Presentation on The Factories Act 1948 THE FACTORIES
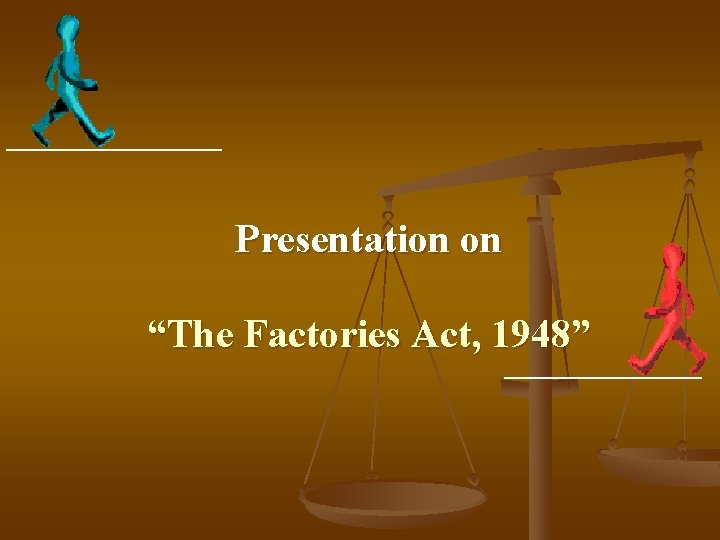
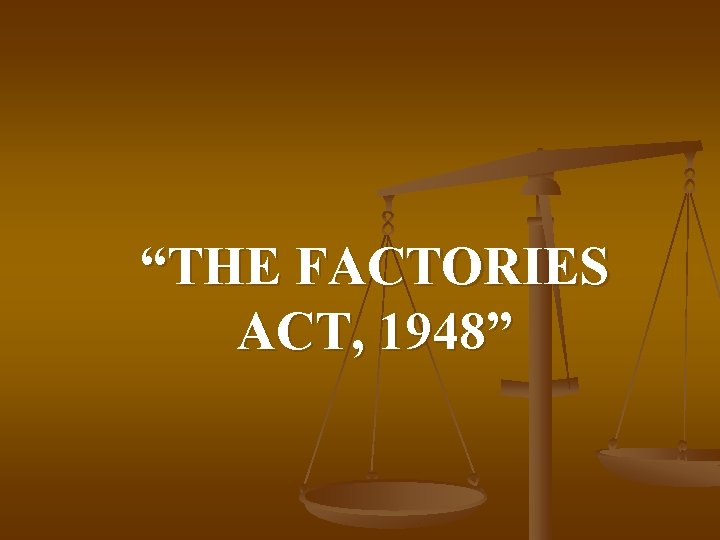
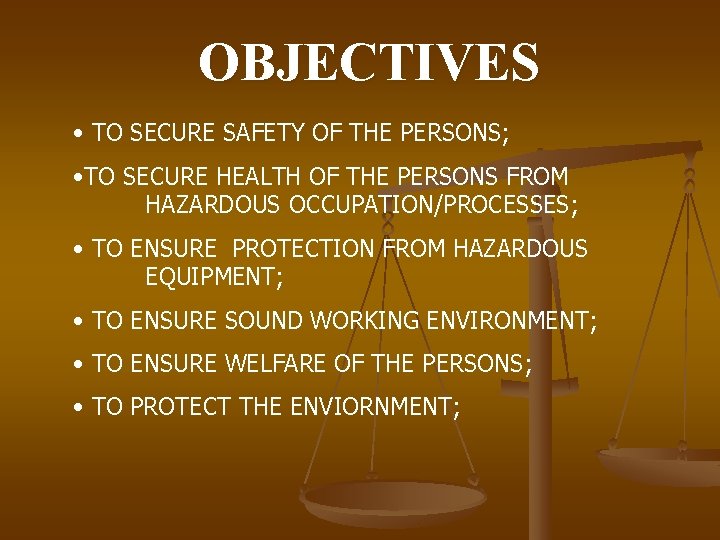
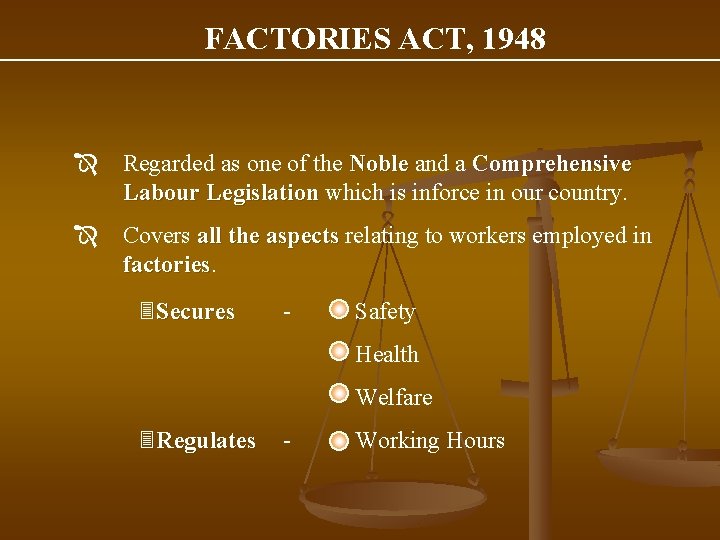
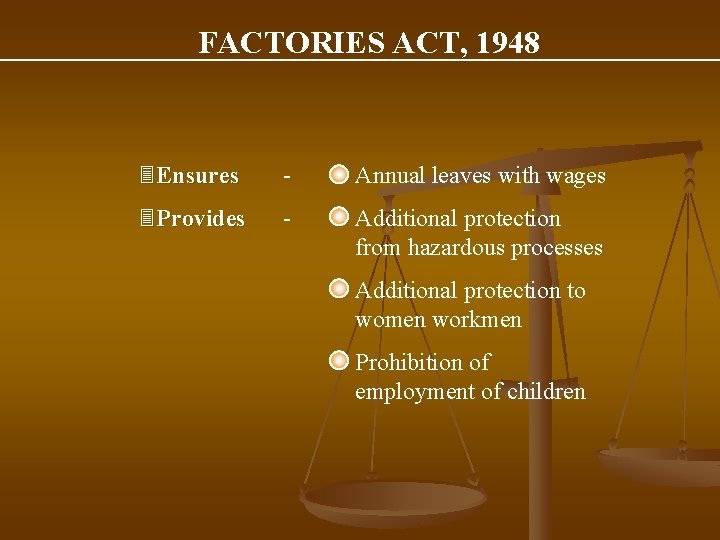
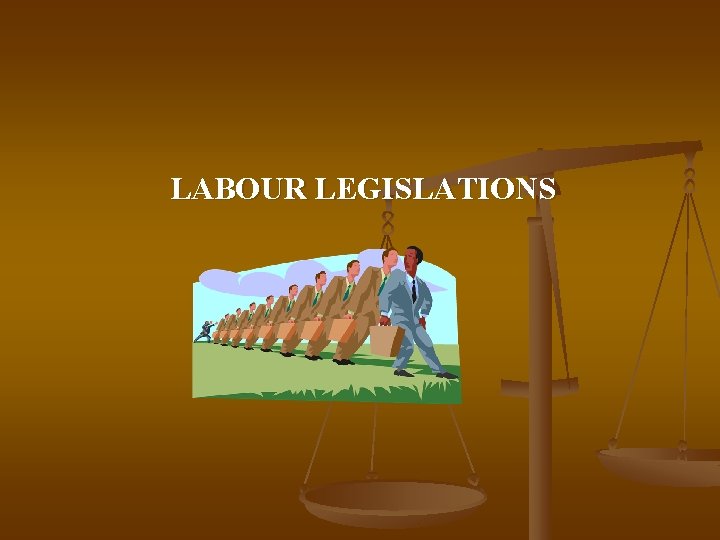
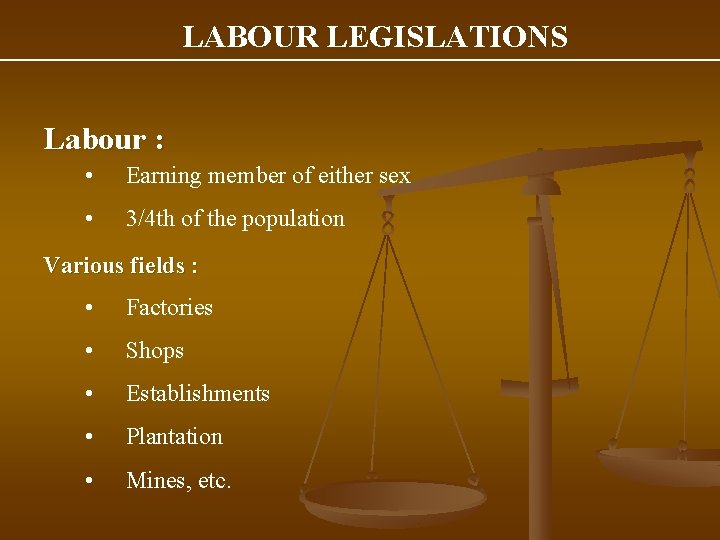
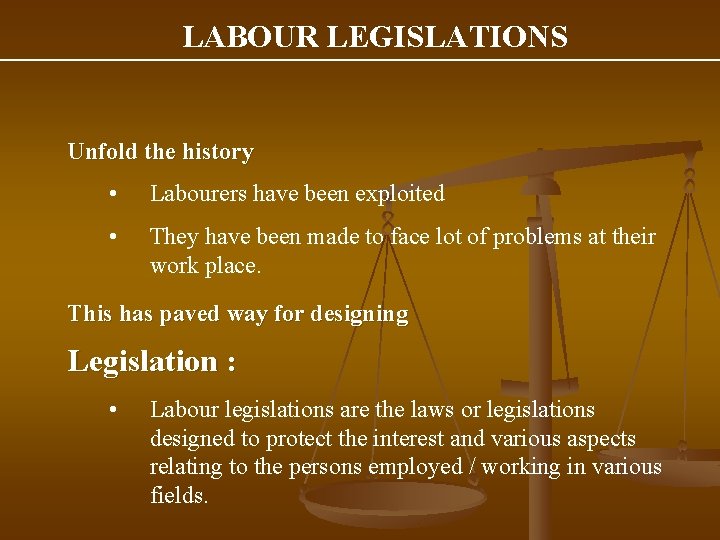
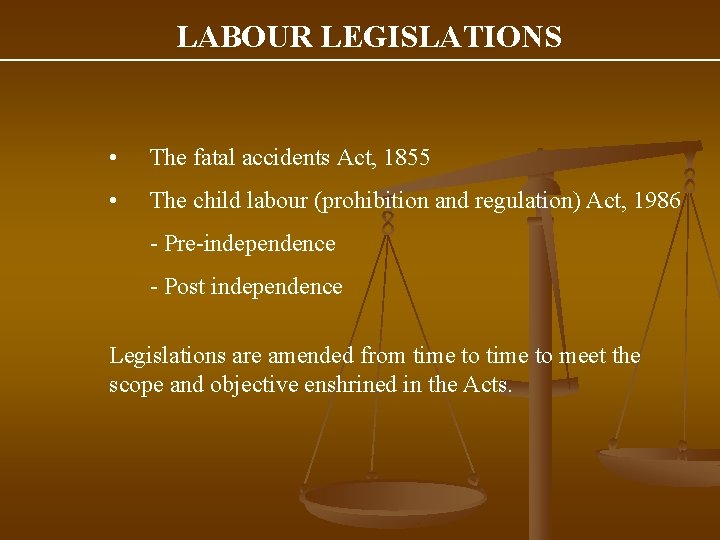
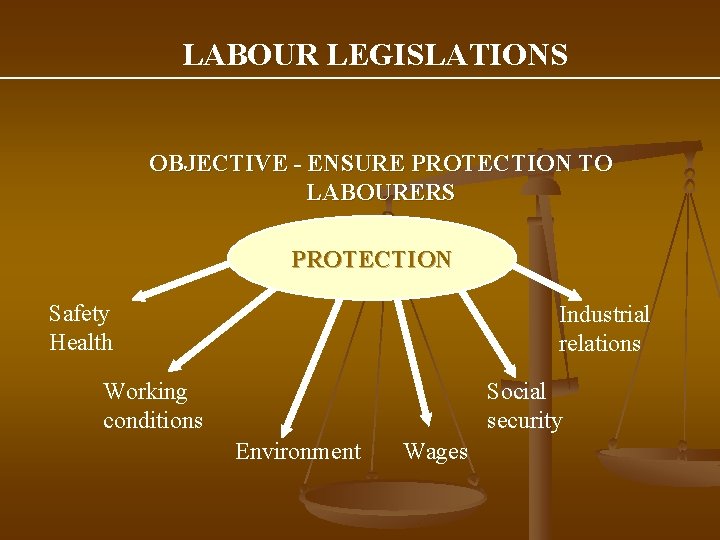
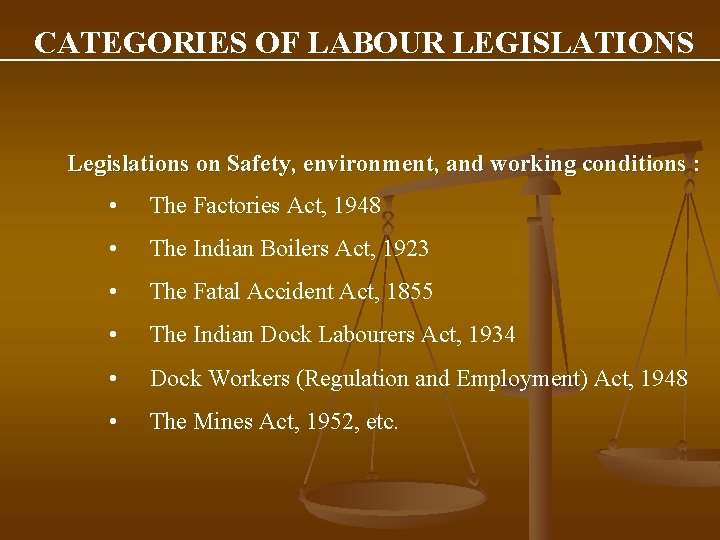
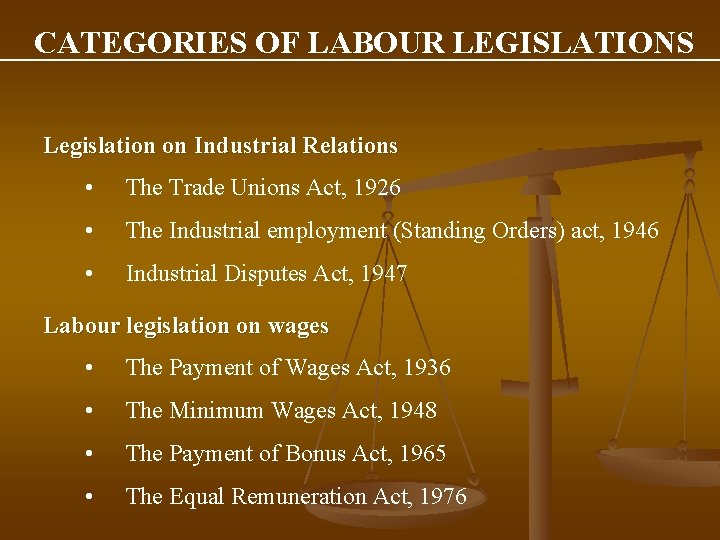
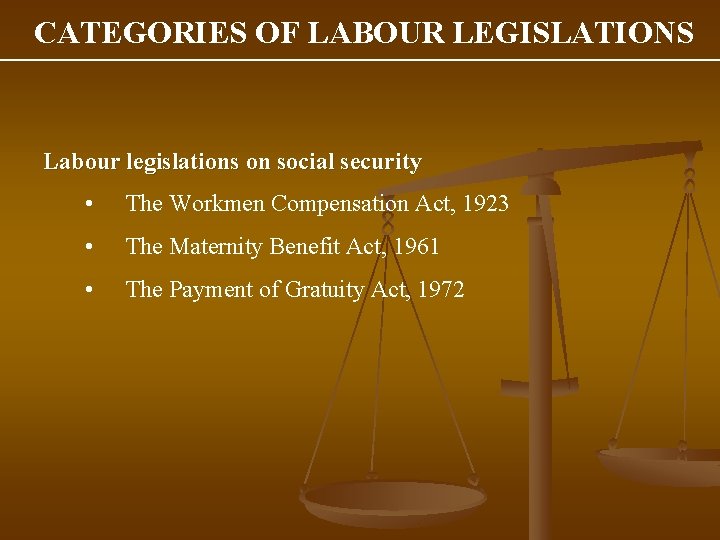
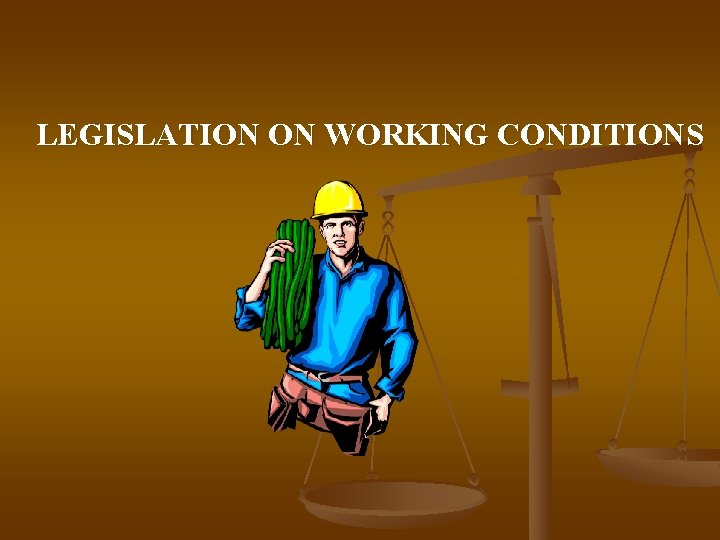
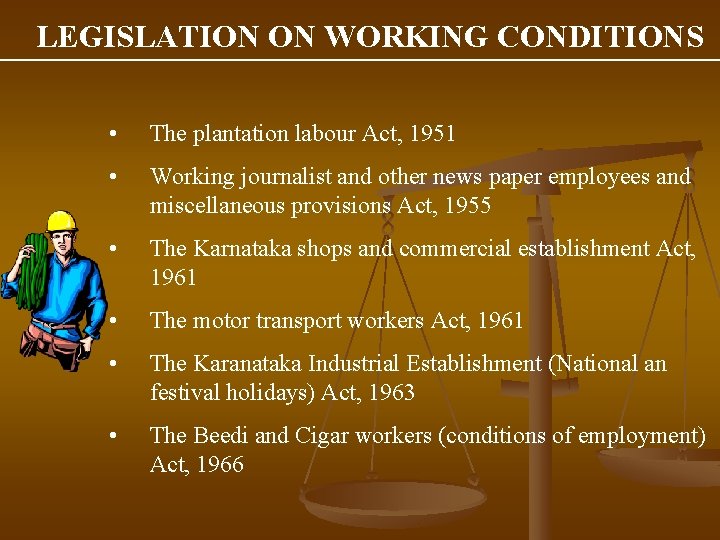
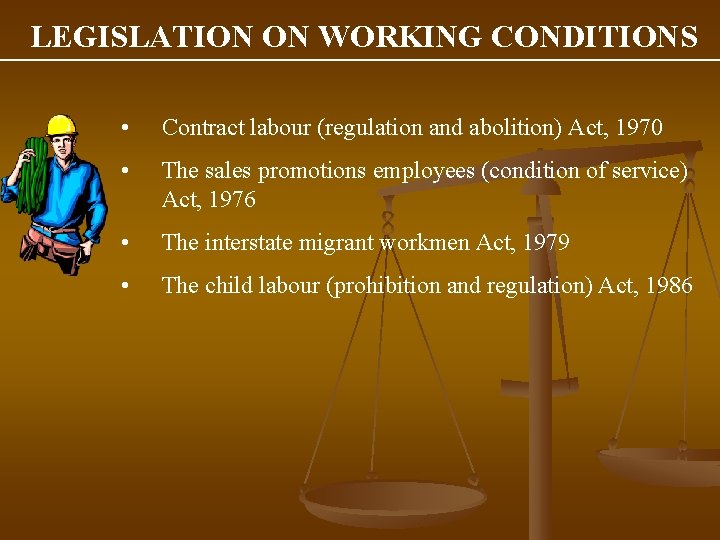
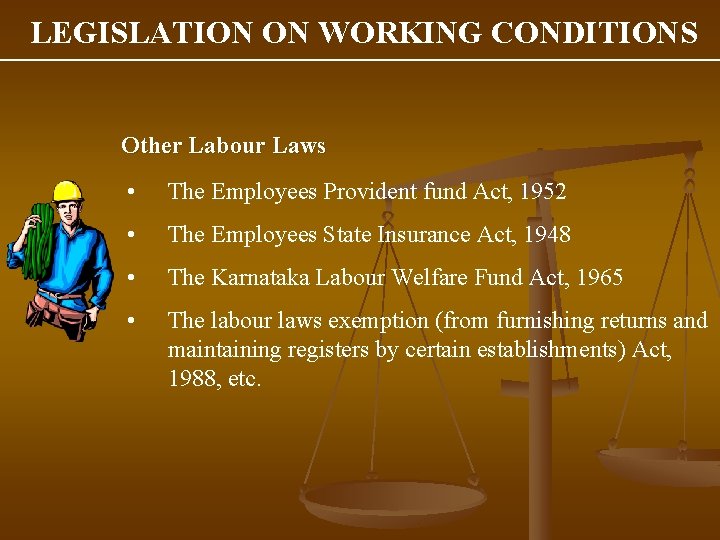
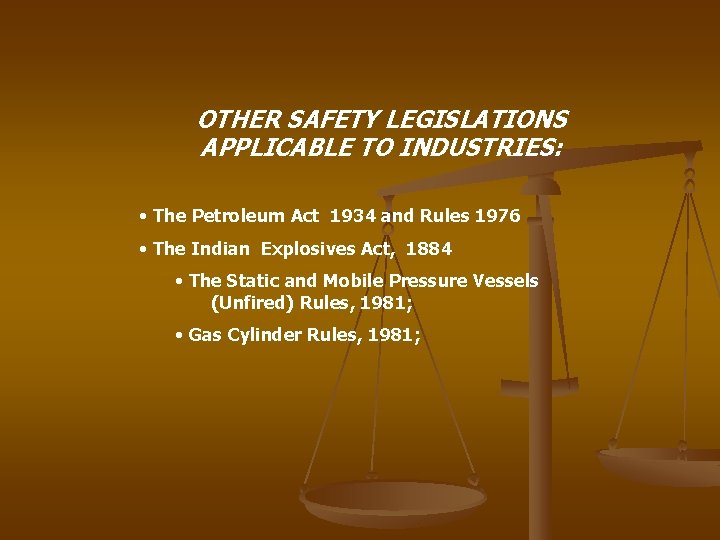
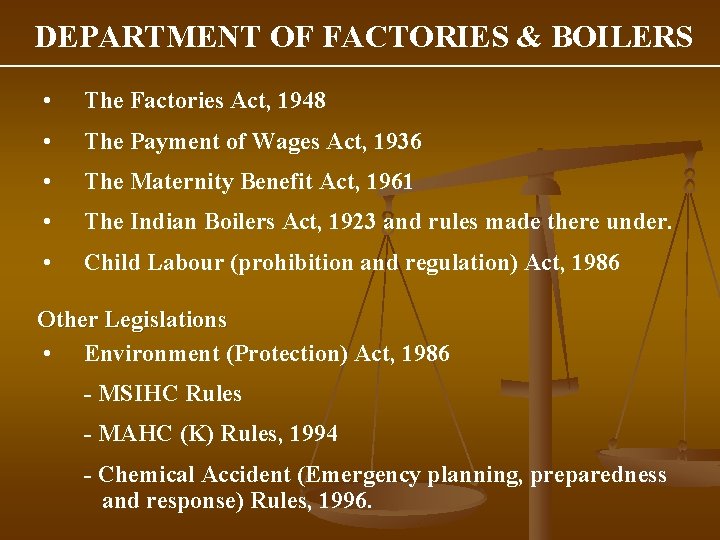
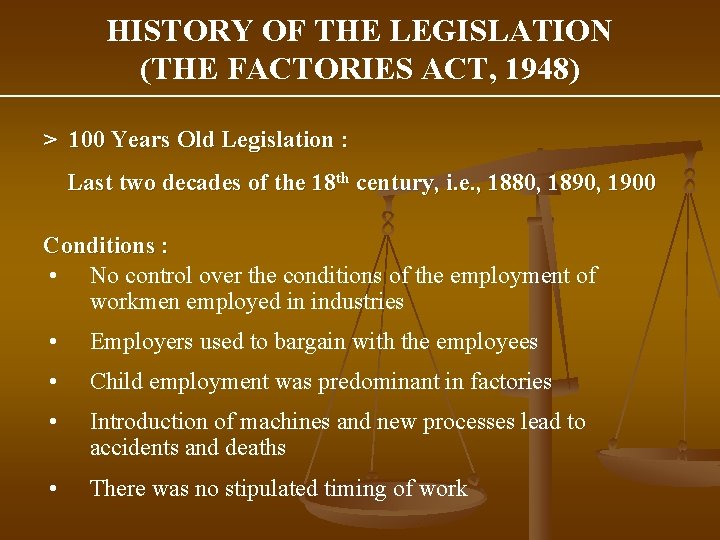
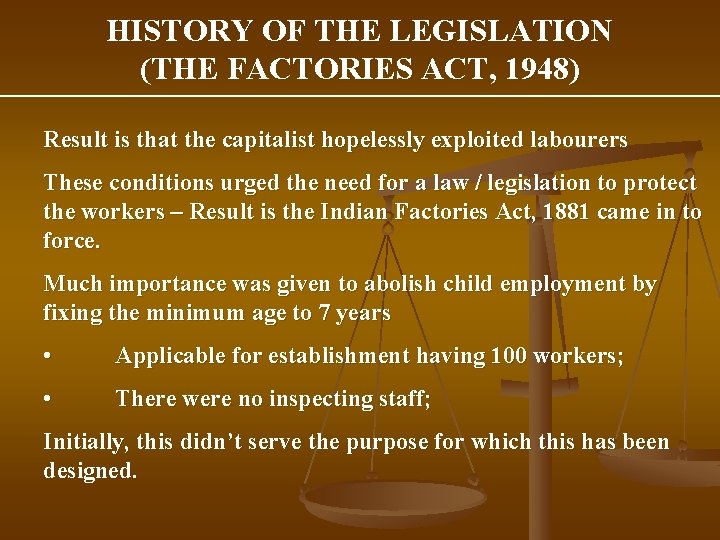
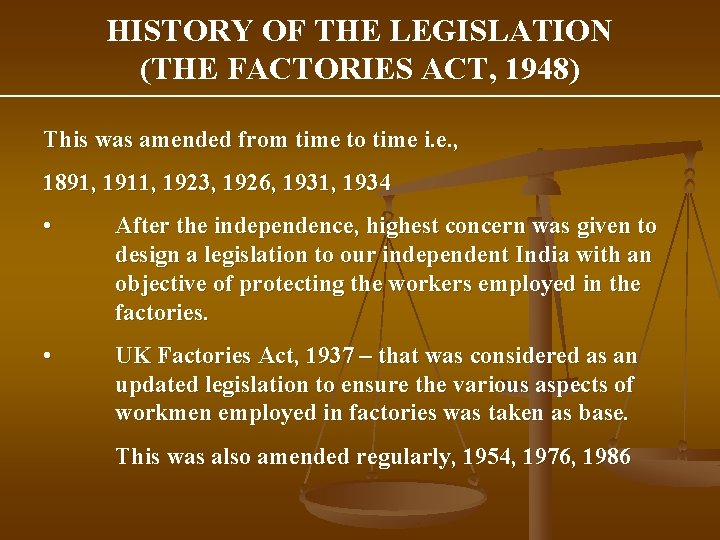
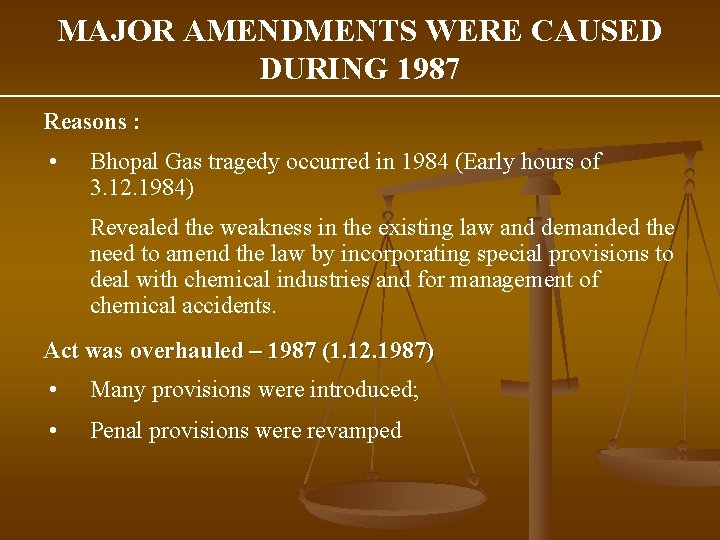
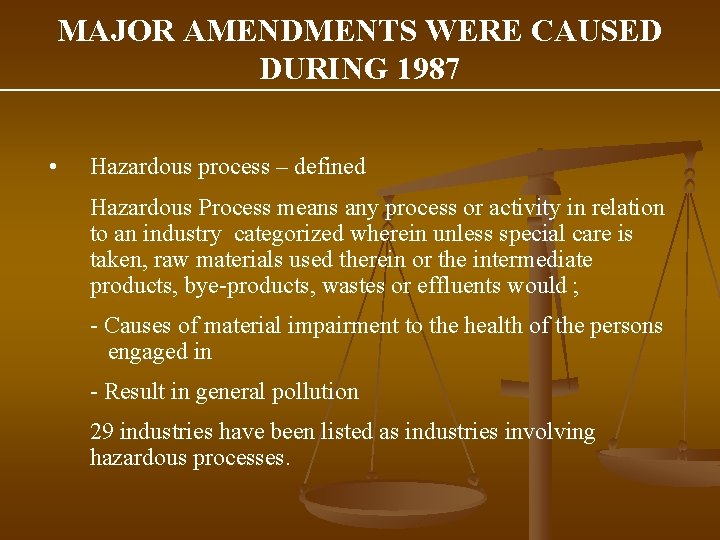
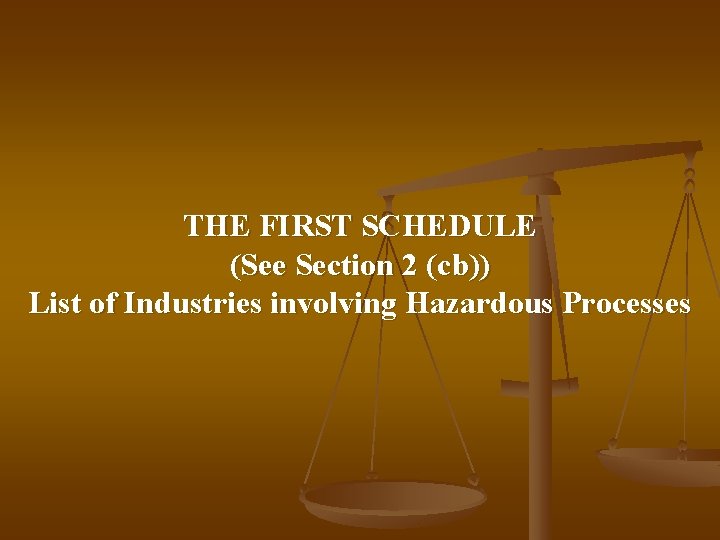
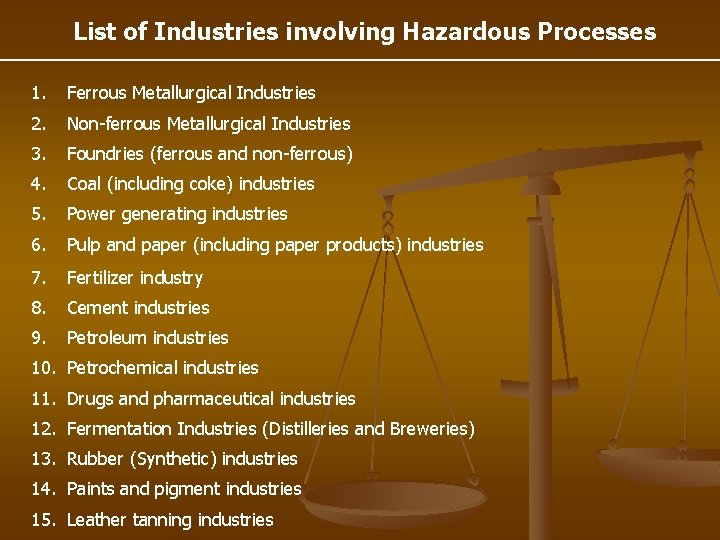
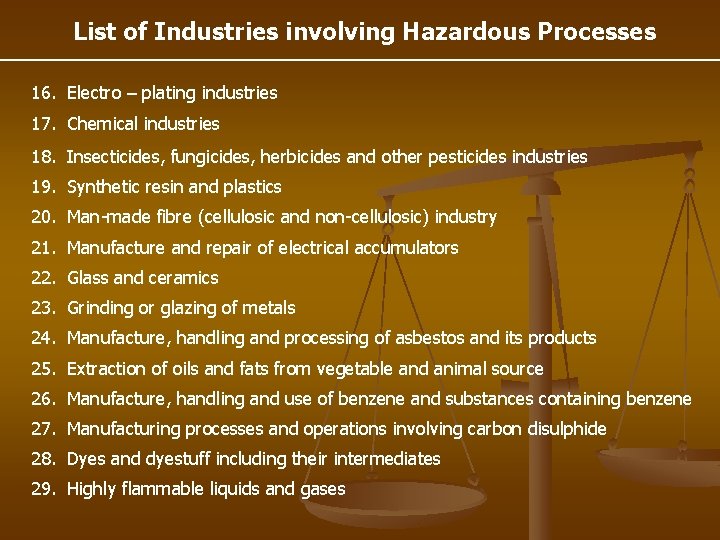
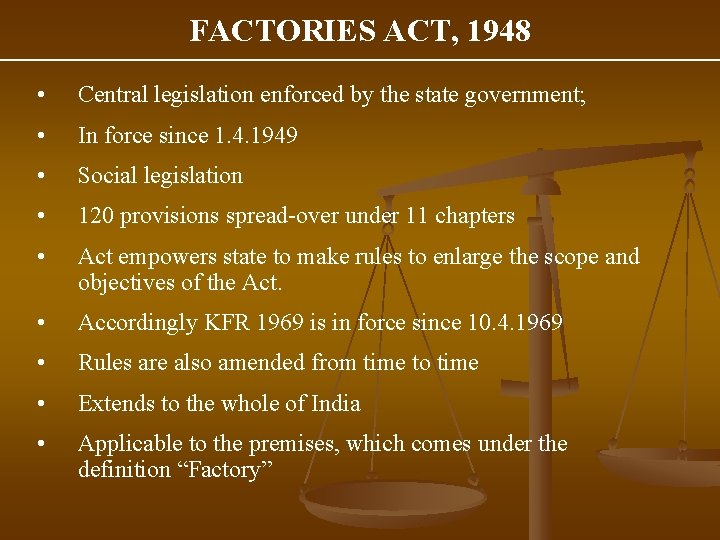
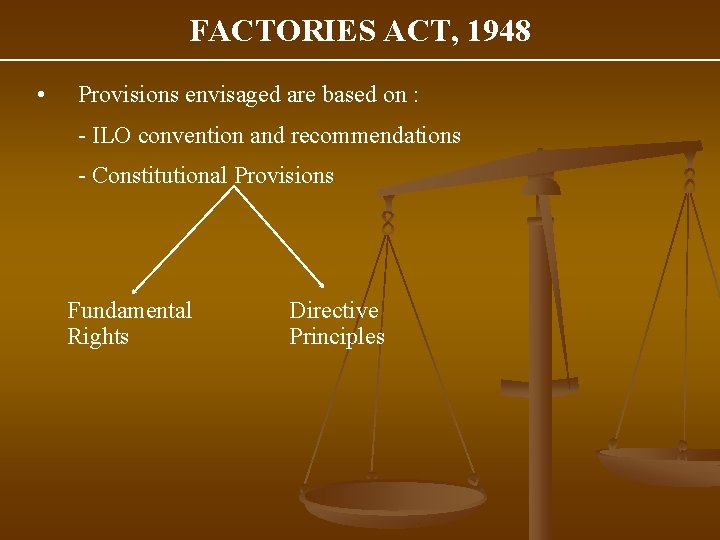
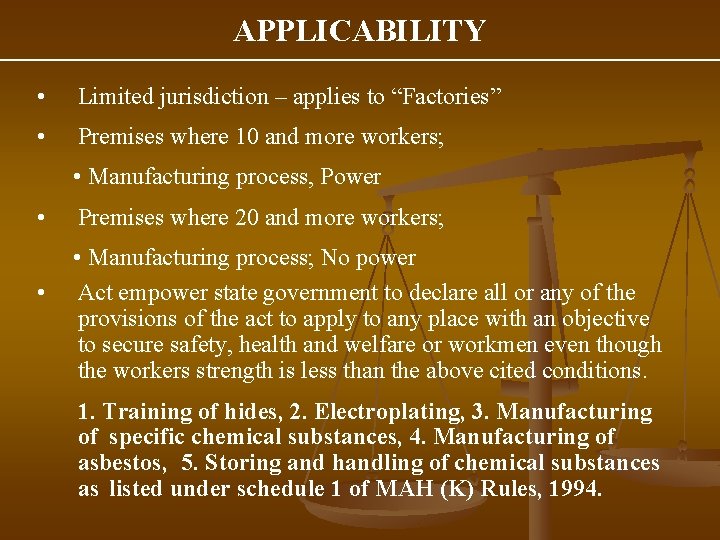
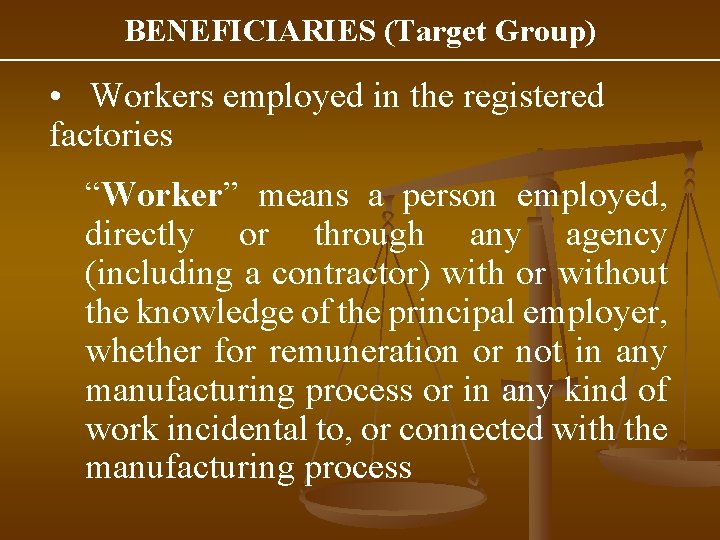
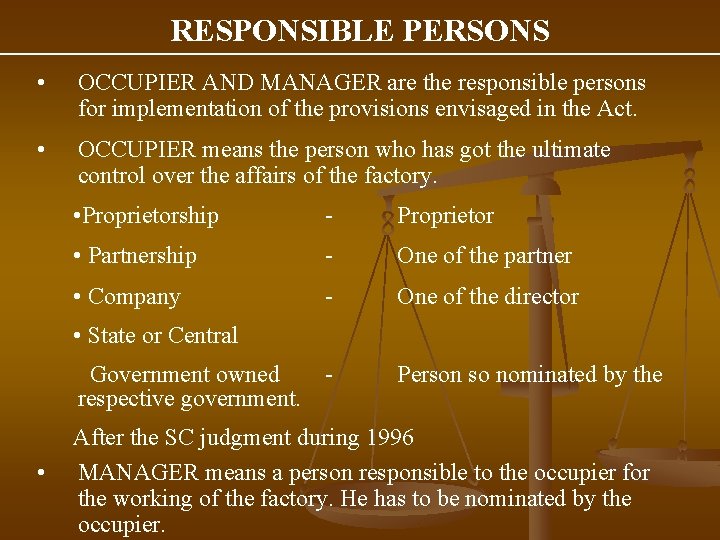
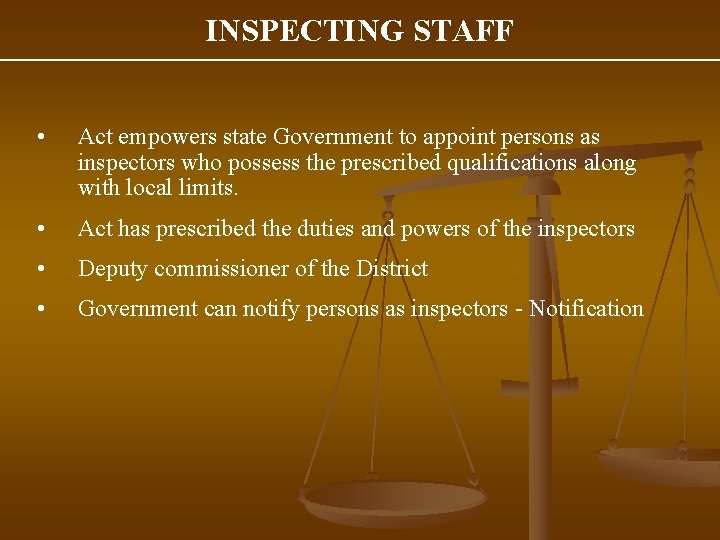
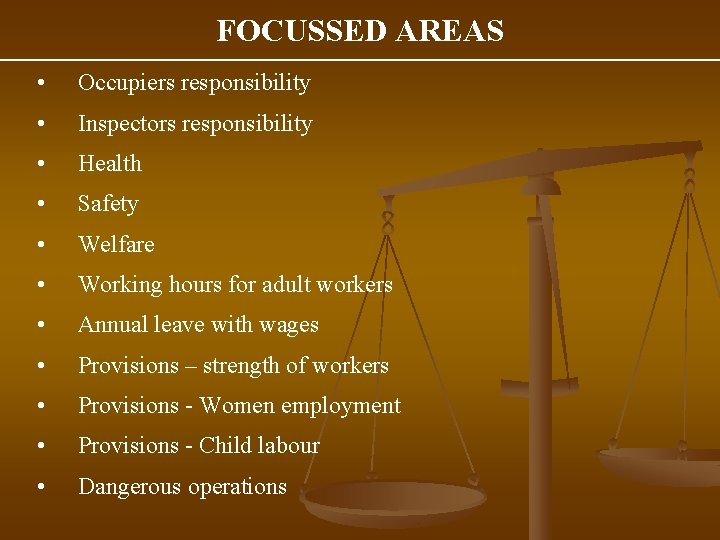
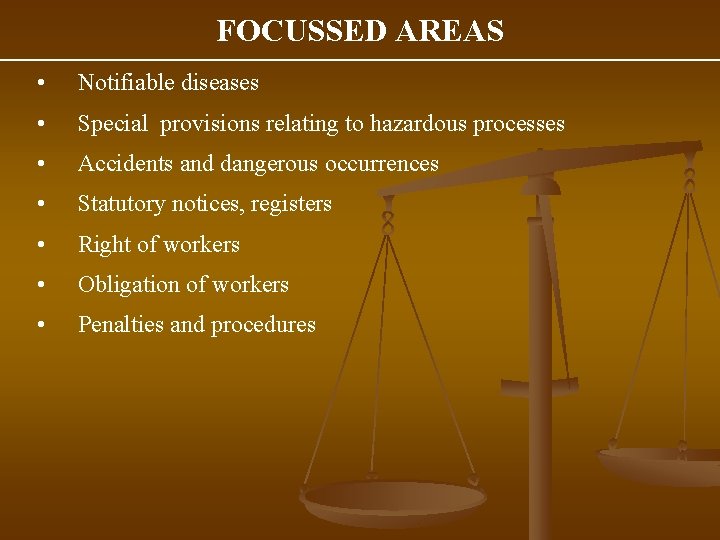
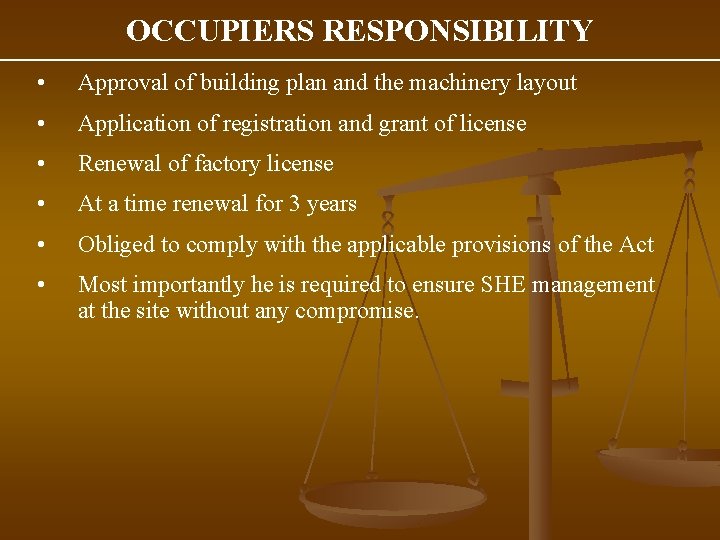
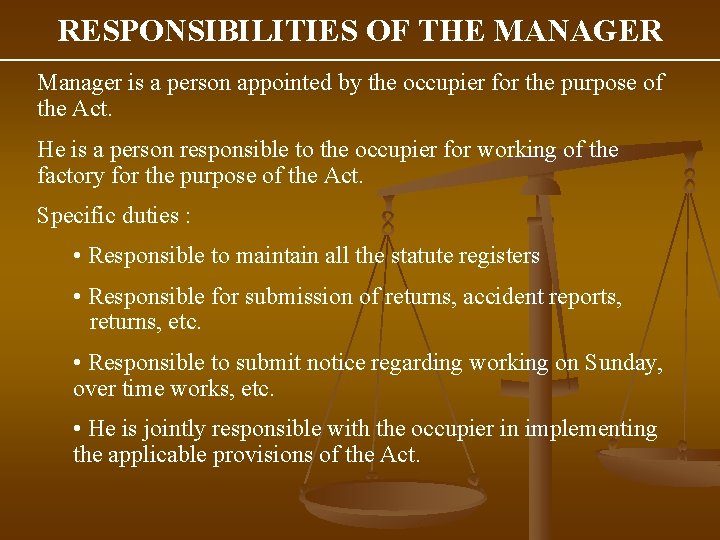
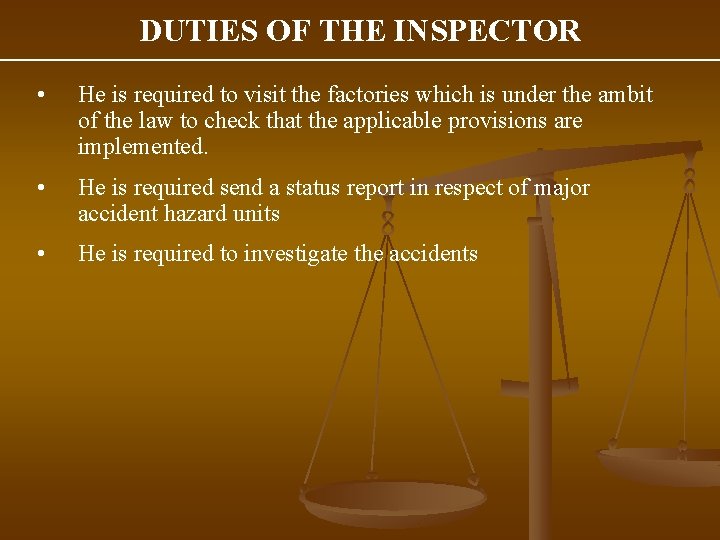
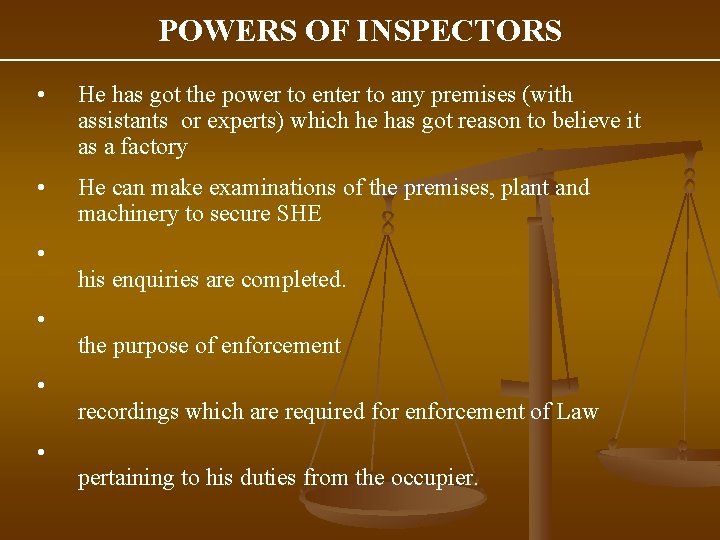
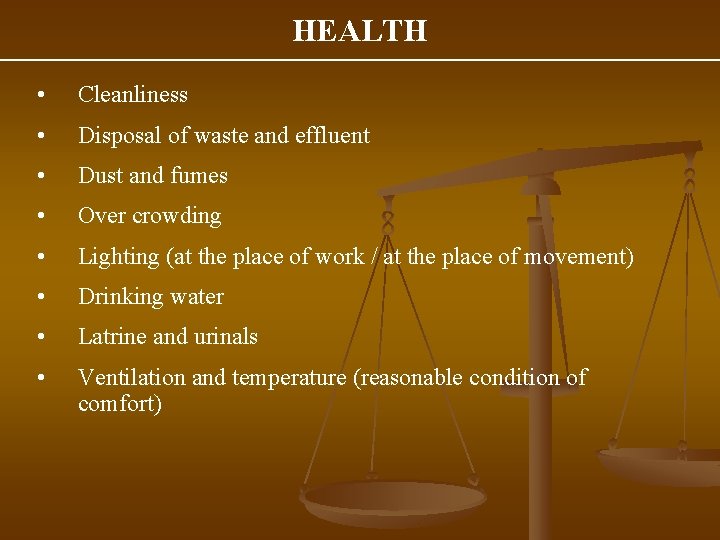
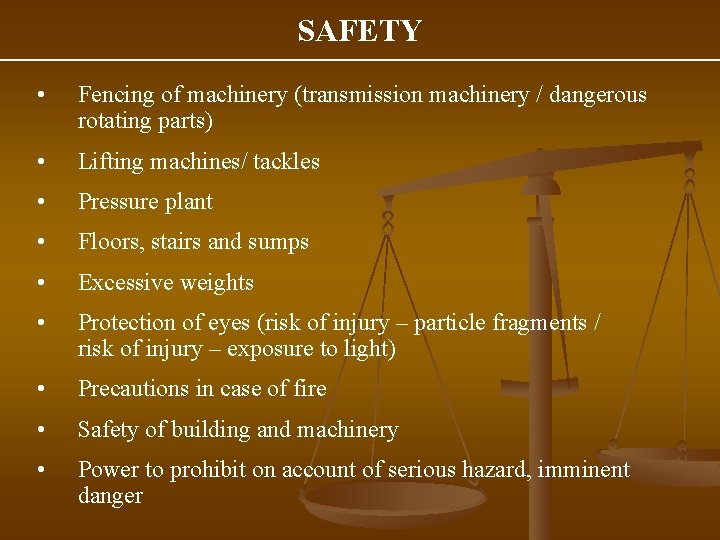
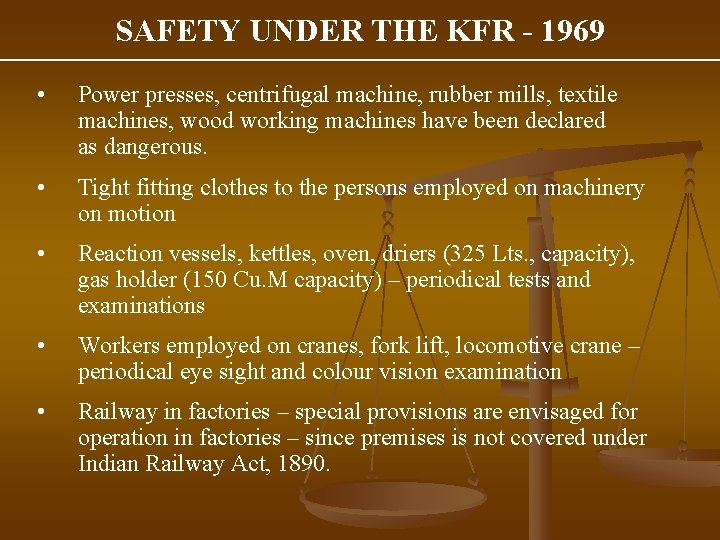
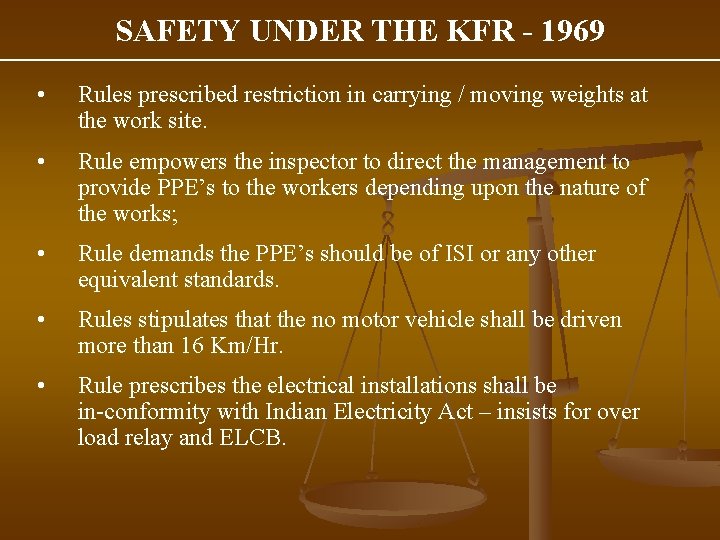
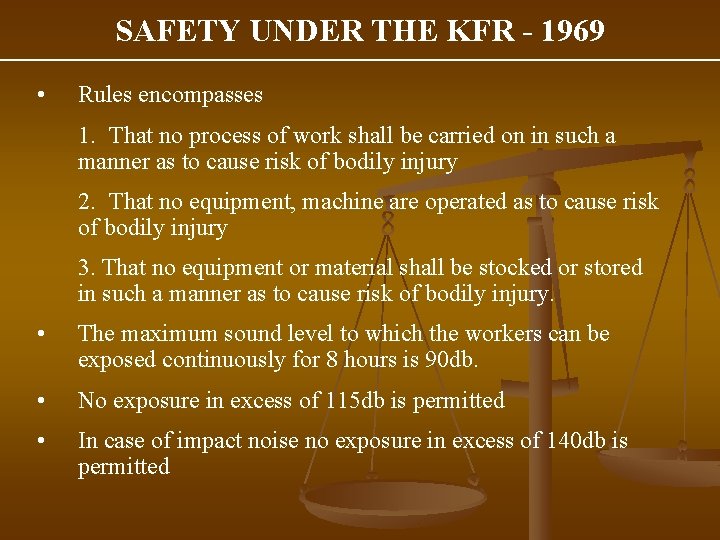
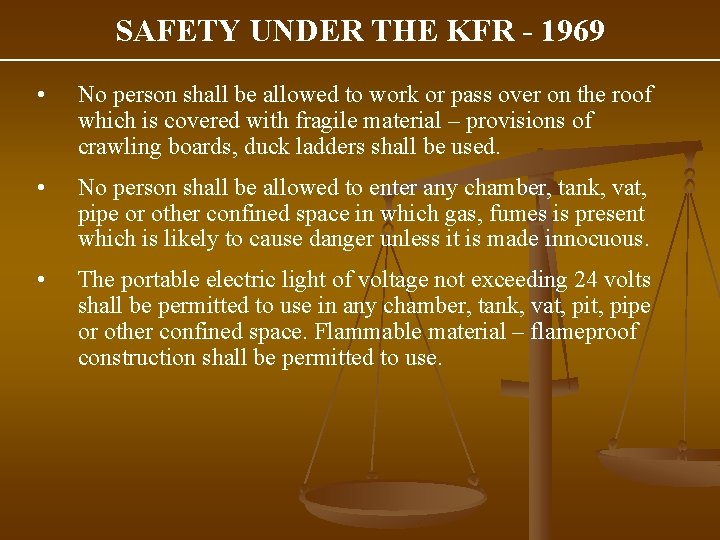
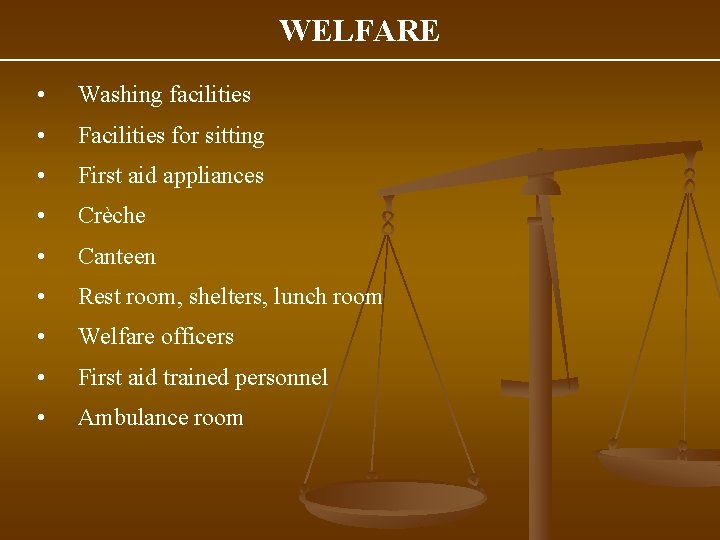
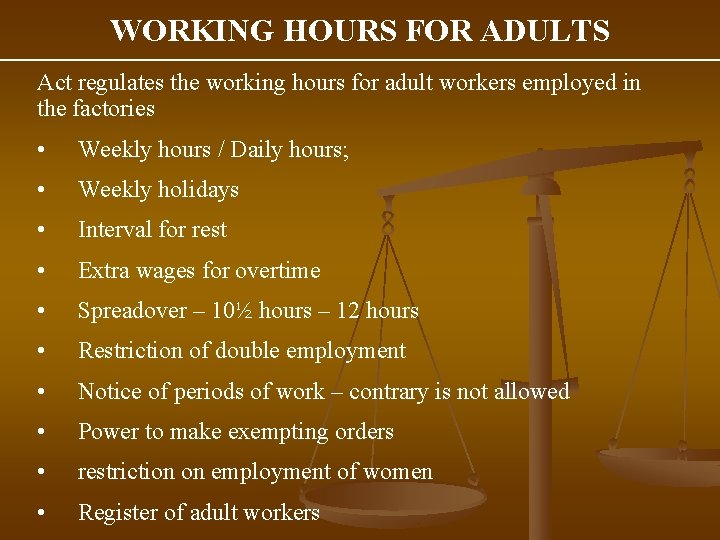
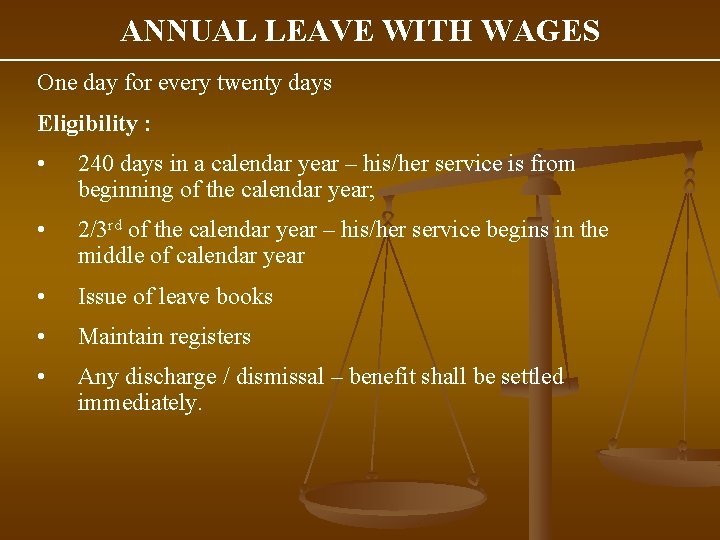
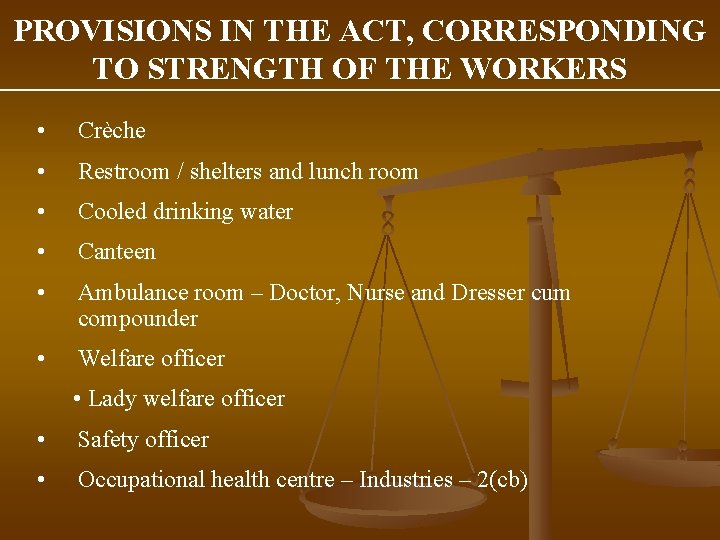
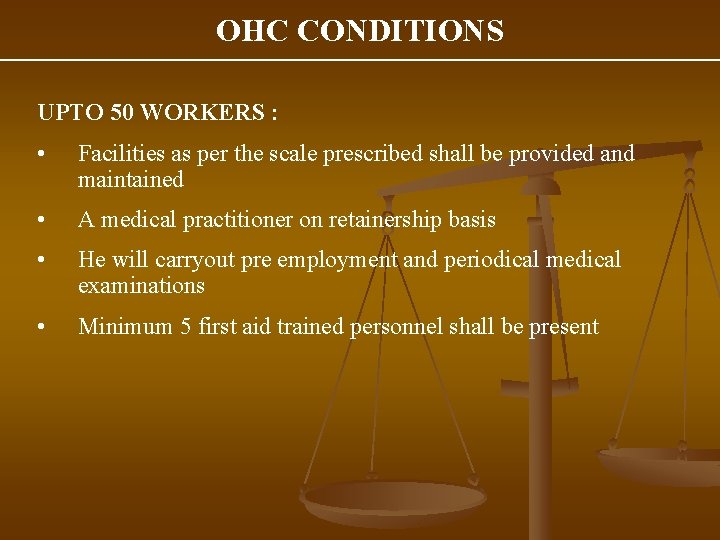

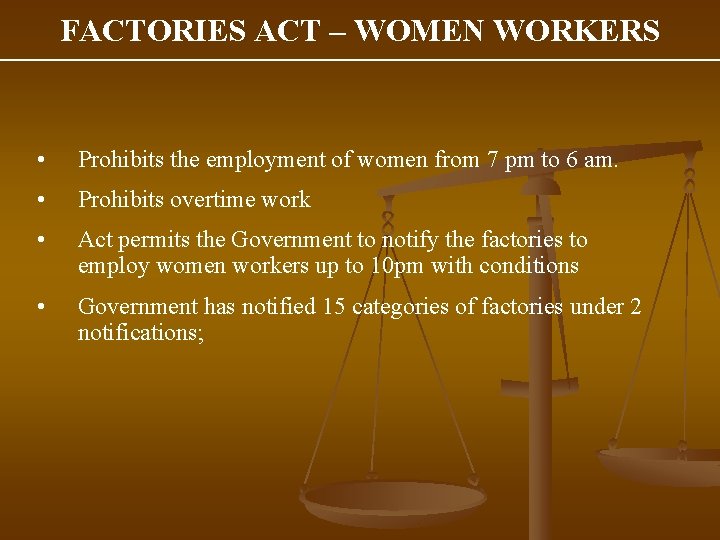
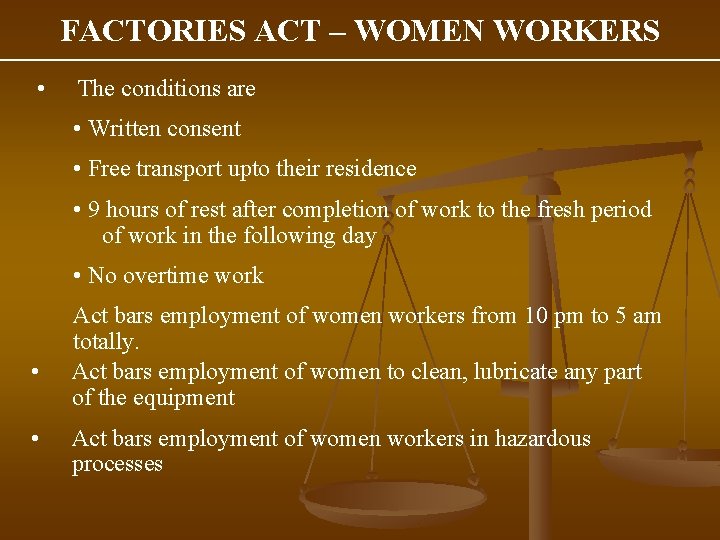
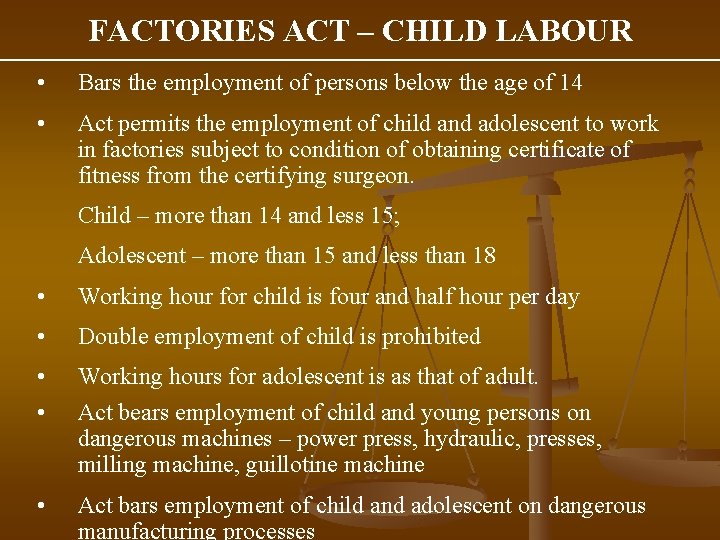
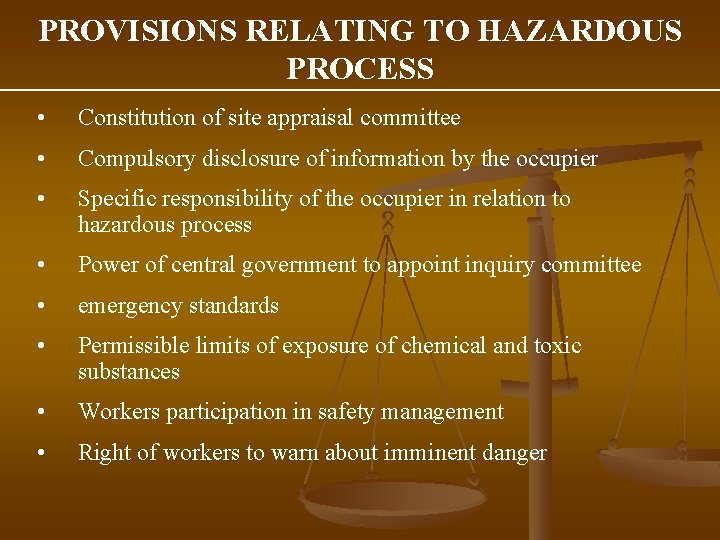
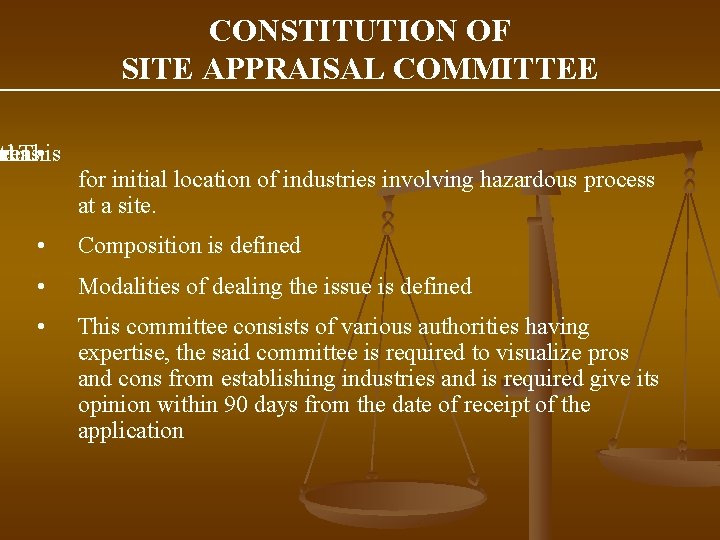
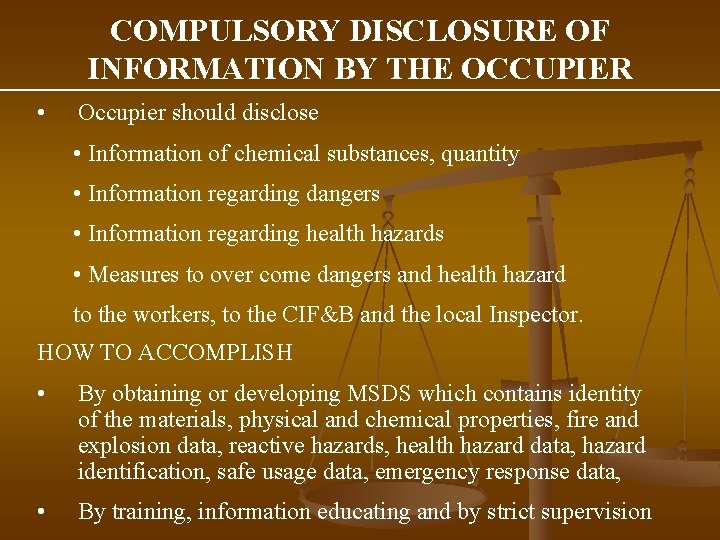

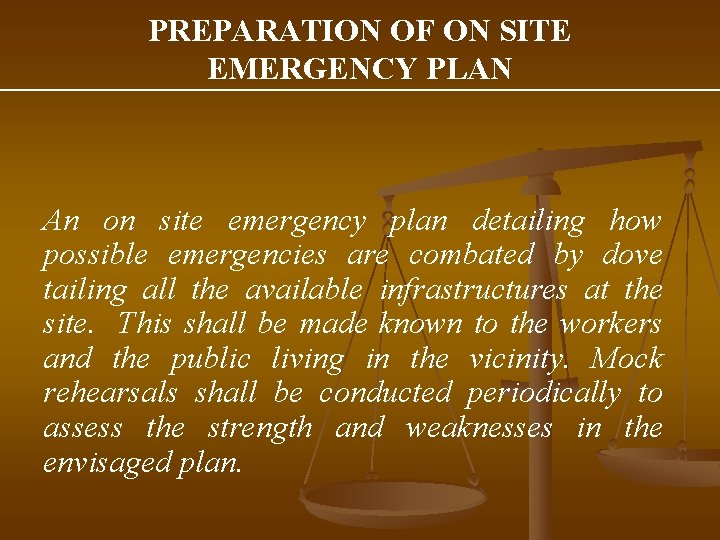
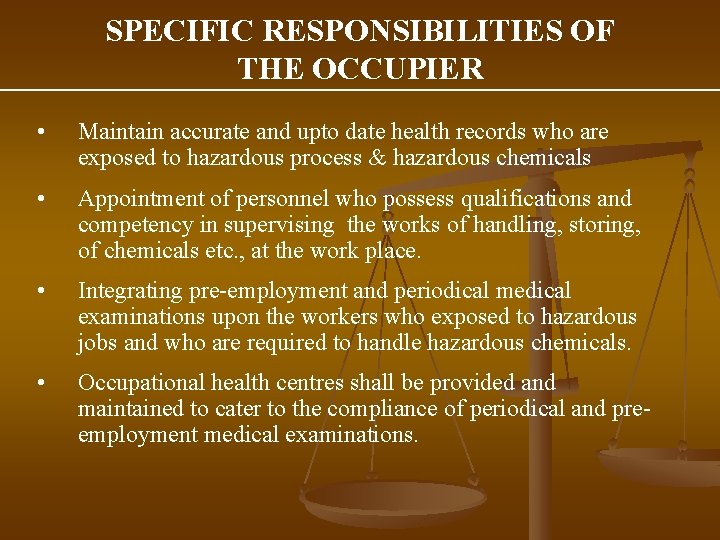
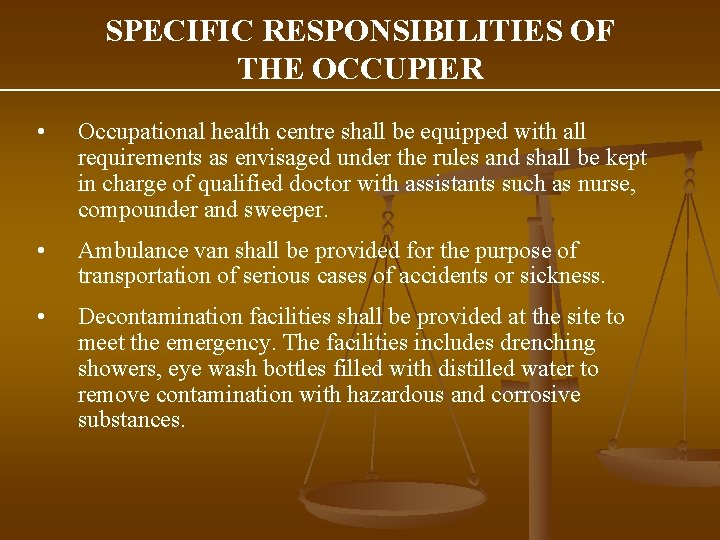
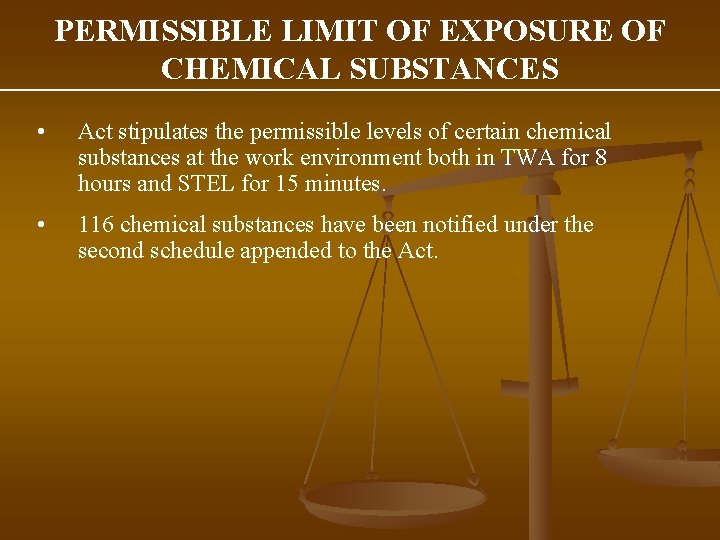
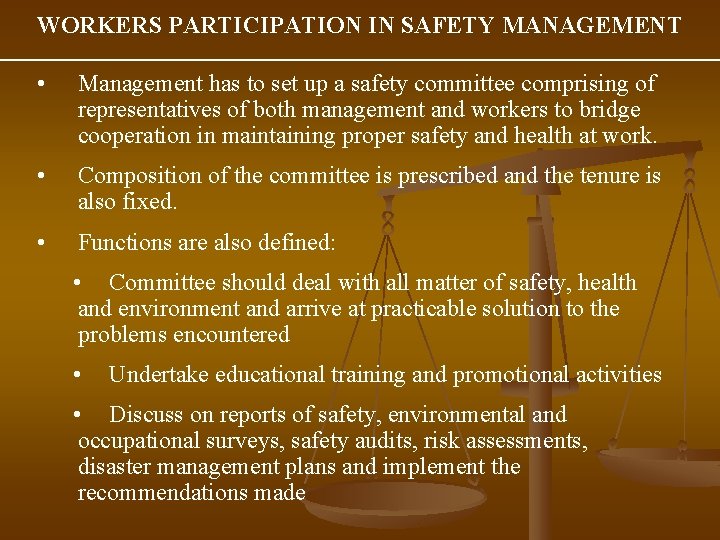
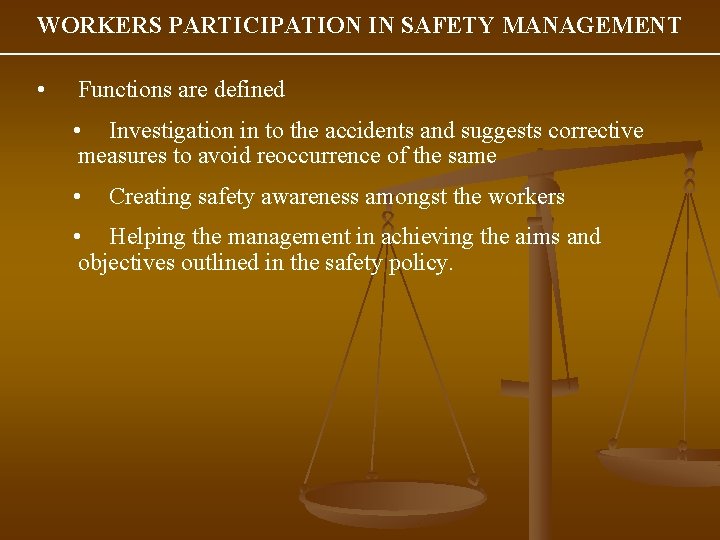
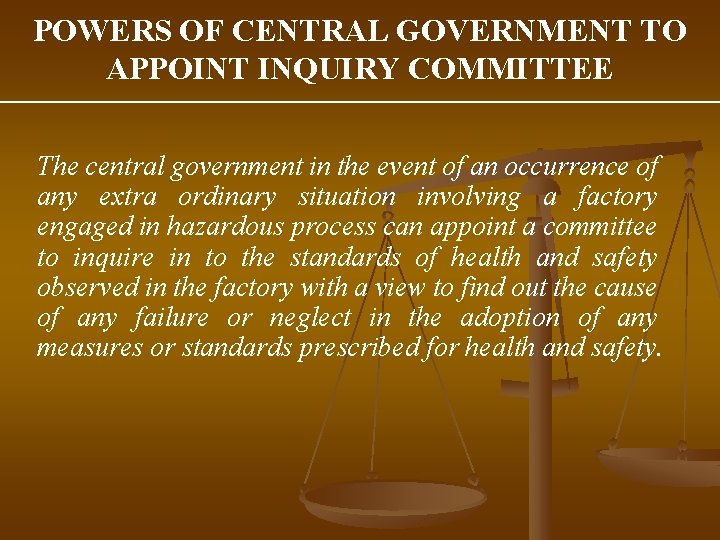
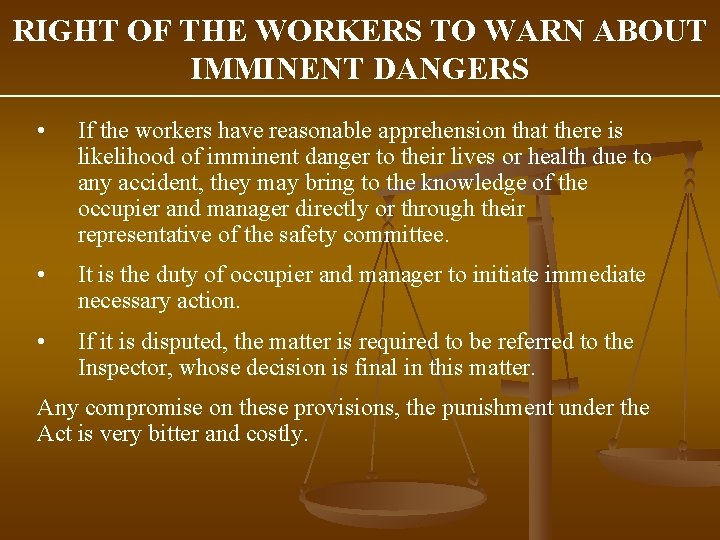
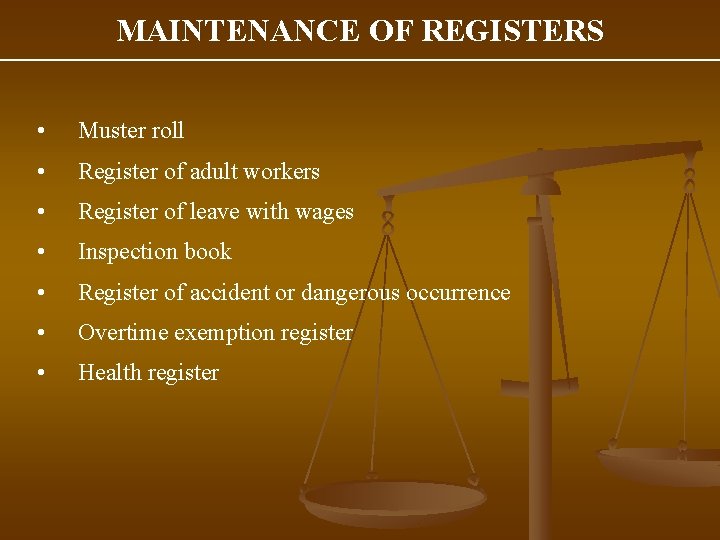
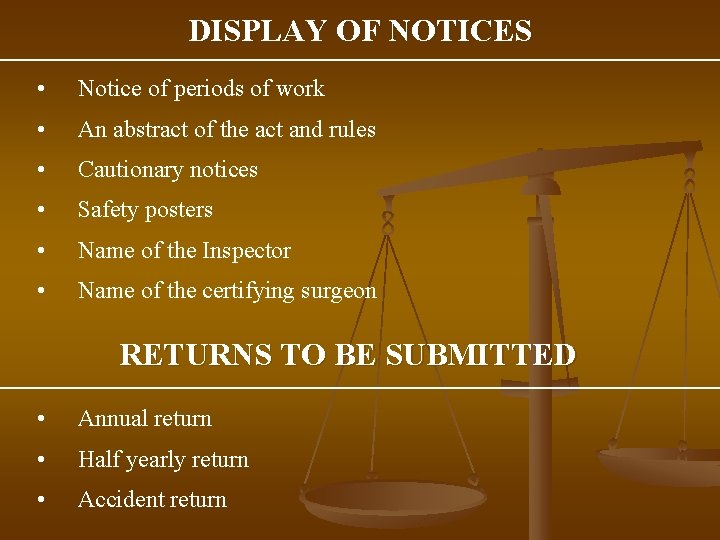
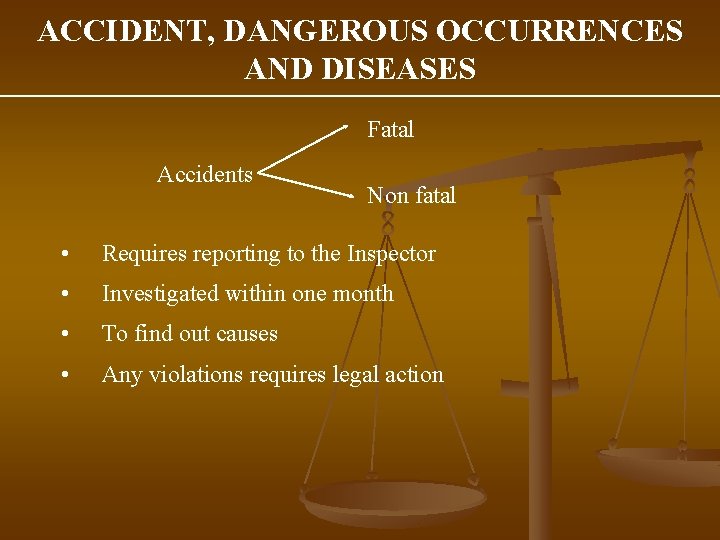
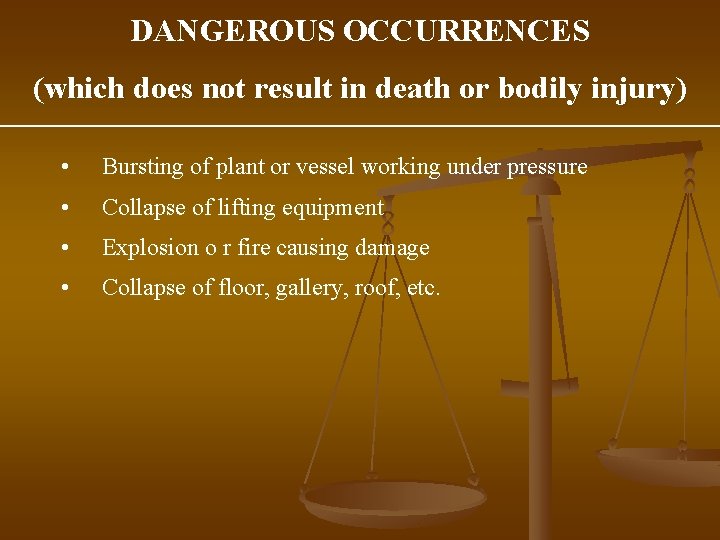
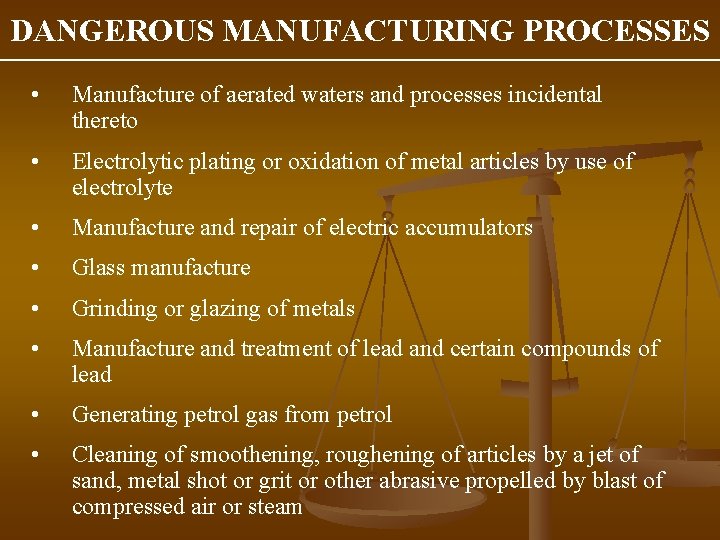
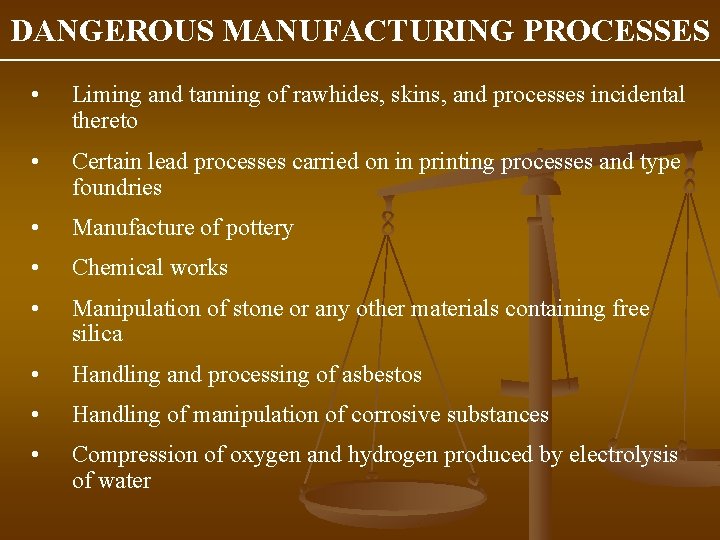
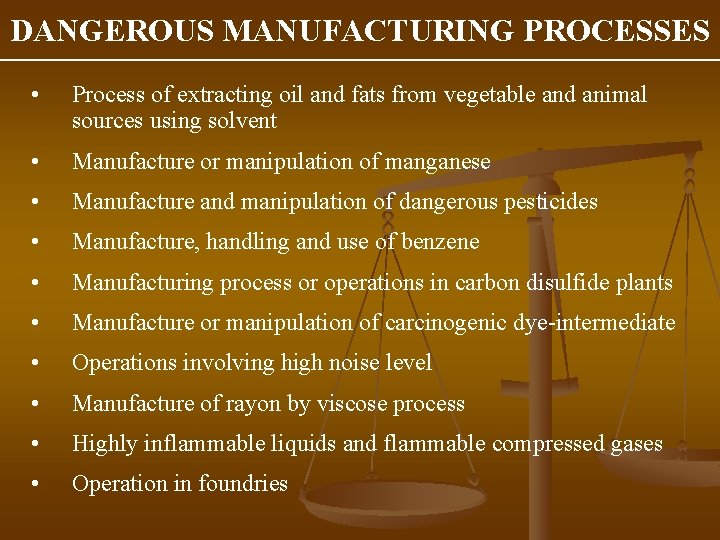
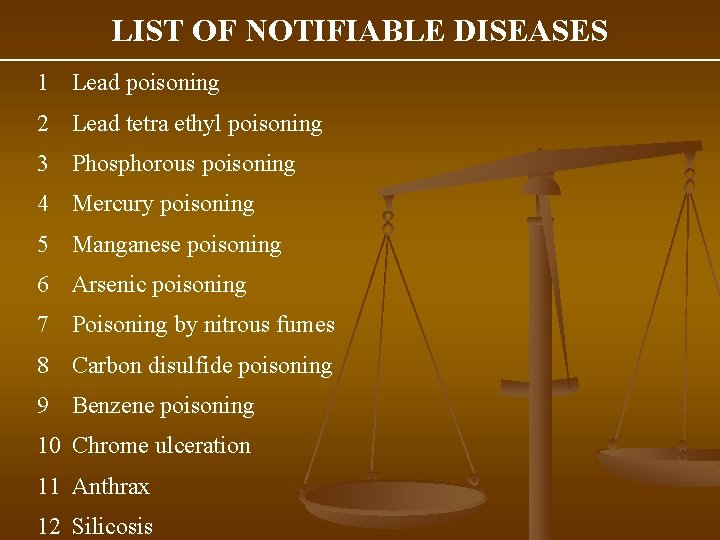
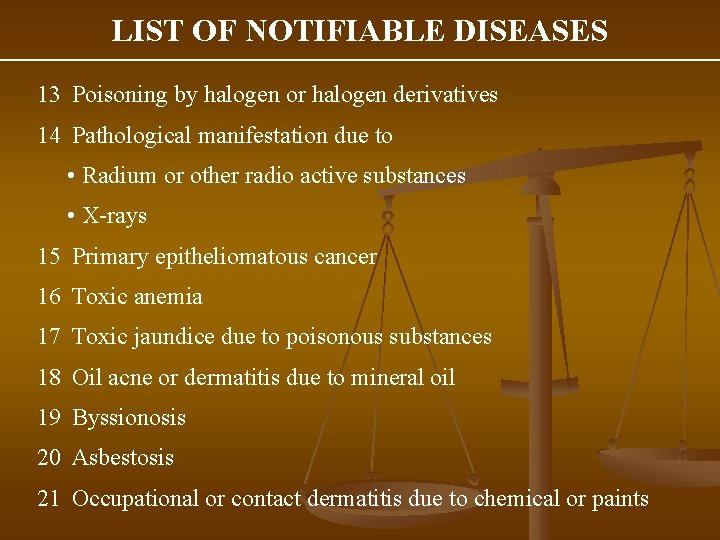
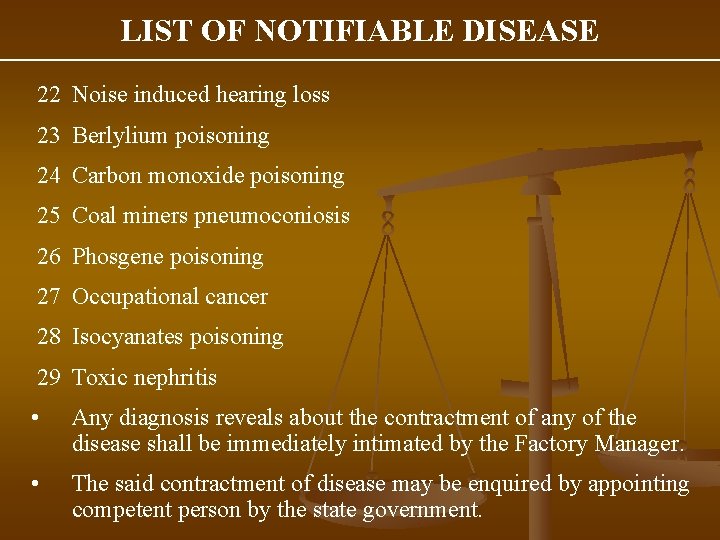
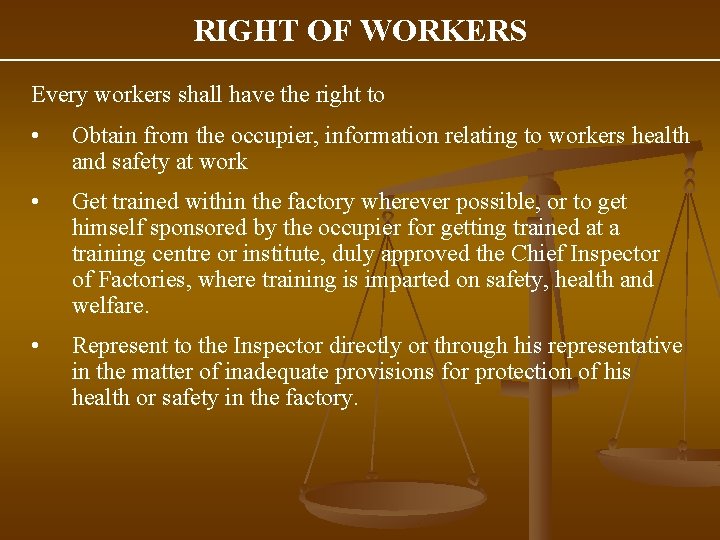
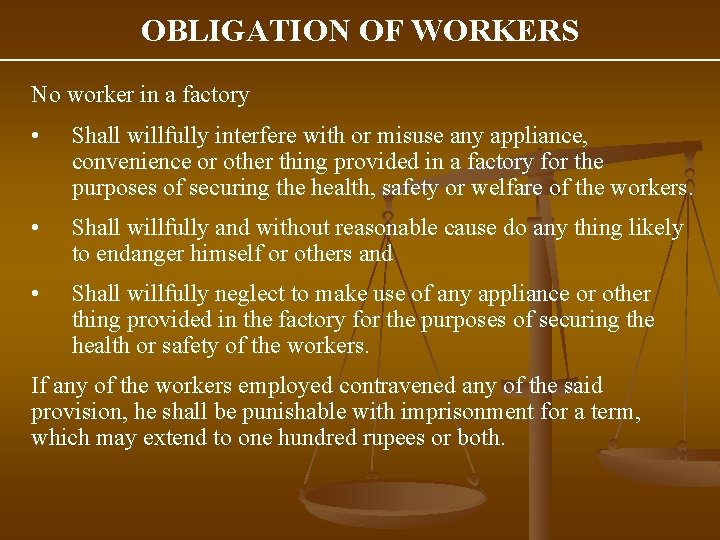
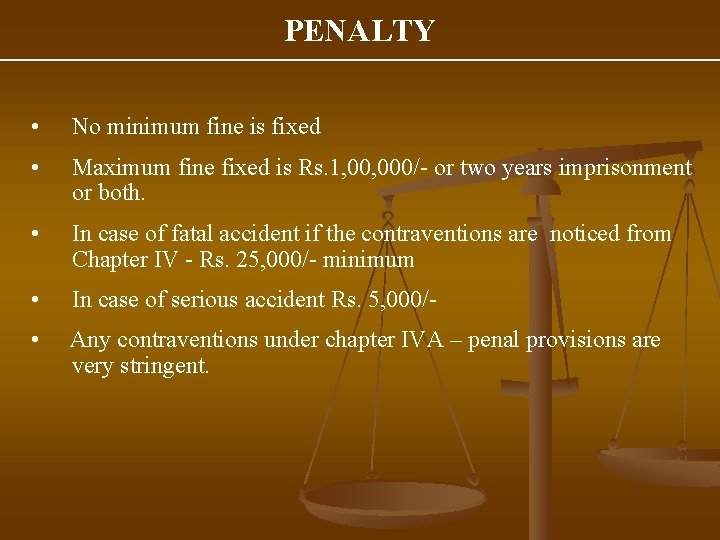
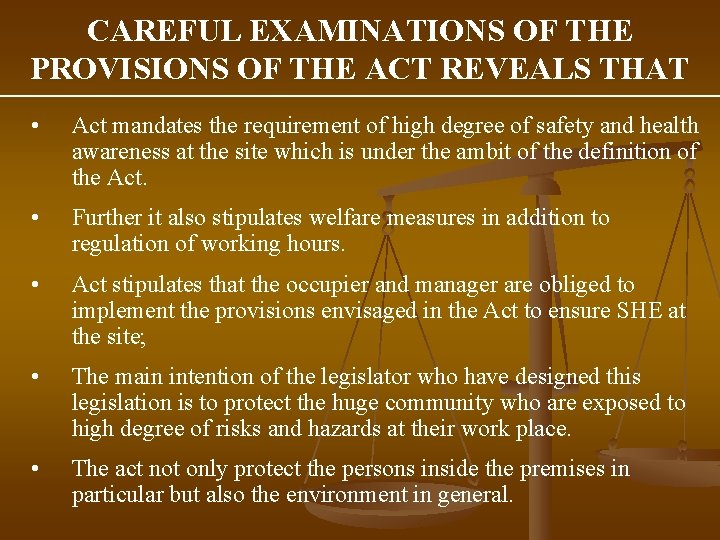
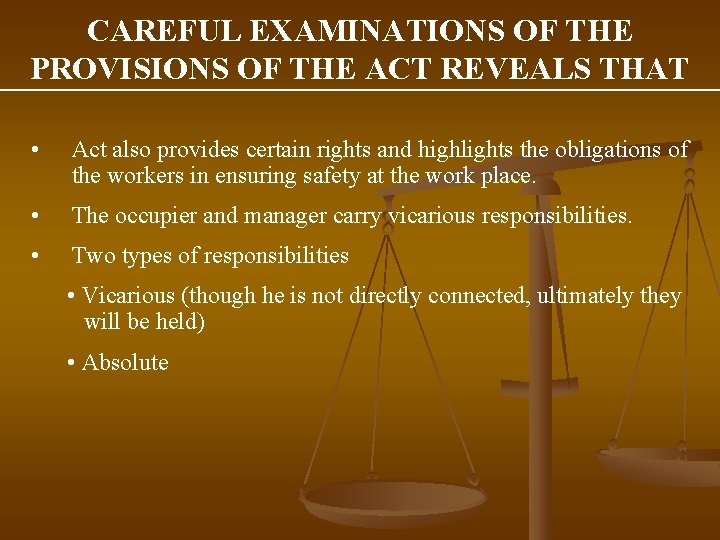
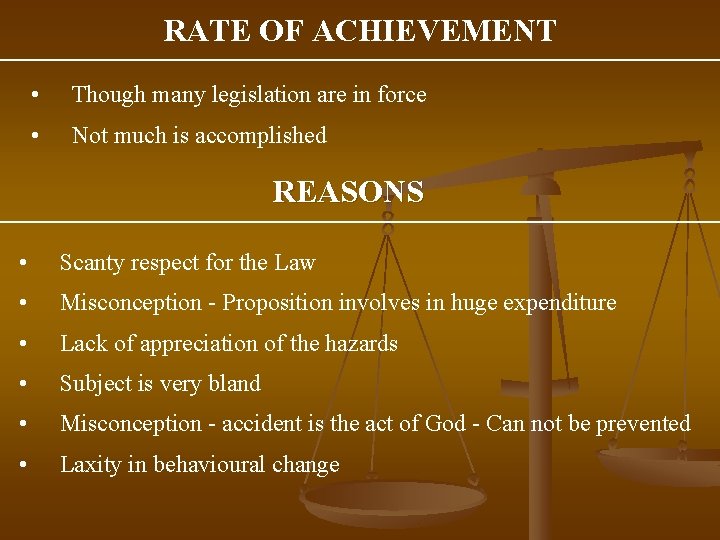
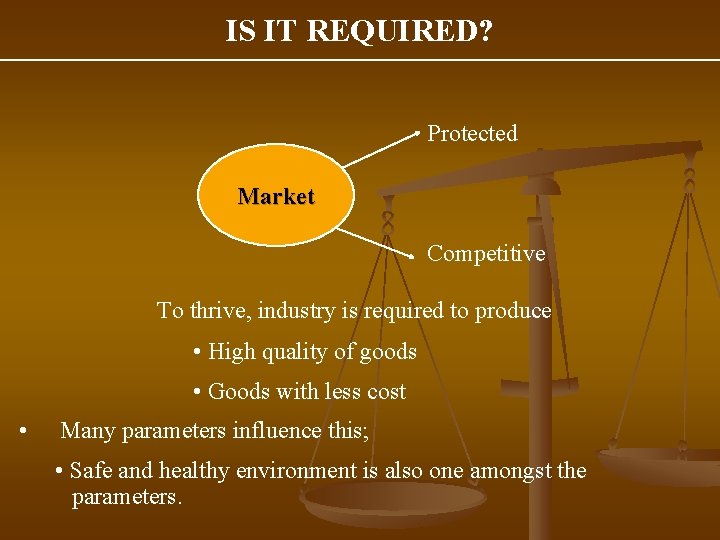
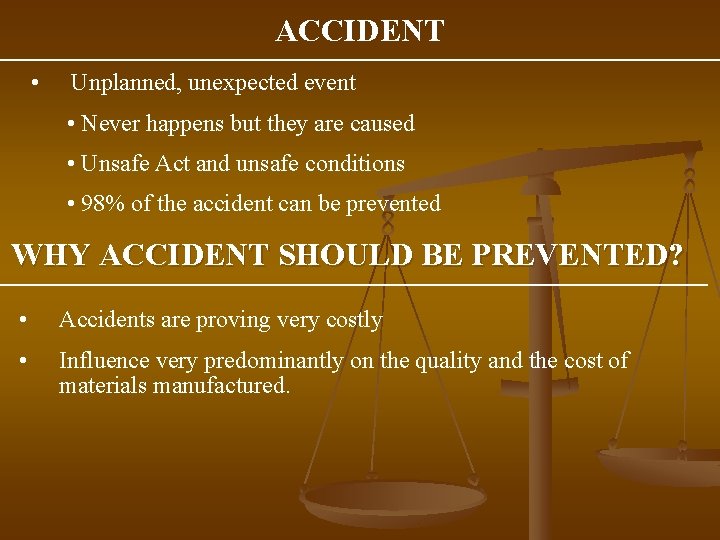
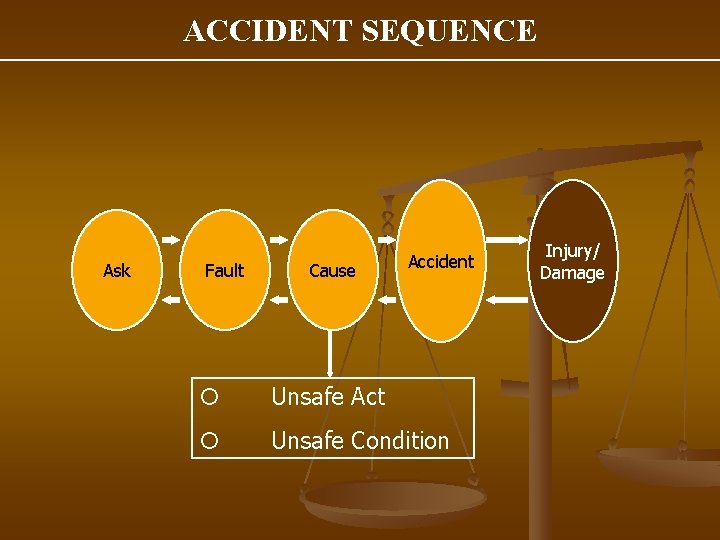
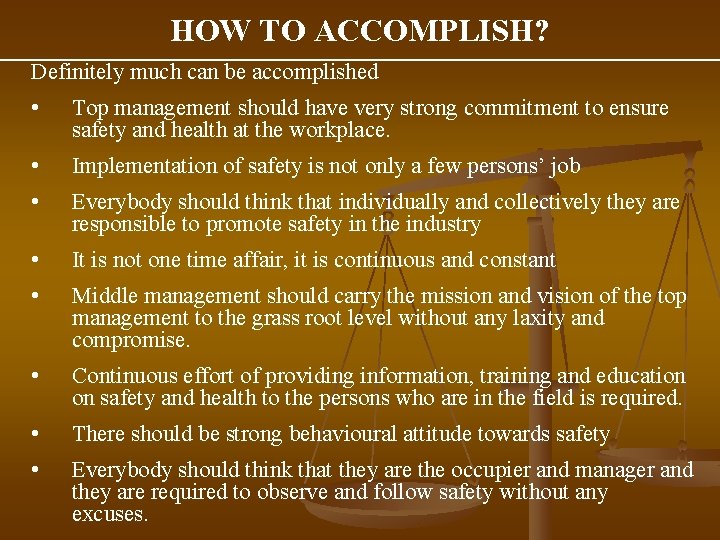
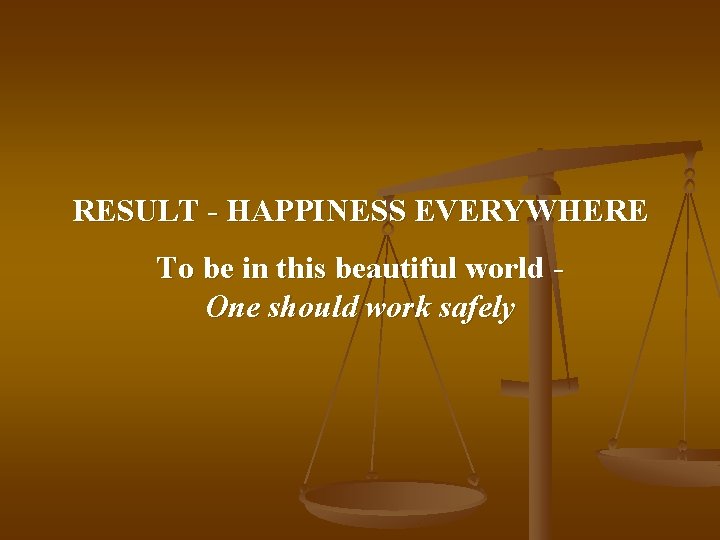
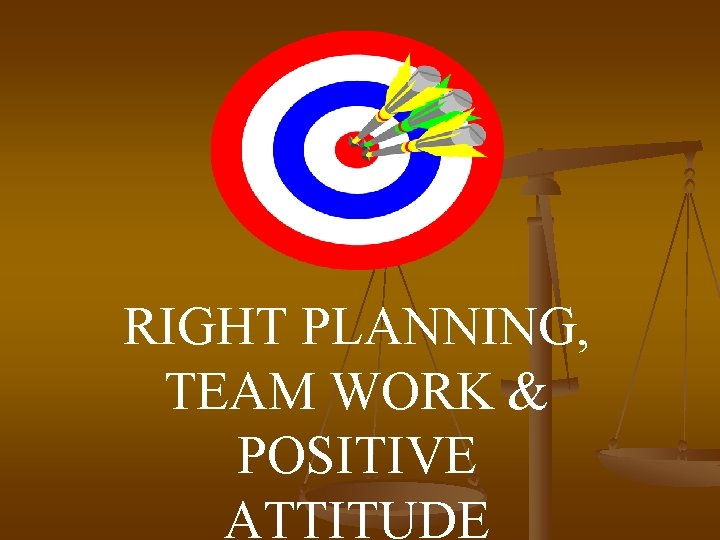
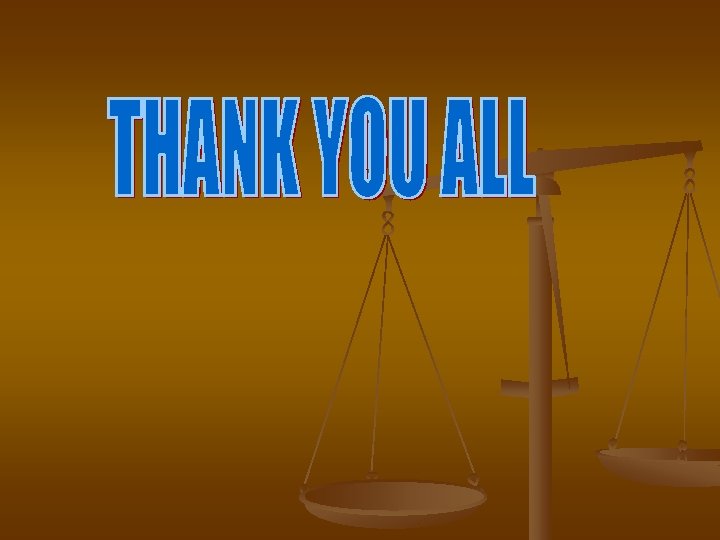
- Slides: 89
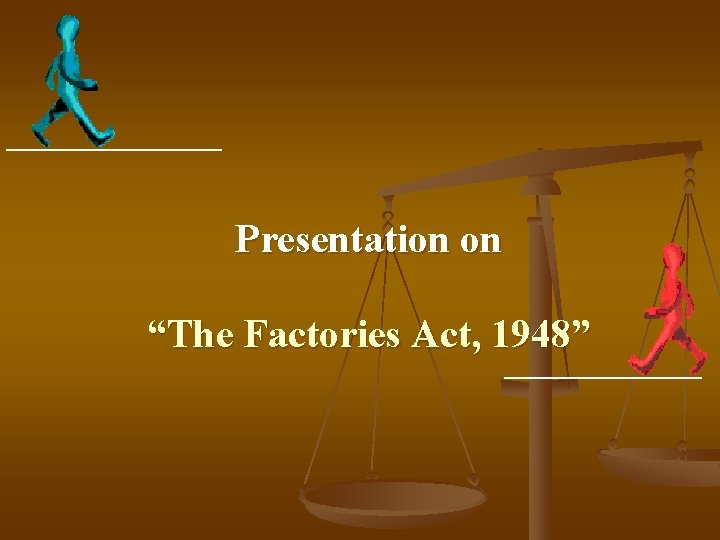
Presentation on “The Factories Act, 1948”
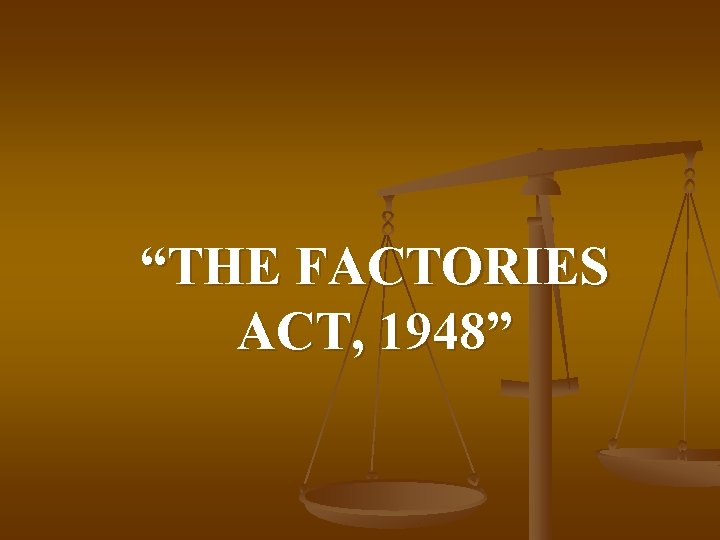
“THE FACTORIES ACT, 1948”
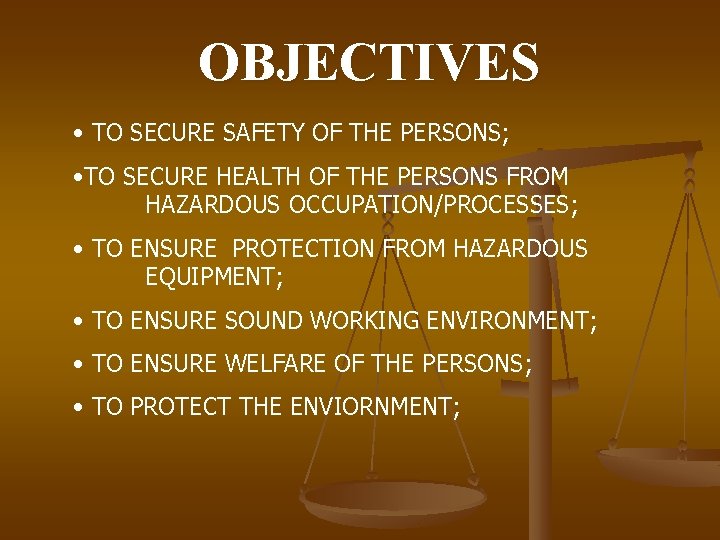
OBJECTIVES • TO SECURE SAFETY OF THE PERSONS; • TO SECURE HEALTH OF THE PERSONS FROM HAZARDOUS OCCUPATION/PROCESSES; • TO ENSURE PROTECTION FROM HAZARDOUS EQUIPMENT; • TO ENSURE SOUND WORKING ENVIRONMENT; • TO ENSURE WELFARE OF THE PERSONS; • TO PROTECT THE ENVIORNMENT;
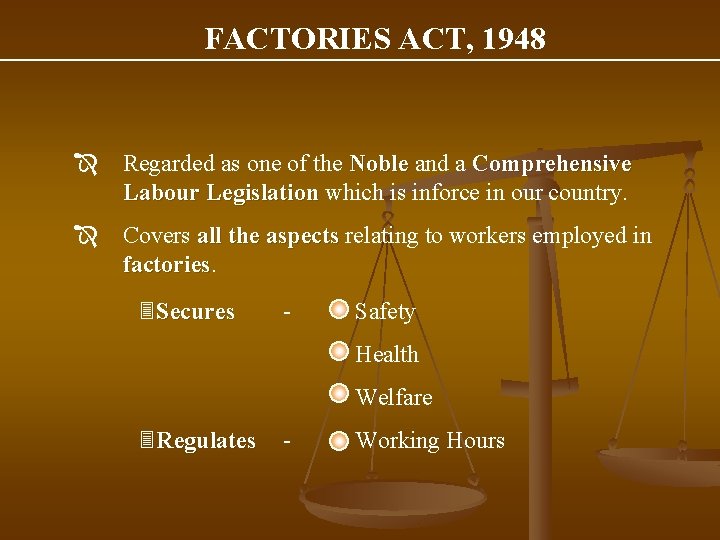
FACTORIES ACT, 1948 Î Regarded as one of the Noble and a Comprehensive Labour Legislation which is inforce in our country. Î Covers all the aspects relating to workers employed in factories 3 Secures - Safety Health Welfare 3 Regulates - Working Hours
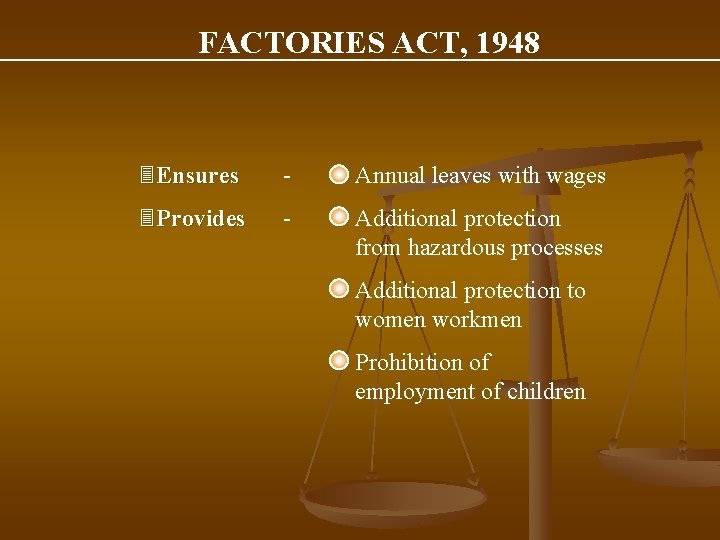
FACTORIES ACT, 1948 3 Ensures - Annual leaves with wages 3 Provides - Additional protection from hazardous processes Additional protection to women workmen Prohibition of employment of children
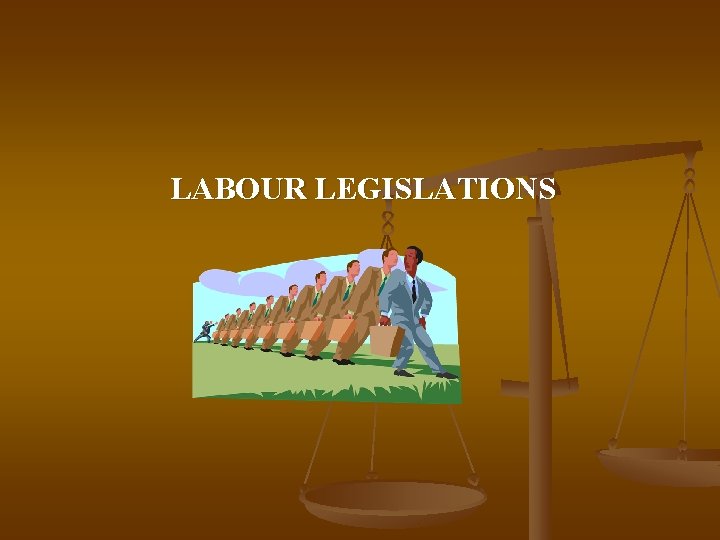
LABOUR LEGISLATIONS
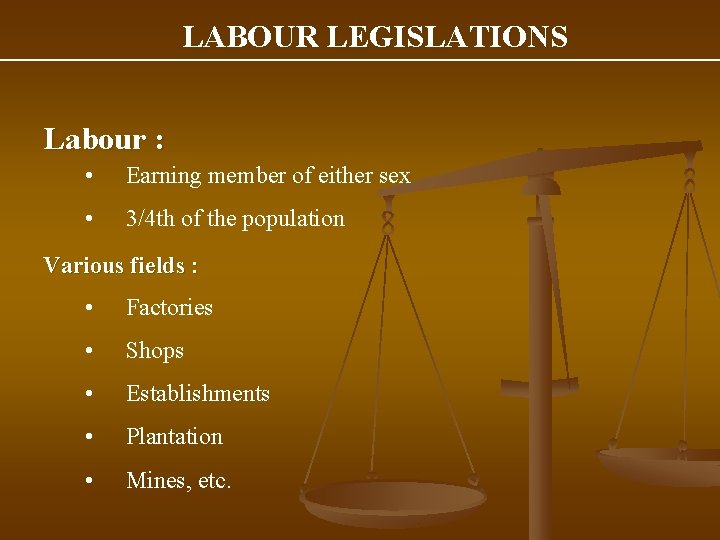
LABOUR LEGISLATIONS Labour : • Earning member of either sex • 3/4 th of the population Various fields : • Factories • Shops • Establishments • Plantation • Mines, etc.
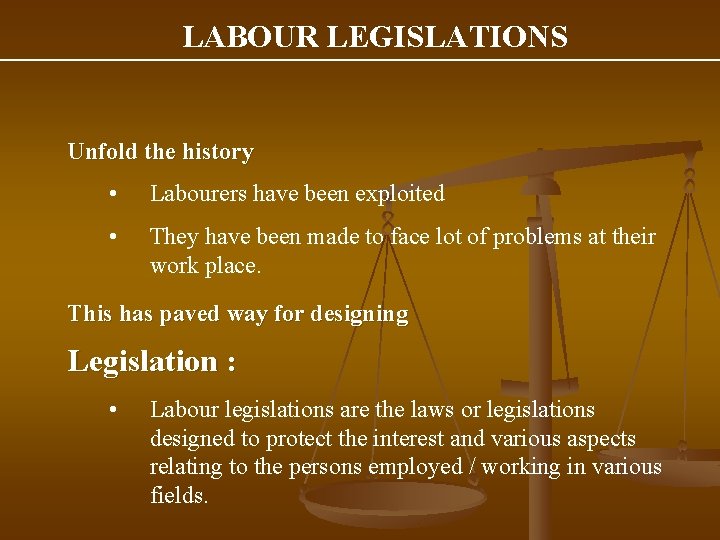
LABOUR LEGISLATIONS Unfold the history • Labourers have been exploited • They have been made to face lot of problems at their work place. This has paved way for designing Legislation : • Labour legislations are the laws or legislations designed to protect the interest and various aspects relating to the persons employed / working in various fields.
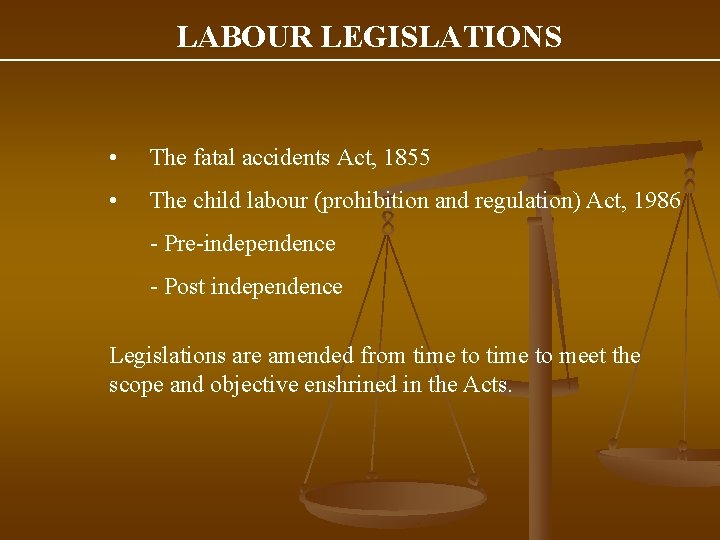
LABOUR LEGISLATIONS • The fatal accidents Act, 1855 • The child labour (prohibition and regulation) Act, 1986 - Pre-independence - Post independence Legislations are amended from time to meet the scope and objective enshrined in the Acts.
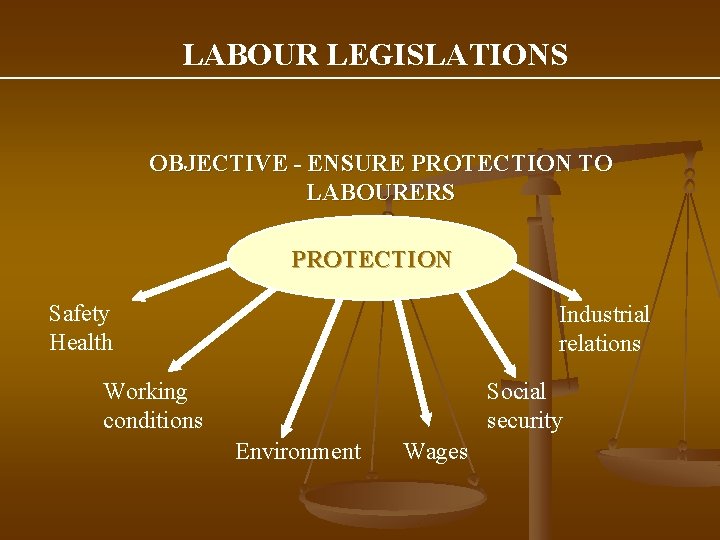
LABOUR LEGISLATIONS OBJECTIVE - ENSURE PROTECTION TO LABOURERS PROTECTION Safety Health Industrial relations Working conditions Social security Environment Wages
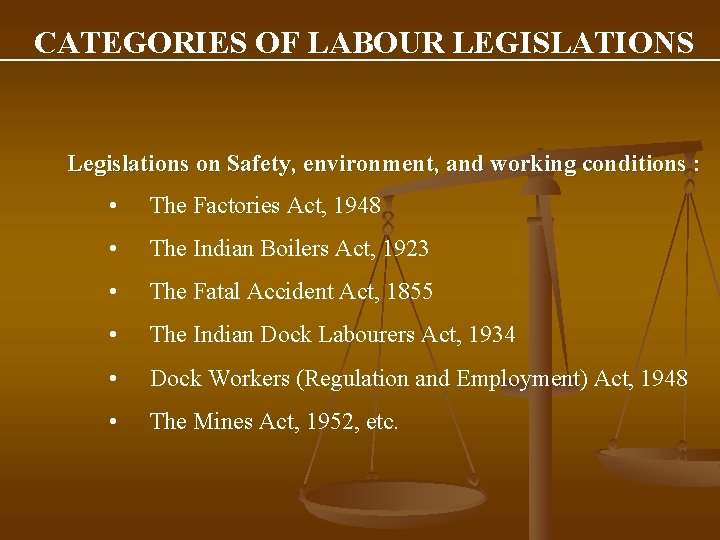
CATEGORIES OF LABOUR LEGISLATIONS Legislations on Safety, environment, and working conditions : • The Factories Act, 1948 • The Indian Boilers Act, 1923 • The Fatal Accident Act, 1855 • The Indian Dock Labourers Act, 1934 • Dock Workers (Regulation and Employment) Act, 1948 • The Mines Act, 1952, etc.
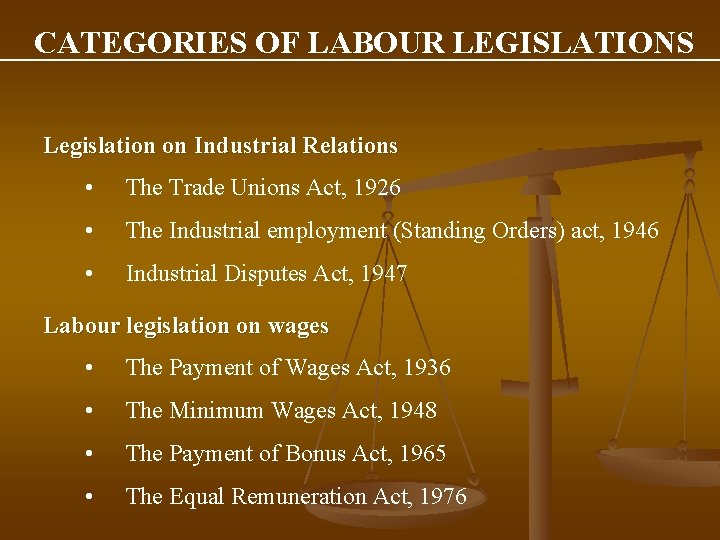
CATEGORIES OF LABOUR LEGISLATIONS Legislation on Industrial Relations • The Trade Unions Act, 1926 • The Industrial employment (Standing Orders) act, 1946 • Industrial Disputes Act, 1947 Labour legislation on wages • The Payment of Wages Act, 1936 • The Minimum Wages Act, 1948 • The Payment of Bonus Act, 1965 • The Equal Remuneration Act, 1976
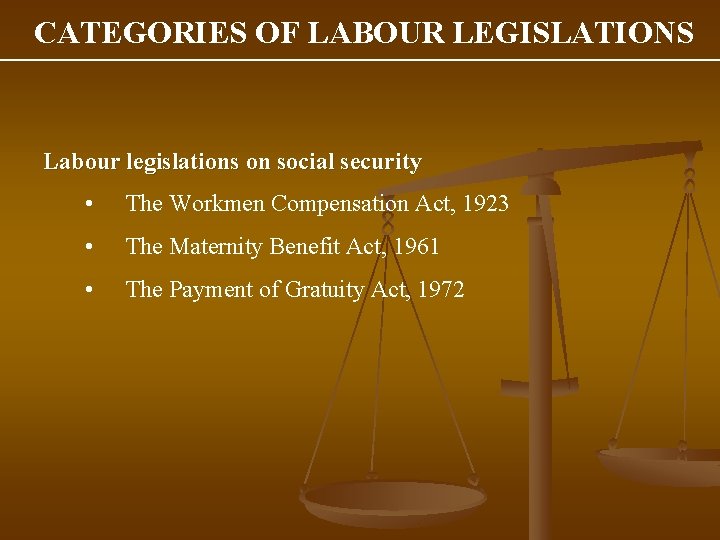
CATEGORIES OF LABOUR LEGISLATIONS Labour legislations on social security • The Workmen Compensation Act, 1923 • The Maternity Benefit Act, 1961 • The Payment of Gratuity Act, 1972
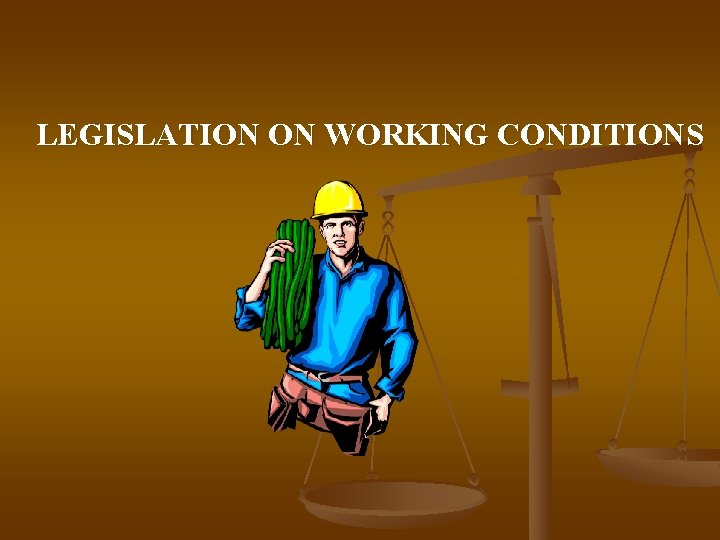
LEGISLATION ON WORKING CONDITIONS
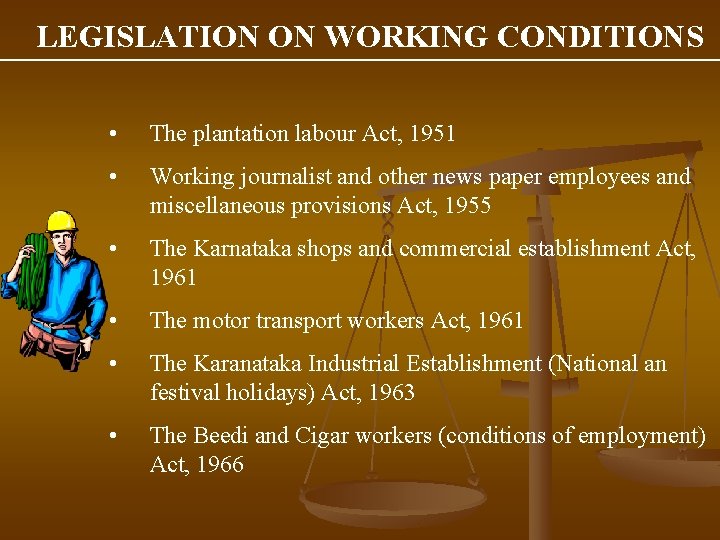
LEGISLATION ON WORKING CONDITIONS • The plantation labour Act, 1951 • Working journalist and other news paper employees and miscellaneous provisions Act, 1955 • The Karnataka shops and commercial establishment Act, 1961 • The motor transport workers Act, 1961 • The Karanataka Industrial Establishment (National an festival holidays) Act, 1963 • The Beedi and Cigar workers (conditions of employment) Act, 1966
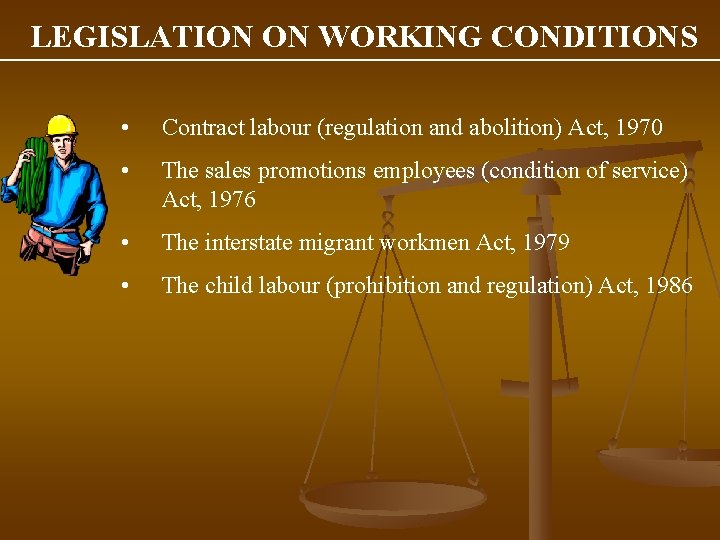
LEGISLATION ON WORKING CONDITIONS • Contract labour (regulation and abolition) Act, 1970 • The sales promotions employees (condition of service) Act, 1976 • The interstate migrant workmen Act, 1979 • The child labour (prohibition and regulation) Act, 1986
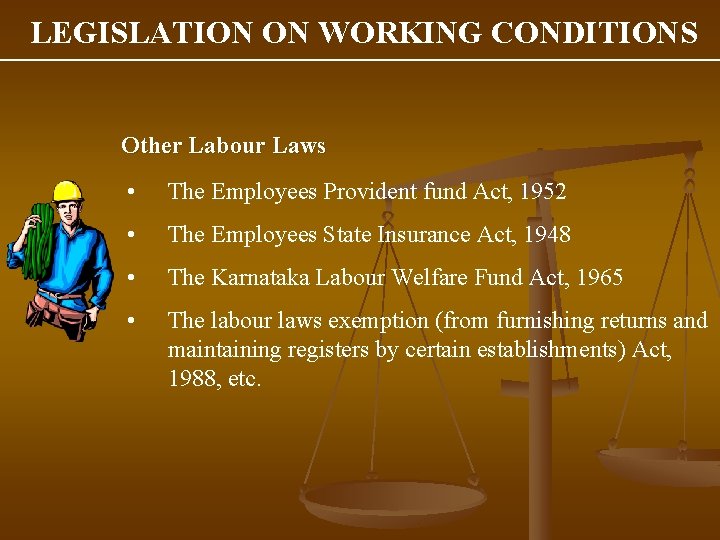
LEGISLATION ON WORKING CONDITIONS Other Labour Laws • The Employees Provident fund Act, 1952 • The Employees State Insurance Act, 1948 • The Karnataka Labour Welfare Fund Act, 1965 • The labour laws exemption (from furnishing returns and maintaining registers by certain establishments) Act, 1988, etc.
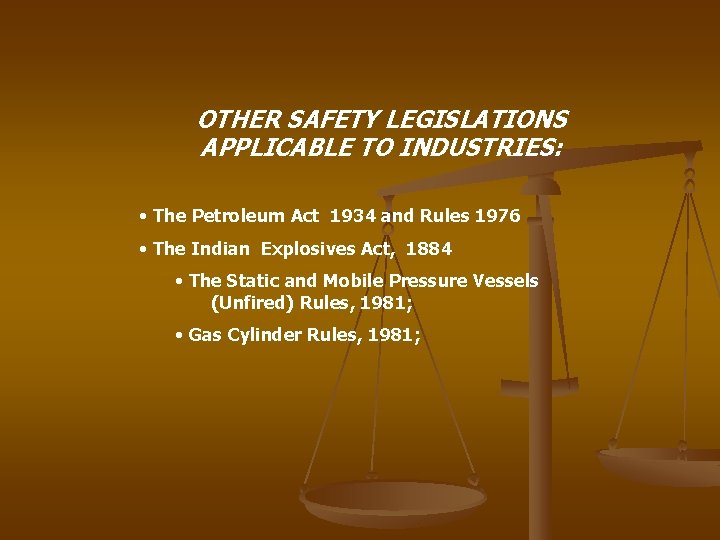
OTHER SAFETY LEGISLATIONS APPLICABLE TO INDUSTRIES: • The Petroleum Act 1934 and Rules 1976 • The Indian Explosives Act, 1884 • The Static and Mobile Pressure Vessels (Unfired) Rules, 1981; • Gas Cylinder Rules, 1981;
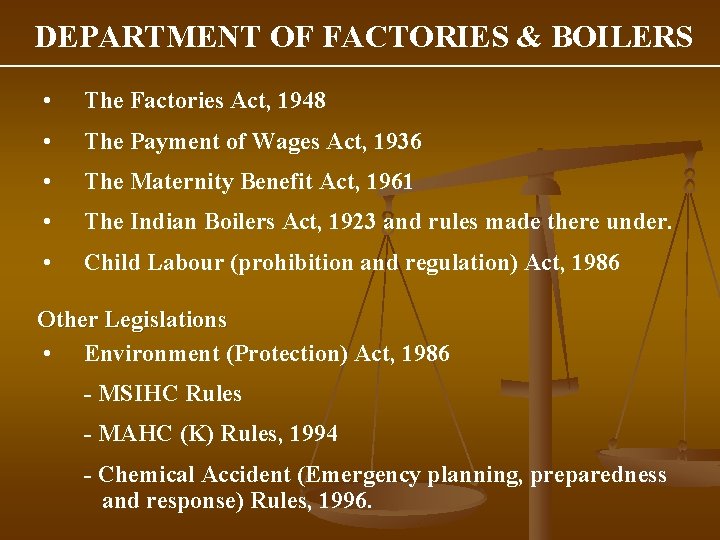
DEPARTMENT OF FACTORIES & BOILERS • The Factories Act, 1948 • The Payment of Wages Act, 1936 • The Maternity Benefit Act, 1961 • The Indian Boilers Act, 1923 and rules made there under. • Child Labour (prohibition and regulation) Act, 1986 Other Legislations • Environment (Protection) Act, 1986 - MSIHC Rules - MAHC (K) Rules, 1994 - Chemical Accident (Emergency planning, preparedness and response) Rules, 1996.
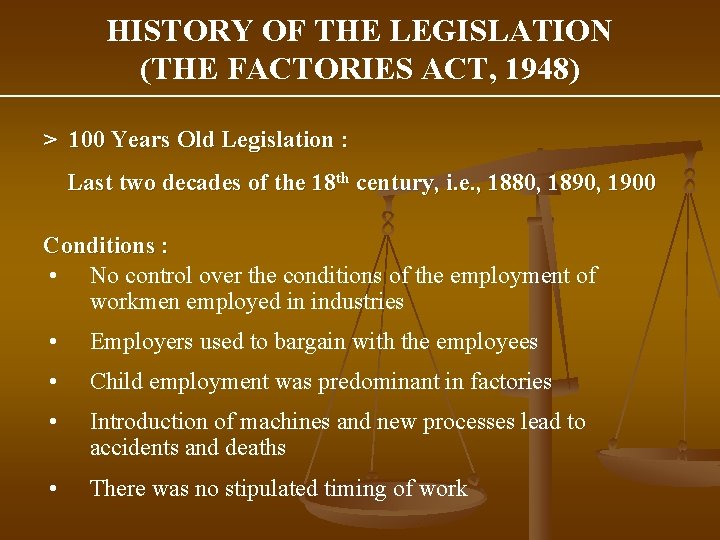
HISTORY OF THE LEGISLATION (THE FACTORIES ACT, 1948) > 100 Years Old Legislation : Last two decades of the 18 th century, i. e. , 1880, 1890, 1900 Conditions : • No control over the conditions of the employment of workmen employed in industries • Employers used to bargain with the employees • Child employment was predominant in factories • Introduction of machines and new processes lead to accidents and deaths • There was no stipulated timing of work
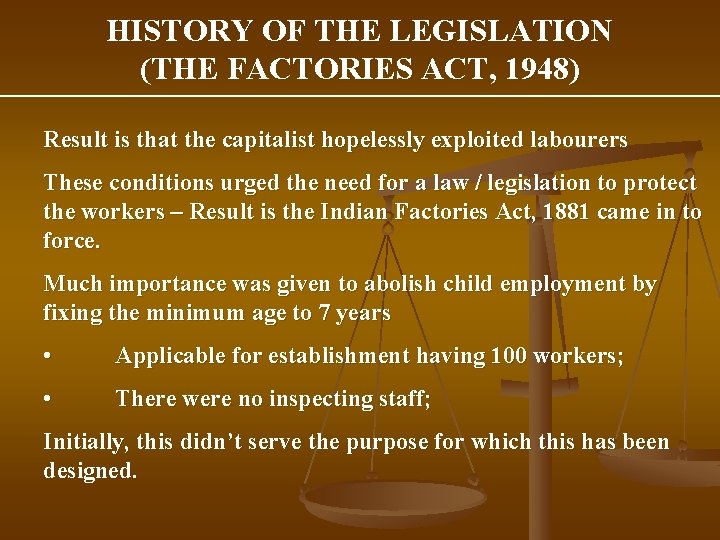
HISTORY OF THE LEGISLATION (THE FACTORIES ACT, 1948) Result is that the capitalist hopelessly exploited labourers These conditions urged the need for a law / legislation to protect the workers – Result is the Indian Factories Act, 1881 came in to force. Much importance was given to abolish child employment by fixing the minimum age to 7 years • Applicable for establishment having 100 workers; • There were no inspecting staff; Initially, this didn’t serve the purpose for which this has been designed.
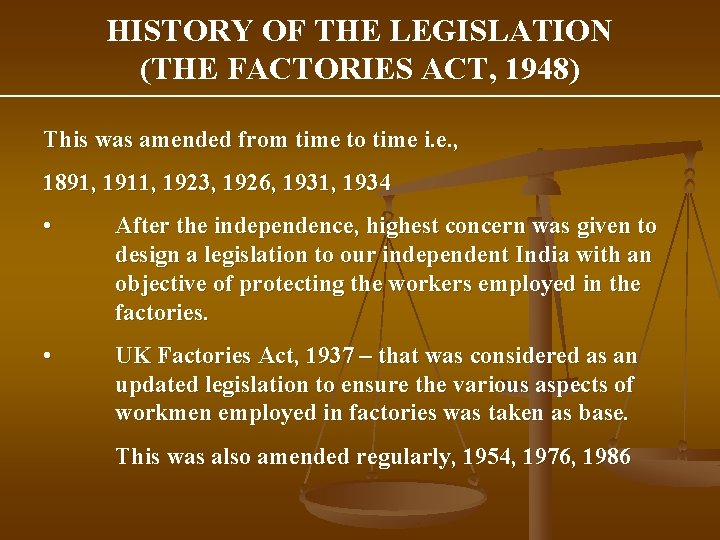
HISTORY OF THE LEGISLATION (THE FACTORIES ACT, 1948) This was amended from time to time i. e. , 1891, 1911, 1923, 1926, 1931, 1934 • After the independence, highest concern was given to design a legislation to our independent India with an objective of protecting the workers employed in the factories. • UK Factories Act, 1937 – that was considered as an updated legislation to ensure the various aspects of workmen employed in factories was taken as base. This was also amended regularly, 1954, 1976, 1986
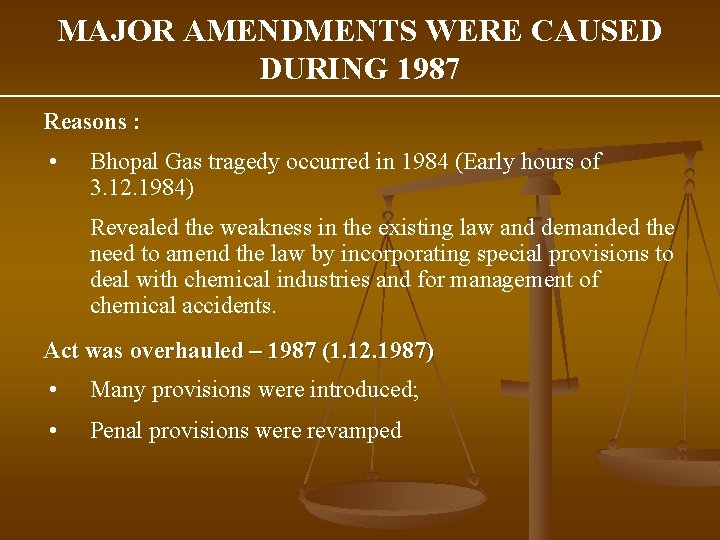
MAJOR AMENDMENTS WERE CAUSED DURING 1987 Reasons : • Bhopal Gas tragedy occurred in 1984 (Early hours of 3. 12. 1984) Revealed the weakness in the existing law and demanded the need to amend the law by incorporating special provisions to deal with chemical industries and for management of chemical accidents. Act was overhauled – 1987 (1. 12. 1987) • Many provisions were introduced; • Penal provisions were revamped
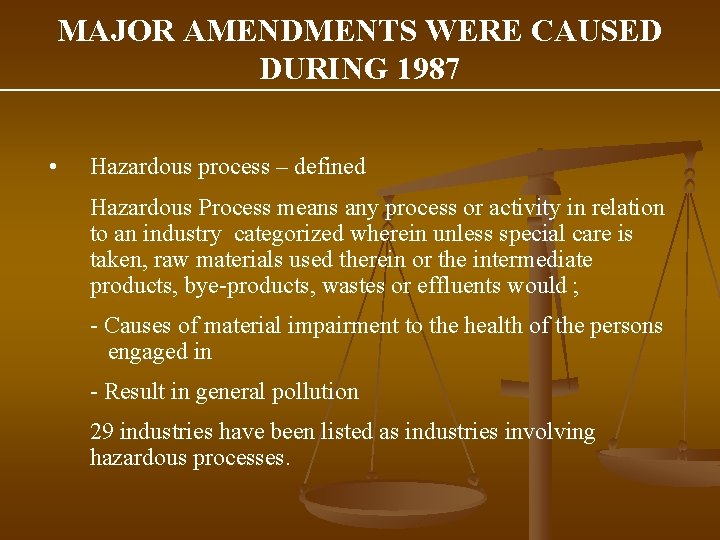
MAJOR AMENDMENTS WERE CAUSED DURING 1987 • Hazardous process – defined Hazardous Process means any process or activity in relation to an industry categorized wherein unless special care is taken, raw materials used therein or the intermediate products, bye-products, wastes or effluents would ; - Causes of material impairment to the health of the persons engaged in - Result in general pollution 29 industries have been listed as industries involving hazardous processes.
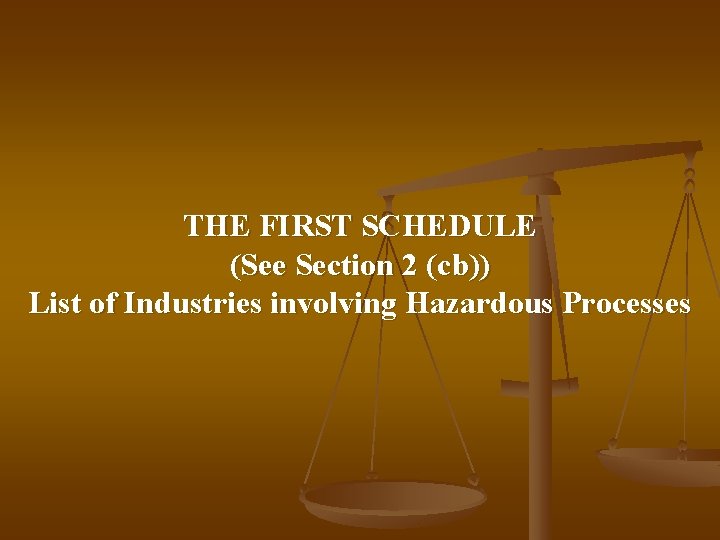
THE FIRST SCHEDULE (See Section 2 (cb)) List of Industries involving Hazardous Processes
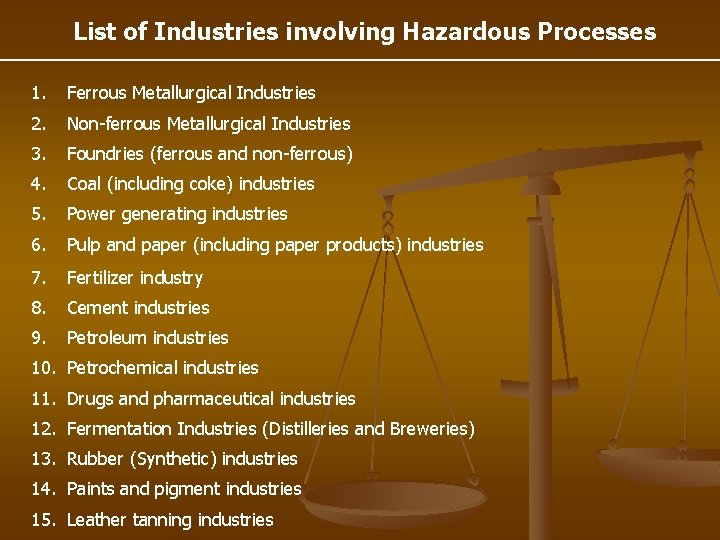
List of Industries involving Hazardous Processes 1. Ferrous Metallurgical Industries 2. Non-ferrous Metallurgical Industries 3. Foundries (ferrous and non-ferrous) 4. Coal (including coke) industries 5. Power generating industries 6. Pulp and paper (including paper products) industries 7. Fertilizer industry 8. Cement industries 9. Petroleum industries 10. Petrochemical industries 11. Drugs and pharmaceutical industries 12. Fermentation Industries (Distilleries and Breweries) 13. Rubber (Synthetic) industries 14. Paints and pigment industries 15. Leather tanning industries
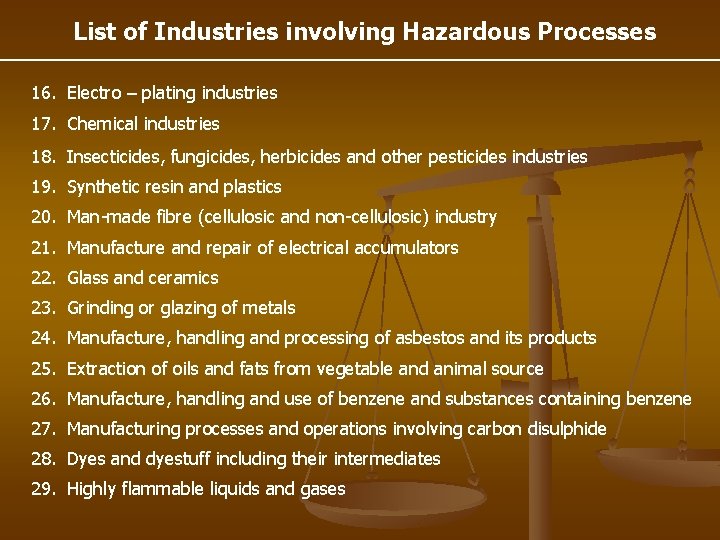
List of Industries involving Hazardous Processes 16. Electro – plating industries 17. Chemical industries 18. Insecticides, fungicides, herbicides and other pesticides industries 19. Synthetic resin and plastics 20. Man-made fibre (cellulosic and non-cellulosic) industry 21. Manufacture and repair of electrical accumulators 22. Glass and ceramics 23. Grinding or glazing of metals 24. Manufacture, handling and processing of asbestos and its products 25. Extraction of oils and fats from vegetable and animal source 26. Manufacture, handling and use of benzene and substances containing benzene 27. Manufacturing processes and operations involving carbon disulphide 28. Dyes and dyestuff including their intermediates 29. Highly flammable liquids and gases
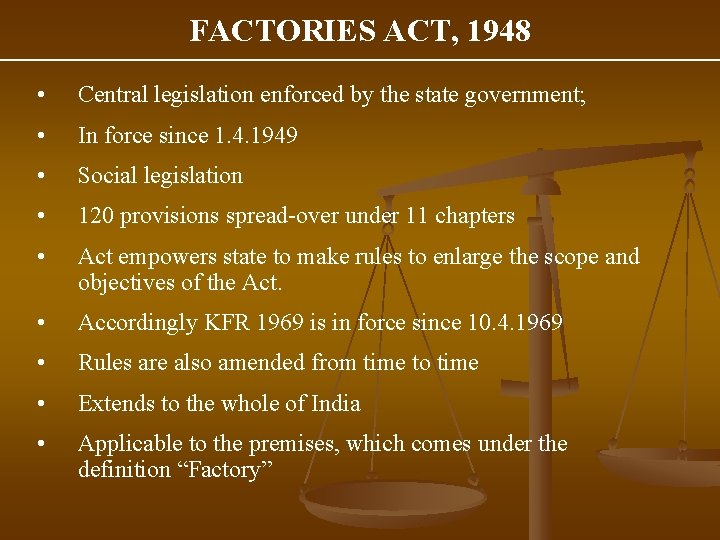
FACTORIES ACT, 1948 • Central legislation enforced by the state government; • In force since 1. 4. 1949 • Social legislation • 120 provisions spread-over under 11 chapters • Act empowers state to make rules to enlarge the scope and objectives of the Act. • Accordingly KFR 1969 is in force since 10. 4. 1969 • Rules are also amended from time to time • Extends to the whole of India • Applicable to the premises, which comes under the definition “Factory”
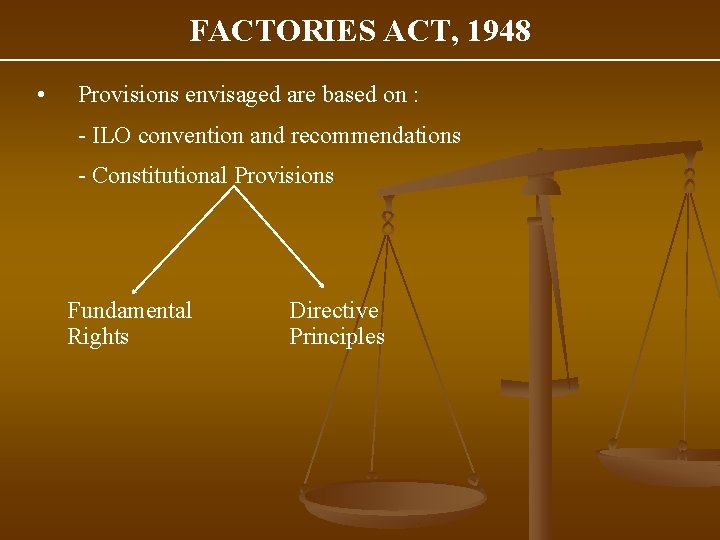
FACTORIES ACT, 1948 • Provisions envisaged are based on : - ILO convention and recommendations - Constitutional Provisions Fundamental Rights Directive Principles
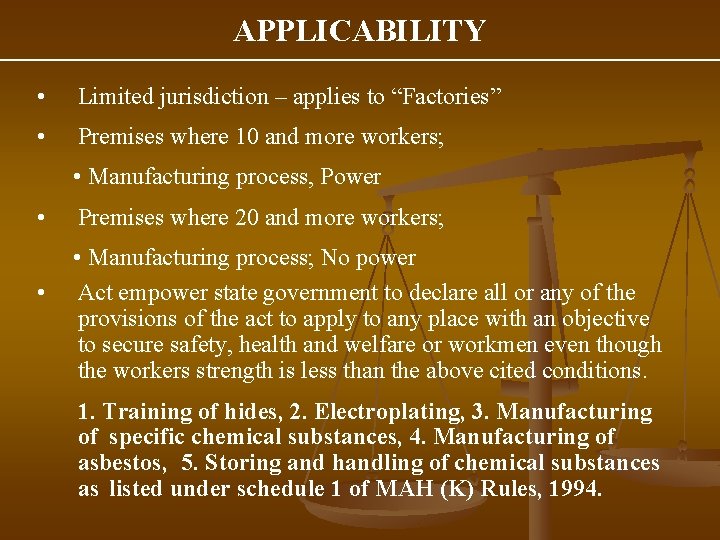
APPLICABILITY • Limited jurisdiction – applies to “Factories” • Premises where 10 and more workers; • Manufacturing process, Power • • Premises where 20 and more workers; • Manufacturing process; No power Act empower state government to declare all or any of the provisions of the act to apply to any place with an objective to secure safety, health and welfare or workmen even though the workers strength is less than the above cited conditions. 1. Training of hides, 2. Electroplating, 3. Manufacturing of specific chemical substances, 4. Manufacturing of asbestos, 5. Storing and handling of chemical substances as listed under schedule 1 of MAH (K) Rules, 1994.
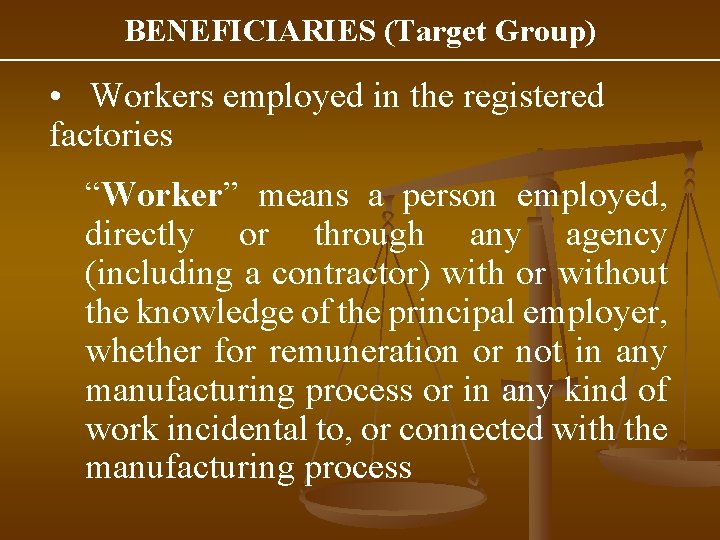
BENEFICIARIES (Target Group) • Workers employed in the registered factories “Worker” means a person employed, directly or through any agency (including a contractor) with or without the knowledge of the principal employer, whether for remuneration or not in any manufacturing process or in any kind of work incidental to, or connected with the manufacturing process
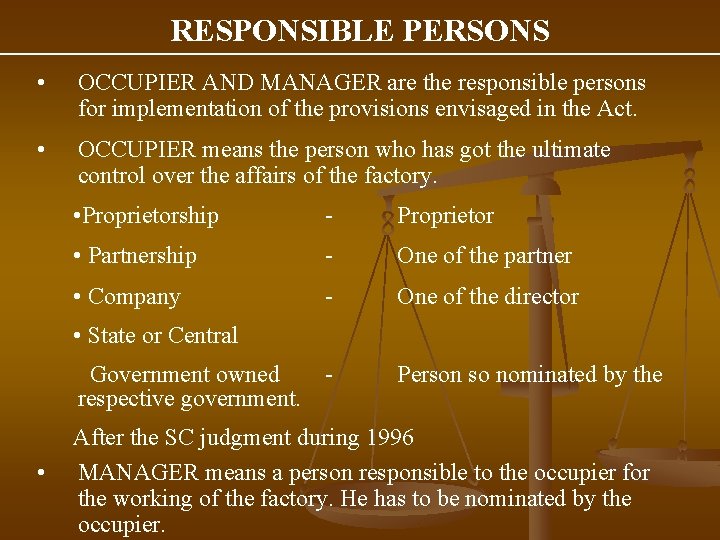
RESPONSIBLE PERSONS • OCCUPIER AND MANAGER are the responsible persons for implementation of the provisions envisaged in the Act. • OCCUPIER means the person who has got the ultimate control over the affairs of the factory. • Proprietorship - Proprietor • Partnership - One of the partner • Company - One of the director • State or Central Government owned respective government. • Person so nominated by the After the SC judgment during 1996 MANAGER means a person responsible to the occupier for the working of the factory. He has to be nominated by the occupier.
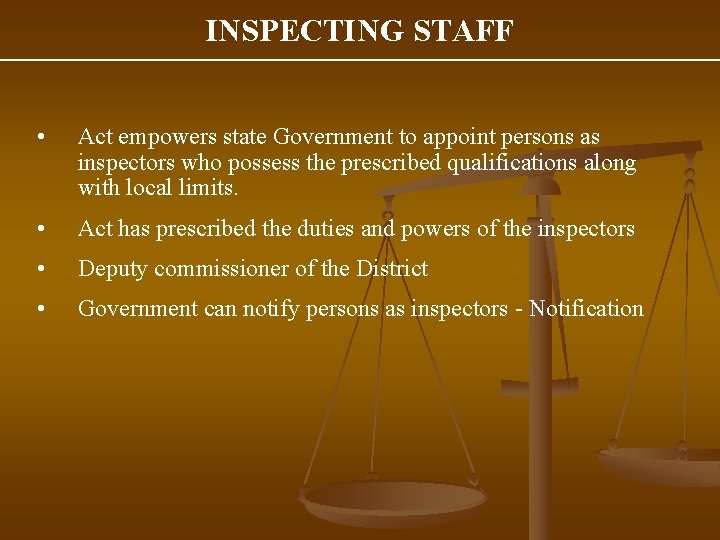
INSPECTING STAFF • Act empowers state Government to appoint persons as inspectors who possess the prescribed qualifications along with local limits. • Act has prescribed the duties and powers of the inspectors • Deputy commissioner of the District • Government can notify persons as inspectors - Notification
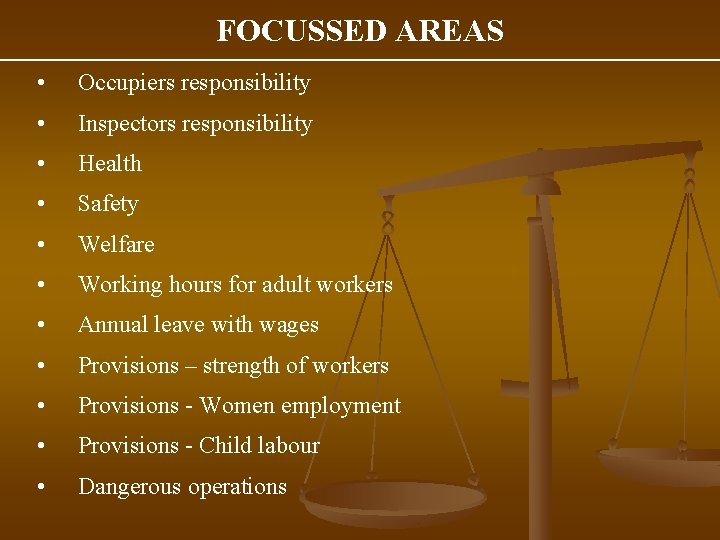
FOCUSSED AREAS • Occupiers responsibility • Inspectors responsibility • Health • Safety • Welfare • Working hours for adult workers • Annual leave with wages • Provisions – strength of workers • Provisions - Women employment • Provisions - Child labour • Dangerous operations
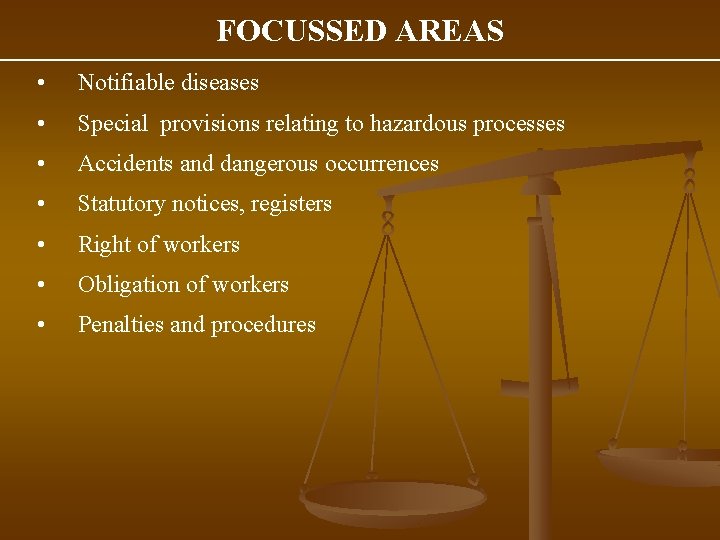
FOCUSSED AREAS • Notifiable diseases • Special provisions relating to hazardous processes • Accidents and dangerous occurrences • Statutory notices, registers • Right of workers • Obligation of workers • Penalties and procedures
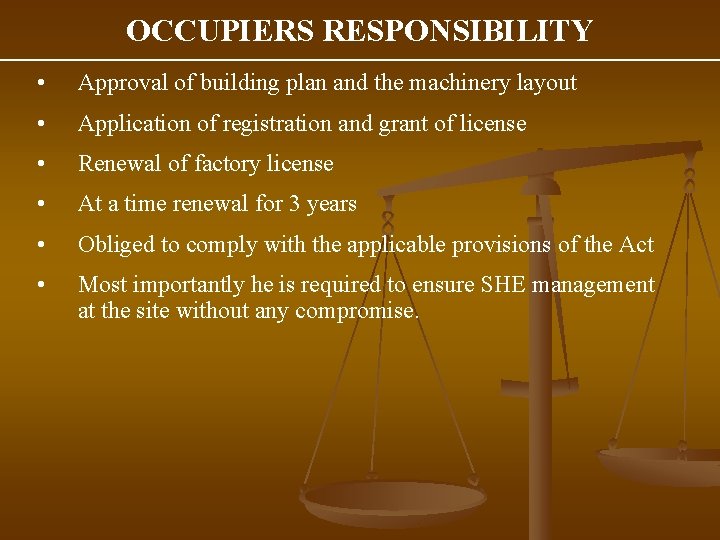
OCCUPIERS RESPONSIBILITY • Approval of building plan and the machinery layout • Application of registration and grant of license • Renewal of factory license • At a time renewal for 3 years • Obliged to comply with the applicable provisions of the Act • Most importantly he is required to ensure SHE management at the site without any compromise.
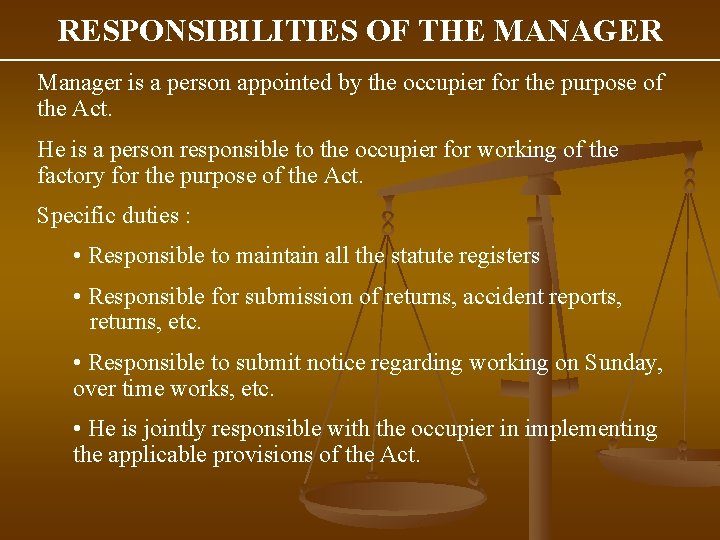
RESPONSIBILITIES OF THE MANAGER Manager is a person appointed by the occupier for the purpose of the Act. He is a person responsible to the occupier for working of the factory for the purpose of the Act. Specific duties : • Responsible to maintain all the statute registers • Responsible for submission of returns, accident reports, returns, etc. • Responsible to submit notice regarding working on Sunday, over time works, etc. • He is jointly responsible with the occupier in implementing the applicable provisions of the Act.
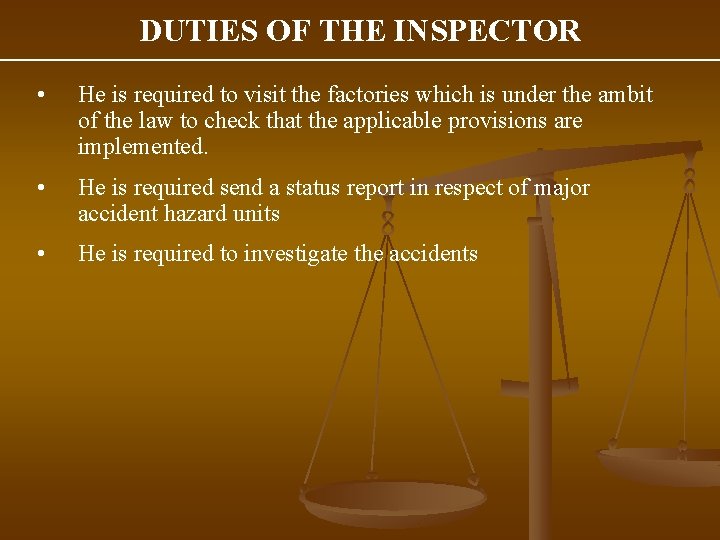
DUTIES OF THE INSPECTOR • He is required to visit the factories which is under the ambit of the law to check that the applicable provisions are implemented. • He is required send a status report in respect of major accident hazard units • He is required to investigate the accidents
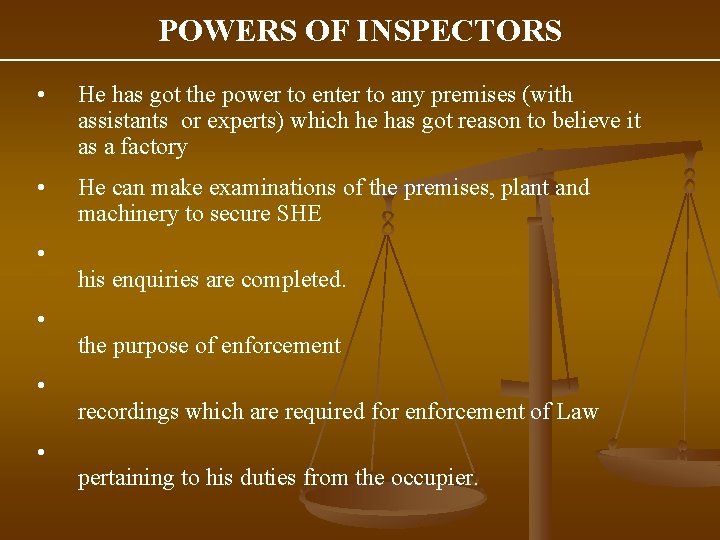
POWERS OF INSPECTORS • He has got the power to enter to any premises (with assistants or experts) which he has got reason to believe it as a factory • He can make examinations of the premises, plant and machinery to secure SHE • • his enquiries are completed. the purpose of enforcement recordings which are required for enforcement of Law pertaining to his duties from the occupier.
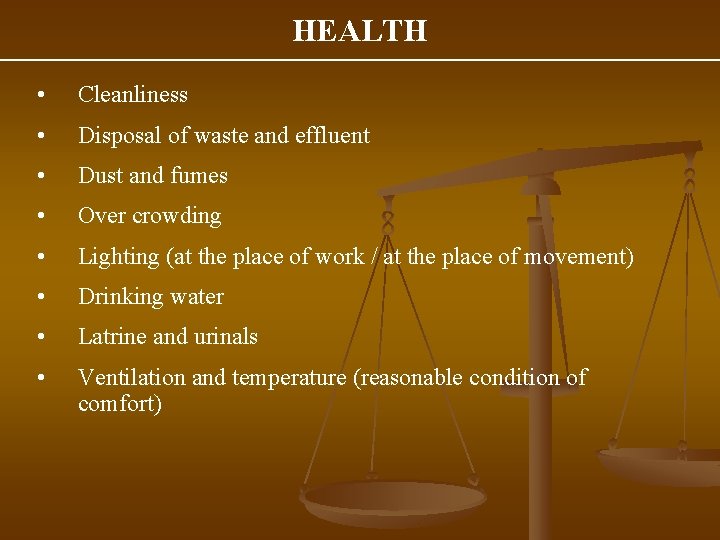
HEALTH • Cleanliness • Disposal of waste and effluent • Dust and fumes • Over crowding • Lighting (at the place of work / at the place of movement) • Drinking water • Latrine and urinals • Ventilation and temperature (reasonable condition of comfort)
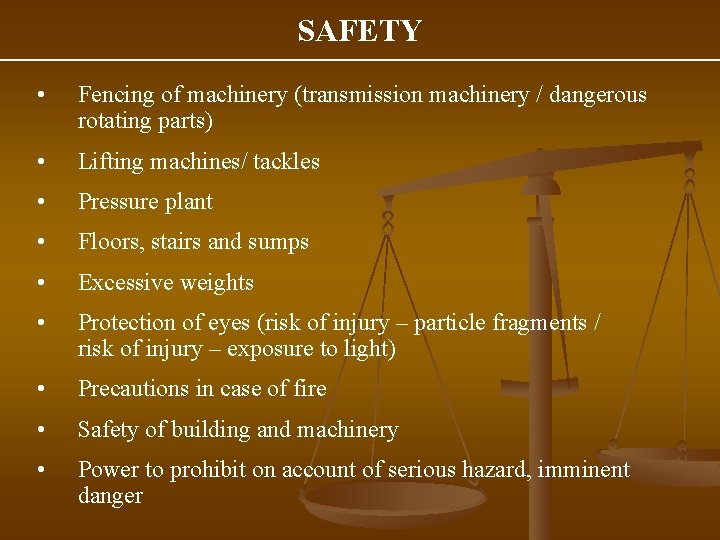
SAFETY • Fencing of machinery (transmission machinery / dangerous rotating parts) • Lifting machines/ tackles • Pressure plant • Floors, stairs and sumps • Excessive weights • Protection of eyes (risk of injury – particle fragments / risk of injury – exposure to light) • Precautions in case of fire • Safety of building and machinery • Power to prohibit on account of serious hazard, imminent danger
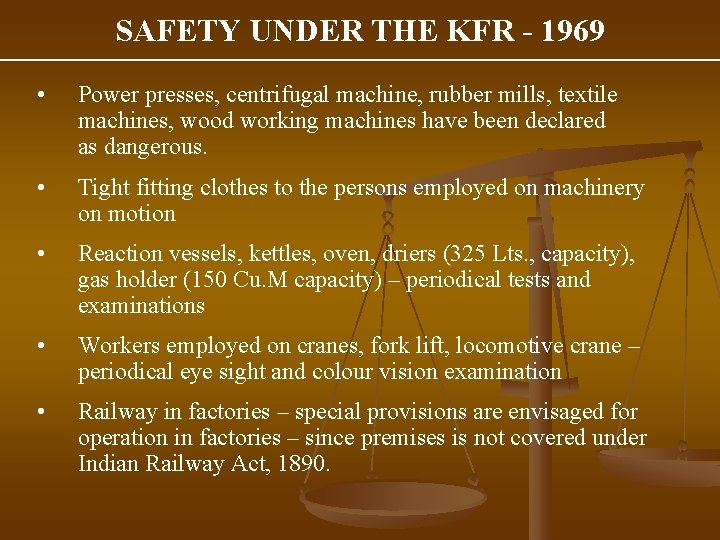
SAFETY UNDER THE KFR - 1969 • Power presses, centrifugal machine, rubber mills, textile machines, wood working machines have been declared as dangerous. • Tight fitting clothes to the persons employed on machinery on motion • Reaction vessels, kettles, oven, driers (325 Lts. , capacity), gas holder (150 Cu. M capacity) – periodical tests and examinations • Workers employed on cranes, fork lift, locomotive crane – periodical eye sight and colour vision examination • Railway in factories – special provisions are envisaged for operation in factories – since premises is not covered under Indian Railway Act, 1890.
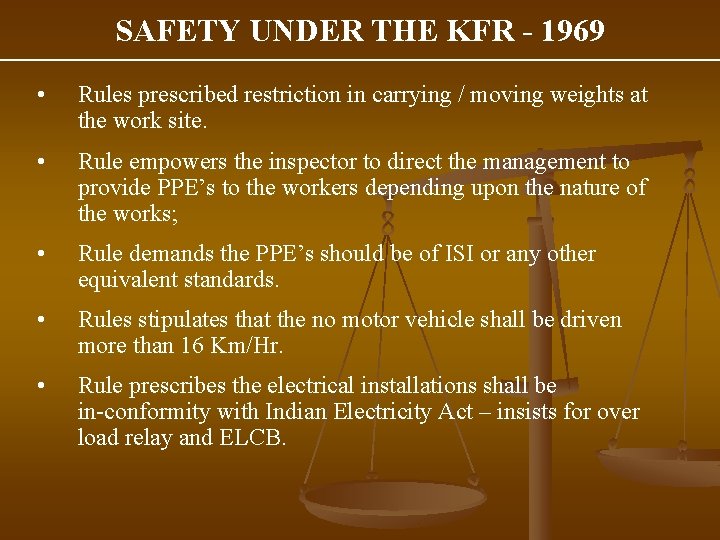
SAFETY UNDER THE KFR - 1969 • Rules prescribed restriction in carrying / moving weights at the work site. • Rule empowers the inspector to direct the management to provide PPE’s to the workers depending upon the nature of the works; • Rule demands the PPE’s should be of ISI or any other equivalent standards. • Rules stipulates that the no motor vehicle shall be driven more than 16 Km/Hr. • Rule prescribes the electrical installations shall be in-conformity with Indian Electricity Act – insists for over load relay and ELCB.
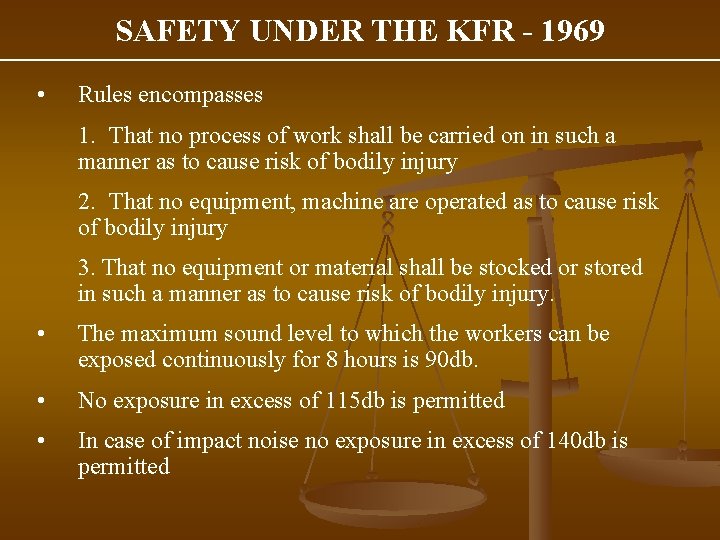
SAFETY UNDER THE KFR - 1969 • Rules encompasses 1. That no process of work shall be carried on in such a manner as to cause risk of bodily injury 2. That no equipment, machine are operated as to cause risk of bodily injury 3. That no equipment or material shall be stocked or stored in such a manner as to cause risk of bodily injury. • The maximum sound level to which the workers can be exposed continuously for 8 hours is 90 db. • No exposure in excess of 115 db is permitted • In case of impact noise no exposure in excess of 140 db is permitted
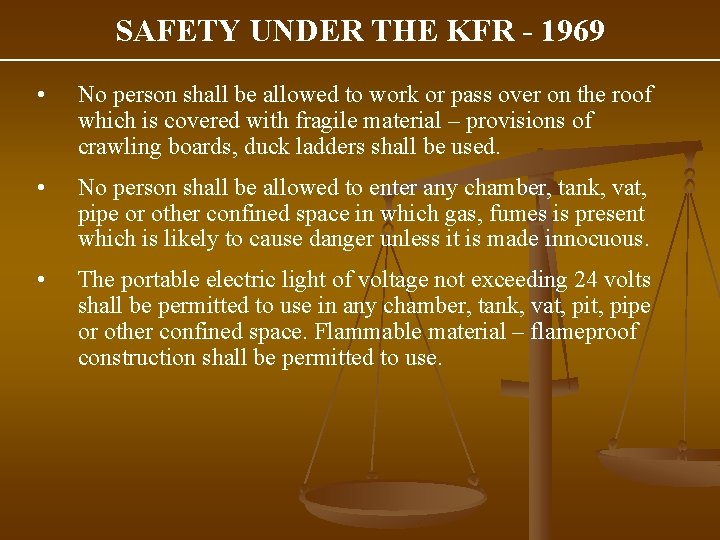
SAFETY UNDER THE KFR - 1969 • No person shall be allowed to work or pass over on the roof which is covered with fragile material – provisions of crawling boards, duck ladders shall be used. • No person shall be allowed to enter any chamber, tank, vat, pipe or other confined space in which gas, fumes is present which is likely to cause danger unless it is made innocuous. • The portable electric light of voltage not exceeding 24 volts shall be permitted to use in any chamber, tank, vat, pipe or other confined space. Flammable material – flameproof construction shall be permitted to use.
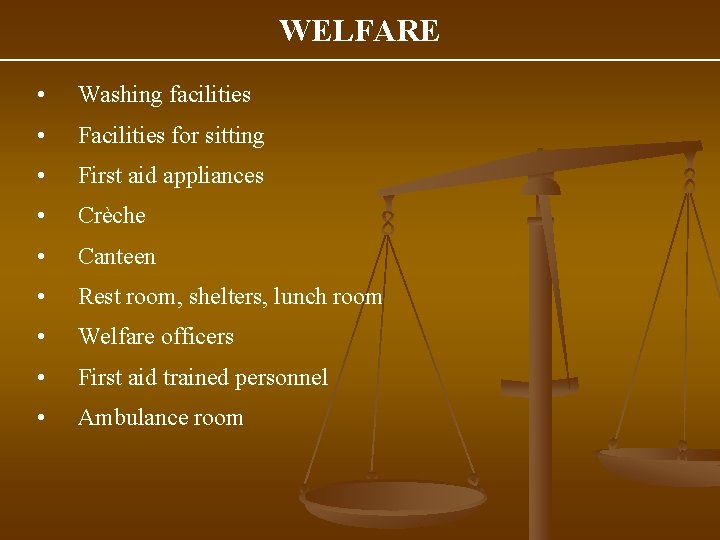
WELFARE • Washing facilities • Facilities for sitting • First aid appliances • Crèche • Canteen • Rest room, shelters, lunch room • Welfare officers • First aid trained personnel • Ambulance room
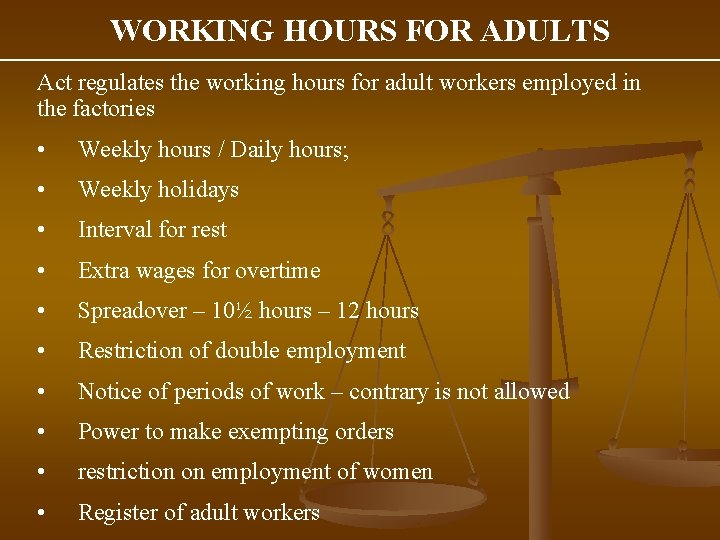
WORKING HOURS FOR ADULTS Act regulates the working hours for adult workers employed in the factories • Weekly hours / Daily hours; • Weekly holidays • Interval for rest • Extra wages for overtime • Spreadover – 10½ hours – 12 hours • Restriction of double employment • Notice of periods of work – contrary is not allowed • Power to make exempting orders • restriction on employment of women • Register of adult workers
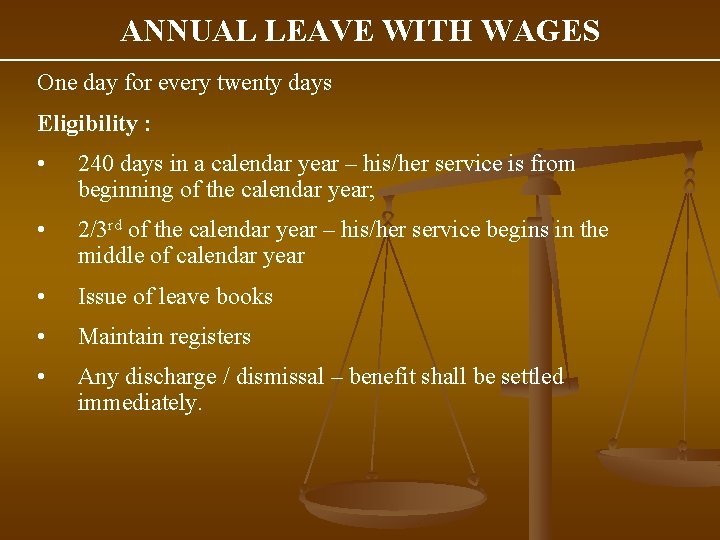
ANNUAL LEAVE WITH WAGES One day for every twenty days Eligibility : • 240 days in a calendar year – his/her service is from beginning of the calendar year; • 2/3 rd of the calendar year – his/her service begins in the middle of calendar year • Issue of leave books • Maintain registers • Any discharge / dismissal – benefit shall be settled immediately.
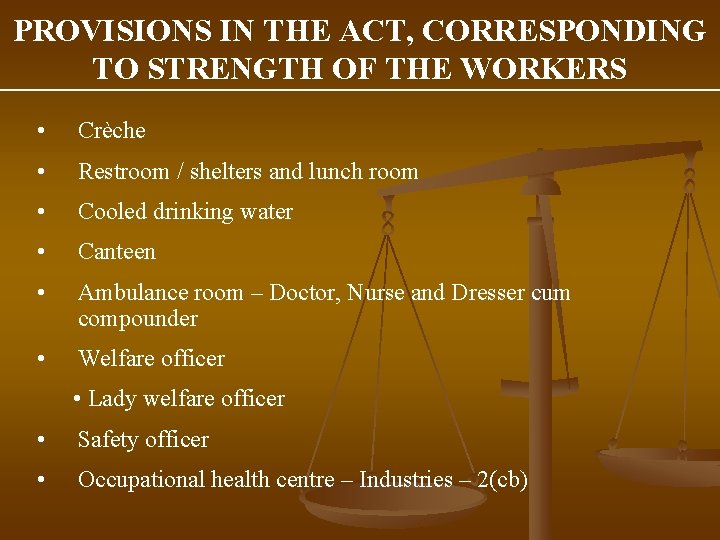
PROVISIONS IN THE ACT, CORRESPONDING TO STRENGTH OF THE WORKERS • Crèche • Restroom / shelters and lunch room • Cooled drinking water • Canteen • Ambulance room – Doctor, Nurse and Dresser cum compounder • Welfare officer • Lady welfare officer • Safety officer • Occupational health centre – Industries – 2(cb)
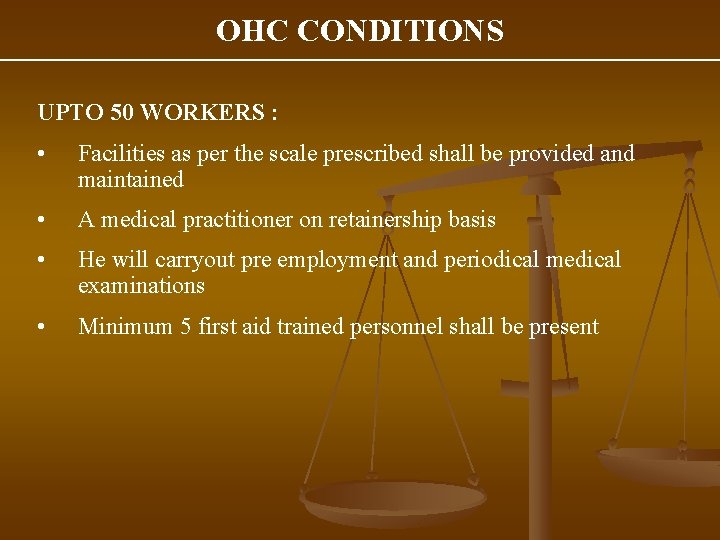
OHC CONDITIONS UPTO 50 WORKERS : • Facilities as per the scale prescribed shall be provided and maintained • A medical practitioner on retainership basis • He will carryout pre employment and periodical medical examinations • Minimum 5 first aid trained personnel shall be present

OHC CONDITIONS FROM 50 TO 200 WORKERS : • A separate room with 15 Sq. Mtr. Area with all the facilities as prescribed under rules • Part time doctor who visit the OHC twice in a week and whose services are readily available in case of emergencies • One qualified dresser cum compounder. MORE THAN 200 WORKERS : • One full time doctor up to 500 workers and one more for every 1000 • Equipped OHC of area 15 Sq. Mtr. • One nurse, dresser cum compounder, sweeper cum wardboy.
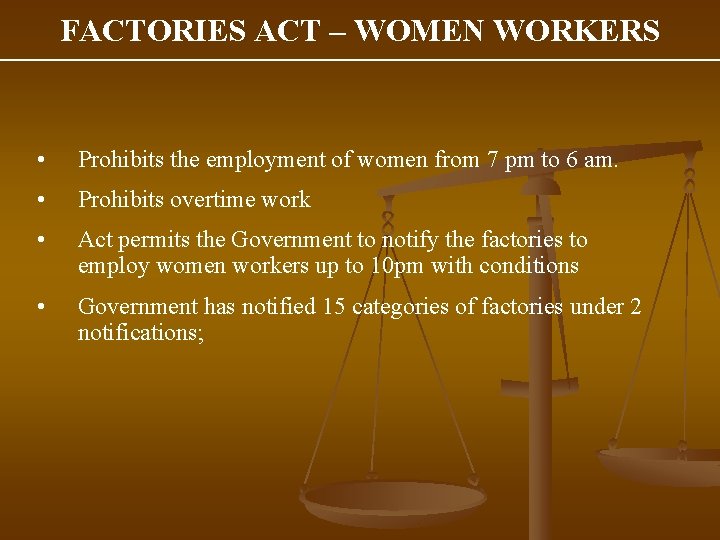
FACTORIES ACT – WOMEN WORKERS • Prohibits the employment of women from 7 pm to 6 am. • Prohibits overtime work • Act permits the Government to notify the factories to employ women workers up to 10 pm with conditions • Government has notified 15 categories of factories under 2 notifications;
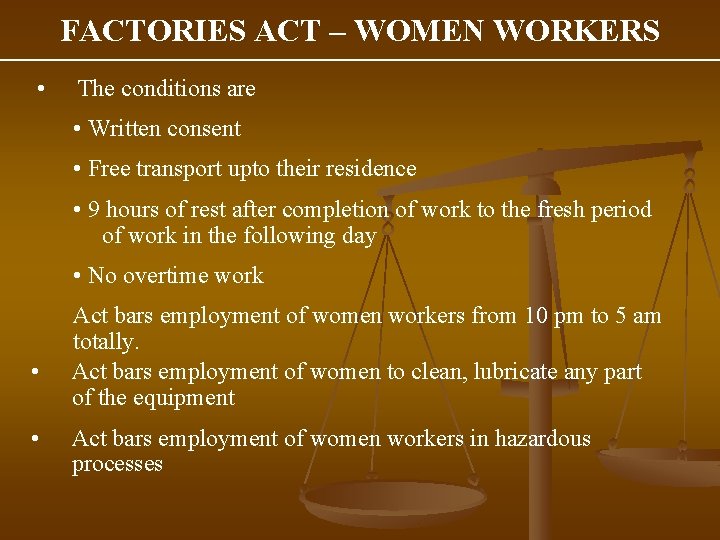
FACTORIES ACT – WOMEN WORKERS • The conditions are • Written consent • Free transport upto their residence • 9 hours of rest after completion of work to the fresh period of work in the following day • No overtime work • • Act bars employment of women workers from 10 pm to 5 am totally. Act bars employment of women to clean, lubricate any part of the equipment Act bars employment of women workers in hazardous processes
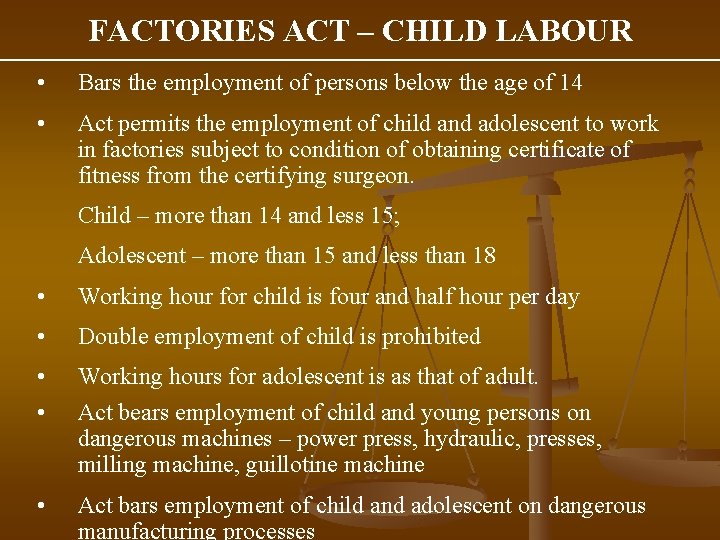
FACTORIES ACT – CHILD LABOUR • Bars the employment of persons below the age of 14 • Act permits the employment of child and adolescent to work in factories subject to condition of obtaining certificate of fitness from the certifying surgeon. Child – more than 14 and less 15; Adolescent – more than 15 and less than 18 • Working hour for child is four and half hour per day • Double employment of child is prohibited • • Working hours for adolescent is as that of adult. • Act bars employment of child and adolescent on dangerous manufacturing processes Act bears employment of child and young persons on dangerous machines – power press, hydraulic, presses, milling machine, guillotine machine
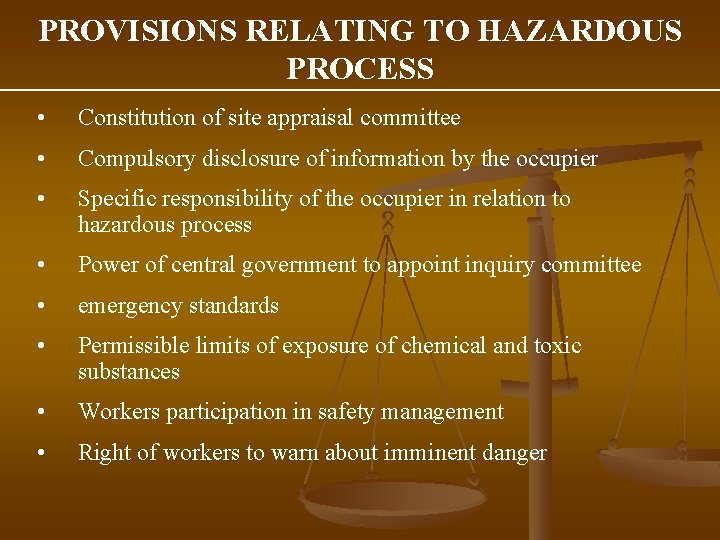
PROVISIONS RELATING TO HAZARDOUS PROCESS • Constitution of site appraisal committee • Compulsory disclosure of information by the occupier • Specific responsibility of the occupier in relation to hazardous process • Power of central government to appoint inquiry committee • emergency standards • Permissible limits of exposure of chemical and toxic substances • Workers participation in safety management • Right of workers to warn about imminent danger
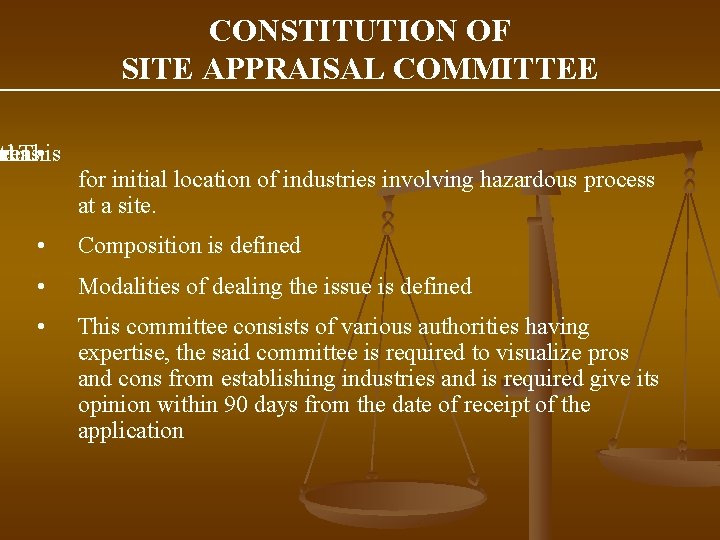
CONSTITUTION OF SITE APPRAISAL COMMITTEE er nnt een t has This • for initial location of industries involving hazardous process at a site. • Composition is defined • Modalities of dealing the issue is defined • This committee consists of various authorities having expertise, the said committee is required to visualize pros and cons from establishing industries and is required give its opinion within 90 days from the date of receipt of the application
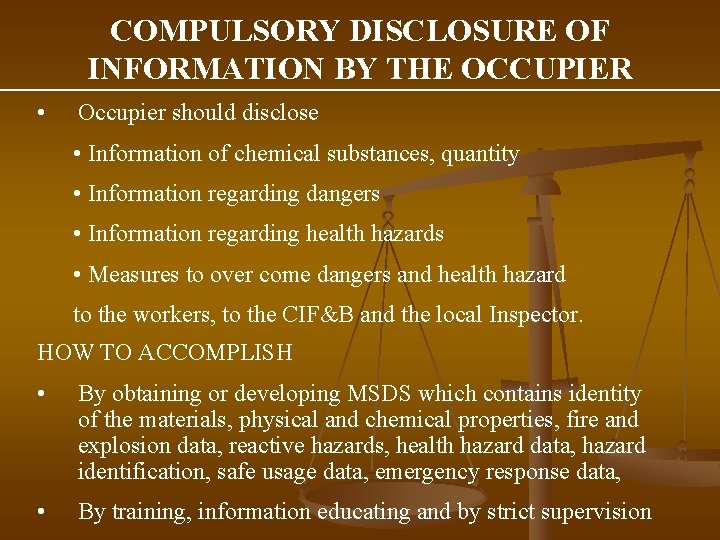
COMPULSORY DISCLOSURE OF INFORMATION BY THE OCCUPIER • Occupier should disclose • Information of chemical substances, quantity • Information regarding dangers • Information regarding health hazards • Measures to over come dangers and health hazard to the workers, to the CIF&B and the local Inspector. HOW TO ACCOMPLISH • By obtaining or developing MSDS which contains identity of the materials, physical and chemical properties, fire and explosion data, reactive hazards, health hazard data, hazard identification, safe usage data, emergency response data, • By training, information educating and by strict supervision

HEALTH AND SAFETY POLICY Occupier should lay down a detailed policy with respect to the health and safety of the workers employed. The Health and Safety Policy should show • The intentions and commitment of the management to provide SHE • Organisational set up to bring out the policy effective • Arrangement for involving the workers • Intention of taking account of SHE performance in considering their career advancement • Fixing responsibility on contractors • Providing resume of SHE performance in their annual report • State intention of integration of SHE in selection of machineries, selection of personnel, etc. , and the
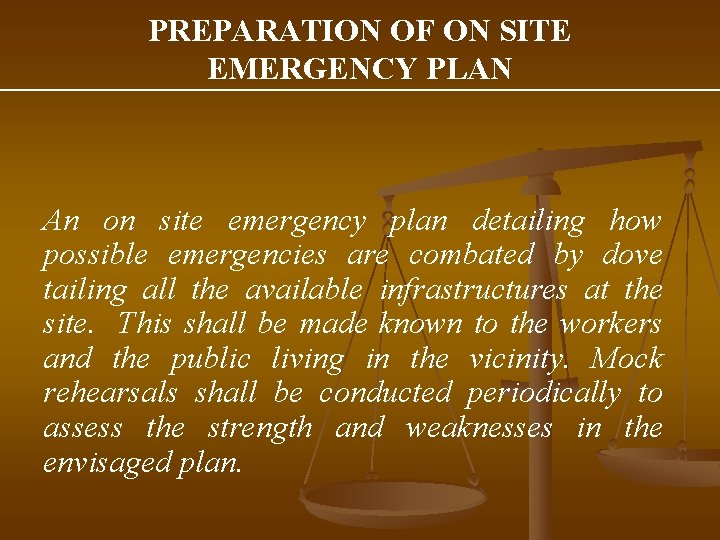
PREPARATION OF ON SITE EMERGENCY PLAN An on site emergency plan detailing how possible emergencies are combated by dove tailing all the available infrastructures at the site. This shall be made known to the workers and the public living in the vicinity. Mock rehearsals shall be conducted periodically to assess the strength and weaknesses in the envisaged plan.
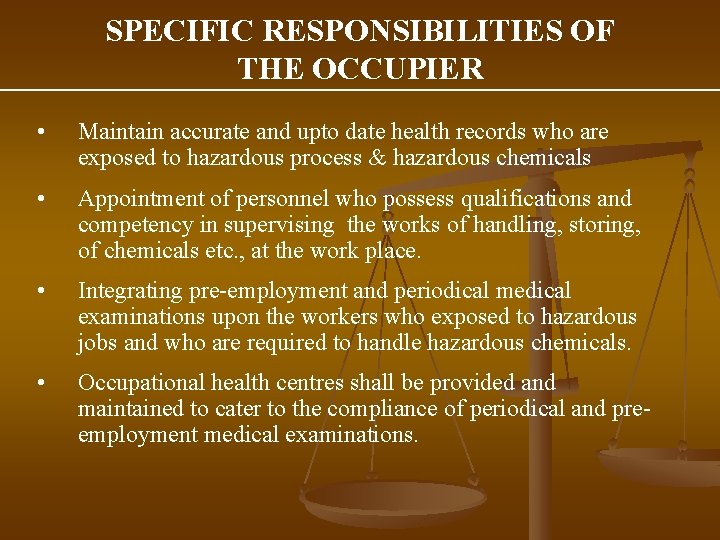
SPECIFIC RESPONSIBILITIES OF THE OCCUPIER • Maintain accurate and upto date health records who are exposed to hazardous process & hazardous chemicals • Appointment of personnel who possess qualifications and competency in supervising the works of handling, storing, of chemicals etc. , at the work place. • Integrating pre-employment and periodical medical examinations upon the workers who exposed to hazardous jobs and who are required to handle hazardous chemicals. • Occupational health centres shall be provided and maintained to cater to the compliance of periodical and preemployment medical examinations.
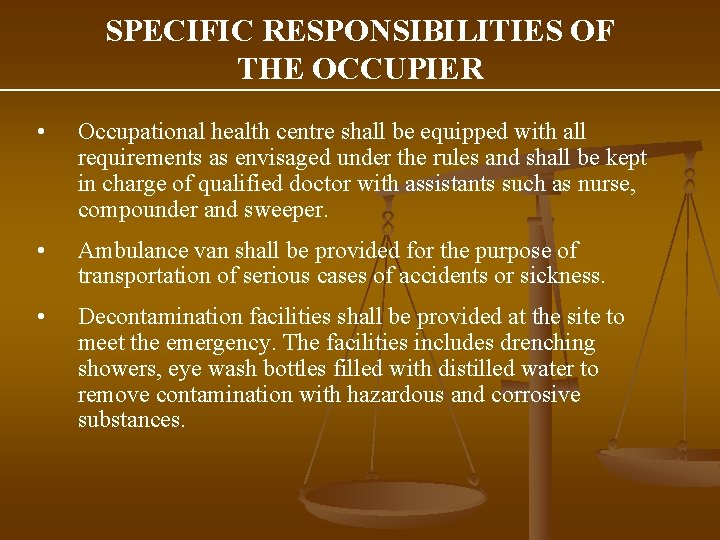
SPECIFIC RESPONSIBILITIES OF THE OCCUPIER • Occupational health centre shall be equipped with all requirements as envisaged under the rules and shall be kept in charge of qualified doctor with assistants such as nurse, compounder and sweeper. • Ambulance van shall be provided for the purpose of transportation of serious cases of accidents or sickness. • Decontamination facilities shall be provided at the site to meet the emergency. The facilities includes drenching showers, eye wash bottles filled with distilled water to remove contamination with hazardous and corrosive substances.
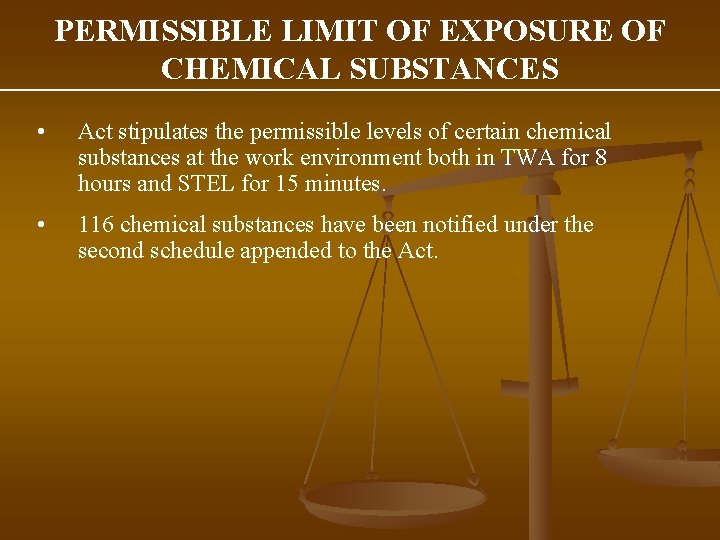
PERMISSIBLE LIMIT OF EXPOSURE OF CHEMICAL SUBSTANCES • Act stipulates the permissible levels of certain chemical substances at the work environment both in TWA for 8 hours and STEL for 15 minutes. • 116 chemical substances have been notified under the second schedule appended to the Act.
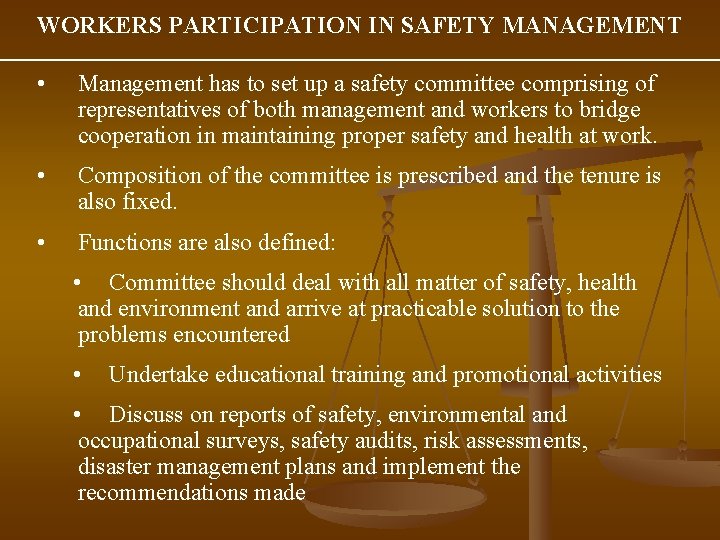
WORKERS PARTICIPATION IN SAFETY MANAGEMENT • Management has to set up a safety committee comprising of representatives of both management and workers to bridge cooperation in maintaining proper safety and health at work. • Composition of the committee is prescribed and the tenure is also fixed. • Functions are also defined: • Committee should deal with all matter of safety, health and environment and arrive at practicable solution to the problems encountered • Undertake educational training and promotional activities • Discuss on reports of safety, environmental and occupational surveys, safety audits, risk assessments, disaster management plans and implement the recommendations made
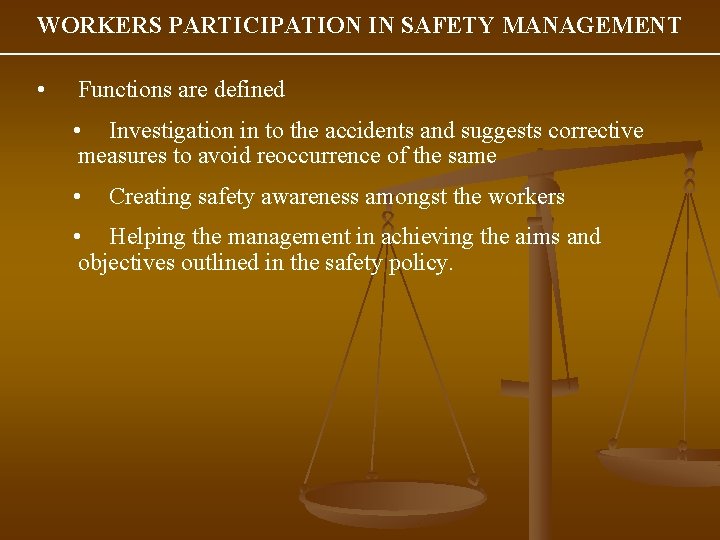
WORKERS PARTICIPATION IN SAFETY MANAGEMENT • Functions are defined • Investigation in to the accidents and suggests corrective measures to avoid reoccurrence of the same • Creating safety awareness amongst the workers • Helping the management in achieving the aims and objectives outlined in the safety policy.
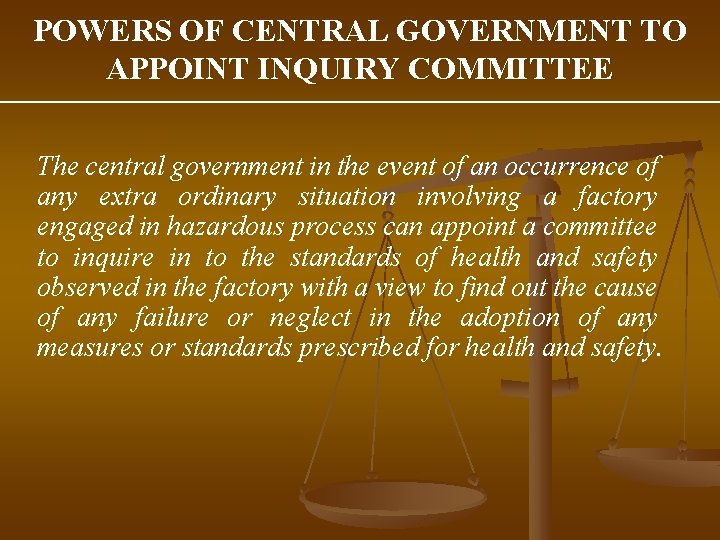
POWERS OF CENTRAL GOVERNMENT TO APPOINT INQUIRY COMMITTEE The central government in the event of an occurrence of any extra ordinary situation involving a factory engaged in hazardous process can appoint a committee to inquire in to the standards of health and safety observed in the factory with a view to find out the cause of any failure or neglect in the adoption of any measures or standards prescribed for health and safety.
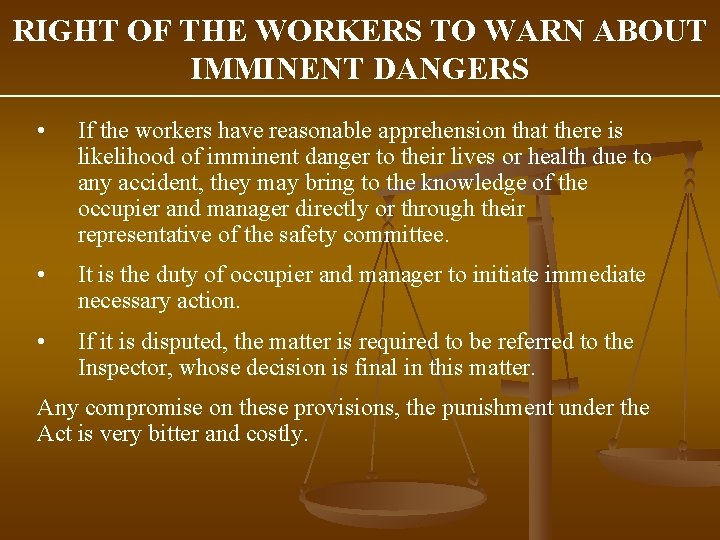
RIGHT OF THE WORKERS TO WARN ABOUT IMMINENT DANGERS • If the workers have reasonable apprehension that there is likelihood of imminent danger to their lives or health due to any accident, they may bring to the knowledge of the occupier and manager directly or through their representative of the safety committee. • It is the duty of occupier and manager to initiate immediate necessary action. • If it is disputed, the matter is required to be referred to the Inspector, whose decision is final in this matter. Any compromise on these provisions, the punishment under the Act is very bitter and costly.
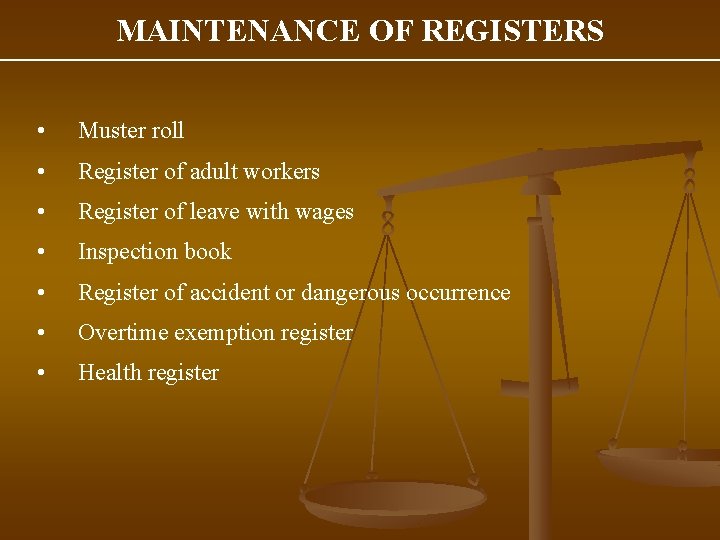
MAINTENANCE OF REGISTERS • Muster roll • Register of adult workers • Register of leave with wages • Inspection book • Register of accident or dangerous occurrence • Overtime exemption register • Health register
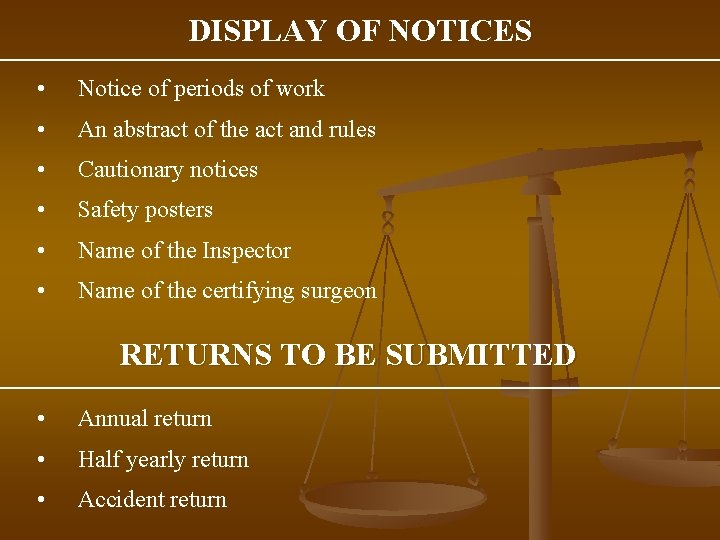
DISPLAY OF NOTICES • Notice of periods of work • An abstract of the act and rules • Cautionary notices • Safety posters • Name of the Inspector • Name of the certifying surgeon RETURNS TO BE SUBMITTED • Annual return • Half yearly return • Accident return
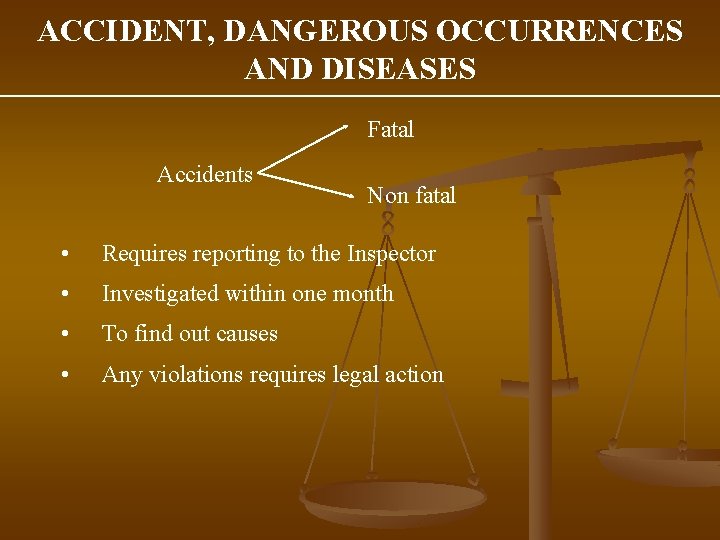
ACCIDENT, DANGEROUS OCCURRENCES AND DISEASES Fatal Accidents Non fatal • Requires reporting to the Inspector • Investigated within one month • To find out causes • Any violations requires legal action
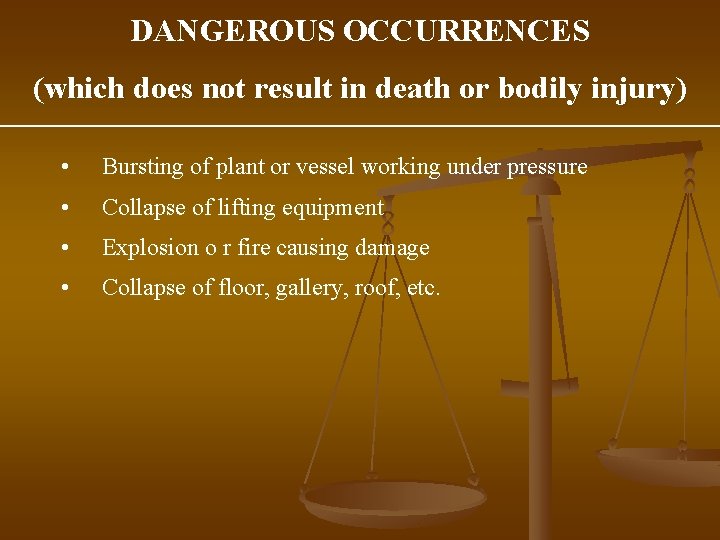
DANGEROUS OCCURRENCES (which does not result in death or bodily injury) • Bursting of plant or vessel working under pressure • Collapse of lifting equipment • Explosion o r fire causing damage • Collapse of floor, gallery, roof, etc.
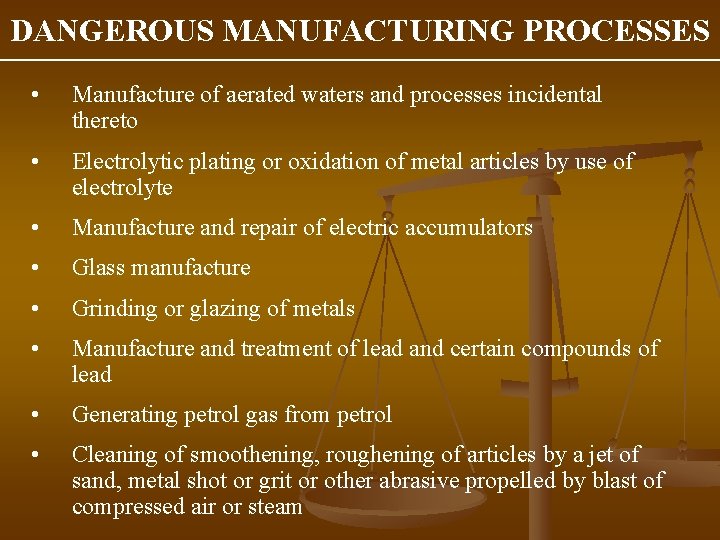
DANGEROUS MANUFACTURING PROCESSES • Manufacture of aerated waters and processes incidental thereto • Electrolytic plating or oxidation of metal articles by use of electrolyte • Manufacture and repair of electric accumulators • Glass manufacture • Grinding or glazing of metals • Manufacture and treatment of lead and certain compounds of lead • Generating petrol gas from petrol • Cleaning of smoothening, roughening of articles by a jet of sand, metal shot or grit or other abrasive propelled by blast of compressed air or steam
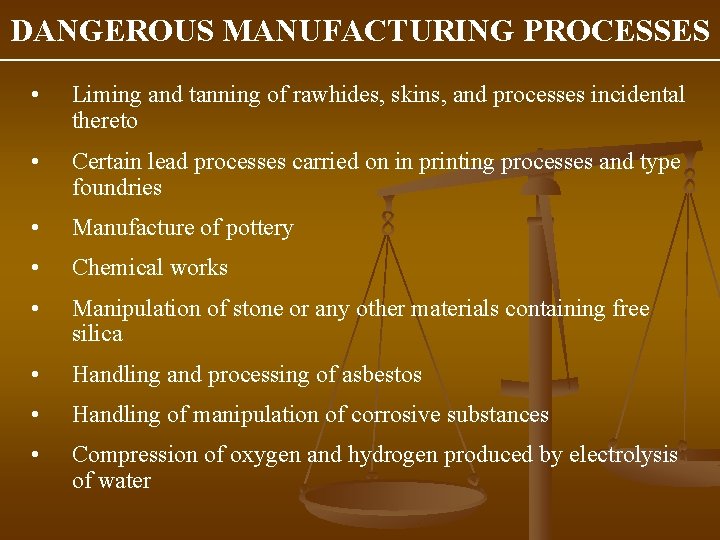
DANGEROUS MANUFACTURING PROCESSES • Liming and tanning of rawhides, skins, and processes incidental thereto • Certain lead processes carried on in printing processes and type foundries • Manufacture of pottery • Chemical works • Manipulation of stone or any other materials containing free silica • Handling and processing of asbestos • Handling of manipulation of corrosive substances • Compression of oxygen and hydrogen produced by electrolysis of water
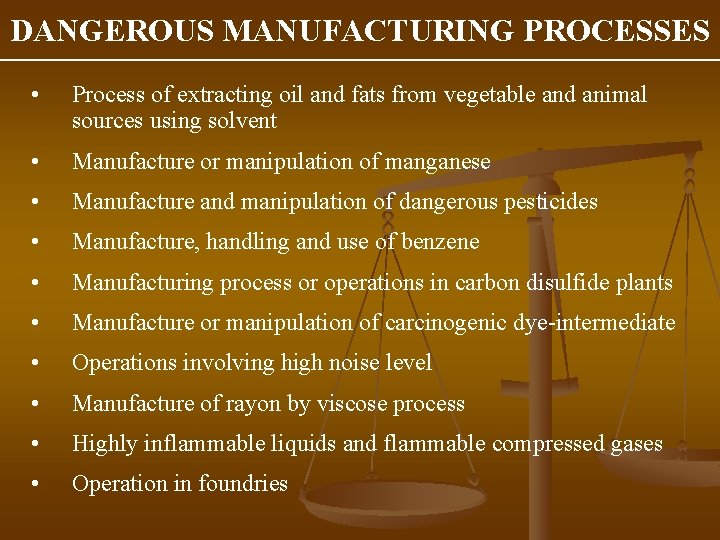
DANGEROUS MANUFACTURING PROCESSES • Process of extracting oil and fats from vegetable and animal sources using solvent • Manufacture or manipulation of manganese • Manufacture and manipulation of dangerous pesticides • Manufacture, handling and use of benzene • Manufacturing process or operations in carbon disulfide plants • Manufacture or manipulation of carcinogenic dye-intermediate • Operations involving high noise level • Manufacture of rayon by viscose process • Highly inflammable liquids and flammable compressed gases • Operation in foundries
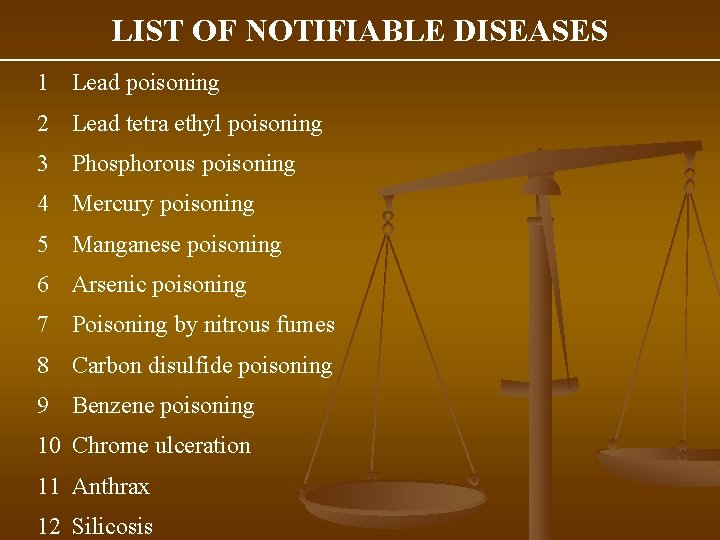
LIST OF NOTIFIABLE DISEASES 1 Lead poisoning 2 Lead tetra ethyl poisoning 3 Phosphorous poisoning 4 Mercury poisoning 5 Manganese poisoning 6 Arsenic poisoning 7 Poisoning by nitrous fumes 8 Carbon disulfide poisoning 9 Benzene poisoning 10 Chrome ulceration 11 Anthrax 12 Silicosis
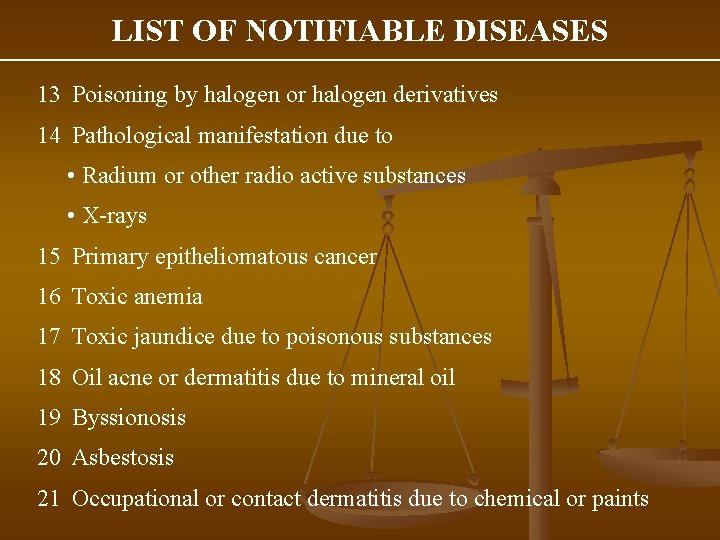
LIST OF NOTIFIABLE DISEASES 13 Poisoning by halogen or halogen derivatives 14 Pathological manifestation due to • Radium or other radio active substances • X-rays 15 Primary epitheliomatous cancer 16 Toxic anemia 17 Toxic jaundice due to poisonous substances 18 Oil acne or dermatitis due to mineral oil 19 Byssionosis 20 Asbestosis 21 Occupational or contact dermatitis due to chemical or paints
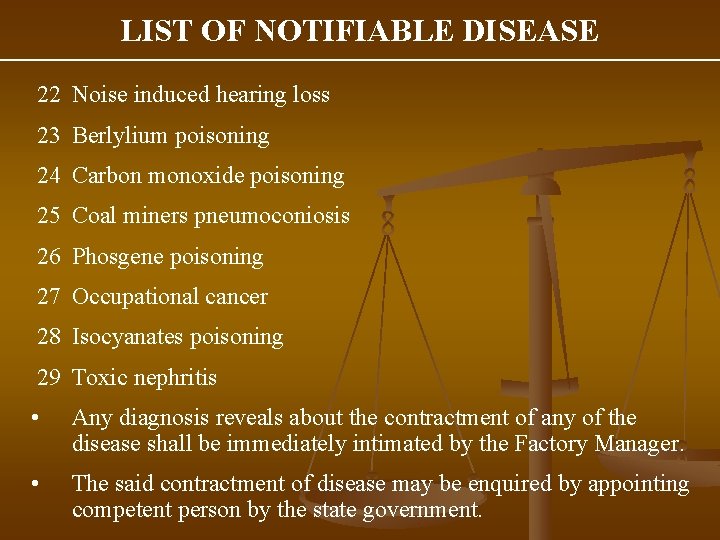
LIST OF NOTIFIABLE DISEASE 22 Noise induced hearing loss 23 Berlylium poisoning 24 Carbon monoxide poisoning 25 Coal miners pneumoconiosis 26 Phosgene poisoning 27 Occupational cancer 28 Isocyanates poisoning 29 Toxic nephritis • Any diagnosis reveals about the contractment of any of the disease shall be immediately intimated by the Factory Manager. • The said contractment of disease may be enquired by appointing competent person by the state government.
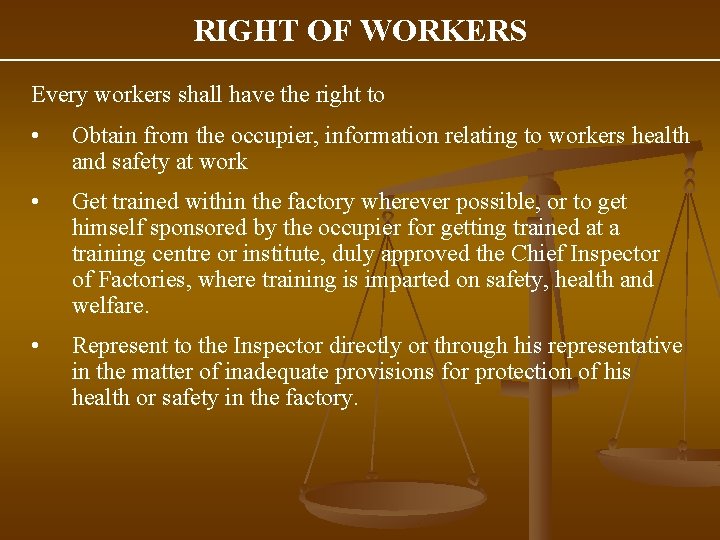
RIGHT OF WORKERS Every workers shall have the right to • Obtain from the occupier, information relating to workers health and safety at work • Get trained within the factory wherever possible, or to get himself sponsored by the occupier for getting trained at a training centre or institute, duly approved the Chief Inspector of Factories, where training is imparted on safety, health and welfare. • Represent to the Inspector directly or through his representative in the matter of inadequate provisions for protection of his health or safety in the factory.
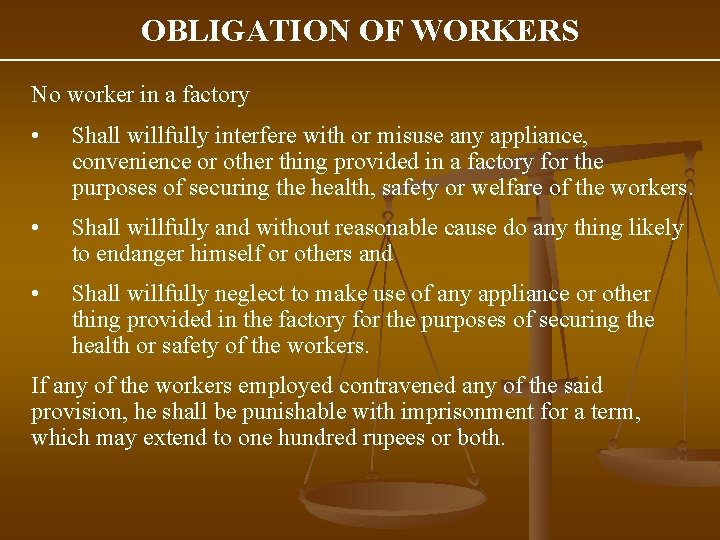
OBLIGATION OF WORKERS No worker in a factory • Shall willfully interfere with or misuse any appliance, convenience or other thing provided in a factory for the purposes of securing the health, safety or welfare of the workers. • Shall willfully and without reasonable cause do any thing likely to endanger himself or others and • Shall willfully neglect to make use of any appliance or other thing provided in the factory for the purposes of securing the health or safety of the workers. If any of the workers employed contravened any of the said provision, he shall be punishable with imprisonment for a term, which may extend to one hundred rupees or both.
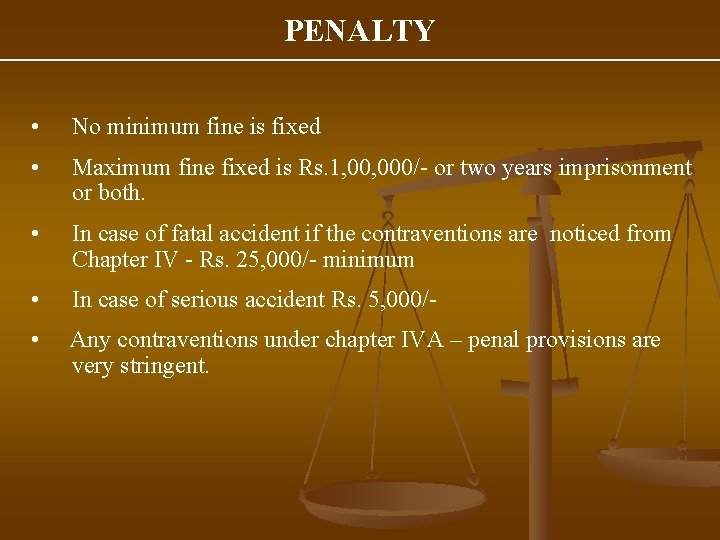
PENALTY • No minimum fine is fixed • Maximum fine fixed is Rs. 1, 000/- or two years imprisonment or both. • In case of fatal accident if the contraventions are noticed from Chapter IV - Rs. 25, 000/- minimum • In case of serious accident Rs. 5, 000/- • Any contraventions under chapter IVA – penal provisions are very stringent.
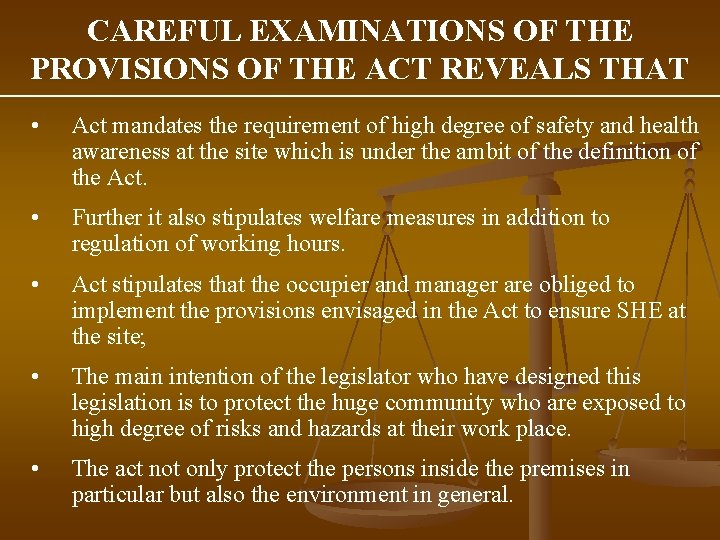
CAREFUL EXAMINATIONS OF THE PROVISIONS OF THE ACT REVEALS THAT • Act mandates the requirement of high degree of safety and health awareness at the site which is under the ambit of the definition of the Act. • Further it also stipulates welfare measures in addition to regulation of working hours. • Act stipulates that the occupier and manager are obliged to implement the provisions envisaged in the Act to ensure SHE at the site; • The main intention of the legislator who have designed this legislation is to protect the huge community who are exposed to high degree of risks and hazards at their work place. • The act not only protect the persons inside the premises in particular but also the environment in general.
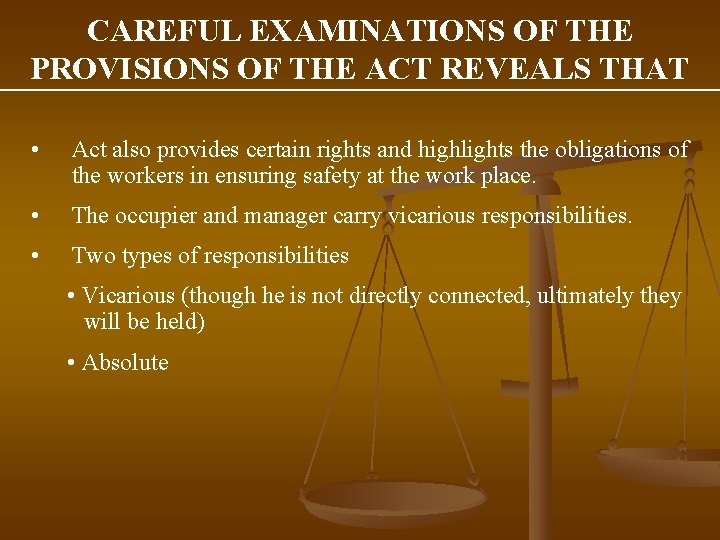
CAREFUL EXAMINATIONS OF THE PROVISIONS OF THE ACT REVEALS THAT • Act also provides certain rights and highlights the obligations of the workers in ensuring safety at the work place. • The occupier and manager carry vicarious responsibilities. • Two types of responsibilities • Vicarious (though he is not directly connected, ultimately they will be held) • Absolute
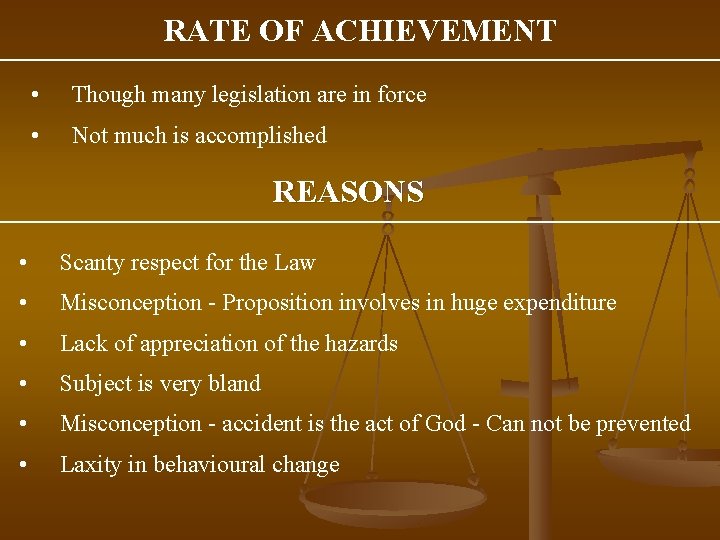
RATE OF ACHIEVEMENT • Though many legislation are in force • Not much is accomplished REASONS • Scanty respect for the Law • Misconception - Proposition involves in huge expenditure • Lack of appreciation of the hazards • Subject is very bland • Misconception - accident is the act of God - Can not be prevented • Laxity in behavioural change
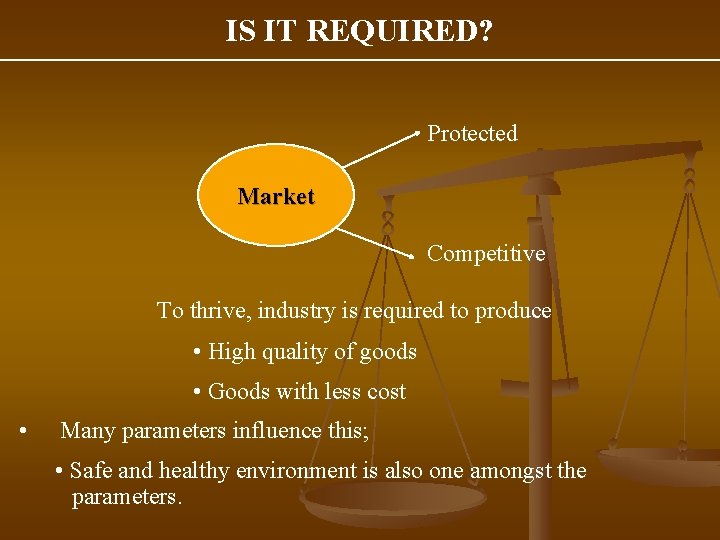
IS IT REQUIRED? Protected Market Competitive To thrive, industry is required to produce • High quality of goods • Goods with less cost • Many parameters influence this; • Safe and healthy environment is also one amongst the parameters.
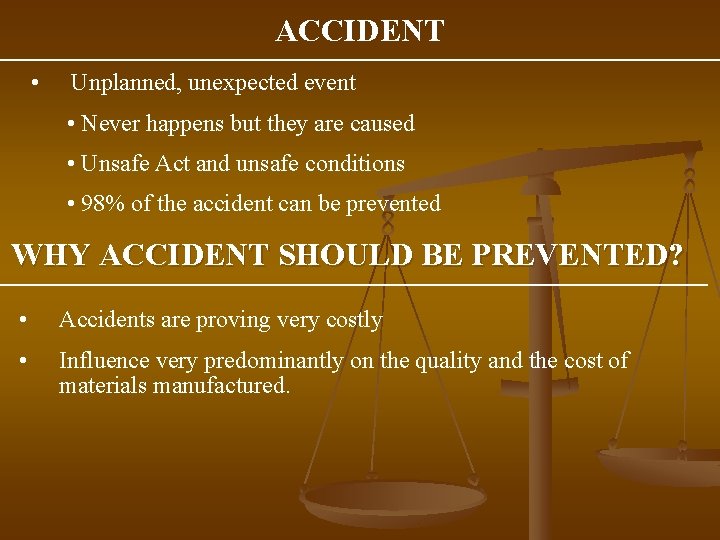
ACCIDENT • Unplanned, unexpected event • Never happens but they are caused • Unsafe Act and unsafe conditions • 98% of the accident can be prevented WHY ACCIDENT SHOULD BE PREVENTED? • Accidents are proving very costly • Influence very predominantly on the quality and the cost of materials manufactured.
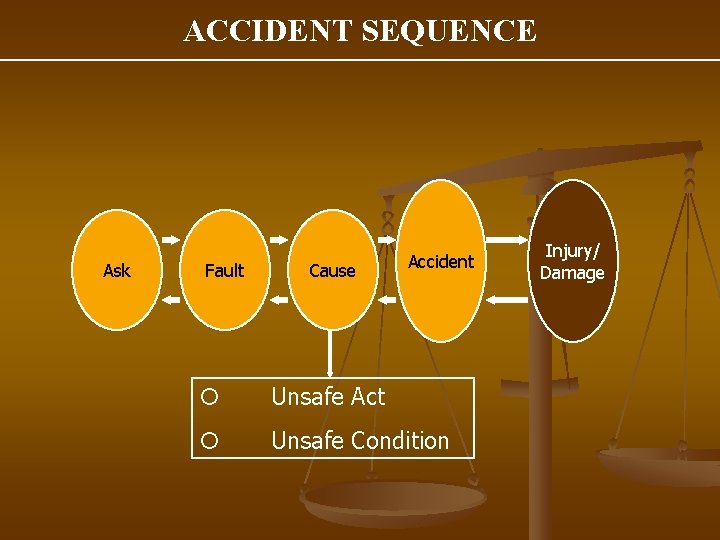
ACCIDENT SEQUENCE Ask Fault Cause Accident ¡ Unsafe Act ¡ Unsafe Condition Injury/ Damage
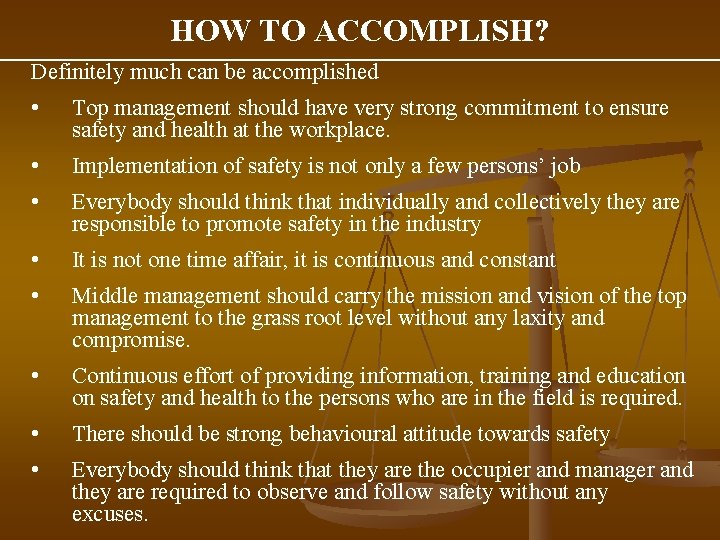
HOW TO ACCOMPLISH? Definitely much can be accomplished • Top management should have very strong commitment to ensure safety and health at the workplace. • Implementation of safety is not only a few persons’ job • Everybody should think that individually and collectively they are responsible to promote safety in the industry • It is not one time affair, it is continuous and constant • Middle management should carry the mission and vision of the top management to the grass root level without any laxity and compromise. • Continuous effort of providing information, training and education on safety and health to the persons who are in the field is required. • There should be strong behavioural attitude towards safety • Everybody should think that they are the occupier and manager and they are required to observe and follow safety without any excuses.
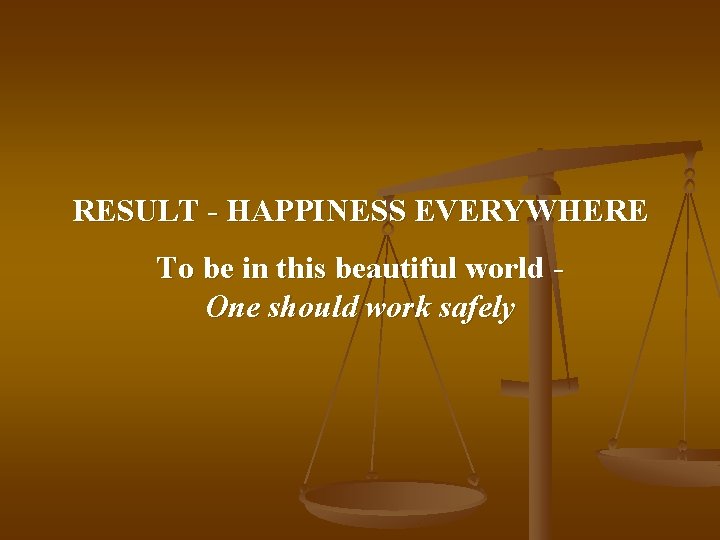
RESULT - HAPPINESS EVERYWHERE To be in this beautiful world One should work safely
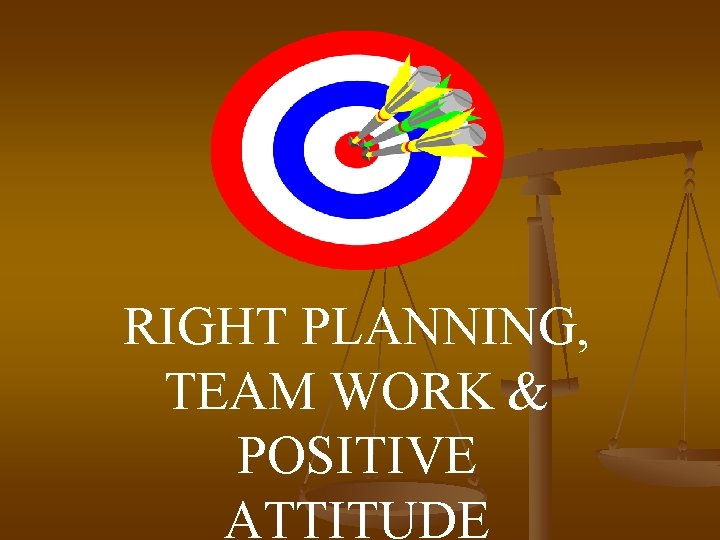
RIGHT PLANNING, TEAM WORK & POSITIVE ATTITUDE
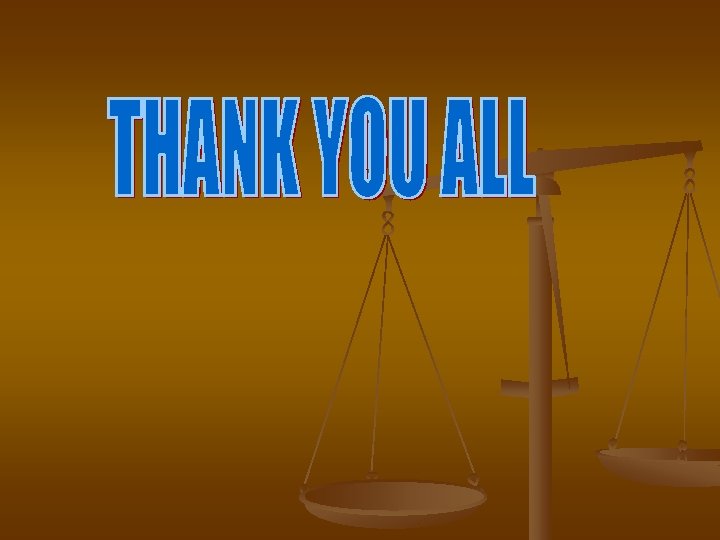
Factories act 1948 notes
Object of the factories act 1948
The minimum wages act 1948
The minimum wage act 1948
Pharmaceutical jurisprudence by mithal
Health problems due to industrialization ppt
Macbeth summary
1948 recording ban
Havighurst 1948
Program tasarım modelleri
Pada 1 februari 1948
Setting of montana 1948
Marie montana 1948
Gail hayden montana 1948
Kirjanik 1899-1948
No. 5, 1948
Currents hannah bottomy
2004-1948
Edward c tolman
Ai 310
December 10 1948
Montana 1948 len
28 juillet 1948
Stephan huber denk pharma
Tuntutan orang melayu dalam ptm 1948
Jackson pollock untitled 1948
1948 transistor
1948 cartoon
Esquema de la guerra civil española
1948 peugeot 203
North korea genocide 1948-1994
Stat grundad 1948
Ttab 700 ultra glide
Drawing hands escher
Le projet d une europe politique depuis 1948
Sejak pembentukannya di bandung pada bulan juli 1948
Evening standard cartoonist
1948 israel map
White city olympics 1948
Cam gear factories
Fumes from factories
Female workers in japanese silk factories dbq answers
Fumes from factories
Aquaculture water treatment
2 ss pipe tianjin
Vesuvius refractory products
How did the flying shuttle change the world
Movies about factories
Solcane
Sic whiskers factories
Self-inductance of a solenoid
Aircraft cable seismic supplier
Tom chothia
Glyphic legend chomik
Permastore
Metal forming part factories
Husky injection molding machine factory
Powder coating extruder
History display board
Pneumatic
1 seg factories
Slt 800 solar light tower
What is factorise
Kookaburra nest factories
Anc kucai
Honey bee wax glands
Elcb factories
Mentovertical diameter
Leopold's maneuver
Hình ảnh bộ gõ cơ thể búng tay
Lp html
Bổ thể
Tỉ lệ cơ thể trẻ em
Chó sói
Thang điểm glasgow
Hát lên người ơi
Môn thể thao bắt đầu bằng từ đua
Thế nào là hệ số cao nhất
Các châu lục và đại dương trên thế giới
Công của trọng lực
Trời xanh đây là của chúng ta thể thơ
Mật thư tọa độ 5x5
Phép trừ bù
độ dài liên kết
Các châu lục và đại dương trên thế giới
Thơ thất ngôn tứ tuyệt đường luật
Quá trình desamine hóa có thể tạo ra
Một số thể thơ truyền thống
Cái miệng xinh xinh thế chỉ nói điều hay thôi
Vẽ hình chiếu vuông góc của vật thể sau