A Performant Antigalloping Device For The 400 k
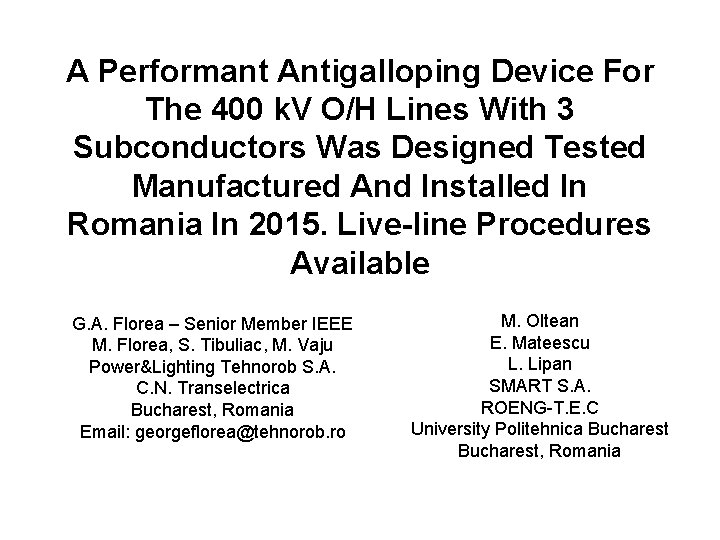
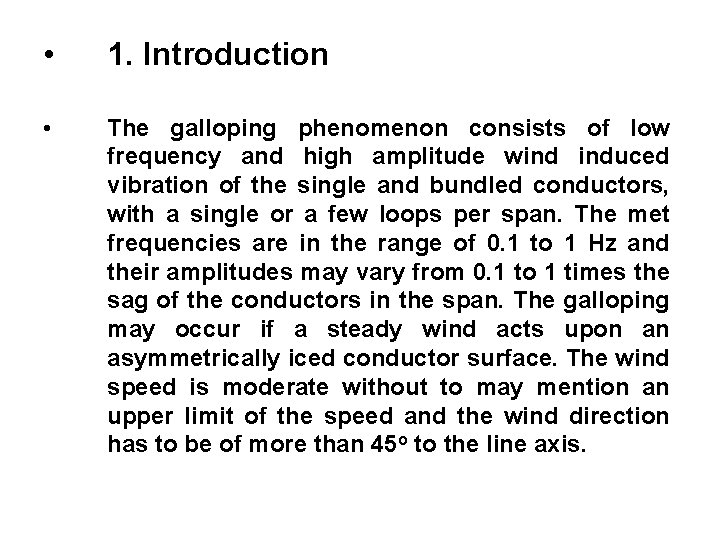
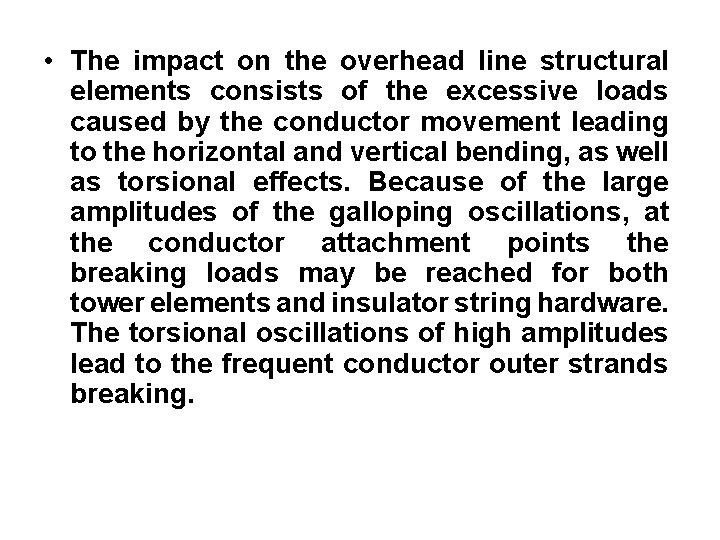
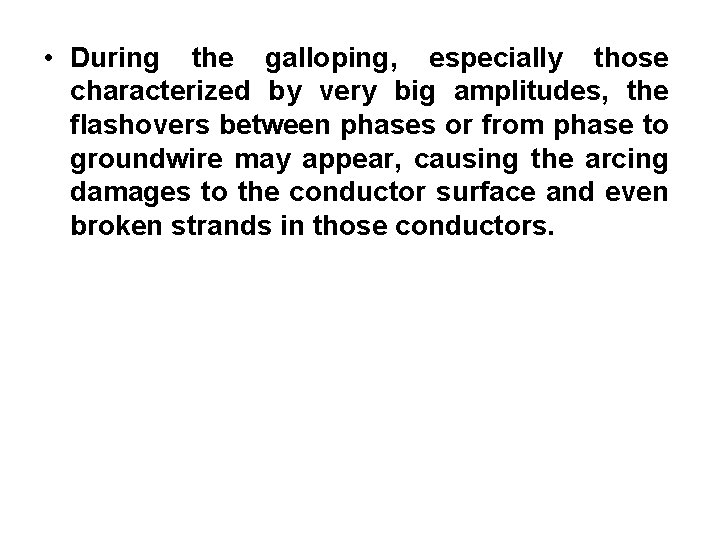
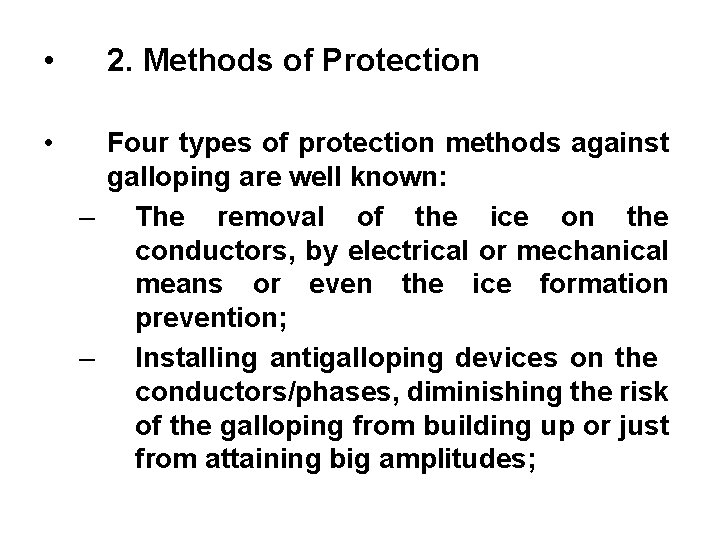
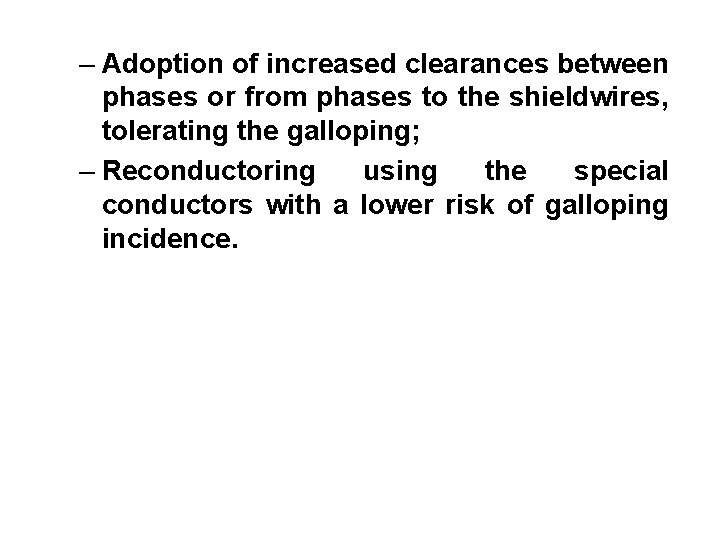
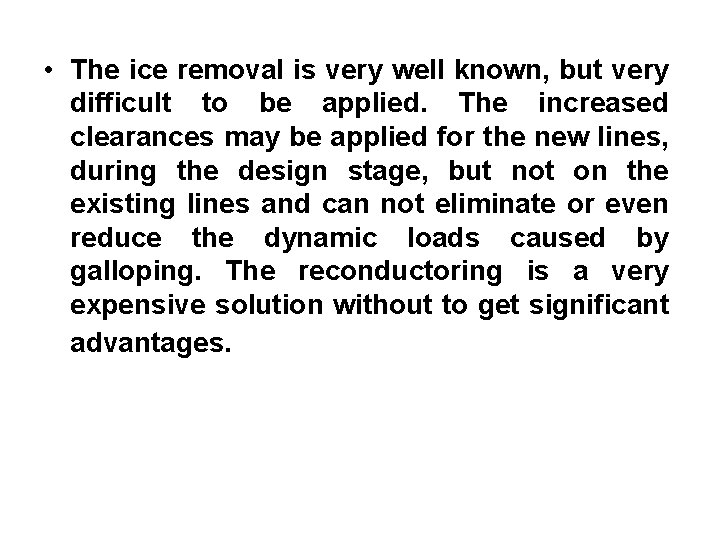
![• Concerning the special antigalloping devices, the CIGRE Brochure no. 322 [1] describes • Concerning the special antigalloping devices, the CIGRE Brochure no. 322 [1] describes](https://slidetodoc.com/presentation_image_h/90e8b453dbf206690ef0d59dc5ec9ab7/image-8.jpg)
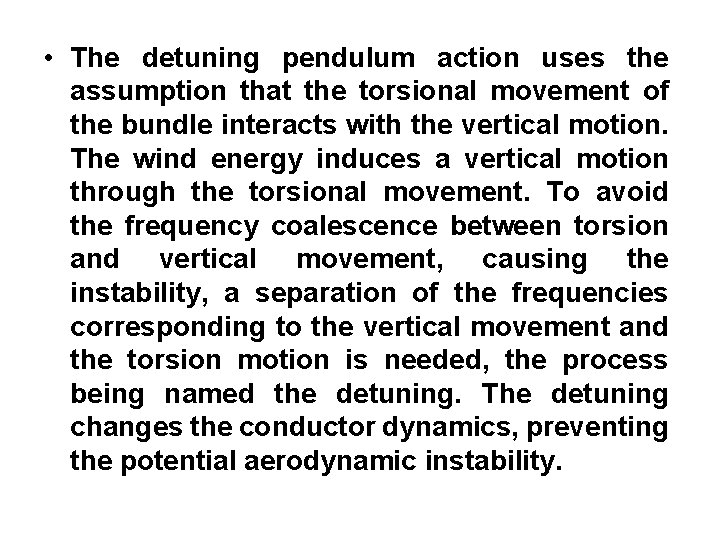
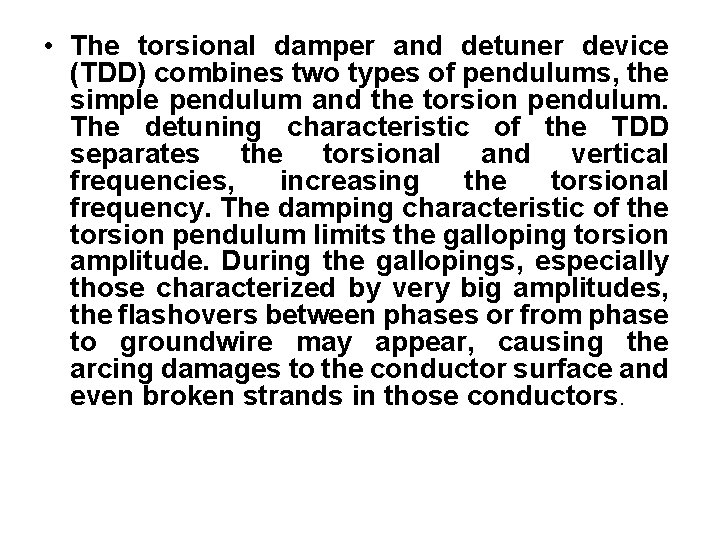
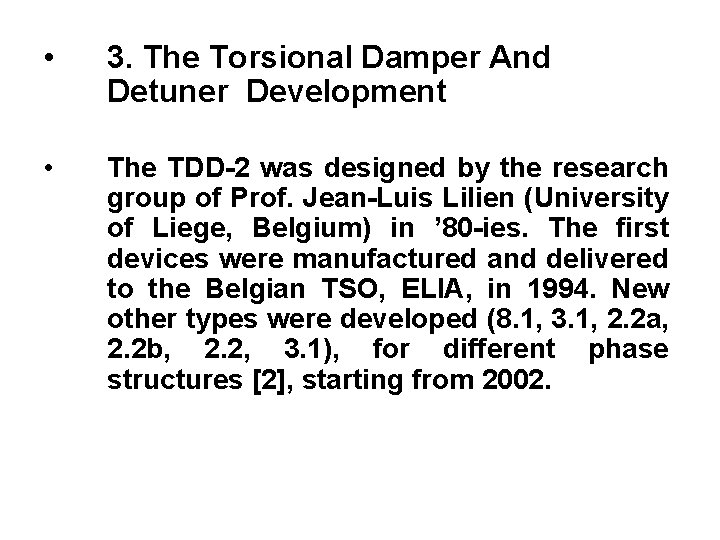
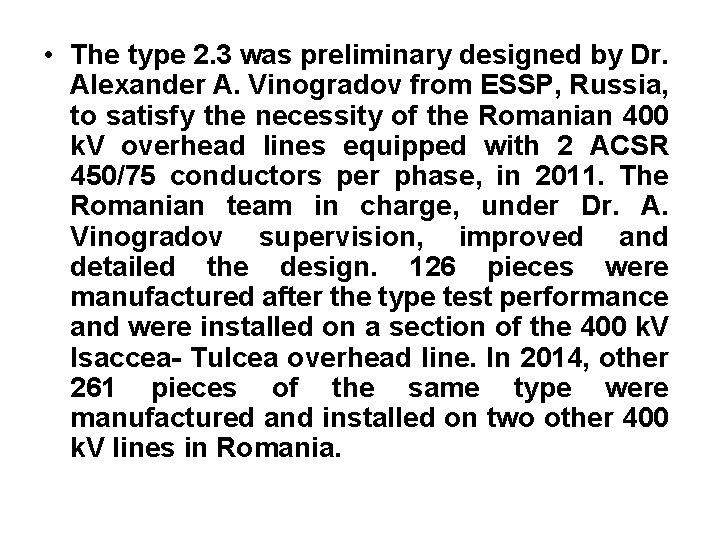
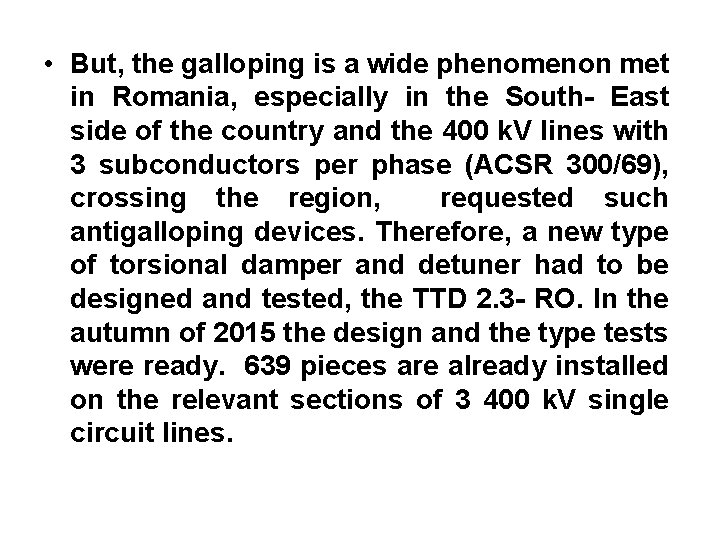
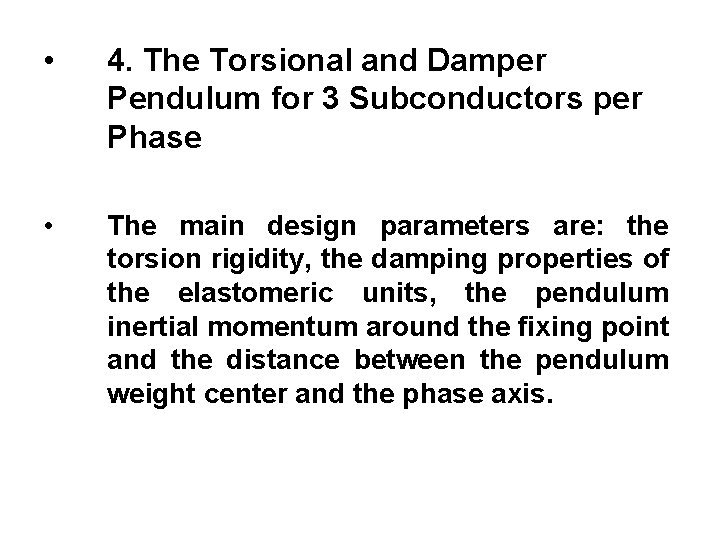
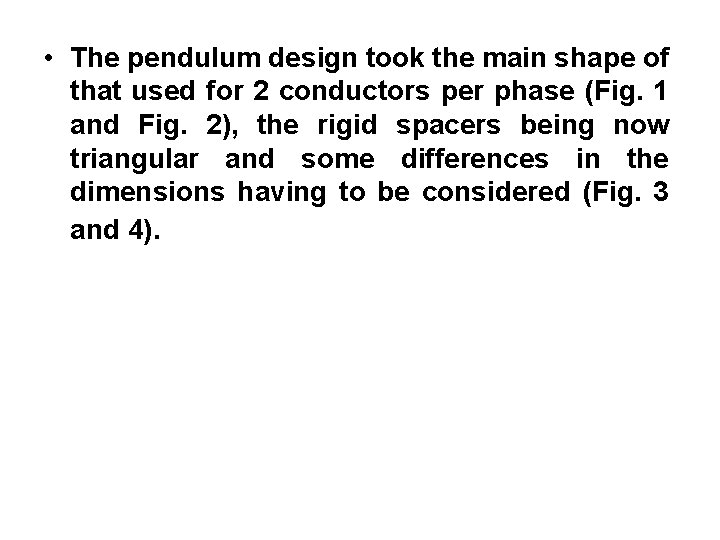
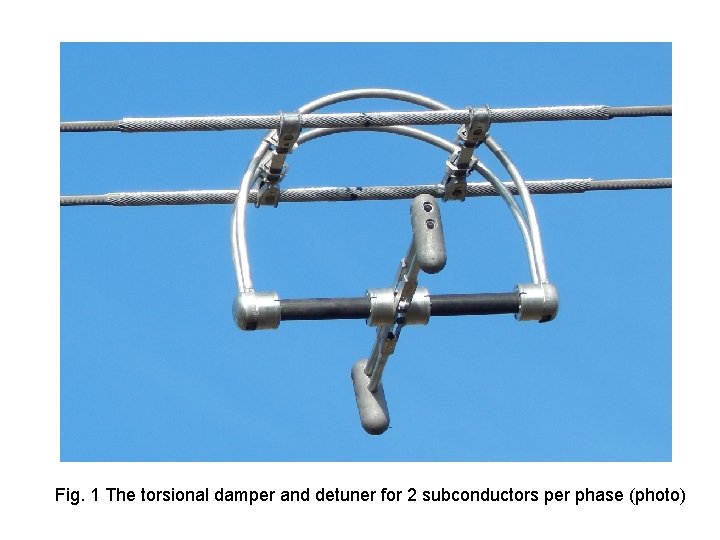
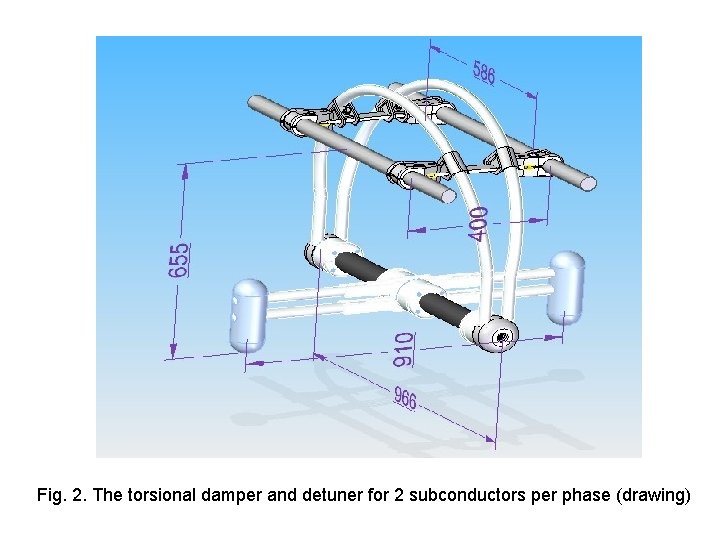
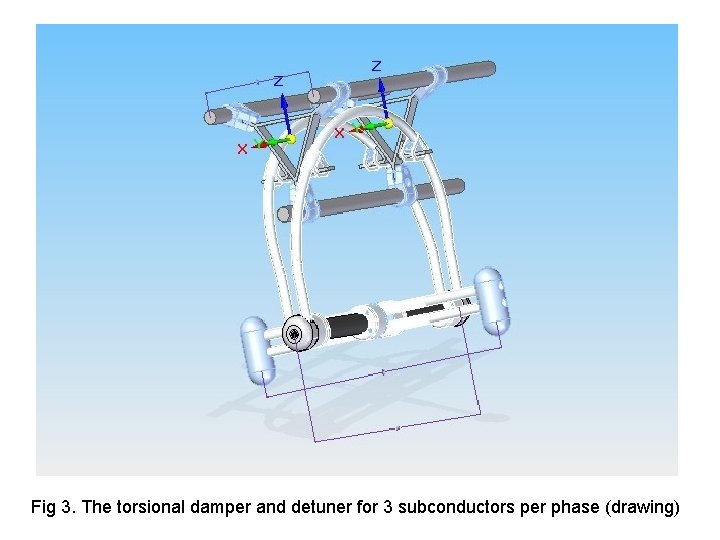
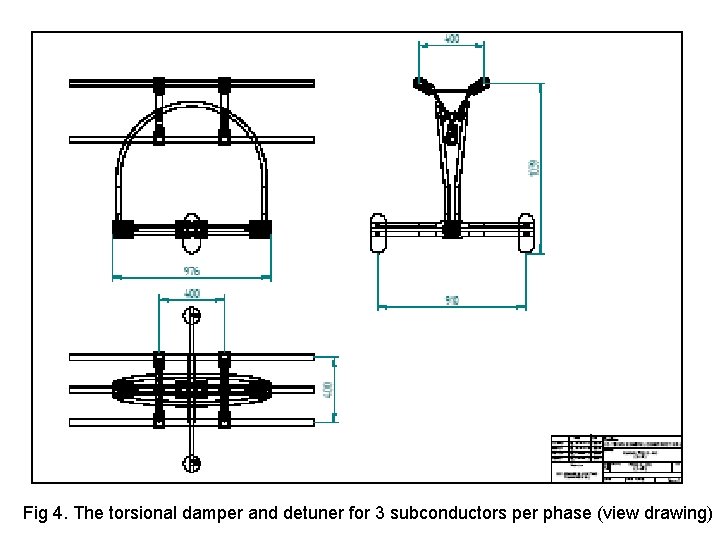
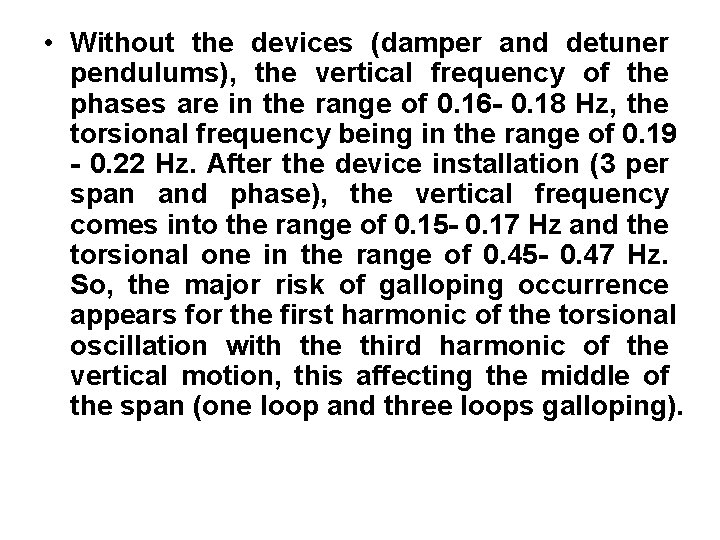
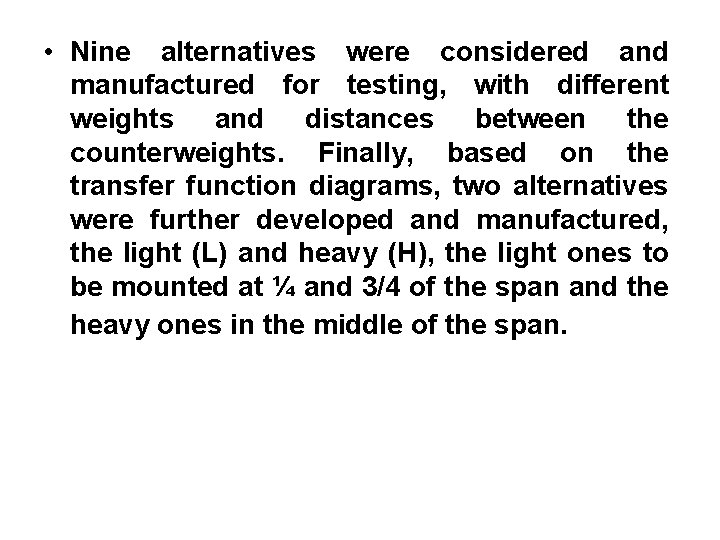

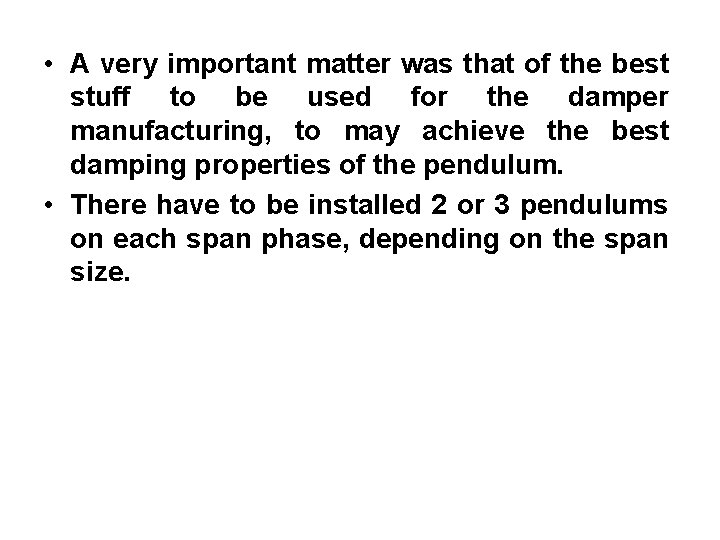
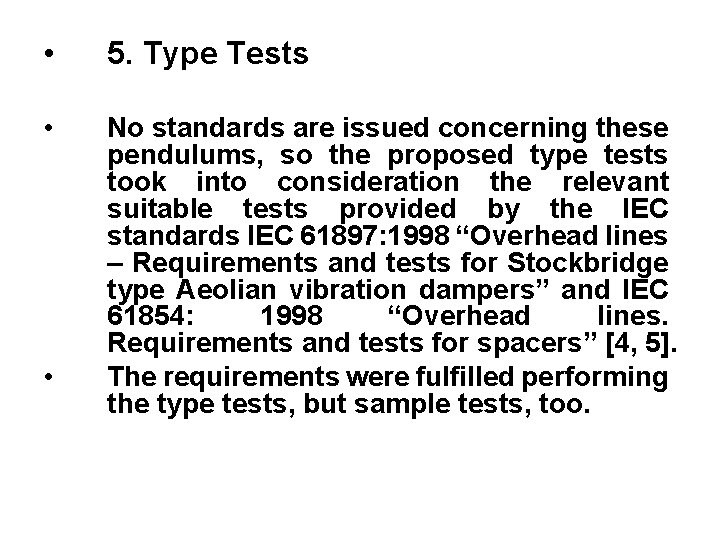
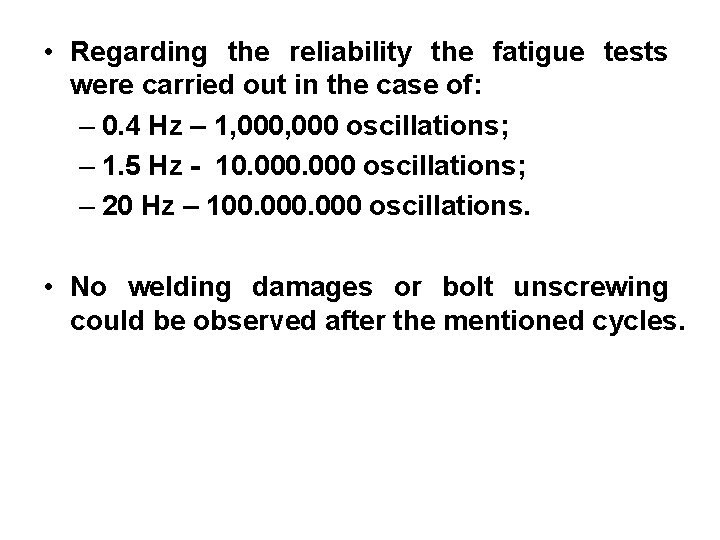
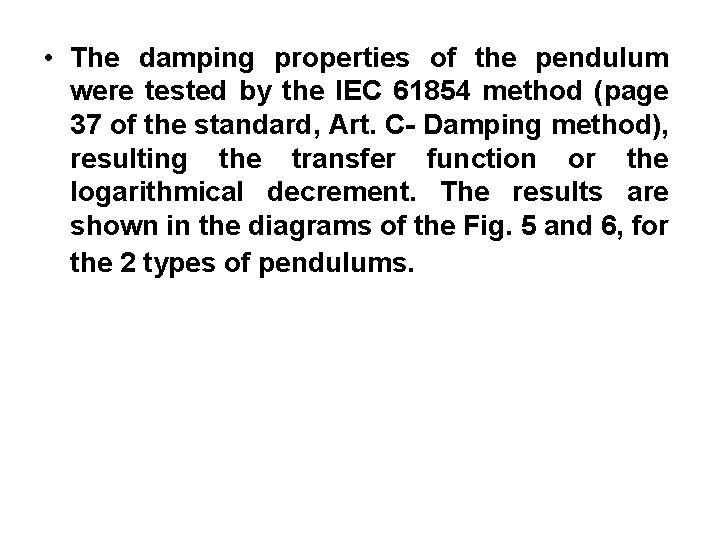
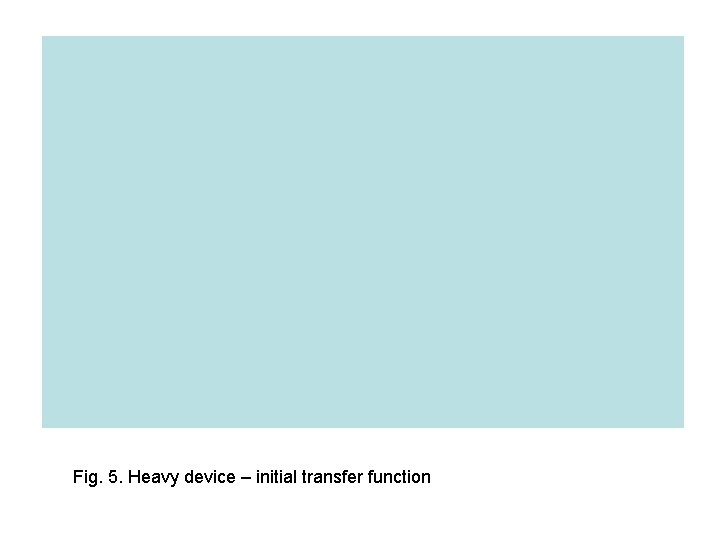
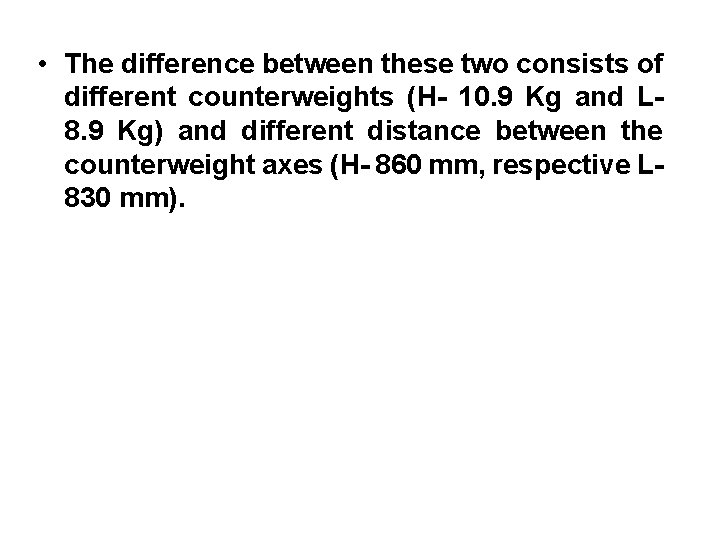
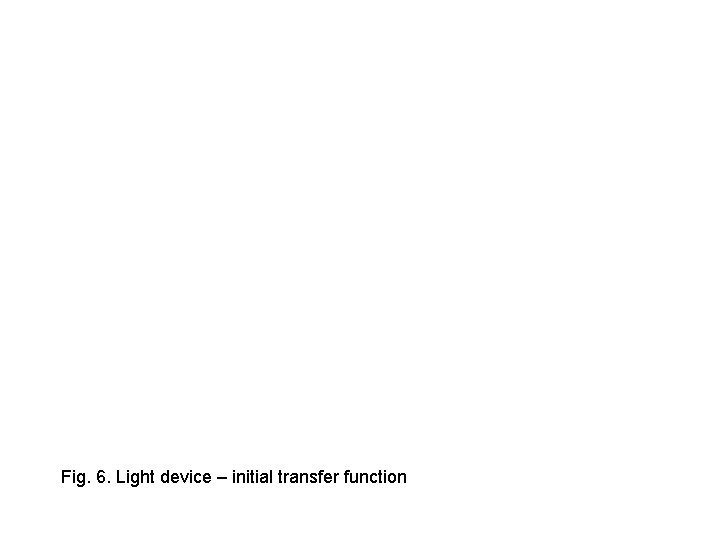
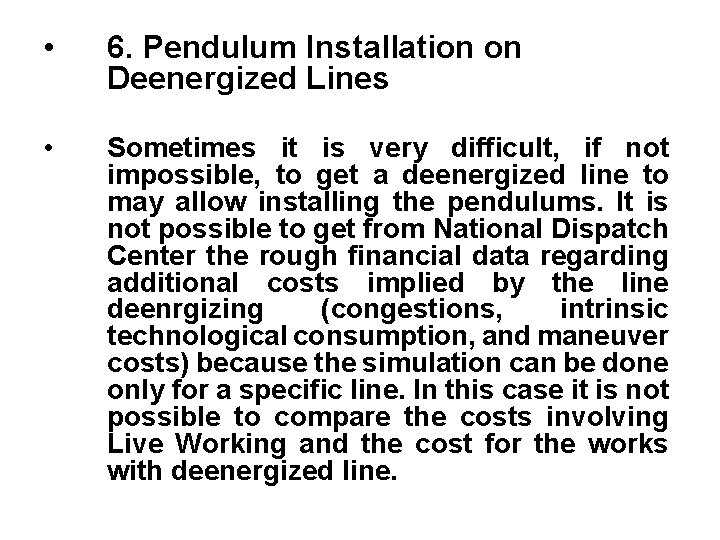
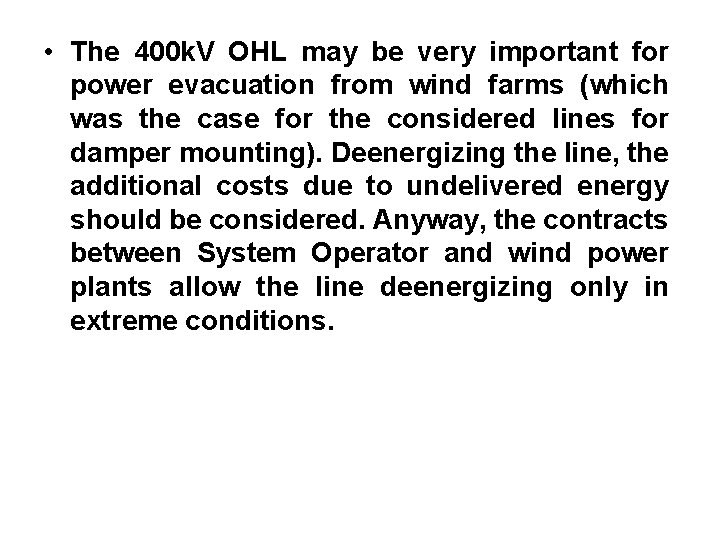
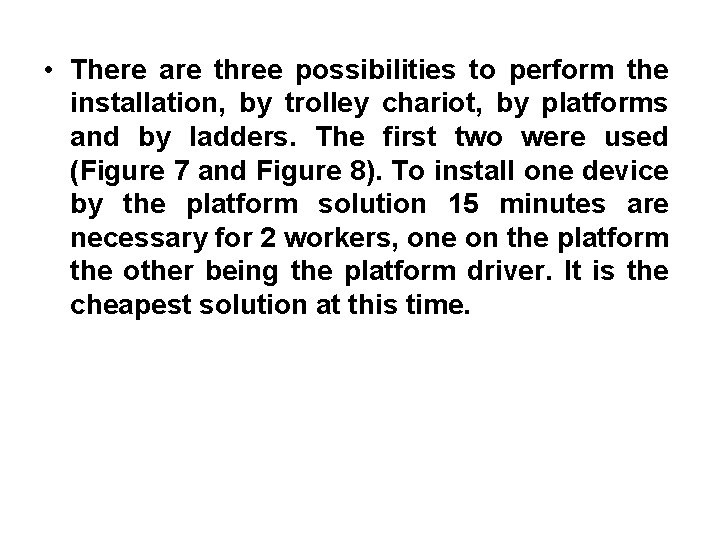
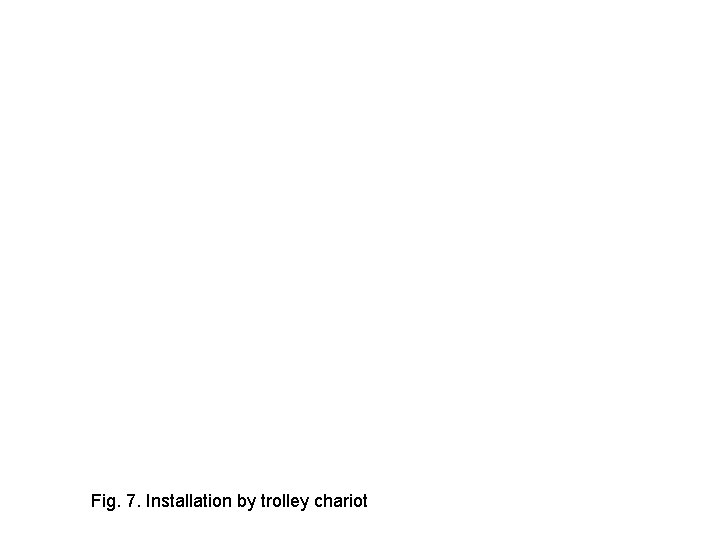
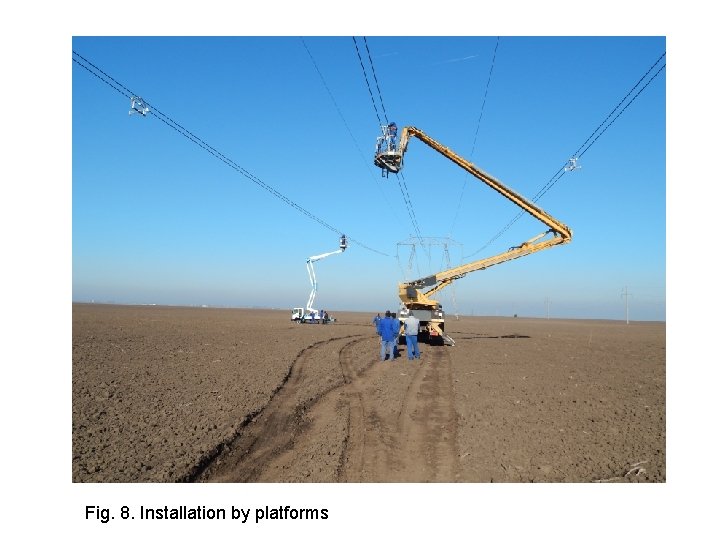
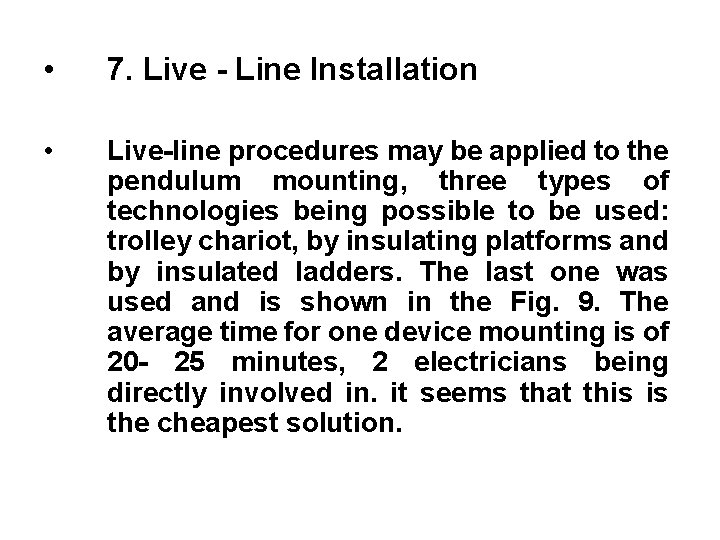
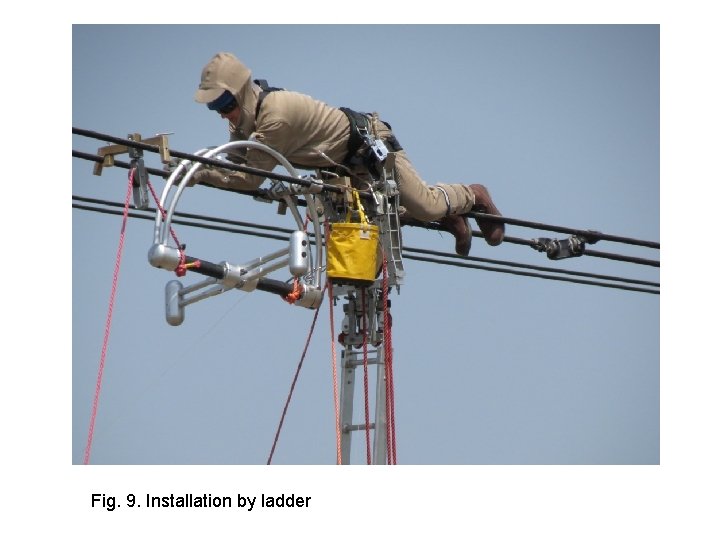
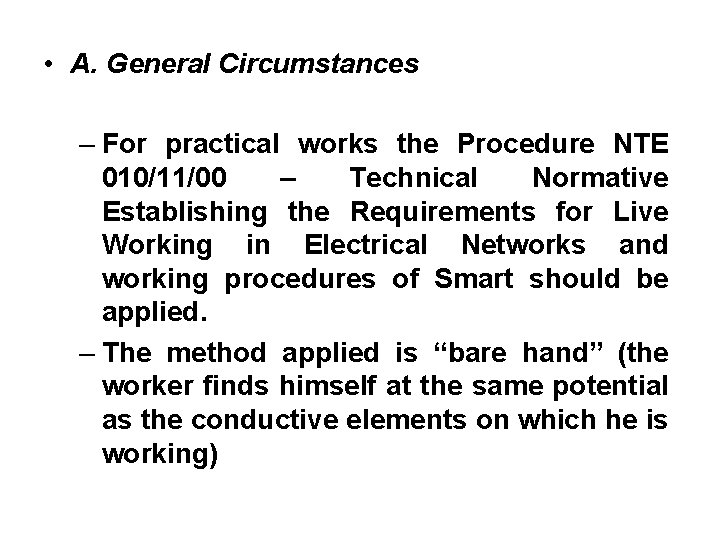
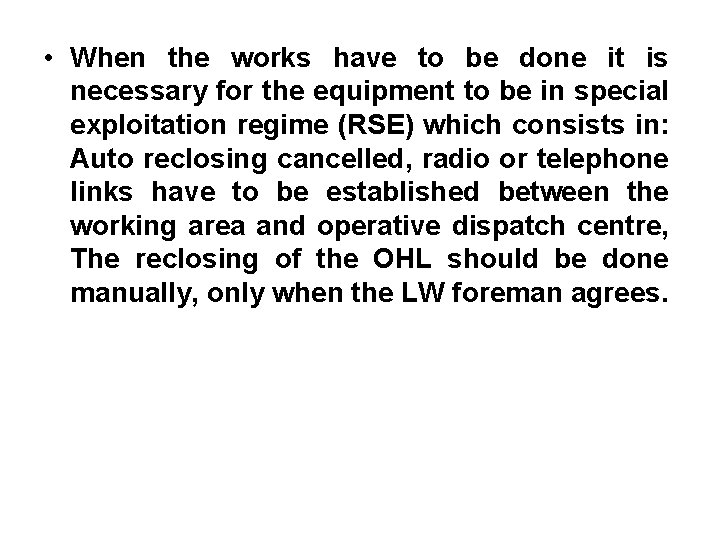
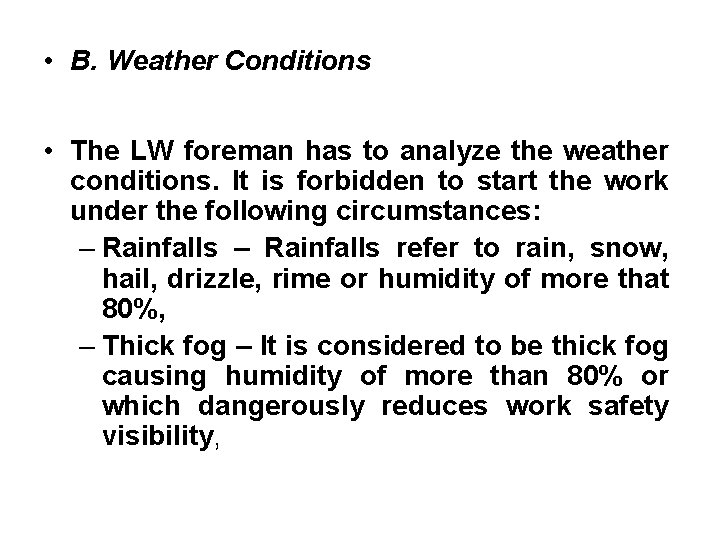
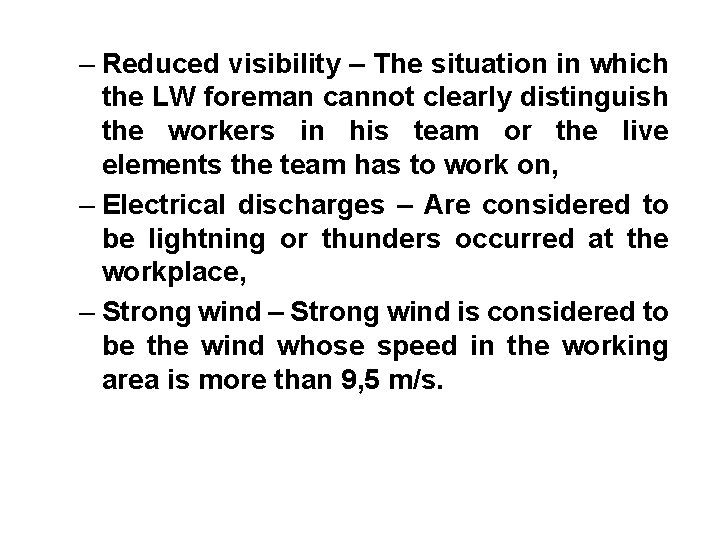
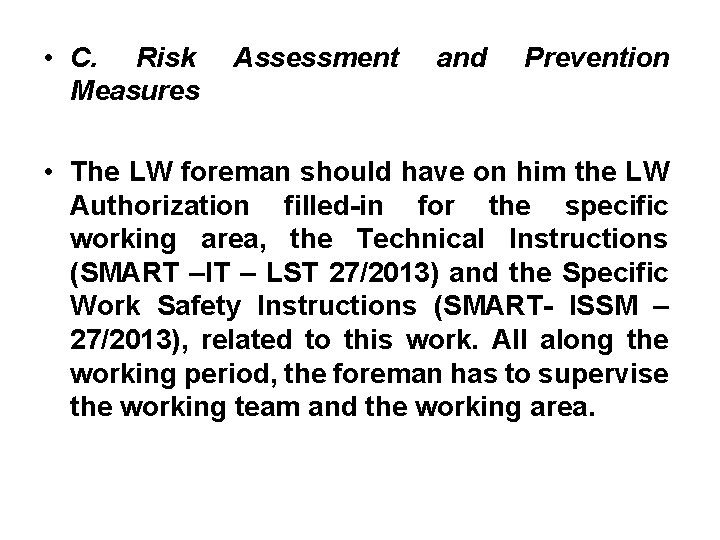
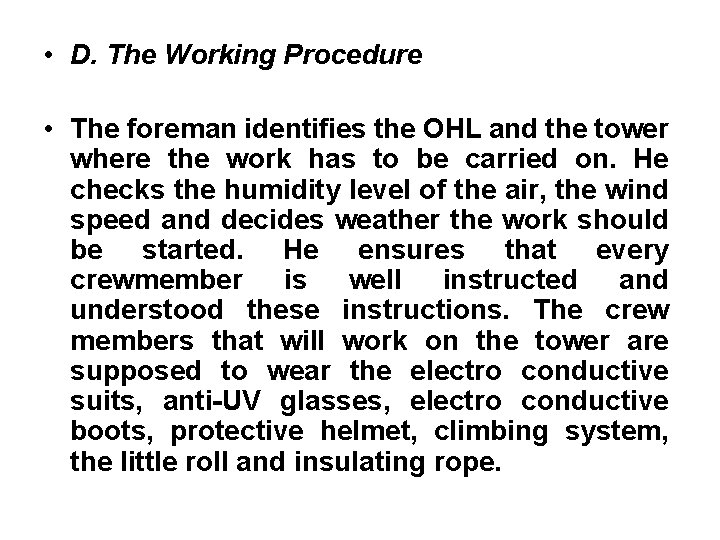
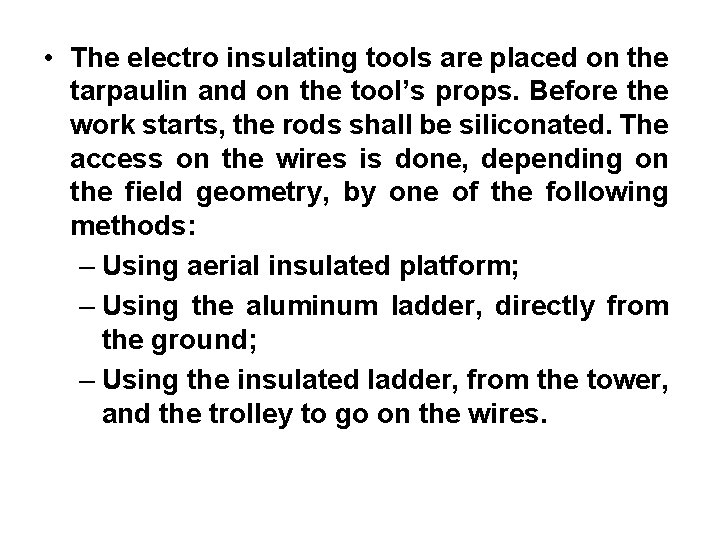
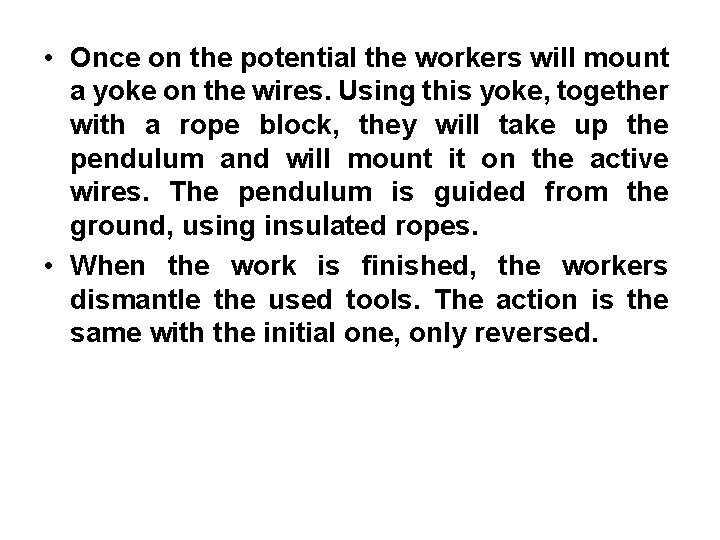
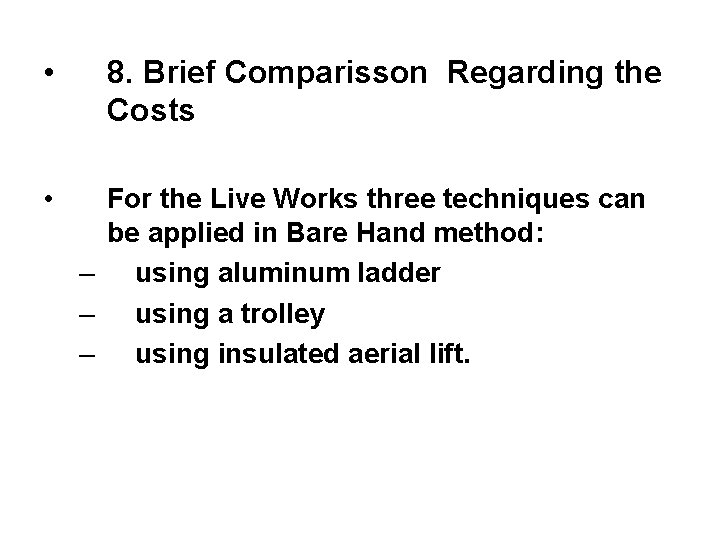
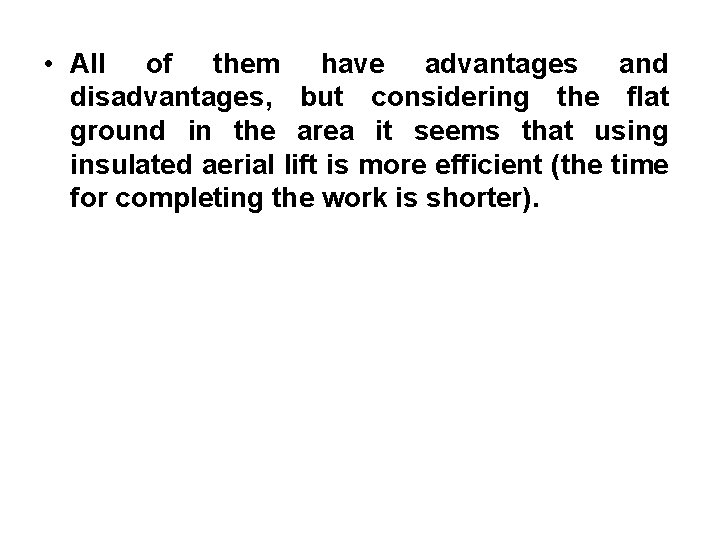
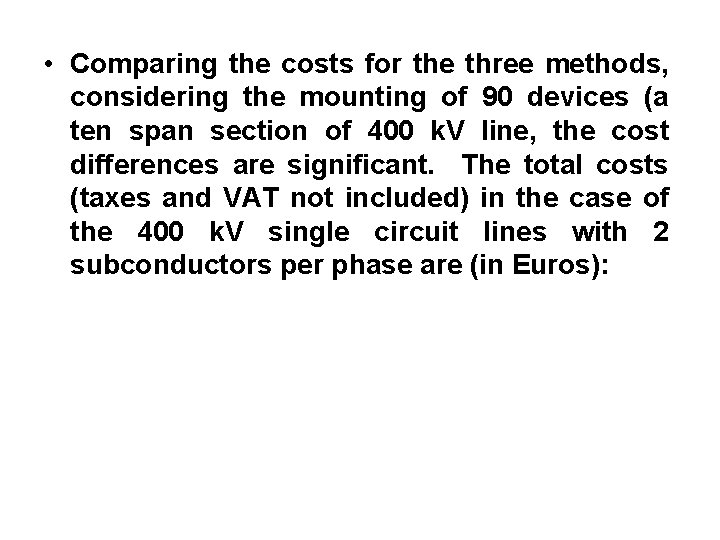
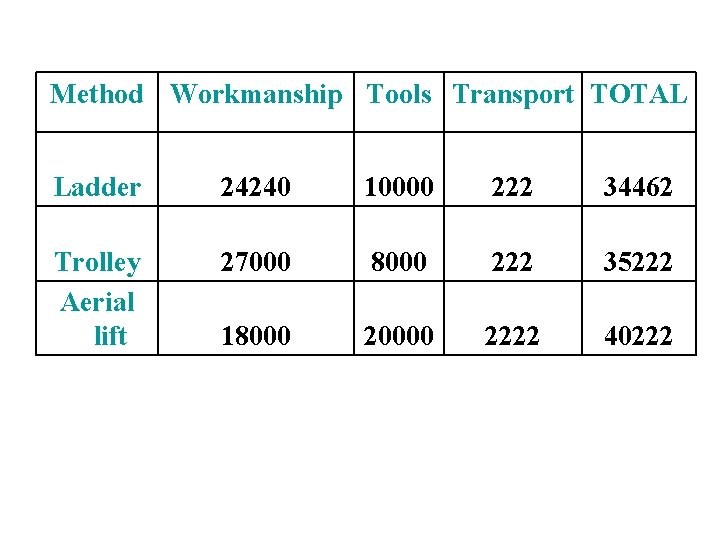
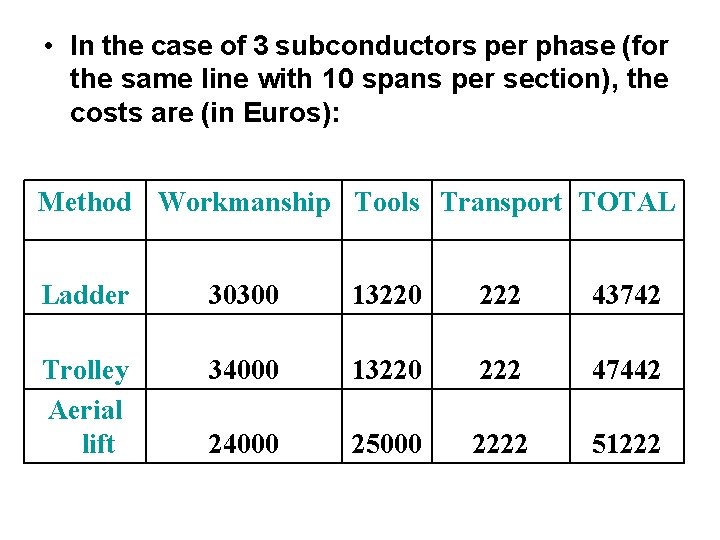
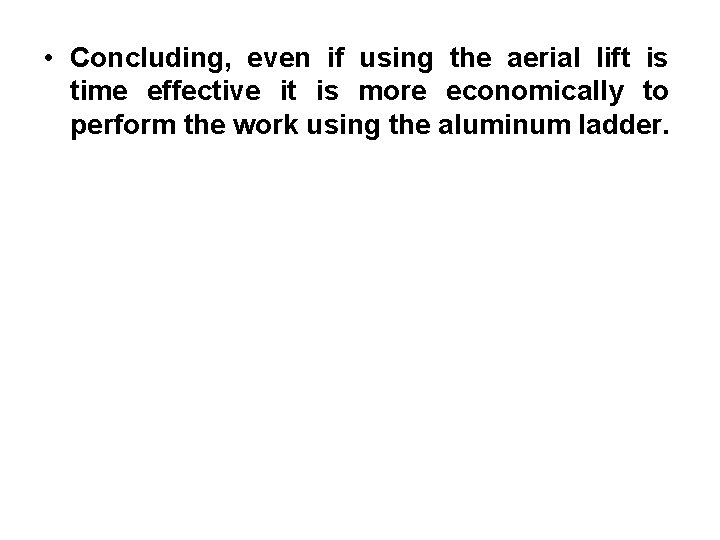
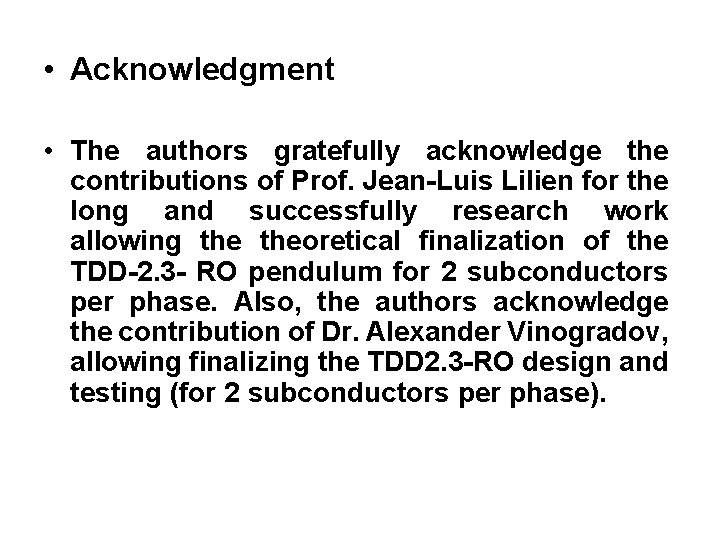
- Slides: 51
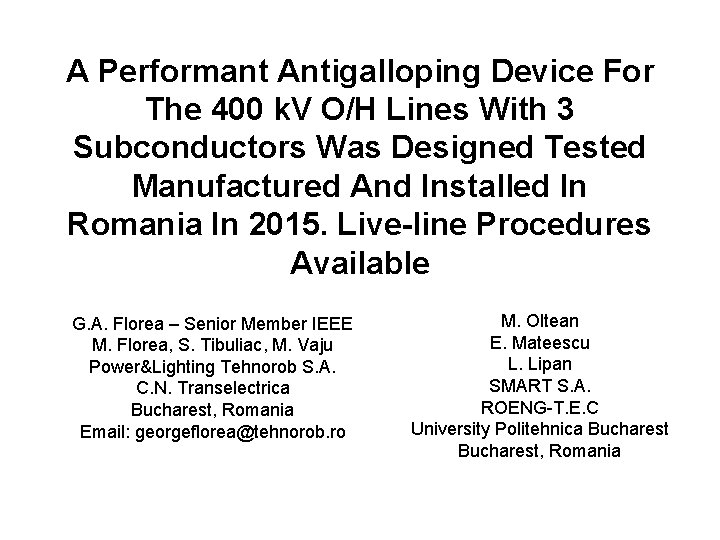
A Performant Antigalloping Device For The 400 k. V O/H Lines With 3 Subconductors Was Designed Tested Manufactured And Installed In Romania In 2015. Live-line Procedures Available G. A. Florea – Senior Member IEEE M. Florea, S. Tibuliac, M. Vaju Power&Lighting Tehnorob S. A. C. N. Transelectrica Bucharest, Romania Email: georgeflorea@tehnorob. ro M. Oltean E. Mateescu L. Lipan SMART S. A. ROENG-T. E. C University Politehnica Bucharest, Romania
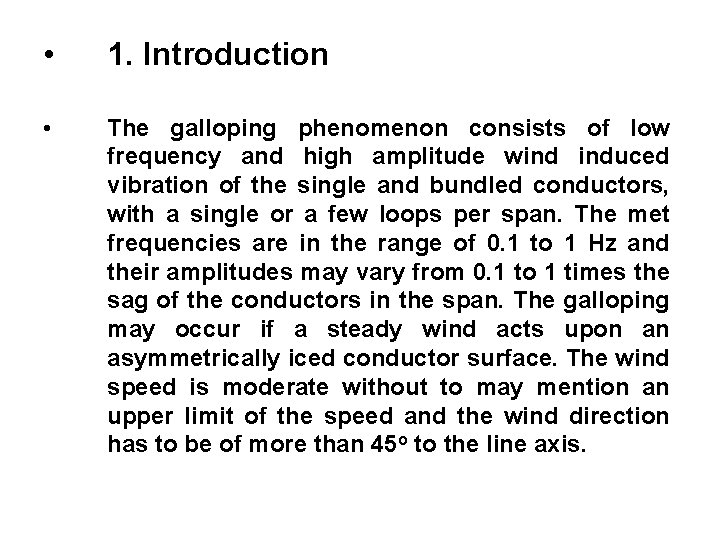
• 1. Introduction • The galloping phenomenon consists of low frequency and high amplitude wind induced vibration of the single and bundled conductors, with a single or a few loops per span. The met frequencies are in the range of 0. 1 to 1 Hz and their amplitudes may vary from 0. 1 to 1 times the sag of the conductors in the span. The galloping may occur if a steady wind acts upon an asymmetrically iced conductor surface. The wind speed is moderate without to may mention an upper limit of the speed and the wind direction has to be of more than 45 o to the line axis.
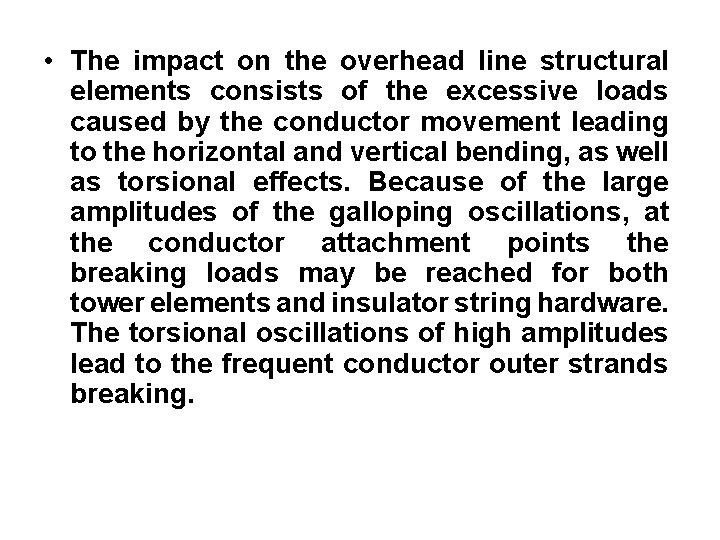
• The impact on the overhead line structural elements consists of the excessive loads caused by the conductor movement leading to the horizontal and vertical bending, as well as torsional effects. Because of the large amplitudes of the galloping oscillations, at the conductor attachment points the breaking loads may be reached for both tower elements and insulator string hardware. The torsional oscillations of high amplitudes lead to the frequent conductor outer strands breaking.
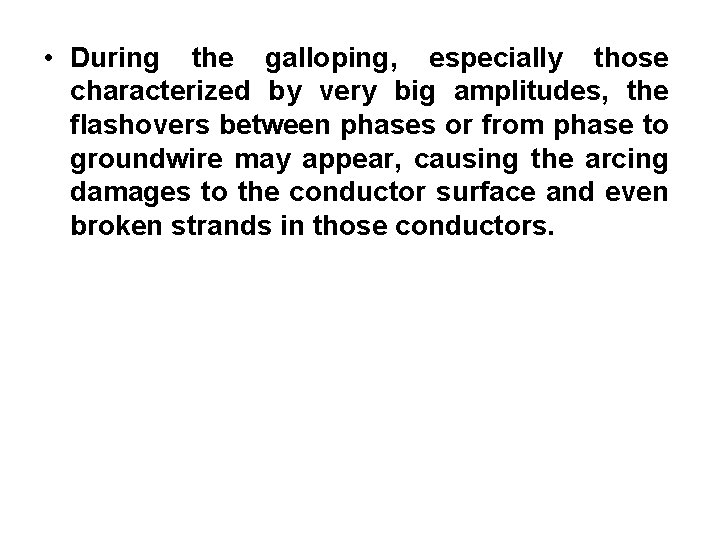
• During the galloping, especially those characterized by very big amplitudes, the flashovers between phases or from phase to groundwire may appear, causing the arcing damages to the conductor surface and even broken strands in those conductors.
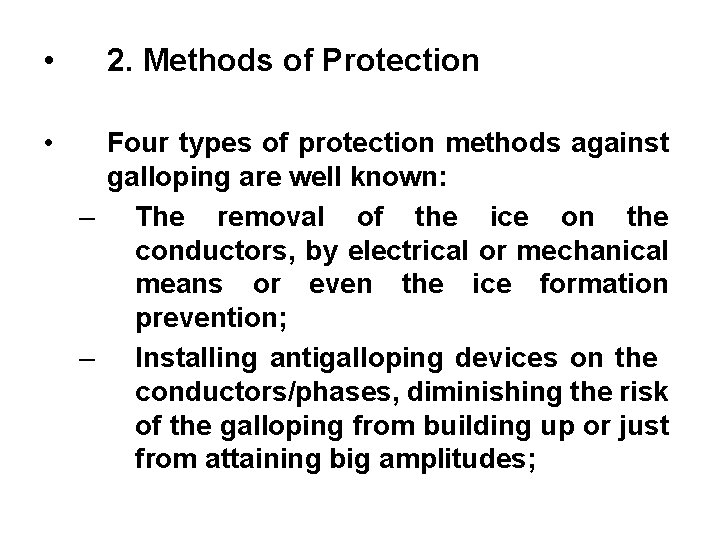
• • 2. Methods of Protection Four types of protection methods against galloping are well known: – The removal of the ice on the conductors, by electrical or mechanical means or even the ice formation prevention; – Installing antigalloping devices on the conductors/phases, diminishing the risk of the galloping from building up or just from attaining big amplitudes;
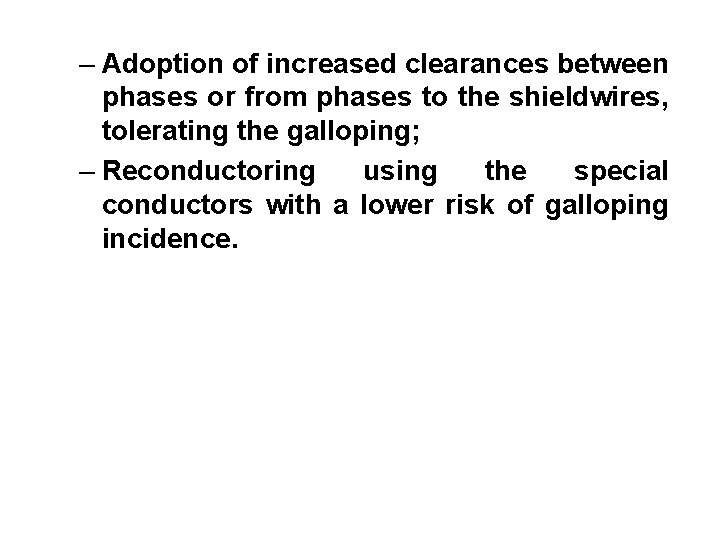
– Adoption of increased clearances between phases or from phases to the shieldwires, tolerating the galloping; – Reconductoring using the special conductors with a lower risk of galloping incidence.
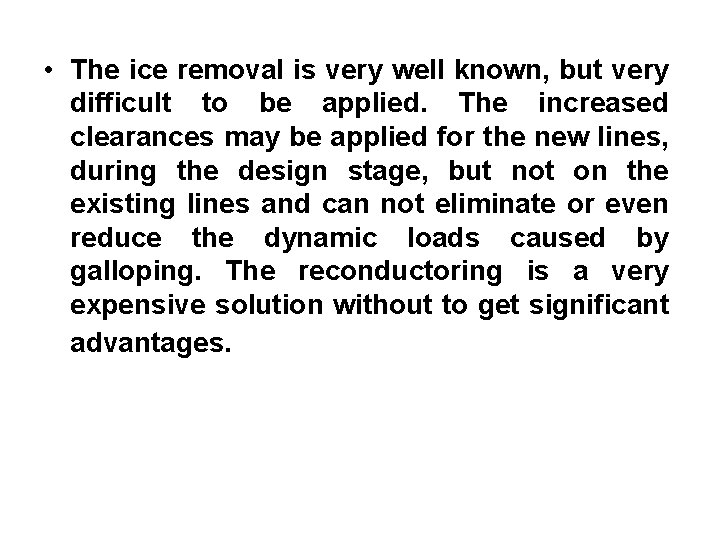
• The ice removal is very well known, but very difficult to be applied. The increased clearances may be applied for the new lines, during the design stage, but not on the existing lines and can not eliminate or even reduce the dynamic loads caused by galloping. The reconductoring is a very expensive solution without to get significant advantages.
![Concerning the special antigalloping devices the CIGRE Brochure no 322 1 describes • Concerning the special antigalloping devices, the CIGRE Brochure no. 322 [1] describes](https://slidetodoc.com/presentation_image_h/90e8b453dbf206690ef0d59dc5ec9ab7/image-8.jpg)
• Concerning the special antigalloping devices, the CIGRE Brochure no. 322 [1] describes 14 types, mentioning their characteristics, advantages and disadvantages. The most used devices are: the rigid and flexible interphase spacers, the air flow spoilers and the detuning pendulums. The best behavior was got by the detuning pendulums, with a galloping amplitude reduction of about 90%.
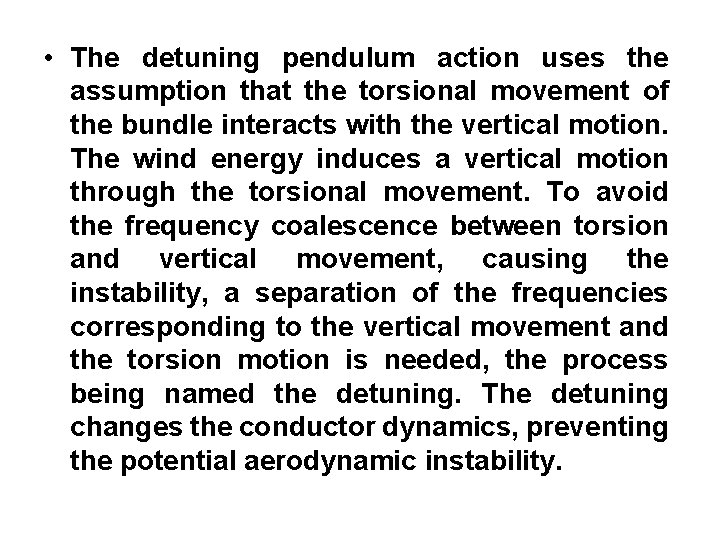
• The detuning pendulum action uses the assumption that the torsional movement of the bundle interacts with the vertical motion. The wind energy induces a vertical motion through the torsional movement. To avoid the frequency coalescence between torsion and vertical movement, causing the instability, a separation of the frequencies corresponding to the vertical movement and the torsion motion is needed, the process being named the detuning. The detuning changes the conductor dynamics, preventing the potential aerodynamic instability.
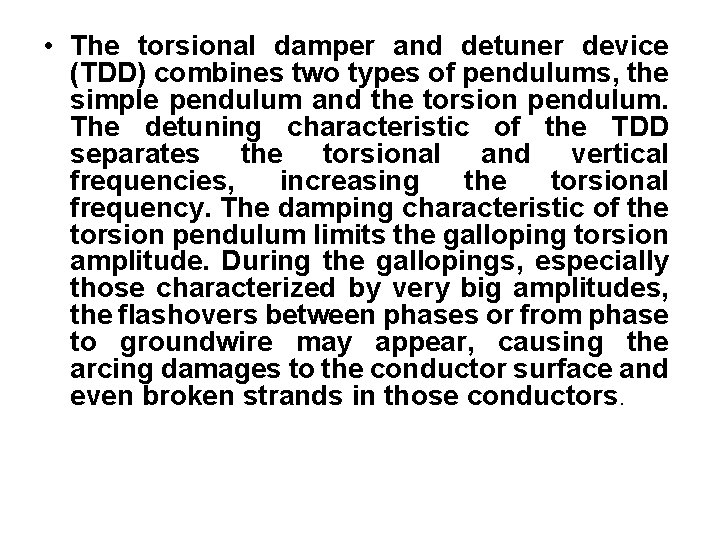
• The torsional damper and detuner device (TDD) combines two types of pendulums, the simple pendulum and the torsion pendulum. The detuning characteristic of the TDD separates the torsional and vertical frequencies, increasing the torsional frequency. The damping characteristic of the torsion pendulum limits the galloping torsion amplitude. During the gallopings, especially those characterized by very big amplitudes, the flashovers between phases or from phase to groundwire may appear, causing the arcing damages to the conductor surface and even broken strands in those conductors.
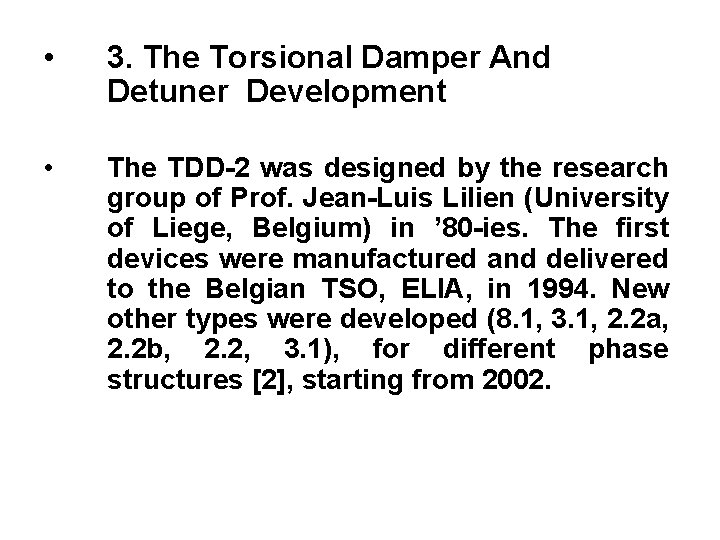
• 3. The Torsional Damper And Detuner Development • The TDD-2 was designed by the research group of Prof. Jean-Luis Lilien (University of Liege, Belgium) in ’ 80 -ies. The first devices were manufactured and delivered to the Belgian TSO, ELIA, in 1994. New other types were developed (8. 1, 3. 1, 2. 2 a, 2. 2 b, 2. 2, 3. 1), for different phase structures [2], starting from 2002.
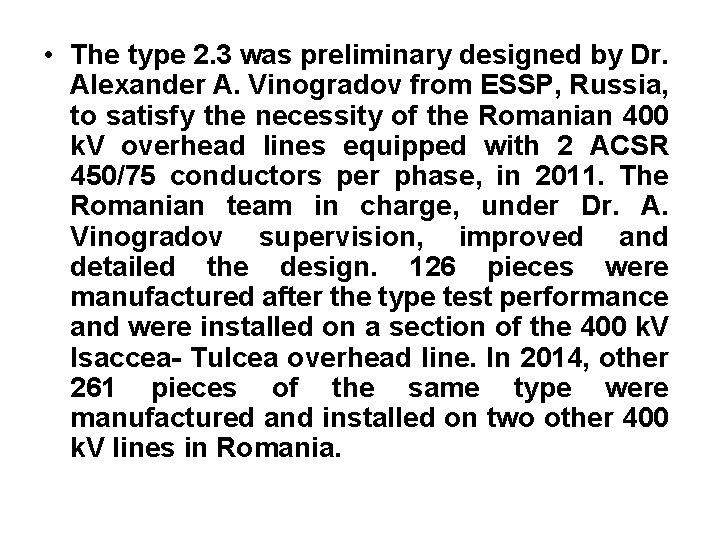
• The type 2. 3 was preliminary designed by Dr. Alexander A. Vinogradov from ESSP, Russia, to satisfy the necessity of the Romanian 400 k. V overhead lines equipped with 2 ACSR 450/75 conductors per phase, in 2011. The Romanian team in charge, under Dr. A. Vinogradov supervision, improved and detailed the design. 126 pieces were manufactured after the type test performance and were installed on a section of the 400 k. V Isaccea- Tulcea overhead line. In 2014, other 261 pieces of the same type were manufactured and installed on two other 400 k. V lines in Romania.
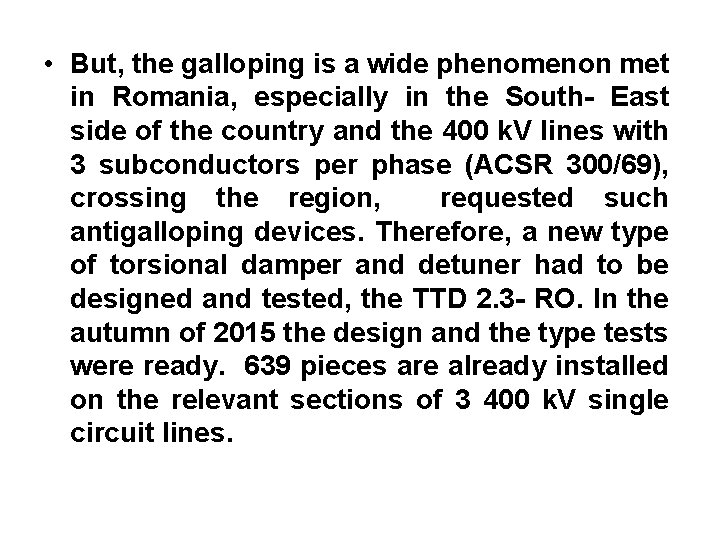
• But, the galloping is a wide phenomenon met in Romania, especially in the South- East side of the country and the 400 k. V lines with 3 subconductors per phase (ACSR 300/69), crossing the region, requested such antigalloping devices. Therefore, a new type of torsional damper and detuner had to be designed and tested, the TTD 2. 3 - RO. In the autumn of 2015 the design and the type tests were ready. 639 pieces are already installed on the relevant sections of 3 400 k. V single circuit lines.
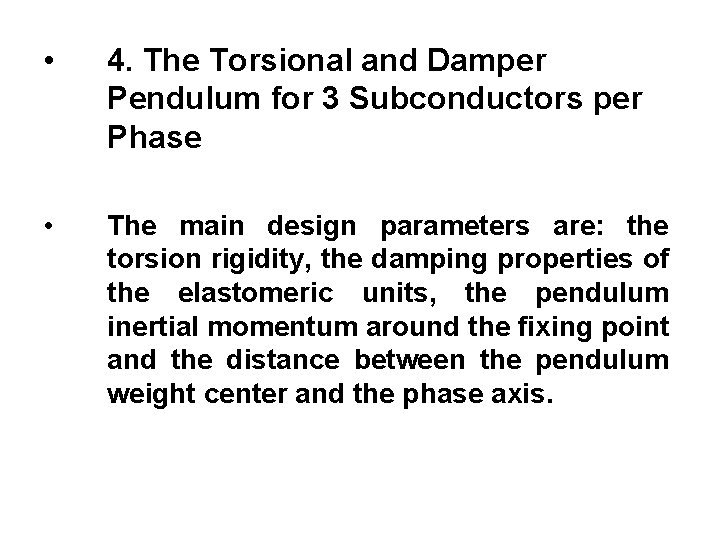
• 4. The Torsional and Damper Pendulum for 3 Subconductors per Phase • The main design parameters are: the torsion rigidity, the damping properties of the elastomeric units, the pendulum inertial momentum around the fixing point and the distance between the pendulum weight center and the phase axis.
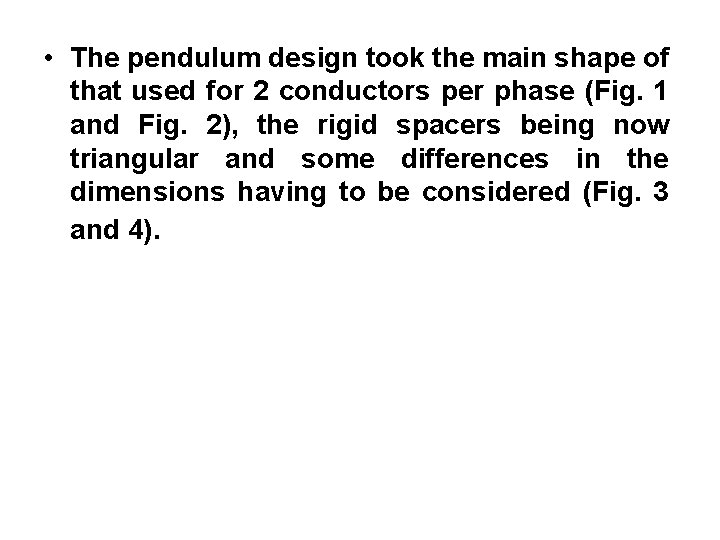
• The pendulum design took the main shape of that used for 2 conductors per phase (Fig. 1 and Fig. 2), the rigid spacers being now triangular and some differences in the dimensions having to be considered (Fig. 3 and 4).
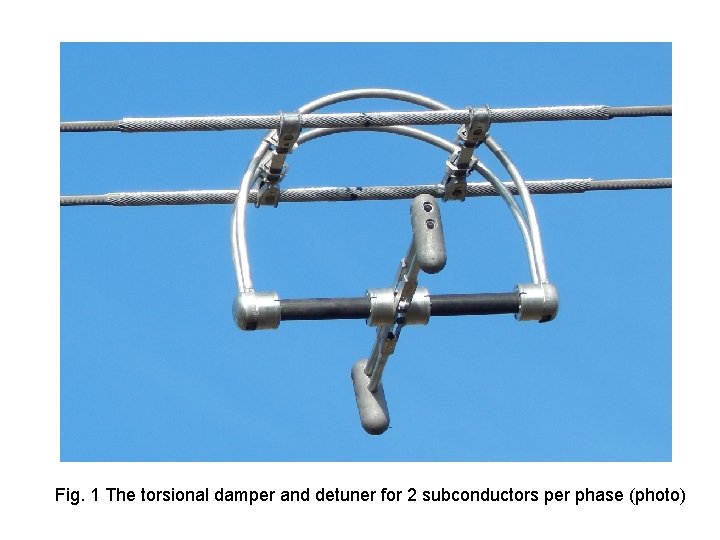
Fig. 1 The torsional damper and detuner for 2 subconductors per phase (photo)
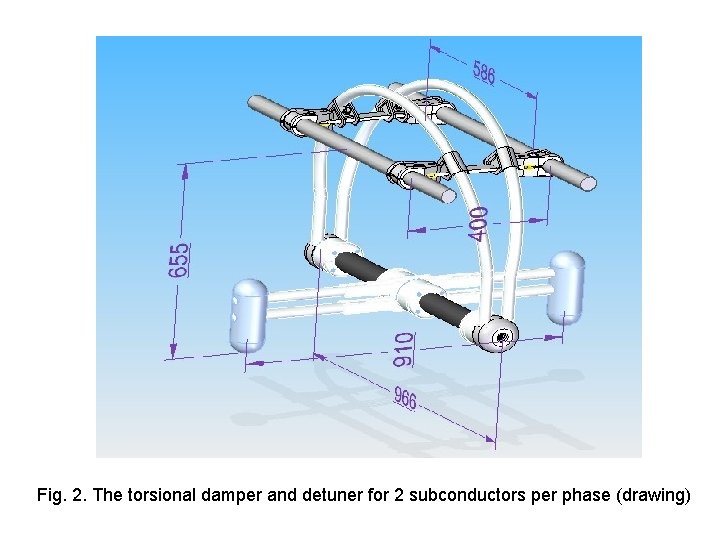
Fig. 2. The torsional damper and detuner for 2 subconductors per phase (drawing)
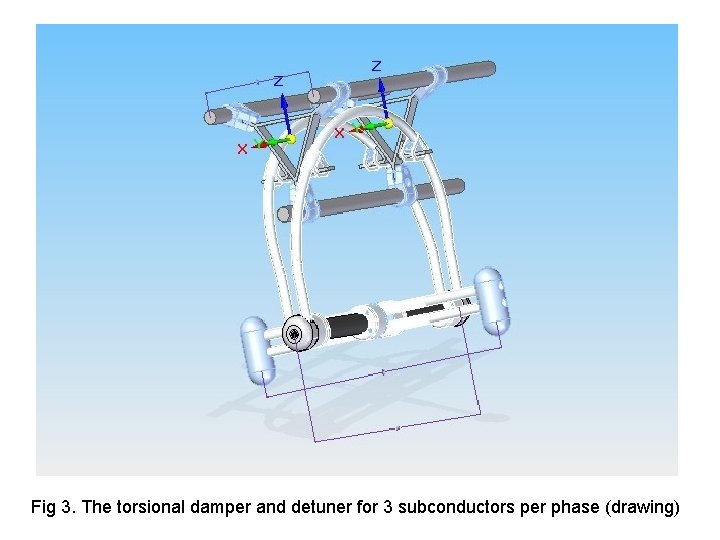
Fig 3. The torsional damper and detuner for 3 subconductors per phase (drawing)
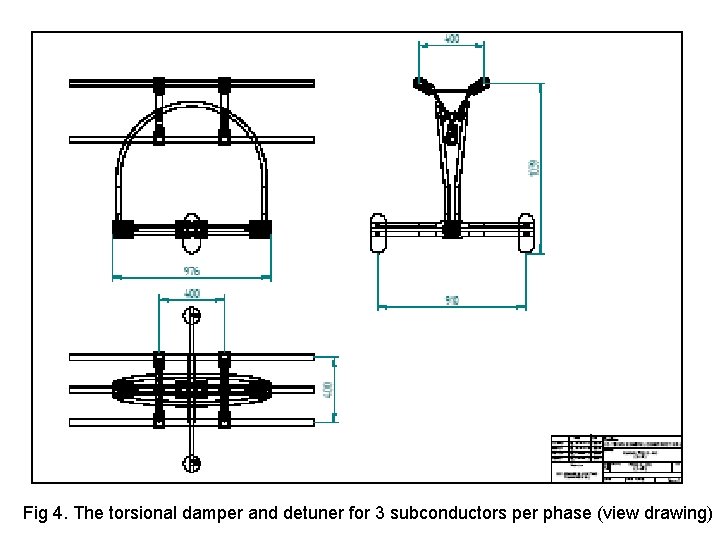
Fig 4. The torsional damper and detuner for 3 subconductors per phase (view drawing)
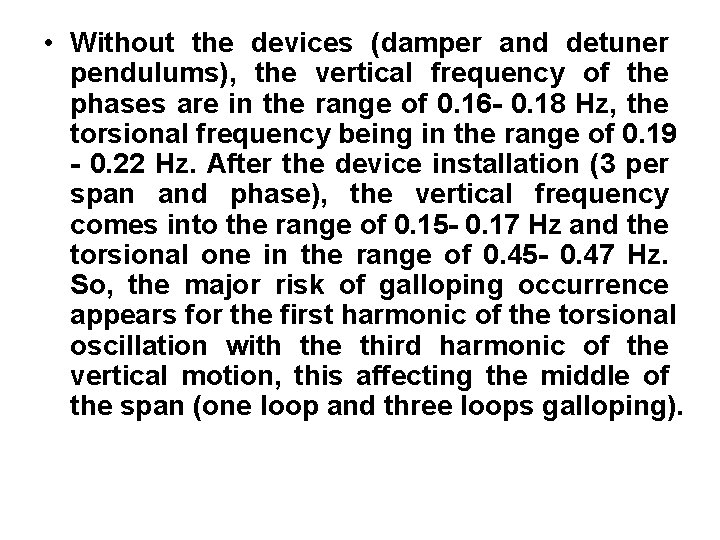
• Without the devices (damper and detuner pendulums), the vertical frequency of the phases are in the range of 0. 16 - 0. 18 Hz, the torsional frequency being in the range of 0. 19 - 0. 22 Hz. After the device installation (3 per span and phase), the vertical frequency comes into the range of 0. 15 - 0. 17 Hz and the torsional one in the range of 0. 45 - 0. 47 Hz. So, the major risk of galloping occurrence appears for the first harmonic of the torsional oscillation with the third harmonic of the vertical motion, this affecting the middle of the span (one loop and three loops galloping).
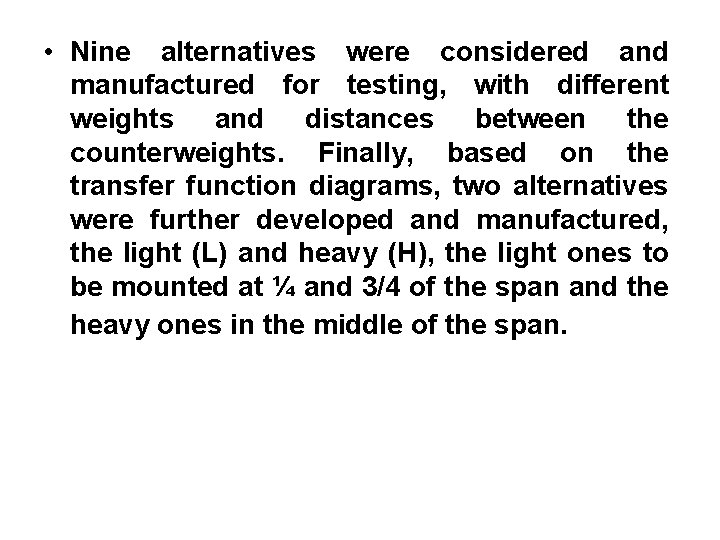
• Nine alternatives were considered and manufactured for testing, with different weights and distances between the counterweights. Finally, based on the transfer function diagrams, two alternatives were further developed and manufactured, the light (L) and heavy (H), the light ones to be mounted at ¼ and 3/4 of the span and the heavy ones in the middle of the span.

• The pendulum structure is composed by 127 components. The most important parts are: the 2 rigid spacers, the 2 tie rods, the elastomeric damper sleeves, the counterweight axes and the 2 counterweights. The pendulum rigid spacers are fixed on the armour rod protected subconductors.
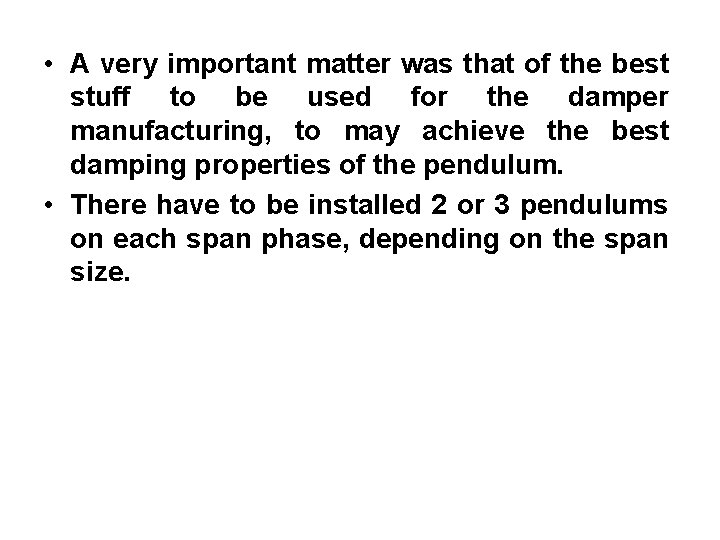
• A very important matter was that of the best stuff to be used for the damper manufacturing, to may achieve the best damping properties of the pendulum. • There have to be installed 2 or 3 pendulums on each span phase, depending on the span size.
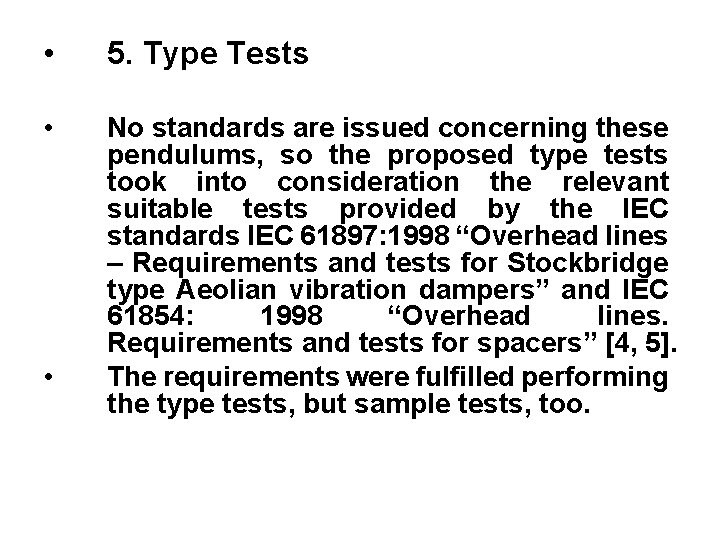
• 5. Type Tests • No standards are issued concerning these pendulums, so the proposed type tests took into consideration the relevant suitable tests provided by the IEC standards IEC 61897: 1998 “Overhead lines – Requirements and tests for Stockbridge type Aeolian vibration dampers” and IEC 61854: 1998 “Overhead lines. Requirements and tests for spacers” [4, 5]. The requirements were fulfilled performing the type tests, but sample tests, too. •
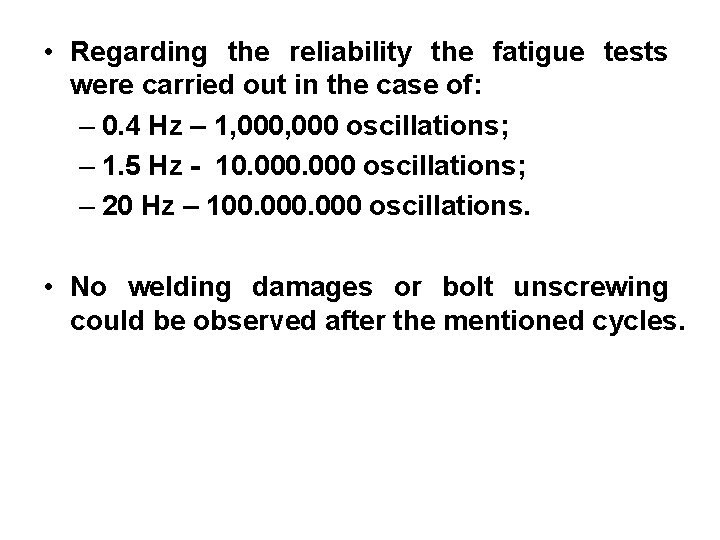
• Regarding the reliability the fatigue tests were carried out in the case of: – 0. 4 Hz – 1, 000 oscillations; – 1. 5 Hz - 10. 000 oscillations; – 20 Hz – 100. 000 oscillations. • No welding damages or bolt unscrewing could be observed after the mentioned cycles.
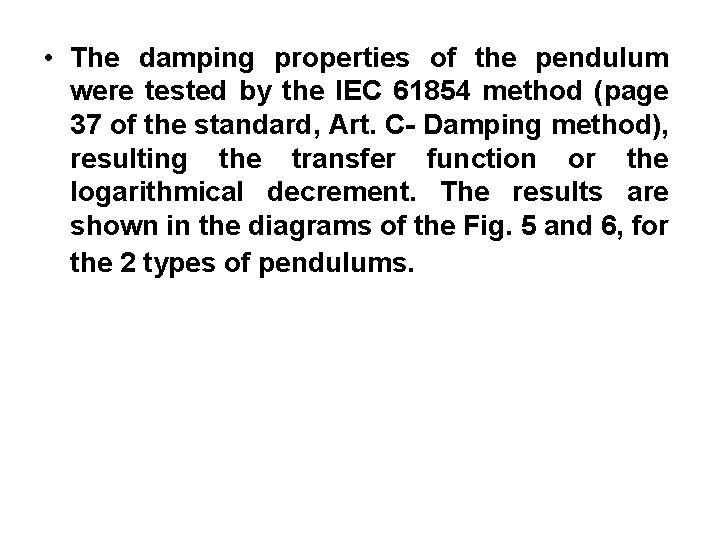
• The damping properties of the pendulum were tested by the IEC 61854 method (page 37 of the standard, Art. C- Damping method), resulting the transfer function or the logarithmical decrement. The results are shown in the diagrams of the Fig. 5 and 6, for the 2 types of pendulums.
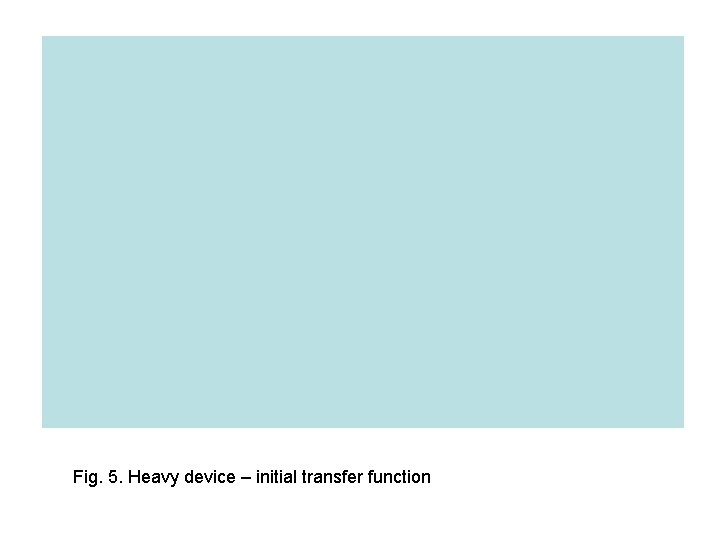
Fig. 5. Heavy device – initial transfer function
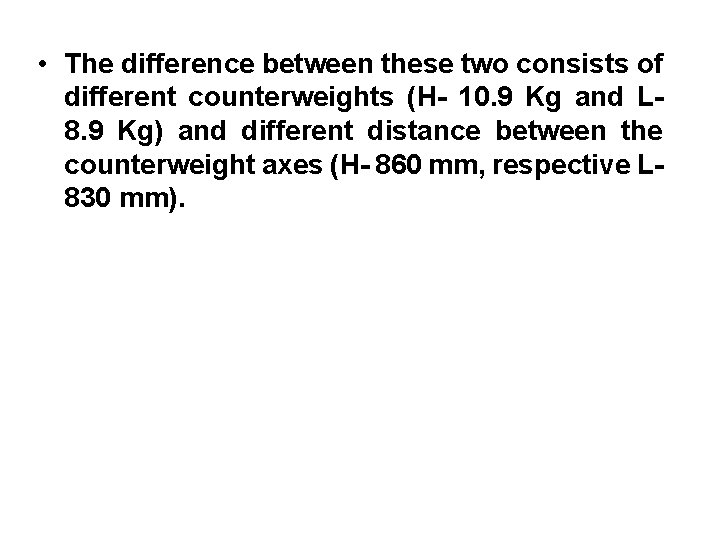
• The difference between these two consists of different counterweights (H- 10. 9 Kg and L 8. 9 Kg) and different distance between the counterweight axes (H- 860 mm, respective L 830 mm).
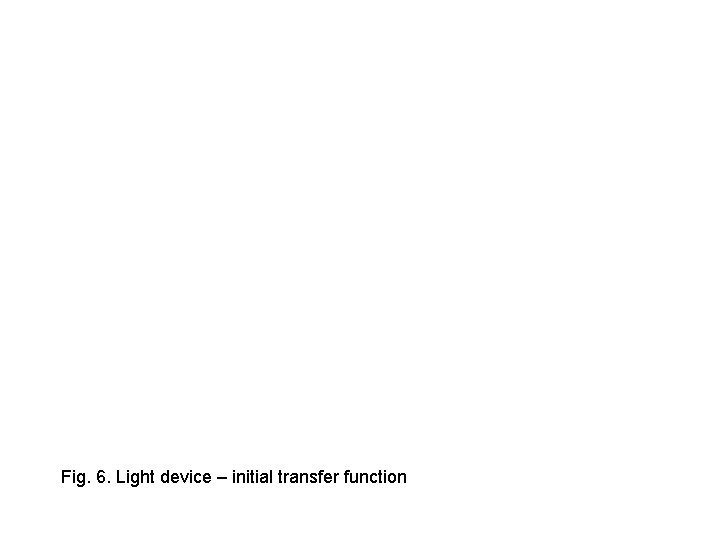
Fig. 6. Light device – initial transfer function
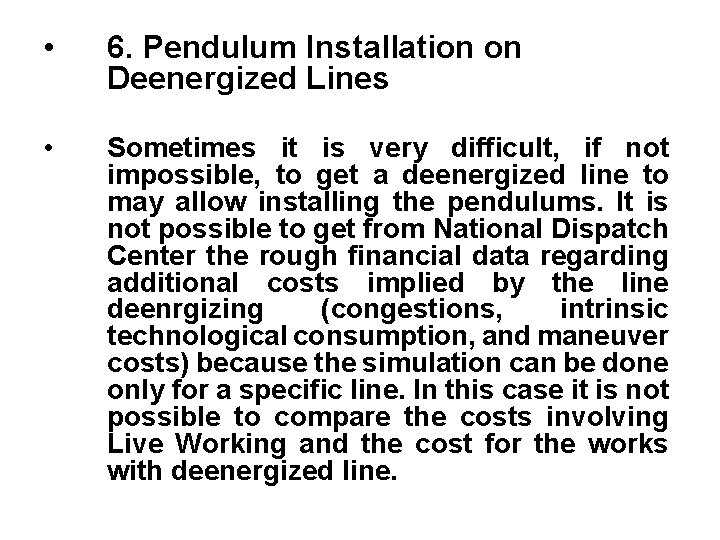
• 6. Pendulum Installation on Deenergized Lines • Sometimes it is very difficult, if not impossible, to get a deenergized line to may allow installing the pendulums. It is not possible to get from National Dispatch Center the rough financial data regarding additional costs implied by the line deenrgizing (congestions, intrinsic technological consumption, and maneuver costs) because the simulation can be done only for a specific line. In this case it is not possible to compare the costs involving Live Working and the cost for the works with deenergized line.
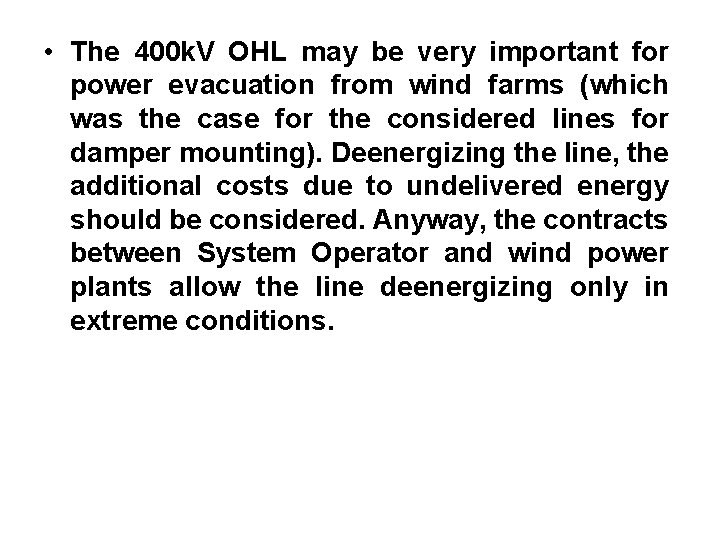
• The 400 k. V OHL may be very important for power evacuation from wind farms (which was the case for the considered lines for damper mounting). Deenergizing the line, the additional costs due to undelivered energy should be considered. Anyway, the contracts between System Operator and wind power plants allow the line deenergizing only in extreme conditions.
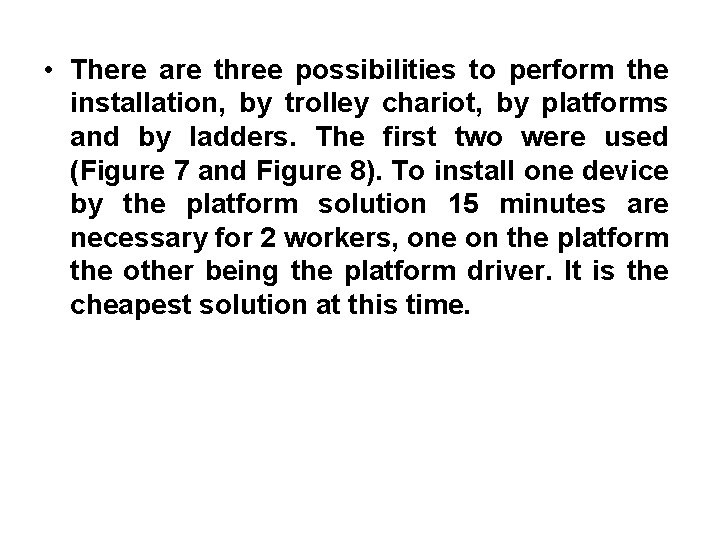
• There are three possibilities to perform the installation, by trolley chariot, by platforms and by ladders. The first two were used (Figure 7 and Figure 8). To install one device by the platform solution 15 minutes are necessary for 2 workers, one on the platform the other being the platform driver. It is the cheapest solution at this time.
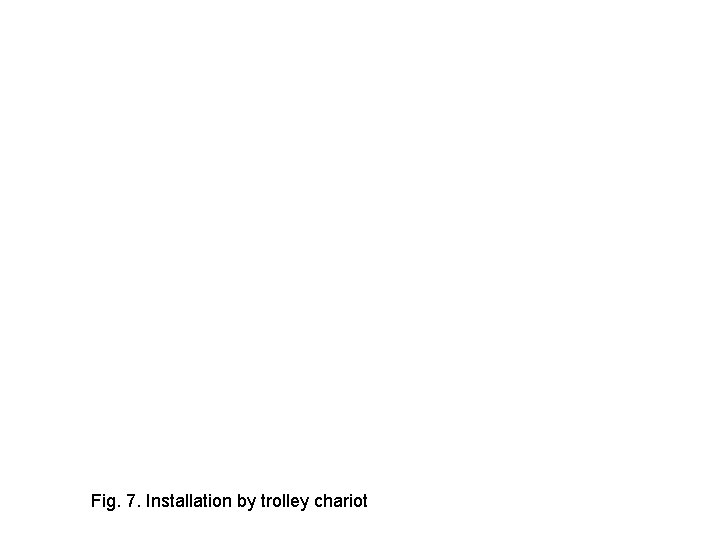
Fig. 7. Installation by trolley chariot
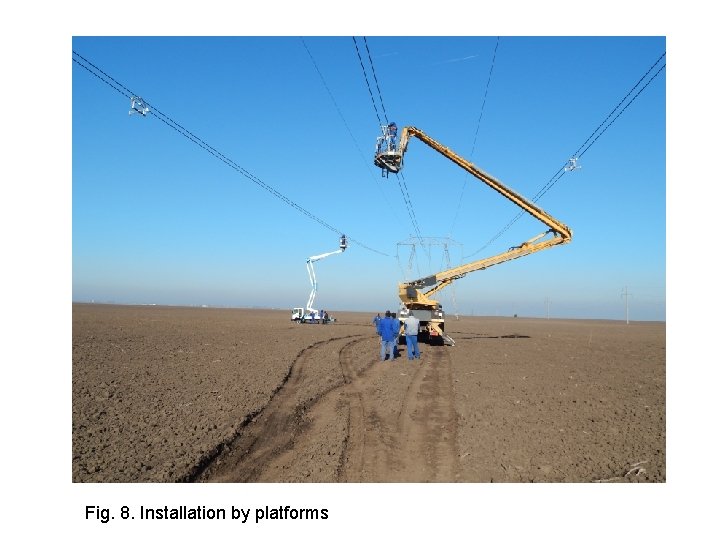
Fig. 8. Installation by platforms
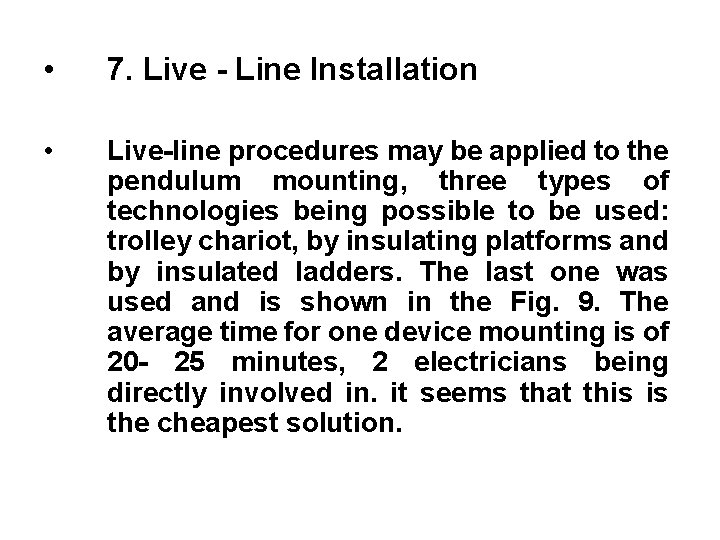
• 7. Live - Line Installation • Live-line procedures may be applied to the pendulum mounting, three types of technologies being possible to be used: trolley chariot, by insulating platforms and by insulated ladders. The last one was used and is shown in the Fig. 9. The average time for one device mounting is of 20 - 25 minutes, 2 electricians being directly involved in. it seems that this is the cheapest solution.
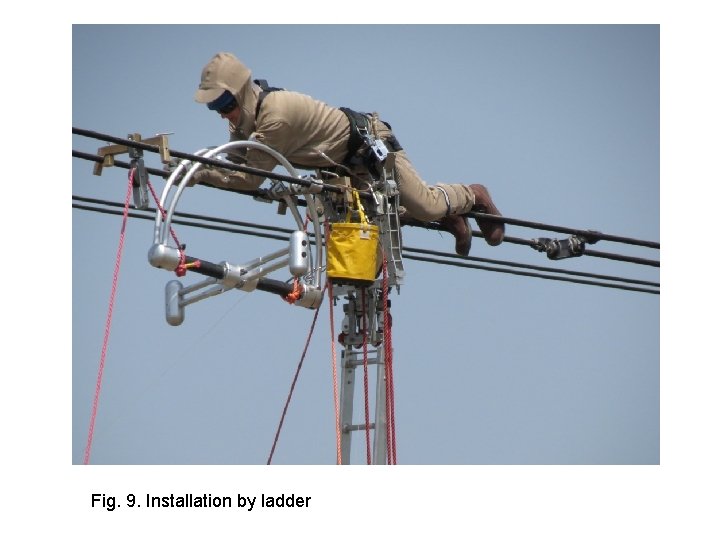
Fig. 9. Installation by ladder
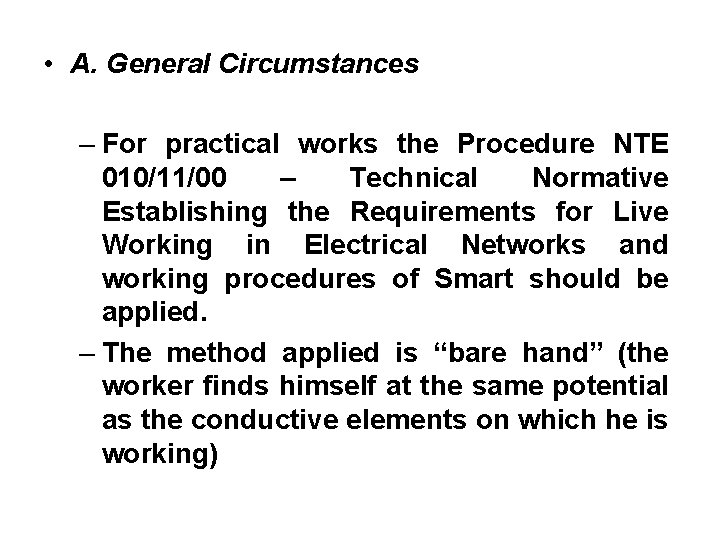
• A. General Circumstances – For practical works the Procedure NTE 010/11/00 – Technical Normative Establishing the Requirements for Live Working in Electrical Networks and working procedures of Smart should be applied. – The method applied is “bare hand” (the worker finds himself at the same potential as the conductive elements on which he is working)
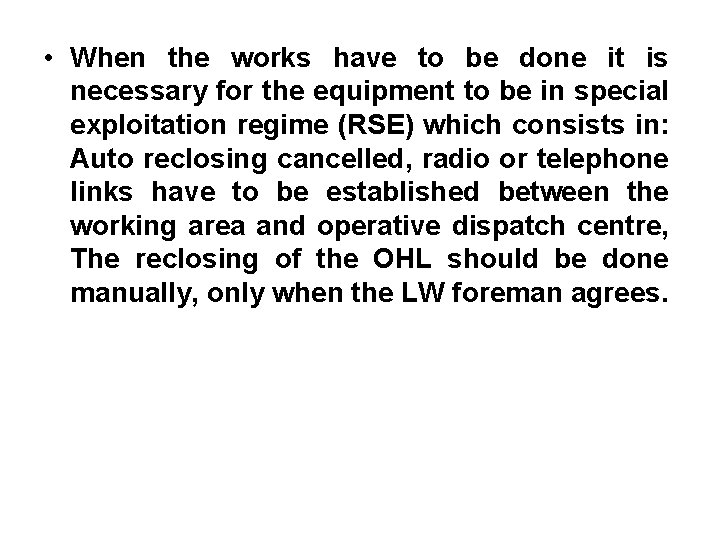
• When the works have to be done it is necessary for the equipment to be in special exploitation regime (RSE) which consists in: Auto reclosing cancelled, radio or telephone links have to be established between the working area and operative dispatch centre, The reclosing of the OHL should be done manually, only when the LW foreman agrees.
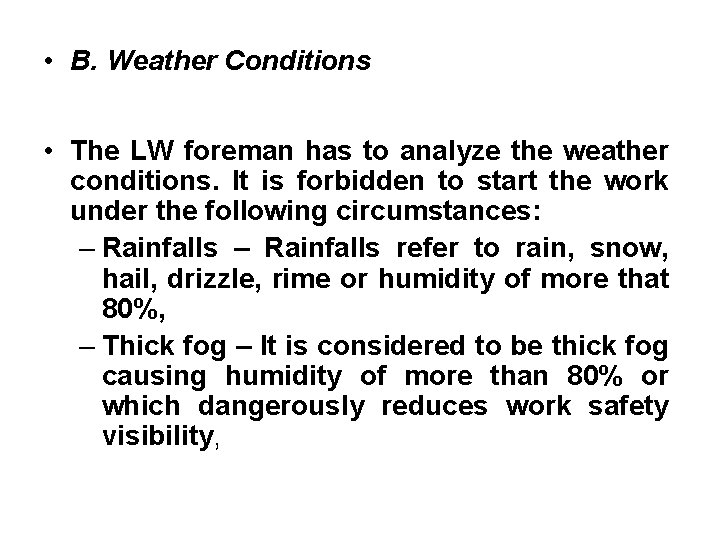
• B. Weather Conditions • The LW foreman has to analyze the weather conditions. It is forbidden to start the work under the following circumstances: – Rainfalls refer to rain, snow, hail, drizzle, rime or humidity of more that 80%, – Thick fog – It is considered to be thick fog causing humidity of more than 80% or which dangerously reduces work safety visibility,
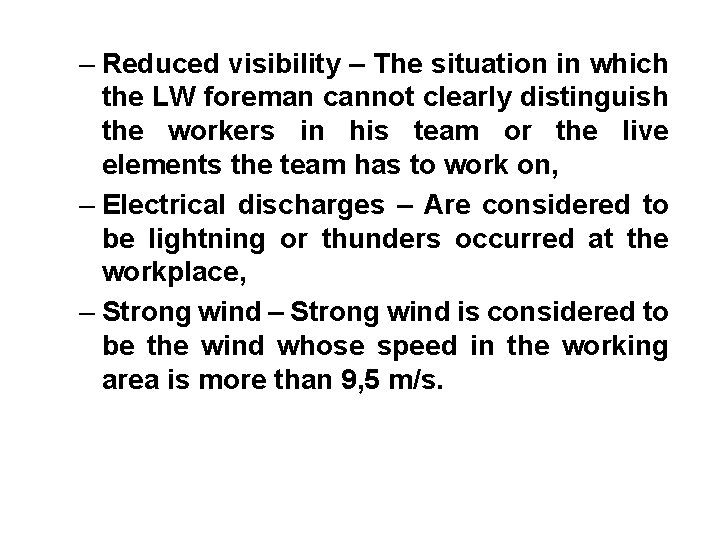
– Reduced visibility – The situation in which the LW foreman cannot clearly distinguish the workers in his team or the live elements the team has to work on, – Electrical discharges – Are considered to be lightning or thunders occurred at the workplace, – Strong wind is considered to be the wind whose speed in the working area is more than 9, 5 m/s.
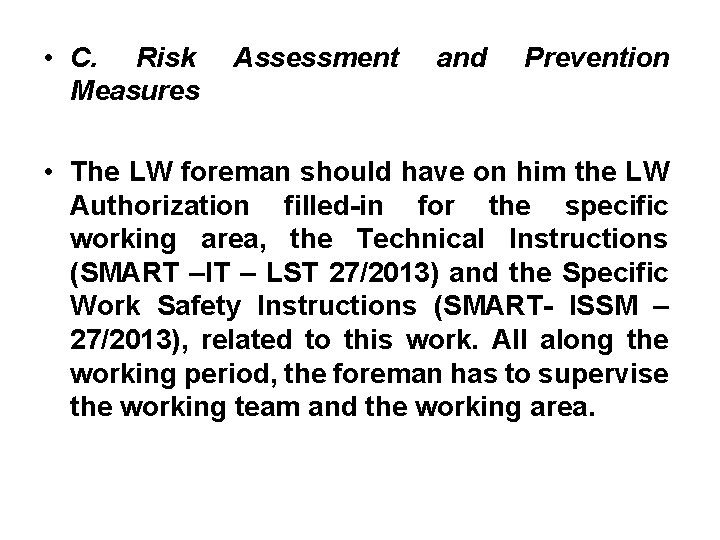
• C. Risk Measures Assessment and Prevention • The LW foreman should have on him the LW Authorization filled-in for the specific working area, the Technical Instructions (SMART –IT – LST 27/2013) and the Specific Work Safety Instructions (SMART- ISSM – 27/2013), related to this work. All along the working period, the foreman has to supervise the working team and the working area.
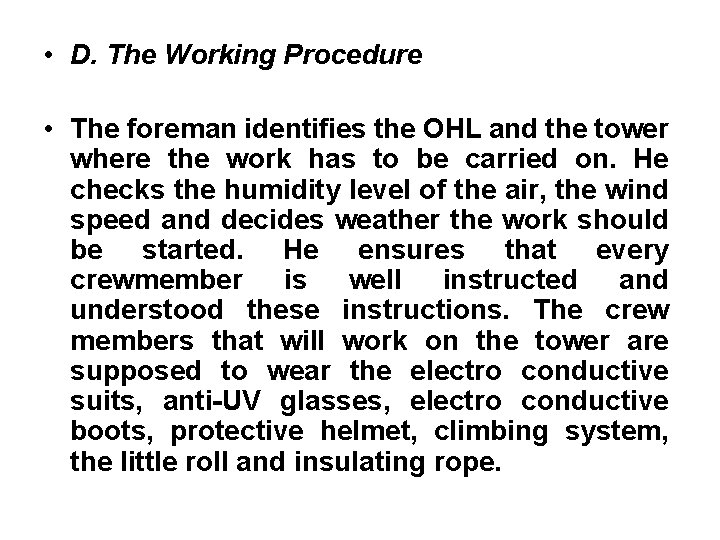
• D. The Working Procedure • The foreman identifies the OHL and the tower where the work has to be carried on. He checks the humidity level of the air, the wind speed and decides weather the work should be started. He ensures that every crewmember is well instructed and understood these instructions. The crew members that will work on the tower are supposed to wear the electro conductive suits, anti-UV glasses, electro conductive boots, protective helmet, climbing system, the little roll and insulating rope.
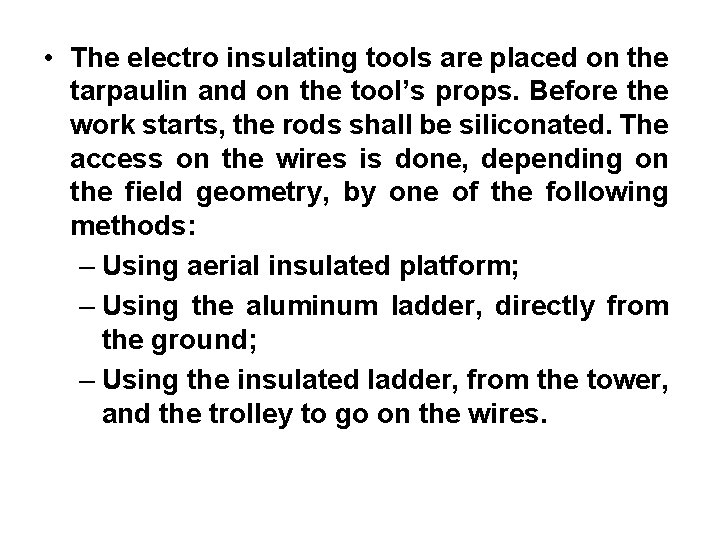
• The electro insulating tools are placed on the tarpaulin and on the tool’s props. Before the work starts, the rods shall be siliconated. The access on the wires is done, depending on the field geometry, by one of the following methods: – Using aerial insulated platform; – Using the aluminum ladder, directly from the ground; – Using the insulated ladder, from the tower, and the trolley to go on the wires.
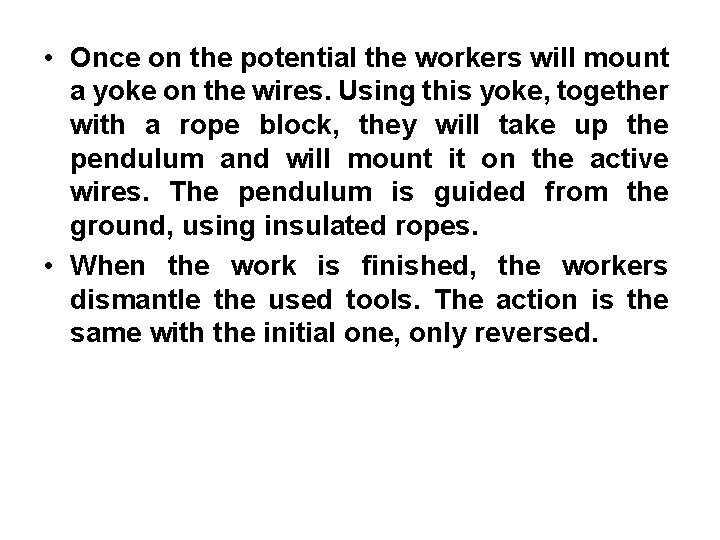
• Once on the potential the workers will mount a yoke on the wires. Using this yoke, together with a rope block, they will take up the pendulum and will mount it on the active wires. The pendulum is guided from the ground, using insulated ropes. • When the work is finished, the workers dismantle the used tools. The action is the same with the initial one, only reversed.
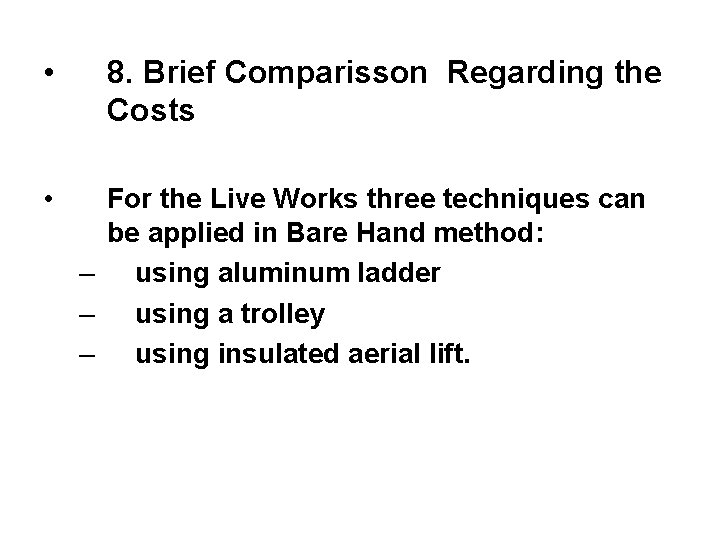
• • 8. Brief Comparisson Regarding the Costs For the Live Works three techniques can be applied in Bare Hand method: – using aluminum ladder – using a trolley – using insulated aerial lift.
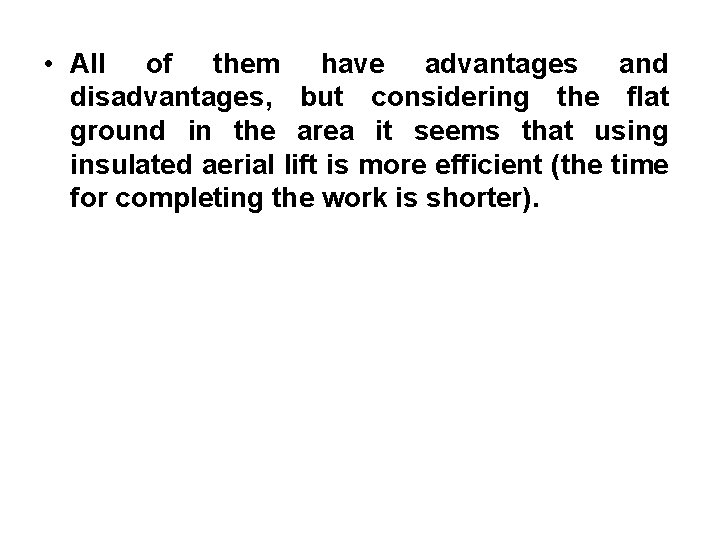
• All of them have advantages and disadvantages, but considering the flat ground in the area it seems that using insulated aerial lift is more efficient (the time for completing the work is shorter).
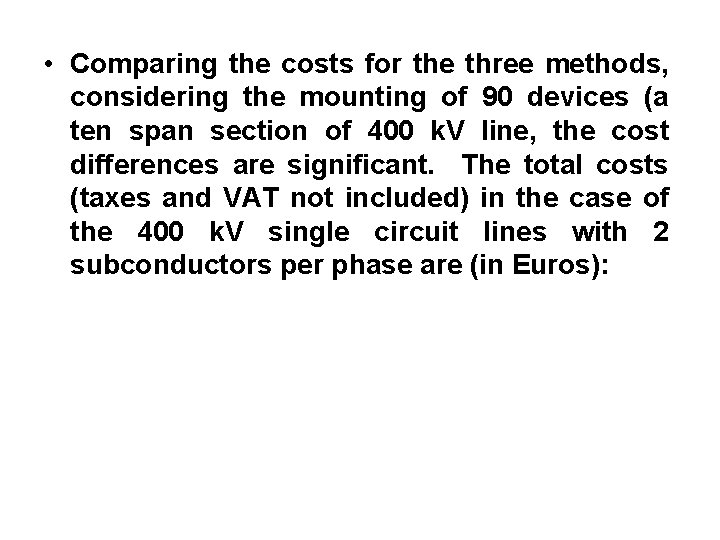
• Comparing the costs for the three methods, considering the mounting of 90 devices (a ten span section of 400 k. V line, the cost differences are significant. The total costs (taxes and VAT not included) in the case of the 400 k. V single circuit lines with 2 subconductors per phase are (in Euros):
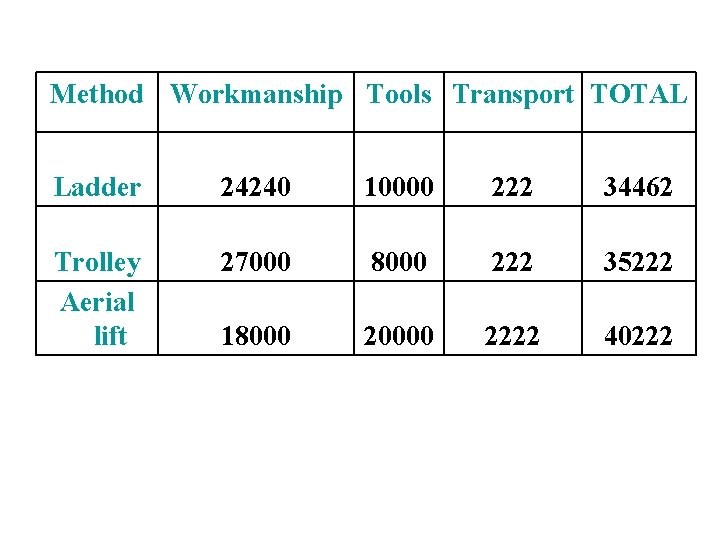
Method Workmanship Tools Transport TOTAL Ladder 24240 10000 222 34462 Trolley Aerial lift 27000 8000 222 35222 18000 20000 2222 40222
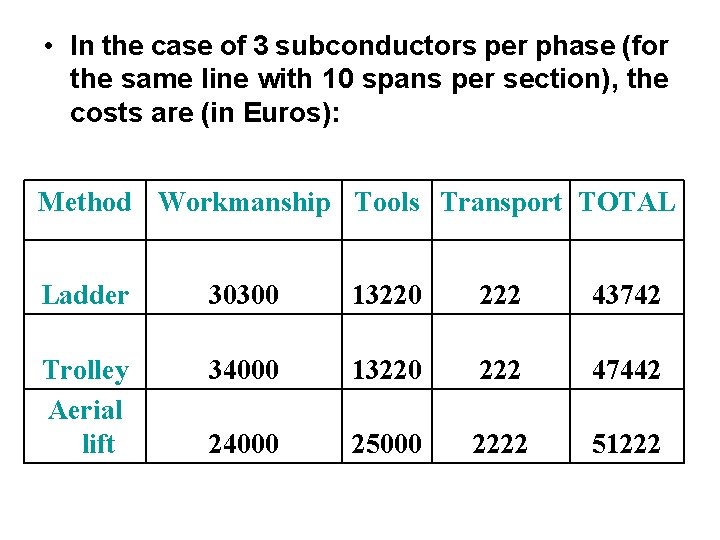
• In the case of 3 subconductors per phase (for the same line with 10 spans per section), the costs are (in Euros): Method Workmanship Tools Transport TOTAL Ladder 30300 13220 222 43742 Trolley Aerial lift 34000 13220 222 47442 24000 25000 2222 51222
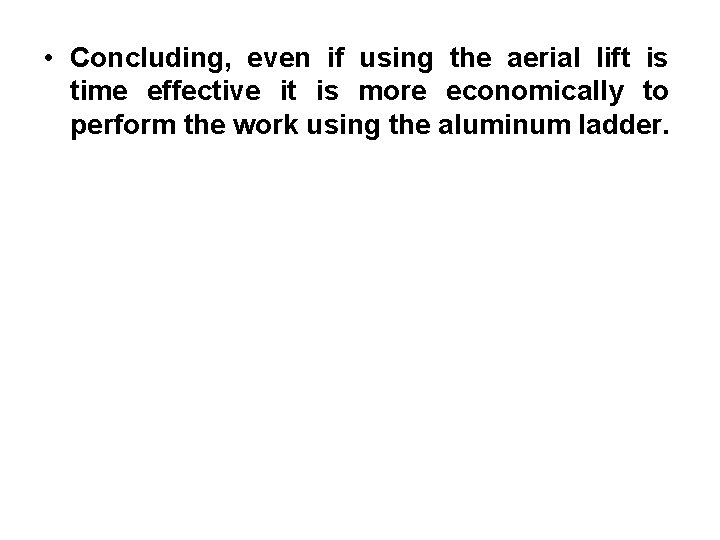
• Concluding, even if using the aerial lift is time effective it is more economically to perform the work using the aluminum ladder.
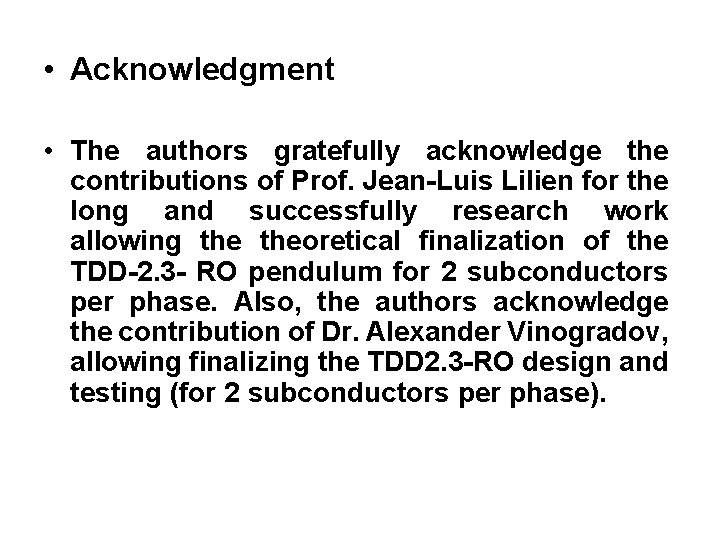
• Acknowledgment • The authors gratefully acknowledge the contributions of Prof. Jean-Luis Lilien for the long and successfully research work allowing theoretical finalization of the TDD-2. 3 - RO pendulum for 2 subconductors per phase. Also, the authors acknowledge the contribution of Dr. Alexander Vinogradov, allowing finalizing the TDD 2. 3 -RO design and testing (for 2 subconductors per phase).
200 + 200 = 400
Mix move match
Internal input devices
Lp 400 essl-canteen management device
A tagout device is preferable to using a lockout device.
Monitor output
Redogör för vad psykologi är
En lathund för arbete med kontinuitetshantering
Mat för idrottare
Ramsa geometriska former
Ledarskapsteorier
Svenskt ramverk för digital samverkan
Antikt plagg i rom
Datorkunskap för nybörjare
Steg för steg rita
Orubbliga rättigheter
Ministerstyre för och nackdelar
Tillitsbaserad ledning
Bat mitza
Nationell inriktning för artificiell intelligens
Bästa kameran för astrofoto
Roliga rim till lärare
Nyckelkompetenser för livslångt lärande
Ro i rom pax
Handledning reflektionsmodellen
Matematisk modellering eksempel
Jätte råtta
Personalliggare bygg undantag
Verktyg för automatisering av utbetalningar
Texter för hinduer tantra
Slyngexcision
I gullregnens månad
Tack för att ni lyssnade bild
Strategi för svensk viltförvaltning
Ledningssystem för verksamhetsinformation
Tack för att ni har lyssnat
Läkarutlåtande för livränta
Klassificeringsstruktur för kommunala verksamheter
Vad står k.r.å.k.a.n för
Centrum för kunskap och säkerhet
Inköpsprocessen steg för steg
Påbyggnader för flakfordon
Tack för att ni lyssnade
Egg för emanuel
Atmosfr
Formel för standardavvikelse
Tidbok för yrkesförare
Rutin för avvikelsehantering
Biologiska arvet
Presentera för publik crossboss
Fspos
Myndigheten för delaktighet