Aluminium Alloys 1302 774 Special topics in Material
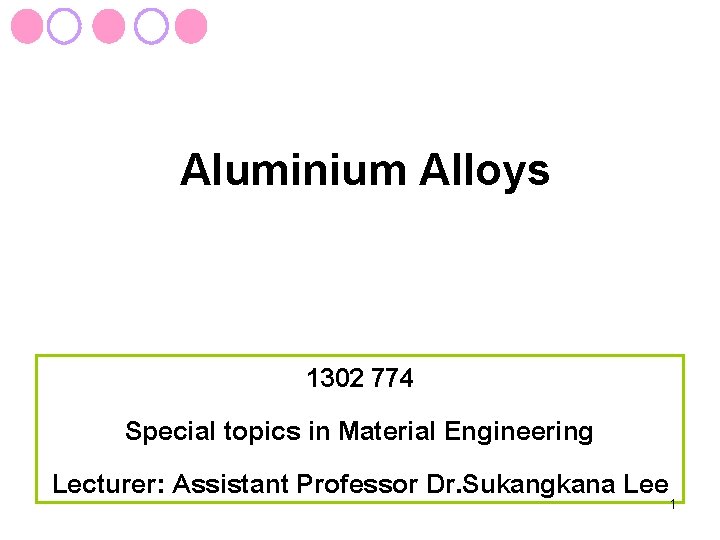
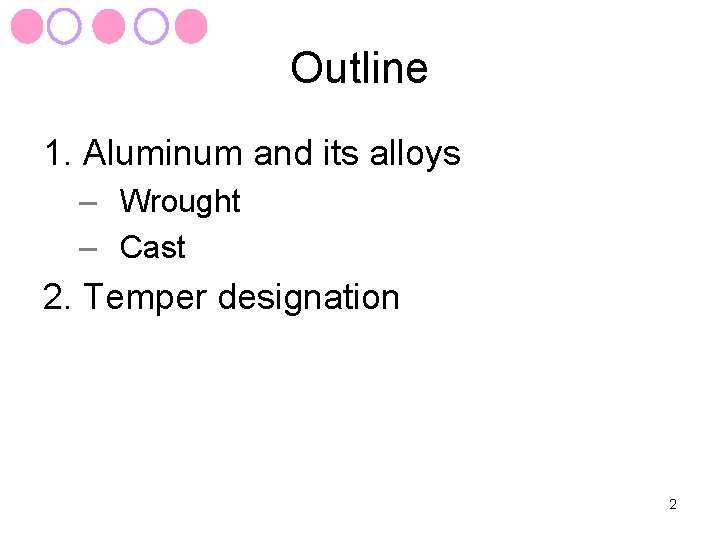
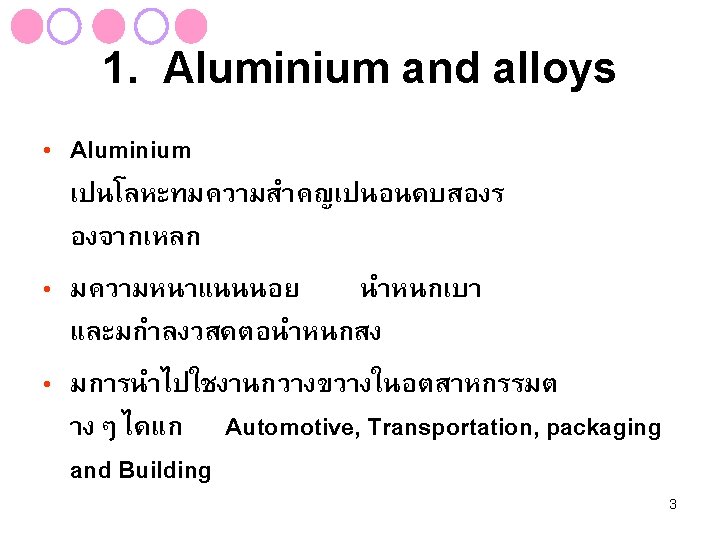
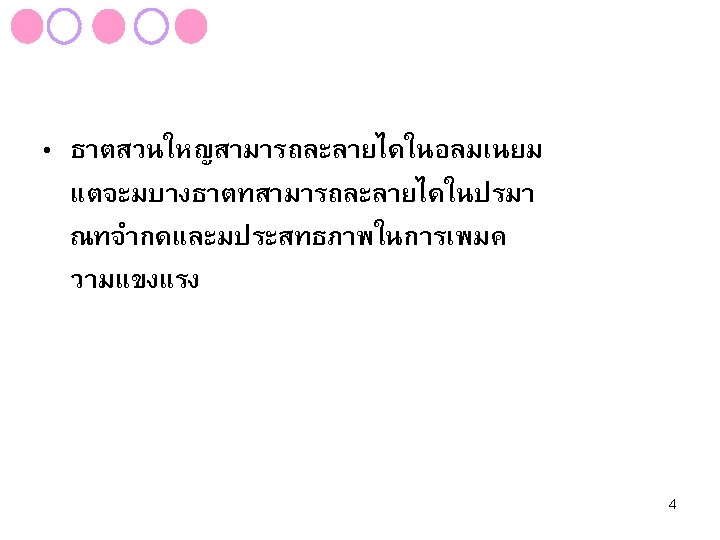
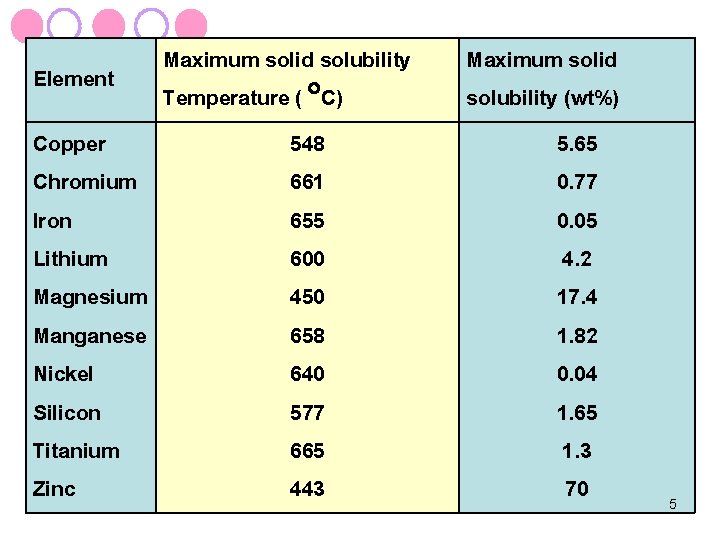
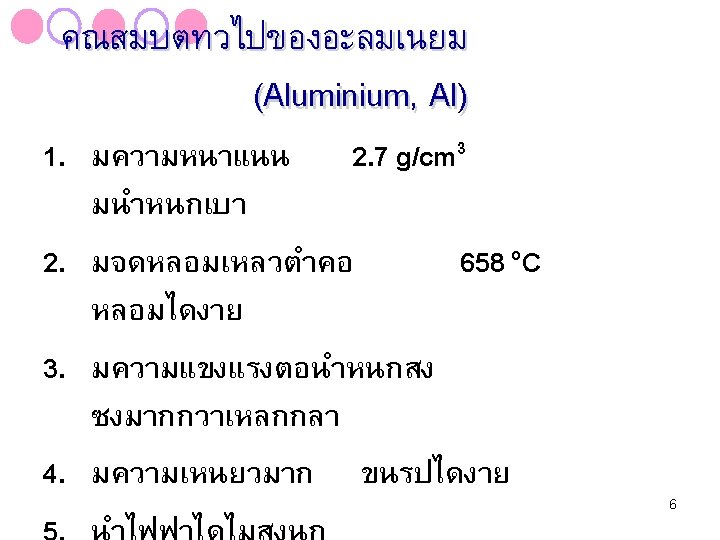
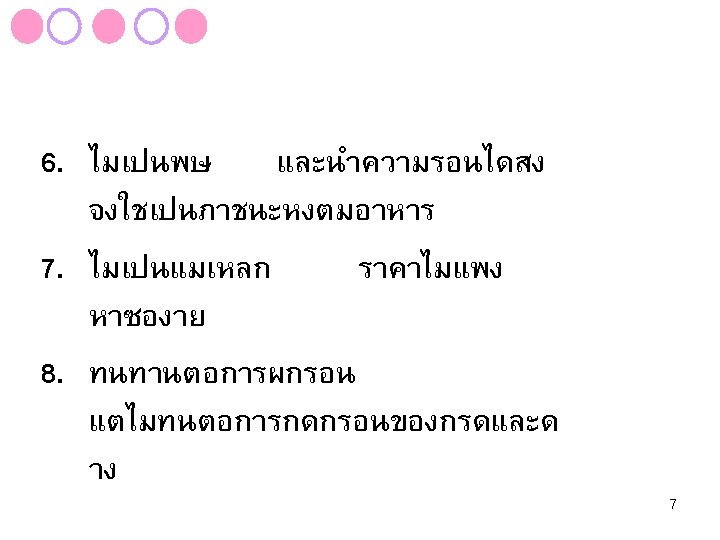
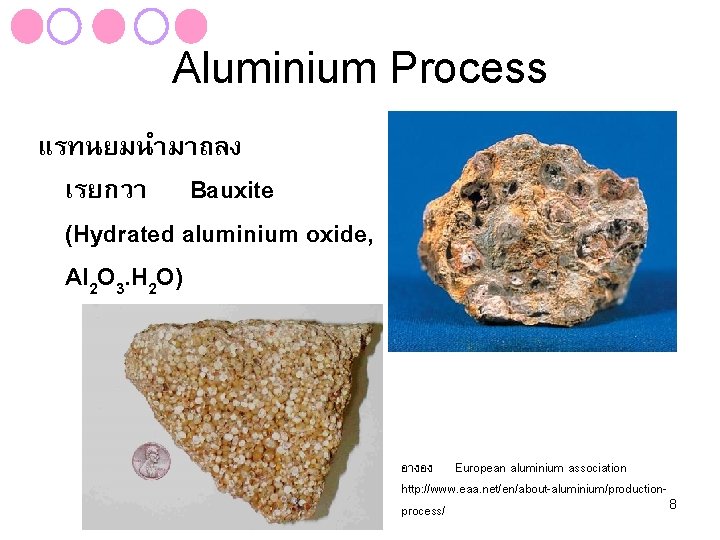
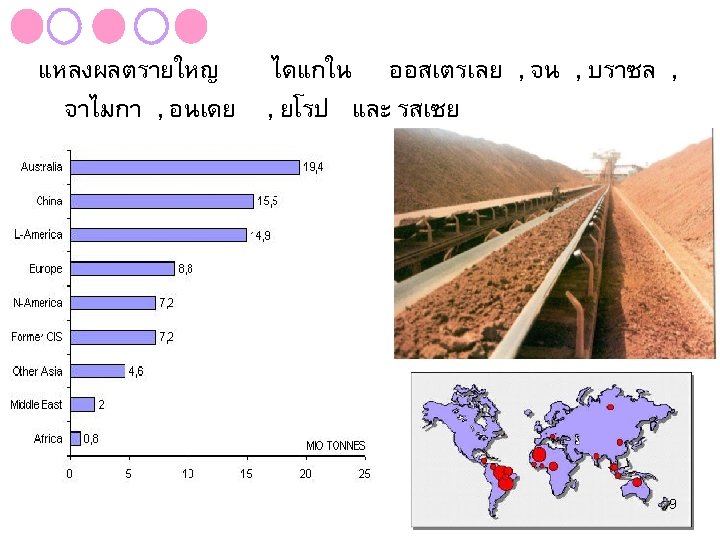
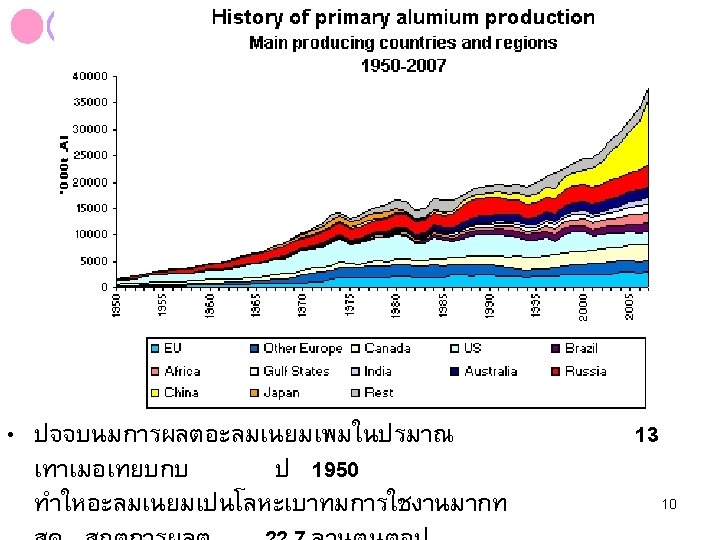
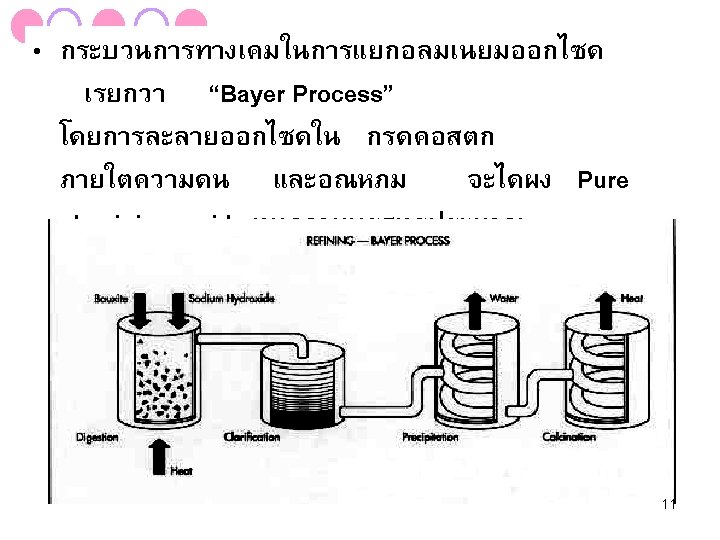
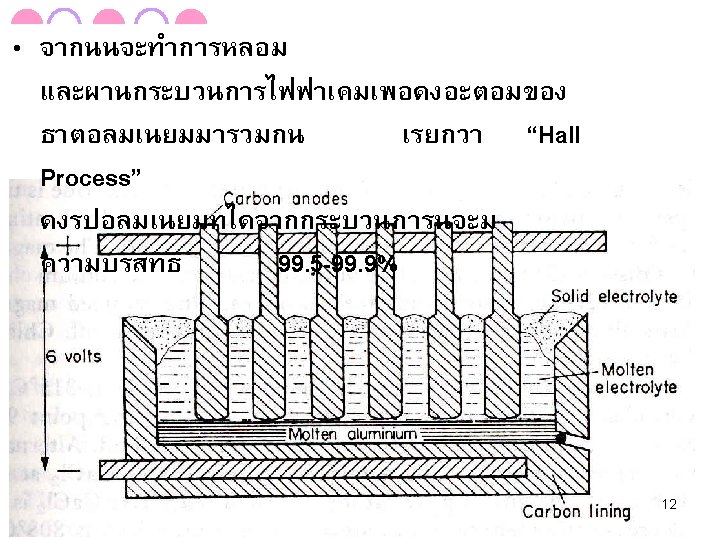
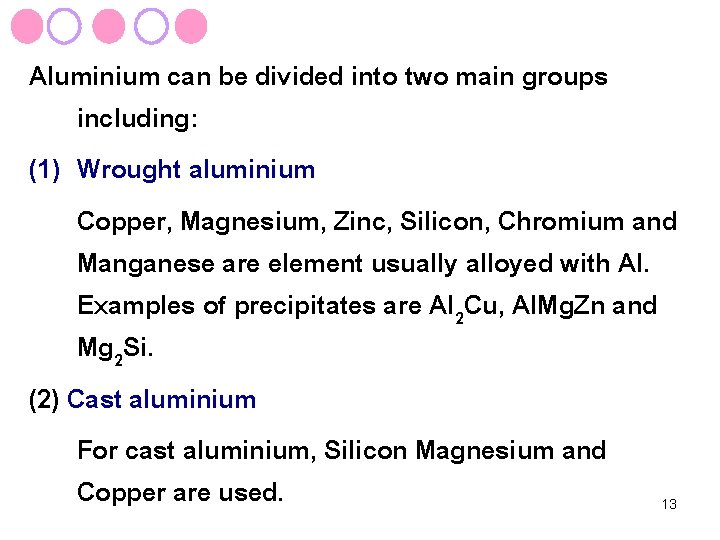
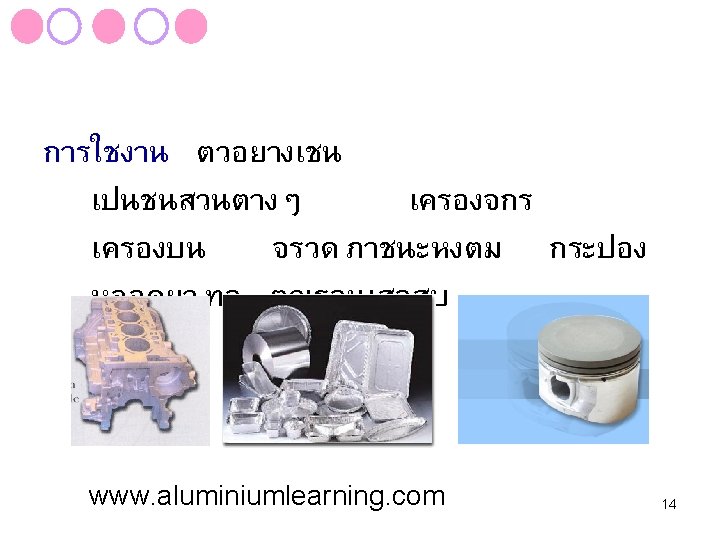
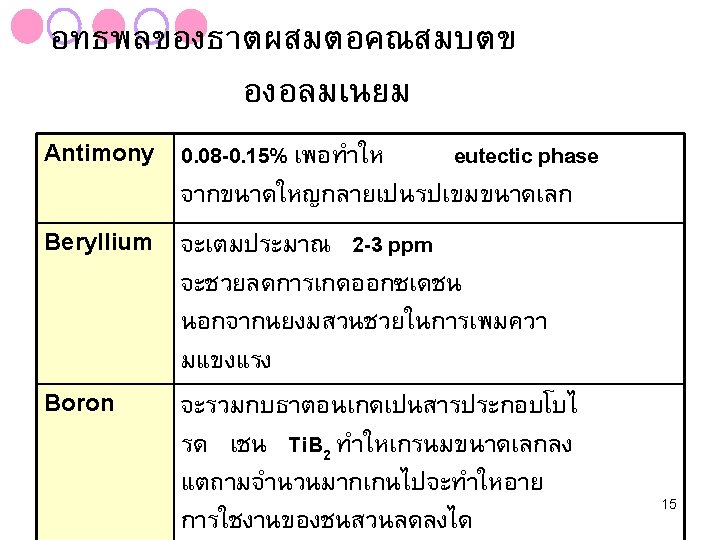
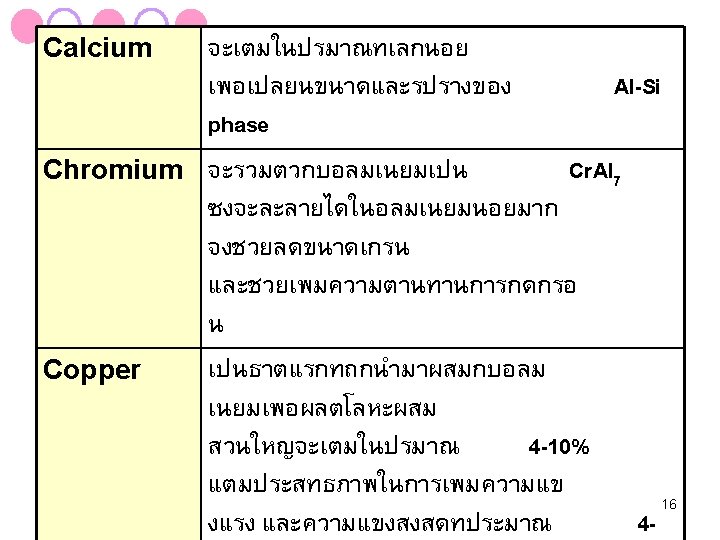
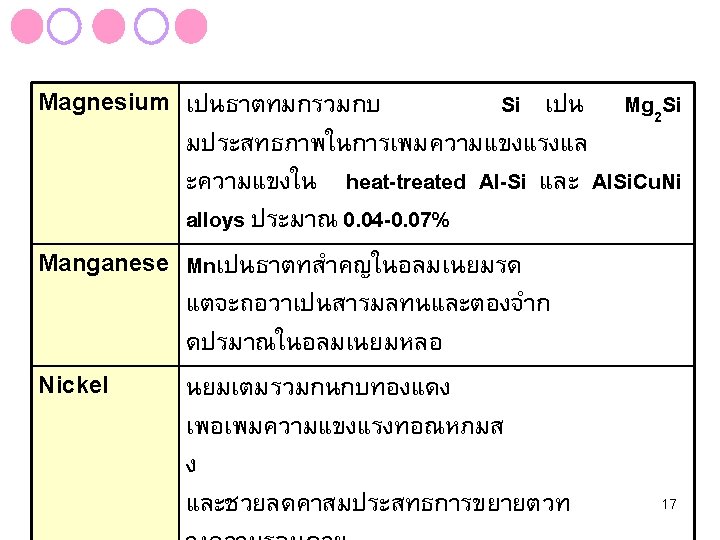
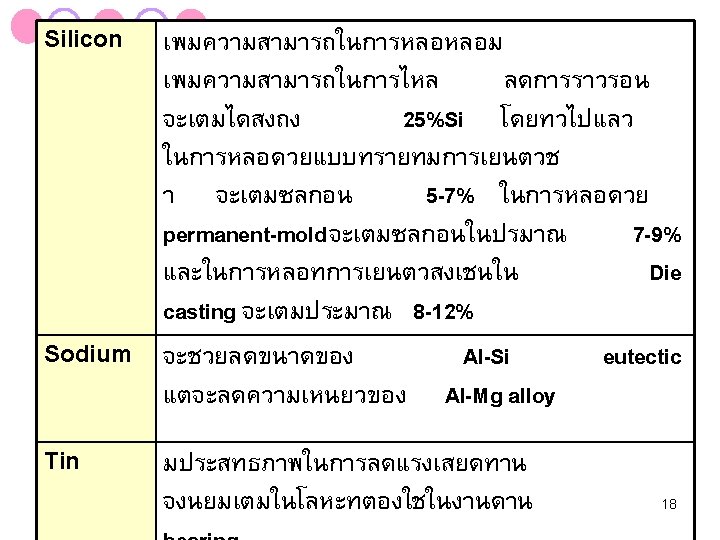
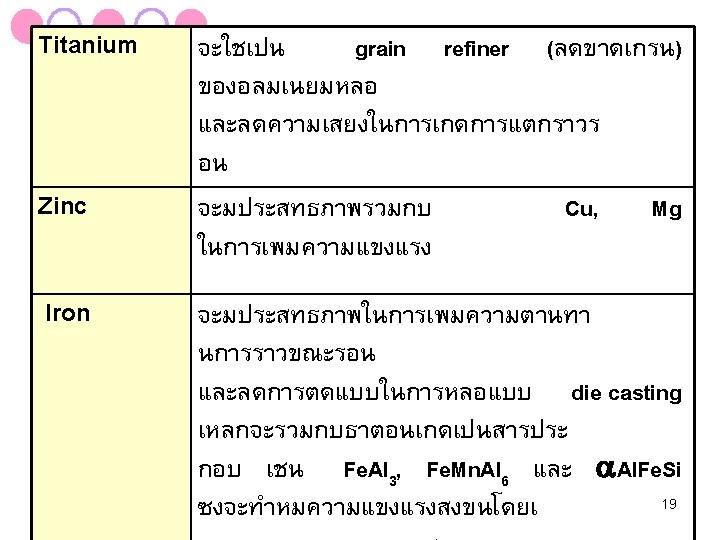
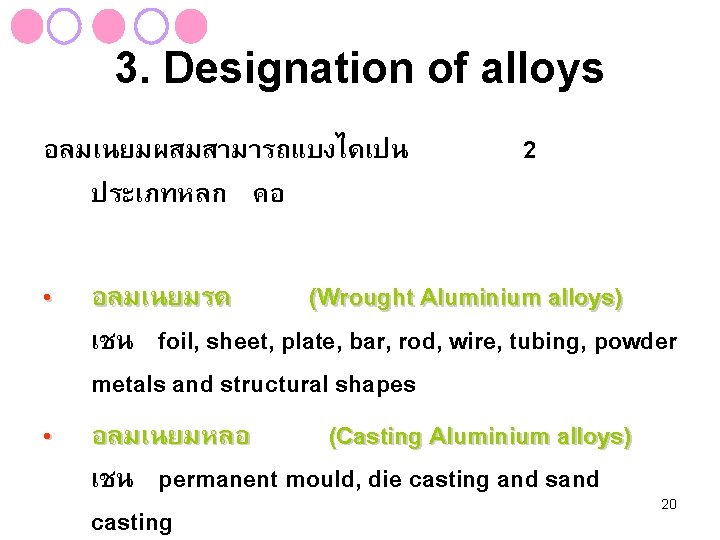
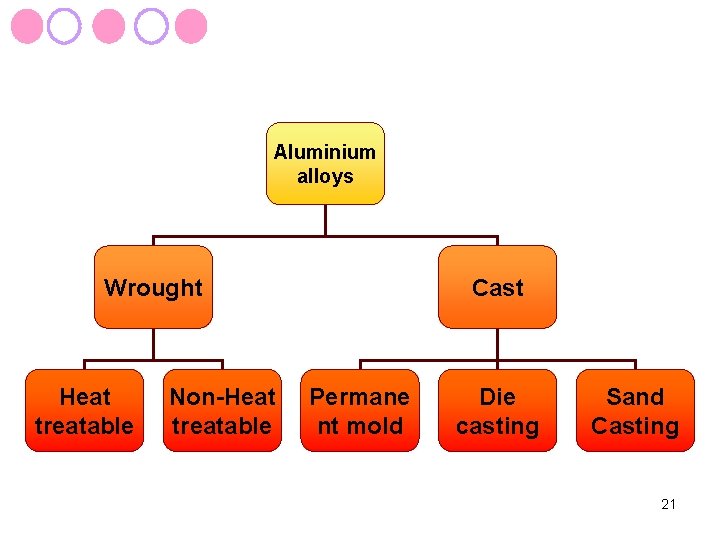
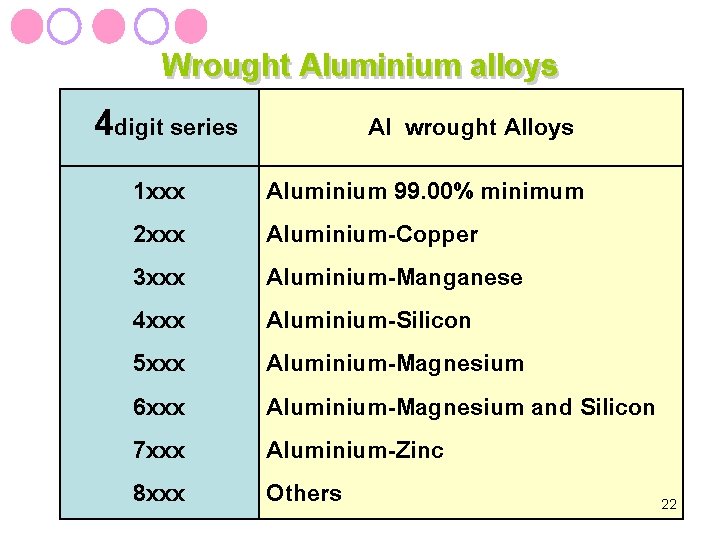
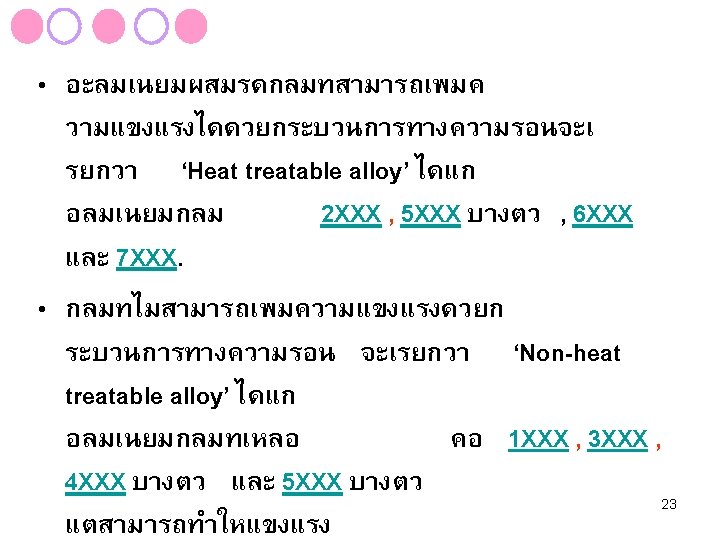
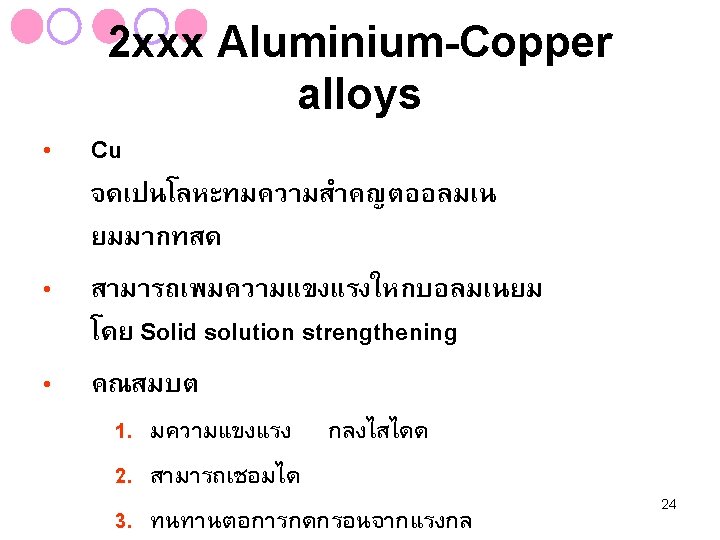
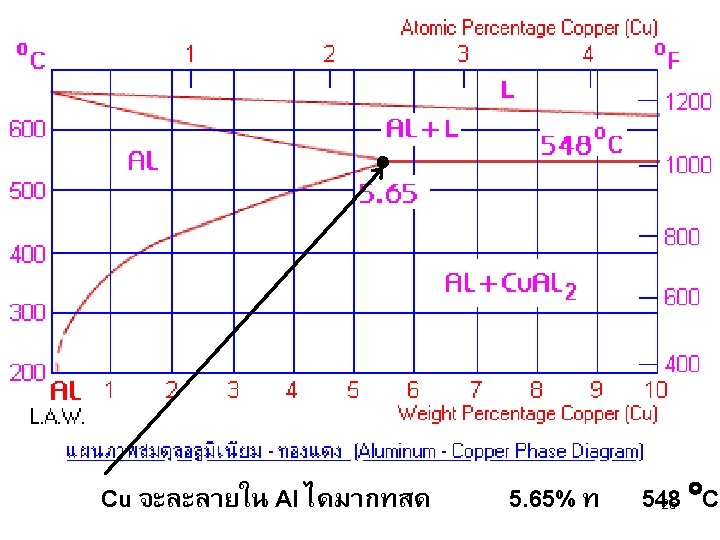
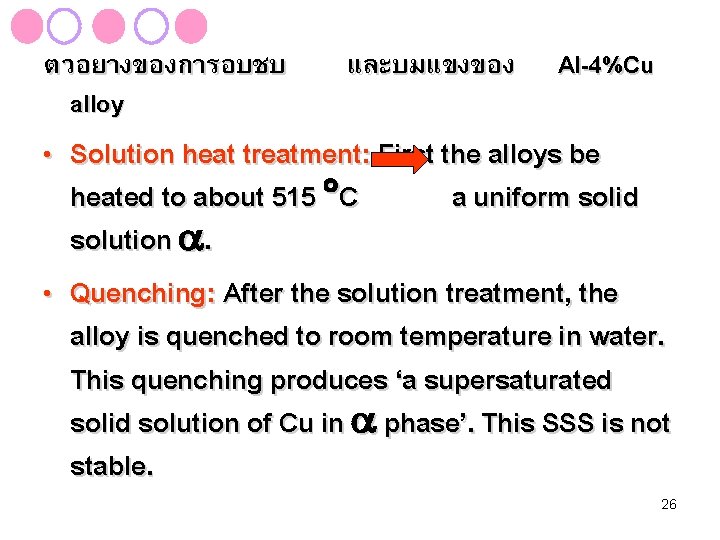
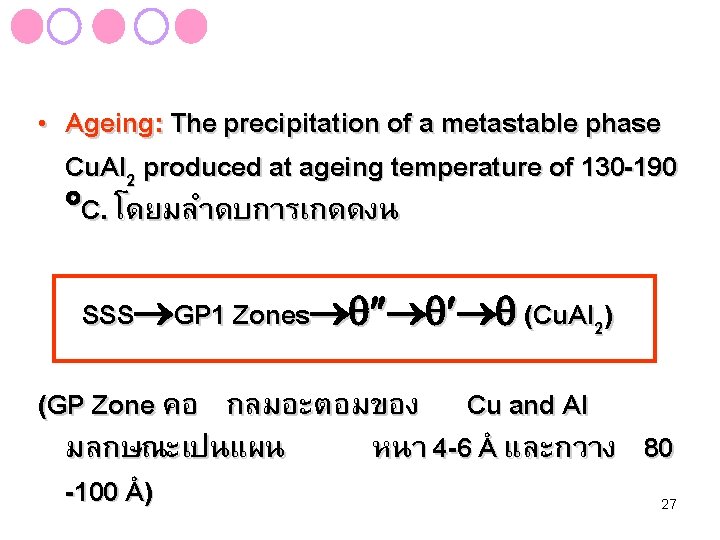
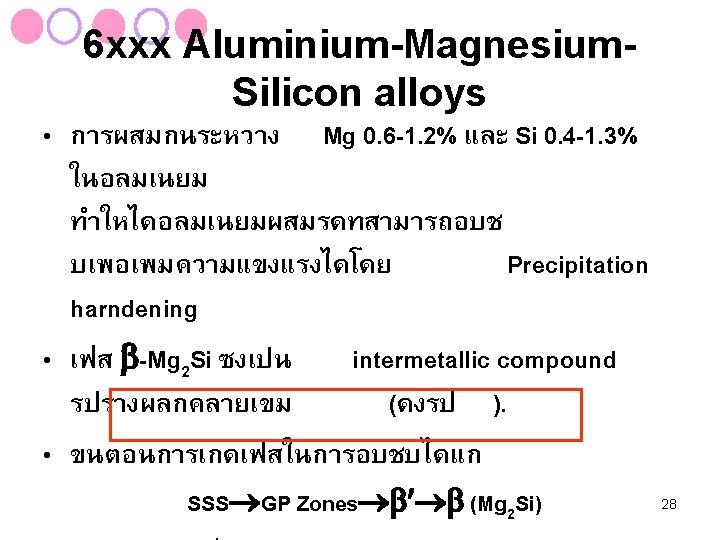
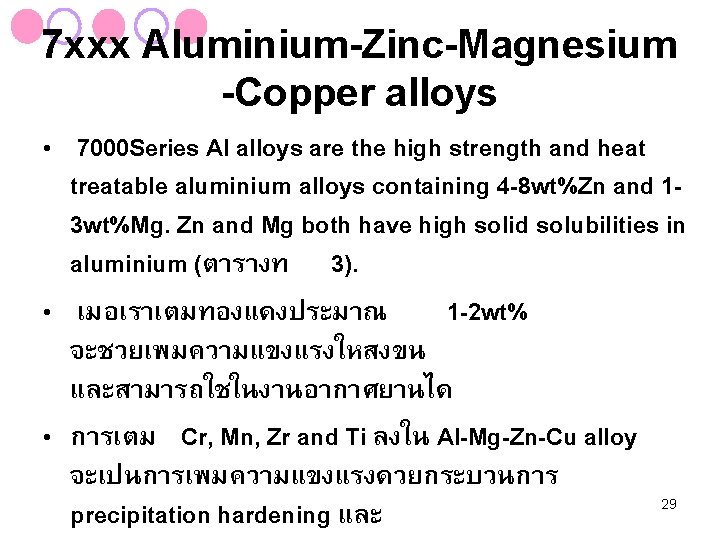
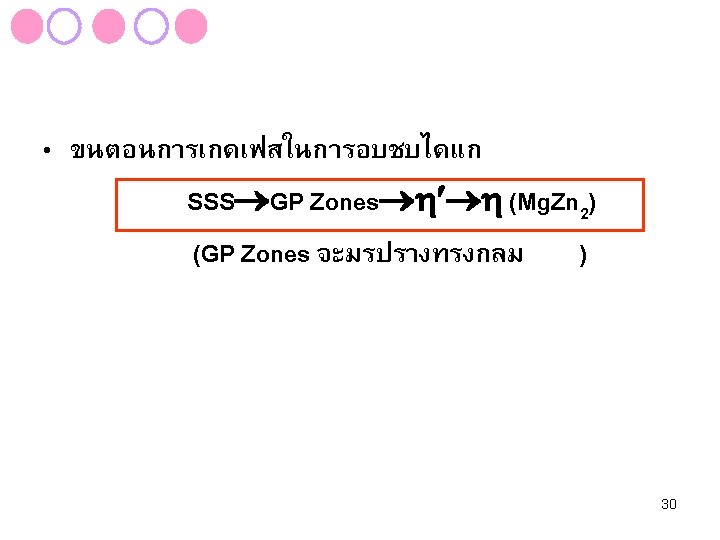
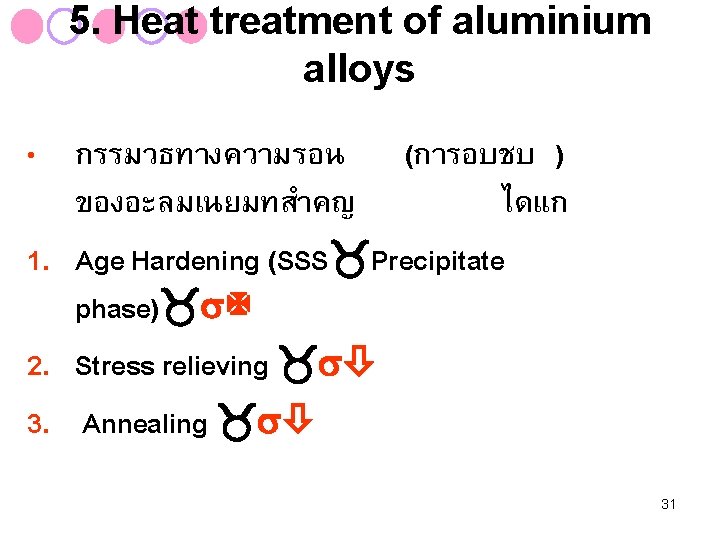
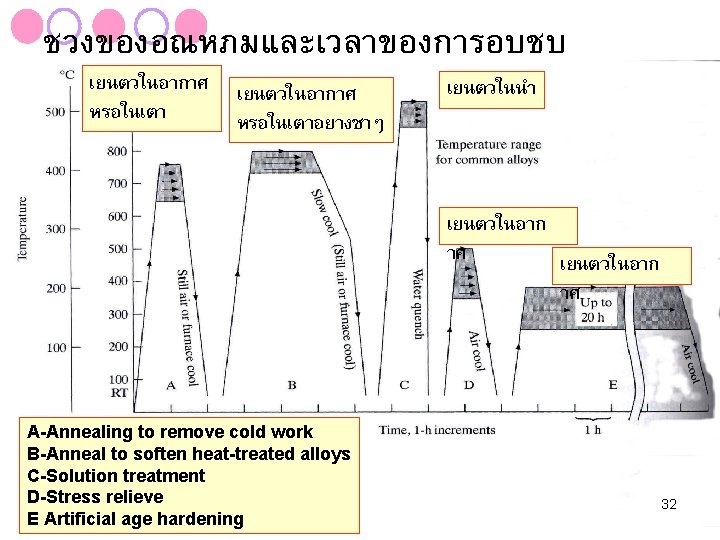
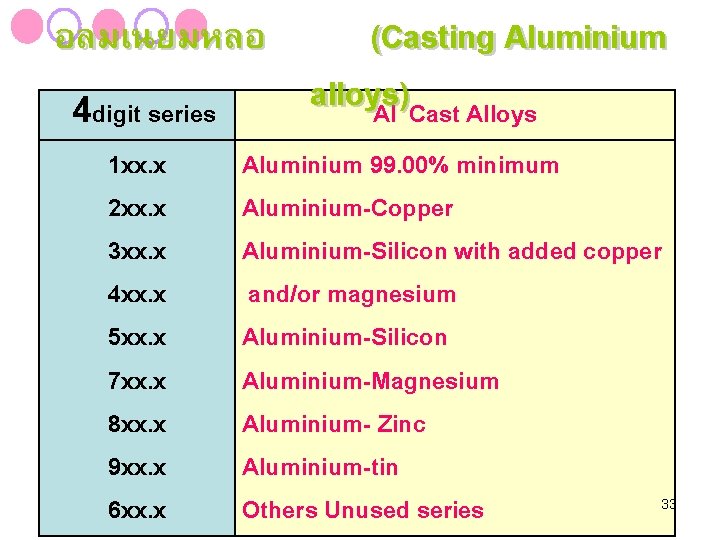
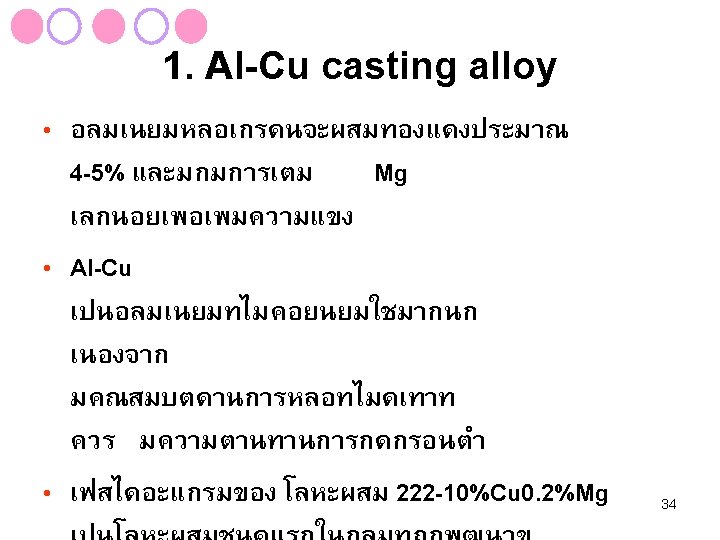
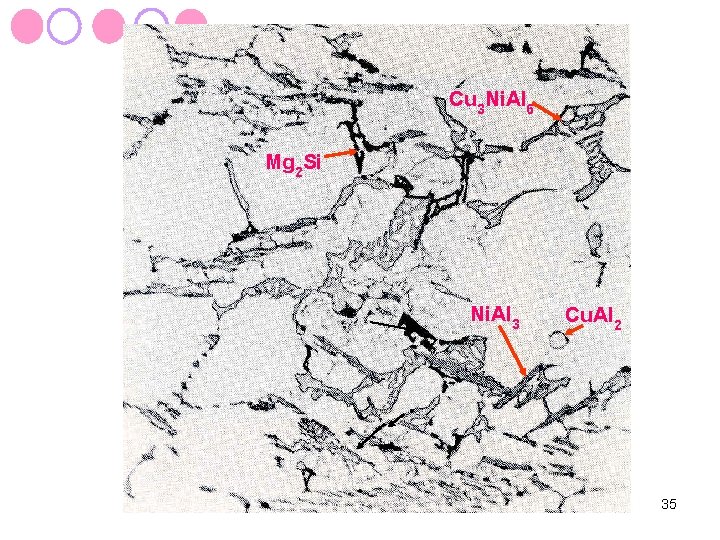
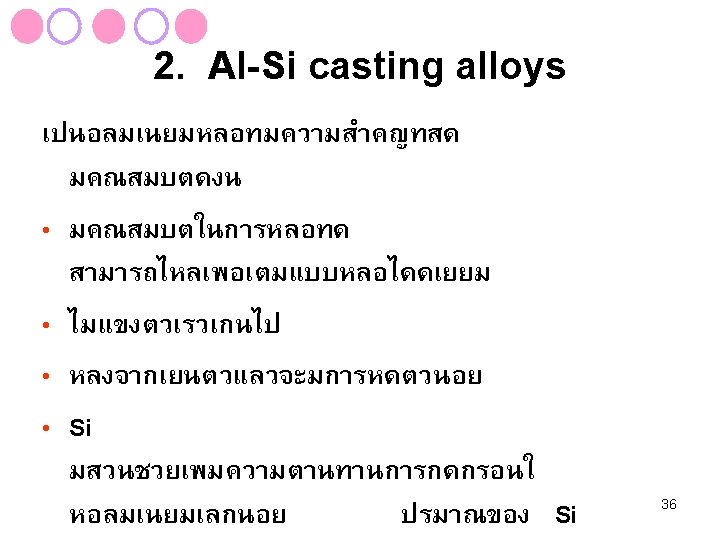
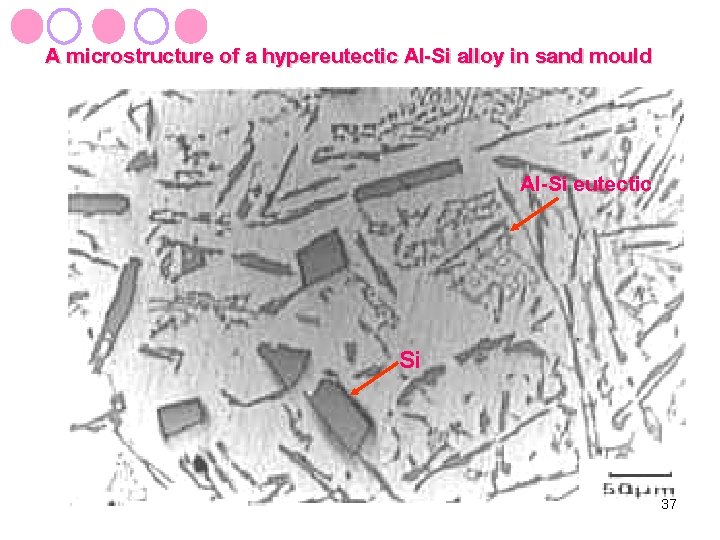
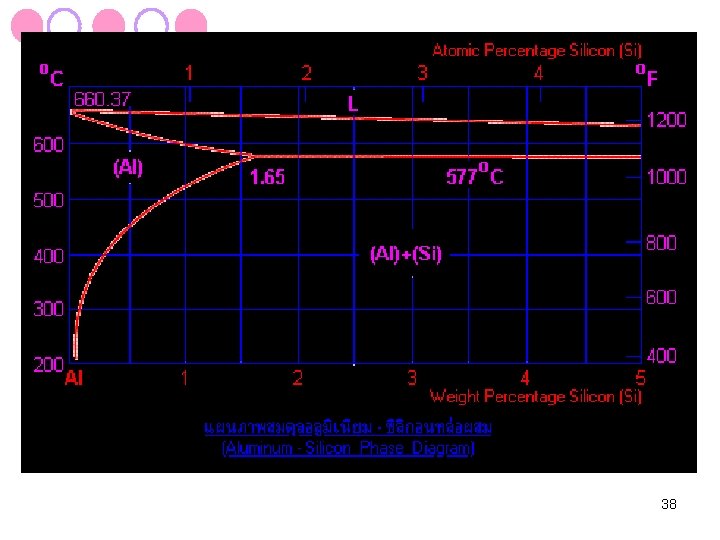
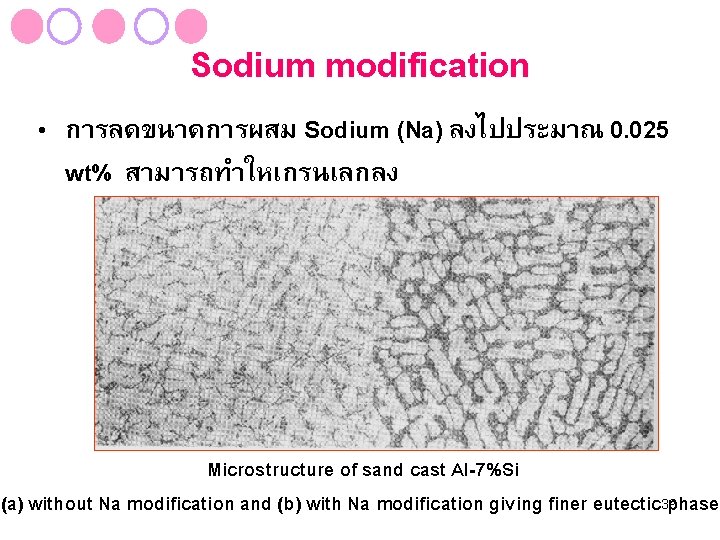
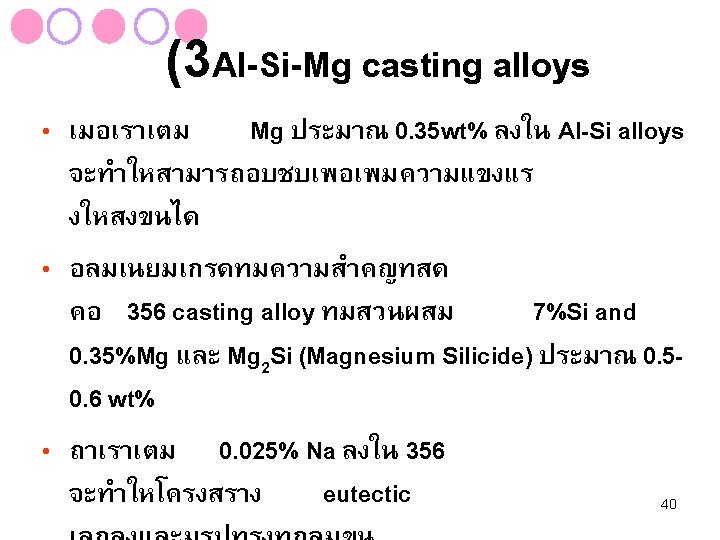
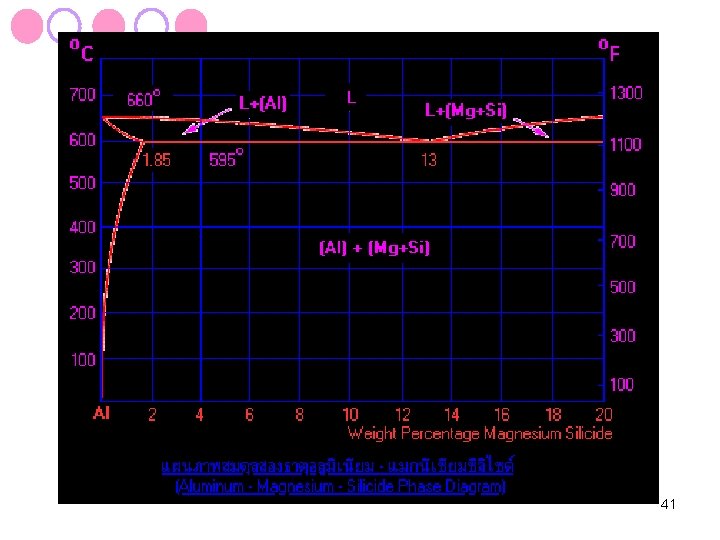
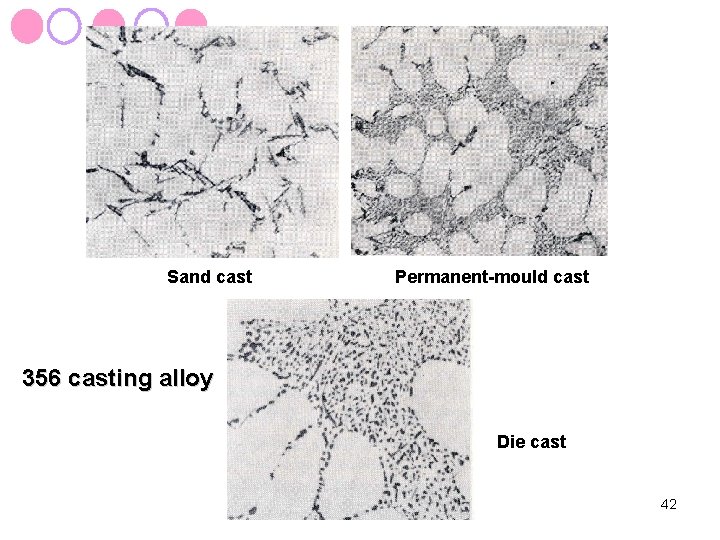
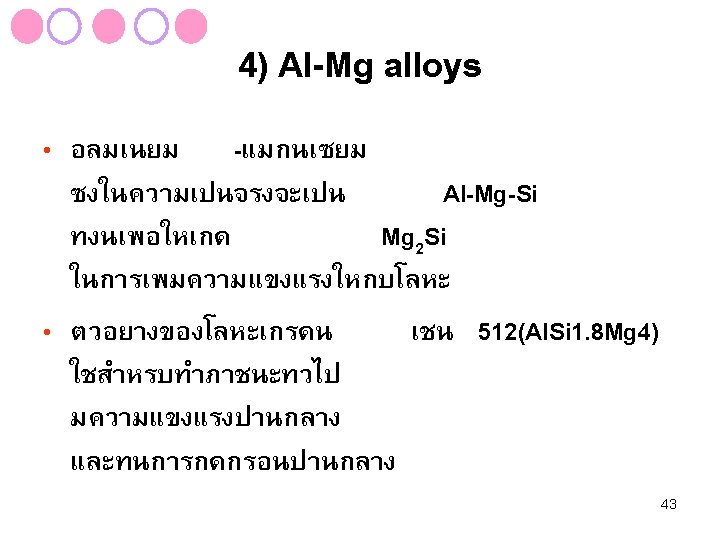
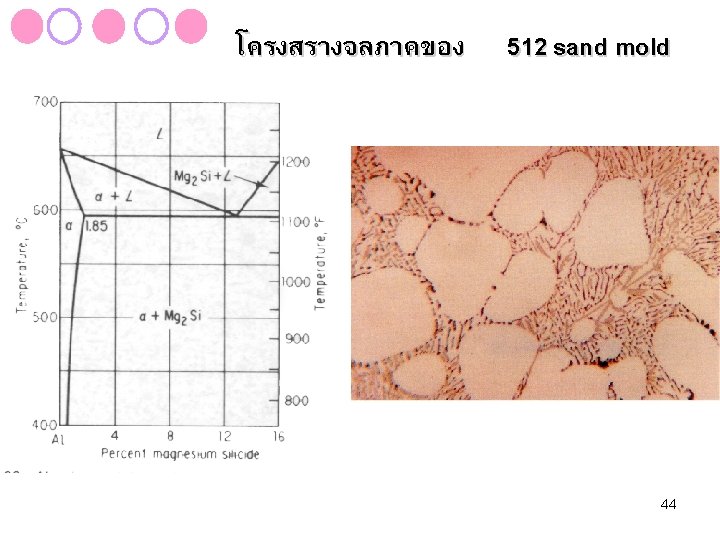
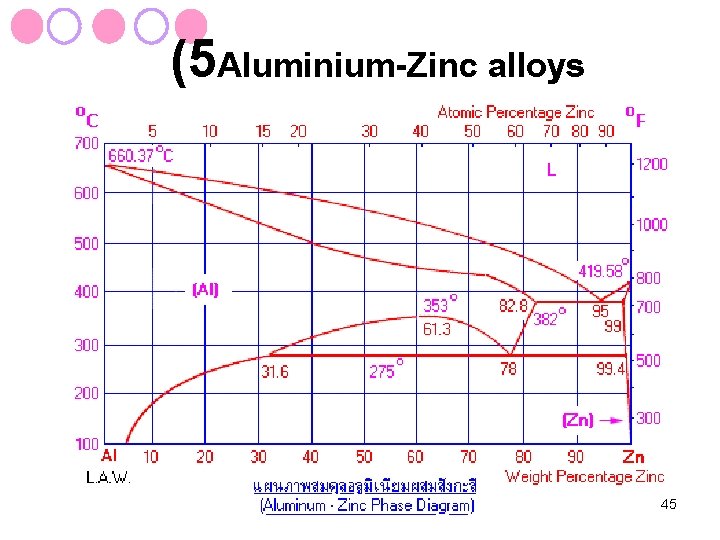
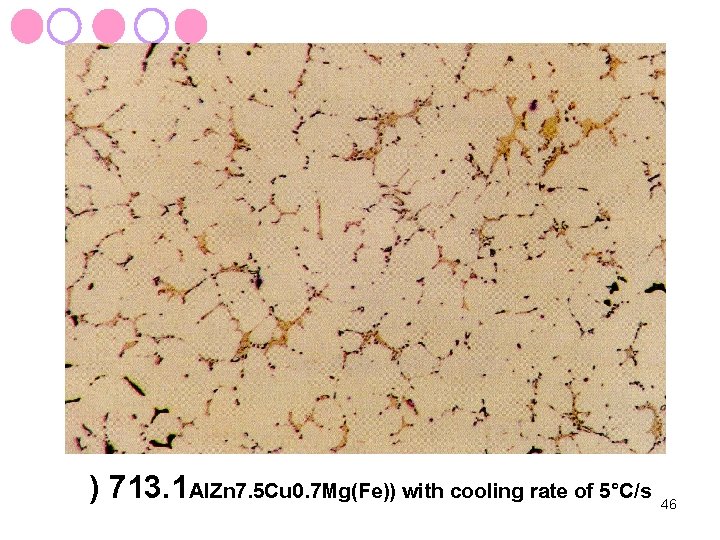
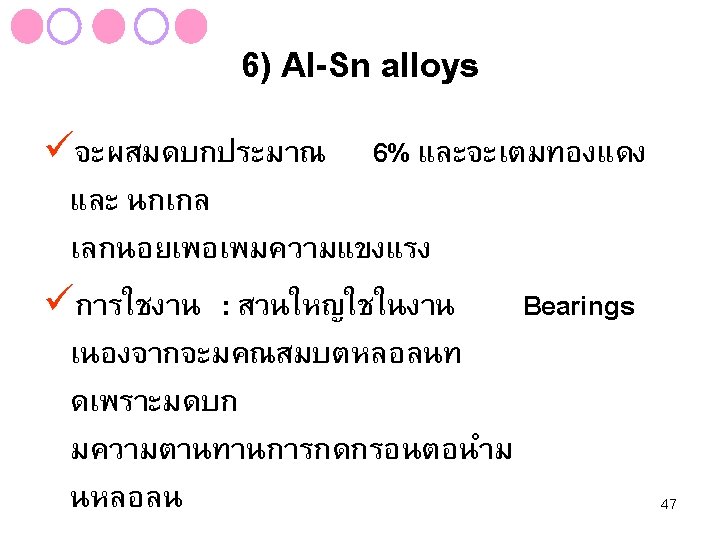
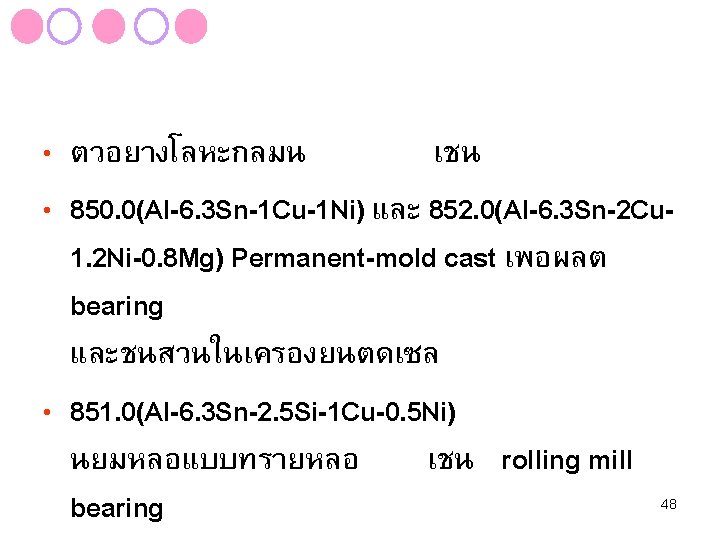
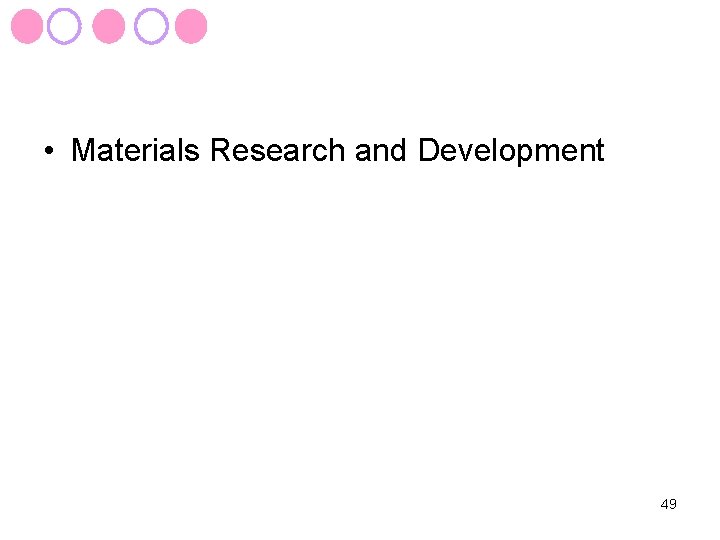
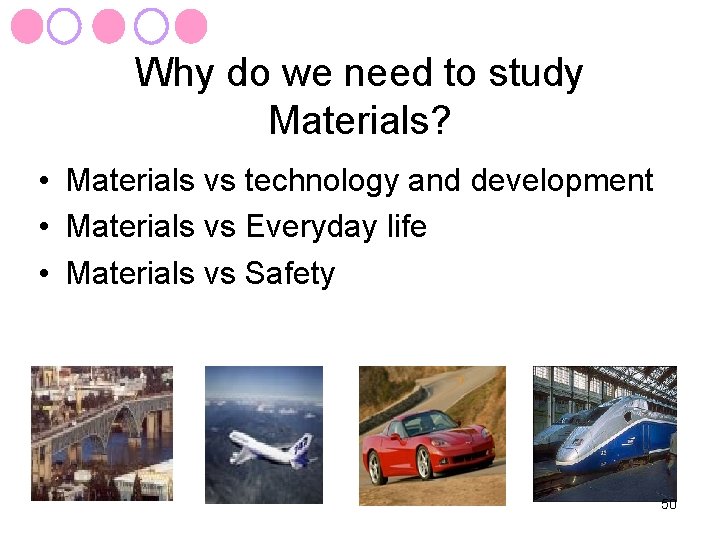
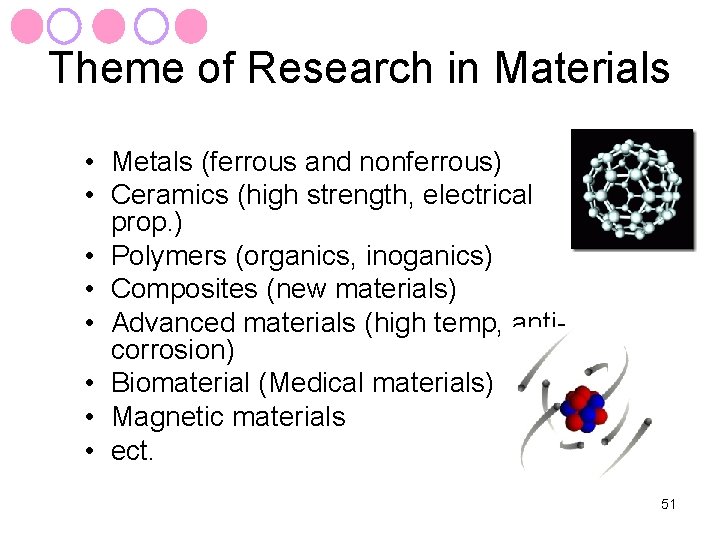
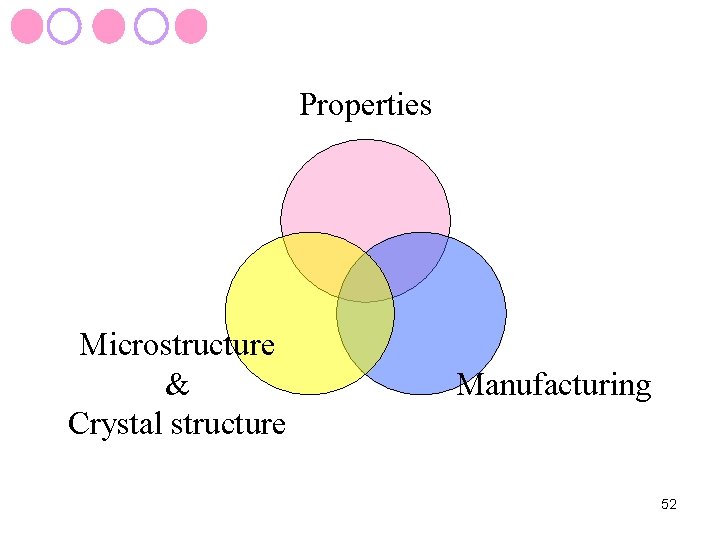
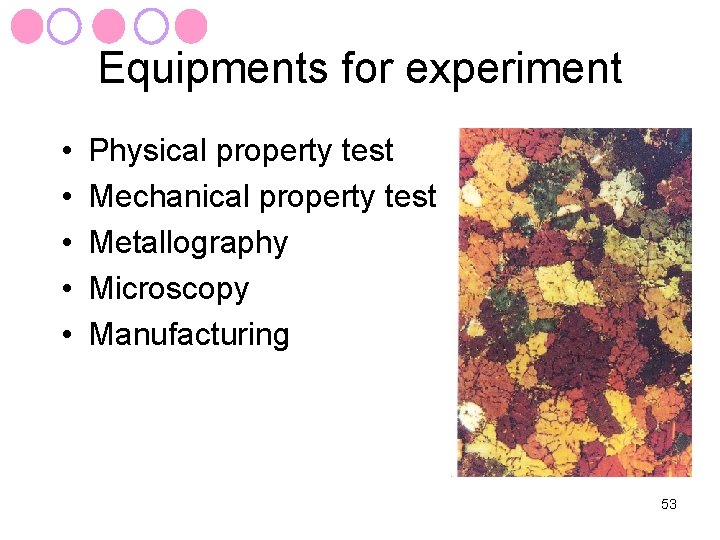
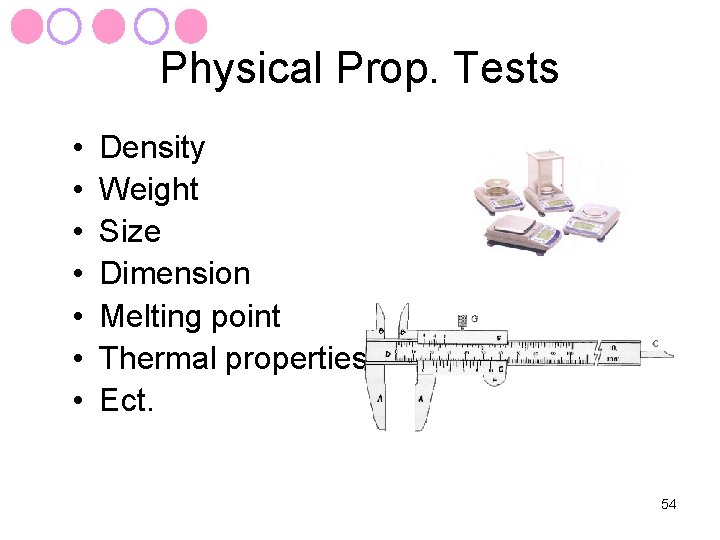
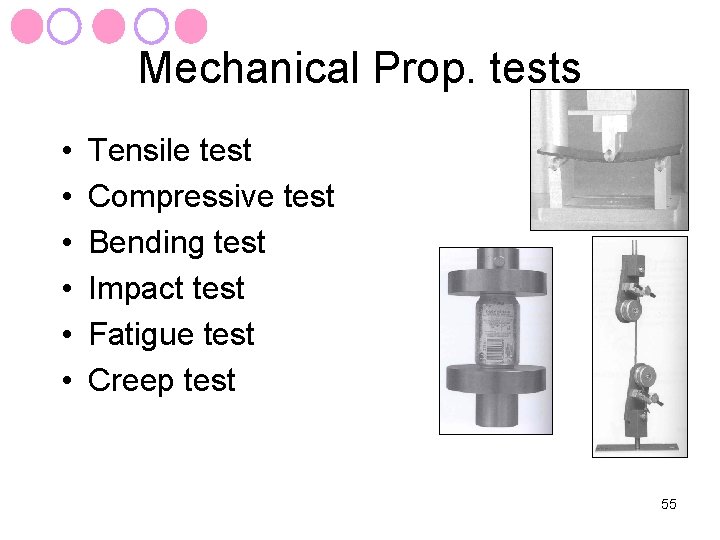
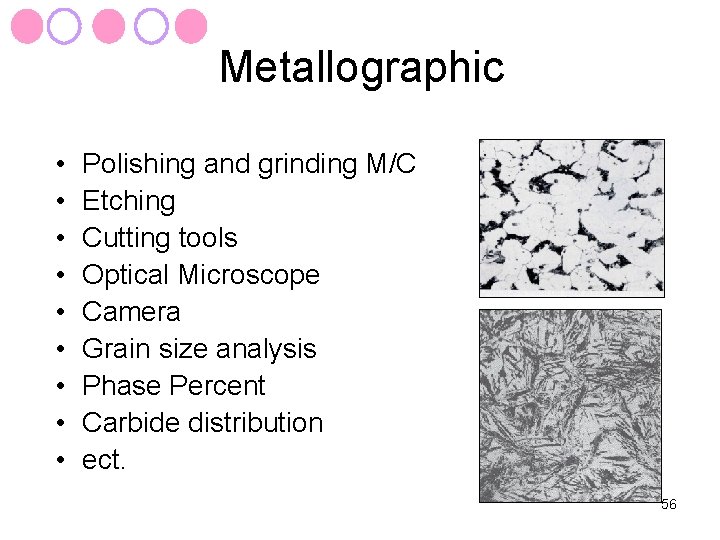
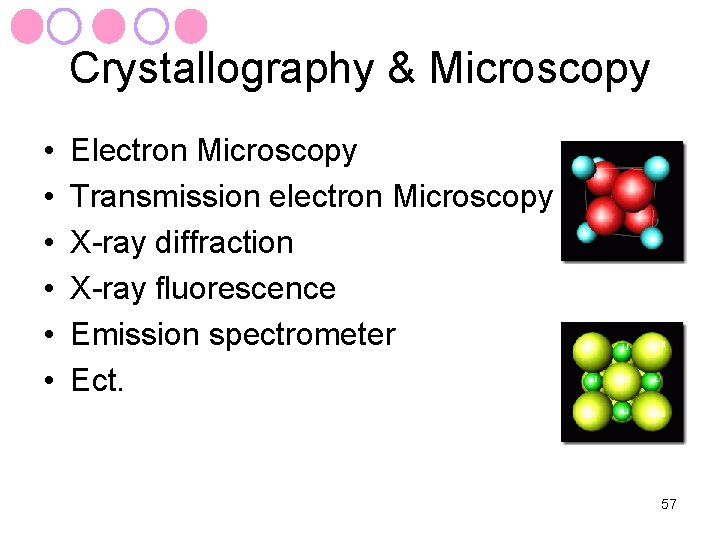
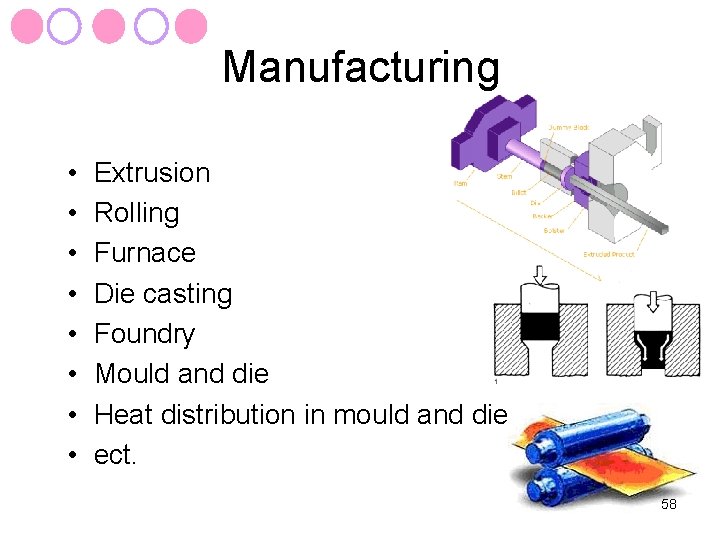
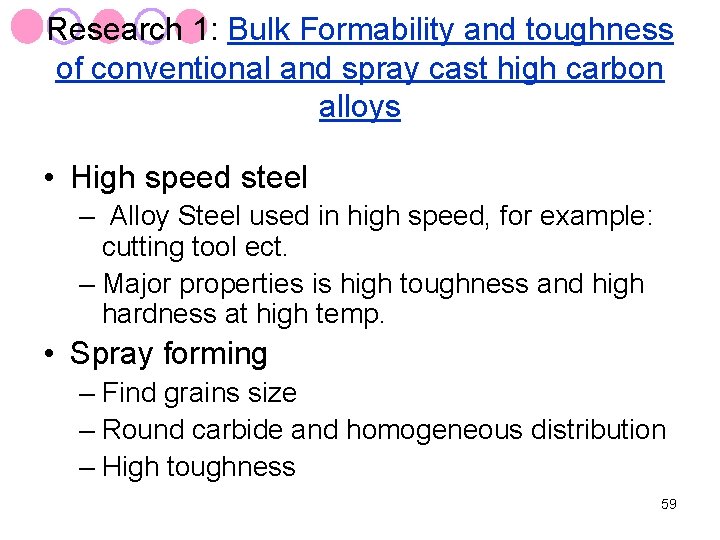
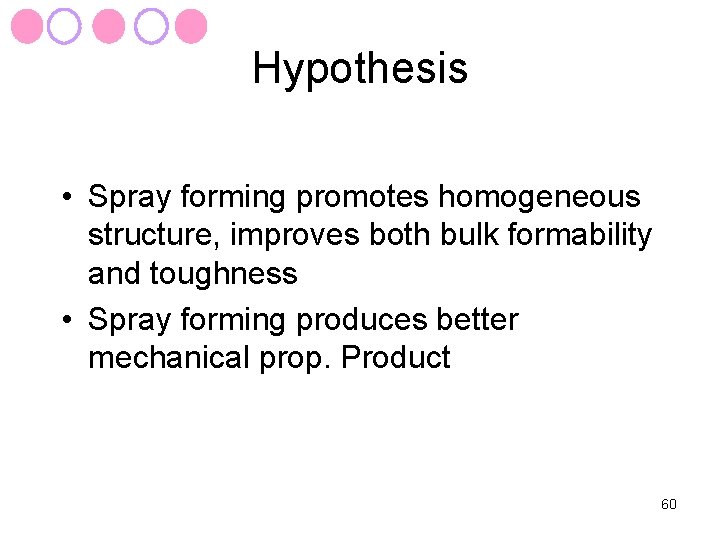
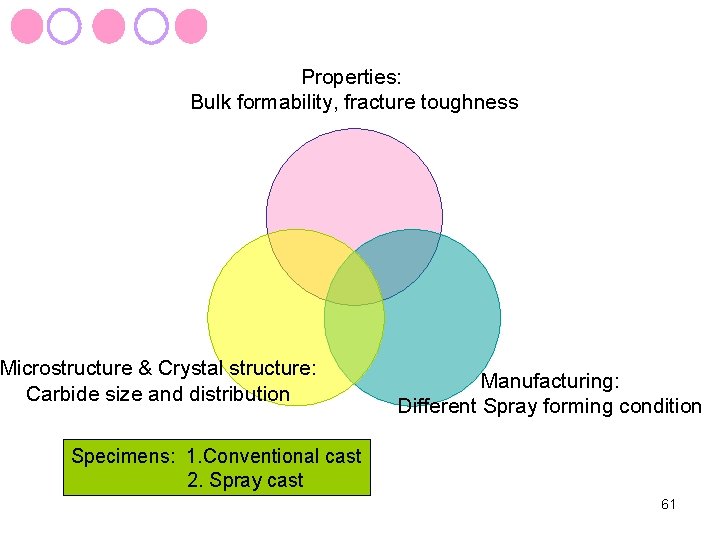
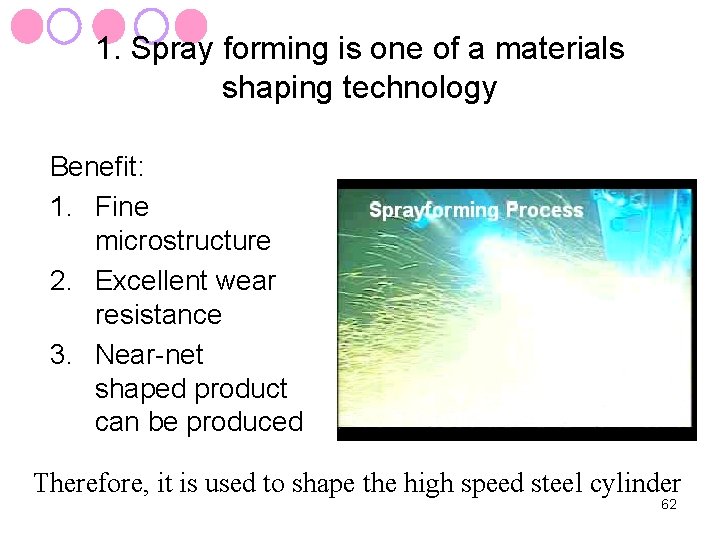
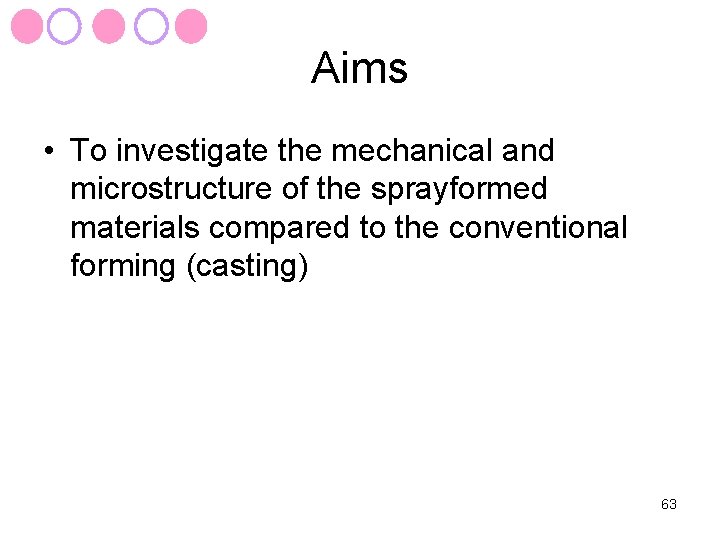
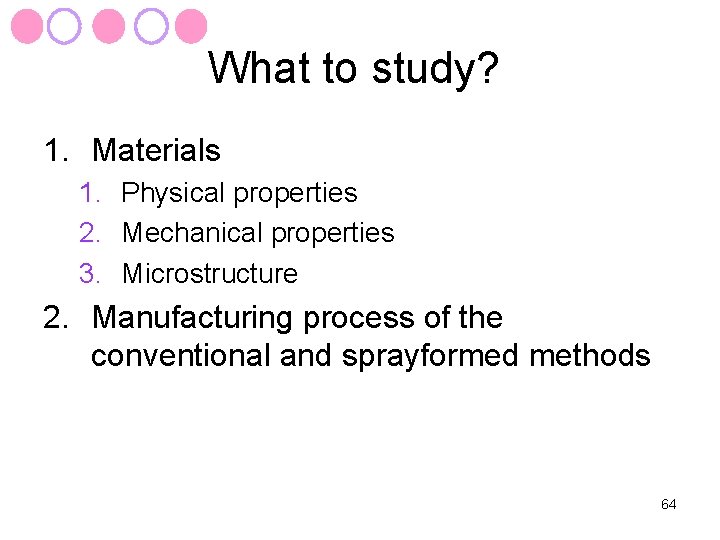
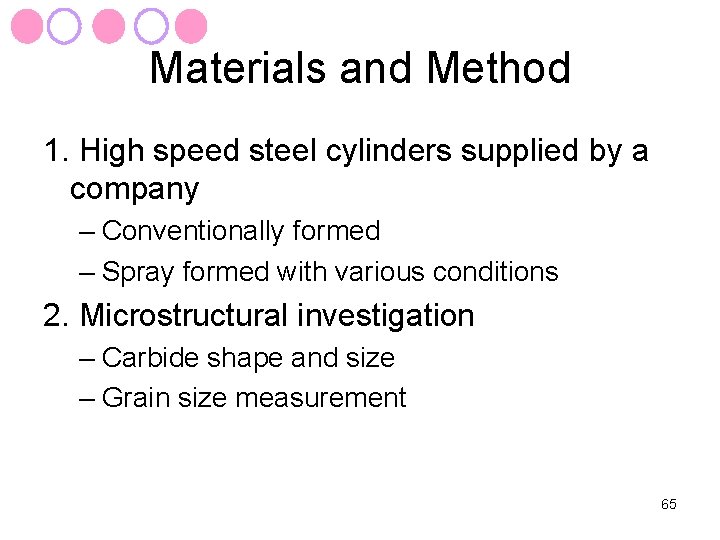
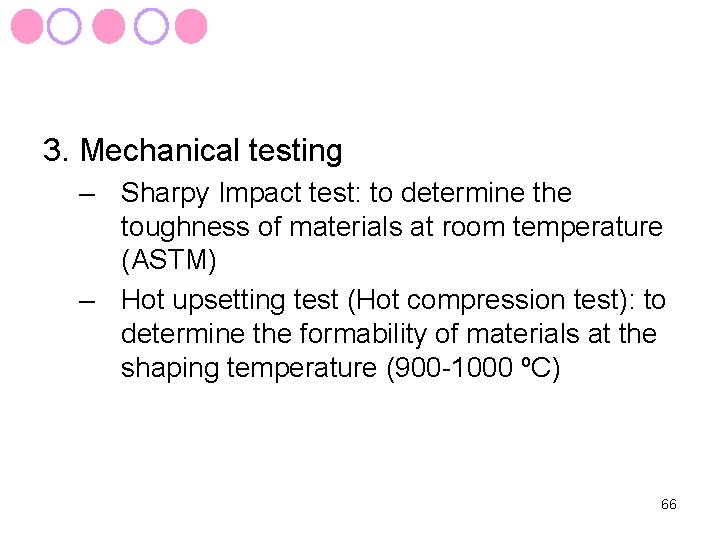
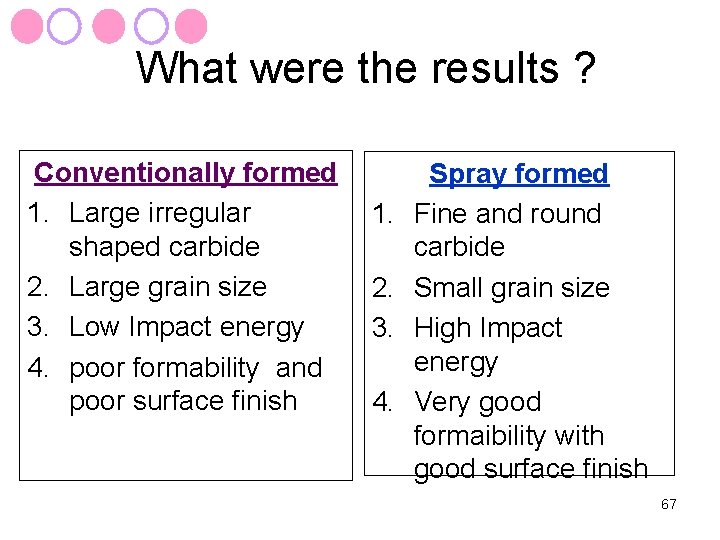
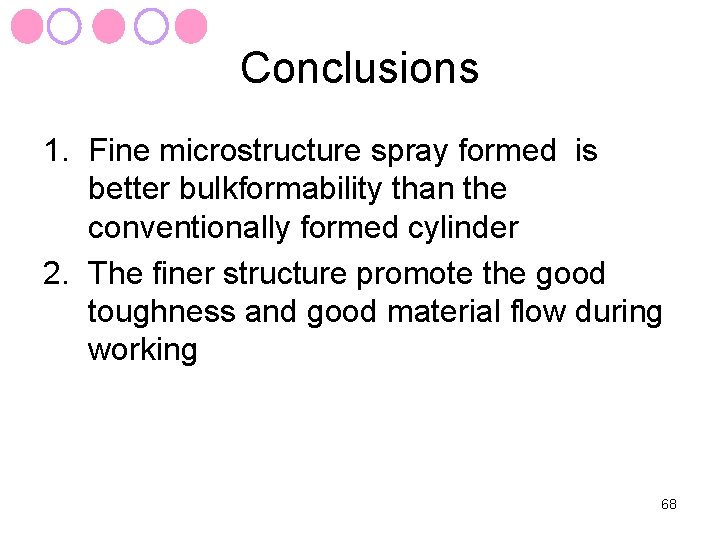
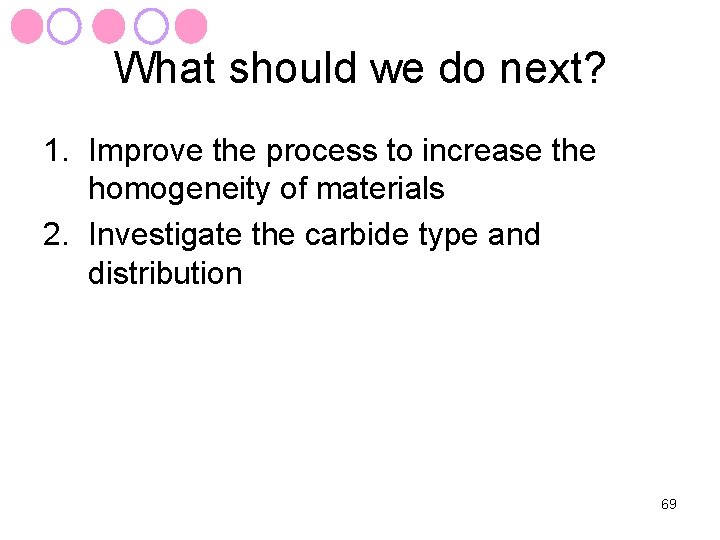
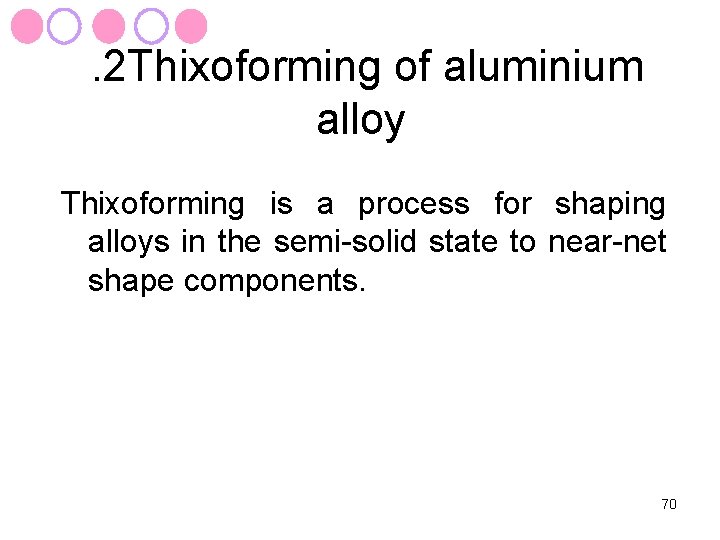
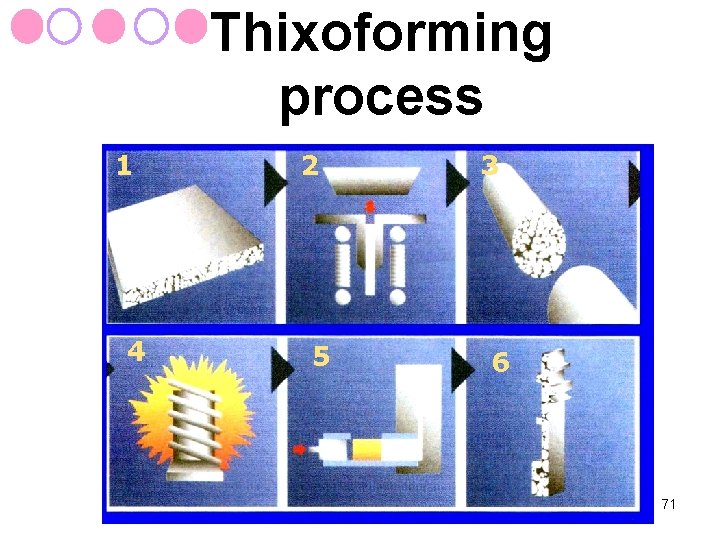
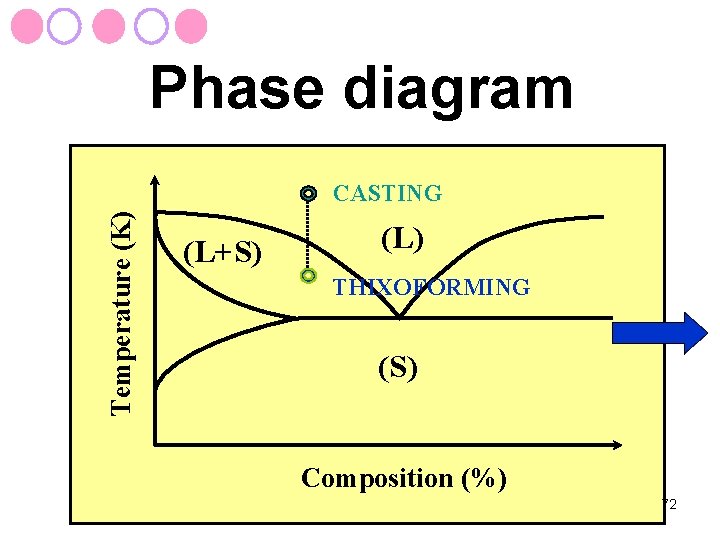

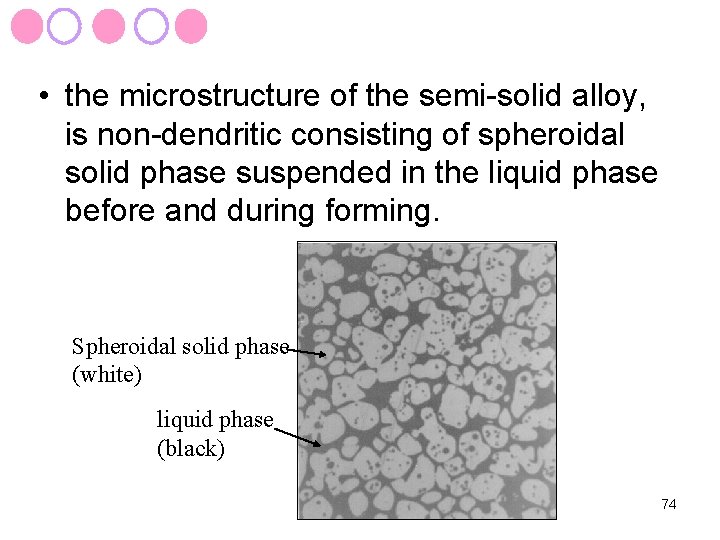
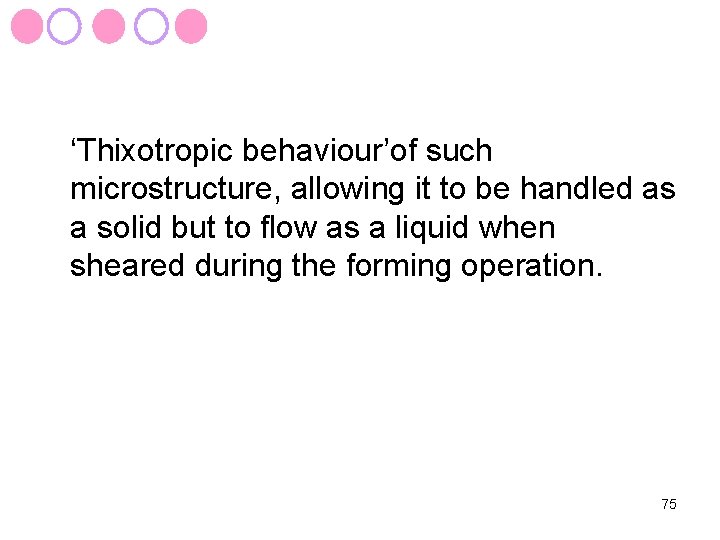
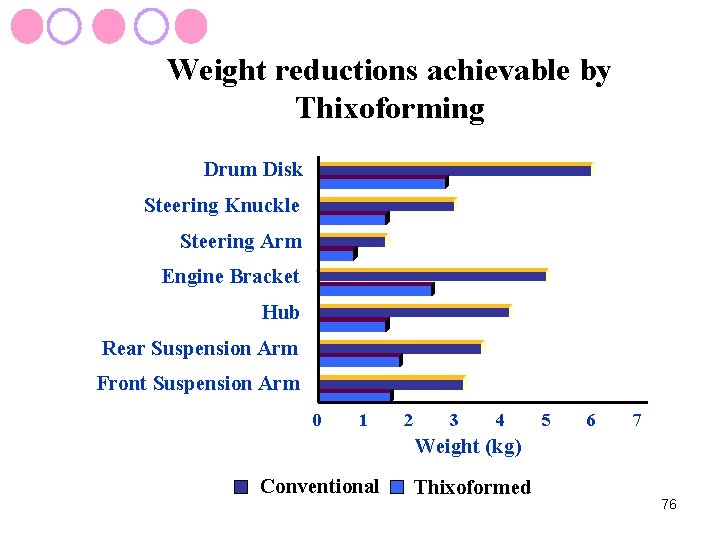
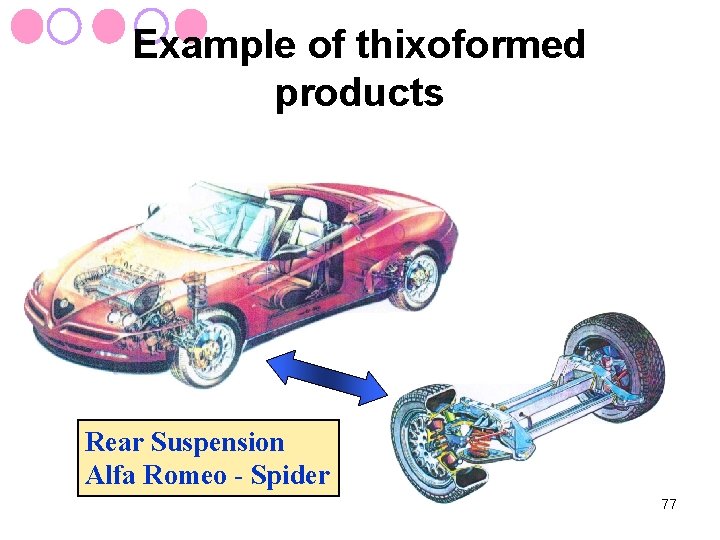
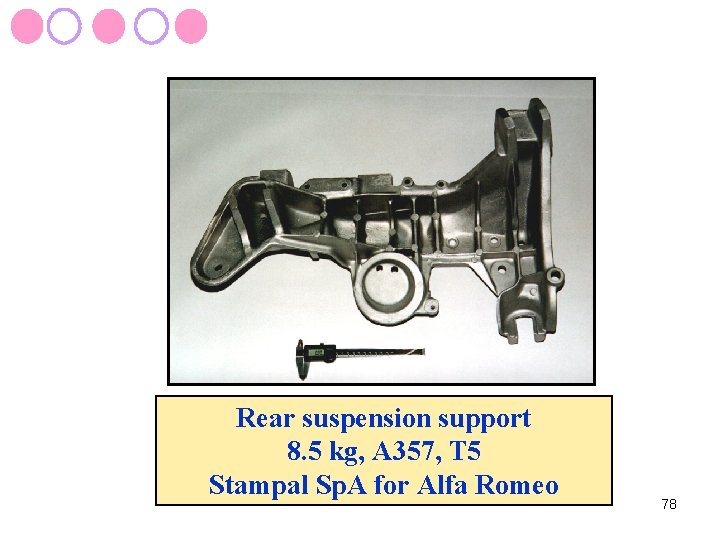
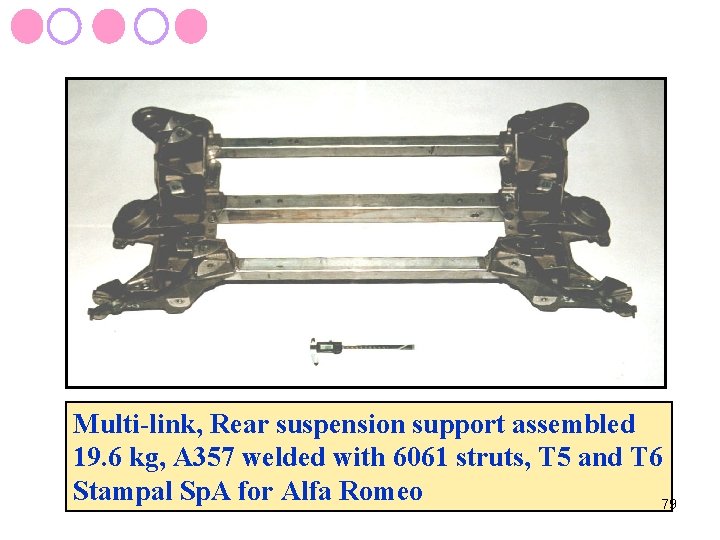
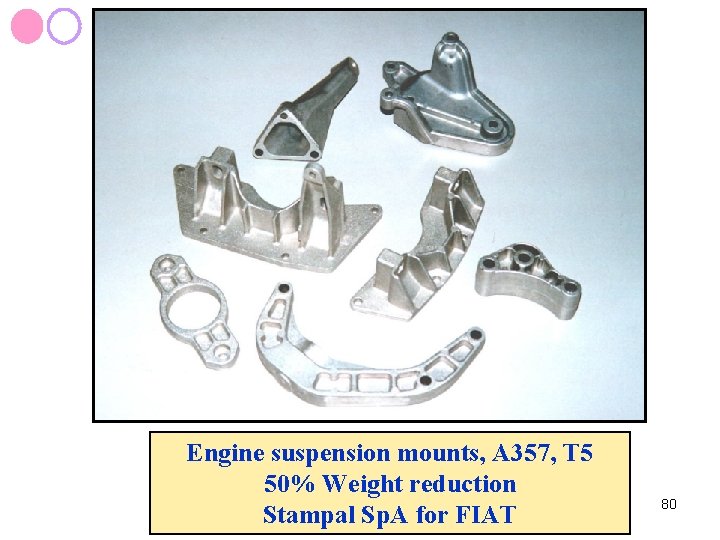
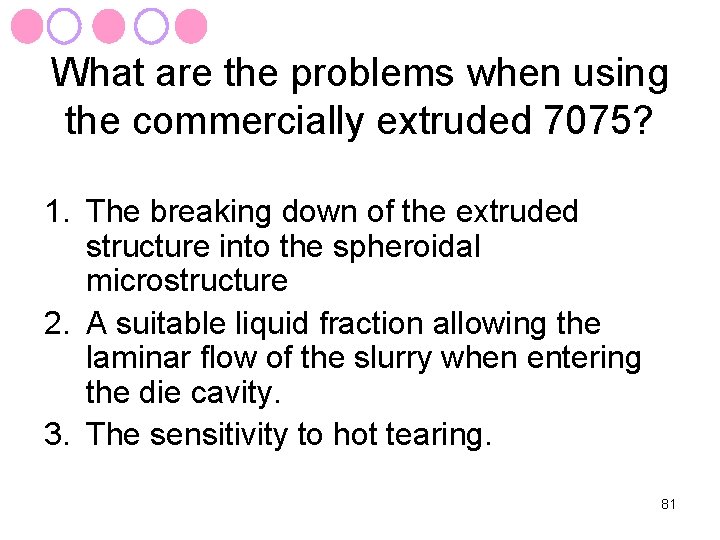
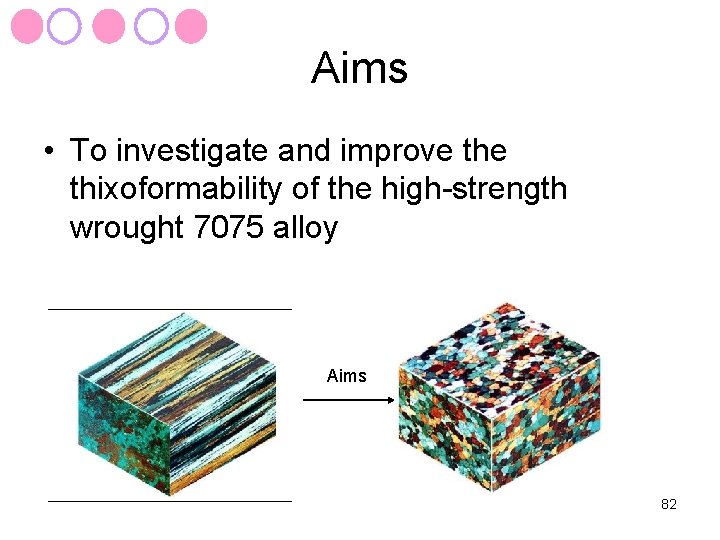
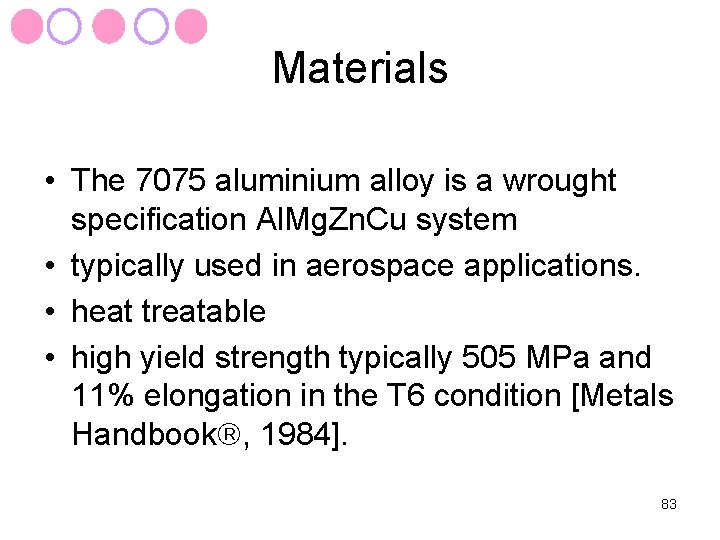
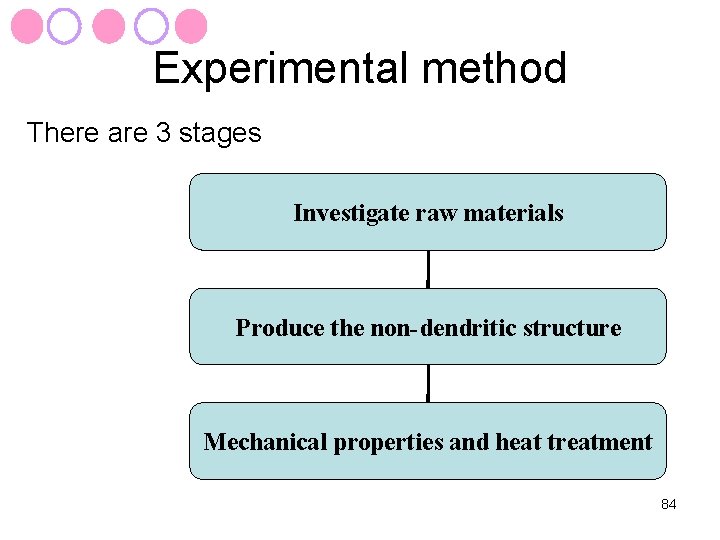
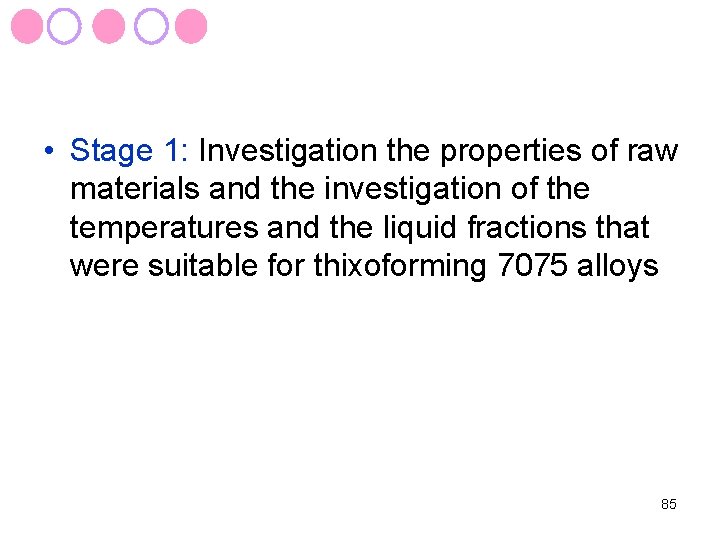
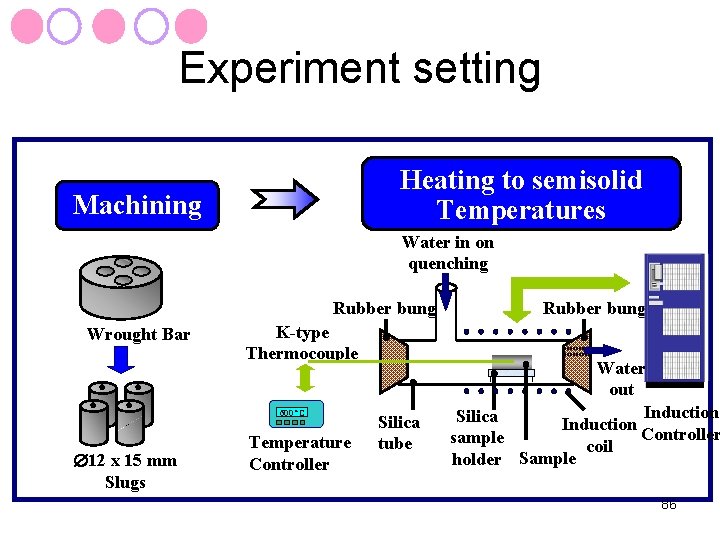
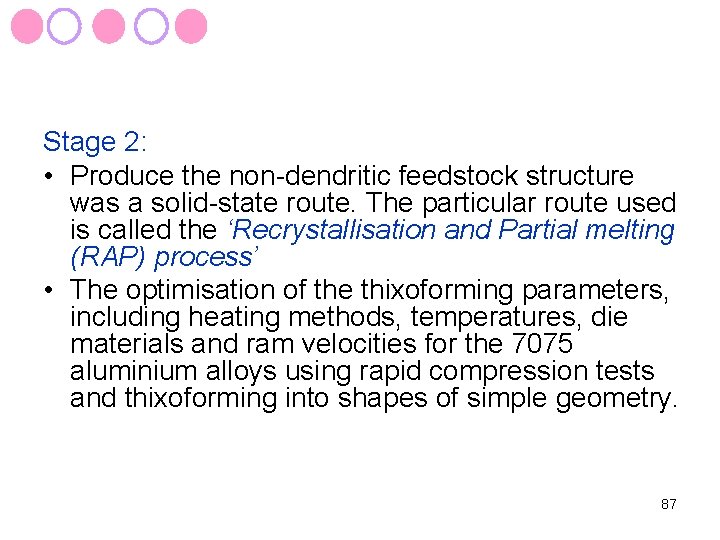
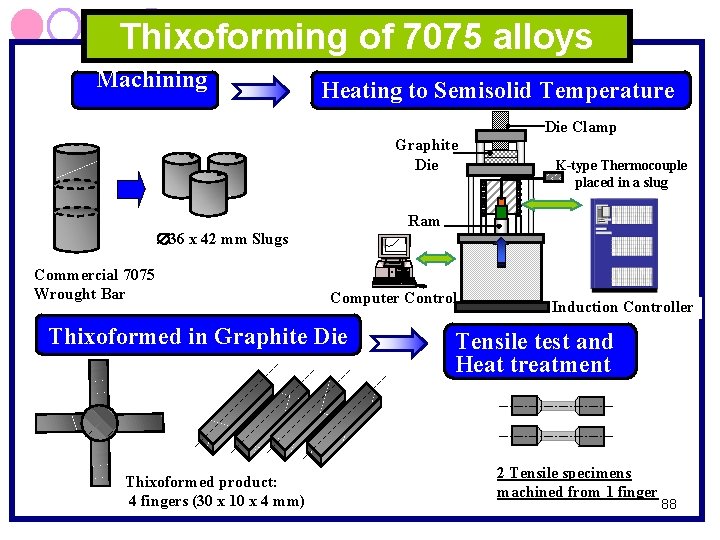
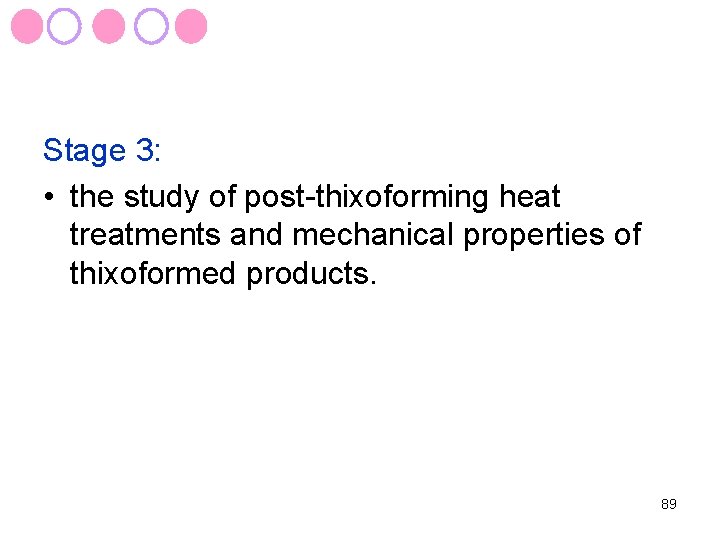
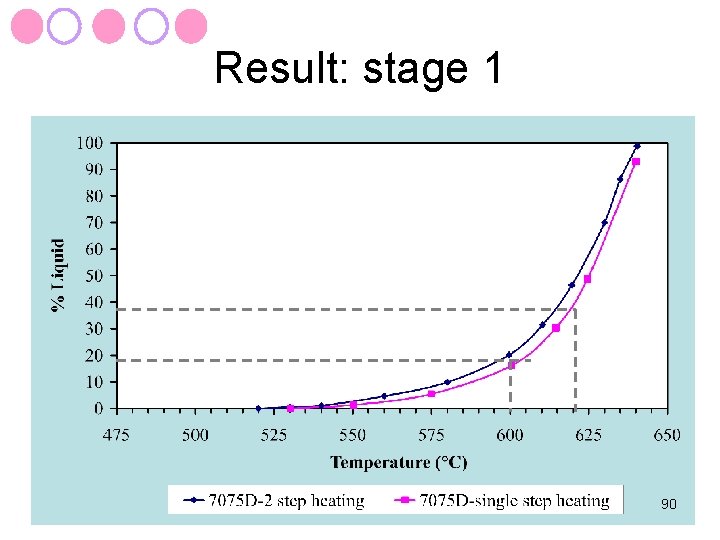
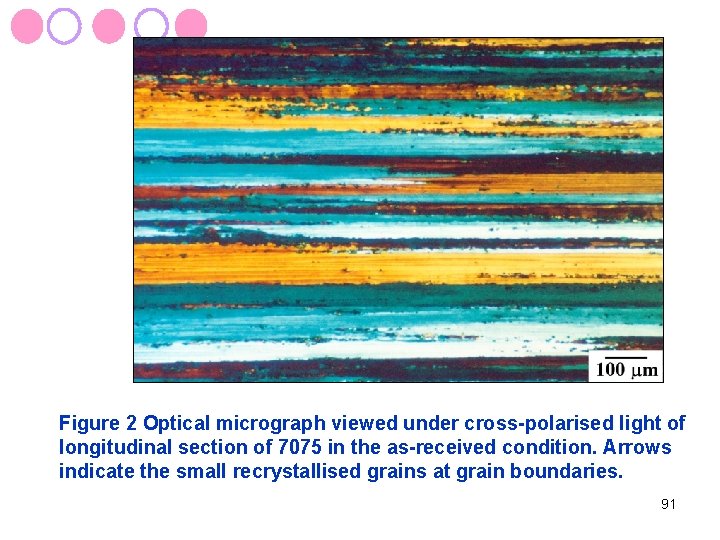
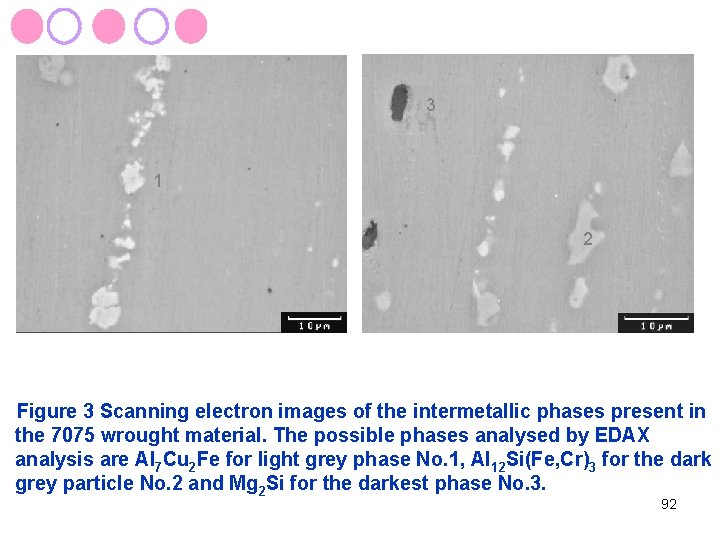
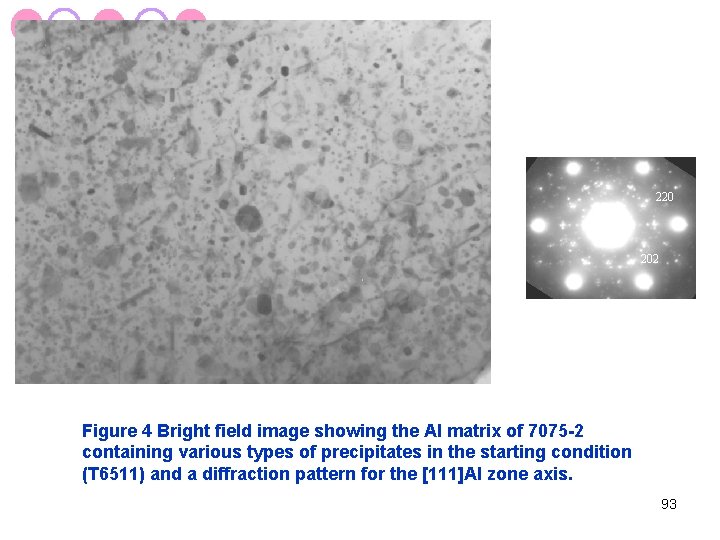
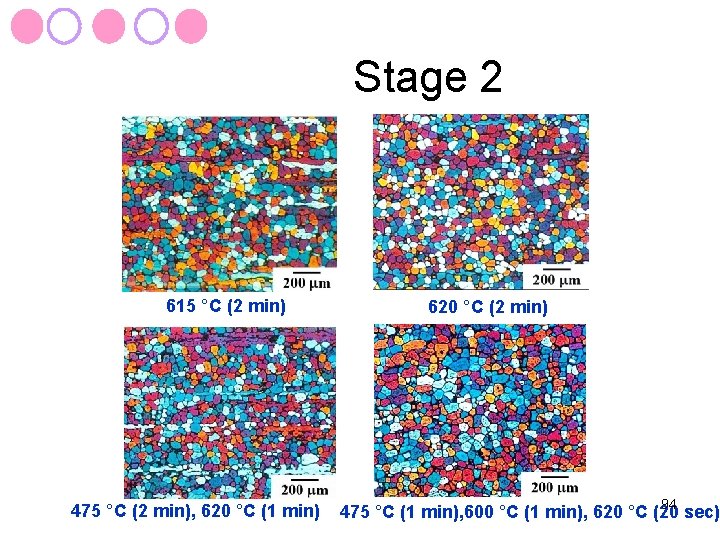
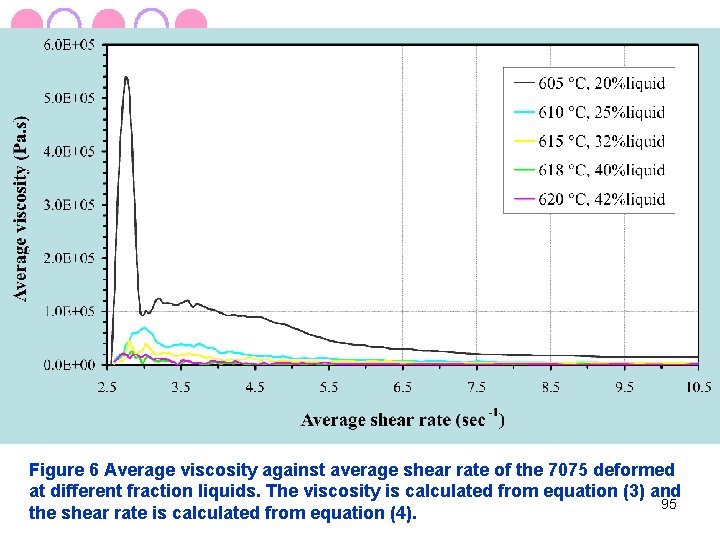
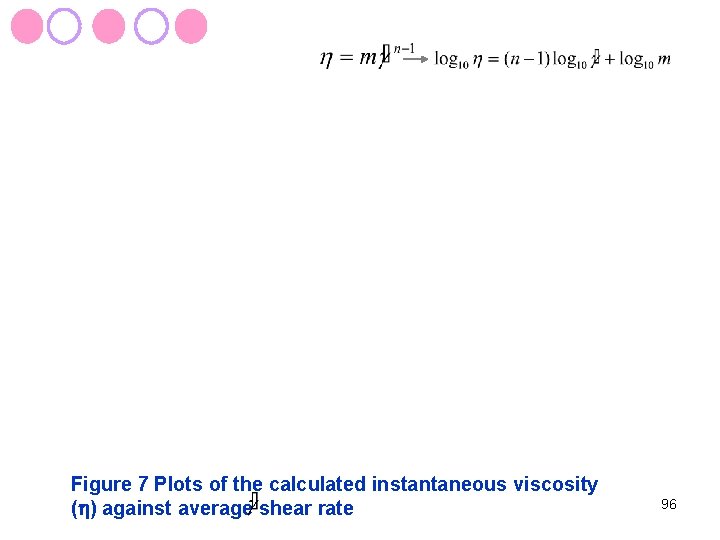
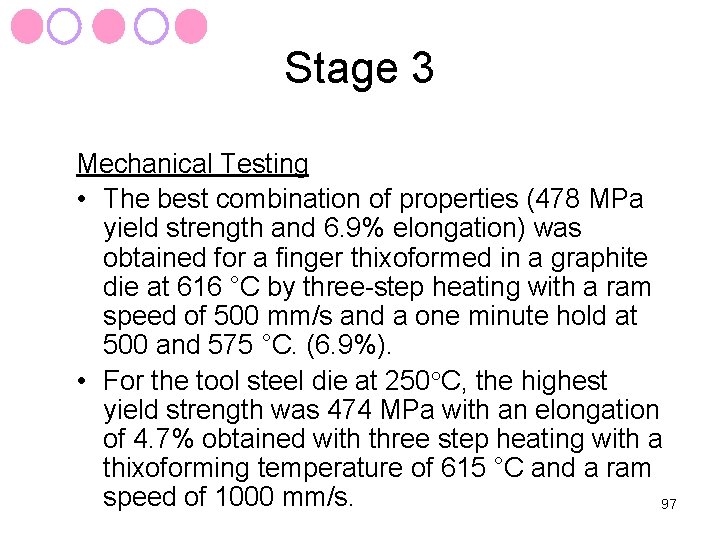
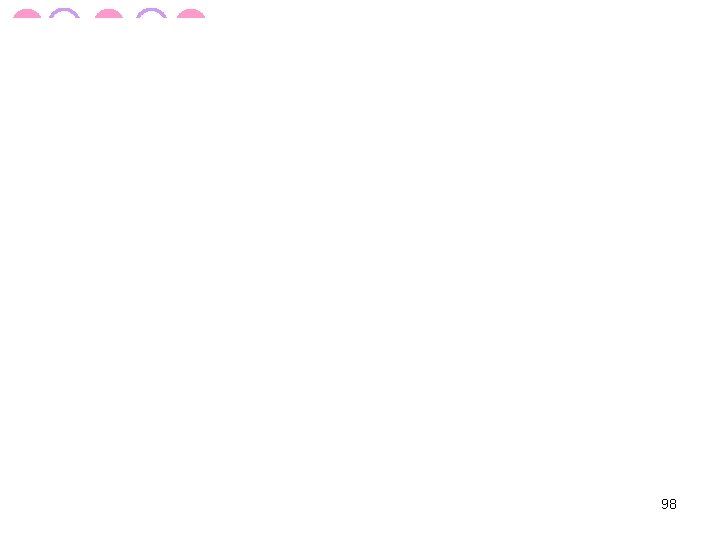
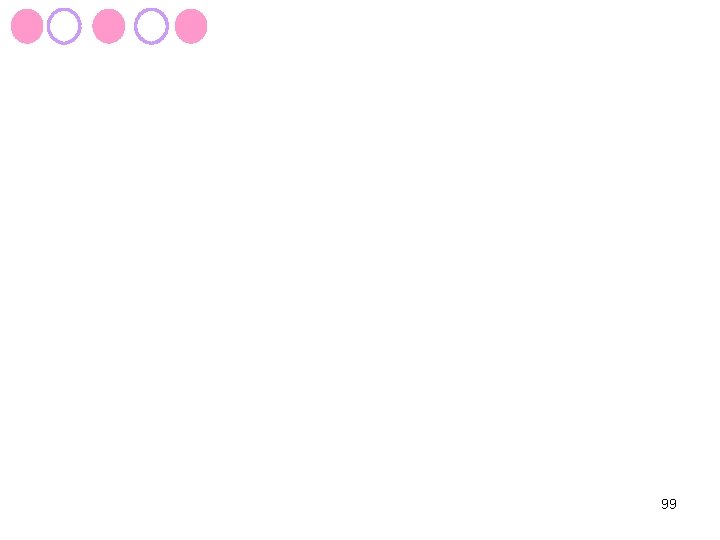
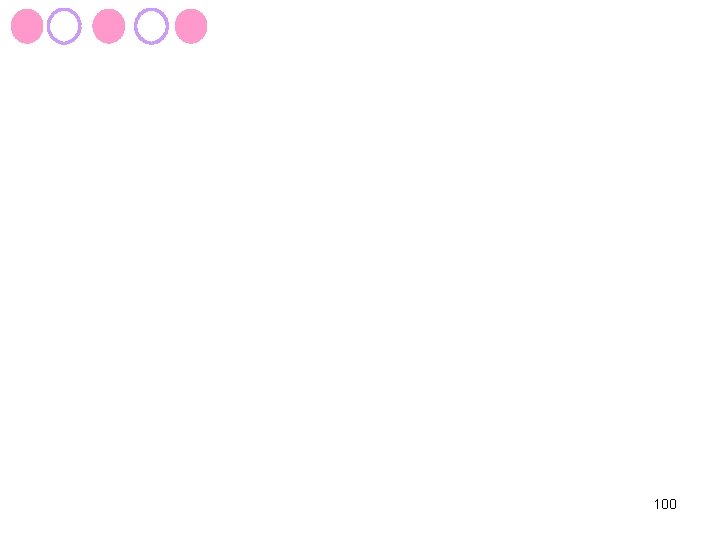
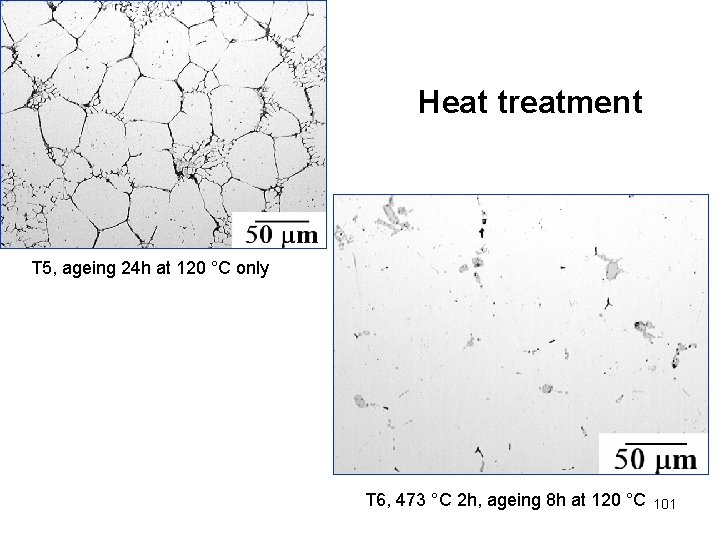
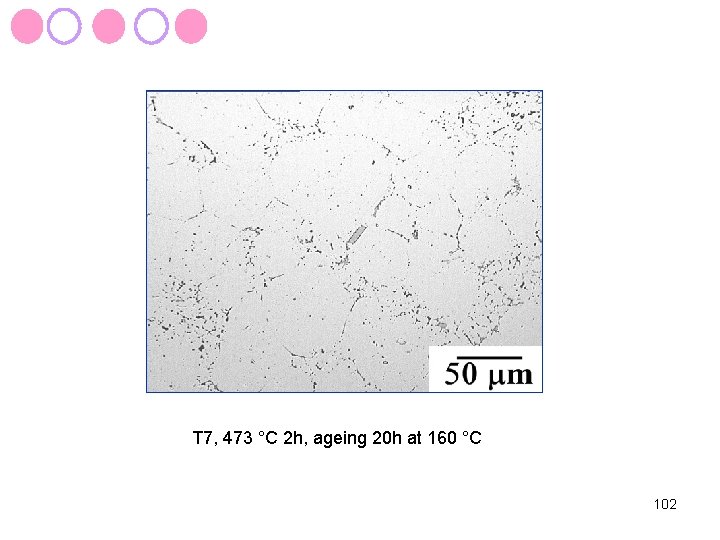
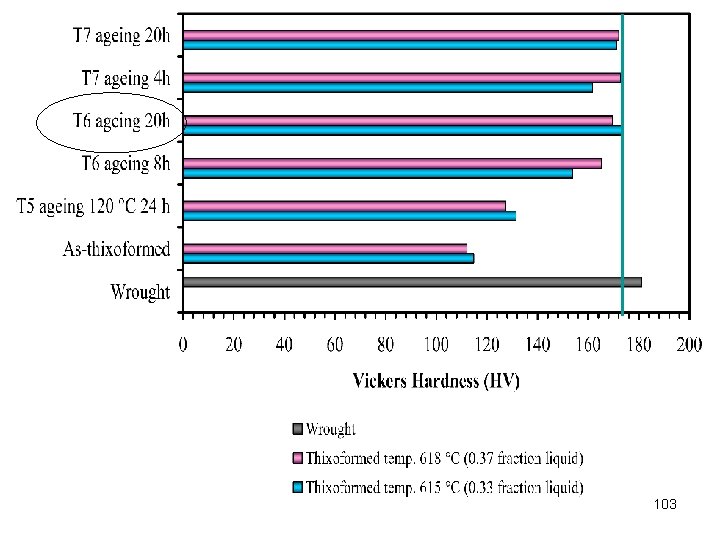
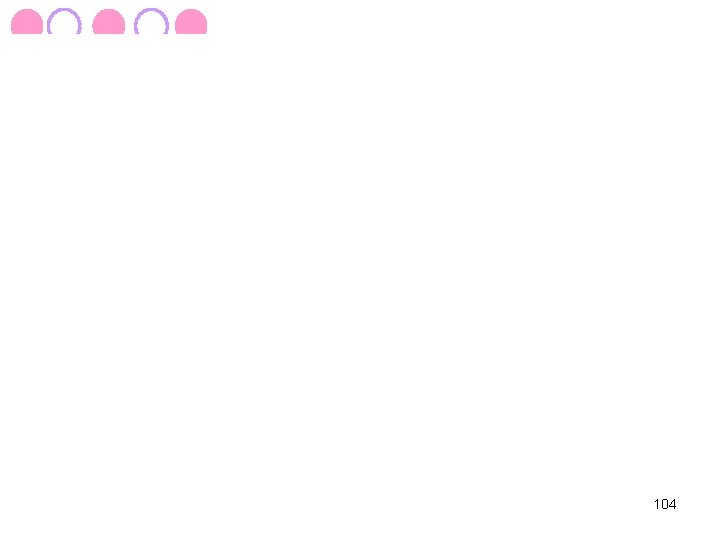
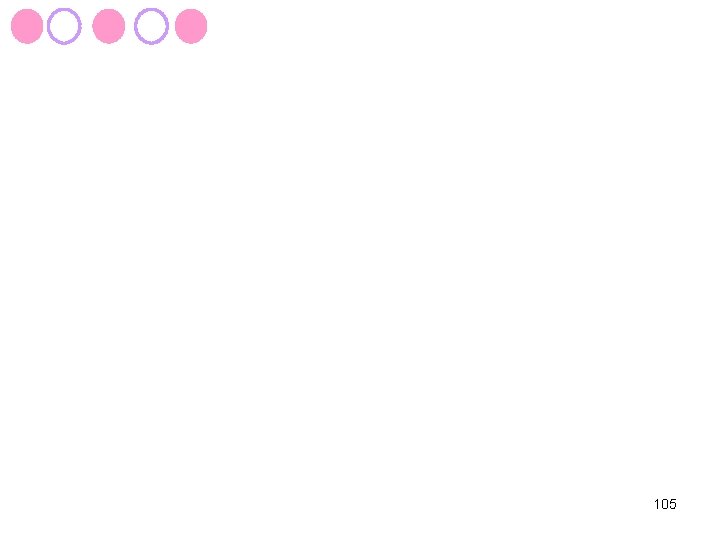
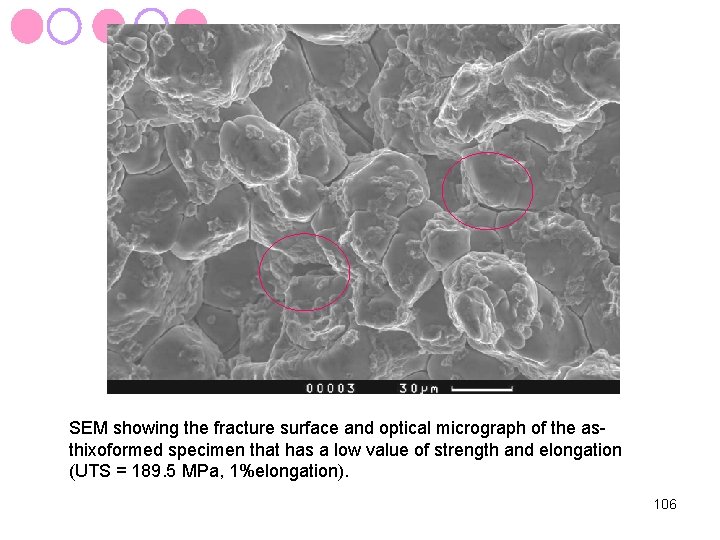
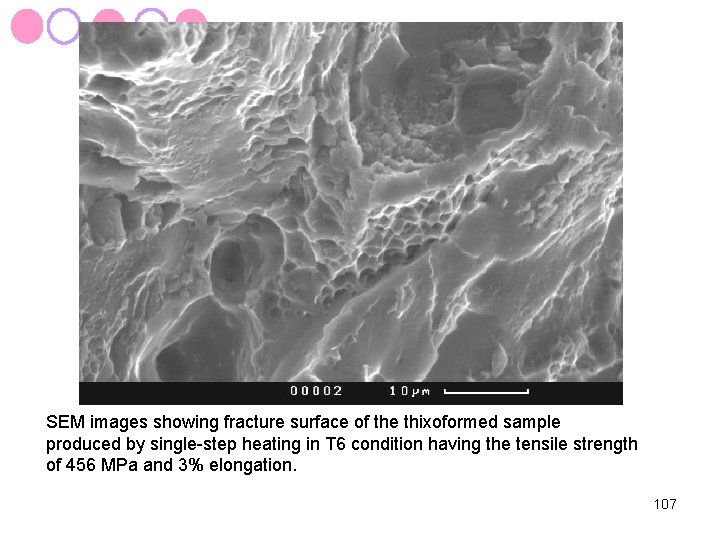
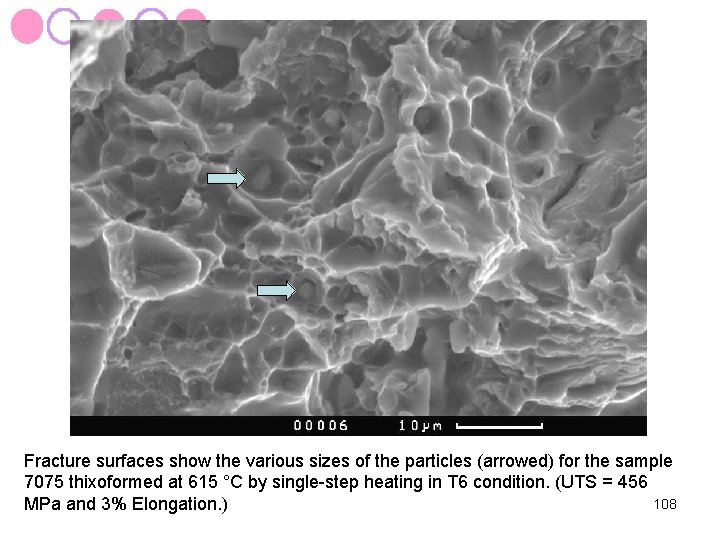
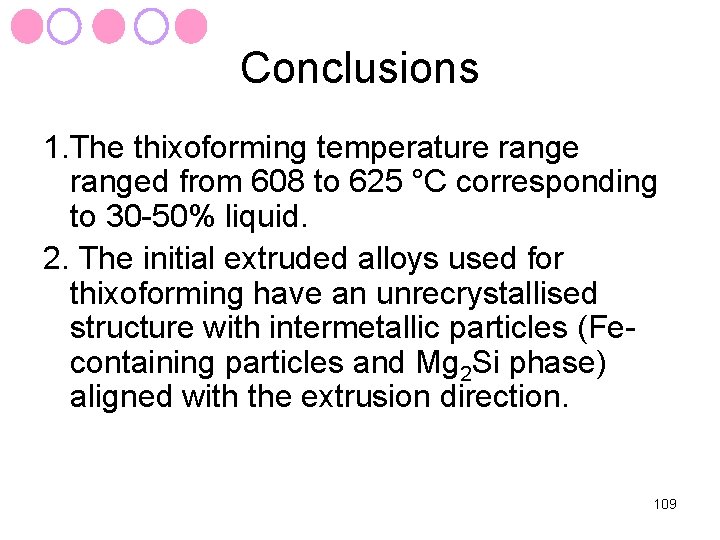
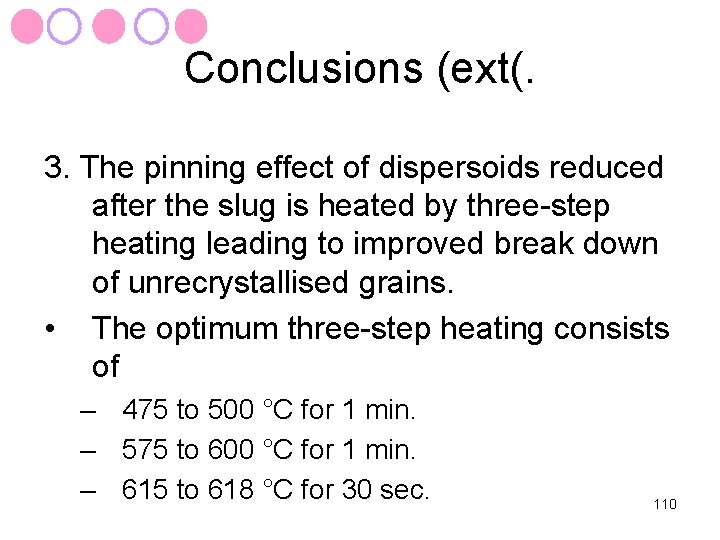
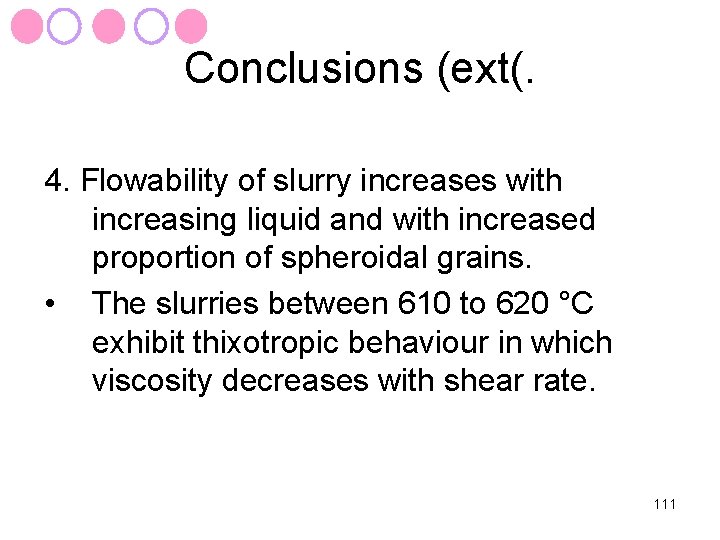
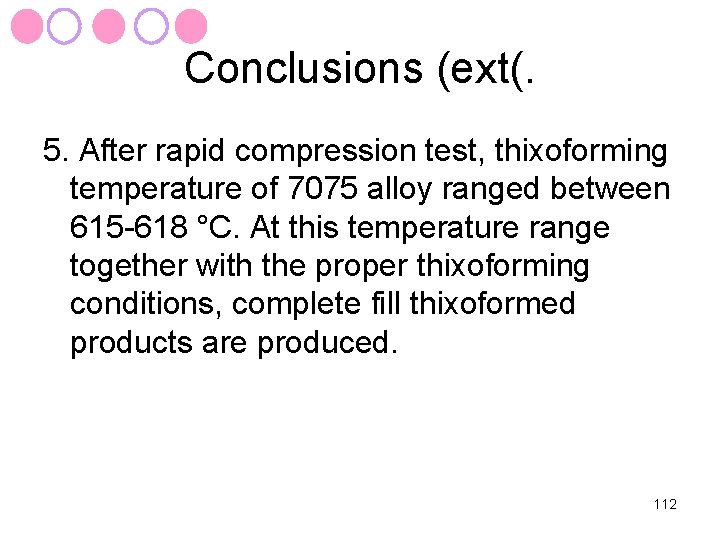
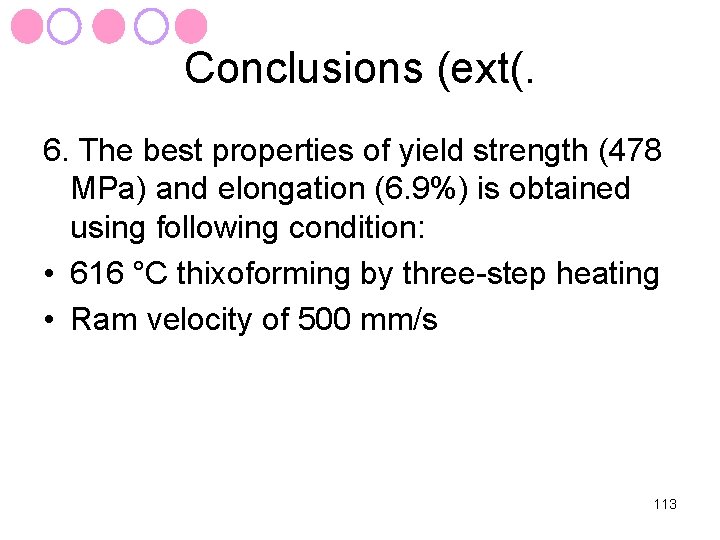
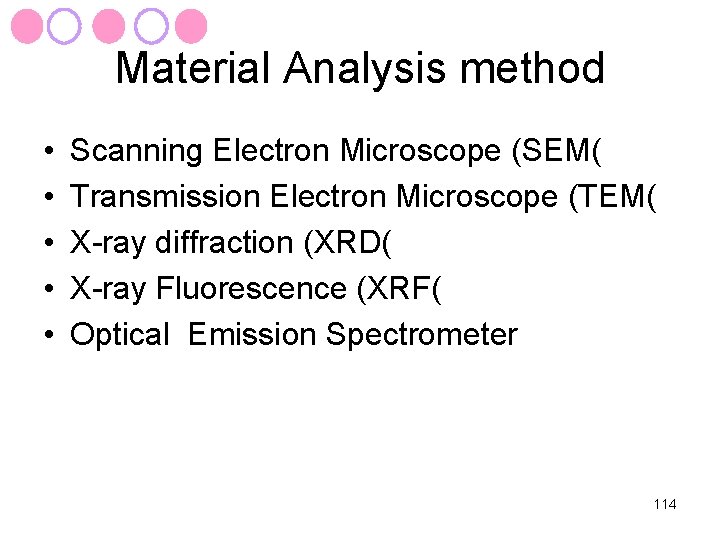
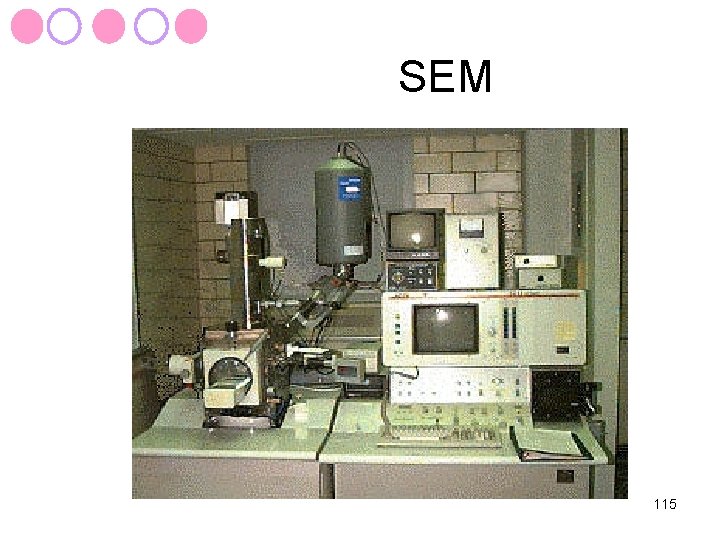
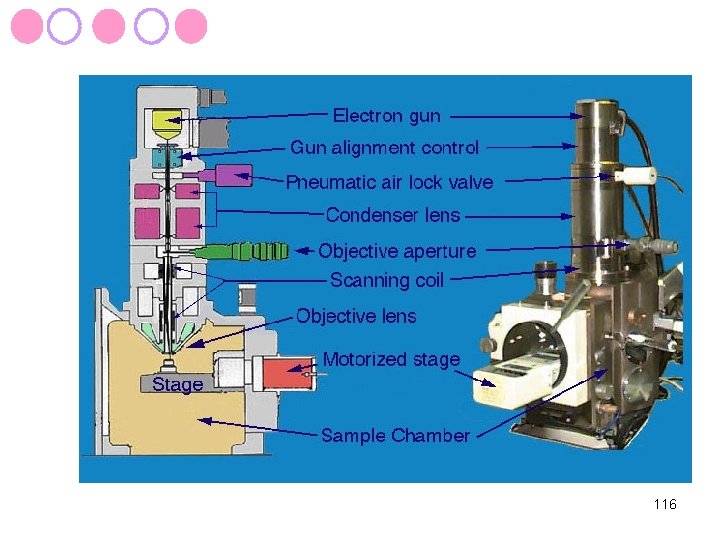
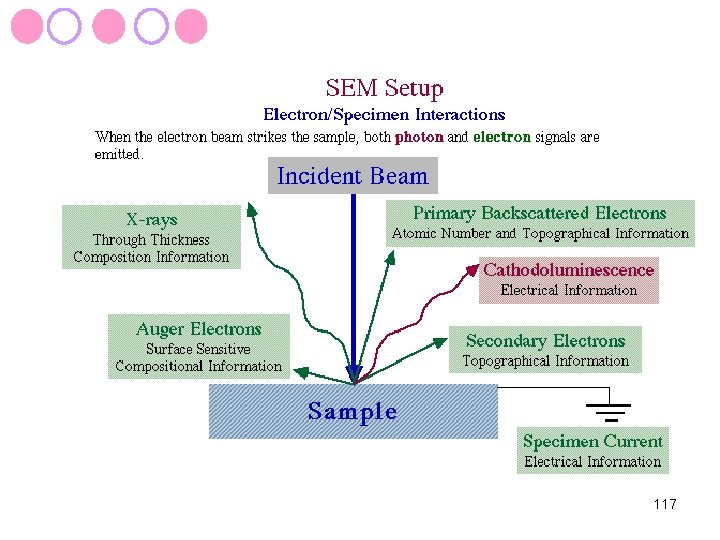
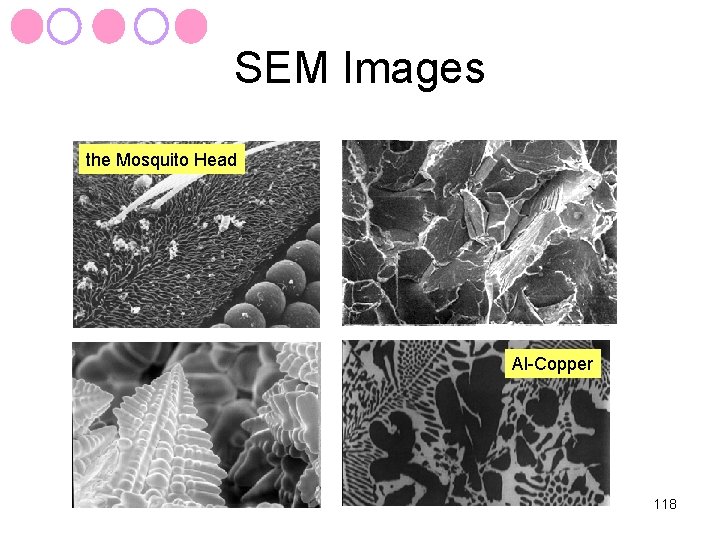
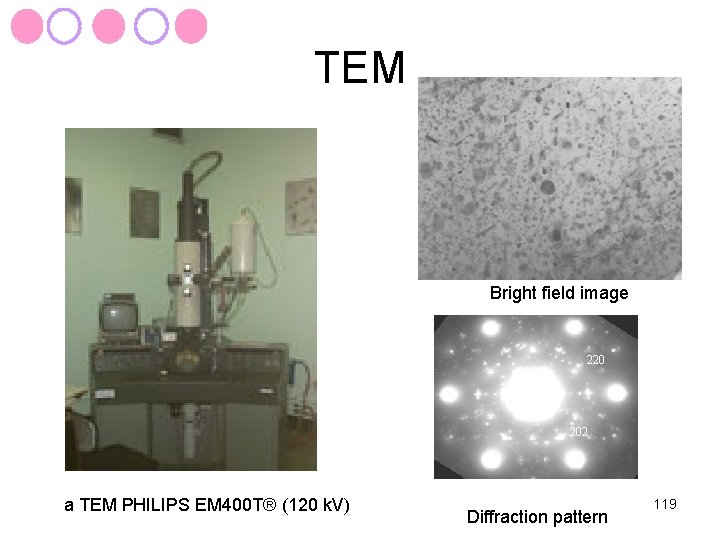
- Slides: 119
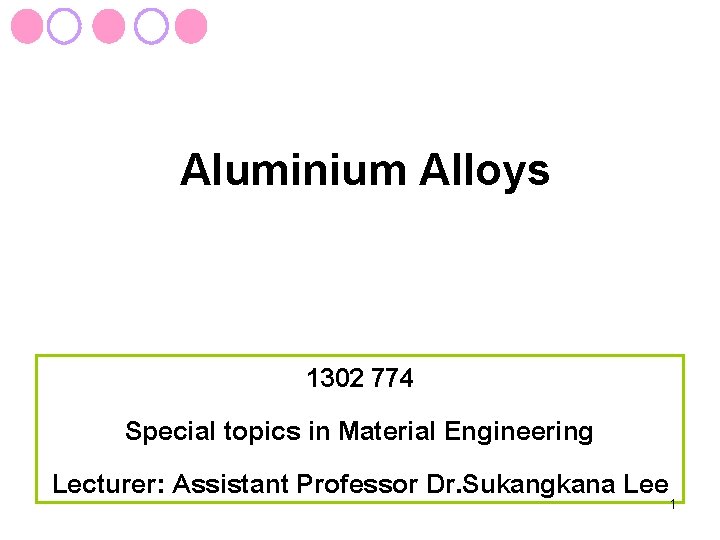
Aluminium Alloys 1302 774 Special topics in Material Engineering Lecturer: Assistant Professor Dr. Sukangkana Lee 1
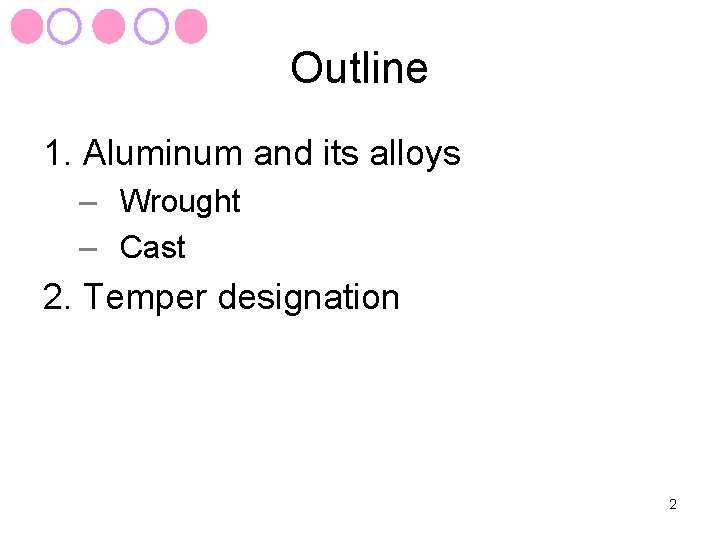
Outline 1. Aluminum and its alloys – Wrought – Cast 2. Temper designation 2
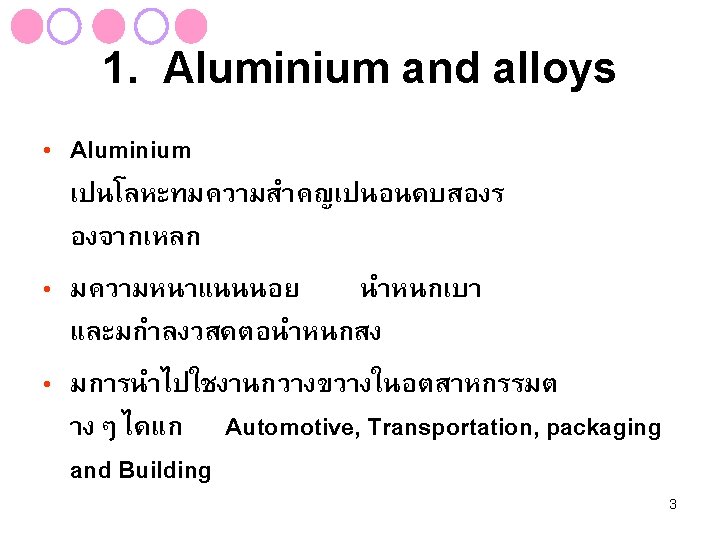
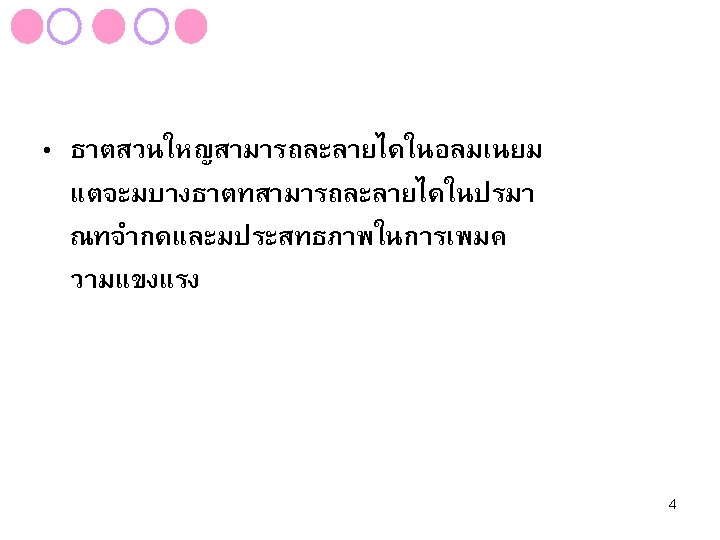
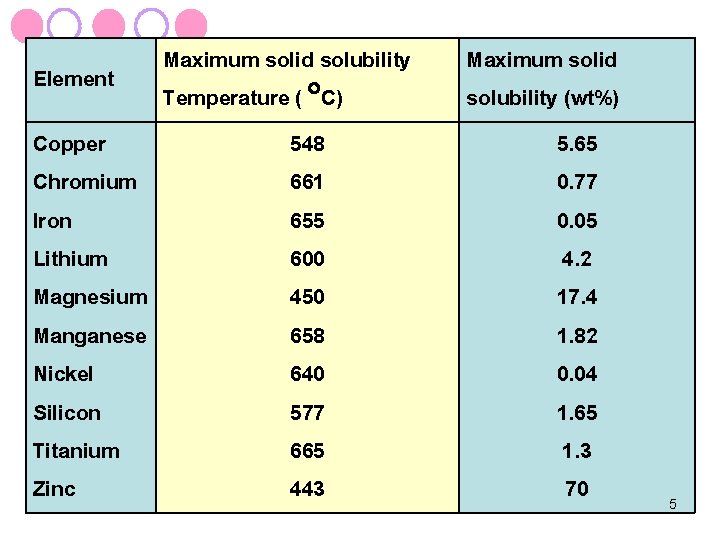
Maximum solid solubility Element Temperature ( C) Copper 548 Chromium 661 Iron 655 Lithium 600 Magnesium 450 Manganese 658 Nickel 640 Silicon 577 Titanium 665 Zinc 443 Maximum solid solubility (wt%) 5. 65 0. 77 0. 05 4. 2 17. 4 1. 82 0. 04 1. 65 1. 3 70 5
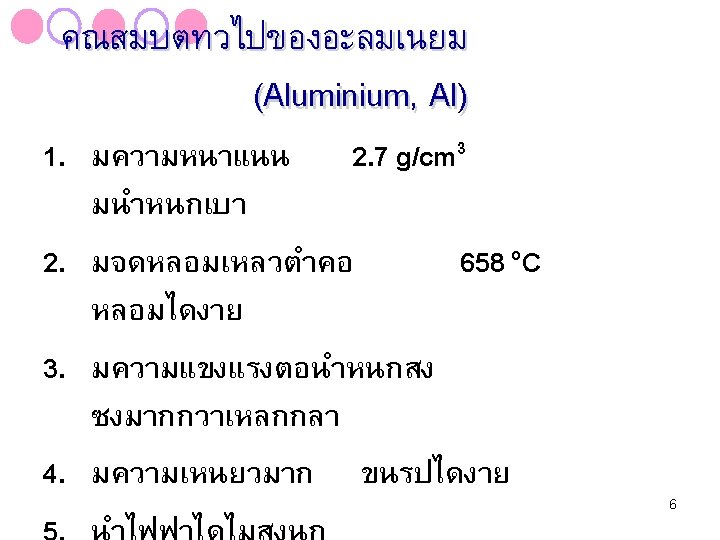
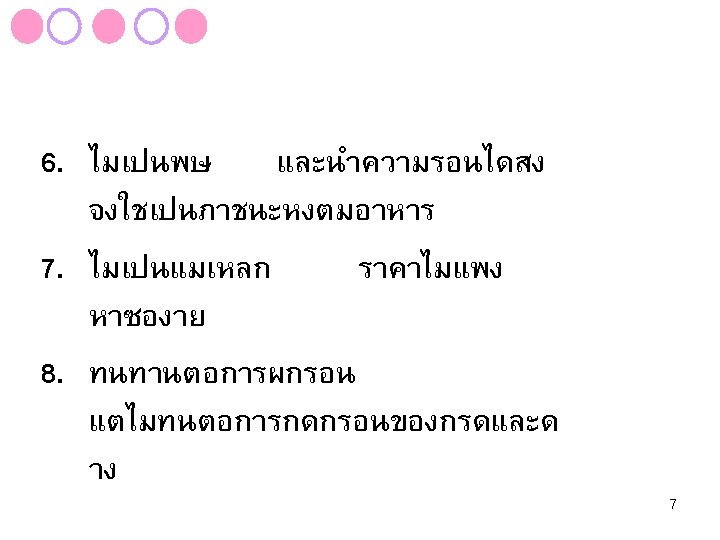
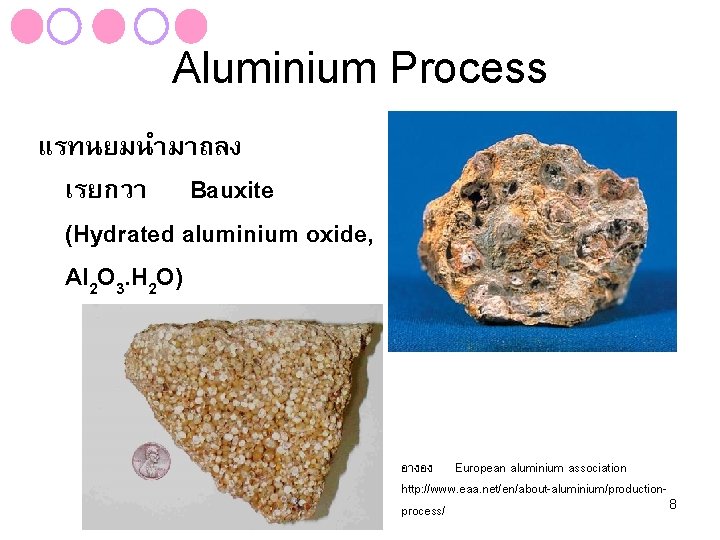
Aluminium Process แรทนยมนำมาถลง เรยกวา Bauxite (Hydrated aluminium oxide, Al 2 O 3. H 2 O) อางอง European aluminium association http: //www. eaa. net/en/about-aluminium/production 8 process/
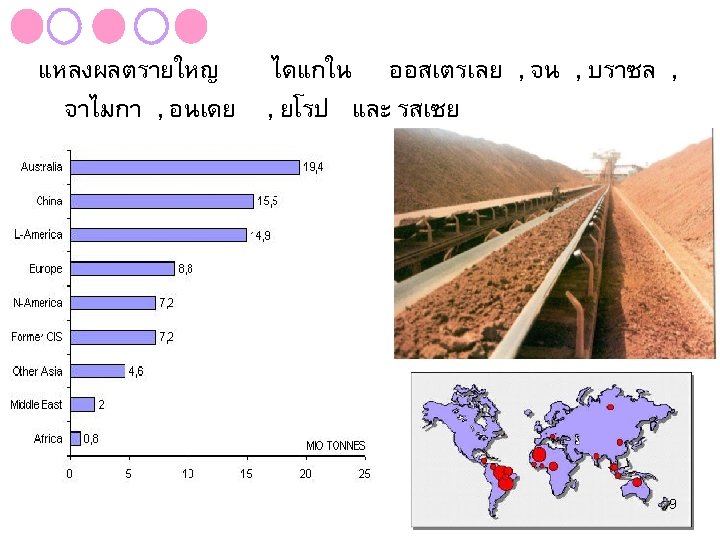
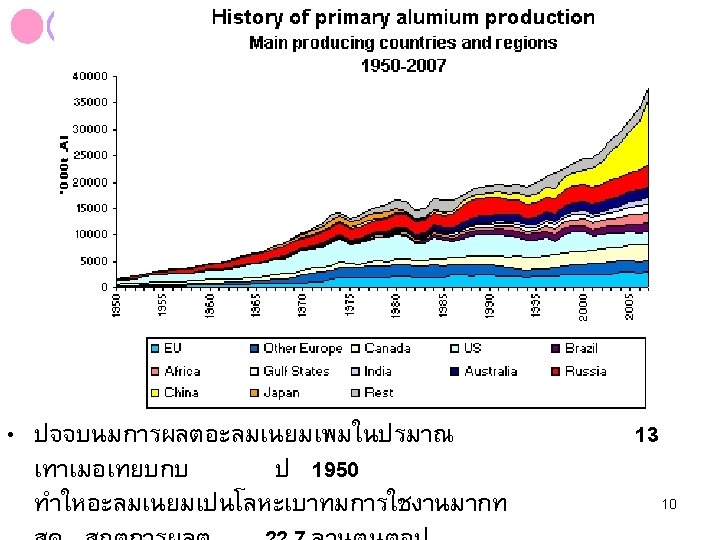
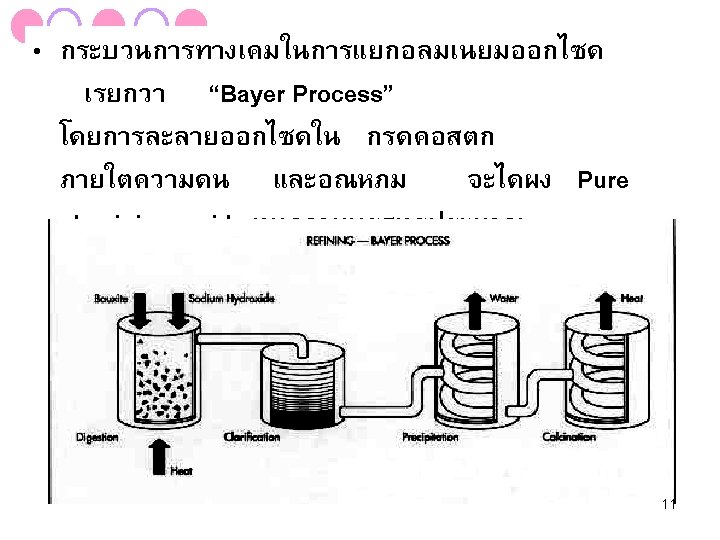
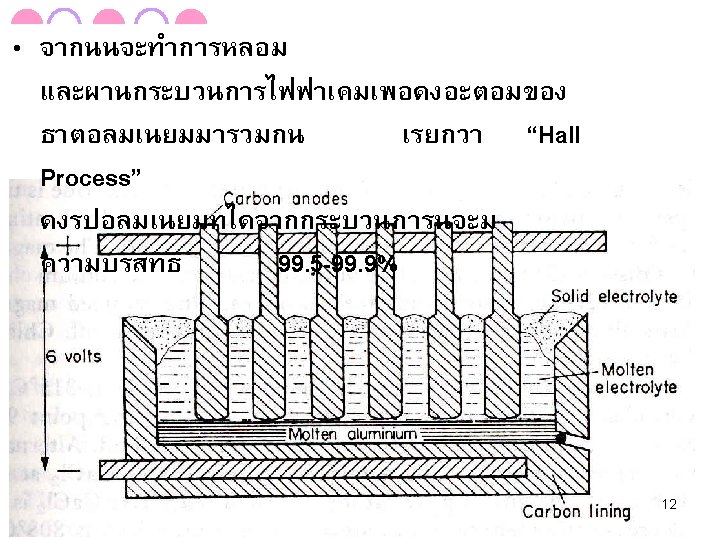
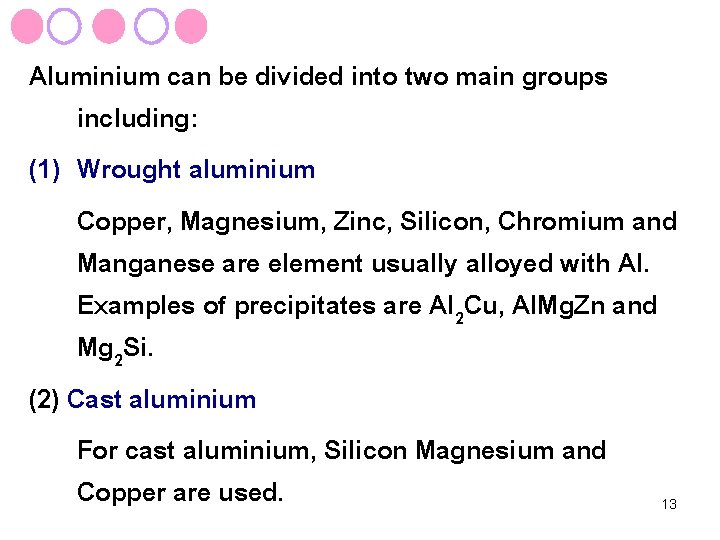
Aluminium can be divided into two main groups including: (1) Wrought aluminium Copper, Magnesium, Zinc, Silicon, Chromium and Manganese are element usually alloyed with Al. Examples of precipitates are Al 2 Cu, Al. Mg. Zn and Mg 2 Si. (2) Cast aluminium For cast aluminium, Silicon Magnesium and Copper are used. 13
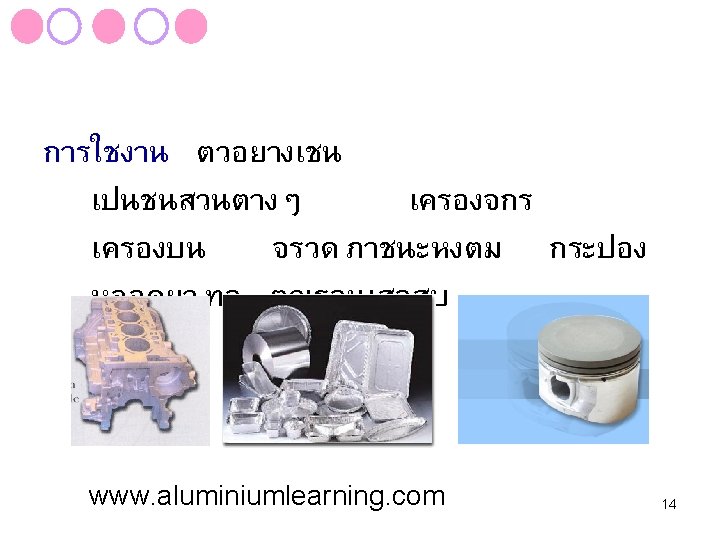
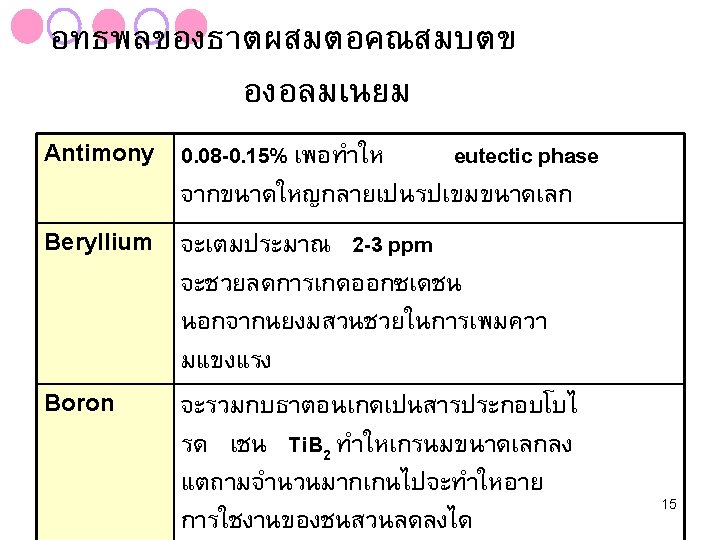
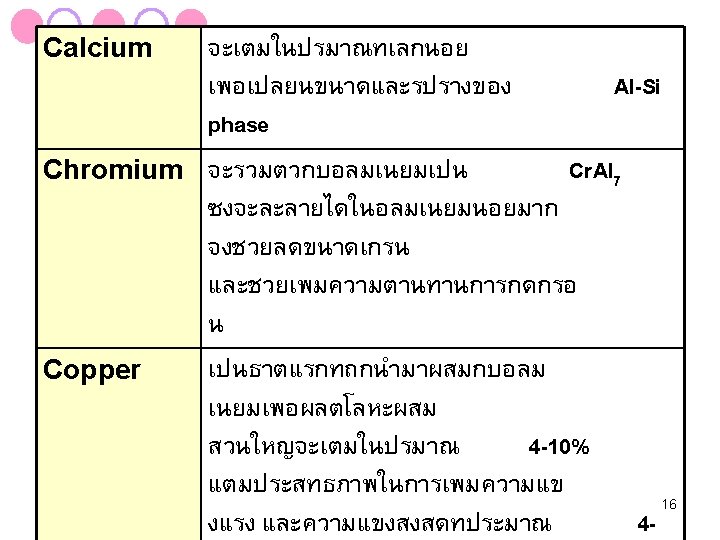
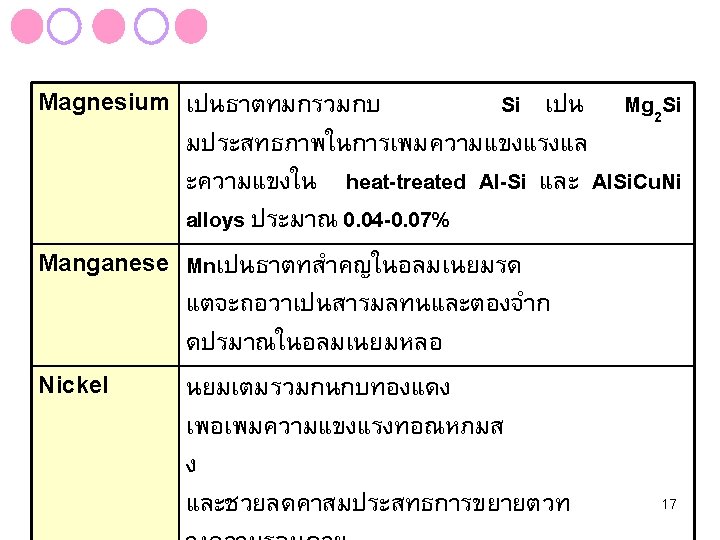
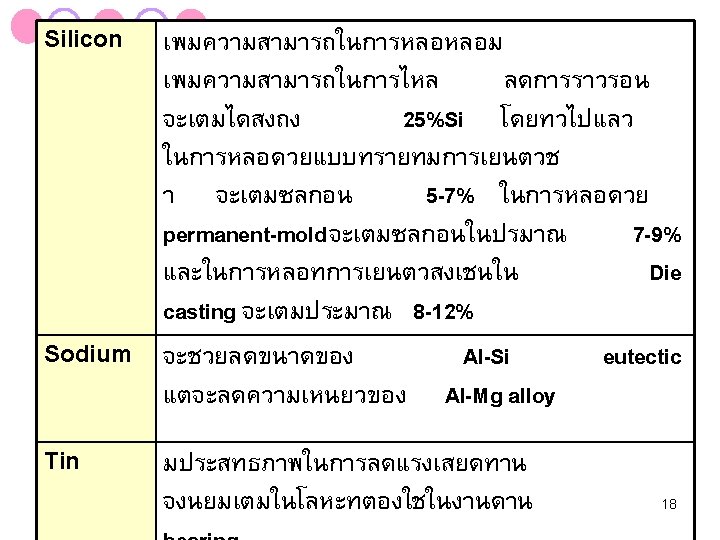
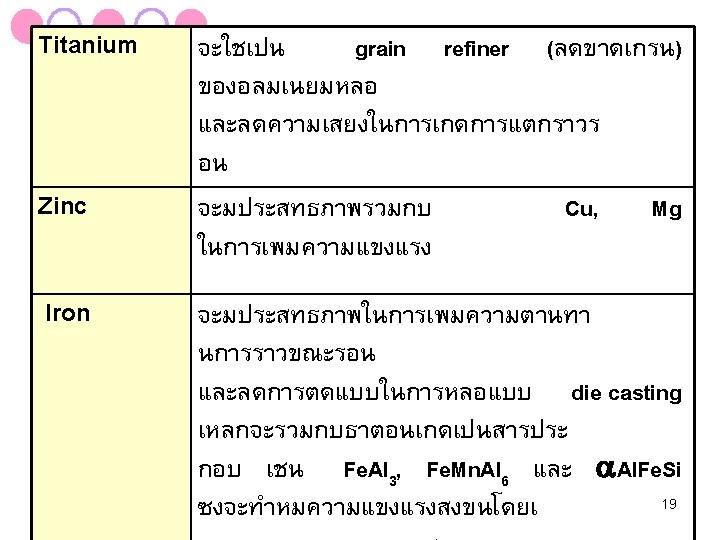
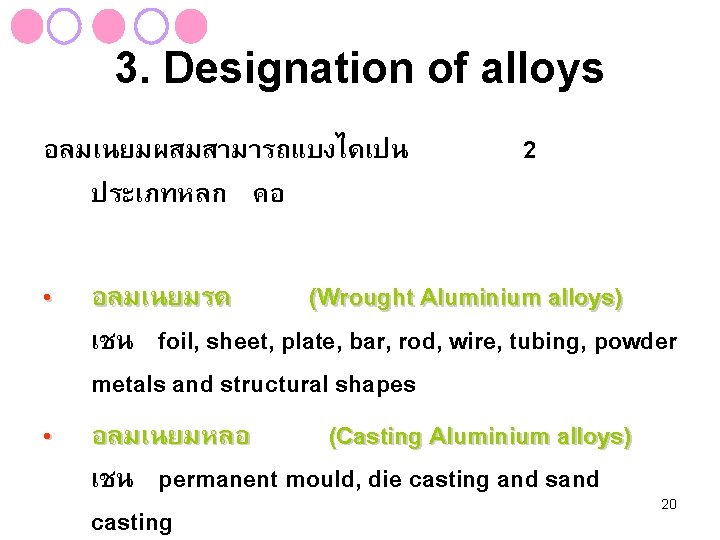
3. Designation of alloys อลมเนยมผสมสามารถแบงไดเปน ประเภทหลก คอ • • 2 อลมเนยมรด (Wrought Aluminium alloys) เชน foil, sheet, plate, bar, rod, wire, tubing, powder metals and structural shapes อลมเนยมหลอ (Casting Aluminium alloys) เชน permanent mould, die casting and sand casting 20
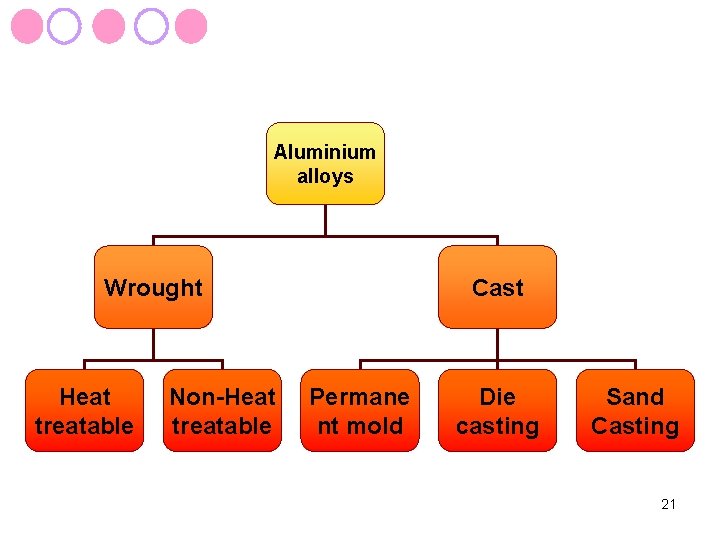
Aluminium alloys Wrought Heat treatable Non-Heat treatable Cast Permane nt mold Die casting Sand Casting 21
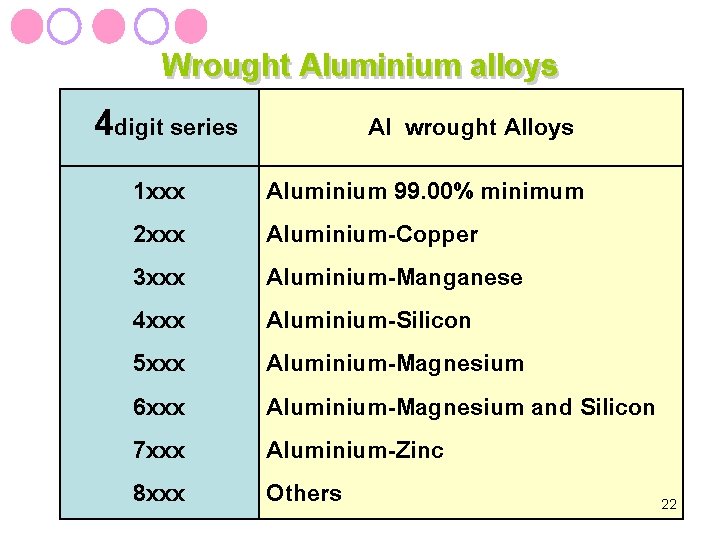
Wrought Aluminium alloys 4 digit series Al wrought Alloys 1 xxx 2 xxx 3 xxx 4 xxx 5 xxx 6 xxx 7 xxx 8 xxx Aluminium 99. 00% minimum Aluminium-Copper Aluminium-Manganese Aluminium-Silicon Aluminium-Magnesium and Silicon Aluminium-Zinc Others 22
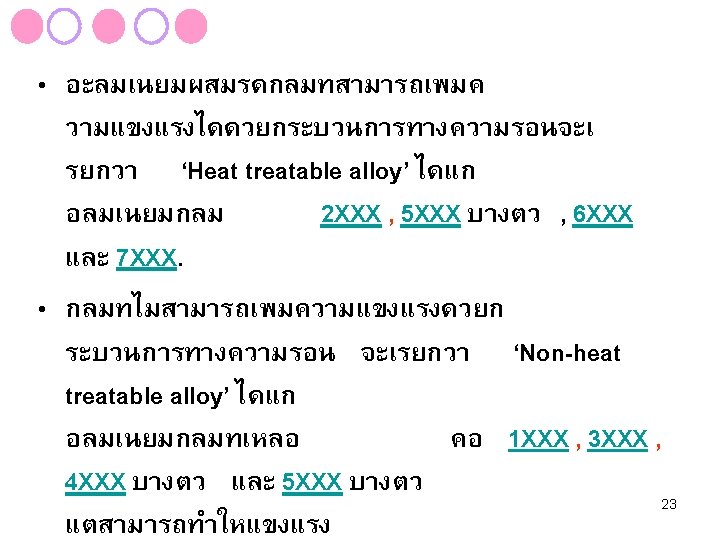
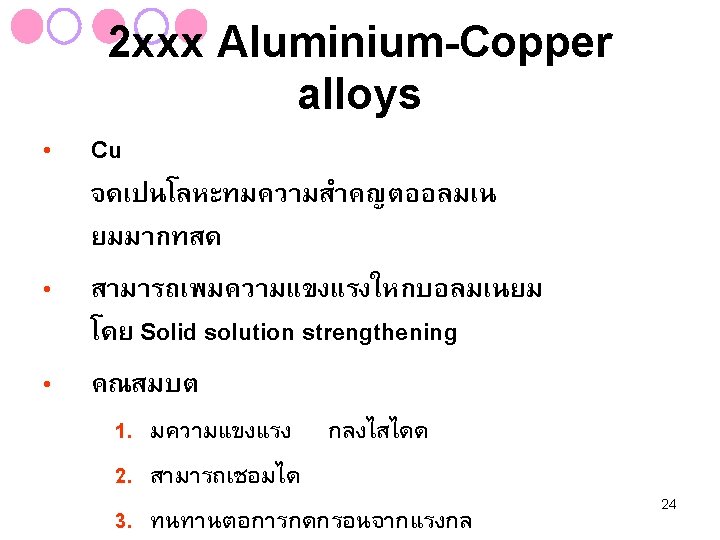
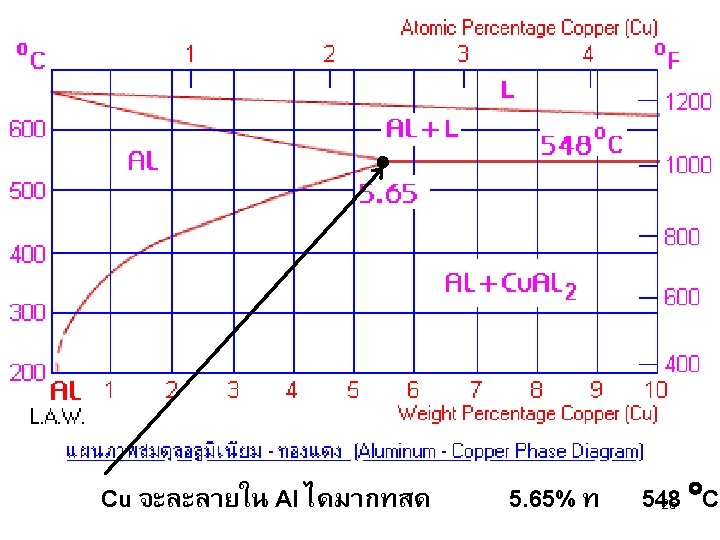
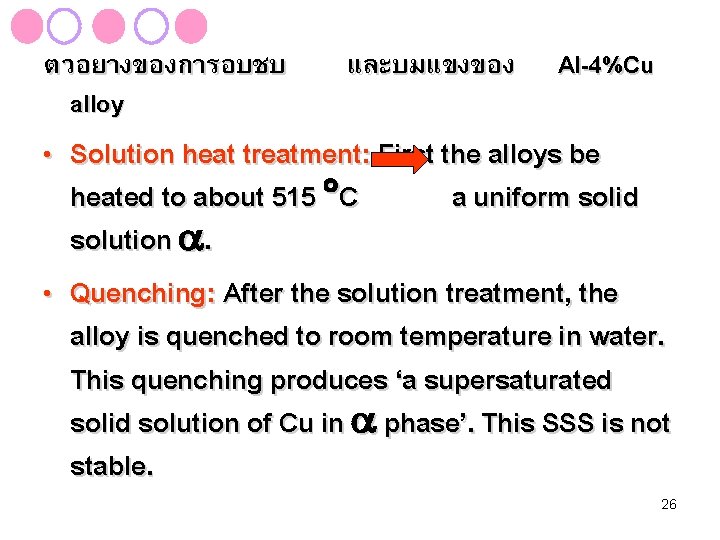
ตวอยางของการอบชบ alloy และบมแขงของ Al-4%Cu • Solution heat treatment: First the alloys be heated to about 515 C a uniform solid solution . • Quenching: After the solution treatment, the alloy is quenched to room temperature in water. This quenching produces ‘a supersaturated solid solution of Cu in phase’. This SSS is not stable. 26
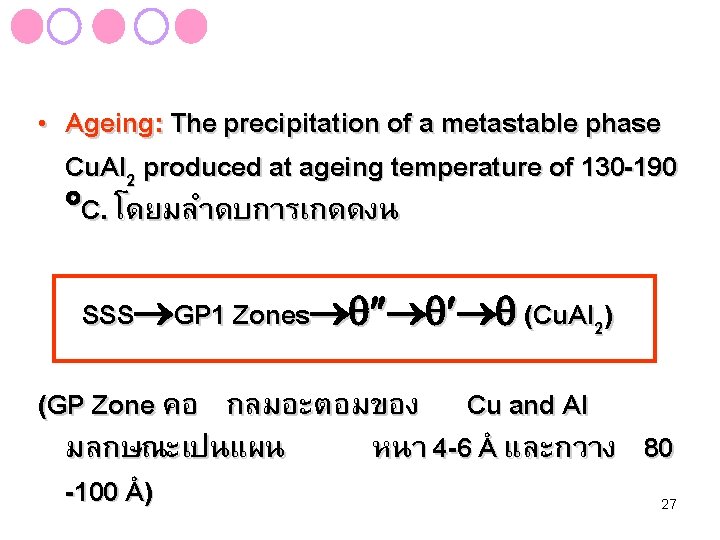
• Ageing: The precipitation of a metastable phase Cu. Al 2 produced at ageing temperature of 130 -190 C. โดยมลำดบการเกดดงน SSS GP 1 Zones (Cu. Al 2) (GP Zone คอ กลมอะตอมของ Cu and Al มลกษณะเปนแผน หนา 4 -6 Å และกวาง 80 -100 Å) 27
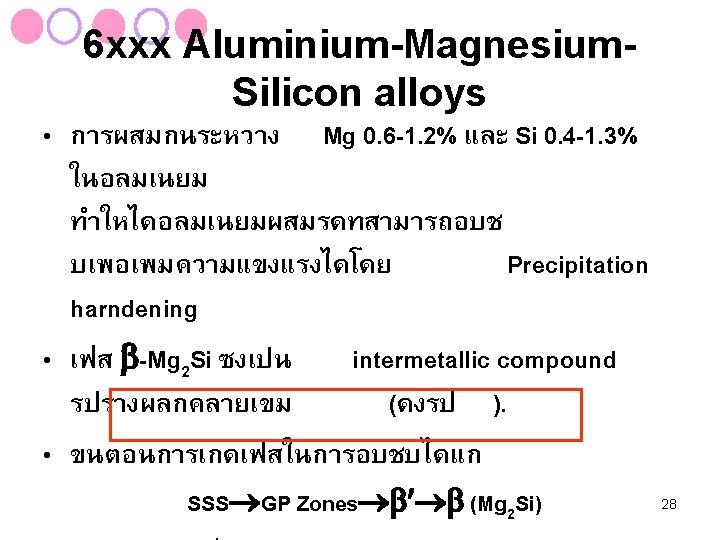
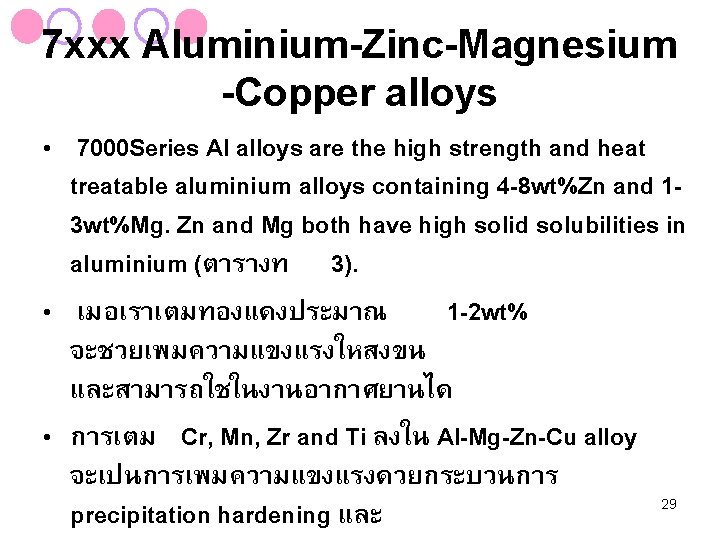
7 xxx Aluminium-Zinc-Magnesium -Copper alloys • 7000 Series Al alloys are the high strength and heat treatable aluminium alloys containing 4 -8 wt%Zn and 13 wt%Mg. Zn and Mg both have high solid solubilities in aluminium (ตารางท 3). • เมอเราเตมทองแดงประมาณ 1 -2 wt% จะชวยเพมความแขงแรงใหสงขน และสามารถใชในงานอากาศยานได • การเตม Cr, Mn, Zr and Ti ลงใน Al-Mg-Zn-Cu alloy จะเปนการเพมความแขงแรงดวยกระบวนการ precipitation hardening และ 29
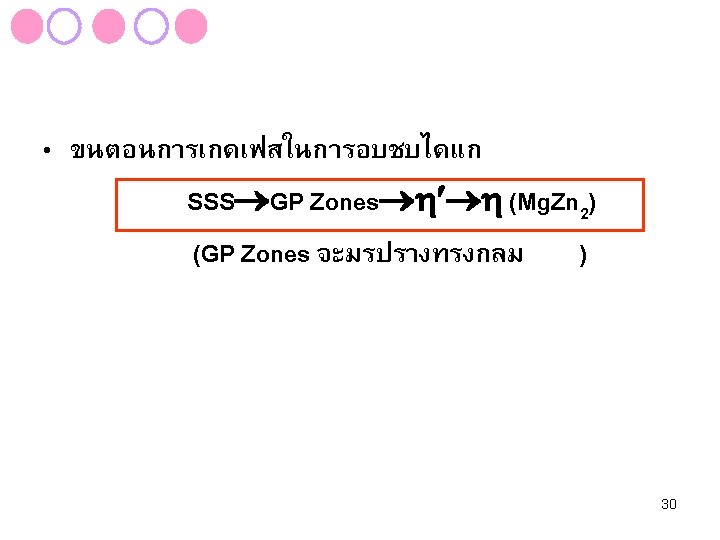
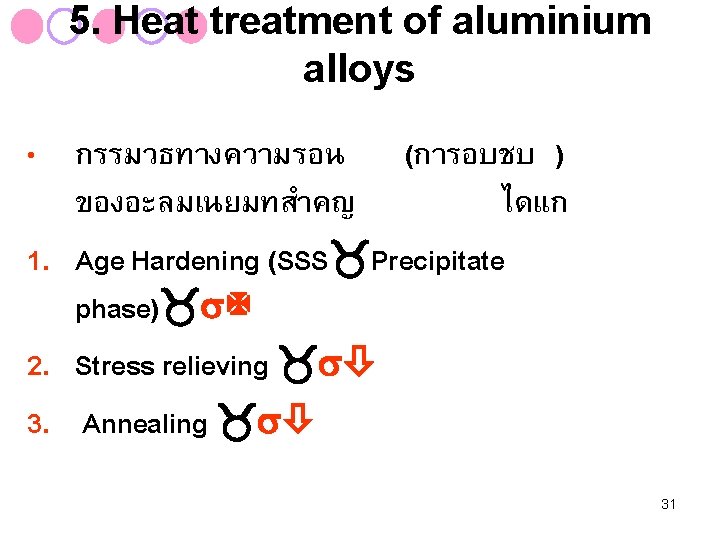
5. Heat treatment of aluminium alloys • กรรมวธทางความรอน (การอบชบ ) ของอะลมเนยมทสำคญ ไดแก 1. Age Hardening (SSS Precipitate phase) 2. Stress relieving 3. Annealing 31
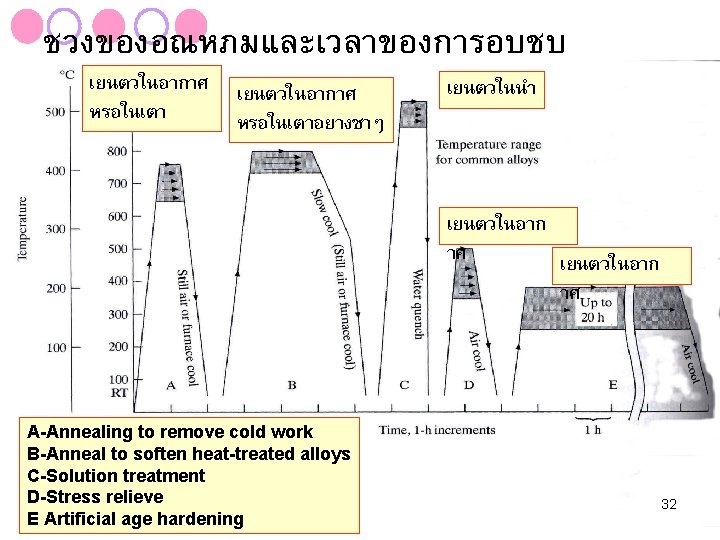
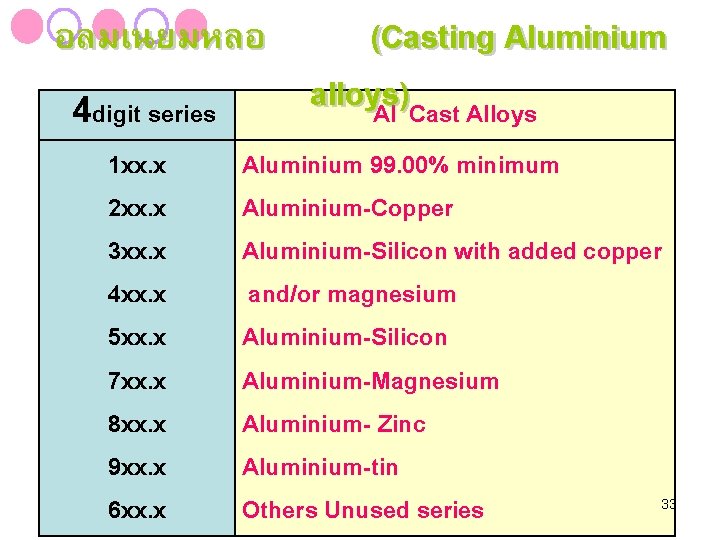
อลมเนยมหลอ 4 digit series 1 xx. x 2 xx. x 3 xx. x 4 xx. x 5 xx. x 7 xx. x 8 xx. x 9 xx. x 6 xx. x (Casting Aluminium alloys) Al Cast Alloys Aluminium 99. 00% minimum Aluminium-Copper Aluminium-Silicon with added copper and/or magnesium Aluminium-Silicon Aluminium-Magnesium Aluminium- Zinc Aluminium-tin Others Unused series 33
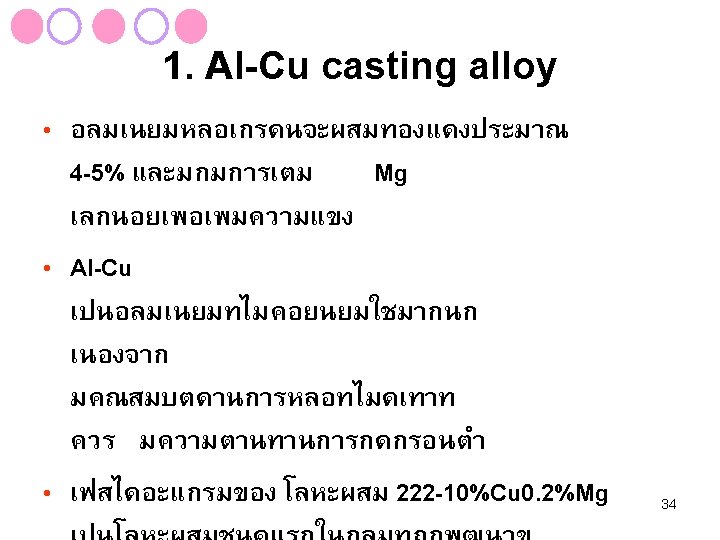
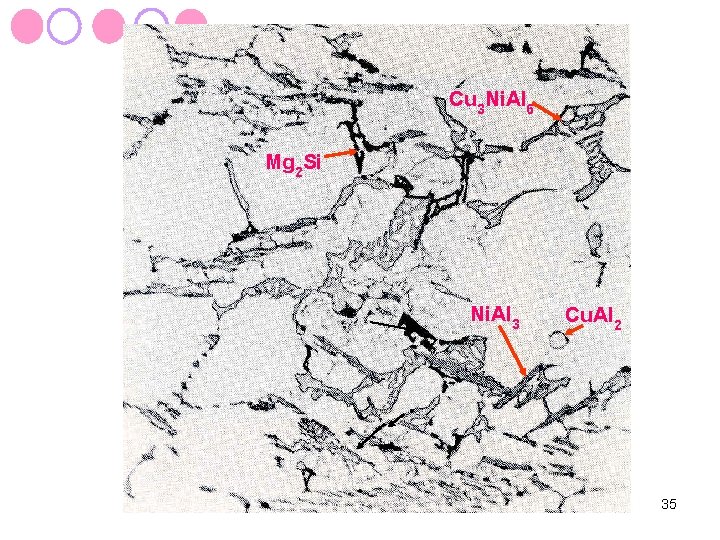
Cu 3 Ni. Al 6 Mg 2 Si Ni. Al 3 Cu. Al 2 35
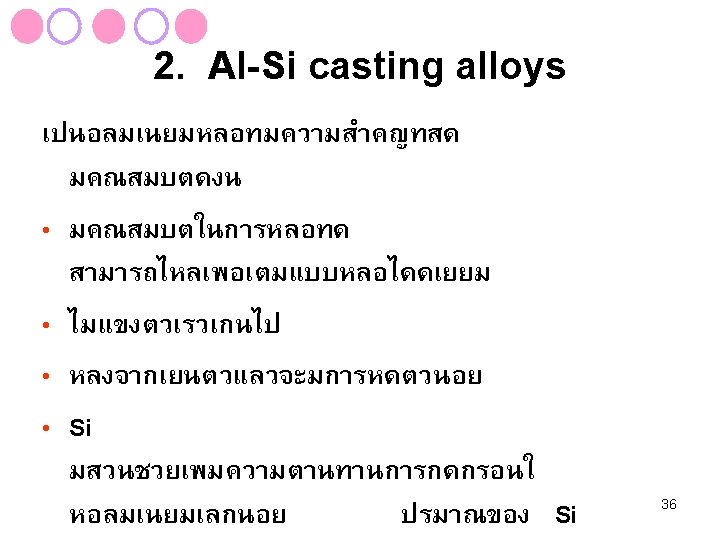
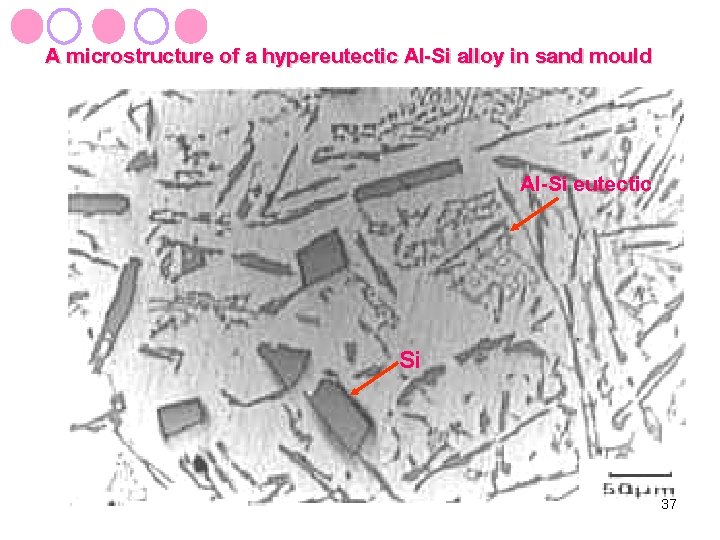
A microstructure of a hypereutectic Al-Si alloy in sand mould Al-Si eutectic Si 37
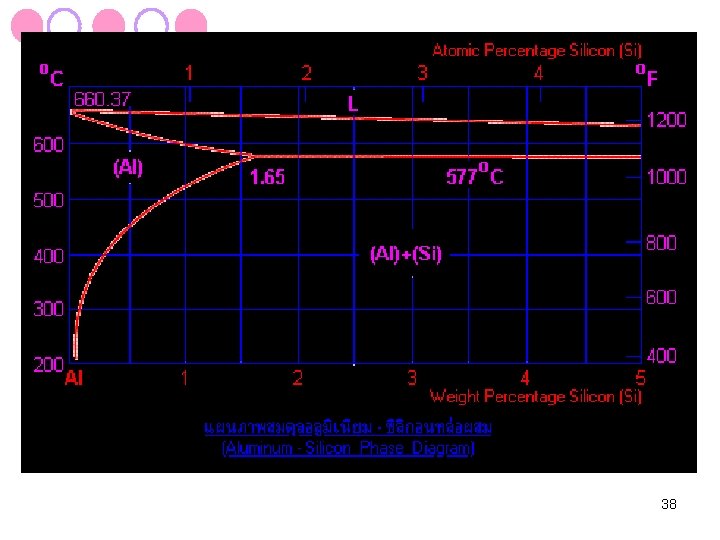
38
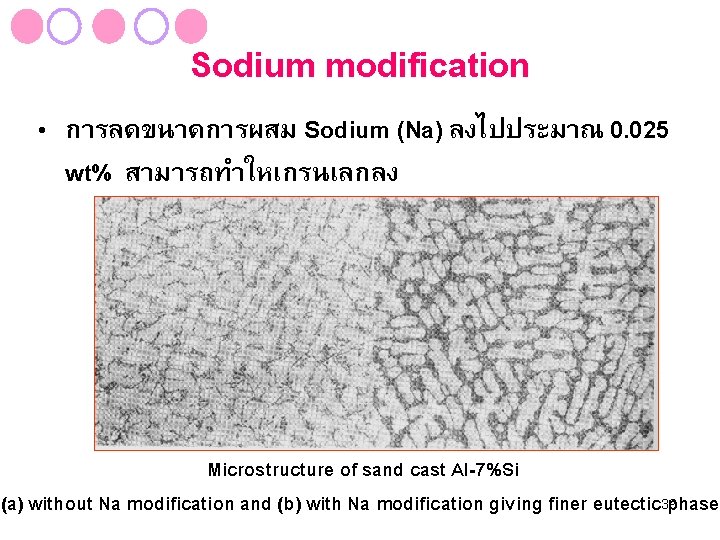
Sodium modification • การลดขนาดการผสม Sodium (Na) ลงไปประมาณ 0. 025 wt% สามารถทำใหเกรนเลกลง Microstructure of sand cast Al-7%Si (a) without Na modification and (b) with Na modification giving finer eutectic 39 phase.
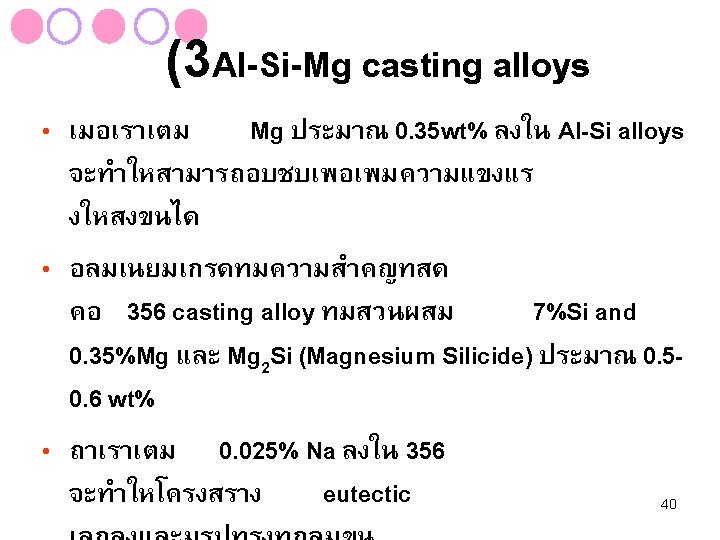
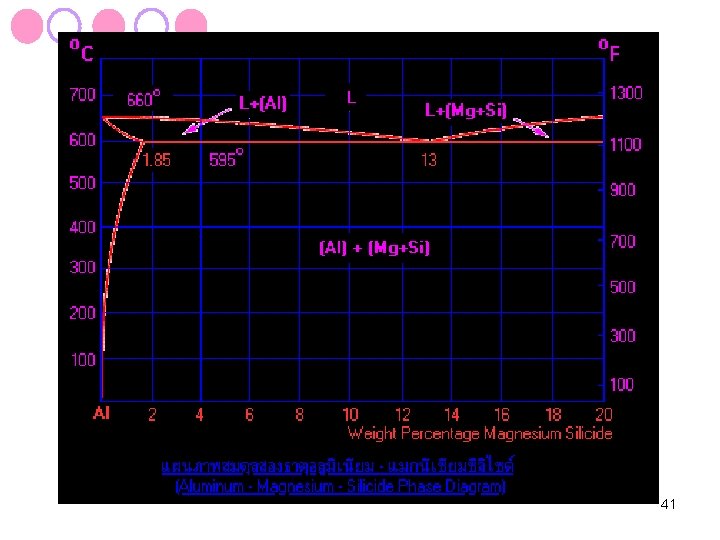
41
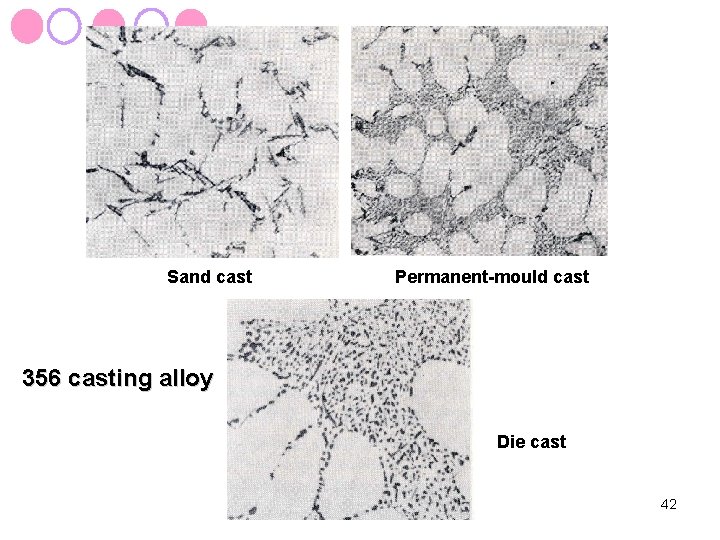
Sand cast Permanent-mould cast 356 casting alloy Die cast 42
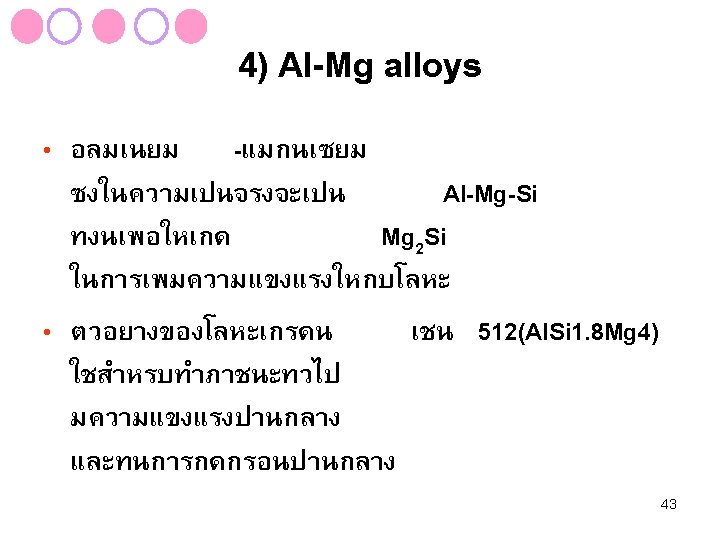
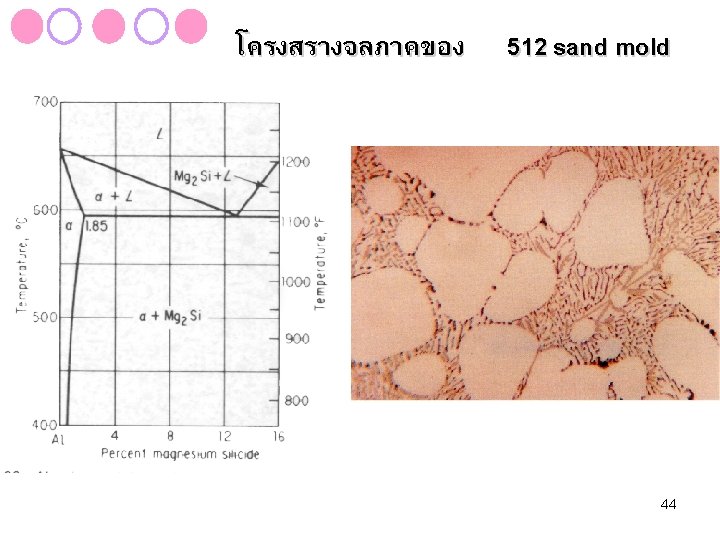
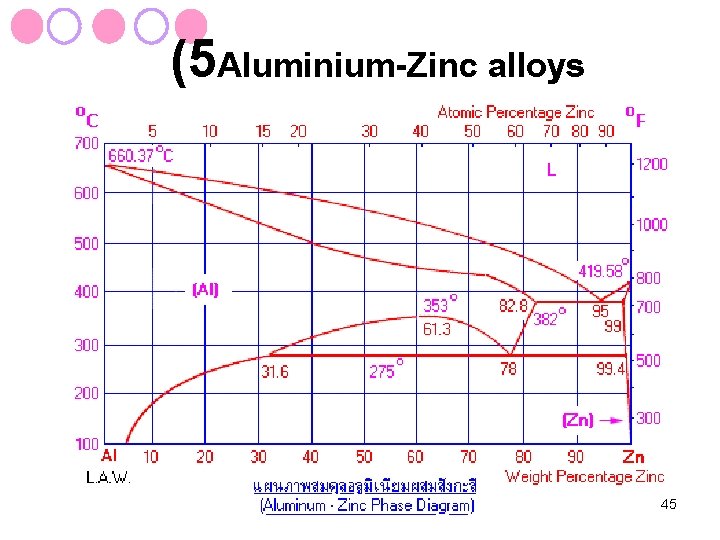
(5 Aluminium-Zinc alloys 45
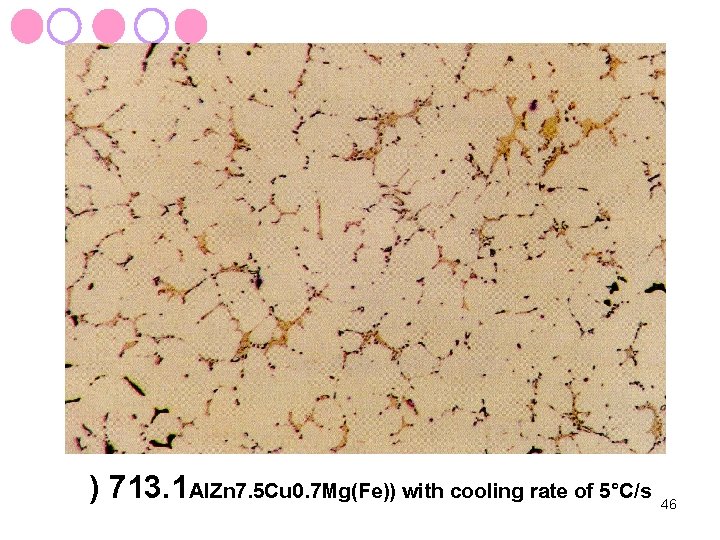
) 713. 1 Al. Zn 7. 5 Cu 0. 7 Mg(Fe)) with cooling rate of 5°C/s 46
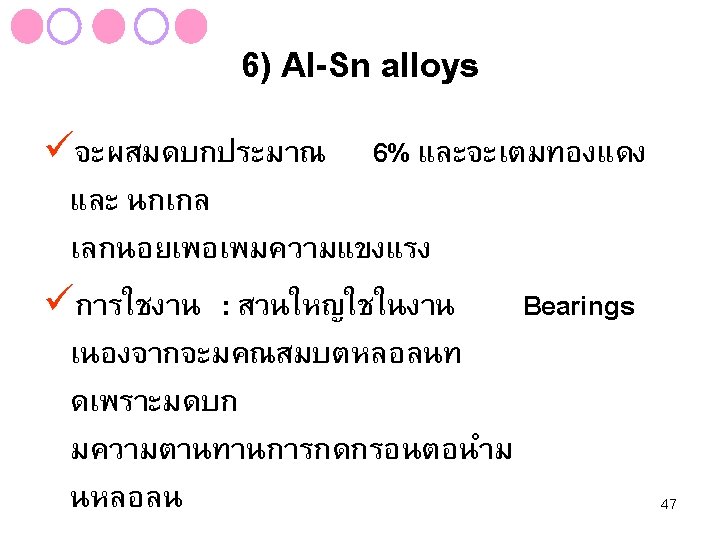
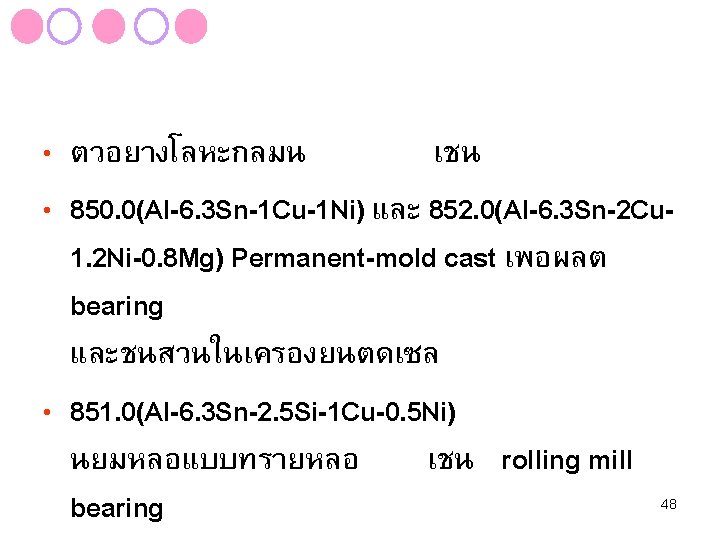
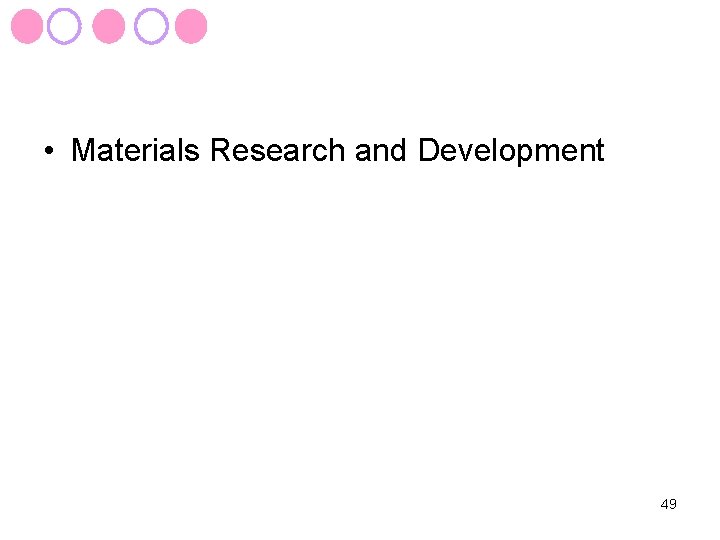
• Materials Research and Development 49
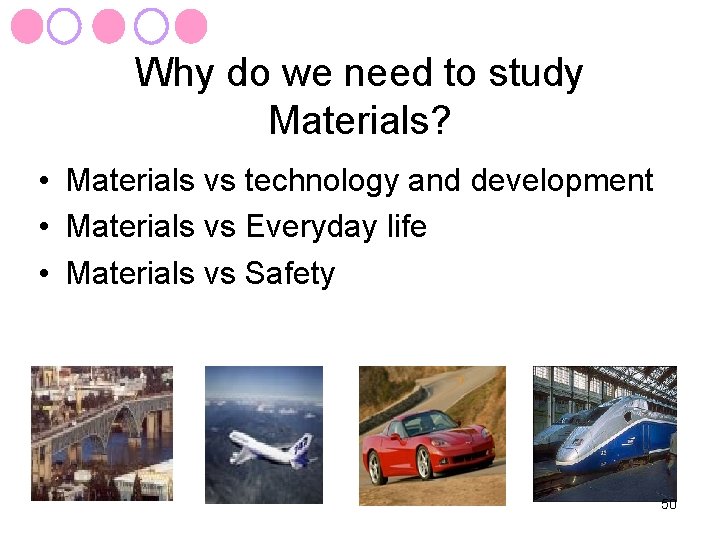
Why do we need to study Materials? • Materials vs technology and development • Materials vs Everyday life • Materials vs Safety 50
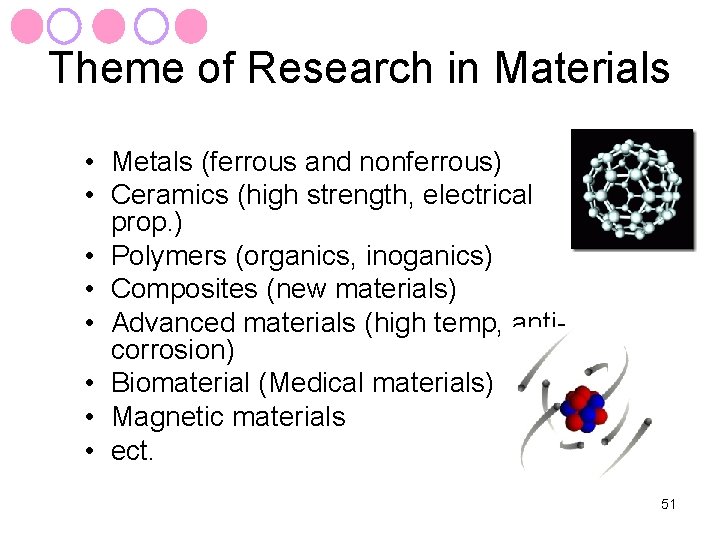
Theme of Research in Materials • Metals (ferrous and nonferrous) • Ceramics (high strength, electrical prop. ) • Polymers (organics, inoganics) • Composites (new materials) • Advanced materials (high temp, anticorrosion) • Biomaterial (Medical materials) • Magnetic materials • ect. 51
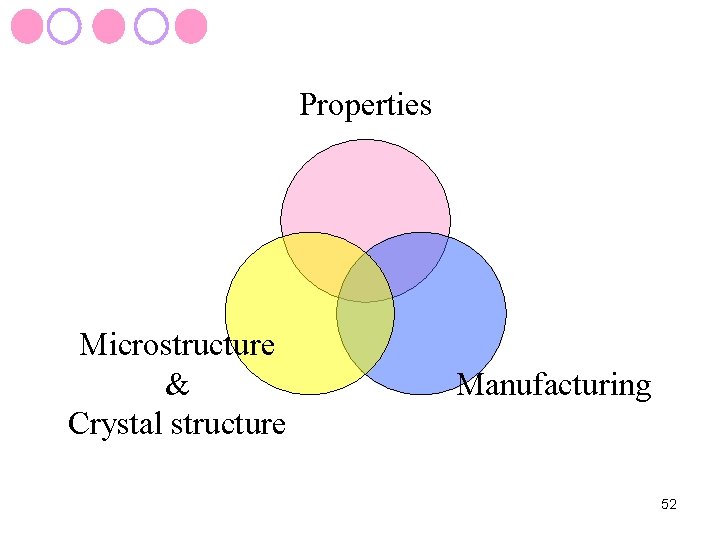
Properties Microstructure & Crystal structure Manufacturing 52
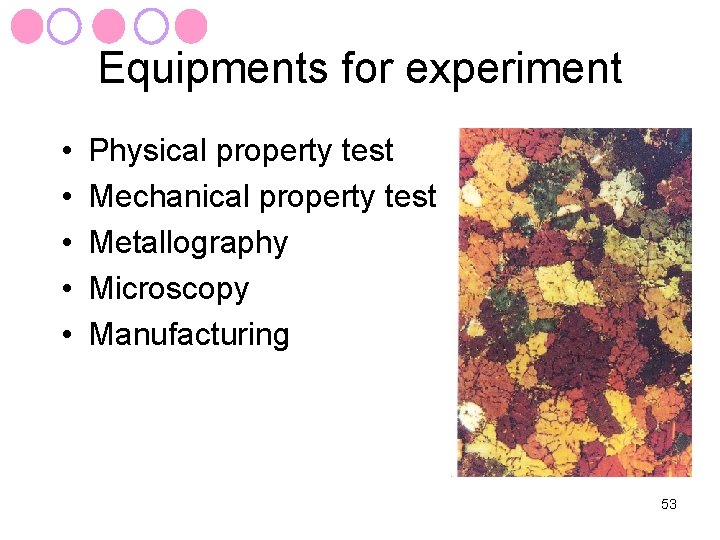
Equipments for experiment • • • Physical property test Mechanical property test Metallography Microscopy Manufacturing 53
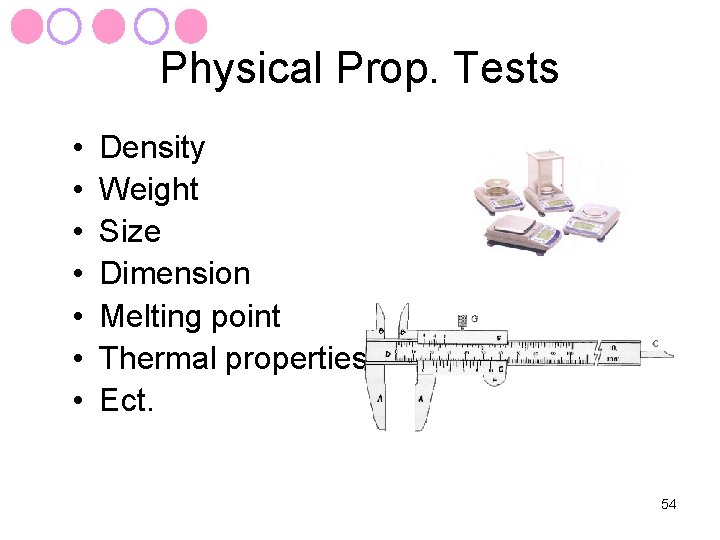
Physical Prop. Tests • • Density Weight Size Dimension Melting point Thermal properties Ect. 54
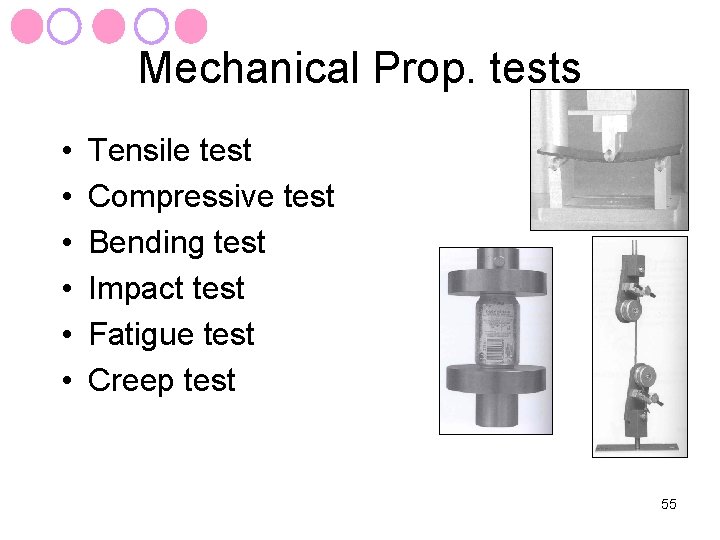
Mechanical Prop. tests • • • Tensile test Compressive test Bending test Impact test Fatigue test Creep test 55
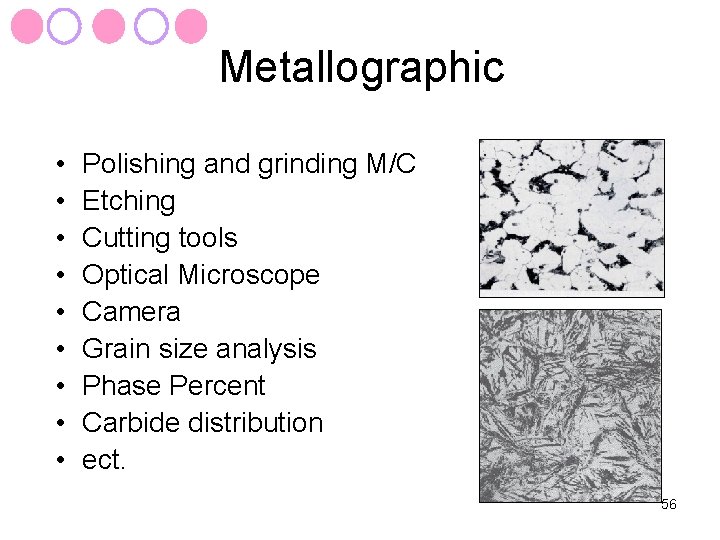
Metallographic • • • Polishing and grinding M/C Etching Cutting tools Optical Microscope Camera Grain size analysis Phase Percent Carbide distribution ect. 56
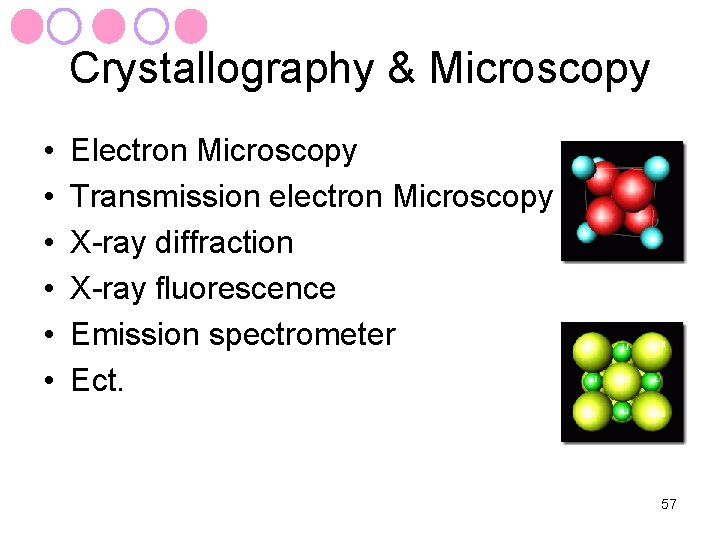
Crystallography & Microscopy • • • Electron Microscopy Transmission electron Microscopy X-ray diffraction X-ray fluorescence Emission spectrometer Ect. 57
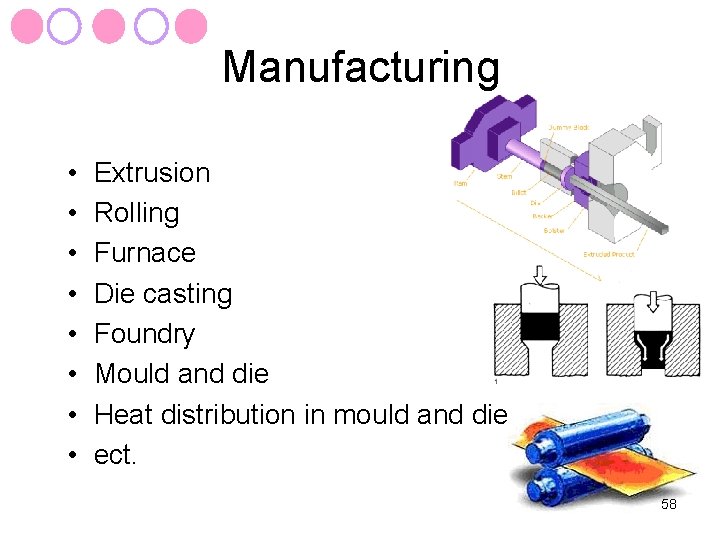
Manufacturing • • Extrusion Rolling Furnace Die casting Foundry Mould and die Heat distribution in mould and die ect. 58
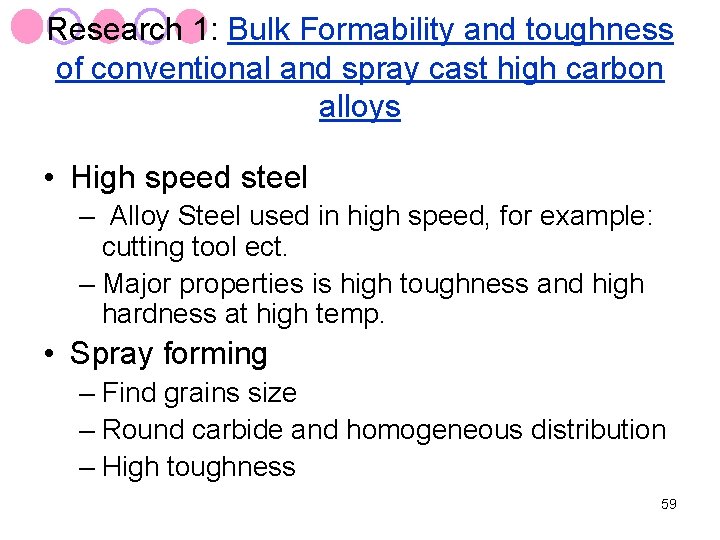
Research 1: Bulk Formability and toughness of conventional and spray cast high carbon alloys • High speed steel – Alloy Steel used in high speed, for example: cutting tool ect. – Major properties is high toughness and high hardness at high temp. • Spray forming – Find grains size – Round carbide and homogeneous distribution – High toughness 59
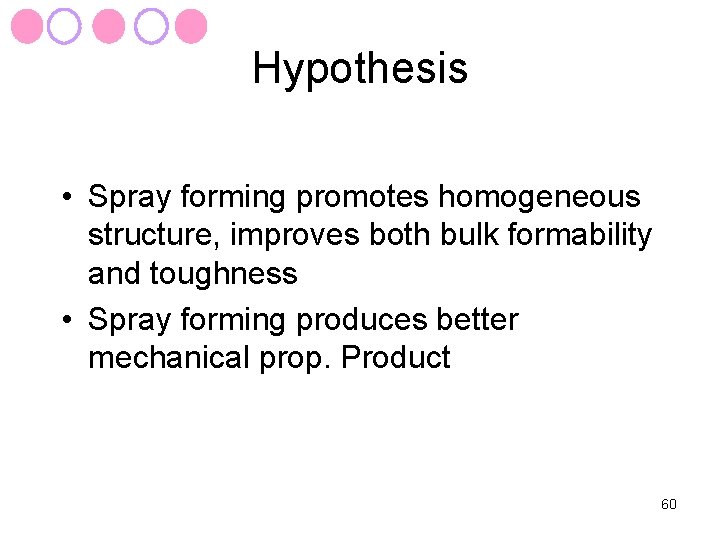
Hypothesis • Spray forming promotes homogeneous structure, improves both bulk formability and toughness • Spray forming produces better mechanical prop. Product 60
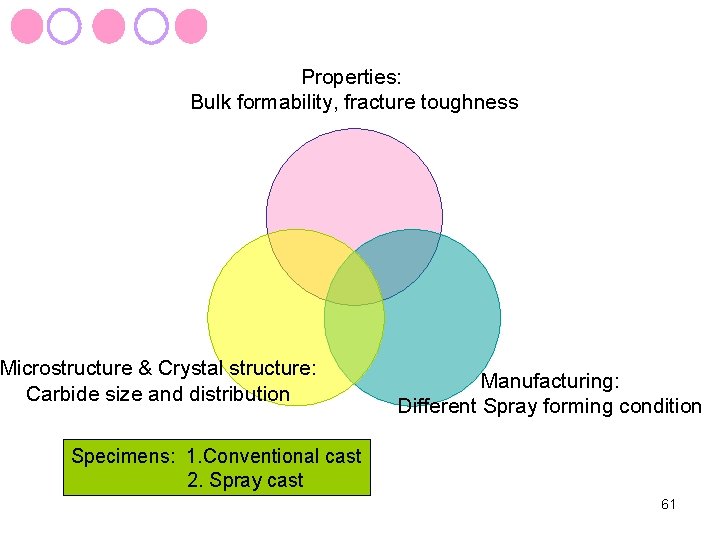
Properties: Bulk formability, fracture toughness Microstructure & Crystal structure: Carbide size and distribution Manufacturing: Different Spray forming condition Specimens: 1. Conventional cast 2. Spray cast 61
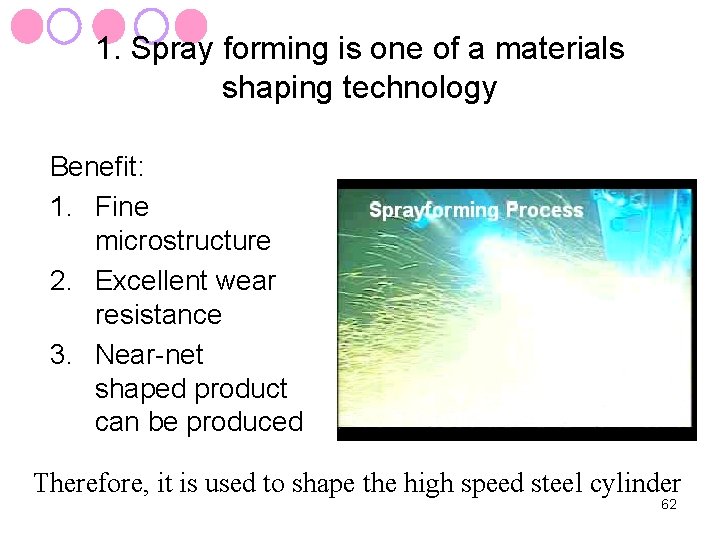
1. Spray forming is one of a materials shaping technology Benefit: 1. Fine microstructure 2. Excellent wear resistance 3. Near-net shaped product can be produced Therefore, it is used to shape the high speed steel cylinder 62
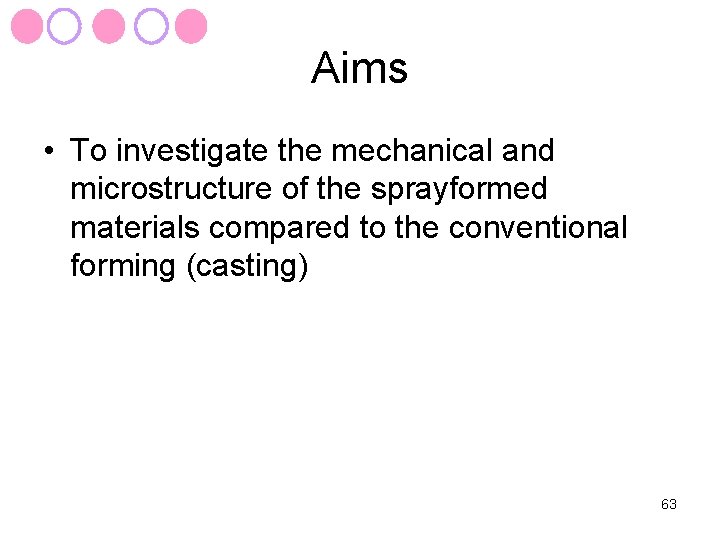
Aims • To investigate the mechanical and microstructure of the sprayformed materials compared to the conventional forming (casting) 63
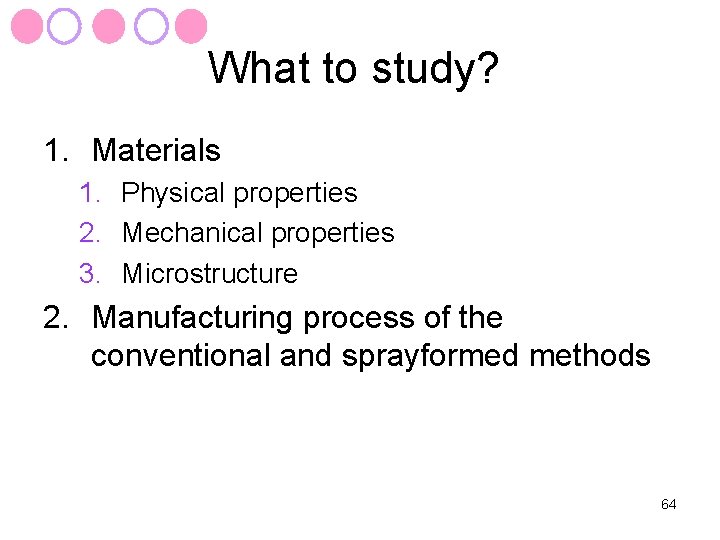
What to study? 1. Materials 1. Physical properties 2. Mechanical properties 3. Microstructure 2. Manufacturing process of the conventional and sprayformed methods 64
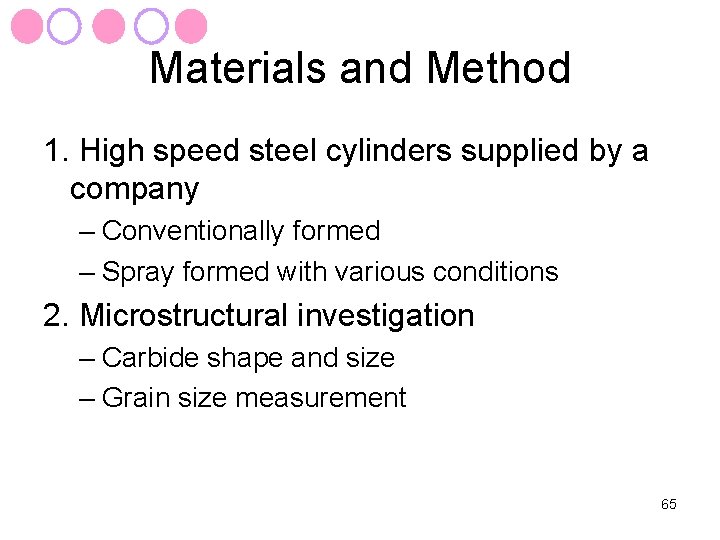
Materials and Method 1. High speed steel cylinders supplied by a company – Conventionally formed – Spray formed with various conditions 2. Microstructural investigation – Carbide shape and size – Grain size measurement 65
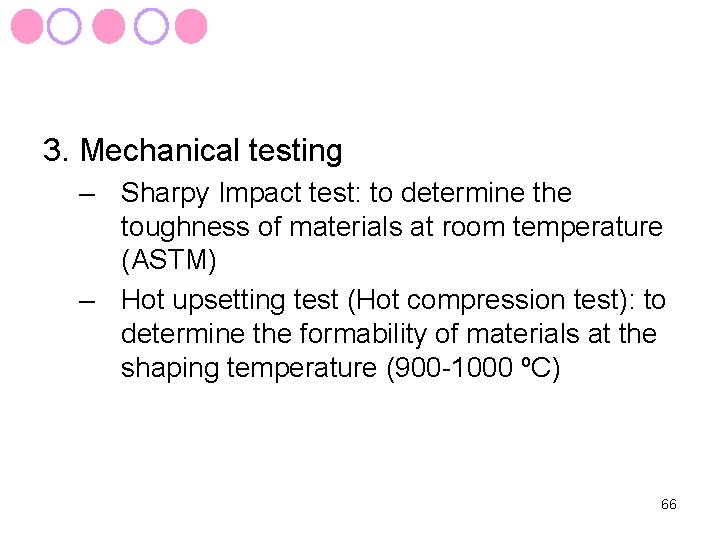
3. Mechanical testing – Sharpy Impact test: to determine the toughness of materials at room temperature (ASTM) – Hot upsetting test (Hot compression test): to determine the formability of materials at the shaping temperature (900 -1000 ºC) 66
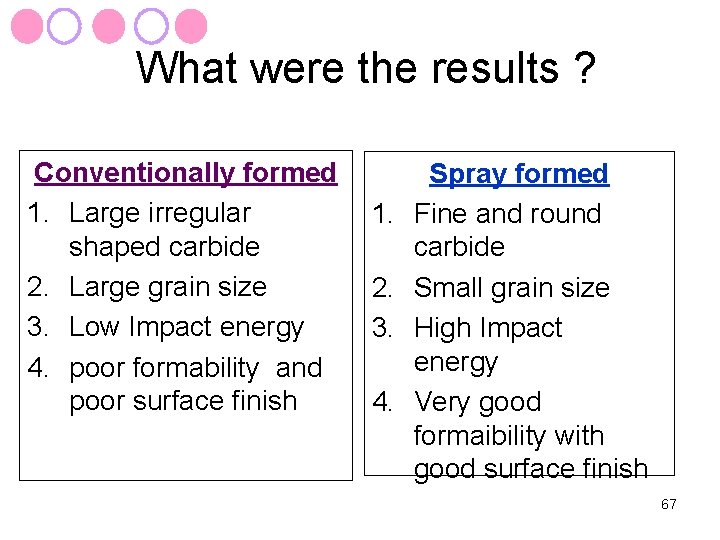
What were the results ? Conventionally formed 1. Large irregular shaped carbide 2. Large grain size 3. Low Impact energy 4. poor formability and poor surface finish 1. 2. 3. 4. Spray formed Fine and round carbide Small grain size High Impact energy Very good formaibility with good surface finish 67
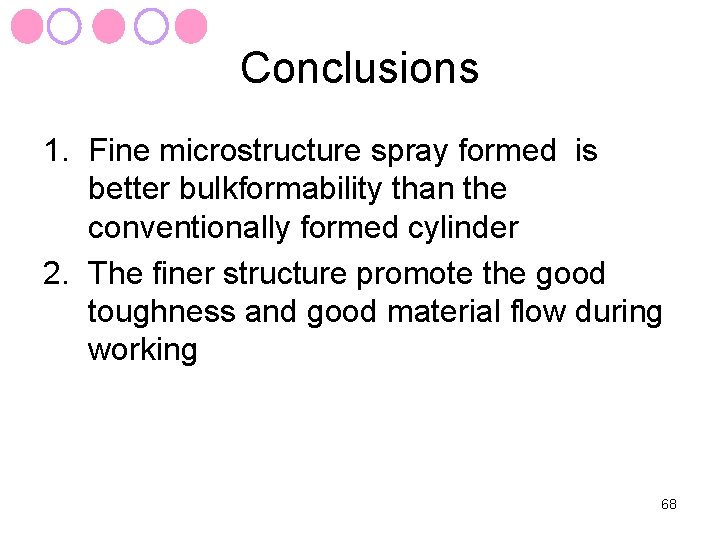
Conclusions 1. Fine microstructure spray formed is better bulkformability than the conventionally formed cylinder 2. The finer structure promote the good toughness and good material flow during working 68
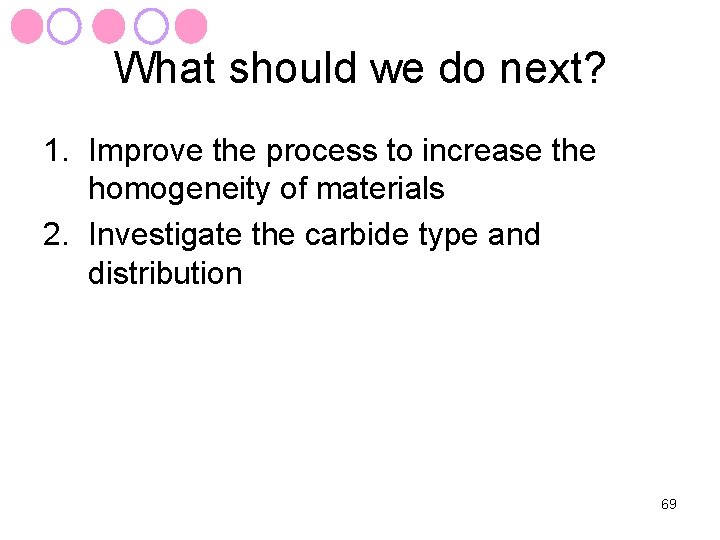
What should we do next? 1. Improve the process to increase the homogeneity of materials 2. Investigate the carbide type and distribution 69
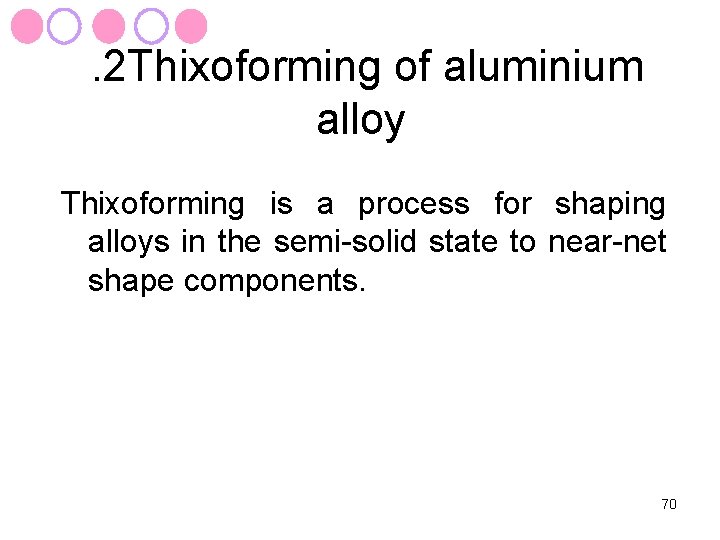
. 2 Thixoforming of aluminium alloy Thixoforming is a process for shaping alloys in the semi-solid state to near-net shape components. 70
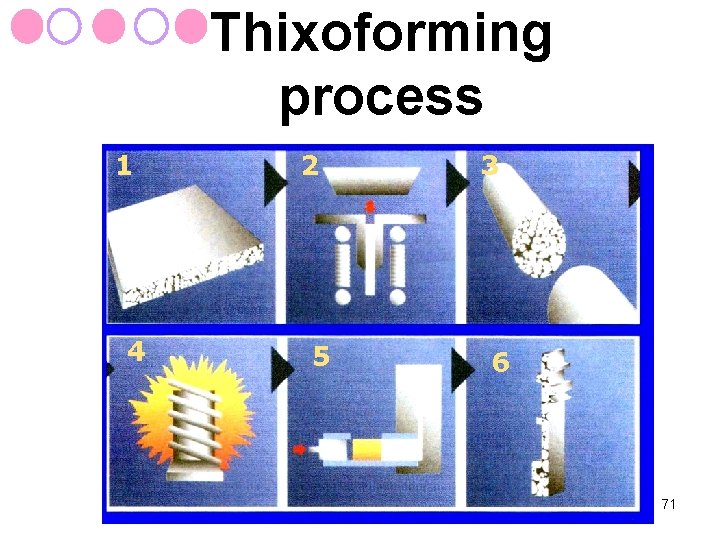
Thixoforming process 1 4 2 5 3 6 71
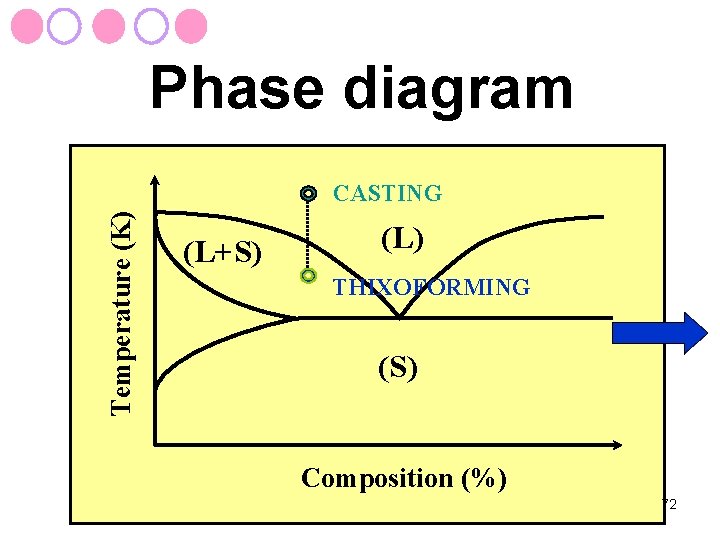
Phase diagram Temperature (K) CASTING (L+S) (L) THIXOFORMING (S) Composition (%) 72

Comparison of microstructures Typical As-cast microstructure Typical As-thixoformed microstructure 73
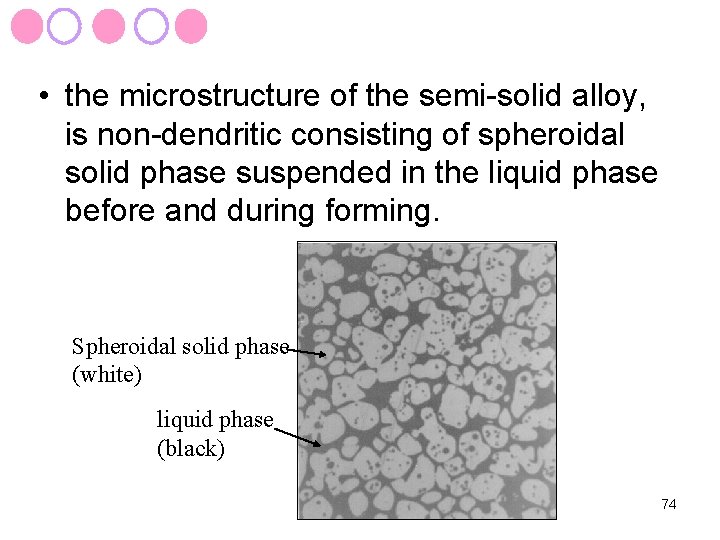
• the microstructure of the semi-solid alloy, is non-dendritic consisting of spheroidal solid phase suspended in the liquid phase before and during forming. Spheroidal solid phase (white) liquid phase (black) 74
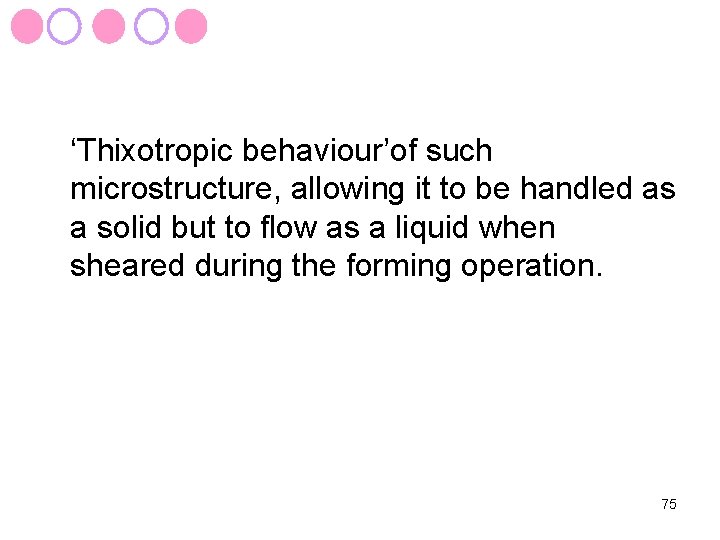
‘Thixotropic behaviour’of such microstructure, allowing it to be handled as a solid but to flow as a liquid when sheared during the forming operation. 75
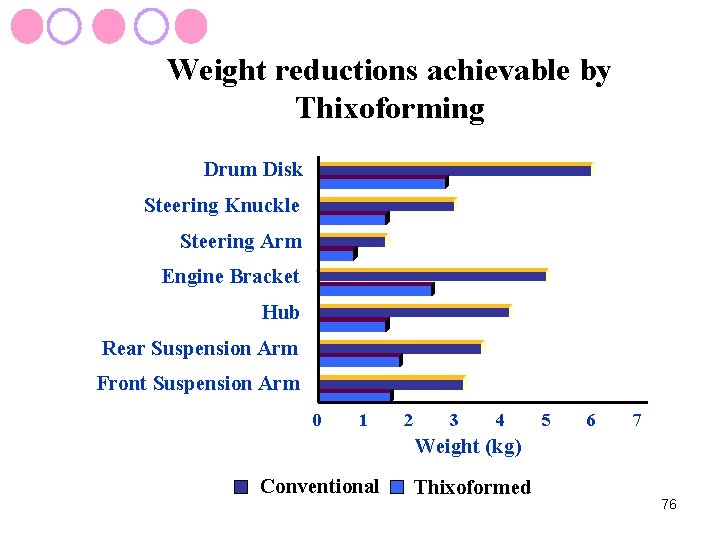
Weight reductions achievable by Thixoforming Drum Disk Steering Knuckle Steering Arm Engine Bracket Hub Rear Suspension Arm Front Suspension Arm 0 1 2 3 4 5 6 7 Weight (kg) Conventional Thixoformed 76
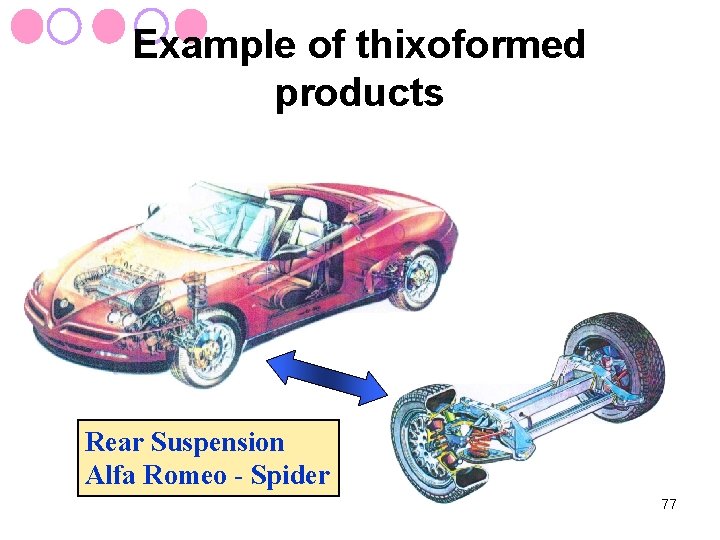
Example of thixoformed products Rear Suspension Alfa Romeo - Spider 77
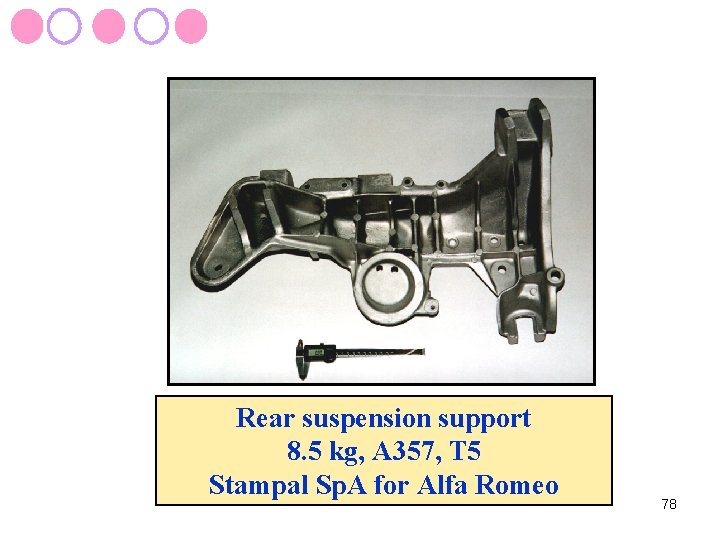
Rear suspension support 8. 5 kg, A 357, T 5 Stampal Sp. A for Alfa Romeo 78
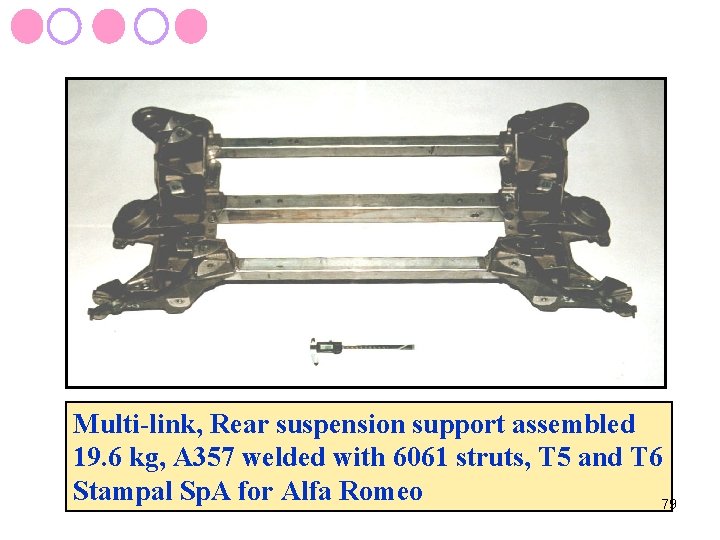
Multi-link, Rear suspension support assembled 19. 6 kg, A 357 welded with 6061 struts, T 5 and T 6 Stampal Sp. A for Alfa Romeo 79
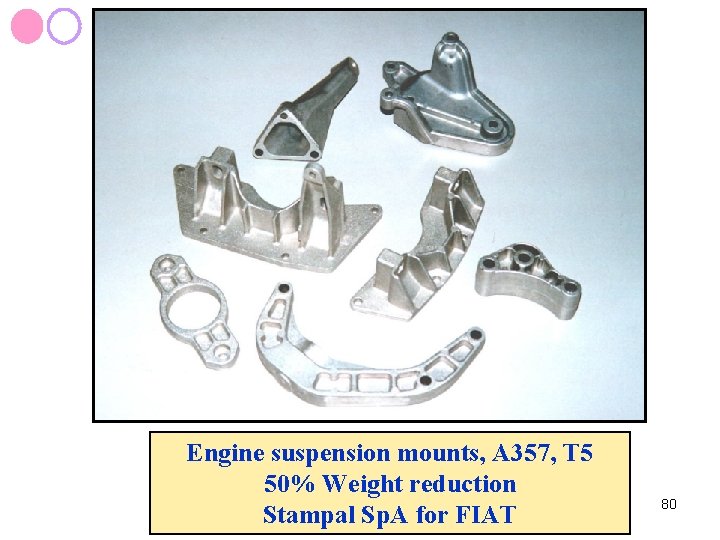
Engine suspension mounts, A 357, T 5 50% Weight reduction Stampal Sp. A for FIAT 80
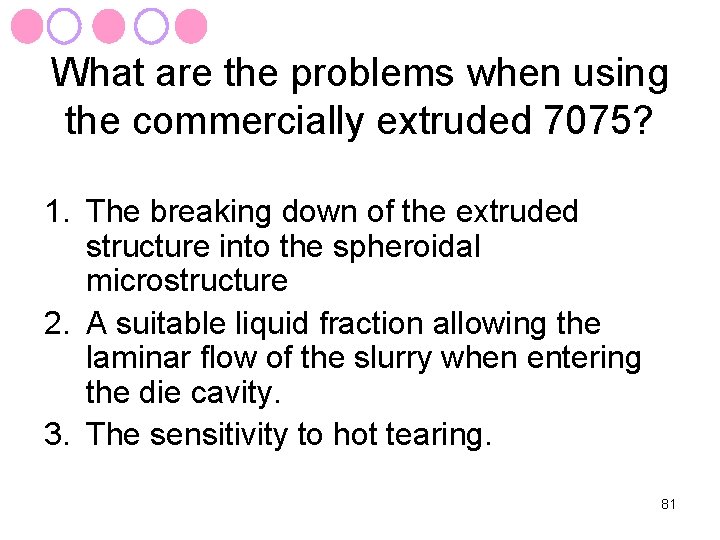
What are the problems when using the commercially extruded 7075? 1. The breaking down of the extruded structure into the spheroidal microstructure 2. A suitable liquid fraction allowing the laminar flow of the slurry when entering the die cavity. 3. The sensitivity to hot tearing. 81
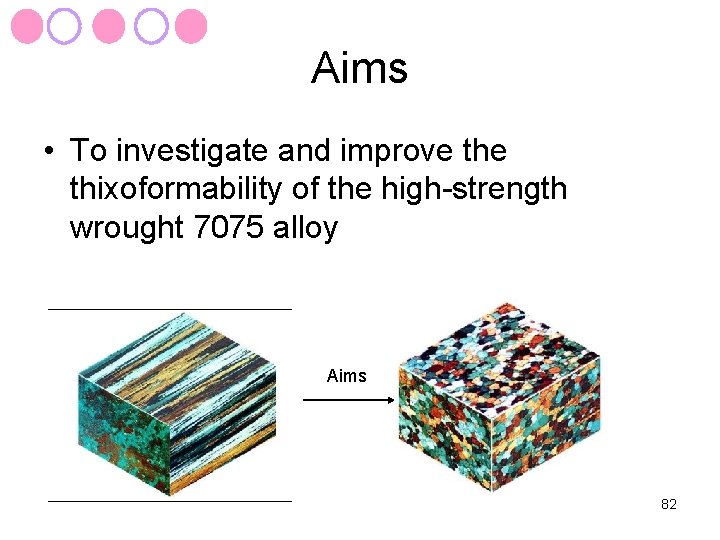
Aims • To investigate and improve thixoformability of the high-strength wrought 7075 alloy Aims 82
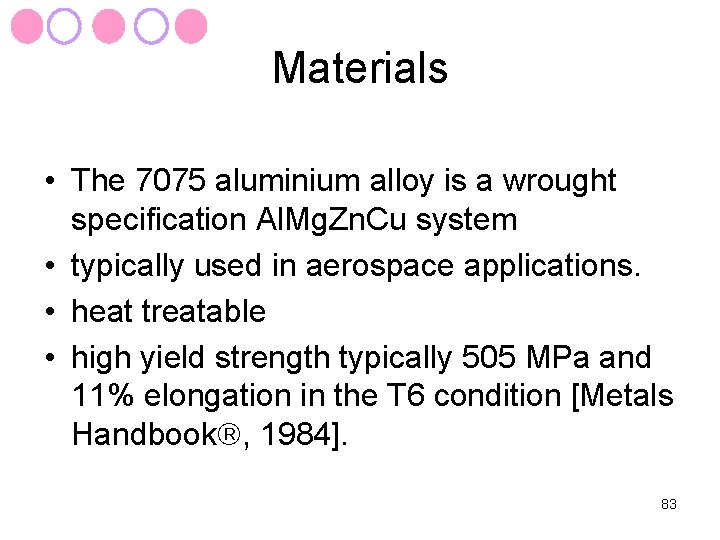
Materials • The 7075 aluminium alloy is a wrought specification Al. Mg. Zn. Cu system • typically used in aerospace applications. • heat treatable • high yield strength typically 505 MPa and 11% elongation in the T 6 condition [Metals Handbook , 1984]. 83
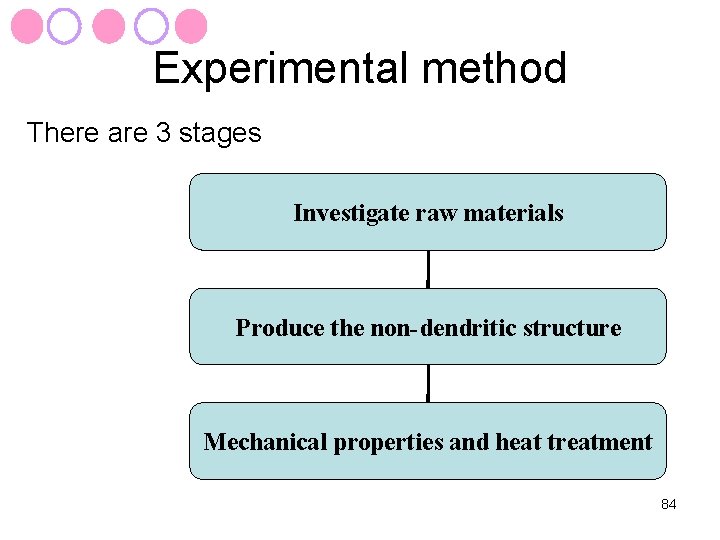
Experimental method There are 3 stages Investigate raw materials Produce the non-dendritic structure Mechanical properties and heat treatment 84
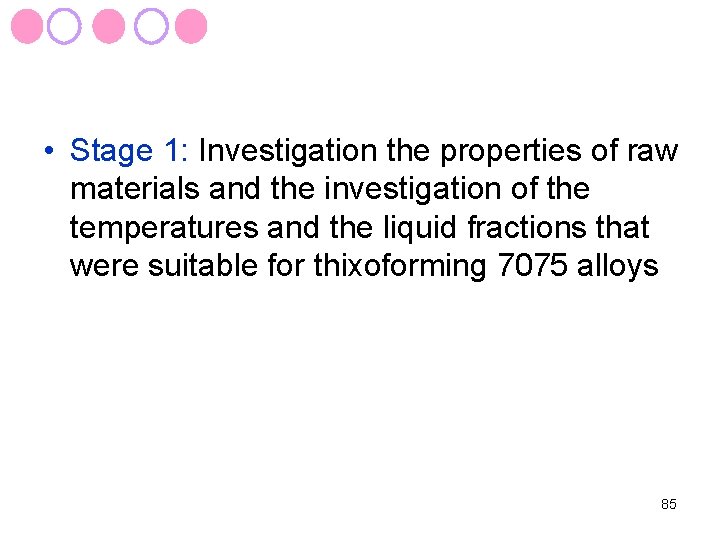
• Stage 1: Investigation the properties of raw materials and the investigation of the temperatures and the liquid fractions that were suitable for thixoforming 7075 alloys 85
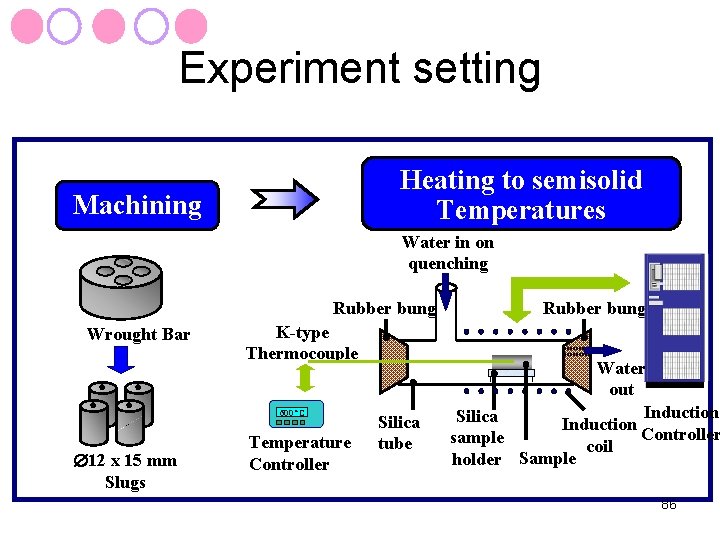
Experiment setting Heating to semisolid Temperatures Machining Water in on quenching Rubber bung Wrought Bar K-type Thermocouple 600 °C 12 x 15 mm Slugs Temperature Controller Silica tube Rubber bung Water out Induction Silica Induction Controller sample coil holder Sample 86
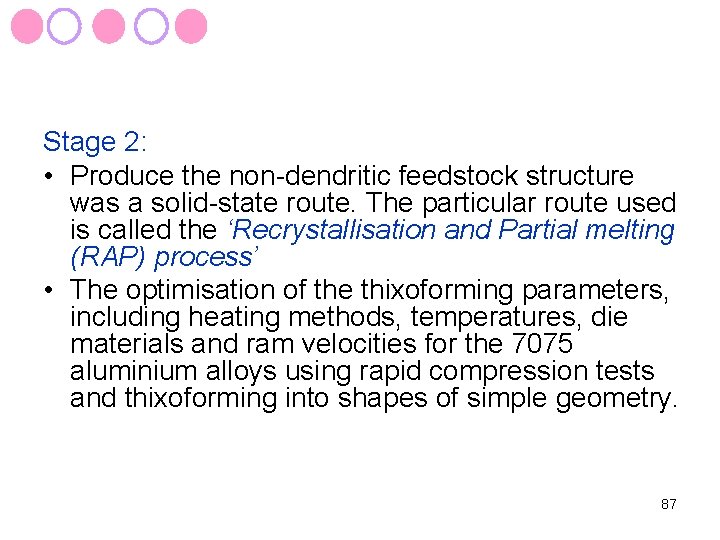
Stage 2: • Produce the non-dendritic feedstock structure was a solid-state route. The particular route used is called the ‘Recrystallisation and Partial melting (RAP) process’ • The optimisation of the thixoforming parameters, including heating methods, temperatures, die materials and ram velocities for the 7075 aluminium alloys using rapid compression tests and thixoforming into shapes of simple geometry. 87
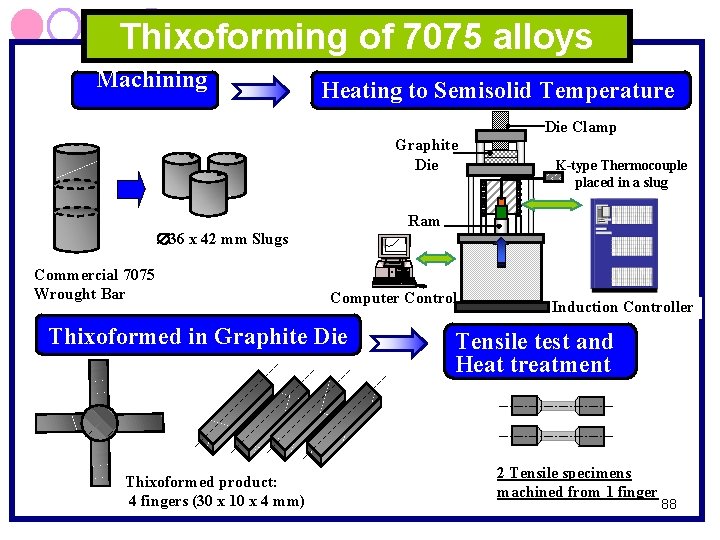
Thixoforming of 7075 alloys Machining Heating to Semisolid Temperature Die Clamp Graphite Die Ram 36 x 42 mm Slugs Commercial 7075 Wrought Bar Computer Control Thixoformed in Graphite Die Thixoformed product: 4 fingers (30 x 10 x 4 mm) K-type Thermocouple placed in a slug Induction Controller Tensile test and Heat treatment 2 Tensile specimens machined from 1 finger 88
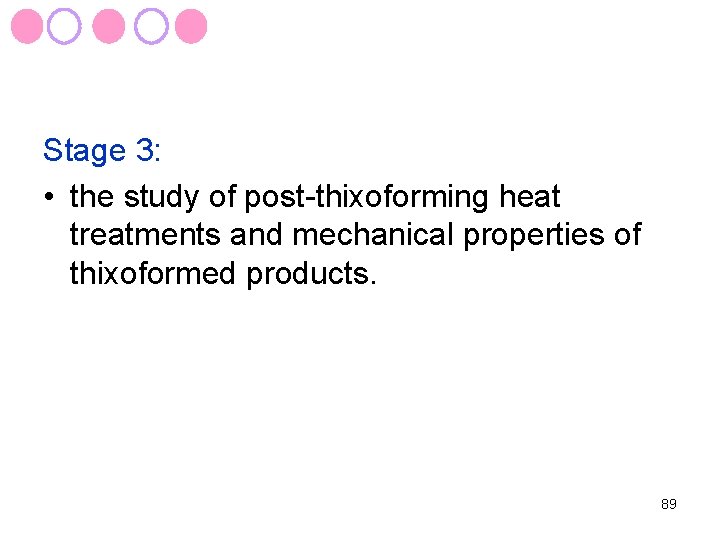
Stage 3: • the study of post-thixoforming heat treatments and mechanical properties of thixoformed products. 89
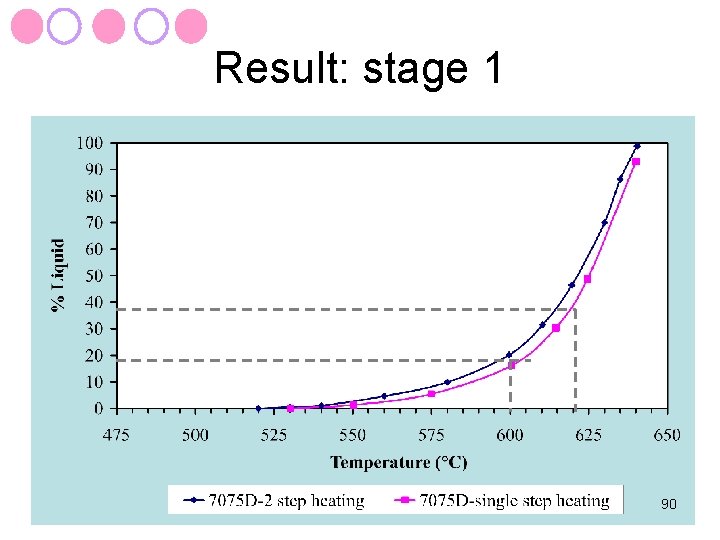
Result: stage 1 90
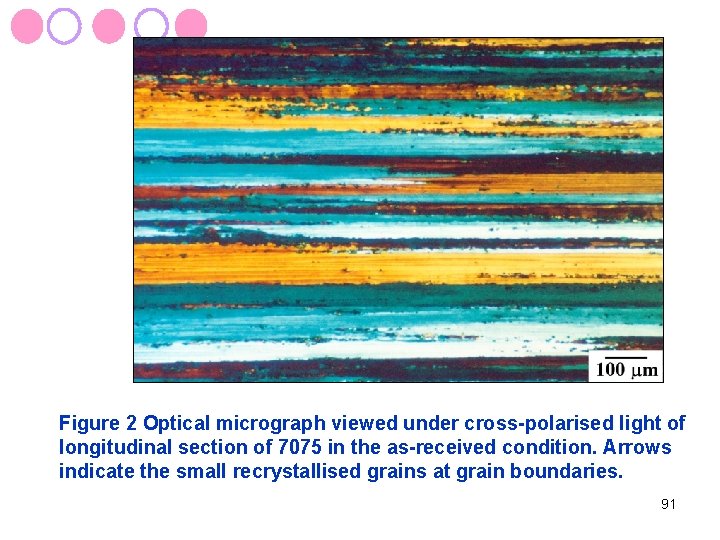
Figure 2 Optical micrograph viewed under cross-polarised light of longitudinal section of 7075 in the as-received condition. Arrows indicate the small recrystallised grains at grain boundaries. 91
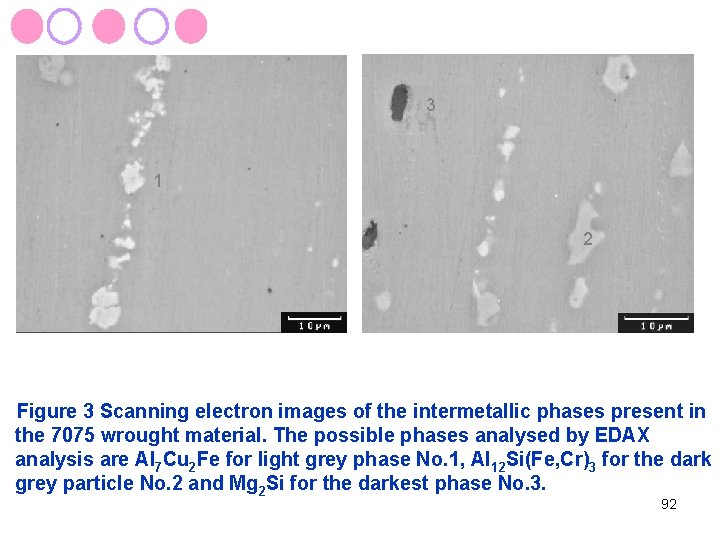
3 1 2 Figure 3 Scanning electron images of the intermetallic phases present in the 7075 wrought material. The possible phases analysed by EDAX analysis are Al 7 Cu 2 Fe for light grey phase No. 1, Al 12 Si(Fe, Cr)3 for the dark grey particle No. 2 and Mg 2 Si for the darkest phase No. 3. 92
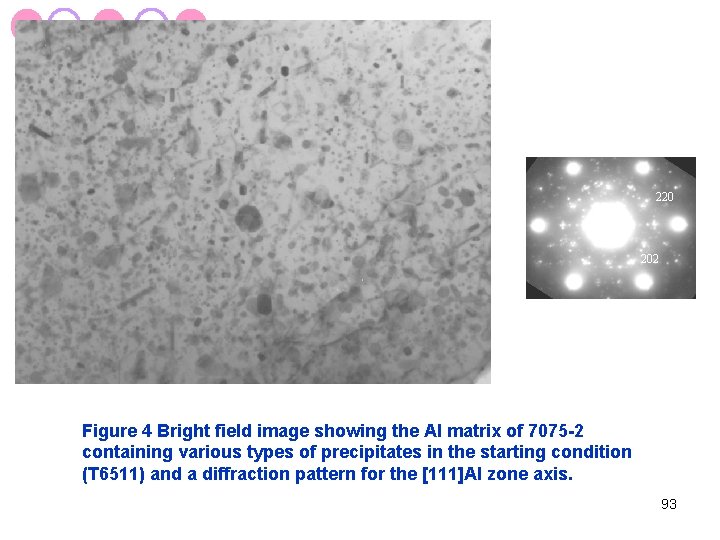
220 202 Figure 4 Bright field image showing the Al matrix of 7075 -2 containing various types of precipitates in the starting condition (T 6511) and a diffraction pattern for the [111]Al zone axis. 93
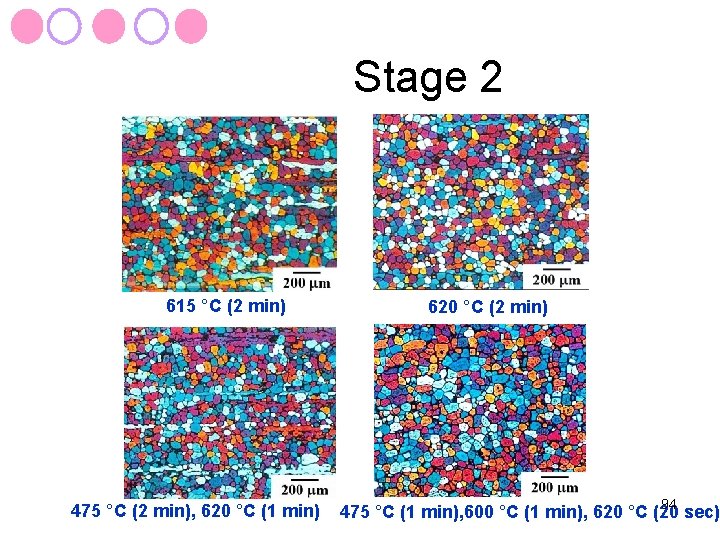
Stage 2 615 °C (2 min) 475 °C (2 min), 620 °C (1 min) 620 °C (2 min) 94 475 °C (1 min), 600 °C (1 min), 620 °C (20 sec)
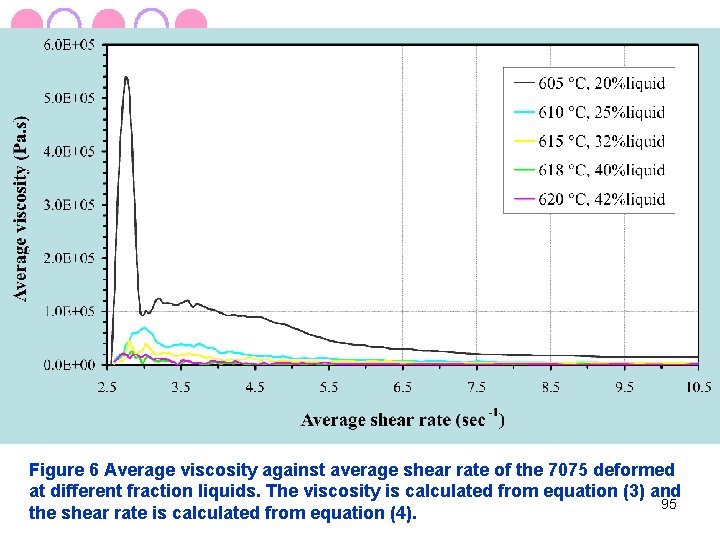
Figure 6 Average viscosity against average shear rate of the 7075 deformed at different fraction liquids. The viscosity is calculated from equation (3) and 95 the shear rate is calculated from equation (4).
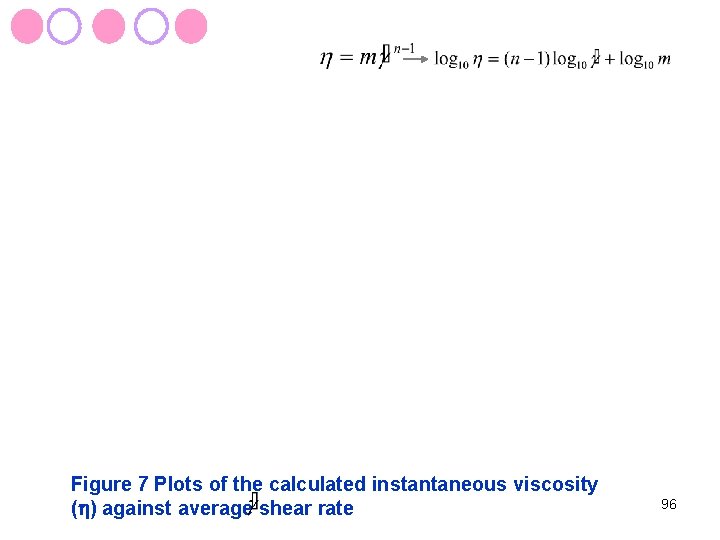
Figure 7 Plots of the calculated instantaneous viscosity ( ) against average shear rate 96
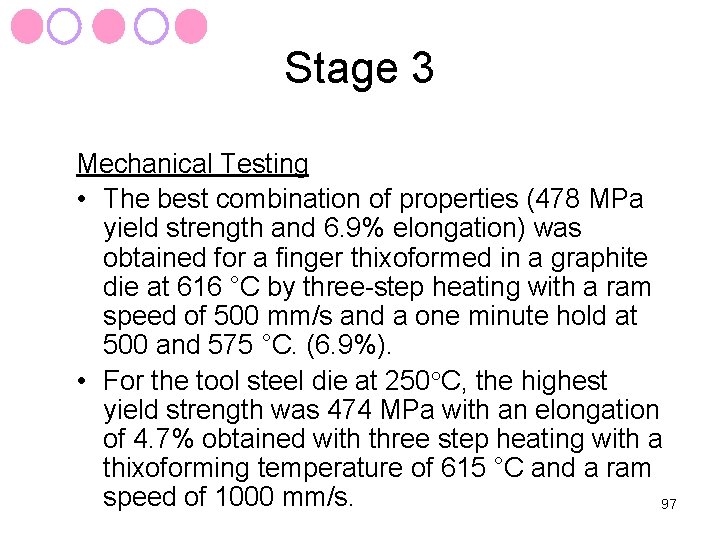
Stage 3 Mechanical Testing • The best combination of properties (478 MPa yield strength and 6. 9% elongation) was obtained for a finger thixoformed in a graphite die at 616 °C by three-step heating with a ram speed of 500 mm/s and a one minute hold at 500 and 575 °C. (6. 9%). • For the tool steel die at 250 C, the highest yield strength was 474 MPa with an elongation of 4. 7% obtained with three step heating with a thixoforming temperature of 615 °C and a ram speed of 1000 mm/s. 97
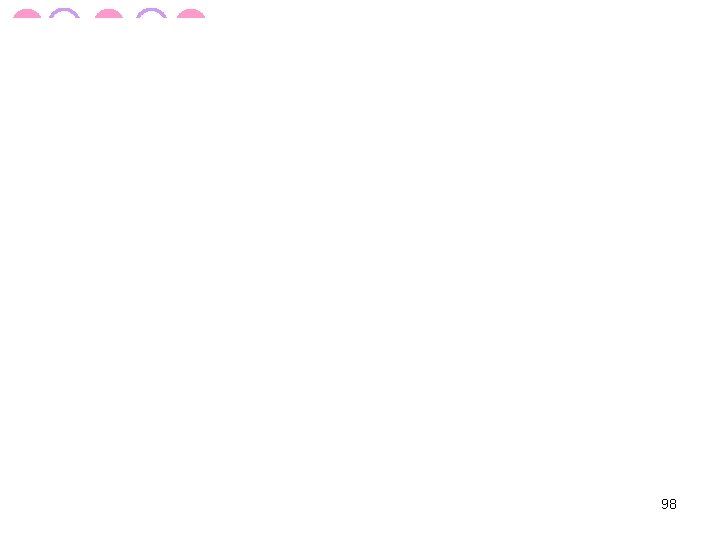
98
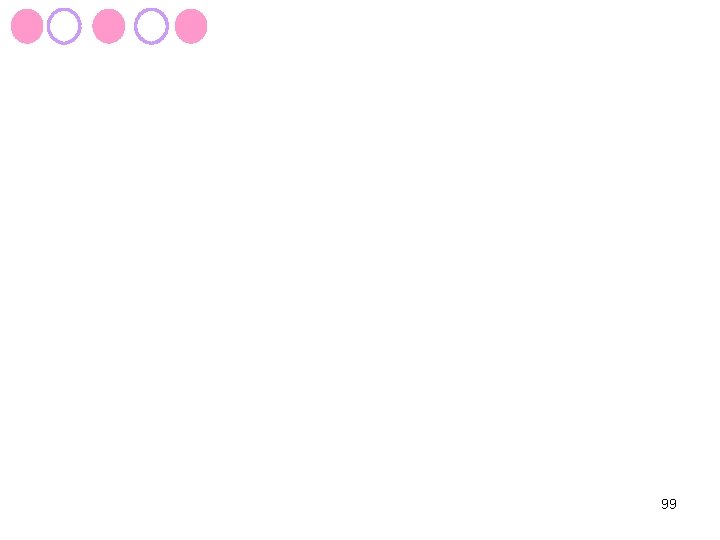
99
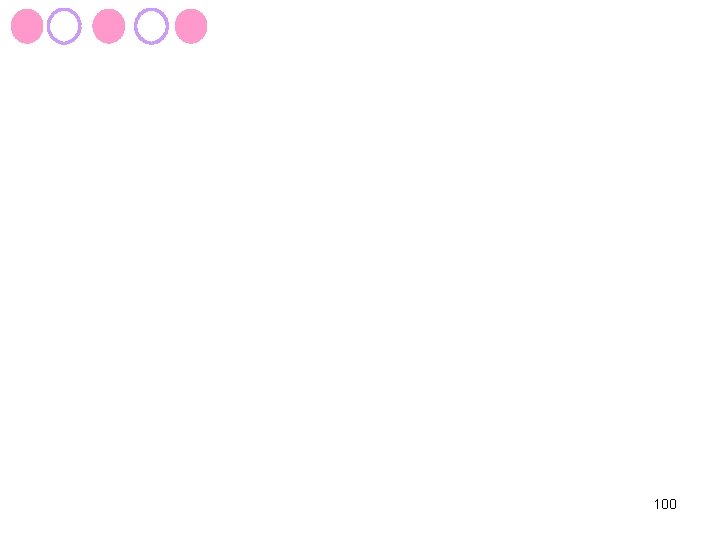
100
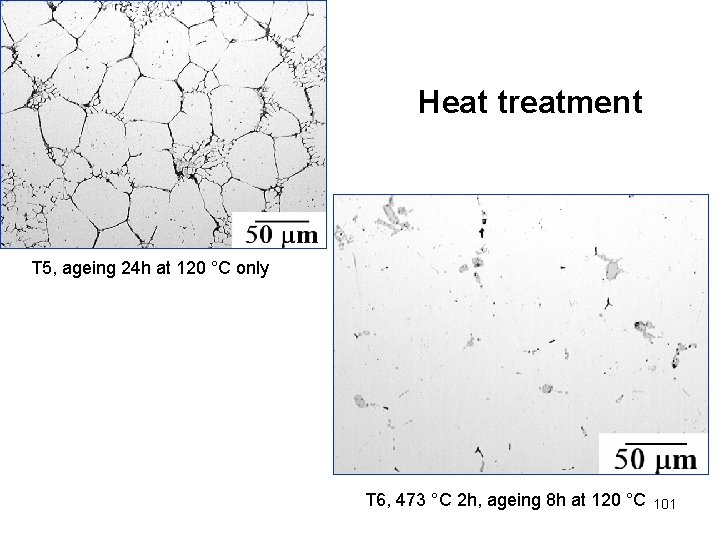
Heat treatment T 5, ageing 24 h at 120 °C only T 6, 473 °C 2 h, ageing 8 h at 120 °C 101
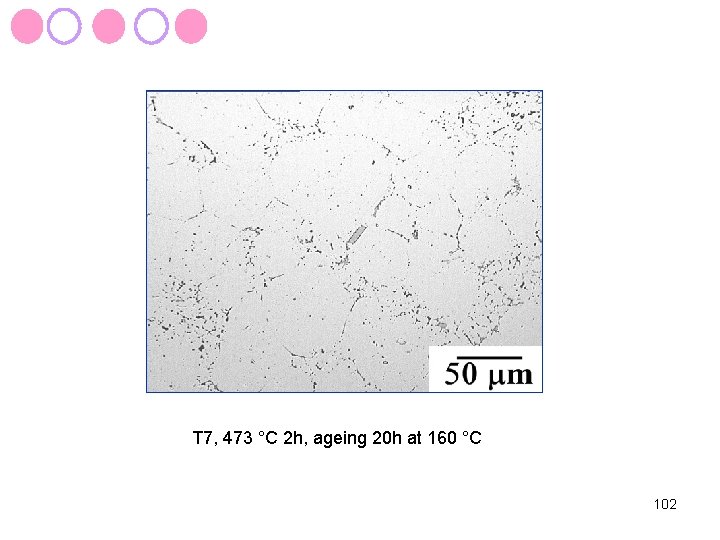
T 7, 473 °C 2 h, ageing 20 h at 160 °C 102
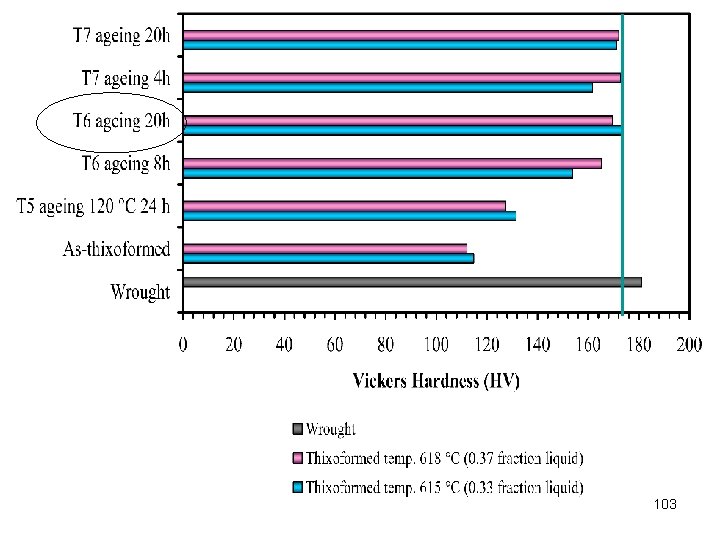
103
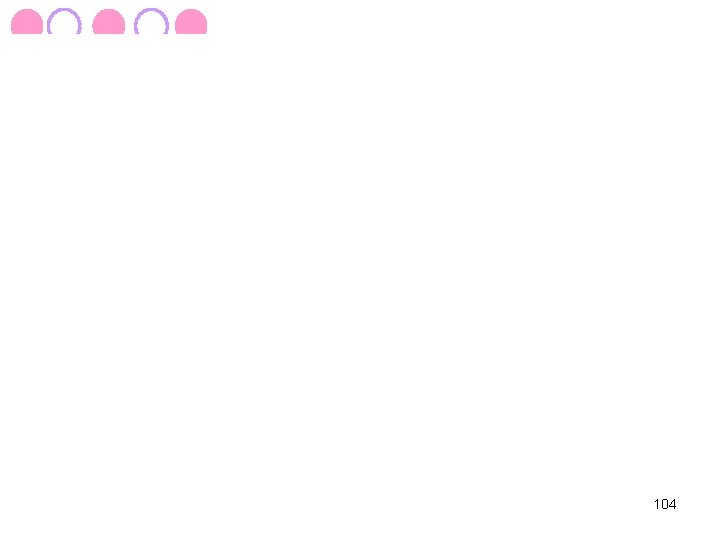
104
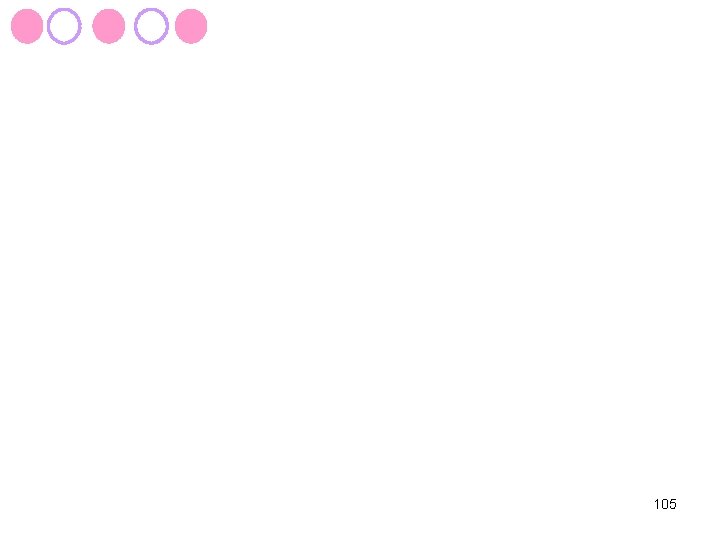
105
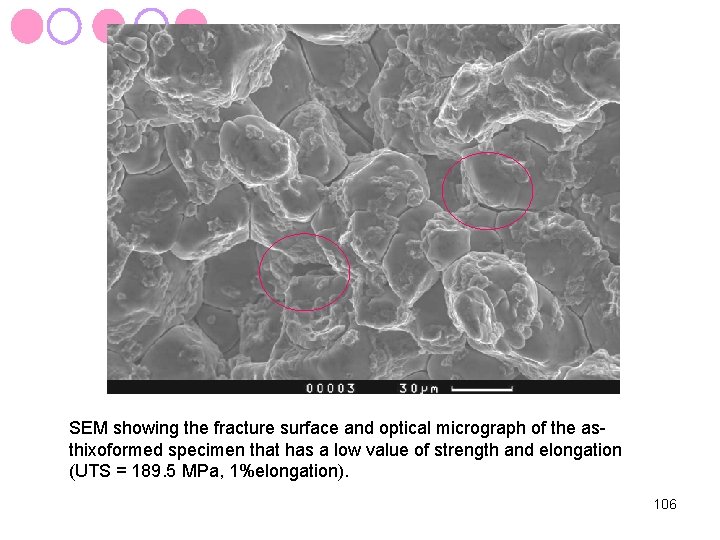
SEM showing the fracture surface and optical micrograph of the asthixoformed specimen that has a low value of strength and elongation (UTS = 189. 5 MPa, 1%elongation). 106
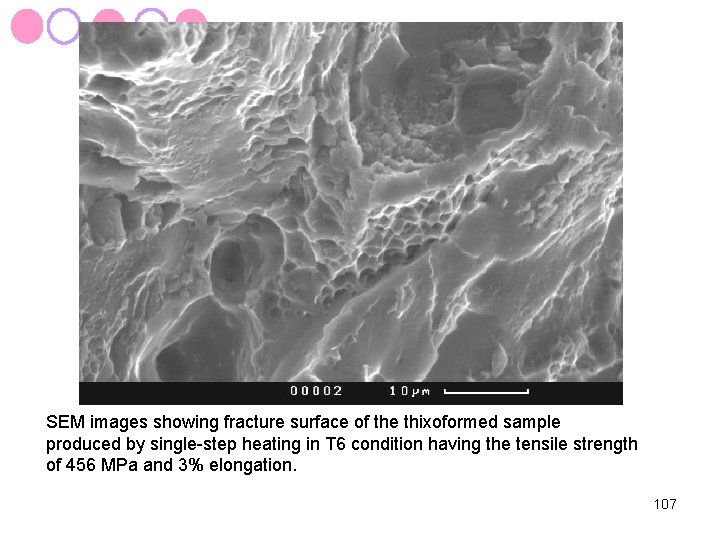
SEM images showing fracture surface of the thixoformed sample produced by single-step heating in T 6 condition having the tensile strength of 456 MPa and 3% elongation. 107
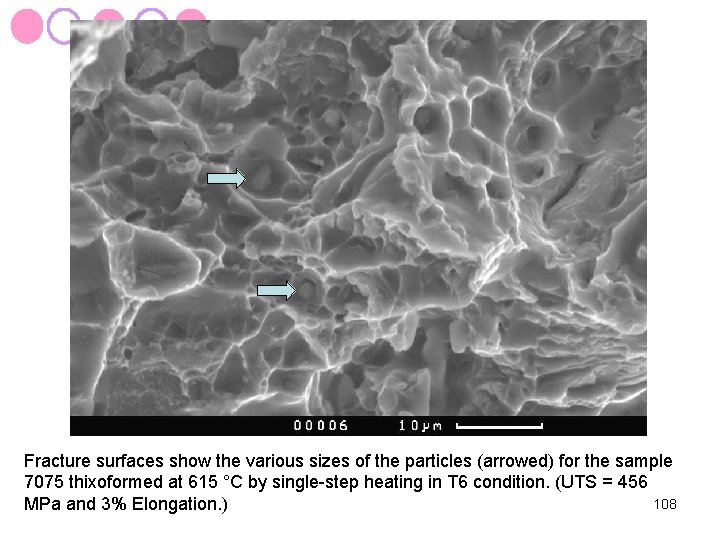
Fracture surfaces show the various sizes of the particles (arrowed) for the sample 7075 thixoformed at 615 °C by single-step heating in T 6 condition. (UTS = 456 108 MPa and 3% Elongation. )
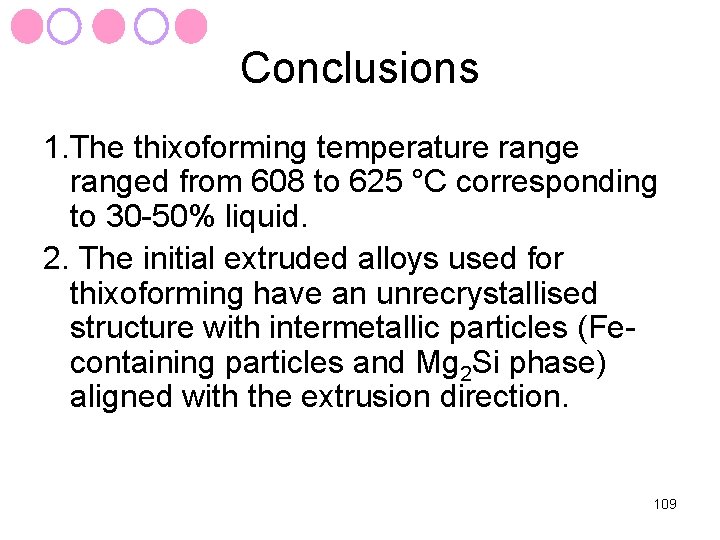
Conclusions 1. The thixoforming temperature ranged from 608 to 625 °C corresponding to 30 -50% liquid. 2. The initial extruded alloys used for thixoforming have an unrecrystallised structure with intermetallic particles (Fecontaining particles and Mg 2 Si phase) aligned with the extrusion direction. 109
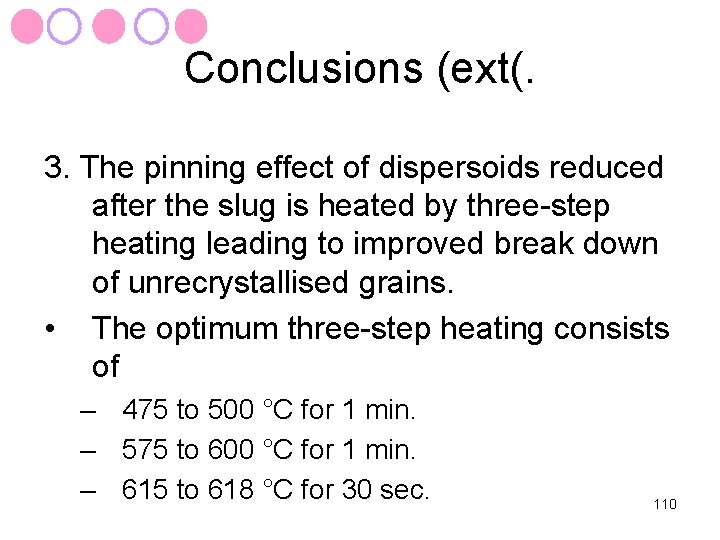
Conclusions (ext(. 3. The pinning effect of dispersoids reduced after the slug is heated by three-step heating leading to improved break down of unrecrystallised grains. • The optimum three-step heating consists of – 475 to 500 °C for 1 min. – 575 to 600 °C for 1 min. – 615 to 618 °C for 30 sec. 110
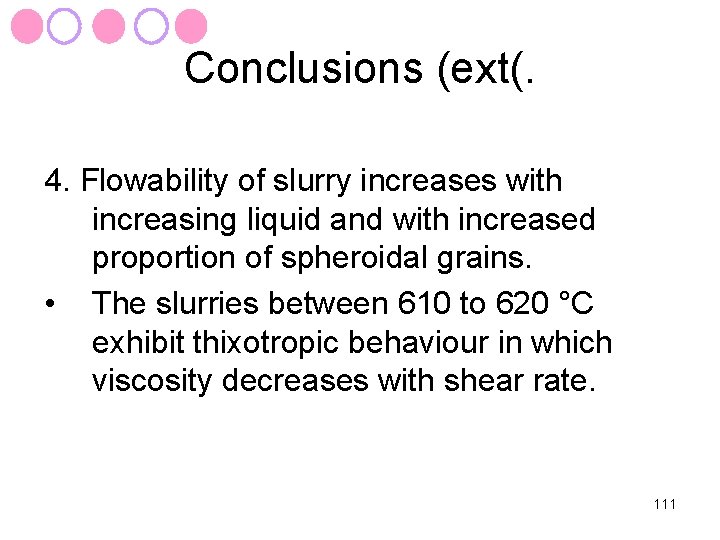
Conclusions (ext(. 4. Flowability of slurry increases with increasing liquid and with increased proportion of spheroidal grains. • The slurries between 610 to 620 °C exhibit thixotropic behaviour in which viscosity decreases with shear rate. 111
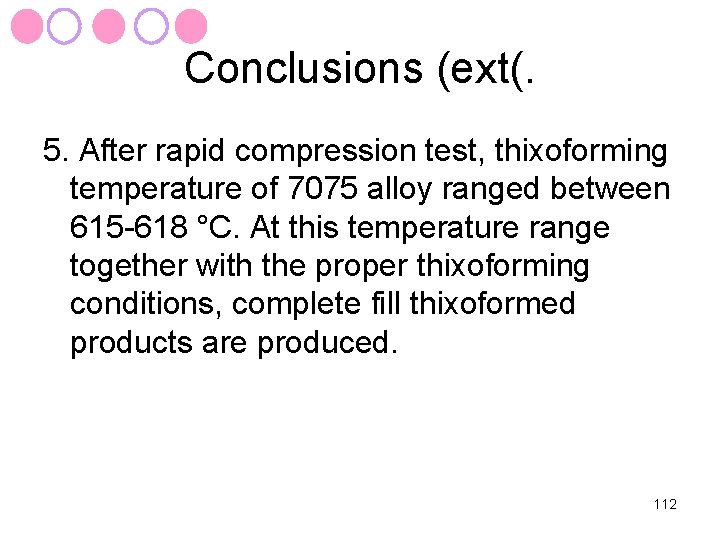
Conclusions (ext(. 5. After rapid compression test, thixoforming temperature of 7075 alloy ranged between 615 -618 °C. At this temperature range together with the proper thixoforming conditions, complete fill thixoformed products are produced. 112
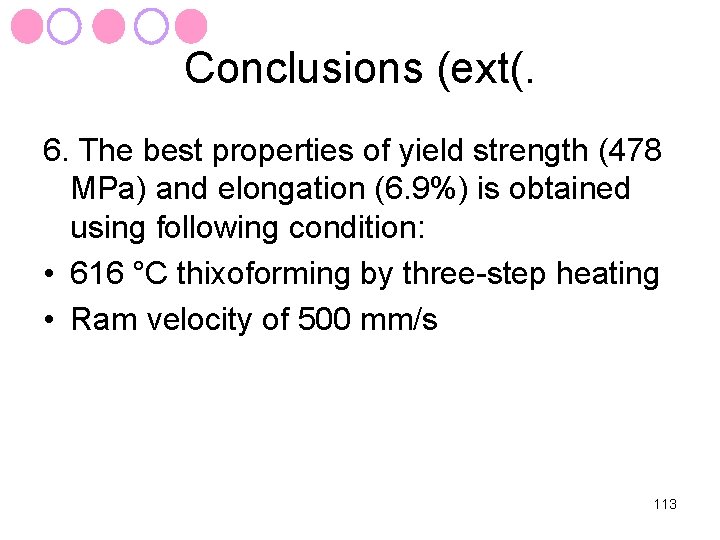
Conclusions (ext(. 6. The best properties of yield strength (478 MPa) and elongation (6. 9%) is obtained using following condition: • 616 °C thixoforming by three-step heating • Ram velocity of 500 mm/s 113
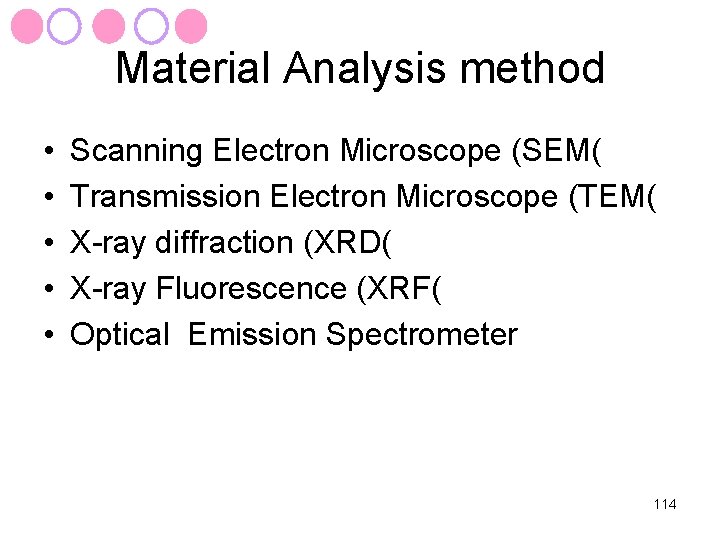
Material Analysis method • • • Scanning Electron Microscope (SEM( Transmission Electron Microscope (TEM( X-ray diffraction (XRD( X-ray Fluorescence (XRF( Optical Emission Spectrometer 114
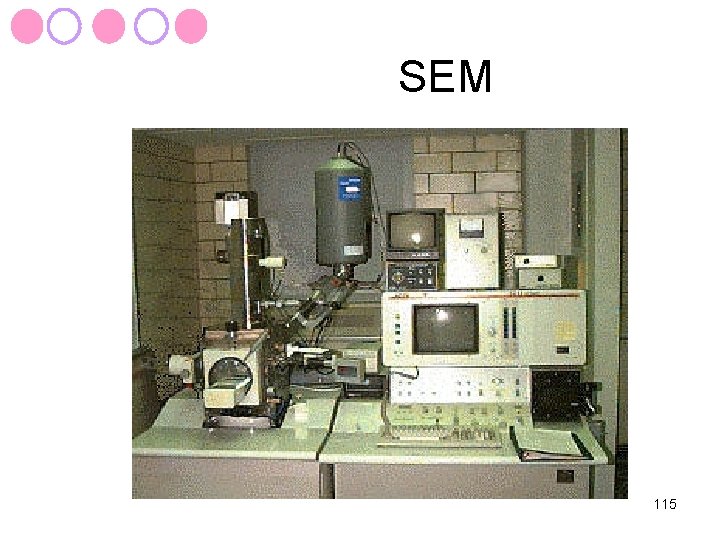
SEM 115
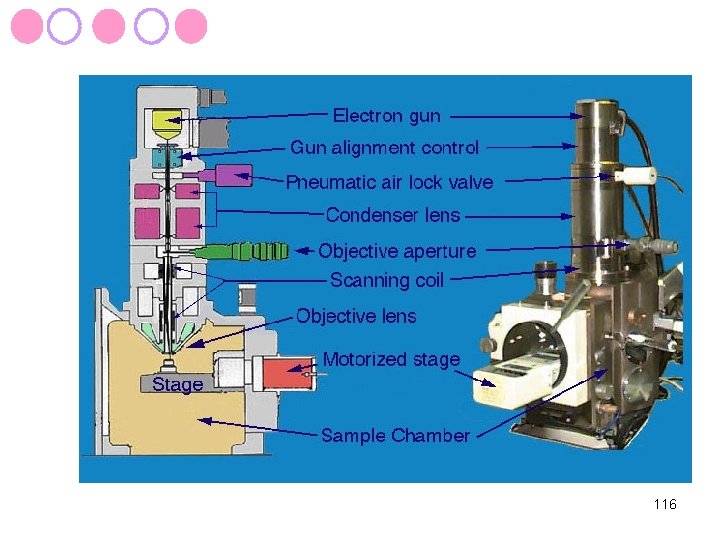
116
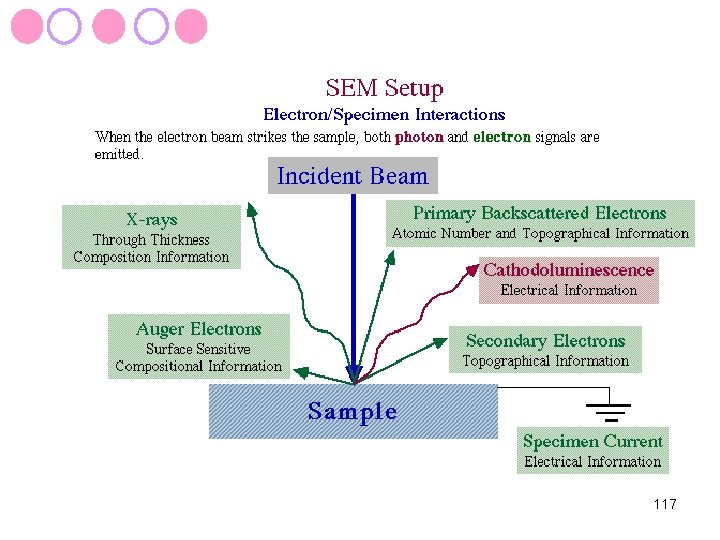
117
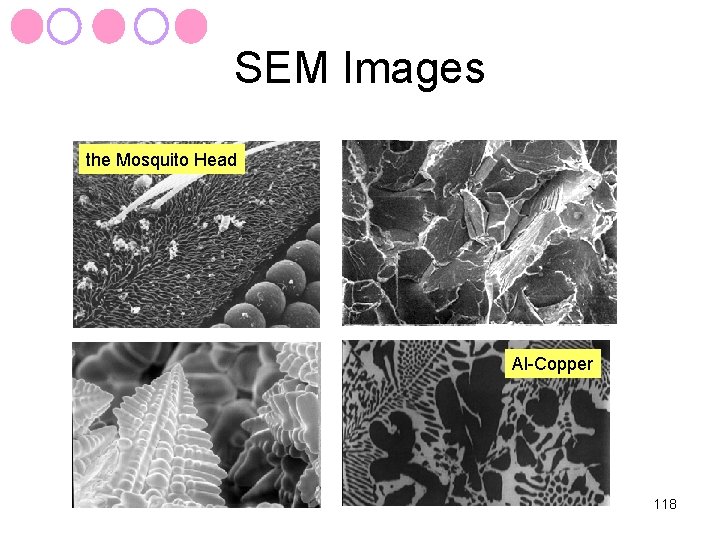
SEM Images the Mosquito Head Al-Copper 118
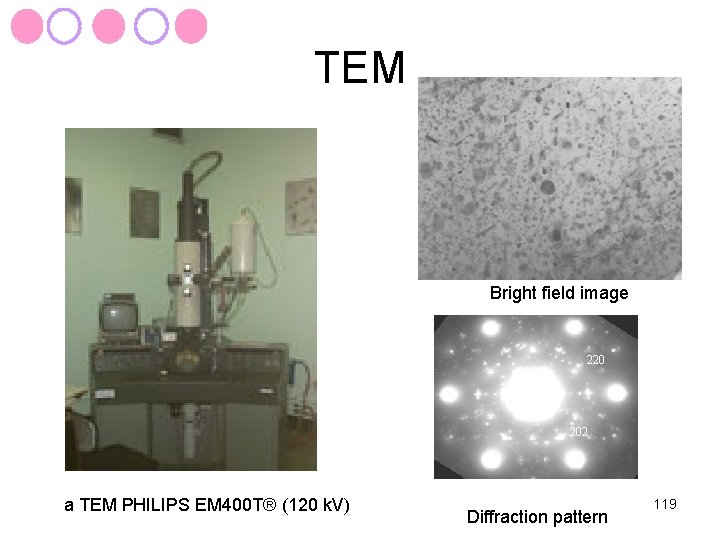
TEM Bright field image 220 202 a TEM PHILIPS EM 400 T® (120 k. V) Diffraction pattern 119
Rheolube 362
Head start performance standards 1302
Calhr 774
Cs 1302
Osmanlı 1302
Dena schlosser
Special investigative topics 3232
Special topics in software engineering
Applications and processing of metal alloys
Uses of pig iron
Wrought metal in cast rpd is used for
Moscow institute of steel and alloys
Properties of dental amalgam
Titanium alloys
Shape memory alloys lecture notes
"re alloys"
Aluminum and its alloys
Difference between antiferromagnetism and ferrimagnetism
Interionic distance formula
Advanced copper alloys
Aluminum and its alloys
Non ferrous alloys definition
Memory shape alloy
Interstital alloys
Application and processing of metal alloys
Adaptive alloys
Development of microstructure in isomorphous alloys
Lightweight alloys
Microfusion cast & alloys
San precision alloys pvt ltd
Magnesium barium alloys
The knowledge language values customs and material objects
Geometrical symbol
Non material culture examples
Standard costing formula
Harmful and useful materials
Material culture example
Flow chart of carded yarn manufacturing
Npa skawina
Sohar aluminium tenders
Anneal aluminium
Eb welding aluminum
Aluminium body stock
Luas jaring-jaring tabung di samping adalah
Pdcb ionic or covalent
Chemical properties of aluminum
What is made up of silicon and aluminium
Sebatang alumunium digantung pada seutas kawat
Chemical reaction example
Leder titan ström
Aluminium designation
China aluminium outlook
Zinkatbeize
Recykling aluminium
Senyawa amfoter
Sohar aluminium tenders
Aluminium paint appearance
Sebatang aluminium panjangnya 2 5 m berpenampang
Silikon aluminium simbol kimia
Odlewnicze stopy aluminium
Aluminium sulfate and calcium hydroxide equation
What is the specific heat capacity of aluminium
Ladespeicher
Jenis jenis zat
Aluminium fluoride market
Gekleurd aluminiumfolie
Aluminium corrosion equation
Extraction of aluminium
Aluminum and oxygen ionic compound
Aluminium + sulphuric acid
Tentukan luas terkecil aluminium
Pengertian klasifikasi umum
Vom bauxit zum aluminium
Herstellung von aluminium
Ecalyptol
Bohr diagram carbon
Debatable and non debatable statements
Tema seminar yang menarik untuk anak muda
How would one use ears for utilizing spare listening time
Demonstration speech ideas
Short example of an expository speech
Engineering drawing topics
Sociolinguistics topics for presentation
Pde project topics
Nature of international finance
Hot topics in patent law
Formulating a research topic
International speech contest topics
Philosophical chairs topics
Informative and surprising essay topics
Security meeting topics
(http //www.history.com/topics/byzantine-empire
History ia sample
What is callus culture
The scarlet letter literary devices
Digital marketing topics
Soil formation ppt
Plsql topics
Vts-0fxyt-e -site:youtube.com
Persuade reported speech
Uil extemp topics
Xuelele
Blank for spectrophotometer
Multi genre project examples
What topics will be covered in this unit
Forklift safety meeting topics
Chemistry extended essay
Advanced topics in computer science
Advanced machine design
April safety topics
Feb advisor
Physics hl ia examples
Topics for philosophical chairs
Extended definition essay examples
Legal topics for presentation
Classification vs division
Group discussion meaning
Introduction to community pharmacy
Example of objective writing
Gmp training for employees