PART I STRESS CONCENTRATION 1 Stress concentration l
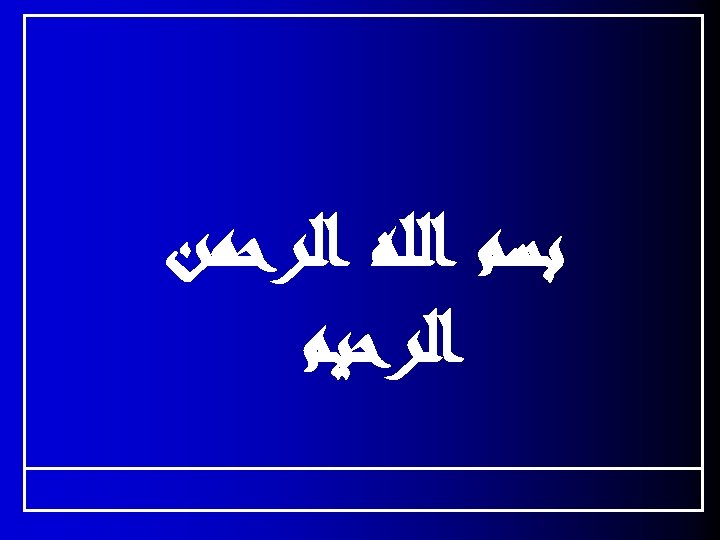
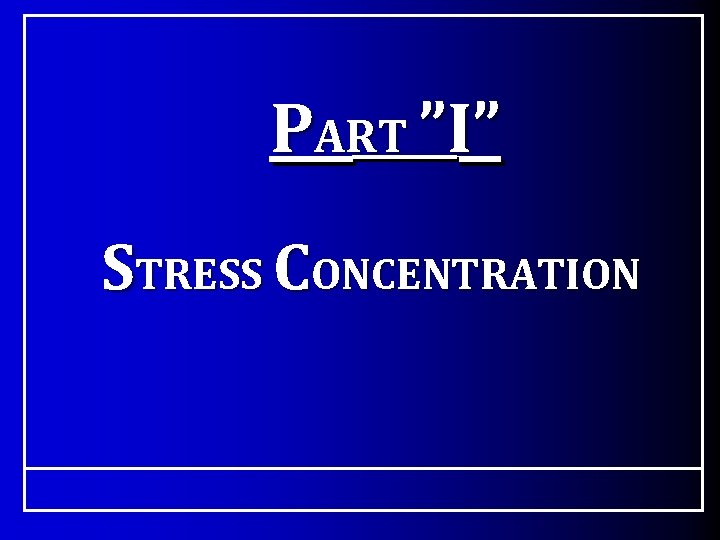
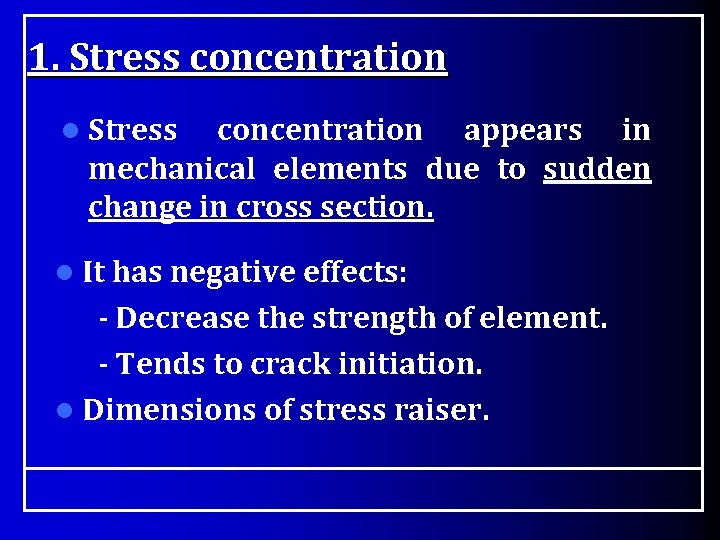
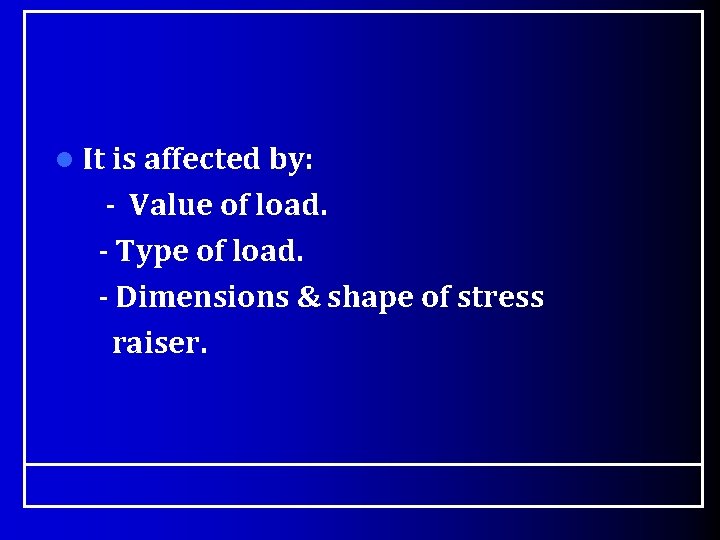
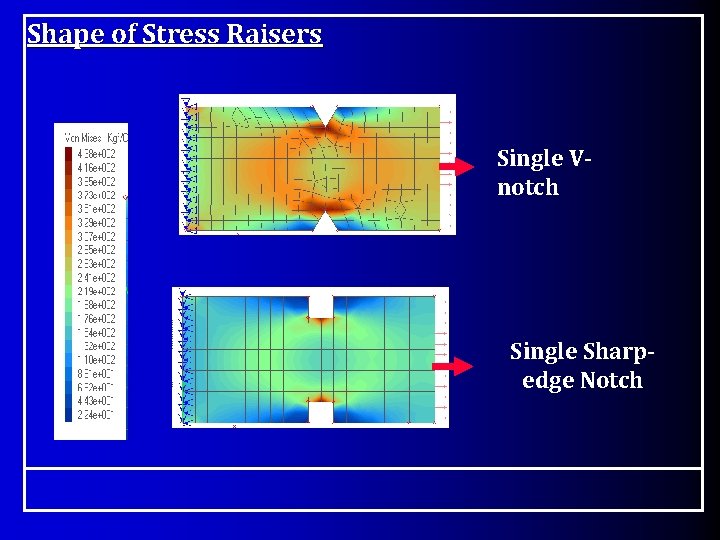
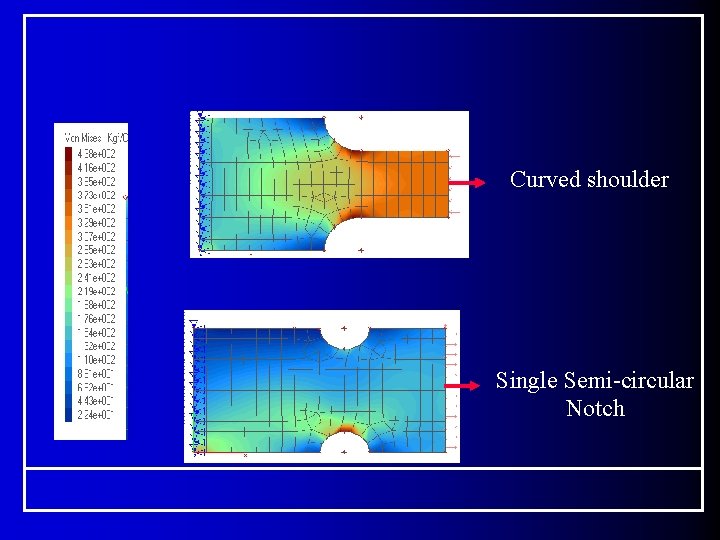
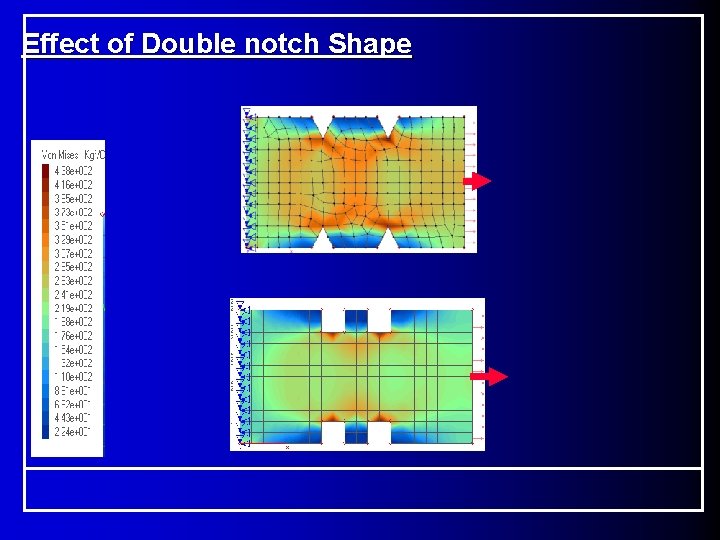
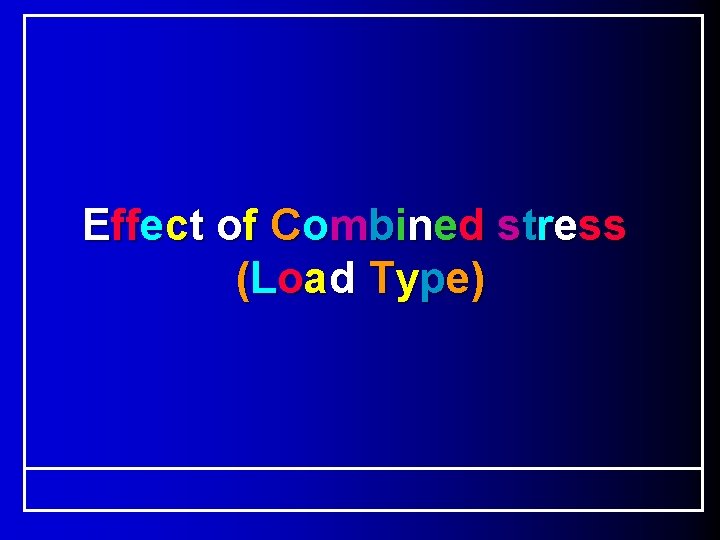
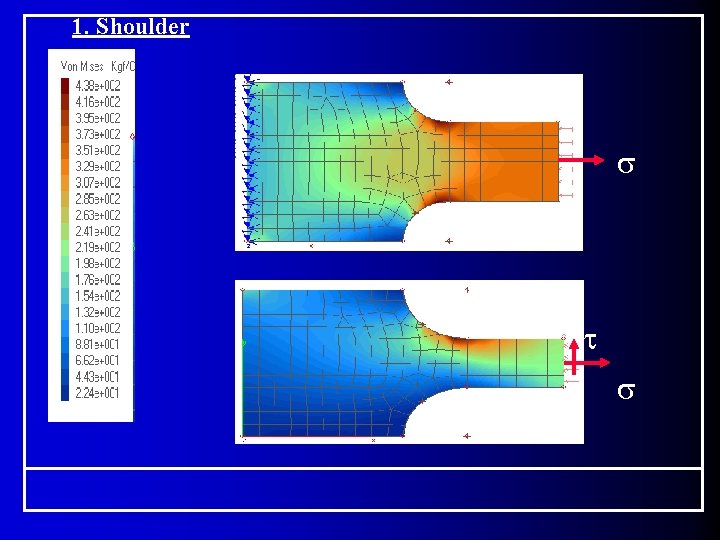
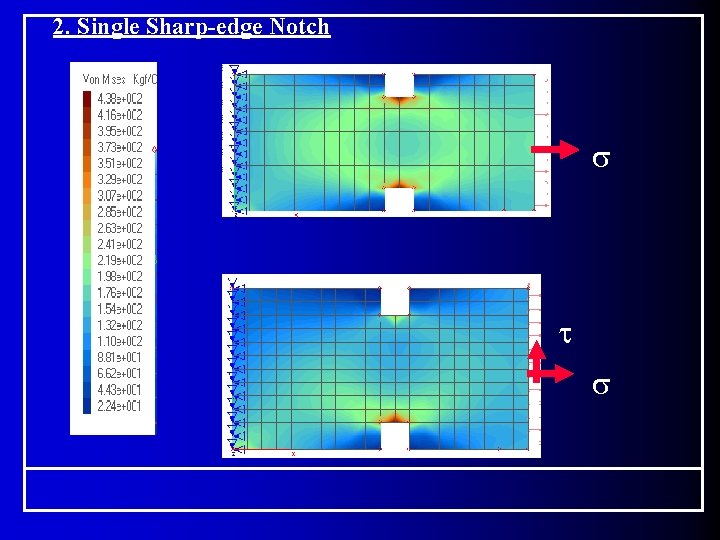
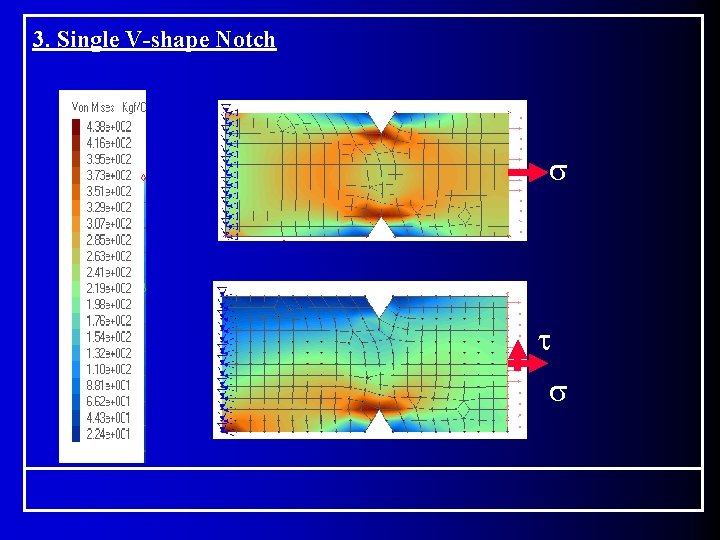
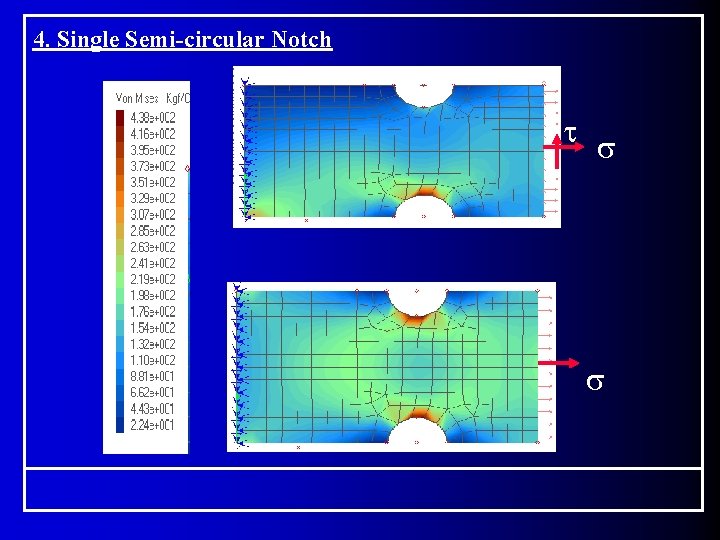
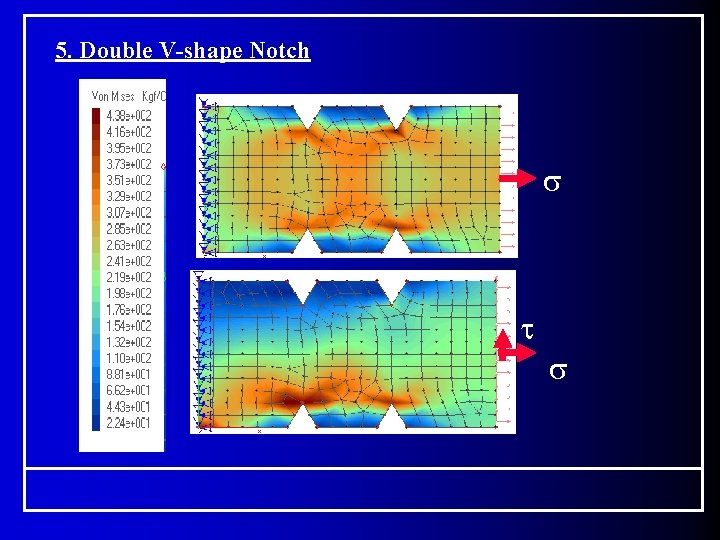
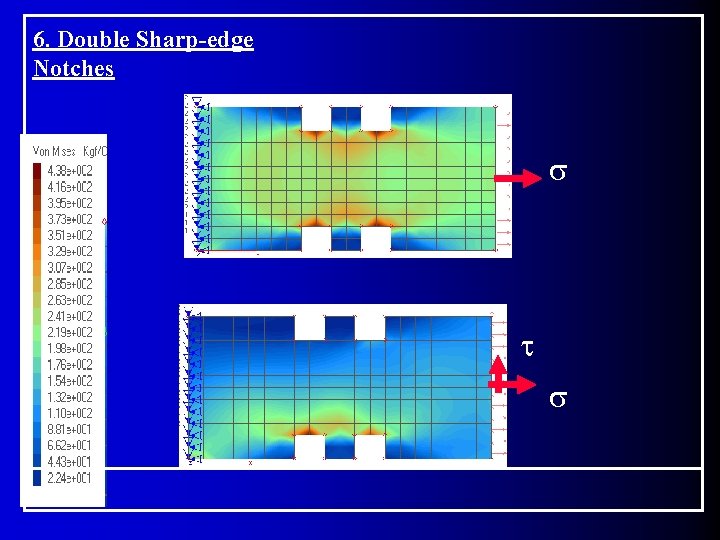
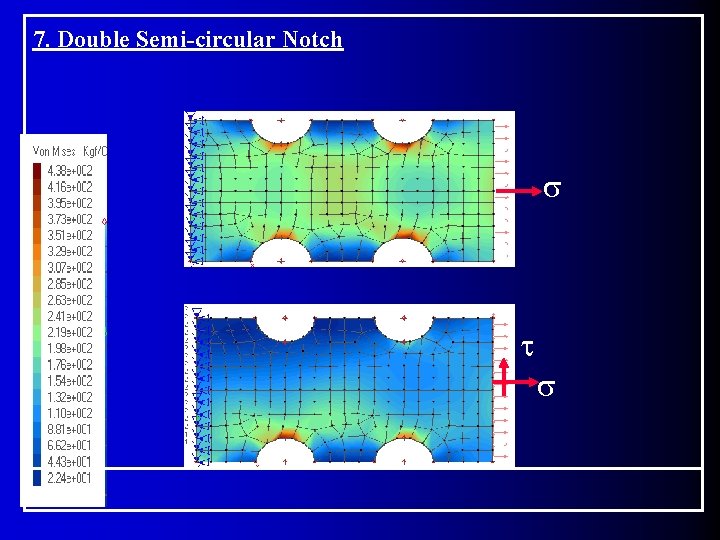
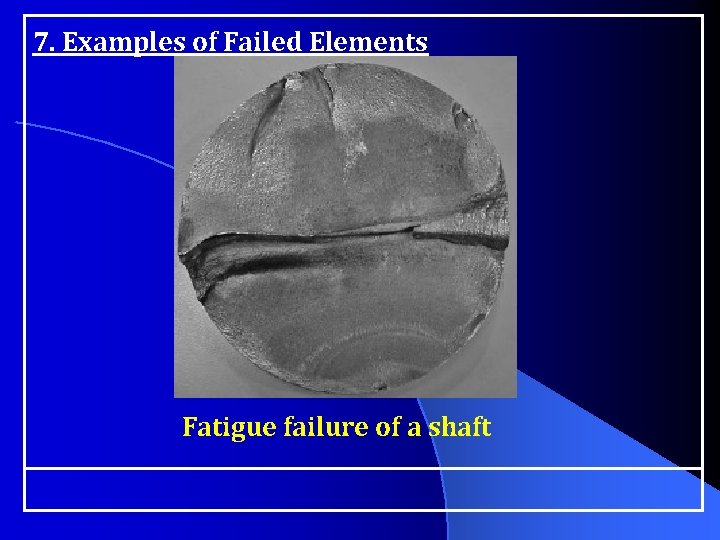
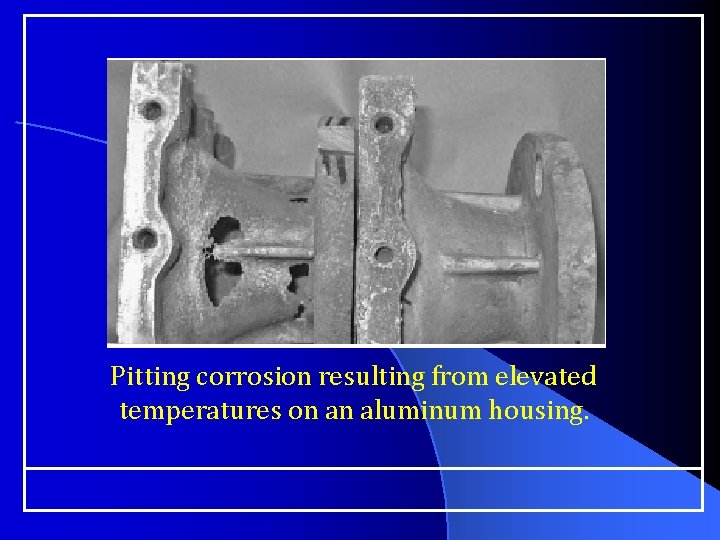
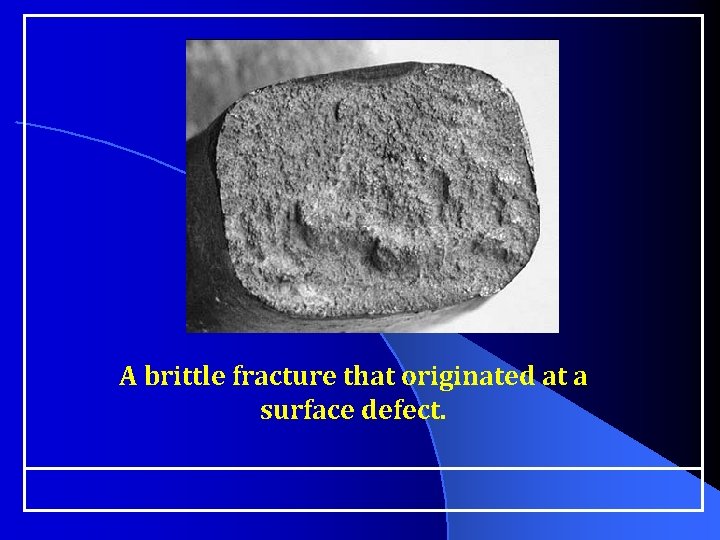
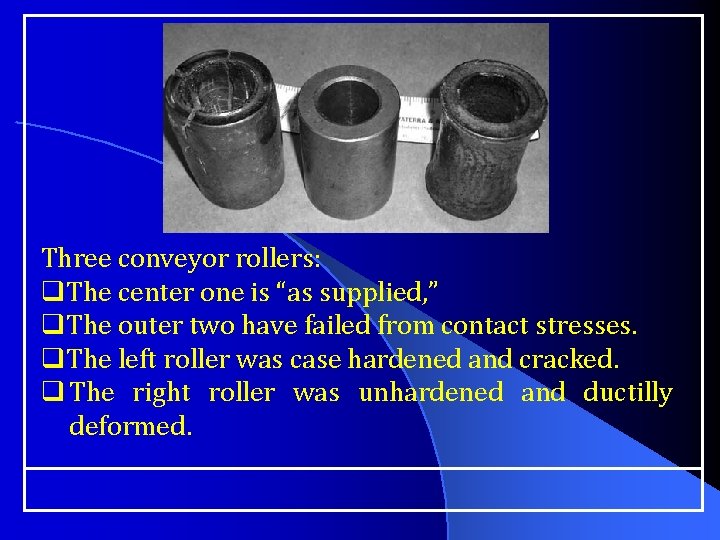
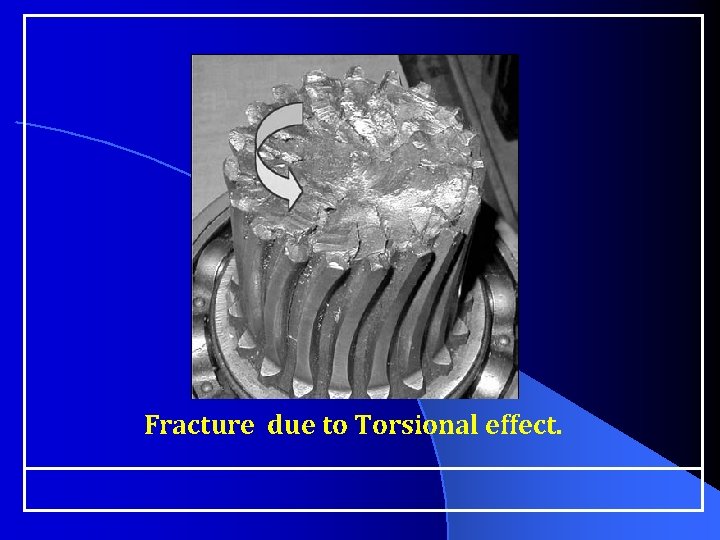
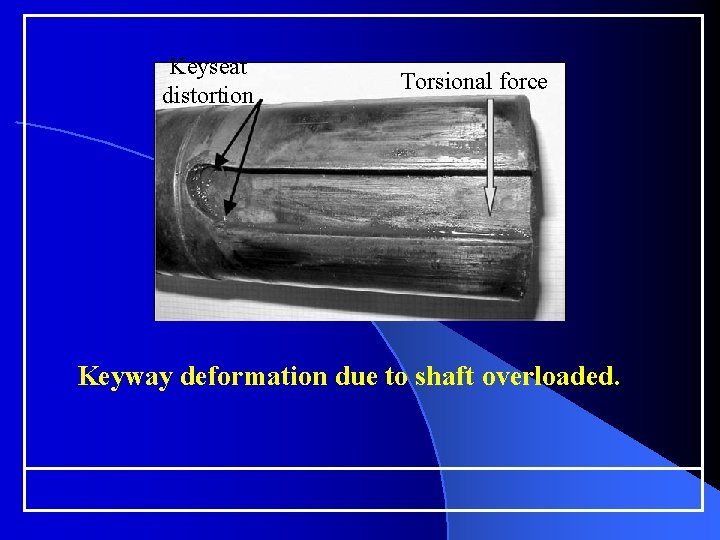
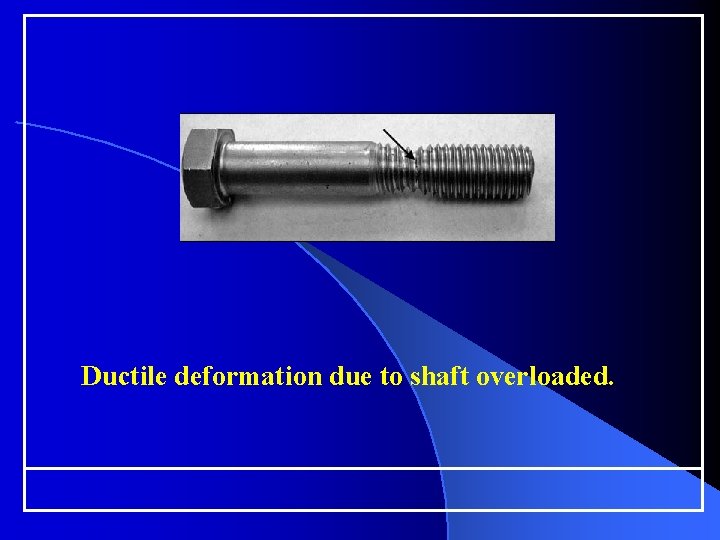
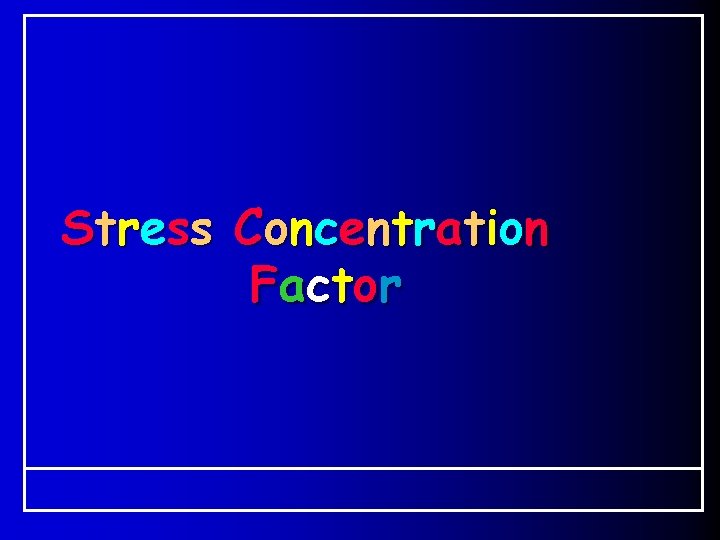
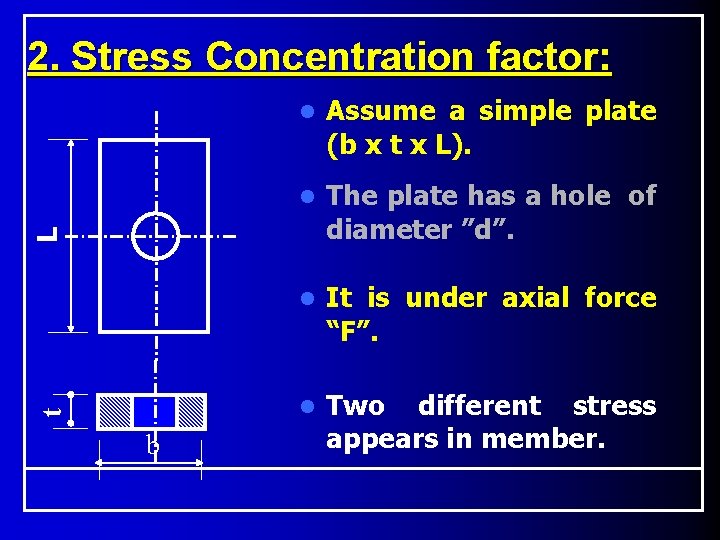
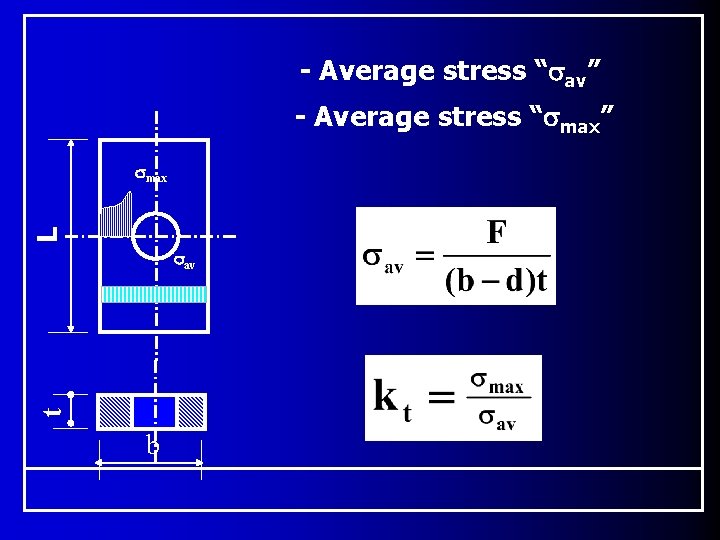
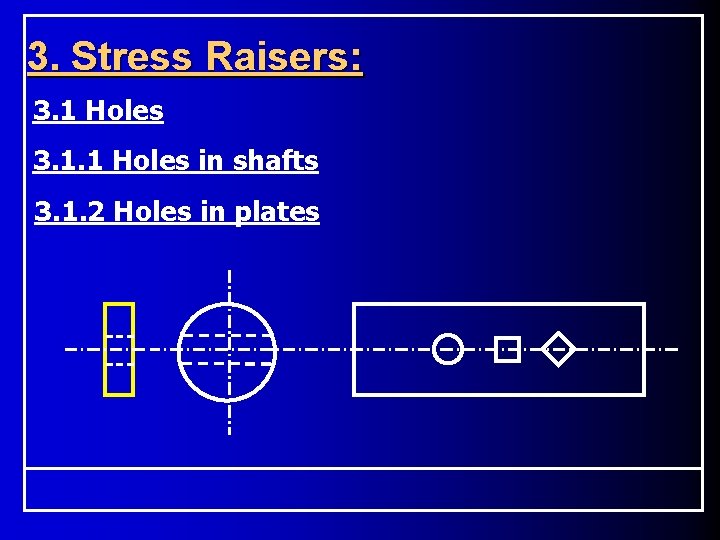
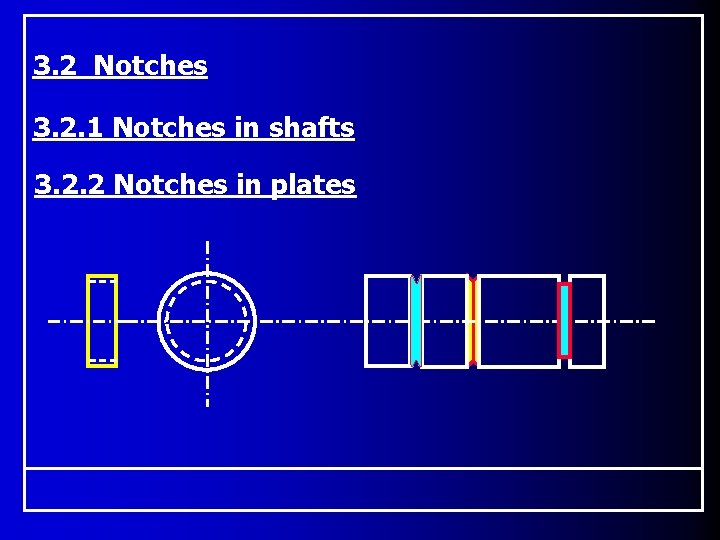
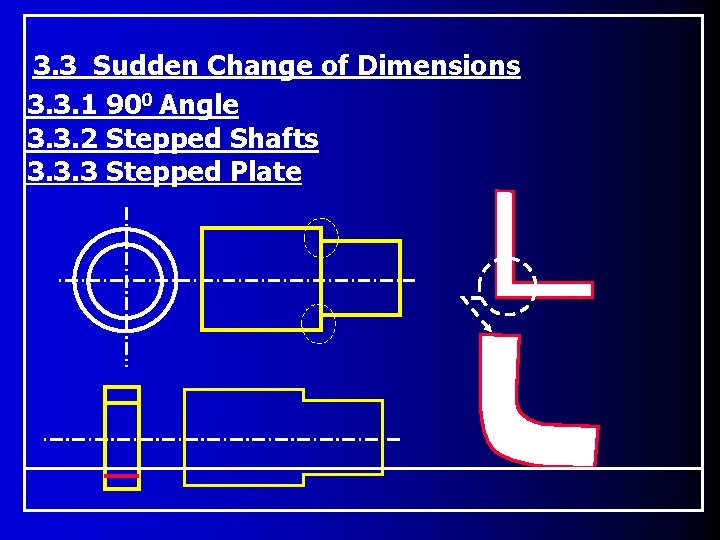
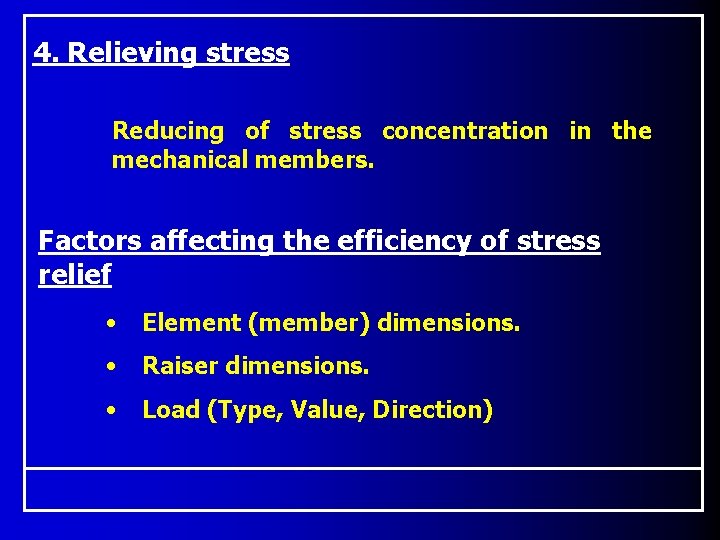
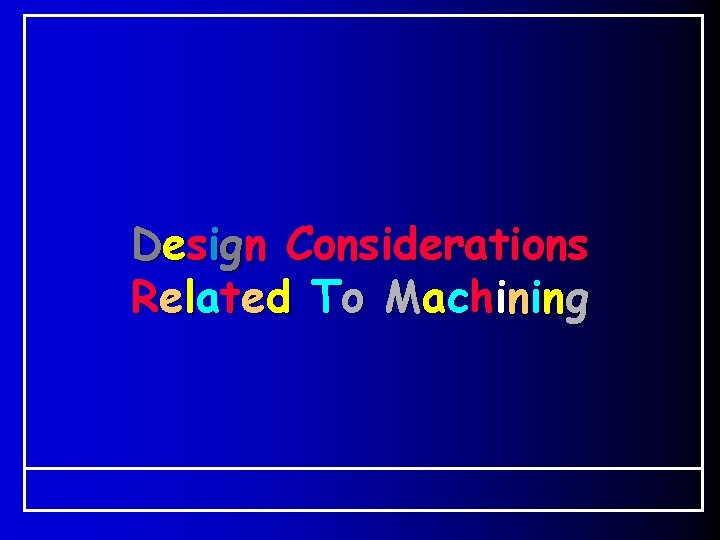
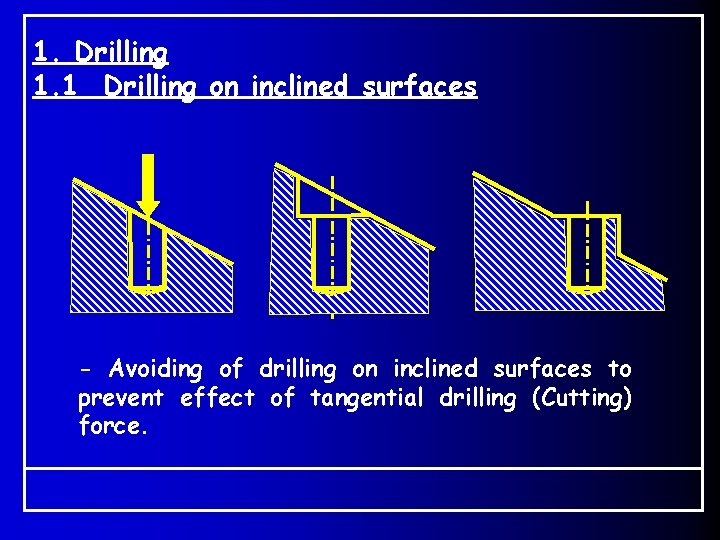

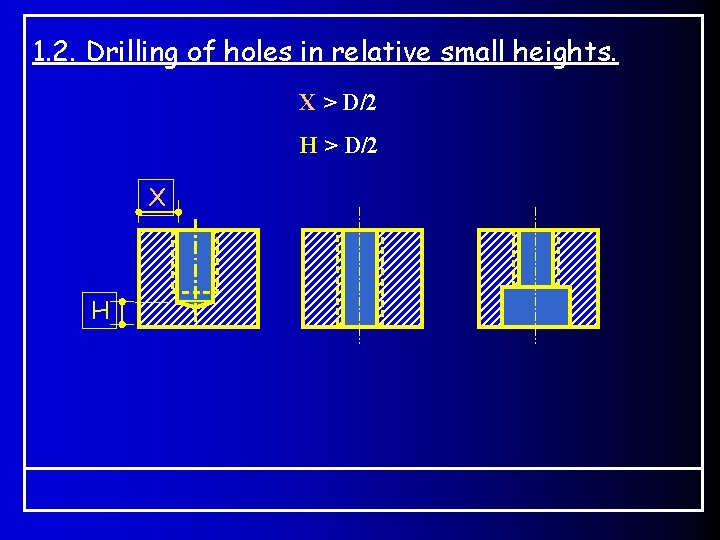
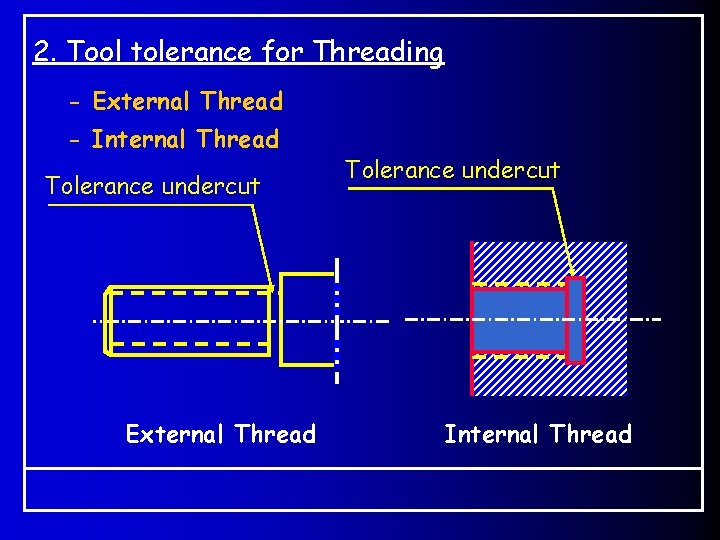
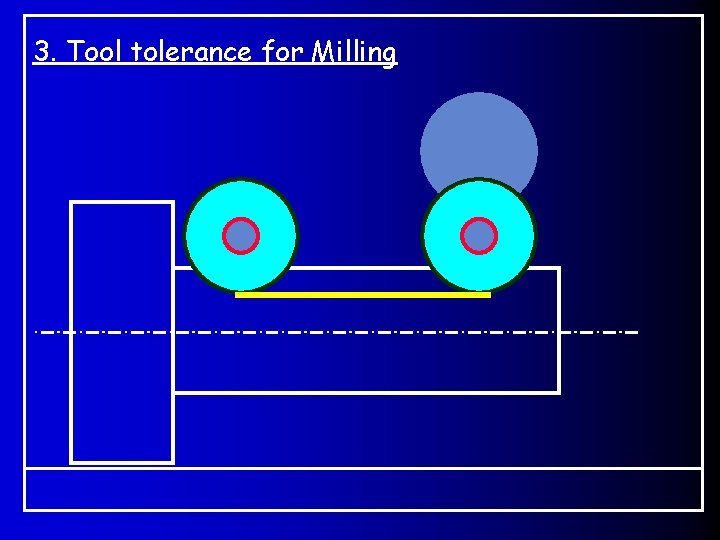
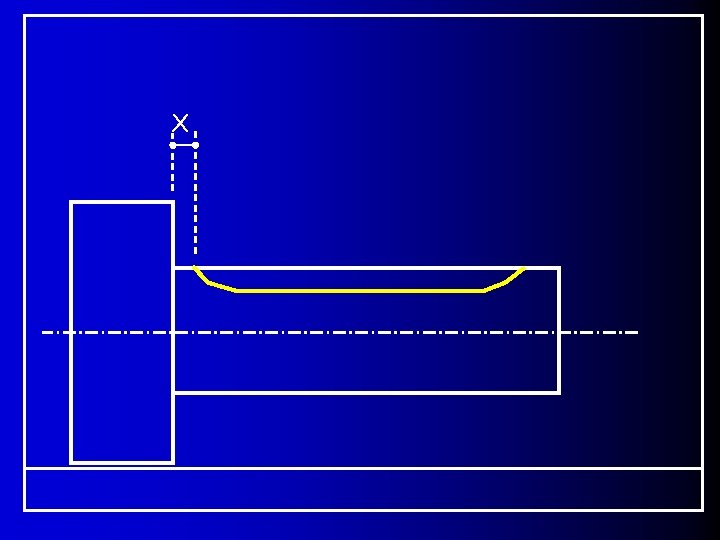
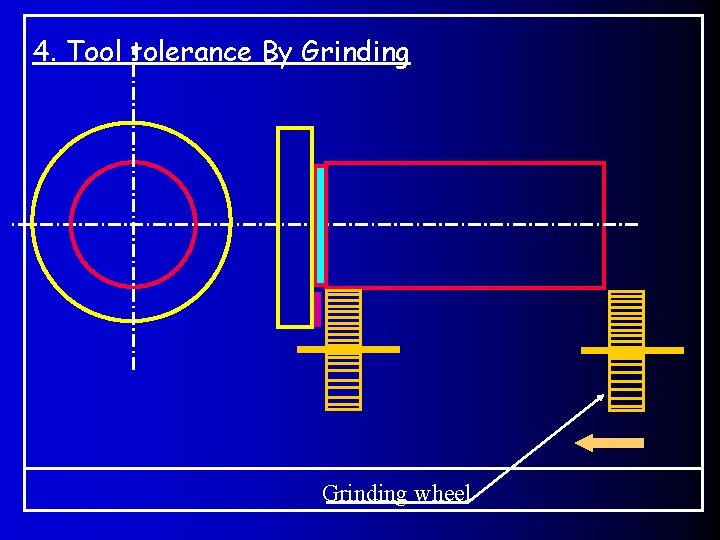
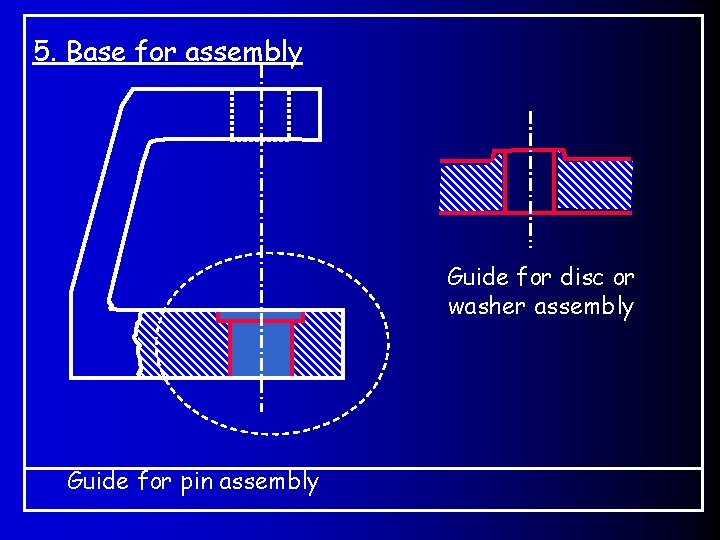
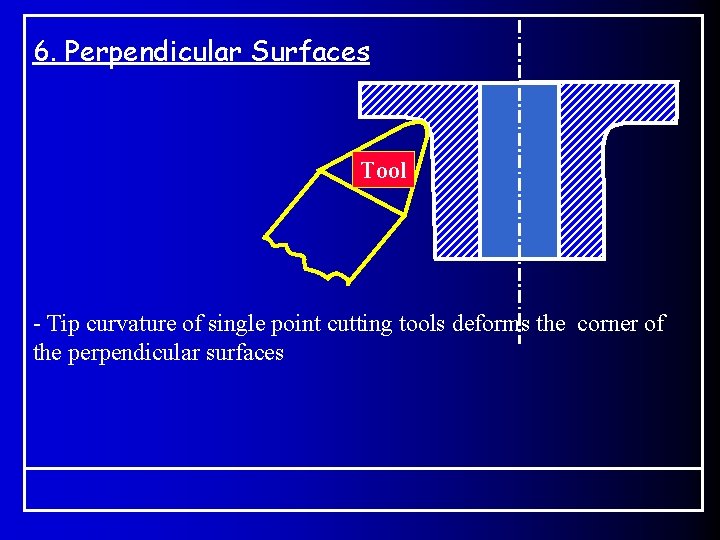
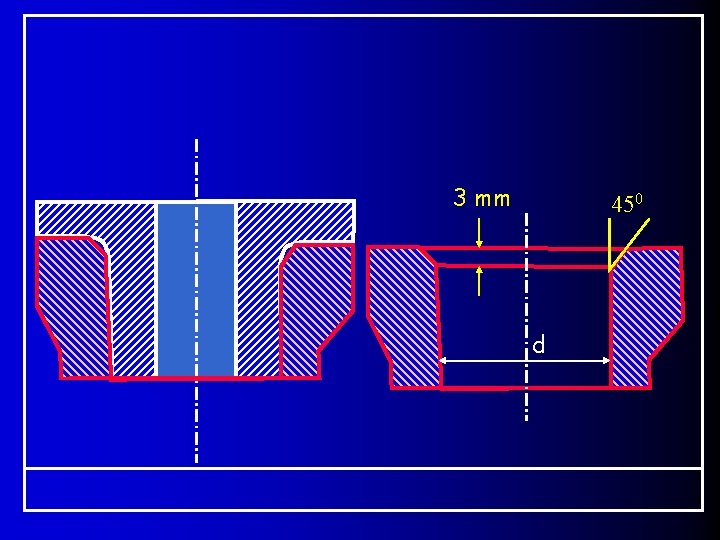
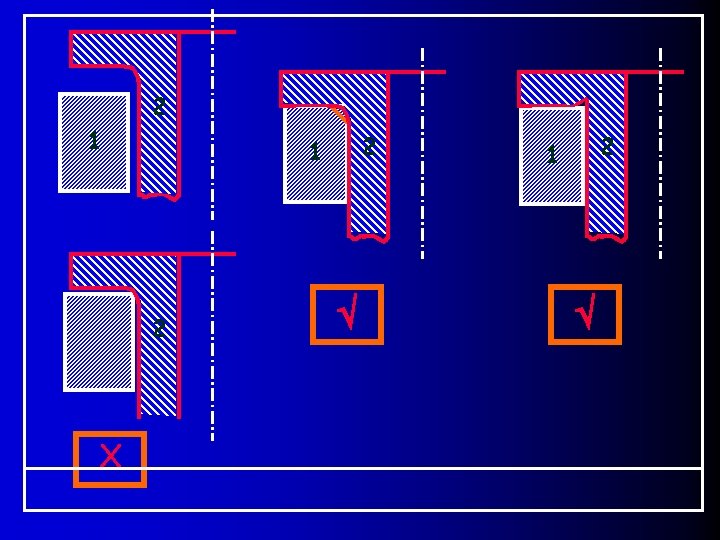
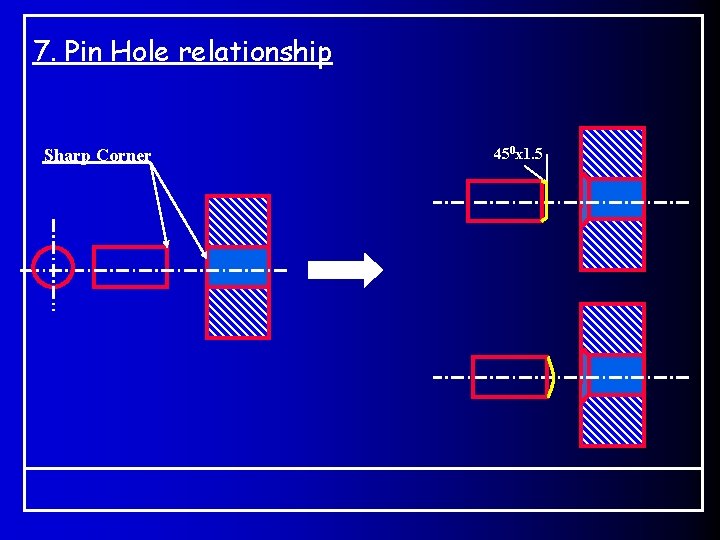
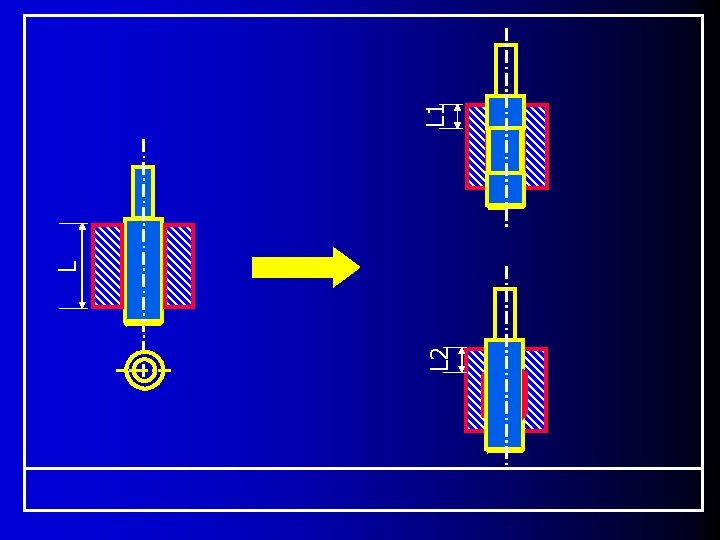
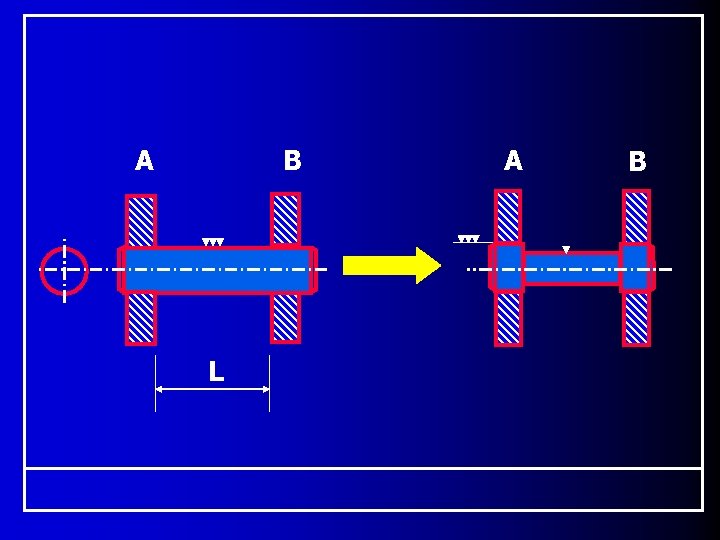
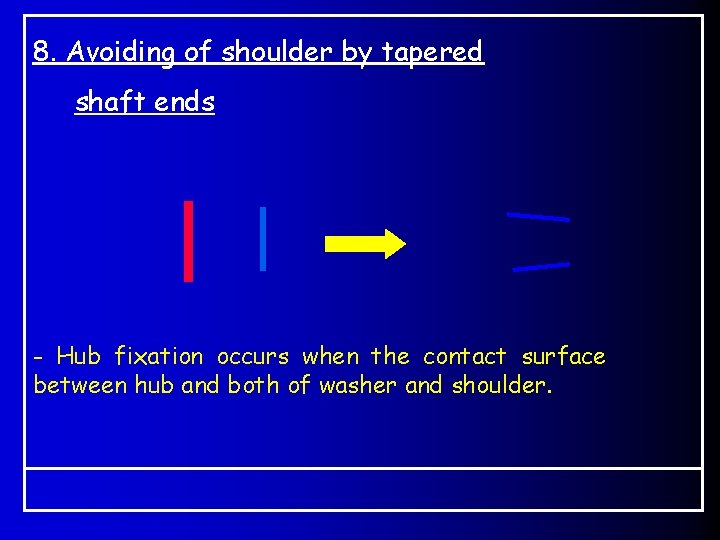
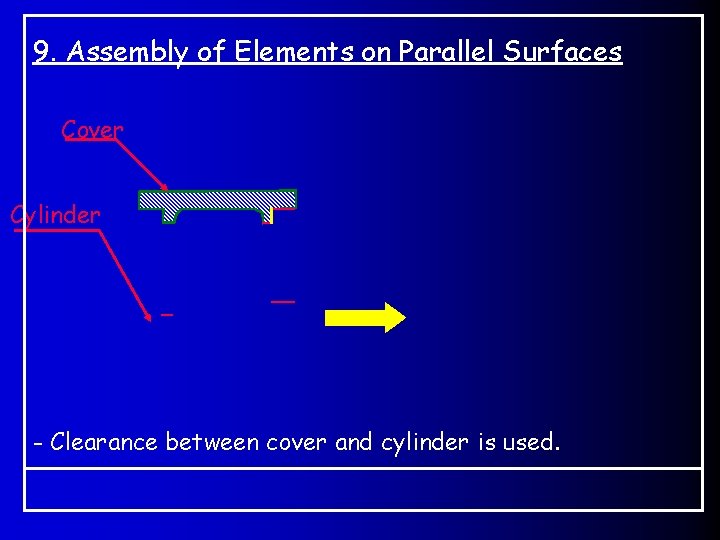
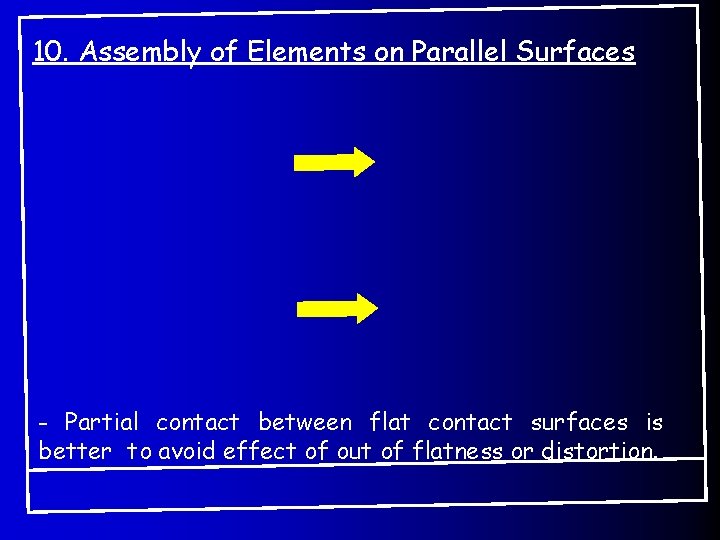
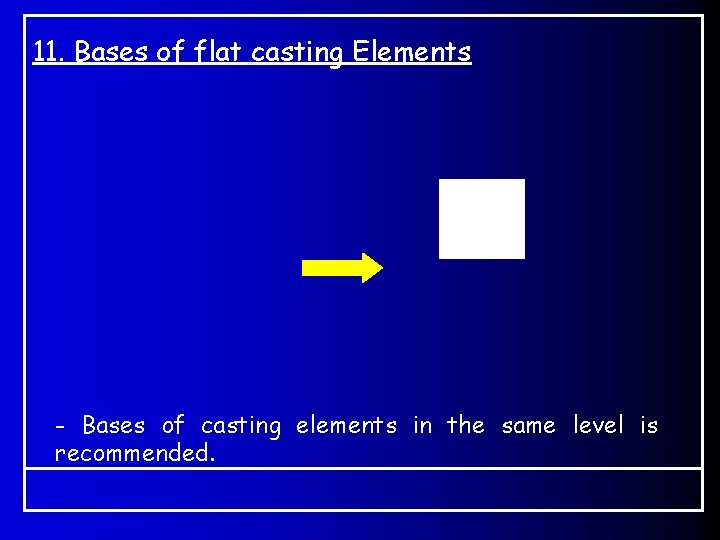
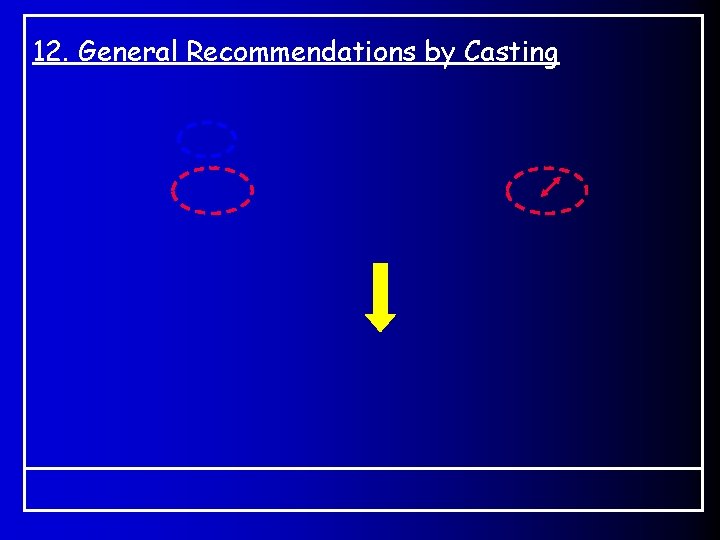
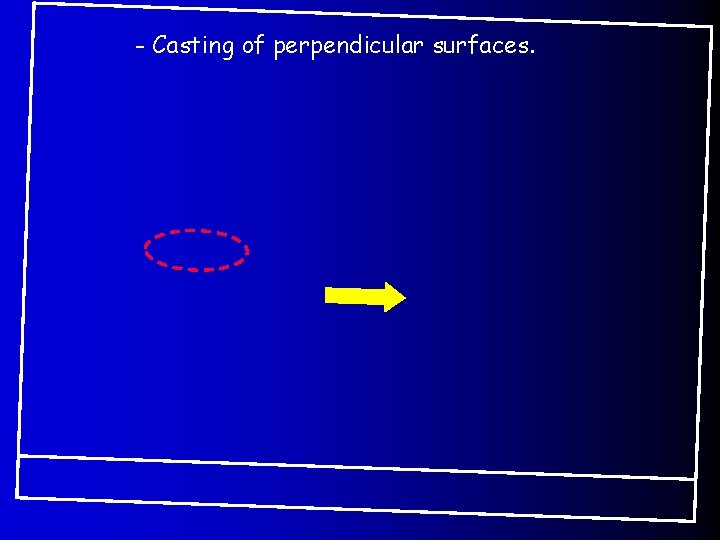
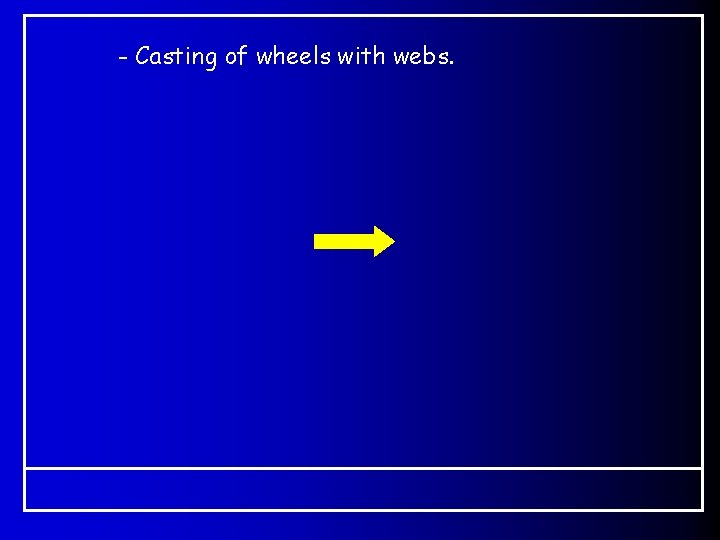
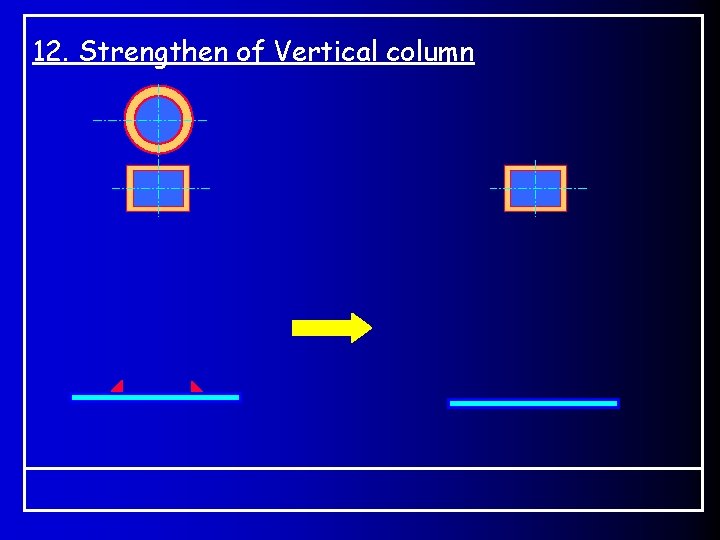
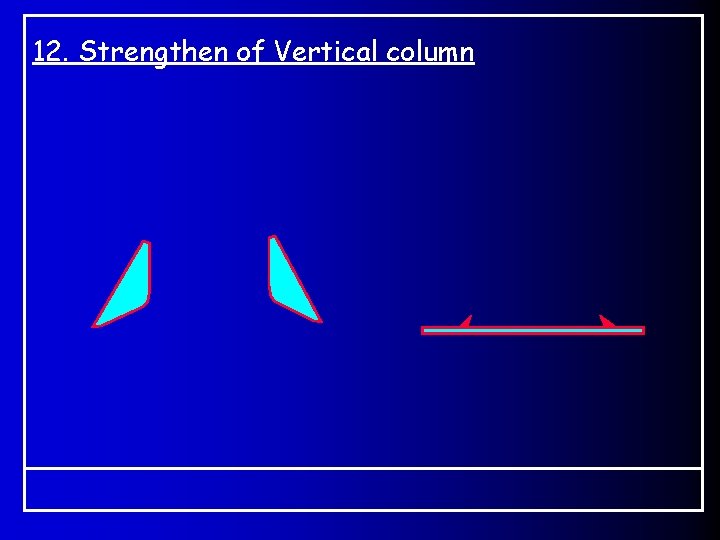
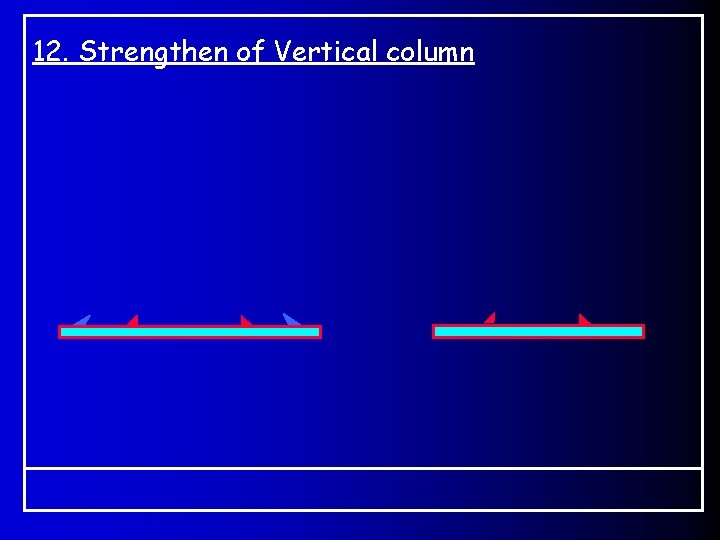
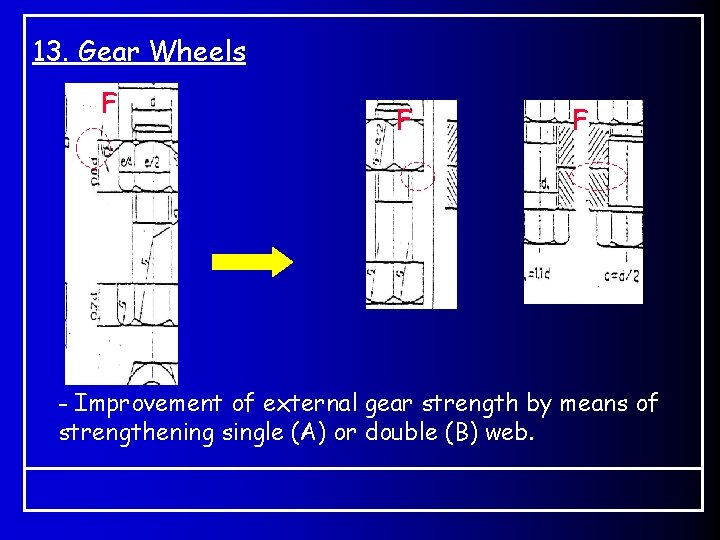
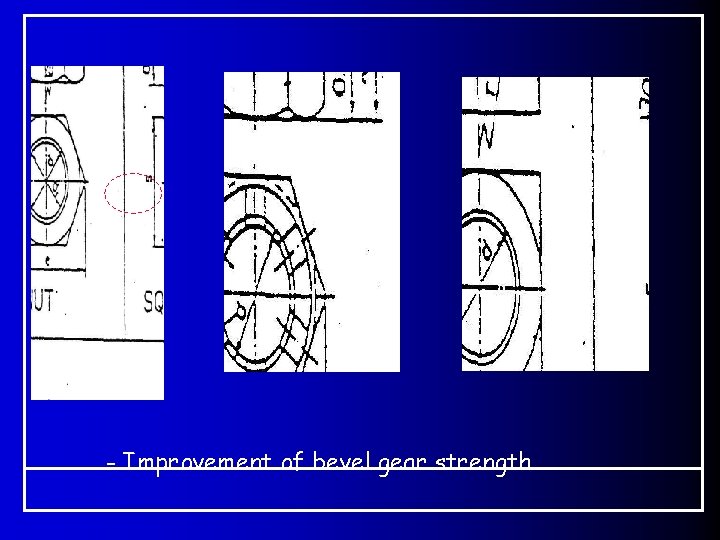
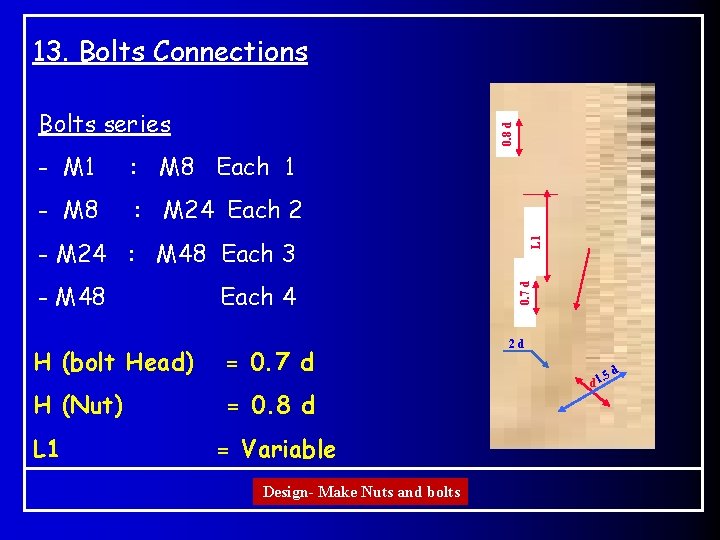
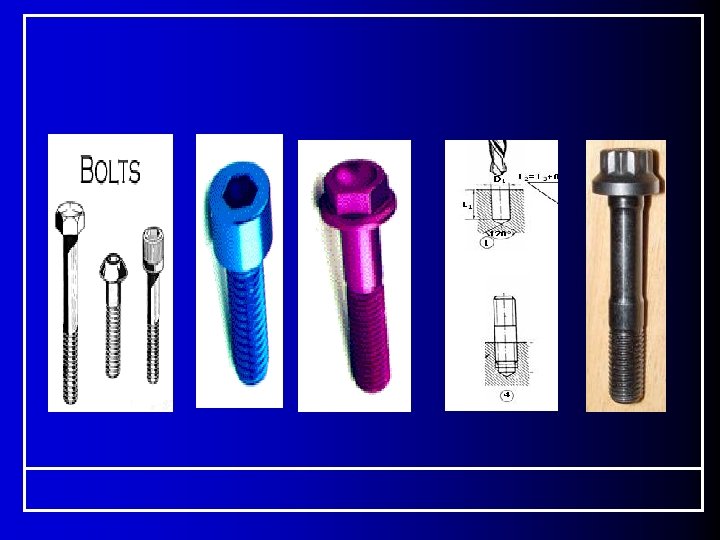
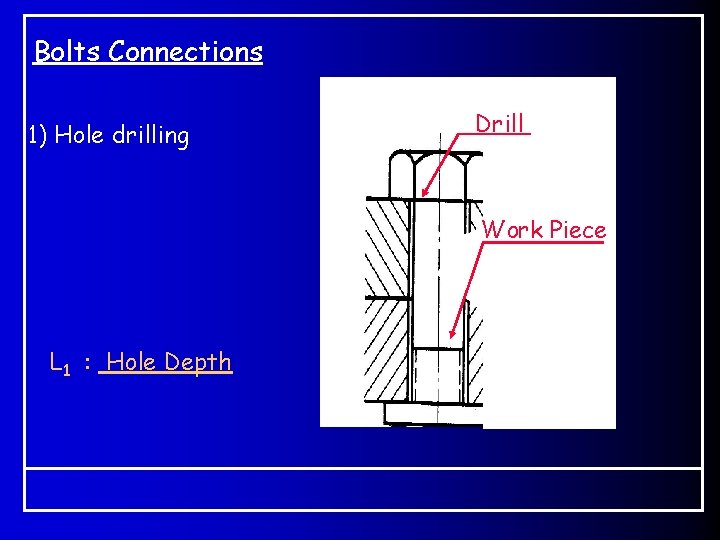
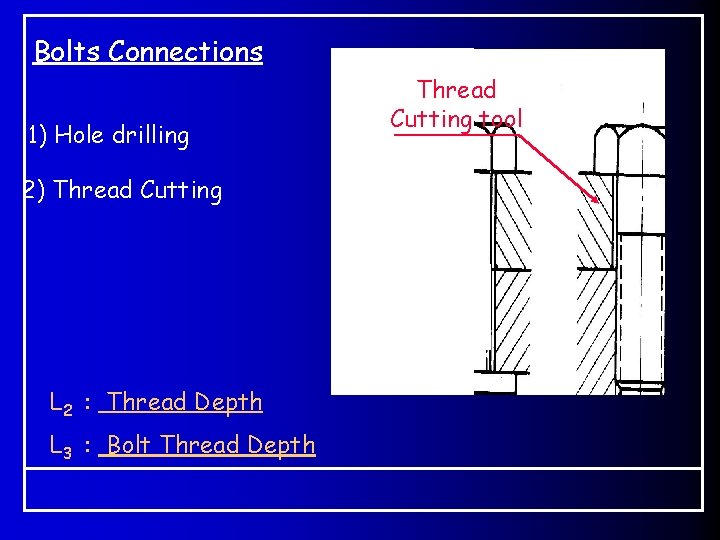
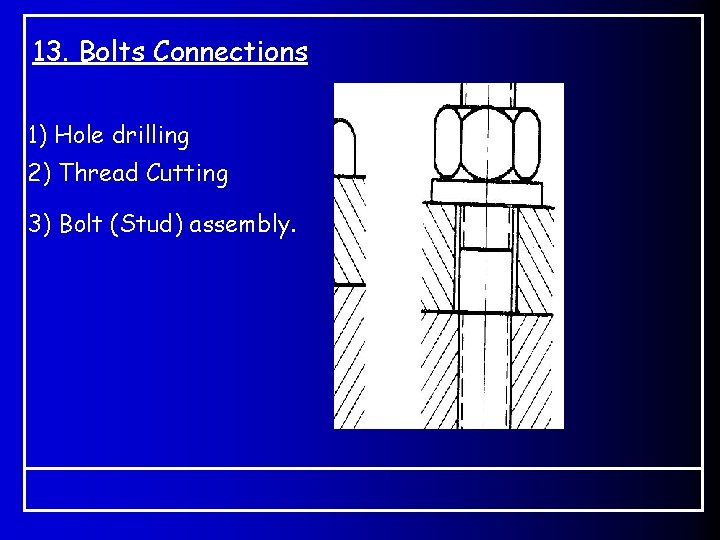
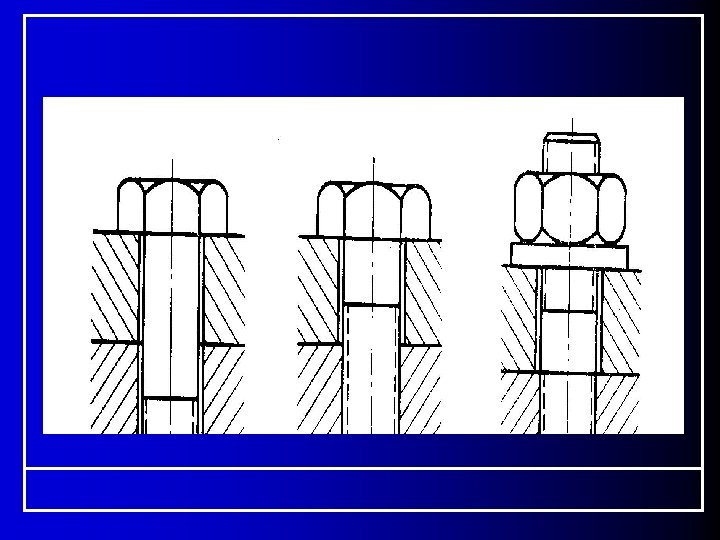
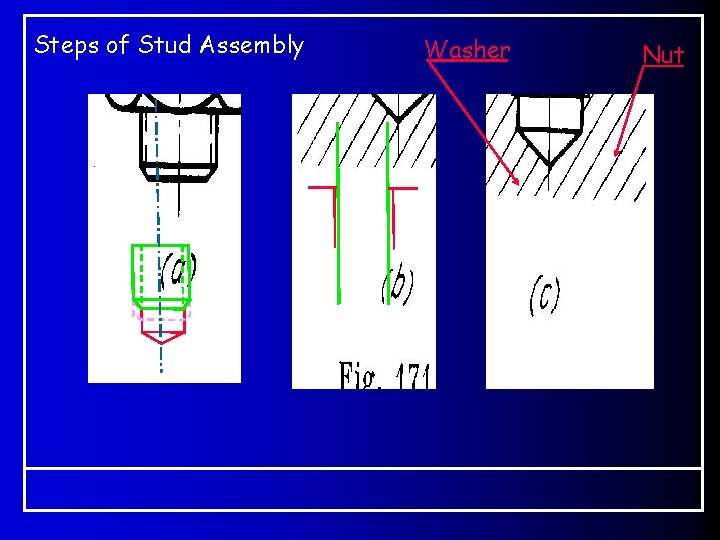
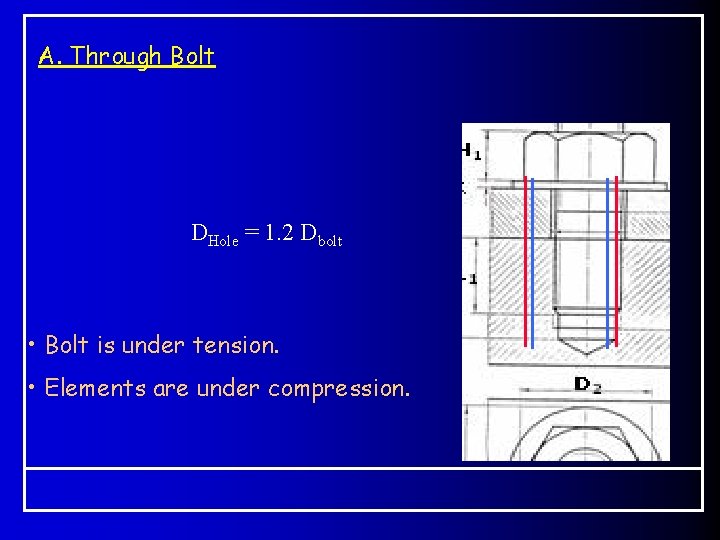
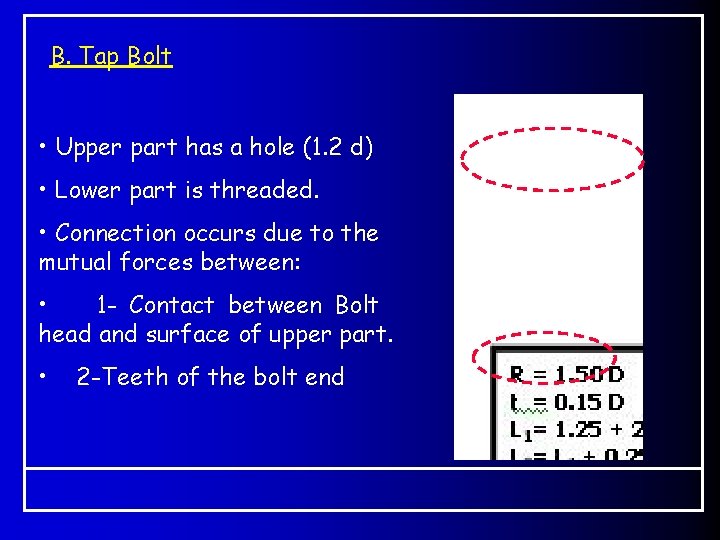
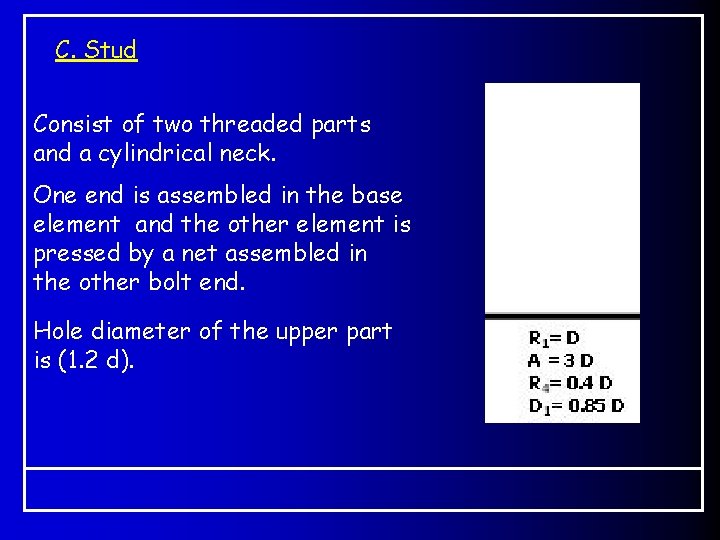
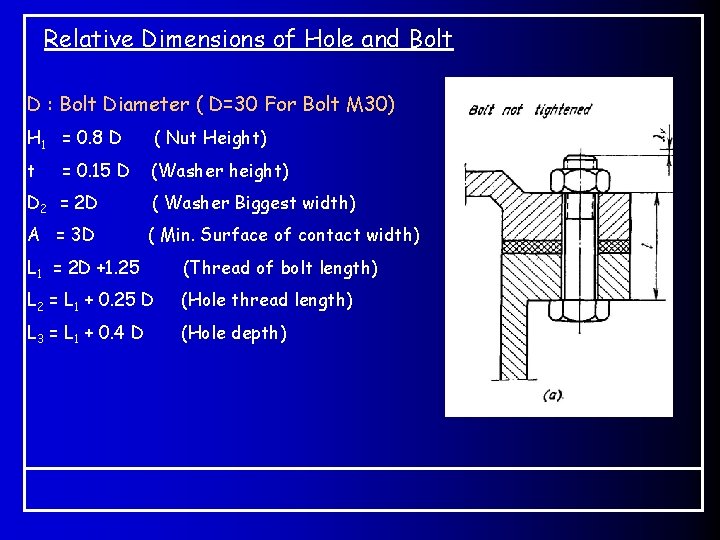
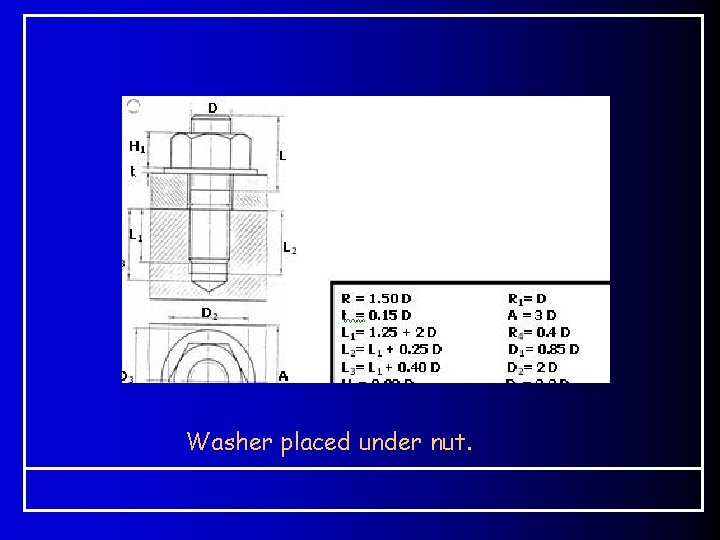
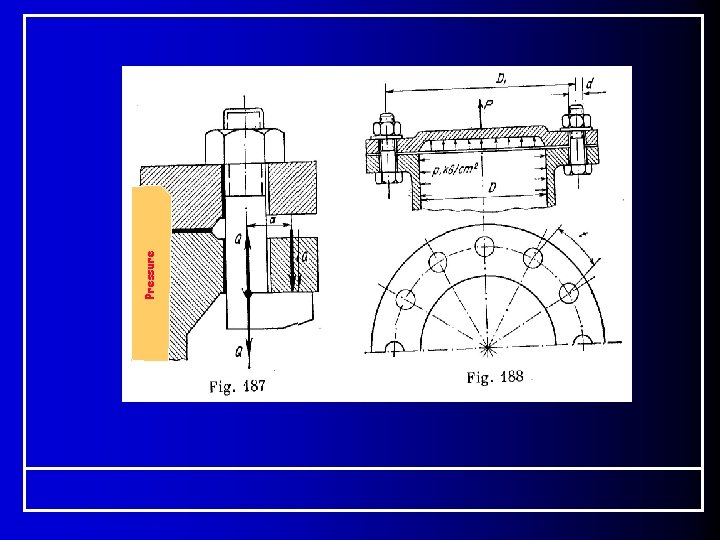
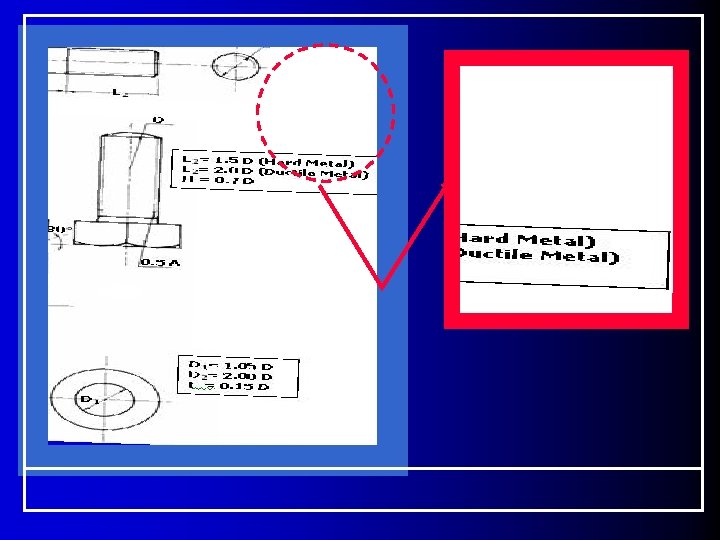
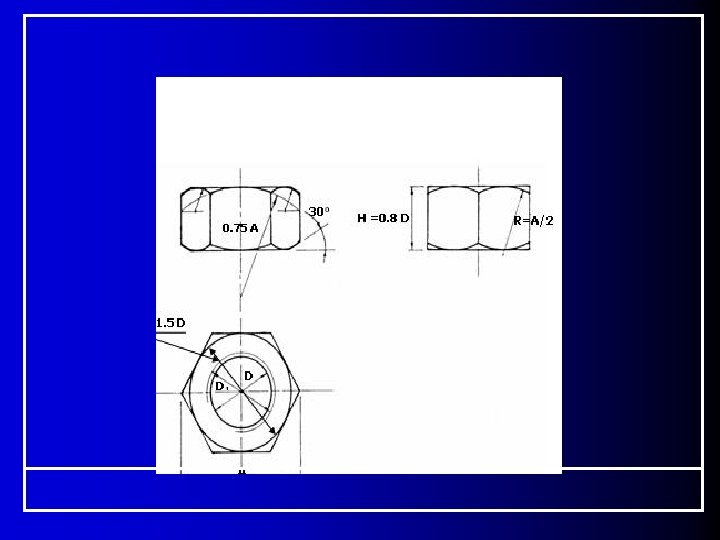
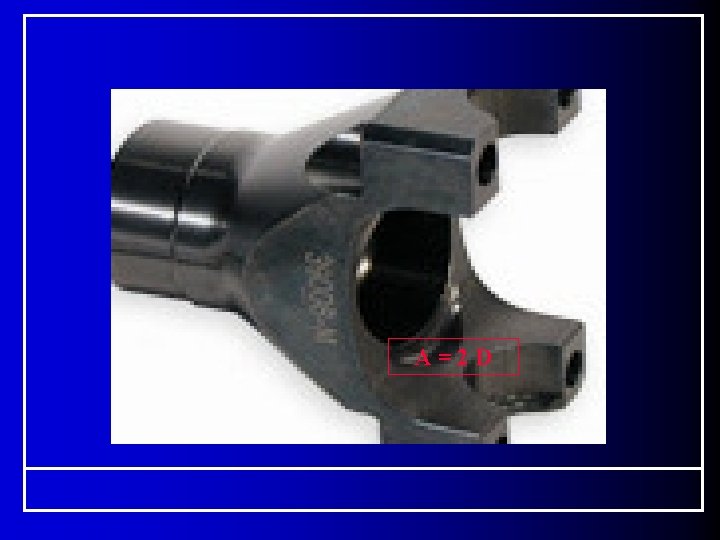
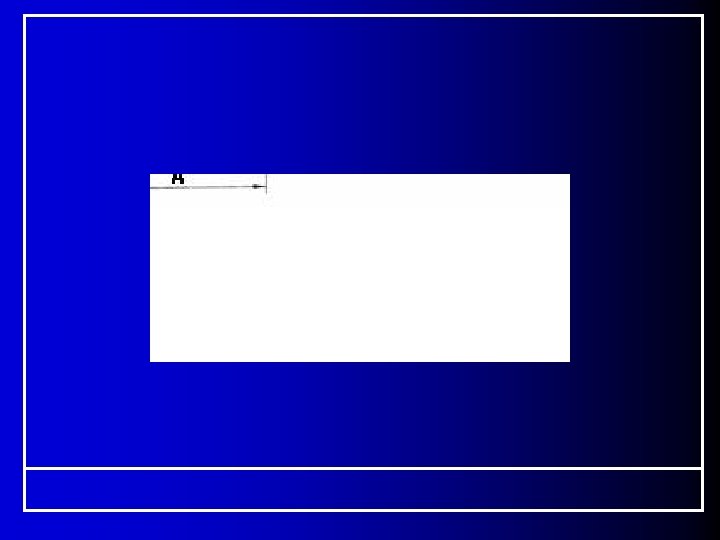
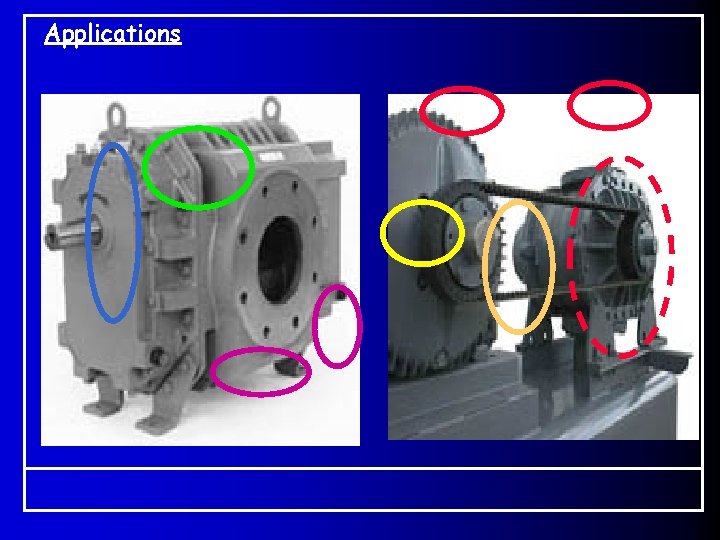
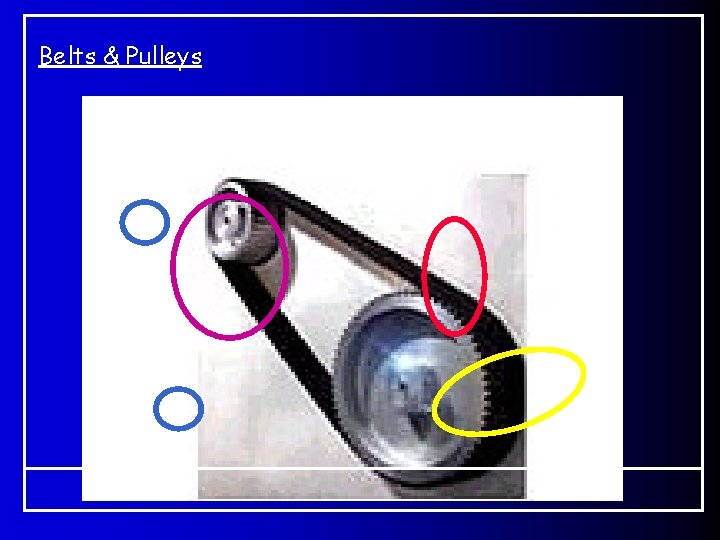
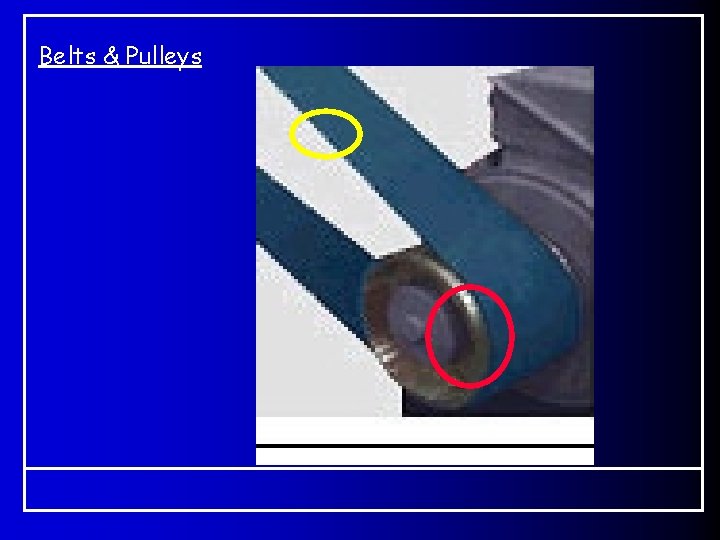
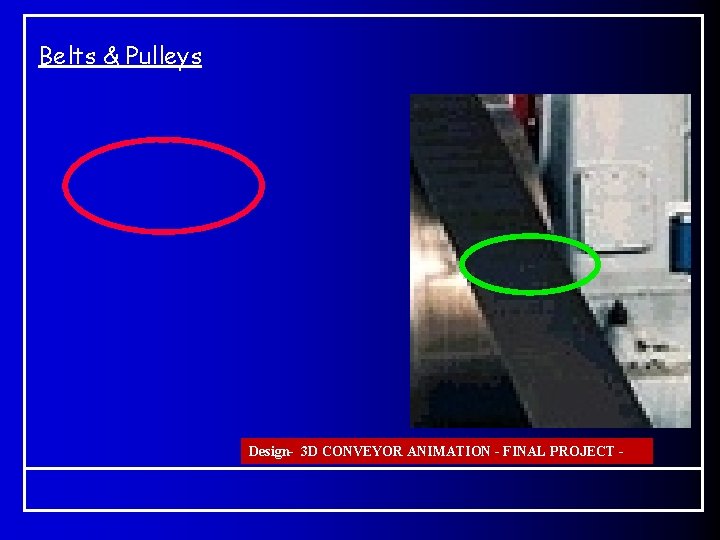
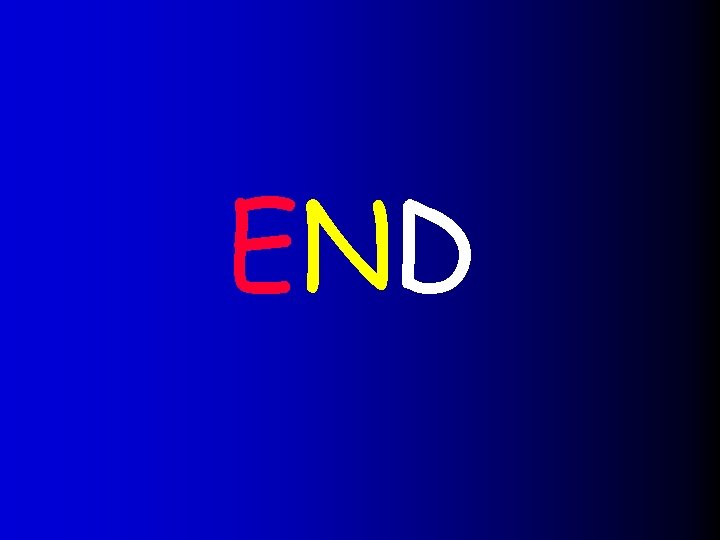
- Slides: 78
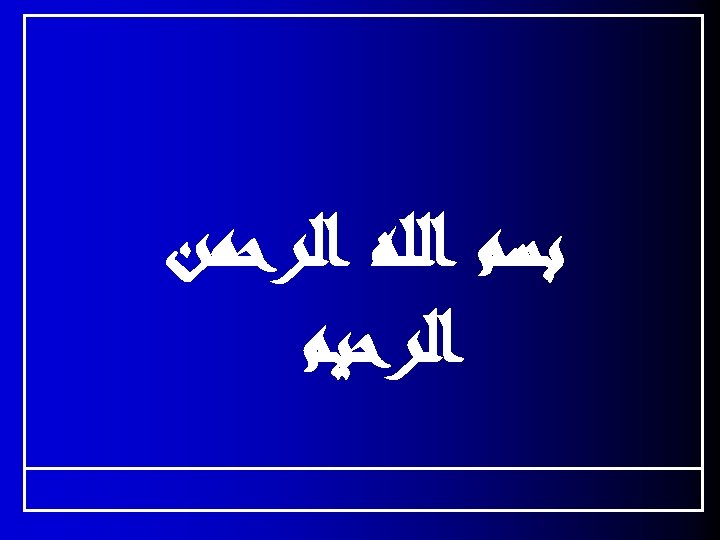
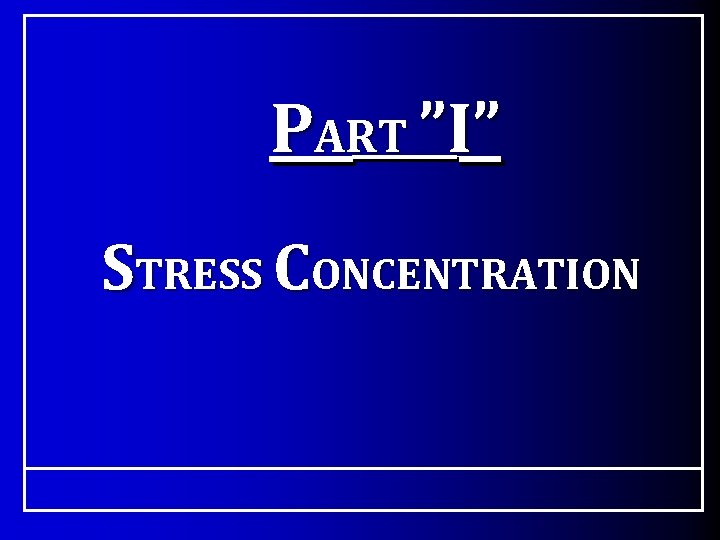
PART ”I” STRESS CONCENTRATION
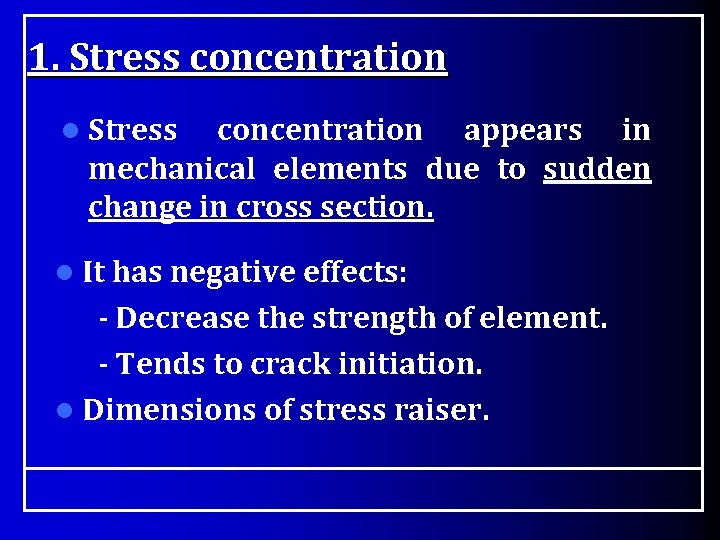
1. Stress concentration l Stress concentration appears in mechanical elements due to sudden change in cross section. l It has negative effects: - Decrease the strength of element. - Tends to crack initiation. l Dimensions of stress raiser.
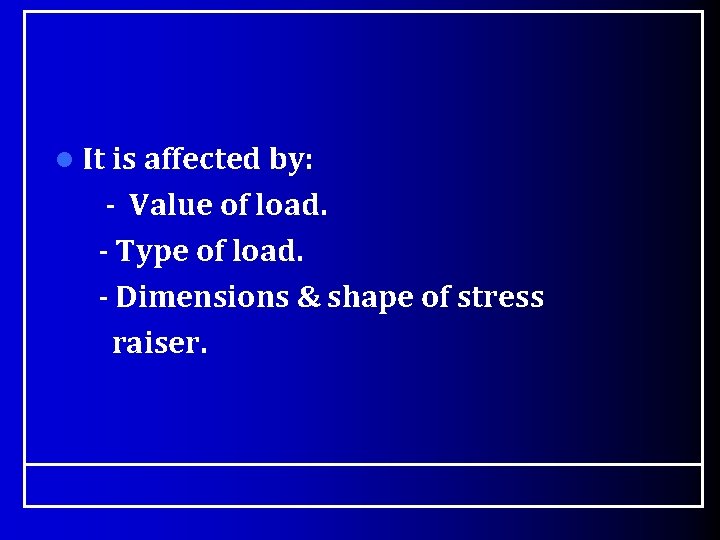
l It is affected by: - Value of load. - Type of load. - Dimensions & shape of stress raiser.
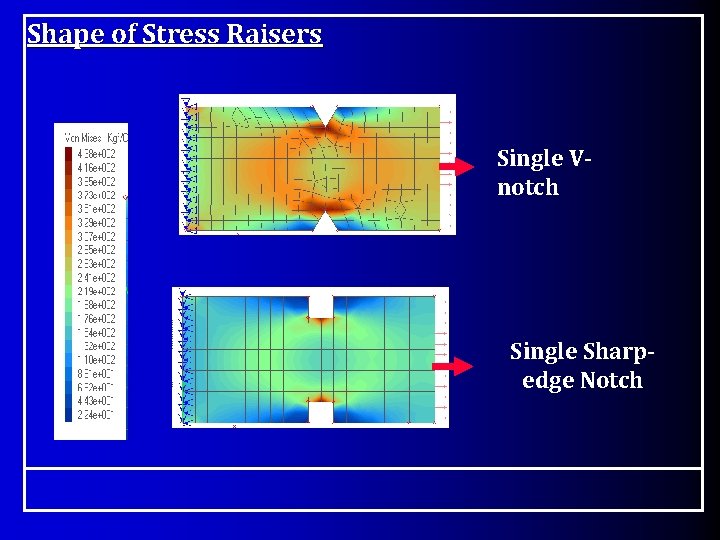
Shape of Stress Raisers Single Vnotch Single Sharpedge Notch
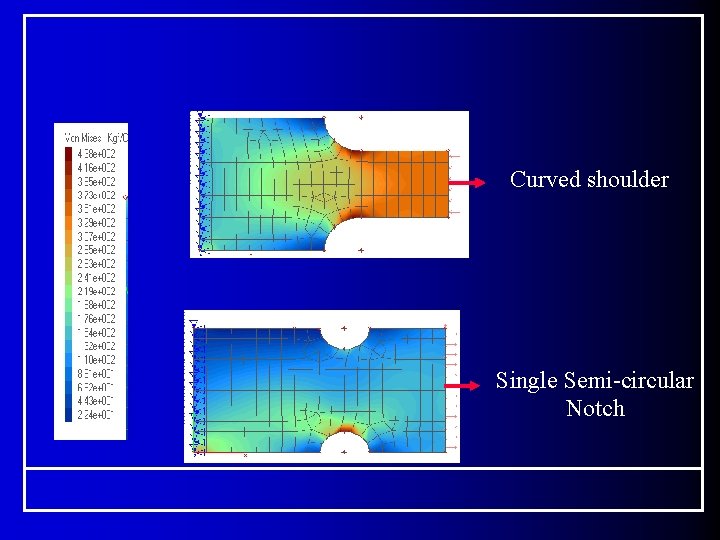
Curved shoulder Single Semi-circular Notch
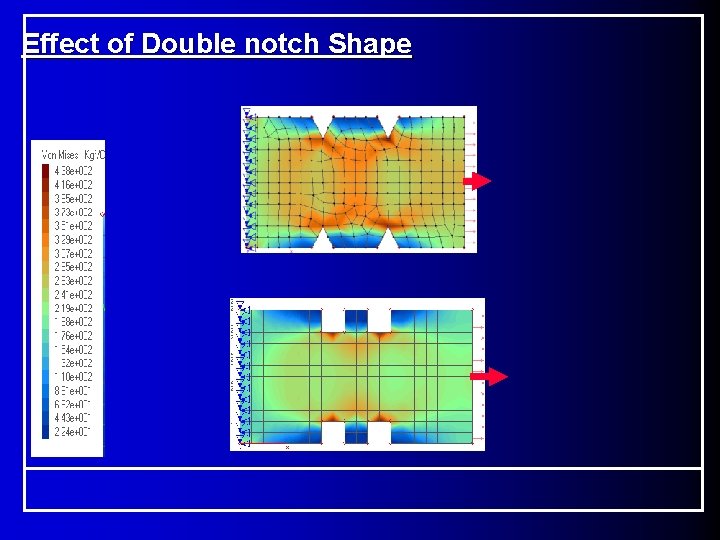
Effect of Double notch Shape
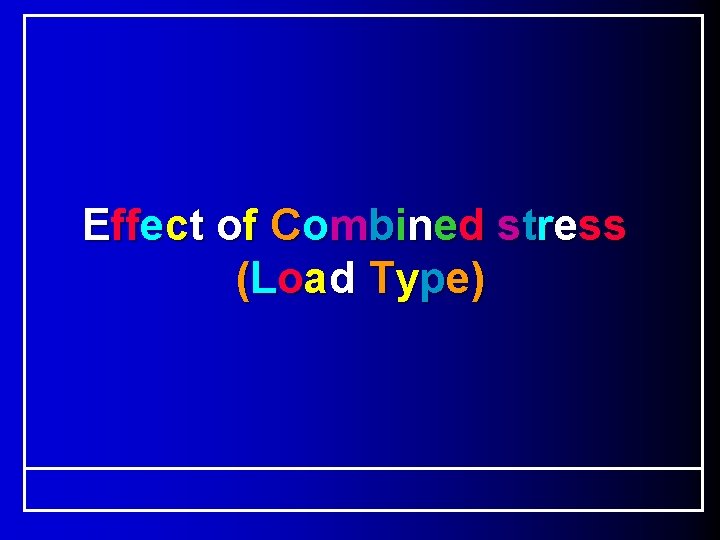
Effect of Combined stress (Load Type)
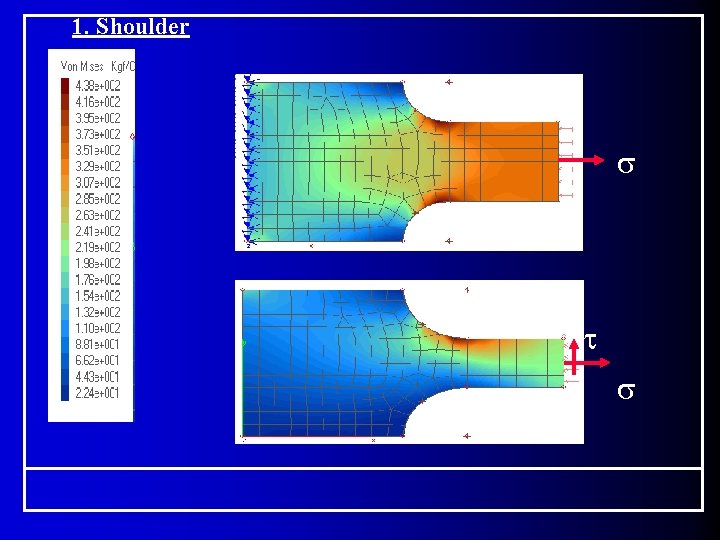
1. Shoulder
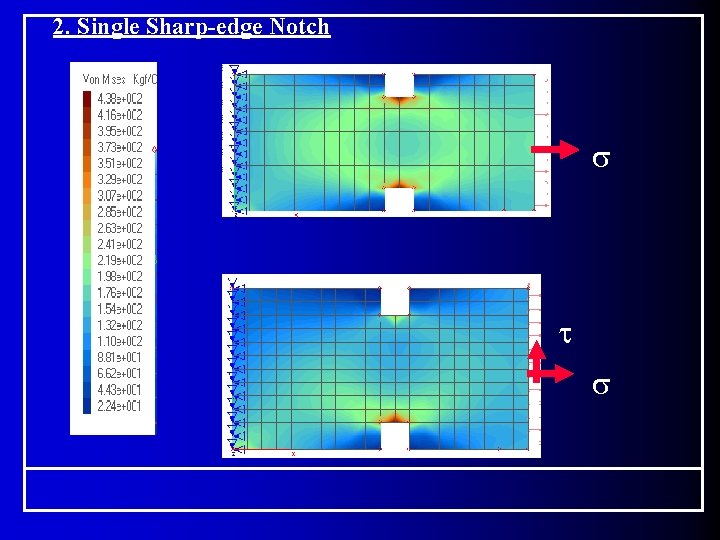
2. Single Sharp-edge Notch
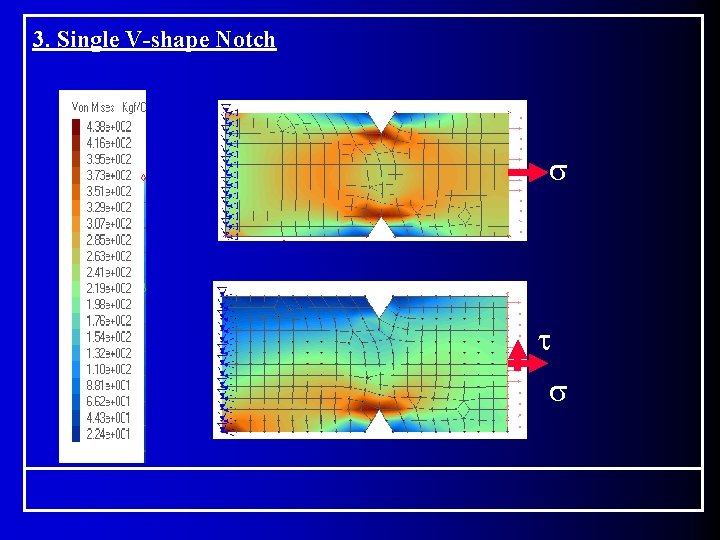
3. Single V-shape Notch
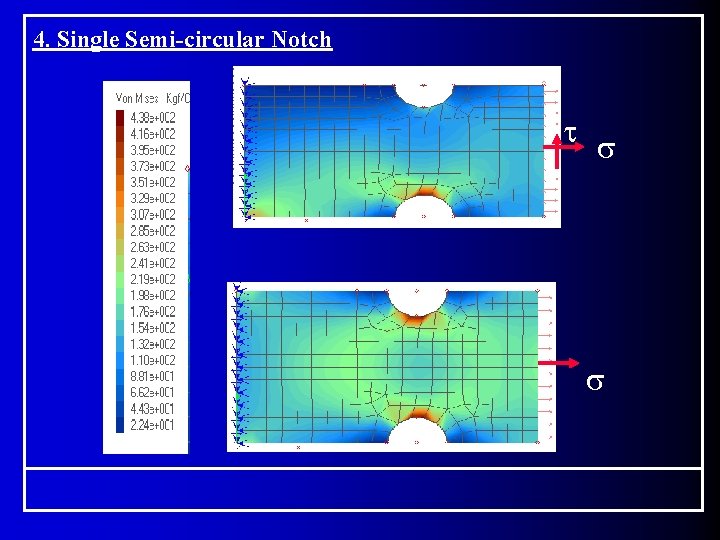
4. Single Semi-circular Notch
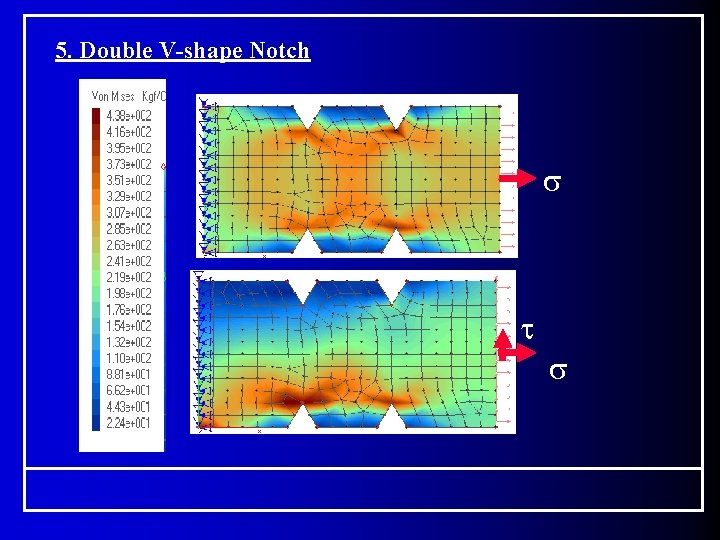
5. Double V-shape Notch
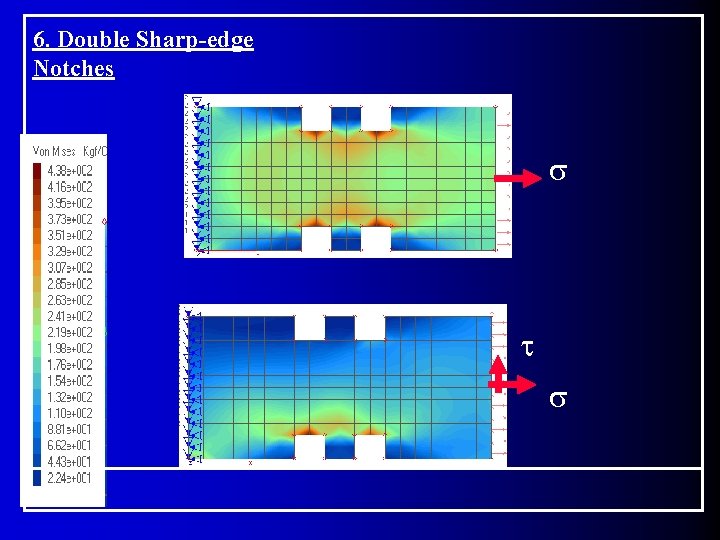
6. Double Sharp-edge Notches
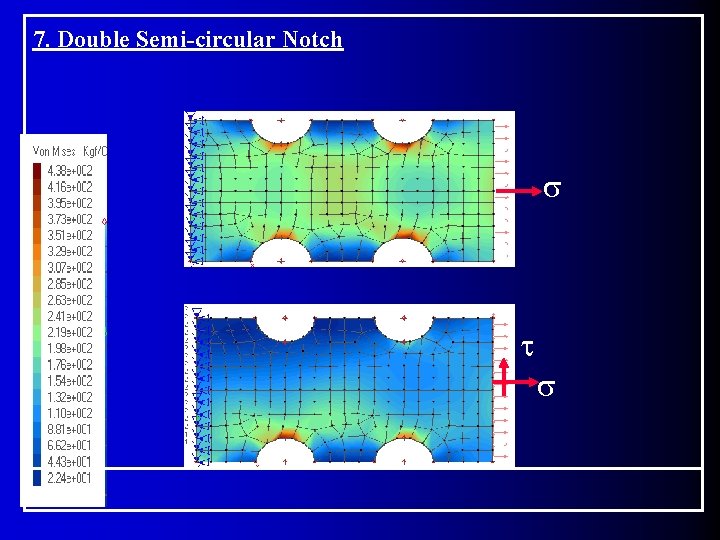
7. Double Semi-circular Notch
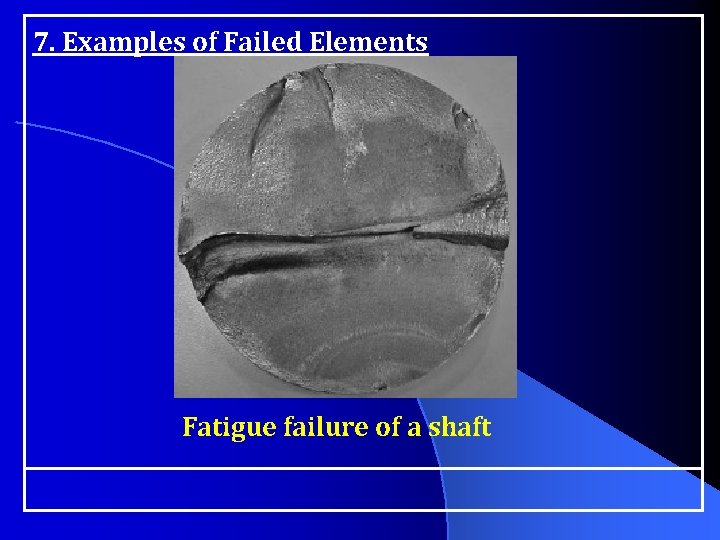
7. Examples of Failed Elements Fatigue failure of a shaft
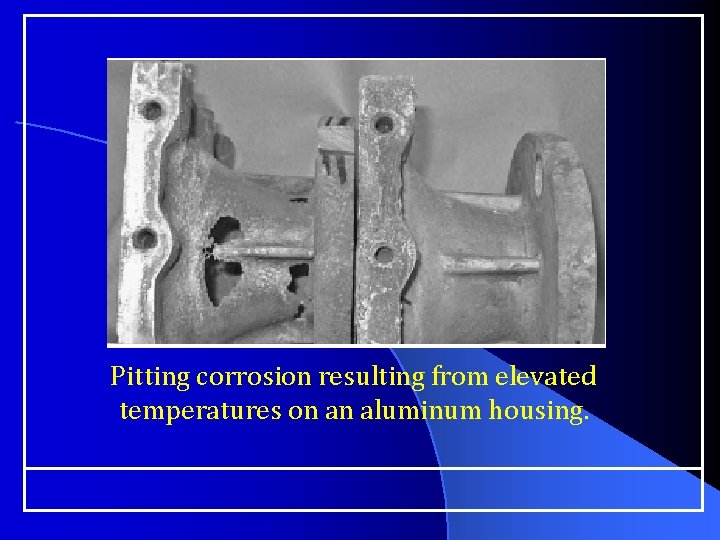
Pitting corrosion resulting from elevated temperatures on an aluminum housing.
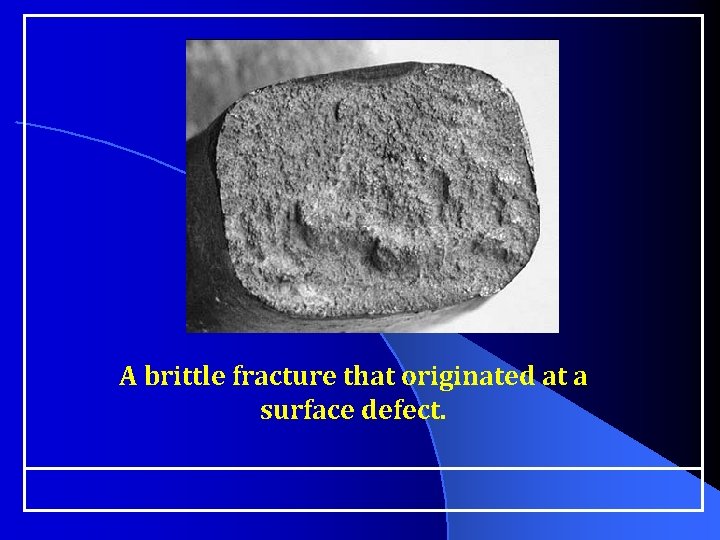
A brittle fracture that originated at a surface defect.
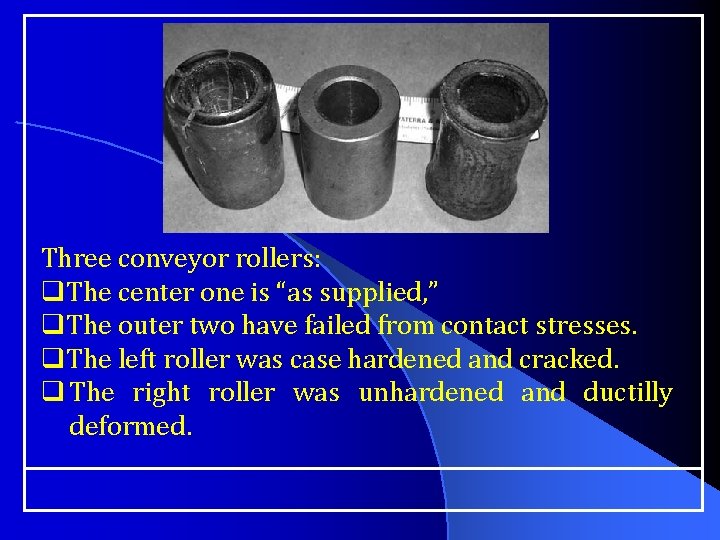
Three conveyor rollers: q. The center one is “as supplied, ” q. The outer two have failed from contact stresses. q. The left roller was case hardened and cracked. q The right roller was unhardened and ductilly deformed.
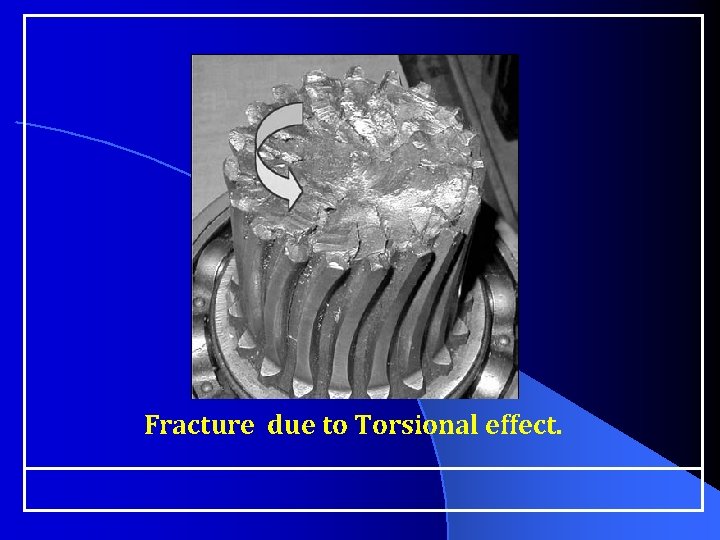
Fracture due to Torsional effect.
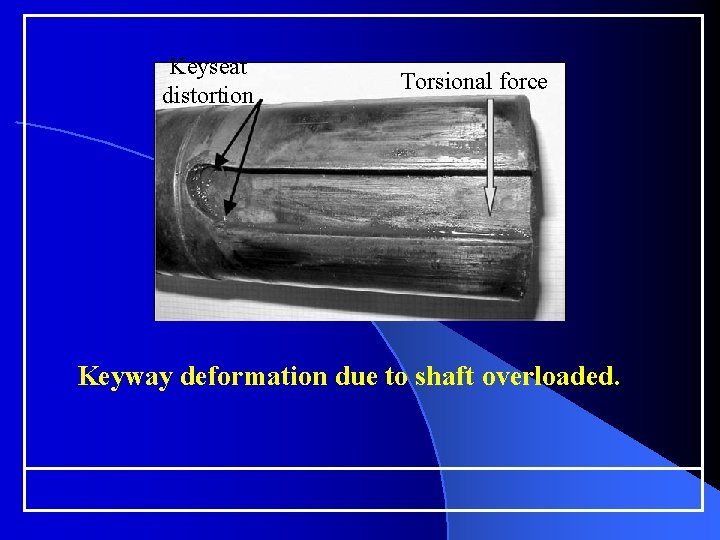
Keyseat distortion Torsional force Keyway deformation due to shaft overloaded.
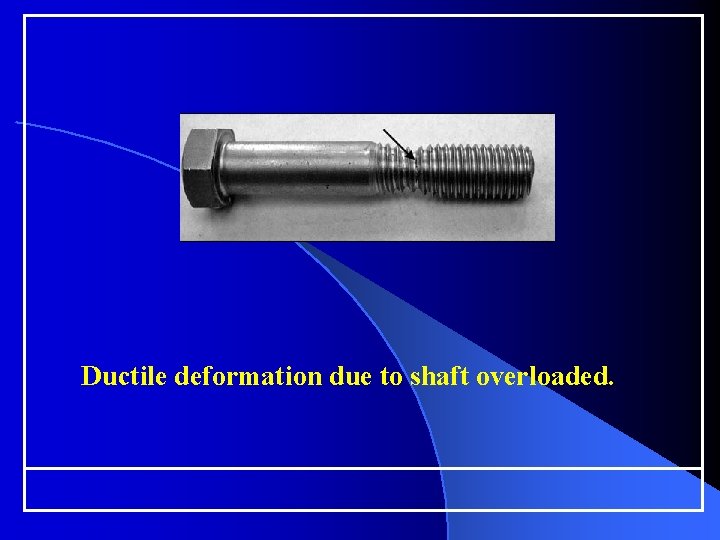
Ductile deformation due to shaft overloaded.
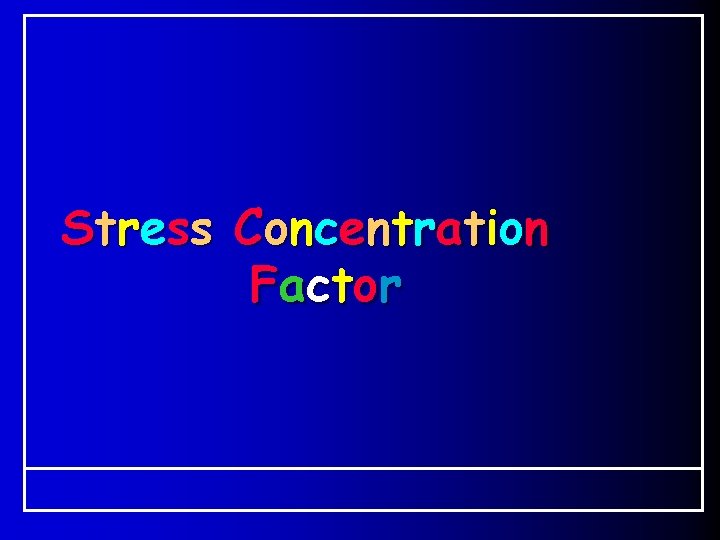
S t r es s C o n c en t r a t i o n F a c to r
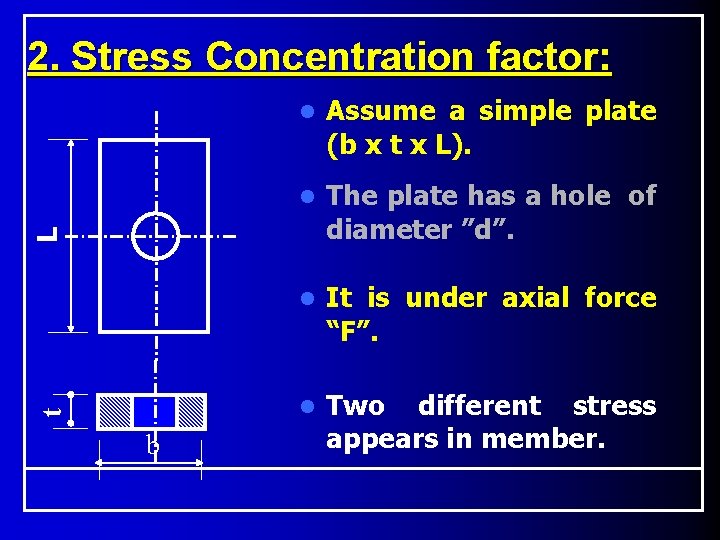
2. Stress Concentration factor: Assume a simple plate (b x t x L). l The plate has a hole of diameter ”d”. l It is under axial force “F”. l Two different stress appears in member. t L l b
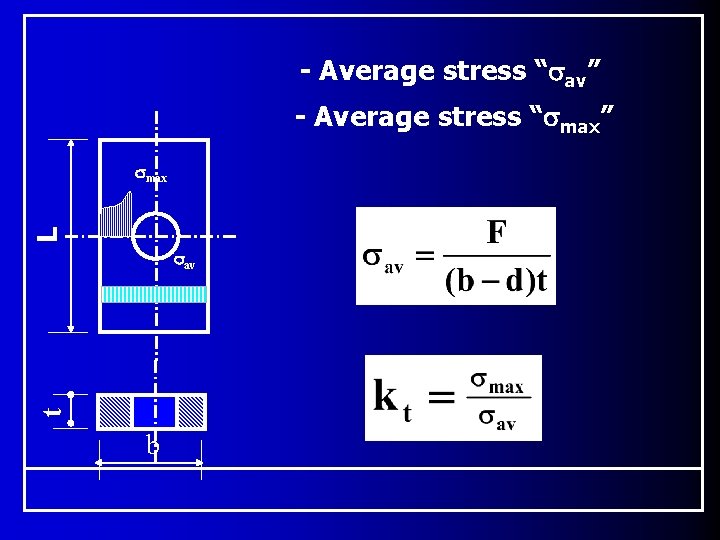
- Average stress “ av” - Average stress “ max” L max t av b
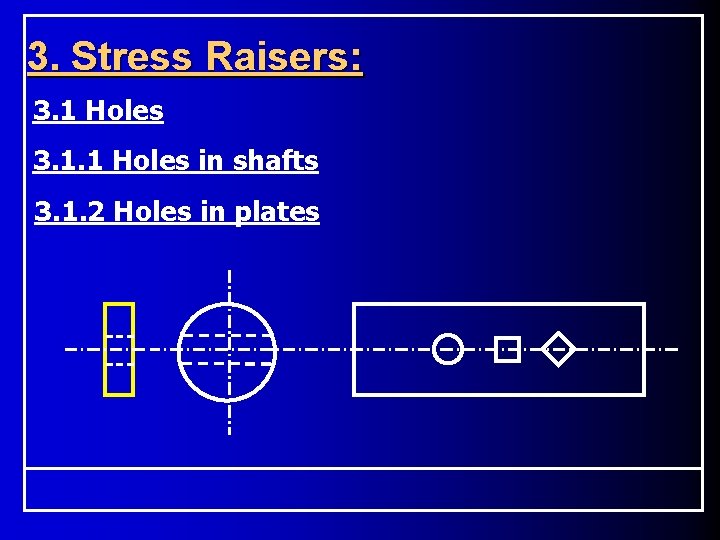
3. Stress Raisers: 3. 1 Holes 3. 1. 1 Holes in shafts 3. 1. 2 Holes in plates
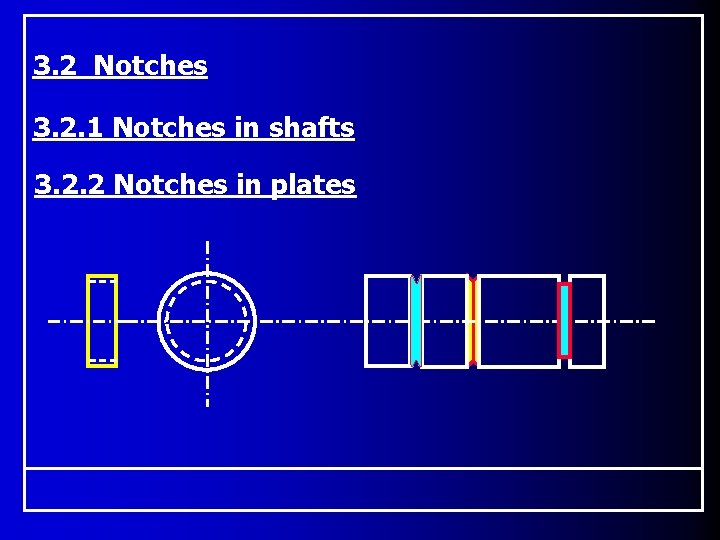
3. 2 Notches 3. 2. 1 Notches in shafts 3. 2. 2 Notches in plates
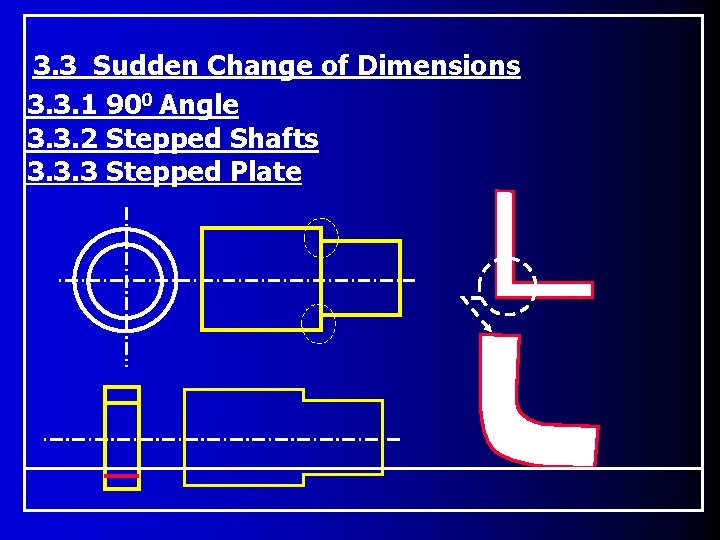
3. 3 Sudden Change of Dimensions 3. 3. 1 900 Angle 3. 3. 2 Stepped Shafts 3. 3. 3 Stepped Plate
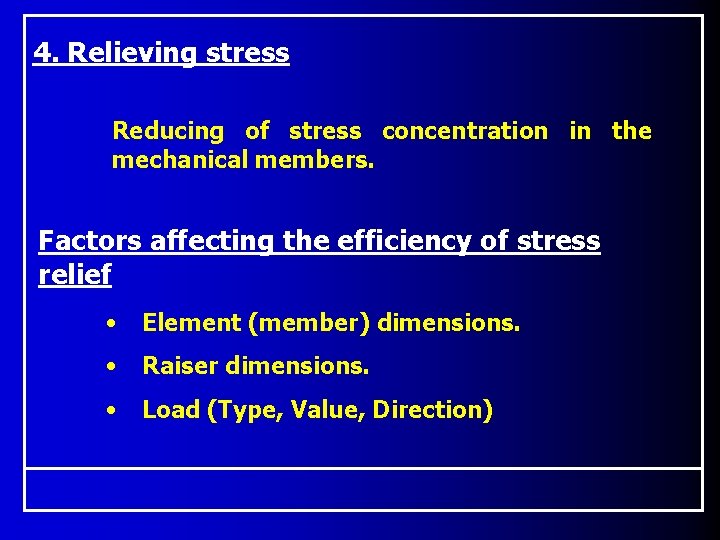
4. Relieving stress Reducing of stress concentration in the mechanical members. Factors affecting the efficiency of stress relief • Element (member) dimensions. • Raiser dimensions. • Load (Type, Value, Direction)
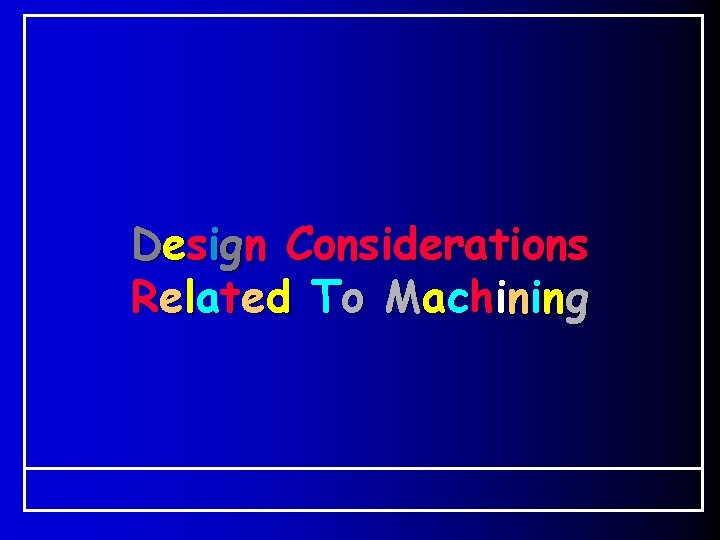
Design Considerations R el a t ed T o M a c h i n g
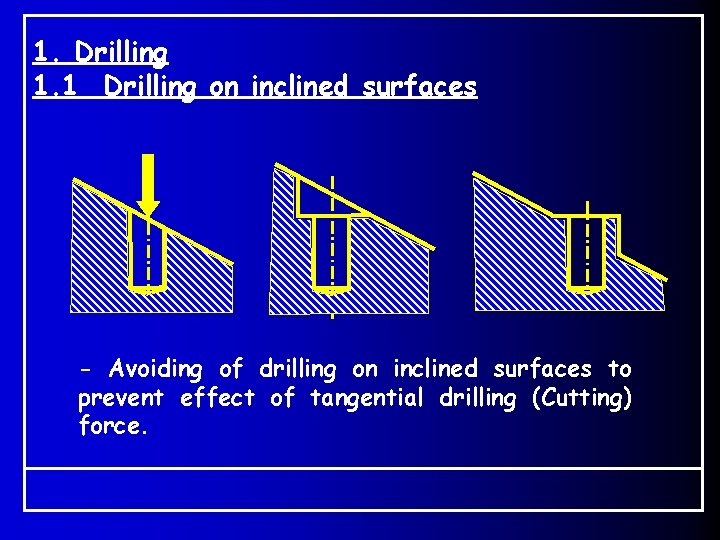
1. Drilling 1. 1 Drilling on inclined surfaces - Avoiding of drilling on inclined surfaces to prevent effect of tangential drilling (Cutting) force.

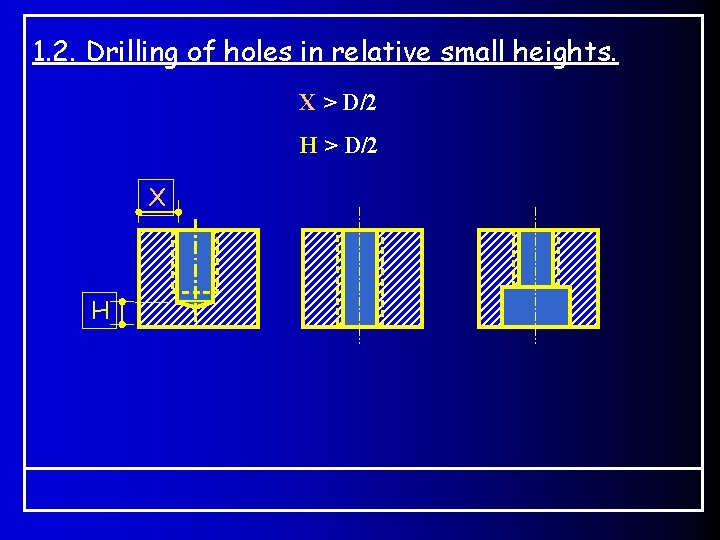
1. 2. Drilling of holes in relative small heights. X > D/2 H > D/2 X H
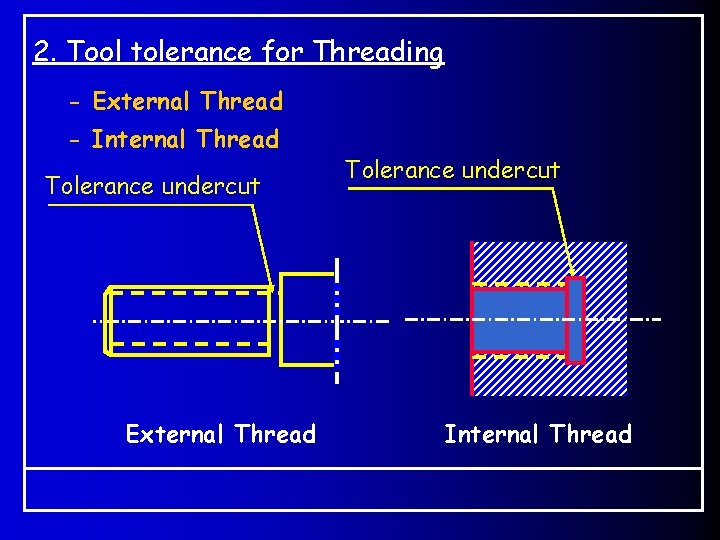
2. Tool tolerance for Threading - External Thread - Internal Thread Tolerance undercut External Thread Tolerance undercut Internal Thread
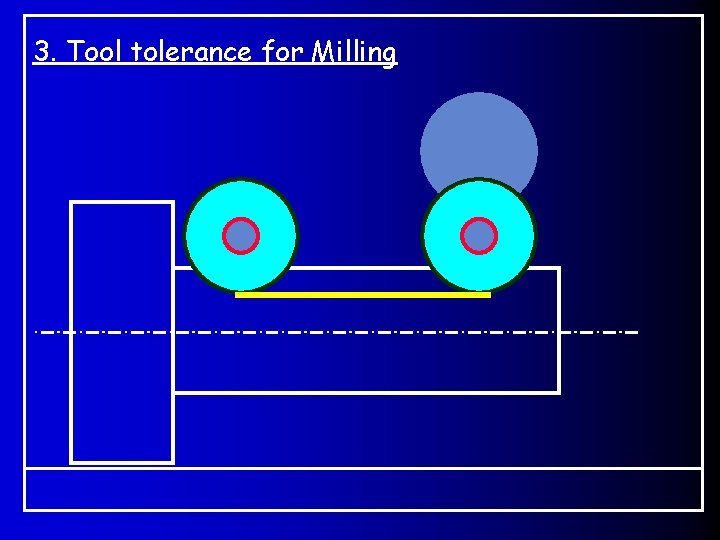
3. Tool tolerance for Milling
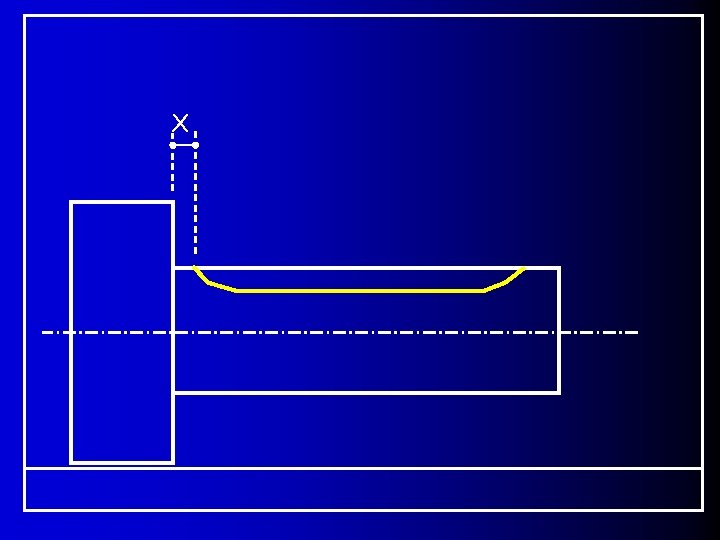
X
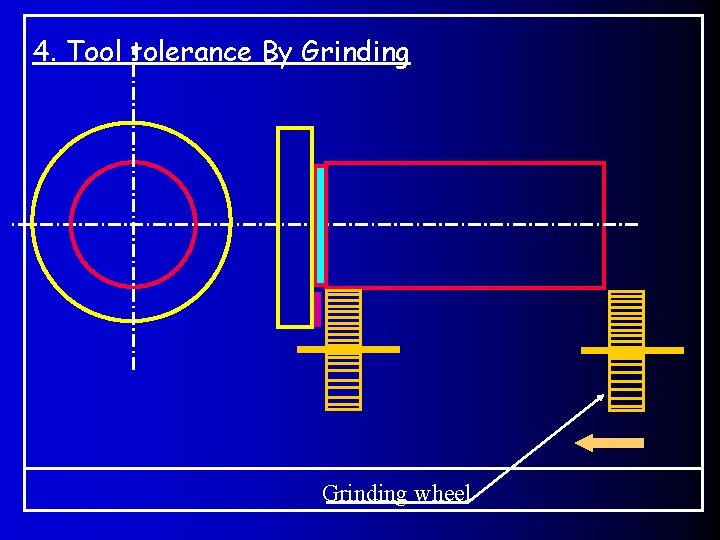
4. Tool tolerance By Grinding wheel
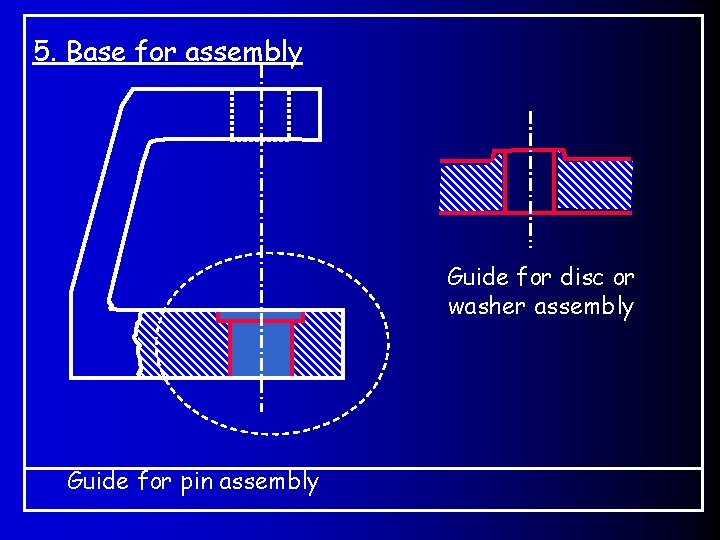
5. Base for assembly Guide for disc or washer assembly Guide for pin assembly
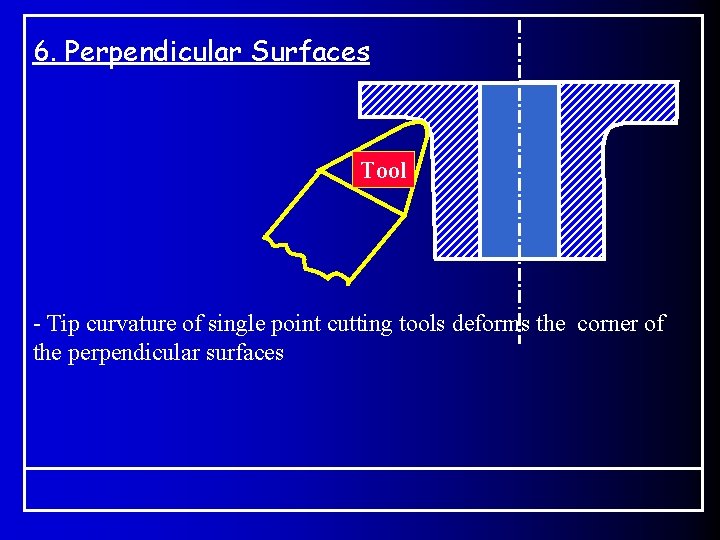
6. Perpendicular Surfaces Tool - Tip curvature of single point cutting tools deforms the corner of the perpendicular surfaces
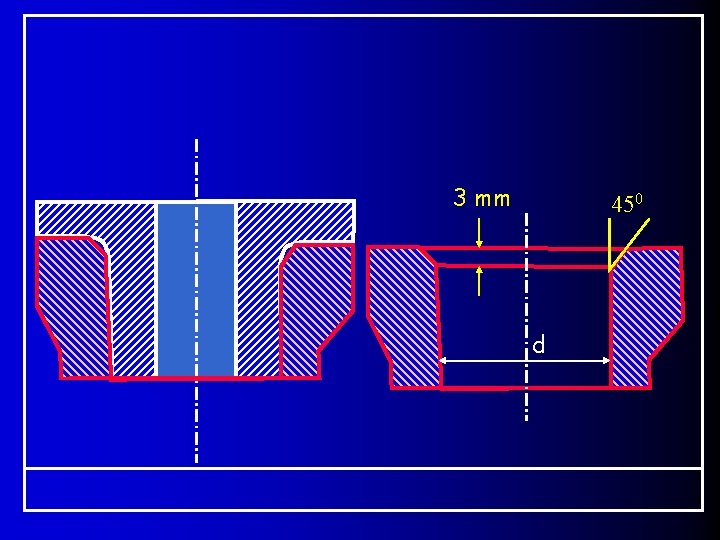
3 mm 450 d
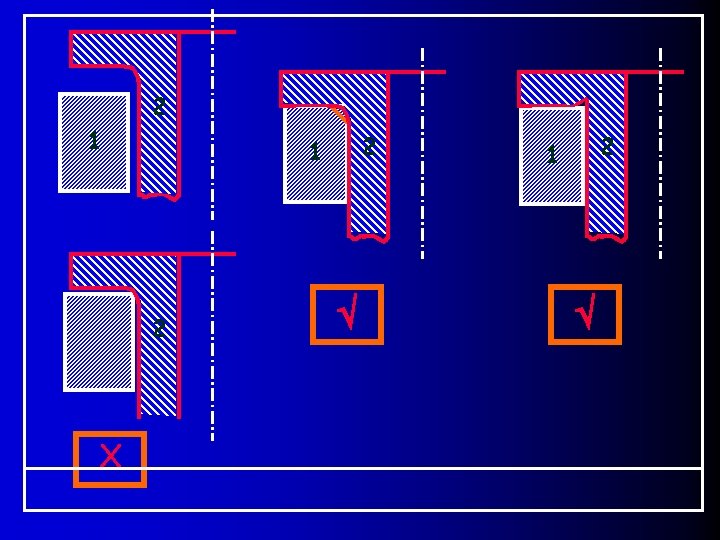
2 1 1 X 2 1 2 2 1
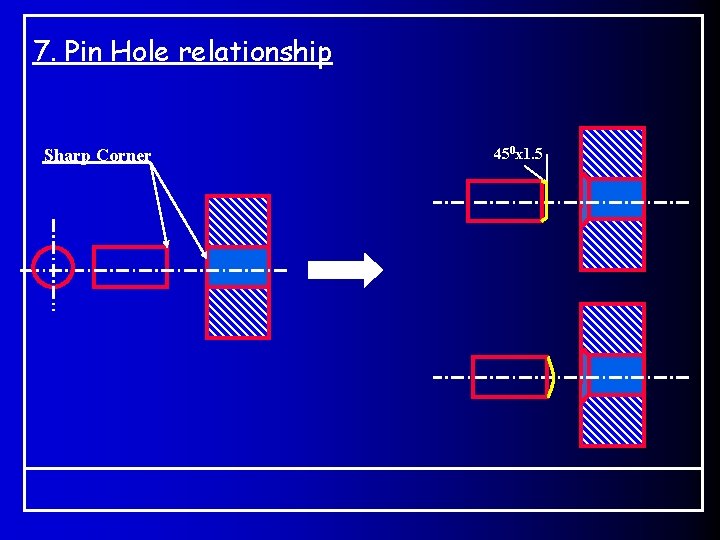
7. Pin Hole relationship Sharp Corner 450 x 1. 5
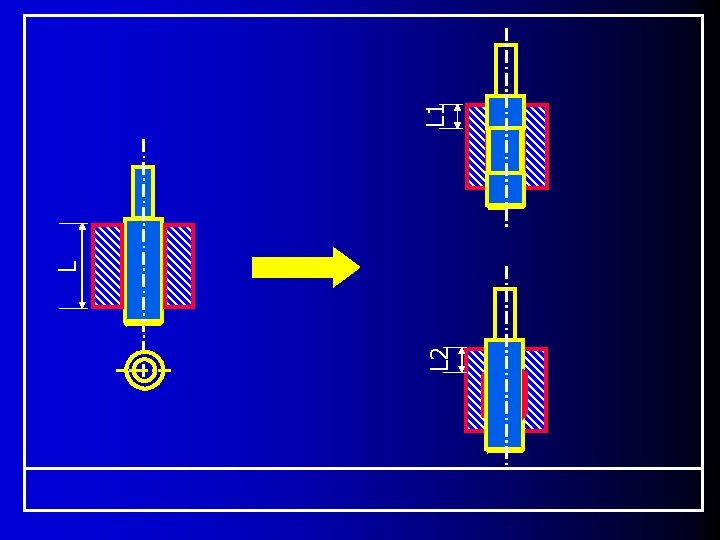
L 2 L L 1
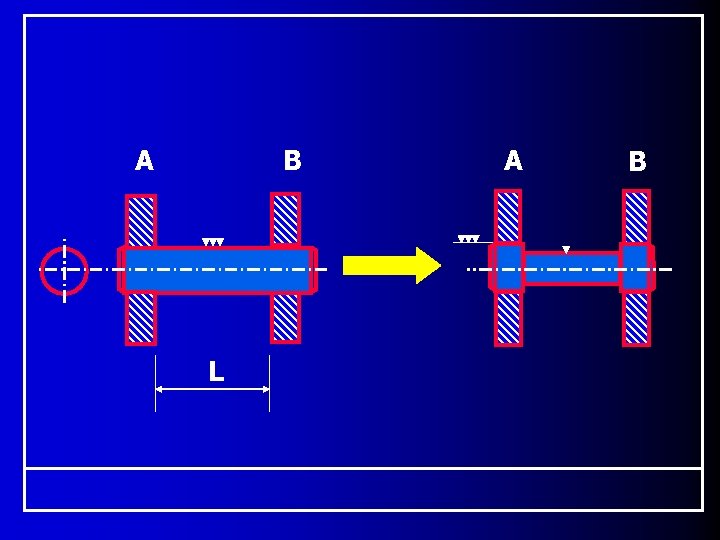
A B L A B
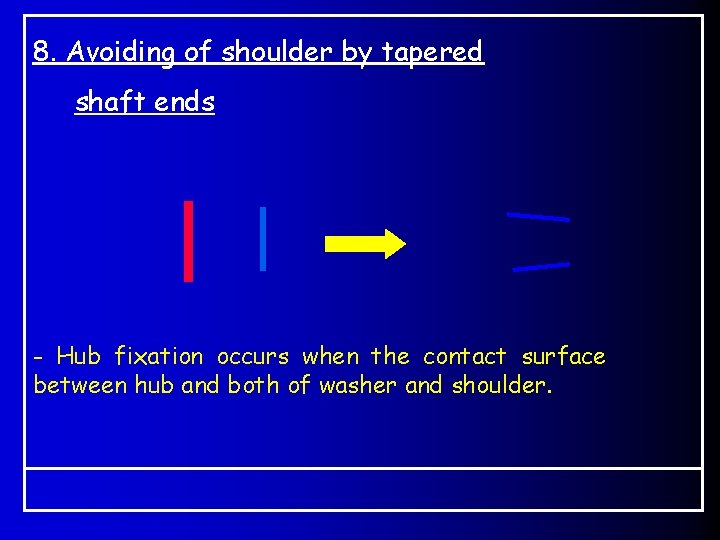
8. Avoiding of shoulder by tapered shaft ends - Hub fixation occurs when the contact surface between hub and both of washer and shoulder.
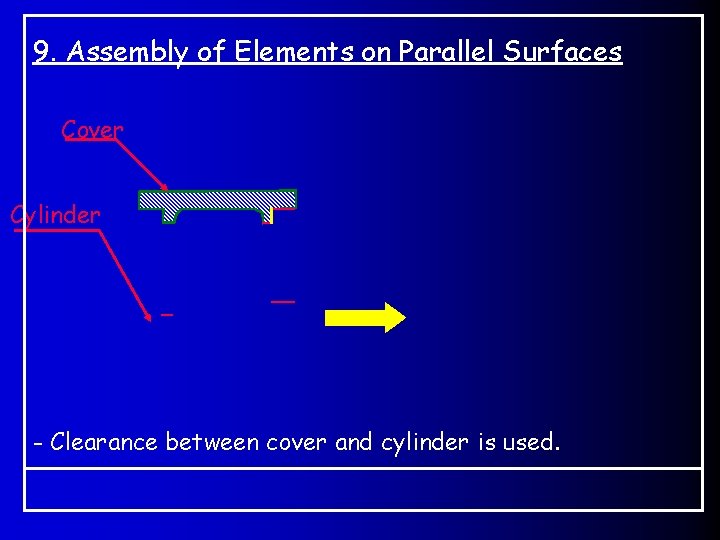
9. Assembly of Elements on Parallel Surfaces Cover Cylinder - Clearance between cover and cylinder is used.
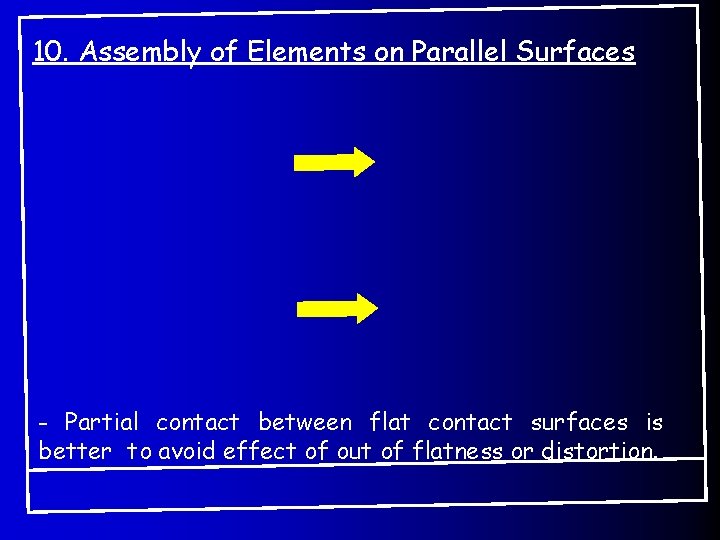
10. Assembly of Elements on Parallel Surfaces - Partial contact between flat contact surfaces is better to avoid effect of out of flatness or distortion.
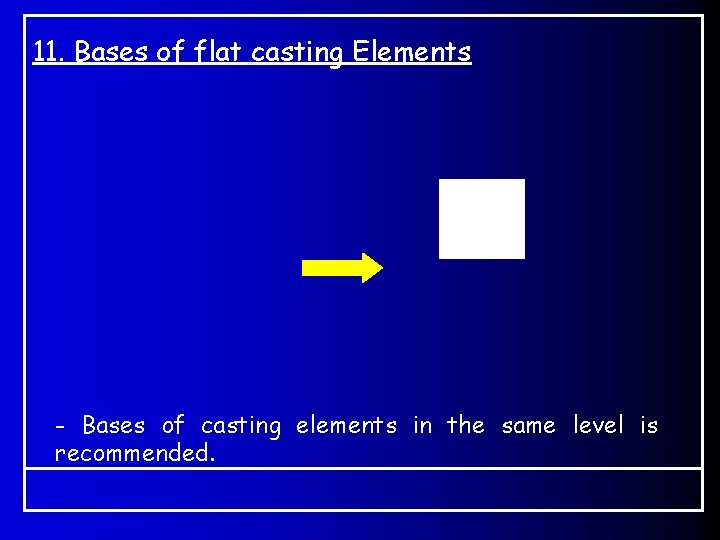
11. Bases of flat casting Elements - Bases of casting elements in the same level is recommended.
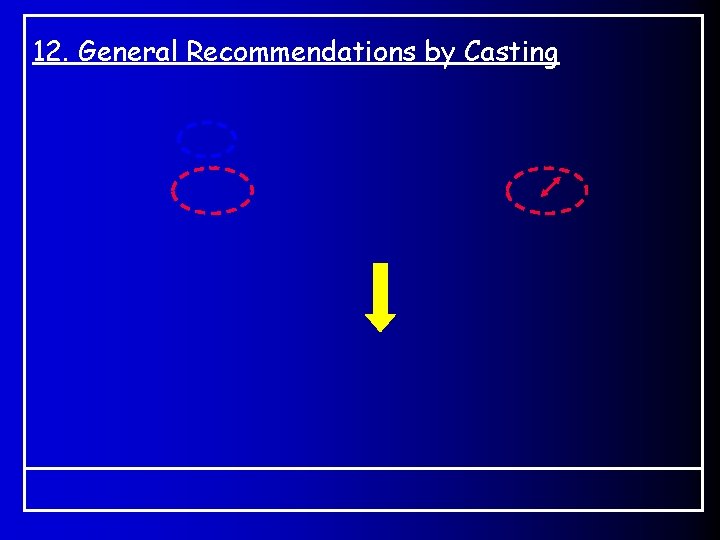
12. General Recommendations by Casting
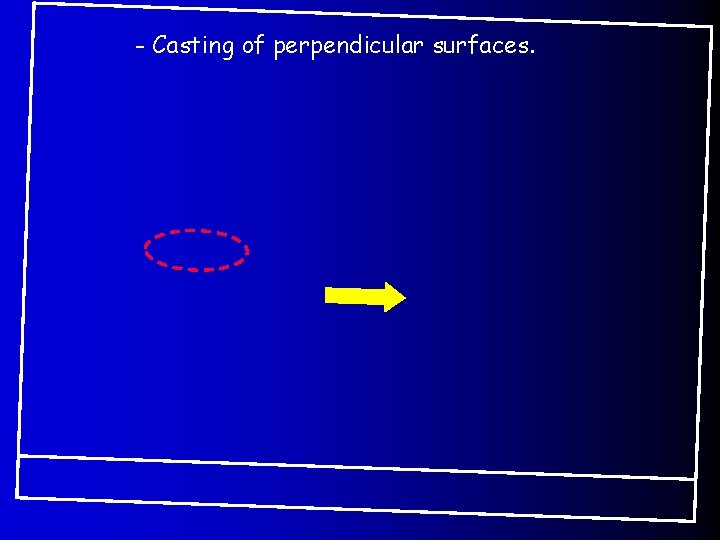
- Casting of perpendicular surfaces.
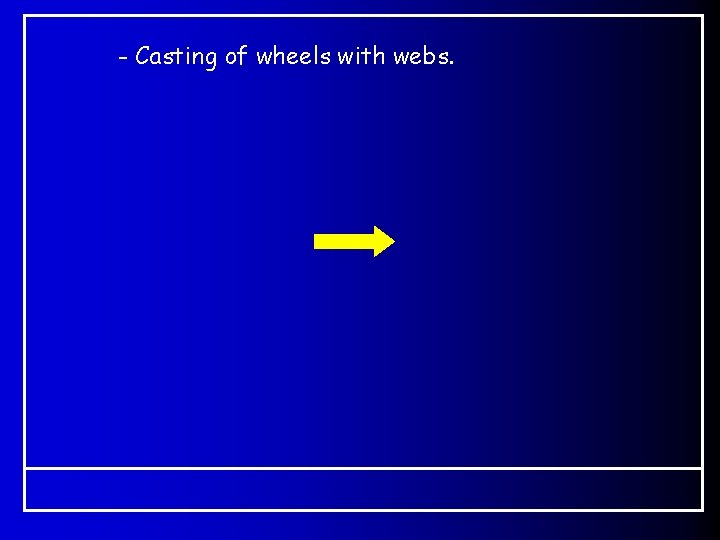
- Casting of wheels with webs.
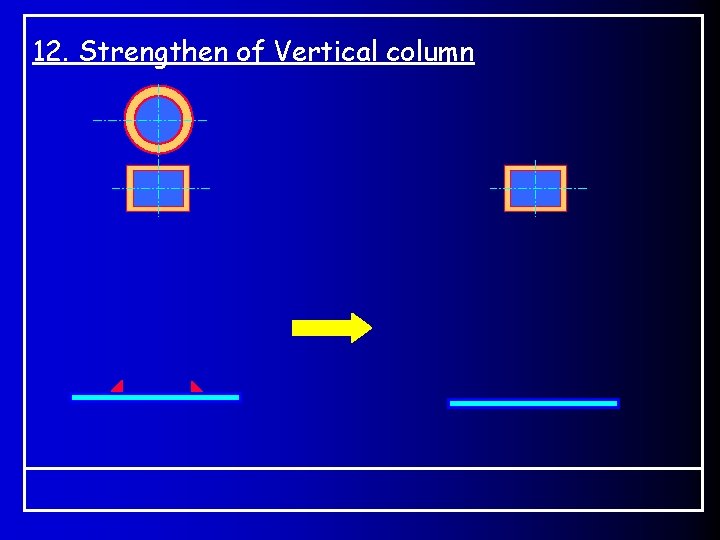
12. Strengthen of Vertical column
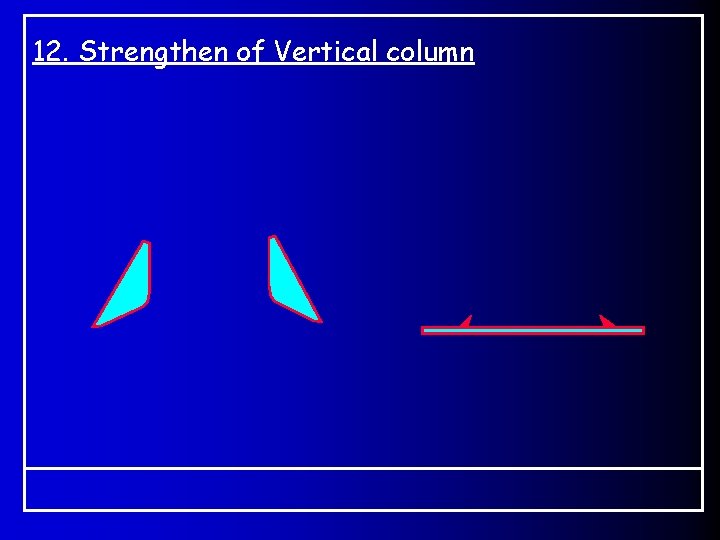
12. Strengthen of Vertical column
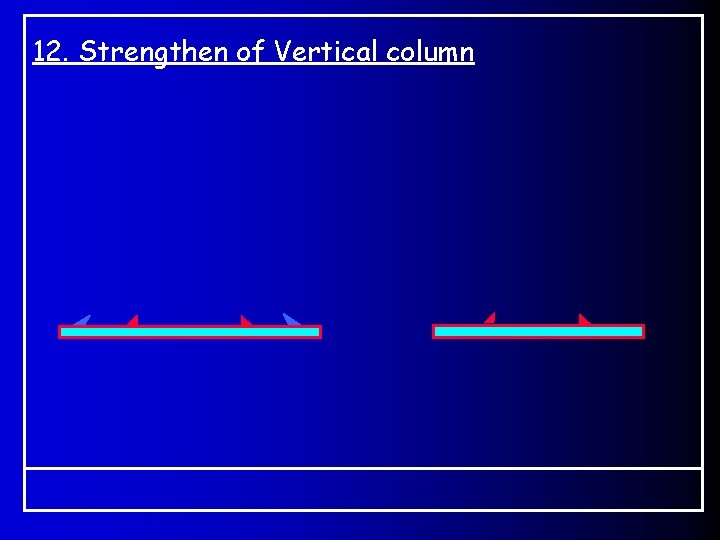
12. Strengthen of Vertical column
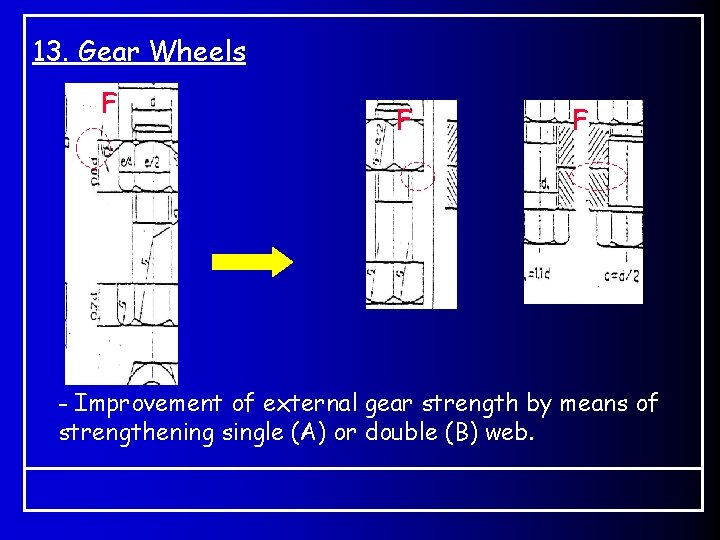
13. Gear Wheels F F F - Improvement of external gear strength by means of strengthening single (A) or double (B) web.
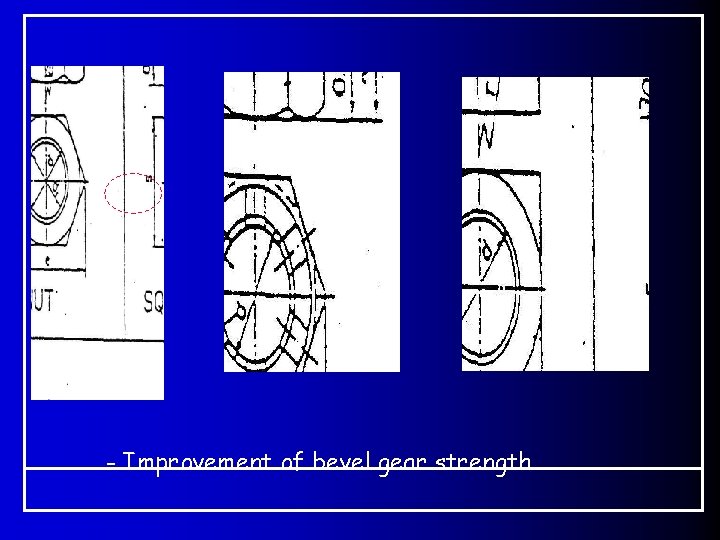
- Improvement of bevel gear strength.
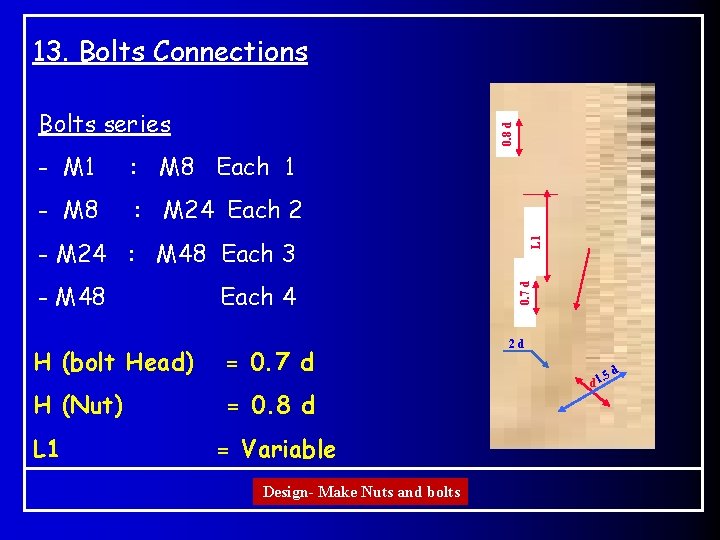
13. Bolts Connections - M 1 : M 8 Each 1 - M 8 : M 24 Each 2 L 1 0. 8 d Bolts series - M 48 Each 4 H (bolt Head) = 0. 7 d H (Nut) = 0. 8 d L 1 = Variable Design- Make Nuts and bolts 0. 7 d - M 24 : M 48 Each 3 2 d 5 d d 1.
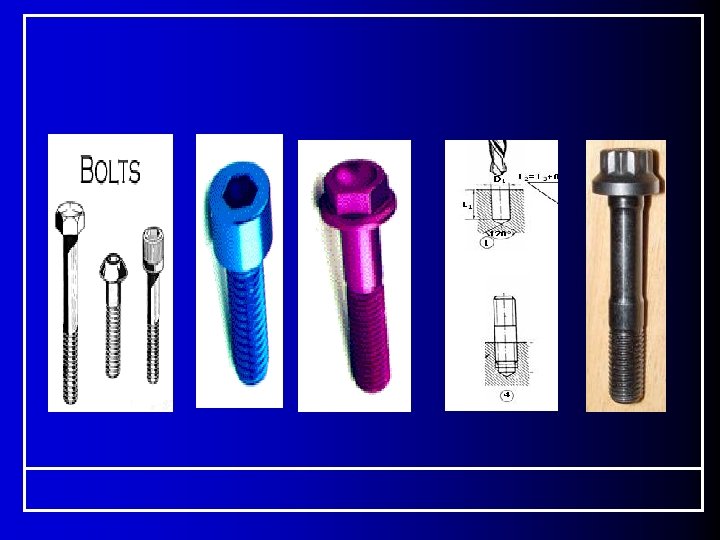
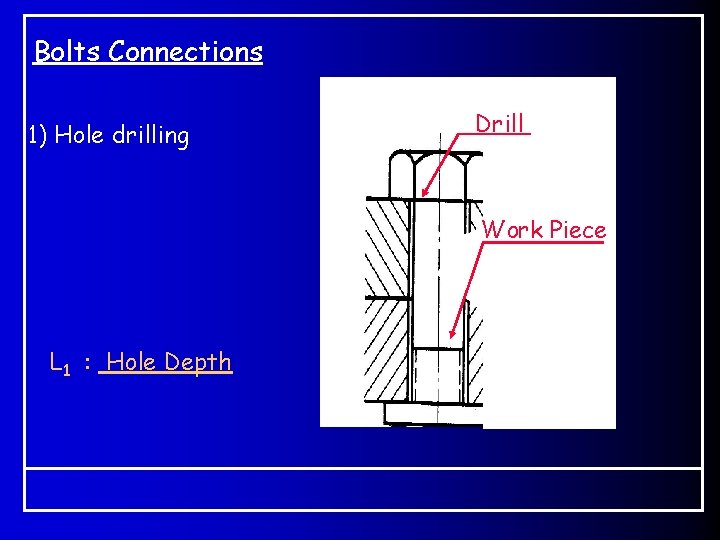
Bolts Connections 1) Hole drilling Drill Work Piece L 1 : Hole Depth
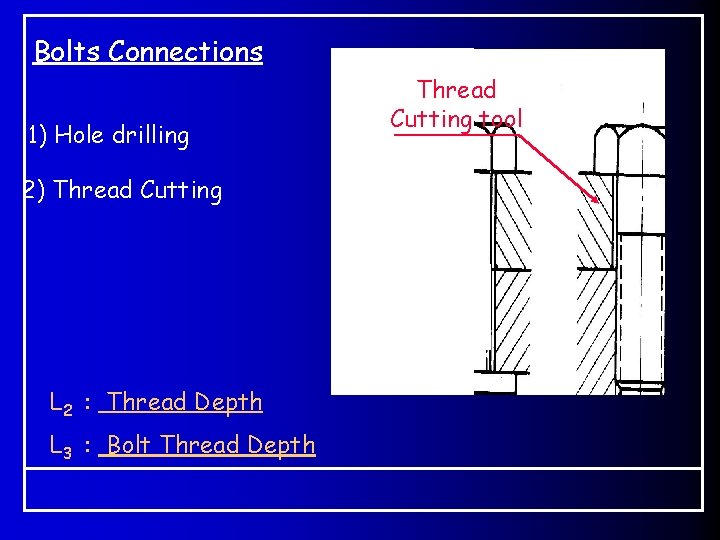
Bolts Connections 1) Hole drilling 2) Thread Cutting L 2 : Thread Depth L 3 : Bolt Thread Depth Thread Cutting tool
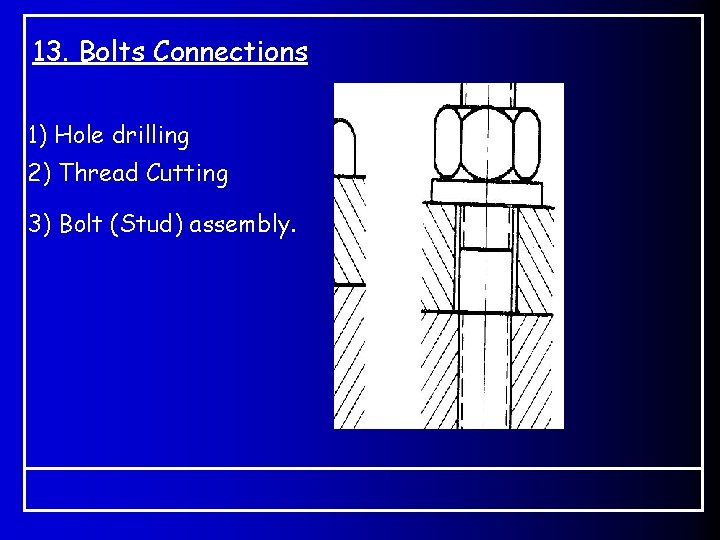
13. Bolts Connections 1) Hole drilling 2) Thread Cutting 3) Bolt (Stud) assembly.
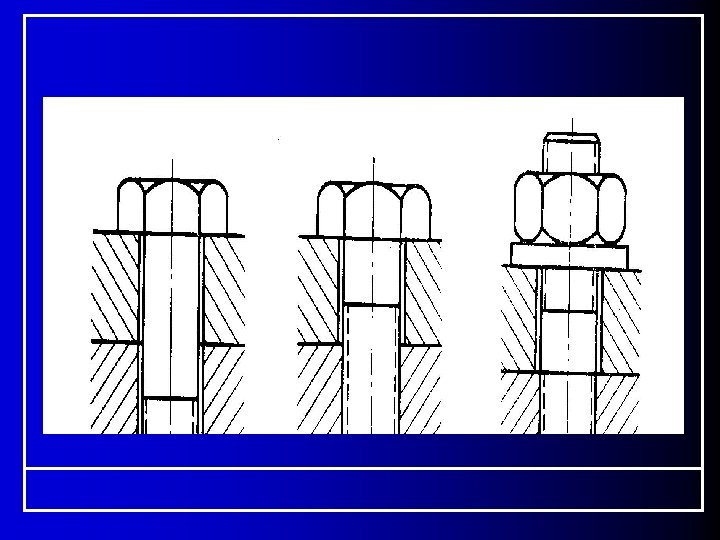
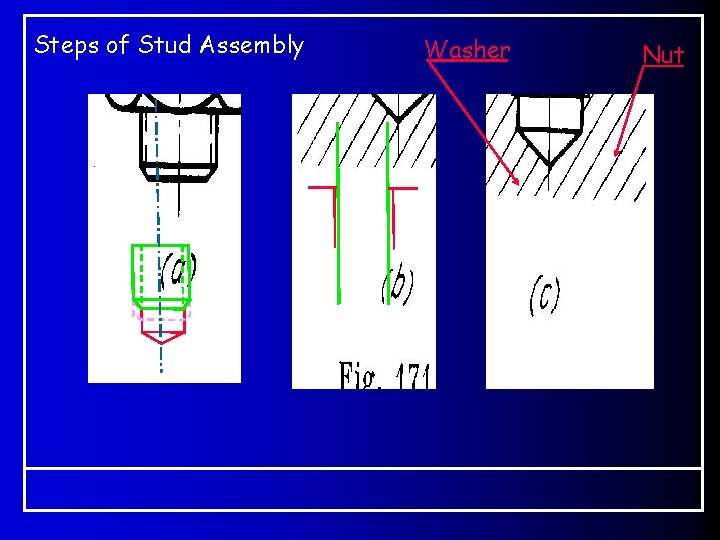
Steps of Stud Assembly Washer Nut
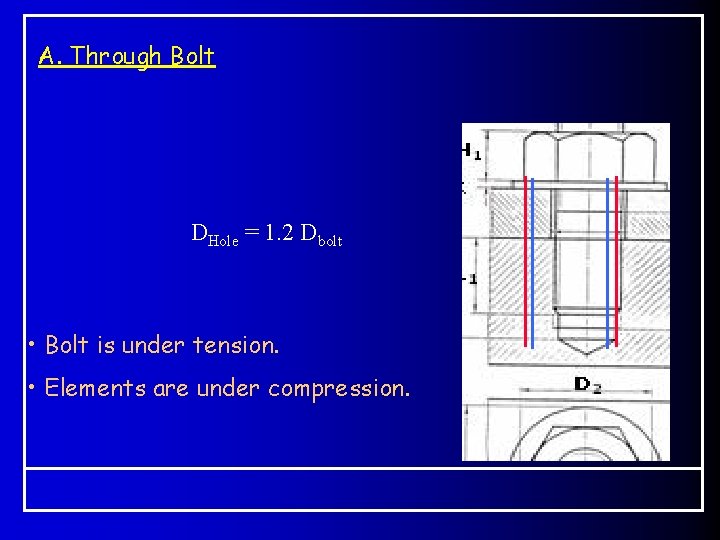
A. Through Bolt DHole = 1. 2 Dbolt • Bolt is under tension. • Elements are under compression.
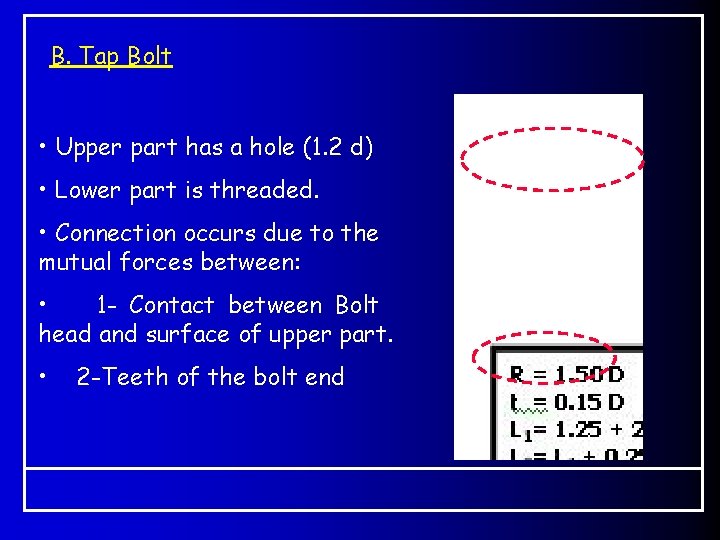
B. Tap Bolt • Upper part has a hole (1. 2 d) • Lower part is threaded. • Connection occurs due to the mutual forces between: • 1 - Contact between Bolt head and surface of upper part. • 2 -Teeth of the bolt end
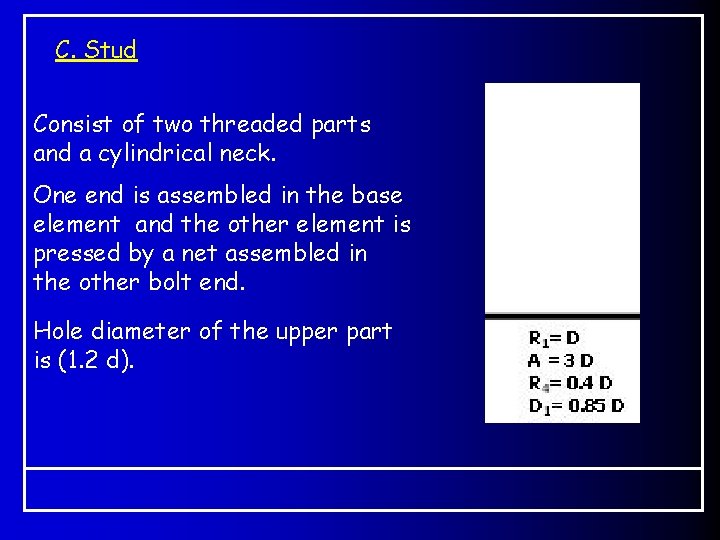
C. Stud Consist of two threaded parts and a cylindrical neck. One end is assembled in the base element and the other element is pressed by a net assembled in the other bolt end. Hole diameter of the upper part is (1. 2 d).
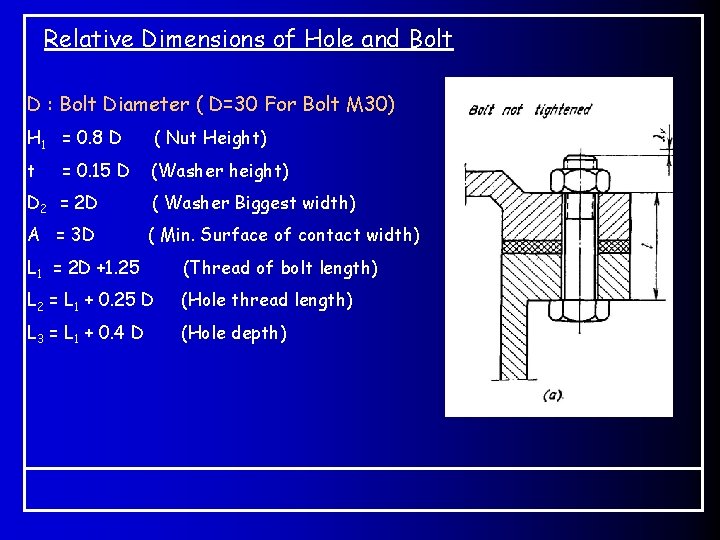
Relative Dimensions of Hole and Bolt D : Bolt Diameter ( D=30 For Bolt M 30) H 1 = 0. 8 D ( Nut Height) t (Washer height) = 0. 15 D D 2 = 2 D ( Washer Biggest width) A = 3 D ( Min. Surface of contact width) L 1 = 2 D +1. 25 (Thread of bolt length) L 2 = L 1 + 0. 25 D (Hole thread length) L 3 = L 1 + 0. 4 D (Hole depth)
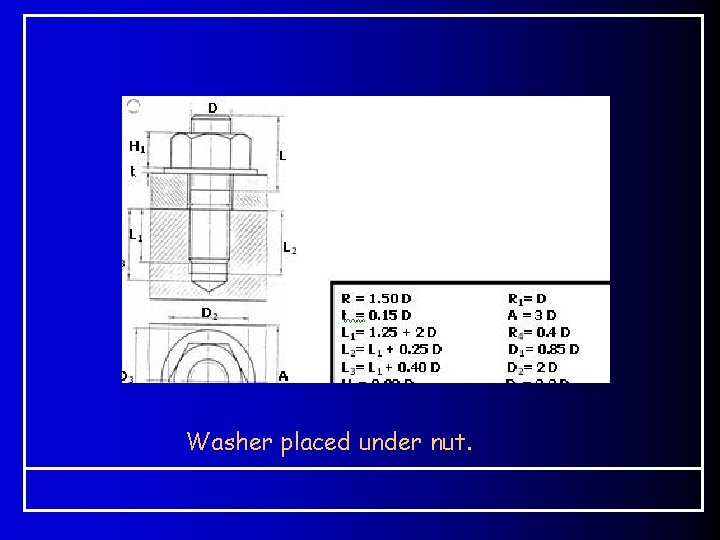
Washer placed under nut.
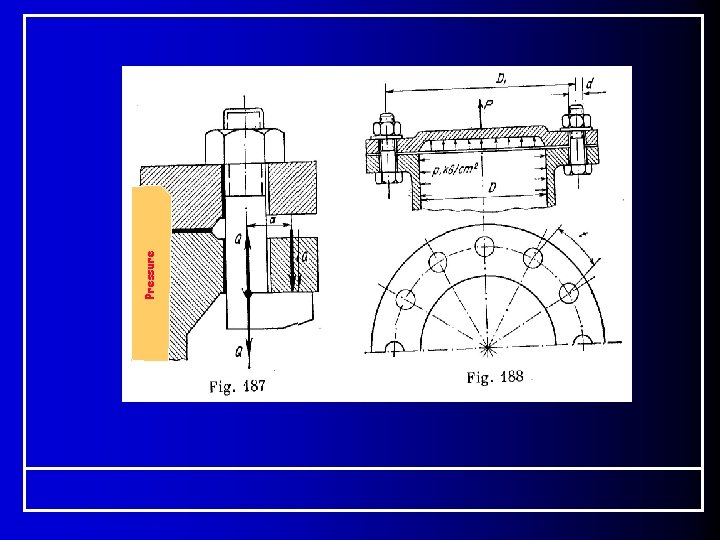
Pressure
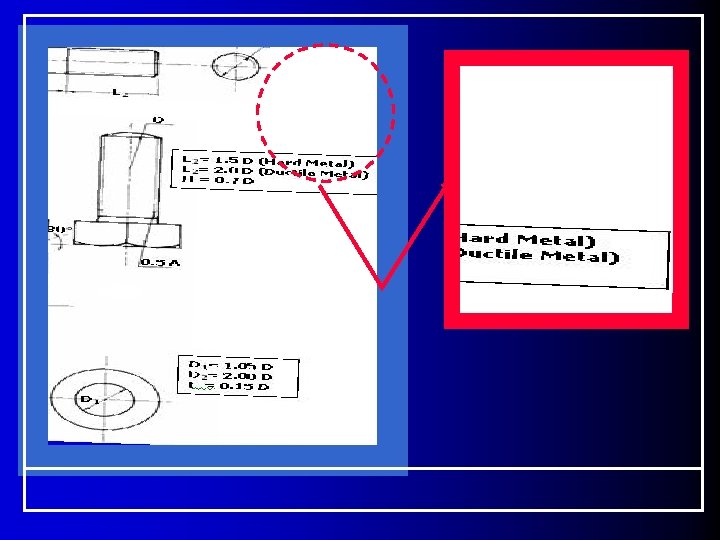
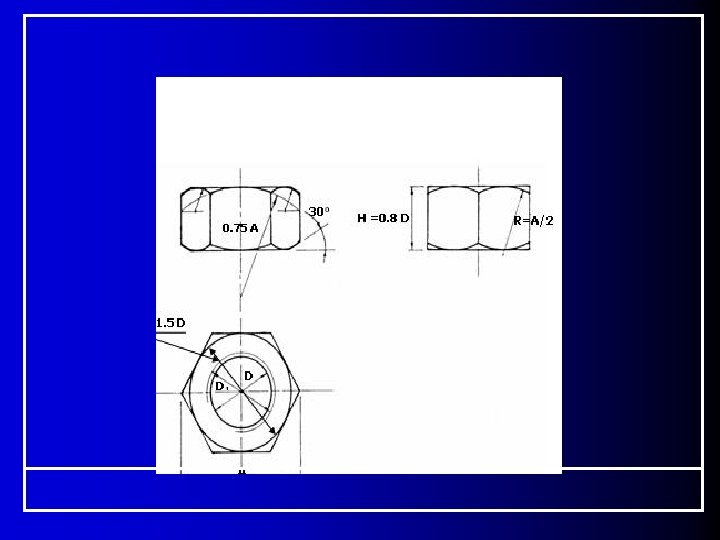
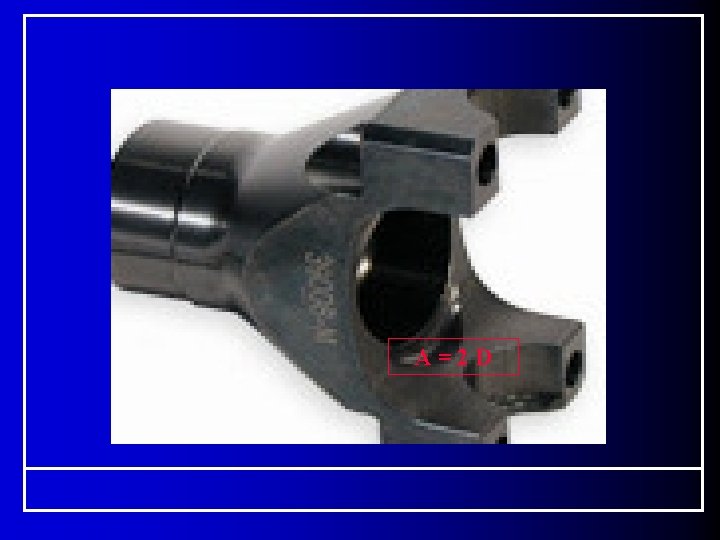
A=2 D
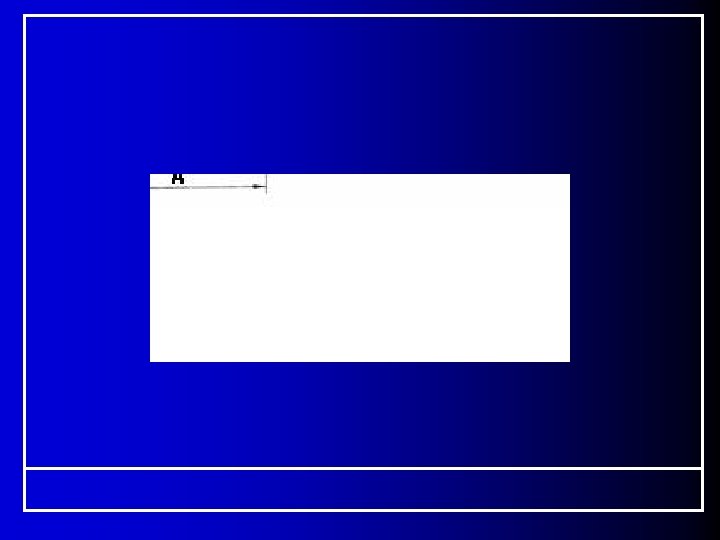
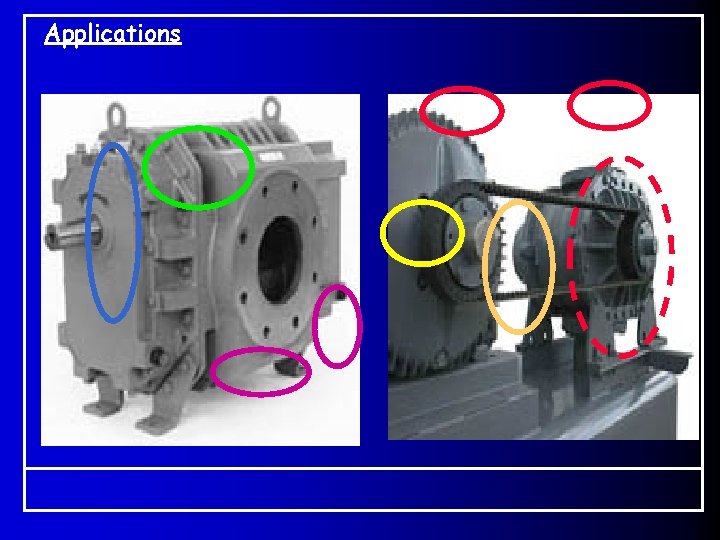
Applications
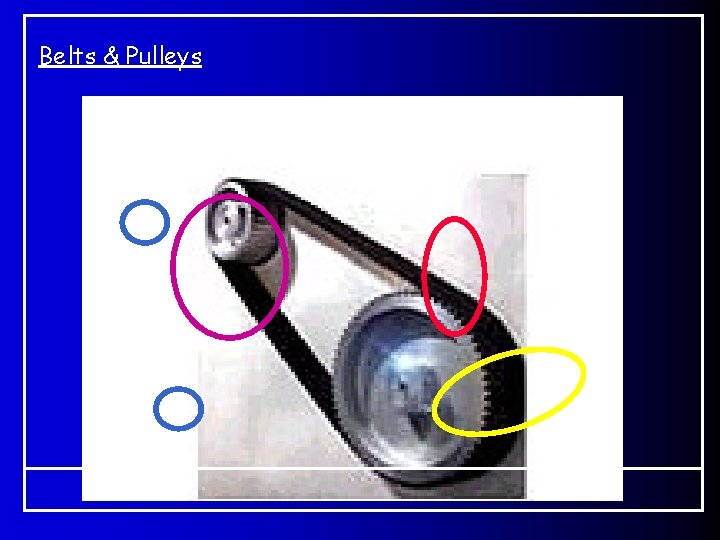
Belts & Pulleys
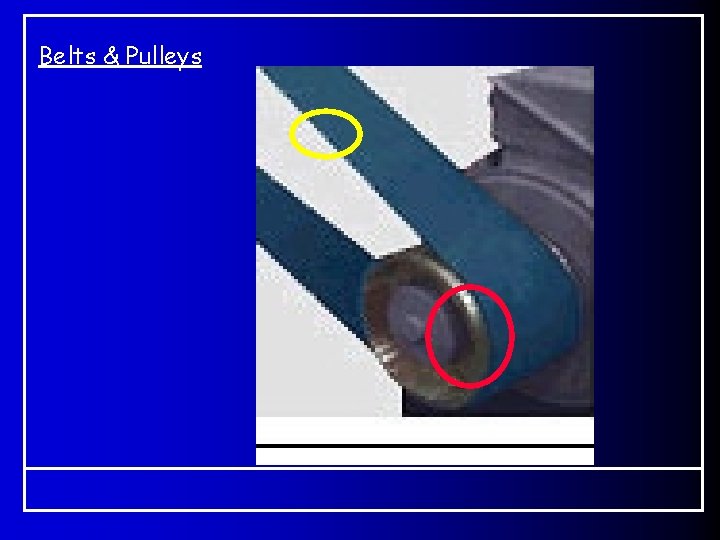
Belts & Pulleys
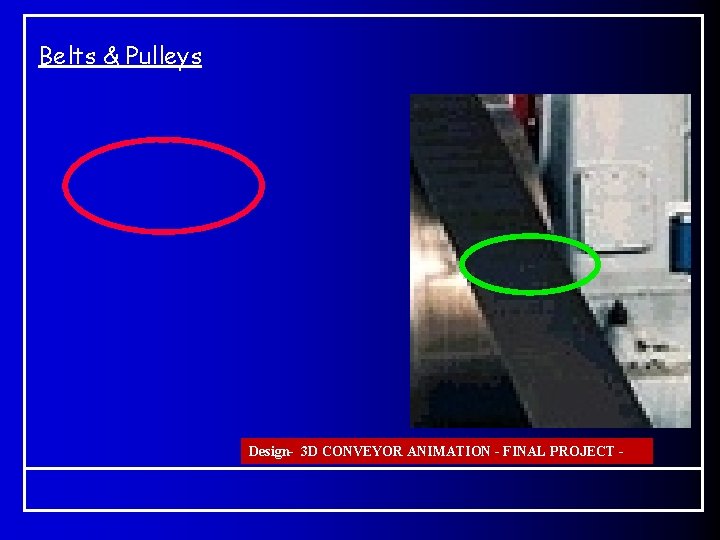
Belts & Pulleys Design- 3 D CONVEYOR ANIMATION - FINAL PROJECT -
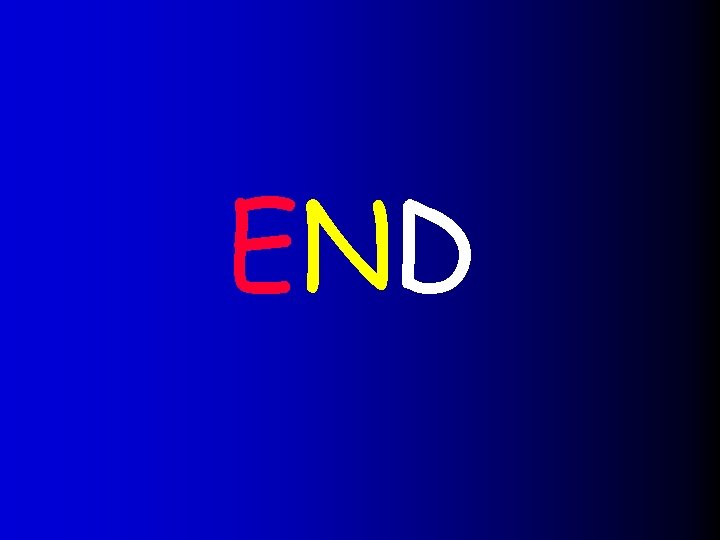
END
Concentration gradient vs concentration difference
Movement of high concentration to low concentration
Levdtwwliqo -site:youtube.com
Stress concentration
Efatigue stress concentration factor
Axial load calculation example
Chapter 10 stress responses and stress management
True stress vs engineering stress
Normal axial stress
Brainpop ratios
Part by part technical description example
Part part whole addition
What are the basic display parts of the bar
Unit ratio definition
미니탭 gage r&r 해석
The part of a shadow surrounding the darkest part
Concentration= moles/volume
How to find percent concentration
Concentration of solution
Concentration in chemical reaction
Sedimentation technique for stool concentration
Alveoli location
The movement of particles from high to low concentration
Faraday's constant electrochemistry
Units for concentration
Proh sub corr facil-alcohol/drug/phone/tobacco
Concentration camps vs internment camps venn diagram
A breath test reflects the alcohol concentration in the:
Gradient de concentration
Difference between focus and concentration
Grams to.moles
How to determine concentration of a solution
Concentration molaire
Novec 123
Fasting plasma glucose concentration
Mac maximum allowable concentration
Bradford assay
Client concentration
Chemical energy
Carrier concentration in intrinsic semiconductor
Camp de concentration sachsenhausen visite
The four-firm concentration ratio
Intrinsic carrier concentration
Are concentration and molarity the same
Solute concentration
Inhalation anesthetics
Concentration
Duhring's rule
Ap concentration examples
The average zinc concentration recovered from a sample
Regulating blood glucose
Lesson 80 bearly alive solution concentration
Transmittance and concentration relationship
Concentration ratio
Concentration
Concentration mass volume triangle
Molarity measurement
Multi-segment marketing
Describe the cash concentration strategies.
Concentration
Single segment concentration
How to find percent concentration
Calculating molarity
Formal ether concentration technique
Moles concentration volume triangle
Enzyme
Quantitative expression of solution concentration
Blood alcohol concentration (bac)
Activity to concentration
Intracellular k concentration
Molarity
Ligation
Ketamine concentration
Dilution in pharmacy
Lesson 80 bearly alive solution concentration
Properties of solutions grade 7
K equilibrium formula
Ww concentration
Carbon dioxide concentration in photosynthesis