QMS Eagle Quality Management System Op Ex Works
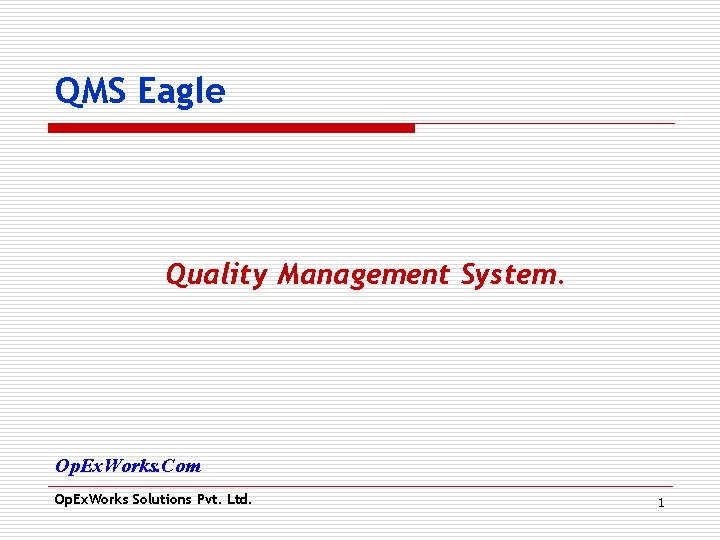
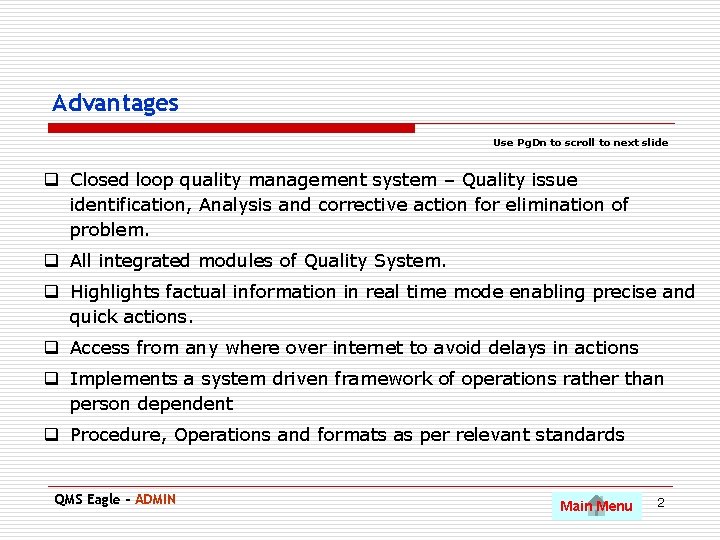
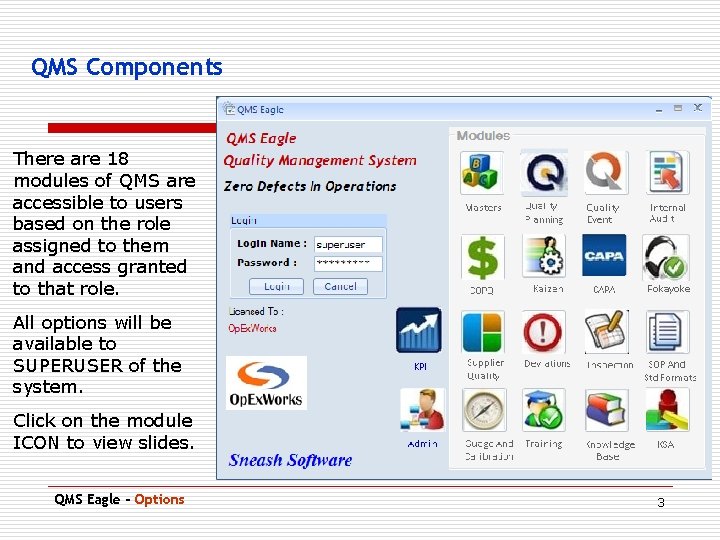
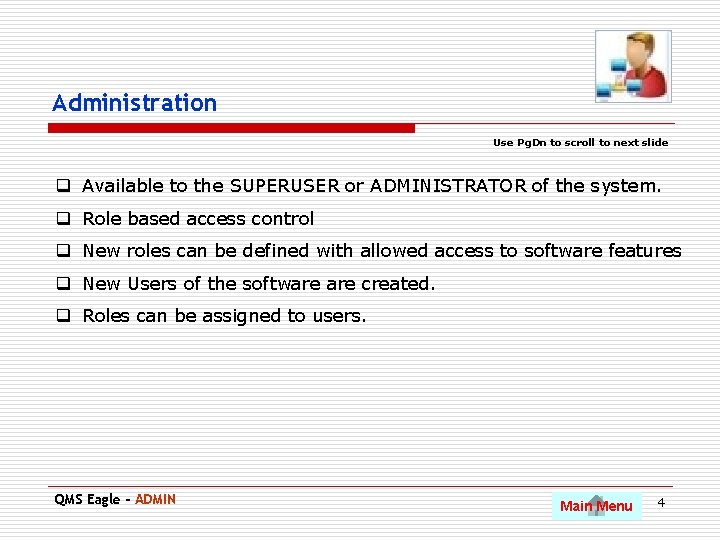
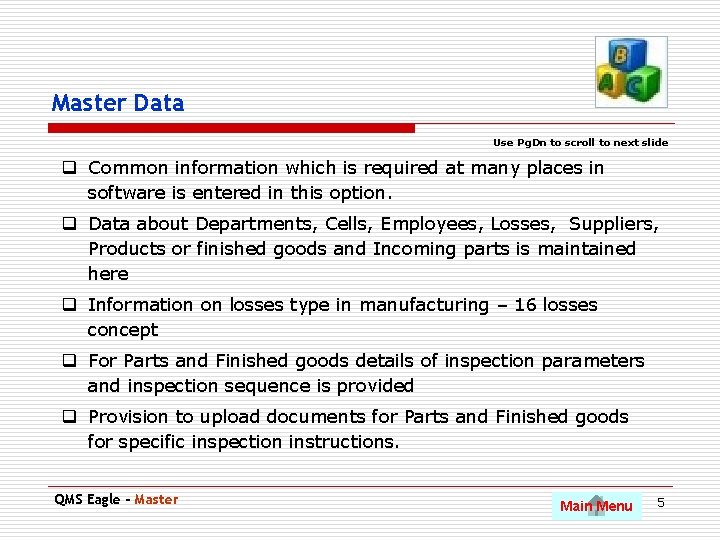
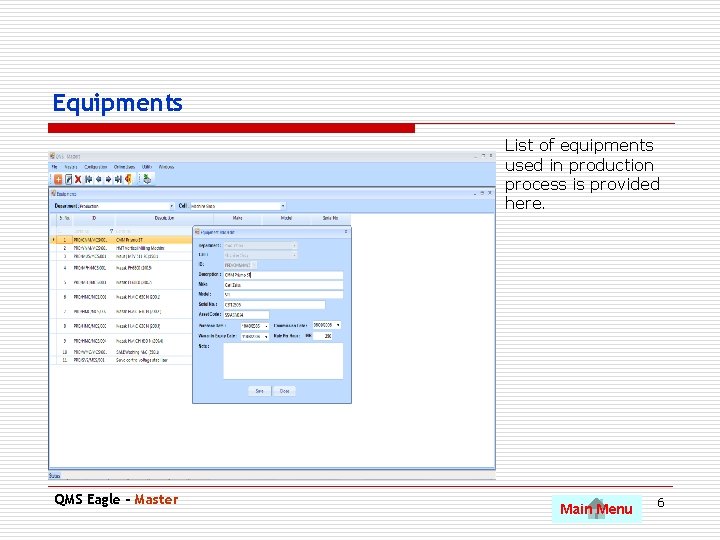
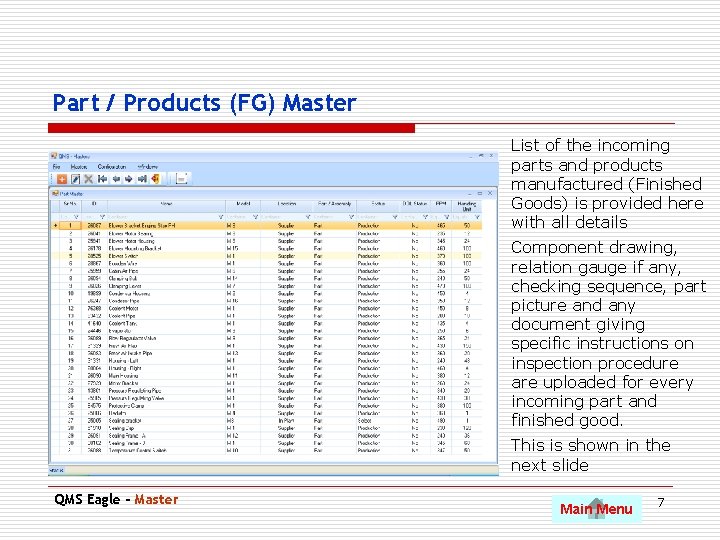
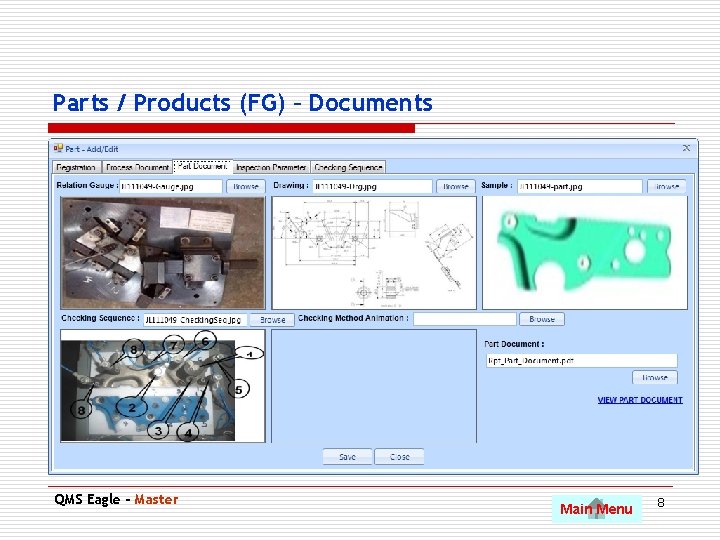
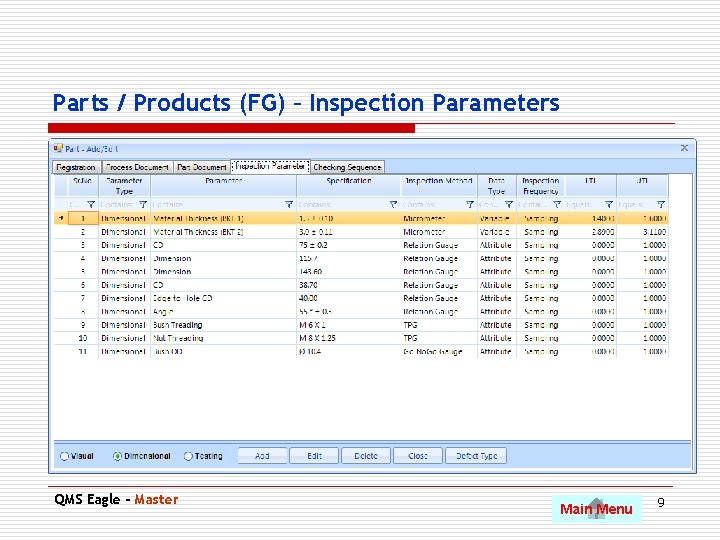
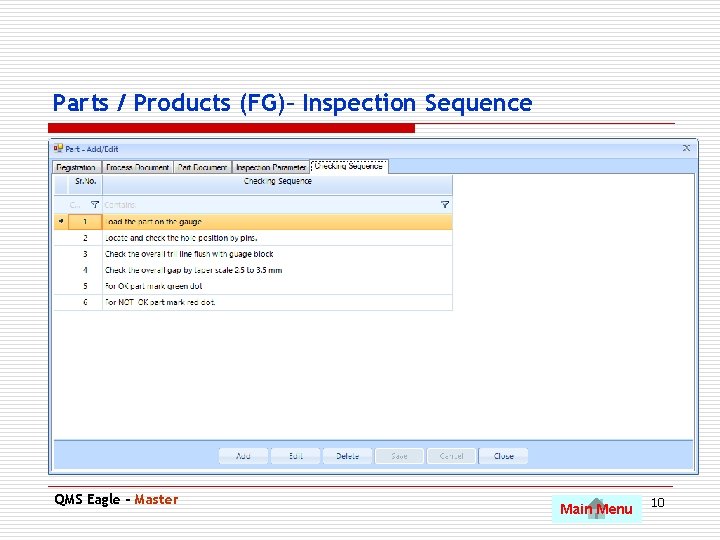
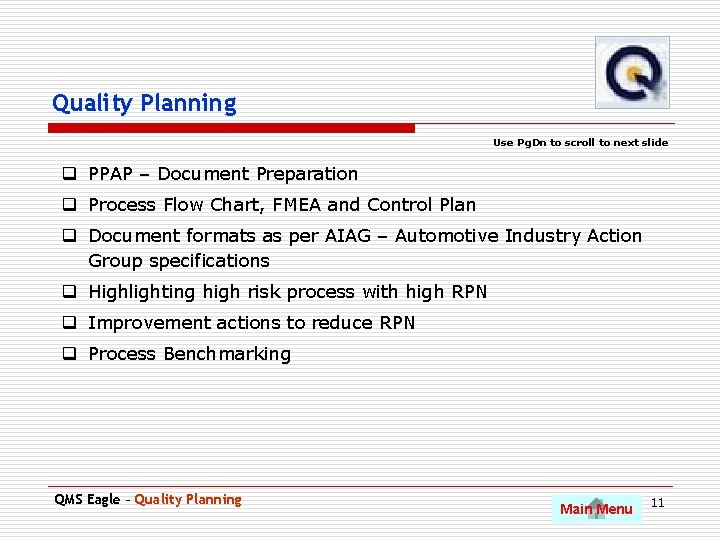
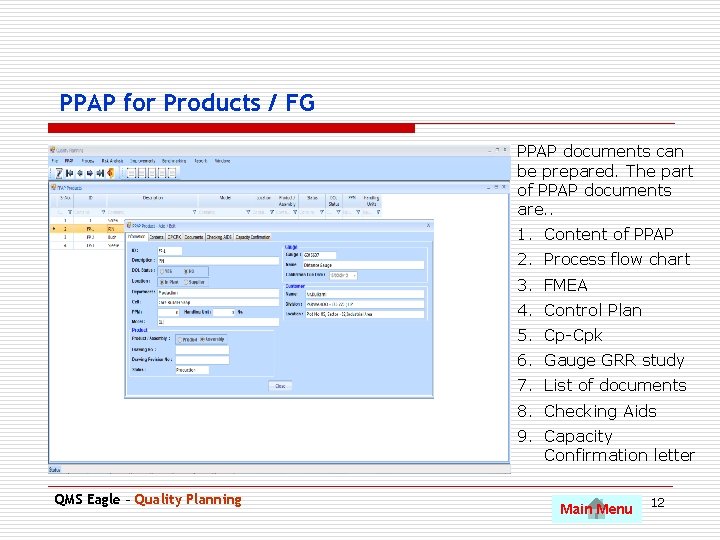
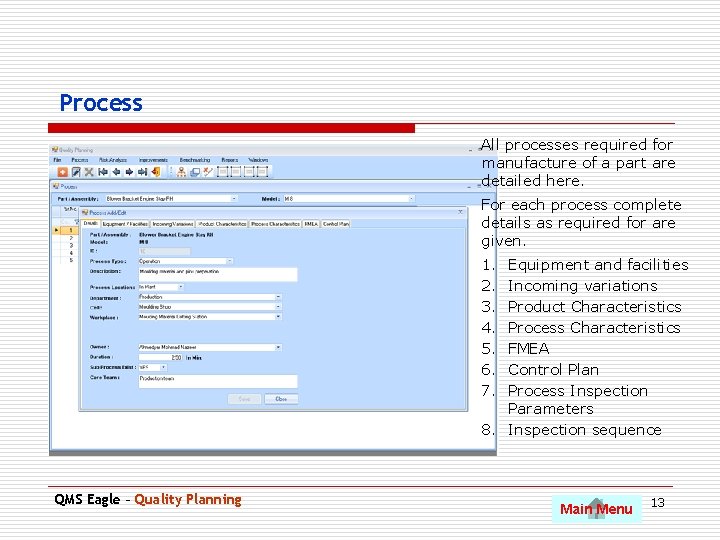
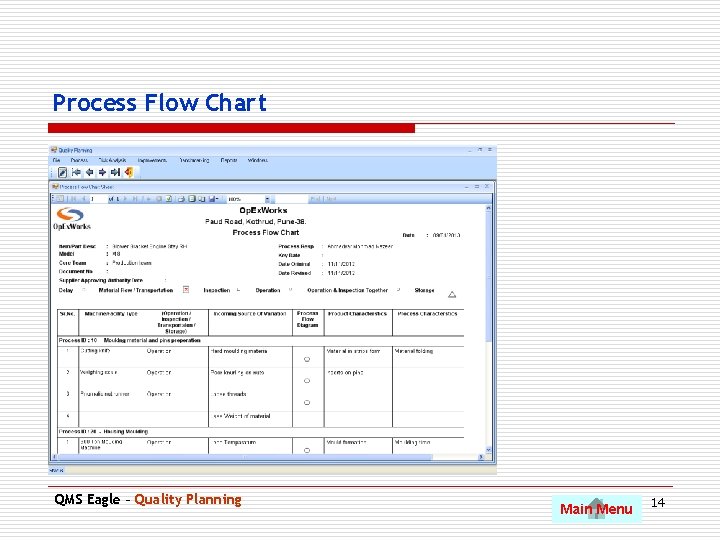
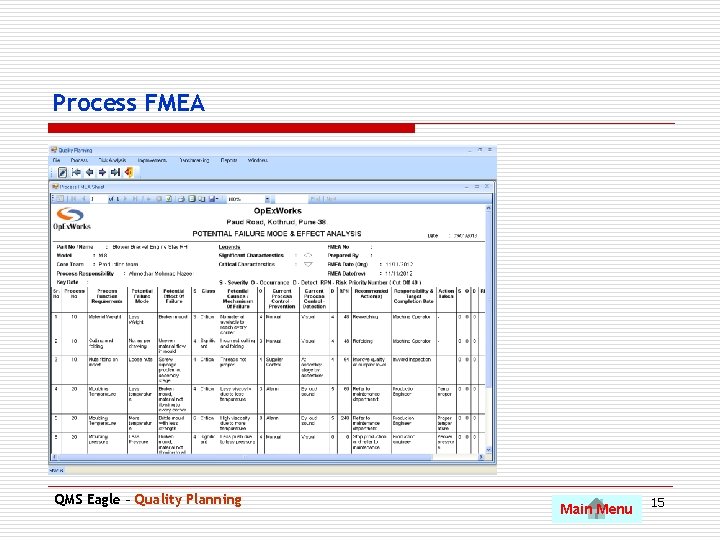
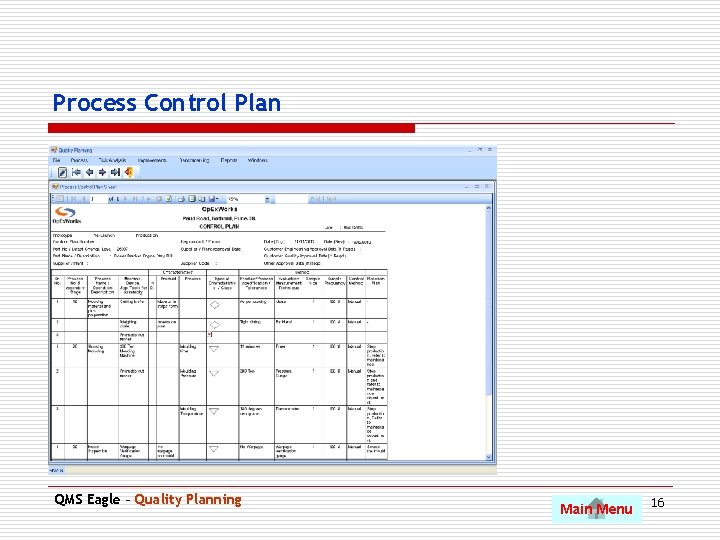
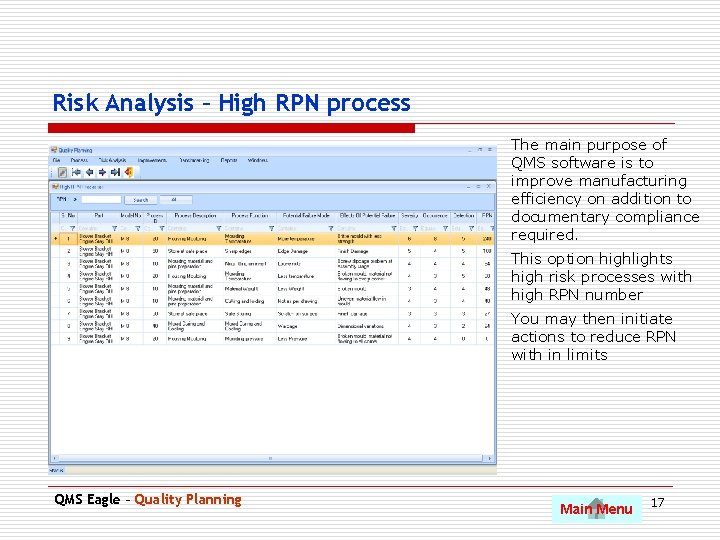
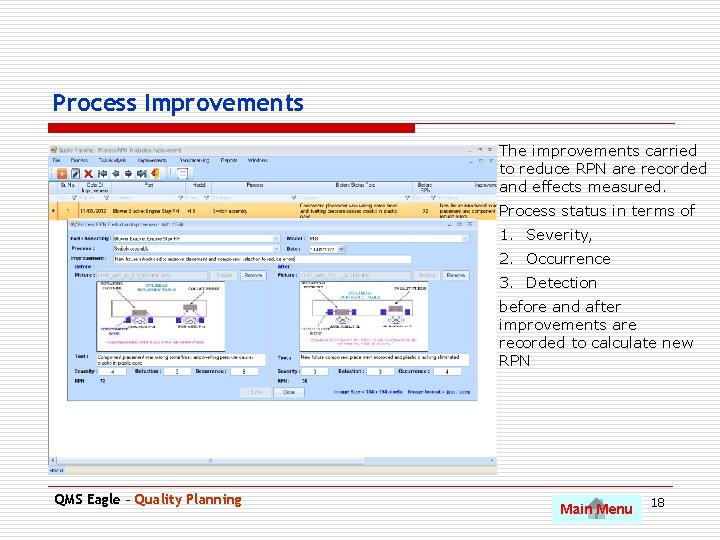
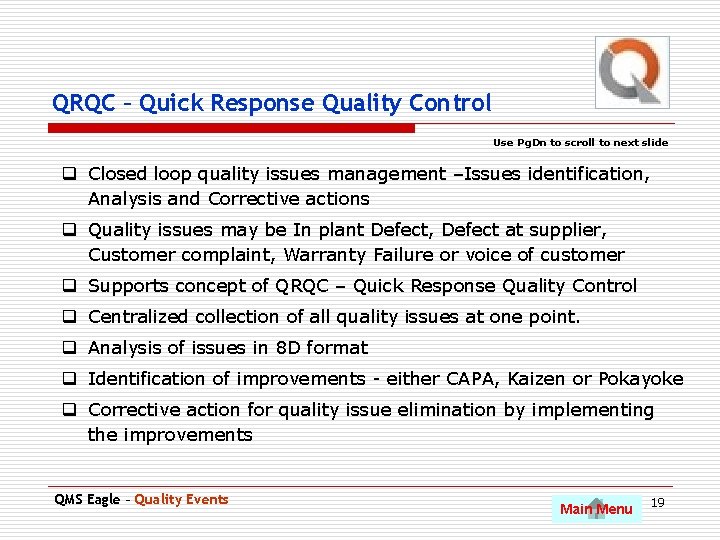
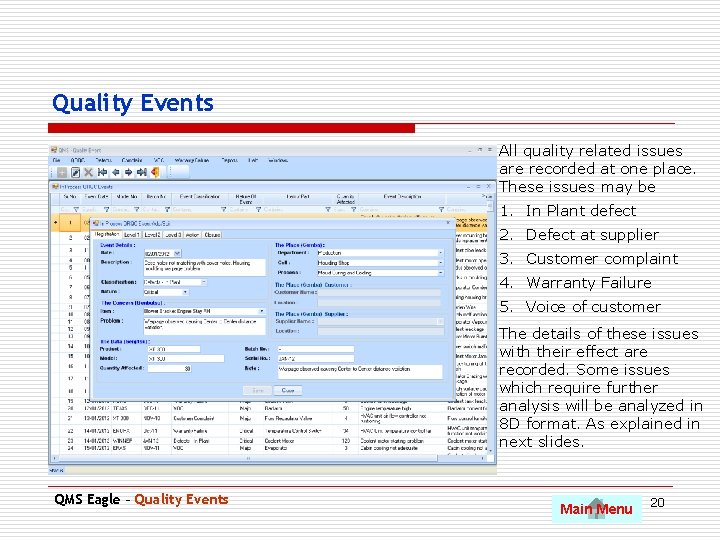
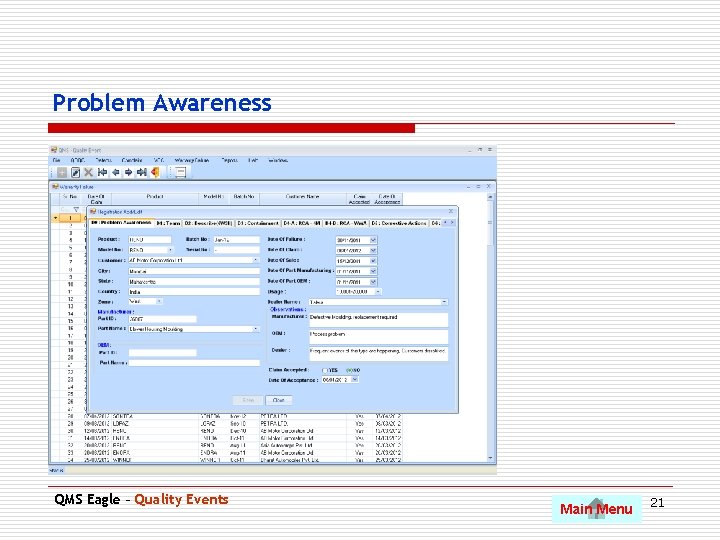
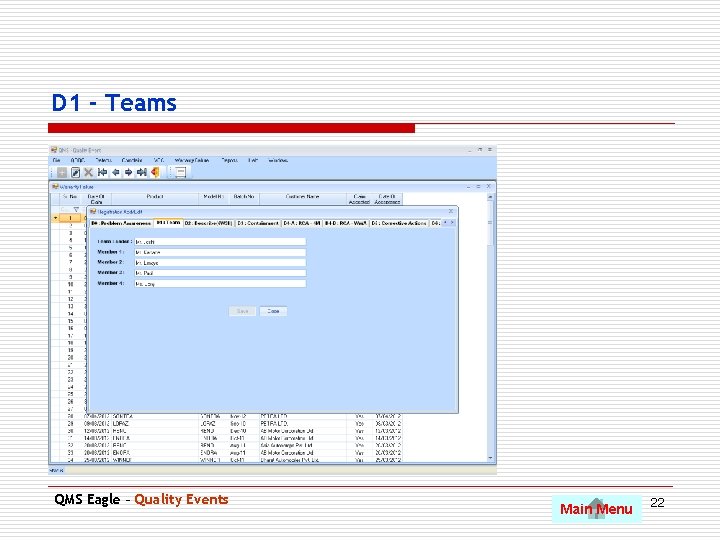
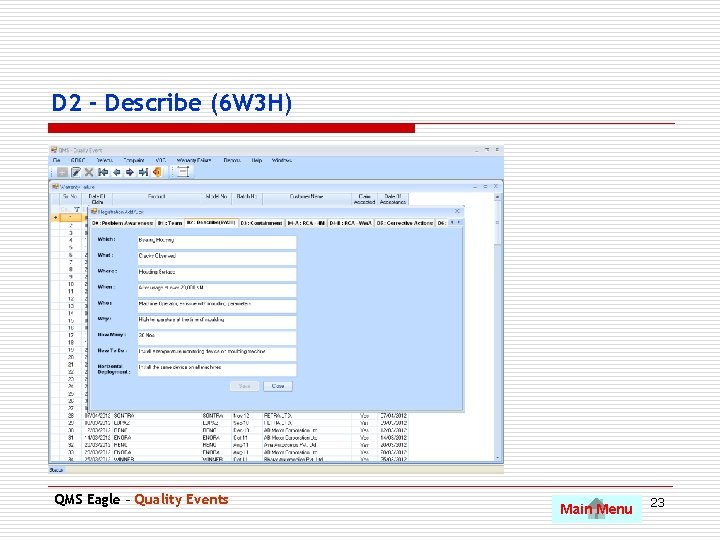
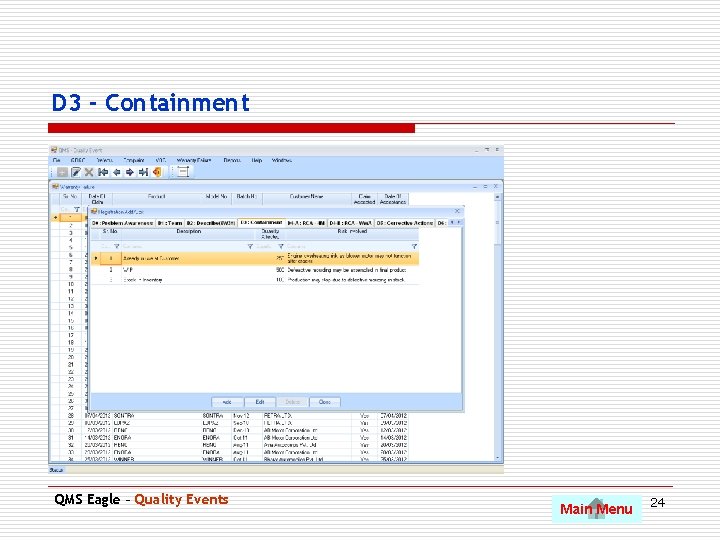
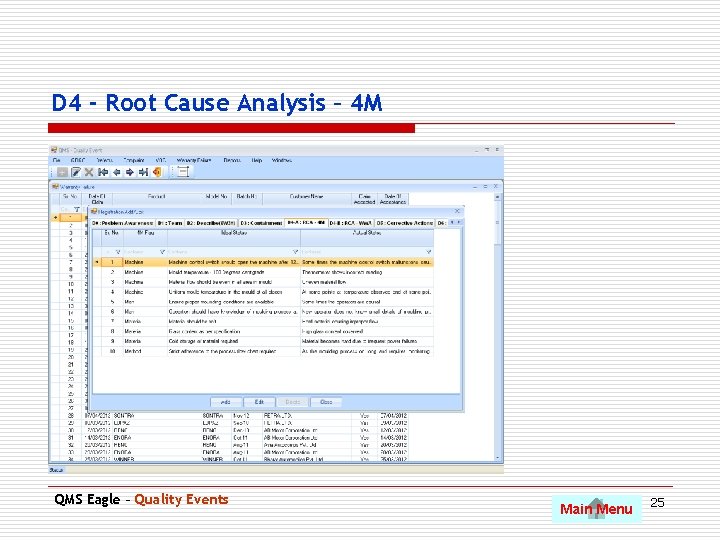
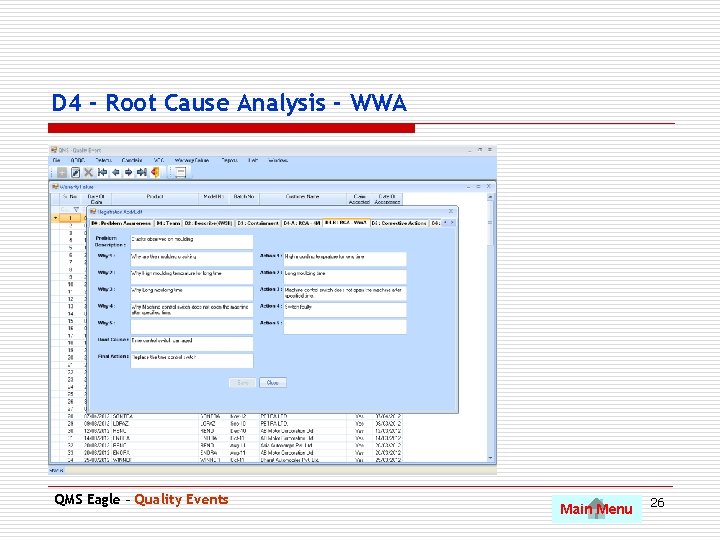
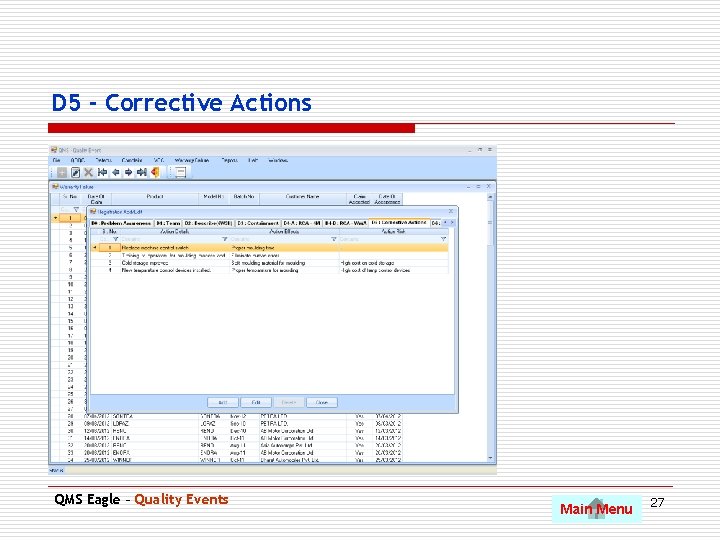
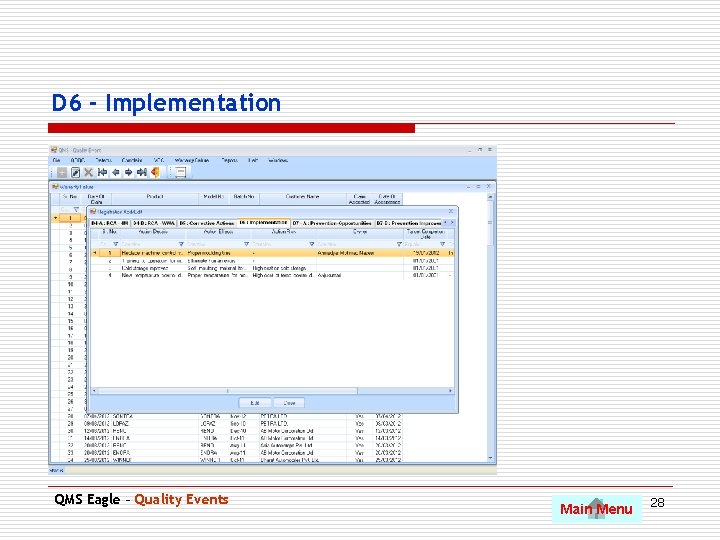
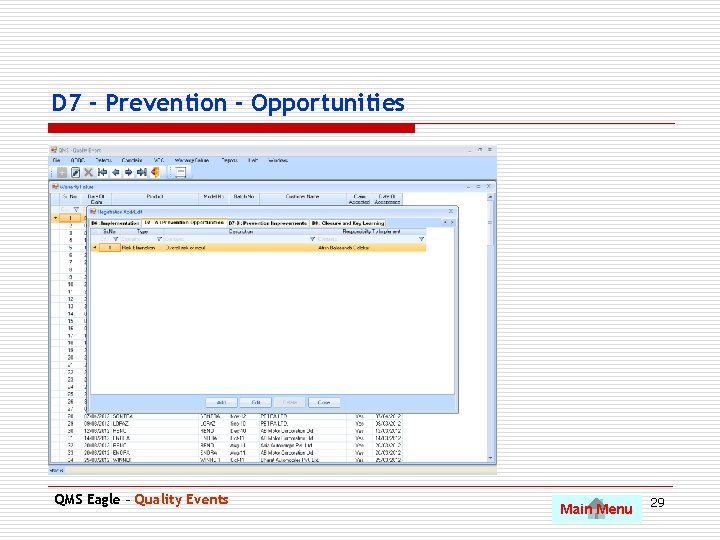
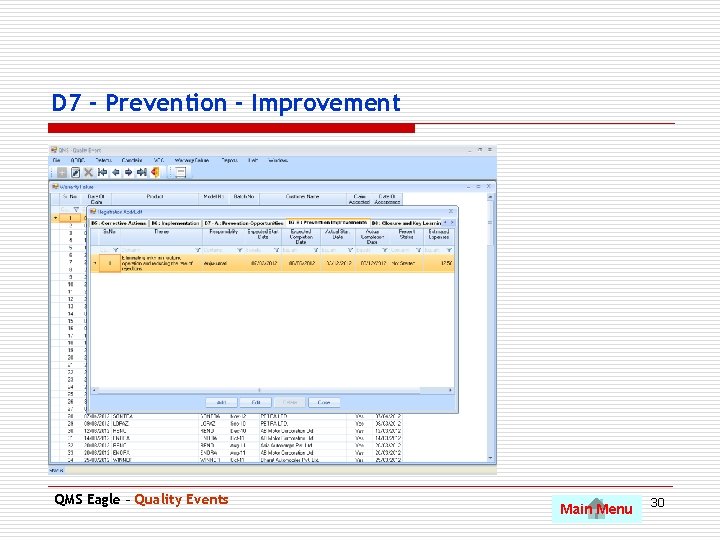

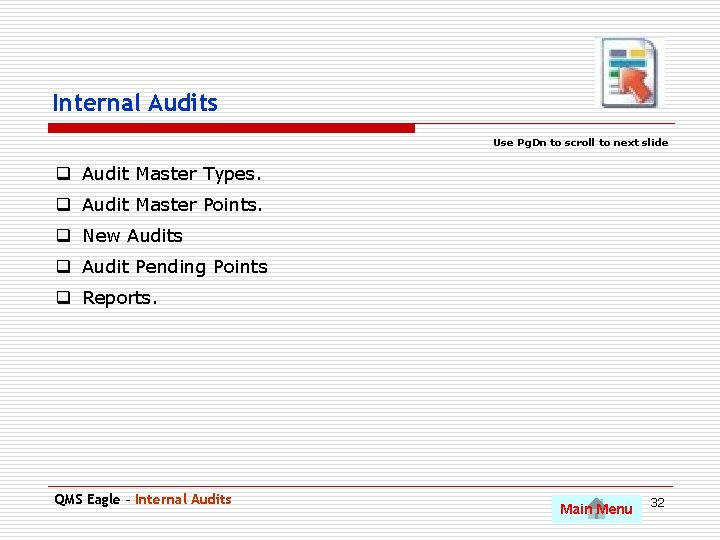
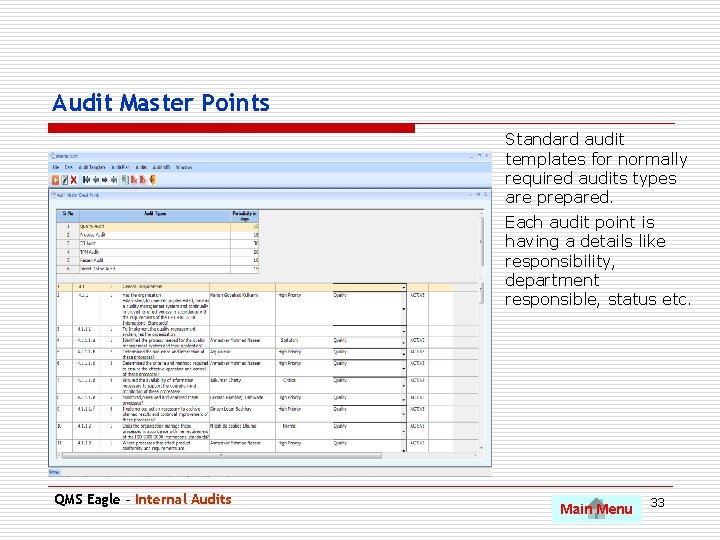
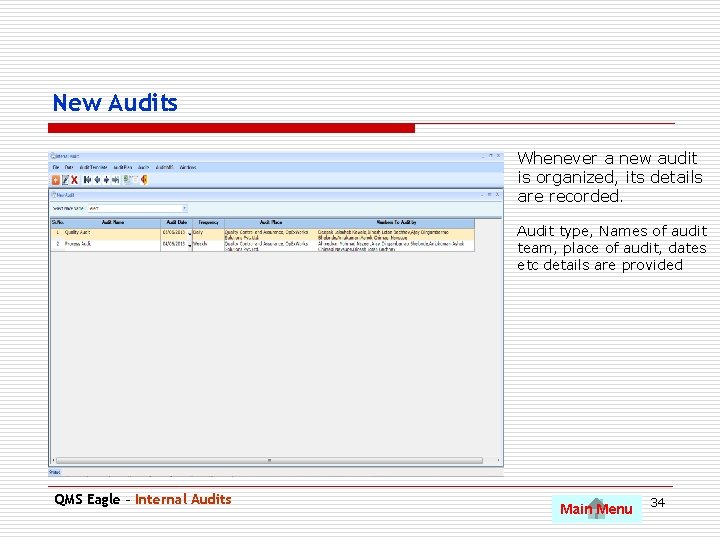
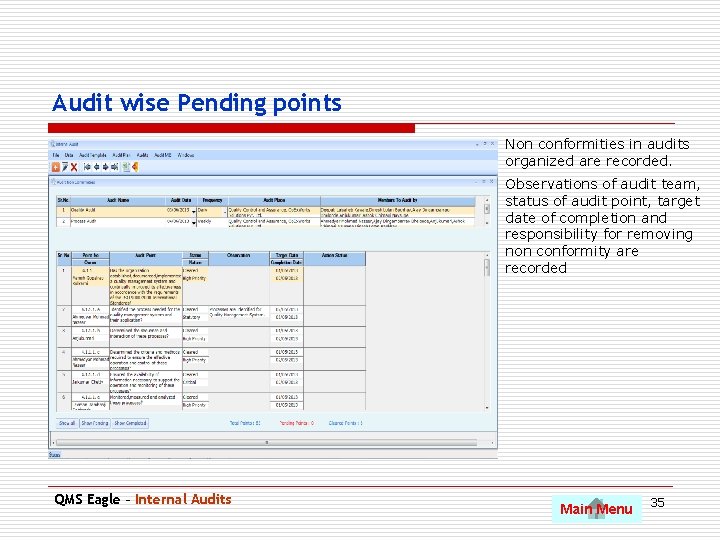
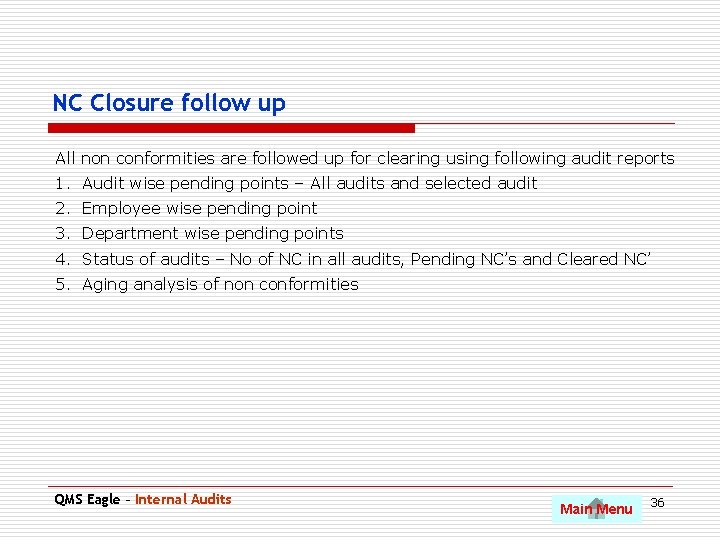
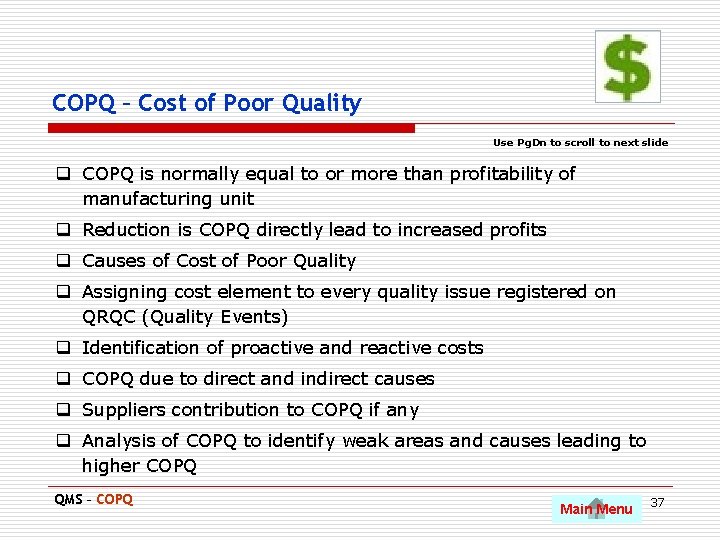
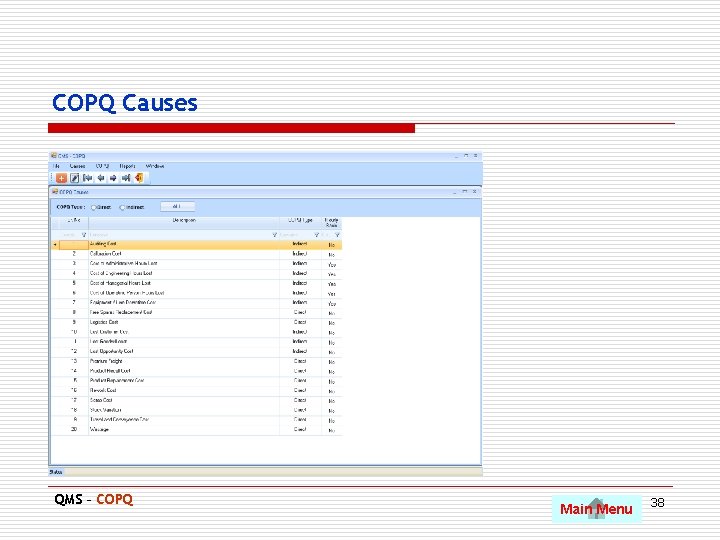
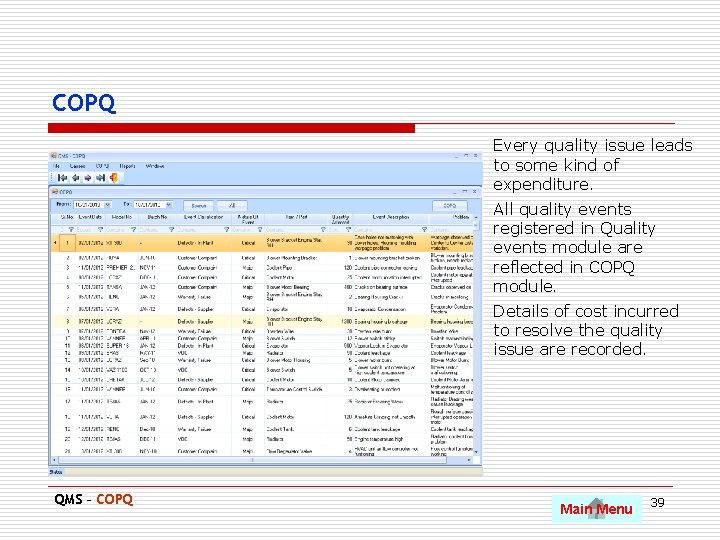
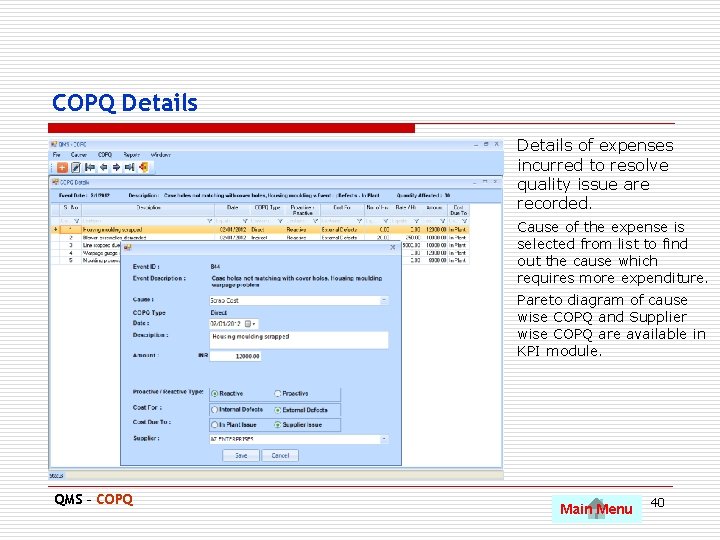
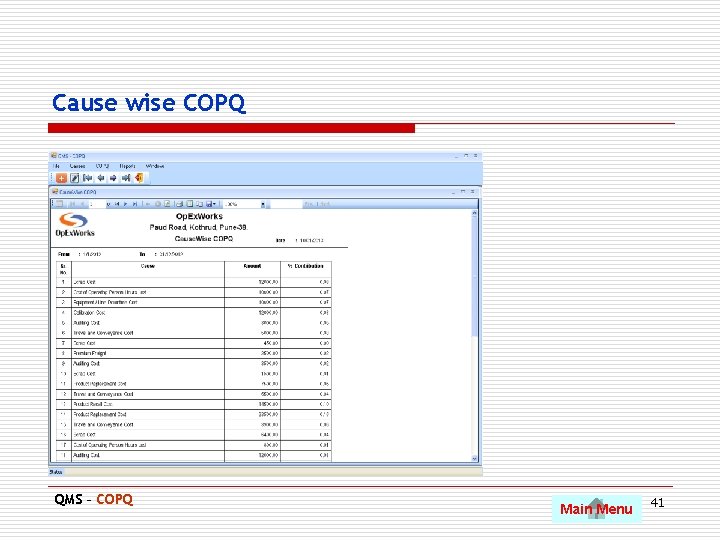
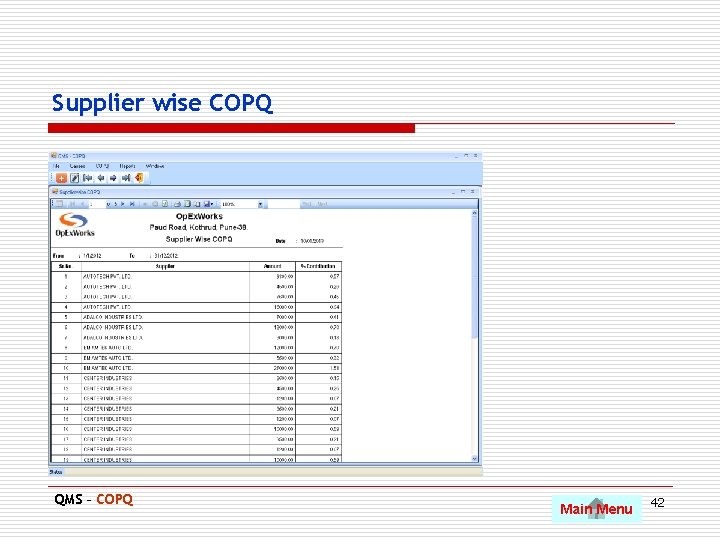
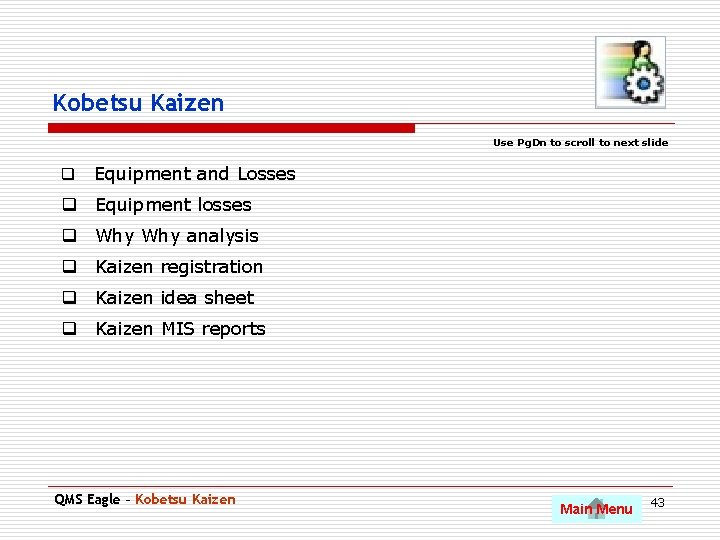
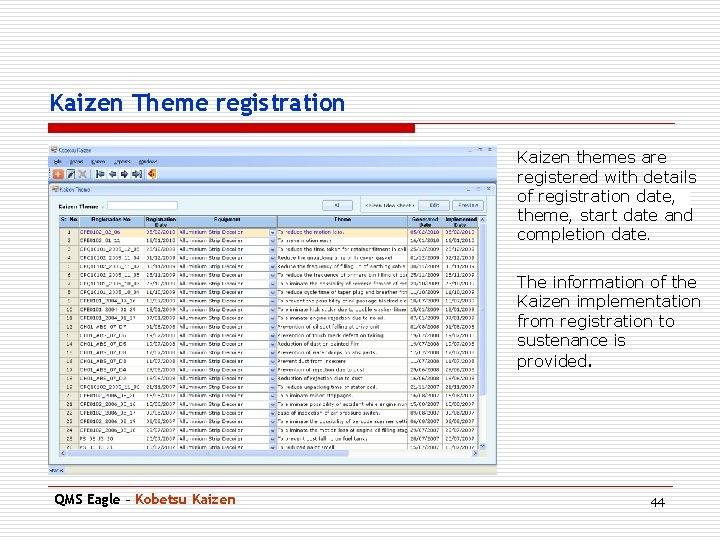
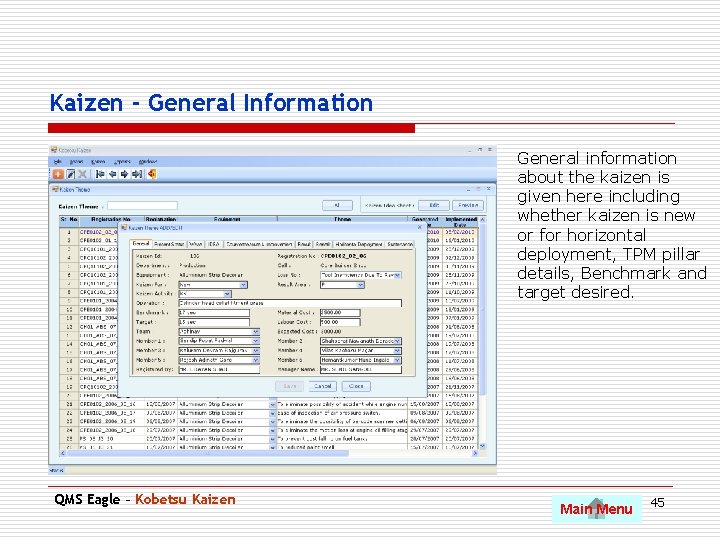
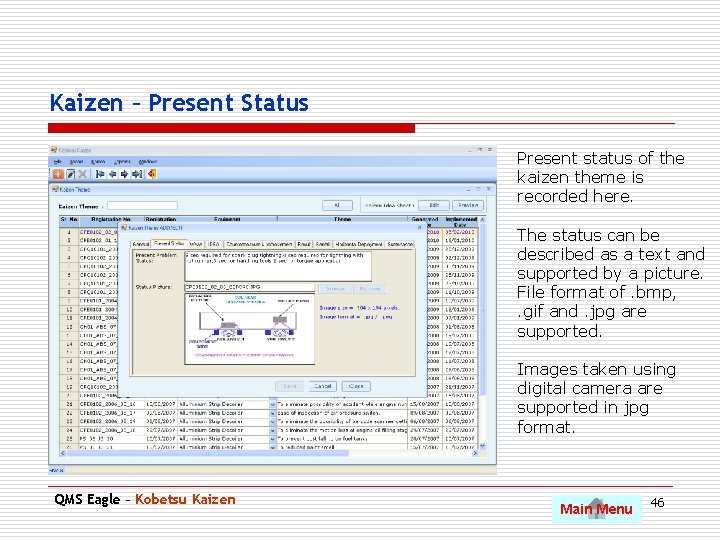
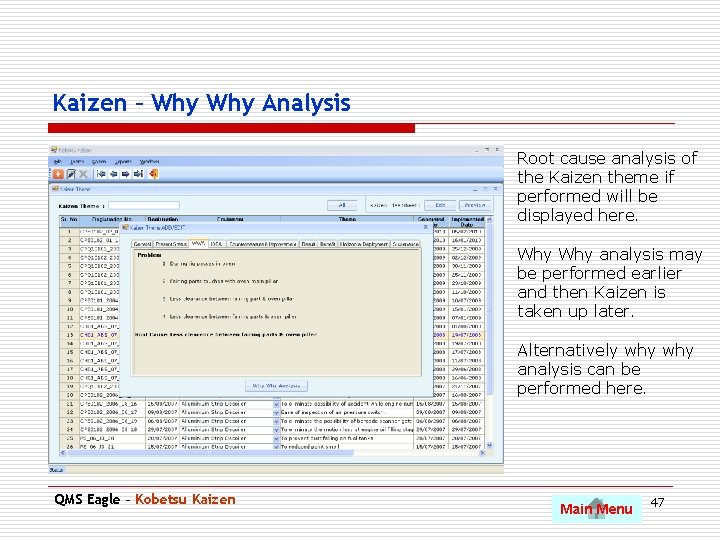
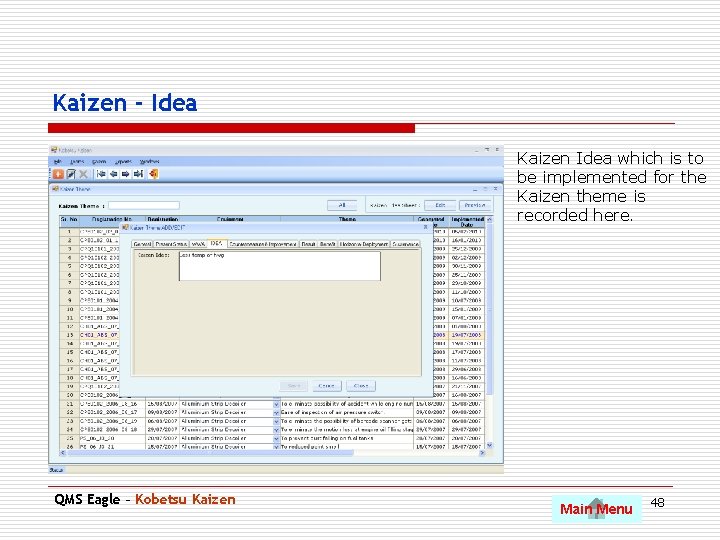
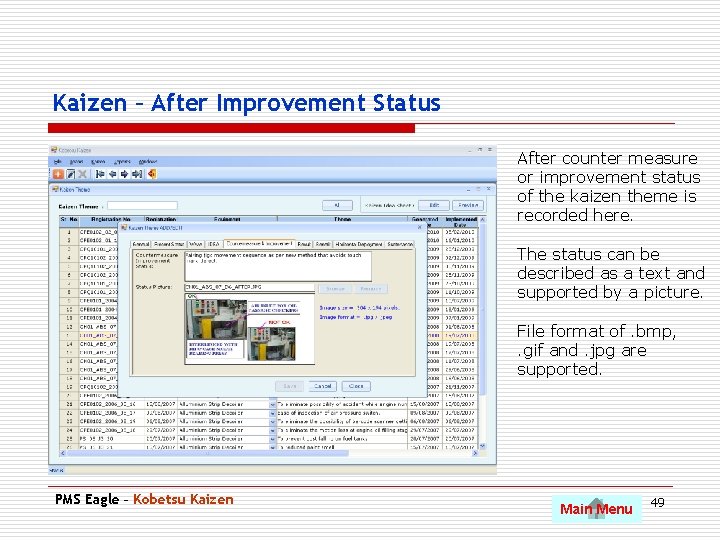
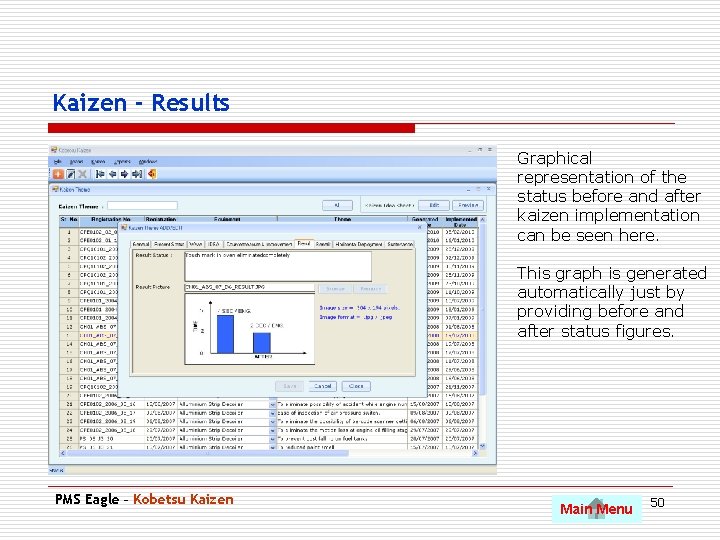
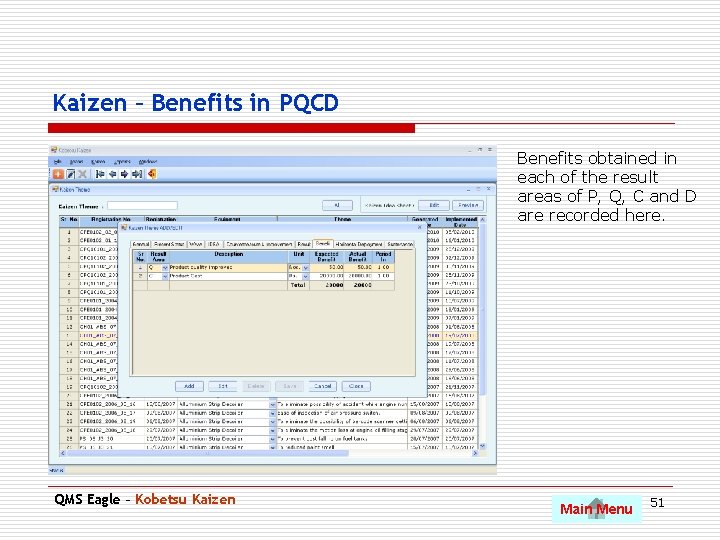
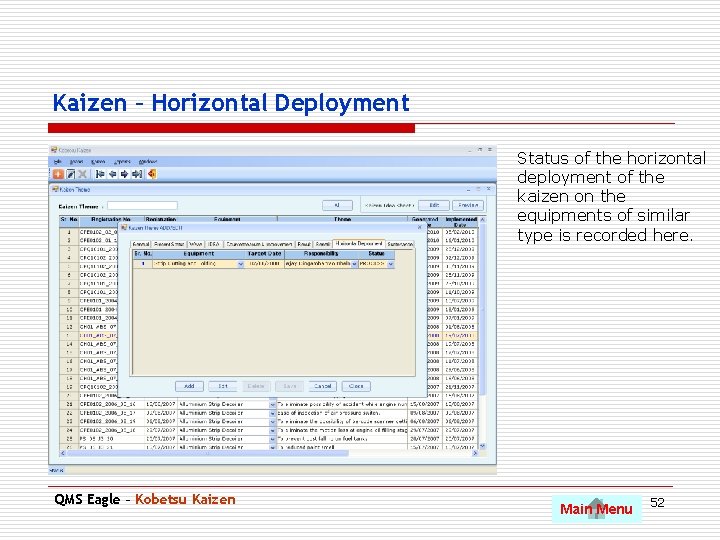
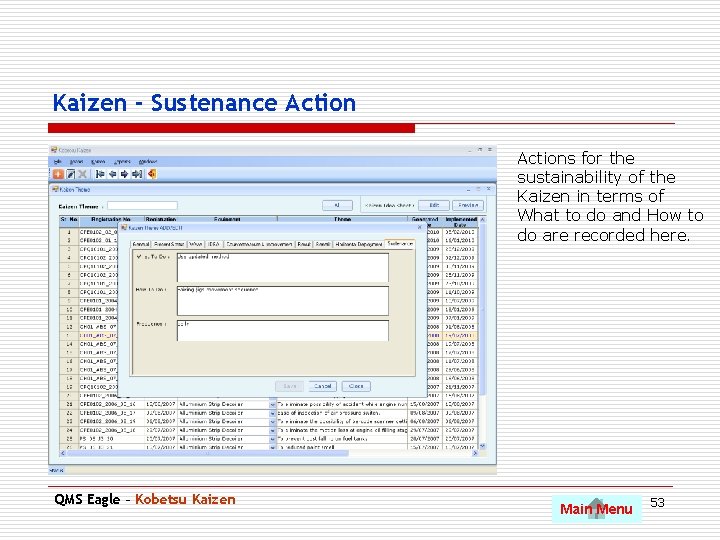
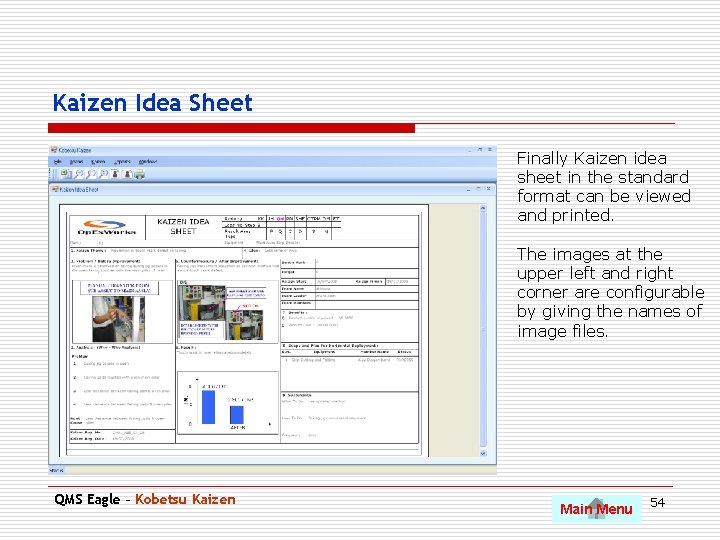
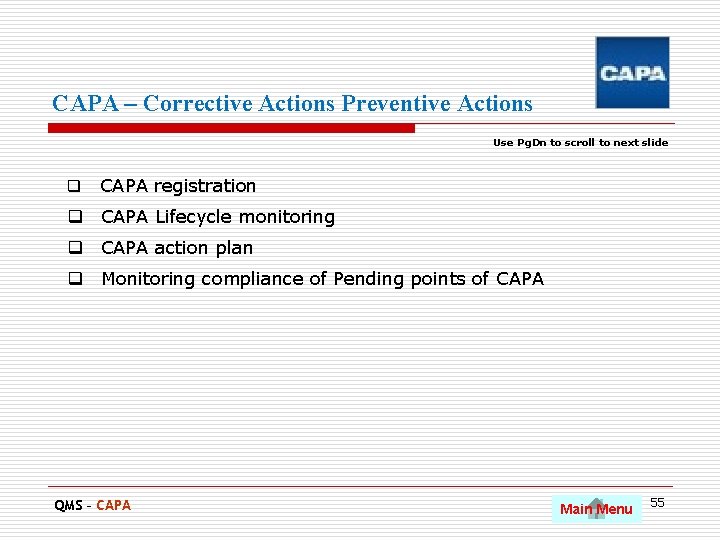
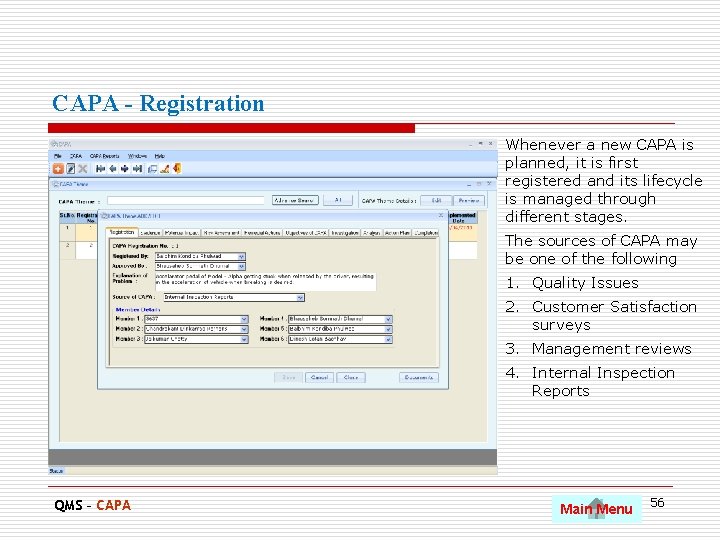
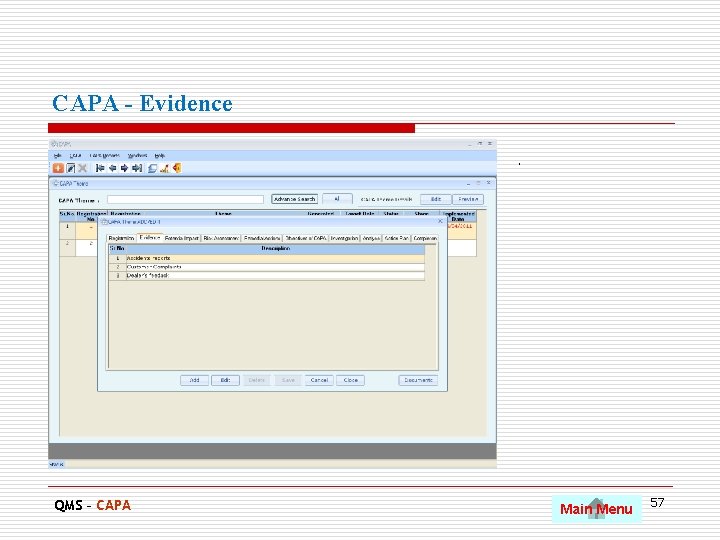
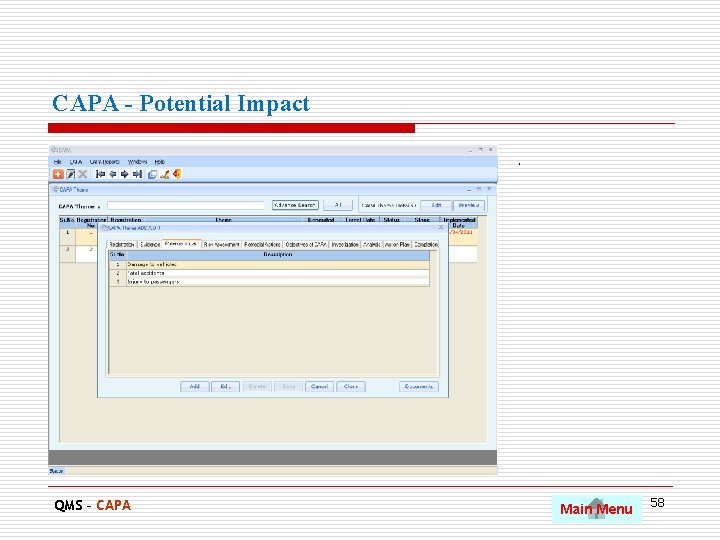
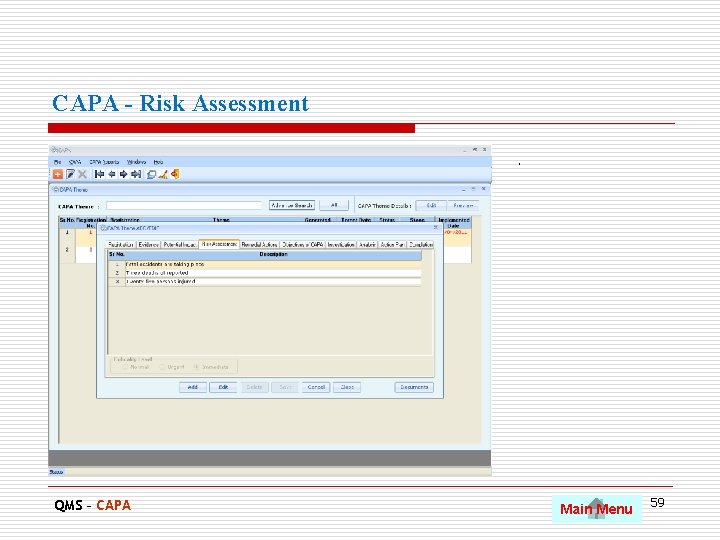
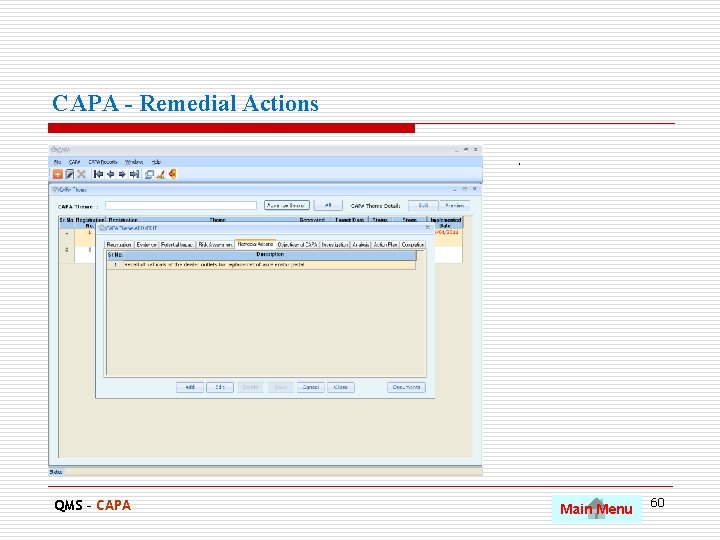
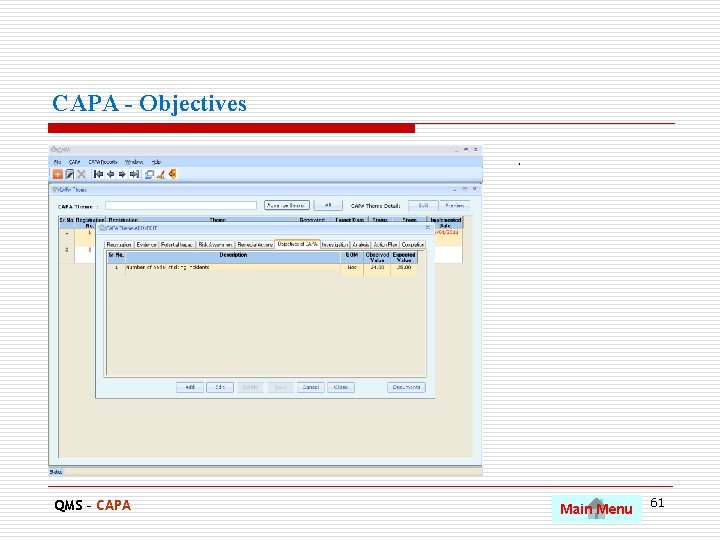
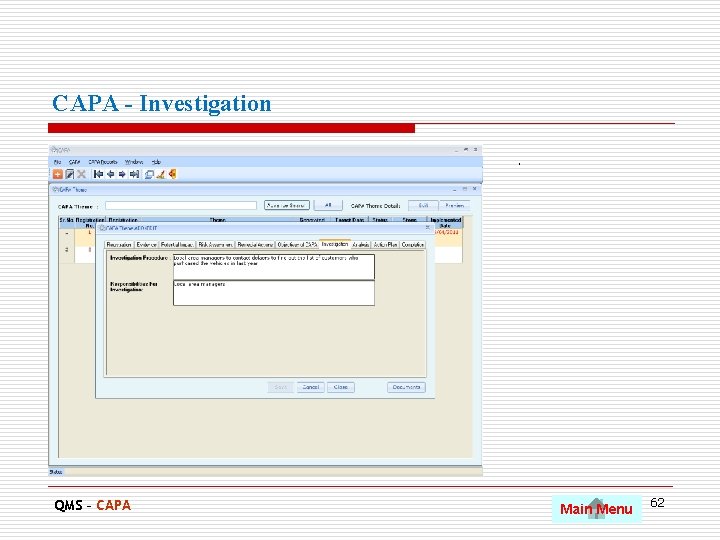
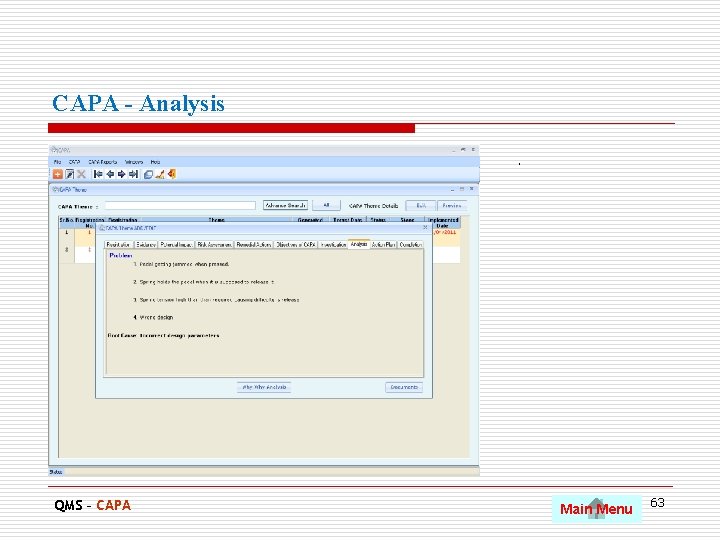
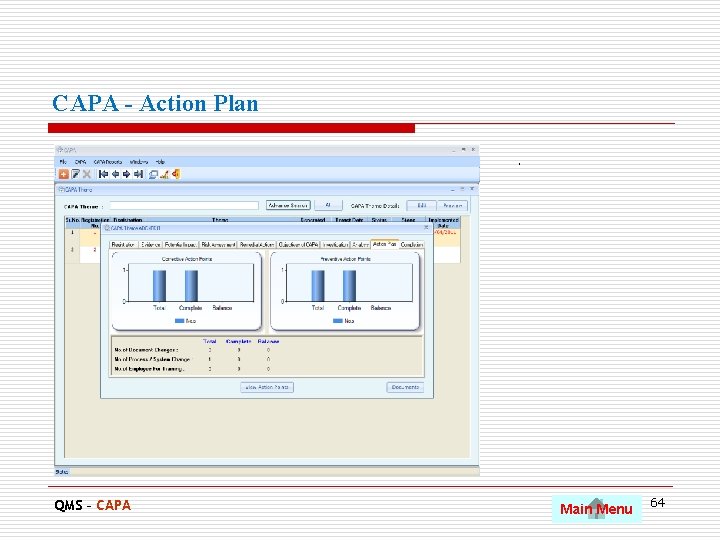
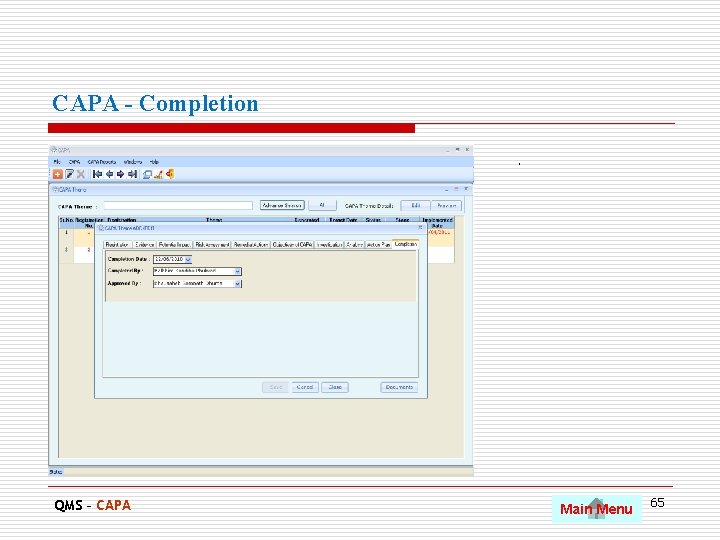
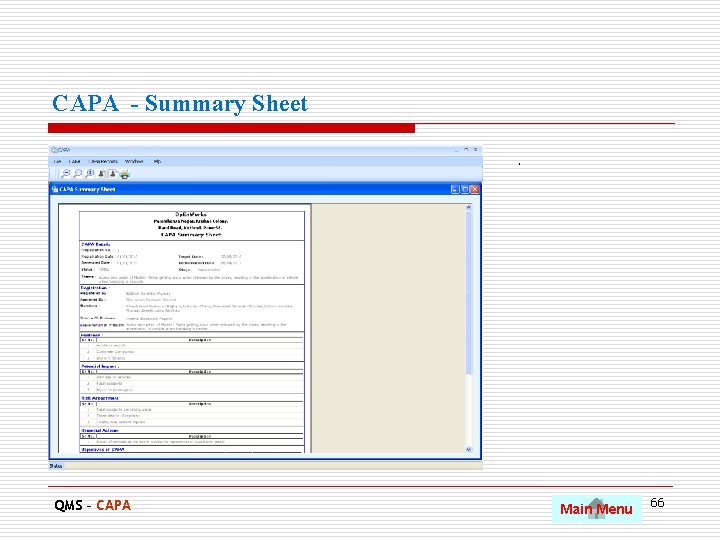
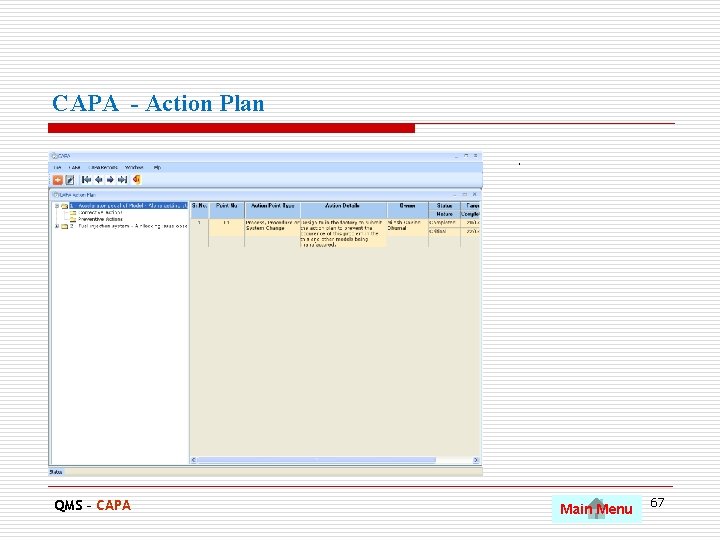
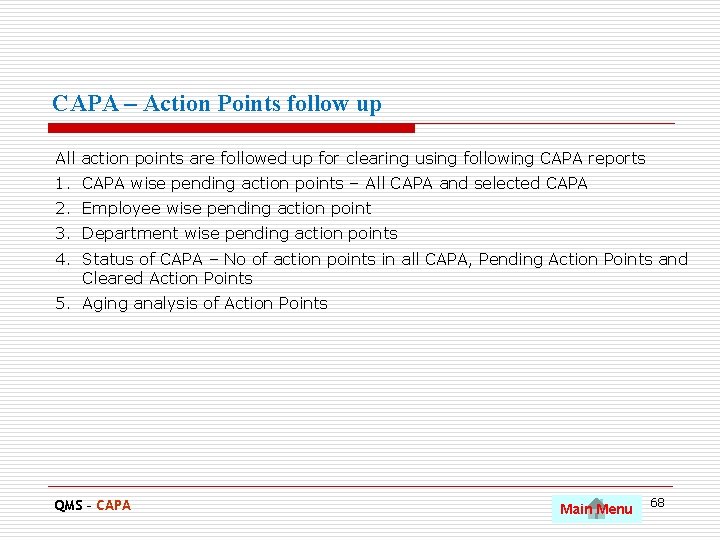
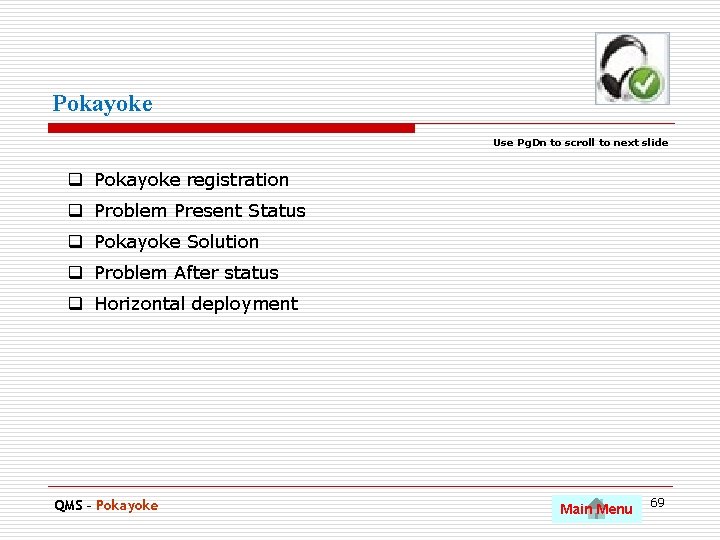
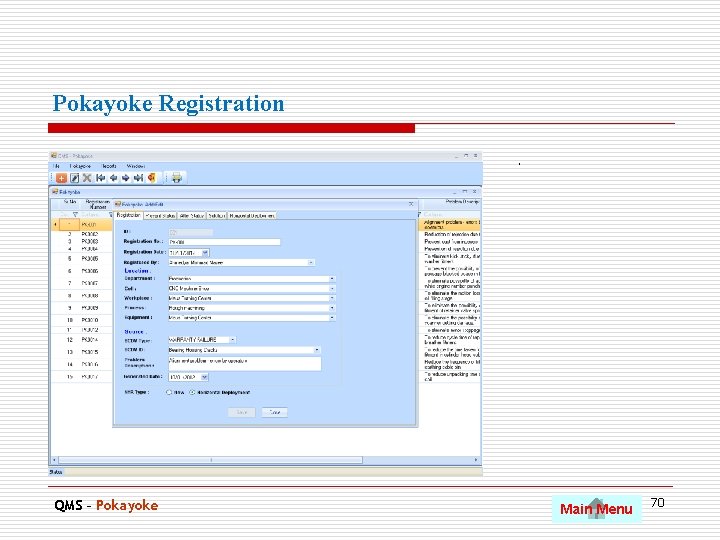

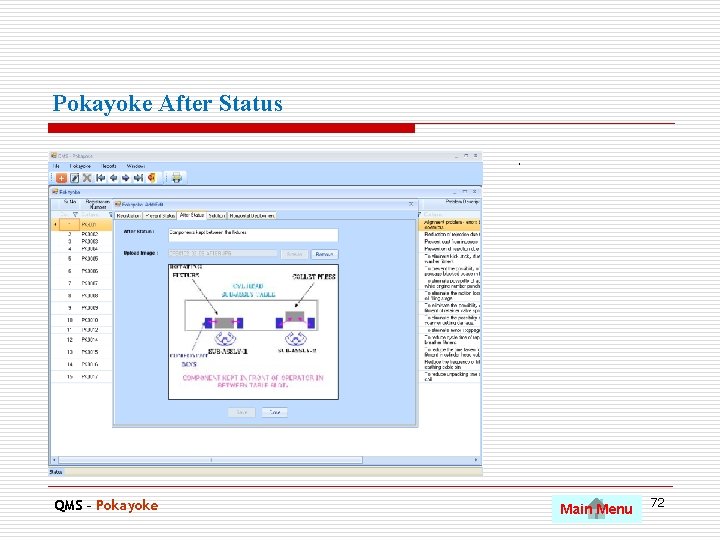
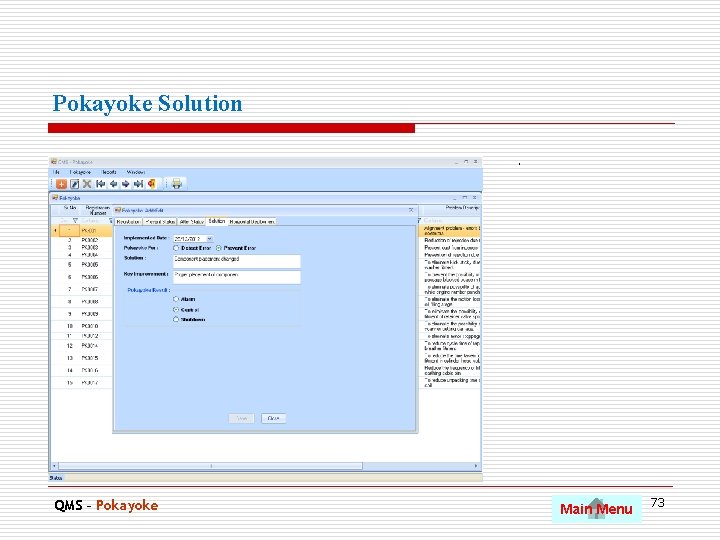
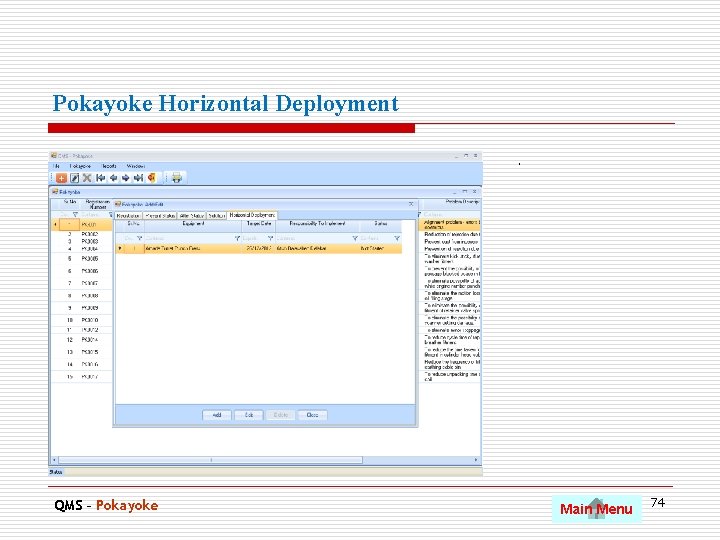
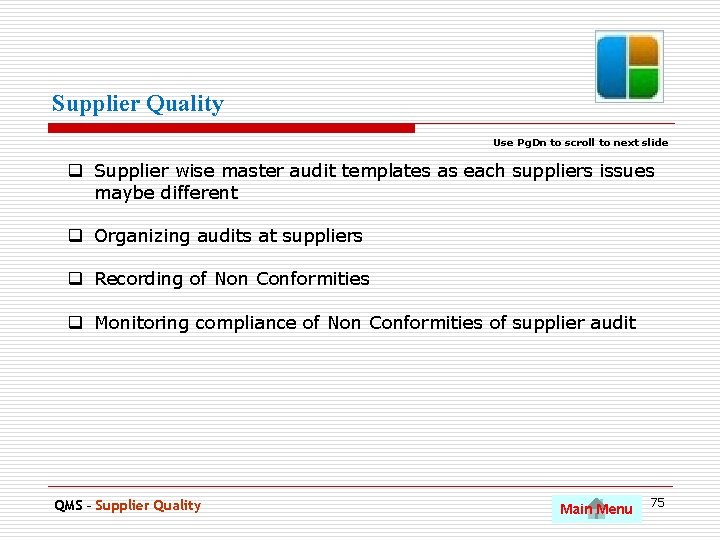
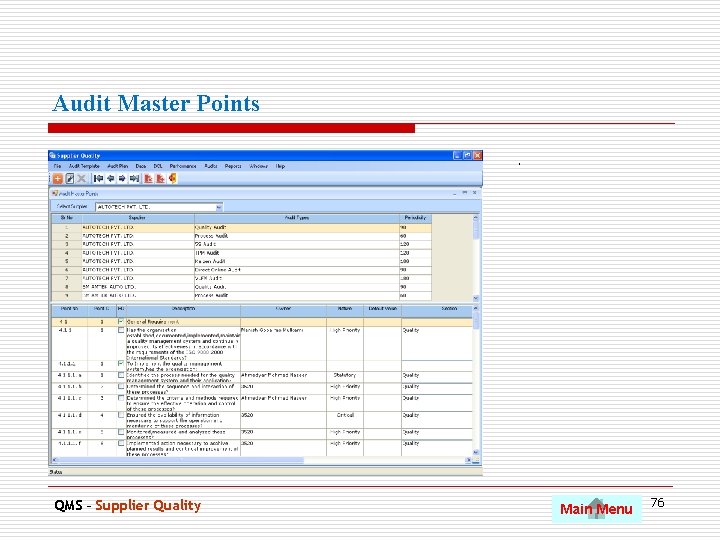
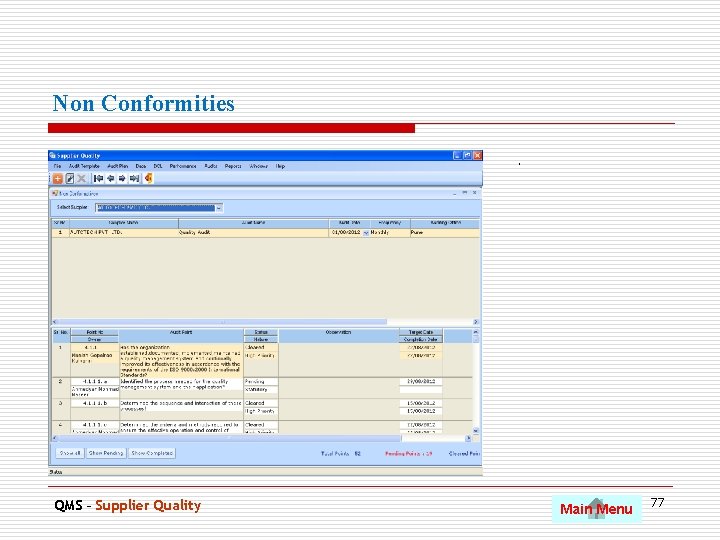
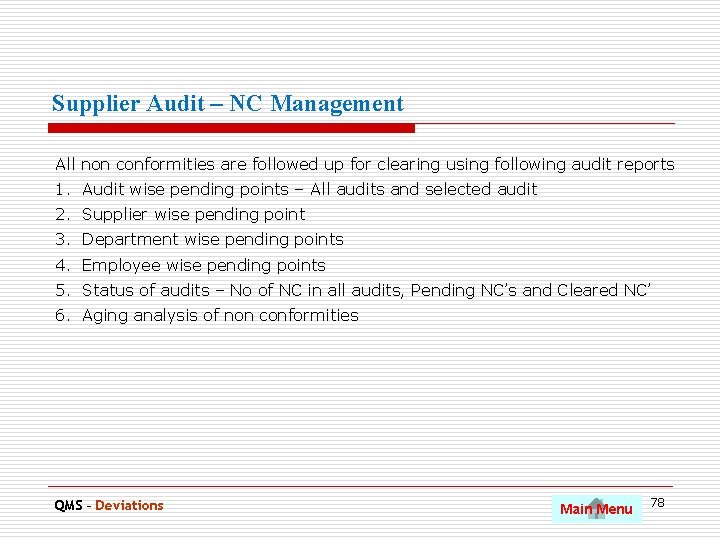
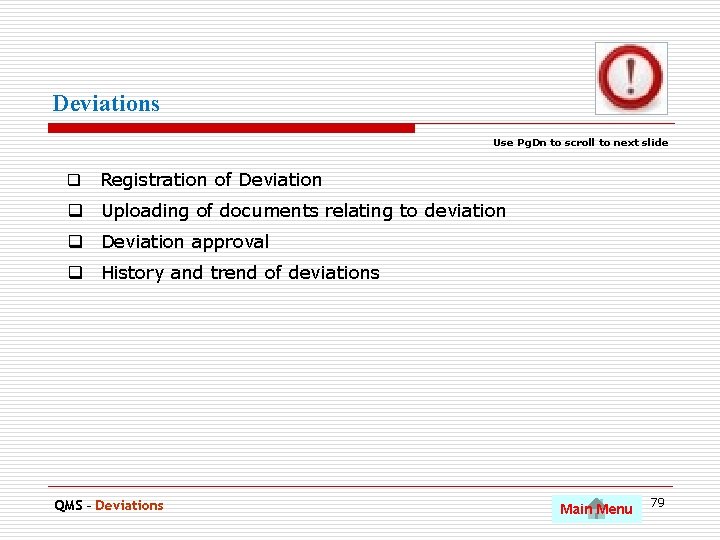
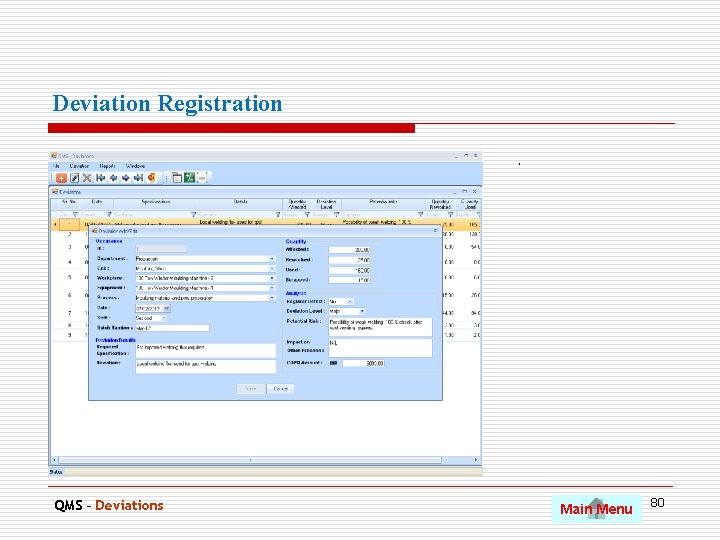
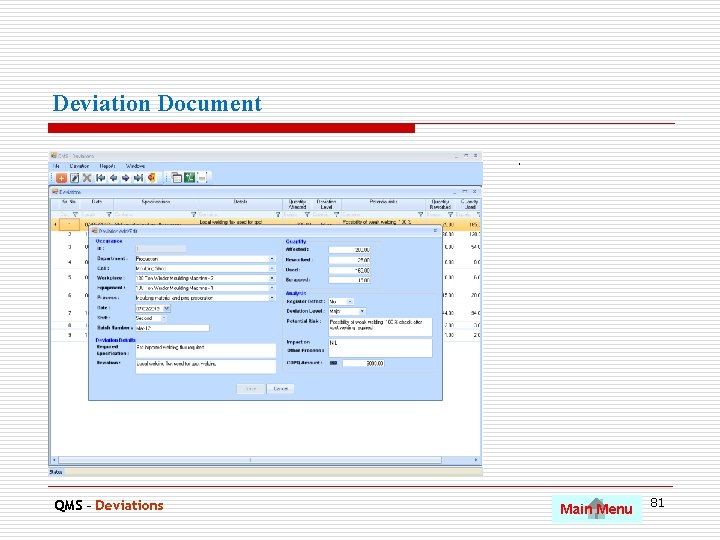
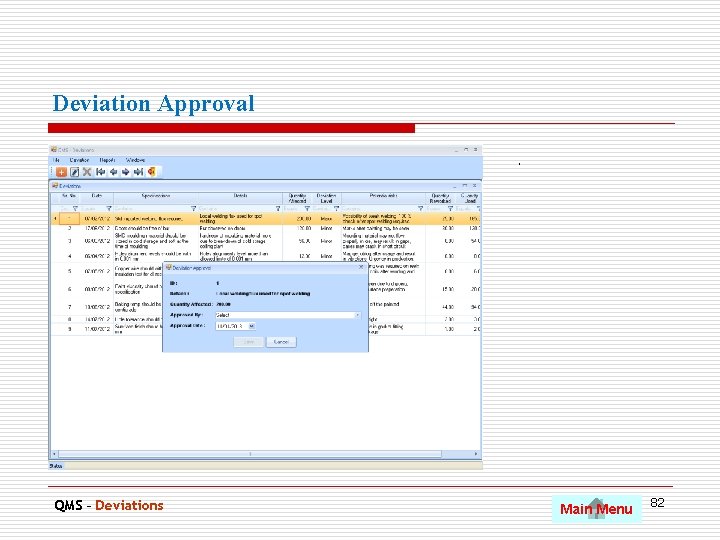
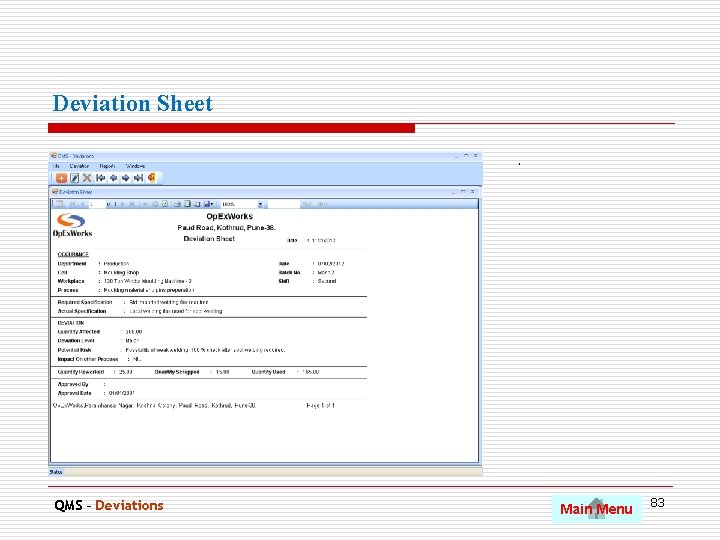

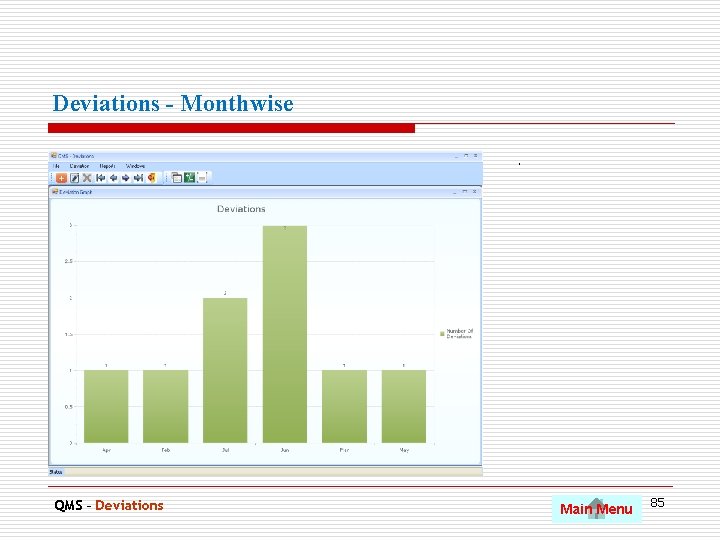
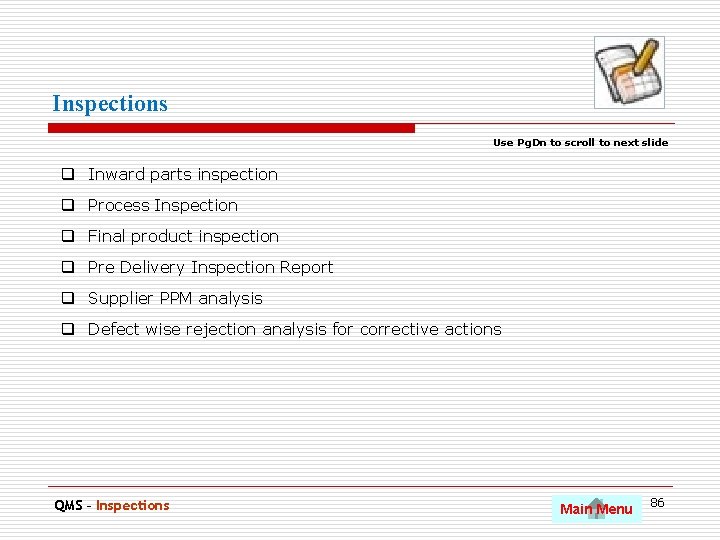
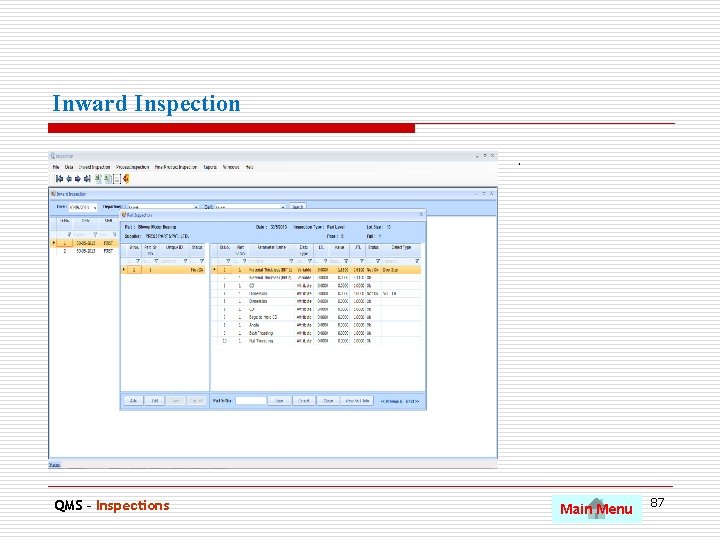
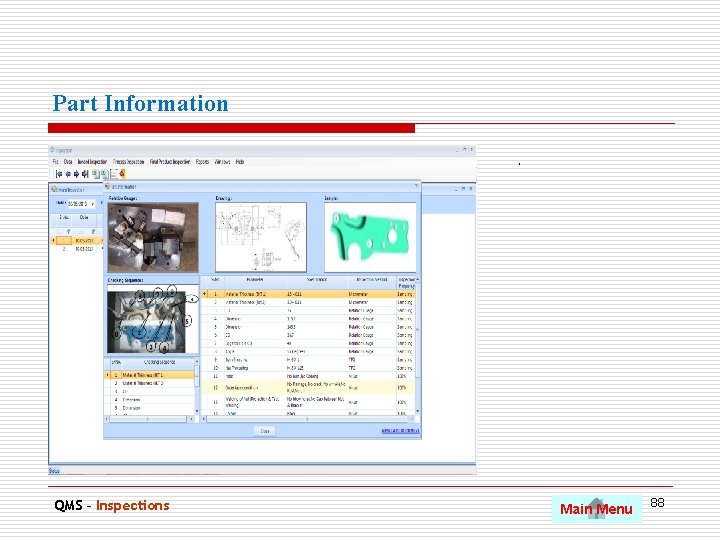
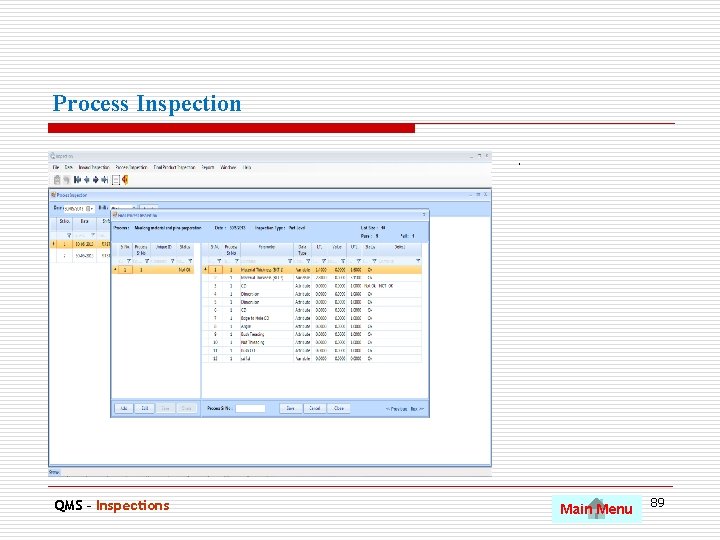
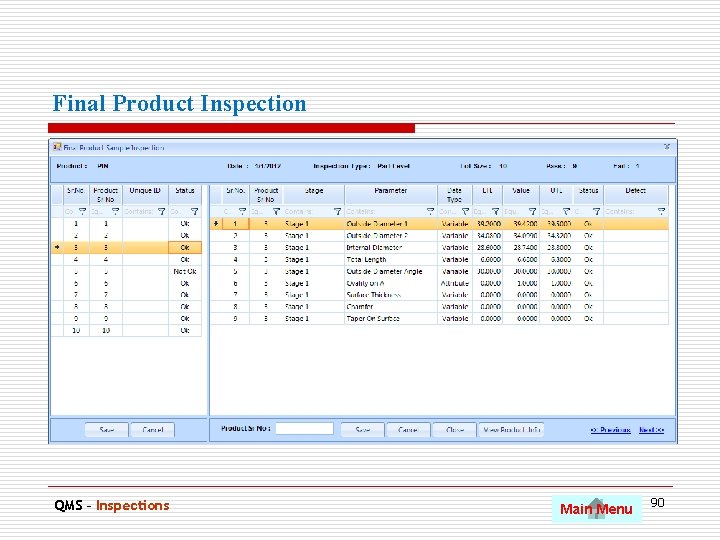
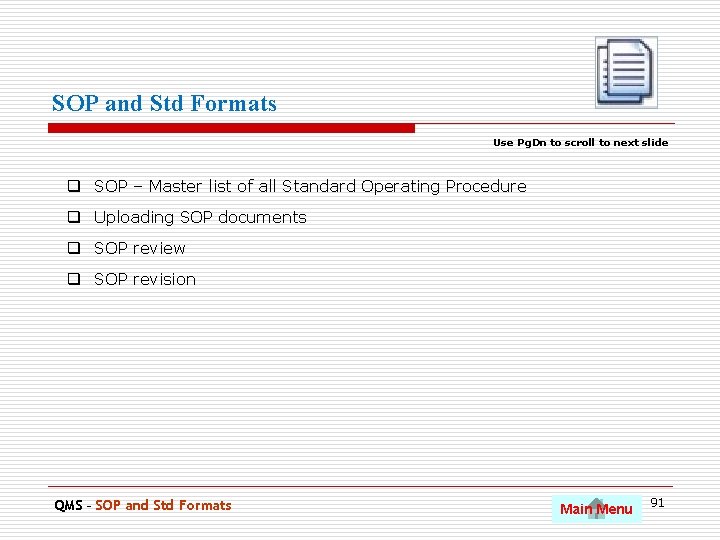
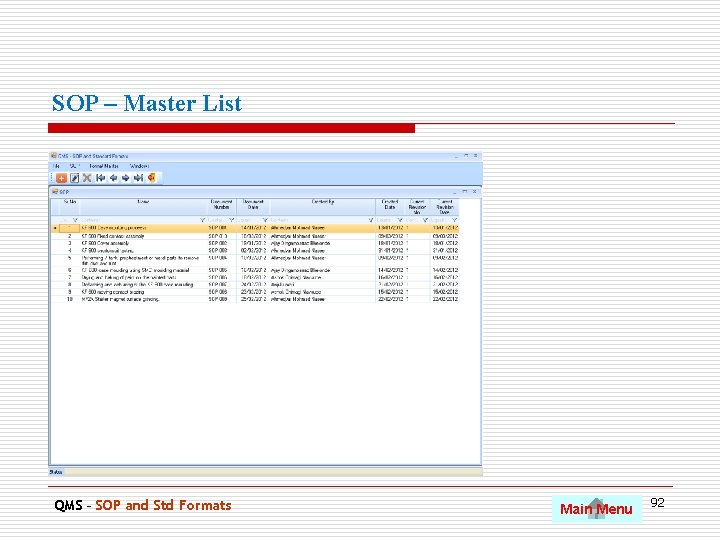
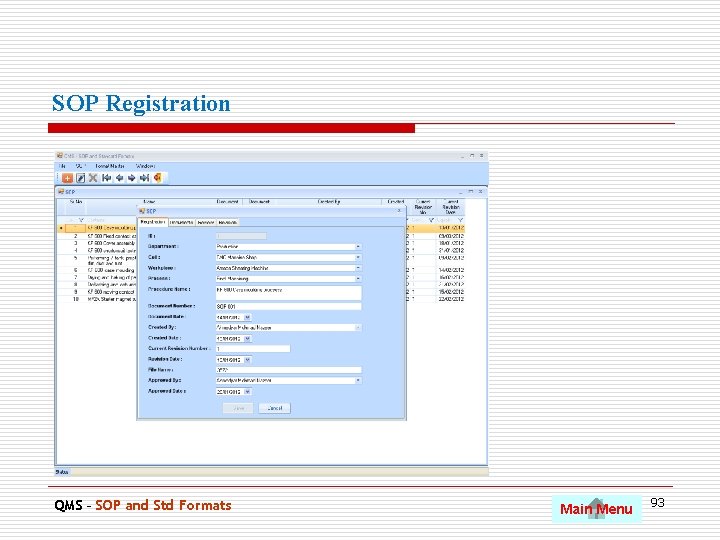
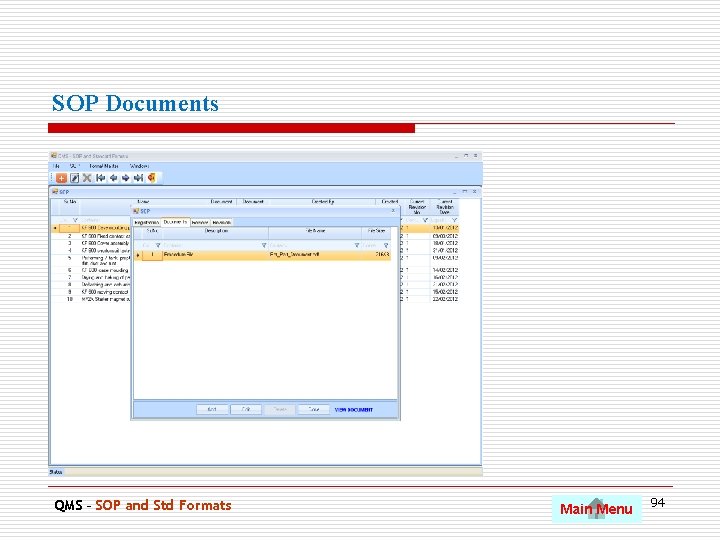
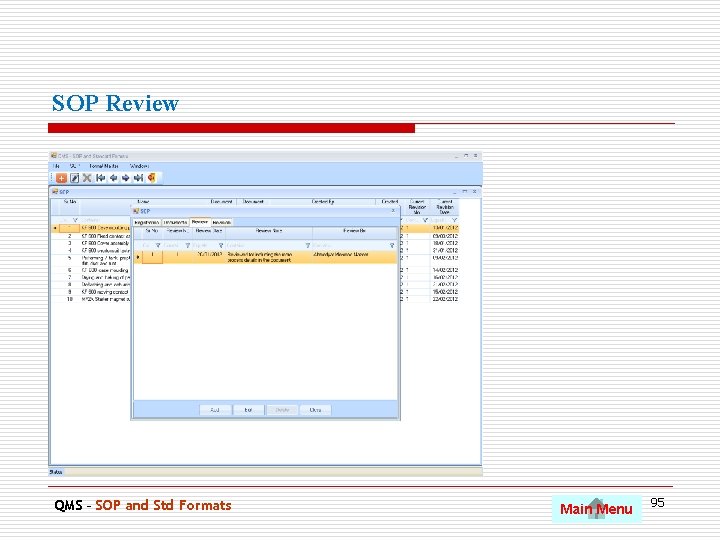
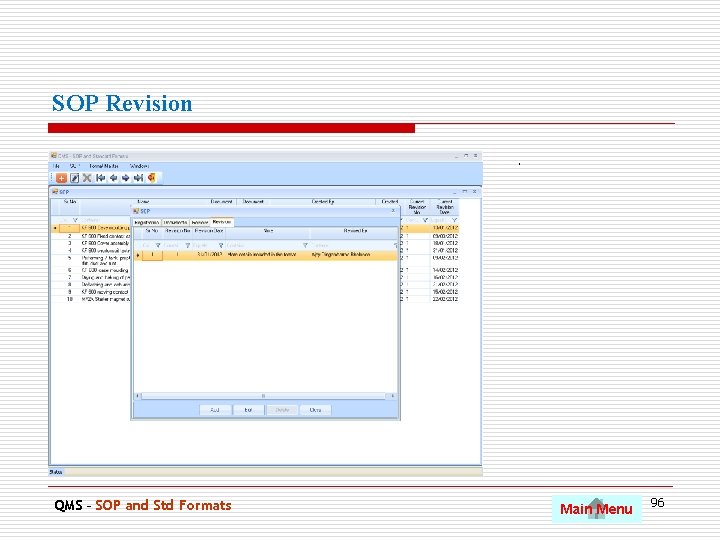
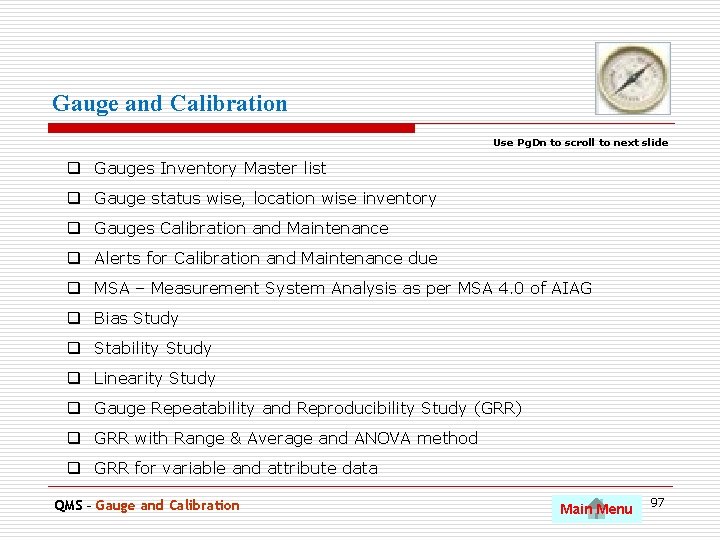
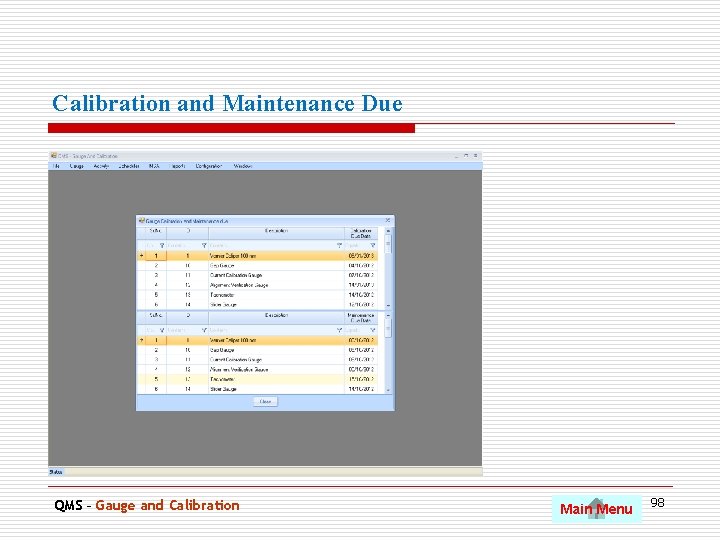
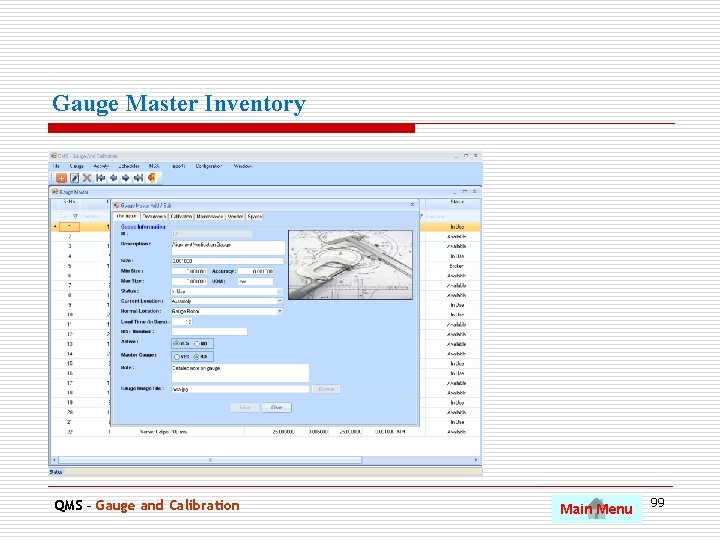
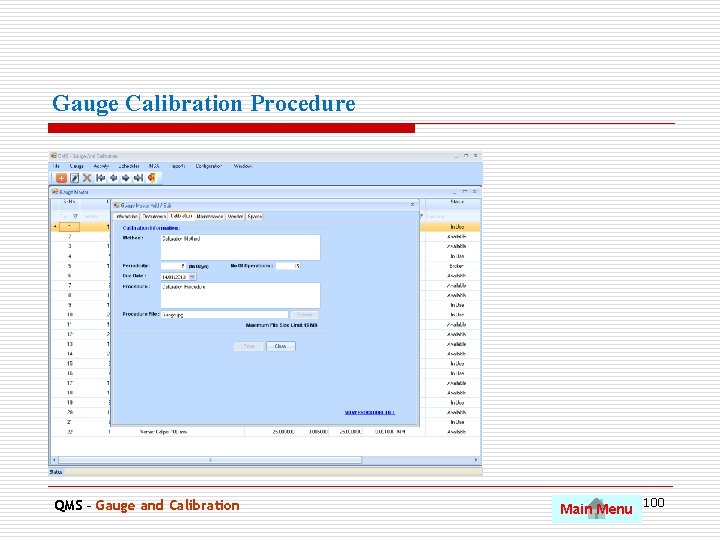
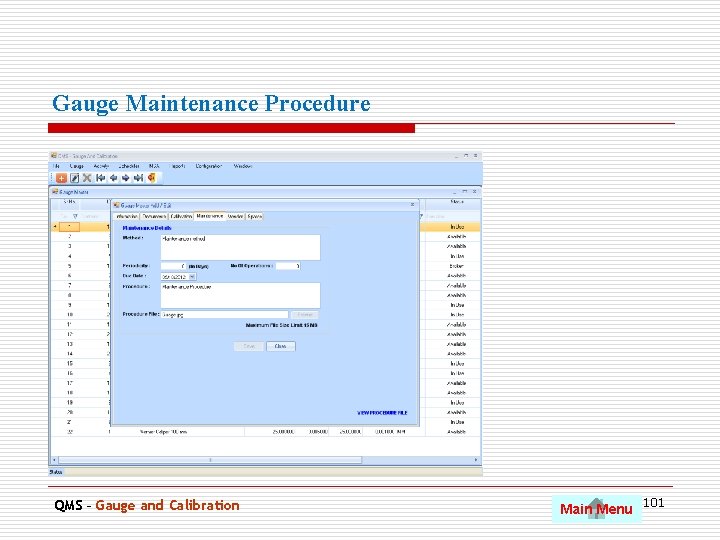
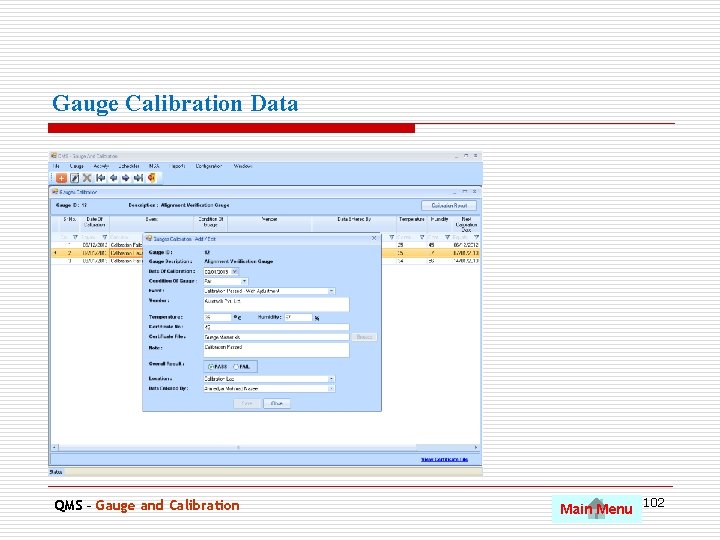
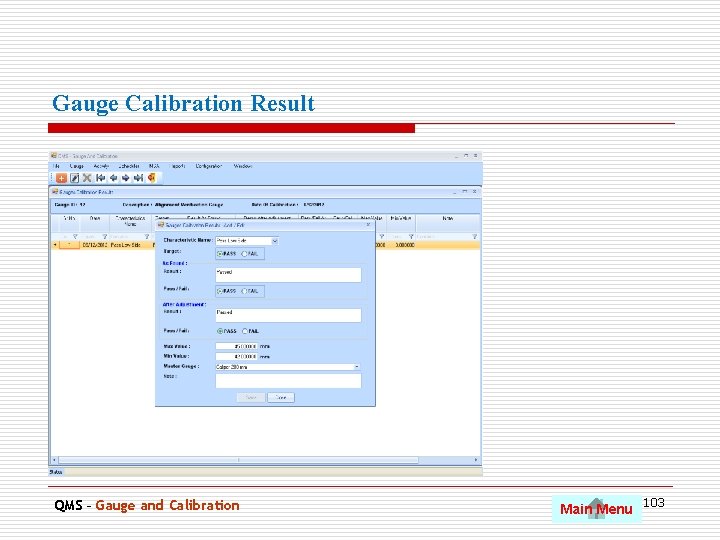
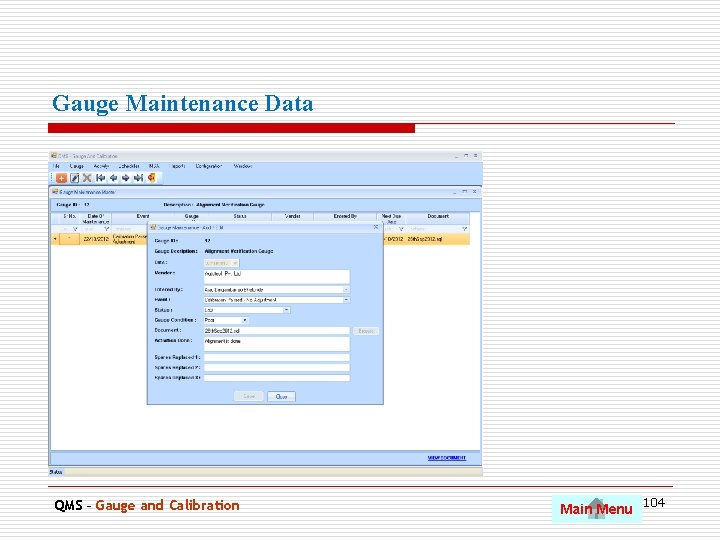
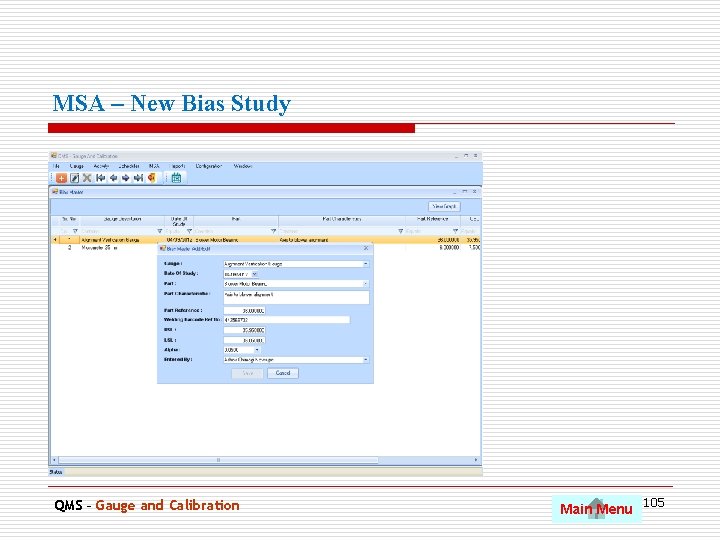
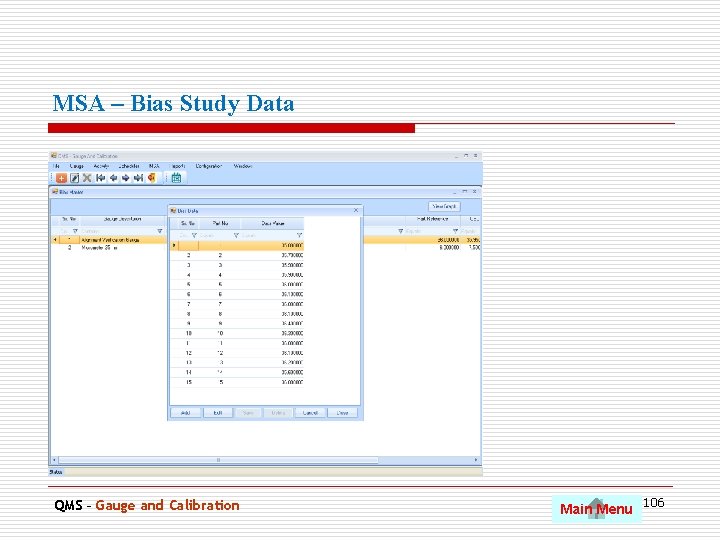
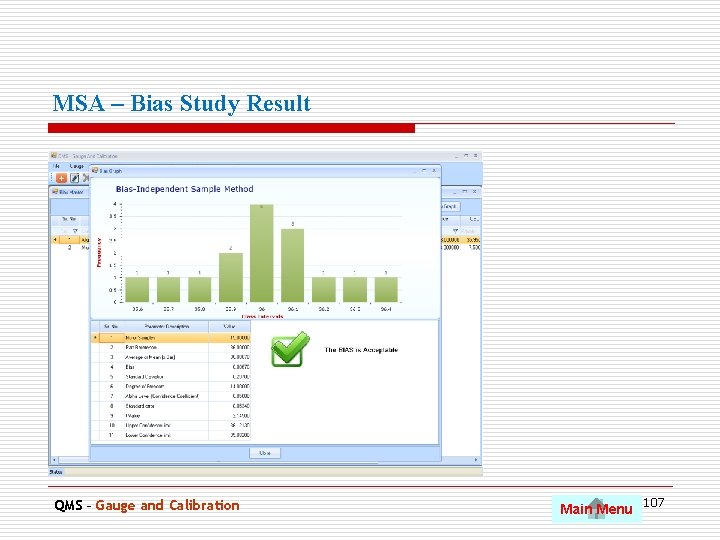
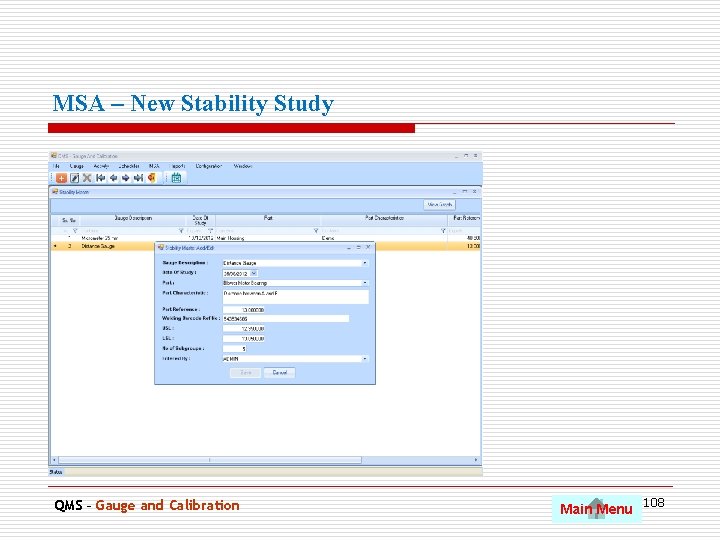
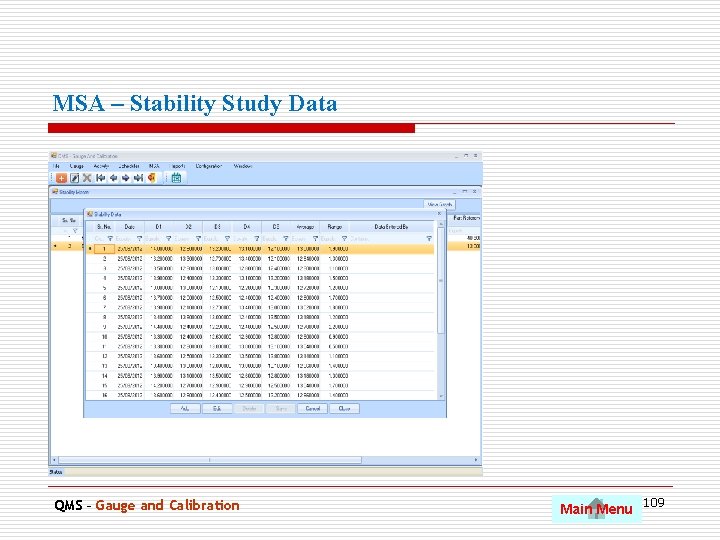
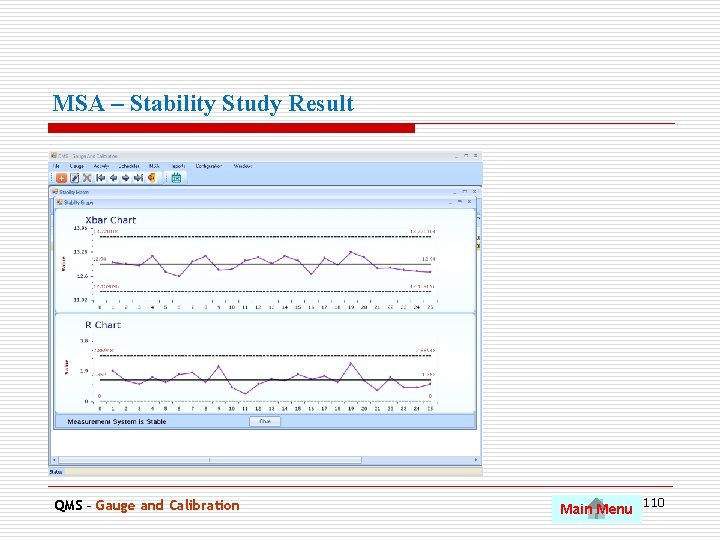
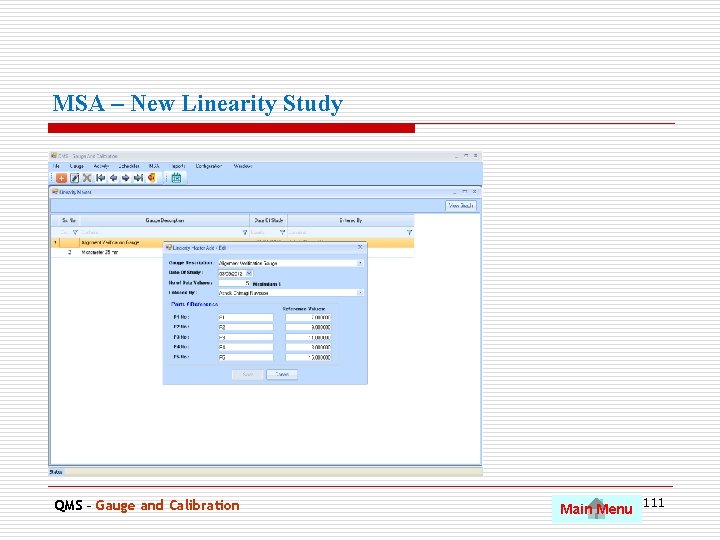
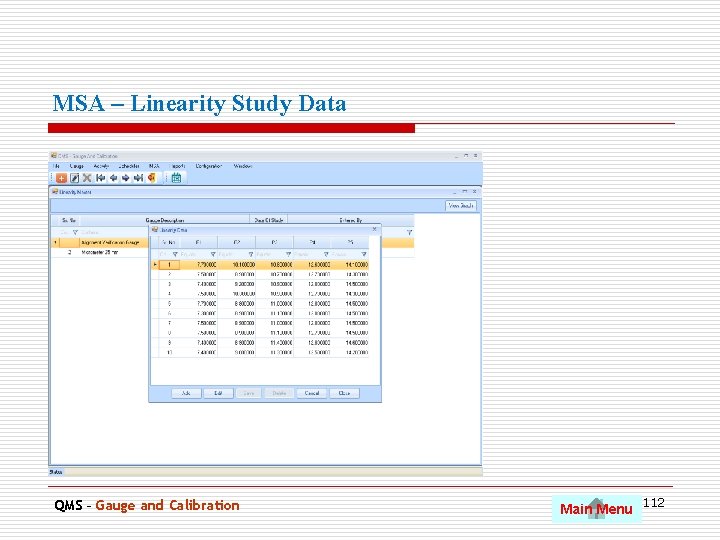
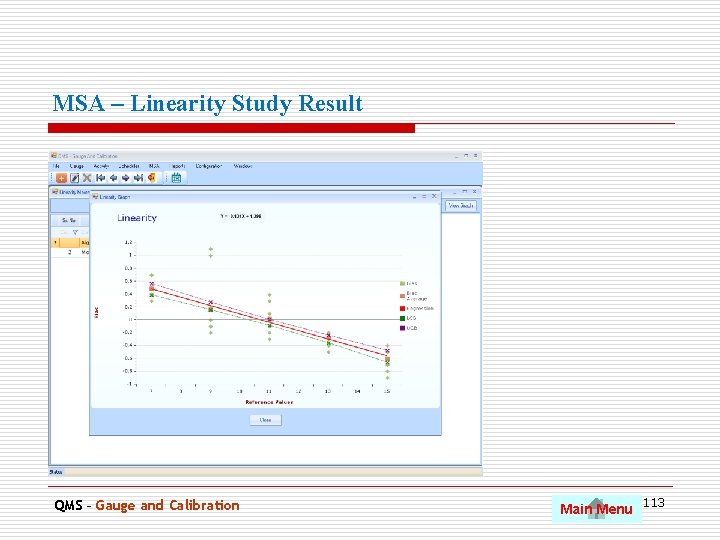
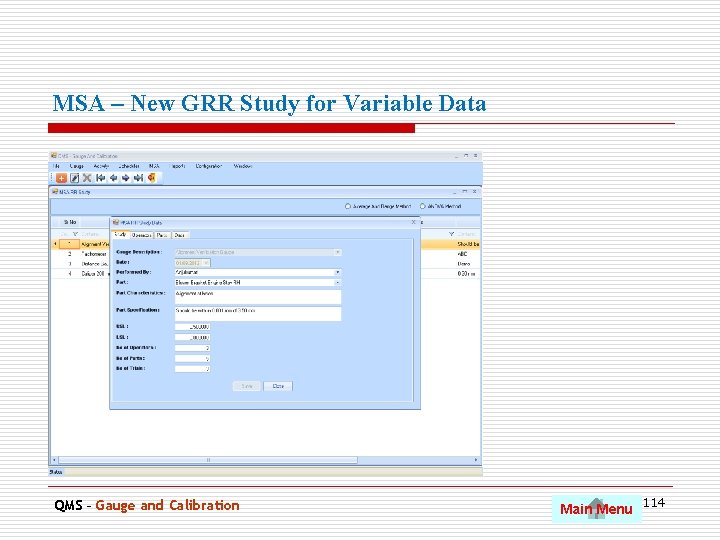
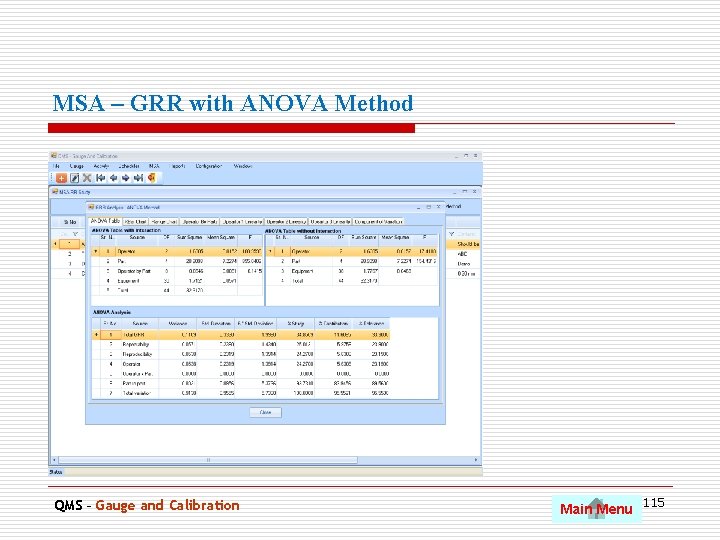
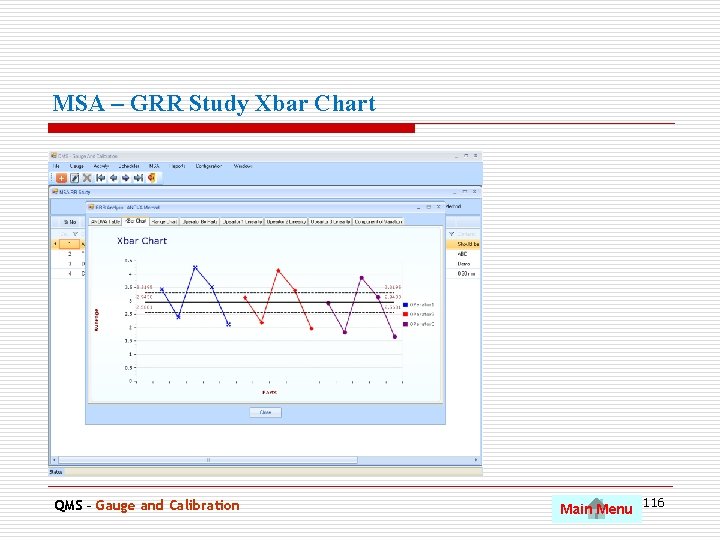
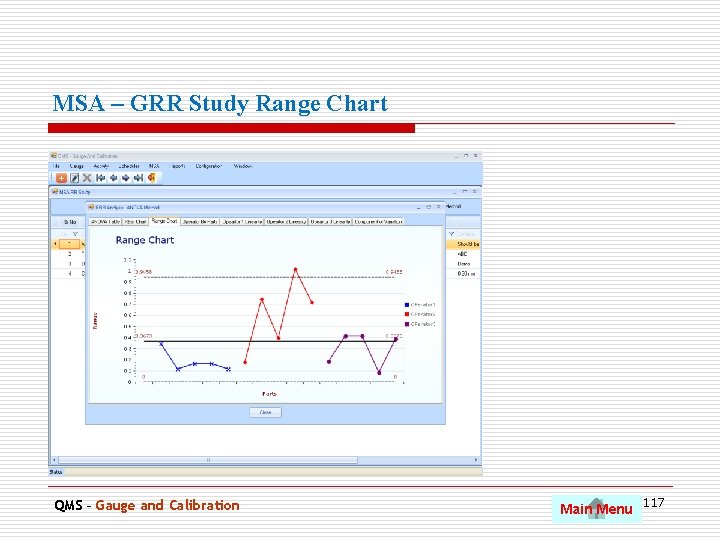
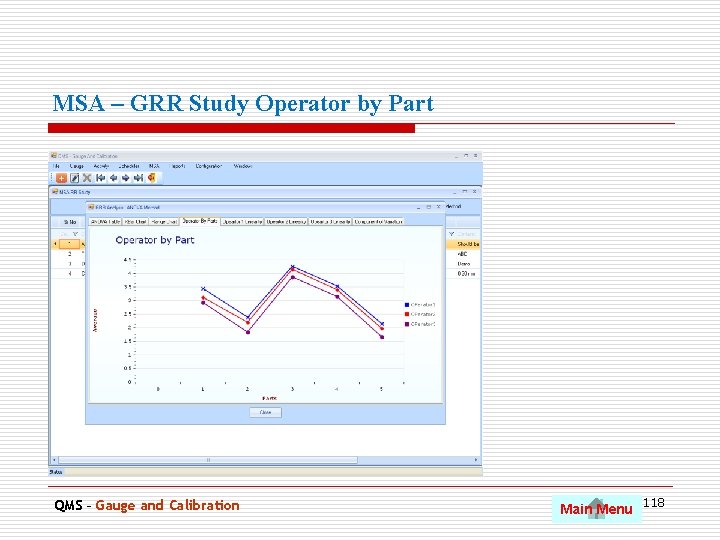
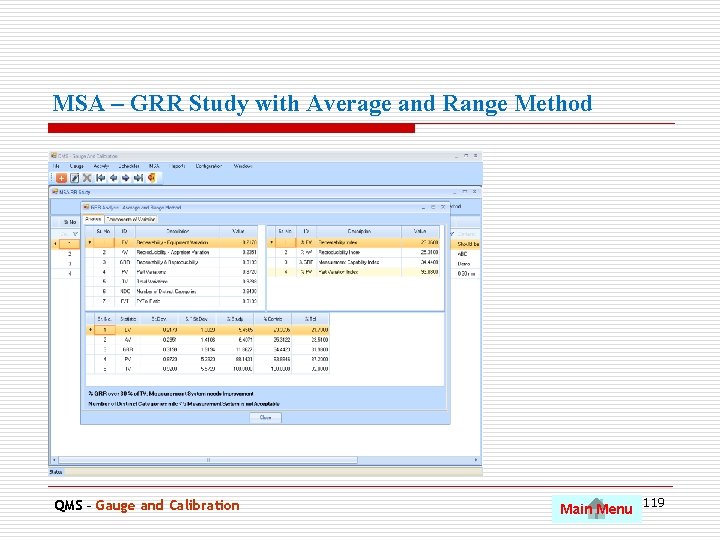
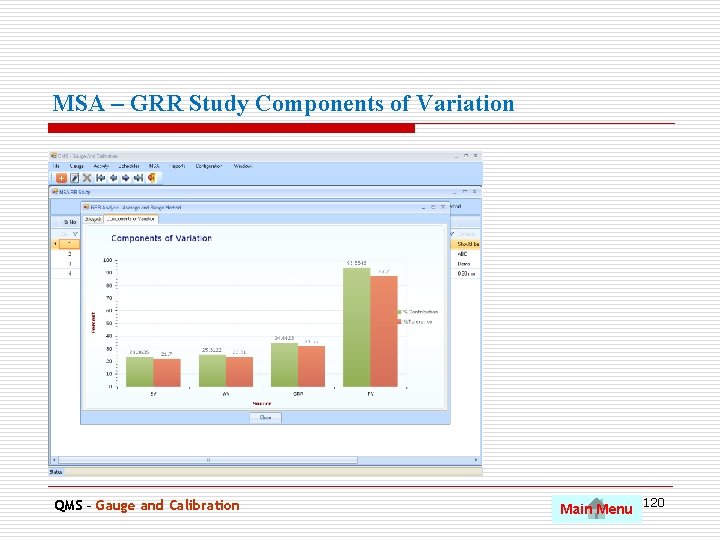
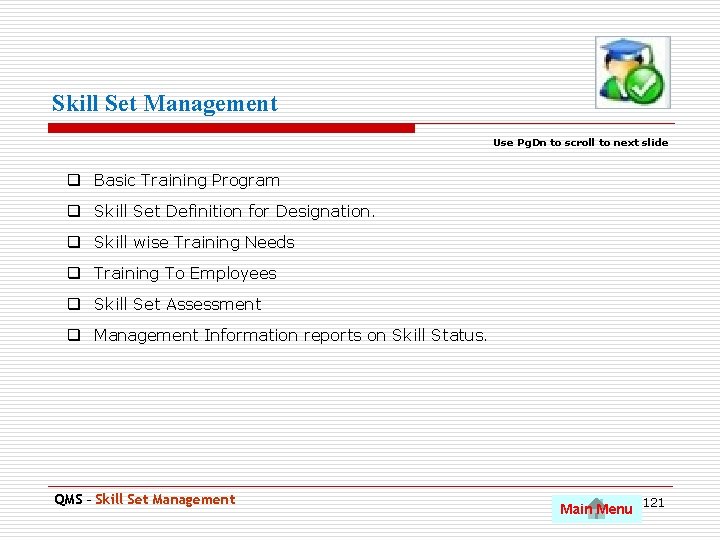
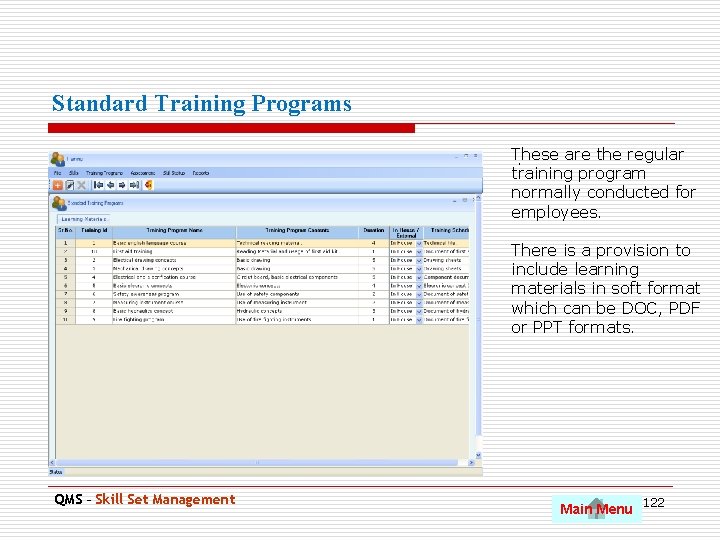
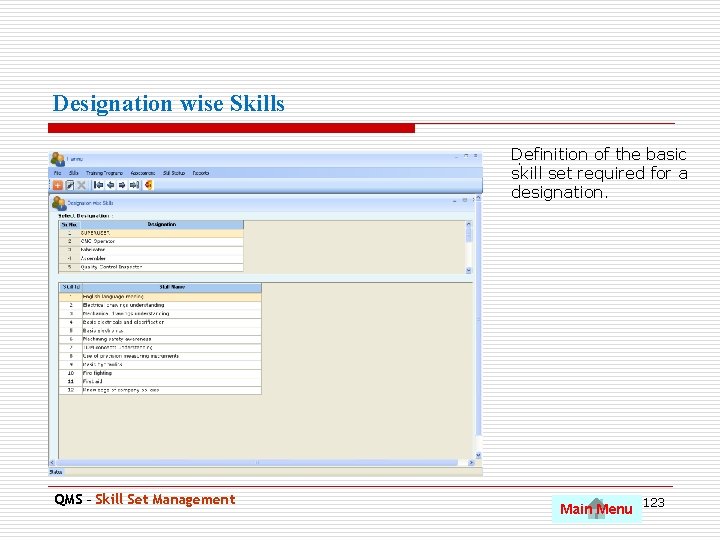
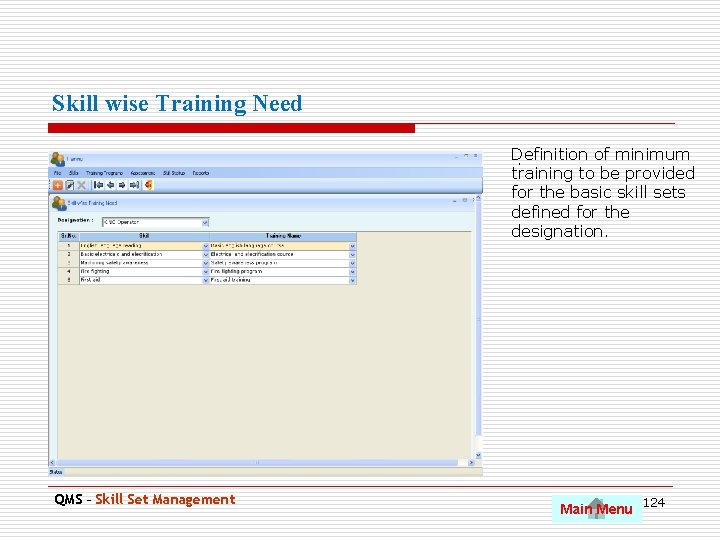
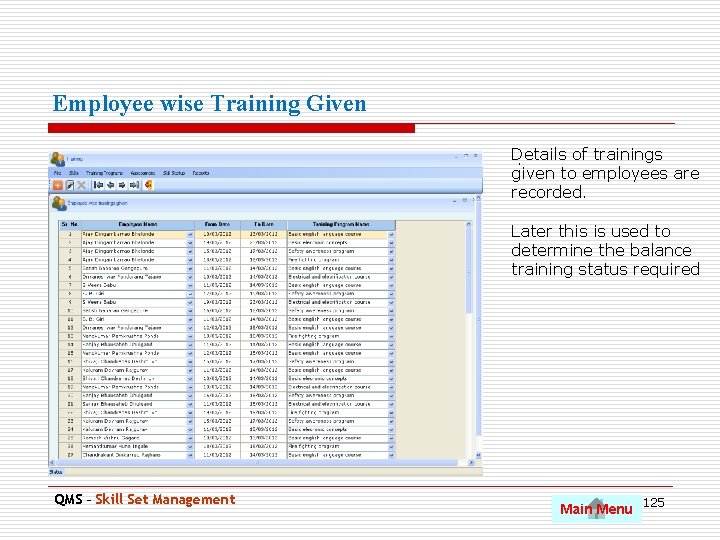
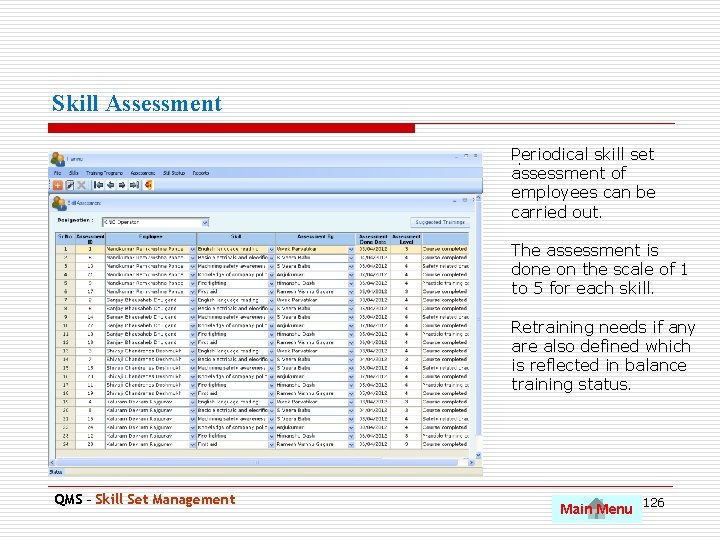

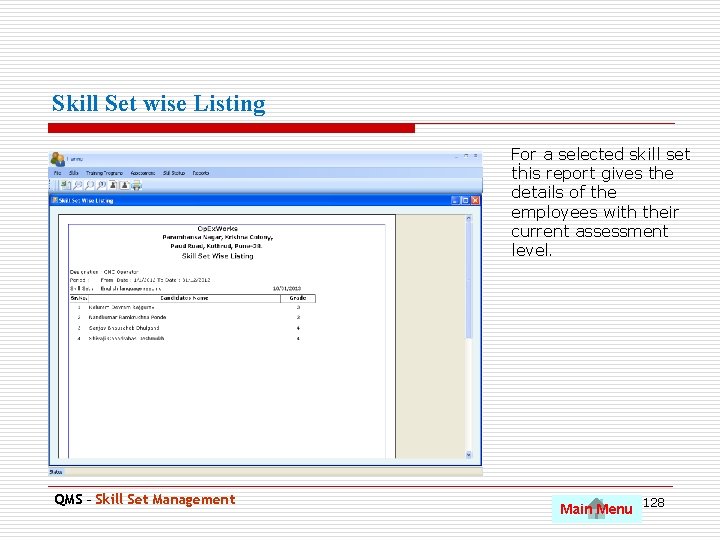
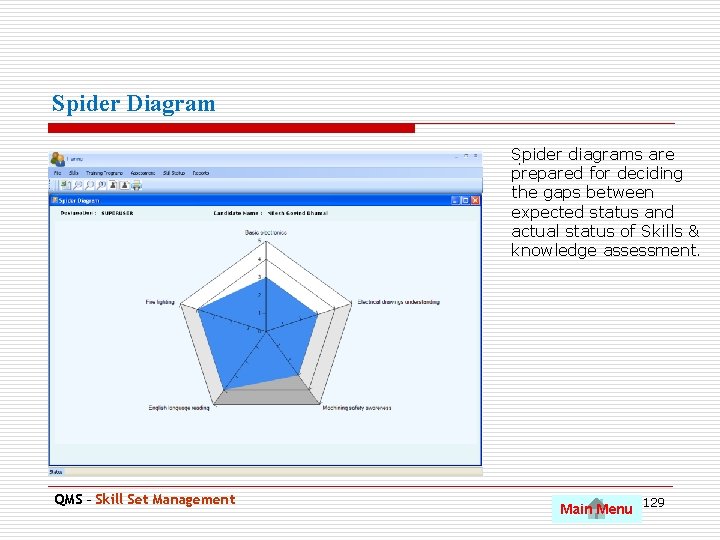
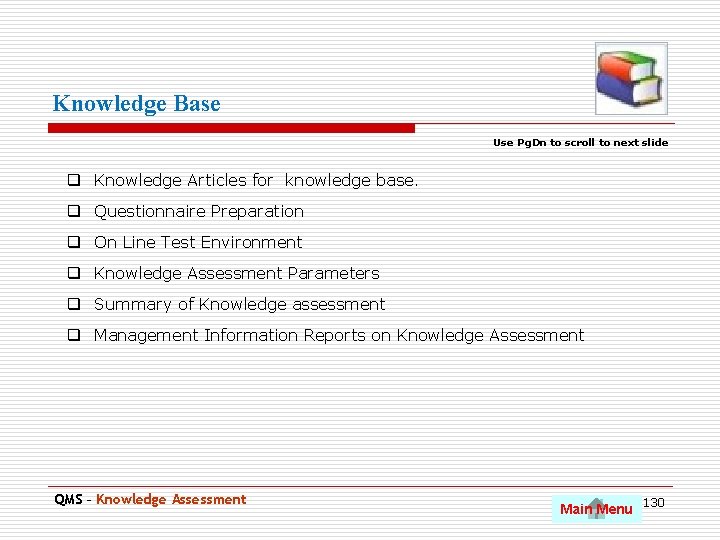
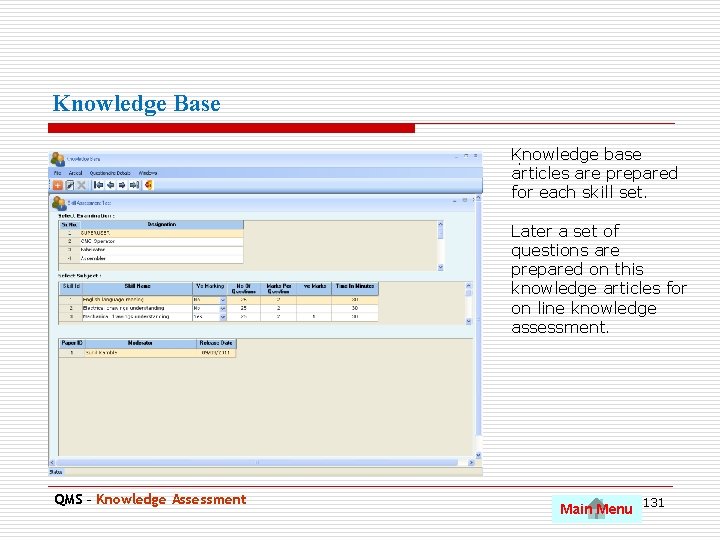
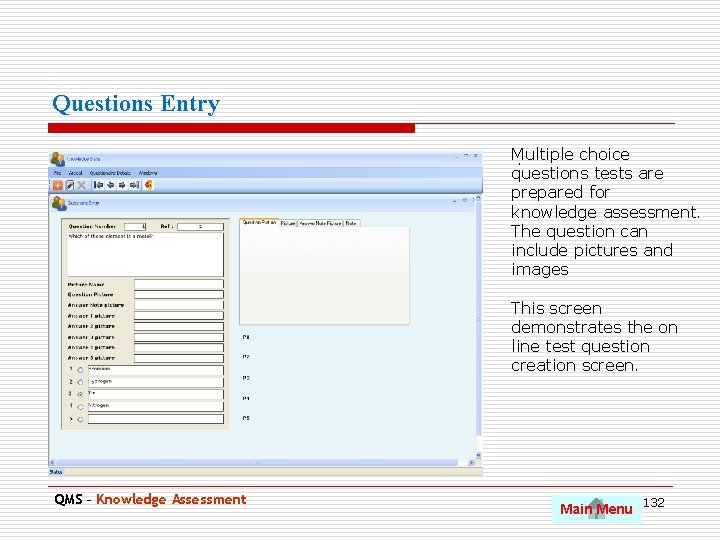
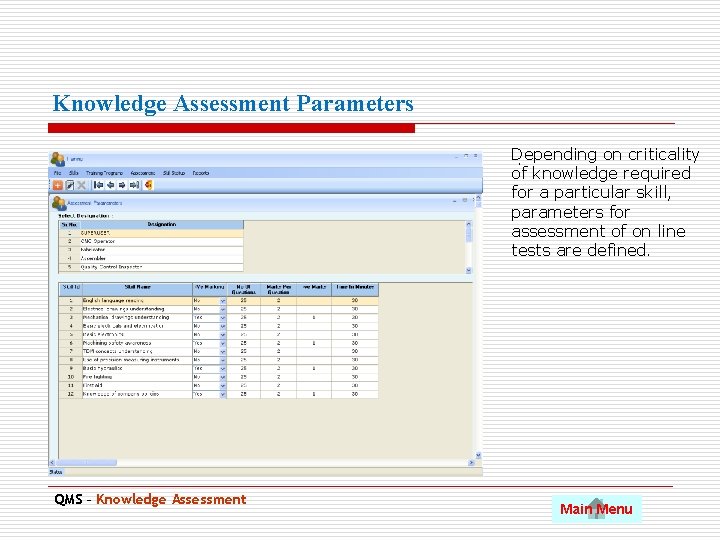
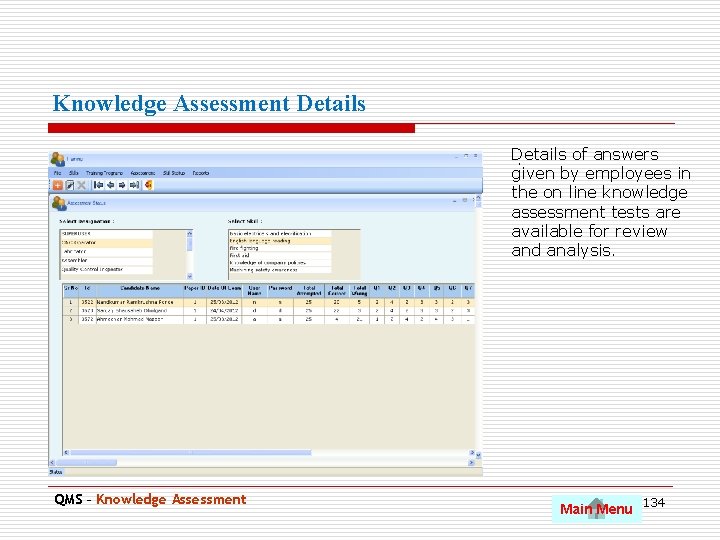
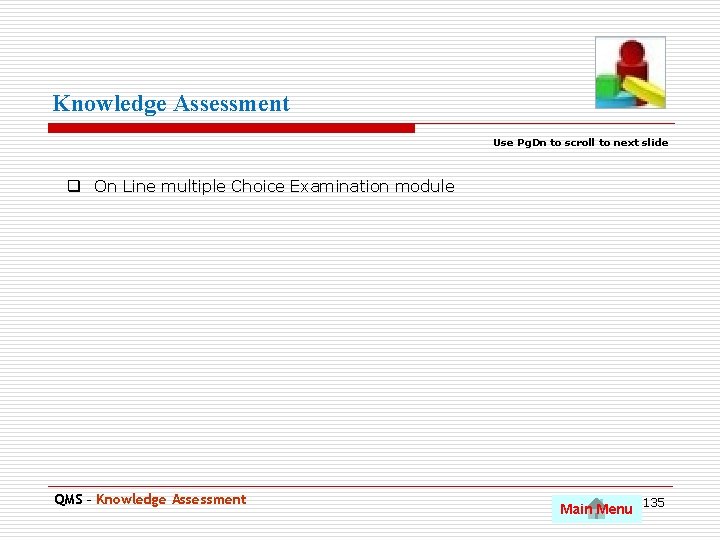
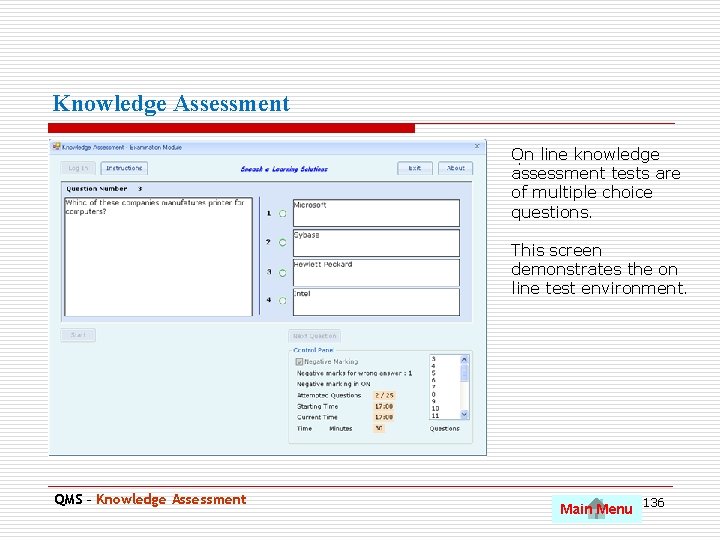
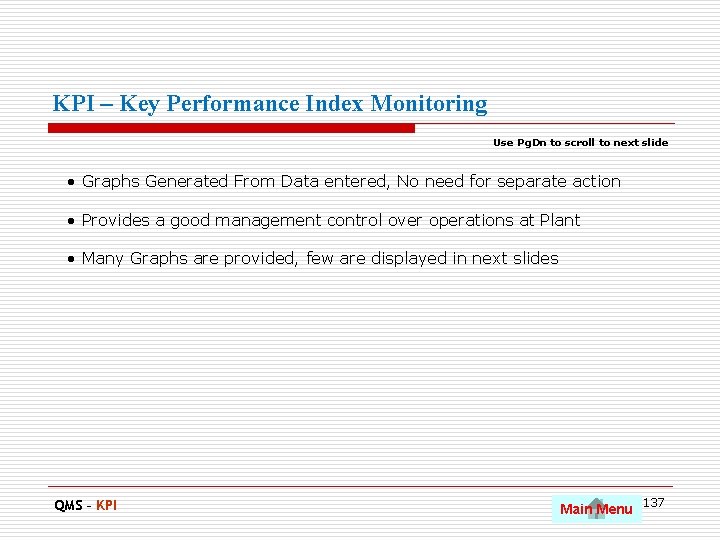
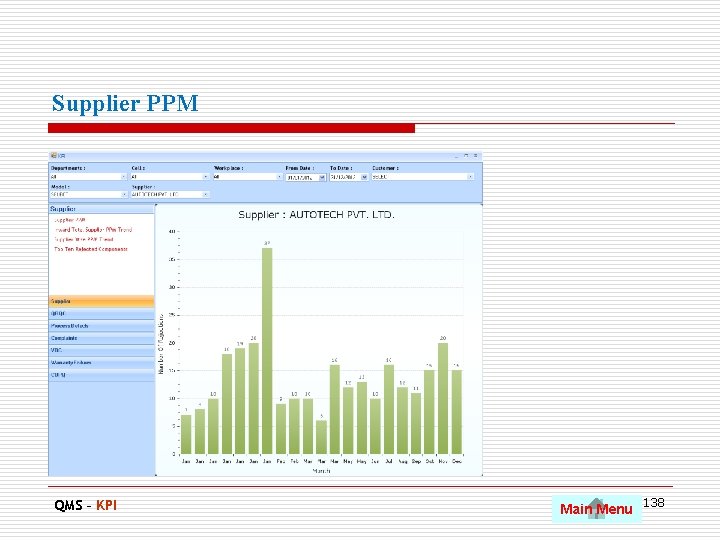
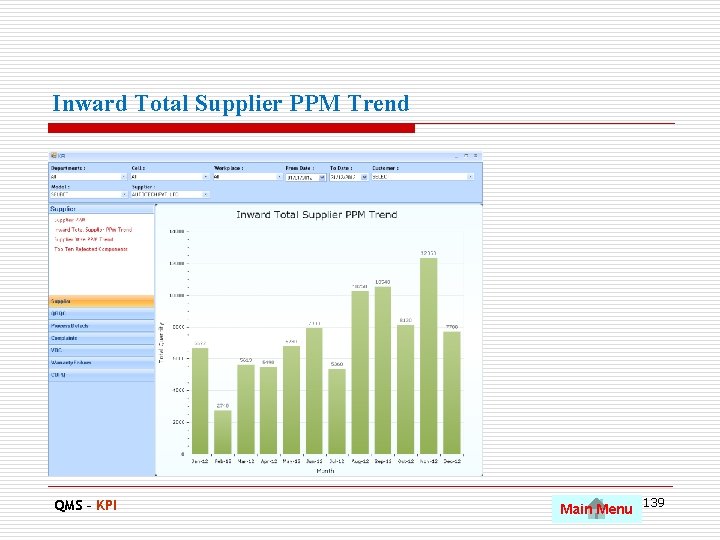
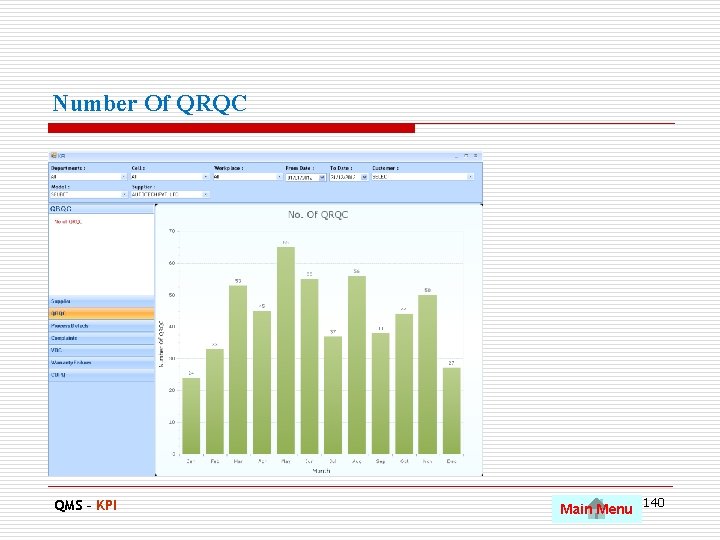
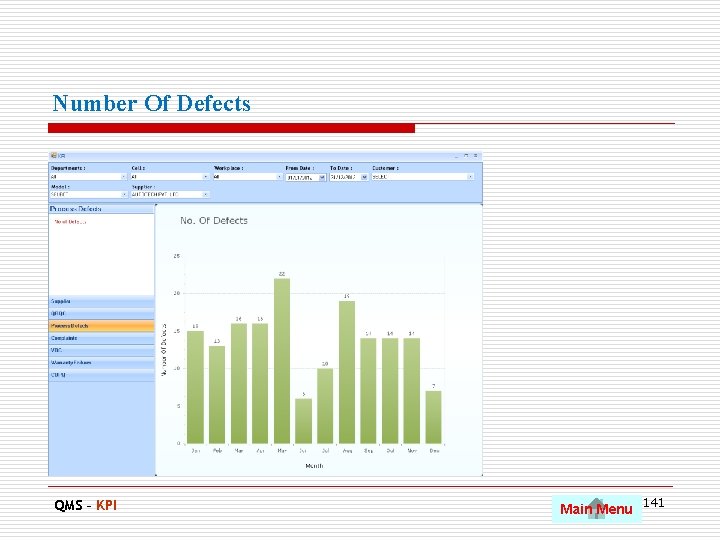
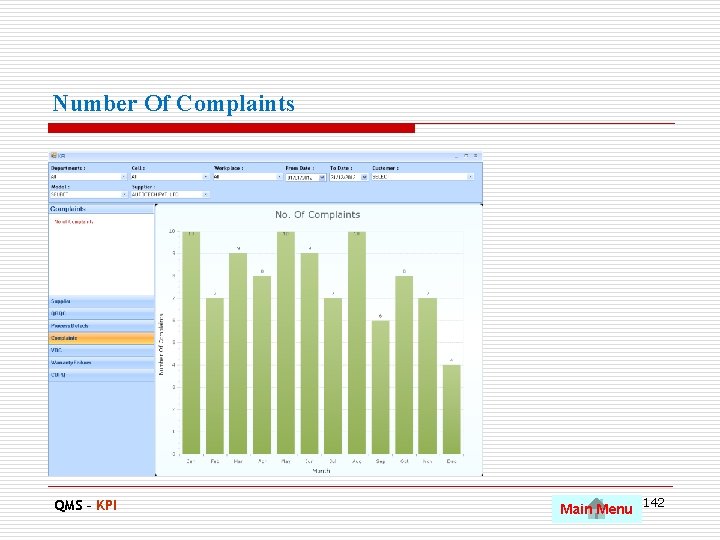
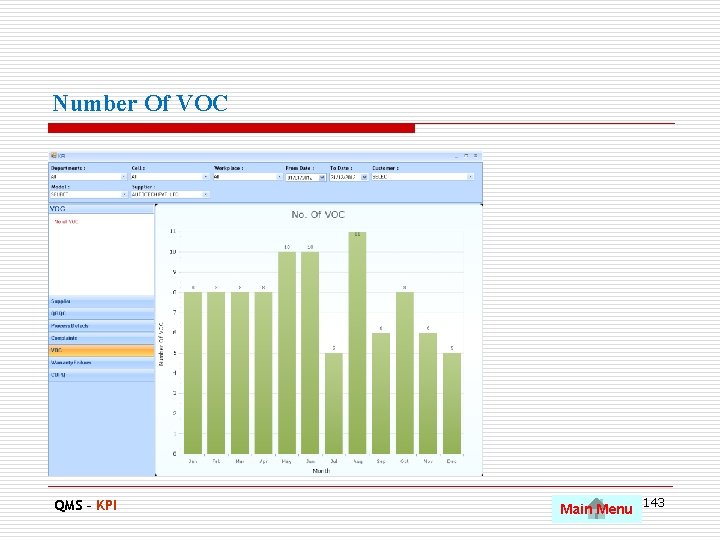
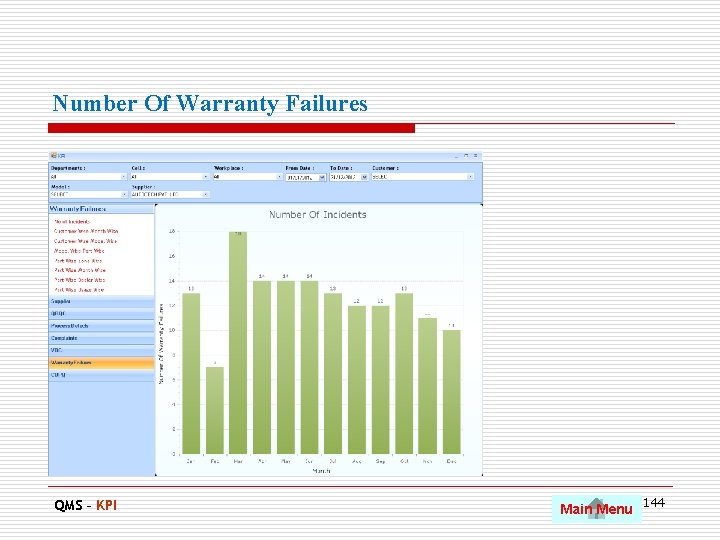
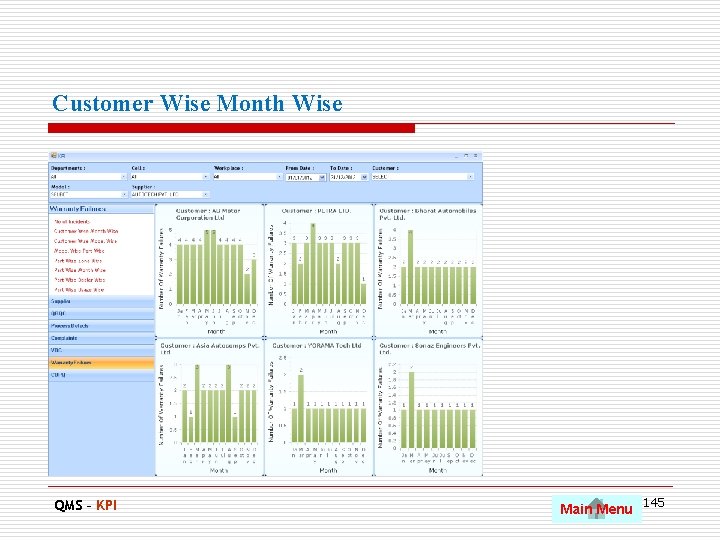
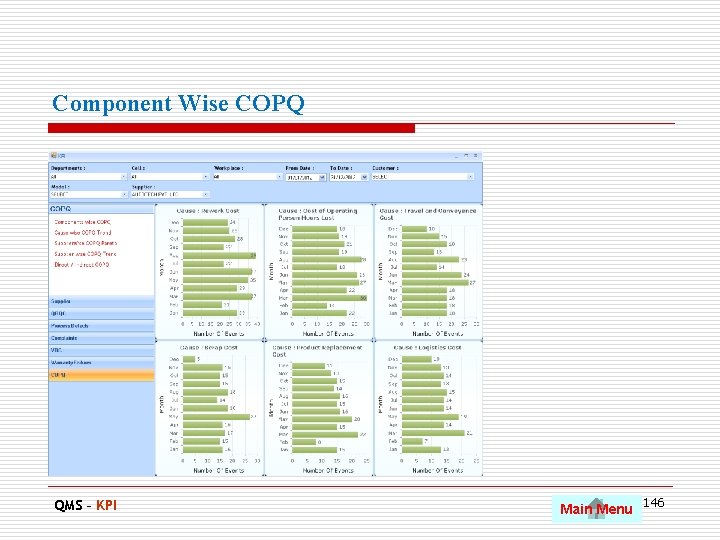
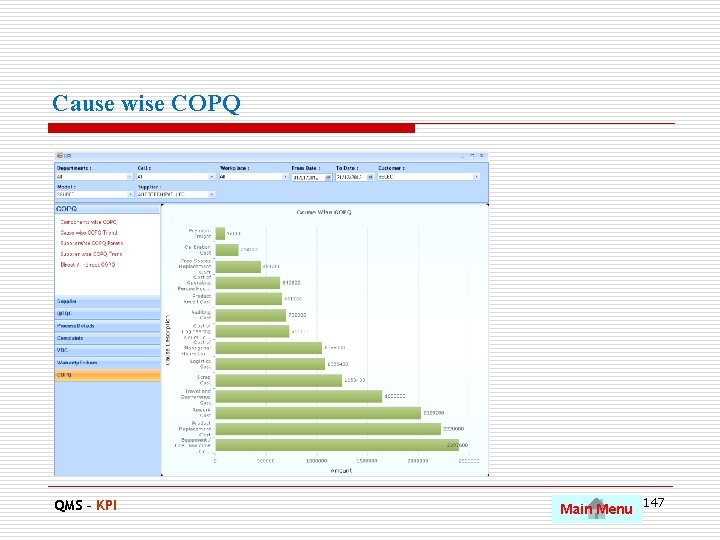
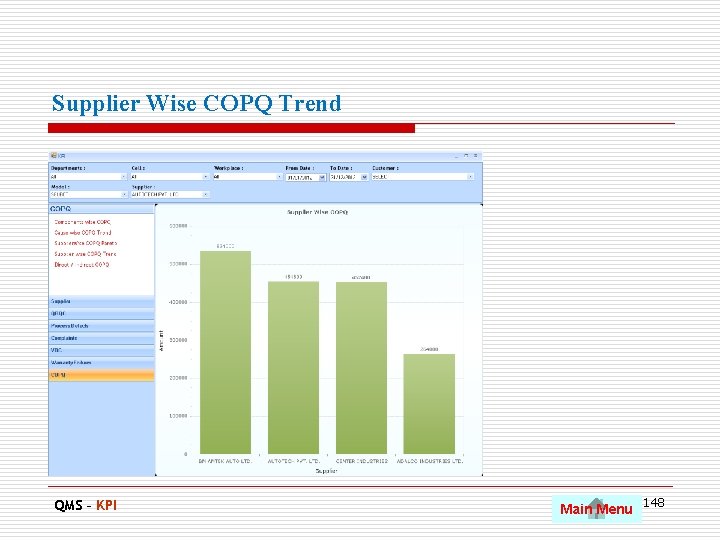
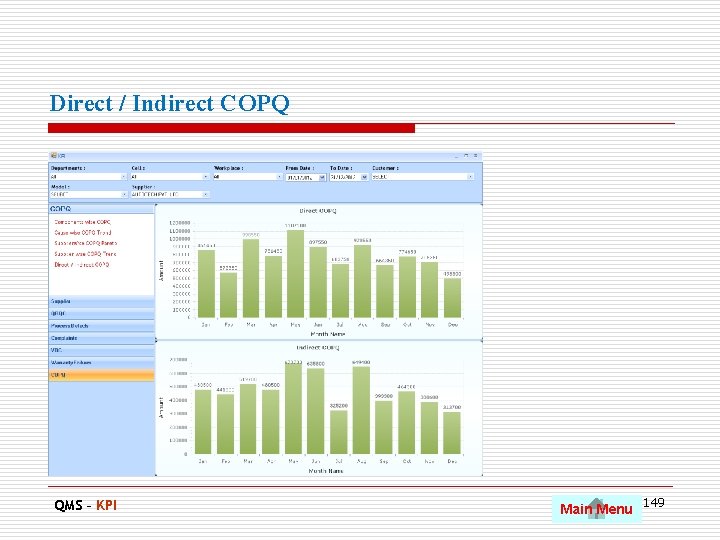
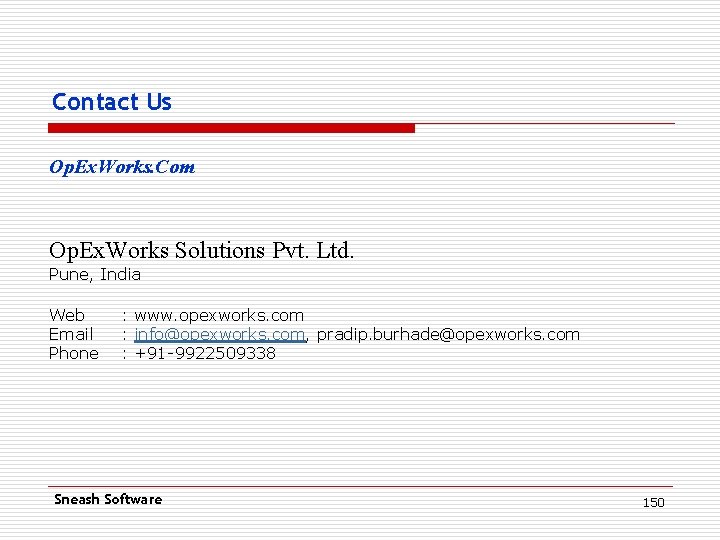
- Slides: 150
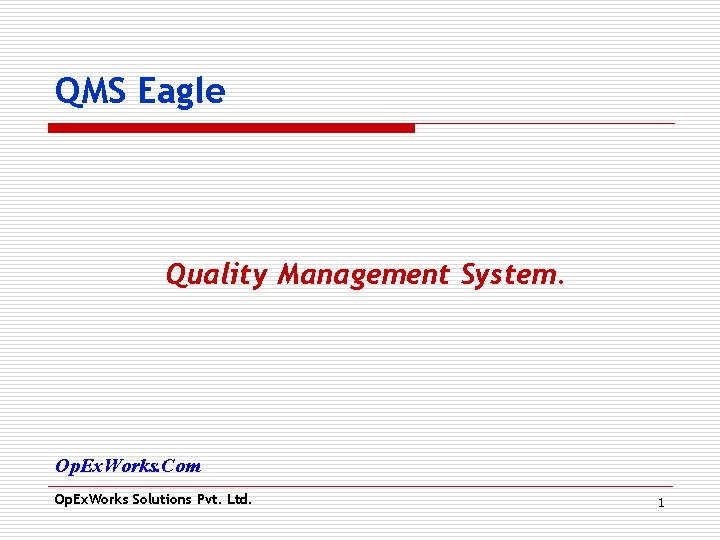
QMS Eagle Quality Management System. Op. Ex. Works. Com Op. Ex. Works Solutions Pvt. Ltd. 1
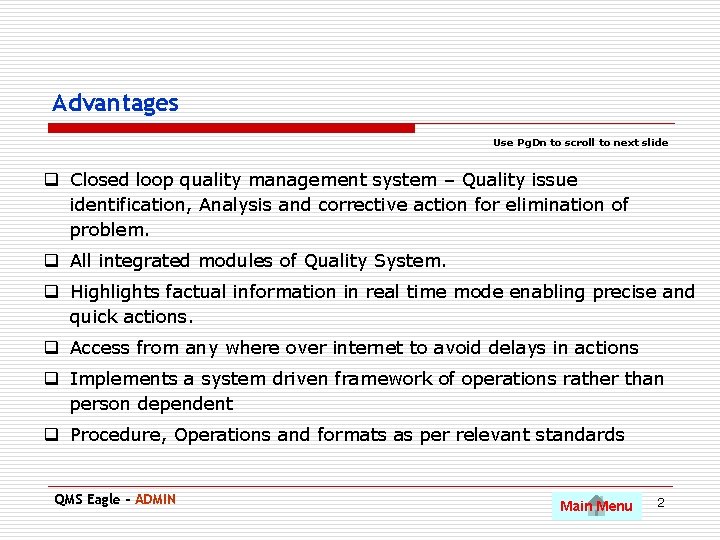
Advantages Use Pg. Dn to scroll to next slide q Closed loop quality management system – Quality issue identification, Analysis and corrective action for elimination of problem. q All integrated modules of Quality System. q Highlights factual information in real time mode enabling precise and quick actions. q Access from any where over internet to avoid delays in actions q Implements a system driven framework of operations rather than person dependent q Procedure, Operations and formats as per relevant standards QMS Eagle - ADMIN Main Menu 2
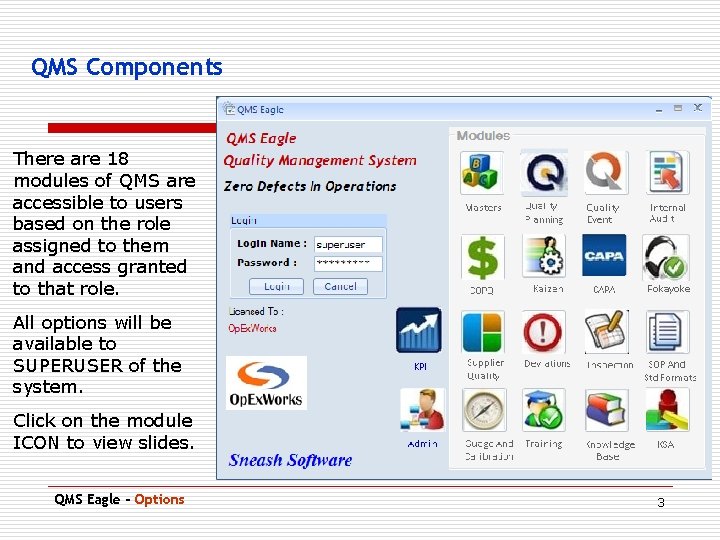
QMS Components There are 18 modules of QMS are accessible to users based on the role assigned to them and access granted to that role. All options will be available to SUPERUSER of the system. Click on the module ICON to view slides. QMS Eagle - Options 3
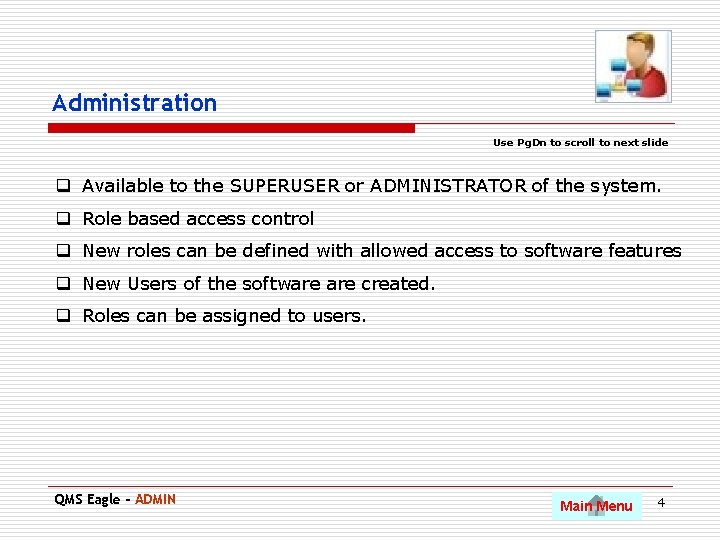
Administration Use Pg. Dn to scroll to next slide q Available to the SUPERUSER or ADMINISTRATOR of the system. q Role based access control q New roles can be defined with allowed access to software features q New Users of the software created. q Roles can be assigned to users. QMS Eagle - ADMIN Main Menu 4
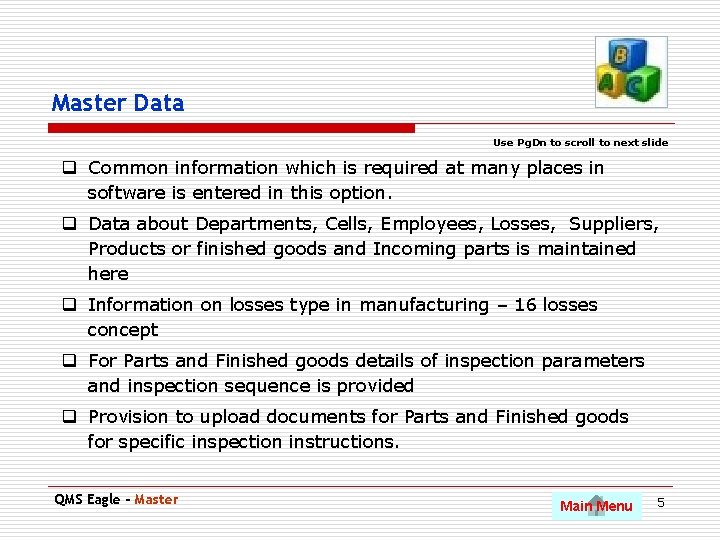
Master Data Use Pg. Dn to scroll to next slide q Common information which is required at many places in software is entered in this option. q Data about Departments, Cells, Employees, Losses, Suppliers, Products or finished goods and Incoming parts is maintained here q Information on losses type in manufacturing – 16 losses concept q For Parts and Finished goods details of inspection parameters and inspection sequence is provided q Provision to upload documents for Parts and Finished goods for specific inspection instructions. QMS Eagle - Master Main Menu 5
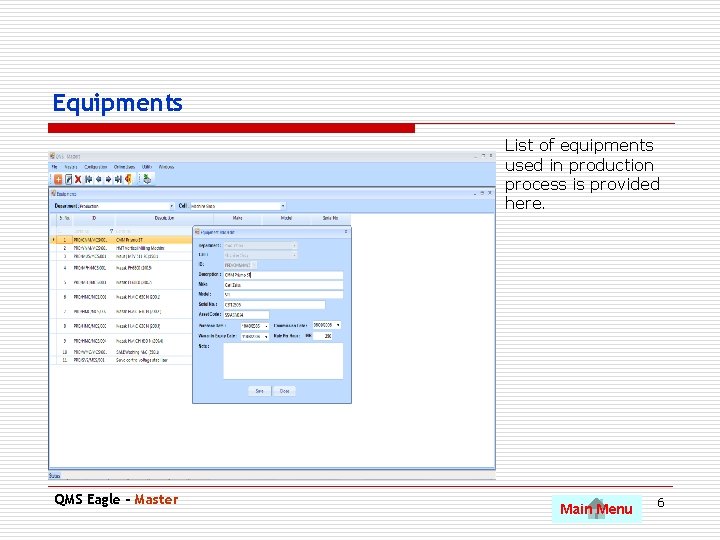
Equipments List of equipments used in production process is provided here. QMS Eagle - Master Main Menu 6
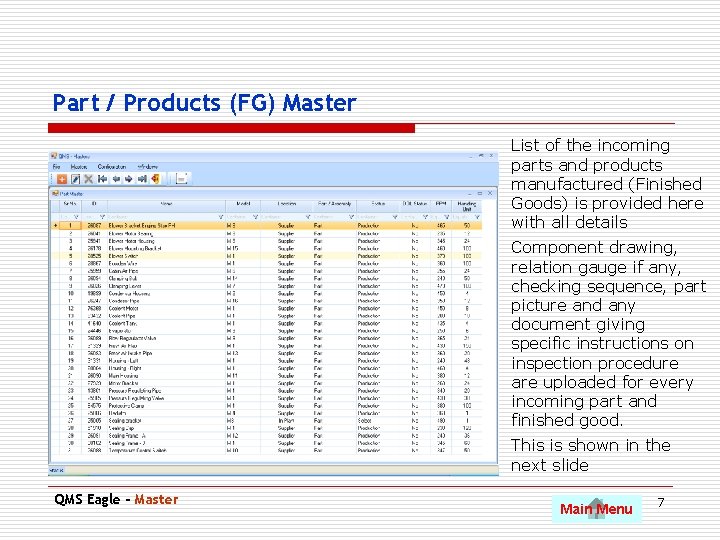
Part / Products (FG) Master List of the incoming parts and products manufactured (Finished Goods) is provided here with all details Component drawing, relation gauge if any, checking sequence, part picture and any document giving specific instructions on inspection procedure are uploaded for every incoming part and finished good. This is shown in the next slide QMS Eagle - Master Main Menu 7
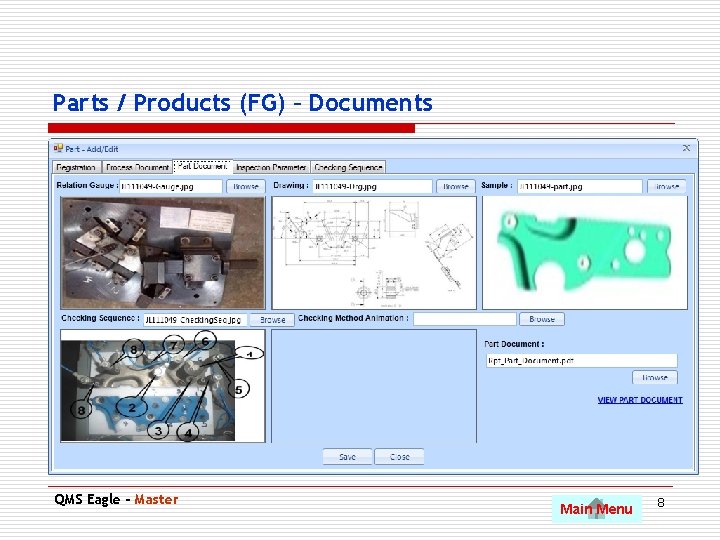
Parts / Products (FG) – Documents. QMS Eagle - Master Main Menu 8
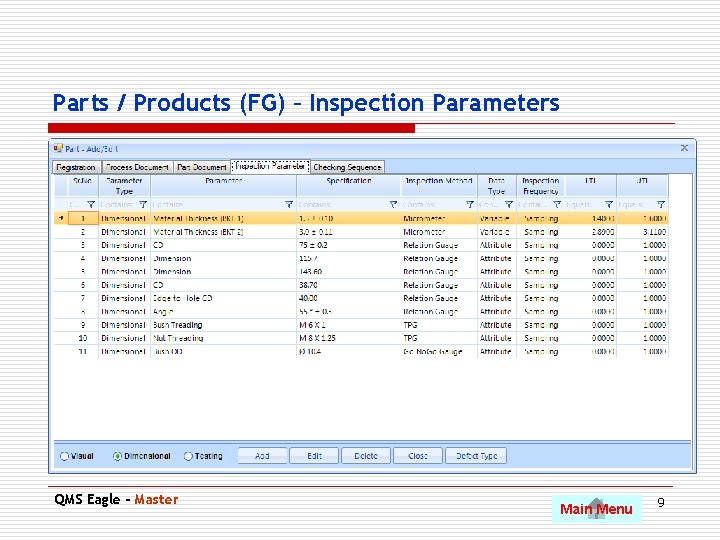
Parts / Products (FG) – Inspection Parameters. QMS Eagle - Master Main Menu 9
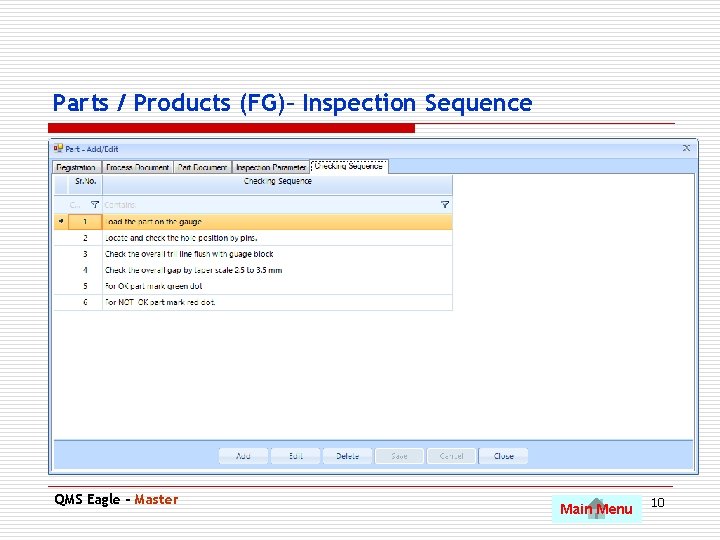
Parts / Products (FG)– Inspection Sequence. QMS Eagle - Master Main Menu 10
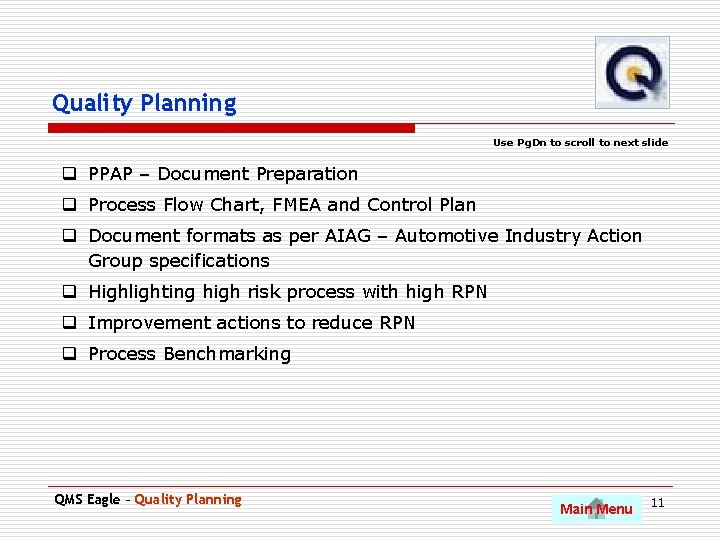
Quality Planning Use Pg. Dn to scroll to next slide q PPAP – Document Preparation q Process Flow Chart, FMEA and Control Plan q Document formats as per AIAG – Automotive Industry Action Group specifications q Highlighting high risk process with high RPN q Improvement actions to reduce RPN q Process Benchmarking QMS Eagle – Quality Planning Main Menu 11
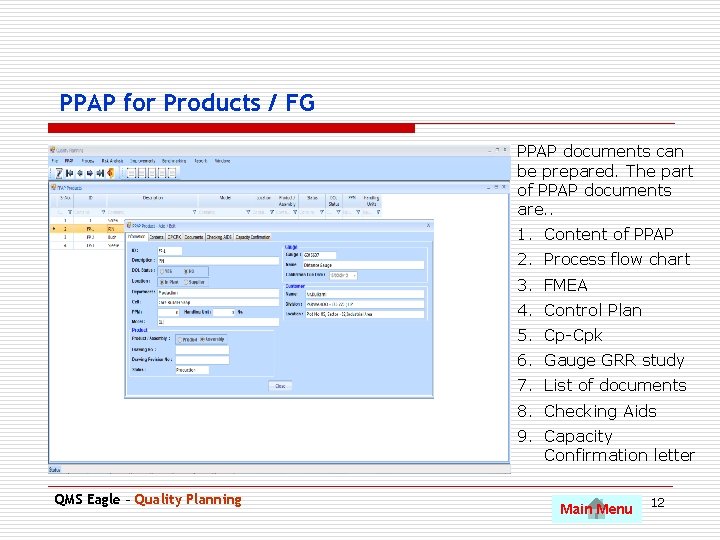
PPAP for Products / FG PPAP documents can be prepared. The part of PPAP documents are. . 1. Content of PPAP 2. Process flow chart 3. FMEA 4. Control Plan 5. Cp-Cpk 6. Gauge GRR study 7. List of documents 8. Checking Aids 9. Capacity Confirmation letter QMS Eagle – Quality Planning Main Menu 12
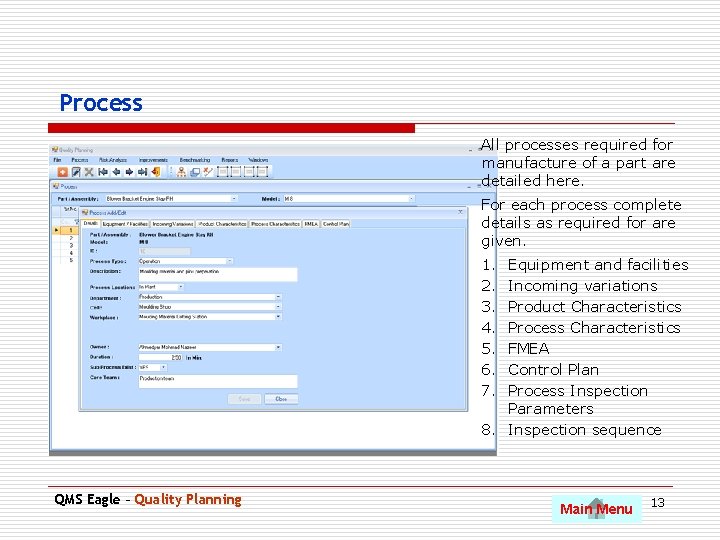
Process All processes required for manufacture of a part are detailed here. For each process complete details as required for are given. 1. 2. 3. 4. 5. 6. 7. Equipment and facilities Incoming variations Product Characteristics Process Characteristics FMEA Control Plan Process Inspection Parameters 8. Inspection sequence QMS Eagle – Quality Planning Main Menu 13
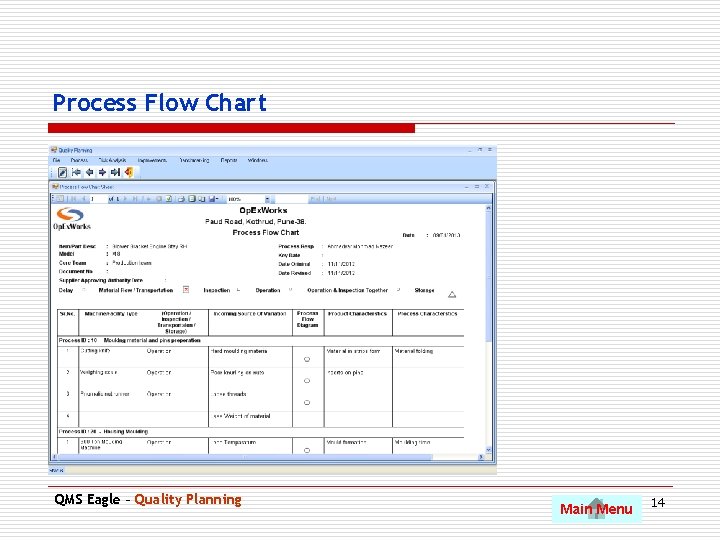
Process Flow Chart QMS Eagle – Quality Planning Main Menu 14
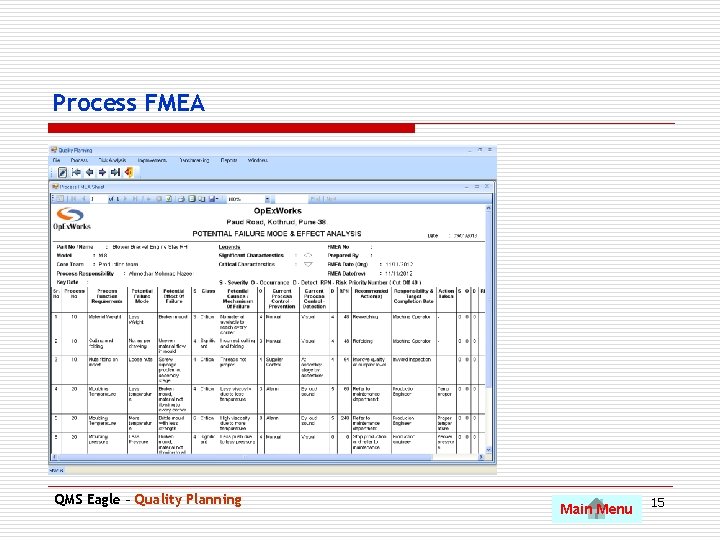
Process FMEA QMS Eagle – Quality Planning Main Menu 15
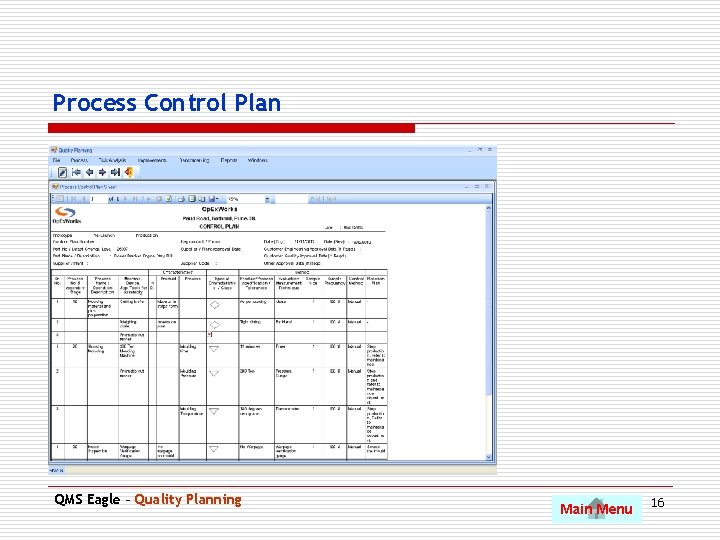
Process Control Plan QMS Eagle – Quality Planning Main Menu 16
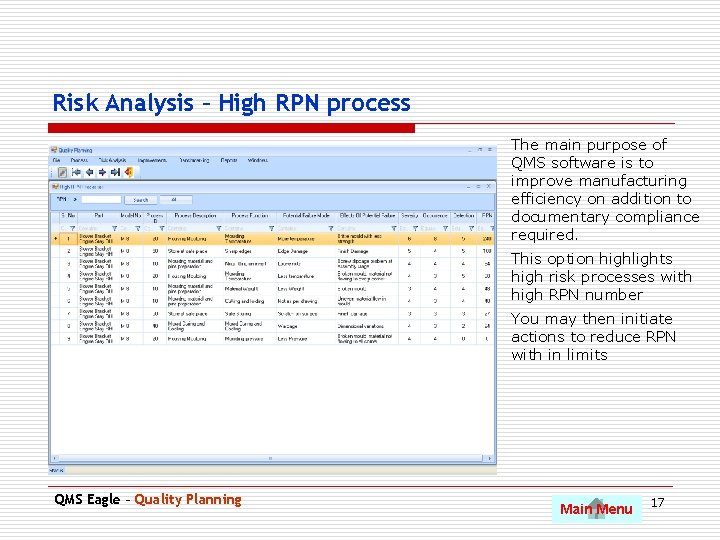
Risk Analysis – High RPN process The main purpose of QMS software is to improve manufacturing efficiency on addition to documentary compliance required. This option highlights high risk processes with high RPN number You may then initiate actions to reduce RPN with in limits QMS Eagle – Quality Planning Main Menu 17
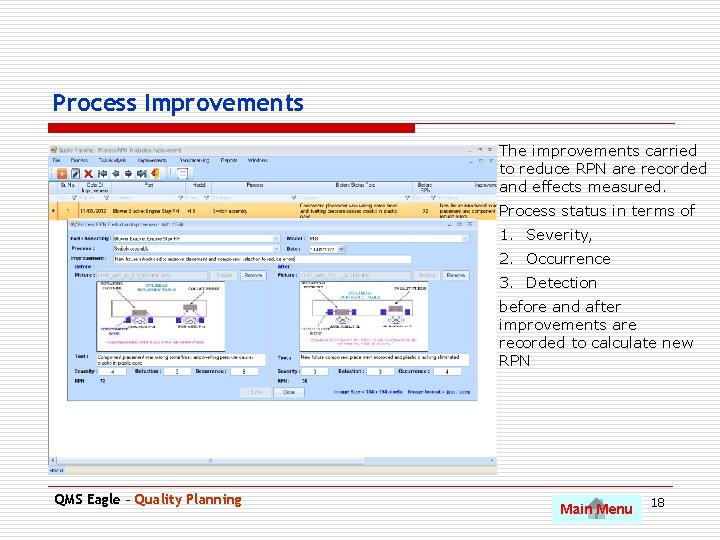
Process Improvements The improvements carried to reduce RPN are recorded and effects measured. Process status in terms of 1. Severity, 2. Occurrence 3. Detection before and after improvements are recorded to calculate new RPN QMS Eagle – Quality Planning Main Menu 18
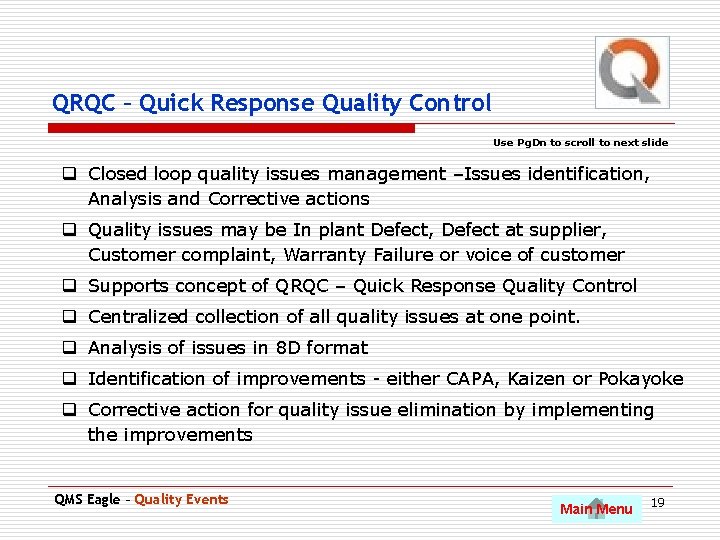
QRQC – Quick Response Quality Control Use Pg. Dn to scroll to next slide q Closed loop quality issues management –Issues identification, Analysis and Corrective actions q Quality issues may be In plant Defect, Defect at supplier, Customer complaint, Warranty Failure or voice of customer q Supports concept of QRQC – Quick Response Quality Control q Centralized collection of all quality issues at one point. q Analysis of issues in 8 D format q Identification of improvements - either CAPA, Kaizen or Pokayoke q Corrective action for quality issue elimination by implementing the improvements QMS Eagle – Quality Events Main Menu 19
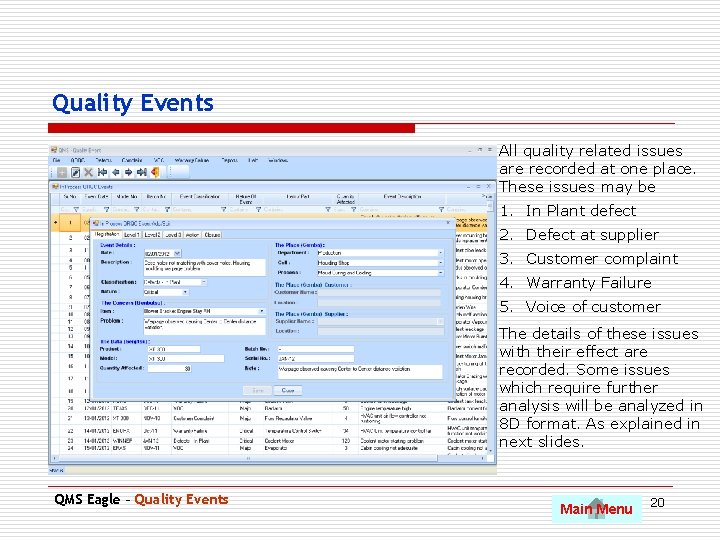
Quality Events All quality related issues are recorded at one place. These issues may be 1. In Plant defect 2. Defect at supplier 3. Customer complaint 4. Warranty Failure 5. Voice of customer The details of these issues with their effect are recorded. Some issues which require further analysis will be analyzed in 8 D format. As explained in next slides. QMS Eagle – Quality Events Main Menu 20
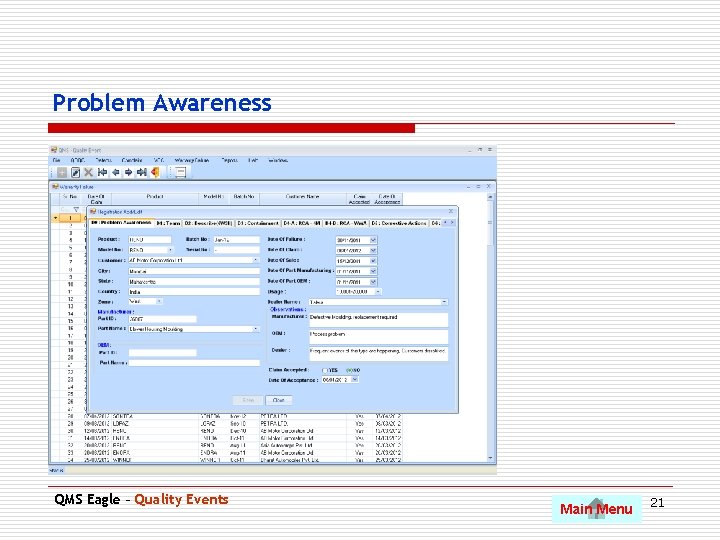
Problem Awareness QMS Eagle – Quality Events Main Menu 21
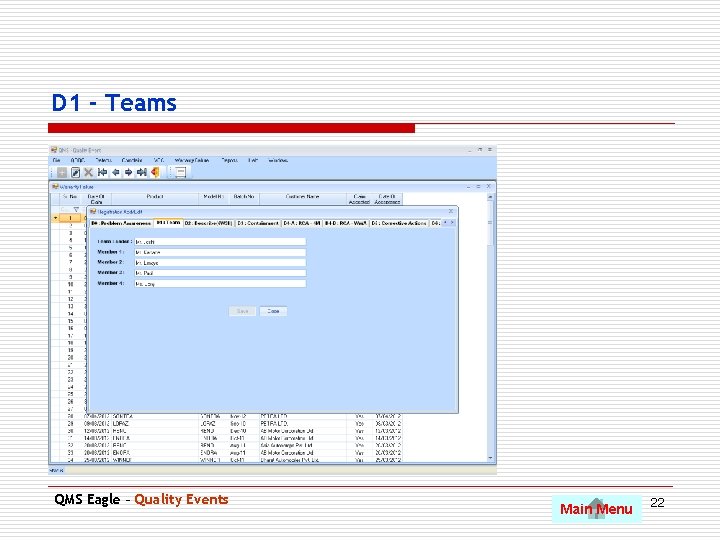
D 1 - Teams QMS Eagle – Quality Events Main Menu 22
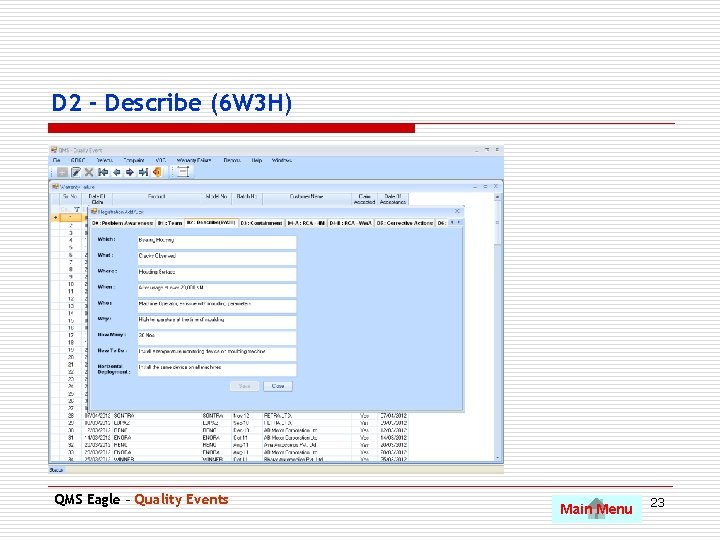
D 2 - Describe (6 W 3 H) QMS Eagle – Quality Events Main Menu 23
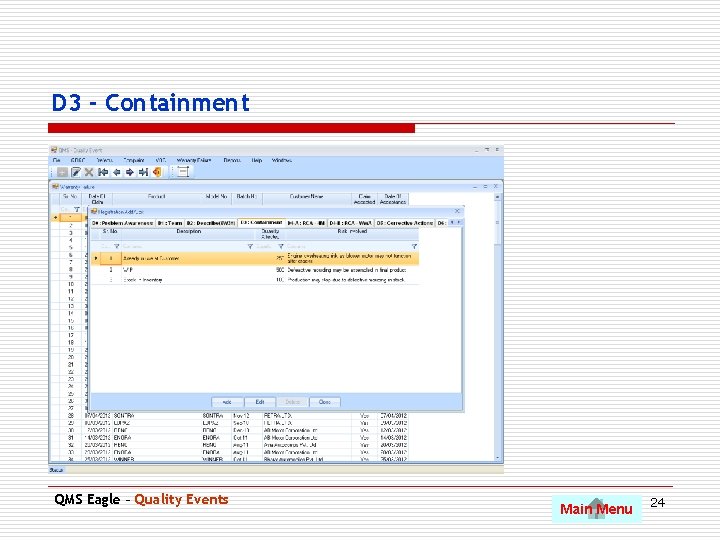
D 3 - Containment QMS Eagle – Quality Events Main Menu 24
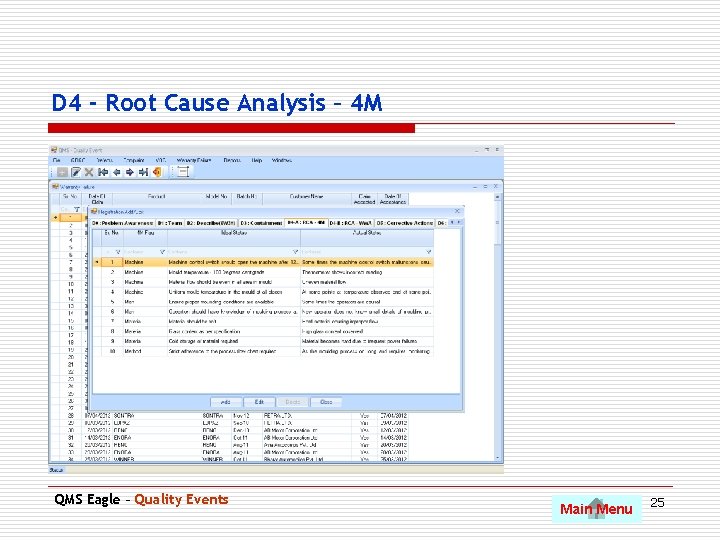
D 4 - Root Cause Analysis – 4 M QMS Eagle – Quality Events Main Menu 25
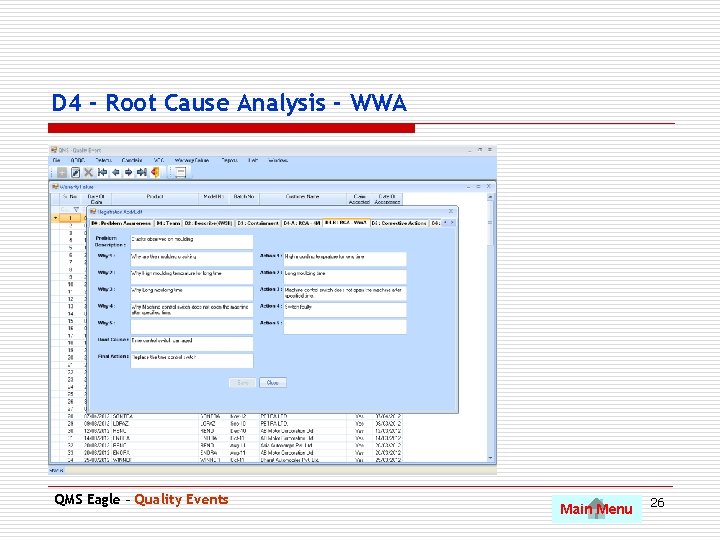
D 4 - Root Cause Analysis - WWA QMS Eagle – Quality Events Main Menu 26
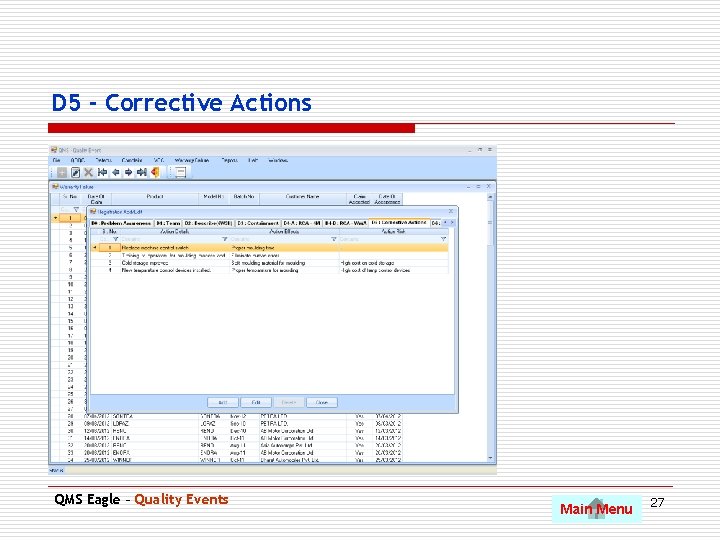
D 5 - Corrective Actions QMS Eagle – Quality Events Main Menu 27
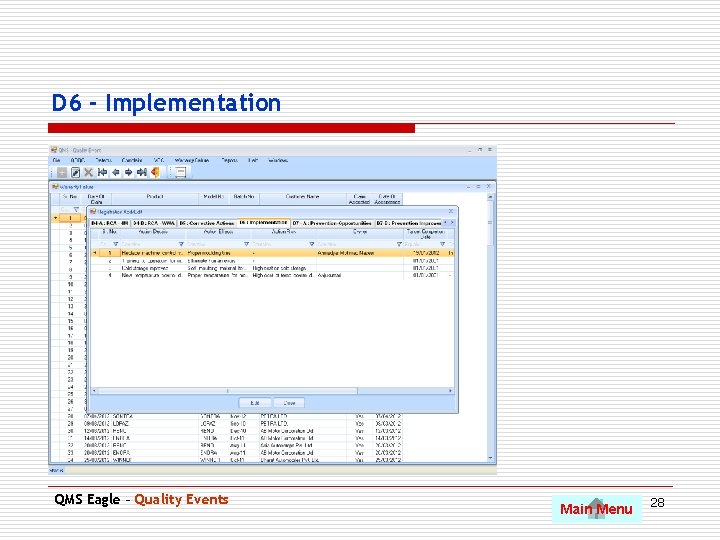
D 6 - Implementation QMS Eagle – Quality Events Main Menu 28
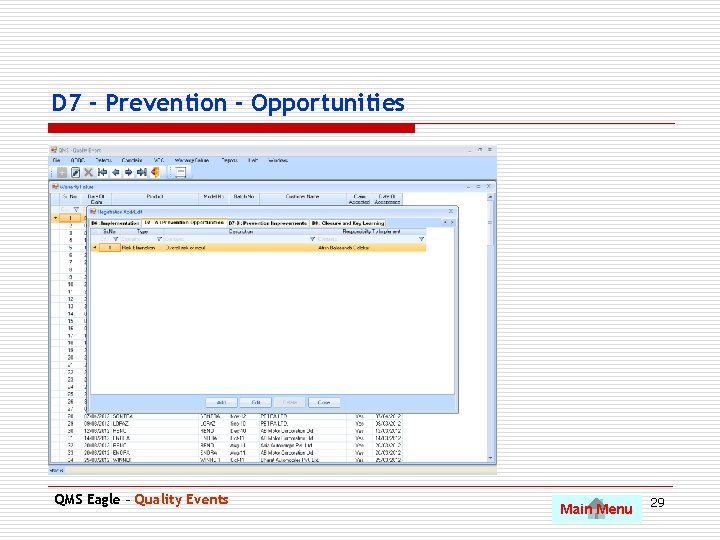
D 7 - Prevention - Opportunities QMS Eagle – Quality Events Main Menu 29
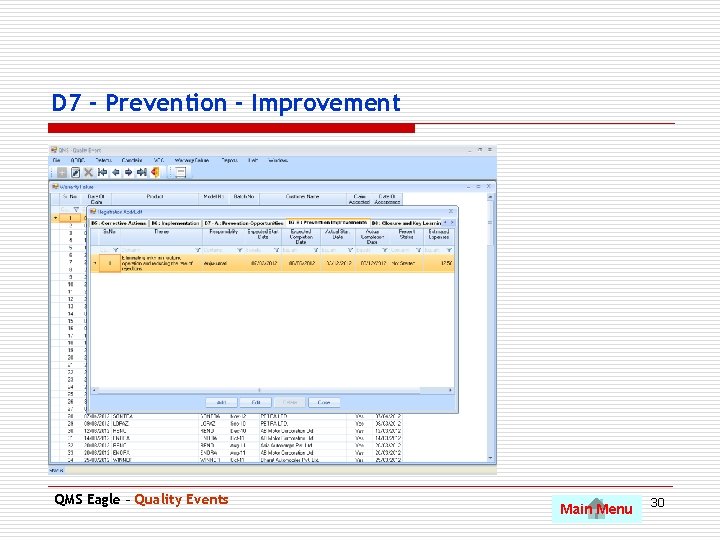
D 7 - Prevention - Improvement QMS Eagle – Quality Events Main Menu 30

D 8 - Closure and Key Learning QMS Eagle – Quality Events Main Menu 31
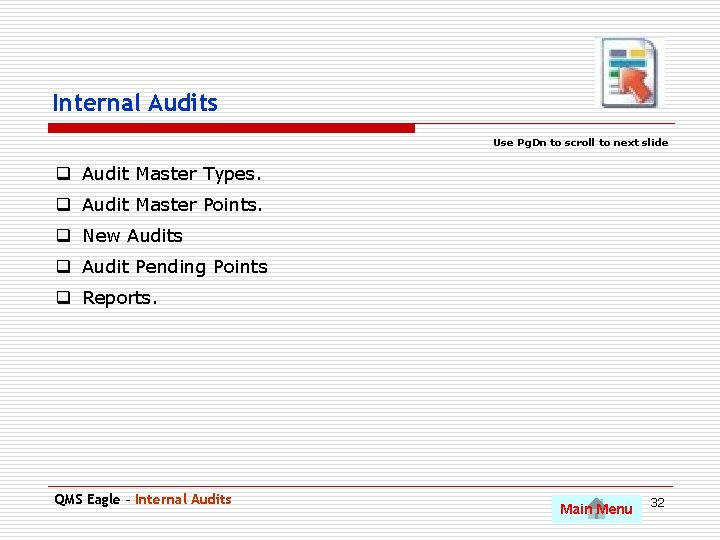
Internal Audits Use Pg. Dn to scroll to next slide q Audit Master Types. q Audit Master Points. q New Audits q Audit Pending Points q Reports. QMS Eagle – Internal Audits Main Menu 32
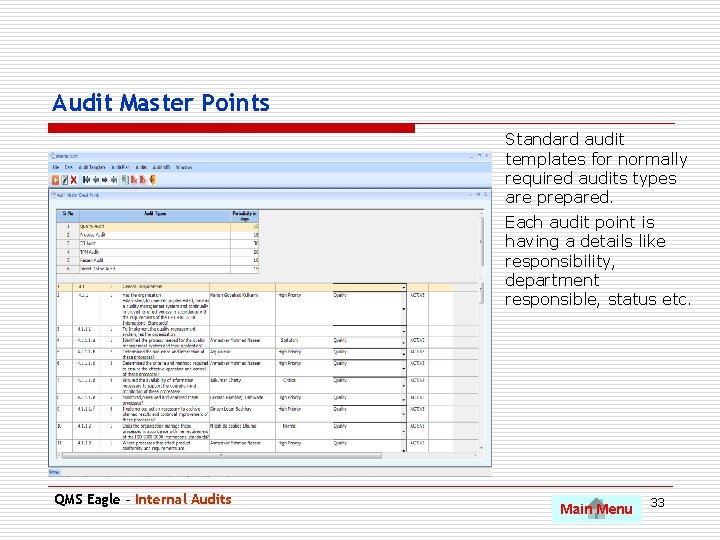
Audit Master Points Standard audit templates for normally required audits types are prepared. Each audit point is having a details like responsibility, department responsible, status etc. QMS Eagle – Internal Audits Main Menu 33
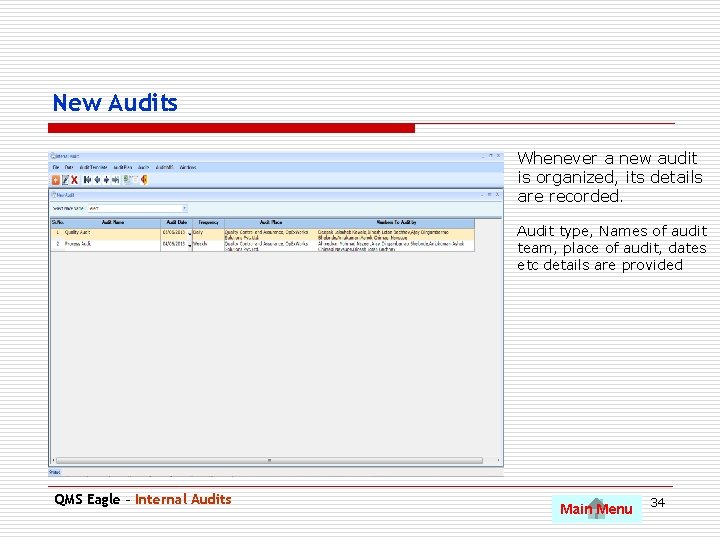
New Audits Whenever a new audit is organized, its details are recorded. Audit type, Names of audit team, place of audit, dates etc details are provided QMS Eagle – Internal Audits Main Menu 34
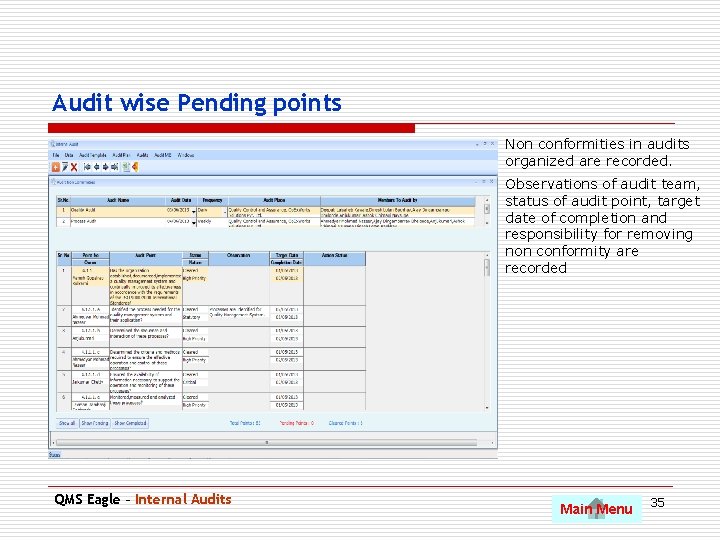
Audit wise Pending points Non conformities in audits organized are recorded. Observations of audit team, status of audit point, target date of completion and responsibility for removing non conformity are recorded QMS Eagle – Internal Audits Main Menu 35
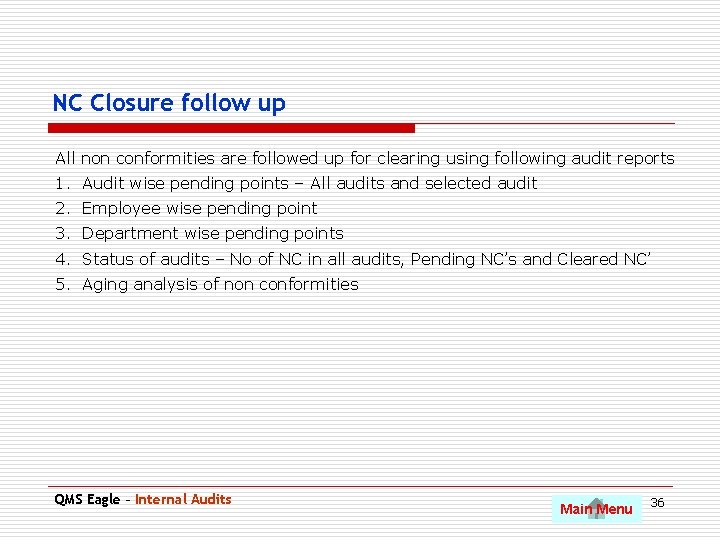
NC Closure follow up All non conformities are followed up for clearing using following audit reports 1. Audit wise pending points – All audits and selected audit 2. Employee wise pending point 3. Department wise pending points 4. Status of audits – No of NC in all audits, Pending NC’s and Cleared NC’ 5. Aging analysis of non conformities QMS Eagle – Internal Audits Main Menu 36
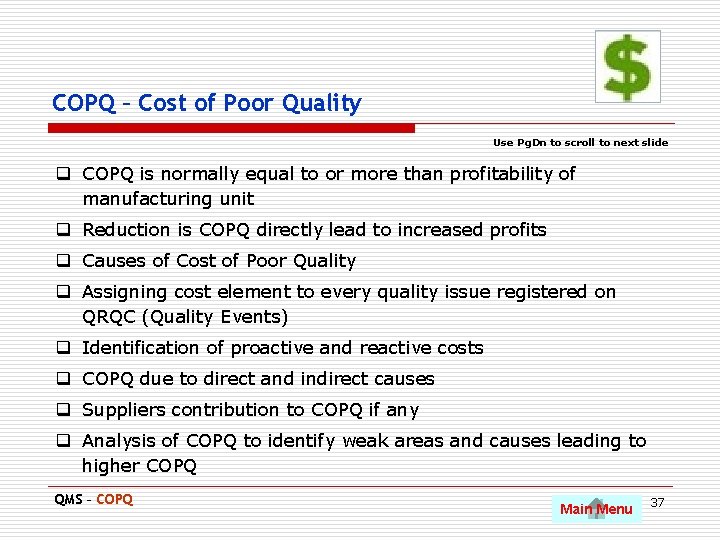
COPQ – Cost of Poor Quality Use Pg. Dn to scroll to next slide q COPQ is normally equal to or more than profitability of manufacturing unit q Reduction is COPQ directly lead to increased profits q Causes of Cost of Poor Quality q Assigning cost element to every quality issue registered on QRQC (Quality Events) q Identification of proactive and reactive costs q COPQ due to direct and indirect causes q Suppliers contribution to COPQ if any q Analysis of COPQ to identify weak areas and causes leading to higher COPQ QMS – COPQ Main Menu 37
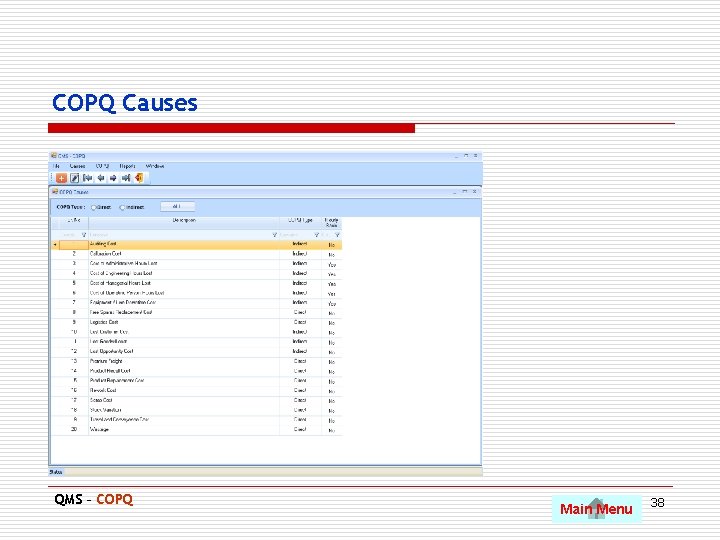
COPQ Causes QMS – COPQ Main Menu 38
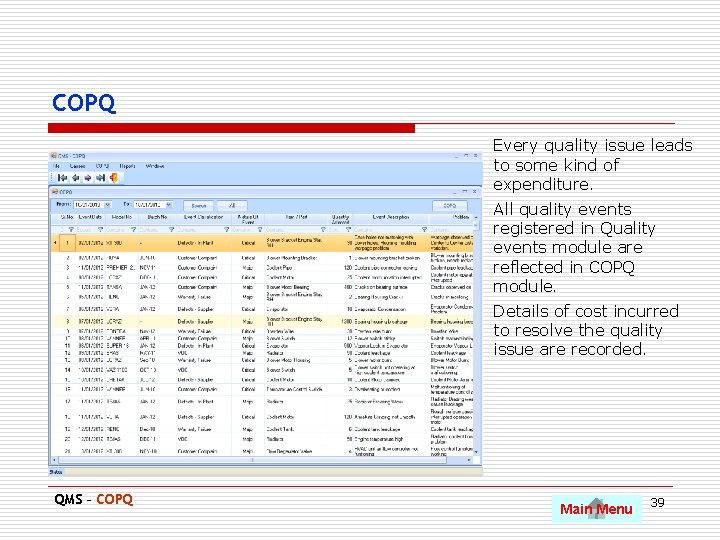
COPQ Every quality issue leads to some kind of expenditure. All quality events registered in Quality events module are reflected in COPQ module. Details of cost incurred to resolve the quality issue are recorded. QMS – COPQ Main Menu 39
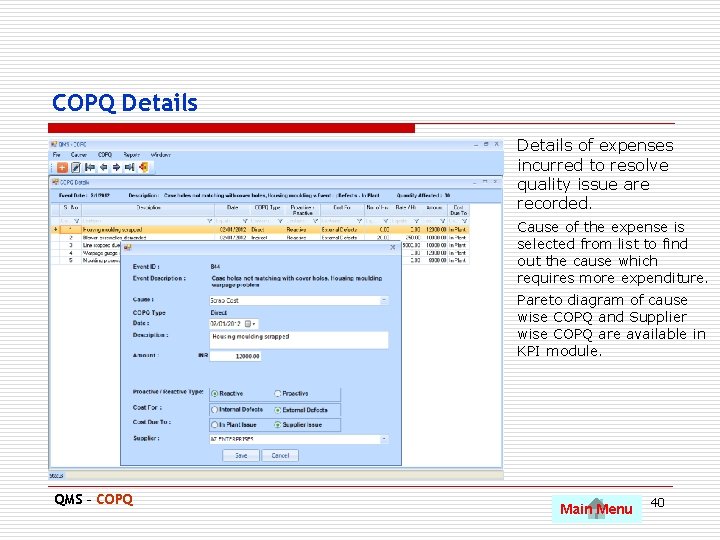
COPQ Details of expenses incurred to resolve quality issue are recorded. Cause of the expense is selected from list to find out the cause which requires more expenditure. Pareto diagram of cause wise COPQ and Supplier wise COPQ are available in KPI module. QMS – COPQ Main Menu 40
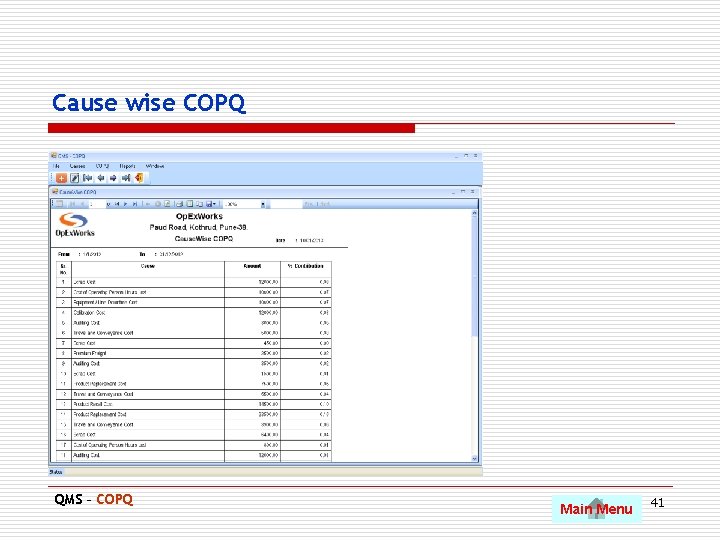
Cause wise COPQ QMS – COPQ Main Menu 41
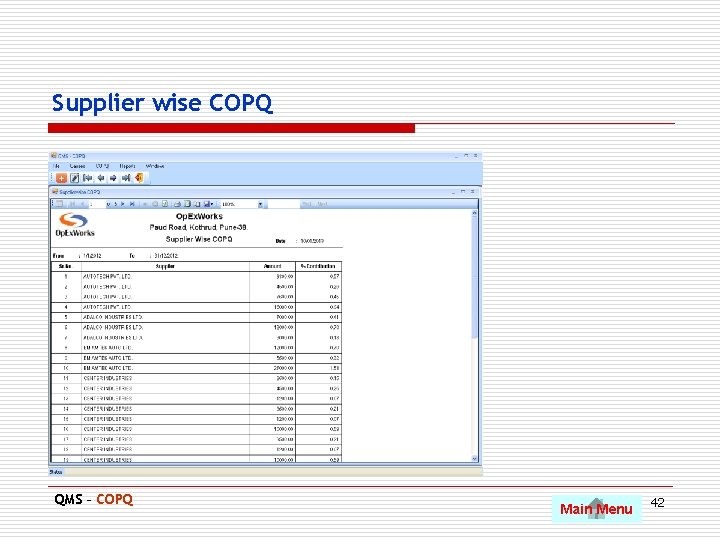
Supplier wise COPQ QMS – COPQ Main Menu 42
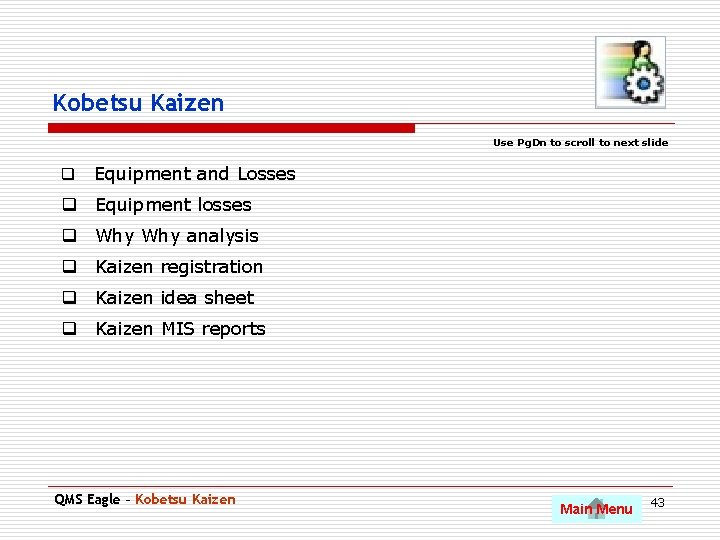
Kobetsu Kaizen Use Pg. Dn to scroll to next slide q Equipment and Losses q Equipment losses q Why analysis q Kaizen registration q Kaizen idea sheet q Kaizen MIS reports QMS Eagle – Kobetsu Kaizen Main Menu 43
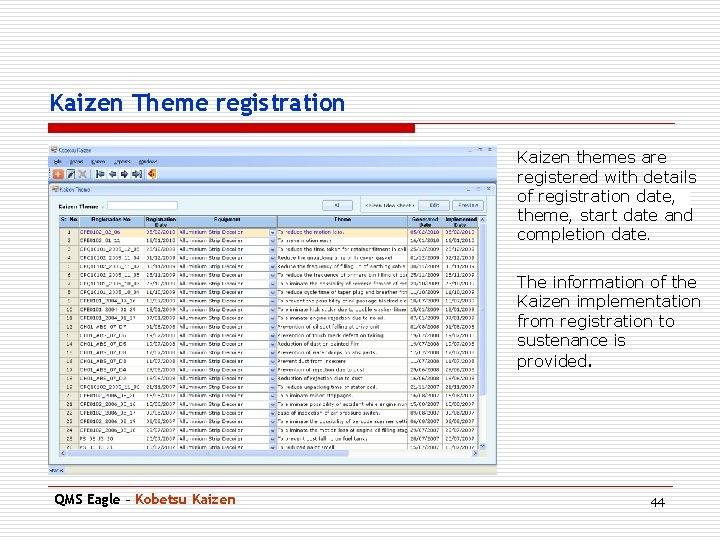
Kaizen Theme registration Kaizen themes are registered with details of registration date, theme, start date and completion date. The information of the Kaizen implementation from registration to sustenance is provided. QMS Eagle – Kobetsu Kaizen 44
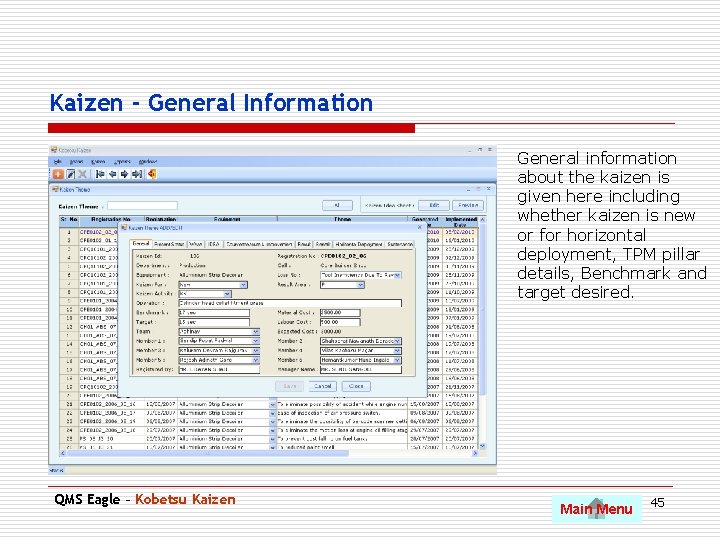
Kaizen - General Information General information about the kaizen is given here including whether kaizen is new or for horizontal deployment, TPM pillar details, Benchmark and target desired. QMS Eagle – Kobetsu Kaizen Main Menu 45
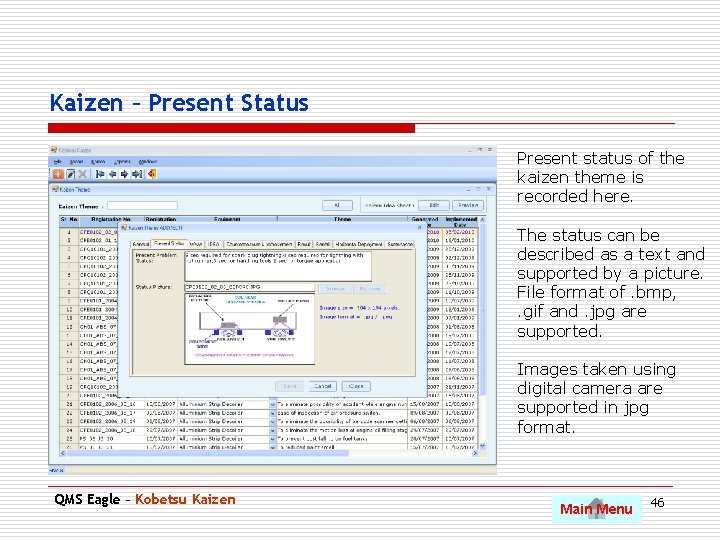
Kaizen – Present Status Present status of the kaizen theme is recorded here. The status can be described as a text and supported by a picture. File format of. bmp, . gif and. jpg are supported. Images taken using digital camera are supported in jpg format. QMS Eagle – Kobetsu Kaizen Main Menu 46
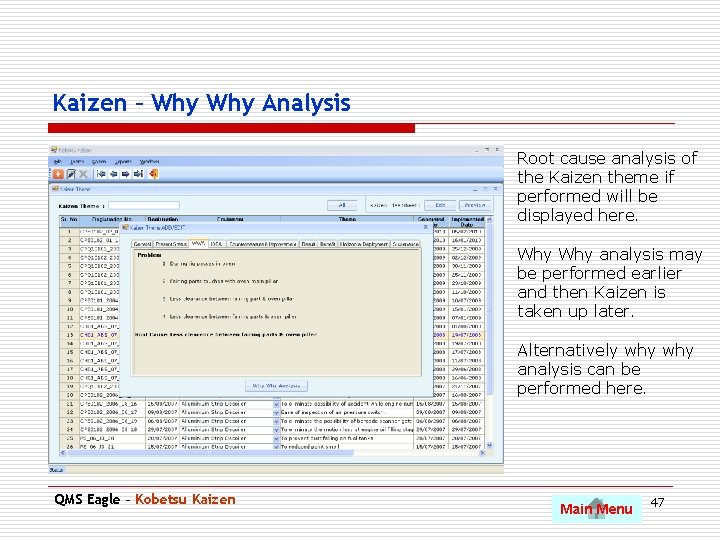
Kaizen – Why Analysis Root cause analysis of the Kaizen theme if performed will be displayed here. Why analysis may be performed earlier and then Kaizen is taken up later. Alternatively why analysis can be performed here. QMS Eagle – Kobetsu Kaizen Main Menu 47
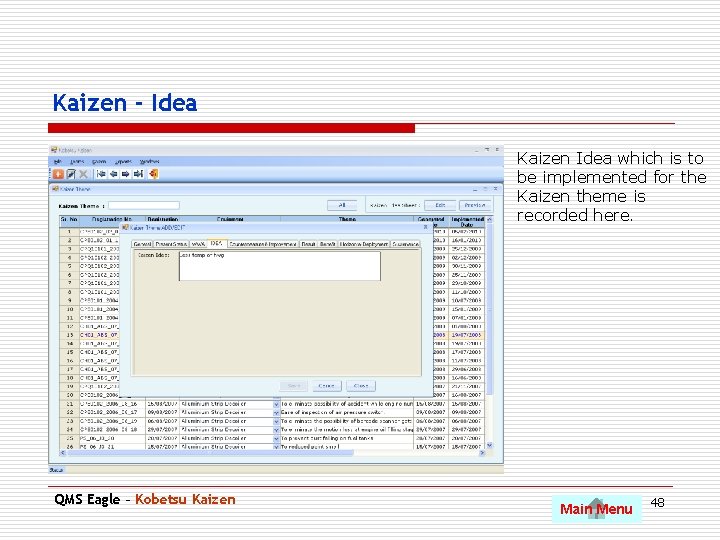
Kaizen - Idea Kaizen Idea which is to be implemented for the Kaizen theme is recorded here. QMS Eagle – Kobetsu Kaizen Main Menu 48
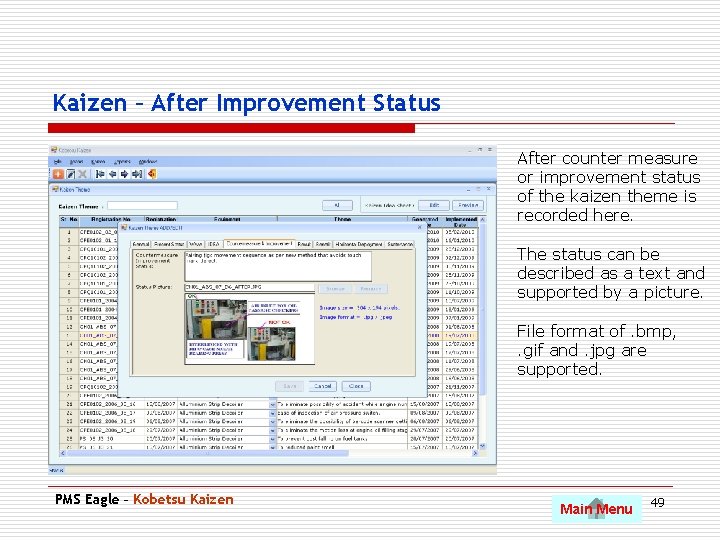
Kaizen – After Improvement Status After counter measure or improvement status of the kaizen theme is recorded here. The status can be described as a text and supported by a picture. File format of. bmp, . gif and. jpg are supported. PMS Eagle – Kobetsu Kaizen Main Menu 49
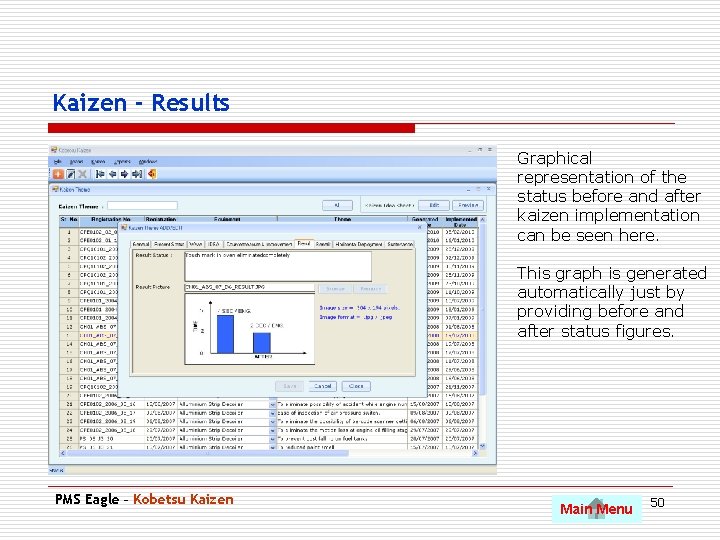
Kaizen - Results Graphical representation of the status before and after kaizen implementation can be seen here. This graph is generated automatically just by providing before and after status figures. PMS Eagle – Kobetsu Kaizen Main Menu 50
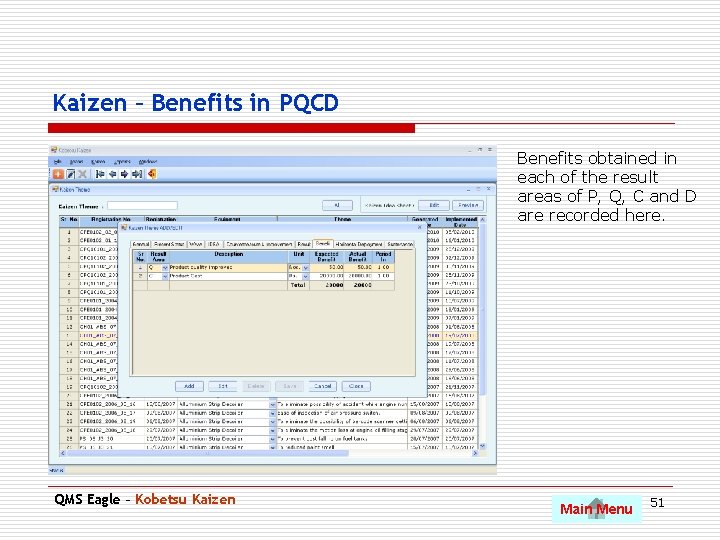
Kaizen – Benefits in PQCD Benefits obtained in each of the result areas of P, Q, C and D are recorded here. QMS Eagle – Kobetsu Kaizen Main Menu 51
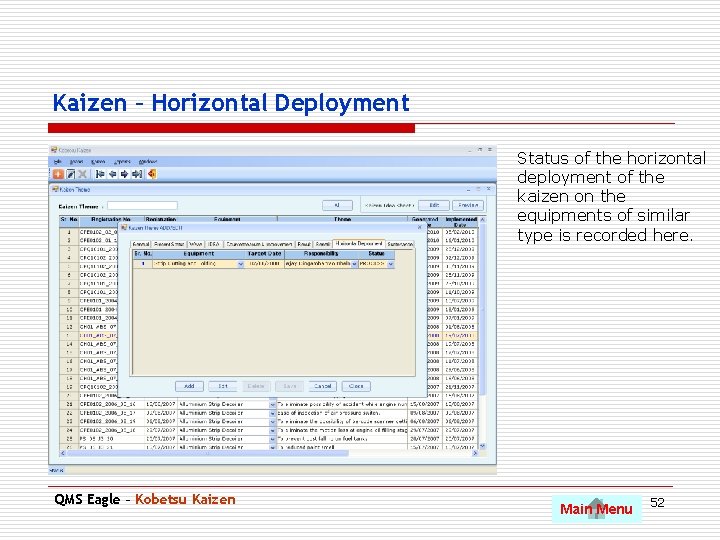
Kaizen – Horizontal Deployment Status of the horizontal deployment of the kaizen on the equipments of similar type is recorded here. QMS Eagle – Kobetsu Kaizen Main Menu 52
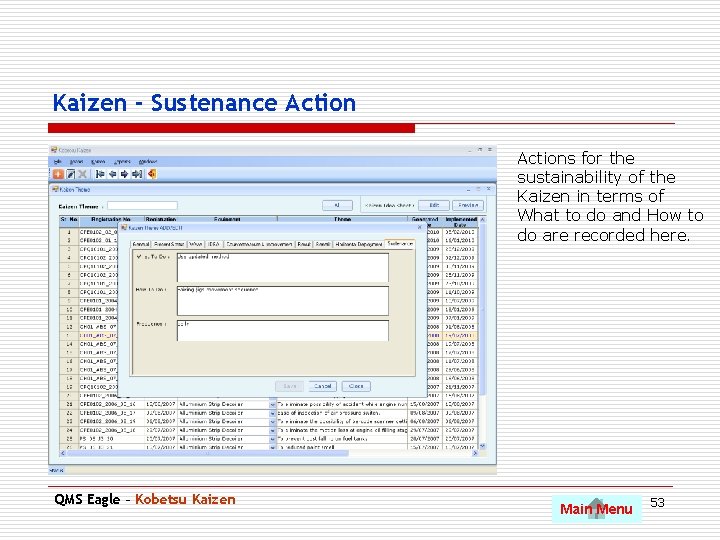
Kaizen - Sustenance Actions for the sustainability of the Kaizen in terms of What to do and How to do are recorded here. QMS Eagle – Kobetsu Kaizen Main Menu 53
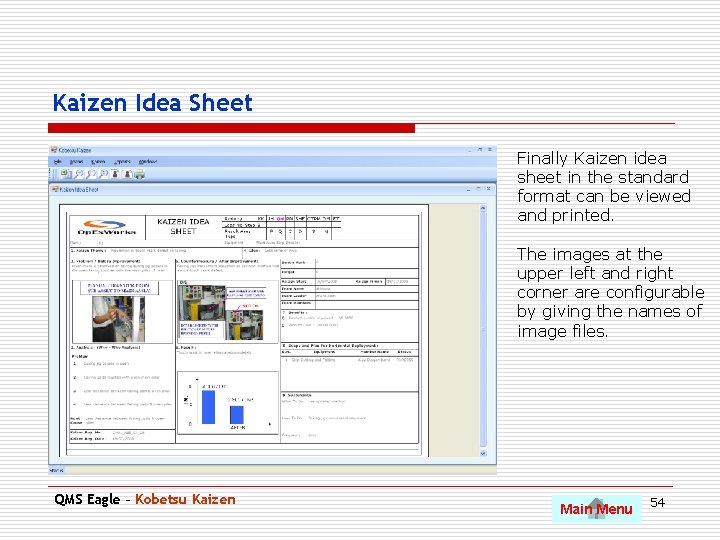
Kaizen Idea Sheet Finally Kaizen idea sheet in the standard format can be viewed and printed. The images at the upper left and right corner are configurable by giving the names of image files. QMS Eagle – Kobetsu Kaizen Main Menu 54
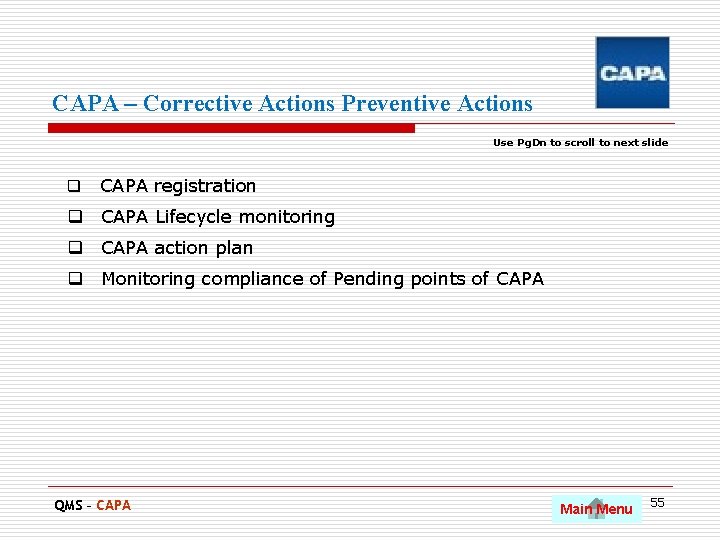
CAPA – Corrective Actions Preventive Actions Use Pg. Dn to scroll to next slide q CAPA registration q CAPA Lifecycle monitoring q CAPA action plan q Monitoring compliance of Pending points of CAPA QMS – CAPA Main Menu 55
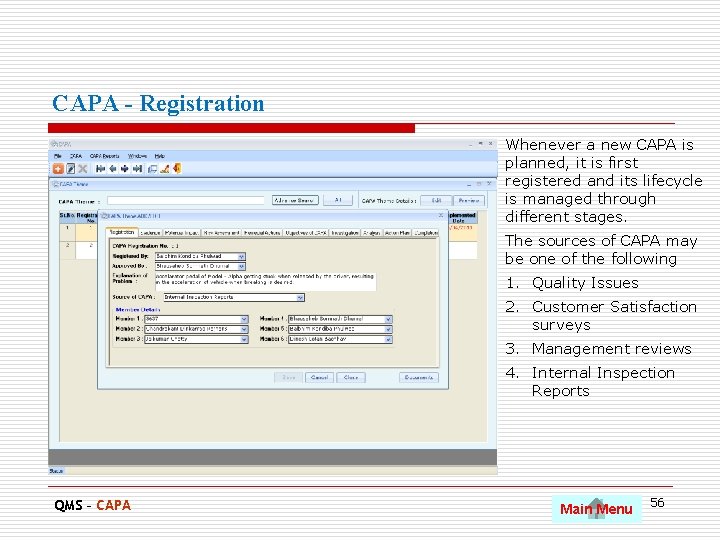
CAPA - Registration Whenever a new CAPA is planned, it is first registered and its lifecycle is managed through different stages. The sources of CAPA may be one of the following 1. Quality Issues 2. Customer Satisfaction surveys 3. Management reviews 4. Internal Inspection Reports QMS – CAPA Main Menu 56
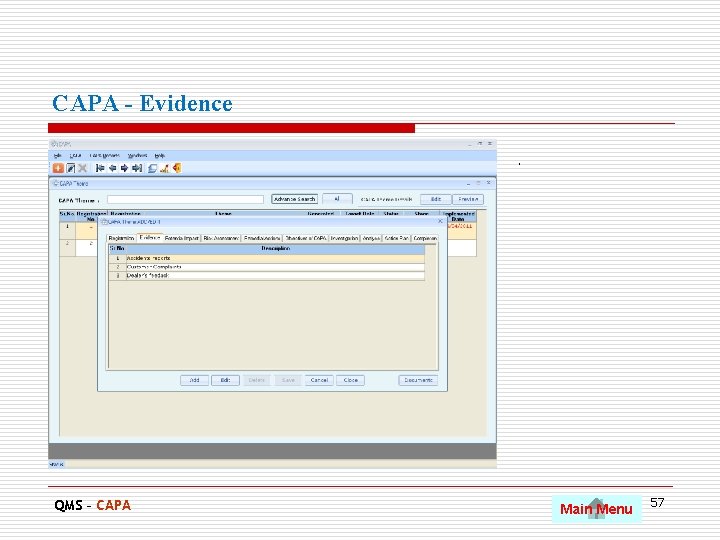
CAPA - Evidence. QMS – CAPA Main Menu 57
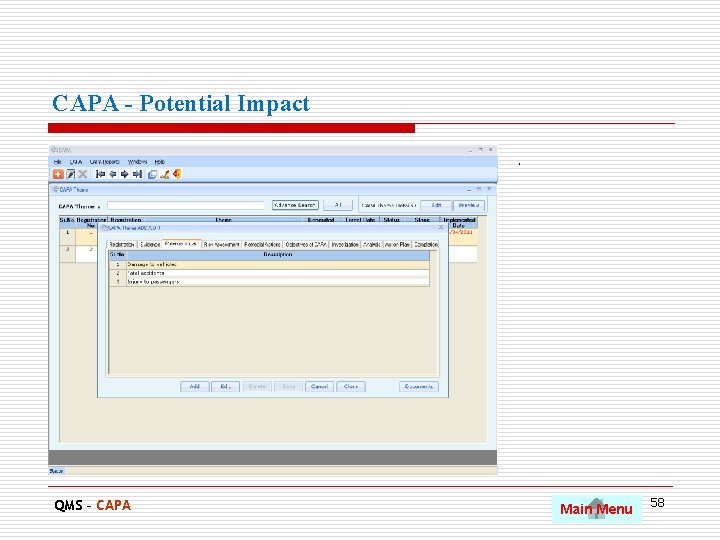
CAPA - Potential Impact. QMS – CAPA Main Menu 58
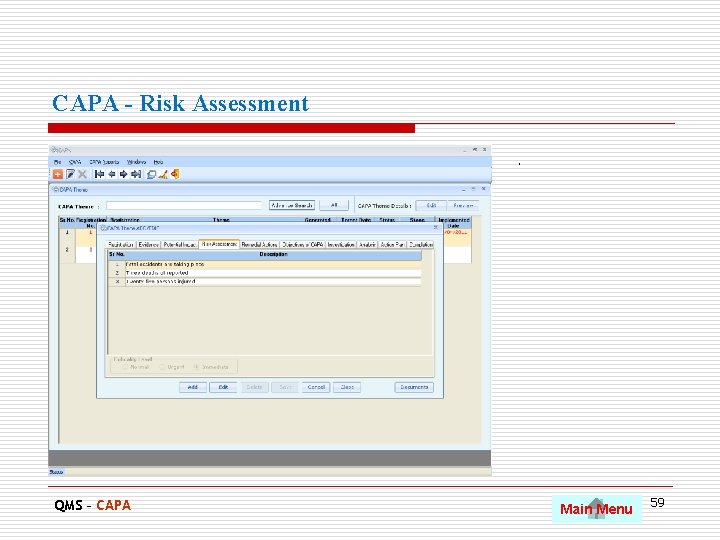
CAPA - Risk Assessment. QMS – CAPA Main Menu 59
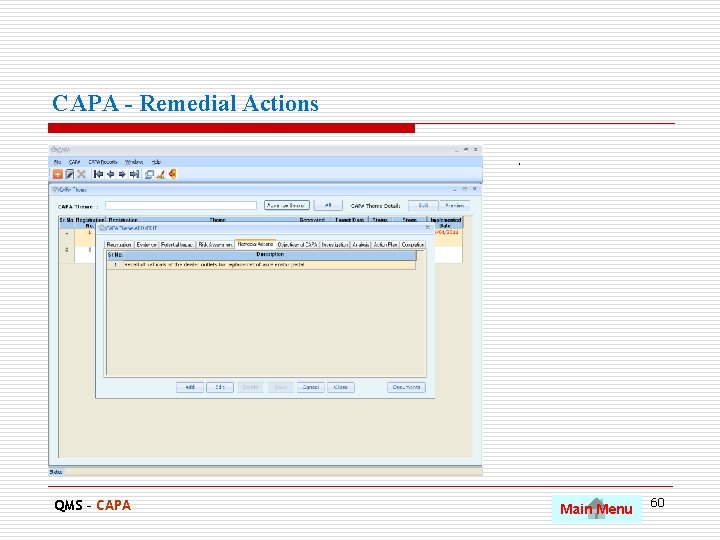
CAPA - Remedial Actions. QMS – CAPA Main Menu 60
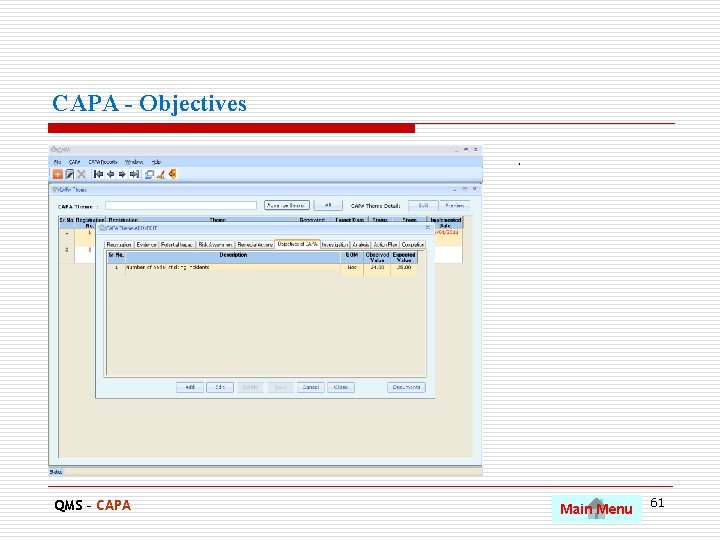
CAPA - Objectives. QMS – CAPA Main Menu 61
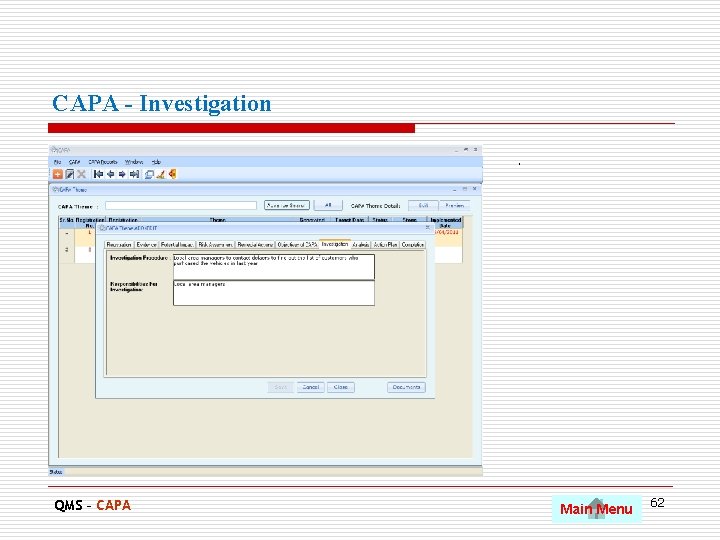
CAPA - Investigation. QMS – CAPA Main Menu 62
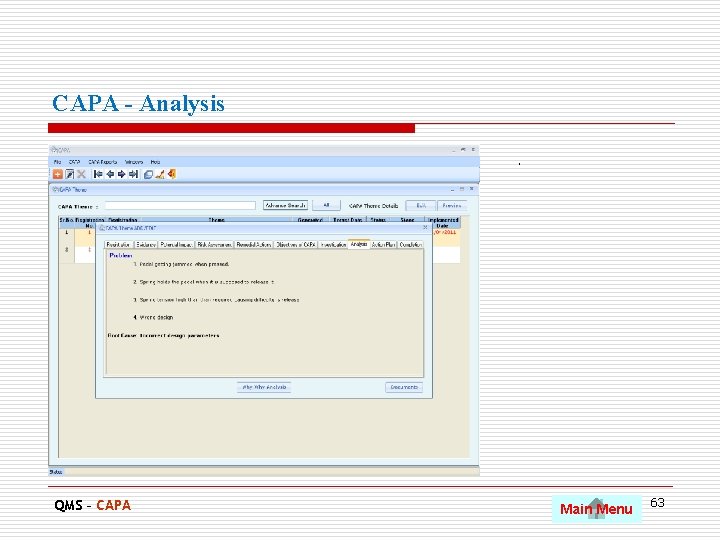
CAPA - Analysis. QMS – CAPA Main Menu 63
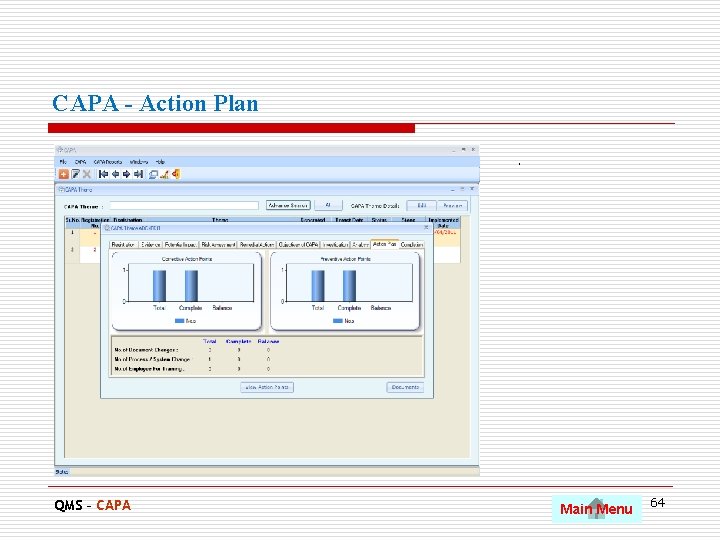
CAPA - Action Plan. QMS – CAPA Main Menu 64
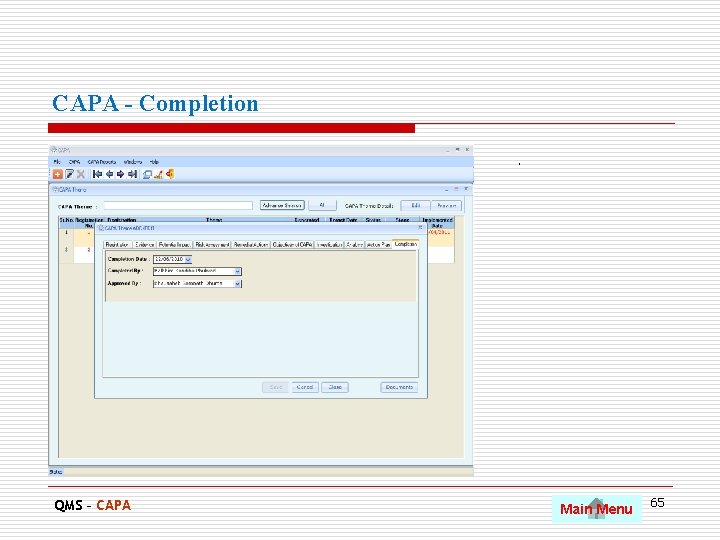
CAPA - Completion. QMS – CAPA Main Menu 65
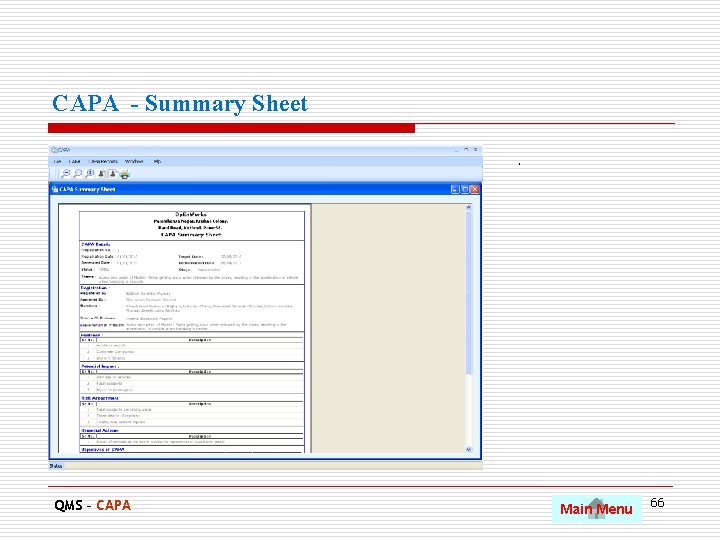
CAPA - Summary Sheet. QMS – CAPA Main Menu 66
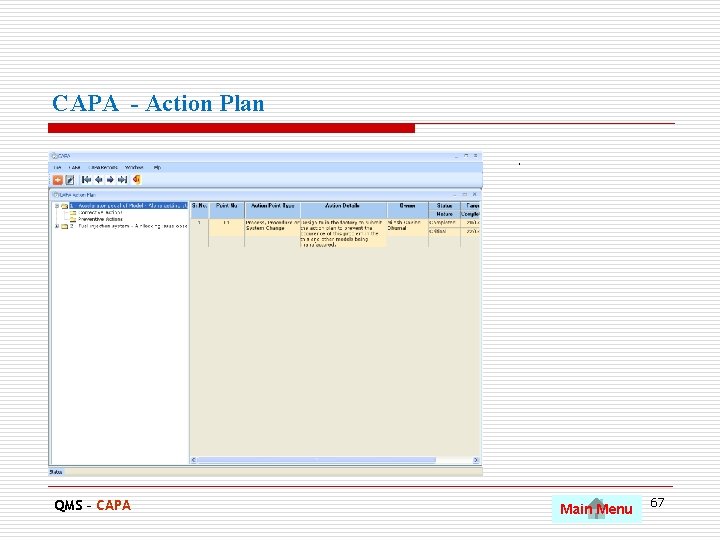
CAPA - Action Plan. QMS – CAPA Main Menu 67
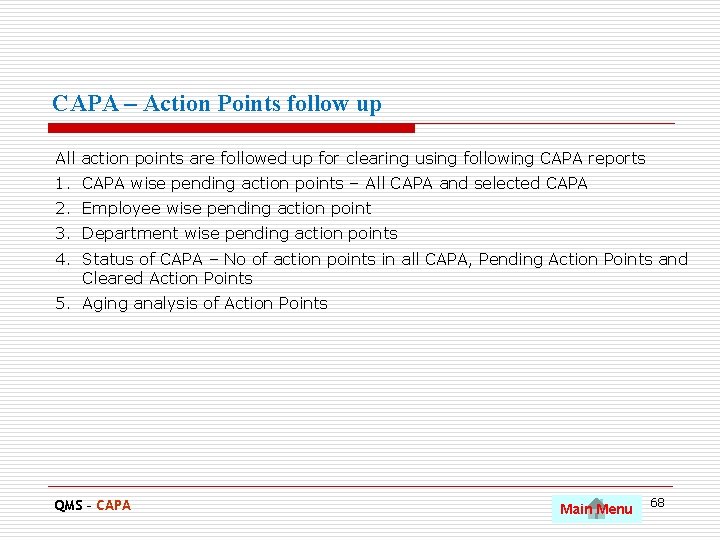
CAPA – Action Points follow up All action points are followed up for clearing using following. CAPA reports 1. CAPA wise pending action points – All CAPA and selected CAPA 2. Employee wise pending action point 3. Department wise pending action points 4. Status of CAPA – No of action points in all CAPA, Pending Action Points and Cleared Action Points 5. Aging analysis of Action Points QMS – CAPA Main Menu 68
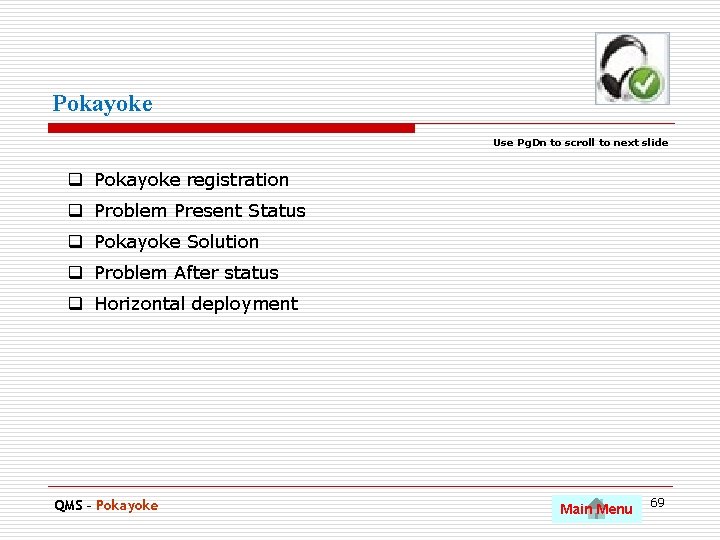
Pokayoke Use Pg. Dn to scroll to next slide q Pokayoke registration q Problem Present Status q Pokayoke Solution q Problem After status q Horizontal deployment QMS – Pokayoke Main Menu 69
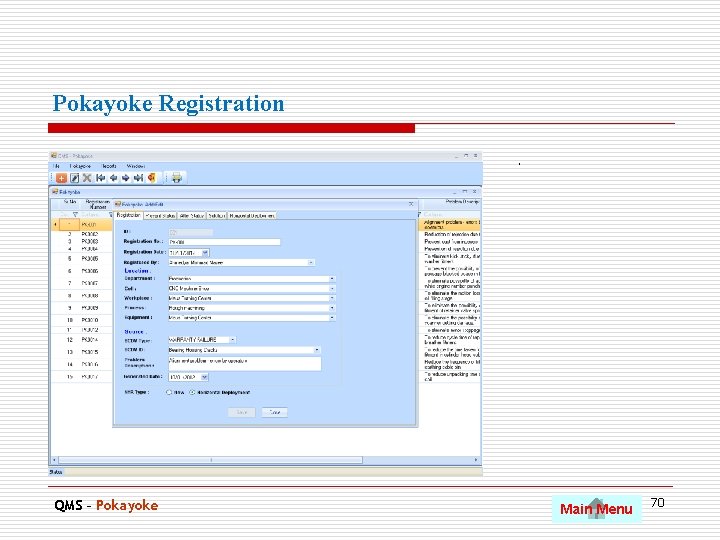
Pokayoke Registration. QMS – Pokayoke Main Menu 70

Pokayoke Present Status. QMS – Pokayoke Main Menu 71
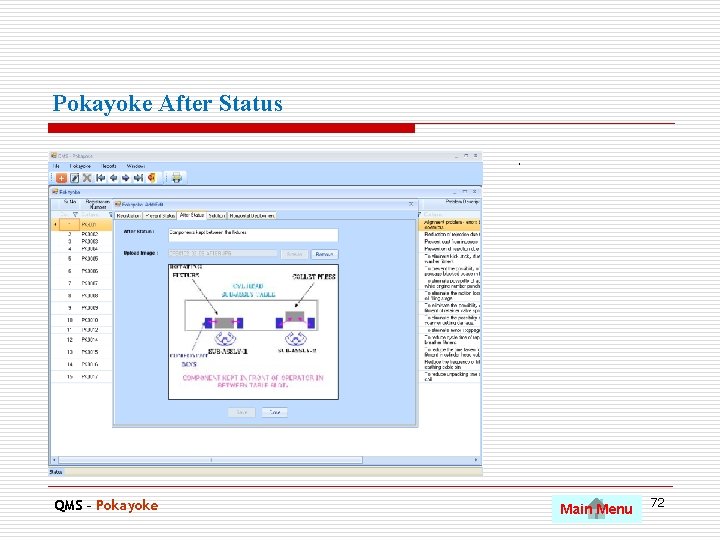
Pokayoke After Status. QMS – Pokayoke Main Menu 72
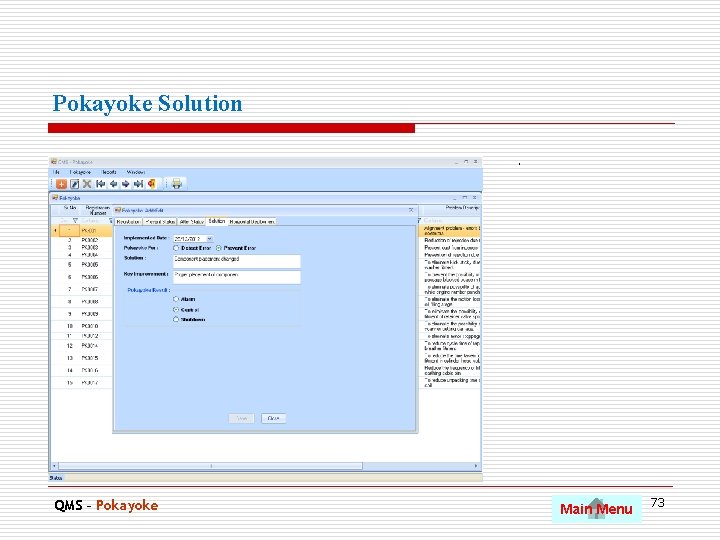
Pokayoke Solution. QMS – Pokayoke Main Menu 73
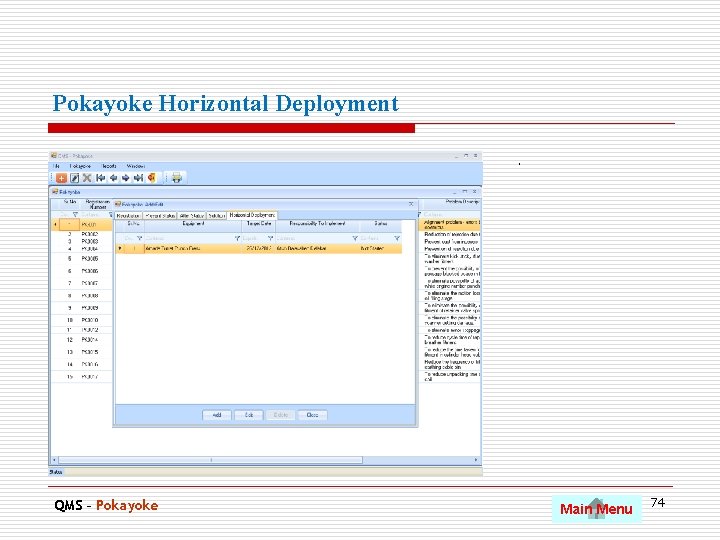
Pokayoke Horizontal Deployment. QMS – Pokayoke Main Menu 74
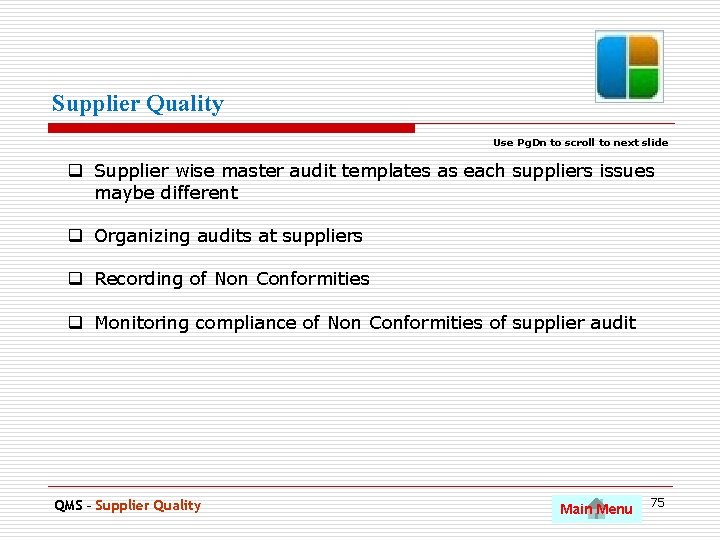
Supplier Quality Use Pg. Dn to scroll to next slide q Supplier wise master audit templates as each suppliers issues maybe different q Organizing audits at suppliers q Recording of Non Conformities q Monitoring compliance of Non Conformities of supplier audit QMS – Supplier Quality Main Menu 75
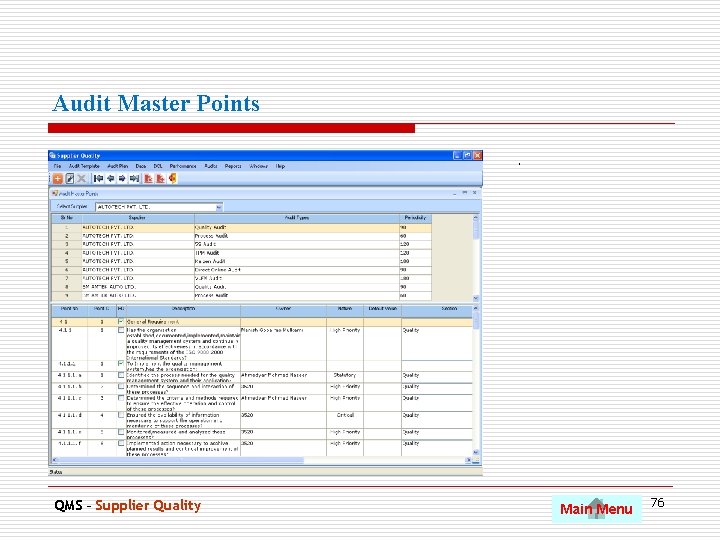
Audit Master Points. QMS – Supplier Quality Main Menu 76
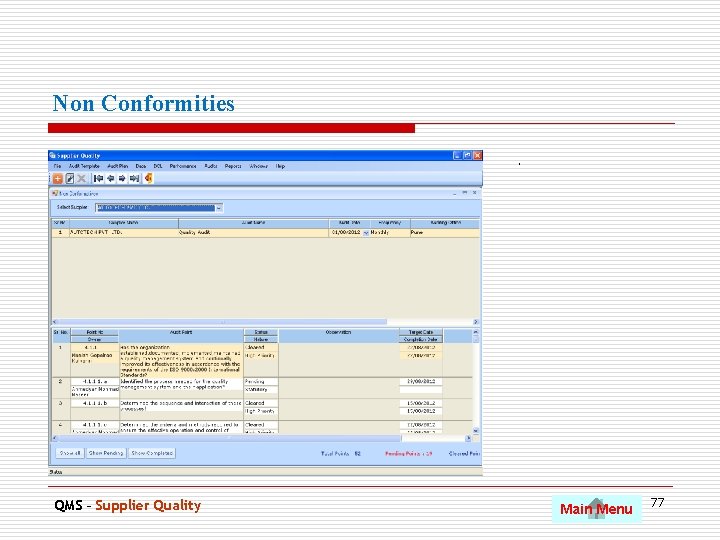
Non Conformities. QMS – Supplier Quality Main Menu 77
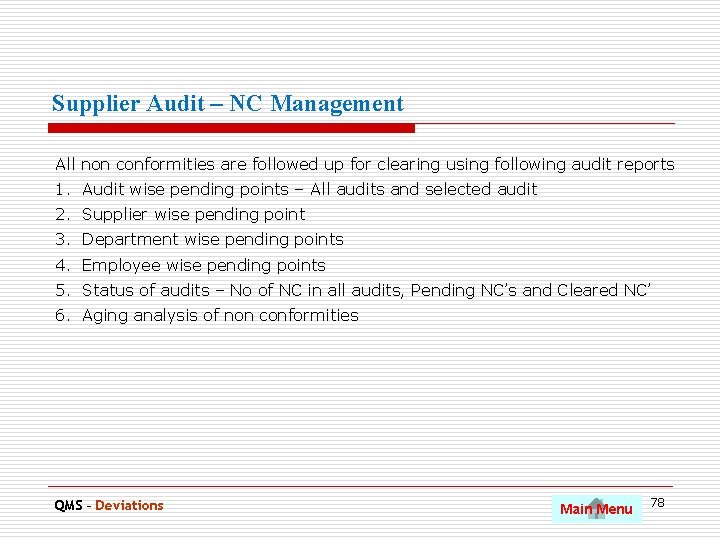
Supplier Audit – NC Management All non conformities are followed up for clearing using following audit reports 1. Audit wise pending points – All audits and selected audit 2. Supplier wise pending point 3. Department wise pending points 4. Employee wise pending points 5. Status of audits – No of NC in all audits, Pending NC’s and Cleared NC’ 6. Aging analysis of non conformities QMS – Deviations Main Menu 78
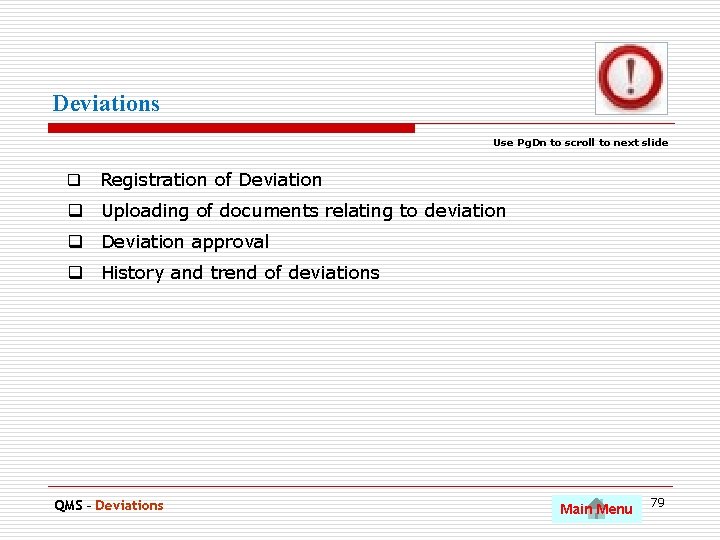
Deviations Use Pg. Dn to scroll to next slide q Registration of Deviation q Uploading of documents relating to deviation q Deviation approval q History and trend of deviations QMS – Deviations Main Menu 79
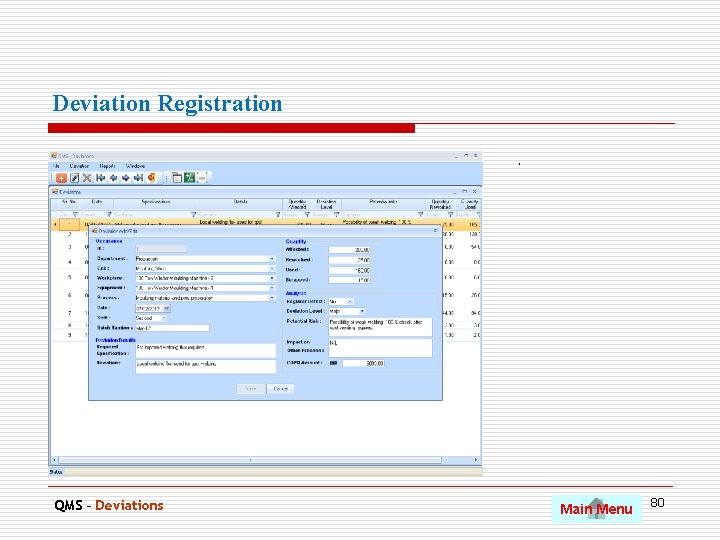
Deviation Registration. QMS – Deviations Main Menu 80
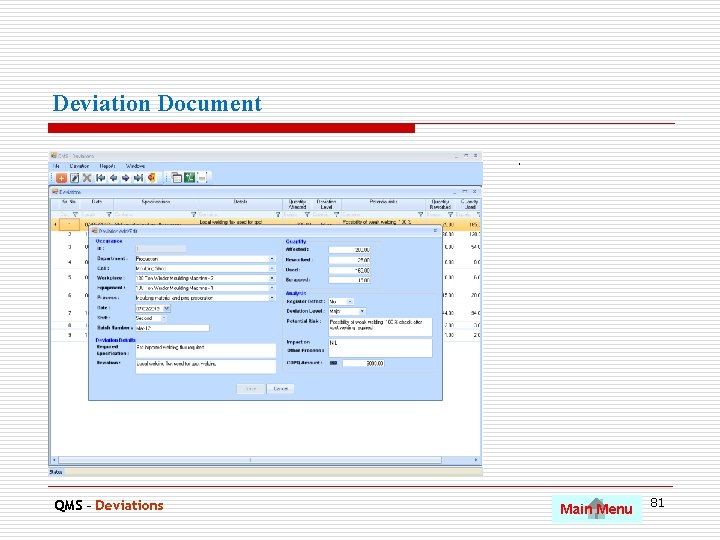
Deviation Document. QMS – Deviations Main Menu 81
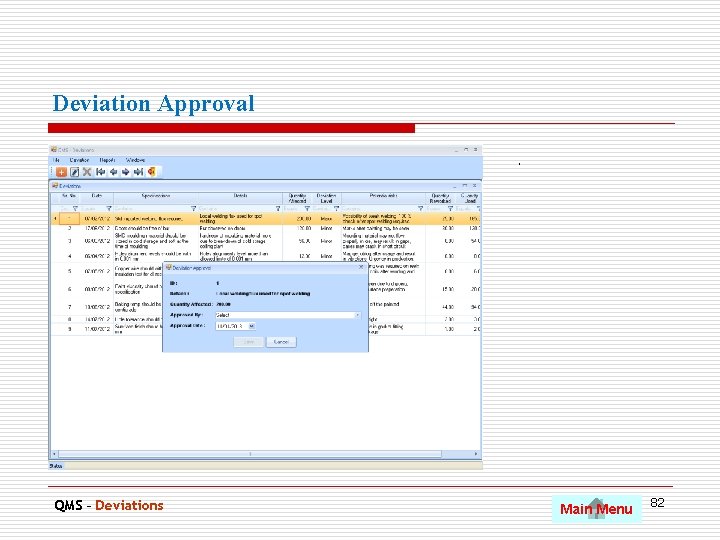
Deviation Approval. QMS – Deviations Main Menu 82
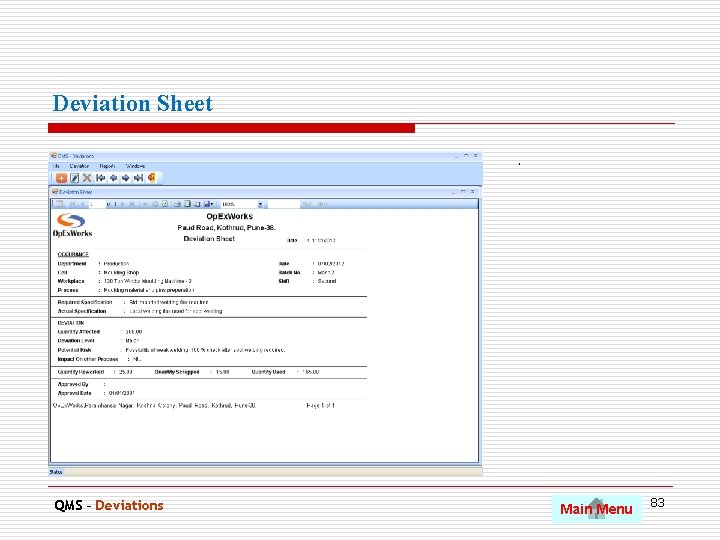
Deviation Sheet. QMS – Deviations Main Menu 83

Deviation Report. QMS – Deviations Main Menu 84
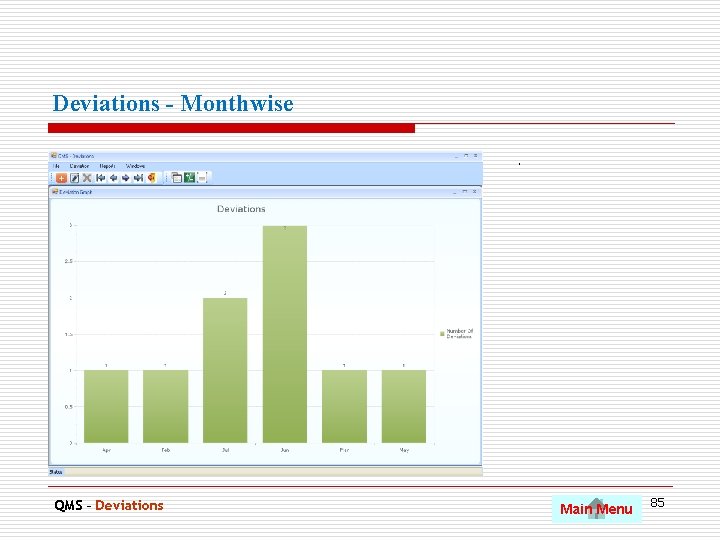
Deviations - Monthwise. QMS – Deviations Main Menu 85
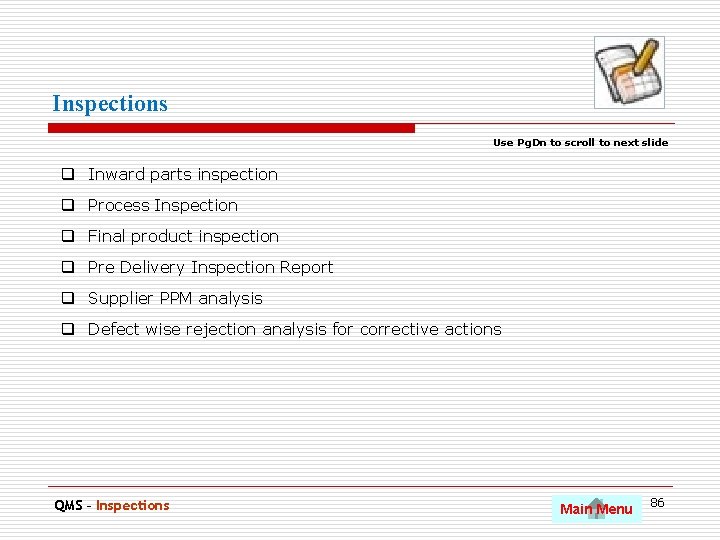
Inspections Use Pg. Dn to scroll to next slide q Inward parts inspection q Process Inspection q Final product inspection q Pre Delivery Inspection Report q Supplier PPM analysis q Defect wise rejection analysis for corrective actions QMS – Inspections Main Menu 86
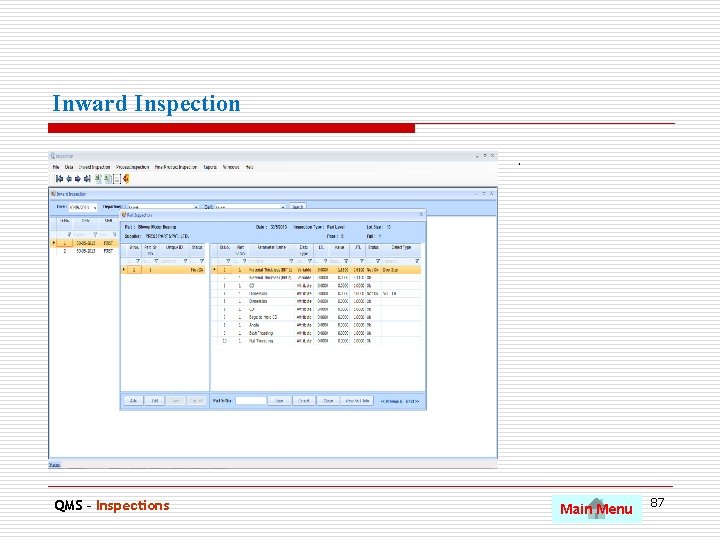
Inward Inspection. QMS – Inspections Main Menu 87
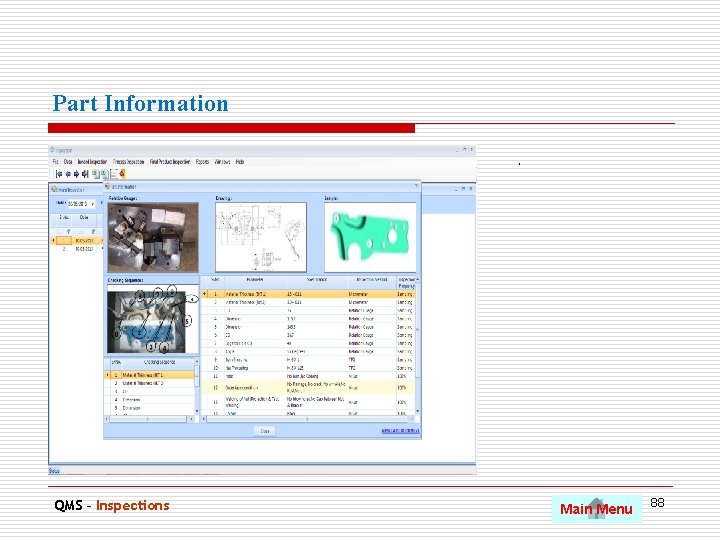
Part Information. QMS – Inspections Main Menu 88
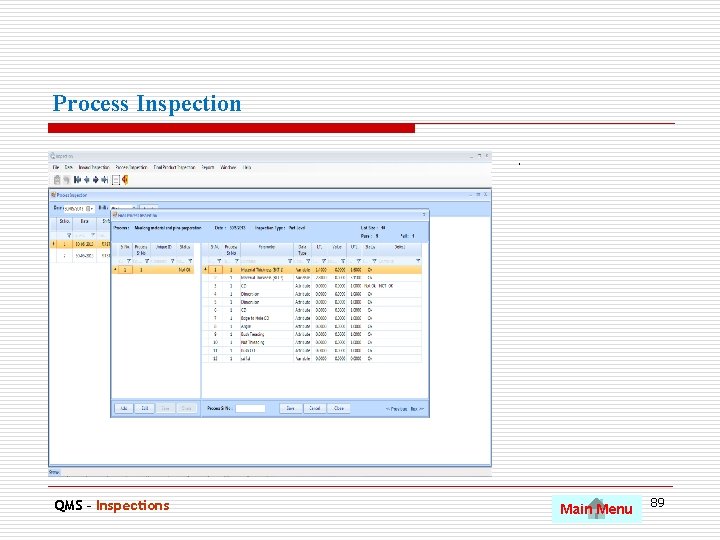
Process Inspection. QMS – Inspections Main Menu 89
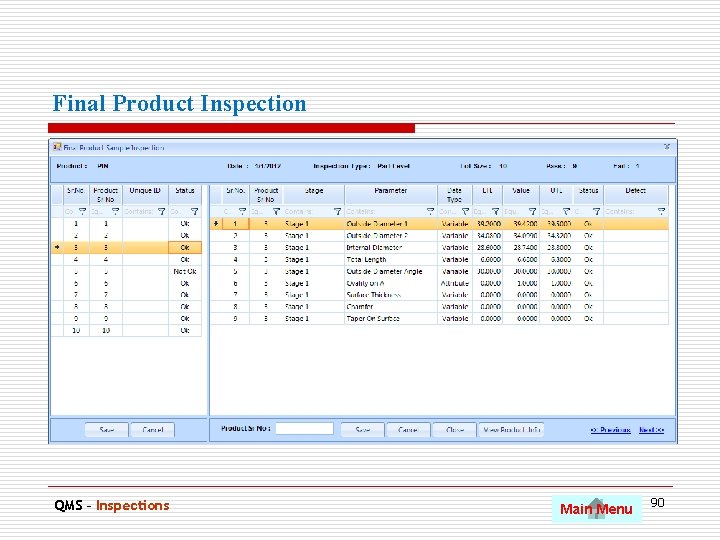
Final Product Inspection. QMS – Inspections Main Menu 90
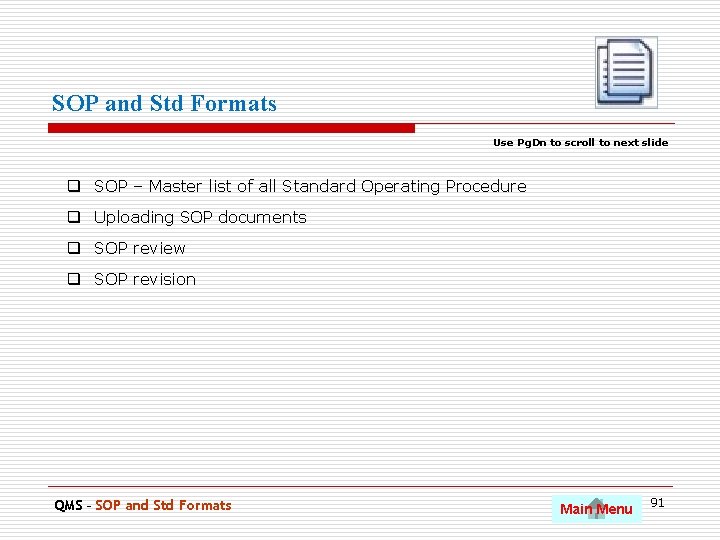
SOP and Std Formats Use Pg. Dn to scroll to next slide q SOP – Master list of all Standard Operating Procedure q Uploading SOP documents q SOP review q SOP revision QMS – SOP and Std Formats Main Menu 91
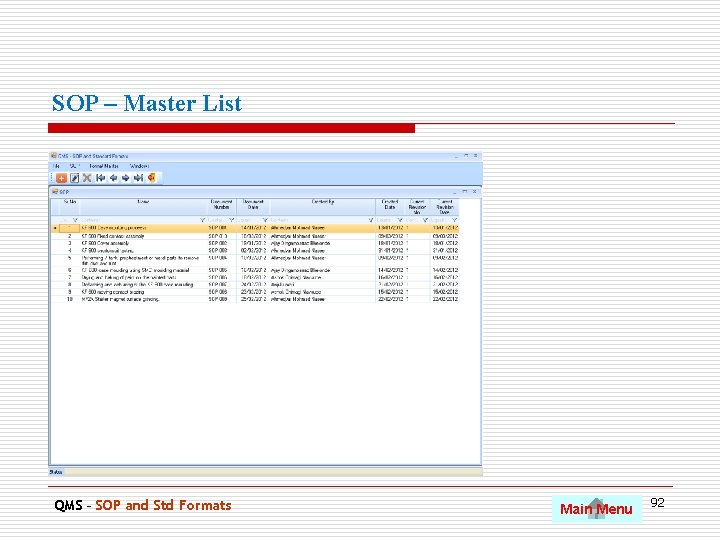
SOP – Master List QMS – SOP and Std Formats Main Menu 92
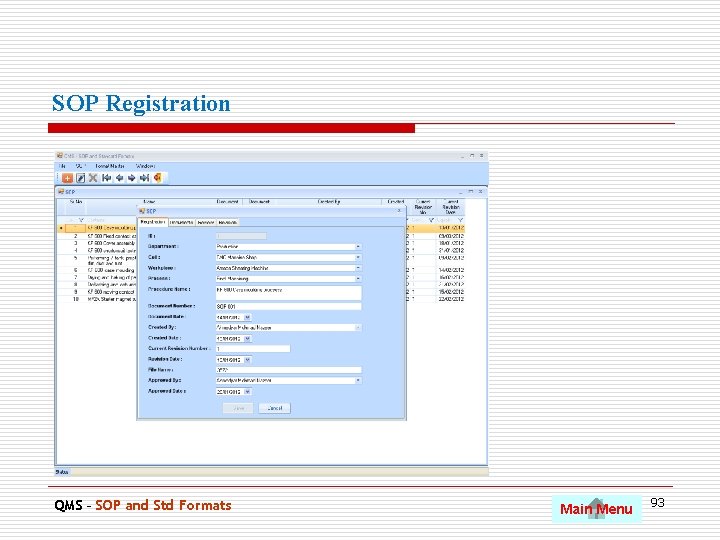
SOP Registration QMS – SOP and Std Formats Main Menu 93
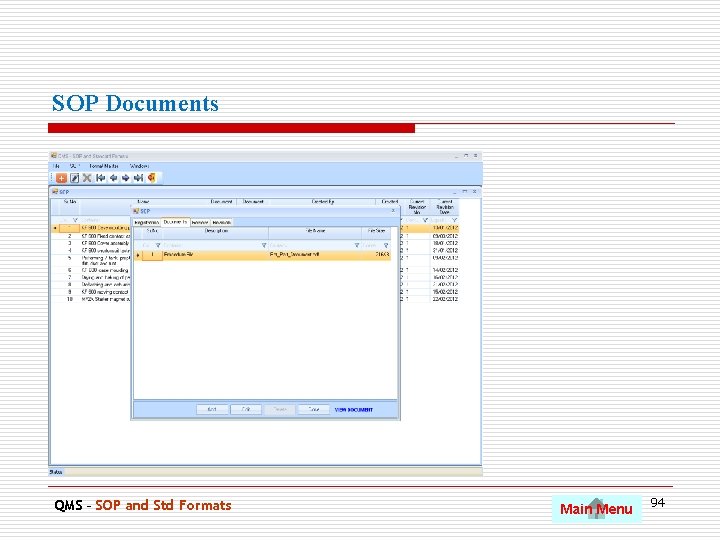
SOP Documents QMS – SOP and Std Formats Main Menu 94
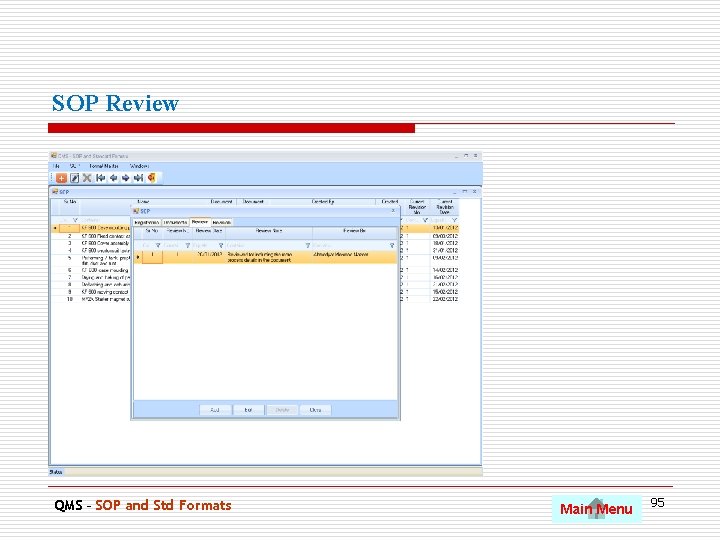
SOP Review QMS – SOP and Std Formats Main Menu 95
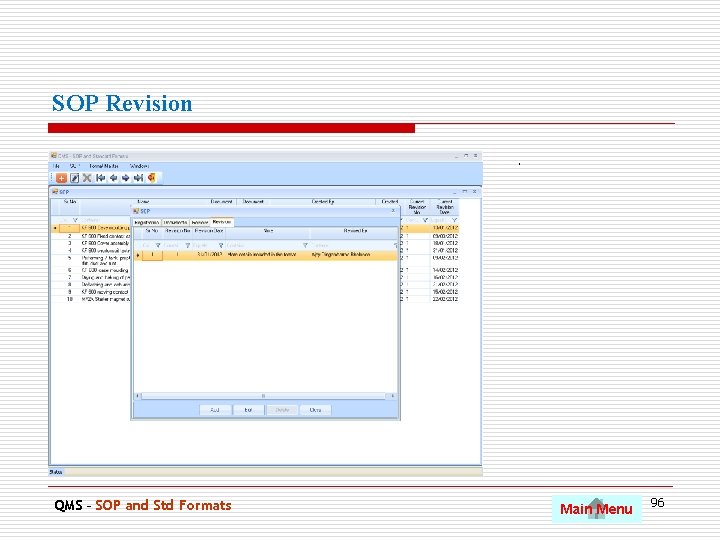
SOP Revision. QMS – SOP and Std Formats Main Menu 96
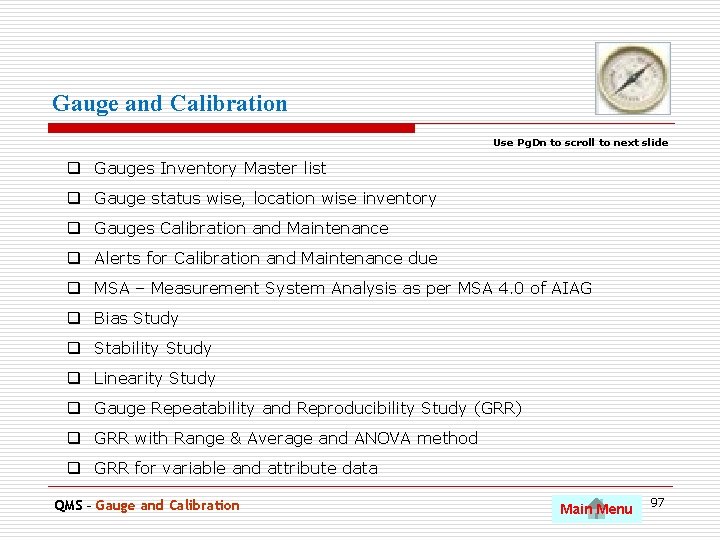
Gauge and Calibration Use Pg. Dn to scroll to next slide q Gauges Inventory Master list q Gauge status wise, location wise inventory q Gauges Calibration and Maintenance q Alerts for Calibration and Maintenance due q MSA – Measurement System Analysis as per MSA 4. 0 of AIAG q Bias Study q Stability Study q Linearity Study q Gauge Repeatability and Reproducibility Study (GRR) q GRR with Range & Average and ANOVA method q GRR for variable and attribute data QMS – Gauge and Calibration Main Menu 97
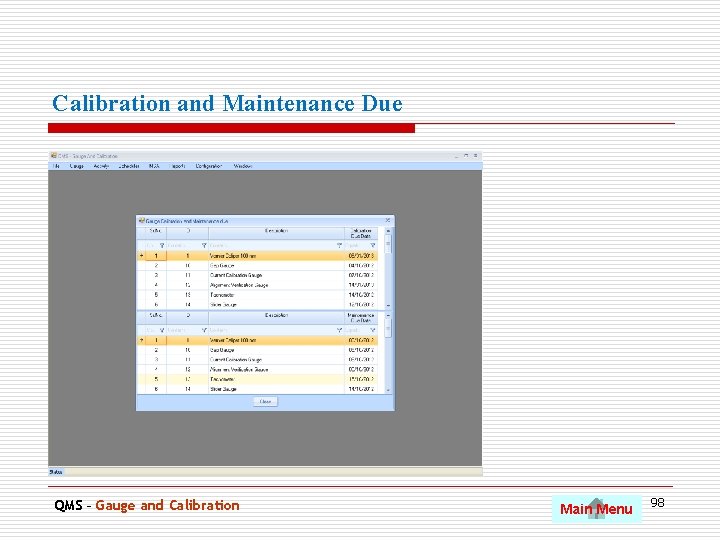
Calibration and Maintenance Due QMS – Gauge and Calibration Main Menu 98
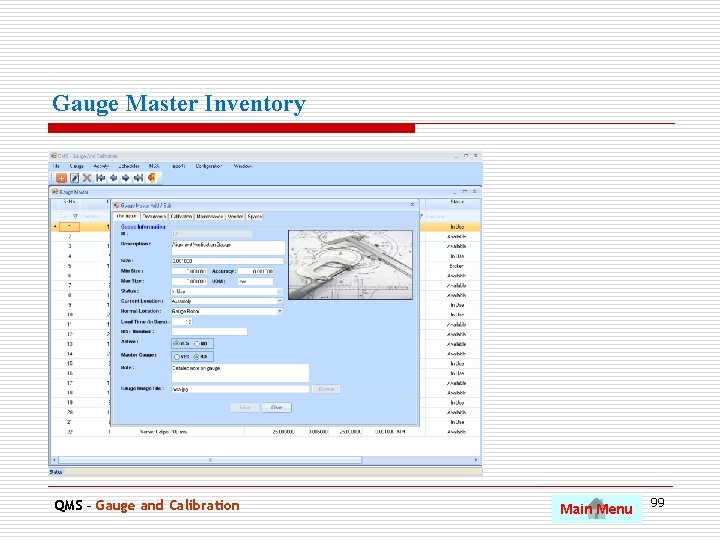
Gauge Master Inventory QMS – Gauge and Calibration Main Menu 99
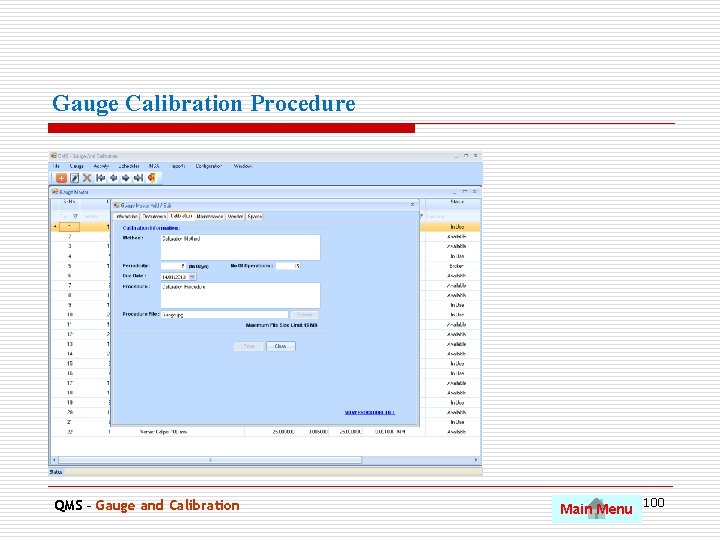
Gauge Calibration Procedure QMS – Gauge and Calibration Main Menu 100
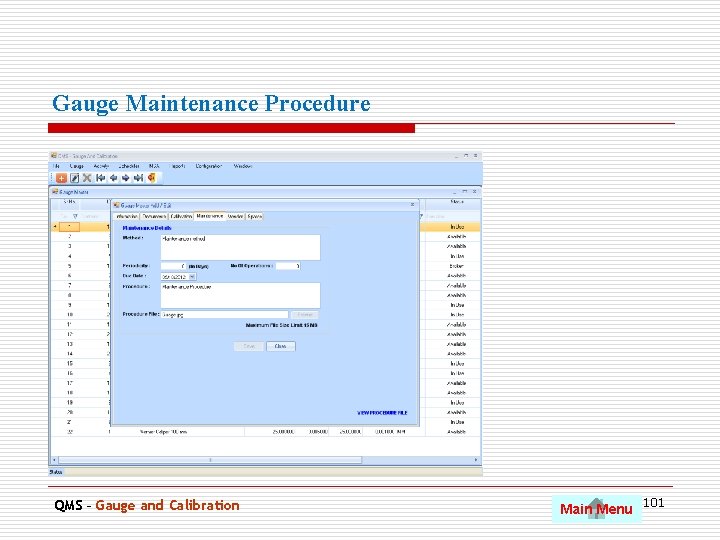
Gauge Maintenance Procedure QMS – Gauge and Calibration Main Menu 101
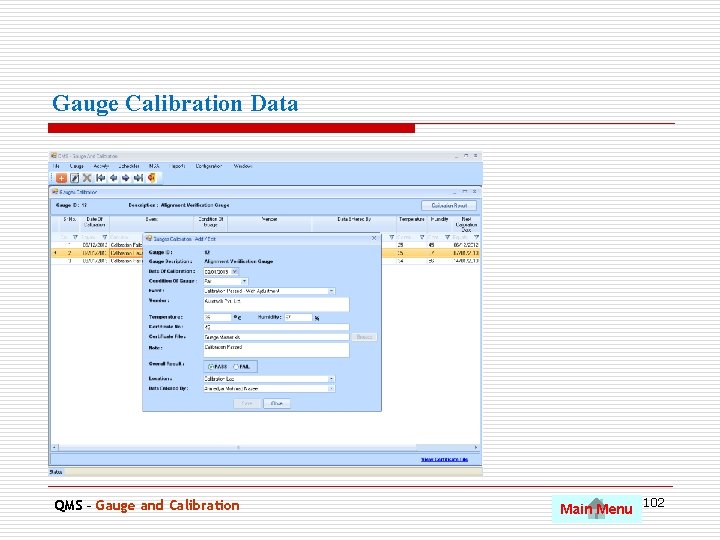
Gauge Calibration Data QMS – Gauge and Calibration Main Menu 102
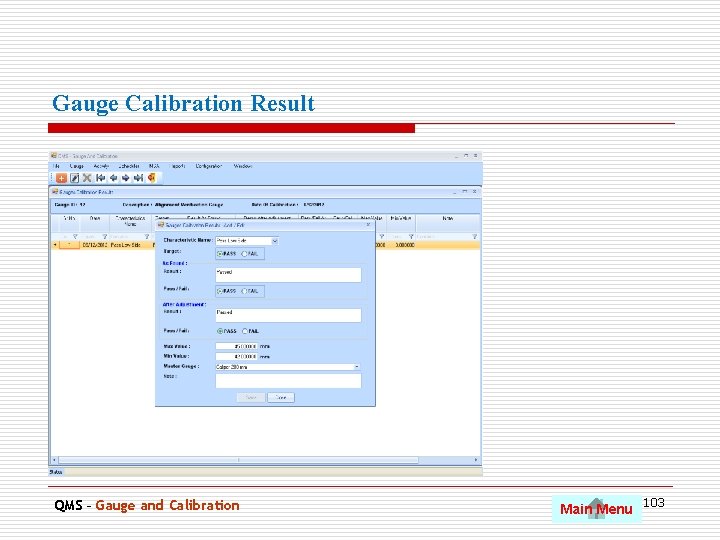
Gauge Calibration Result QMS – Gauge and Calibration Main Menu 103
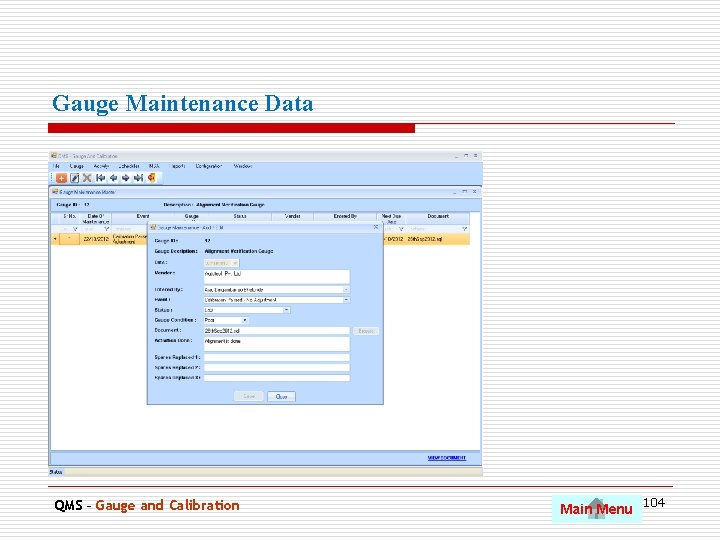
Gauge Maintenance Data QMS – Gauge and Calibration Main Menu 104
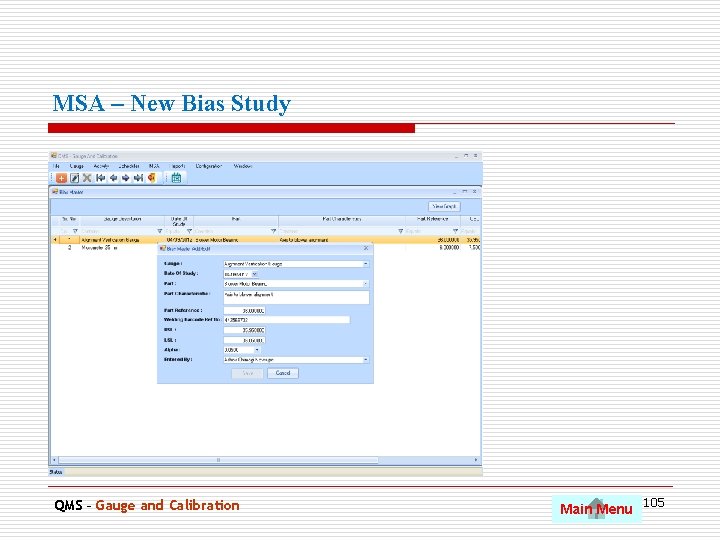
MSA – New Bias Study QMS – Gauge and Calibration Main Menu 105
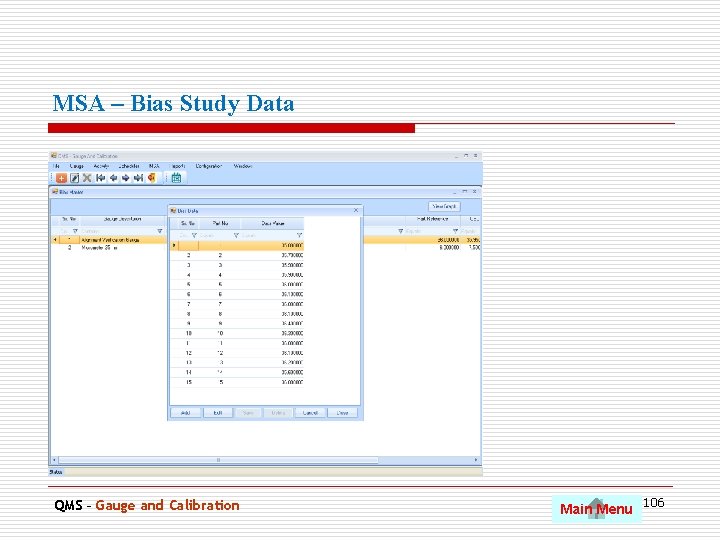
MSA – Bias Study Data QMS – Gauge and Calibration Main Menu 106
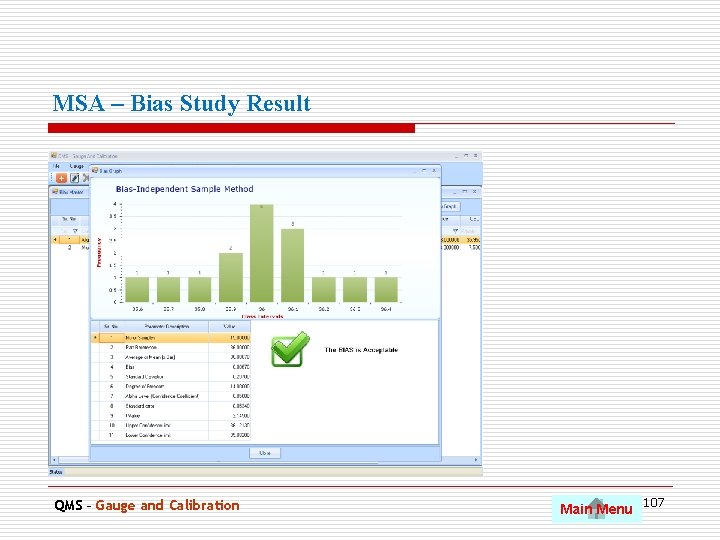
MSA – Bias Study Result QMS – Gauge and Calibration Main Menu 107
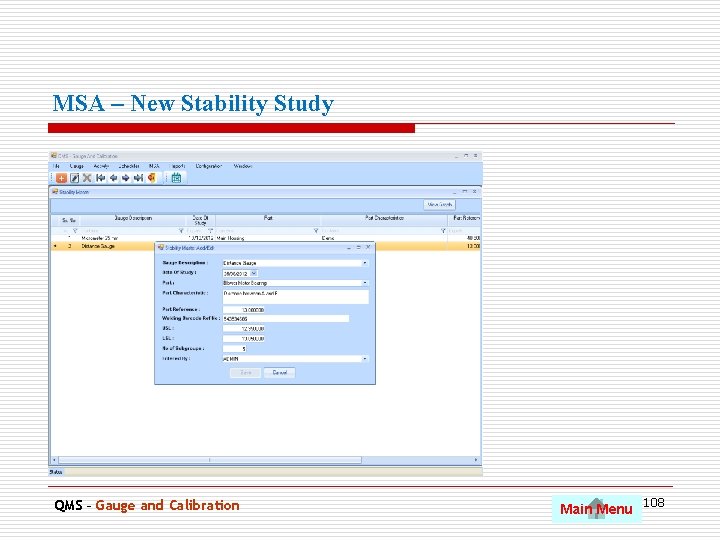
MSA – New Stability Study QMS – Gauge and Calibration Main Menu 108
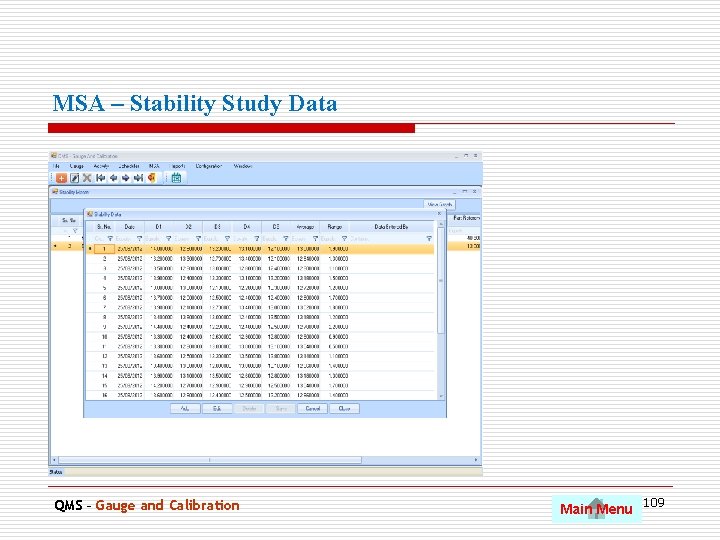
MSA – Stability Study Data QMS – Gauge and Calibration Main Menu 109
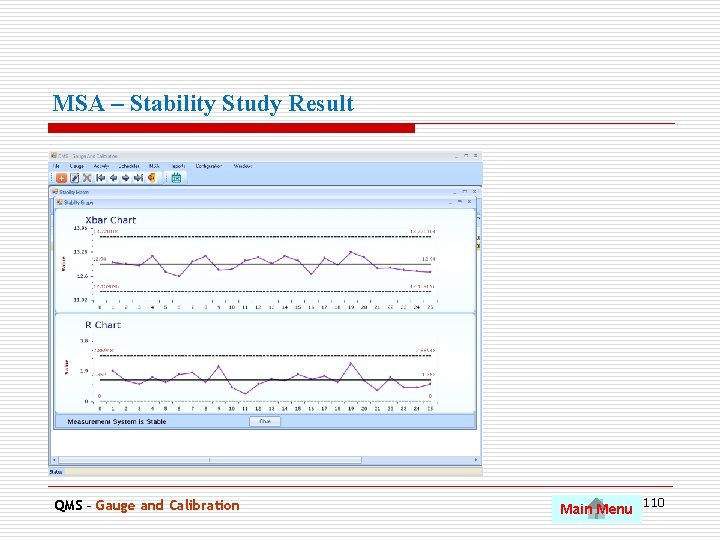
MSA – Stability Study Result QMS – Gauge and Calibration Main Menu 110
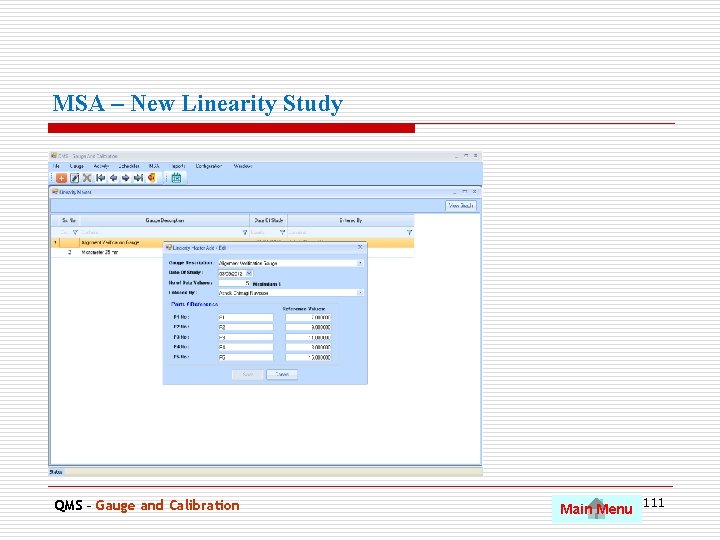
MSA – New Linearity Study QMS – Gauge and Calibration Main Menu 111
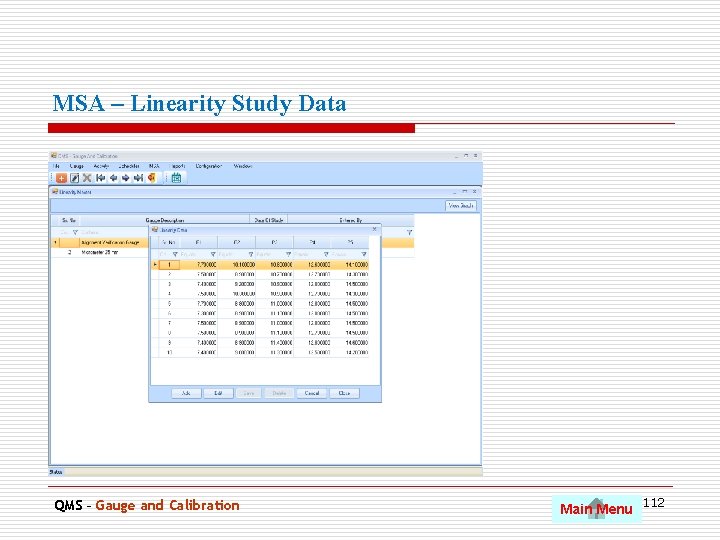
MSA – Linearity Study Data QMS – Gauge and Calibration Main Menu 112
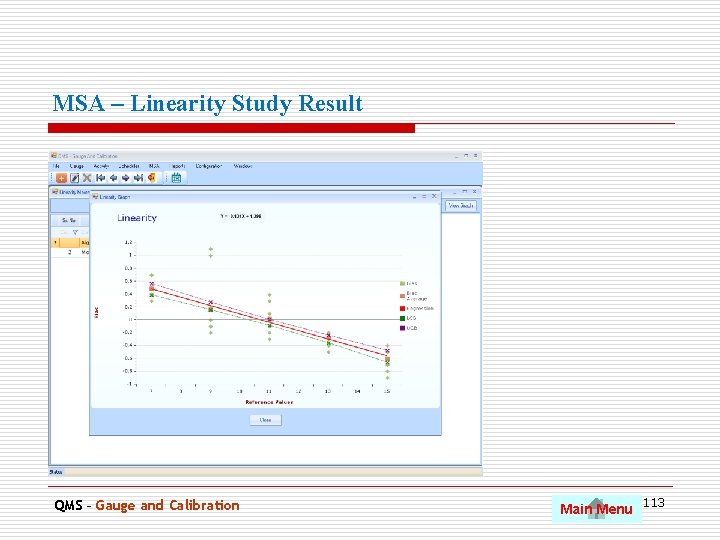
MSA – Linearity Study Result QMS – Gauge and Calibration Main Menu 113
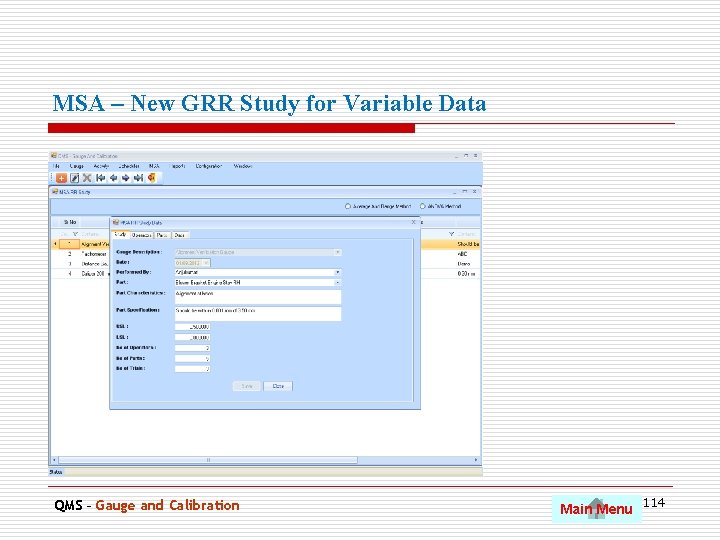
MSA – New GRR Study for Variable Data QMS – Gauge and Calibration Main Menu 114
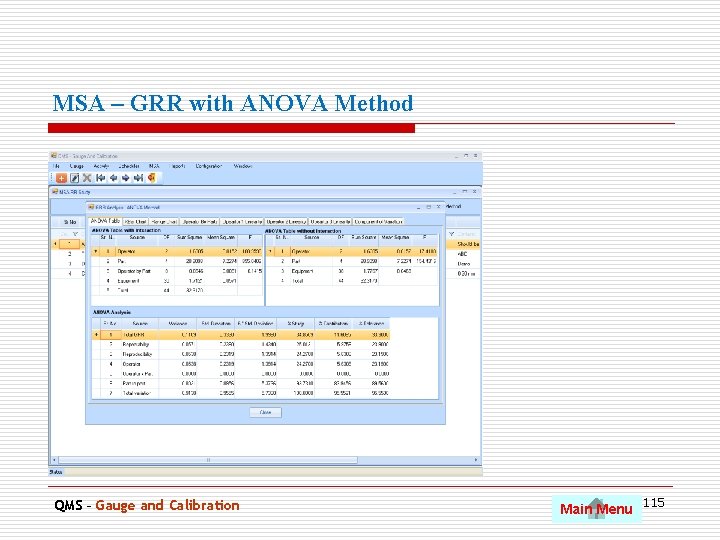
MSA – GRR with ANOVA Method QMS – Gauge and Calibration Main Menu 115
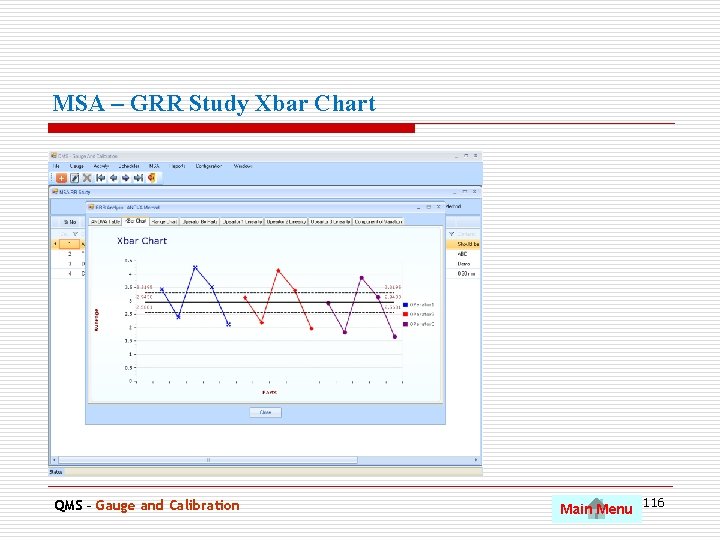
MSA – GRR Study Xbar Chart QMS – Gauge and Calibration Main Menu 116
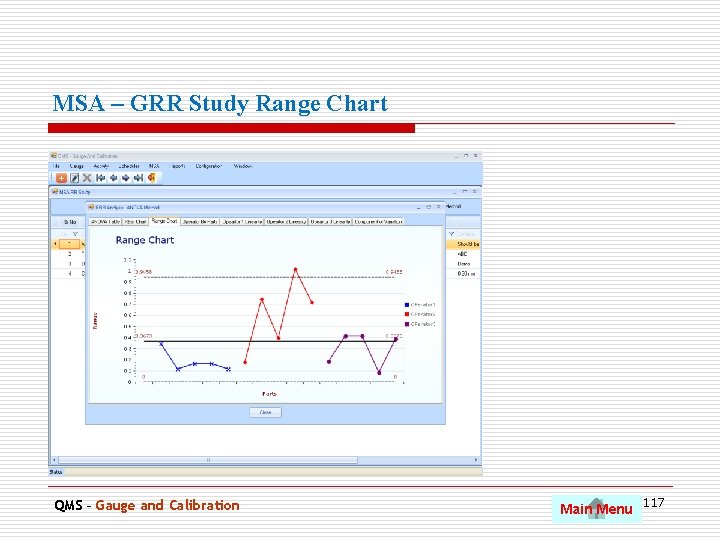
MSA – GRR Study Range Chart QMS – Gauge and Calibration Main Menu 117
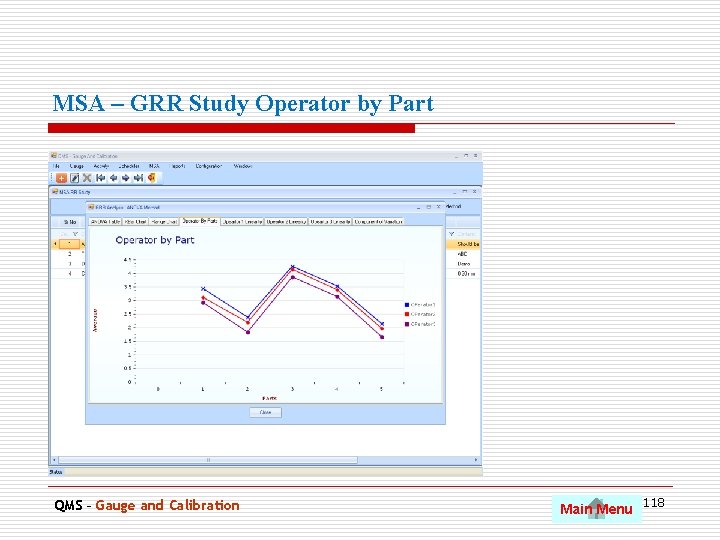
MSA – GRR Study Operator by Part QMS – Gauge and Calibration Main Menu 118
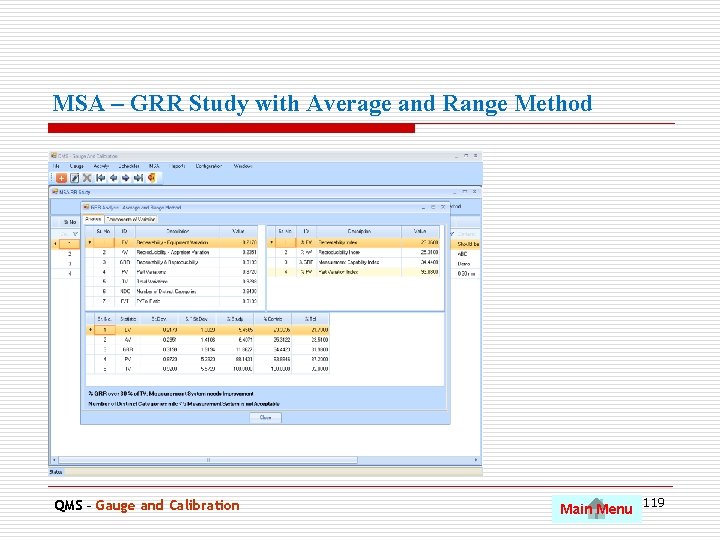
MSA – GRR Study with Average and Range Method QMS – Gauge and Calibration Main Menu 119
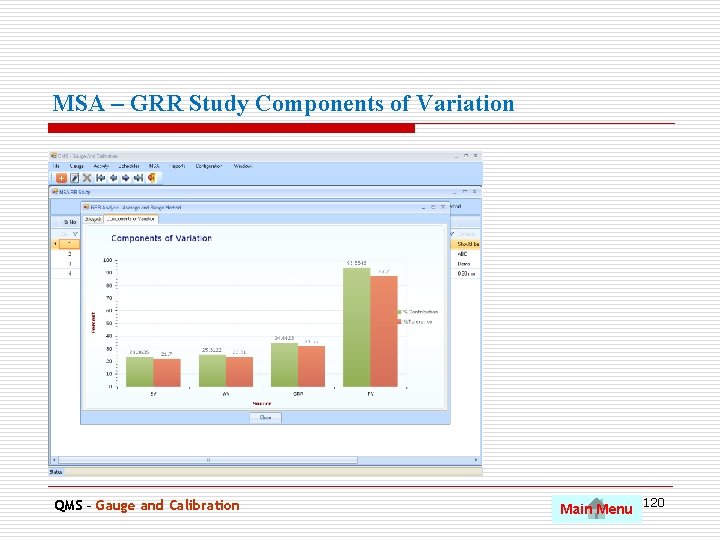
MSA – GRR Study Components of Variation QMS – Gauge and Calibration Main Menu 120
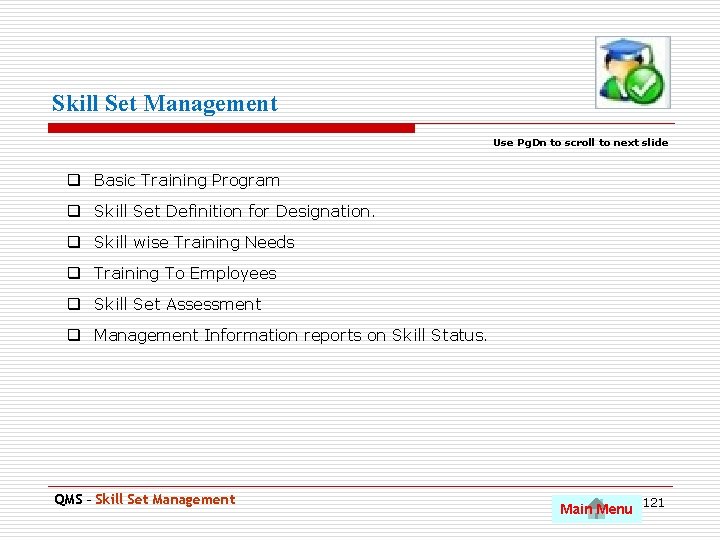
Skill Set Management Use Pg. Dn to scroll to next slide q Basic Training Program q Skill Set Definition for Designation. q Skill wise Training Needs q Training To Employees q Skill Set Assessment q Management Information reports on Skill Status. QMS – Skill Set Management Main Menu 121
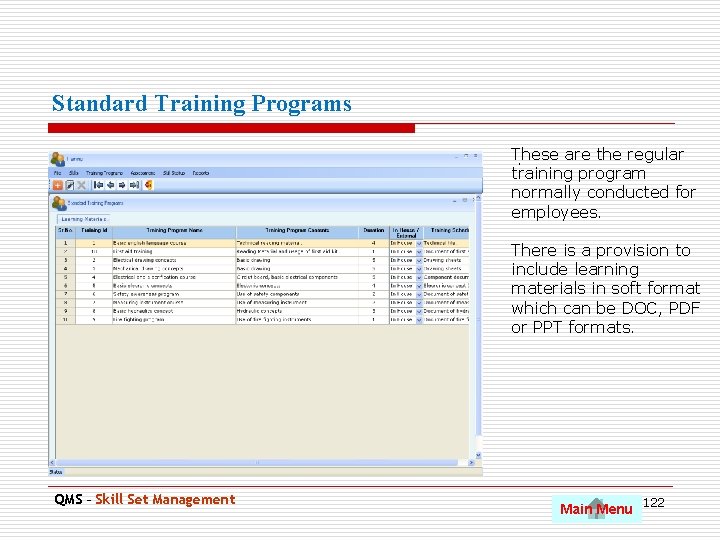
Standard Training Programs These are the regular. training program normally conducted for employees. There is a provision to include learning materials in soft format which can be DOC, PDF or PPT formats. QMS – Skill Set Management Main Menu 122
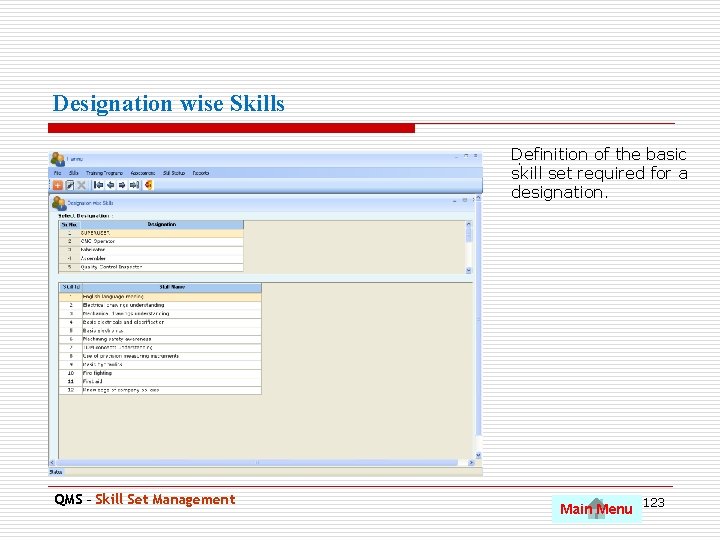
Designation wise Skills Definition of the basic. skill set required for a designation. QMS – Skill Set Management Main Menu 123
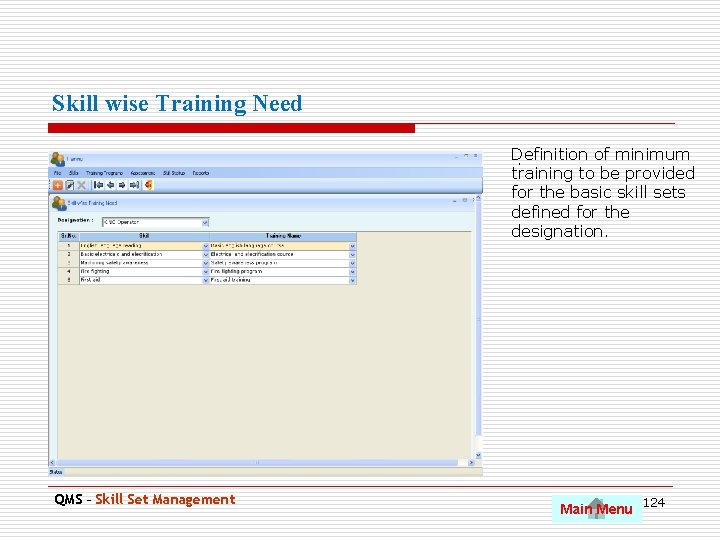
Skill wise Training Need Definition of minimum. training to be provided for the basic skill sets defined for the designation. QMS – Skill Set Management Main Menu 124
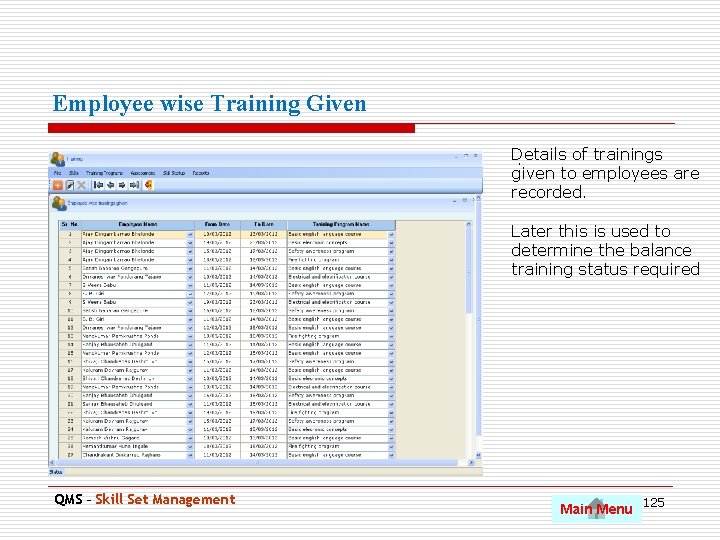
Employee wise Training Given Details of trainings. given to employees are recorded. Later this is used to determine the balance training status required QMS – Skill Set Management Main Menu 125
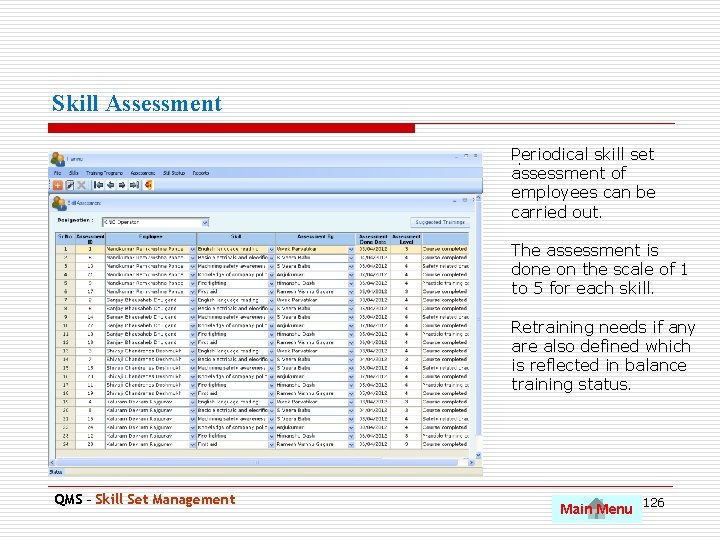
Skill Assessment Periodical skill set. assessment of employees can be carried out. The assessment is done on the scale of 1 to 5 for each skill. Retraining needs if any are also defined which is reflected in balance training status. QMS – Skill Set Management Main Menu 126

Designation wise / Skill Set wise Population This report provides. the average assessment level of employees for the skill set required for a designation. Useful for planning training for employees. QMS – Skill Set Management Main Menu 127
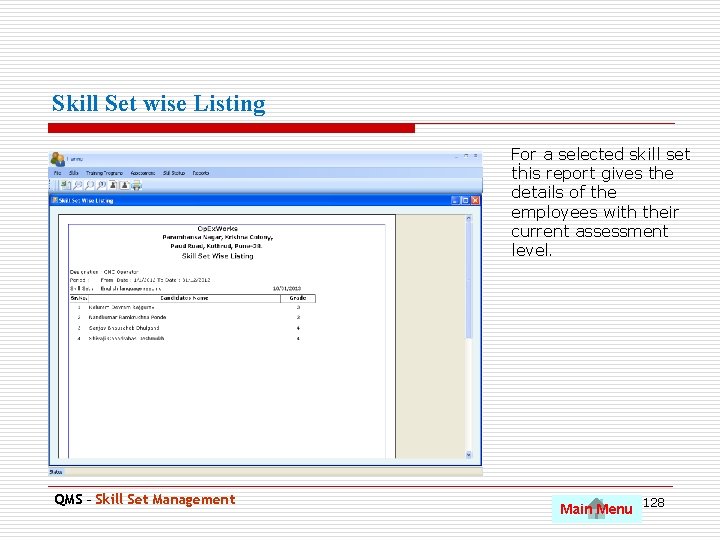
Skill Set wise Listing For. a selected skill set this report gives the details of the employees with their current assessment level. QMS – Skill Set Management Main Menu 128
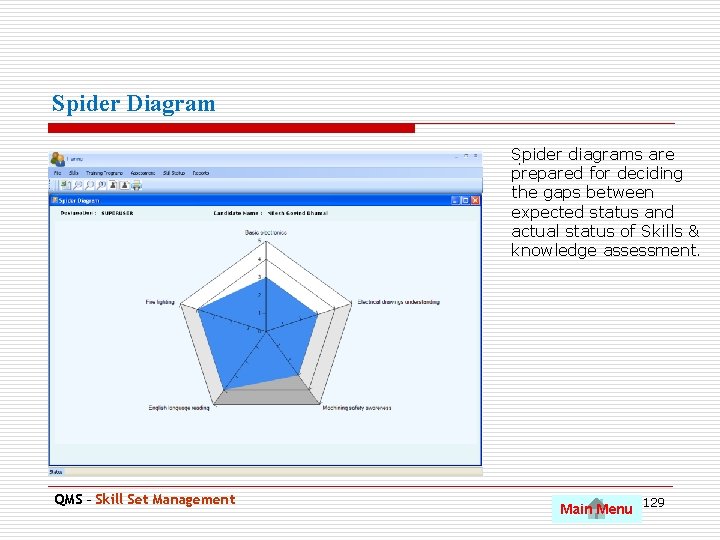
Spider Diagram Spider diagrams are. prepared for deciding the gaps between expected status and actual status of Skills & knowledge assessment. QMS – Skill Set Management Main Menu 129
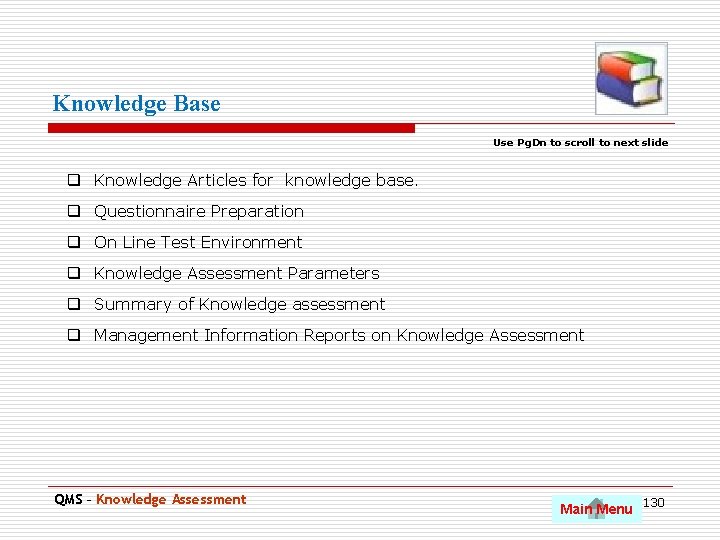
Knowledge Base Use Pg. Dn to scroll to next slide q Knowledge Articles for knowledge base. q Questionnaire Preparation q On Line Test Environment q Knowledge Assessment Parameters q Summary of Knowledge assessment q Management Information Reports on Knowledge Assessment QMS – Knowledge Assessment Main Menu 130
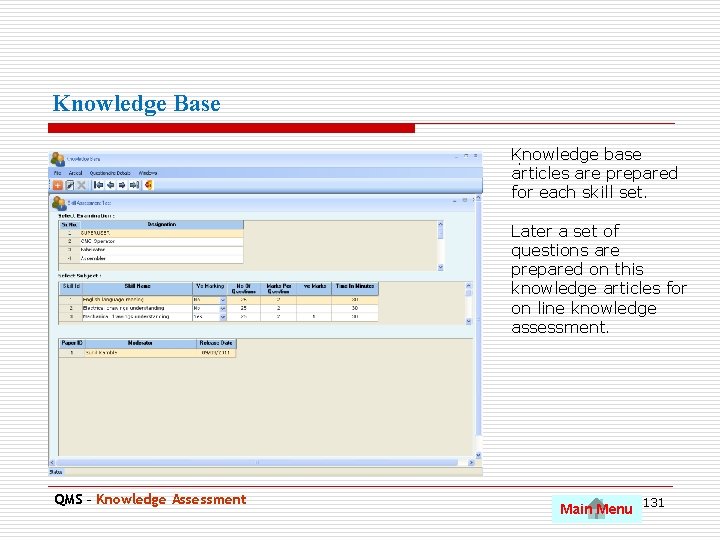
Knowledge Base Knowledge base. articles are prepared for each skill set. Later a set of questions are prepared on this knowledge articles for on line knowledge assessment. QMS – Knowledge Assessment Main Menu 131
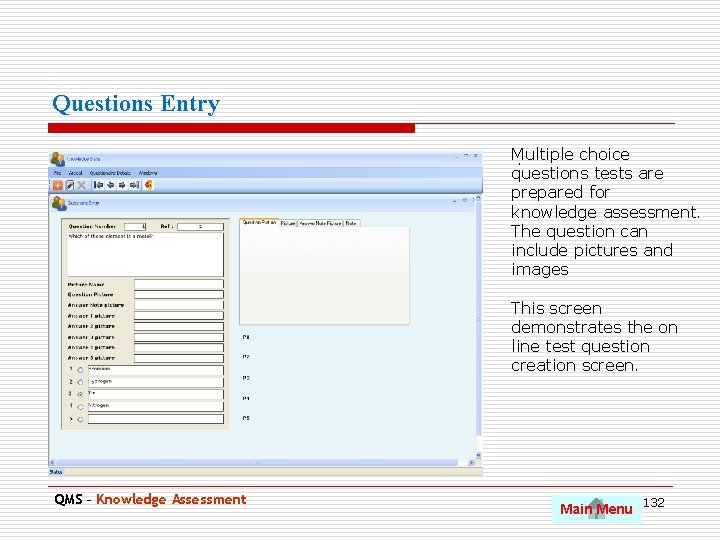
Questions Entry Multiple choice. questions tests are prepared for knowledge assessment. The question can include pictures and images This screen demonstrates the on line test question creation screen. QMS – Knowledge Assessment Main Menu 132
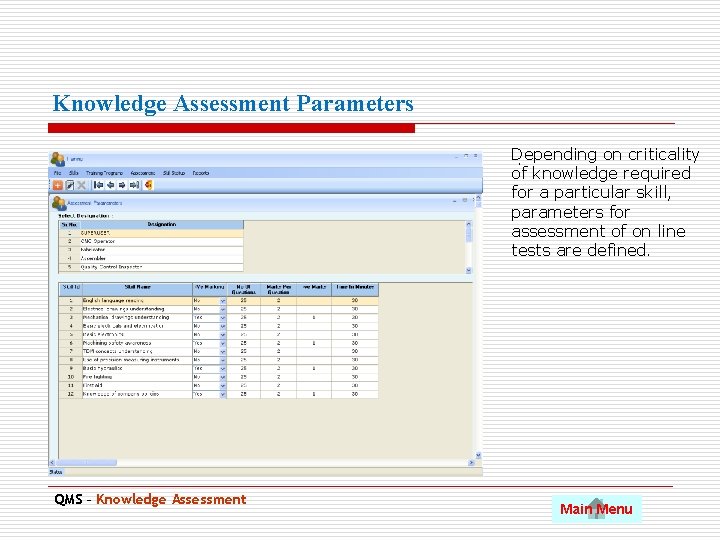
Knowledge Assessment Parameters Depending on criticality. of knowledge required for a particular skill, parameters for assessment of on line tests are defined. QMS – Knowledge Assessment Main Menu
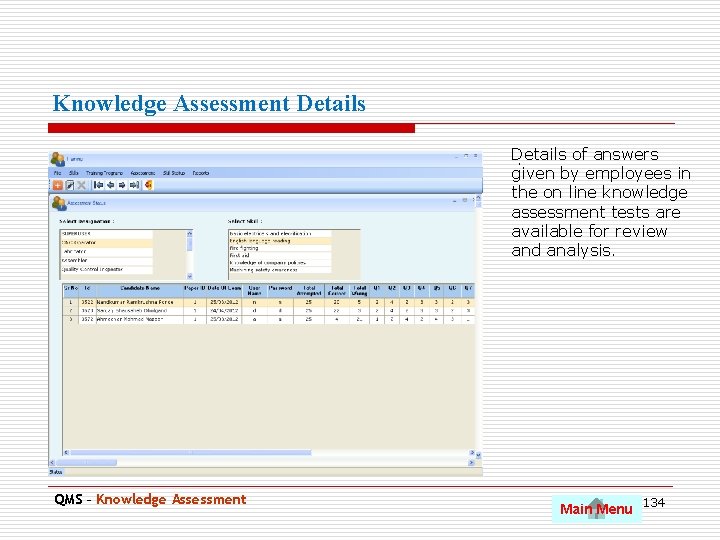
Knowledge Assessment Details of answers. given by employees in the on line knowledge assessment tests are available for review and analysis. QMS – Knowledge Assessment Main Menu 134
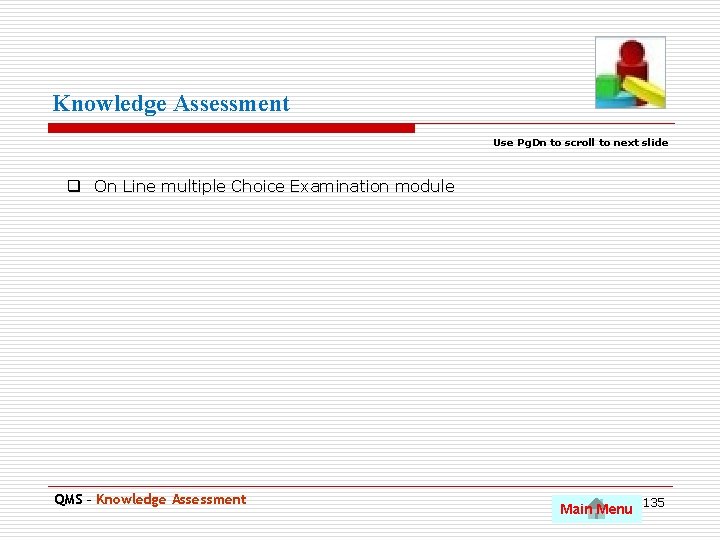
Knowledge Assessment Use Pg. Dn to scroll to next slide q On Line multiple Choice Examination module QMS – Knowledge Assessment Main Menu 135
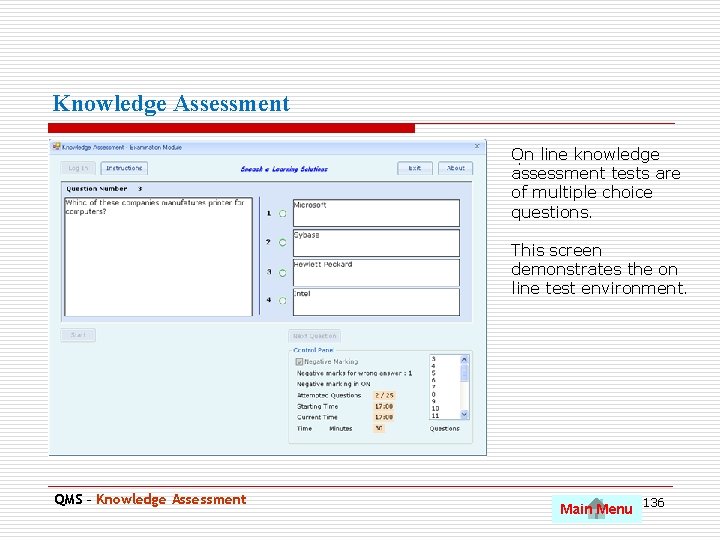
Knowledge Assessment On. line knowledge assessment tests are of multiple choice questions. This screen demonstrates the on line test environment. QMS – Knowledge Assessment Main Menu 136
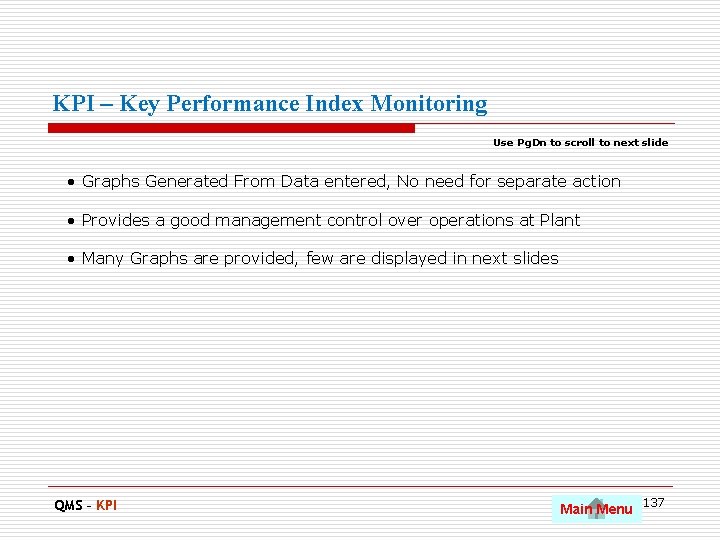
KPI – Key Performance Index Monitoring Use Pg. Dn to scroll to next slide • Graphs Generated From Data entered, No need for separate action • Provides a good management control over operations at Plant • Many Graphs are provided, few are displayed in next slides QMS – KPI Main Menu 137
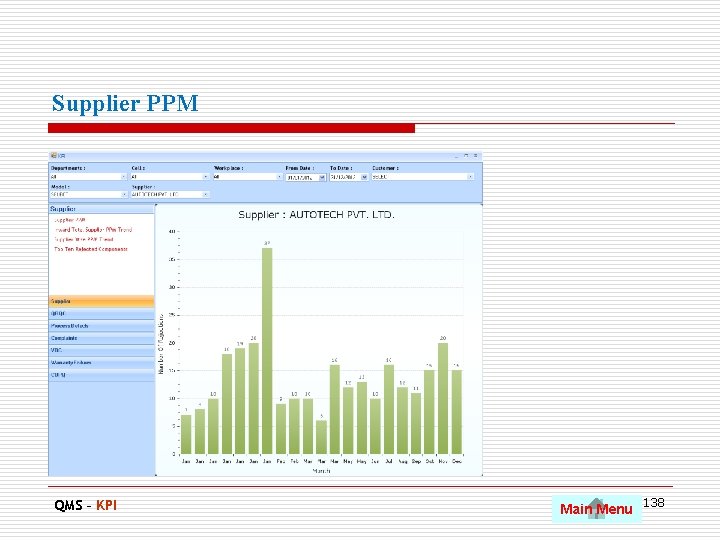
Supplier PPM QMS – KPI Main Menu 138
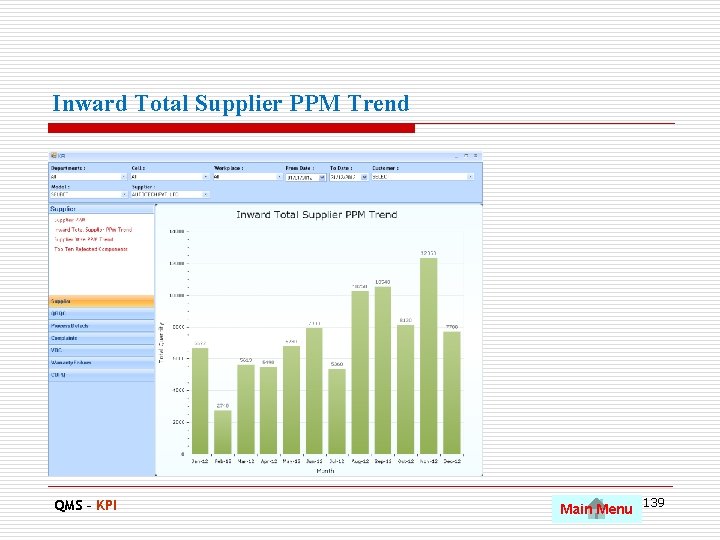
Inward Total Supplier PPM Trend QMS – KPI Main Menu 139
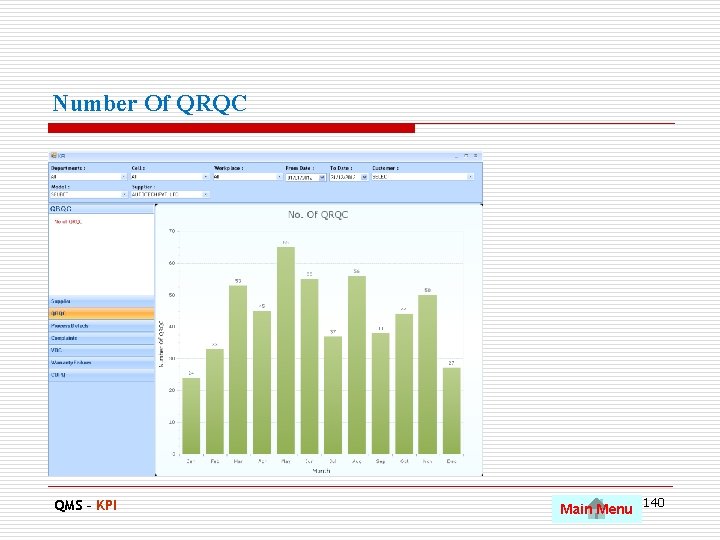
Number Of QRQC QMS – KPI Main Menu 140
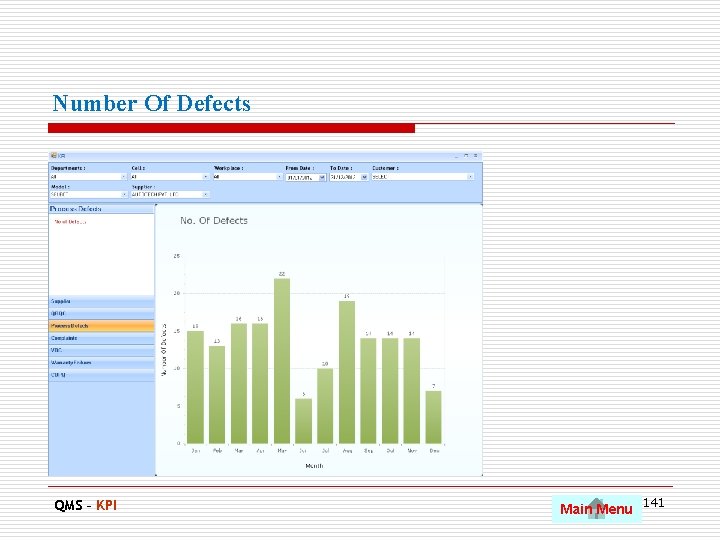
Number Of Defects QMS – KPI Main Menu 141
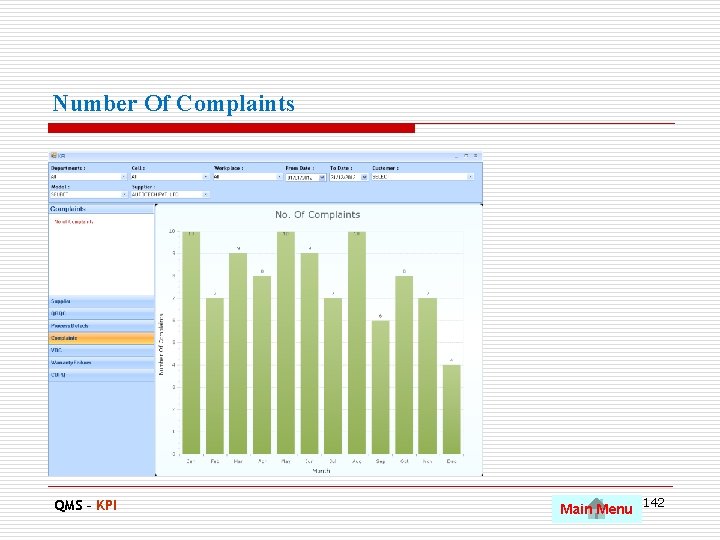
Number Of Complaints QMS – KPI Main Menu 142
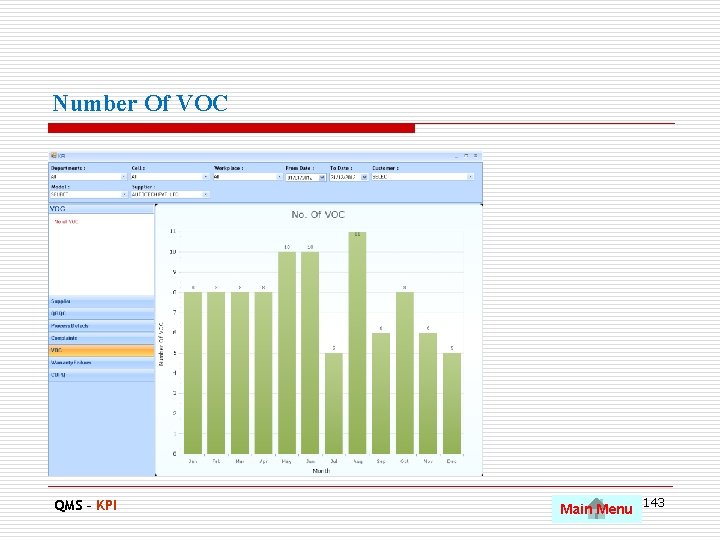
Number Of VOC QMS – KPI Main Menu 143
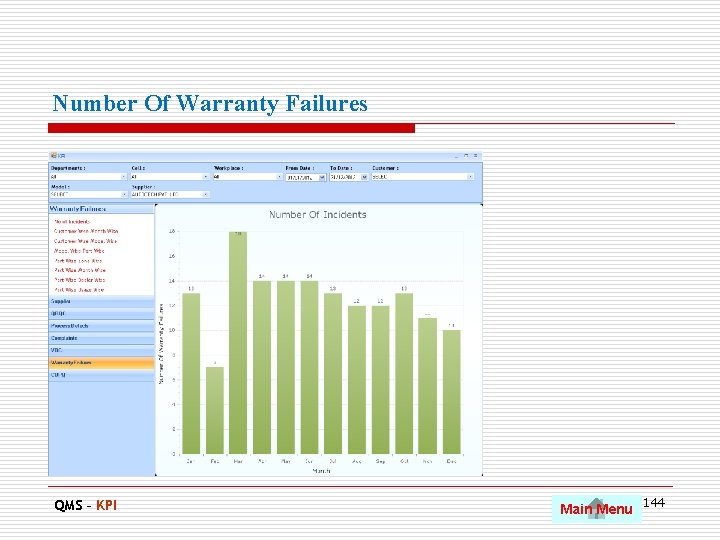
Number Of Warranty Failures QMS – KPI Main Menu 144
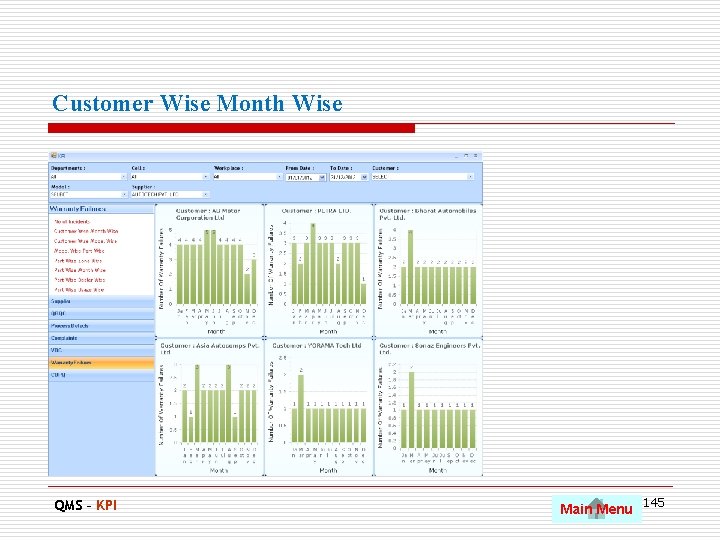
Customer Wise Month Wise QMS – KPI Main Menu 145
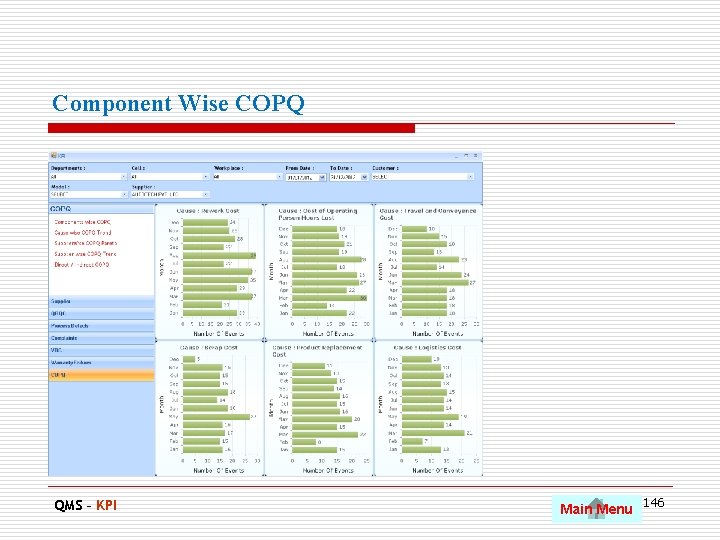
Component Wise COPQ QMS – KPI Main Menu 146
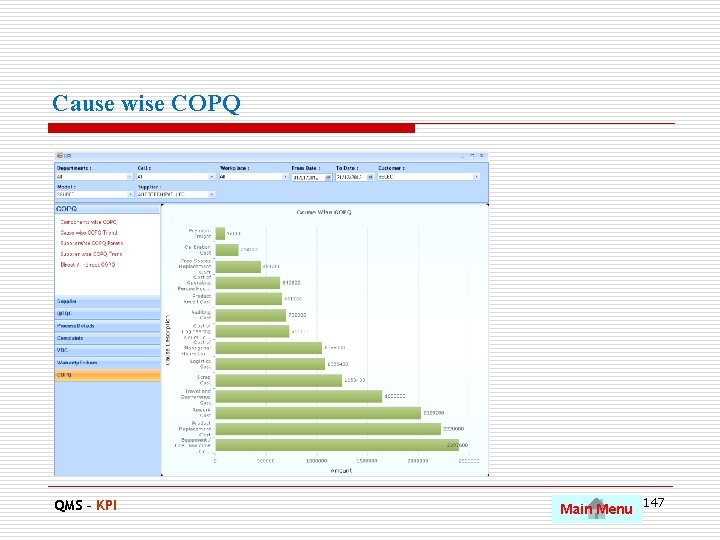
Cause wise COPQ QMS – KPI Main Menu 147
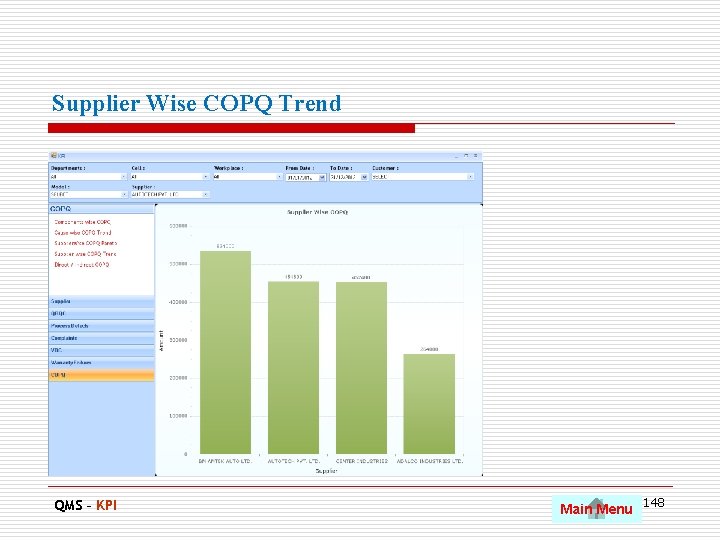
Supplier Wise COPQ Trend QMS – KPI Main Menu 148
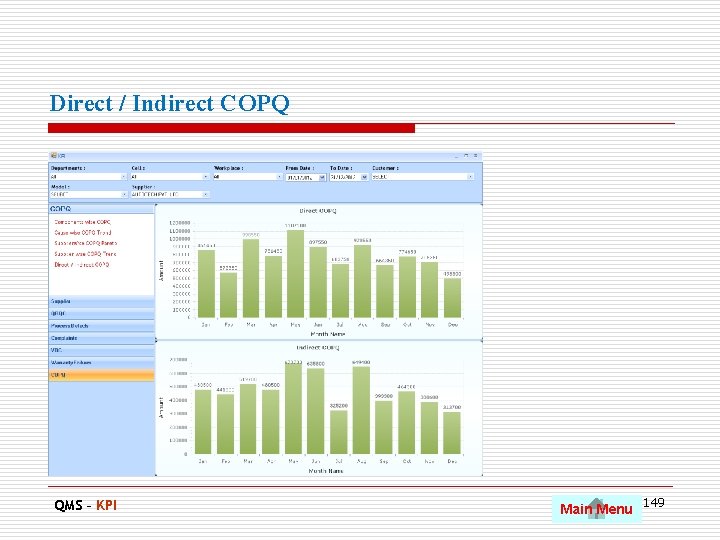
Direct / Indirect COPQ QMS – KPI Main Menu 149
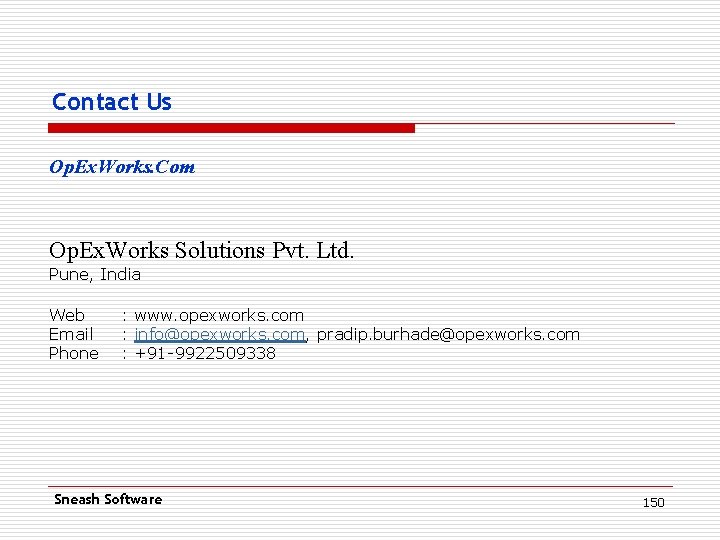
Contact Us Op. Ex. Works. Com Op. Ex. Works Solutions Pvt. Ltd. Pune, India Web Email Phone : www. opexworks. com : info@opexworks. com, pradip. burhade@opexworks. com : +91 -9922509338 Sneash Software 150
Incompetent
Master qms
Qms documentation structure
Qms school training toolkit
Kfu
Qms
Proprofs.com
Enterprise wide quality integrated management system
Verse qms
Internal failure costs examples
Qms
Street works book
Operations and quality management
Enterprise resource planning lecture notes ppt
Operations management with total quality management book
Poka yoke
Total quality management system
Laboratory quality management system definition
Evolution of quality management system
7 principles of quality management system
Pillars of quality management system
Iqms tutorial
Quality management system
"quality management system"
Defence infrastructure panel
"quality management system"
Quality assurance vs quality control
Project quality management pmp
Pmbok quality assurance vs quality control
Define quality assurance in nursing
Compliance vs quality
Basic concepts of quality assurance
American quality gurus
Quality is free
What is tqm
Operating system
How the nervous system works
Public works roofing system
Digestive system parts
How your muscular system works
Why did eagles almost go extinct
Heards ferry eagle alliance
Zea eagle
Eagle scout mentor pin script
Eagle lifespan 70 years
Scullery sink definition
Http eagle-squad.fr
Fanatic eagle 126
Connotation and denotation in poetry
Eagles baseball club
If an eagle and a bumblebee are traveling at 10m/s
Eagle eye anatomy
Blue eagle shipping
Eagle project coach
7 principles of an eagle powerpoint
Leadership lessons from an eagle
Umw eagle one
Chain of friendship ww1
Soaring eagle nursery
Eagle project fundraising
Eagle's nest sinkhole
Listed below
Golden eagle regional park
Corkery v carpenter
Eagle product inspection headquarters
Basic cheer jumps
Black eagle
Pcb designprozess
Bald eagle phylum
Bald eagle food web
Rideles
Trophic level examples
Eagle scout worksheet
Eagle creek land and development
Characteristics of the class aves
Black eagle logistics
I rise up like an eagle
Jove's eagle
Eagle images
Eagle gate college login
Eagle mhc
What does the eagle on the ffa emblem mean
Eagle worldwide ministries
Eagle court of honor invocation
Eagle
Linn's sloth
Craig mallett
Eagle scout marines
Golden eagle pride scout
Eagle pcb design
Jeep/eagle introduces a new product
Fly eagle fly characterisation
Eagle plains public school
Eagle communication
Eagle landing middle school
Eagle cabs
Eagle bluff dorms
Fvpd stock
Eagle proteus
Eagle africa mbao pension
Eagle insulation
Michigan imputation server
Pyramid levels of management
Top management middle management first line management
Middle level management
Activity diagram for gym management system
System architecture diagram for hospital management system
Total quality management tools and techniques
Lean production and quality management
Tqm evolution
Tqm definition
14 principles of total quality management
Total quality management founder
Books on total quality management
Tqm in hospitality industry
Benchmarking in total quality management
Philosophies of total quality management
Quality management techniques
Software quality management plan
Conclusion for quality management
Quality management for organizational excellence
Dtrtrtft
Quality and operations management
Project quality management definition
Chapter 9 management of quality
What are quality standards in project management
Total quality management of kfc pdf
Kaizen in tqm
Introduction to quality management
Project quality management lecture notes
John talburt
Data quality management best practices
Toyota total quality management
Sqc of filling processes
Operations management chapter 10 quality control solutions
How to achieve tqm
Sqm quality management
Sap quality management
Quality management tools
Pmbok
Control chart precision accuracy pmp
Managing quality in operations management
Design of experiments pmp example
Introduction to total quality management
Qfd in total quality management
Quality assurance card
Agriculture quality management
Water quality management in india
Quality control data management
Total quality management wikipedia
Quality management software for farmers