Critical Design Review CDR Florida Institute of Technology
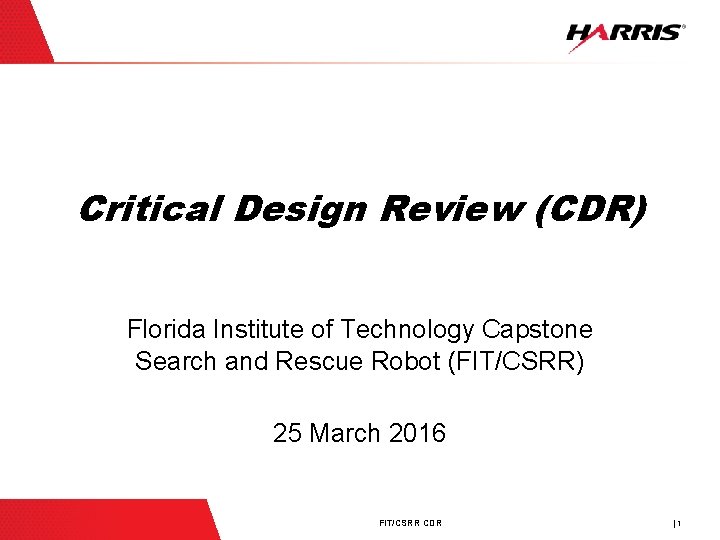
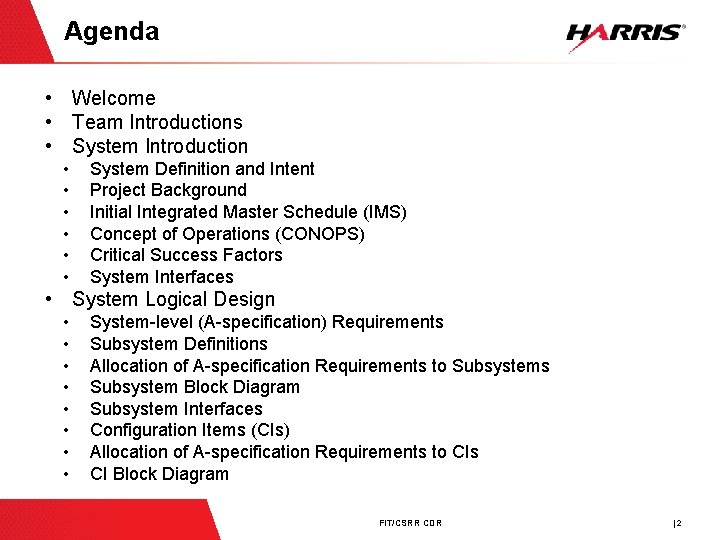
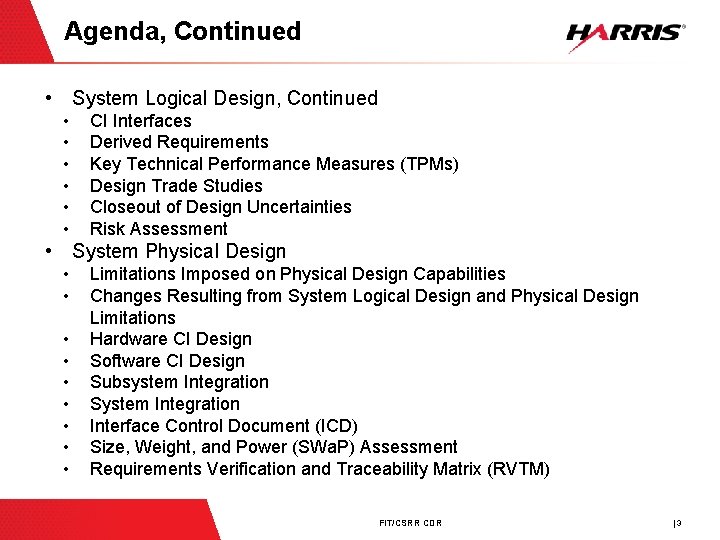
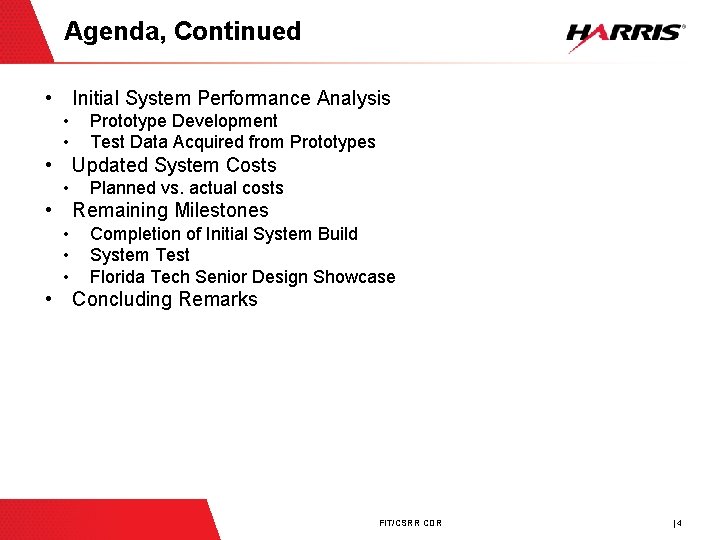

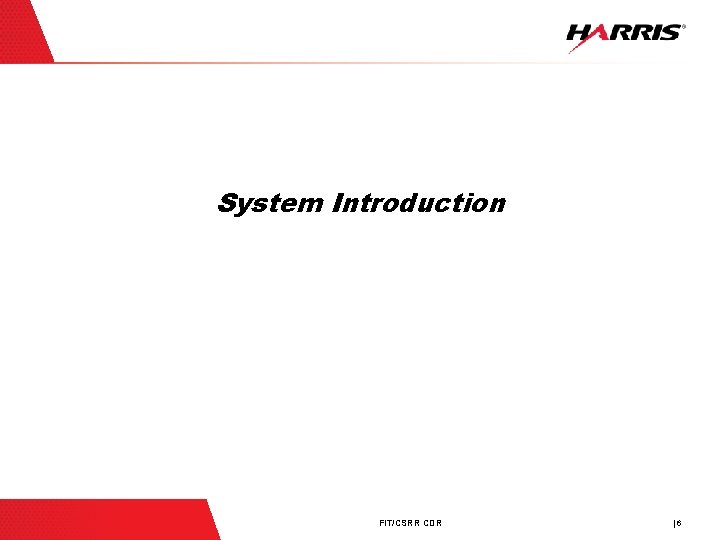
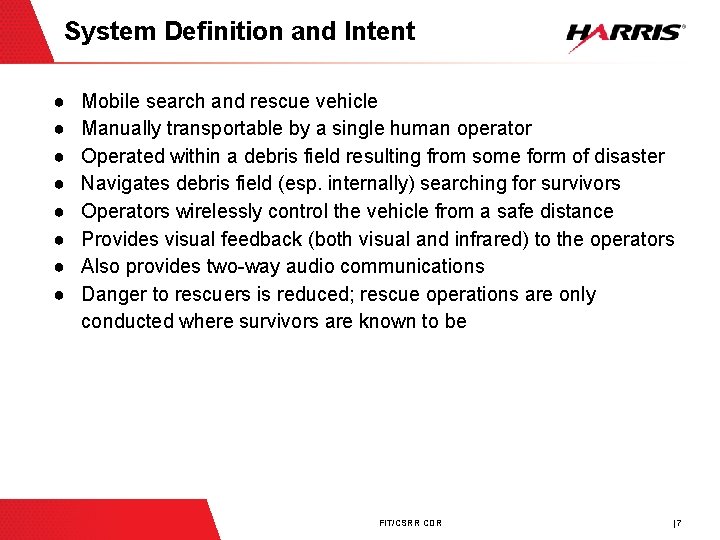
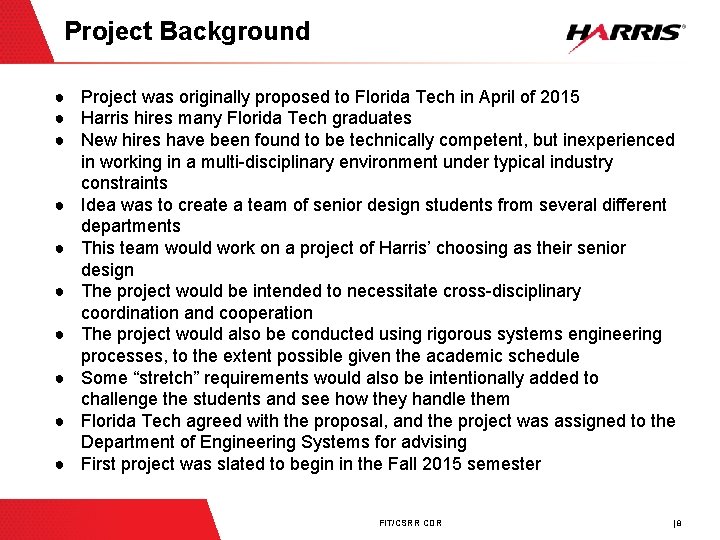
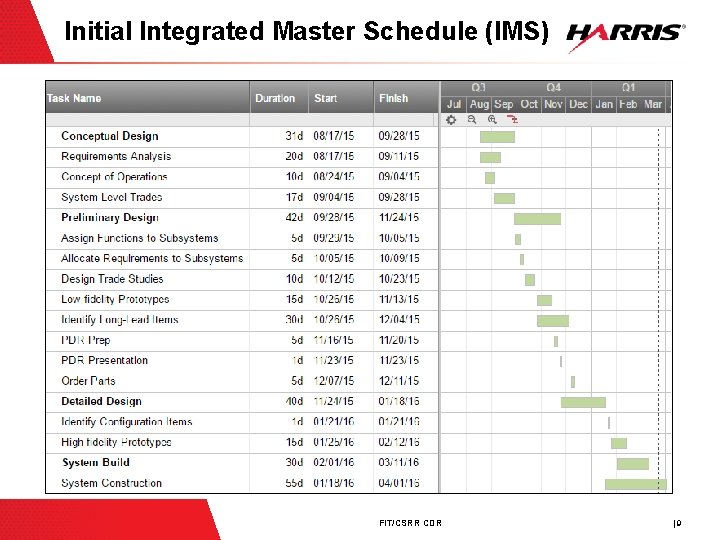
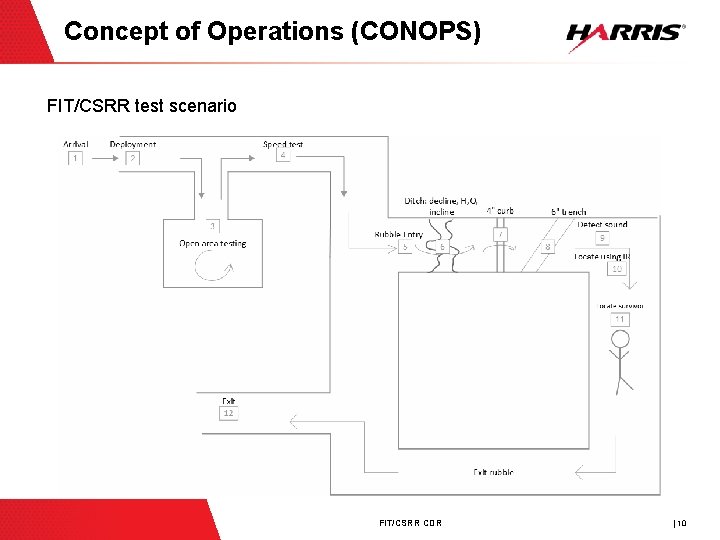
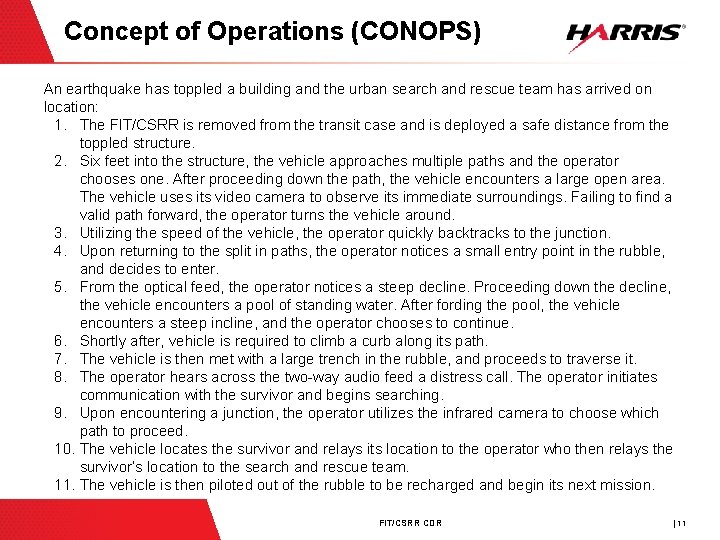
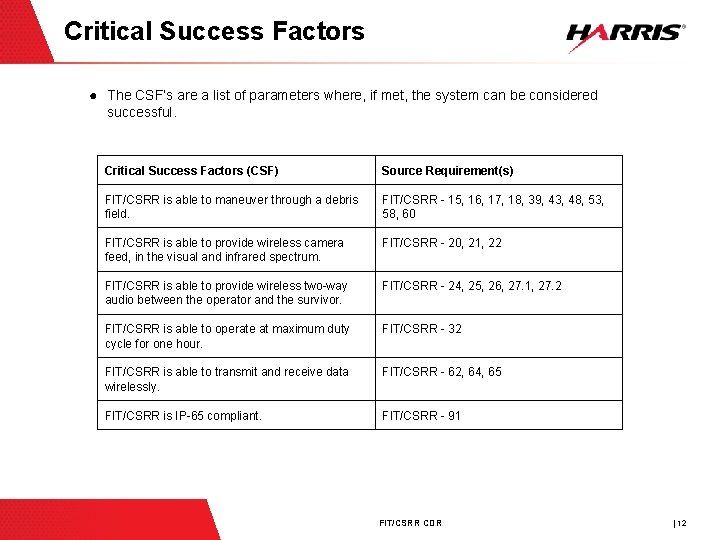
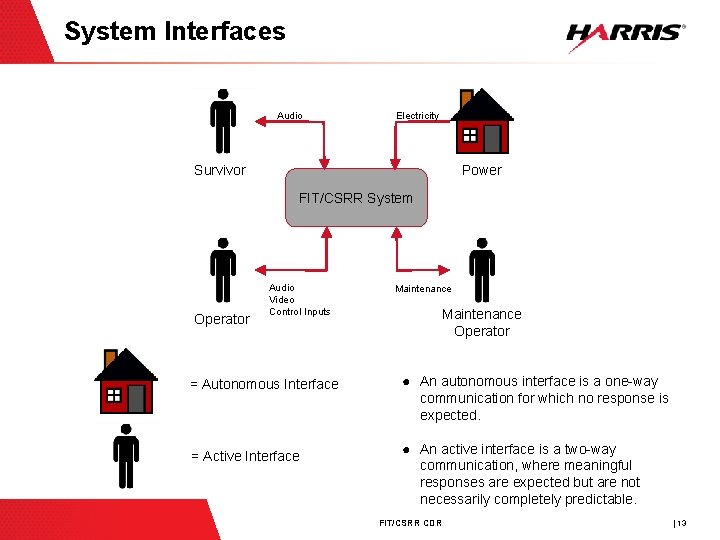
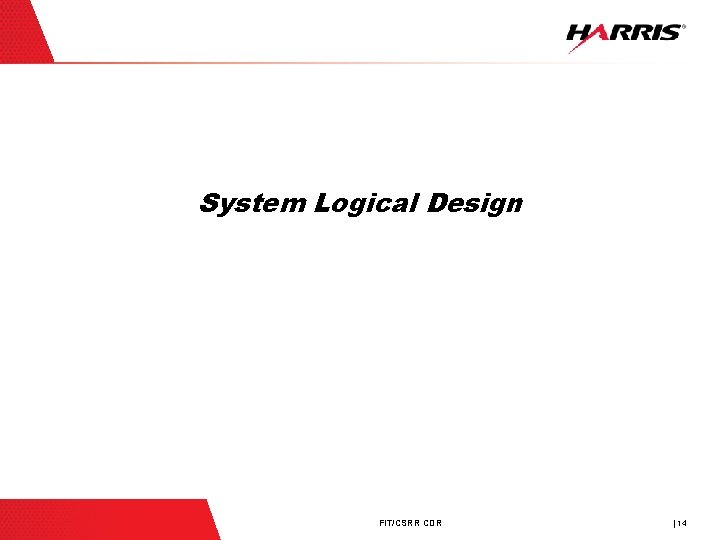
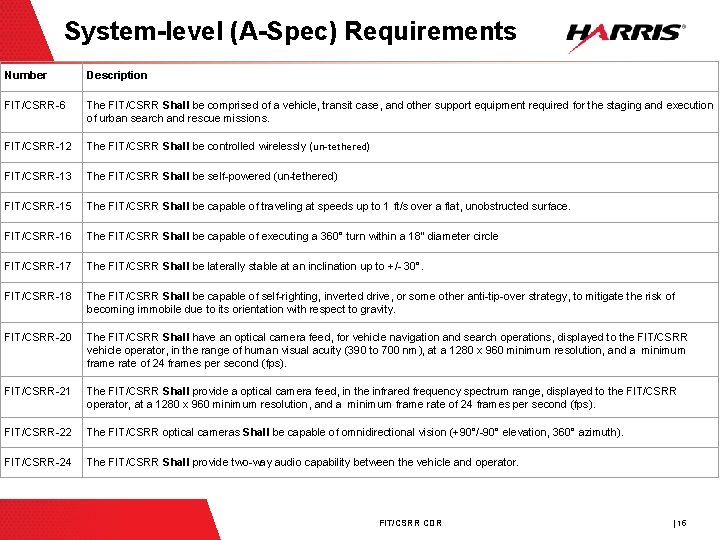
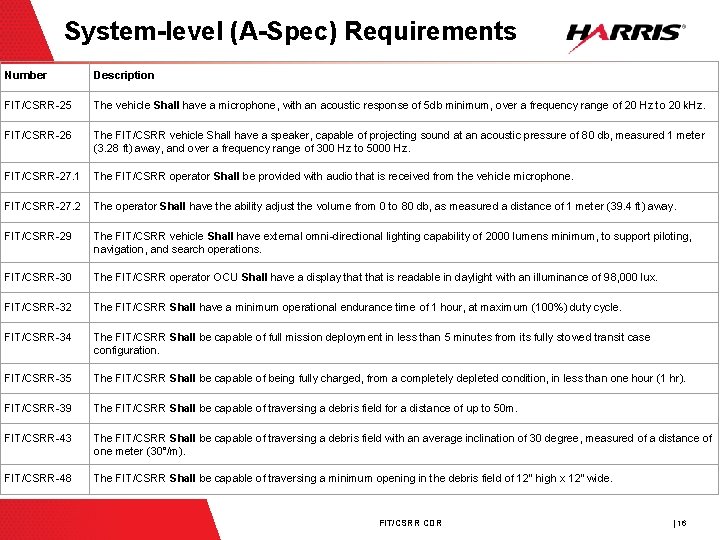
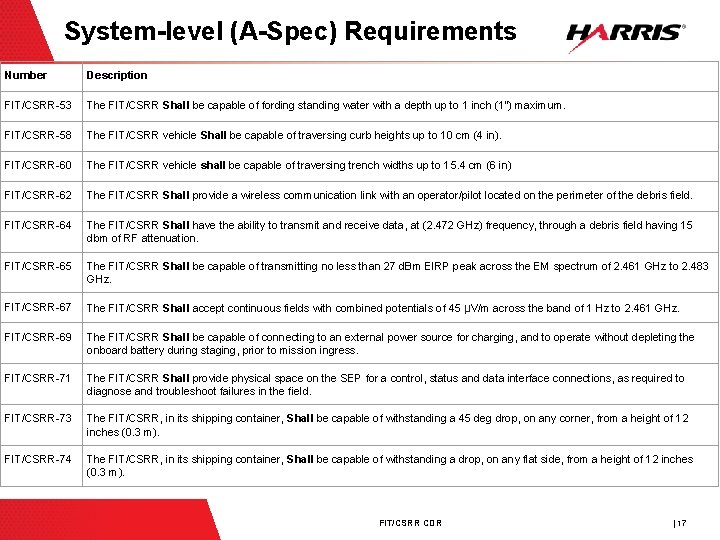
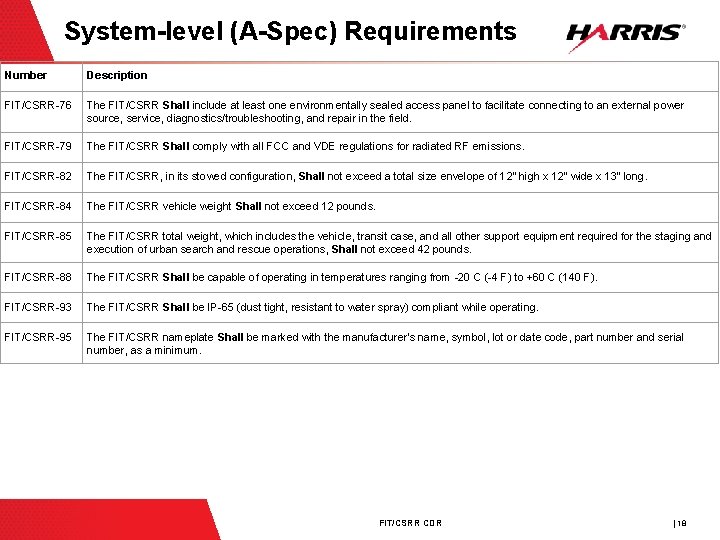
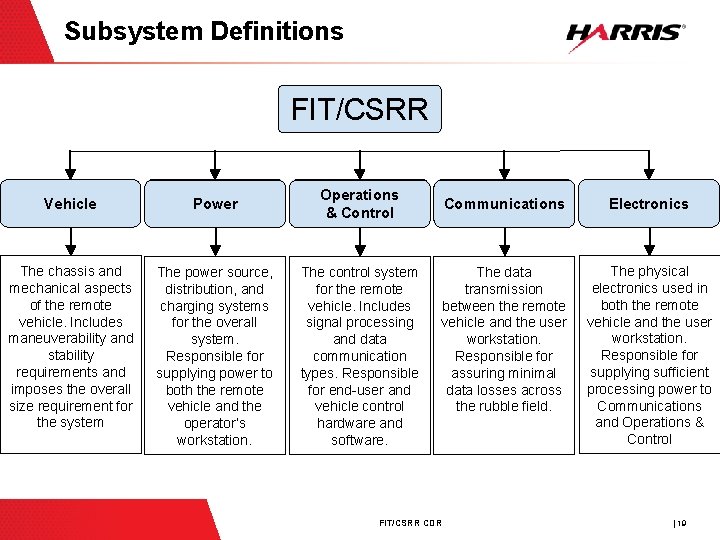
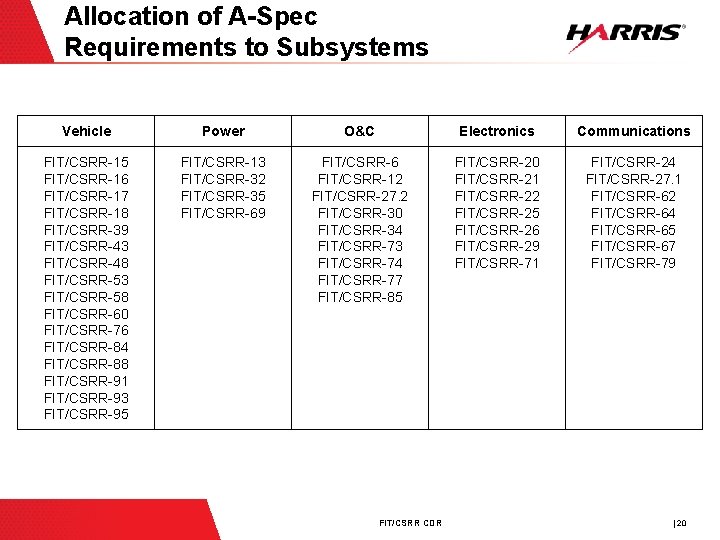
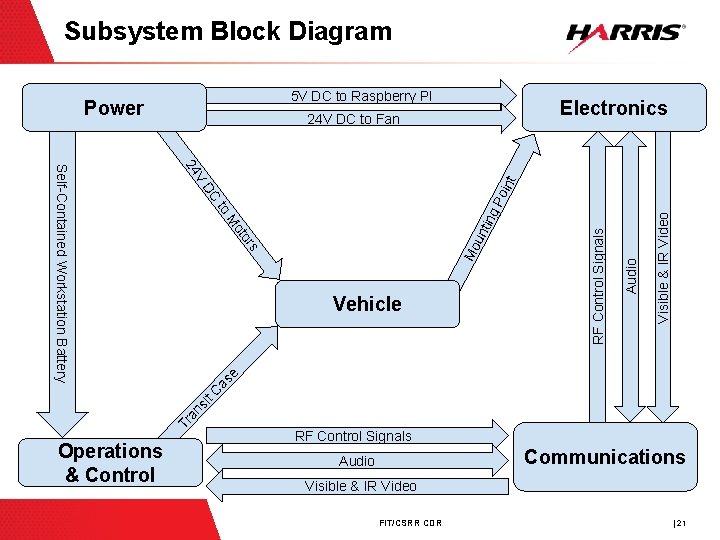

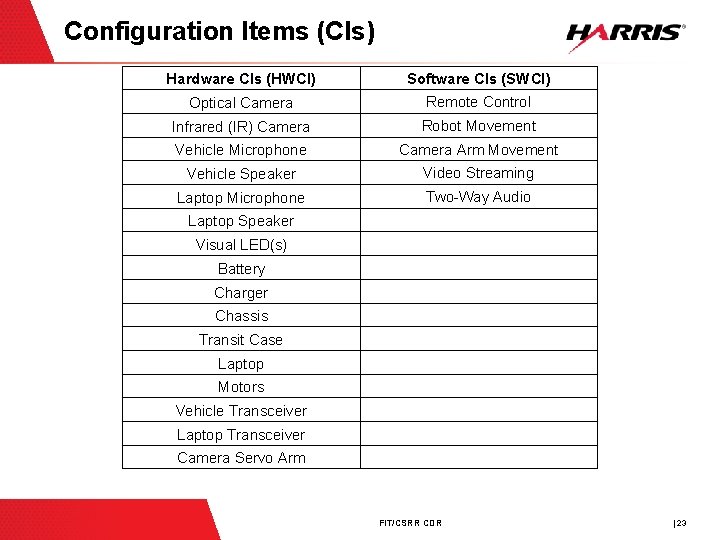
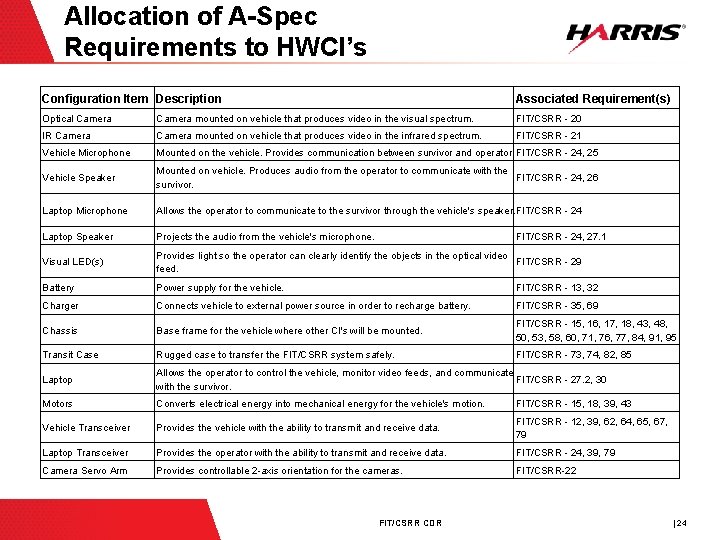
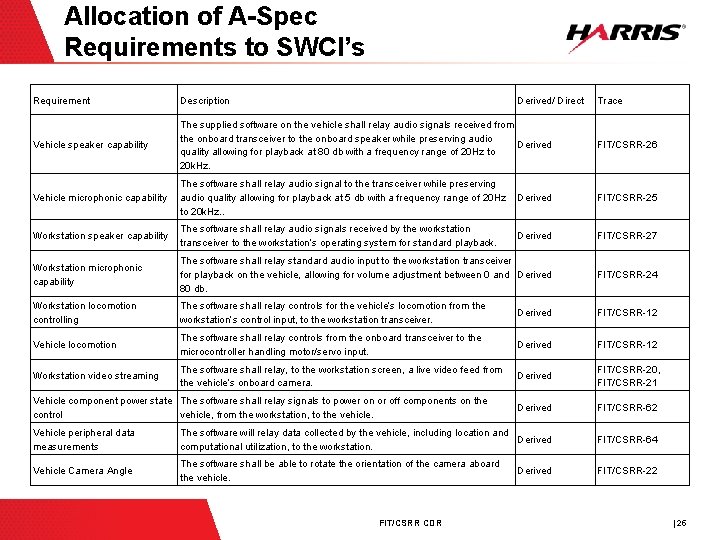
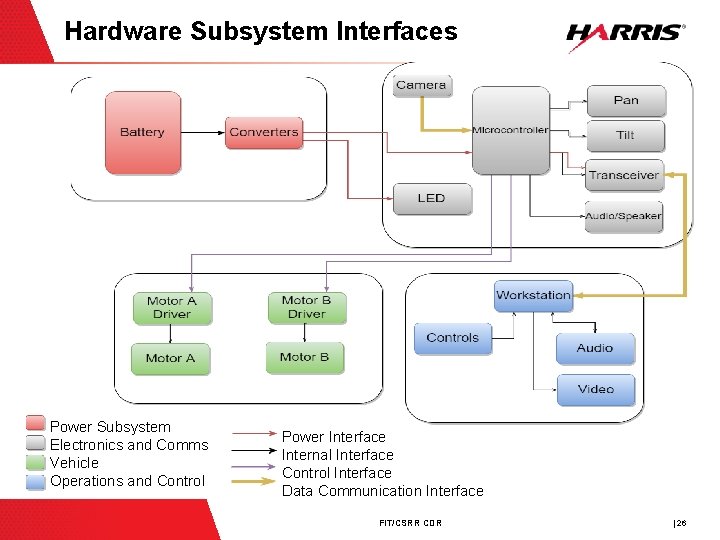
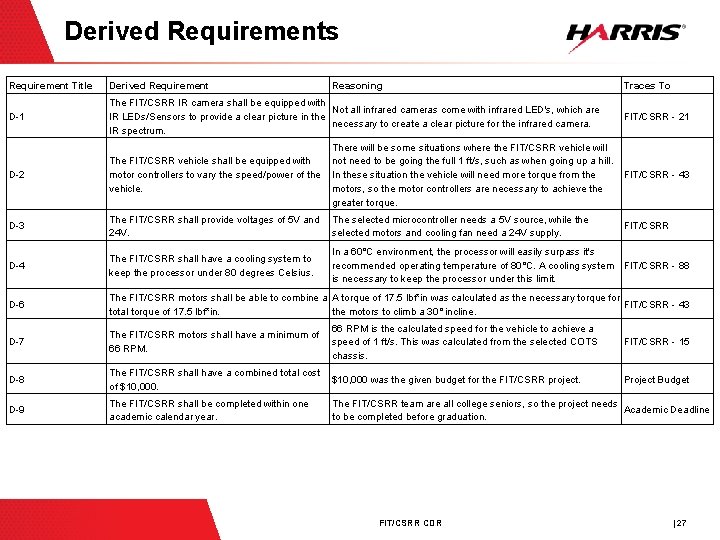
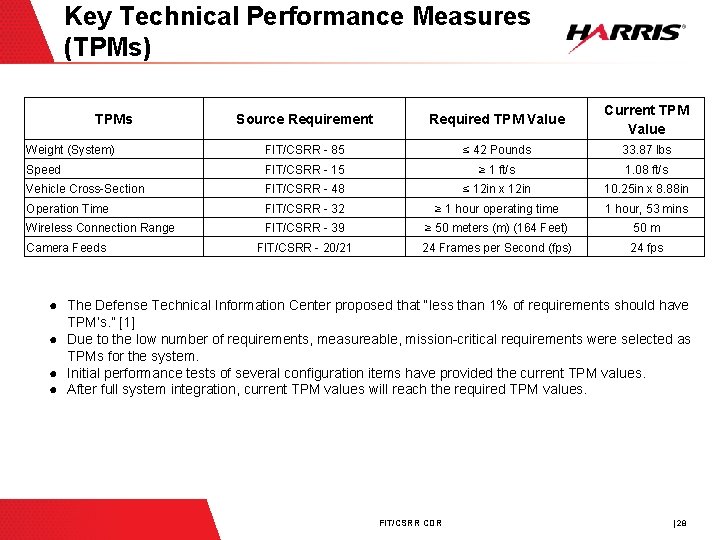
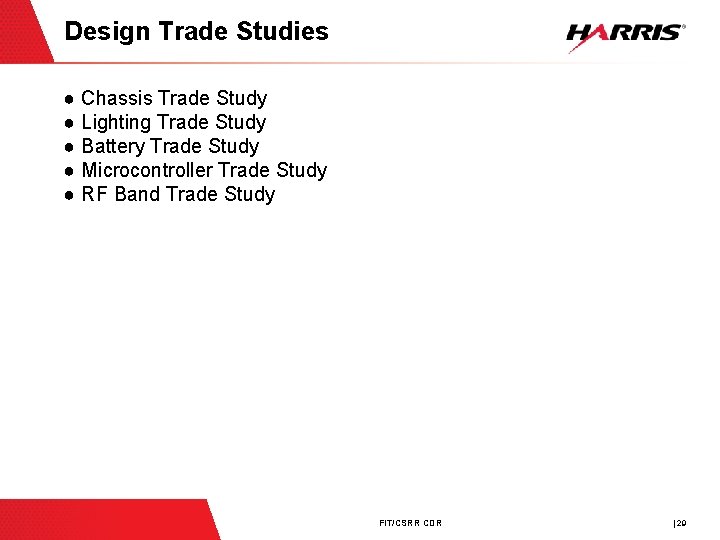
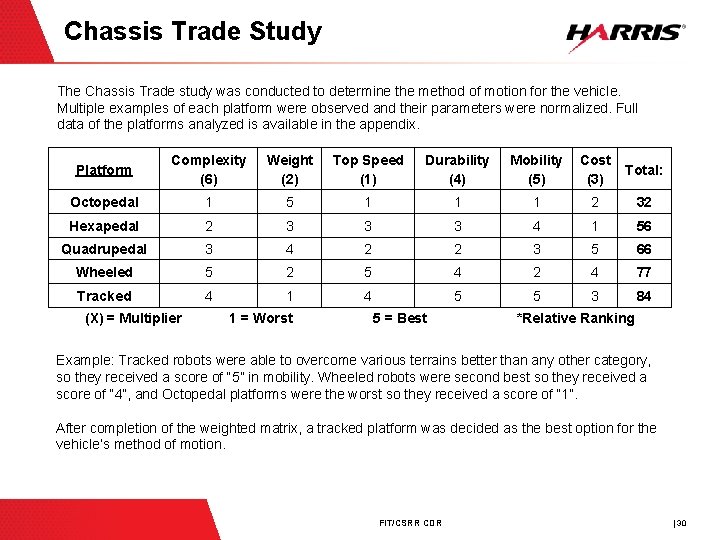
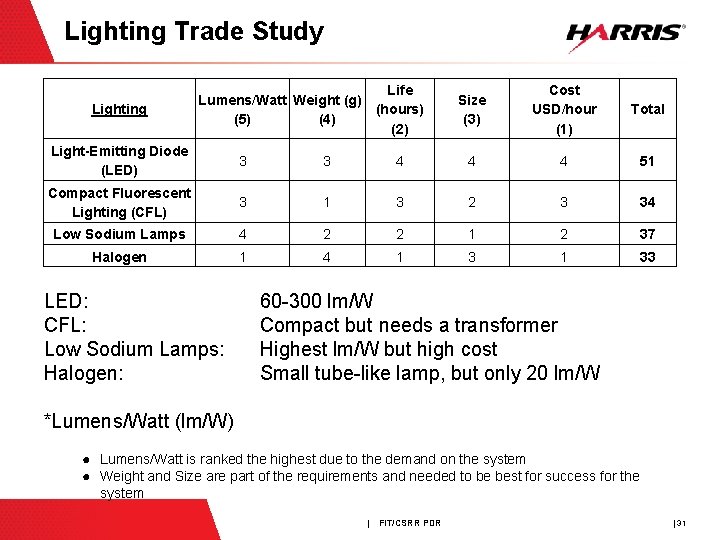
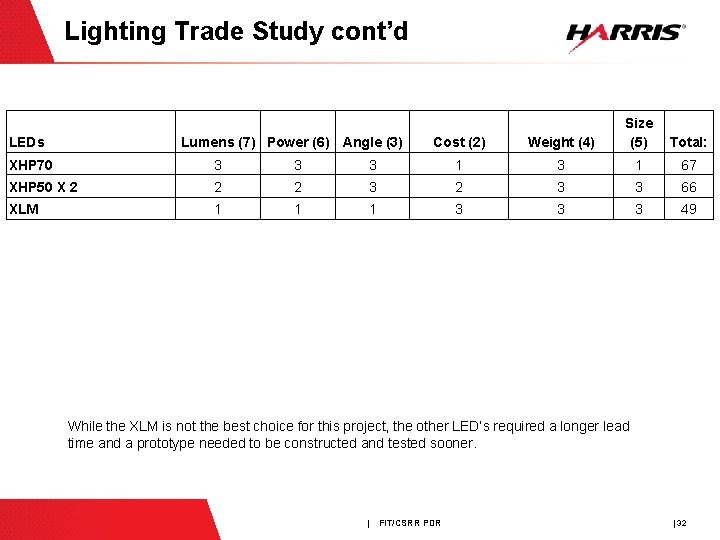
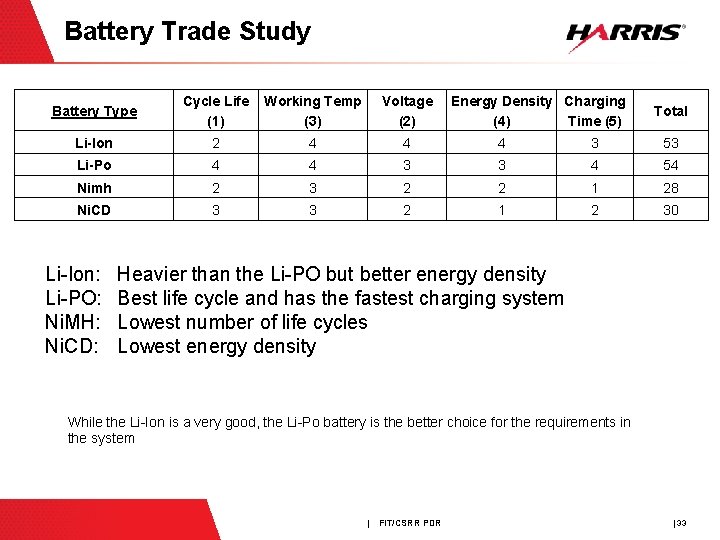
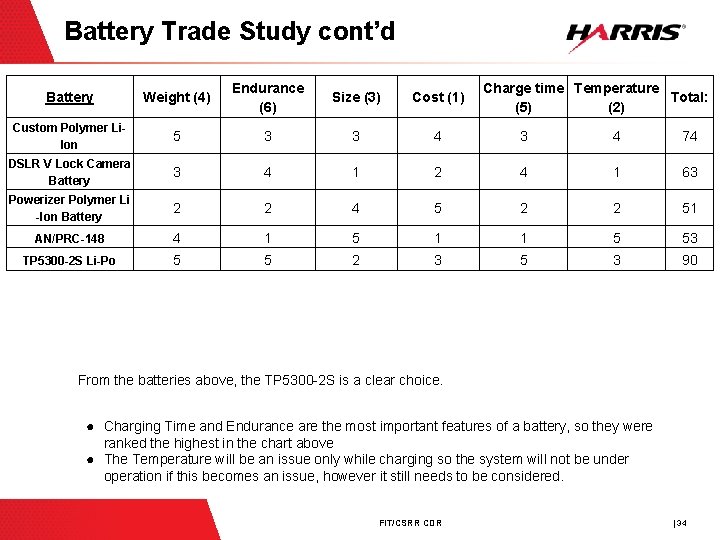
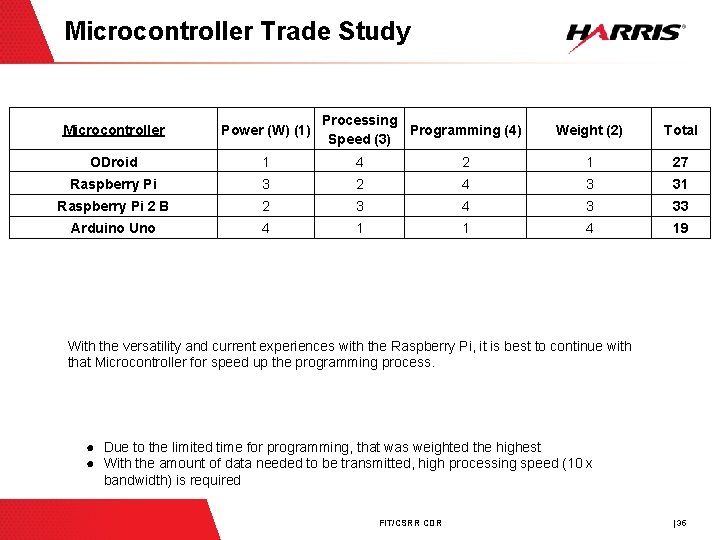
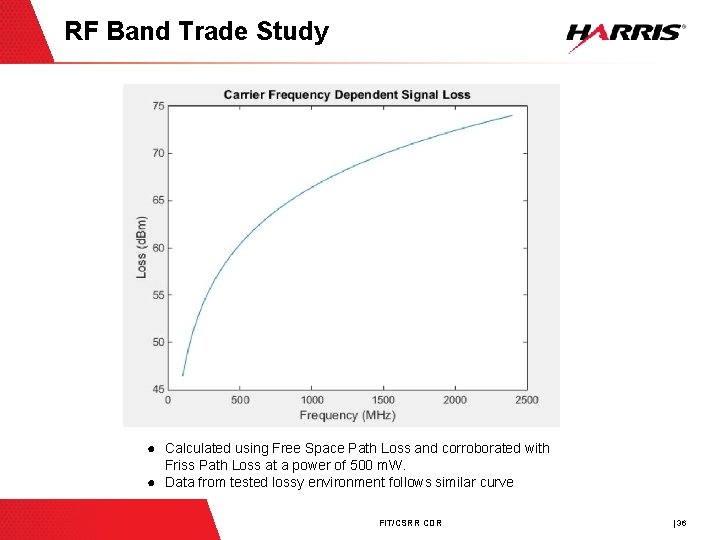
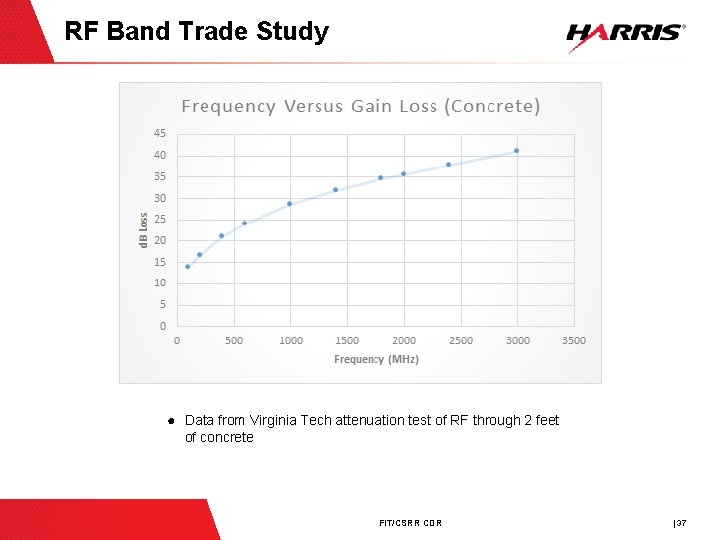
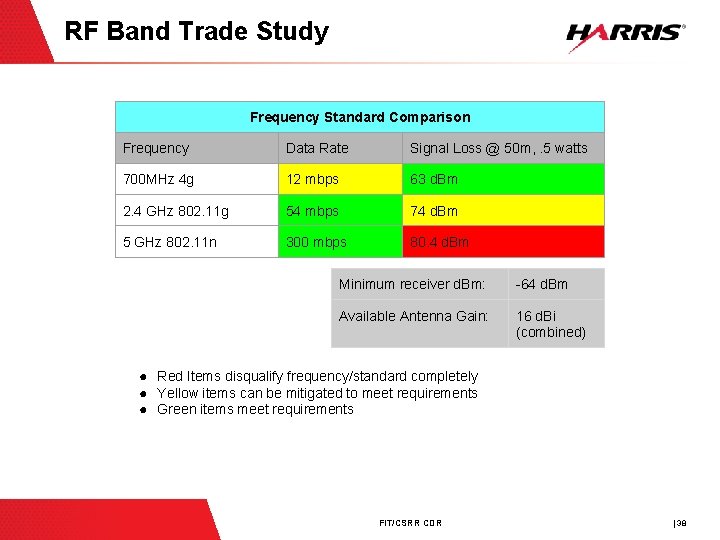
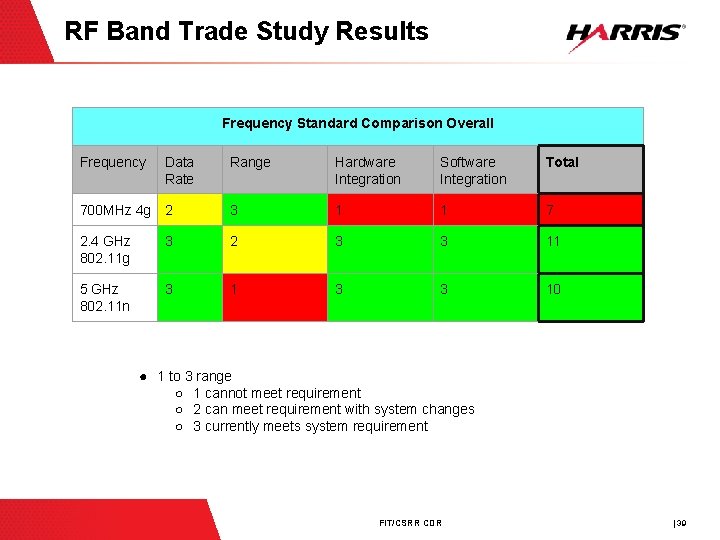
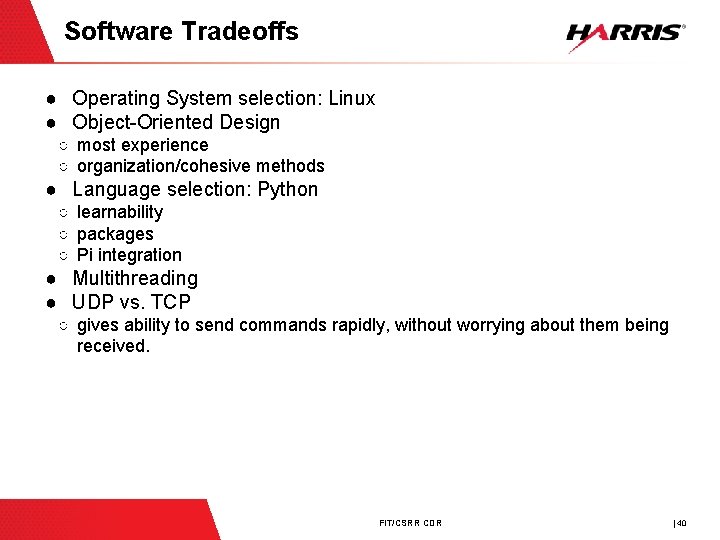
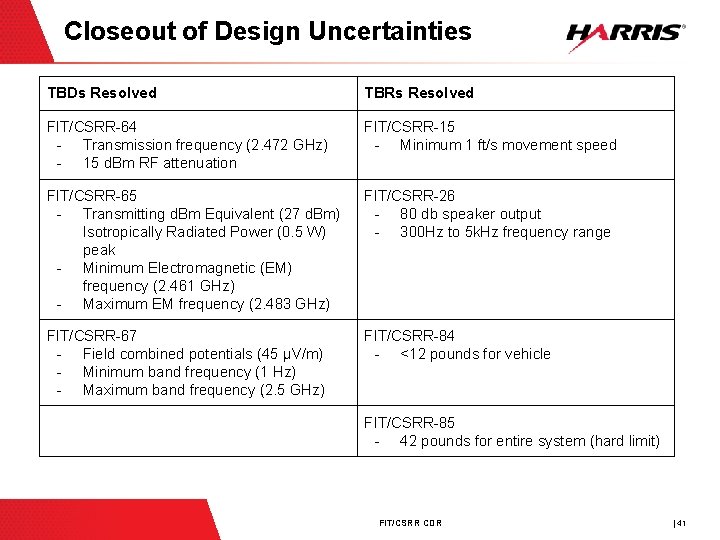
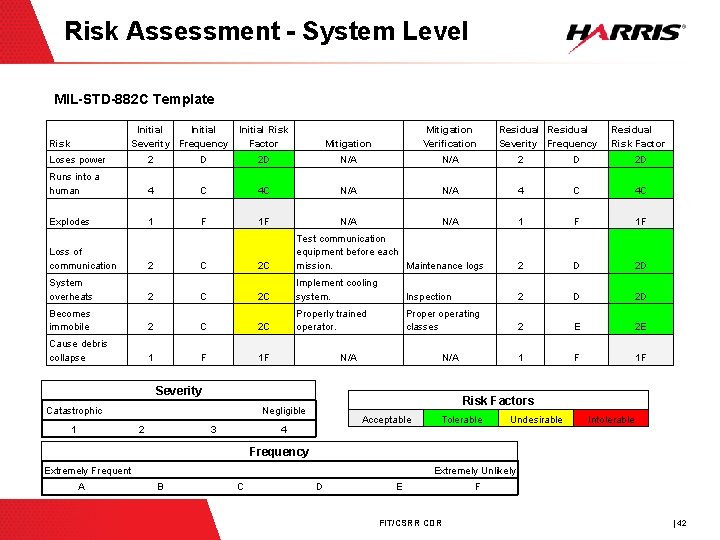
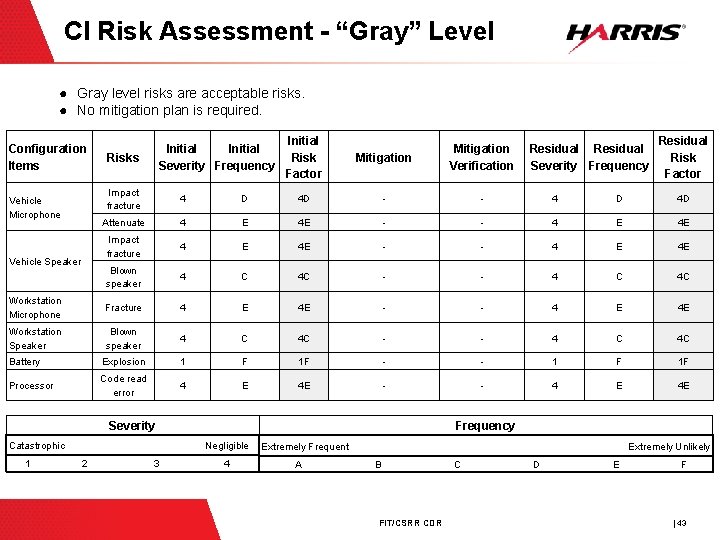
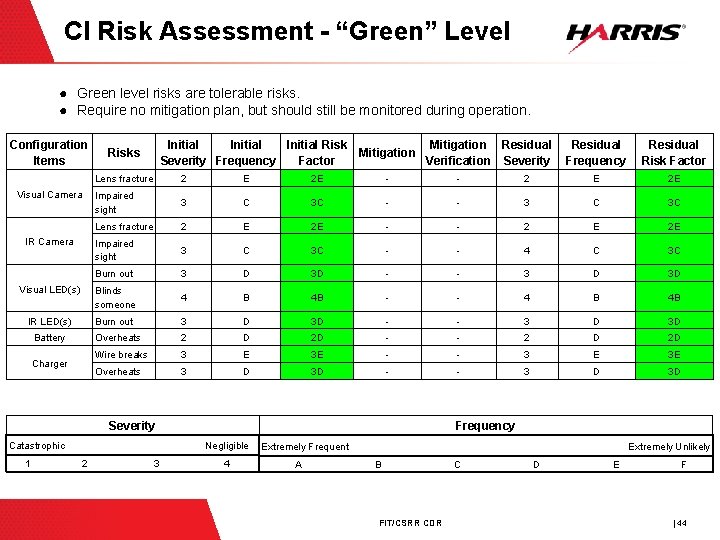
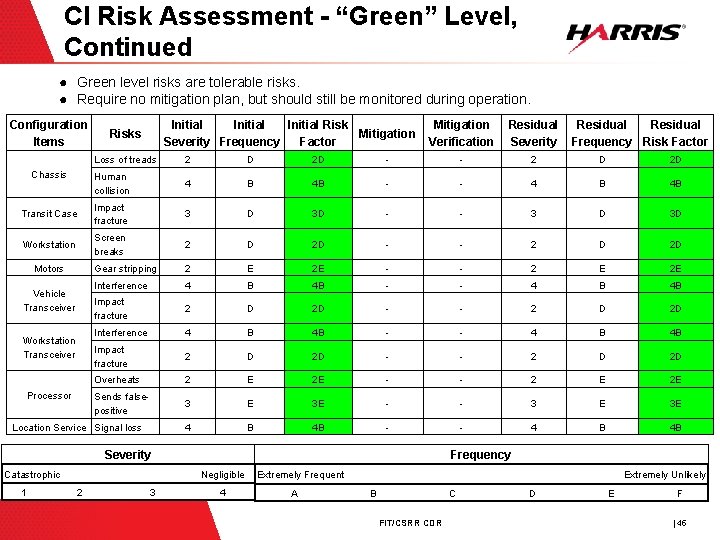

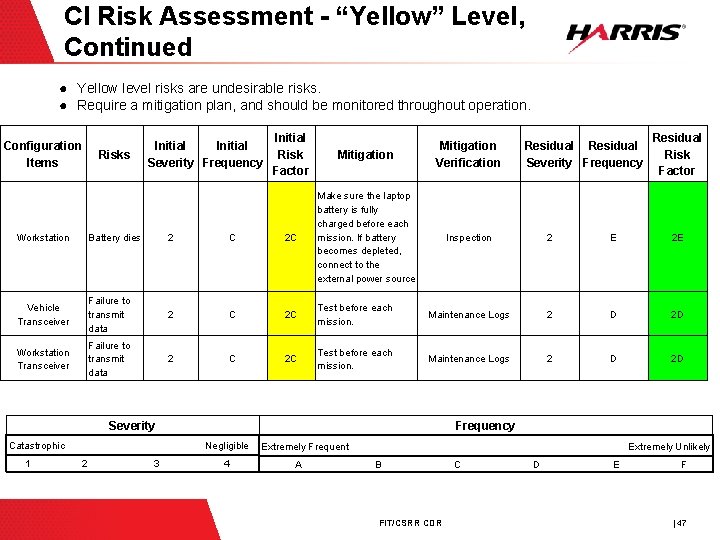
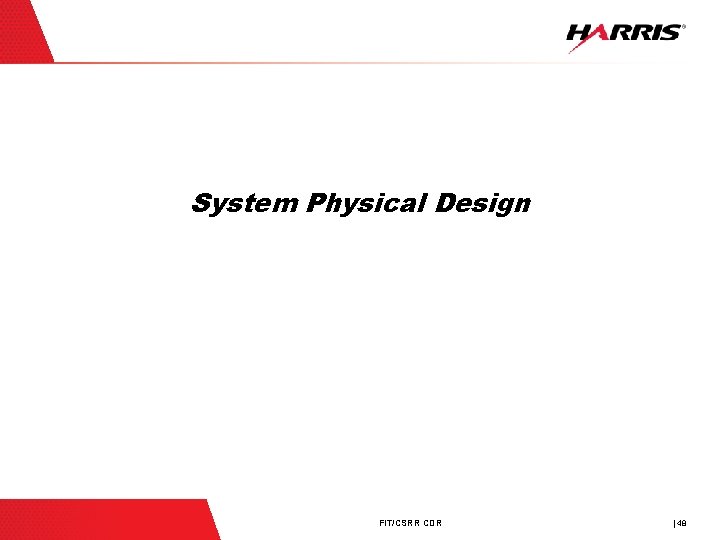
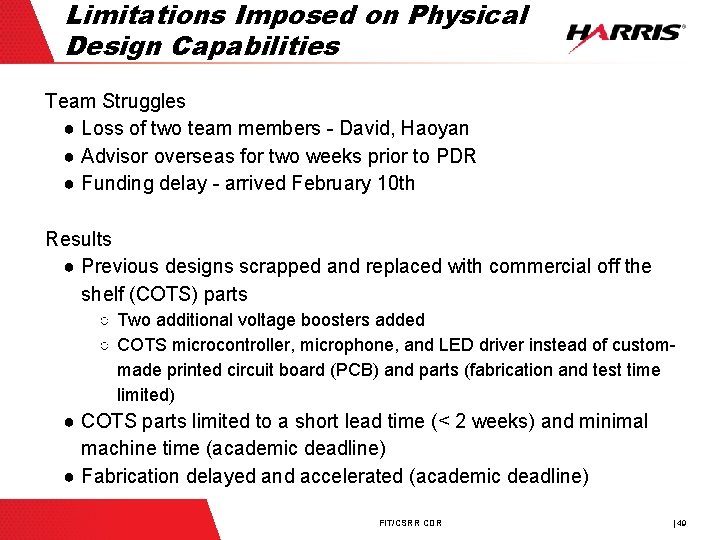
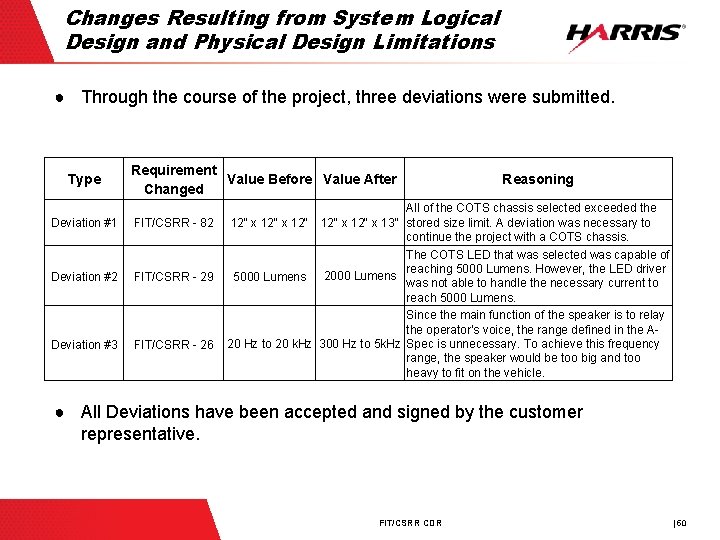
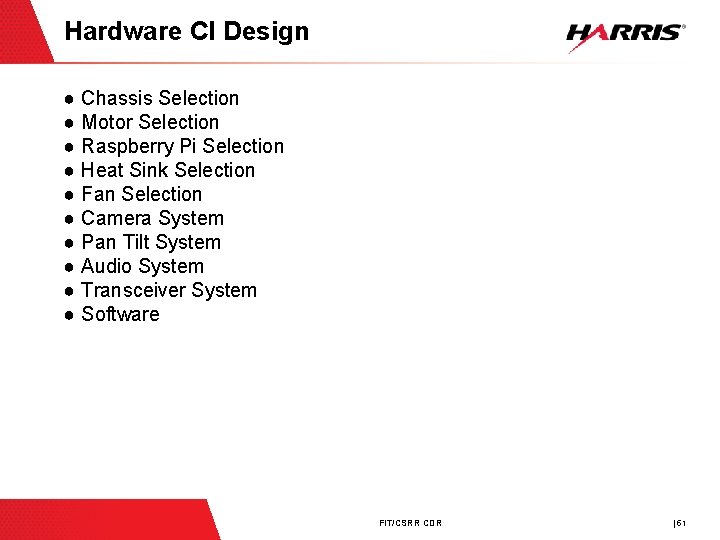
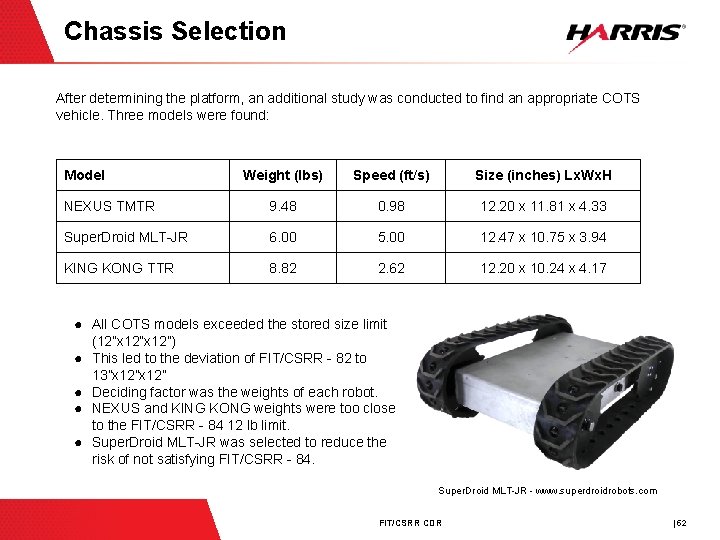
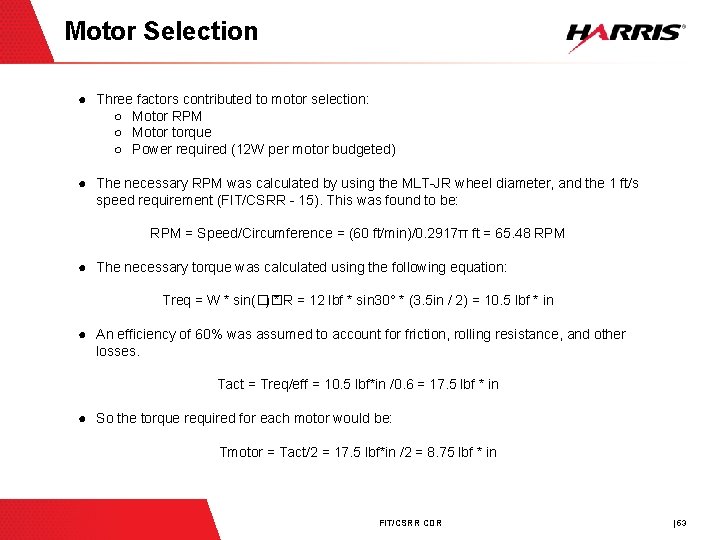
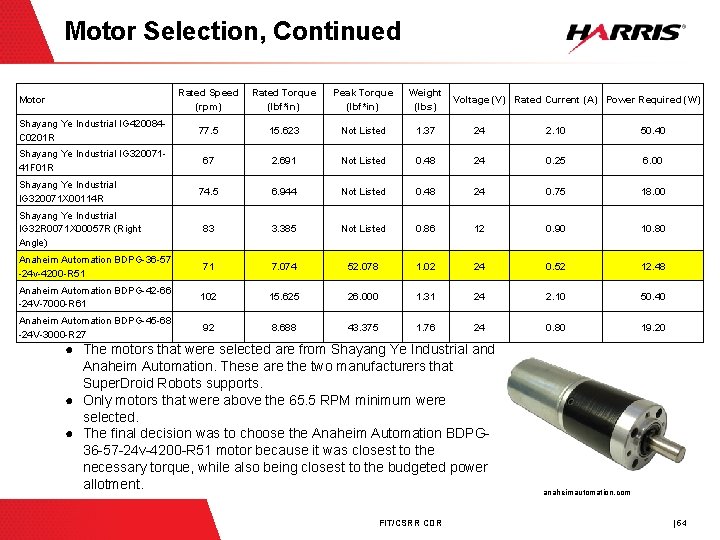
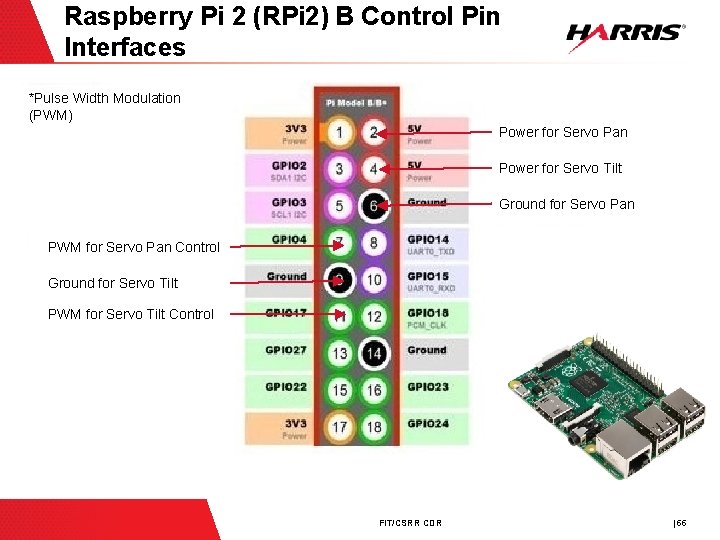
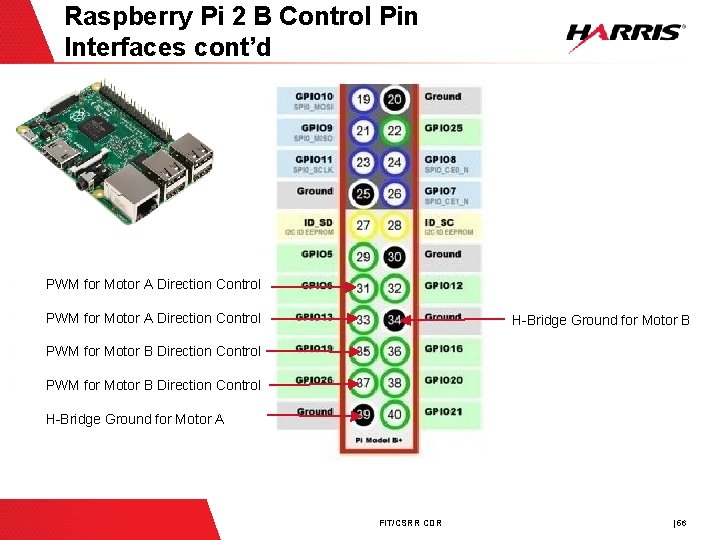
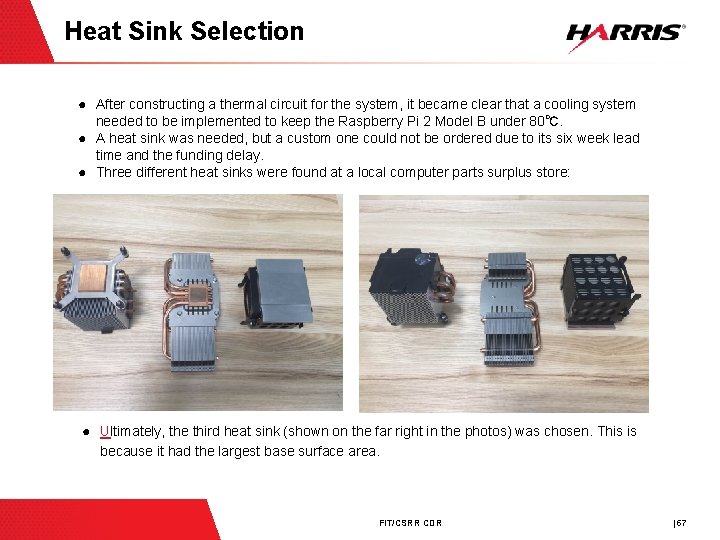
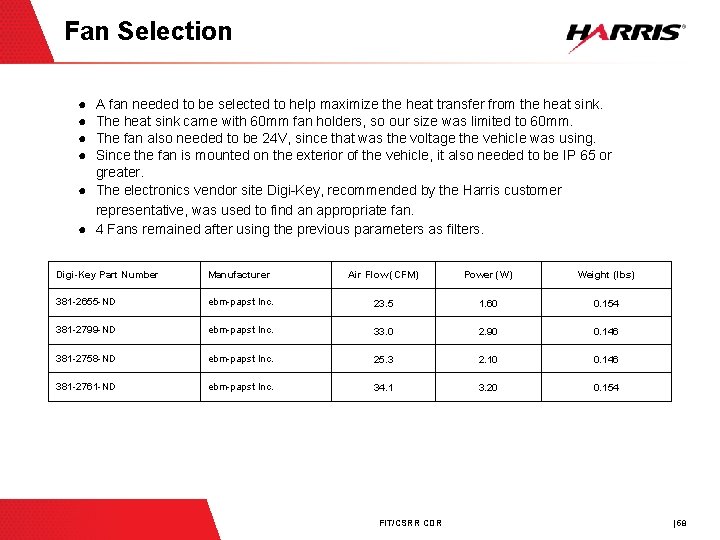
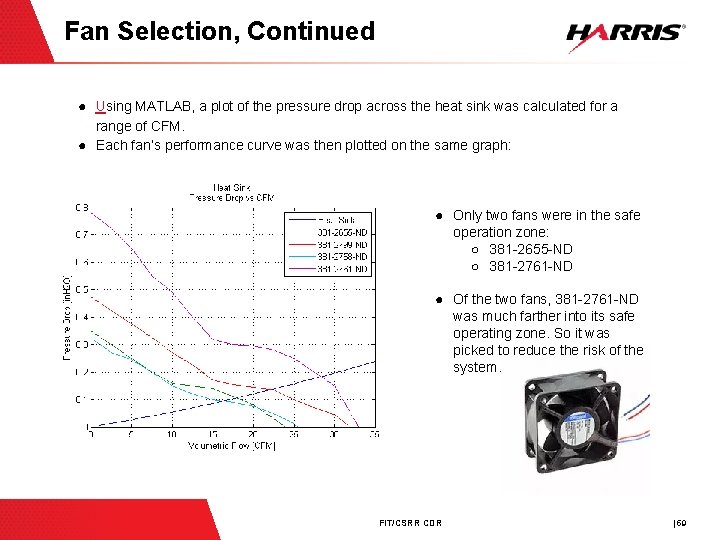
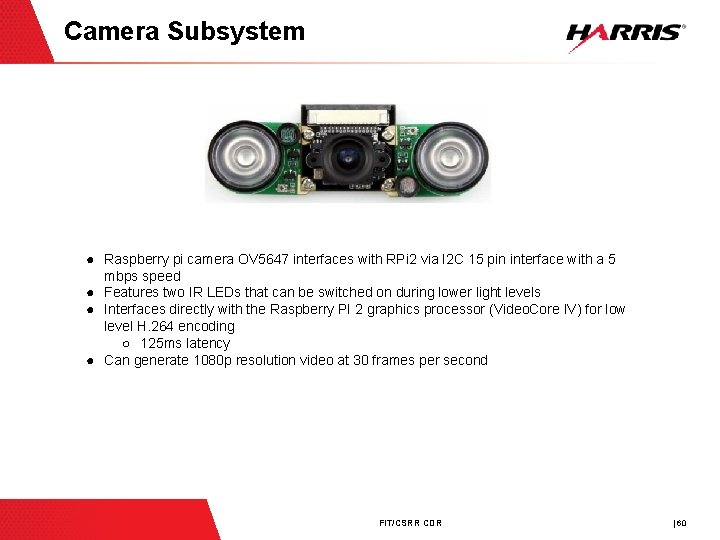
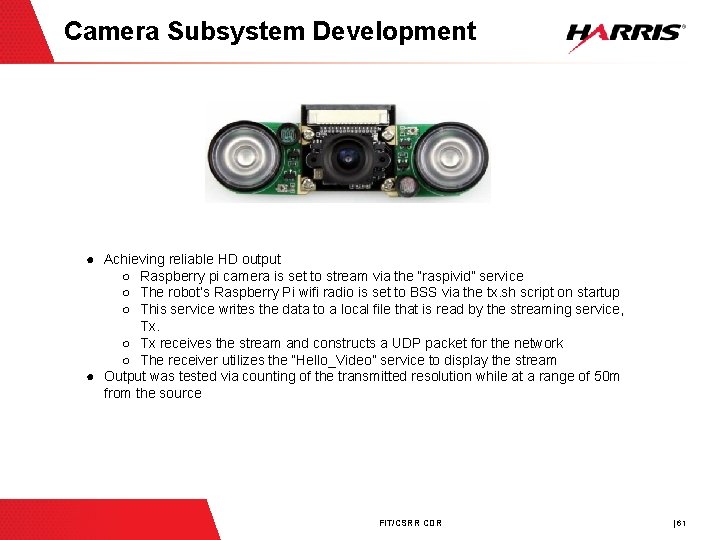
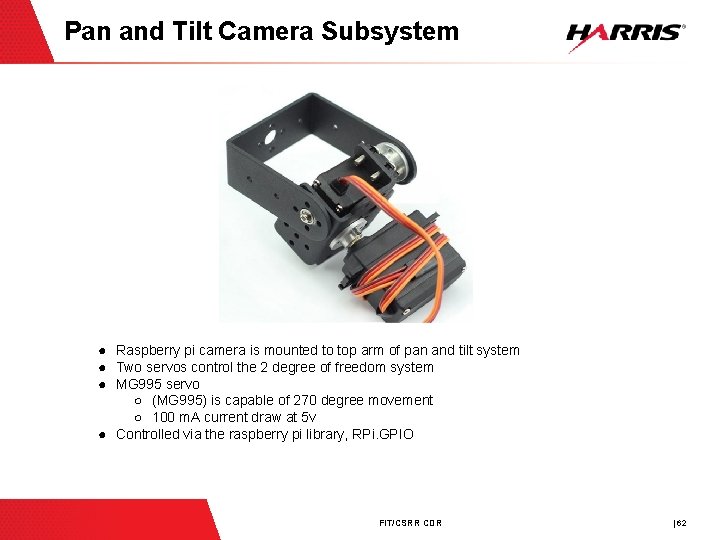
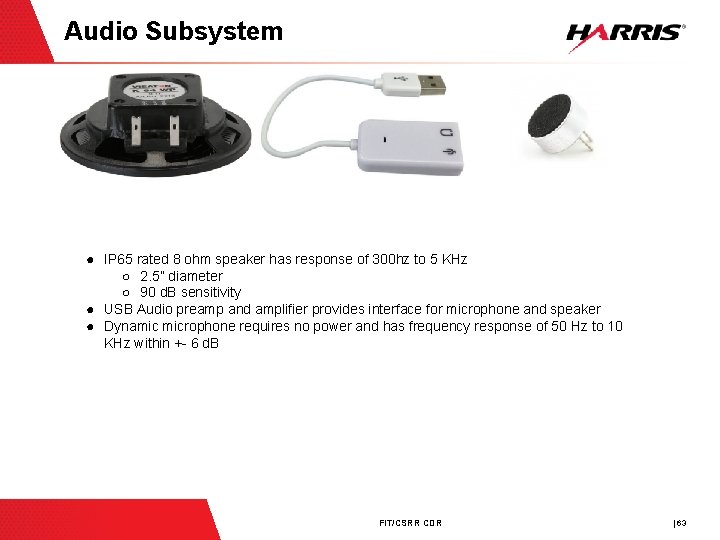
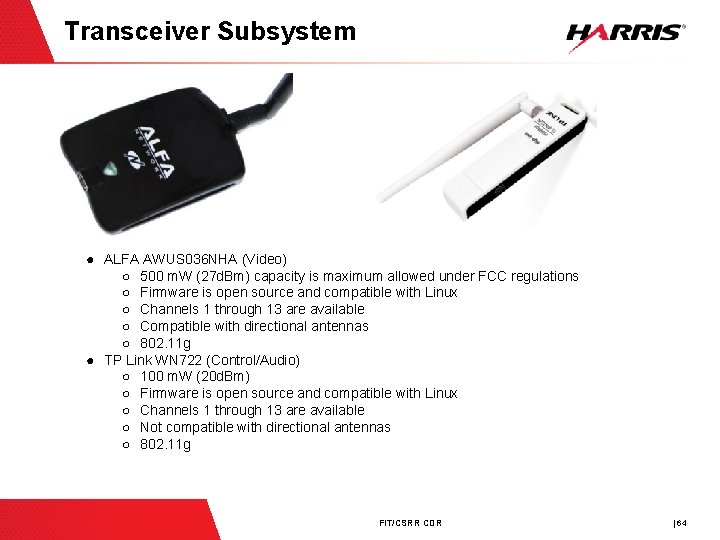
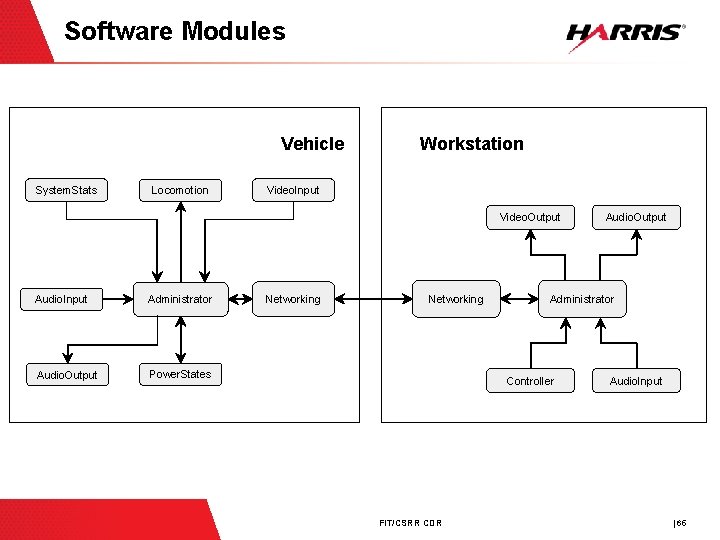
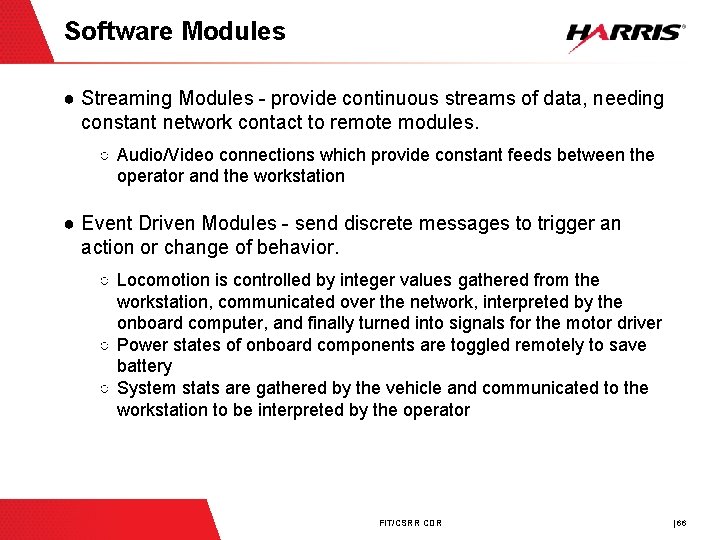
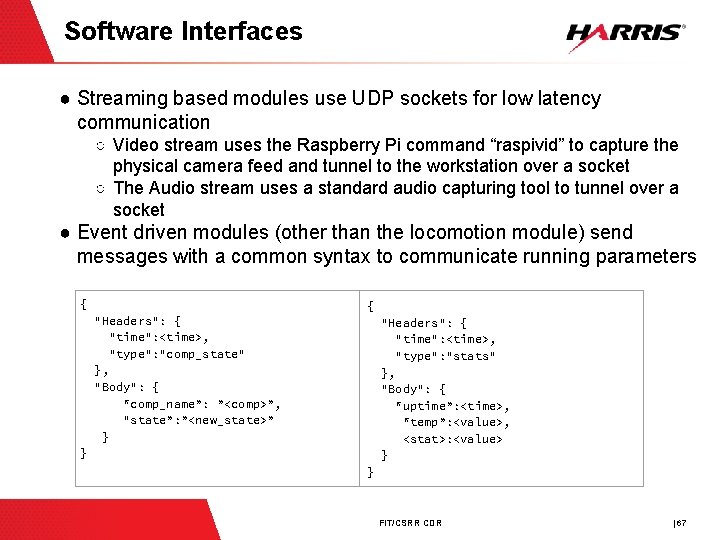
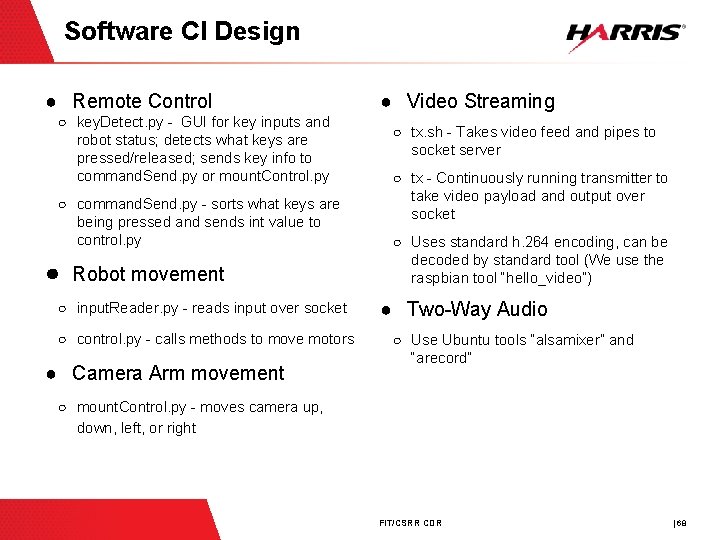
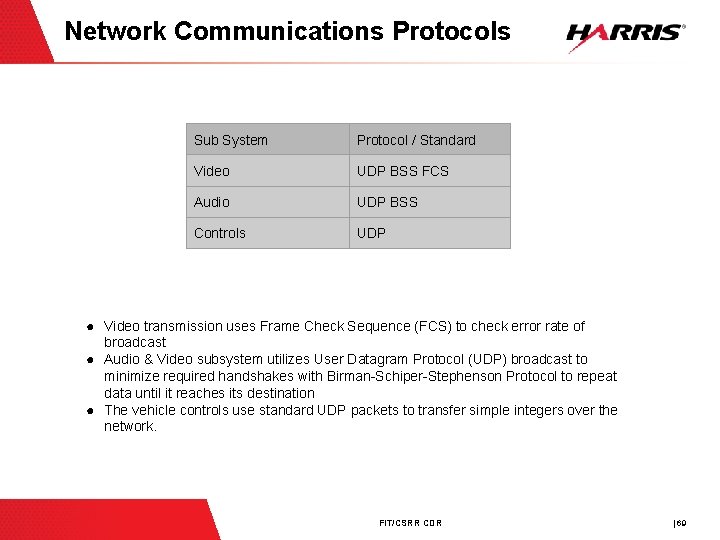
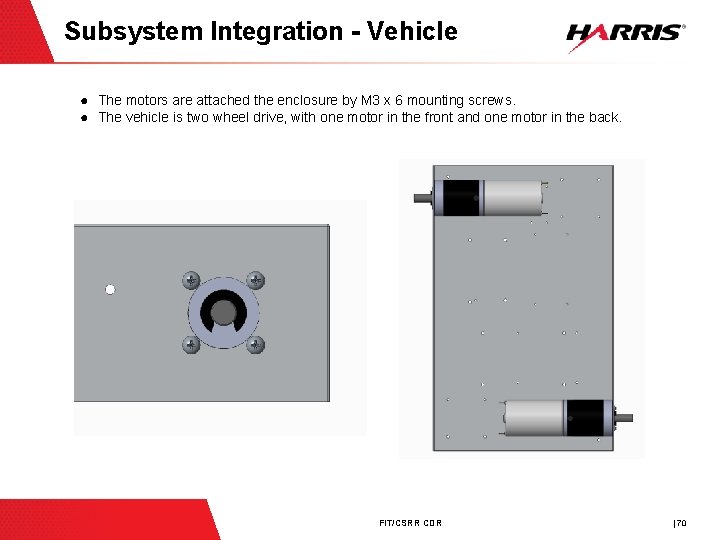
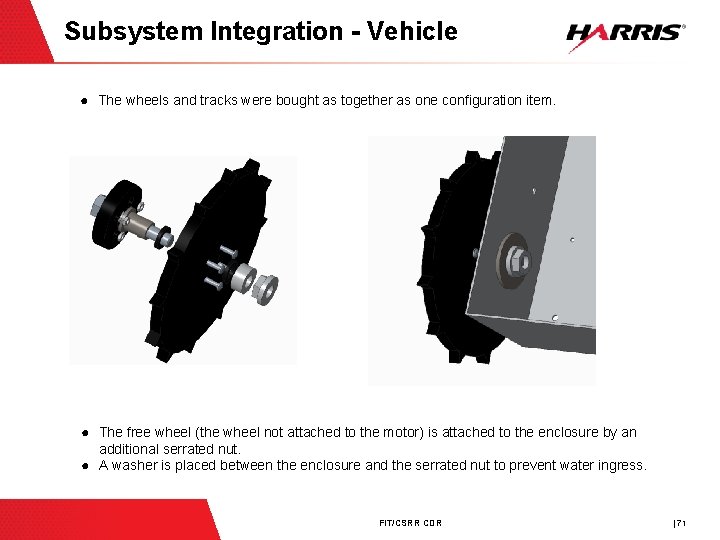
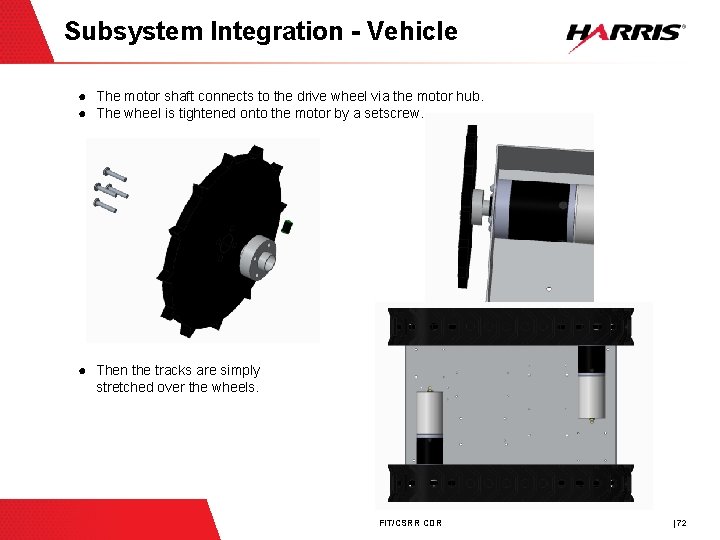
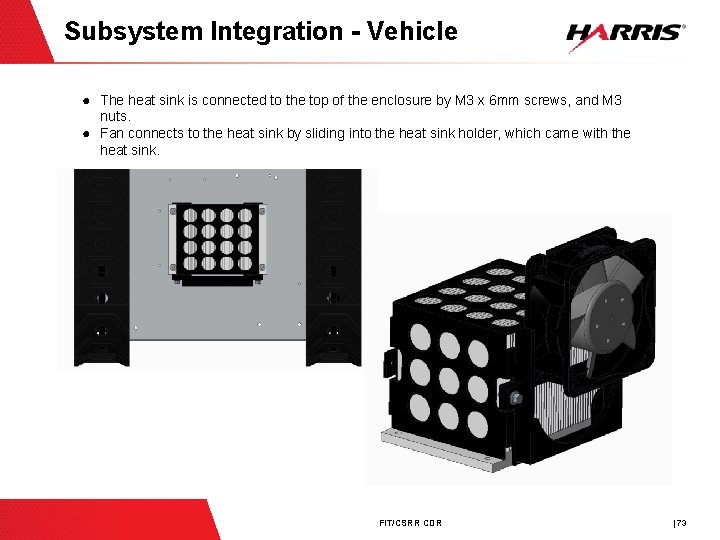
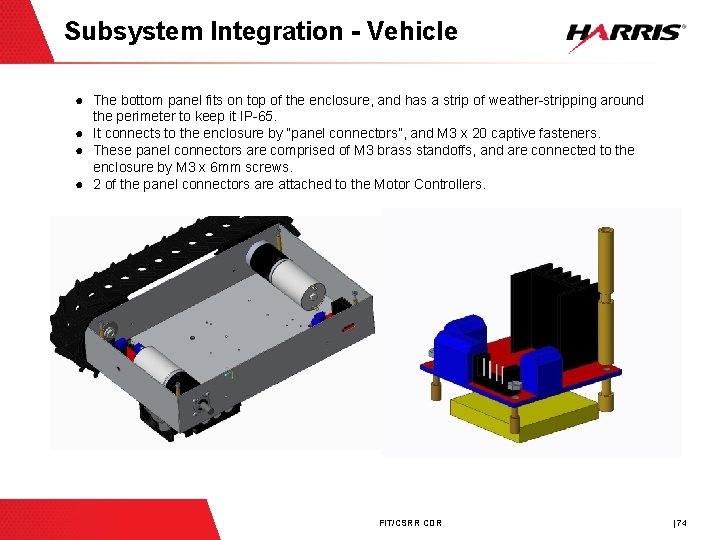
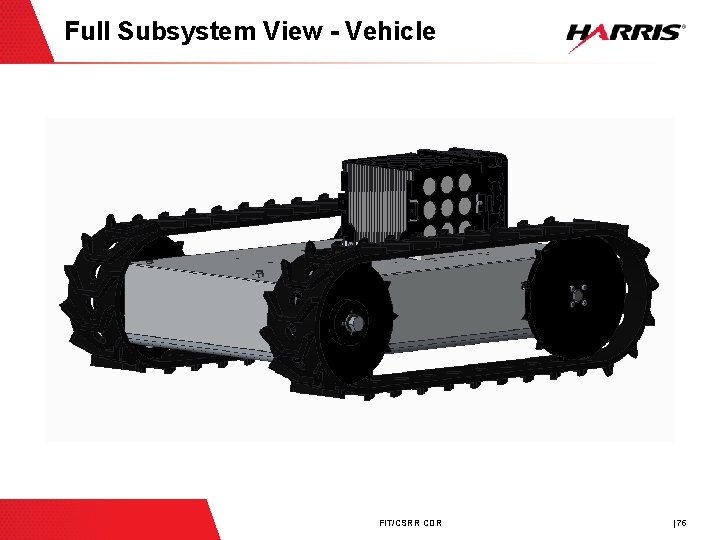
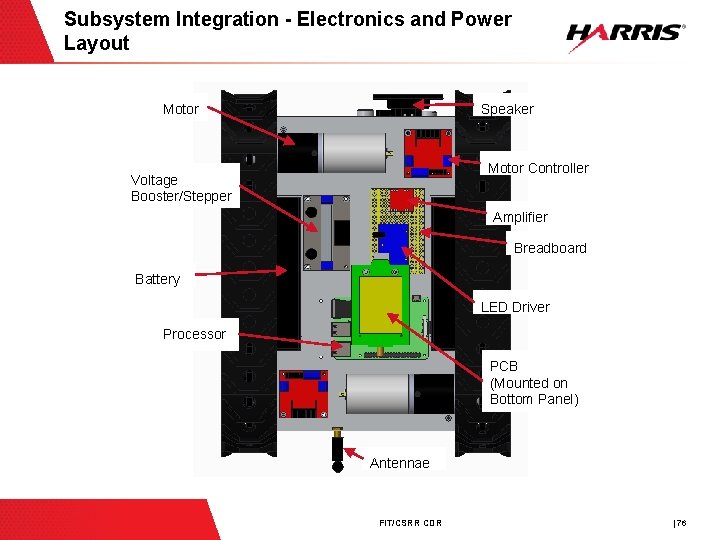
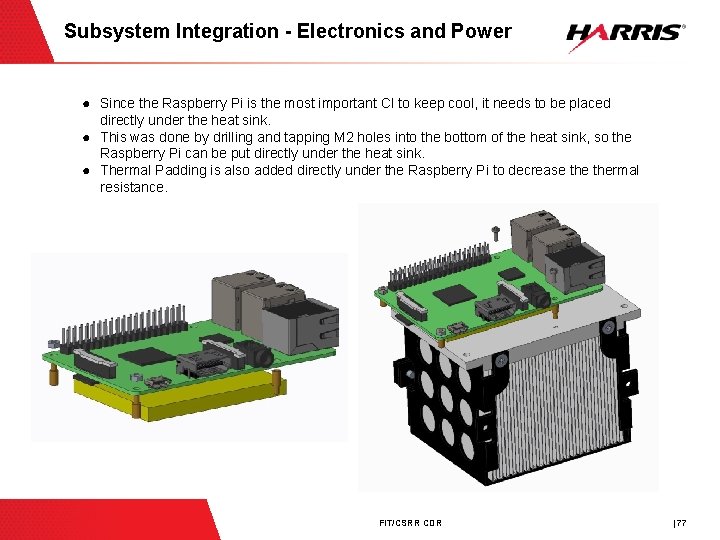
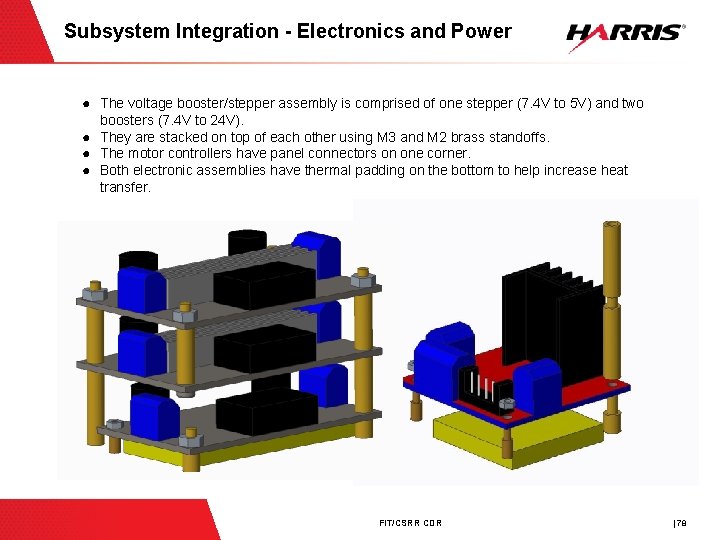
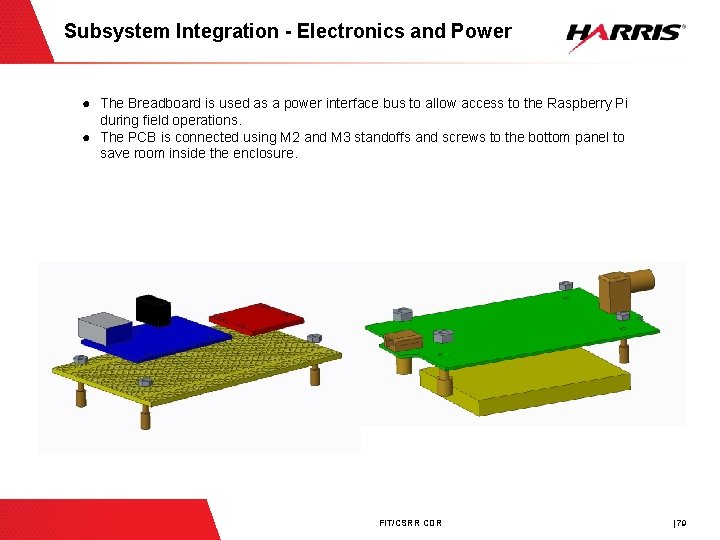
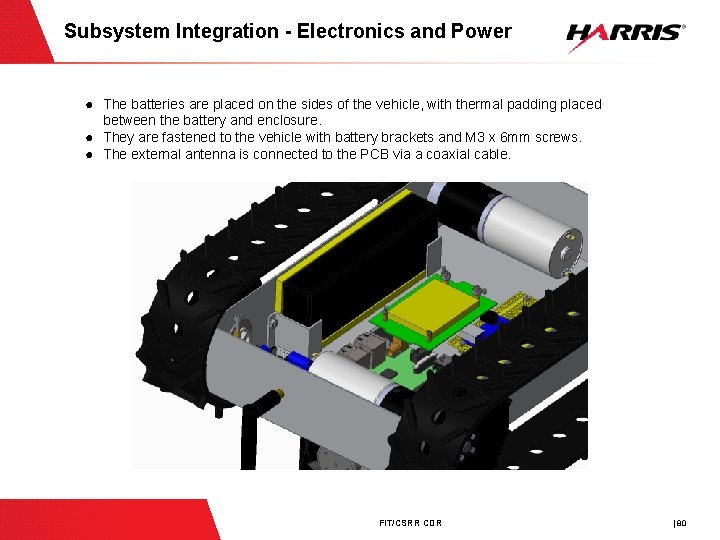
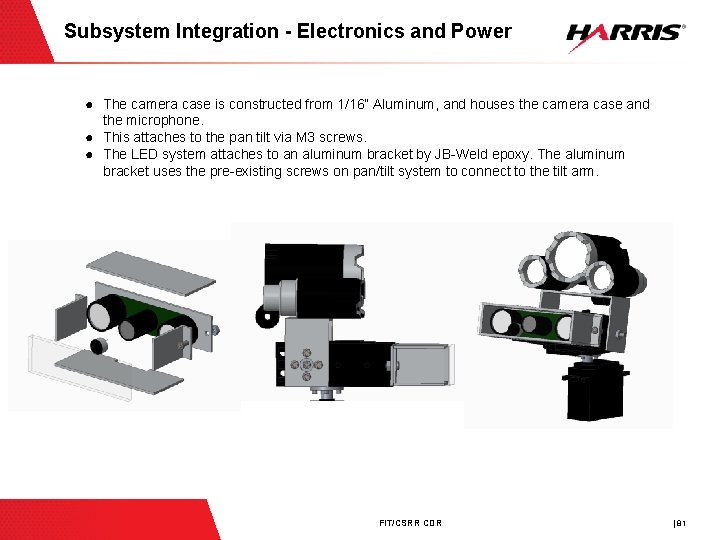
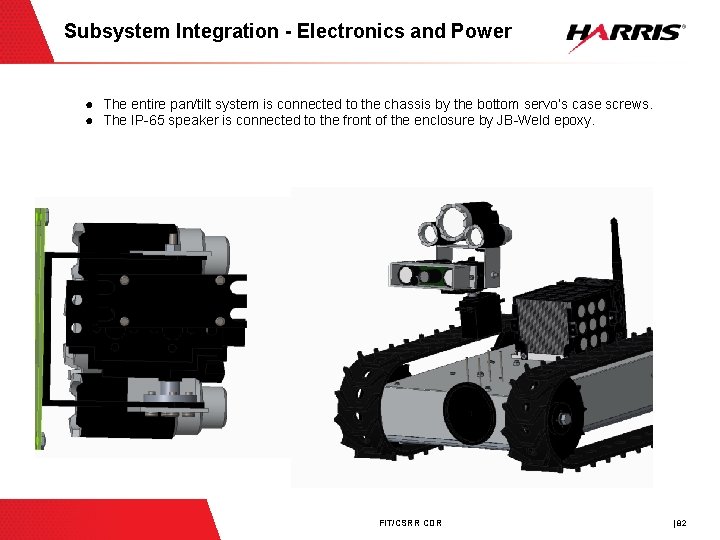
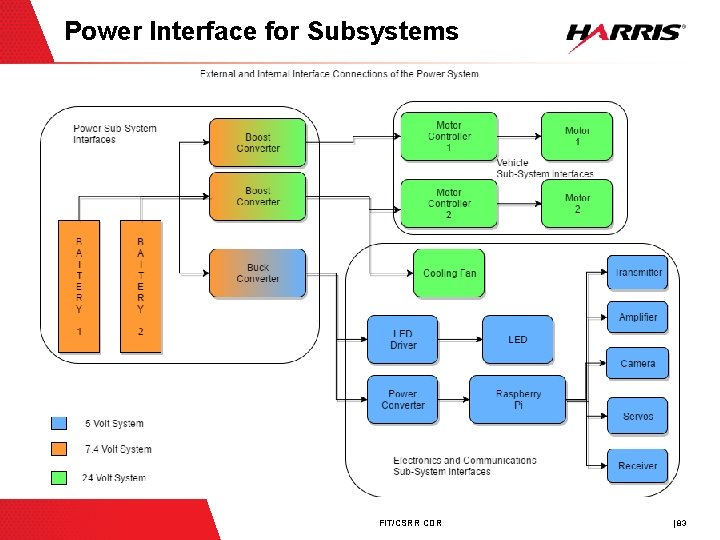
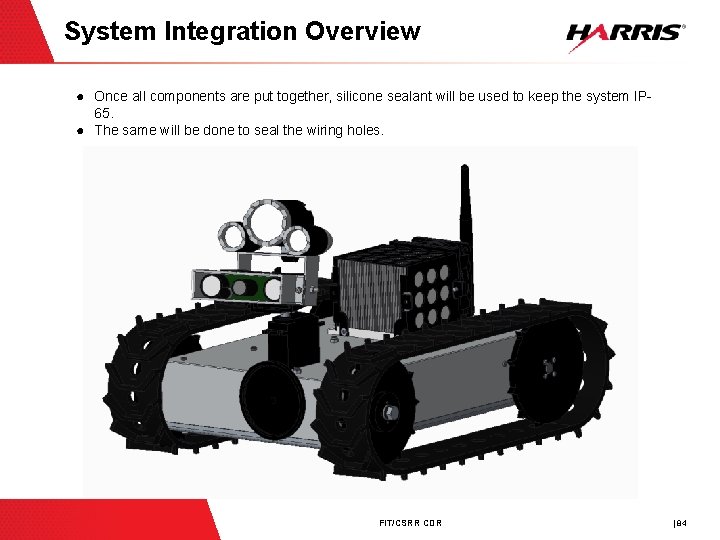
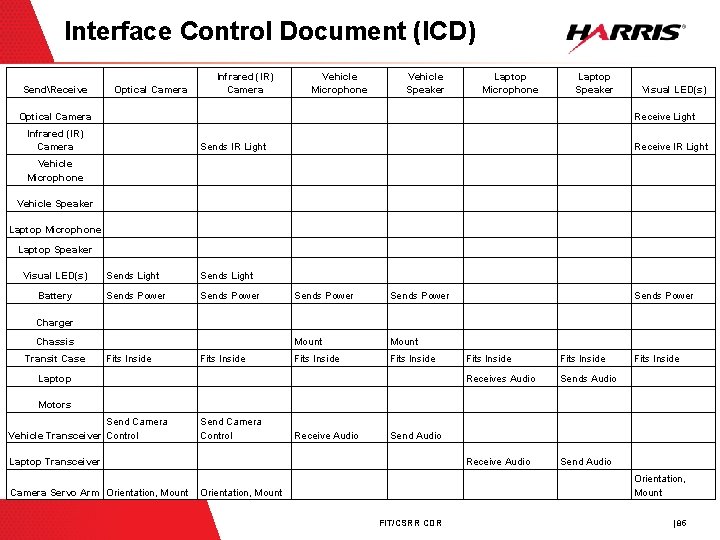
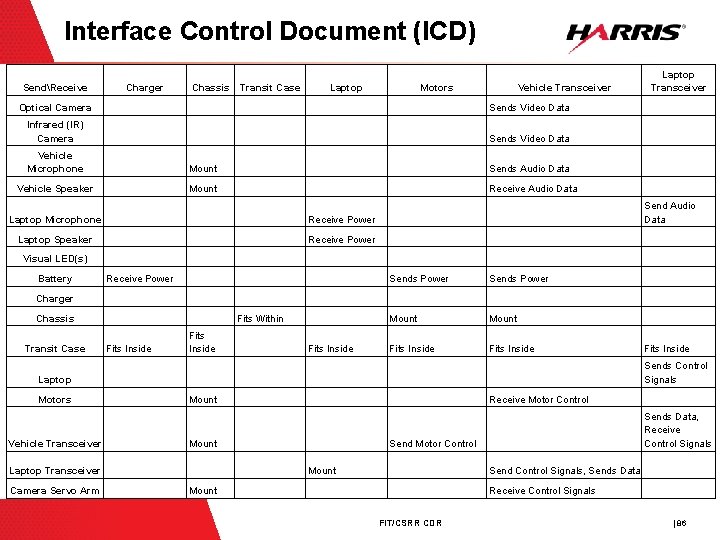
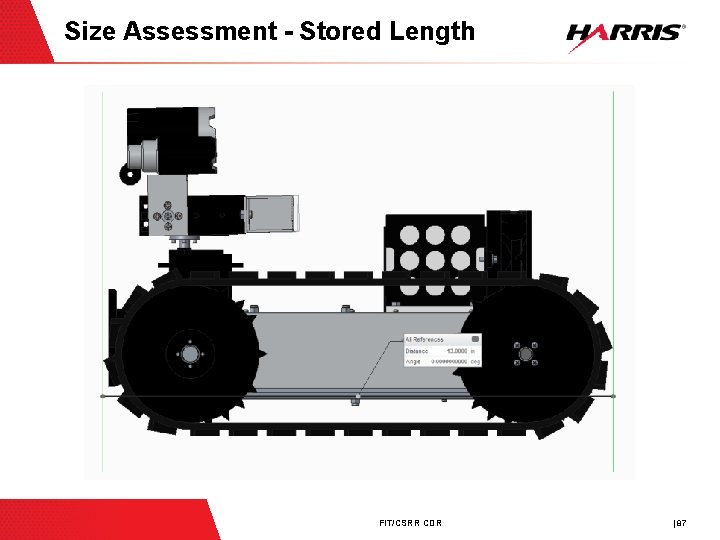
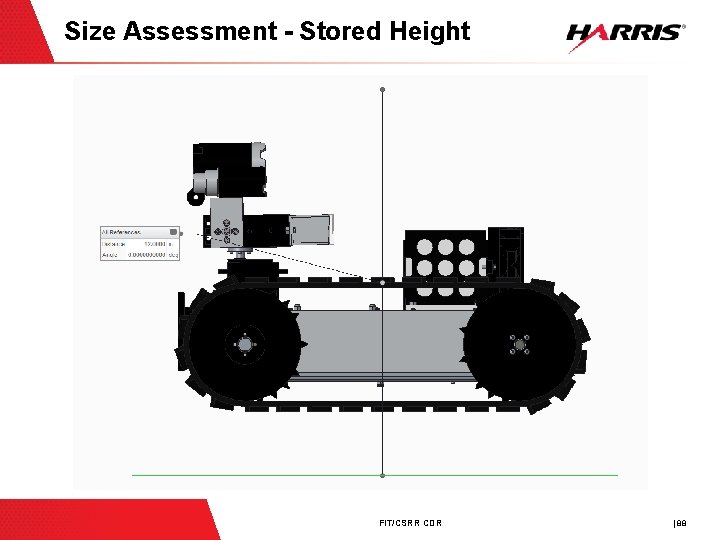
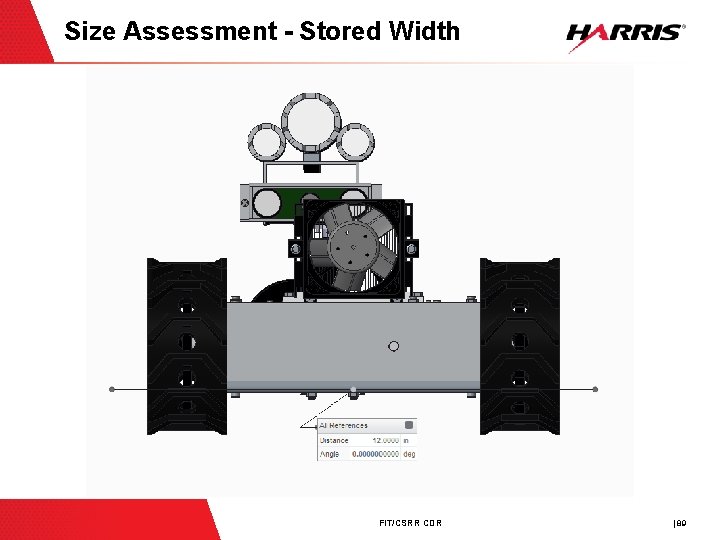
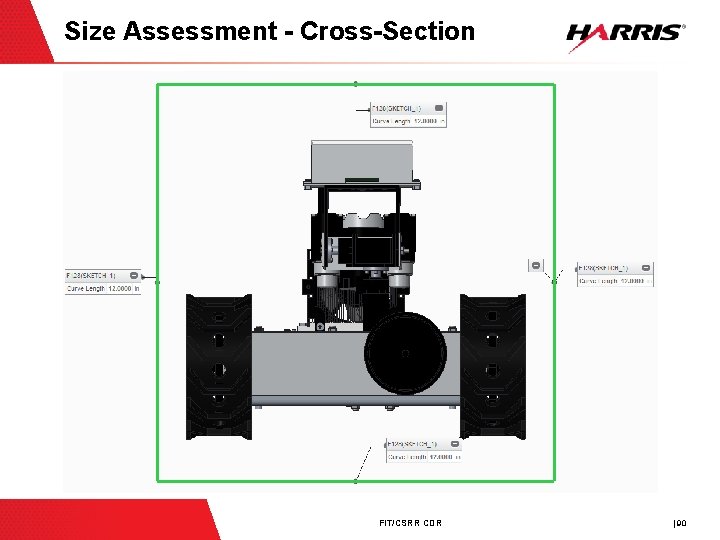
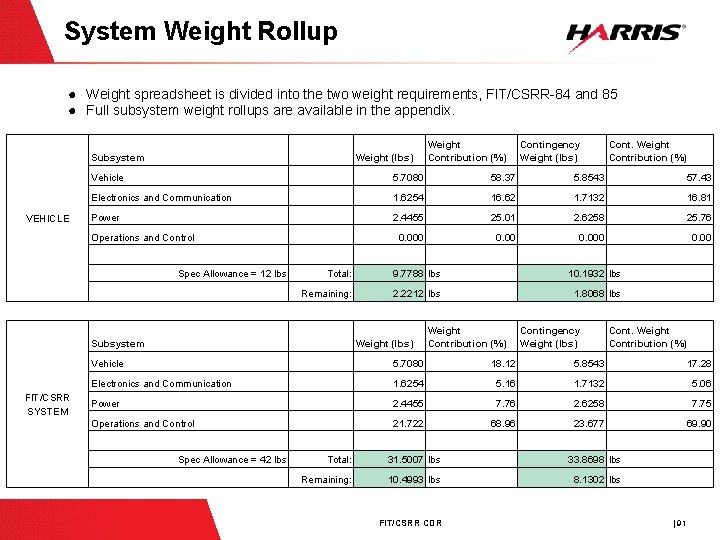
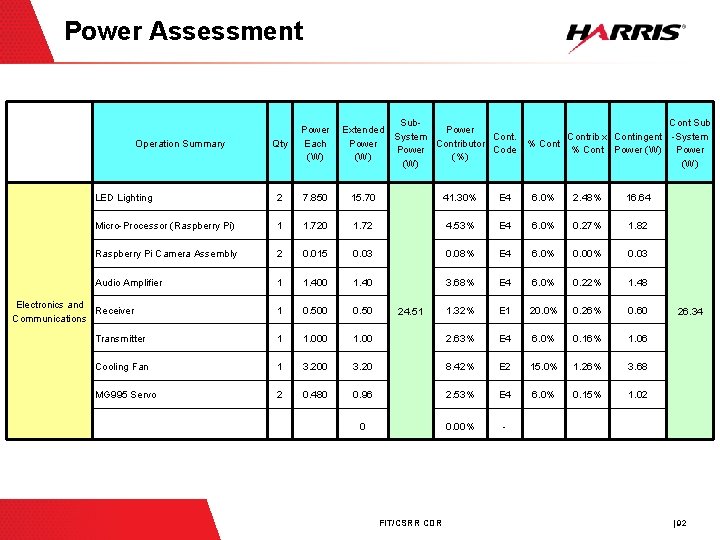
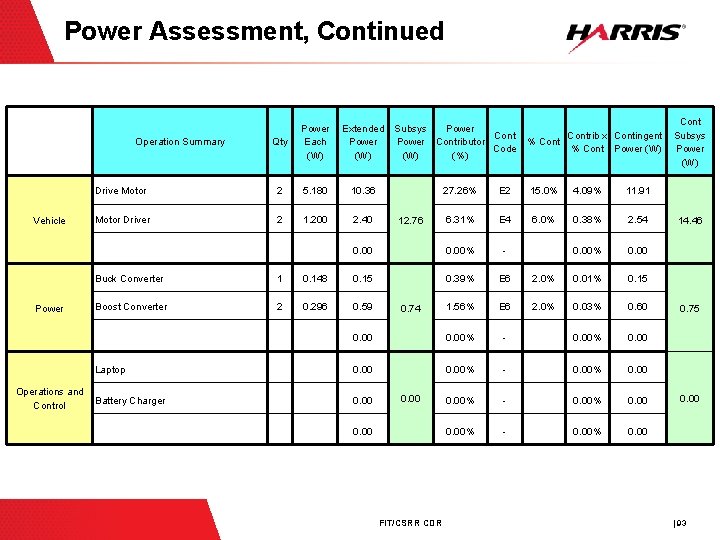
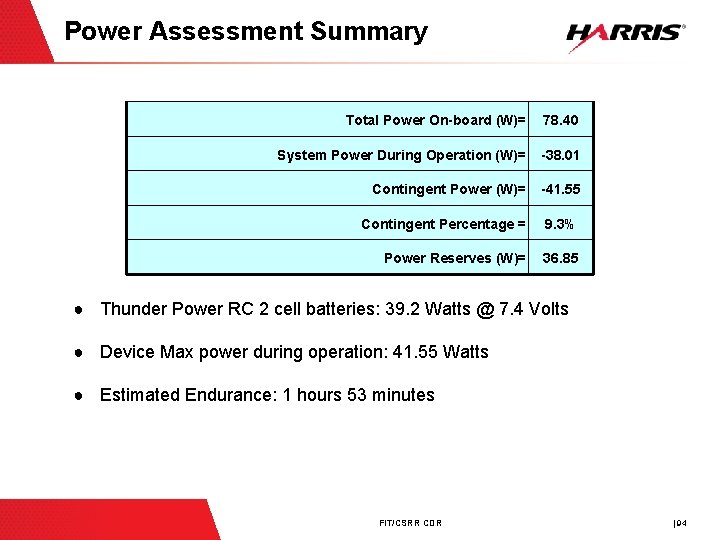
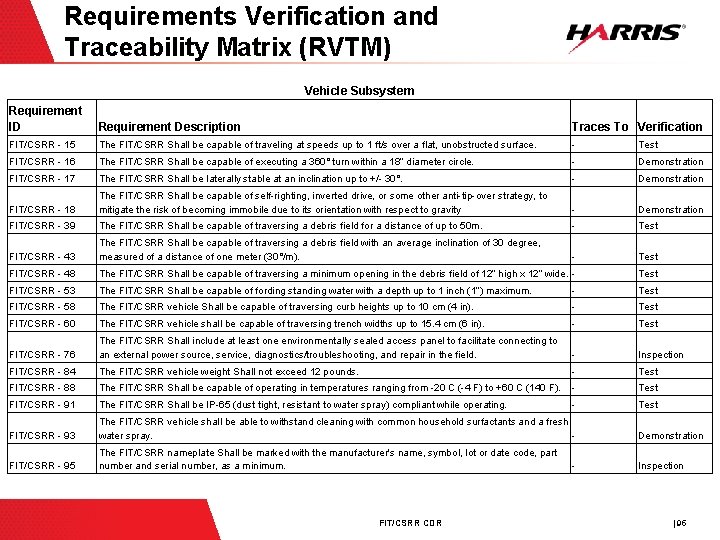
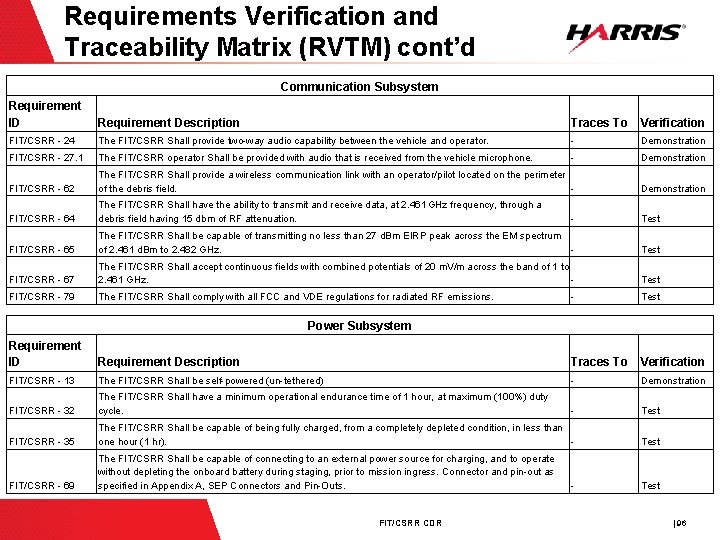
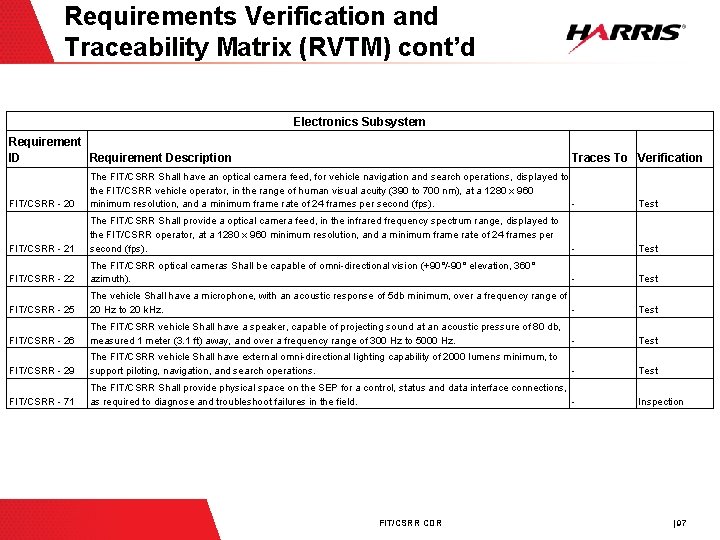
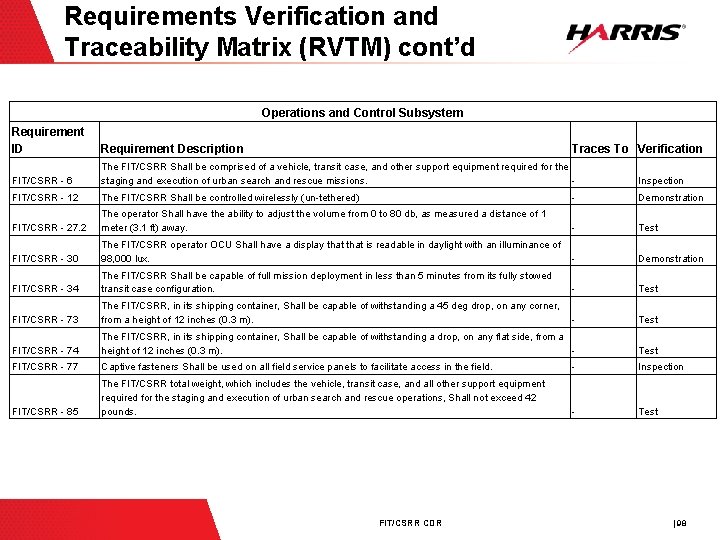
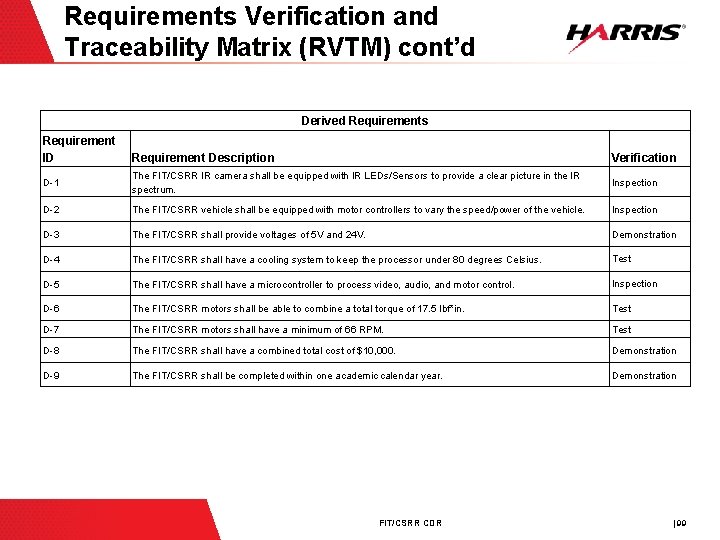
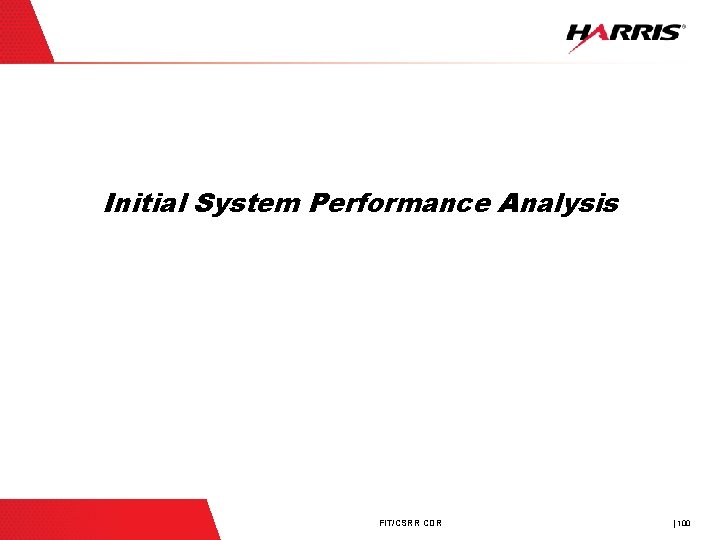
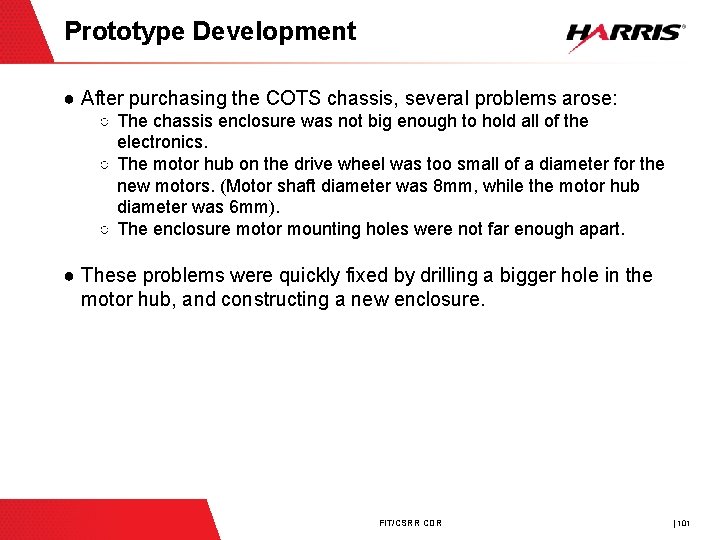
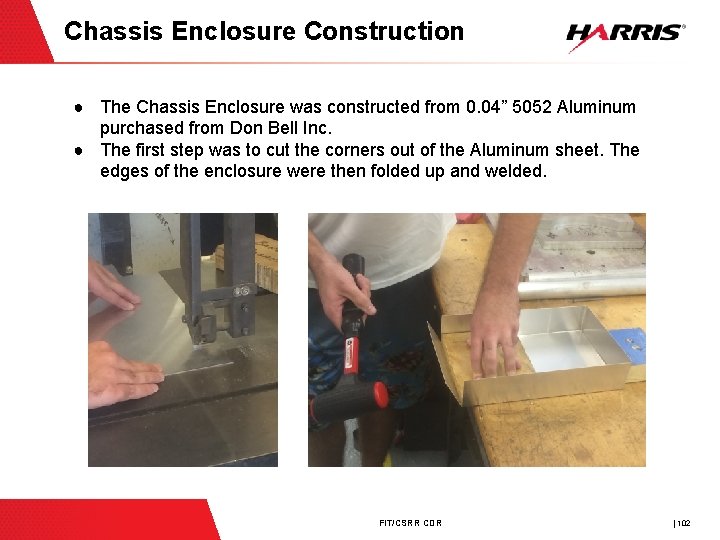
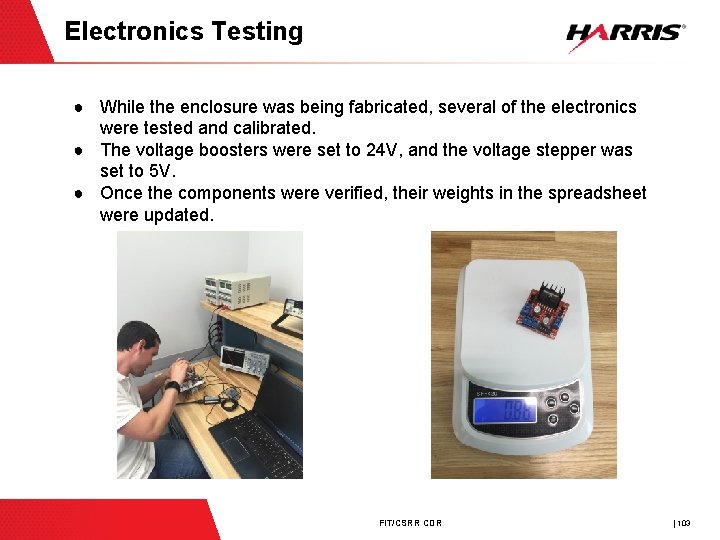
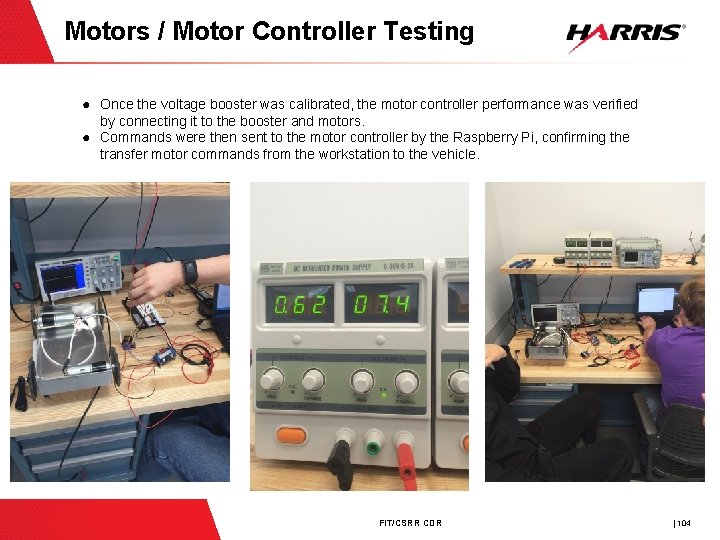
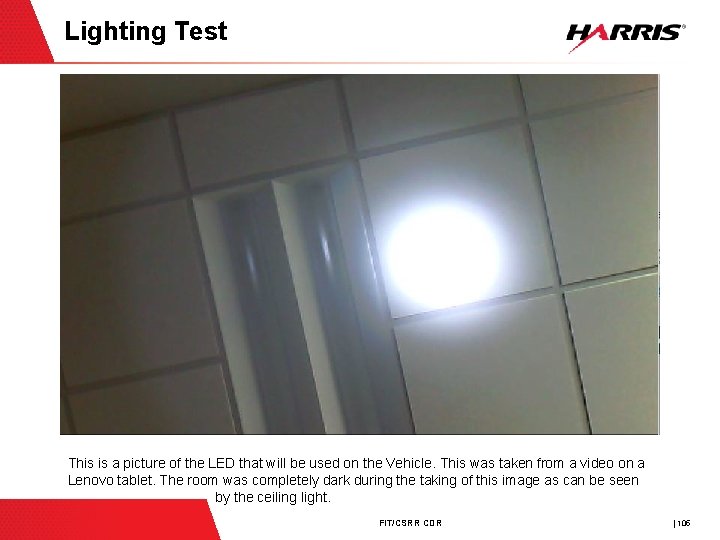
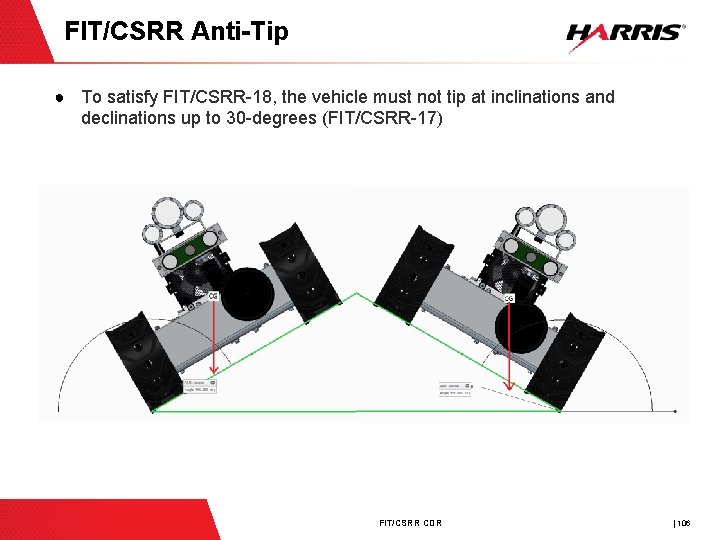
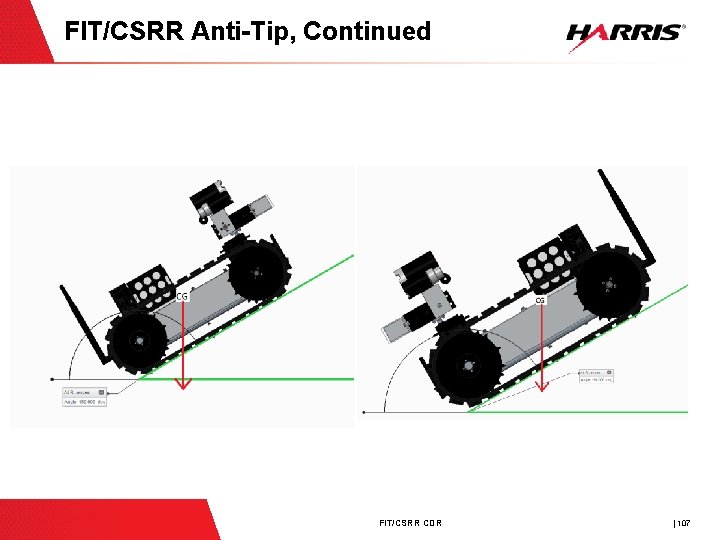
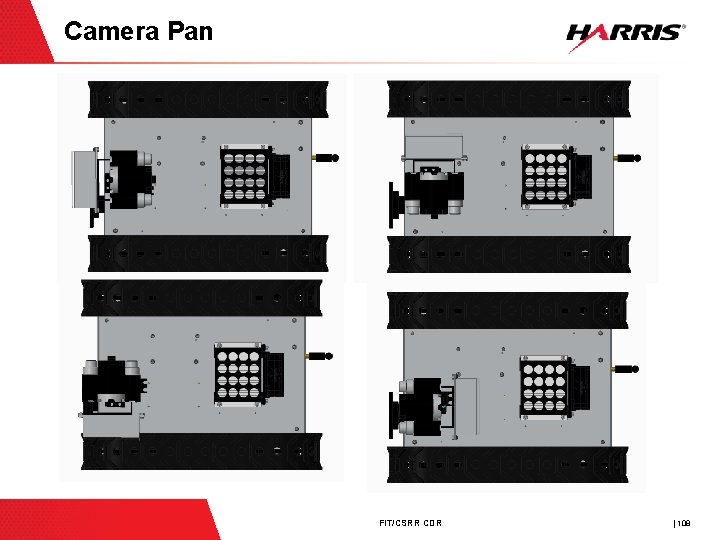
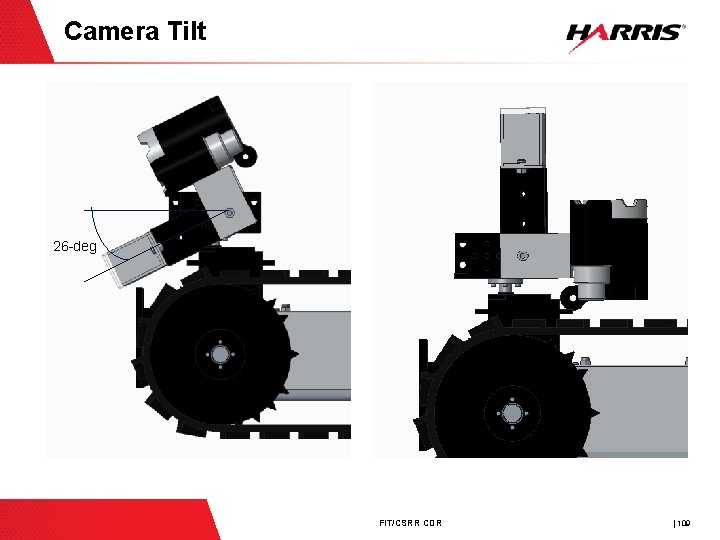
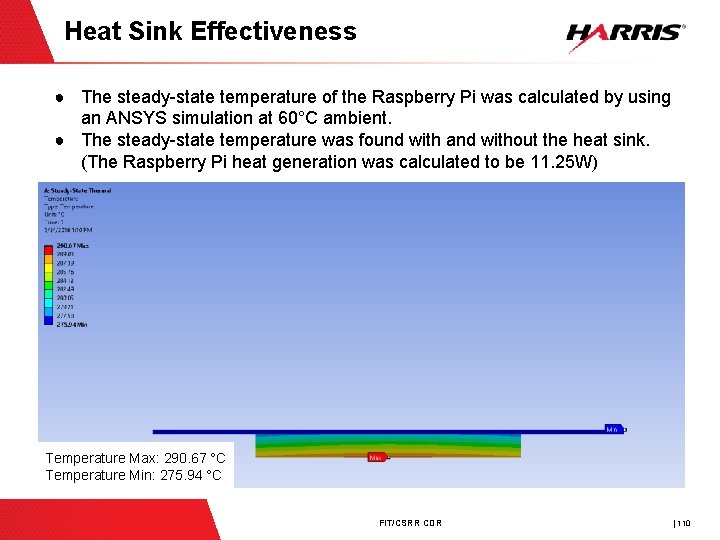
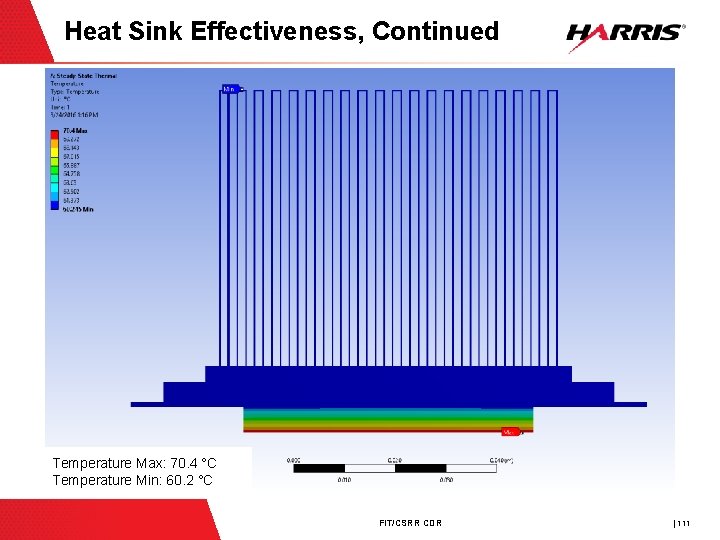
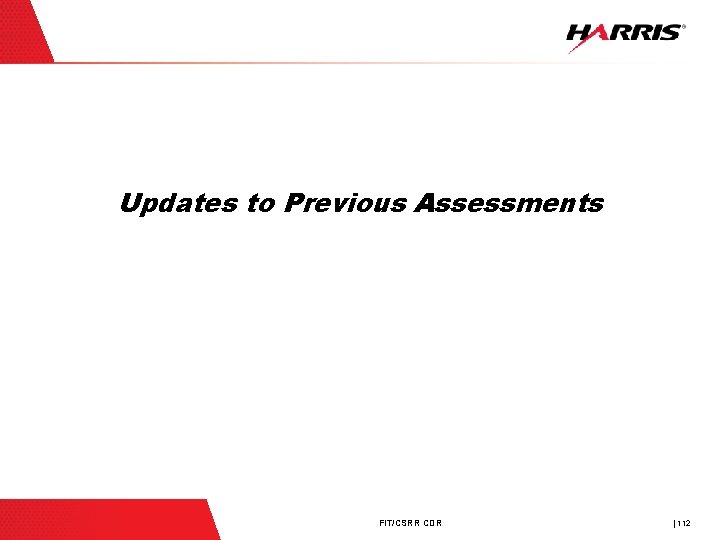
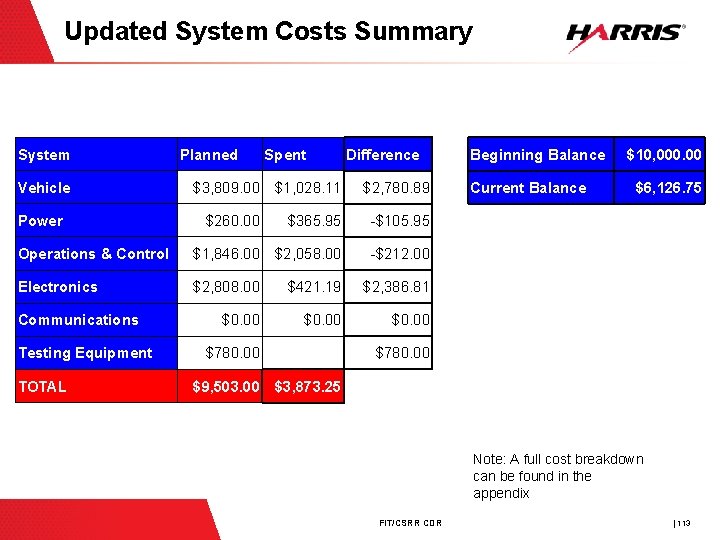
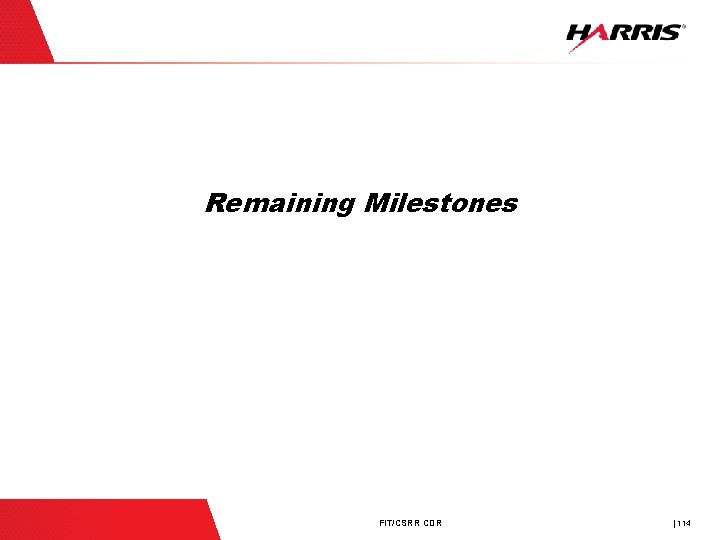
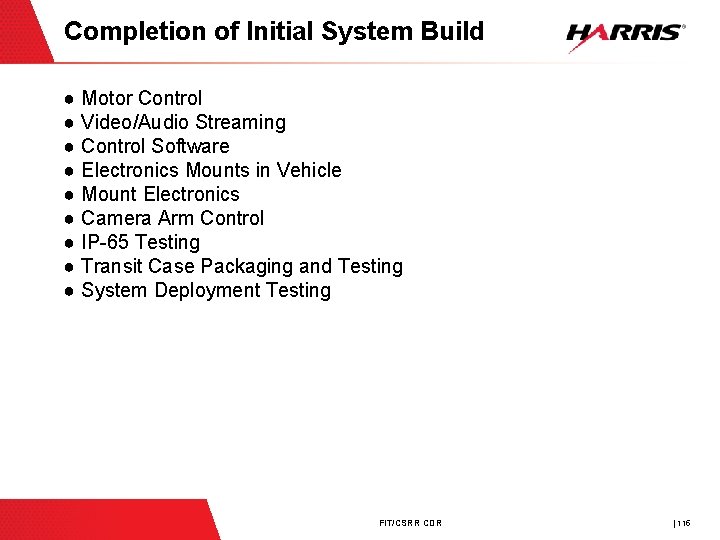
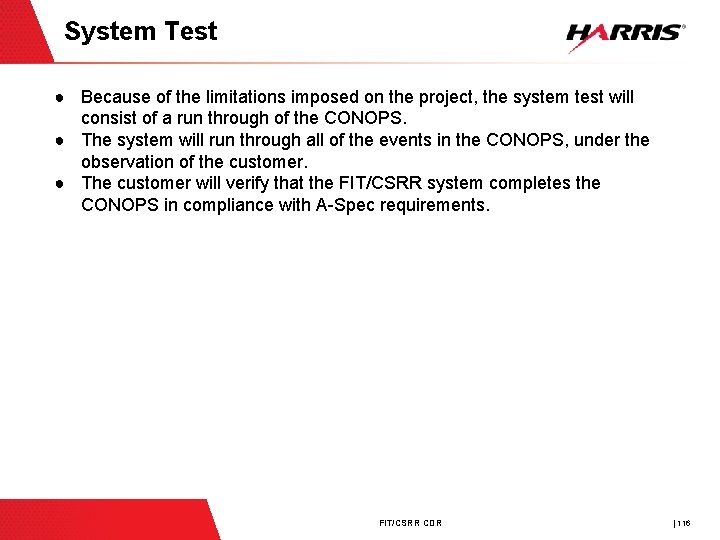
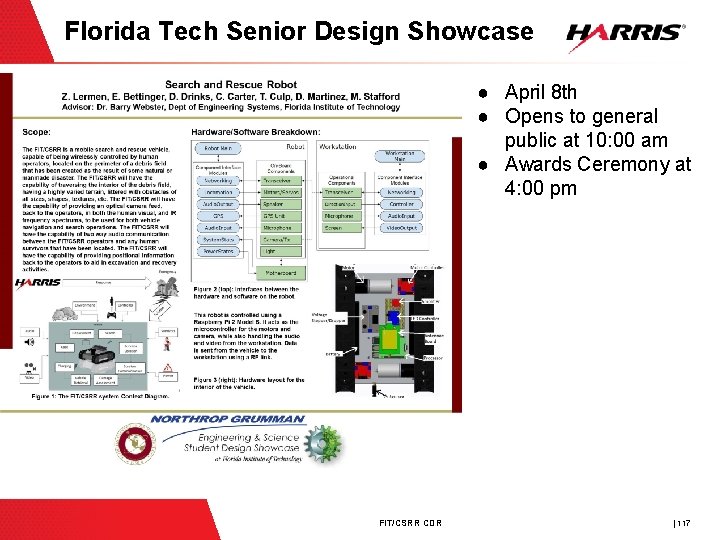
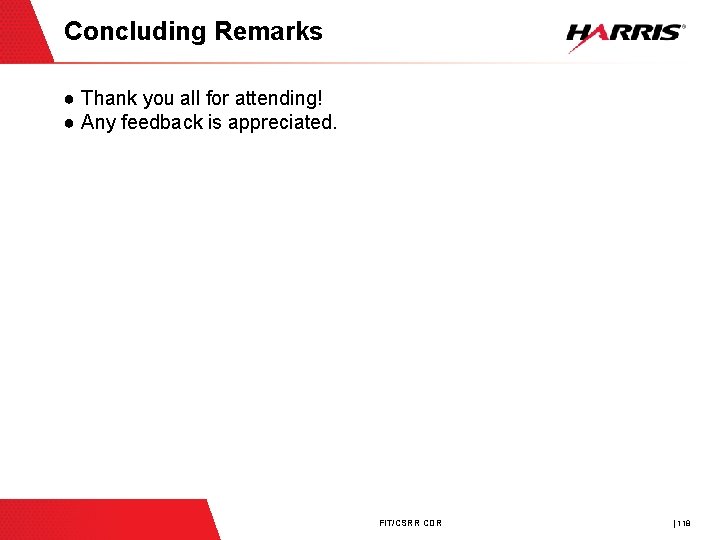
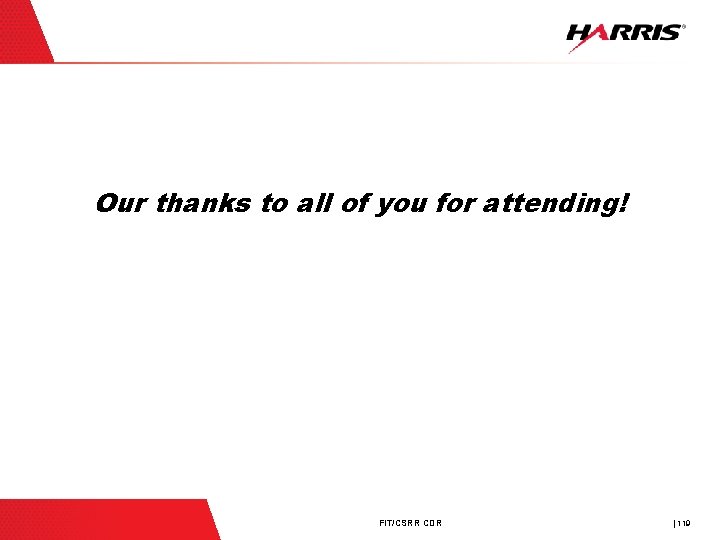
![References – IEEE Standard [1]J. Oakes, R. Botta and T. Bahill, “Technical Performance Measures”, References – IEEE Standard [1]J. Oakes, R. Botta and T. Bahill, “Technical Performance Measures”,](https://slidetodoc.com/presentation_image_h/882432d770b2194ab374350724101881/image-120.jpg)
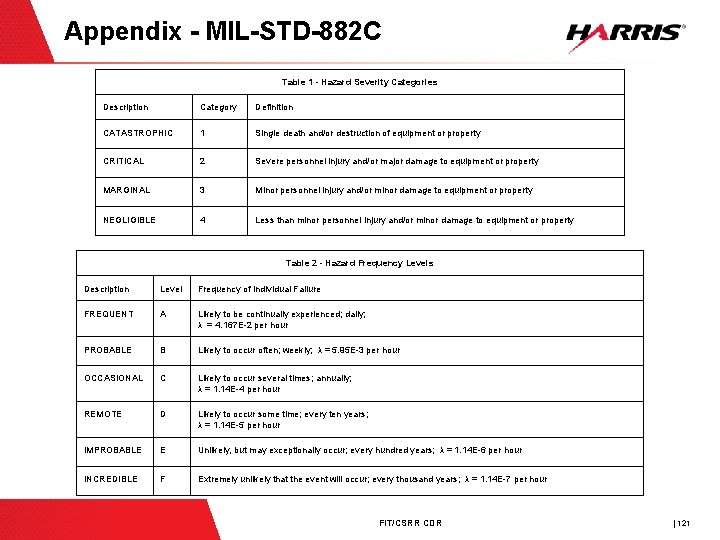
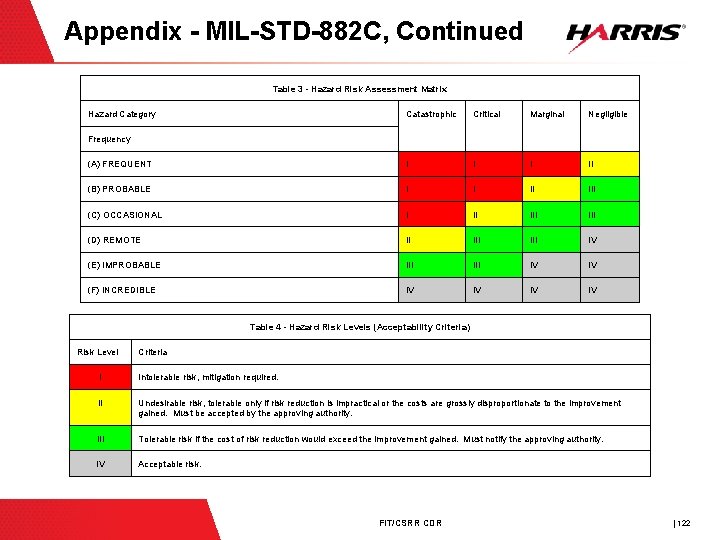
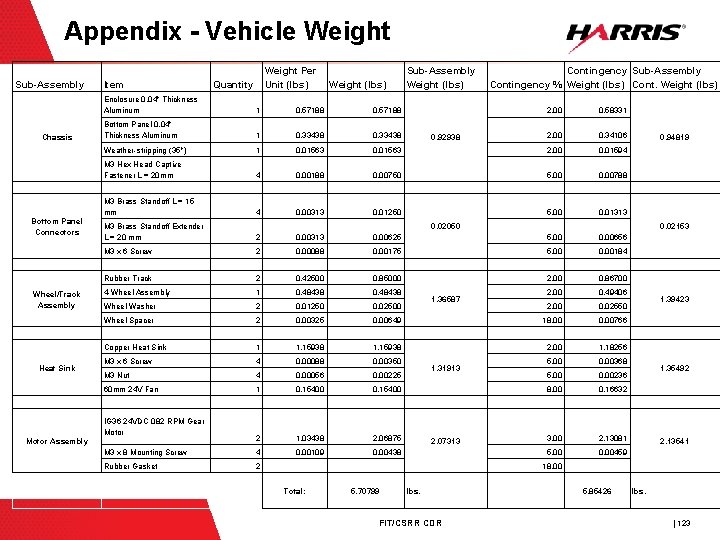
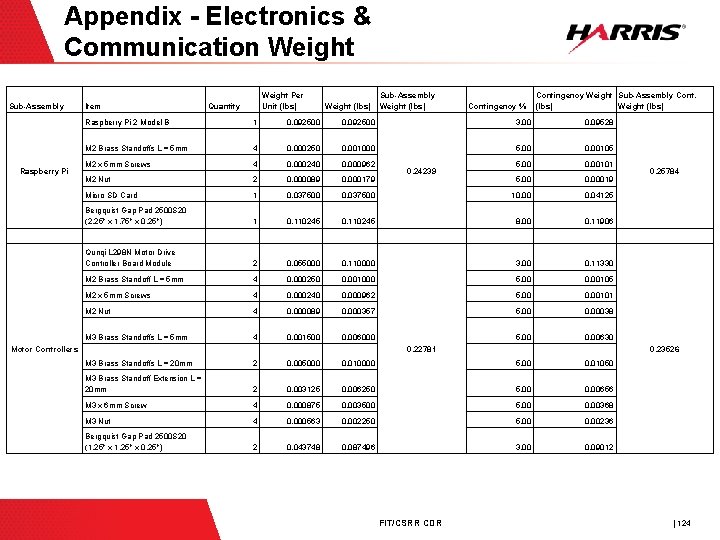
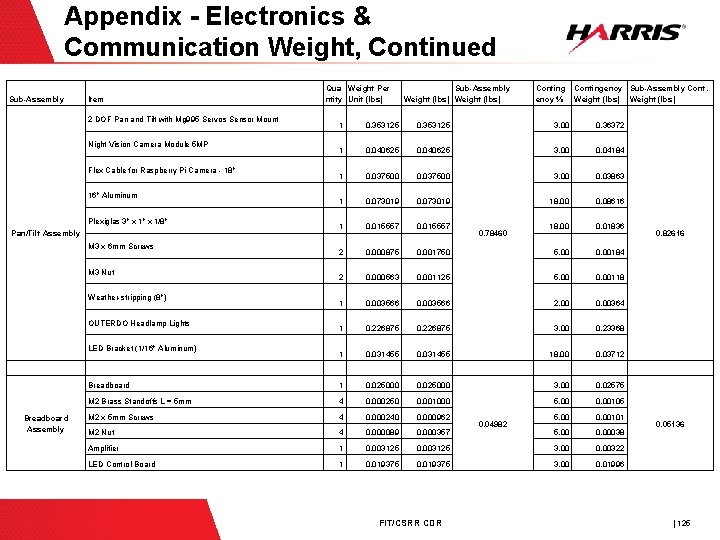
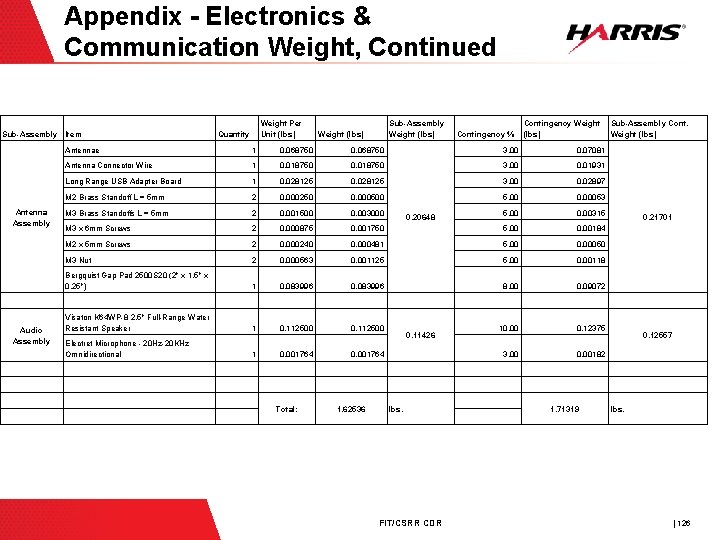
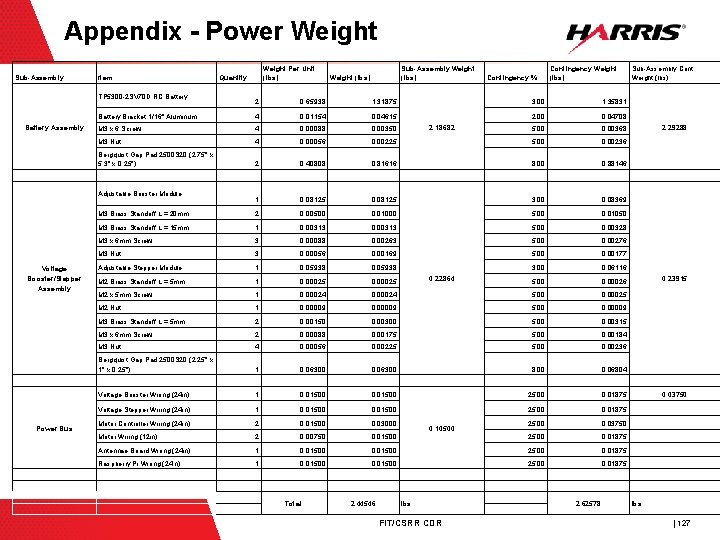
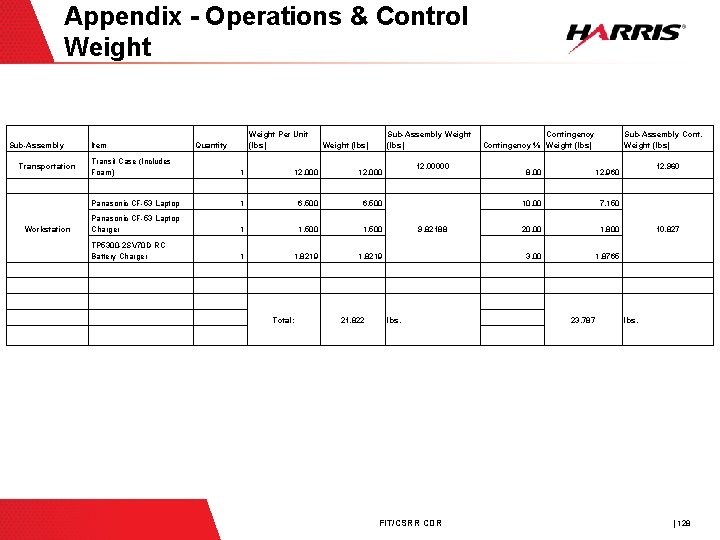
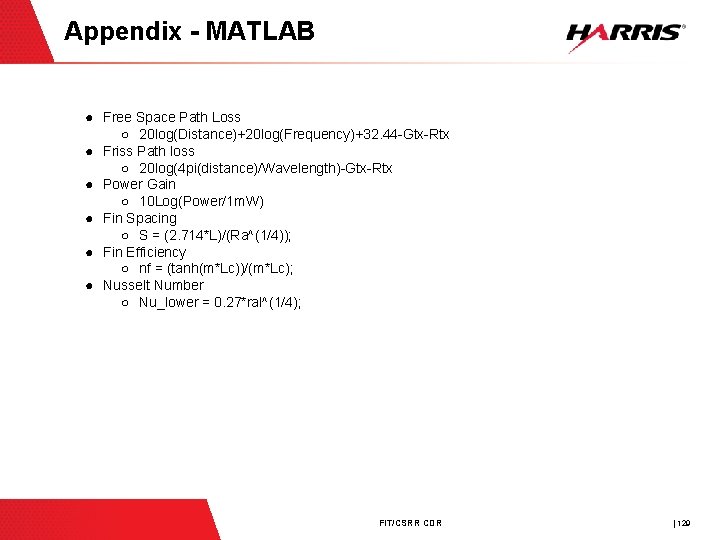
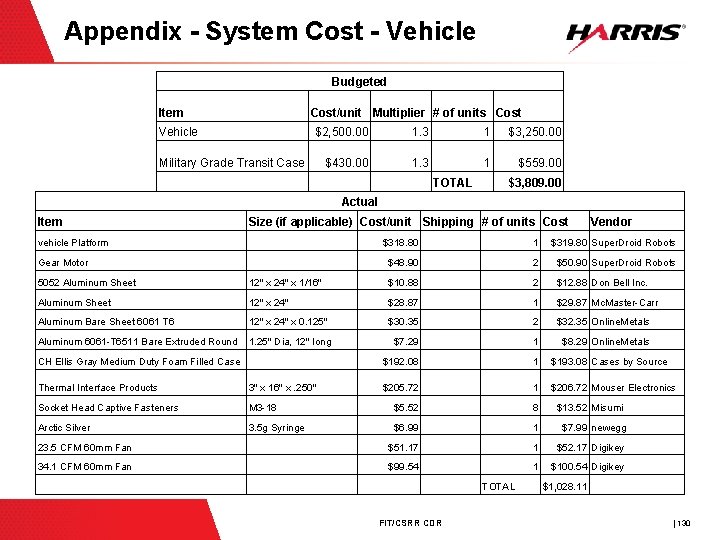
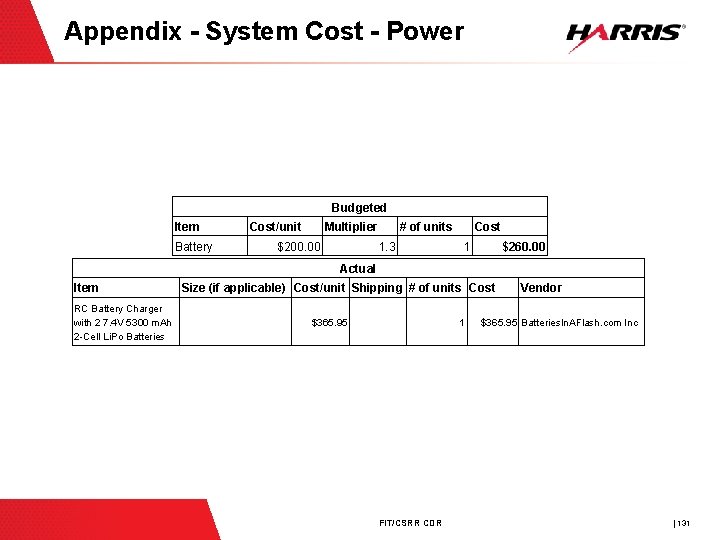
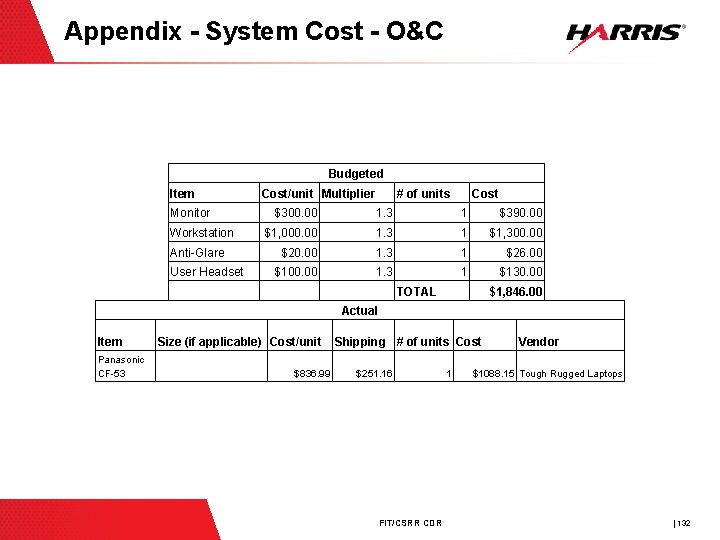
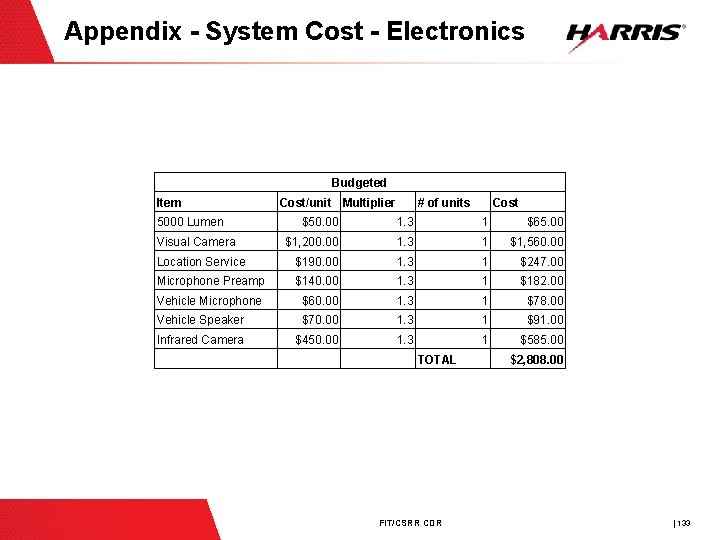
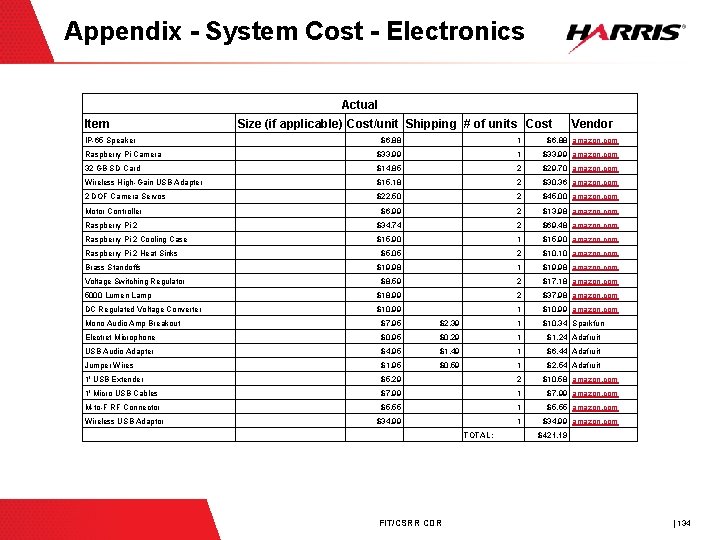
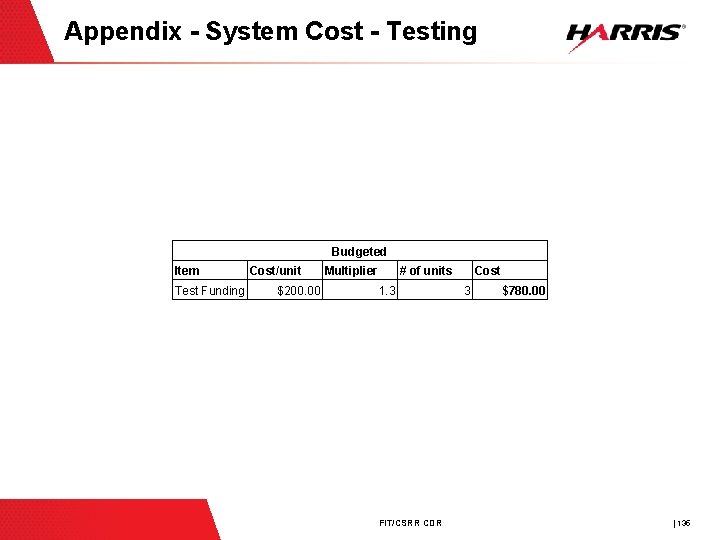
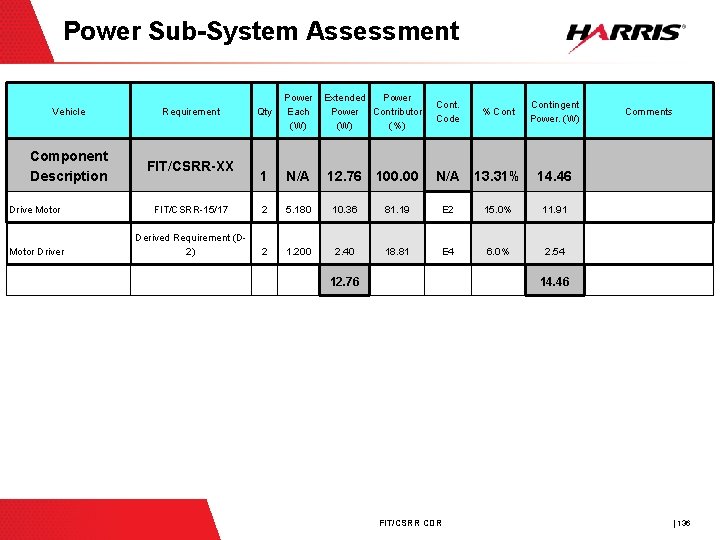
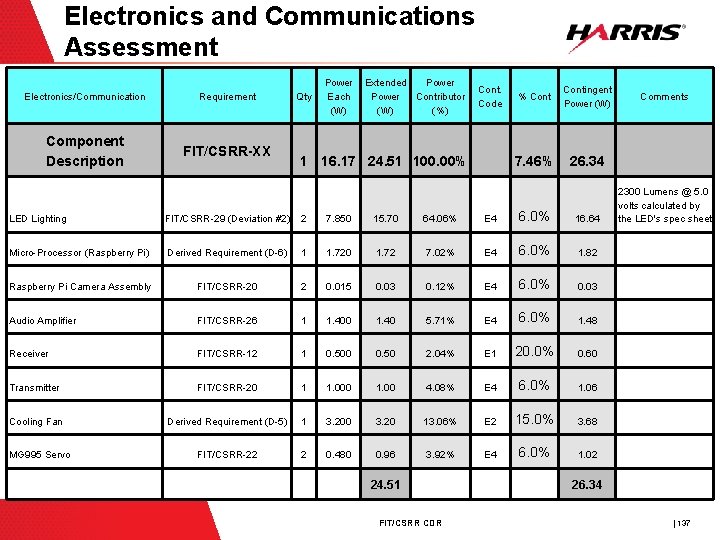
- Slides: 137
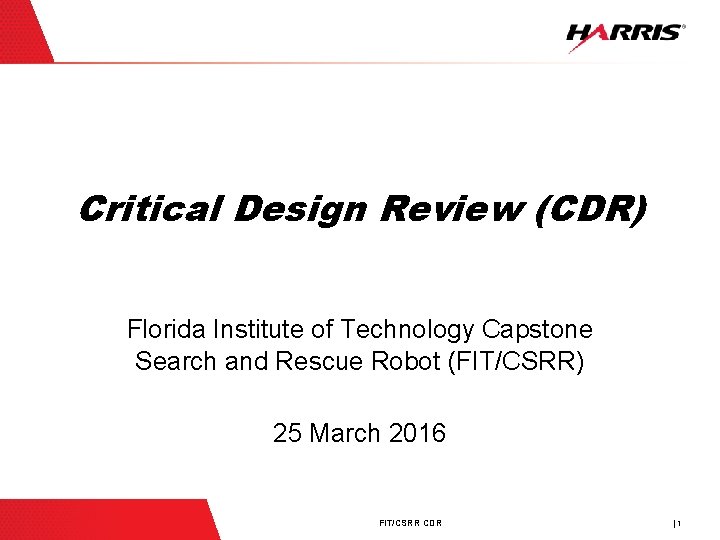
Critical Design Review (CDR) Florida Institute of Technology Capstone Search and Rescue Robot (FIT/CSRR) 25 March 2016 FIT/CSRR CDR | 1
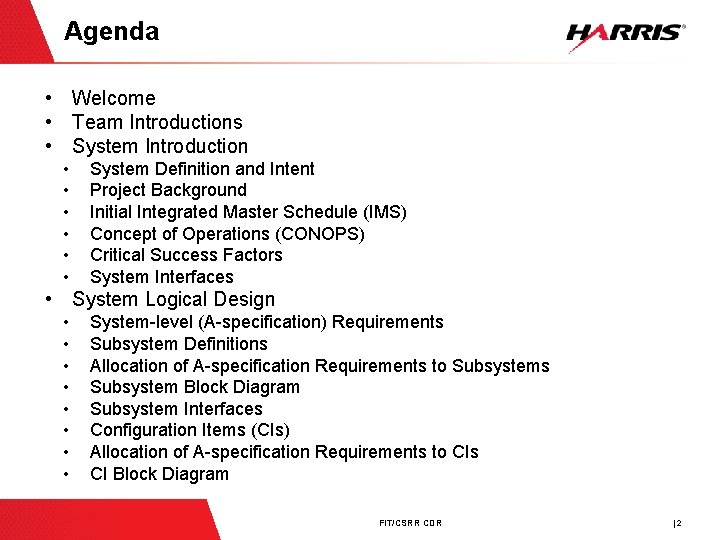
Agenda • Welcome • Team Introductions • System Introduction • • • System Definition and Intent Project Background Initial Integrated Master Schedule (IMS) Concept of Operations (CONOPS) Critical Success Factors System Interfaces • System Logical Design • • System-level (A-specification) Requirements Subsystem Definitions Allocation of A-specification Requirements to Subsystems Subsystem Block Diagram Subsystem Interfaces Configuration Items (CIs) Allocation of A-specification Requirements to CIs CI Block Diagram FIT/CSRR CDR | 2
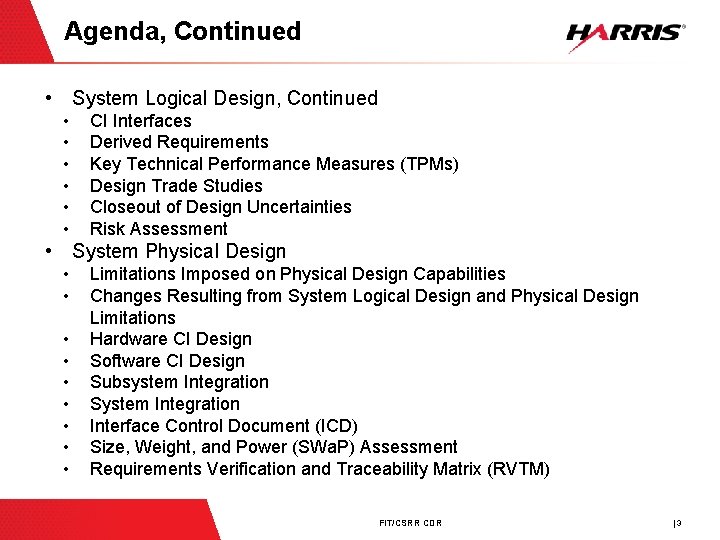
Agenda, Continued • System Logical Design, Continued • • • CI Interfaces Derived Requirements Key Technical Performance Measures (TPMs) Design Trade Studies Closeout of Design Uncertainties Risk Assessment • System Physical Design • • • Limitations Imposed on Physical Design Capabilities Changes Resulting from System Logical Design and Physical Design Limitations Hardware CI Design Software CI Design Subsystem Integration System Integration Interface Control Document (ICD) Size, Weight, and Power (SWa. P) Assessment Requirements Verification and Traceability Matrix (RVTM) FIT/CSRR CDR | 3
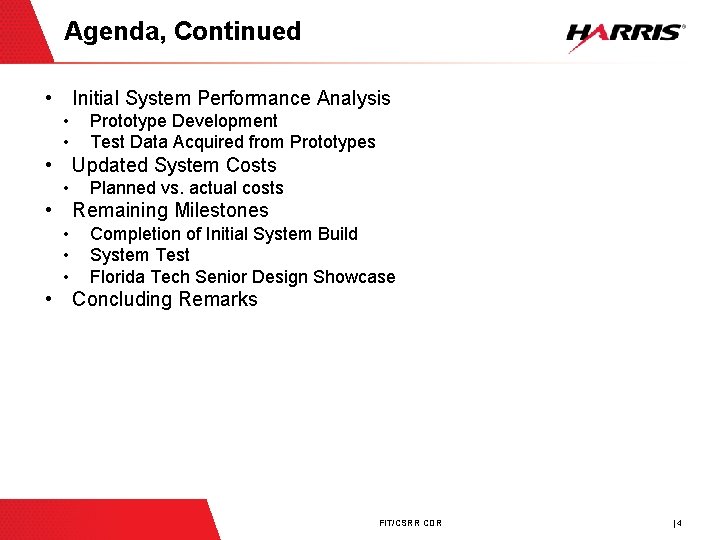
Agenda, Continued • Initial System Performance Analysis • • Prototype Development Test Data Acquired from Prototypes • Updated System Costs • Planned vs. actual costs • Remaining Milestones • • • Completion of Initial System Build System Test Florida Tech Senior Design Showcase • Concluding Remarks FIT/CSRR CDR | 4

Team Introductions Team Advisor Project Foreman Computer Engineering Computer Science Dr. Barry Webster Zackary Lermen Dale Drinks Tyler Culp Milton Stafford Electrical Engineering Christopher Carter Mechanical Engineering Eric Bettinger Software Engineering Devin Martinez FIT/CSRR CDR | 5
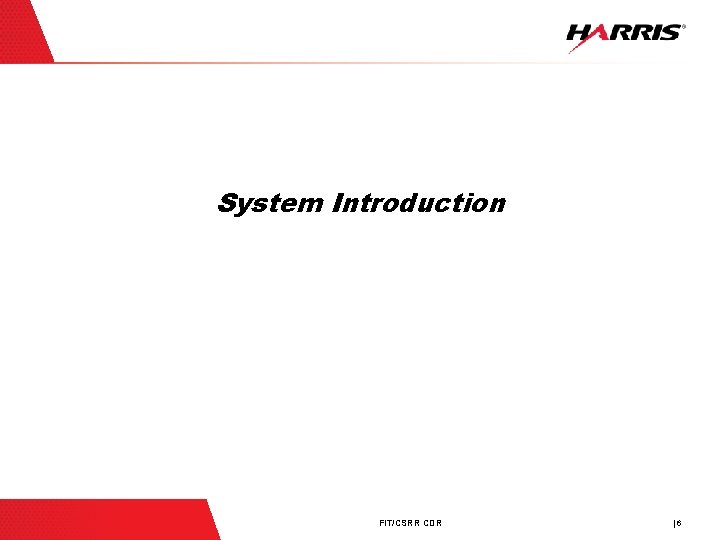
System Introduction FIT/CSRR CDR | 6
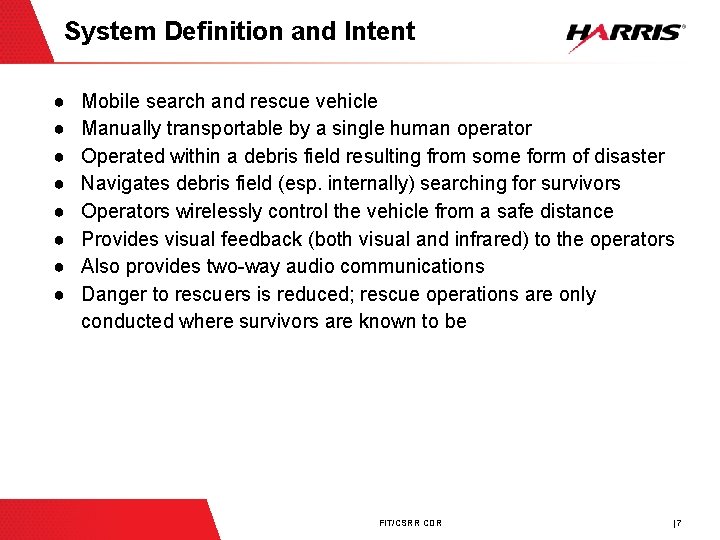
System Definition and Intent ● ● ● ● Mobile search and rescue vehicle Manually transportable by a single human operator Operated within a debris field resulting from some form of disaster Navigates debris field (esp. internally) searching for survivors Operators wirelessly control the vehicle from a safe distance Provides visual feedback (both visual and infrared) to the operators Also provides two-way audio communications Danger to rescuers is reduced; rescue operations are only conducted where survivors are known to be FIT/CSRR CDR | 7
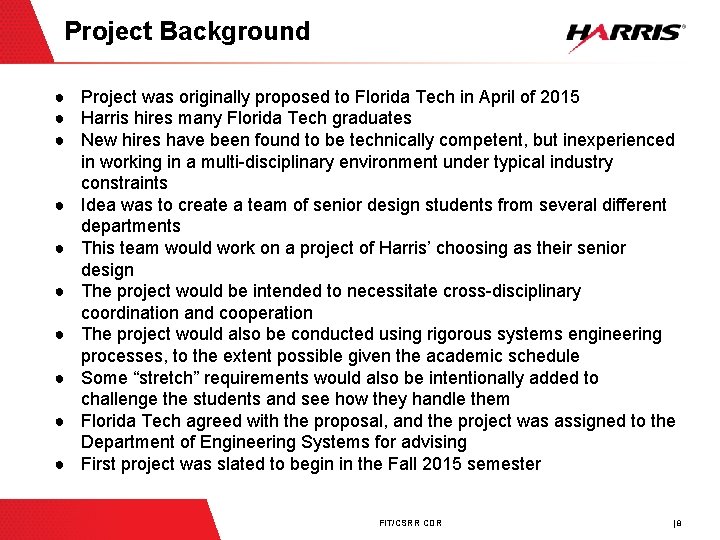
Project Background ● Project was originally proposed to Florida Tech in April of 2015 ● Harris hires many Florida Tech graduates ● New hires have been found to be technically competent, but inexperienced in working in a multi-disciplinary environment under typical industry constraints ● Idea was to create a team of senior design students from several different departments ● This team would work on a project of Harris’ choosing as their senior design ● The project would be intended to necessitate cross-disciplinary coordination and cooperation ● The project would also be conducted using rigorous systems engineering processes, to the extent possible given the academic schedule ● Some “stretch” requirements would also be intentionally added to challenge the students and see how they handle them ● Florida Tech agreed with the proposal, and the project was assigned to the Department of Engineering Systems for advising ● First project was slated to begin in the Fall 2015 semester FIT/CSRR CDR | 8
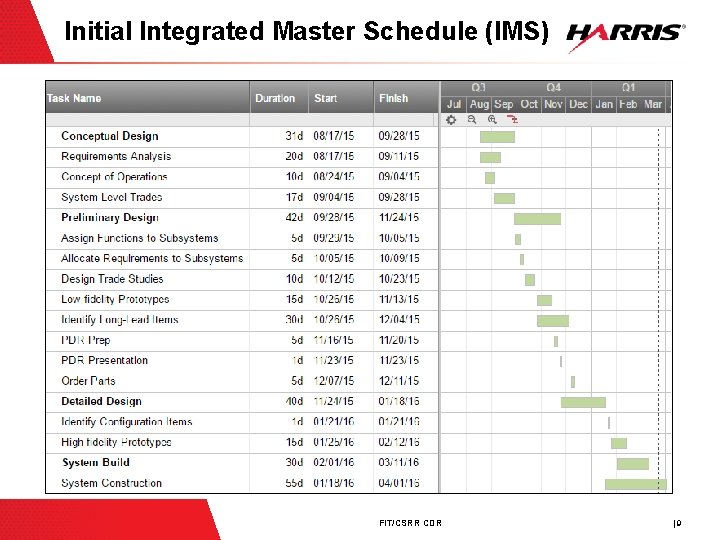
Initial Integrated Master Schedule (IMS) FIT/CSRR CDR | 9
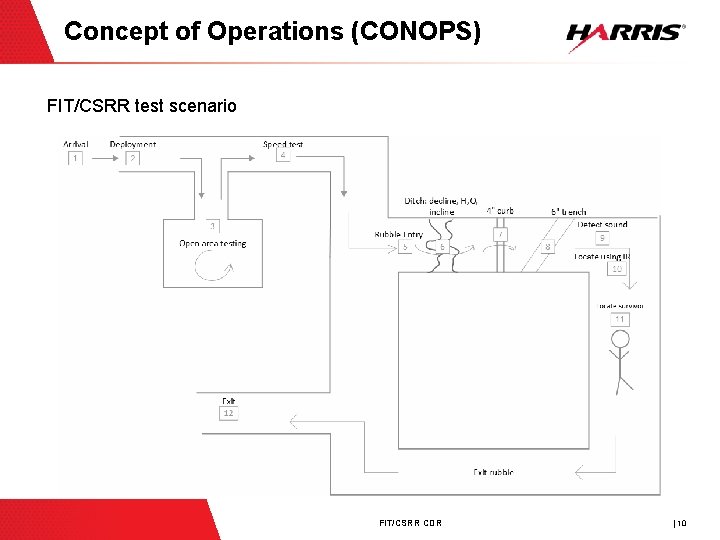
Concept of Operations (CONOPS) FIT/CSRR test scenario FIT/CSRR CDR | 10
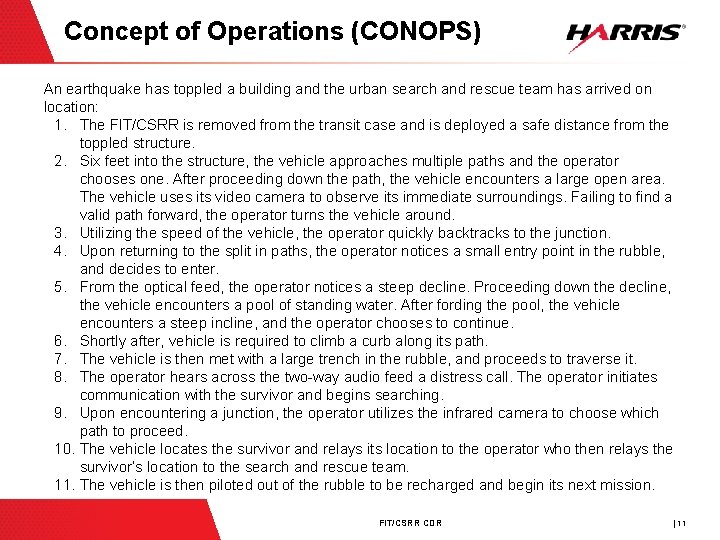
Concept of Operations (CONOPS) An earthquake has toppled a building and the urban search and rescue team has arrived on location: 1. The FIT/CSRR is removed from the transit case and is deployed a safe distance from the toppled structure. 2. Six feet into the structure, the vehicle approaches multiple paths and the operator chooses one. After proceeding down the path, the vehicle encounters a large open area. The vehicle uses its video camera to observe its immediate surroundings. Failing to find a valid path forward, the operator turns the vehicle around. 3. Utilizing the speed of the vehicle, the operator quickly backtracks to the junction. 4. Upon returning to the split in paths, the operator notices a small entry point in the rubble, and decides to enter. 5. From the optical feed, the operator notices a steep decline. Proceeding down the decline, the vehicle encounters a pool of standing water. After fording the pool, the vehicle encounters a steep incline, and the operator chooses to continue. 6. Shortly after, vehicle is required to climb a curb along its path. 7. The vehicle is then met with a large trench in the rubble, and proceeds to traverse it. 8. The operator hears across the two-way audio feed a distress call. The operator initiates communication with the survivor and begins searching. 9. Upon encountering a junction, the operator utilizes the infrared camera to choose which path to proceed. 10. The vehicle locates the survivor and relays its location to the operator who then relays the survivor’s location to the search and rescue team. 11. The vehicle is then piloted out of the rubble to be recharged and begin its next mission. FIT/CSRR CDR | 11
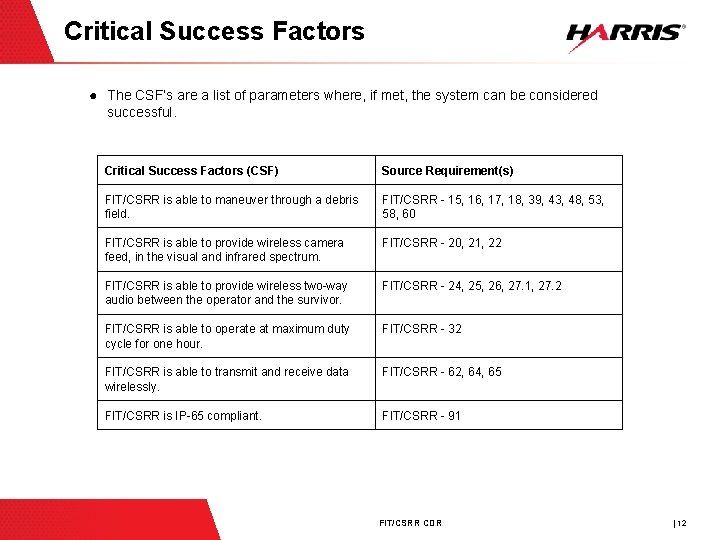
Critical Success Factors ● The CSF’s are a list of parameters where, if met, the system can be considered successful. Critical Success Factors (CSF) Source Requirement(s) FIT/CSRR is able to maneuver through a debris field. FIT/CSRR - 15, 16, 17, 18, 39, 43, 48, 53, 58, 60 FIT/CSRR is able to provide wireless camera feed, in the visual and infrared spectrum. FIT/CSRR - 20, 21, 22 FIT/CSRR is able to provide wireless two-way audio between the operator and the survivor. FIT/CSRR - 24, 25, 26, 27. 1, 27. 2 FIT/CSRR is able to operate at maximum duty cycle for one hour. FIT/CSRR - 32 FIT/CSRR is able to transmit and receive data wirelessly. FIT/CSRR - 62, 64, 65 FIT/CSRR is IP-65 compliant. FIT/CSRR - 91 FIT/CSRR CDR | 12
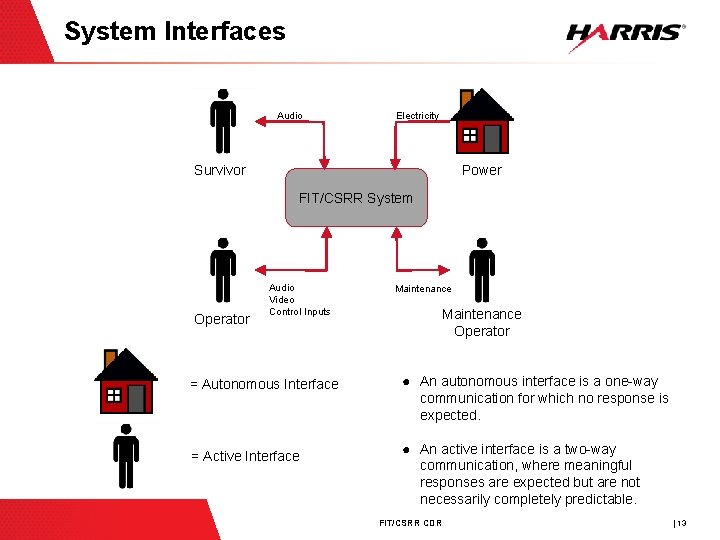
System Interfaces Audio Electricity Survivor Power FIT/CSRR System Operator Audio Video Control Inputs = Autonomous Interface = Active Interface Maintenance Operator ● An autonomous interface is a one-way communication for which no response is expected. ● An active interface is a two-way communication, where meaningful responses are expected but are not necessarily completely predictable. FIT/CSRR CDR | 13
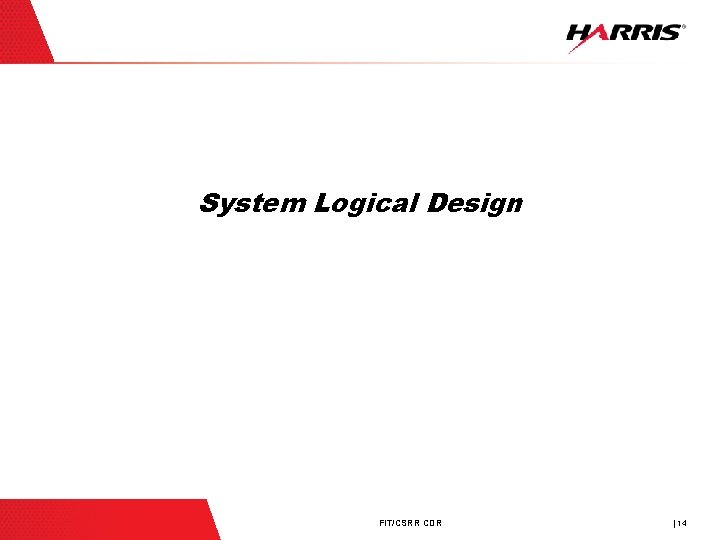
System Logical Design FIT/CSRR CDR | 14
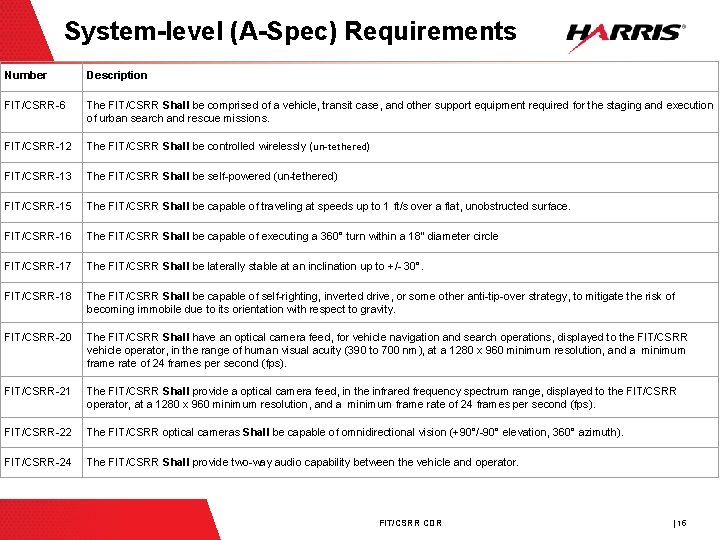
System-level (A-Spec) Requirements Number Description FIT/CSRR-6 The FIT/CSRR Shall be comprised of a vehicle, transit case, and other support equipment required for the staging and execution of urban search and rescue missions. FIT/CSRR-12 The FIT/CSRR Shall be controlled wirelessly (un-tethered) FIT/CSRR-13 The FIT/CSRR Shall be self-powered (un-tethered) FIT/CSRR-15 The FIT/CSRR Shall be capable of traveling at speeds up to 1 ft/s over a flat, unobstructed surface. FIT/CSRR-16 The FIT/CSRR Shall be capable of executing a 360° turn within a 18” diameter circle FIT/CSRR-17 The FIT/CSRR Shall be laterally stable at an inclination up to +/- 30°. FIT/CSRR-18 The FIT/CSRR Shall be capable of self-righting, inverted drive, or some other anti-tip-over strategy, to mitigate the risk of becoming immobile due to its orientation with respect to gravity. FIT/CSRR-20 The FIT/CSRR Shall have an optical camera feed, for vehicle navigation and search operations, displayed to the FIT/CSRR vehicle operator, in the range of human visual acuity (390 to 700 nm), at a 1280 x 960 minimum resolution, and a minimum frame rate of 24 frames per second (fps). FIT/CSRR-21 The FIT/CSRR Shall provide a optical camera feed, in the infrared frequency spectrum range, displayed to the FIT/CSRR operator, at a 1280 x 960 minimum resolution, and a minimum frame rate of 24 frames per second (fps). FIT/CSRR-22 The FIT/CSRR optical cameras Shall be capable of omnidirectional vision (+90°/-90° elevation, 360° azimuth). FIT/CSRR-24 The FIT/CSRR Shall provide two-way audio capability between the vehicle and operator. FIT/CSRR CDR | 15
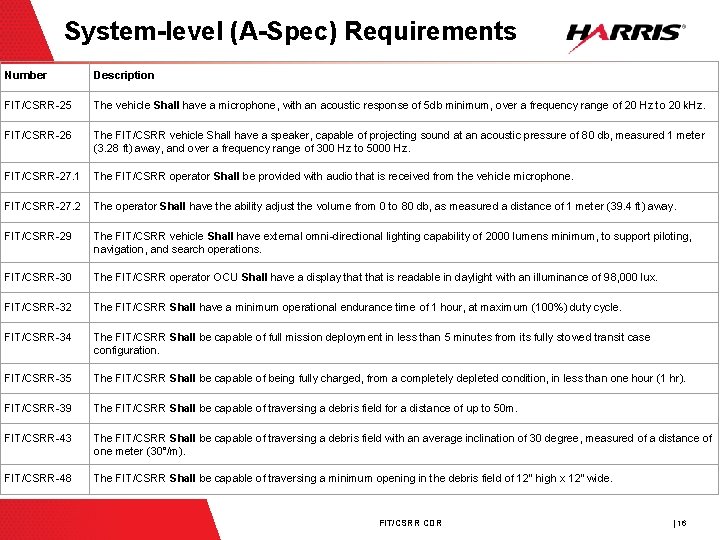
System-level (A-Spec) Requirements Number Description FIT/CSRR-25 The vehicle Shall have a microphone, with an acoustic response of 5 db minimum, over a frequency range of 20 Hz to 20 k. Hz. FIT/CSRR-26 The FIT/CSRR vehicle Shall have a speaker, capable of projecting sound at an acoustic pressure of 80 db, measured 1 meter (3. 28 ft) away, and over a frequency range of 300 Hz to 5000 Hz. FIT/CSRR-27. 1 The FIT/CSRR operator Shall be provided with audio that is received from the vehicle microphone. FIT/CSRR-27. 2 The operator Shall have the ability adjust the volume from 0 to 80 db, as measured a distance of 1 meter (39. 4 ft) away. FIT/CSRR-29 The FIT/CSRR vehicle Shall have external omni-directional lighting capability of 2000 lumens minimum, to support piloting, navigation, and search operations. FIT/CSRR-30 The FIT/CSRR operator OCU Shall have a display that is readable in daylight with an illuminance of 98, 000 lux. FIT/CSRR-32 The FIT/CSRR Shall have a minimum operational endurance time of 1 hour, at maximum (100%) duty cycle. FIT/CSRR-34 The FIT/CSRR Shall be capable of full mission deployment in less than 5 minutes from its fully stowed transit case configuration. FIT/CSRR-35 The FIT/CSRR Shall be capable of being fully charged, from a completely depleted condition, in less than one hour (1 hr). FIT/CSRR-39 The FIT/CSRR Shall be capable of traversing a debris field for a distance of up to 50 m. FIT/CSRR-43 The FIT/CSRR Shall be capable of traversing a debris field with an average inclination of 30 degree, measured of a distance of one meter (30°/m). FIT/CSRR-48 The FIT/CSRR Shall be capable of traversing a minimum opening in the debris field of 12” high x 12” wide. FIT/CSRR CDR | 16
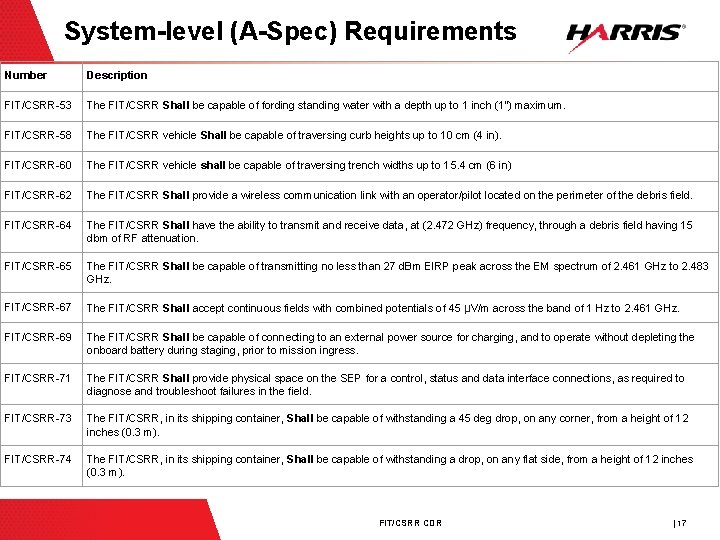
System-level (A-Spec) Requirements Number Description FIT/CSRR-53 The FIT/CSRR Shall be capable of fording standing water with a depth up to 1 inch (1”) maximum. FIT/CSRR-58 The FIT/CSRR vehicle Shall be capable of traversing curb heights up to 10 cm (4 in). FIT/CSRR-60 The FIT/CSRR vehicle shall be capable of traversing trench widths up to 15. 4 cm (6 in) FIT/CSRR-62 The FIT/CSRR Shall provide a wireless communication link with an operator/pilot located on the perimeter of the debris field. FIT/CSRR-64 The FIT/CSRR Shall have the ability to transmit and receive data, at (2. 472 GHz) frequency, through a debris field having 15 dbm of RF attenuation. FIT/CSRR-65 The FIT/CSRR Shall be capable of transmitting no less than 27 d. Bm EIRP peak across the EM spectrum of 2. 461 GHz to 2. 483 GHz. FIT/CSRR-67 The FIT/CSRR Shall accept continuous fields with combined potentials of 45 μV/m across the band of 1 Hz to 2. 461 GHz. FIT/CSRR-69 The FIT/CSRR Shall be capable of connecting to an external power source for charging, and to operate without depleting the onboard battery during staging, prior to mission ingress. FIT/CSRR-71 The FIT/CSRR Shall provide physical space on the SEP for a control, status and data interface connections, as required to diagnose and troubleshoot failures in the field. FIT/CSRR-73 The FIT/CSRR, in its shipping container, Shall be capable of withstanding a 45 deg drop, on any corner, from a height of 12 inches (0. 3 m). FIT/CSRR-74 The FIT/CSRR, in its shipping container, Shall be capable of withstanding a drop, on any flat side, from a height of 12 inches (0. 3 m). FIT/CSRR CDR | 17
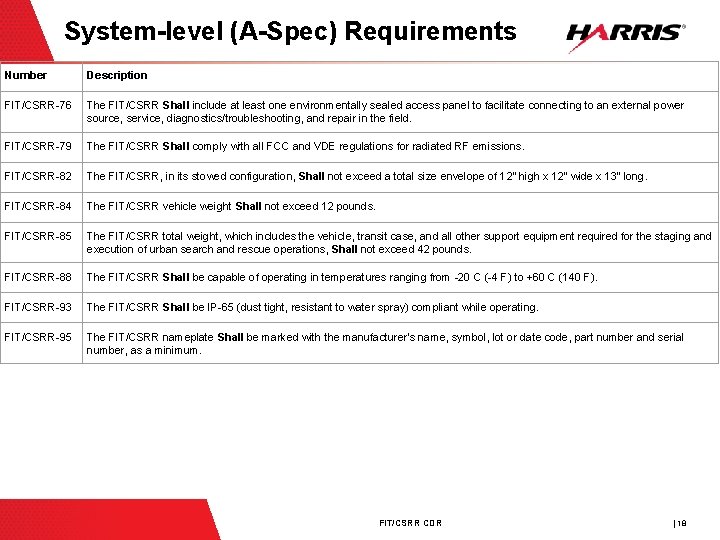
System-level (A-Spec) Requirements Number Description FIT/CSRR-76 The FIT/CSRR Shall include at least one environmentally sealed access panel to facilitate connecting to an external power source, service, diagnostics/troubleshooting, and repair in the field. FIT/CSRR-79 The FIT/CSRR Shall comply with all FCC and VDE regulations for radiated RF emissions. FIT/CSRR-82 The FIT/CSRR, in its stowed configuration, Shall not exceed a total size envelope of 12” high x 12” wide x 13” long. FIT/CSRR-84 The FIT/CSRR vehicle weight Shall not exceed 12 pounds. FIT/CSRR-85 The FIT/CSRR total weight, which includes the vehicle, transit case, and all other support equipment required for the staging and execution of urban search and rescue operations, Shall not exceed 42 pounds. FIT/CSRR-88 The FIT/CSRR Shall be capable of operating in temperatures ranging from -20 C (-4 F) to +60 C (140 F). FIT/CSRR-93 The FIT/CSRR Shall be IP-65 (dust tight, resistant to water spray) compliant while operating. FIT/CSRR-95 The FIT/CSRR nameplate Shall be marked with the manufacturer's name, symbol, lot or date code, part number and serial number, as a minimum. FIT/CSRR CDR | 18
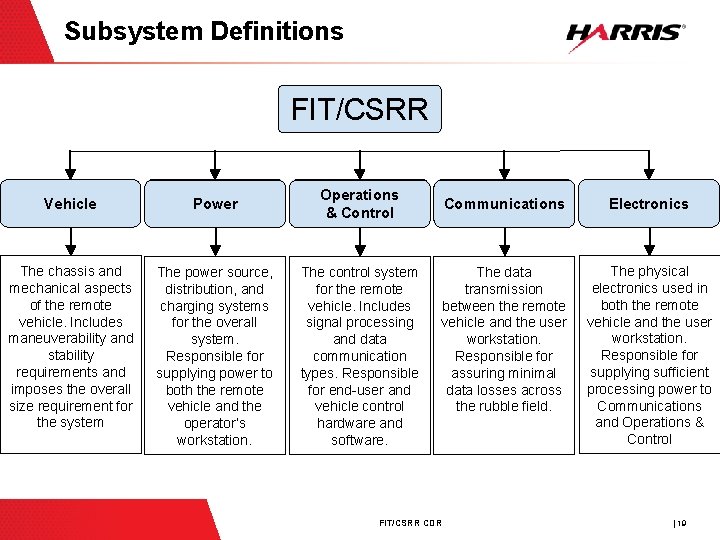
Subsystem Definitions FIT/CSRR Vehicle Power Operations Control &&Control The chassis and mechanical aspects of the remote vehicle. Includes maneuverability and stability requirements and imposes the overall size requirement for the system The power source, distribution, and charging systems for the overall system. Responsible for supplying power to both the remote vehicle and the operator’s workstation. The control system for the remote vehicle. Includes signal processing and data communication types. Responsible for end-user and vehicle control hardware and software. Communicat ions Communications Electronics The data transmission between the remote vehicle and the user workstation. Responsible for assuring minimal data losses across the rubble field. The physical electronics used in both the remote vehicle and the user workstation. Responsible for supplying sufficient processing power to Communications and Operations & Control FIT/CSRR CDR | 19
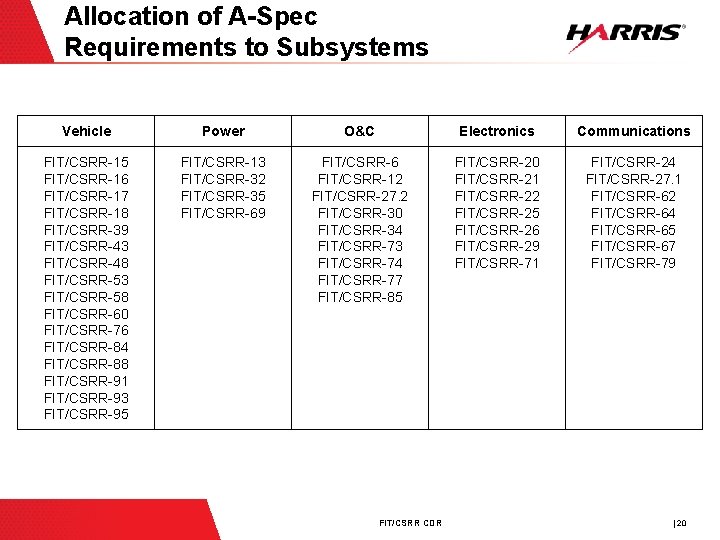
Allocation of A-Spec Requirements to Subsystems Vehicle Power O&C Electronics Communications FIT/CSRR-15 FIT/CSRR-16 FIT/CSRR-17 FIT/CSRR-18 FIT/CSRR-39 FIT/CSRR-43 FIT/CSRR-48 FIT/CSRR-53 FIT/CSRR-58 FIT/CSRR-60 FIT/CSRR-76 FIT/CSRR-84 FIT/CSRR-88 FIT/CSRR-91 FIT/CSRR-93 FIT/CSRR-95 FIT/CSRR-13 FIT/CSRR-32 FIT/CSRR-35 FIT/CSRR-69 FIT/CSRR-6 FIT/CSRR-12 FIT/CSRR-27. 2 FIT/CSRR-30 FIT/CSRR-34 FIT/CSRR-73 FIT/CSRR-74 FIT/CSRR-77 FIT/CSRR-85 FIT/CSRR-20 FIT/CSRR-21 FIT/CSRR-22 FIT/CSRR-25 FIT/CSRR-26 FIT/CSRR-29 FIT/CSRR-71 FIT/CSRR-24 FIT/CSRR-27. 1 FIT/CSRR-62 FIT/CSRR-64 FIT/CSRR-65 FIT/CSRR-67 FIT/CSRR-79 FIT/CSRR CDR | 20
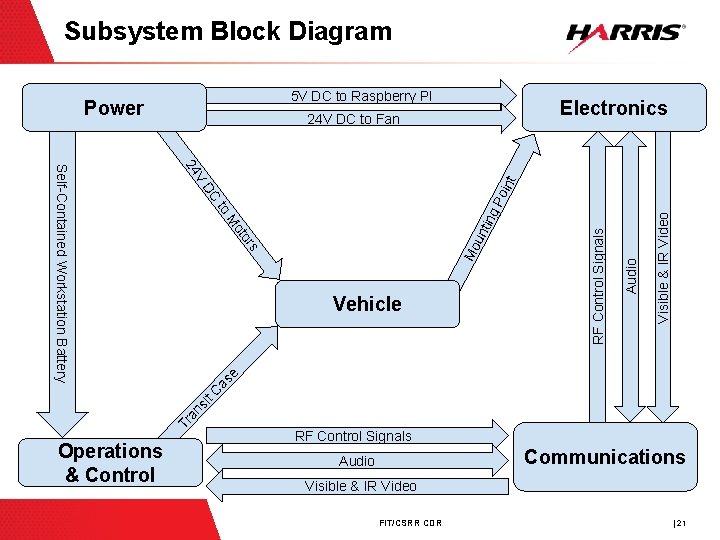
Subsystem Block Diagram 5 V DC to Raspberry PI Power Electronics 24 V DC to Fan 24 Tr a Visible & IR Video Audio ns it C as e RF Control Signals s Mo u or ot ntin M to g P oin t DC V Self-Contained Workstation Battery Vehicle Operations & Control RF Control Signals Communications Audio Visible & IR Video FIT/CSRR CDR | 21

Subsystem Interfaces ● Mounting Points ○ Physical mounting points for hardware ● Audio ○ 2 -way audio communication between the survivor and operator ● Visible & IR Video ○ 1 -way live video feed from the vehicle to the operator ● RF Control Signals ○ motor control, camera arm control, and camera control ● 24 V DC to Motors ○ Power at 24 V supplied to the motors ● 5 V DC to Raspberry Pi ○ Power at 5 V supplied to the microcontroller ● 24 V DC to Fan ○ Power at 24 V supplied to the fan ● Self-Contained Workstation Battery ○ Laptop is equipped with an internal battery ● Transit Case ○ Transit case to carry the vehicle and other support equipment FIT/CSRR CDR | 22
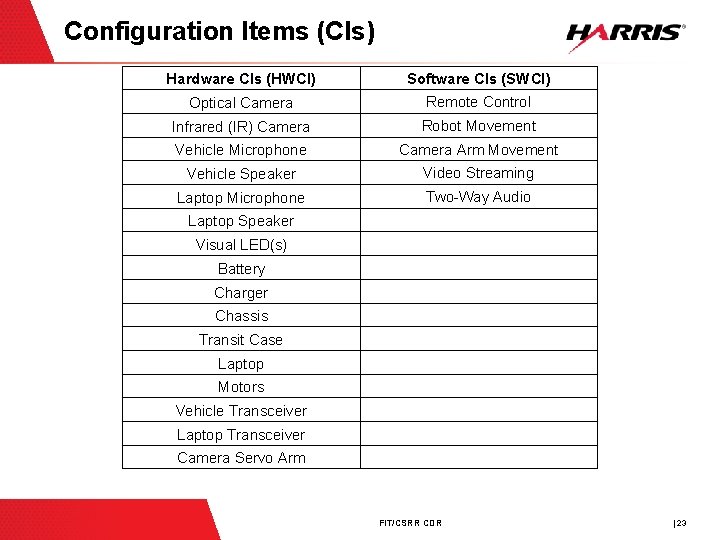
Configuration Items (CIs) Hardware CIs (HWCI) Software CIs (SWCI) Optical Camera Remote Control Infrared (IR) Camera Robot Movement Vehicle Microphone Camera Arm Movement Vehicle Speaker Video Streaming Laptop Microphone Two-Way Audio Laptop Speaker Visual LED(s) Battery Charger Chassis Transit Case Laptop Motors Vehicle Transceiver Laptop Transceiver Camera Servo Arm FIT/CSRR CDR | 23
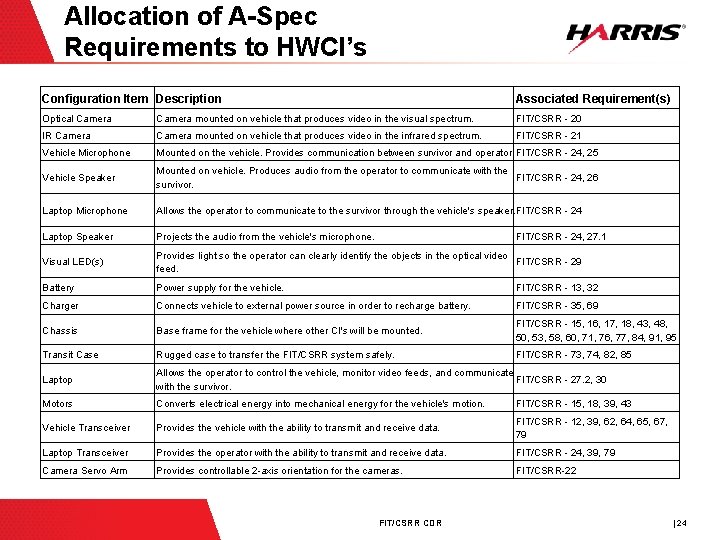
Allocation of A-Spec Requirements to HWCI’s Configuration Item Description Associated Requirement(s) Optical Camera mounted on vehicle that produces video in the visual spectrum. FIT/CSRR - 20 IR Camera mounted on vehicle that produces video in the infrared spectrum. FIT/CSRR - 21 Vehicle Microphone Mounted on the vehicle. Provides communication between survivor and operator. FIT/CSRR - 24, 25 Vehicle Speaker Mounted on vehicle. Produces audio from the operator to communicate with the FIT/CSRR - 24, 26 survivor. Laptop Microphone Allows the operator to communicate to the survivor through the vehicle's speaker. FIT/CSRR - 24 Laptop Speaker Projects the audio from the vehicle's microphone. Visual LED(s) Provides light so the operator can clearly identify the objects in the optical video FIT/CSRR - 29 feed. Battery Power supply for the vehicle. FIT/CSRR - 13, 32 Charger Connects vehicle to external power source in order to recharge battery. FIT/CSRR - 35, 69 Chassis Base frame for the vehicle where other CI's will be mounted. FIT/CSRR - 15, 16, 17, 18, 43, 48, 50, 53, 58, 60, 71, 76, 77, 84, 91, 95 Transit Case Rugged case to transfer the FIT/CSRR system safely. FIT/CSRR - 73, 74, 82, 85 Laptop Allows the operator to control the vehicle, monitor video feeds, and communicate FIT/CSRR - 27. 2, 30 with the survivor. Motors Converts electrical energy into mechanical energy for the vehicle's motion. FIT/CSRR - 15, 18, 39, 43 Vehicle Transceiver Provides the vehicle with the ability to transmit and receive data. FIT/CSRR - 12, 39, 62, 64, 65, 67, 79 Laptop Transceiver Provides the operator with the ability to transmit and receive data. FIT/CSRR - 24, 39, 79 Camera Servo Arm Provides controllable 2 -axis orientation for the cameras. FIT/CSRR-22 FIT/CSRR - 24, 27. 1 FIT/CSRR CDR | 24
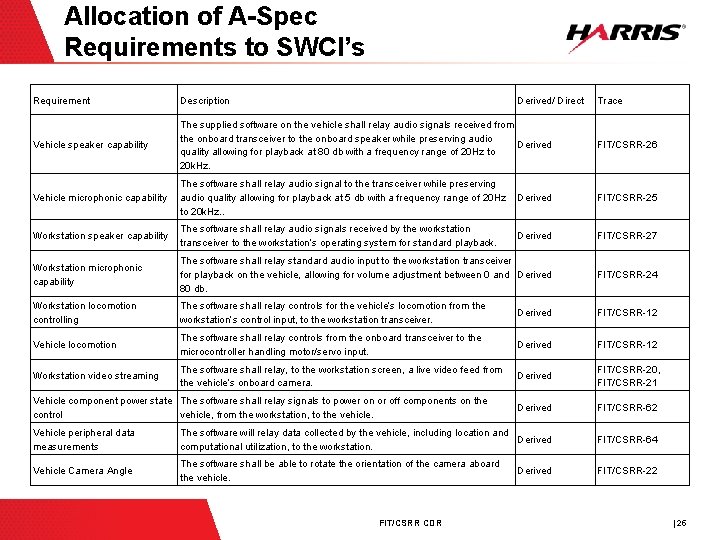
Allocation of A-Spec Requirements to SWCI’s Requirement Description Derived/ Direct Vehicle speaker capability The supplied software on the vehicle shall relay audio signals received from the onboard transceiver to the onboard speaker while preserving audio Derived quality allowing for playback at 80 db with a frequency range of 20 Hz to 20 k. Hz. FIT/CSRR-26 Vehicle microphonic capability The software shall relay audio signal to the transceiver while preserving audio quality allowing for playback at 5 db with a frequency range of 20 Hz Derived to 20 k. Hz. . FIT/CSRR-25 Workstation speaker capability The software shall relay audio signals received by the workstation transceiver to the workstation’s operating system for standard playback. Derived FIT/CSRR-27 Workstation microphonic capability The software shall relay standard audio input to the workstation transceiver for playback on the vehicle, allowing for volume adjustment between 0 and Derived 80 db. FIT/CSRR-24 Workstation locomotion controlling The software shall relay controls for the vehicle’s locomotion from the workstation’s control input, to the workstation transceiver. Derived FIT/CSRR-12 Vehicle locomotion The software shall relay controls from the onboard transceiver to the microcontroller handling motor/servo input. Derived FIT/CSRR-12 Workstation video streaming The software shall relay, to the workstation screen, a live video feed from the vehicle’s onboard camera. Derived FIT/CSRR-20, FIT/CSRR-21 Derived FIT/CSRR-62 Vehicle peripheral data measurements The software will relay data collected by the vehicle, including location and Derived computational utilization, to the workstation. FIT/CSRR-64 Vehicle Camera Angle The software shall be able to rotate the orientation of the camera aboard the vehicle. FIT/CSRR-22 Vehicle component power state The software shall relay signals to power on or off components on the control vehicle, from the workstation, to the vehicle. FIT/CSRR CDR Derived Trace | 25
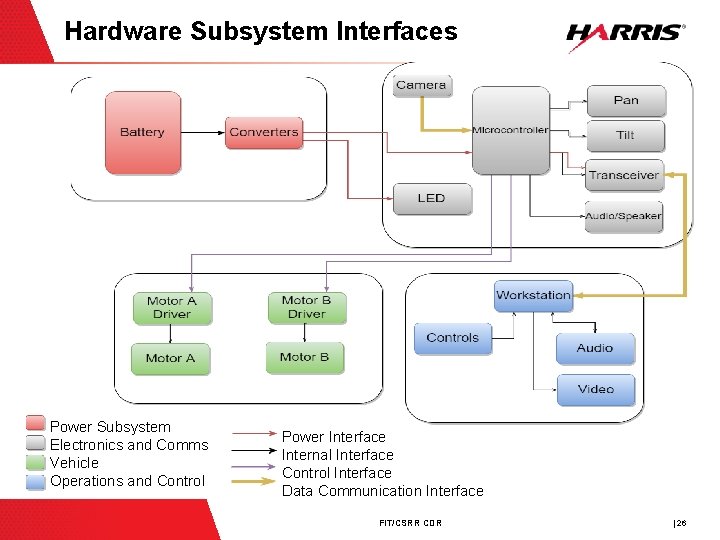
Hardware Subsystem Interfaces Power Subsystem Electronics and Comms Vehicle Operations and Control Power Interface Internal Interface Control Interface Data Communication Interface FIT/CSRR CDR | 26
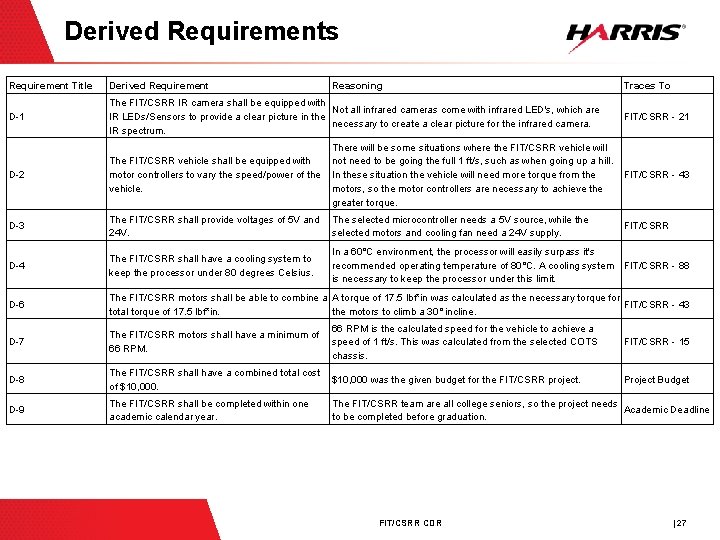
Derived Requirements Requirement Title Derived Requirement Reasoning Traces To D-1 The FIT/CSRR IR camera shall be equipped with Not all infrared cameras come with infrared LED's, which are IR LEDs/Sensors to provide a clear picture in the necessary to create a clear picture for the infrared camera. IR spectrum. D-2 There will be some situations where the FIT/CSRR vehicle will not need to be going the full 1 ft/s, such as when going up a hill. The FIT/CSRR vehicle shall be equipped with FIT/CSRR - 43 motor controllers to vary the speed/power of the In these situation the vehicle will need more torque from the vehicle. motors, so the motor controllers are necessary to achieve the greater torque. D-3 The FIT/CSRR shall provide voltages of 5 V and The selected microcontroller needs a 5 V source, while the 24 V. selected motors and cooling fan need a 24 V supply. D-4 The FIT/CSRR shall have a cooling system to keep the processor under 80 degrees Celsius. D-6 The FIT/CSRR motors shall be able to combine a A torque of 17. 5 lbf*in was calculated as the necessary torque for FIT/CSRR - 43 total torque of 17. 5 lbf*in. the motors to climb a 30° incline. D-7 The FIT/CSRR motors shall have a minimum of 66 RPM. D-8 The FIT/CSRR shall have a combined total cost $10, 000 was the given budget for the FIT/CSRR project. of $10, 000. D-9 The FIT/CSRR shall be completed within one academic calendar year. FIT/CSRR - 21 FIT/CSRR In a 60°C environment, the processor will easily surpass it's recommended operating temperature of 80°C. A cooling system FIT/CSRR - 88 is necessary to keep the processor under this limit. 66 RPM is the calculated speed for the vehicle to achieve a speed of 1 ft/s. This was calculated from the selected COTS chassis. FIT/CSRR - 15 Project Budget The FIT/CSRR team are all college seniors, so the project needs Academic Deadline to be completed before graduation. FIT/CSRR CDR | 27
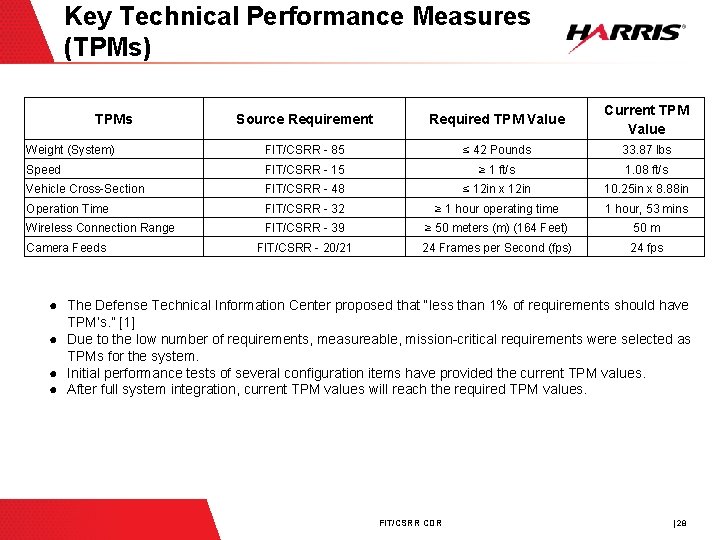
Key Technical Performance Measures (TPMs) Source Requirement Required TPM Value Current TPM Value Weight (System) FIT/CSRR - 85 ≤ 42 Pounds 33. 87 lbs Speed FIT/CSRR - 15 ≥ 1 ft/s 1. 08 ft/s Vehicle Cross-Section FIT/CSRR - 48 ≤ 12 in x 12 in 10. 25 in x 8. 88 in Operation Time FIT/CSRR - 32 ≥ 1 hour operating time 1 hour, 53 mins Wireless Connection Range FIT/CSRR - 39 ≥ 50 meters (m) (164 Feet) 50 m FIT/CSRR - 20/21 24 Frames per Second (fps) 24 fps TPMs Camera Feeds ● The Defense Technical Information Center proposed that “less than 1% of requirements should have TPM’s. ” [1] ● Due to the low number of requirements, measureable, mission-critical requirements were selected as TPMs for the system. ● Initial performance tests of several configuration items have provided the current TPM values. ● After full system integration, current TPM values will reach the required TPM values. FIT/CSRR CDR | 28
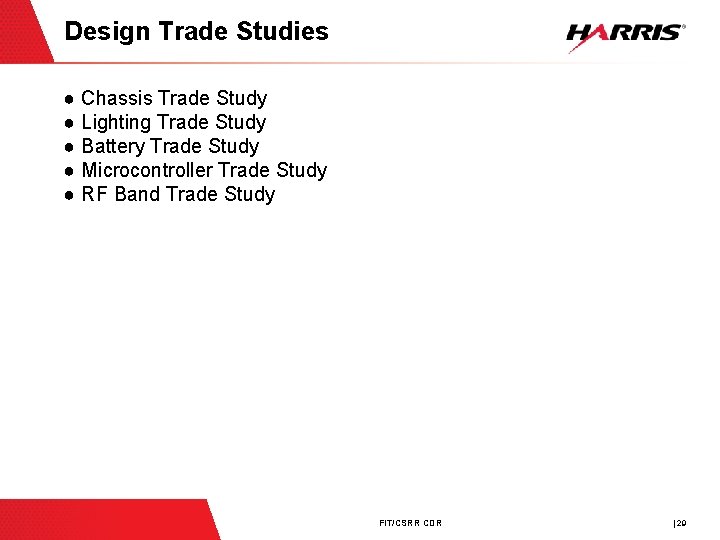
Design Trade Studies ● Chassis Trade Study ● Lighting Trade Study ● Battery Trade Study ● Microcontroller Trade Study ● RF Band Trade Study FIT/CSRR CDR | 29
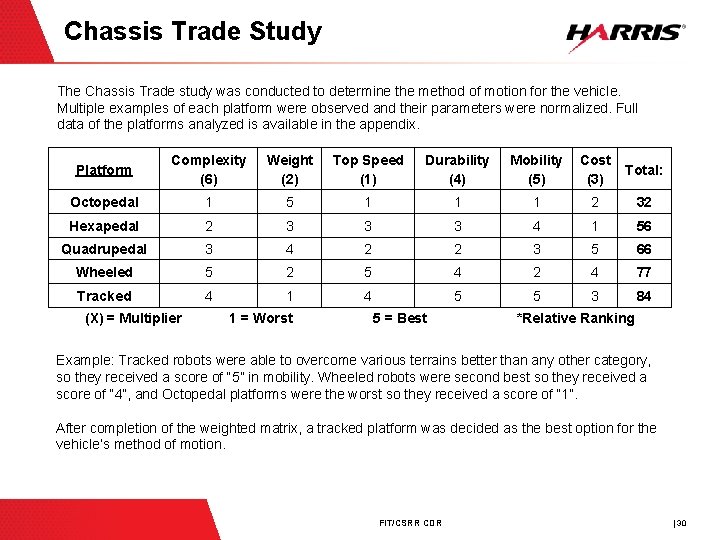
Chassis Trade Study The Chassis Trade study was conducted to determine the method of motion for the vehicle. Multiple examples of each platform were observed and their parameters were normalized. Full data of the platforms analyzed is available in the appendix. Platform Complexity (6) Weight (2) Top Speed (1) Durability (4) Mobility (5) Cost (3) Total: Octopedal 1 5 1 1 1 2 32 Hexapedal 2 3 3 3 4 1 56 Quadrupedal 3 4 2 2 3 5 66 Wheeled 5 2 5 4 2 4 77 Tracked 4 1 4 5 5 3 84 (X) = Multiplier 1 = Worst 5 = Best *Relative Ranking Example: Tracked robots were able to overcome various terrains better than any other category, so they received a score of “ 5” in mobility. Wheeled robots were second best so they received a score of “ 4”, and Octopedal platforms were the worst so they received a score of “ 1”. After completion of the weighted matrix, a tracked platform was decided as the best option for the vehicle’s method of motion. FIT/CSRR CDR | 30
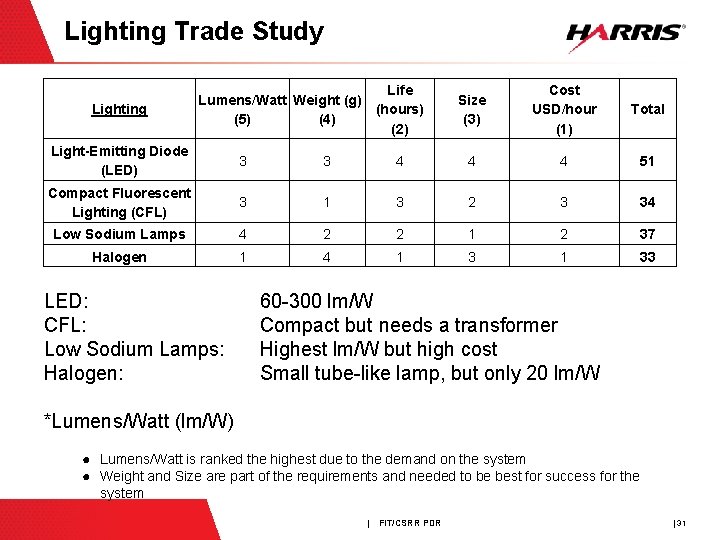
Lighting Trade Study Lighting Lumens/Watt Weight (g) (5) (4) Life (hours) (2) Size (3) Cost USD/hour (1) Total Light-Emitting Diode (LED) 3 3 4 4 4 51 Compact Fluorescent Lighting (CFL) 3 1 3 2 3 34 Low Sodium Lamps 4 2 2 1 2 37 Halogen 1 4 1 33 LED: CFL: Low Sodium Lamps: Halogen: 60 -300 lm/W Compact but needs a transformer Highest lm/W but high cost Small tube-like lamp, but only 20 lm/W *Lumens/Watt (lm/W) ● Lumens/Watt is ranked the highest due to the demand on the system ● Weight and Size are part of the requirements and needed to be best for success for the system | FIT/CSRR PDR | 31
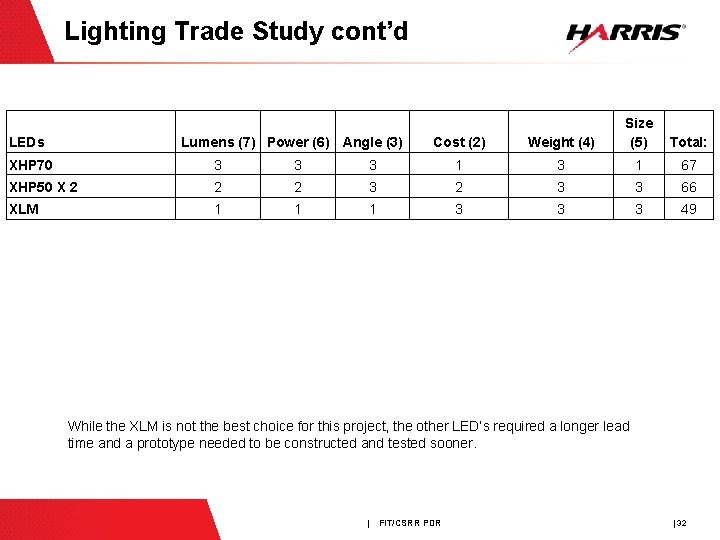
Lighting Trade Study cont’d LEDs Lumens (7) Power (6) Angle (3) Cost (2) Weight (4) Size (5) Total: XHP 70 3 3 3 1 67 XHP 50 X 2 2 2 3 3 66 XLM 1 1 1 3 3 3 49 While the XLM is not the best choice for this project, the other LED’s required a longer lead time and a prototype needed to be constructed and tested sooner. | FIT/CSRR PDR | 32
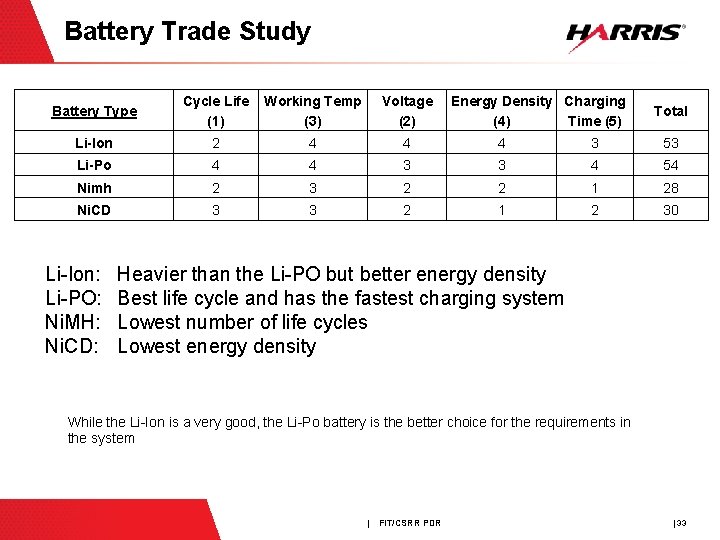
Battery Trade Study Battery Type Cycle Life (1) Working Temp (3) Voltage (2) Li-Ion 2 4 4 4 3 53 Li-Po 4 4 3 3 4 54 Nimh 2 3 2 2 1 28 Ni. CD 3 3 2 1 2 30 Li-Ion: Li-PO: Ni. MH: Ni. CD: Energy Density Charging (4) Time (5) Total Heavier than the Li-PO but better energy density Best life cycle and has the fastest charging system Lowest number of life cycles Lowest energy density While the Li-Ion is a very good, the Li-Po battery is the better choice for the requirements in the system | FIT/CSRR PDR | 33
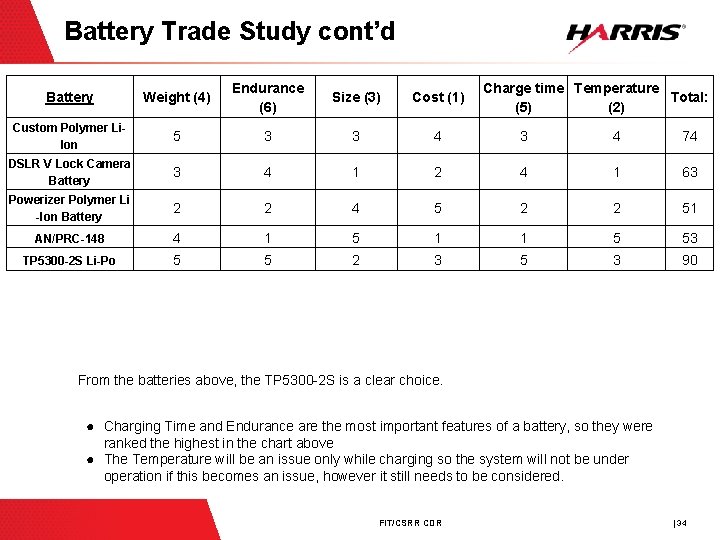
Battery Trade Study cont’d Battery Weight (4) Endurance (6) Size (3) Cost (1) Charge time Temperature Total: (5) (2) Custom Polymer Li. Ion 5 3 3 4 74 DSLR V Lock Camera Battery 3 4 1 2 4 1 63 Powerizer Polymer Li -Ion Battery 2 2 4 5 2 2 51 AN/PRC-148 4 1 5 1 1 5 53 TP 5300 -2 S Li-Po 5 5 2 3 5 3 90 From the batteries above, the TP 5300 -2 S is a clear choice. ● Charging Time and Endurance are the most important features of a battery, so they were ranked the highest in the chart above ● The Temperature will be an issue only while charging so the system will not be under operation if this becomes an issue, however it still needs to be considered. FIT/CSRR CDR | 34
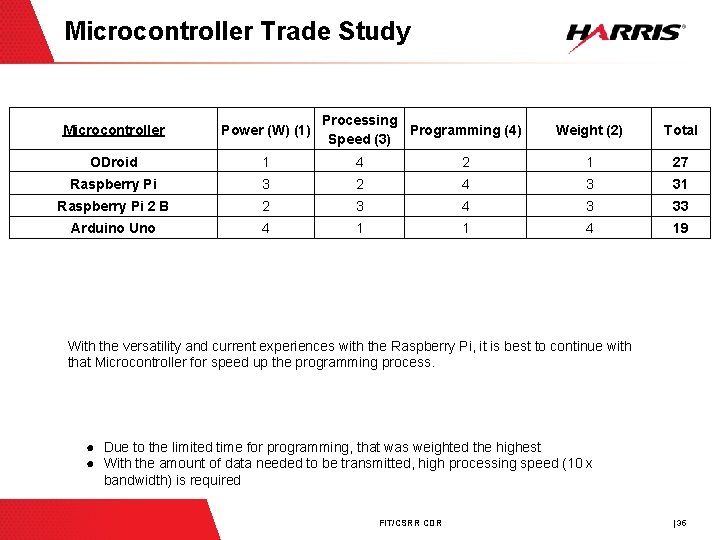
Microcontroller Trade Study Processing Programming (4) Speed (3) Microcontroller Power (W) (1) Weight (2) Total ODroid 1 4 2 1 27 Raspberry Pi 3 2 4 3 31 Raspberry Pi 2 B 2 3 4 3 33 Arduino Uno 4 1 1 4 19 With the versatility and current experiences with the Raspberry Pi, it is best to continue with that Microcontroller for speed up the programming process. ● Due to the limited time for programming, that was weighted the highest ● With the amount of data needed to be transmitted, high processing speed (10 x bandwidth) is required FIT/CSRR CDR | 35
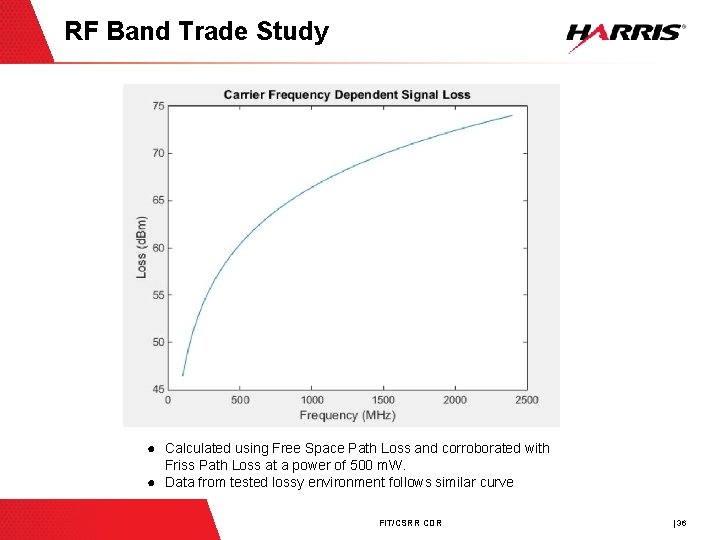
RF Band Trade Study ● Calculated using Free Space Path Loss and corroborated with Friss Path Loss at a power of 500 m. W. ● Data from tested lossy environment follows similar curve FIT/CSRR CDR | 36
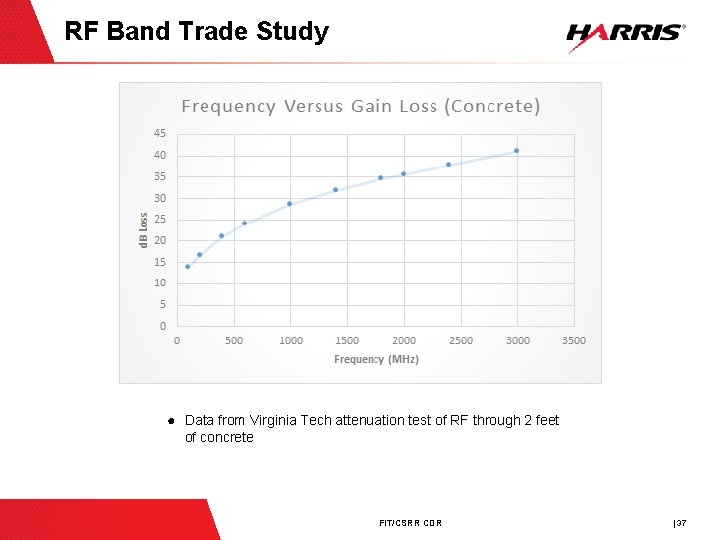
RF Band Trade Study ● Data from Virginia Tech attenuation test of RF through 2 feet of concrete FIT/CSRR CDR | 37
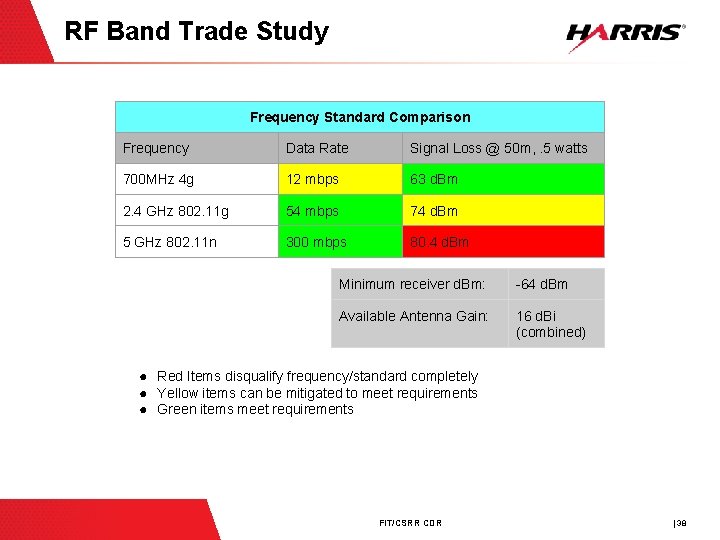
RF Band Trade Study Frequency Standard Comparison Frequency Data Rate Signal Loss @ 50 m, . 5 watts 700 MHz 4 g 12 mbps 63 d. Bm 2. 4 GHz 802. 11 g 54 mbps 74 d. Bm 5 GHz 802. 11 n 300 mbps 80. 4 d. Bm Minimum receiver d. Bm: -64 d. Bm Available Antenna Gain: 16 d. Bi (combined) ● Red Items disqualify frequency/standard completely ● Yellow items can be mitigated to meet requirements ● Green items meet requirements FIT/CSRR CDR | 38
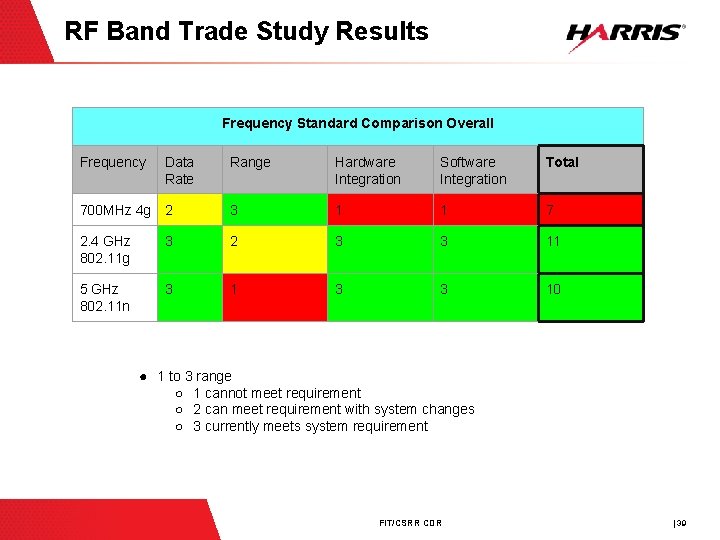
RF Band Trade Study Results Frequency Standard Comparison Overall Frequency Data Rate Range Hardware Integration Software Integration Total 700 MHz 4 g 2 3 1 1 7 2. 4 GHz 802. 11 g 3 2 3 3 11 5 GHz 802. 11 n 3 1 3 3 10 ● 1 to 3 range ○ 1 cannot meet requirement ○ 2 can meet requirement with system changes ○ 3 currently meets system requirement FIT/CSRR CDR | 39
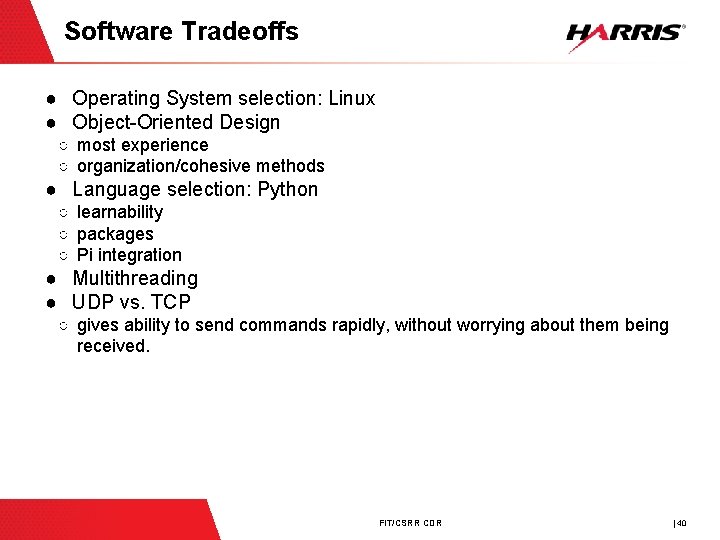
Software Tradeoffs ● Operating System selection: Linux ● Object-Oriented Design ○ most experience ○ organization/cohesive methods ● Language selection: Python ○ learnability ○ packages ○ Pi integration ● Multithreading ● UDP vs. TCP ○ gives ability to send commands rapidly, without worrying about them being received. FIT/CSRR CDR | 40
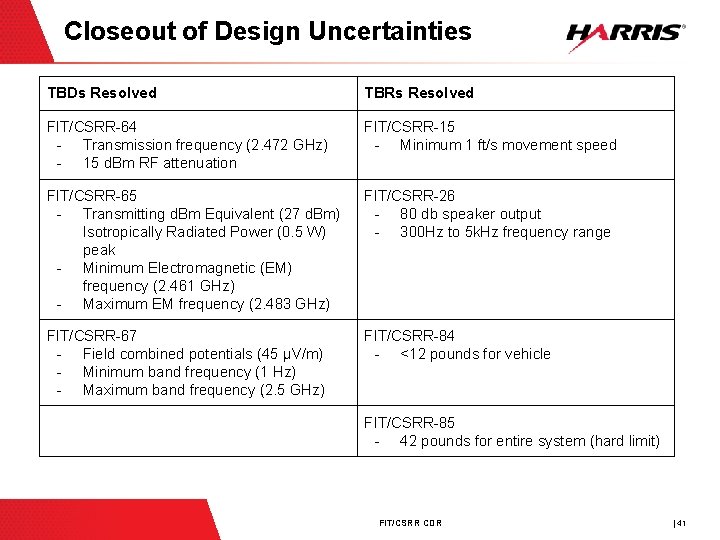
Closeout of Design Uncertainties TBDs Resolved TBRs Resolved FIT/CSRR-64 - Transmission frequency (2. 472 GHz) - 15 d. Bm RF attenuation FIT/CSRR-15 - Minimum 1 ft/s movement speed FIT/CSRR-65 - Transmitting d. Bm Equivalent (27 d. Bm) Isotropically Radiated Power (0. 5 W) peak - Minimum Electromagnetic (EM) frequency (2. 461 GHz) - Maximum EM frequency (2. 483 GHz) FIT/CSRR-26 - 80 db speaker output - 300 Hz to 5 k. Hz frequency range FIT/CSRR-67 - Field combined potentials (45 µV/m) - Minimum band frequency (1 Hz) - Maximum band frequency (2. 5 GHz) FIT/CSRR-84 - <12 pounds for vehicle FIT/CSRR-85 - 42 pounds for entire system (hard limit) FIT/CSRR CDR | 41
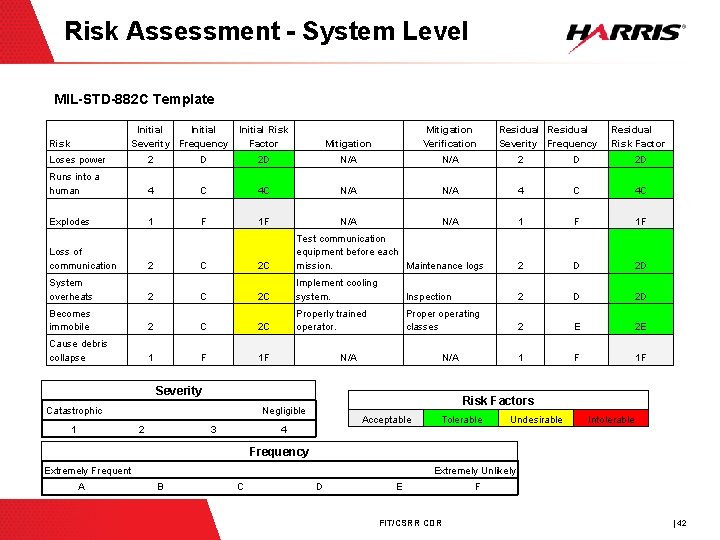
Risk Assessment - System Level MIL-STD-882 C Template Initial Severity Frequency Risk Initial Risk Factor Mitigation Verification Residual Severity Frequency Residual Risk Factor Loses power 2 D 2 D N/A 2 D 2 D Runs into a human 4 C 4 C N/A 4 C 4 C Explodes 1 F 1 F N/A 1 F 1 F 2 D 2 D Loss of communication 2 C 2 C Test communication equipment before each mission. Maintenance logs System overheats 2 C 2 C Implement cooling system. Inspection 2 D 2 D Becomes immobile 2 C 2 C Properly trained operator. Properating classes 2 E 2 E Cause debris collapse 1 F 1 F N/A Severity Catastrophic 1 Risk Factors Negligible 2 3 Acceptable 4 Tolerable Undesirable Intolerable Frequency Extremely Frequent A Extremely Unlikely B C D E FIT/CSRR CDR F | 42
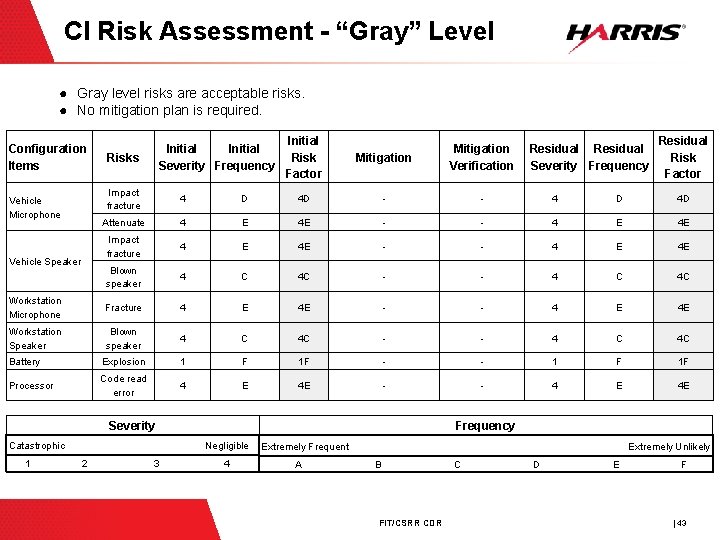
CI Risk Assessment - “Gray” Level ● Gray level risks are acceptable risks. ● No mitigation plan is required. Configuration Items Initial Severity Frequency Risks Initial Risk Factor Mitigation Verification Residual Severity Frequency Residual Risk Factor Impact fracture 4 D 4 D - - 4 D 4 D Attenuate 4 E 4 E - - 4 E 4 E Impact fracture 4 E 4 E - - 4 E 4 E Blown speaker 4 C 4 C - - 4 C 4 C Workstation Microphone Fracture 4 E 4 E - - 4 E 4 E Workstation Speaker Blown speaker 4 C 4 C - - 4 C 4 C Battery Explosion 1 F 1 F - - 1 F 1 F Processor Code read error 4 E 4 E - - 4 E 4 E Vehicle Microphone Vehicle Speaker Severity Catastrophic 1 Frequency Negligible 2 3 4 Extremely Frequent A Extremely Unlikely B FIT/CSRR CDR C D E F | 43
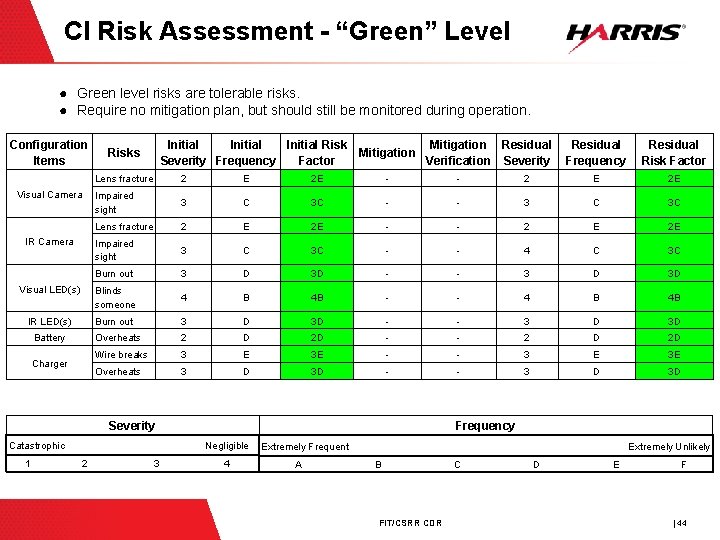
CI Risk Assessment - “Green” Level ● Green level risks are tolerable risks. ● Require no mitigation plan, but should still be monitored during operation. Configuration Items Initial Risk Severity Frequency Factor Risks Mitigation Residual Verification Severity Residual Frequency Residual Risk Factor Lens fracture 2 E 2 E - - 2 E 2 E Impaired sight 3 C 3 C - - 3 C 3 C Lens fracture 2 E 2 E - - 2 E 2 E Impaired sight 3 C 3 C - - 4 C 3 C Burn out 3 D 3 D - - 3 D 3 D Visual LED(s) Blinds someone 4 B 4 B - - 4 B 4 B IR LED(s) Burn out 3 D 3 D - - 3 D 3 D Overheats 2 D 2 D - - 2 D 2 D Wire breaks 3 E 3 E - - 3 E 3 E Overheats 3 D 3 D - - 3 D 3 D Visual Camera IR Camera Battery Charger Severity Catastrophic 1 Frequency Negligible 2 3 4 Extremely Frequent A Extremely Unlikely B FIT/CSRR CDR C D E F | 44
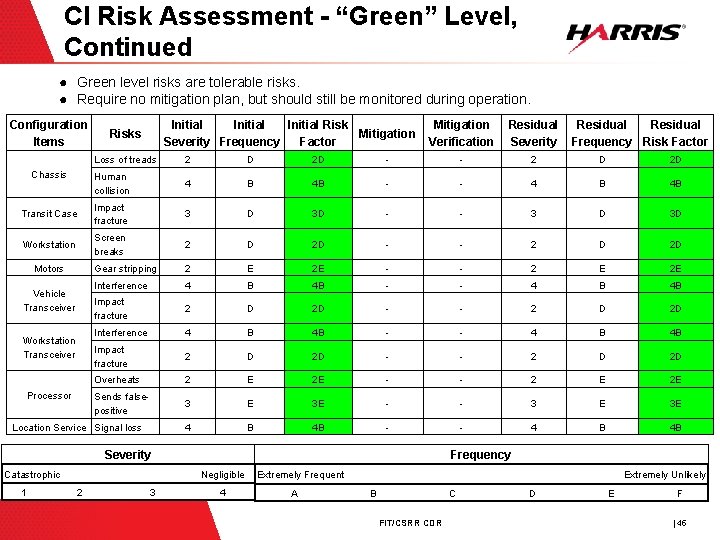
CI Risk Assessment - “Green” Level, Continued ● Green level risks are tolerable risks. ● Require no mitigation plan, but should still be monitored during operation. Configuration Items Initial Risk Mitigation Severity Frequency Factor Risks Mitigation Verification Residual Severity Residual Frequency Risk Factor Loss of treads 2 D 2 D - - 2 D 2 D Human collision 4 B 4 B - - 4 B 4 B Transit Case Impact fracture 3 D 3 D - - 3 D 3 D Workstation Screen breaks 2 D 2 D - - 2 D 2 D Gear stripping 2 E 2 E - - 2 E 2 E Interference 4 B 4 B - - 4 B 4 B Impact fracture 2 D 2 D - - 2 D 2 D Overheats 2 E 2 E - - 2 E 2 E Sends falsepositive 3 E 3 E - - 3 E 3 E 4 B 4 B - - 4 B 4 B Chassis Motors Vehicle Transceiver Workstation Transceiver Processor Location Service Signal loss Severity Catastrophic 1 Frequency Negligible 2 3 4 Extremely Frequent A Extremely Unlikely B C FIT/CSRR CDR D E F | 45

CI Risk Assessment - “Yellow” Level ● Yellow level risks are undesirable risks. ● Require a mitigation plan, and should be monitored throughout operation. Configuration Items Risks Initial Severity Frequency Fully depletes during mission Battery 2 Becomes stuck Chassis C 2 C Initial Risk Factor Mitigation Verification Mitigation 1 2 C 2 D 2 D 2 C Properator training. This is so the operator knows the limits of the vehicle's mobility. 2 D 2 D Operation classes Frequency Negligible 2 3 Residual Risk Factor Make sure the battery is fully charged before each mission. Have the operator trained Inspection/Operation enough so they don't classes leave the vehicle out for longer than an hour. Severity Catastrophic Residual Severity Frequency 4 Extremely Frequent A Extremely Unlikely B FIT/CSRR CDR C D E F | 46
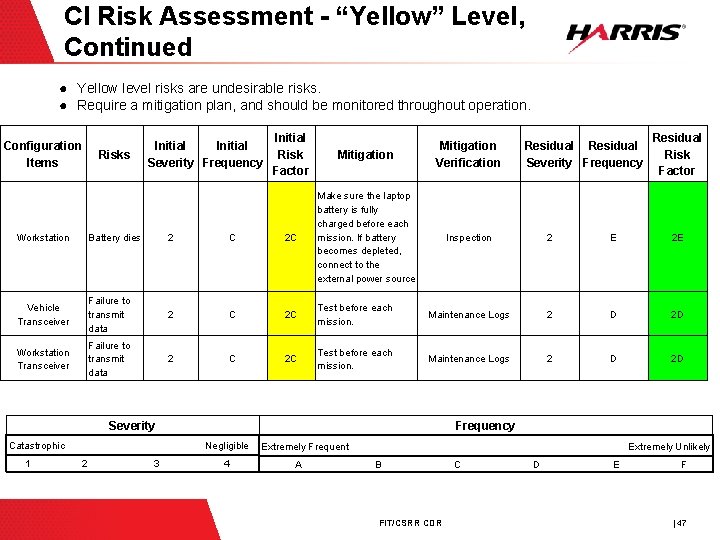
CI Risk Assessment - “Yellow” Level, Continued ● Yellow level risks are undesirable risks. ● Require a mitigation plan, and should be monitored throughout operation. Configuration Items Risks Initial Severity Frequency Initial Risk Factor Mitigation Verification Inspection 2 E 2 E Residual Severity Frequency Residual Risk Factor Workstation Battery dies 2 C 2 C Make sure the laptop battery is fully charged before each mission. If battery becomes depleted, connect to the external power source. Vehicle Transceiver Failure to transmit data 2 C 2 C Test before each mission. Maintenance Logs 2 D 2 D Workstation Transceiver Failure to transmit data 2 C 2 C Test before each mission. Maintenance Logs 2 D 2 D Severity Catastrophic 1 Frequency Negligible 2 3 4 Extremely Frequent A Extremely Unlikely B FIT/CSRR CDR C D E F | 47
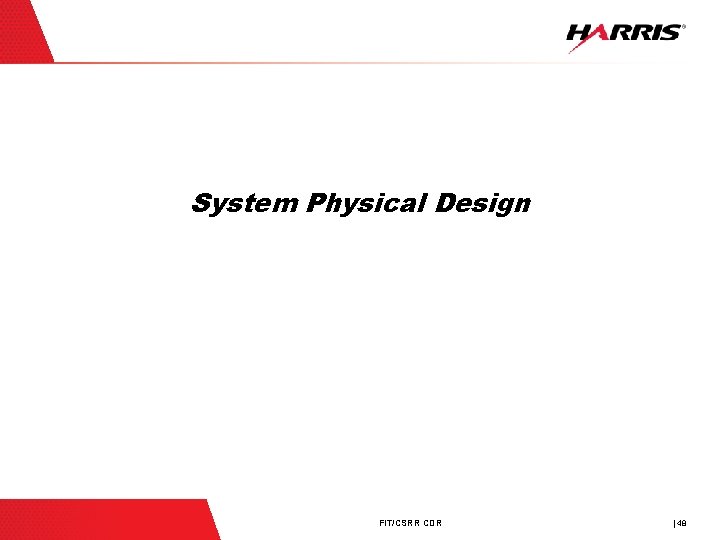
System Physical Design FIT/CSRR CDR | 48
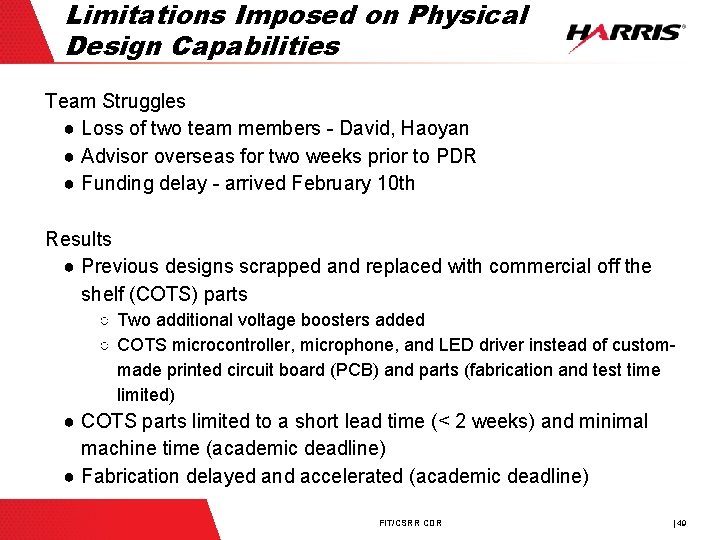
Limitations Imposed on Physical Design Capabilities Team Struggles ● Loss of two team members - David, Haoyan ● Advisor overseas for two weeks prior to PDR ● Funding delay - arrived February 10 th Results ● Previous designs scrapped and replaced with commercial off the shelf (COTS) parts ○ Two additional voltage boosters added ○ COTS microcontroller, microphone, and LED driver instead of custommade printed circuit board (PCB) and parts (fabrication and test time limited) ● COTS parts limited to a short lead time (< 2 weeks) and minimal machine time (academic deadline) ● Fabrication delayed and accelerated (academic deadline) FIT/CSRR CDR | 49
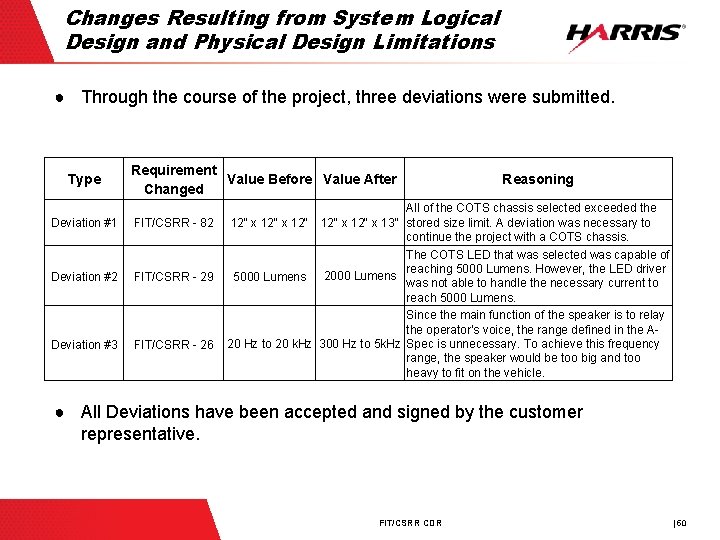
Changes Resulting from System Logical Design and Physical Design Limitations ● Through the course of the project, three deviations were submitted. Type Requirement Value Before Value After Changed Deviation #1 FIT/CSRR - 82 Deviation #2 FIT/CSRR - 29 Deviation #3 FIT/CSRR - 26 Reasoning All of the COTS chassis selected exceeded the 12" x 13" stored size limit. A deviation was necessary to continue the project with a COTS chassis. The COTS LED that was selected was capable of reaching 5000 Lumens. However, the LED driver 5000 Lumens 2000 Lumens was not able to handle the necessary current to reach 5000 Lumens. Since the main function of the speaker is to relay the operator's voice, the range defined in the A 20 Hz to 20 k. Hz 300 Hz to 5 k. Hz Spec is unnecessary. To achieve this frequency range, the speaker would be too big and too heavy to fit on the vehicle. 12" x 12" ● All Deviations have been accepted and signed by the customer representative. FIT/CSRR CDR | 50
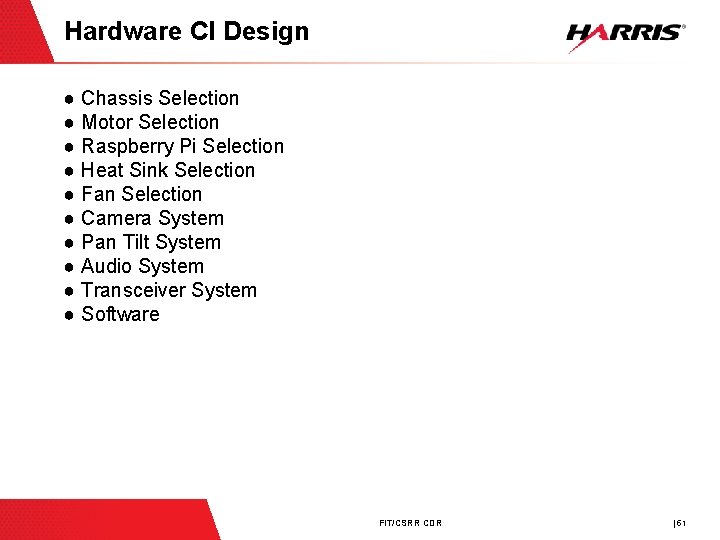
Hardware CI Design ● Chassis Selection ● Motor Selection ● Raspberry Pi Selection ● Heat Sink Selection ● Fan Selection ● Camera System ● Pan Tilt System ● Audio System ● Transceiver System ● Software FIT/CSRR CDR | 51
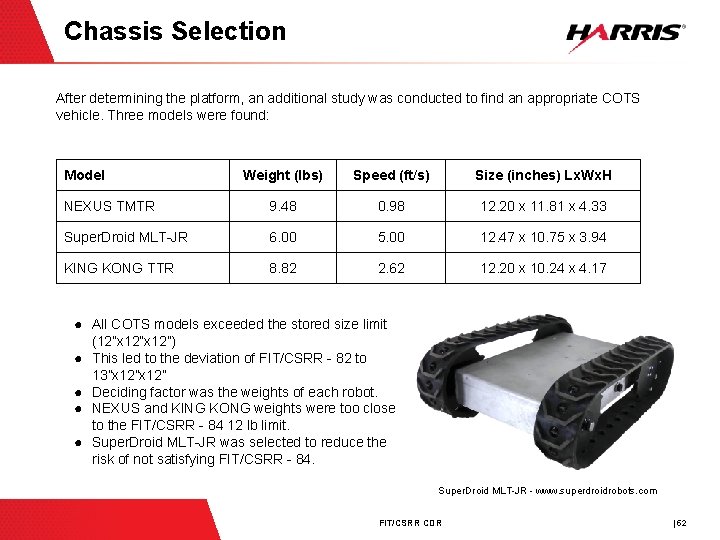
Chassis Selection After determining the platform, an additional study was conducted to find an appropriate COTS vehicle. Three models were found: Model Weight (lbs) Speed (ft/s) Size (inches) Lx. Wx. H NEXUS TMTR 9. 48 0. 98 12. 20 x 11. 81 x 4. 33 Super. Droid MLT-JR 6. 00 5. 00 12. 47 x 10. 75 x 3. 94 KING KONG TTR 8. 82 2. 62 12. 20 x 10. 24 x 4. 17 ● All COTS models exceeded the stored size limit (12”x 12”) ● This led to the deviation of FIT/CSRR - 82 to 13”x 12” ● Deciding factor was the weights of each robot. ● NEXUS and KING KONG weights were too close to the FIT/CSRR - 84 12 lb limit. ● Super. Droid MLT-JR was selected to reduce the risk of not satisfying FIT/CSRR - 84. Super. Droid MLT-JR - www. superdroidrobots. com FIT/CSRR CDR | 52
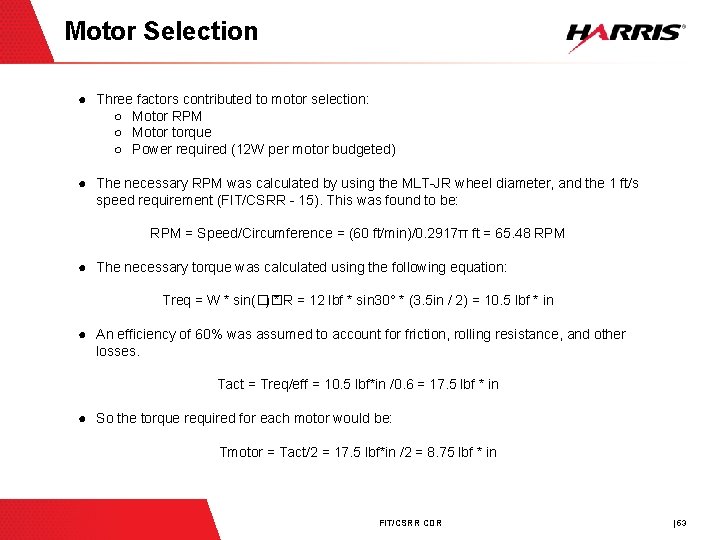
Motor Selection ● Three factors contributed to motor selection: ○ Motor RPM ○ Motor torque ○ Power required (12 W per motor budgeted) ● The necessary RPM was calculated by using the MLT-JR wheel diameter, and the 1 ft/s speed requirement (FIT/CSRR - 15). This was found to be: RPM = Speed/Circumference = (60 ft/min)/0. 2917π ft = 65. 48 RPM ● The necessary torque was calculated using the following equation: Treq = W * sin(�� ) * R = 12 lbf * sin 30° * (3. 5 in / 2) = 10. 5 lbf * in ● An efficiency of 60% was assumed to account for friction, rolling resistance, and other losses. Tact = Treq/eff = 10. 5 lbf*in /0. 6 = 17. 5 lbf * in ● So the torque required for each motor would be: Tmotor = Tact/2 = 17. 5 lbf*in /2 = 8. 75 lbf * in FIT/CSRR CDR | 53
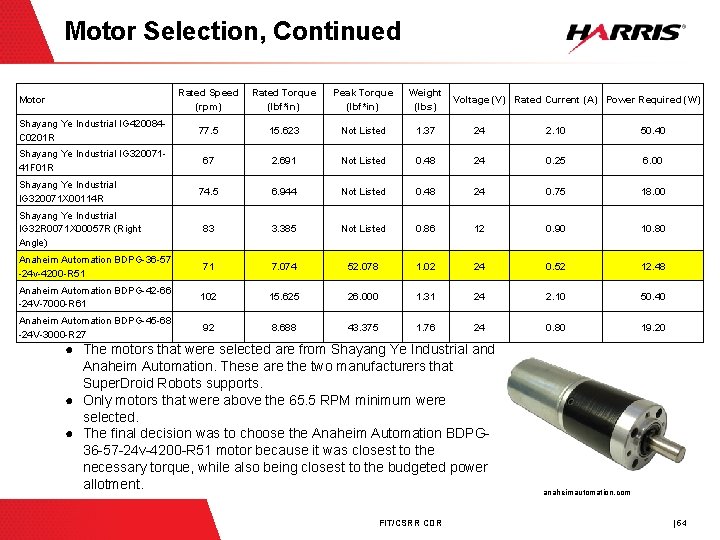
Motor Selection, Continued Rated Speed (rpm) Rated Torque (lbf*in) Peak Torque (lbf*in) Weight (lbs) Shayang Ye Industrial IG 420084 C 0201 R 77. 5 15. 623 Not Listed 1. 37 24 2. 10 50. 40 Shayang Ye Industrial IG 32007141 F 01 R 67 2. 691 Not Listed 0. 48 24 0. 25 6. 00 74. 5 6. 944 Not Listed 0. 48 24 0. 75 18. 00 Shayang Ye Industrial IG 32 R 0071 X 00057 R (Right Angle) 83 3. 385 Not Listed 0. 86 12 0. 90 10. 80 Anaheim Automation BDPG-36 -57 -24 v-4200 -R 51 71 7. 074 52. 078 1. 02 24 0. 52 12. 48 Anaheim Automation BDPG-42 -66 -24 V-7000 -R 61 102 15. 625 26. 000 1. 31 24 2. 10 50. 40 Anaheim Automation BDPG-45 -68 -24 V-3000 -R 27 92 8. 688 43. 375 1. 76 24 0. 80 19. 20 Motor Shayang Ye Industrial IG 320071 X 00114 R Voltage (V) Rated Current (A) Power Required (W) ● The motors that were selected are from Shayang Ye Industrial and Anaheim Automation. These are the two manufacturers that Super. Droid Robots supports. ● Only motors that were above the 65. 5 RPM minimum were selected. ● The final decision was to choose the Anaheim Automation BDPG 36 -57 -24 v-4200 -R 51 motor because it was closest to the necessary torque, while also being closest to the budgeted power allotment. FIT/CSRR CDR anaheimautomation. com | 54
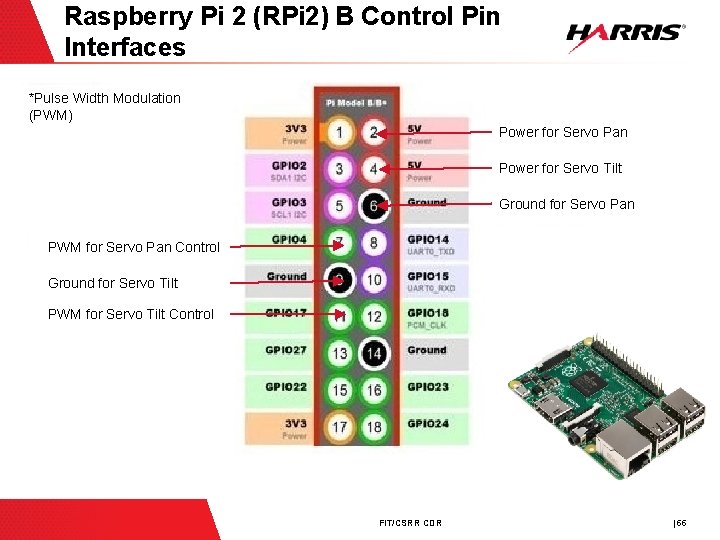
Raspberry Pi 2 (RPi 2) B Control Pin Interfaces *Pulse Width Modulation (PWM) Power for Servo Pan Power for Servo Tilt Ground for Servo Pan PWM for Servo Pan Control Ground for Servo Tilt PWM for Servo Tilt Control FIT/CSRR CDR | 55
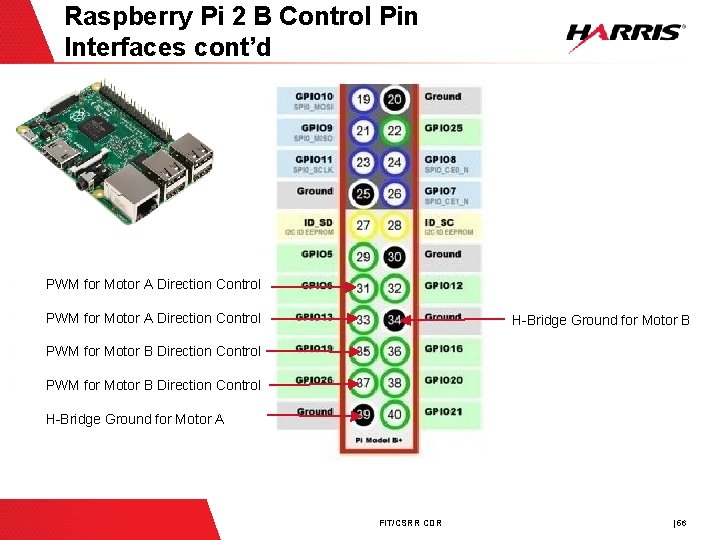
Raspberry Pi 2 B Control Pin Interfaces cont’d PWM for Motor A Direction Control H-Bridge Ground for Motor B PWM for Motor B Direction Control H-Bridge Ground for Motor A FIT/CSRR CDR | 56
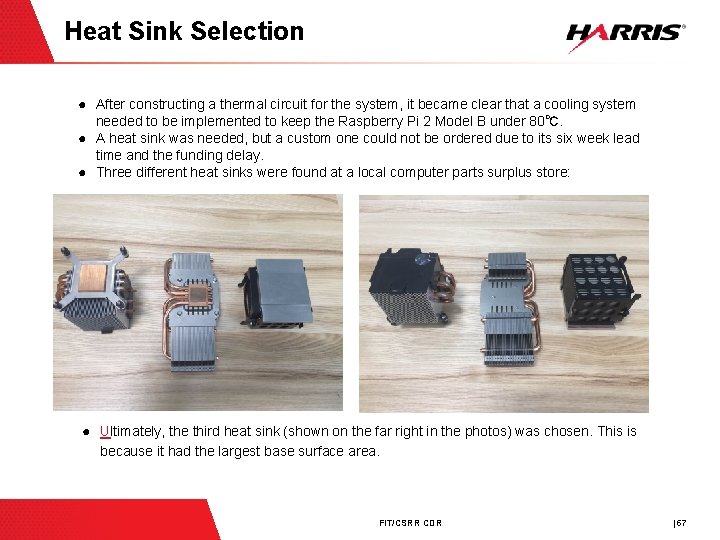
Heat Sink Selection ● After constructing a thermal circuit for the system, it became clear that a cooling system needed to be implemented to keep the Raspberry Pi 2 Model B under 80℃. ● A heat sink was needed, but a custom one could not be ordered due to its six week lead time and the funding delay. ● Three different heat sinks were found at a local computer parts surplus store: ● Ultimately, the third heat sink (shown on the far right in the photos) was chosen. This is because it had the largest base surface area. FIT/CSRR CDR | 57
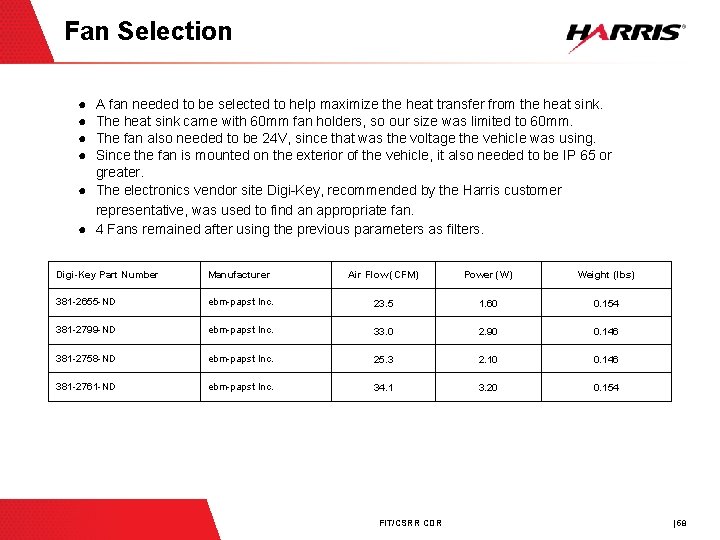
Fan Selection ● ● A fan needed to be selected to help maximize the heat transfer from the heat sink. The heat sink came with 60 mm fan holders, so our size was limited to 60 mm. The fan also needed to be 24 V, since that was the voltage the vehicle was using. Since the fan is mounted on the exterior of the vehicle, it also needed to be IP 65 or greater. ● The electronics vendor site Digi-Key, recommended by the Harris customer representative, was used to find an appropriate fan. ● 4 Fans remained after using the previous parameters as filters. Digi-Key Part Number Manufacturer Air Flow (CFM) Power (W) Weight (lbs) 381 -2655 -ND ebm-papst Inc. 23. 5 1. 60 0. 154 381 -2799 -ND ebm-papst Inc. 33. 0 2. 90 0. 146 381 -2758 -ND ebm-papst Inc. 25. 3 2. 10 0. 146 381 -2761 -ND ebm-papst Inc. 34. 1 3. 20 0. 154 FIT/CSRR CDR | 58
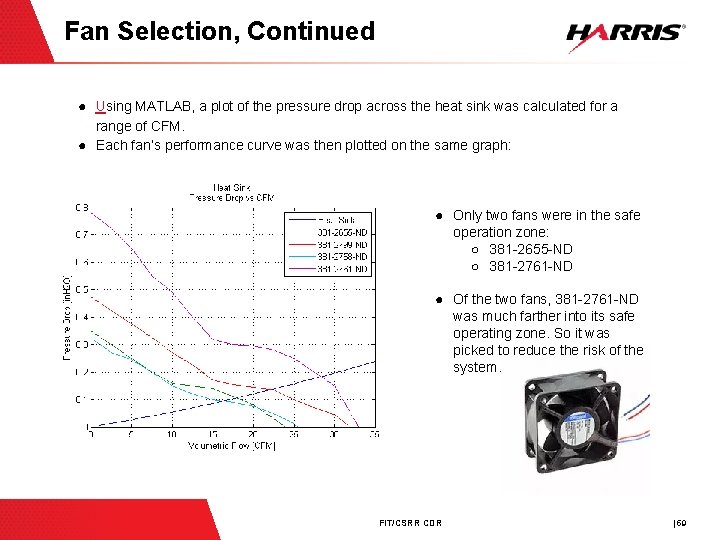
Fan Selection, Continued ● Using MATLAB, a plot of the pressure drop across the heat sink was calculated for a range of CFM. ● Each fan’s performance curve was then plotted on the same graph: ● Only two fans were in the safe operation zone: ○ 381 -2655 -ND ○ 381 -2761 -ND ● Of the two fans, 381 -2761 -ND was much farther into its safe operating zone. So it was picked to reduce the risk of the system. FIT/CSRR CDR | 59
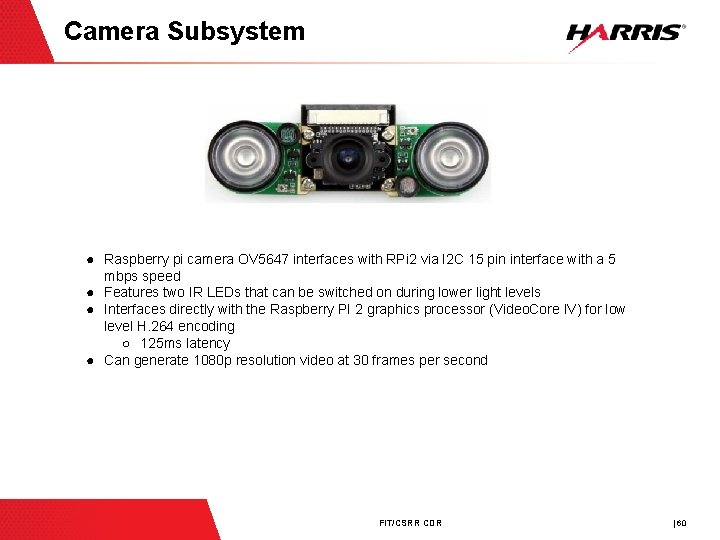
Camera Subsystem ● Raspberry pi camera OV 5647 interfaces with RPi 2 via I 2 C 15 pin interface with a 5 mbps speed ● Features two IR LEDs that can be switched on during lower light levels ● Interfaces directly with the Raspberry PI 2 graphics processor (Video. Core IV) for low level H. 264 encoding ○ 125 ms latency ● Can generate 1080 p resolution video at 30 frames per second FIT/CSRR CDR | 60
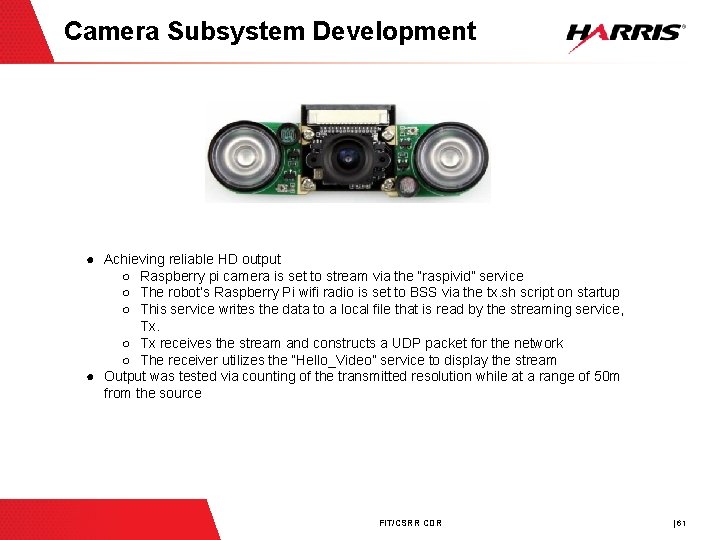
Camera Subsystem Development ● Achieving reliable HD output ○ Raspberry pi camera is set to stream via the “raspivid” service ○ The robot’s Raspberry Pi wifi radio is set to BSS via the tx. sh script on startup ○ This service writes the data to a local file that is read by the streaming service, Tx. ○ Tx receives the stream and constructs a UDP packet for the network ○ The receiver utilizes the “Hello_Video” service to display the stream ● Output was tested via counting of the transmitted resolution while at a range of 50 m from the source FIT/CSRR CDR | 61
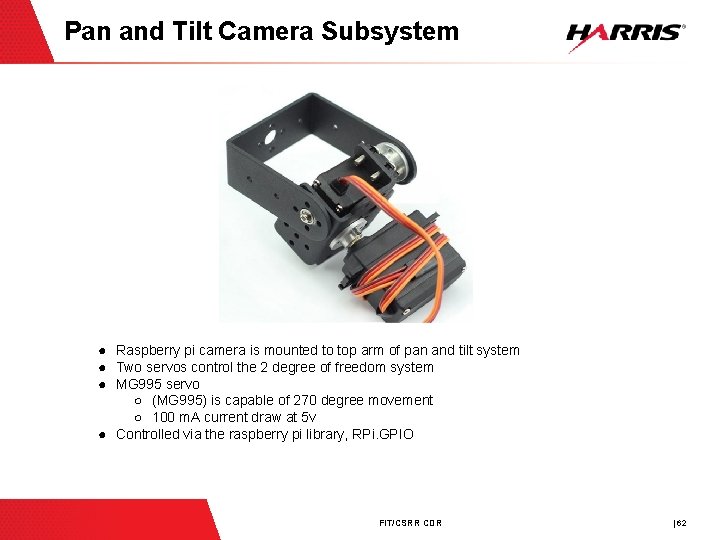
Pan and Tilt Camera Subsystem ● Raspberry pi camera is mounted to top arm of pan and tilt system ● Two servos control the 2 degree of freedom system ● MG 995 servo ○ (MG 995) is capable of 270 degree movement ○ 100 m. A current draw at 5 v ● Controlled via the raspberry pi library, RPi. GPIO FIT/CSRR CDR | 62
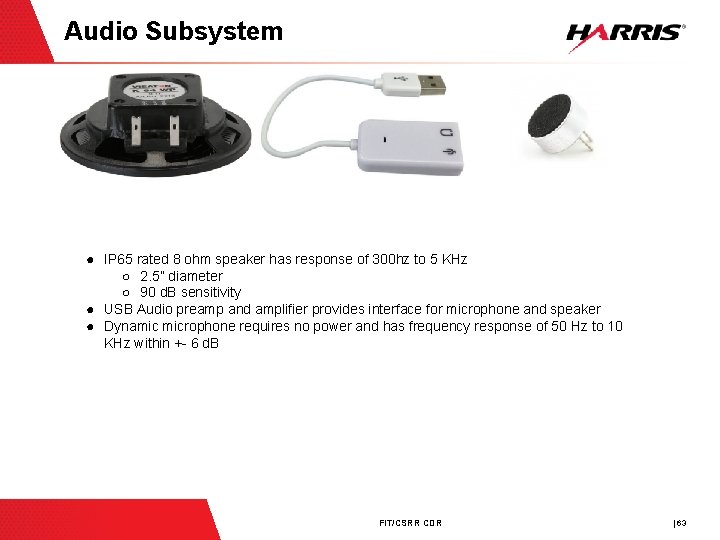
Audio Subsystem ● IP 65 rated 8 ohm speaker has response of 300 hz to 5 KHz ○ 2. 5” diameter ○ 90 d. B sensitivity ● USB Audio preamp and amplifier provides interface for microphone and speaker ● Dynamic microphone requires no power and has frequency response of 50 Hz to 10 KHz within +- 6 d. B FIT/CSRR CDR | 63
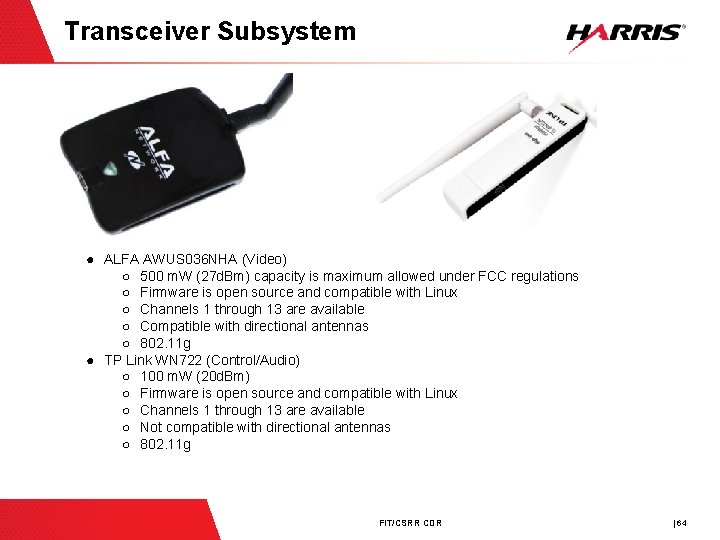
Transceiver Subsystem ● ALFA AWUS 036 NHA (Video) ○ 500 m. W (27 d. Bm) capacity is maximum allowed under FCC regulations ○ Firmware is open source and compatible with Linux ○ Channels 1 through 13 are available ○ Compatible with directional antennas ○ 802. 11 g ● TP Link WN 722 (Control/Audio) ○ 100 m. W (20 d. Bm) ○ Firmware is open source and compatible with Linux ○ Channels 1 through 13 are available ○ Not compatible with directional antennas ○ 802. 11 g FIT/CSRR CDR | 64
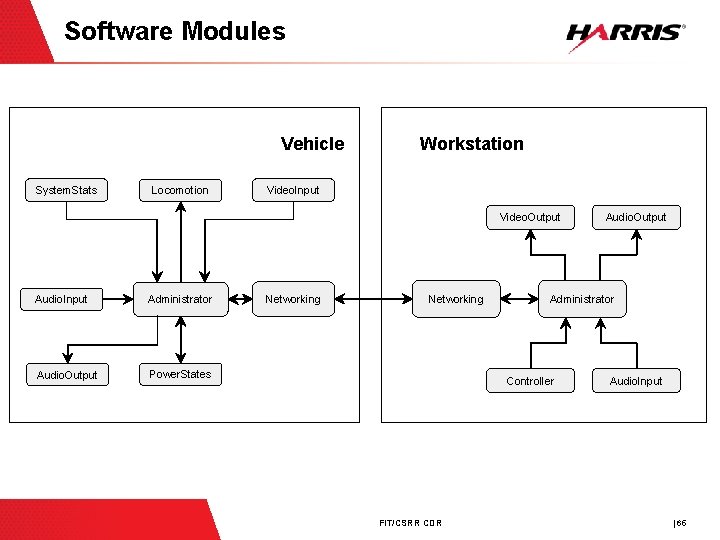
Software Modules Vehicle System. Stats Locomotion Workstation Video. Input Video. Output Audio. Output Audio. Input Administrator Audio. Output Power. States Networking Administrator Controller FIT/CSRR CDR Audio. Input | 65
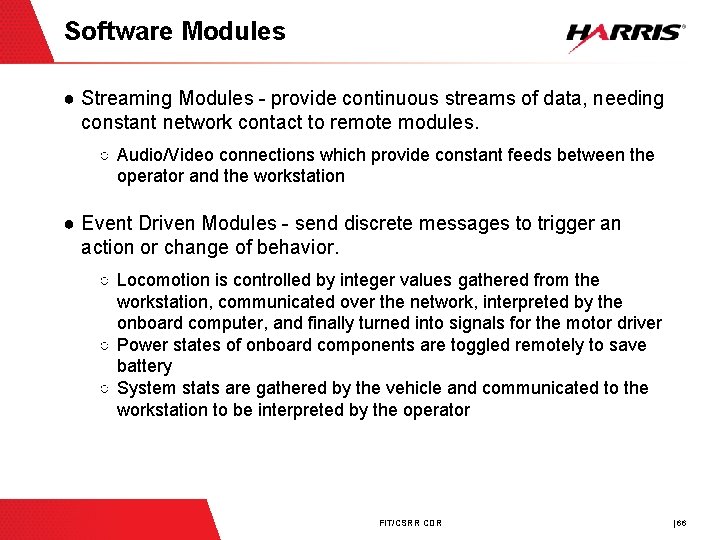
Software Modules ● Streaming Modules - provide continuous streams of data, needing constant network contact to remote modules. ○ Audio/Video connections which provide constant feeds between the operator and the workstation ● Event Driven Modules - send discrete messages to trigger an action or change of behavior. ○ Locomotion is controlled by integer values gathered from the workstation, communicated over the network, interpreted by the onboard computer, and finally turned into signals for the motor driver ○ Power states of onboard components are toggled remotely to save battery ○ System stats are gathered by the vehicle and communicated to the workstation to be interpreted by the operator FIT/CSRR CDR | 66
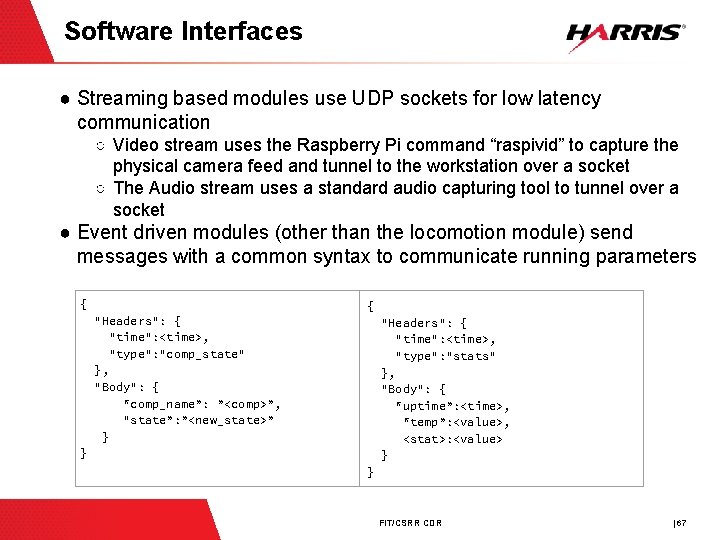
Software Interfaces ● Streaming based modules use UDP sockets for low latency communication ○ Video stream uses the Raspberry Pi command “raspivid” to capture the physical camera feed and tunnel to the workstation over a socket ○ The Audio stream uses a standard audio capturing tool to tunnel over a socket ● Event driven modules (other than the locomotion module) send messages with a common syntax to communicate running parameters { "Headers": { "time": <time>, "type": "comp_state" }, "Body": { “comp_name”: ”<comp>”, "state”: ”<new_state>” } { "Headers": { "time": <time>, "type": "stats" }, "Body": { “uptime”: <time>, “temp”: <value>, <stat>: <value> } } } FIT/CSRR CDR | 67
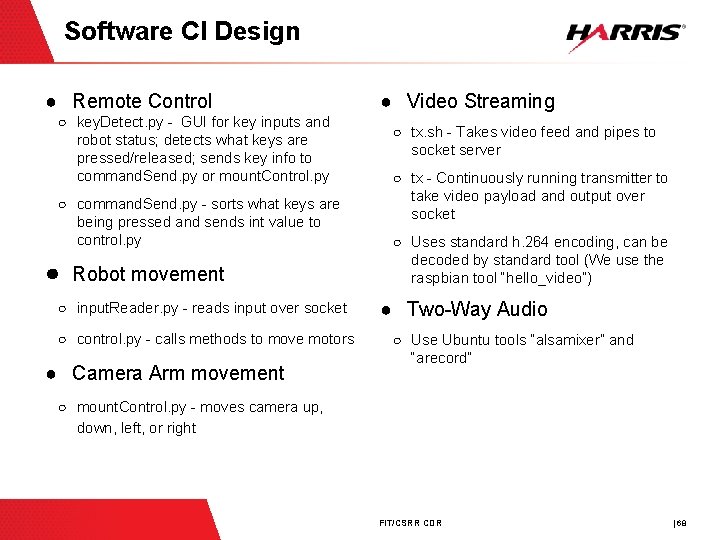
Software CI Design ● Remote Control ○ key. Detect. py - GUI for key inputs and robot status; detects what keys are pressed/released; sends key info to command. Send. py or mount. Control. py ○ command. Send. py - sorts what keys are being pressed and sends int value to control. py ● Robot movement ○ input. Reader. py - reads input over socket ○ control. py - calls methods to move motors ● Camera Arm movement ● Video Streaming ○ tx. sh - Takes video feed and pipes to socket server ○ tx - Continuously running transmitter to take video payload and output over socket ○ Uses standard h. 264 encoding, can be decoded by standard tool (We use the raspbian tool “hello_video”) ● Two-Way Audio ○ Use Ubuntu tools “alsamixer” and “arecord” ○ mount. Control. py - moves camera up, down, left, or right FIT/CSRR CDR | 68
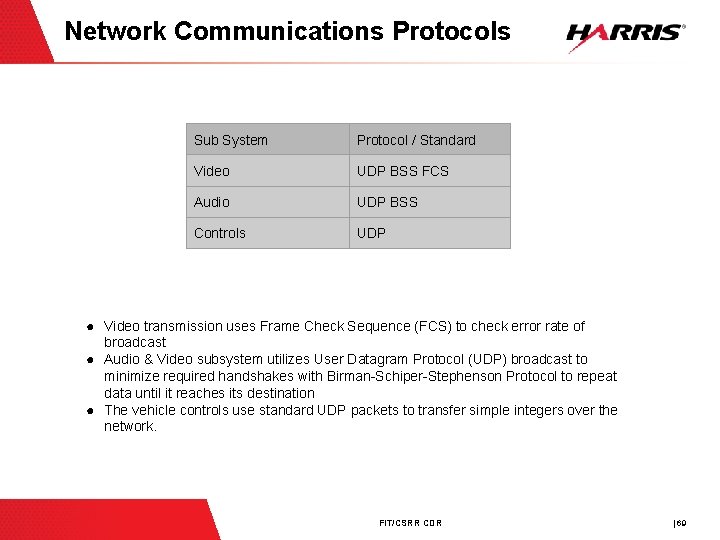
Network Communications Protocols Sub System Protocol / Standard Video UDP BSS FCS Audio UDP BSS Controls UDP ● Video transmission uses Frame Check Sequence (FCS) to check error rate of broadcast ● Audio & Video subsystem utilizes User Datagram Protocol (UDP) broadcast to minimize required handshakes with Birman-Schiper-Stephenson Protocol to repeat data until it reaches its destination ● The vehicle controls use standard UDP packets to transfer simple integers over the network. FIT/CSRR CDR | 69
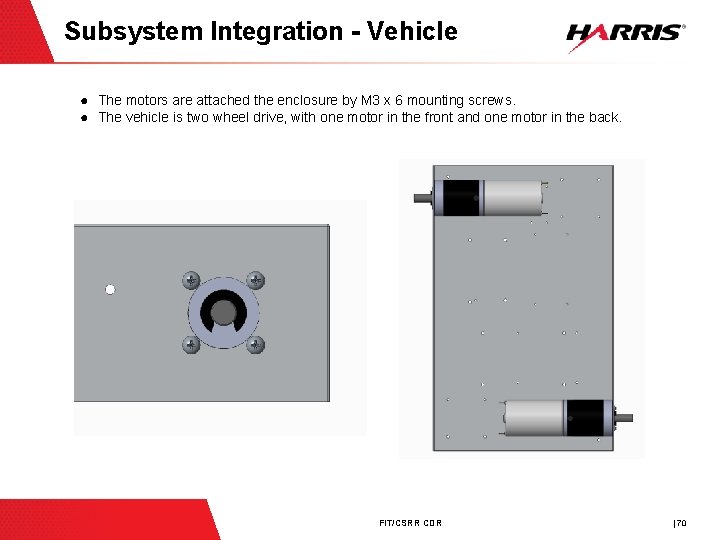
Subsystem Integration - Vehicle ● The motors are attached the enclosure by M 3 x 6 mounting screws. ● The vehicle is two wheel drive, with one motor in the front and one motor in the back. FIT/CSRR CDR | 70
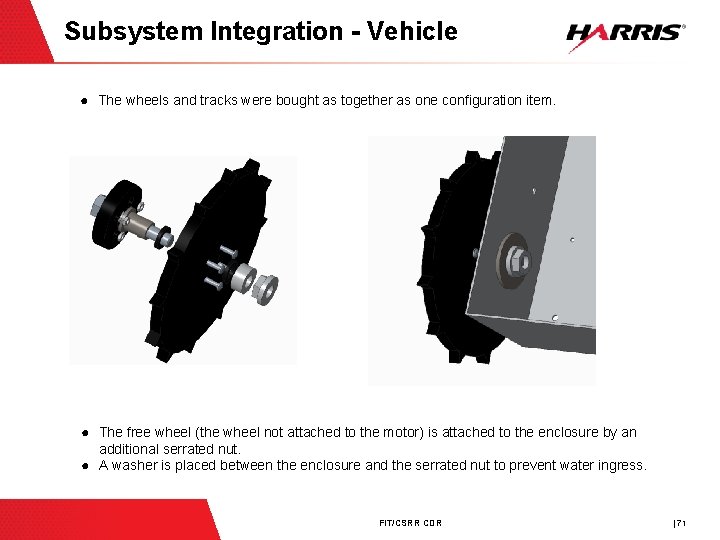
Subsystem Integration - Vehicle ● The wheels and tracks were bought as together as one configuration item. ● The free wheel (the wheel not attached to the motor) is attached to the enclosure by an additional serrated nut. ● A washer is placed between the enclosure and the serrated nut to prevent water ingress. FIT/CSRR CDR | 71
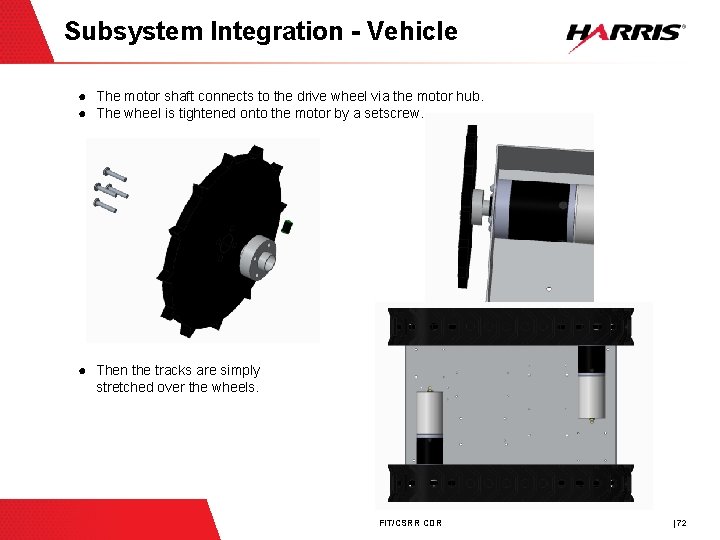
Subsystem Integration - Vehicle ● The motor shaft connects to the drive wheel via the motor hub. ● The wheel is tightened onto the motor by a setscrew. ● Then the tracks are simply stretched over the wheels. FIT/CSRR CDR | 72
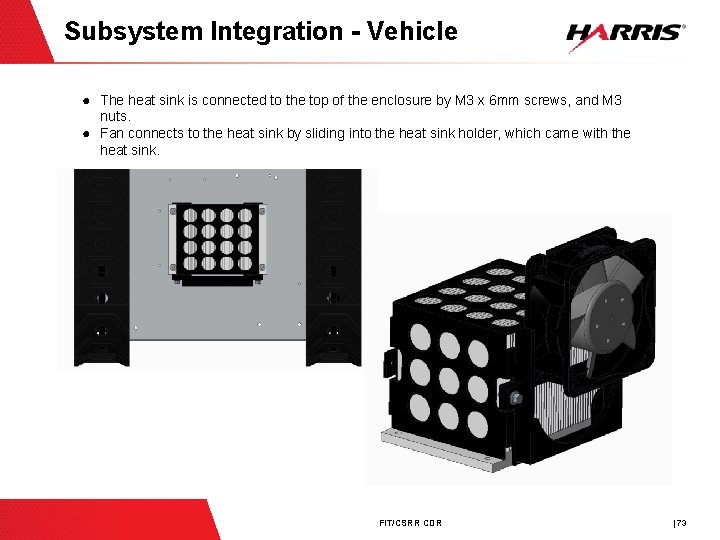
Subsystem Integration - Vehicle ● The heat sink is connected to the top of the enclosure by M 3 x 6 mm screws, and M 3 nuts. ● Fan connects to the heat sink by sliding into the heat sink holder, which came with the heat sink. FIT/CSRR CDR | 73
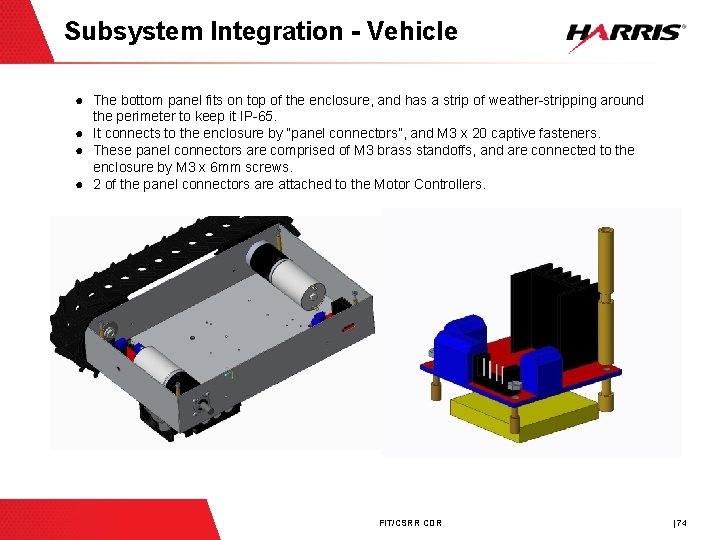
Subsystem Integration - Vehicle ● The bottom panel fits on top of the enclosure, and has a strip of weather-stripping around the perimeter to keep it IP-65. ● It connects to the enclosure by “panel connectors”, and M 3 x 20 captive fasteners. ● These panel connectors are comprised of M 3 brass standoffs, and are connected to the enclosure by M 3 x 6 mm screws. ● 2 of the panel connectors are attached to the Motor Controllers. FIT/CSRR CDR | 74
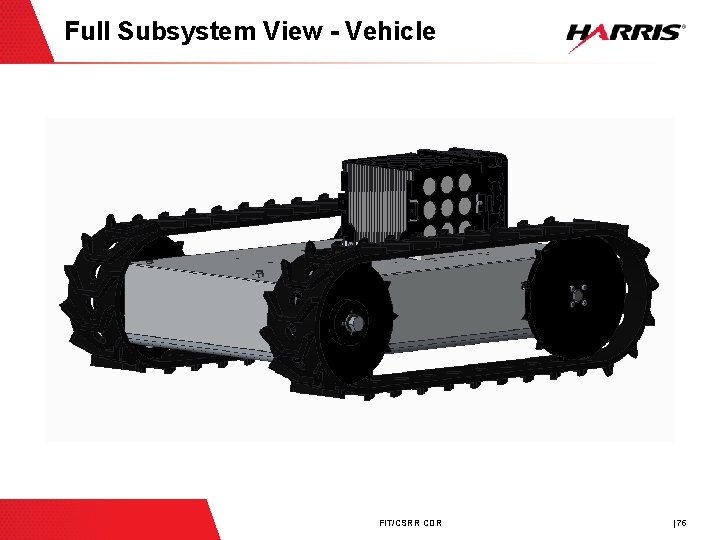
Full Subsystem View - Vehicle FIT/CSRR CDR | 75
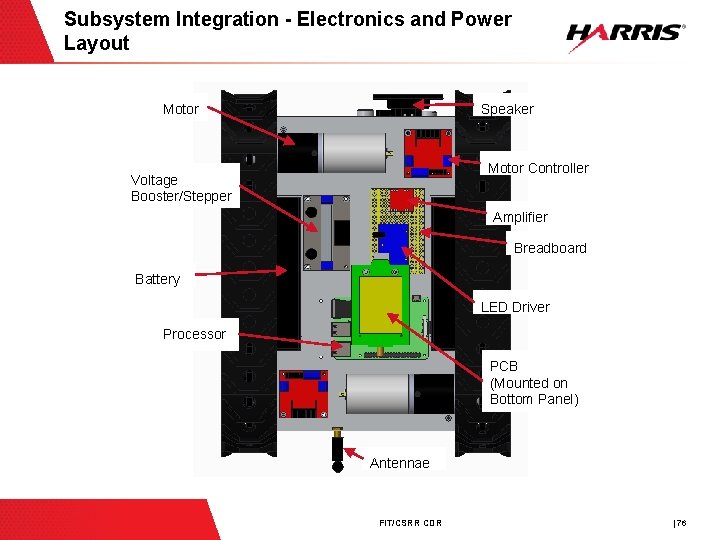
Subsystem Integration - Electronics and Power Layout Motor Speaker Motor Controller Voltage Booster/Stepper Amplifier Breadboard Battery LED Driver Processor PCB (Mounted on Bottom Panel) Antennae FIT/CSRR CDR | 76
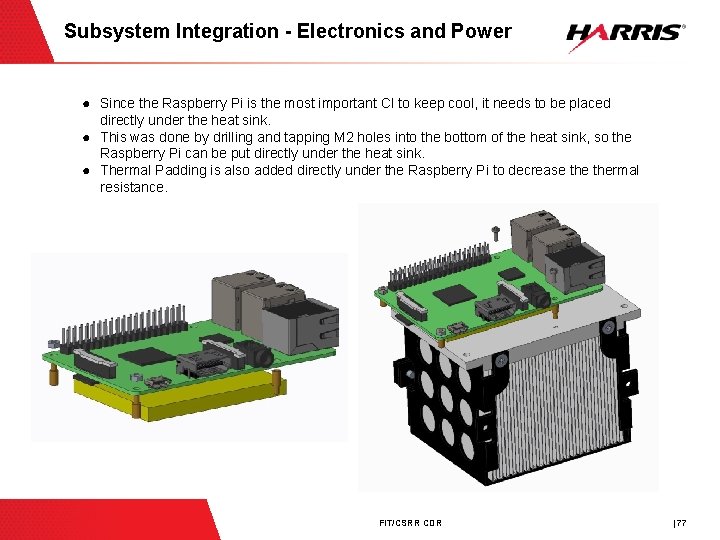
Subsystem Integration - Electronics and Power ● Since the Raspberry Pi is the most important CI to keep cool, it needs to be placed directly under the heat sink. ● This was done by drilling and tapping M 2 holes into the bottom of the heat sink, so the Raspberry Pi can be put directly under the heat sink. ● Thermal Padding is also added directly under the Raspberry Pi to decrease thermal resistance. FIT/CSRR CDR | 77
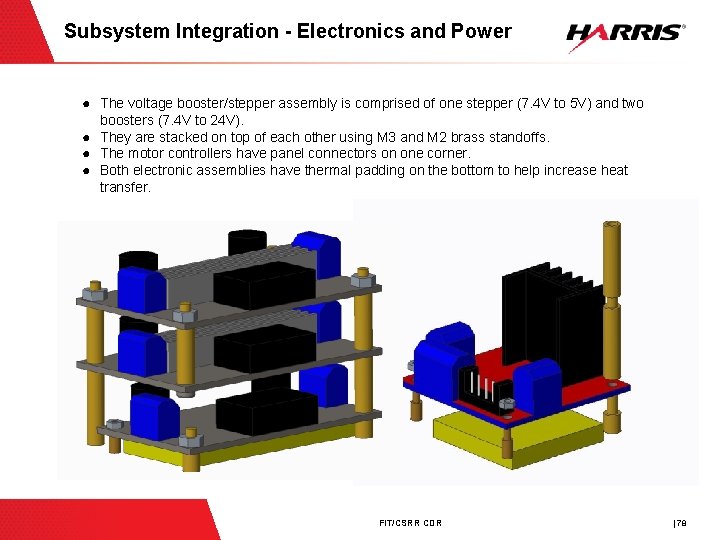
Subsystem Integration - Electronics and Power ● The voltage booster/stepper assembly is comprised of one stepper (7. 4 V to 5 V) and two boosters (7. 4 V to 24 V). ● They are stacked on top of each other using M 3 and M 2 brass standoffs. ● The motor controllers have panel connectors on one corner. ● Both electronic assemblies have thermal padding on the bottom to help increase heat transfer. FIT/CSRR CDR | 78
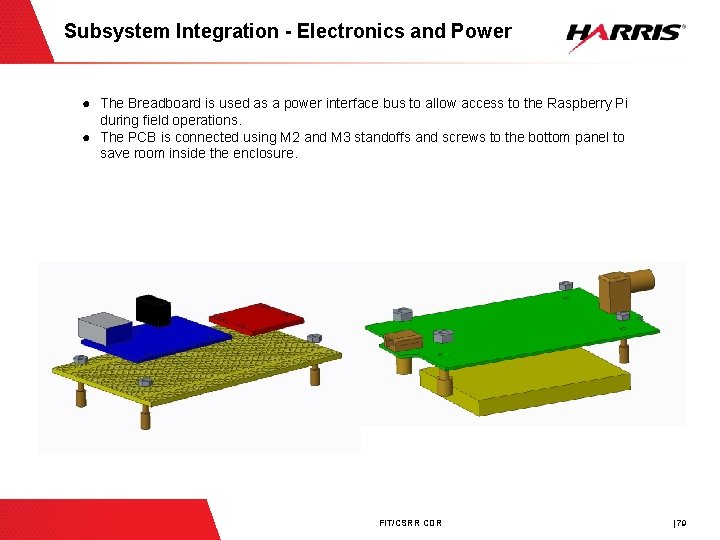
Subsystem Integration - Electronics and Power ● The Breadboard is used as a power interface bus to allow access to the Raspberry Pi during field operations. ● The PCB is connected using M 2 and M 3 standoffs and screws to the bottom panel to save room inside the enclosure. FIT/CSRR CDR | 79
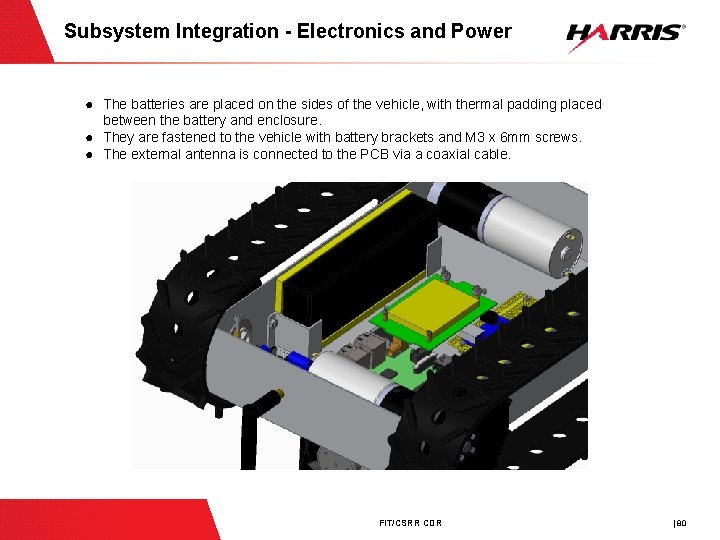
Subsystem Integration - Electronics and Power ● The batteries are placed on the sides of the vehicle, with thermal padding placed between the battery and enclosure. ● They are fastened to the vehicle with battery brackets and M 3 x 6 mm screws. ● The external antenna is connected to the PCB via a coaxial cable. FIT/CSRR CDR | 80
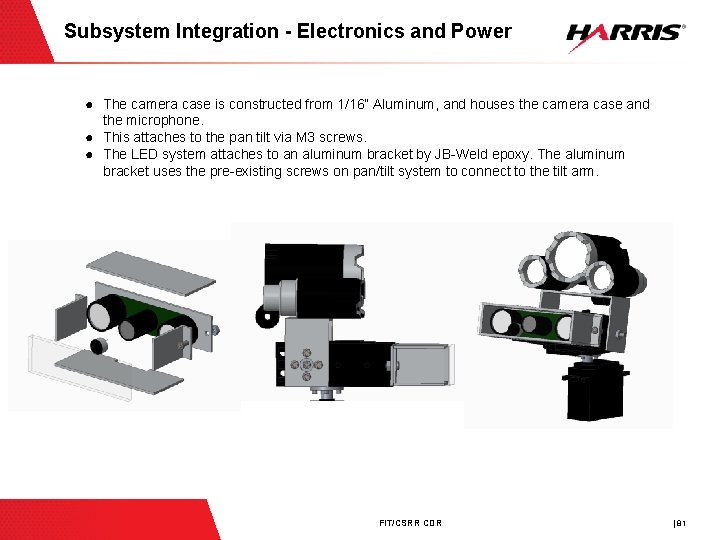
Subsystem Integration - Electronics and Power ● The camera case is constructed from 1/16” Aluminum, and houses the camera case and the microphone. ● This attaches to the pan tilt via M 3 screws. ● The LED system attaches to an aluminum bracket by JB-Weld epoxy. The aluminum bracket uses the pre-existing screws on pan/tilt system to connect to the tilt arm. FIT/CSRR CDR | 81
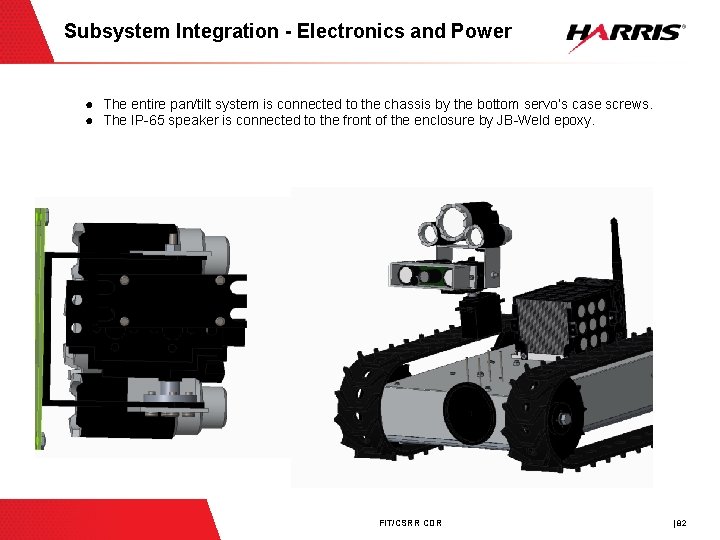
Subsystem Integration - Electronics and Power ● The entire pan/tilt system is connected to the chassis by the bottom servo’s case screws. ● The IP-65 speaker is connected to the front of the enclosure by JB-Weld epoxy. FIT/CSRR CDR | 82
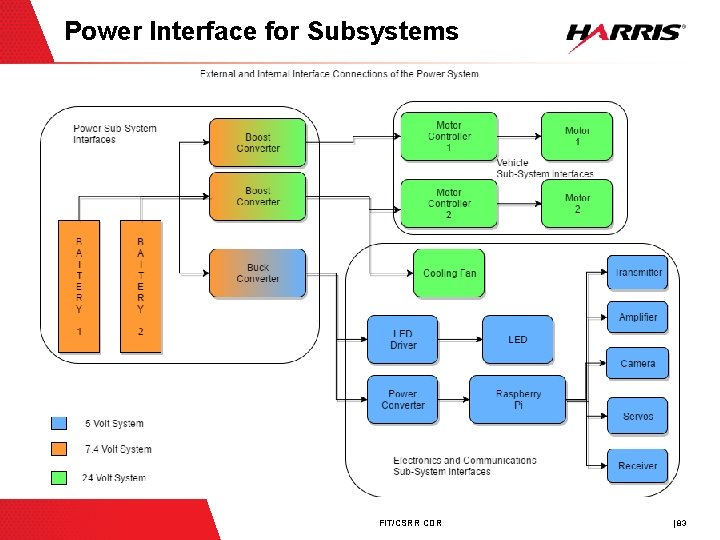
Power Interface for Subsystems FIT/CSRR CDR | 83
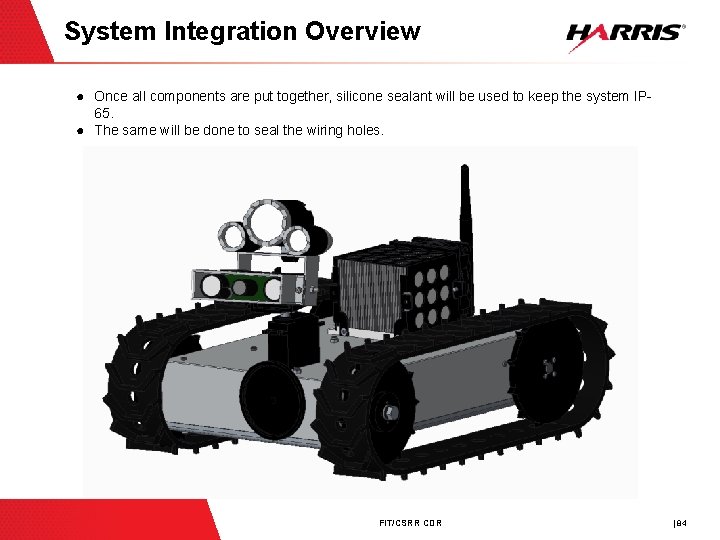
System Integration Overview ● Once all components are put together, silicone sealant will be used to keep the system IP 65. ● The same will be done to seal the wiring holes. FIT/CSRR CDR | 84
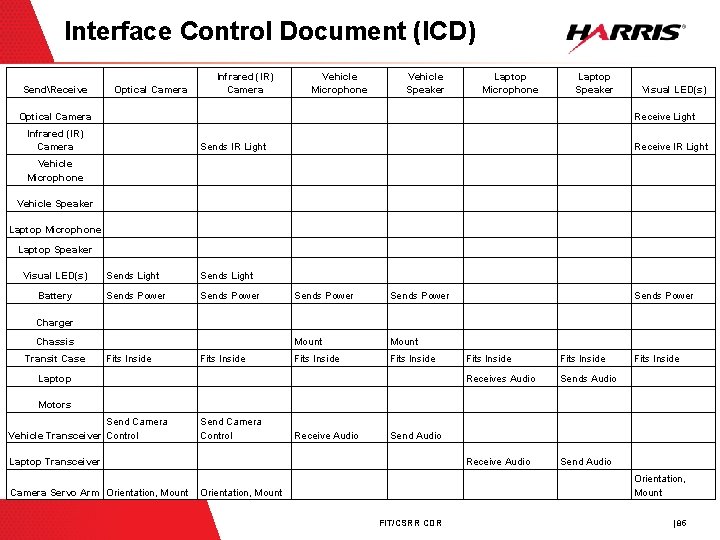
Interface Control Document (ICD) SendReceive Optical Camera Infrared (IR) Camera Vehicle Microphone Vehicle Speaker Laptop Microphone Laptop Speaker Optical Camera Visual LED(s) Receive Light Infrared (IR) Camera Sends IR Light Receive IR Light Vehicle Microphone Vehicle Speaker Laptop Microphone Laptop Speaker Visual LED(s) Battery Sends Light Sends Power Mount Fits Inside Sends Power Charger Chassis Transit Case Fits Inside Laptop Fits Inside Receives Audio Sends Audio Receive Audio Send Audio Fits Inside Motors Send Camera Vehicle Transceiver Control Send Camera Control Receive Audio Send Audio Laptop Transceiver Camera Servo Arm Orientation, Mount FIT/CSRR CDR | 85
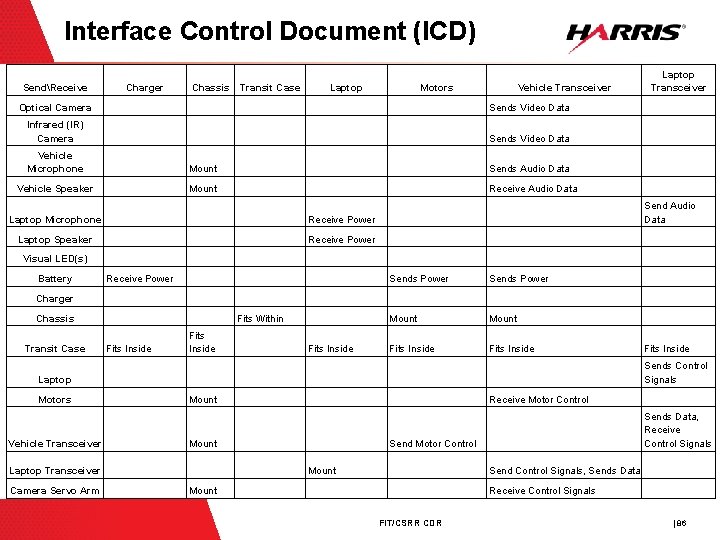
Interface Control Document (ICD) SendReceive Charger Chassis Transit Case Laptop Motors Vehicle Transceiver Optical Camera Sends Video Data Infrared (IR) Camera Sends Video Data Vehicle Microphone Mount Sends Audio Data Vehicle Speaker Mount Receive Audio Data Laptop Microphone Receive Power Laptop Speaker Receive Power Laptop Transceiver Send Audio Data Visual LED(s) Battery Receive Power Sends Power Mount Fits Inside Charger Chassis Transit Case Fits Within Fits Inside Sends Control Signals Laptop Motors Vehicle Transceiver Mount Receive Motor Control Mount Laptop Transceiver Camera Servo Arm Fits Inside Sends Data, Receive Control Signals Send Motor Control Mount Send Control Signals, Sends Data Mount Receive Control Signals FIT/CSRR CDR | 86
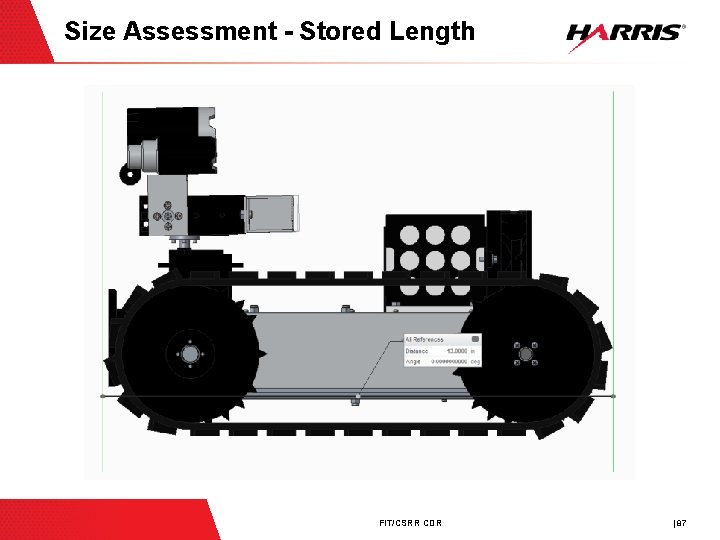
Size Assessment - Stored Length FIT/CSRR CDR | 87
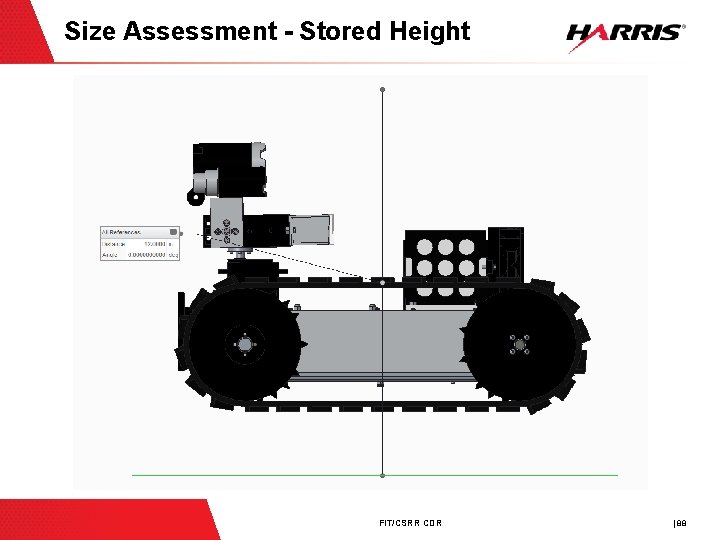
Size Assessment - Stored Height FIT/CSRR CDR | 88
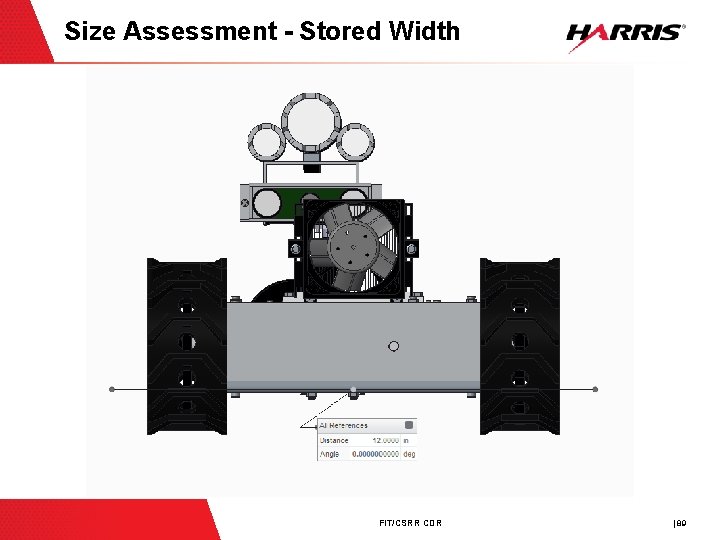
Size Assessment - Stored Width FIT/CSRR CDR | 89
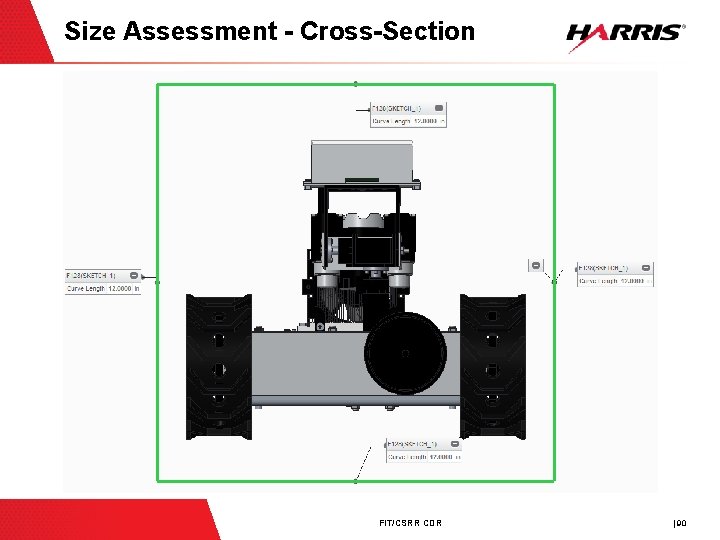
Size Assessment - Cross-Section FIT/CSRR CDR | 90
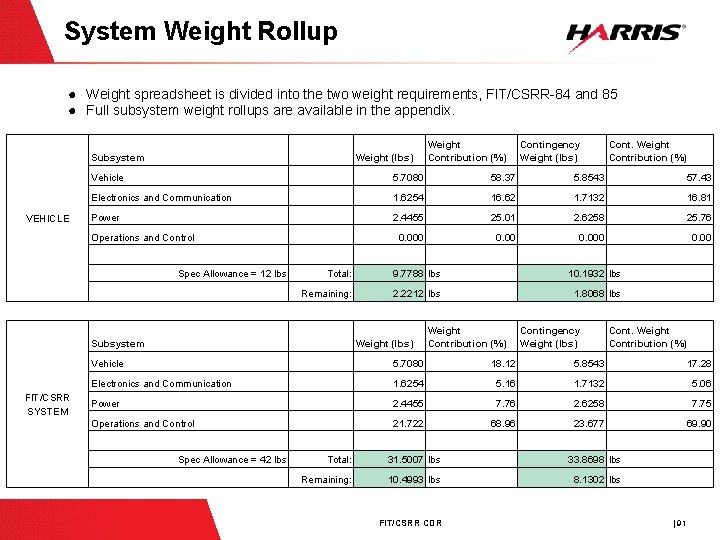
System Weight Rollup ● Weight spreadsheet is divided into the two weight requirements, FIT/CSRR-84 and 85 ● Full subsystem weight rollups are available in the appendix. Subsystem VEHICLE Weight (lbs) Contingency Weight (lbs) Cont. Weight Contribution (%) Vehicle 5. 7080 58. 37 5. 8543 57. 43 Electronics and Communication 1. 6254 16. 62 1. 7132 16. 81 Power 2. 4455 25. 01 2. 6258 25. 76 0. 000 0. 00 Operations and Control Spec Allowance = 12 lbs Total: 9. 7788 lbs 10. 1932 lbs Remaining: 2. 2212 lbs 1. 8068 lbs Subsystem FIT/CSRR SYSTEM Weight Contribution (%) Weight (lbs) Weight Contribution (%) Contingency Weight (lbs) Cont. Weight Contribution (%) Vehicle 5. 7080 18. 12 5. 8543 17. 28 Electronics and Communication 1. 6254 5. 16 1. 7132 5. 06 Power 2. 4455 7. 76 2. 6258 7. 75 Operations and Control 21. 722 68. 96 23. 677 69. 90 Spec Allowance = 42 lbs Total: 31. 5007 lbs 33. 8698 lbs Remaining: 10. 4993 lbs 8. 1302 lbs FIT/CSRR CDR | 91
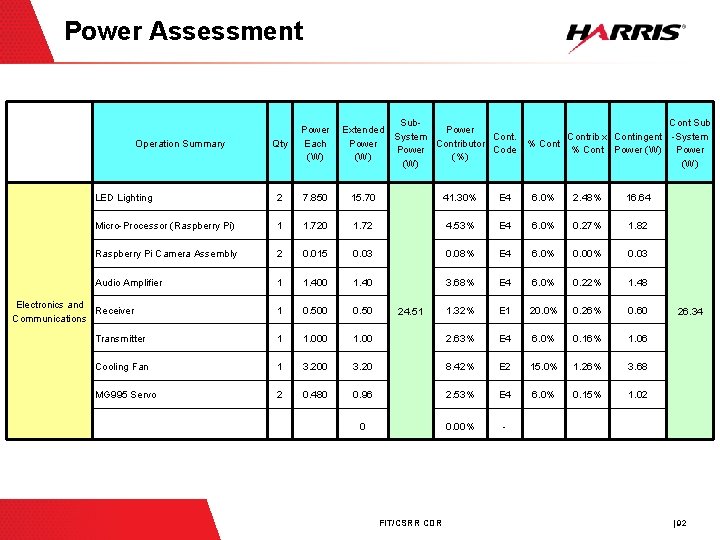
Power Assessment Operation Summary Qty Sub. Cont Sub Power Extended Power System Contrib x Contingent -System % Cont Each Power Contributor Power Code % Cont Power (W) (W) (%) (W) LED Lighting 2 7. 850 15. 70 41. 30% E 4 6. 0% 2. 48% 16. 64 Micro-Processor (Raspberry Pi) 1 1. 720 1. 72 4. 53% E 4 6. 0% 0. 27% 1. 82 Raspberry Pi Camera Assembly 2 0. 015 0. 03 0. 08% E 4 6. 0% 0. 03 Audio Amplifier 1 1. 400 1. 40 3. 68% E 4 6. 0% 0. 22% 1. 48 1 0. 500 0. 50 1. 32% E 1 20. 0% 0. 26% 0. 60 Transmitter 1 1. 000 1. 00 2. 63% E 4 6. 0% 0. 16% 1. 06 Cooling Fan 1 3. 200 3. 20 8. 42% E 2 15. 0% 1. 26% 3. 68 MG 995 Servo 2 0. 480 0. 96 2. 53% E 4 6. 0% 0. 15% 1. 02 0 0. 00% - Electronics and Receiver Communications 24. 51 FIT/CSRR CDR 26. 34 | 92
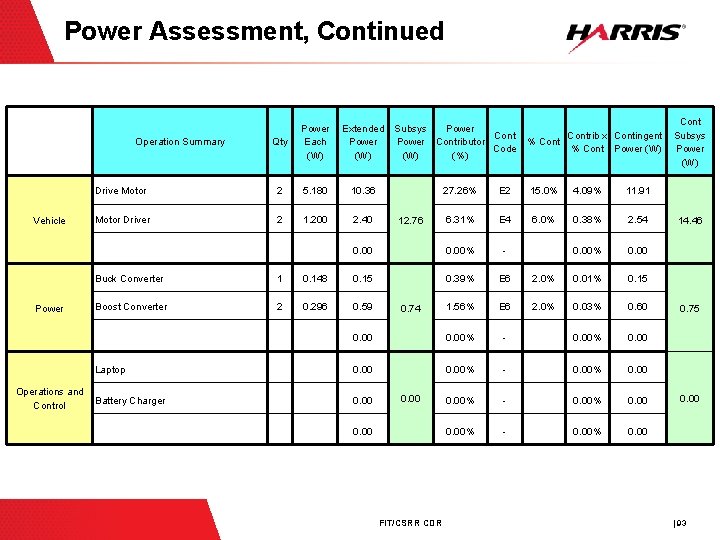
Power Assessment, Continued Operation Summary Vehicle Power Qty Cont Power Extended Subsys Power Contrib x Contingent Subsys Each Power Contributor % Cont Code % Cont Power (W) (W) (%) (W) Drive Motor 2 5. 180 10. 36 27. 26% E 2 15. 0% 4. 09% 11. 91 Motor Driver 2 1. 200 2. 40 6. 31% E 4 6. 0% 0. 38% 2. 54 0. 00% - 0. 00% 0. 00 0. 39% E 6 2. 0% 0. 01% 0. 15 1. 56% E 6 2. 0% 0. 03% 0. 60 0. 00% - 0. 00% 0. 00 Buck Converter 1 0. 148 0. 15 Boost Converter 2 0. 296 0. 59 Laptop Operations and Battery Charger Control 0. 00 12. 76 0. 74 0. 00 FIT/CSRR CDR 14. 46 0. 75 0. 00 | 93
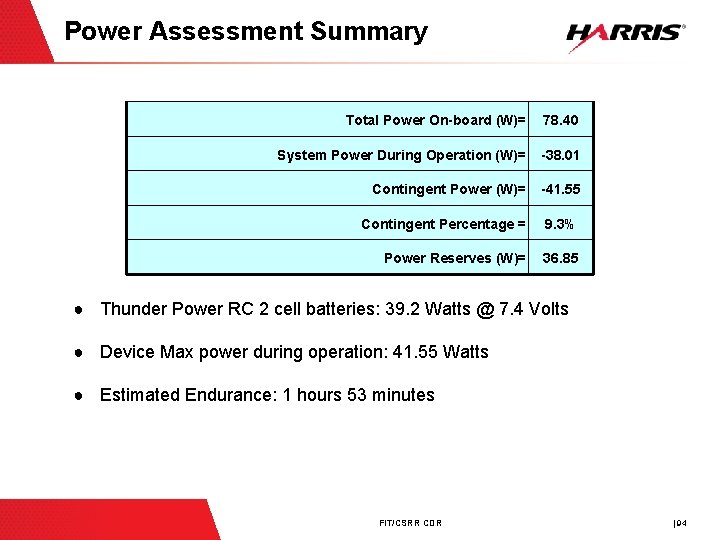
Power Assessment Summary Total Power On-board (W)= 78. 40 System Power During Operation (W)= -38. 01 Contingent Power (W)= -41. 55 Contingent Percentage = 9. 3% Power Reserves (W)= 36. 85 ● Thunder Power RC 2 cell batteries: 39. 2 Watts @ 7. 4 Volts ● Device Max power during operation: 41. 55 Watts ● Estimated Endurance: 1 hours 53 minutes FIT/CSRR CDR | 94
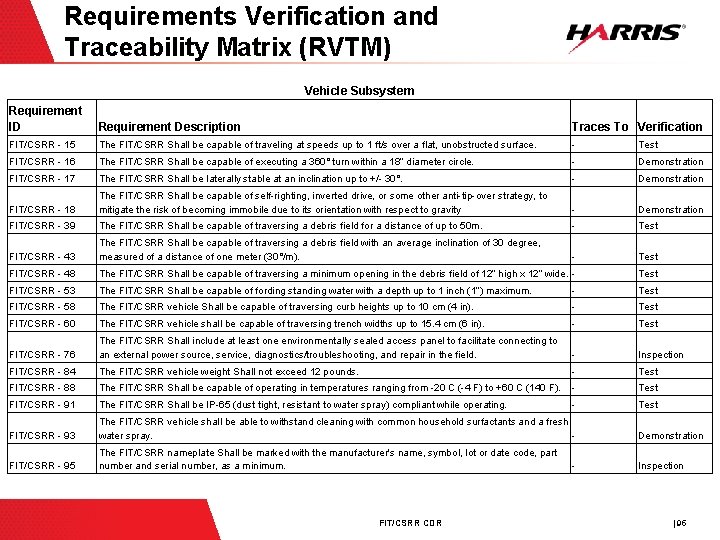
Requirements Verification and Traceability Matrix (RVTM) Vehicle Subsystem Requirement ID Requirement Description Traces To Verification FIT/CSRR - 15 The FIT/CSRR Shall be capable of traveling at speeds up to 1 ft/s over a flat, unobstructed surface. - Test FIT/CSRR - 16 The FIT/CSRR Shall be capable of executing a 360° turn within a 18” diameter circle. - Demonstration FIT/CSRR - 17 The FIT/CSRR Shall be laterally stable at an inclination up to +/- 30°. - Demonstration FIT/CSRR - 18 The FIT/CSRR Shall be capable of self-righting, inverted drive, or some other anti-tip-over strategy, to mitigate the risk of becoming immobile due to its orientation with respect to gravity - Demonstration FIT/CSRR - 39 The FIT/CSRR Shall be capable of traversing a debris field for a distance of up to 50 m. - Test FIT/CSRR - 43 The FIT/CSRR Shall be capable of traversing a debris field with an average inclination of 30 degree, measured of a distance of one meter (30°/m). - Test FIT/CSRR - 48 The FIT/CSRR Shall be capable of traversing a minimum opening in the debris field of 12” high x 12” wide. - Test FIT/CSRR - 53 The FIT/CSRR Shall be capable of fording standing water with a depth up to 1 inch (1”) maximum. - Test FIT/CSRR - 58 The FIT/CSRR vehicle Shall be capable of traversing curb heights up to 10 cm (4 in). - Test FIT/CSRR - 60 The FIT/CSRR vehicle shall be capable of traversing trench widths up to 15. 4 cm (6 in). - Test FIT/CSRR - 76 The FIT/CSRR Shall include at least one environmentally sealed access panel to facilitate connecting to an external power source, service, diagnostics/troubleshooting, and repair in the field. - Inspection FIT/CSRR - 84 The FIT/CSRR vehicle weight Shall not exceed 12 pounds. - Test FIT/CSRR - 88 The FIT/CSRR Shall be capable of operating in temperatures ranging from -20 C (-4 F) to +60 C (140 F). - Test FIT/CSRR - 91 The FIT/CSRR Shall be IP-65 (dust tight, resistant to water spray) compliant while operating. - Test FIT/CSRR - 93 The FIT/CSRR vehicle shall be able to withstand cleaning with common household surfactants and a fresh water spray. - Demonstration FIT/CSRR - 95 The FIT/CSRR nameplate Shall be marked with the manufacturer's name, symbol, lot or date code, part number and serial number, as a minimum. Inspection FIT/CSRR CDR - | 95
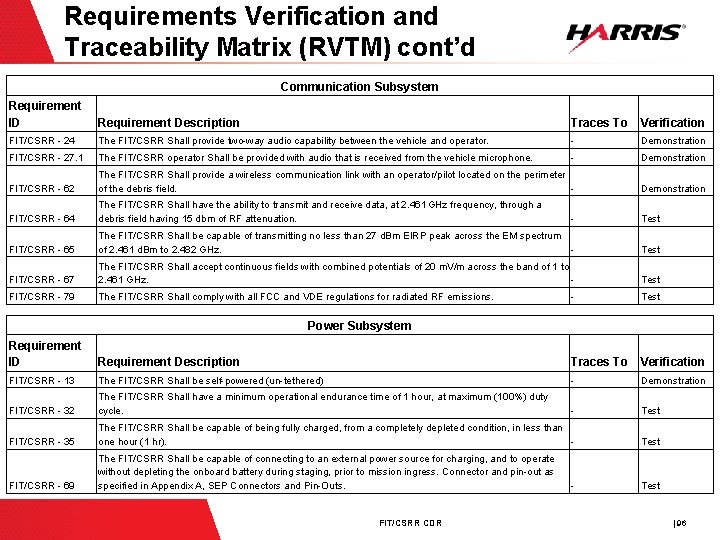
Requirements Verification and Traceability Matrix (RVTM) cont’d Communication Subsystem Requirement ID Requirement Description Traces To Verification FIT/CSRR - 24 The FIT/CSRR Shall provide two-way audio capability between the vehicle and operator. - Demonstration FIT/CSRR - 27. 1 The FIT/CSRR operator Shall be provided with audio that is received from the vehicle microphone. - Demonstration FIT/CSRR - 62 The FIT/CSRR Shall provide a wireless communication link with an operator/pilot located on the perimeter of the debris field. - Demonstration FIT/CSRR - 64 The FIT/CSRR Shall have the ability to transmit and receive data, at 2. 461 GHz frequency, through a debris field having 15 dbm of RF attenuation. - Test FIT/CSRR - 65 The FIT/CSRR Shall be capable of transmitting no less than 27 d. Bm EIRP peak across the EM spectrum of 2. 461 d. Bm to 2. 482 GHz. - Test FIT/CSRR - 67 The FIT/CSRR Shall accept continuous fields with combined potentials of 20 m. V/m across the band of 1 to 2. 461 GHz. - Test FIT/CSRR - 79 The FIT/CSRR Shall comply with all FCC and VDE regulations for radiated RF emissions. - Test Power Subsystem Requirement ID Requirement Description Traces To Verification FIT/CSRR - 13 The FIT/CSRR Shall be self-powered (un-tethered) - Demonstration FIT/CSRR - 32 The FIT/CSRR Shall have a minimum operational endurance time of 1 hour, at maximum (100%) duty cycle. - Test FIT/CSRR - 35 The FIT/CSRR Shall be capable of being fully charged, from a completely depleted condition, in less than one hour (1 hr). - Test FIT/CSRR - 69 The FIT/CSRR Shall be capable of connecting to an external power source for charging, and to operate without depleting the onboard battery during staging, prior to mission ingress. Connector and pin-out as specified in Appendix A, SEP Connectors and Pin-Outs. Test FIT/CSRR CDR - | 96
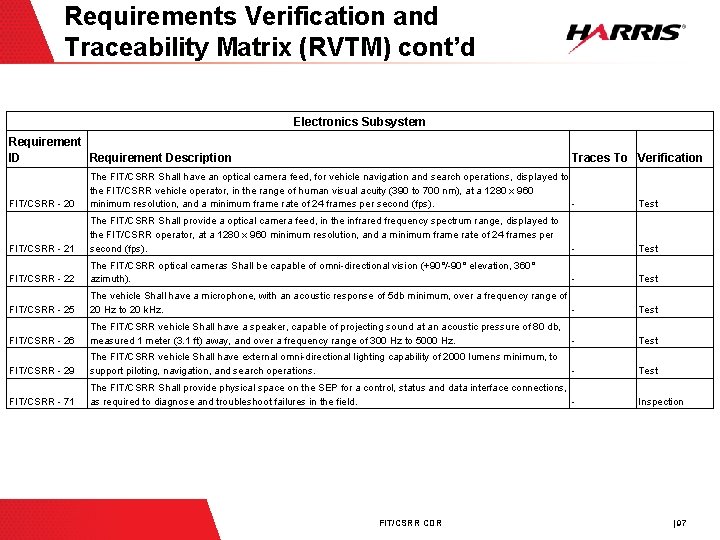
Requirements Verification and Traceability Matrix (RVTM) cont’d Electronics Subsystem Requirement ID Requirement Description Traces To Verification FIT/CSRR - 20 The FIT/CSRR Shall have an optical camera feed, for vehicle navigation and search operations, displayed to the FIT/CSRR vehicle operator, in the range of human visual acuity (390 to 700 nm), at a 1280 x 960 minimum resolution, and a minimum frame rate of 24 frames per second (fps). - Test FIT/CSRR - 21 The FIT/CSRR Shall provide a optical camera feed, in the infrared frequency spectrum range, displayed to the FIT/CSRR operator, at a 1280 x 960 minimum resolution, and a minimum frame rate of 24 frames per second (fps). - Test FIT/CSRR - 22 The FIT/CSRR optical cameras Shall be capable of omni-directional vision (+90°/-90° elevation, 360° azimuth). - Test FIT/CSRR - 25 The vehicle Shall have a microphone, with an acoustic response of 5 db minimum, over a frequency range of 20 Hz to 20 k. Hz. - Test FIT/CSRR - 26 The FIT/CSRR vehicle Shall have a speaker, capable of projecting sound at an acoustic pressure of 80 db, measured 1 meter (3. 1 ft) away, and over a frequency range of 300 Hz to 5000 Hz. - Test FIT/CSRR - 29 The FIT/CSRR vehicle Shall have external omni-directional lighting capability of 2000 lumens minimum, to support piloting, navigation, and search operations. Test FIT/CSRR - 71 The FIT/CSRR Shall provide physical space on the SEP for a control, status and data interface connections, as required to diagnose and troubleshoot failures in the field. - FIT/CSRR CDR - Inspection | 97
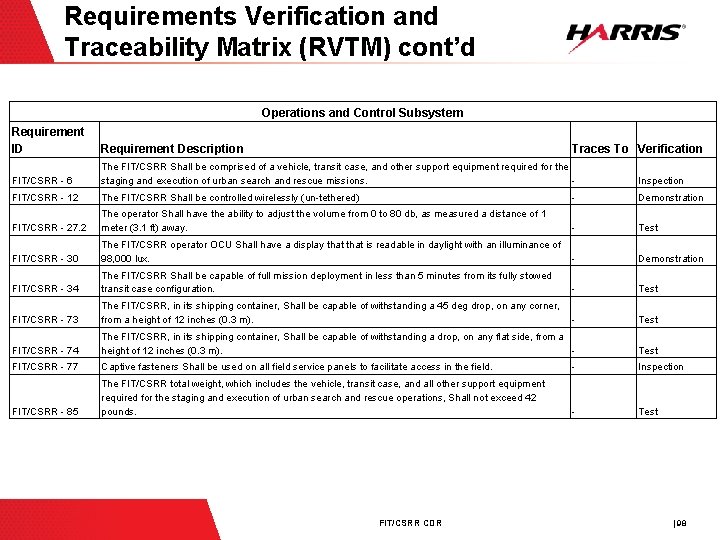
Requirements Verification and Traceability Matrix (RVTM) cont’d Operations and Control Subsystem Requirement ID Requirement Description FIT/CSRR - 6 The FIT/CSRR Shall be comprised of a vehicle, transit case, and other support equipment required for the staging and execution of urban search and rescue missions. - Inspection FIT/CSRR - 12 The FIT/CSRR Shall be controlled wirelessly (un-tethered) - Demonstration FIT/CSRR - 27. 2 The operator Shall have the ability to adjust the volume from 0 to 80 db, as measured a distance of 1 meter (3. 1 ft) away. - Test FIT/CSRR - 30 The FIT/CSRR operator OCU Shall have a display that is readable in daylight with an illuminance of 98, 000 lux. - Demonstration FIT/CSRR - 34 The FIT/CSRR Shall be capable of full mission deployment in less than 5 minutes from its fully stowed transit case configuration. - Test FIT/CSRR - 73 The FIT/CSRR, in its shipping container, Shall be capable of withstanding a 45 deg drop, on any corner, from a height of 12 inches (0. 3 m). - Test FIT/CSRR - 74 The FIT/CSRR, in its shipping container, Shall be capable of withstanding a drop, on any flat side, from a height of 12 inches (0. 3 m). - Test FIT/CSRR - 77 Captive fasteners Shall be used on all field service panels to facilitate access in the field. - Inspection FIT/CSRR - 85 The FIT/CSRR total weight, which includes the vehicle, transit case, and all other support equipment required for the staging and execution of urban search and rescue operations, Shall not exceed 42 pounds. - Test Traces To Verification FIT/CSRR CDR | 98
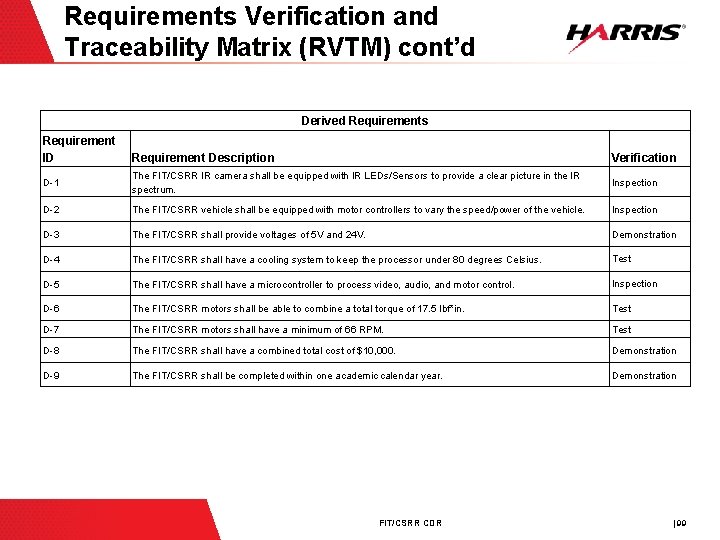
Requirements Verification and Traceability Matrix (RVTM) cont’d Derived Requirements Requirement ID Requirement Description Verification D-1 The FIT/CSRR IR camera shall be equipped with IR LEDs/Sensors to provide a clear picture in the IR spectrum. Inspection D-2 The FIT/CSRR vehicle shall be equipped with motor controllers to vary the speed/power of the vehicle. Inspection D-3 The FIT/CSRR shall provide voltages of 5 V and 24 V. Demonstration D-4 The FIT/CSRR shall have a cooling system to keep the processor under 80 degrees Celsius. Test D-5 The FIT/CSRR shall have a microcontroller to process video, audio, and motor control. Inspection D-6 The FIT/CSRR motors shall be able to combine a total torque of 17. 5 lbf*in. Test D-7 The FIT/CSRR motors shall have a minimum of 66 RPM. Test D-8 The FIT/CSRR shall have a combined total cost of $10, 000. Demonstration D-9 The FIT/CSRR shall be completed within one academic calendar year. Demonstration FIT/CSRR CDR | 99
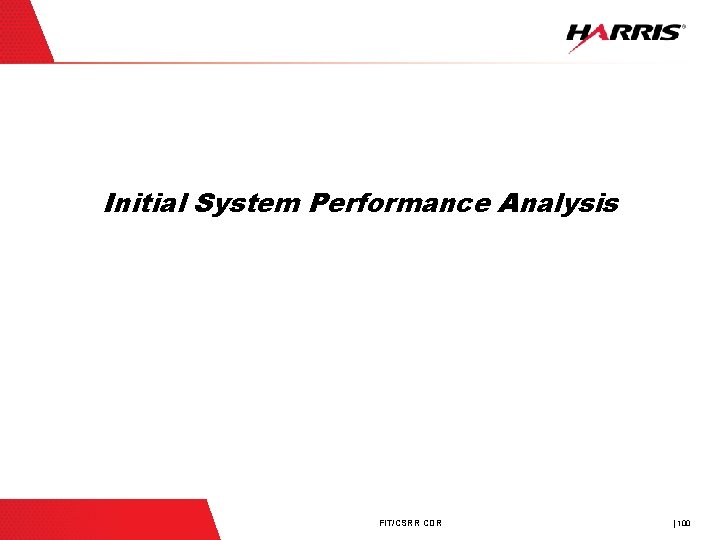
Initial System Performance Analysis FIT/CSRR CDR | 100
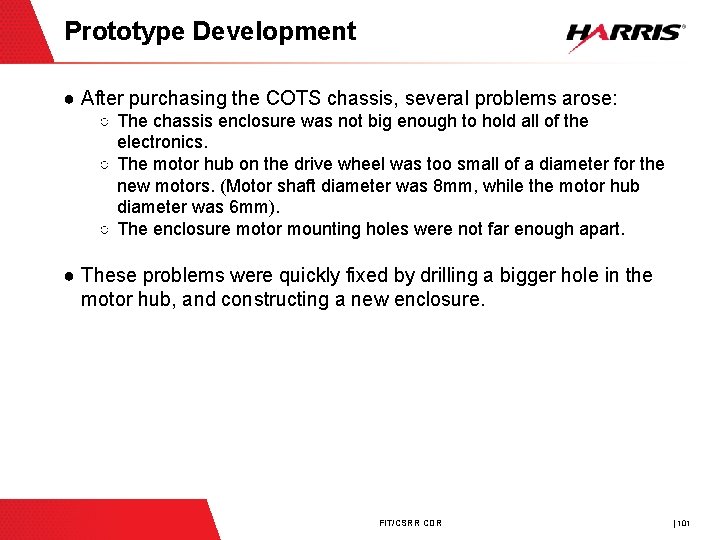
Prototype Development ● After purchasing the COTS chassis, several problems arose: ○ The chassis enclosure was not big enough to hold all of the electronics. ○ The motor hub on the drive wheel was too small of a diameter for the new motors. (Motor shaft diameter was 8 mm, while the motor hub diameter was 6 mm). ○ The enclosure motor mounting holes were not far enough apart. ● These problems were quickly fixed by drilling a bigger hole in the motor hub, and constructing a new enclosure. FIT/CSRR CDR | 101
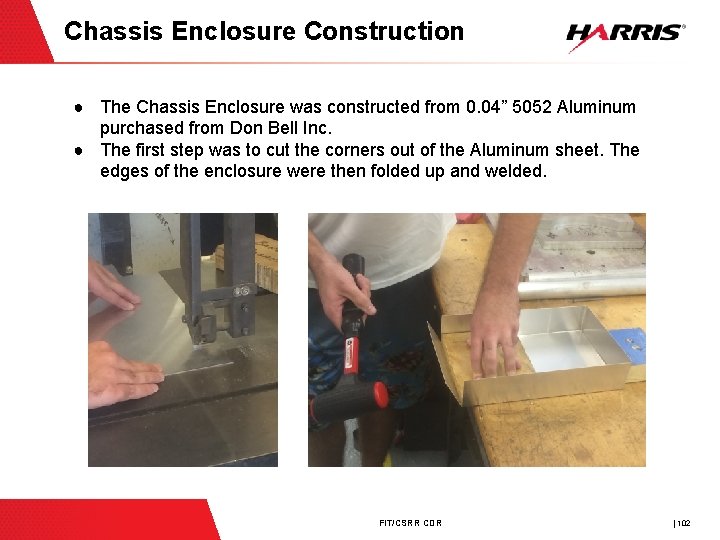
Chassis Enclosure Construction ● The Chassis Enclosure was constructed from 0. 04” 5052 Aluminum purchased from Don Bell Inc. ● The first step was to cut the corners out of the Aluminum sheet. The edges of the enclosure were then folded up and welded. FIT/CSRR CDR | 102
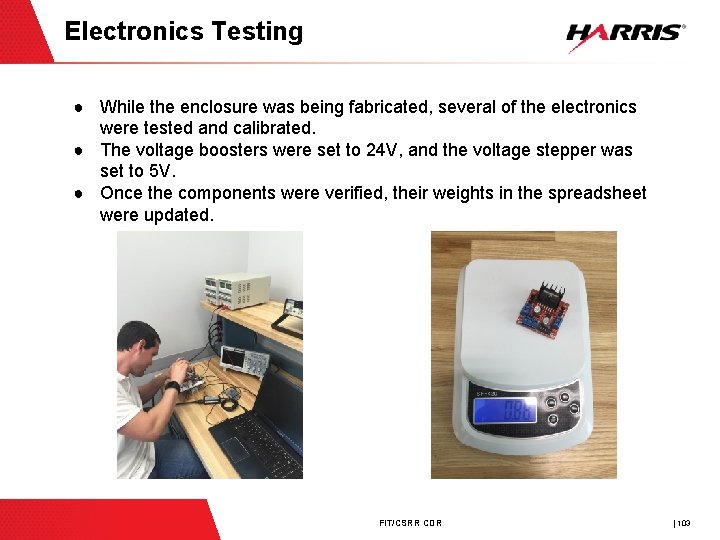
Electronics Testing ● While the enclosure was being fabricated, several of the electronics were tested and calibrated. ● The voltage boosters were set to 24 V, and the voltage stepper was set to 5 V. ● Once the components were verified, their weights in the spreadsheet were updated. FIT/CSRR CDR | 103
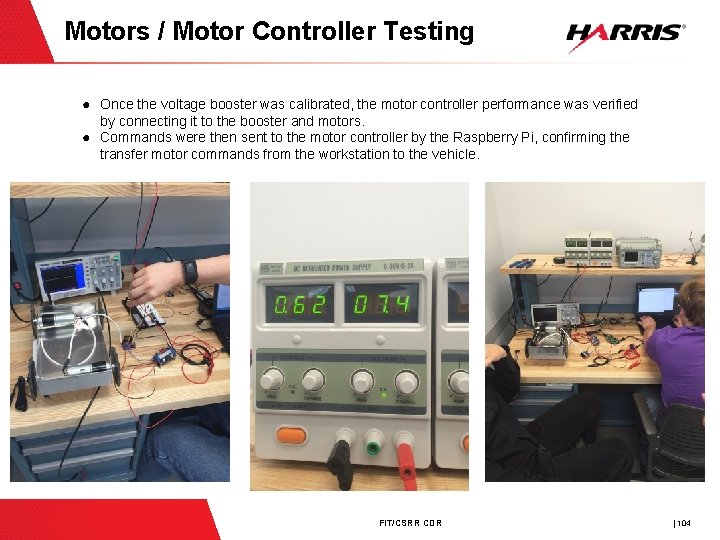
Motors / Motor Controller Testing ● Once the voltage booster was calibrated, the motor controller performance was verified by connecting it to the booster and motors. ● Commands were then sent to the motor controller by the Raspberry Pi, confirming the transfer motor commands from the workstation to the vehicle. FIT/CSRR CDR | 104
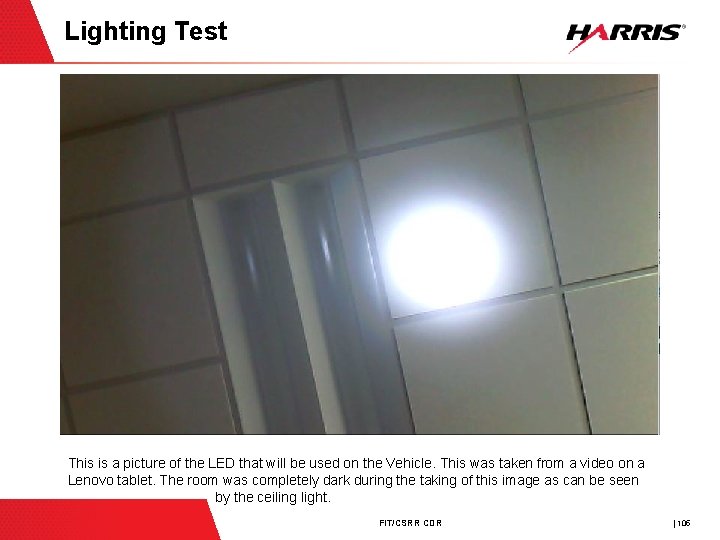
Lighting Test This is a picture of the LED that will be used on the Vehicle. This was taken from a video on a Lenovo tablet. The room was completely dark during the taking of this image as can be seen by the ceiling light. FIT/CSRR CDR | 105
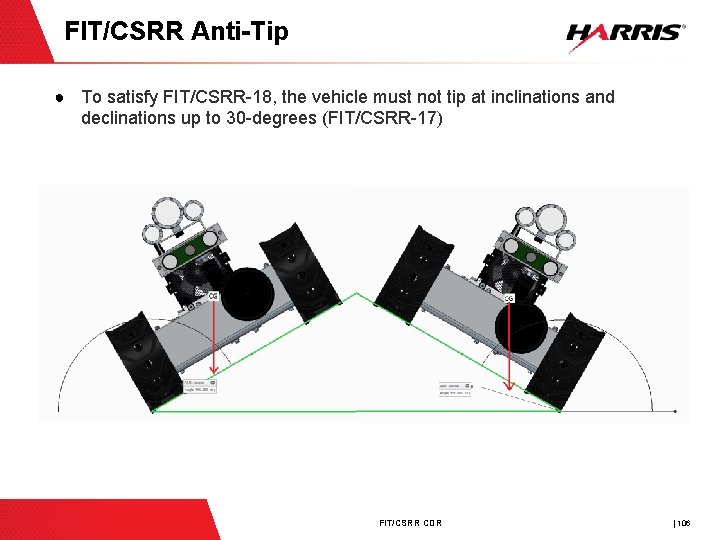
FIT/CSRR Anti-Tip ● To satisfy FIT/CSRR-18, the vehicle must not tip at inclinations and declinations up to 30 -degrees (FIT/CSRR-17) FIT/CSRR CDR | 106
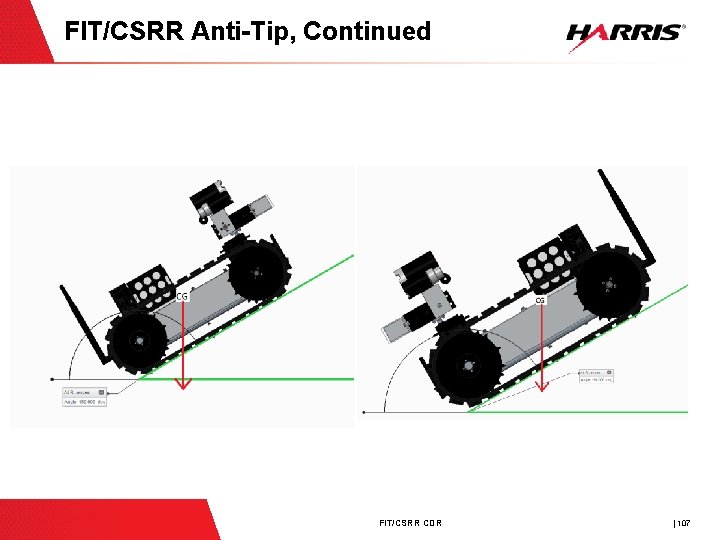
FIT/CSRR Anti-Tip, Continued FIT/CSRR CDR | 107
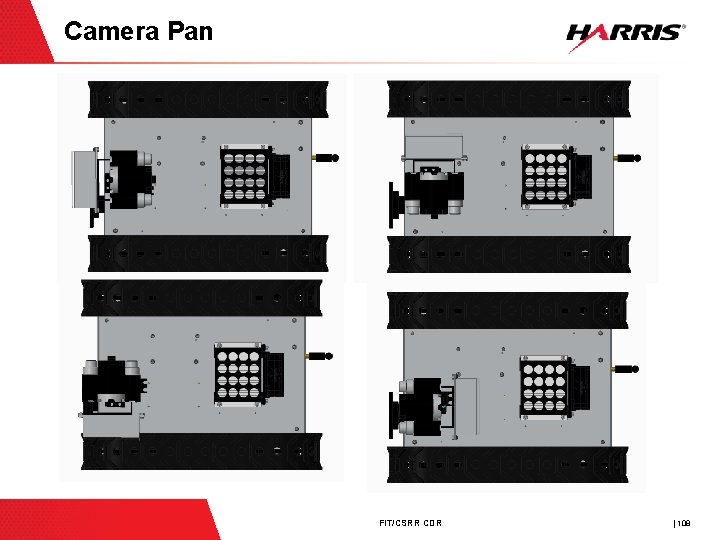
Camera Pan FIT/CSRR CDR | 108
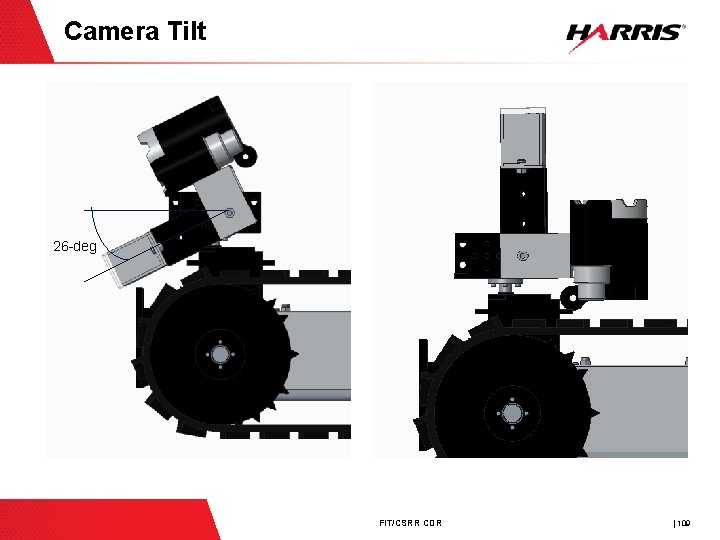
Camera Tilt 26 -deg FIT/CSRR CDR | 109
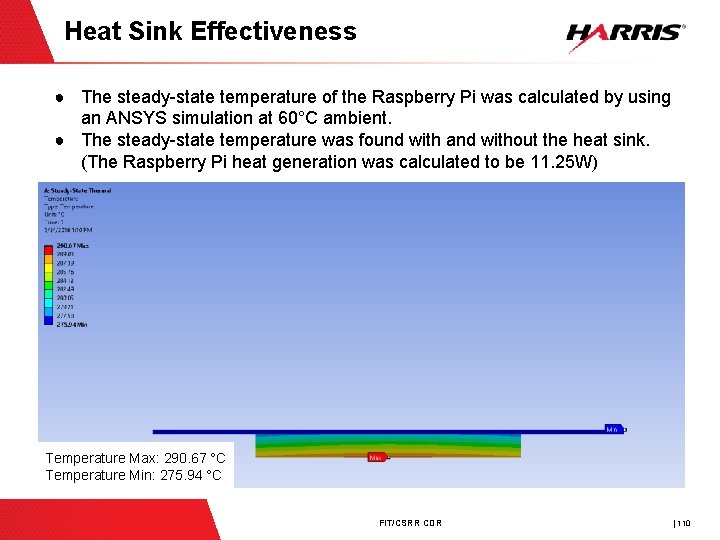
Heat Sink Effectiveness ● The steady-state temperature of the Raspberry Pi was calculated by using an ANSYS simulation at 60°C ambient. ● The steady-state temperature was found with and without the heat sink. (The Raspberry Pi heat generation was calculated to be 11. 25 W) Temperature Max: 290. 67 °C Temperature Min: 275. 94 °C FIT/CSRR CDR | 110
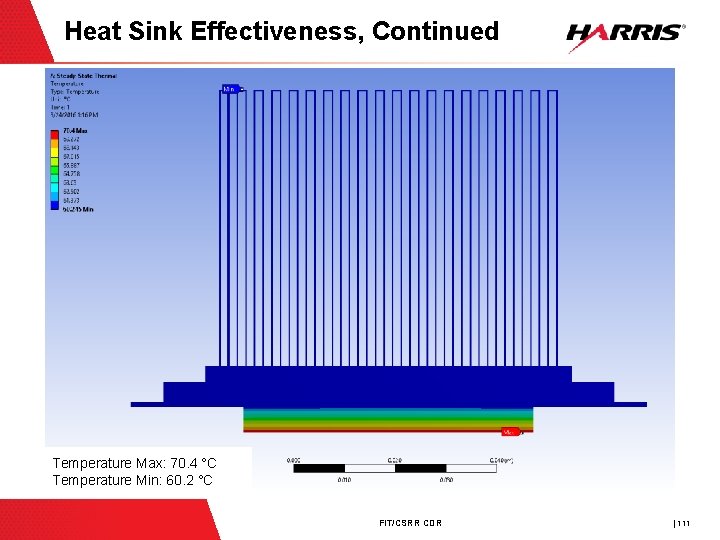
Heat Sink Effectiveness, Continued Temperature Max: 70. 4 °C Temperature Min: 60. 2 °C FIT/CSRR CDR | 111
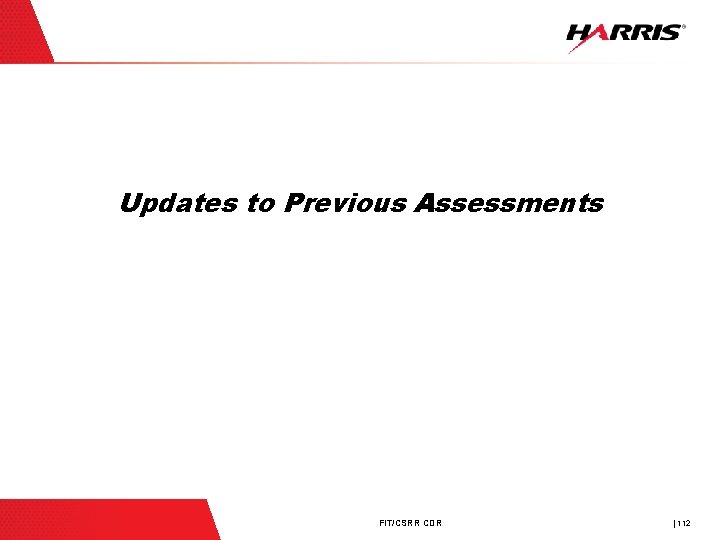
Updates to Previous Assessments FIT/CSRR CDR | 112
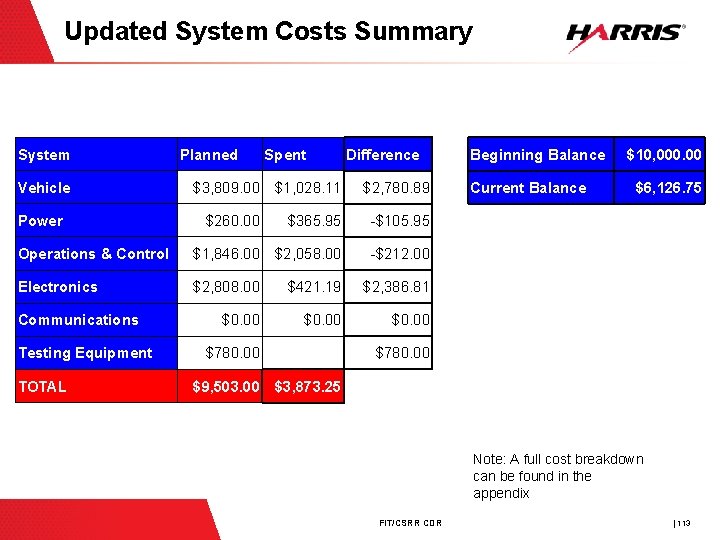
Updated System Costs Summary System Vehicle Planned Spent Difference $3, 809. 00 $1, 028. 11 $2, 780. 89 $260. 00 $365. 95 -$105. 95 Operations & Control $1, 846. 00 $2, 058. 00 -$212. 00 Electronics $2, 808. 00 $421. 19 $2, 386. 81 $0. 00 Power Communications Testing Equipment TOTAL $780. 00 $9, 503. 00 Beginning Balance Current Balance $10, 000. 00 $6, 126. 75 $780. 00 $3, 873. 25 Note: A full cost breakdown can be found in the appendix FIT/CSRR CDR | 113
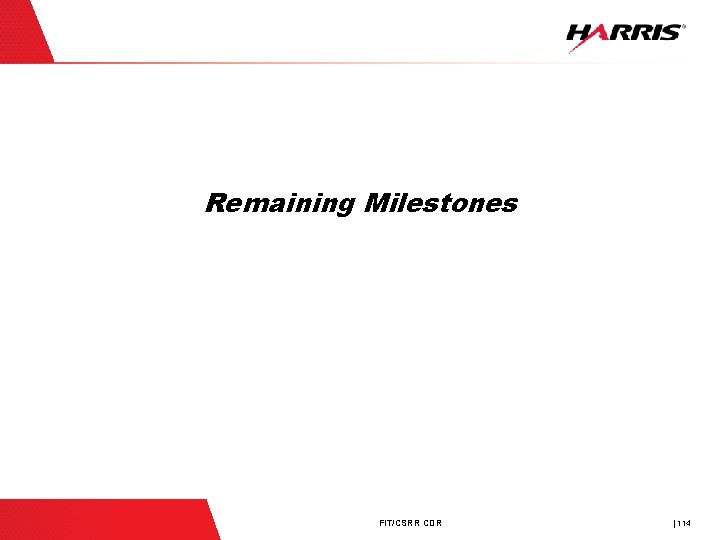
Remaining Milestones FIT/CSRR CDR | 114
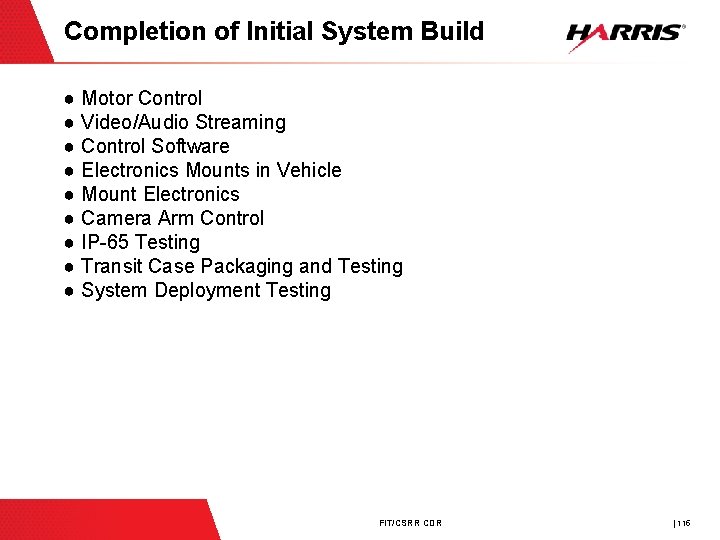
Completion of Initial System Build ● Motor Control ● Video/Audio Streaming ● Control Software ● Electronics Mounts in Vehicle ● Mount Electronics ● Camera Arm Control ● IP-65 Testing ● Transit Case Packaging and Testing ● System Deployment Testing FIT/CSRR CDR | 115
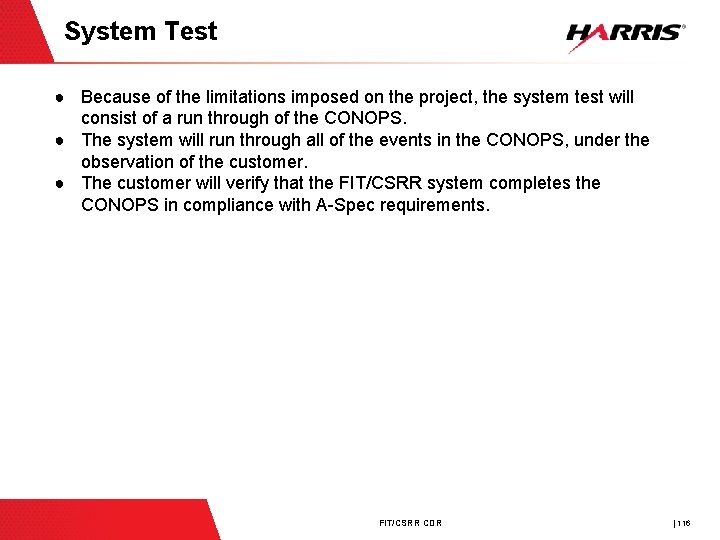
System Test ● Because of the limitations imposed on the project, the system test will consist of a run through of the CONOPS. ● The system will run through all of the events in the CONOPS, under the observation of the customer. ● The customer will verify that the FIT/CSRR system completes the CONOPS in compliance with A-Spec requirements. FIT/CSRR CDR | 116
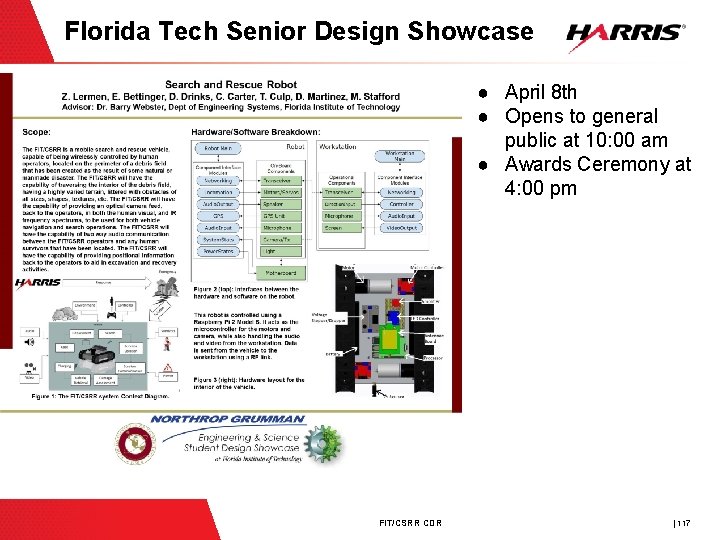
Florida Tech Senior Design Showcase ● April 8 th ● Opens to general public at 10: 00 am ● Awards Ceremony at 4: 00 pm FIT/CSRR CDR | 117
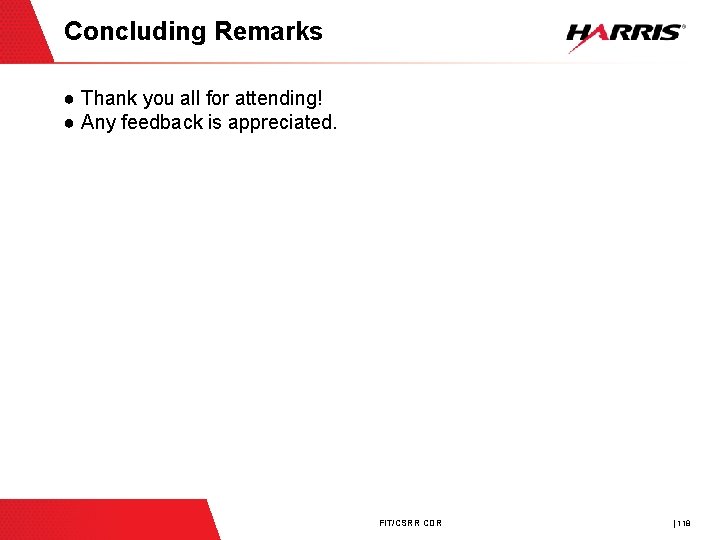
Concluding Remarks ● Thank you all for attending! ● Any feedback is appreciated. FIT/CSRR CDR | 118
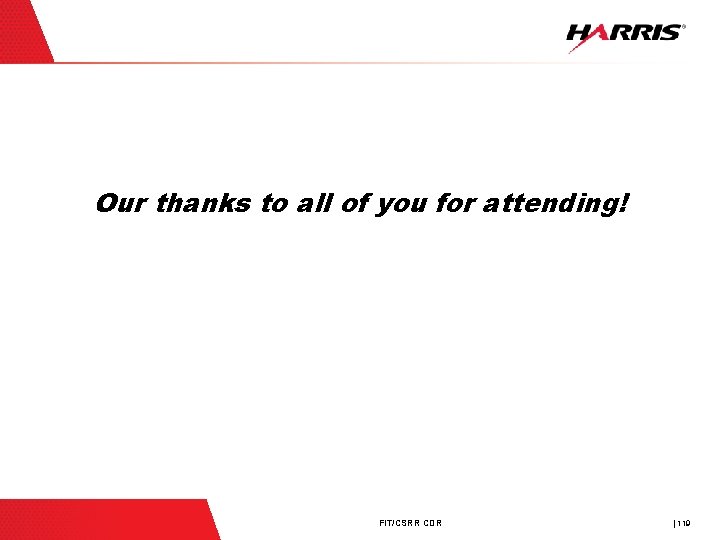
Our thanks to all of you for attending! FIT/CSRR CDR | 119
![References IEEE Standard 1J Oakes R Botta and T Bahill Technical Performance Measures References – IEEE Standard [1]J. Oakes, R. Botta and T. Bahill, “Technical Performance Measures”,](https://slidetodoc.com/presentation_image_h/882432d770b2194ab374350724101881/image-120.jpg)
References – IEEE Standard [1]J. Oakes, R. Botta and T. Bahill, “Technical Performance Measures”, http: //www. dtic. mil/ndia/2005 systems/wednesday/oakes. pdf, 2005 FIT/CSRR CDR | 120
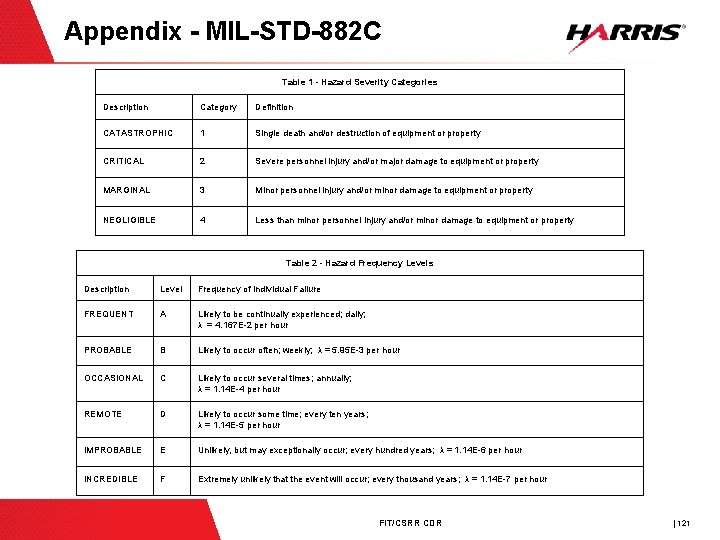
Appendix - MIL-STD-882 C Table 1 - Hazard Severity Categories Description Category Definition CATASTROPHIC 1 Single death and/or destruction of equipment or property CRITICAL 2 Severe personnel injury and/or major damage to equipment or property MARGINAL 3 Minor personnel injury and/or minor damage to equipment or property NEGLIGIBLE 4 Less than minor personnel injury and/or minor damage to equipment or property Table 2 - Hazard Frequency Levels Description Level Frequency of Individual Failure FREQUENT A Likely to be continually experienced; daily; λ = 4. 167 E-2 per hour PROBABLE B Likely to occur often; weekly; λ = 5. 95 E-3 per hour OCCASIONAL C Likely to occur several times; annually; λ = 1. 14 E-4 per hour REMOTE D Likely to occur some time; every ten years; λ = 1. 14 E-5 per hour IMPROBABLE E Unlikely, but may exceptionally occur; every hundred years; λ = 1. 14 E-6 per hour INCREDIBLE F Extremely unlikely that the event will occur; every thousand years; λ = 1. 14 E-7 per hour FIT/CSRR CDR | 121
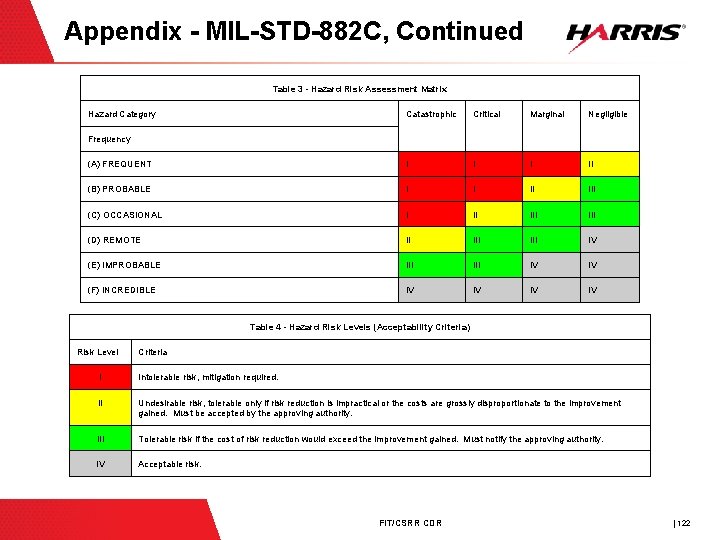
Appendix - MIL-STD-882 C, Continued Table 3 - Hazard Risk Assessment Matrix Hazard Category Catastrophic Critical Marginal Negligible (A) FREQUENT I II (B) PROBABLE I I II III (C) OCCASIONAL I II III (D) REMOTE II III IV (E) IMPROBABLE III IV IV (F) INCREDIBLE IV IV Frequency Table 4 - Hazard Risk Levels (Acceptability Criteria) Risk Level Criteria I Intolerable risk, mitigation required. II Undesirable risk, tolerable only if risk reduction is impractical or the costs are grossly disproportionate to the improvement gained. Must be accepted by the approving authority. III Tolerable risk if the cost of risk reduction would exceed the improvement gained. Must notify the approving authority. IV Acceptable risk. FIT/CSRR CDR | 122
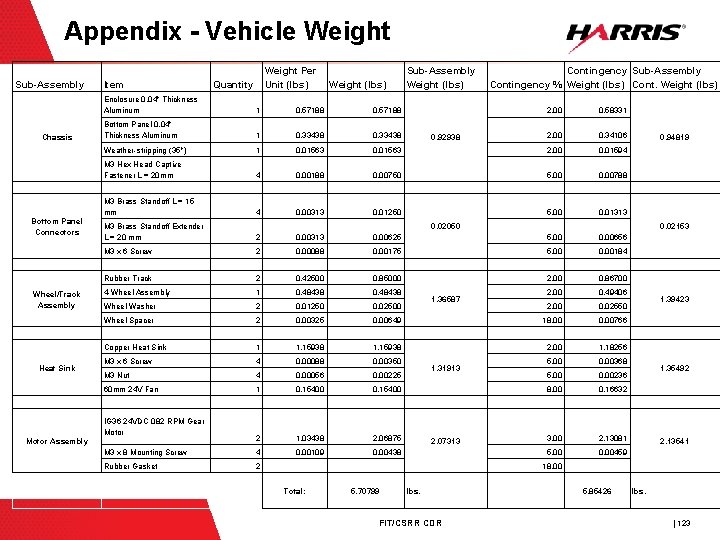
Appendix - Vehicle Weight Sub-Assembly Chassis Bottom Panel Connectors Wheel/Track Assembly Heat Sink Motor Assembly Item Weight Per Unit (lbs) Quantity Weight (lbs) Enclosure 0. 04" Thickness Aluminum 1 0. 57188 Bottom Panel 0. 04" Thickness Aluminum 1 0. 33438 Weather-stripping (35") 1 0. 01563 M 3 Hex Head Captive Fastener L = 20 mm 4 M 3 Brass Standoff L = 15 mm Sub-Assembly Weight (lbs) Contingency Sub-Assembly Contingency % Weight (lbs) Cont. Weight (lbs) 2. 00 0. 58331 2. 00 0. 34106 0. 01563 2. 00 0. 01594 0. 00188 0. 00750 5. 00 0. 00788 4 0. 00313 0. 01250 5. 00 0. 01313 M 3 Brass Standoff Extender L = 20 mm 2 0. 00313 0. 00625 5. 00 0. 00656 M 3 x 6 Screw 2 0. 00088 0. 00175 5. 00 0. 00184 Rubber Track 2 0. 42500 0. 85000 2. 00 0. 86700 4 -Wheel Assembly 1 0. 48438 2. 00 0. 49406 Wheel Washer 2 0. 01250 0. 02500 2. 00 0. 02550 Wheel Spacer 2 0. 00325 0. 00649 18. 00 0. 00766 Copper Heat Sink 1 1. 15938 2. 00 1. 18256 M 3 x 6 Screw 4 0. 00088 0. 00350 5. 00 0. 00368 M 3 Nut 4 0. 00056 0. 00225 5. 00 0. 00236 60 mm 24 V Fan 1 0. 15400 8. 00 0. 16632 3. 00 2. 13081 5. 00 0. 00459 IG 36 24 VDC 082 RPM Gear Motor 0. 92938 0. 94819 0. 02050 2 1. 03438 2. 06875 M 3 x 8 Mounting Screw 4 0. 00109 0. 00438 Rubber Gasket 2 1. 36587 1. 31913 2. 07313 0. 02153 1. 39423 1. 35492 2. 13541 18. 00 Total: 5. 70799 lbs. FIT/CSRR CDR 5. 85426 lbs. | 123
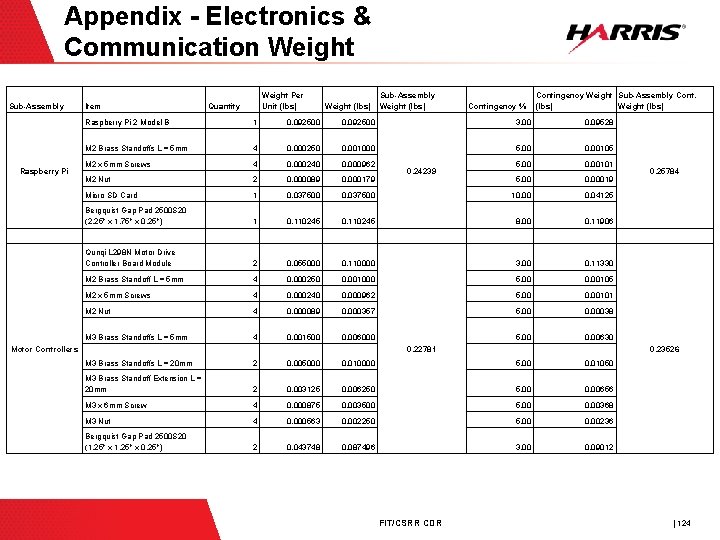
Appendix - Electronics & Communication Weight Sub-Assembly Raspberry Pi Item Weight Per Unit (lbs) Quantity Weight (lbs) Sub-Assembly Weight (lbs) Contingency % Contingency Weight Sub-Assembly Cont. (lbs) Weight (lbs) Raspberry Pi 2 Model B 1 0. 092500 3. 00 0. 09528 M 2 Brass Standoffs L = 5 mm 4 0. 000250 0. 001000 5. 00 0. 00105 M 2 x 5 mm Screws 4 0. 000240 0. 000962 5. 00 0. 00101 M 2 Nut 2 0. 000089 0. 000179 5. 00 0. 00019 Micro SD Card 1 0. 037500 10. 00 0. 04125 Bergquist Gap Pad 2500 S 20 (2. 25" x 1. 75" x 0. 25") 1 0. 110245 8. 00 0. 11906 Qunqi L 298 N Motor Drive Controller Board Module 2 0. 055000 0. 110000 3. 00 0. 11330 M 2 Brass Standoff L = 5 mm 4 0. 000250 0. 001000 5. 00 0. 00105 M 2 x 5 mm Screws 4 0. 000240 0. 000962 5. 00 0. 00101 M 2 Nut 4 0. 000089 0. 000357 5. 00 0. 00038 M 3 Brass Standoffs L = 5 mm 4 0. 001500 0. 006000 5. 00 0. 00630 M 3 Brass Standoffs L = 20 mm 2 0. 005000 0. 010000 5. 00 0. 01050 M 3 Brass Standoff Extension L = 20 mm 2 0. 003125 0. 006250 5. 00 0. 00656 M 3 x 6 mm Screw 4 0. 000875 0. 003500 5. 00 0. 00368 M 3 Nut 4 0. 000563 0. 002250 5. 00 0. 00236 Bergquist Gap Pad 2500 S 20 (1. 25" x 0. 25") 2 0. 043748 0. 087496 3. 00 0. 09012 Motor Controllers 0. 24239 0. 22781 FIT/CSRR CDR 0. 25784 0. 23526 | 124
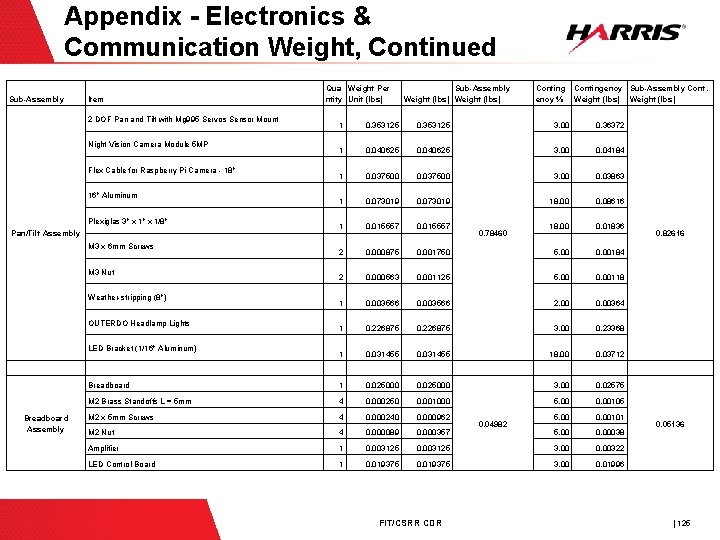
Appendix - Electronics & Communication Weight, Continued Sub-Assembly Item 2 DOF Pan and Tilt with Mg 995 Servos Sensor Mount Sub-Assembly Weight (lbs) Conting ency % Contingency Sub-Assembly Cont. Weight (lbs) 1 0. 353125 3. 00 0. 36372 1 0. 040625 3. 00 0. 04184 1 0. 037500 3. 00 0. 03863 1 0. 073019 18. 00 0. 08616 1 0. 015557 18. 00 0. 01836 2 0. 000875 0. 001750 5. 00 0. 00184 2 0. 000563 0. 001125 5. 00 0. 00118 1 0. 003566 2. 00 0. 00364 1 0. 226875 3. 00 0. 23368 1 0. 031455 18. 00 0. 03712 Breadboard 1 0. 025000 3. 00 0. 02575 M 2 Brass Standoffs L = 5 mm 4 0. 000250 0. 001000 5. 00 0. 00105 M 2 x 5 mm Screws 4 0. 000240 0. 000962 5. 00 0. 00101 M 2 Nut 4 0. 000089 0. 000357 5. 00 0. 00038 Amplifier 1 0. 003125 3. 00 0. 00322 LED Control Board 1 0. 019375 3. 00 0. 01996 Night Vision Camera Module 5 MP Flex Cable for Raspberry Pi Camera - 18" 16" Aluminum Plexiglas 3" x 1/8" Pan/Tilt Assembly M 3 x 6 mm Screws M 3 Nut Weather-stripping (8") OUTERDO Headlamp Lights LED Bracket (1/16" Aluminum) Breadboard Assembly Qua Weight Per ntity Unit (lbs) FIT/CSRR CDR 0. 78460 0. 04982 0. 82616 0. 05136 | 125
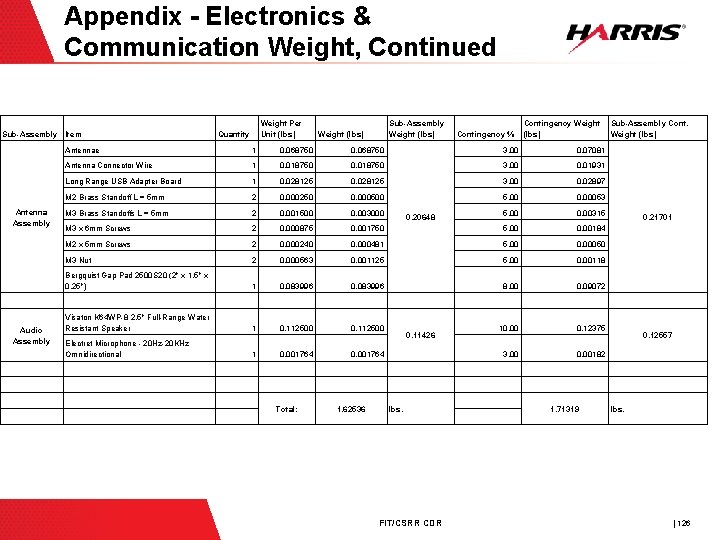
Appendix - Electronics & Communication Weight, Continued Sub-Assembly Item Antenna Assembly Audio Assembly Weight Per Unit (lbs) Quantity Sub-Assembly Weight (lbs) Contingency % Contingency Weight (lbs) Antennae 1 0. 068750 3. 00 0. 07081 Antenna Connector Wire 1 0. 018750 3. 00 0. 01931 Long Range USB Adapter Board 1 0. 028125 3. 00 0. 02897 M 2 Brass Standoff L = 5 mm 2 0. 000250 0. 000500 5. 00 0. 00053 M 3 Brass Standoffs L = 5 mm 2 0. 001500 0. 003000 5. 00 0. 00315 M 3 x 6 mm Screws 2 0. 000875 0. 001750 5. 00 0. 00184 M 2 x 5 mm Screws 2 0. 000240 0. 000481 5. 00 0. 00050 M 3 Nut 2 0. 000563 0. 001125 5. 00 0. 00118 Bergquist Gap Pad 2500 S 20 (2" x 1. 5" x 0. 25") 1 0. 083996 8. 00 0. 09072 Visaton K 64 WP-8 2. 5" Full-Range Water Resistant Speaker 1 0. 112500 10. 00 0. 12375 Electret Microphone - 20 Hz-20 KHz Omnidirectional 1 0. 001764 3. 00 0. 00182 Total: 1. 62536 0. 20648 0. 11426 lbs. FIT/CSRR CDR 1. 71319 Sub-Assembly Cont. Weight (lbs) 0. 21701 0. 12557 lbs. | 126
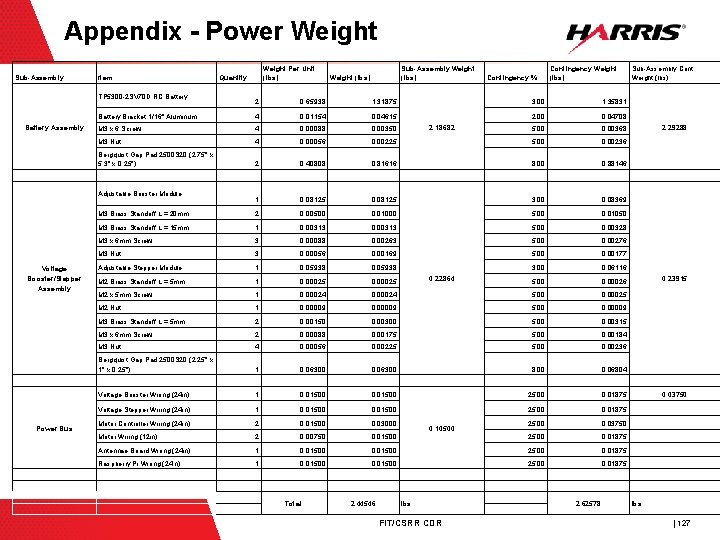
Appendix - Power Weight Sub-Assembly Item TP 5300 -2 SV 70 D RC Battery Assembly Power Bus Sub-Assembly Weight (lbs) Contingency % Contingency Weight (lbs) 2 0. 65938 1. 31875 3. 00 1. 35831 Battery Bracket 1/16" Aluminum 4 0. 01154 0. 04615 2. 00 0. 04708 M 3 x 6 Screw 4 0. 00088 0. 00350 5. 00 0. 00368 M 3 Nut 4 0. 00056 0. 00225 5. 00 0. 00236 Bergquist Gap Pad 2500 S 20 (2. 75" x 5. 3" x 0. 25") 2 0. 40808 0. 81616 8. 00 0. 88146 1 0. 08125 3. 00 0. 08369 M 3 Brass Standoff L = 20 mm 2 0. 00500 0. 01000 5. 00 0. 01050 M 3 Brass Standoff L = 15 mm 1 0. 00313 5. 00 0. 00328 M 3 x 6 mm Screw 3 0. 00088 0. 00263 5. 00 0. 00276 M 3 Nut 3 0. 00056 0. 00169 5. 00 0. 00177 Adjustable Stepper Module 1 0. 05938 3. 00 0. 06116 5. 00 0. 00026 Adjustable Booster Module Voltage Booster/Stepper Assembly Weight Per Unit (lbs) Quantity 2. 18682 0. 22864 M 2 Brass Standoff L = 5 mm 1 0. 00025 M 2 x 5 mm Screw 1 0. 00024 5. 00 0. 00025 M 2 Nut 1 0. 00009 5. 00 0. 00009 M 3 Brass Standoff L = 5 mm 2 0. 00150 0. 00300 5. 00 0. 00315 M 3 x 6 mm Screw 2 0. 00088 0. 00175 5. 00 0. 00184 M 3 Nut 4 0. 00056 0. 00225 5. 00 0. 00236 Bergquist Gap Pad 2500 S 20 (2. 25" x 1" x 0. 25") 1 0. 06300 8. 00 0. 06804 Voltage Booster Wiring (24 in) 1 0. 01500 25. 00 0. 01875 Voltage Stepper Wiring (24 in) 1 0. 01500 25. 00 0. 01875 Motor Controller Wiring (24 in) 2 0. 01500 0. 03000 25. 00 0. 03750 Motor Wiring (12 in) 2 0. 00750 0. 01500 25. 00 0. 01875 Antennae Board Wiring (24 in) 1 0. 01500 25. 00 0. 01875 Raspberry Pi Wiring (24 in) 1 0. 01500 25. 00 0. 01875 Total: 2. 44546 0. 10500 lbs. FIT/CSRR CDR 2. 62578 Sub-Assembly Cont. Weight (lbs) 2. 29288 0. 23915 0. 03750 lbs. | 127
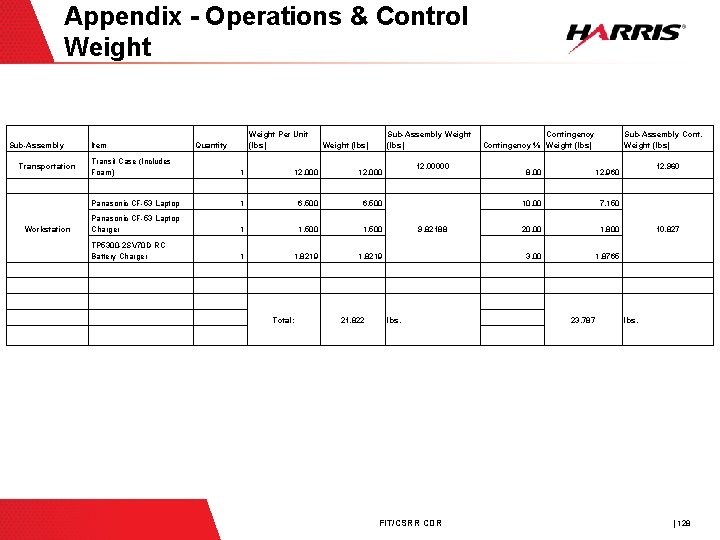
Appendix - Operations & Control Weight Sub-Assembly Transportation Workstation Item Weight Per Unit (lbs) Quantity Sub-Assembly Weight (lbs) Transit Case (Includes Foam) 1 12. 000 Panasonic CF-53 Laptop 1 6. 500 Panasonic CF-53 Laptop Charger 1 1. 500 TP 5300 -2 SV 70 D RC Battery Charger 1 1. 8219 12. 00000 9. 82188 Contingency % Weight (lbs) Sub-Assembly Cont. Weight (lbs) 8. 00 12. 960 10. 00 7. 150 20. 00 1. 800 3. 00 1. 8765 12. 960 10. 827 Total: 21. 822 lbs. FIT/CSRR CDR 23. 787 lbs. | 128
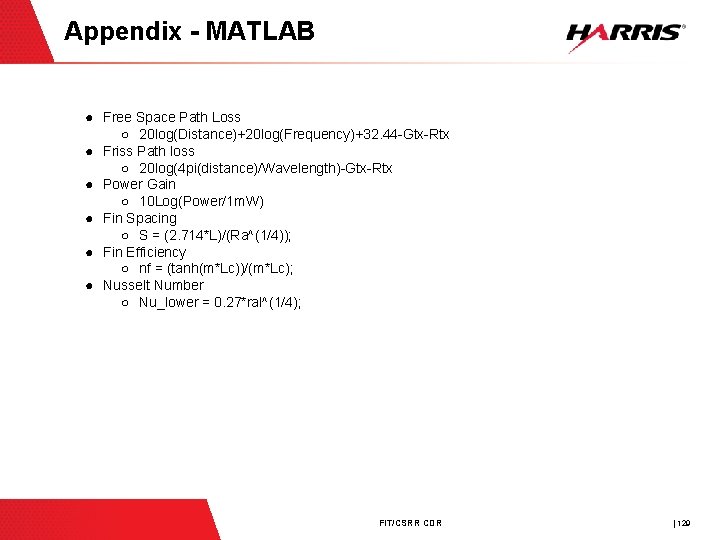
Appendix - MATLAB ● Free Space Path Loss ○ 20 log(Distance)+20 log(Frequency)+32. 44 -Gtx-Rtx ● Friss Path loss ○ 20 log(4 pi(distance)/Wavelength)-Gtx-Rtx ● Power Gain ○ 10 Log(Power/1 m. W) ● Fin Spacing ○ S = (2. 714*L)/(Ra^(1/4)); ● Fin Efficiency ○ nf = (tanh(m*Lc))/(m*Lc); ● Nusselt Number ○ Nu_lower = 0. 27*ral^(1/4); FIT/CSRR CDR | 129
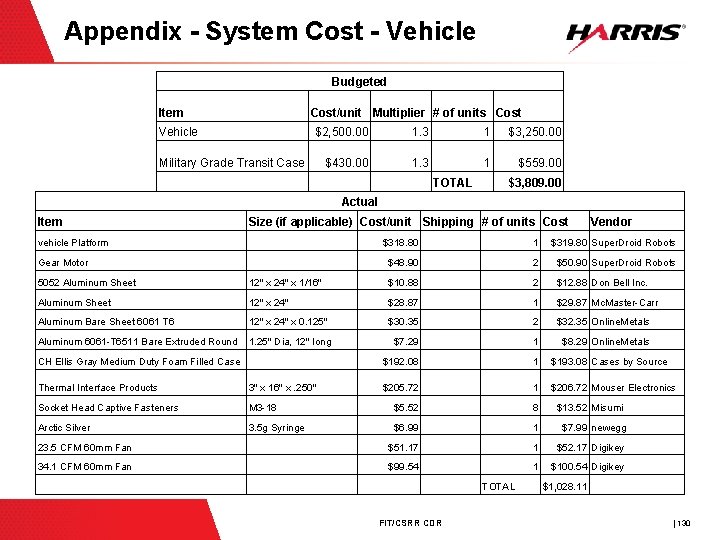
Appendix - System Cost - Vehicle Budgeted Item Cost/unit Multiplier # of units Cost Vehicle $2, 500. 00 1. 3 1 $3, 250. 00 $430. 00 1. 3 1 $559. 00 Military Grade Transit Case TOTAL $3, 809. 00 Actual Item Size (if applicable) Cost/unit Shipping # of units Cost vehicle Platform Gear Motor Vendor $318. 80 1 $319. 80 Super. Droid Robots $48. 90 2 $50. 90 Super. Droid Robots 5052 Aluminum Sheet 12" x 24" x 1/16" $10. 88 2 $12. 88 Don Bell Inc. Aluminum Sheet 12" x 24" $28. 87 1 $29. 87 Mc. Master-Carr Aluminum Bare Sheet 6061 T 6 12" x 24" x 0. 125" $30. 35 2 $32. 35 Online. Metals Aluminum 6061 -T 6511 Bare Extruded Round 1. 25" Dia, 12" long $7. 29 1 $8. 29 Online. Metals $192. 08 1 $193. 08 Cases by Source $205. 72 1 $206. 72 Mouser Electronics CH Ellis Gray Medium Duty Foam Filled Case Thermal Interface Products 3" x 16" x. 250" Socket Head Captive Fasteners M 3 -18 $5. 52 8 Arctic Silver 3. 5 g Syringe $6. 99 1 $7. 99 newegg 23. 5 CFM 60 mm Fan $51. 17 1 $52. 17 Digikey 34. 1 CFM 60 mm Fan $99. 54 1 $100. 54 Digikey TOTAL FIT/CSRR CDR $13. 52 Misumi $1, 028. 11 | 130
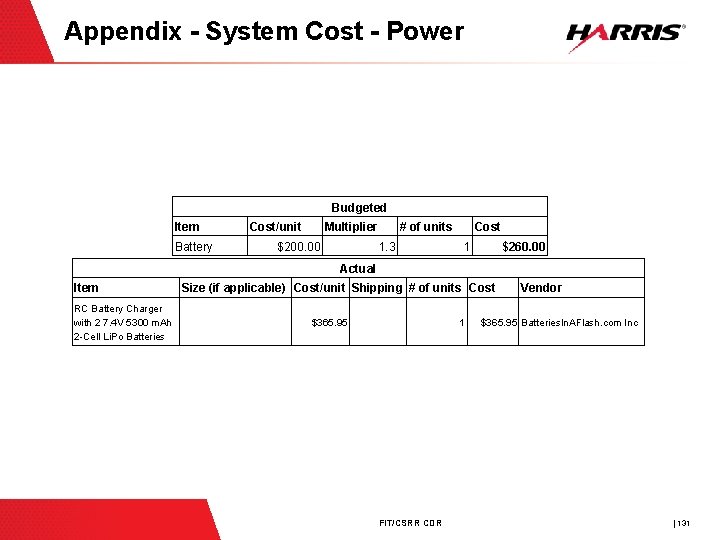
Appendix - System Cost - Power Budgeted Item Battery Cost/unit Multiplier $200. 00 # of units 1. 3 Cost 1 $260. 00 Actual Item RC Battery Charger with 2 7. 4 V 5300 m. Ah 2 -Cell Li. Po Batteries Size (if applicable) Cost/unit Shipping # of units Cost $365. 95 1 FIT/CSRR CDR Vendor $365. 95 Batteries. In. AFlash. com Inc | 131
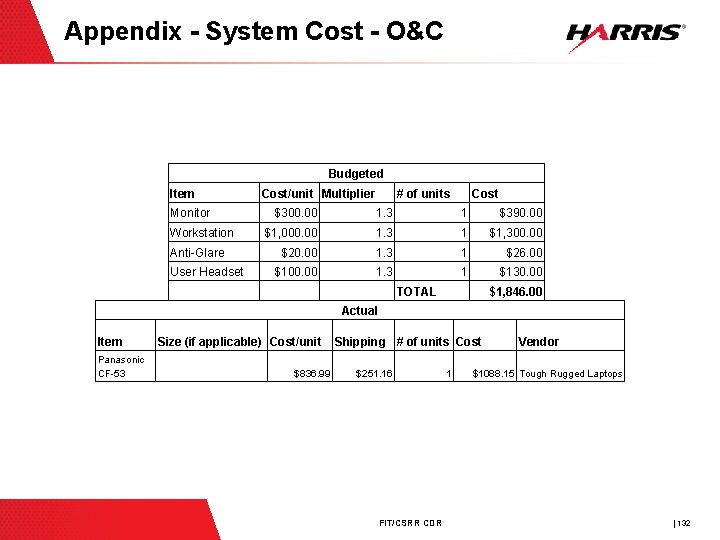
Appendix - System Cost - O&C Budgeted Item Monitor Workstation Anti-Glare User Headset Cost/unit Multiplier # of units Cost $300. 00 1. 3 1 $390. 00 $1, 000. 00 1. 3 1 $1, 300. 00 $20. 00 1. 3 1 $26. 00 $100. 00 1. 3 1 $130. 00 TOTAL $1, 846. 00 Actual Item Panasonic CF-53 Size (if applicable) Cost/unit $836. 99 Shipping # of units Cost $251. 16 FIT/CSRR CDR 1 Vendor $1088. 15 Tough Rugged Laptops | 132
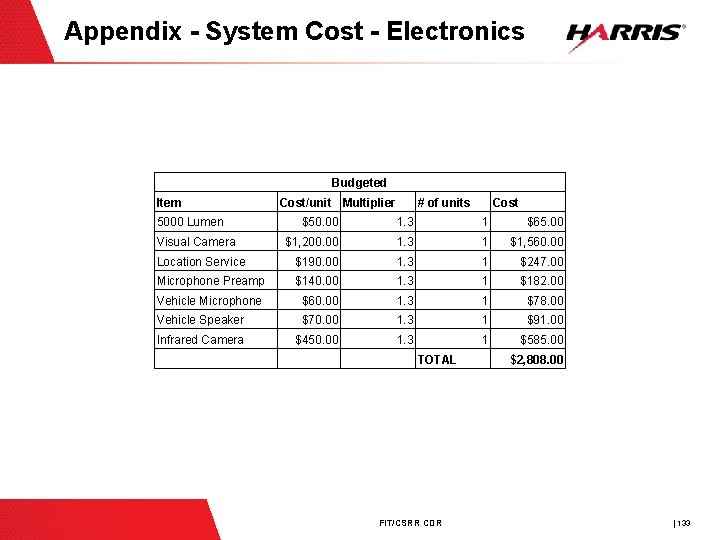
Appendix - System Cost - Electronics Budgeted Item 5000 Lumen Cost/unit Multiplier # of units Cost $50. 00 1. 3 1 $65. 00 $1, 200. 00 1. 3 1 $1, 560. 00 Location Service $190. 00 1. 3 1 $247. 00 Microphone Preamp $140. 00 1. 3 1 $182. 00 Vehicle Microphone $60. 00 1. 3 1 $78. 00 Vehicle Speaker $70. 00 1. 3 1 $91. 00 Infrared Camera $450. 00 1. 3 1 $585. 00 Visual Camera TOTAL FIT/CSRR CDR $2, 808. 00 | 133
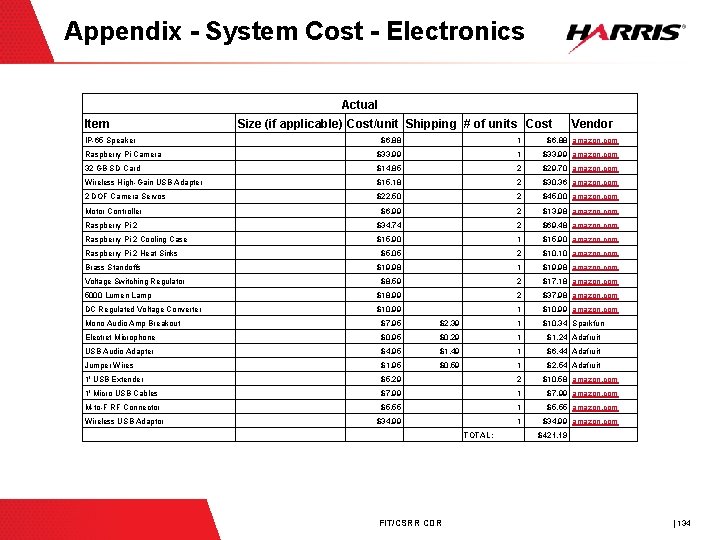
Appendix - System Cost - Electronics Actual Item IP-65 Speaker Size (if applicable) Cost/unit Shipping # of units Cost Vendor $6. 88 1 $6. 88 amazon. com Raspberry Pi Camera $33. 99 1 $33. 99 amazon. com 32 GB SD Card $14. 85 2 $29. 70 amazon. com Wireless High-Gain USB Adapter $15. 18 2 $30. 36 amazon. com 2 DOF Camera Servos $22. 50 2 $45. 00 amazon. com Motor Controller $6. 99 2 $13. 98 amazon. com Raspberry Pi 2 $34. 74 2 $69. 48 amazon. com Raspberry Pi 2 Cooling Case $15. 90 1 $15. 90 amazon. com $5. 05 2 $10. 10 amazon. com $19. 98 1 $19. 98 amazon. com $8. 59 2 $17. 18 amazon. com 5000 Lumen Lamp $18. 99 2 $37. 98 amazon. com DC Regulated Voltage Converter $10. 99 1 $10. 99 amazon. com Raspberry Pi 2 Heat Sinks Brass Standoffs Voltage Switching Regulator Mono Audio Amp Breakout $7. 95 $2. 39 1 $10. 34 Sparkfun Electret Microphone $0. 95 $0. 29 1 $1. 24 Adafruit USB Audio Adapter $4. 95 $1. 49 1 $6. 44 Adafruit Jumper Wires $1. 95 $0. 59 1 $2. 54 Adafruit 1' USB Extender $5. 29 2 $10. 58 amazon. com 1' Micro USB Cables $7. 99 1 $7. 99 amazon. com M-to-F RF Connector $5. 55 1 $5. 55 amazon. com Wireless USB Adaptor $34. 99 1 TOTAL: FIT/CSRR CDR $34. 99 amazon. com $421. 19 | 134
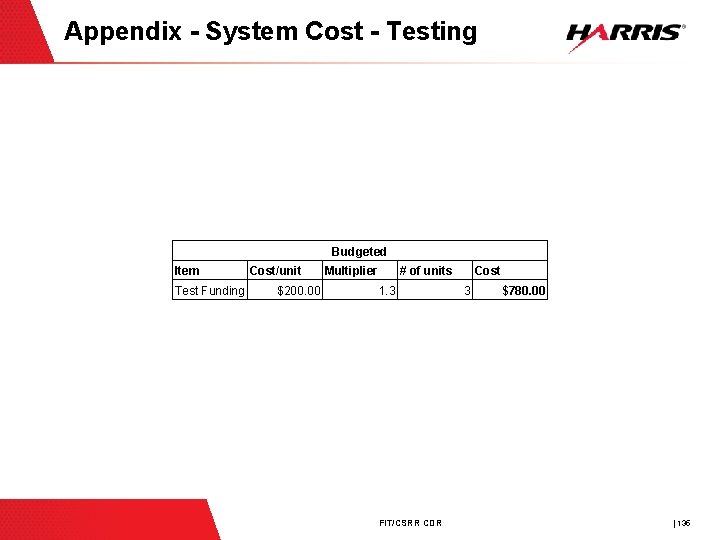
Appendix - System Cost - Testing Budgeted Item Test Funding Cost/unit $200. 00 Multiplier # of units 1. 3 FIT/CSRR CDR Cost 3 $780. 00 | 135
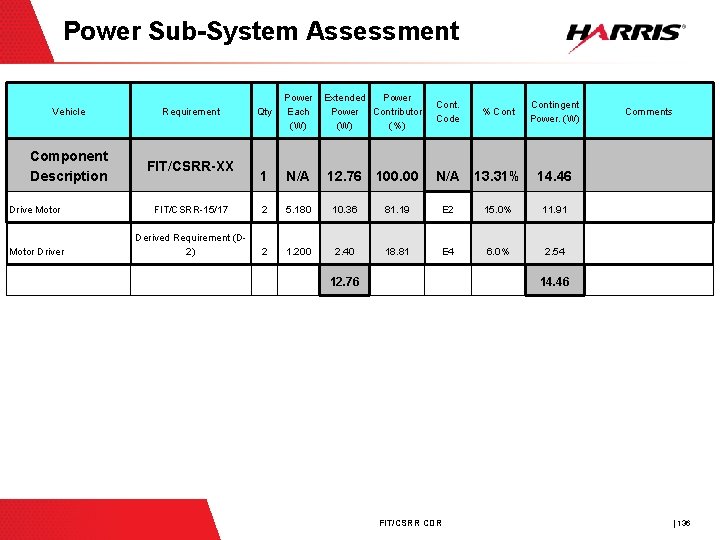
Power Sub-System Assessment Vehicle Requirement Component Description FIT/CSRR-XX Power Extended Power Each Power Contributor (W) (%) Cont. Code % Contingent Power. (W) 1 N/A 13. 31% 14. 46 Qty 12. 76 100. 00 Drive Motor FIT/CSRR-15/17 2 5. 180 10. 36 81. 19 E 2 15. 0% 11. 91 Motor Driver Derived Requirement (D 2) 2 1. 200 2. 40 18. 81 E 4 6. 0% 2. 54 12. 76 Comments 14. 46 FIT/CSRR CDR | 136
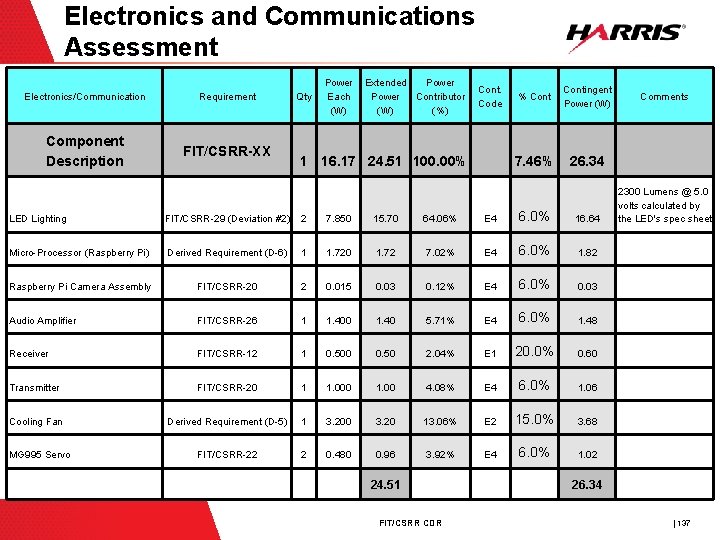
Electronics and Communications Assessment Electronics/Communication Requirement Component Description FIT/CSRR-XX Qty Power Extended Power Each Power Contributor (W) (%) Cont. Code 1 16. 17 24. 51 100. 00% % Contingent Power (W) 7. 46% 26. 34 LED Lighting FIT/CSRR-29 (Deviation #2) 2 7. 850 15. 70 64. 06% E 4 6. 0% 16. 64 Micro-Processor (Raspberry Pi) Derived Requirement (D-6) 1 1. 720 1. 72 7. 02% E 4 6. 0% 1. 82 Raspberry Pi Camera Assembly FIT/CSRR-20 2 0. 015 0. 03 0. 12% E 4 6. 0% 0. 03 Audio Amplifier FIT/CSRR-26 1 1. 400 1. 40 5. 71% E 4 6. 0% 1. 48 Receiver FIT/CSRR-12 1 0. 500 0. 50 2. 04% E 1 20. 0% 0. 60 Transmitter FIT/CSRR-20 1 1. 000 1. 00 4. 08% E 4 6. 0% 1. 06 Cooling Fan Derived Requirement (D-5) 1 3. 200 3. 20 13. 06% E 2 15. 0% 3. 68 FIT/CSRR-22 2 0. 480 0. 96 3. 92% E 4 6. 0% 1. 02 MG 995 Servo 24. 51 FIT/CSRR CDR Comments 2300 Lumens @ 5. 0 volts calculated by the LED's spec sheet 26. 34 | 137
Critical design review
Cdr critical design review
Critical semi critical and non critical instruments
Semi-critical
Critical design review
Critical design review template
Critical design review
Critical design review
Pdr cdr project management
Pdr cdr project management
Net population growth formula
Delta cdr
Cdr
Cdr
Cdr vs cdrw
Cdr analysis in excel
Cdr winkel
Front end schedule
Broad areas of corporate restructuring
Radiology
Cdr rental
Ketan computers cdr analysis
Cdr
Program cdr
Alok mohan
International arctic buoy program
Asset classification norms
Cdr websams
Dr maureen padden
Slidetodoc.com
Www.kent.k12.wa.us frequently used links
Florida us history eoc review
Calc institute of technology
Vidhyadeep institute of engineering and technology
Waterford institute of technology vacancies
Ulsan national institute of science and technology
National assistive technology research institute
Masdar institute of science and technology
Madhav institute of technology and science
Saio grenoble
Gastechnology
De lin institute of technology
Dbs institute of technology
Materials technology institute
Bms institute of technology & management
Vocational education uae
Courseweb.sliit.lk
Sagar institute of research and technology
Prajnanananda institute of technology & management
National institute of standards and technology
Monohakobi technology institute
Schorarly
Netherland maritime institute of technology
Stevens institute of technology
Reel to reel institute
Kth royal institute of technology notable alumni
Indian institute of space science and technology
Brno institute of technology
Mutiyanganaya
Shri dadaji institute of technology and science
Prof ram meghe institute of technology and research
Monohakobi technology institute
Mandava institute of engineering and technology
Illinois institute of technology toefl requirement
Swami vivekanand institute of technology and management
Fromme423
Swiss federal institute of technology
Itg gopeshwar
Saigon institute for techniques & technology
Hong kong institute for data science
Dublin institute of technology college of business
National institute of agricultural technology
Industrial technology research institute
Corporate institute of science and technology bhopal
Addis ababa university institute of technology
Poam examples
Performance review institute
Startup institute review
Performance review institute
Introductory performance review
Ucl critical review
The critical literature review chapter 4
Whats a good review to write
Statistik inferensial menurut para ahli
Computer technology review
Columbia science and technology law review
Chapter review motion part a vocabulary review answer key
Ap gov review final exam review
Narrative review vs systematic review
What is inclusion and exclusion criteria
Narrative review vs systematic review
Y5zone singapore
Safety critical design
Sample design and technology gcse examination paper answers
Sample design and technology gcse examination paper answers
Sample design and technology gcse examination paper answers
Types of forces in technology
Moscow state university of design and technology
Design technology gcse coursework examples
Learning through design and technology
Eduqas product design a level
Design and technology tools
The technology design process
Sample design and technology gcse examination paper answers
Principles of educational technology
Industrial technology design
Why is product analysis useful to a designer
Design technology in embedded system
Aqa design and technology past papers
What is sustainability in design and technology
Design technology a level
Nuffield aesthetics singapore
Design technology
Radio frequency design and technology
Design and technology
Digital technologies victorian curriculum
Gcse design and technology coursework examples 2019
Bubble matching digital logic
Preliminary design review example
Formal design review
Gmp design review
Billy blue college of design reviews
Formal design review
Design review example
Principles of hair design chapter 14
Interim design review
Lna
5 welding symbols
Fea study
Cable installation design review
Ebay website design review
Design review presentation
Social impact statement for early design review
Pdr preliminary design review
Preliminary design review example
Conceptual design review template
Design review report
Conceptual design review