Office of Safety Health Consultation presents Control of
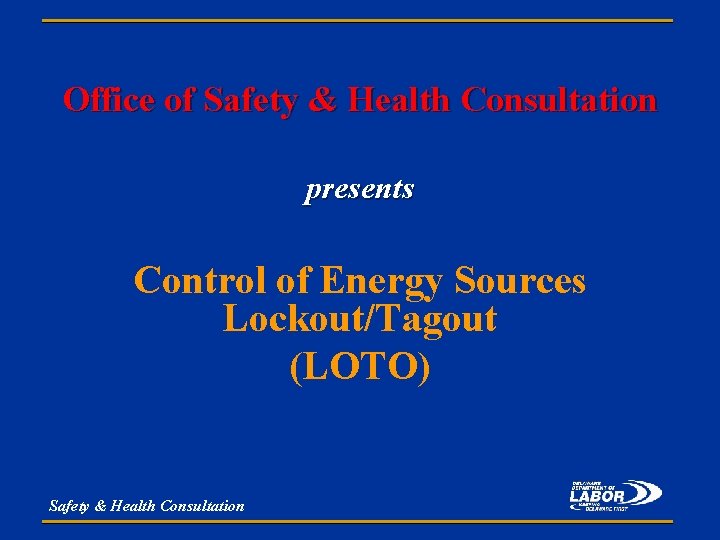
![GENERAL ENVIRONMENT CONTROLS [1910. 141 – 147] 29 CFR 1910 SUBPARTS 147(c)(4)(i) 579 LOCKOUT/TAGOUT GENERAL ENVIRONMENT CONTROLS [1910. 141 – 147] 29 CFR 1910 SUBPARTS 147(c)(4)(i) 579 LOCKOUT/TAGOUT](https://slidetodoc.com/presentation_image_h/7daeaa200841f094425eb609a565fe52/image-2.jpg)
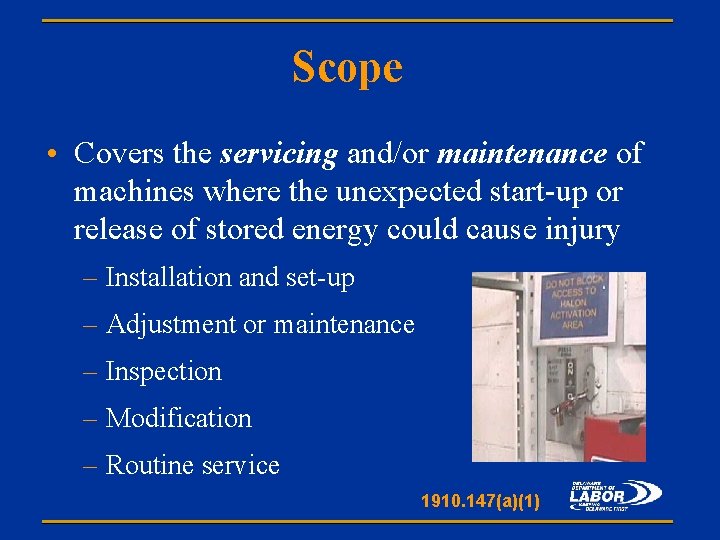
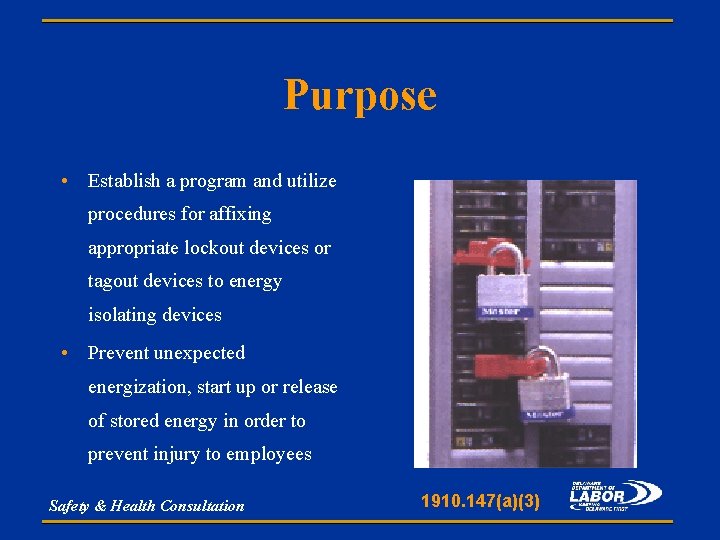
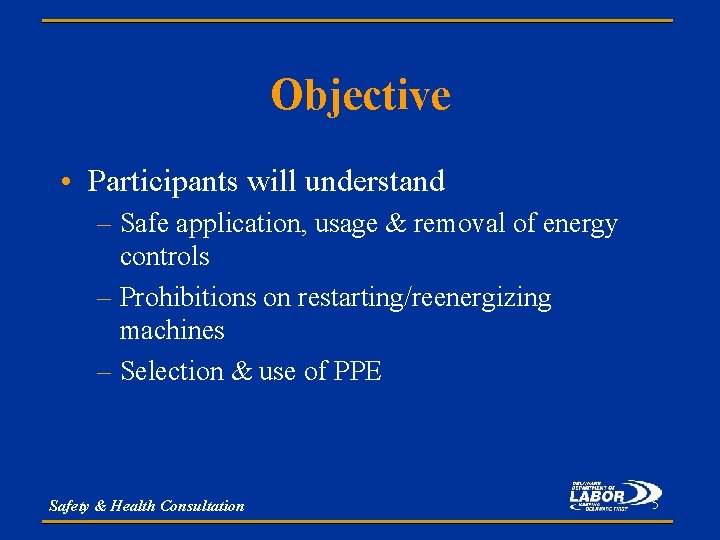
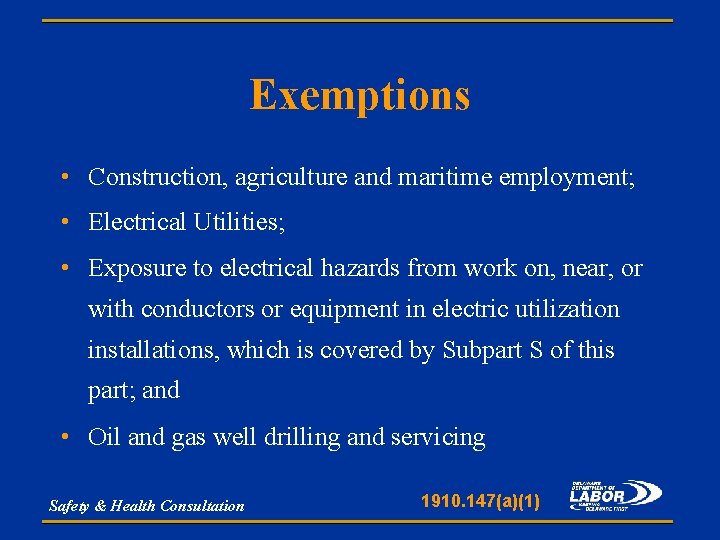

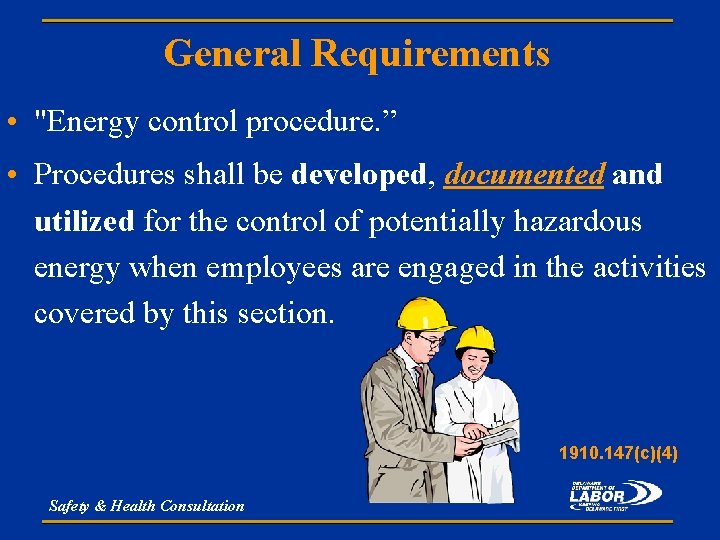
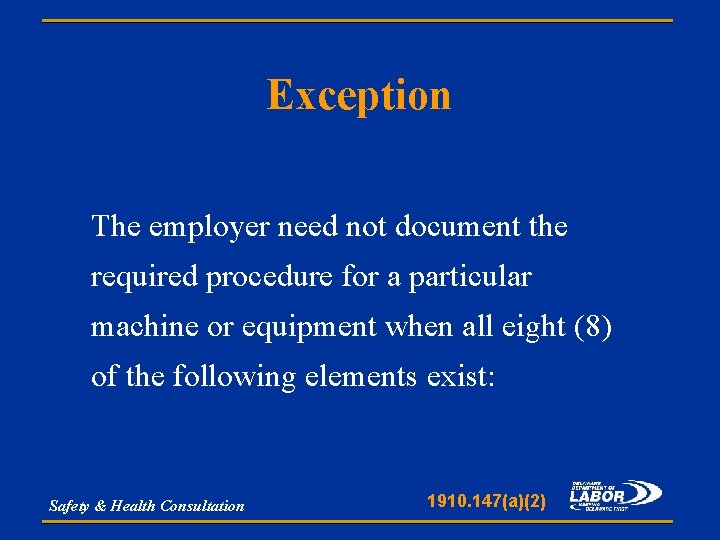
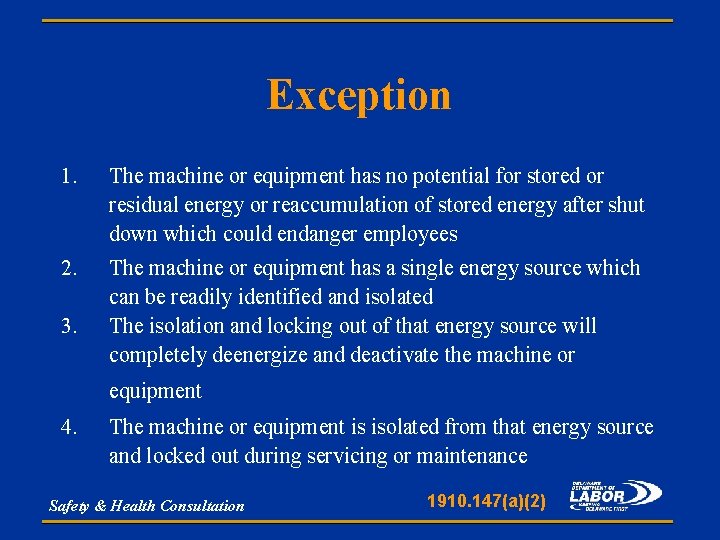
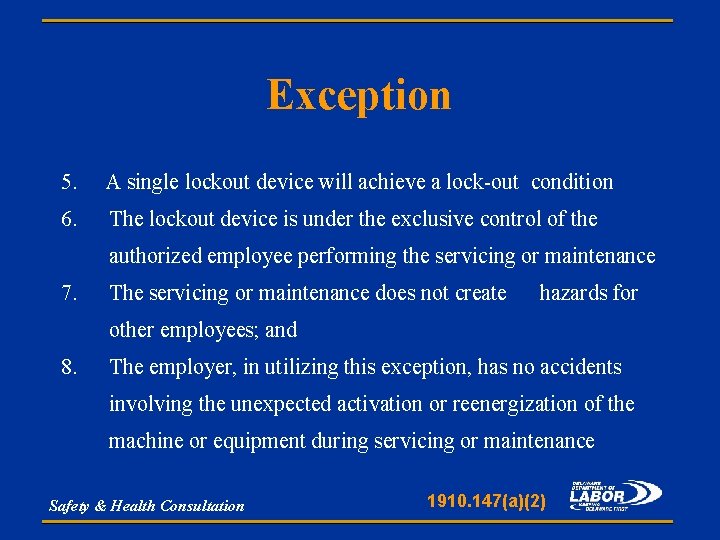
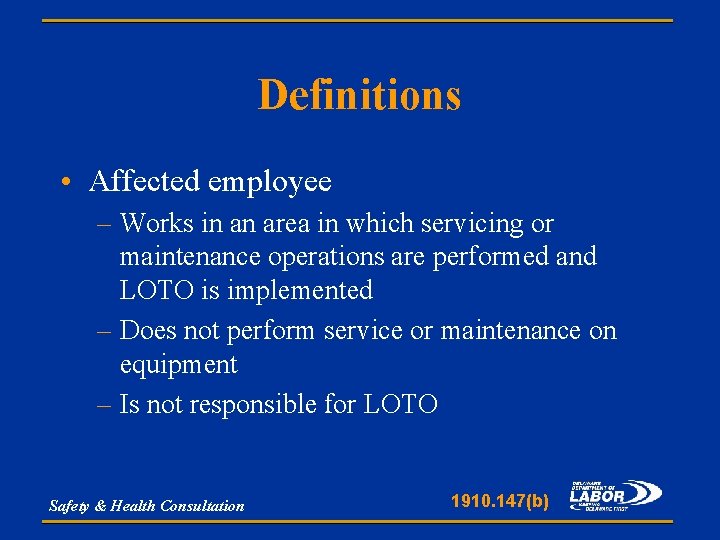
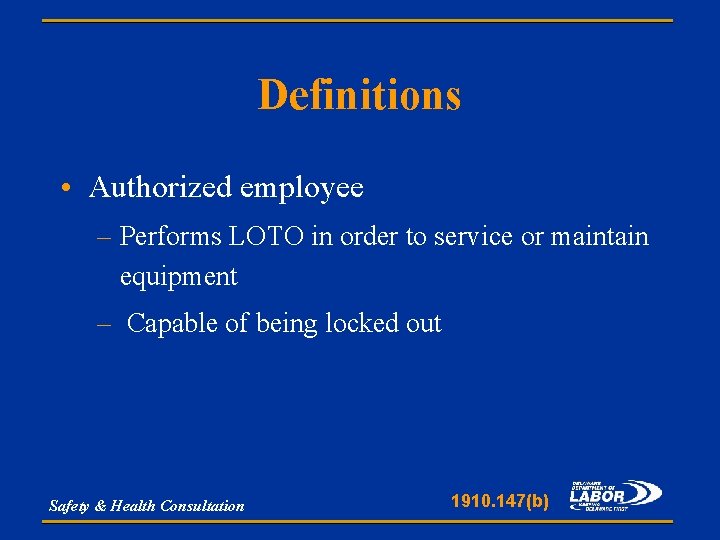
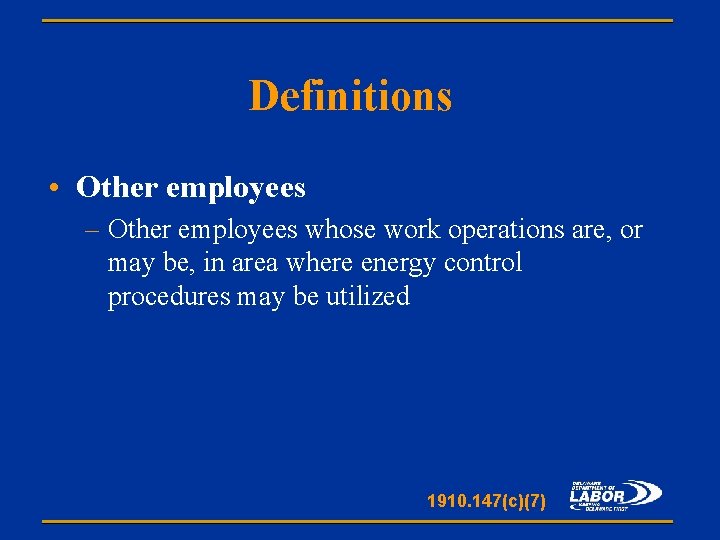
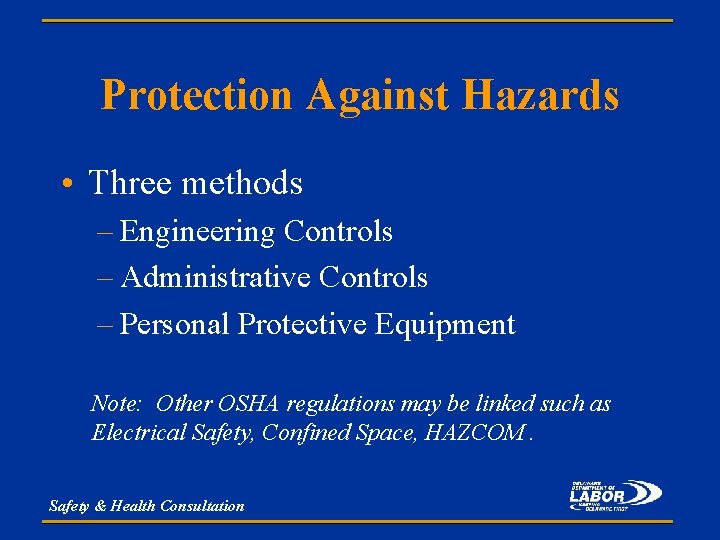
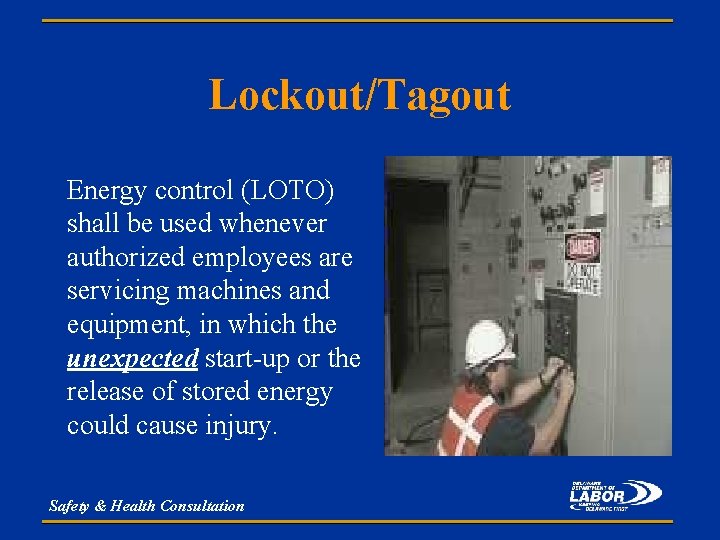
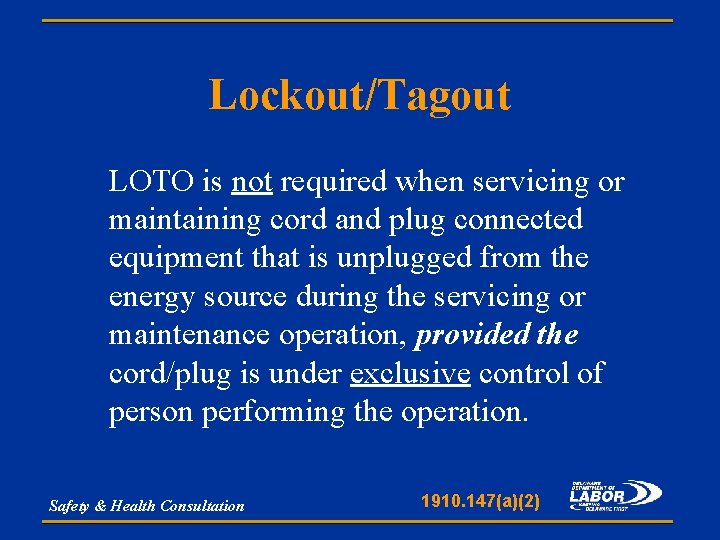
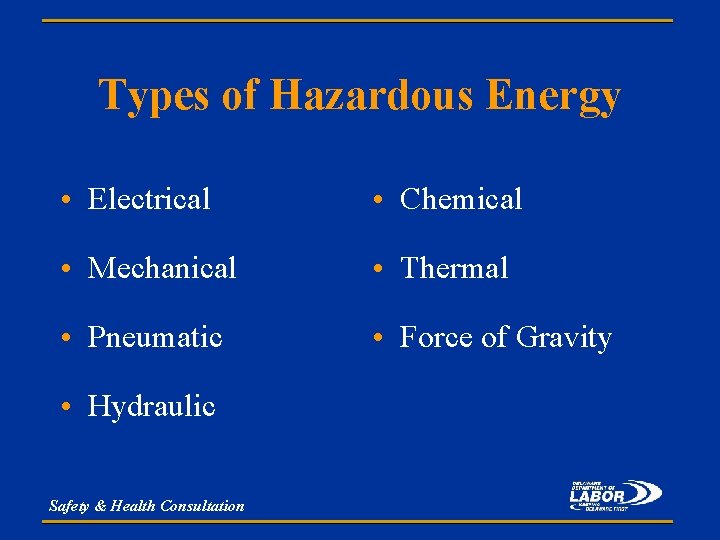
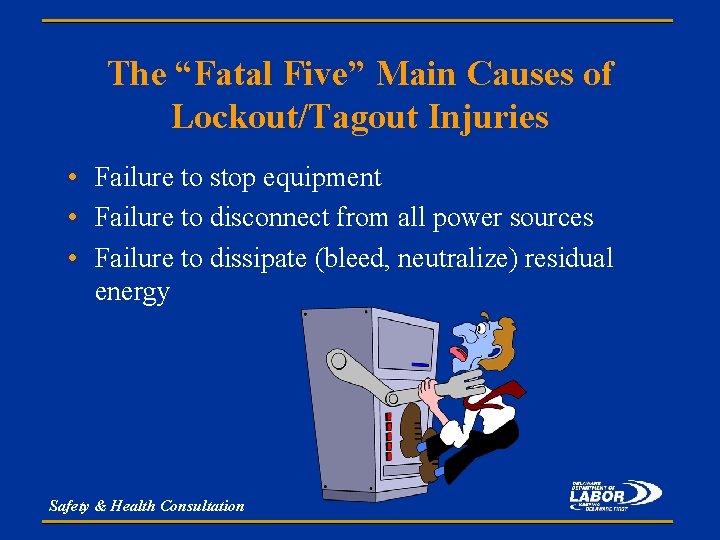
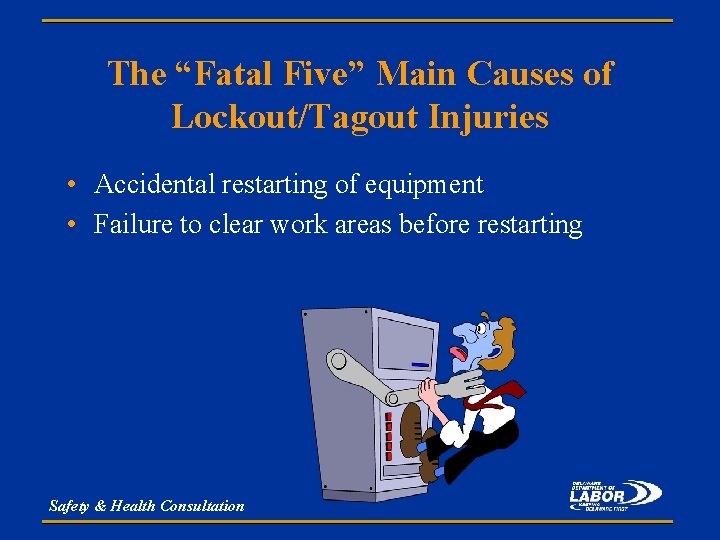
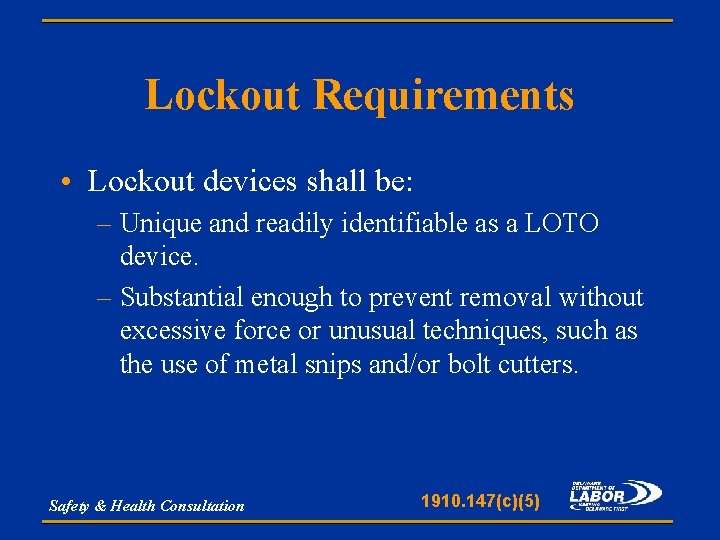
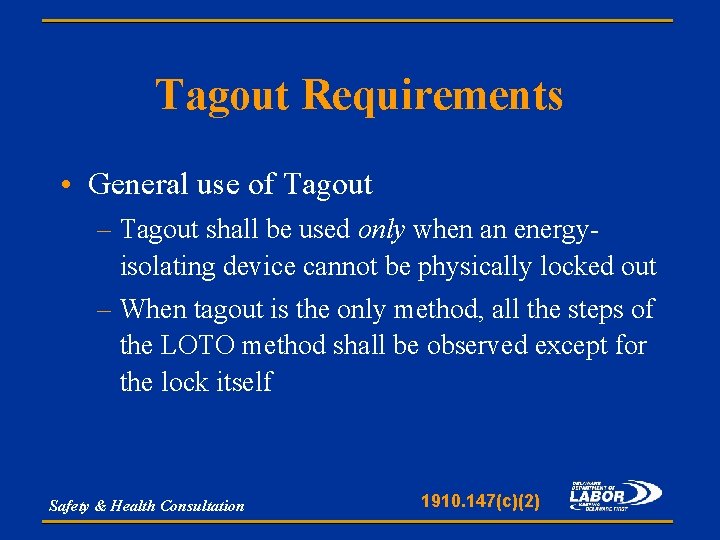
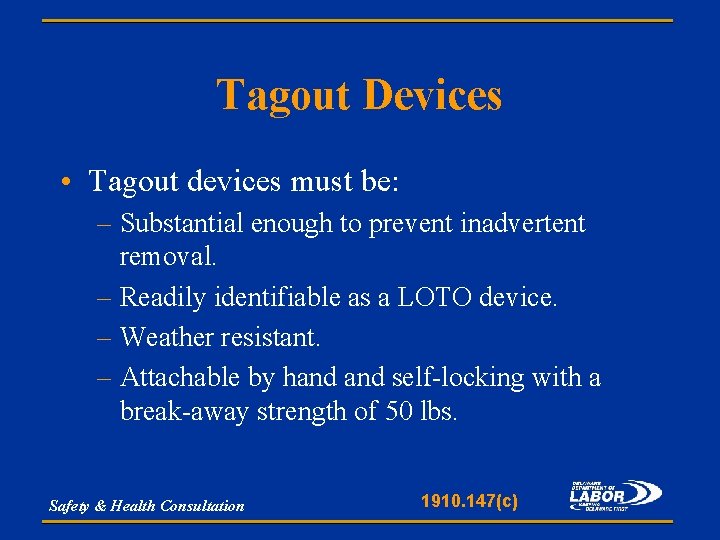
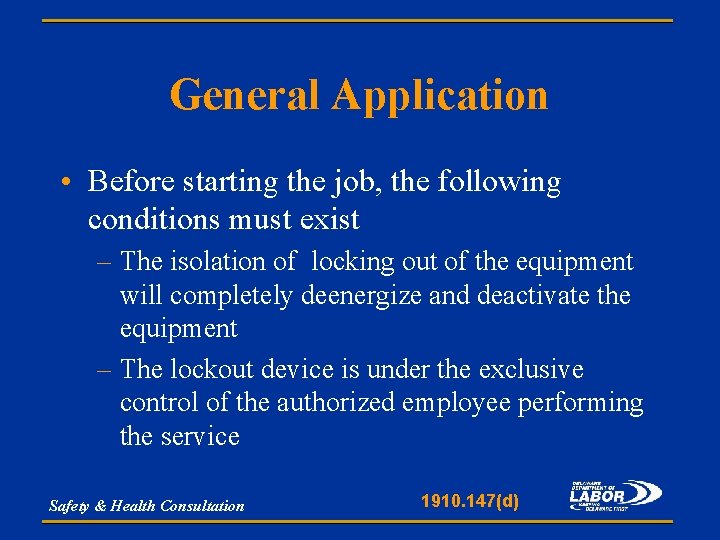
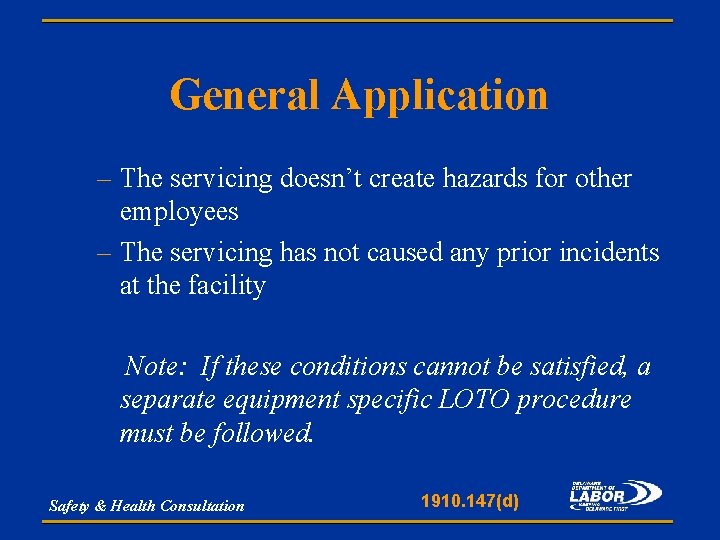
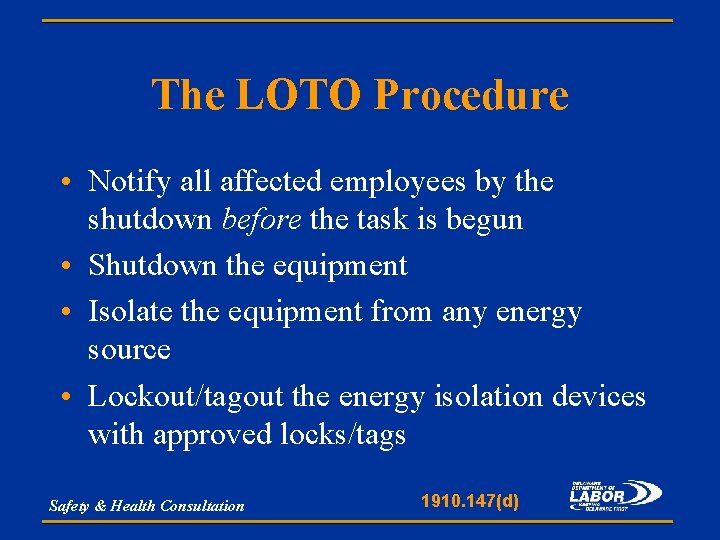
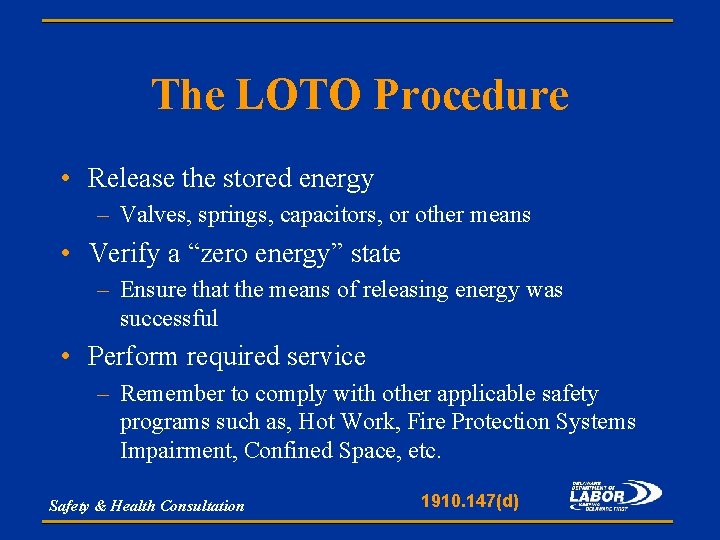
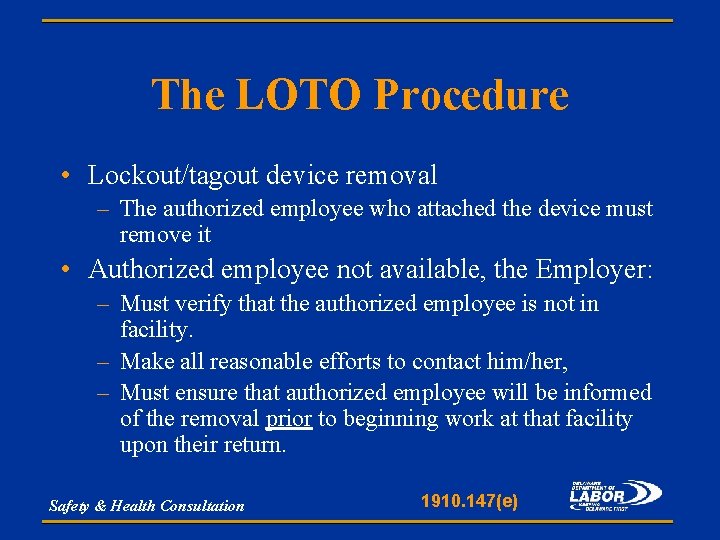
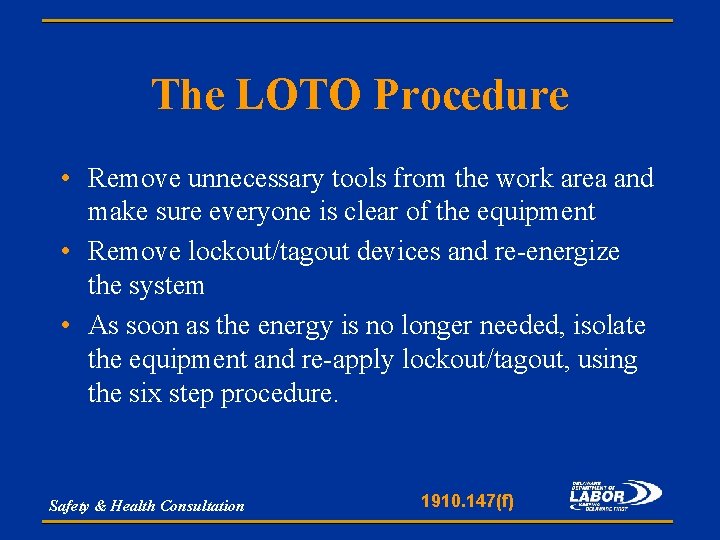
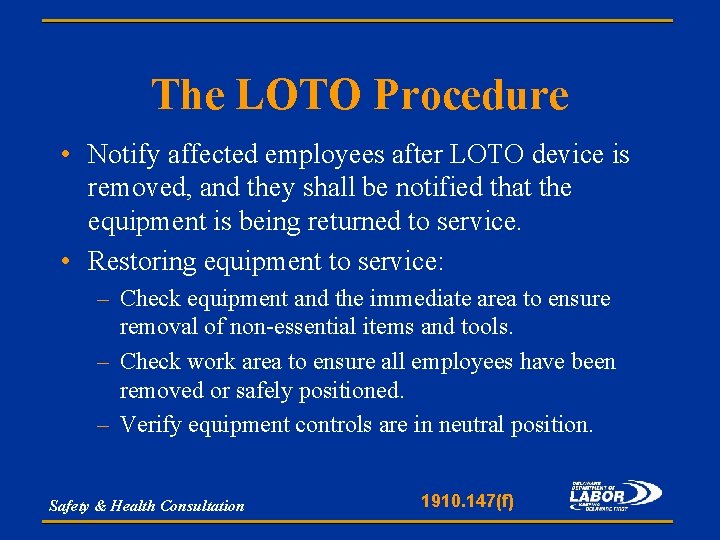
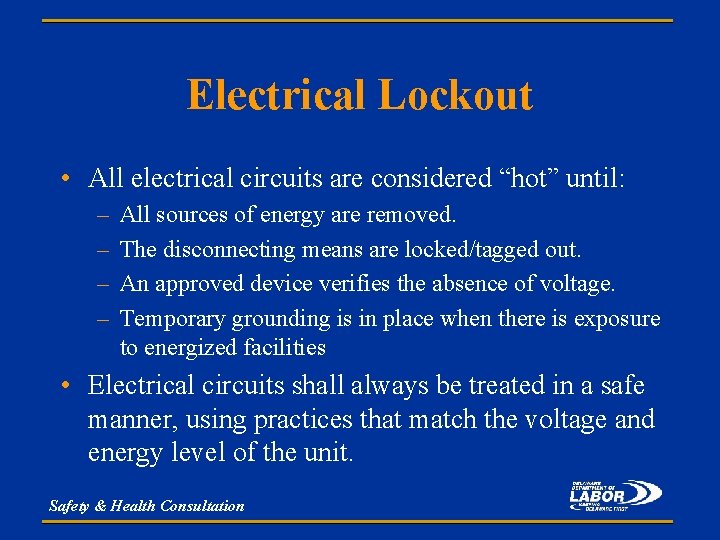
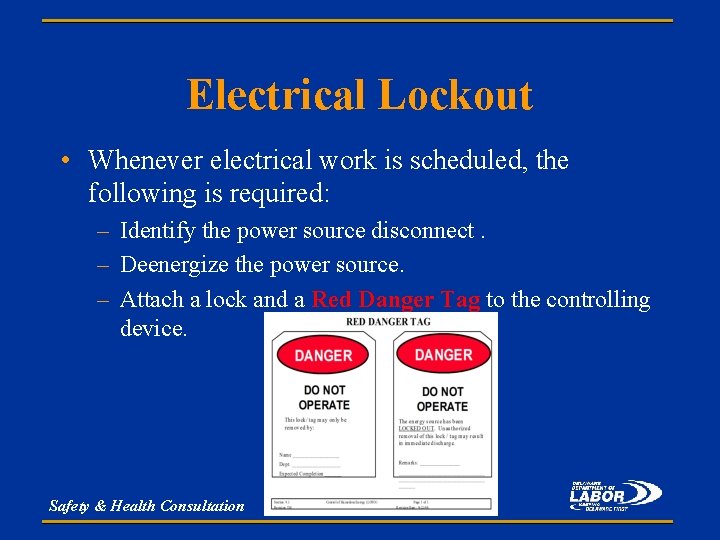
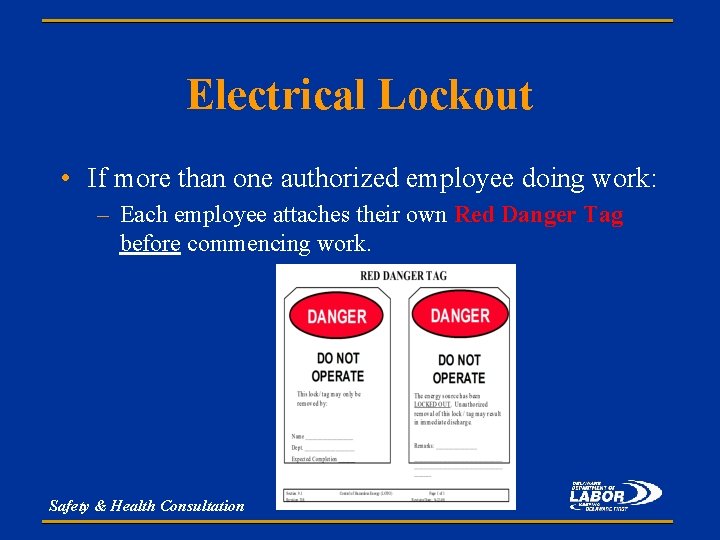
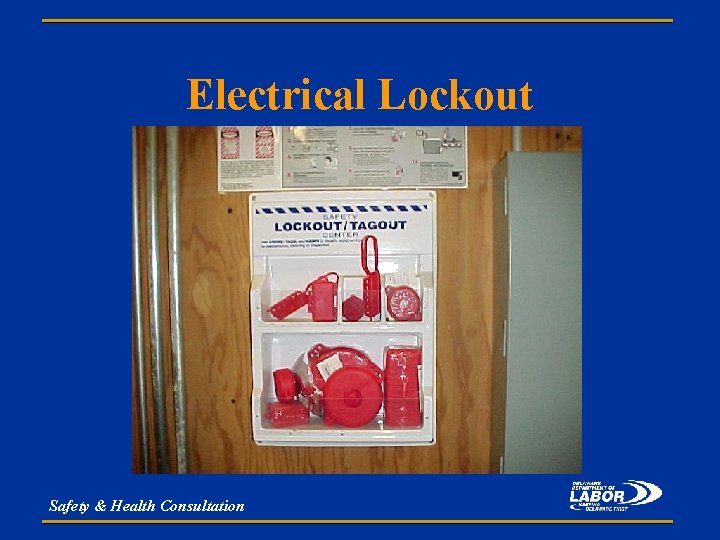
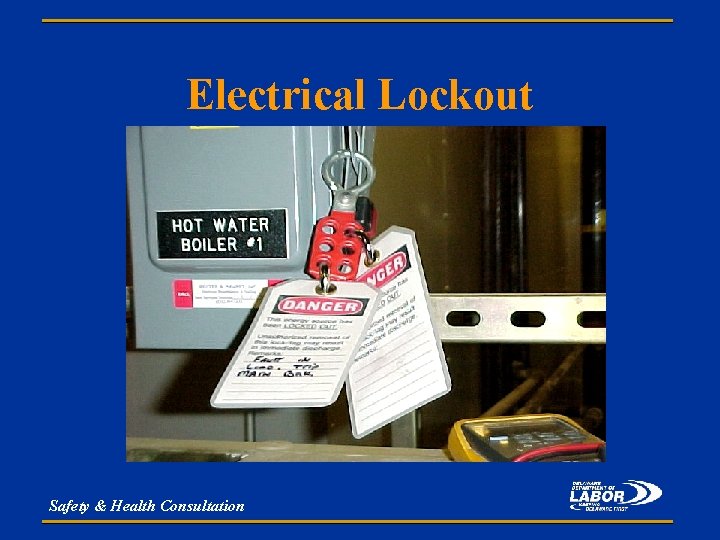
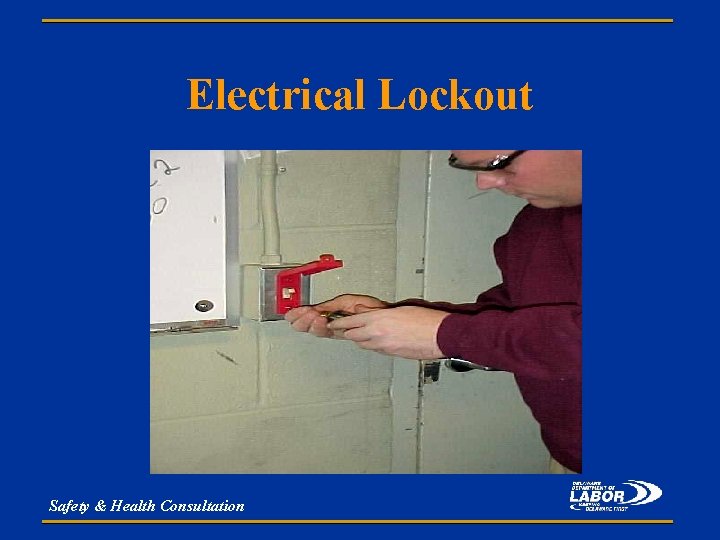
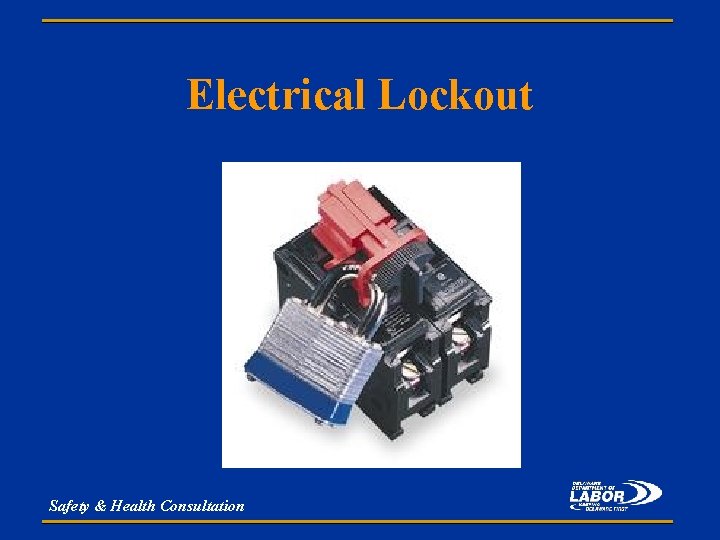
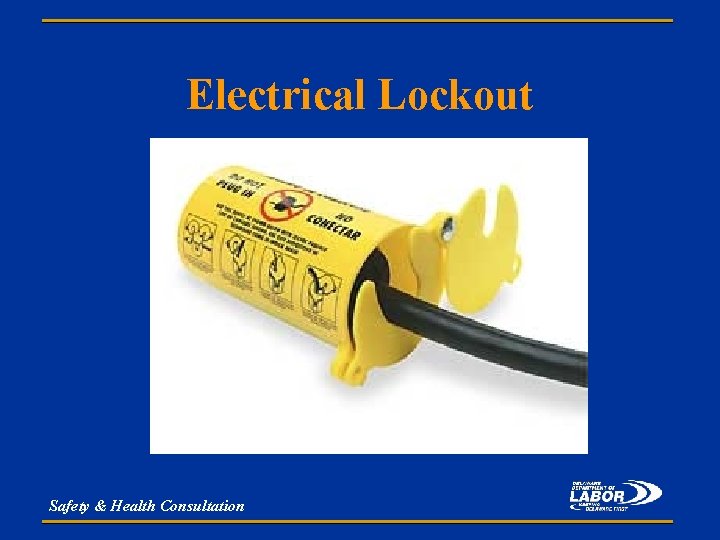

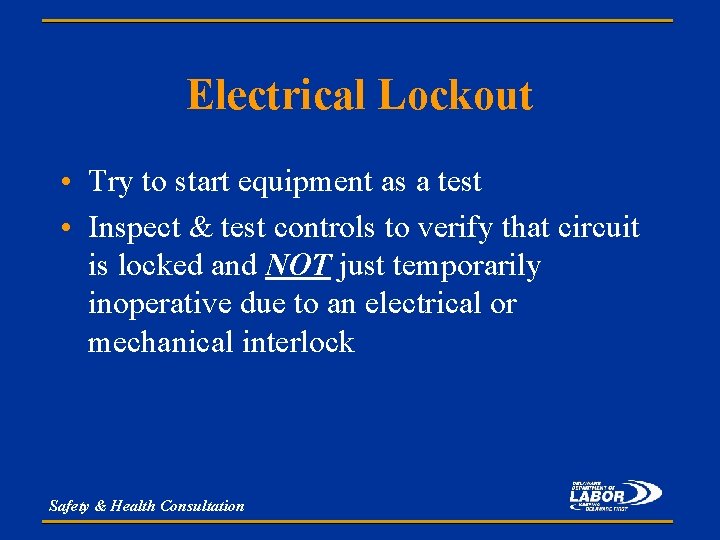
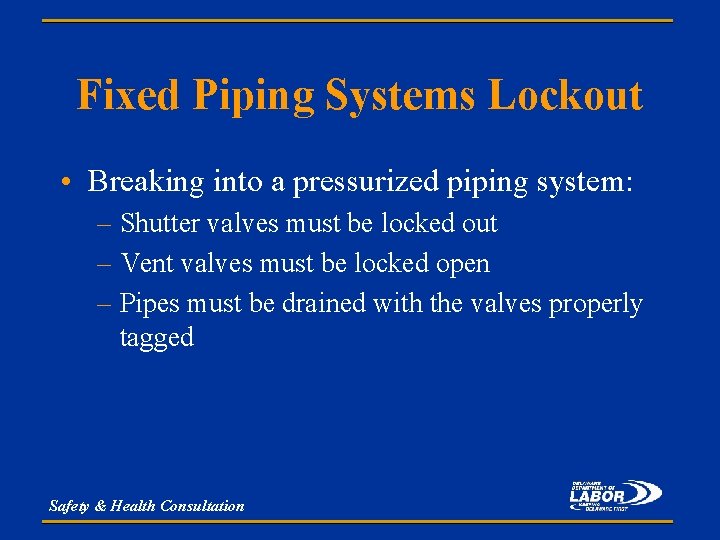
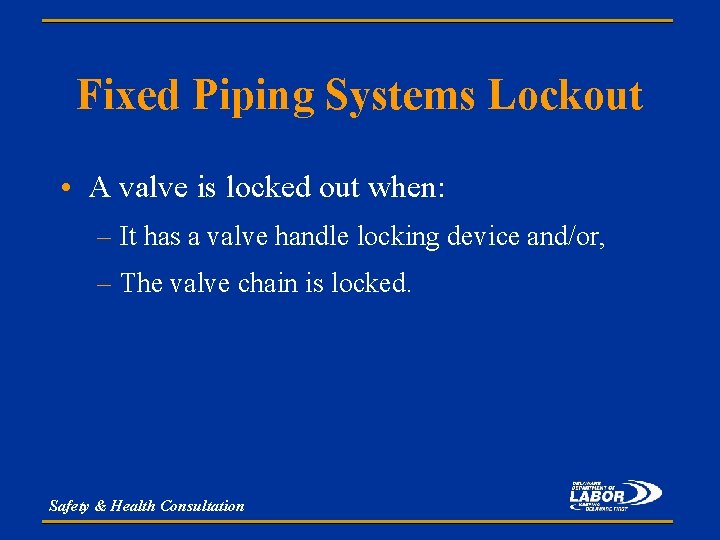
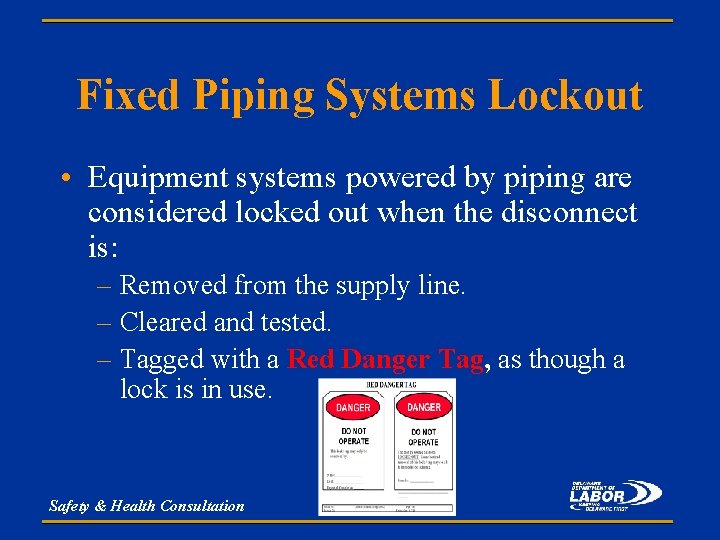
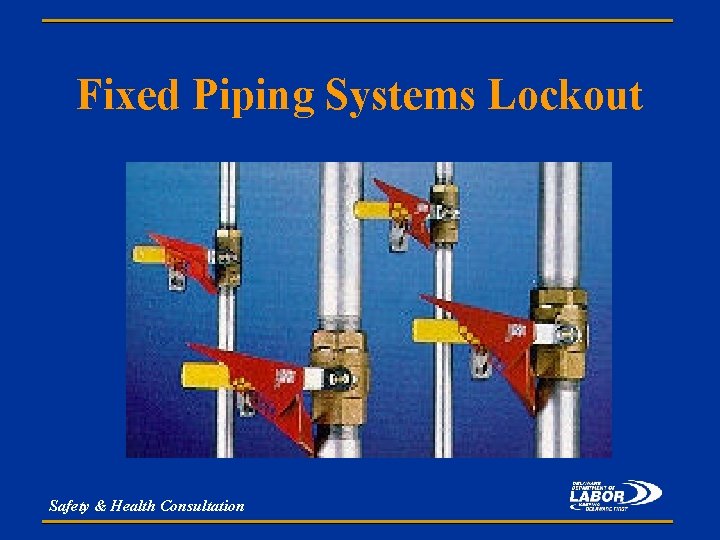

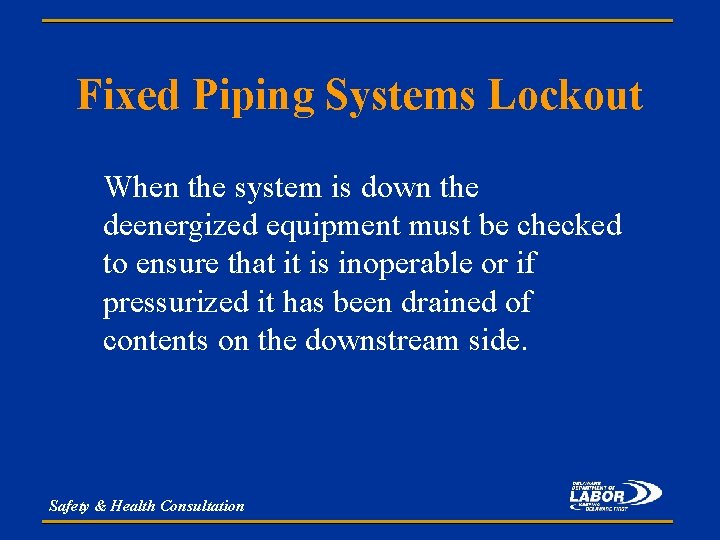
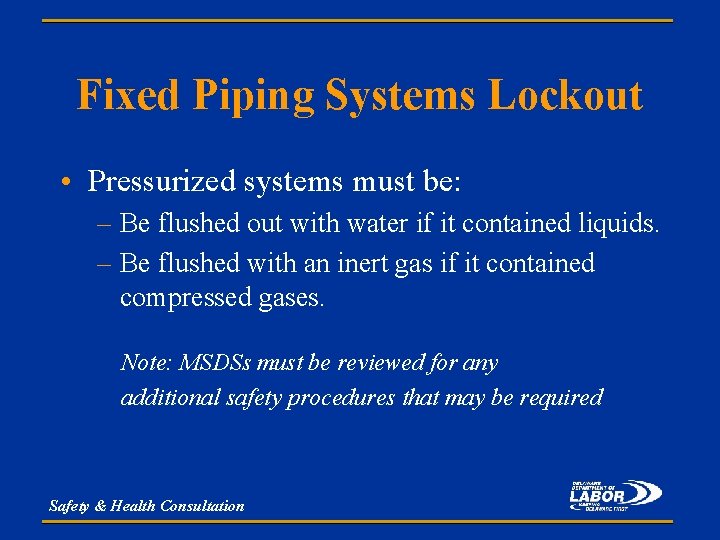
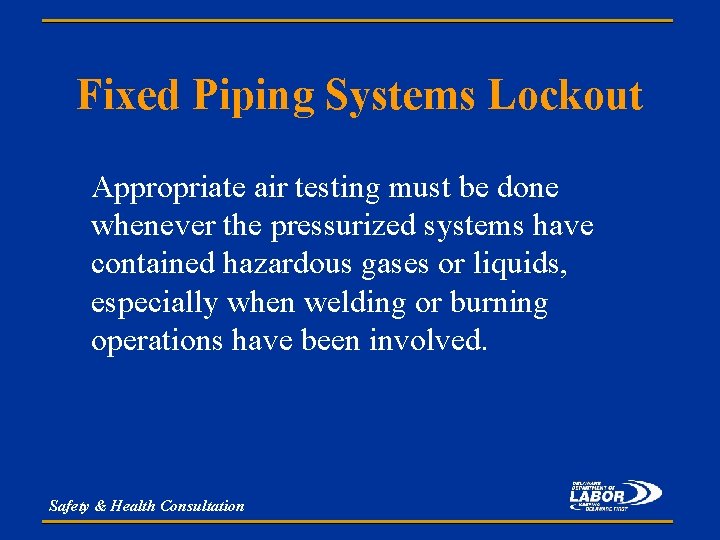
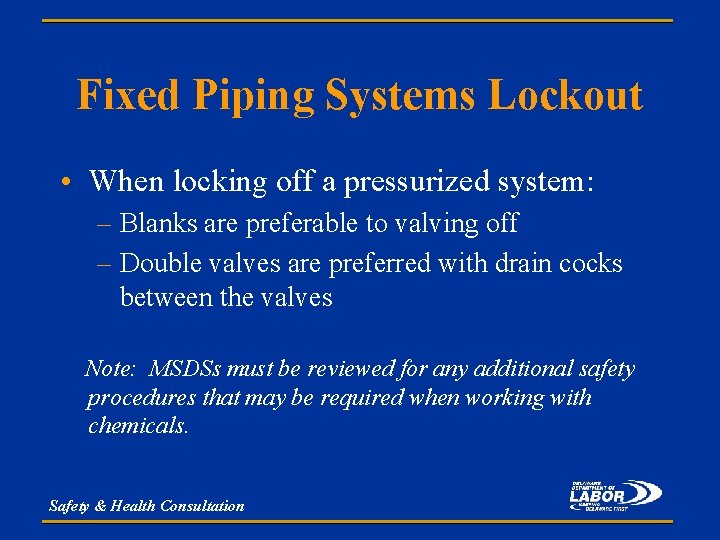
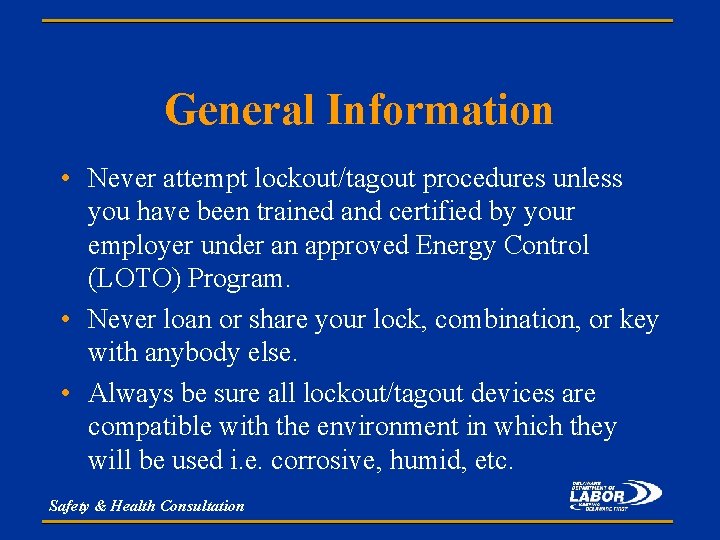
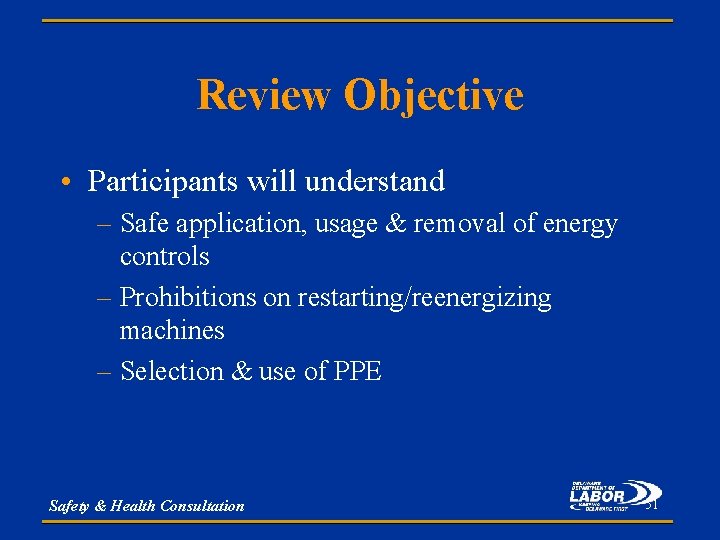
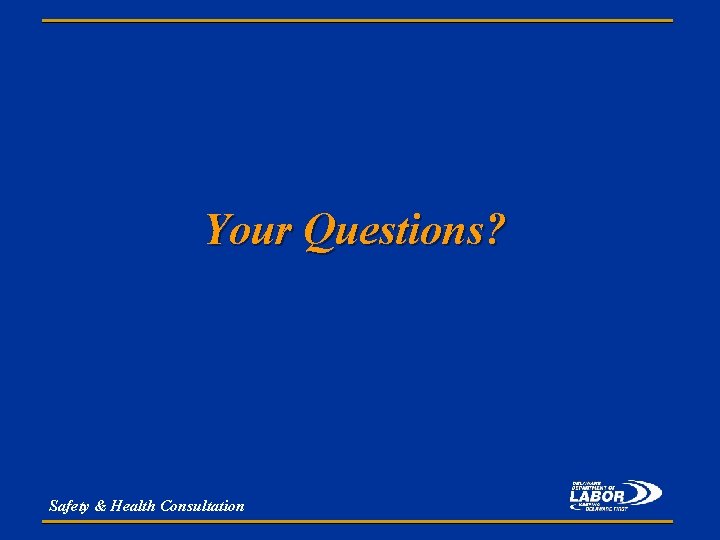
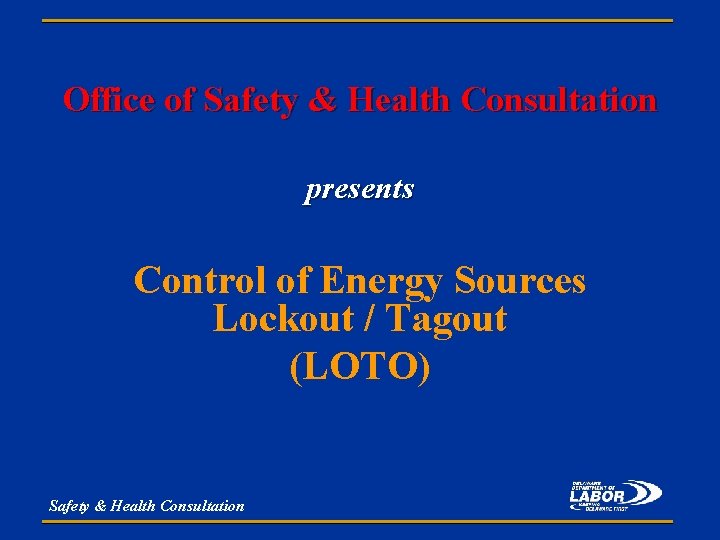
- Slides: 53
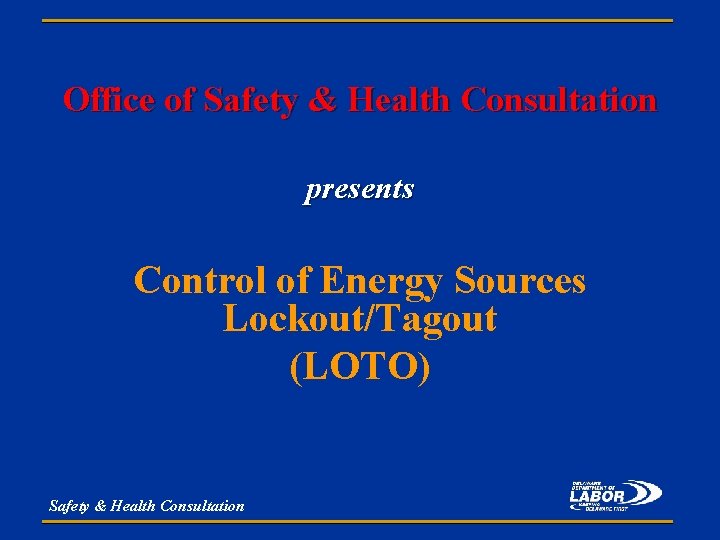
Office of Safety & Health Consultation presents Control of Energy Sources Lockout/Tagout (LOTO) Safety & Health Consultation
![GENERAL ENVIRONMENT CONTROLS 1910 141 147 29 CFR 1910 SUBPARTS 147c4i 579 LOCKOUTTAGOUT GENERAL ENVIRONMENT CONTROLS [1910. 141 – 147] 29 CFR 1910 SUBPARTS 147(c)(4)(i) 579 LOCKOUT/TAGOUT](https://slidetodoc.com/presentation_image_h/7daeaa200841f094425eb609a565fe52/image-2.jpg)
GENERAL ENVIRONMENT CONTROLS [1910. 141 – 147] 29 CFR 1910 SUBPARTS 147(c)(4)(i) 579 LOCKOUT/TAGOUT – PROGRAM 147(c)(1) 508 LOCKOUT/TAGOUT – PERIODIC INSPECTIONS 432 147(c)(6)(i) 147(c)(7)(i) 147(c)(4)(ii) SUBPART J LOCKOUT/TAGOUT – DEVELOPED PROCEDURES LOCKOUT/TAGOUT – GENERAL TRAINING 258 LOCKOUT/TAGOUT – SPECIFIC/ENFORCEMENT OF PROCEDURES 173 2 NUMBER OF SERIOUS VIOLATIONS – FY 2014
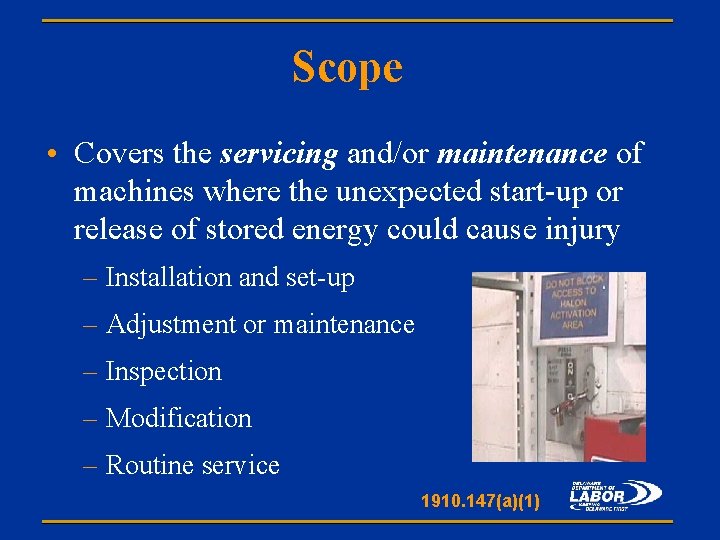
Scope • Covers the servicing and/or maintenance of machines where the unexpected start-up or release of stored energy could cause injury – Installation and set-up – Adjustment or maintenance – Inspection – Modification – Routine service 1910. 147(a)(1)
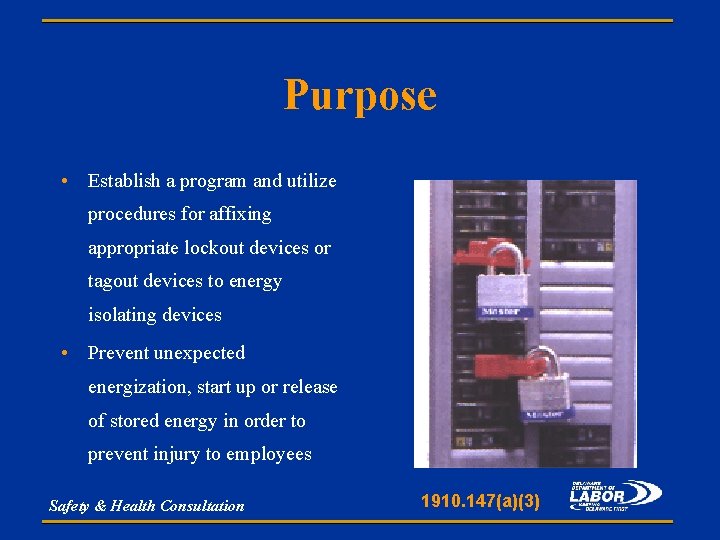
Purpose • Establish a program and utilize procedures for affixing appropriate lockout devices or tagout devices to energy isolating devices • Prevent unexpected energization, start up or release of stored energy in order to prevent injury to employees Safety & Health Consultation 1910. 147(a)(3)
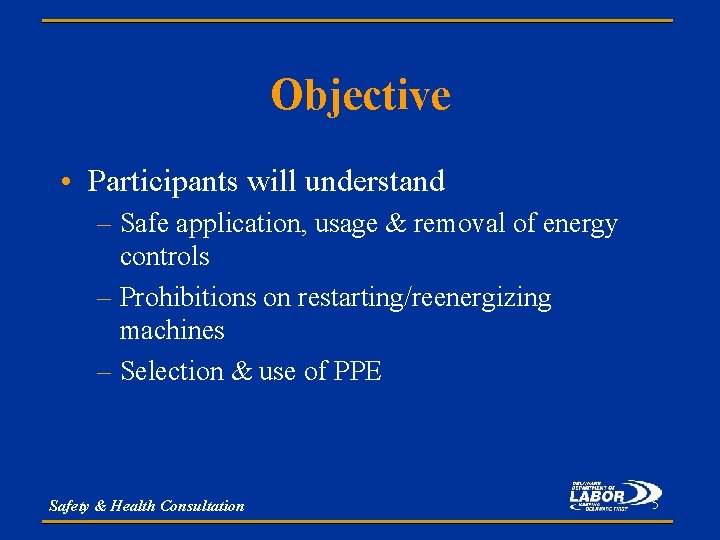
Objective • Participants will understand – Safe application, usage & removal of energy controls – Prohibitions on restarting/reenergizing machines – Selection & use of PPE Safety & Health Consultation 5
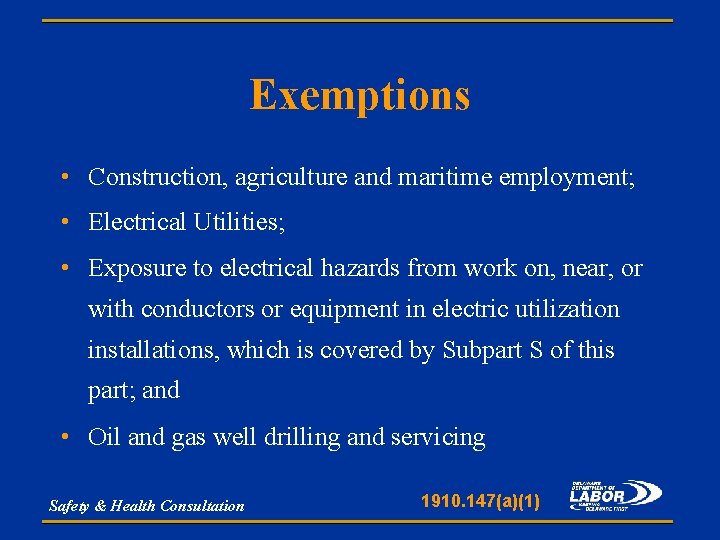
Exemptions • Construction, agriculture and maritime employment; • Electrical Utilities; • Exposure to electrical hazards from work on, near, or with conductors or equipment in electric utilization installations, which is covered by Subpart S of this part; and • Oil and gas well drilling and servicing Safety & Health Consultation 1910. 147(a)(1)

General Requirements • The employer shall establish a program consisting of: – Energy control procedures, – Employee training and, – Periodic inspections • To ensure that before any employee performs any servicing or maintenance on a machine or equipment where the unexpected energizing, startup or release of stored energy could occur and cause injury, the machine or equipment shall be isolated from the energy source and rendered inoperative. Safety & Health Consultation 1910. 147(c)
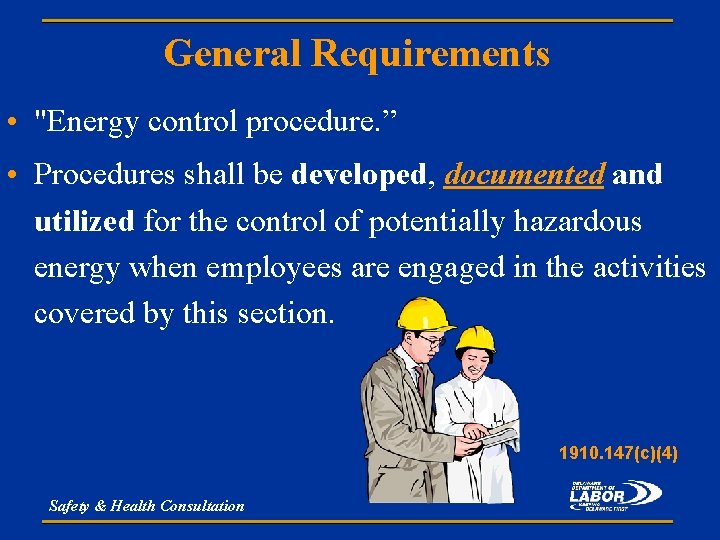
General Requirements • "Energy control procedure. ” • Procedures shall be developed, documented and utilized for the control of potentially hazardous energy when employees are engaged in the activities covered by this section. 1910. 147(c)(4) Safety & Health Consultation
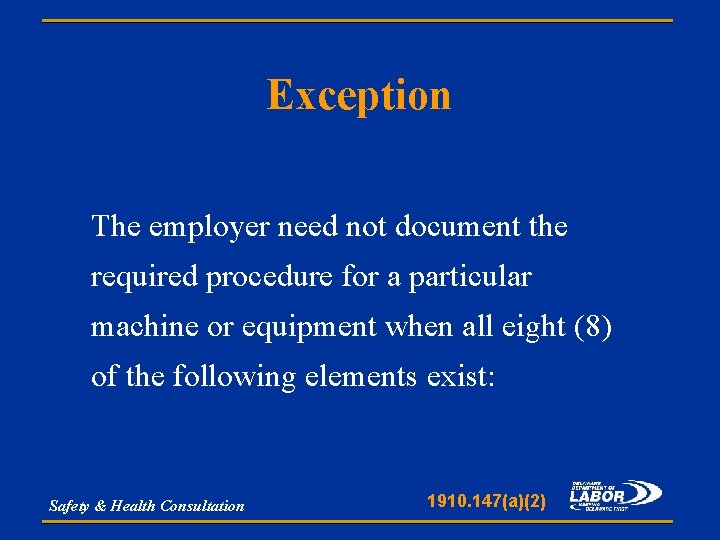
Exception The employer need not document the required procedure for a particular machine or equipment when all eight (8) of the following elements exist: Safety & Health Consultation 1910. 147(a)(2)
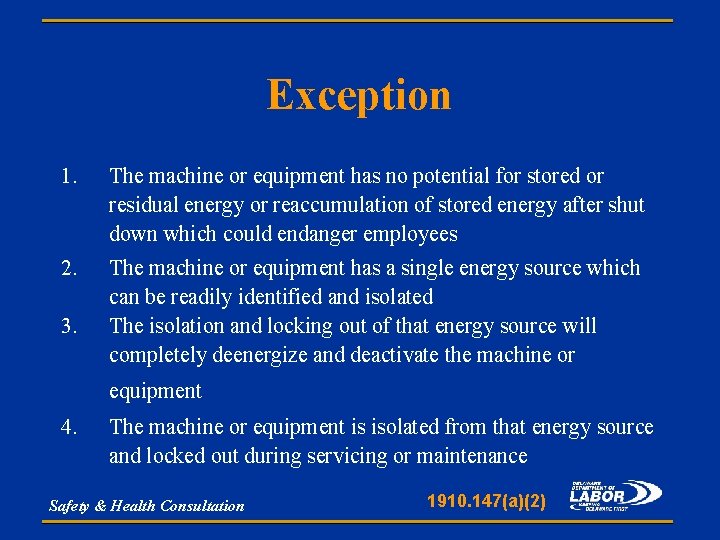
Exception 1. The machine or equipment has no potential for stored or residual energy or reaccumulation of stored energy after shut down which could endanger employees 2. The machine or equipment has a single energy source which can be readily identified and isolated The isolation and locking out of that energy source will completely deenergize and deactivate the machine or 3. equipment 4. The machine or equipment is isolated from that energy source and locked out during servicing or maintenance Safety & Health Consultation 1910. 147(a)(2)
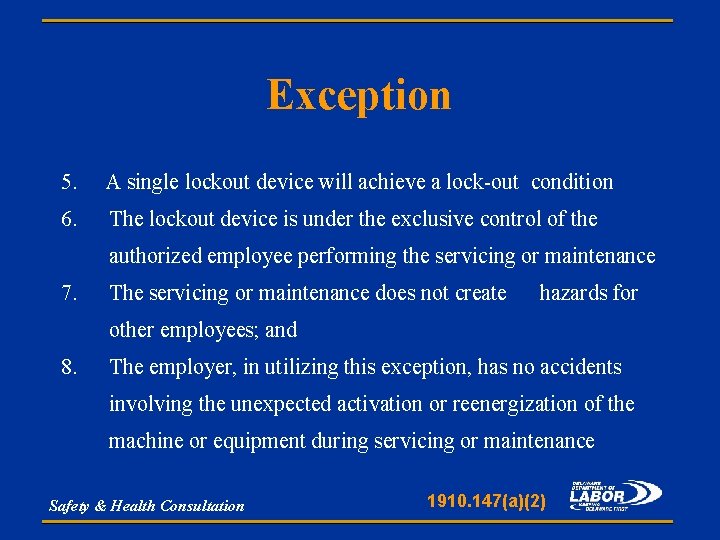
Exception 5. A single lockout device will achieve a lock-out condition 6. The lockout device is under the exclusive control of the authorized employee performing the servicing or maintenance 7. The servicing or maintenance does not create hazards for other employees; and 8. The employer, in utilizing this exception, has no accidents involving the unexpected activation or reenergization of the machine or equipment during servicing or maintenance Safety & Health Consultation 1910. 147(a)(2)
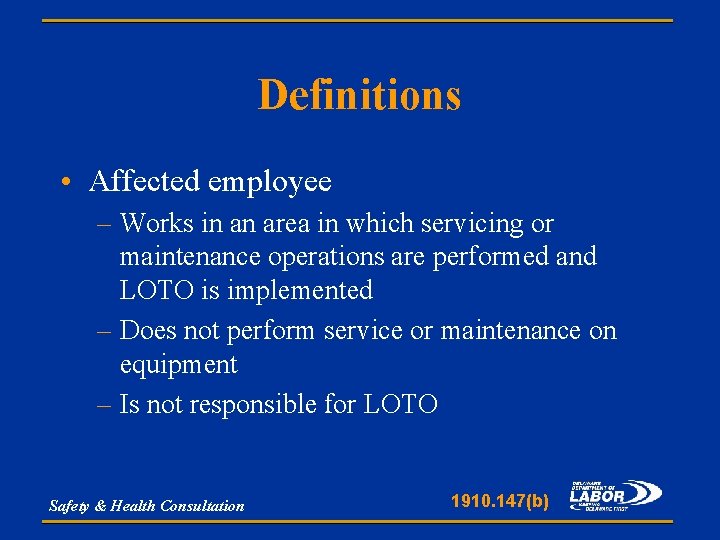
Definitions • Affected employee – Works in an area in which servicing or maintenance operations are performed and LOTO is implemented – Does not perform service or maintenance on equipment – Is not responsible for LOTO Safety & Health Consultation 1910. 147(b)
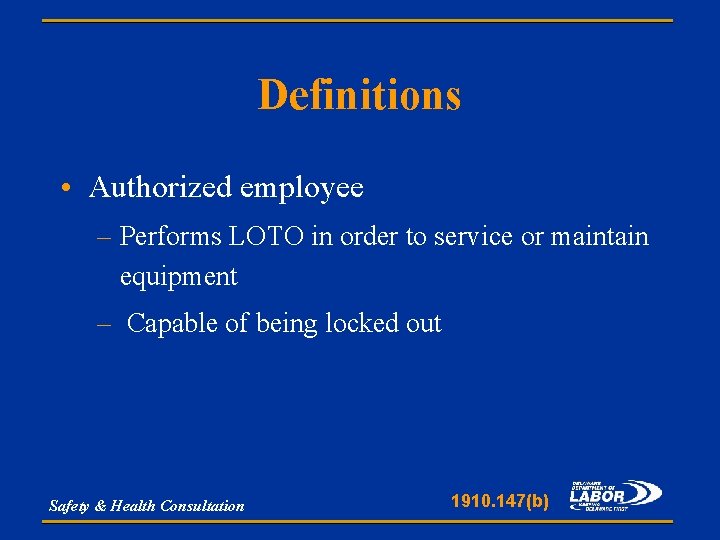
Definitions • Authorized employee – Performs LOTO in order to service or maintain equipment – Capable of being locked out Safety & Health Consultation 1910. 147(b)
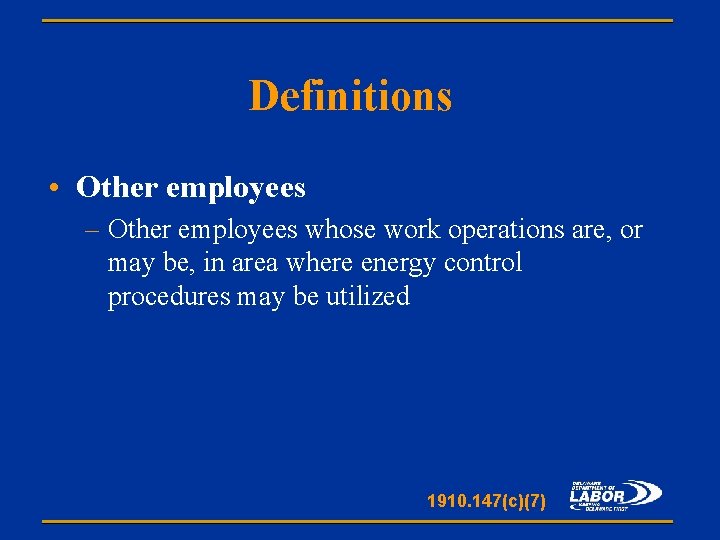
Definitions • Other employees – Other employees whose work operations are, or may be, in area where energy control procedures may be utilized 1910. 147(c)(7)
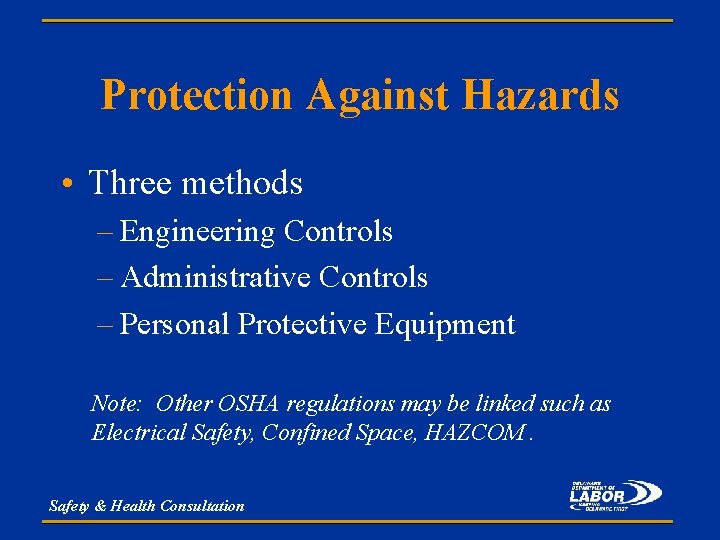
Protection Against Hazards • Three methods – Engineering Controls – Administrative Controls – Personal Protective Equipment Note: Other OSHA regulations may be linked such as Electrical Safety, Confined Space, HAZCOM. Safety & Health Consultation
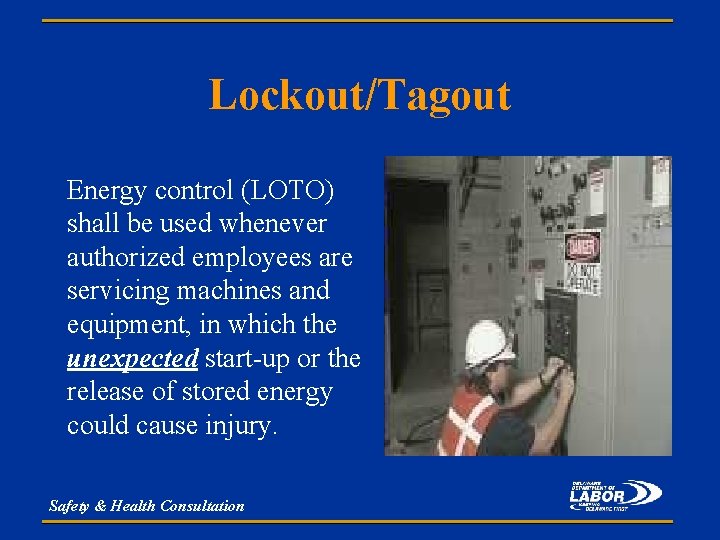
Lockout/Tagout Energy control (LOTO) shall be used whenever authorized employees are servicing machines and equipment, in which the unexpected start-up or the release of stored energy could cause injury. Safety & Health Consultation
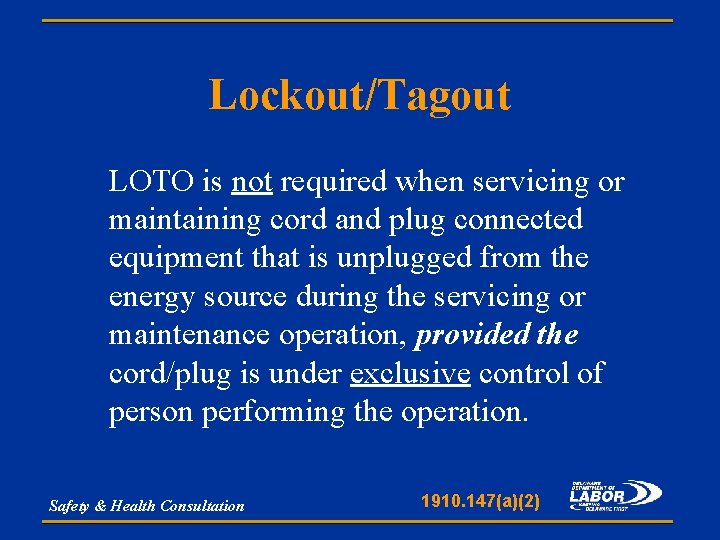
Lockout/Tagout LOTO is not required when servicing or maintaining cord and plug connected equipment that is unplugged from the energy source during the servicing or maintenance operation, provided the cord/plug is under exclusive control of person performing the operation. Safety & Health Consultation 1910. 147(a)(2)
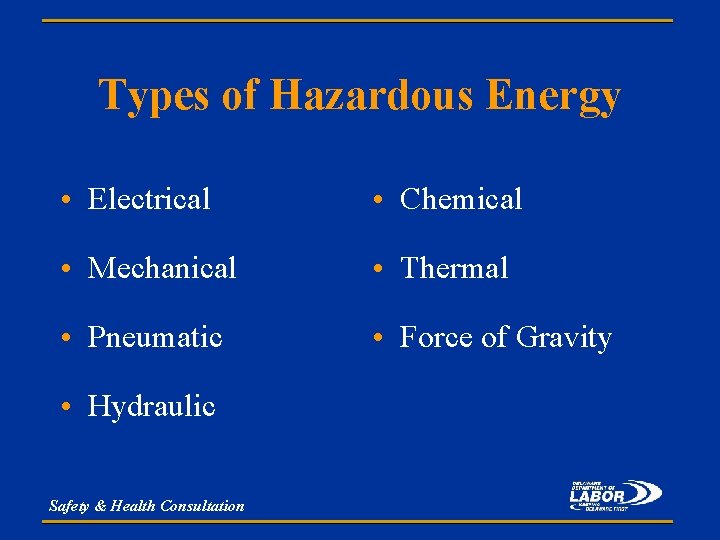
Types of Hazardous Energy • Electrical • Chemical • Mechanical • Thermal • Pneumatic • Force of Gravity • Hydraulic Safety & Health Consultation
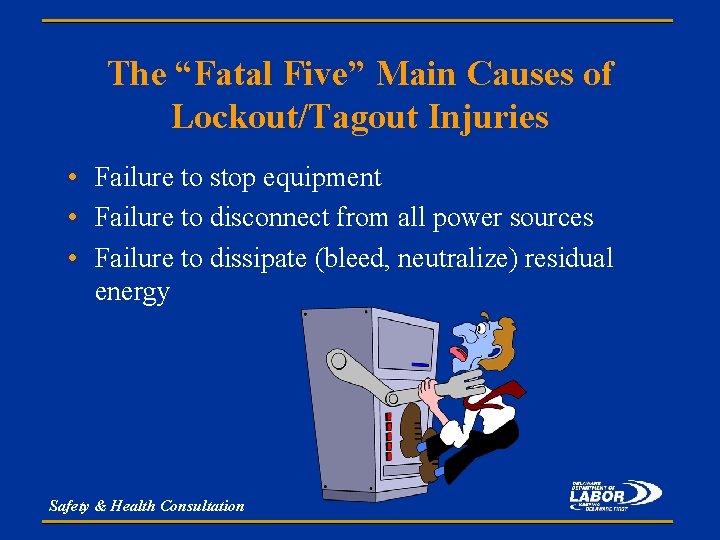
The “Fatal Five” Main Causes of Lockout/Tagout Injuries • Failure to stop equipment • Failure to disconnect from all power sources • Failure to dissipate (bleed, neutralize) residual energy Safety & Health Consultation
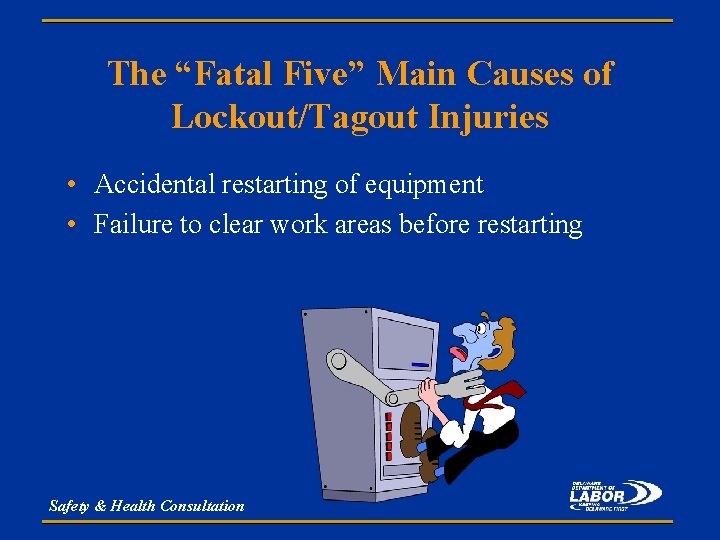
The “Fatal Five” Main Causes of Lockout/Tagout Injuries • Accidental restarting of equipment • Failure to clear work areas before restarting Safety & Health Consultation
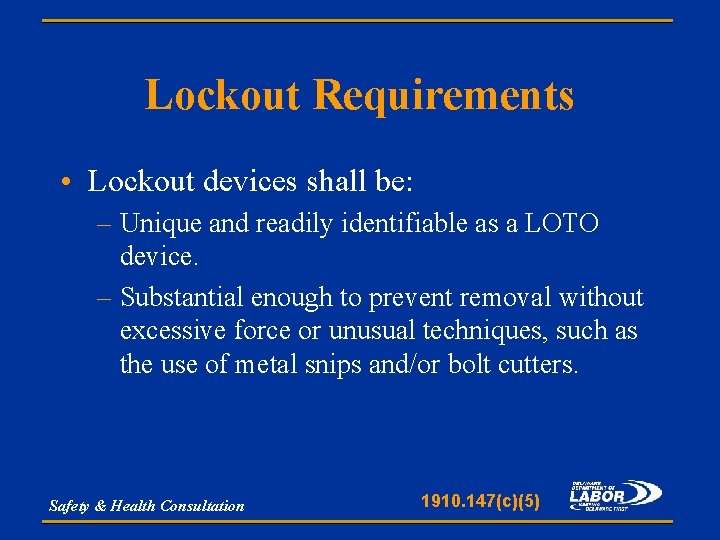
Lockout Requirements • Lockout devices shall be: – Unique and readily identifiable as a LOTO device. – Substantial enough to prevent removal without excessive force or unusual techniques, such as the use of metal snips and/or bolt cutters. Safety & Health Consultation 1910. 147(c)(5)
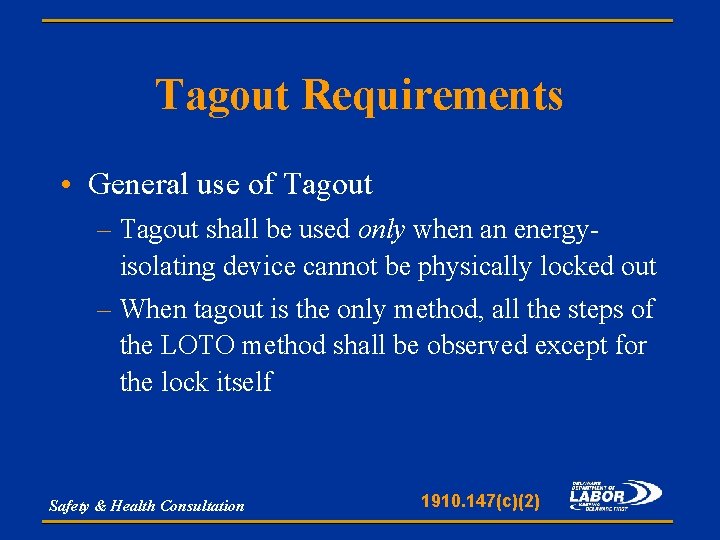
Tagout Requirements • General use of Tagout – Tagout shall be used only when an energyisolating device cannot be physically locked out – When tagout is the only method, all the steps of the LOTO method shall be observed except for the lock itself Safety & Health Consultation 1910. 147(c)(2)
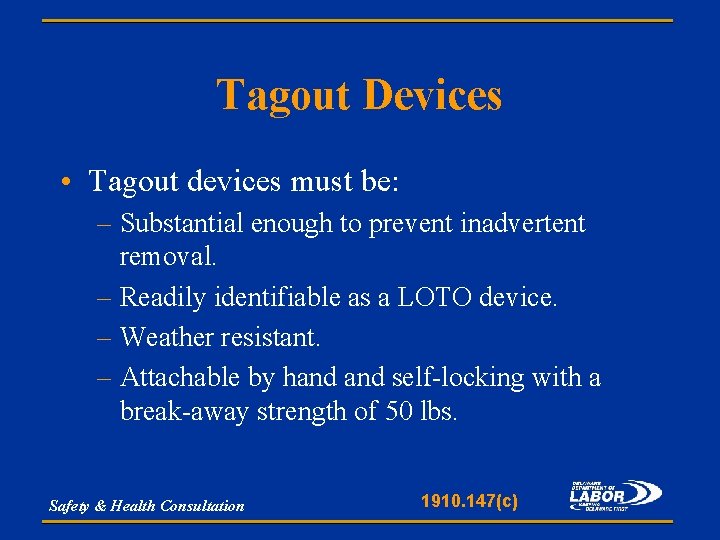
Tagout Devices • Tagout devices must be: – Substantial enough to prevent inadvertent removal. – Readily identifiable as a LOTO device. – Weather resistant. – Attachable by hand self-locking with a break-away strength of 50 lbs. Safety & Health Consultation 1910. 147(c)
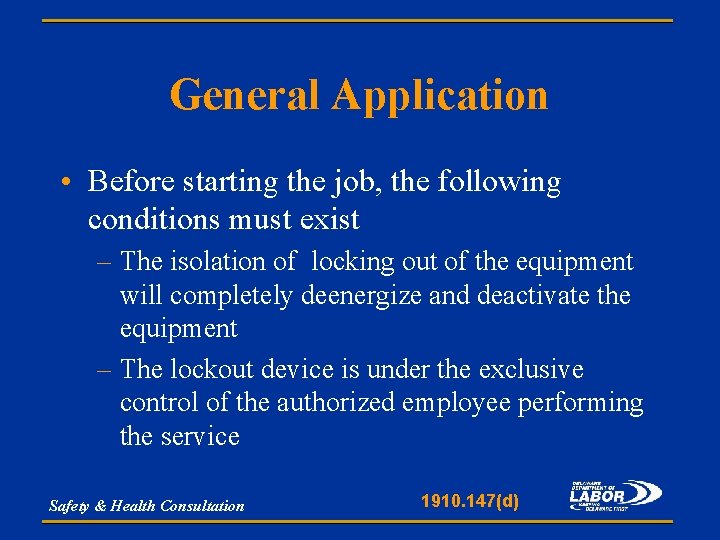
General Application • Before starting the job, the following conditions must exist – The isolation of locking out of the equipment will completely deenergize and deactivate the equipment – The lockout device is under the exclusive control of the authorized employee performing the service Safety & Health Consultation 1910. 147(d)
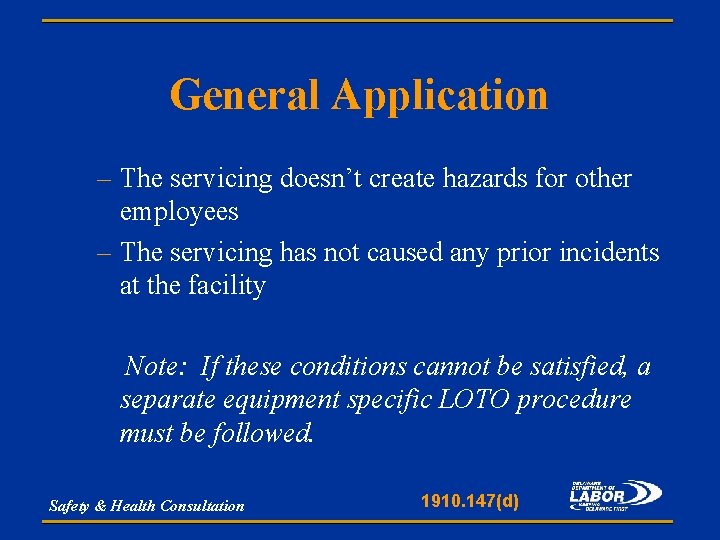
General Application – The servicing doesn’t create hazards for other employees – The servicing has not caused any prior incidents at the facility Note: If these conditions cannot be satisfied, a separate equipment specific LOTO procedure must be followed. Safety & Health Consultation 1910. 147(d)
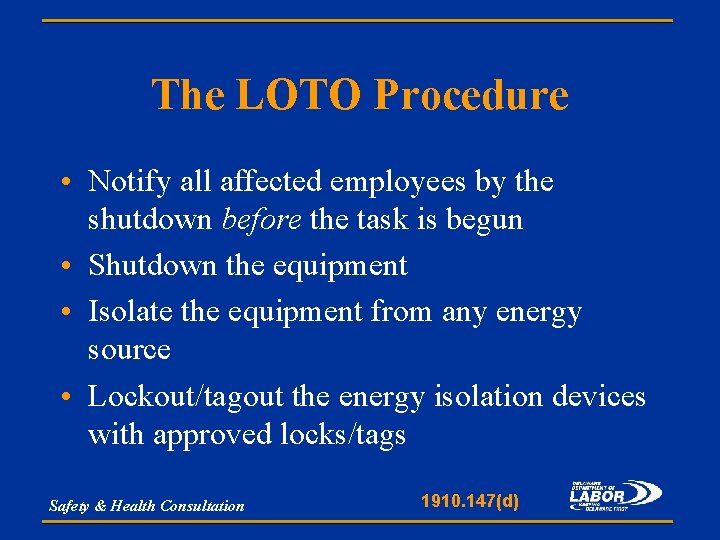
The LOTO Procedure • Notify all affected employees by the shutdown before the task is begun • Shutdown the equipment • Isolate the equipment from any energy source • Lockout/tagout the energy isolation devices with approved locks/tags Safety & Health Consultation 1910. 147(d)
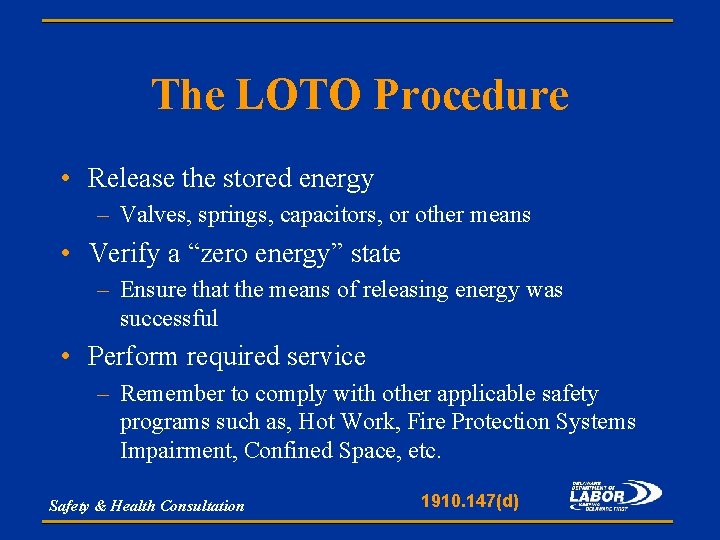
The LOTO Procedure • Release the stored energy – Valves, springs, capacitors, or other means • Verify a “zero energy” state – Ensure that the means of releasing energy was successful • Perform required service – Remember to comply with other applicable safety programs such as, Hot Work, Fire Protection Systems Impairment, Confined Space, etc. Safety & Health Consultation 1910. 147(d)
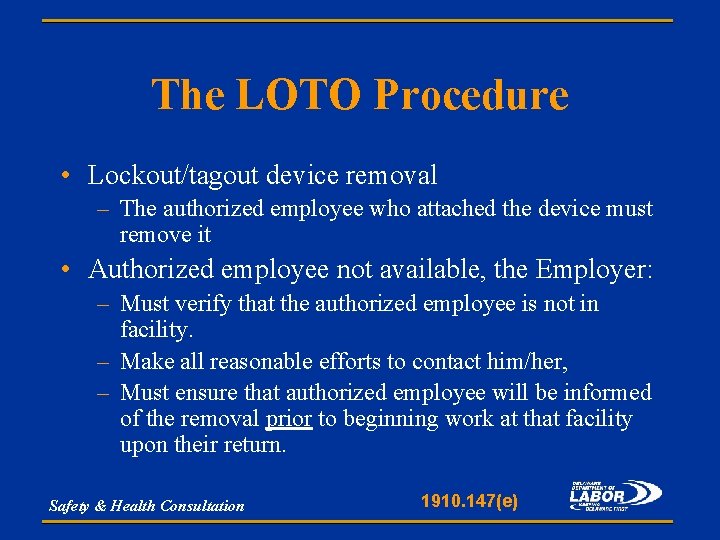
The LOTO Procedure • Lockout/tagout device removal – The authorized employee who attached the device must remove it • Authorized employee not available, the Employer: – Must verify that the authorized employee is not in facility. – Make all reasonable efforts to contact him/her, – Must ensure that authorized employee will be informed of the removal prior to beginning work at that facility upon their return. Safety & Health Consultation 1910. 147(e)
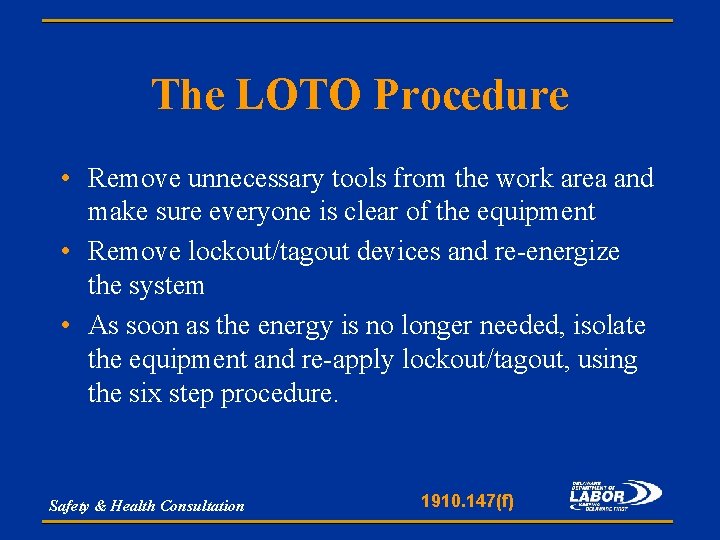
The LOTO Procedure • Remove unnecessary tools from the work area and make sure everyone is clear of the equipment • Remove lockout/tagout devices and re-energize the system • As soon as the energy is no longer needed, isolate the equipment and re-apply lockout/tagout, using the six step procedure. Safety & Health Consultation 1910. 147(f)
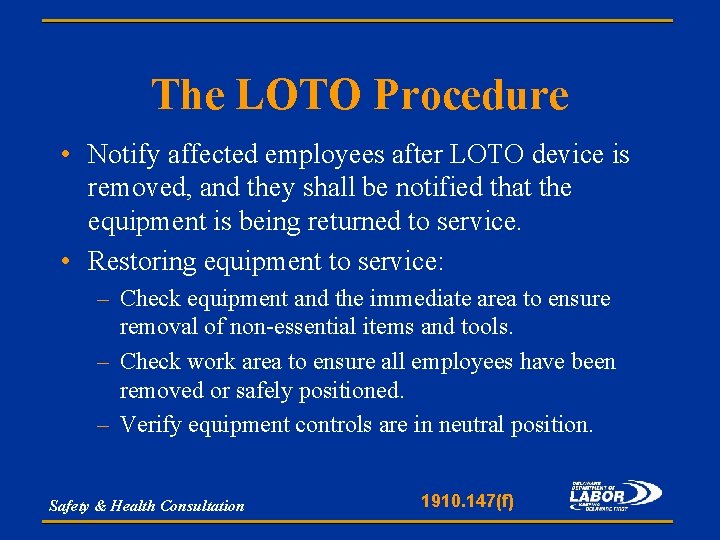
The LOTO Procedure • Notify affected employees after LOTO device is removed, and they shall be notified that the equipment is being returned to service. • Restoring equipment to service: – Check equipment and the immediate area to ensure removal of non-essential items and tools. – Check work area to ensure all employees have been removed or safely positioned. – Verify equipment controls are in neutral position. Safety & Health Consultation 1910. 147(f)
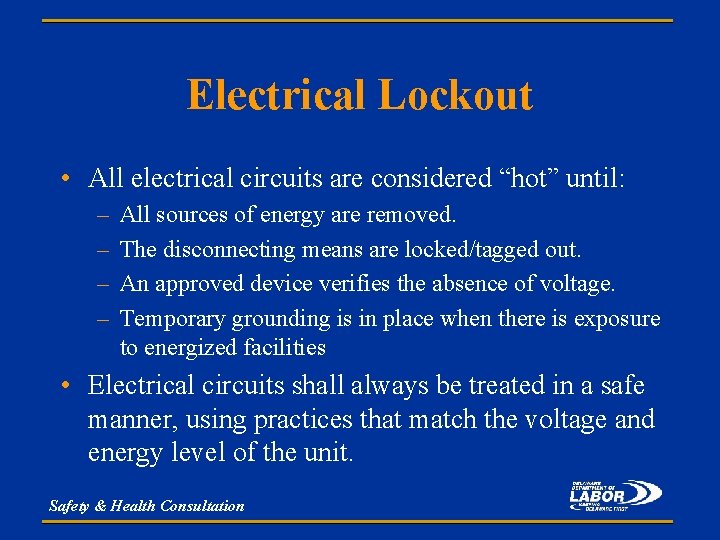
Electrical Lockout • All electrical circuits are considered “hot” until: – – All sources of energy are removed. The disconnecting means are locked/tagged out. An approved device verifies the absence of voltage. Temporary grounding is in place when there is exposure to energized facilities • Electrical circuits shall always be treated in a safe manner, using practices that match the voltage and energy level of the unit. Safety & Health Consultation
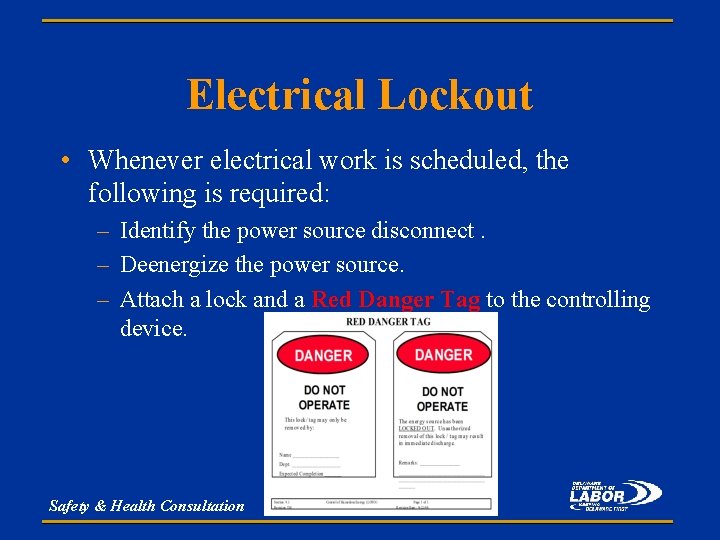
Electrical Lockout • Whenever electrical work is scheduled, the following is required: – Identify the power source disconnect. – Deenergize the power source. – Attach a lock and a Red Danger Tag to the controlling device. Safety & Health Consultation
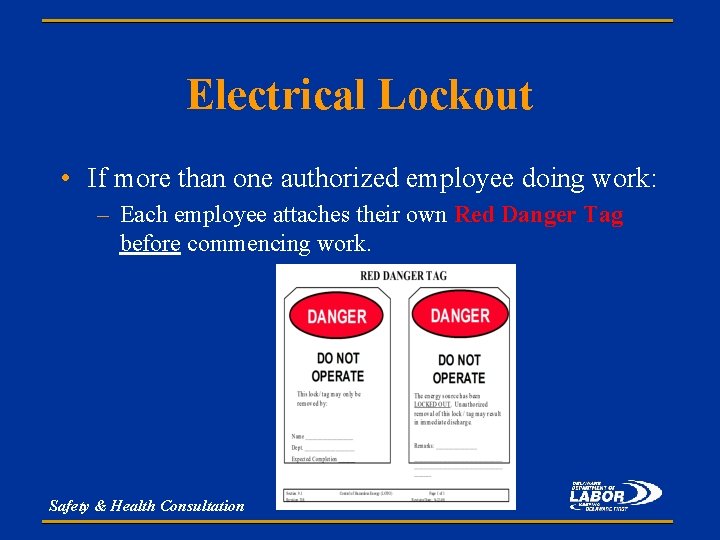
Electrical Lockout • If more than one authorized employee doing work: – Each employee attaches their own Red Danger Tag before commencing work. Safety & Health Consultation
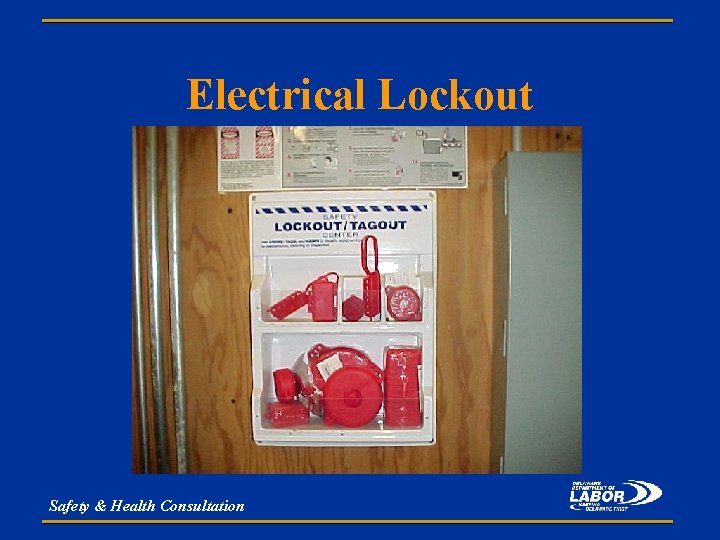
Electrical Lockout Safety & Health Consultation
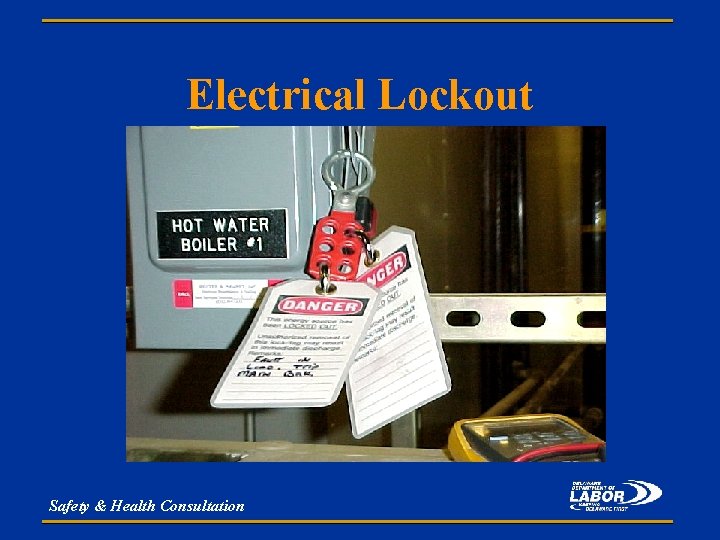
Electrical Lockout Safety & Health Consultation
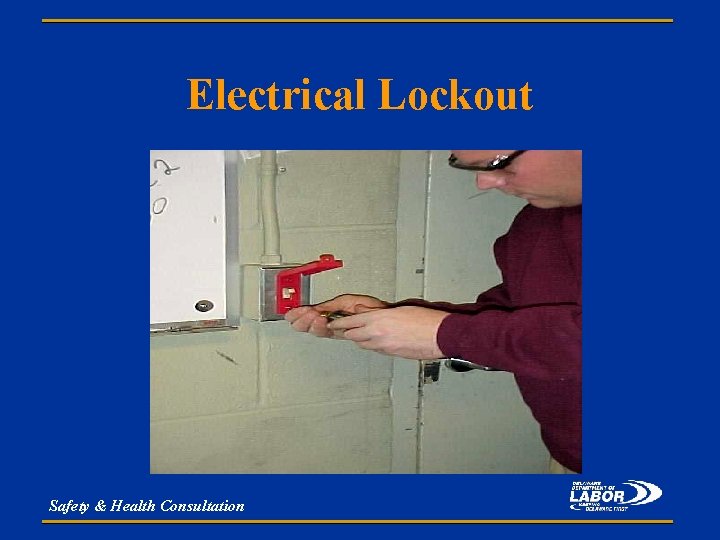
Electrical Lockout Safety & Health Consultation
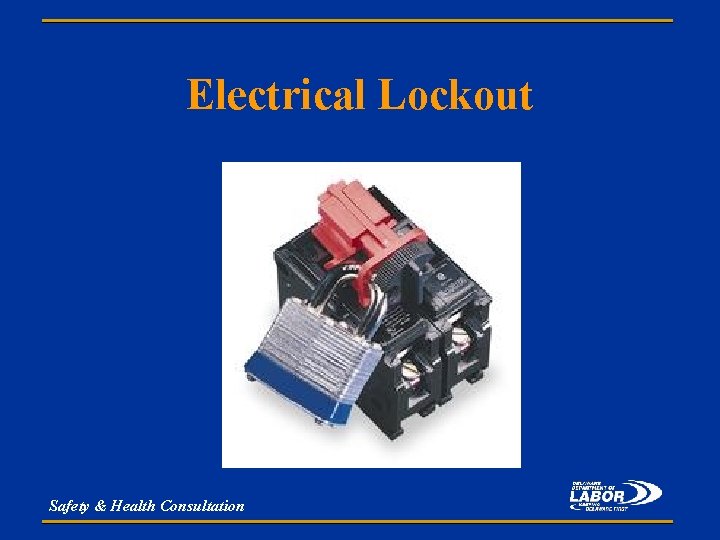
Electrical Lockout Safety & Health Consultation
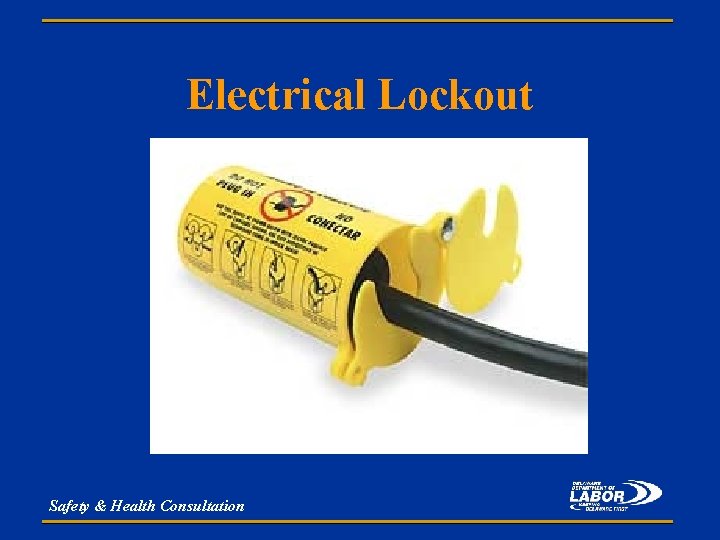
Electrical Lockout Safety & Health Consultation

Electrical Lockout • Prior to beginning equipment work: – Test voltmeter on known circuit to verify working order. – Test equipment on the downstream/tagged out side of the controlling device. – If equipment is wired directly to breaker box, test downstream of the box actuator device. Safety & Health Consultation
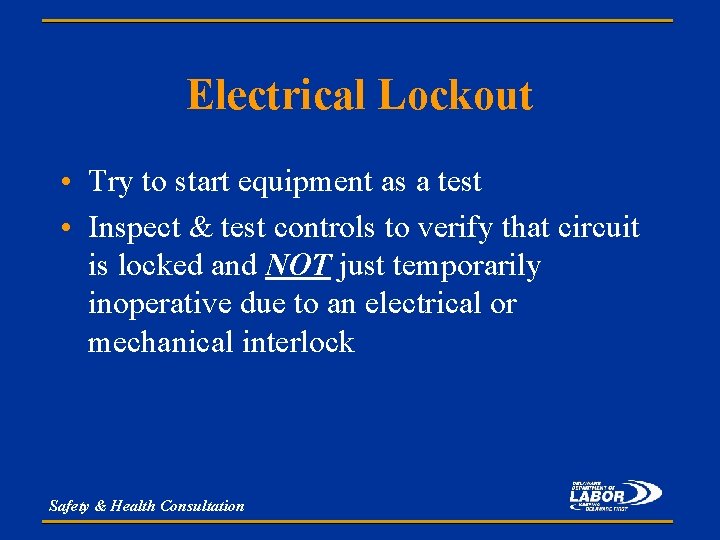
Electrical Lockout • Try to start equipment as a test • Inspect & test controls to verify that circuit is locked and NOT just temporarily inoperative due to an electrical or mechanical interlock Safety & Health Consultation
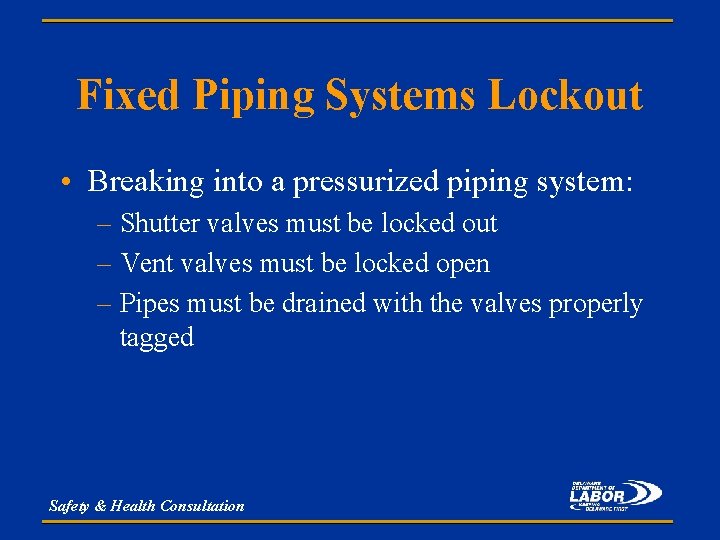
Fixed Piping Systems Lockout • Breaking into a pressurized piping system: – Shutter valves must be locked out – Vent valves must be locked open – Pipes must be drained with the valves properly tagged Safety & Health Consultation
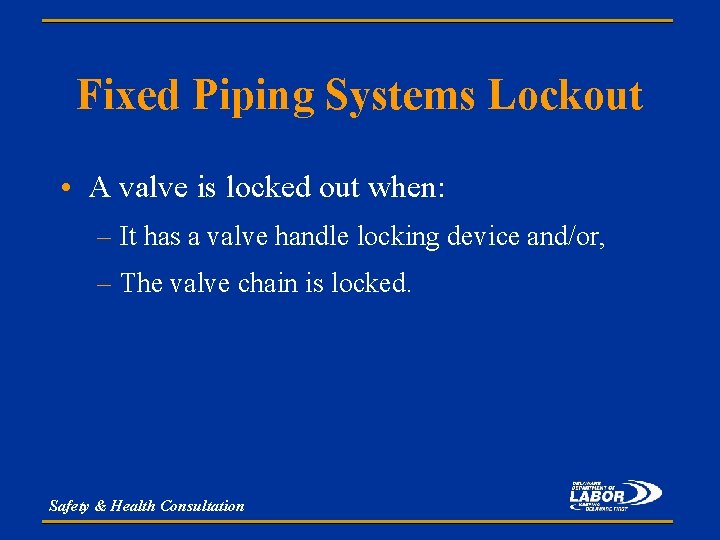
Fixed Piping Systems Lockout • A valve is locked out when: – It has a valve handle locking device and/or, – The valve chain is locked. Safety & Health Consultation
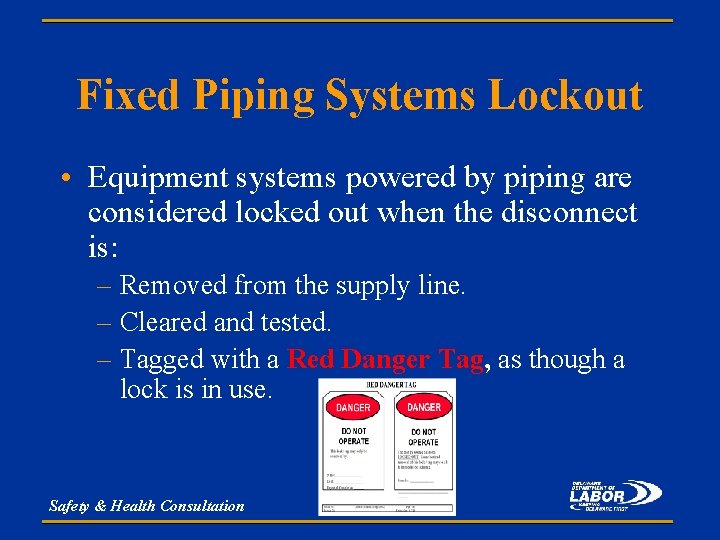
Fixed Piping Systems Lockout • Equipment systems powered by piping are considered locked out when the disconnect is: – Removed from the supply line. – Cleared and tested. – Tagged with a Red Danger Tag, as though a lock is in use. Safety & Health Consultation
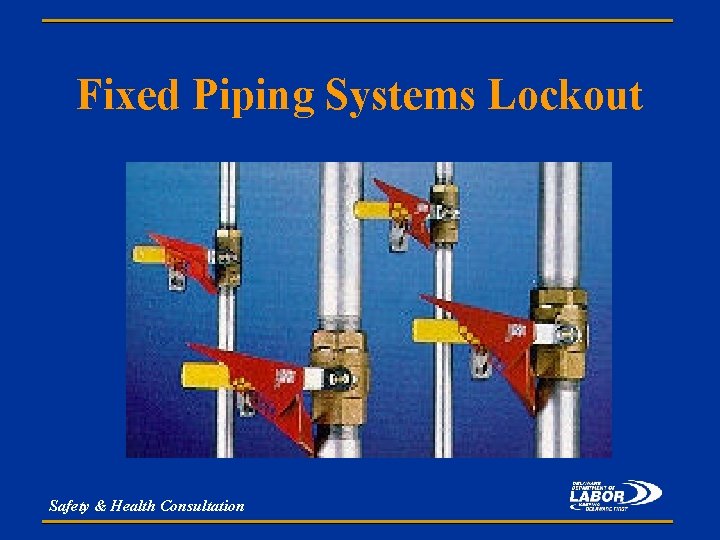
Fixed Piping Systems Lockout Safety & Health Consultation

Fixed Piping Systems Lockout Safety & Health Consultation
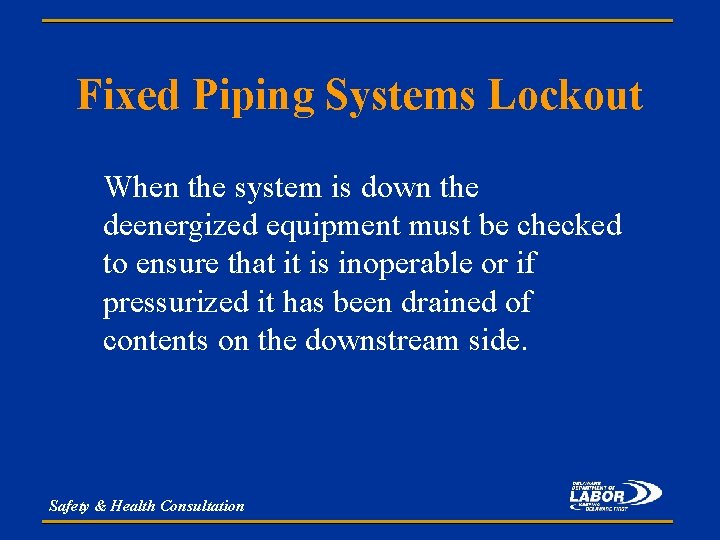
Fixed Piping Systems Lockout When the system is down the deenergized equipment must be checked to ensure that it is inoperable or if pressurized it has been drained of contents on the downstream side. Safety & Health Consultation
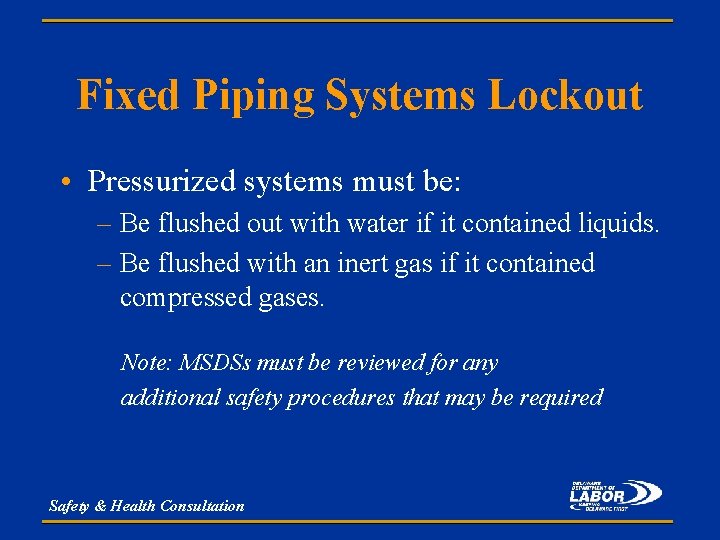
Fixed Piping Systems Lockout • Pressurized systems must be: – Be flushed out with water if it contained liquids. – Be flushed with an inert gas if it contained compressed gases. Note: MSDSs must be reviewed for any additional safety procedures that may be required Safety & Health Consultation
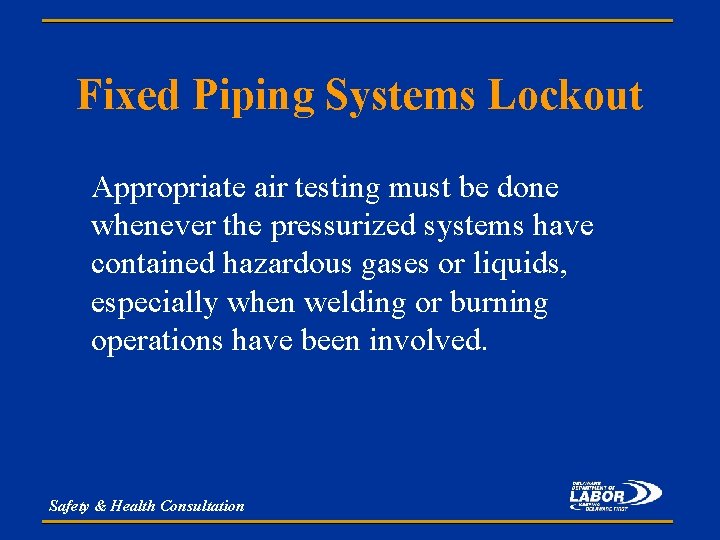
Fixed Piping Systems Lockout Appropriate air testing must be done whenever the pressurized systems have contained hazardous gases or liquids, especially when welding or burning operations have been involved. Safety & Health Consultation
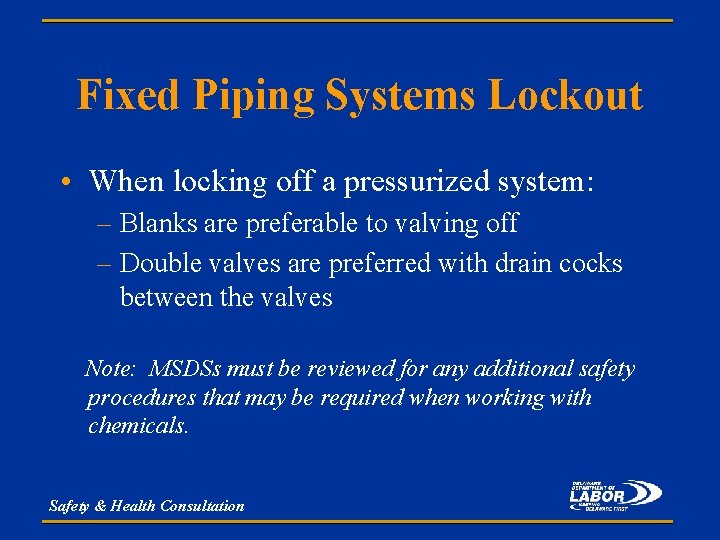
Fixed Piping Systems Lockout • When locking off a pressurized system: – Blanks are preferable to valving off – Double valves are preferred with drain cocks between the valves Note: MSDSs must be reviewed for any additional safety procedures that may be required when working with chemicals. Safety & Health Consultation
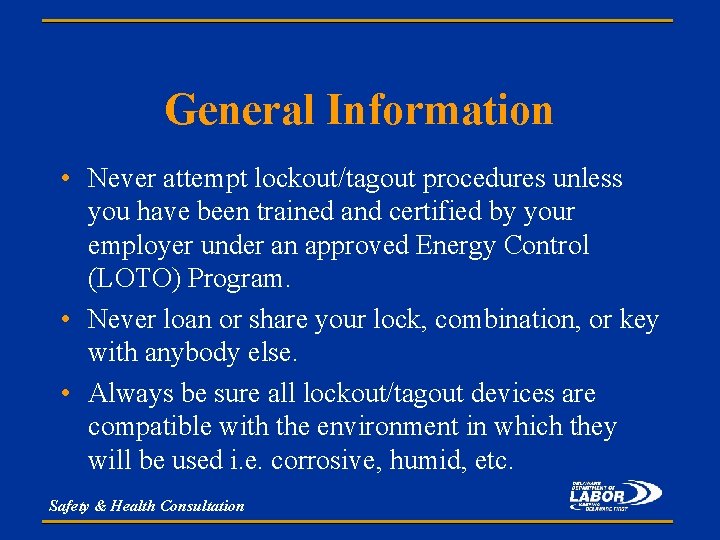
General Information • Never attempt lockout/tagout procedures unless you have been trained and certified by your employer under an approved Energy Control (LOTO) Program. • Never loan or share your lock, combination, or key with anybody else. • Always be sure all lockout/tagout devices are compatible with the environment in which they will be used i. e. corrosive, humid, etc. Safety & Health Consultation
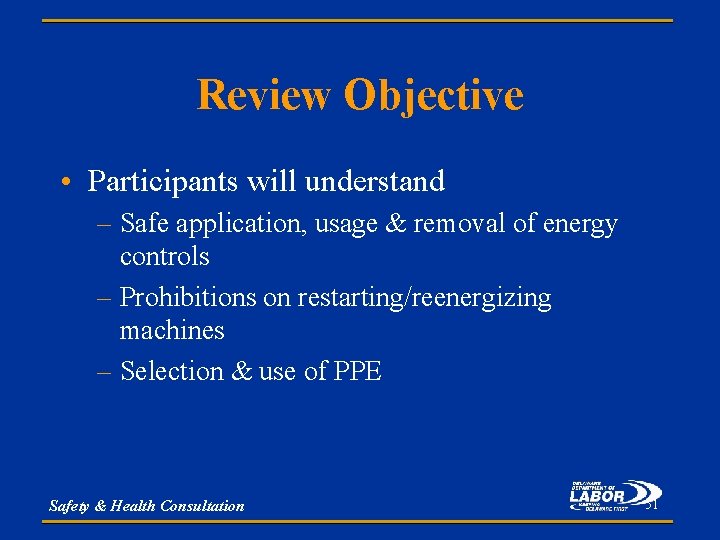
Review Objective • Participants will understand – Safe application, usage & removal of energy controls – Prohibitions on restarting/reenergizing machines – Selection & use of PPE Safety & Health Consultation 51
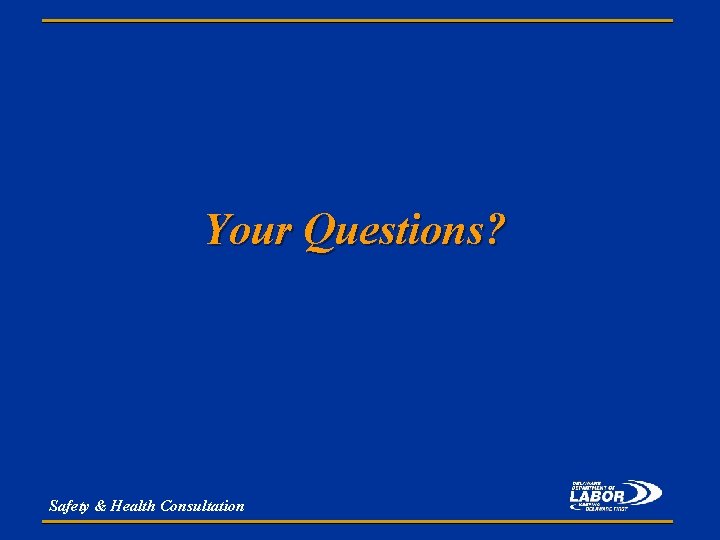
Your Questions? Safety & Health Consultation
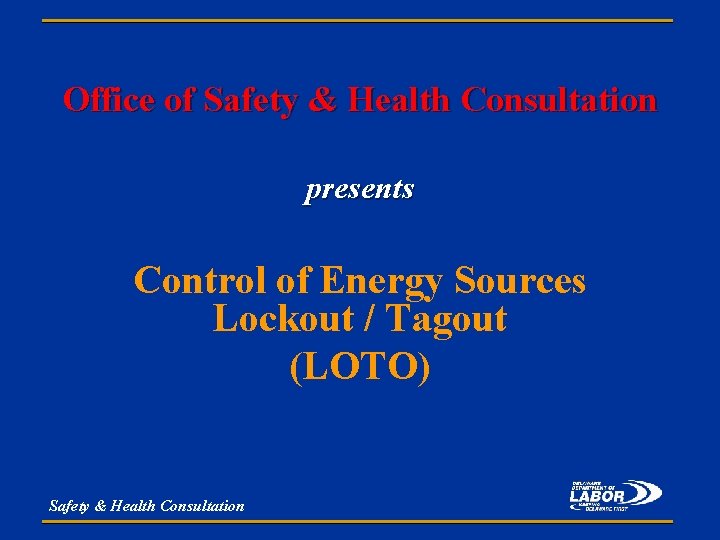
Office of Safety & Health Consultation presents Control of Energy Sources Lockout / Tagout (LOTO) Safety & Health Consultation