POWER SYSTEM COMMISSIONING AND MAINTENANCE PRACTICE DET 3103

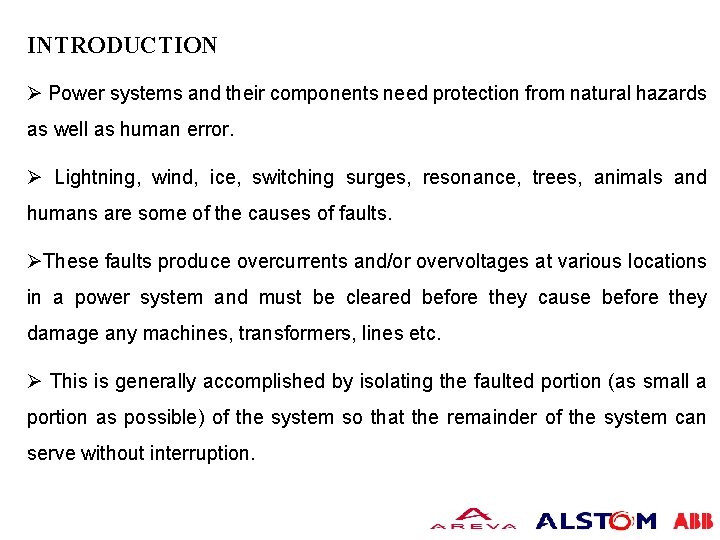
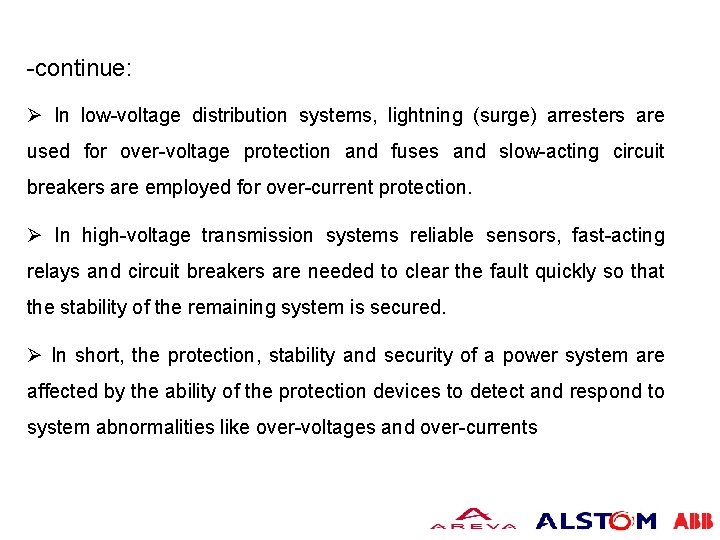
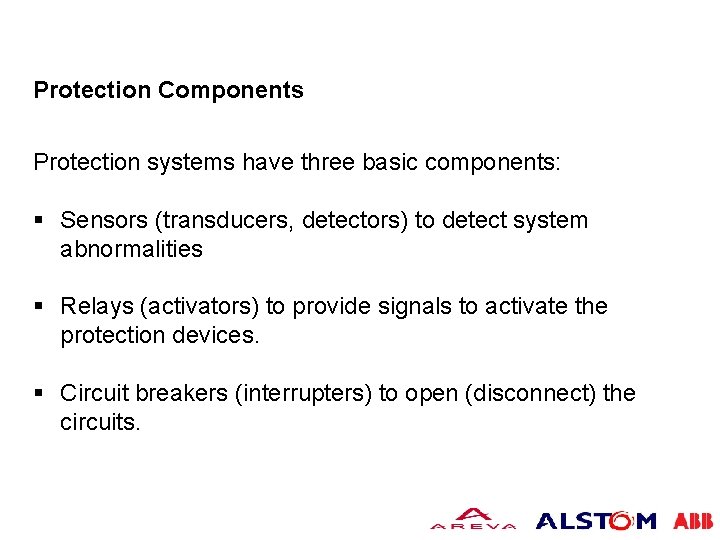
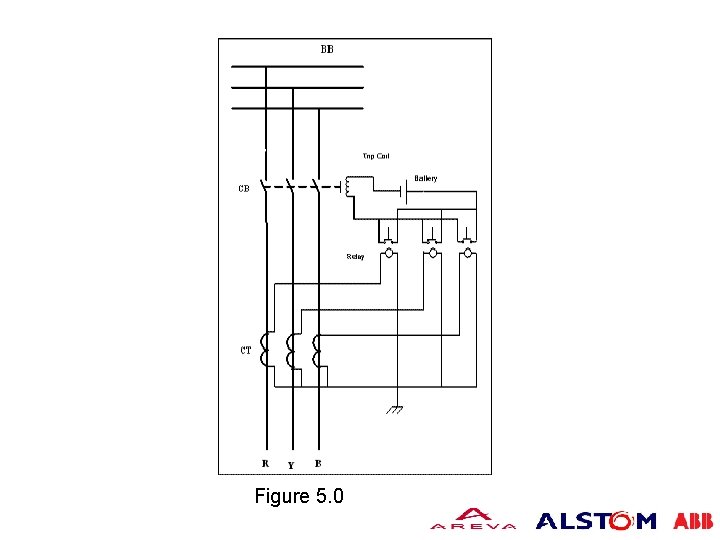
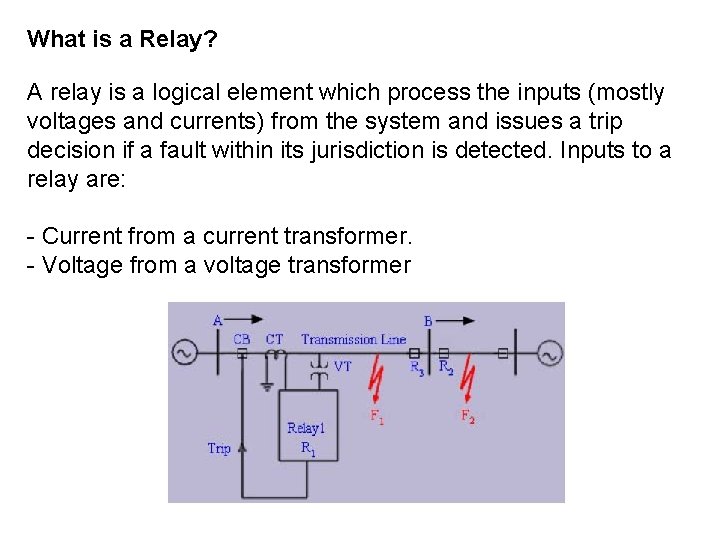
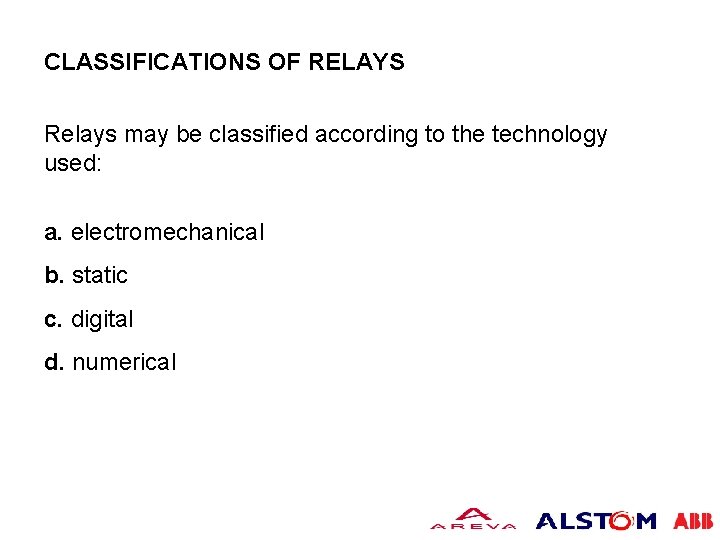
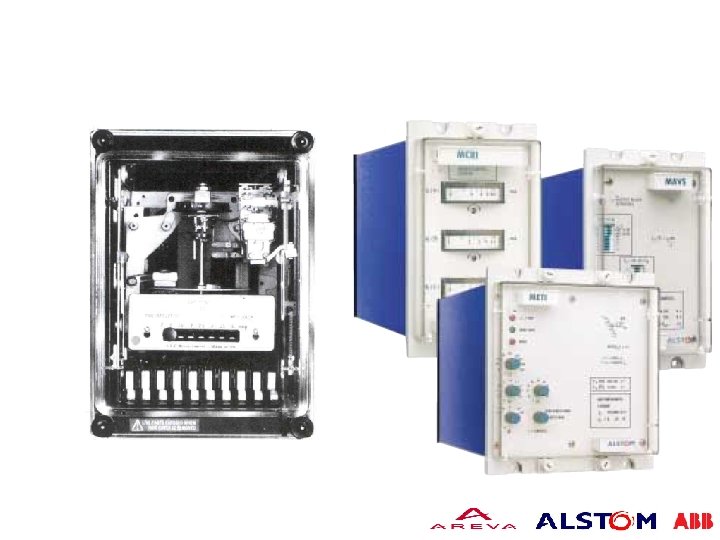
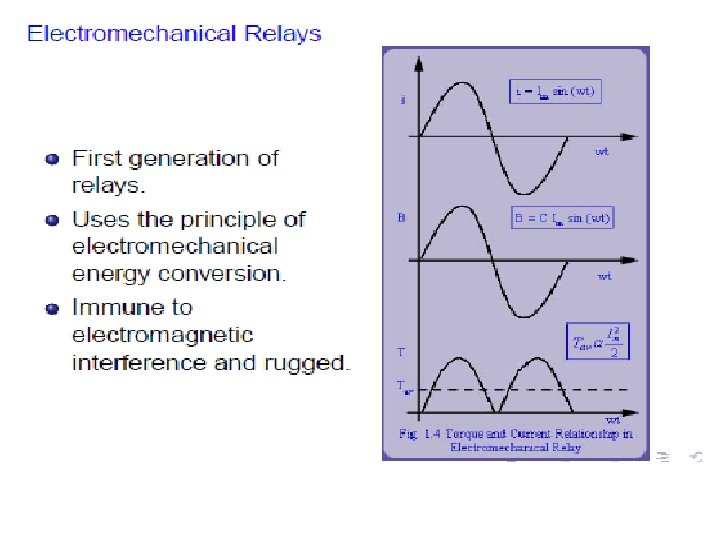
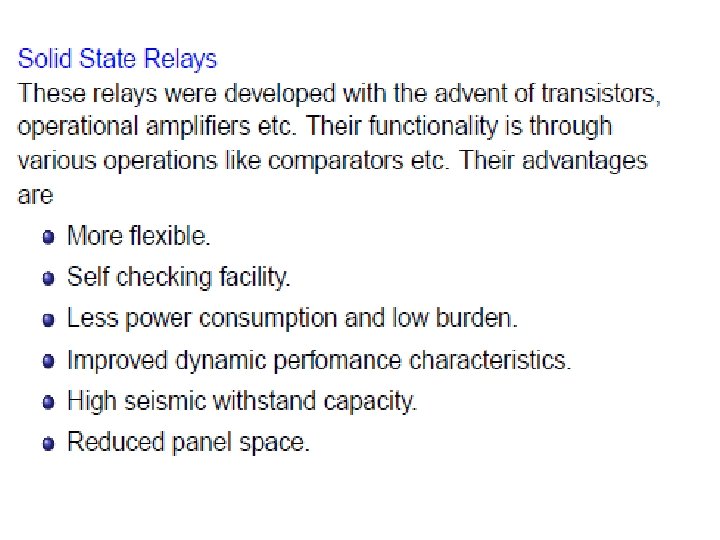
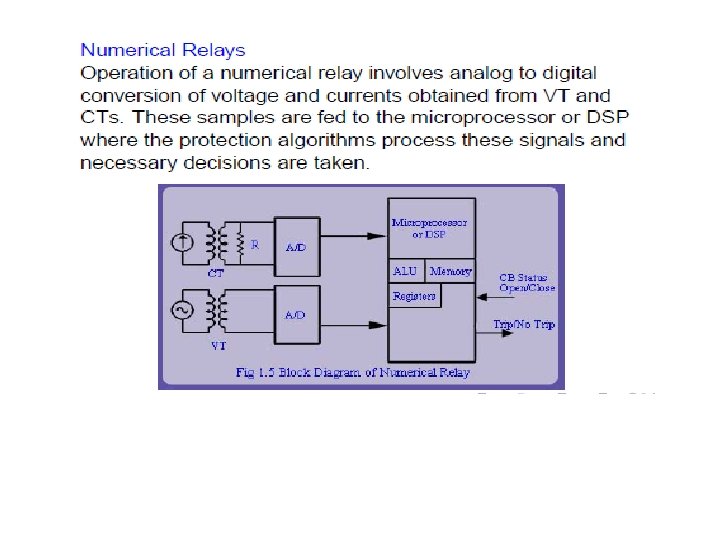
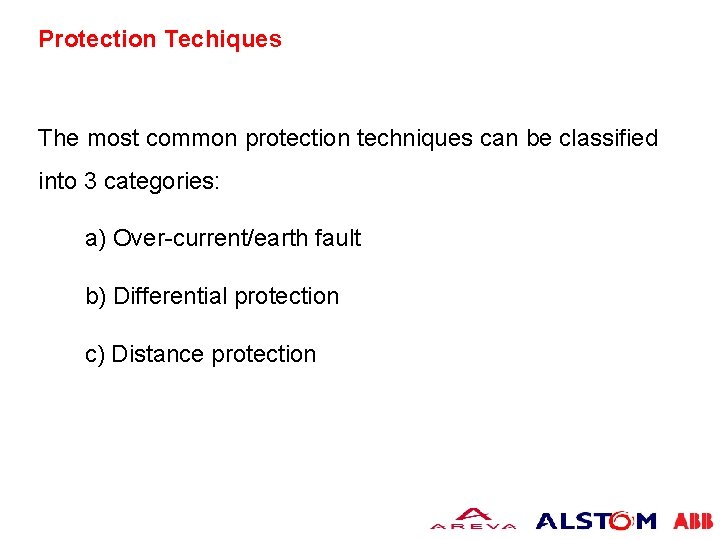
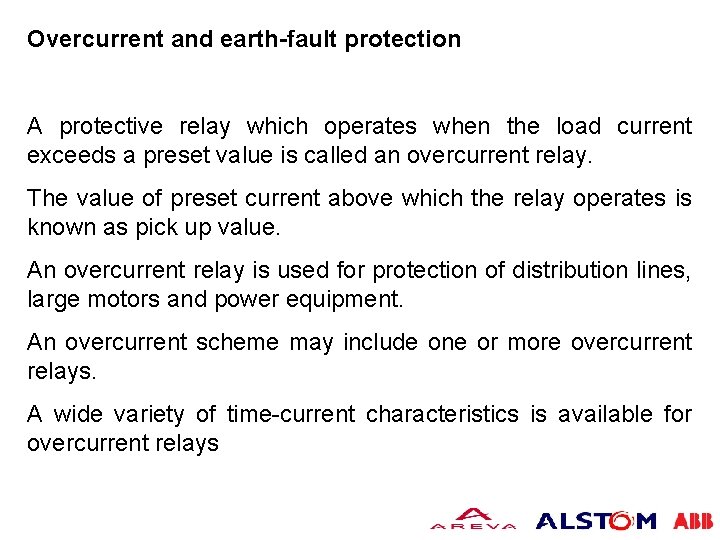
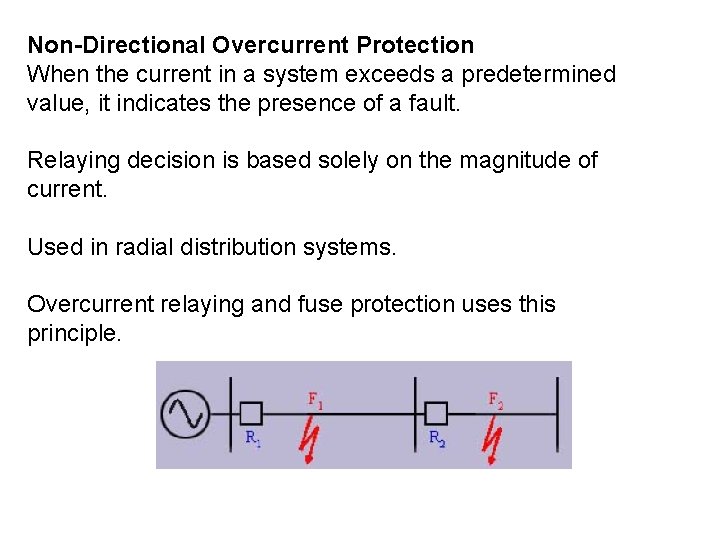
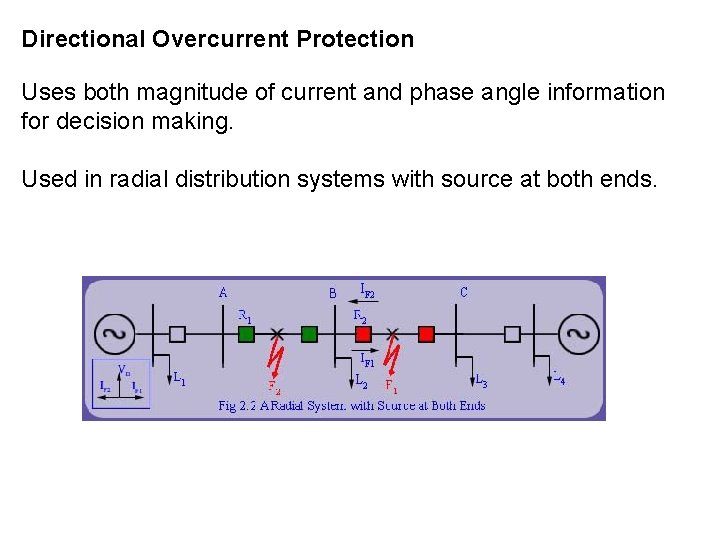
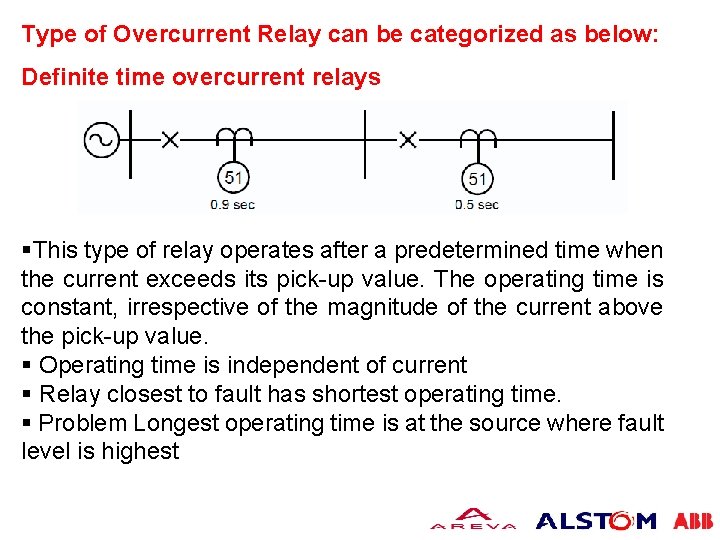
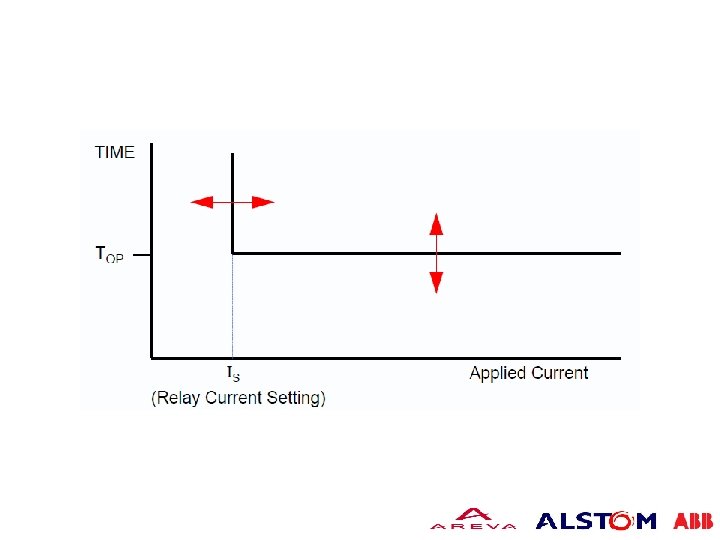
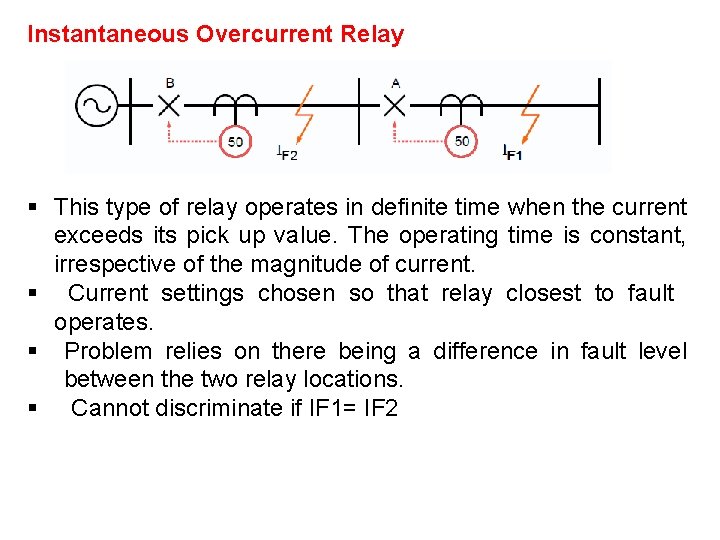
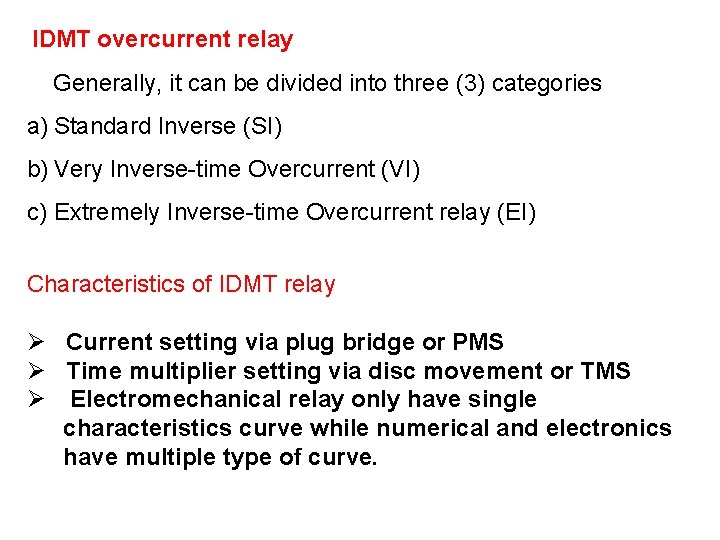
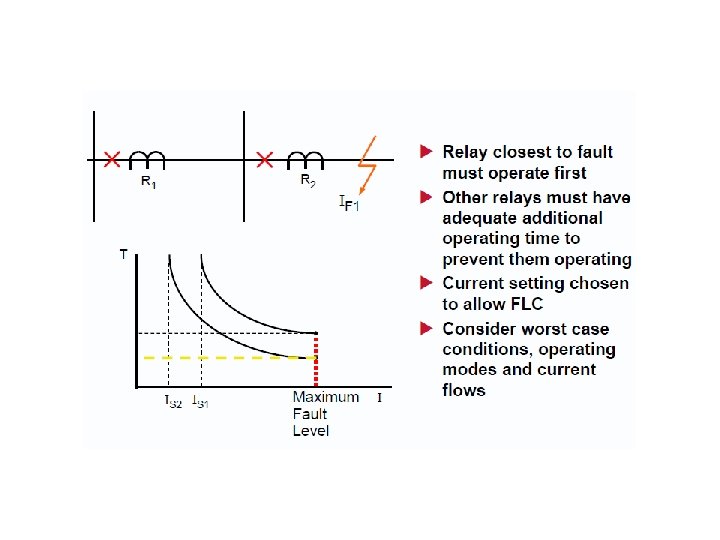
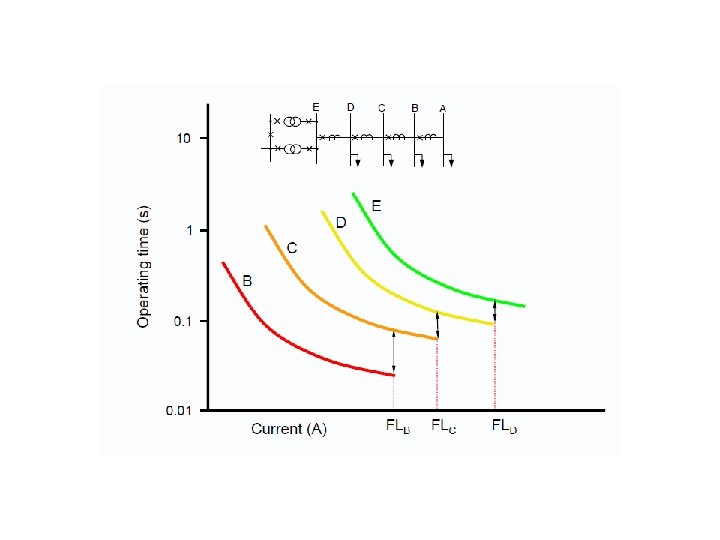
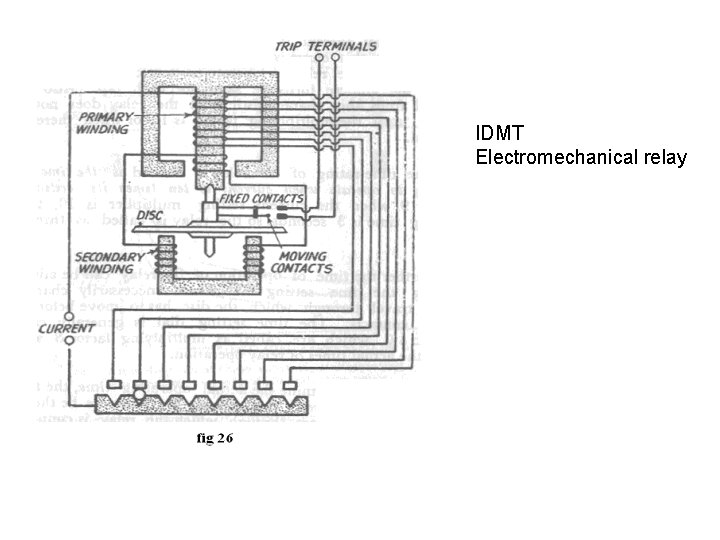
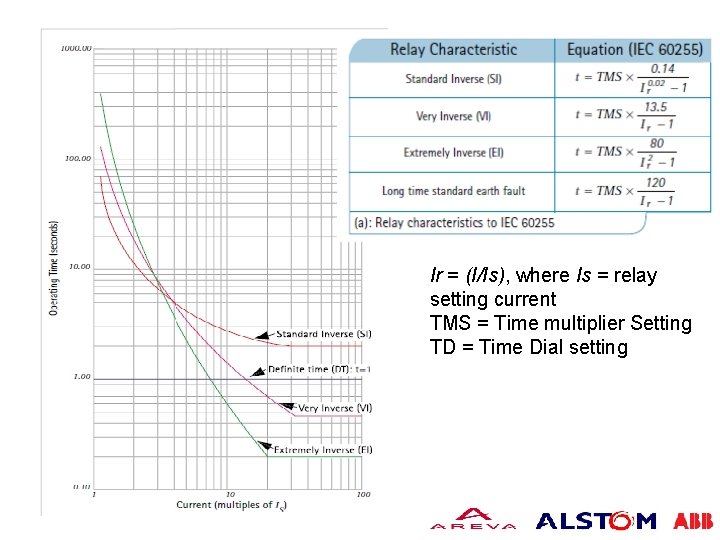
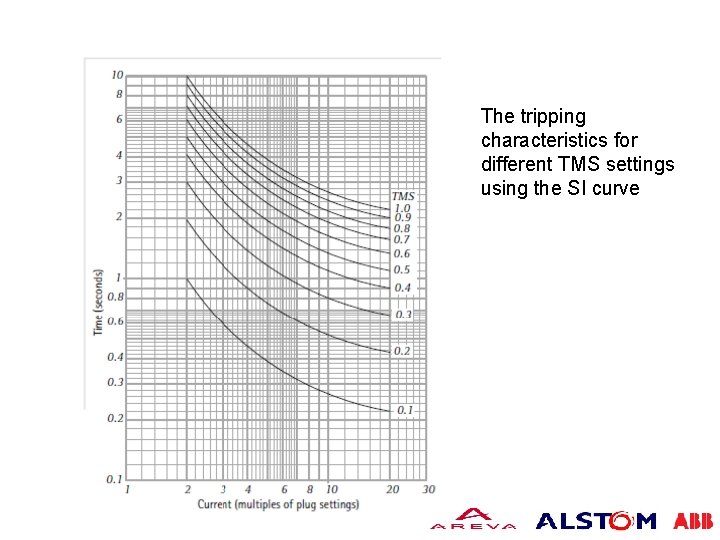
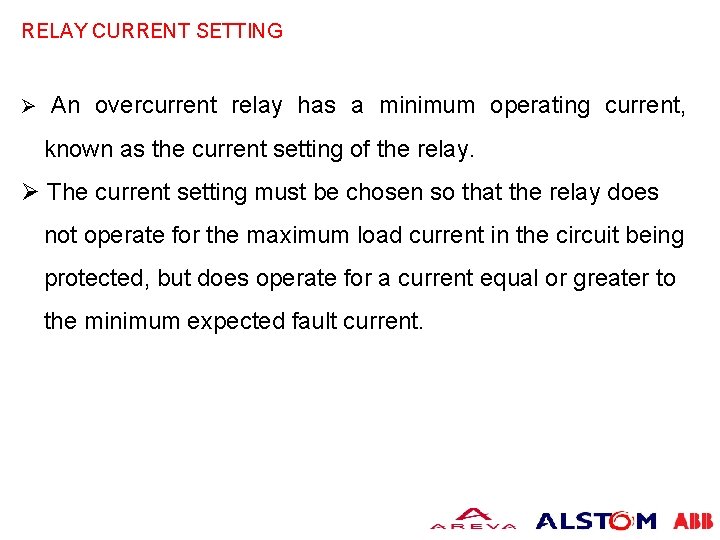
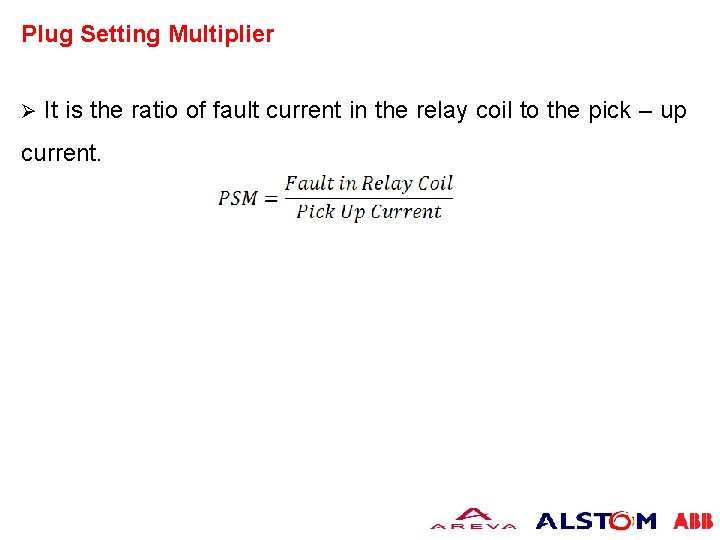
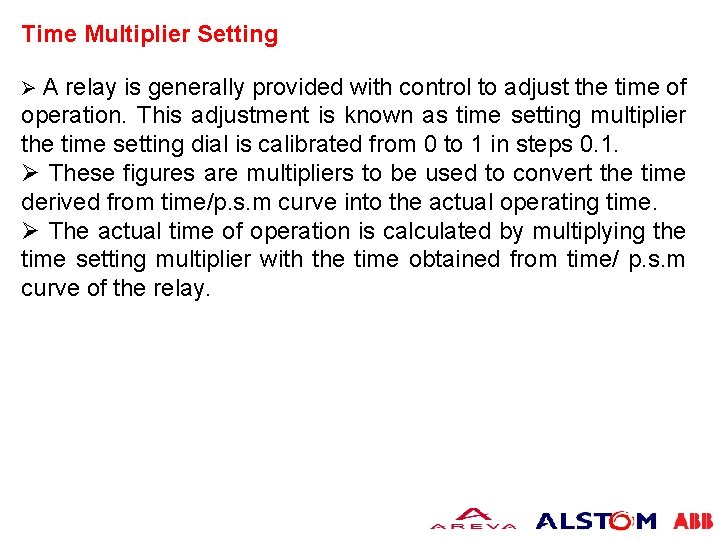
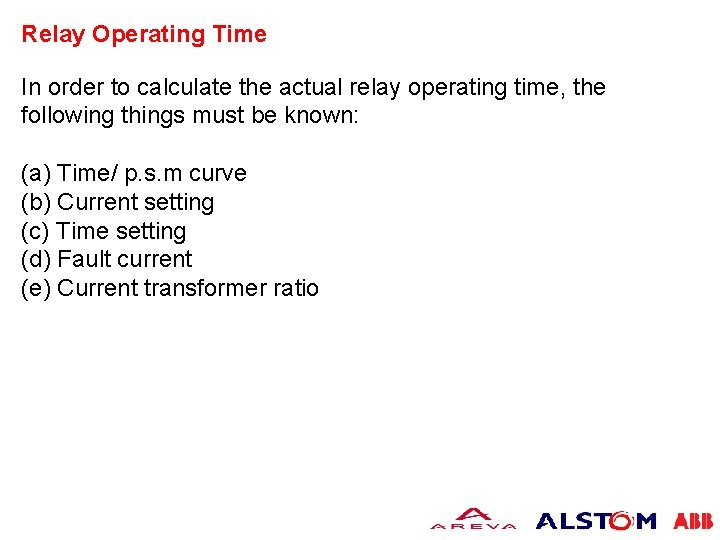
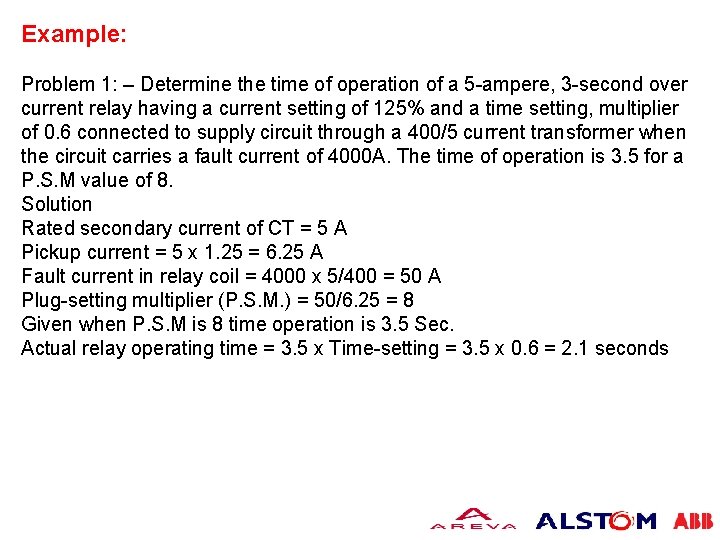
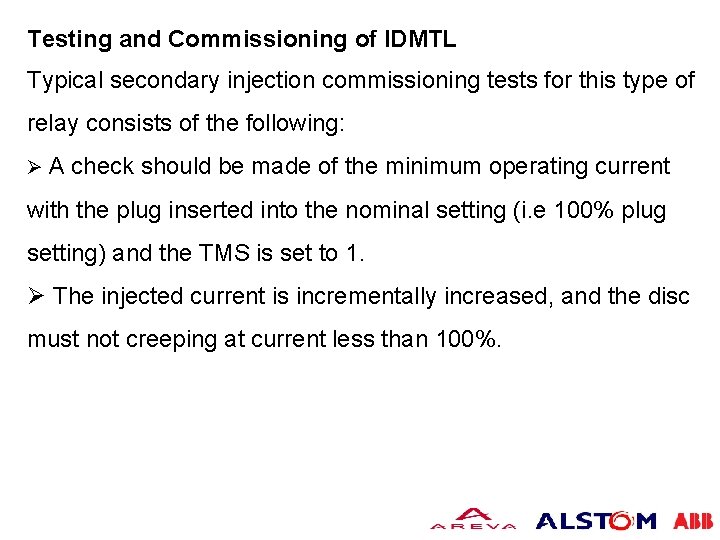

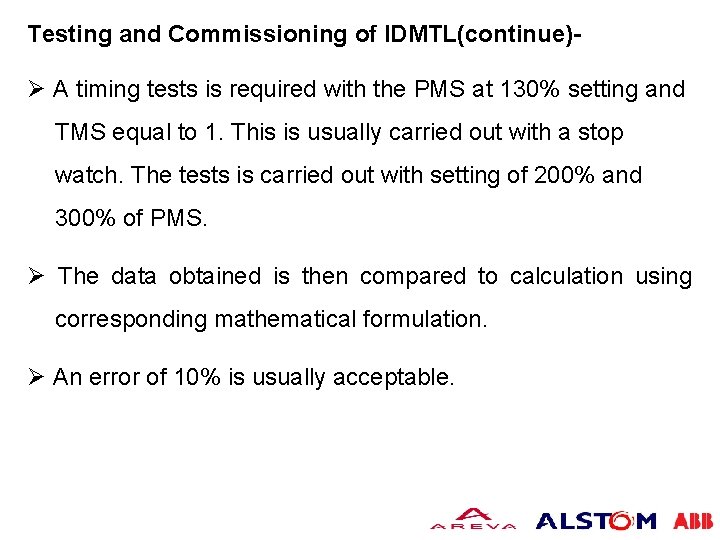
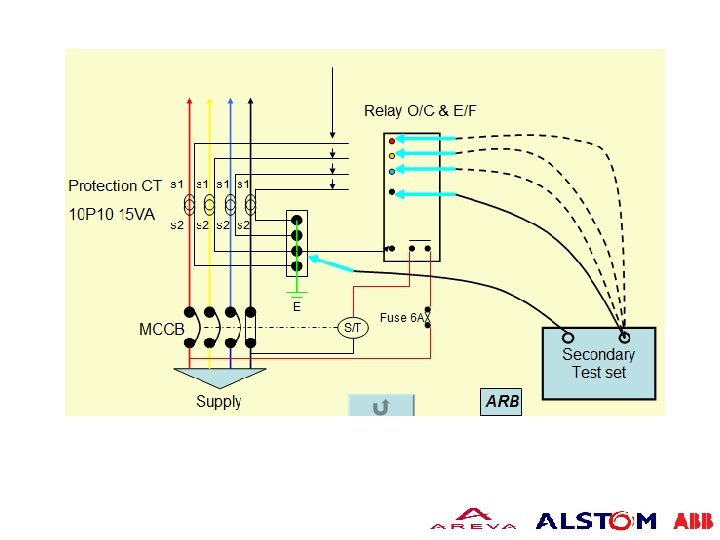
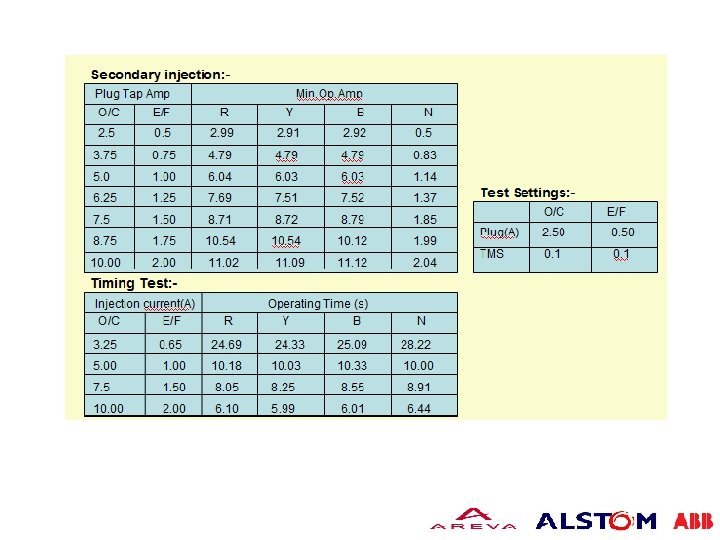
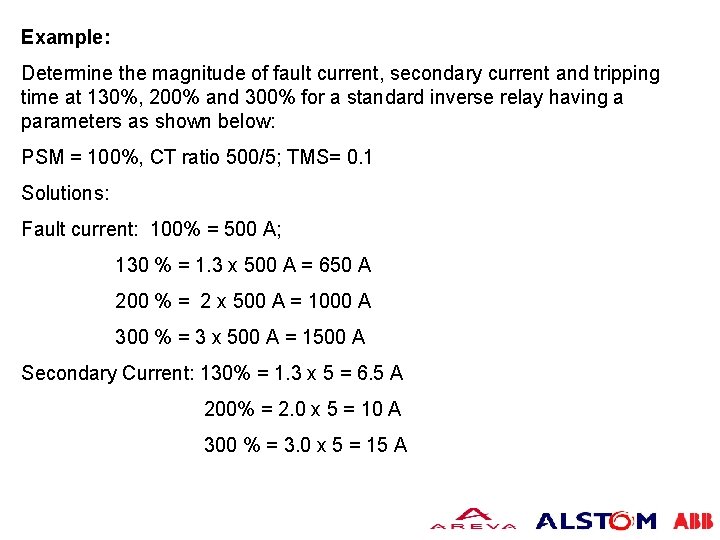
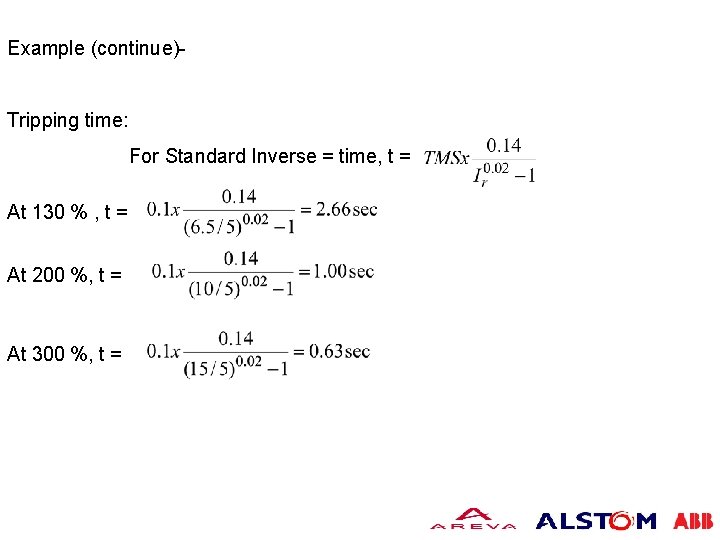
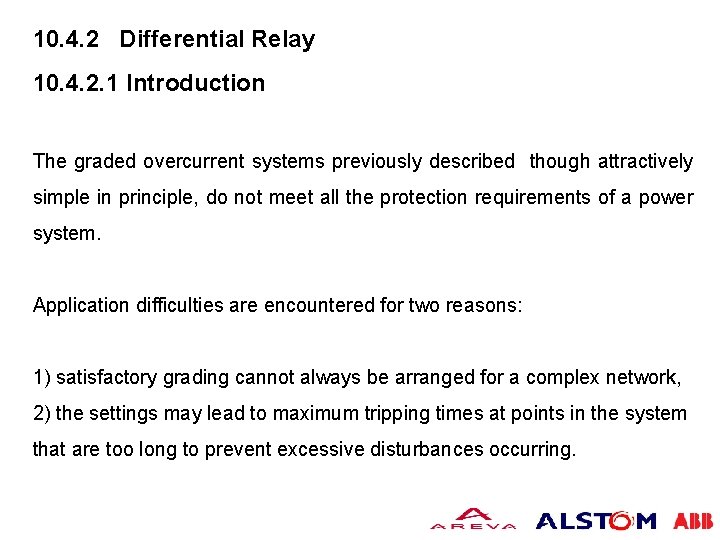
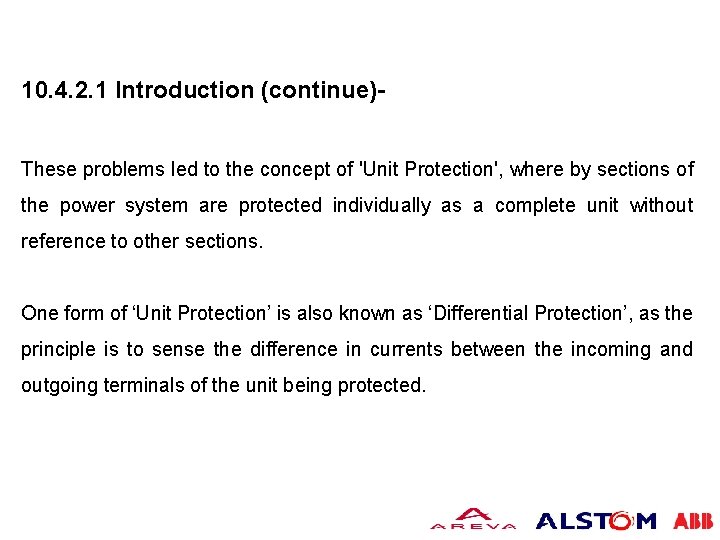
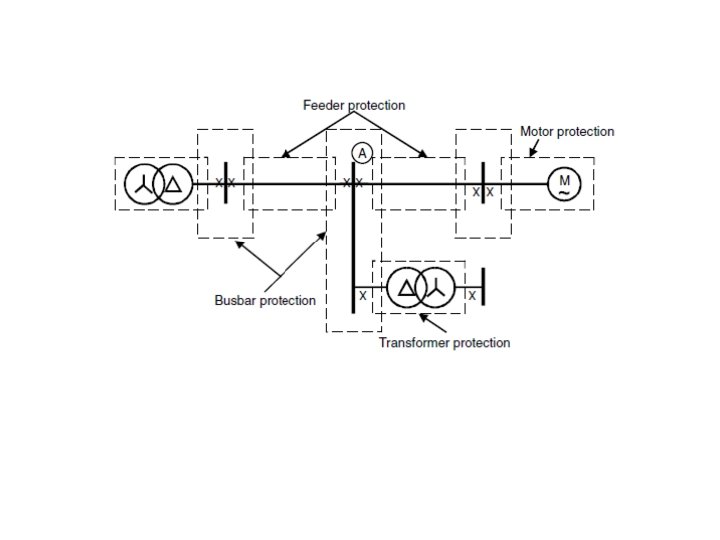
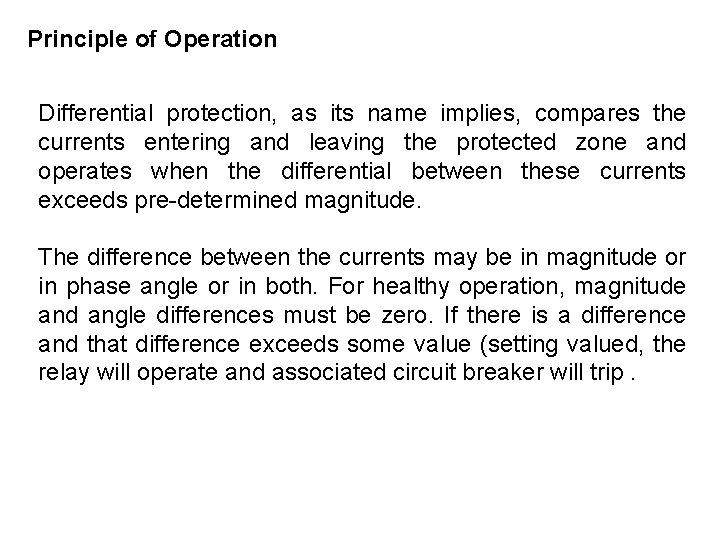
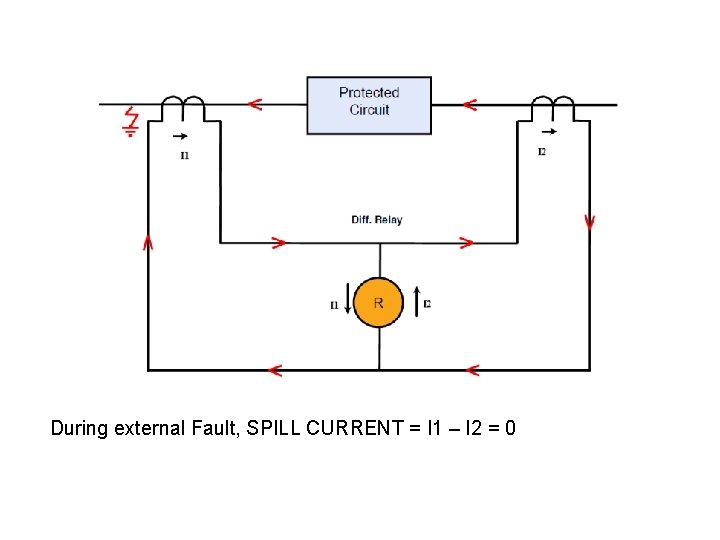
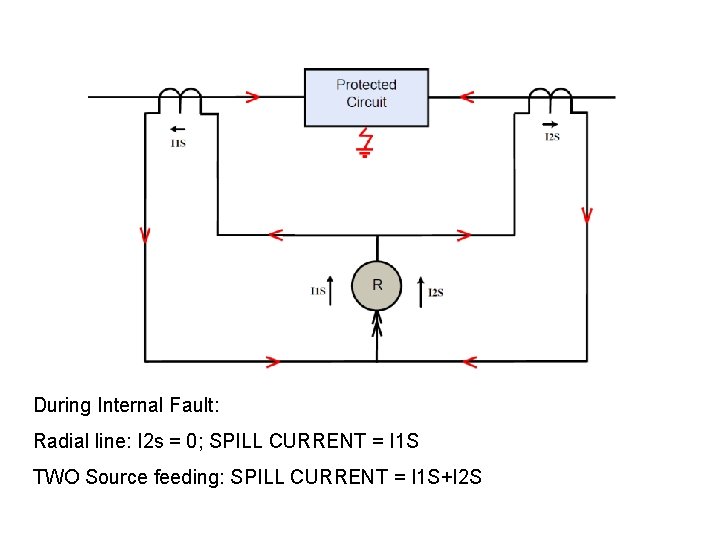
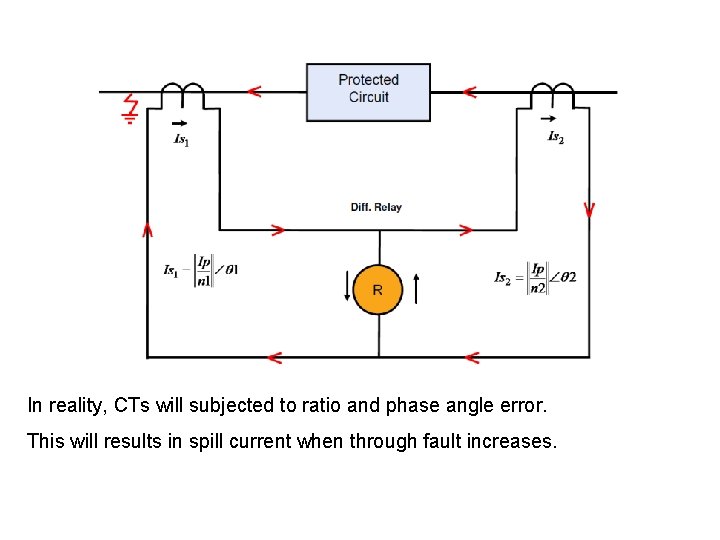
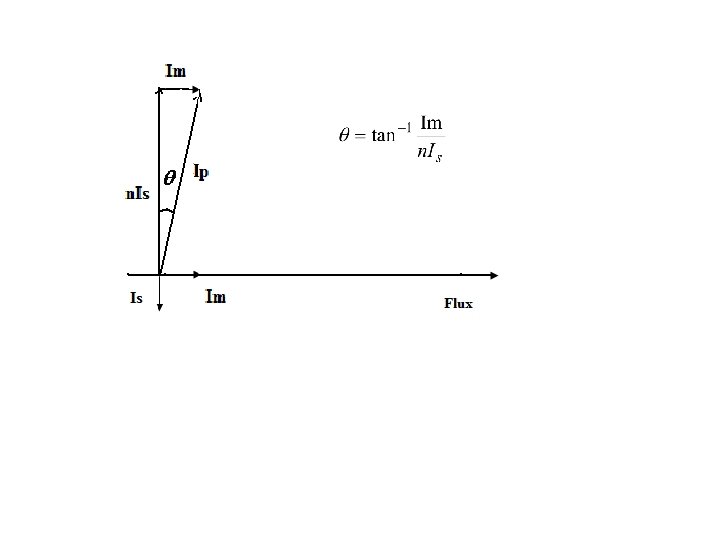
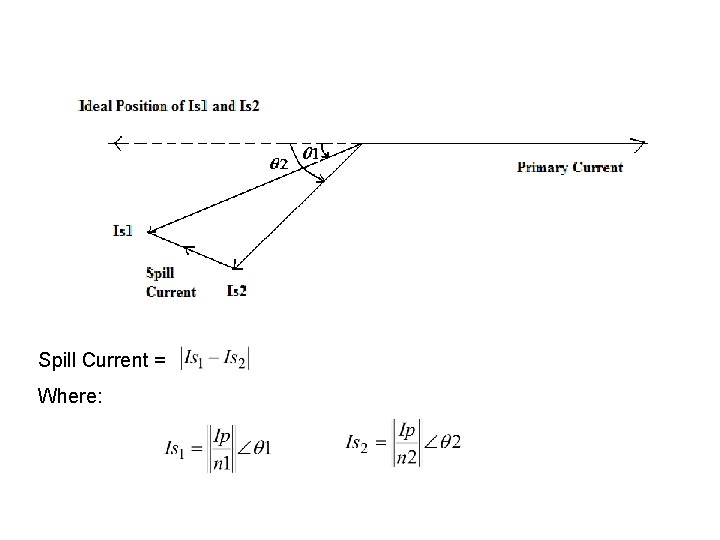
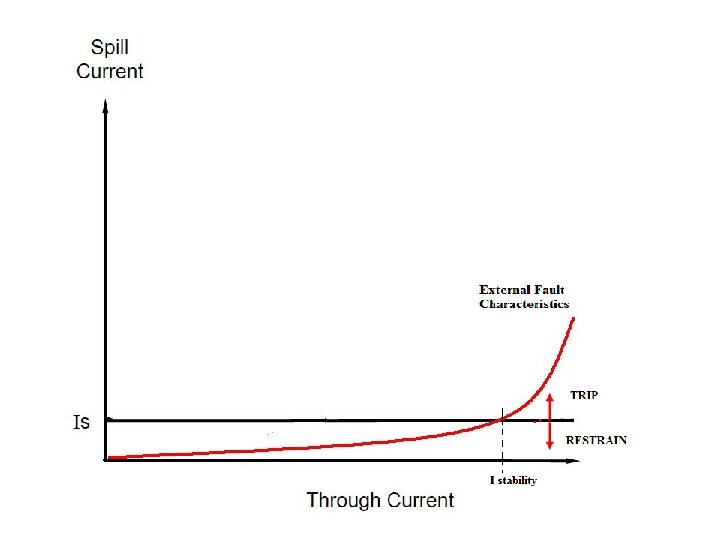
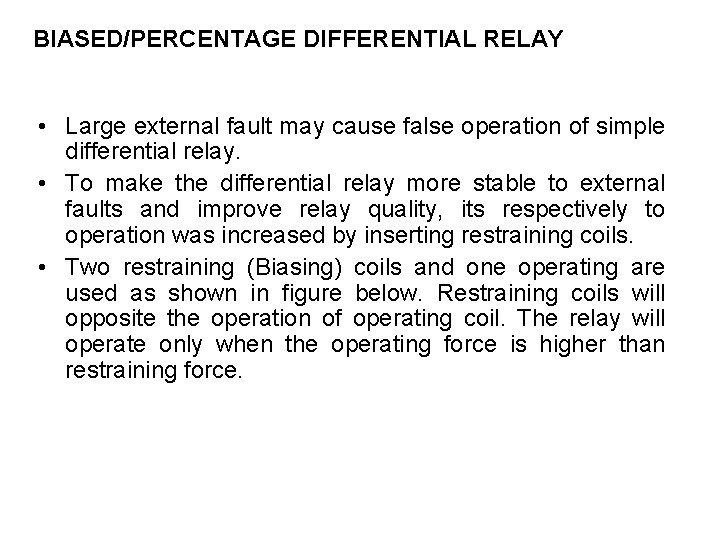
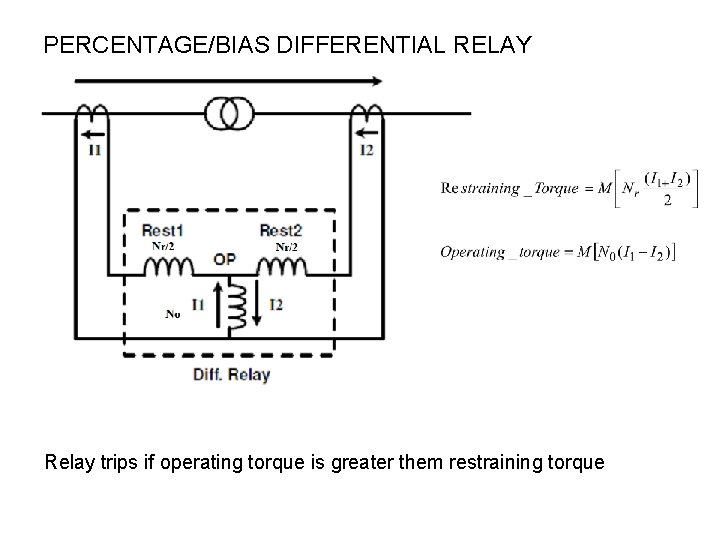
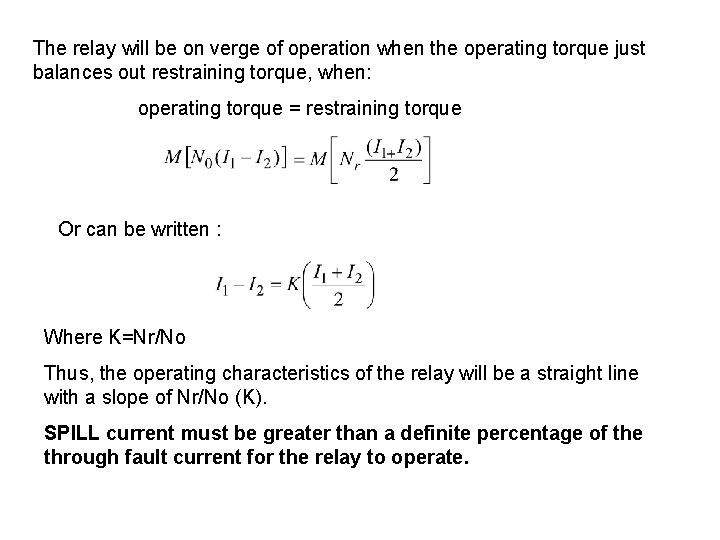
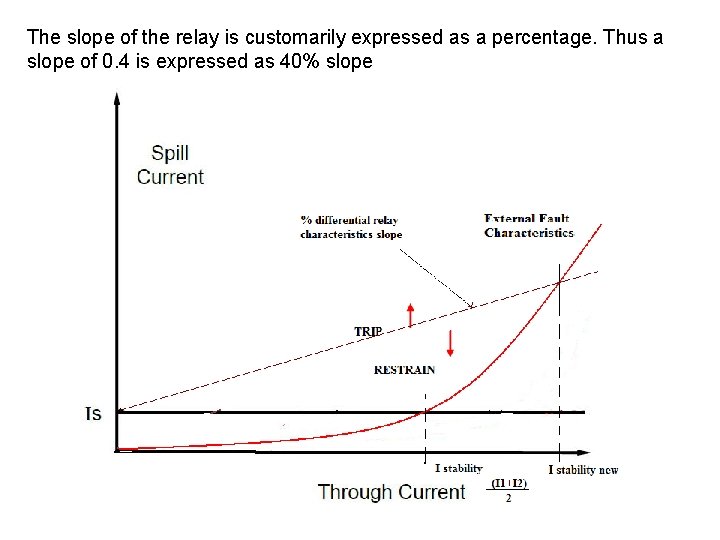
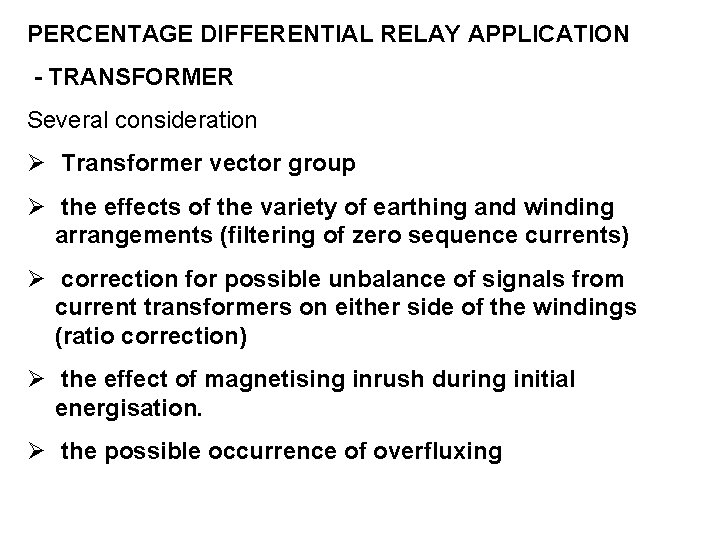
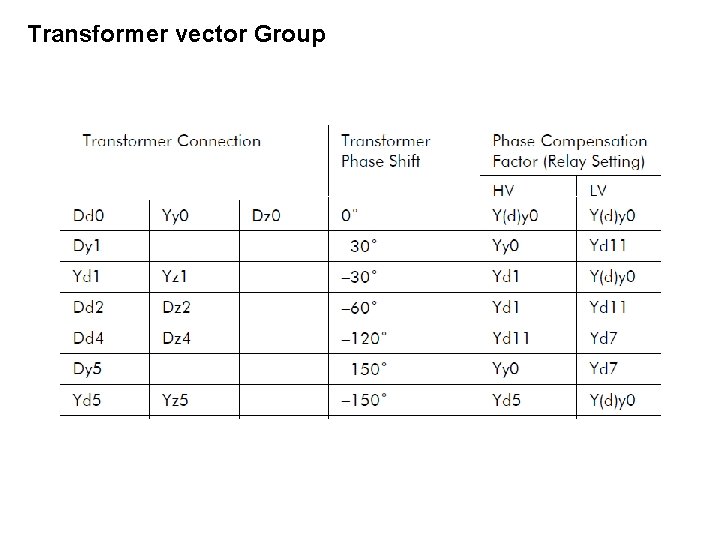
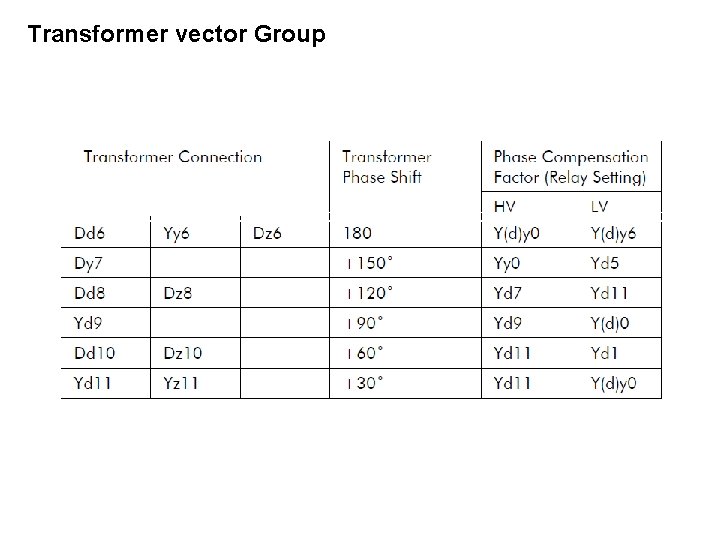
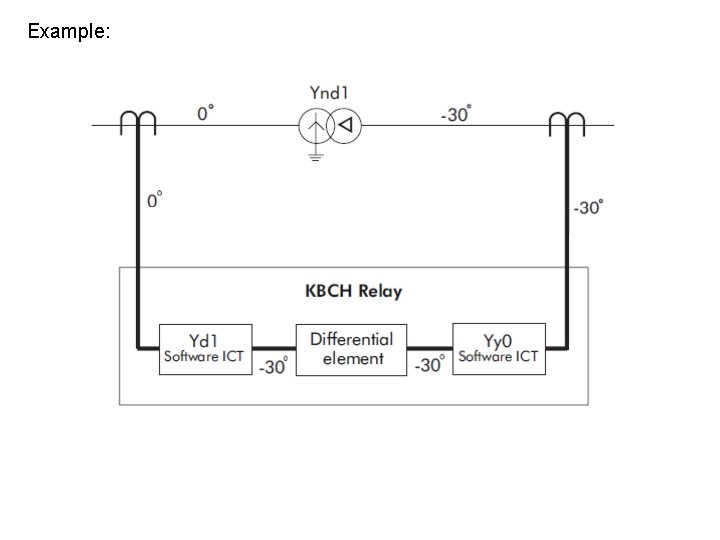
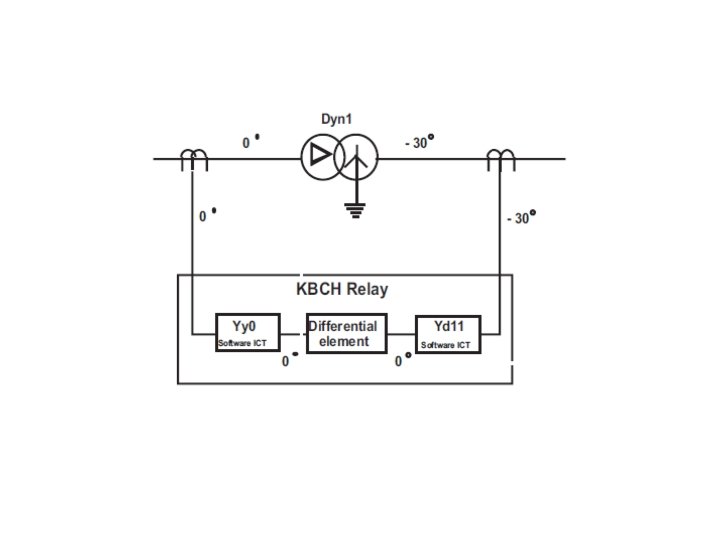
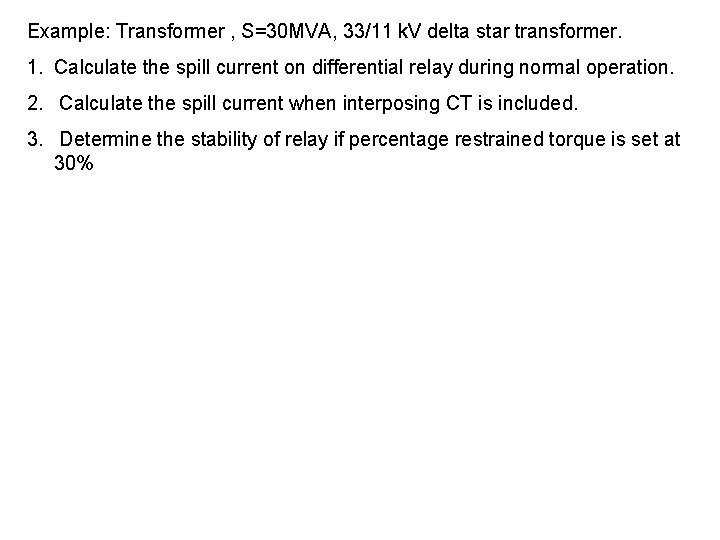
- Slides: 56

POWER SYSTEM COMMISSIONING AND MAINTENANCE PRACTICE DET 310/3 CHAPTER 10 PROTECTIVE RELAY
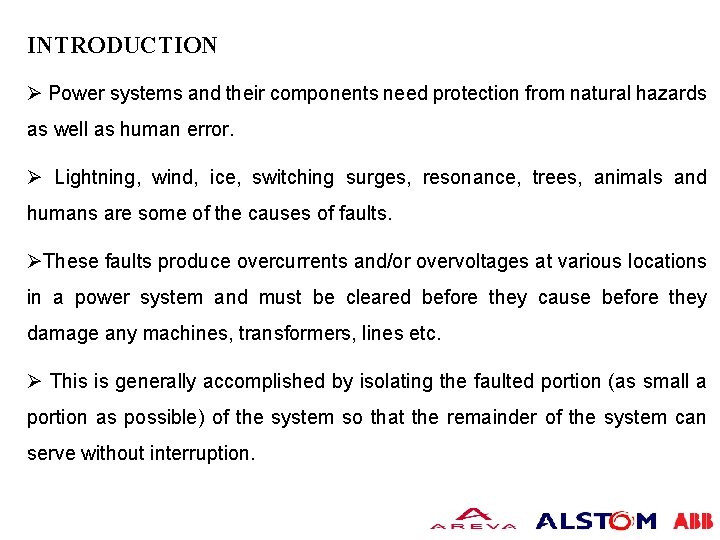
INTRODUCTION Ø Power systems and their components need protection from natural hazards as well as human error. Ø Lightning, wind, ice, switching surges, resonance, trees, animals and humans are some of the causes of faults. ØThese faults produce overcurrents and/or overvoltages at various locations in a power system and must be cleared before they cause before they damage any machines, transformers, lines etc. Ø This is generally accomplished by isolating the faulted portion (as small a portion as possible) of the system so that the remainder of the system can serve without interruption.
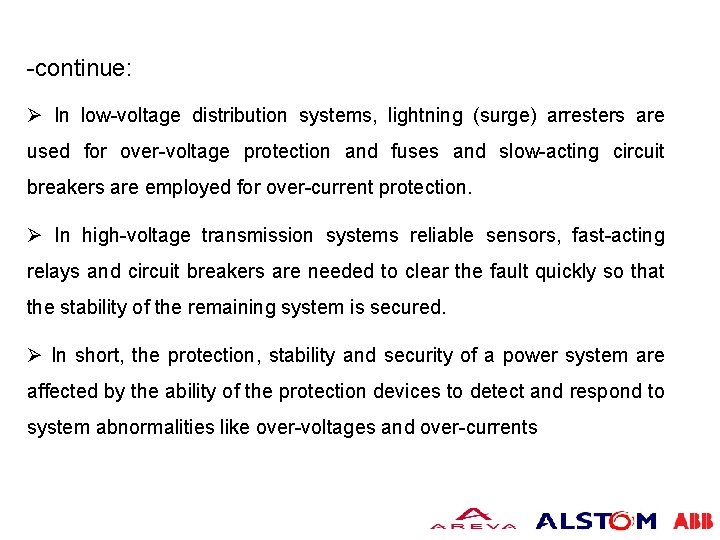
-continue: Ø In low-voltage distribution systems, lightning (surge) arresters are used for over-voltage protection and fuses and slow-acting circuit breakers are employed for over-current protection. Ø In high-voltage transmission systems reliable sensors, fast-acting relays and circuit breakers are needed to clear the fault quickly so that the stability of the remaining system is secured. Ø In short, the protection, stability and security of a power system are affected by the ability of the protection devices to detect and respond to system abnormalities like over-voltages and over-currents
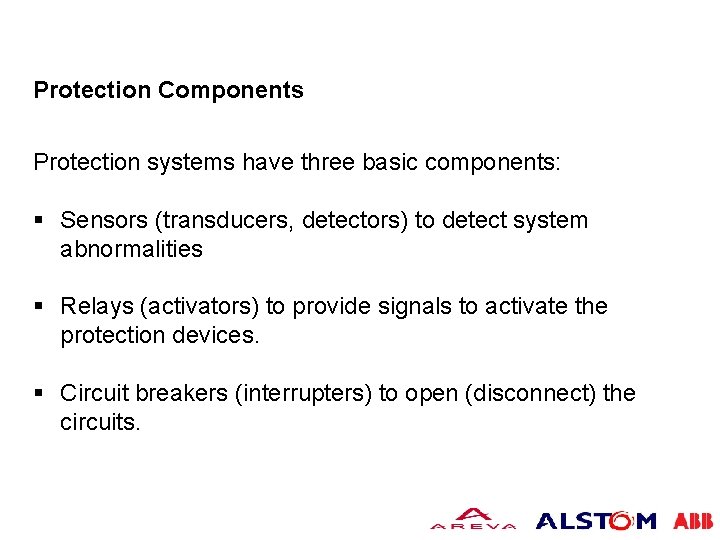
Protection Components Protection systems have three basic components: § Sensors (transducers, detectors) to detect system abnormalities § Relays (activators) to provide signals to activate the protection devices. § Circuit breakers (interrupters) to open (disconnect) the circuits.
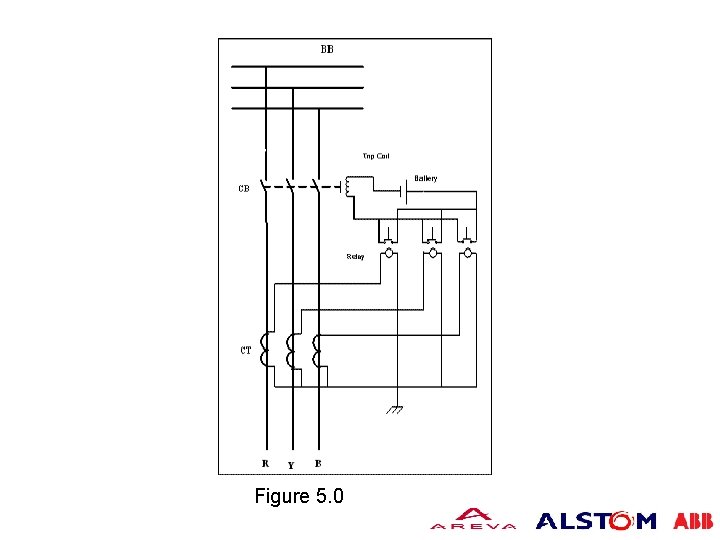
Figure 5. 0
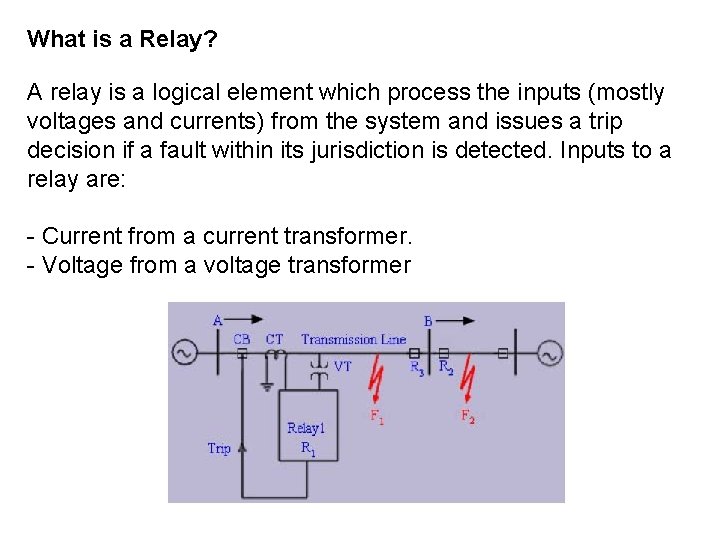
What is a Relay? A relay is a logical element which process the inputs (mostly voltages and currents) from the system and issues a trip decision if a fault within its jurisdiction is detected. Inputs to a relay are: - Current from a current transformer. - Voltage from a voltage transformer
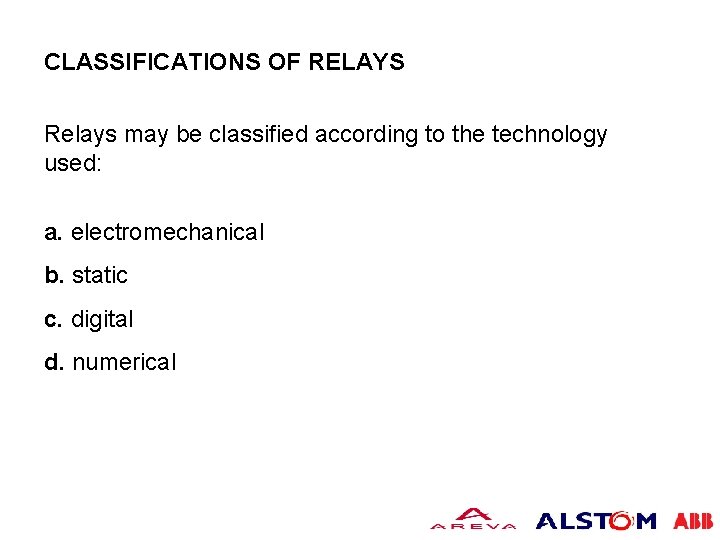
CLASSIFICATIONS OF RELAYS Relays may be classified according to the technology used: a. electromechanical b. static c. digital d. numerical
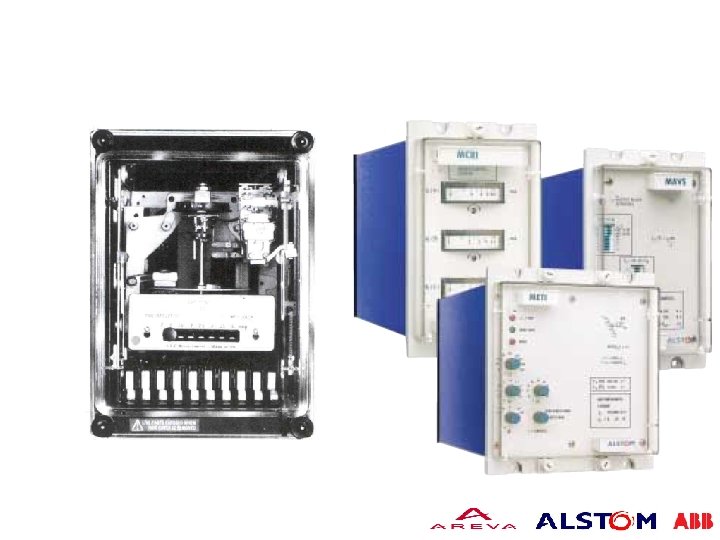
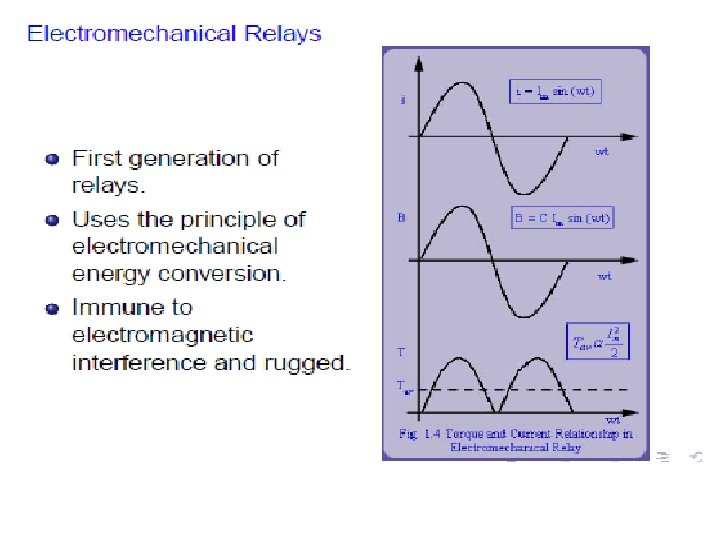
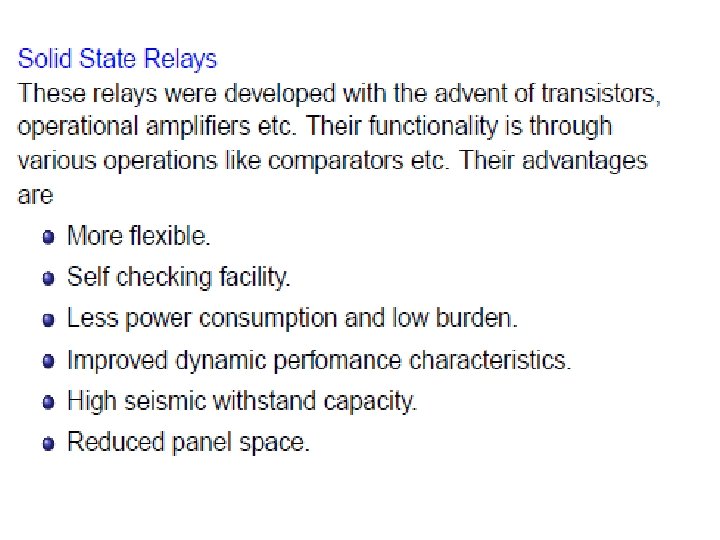
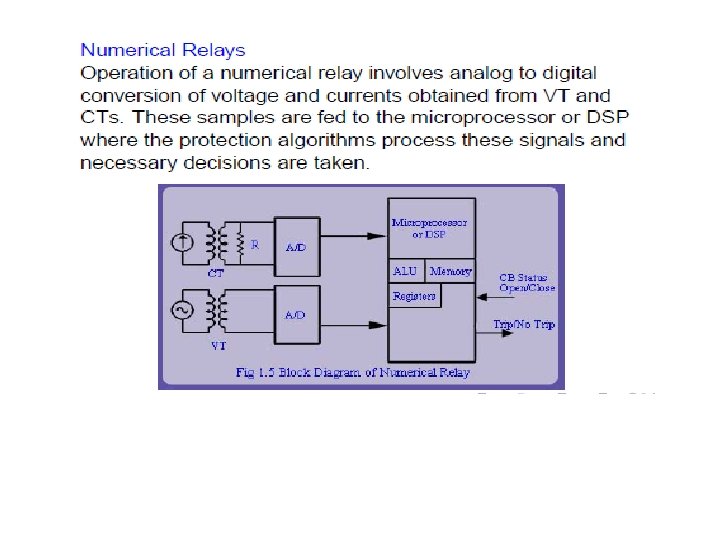
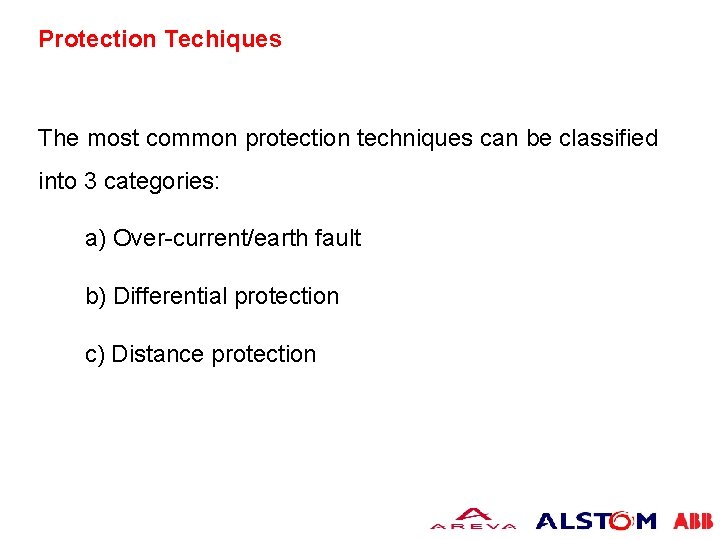
Protection Techiques The most common protection techniques can be classified into 3 categories: a) Over-current/earth fault b) Differential protection c) Distance protection
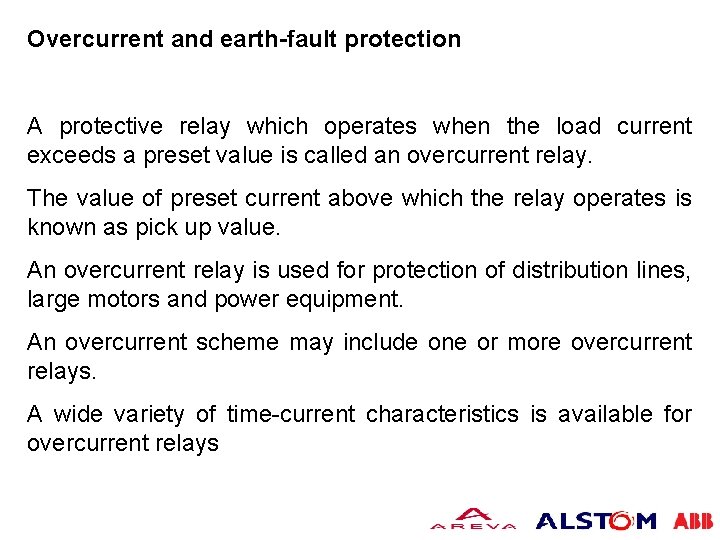
Overcurrent and earth-fault protection A protective relay which operates when the load current exceeds a preset value is called an overcurrent relay. The value of preset current above which the relay operates is known as pick up value. An overcurrent relay is used for protection of distribution lines, large motors and power equipment. An overcurrent scheme may include one or more overcurrent relays. A wide variety of time-current characteristics is available for overcurrent relays
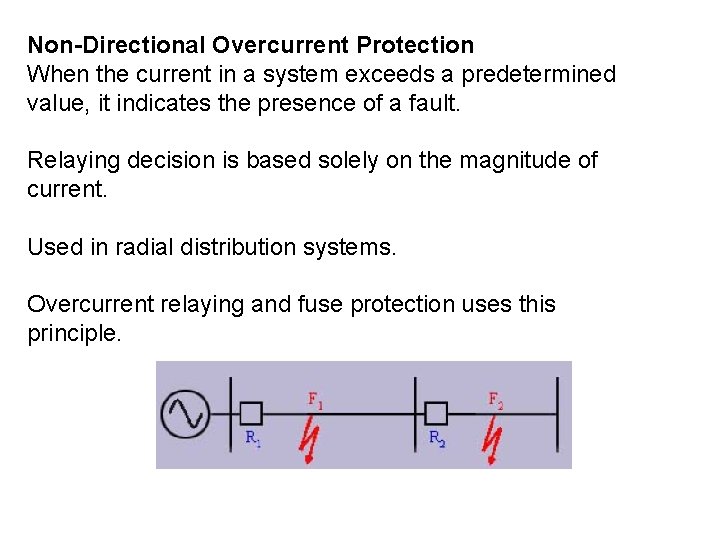
Non-Directional Overcurrent Protection When the current in a system exceeds a predetermined value, it indicates the presence of a fault. Relaying decision is based solely on the magnitude of current. Used in radial distribution systems. Overcurrent relaying and fuse protection uses this principle.
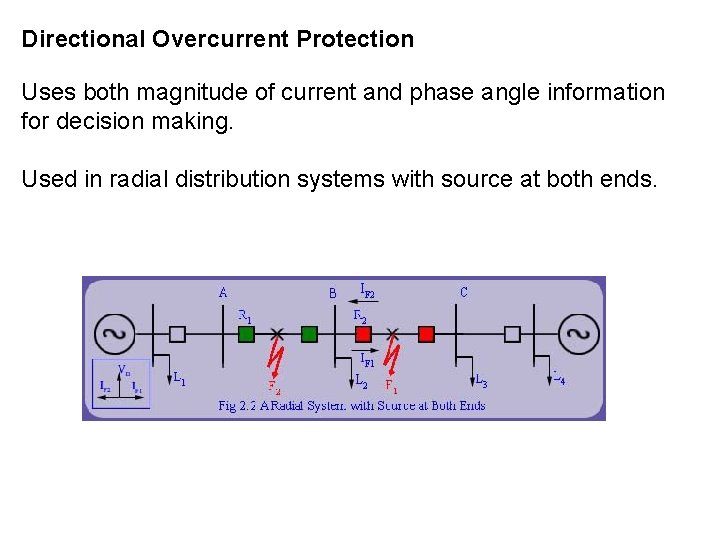
Directional Overcurrent Protection Uses both magnitude of current and phase angle information for decision making. Used in radial distribution systems with source at both ends.
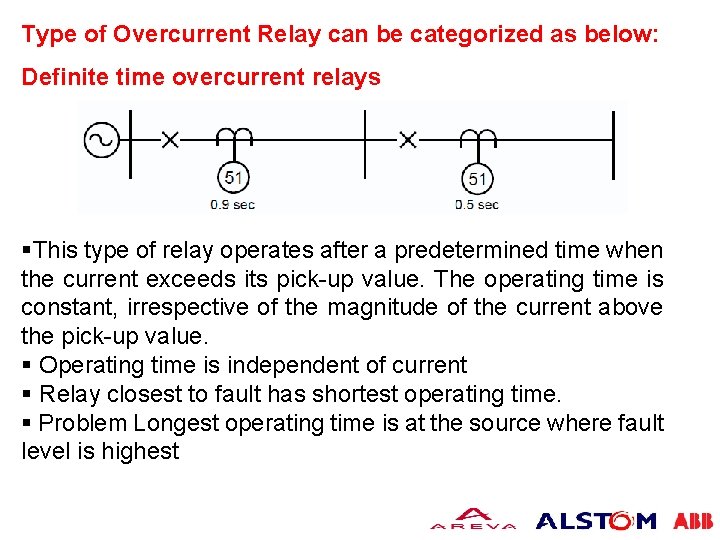
Type of Overcurrent Relay can be categorized as below: Definite time overcurrent relays §This type of relay operates after a predetermined time when the current exceeds its pick-up value. The operating time is constant, irrespective of the magnitude of the current above the pick-up value. § Operating time is independent of current § Relay closest to fault has shortest operating time. § Problem Longest operating time is at the source where fault level is highest
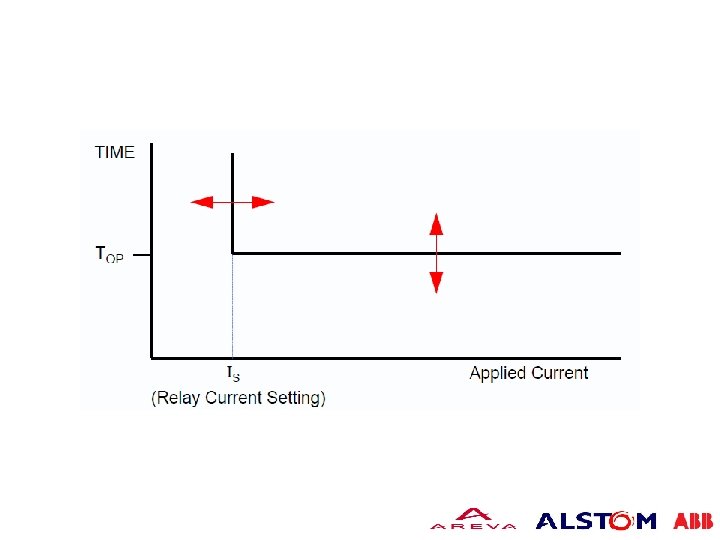
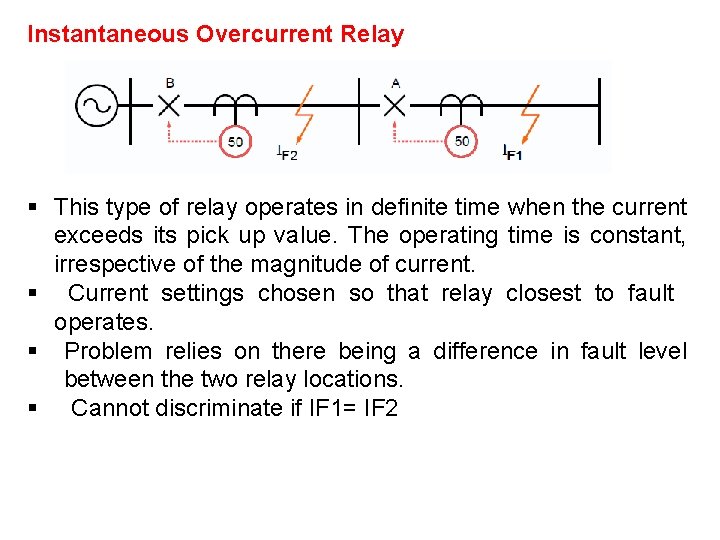
Instantaneous Overcurrent Relay § This type of relay operates in definite time when the current exceeds its pick up value. The operating time is constant, irrespective of the magnitude of current. § Current settings chosen so that relay closest to fault operates. § Problem relies on there being a difference in fault level between the two relay locations. § Cannot discriminate if IF 1= IF 2
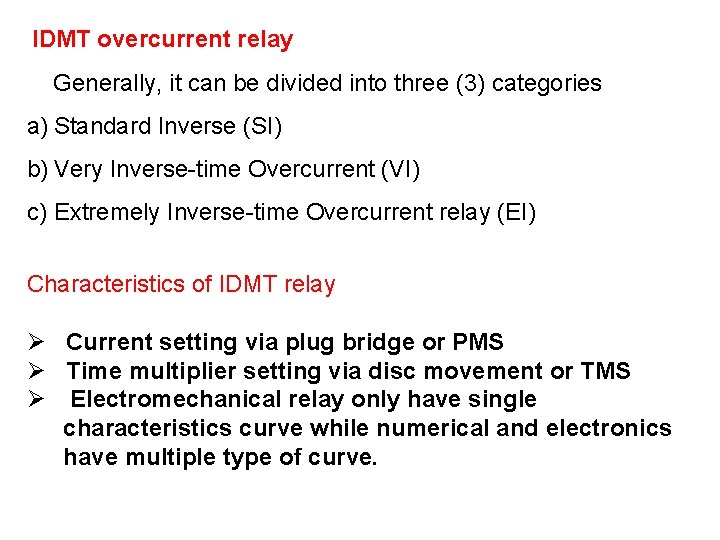
IDMT overcurrent relay Generally, it can be divided into three (3) categories a) Standard Inverse (SI) b) Very Inverse-time Overcurrent (VI) c) Extremely Inverse-time Overcurrent relay (EI) Characteristics of IDMT relay Ø Current setting via plug bridge or PMS Ø Time multiplier setting via disc movement or TMS Ø Electromechanical relay only have single characteristics curve while numerical and electronics have multiple type of curve.
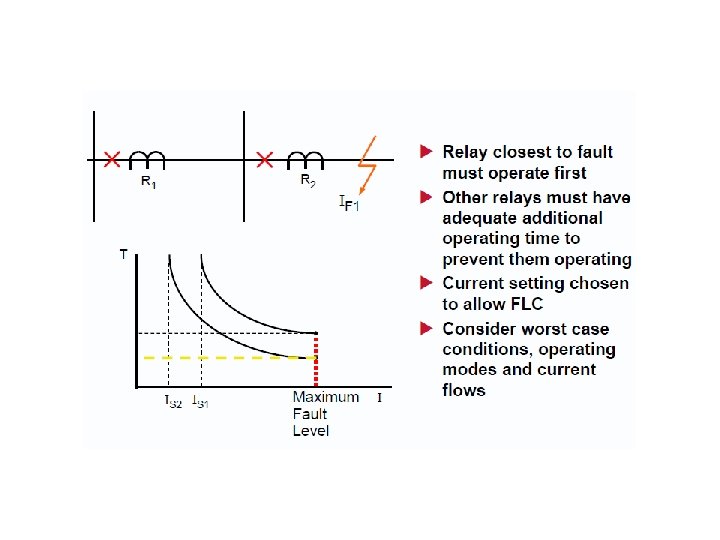
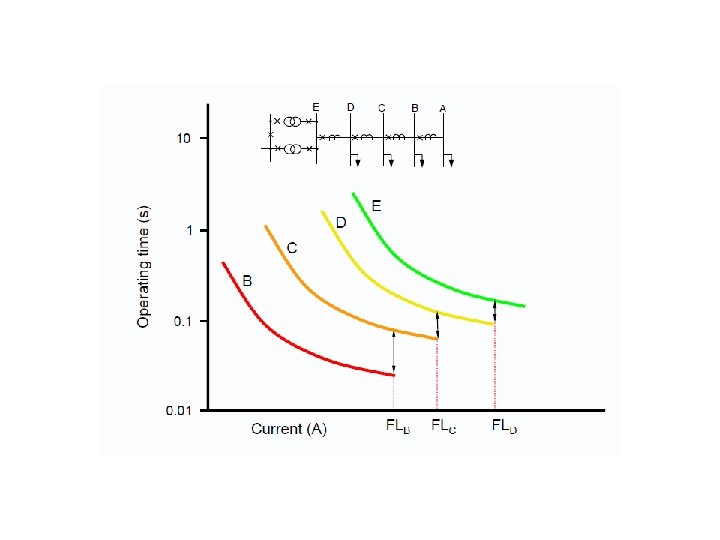
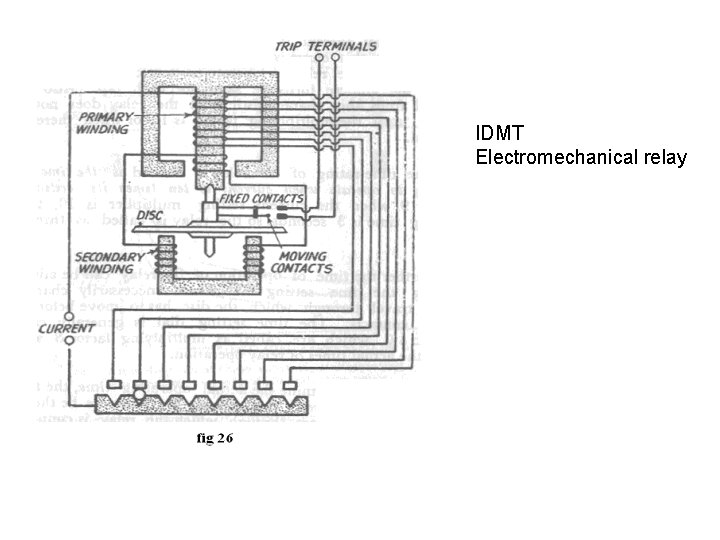
IDMT Electromechanical relay
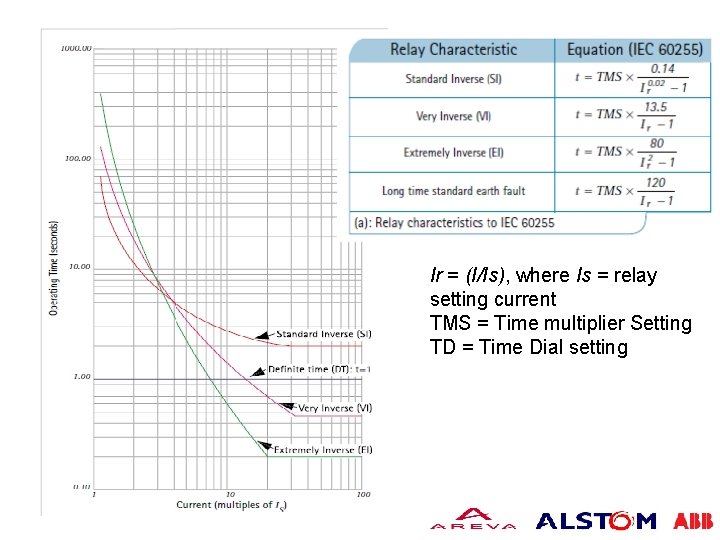
Ir = (I/Is), where Is = relay setting current TMS = Time multiplier Setting TD = Time Dial setting
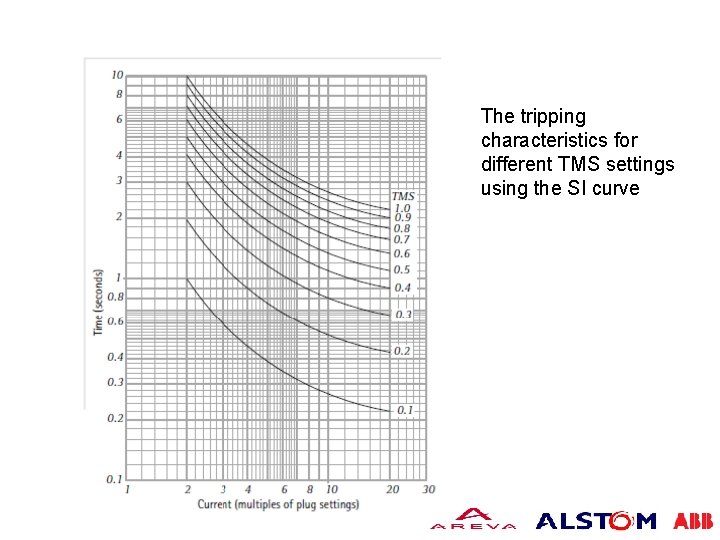
The tripping characteristics for different TMS settings using the SI curve
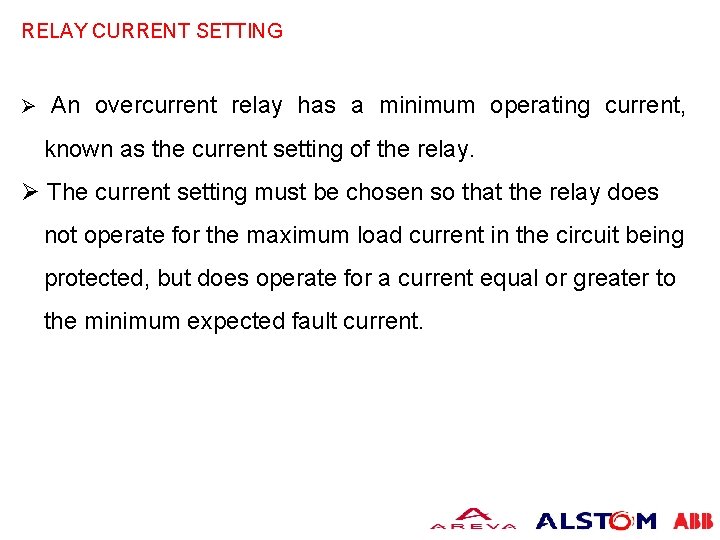
RELAY CURRENT SETTING Ø An overcurrent relay has a minimum operating current, known as the current setting of the relay. Ø The current setting must be chosen so that the relay does not operate for the maximum load current in the circuit being protected, but does operate for a current equal or greater to the minimum expected fault current.
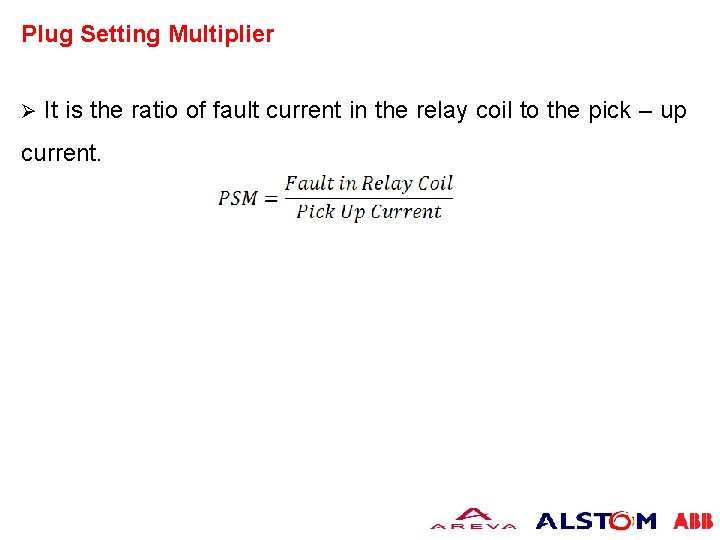
Plug Setting Multiplier Ø It is the ratio of fault current in the relay coil to the pick – up current.
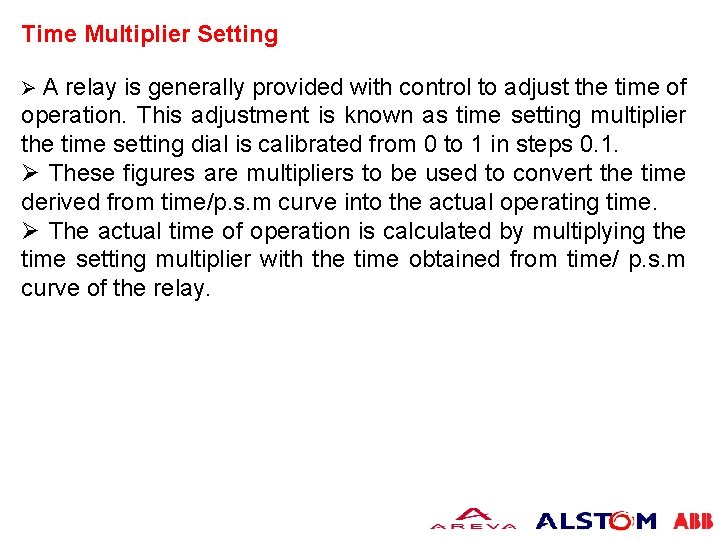
Time Multiplier Setting Ø A relay is generally provided with control to adjust the time of operation. This adjustment is known as time setting multiplier the time setting dial is calibrated from 0 to 1 in steps 0. 1. Ø These figures are multipliers to be used to convert the time derived from time/p. s. m curve into the actual operating time. Ø The actual time of operation is calculated by multiplying the time setting multiplier with the time obtained from time/ p. s. m curve of the relay.
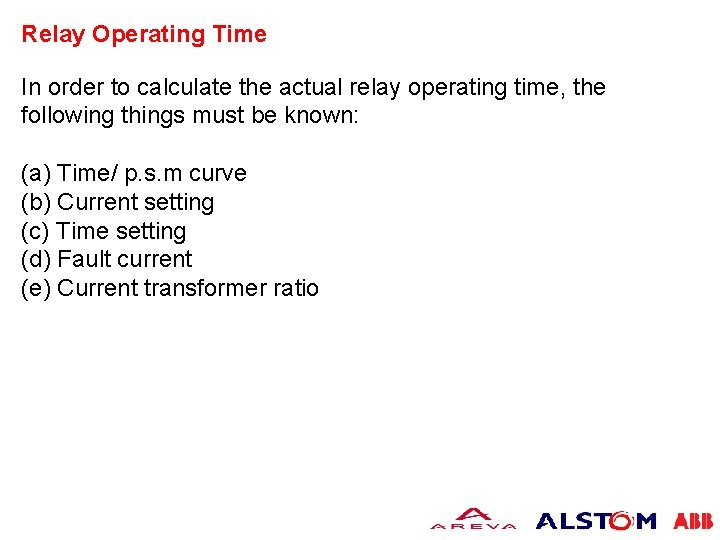
Relay Operating Time In order to calculate the actual relay operating time, the following things must be known: (a) Time/ p. s. m curve (b) Current setting (c) Time setting (d) Fault current (e) Current transformer ratio
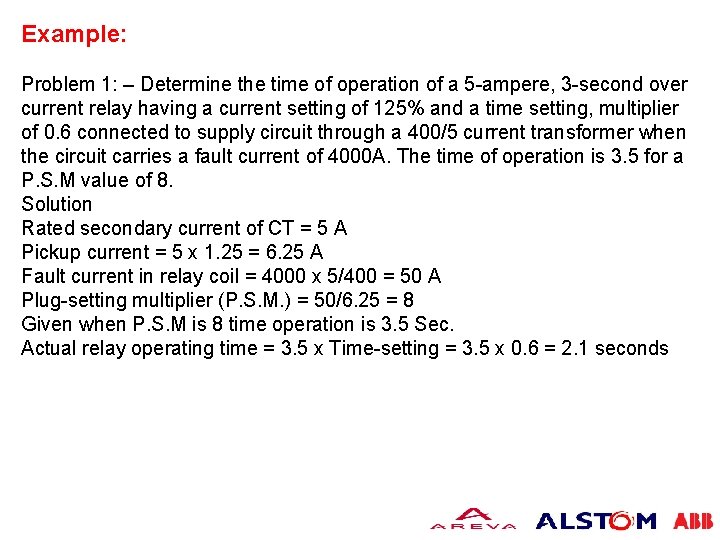
Example: Problem 1: – Determine the time of operation of a 5 -ampere, 3 -second over current relay having a current setting of 125% and a time setting, multiplier of 0. 6 connected to supply circuit through a 400/5 current transformer when the circuit carries a fault current of 4000 A. The time of operation is 3. 5 for a P. S. M value of 8. Solution Rated secondary current of CT = 5 A Pickup current = 5 x 1. 25 = 6. 25 A Fault current in relay coil = 4000 x 5/400 = 50 A Plug-setting multiplier (P. S. M. ) = 50/6. 25 = 8 Given when P. S. M is 8 time operation is 3. 5 Sec. Actual relay operating time = 3. 5 x Time-setting = 3. 5 x 0. 6 = 2. 1 seconds
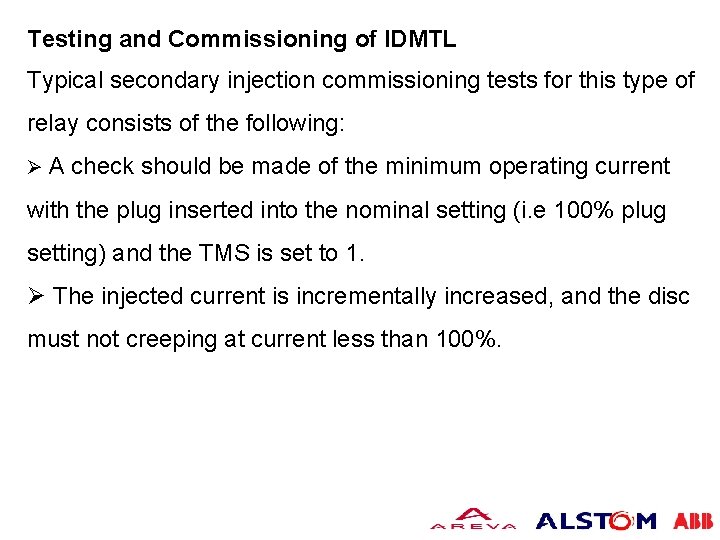
Testing and Commissioning of IDMTL Typical secondary injection commissioning tests for this type of relay consists of the following: Ø A check should be made of the minimum operating current with the plug inserted into the nominal setting (i. e 100% plug setting) and the TMS is set to 1. Ø The injected current is incrementally increased, and the disc must not creeping at current less than 100%.

Testing and Commissioning of IDMTL Ø Full travel of disc must occur, and relay flag must have dropped with an injected current less than 130% of setting. Ø The current should be then incrementally reduced to enable the disc to reset, which occur at a current less than 70% of the pick-up current
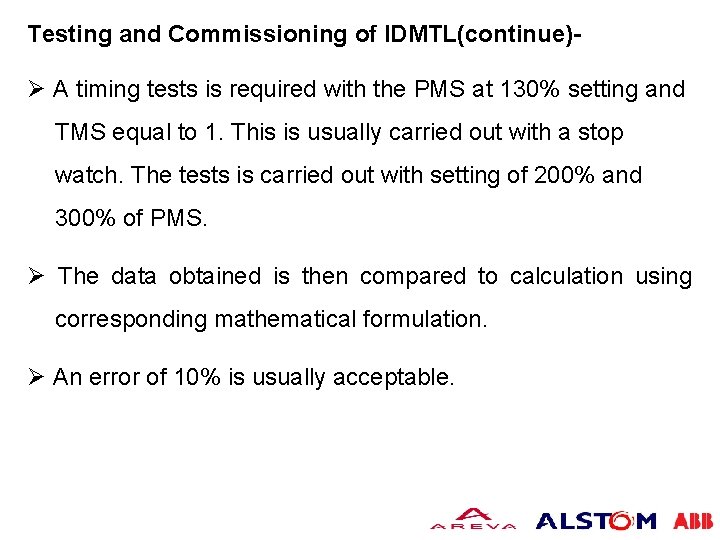
Testing and Commissioning of IDMTL(continue)- Ø A timing tests is required with the PMS at 130% setting and TMS equal to 1. This is usually carried out with a stop watch. The tests is carried out with setting of 200% and 300% of PMS. Ø The data obtained is then compared to calculation using corresponding mathematical formulation. Ø An error of 10% is usually acceptable.
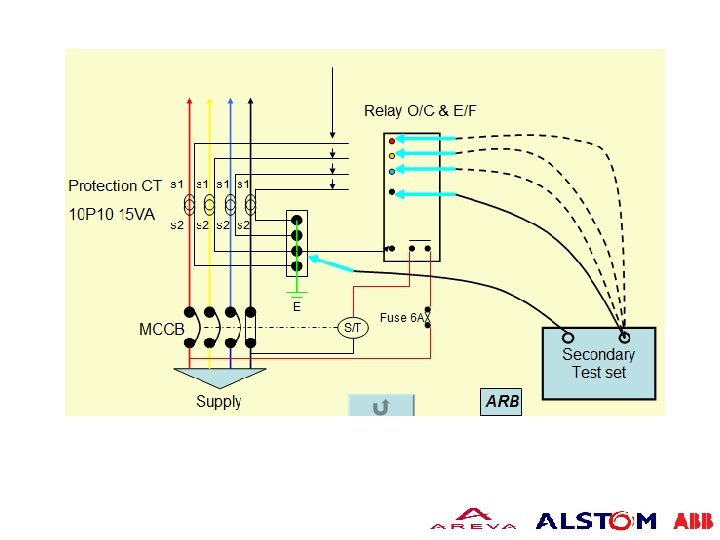
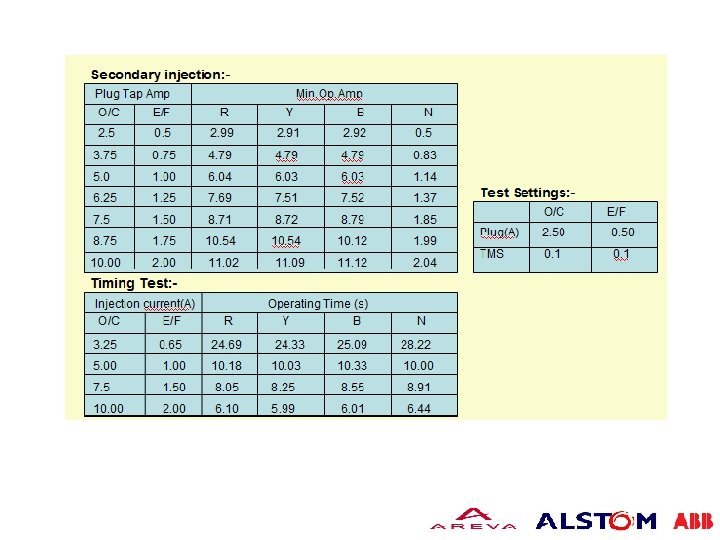
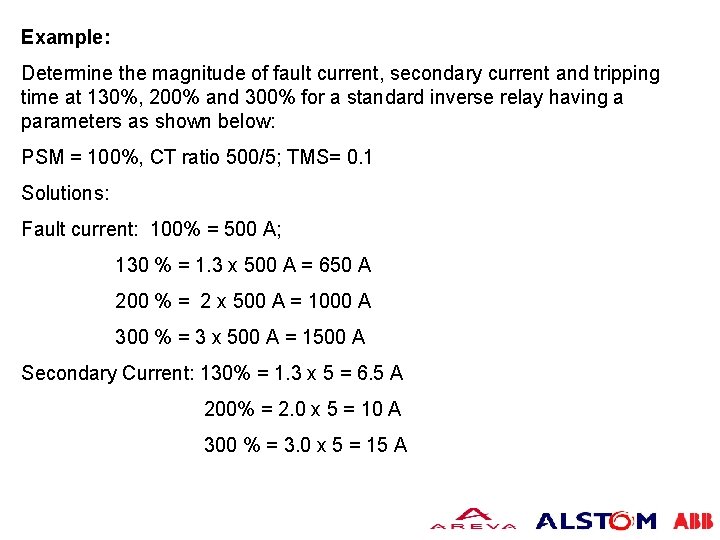
Example: Determine the magnitude of fault current, secondary current and tripping time at 130%, 200% and 300% for a standard inverse relay having a parameters as shown below: PSM = 100%, CT ratio 500/5; TMS= 0. 1 Solutions: Fault current: 100% = 500 A; 130 % = 1. 3 x 500 A = 650 A 200 % = 2 x 500 A = 1000 A 300 % = 3 x 500 A = 1500 A Secondary Current: 130% = 1. 3 x 5 = 6. 5 A 200% = 2. 0 x 5 = 10 A 300 % = 3. 0 x 5 = 15 A
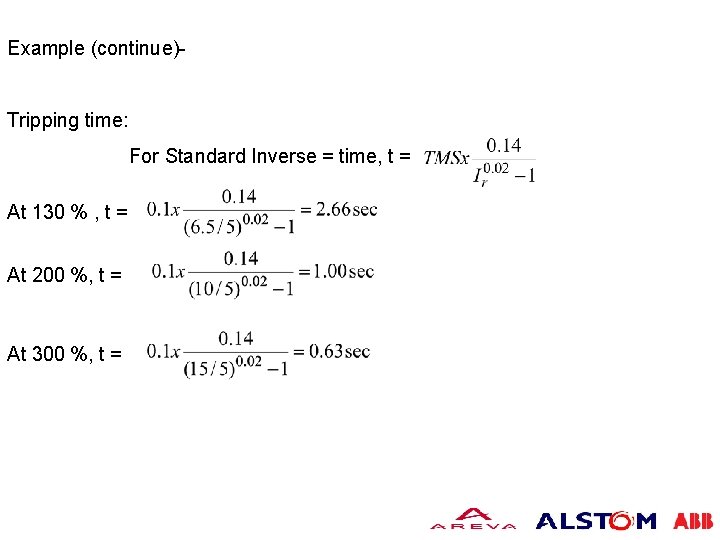
Example (continue)Tripping time: For Standard Inverse = time, t = At 130 % , t = At 200 %, t = At 300 %, t =
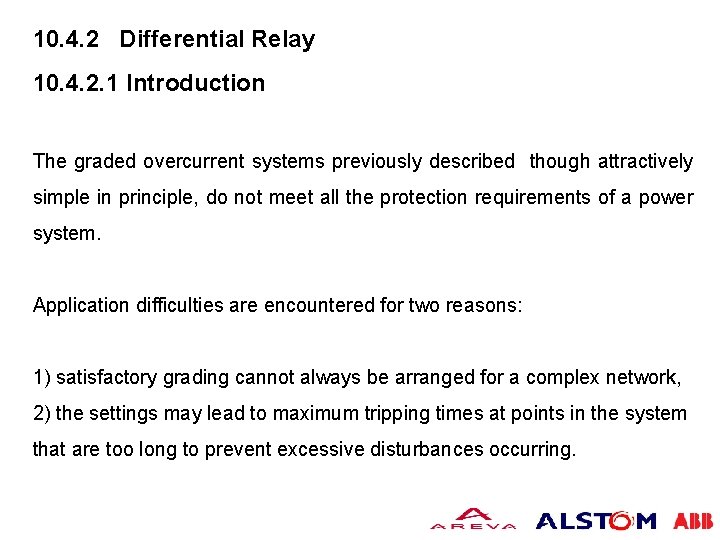
10. 4. 2 Differential Relay 10. 4. 2. 1 Introduction The graded overcurrent systems previously described though attractively simple in principle, do not meet all the protection requirements of a power system. Application difficulties are encountered for two reasons: 1) satisfactory grading cannot always be arranged for a complex network, 2) the settings may lead to maximum tripping times at points in the system that are too long to prevent excessive disturbances occurring.
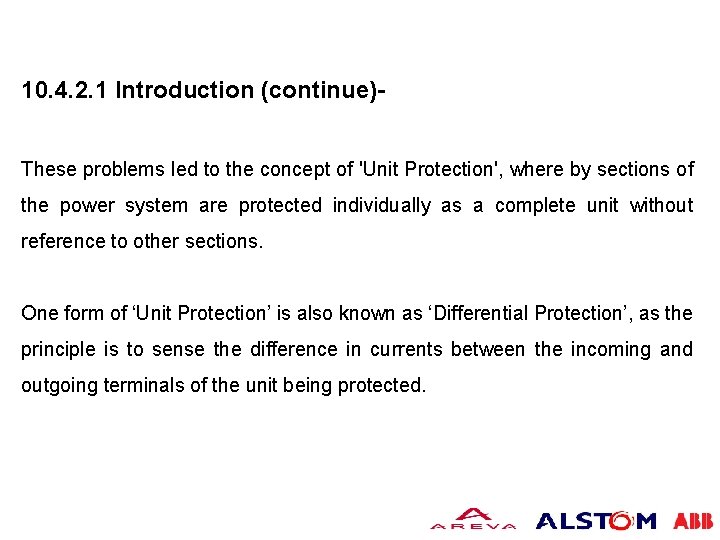
10. 4. 2. 1 Introduction (continue)These problems led to the concept of 'Unit Protection', where by sections of the power system are protected individually as a complete unit without reference to other sections. One form of ‘Unit Protection’ is also known as ‘Differential Protection’, as the principle is to sense the difference in currents between the incoming and outgoing terminals of the unit being protected.
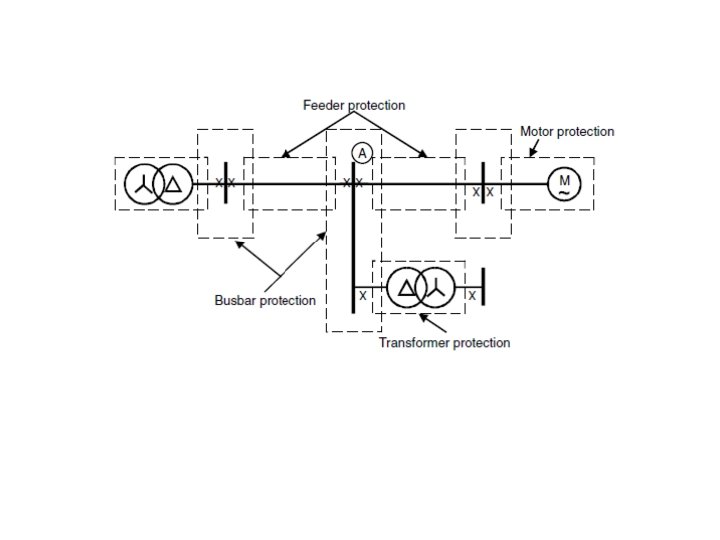
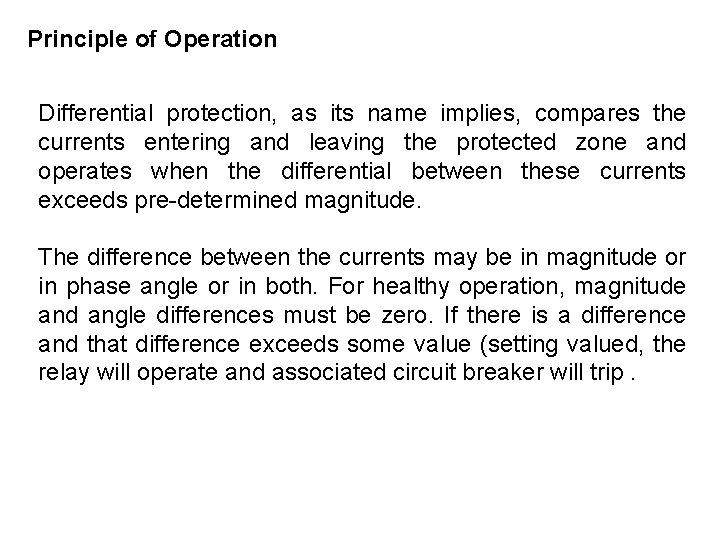
Principle of Operation Differential protection, as its name implies, compares the currents entering and leaving the protected zone and operates when the differential between these currents exceeds pre-determined magnitude. The difference between the currents may be in magnitude or in phase angle or in both. For healthy operation, magnitude and angle differences must be zero. If there is a difference and that difference exceeds some value (setting valued, the relay will operate and associated circuit breaker will trip.
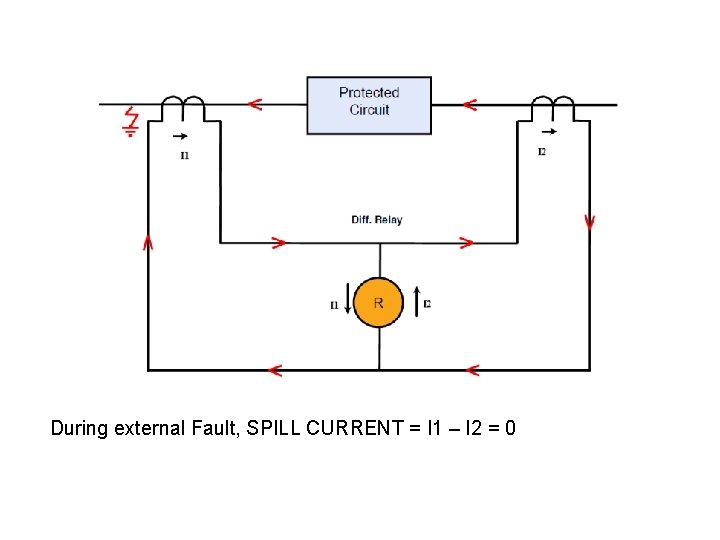
During external Fault, SPILL CURRENT = I 1 – I 2 = 0
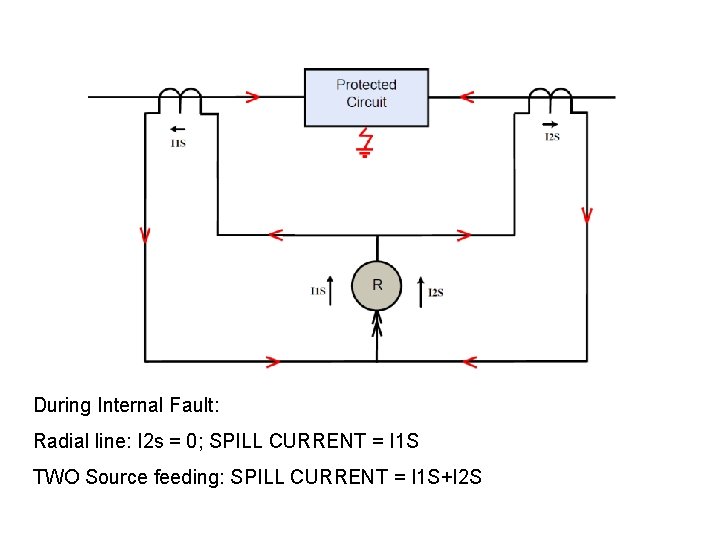
During Internal Fault: Radial line: I 2 s = 0; SPILL CURRENT = I 1 S TWO Source feeding: SPILL CURRENT = I 1 S+I 2 S
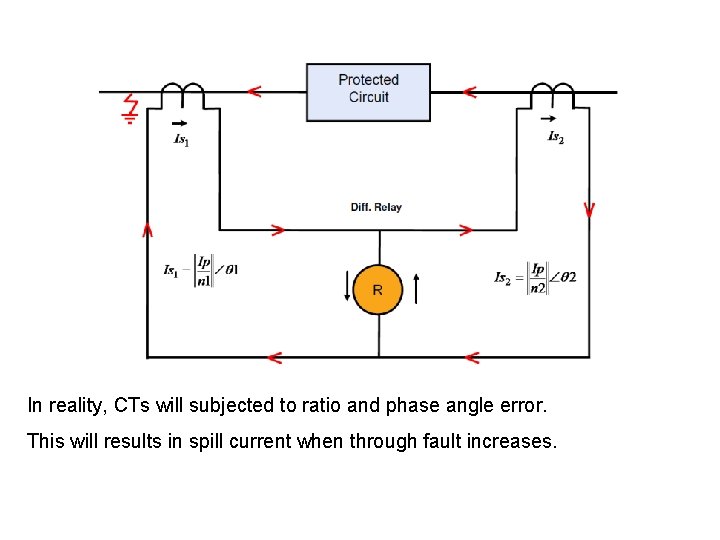
In reality, CTs will subjected to ratio and phase angle error. This will results in spill current when through fault increases.
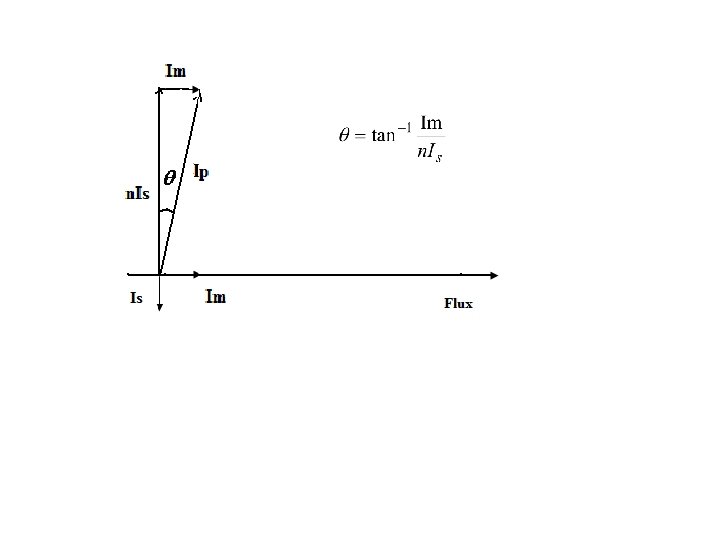
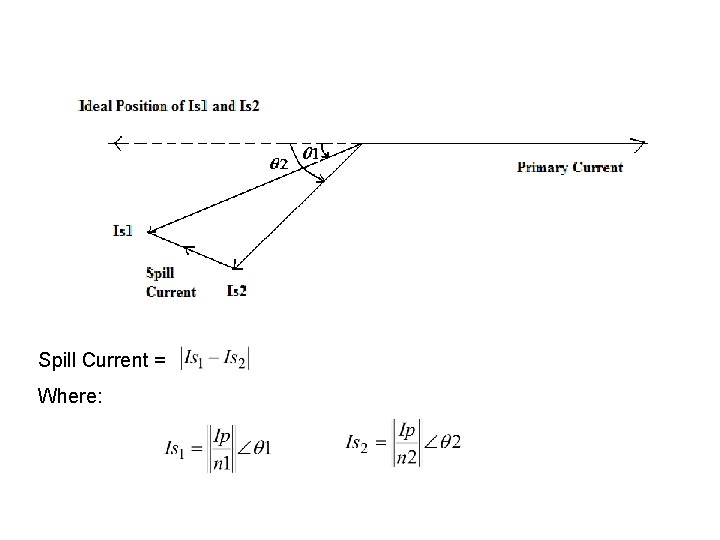
Spill Current = Where:
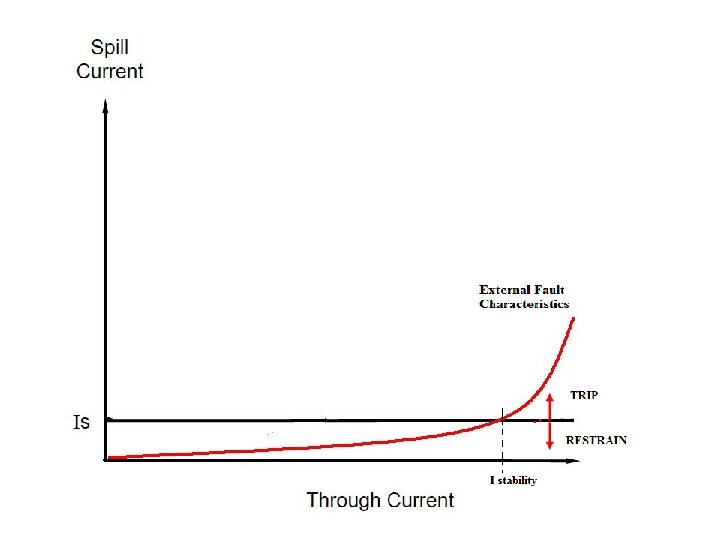
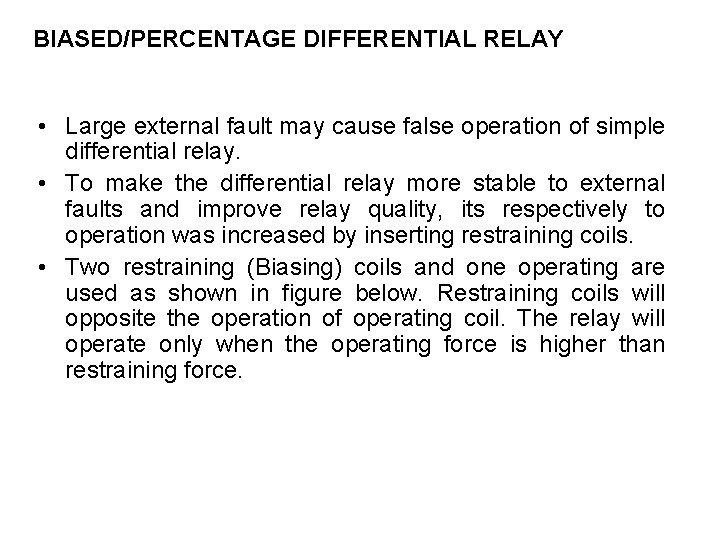
BIASED/PERCENTAGE DIFFERENTIAL RELAY • Large external fault may cause false operation of simple differential relay. • To make the differential relay more stable to external faults and improve relay quality, its respectively to operation was increased by inserting restraining coils. • Two restraining (Biasing) coils and one operating are used as shown in figure below. Restraining coils will opposite the operation of operating coil. The relay will operate only when the operating force is higher than restraining force.
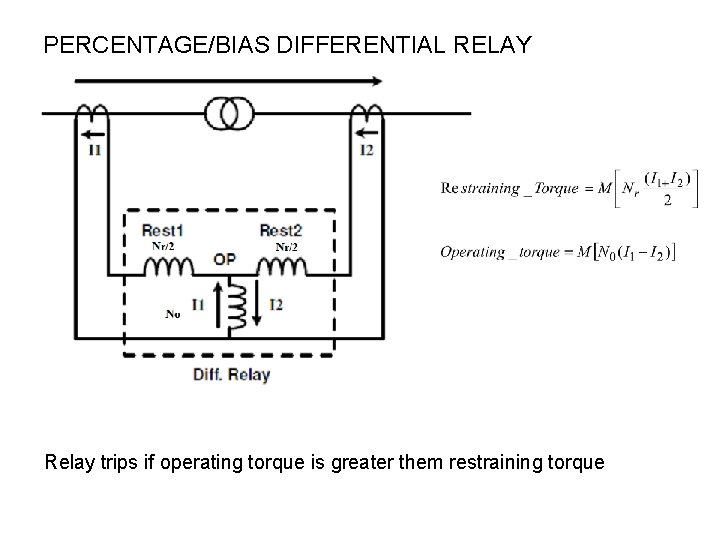
PERCENTAGE/BIAS DIFFERENTIAL RELAY Relay trips if operating torque is greater them restraining torque
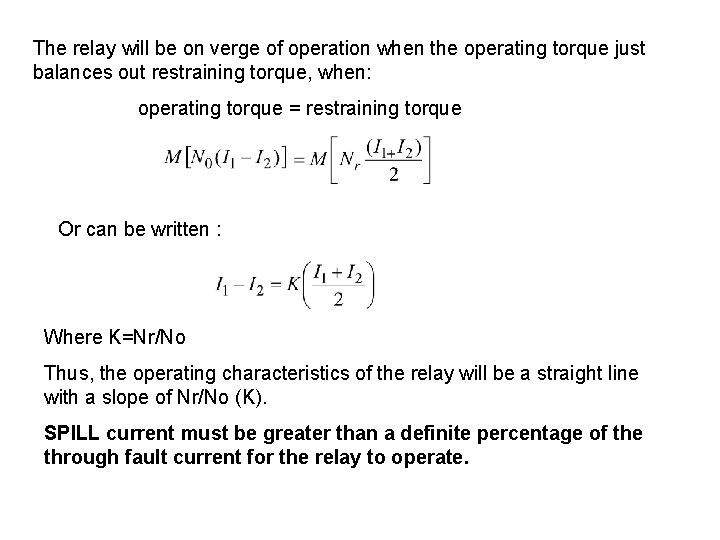
The relay will be on verge of operation when the operating torque just balances out restraining torque, when: operating torque = restraining torque Or can be written : Where K=Nr/No Thus, the operating characteristics of the relay will be a straight line with a slope of Nr/No (K). SPILL current must be greater than a definite percentage of the through fault current for the relay to operate.
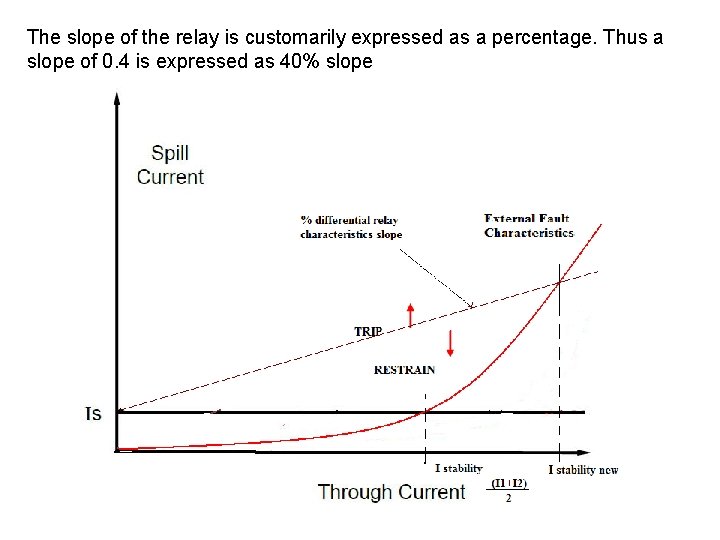
The slope of the relay is customarily expressed as a percentage. Thus a slope of 0. 4 is expressed as 40% slope
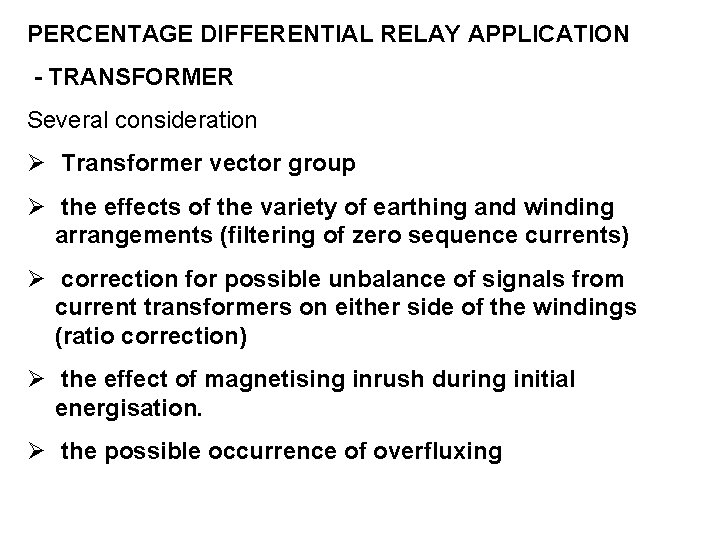
PERCENTAGE DIFFERENTIAL RELAY APPLICATION - TRANSFORMER Several consideration Ø Transformer vector group Ø the effects of the variety of earthing and winding arrangements (filtering of zero sequence currents) Ø correction for possible unbalance of signals from current transformers on either side of the windings (ratio correction) Ø the effect of magnetising inrush during initial energisation. Ø the possible occurrence of overfluxing
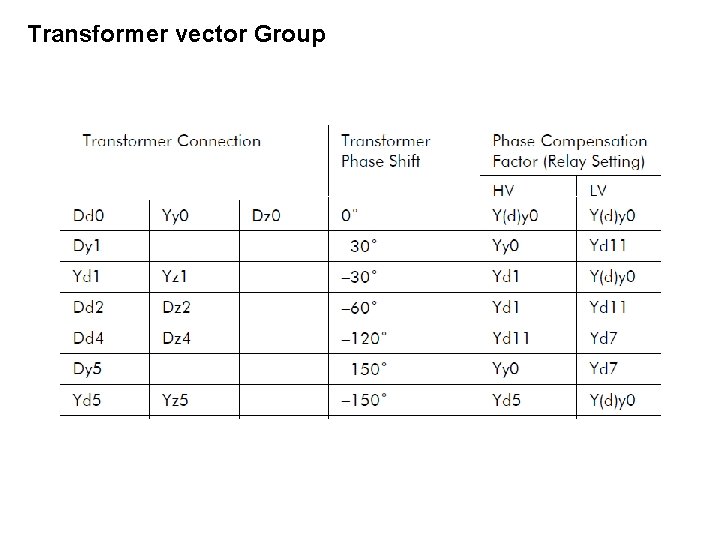
Transformer vector Group
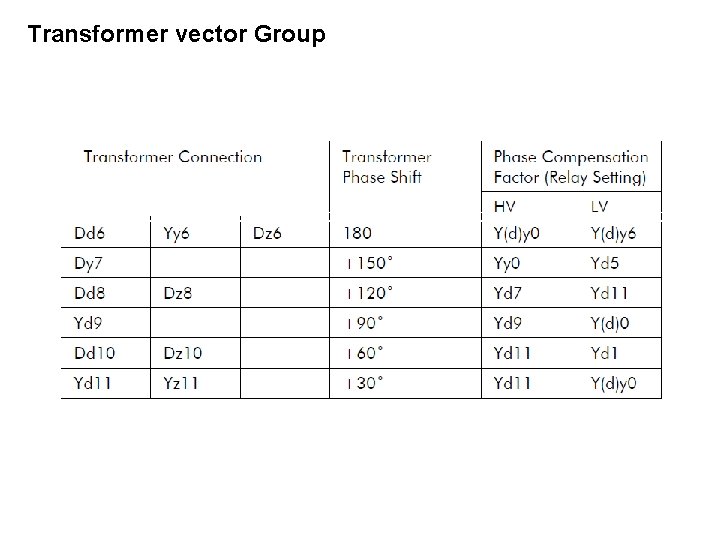
Transformer vector Group
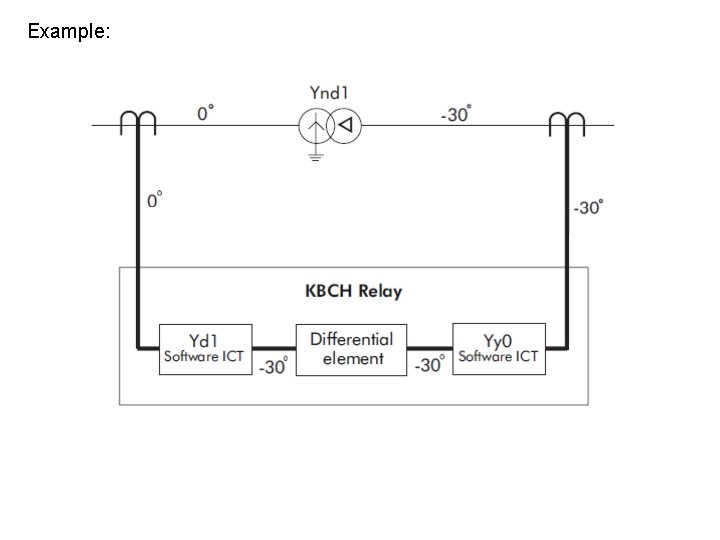
Example:
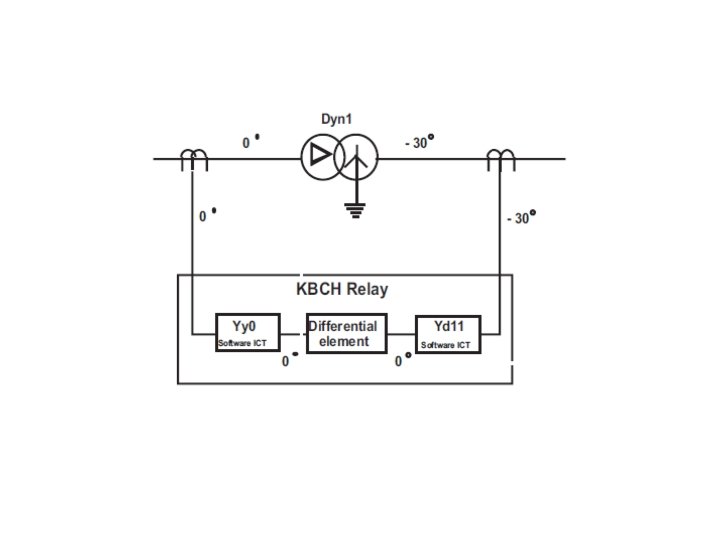
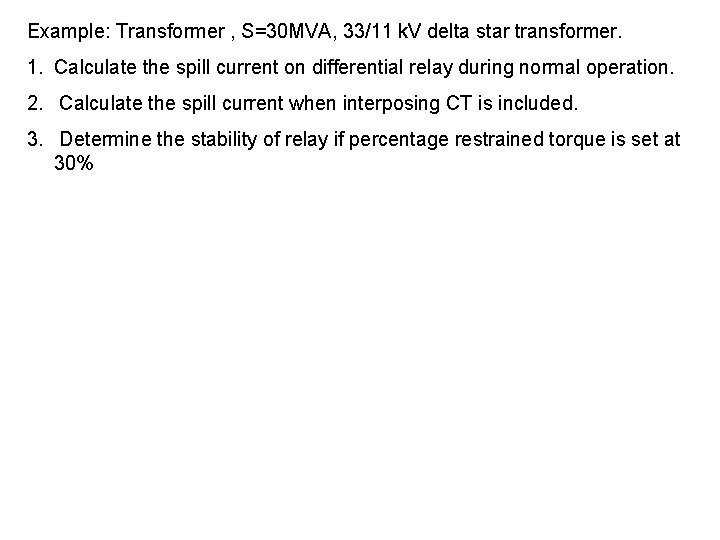
Example: Transformer , S=30 MVA, 33/11 k. V delta star transformer. 1. Calculate the spill current on differential relay during normal operation. 2. Calculate the spill current when interposing CT is included. 3. Determine the stability of relay if percentage restrained torque is set at 30%
Pep 3103
Power system commissioning
Det beskrivende og det komplekse kulturbegreb
Stenpelare och gud
Integrated commissioning and progress system
Hmsweb
Central commissioning facility research management system
Power trianlge
Preventive and predictive maintenance of hydro power plant
Mao maintenance of power
Commissioning cycle
Amedd commissioning programs
Commissioning cycle
Ecs commissioning
Fortis commissioning sheet
Timeline jwst
Commissioning cycle
Value based commissioning
Vacuum systems commissioning
Dominik sikora
Dr nicola burbidge
Commissioning
Aabc commissioning group
Pod point lidl
Croydon clinical commissioning group
Tpc online tracking
Power angle curve in power system stability
System maintenance and review
System maintenance must be performed to
Practice assessor and practice supervisor
Indføleligt
Hvor i det periodiske system står atomer med 5 skaller?
Det periodiske system hovedgrupper
Pensum for 9 klasse
Solar power satellites and microwave power transmission
Actual power and potential power
Dispersive power of a grating
Ns5 maintenance system
File system maintenance
Fleet maintenance management system best practices
Spmig database
Ns5 maintenance system
Colt international uk
File system maintenance
Explain system maintenance
Maintenance decision support system
Truth maintenance system
Is earth an open or closed system
Circularory system
Importance of recording and reporting in nursing
Flex28024a
Power of a power property
General power rule
Powerbi in powerpoint
Power delivered vs power absorbed
Power system dynamics and stability lecture notes
Power system dynamics and stability lecture notes