Coupled EMThermalStructural ANSYS Simulation of the FETS 4
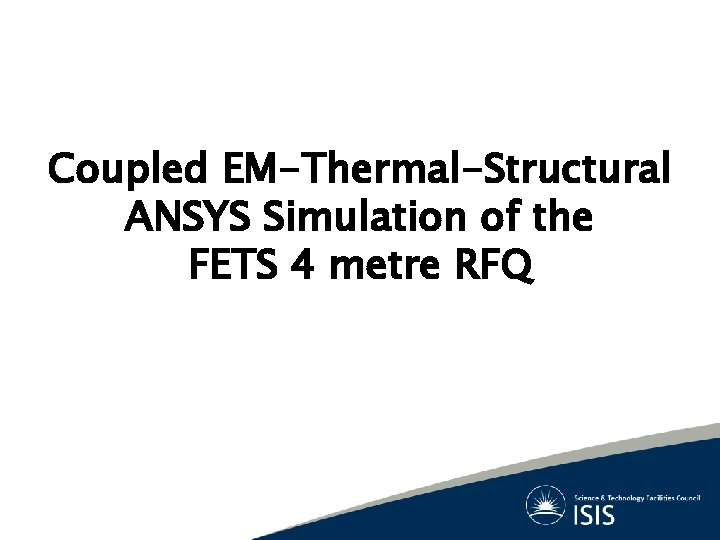
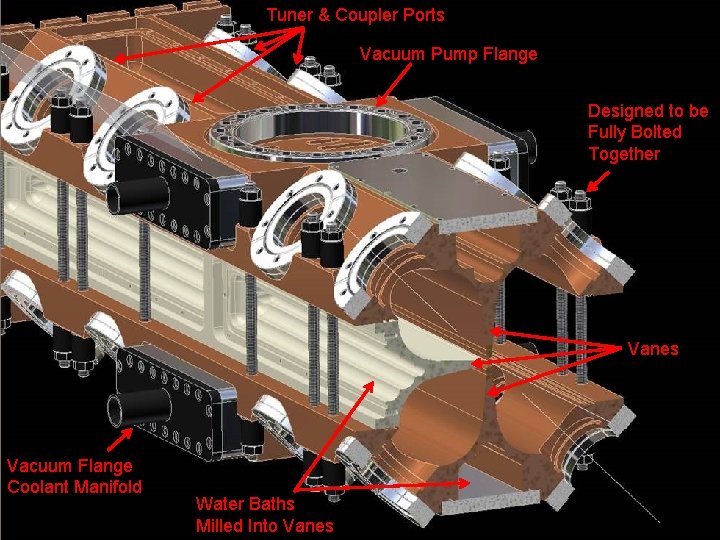
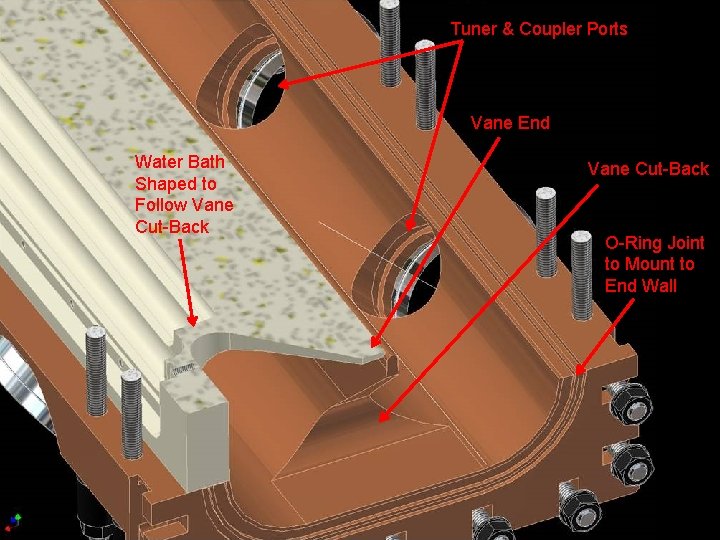
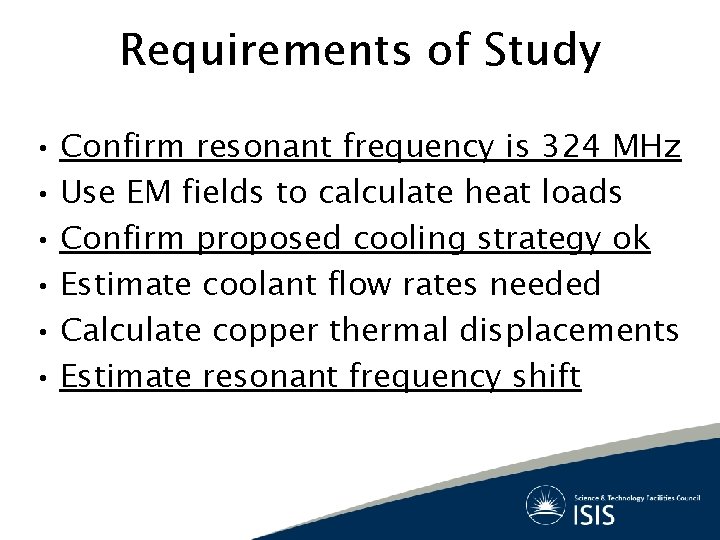
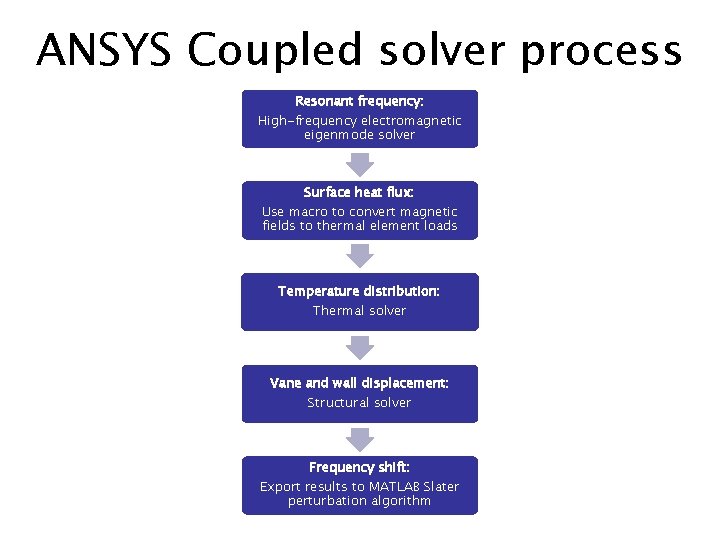
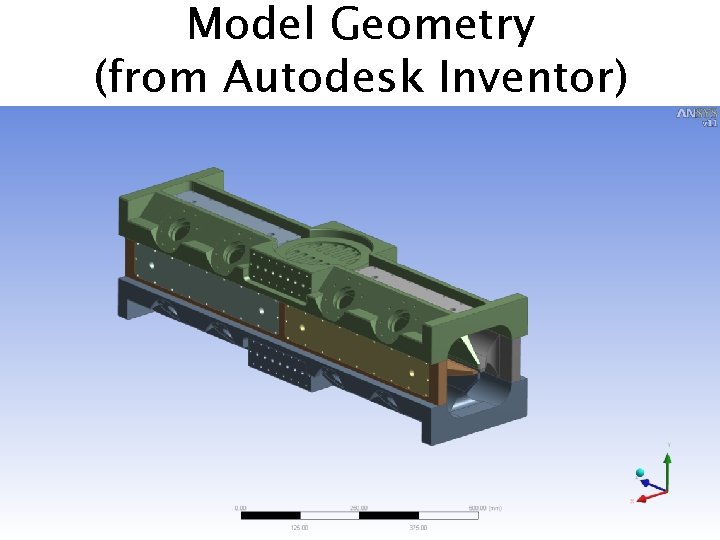
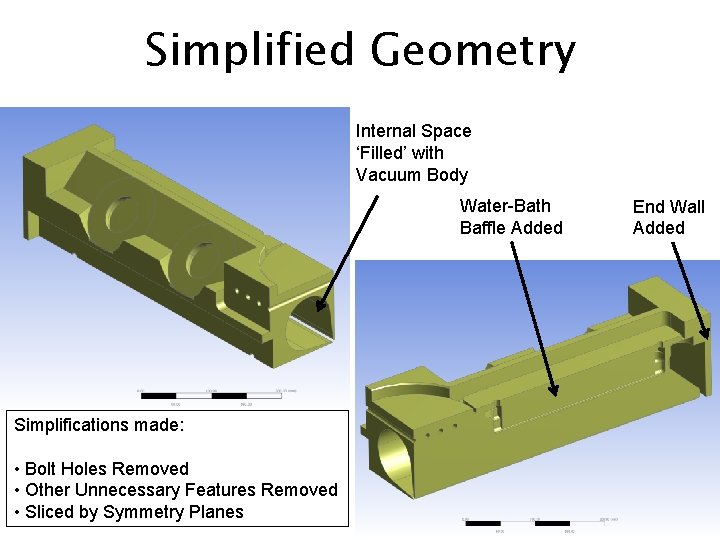
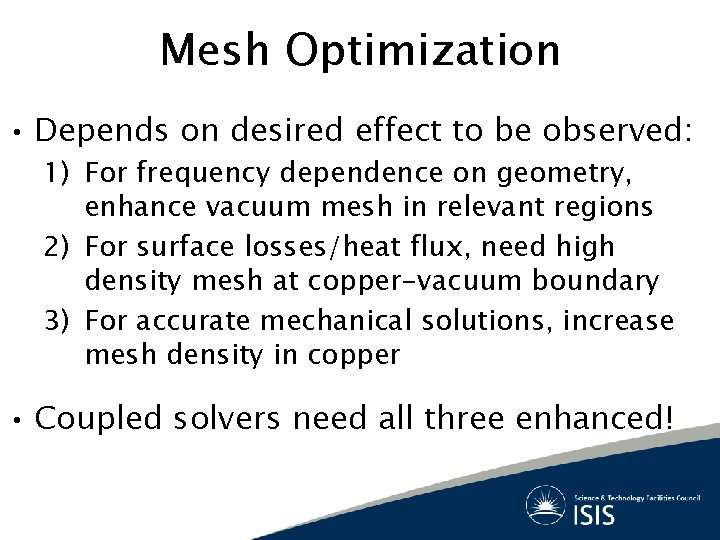
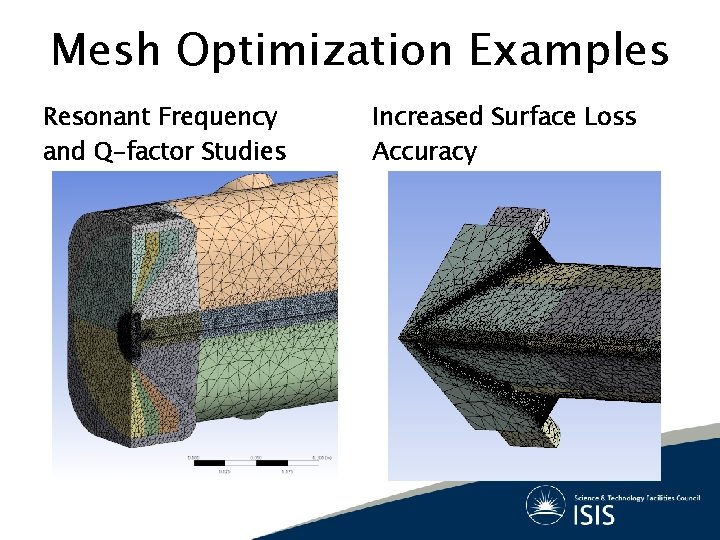
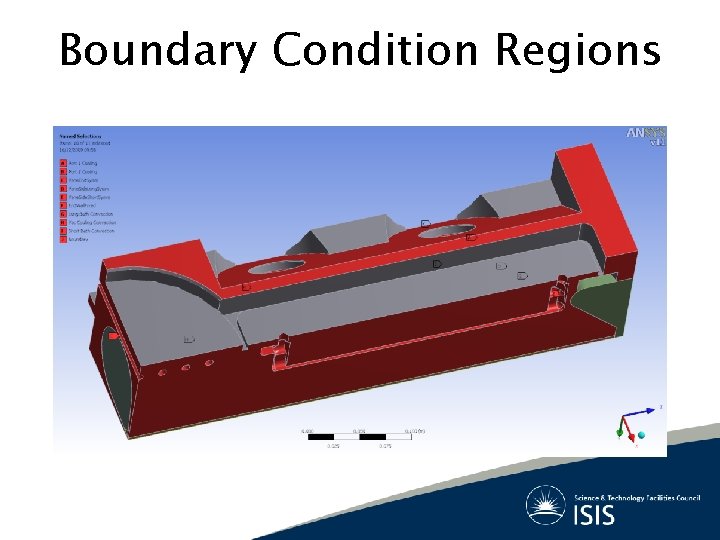
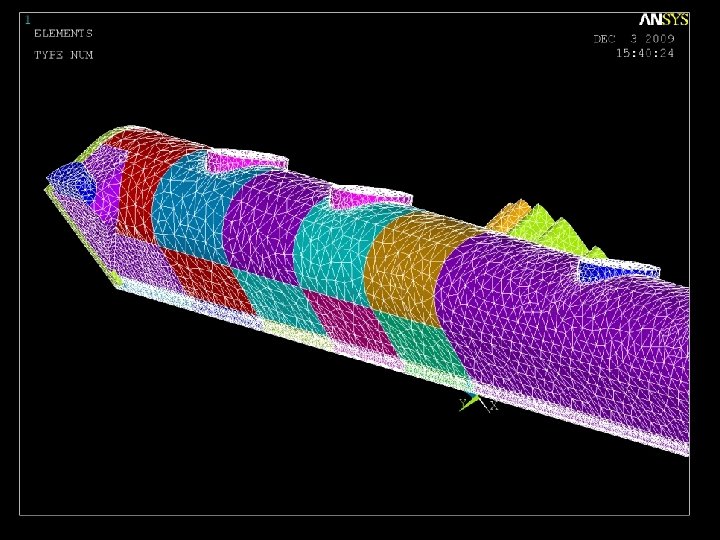
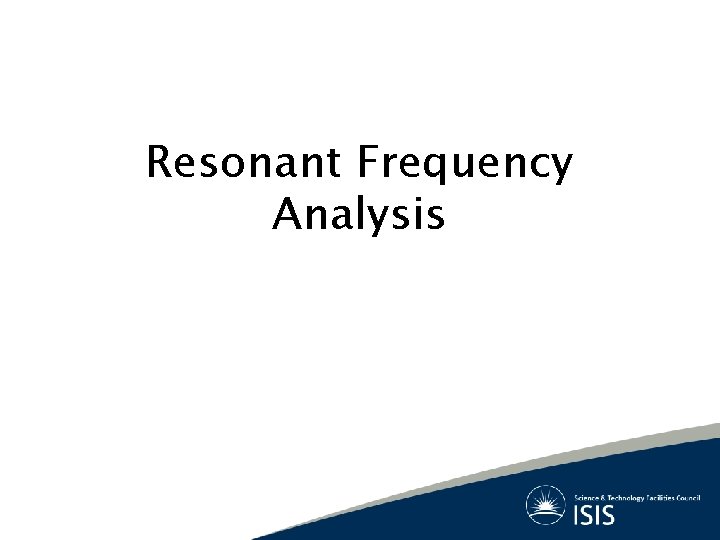
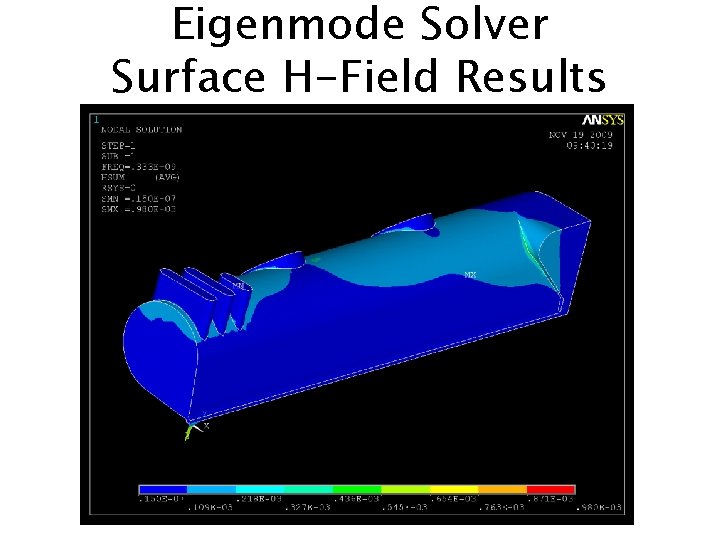
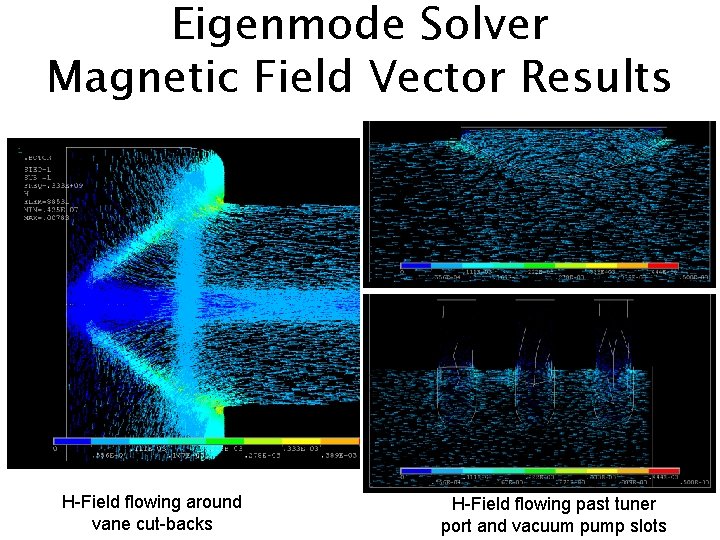
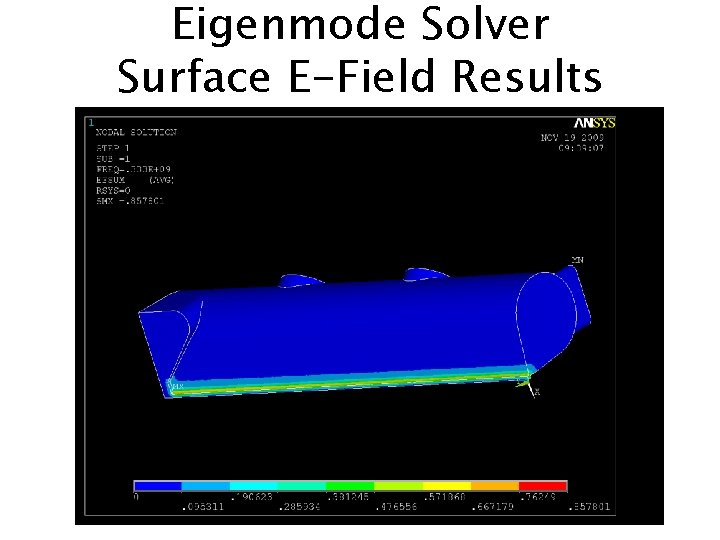
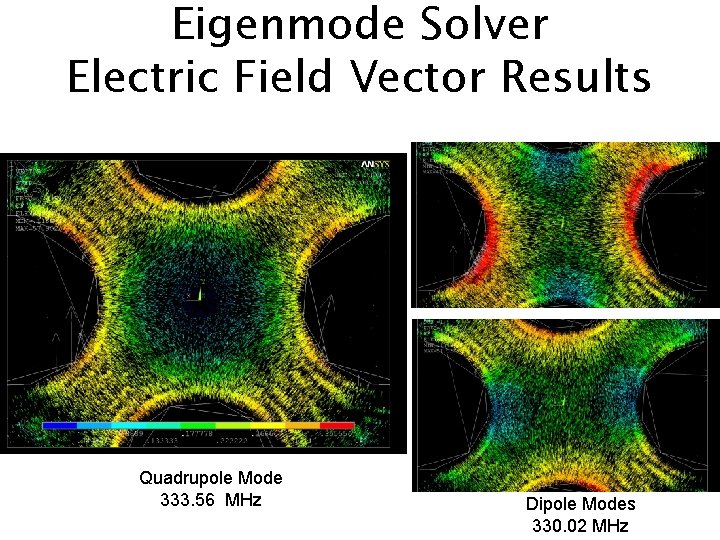
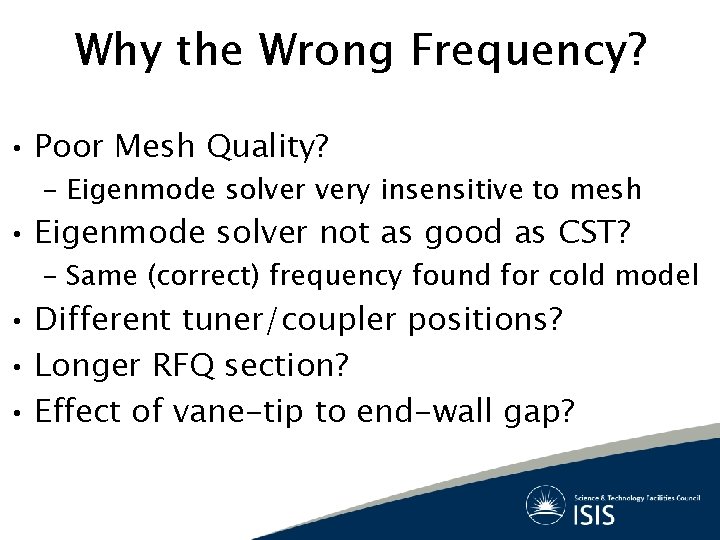
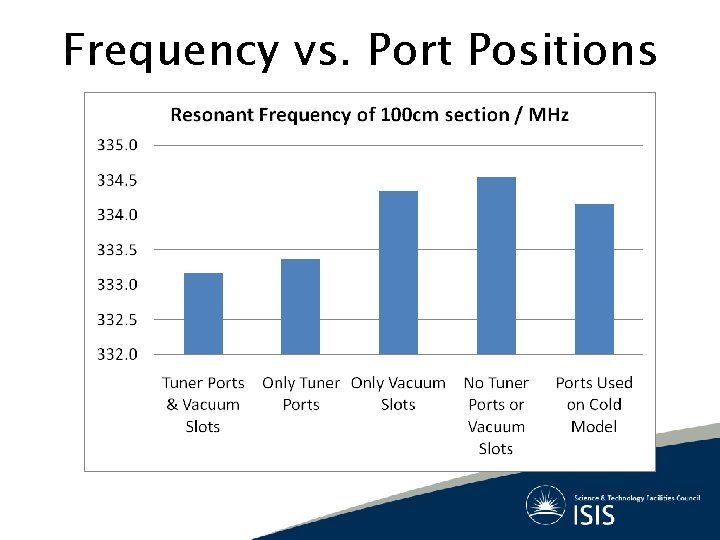
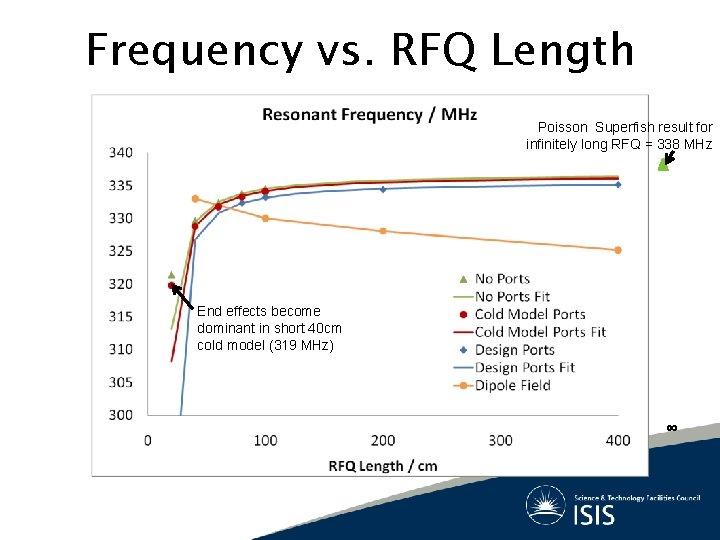
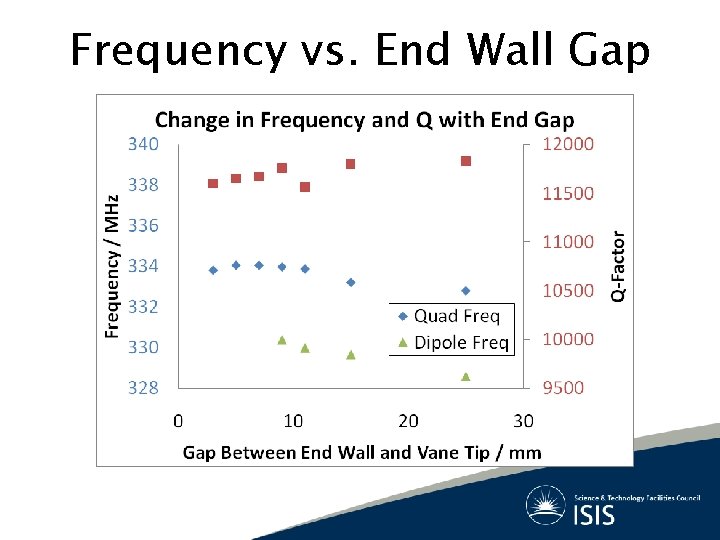
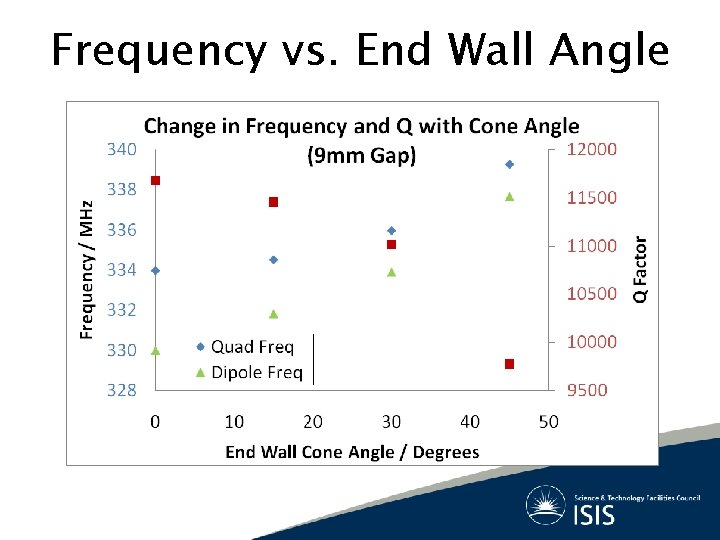
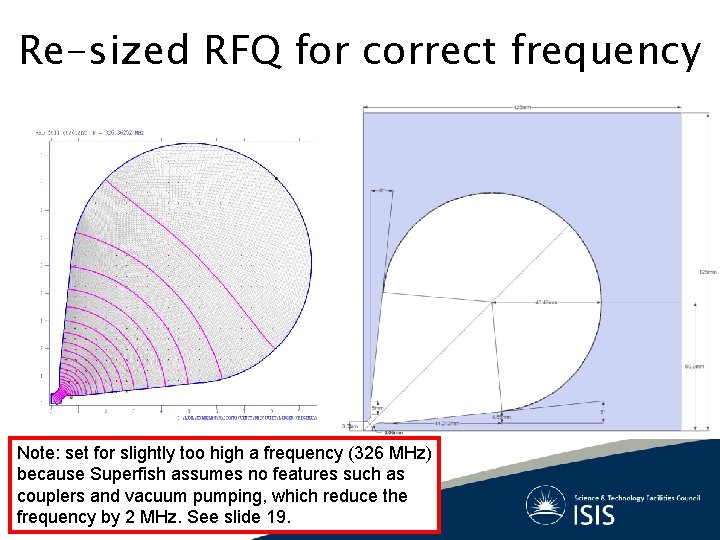
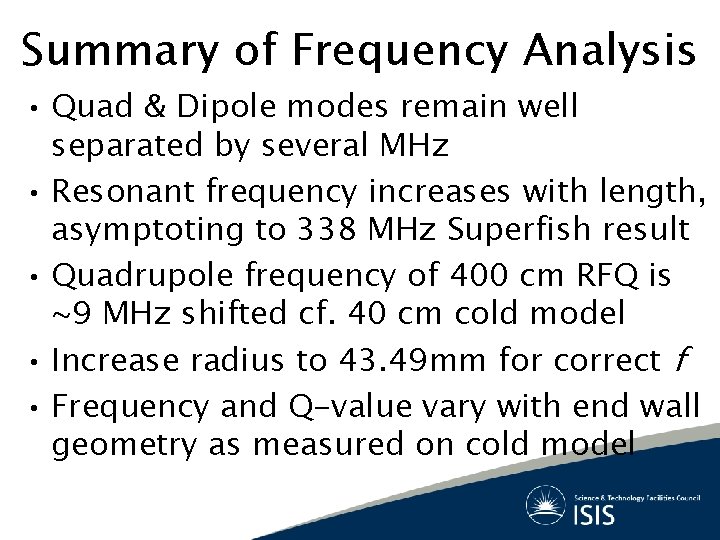
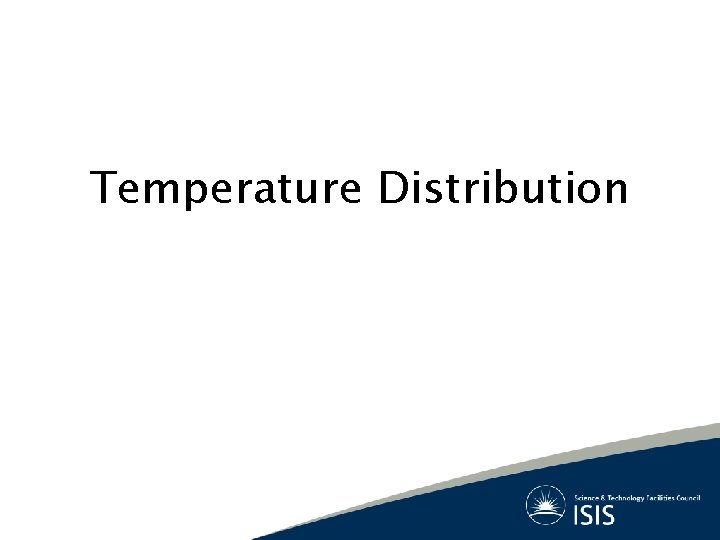
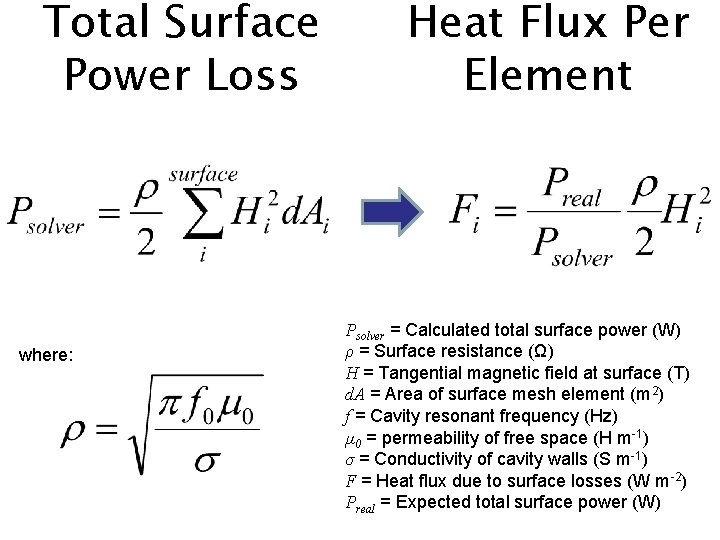
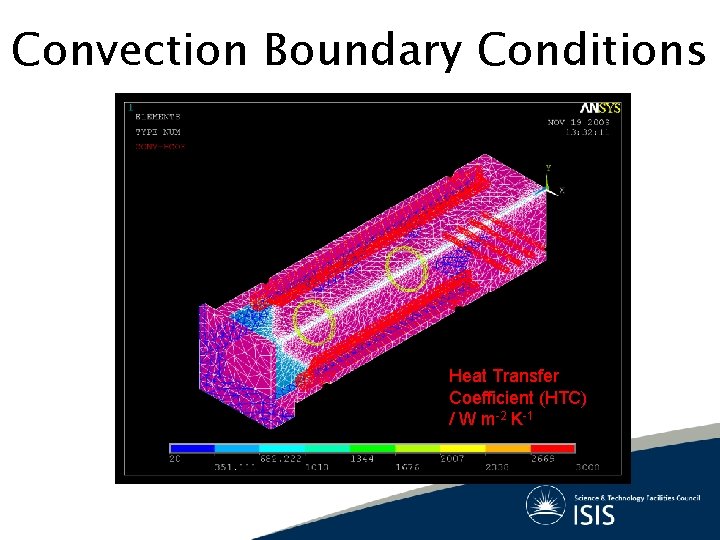
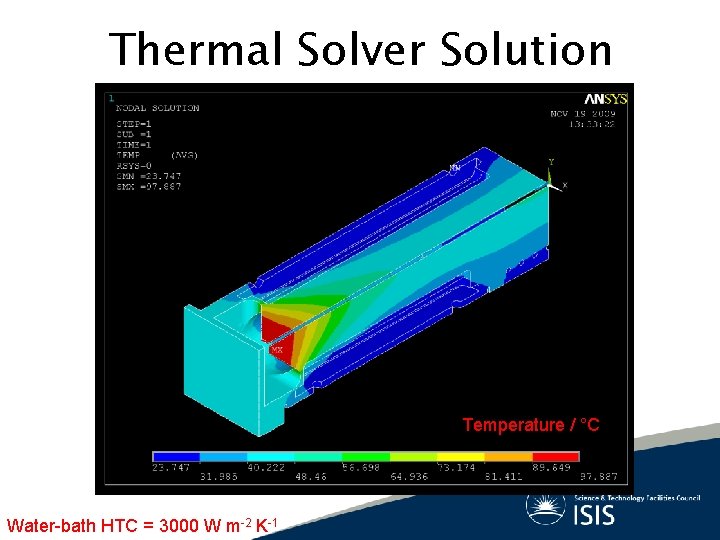
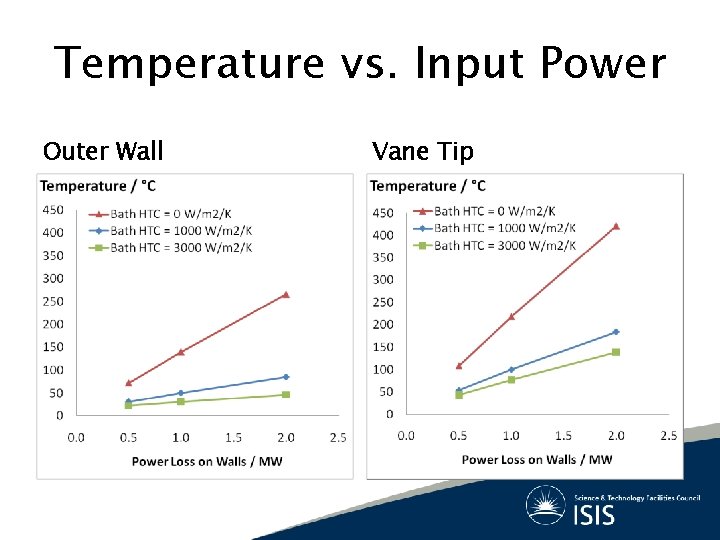
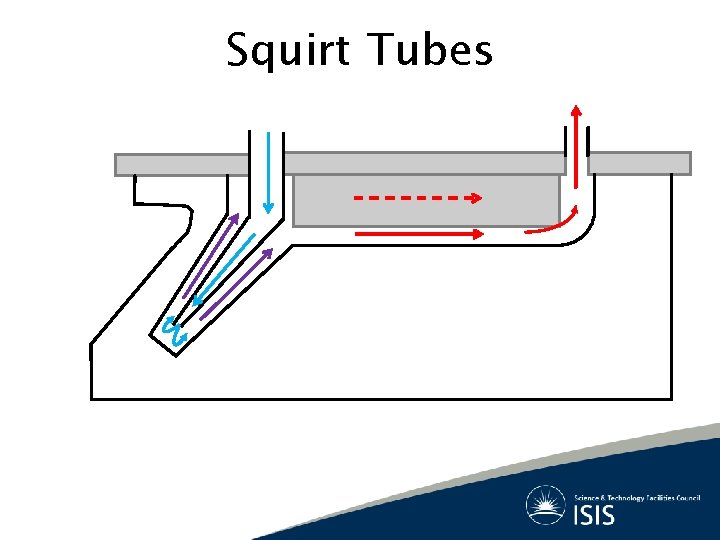
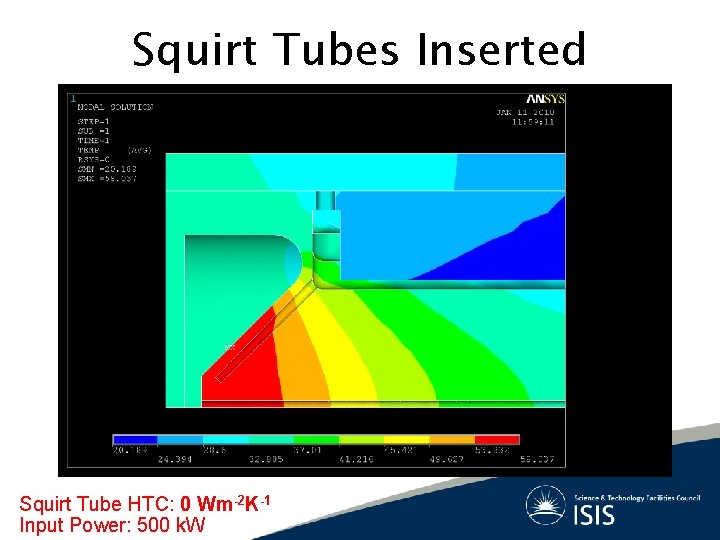
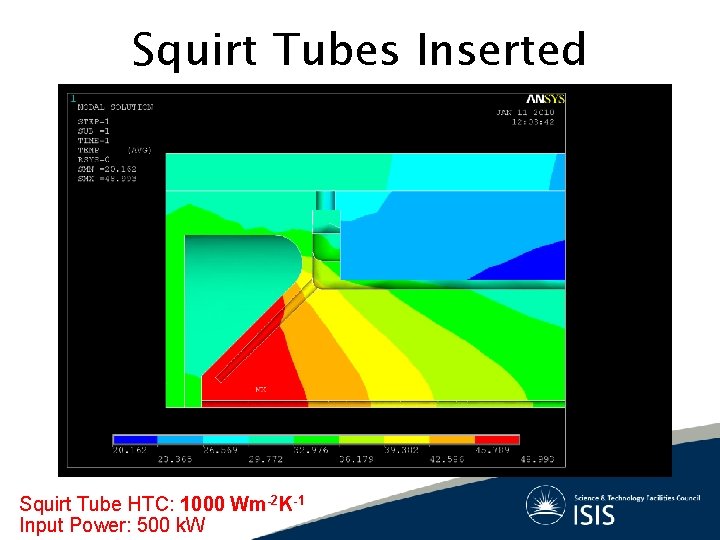
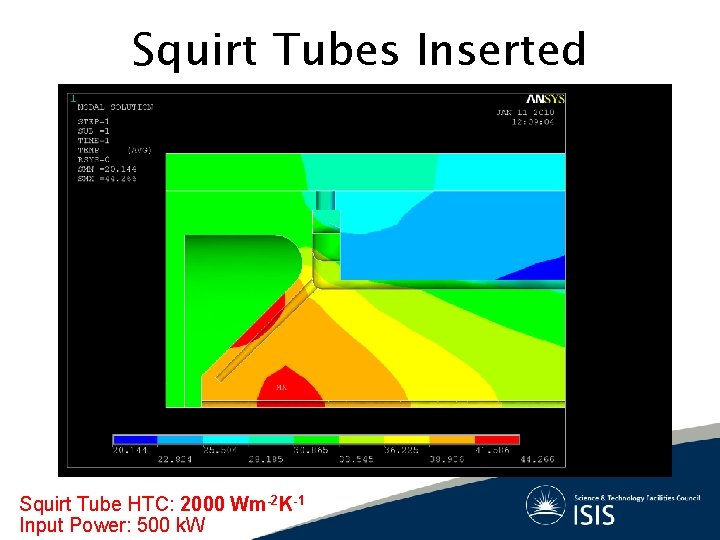
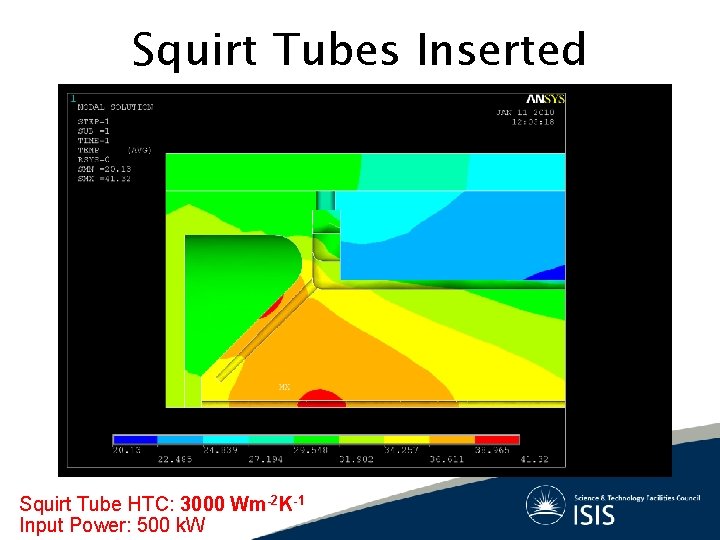
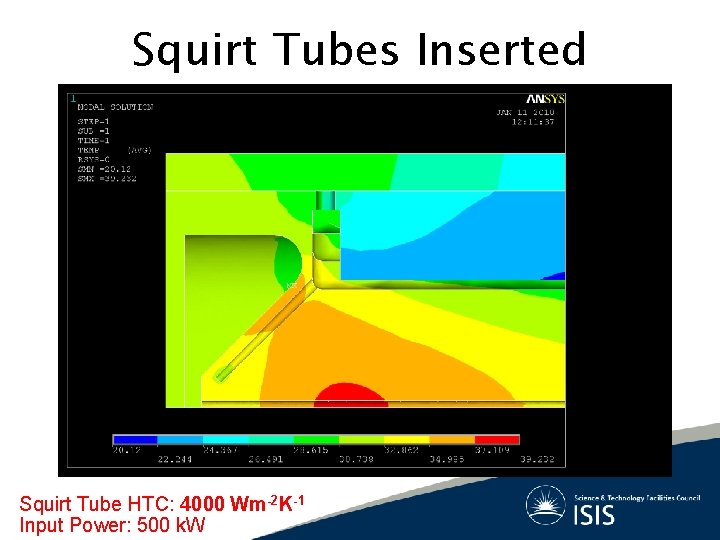
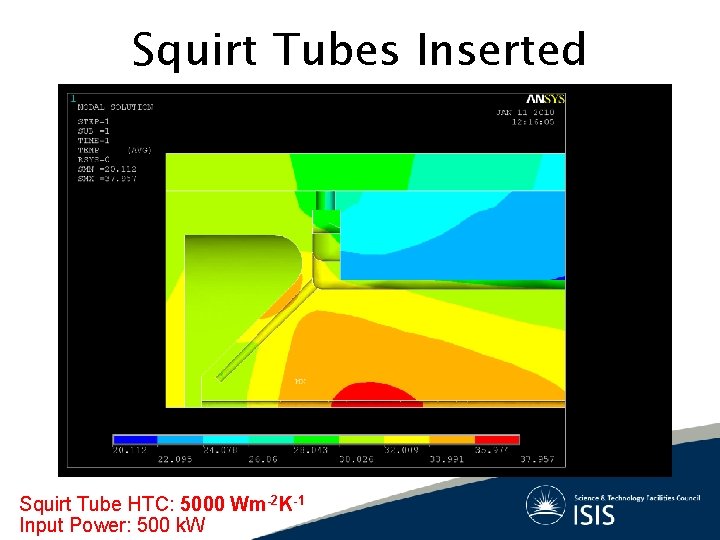
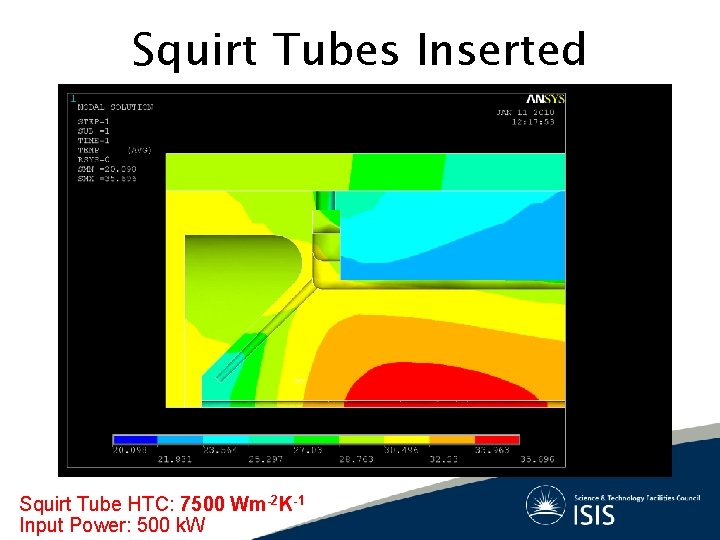
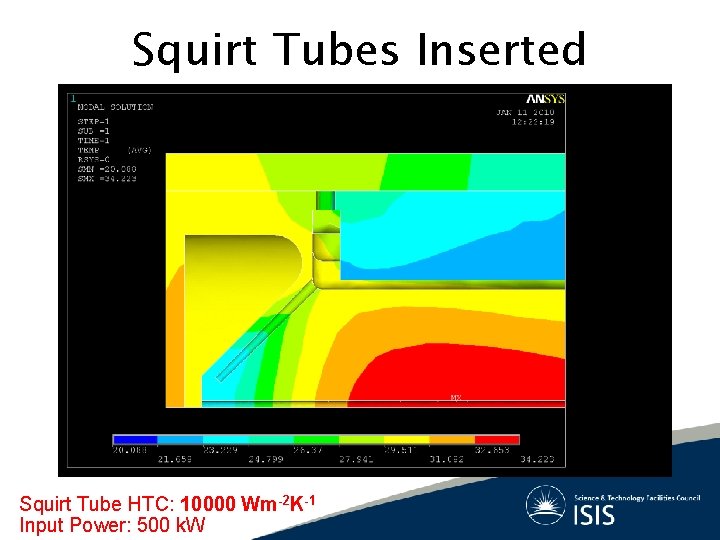
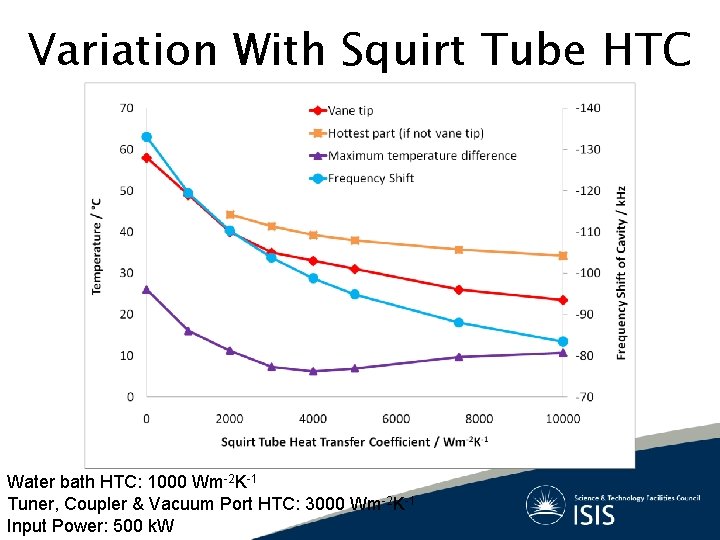
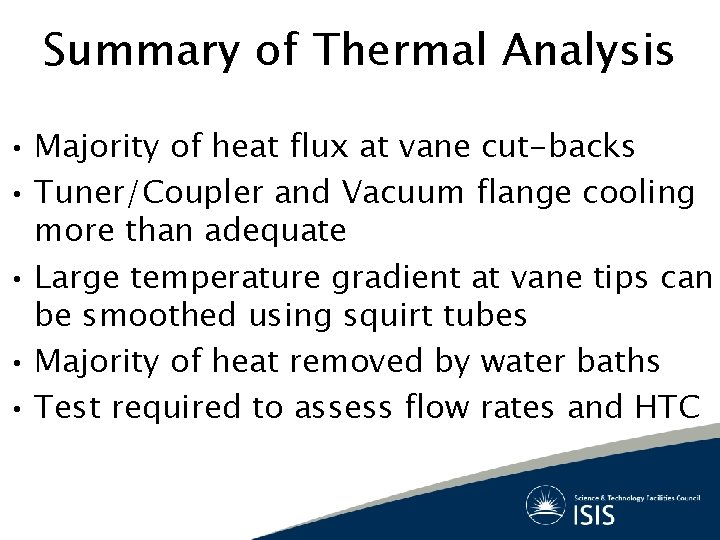
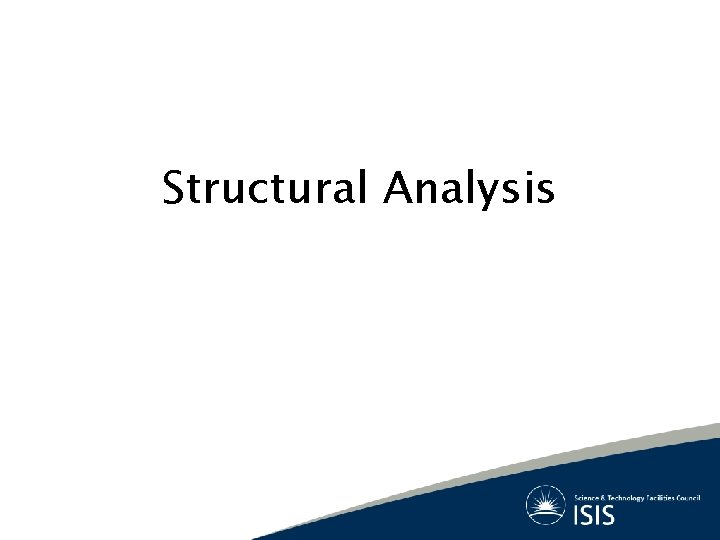
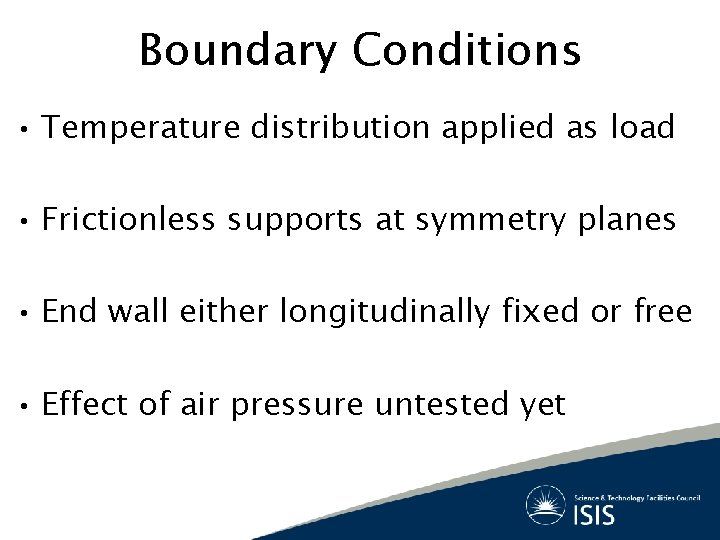
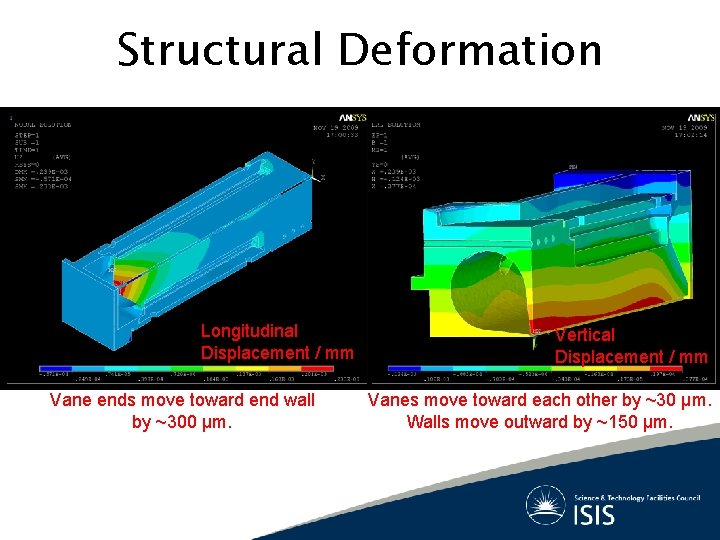
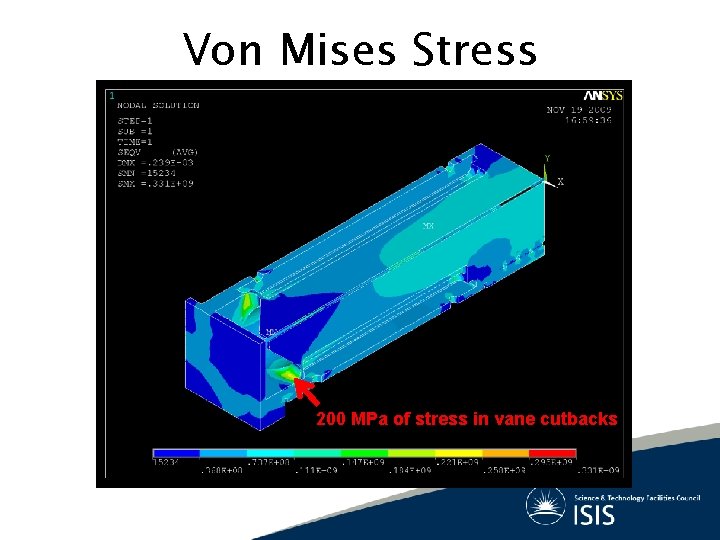
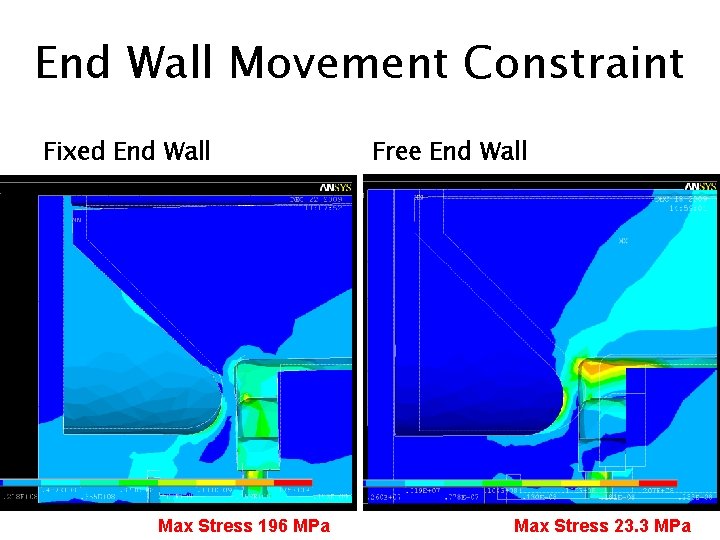
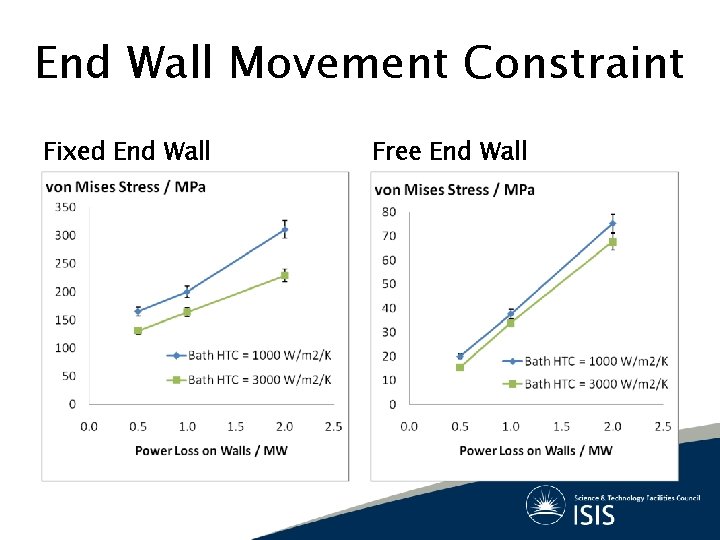
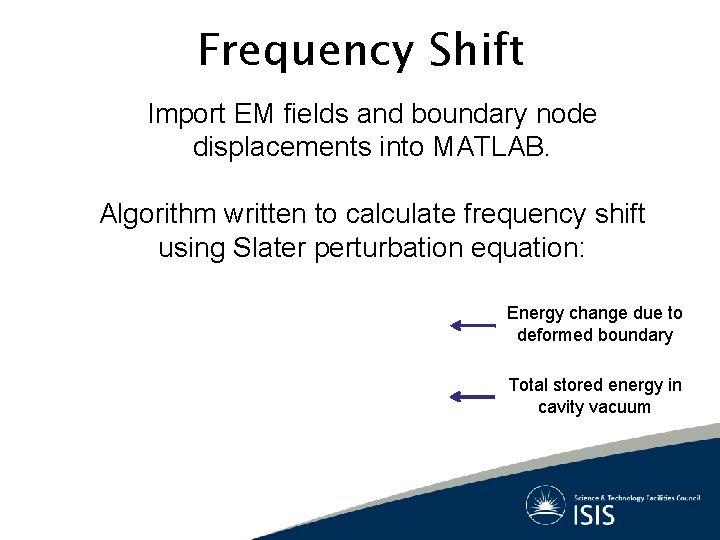
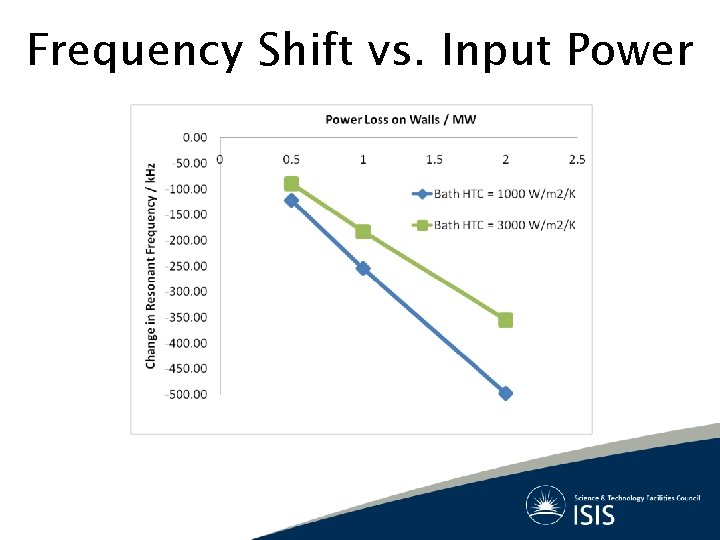
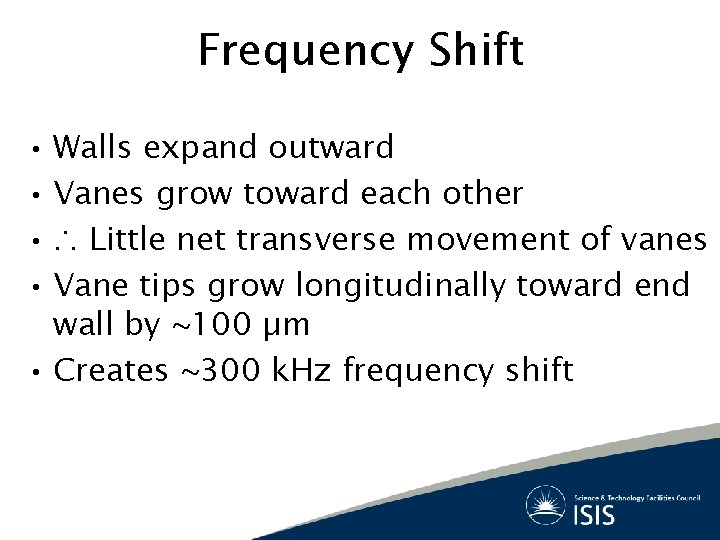
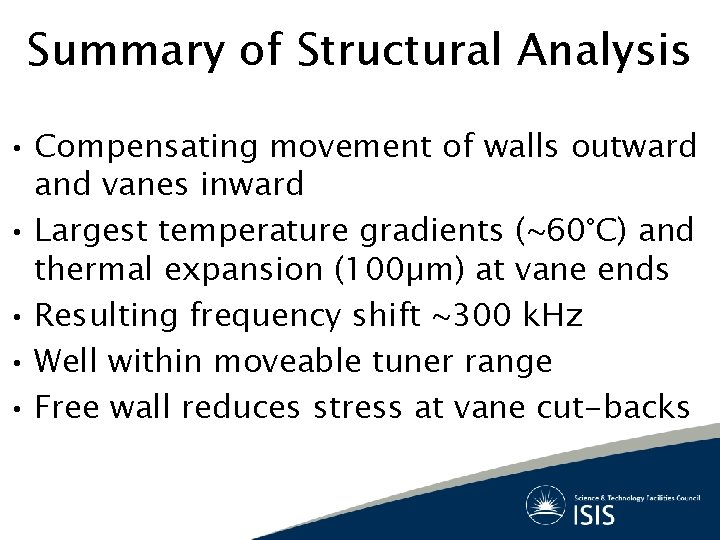
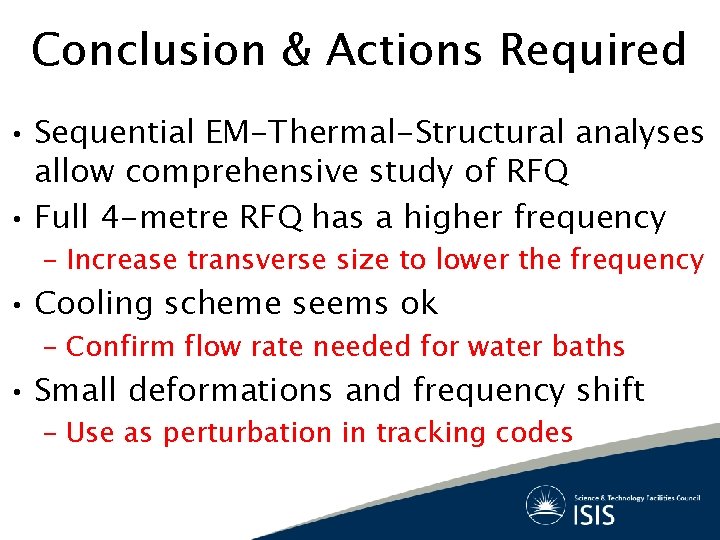
- Slides: 50
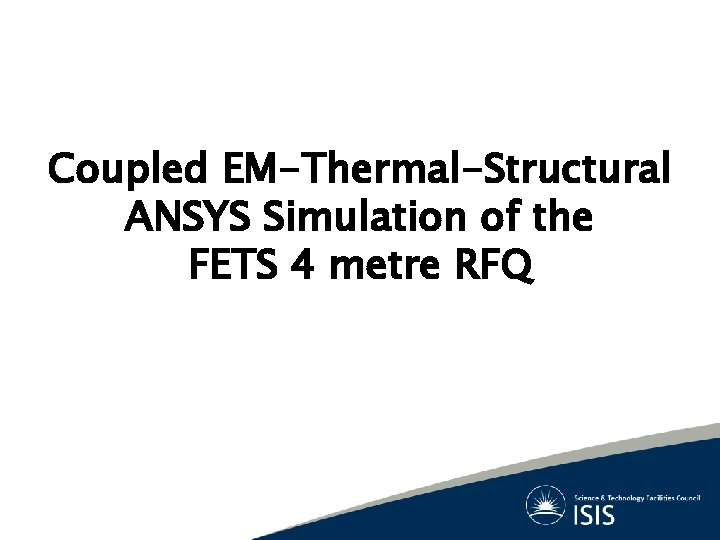
Coupled EM-Thermal-Structural ANSYS Simulation of the FETS 4 metre RFQ
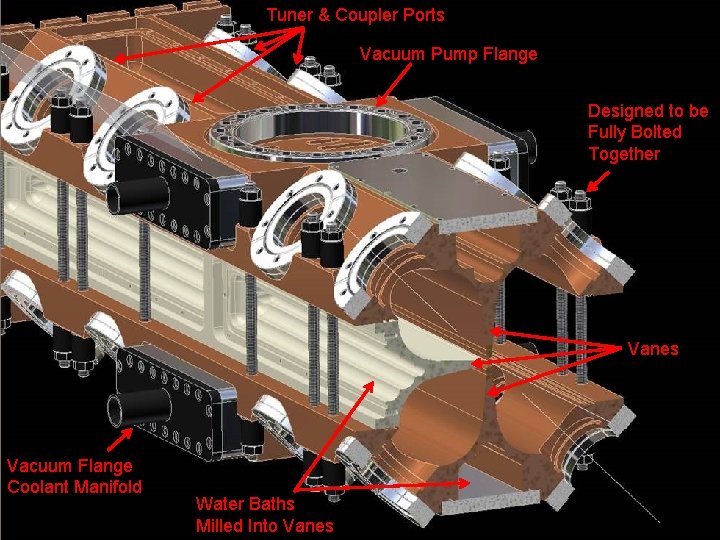
Tuner & Coupler Ports Vacuum Pump Flange Designed to be Fully Bolted Together Vanes Vacuum Flange Coolant Manifold Water Baths Milled Into Vanes
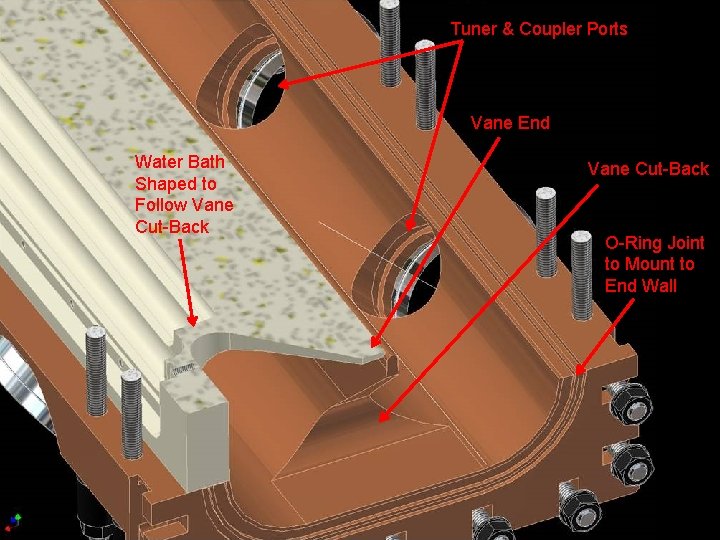
Tuner & Coupler Ports Vane End Water Bath Shaped to Follow Vane Cut-Back O-Ring Joint to Mount to End Wall
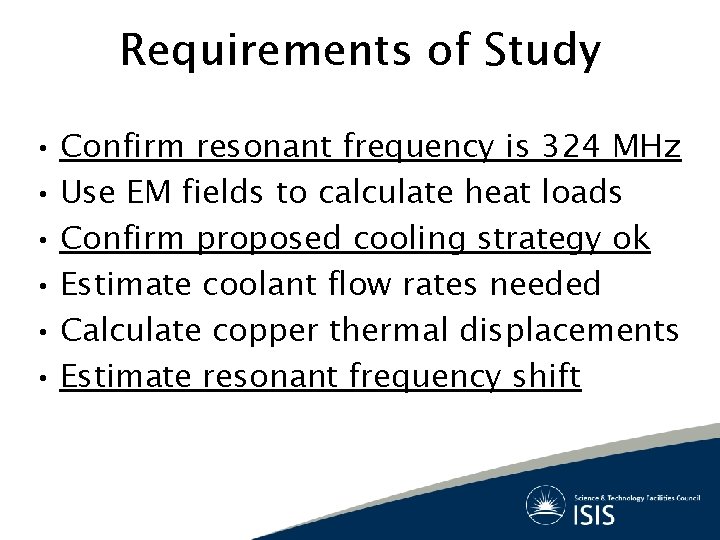
Requirements of Study • Confirm resonant frequency is 324 MHz • Use EM fields to calculate heat loads • Confirm proposed cooling strategy ok • Estimate coolant flow rates needed • Calculate copper thermal displacements • Estimate resonant frequency shift
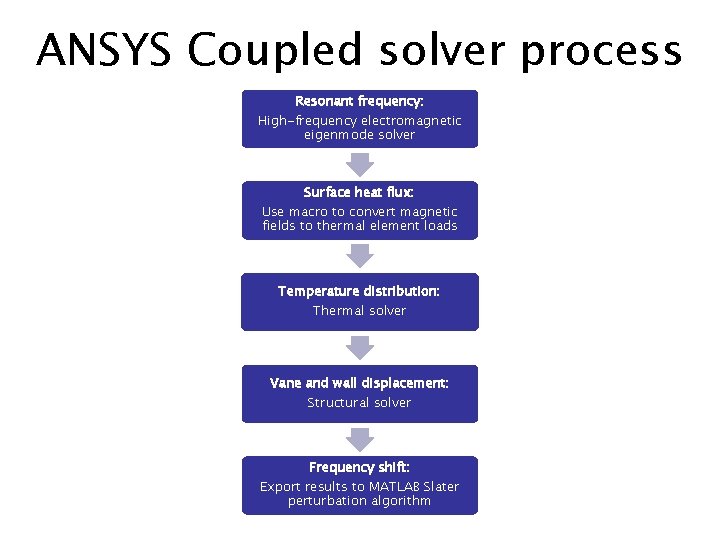
ANSYS Coupled solver process Resonant frequency: High-frequency electromagnetic eigenmode solver Surface heat flux: Use macro to convert magnetic fields to thermal element loads Temperature distribution: Thermal solver Vane and wall displacement: Structural solver Frequency shift: Export results to MATLAB Slater perturbation algorithm
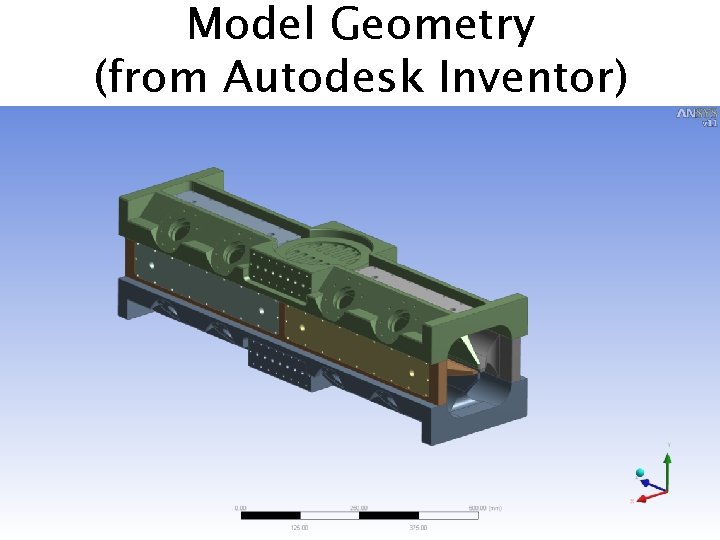
Model Geometry (from Autodesk Inventor)
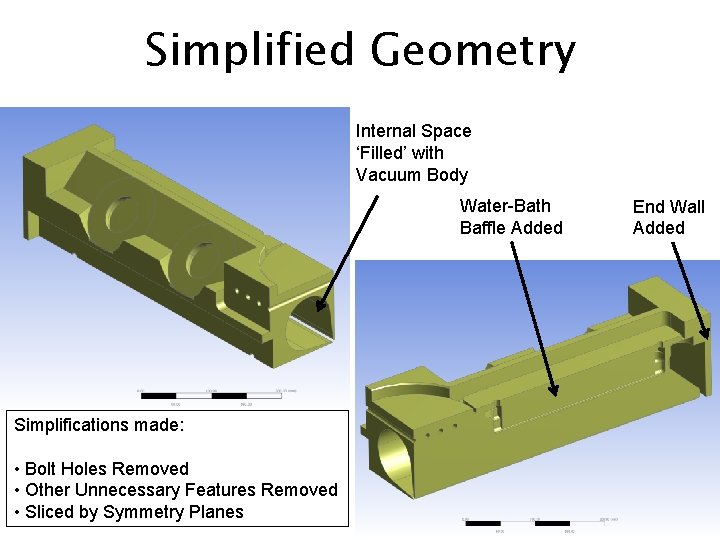
Simplified Geometry Internal Space ‘Filled’ with Vacuum Body Water-Bath Baffle Added Simplifications made: • Bolt Holes Removed • Other Unnecessary Features Removed • Sliced by Symmetry Planes End Wall Added
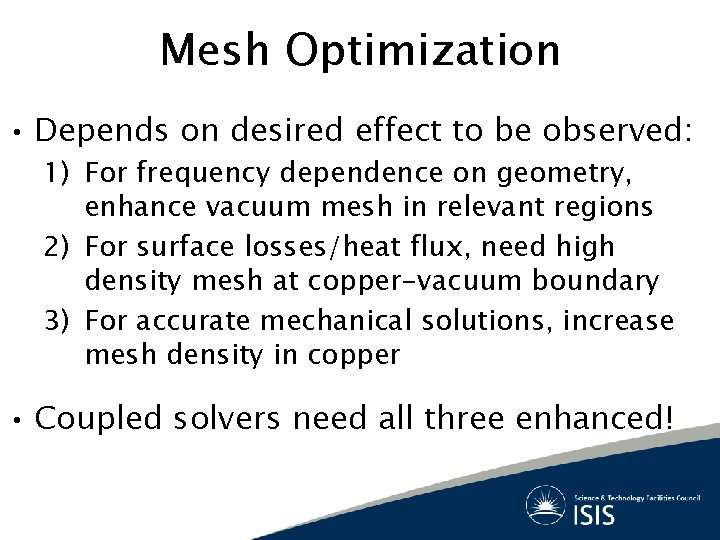
Mesh Optimization • Depends on desired effect to be observed: 1) For frequency dependence on geometry, enhance vacuum mesh in relevant regions 2) For surface losses/heat flux, need high density mesh at copper-vacuum boundary 3) For accurate mechanical solutions, increase mesh density in copper • Coupled solvers need all three enhanced!
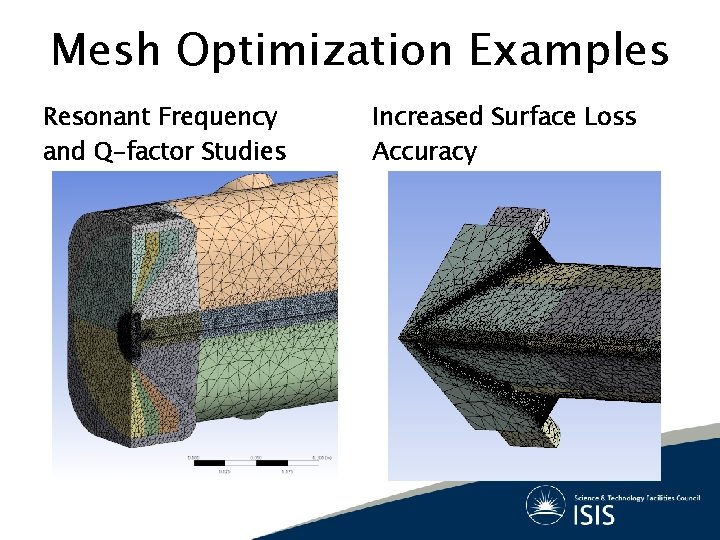
Mesh Optimization Examples Resonant Frequency and Q-factor Studies Increased Surface Loss Accuracy
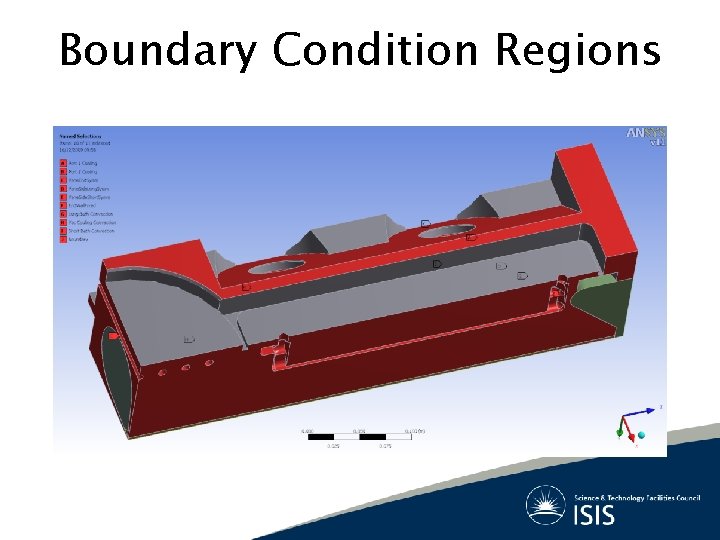
Boundary Condition Regions
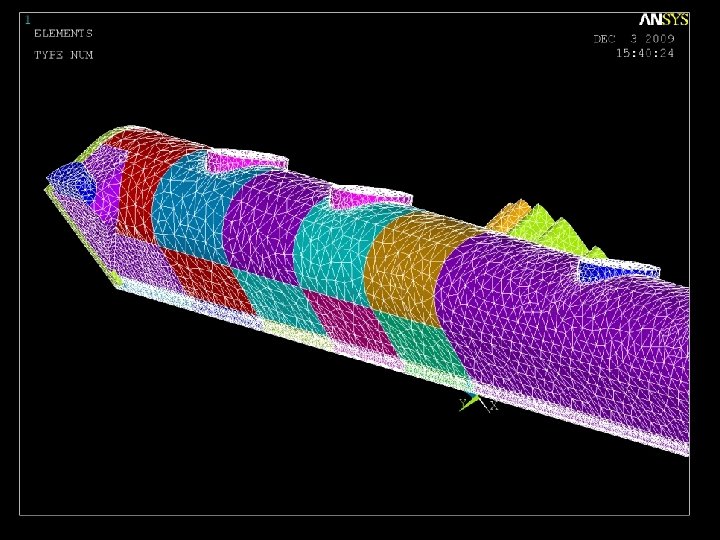
Transfer to ANSYS Classic • Different ‘bodies’ are different mesh types • Assign boundary condition to node groups
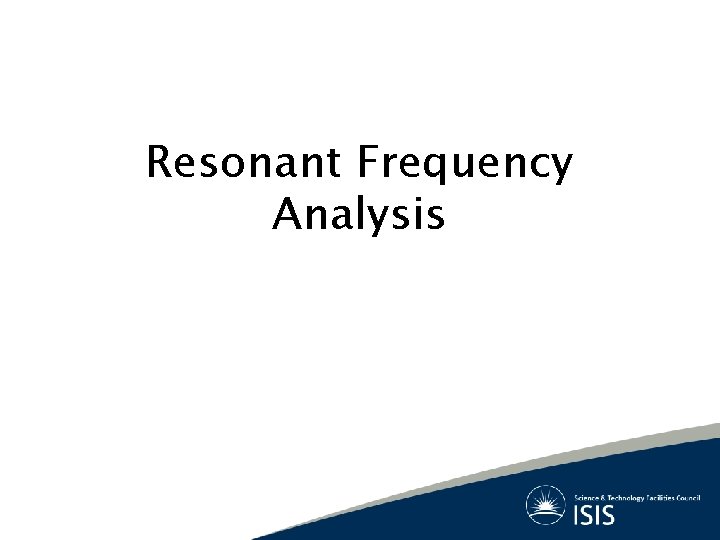
Resonant Frequency Analysis
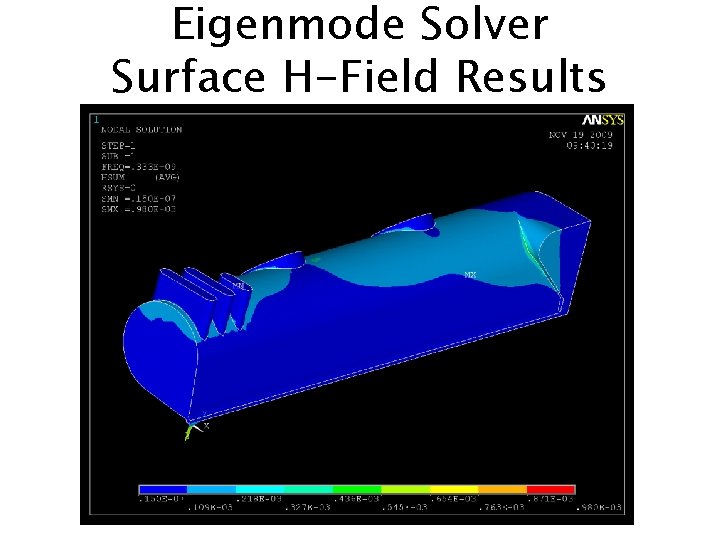
Eigenmode Solver Surface H-Field Results
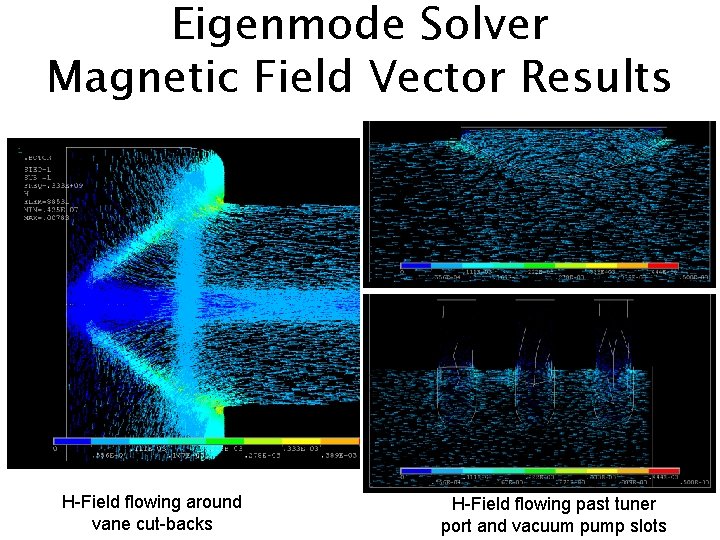
Eigenmode Solver Magnetic Field Vector Results H-Field flowing around vane cut-backs H-Field flowing past tuner port and vacuum pump slots
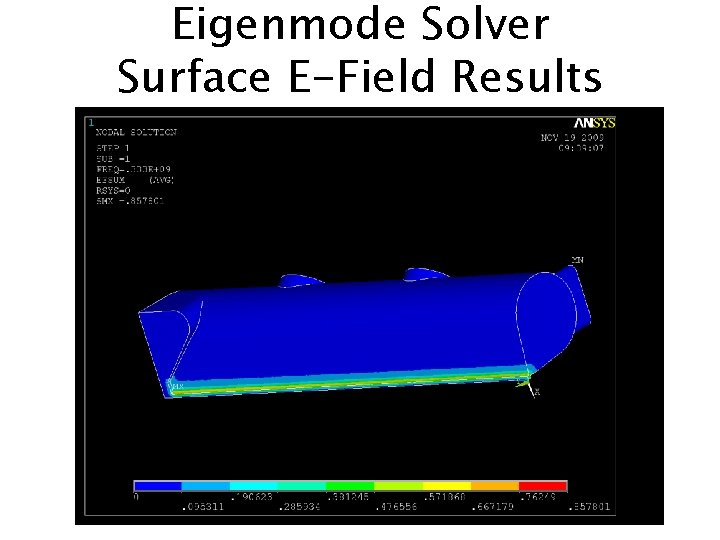
Eigenmode Solver Surface E-Field Results
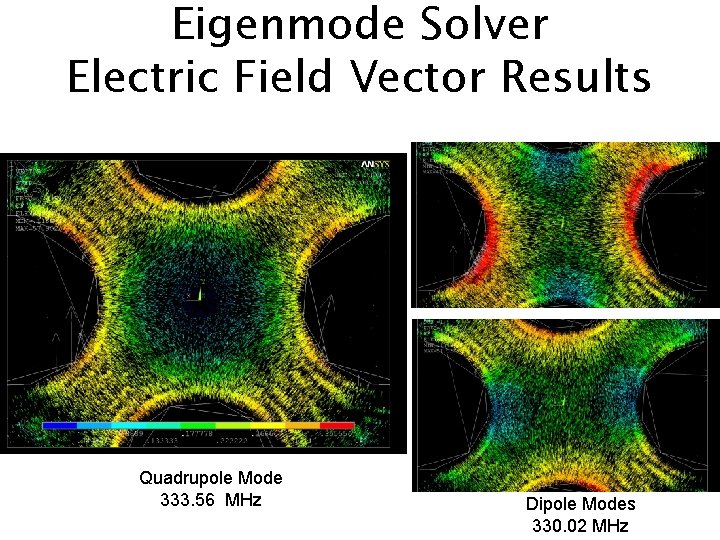
Eigenmode Solver Electric Field Vector Results Quadrupole Mode 333. 56 MHz Dipole Modes 330. 02 MHz
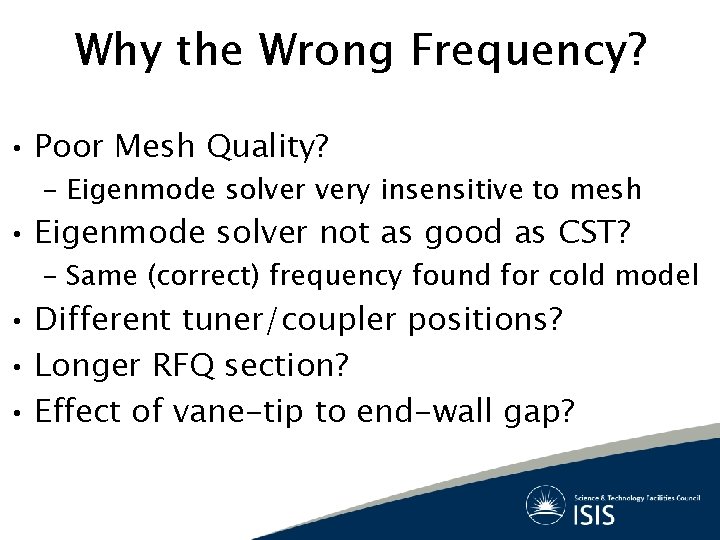
Why the Wrong Frequency? • Poor Mesh Quality? – Eigenmode solver very insensitive to mesh • Eigenmode solver not as good as CST? – Same (correct) frequency found for cold model • Different tuner/coupler positions? • Longer RFQ section? • Effect of vane-tip to end-wall gap?
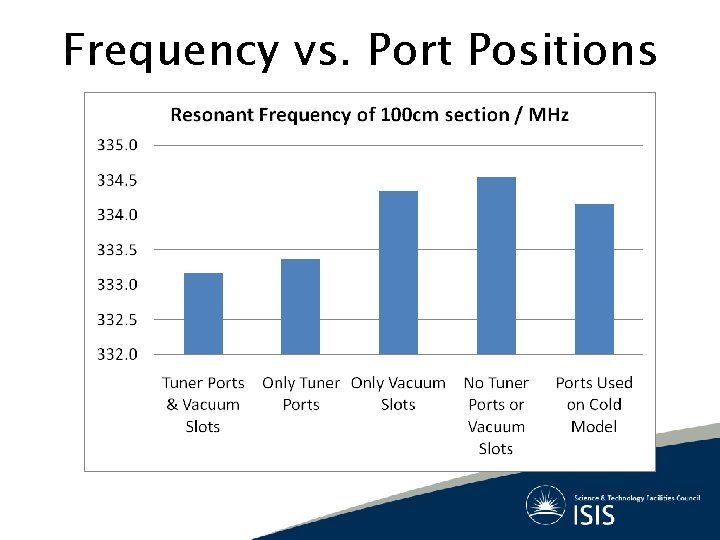
Frequency vs. Port Positions
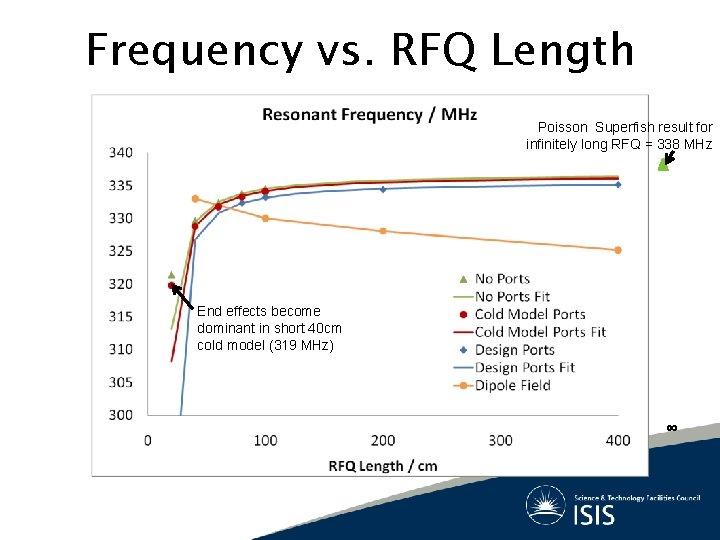
Frequency vs. RFQ Length Poisson Superfish result for infinitely long RFQ = 338 MHz End effects become dominant in short 40 cm cold model (319 MHz) ∞
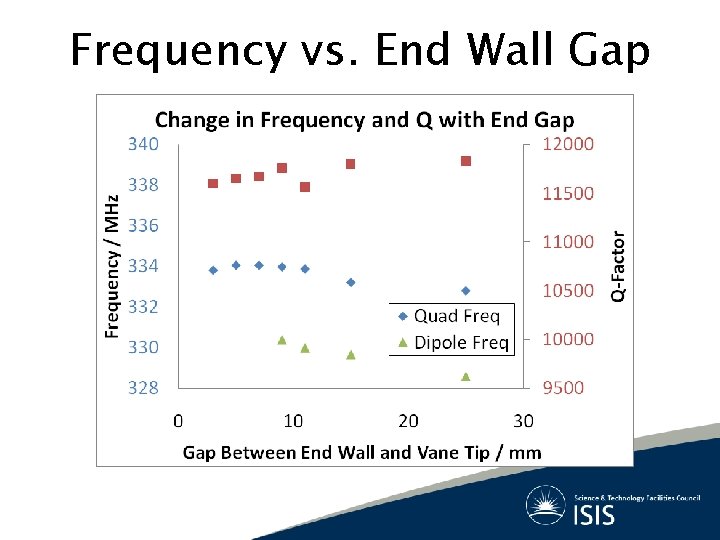
Frequency vs. End Wall Gap
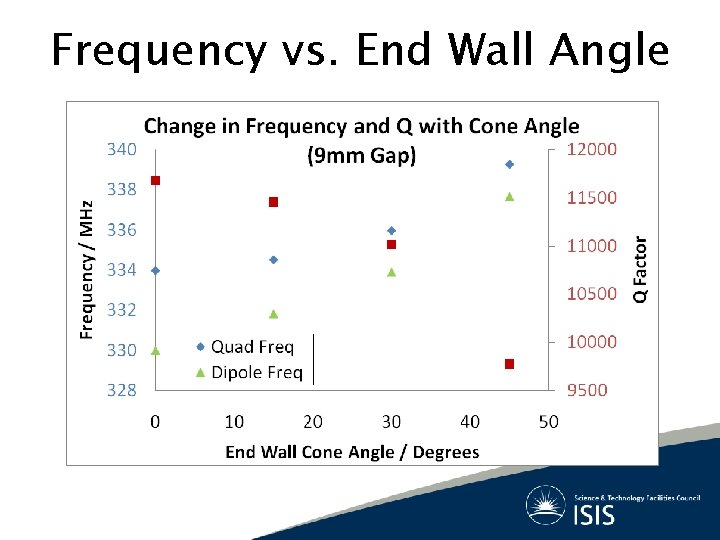
Frequency vs. End Wall Angle
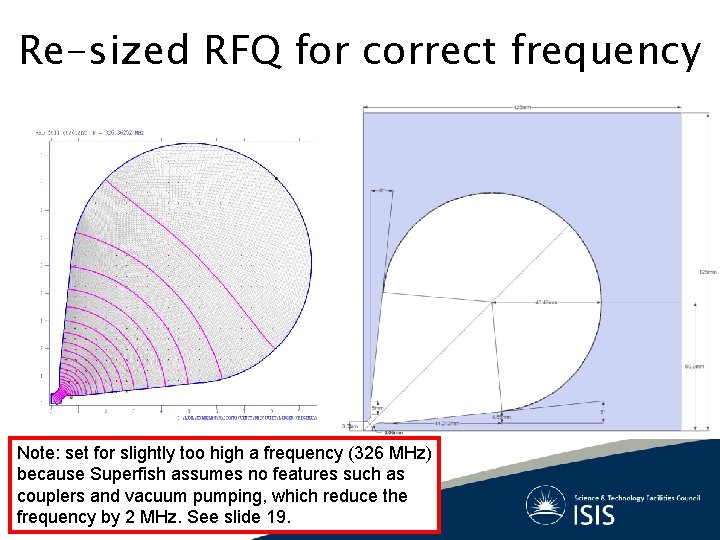
Re-sized RFQ for correct frequency Note: set for slightly too high a frequency (326 MHz) because Superfish assumes no features such as couplers and vacuum pumping, which reduce the frequency by 2 MHz. See slide 19.
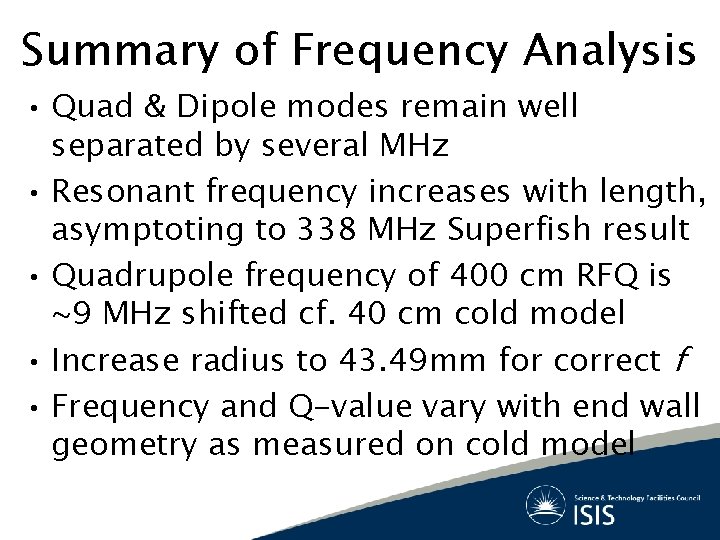
Summary of Frequency Analysis • Quad & Dipole modes remain well separated by several MHz • Resonant frequency increases with length, asymptoting to 338 MHz Superfish result • Quadrupole frequency of 400 cm RFQ is ~9 MHz shifted cf. 40 cm cold model • Increase radius to 43. 49 mm for correct f • Frequency and Q-value vary with end wall geometry as measured on cold model
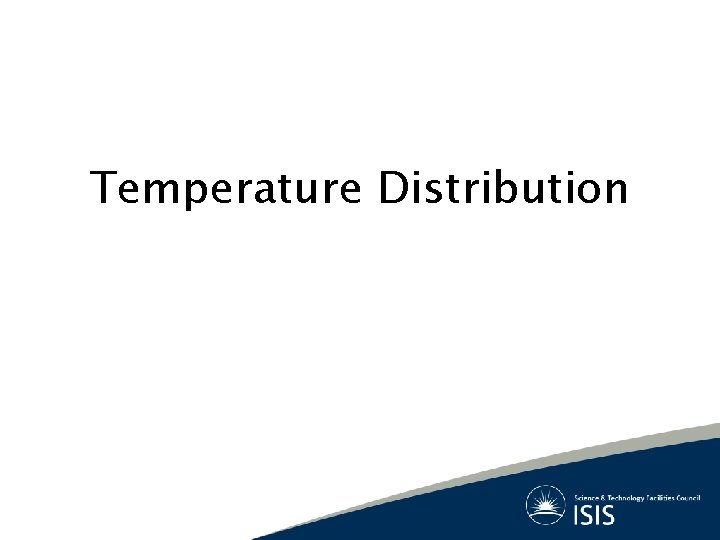
Temperature Distribution
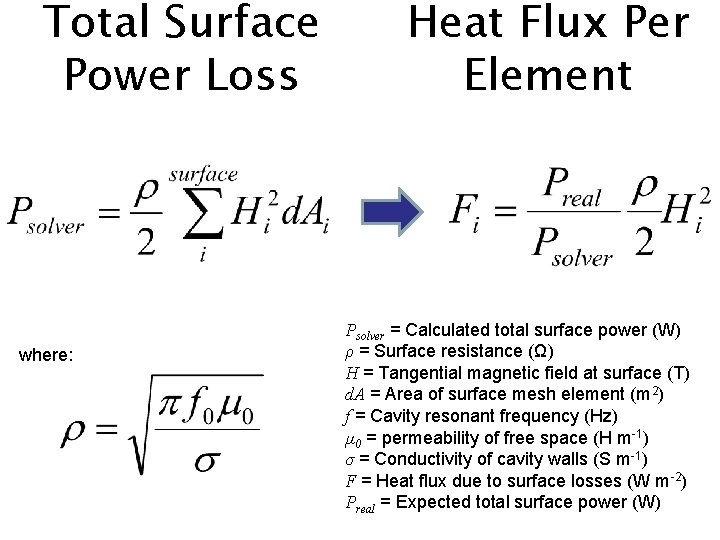
Total Surface Power Loss where: Heat Flux Per Element Psolver = Calculated total surface power (W) ρ = Surface resistance (Ω) H = Tangential magnetic field at surface (T) d. A = Area of surface mesh element (m 2) f = Cavity resonant frequency (Hz) µ 0 = permeability of free space (H m-1) σ = Conductivity of cavity walls (S m-1) F = Heat flux due to surface losses (W m-2) Preal = Expected total surface power (W)
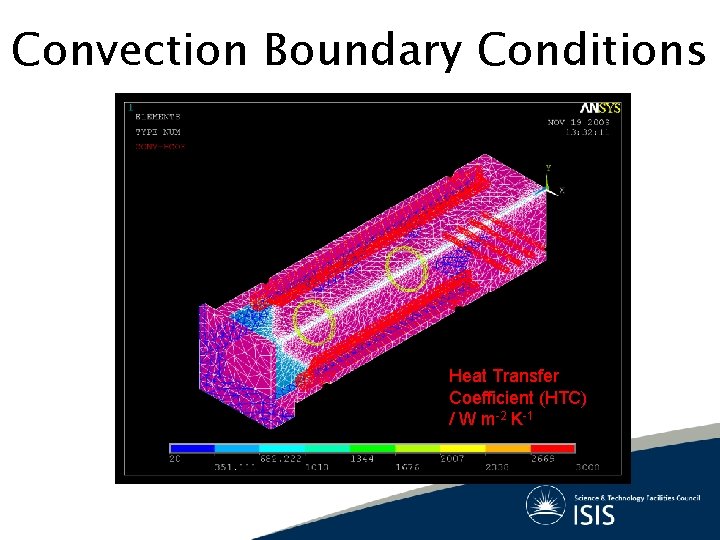
Convection Boundary Conditions Heat Transfer Coefficient (HTC) / W m-2 K-1
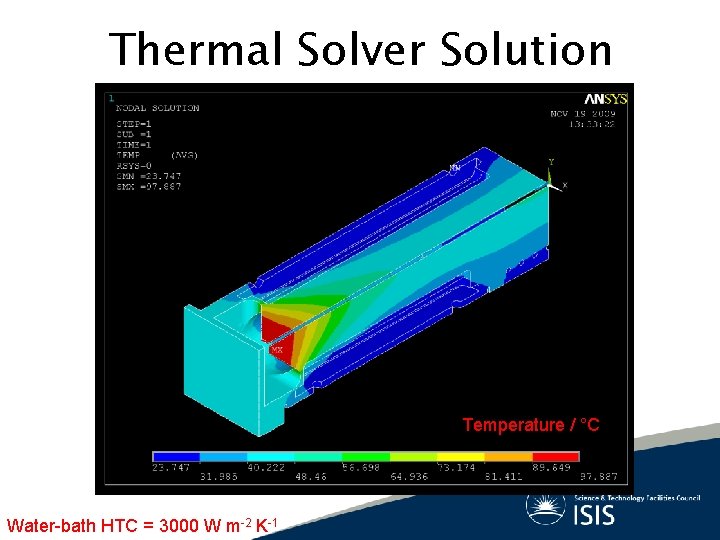
Thermal Solver Solution Temperature / °C Water-bath HTC = 3000 W m-2 K-1
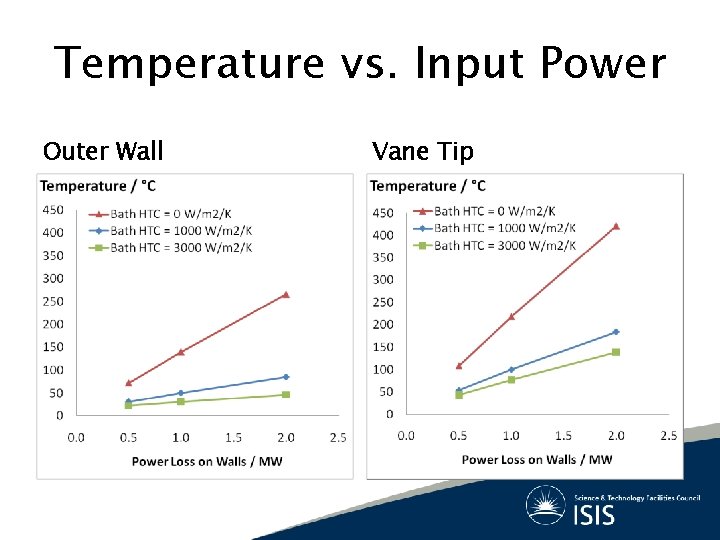
Temperature vs. Input Power Outer Wall Vane Tip
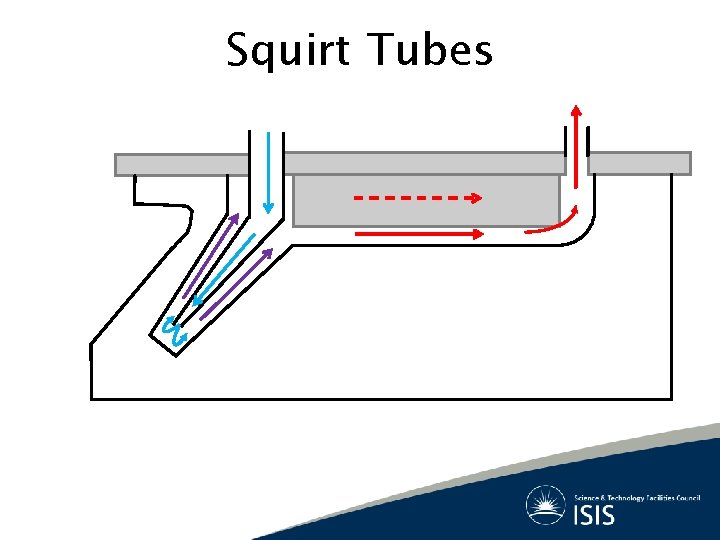
Squirt Tubes
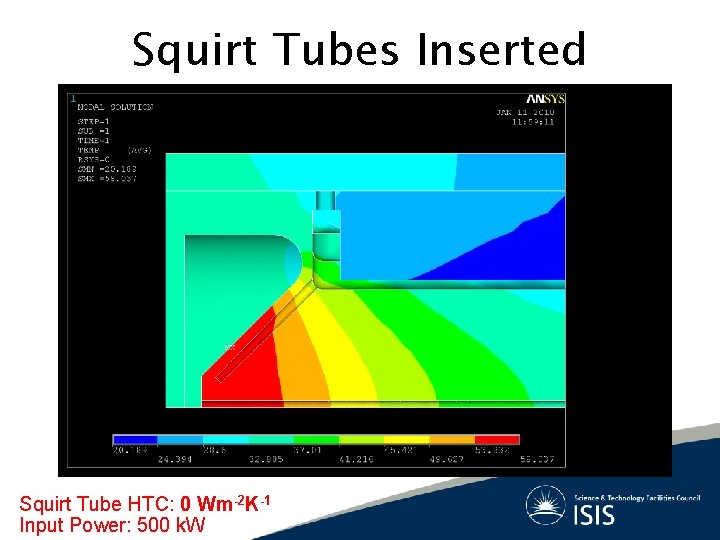
Squirt Tubes Inserted Squirt Tube HTC: 0 Wm-2 K-1 Input Power: 500 k. W
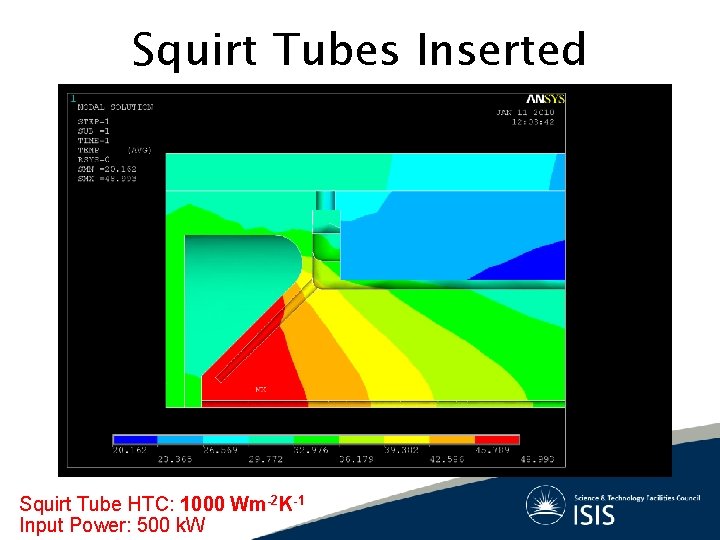
Squirt Tubes Inserted Squirt Tube HTC: 1000 Wm-2 K-1 Input Power: 500 k. W
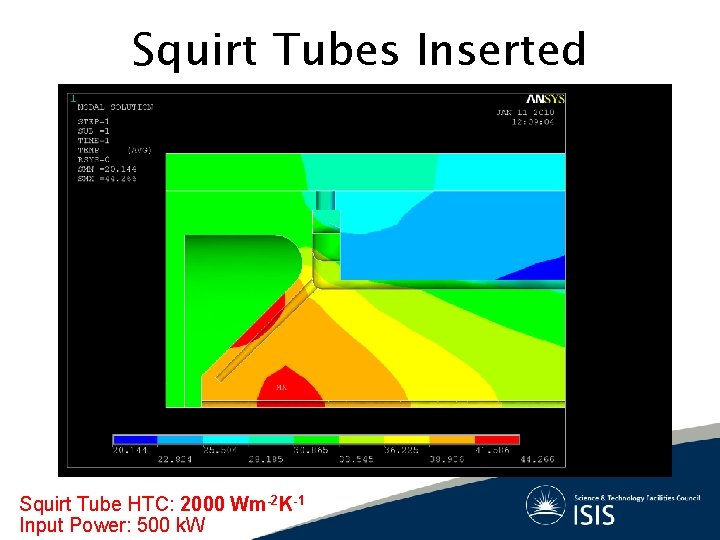
Squirt Tubes Inserted Squirt Tube HTC: 2000 Wm-2 K-1 Input Power: 500 k. W
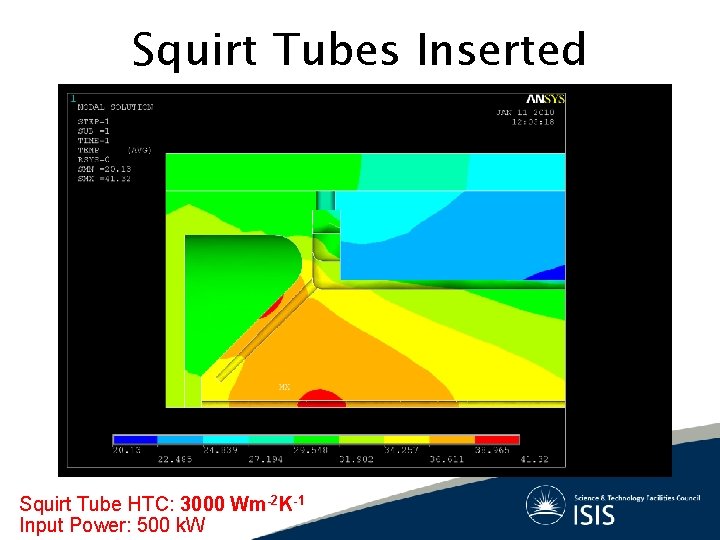
Squirt Tubes Inserted Squirt Tube HTC: 3000 Wm-2 K-1 Input Power: 500 k. W
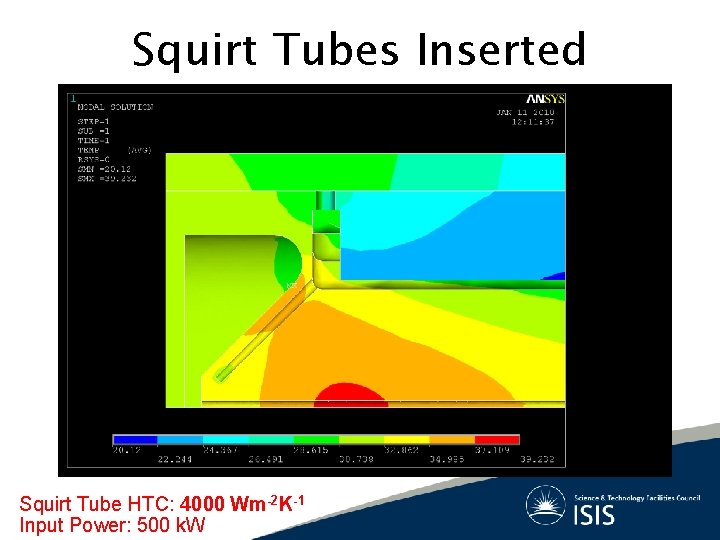
Squirt Tubes Inserted Squirt Tube HTC: 4000 Wm-2 K-1 Input Power: 500 k. W
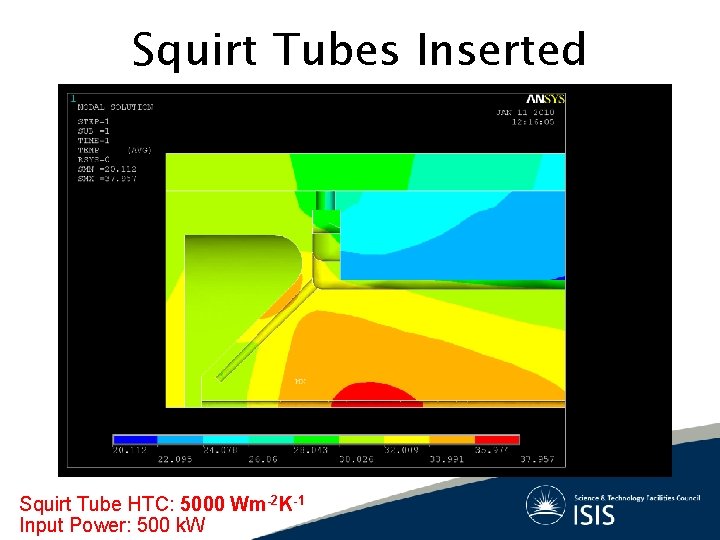
Squirt Tubes Inserted Squirt Tube HTC: 5000 Wm-2 K-1 Input Power: 500 k. W
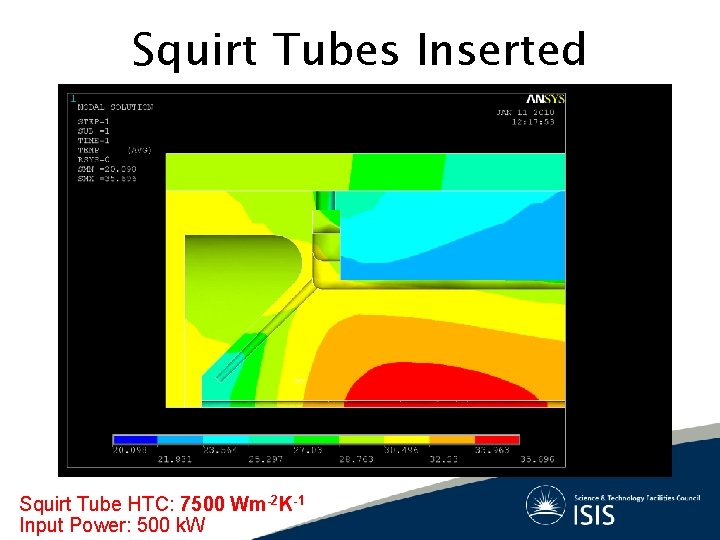
Squirt Tubes Inserted Squirt Tube HTC: 7500 Wm-2 K-1 Input Power: 500 k. W
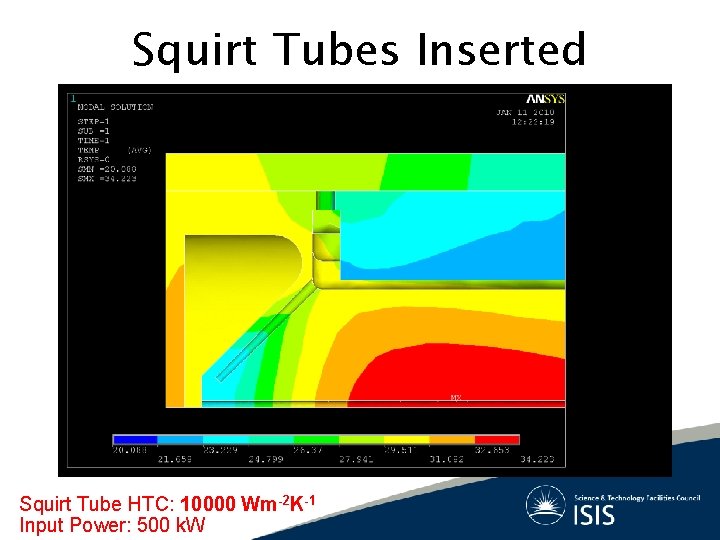
Squirt Tubes Inserted Squirt Tube HTC: 10000 Wm-2 K-1 Input Power: 500 k. W
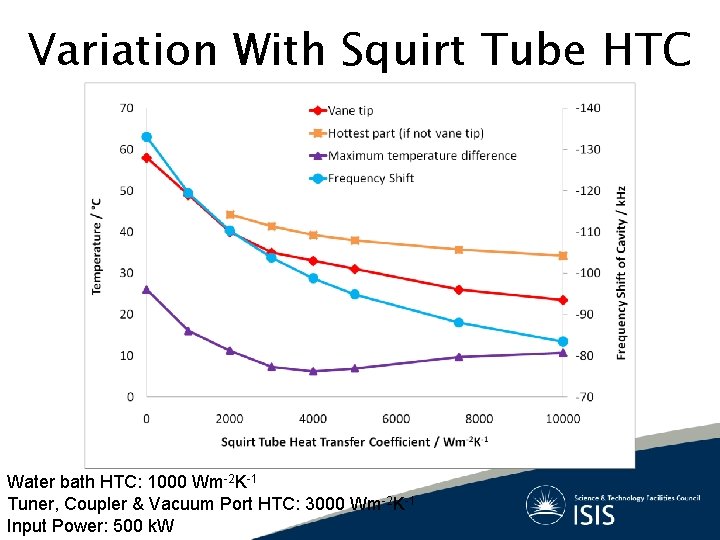
Variation With Squirt Tube HTC Water bath HTC: 1000 Wm-2 K-1 Tuner, Coupler & Vacuum Port HTC: 3000 Wm-2 K-1 Input Power: 500 k. W
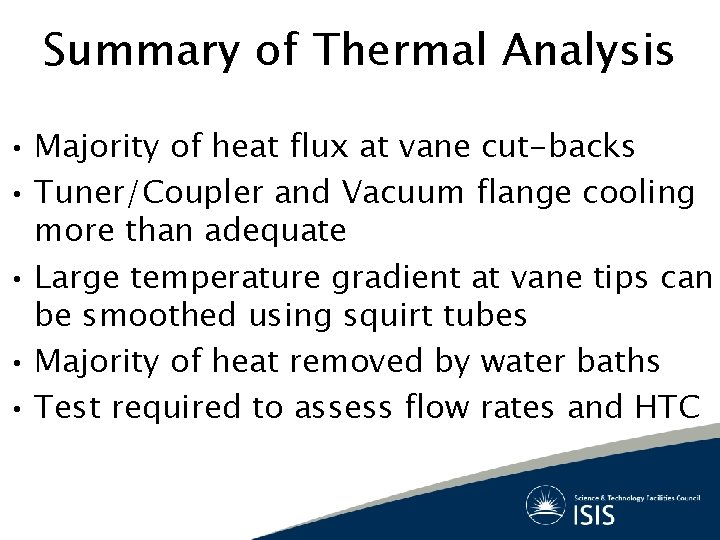
Summary of Thermal Analysis • Majority of heat flux at vane cut-backs • Tuner/Coupler and Vacuum flange cooling more than adequate • Large temperature gradient at vane tips can be smoothed using squirt tubes • Majority of heat removed by water baths • Test required to assess flow rates and HTC
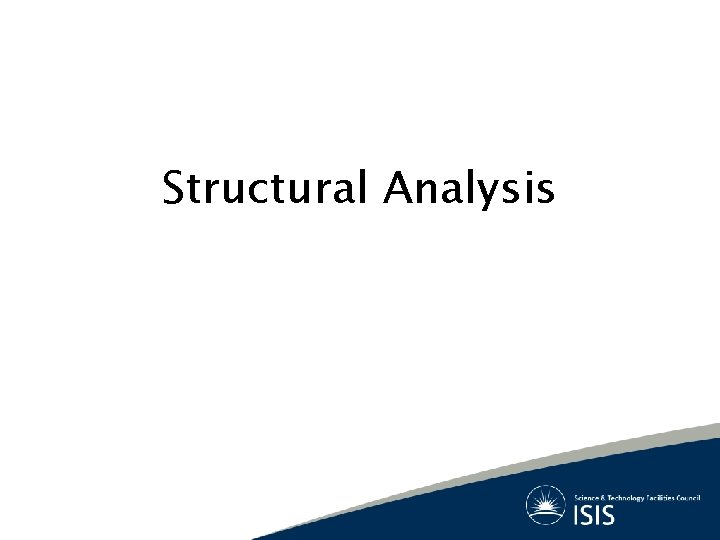
Structural Analysis
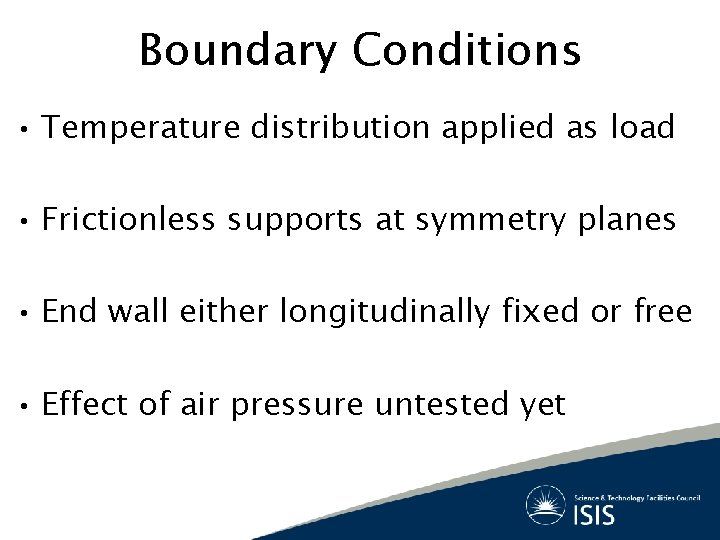
Boundary Conditions • Temperature distribution applied as load • Frictionless supports at symmetry planes • End wall either longitudinally fixed or free • Effect of air pressure untested yet
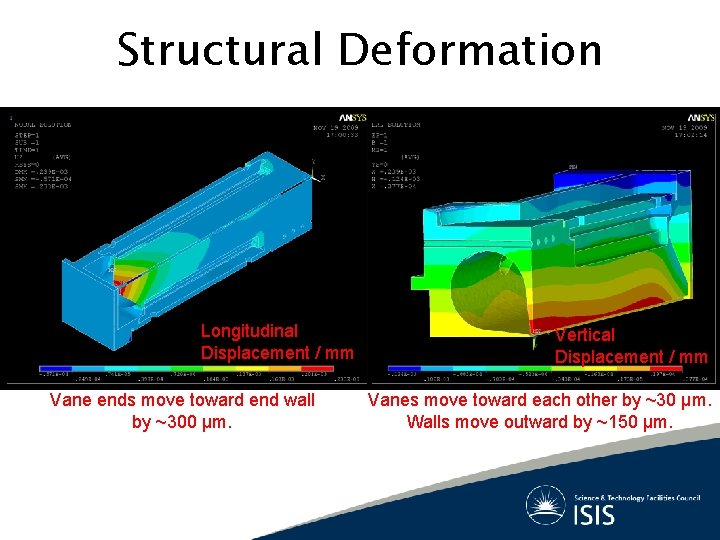
Structural Deformation Longitudinal Displacement / mm Vane ends move toward end wall by ~300 µm. Vertical Displacement / mm Vanes move toward each other by ~30 µm. Walls move outward by ~150 µm.
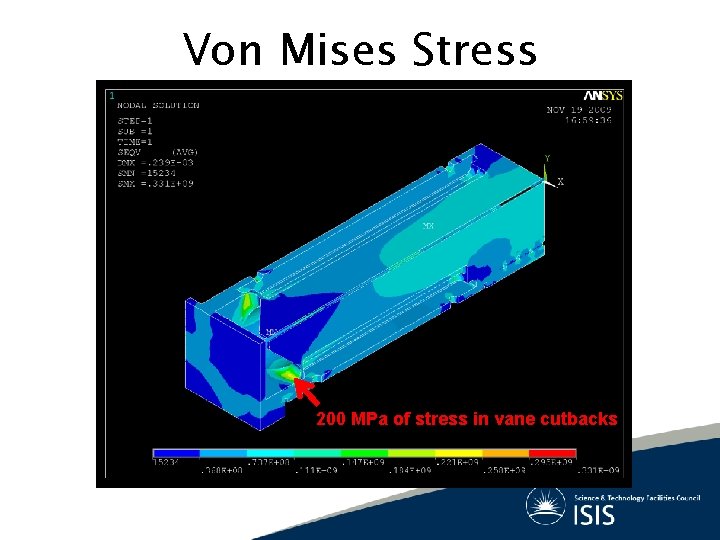
Von Mises Stress 200 MPa of stress in vane cutbacks
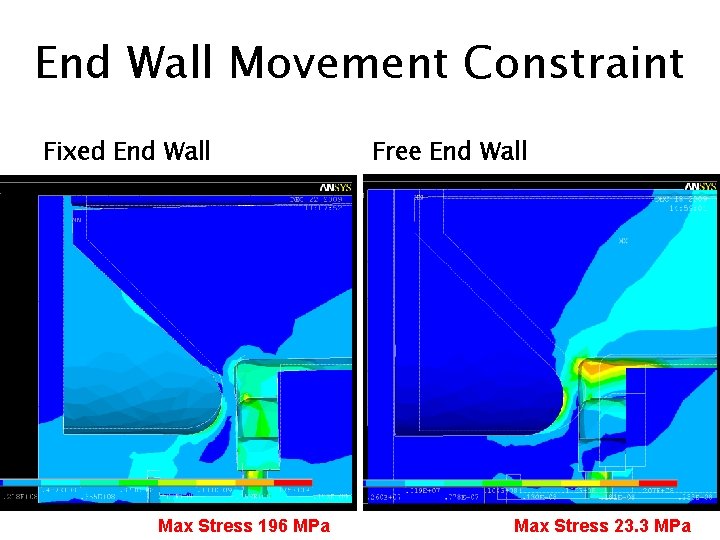
End Wall Movement Constraint Fixed End Wall Max Stress 196 MPa Free End Wall Max Stress 23. 3 MPa
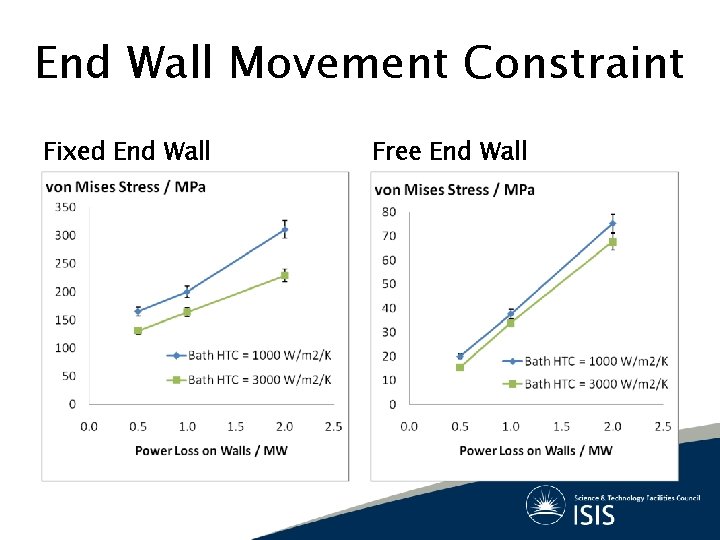
End Wall Movement Constraint Fixed End Wall Free End Wall
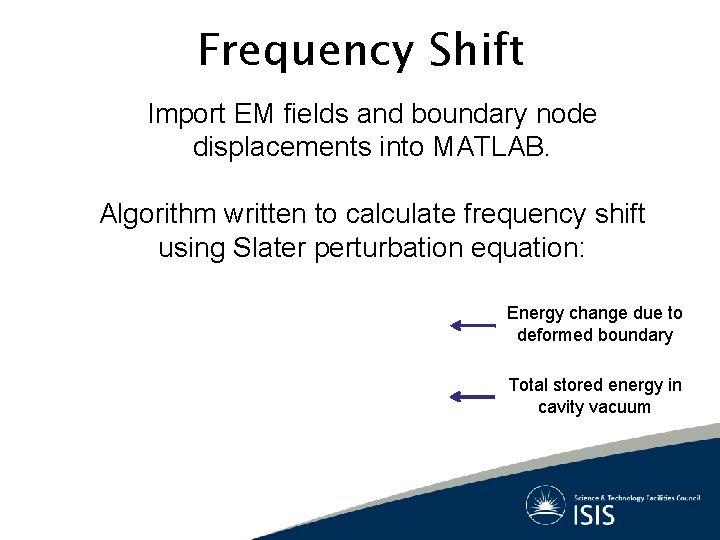
Frequency Shift Import EM fields and boundary node displacements into MATLAB. Algorithm written to calculate frequency shift using Slater perturbation equation: Energy change due to deformed boundary Total stored energy in cavity vacuum
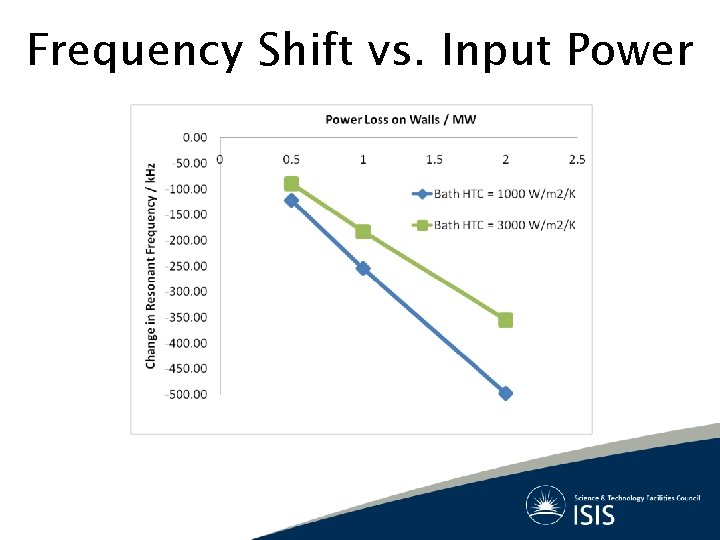
Frequency Shift vs. Input Power
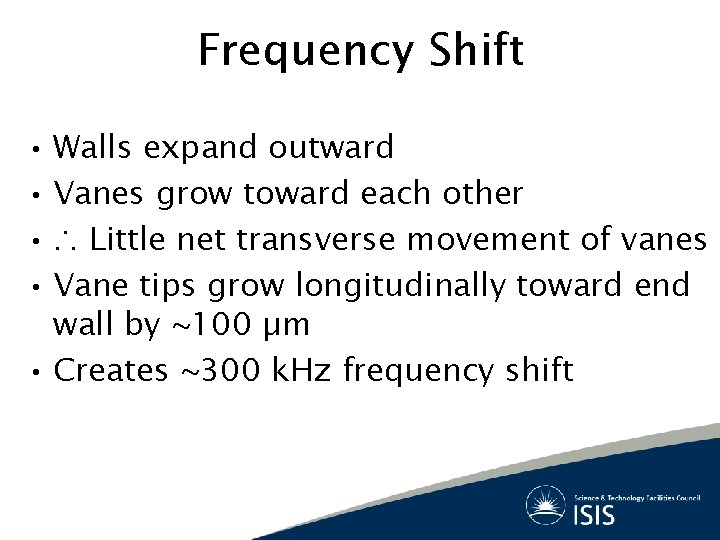
Frequency Shift • Walls expand outward • Vanes grow toward each other • ∴ Little net transverse movement of vanes • Vane tips grow longitudinally toward end wall by ~100 µm • Creates ~300 k. Hz frequency shift
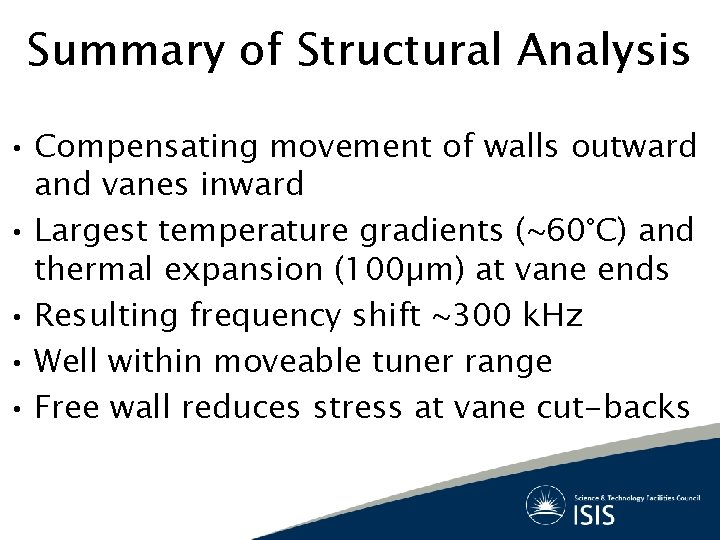
Summary of Structural Analysis • Compensating movement of walls outward and vanes inward • Largest temperature gradients (~60°C) and thermal expansion (100µm) at vane ends • Resulting frequency shift ~300 k. Hz • Well within moveable tuner range • Free wall reduces stress at vane cut-backs
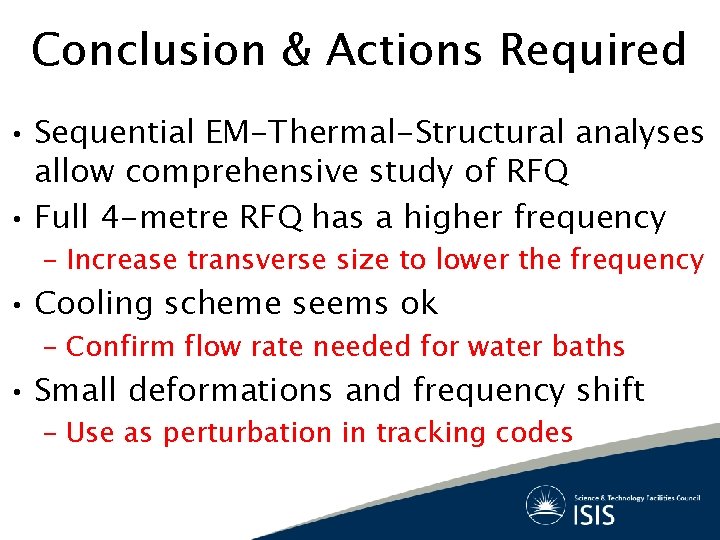
Conclusion & Actions Required • Sequential EM-Thermal-Structural analyses allow comprehensive study of RFQ • Full 4 -metre RFQ has a higher frequency – Increase transverse size to lower the frequency • Cooling scheme seems ok – Confirm flow rate needed for water baths • Small deformations and frequency shift – Use as perturbation in tracking codes
De que estan fets els ossos
Fets històrics importants
Ansys simulation
Sr latch with nor gates
Block diagram 8086
Coupled line coupler
Capacitor coupled non inverting amplifier
All resources are tightly coupled in computing paradigm of
Membrane transport
Amplifier
Ecl gate
Multistage amplifier
Highly aligned loosely coupled meaning
3 port network
Magnetically coupled circuits lecture notes
Complex impedances
Magnetic coupled circuits
Synchronous motor equations
Coupled model intercomparison project phase 5
Charge coupled device
Example of claim
3 port network
Explain system models for distributed and cloud computing
Charge coupled device detector
Gibbs free energy
Coupled circuits
Inductively coupled plasma
Tanya leise amherst
Emitter coupled differential amplifier
Coupled oscillations
Tightly coupled multiprocessor
Netflix freedom and responsibility
Hazeltine neutralization
Coupled reaction
Làm thế nào để 102-1=99
Cong thức tính động năng
Tỉ lệ cơ thể trẻ em
Lời thề hippocrates
đại từ thay thế
Vẽ hình chiếu đứng bằng cạnh của vật thể
Quá trình desamine hóa có thể tạo ra
Môn thể thao bắt đầu bằng từ chạy
Hát kết hợp bộ gõ cơ thể
Sự nuôi và dạy con của hươu
Thế nào là mạng điện lắp đặt kiểu nổi
Dạng đột biến một nhiễm là
Biện pháp chống mỏi cơ
Phản ứng thế ankan
Chó sói
Thiếu nhi thế giới liên hoan
điện thế nghỉ