Management of Facilities Production Facilities Production facilities form
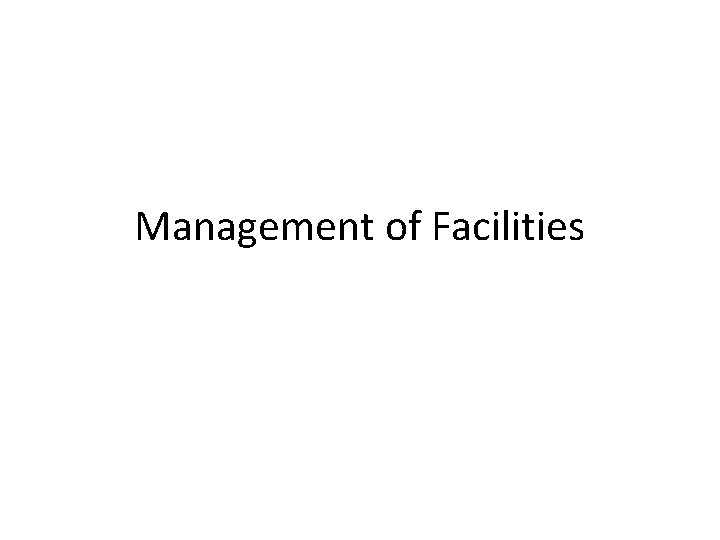
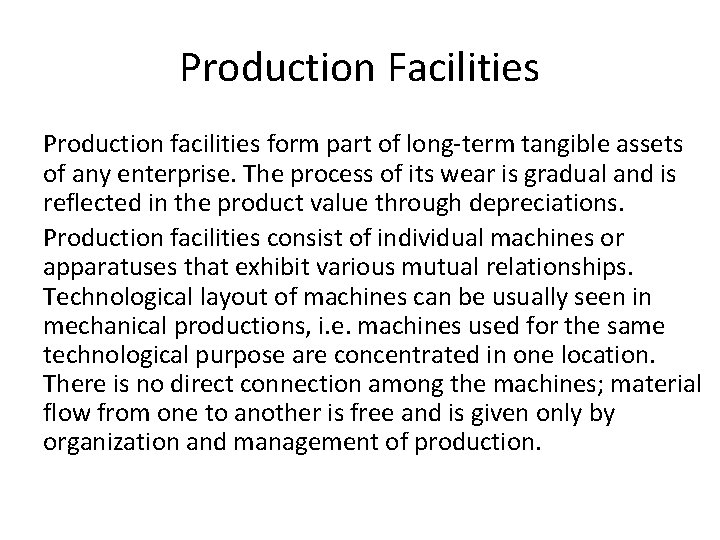
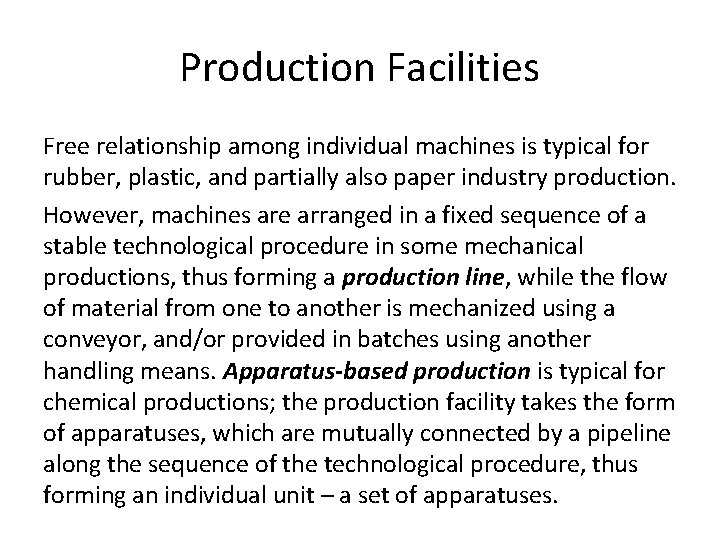
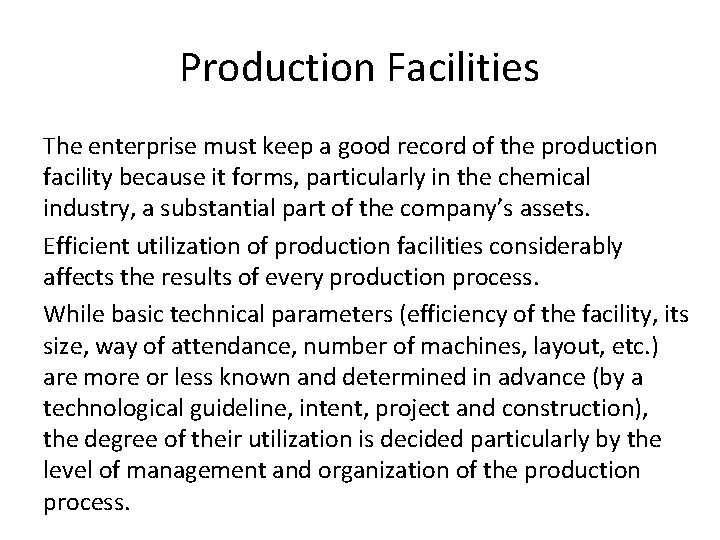
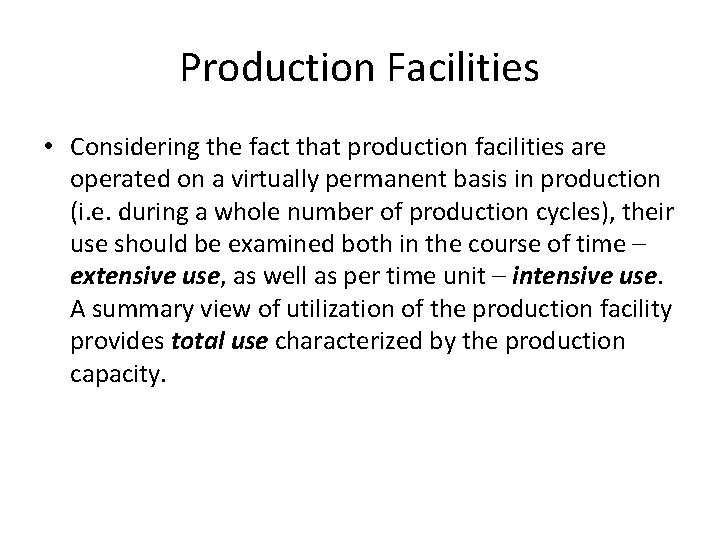
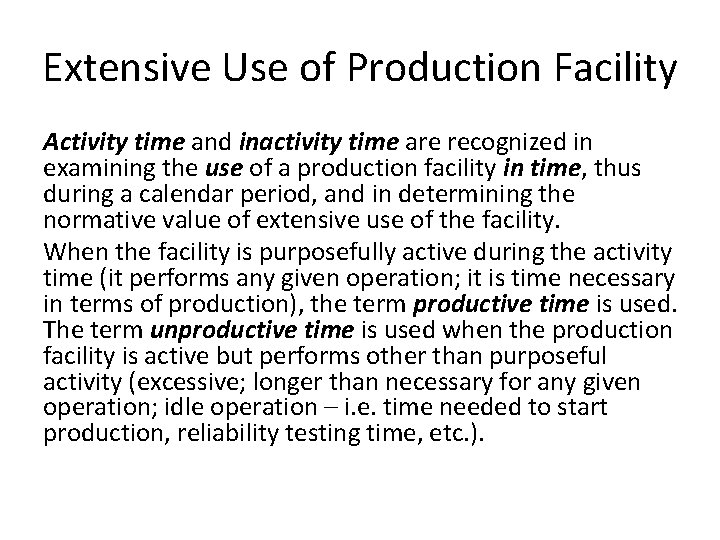

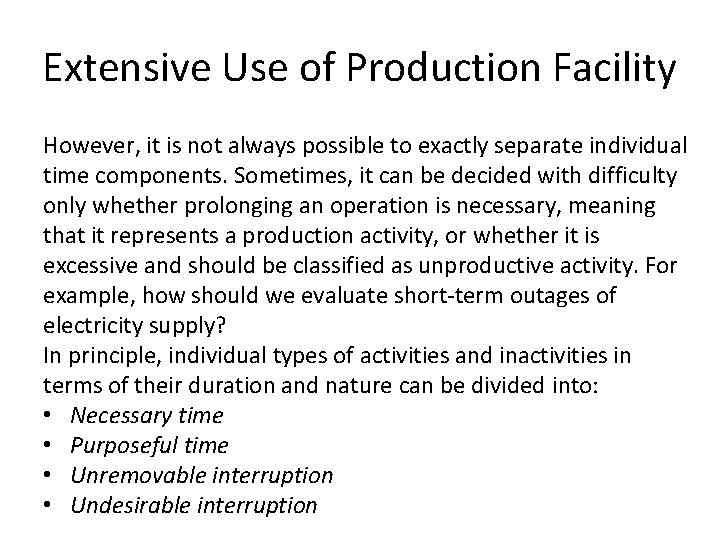
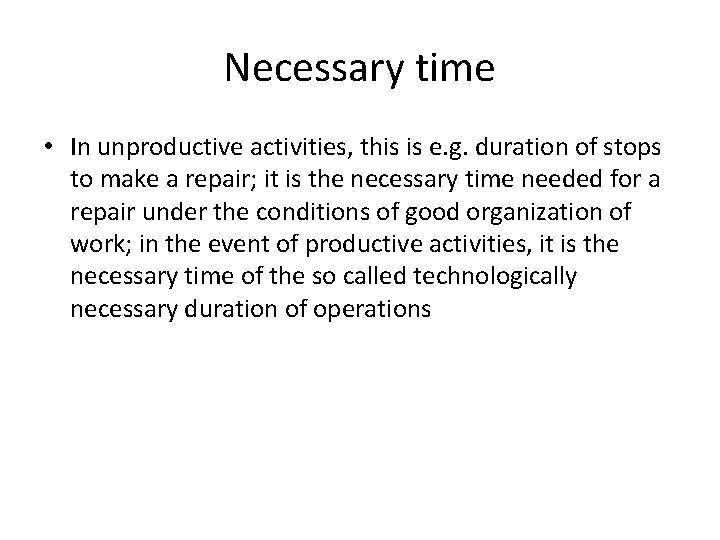
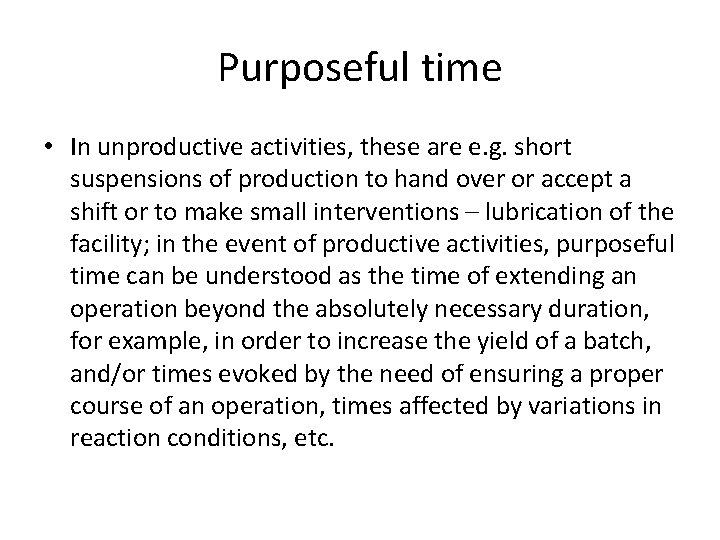
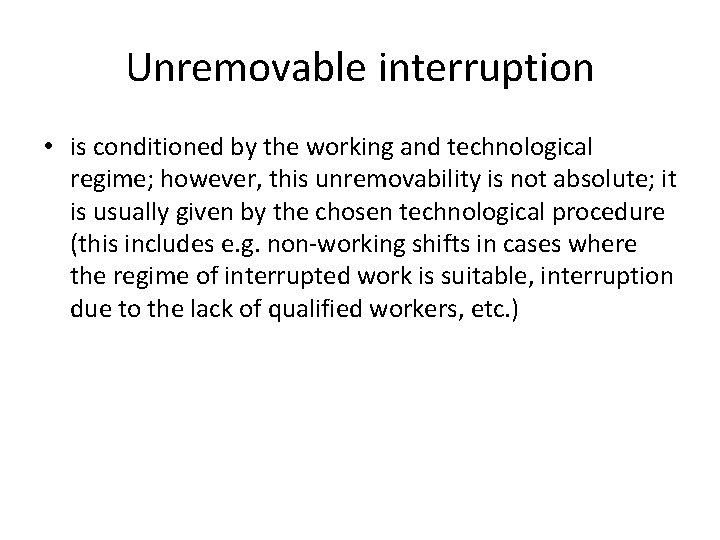
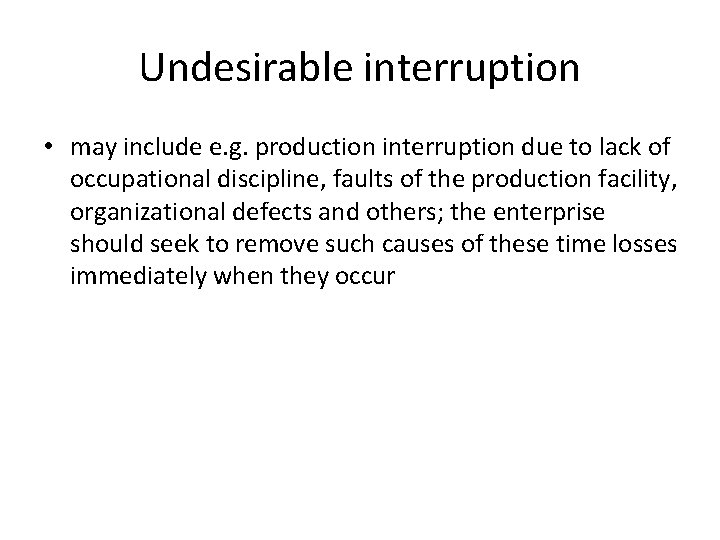
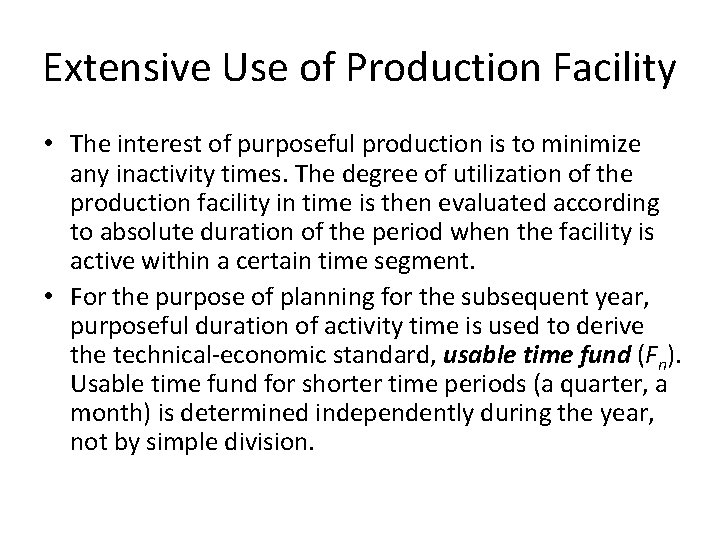
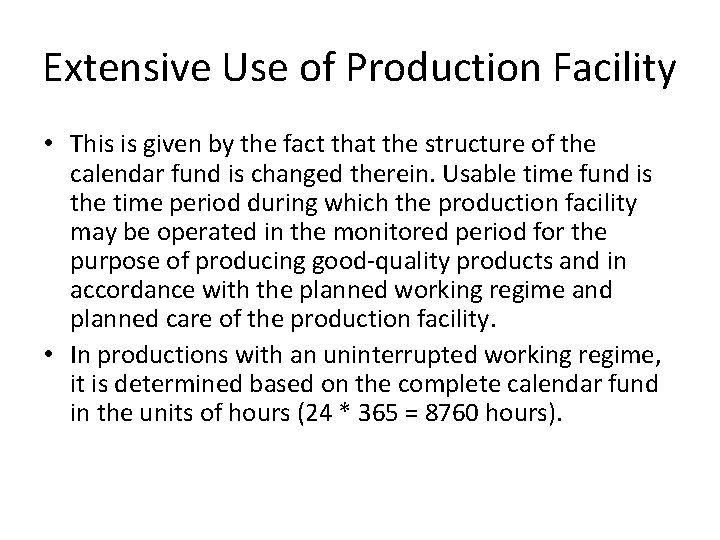
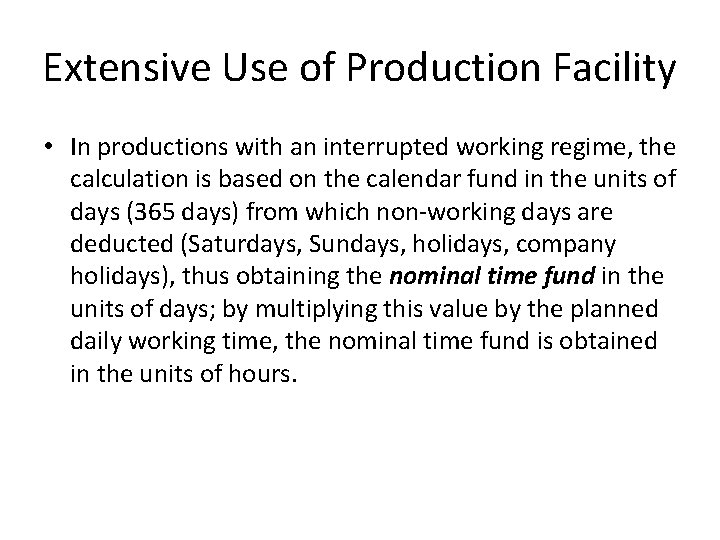
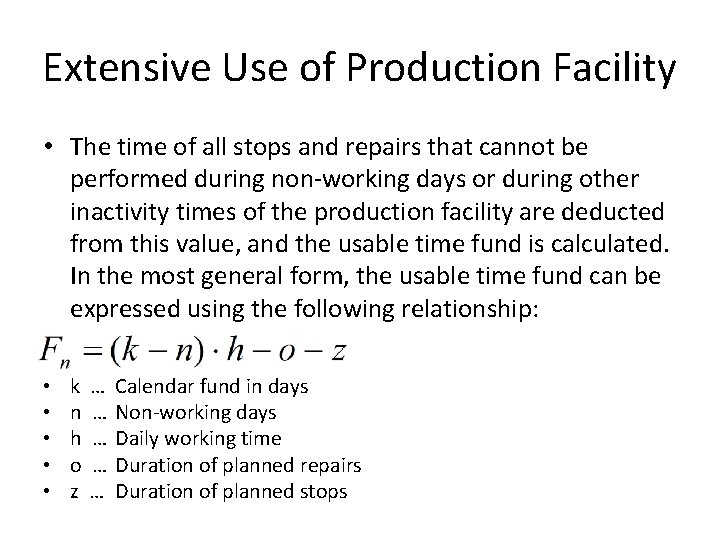
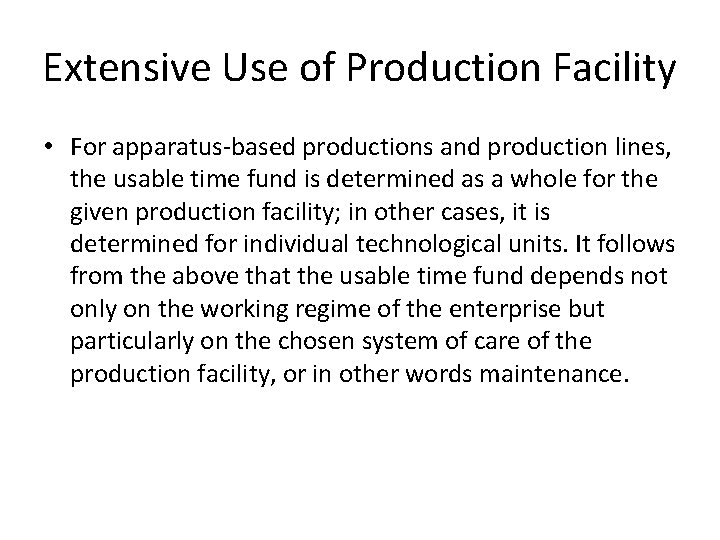
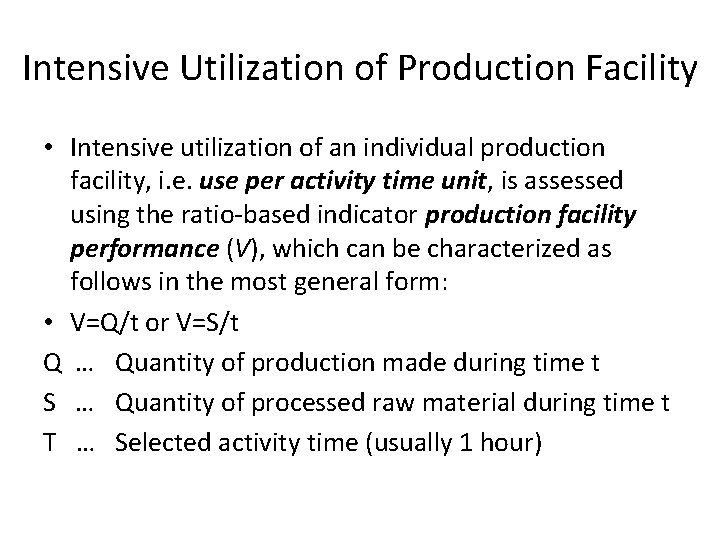
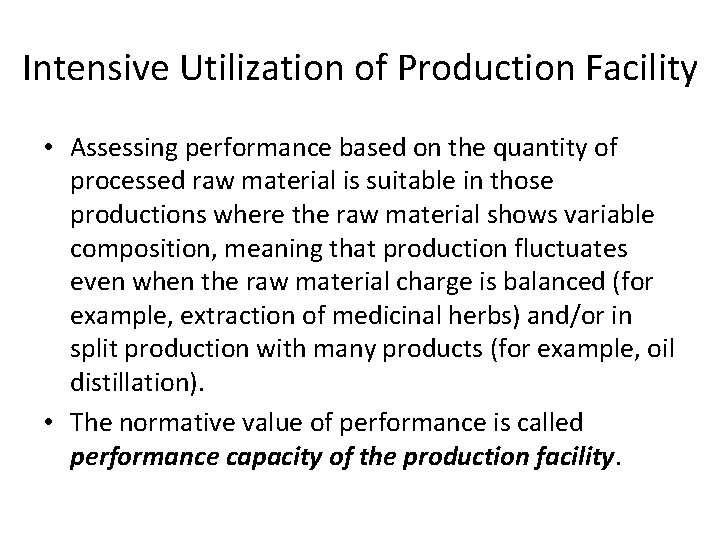
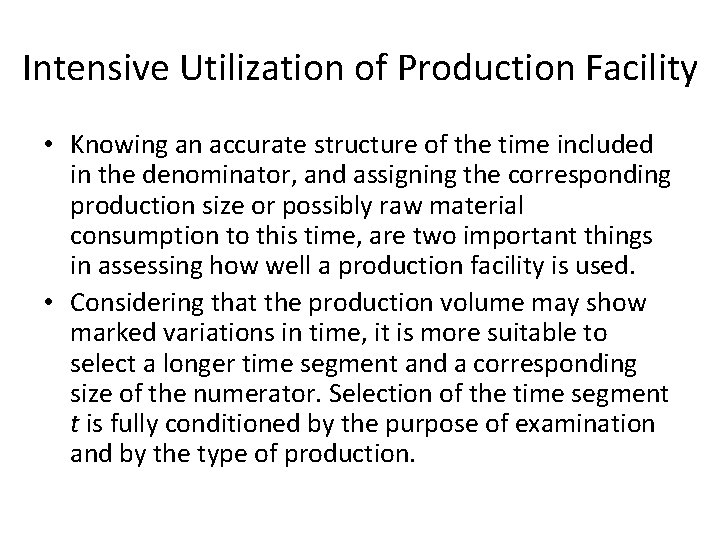
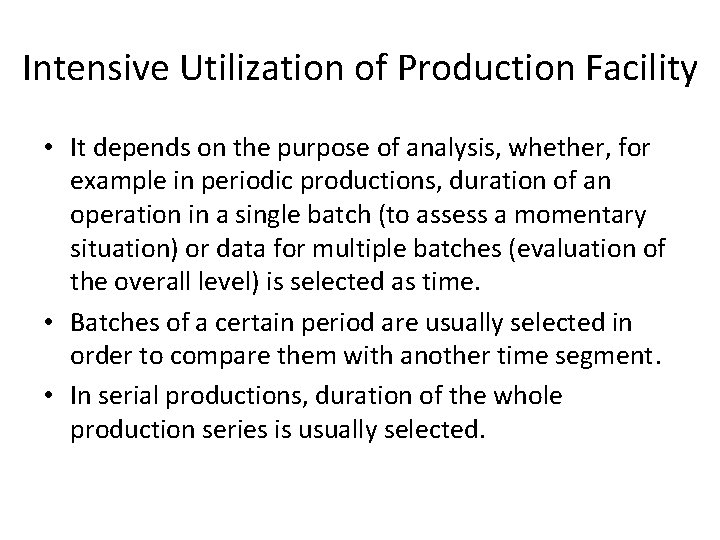
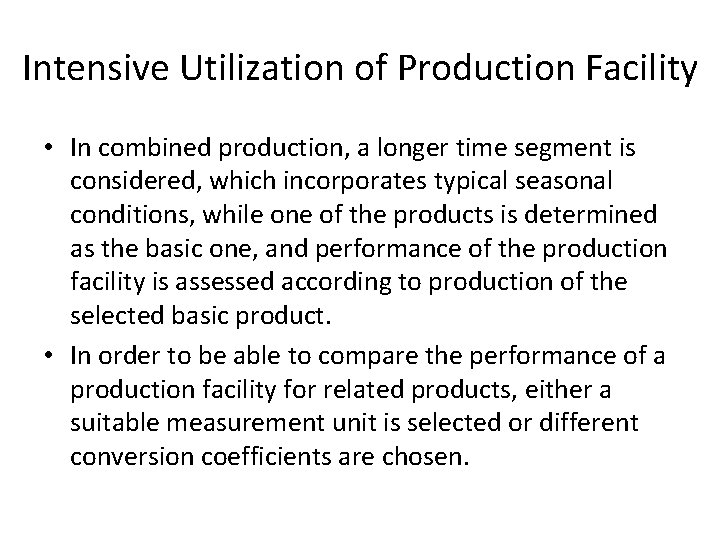
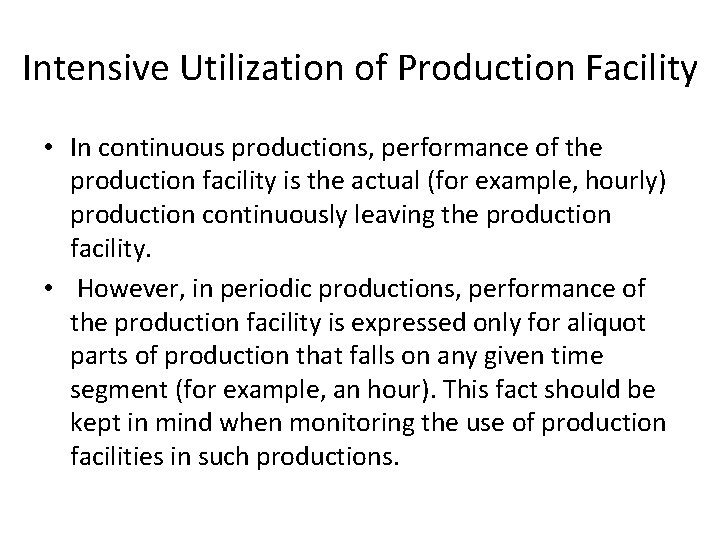
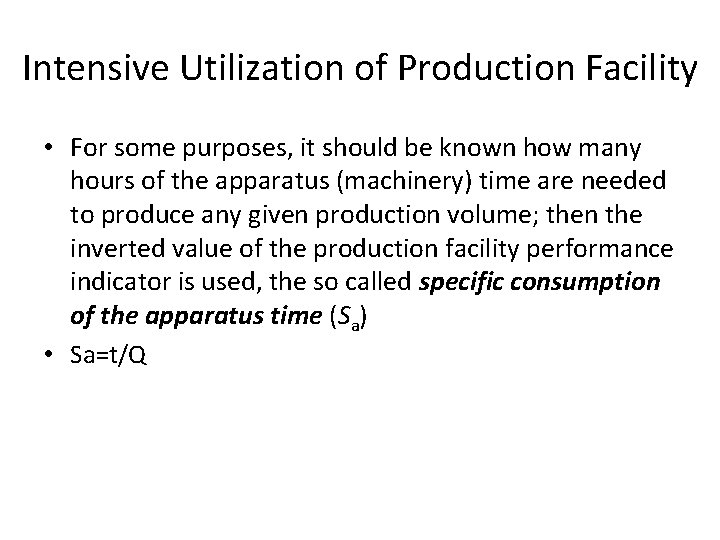
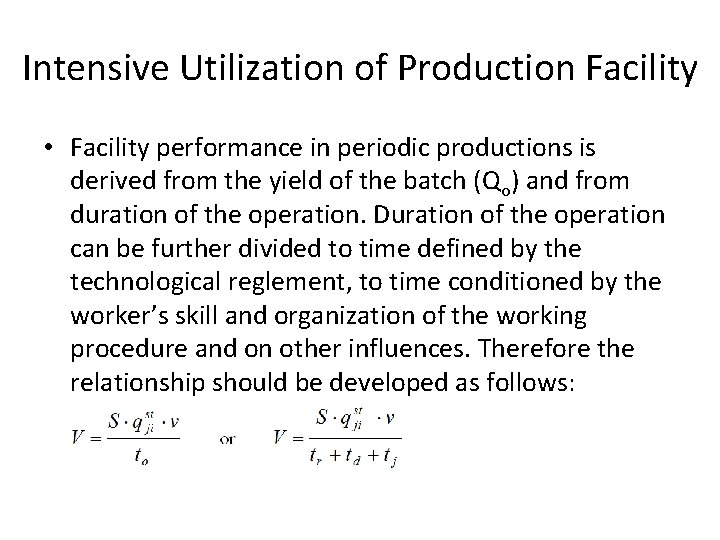
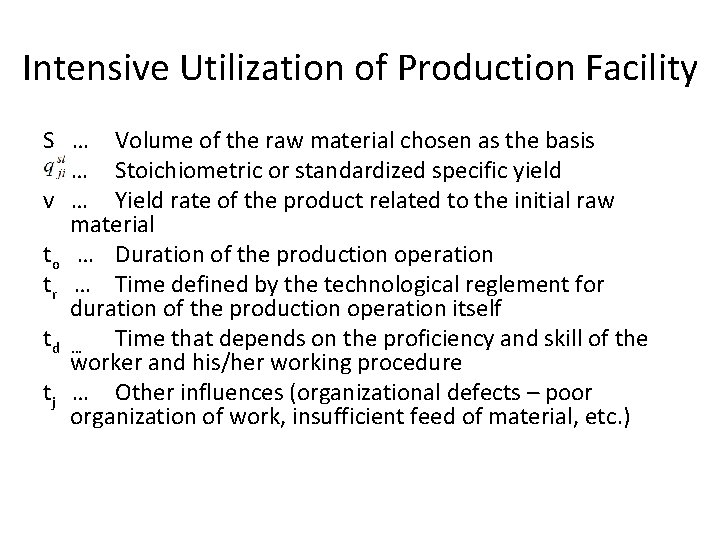
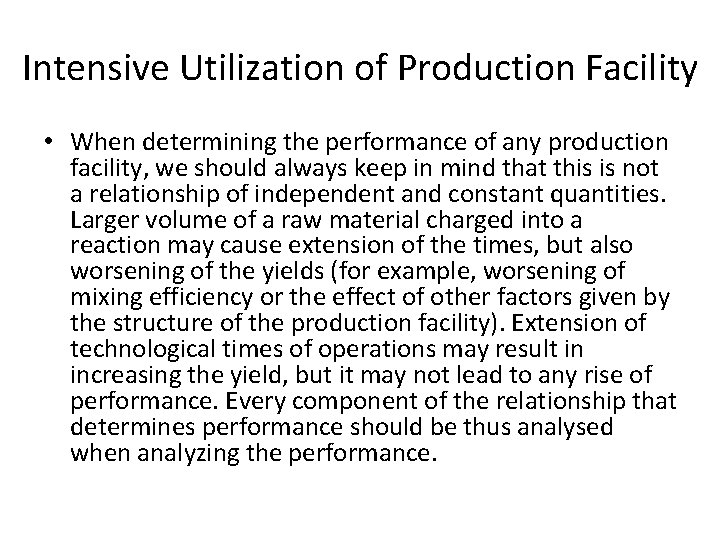
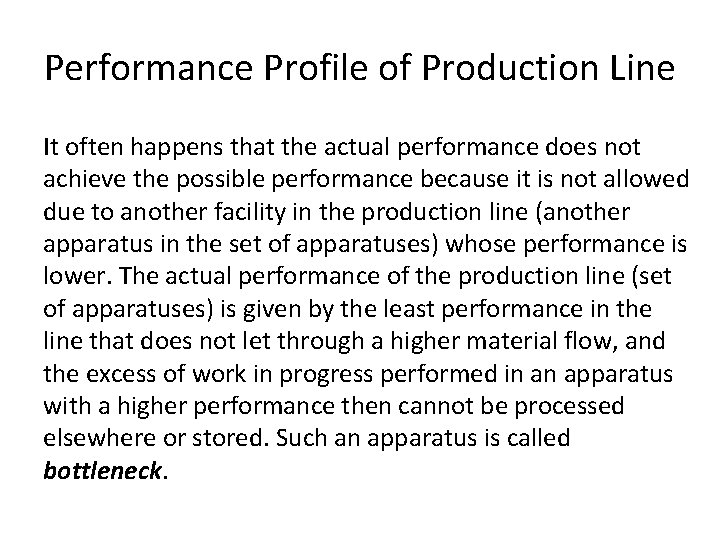
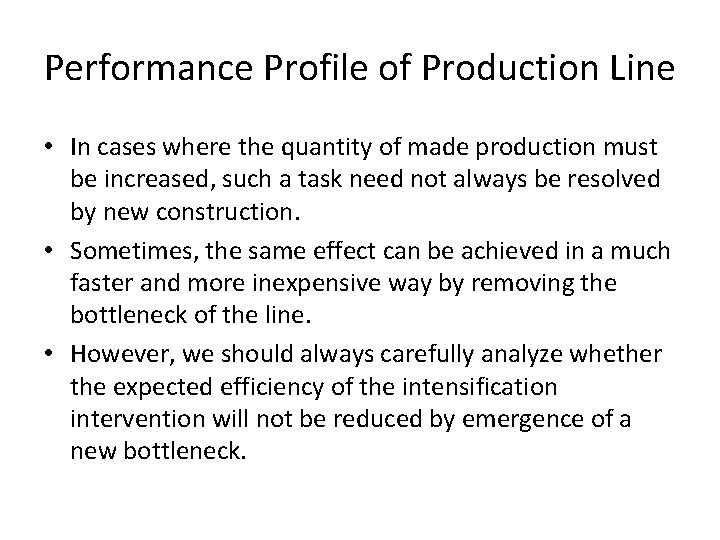
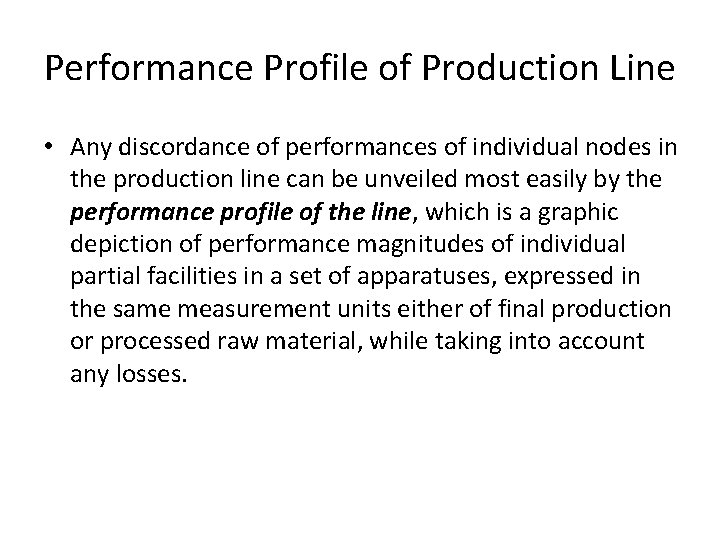
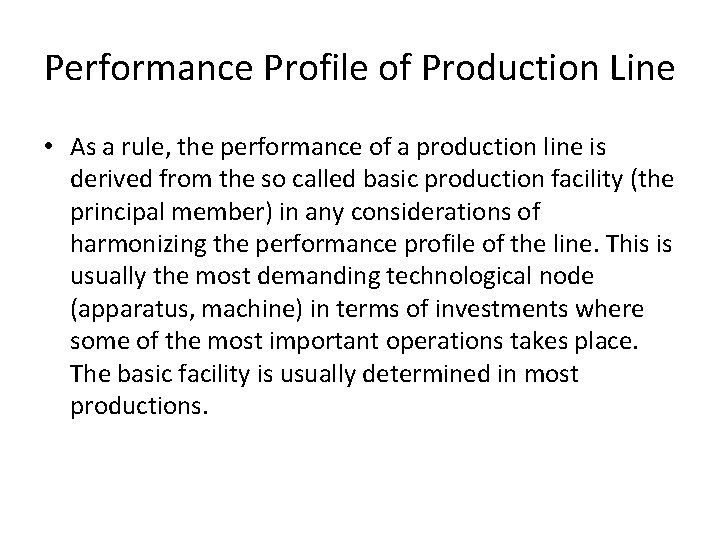
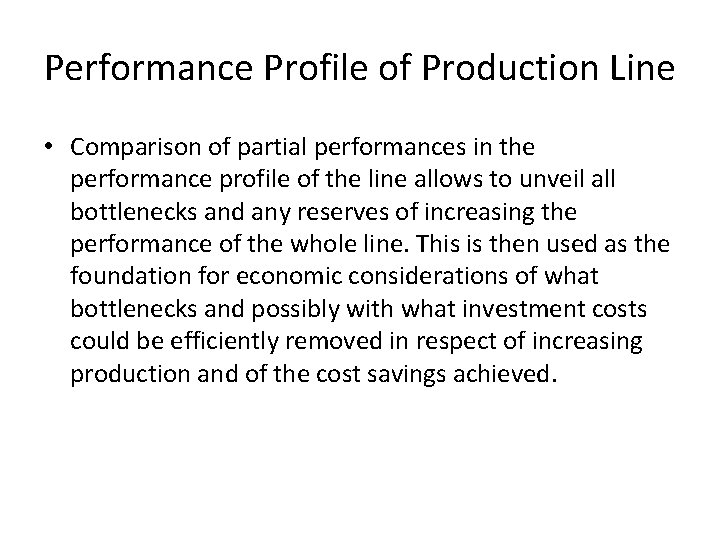
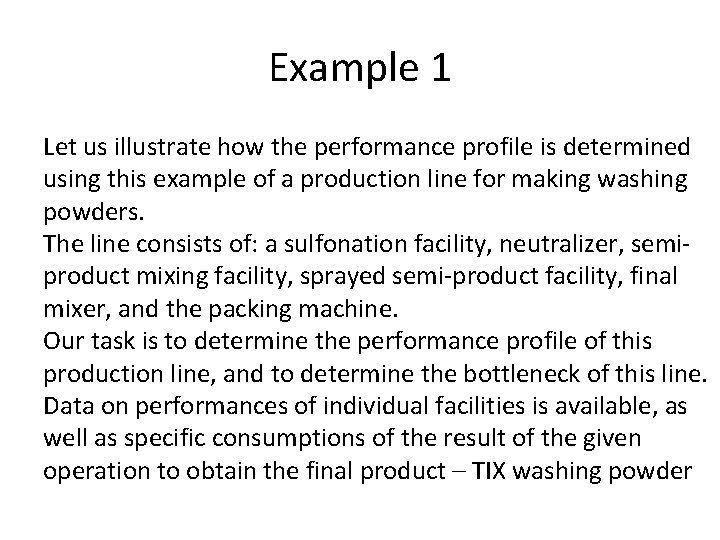
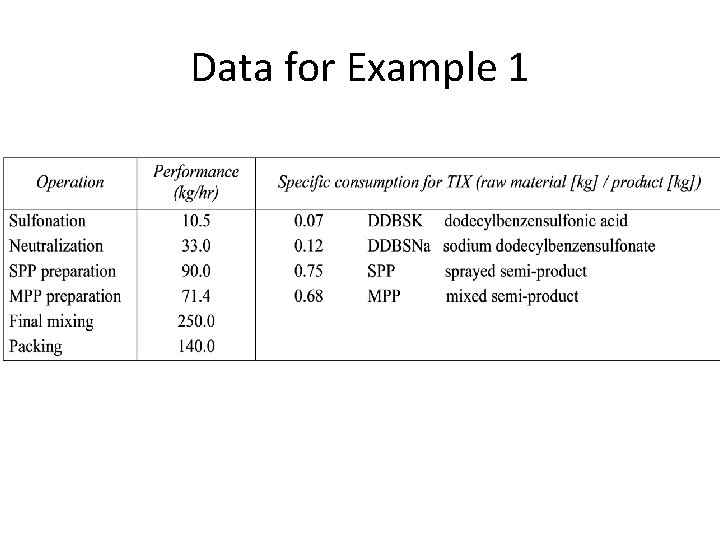
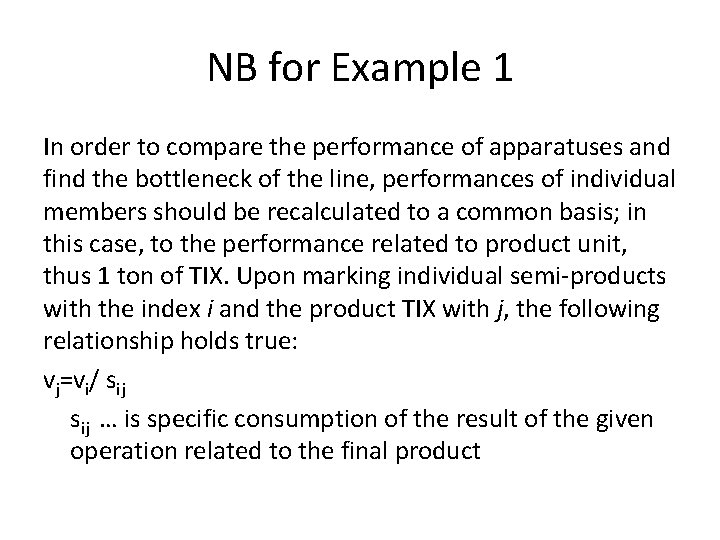
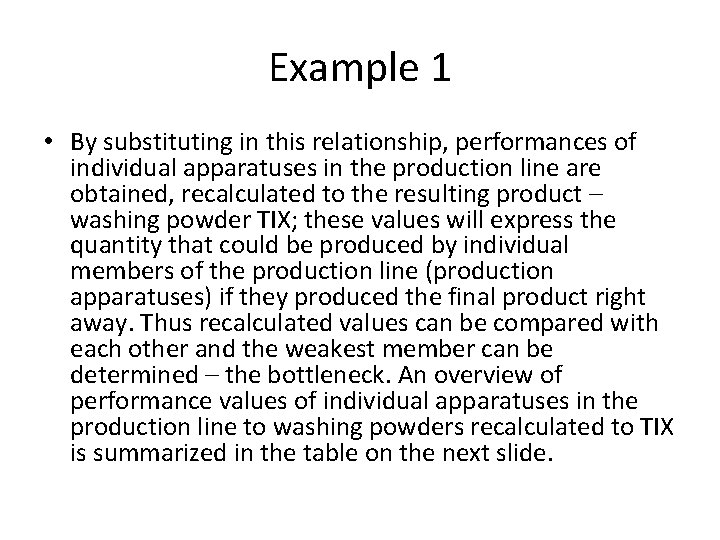
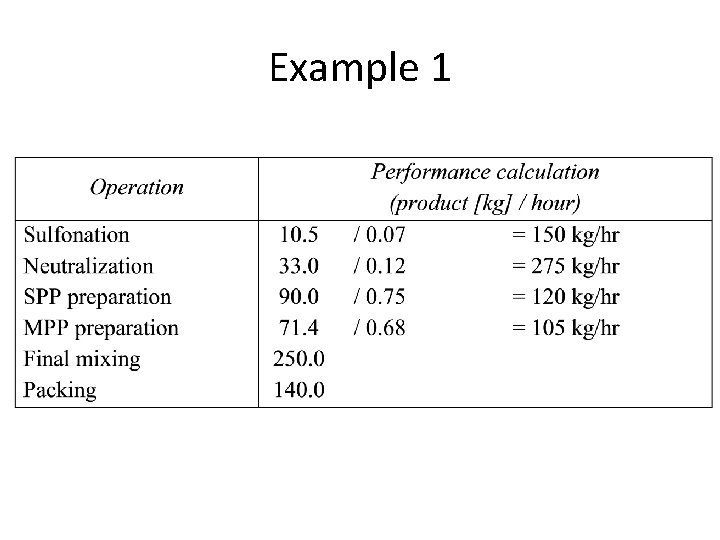
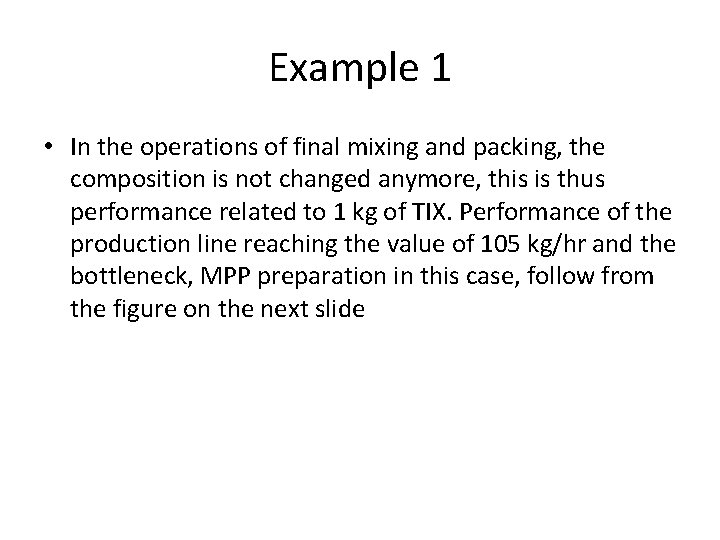
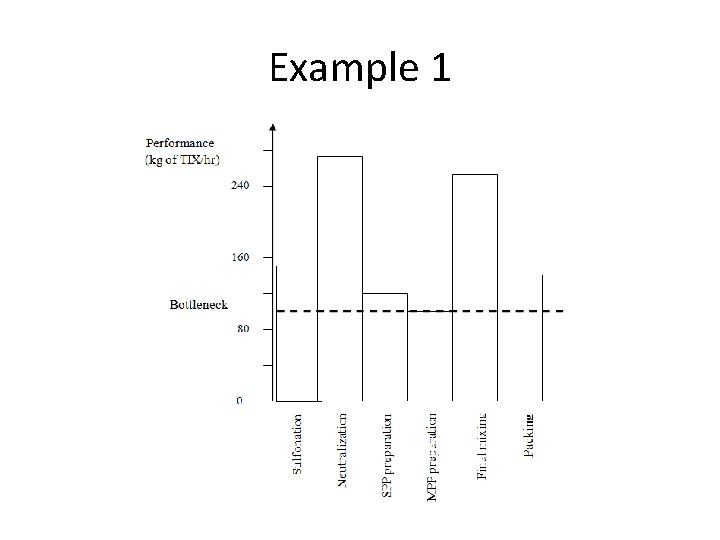
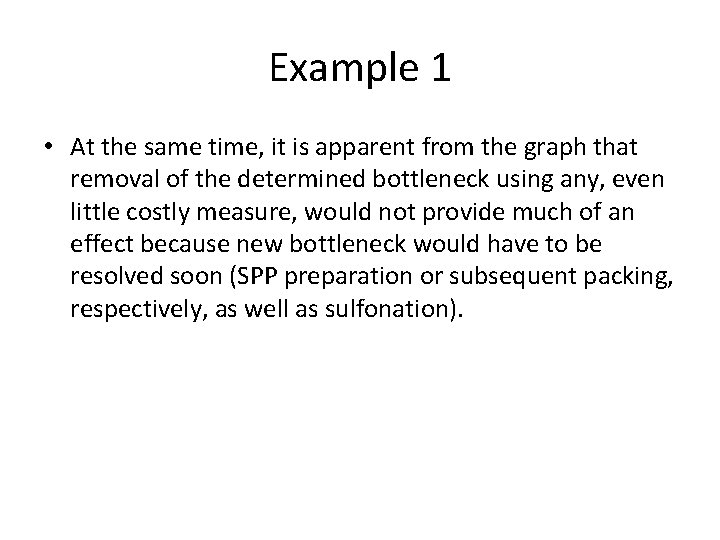
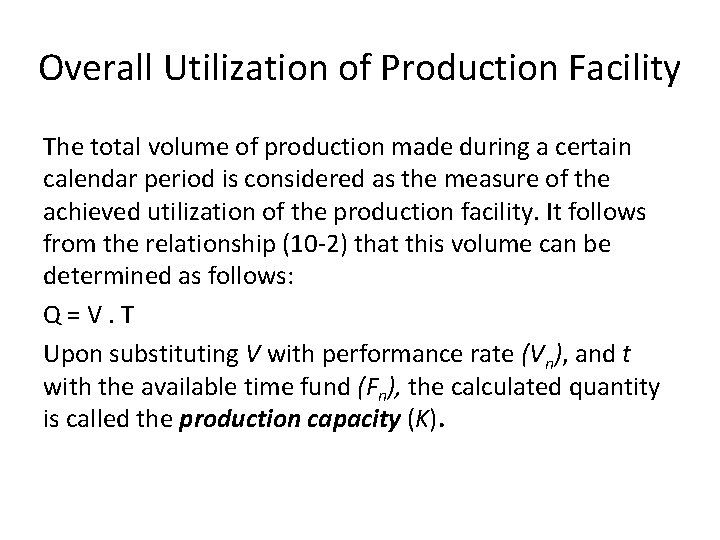
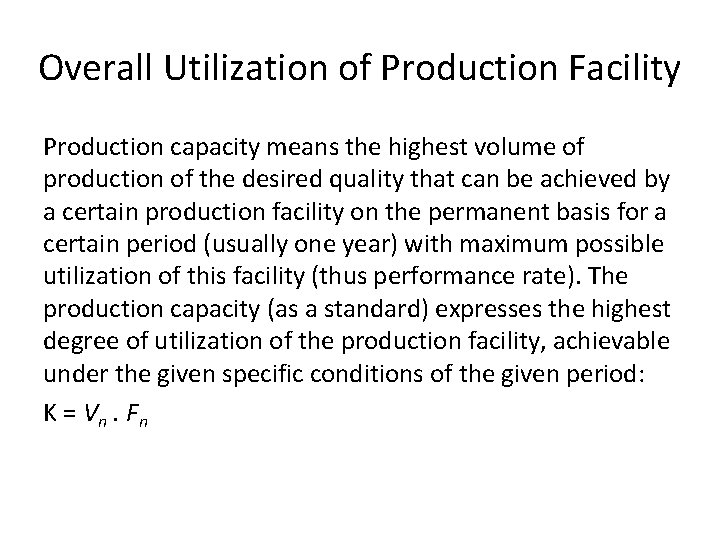
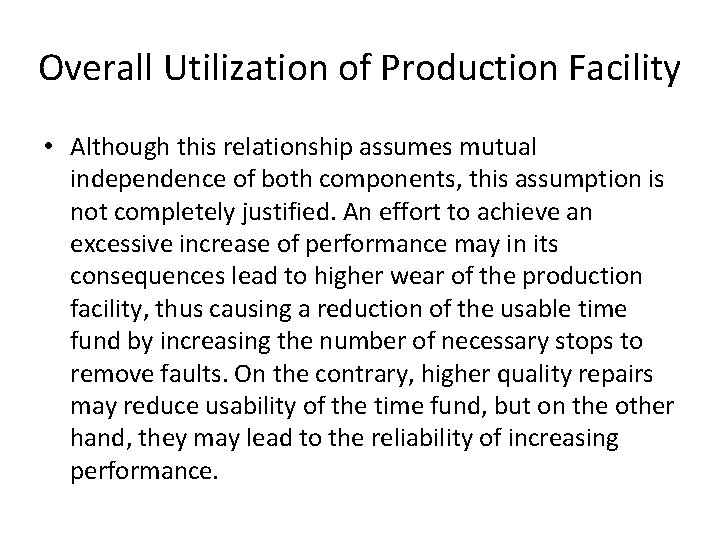
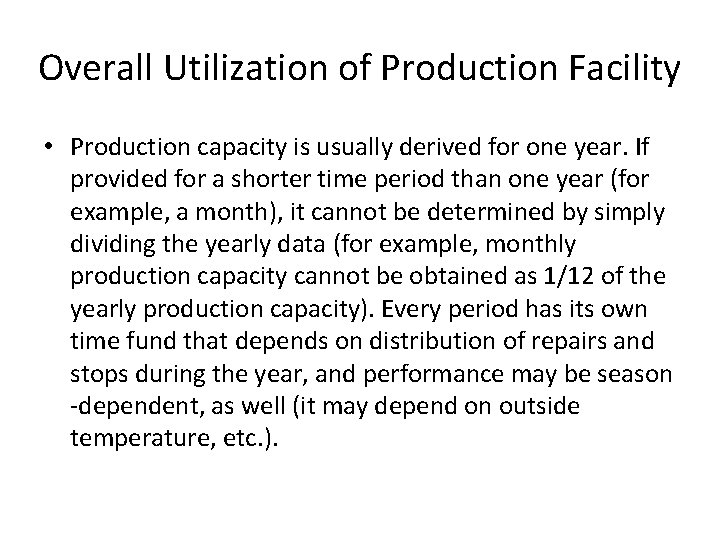
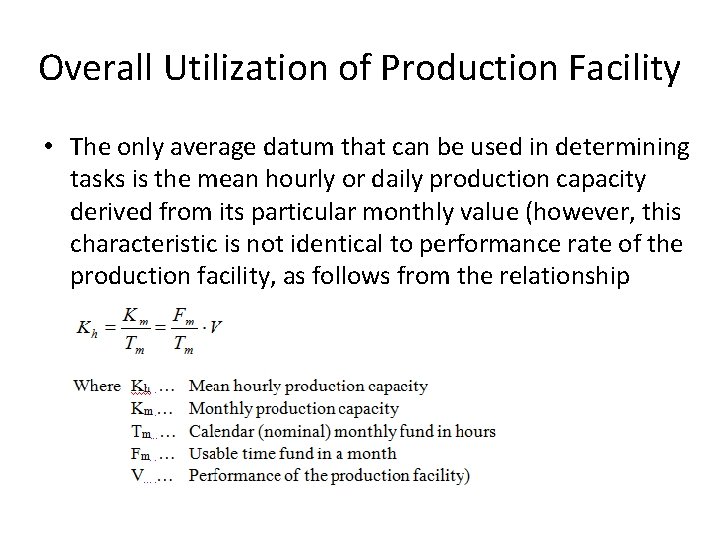
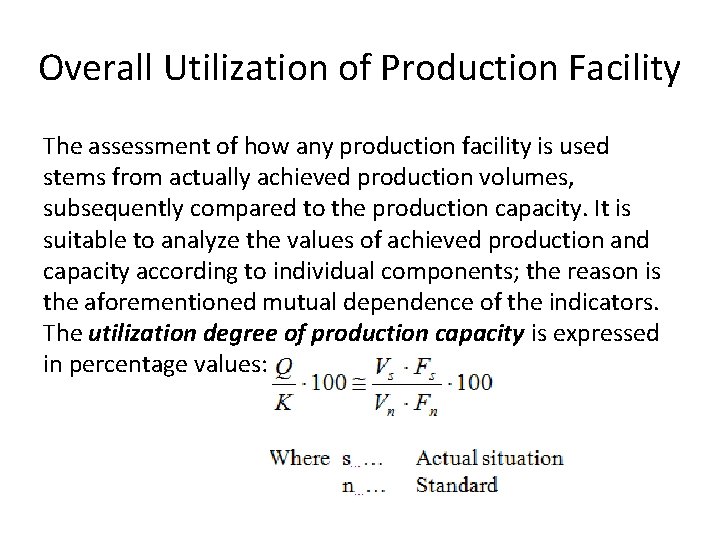
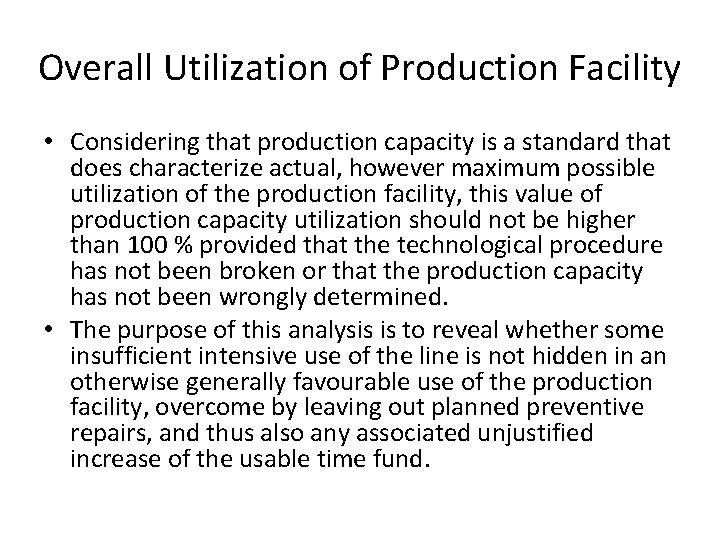
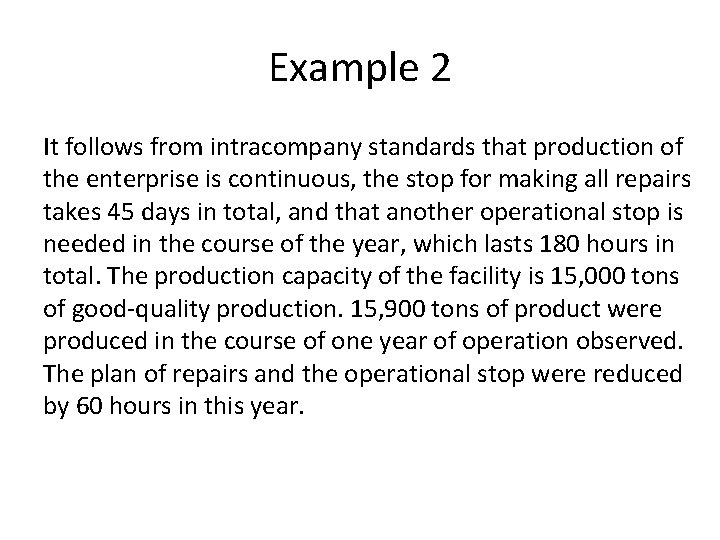
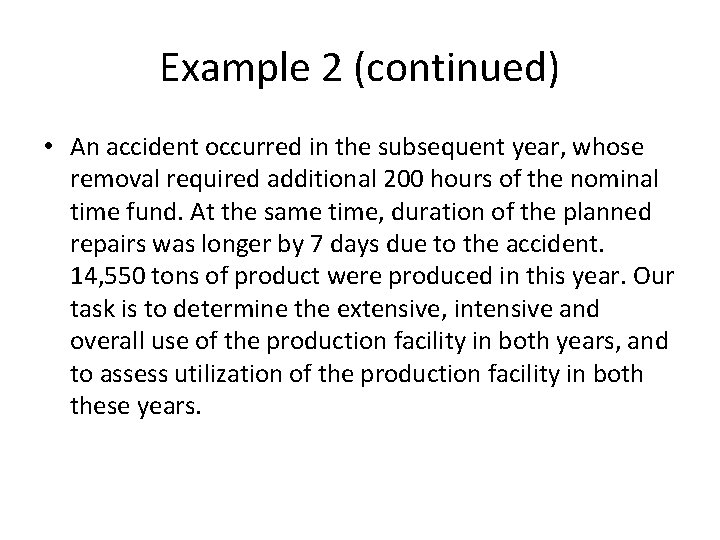
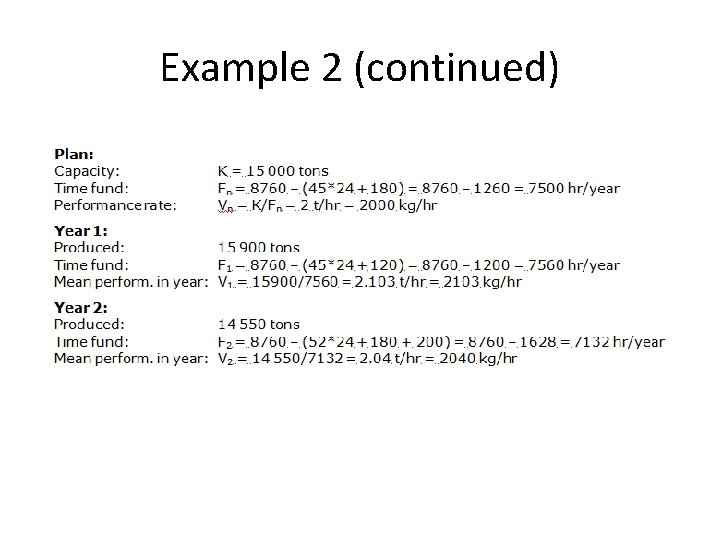
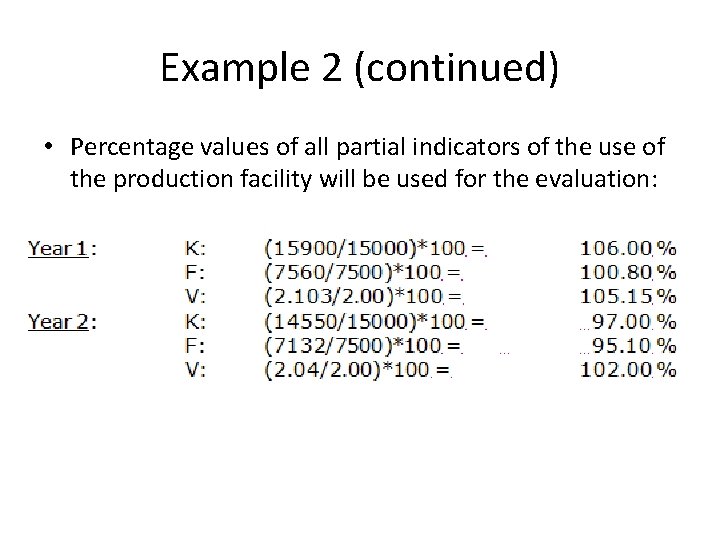
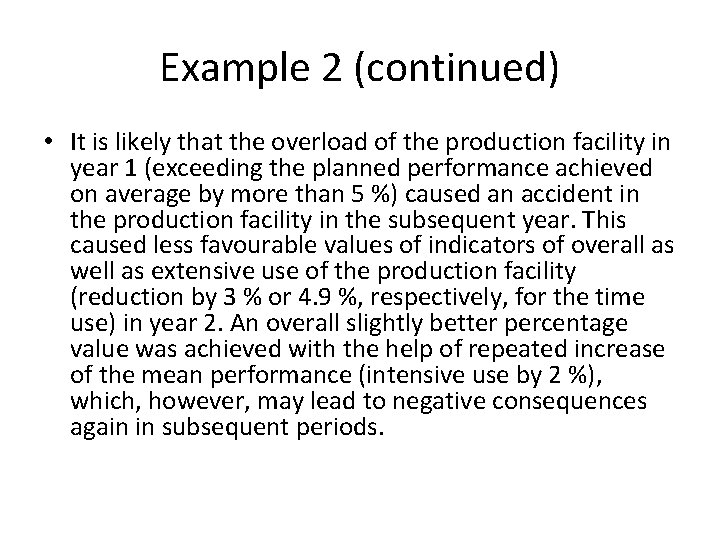
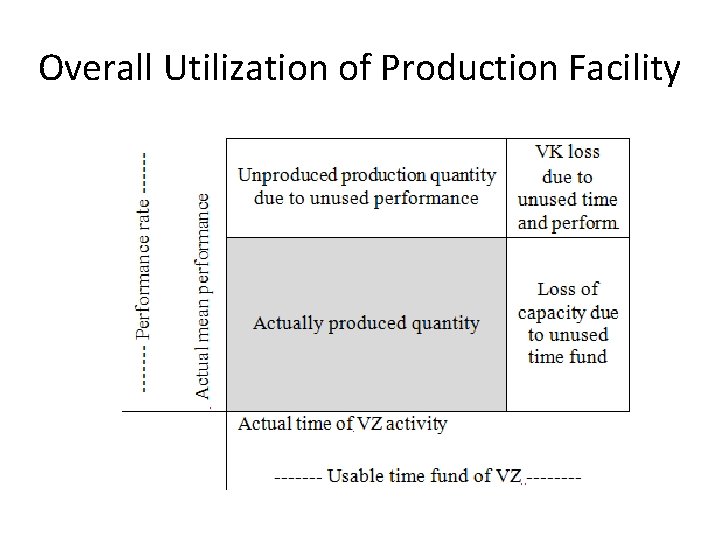
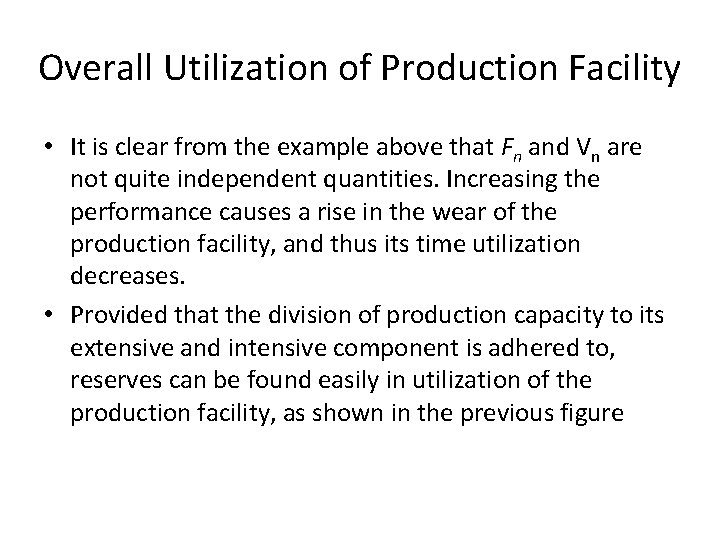
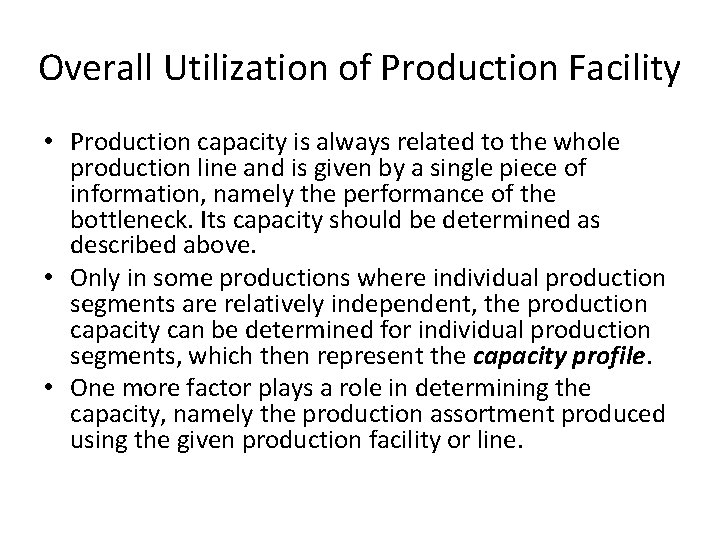
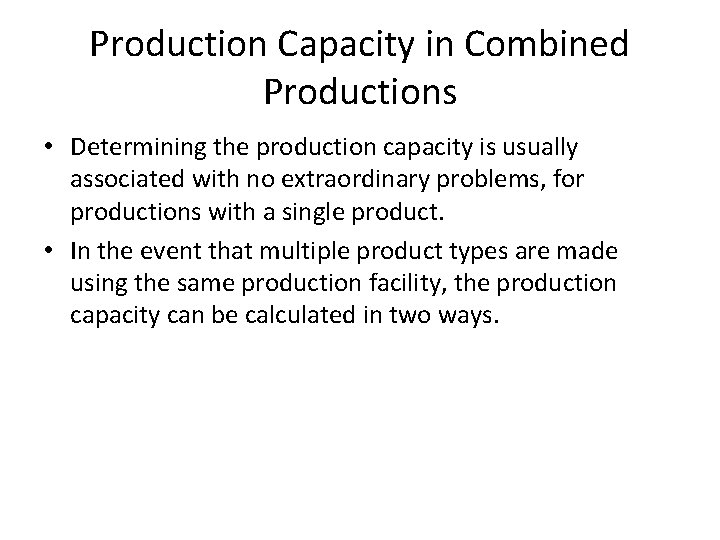
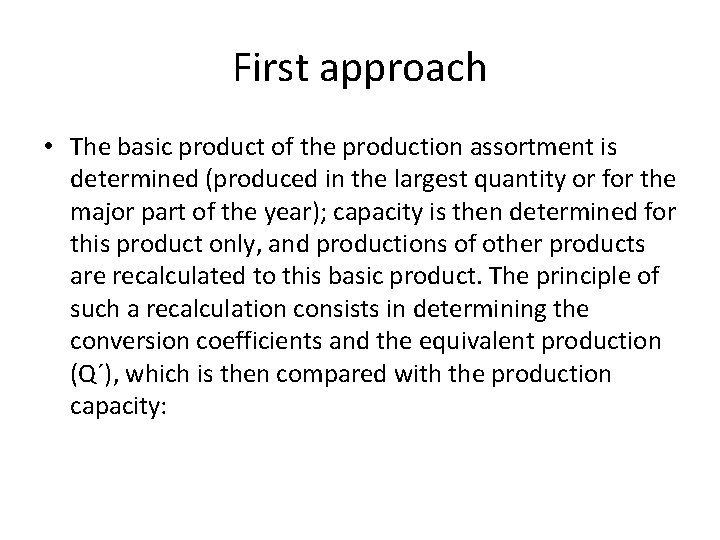
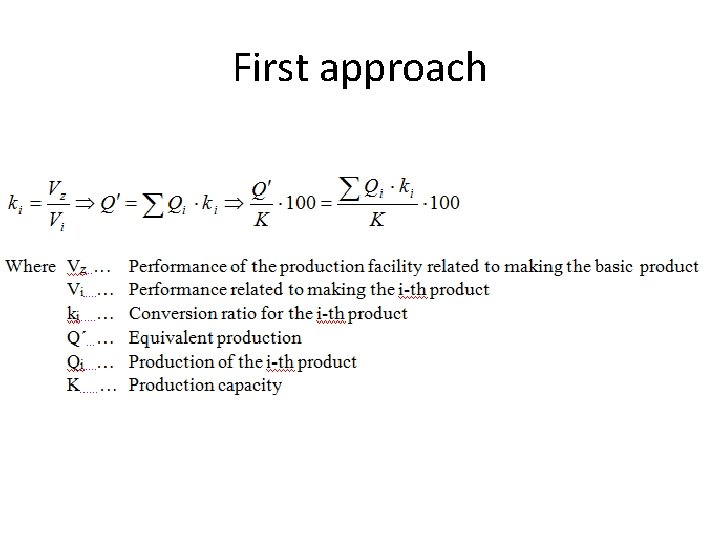
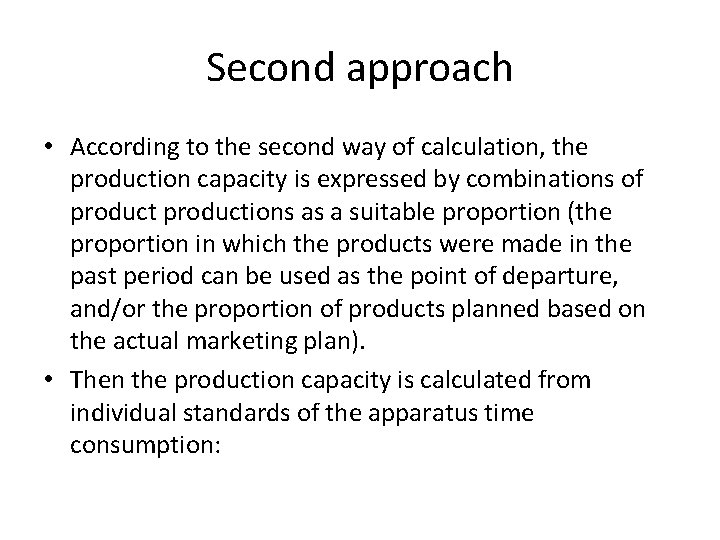
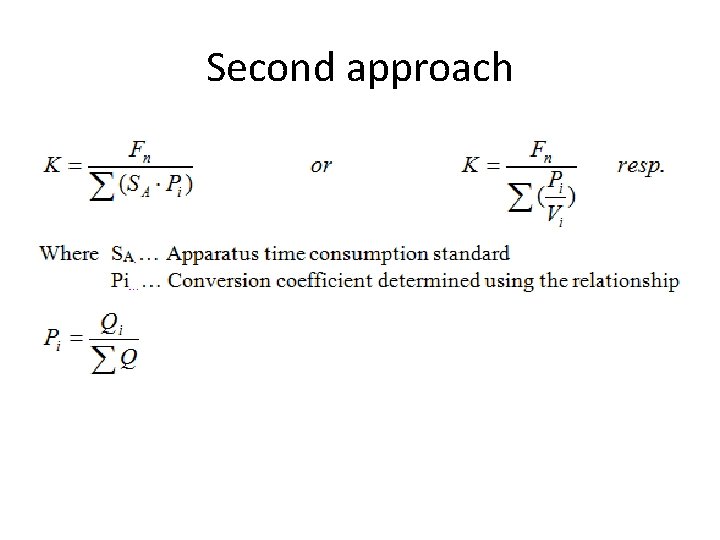

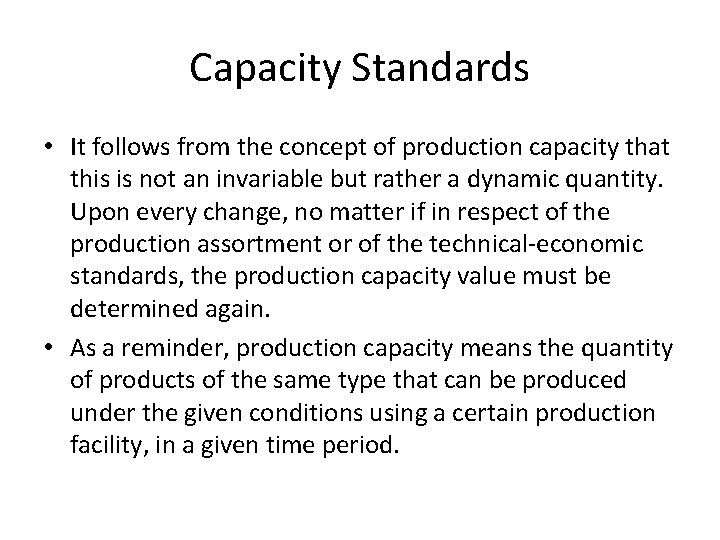
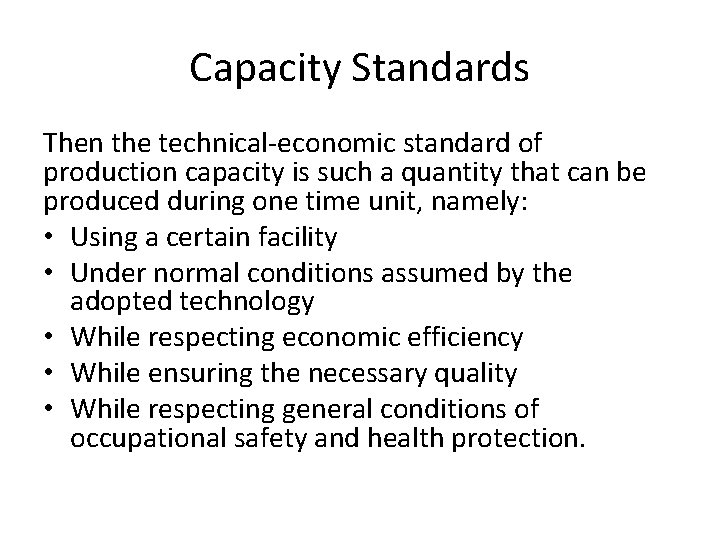
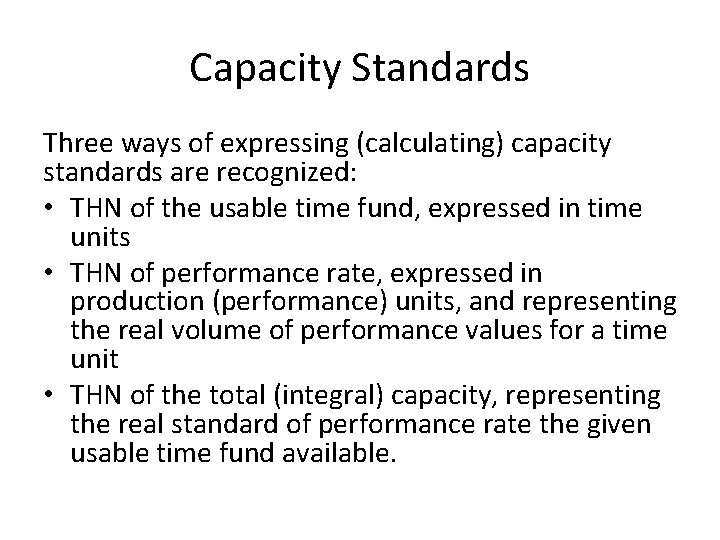
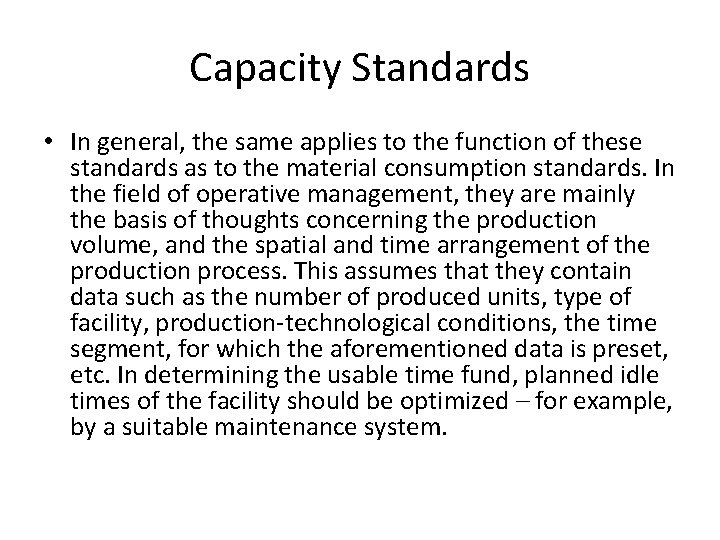
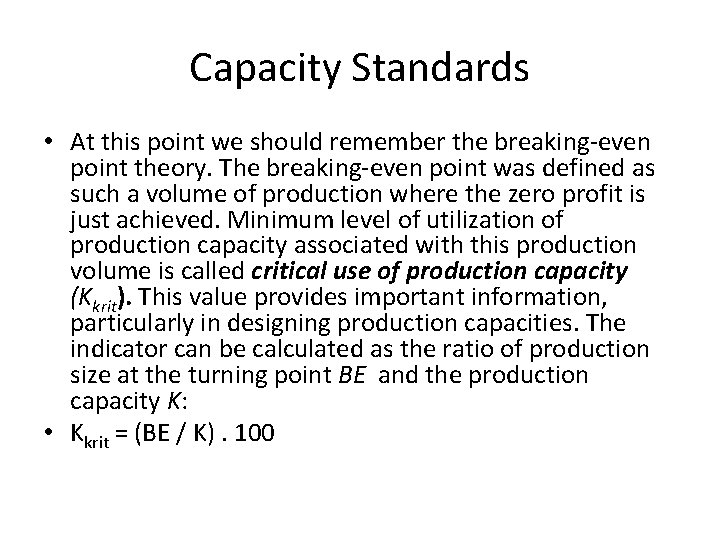
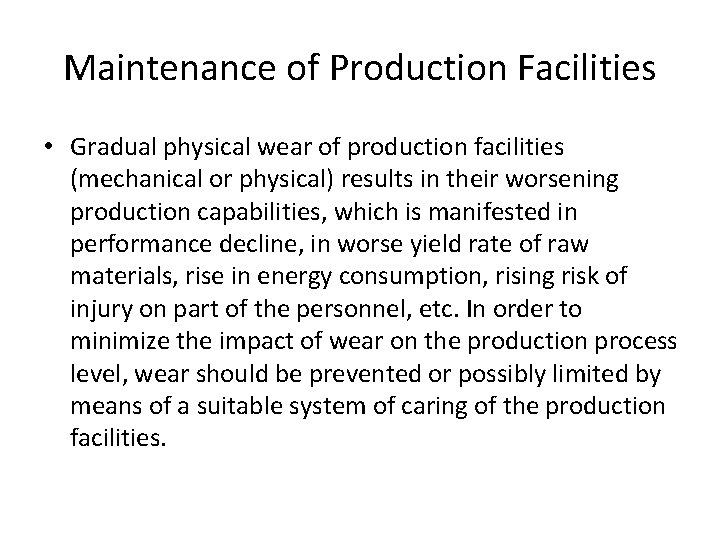
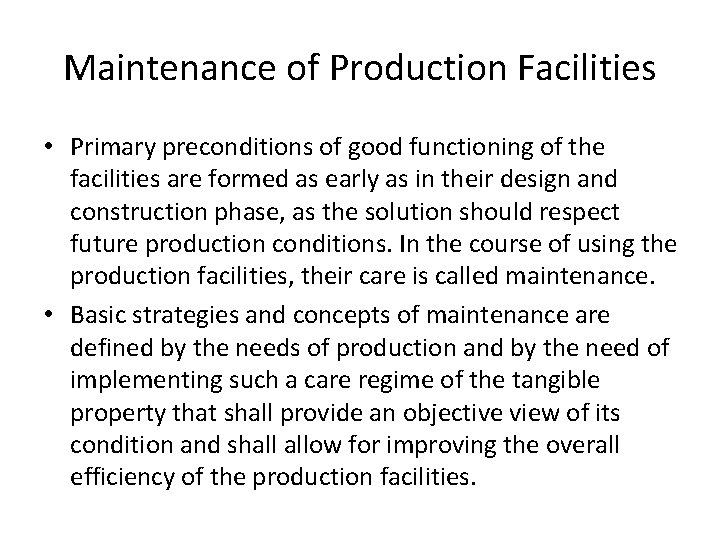
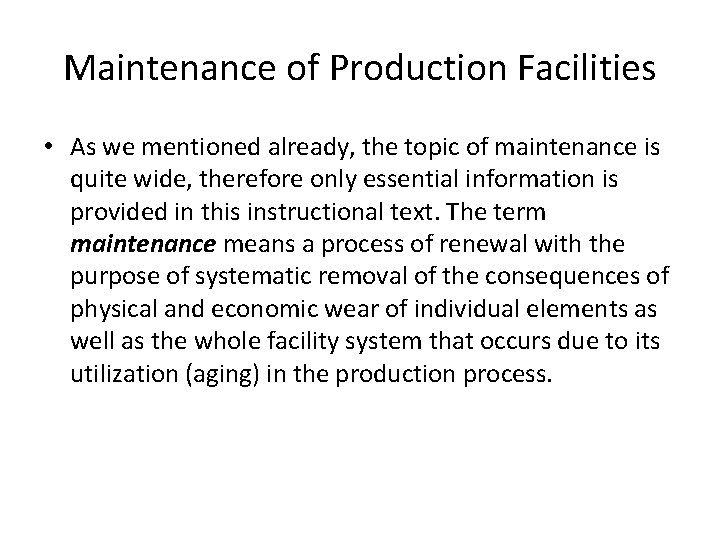

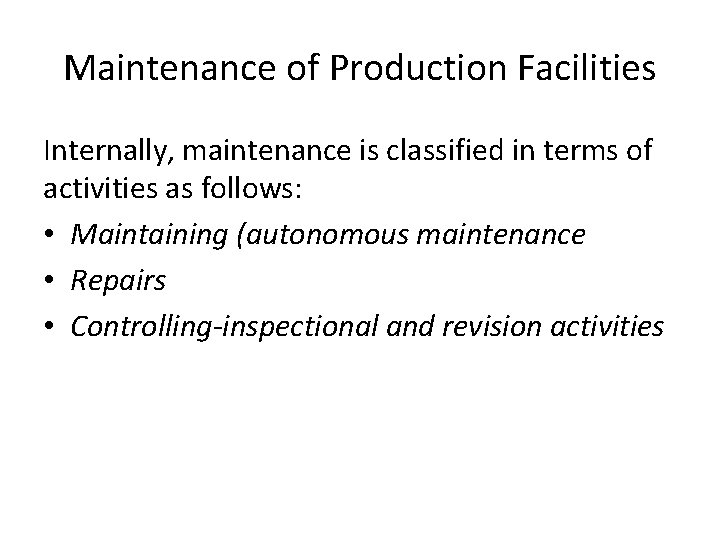
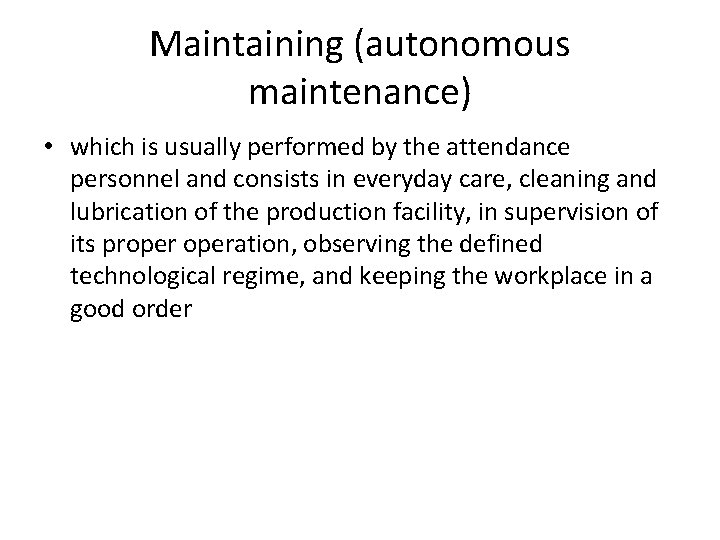
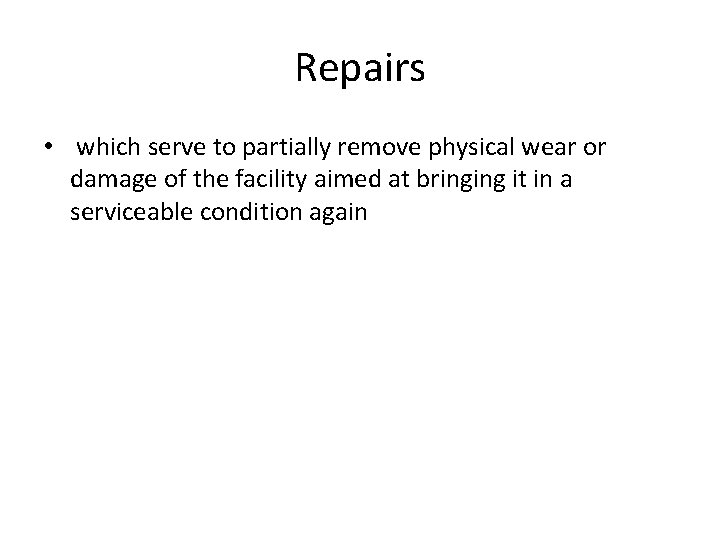
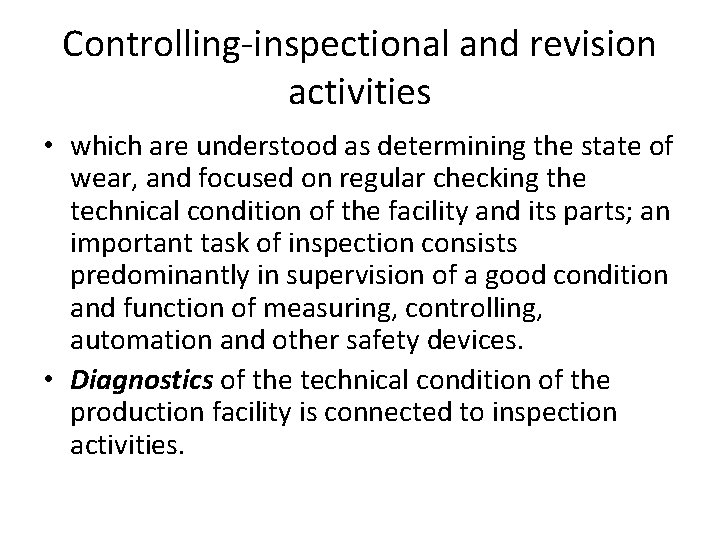
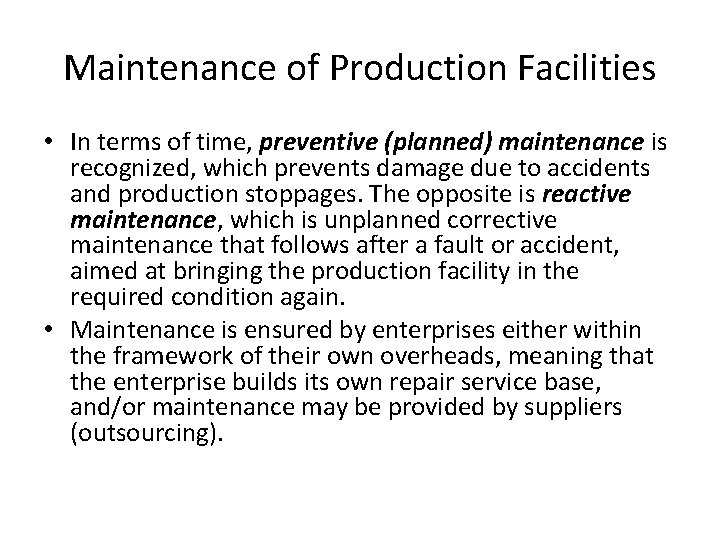
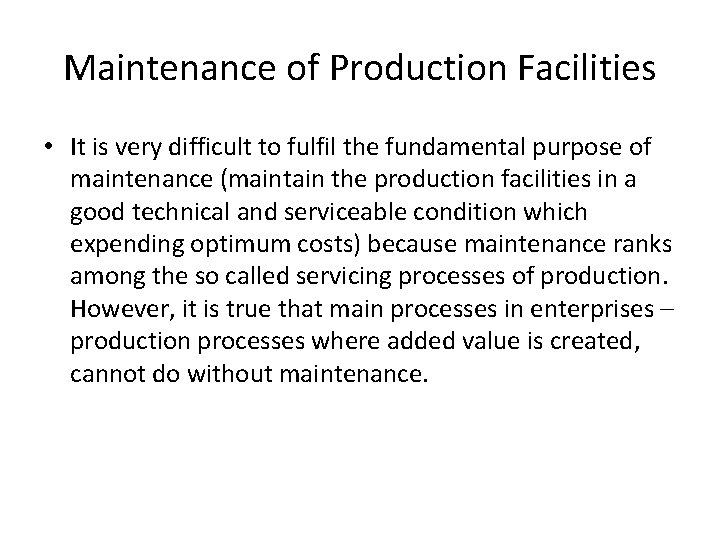
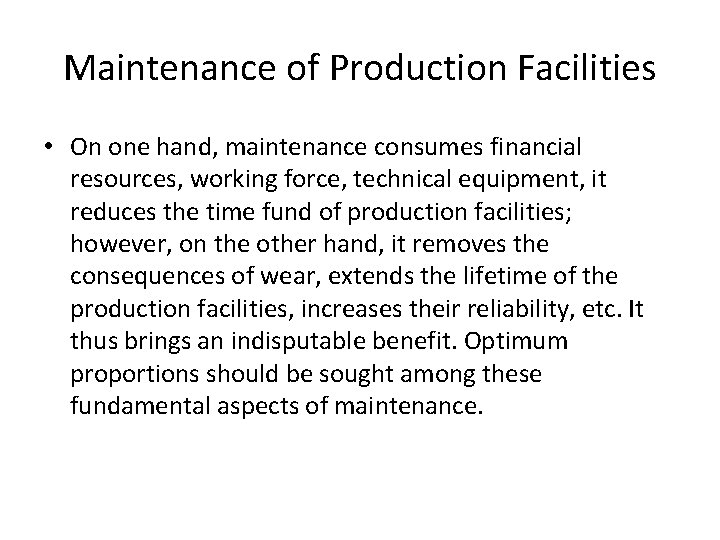
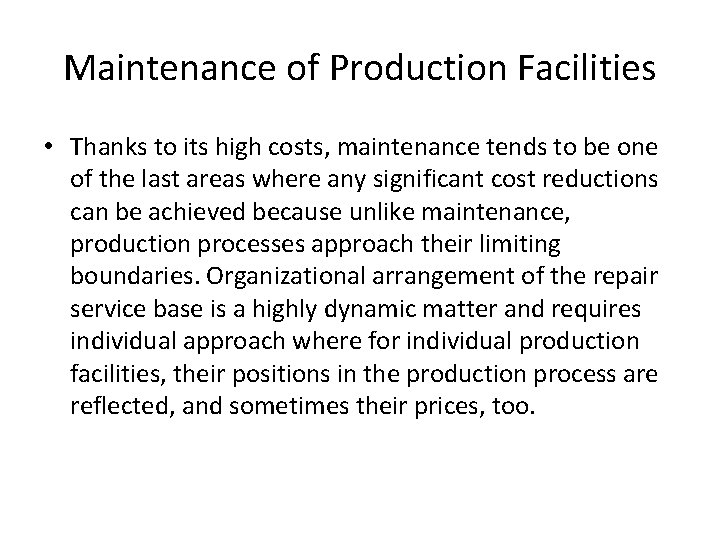
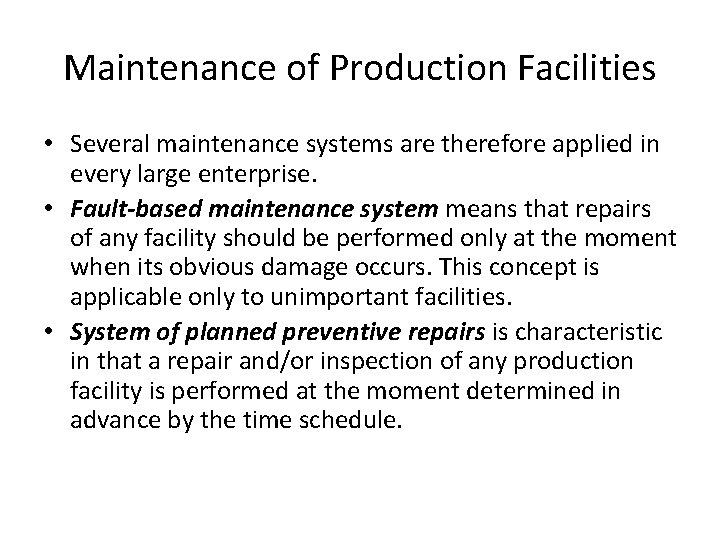
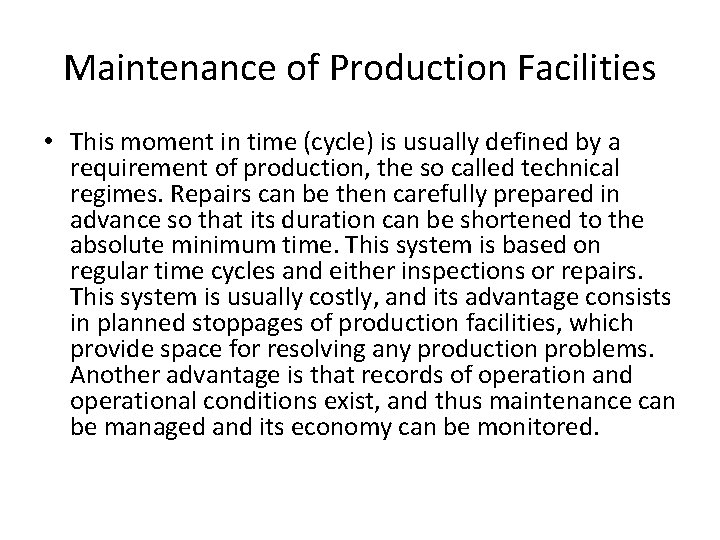
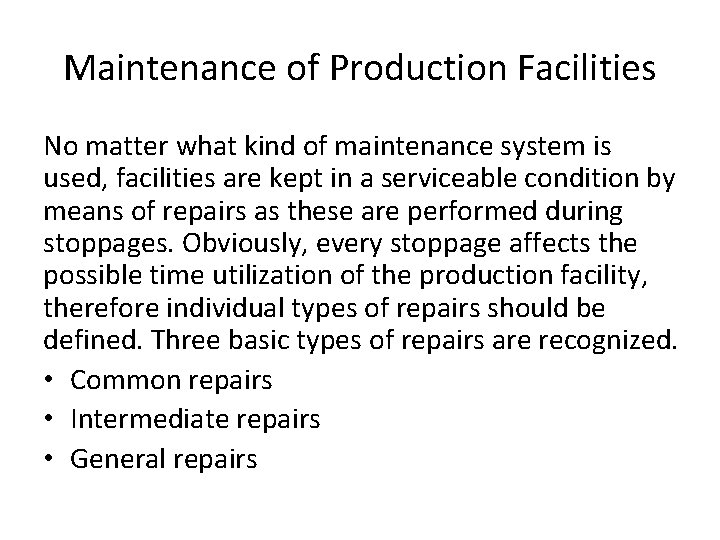
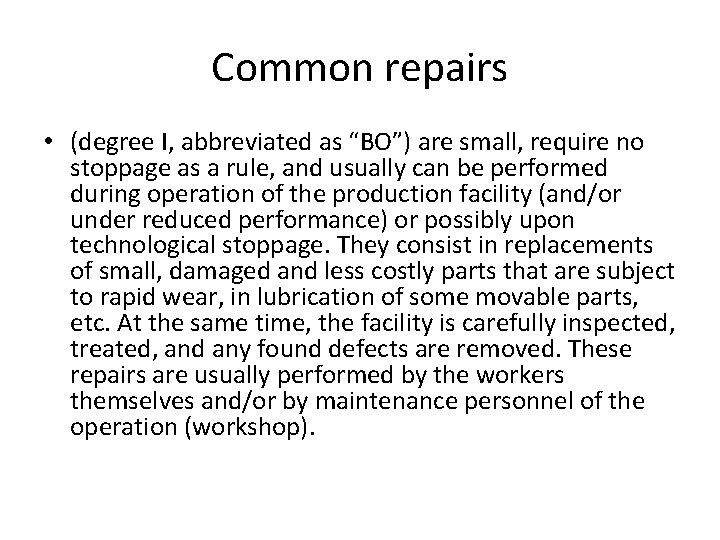
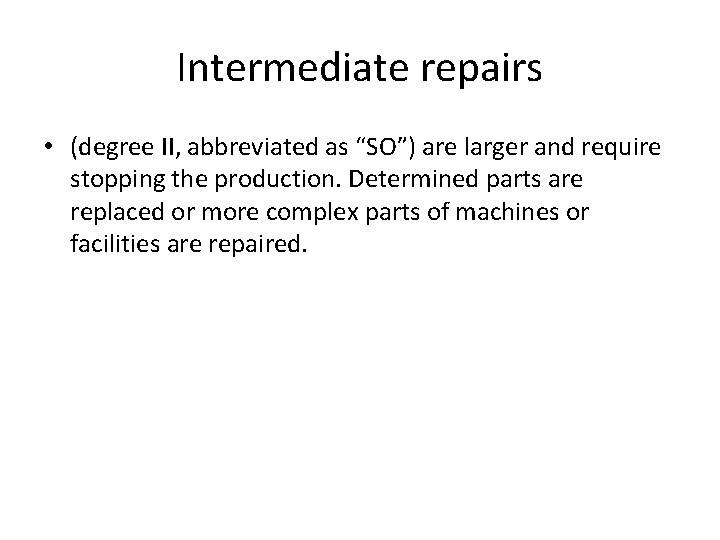
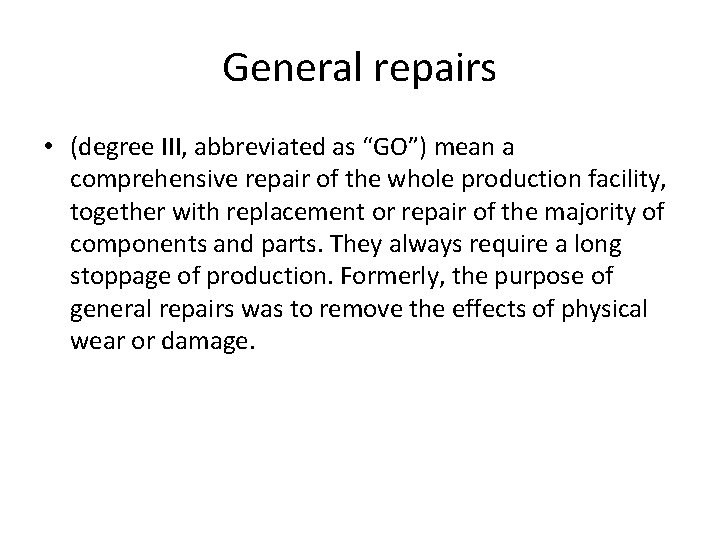
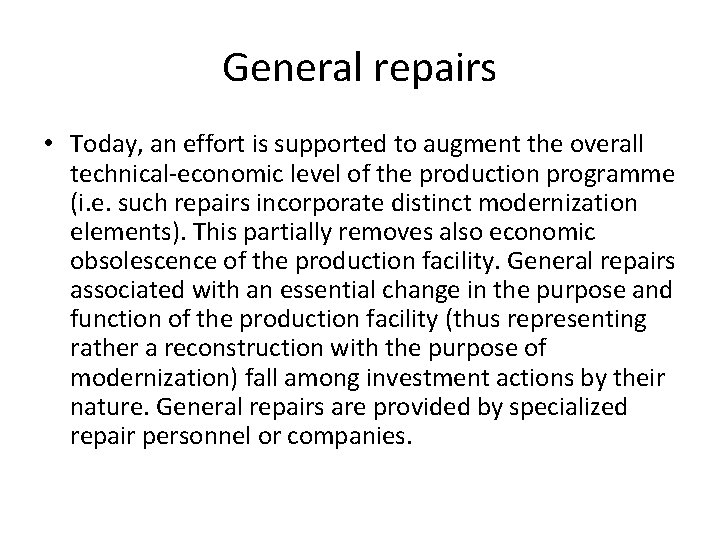
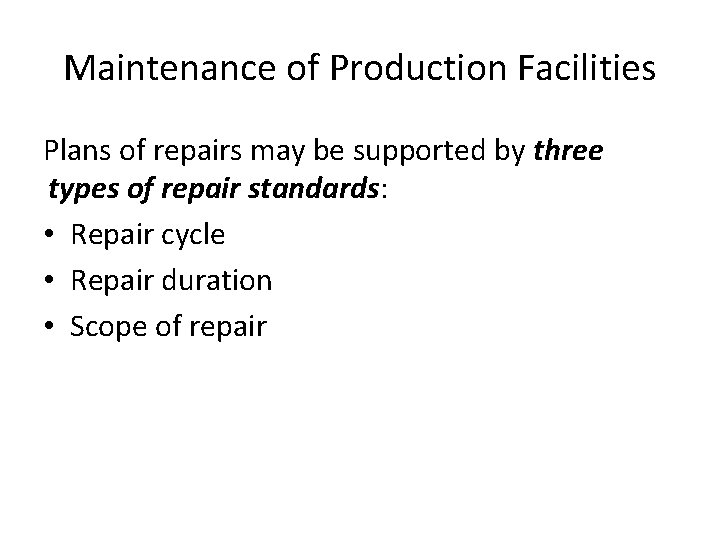
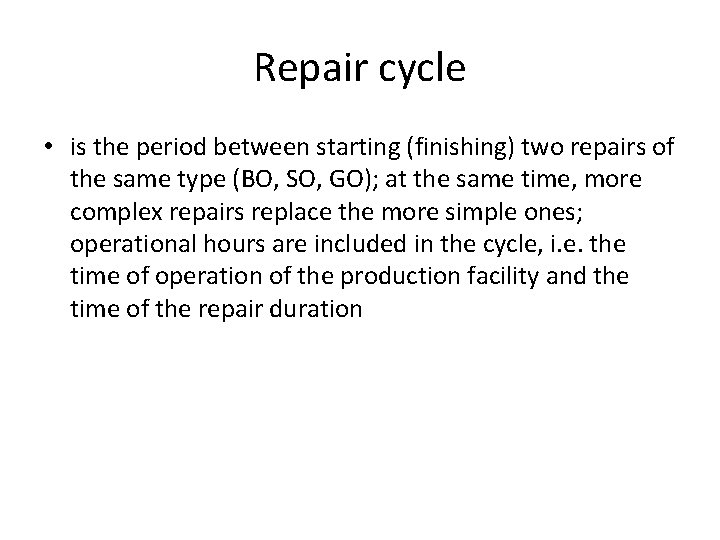
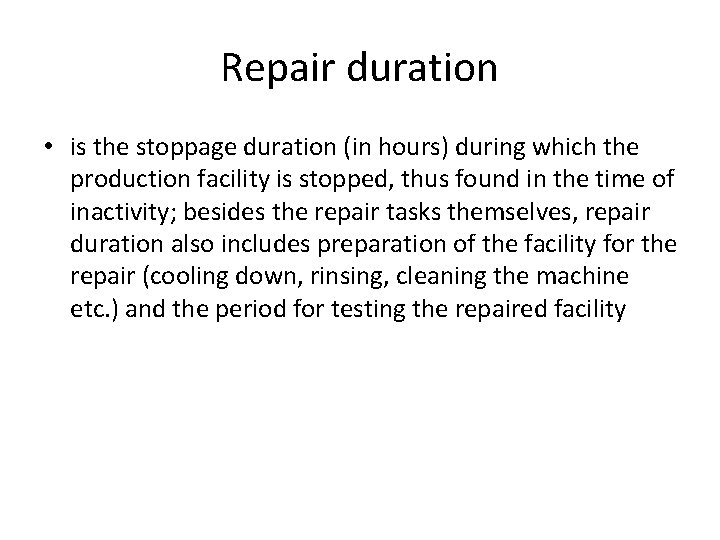
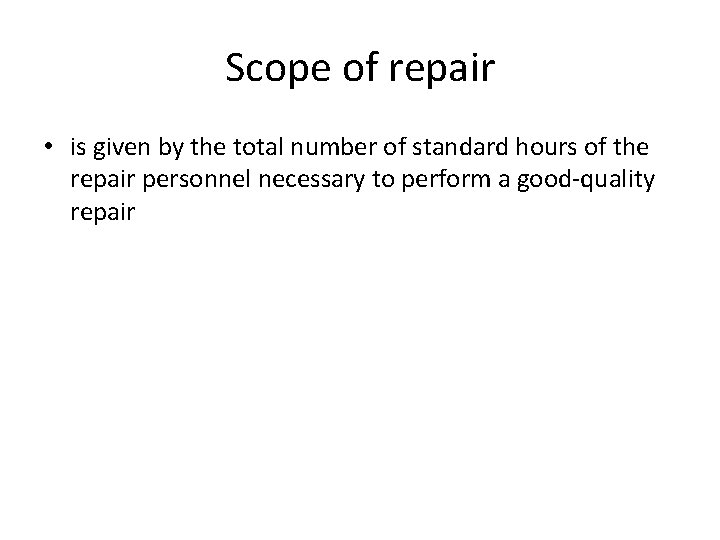
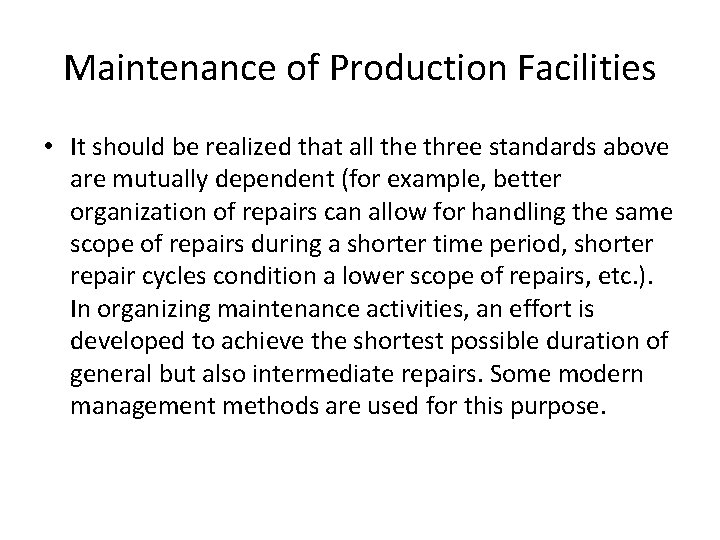
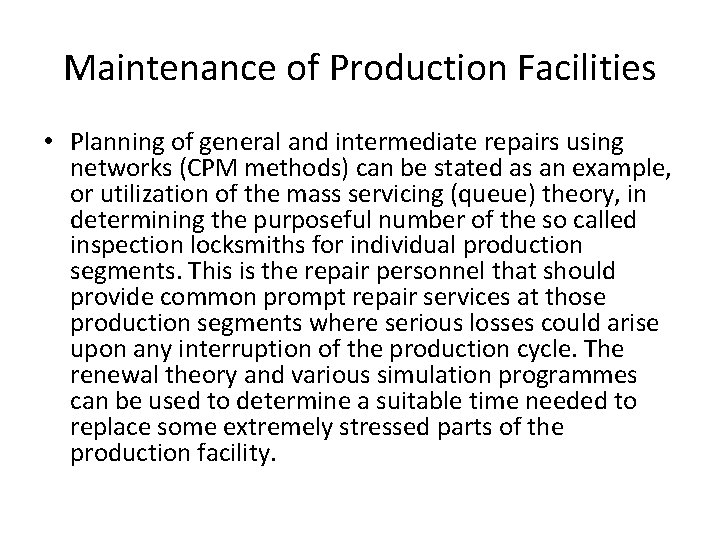
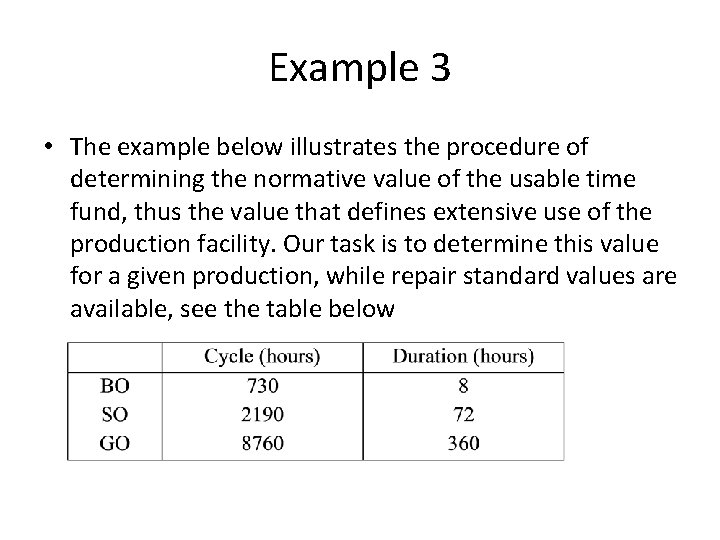
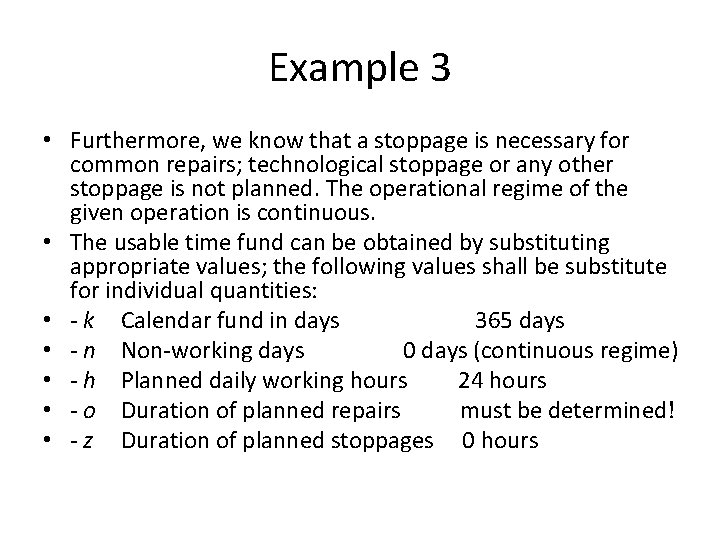
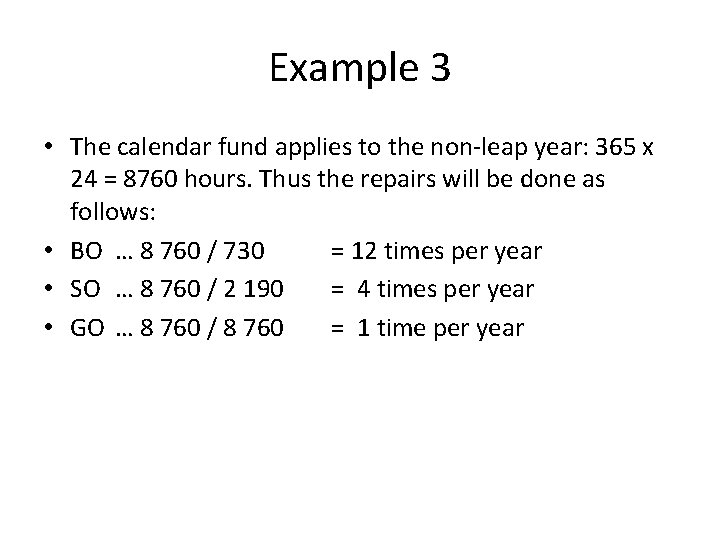
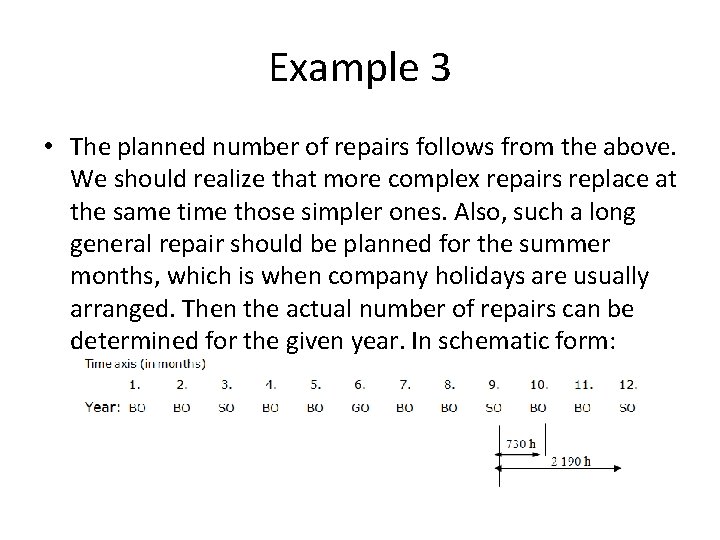
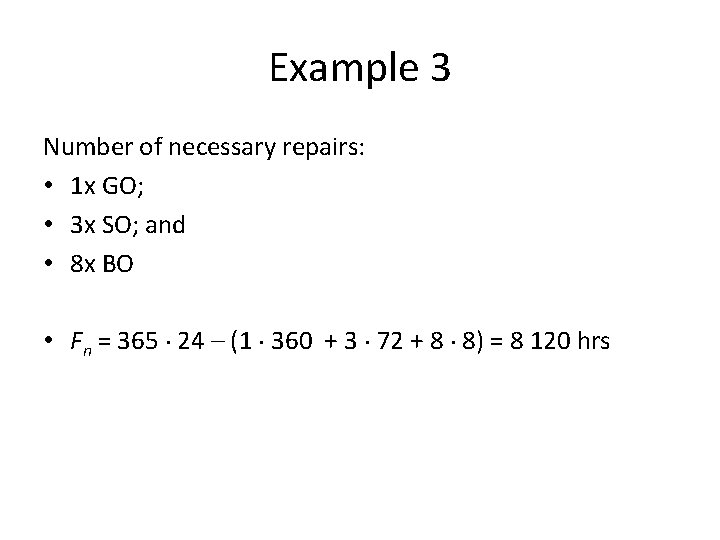
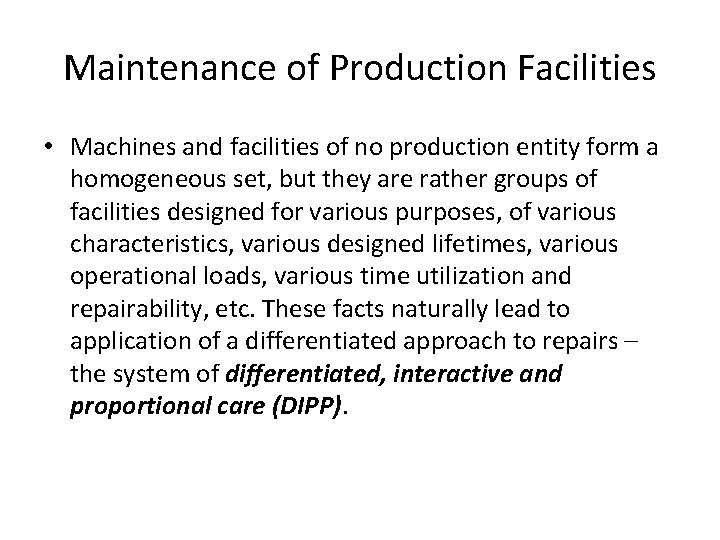
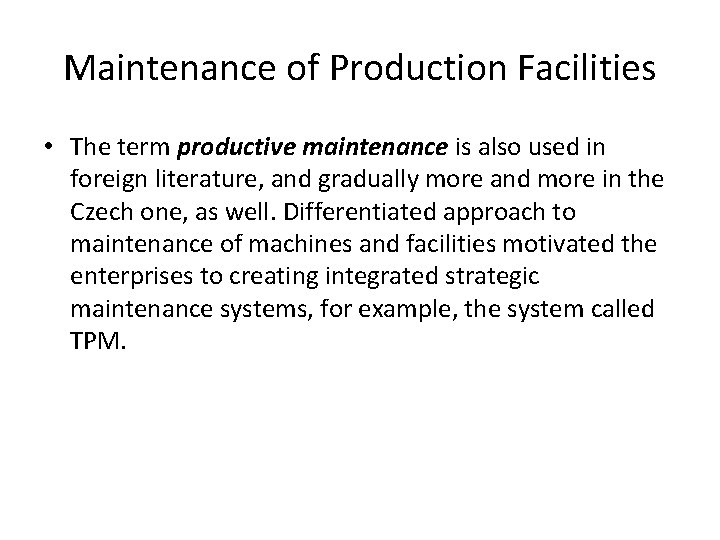
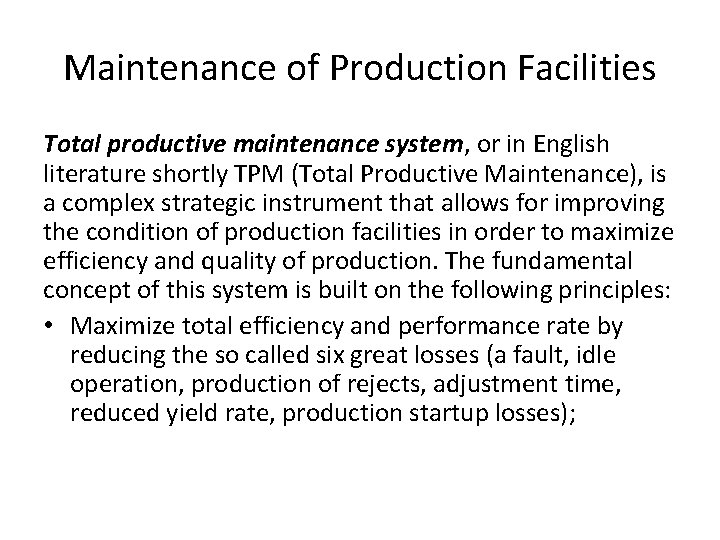
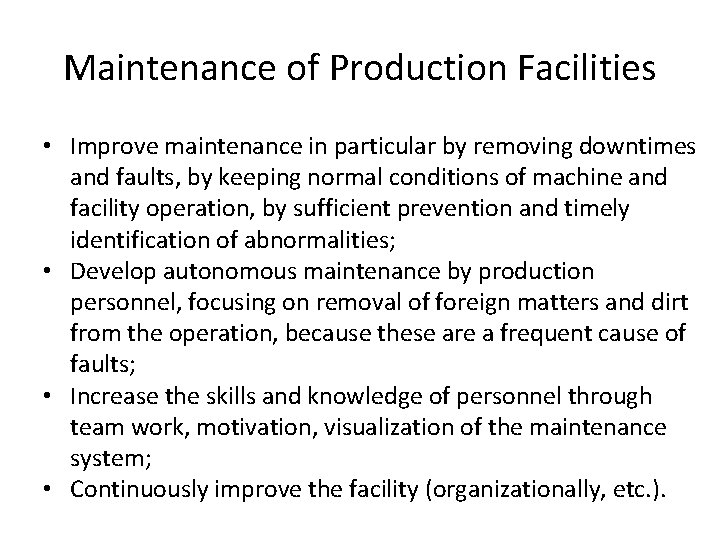
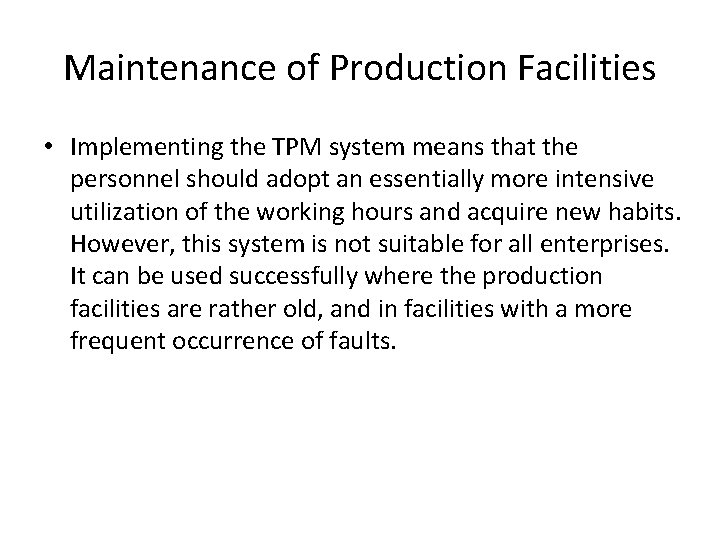
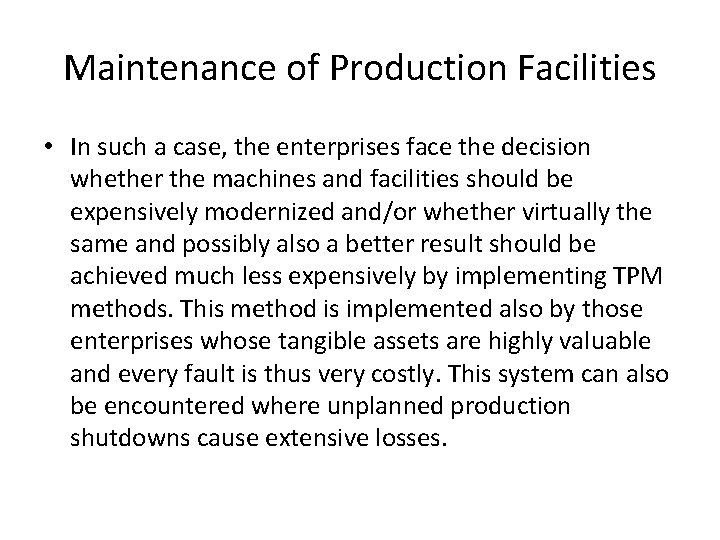
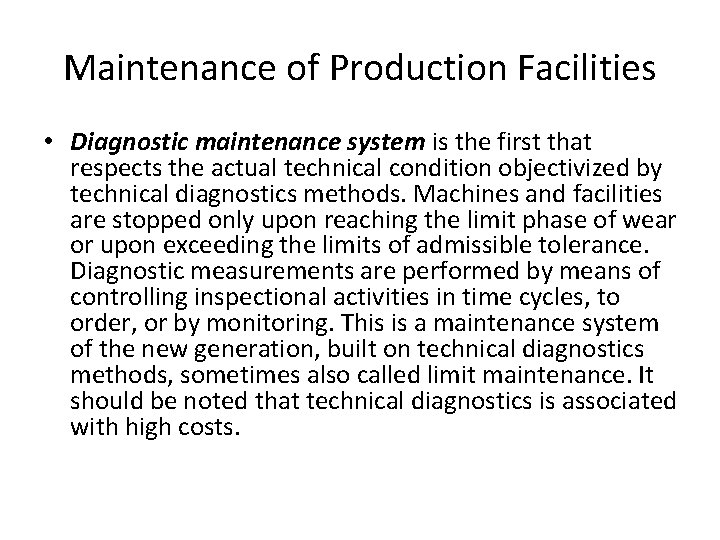
- Slides: 103
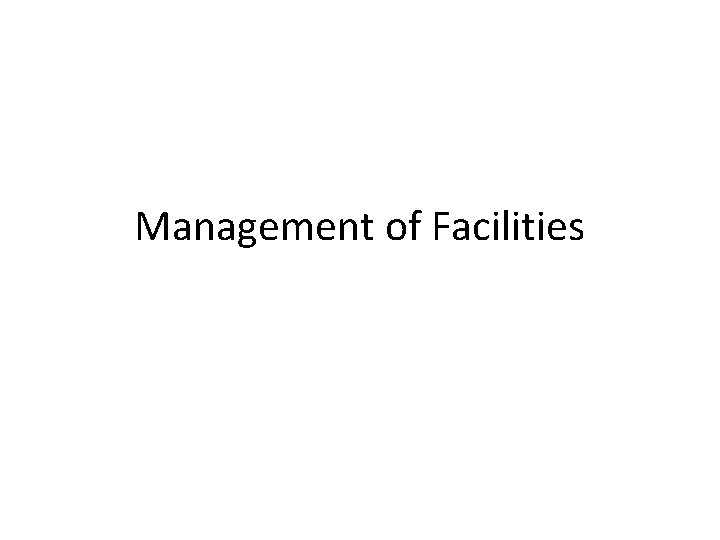
Management of Facilities
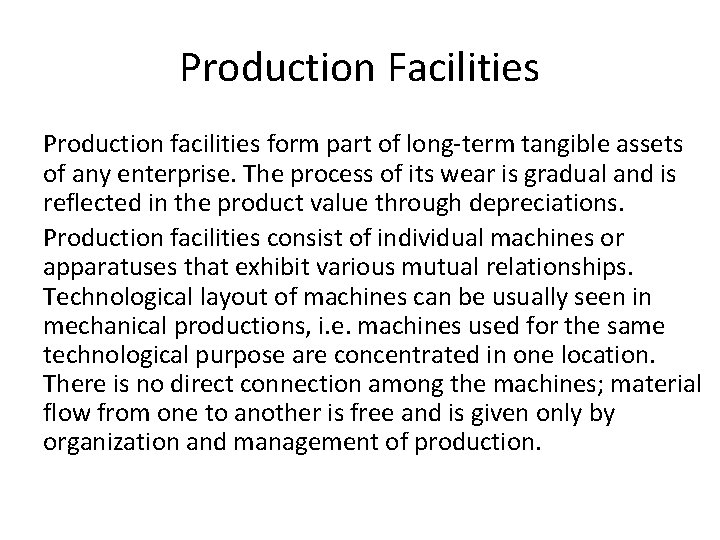
Production Facilities Production facilities form part of long-term tangible assets of any enterprise. The process of its wear is gradual and is reflected in the product value through depreciations. Production facilities consist of individual machines or apparatuses that exhibit various mutual relationships. Technological layout of machines can be usually seen in mechanical productions, i. e. machines used for the same technological purpose are concentrated in one location. There is no direct connection among the machines; material flow from one to another is free and is given only by organization and management of production.
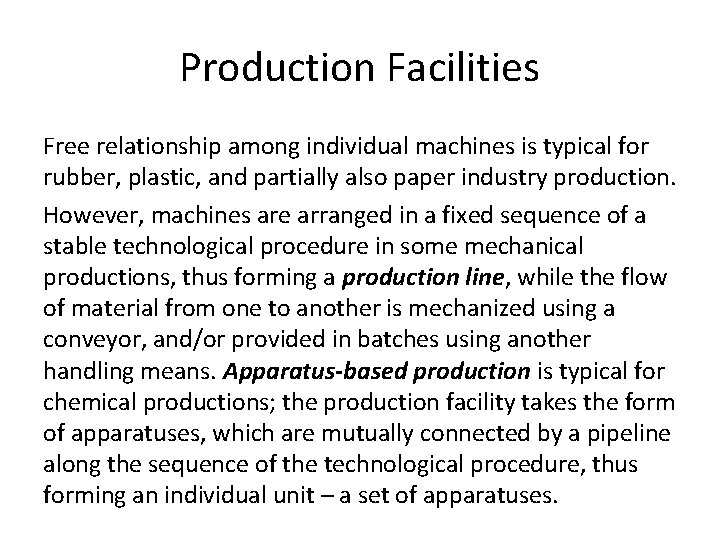
Production Facilities Free relationship among individual machines is typical for rubber, plastic, and partially also paper industry production. However, machines are arranged in a fixed sequence of a stable technological procedure in some mechanical productions, thus forming a production line, while the flow of material from one to another is mechanized using a conveyor, and/or provided in batches using another handling means. Apparatus-based production is typical for chemical productions; the production facility takes the form of apparatuses, which are mutually connected by a pipeline along the sequence of the technological procedure, thus forming an individual unit – a set of apparatuses.
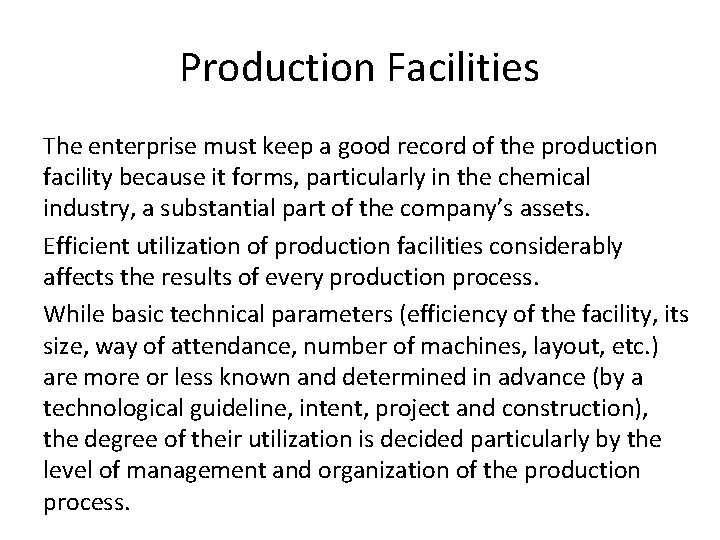
Production Facilities The enterprise must keep a good record of the production facility because it forms, particularly in the chemical industry, a substantial part of the company’s assets. Efficient utilization of production facilities considerably affects the results of every production process. While basic technical parameters (efficiency of the facility, its size, way of attendance, number of machines, layout, etc. ) are more or less known and determined in advance (by a technological guideline, intent, project and construction), the degree of their utilization is decided particularly by the level of management and organization of the production process.
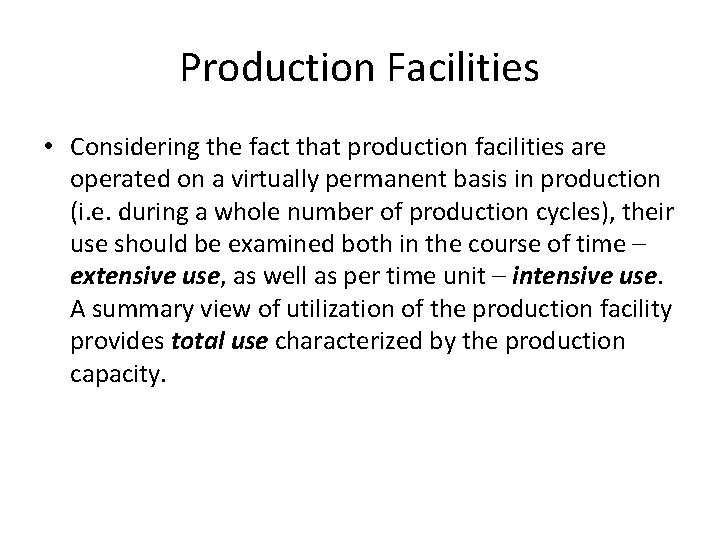
Production Facilities • Considering the fact that production facilities are operated on a virtually permanent basis in production (i. e. during a whole number of production cycles), their use should be examined both in the course of time – extensive use, as well as per time unit – intensive use. A summary view of utilization of the production facility provides total use characterized by the production capacity.
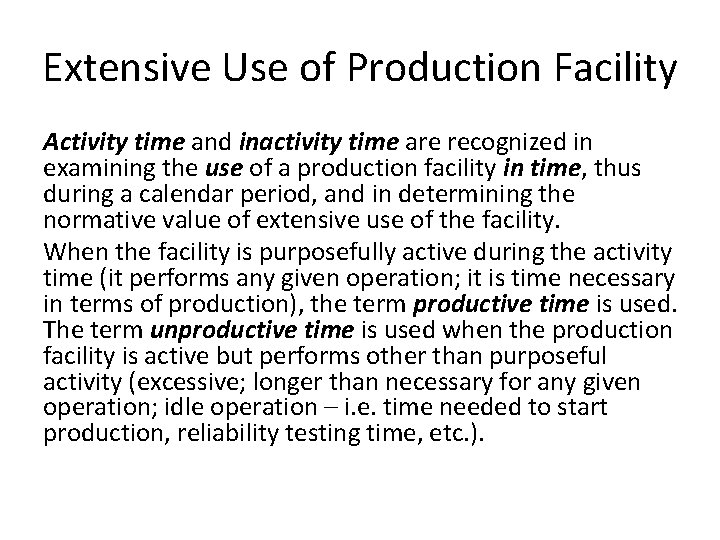
Extensive Use of Production Facility Activity time and inactivity time are recognized in examining the use of a production facility in time, thus during a calendar period, and in determining the normative value of extensive use of the facility. When the facility is purposefully active during the activity time (it performs any given operation; it is time necessary in terms of production), the term productive time is used. The term unproductive time is used when the production facility is active but performs other than purposeful activity (excessive; longer than necessary for any given operation; idle operation – i. e. time needed to start production, reliability testing time, etc. ).

Extensive Use of Production Facility There may be many causes of interrupting activity, i. e. causes of inactivity time of the production facility, and they follow from: • Condition of the production facility (fault) • Technological conditions and regime of production (catalyst replacement, machine adjustment) • From production organization and management (change of made products, preparation and cleaning of the workplace, material transfer, unavailable attendance personnel, faults) • From the working regime (compulsory pauses at work, other than working shifts) • From lack of discipline of the workers, etc.
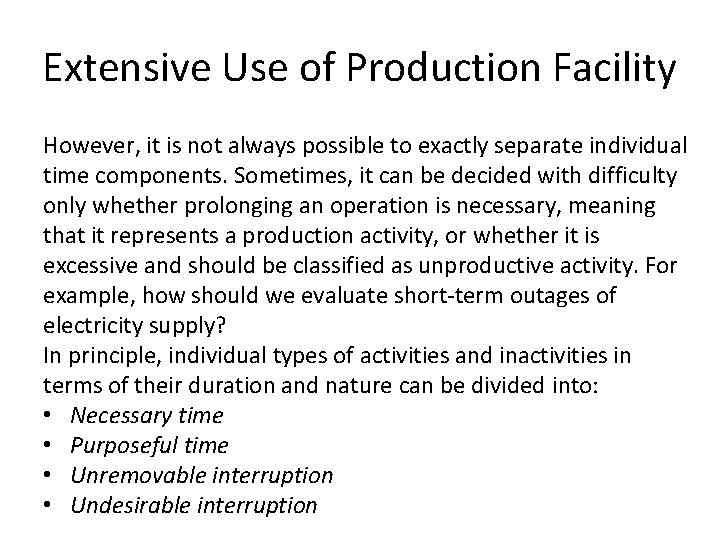
Extensive Use of Production Facility However, it is not always possible to exactly separate individual time components. Sometimes, it can be decided with difficulty only whether prolonging an operation is necessary, meaning that it represents a production activity, or whether it is excessive and should be classified as unproductive activity. For example, how should we evaluate short-term outages of electricity supply? In principle, individual types of activities and inactivities in terms of their duration and nature can be divided into: • Necessary time • Purposeful time • Unremovable interruption • Undesirable interruption
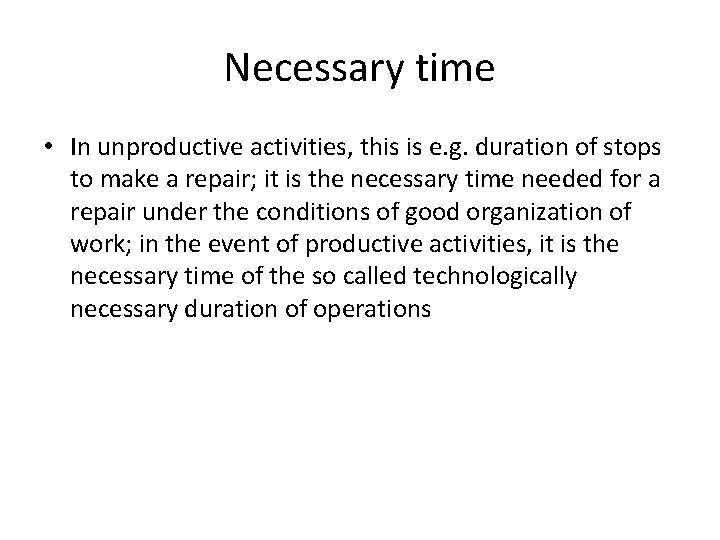
Necessary time • In unproductive activities, this is e. g. duration of stops to make a repair; it is the necessary time needed for a repair under the conditions of good organization of work; in the event of productive activities, it is the necessary time of the so called technologically necessary duration of operations
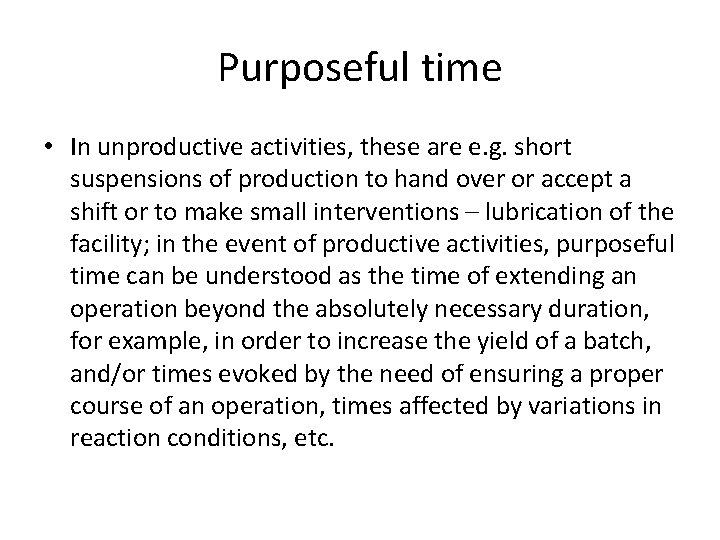
Purposeful time • In unproductive activities, these are e. g. short suspensions of production to hand over or accept a shift or to make small interventions – lubrication of the facility; in the event of productive activities, purposeful time can be understood as the time of extending an operation beyond the absolutely necessary duration, for example, in order to increase the yield of a batch, and/or times evoked by the need of ensuring a proper course of an operation, times affected by variations in reaction conditions, etc.
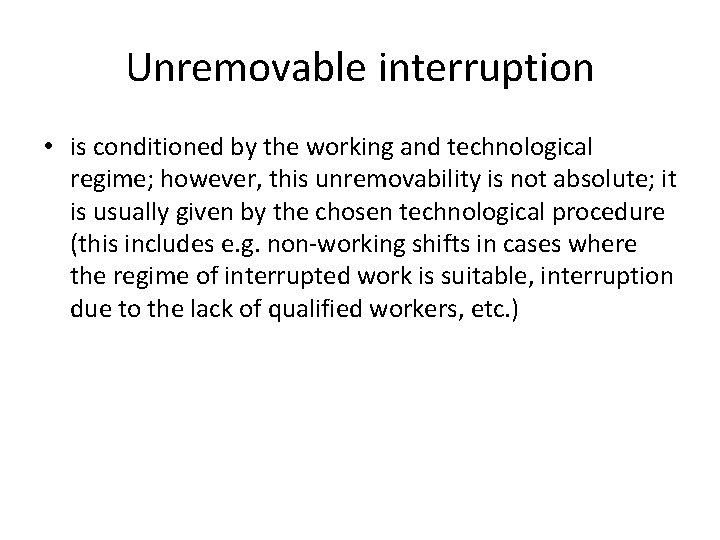
Unremovable interruption • is conditioned by the working and technological regime; however, this unremovability is not absolute; it is usually given by the chosen technological procedure (this includes e. g. non-working shifts in cases where the regime of interrupted work is suitable, interruption due to the lack of qualified workers, etc. )
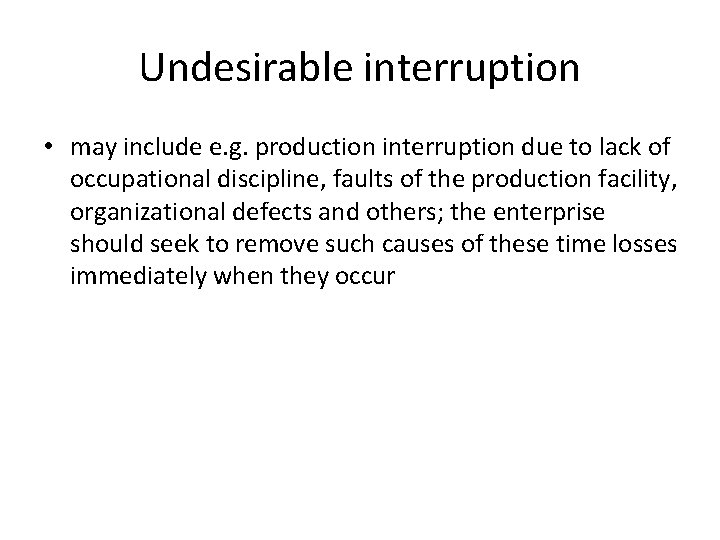
Undesirable interruption • may include e. g. production interruption due to lack of occupational discipline, faults of the production facility, organizational defects and others; the enterprise should seek to remove such causes of these time losses immediately when they occur
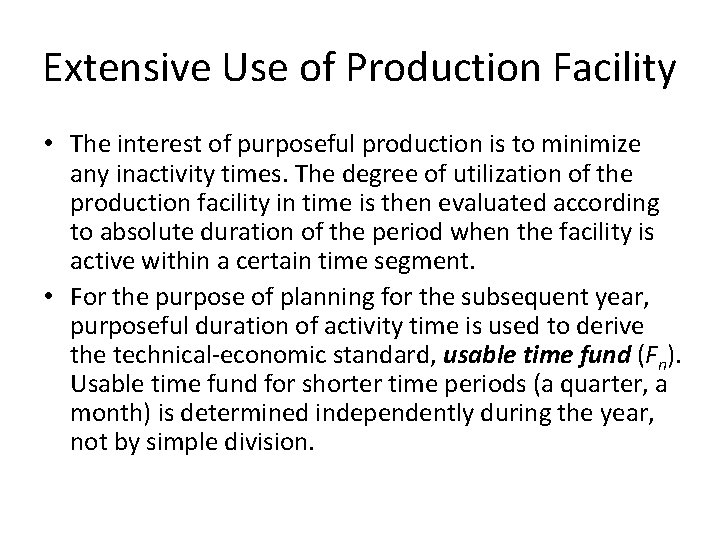
Extensive Use of Production Facility • The interest of purposeful production is to minimize any inactivity times. The degree of utilization of the production facility in time is then evaluated according to absolute duration of the period when the facility is active within a certain time segment. • For the purpose of planning for the subsequent year, purposeful duration of activity time is used to derive the technical-economic standard, usable time fund (Fn). Usable time fund for shorter time periods (a quarter, a month) is determined independently during the year, not by simple division.
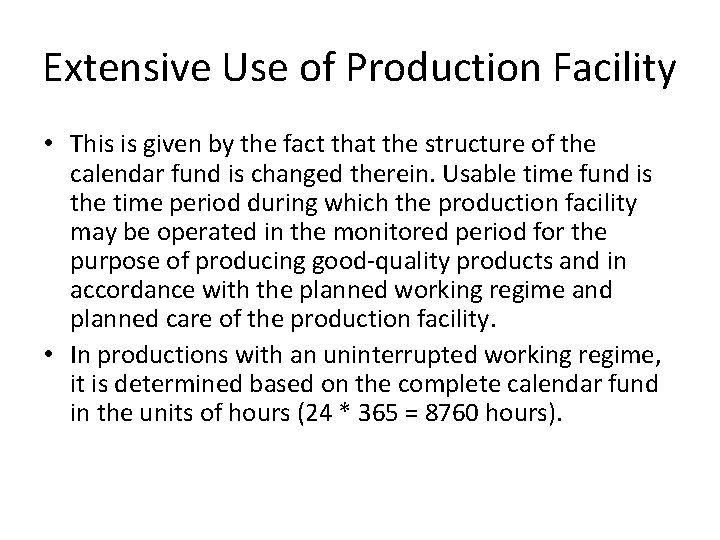
Extensive Use of Production Facility • This is given by the fact that the structure of the calendar fund is changed therein. Usable time fund is the time period during which the production facility may be operated in the monitored period for the purpose of producing good-quality products and in accordance with the planned working regime and planned care of the production facility. • In productions with an uninterrupted working regime, it is determined based on the complete calendar fund in the units of hours (24 * 365 = 8760 hours).
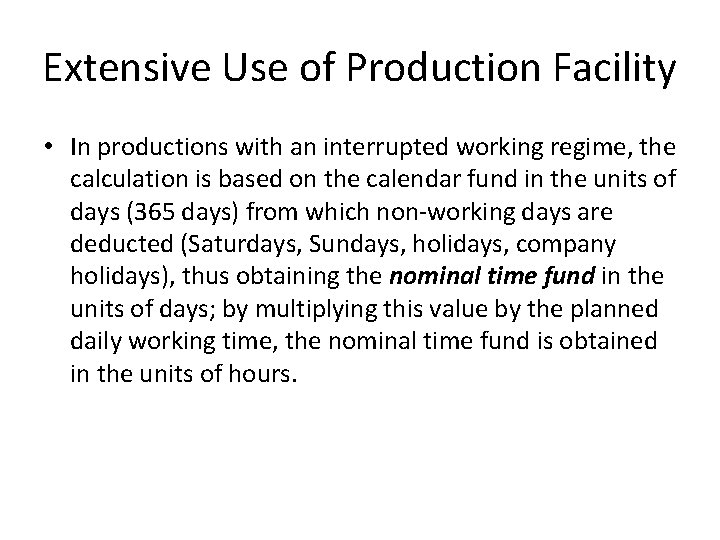
Extensive Use of Production Facility • In productions with an interrupted working regime, the calculation is based on the calendar fund in the units of days (365 days) from which non-working days are deducted (Saturdays, Sundays, holidays, company holidays), thus obtaining the nominal time fund in the units of days; by multiplying this value by the planned daily working time, the nominal time fund is obtained in the units of hours.
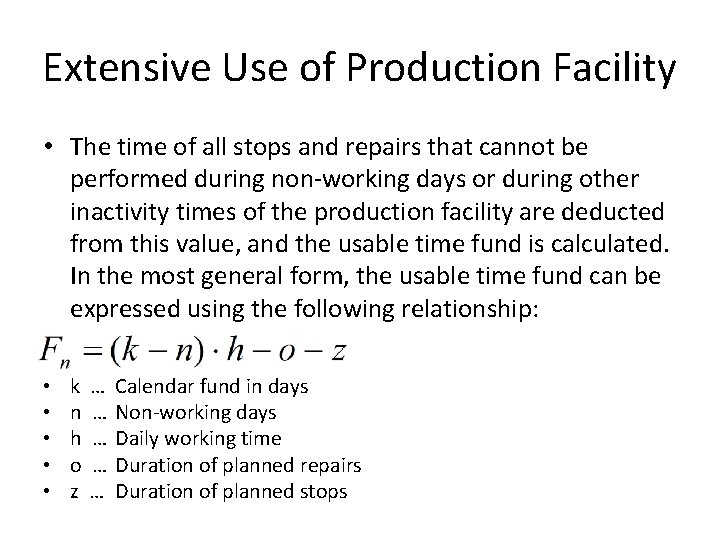
Extensive Use of Production Facility • The time of all stops and repairs that cannot be performed during non-working days or during other inactivity times of the production facility are deducted from this value, and the usable time fund is calculated. In the most general form, the usable time fund can be expressed using the following relationship: • • • k n h o z … … … Calendar fund in days Non-working days Daily working time Duration of planned repairs Duration of planned stops
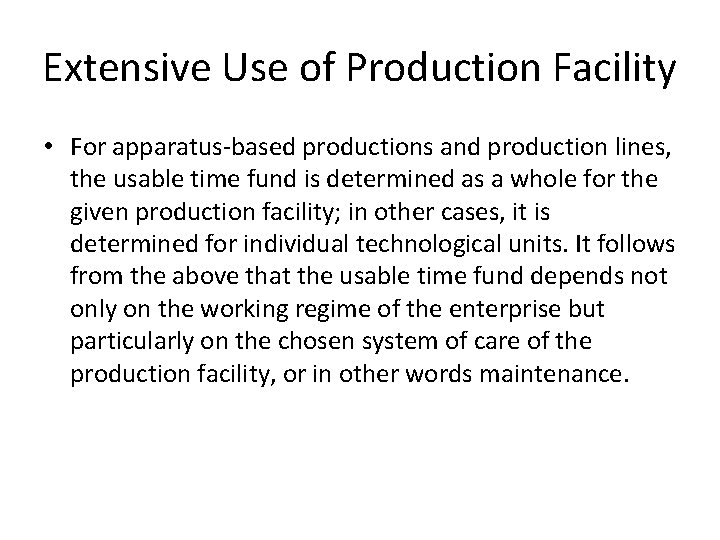
Extensive Use of Production Facility • For apparatus-based productions and production lines, the usable time fund is determined as a whole for the given production facility; in other cases, it is determined for individual technological units. It follows from the above that the usable time fund depends not only on the working regime of the enterprise but particularly on the chosen system of care of the production facility, or in other words maintenance.
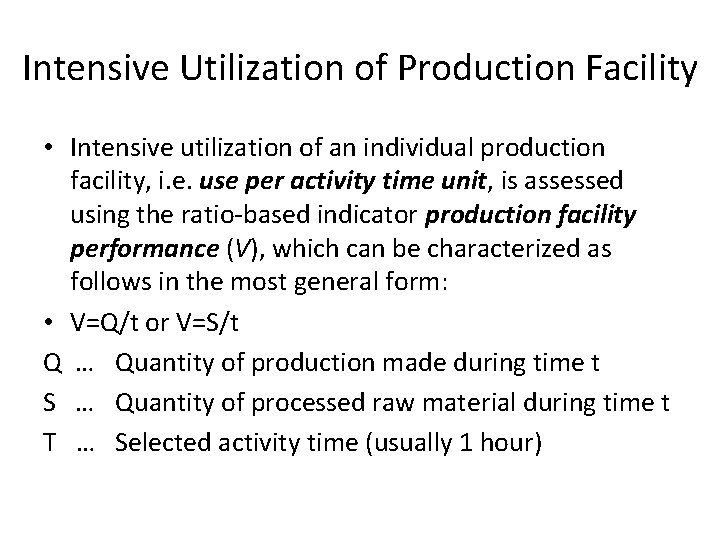
Intensive Utilization of Production Facility • Intensive utilization of an individual production facility, i. e. use per activity time unit, is assessed using the ratio-based indicator production facility performance (V), which can be characterized as follows in the most general form: • V=Q/t or V=S/t Q … Quantity of production made during time t S … Quantity of processed raw material during time t T … Selected activity time (usually 1 hour)
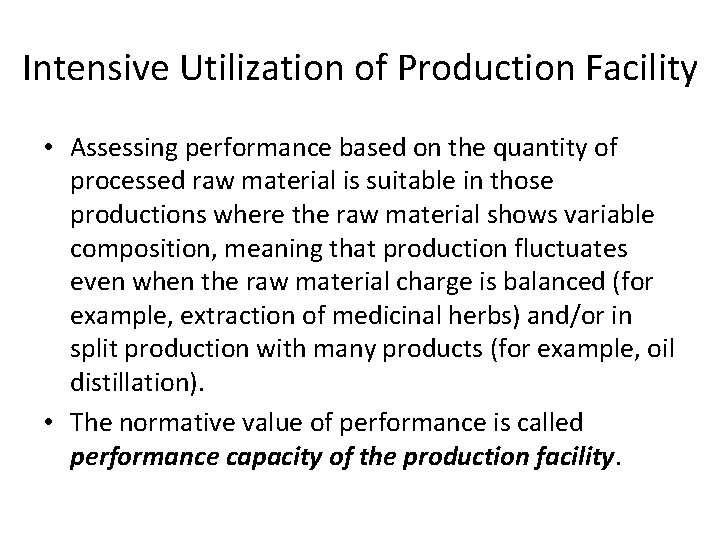
Intensive Utilization of Production Facility • Assessing performance based on the quantity of processed raw material is suitable in those productions where the raw material shows variable composition, meaning that production fluctuates even when the raw material charge is balanced (for example, extraction of medicinal herbs) and/or in split production with many products (for example, oil distillation). • The normative value of performance is called performance capacity of the production facility.
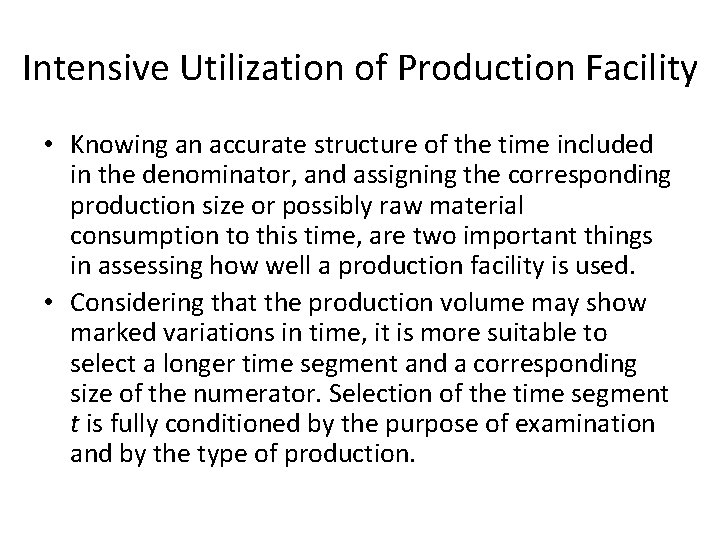
Intensive Utilization of Production Facility • Knowing an accurate structure of the time included in the denominator, and assigning the corresponding production size or possibly raw material consumption to this time, are two important things in assessing how well a production facility is used. • Considering that the production volume may show marked variations in time, it is more suitable to select a longer time segment and a corresponding size of the numerator. Selection of the time segment t is fully conditioned by the purpose of examination and by the type of production.
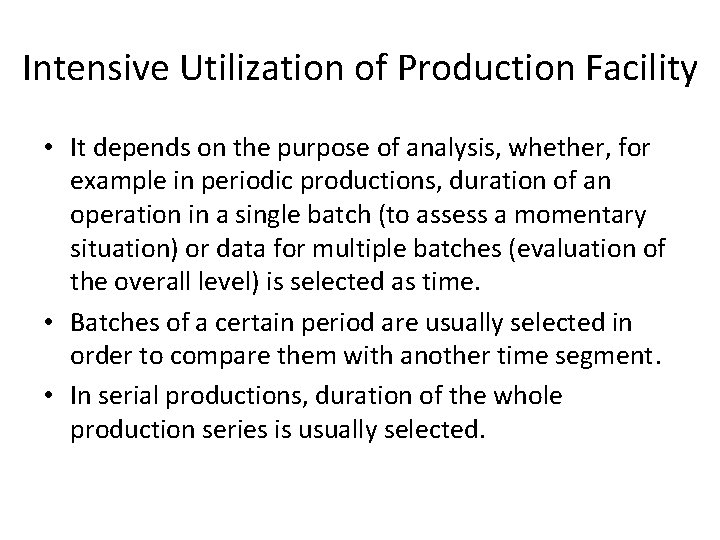
Intensive Utilization of Production Facility • It depends on the purpose of analysis, whether, for example in periodic productions, duration of an operation in a single batch (to assess a momentary situation) or data for multiple batches (evaluation of the overall level) is selected as time. • Batches of a certain period are usually selected in order to compare them with another time segment. • In serial productions, duration of the whole production series is usually selected.
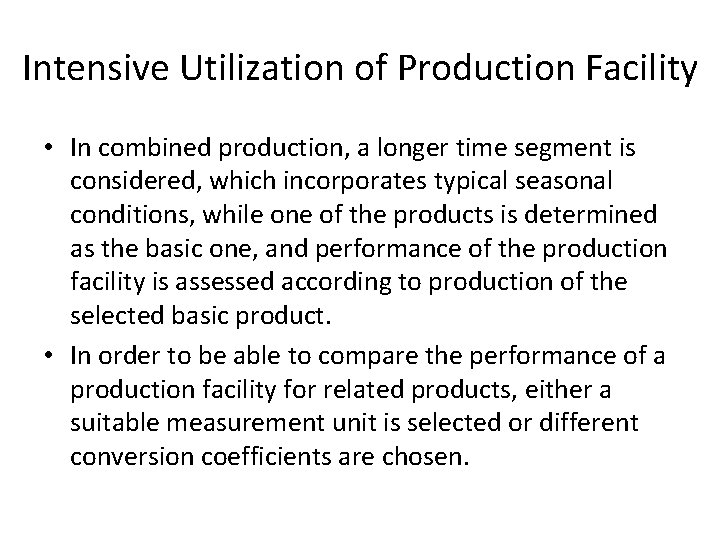
Intensive Utilization of Production Facility • In combined production, a longer time segment is considered, which incorporates typical seasonal conditions, while one of the products is determined as the basic one, and performance of the production facility is assessed according to production of the selected basic product. • In order to be able to compare the performance of a production facility for related products, either a suitable measurement unit is selected or different conversion coefficients are chosen.
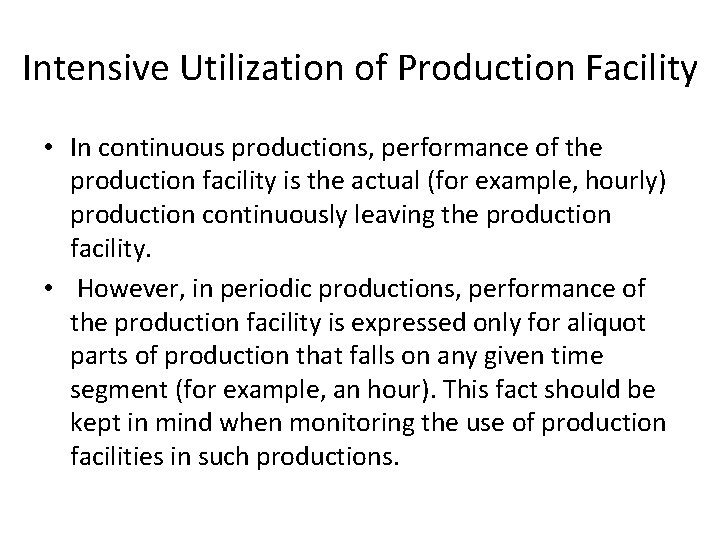
Intensive Utilization of Production Facility • In continuous productions, performance of the production facility is the actual (for example, hourly) production continuously leaving the production facility. • However, in periodic productions, performance of the production facility is expressed only for aliquot parts of production that falls on any given time segment (for example, an hour). This fact should be kept in mind when monitoring the use of production facilities in such productions.
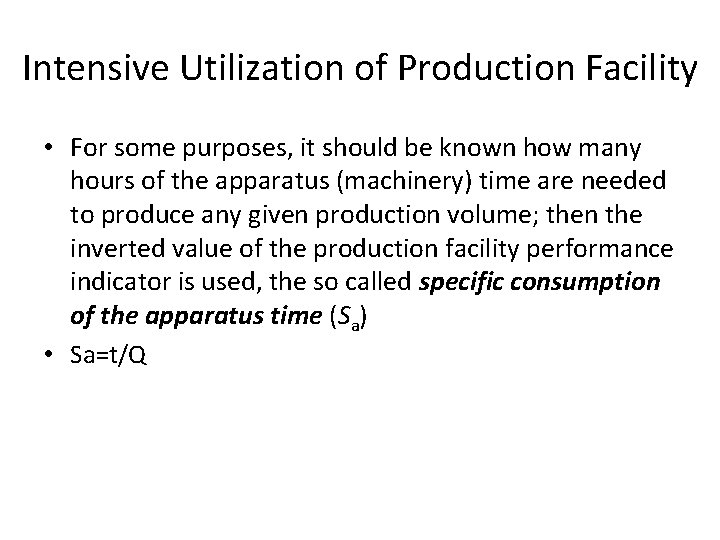
Intensive Utilization of Production Facility • For some purposes, it should be known how many hours of the apparatus (machinery) time are needed to produce any given production volume; then the inverted value of the production facility performance indicator is used, the so called specific consumption of the apparatus time (Sa) • Sa=t/Q
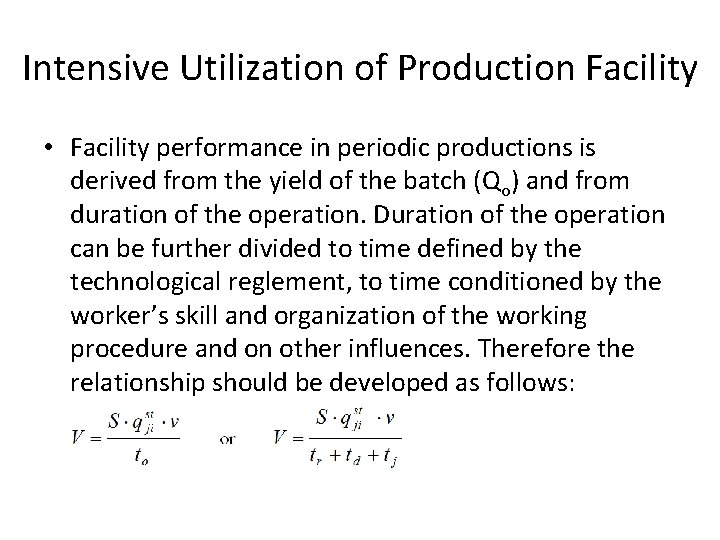
Intensive Utilization of Production Facility • Facility performance in periodic productions is derived from the yield of the batch (Qo) and from duration of the operation. Duration of the operation can be further divided to time defined by the technological reglement, to time conditioned by the worker’s skill and organization of the working procedure and on other influences. Therefore the relationship should be developed as follows:
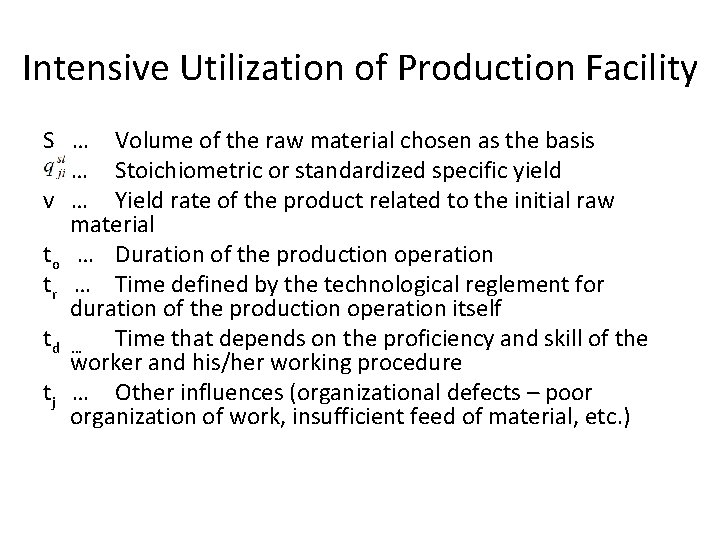
Intensive Utilization of Production Facility S … Volume of the raw material chosen as the basis … Stoichiometric or standardized specific yield v … Yield rate of the product related to the initial raw material to … Duration of the production operation tr … Time defined by the technological reglement for duration of the production operation itself td … Time that depends on the proficiency and skill of the worker and his/her working procedure tj … Other influences (organizational defects – poor organization of work, insufficient feed of material, etc. )
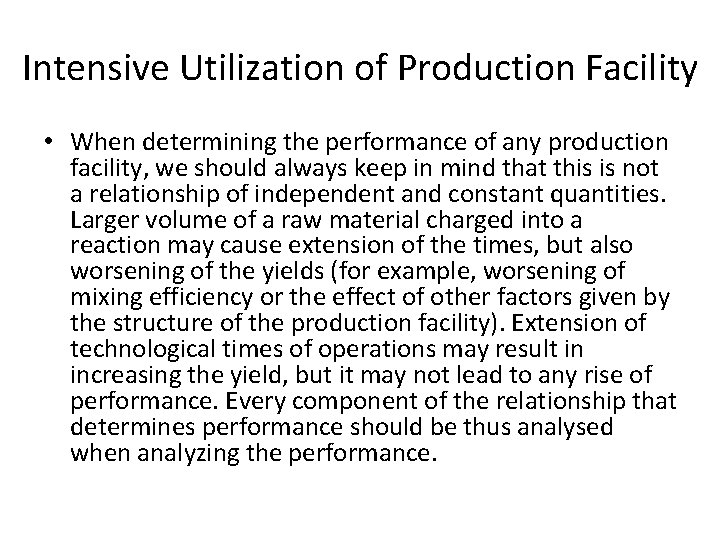
Intensive Utilization of Production Facility • When determining the performance of any production facility, we should always keep in mind that this is not a relationship of independent and constant quantities. Larger volume of a raw material charged into a reaction may cause extension of the times, but also worsening of the yields (for example, worsening of mixing efficiency or the effect of other factors given by the structure of the production facility). Extension of technological times of operations may result in increasing the yield, but it may not lead to any rise of performance. Every component of the relationship that determines performance should be thus analysed when analyzing the performance.
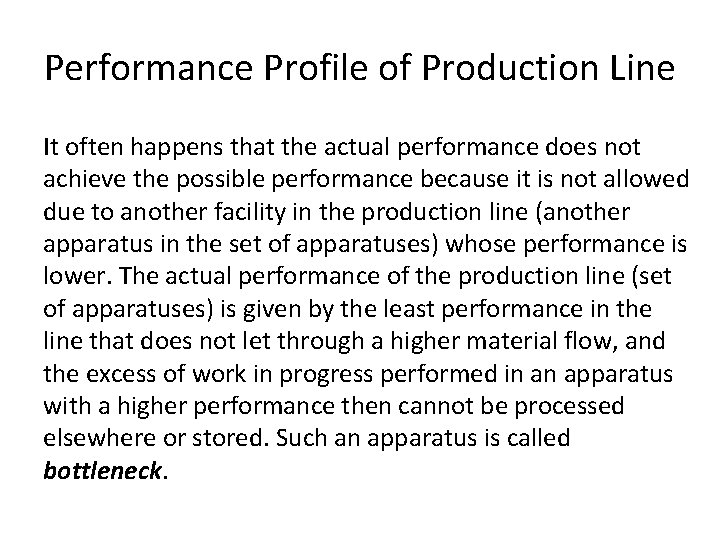
Performance Profile of Production Line It often happens that the actual performance does not achieve the possible performance because it is not allowed due to another facility in the production line (another apparatus in the set of apparatuses) whose performance is lower. The actual performance of the production line (set of apparatuses) is given by the least performance in the line that does not let through a higher material flow, and the excess of work in progress performed in an apparatus with a higher performance then cannot be processed elsewhere or stored. Such an apparatus is called bottleneck.
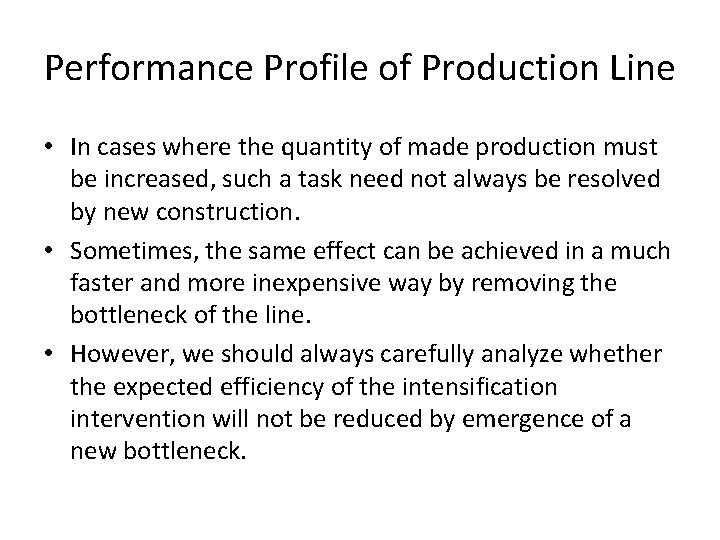
Performance Profile of Production Line • In cases where the quantity of made production must be increased, such a task need not always be resolved by new construction. • Sometimes, the same effect can be achieved in a much faster and more inexpensive way by removing the bottleneck of the line. • However, we should always carefully analyze whether the expected efficiency of the intensification intervention will not be reduced by emergence of a new bottleneck.
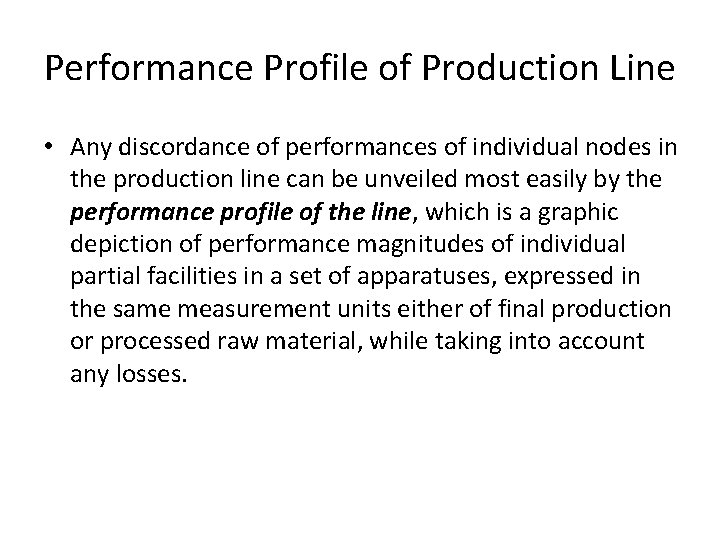
Performance Profile of Production Line • Any discordance of performances of individual nodes in the production line can be unveiled most easily by the performance profile of the line, which is a graphic depiction of performance magnitudes of individual partial facilities in a set of apparatuses, expressed in the same measurement units either of final production or processed raw material, while taking into account any losses.
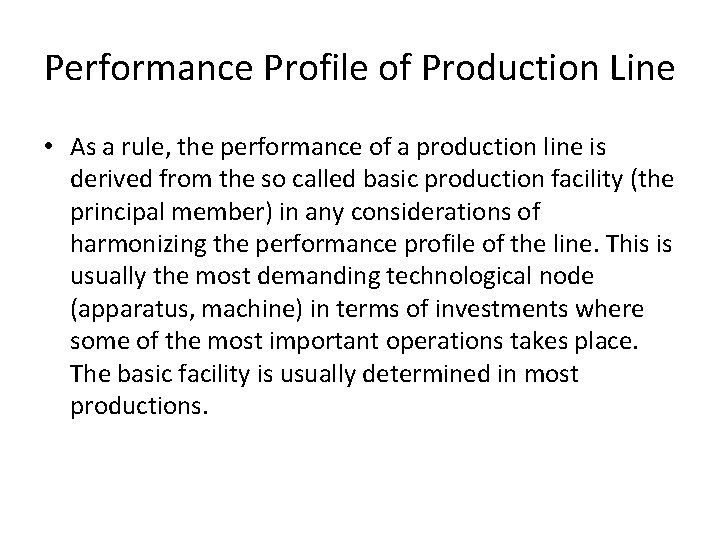
Performance Profile of Production Line • As a rule, the performance of a production line is derived from the so called basic production facility (the principal member) in any considerations of harmonizing the performance profile of the line. This is usually the most demanding technological node (apparatus, machine) in terms of investments where some of the most important operations takes place. The basic facility is usually determined in most productions.
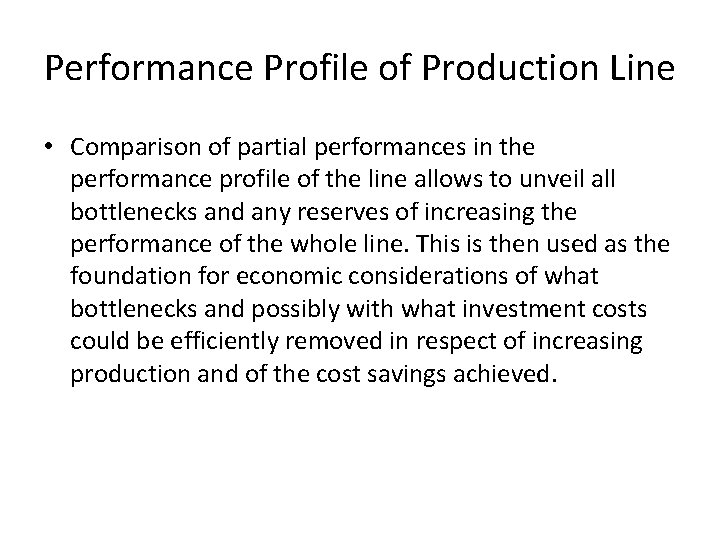
Performance Profile of Production Line • Comparison of partial performances in the performance profile of the line allows to unveil all bottlenecks and any reserves of increasing the performance of the whole line. This is then used as the foundation for economic considerations of what bottlenecks and possibly with what investment costs could be efficiently removed in respect of increasing production and of the cost savings achieved.
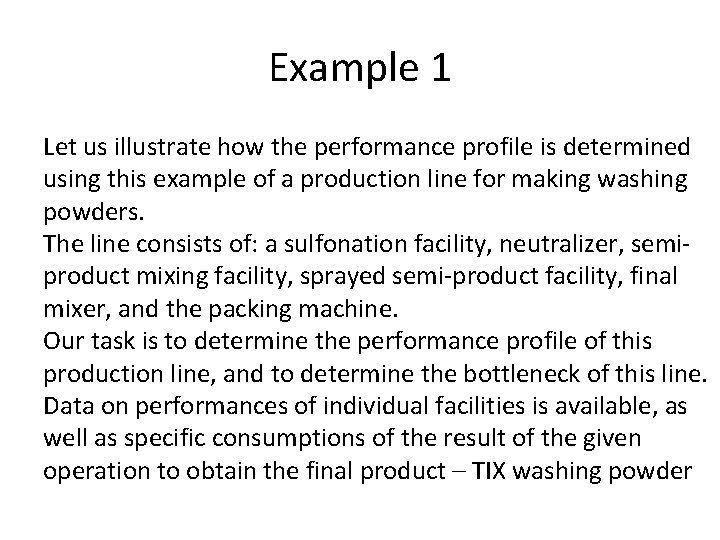
Example 1 Let us illustrate how the performance profile is determined using this example of a production line for making washing powders. The line consists of: a sulfonation facility, neutralizer, semiproduct mixing facility, sprayed semi-product facility, final mixer, and the packing machine. Our task is to determine the performance profile of this production line, and to determine the bottleneck of this line. Data on performances of individual facilities is available, as well as specific consumptions of the result of the given operation to obtain the final product – TIX washing powder
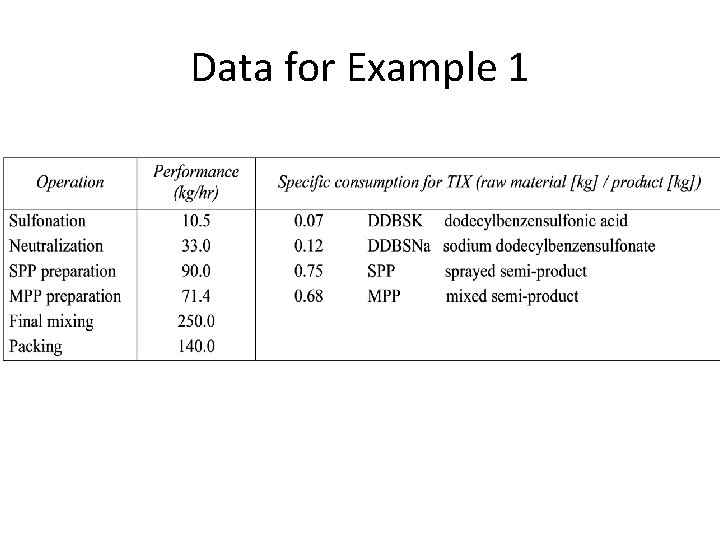
Data for Example 1
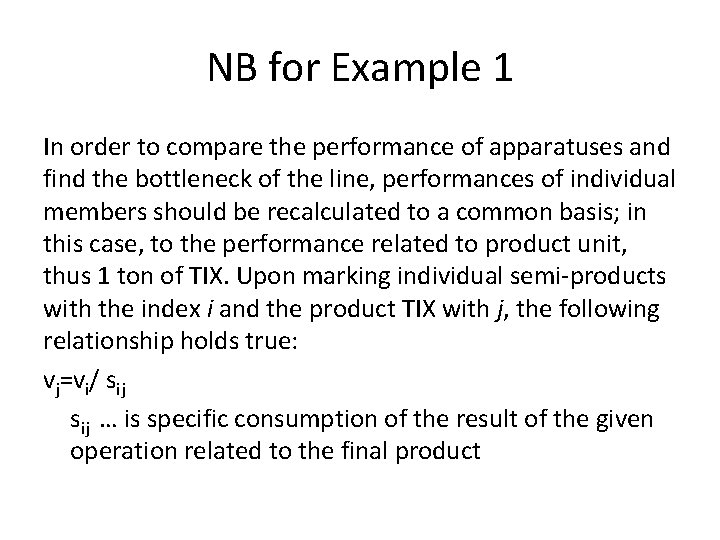
NB for Example 1 In order to compare the performance of apparatuses and find the bottleneck of the line, performances of individual members should be recalculated to a common basis; in this case, to the performance related to product unit, thus 1 ton of TIX. Upon marking individual semi-products with the index i and the product TIX with j, the following relationship holds true: vj=vi/ sij … is specific consumption of the result of the given operation related to the final product
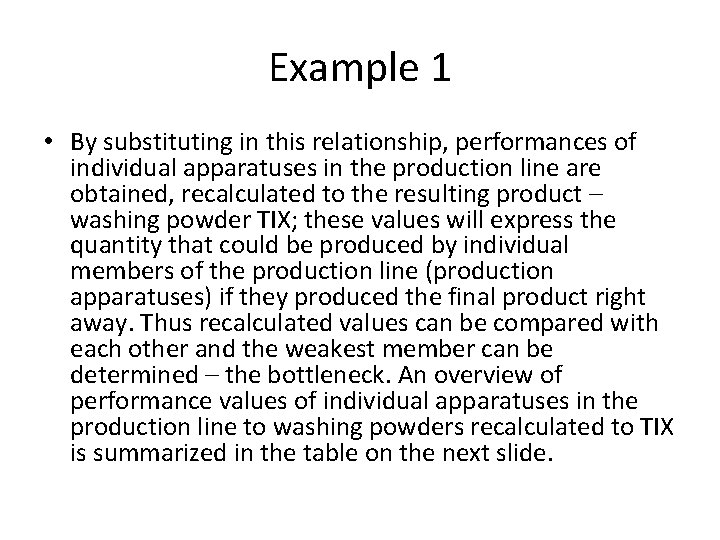
Example 1 • By substituting in this relationship, performances of individual apparatuses in the production line are obtained, recalculated to the resulting product – washing powder TIX; these values will express the quantity that could be produced by individual members of the production line (production apparatuses) if they produced the final product right away. Thus recalculated values can be compared with each other and the weakest member can be determined – the bottleneck. An overview of performance values of individual apparatuses in the production line to washing powders recalculated to TIX is summarized in the table on the next slide.
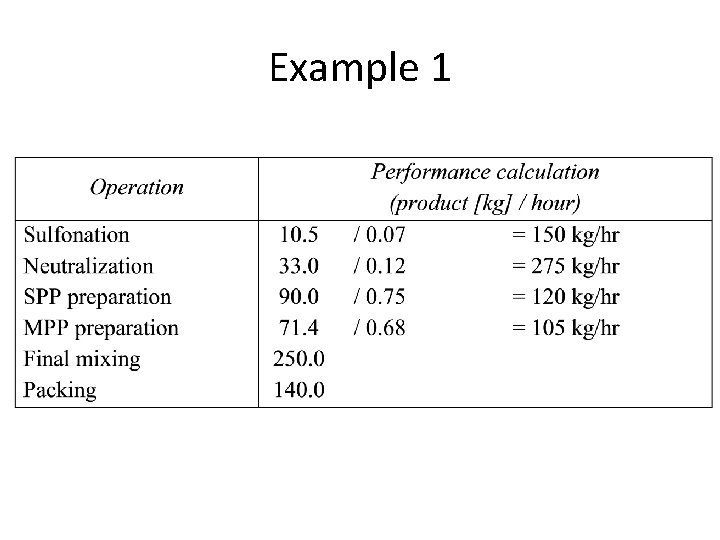
Example 1
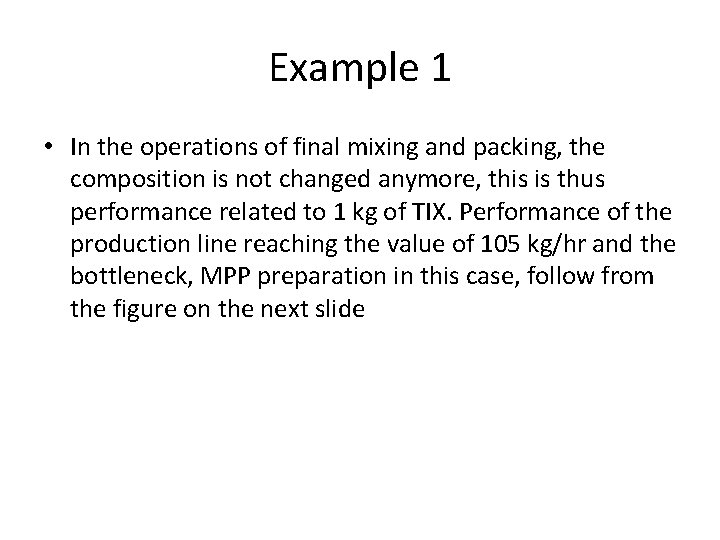
Example 1 • In the operations of final mixing and packing, the composition is not changed anymore, this is thus performance related to 1 kg of TIX. Performance of the production line reaching the value of 105 kg/hr and the bottleneck, MPP preparation in this case, follow from the figure on the next slide
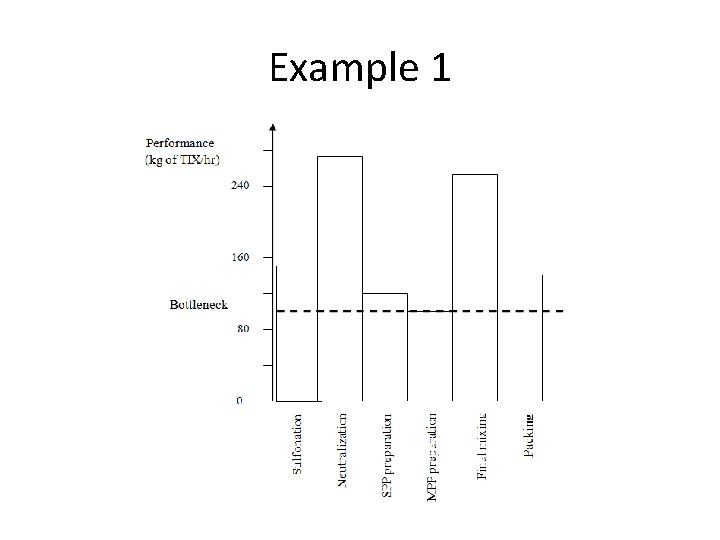
Example 1
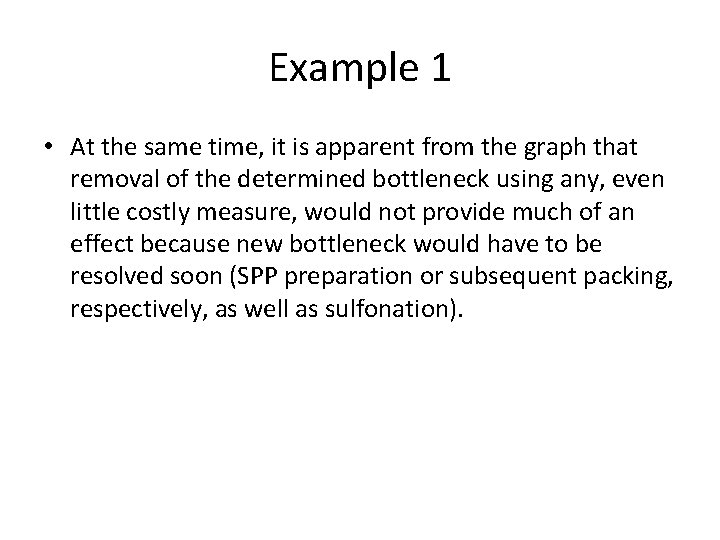
Example 1 • At the same time, it is apparent from the graph that removal of the determined bottleneck using any, even little costly measure, would not provide much of an effect because new bottleneck would have to be resolved soon (SPP preparation or subsequent packing, respectively, as well as sulfonation).
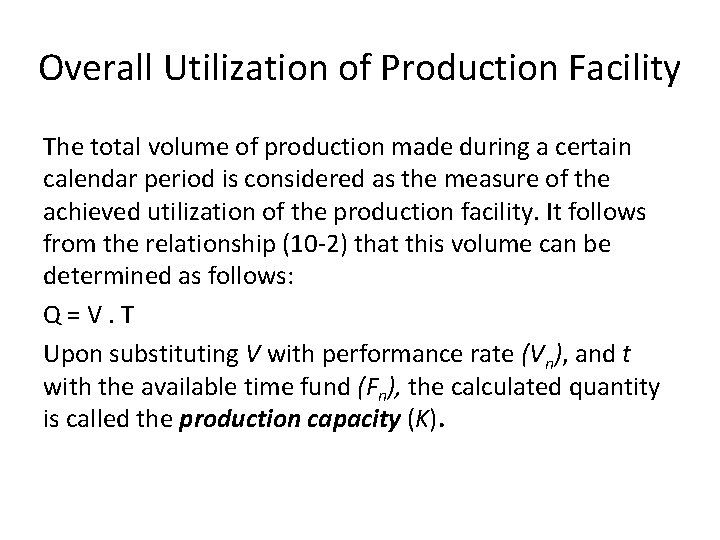
Overall Utilization of Production Facility The total volume of production made during a certain calendar period is considered as the measure of the achieved utilization of the production facility. It follows from the relationship (10 -2) that this volume can be determined as follows: Q=V. T Upon substituting V with performance rate (Vn), and t with the available time fund (Fn), the calculated quantity is called the production capacity (K).
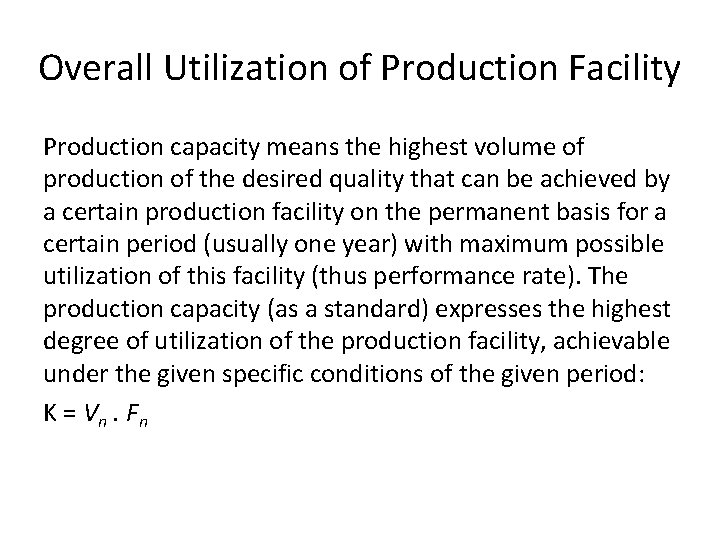
Overall Utilization of Production Facility Production capacity means the highest volume of production of the desired quality that can be achieved by a certain production facility on the permanent basis for a certain period (usually one year) with maximum possible utilization of this facility (thus performance rate). The production capacity (as a standard) expresses the highest degree of utilization of the production facility, achievable under the given specific conditions of the given period: K = Vn. F n
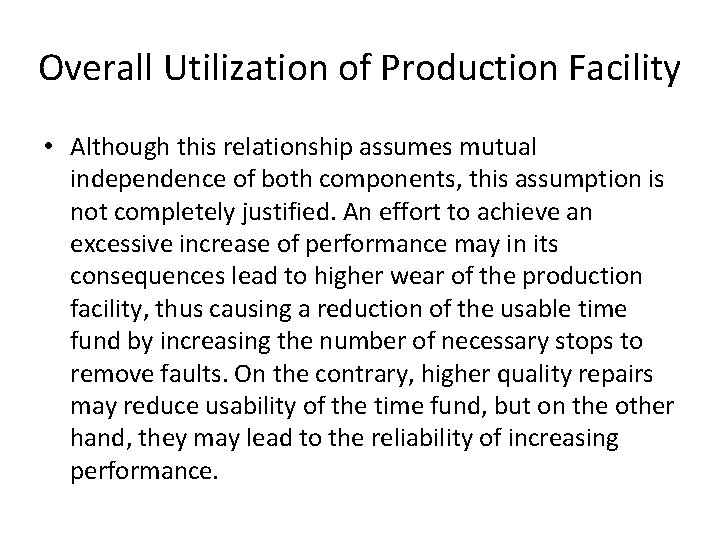
Overall Utilization of Production Facility • Although this relationship assumes mutual independence of both components, this assumption is not completely justified. An effort to achieve an excessive increase of performance may in its consequences lead to higher wear of the production facility, thus causing a reduction of the usable time fund by increasing the number of necessary stops to remove faults. On the contrary, higher quality repairs may reduce usability of the time fund, but on the other hand, they may lead to the reliability of increasing performance.
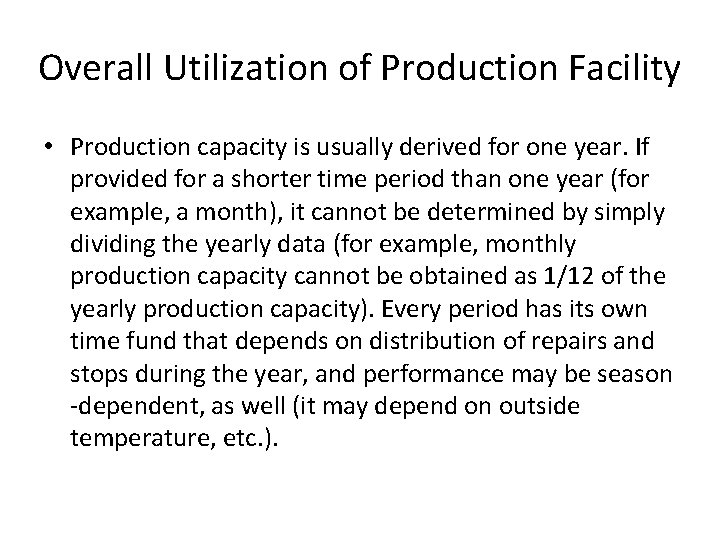
Overall Utilization of Production Facility • Production capacity is usually derived for one year. If provided for a shorter time period than one year (for example, a month), it cannot be determined by simply dividing the yearly data (for example, monthly production capacity cannot be obtained as 1/12 of the yearly production capacity). Every period has its own time fund that depends on distribution of repairs and stops during the year, and performance may be season -dependent, as well (it may depend on outside temperature, etc. ).
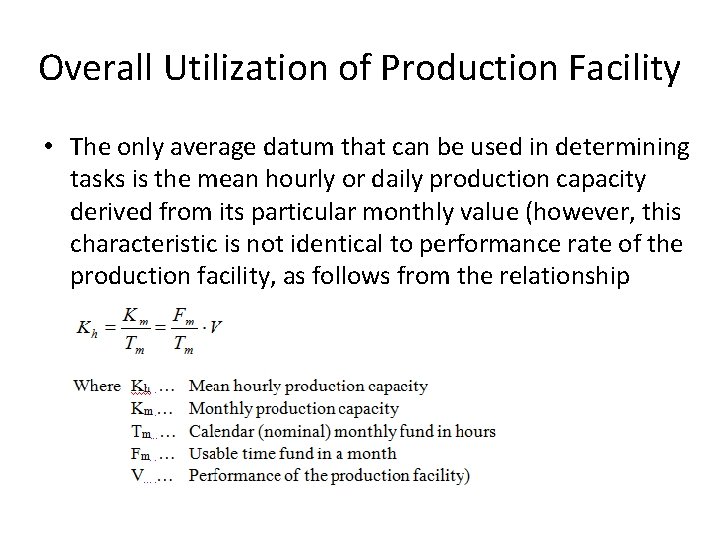
Overall Utilization of Production Facility • The only average datum that can be used in determining tasks is the mean hourly or daily production capacity derived from its particular monthly value (however, this characteristic is not identical to performance rate of the production facility, as follows from the relationship
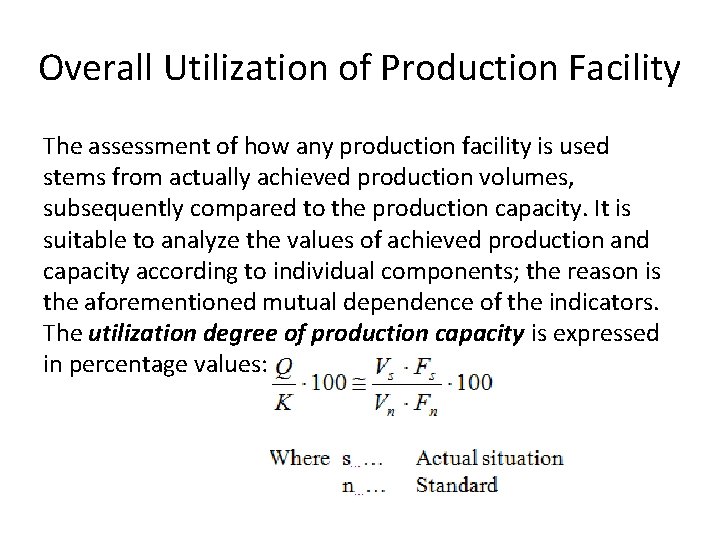
Overall Utilization of Production Facility The assessment of how any production facility is used stems from actually achieved production volumes, subsequently compared to the production capacity. It is suitable to analyze the values of achieved production and capacity according to individual components; the reason is the aforementioned mutual dependence of the indicators. The utilization degree of production capacity is expressed in percentage values:
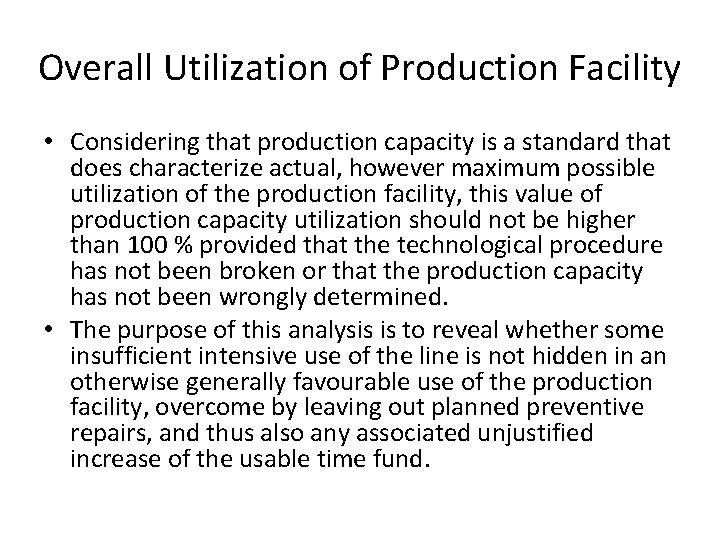
Overall Utilization of Production Facility • Considering that production capacity is a standard that does characterize actual, however maximum possible utilization of the production facility, this value of production capacity utilization should not be higher than 100 % provided that the technological procedure has not been broken or that the production capacity has not been wrongly determined. • The purpose of this analysis is to reveal whether some insufficient intensive use of the line is not hidden in an otherwise generally favourable use of the production facility, overcome by leaving out planned preventive repairs, and thus also any associated unjustified increase of the usable time fund.
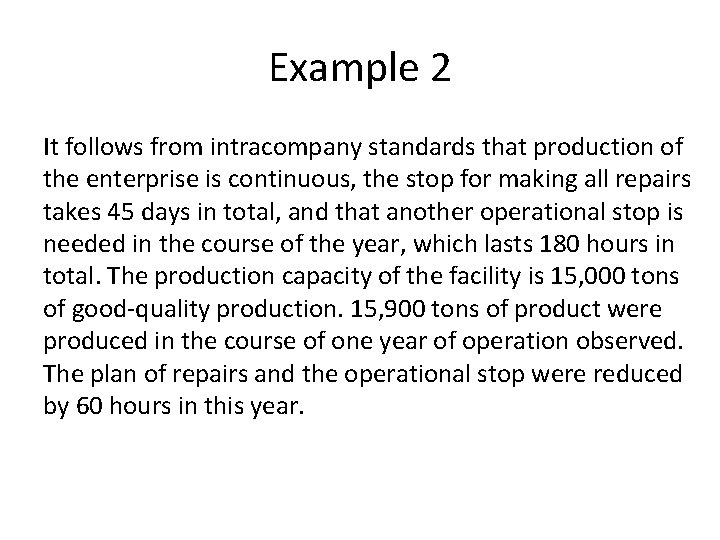
Example 2 It follows from intracompany standards that production of the enterprise is continuous, the stop for making all repairs takes 45 days in total, and that another operational stop is needed in the course of the year, which lasts 180 hours in total. The production capacity of the facility is 15, 000 tons of good-quality production. 15, 900 tons of product were produced in the course of one year of operation observed. The plan of repairs and the operational stop were reduced by 60 hours in this year.
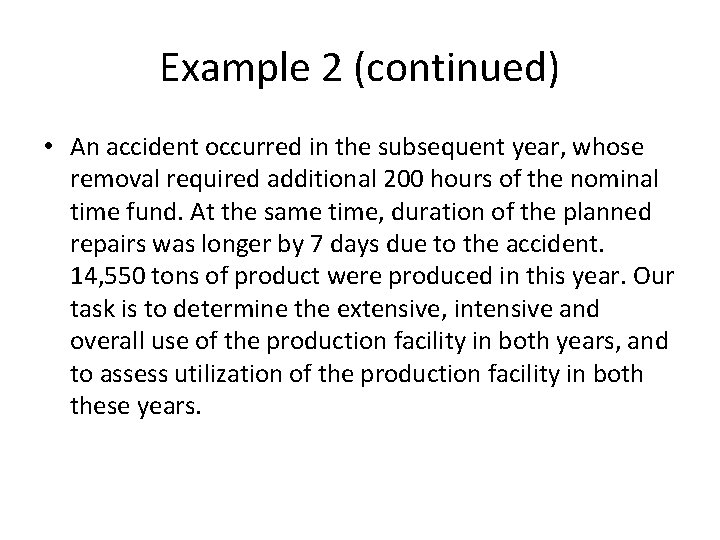
Example 2 (continued) • An accident occurred in the subsequent year, whose removal required additional 200 hours of the nominal time fund. At the same time, duration of the planned repairs was longer by 7 days due to the accident. 14, 550 tons of product were produced in this year. Our task is to determine the extensive, intensive and overall use of the production facility in both years, and to assess utilization of the production facility in both these years.
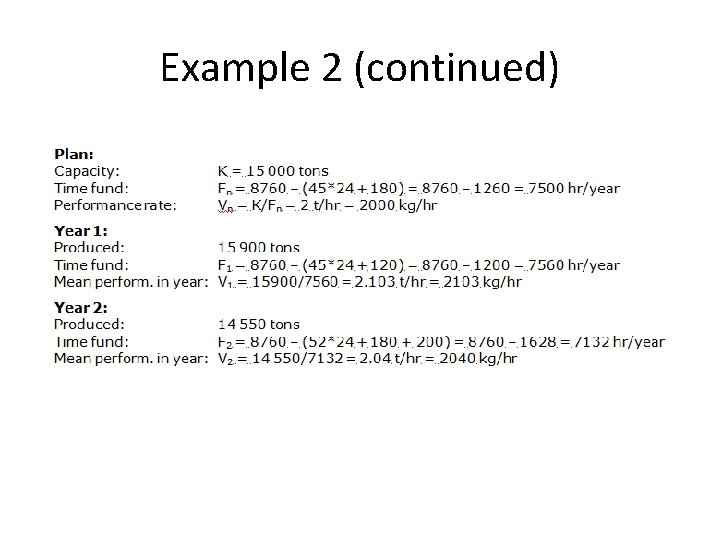
Example 2 (continued)
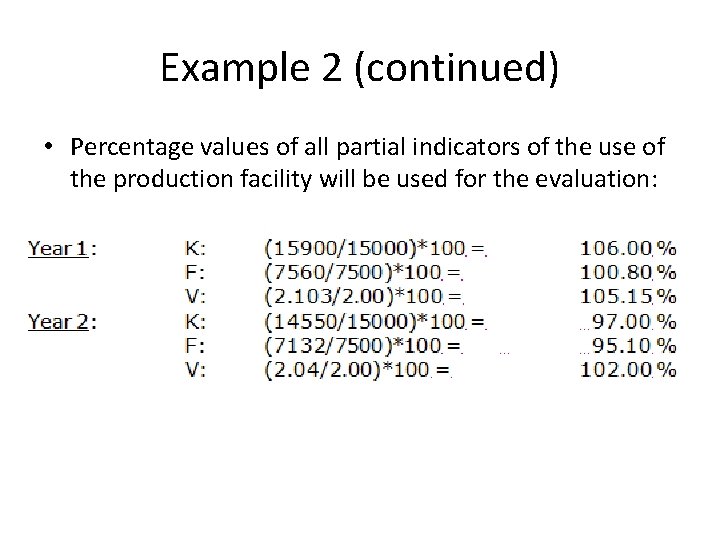
Example 2 (continued) • Percentage values of all partial indicators of the use of the production facility will be used for the evaluation:
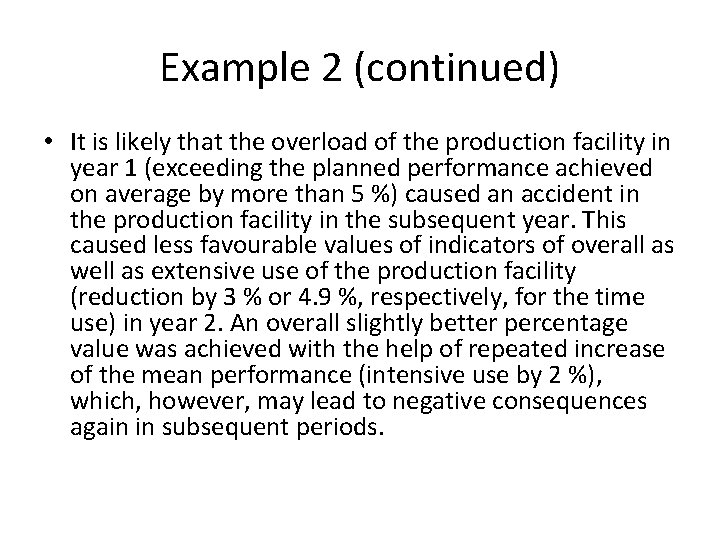
Example 2 (continued) • It is likely that the overload of the production facility in year 1 (exceeding the planned performance achieved on average by more than 5 %) caused an accident in the production facility in the subsequent year. This caused less favourable values of indicators of overall as well as extensive use of the production facility (reduction by 3 % or 4. 9 %, respectively, for the time use) in year 2. An overall slightly better percentage value was achieved with the help of repeated increase of the mean performance (intensive use by 2 %), which, however, may lead to negative consequences again in subsequent periods.
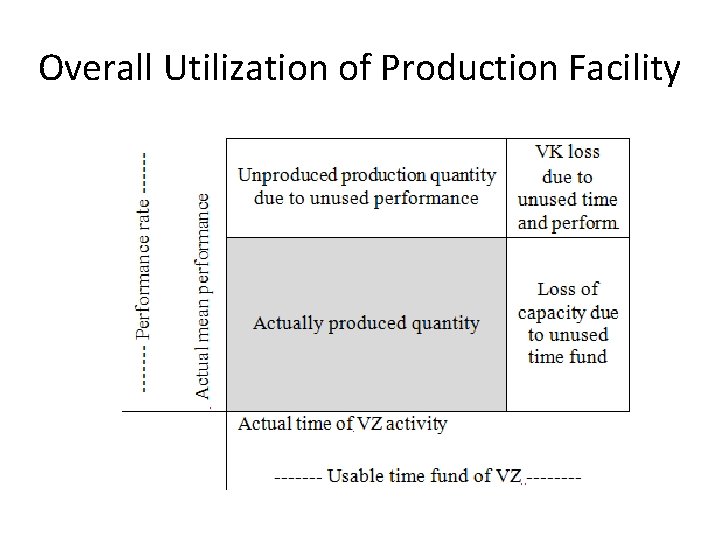
Overall Utilization of Production Facility
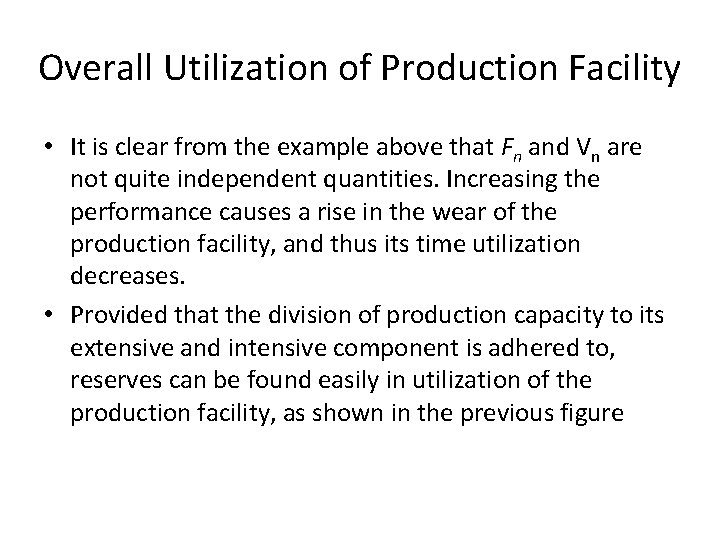
Overall Utilization of Production Facility • It is clear from the example above that Fn and Vn are not quite independent quantities. Increasing the performance causes a rise in the wear of the production facility, and thus its time utilization decreases. • Provided that the division of production capacity to its extensive and intensive component is adhered to, reserves can be found easily in utilization of the production facility, as shown in the previous figure
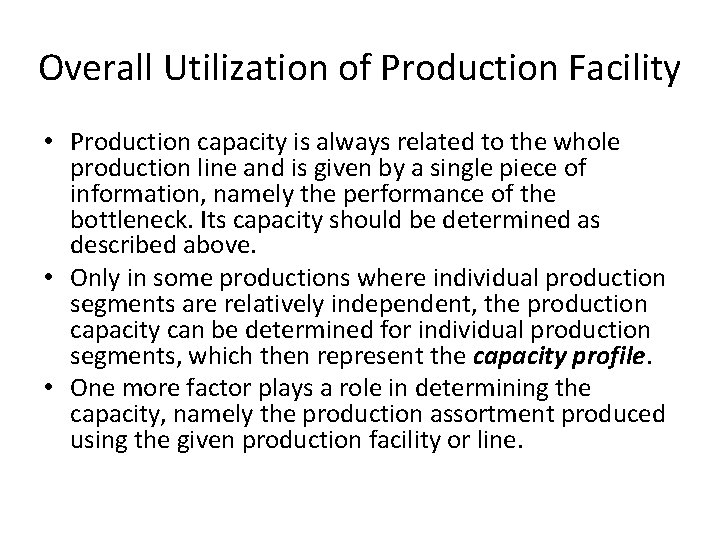
Overall Utilization of Production Facility • Production capacity is always related to the whole production line and is given by a single piece of information, namely the performance of the bottleneck. Its capacity should be determined as described above. • Only in some productions where individual production segments are relatively independent, the production capacity can be determined for individual production segments, which then represent the capacity profile. • One more factor plays a role in determining the capacity, namely the production assortment produced using the given production facility or line.
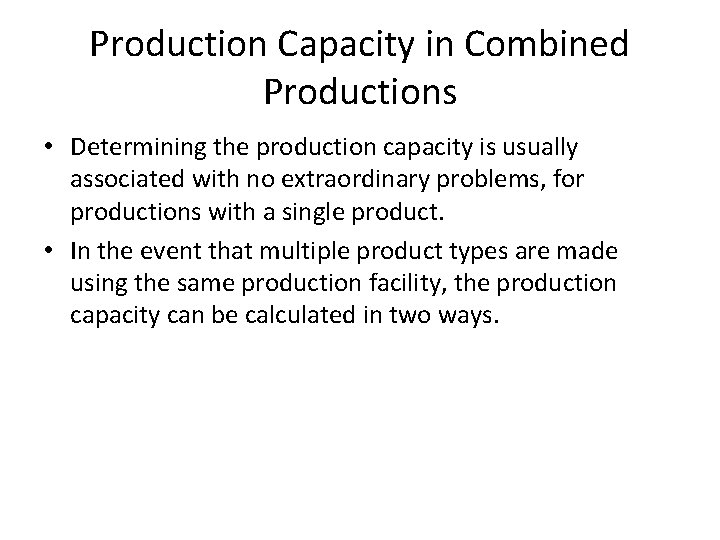
Production Capacity in Combined Productions • Determining the production capacity is usually associated with no extraordinary problems, for productions with a single product. • In the event that multiple product types are made using the same production facility, the production capacity can be calculated in two ways.
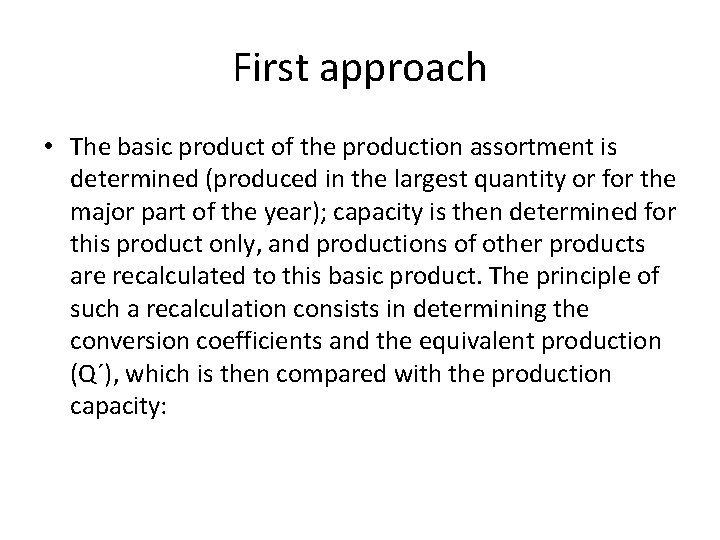
First approach • The basic product of the production assortment is determined (produced in the largest quantity or for the major part of the year); capacity is then determined for this product only, and productions of other products are recalculated to this basic product. The principle of such a recalculation consists in determining the conversion coefficients and the equivalent production (Q´), which is then compared with the production capacity:
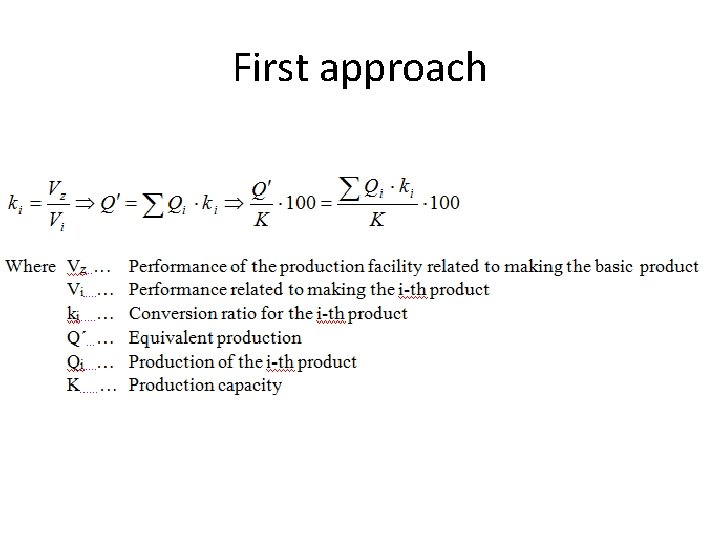
First approach
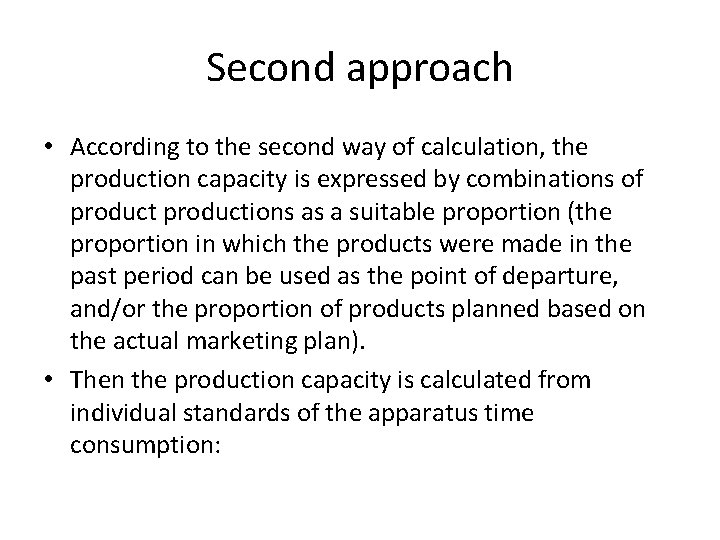
Second approach • According to the second way of calculation, the production capacity is expressed by combinations of productions as a suitable proportion (the proportion in which the products were made in the past period can be used as the point of departure, and/or the proportion of products planned based on the actual marketing plan). • Then the production capacity is calculated from individual standards of the apparatus time consumption:
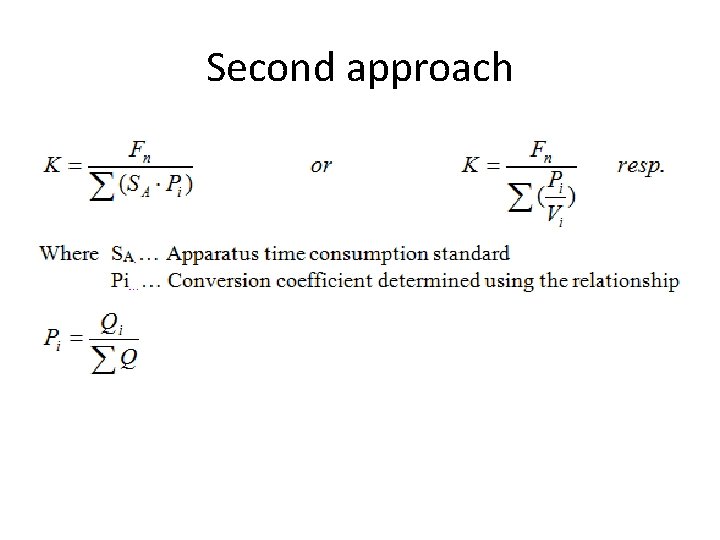
Second approach

Production Capacity in Combined Productions • In the case of assortment production performed using a single production facility, various instruments of operative production management can also be used in respect of the production capacity. • For example, the mathematical algorithm used to determine optimum sizes of deliveries of the common raw material supplies can be applied. • However, in the case of assortment production, it is applied to determining an optimum size of production batches of individual products within the whole assortment range.
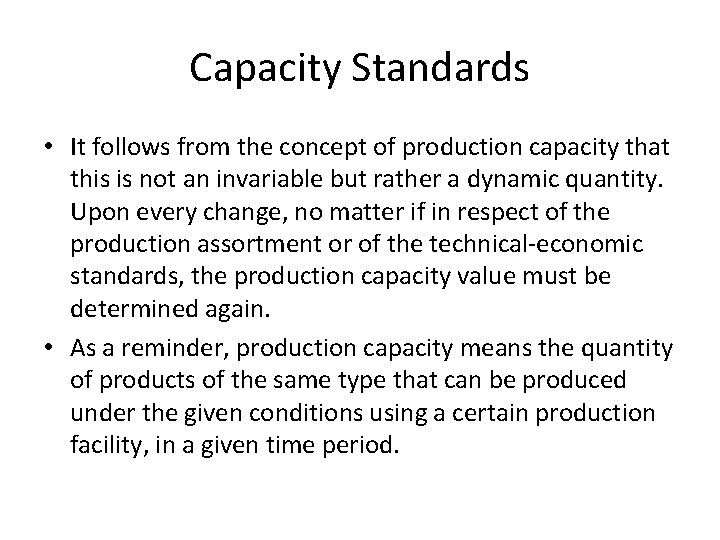
Capacity Standards • It follows from the concept of production capacity that this is not an invariable but rather a dynamic quantity. Upon every change, no matter if in respect of the production assortment or of the technical-economic standards, the production capacity value must be determined again. • As a reminder, production capacity means the quantity of products of the same type that can be produced under the given conditions using a certain production facility, in a given time period.
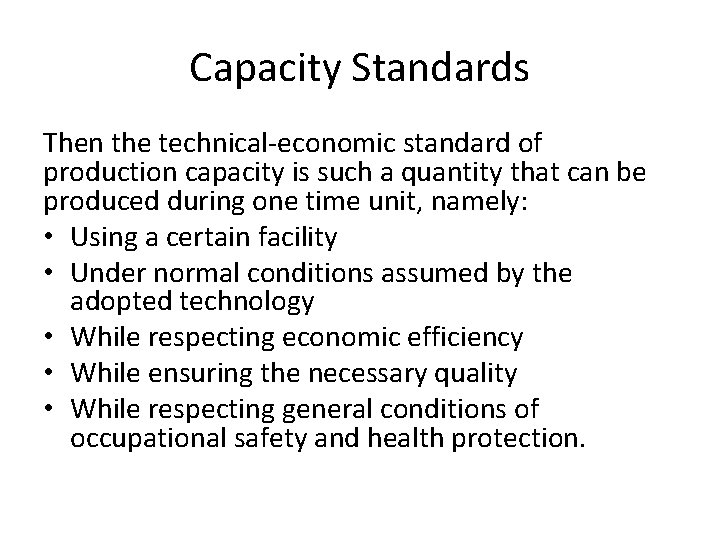
Capacity Standards Then the technical-economic standard of production capacity is such a quantity that can be produced during one time unit, namely: • Using a certain facility • Under normal conditions assumed by the adopted technology • While respecting economic efficiency • While ensuring the necessary quality • While respecting general conditions of occupational safety and health protection.
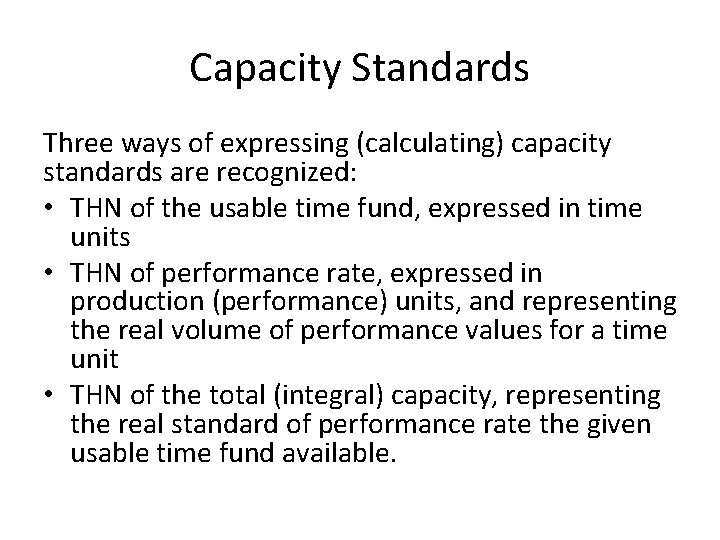
Capacity Standards Three ways of expressing (calculating) capacity standards are recognized: • THN of the usable time fund, expressed in time units • THN of performance rate, expressed in production (performance) units, and representing the real volume of performance values for a time unit • THN of the total (integral) capacity, representing the real standard of performance rate the given usable time fund available.
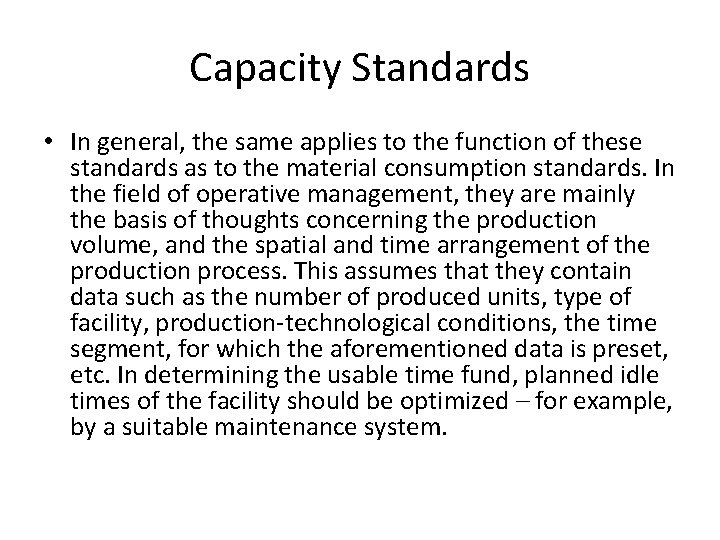
Capacity Standards • In general, the same applies to the function of these standards as to the material consumption standards. In the field of operative management, they are mainly the basis of thoughts concerning the production volume, and the spatial and time arrangement of the production process. This assumes that they contain data such as the number of produced units, type of facility, production-technological conditions, the time segment, for which the aforementioned data is preset, etc. In determining the usable time fund, planned idle times of the facility should be optimized – for example, by a suitable maintenance system.
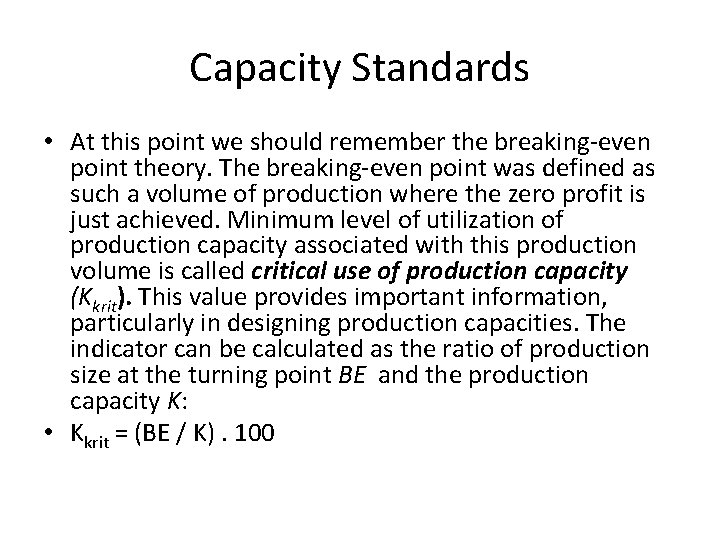
Capacity Standards • At this point we should remember the breaking-even point theory. The breaking-even point was defined as such a volume of production where the zero profit is just achieved. Minimum level of utilization of production capacity associated with this production volume is called critical use of production capacity (Kkrit). This value provides important information, particularly in designing production capacities. The indicator can be calculated as the ratio of production size at the turning point BE and the production capacity K: • Kkrit = (BE / K). 100
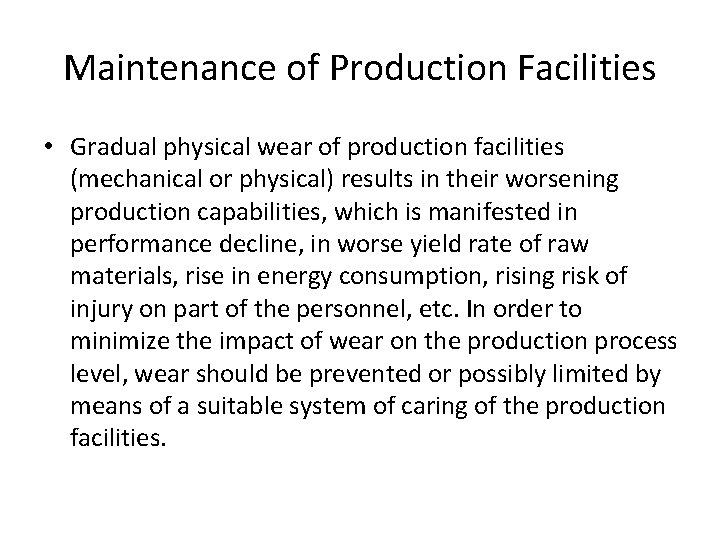
Maintenance of Production Facilities • Gradual physical wear of production facilities (mechanical or physical) results in their worsening production capabilities, which is manifested in performance decline, in worse yield rate of raw materials, rise in energy consumption, rising risk of injury on part of the personnel, etc. In order to minimize the impact of wear on the production process level, wear should be prevented or possibly limited by means of a suitable system of caring of the production facilities.
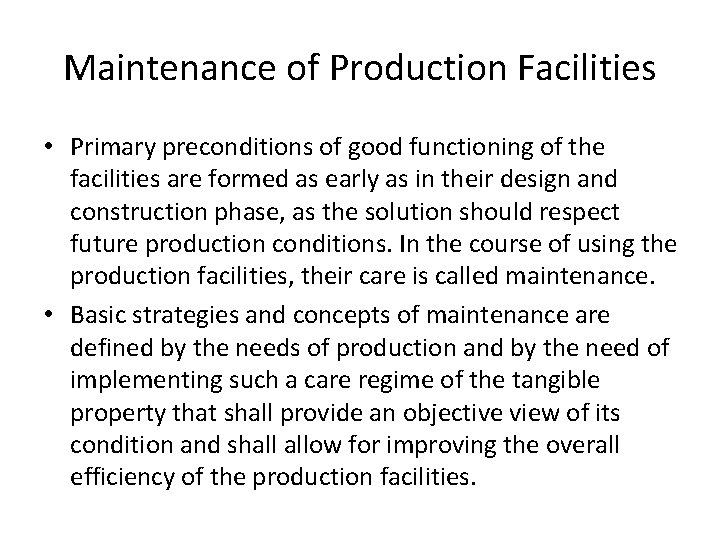
Maintenance of Production Facilities • Primary preconditions of good functioning of the facilities are formed as early as in their design and construction phase, as the solution should respect future production conditions. In the course of using the production facilities, their care is called maintenance. • Basic strategies and concepts of maintenance are defined by the needs of production and by the need of implementing such a care regime of the tangible property that shall provide an objective view of its condition and shall allow for improving the overall efficiency of the production facilities.
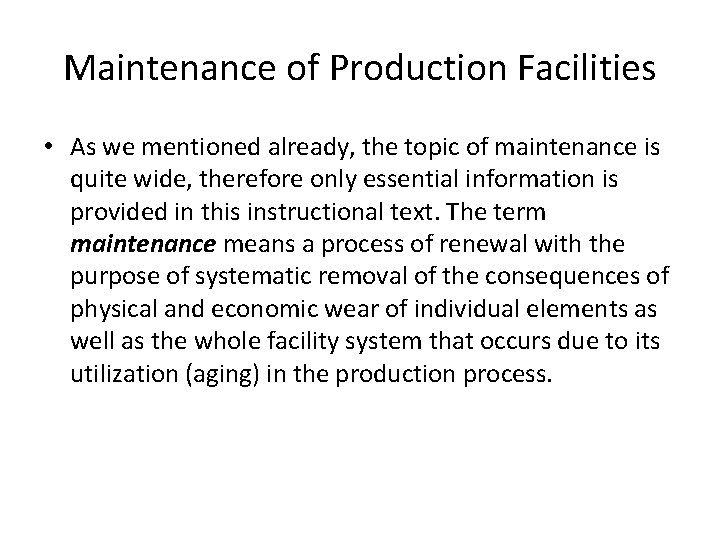
Maintenance of Production Facilities • As we mentioned already, the topic of maintenance is quite wide, therefore only essential information is provided in this instructional text. The term maintenance means a process of renewal with the purpose of systematic removal of the consequences of physical and economic wear of individual elements as well as the whole facility system that occurs due to its utilization (aging) in the production process.

Maintenance of Production Facilities • The aim of maintenance consists in systematic keeping of the production facilities in a good technical, serviceable and reliable condition while expending optimum costs. The maintenance system itself is a set of elements having the nature of organizational, material, financial and other data. This data then makes it possible to perform maintenance in the given conditions to make sure that it is timely, economic and reliable. Upon applying the most basic view, the maintenance system can be classified according to the following perspectives.
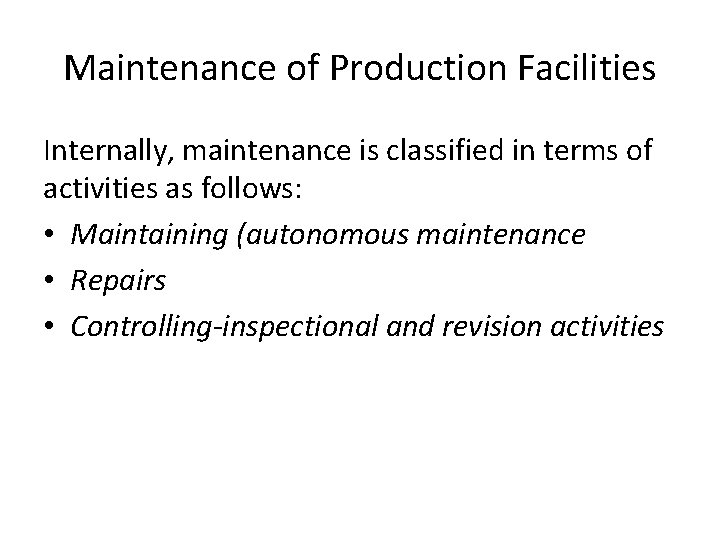
Maintenance of Production Facilities Internally, maintenance is classified in terms of activities as follows: • Maintaining (autonomous maintenance • Repairs • Controlling-inspectional and revision activities
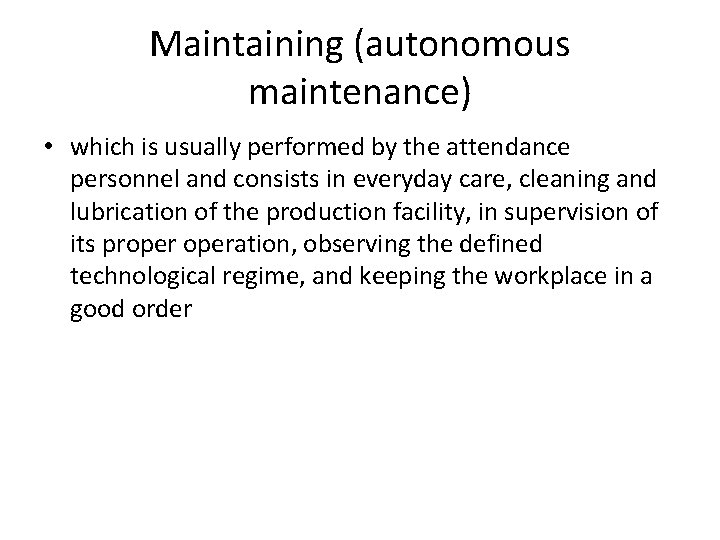
Maintaining (autonomous maintenance) • which is usually performed by the attendance personnel and consists in everyday care, cleaning and lubrication of the production facility, in supervision of its properation, observing the defined technological regime, and keeping the workplace in a good order
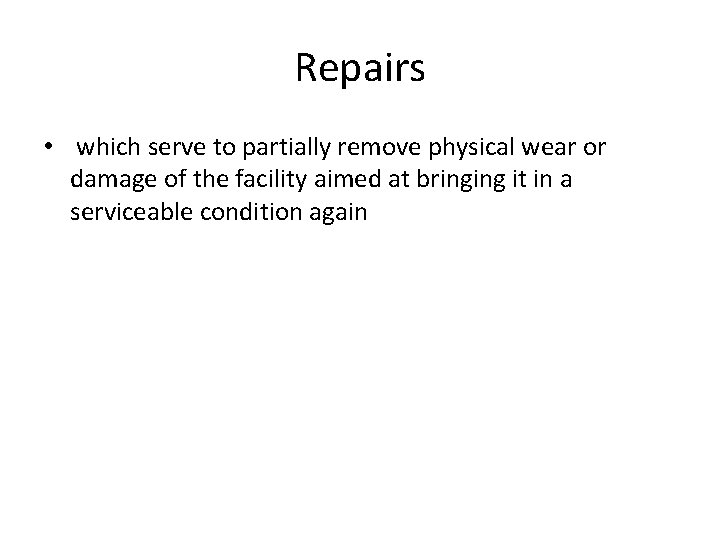
Repairs • which serve to partially remove physical wear or damage of the facility aimed at bringing it in a serviceable condition again
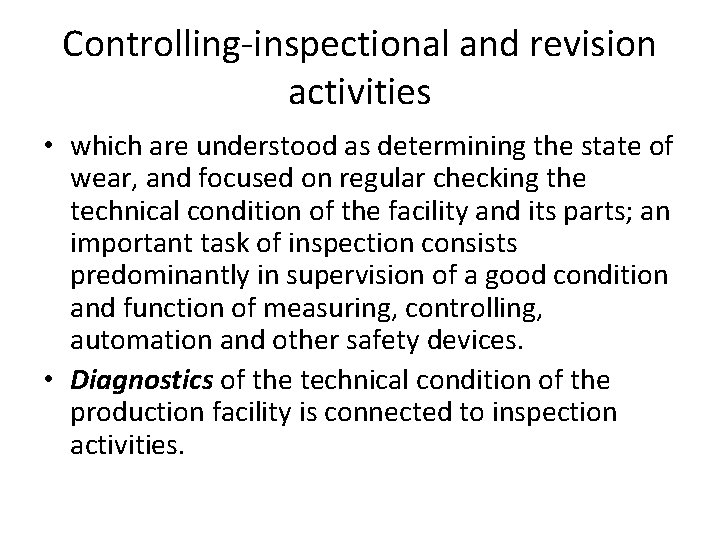
Controlling-inspectional and revision activities • which are understood as determining the state of wear, and focused on regular checking the technical condition of the facility and its parts; an important task of inspection consists predominantly in supervision of a good condition and function of measuring, controlling, automation and other safety devices. • Diagnostics of the technical condition of the production facility is connected to inspection activities.
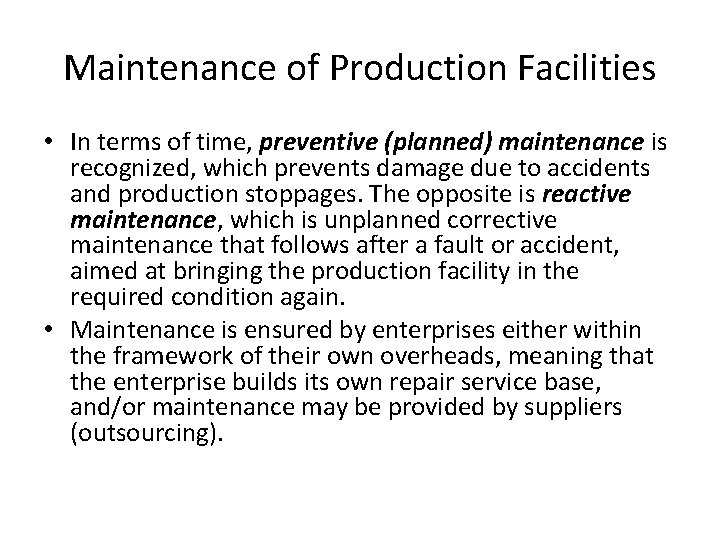
Maintenance of Production Facilities • In terms of time, preventive (planned) maintenance is recognized, which prevents damage due to accidents and production stoppages. The opposite is reactive maintenance, which is unplanned corrective maintenance that follows after a fault or accident, aimed at bringing the production facility in the required condition again. • Maintenance is ensured by enterprises either within the framework of their own overheads, meaning that the enterprise builds its own repair service base, and/or maintenance may be provided by suppliers (outsourcing).
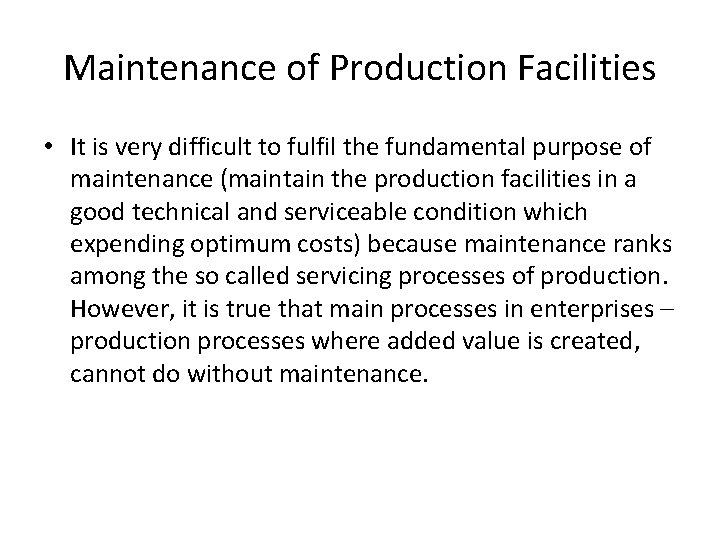
Maintenance of Production Facilities • It is very difficult to fulfil the fundamental purpose of maintenance (maintain the production facilities in a good technical and serviceable condition which expending optimum costs) because maintenance ranks among the so called servicing processes of production. However, it is true that main processes in enterprises – production processes where added value is created, cannot do without maintenance.
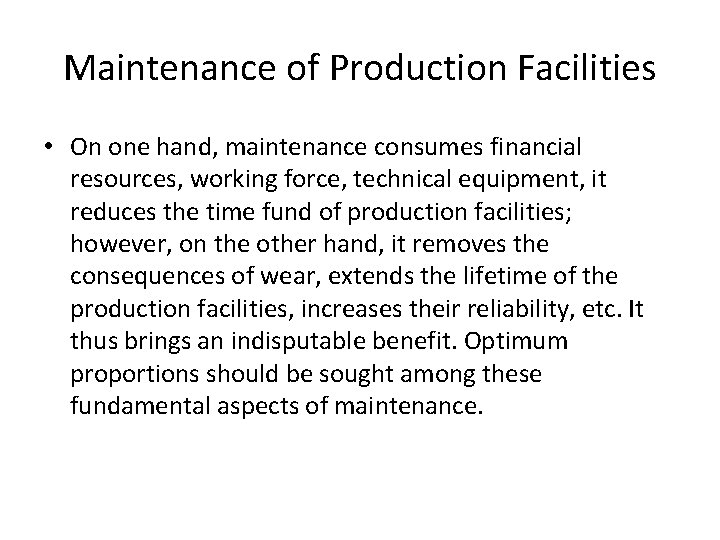
Maintenance of Production Facilities • On one hand, maintenance consumes financial resources, working force, technical equipment, it reduces the time fund of production facilities; however, on the other hand, it removes the consequences of wear, extends the lifetime of the production facilities, increases their reliability, etc. It thus brings an indisputable benefit. Optimum proportions should be sought among these fundamental aspects of maintenance.
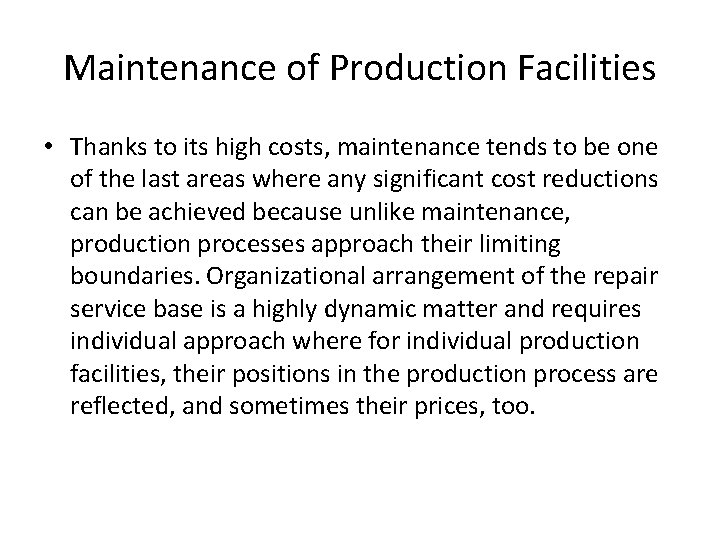
Maintenance of Production Facilities • Thanks to its high costs, maintenance tends to be one of the last areas where any significant cost reductions can be achieved because unlike maintenance, production processes approach their limiting boundaries. Organizational arrangement of the repair service base is a highly dynamic matter and requires individual approach where for individual production facilities, their positions in the production process are reflected, and sometimes their prices, too.
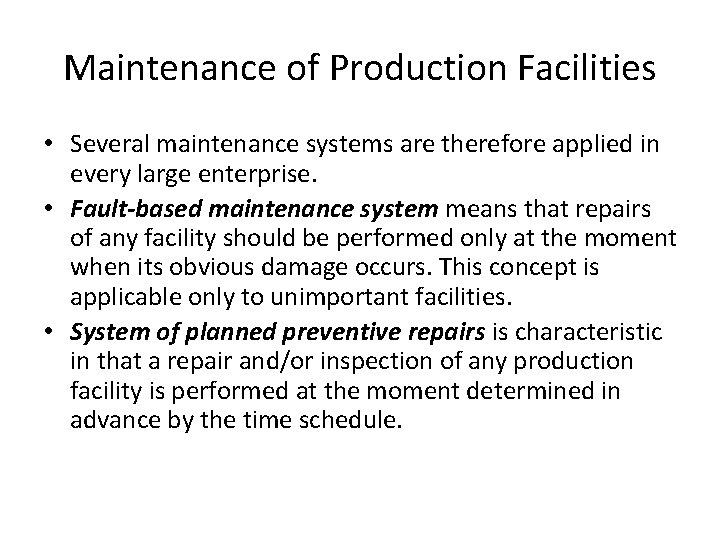
Maintenance of Production Facilities • Several maintenance systems are therefore applied in every large enterprise. • Fault-based maintenance system means that repairs of any facility should be performed only at the moment when its obvious damage occurs. This concept is applicable only to unimportant facilities. • System of planned preventive repairs is characteristic in that a repair and/or inspection of any production facility is performed at the moment determined in advance by the time schedule.
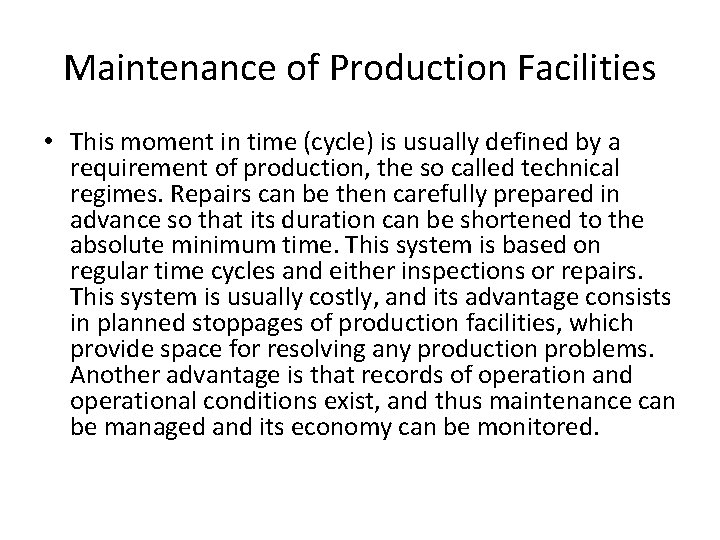
Maintenance of Production Facilities • This moment in time (cycle) is usually defined by a requirement of production, the so called technical regimes. Repairs can be then carefully prepared in advance so that its duration can be shortened to the absolute minimum time. This system is based on regular time cycles and either inspections or repairs. This system is usually costly, and its advantage consists in planned stoppages of production facilities, which provide space for resolving any production problems. Another advantage is that records of operation and operational conditions exist, and thus maintenance can be managed and its economy can be monitored.
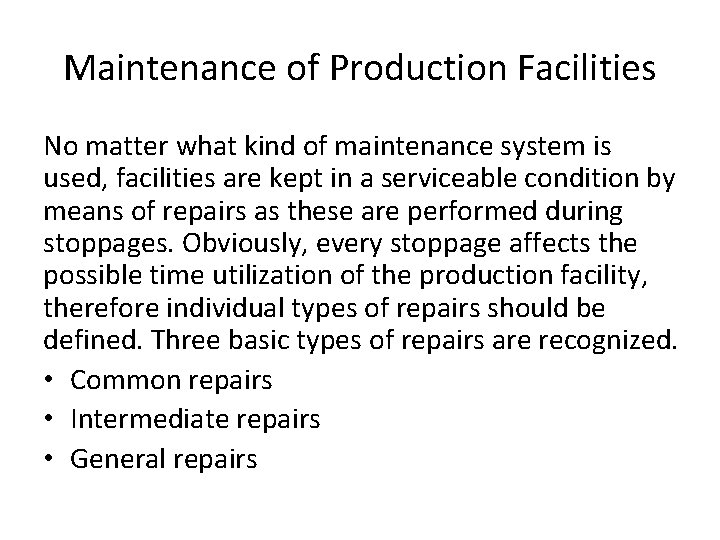
Maintenance of Production Facilities No matter what kind of maintenance system is used, facilities are kept in a serviceable condition by means of repairs as these are performed during stoppages. Obviously, every stoppage affects the possible time utilization of the production facility, therefore individual types of repairs should be defined. Three basic types of repairs are recognized. • Common repairs • Intermediate repairs • General repairs
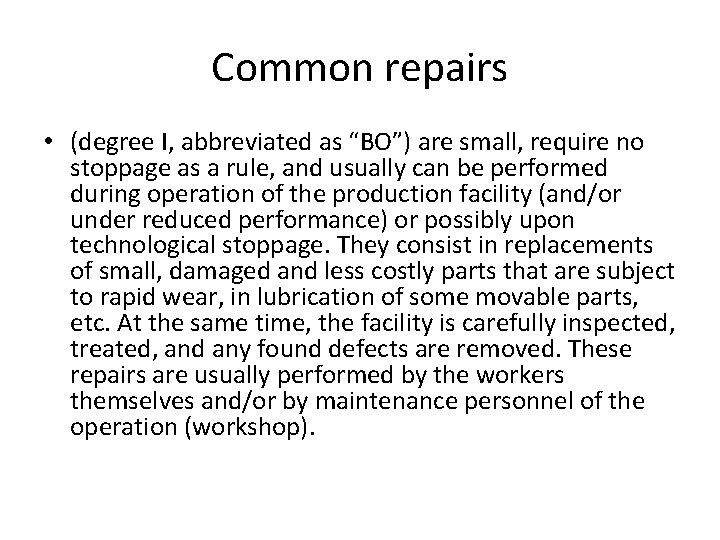
Common repairs • (degree I, abbreviated as “BO”) are small, require no stoppage as a rule, and usually can be performed during operation of the production facility (and/or under reduced performance) or possibly upon technological stoppage. They consist in replacements of small, damaged and less costly parts that are subject to rapid wear, in lubrication of some movable parts, etc. At the same time, the facility is carefully inspected, treated, and any found defects are removed. These repairs are usually performed by the workers themselves and/or by maintenance personnel of the operation (workshop).
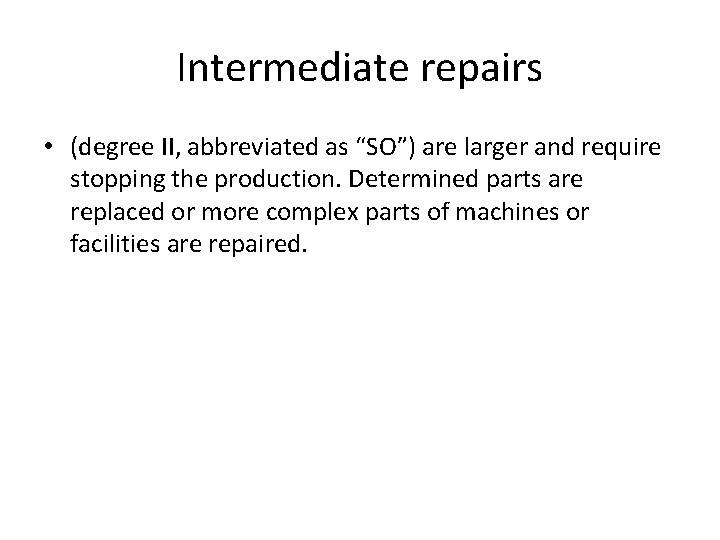
Intermediate repairs • (degree II, abbreviated as “SO”) are larger and require stopping the production. Determined parts are replaced or more complex parts of machines or facilities are repaired.
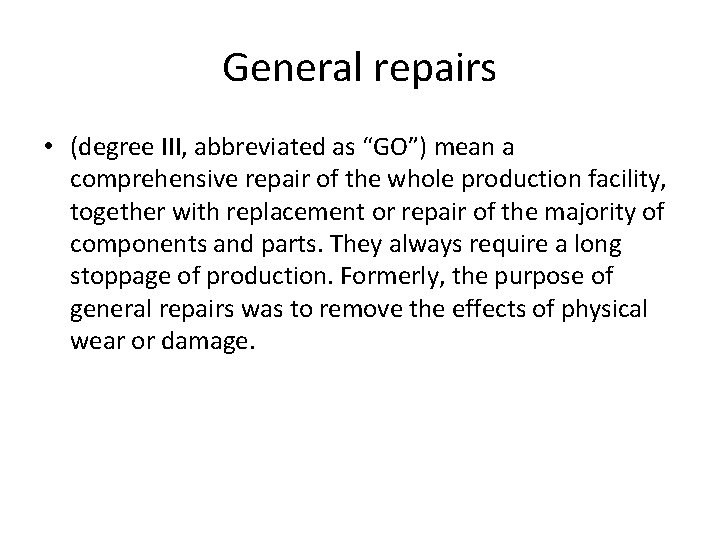
General repairs • (degree III, abbreviated as “GO”) mean a comprehensive repair of the whole production facility, together with replacement or repair of the majority of components and parts. They always require a long stoppage of production. Formerly, the purpose of general repairs was to remove the effects of physical wear or damage.
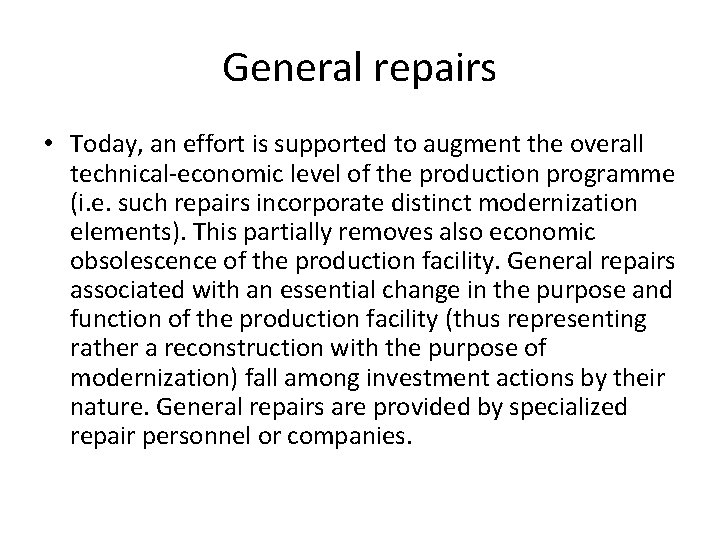
General repairs • Today, an effort is supported to augment the overall technical-economic level of the production programme (i. e. such repairs incorporate distinct modernization elements). This partially removes also economic obsolescence of the production facility. General repairs associated with an essential change in the purpose and function of the production facility (thus representing rather a reconstruction with the purpose of modernization) fall among investment actions by their nature. General repairs are provided by specialized repair personnel or companies.
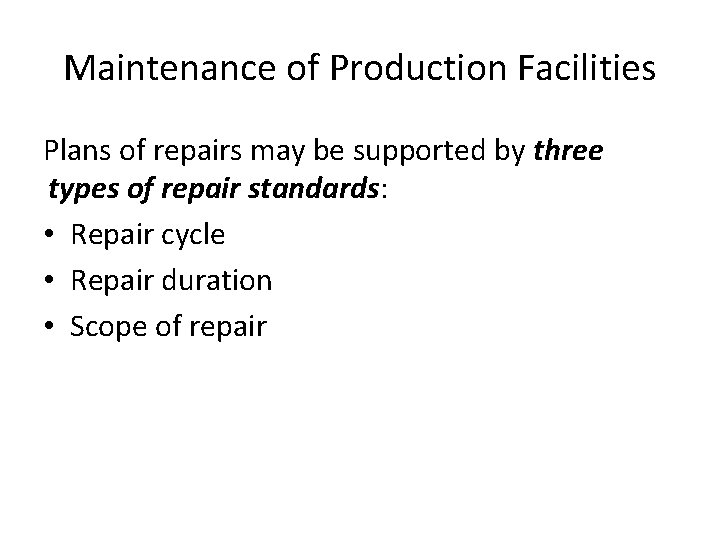
Maintenance of Production Facilities Plans of repairs may be supported by three types of repair standards: • Repair cycle • Repair duration • Scope of repair
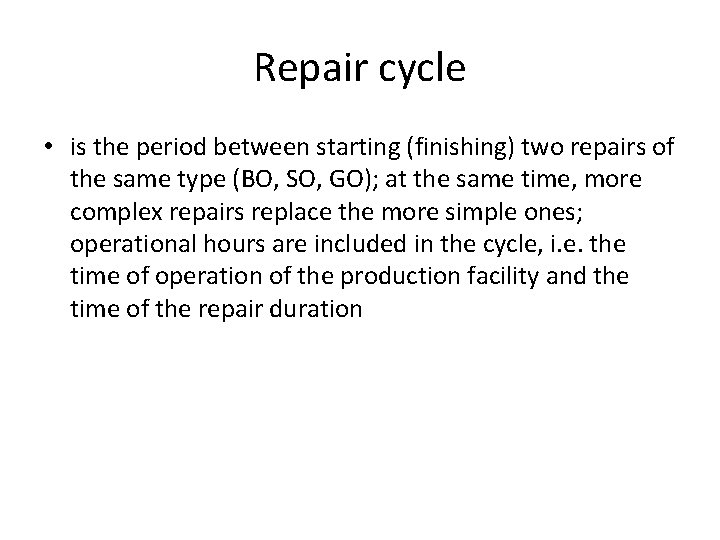
Repair cycle • is the period between starting (finishing) two repairs of the same type (BO, SO, GO); at the same time, more complex repairs replace the more simple ones; operational hours are included in the cycle, i. e. the time of operation of the production facility and the time of the repair duration
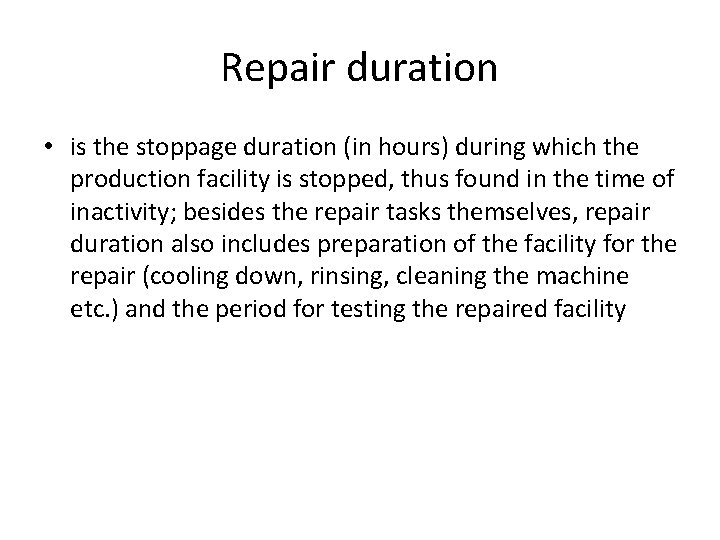
Repair duration • is the stoppage duration (in hours) during which the production facility is stopped, thus found in the time of inactivity; besides the repair tasks themselves, repair duration also includes preparation of the facility for the repair (cooling down, rinsing, cleaning the machine etc. ) and the period for testing the repaired facility
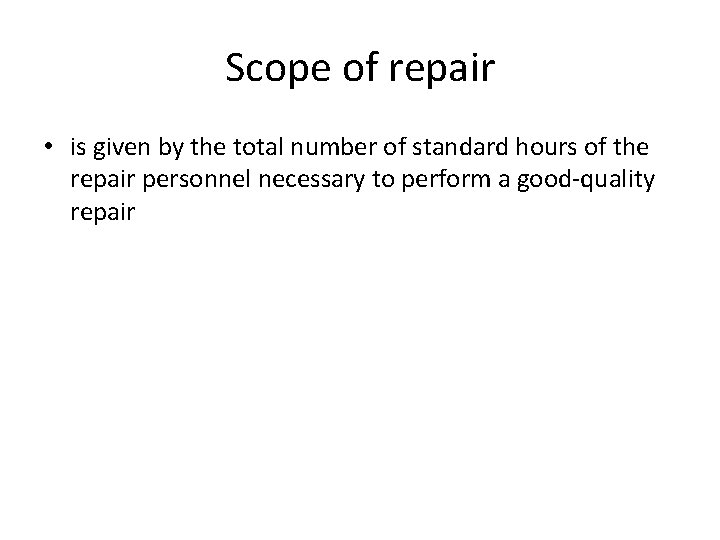
Scope of repair • is given by the total number of standard hours of the repair personnel necessary to perform a good-quality repair
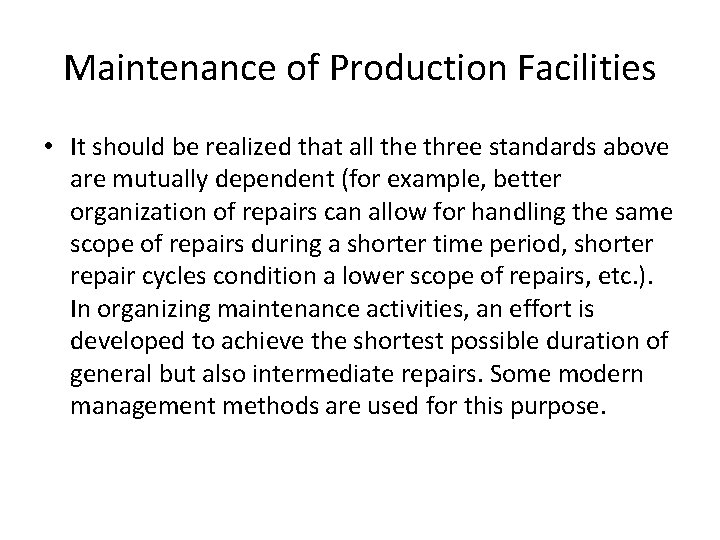
Maintenance of Production Facilities • It should be realized that all the three standards above are mutually dependent (for example, better organization of repairs can allow for handling the same scope of repairs during a shorter time period, shorter repair cycles condition a lower scope of repairs, etc. ). In organizing maintenance activities, an effort is developed to achieve the shortest possible duration of general but also intermediate repairs. Some modern management methods are used for this purpose.
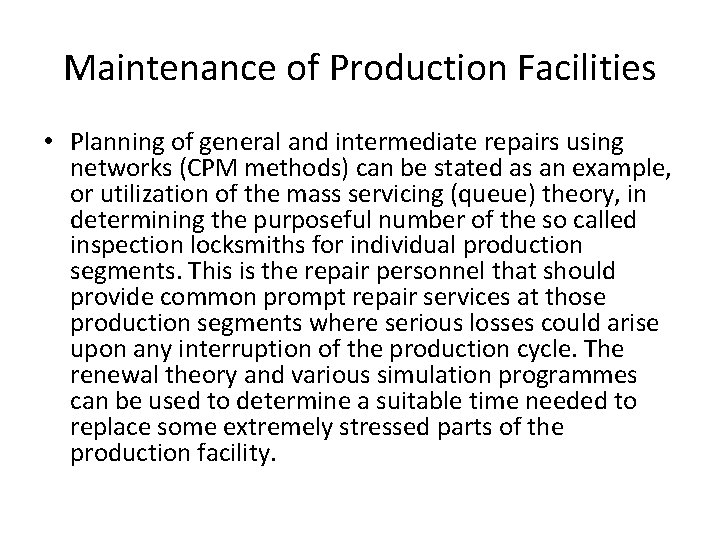
Maintenance of Production Facilities • Planning of general and intermediate repairs using networks (CPM methods) can be stated as an example, or utilization of the mass servicing (queue) theory, in determining the purposeful number of the so called inspection locksmiths for individual production segments. This is the repair personnel that should provide common prompt repair services at those production segments where serious losses could arise upon any interruption of the production cycle. The renewal theory and various simulation programmes can be used to determine a suitable time needed to replace some extremely stressed parts of the production facility.
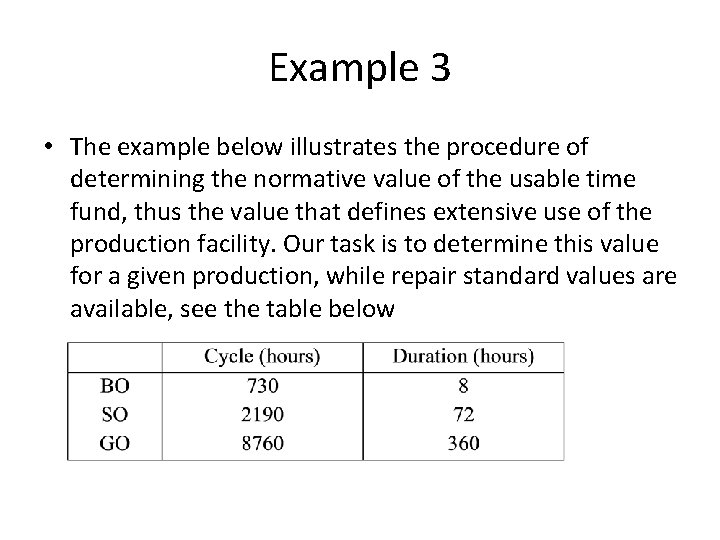
Example 3 • The example below illustrates the procedure of determining the normative value of the usable time fund, thus the value that defines extensive use of the production facility. Our task is to determine this value for a given production, while repair standard values are available, see the table below
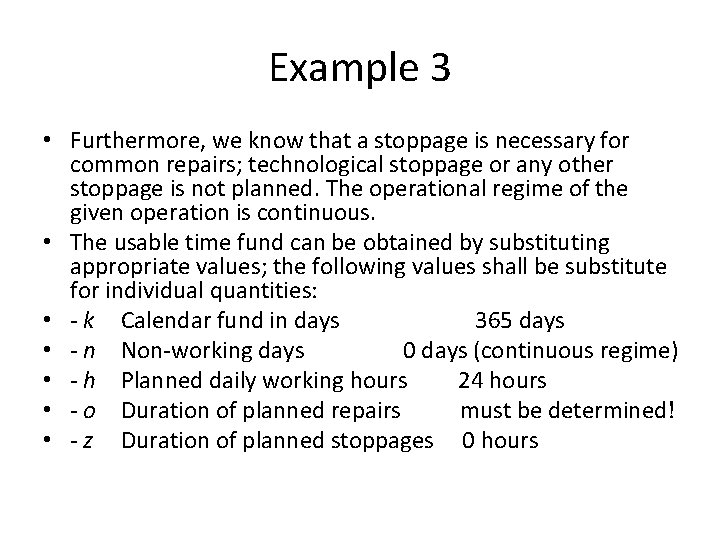
Example 3 • Furthermore, we know that a stoppage is necessary for common repairs; technological stoppage or any other stoppage is not planned. The operational regime of the given operation is continuous. • The usable time fund can be obtained by substituting appropriate values; the following values shall be substitute for individual quantities: • - k Calendar fund in days 365 days • - n Non-working days 0 days (continuous regime) • - h Planned daily working hours 24 hours • - o Duration of planned repairs must be determined! • - z Duration of planned stoppages 0 hours
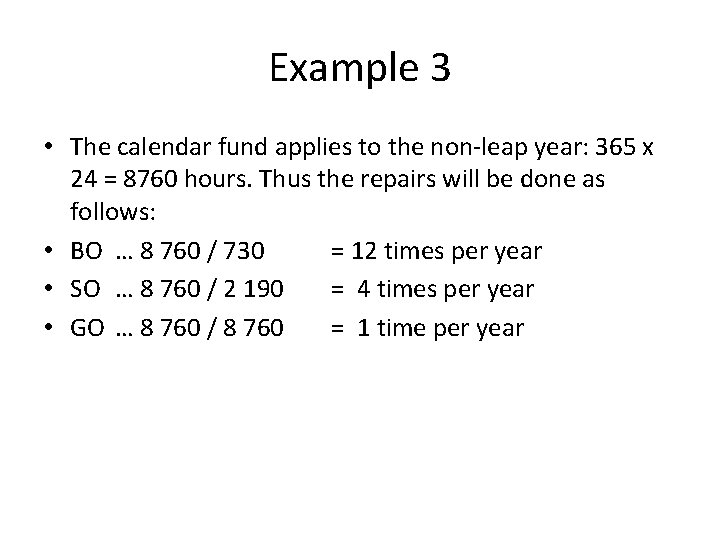
Example 3 • The calendar fund applies to the non-leap year: 365 x 24 = 8760 hours. Thus the repairs will be done as follows: • BO … 8 760 / 730 = 12 times per year • SO … 8 760 / 2 190 = 4 times per year • GO … 8 760 / 8 760 = 1 time per year
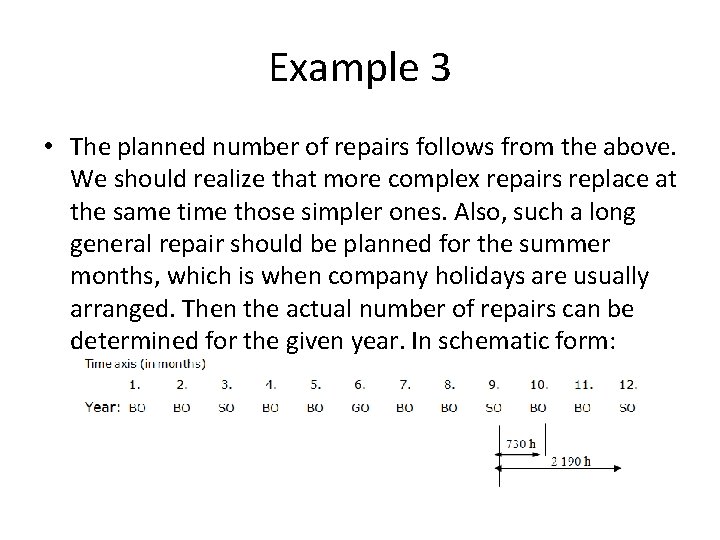
Example 3 • The planned number of repairs follows from the above. We should realize that more complex repairs replace at the same time those simpler ones. Also, such a long general repair should be planned for the summer months, which is when company holidays are usually arranged. Then the actual number of repairs can be determined for the given year. In schematic form:
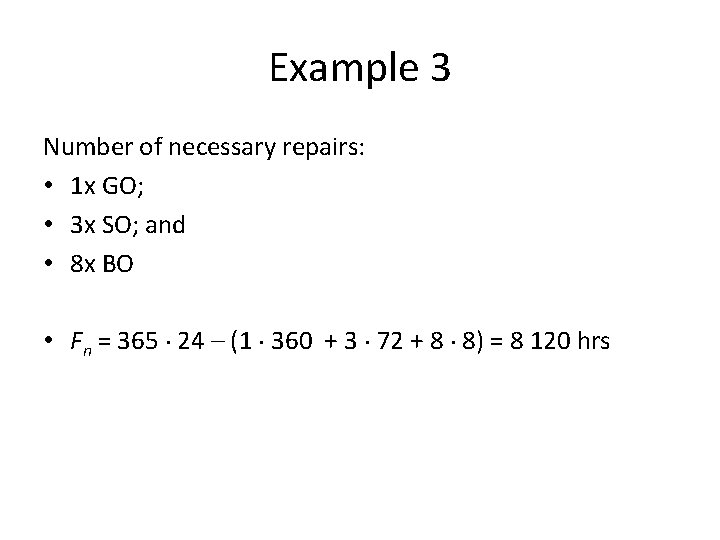
Example 3 Number of necessary repairs: • 1 x GO; • 3 x SO; and • 8 x BO • Fn = 365 24 – (1 360 + 3 72 + 8 8) = 8 120 hrs
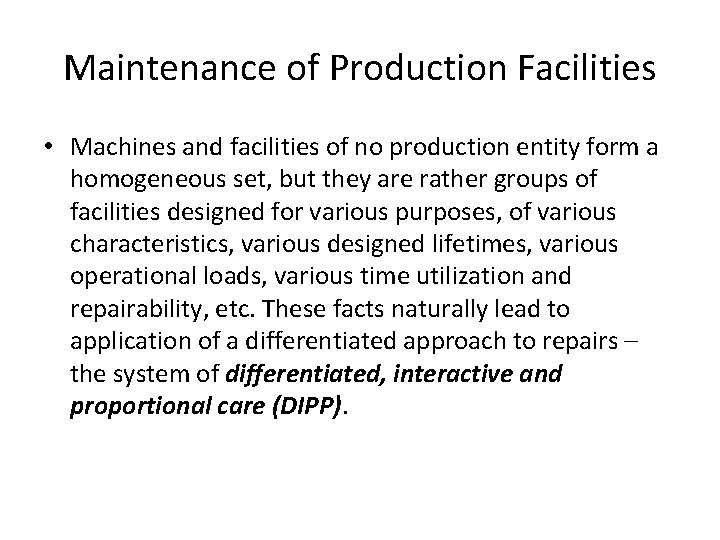
Maintenance of Production Facilities • Machines and facilities of no production entity form a homogeneous set, but they are rather groups of facilities designed for various purposes, of various characteristics, various designed lifetimes, various operational loads, various time utilization and repairability, etc. These facts naturally lead to application of a differentiated approach to repairs – the system of differentiated, interactive and proportional care (DIPP).
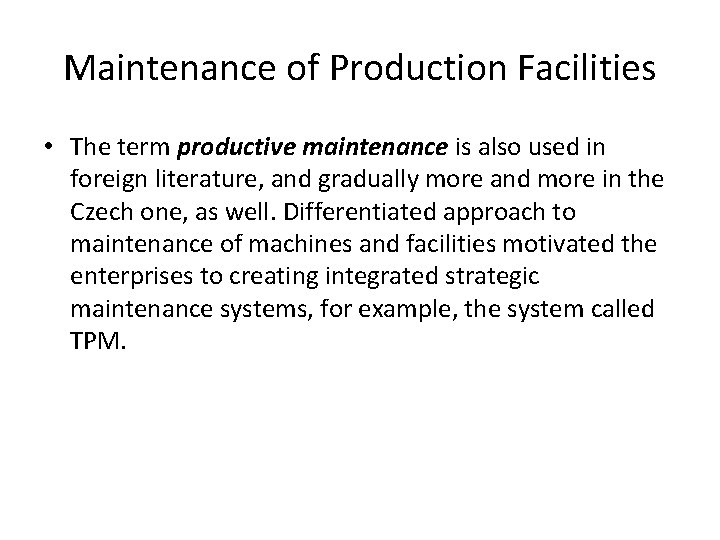
Maintenance of Production Facilities • The term productive maintenance is also used in foreign literature, and gradually more and more in the Czech one, as well. Differentiated approach to maintenance of machines and facilities motivated the enterprises to creating integrated strategic maintenance systems, for example, the system called TPM.
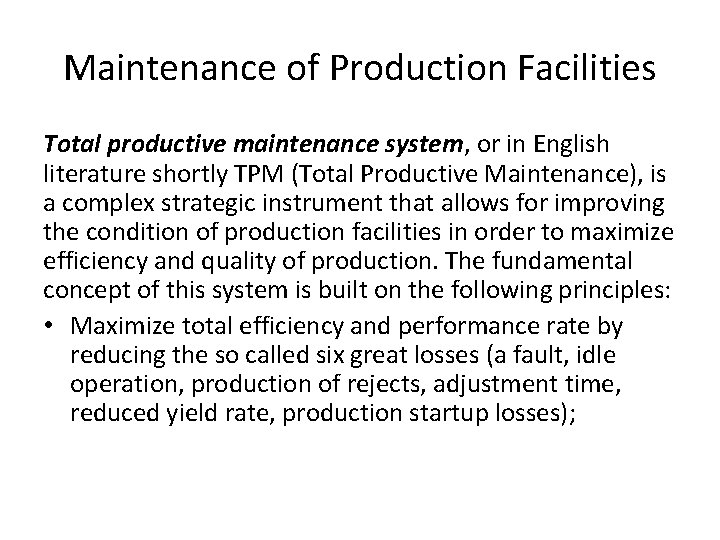
Maintenance of Production Facilities Total productive maintenance system, or in English literature shortly TPM (Total Productive Maintenance), is a complex strategic instrument that allows for improving the condition of production facilities in order to maximize efficiency and quality of production. The fundamental concept of this system is built on the following principles: • Maximize total efficiency and performance rate by reducing the so called six great losses (a fault, idle operation, production of rejects, adjustment time, reduced yield rate, production startup losses);
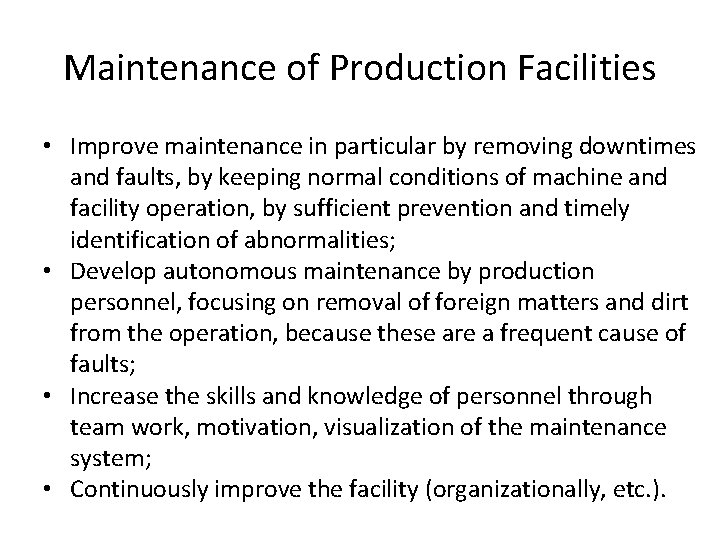
Maintenance of Production Facilities • Improve maintenance in particular by removing downtimes and faults, by keeping normal conditions of machine and facility operation, by sufficient prevention and timely identification of abnormalities; • Develop autonomous maintenance by production personnel, focusing on removal of foreign matters and dirt from the operation, because these are a frequent cause of faults; • Increase the skills and knowledge of personnel through team work, motivation, visualization of the maintenance system; • Continuously improve the facility (organizationally, etc. ).
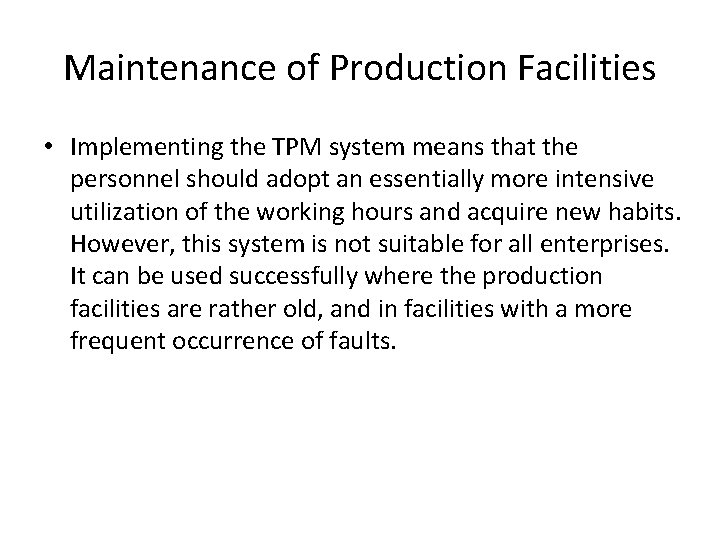
Maintenance of Production Facilities • Implementing the TPM system means that the personnel should adopt an essentially more intensive utilization of the working hours and acquire new habits. However, this system is not suitable for all enterprises. It can be used successfully where the production facilities are rather old, and in facilities with a more frequent occurrence of faults.
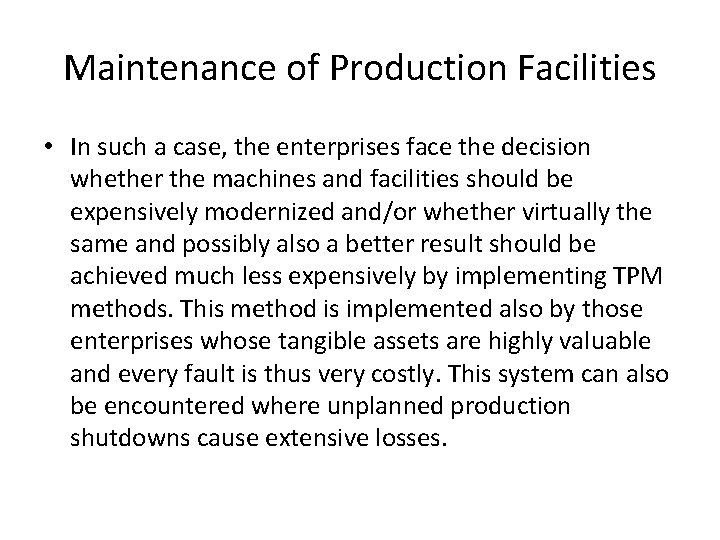
Maintenance of Production Facilities • In such a case, the enterprises face the decision whether the machines and facilities should be expensively modernized and/or whether virtually the same and possibly also a better result should be achieved much less expensively by implementing TPM methods. This method is implemented also by those enterprises whose tangible assets are highly valuable and every fault is thus very costly. This system can also be encountered where unplanned production shutdowns cause extensive losses.
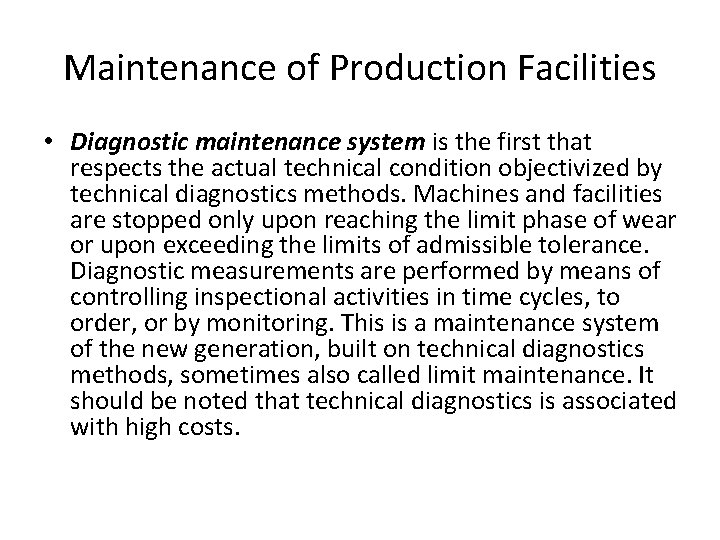
Maintenance of Production Facilities • Diagnostic maintenance system is the first that respects the actual technical condition objectivized by technical diagnostics methods. Machines and facilities are stopped only upon reaching the limit phase of wear or upon exceeding the limits of admissible tolerance. Diagnostic measurements are performed by means of controlling inspectional activities in time cycles, to order, or by monitoring. This is a maintenance system of the new generation, built on technical diagnostics methods, sometimes also called limit maintenance. It should be noted that technical diagnostics is associated with high costs.
Alir produksi multimedia
Present continuous negative and interrogative
Sss facility management services
Dansk facilities management netværk
Student facility management
Facilities business continuity plan
Safe facilities and pest management
Duke facilities management
Top management middle management first line management
Top management middle management first line management
Middle level management
The most common form of production deviance is
Lean production and quality management
Production planning inventory control
Facility layout types
Demand forecasting in operations management
Production management deals with decision making also
Apics certification meaning
Toyota production system operations management
Operations management functions
Production operations definition
Game production and management
Operations management product design
Elements of production management
Introduction to production management
Elements of production management
Historical development of operations management
What is forecasting in operations management
Smart welding manager
Historical evolution of operations management
Nature of production management
Cdm welfare facilities
Seperation
Methods of shopping
In keeping equipment and facilities safe and sanitary
Aif ago and anop
Lockheed martin georgia
Article 7 behavioral health residential facilities
Disqualification of testing facility
Mdoc satellite facilities
Fairfax county pfm
Facility planning definition
Examples of facilities
Conversation in hotel reservation
Cleaning public areas facilities and equipment
Receiving and storing
Hotel classifications
Iso 17025 environmental conditions
Nys environmental facilities corporation
Supporting facilities example
Framework for structuring drivers
Short-term scheduling in operations management
Vinci facilities maximo
Facilities planning hierarchy
Esi hospital chennai kk nagar
Supporting facilities
Ada fitness center
Lesson 2 healthcare facilities
Yakin aja
Iuss health facility guidelines
Reject allowance problem facilities planning
Conventional facilities
Desired response time and number of facilities
Sanitary facilities and equipment
Facilities on the titanic
Spokane public facilities district
33cfr105
Facilities vocabulary
Facility layout
Fixed facilities in transportation
Adjectives for facilities
Facility planning
Factors influencing network design decision
Facilities shipping agency
Ancillary facilities construction
Ucsf facilities services
Instructional facilities
Providing support services facilities and other amenities
Public facilities relate to people's
Aaf audit automation facilities
Work breakdown structure for planning a trip
Caucalor
Physical layout of nursing unit
Hannah hall oakland university
Advantages of broadcast advertising
Facilities planning
Healthcare facilities accreditation program
Facilities planning definition
Craft layout example
Translators and facilities of languages
Titanic facilities
"facilities survey inc." cms or cmms
Facilities exchange
Marine facilities planning
Fairfax county public facilities manual
Leadership styles in correctional facilities
What's vertex form
How to convert polar form to rectangular form
Transformation of exponential functions
Multiplying complex numbers in trig form
Circle standard form
General to standard form
Rectangular form complex numbers
How to find certex