Stevens Institute of Technology Mechanical Engineering Dept Senior
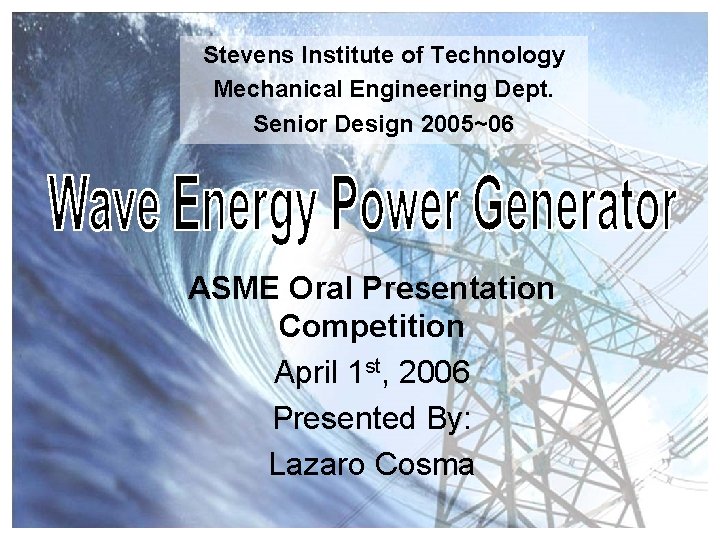
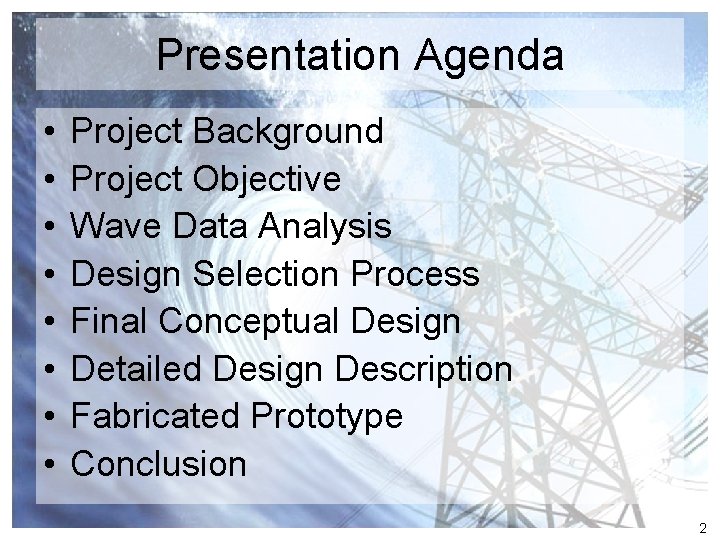
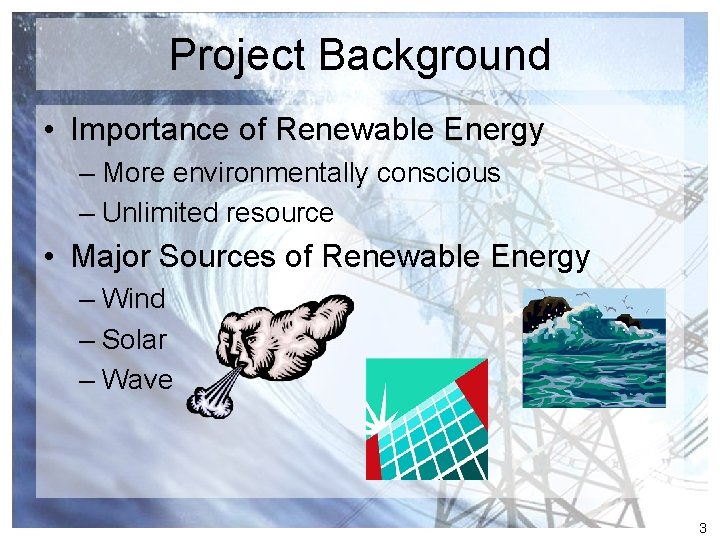
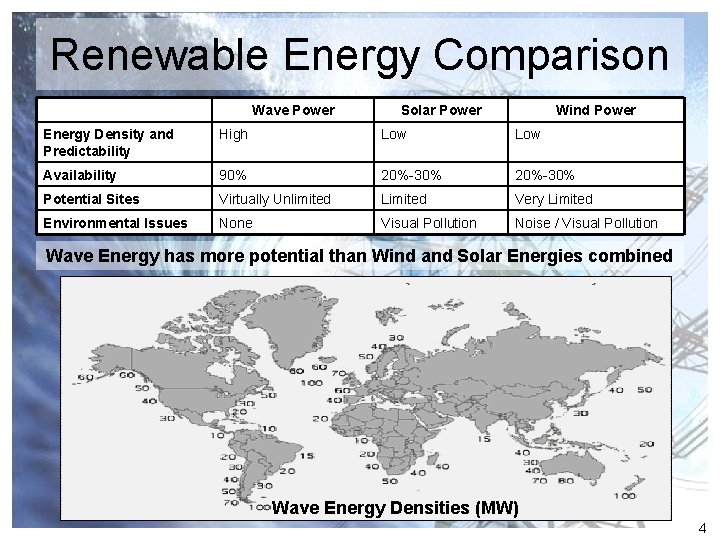
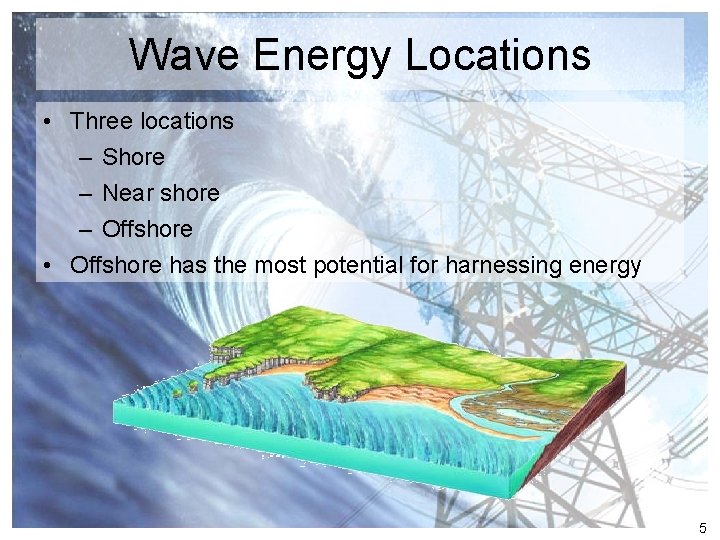
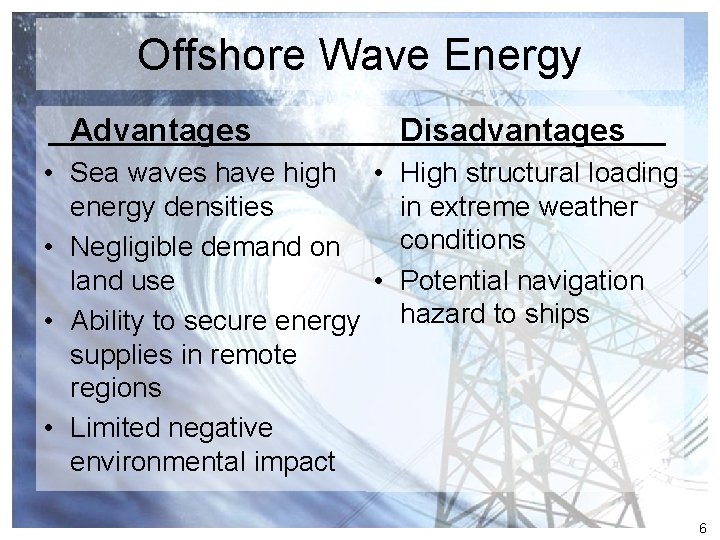
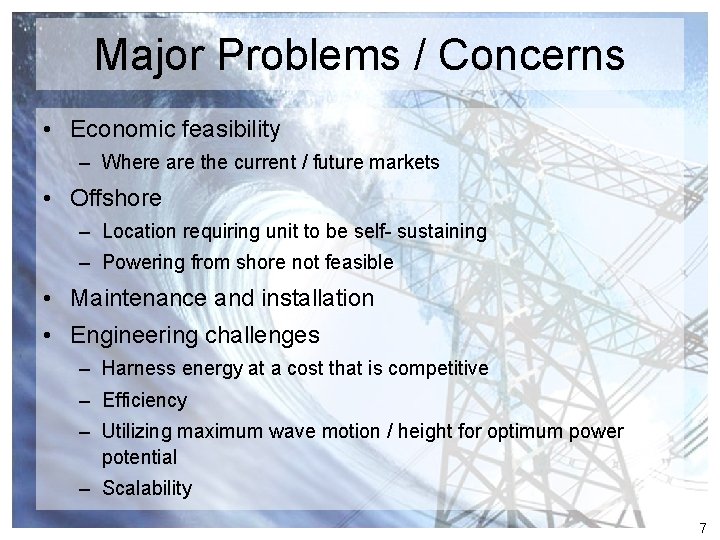
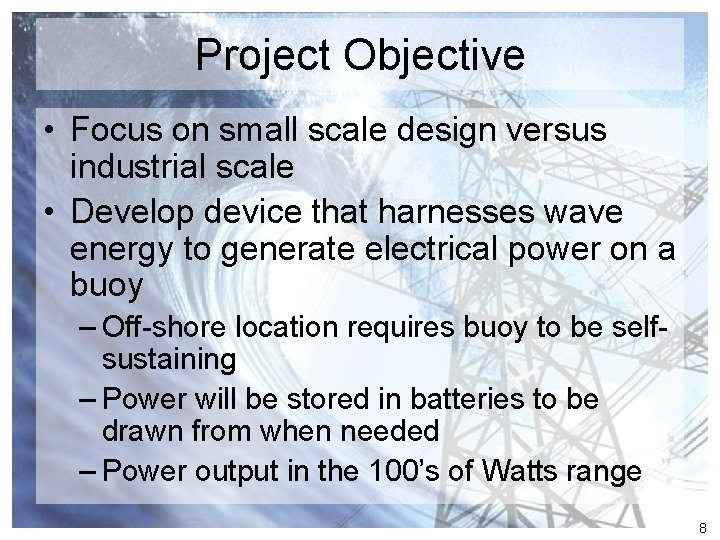
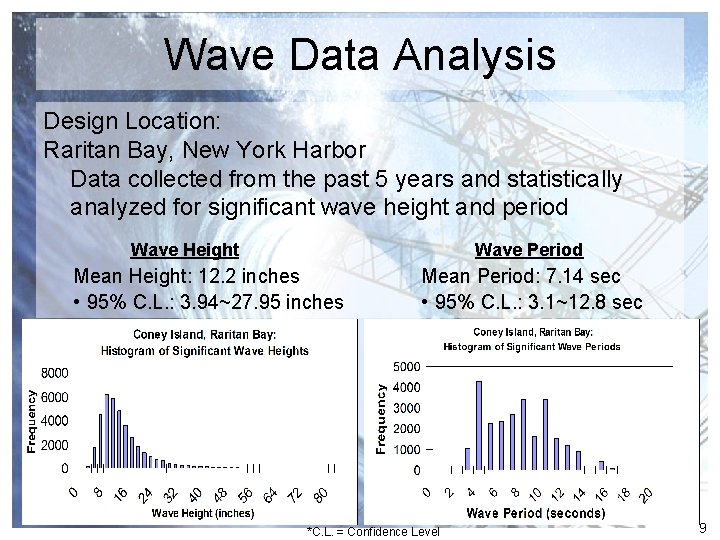
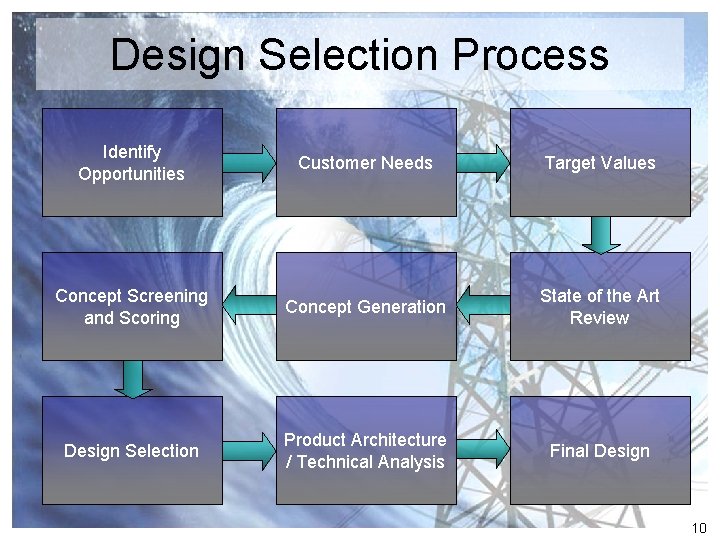
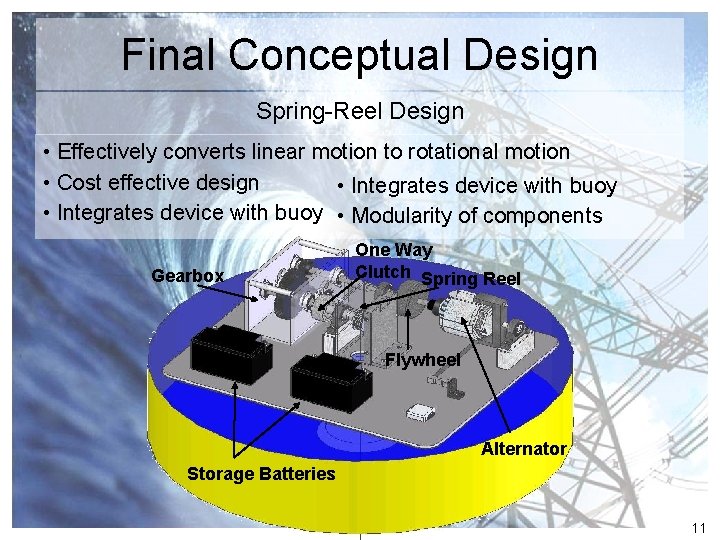
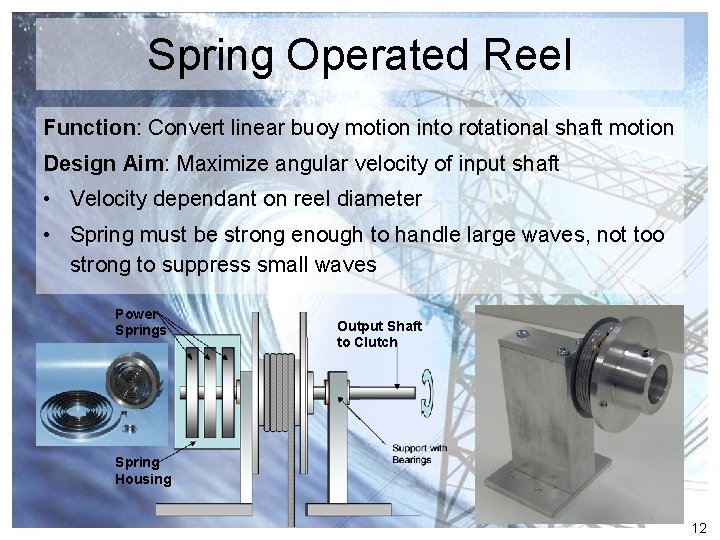
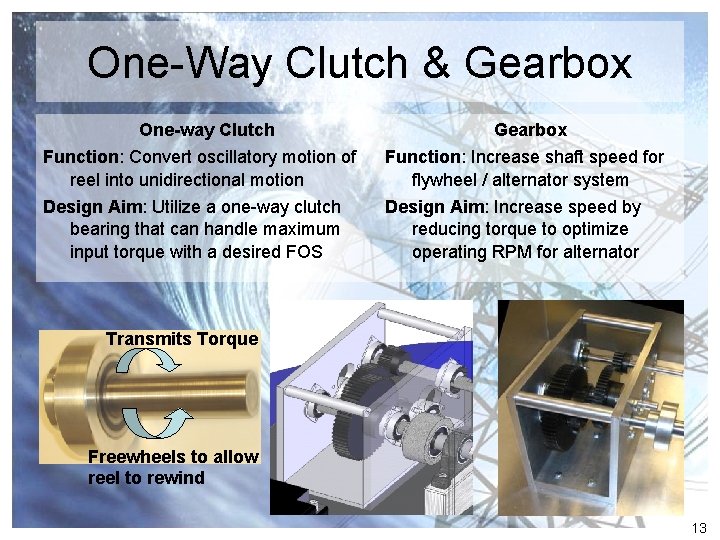
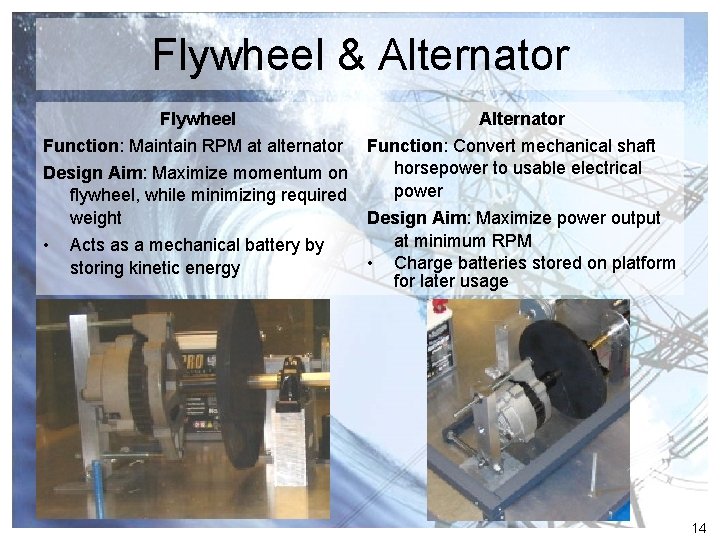
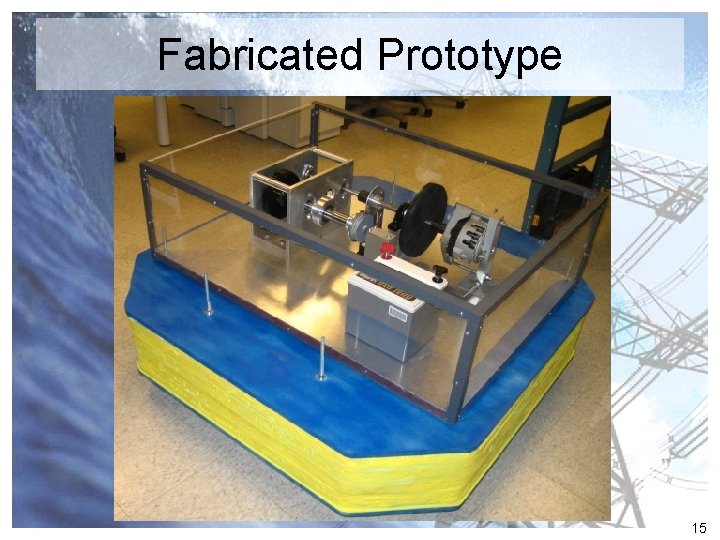
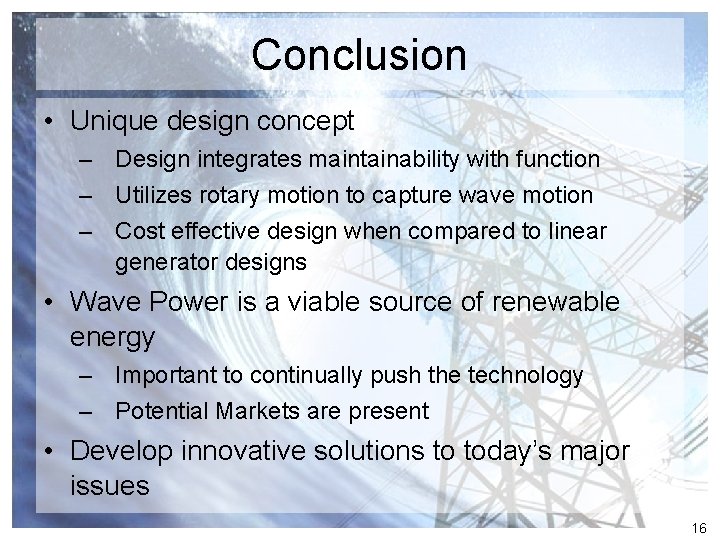
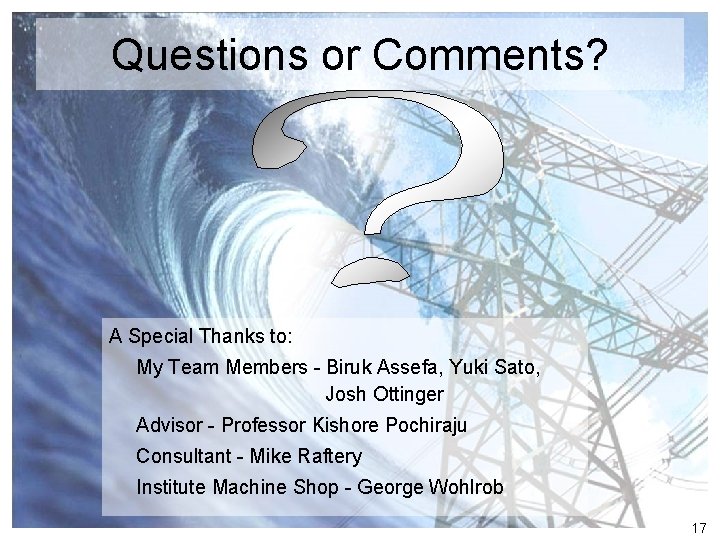
- Slides: 17
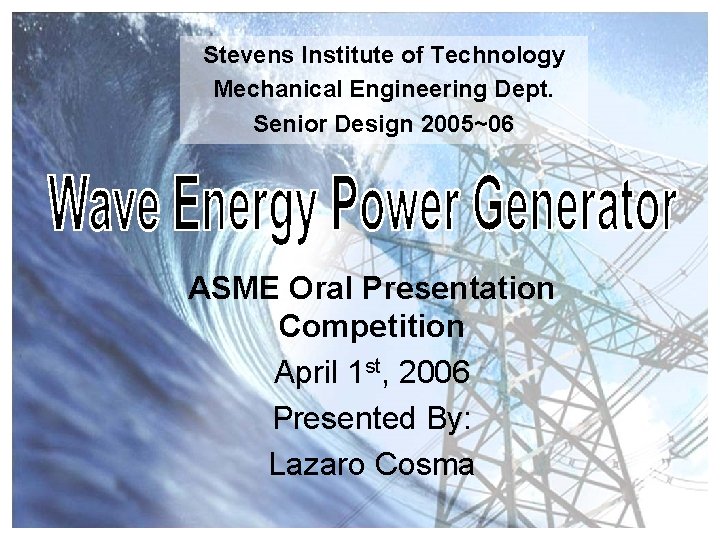
Stevens Institute of Technology Mechanical Engineering Dept. Senior Design 2005~06 ASME Oral Presentation Competition April 1 st, 2006 Presented By: Lazaro Cosma
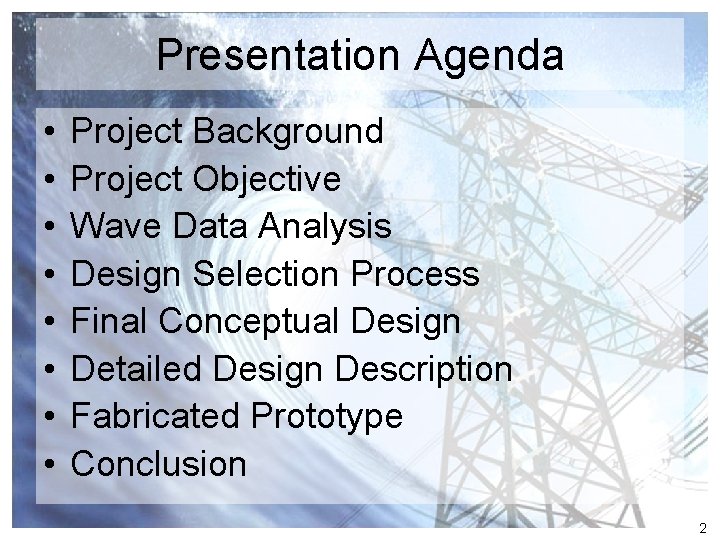
Presentation Agenda • • Project Background Project Objective Wave Data Analysis Design Selection Process Final Conceptual Design Detailed Design Description Fabricated Prototype Conclusion 2
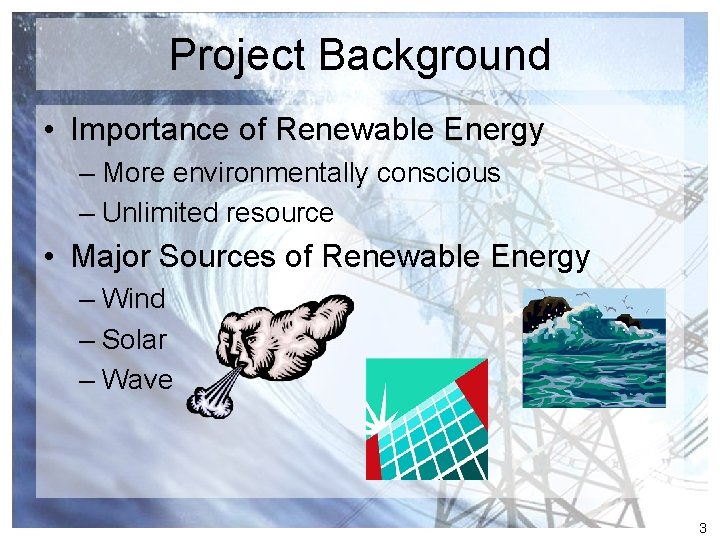
Project Background • Importance of Renewable Energy – More environmentally conscious – Unlimited resource • Major Sources of Renewable Energy – Wind – Solar – Wave 3
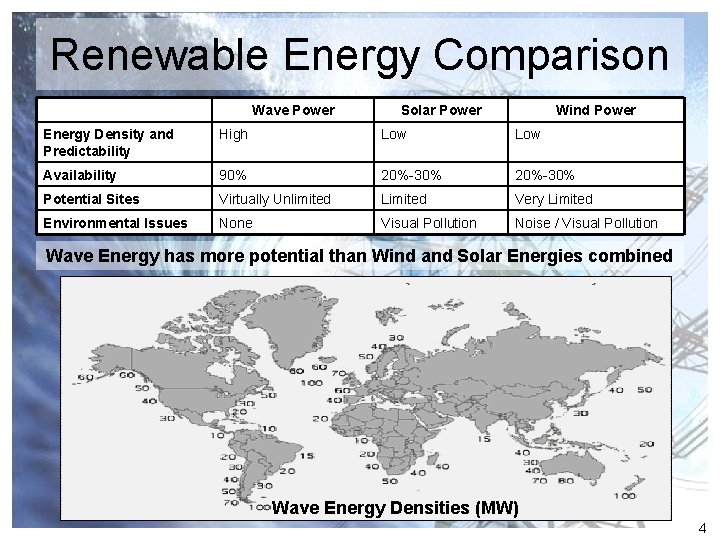
Renewable Energy Comparison Wave Power Solar Power Wind Power Energy Density and Predictability High Low Availability 90% 20%-30% Potential Sites Virtually Unlimited Limited Very Limited Environmental Issues None Visual Pollution Noise / Visual Pollution Wave Energy has more potential than Wind and Solar Energies combined Wave Energy Densities (MW) 4
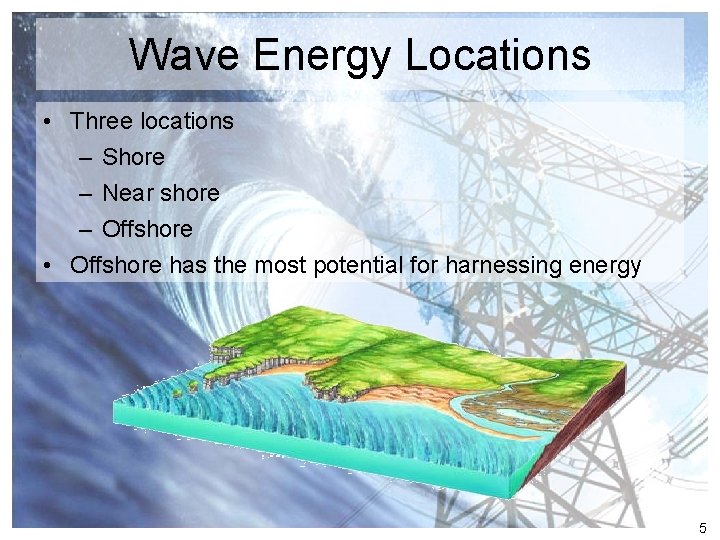
Wave Energy Locations • Three locations – Shore – Near shore – Offshore • Offshore has the most potential for harnessing energy 5
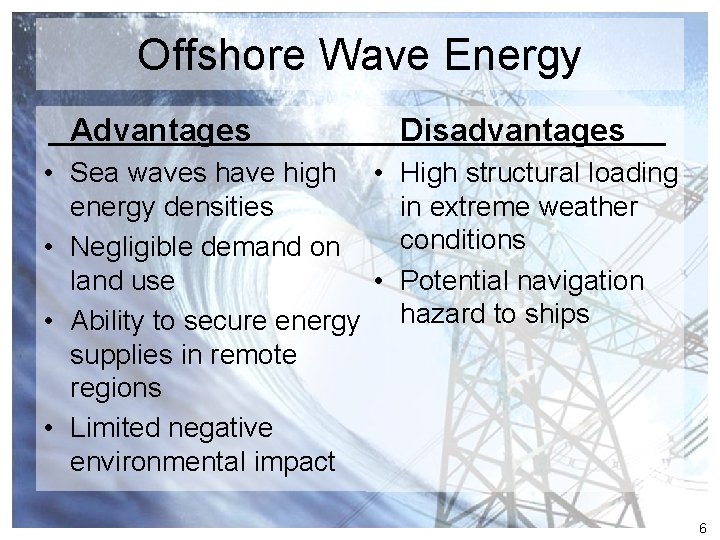
Offshore Wave Energy Advantages Disadvantages • Sea waves have high • High structural loading energy densities in extreme weather conditions • Negligible demand on land use • Potential navigation • Ability to secure energy hazard to ships supplies in remote regions • Limited negative environmental impact 6
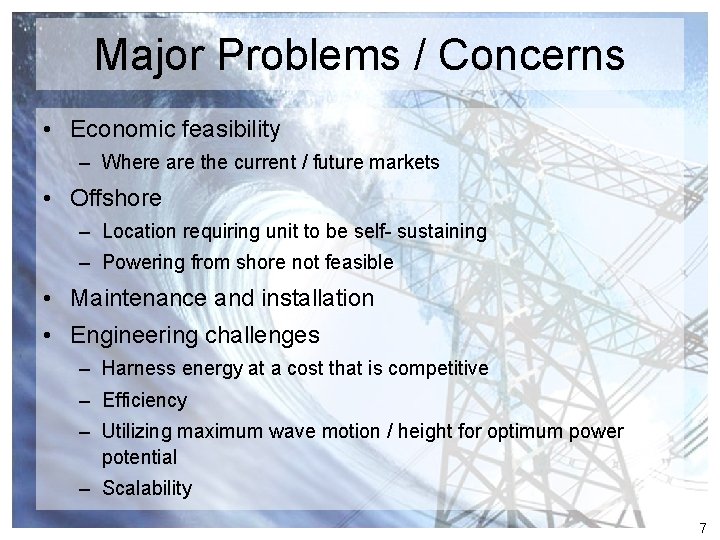
Major Problems / Concerns • Economic feasibility – Where are the current / future markets • Offshore – Location requiring unit to be self- sustaining – Powering from shore not feasible • Maintenance and installation • Engineering challenges – Harness energy at a cost that is competitive – Efficiency – Utilizing maximum wave motion / height for optimum power potential – Scalability 7
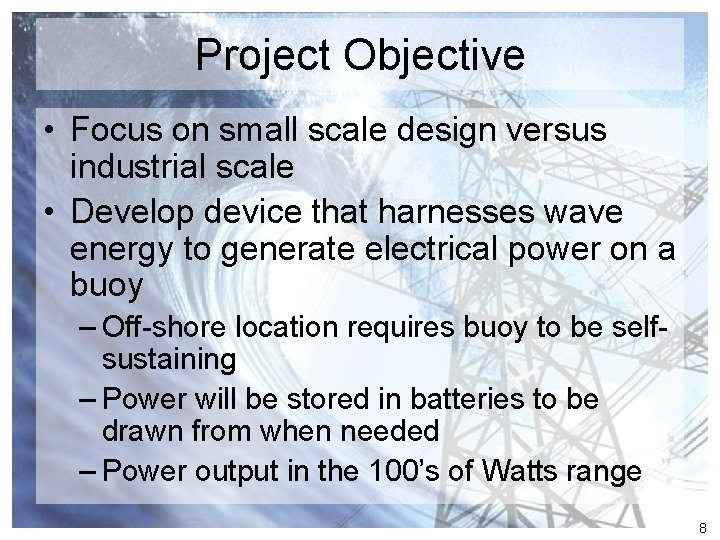
Project Objective • Focus on small scale design versus industrial scale • Develop device that harnesses wave energy to generate electrical power on a buoy – Off-shore location requires buoy to be selfsustaining – Power will be stored in batteries to be drawn from when needed – Power output in the 100’s of Watts range 8
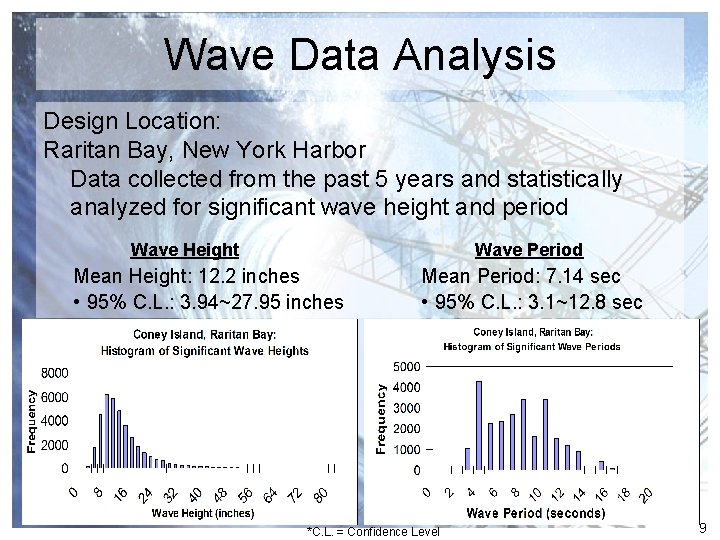
Wave Data Analysis Design Location: Raritan Bay, New York Harbor Data collected from the past 5 years and statistically analyzed for significant wave height and period Wave Height Wave Period Mean Height: 12. 2 inches • 95% C. L. : 3. 94~27. 95 inches Mean Period: 7. 14 sec • 95% C. L. : 3. 1~12. 8 sec *C. L. = Confidence Level 9
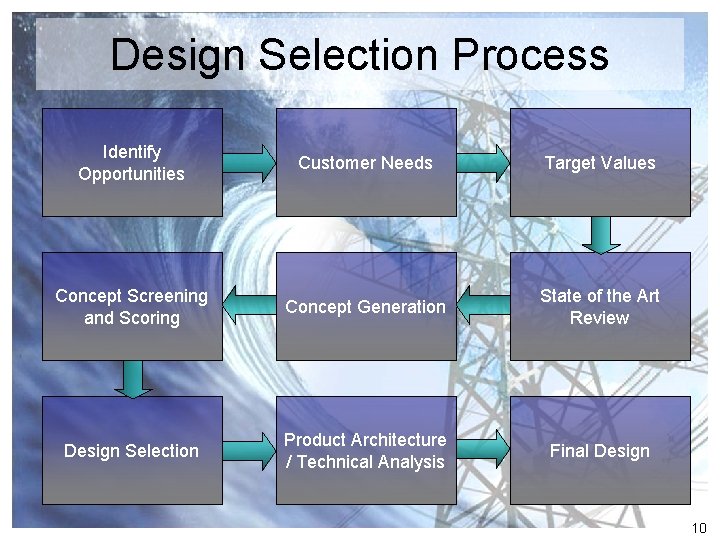
Design Selection Process Identify Opportunities Customer Needs Target Values Concept Screening and Scoring Concept Generation State of the Art Review Design Selection Product Architecture / Technical Analysis Final Design 10
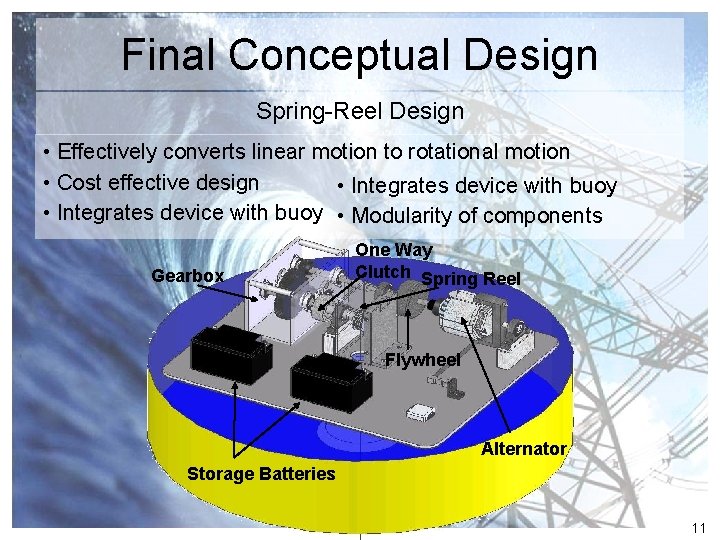
Final Conceptual Design Spring-Reel Design • Effectively converts linear motion to rotational motion • Cost effective design • Integrates device with buoy • Modularity of components Gearbox One Way Clutch Spring Reel Flywheel Alternator Storage Batteries 11
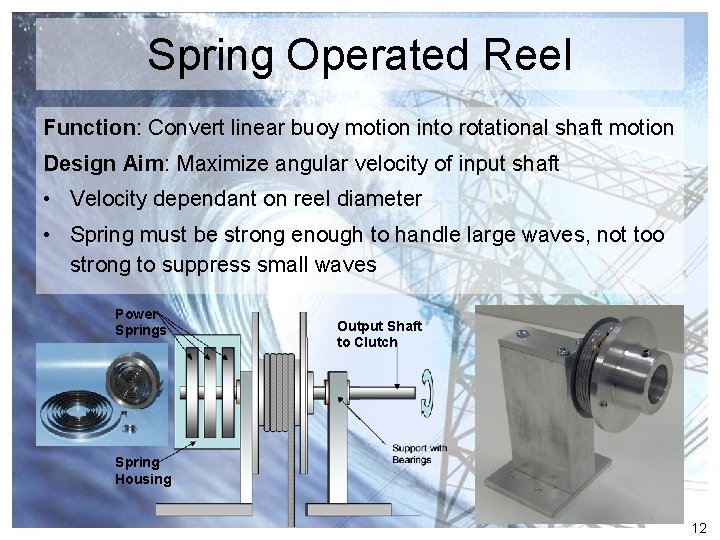
Spring Operated Reel Function: Convert linear buoy motion into rotational shaft motion Design Aim: Maximize angular velocity of input shaft • Velocity dependant on reel diameter • Spring must be strong enough to handle large waves, not too strong to suppress small waves Power Springs Output Shaft to Clutch Spring Housing 12
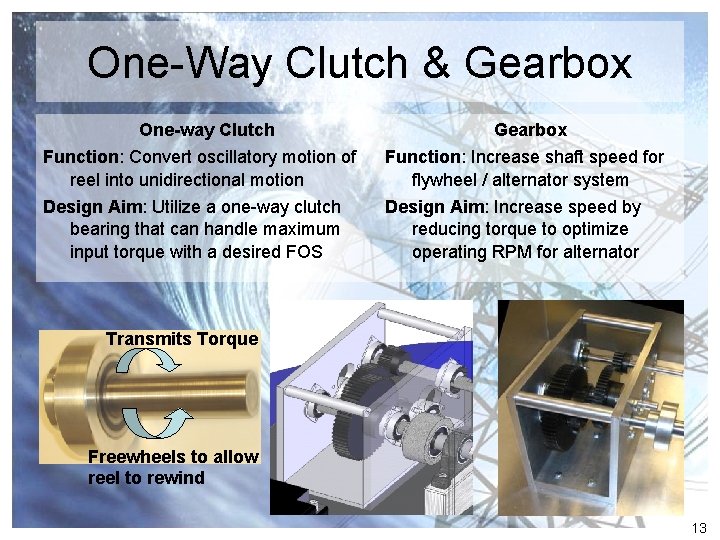
One-Way Clutch & Gearbox One-way Clutch Function: Convert oscillatory motion of reel into unidirectional motion Design Aim: Utilize a one-way clutch bearing that can handle maximum input torque with a desired FOS Gearbox Function: Increase shaft speed for flywheel / alternator system Design Aim: Increase speed by reducing torque to optimize operating RPM for alternator Transmits Torque Freewheels to allow reel to rewind 13
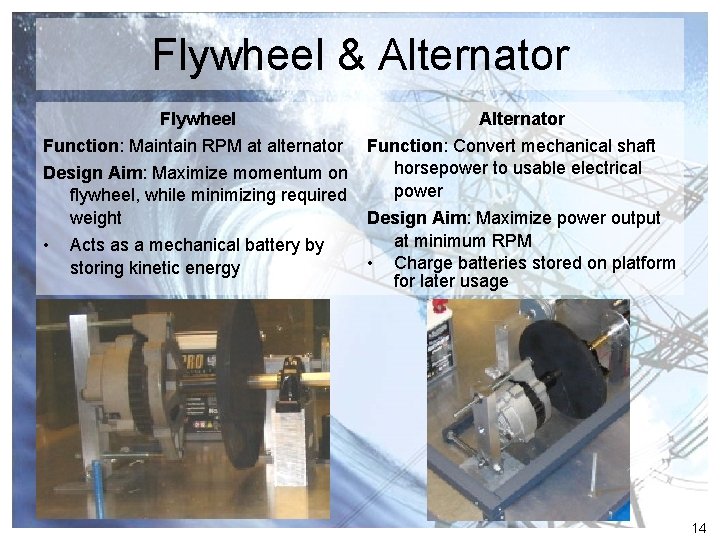
Flywheel & Alternator Flywheel Function: Maintain RPM at alternator Design Aim: Maximize momentum on flywheel, while minimizing required weight • Acts as a mechanical battery by storing kinetic energy Alternator Function: Convert mechanical shaft horsepower to usable electrical power Design Aim: Maximize power output at minimum RPM • Charge batteries stored on platform for later usage 14
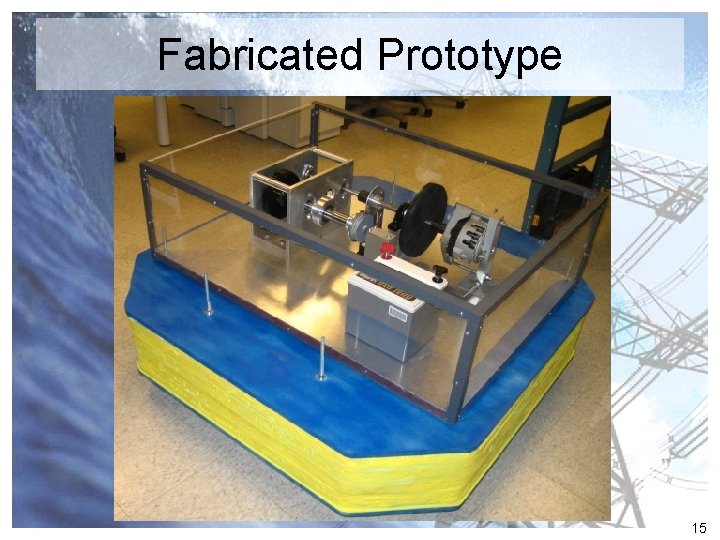
Fabricated Prototype 15
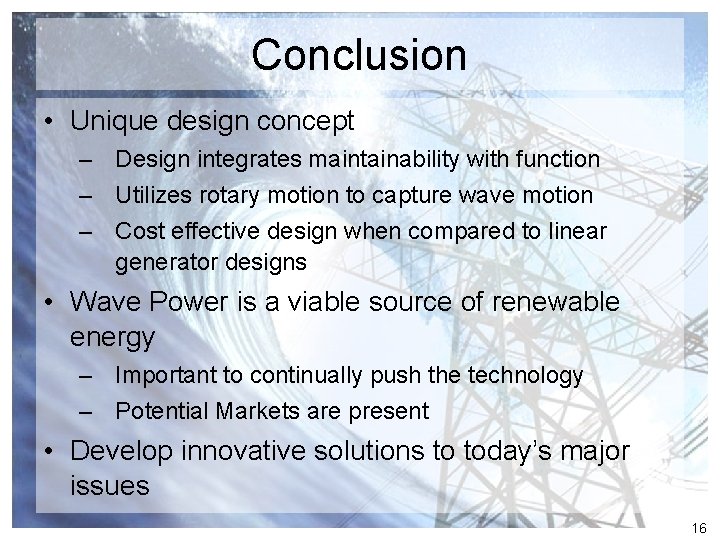
Conclusion • Unique design concept – Design integrates maintainability with function – Utilizes rotary motion to capture wave motion – Cost effective design when compared to linear generator designs • Wave Power is a viable source of renewable energy – Important to continually push the technology – Potential Markets are present • Develop innovative solutions to today’s major issues 16
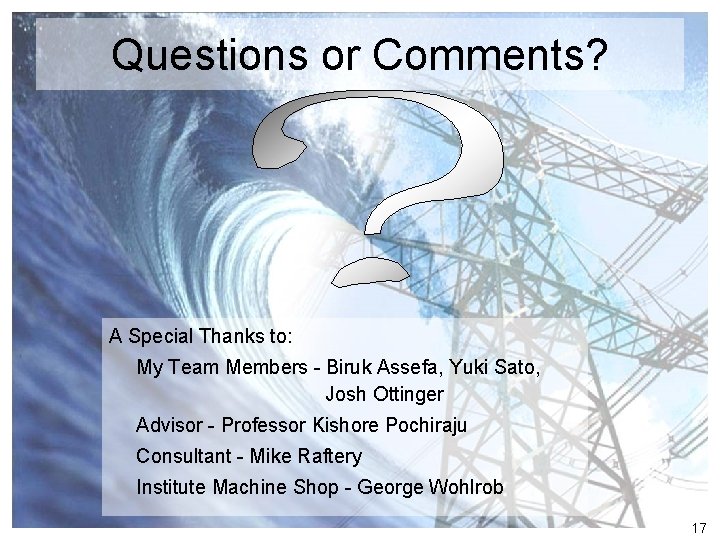
Questions or Comments? A Special Thanks to: My Team Members - Biruk Assefa, Yuki Sato, Josh Ottinger Advisor - Professor Kishore Pochiraju Consultant - Mike Raftery Institute Machine Shop - George Wohlrob 17
Reel to reel institute
Stevens institute of technology mechanical engineering
Stevens institute of technology
Marybeth murphy stevens institute
Vidhyadeep institute of engineering and technology
Mandava institute of engineering and technology
Actual mechanical advantage vs ideal mechanical advantage
Usc innovation
Lyrics to peace train by cat stevens
Lake stevens high school pool
Cs 541 stevens
Smart and stevens cohabitation
Bryn stevens
Smart and stevens cohabitation
Evelyn stevens marianismo
Liesbet stevens echtgenoot
Han haitjema
Jubilee resources freemasonry