Thermal noise overview Ronny Nawrodt Institute for Gravitational
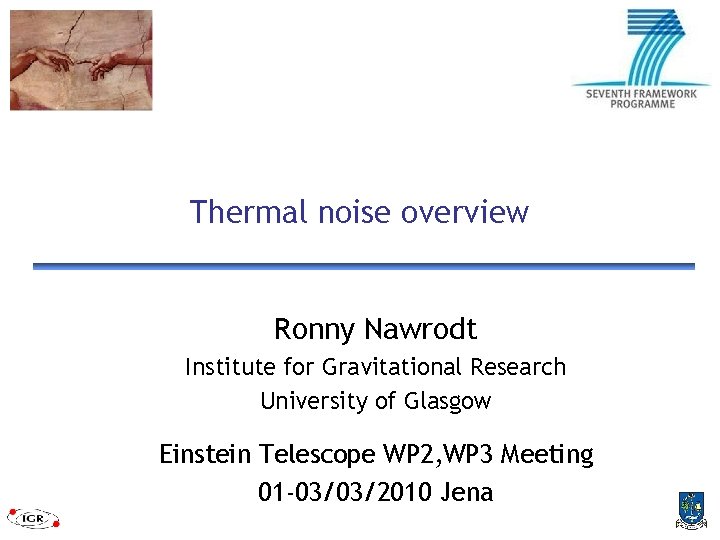
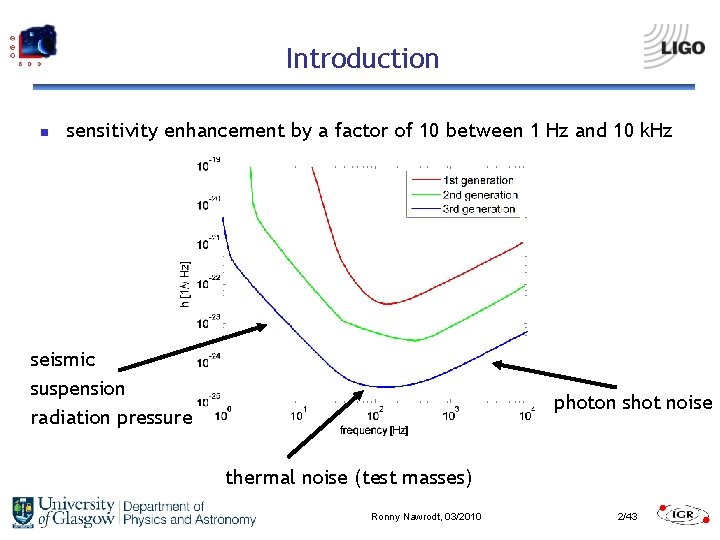
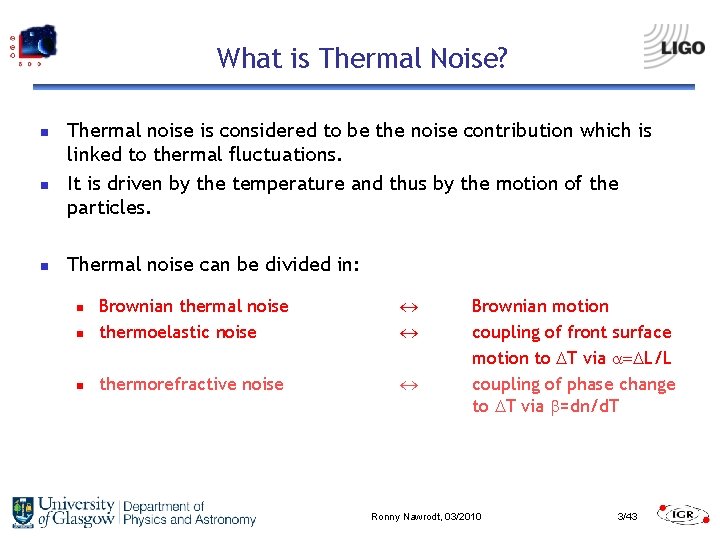
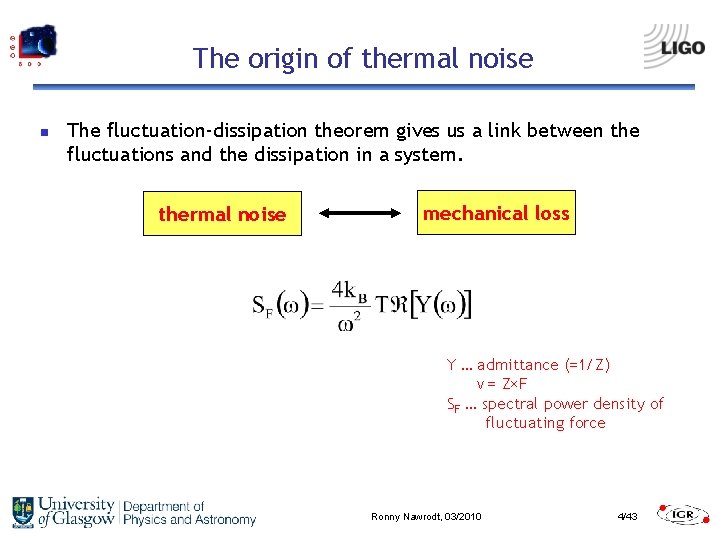
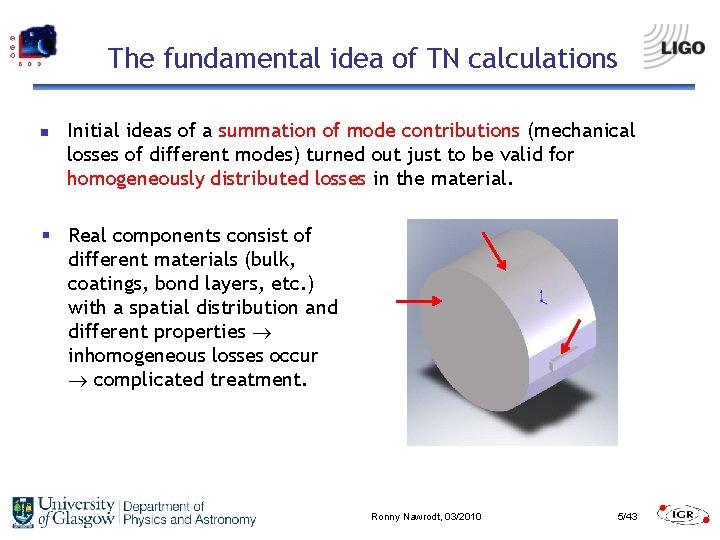
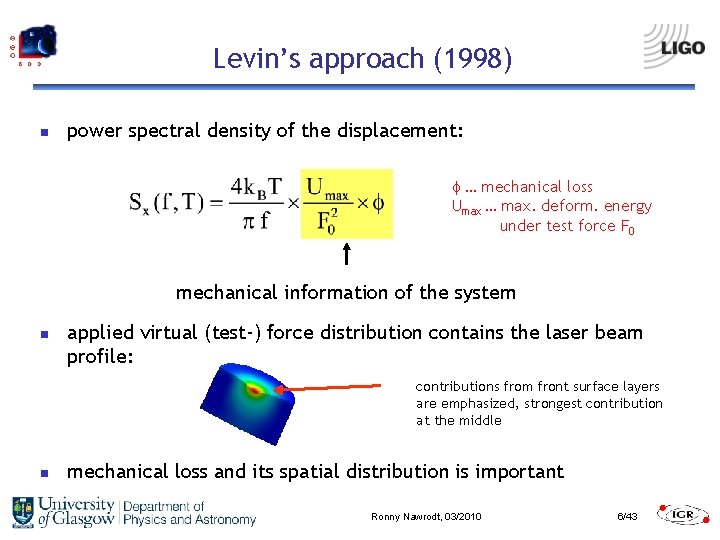
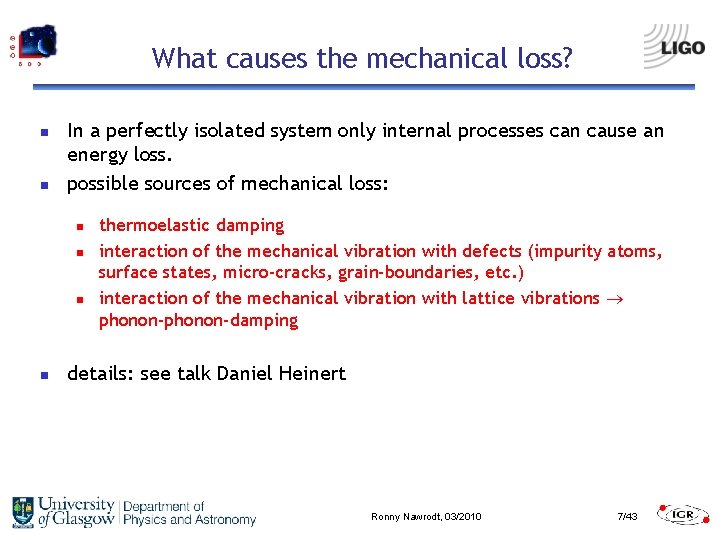
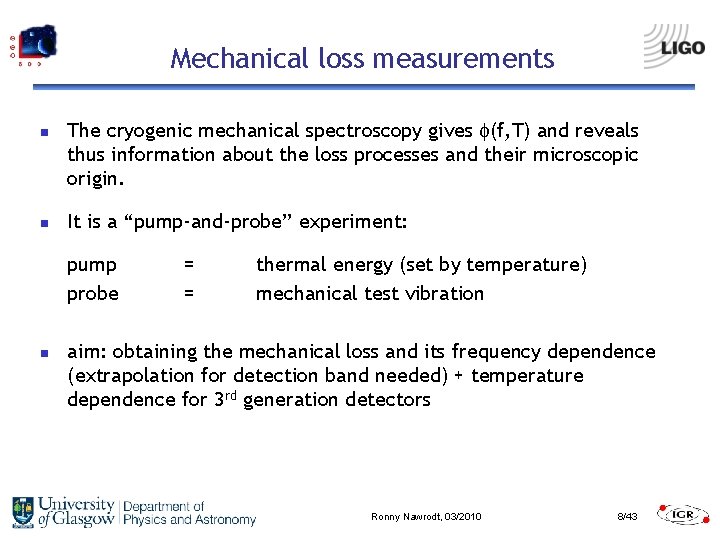
![Bulk material thermal noise calculation n thermoelastic noise: [Braginsky 1999] [Liu, Thorne 2000] n Bulk material thermal noise calculation n thermoelastic noise: [Braginsky 1999] [Liu, Thorne 2000] n](https://slidetodoc.com/presentation_image_h/2da57d1ee41f9d5051157a1634b101c2/image-9.jpg)
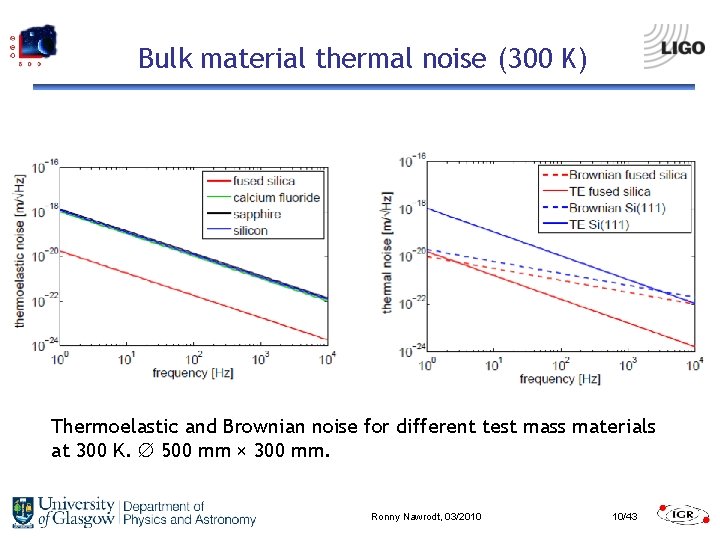
![Coating thermal noise calculation n thermoelastic noise: [Braginsky, Fejer et al. 2004] n Brownian Coating thermal noise calculation n thermoelastic noise: [Braginsky, Fejer et al. 2004] n Brownian](https://slidetodoc.com/presentation_image_h/2da57d1ee41f9d5051157a1634b101c2/image-11.jpg)
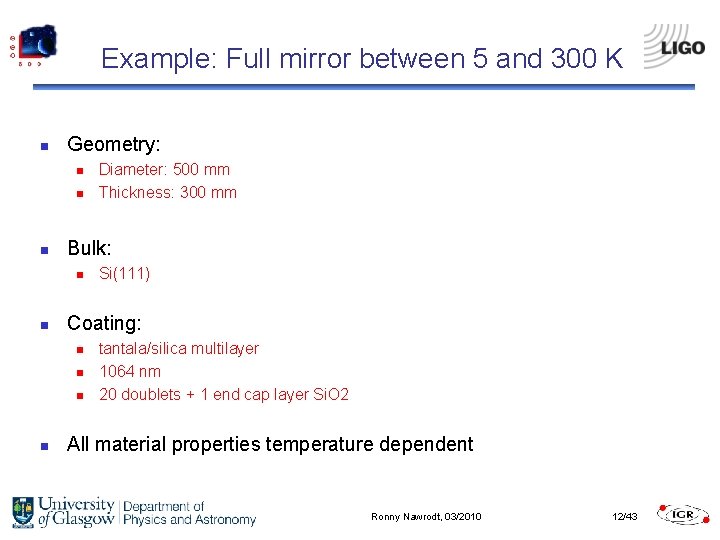
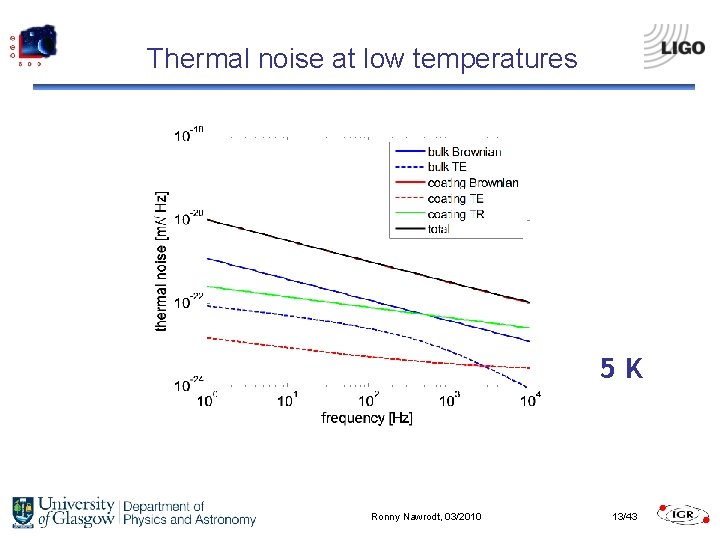
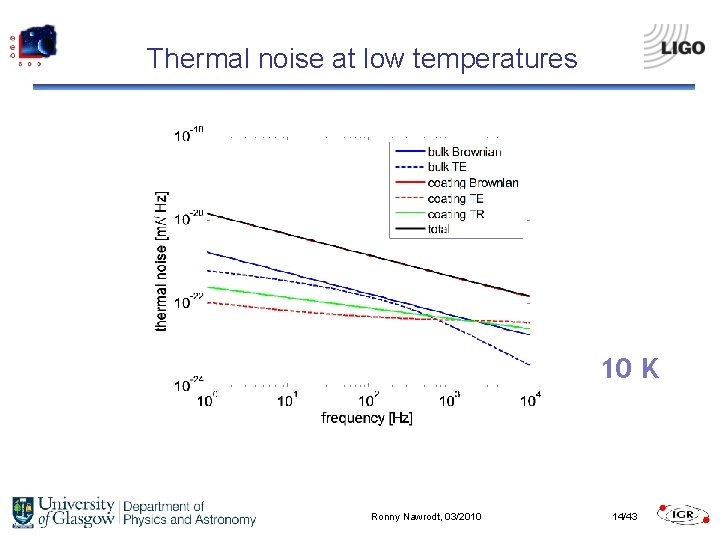
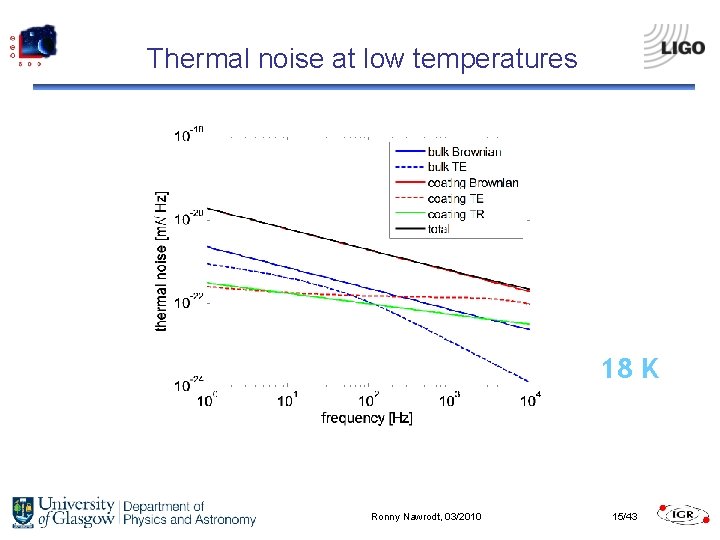
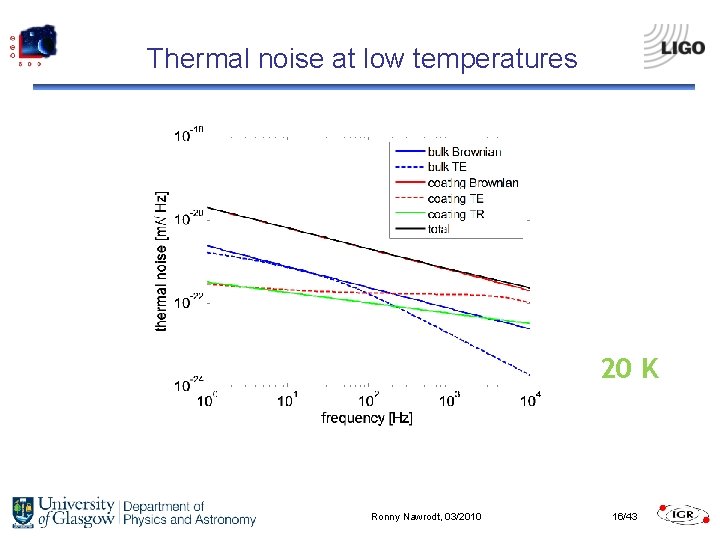
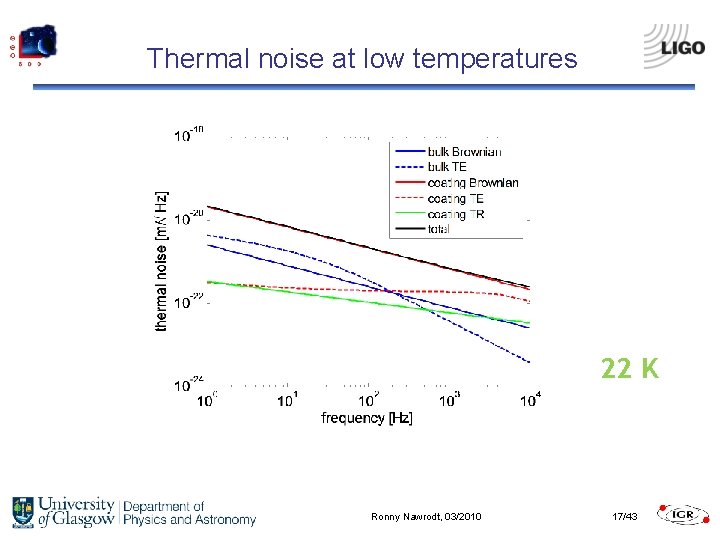
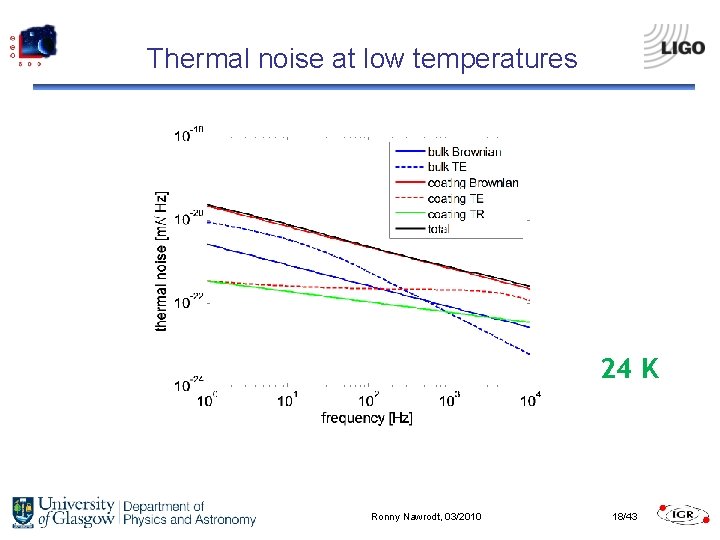

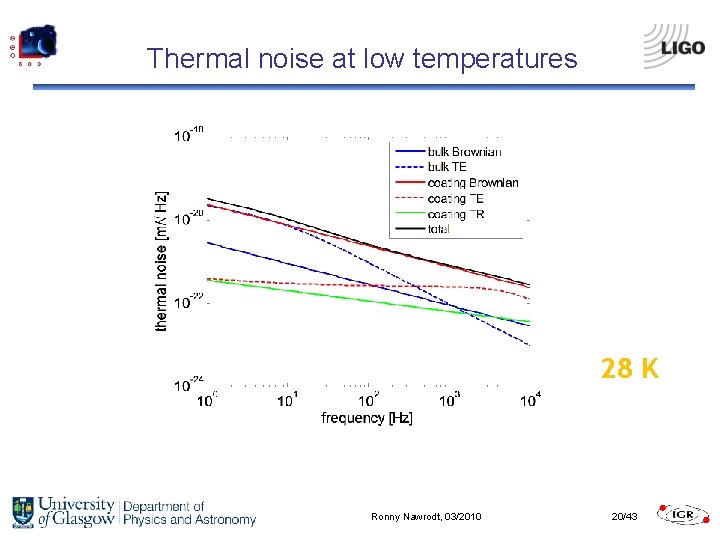
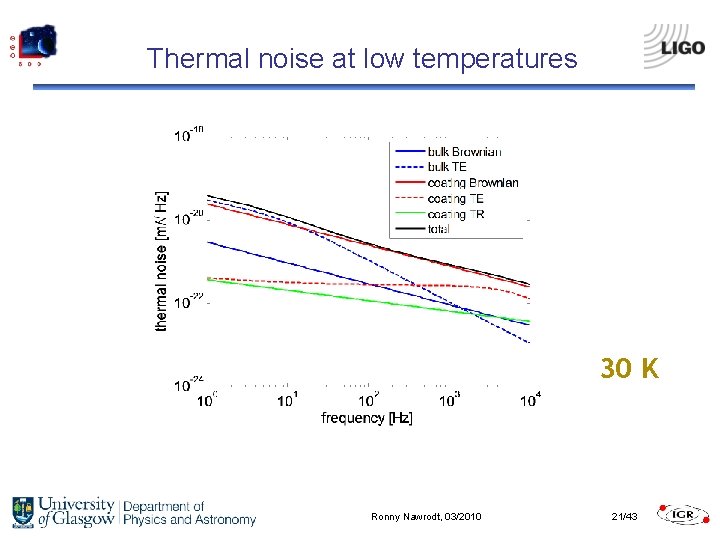
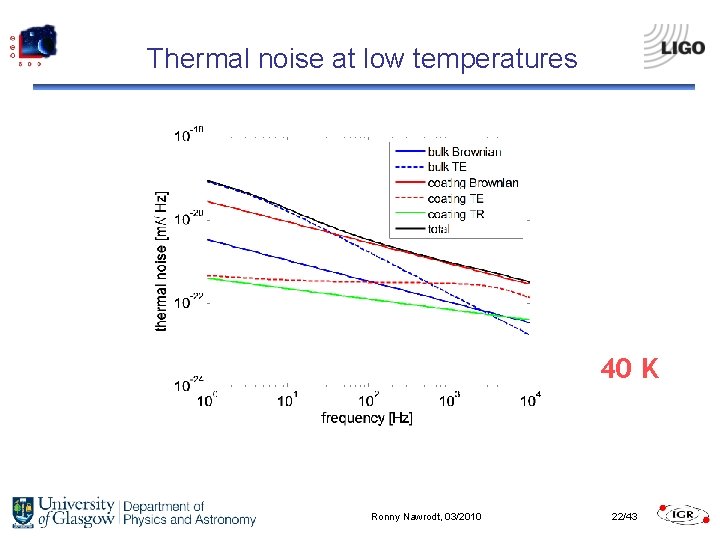
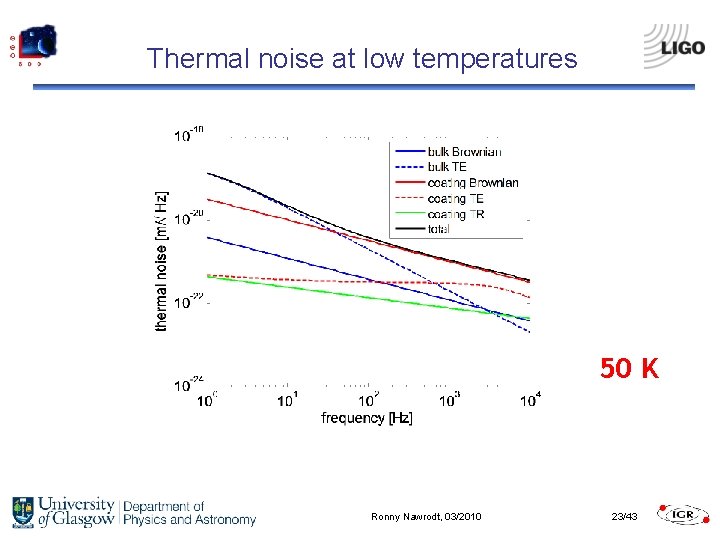
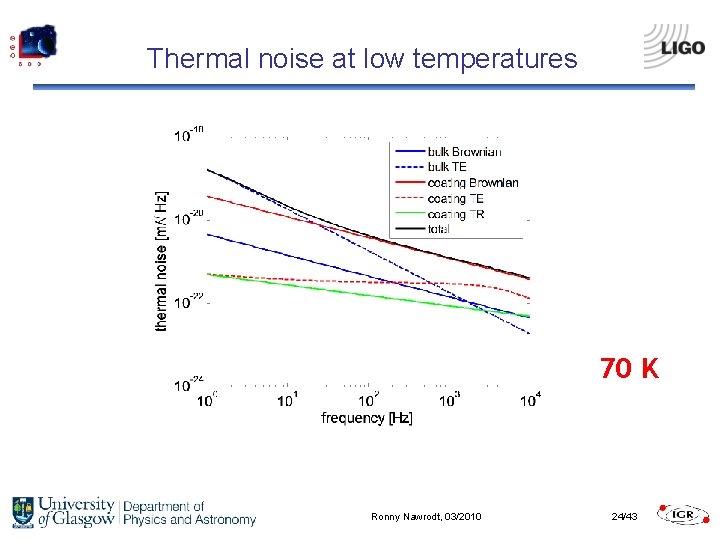
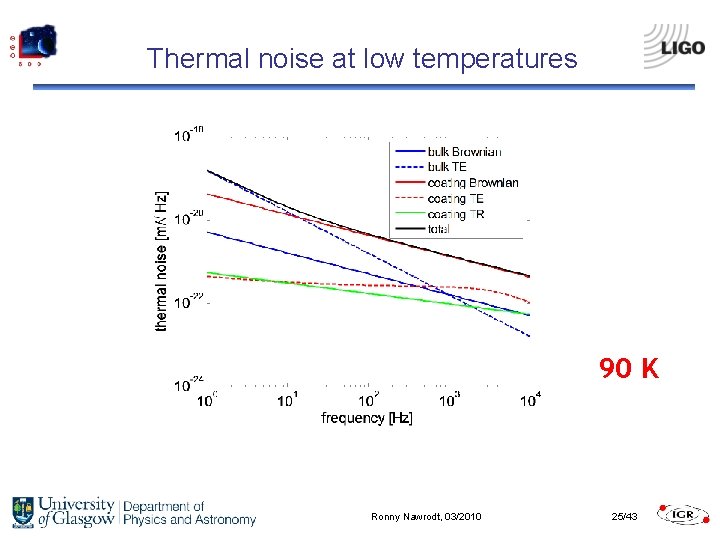
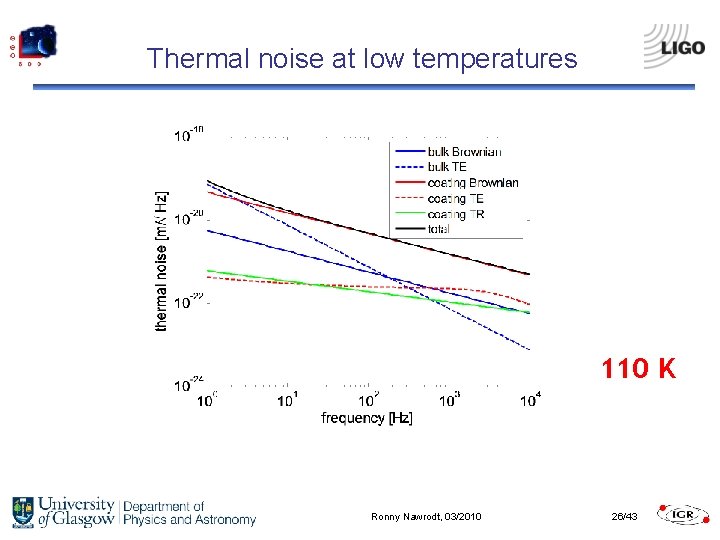
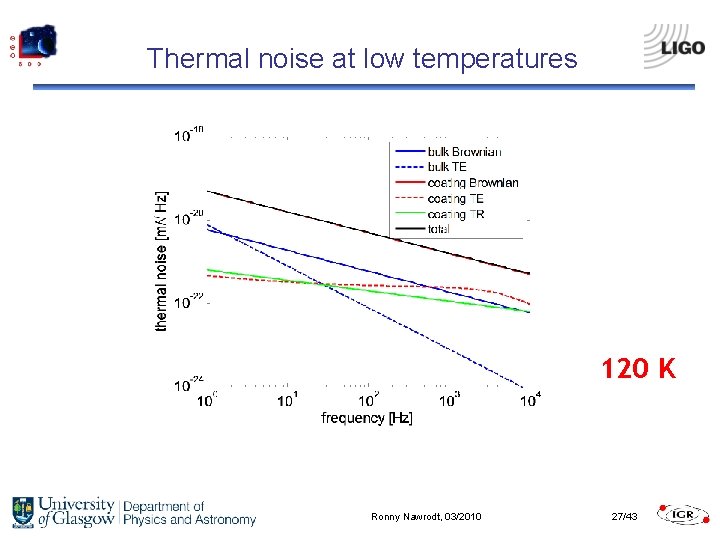

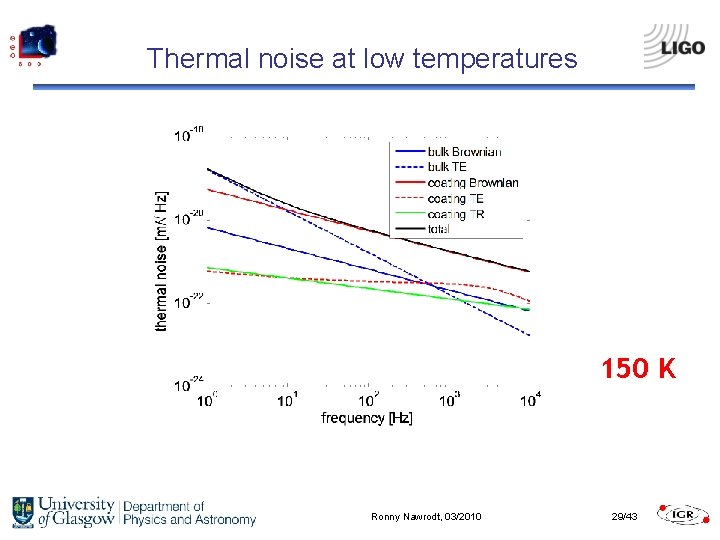
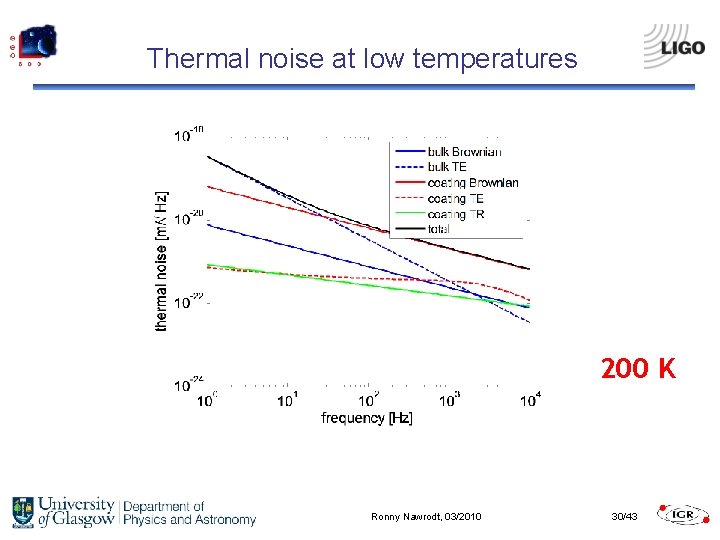
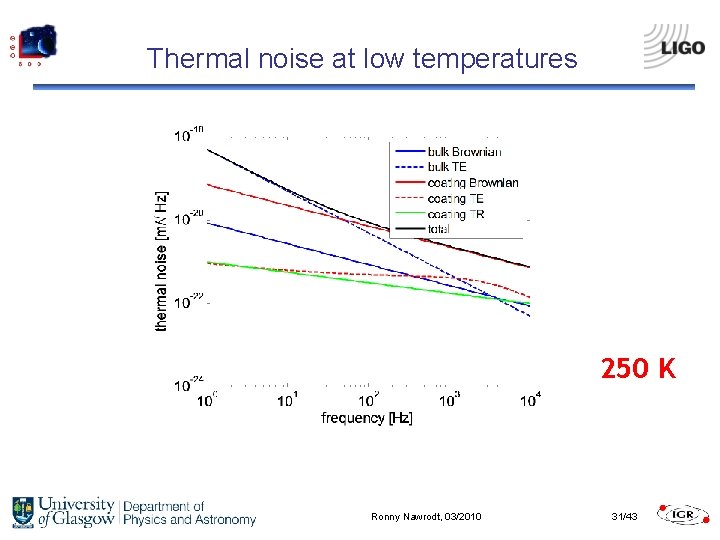
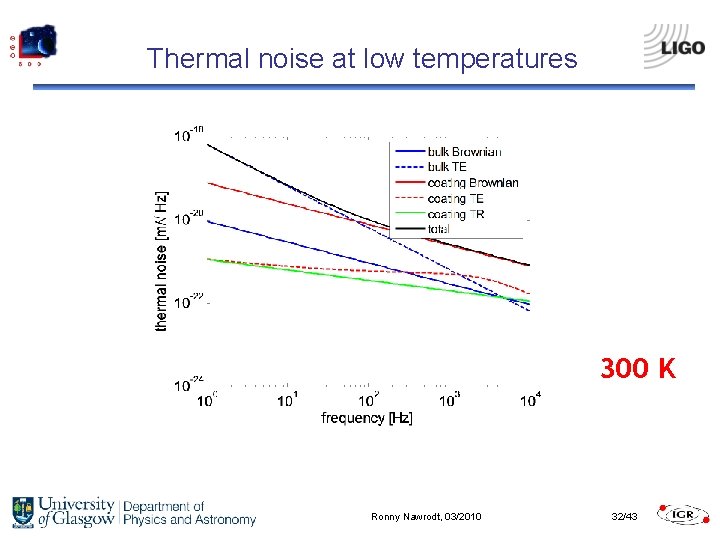
![Example calculation n simplified layout: 10 km [S. Hild] Si(111) + HR stack, 20 Example calculation n simplified layout: 10 km [S. Hild] Si(111) + HR stack, 20](https://slidetodoc.com/presentation_image_h/2da57d1ee41f9d5051157a1634b101c2/image-33.jpg)
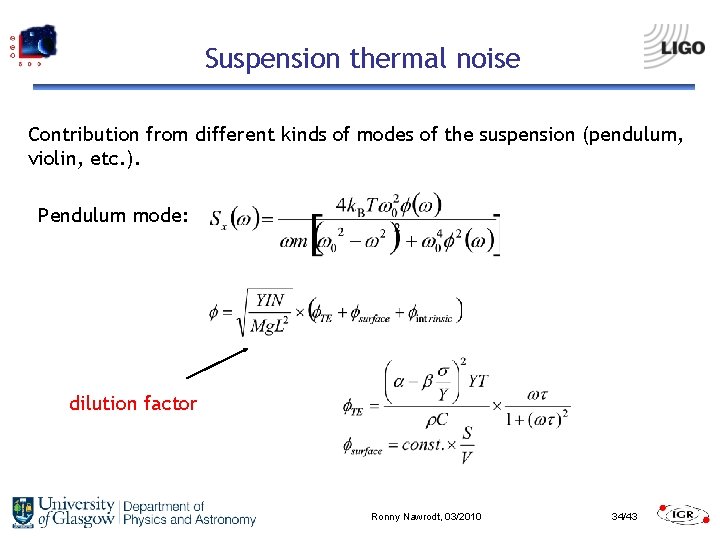
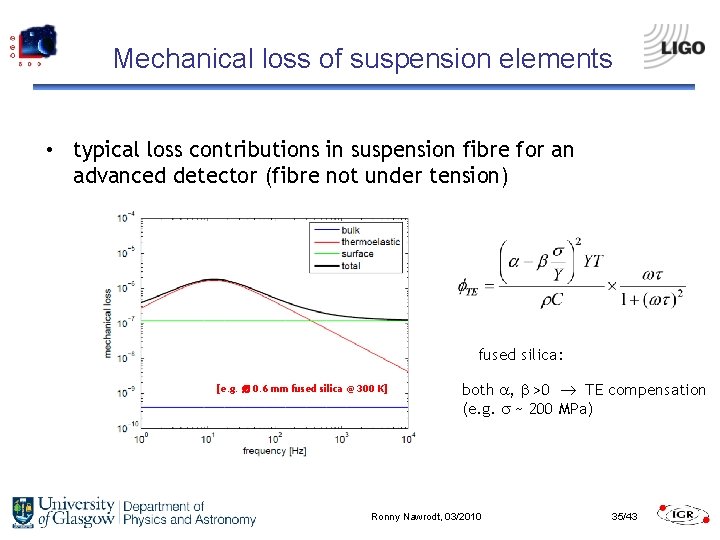
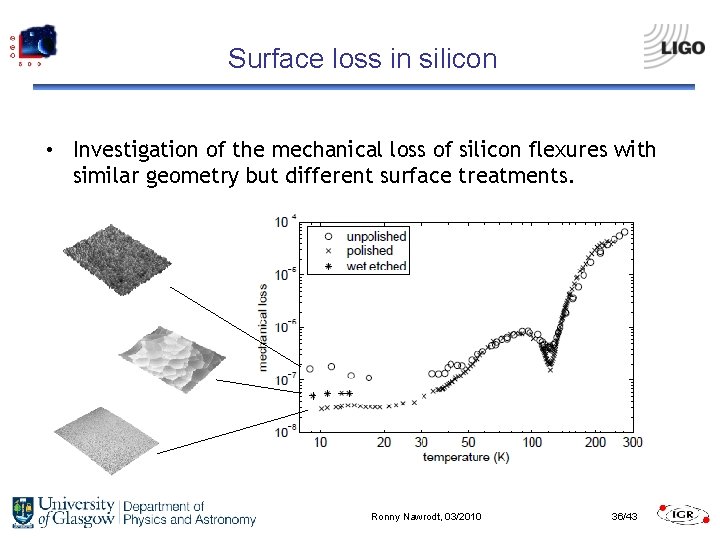
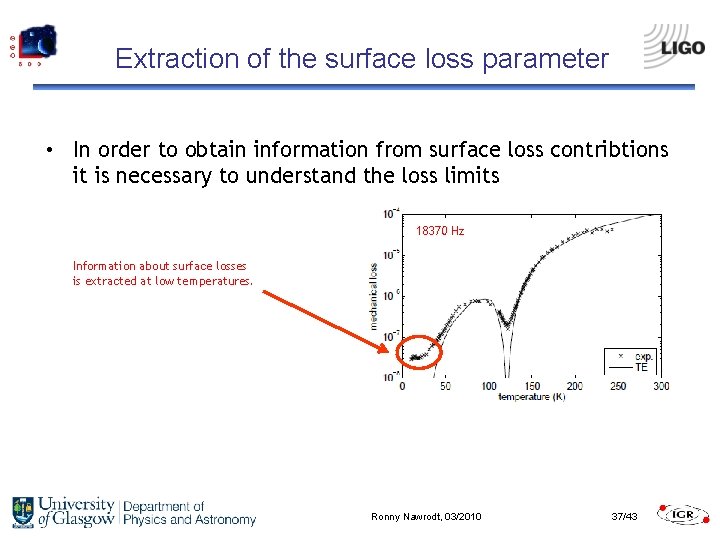
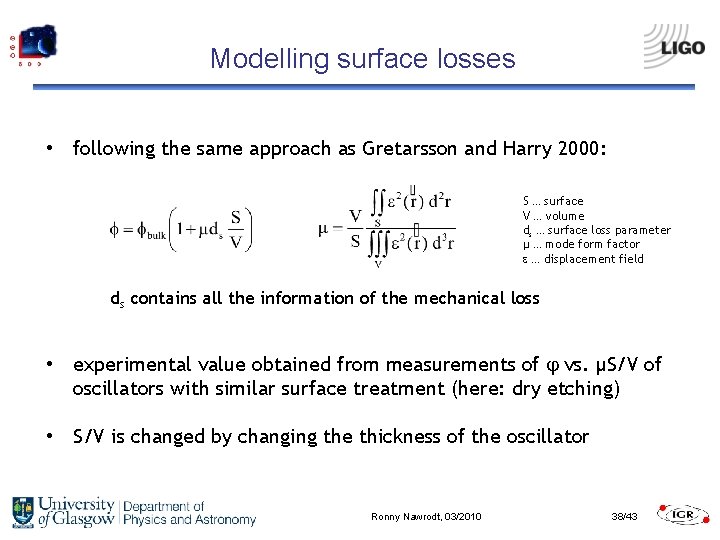
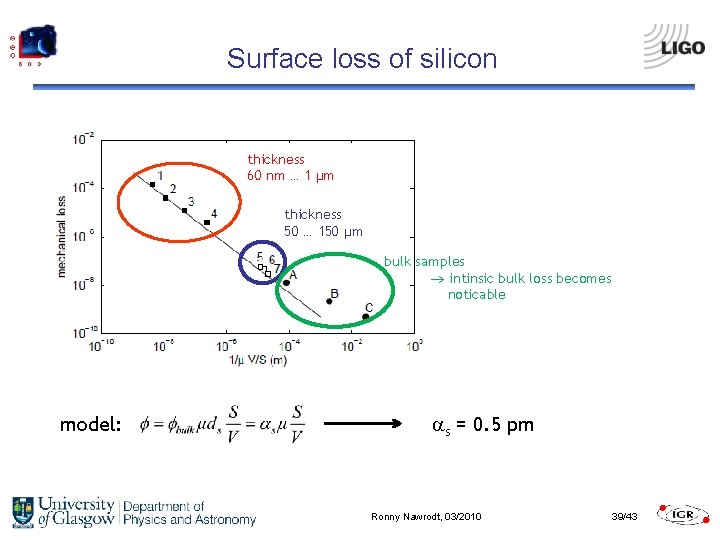
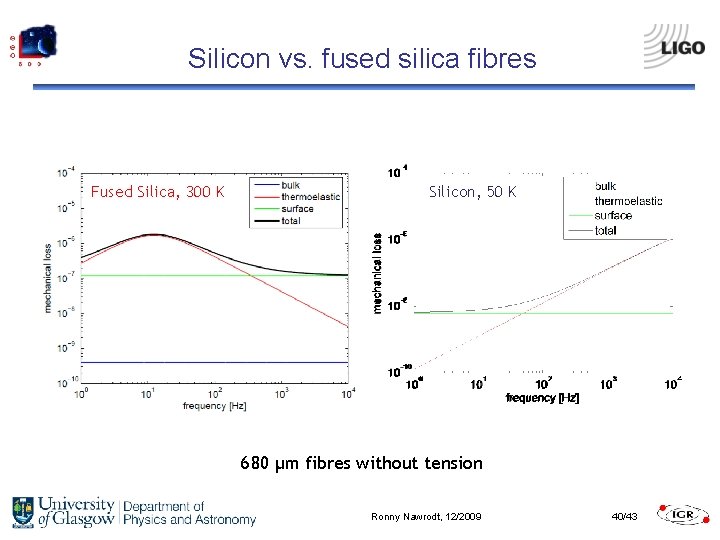
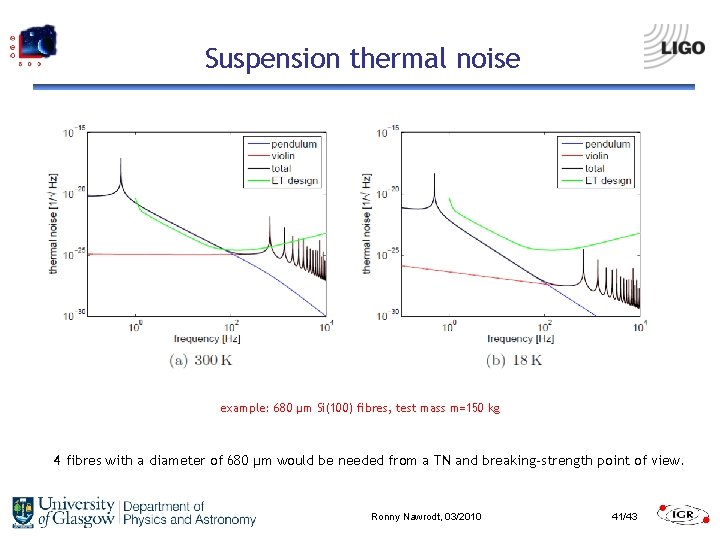
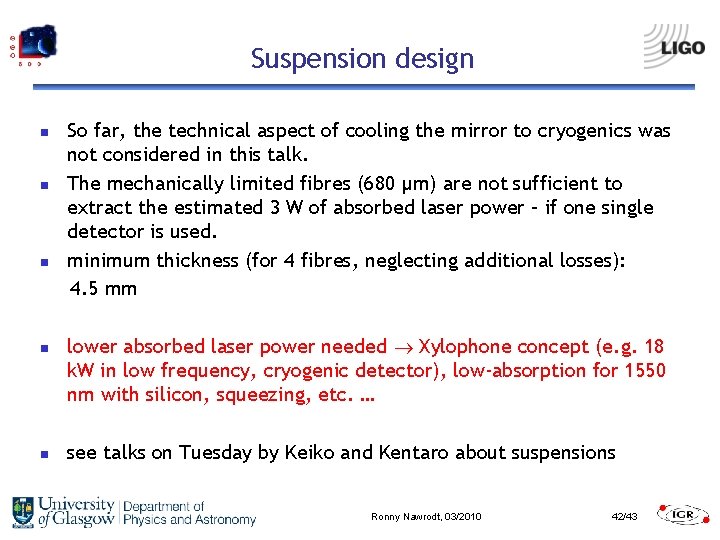
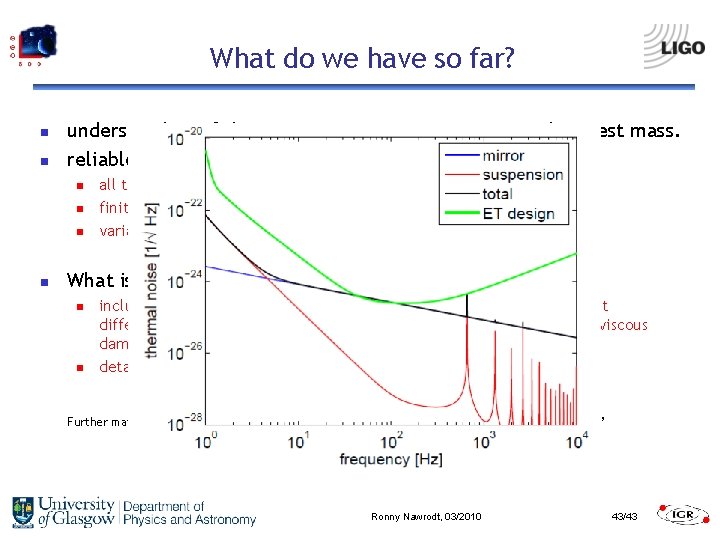
- Slides: 43
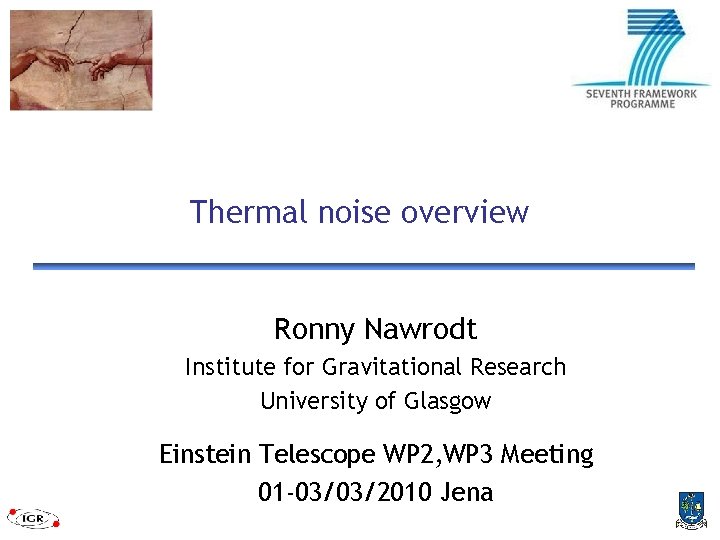
Thermal noise overview Ronny Nawrodt Institute for Gravitational Research University of Glasgow Einstein Telescope WP 2, WP 3 Meeting 01 -03/03/2010 Jena
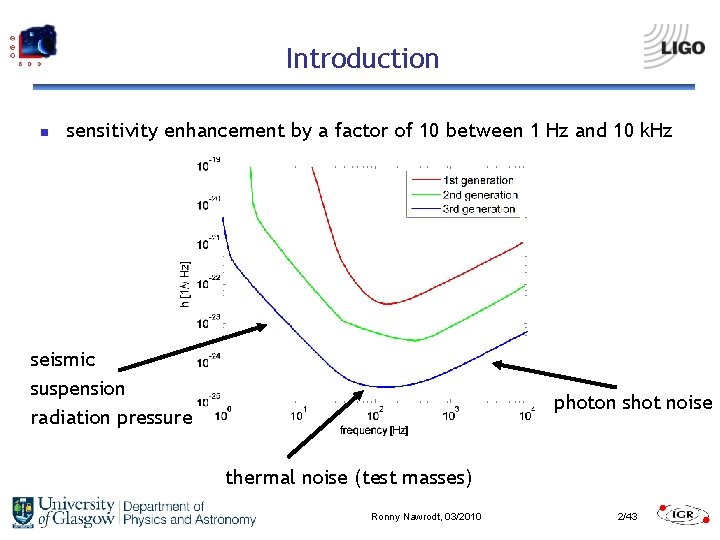
Introduction n sensitivity enhancement by a factor of 10 between 1 Hz and 10 k. Hz seismic suspension radiation pressure photon shot noise thermal noise (test masses) Ronny Nawrodt, 03/2010 2/43
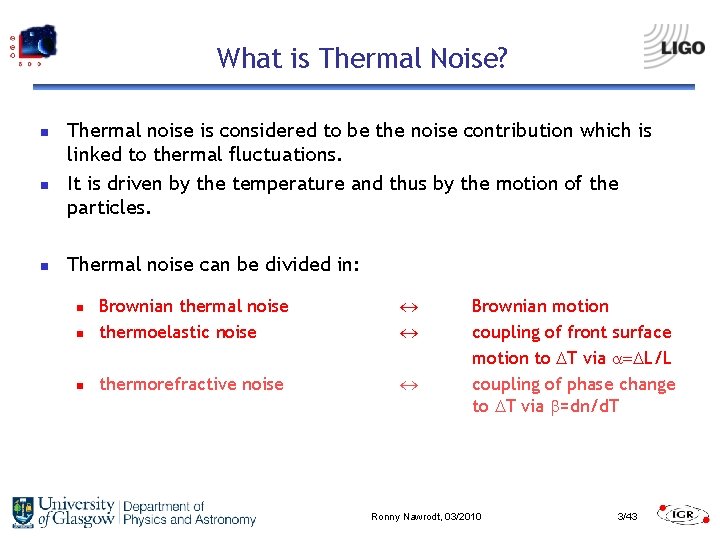
What is Thermal Noise? n n n Thermal noise is considered to be the noise contribution which is linked to thermal fluctuations. It is driven by the temperature and thus by the motion of the particles. Thermal noise can be divided in: n Brownian thermal noise thermoelastic noise n thermorefractive noise n Brownian motion coupling of front surface motion to DT via =DL/L coupling of phase change to DT via =dn/d. T Ronny Nawrodt, 03/2010 3/43
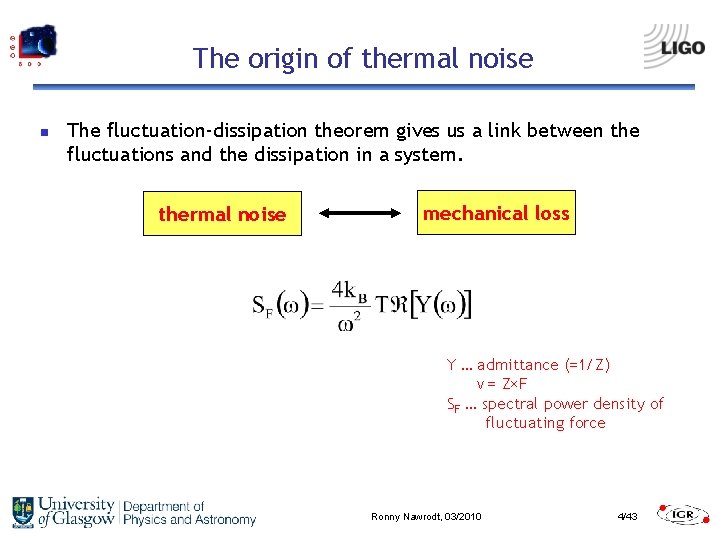
The origin of thermal noise n The fluctuation-dissipation theorem gives us a link between the fluctuations and the dissipation in a system. thermal noise mechanical loss Y … admittance (=1/Z) v = Z×F SF … spectral power density of fluctuating force Ronny Nawrodt, 03/2010 4/43
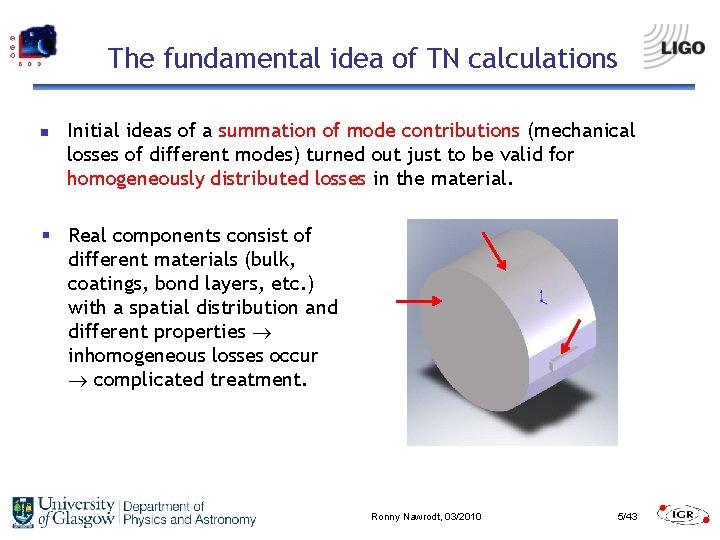
The fundamental idea of TN calculations n Initial ideas of a summation of mode contributions (mechanical losses of different modes) turned out just to be valid for homogeneously distributed losses in the material. § Real components consist of different materials (bulk, coatings, bond layers, etc. ) with a spatial distribution and different properties inhomogeneous losses occur complicated treatment. Ronny Nawrodt, 03/2010 5/43
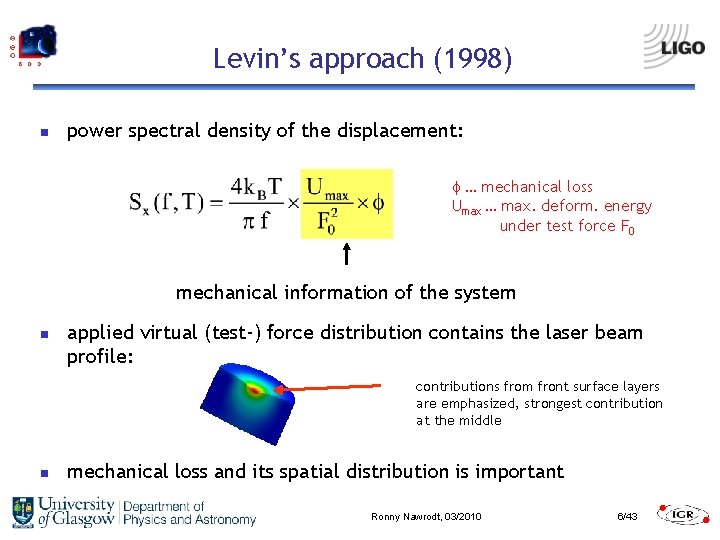
Levin’s approach (1998) n power spectral density of the displacement: … mechanical loss Umax … max. deform. energy under test force F 0 mechanical information of the system n applied virtual (test-) force distribution contains the laser beam profile: contributions from front surface layers are emphasized, strongest contribution at the middle n mechanical loss and its spatial distribution is important Ronny Nawrodt, 03/2010 6/43
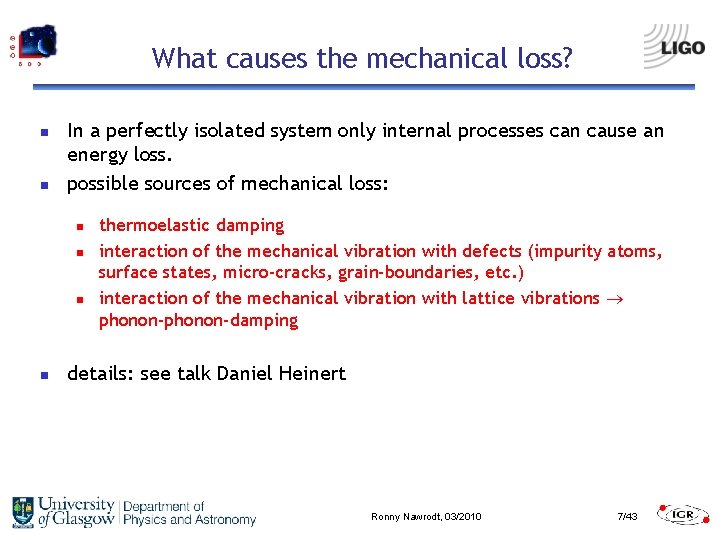
What causes the mechanical loss? n n In a perfectly isolated system only internal processes can cause an energy loss. possible sources of mechanical loss: n n thermoelastic damping interaction of the mechanical vibration with defects (impurity atoms, surface states, micro-cracks, grain-boundaries, etc. ) interaction of the mechanical vibration with lattice vibrations phonon-damping details: see talk Daniel Heinert Ronny Nawrodt, 03/2010 7/43
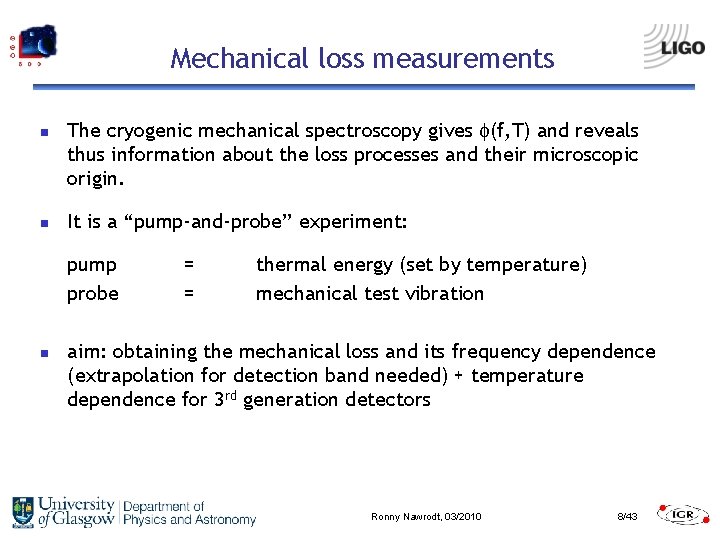
Mechanical loss measurements n n The cryogenic mechanical spectroscopy gives (f, T) and reveals thus information about the loss processes and their microscopic origin. It is a “pump-and-probe” experiment: pump probe n = = thermal energy (set by temperature) mechanical test vibration aim: obtaining the mechanical loss and its frequency dependence (extrapolation for detection band needed) + temperature dependence for 3 rd generation detectors Ronny Nawrodt, 03/2010 8/43
![Bulk material thermal noise calculation n thermoelastic noise Braginsky 1999 Liu Thorne 2000 n Bulk material thermal noise calculation n thermoelastic noise: [Braginsky 1999] [Liu, Thorne 2000] n](https://slidetodoc.com/presentation_image_h/2da57d1ee41f9d5051157a1634b101c2/image-9.jpg)
Bulk material thermal noise calculation n thermoelastic noise: [Braginsky 1999] [Liu, Thorne 2000] n Brownian thermal noise: [Liu, Thorne 2000] [Liu, Thorne 2000, Bondu, Hello, Vinet 1998] Ronny Nawrodt, 03/2010 9/43
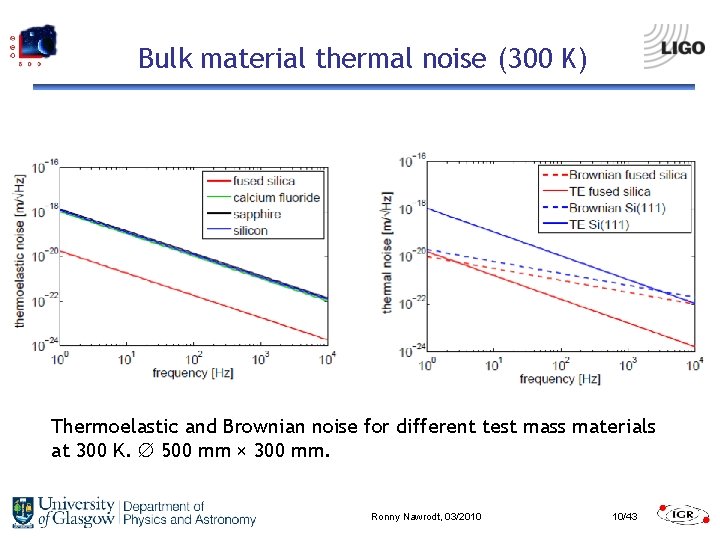
Bulk material thermal noise (300 K) Thermoelastic and Brownian noise for different test mass materials at 300 K. 500 mm × 300 mm. Ronny Nawrodt, 03/2010 10/43
![Coating thermal noise calculation n thermoelastic noise Braginsky Fejer et al 2004 n Brownian Coating thermal noise calculation n thermoelastic noise: [Braginsky, Fejer et al. 2004] n Brownian](https://slidetodoc.com/presentation_image_h/2da57d1ee41f9d5051157a1634b101c2/image-11.jpg)
Coating thermal noise calculation n thermoelastic noise: [Braginsky, Fejer et al. 2004] n Brownian thermal noise: [Harry et al. 2002] Finite size corrections: [Somiya, Yamamoto 2009] increase of thermal noise if mirror is „too thin“, roughly thickness < radius, corrections for an advanced detector ~ 5% Ronny Nawrodt, 03/2010 11/43
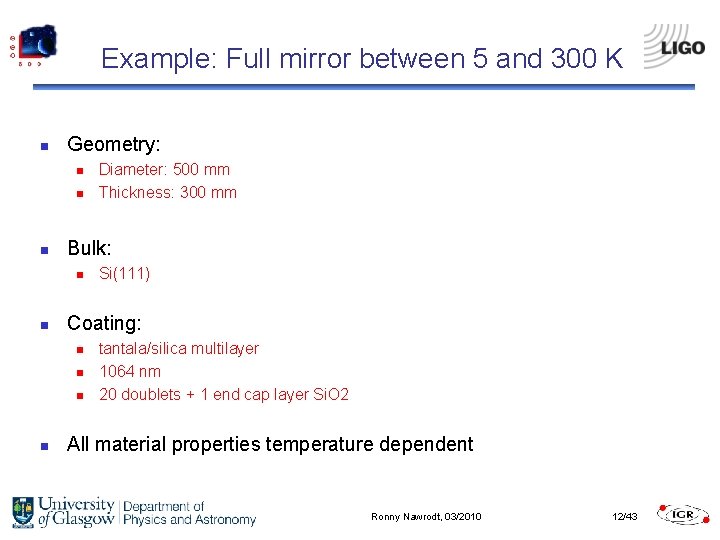
Example: Full mirror between 5 and 300 K n Geometry: n n n Bulk: n n Si(111) Coating: n n Diameter: 500 mm Thickness: 300 mm tantala/silica multilayer 1064 nm 20 doublets + 1 end cap layer Si. O 2 All material properties temperature dependent Ronny Nawrodt, 03/2010 12/43
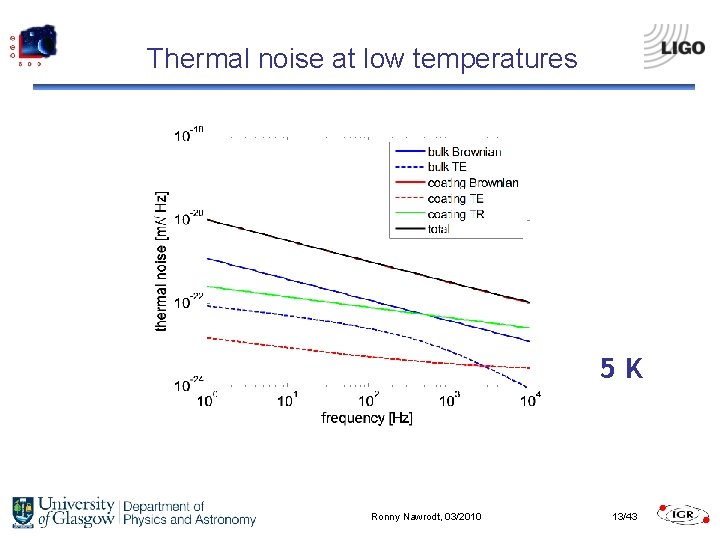
Thermal noise at low temperatures 5 K Ronny Nawrodt, 03/2010 13/43
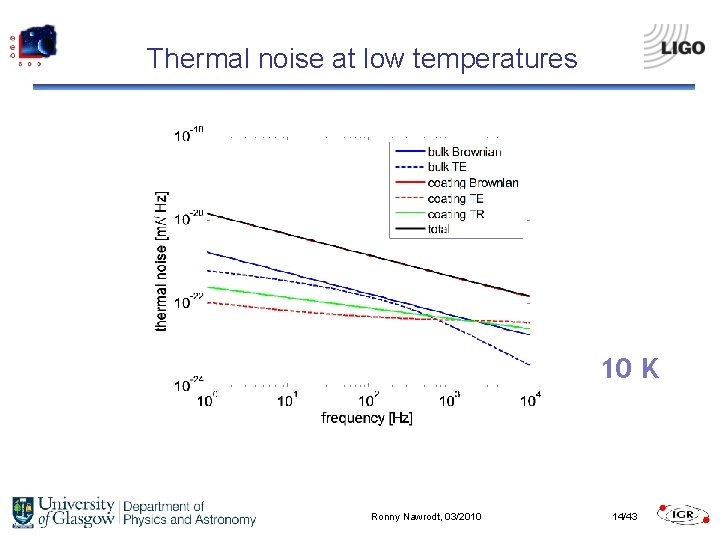
Thermal noise at low temperatures 10 K Ronny Nawrodt, 03/2010 14/43
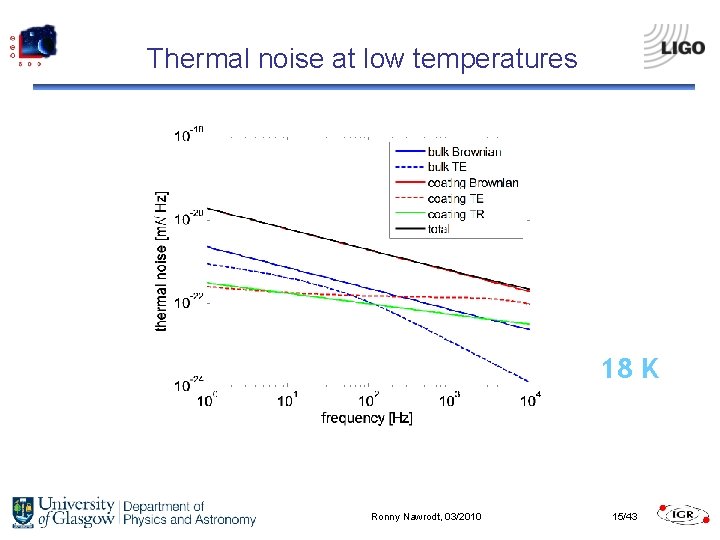
Thermal noise at low temperatures 18 K Ronny Nawrodt, 03/2010 15/43
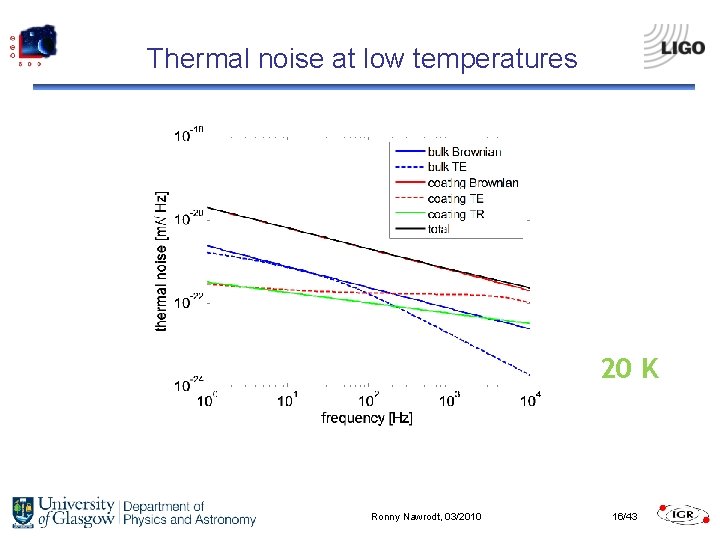
Thermal noise at low temperatures 20 K Ronny Nawrodt, 03/2010 16/43
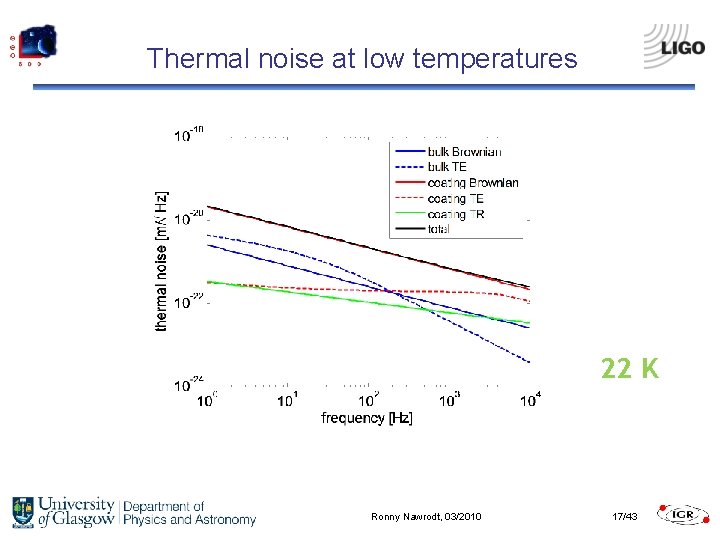
Thermal noise at low temperatures 22 K Ronny Nawrodt, 03/2010 17/43
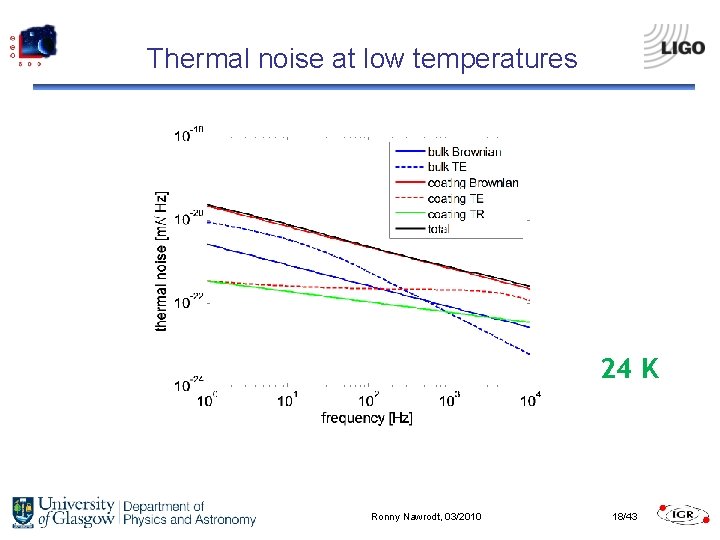
Thermal noise at low temperatures 24 K Ronny Nawrodt, 03/2010 18/43

Thermal noise at low temperatures 26 K Ronny Nawrodt, 03/2010 19/43
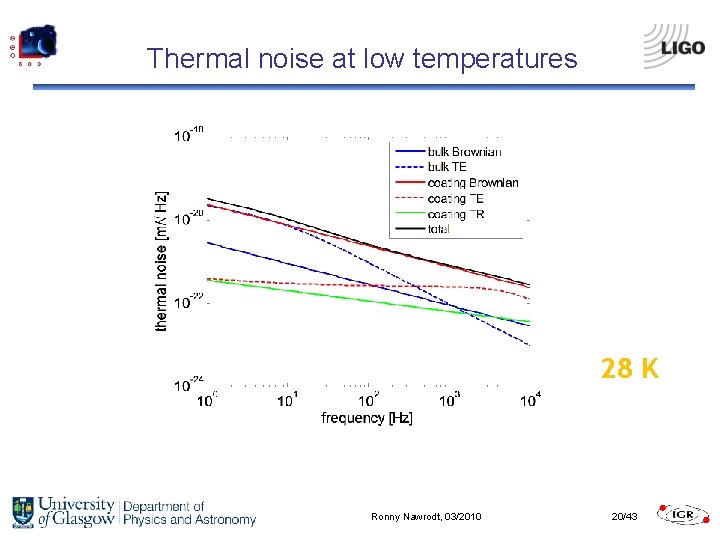
Thermal noise at low temperatures 28 K Ronny Nawrodt, 03/2010 20/43
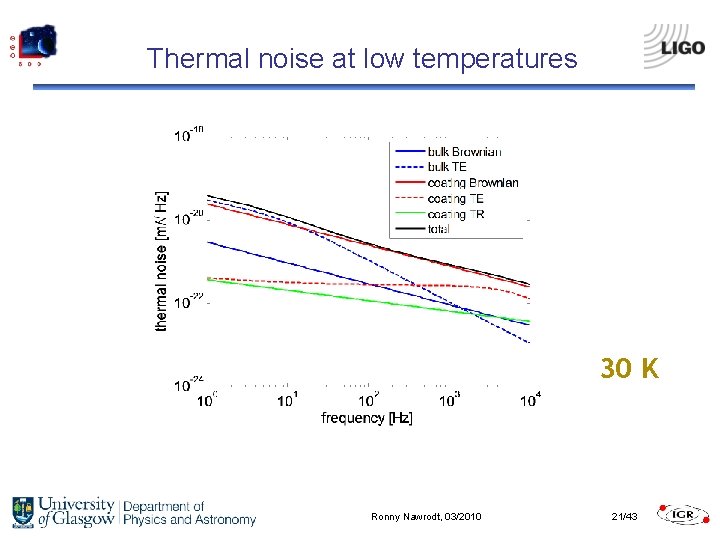
Thermal noise at low temperatures 30 K Ronny Nawrodt, 03/2010 21/43
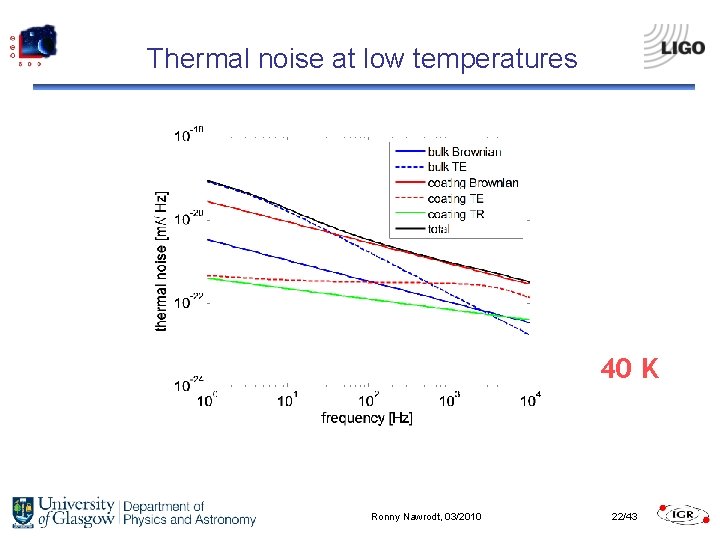
Thermal noise at low temperatures 40 K Ronny Nawrodt, 03/2010 22/43
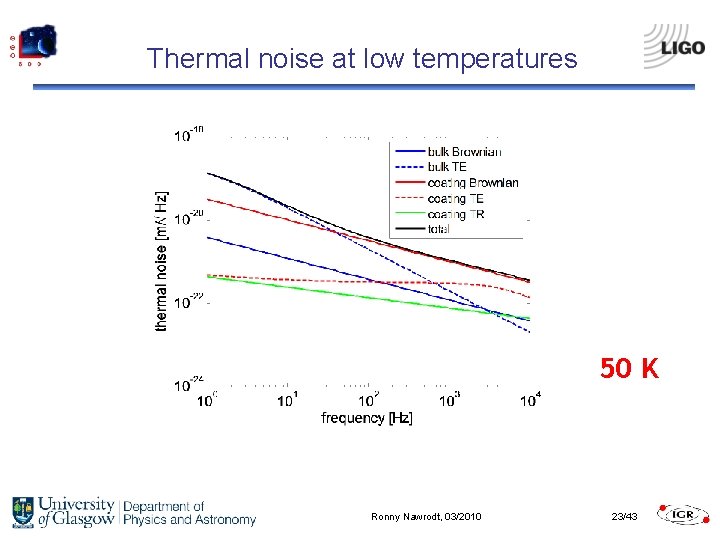
Thermal noise at low temperatures 50 K Ronny Nawrodt, 03/2010 23/43
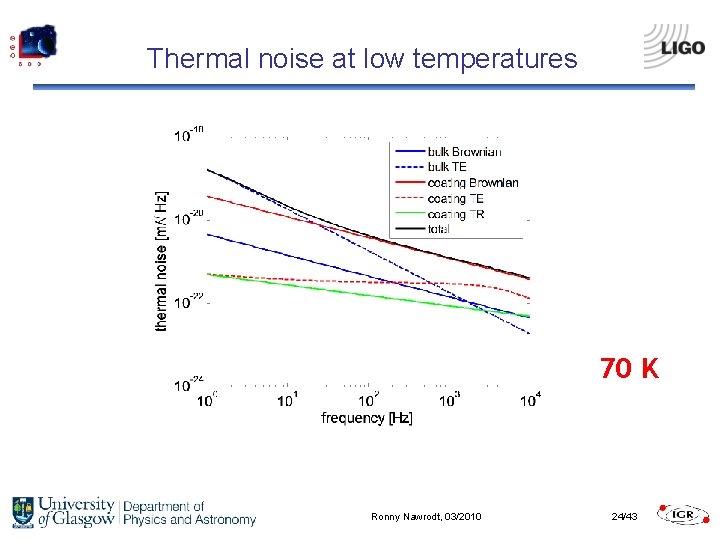
Thermal noise at low temperatures 70 K Ronny Nawrodt, 03/2010 24/43
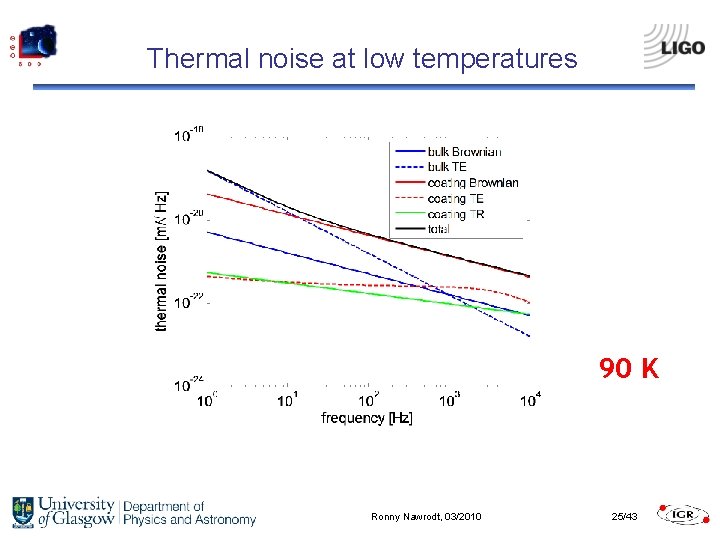
Thermal noise at low temperatures 90 K Ronny Nawrodt, 03/2010 25/43
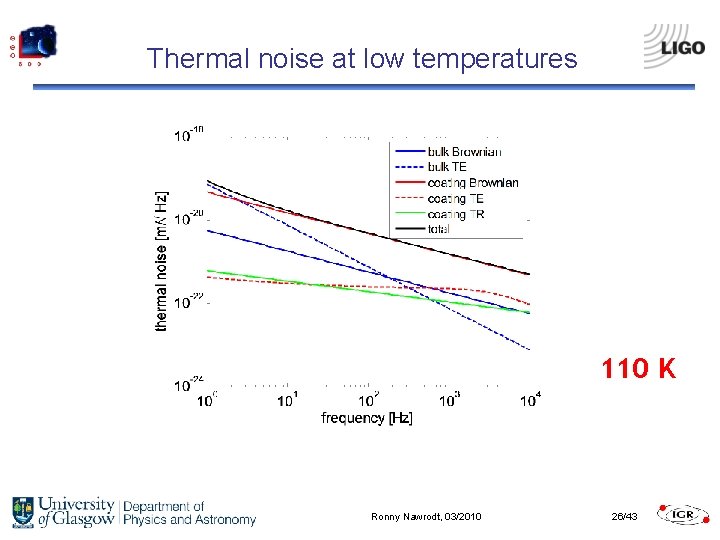
Thermal noise at low temperatures 110 K Ronny Nawrodt, 03/2010 26/43
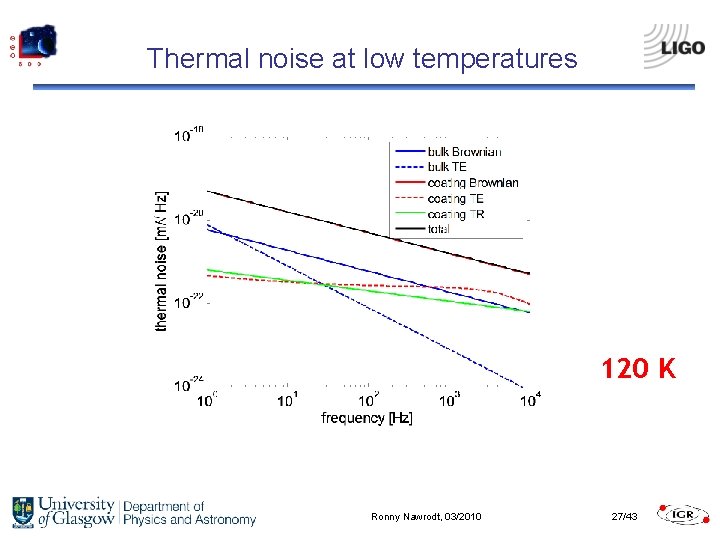
Thermal noise at low temperatures 120 K Ronny Nawrodt, 03/2010 27/43

Thermal noise at low temperatures 130 K Ronny Nawrodt, 03/2010 28/43
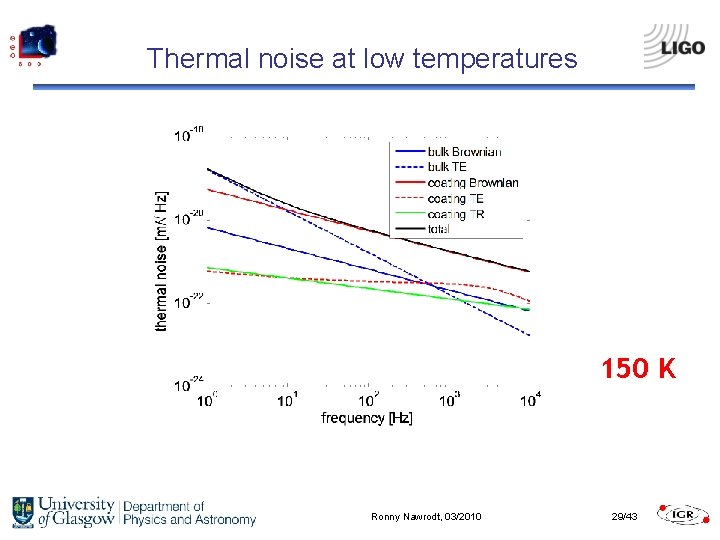
Thermal noise at low temperatures 150 K Ronny Nawrodt, 03/2010 29/43
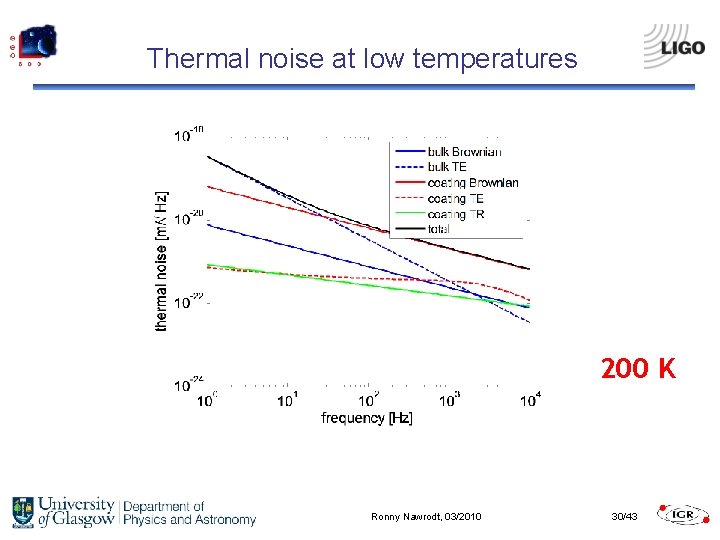
Thermal noise at low temperatures 200 K Ronny Nawrodt, 03/2010 30/43
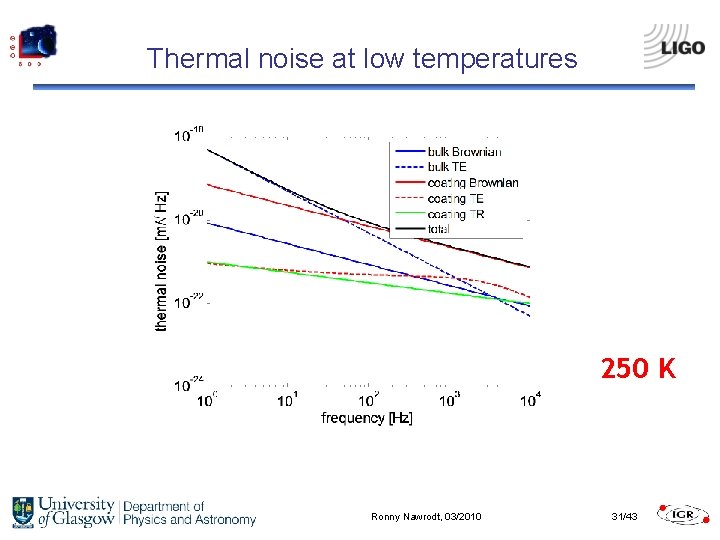
Thermal noise at low temperatures 250 K Ronny Nawrodt, 03/2010 31/43
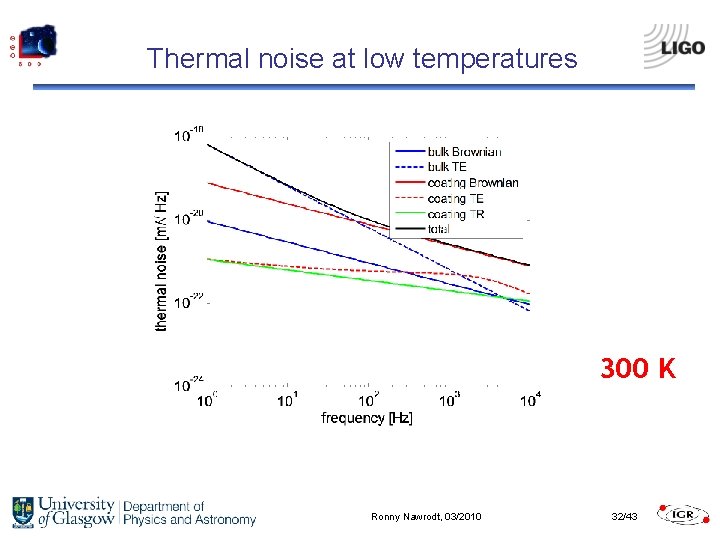
Thermal noise at low temperatures 300 K Ronny Nawrodt, 03/2010 32/43
![Example calculation n simplified layout 10 km S Hild Si111 HR stack 20 Example calculation n simplified layout: 10 km [S. Hild] Si(111) + HR stack, 20](https://slidetodoc.com/presentation_image_h/2da57d1ee41f9d5051157a1634b101c2/image-33.jpg)
Example calculation n simplified layout: 10 km [S. Hild] Si(111) + HR stack, 20 K 4 identical components, 10 km arm length Ronny Nawrodt, 03/2010 33/43
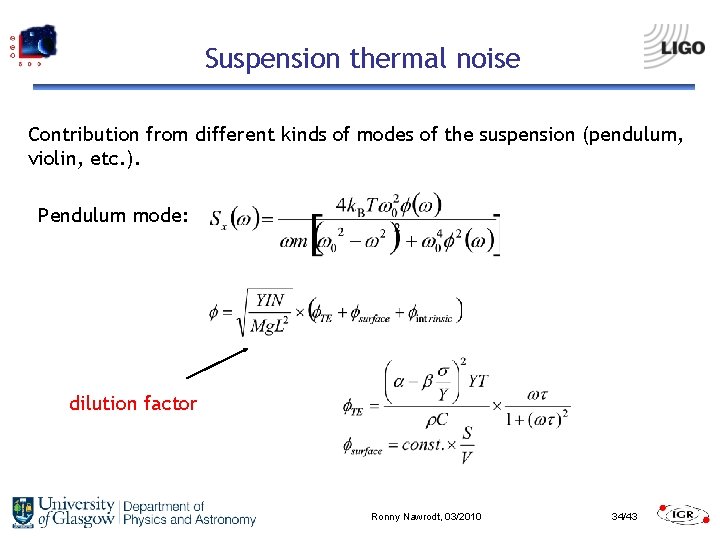
Suspension thermal noise Contribution from different kinds of modes of the suspension (pendulum, violin, etc. ). Pendulum mode: dilution factor Ronny Nawrodt, 03/2010 34/43
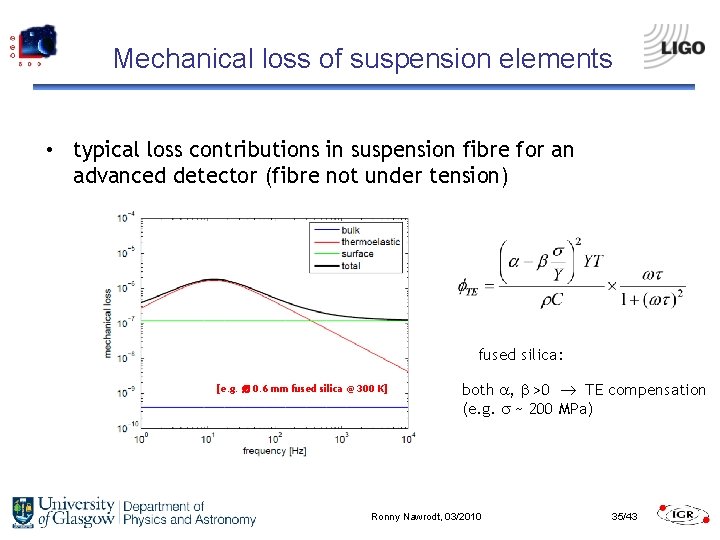
Mechanical loss of suspension elements • typical loss contributions in suspension fibre for an advanced detector (fibre not under tension) fused silica: [e. g. 0. 6 mm fused silica @ 300 K] both , >0 TE compensation (e. g. ~ 200 MPa) Ronny Nawrodt, 03/2010 35/43
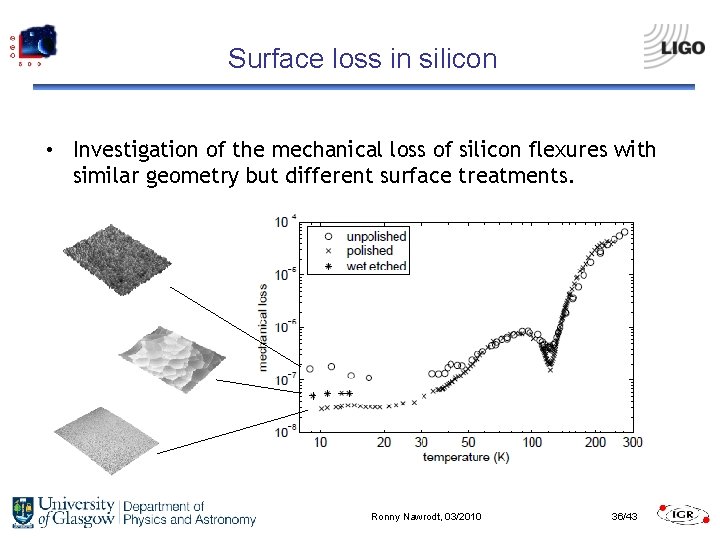
Surface loss in silicon • Investigation of the mechanical loss of silicon flexures with similar geometry but different surface treatments. Ronny Nawrodt, 03/2010 36/43
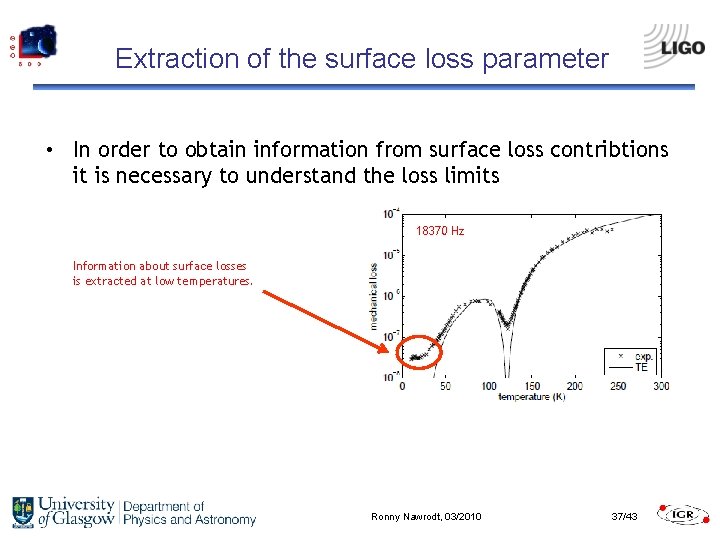
Extraction of the surface loss parameter • In order to obtain information from surface loss contribtions it is necessary to understand the loss limits 18370 Hz Information about surface losses is extracted at low temperatures. Ronny Nawrodt, 03/2010 37/43
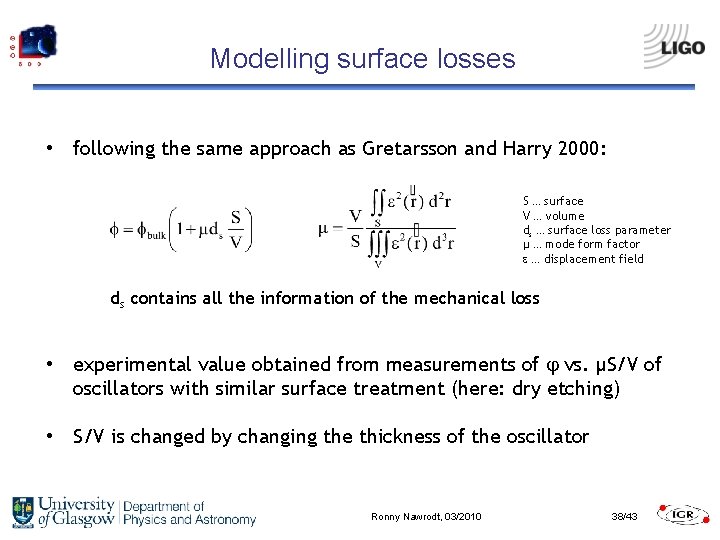
Modelling surface losses • following the same approach as Gretarsson and Harry 2000: S … surface V … volume ds … surface loss parameter µ … mode form factor … displacement field ds contains all the information of the mechanical loss • experimental value obtained from measurements of vs. µS/V of oscillators with similar surface treatment (here: dry etching) • S/V is changed by changing the thickness of the oscillator Ronny Nawrodt, 03/2010 38/43
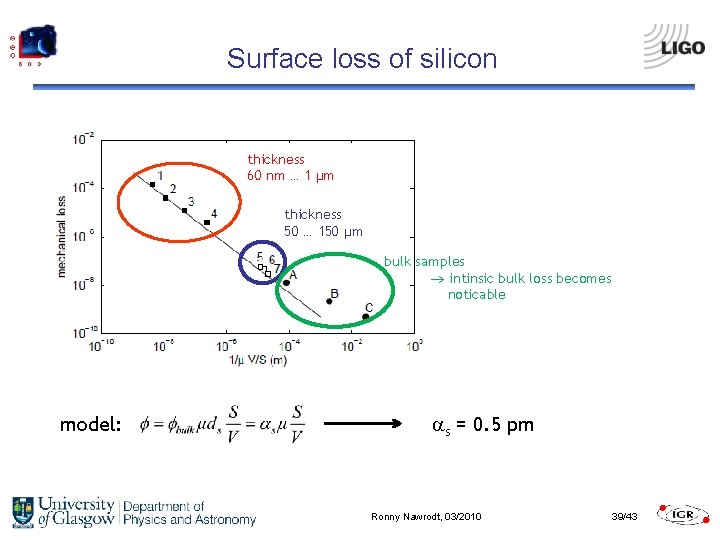
Surface loss of silicon thickness 60 nm … 1 µm thickness 50 … 150 µm bulk samples intinsic bulk loss becomes noticable model: s = 0. 5 pm Ronny Nawrodt, 03/2010 39/43
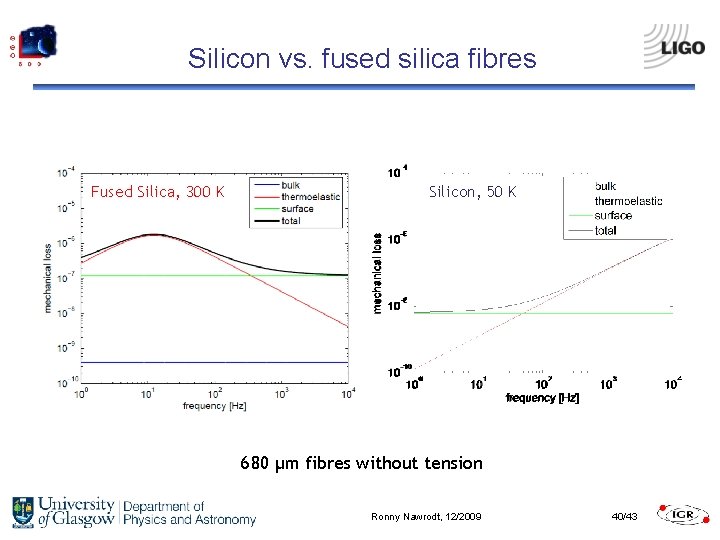
Silicon vs. fused silica fibres Fused Silica, 300 K Silicon, 300 50 KK 680 µm fibres without tension Ronny Nawrodt, 12/2009 40/43
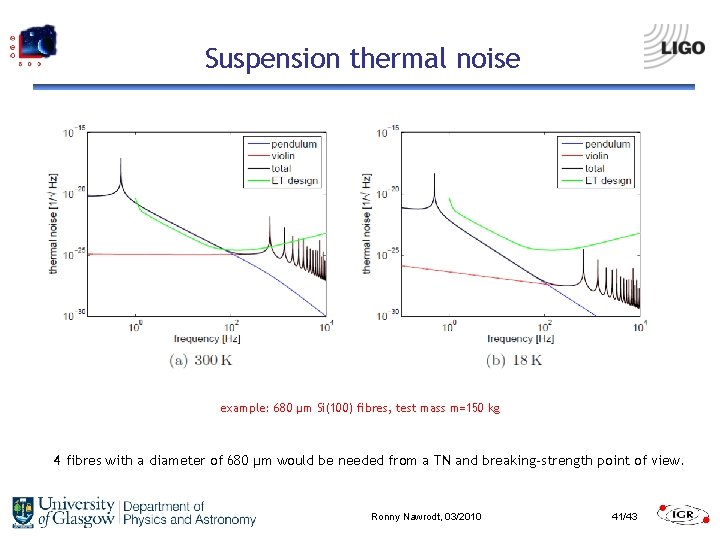
Suspension thermal noise example: 680 µm Si(100) fibres, test mass m=150 kg 4 fibres with a diameter of 680 µm would be needed from a TN and breaking-strength point of view. Ronny Nawrodt, 03/2010 41/43
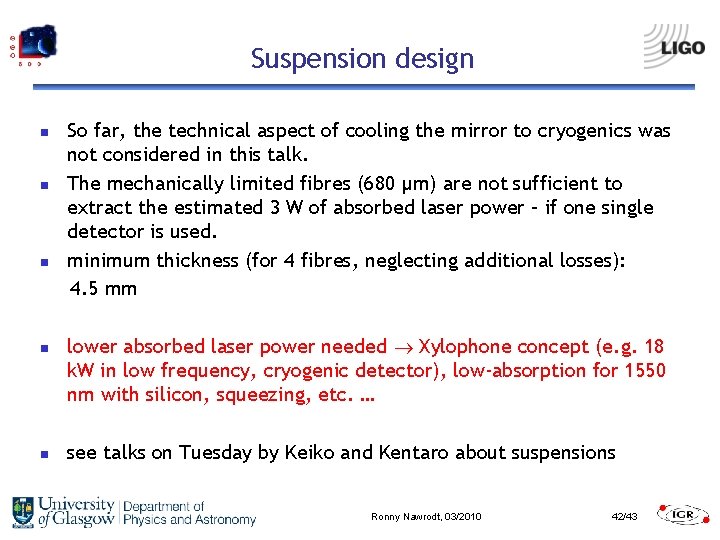
Suspension design n n So far, the technical aspect of cooling the mirror to cryogenics was not considered in this talk. The mechanically limited fibres (680 µm) are not sufficient to extract the estimated 3 W of absorbed laser power – if one single detector is used. minimum thickness (for 4 fibres, neglecting additional losses): 4. 5 mm lower absorbed laser power needed Xylophone concept (e. g. 18 k. W in low frequency, cryogenic detector), low-absorption for 1550 nm with silicon, squeezing, etc. … see talks on Tuesday by Keiko and Kentaro about suspensions Ronny Nawrodt, 03/2010 42/43
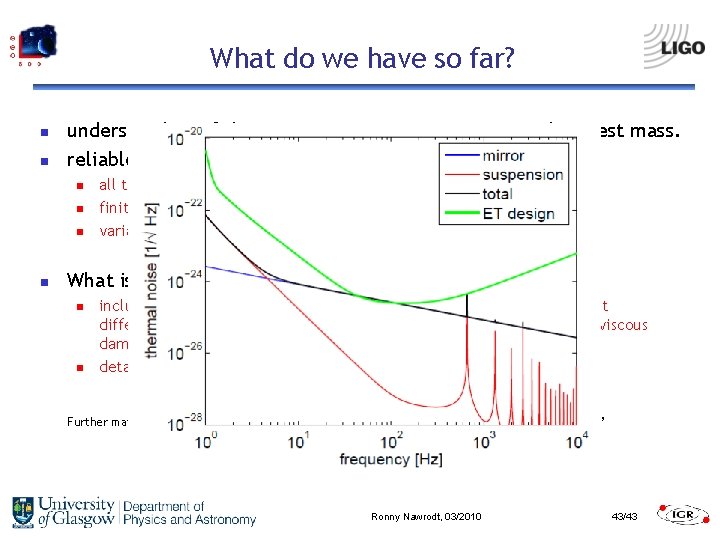
What do we have so far? n n understanding of the main noise sources in a potential ET test mass. reliable Matlab code for TN calculation including: n n all thermal noise sources finite test mass size variable (temperature dependent) material properties What is needed in the near future? n n including detailed suspension thermal noise (different temperatures at different stages, coupling from upper to lower stages, structural and viscous damping VIR-015 E-09 document) detailed documentation Further material: ET-notes ET-021 -09, ET-027 -09 and GRG article special issue “Einstein Telescope” Ronny Nawrodt, 03/2010 43/43
Kronny
Nawrodt
Companding in pcm
Rumus thermal noise
Thermal noise in analog communication
Thermal noise is a wide sense stationary process.
Thermal noise
Section 3 using thermal energy worksheet answer key
Thermal transfer vs direct thermal printing
Ronny chaing
Ronny depoortere
Ronny kohavi
Ronny dillen
Ronny pieters
Ronny decorte
Ronny wickström
Ronny krashinsky
Ronny dalene
Ronny krashinsky
Myndigheten för delaktighet
Presentera för publik crossboss
Mall debattartikel
Kung som dog 1611
Förklara densitet för barn
Tobinskatten för och nackdelar
Tack för att ni lyssnade bild
Tack för att ni har lyssnat
Referatmarkeringar
Karttecken höjdkurva
Luftstrupen för medicinare
Verifikationsplan
Rbk-mätning
Lufttryck formel
Vilka tal pekar pilarna på
Särskild löneskatt för pensionskostnader
Elektronik för barn
Borra hål för knoppar
Smärtskolan kunskap för livet
Bris för vuxna
Jiddisch
Trög för kemist
Delegerande ledarstil
Indikation för kejsarsnitt på moderns önskan
Datorkunskap för nybörjare