TOTAL QUALITY MANAGEMENT AND QUALITY MANAGEMENT PHILOSOPHIES Dr
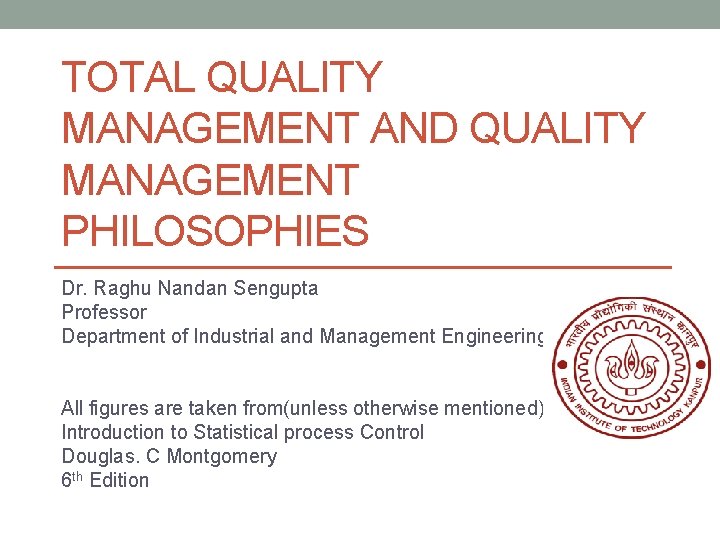
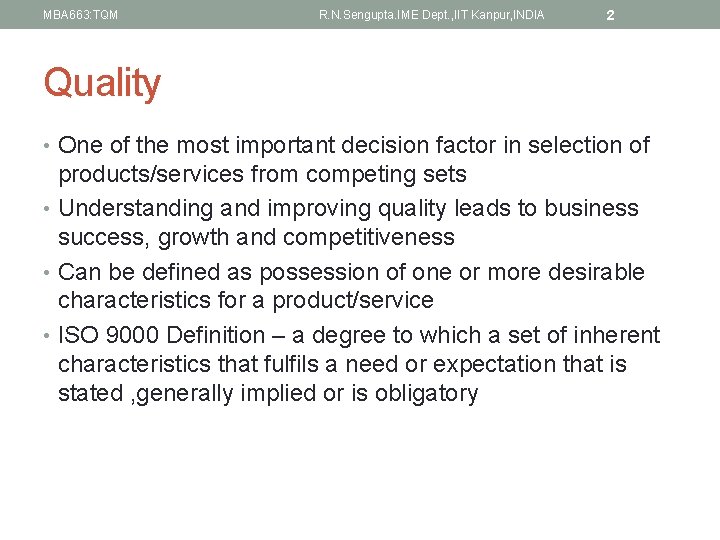
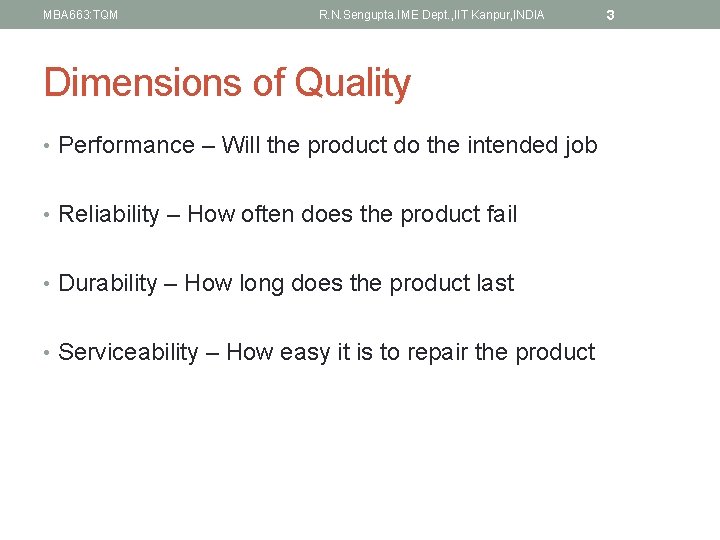
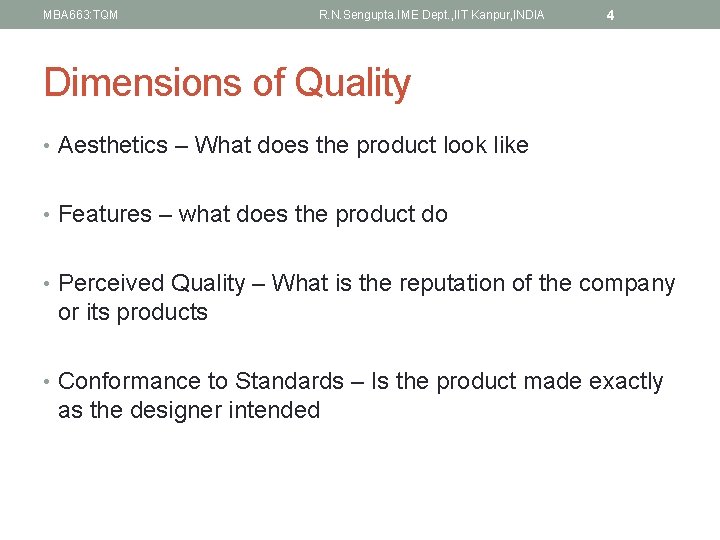
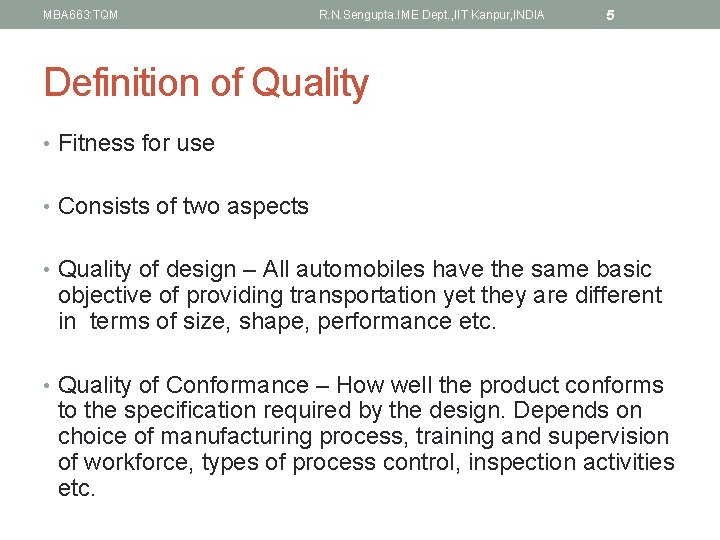
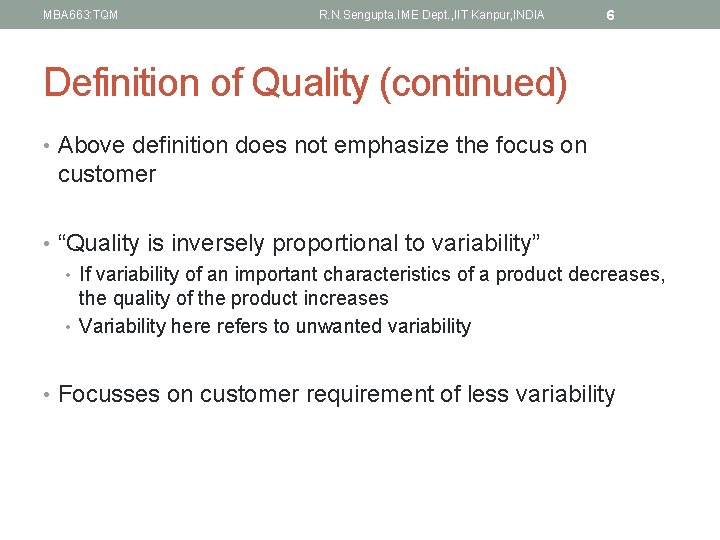
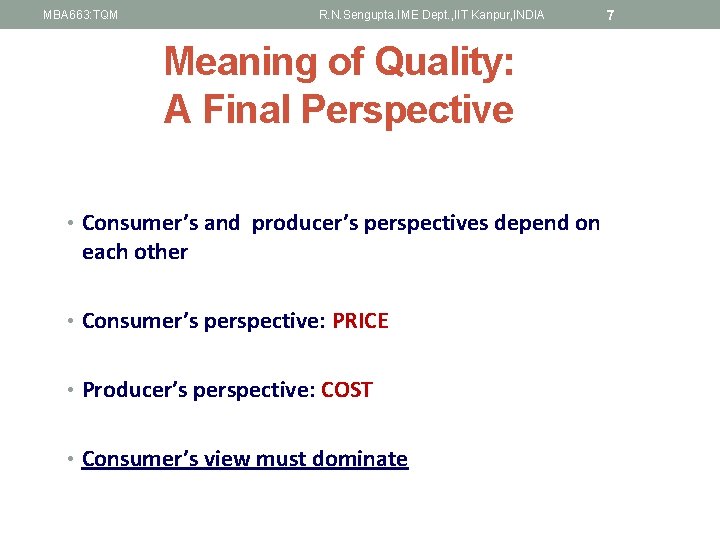
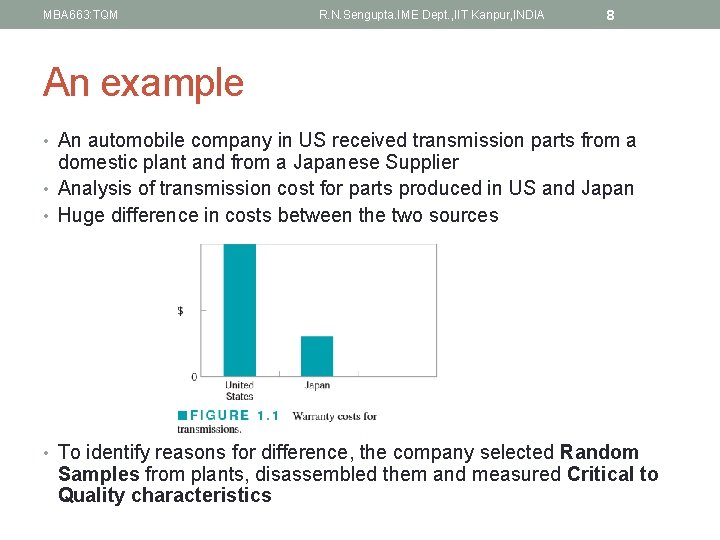
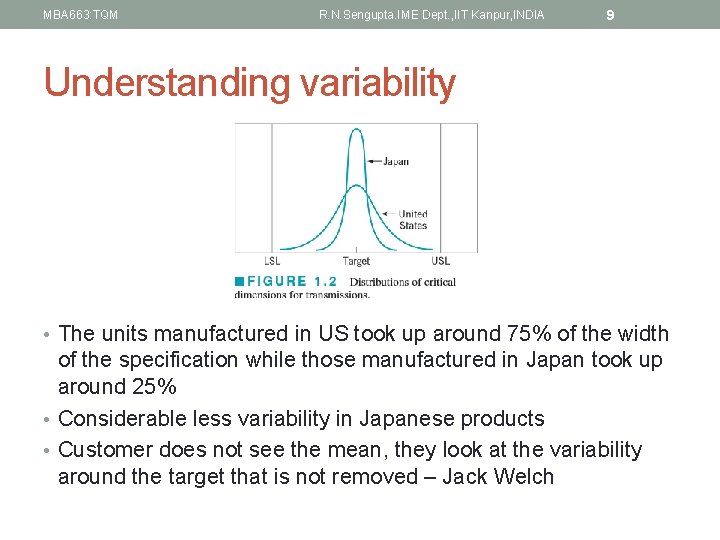
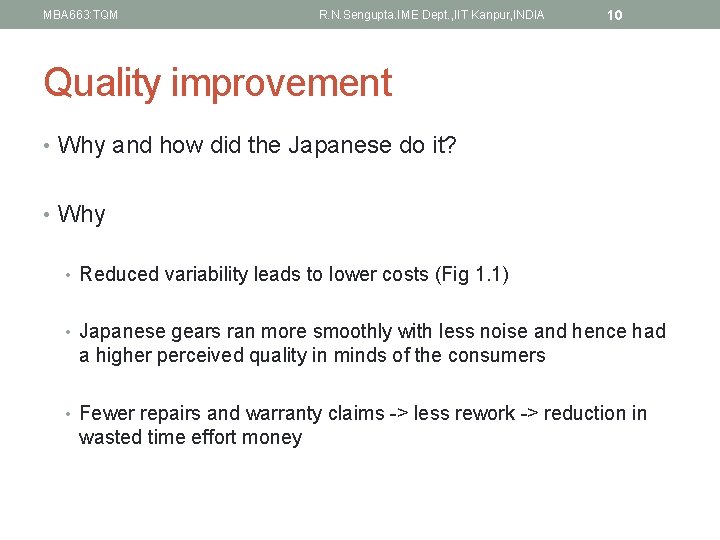
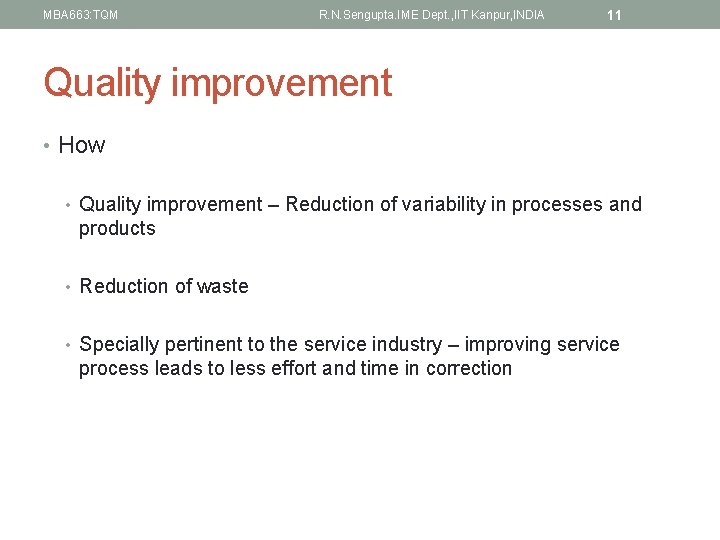
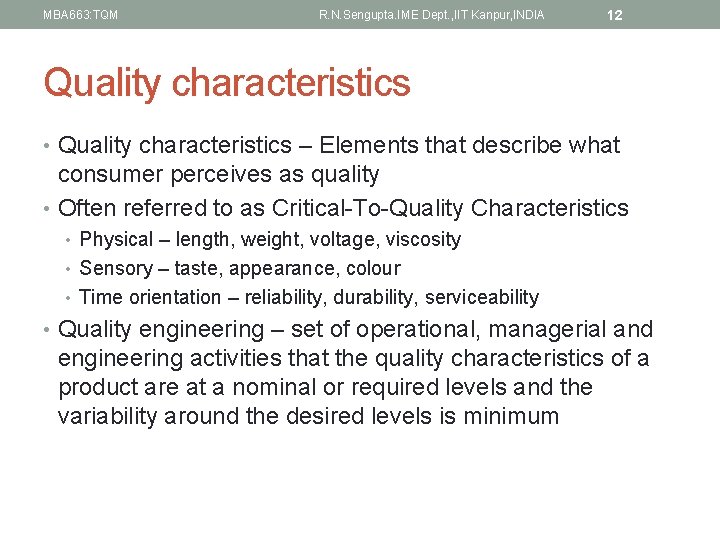
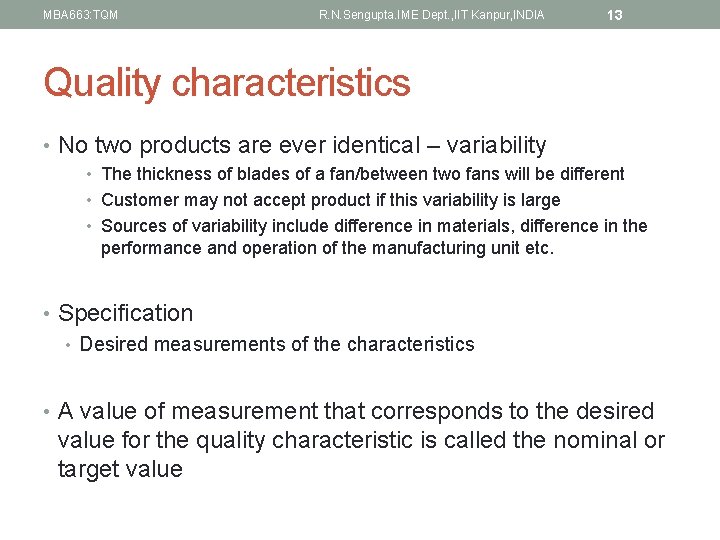
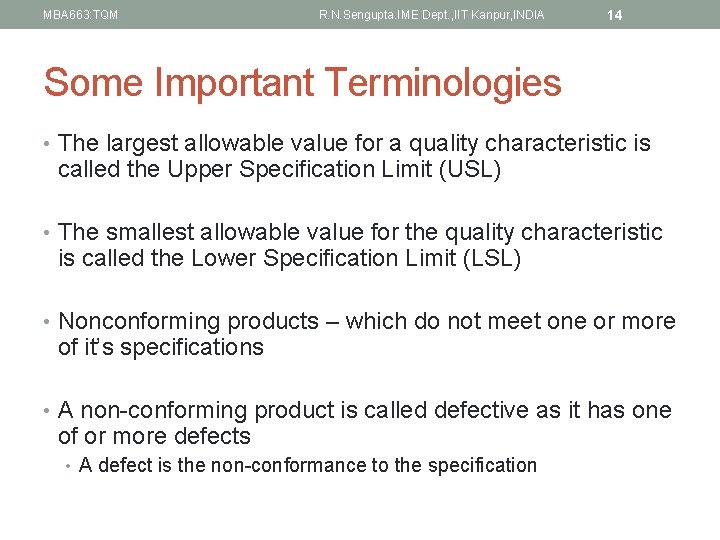
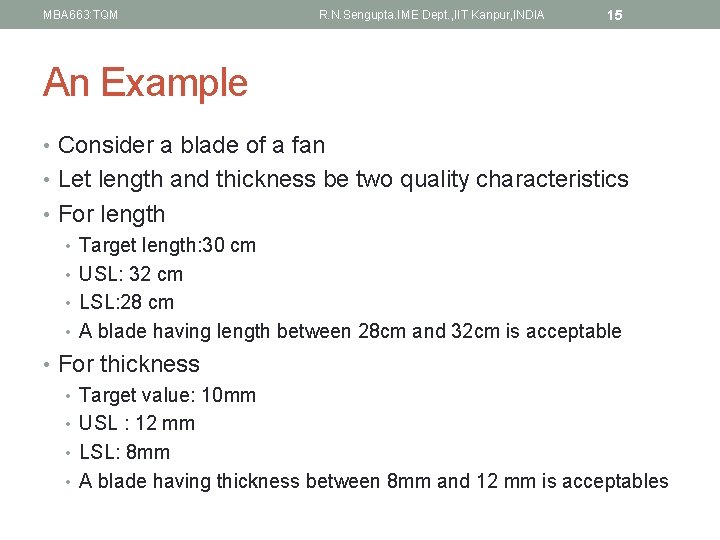
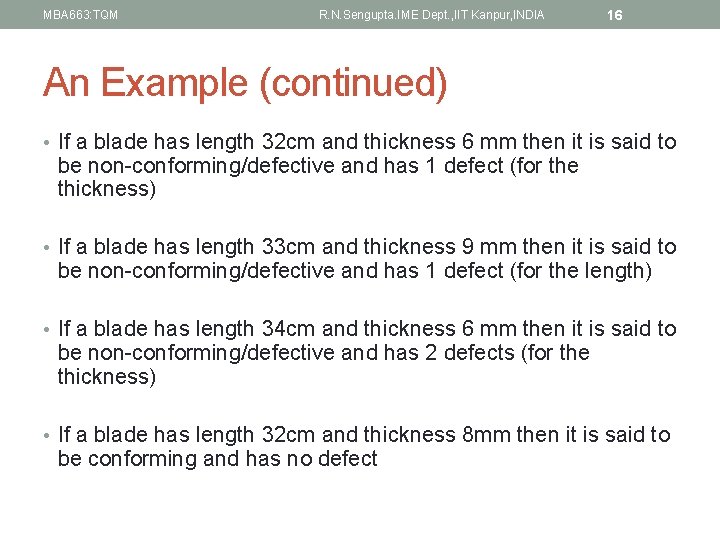
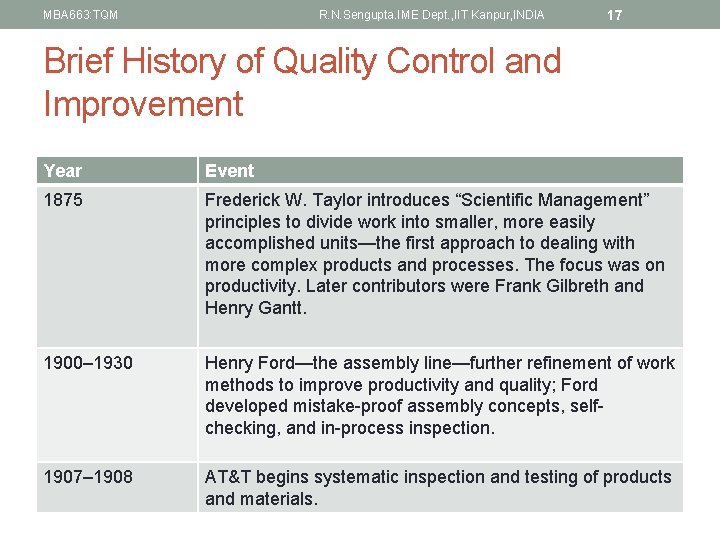
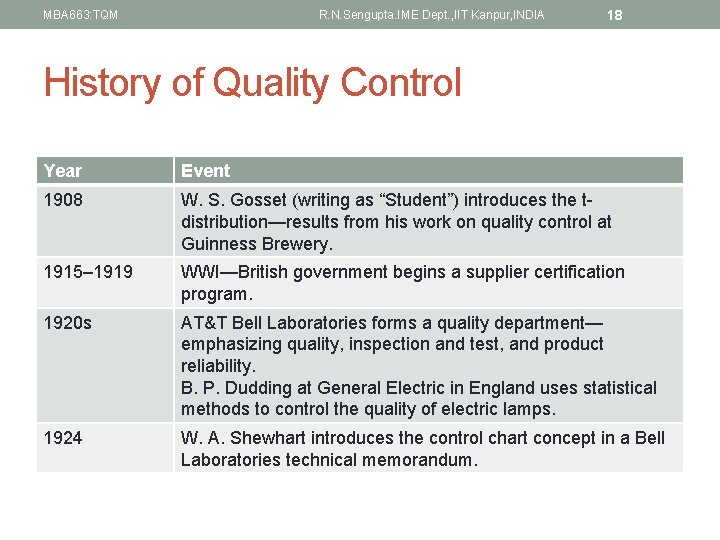
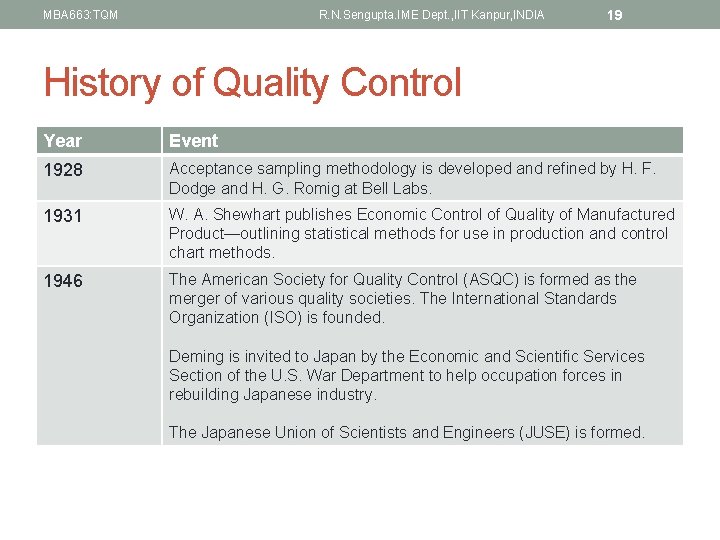
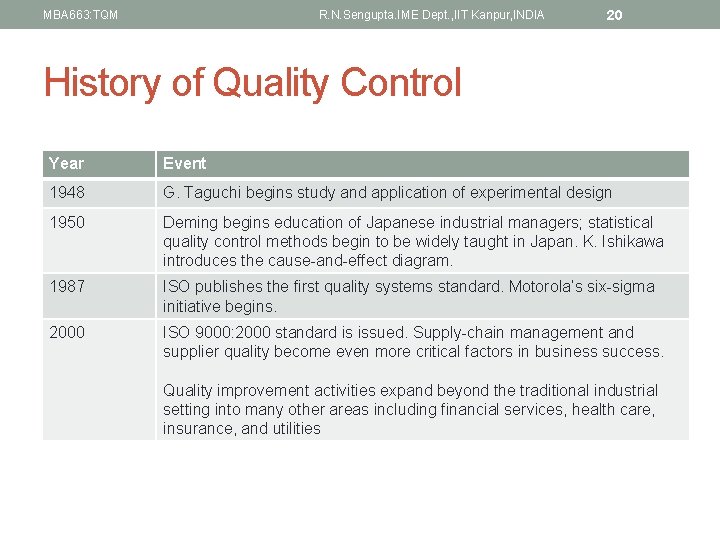
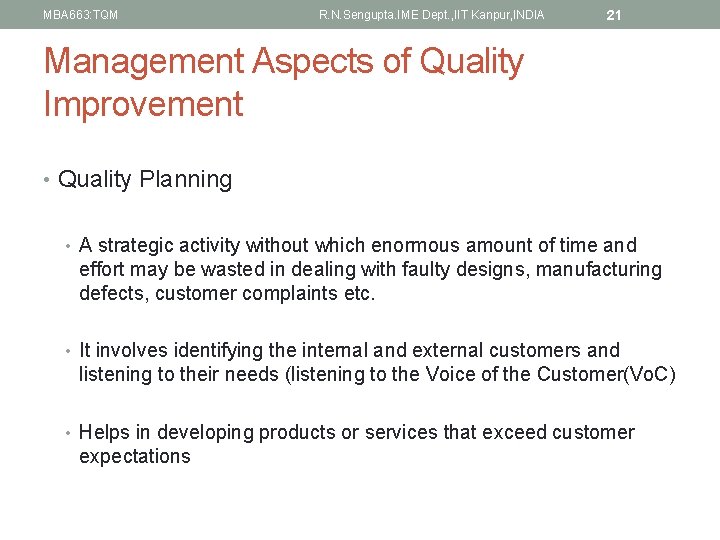
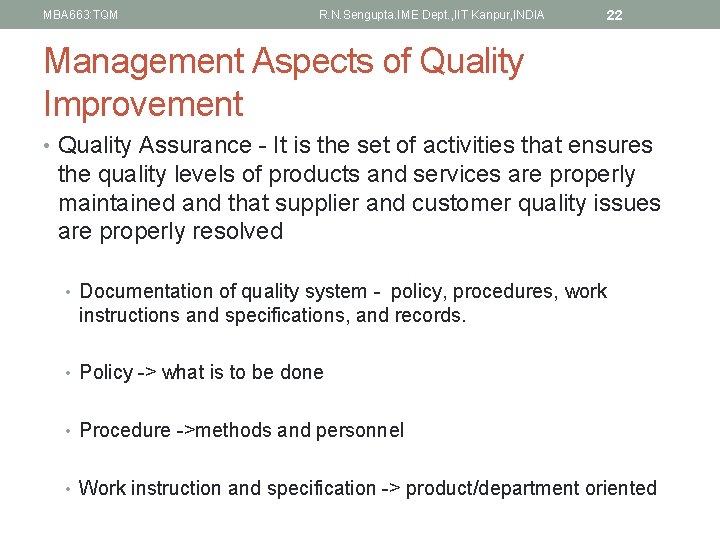
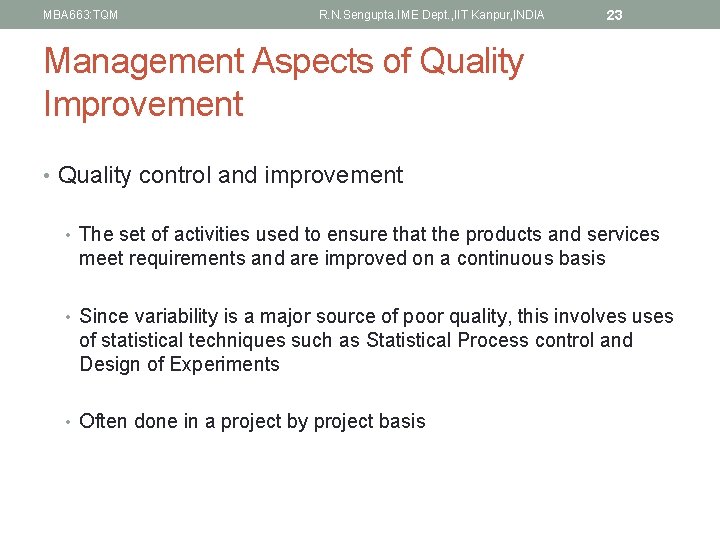
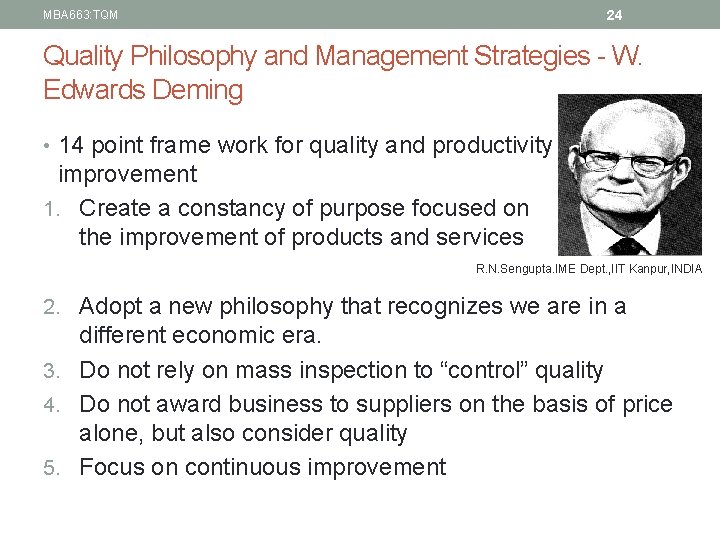
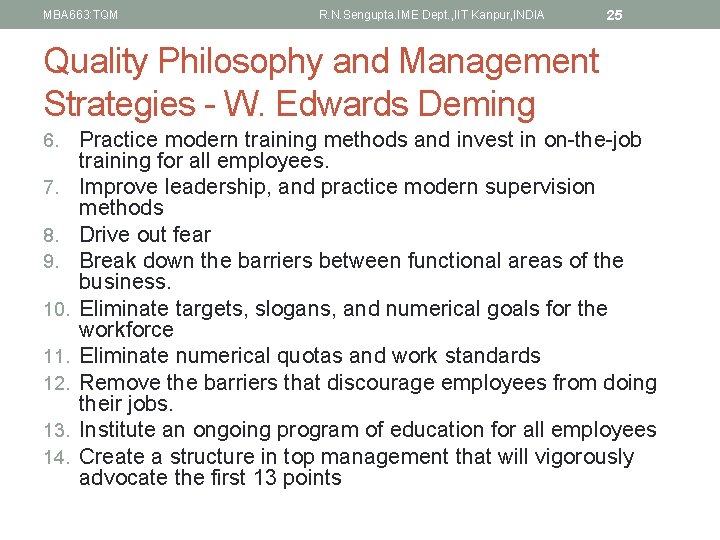
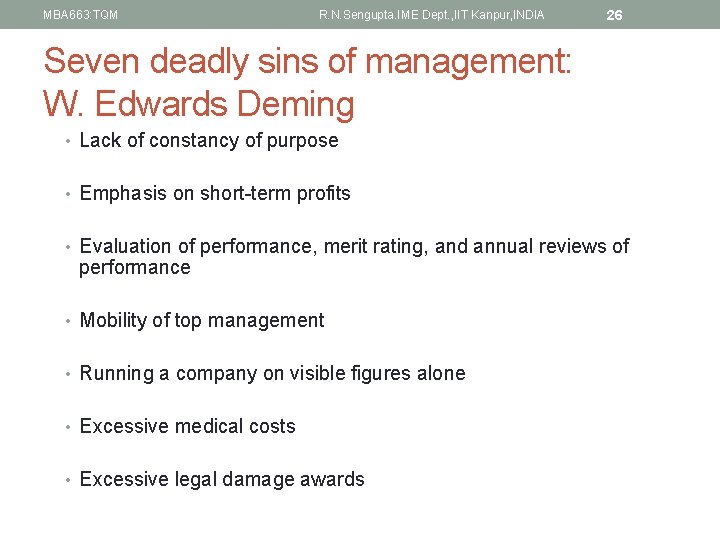
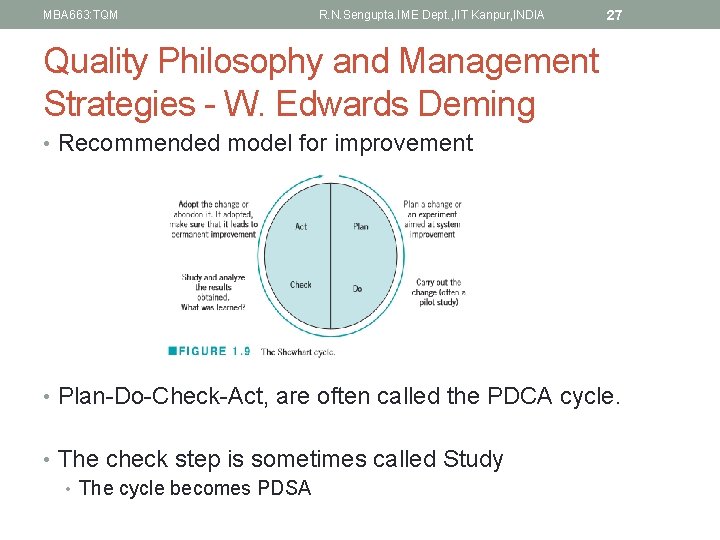
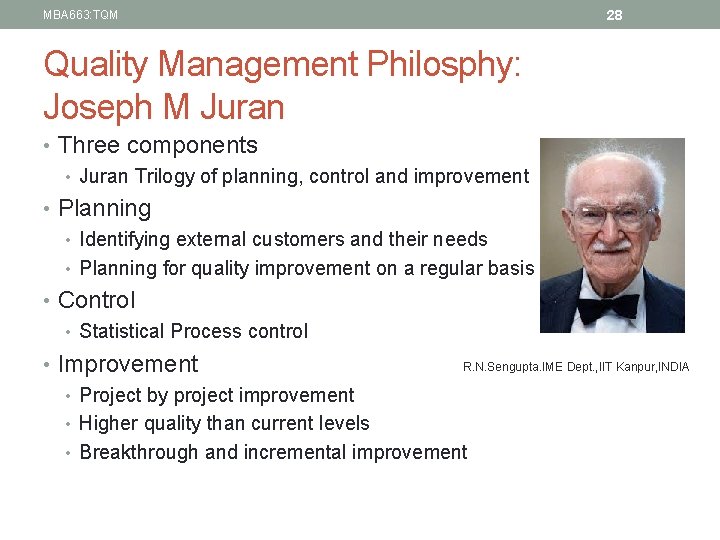
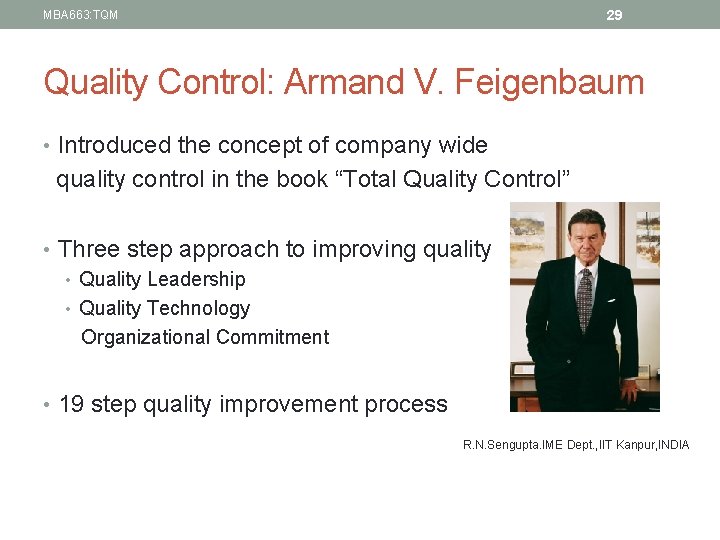
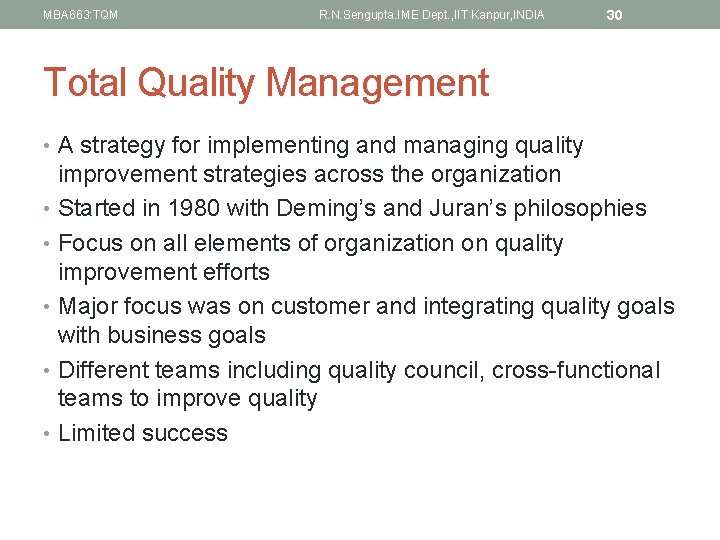
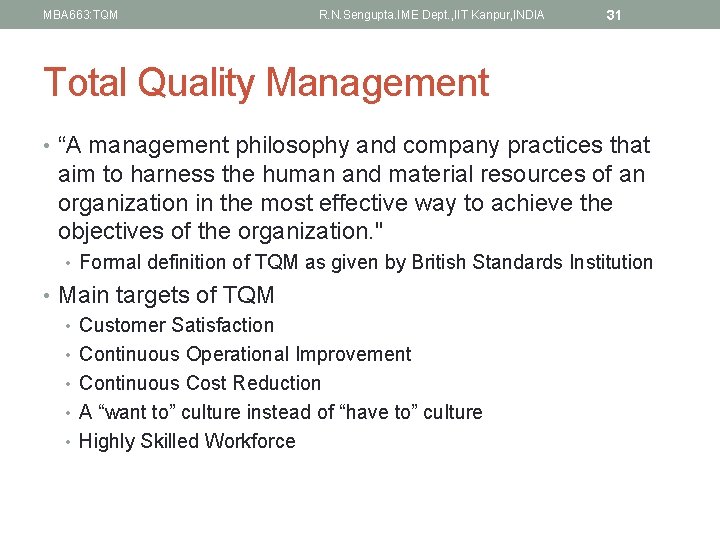
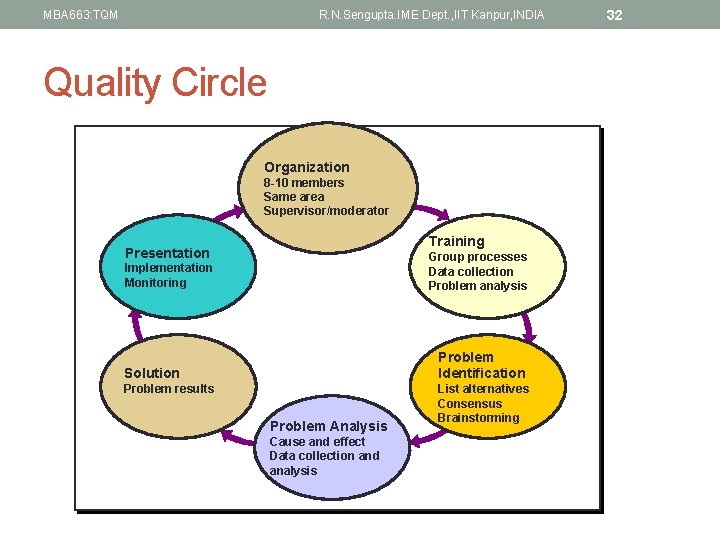
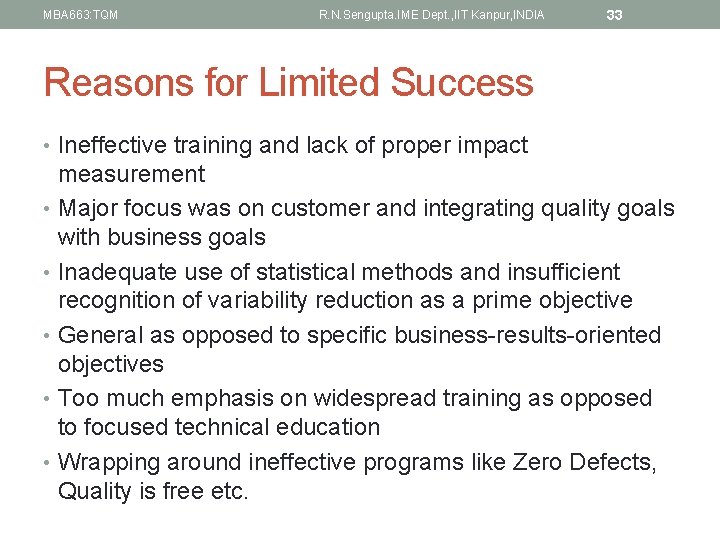
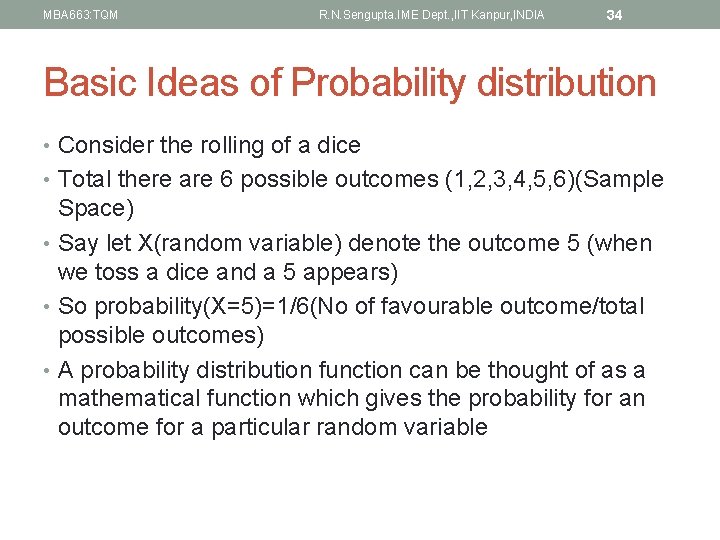
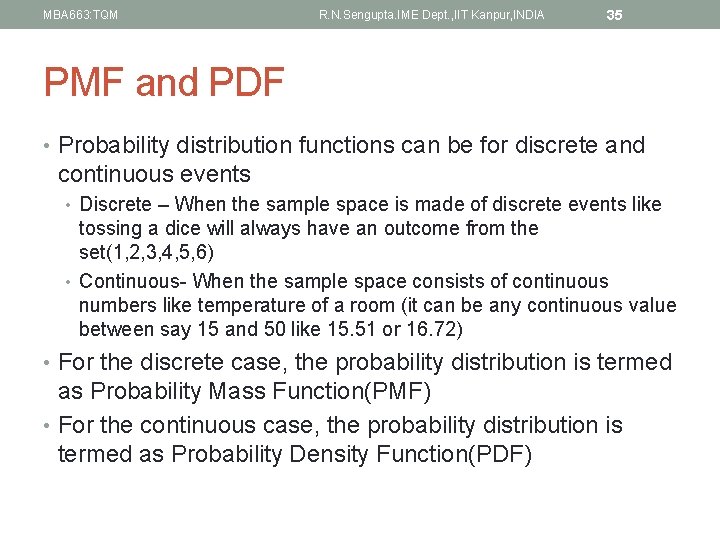
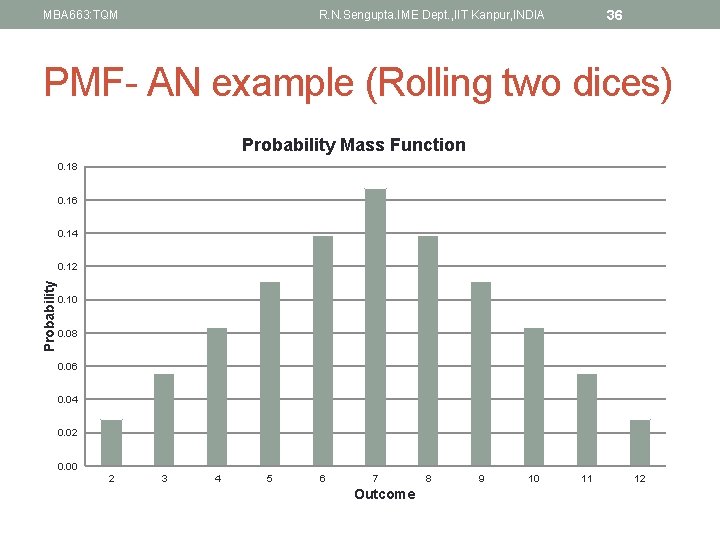
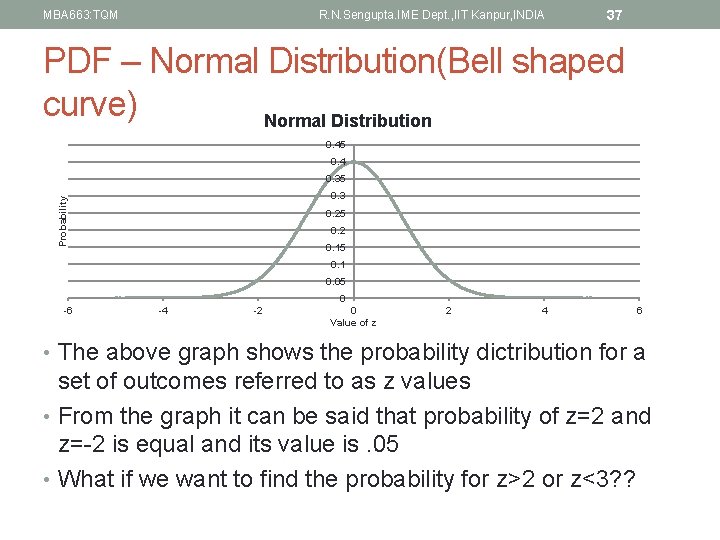
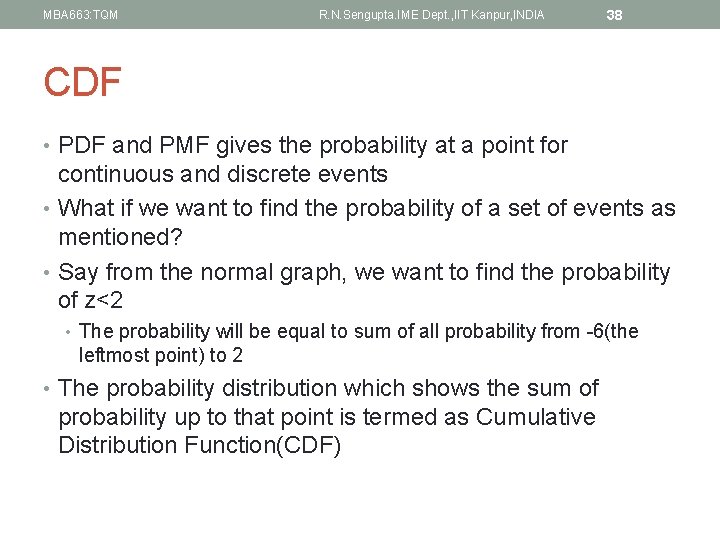
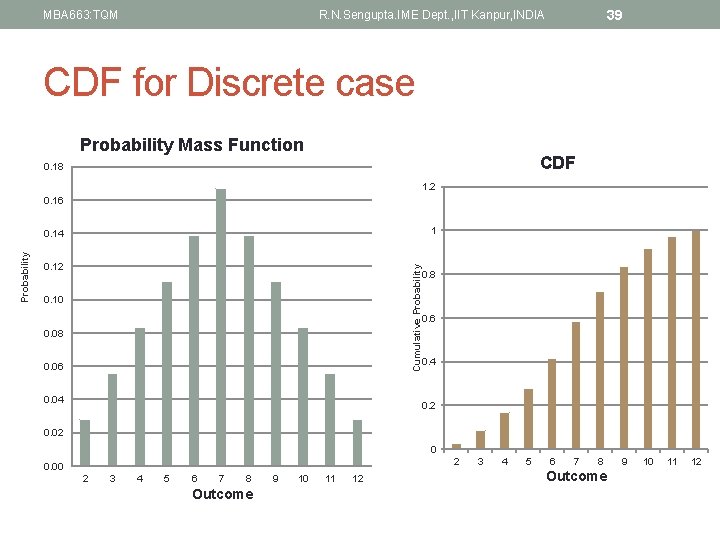
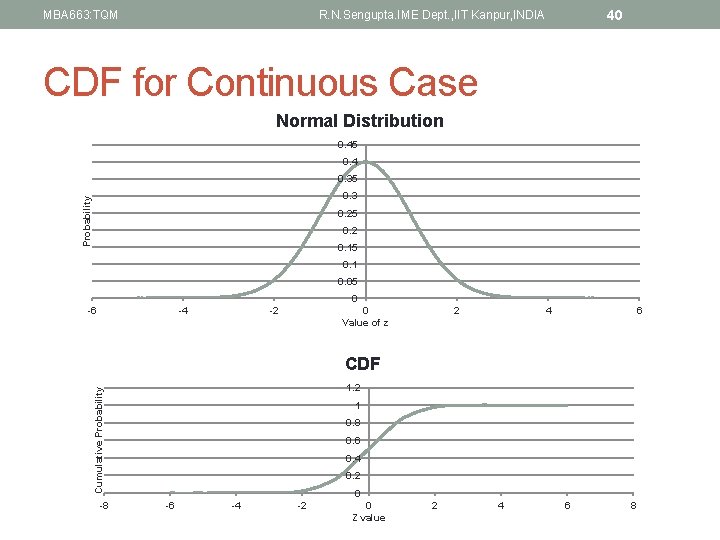
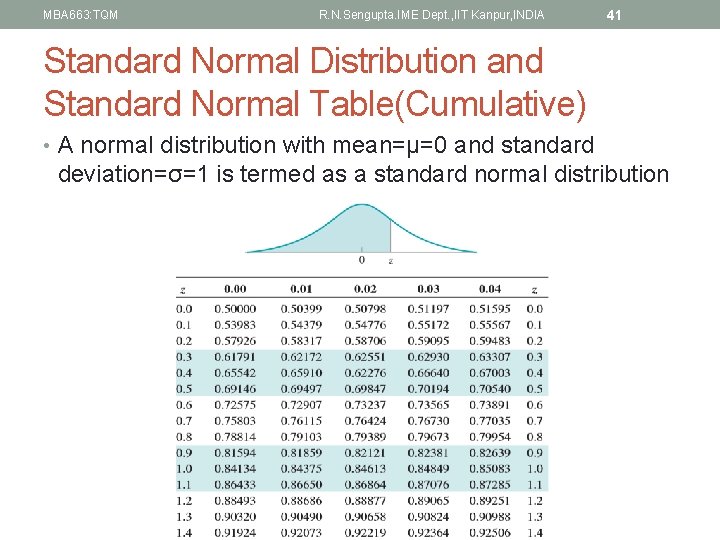
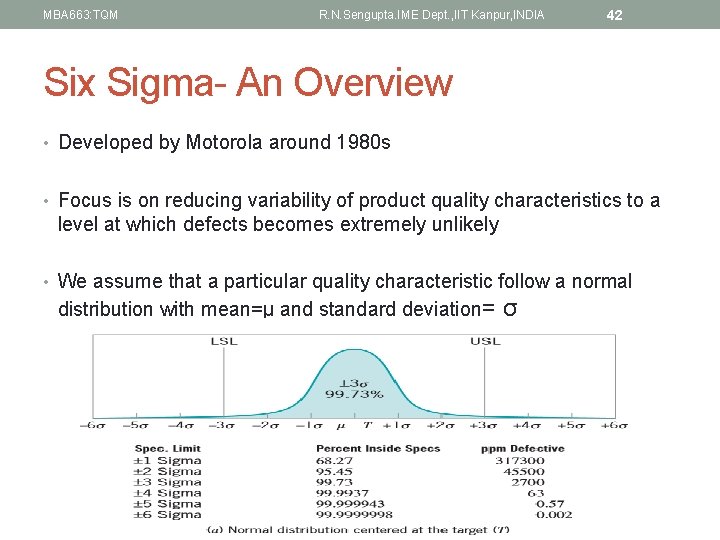
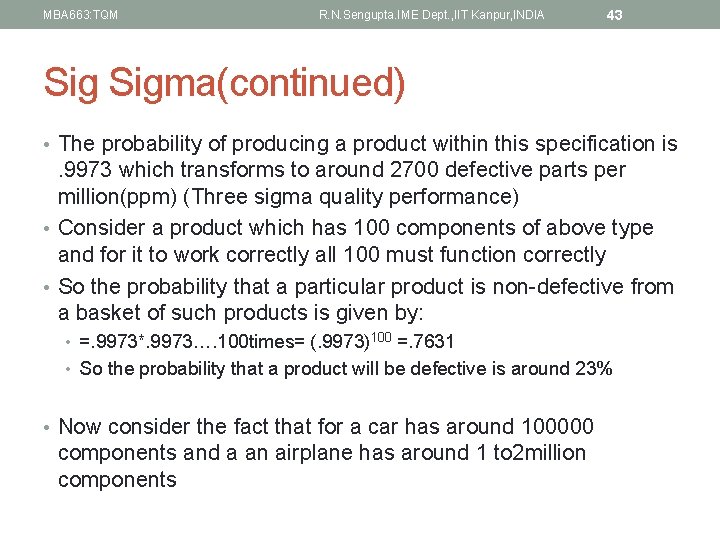
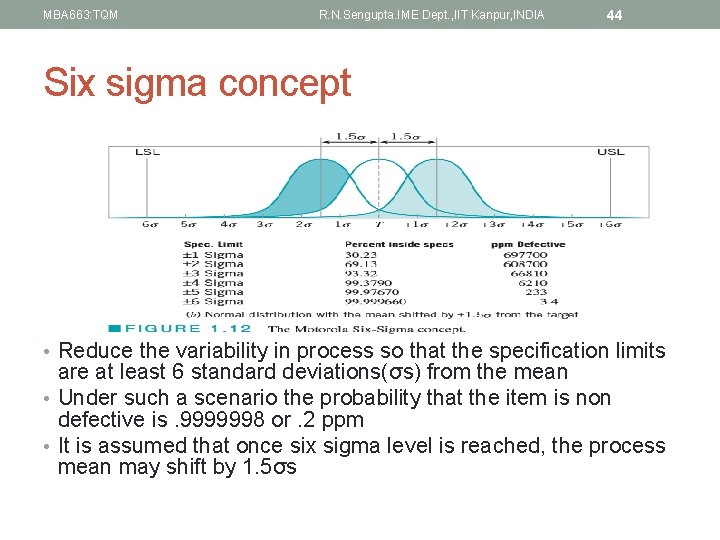
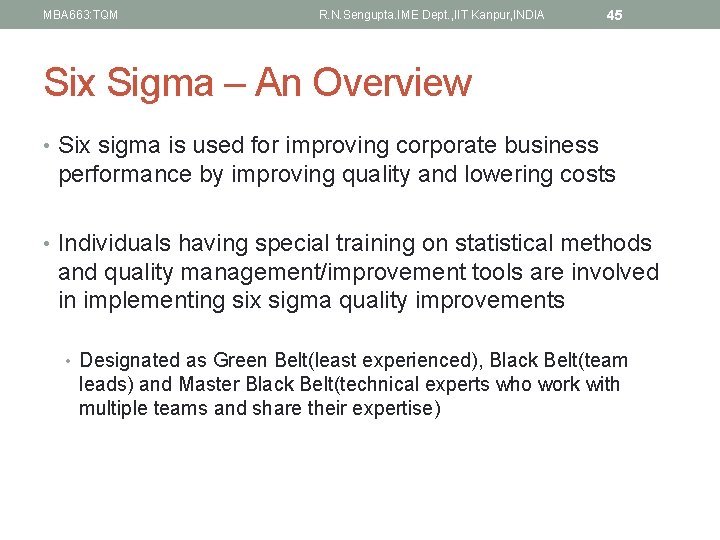
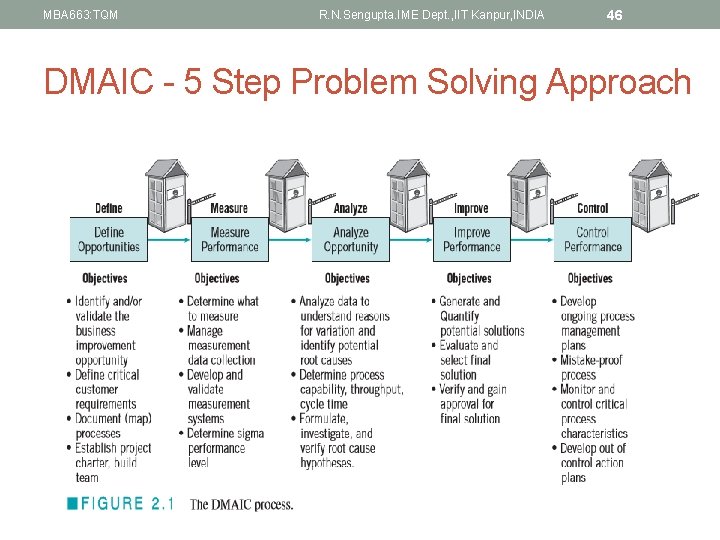
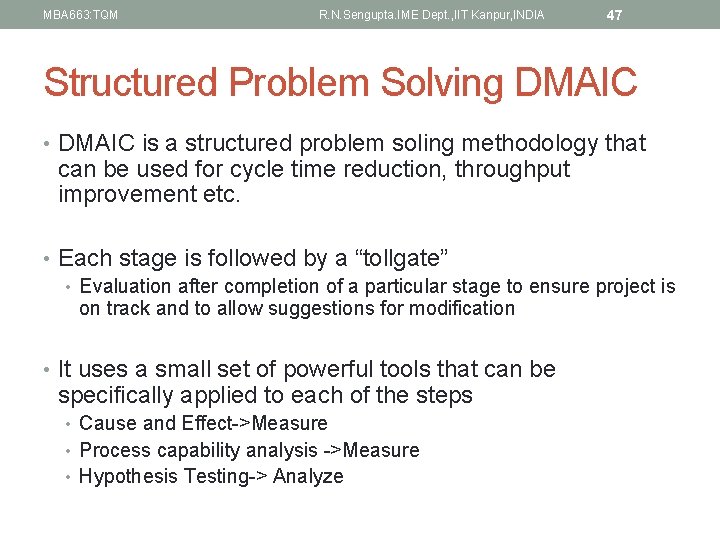
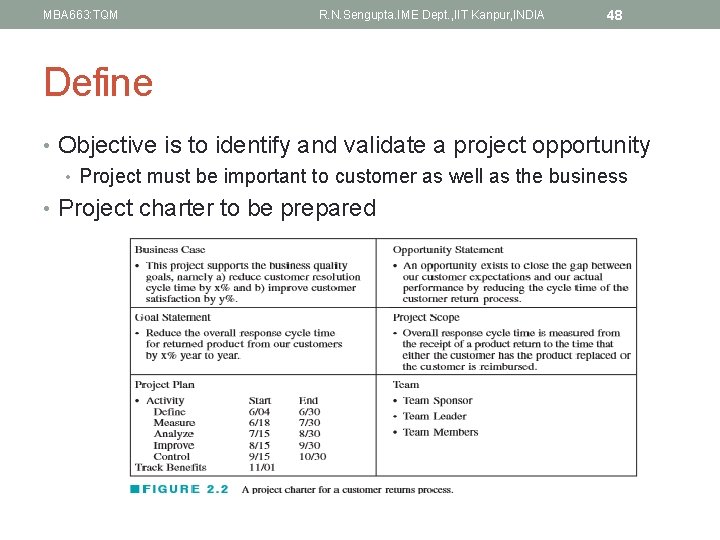
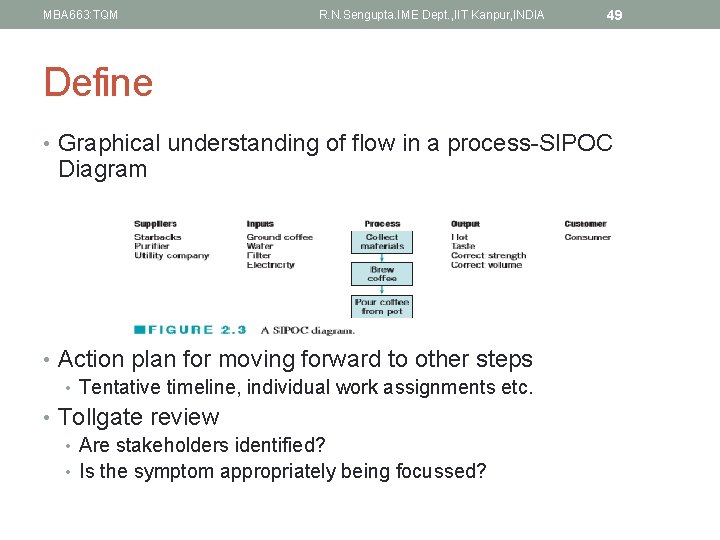
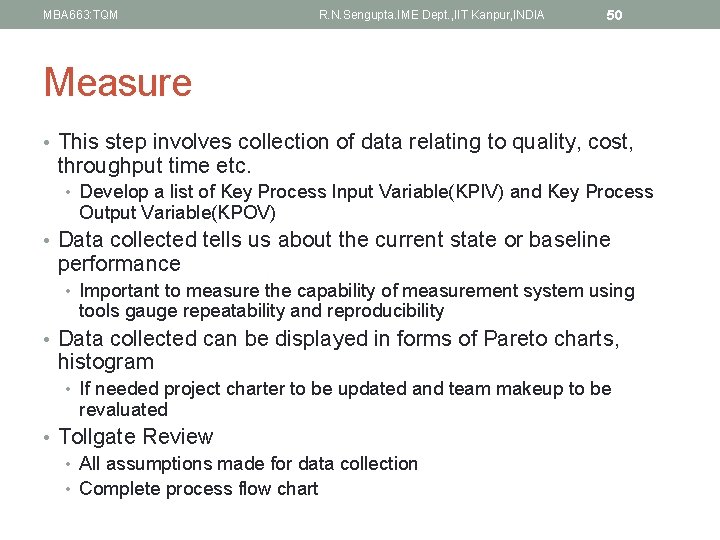
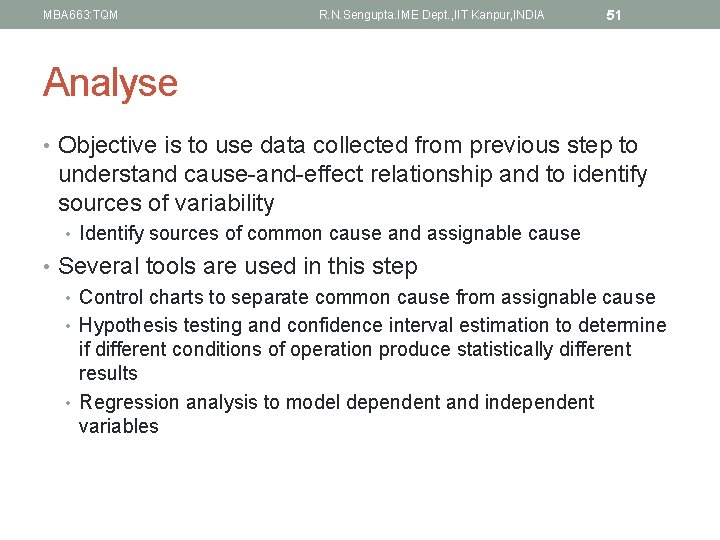
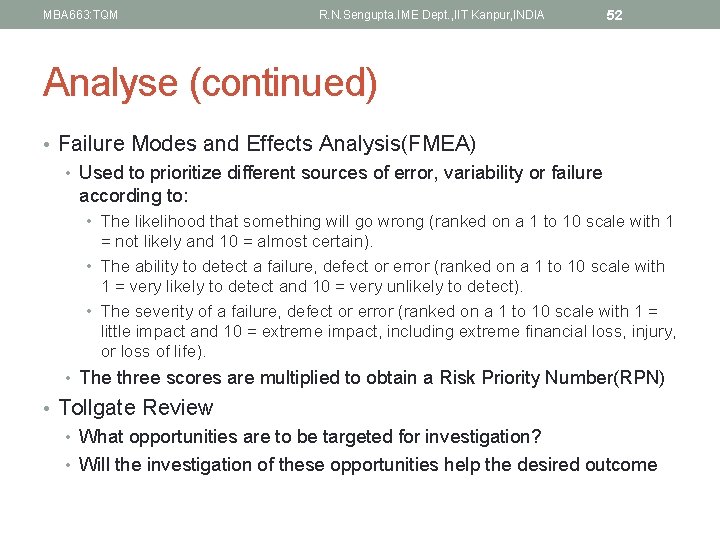
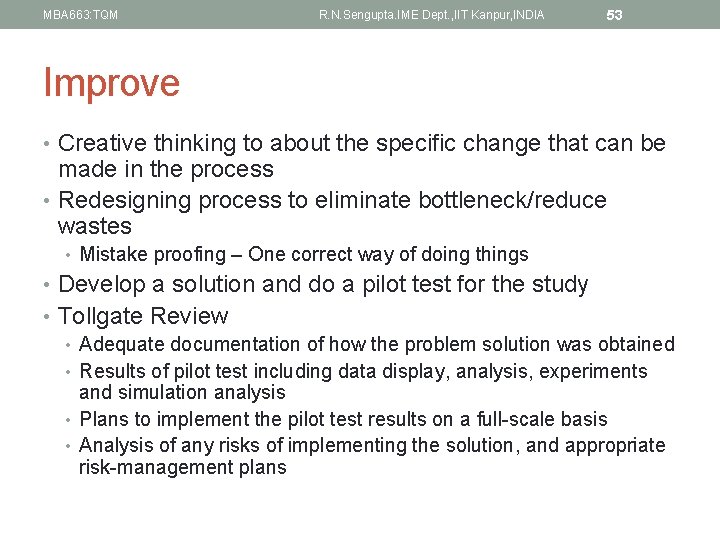
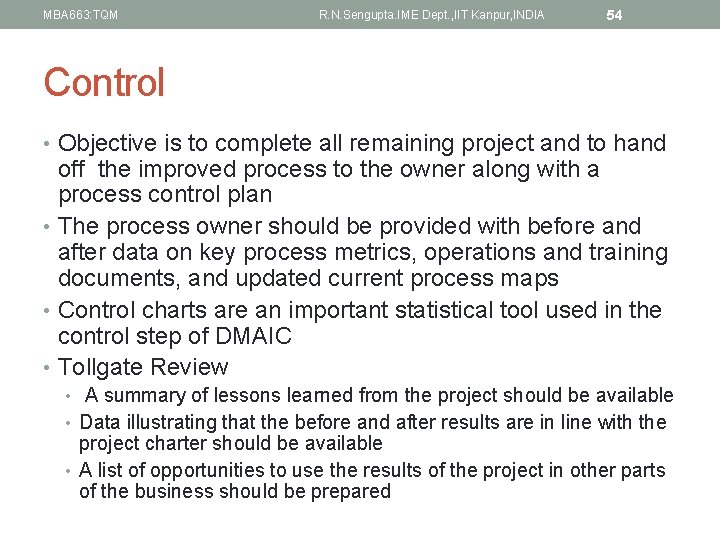
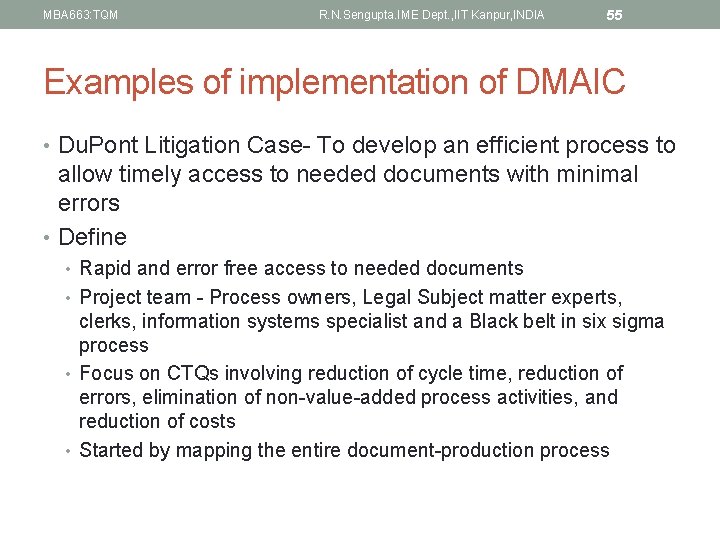
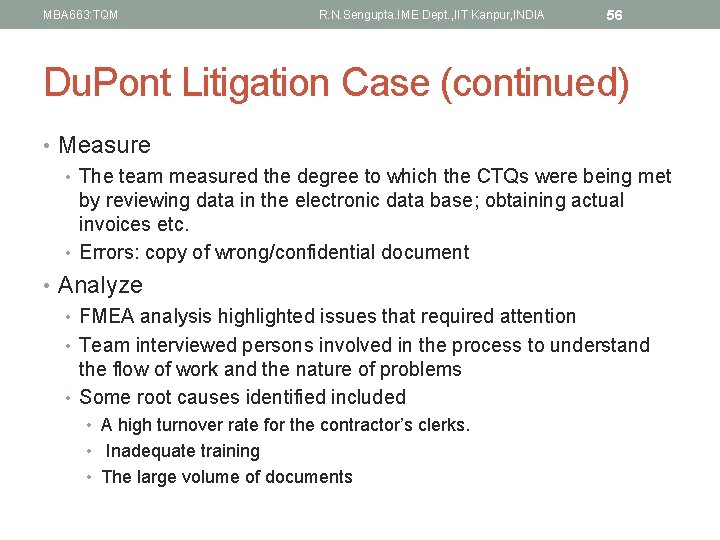
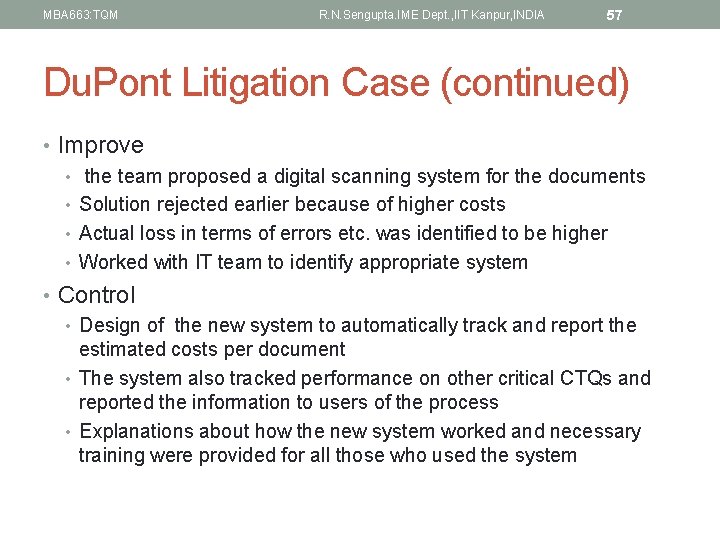
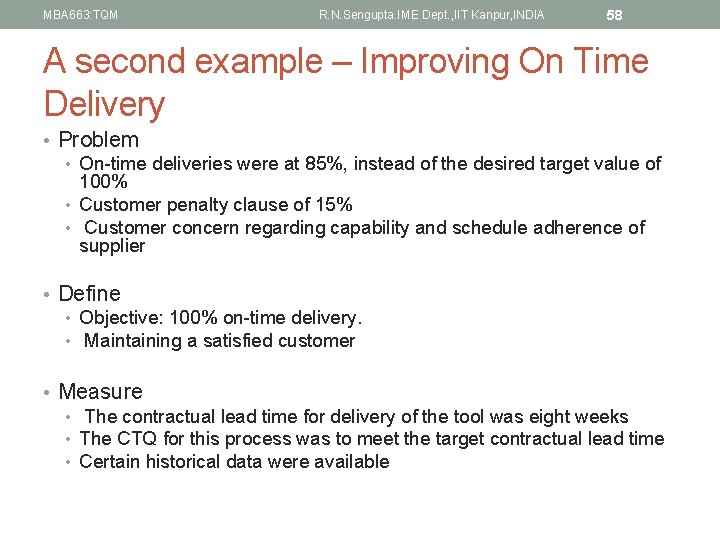
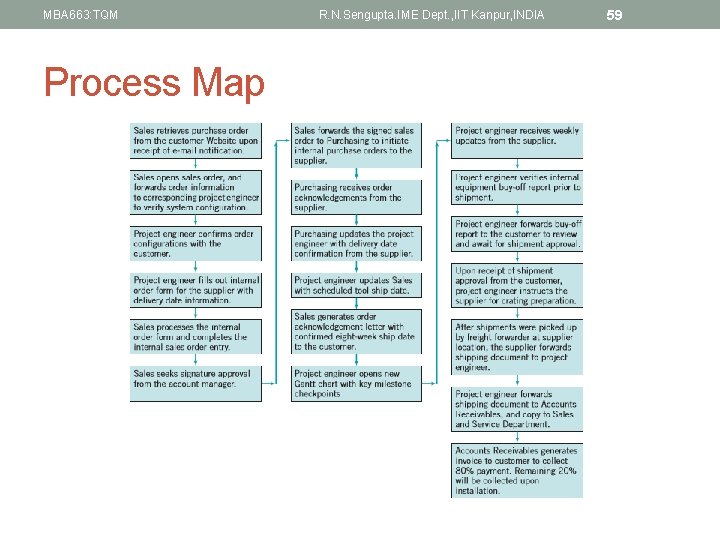
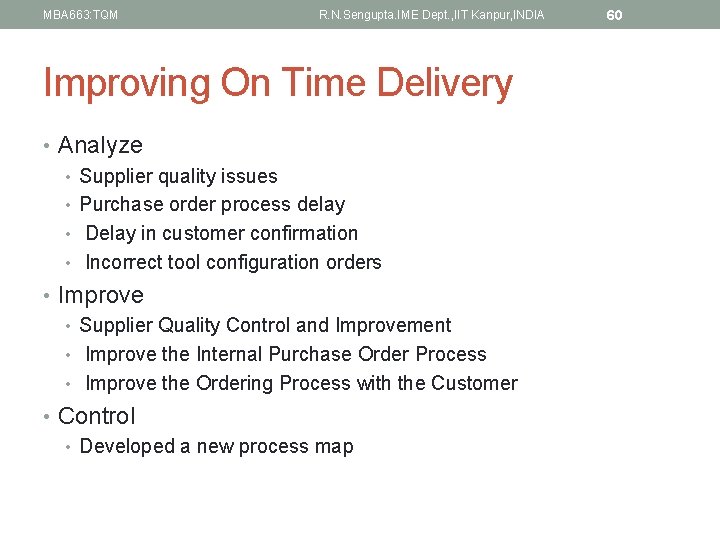
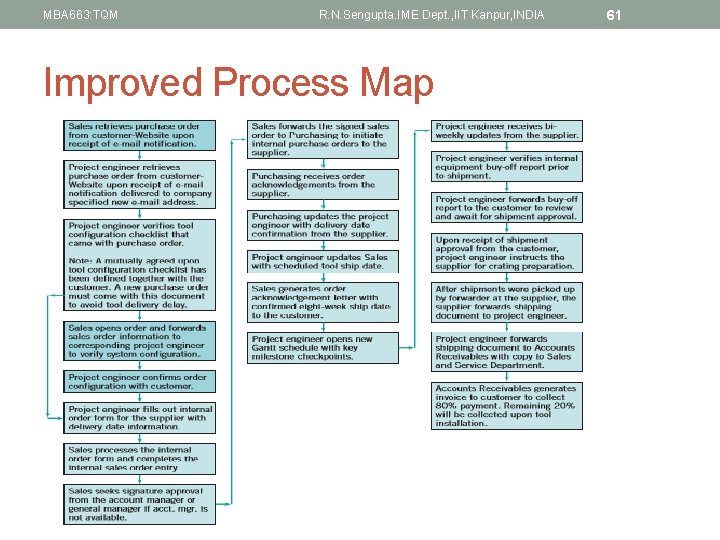
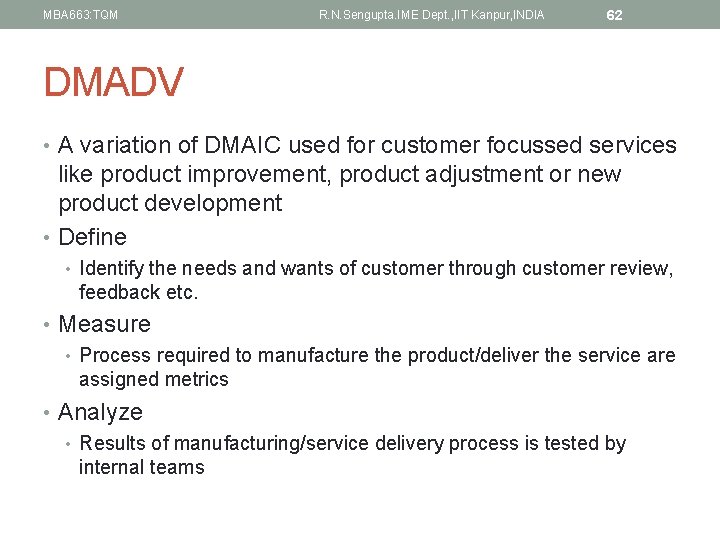
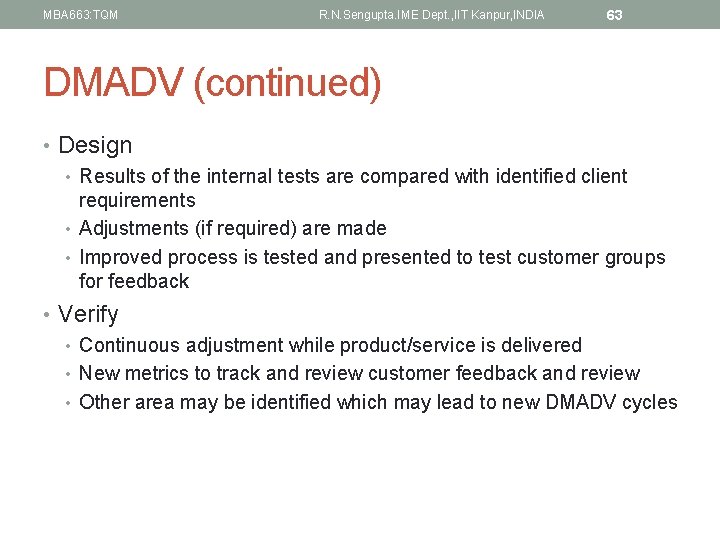
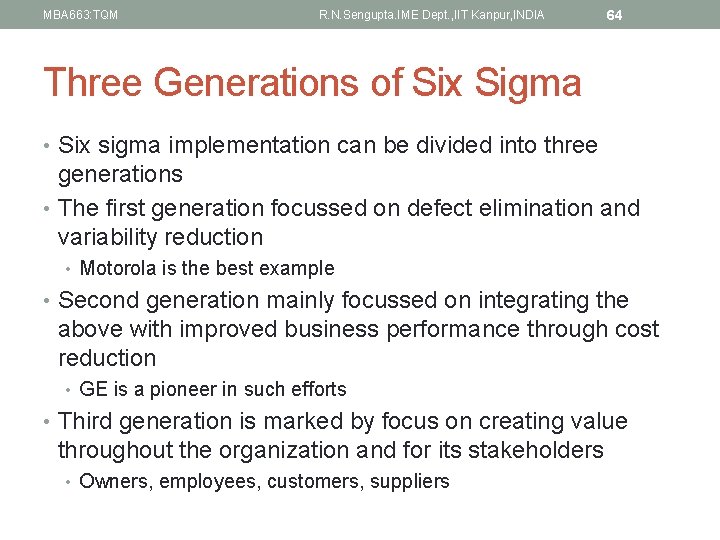
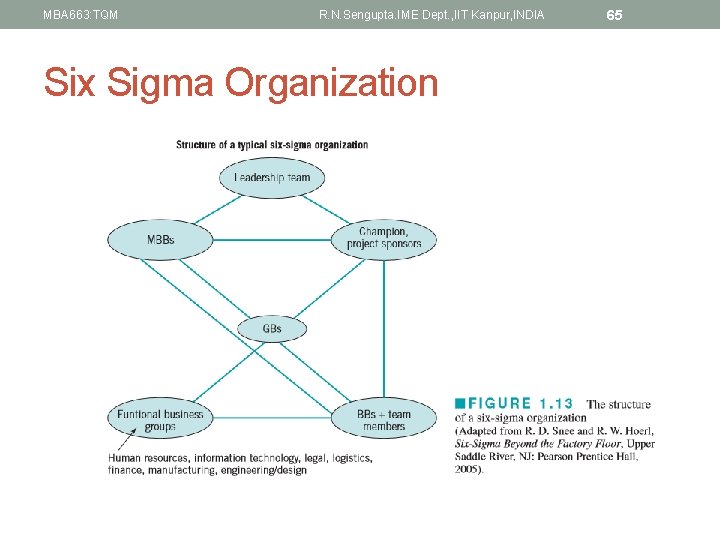
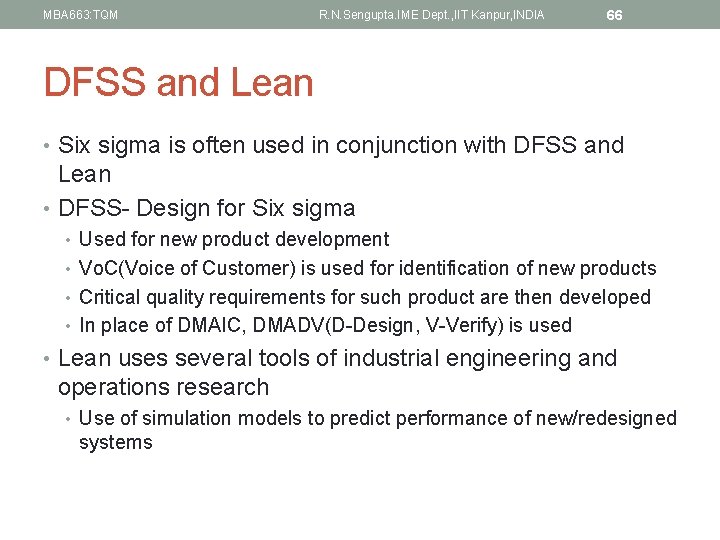
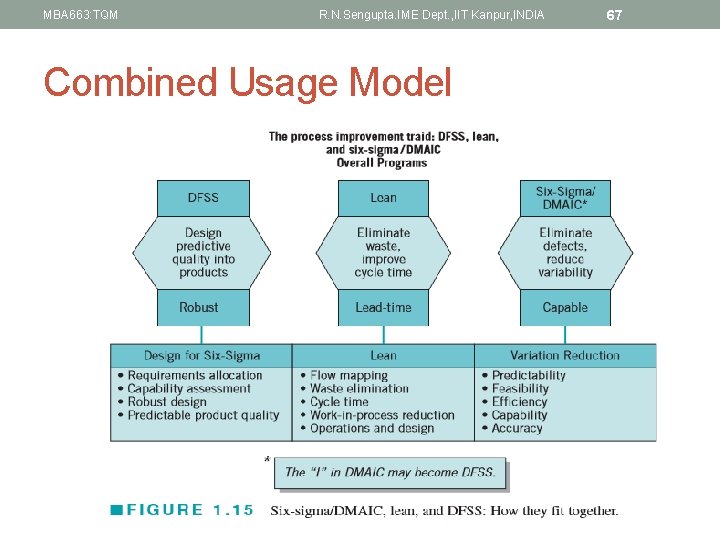
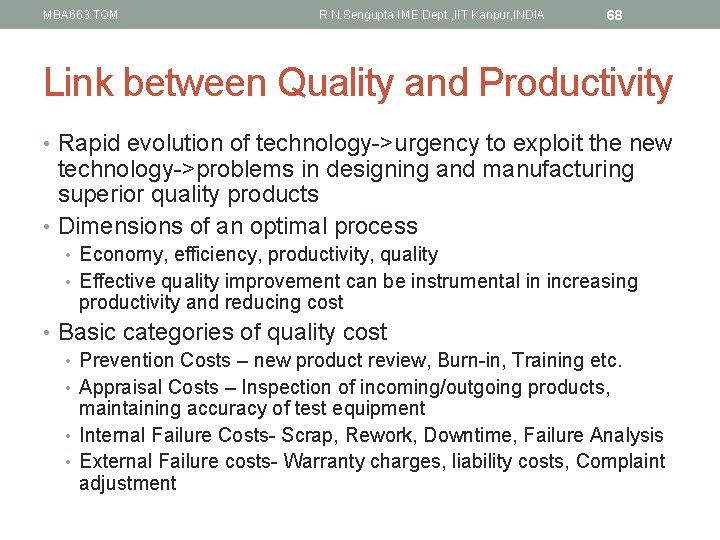
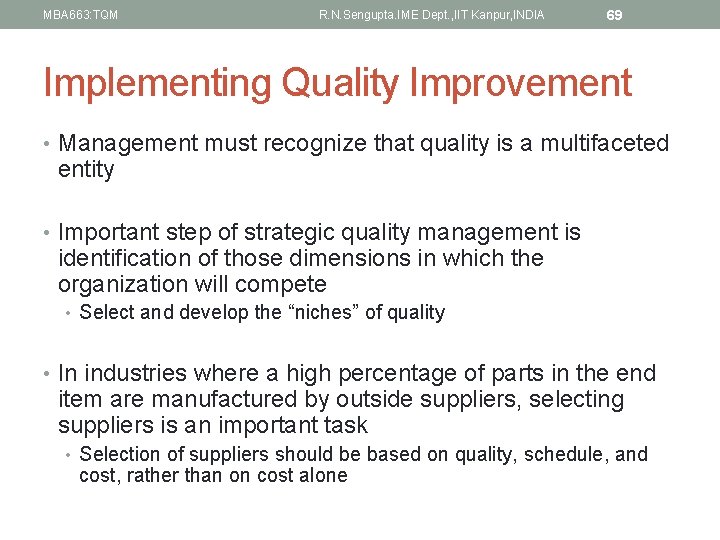
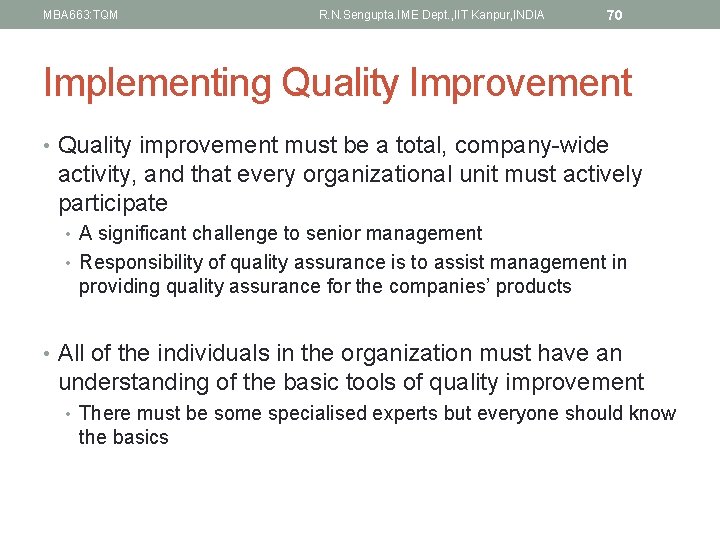
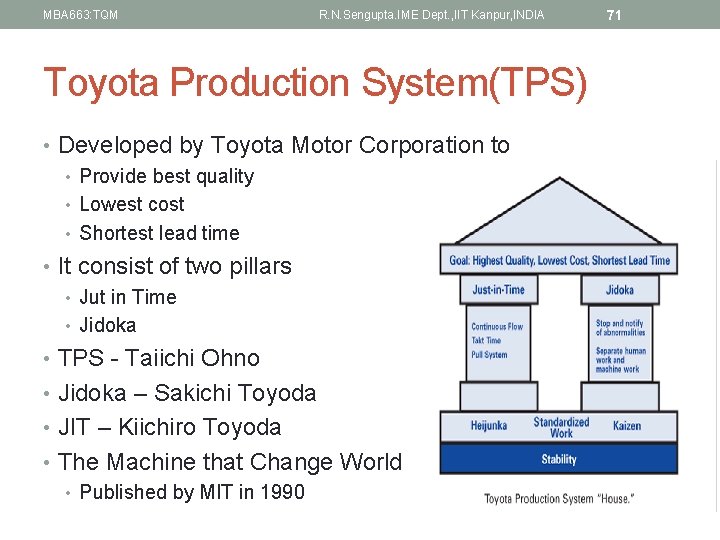
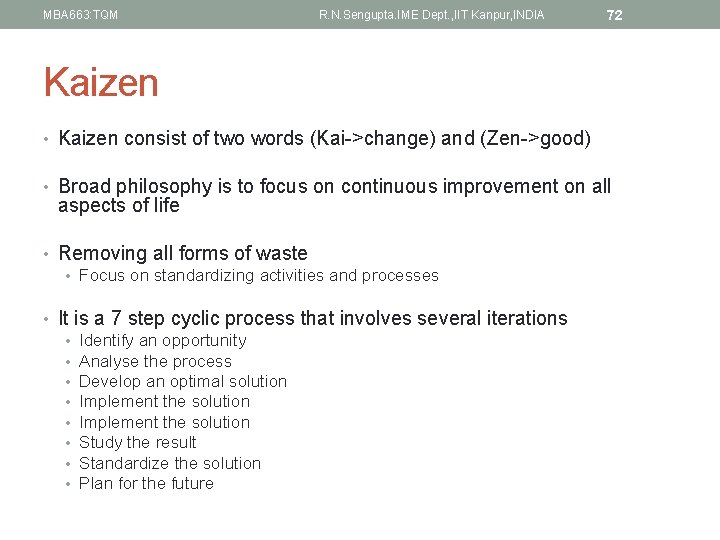
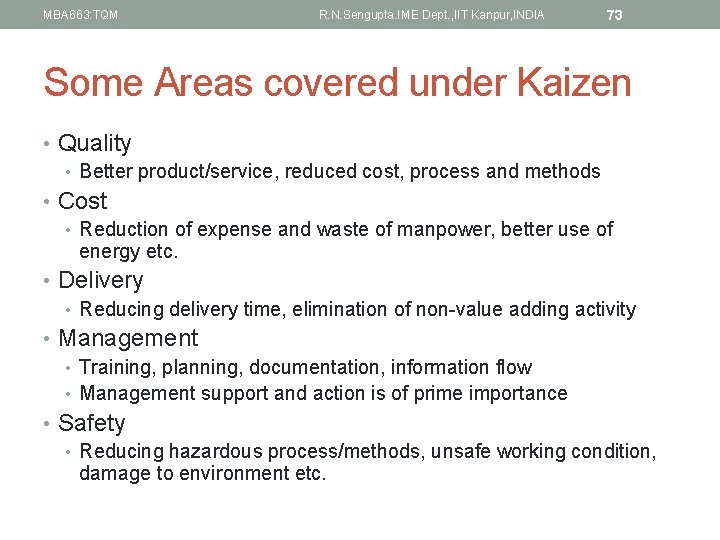
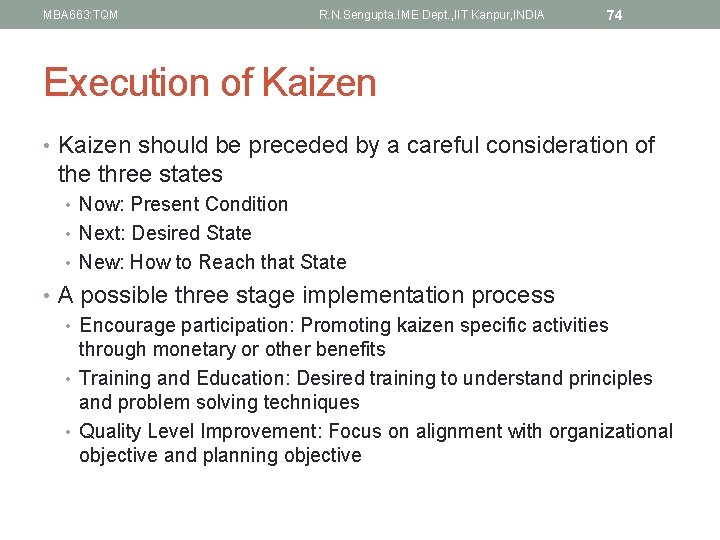
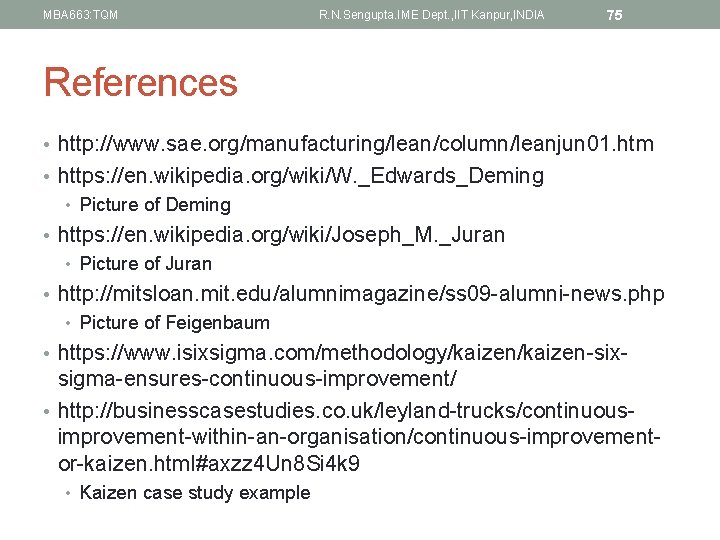
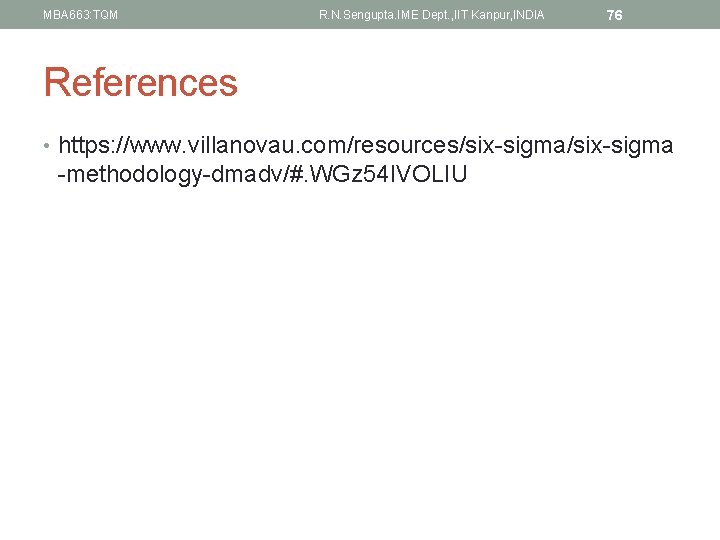
- Slides: 76
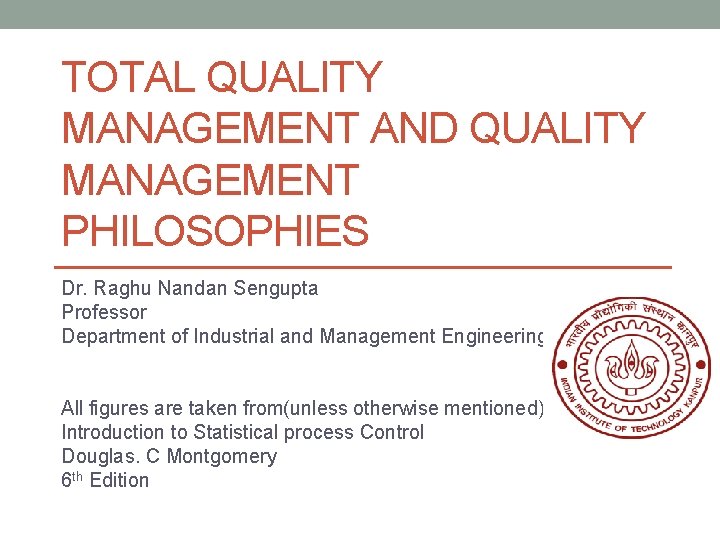
TOTAL QUALITY MANAGEMENT AND QUALITY MANAGEMENT PHILOSOPHIES Dr. Raghu Nandan Sengupta Professor Department of Industrial and Management Engineering All figures are taken from(unless otherwise mentioned): Introduction to Statistical process Control Douglas. C Montgomery 6 th Edition
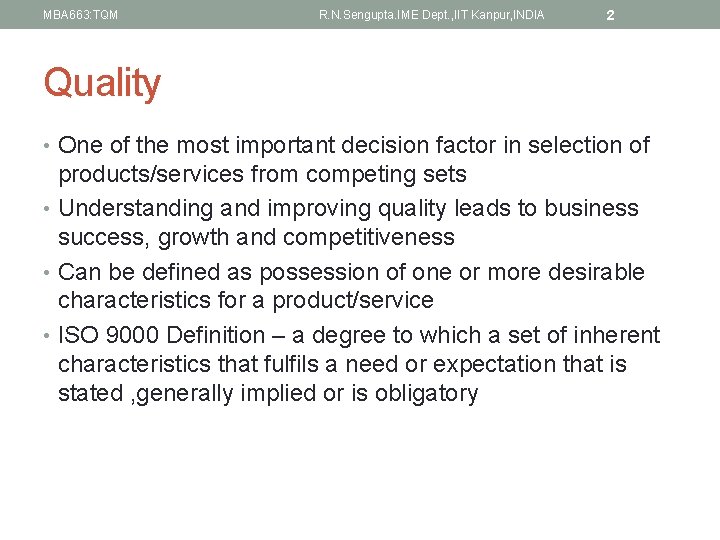
MBA 663: TQM R. N. Sengupta. IME Dept. , IIT Kanpur, INDIA 2 Quality • One of the most important decision factor in selection of products/services from competing sets • Understanding and improving quality leads to business success, growth and competitiveness • Can be defined as possession of one or more desirable characteristics for a product/service • ISO 9000 Definition – a degree to which a set of inherent characteristics that fulfils a need or expectation that is stated , generally implied or is obligatory
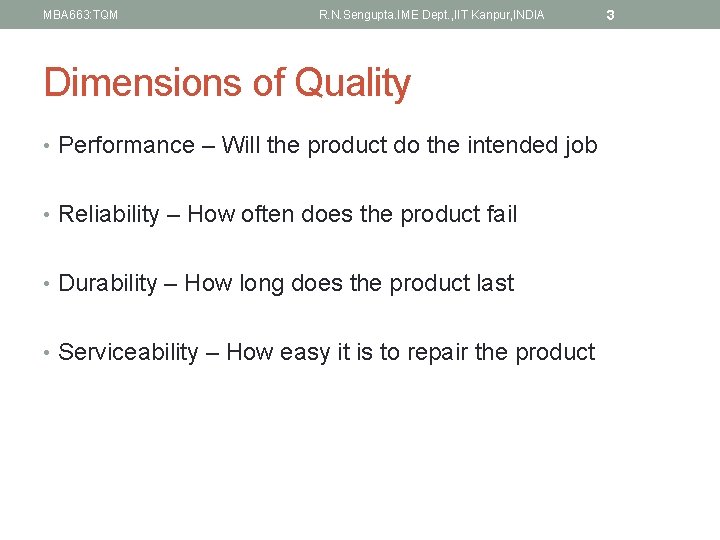
MBA 663: TQM R. N. Sengupta. IME Dept. , IIT Kanpur, INDIA Dimensions of Quality • Performance – Will the product do the intended job • Reliability – How often does the product fail • Durability – How long does the product last • Serviceability – How easy it is to repair the product 3
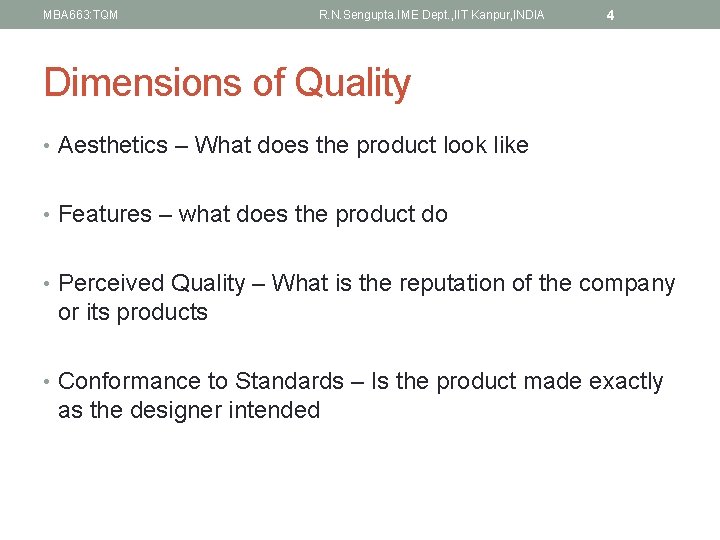
MBA 663: TQM R. N. Sengupta. IME Dept. , IIT Kanpur, INDIA 4 Dimensions of Quality • Aesthetics – What does the product look like • Features – what does the product do • Perceived Quality – What is the reputation of the company or its products • Conformance to Standards – Is the product made exactly as the designer intended
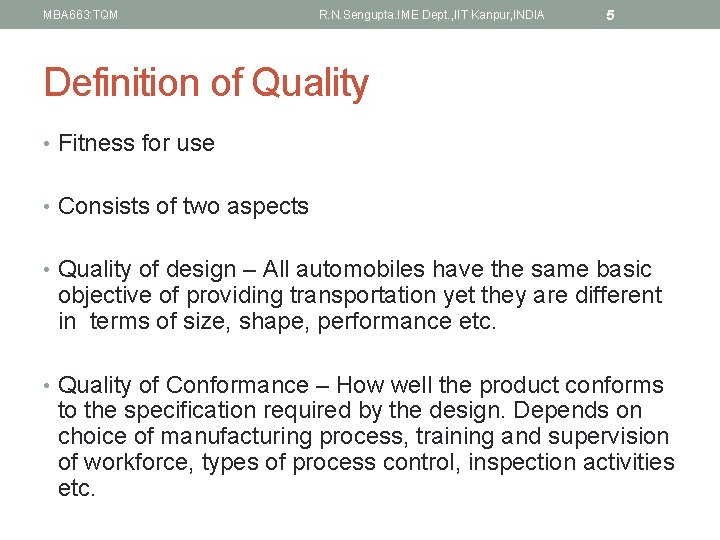
MBA 663: TQM R. N. Sengupta. IME Dept. , IIT Kanpur, INDIA 5 Definition of Quality • Fitness for use • Consists of two aspects • Quality of design – All automobiles have the same basic objective of providing transportation yet they are different in terms of size, shape, performance etc. • Quality of Conformance – How well the product conforms to the specification required by the design. Depends on choice of manufacturing process, training and supervision of workforce, types of process control, inspection activities etc.
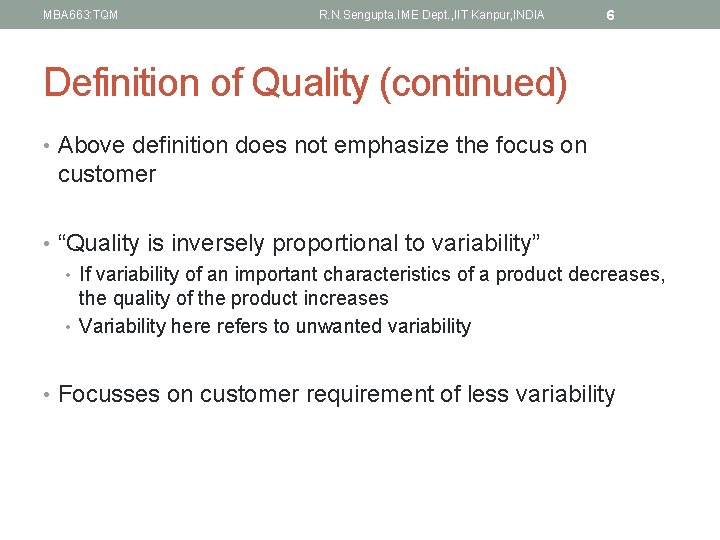
MBA 663: TQM R. N. Sengupta. IME Dept. , IIT Kanpur, INDIA 6 Definition of Quality (continued) • Above definition does not emphasize the focus on customer • “Quality is inversely proportional to variability” • If variability of an important characteristics of a product decreases, the quality of the product increases • Variability here refers to unwanted variability • Focusses on customer requirement of less variability
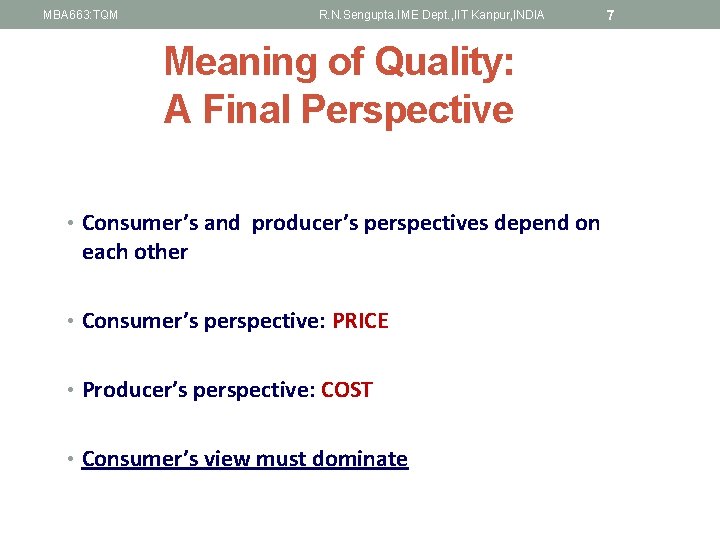
MBA 663: TQM R. N. Sengupta. IME Dept. , IIT Kanpur, INDIA Meaning of Quality: A Final Perspective • Consumer’s and producer’s perspectives depend on each other • Consumer’s perspective: PRICE • Producer’s perspective: COST • Consumer’s view must dominate 7
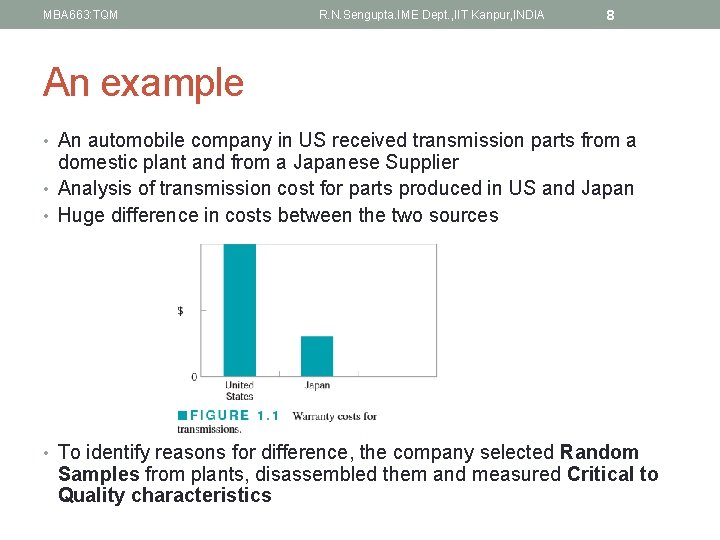
MBA 663: TQM R. N. Sengupta. IME Dept. , IIT Kanpur, INDIA 8 An example • An automobile company in US received transmission parts from a domestic plant and from a Japanese Supplier • Analysis of transmission cost for parts produced in US and Japan • Huge difference in costs between the two sources • To identify reasons for difference, the company selected Random Samples from plants, disassembled them and measured Critical to Quality characteristics
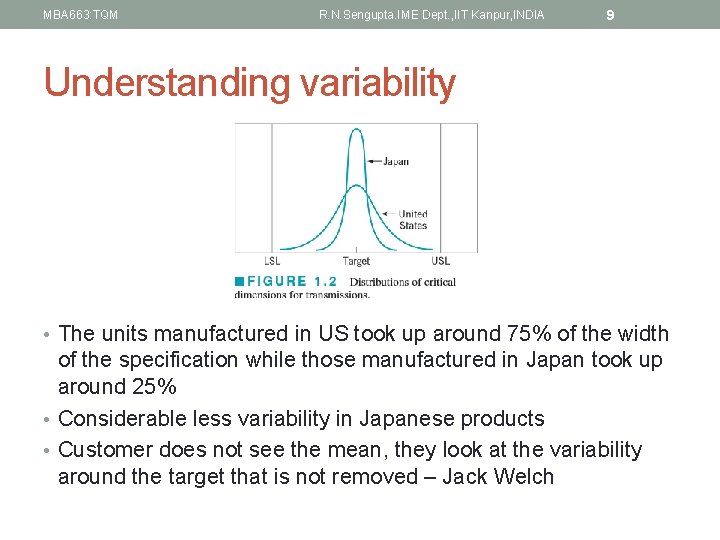
MBA 663: TQM R. N. Sengupta. IME Dept. , IIT Kanpur, INDIA 9 Understanding variability • The units manufactured in US took up around 75% of the width of the specification while those manufactured in Japan took up around 25% • Considerable less variability in Japanese products • Customer does not see the mean, they look at the variability around the target that is not removed – Jack Welch
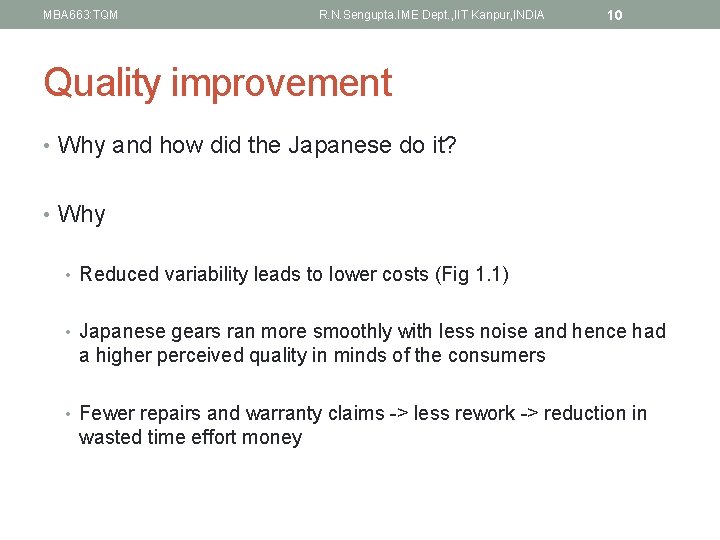
MBA 663: TQM R. N. Sengupta. IME Dept. , IIT Kanpur, INDIA 10 Quality improvement • Why and how did the Japanese do it? • Why • Reduced variability leads to lower costs (Fig 1. 1) • Japanese gears ran more smoothly with less noise and hence had a higher perceived quality in minds of the consumers • Fewer repairs and warranty claims -> less rework -> reduction in wasted time effort money
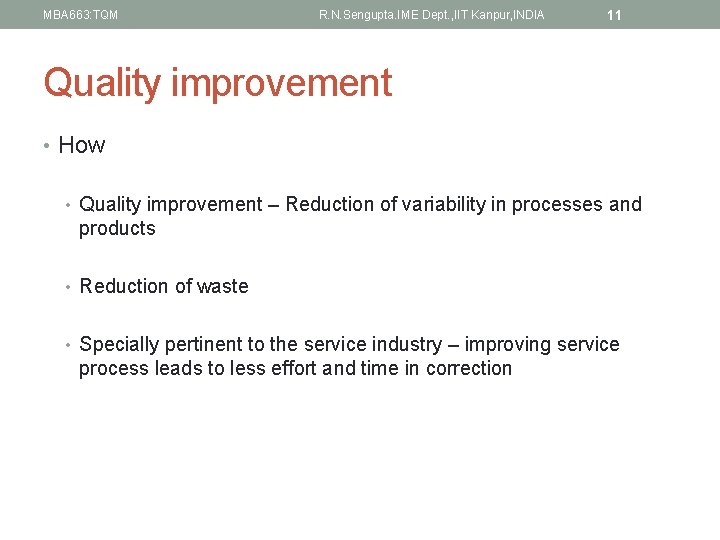
MBA 663: TQM R. N. Sengupta. IME Dept. , IIT Kanpur, INDIA 11 Quality improvement • How • Quality improvement – Reduction of variability in processes and products • Reduction of waste • Specially pertinent to the service industry – improving service process leads to less effort and time in correction
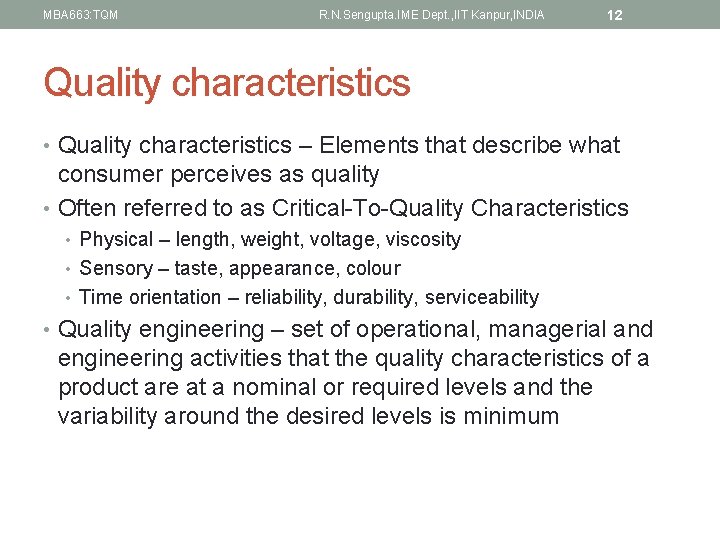
MBA 663: TQM R. N. Sengupta. IME Dept. , IIT Kanpur, INDIA 12 Quality characteristics • Quality characteristics – Elements that describe what consumer perceives as quality • Often referred to as Critical-To-Quality Characteristics • Physical – length, weight, voltage, viscosity • Sensory – taste, appearance, colour • Time orientation – reliability, durability, serviceability • Quality engineering – set of operational, managerial and engineering activities that the quality characteristics of a product are at a nominal or required levels and the variability around the desired levels is minimum
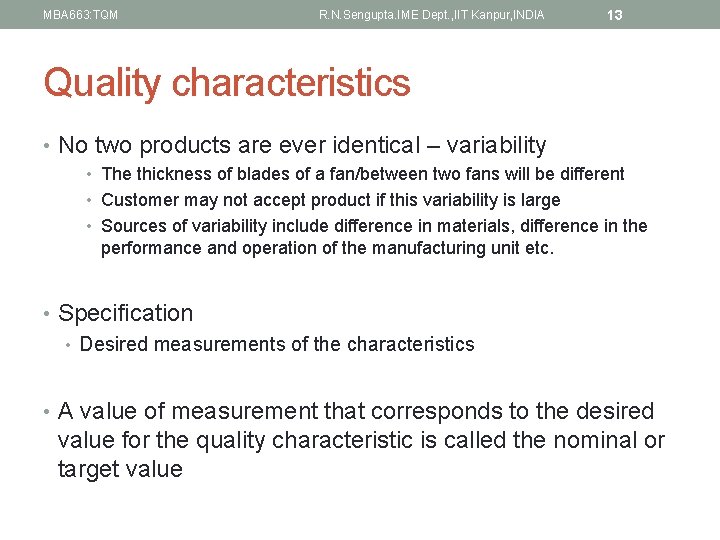
MBA 663: TQM R. N. Sengupta. IME Dept. , IIT Kanpur, INDIA 13 Quality characteristics • No two products are ever identical – variability • The thickness of blades of a fan/between two fans will be different • Customer may not accept product if this variability is large • Sources of variability include difference in materials, difference in the performance and operation of the manufacturing unit etc. • Specification • Desired measurements of the characteristics • A value of measurement that corresponds to the desired value for the quality characteristic is called the nominal or target value
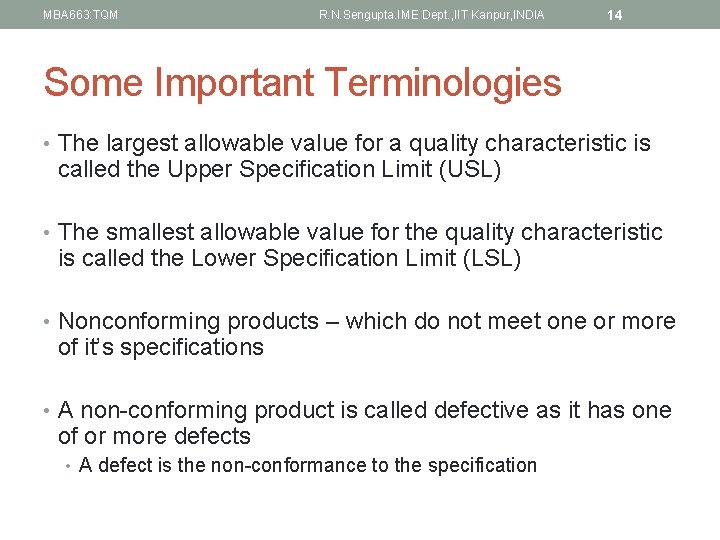
MBA 663: TQM R. N. Sengupta. IME Dept. , IIT Kanpur, INDIA 14 Some Important Terminologies • The largest allowable value for a quality characteristic is called the Upper Specification Limit (USL) • The smallest allowable value for the quality characteristic is called the Lower Specification Limit (LSL) • Nonconforming products – which do not meet one or more of it’s specifications • A non-conforming product is called defective as it has one of or more defects • A defect is the non-conformance to the specification
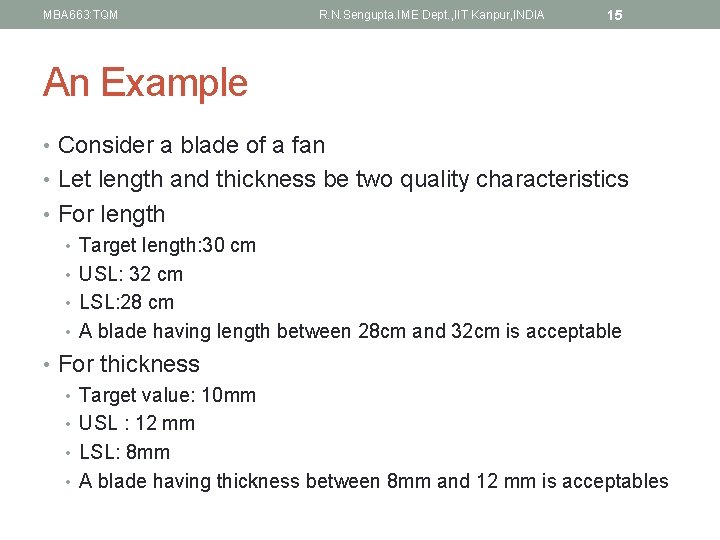
MBA 663: TQM R. N. Sengupta. IME Dept. , IIT Kanpur, INDIA 15 An Example • Consider a blade of a fan • Let length and thickness be two quality characteristics • For length • Target length: 30 cm • USL: 32 cm • LSL: 28 cm • A blade having length between 28 cm and 32 cm is acceptable • For thickness • Target value: 10 mm • USL : 12 mm • LSL: 8 mm • A blade having thickness between 8 mm and 12 mm is acceptables
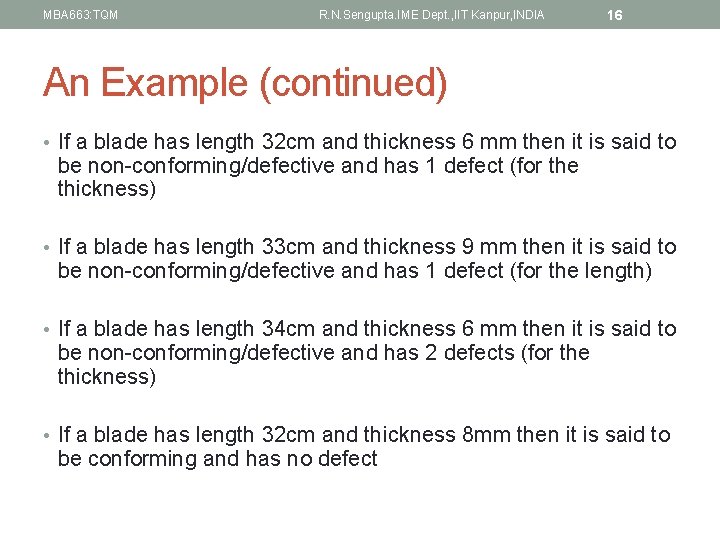
MBA 663: TQM R. N. Sengupta. IME Dept. , IIT Kanpur, INDIA 16 An Example (continued) • If a blade has length 32 cm and thickness 6 mm then it is said to be non-conforming/defective and has 1 defect (for the thickness) • If a blade has length 33 cm and thickness 9 mm then it is said to be non-conforming/defective and has 1 defect (for the length) • If a blade has length 34 cm and thickness 6 mm then it is said to be non-conforming/defective and has 2 defects (for the thickness) • If a blade has length 32 cm and thickness 8 mm then it is said to be conforming and has no defect
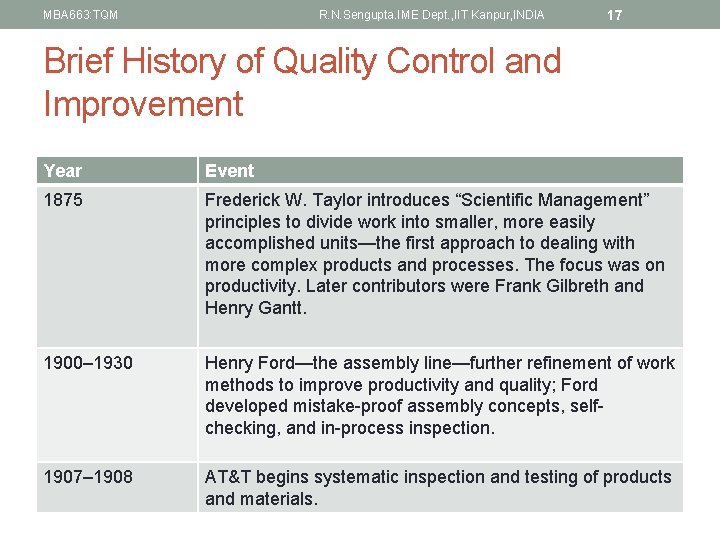
MBA 663: TQM R. N. Sengupta. IME Dept. , IIT Kanpur, INDIA 17 Brief History of Quality Control and Improvement Year Event 1875 Frederick W. Taylor introduces “Scientific Management” principles to divide work into smaller, more easily accomplished units—the first approach to dealing with more complex products and processes. The focus was on productivity. Later contributors were Frank Gilbreth and Henry Gantt. 1900– 1930 Henry Ford—the assembly line—further refinement of work methods to improve productivity and quality; Ford developed mistake-proof assembly concepts, selfchecking, and in-process inspection. 1907– 1908 AT&T begins systematic inspection and testing of products and materials.
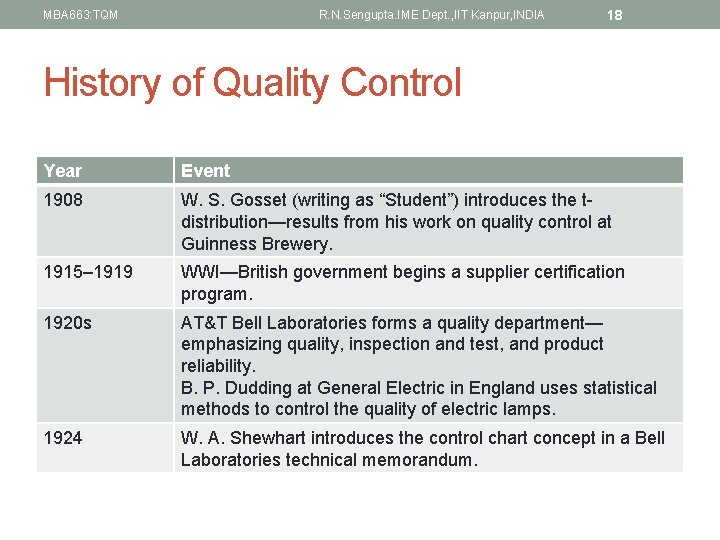
MBA 663: TQM R. N. Sengupta. IME Dept. , IIT Kanpur, INDIA 18 History of Quality Control Year Event 1908 W. S. Gosset (writing as “Student”) introduces the tdistribution—results from his work on quality control at Guinness Brewery. 1915– 1919 WWI—British government begins a supplier certification program. 1920 s AT&T Bell Laboratories forms a quality department— emphasizing quality, inspection and test, and product reliability. B. P. Dudding at General Electric in England uses statistical methods to control the quality of electric lamps. 1924 W. A. Shewhart introduces the control chart concept in a Bell Laboratories technical memorandum.
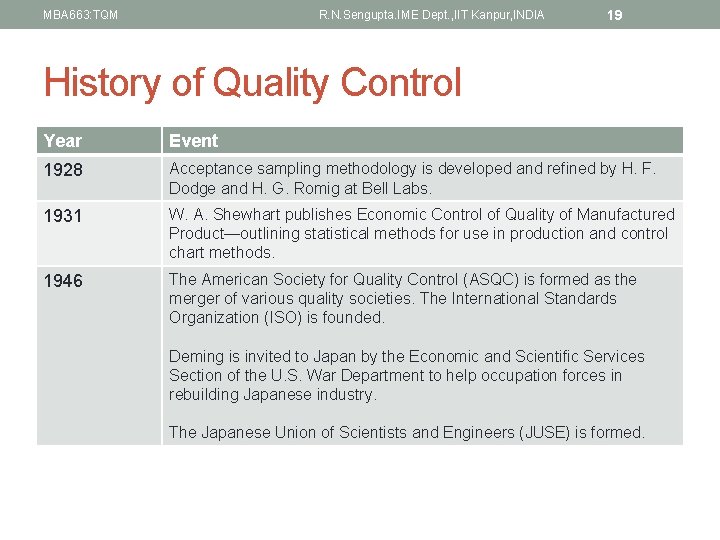
MBA 663: TQM R. N. Sengupta. IME Dept. , IIT Kanpur, INDIA 19 History of Quality Control Year Event 1928 Acceptance sampling methodology is developed and refined by H. F. Dodge and H. G. Romig at Bell Labs. 1931 W. A. Shewhart publishes Economic Control of Quality of Manufactured Product—outlining statistical methods for use in production and control chart methods. 1946 The American Society for Quality Control (ASQC) is formed as the merger of various quality societies. The International Standards Organization (ISO) is founded. Deming is invited to Japan by the Economic and Scientific Services Section of the U. S. War Department to help occupation forces in rebuilding Japanese industry. The Japanese Union of Scientists and Engineers (JUSE) is formed.
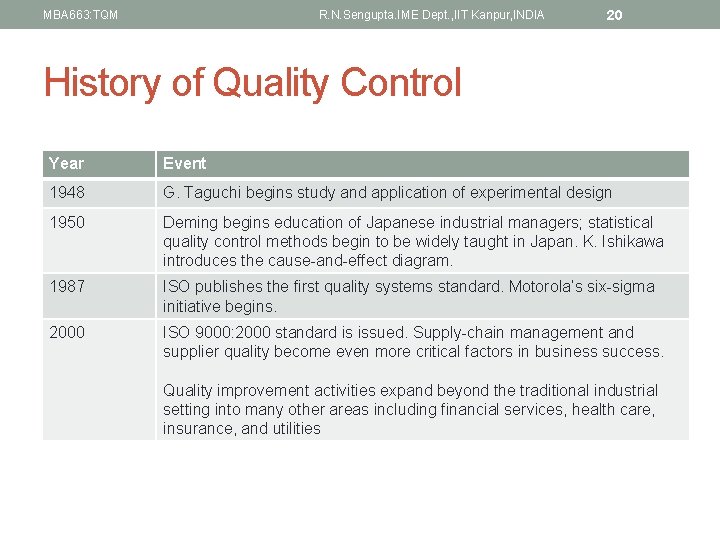
MBA 663: TQM R. N. Sengupta. IME Dept. , IIT Kanpur, INDIA 20 History of Quality Control Year Event 1948 G. Taguchi begins study and application of experimental design 1950 Deming begins education of Japanese industrial managers; statistical quality control methods begin to be widely taught in Japan. K. Ishikawa introduces the cause-and-effect diagram. 1987 ISO publishes the first quality systems standard. Motorola’s six-sigma initiative begins. 2000 ISO 9000: 2000 standard is issued. Supply-chain management and supplier quality become even more critical factors in business success. Quality improvement activities expand beyond the traditional industrial setting into many other areas including financial services, health care, insurance, and utilities
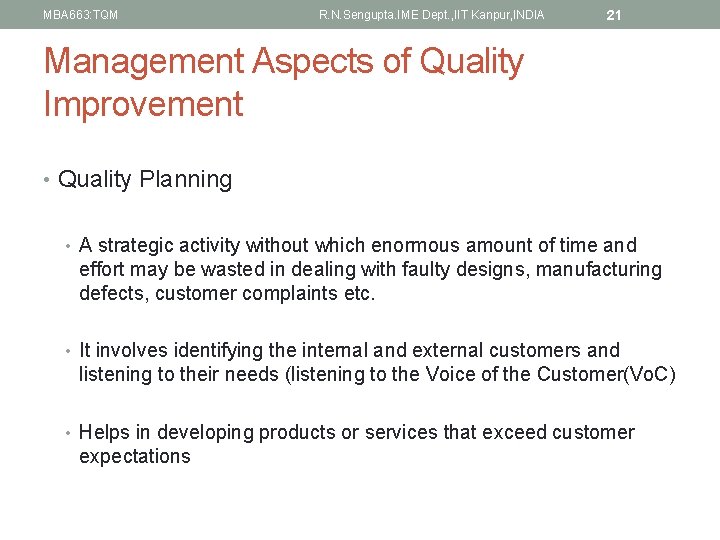
MBA 663: TQM R. N. Sengupta. IME Dept. , IIT Kanpur, INDIA 21 Management Aspects of Quality Improvement • Quality Planning • A strategic activity without which enormous amount of time and effort may be wasted in dealing with faulty designs, manufacturing defects, customer complaints etc. • It involves identifying the internal and external customers and listening to their needs (listening to the Voice of the Customer(Vo. C) • Helps in developing products or services that exceed customer expectations
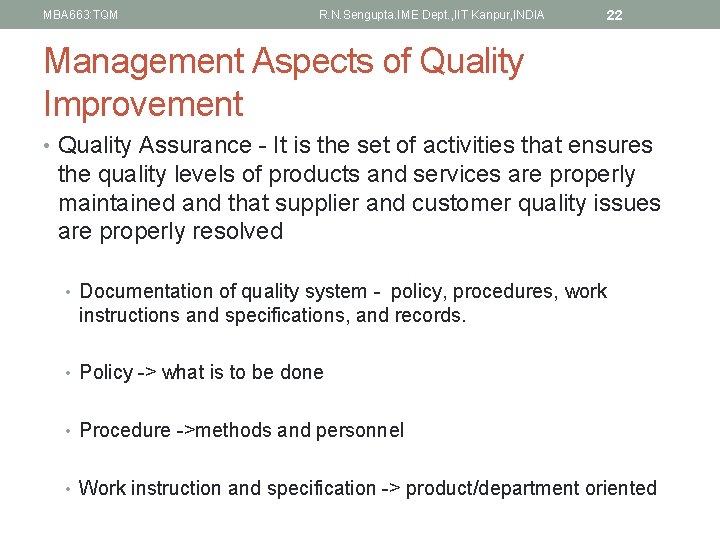
MBA 663: TQM R. N. Sengupta. IME Dept. , IIT Kanpur, INDIA 22 Management Aspects of Quality Improvement • Quality Assurance - It is the set of activities that ensures the quality levels of products and services are properly maintained and that supplier and customer quality issues are properly resolved • Documentation of quality system - policy, procedures, work instructions and specifications, and records. • Policy -> what is to be done • Procedure ->methods and personnel • Work instruction and specification -> product/department oriented
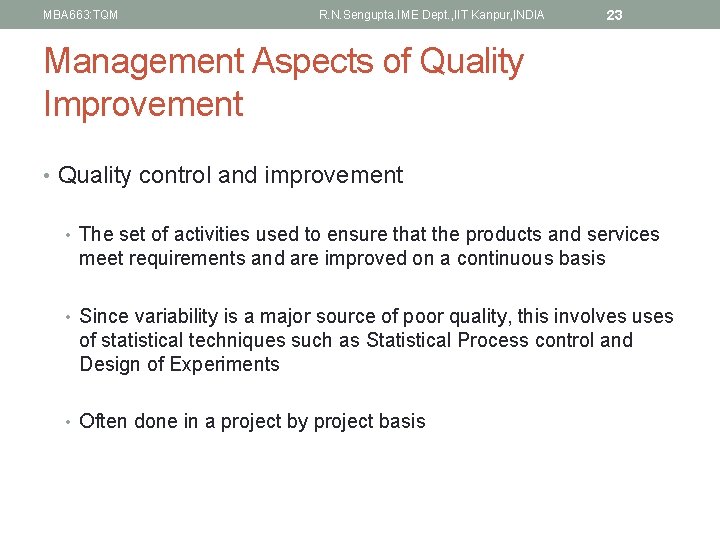
MBA 663: TQM R. N. Sengupta. IME Dept. , IIT Kanpur, INDIA 23 Management Aspects of Quality Improvement • Quality control and improvement • The set of activities used to ensure that the products and services meet requirements and are improved on a continuous basis • Since variability is a major source of poor quality, this involves uses of statistical techniques such as Statistical Process control and Design of Experiments • Often done in a project by project basis
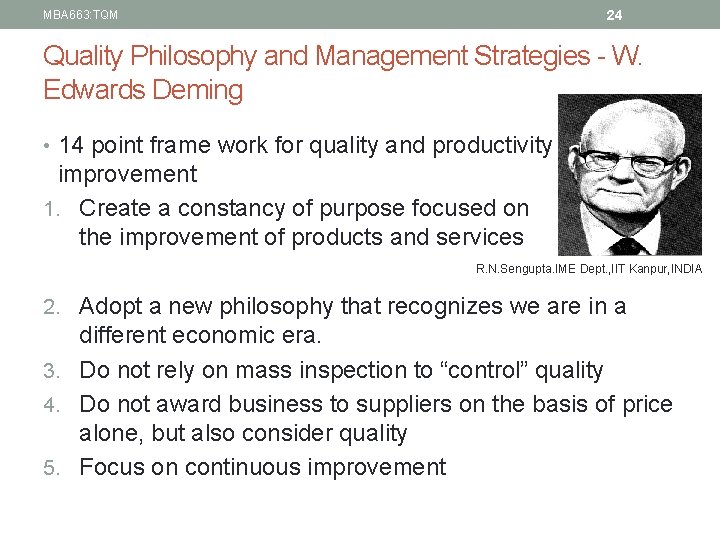
24 MBA 663: TQM Quality Philosophy and Management Strategies - W. Edwards Deming • 14 point frame work for quality and productivity improvement 1. Create a constancy of purpose focused on the improvement of products and services R. N. Sengupta. IME Dept. , IIT Kanpur, INDIA 2. Adopt a new philosophy that recognizes we are in a different economic era. 3. Do not rely on mass inspection to “control” quality 4. Do not award business to suppliers on the basis of price alone, but also consider quality 5. Focus on continuous improvement
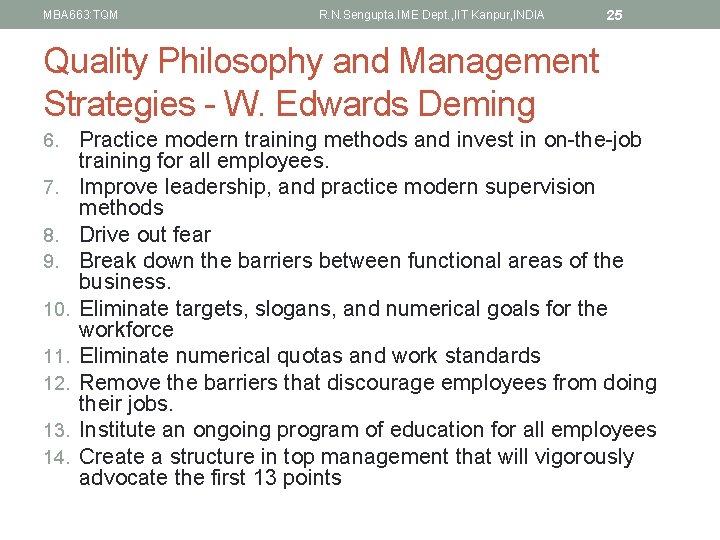
MBA 663: TQM R. N. Sengupta. IME Dept. , IIT Kanpur, INDIA 25 Quality Philosophy and Management Strategies - W. Edwards Deming 6. 7. 8. 9. 10. 11. 12. 13. 14. Practice modern training methods and invest in on-the-job training for all employees. Improve leadership, and practice modern supervision methods Drive out fear Break down the barriers between functional areas of the business. Eliminate targets, slogans, and numerical goals for the workforce Eliminate numerical quotas and work standards Remove the barriers that discourage employees from doing their jobs. Institute an ongoing program of education for all employees Create a structure in top management that will vigorously advocate the first 13 points
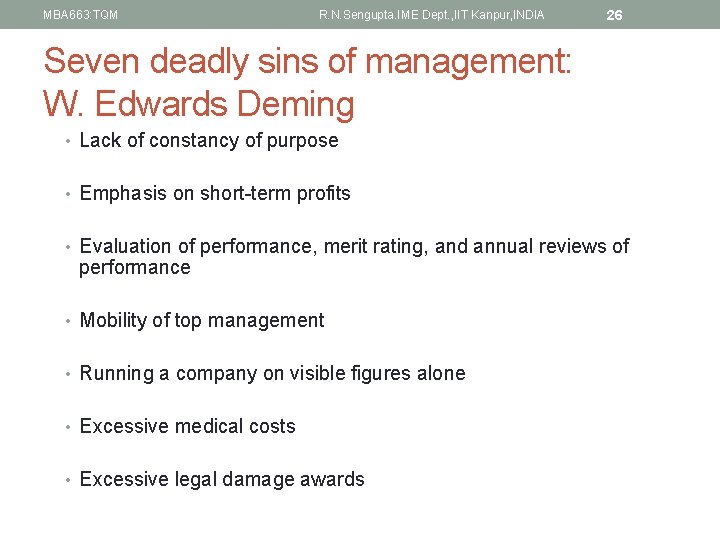
MBA 663: TQM R. N. Sengupta. IME Dept. , IIT Kanpur, INDIA 26 Seven deadly sins of management: W. Edwards Deming • Lack of constancy of purpose • Emphasis on short-term profits • Evaluation of performance, merit rating, and annual reviews of performance • Mobility of top management • Running a company on visible figures alone • Excessive medical costs • Excessive legal damage awards
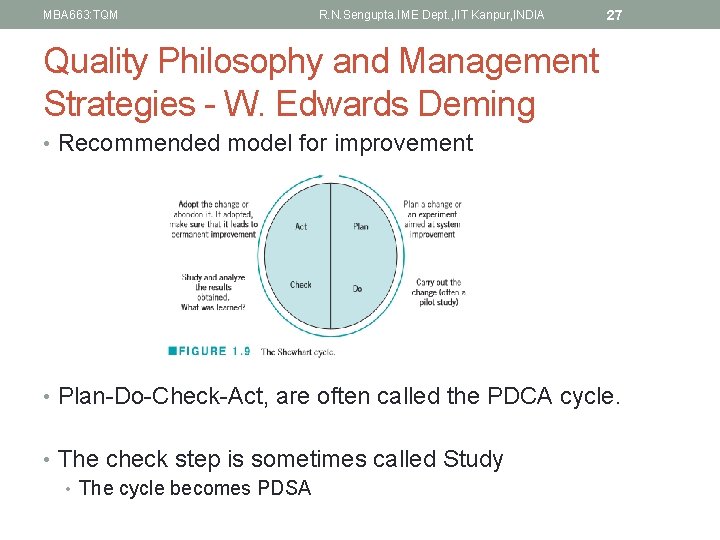
MBA 663: TQM R. N. Sengupta. IME Dept. , IIT Kanpur, INDIA 27 Quality Philosophy and Management Strategies - W. Edwards Deming • Recommended model for improvement • Plan-Do-Check-Act, are often called the PDCA cycle. • The check step is sometimes called Study • The cycle becomes PDSA
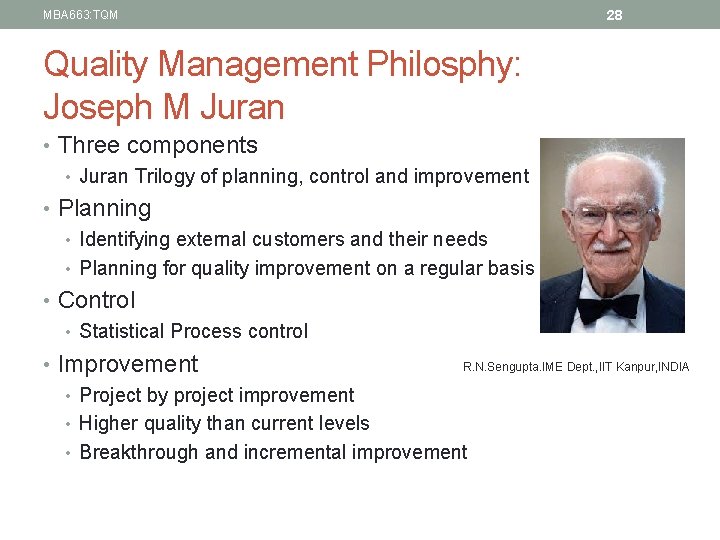
MBA 663: TQM 28 Quality Management Philosphy: Joseph M Juran • Three components • Juran Trilogy of planning, control and improvement • Planning • Identifying external customers and their needs • Planning for quality improvement on a regular basis • Control • Statistical Process control R. N. Sengupta. IME Dept. , IIT Kanpur, INDIA • Improvement • Project by project improvement • Higher quality than current levels • Breakthrough and incremental improvement
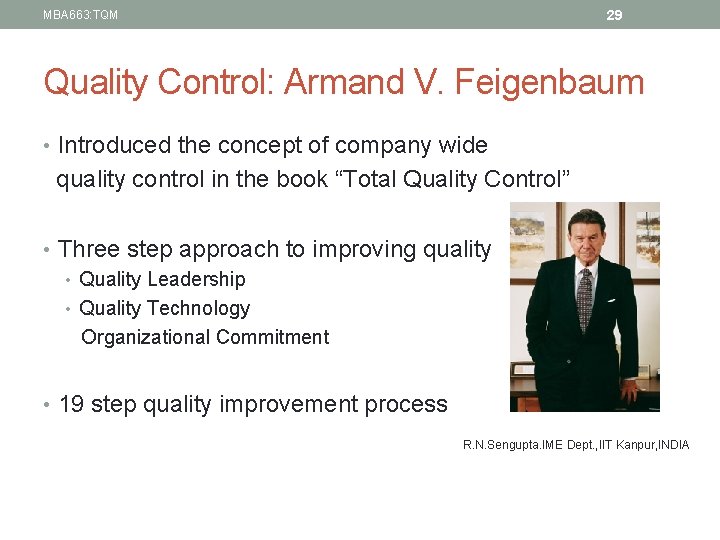
29 MBA 663: TQM Quality Control: Armand V. Feigenbaum • Introduced the concept of company wide quality control in the book “Total Quality Control” • Three step approach to improving quality • Quality Leadership • Quality Technology Organizational Commitment • 19 step quality improvement process R. N. Sengupta. IME Dept. , IIT Kanpur, INDIA
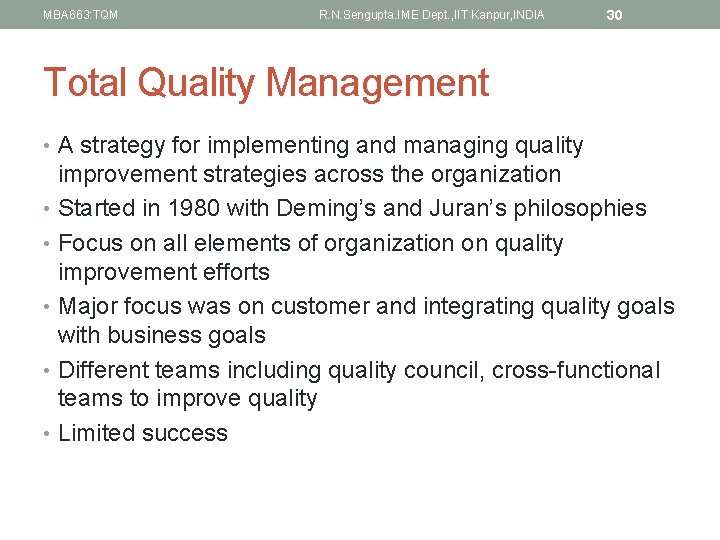
MBA 663: TQM R. N. Sengupta. IME Dept. , IIT Kanpur, INDIA 30 Total Quality Management • A strategy for implementing and managing quality improvement strategies across the organization • Started in 1980 with Deming’s and Juran’s philosophies • Focus on all elements of organization on quality improvement efforts • Major focus was on customer and integrating quality goals with business goals • Different teams including quality council, cross-functional teams to improve quality • Limited success
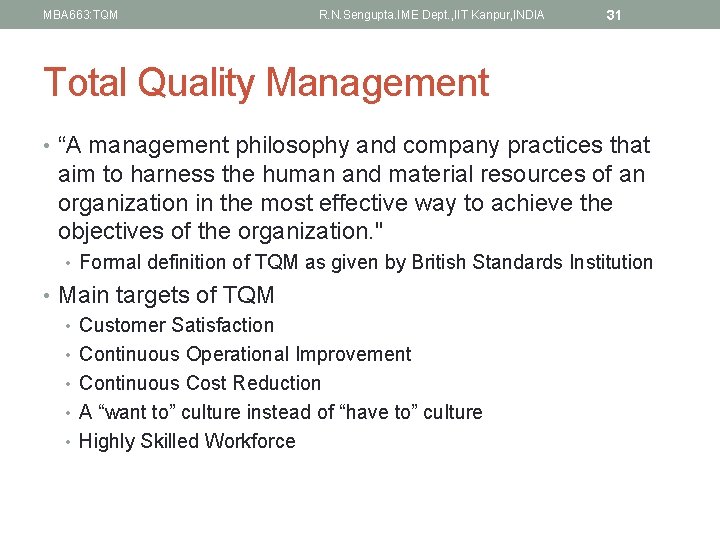
MBA 663: TQM R. N. Sengupta. IME Dept. , IIT Kanpur, INDIA 31 Total Quality Management • “A management philosophy and company practices that aim to harness the human and material resources of an organization in the most effective way to achieve the objectives of the organization. " • Formal definition of TQM as given by British Standards Institution • Main targets of TQM • Customer Satisfaction • Continuous Operational Improvement • Continuous Cost Reduction • A “want to” culture instead of “have to” culture • Highly Skilled Workforce
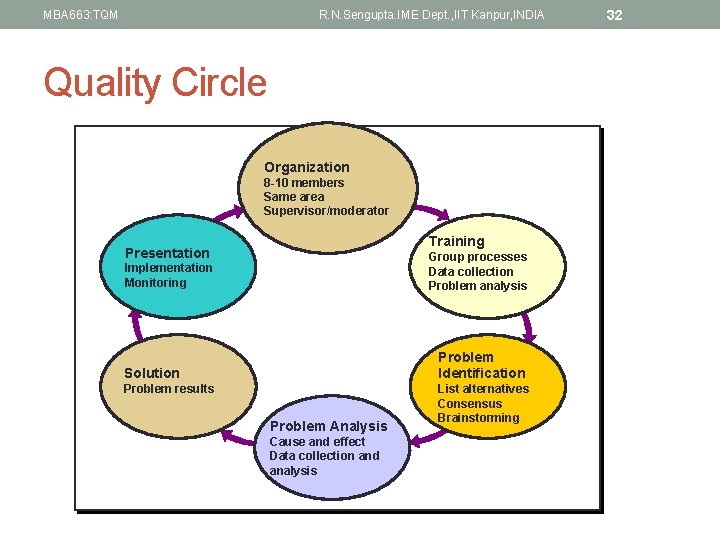
MBA 663: TQM R. N. Sengupta. IME Dept. , IIT Kanpur, INDIA Quality Circle Organization 8 -10 members Same area Supervisor/moderator Training Presentation Group processes Data collection Problem analysis Implementation Monitoring Problem Identification Solution Problem results Problem Analysis Cause and effect Data collection and analysis List alternatives Consensus Brainstorming 32
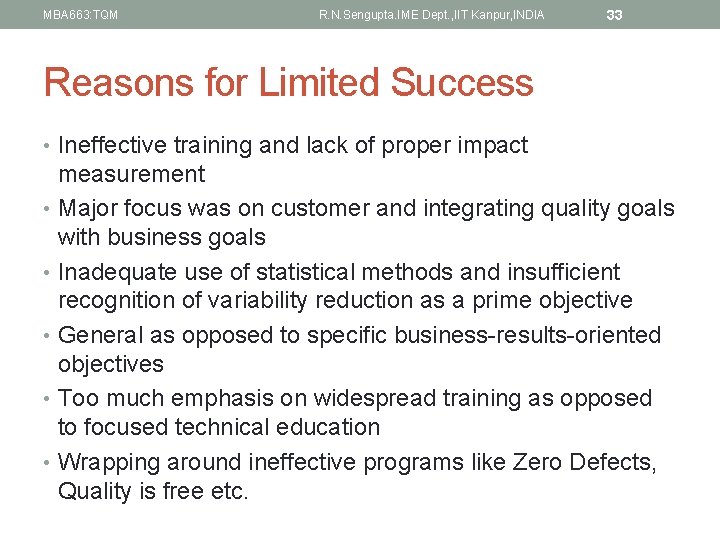
MBA 663: TQM R. N. Sengupta. IME Dept. , IIT Kanpur, INDIA 33 Reasons for Limited Success • Ineffective training and lack of proper impact measurement • Major focus was on customer and integrating quality goals with business goals • Inadequate use of statistical methods and insufficient recognition of variability reduction as a prime objective • General as opposed to specific business-results-oriented objectives • Too much emphasis on widespread training as opposed to focused technical education • Wrapping around ineffective programs like Zero Defects, Quality is free etc.
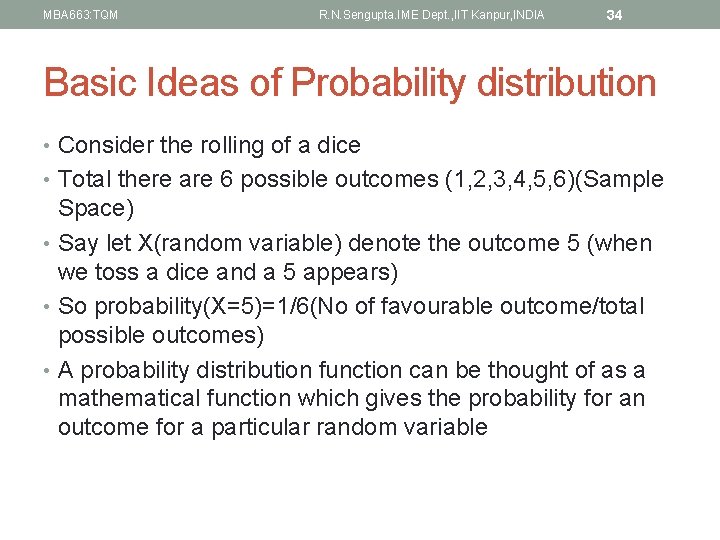
MBA 663: TQM R. N. Sengupta. IME Dept. , IIT Kanpur, INDIA 34 Basic Ideas of Probability distribution • Consider the rolling of a dice • Total there are 6 possible outcomes (1, 2, 3, 4, 5, 6)(Sample Space) • Say let X(random variable) denote the outcome 5 (when we toss a dice and a 5 appears) • So probability(X=5)=1/6(No of favourable outcome/total possible outcomes) • A probability distribution function can be thought of as a mathematical function which gives the probability for an outcome for a particular random variable
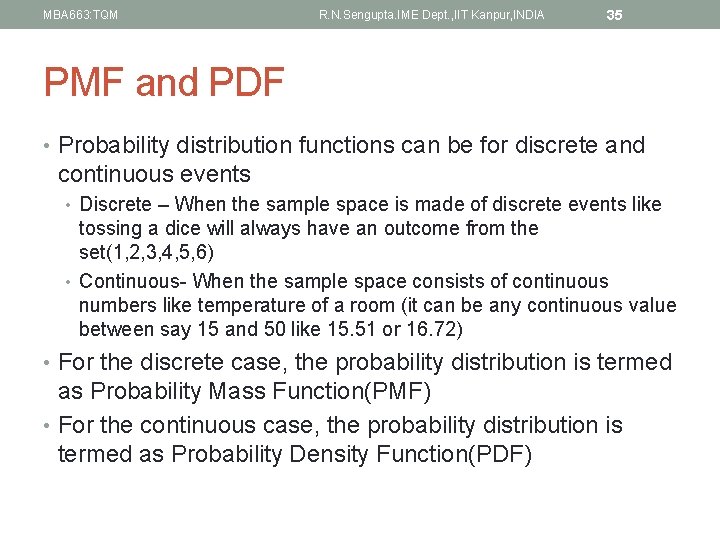
MBA 663: TQM R. N. Sengupta. IME Dept. , IIT Kanpur, INDIA 35 PMF and PDF • Probability distribution functions can be for discrete and continuous events • Discrete – When the sample space is made of discrete events like tossing a dice will always have an outcome from the set(1, 2, 3, 4, 5, 6) • Continuous- When the sample space consists of continuous numbers like temperature of a room (it can be any continuous value between say 15 and 50 like 15. 51 or 16. 72) • For the discrete case, the probability distribution is termed as Probability Mass Function(PMF) • For the continuous case, the probability distribution is termed as Probability Density Function(PDF)
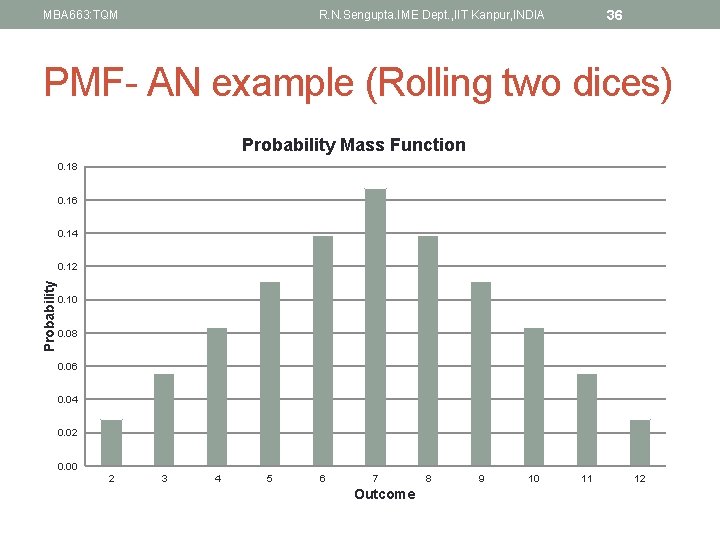
MBA 663: TQM 36 R. N. Sengupta. IME Dept. , IIT Kanpur, INDIA PMF- AN example (Rolling two dices) Probability Mass Function 0. 18 0. 16 0. 14 Probability 0. 12 0. 10 0. 08 0. 06 0. 04 0. 02 0. 00 2 3 4 5 6 7 Outcome 8 9 10 11 12
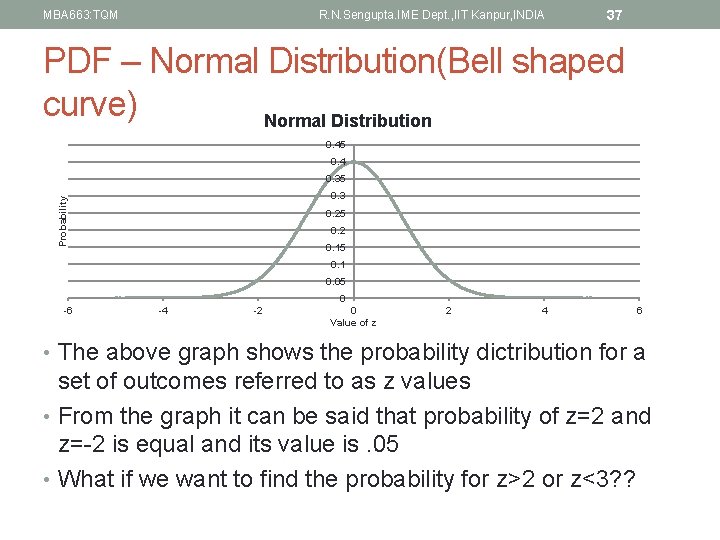
MBA 663: TQM R. N. Sengupta. IME Dept. , IIT Kanpur, INDIA 37 PDF – Normal Distribution(Bell shaped curve) Normal Distribution 0. 45 0. 4 0. 35 Probability 0. 3 0. 25 0. 2 0. 15 0. 1 0. 05 0 -6 -4 -2 0 Value of z 2 4 6 • The above graph shows the probability dictribution for a set of outcomes referred to as z values • From the graph it can be said that probability of z=2 and z=-2 is equal and its value is. 05 • What if we want to find the probability for z>2 or z<3? ?
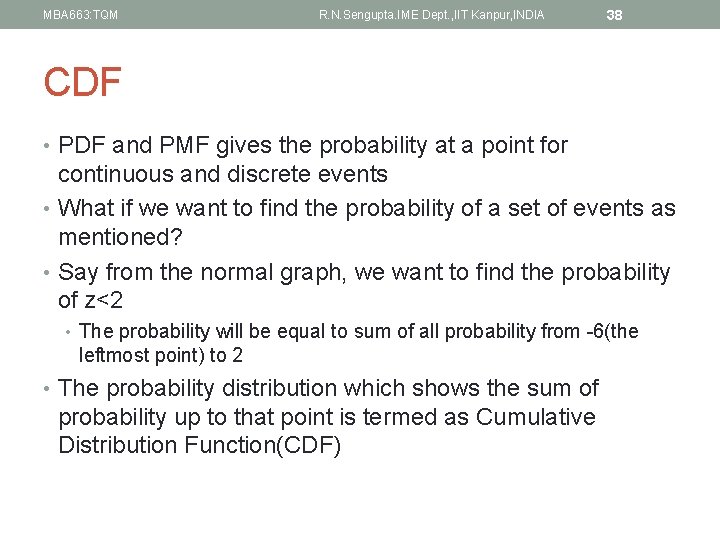
MBA 663: TQM R. N. Sengupta. IME Dept. , IIT Kanpur, INDIA 38 CDF • PDF and PMF gives the probability at a point for continuous and discrete events • What if we want to find the probability of a set of events as mentioned? • Say from the normal graph, we want to find the probability of z<2 • The probability will be equal to sum of all probability from -6(the leftmost point) to 2 • The probability distribution which shows the sum of probability up to that point is termed as Cumulative Distribution Function(CDF)
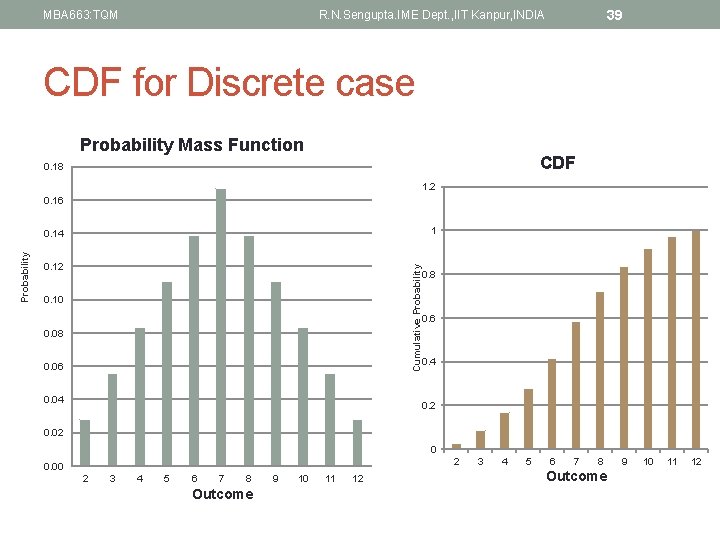
MBA 663: TQM 39 R. N. Sengupta. IME Dept. , IIT Kanpur, INDIA CDF for Discrete case Probability Mass Function CDF 0. 18 1. 2 0. 16 1 0. 12 Cumulative Probability 0. 14 0. 10 0. 08 0. 06 0. 04 0. 8 0. 6 0. 4 0. 2 0. 02 0 2 0. 00 2 3 4 5 6 7 8 Outcome 9 10 11 12
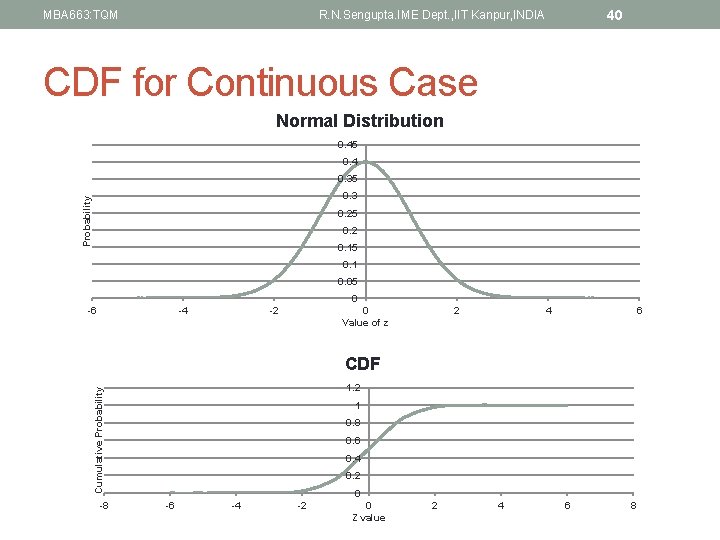
MBA 663: TQM 40 R. N. Sengupta. IME Dept. , IIT Kanpur, INDIA CDF for Continuous Case Normal Distribution 0. 45 0. 4 0. 35 Probability 0. 3 0. 25 0. 2 0. 15 0. 1 0. 05 0 -6 -4 -2 0 Value of z 2 4 6 CDF Cumulative Probability 1. 2 -8 1 0. 8 0. 6 0. 4 0. 2 0 -6 -4 -2 0 Z value 2 4 6 8
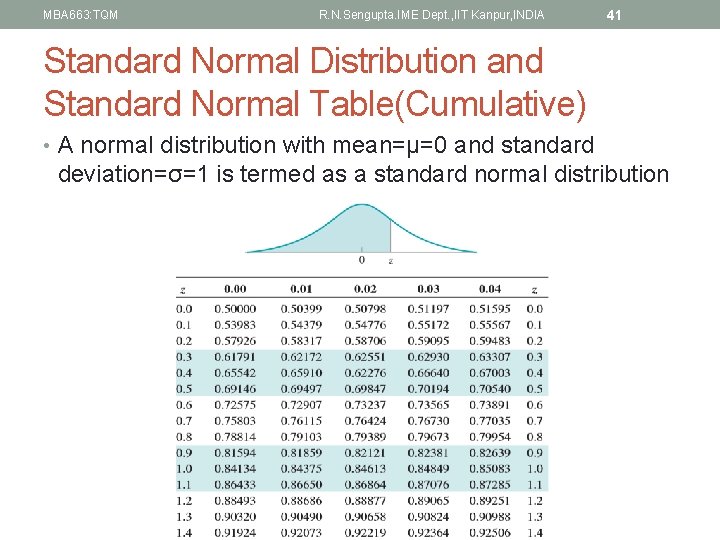
MBA 663: TQM R. N. Sengupta. IME Dept. , IIT Kanpur, INDIA 41 Standard Normal Distribution and Standard Normal Table(Cumulative) • A normal distribution with mean=μ=0 and standard deviation=σ=1 is termed as a standard normal distribution
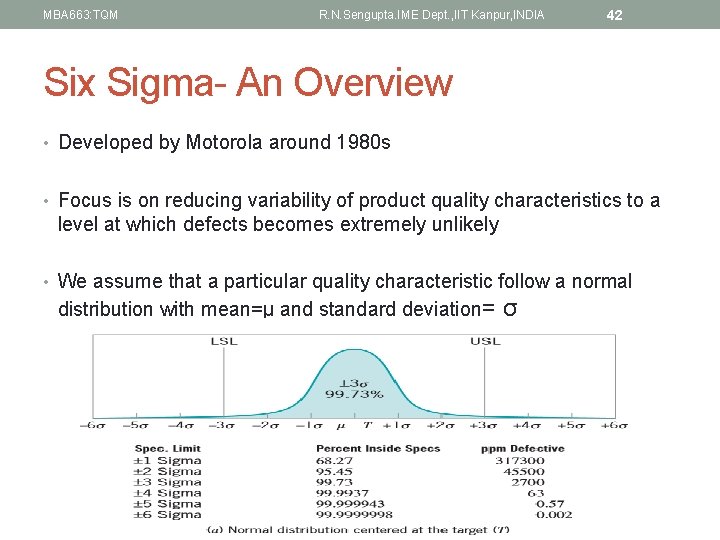
MBA 663: TQM R. N. Sengupta. IME Dept. , IIT Kanpur, INDIA 42 Six Sigma- An Overview • Developed by Motorola around 1980 s • Focus is on reducing variability of product quality characteristics to a level at which defects becomes extremely unlikely • We assume that a particular quality characteristic follow a normal distribution with mean=μ and standard deviation= σ
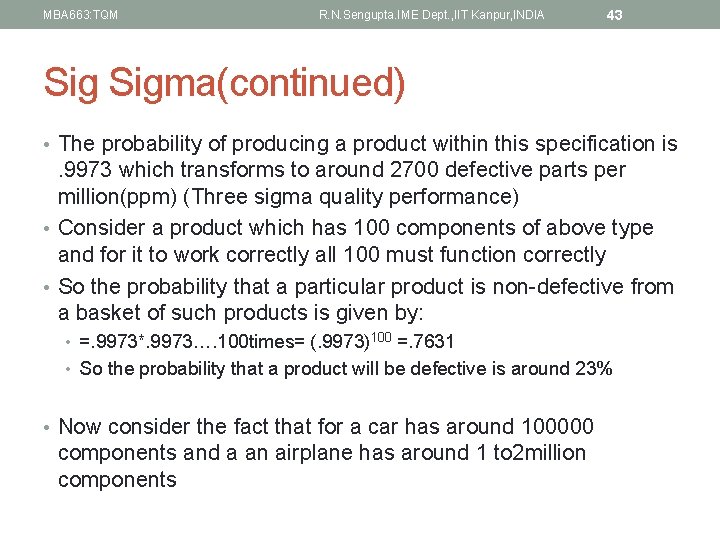
MBA 663: TQM R. N. Sengupta. IME Dept. , IIT Kanpur, INDIA 43 Sigma(continued) • The probability of producing a product within this specification is . 9973 which transforms to around 2700 defective parts per million(ppm) (Three sigma quality performance) • Consider a product which has 100 components of above type and for it to work correctly all 100 must function correctly • So the probability that a particular product is non-defective from a basket of such products is given by: • =. 9973*. 9973…. 100 times= (. 9973)100 =. 7631 • So the probability that a product will be defective is around 23% • Now consider the fact that for a car has around 100000 components and a an airplane has around 1 to 2 million components
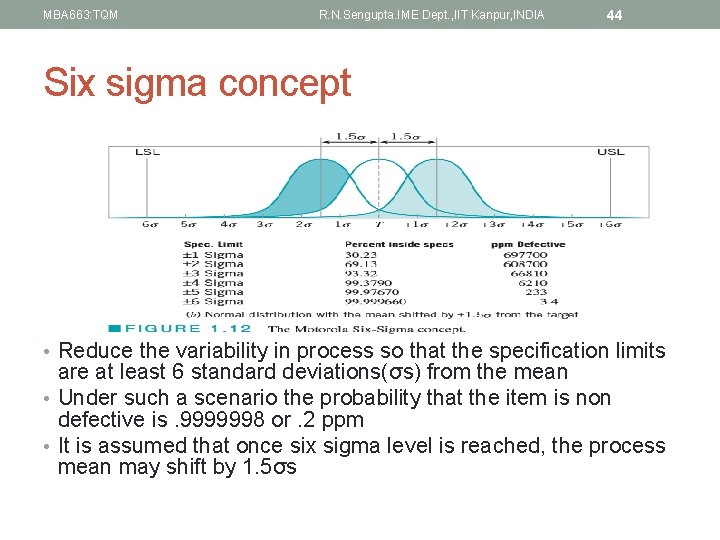
MBA 663: TQM R. N. Sengupta. IME Dept. , IIT Kanpur, INDIA 44 Six sigma concept • Reduce the variability in process so that the specification limits are at least 6 standard deviations(σs) from the mean • Under such a scenario the probability that the item is non defective is. 9999998 or. 2 ppm • It is assumed that once six sigma level is reached, the process mean may shift by 1. 5σs
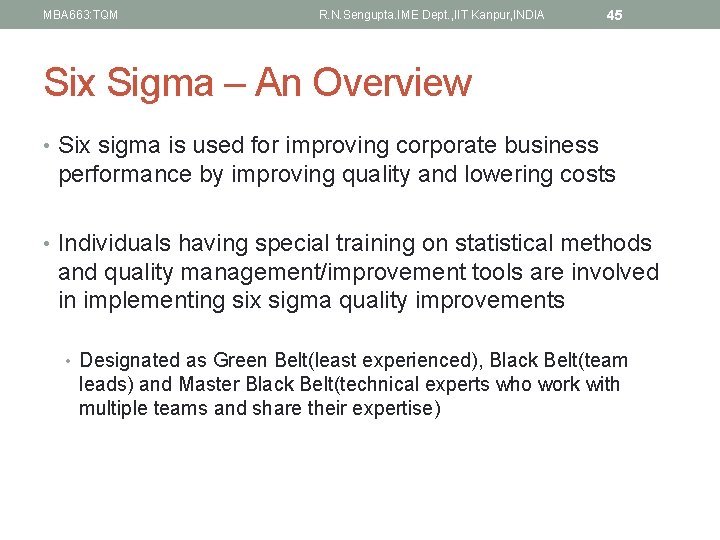
MBA 663: TQM R. N. Sengupta. IME Dept. , IIT Kanpur, INDIA 45 Six Sigma – An Overview • Six sigma is used for improving corporate business performance by improving quality and lowering costs • Individuals having special training on statistical methods and quality management/improvement tools are involved in implementing six sigma quality improvements • Designated as Green Belt(least experienced), Black Belt(team leads) and Master Black Belt(technical experts who work with multiple teams and share their expertise)
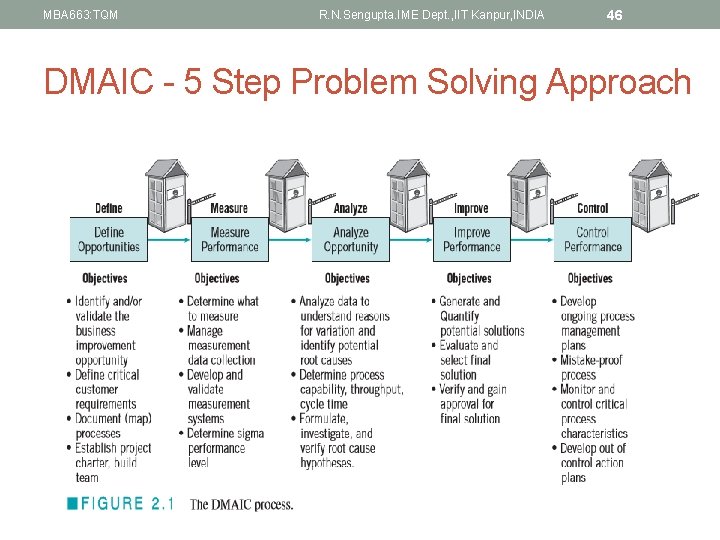
MBA 663: TQM R. N. Sengupta. IME Dept. , IIT Kanpur, INDIA 46 DMAIC - 5 Step Problem Solving Approach
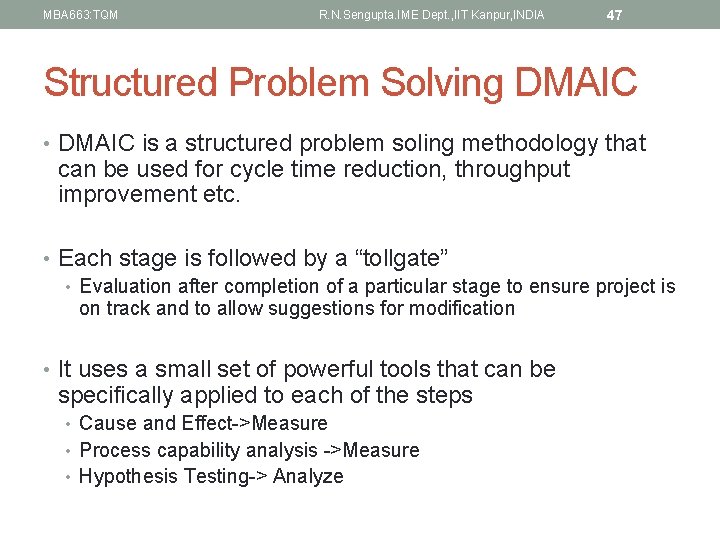
MBA 663: TQM R. N. Sengupta. IME Dept. , IIT Kanpur, INDIA 47 Structured Problem Solving DMAIC • DMAIC is a structured problem soling methodology that can be used for cycle time reduction, throughput improvement etc. • Each stage is followed by a “tollgate” • Evaluation after completion of a particular stage to ensure project is on track and to allow suggestions for modification • It uses a small set of powerful tools that can be specifically applied to each of the steps • Cause and Effect->Measure • Process capability analysis ->Measure • Hypothesis Testing-> Analyze
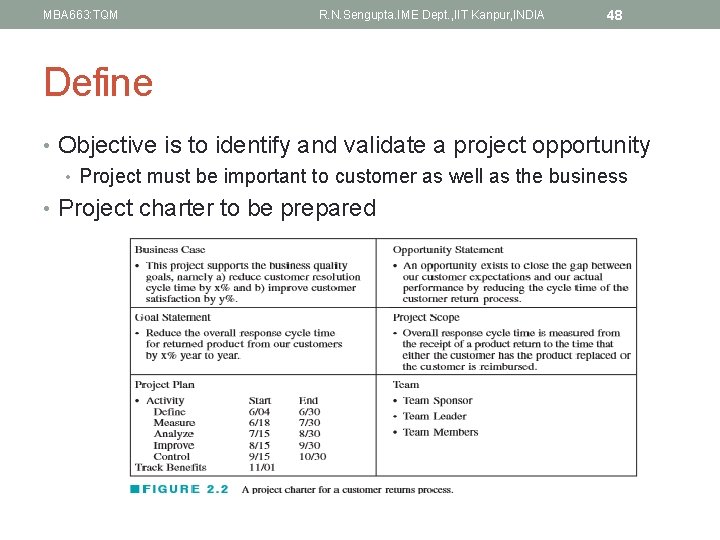
MBA 663: TQM R. N. Sengupta. IME Dept. , IIT Kanpur, INDIA 48 Define • Objective is to identify and validate a project opportunity • Project must be important to customer as well as the business • Project charter to be prepared
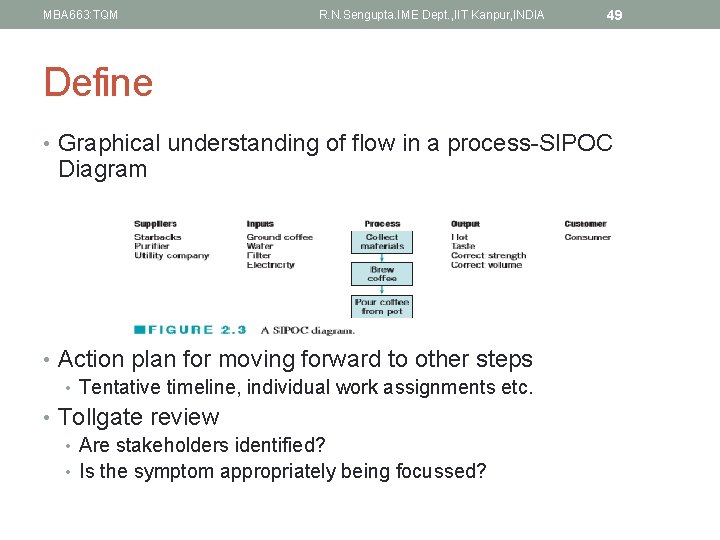
MBA 663: TQM R. N. Sengupta. IME Dept. , IIT Kanpur, INDIA 49 Define • Graphical understanding of flow in a process-SIPOC Diagram • Action plan for moving forward to other steps • Tentative timeline, individual work assignments etc. • Tollgate review • Are stakeholders identified? • Is the symptom appropriately being focussed?
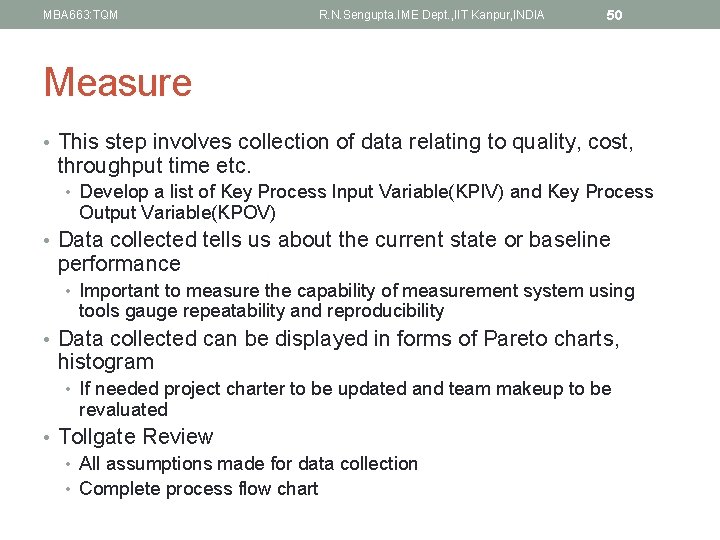
MBA 663: TQM R. N. Sengupta. IME Dept. , IIT Kanpur, INDIA 50 Measure • This step involves collection of data relating to quality, cost, throughput time etc. • Develop a list of Key Process Input Variable(KPIV) and Key Process Output Variable(KPOV) • Data collected tells us about the current state or baseline performance • Important to measure the capability of measurement system using tools gauge repeatability and reproducibility • Data collected can be displayed in forms of Pareto charts, histogram • If needed project charter to be updated and team makeup to be revaluated • Tollgate Review • All assumptions made for data collection • Complete process flow chart
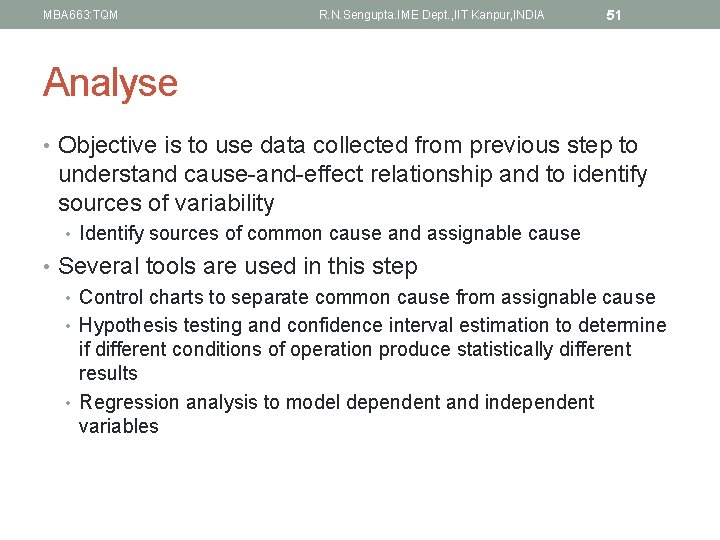
MBA 663: TQM R. N. Sengupta. IME Dept. , IIT Kanpur, INDIA 51 Analyse • Objective is to use data collected from previous step to understand cause-and-effect relationship and to identify sources of variability • Identify sources of common cause and assignable cause • Several tools are used in this step • Control charts to separate common cause from assignable cause • Hypothesis testing and confidence interval estimation to determine if different conditions of operation produce statistically different results • Regression analysis to model dependent and independent variables
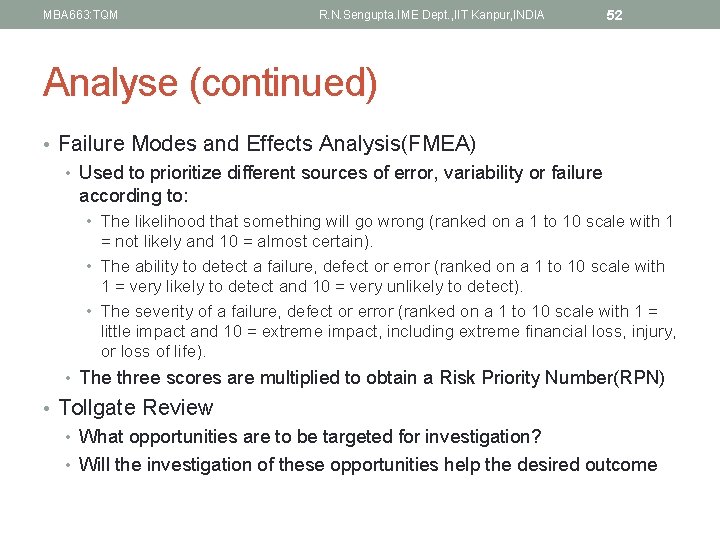
MBA 663: TQM R. N. Sengupta. IME Dept. , IIT Kanpur, INDIA 52 Analyse (continued) • Failure Modes and Effects Analysis(FMEA) • Used to prioritize different sources of error, variability or failure according to: • The likelihood that something will go wrong (ranked on a 1 to 10 scale with 1 = not likely and 10 = almost certain). • The ability to detect a failure, defect or error (ranked on a 1 to 10 scale with 1 = very likely to detect and 10 = very unlikely to detect). • The severity of a failure, defect or error (ranked on a 1 to 10 scale with 1 = little impact and 10 = extreme impact, including extreme financial loss, injury, or loss of life). • The three scores are multiplied to obtain a Risk Priority Number(RPN) • Tollgate Review • What opportunities are to be targeted for investigation? • Will the investigation of these opportunities help the desired outcome
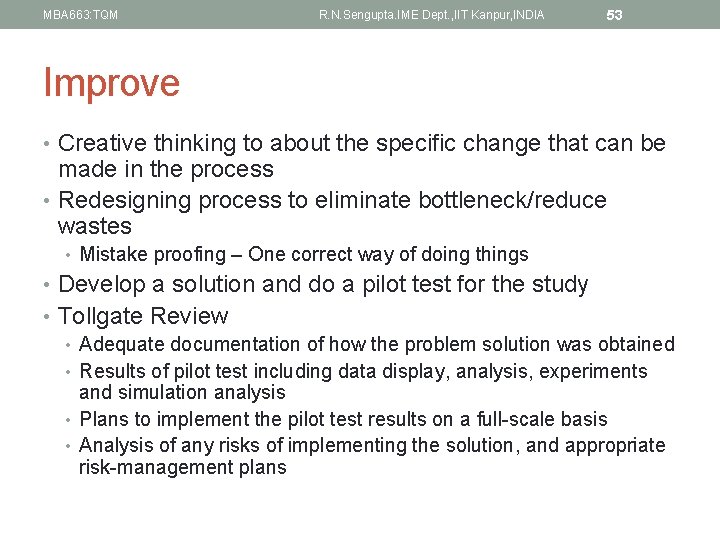
MBA 663: TQM R. N. Sengupta. IME Dept. , IIT Kanpur, INDIA 53 Improve • Creative thinking to about the specific change that can be made in the process • Redesigning process to eliminate bottleneck/reduce wastes • Mistake proofing – One correct way of doing things • Develop a solution and do a pilot test for the study • Tollgate Review • Adequate documentation of how the problem solution was obtained • Results of pilot test including data display, analysis, experiments and simulation analysis • Plans to implement the pilot test results on a full-scale basis • Analysis of any risks of implementing the solution, and appropriate risk-management plans
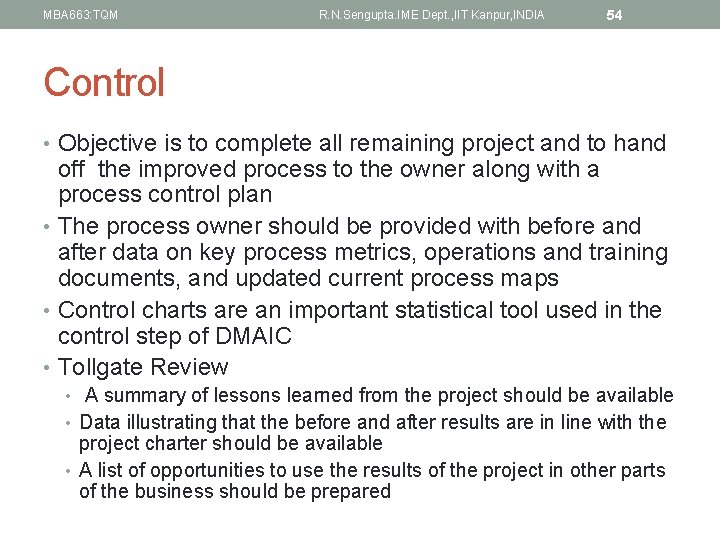
MBA 663: TQM R. N. Sengupta. IME Dept. , IIT Kanpur, INDIA 54 Control • Objective is to complete all remaining project and to hand off the improved process to the owner along with a process control plan • The process owner should be provided with before and after data on key process metrics, operations and training documents, and updated current process maps • Control charts are an important statistical tool used in the control step of DMAIC • Tollgate Review • A summary of lessons learned from the project should be available • Data illustrating that the before and after results are in line with the project charter should be available • A list of opportunities to use the results of the project in other parts of the business should be prepared
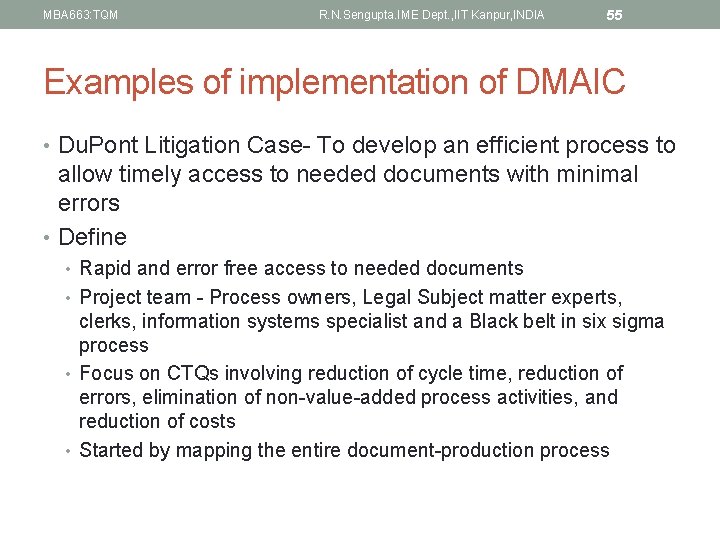
MBA 663: TQM R. N. Sengupta. IME Dept. , IIT Kanpur, INDIA 55 Examples of implementation of DMAIC • Du. Pont Litigation Case- To develop an efficient process to allow timely access to needed documents with minimal errors • Define • Rapid and error free access to needed documents • Project team - Process owners, Legal Subject matter experts, clerks, information systems specialist and a Black belt in six sigma process • Focus on CTQs involving reduction of cycle time, reduction of errors, elimination of non-value-added process activities, and reduction of costs • Started by mapping the entire document-production process
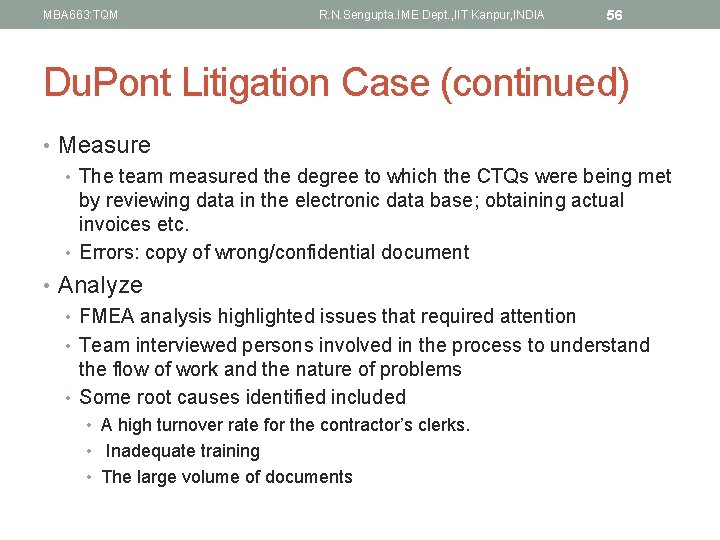
MBA 663: TQM R. N. Sengupta. IME Dept. , IIT Kanpur, INDIA 56 Du. Pont Litigation Case (continued) • Measure • The team measured the degree to which the CTQs were being met by reviewing data in the electronic data base; obtaining actual invoices etc. • Errors: copy of wrong/confidential document • Analyze • FMEA analysis highlighted issues that required attention • Team interviewed persons involved in the process to understand the flow of work and the nature of problems • Some root causes identified included • A high turnover rate for the contractor’s clerks. • Inadequate training • The large volume of documents
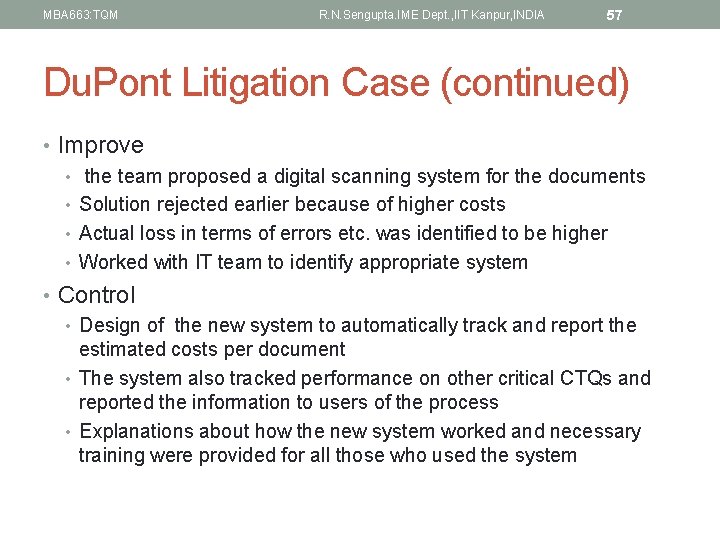
MBA 663: TQM R. N. Sengupta. IME Dept. , IIT Kanpur, INDIA 57 Du. Pont Litigation Case (continued) • Improve • the team proposed a digital scanning system for the documents • Solution rejected earlier because of higher costs • Actual loss in terms of errors etc. was identified to be higher • Worked with IT team to identify appropriate system • Control • Design of the new system to automatically track and report the estimated costs per document • The system also tracked performance on other critical CTQs and reported the information to users of the process • Explanations about how the new system worked and necessary training were provided for all those who used the system
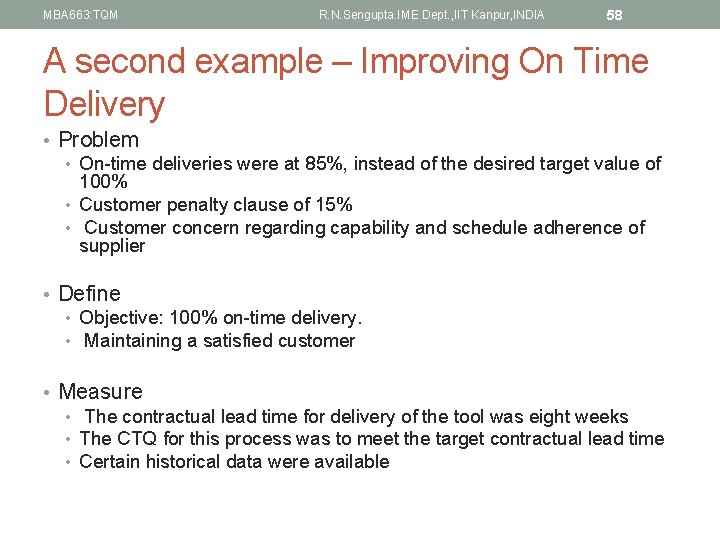
MBA 663: TQM R. N. Sengupta. IME Dept. , IIT Kanpur, INDIA 58 A second example – Improving On Time Delivery • Problem • On-time deliveries were at 85%, instead of the desired target value of 100% • Customer penalty clause of 15% • Customer concern regarding capability and schedule adherence of supplier • Define • Objective: 100% on-time delivery. • Maintaining a satisfied customer • Measure • The contractual lead time for delivery of the tool was eight weeks • The CTQ for this process was to meet the target contractual lead time • Certain historical data were available
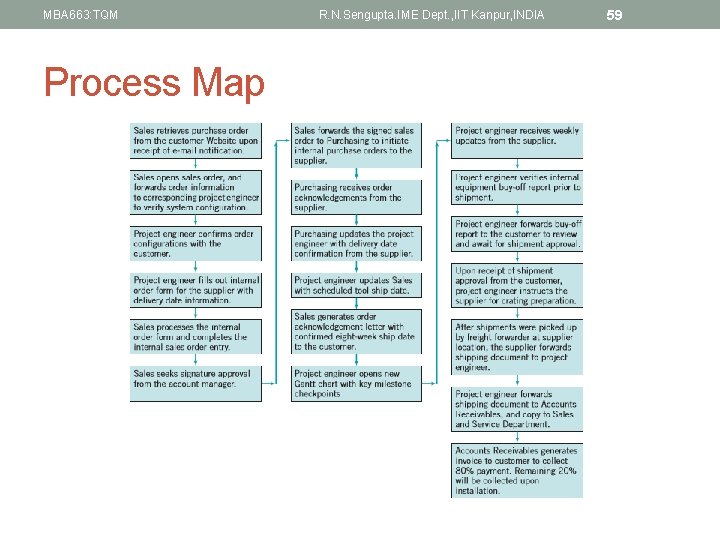
MBA 663: TQM Process Map R. N. Sengupta. IME Dept. , IIT Kanpur, INDIA 59
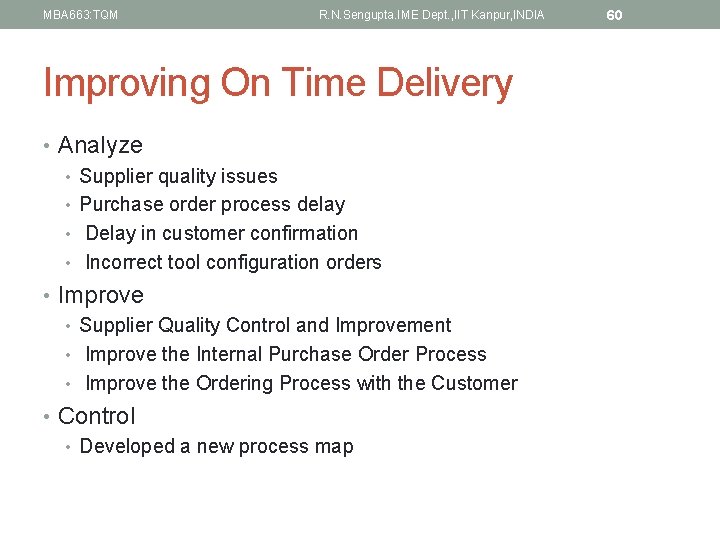
MBA 663: TQM R. N. Sengupta. IME Dept. , IIT Kanpur, INDIA Improving On Time Delivery • Analyze • Supplier quality issues • Purchase order process delay • Delay in customer confirmation • Incorrect tool configuration orders • Improve • Supplier Quality Control and Improvement • Improve the Internal Purchase Order Process • Improve the Ordering Process with the Customer • Control • Developed a new process map 60
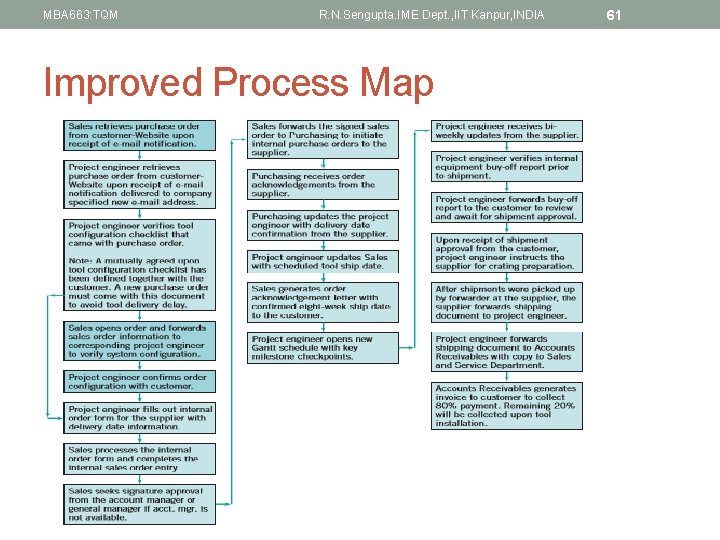
MBA 663: TQM R. N. Sengupta. IME Dept. , IIT Kanpur, INDIA Improved Process Map 61
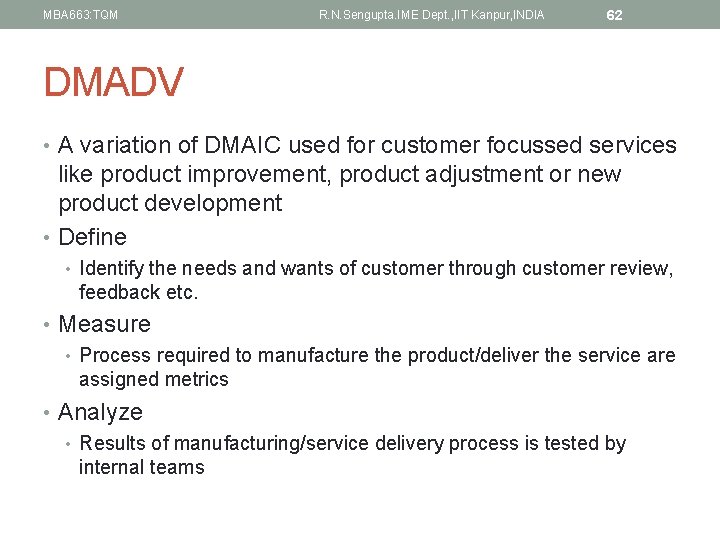
MBA 663: TQM R. N. Sengupta. IME Dept. , IIT Kanpur, INDIA 62 DMADV • A variation of DMAIC used for customer focussed services like product improvement, product adjustment or new product development • Define • Identify the needs and wants of customer through customer review, feedback etc. • Measure • Process required to manufacture the product/deliver the service are assigned metrics • Analyze • Results of manufacturing/service delivery process is tested by internal teams
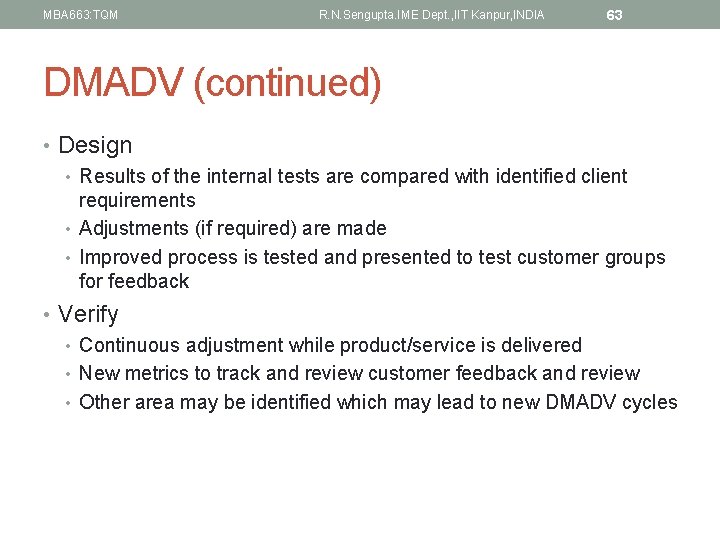
MBA 663: TQM R. N. Sengupta. IME Dept. , IIT Kanpur, INDIA 63 DMADV (continued) • Design • Results of the internal tests are compared with identified client requirements • Adjustments (if required) are made • Improved process is tested and presented to test customer groups for feedback • Verify • Continuous adjustment while product/service is delivered • New metrics to track and review customer feedback and review • Other area may be identified which may lead to new DMADV cycles
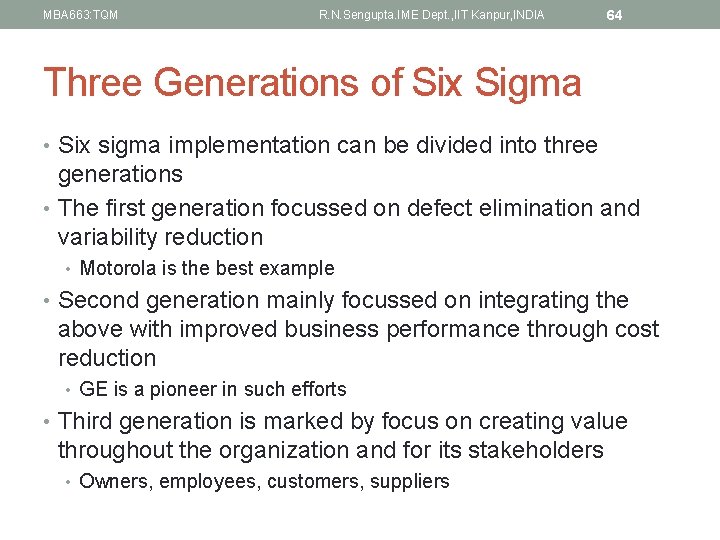
MBA 663: TQM R. N. Sengupta. IME Dept. , IIT Kanpur, INDIA 64 Three Generations of Six Sigma • Six sigma implementation can be divided into three generations • The first generation focussed on defect elimination and variability reduction • Motorola is the best example • Second generation mainly focussed on integrating the above with improved business performance through cost reduction • GE is a pioneer in such efforts • Third generation is marked by focus on creating value throughout the organization and for its stakeholders • Owners, employees, customers, suppliers
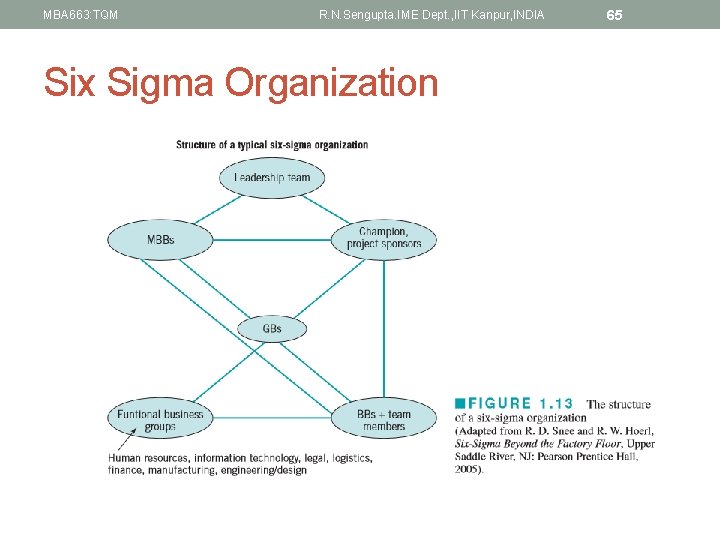
MBA 663: TQM R. N. Sengupta. IME Dept. , IIT Kanpur, INDIA Six Sigma Organization 65
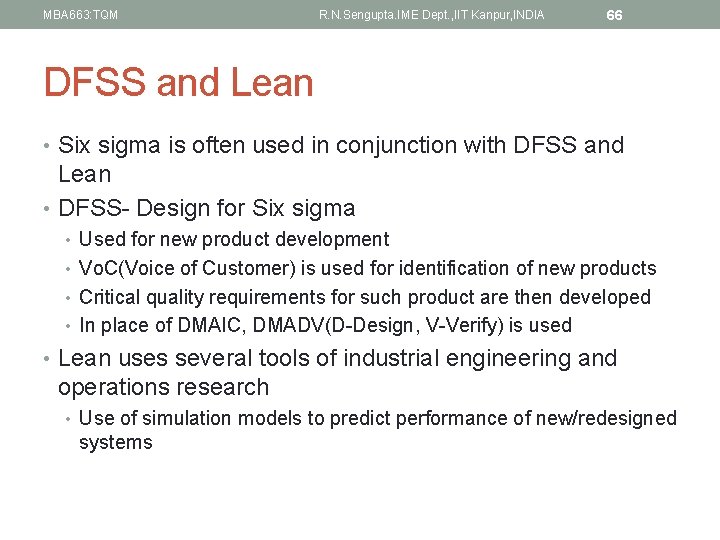
MBA 663: TQM R. N. Sengupta. IME Dept. , IIT Kanpur, INDIA 66 DFSS and Lean • Six sigma is often used in conjunction with DFSS and Lean • DFSS- Design for Six sigma • Used for new product development • Vo. C(Voice of Customer) is used for identification of new products • Critical quality requirements for such product are then developed • In place of DMAIC, DMADV(D-Design, V-Verify) is used • Lean uses several tools of industrial engineering and operations research • Use of simulation models to predict performance of new/redesigned systems
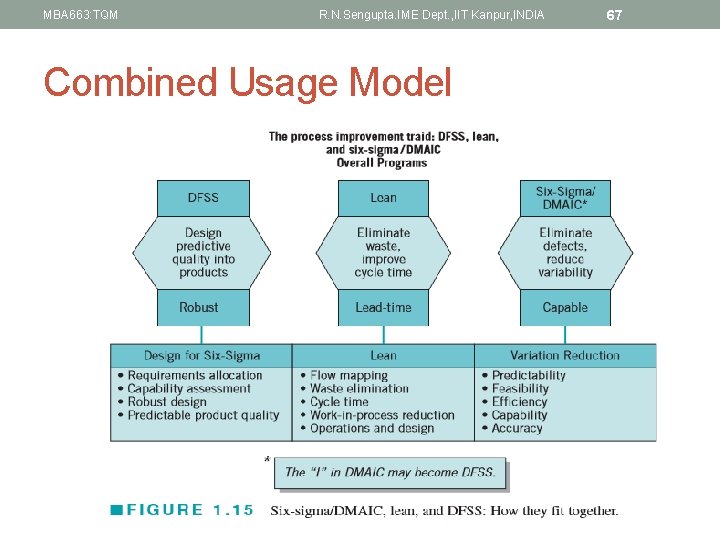
MBA 663: TQM R. N. Sengupta. IME Dept. , IIT Kanpur, INDIA Combined Usage Model 67
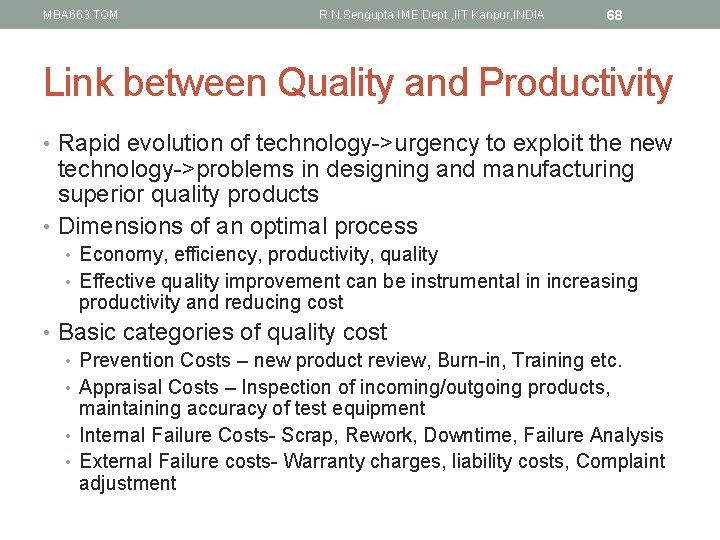
MBA 663: TQM R. N. Sengupta. IME Dept. , IIT Kanpur, INDIA 68 Link between Quality and Productivity • Rapid evolution of technology->urgency to exploit the new technology->problems in designing and manufacturing superior quality products • Dimensions of an optimal process • Economy, efficiency, productivity, quality • Effective quality improvement can be instrumental in increasing productivity and reducing cost • Basic categories of quality cost • Prevention Costs – new product review, Burn-in, Training etc. • Appraisal Costs – Inspection of incoming/outgoing products, maintaining accuracy of test equipment • Internal Failure Costs- Scrap, Rework, Downtime, Failure Analysis • External Failure costs- Warranty charges, liability costs, Complaint adjustment
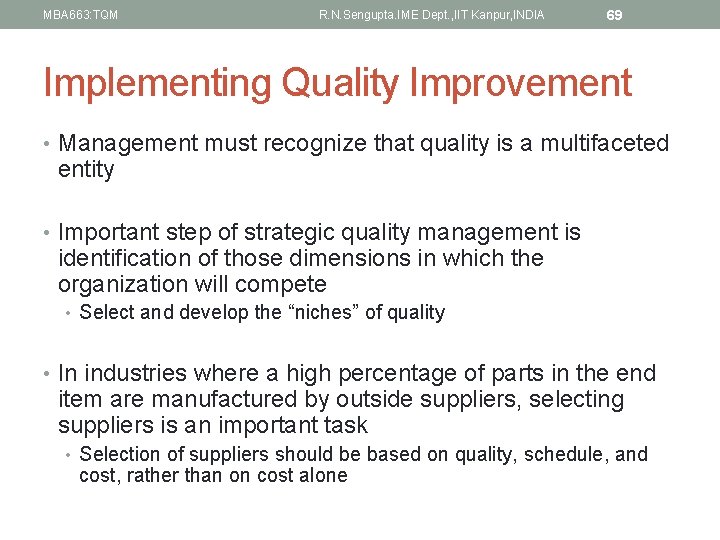
MBA 663: TQM R. N. Sengupta. IME Dept. , IIT Kanpur, INDIA 69 Implementing Quality Improvement • Management must recognize that quality is a multifaceted entity • Important step of strategic quality management is identification of those dimensions in which the organization will compete • Select and develop the “niches” of quality • In industries where a high percentage of parts in the end item are manufactured by outside suppliers, selecting suppliers is an important task • Selection of suppliers should be based on quality, schedule, and cost, rather than on cost alone
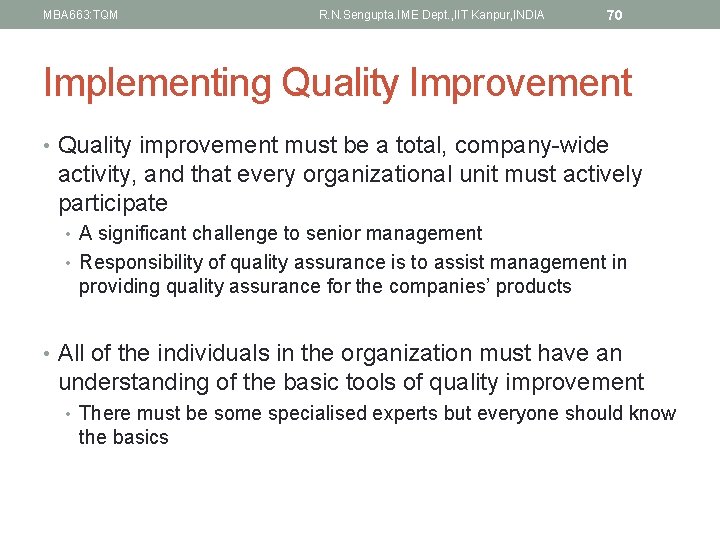
MBA 663: TQM R. N. Sengupta. IME Dept. , IIT Kanpur, INDIA 70 Implementing Quality Improvement • Quality improvement must be a total, company-wide activity, and that every organizational unit must actively participate • A significant challenge to senior management • Responsibility of quality assurance is to assist management in providing quality assurance for the companies’ products • All of the individuals in the organization must have an understanding of the basic tools of quality improvement • There must be some specialised experts but everyone should know the basics
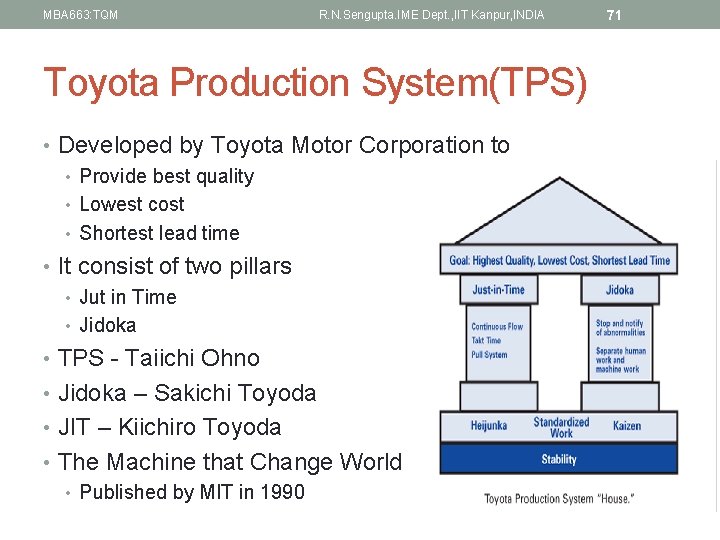
MBA 663: TQM R. N. Sengupta. IME Dept. , IIT Kanpur, INDIA Toyota Production System(TPS) • Developed by Toyota Motor Corporation to • Provide best quality • Lowest cost • Shortest lead time • It consist of two pillars • Jut in Time • Jidoka • TPS - Taiichi Ohno • Jidoka – Sakichi Toyoda • JIT – Kiichiro Toyoda • The Machine that Change World • Published by MIT in 1990 71
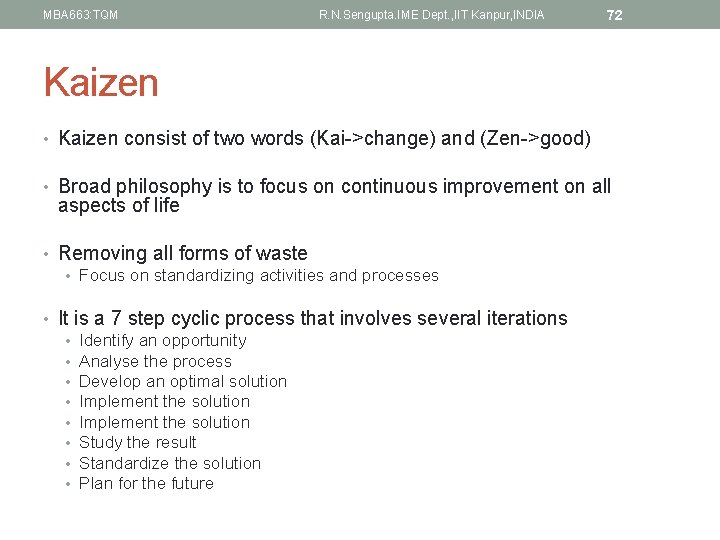
MBA 663: TQM R. N. Sengupta. IME Dept. , IIT Kanpur, INDIA 72 Kaizen • Kaizen consist of two words (Kai->change) and (Zen->good) • Broad philosophy is to focus on continuous improvement on all aspects of life • Removing all forms of waste • Focus on standardizing activities and processes • It is a 7 step cyclic process that involves several iterations • Identify an opportunity • Analyse the process • Develop an optimal solution • Implement the solution • Study the result • Standardize the solution • Plan for the future
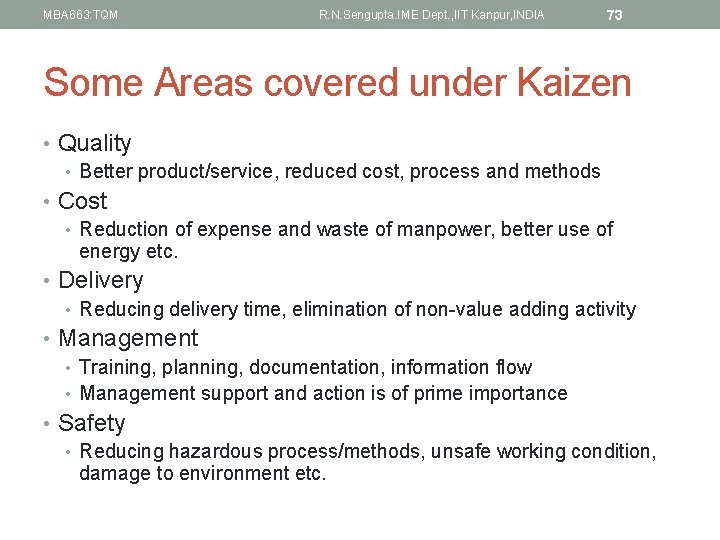
MBA 663: TQM R. N. Sengupta. IME Dept. , IIT Kanpur, INDIA 73 Some Areas covered under Kaizen • Quality • Better product/service, reduced cost, process and methods • Cost • Reduction of expense and waste of manpower, better use of energy etc. • Delivery • Reducing delivery time, elimination of non-value adding activity • Management • Training, planning, documentation, information flow • Management support and action is of prime importance • Safety • Reducing hazardous process/methods, unsafe working condition, damage to environment etc.
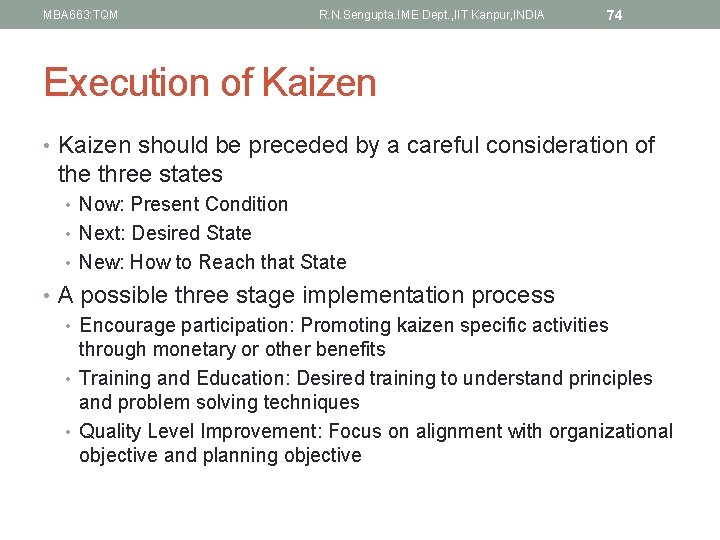
MBA 663: TQM R. N. Sengupta. IME Dept. , IIT Kanpur, INDIA 74 Execution of Kaizen • Kaizen should be preceded by a careful consideration of the three states • Now: Present Condition • Next: Desired State • New: How to Reach that State • A possible three stage implementation process • Encourage participation: Promoting kaizen specific activities through monetary or other benefits • Training and Education: Desired training to understand principles and problem solving techniques • Quality Level Improvement: Focus on alignment with organizational objective and planning objective
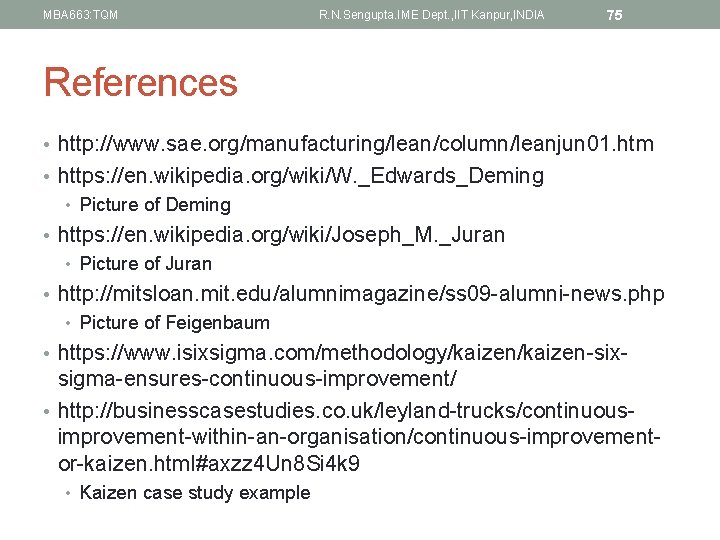
MBA 663: TQM R. N. Sengupta. IME Dept. , IIT Kanpur, INDIA 75 References • http: //www. sae. org/manufacturing/lean/column/leanjun 01. htm • https: //en. wikipedia. org/wiki/W. _Edwards_Deming • Picture of Deming • https: //en. wikipedia. org/wiki/Joseph_M. _Juran • Picture of Juran • http: //mitsloan. mit. edu/alumnimagazine/ss 09 -alumni-news. php • Picture of Feigenbaum • https: //www. isixsigma. com/methodology/kaizen-six- sigma-ensures-continuous-improvement/ • http: //businesscasestudies. co. uk/leyland-trucks/continuousimprovement-within-an-organisation/continuous-improvementor-kaizen. html#axzz 4 Un 8 Si 4 k 9 • Kaizen case study example
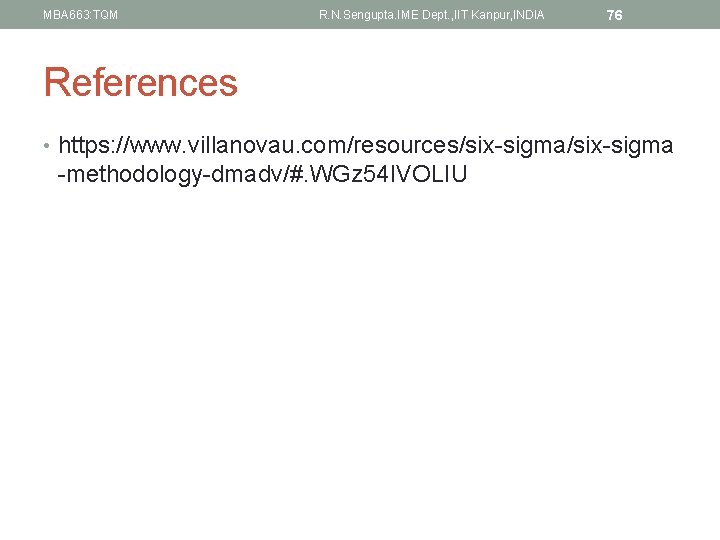
MBA 663: TQM R. N. Sengupta. IME Dept. , IIT Kanpur, INDIA 76 References • https: //www. villanovau. com/resources/six-sigma -methodology-dmadv/#. WGz 54 IVOLIU
Total iit in india
What is tqm? *
Contemporary management practices
What is tqm
Four marketing management philosophies
Total quality tools
Individual factors moral philosophies and values
Research philosophies and approaches
What is total quality managment
Quality management definition
Poka yoka
Total quality managment
Evolution of tqm
Antecedents of modern quality management
Tqm book
Tqm in hospitality industry
Benchmarking in total quality management
Juran's three role model
Ana quality assurance model
Kfc tqm
Six sigma iso 9000
Total data quality management
Toyota total quality management
7 principles of quality management
Iqc and eqc
Introduction to quality management
Qfd in total quality management
Total quality management wikipedia
Total quality management in erp
Quality management for agriculture
Airline ticket
Total quality managemen
Definisi total quality management
Tourism: principles, practices, philosophies
Comparing economic philosophies worksheet answers
Philosophy of extension education
Types of investment philosophies
Damodaran investment philosophies
Marketing philosophies
5 theories of art
Lessons from ants
5 philosophies of education
Chinese philosophies comparison chart
Applying moral philosophies to business ethics
5 educational philosophies
In grendel, john gardner uses
Confucianism legalism and daoism chart
List the three chinese philosophies
Unidad 3 razones financieras
Total revenues minus total costs equals
Total revenues minus total costs equals
Total revenues minus total costs equals
Total revenue minus total expenses
Total quality control tqc
Total quality assurance
Pengertian tqs
Motivating people for total quality
Perform quality assurance
Concepts of quality control
Total management and training
Operations and quality management
Pmp quality management
Pmbok quality assurance vs quality control
Compliance vs quality
Quality is free
What is tqm
Total value management
Total supply chain management
Total value management
Life cycle logistics definition
Total cost management
Total records information management
Total maintenance service
Tpm process
Estructura del tpm
Total resource management
Total responsibility management