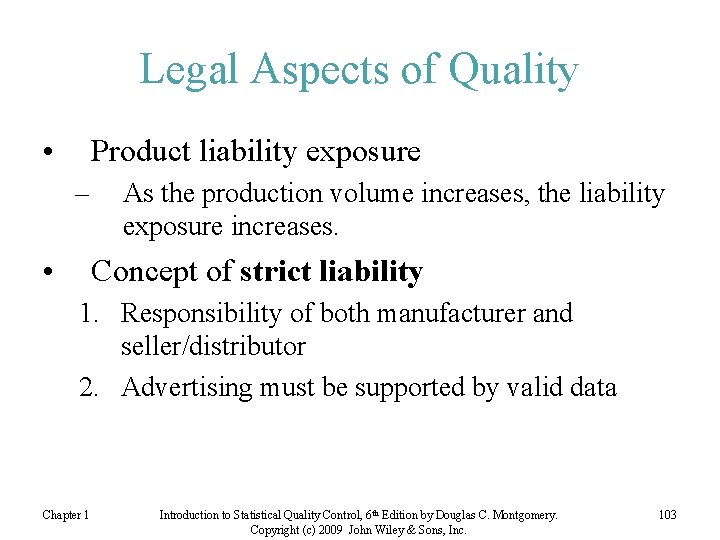
Legal Aspects of Quality • Product liability exposure – • As the production volume increases, the liability exposure increases. Concept of strict liability 1. Responsibility of both manufacturer and seller/distributor 2. Advertising must be supported by valid data Chapter 1 Introduction to Statistical Quality Control, 6 th Edition by Douglas C. Montgomery. Copyright (c) 2009 John Wiley & Sons, Inc. 103
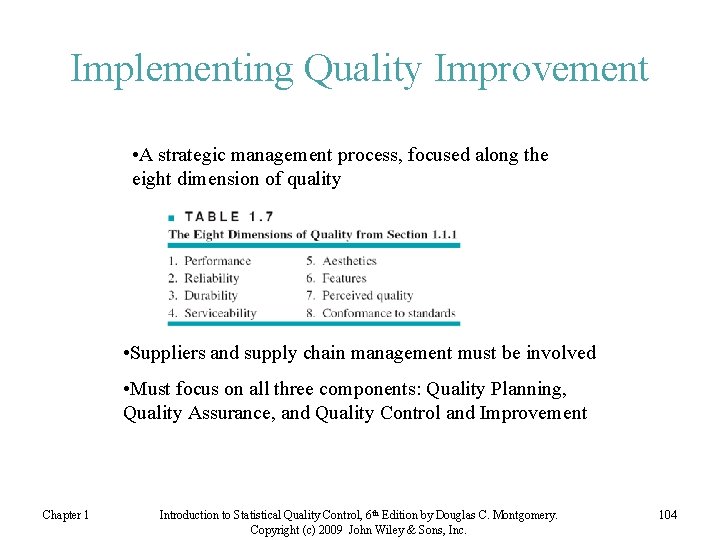
Implementing Quality Improvement • A strategic management process, focused along the eight dimension of quality • Suppliers and supply chain management must be involved • Must focus on all three components: Quality Planning, Quality Assurance, and Quality Control and Improvement Chapter 1 Introduction to Statistical Quality Control, 6 th Edition by Douglas C. Montgomery. Copyright (c) 2009 John Wiley & Sons, Inc. 104
Introduction to statistical quality control
Introduction to statistical quality control
What is sqc in operations management
Statistical quality control in operations management
Pengertian total quality management
Statistical quality control
Quality assurance vs quality control
Quality control vs quality assurance pmp
Pmbok quality assurance vs quality control
Concepts of quality control
Introduction to quality control
Introduction to quality control
Statistical quality assurance in software engineering
Statistical software quality assurance
Statistical process control ppt
Statistical control in research
Statistical inventory control
Statistical process control tutorial
Mssc introduction to spc
Quality
20%ของ300
Statistical process control definition
Statistical process control
Operations management chapter 10 quality control solutions
Introduction to quantum statistical mechanics
Ana model of quality assurance
Quality improvement vs quality assurance
Quality management gurus
Quality is free
Old quality vs new quality
Qa ipc
Tqm tqc
Acceptance sampling procedure
Average run length in quality control
Software quality plan
Quality control log examples
Subway quality control
Rick benson iris
Quality control in business plan
Quality determination
Receiving of materials
Quality control in blood bank pdf
Quality control of fresh fruits and vegetables
Quality control analysis of beer
Quality control in hematology wikipedia
Qrqc methodology
Clarity test for parenterals
Quality assurance definition
Quality control circle
Quality control documentation
Sterilization quality control
Dqc data quality control
Attribute control charts
Average run length in quality control
What is sampling plan in quality control
What is sampling plan in quality control
Westgard rules
Six sigma methodology defines three core steps
Quality control assay
Quality control chart
Quality control personnel
Aec quality control
7 quality control tools
Quality control approved by rf
Mbaknol.com
Third party quality control
Quality v
Internal quality control
Quality control painting
Quality control methods for medicinal plant materials
What is quality control definition
Internal and external qc
Purpose of quality control
Qcp quality control plan
Extrusion quality control
Quality control program
Natural tolerance
Internal quality control laboratory
Westgard rules explained
Objectives of caqc
Ulu icma
Aqc quality control
Dna hybridization microarray
Quality control data management
Juran histogram
Qa
Contoh kegiatan quality control di rumah sakit
Leather quality control
Istat quality control procedure
Quality control bureau
Weakness of toyota
Apply quality control
Data quality control techniques
Importance of quality in pharmaceutical industry
Quality control plan
Content uniformity definition
Pcb quality assurance
Quality control formula
High-quality reagents
Quality control tools and techniques
Software quality control checklist