Concentration factors Shape Factor or Stress Concentration Factor
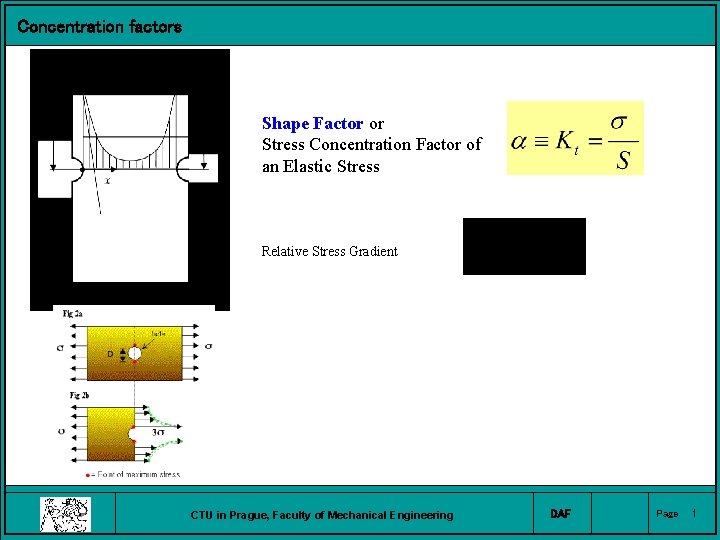
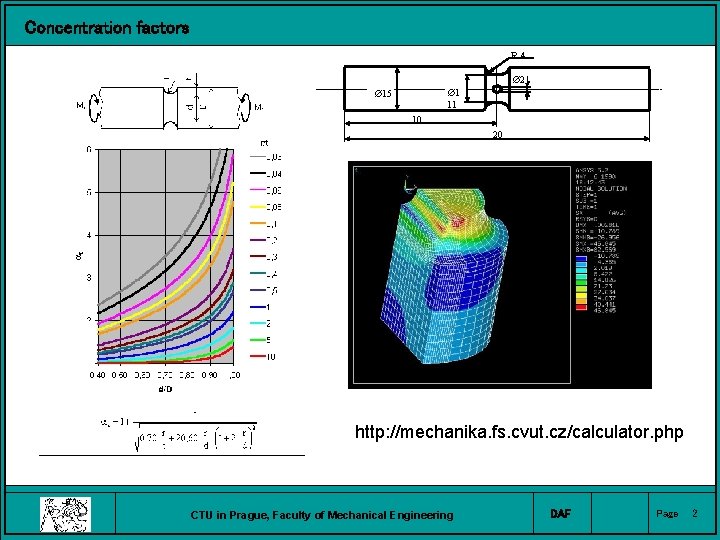
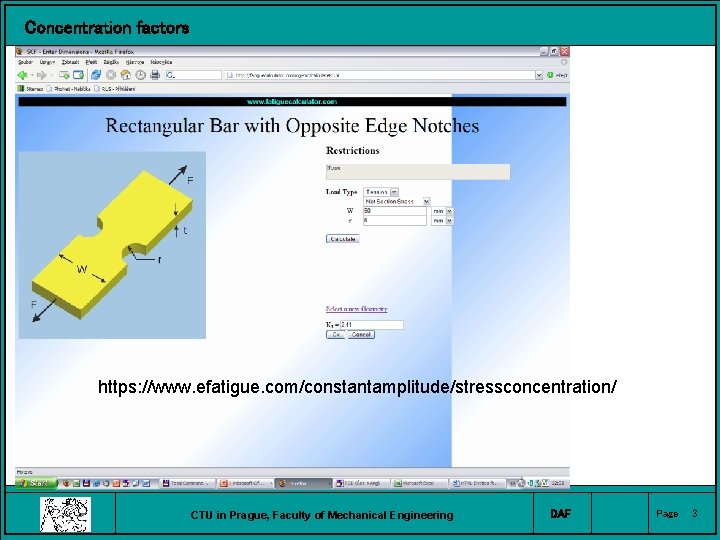
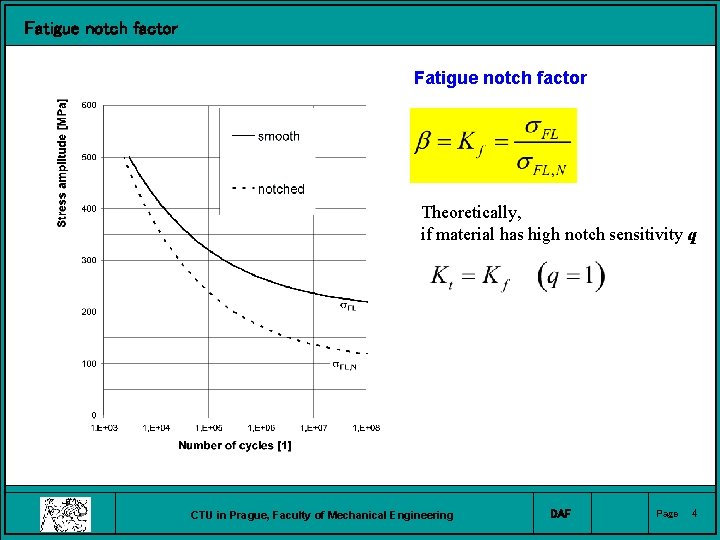

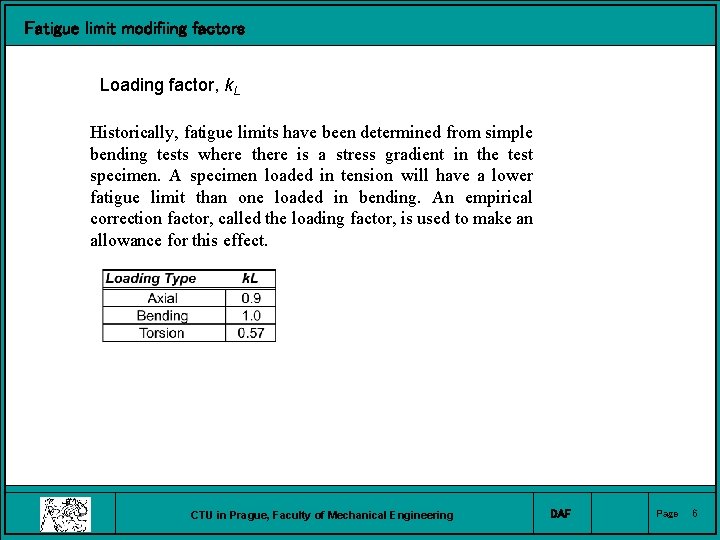
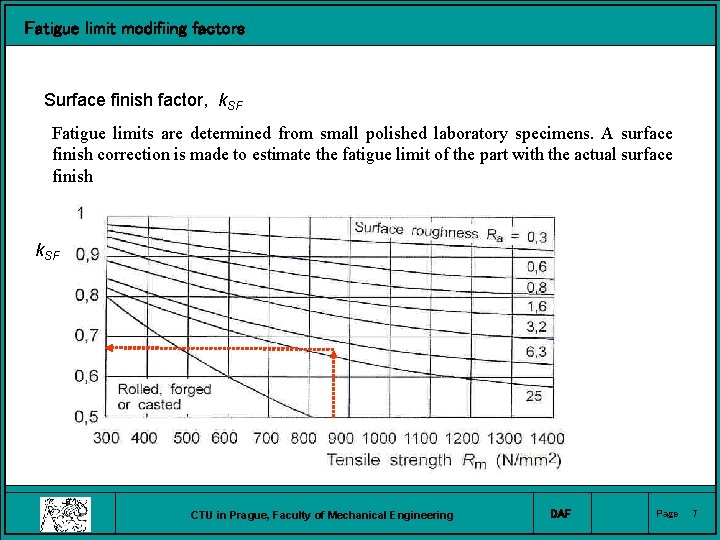
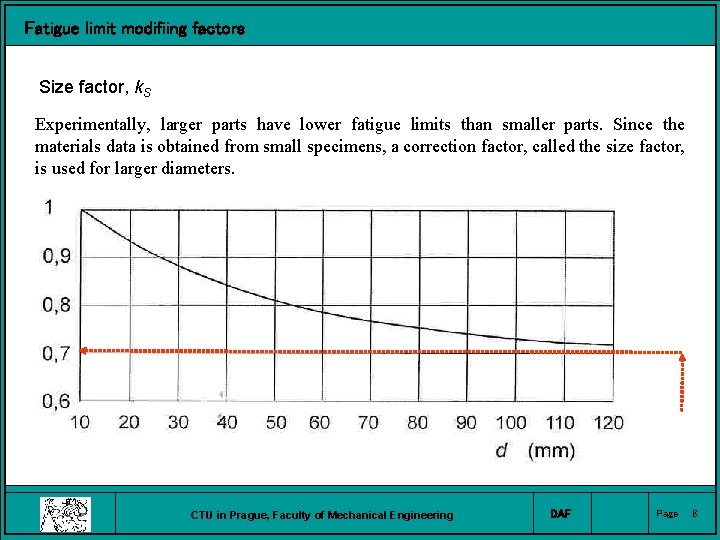
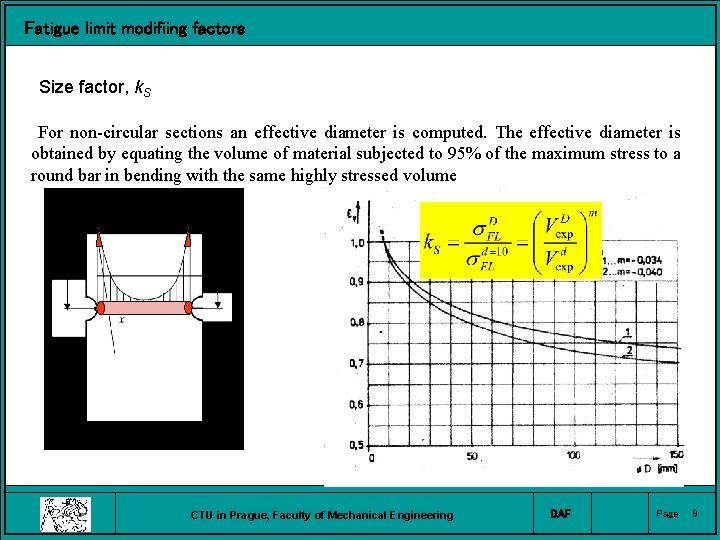
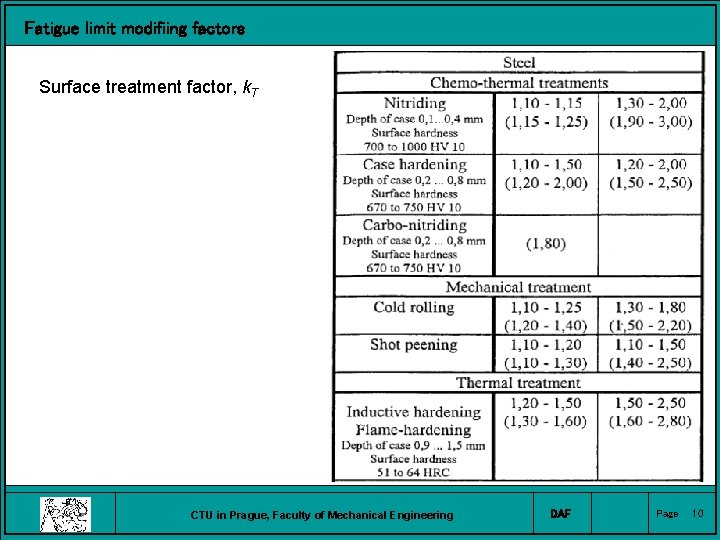
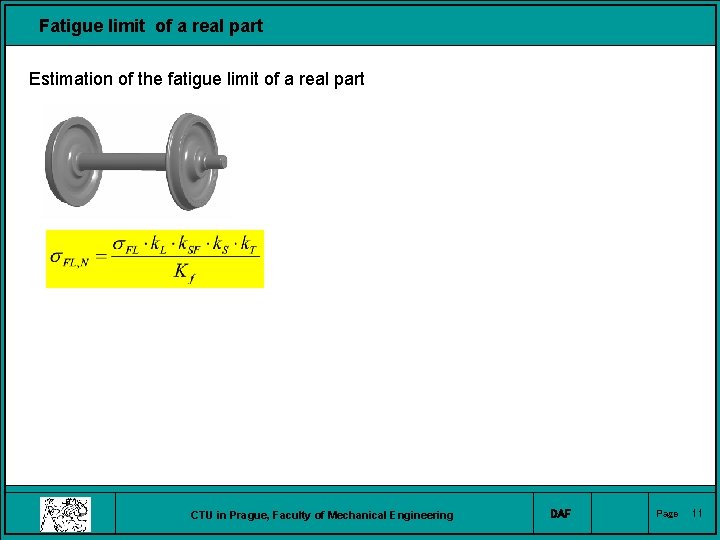
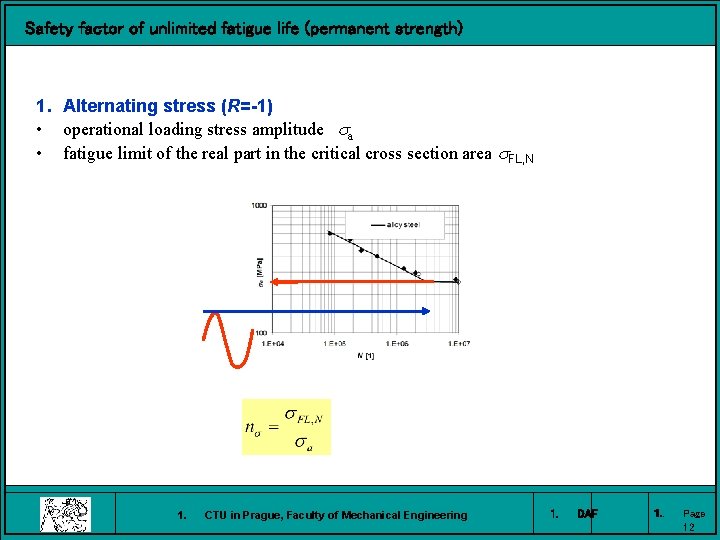
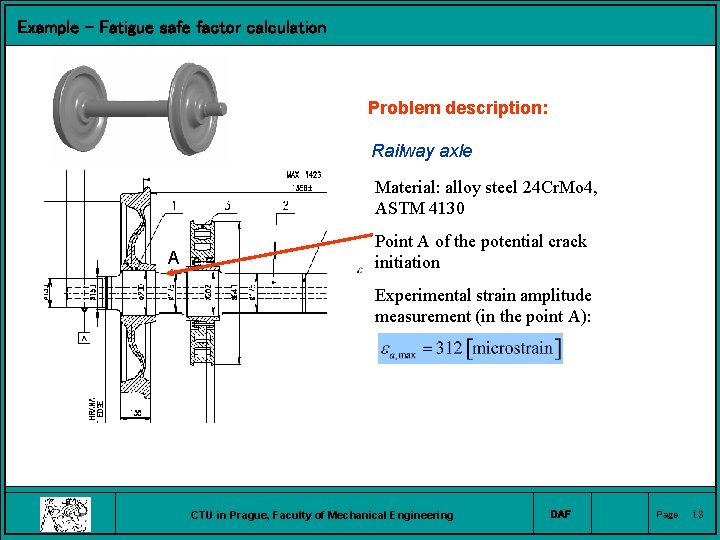
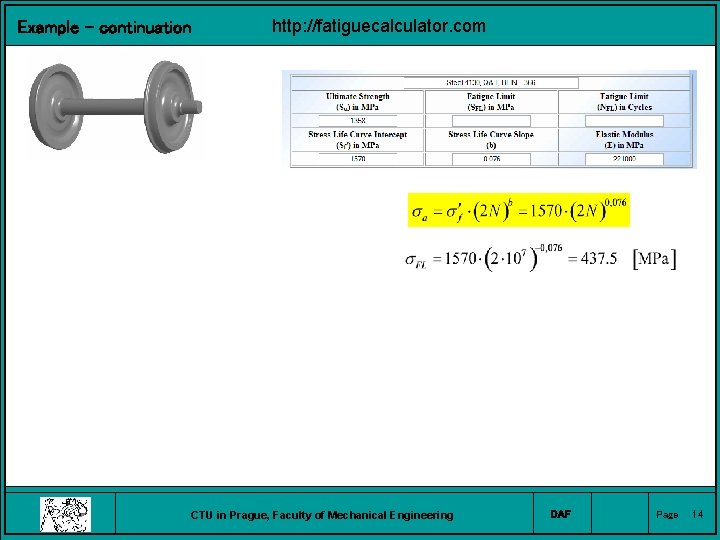
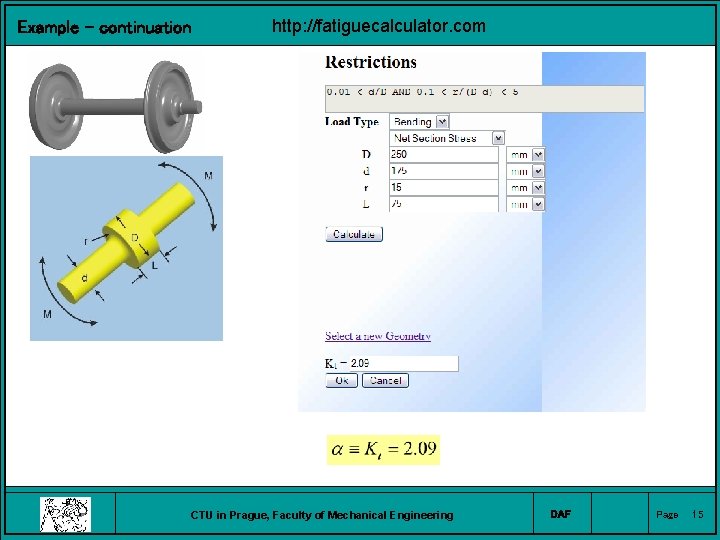

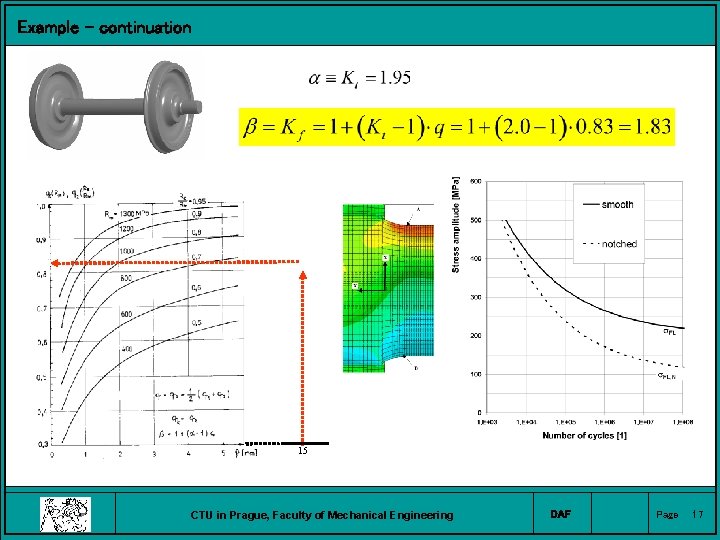
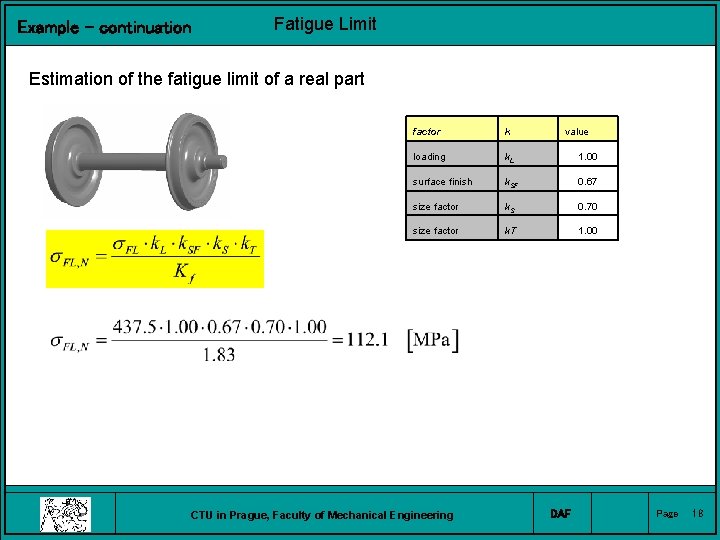
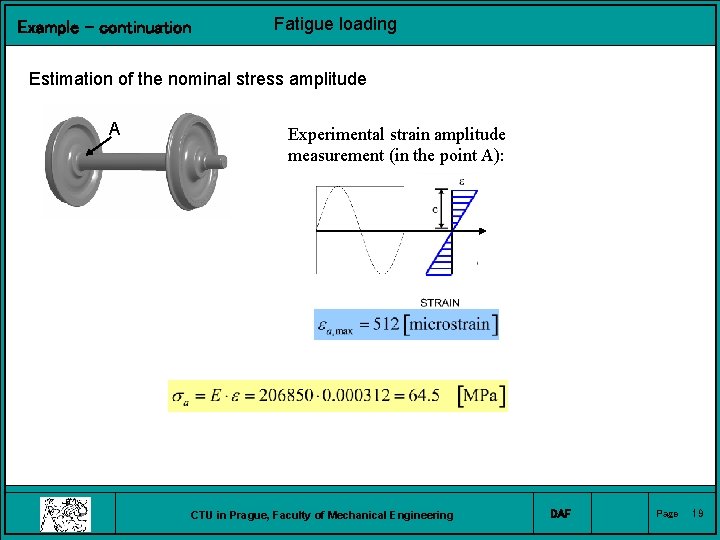
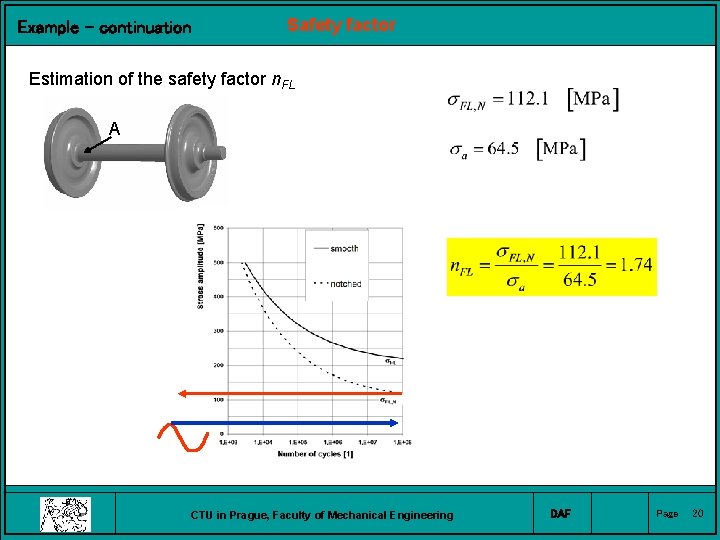
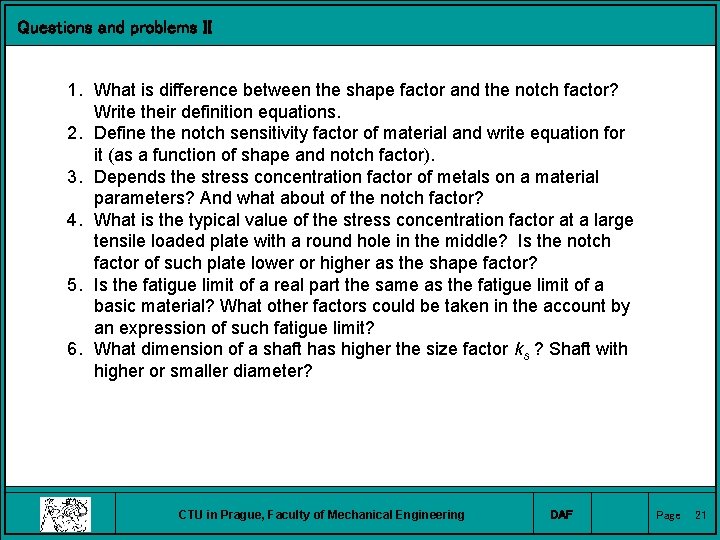
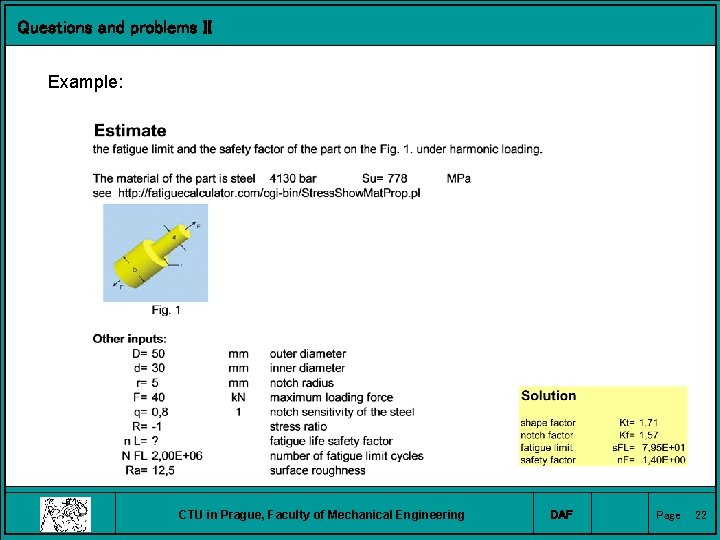
- Slides: 22
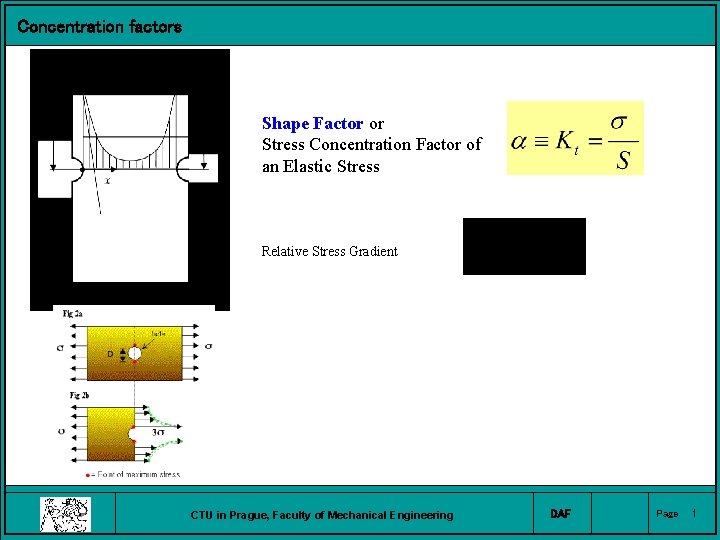
Concentration factors Shape Factor or Stress Concentration Factor of an Elastic Stress Relative Stress Gradient CTU in Prague, Faculty of Mechanical Engineering DAF Page 1
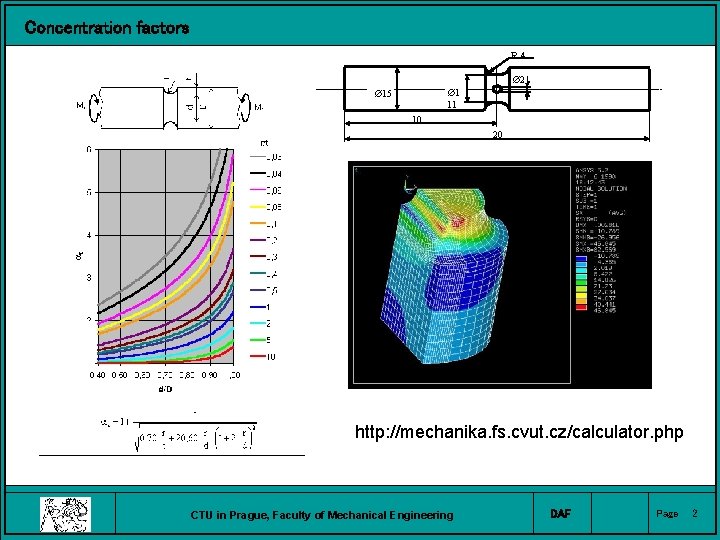
Concentration factors R 4 2 1 11 15 10 20 http: //mechanika. fs. cvut. cz/calculator. php CTU in Prague, Faculty of Mechanical Engineering DAF Page 2
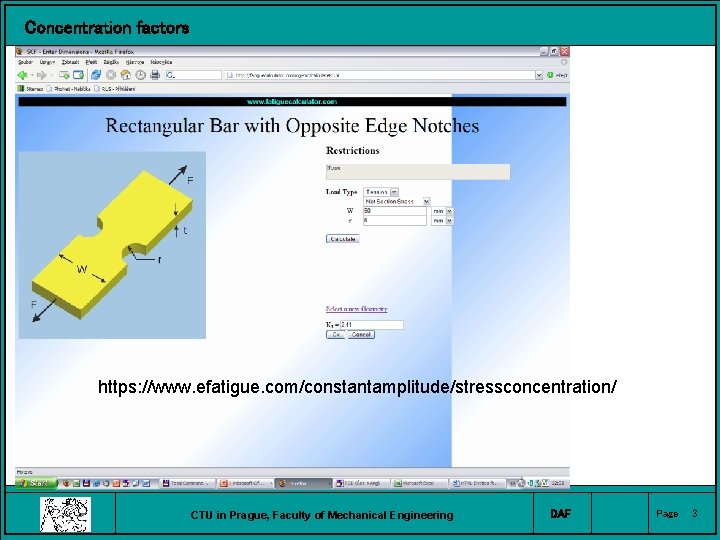
Concentration factors https: //www. efatigue. com/constantamplitude/stressconcentration/ CTU in Prague, Faculty of Mechanical Engineering DAF Page 3
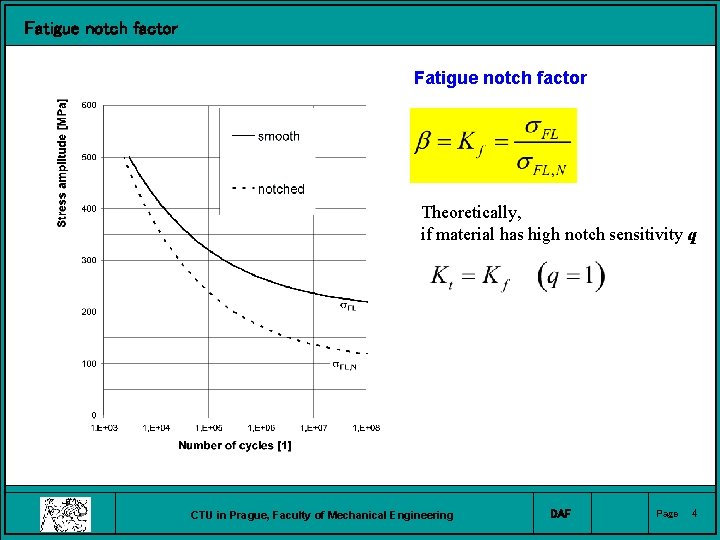
Fatigue notch factor Theoretically, if material has high notch sensitivity q CTU in Prague, Faculty of Mechanical Engineering DAF Page 4

Fatigue notch factor, Kf and notch sensitivity factor, q Experiments have shown that the effect of notches is less than that the estimated effect according a traditional stress concentration factor, Kt. The fatigue notch factor, Kf , can be described as the effective stress concentration in fatigue. This effect is dealt with using a notch sensitivity factor, q. Notch radius CTU in Prague, Faculty of Mechanical Engineering DAF Page 5
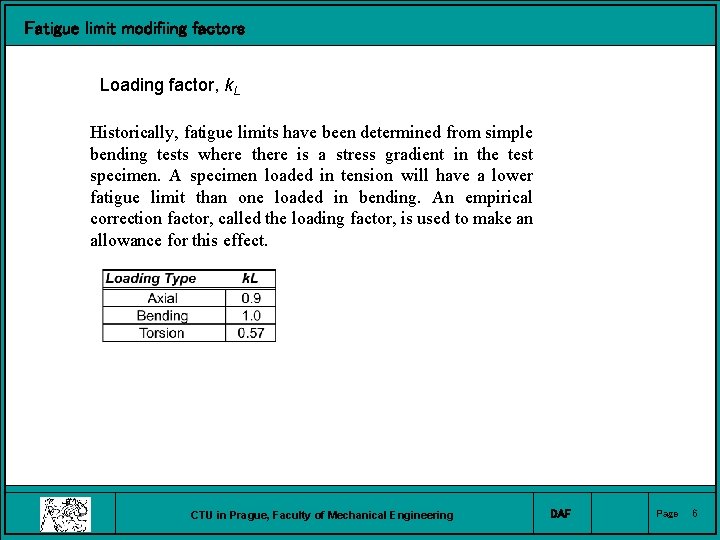
Fatigue limit modifiing factors Loading factor, k. L Historically, fatigue limits have been determined from simple bending tests where there is a stress gradient in the test specimen. A specimen loaded in tension will have a lower fatigue limit than one loaded in bending. An empirical correction factor, called the loading factor, is used to make an allowance for this effect. CTU in Prague, Faculty of Mechanical Engineering DAF Page 6
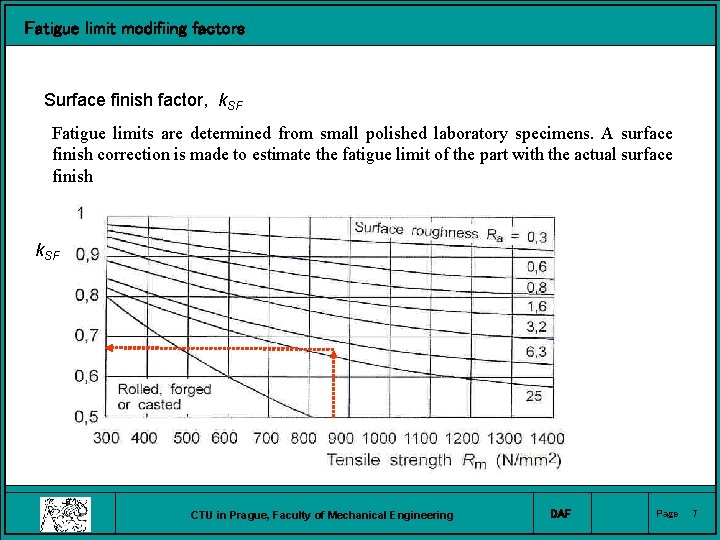
Fatigue limit modifiing factors Surface finish factor, k. SF Fatigue limits are determined from small polished laboratory specimens. A surface finish correction is made to estimate the fatigue limit of the part with the actual surface finish k. SF CTU in Prague, Faculty of Mechanical Engineering DAF Page 7
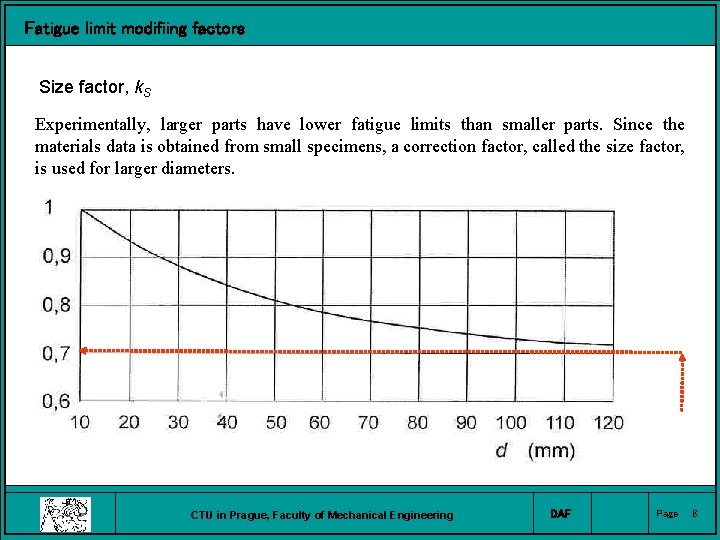
Fatigue limit modifiing factors Size factor, k. S Experimentally, larger parts have lower fatigue limits than smaller parts. Since the materials data is obtained from small specimens, a correction factor, called the size factor, is used for larger diameters. CTU in Prague, Faculty of Mechanical Engineering DAF Page 8
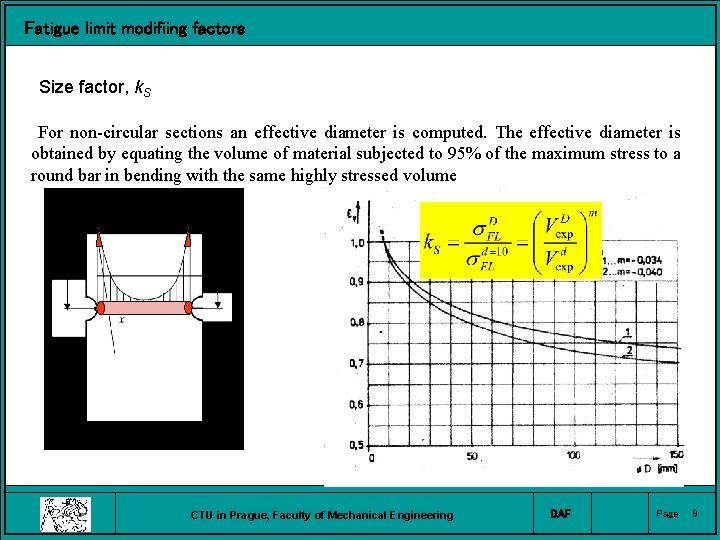
Fatigue limit modifiing factors Size factor, k. S For non-circular sections an effective diameter is computed. The effective diameter is obtained by equating the volume of material subjected to 95% of the maximum stress to a round bar in bending with the same highly stressed volume CTU in Prague, Faculty of Mechanical Engineering DAF Page 9
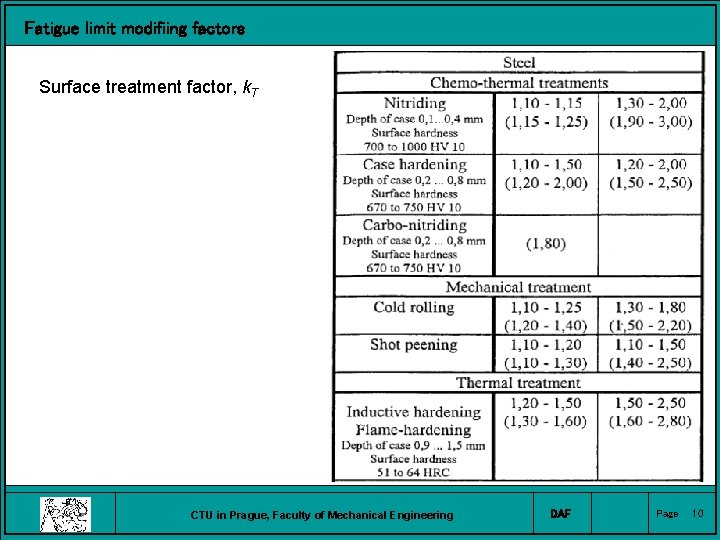
Fatigue limit modifiing factors Surface treatment factor, k. T CTU in Prague, Faculty of Mechanical Engineering DAF Page 10
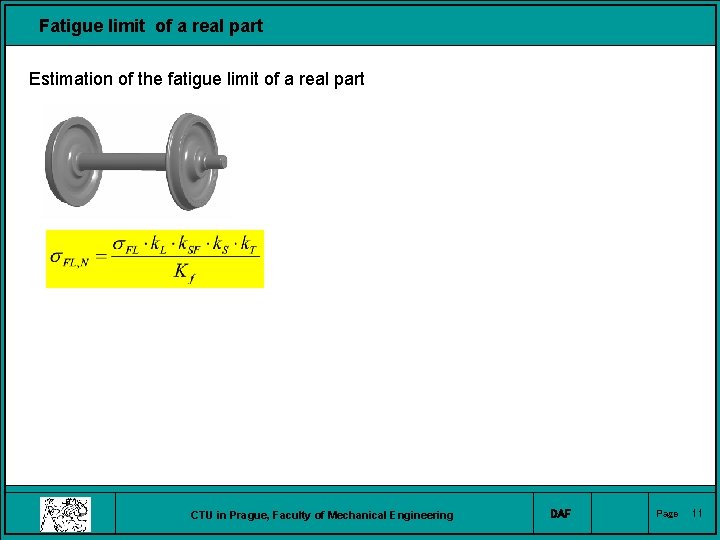
Fatigue limit of a real part Estimation of the fatigue limit of a real part CTU in Prague, Faculty of Mechanical Engineering DAF Page 11
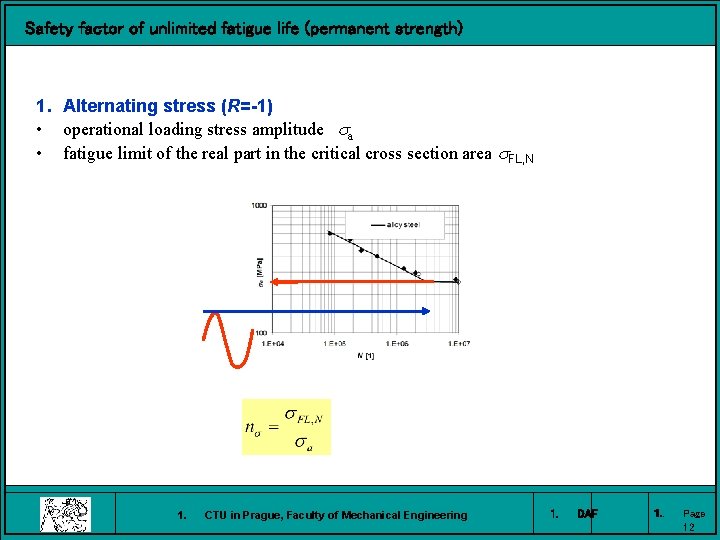
Safety factor of unlimited fatigue life (permanent strength) 1. Alternating stress (R=-1) • operational loading stress amplitude sa • fatigue limit of the real part in the critical cross section area s. FL, N 1. CTU in Prague, Faculty of Mechanical Engineering 1. DAF 1. 1. Page 12
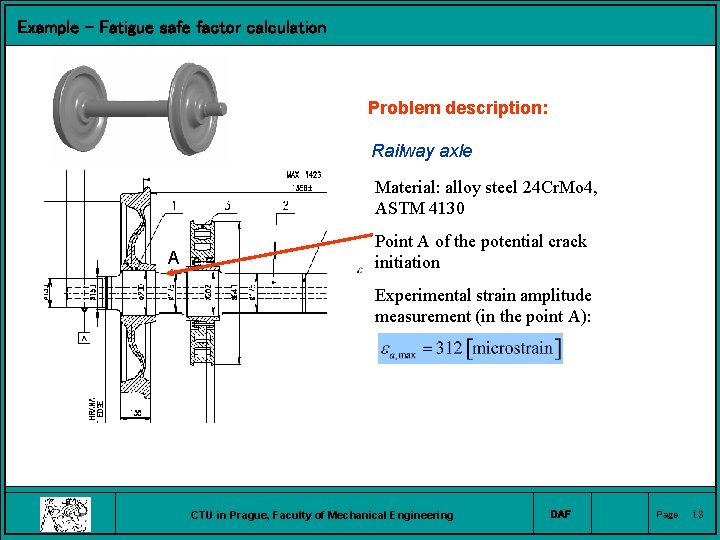
Example – Fatigue safe factor calculation Problem description: Railway axle Material: alloy steel 24 Cr. Mo 4, ASTM 4130 A Point A of the potential crack initiation Experimental strain amplitude measurement (in the point A): CTU in Prague, Faculty of Mechanical Engineering DAF Page 13
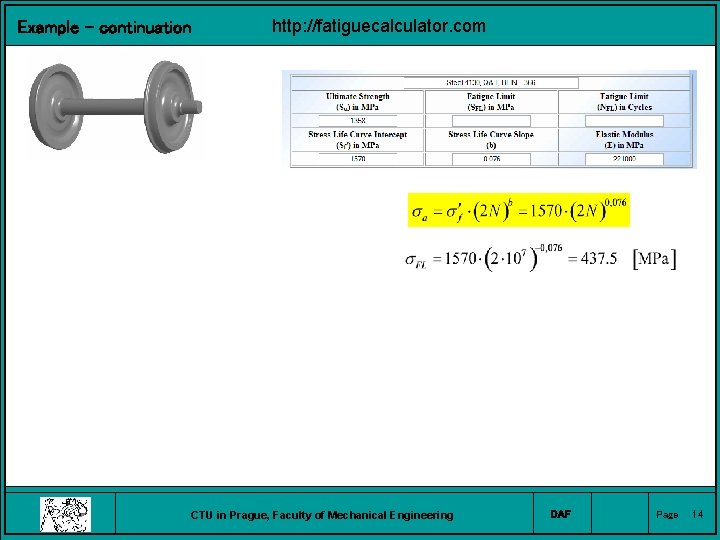
Example – continuation http: //fatiguecalculator. com CTU in Prague, Faculty of Mechanical Engineering DAF Page 14
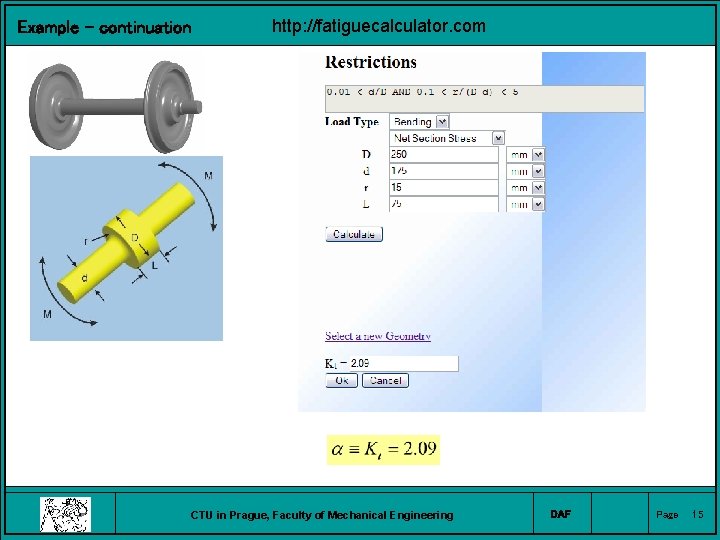
Example – continuation http: //fatiguecalculator. com CTU in Prague, Faculty of Mechanical Engineering DAF Page 15

Example – continuation FEM Calculation – CTU Prague Wheel Braking disc Axle CTU in Prague, Faculty of Mechanical Engineering DAF Page 16
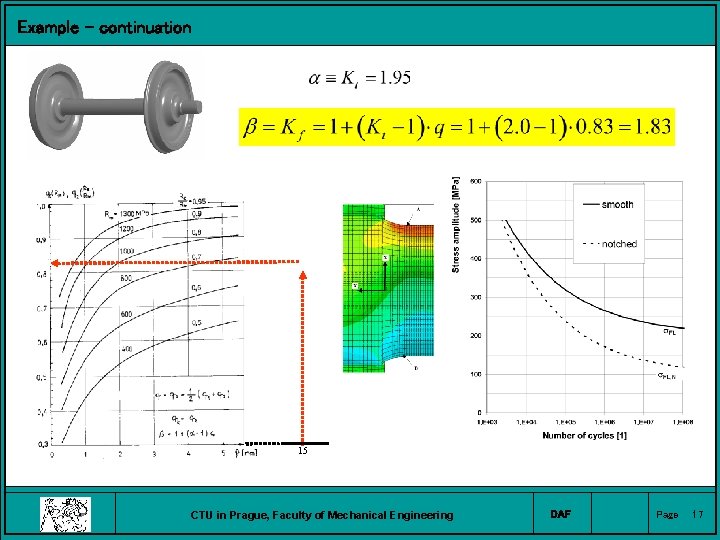
Example – continuation 15 CTU in Prague, Faculty of Mechanical Engineering DAF Page 17
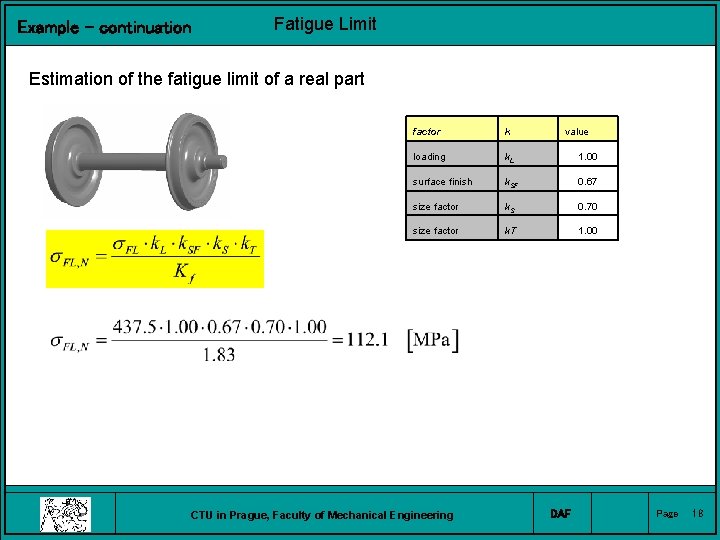
Example – continuation Fatigue Limit Estimation of the fatigue limit of a real part factor k loading k. L 1. 00 surface finish k. SF 0. 67 size factor k. S 0. 70 size factor k. T 1. 00 CTU in Prague, Faculty of Mechanical Engineering value DAF Page 18
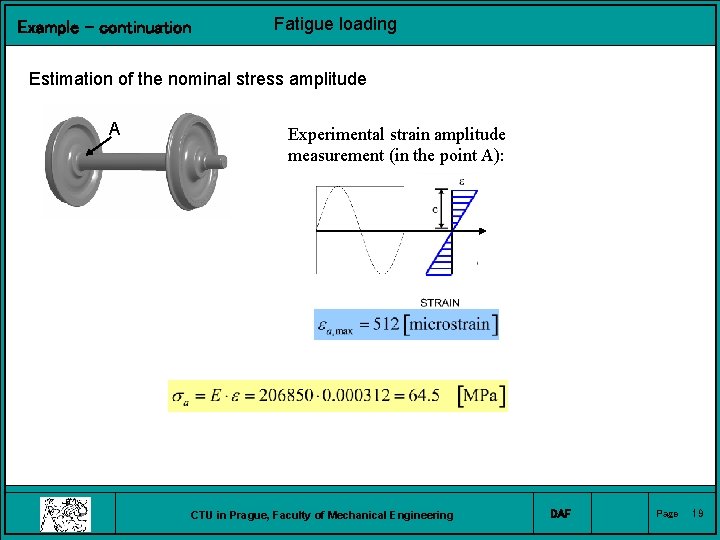
Example – continuation Fatigue loading Estimation of the nominal stress amplitude A Experimental strain amplitude measurement (in the point A): CTU in Prague, Faculty of Mechanical Engineering DAF Page 19
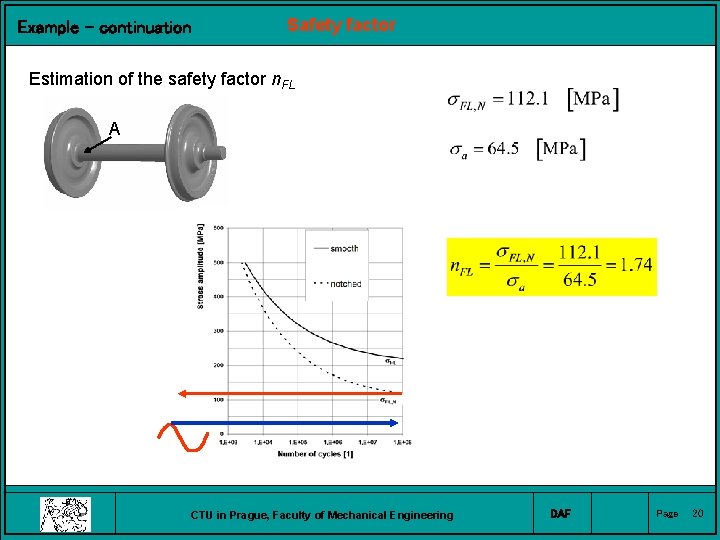
Example – continuation Safety factor Estimation of the safety factor n. FL A CTU in Prague, Faculty of Mechanical Engineering DAF Page 20
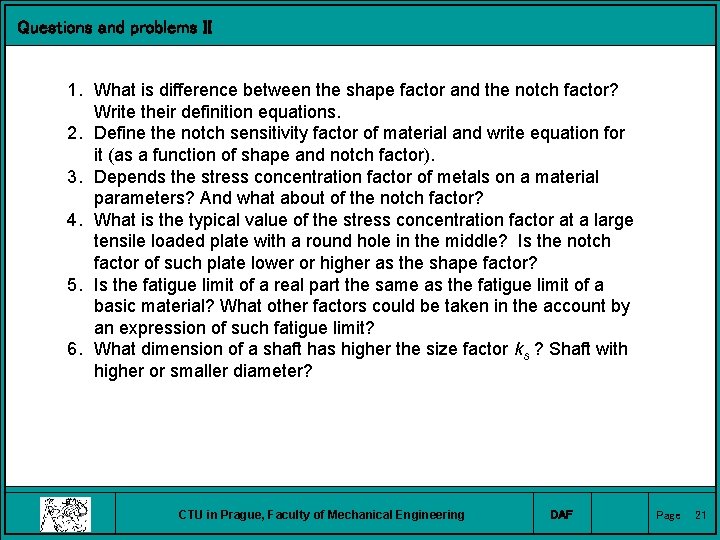
Questions and problems II 1. What is difference between the shape factor and the notch factor? Write their definition equations. 2. Define the notch sensitivity factor of material and write equation for it (as a function of shape and notch factor). 3. Depends the stress concentration factor of metals on a material parameters? And what about of the notch factor? 4. What is the typical value of the stress concentration factor at a large tensile loaded plate with a round hole in the middle? Is the notch factor of such plate lower or higher as the shape factor? 5. Is the fatigue limit of a real part the same as the fatigue limit of a basic material? What other factors could be taken in the account by an expression of such fatigue limit? 6. What dimension of a shaft has higher the size factor ks ? Shaft with higher or smaller diameter? CTU in Prague, Faculty of Mechanical Engineering DAF Page 21
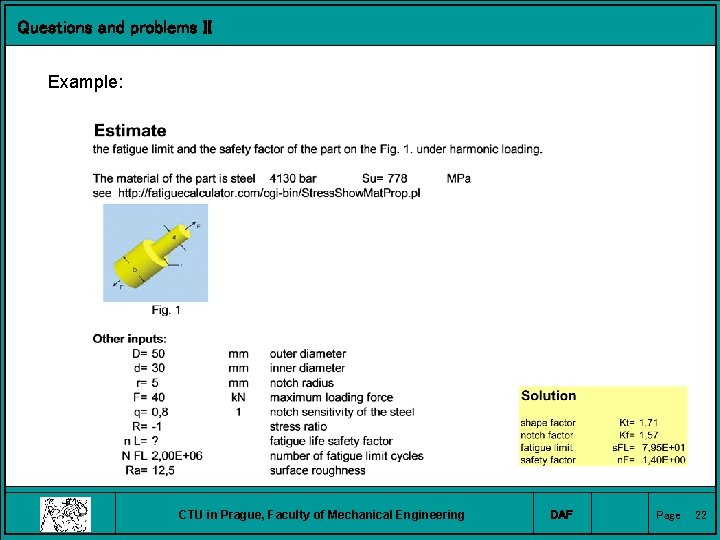
Questions and problems II Example: CTU in Prague, Faculty of Mechanical Engineering DAF Page 22
Efatigue stress concentration factor
Concentration gradient
Movement of high concentration to low concentration
Stress concentration
Stress concentration
7kt tube
True strain formula
Normal stress vs axial stress
Chapter 10 stress responses and stress management
Aerofoil shapes
Shape matching and object recognition using shape contexts
Template matching
What factors shape the climate in canada
Shape
Situation vs site factors
Is wood biotic or abiotic
Abiotic vs biotic factors
Aboitic environment
Is mud abiotic or biotic
Site vs location
What are the factors of 8
Highest common factor
Factors of 8