FACULTY Mr Lee Alves Vice President Simpler Consulting
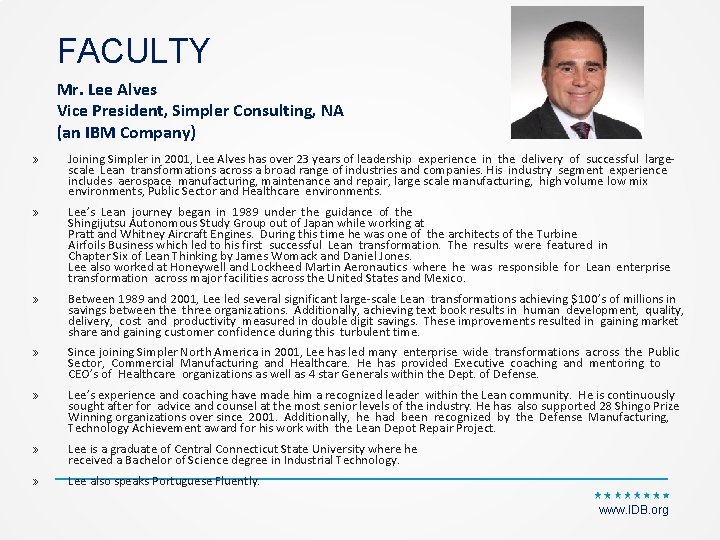
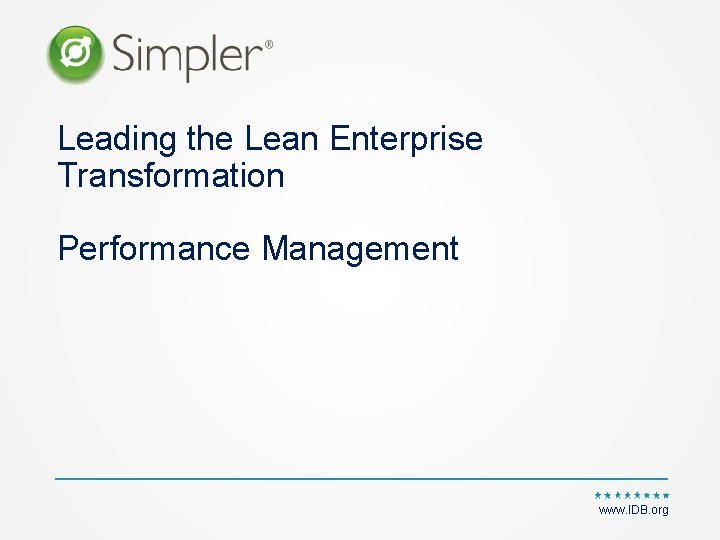

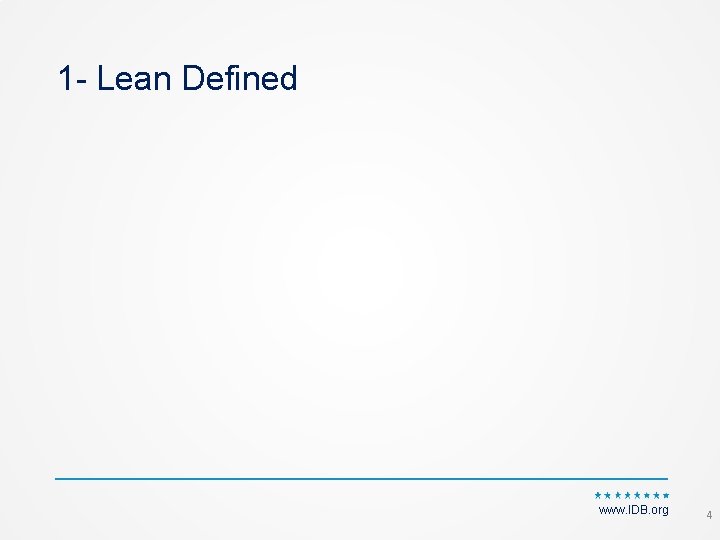
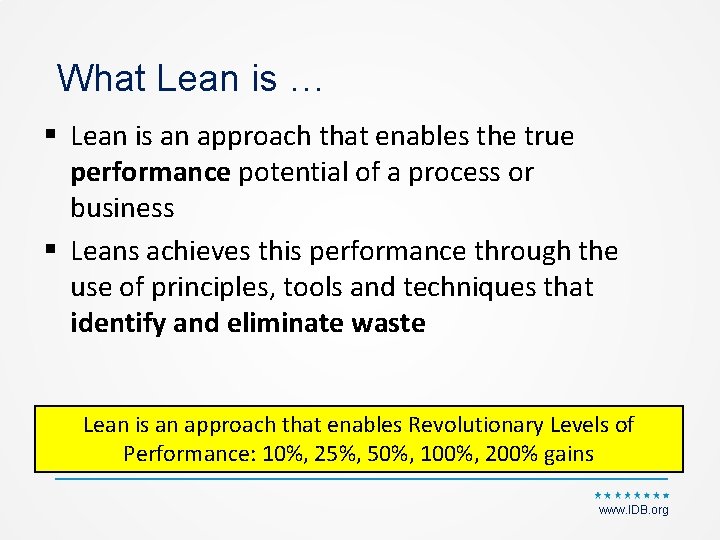
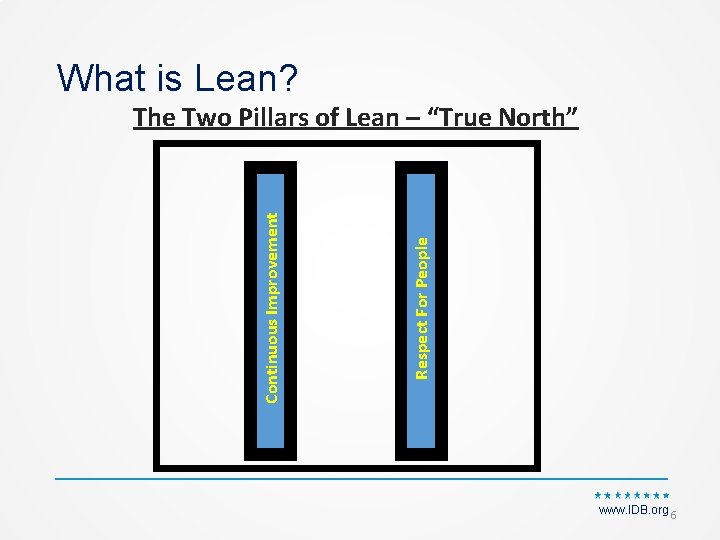
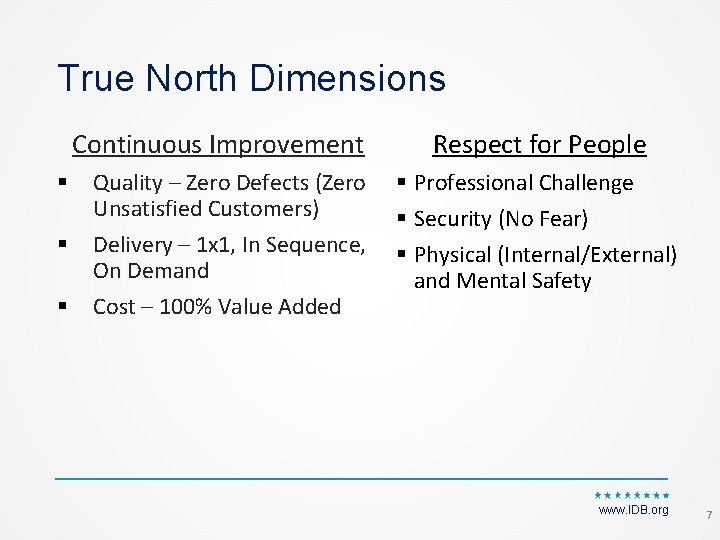
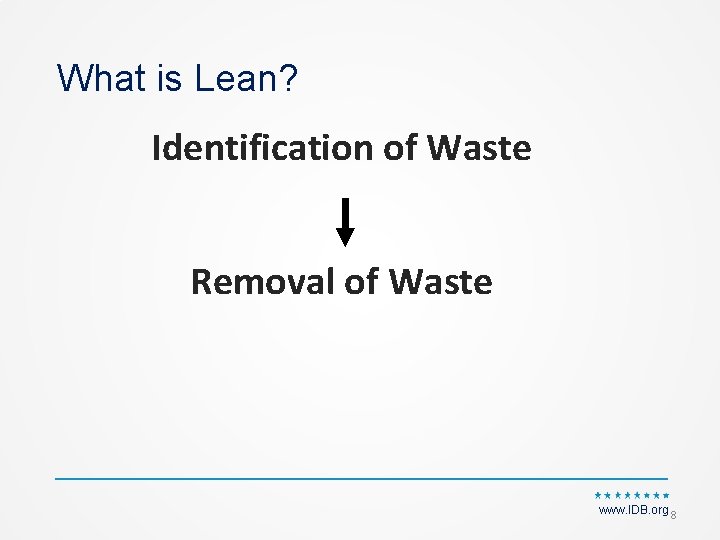
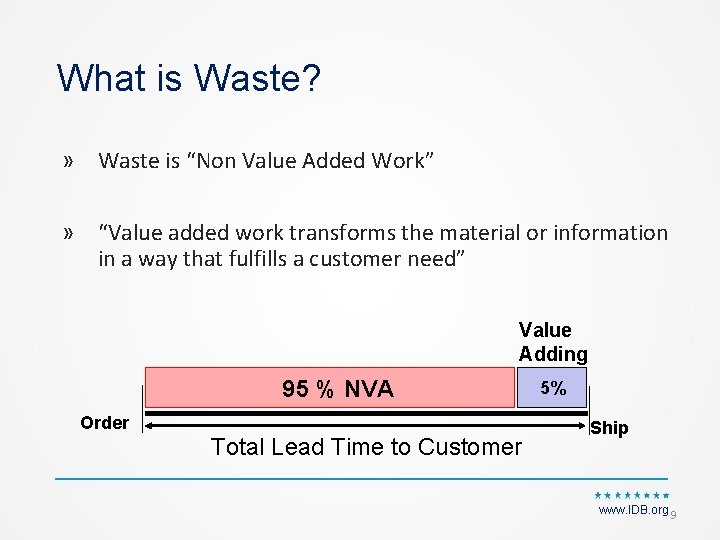
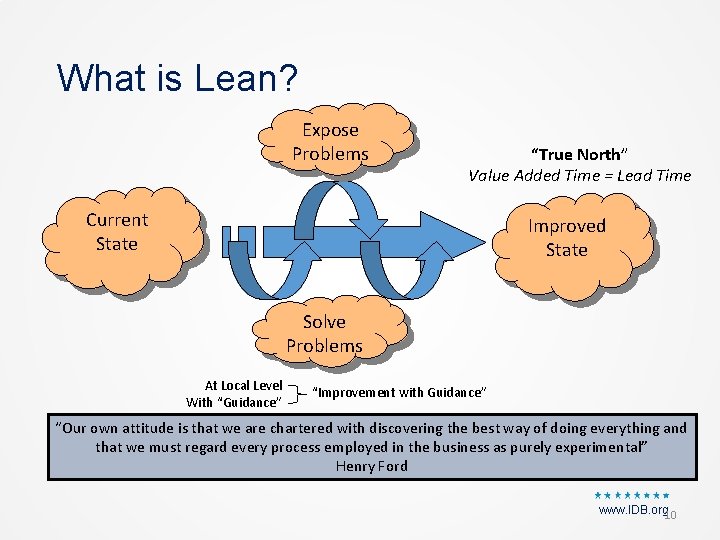
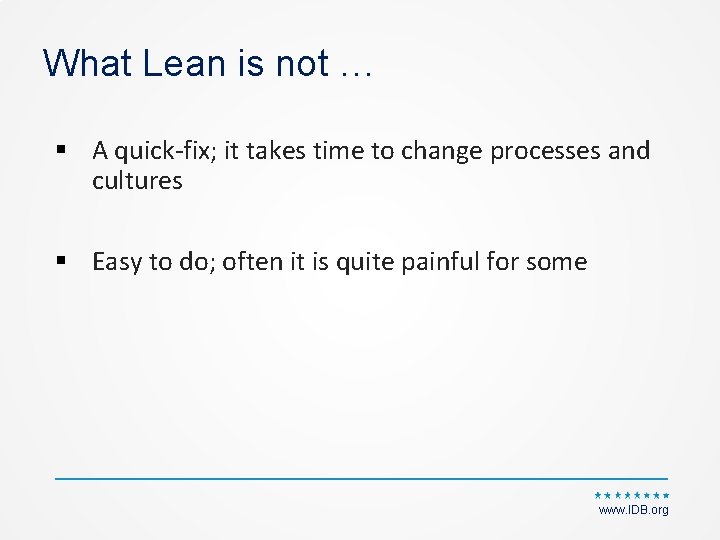
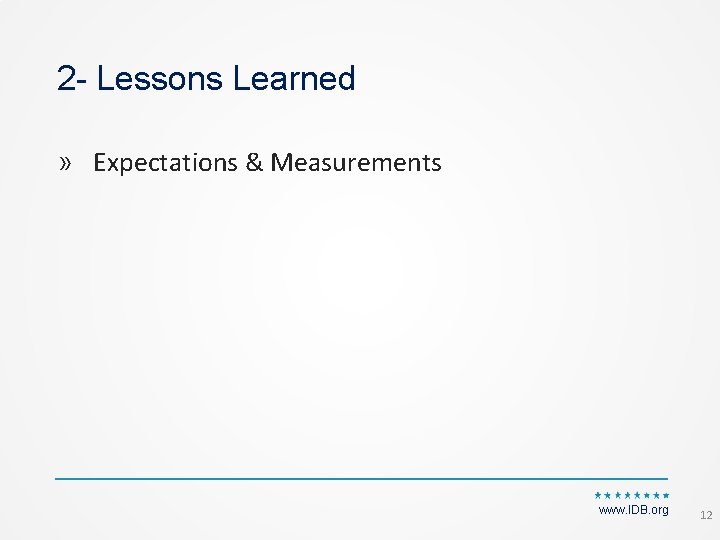
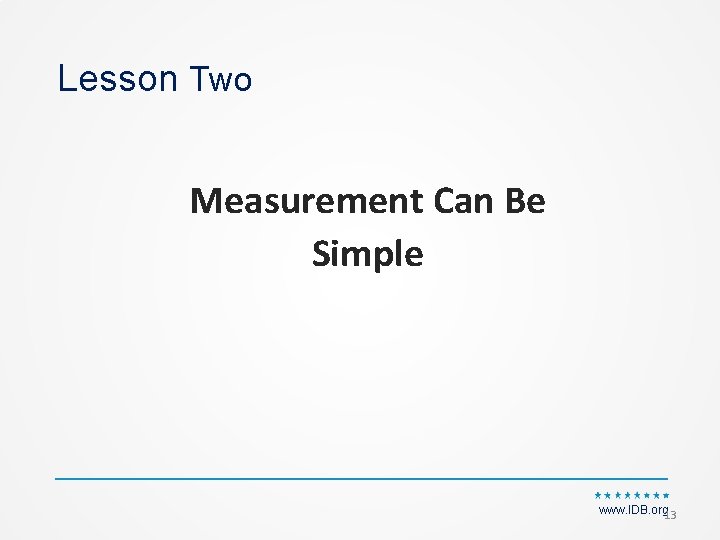
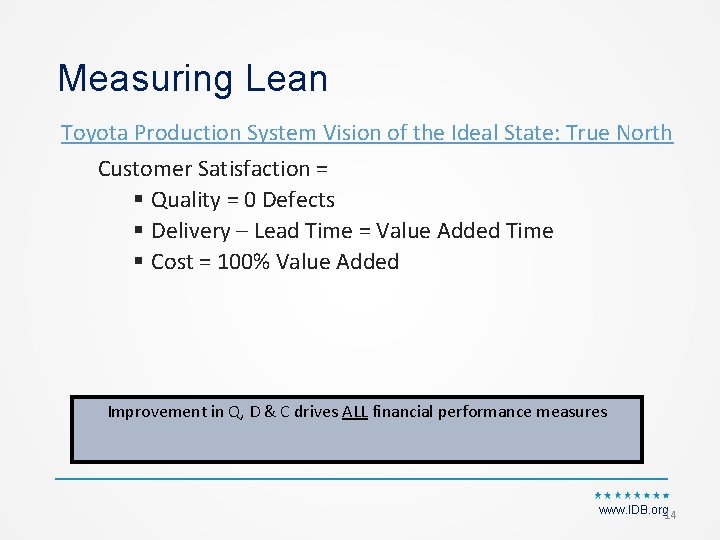
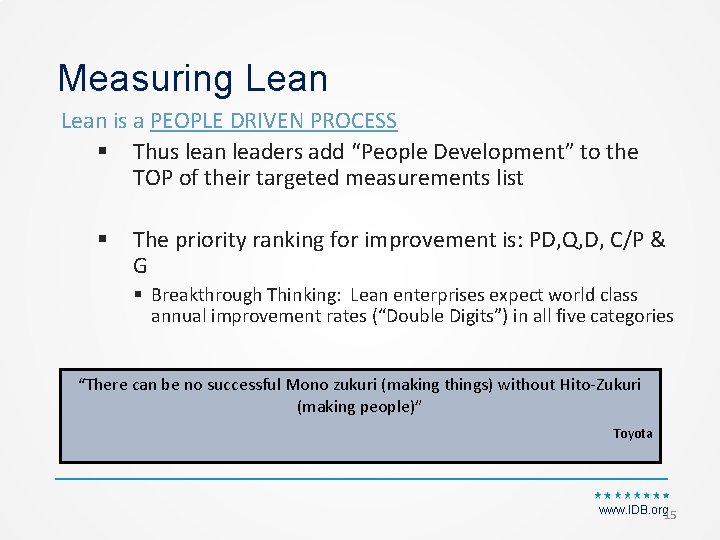
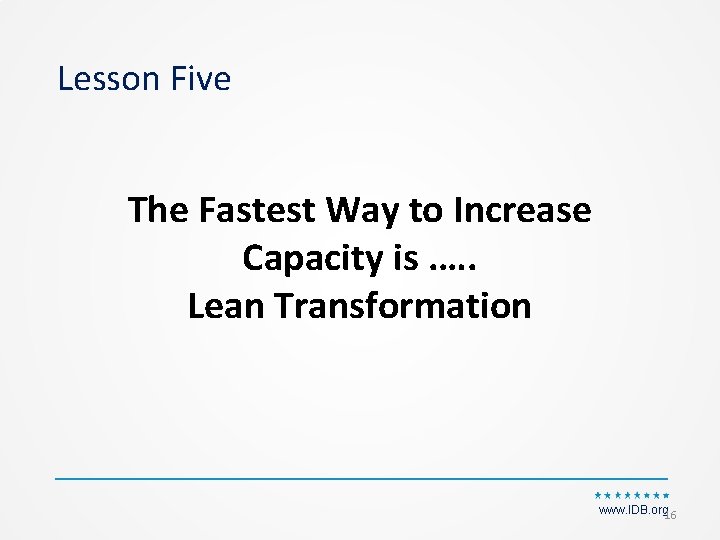
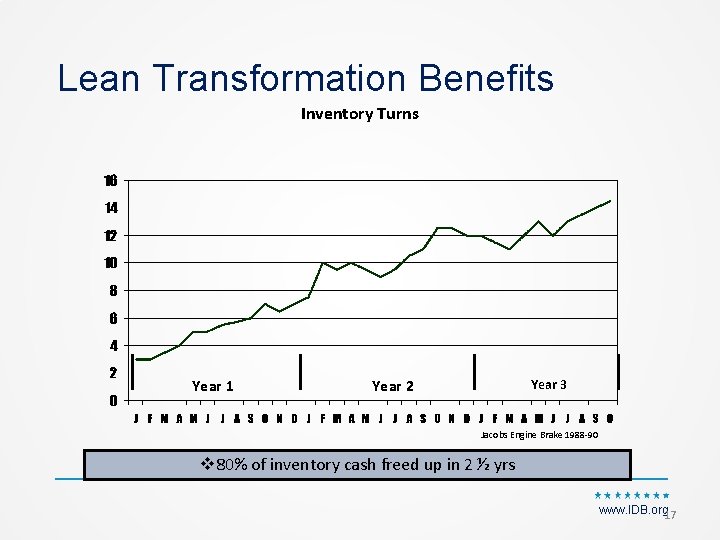
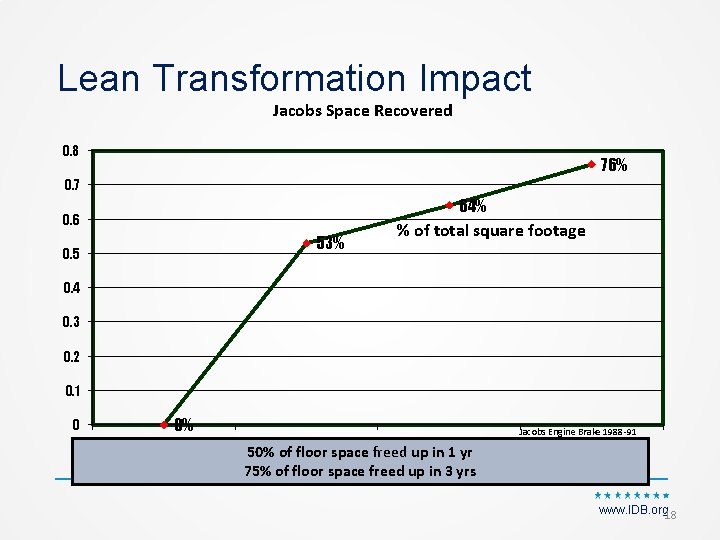
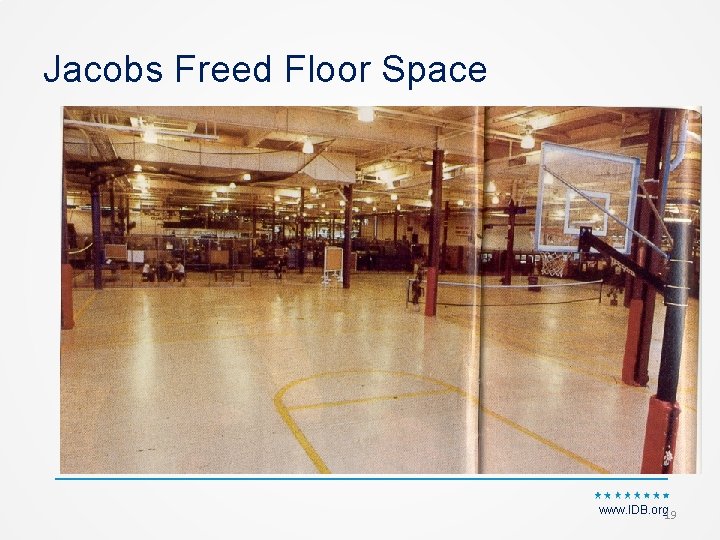
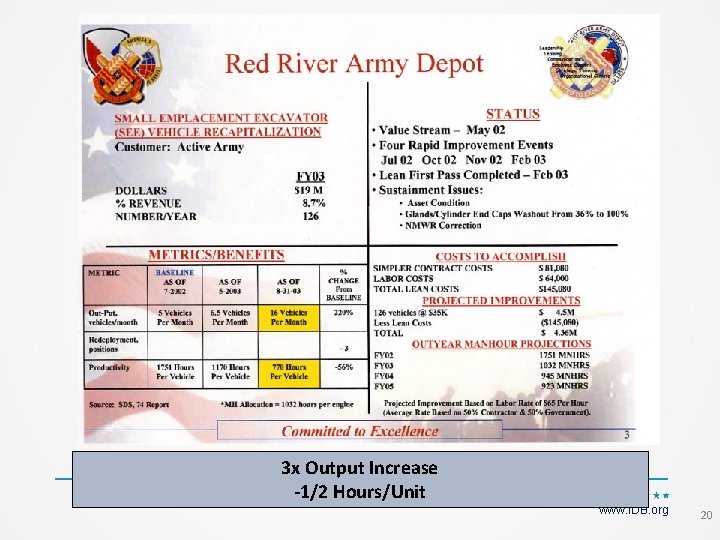
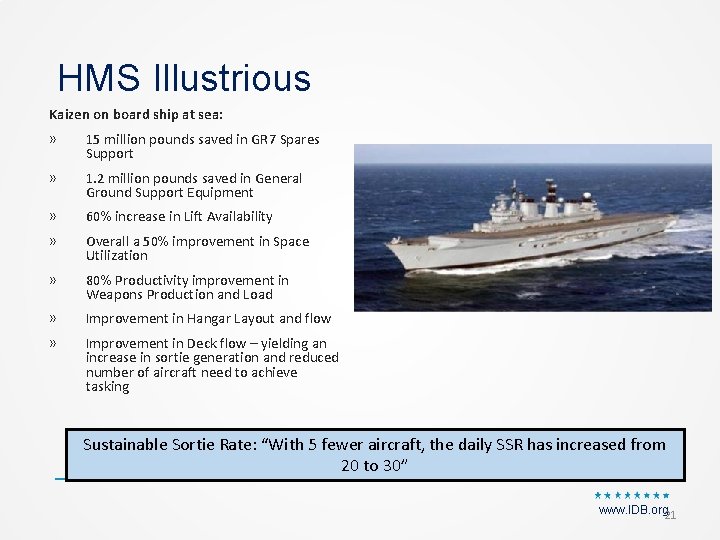
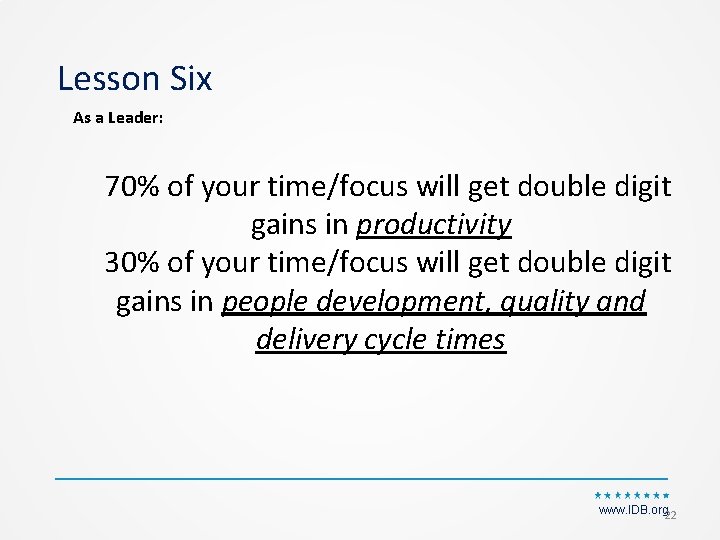
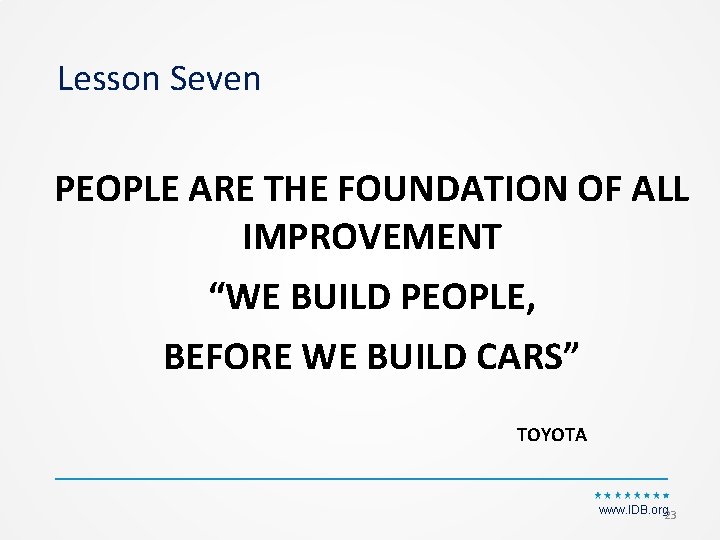
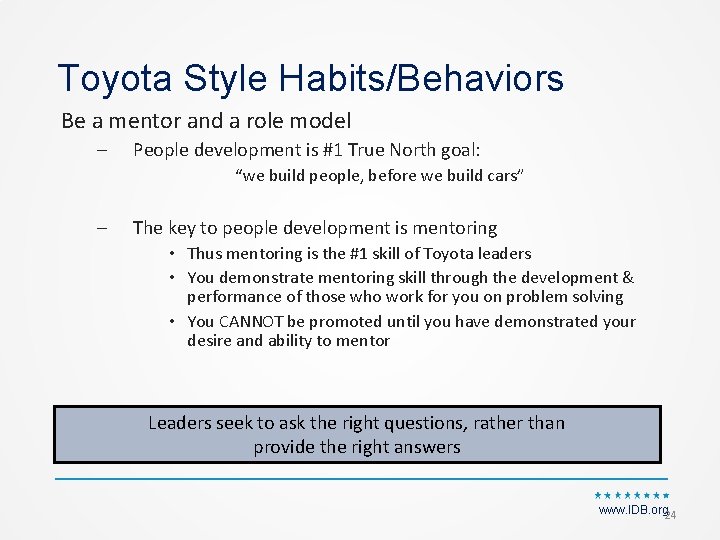
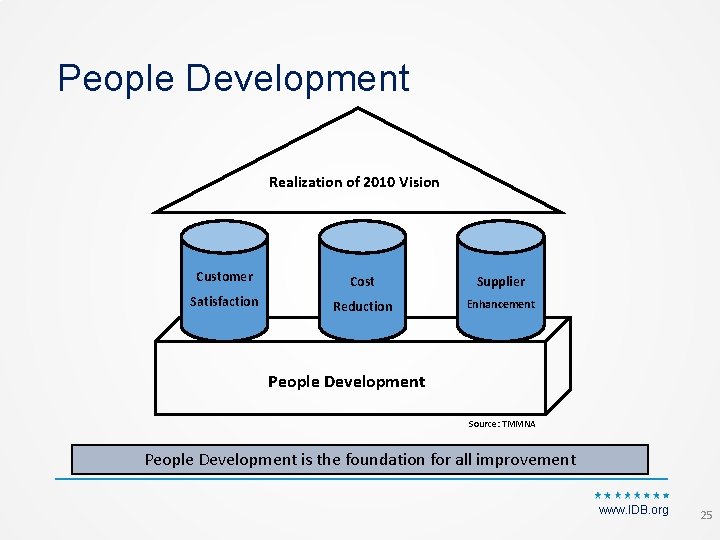
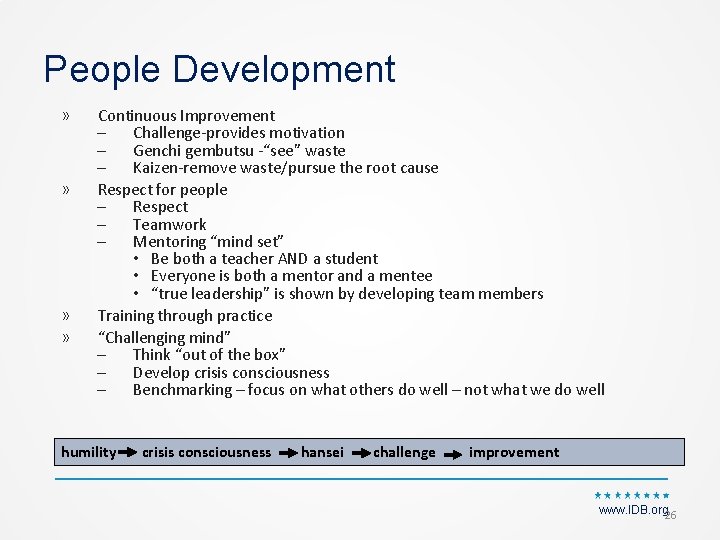
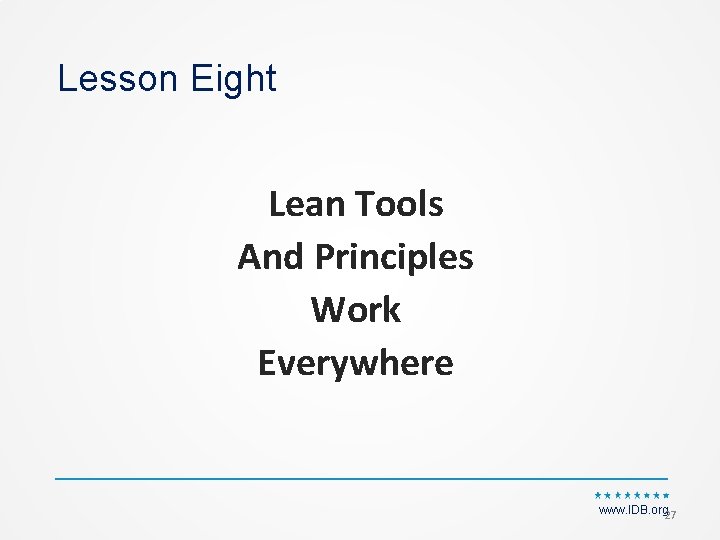
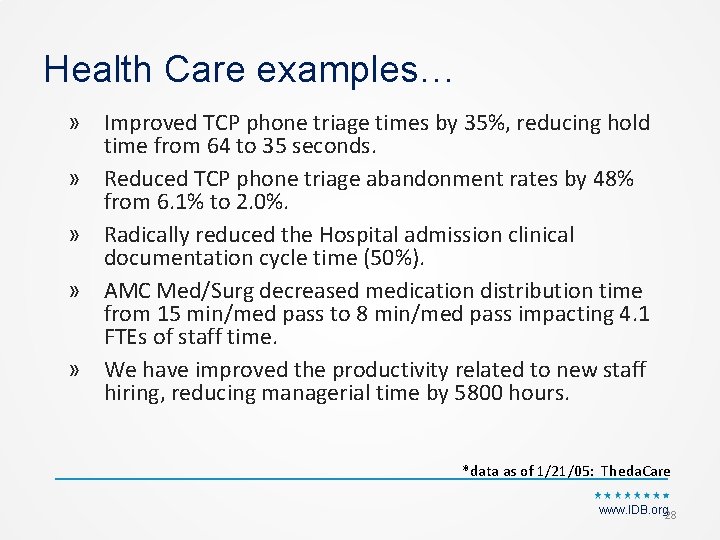
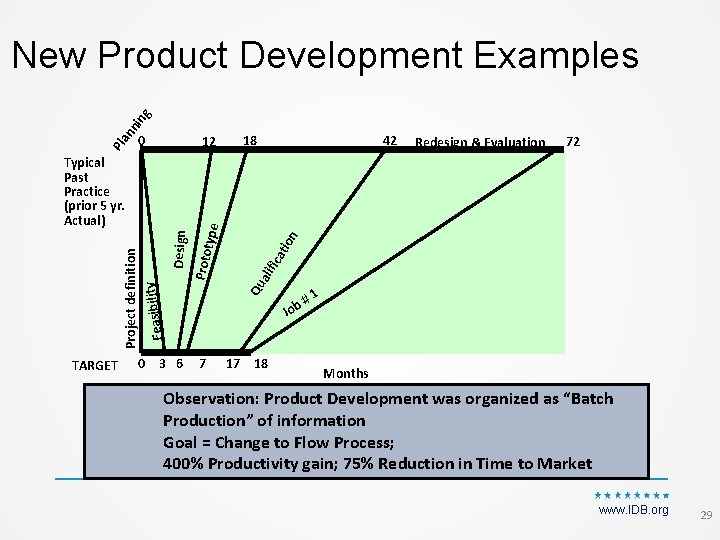
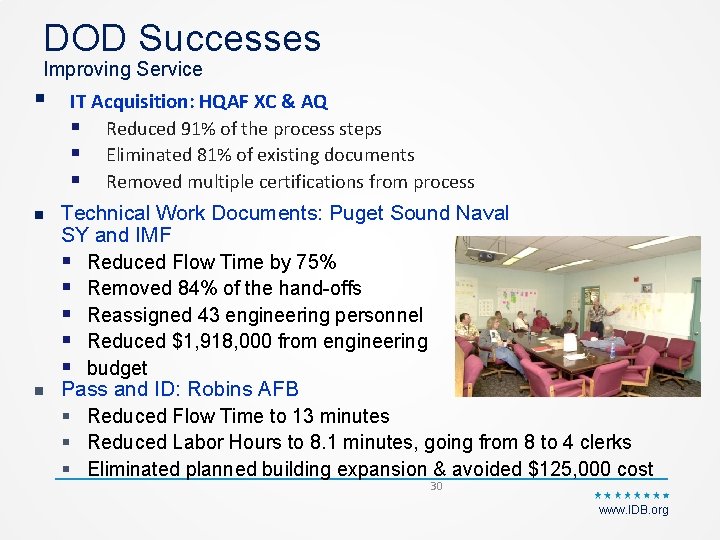
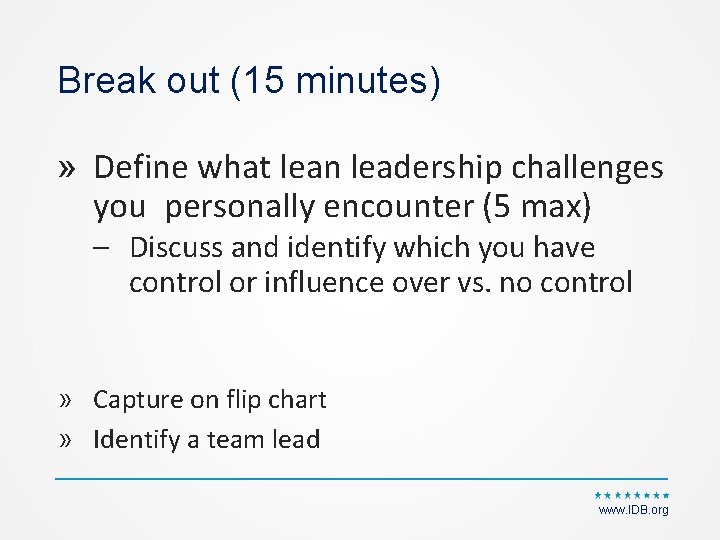
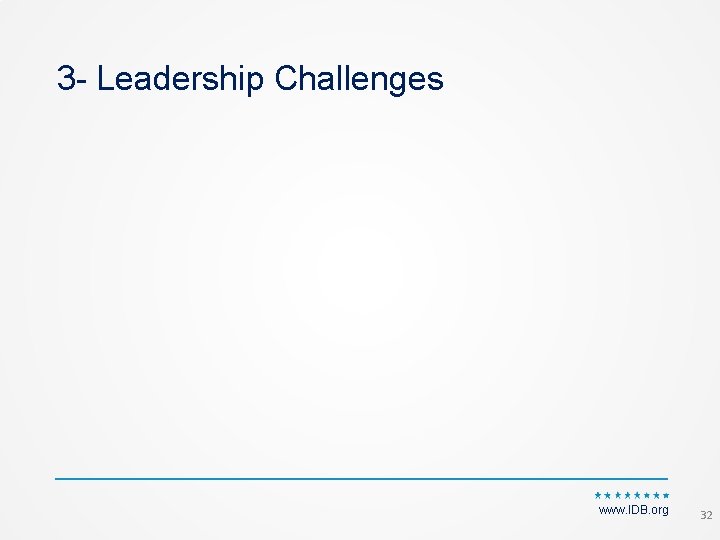
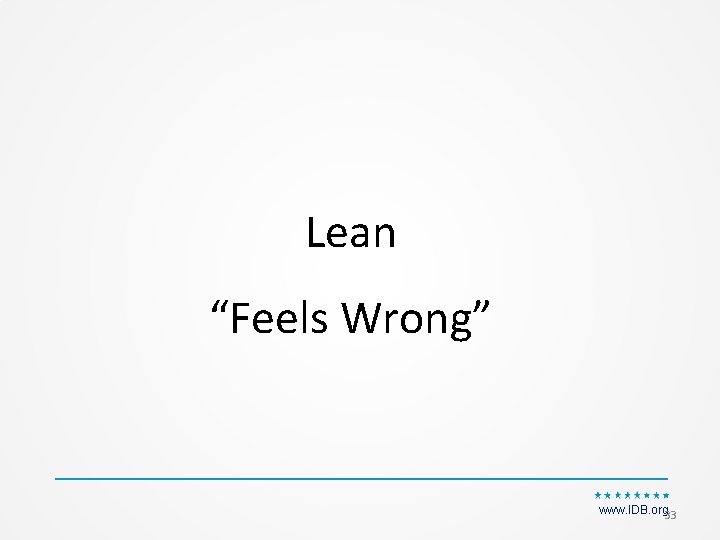
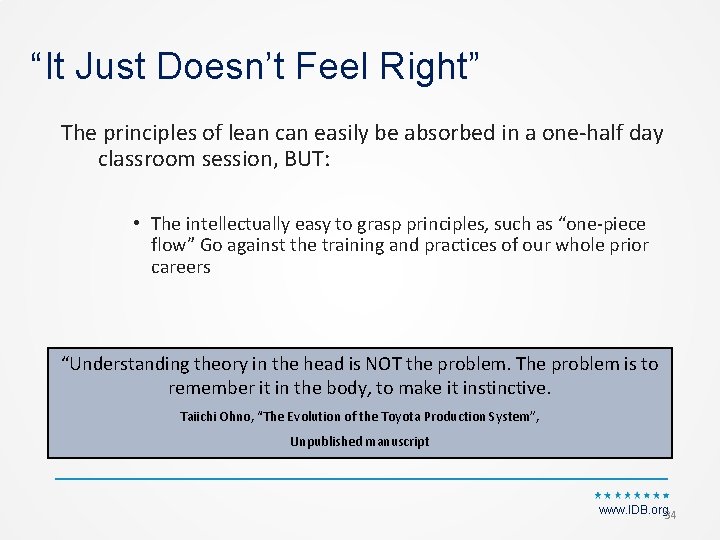
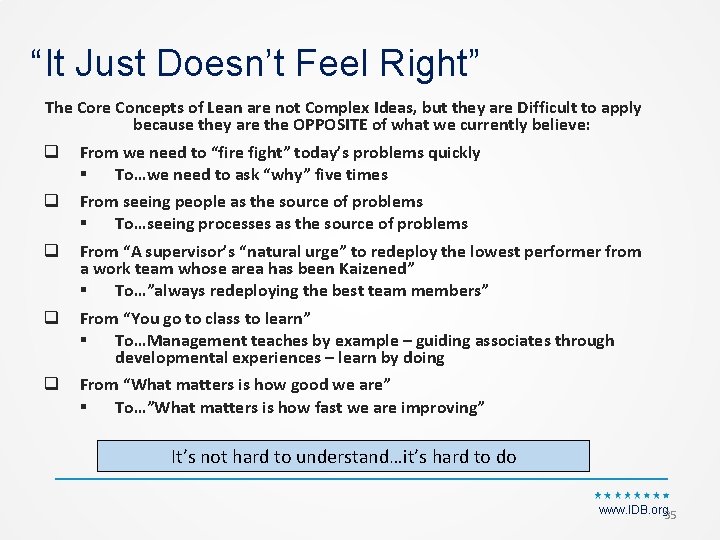
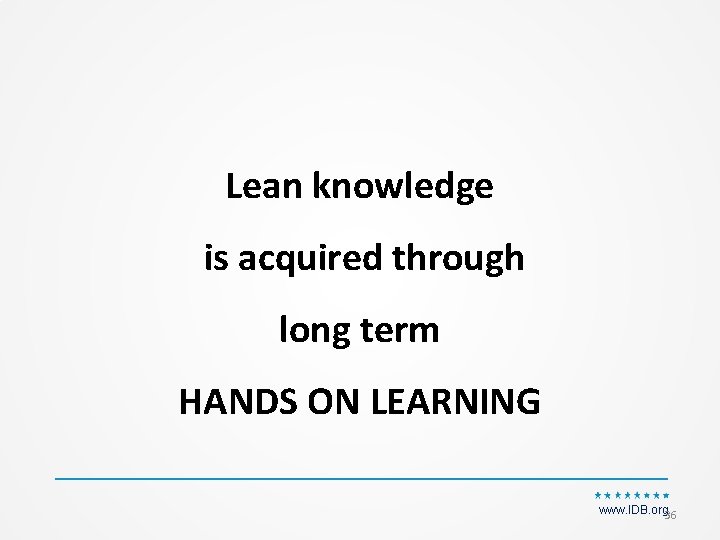
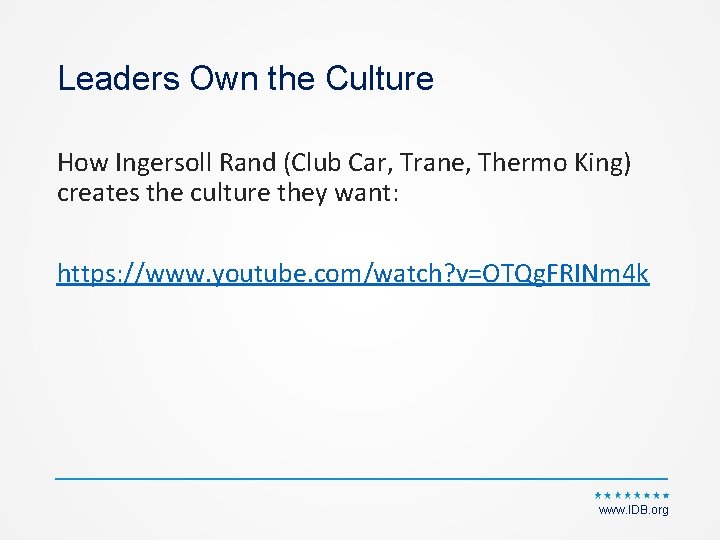
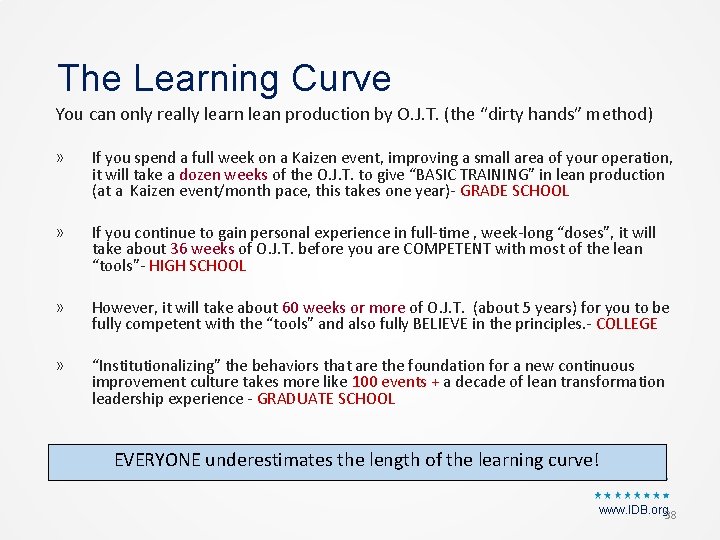
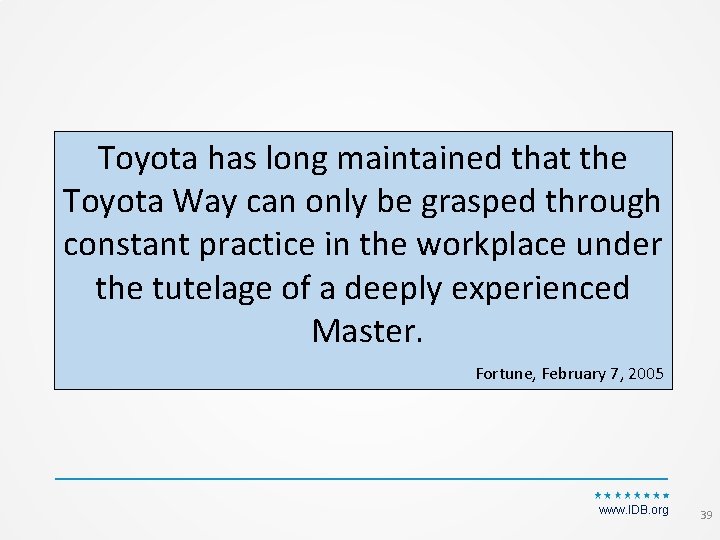
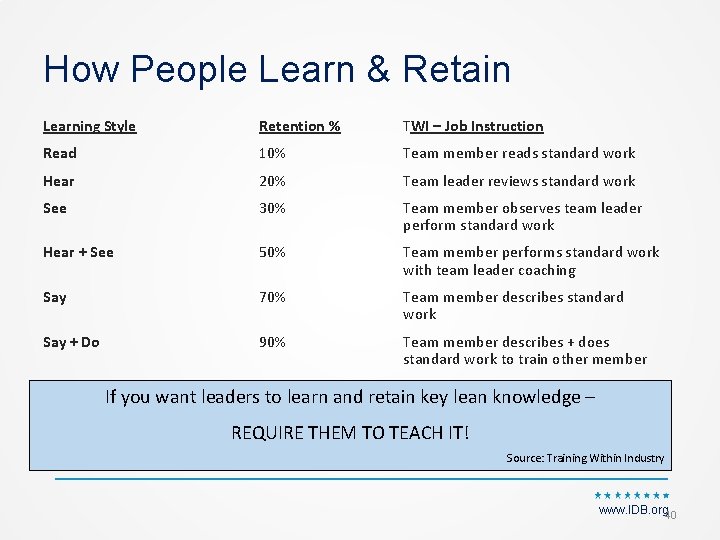
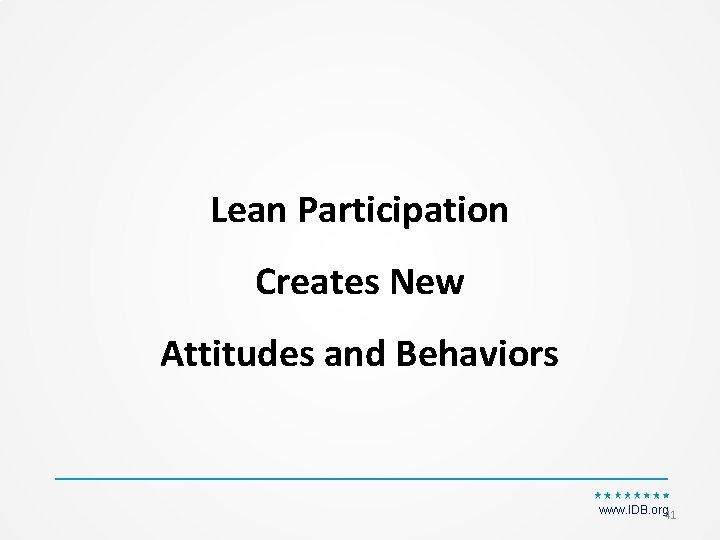
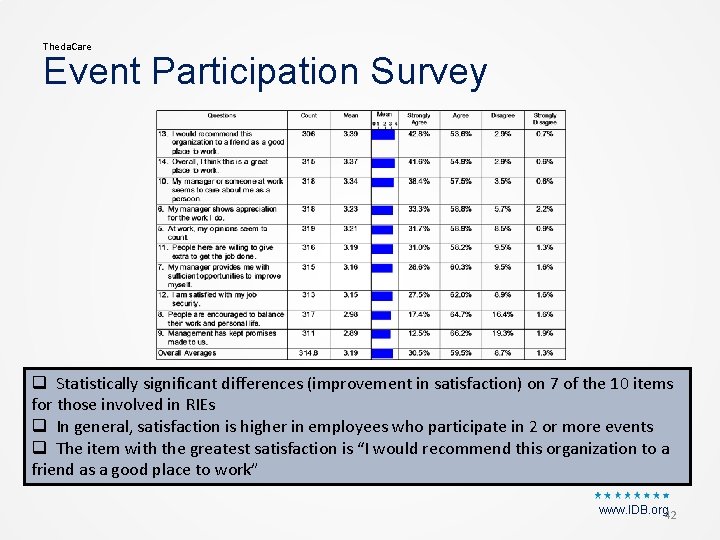
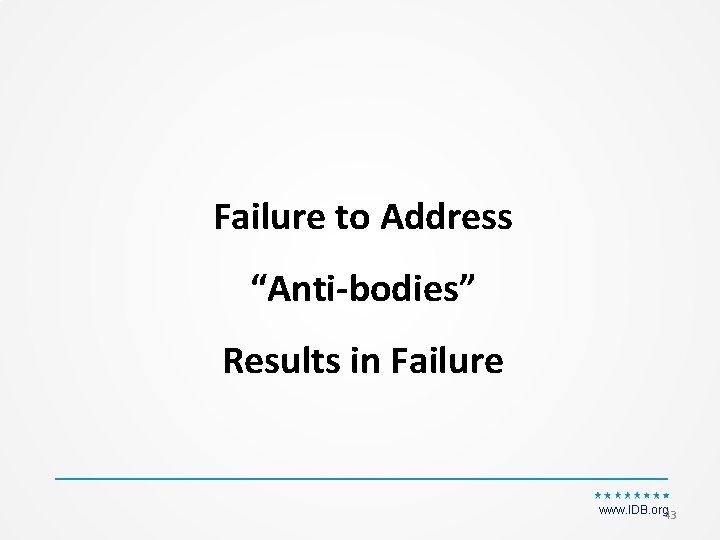
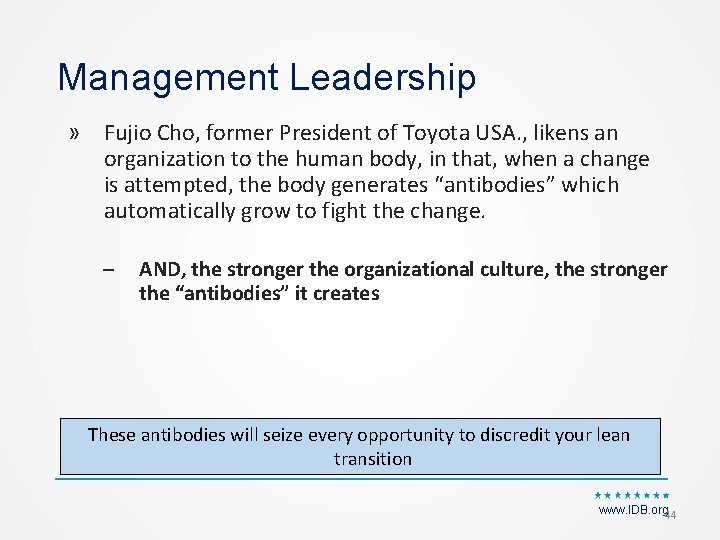
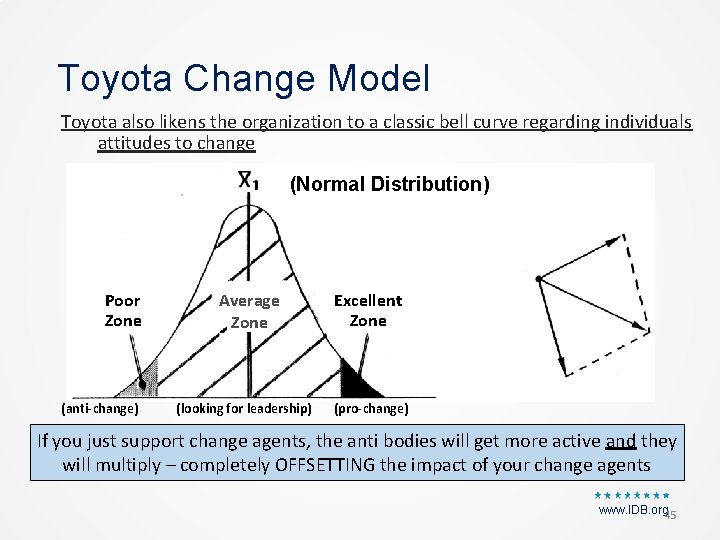
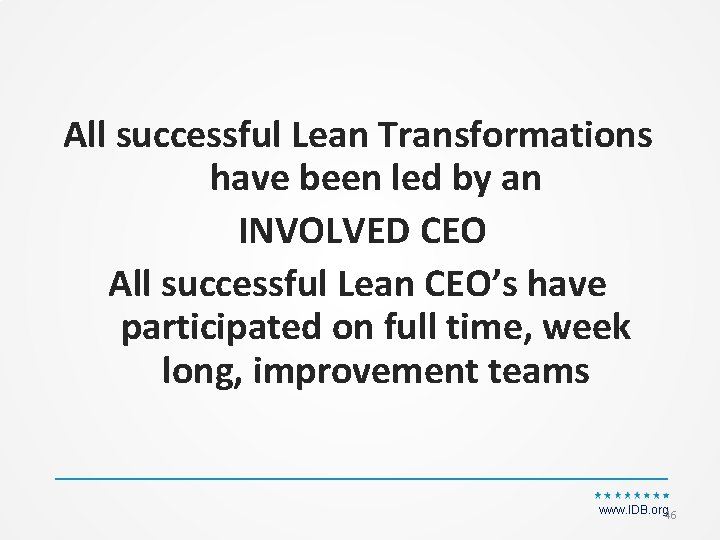
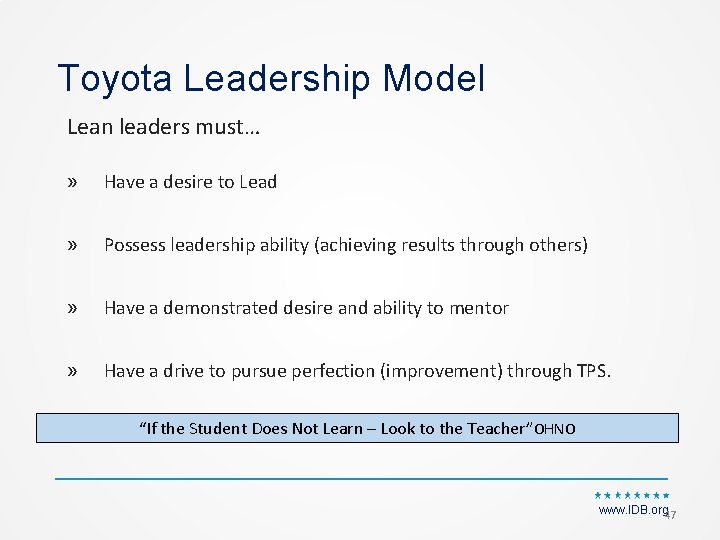
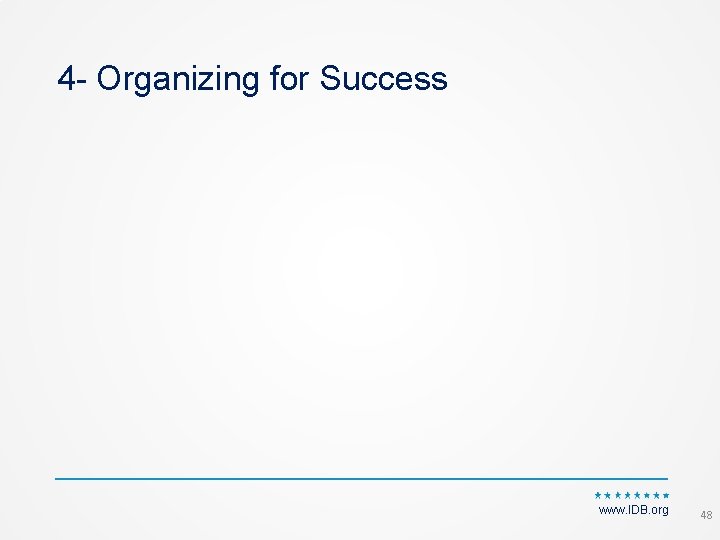
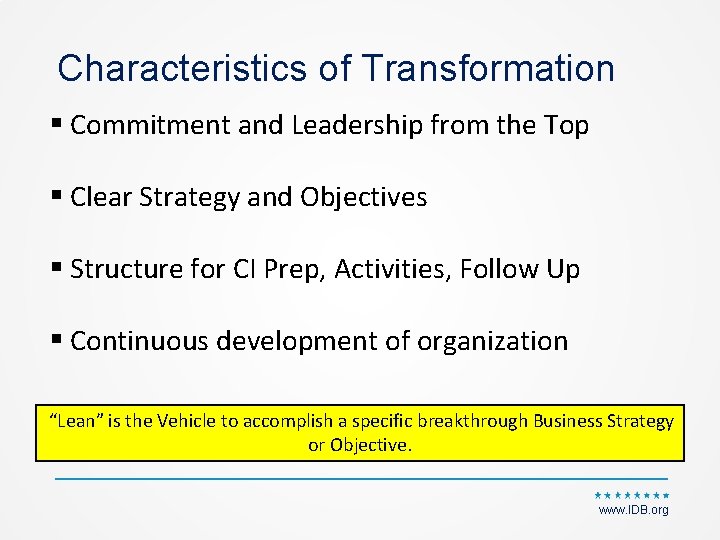
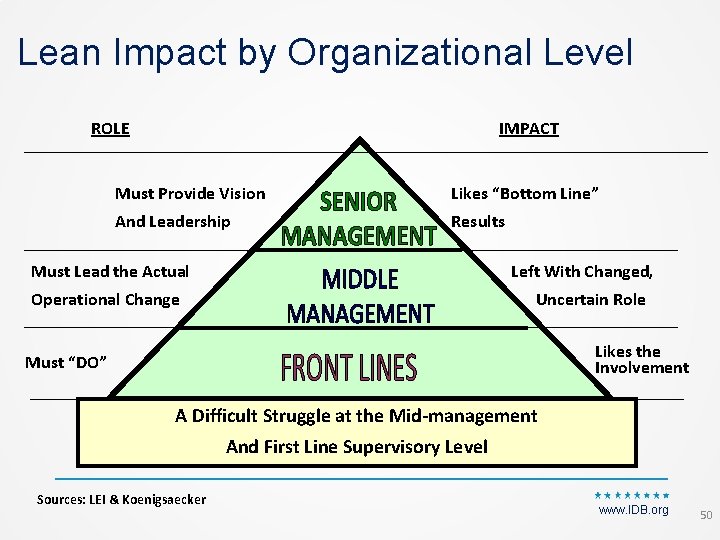
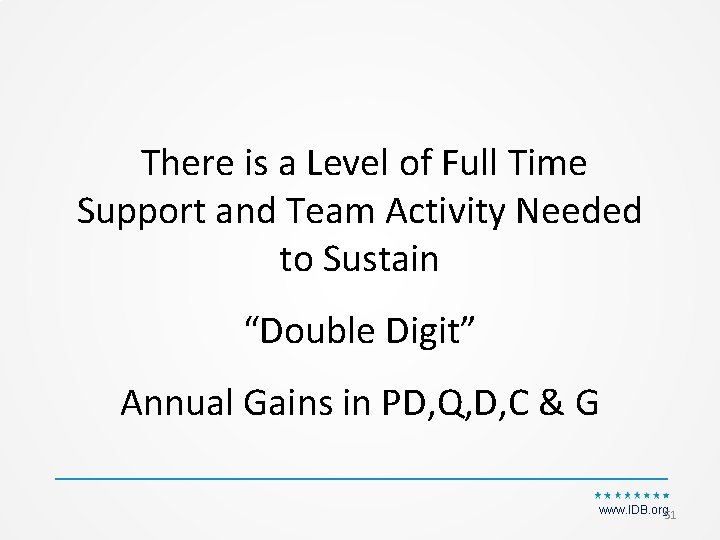
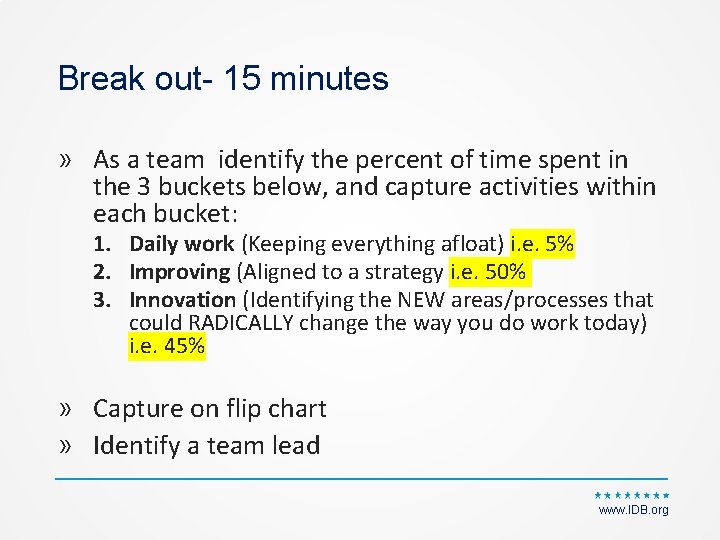
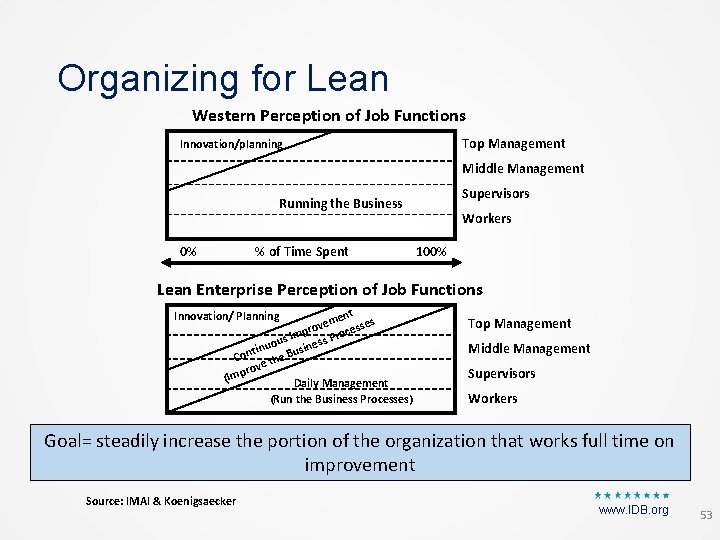
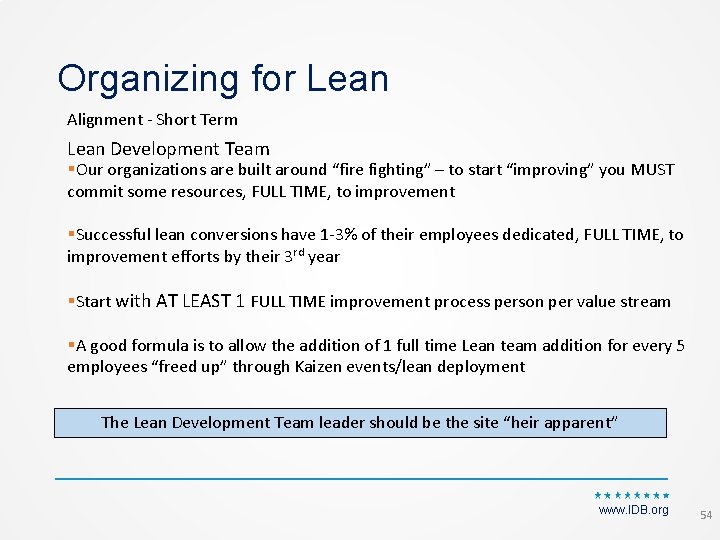
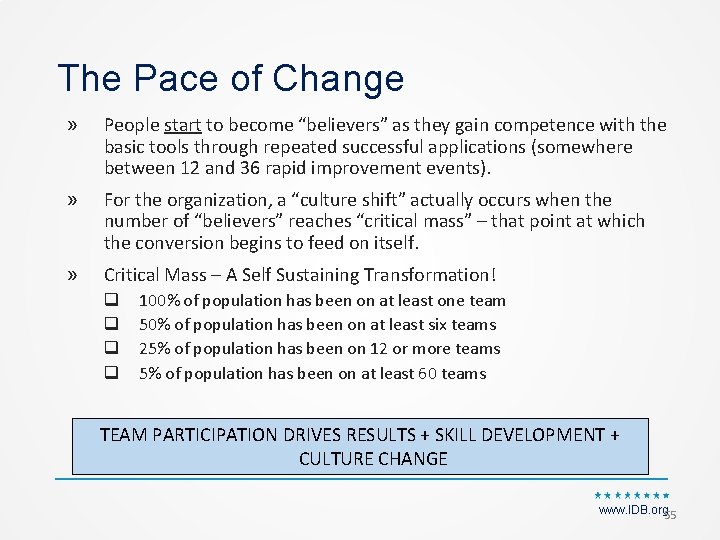
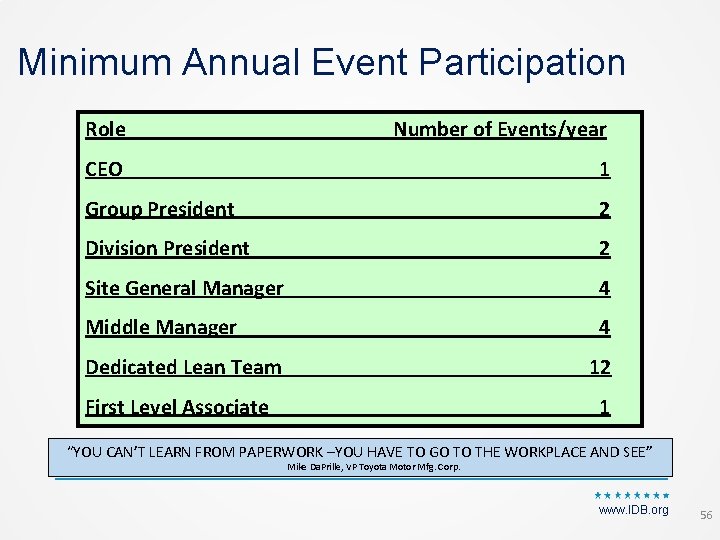
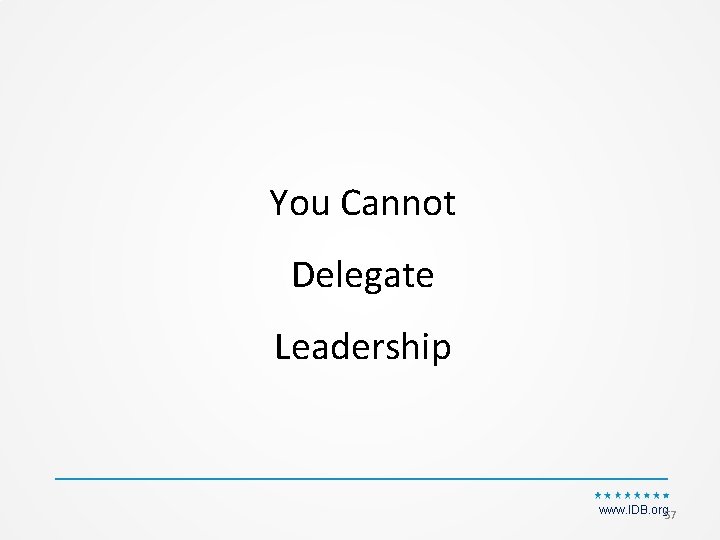
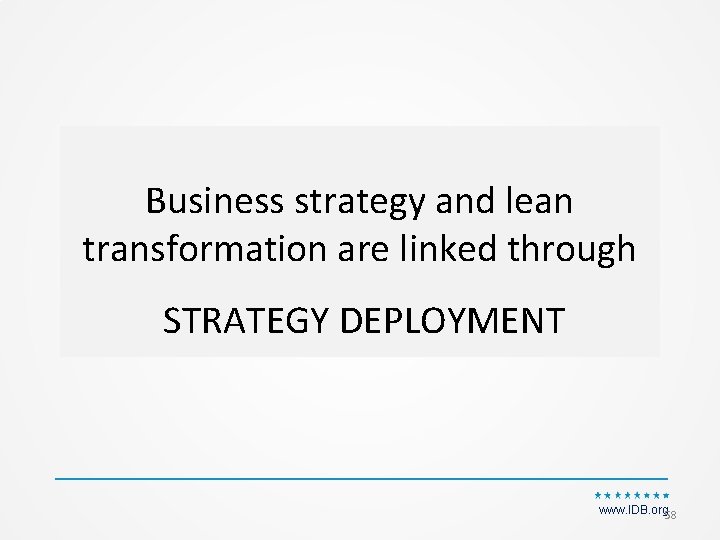
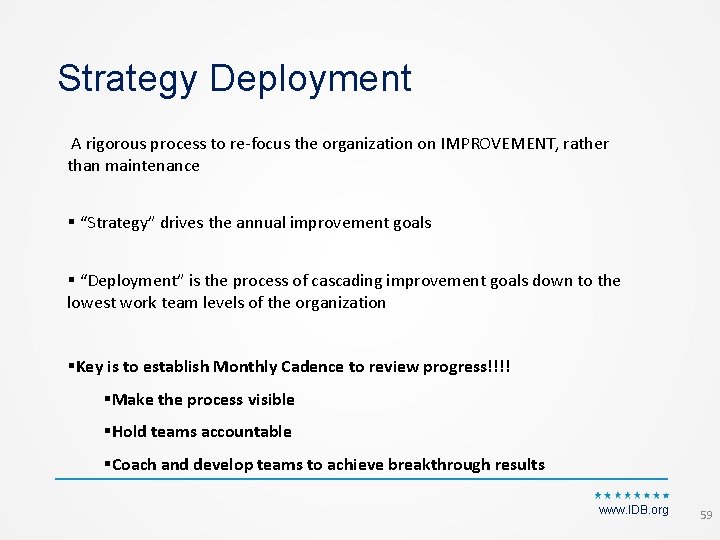
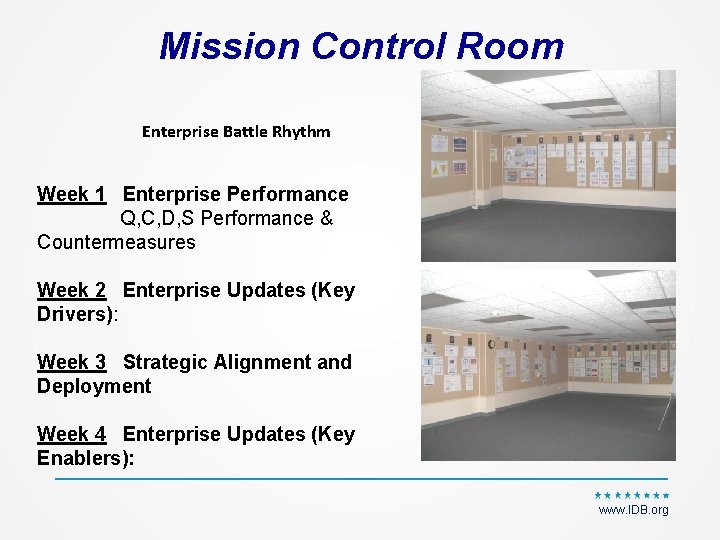
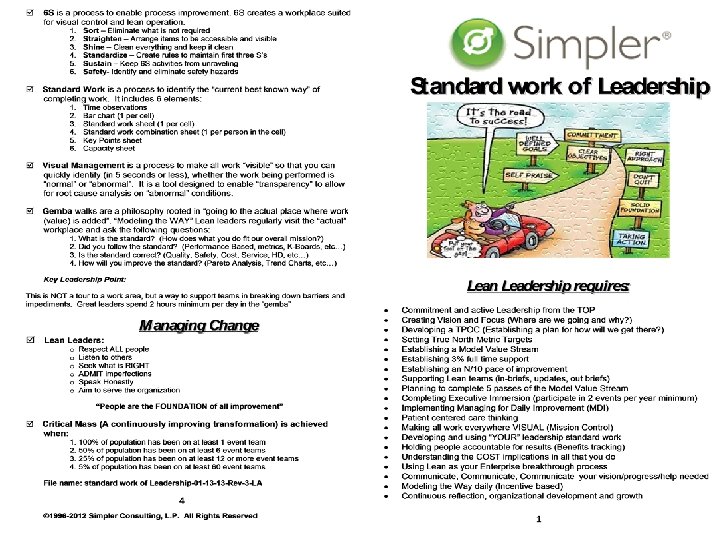
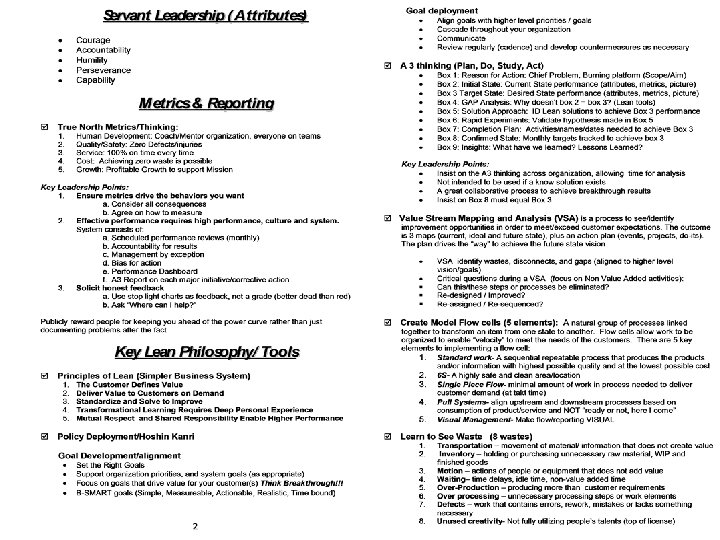
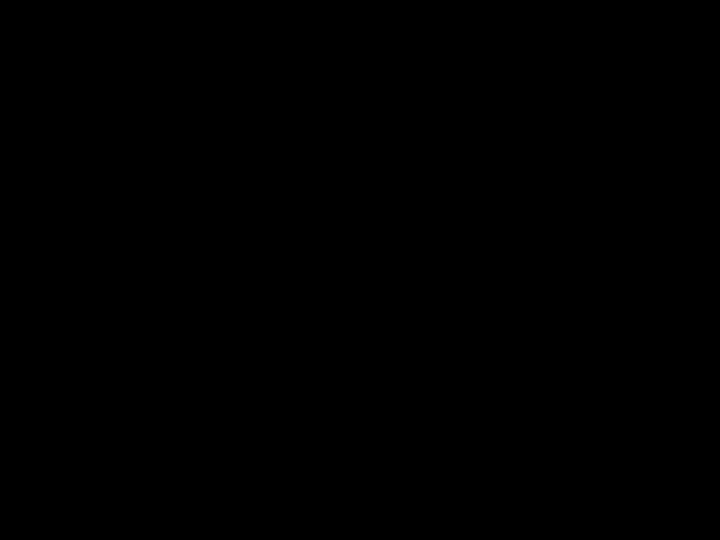
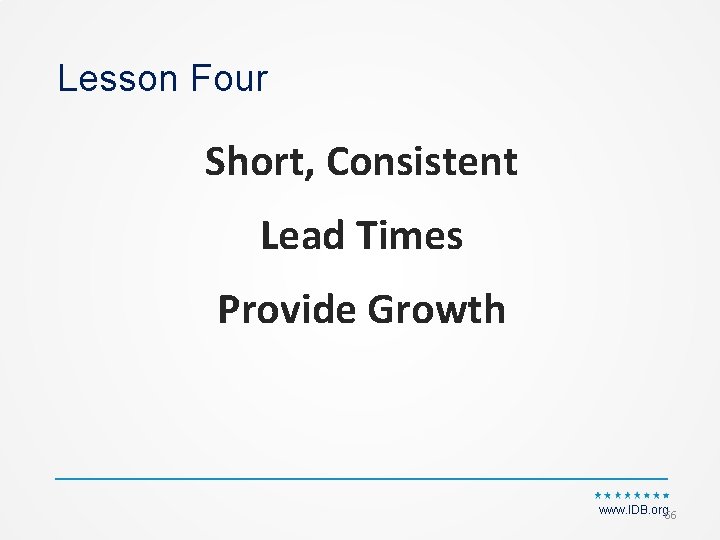
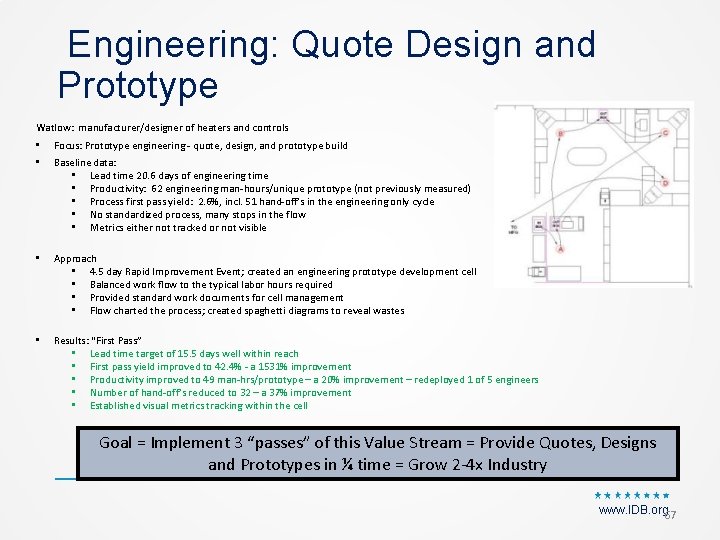
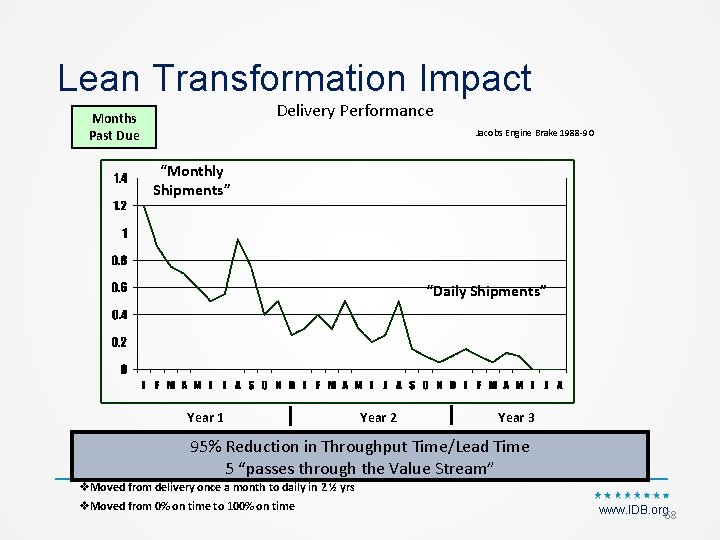
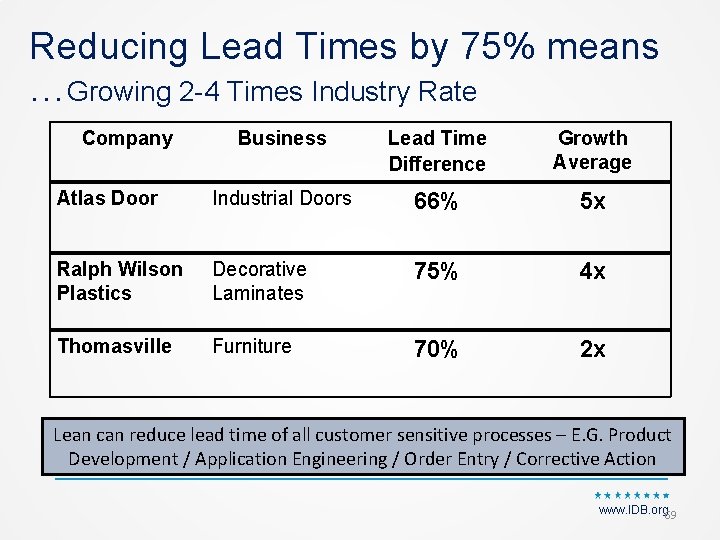
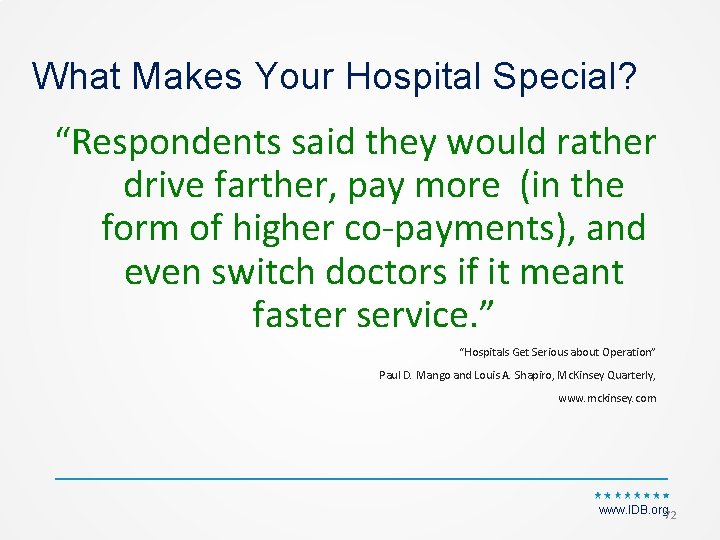
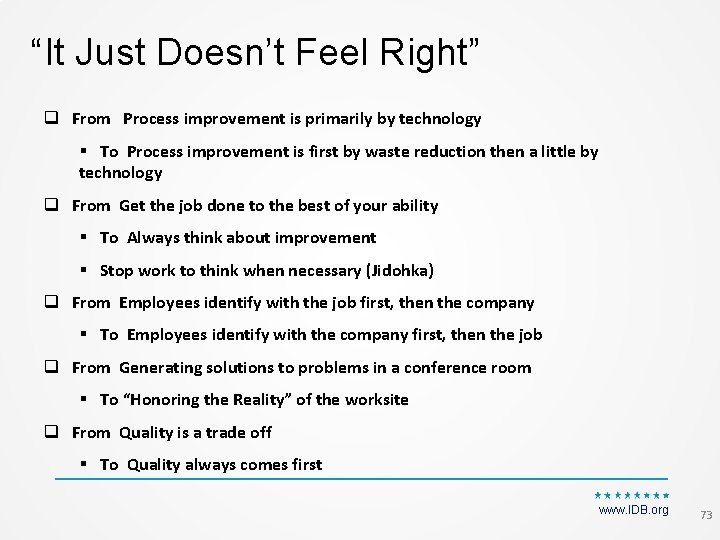
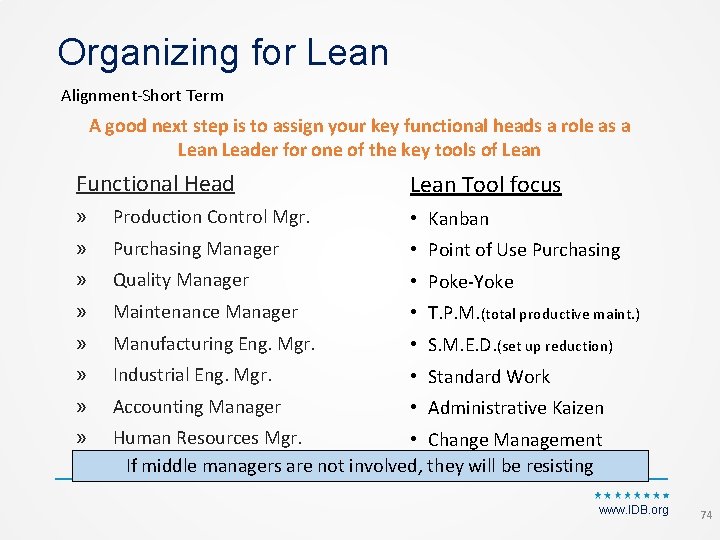
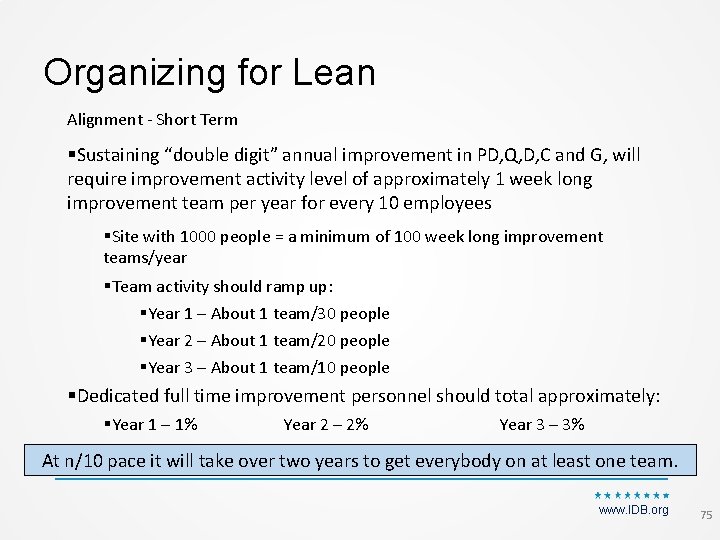
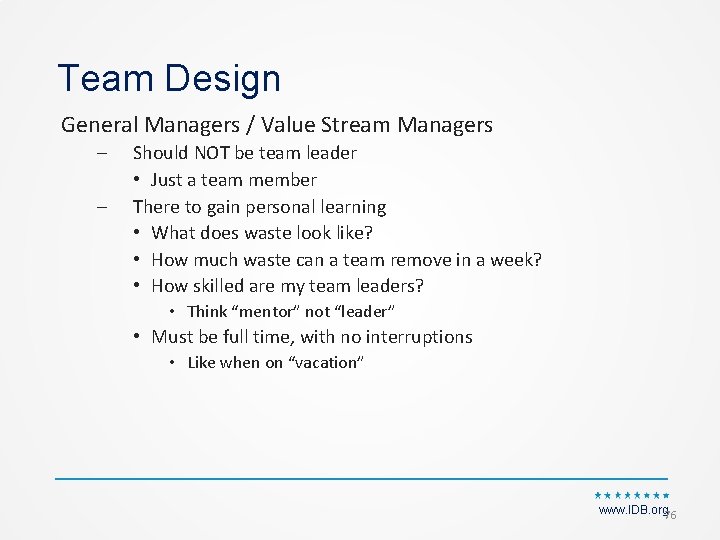
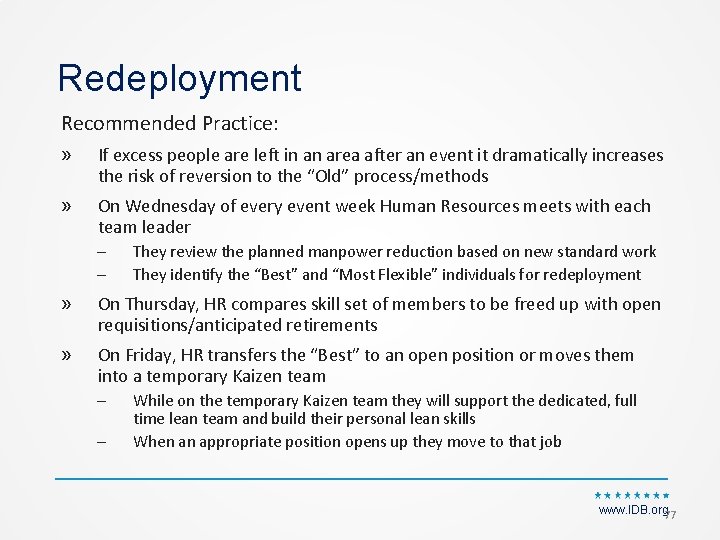
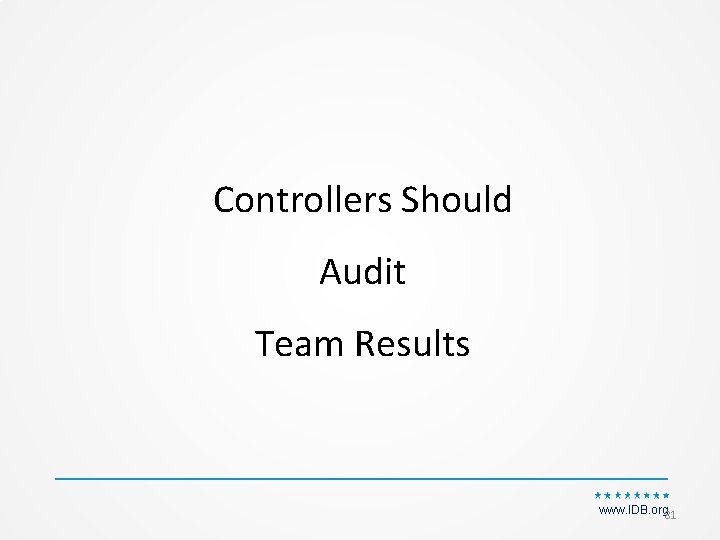
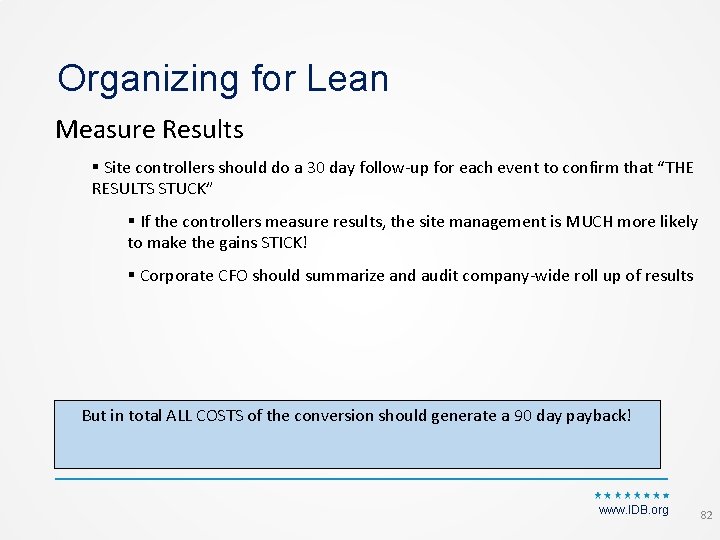
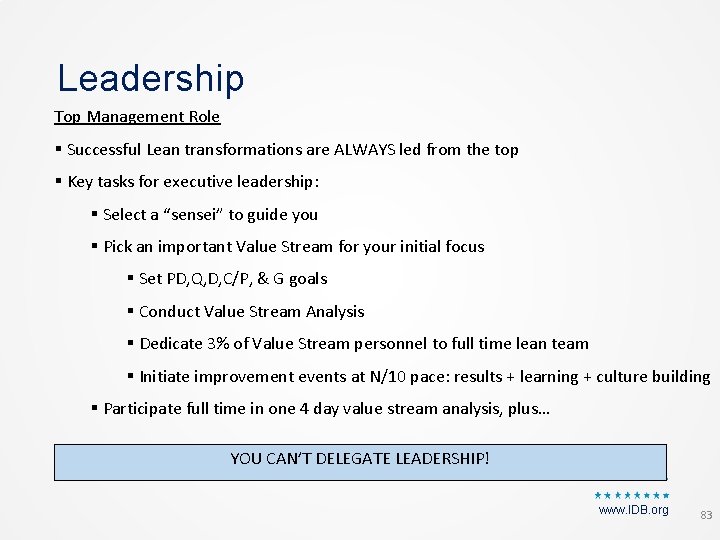
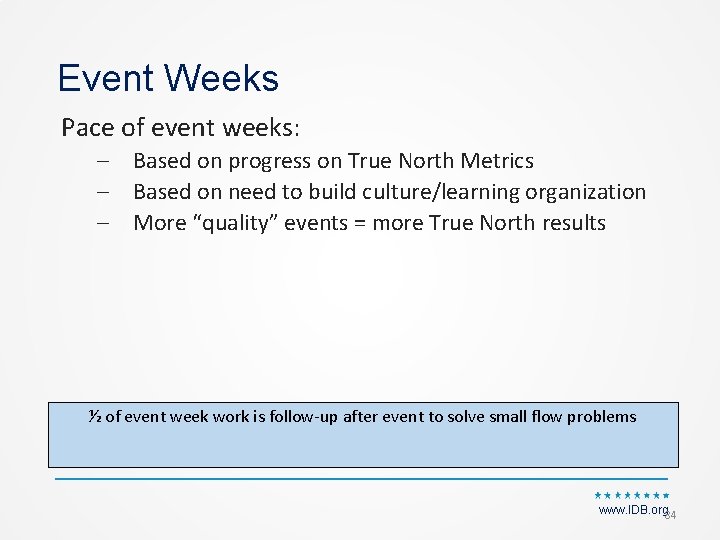
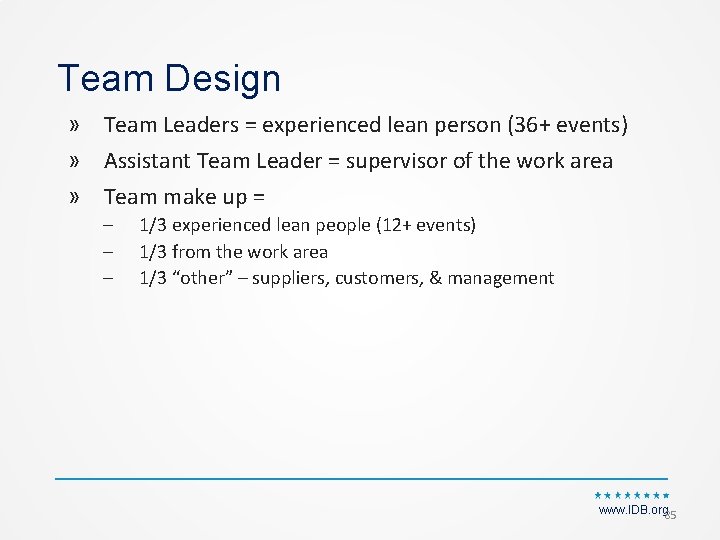
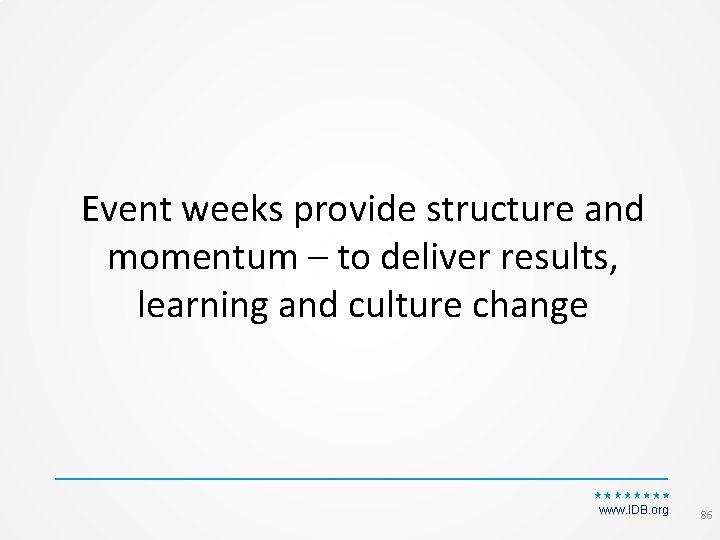
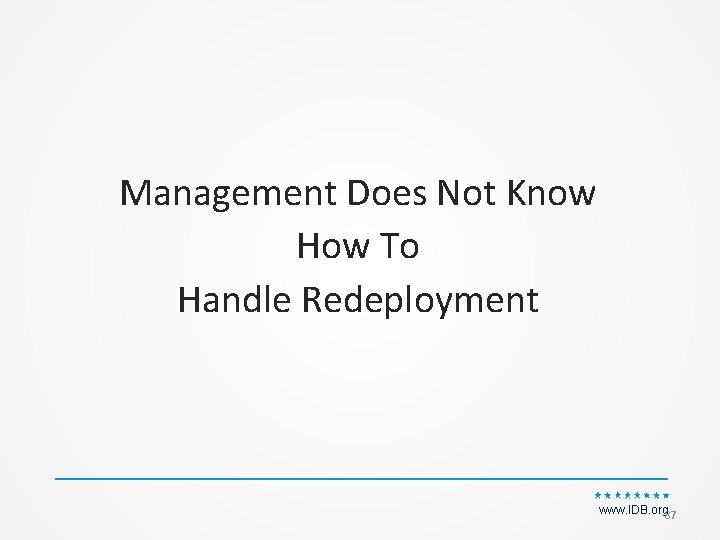
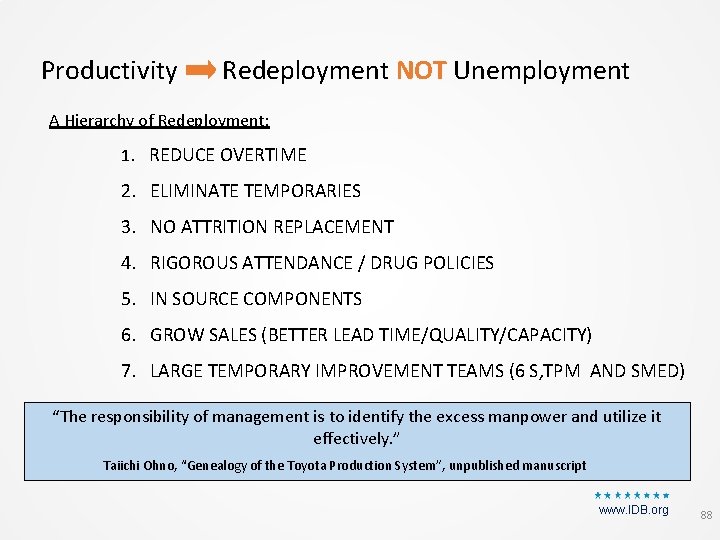
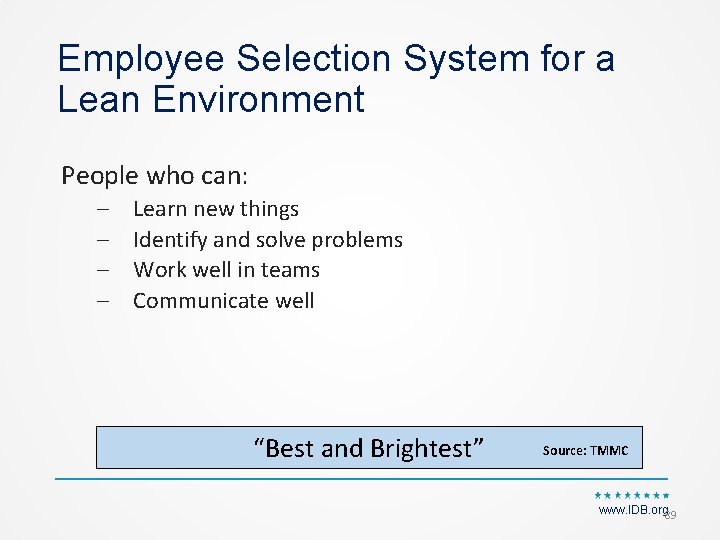
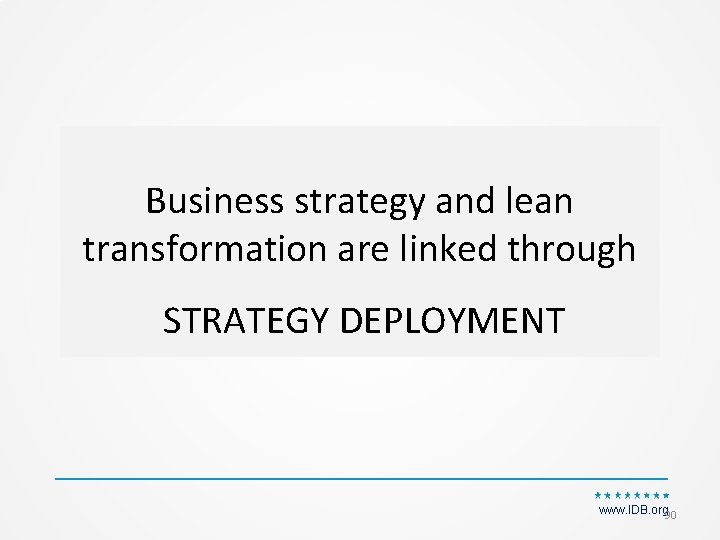
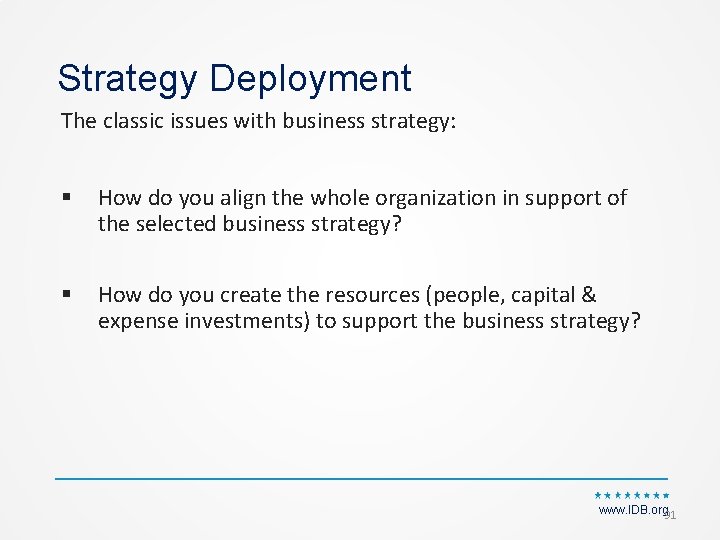
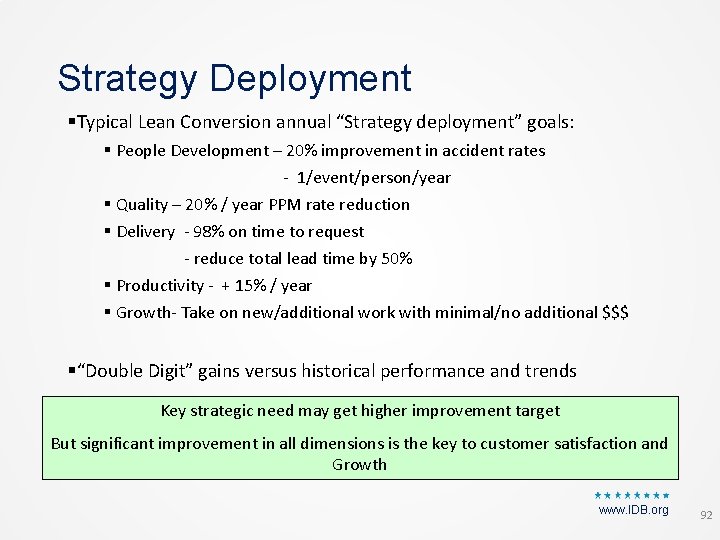
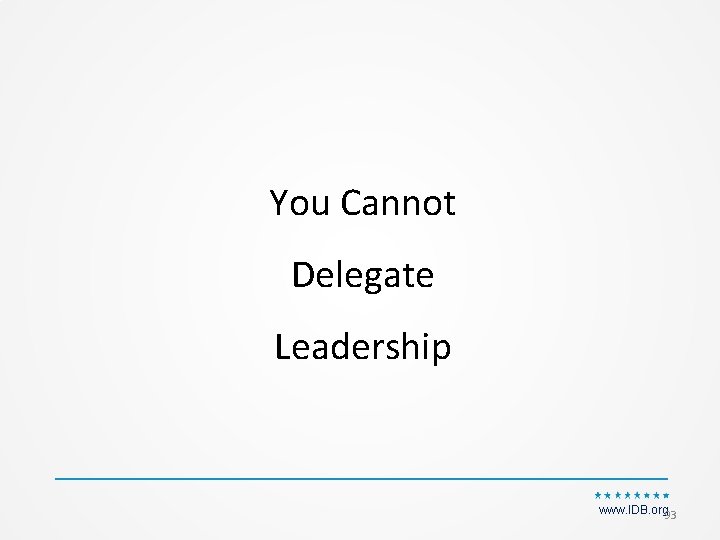
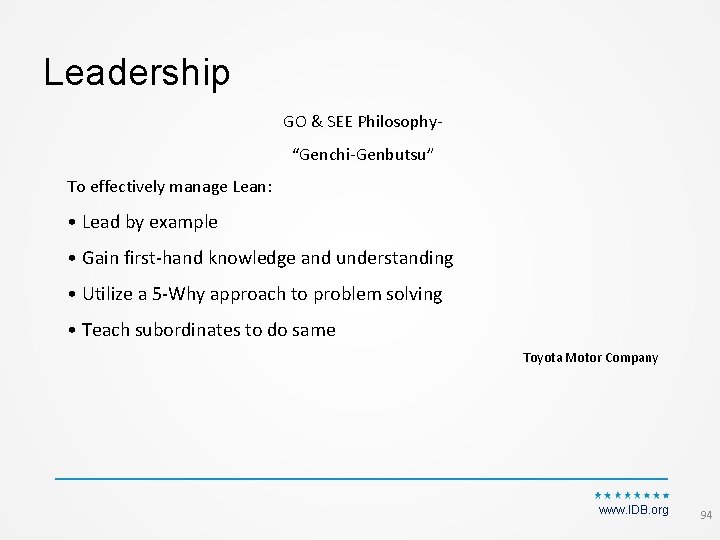
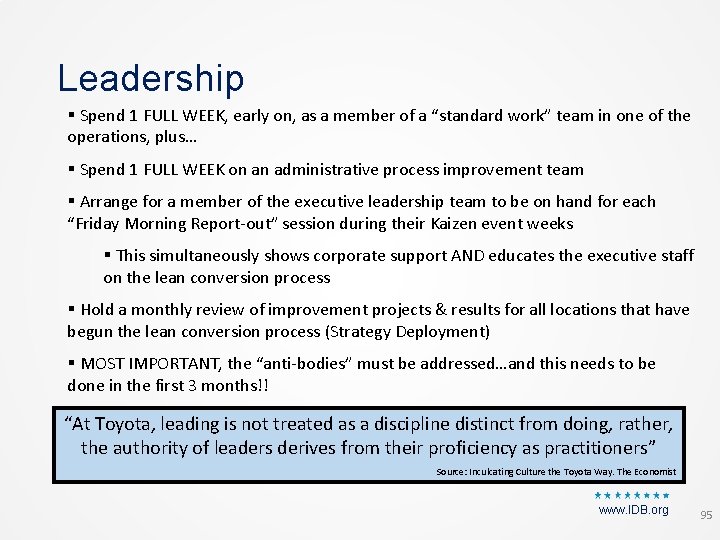
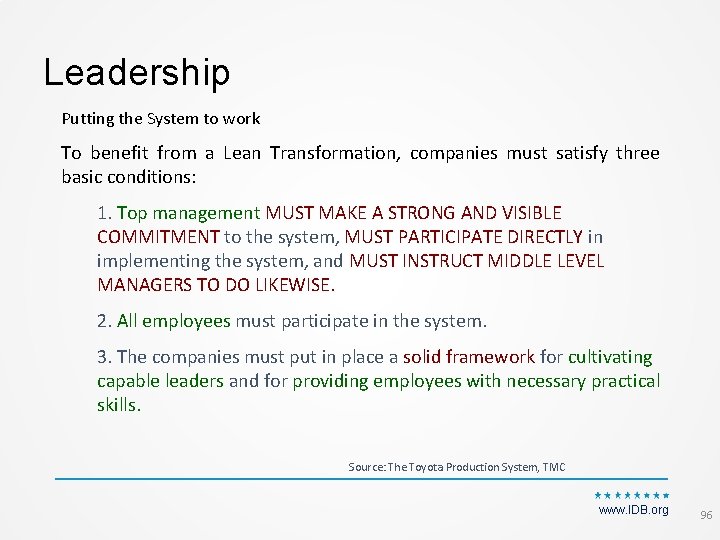
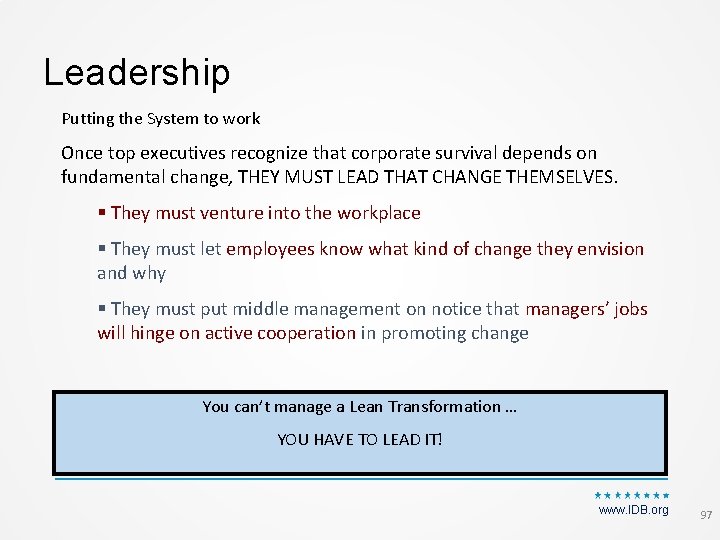
- Slides: 90
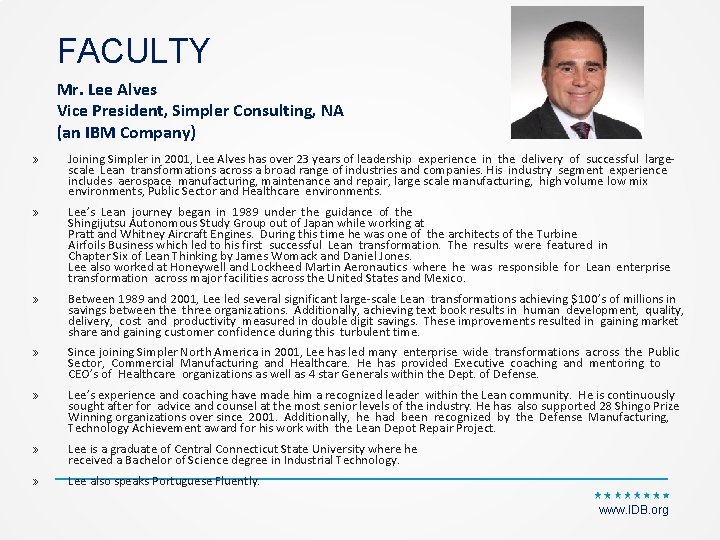
FACULTY Mr. Lee Alves Vice President, Simpler Consulting, NA (an IBM Company) » Joining Simpler in 2001, Lee Alves has over 23 years of leadership experience in the delivery of successful large‐ scale Lean transformations across a broad range of industries and companies. His industry segment experience includes aerospace manufacturing, maintenance and repair, large scale manufacturing, high volume low mix environments, Public Sector and Healthcare environments. » Lee’s Lean journey began in 1989 under the guidance of the Shingijutsu Autonomous Study Group out of Japan while working at Pratt and Whitney Aircraft Engines. During this time he was one of the architects of the Turbine Airfoils Business which led to his first successful Lean transformation. The results were featured in Chapter Six of Lean Thinking by James Womack and Daniel Jones. Lee also worked at Honeywell and Lockheed Martin Aeronautics where he was responsible for Lean enterprise transformation across major facilities across the United States and Mexico. » Between 1989 and 2001, Lee led several significant large‐scale Lean transformations achieving $100’s of millions in savings between the three organizations. Additionally, achieving text book results in human development, quality, delivery, cost and productivity measured in double digit savings. These improvements resulted in gaining market share and gaining customer confidence during this turbulent time. » Since joining Simpler North America in 2001, Lee has led many enterprise wide transformations across the Public Sector, Commercial Manufacturing and Healthcare. He has provided Executive coaching and mentoring to CEO’s of Healthcare organizations as well as 4 star Generals within the Dept. of Defense. » Lee’s experience and coaching have made him a recognized leader within the Lean community. He is continuously sought after for advice and counsel at the most senior levels of the industry. He has also supported 28 Shingo Prize Winning organizations over since 2001. Additionally, he had been recognized by the Defense Manufacturing, Technology Achievement award for his work with the Lean Depot Repair Project. » Lee is a graduate of Central Connecticut State University where he received a Bachelor of Science degree in Industrial Technology. » Lee also speaks Portuguese Fluently. www. IDB. org
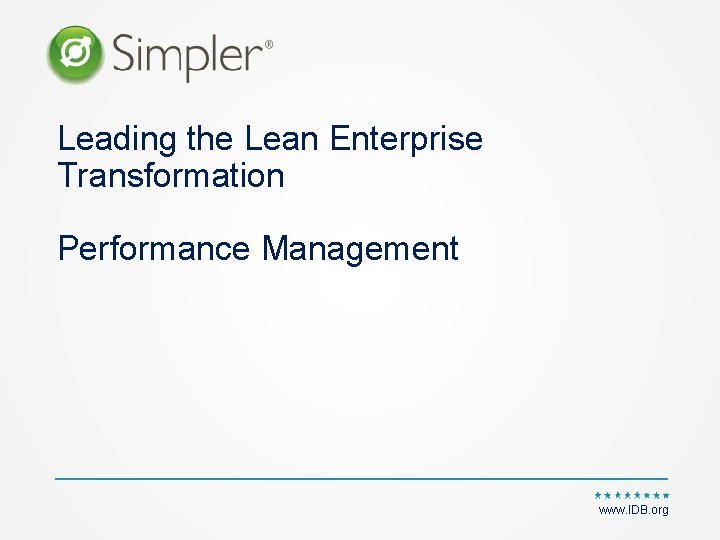
Leading the Lean Enterprise Transformation Performance Management www. IDB. org

Major Themes 1. 2. 3. 4. Lean Defined (Level setting) Expectations & Measurements Lean Leadership Challenges Organizing for Success Prefaced by what is meant by “Lean, ” lessons were selected specifically for your Executive Workshop www. IDB. org 3
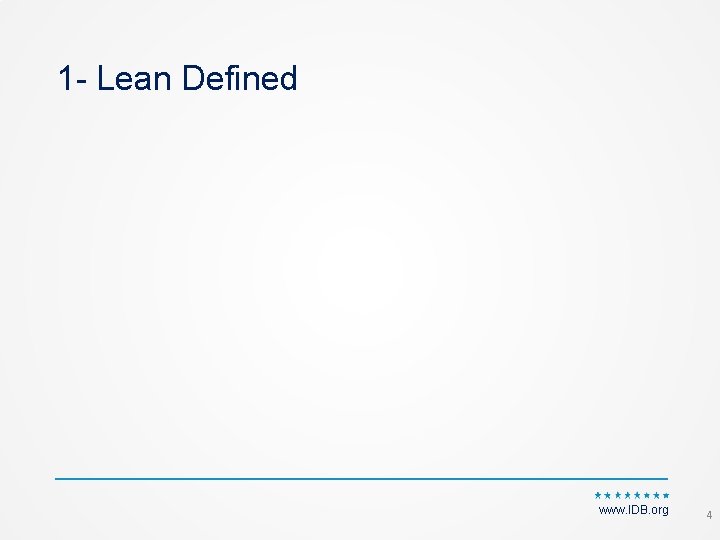
1 - Lean Defined www. IDB. org 4
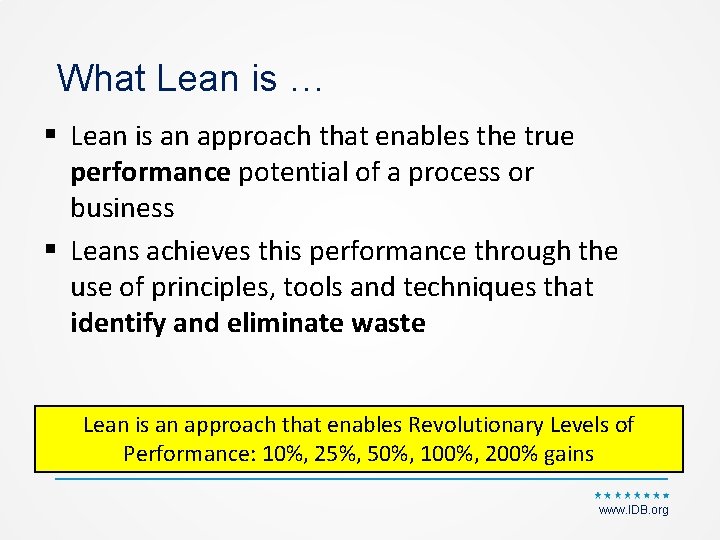
What Lean is … § Lean is an approach that enables the true performance potential of a process or business § Leans achieves this performance through the use of principles, tools and techniques that identify and eliminate waste Lean is an approach that enables Revolutionary Levels of Performance: 10%, 25%, 50%, 100%, 200% gains www. IDB. org
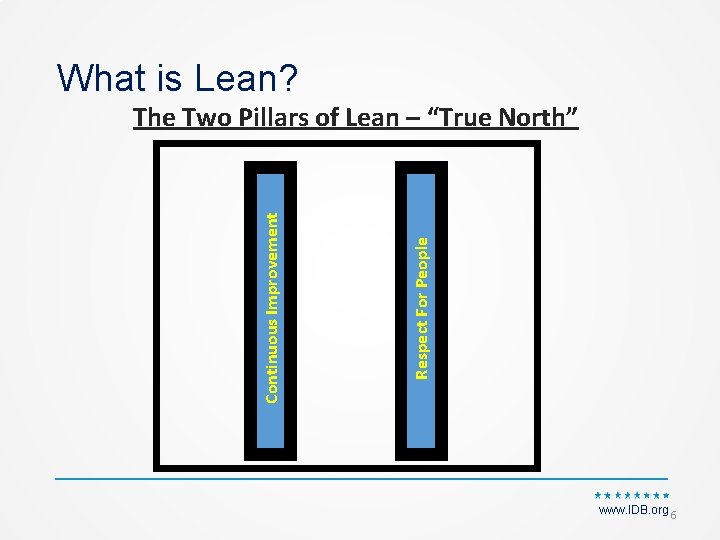
What is Lean? Respect For People Continuous Improvement The Two Pillars of Lean – “True North” www. IDB. org 6
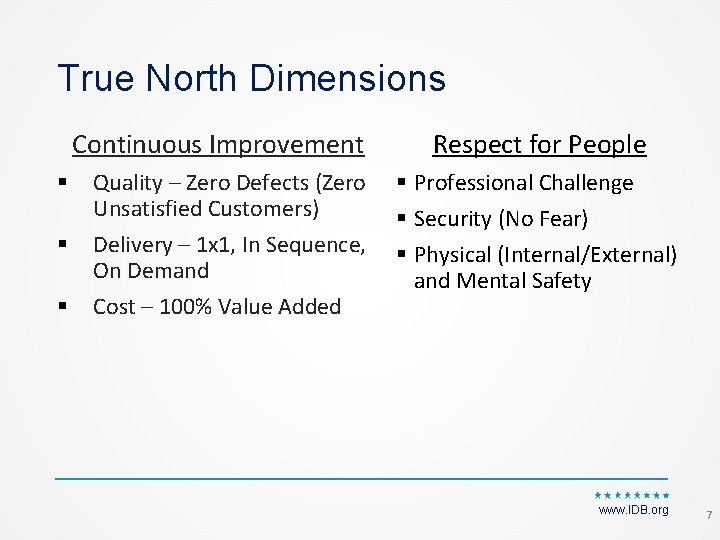
True North Dimensions Continuous Improvement § § § Quality – Zero Defects (Zero Unsatisfied Customers) Delivery – 1 x 1, In Sequence, On Demand Cost – 100% Value Added Respect for People § Professional Challenge § Security (No Fear) § Physical (Internal/External) and Mental Safety www. IDB. org 7
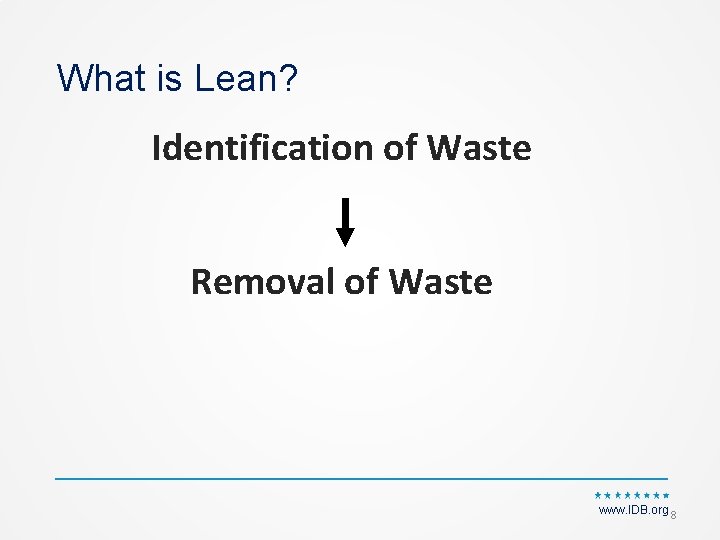
What is Lean? Identification of Waste Removal of Waste www. IDB. org 8
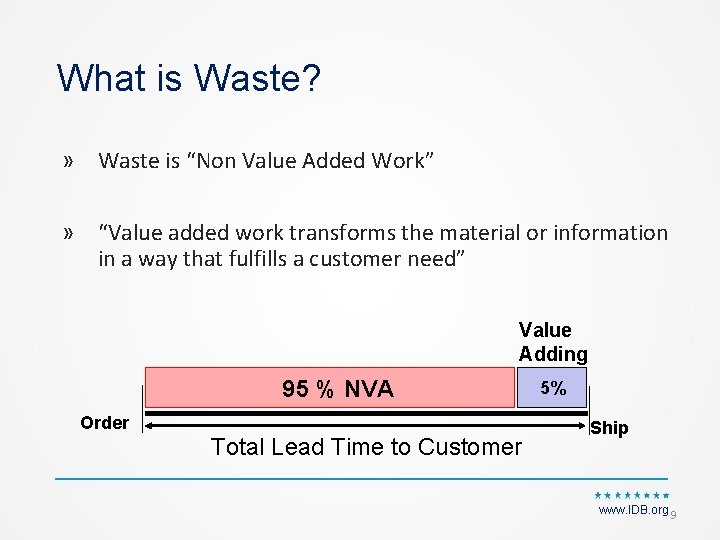
What is Waste? » Waste is “Non Value Added Work” » “Value added work transforms the material or information in a way that fulfills a customer need” Value Adding 95 % NVA Order Total Lead Time to Customer 5% Ship www. IDB. org 9
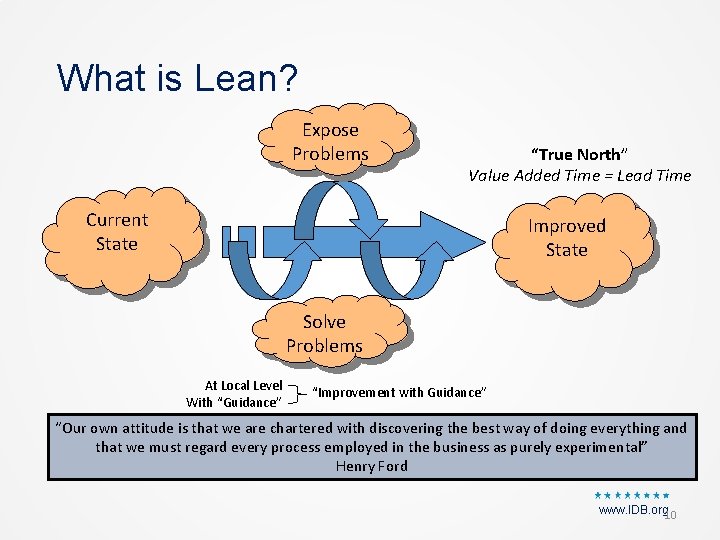
What is Lean? Expose Problems “True North” Value Added Time = Lead Time Current State Improved State Solve Problems At Local Level With “Guidance” “Improvement with Guidance” “Our own attitude is that we are chartered with discovering the best way of doing everything and that we must regard every process employed in the business as purely experimental” Henry Ford www. IDB. org 10
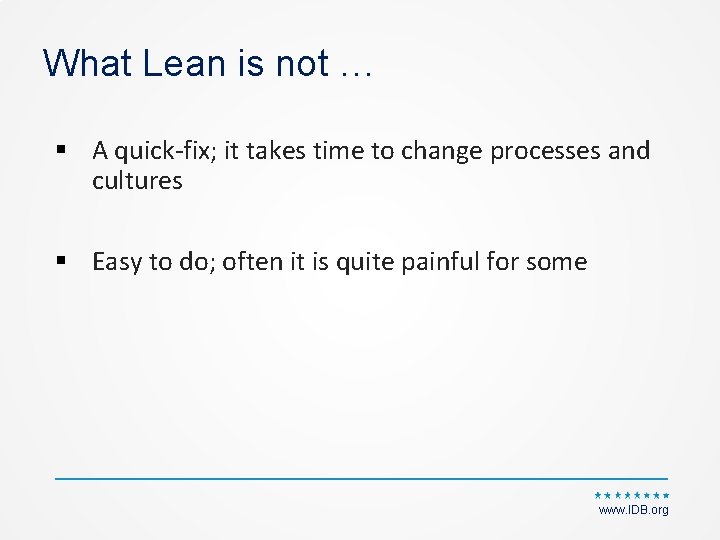
What Lean is not … § A quick‐fix; it takes time to change processes and cultures § Easy to do; often it is quite painful for some www. IDB. org
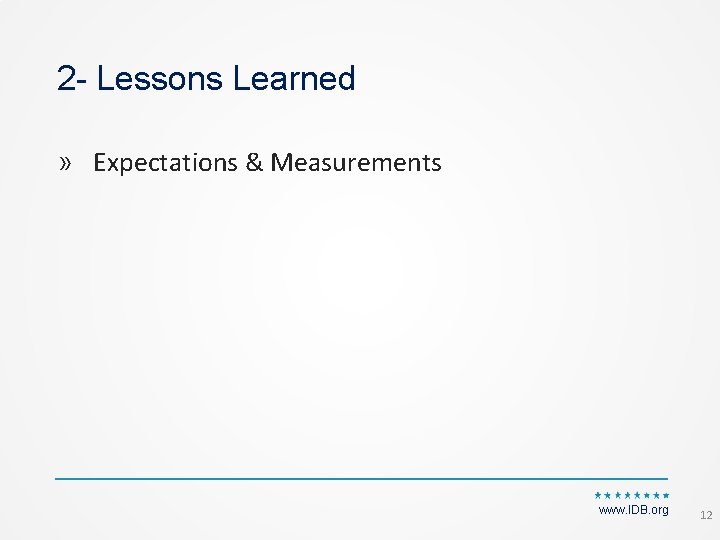
2 - Lessons Learned » Expectations & Measurements www. IDB. org 12
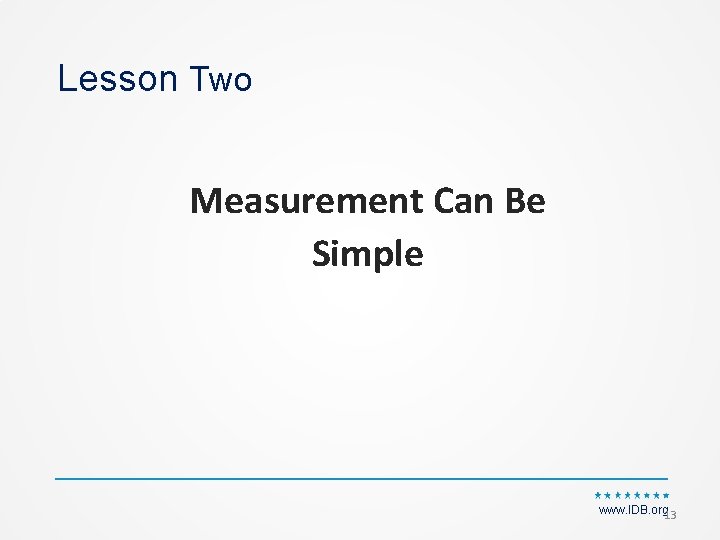
Lesson Two Measurement Can Be Simple www. IDB. org 13
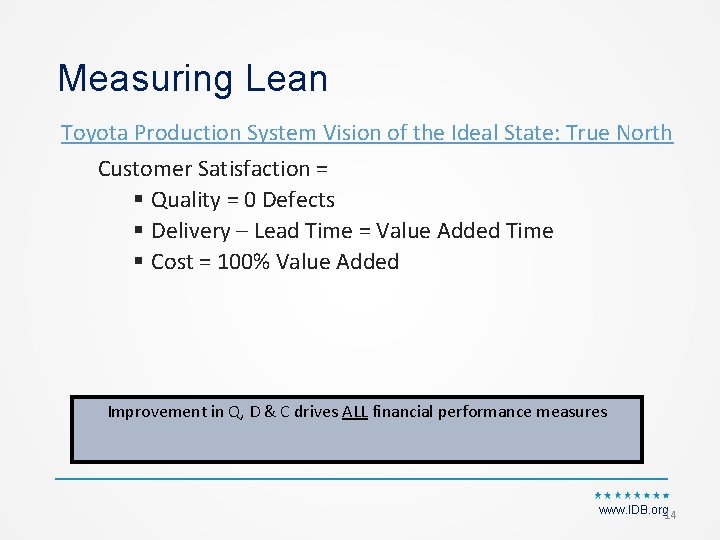
Measuring Lean Toyota Production System Vision of the Ideal State: True North Customer Satisfaction = § Quality = 0 Defects § Delivery – Lead Time = Value Added Time § Cost = 100% Value Added Improvement in Q, D & C drives ALL financial performance measures www. IDB. org 14
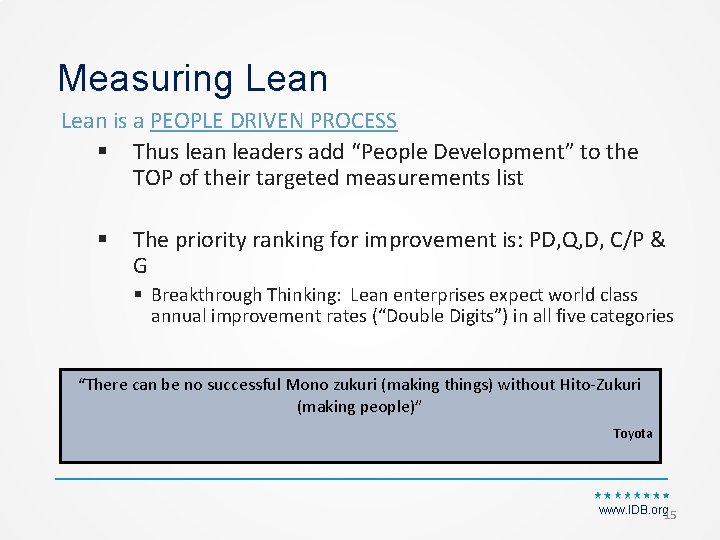
Measuring Lean is a PEOPLE DRIVEN PROCESS § Thus lean leaders add “People Development” to the TOP of their targeted measurements list § The priority ranking for improvement is: PD, Q, D, C/P & G § Breakthrough Thinking: Lean enterprises expect world class annual improvement rates (“Double Digits”) in all five categories “There can be no successful Mono zukuri (making things) without Hito‐Zukuri (making people)” Toyota www. IDB. org 15
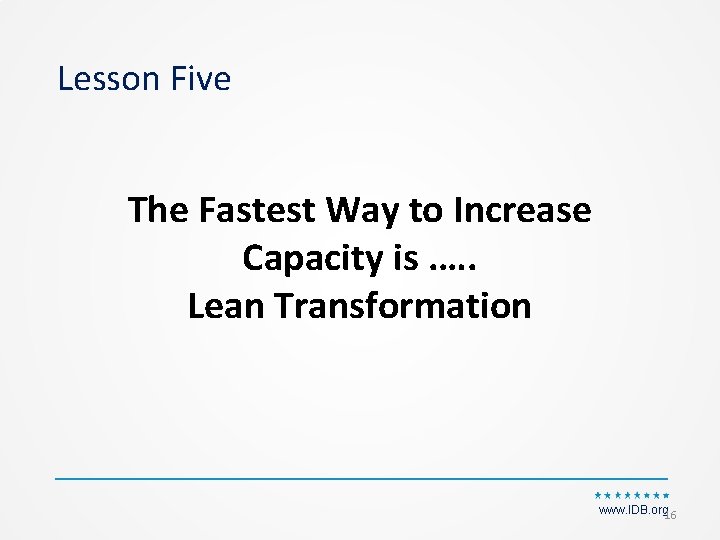
Lesson Five The Fastest Way to Increase Capacity is. …. Lean Transformation www. IDB. org 16
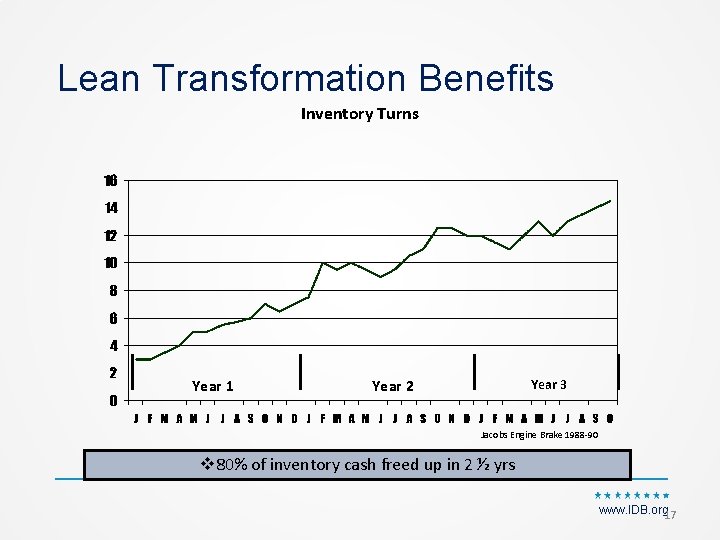
Lean Transformation Benefits Inventory Turns Year 1 Year 2 Year 3 Jacobs Engine Brake 1988‐ 90 v 80% of inventory cash freed up in 2 ½ yrs www. IDB. org 17
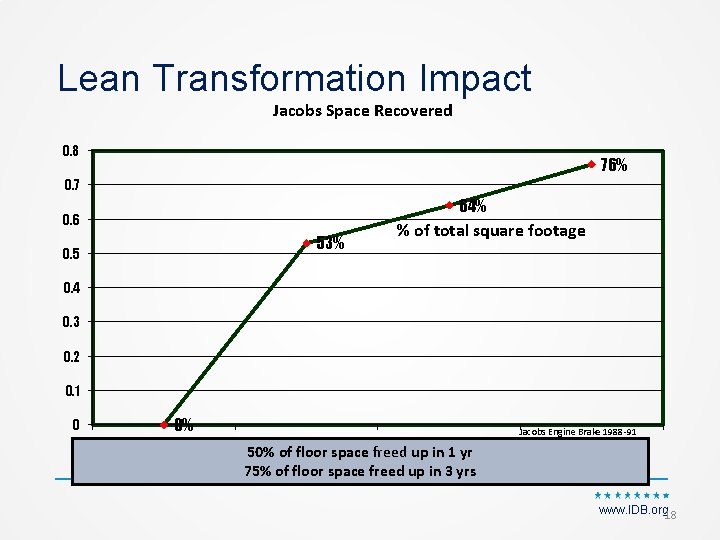
Lean Transformation Impact Jacobs Space Recovered 0. 8 76% 0. 7 64% 0. 6 53% 0. 5 % of total square footage 0. 4 0. 3 0. 2 0. 1 0 0% Year 1 2 space freed up Year 3 50% of. Year floor in 1 yr 75% of floor space freed up in 3 yrs Jacobs Engine Brake 1988‐ 91 Year 4 www. IDB. org 18
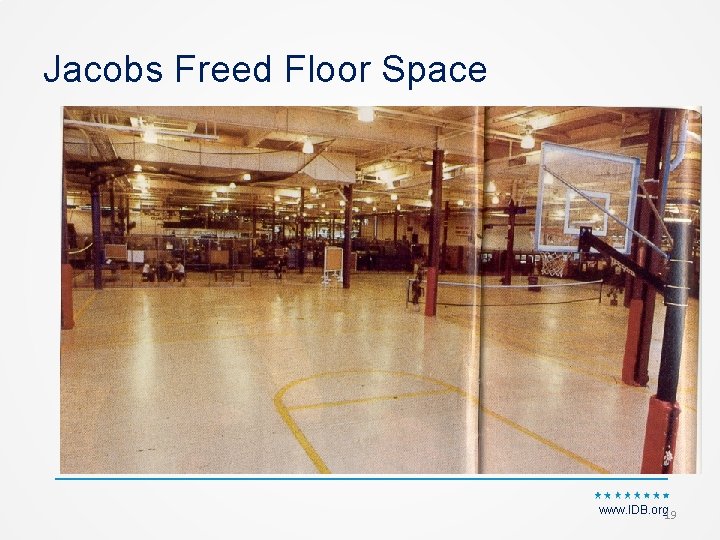
Jacobs Freed Floor Space www. IDB. org 19
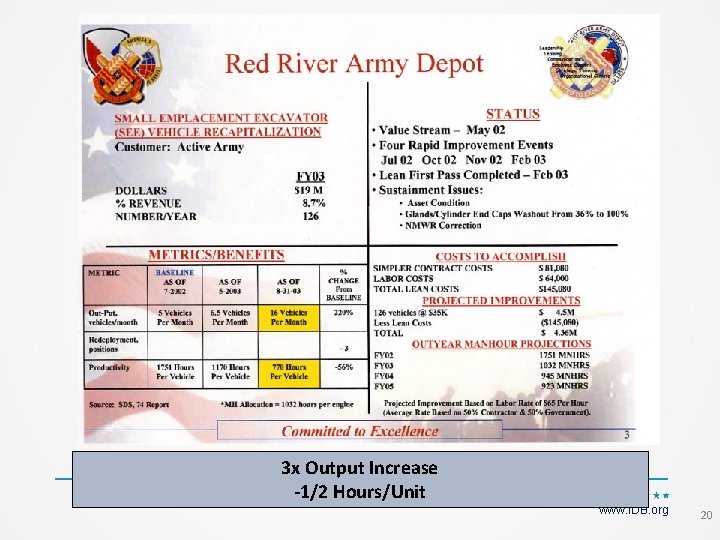
3 x Output Increase -1/2 Hours/Unit www. IDB. org 20
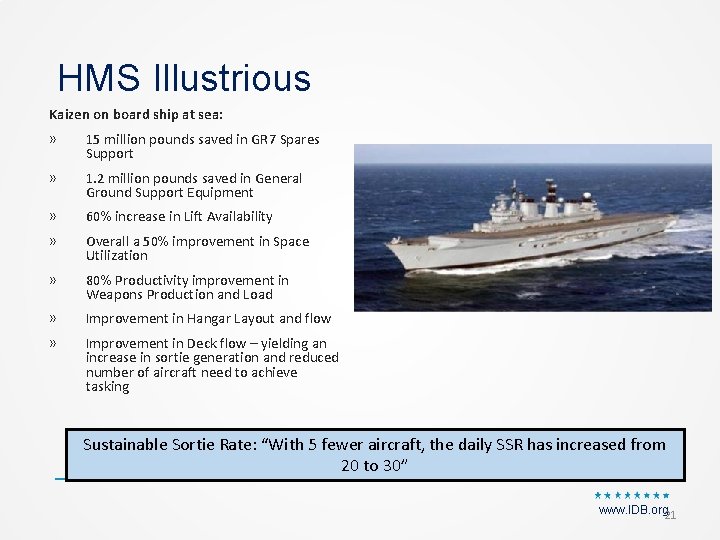
HMS Illustrious Kaizen on board ship at sea: » 15 million pounds saved in GR 7 Spares Support » 1. 2 million pounds saved in General Ground Support Equipment » 60% increase in Lift Availability » Overall a 50% improvement in Space Utilization » 80% Productivity improvement in Weapons Production and Load » Improvement in Hangar Layout and flow » Improvement in Deck flow – yielding an increase in sortie generation and reduced number of aircraft need to achieve tasking Sustainable Sortie Rate: “With 5 fewer aircraft, the daily SSR has increased from 20 to 30” www. IDB. org 21
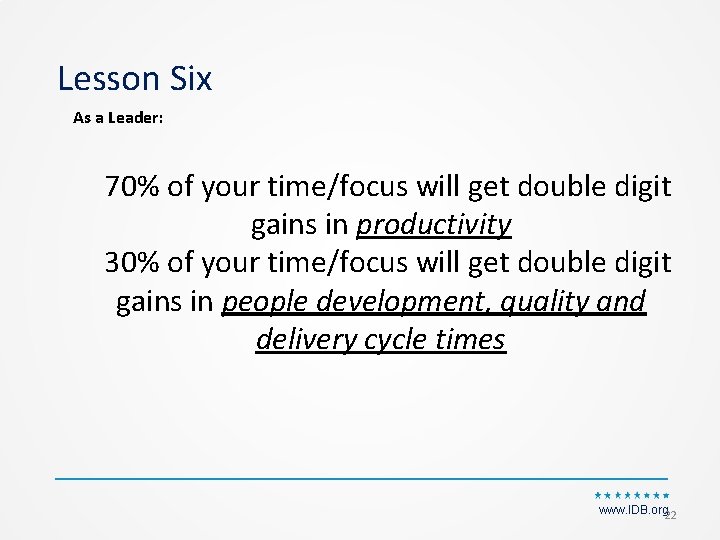
Lesson Six As a Leader: 70% of your time/focus will get double digit gains in productivity 30% of your time/focus will get double digit gains in people development, quality and delivery cycle times www. IDB. org 22
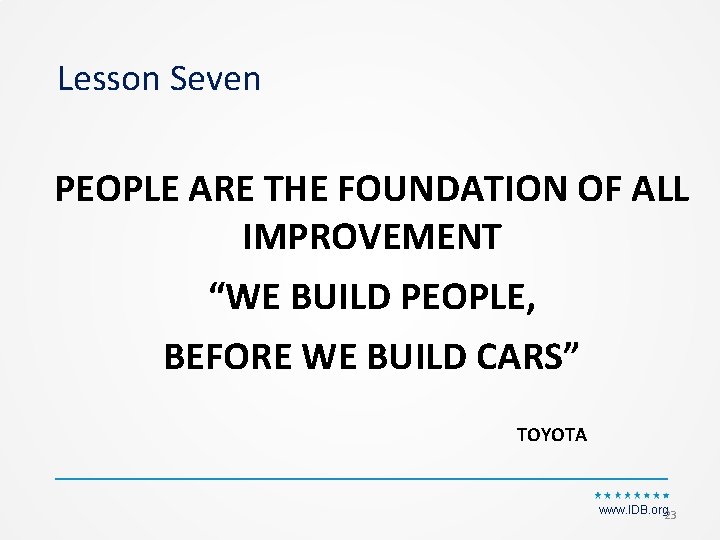
Lesson Seven PEOPLE ARE THE FOUNDATION OF ALL IMPROVEMENT “WE BUILD PEOPLE, BEFORE WE BUILD CARS” TOYOTA www. IDB. org 23
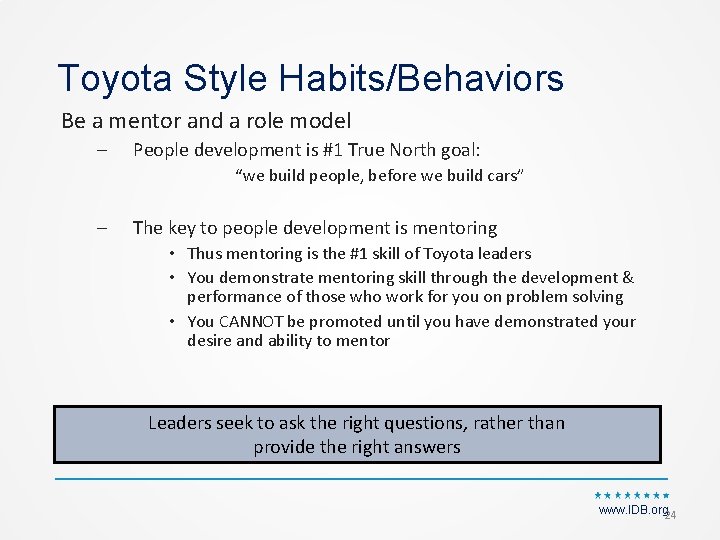
Toyota Style Habits/Behaviors Be a mentor and a role model – People development is #1 True North goal: “we build people, before we build cars” – The key to people development is mentoring • Thus mentoring is the #1 skill of Toyota leaders • You demonstrate mentoring skill through the development & performance of those who work for you on problem solving • You CANNOT be promoted until you have demonstrated your desire and ability to mentor Leaders seek to ask the right questions, rather than provide the right answers www. IDB. org 24
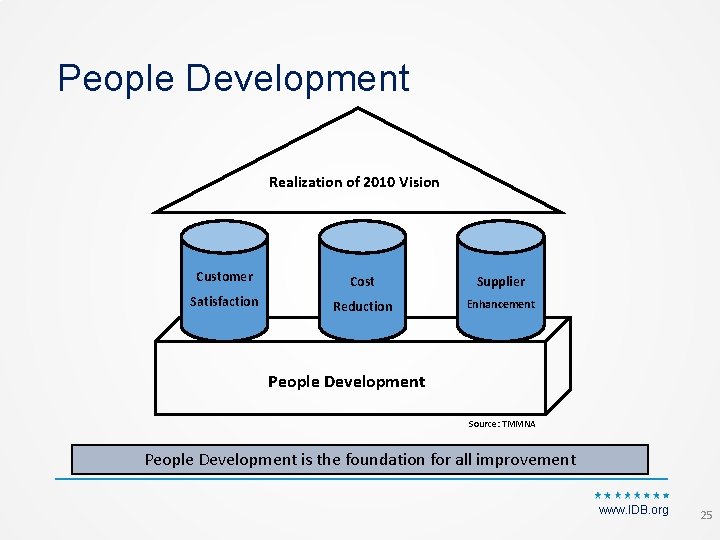
People Development Realization of 2010 Vision Customer Cost Supplier Satisfaction Reduction Enhancement People Development Source: TMMNA People Development is the foundation for all improvement www. IDB. org 25
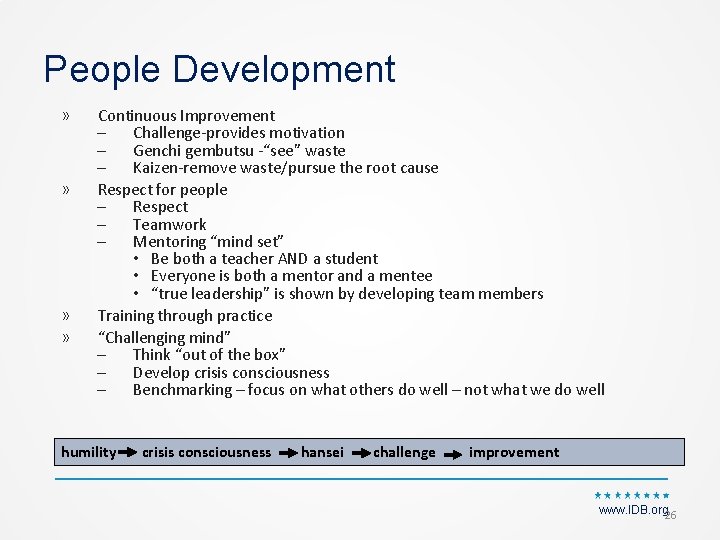
People Development » » » » Continuous Improvement – Challenge‐provides motivation – Genchi gembutsu ‐“see” waste – Kaizen‐remove waste/pursue the root cause Respect for people – Respect – Teamwork – Mentoring “mind set” • Be both a teacher AND a student • Everyone is both a mentor and a mentee • “true leadership” is shown by developing team members Training through practice “Challenging mind” – Think “out of the box” – Develop crisis consciousness – Benchmarking – focus on what others do well – not what we do well humility crisis consciousness hansei challenge improvement www. IDB. org 26
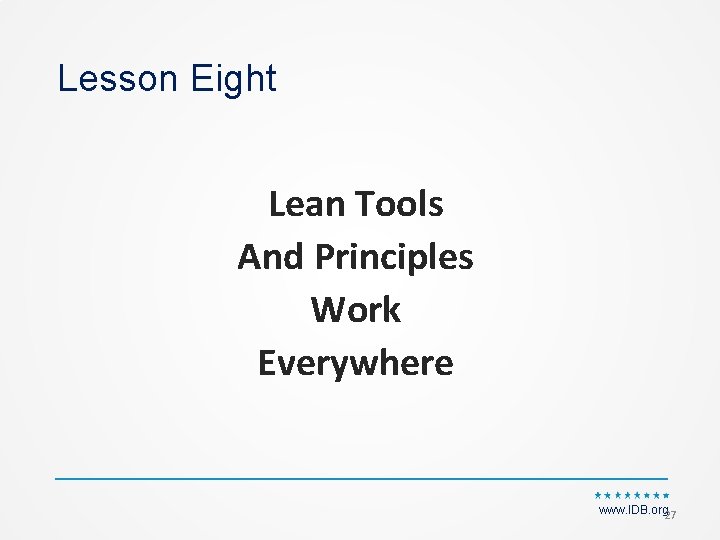
Lesson Eight Lean Tools And Principles Work Everywhere www. IDB. org 27
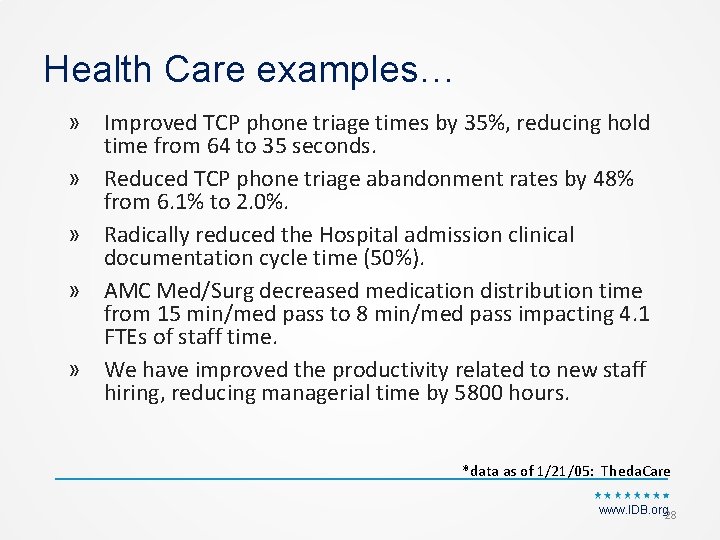
Health Care examples… » Improved TCP phone triage times by 35%, reducing hold time from 64 to 35 seconds. » Reduced TCP phone triage abandonment rates by 48% from 6. 1% to 2. 0%. » Radically reduced the Hospital admission clinical documentation cycle time (50%). » AMC Med/Surg decreased medication distribution time from 15 min/med pass to 8 min/med pass impacting 4. 1 FTEs of staff time. » We have improved the productivity related to new staff hiring, reducing managerial time by 5800 hours. *data as of 1/21/05: Theda. Care www. IDB. org 28
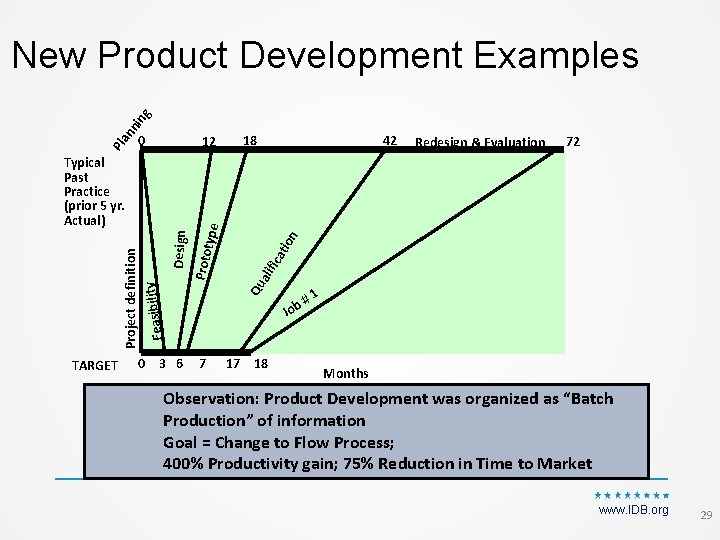
TARGET 0 3 6 7 72 ati o n Redesign & Evaluation fic Qu Design Project definition Feasibility Typical Past Practice (prior 5 yr. Actual) 42 18 type 12 ali 0 Proto Pla nn ing New Product Development Examples 17 18 # Job 1 Months Observation: Product Development was organized as “Batch Production” of information Goal = Change to Flow Process; 400% Productivity gain; 75% Reduction in Time to Market www. IDB. org 29
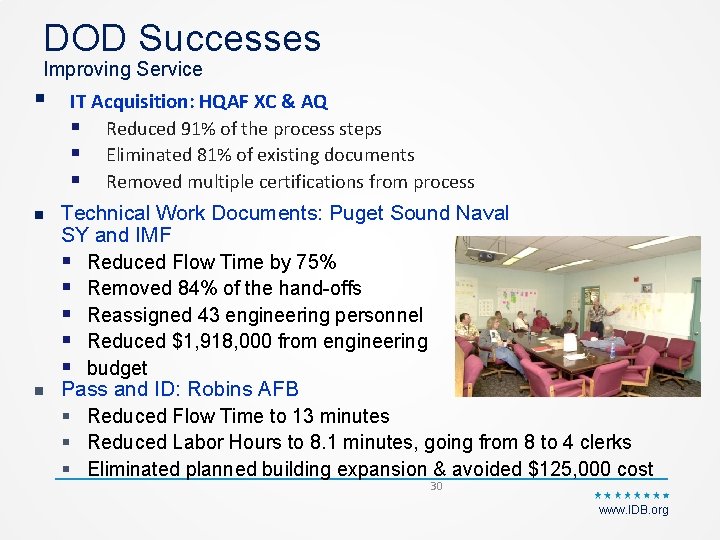
DOD Successes Improving Service § IT Acquisition: HQAF XC & AQ § Reduced 91% of the process steps § Eliminated 81% of existing documents § Removed multiple certifications from process n n Technical Work Documents: Puget Sound Naval SY and IMF § Reduced Flow Time by 75% § Removed 84% of the hand-offs § Reassigned 43 engineering personnel § Reduced $1, 918, 000 from engineering § budget Pass and ID: Robins AFB § Reduced Flow Time to 13 minutes § Reduced Labor Hours to 8. 1 minutes, going from 8 to 4 clerks § Eliminated planned building expansion & avoided $125, 000 cost 30 www. IDB. org
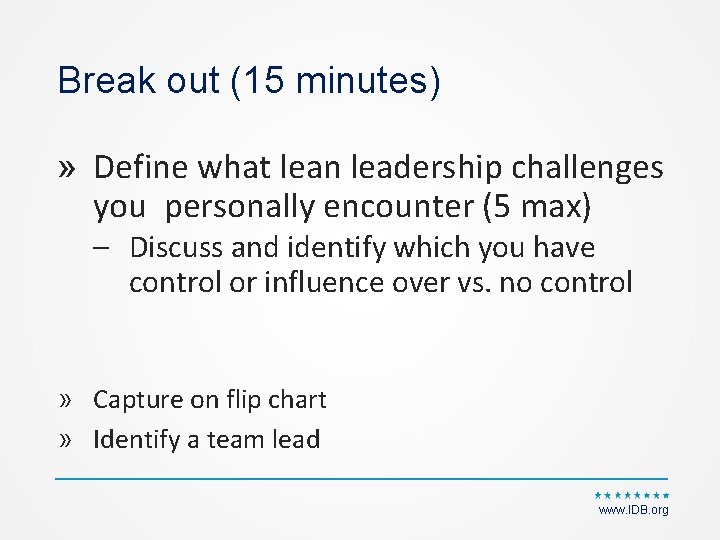
Break out (15 minutes) » Define what lean leadership challenges you personally encounter (5 max) – Discuss and identify which you have control or influence over vs. no control » Capture on flip chart » Identify a team lead www. IDB. org
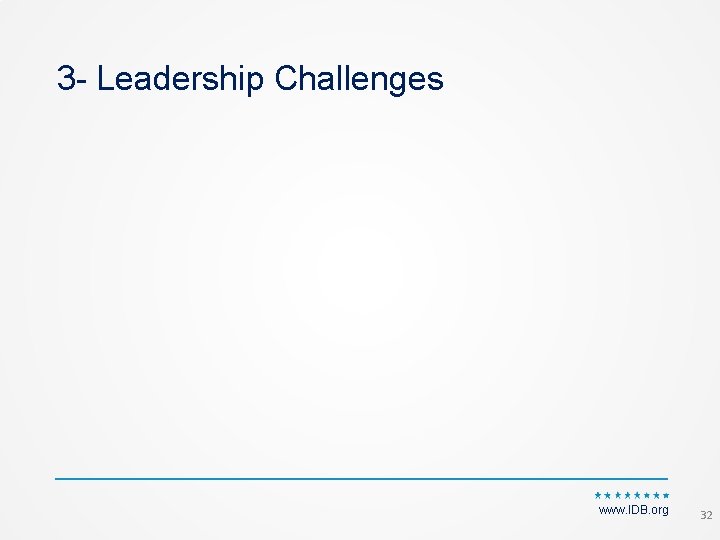
3 - Leadership Challenges www. IDB. org 32
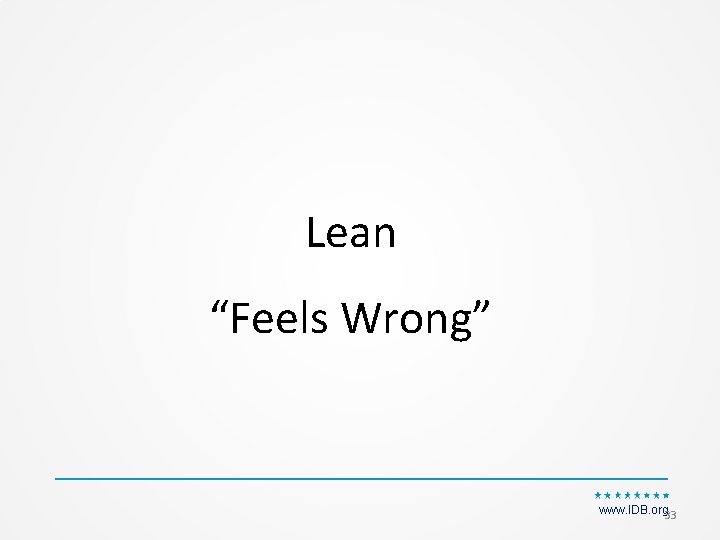
Lean “Feels Wrong” www. IDB. org 33
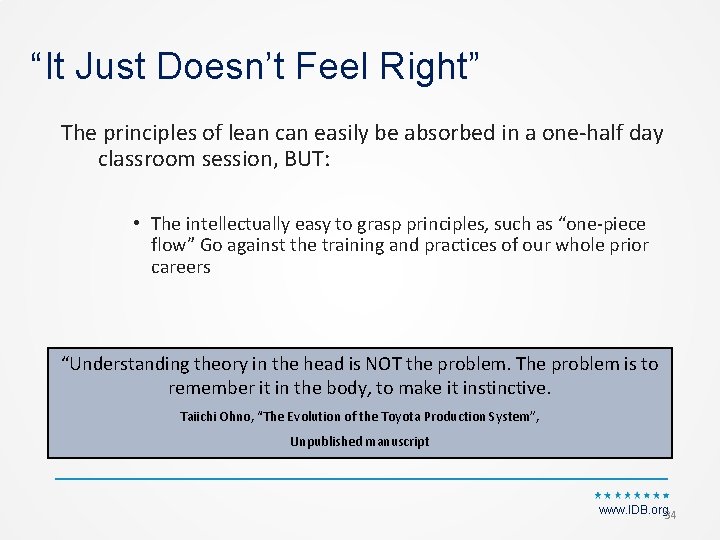
“It Just Doesn’t Feel Right” The principles of lean can easily be absorbed in a one‐half day classroom session, BUT: • The intellectually easy to grasp principles, such as “one‐piece flow” Go against the training and practices of our whole prior careers “Understanding theory in the head is NOT the problem. The problem is to remember it in the body, to make it instinctive. Taiichi Ohno, “The Evolution of the Toyota Production System”, Unpublished manuscript www. IDB. org 34
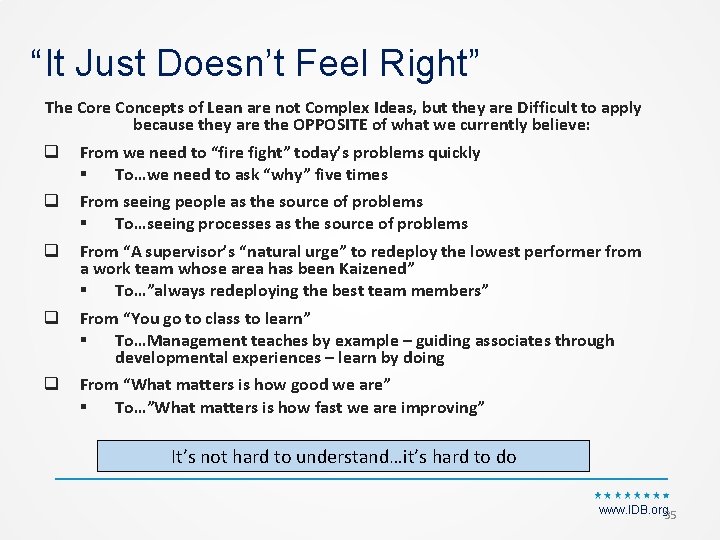
“It Just Doesn’t Feel Right” The Core Concepts of Lean are not Complex Ideas, but they are Difficult to apply because they are the OPPOSITE of what we currently believe: q From we need to “fire fight” today’s problems quickly § To…we need to ask “why” five times q From seeing people as the source of problems § To…seeing processes as the source of problems q From “A supervisor’s “natural urge” to redeploy the lowest performer from a work team whose area has been Kaizened” § To…”always redeploying the best team members” q From “You go to class to learn” § To…Management teaches by example – guiding associates through developmental experiences – learn by doing q From “What matters is how good we are” § To…”What matters is how fast we are improving” It’s not hard to understand…it’s hard to do www. IDB. org 35
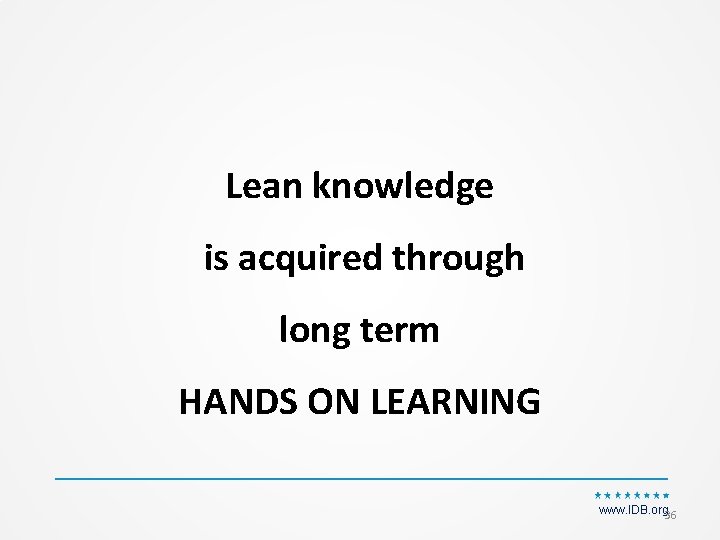
Lean knowledge is acquired through long term HANDS ON LEARNING www. IDB. org 36
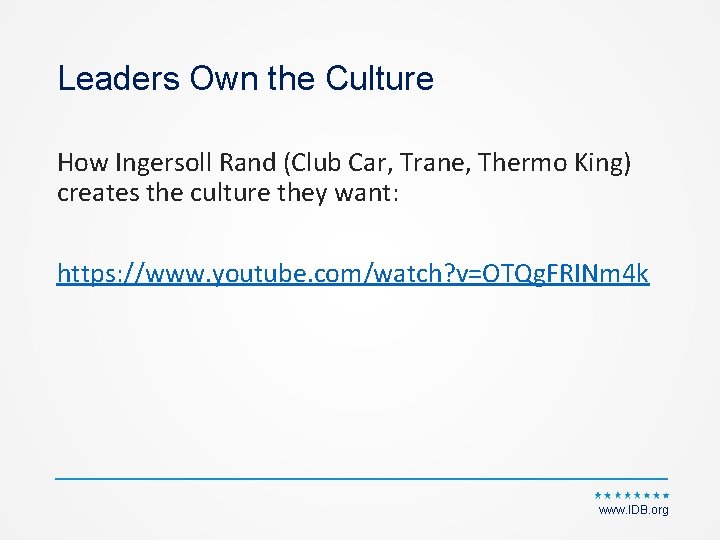
Leaders Own the Culture How Ingersoll Rand (Club Car, Trane, Thermo King) creates the culture they want: https: //www. youtube. com/watch? v=OTQg. FRINm 4 k www. IDB. org
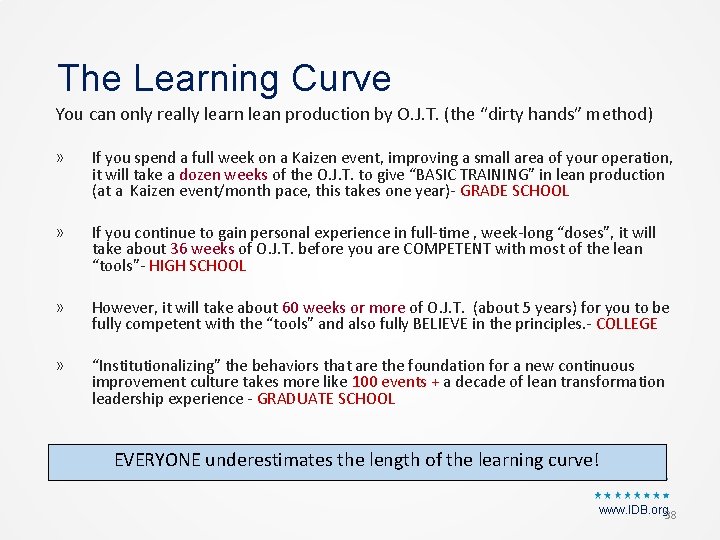
The Learning Curve You can only really learn lean production by O. J. T. (the “dirty hands” method) » If you spend a full week on a Kaizen event, improving a small area of your operation, it will take a dozen weeks of the O. J. T. to give “BASIC TRAINING” in lean production (at a Kaizen event/month pace, this takes one year)‐ GRADE SCHOOL » If you continue to gain personal experience in full‐time , week‐long “doses”, it will take about 36 weeks of O. J. T. before you are COMPETENT with most of the lean “tools”‐ HIGH SCHOOL » However, it will take about 60 weeks or more of O. J. T. (about 5 years) for you to be fully competent with the “tools” and also fully BELIEVE in the principles. ‐ COLLEGE » “Institutionalizing” the behaviors that are the foundation for a new continuous improvement culture takes more like 100 events + a decade of lean transformation leadership experience ‐ GRADUATE SCHOOL EVERYONE underestimates the length of the learning curve! www. IDB. org 38
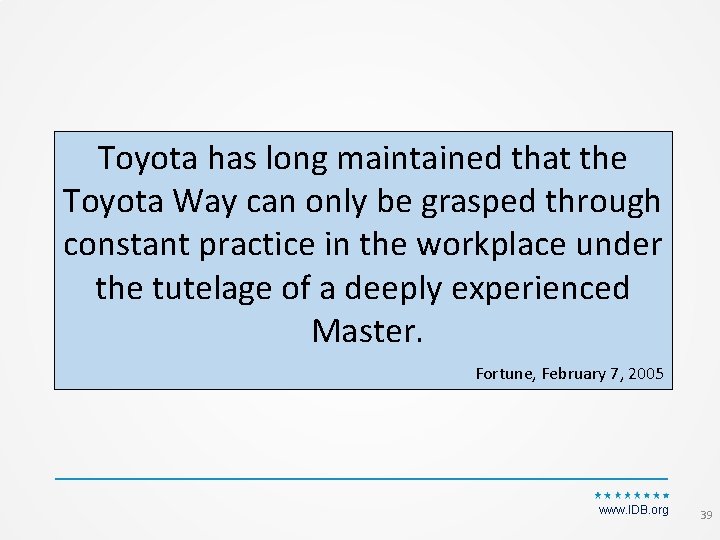
Toyota has long maintained that the Toyota Way can only be grasped through constant practice in the workplace under the tutelage of a deeply experienced Master. Fortune, February 7, 2005 www. IDB. org 39
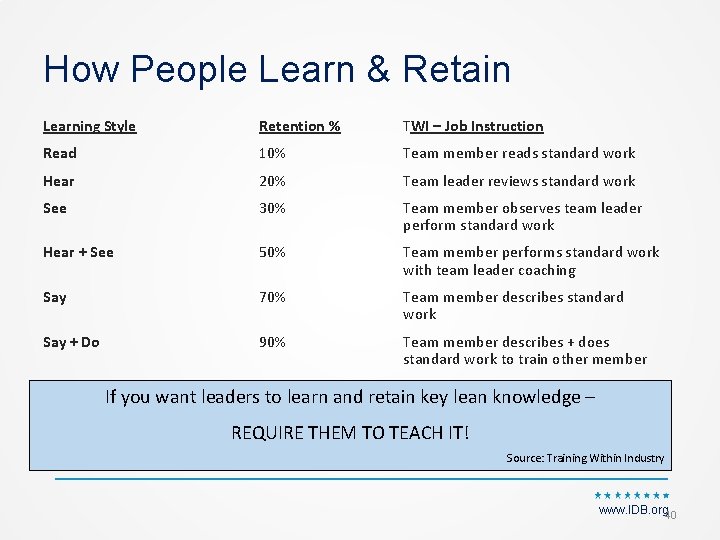
How People Learn & Retain Learning Style Retention % TWI – Job Instruction Read 10% Team member reads standard work Hear 20% Team leader reviews standard work See 30% Team member observes team leader perform standard work Hear + See 50% Team member performs standard work with team leader coaching Say 70% Team member describes standard work 90% Team member describes + does standard work to train other member Say + Do If you want leaders to learn and retain key lean knowledge – REQUIRE THEM TO TEACH IT! Source: Training Within Industry www. IDB. org 40
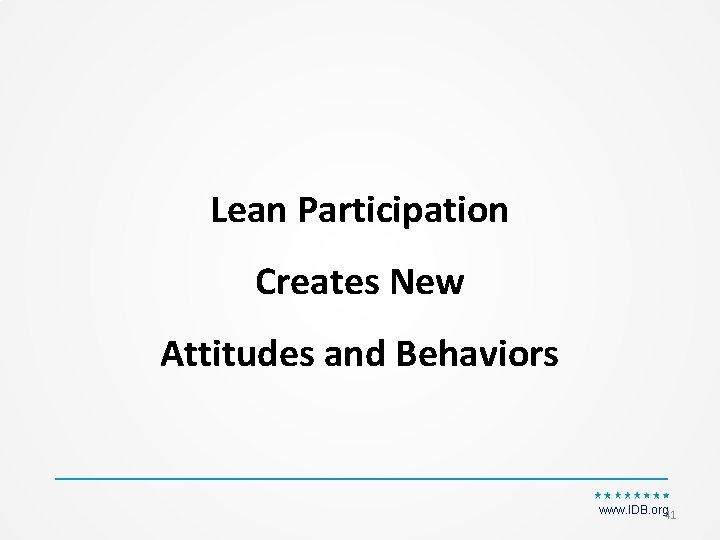
Lean Participation Creates New Attitudes and Behaviors www. IDB. org 41
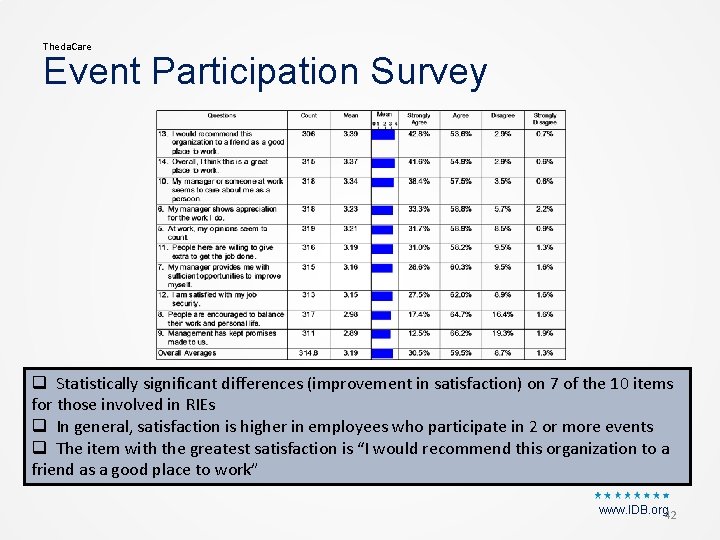
Theda. Care Event Participation Survey q Statistically significant differences (improvement in satisfaction) on 7 of the 10 items for those involved in RIEs q In general, satisfaction is higher in employees who participate in 2 or more events q The item with the greatest satisfaction is “I would recommend this organization to a friend as a good place to work” www. IDB. org 42
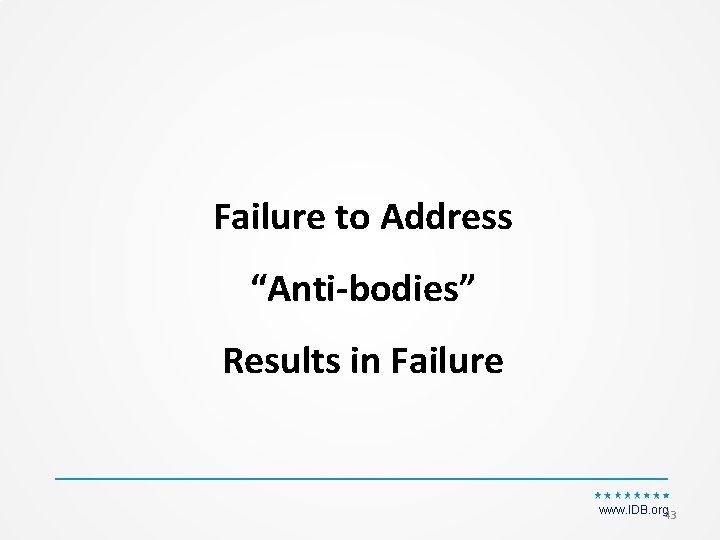
Failure to Address “Anti-bodies” Results in Failure www. IDB. org 43
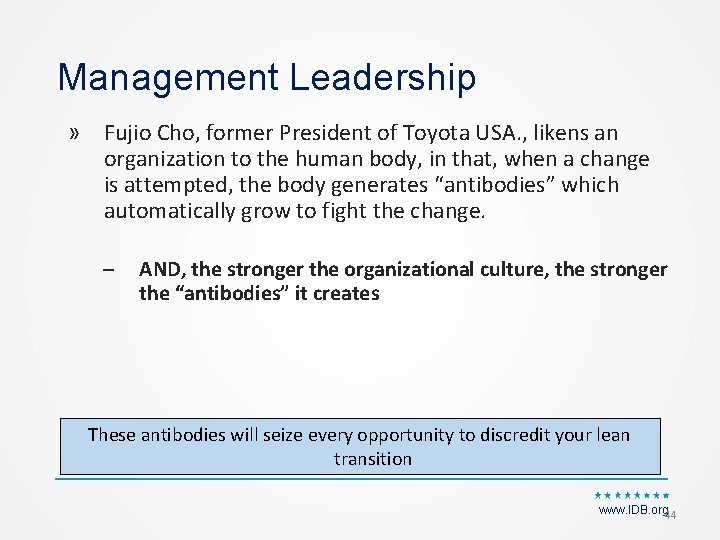
Management Leadership » Fujio Cho, former President of Toyota USA. , likens an organization to the human body, in that, when a change is attempted, the body generates “antibodies” which automatically grow to fight the change. – AND, the stronger the organizational culture, the stronger the “antibodies” it creates These antibodies will seize every opportunity to discredit your lean transition www. IDB. org 44
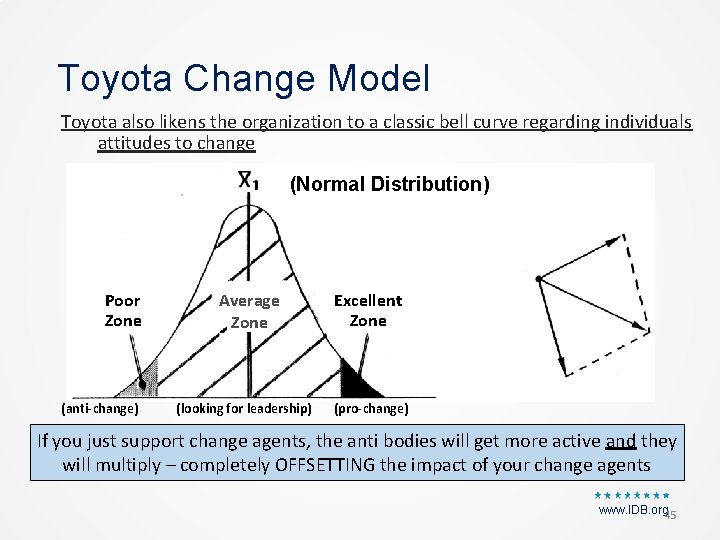
Toyota Change Model Toyota also likens the organization to a classic bell curve regarding individuals attitudes to change (Normal Distribution) Poor Zone (anti-change) Average Zone (looking for leadership) Excellent Zone (pro-change) If you just support change agents, the anti bodies will get more active and they will multiply – completely OFFSETTING the impact of your change agents www. IDB. org 45
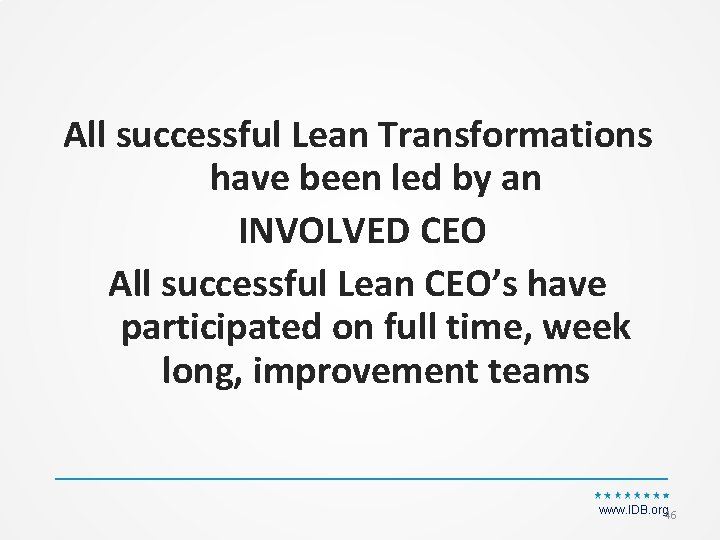
All successful Lean Transformations have been led by an INVOLVED CEO All successful Lean CEO’s have participated on full time, week long, improvement teams www. IDB. org 46
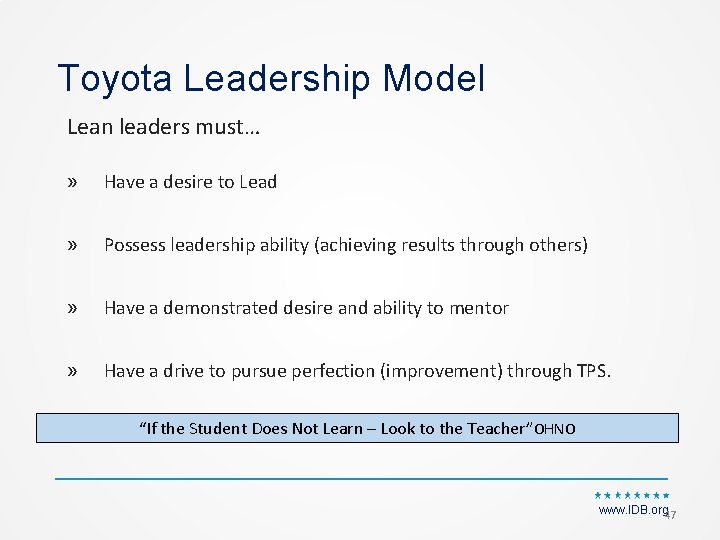
Toyota Leadership Model Lean leaders must… » Have a desire to Lead » Possess leadership ability (achieving results through others) » Have a demonstrated desire and ability to mentor » Have a drive to pursue perfection (improvement) through TPS. “If the Student Does Not Learn – Look to the Teacher”OHNO www. IDB. org 47
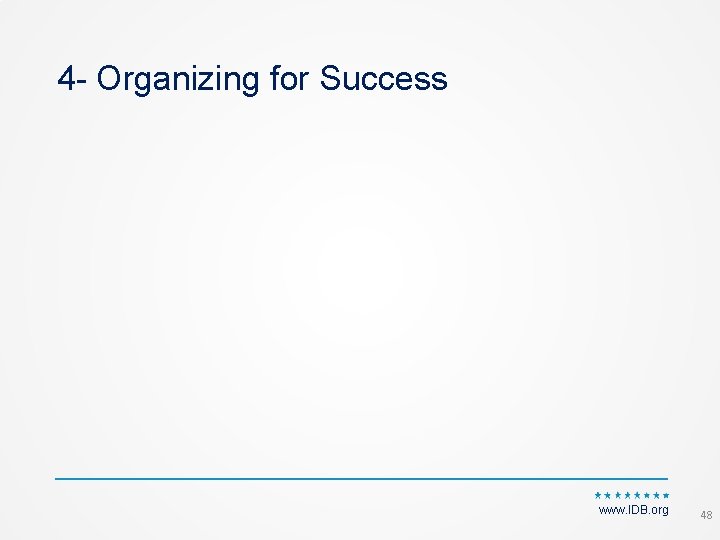
4 - Organizing for Success www. IDB. org 48
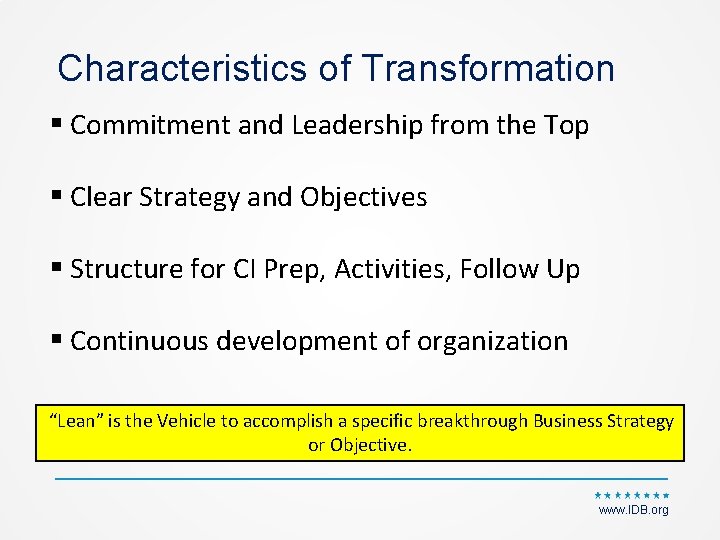
Characteristics of Transformation § Commitment and Leadership from the Top § Clear Strategy and Objectives § Structure for CI Prep, Activities, Follow Up § Continuous development of organization “Lean” is the Vehicle to accomplish a specific breakthrough Business Strategy or Objective. www. IDB. org
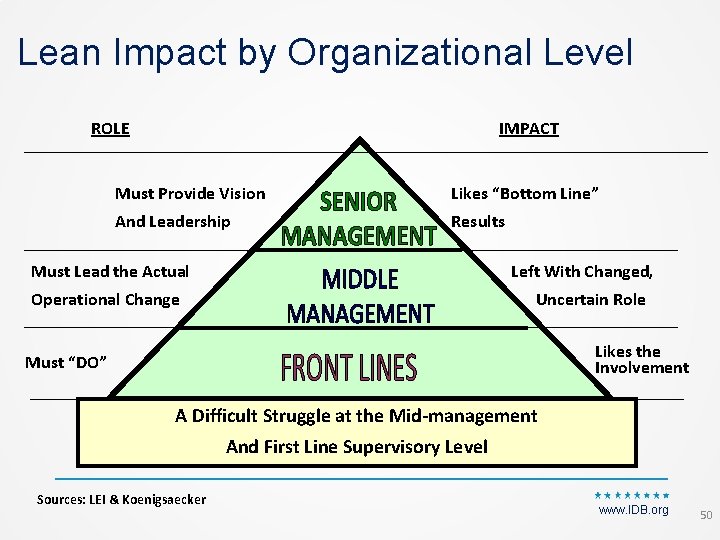
Lean Impact by Organizational Level ROLE IMPACT Must Provide Vision Likes “Bottom Line” And Leadership Results Must Lead the Actual Left With Changed, Operational Change Uncertain Role Likes the Involvement Must “DO” A Difficult Struggle at the Mid-management And First Line Supervisory Level Sources: LEI & Koenigsaecker www. IDB. org 50
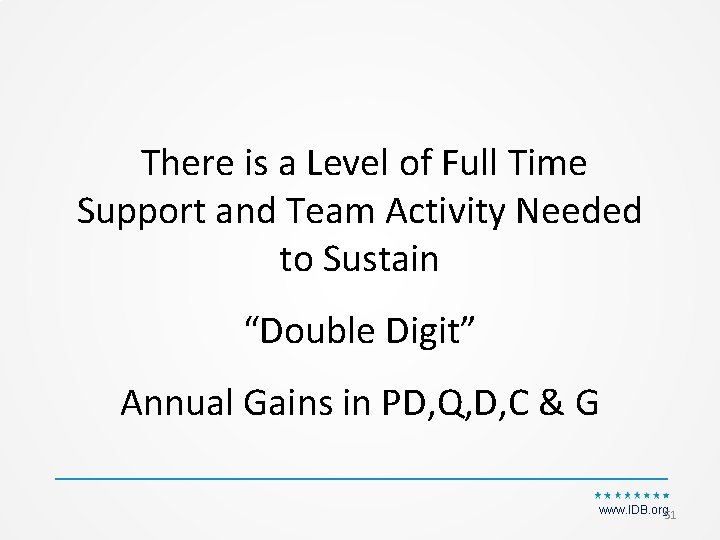
There is a Level of Full Time Support and Team Activity Needed to Sustain “Double Digit” Annual Gains in PD, Q, D, C & G www. IDB. org 51
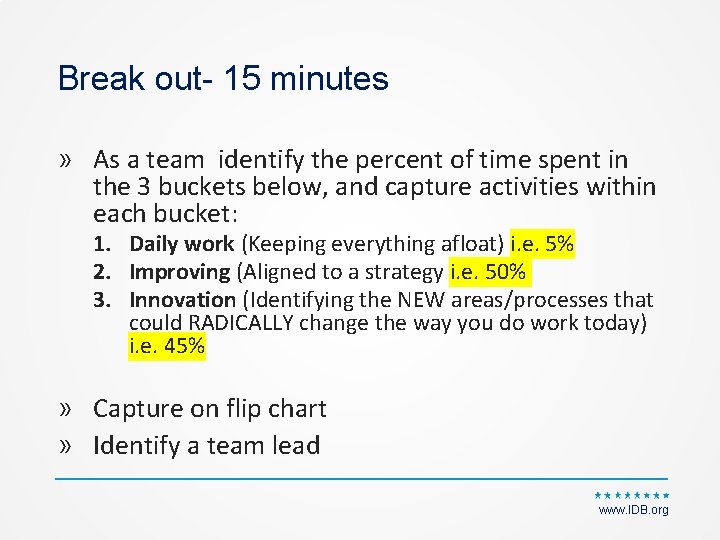
Break out- 15 minutes » As a team identify the percent of time spent in the 3 buckets below, and capture activities within each bucket: 1. Daily work (Keeping everything afloat) i. e. 5% 2. Improving (Aligned to a strategy i. e. 50% 3. Innovation (Identifying the NEW areas/processes that could RADICALLY change the way you do work today) i. e. 45% » Capture on flip chart » Identify a team lead www. IDB. org
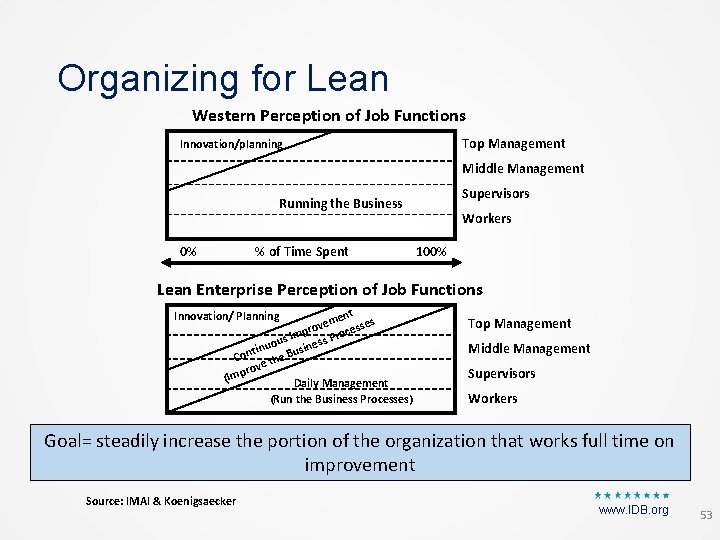
Organizing for Lean Western Perception of Job Functions Top Management Innovation/planning Middle Management Supervisors Running the Business 0% % of Time Spent Workers 100% Lean Enterprise Perception of Job Functions t men ses e v s o mpr s Proce I s ou es tinu Busin n o C he ve t o r (Imp Daily Management (Run the Business Processes) Innovation/ Planning Top Management Middle Management Supervisors Workers Goal= steadily increase the portion of the organization that works full time on improvement Source: IMAI & Koenigsaecker www. IDB. org 53
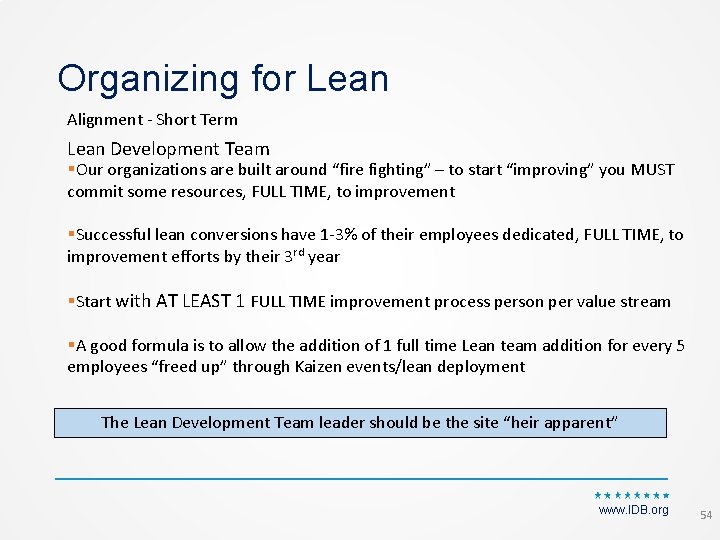
Organizing for Lean Alignment ‐ Short Term Lean Development Team §Our organizations are built around “fire fighting” – to start “improving” you MUST commit some resources, FULL TIME, to improvement §Successful lean conversions have 1‐ 3% of their employees dedicated, FULL TIME, to improvement efforts by their 3 rd year §Start with AT LEAST 1 FULL TIME improvement process person per value stream §A good formula is to allow the addition of 1 full time Lean team addition for every 5 employees “freed up” through Kaizen events/lean deployment The Lean Development Team leader should be the site “heir apparent” www. IDB. org 54
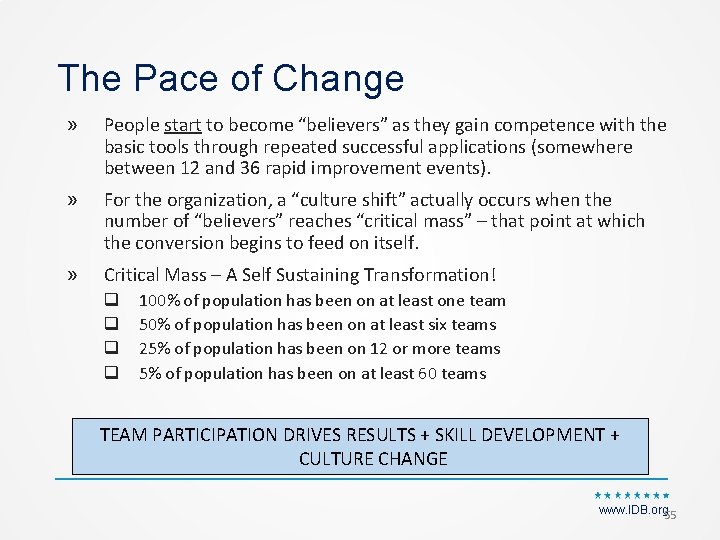
The Pace of Change » People start to become “believers” as they gain competence with the basic tools through repeated successful applications (somewhere between 12 and 36 rapid improvement events). » For the organization, a “culture shift” actually occurs when the number of “believers” reaches “critical mass” – that point at which the conversion begins to feed on itself. » Critical Mass – A Self Sustaining Transformation! q q 100% of population has been on at least one team 50% of population has been on at least six teams 25% of population has been on 12 or more teams 5% of population has been on at least 60 teams TEAM PARTICIPATION DRIVES RESULTS + SKILL DEVELOPMENT + CULTURE CHANGE www. IDB. org 55
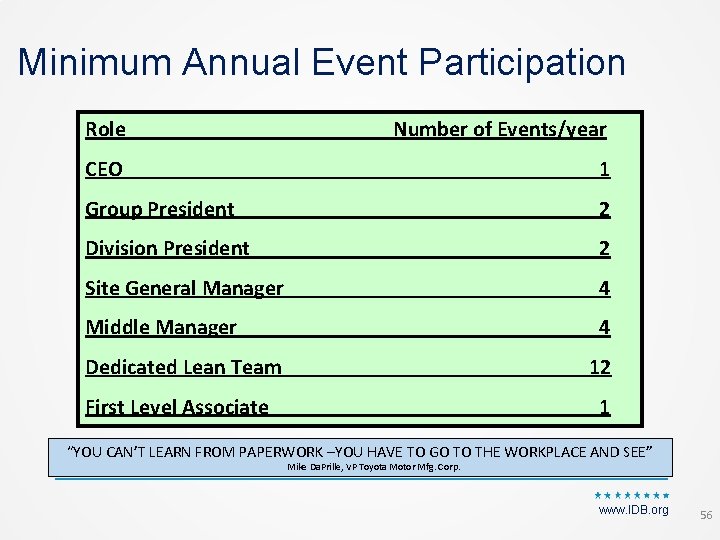
Minimum Annual Event Participation Role Number of Events/year CEO 1 Group President 2 Division President 2 Site General Manager 4 Middle Manager 4 Dedicated Lean Team 12 First Level Associate 1 “YOU CAN’T LEARN FROM PAPERWORK –YOU HAVE TO GO TO THE WORKPLACE AND SEE” Mike Da. Prille, VP Toyota Motor Mfg. Corp. www. IDB. org 56
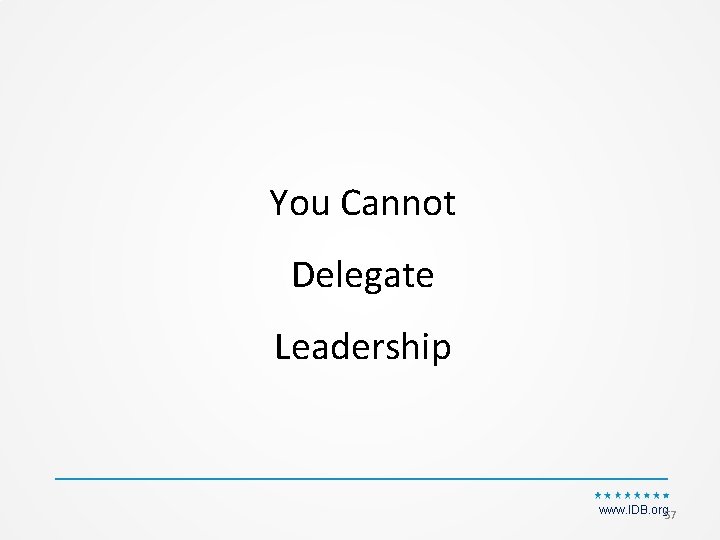
You Cannot Delegate Leadership www. IDB. org 57
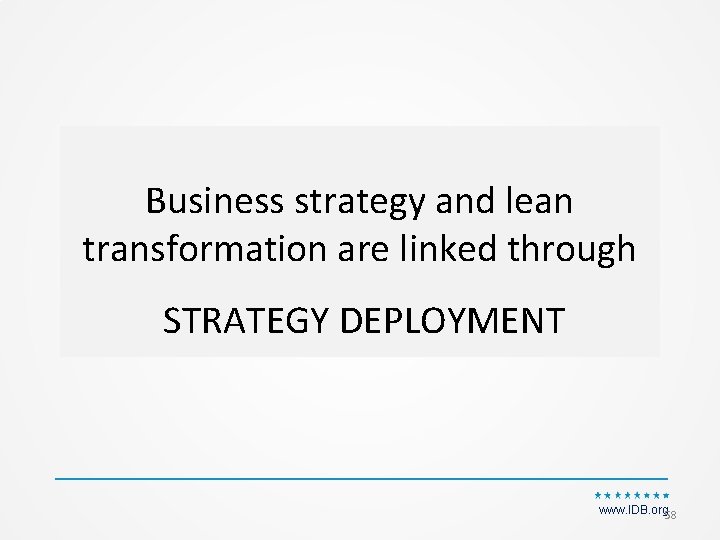
Business strategy and lean transformation are linked through STRATEGY DEPLOYMENT www. IDB. org 58
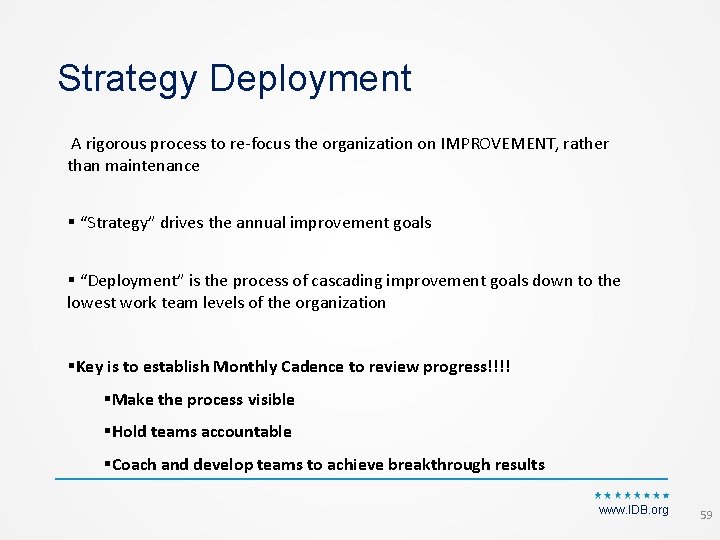
Strategy Deployment A rigorous process to re‐focus the organization on IMPROVEMENT, rather than maintenance § “Strategy” drives the annual improvement goals § “Deployment” is the process of cascading improvement goals down to the lowest work team levels of the organization §Key is to establish Monthly Cadence to review progress!!!! §Make the process visible §Hold teams accountable §Coach and develop teams to achieve breakthrough results www. IDB. org 59
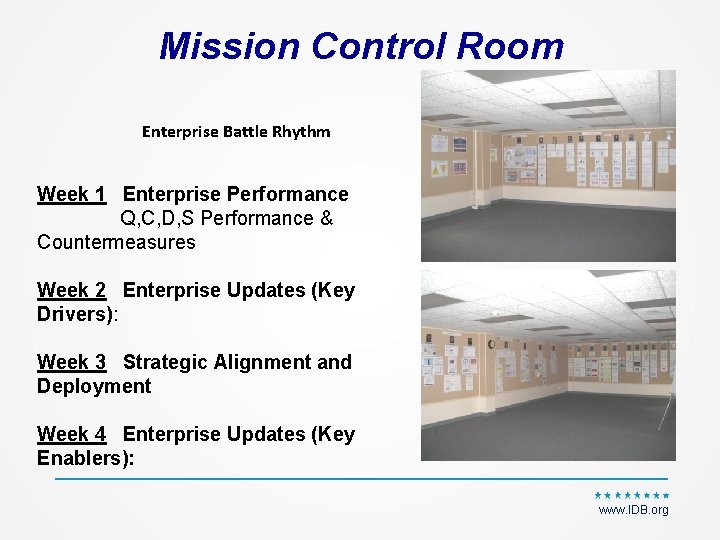
Mission Control Room Enterprise Battle Rhythm Week 1 Enterprise Performance Q, C, D, S Performance & Countermeasures Week 2 Enterprise Updates (Key Drivers): Week 3 Strategic Alignment and Deployment Week 4 Enterprise Updates (Key Enablers): www. IDB. org
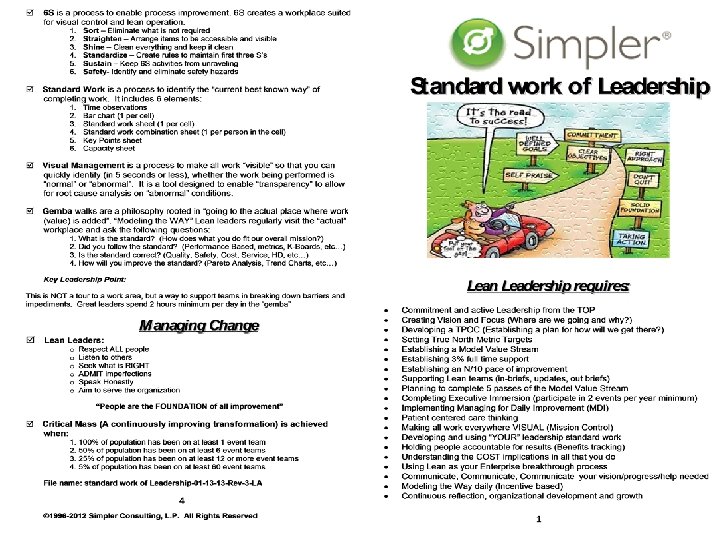
61
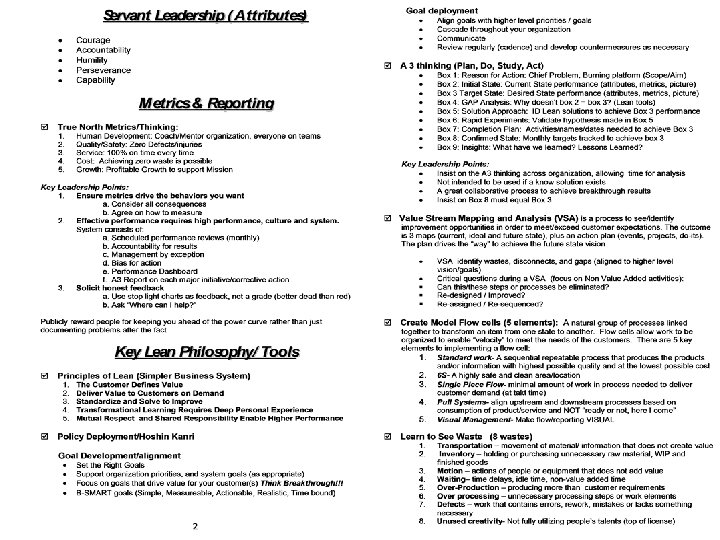
62
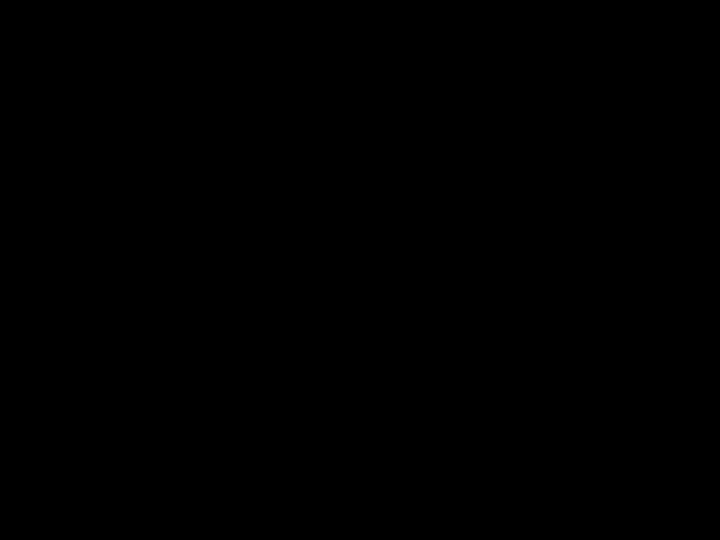
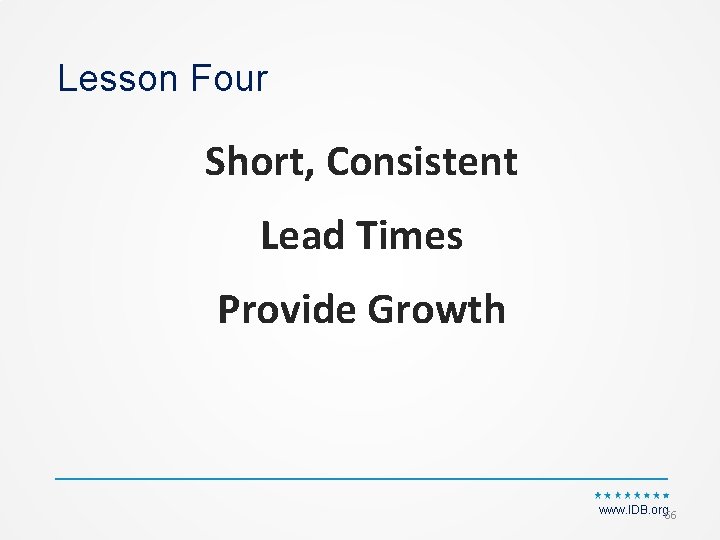
Lesson Four Short, Consistent Lead Times Provide Growth www. IDB. org 66
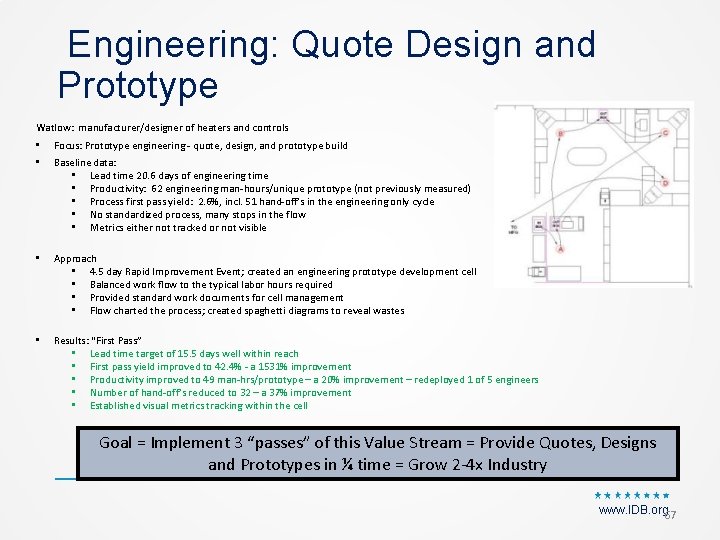
Engineering: Quote Design and Prototype Watlow: manufacturer/designer of heaters and controls • Focus: Prototype engineering ‐ quote, design, and prototype build • Baseline data: • Lead time 20. 6 days of engineering time • Productivity: 62 engineering man‐hours/unique prototype (not previously measured) • Process first pass yield: 2. 6%, incl. 51 hand‐off’s in the engineering only cycle • No standardized process, many stops in the flow • Metrics either not tracked or not visible • Approach • 4. 5 day Rapid Improvement Event; created an engineering prototype development cell • Balanced work flow to the typical labor hours required • Provided standard work documents for cell management • Flow charted the process; created spaghetti diagrams to reveal wastes • Results: “First Pass” • Lead time target of 15. 5 days well within reach • First pass yield improved to 42. 4% ‐ a 1531% improvement • Productivity improved to 49 man‐hrs/prototype – a 20% improvement – redeployed 1 of 5 engineers • Number of hand‐off’s reduced to 32 – a 37% improvement • Established visual metrics tracking within the cell Goal = Implement 3 “passes” of this Value Stream = Provide Quotes, Designs and Prototypes in ¼ time = Grow 2‐ 4 x Industry www. IDB. org 67
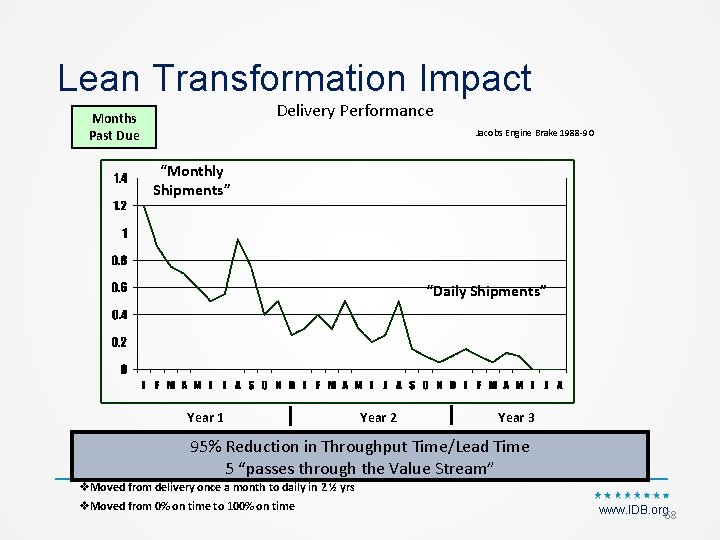
Lean Transformation Impact Delivery Performance Months Past Due Jacobs Engine Brake 1988‐ 90 “Monthly Shipments” “Daily Shipments” Year 1 Year 2 Year 3 95% Reduction in Throughput Time/Lead Time 5 “passes through the Value Stream” v. Moved from delivery once a month to daily in 2 ½ yrs v. Moved from 0% on time to 100% on time www. IDB. org 68
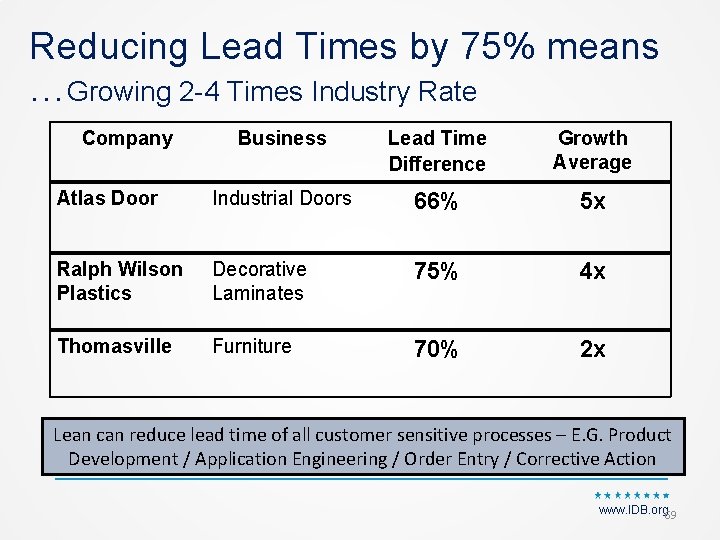
Reducing Lead Times by 75% means …Growing 2 -4 Times Industry Rate Company Business Lead Time Difference Growth Average Atlas Door Industrial Doors 66% 5 x Ralph Wilson Plastics Decorative Laminates 75% 4 x Thomasville Furniture 70% 2 x Lean can reduce lead time of all customer sensitive processes – E. G. Product Development / Application Engineering / Order Entry / Corrective Action www. IDB. org 69
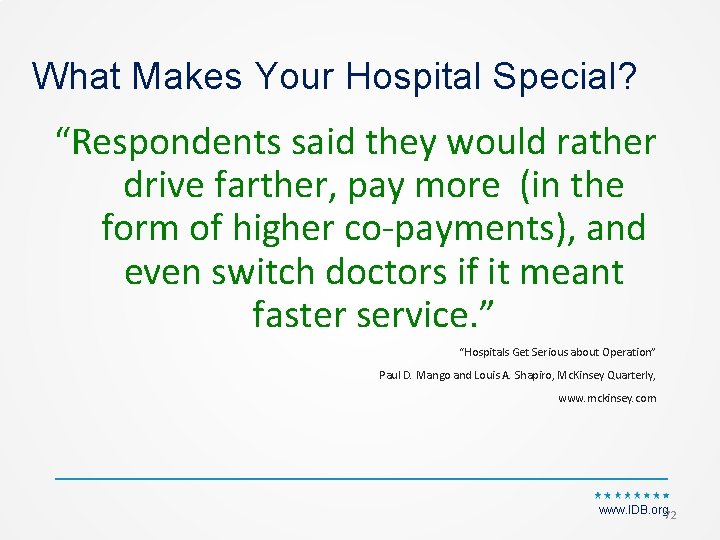
What Makes Your Hospital Special? “Respondents said they would rather drive farther, pay more (in the form of higher co‐payments), and even switch doctors if it meant faster service. ” “Hospitals Get Serious about Operation” Paul D. Mango and Louis A. Shapiro, Mc. Kinsey Quarterly, www. mckinsey. com www. IDB. org 72
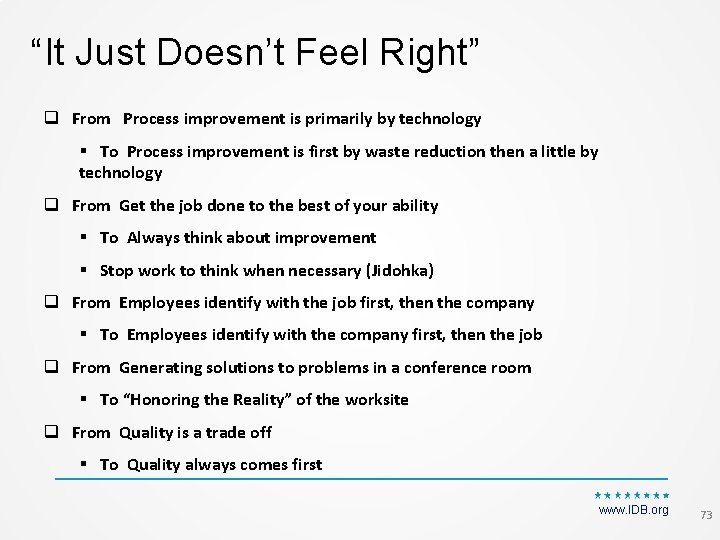
“It Just Doesn’t Feel Right” q From Process improvement is primarily by technology § To Process improvement is first by waste reduction then a little by technology q From Get the job done to the best of your ability § To Always think about improvement § Stop work to think when necessary (Jidohka) q From Employees identify with the job first, then the company § To Employees identify with the company first, then the job q From Generating solutions to problems in a conference room § To “Honoring the Reality” of the worksite q From Quality is a trade off § To Quality always comes first www. IDB. org 73
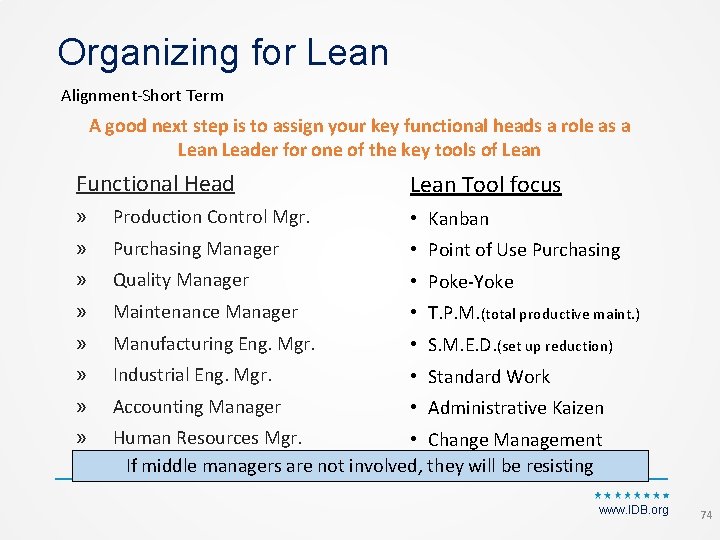
Organizing for Lean Alignment‐Short Term A good next step is to assign your key functional heads a role as a Lean Leader for one of the key tools of Lean Functional Head Lean Tool focus » Production Control Mgr. • Kanban » Purchasing Manager • Point of Use Purchasing » Quality Manager • Poke‐Yoke » Maintenance Manager • T. P. M. (total productive maint. ) » Manufacturing Eng. Mgr. • S. M. E. D. (set up reduction) » Industrial Eng. Mgr. • Standard Work » Accounting Manager • Administrative Kaizen » Human Resources Mgr. • Change Management If middle managers are not involved, they will be resisting www. IDB. org 74
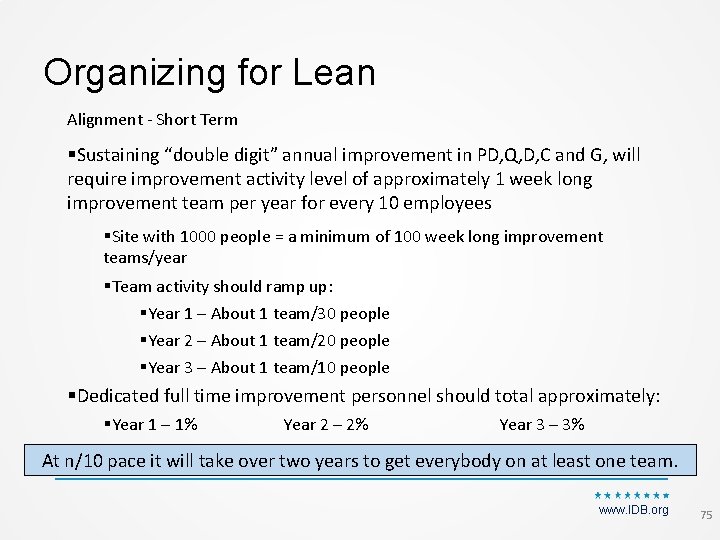
Organizing for Lean Alignment ‐ Short Term §Sustaining “double digit” annual improvement in PD, Q, D, C and G, will require improvement activity level of approximately 1 week long improvement team per year for every 10 employees §Site with 1000 people = a minimum of 100 week long improvement teams/year §Team activity should ramp up: §Year 1 – About 1 team/30 people §Year 2 – About 1 team/20 people §Year 3 – About 1 team/10 people §Dedicated full time improvement personnel should total approximately: §Year 1 – 1% Year 2 – 2% Year 3 – 3% At n/10 pace it will take over two years to get everybody on at least one team. www. IDB. org 75
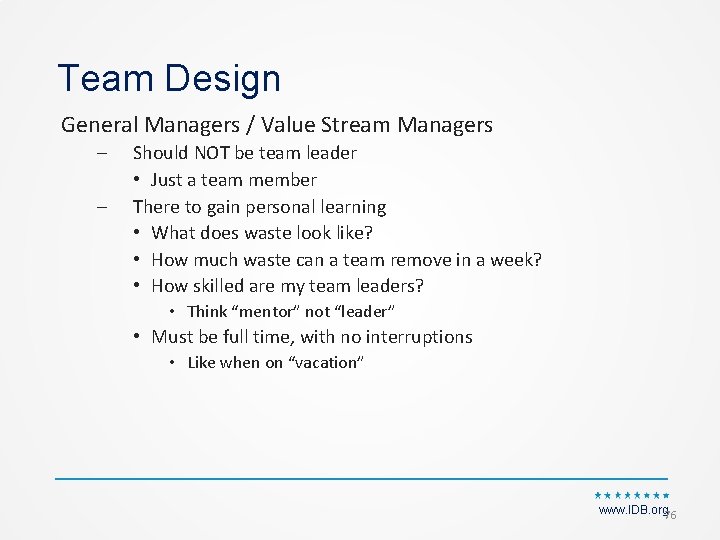
Team Design General Managers / Value Stream Managers – – Should NOT be team leader • Just a team member There to gain personal learning • What does waste look like? • How much waste can a team remove in a week? • How skilled are my team leaders? • Think “mentor” not “leader” • Must be full time, with no interruptions • Like when on “vacation” www. IDB. org 76
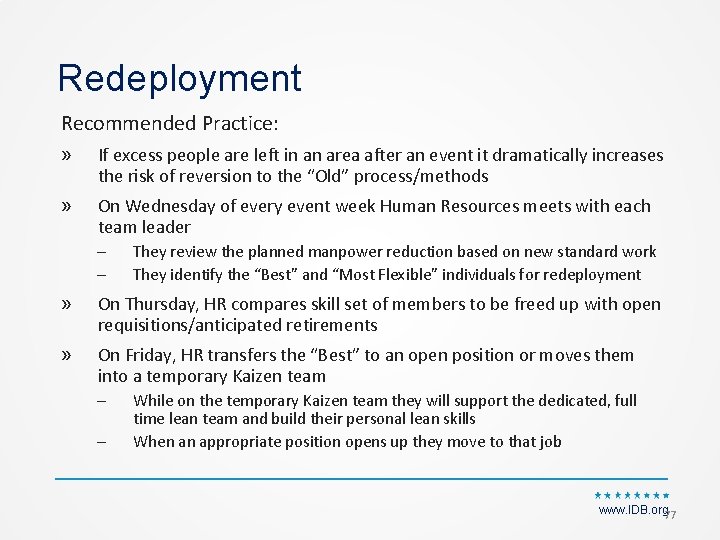
Redeployment Recommended Practice: » If excess people are left in an area after an event it dramatically increases the risk of reversion to the “Old” process/methods » On Wednesday of every event week Human Resources meets with each team leader – – They review the planned manpower reduction based on new standard work They identify the “Best” and “Most Flexible” individuals for redeployment » On Thursday, HR compares skill set of members to be freed up with open requisitions/anticipated retirements » On Friday, HR transfers the “Best” to an open position or moves them into a temporary Kaizen team – – While on the temporary Kaizen team they will support the dedicated, full time lean team and build their personal lean skills When an appropriate position opens up they move to that job www. IDB. org 77
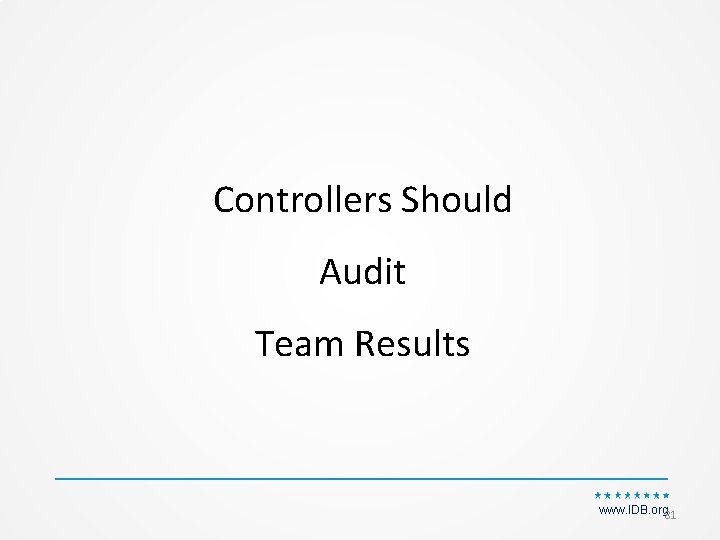
Controllers Should Audit Team Results www. IDB. org 81
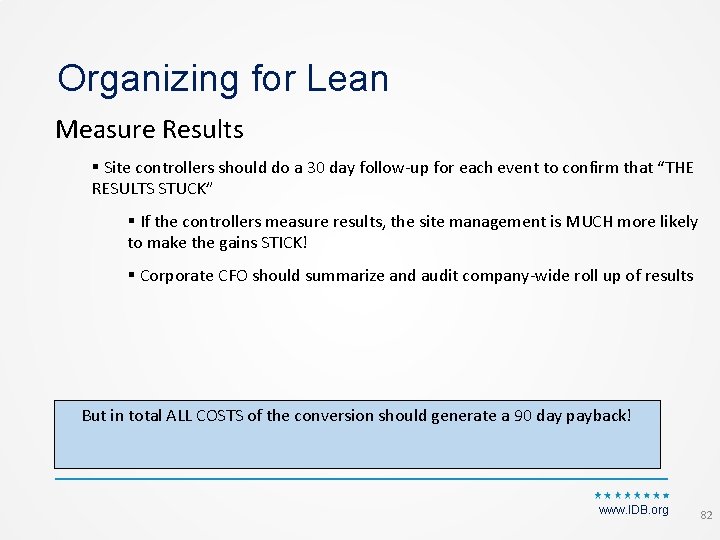
Organizing for Lean Measure Results § Site controllers should do a 30 day follow‐up for each event to confirm that “THE RESULTS STUCK” § If the controllers measure results, the site management is MUCH more likely to make the gains STICK! § Corporate CFO should summarize and audit company‐wide roll up of results But in total ALL COSTS of the conversion should generate a 90 day payback! www. IDB. org 82
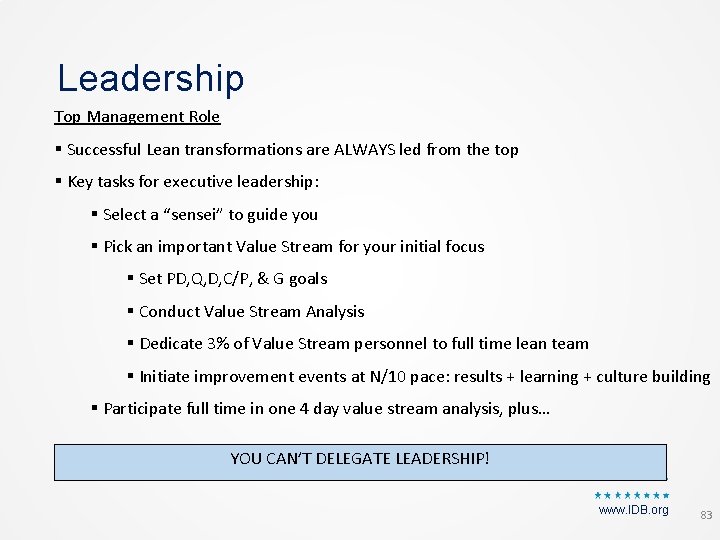
Leadership Top Management Role § Successful Lean transformations are ALWAYS led from the top § Key tasks for executive leadership: § Select a “sensei” to guide you § Pick an important Value Stream for your initial focus § Set PD, Q, D, C/P, & G goals § Conduct Value Stream Analysis § Dedicate 3% of Value Stream personnel to full time lean team § Initiate improvement events at N/10 pace: results + learning + culture building § Participate full time in one 4 day value stream analysis, plus… YOU CAN’T DELEGATE LEADERSHIP! www. IDB. org 83
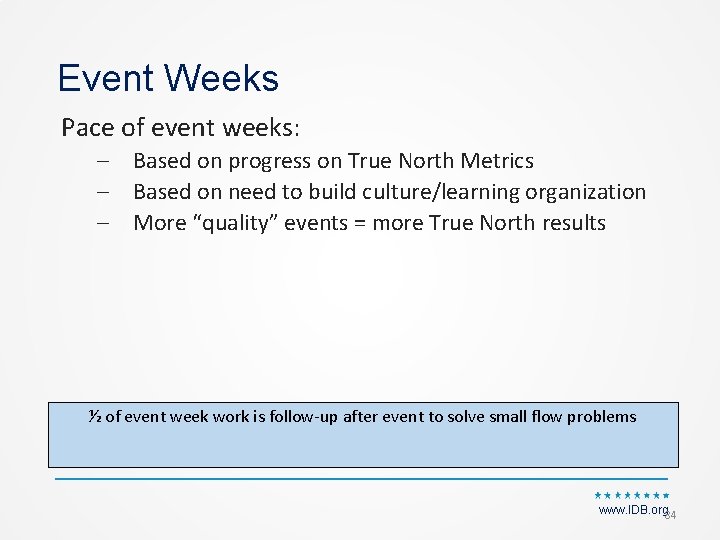
Event Weeks Pace of event weeks: – Based on progress on True North Metrics – Based on need to build culture/learning organization – More “quality” events = more True North results ½ of event week work is follow‐up after event to solve small flow problems www. IDB. org 84
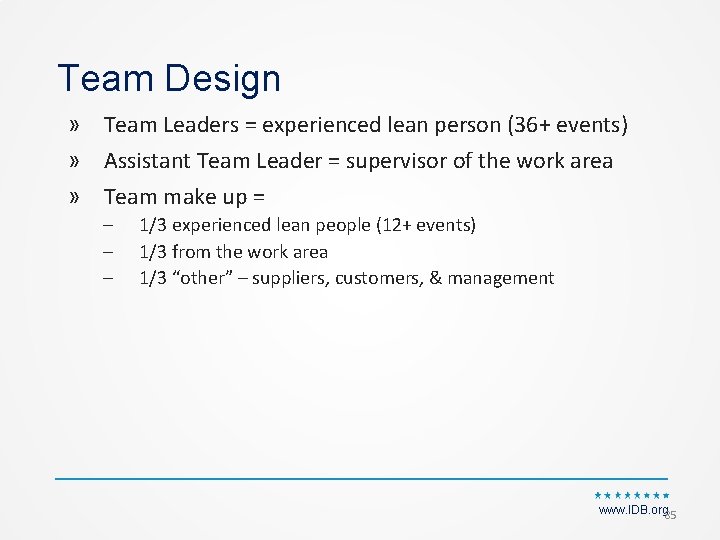
Team Design » Team Leaders = experienced lean person (36+ events) » Assistant Team Leader = supervisor of the work area » Team make up = – – – 1/3 experienced lean people (12+ events) 1/3 from the work area 1/3 “other” – suppliers, customers, & management www. IDB. org 85
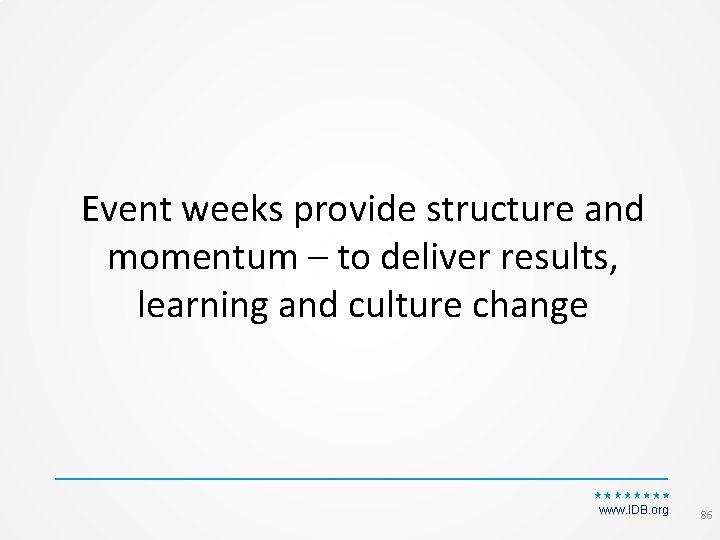
Event weeks provide structure and momentum – to deliver results, learning and culture change www. IDB. org 86
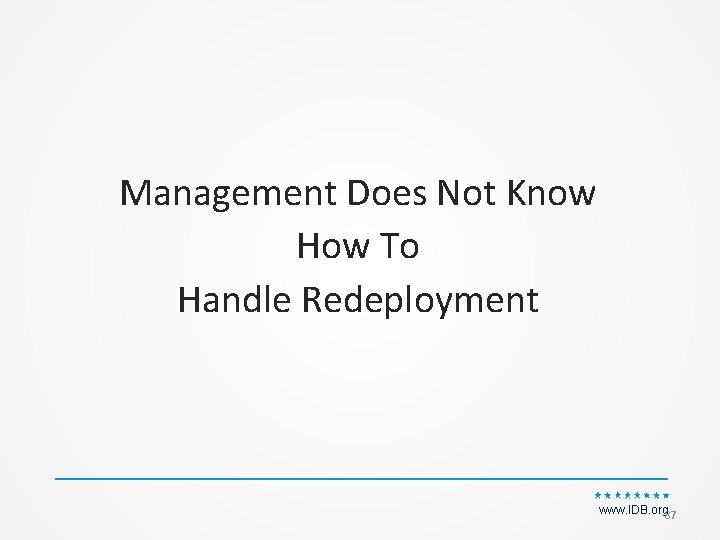
Management Does Not Know How To Handle Redeployment www. IDB. org 87
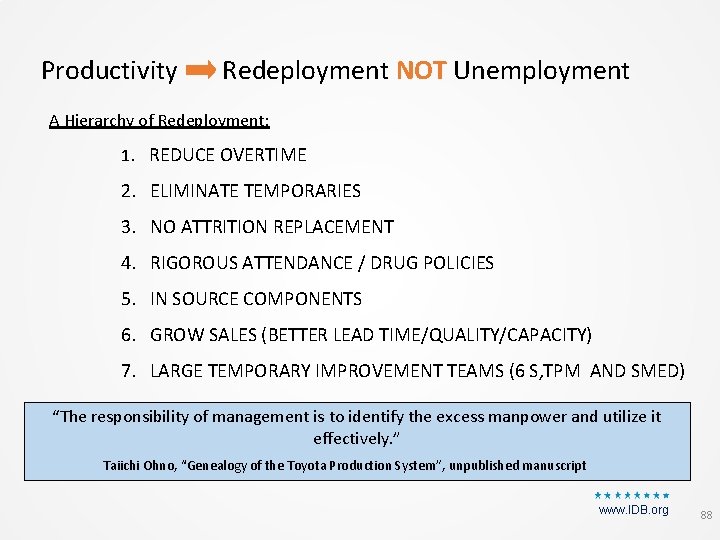
Productivity Redeployment NOT Unemployment A Hierarchy of Redeployment: 1. REDUCE OVERTIME 2. ELIMINATE TEMPORARIES 3. NO ATTRITION REPLACEMENT 4. RIGOROUS ATTENDANCE / DRUG POLICIES 5. IN SOURCE COMPONENTS 6. GROW SALES (BETTER LEAD TIME/QUALITY/CAPACITY) 7. LARGE TEMPORARY IMPROVEMENT TEAMS (6 S, TPM AND SMED) “The responsibility of management is to identify the excess manpower and utilize it effectively. ” Taiichi Ohno, “Genealogy of the Toyota Production System”, unpublished manuscript www. IDB. org 88
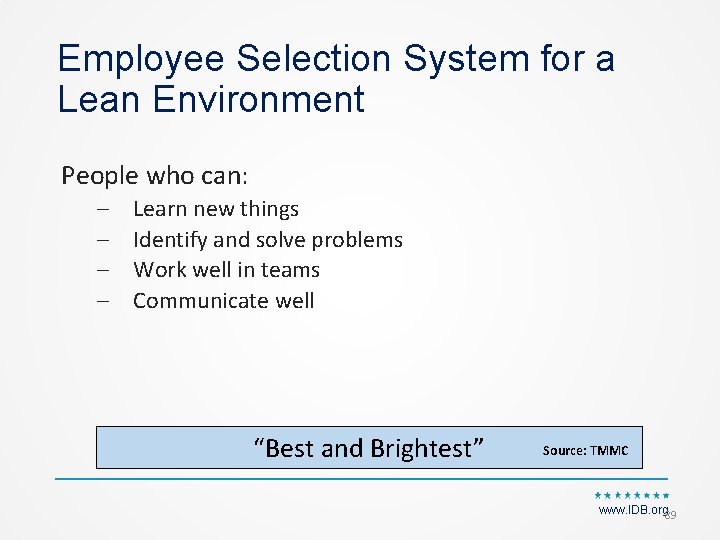
Employee Selection System for a Lean Environment People who can: – – Learn new things Identify and solve problems Work well in teams Communicate well “Best and Brightest” Source: TMMC www. IDB. org 89
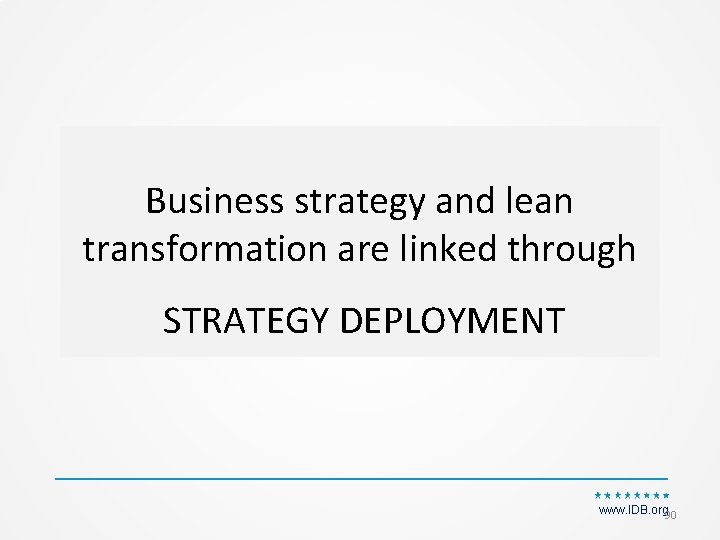
Business strategy and lean transformation are linked through STRATEGY DEPLOYMENT www. IDB. org 90
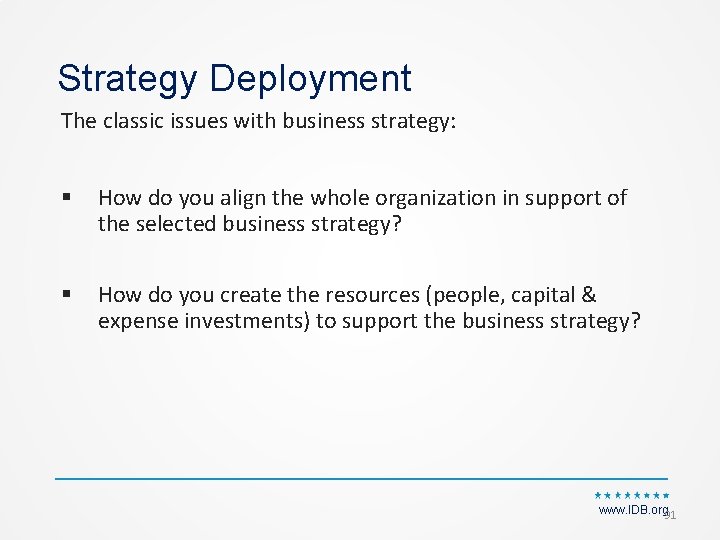
Strategy Deployment The classic issues with business strategy: § How do you align the whole organization in support of the selected business strategy? § How do you create the resources (people, capital & expense investments) to support the business strategy? www. IDB. org 91
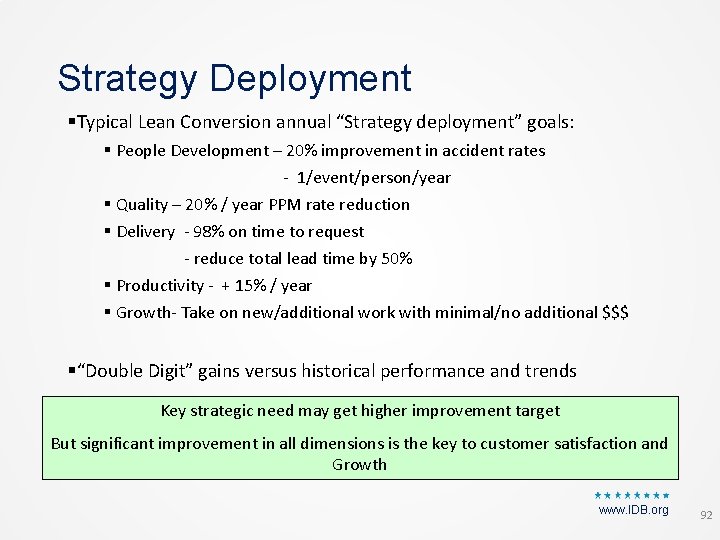
Strategy Deployment §Typical Lean Conversion annual “Strategy deployment” goals: § People Development – 20% improvement in accident rates ‐ 1/event/person/year § Quality – 20% / year PPM rate reduction § Delivery ‐ 98% on time to request ‐ reduce total lead time by 50% § Productivity ‐ + 15% / year § Growth‐ Take on new/additional work with minimal/no additional $$$ §“Double Digit” gains versus historical performance and trends Key strategic need may get higher improvement target But significant improvement in all dimensions is the key to customer satisfaction and Growth www. IDB. org 92
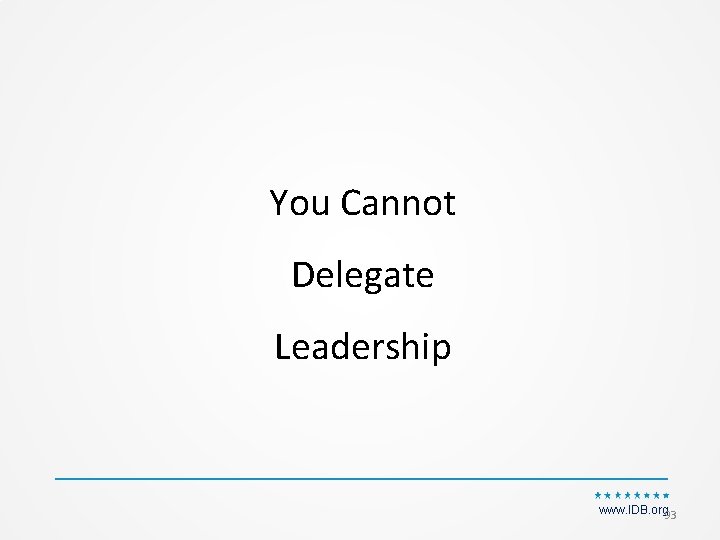
You Cannot Delegate Leadership www. IDB. org 93
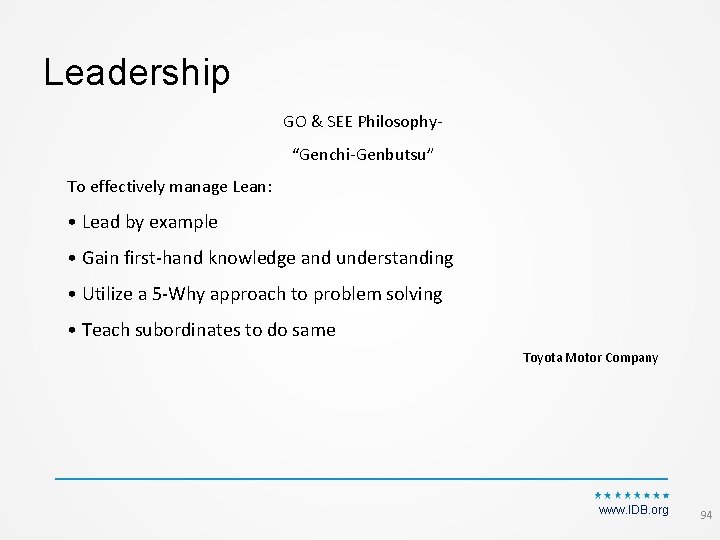
Leadership GO & SEE Philosophy‐ “Genchi‐Genbutsu” To effectively manage Lean: • Lead by example • Gain first‐hand knowledge and understanding • Utilize a 5‐Why approach to problem solving • Teach subordinates to do same Toyota Motor Company www. IDB. org 94
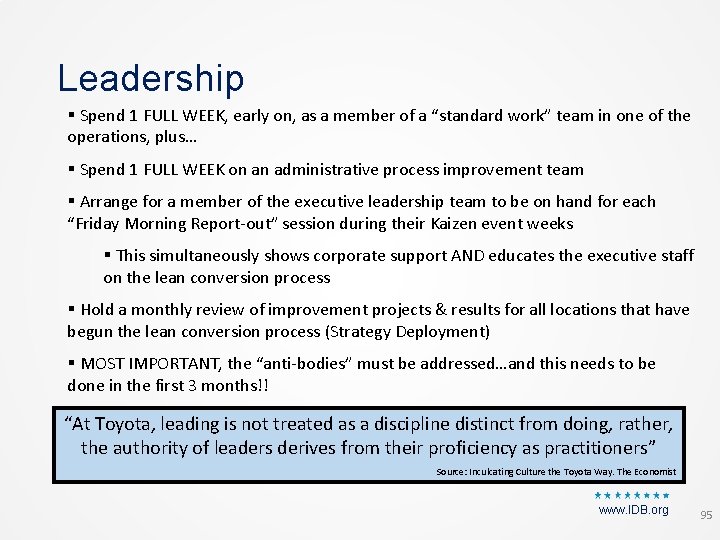
Leadership § Spend 1 FULL WEEK, early on, as a member of a “standard work” team in one of the operations, plus… § Spend 1 FULL WEEK on an administrative process improvement team § Arrange for a member of the executive leadership team to be on hand for each “Friday Morning Report‐out” session during their Kaizen event weeks § This simultaneously shows corporate support AND educates the executive staff on the lean conversion process § Hold a monthly review of improvement projects & results for all locations that have begun the lean conversion process (Strategy Deployment) § MOST IMPORTANT, the “anti‐bodies” must be addressed…and this needs to be done in the first 3 months!! “At Toyota, leading is not treated as a discipline distinct from doing, rather, the authority of leaders derives from their proficiency as practitioners” Source: Inculcating Culture the Toyota Way. The Economist www. IDB. org 95
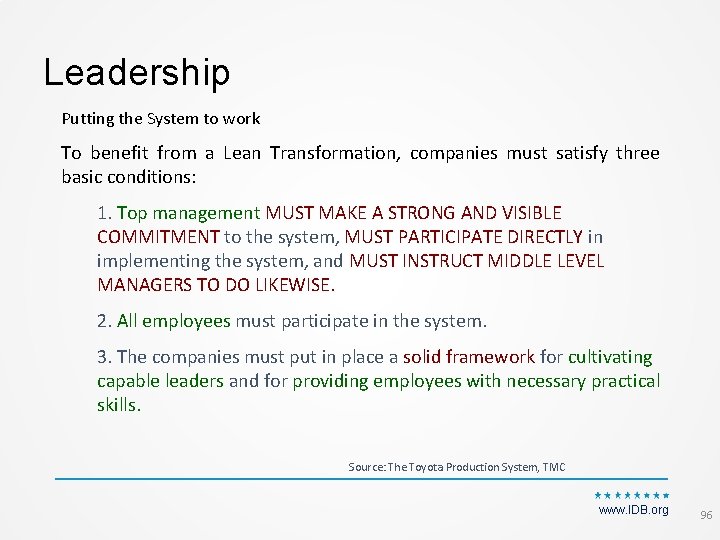
Leadership Putting the System to work To benefit from a Lean Transformation, companies must satisfy three basic conditions: 1. Top management MUST MAKE A STRONG AND VISIBLE COMMITMENT to the system, MUST PARTICIPATE DIRECTLY in implementing the system, and MUST INSTRUCT MIDDLE LEVEL MANAGERS TO DO LIKEWISE. 2. All employees must participate in the system. 3. The companies must put in place a solid framework for cultivating capable leaders and for providing employees with necessary practical skills. Source: The Toyota Production System, TMC www. IDB. org 96
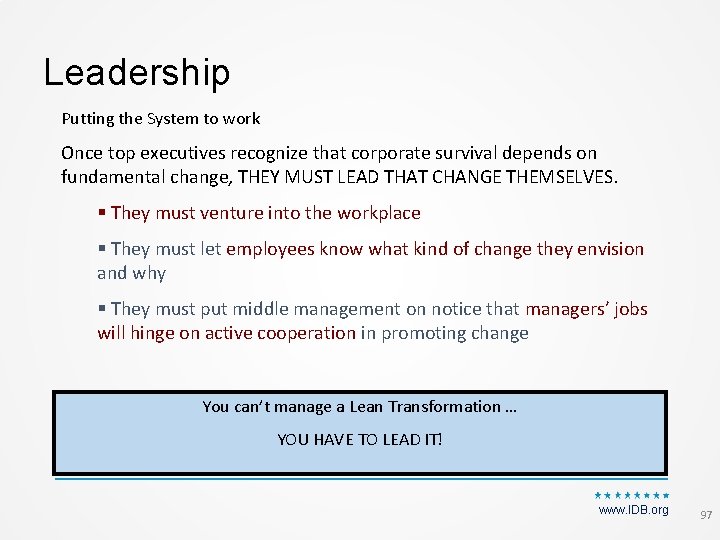
Leadership Putting the System to work Once top executives recognize that corporate survival depends on fundamental change, THEY MUST LEAD THAT CHANGE THEMSELVES. § They must venture into the workplace § They must let employees know what kind of change they envision and why § They must put middle management on notice that managers’ jobs will hinge on active cooperation in promoting change You can’t manage a Lean Transformation … YOU HAVE TO LEAD IT! www. IDB. org 97
President vice president treasurer secretary
Lee alves
Vice president membership
Senior regional vice president
Age of vice president
Ffa parliamentarian symbol
Vice president duties in a club
What ffa officer is stationed by the flag
Vice president training
Senior regional vice president
Mary jo fitzpatrick is the vice president
Vice president training
Lee tait
Senior regional vice president
Senior regional vice president
Microsoft executive vice president
Lee kong chian faculty of engineering and science
Lee kong chian faculty of engineering and science
Process of changing food into simpler substances
Vowel distortions
Solve a simpler problem strategy
Solve a simpler problem examples
What do vice presidents do in clubs
Vice reinos espanhois
Více hlásek než písmen
Folk gang sign
Ano ang pamumuhay sa espanya
Xxx vice-chair
Tanuvas vice chancellor
Extremism in the defense of liberty
Inherent vice of capitalism
Conversion of work into heat and vice versa
Bod zvratu pro více produktů
Vice-laden
Changing decimals to fractions and vice versa
Party is such sweet sorrow vice game
Inherent vice definition
A poesia lírica de castro alves também apresenta
Rubem alves passaros engaiolados
Embriologia comparada exemplos
Javeleta
Agrupamento escolas alves redol
Carlos augusto alves santana
Bruno alves pinto
Joannabelle ng
Historia geral e do brasil jose alves de freitas neto
José júlio alves alferes
Então longe de ti
Kelynn midori alves
Rubem alves a complicada arte de ver
Gametas
Alecsander alves altura
Versos decassilabos
Elizeu barroso alves
Jabuticaba poema
Davis alves
Estudo longitudinal
Halliburton engineering global programs
Rubem alves a arte de educar
Comernity
Piçarras celk
A pipoca rubem alves
Profamilka
Usi faculty
Brenton diaz york university
Feri maribor
Singularity executive program
Maastricht faculty of law
Cme invitation format
Mendel university - faculty of business and economics
Thin and thick smear
Iit delhi eacademics
Mcgill medicine supporting documents
Importance of faculty in higher education
Fsu new faculty orientation
Imnu faculty
Faculty information system unt
Uab comp clinic
Kfupm clinic
Etfbl
Sjsu faculty affairs
Chronicle salary data
Ucl computers
St.anns college chirala materials
Advice for new faculty members
Faculty of civil engineering ctu prague
Faculty introduction speech
Applied medical sciences
John von neumann faculty of informatics
Bu pemba curriculum
Penn state neurosurgery faculty