INTODUCTION TO WELDING PROCESS WELDING PROCESS The welding
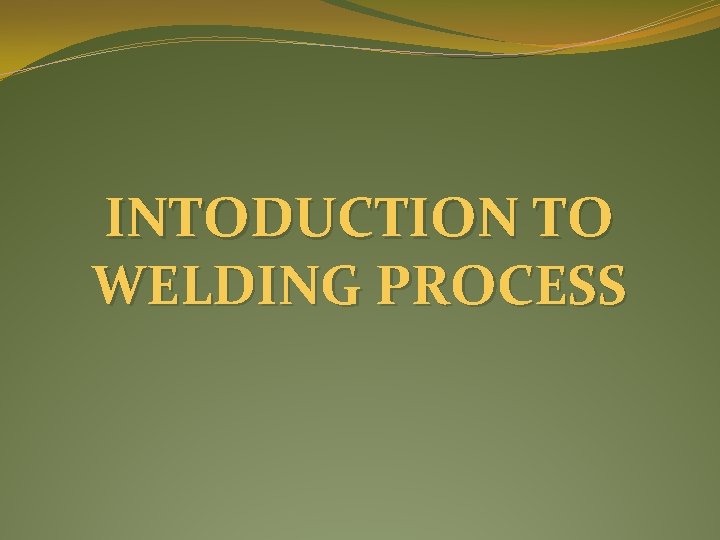
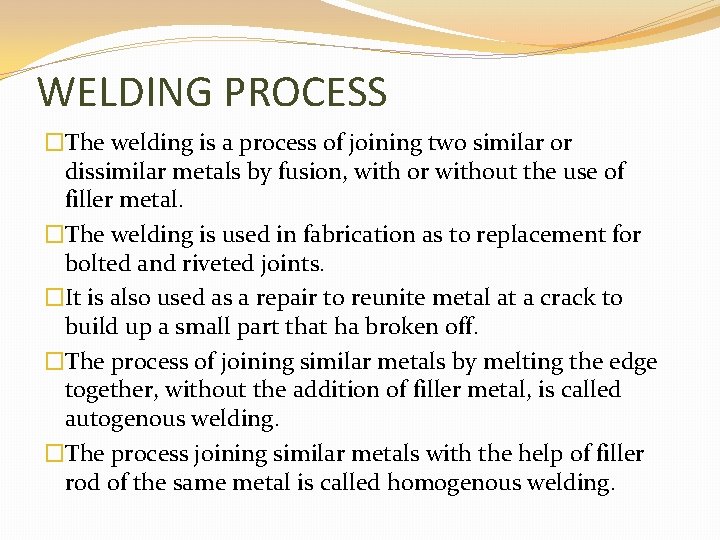
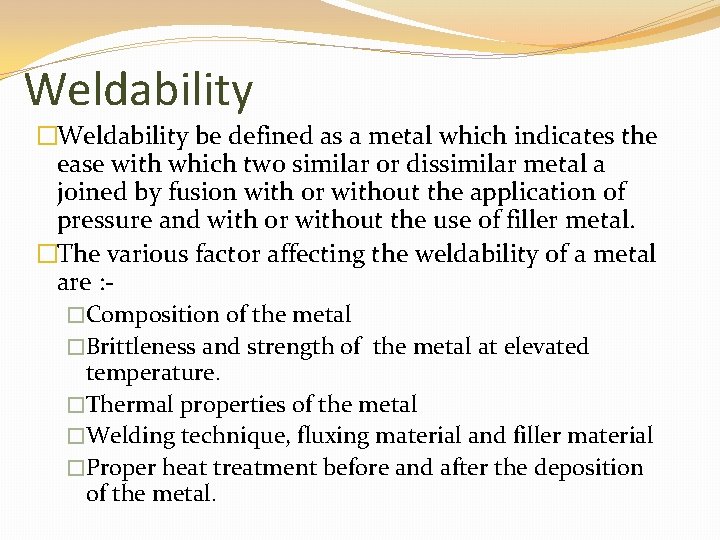
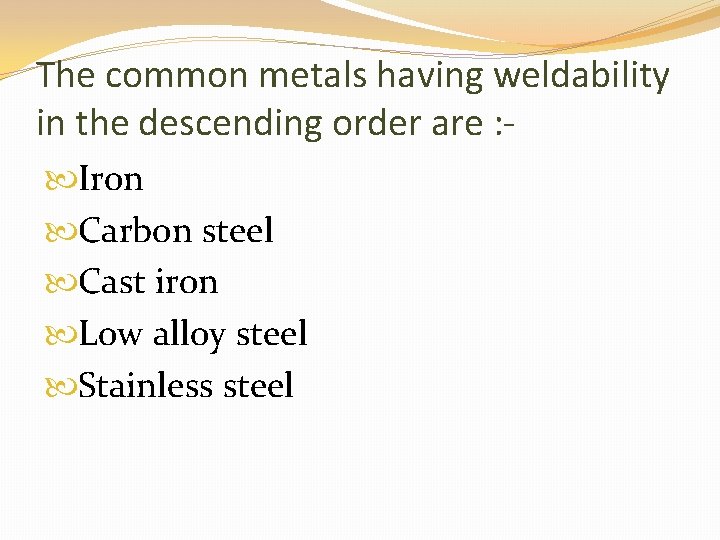
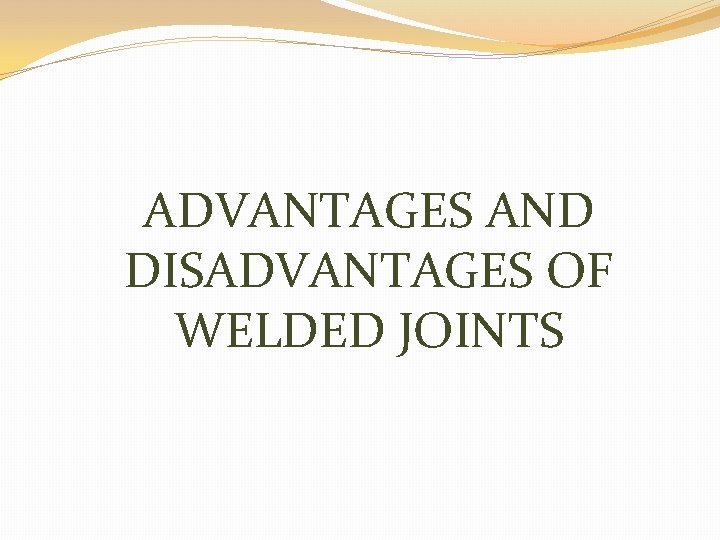
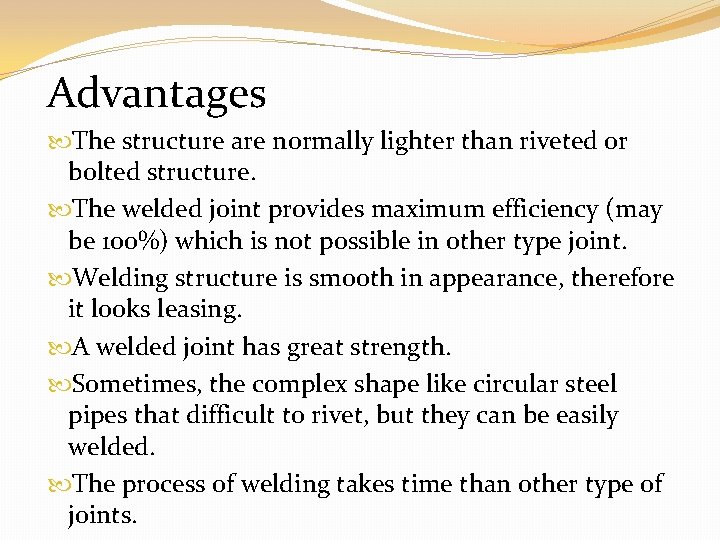
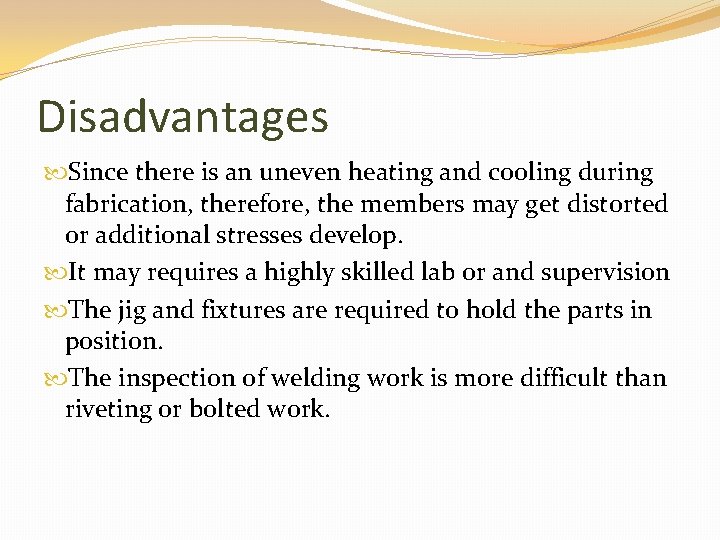
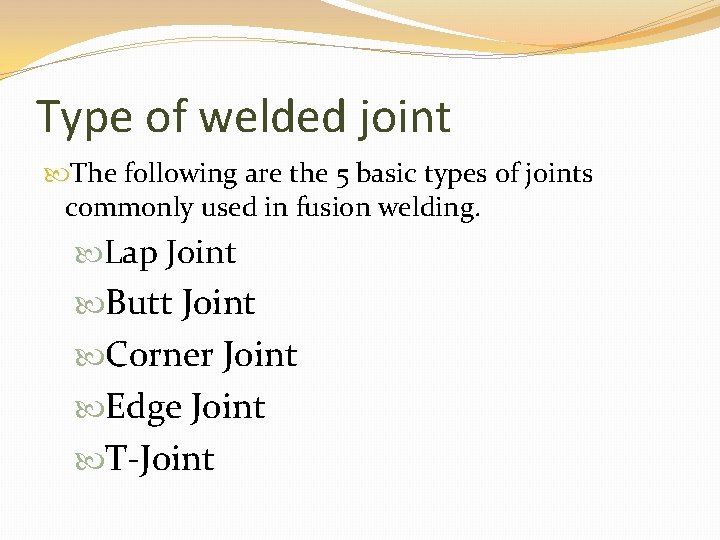
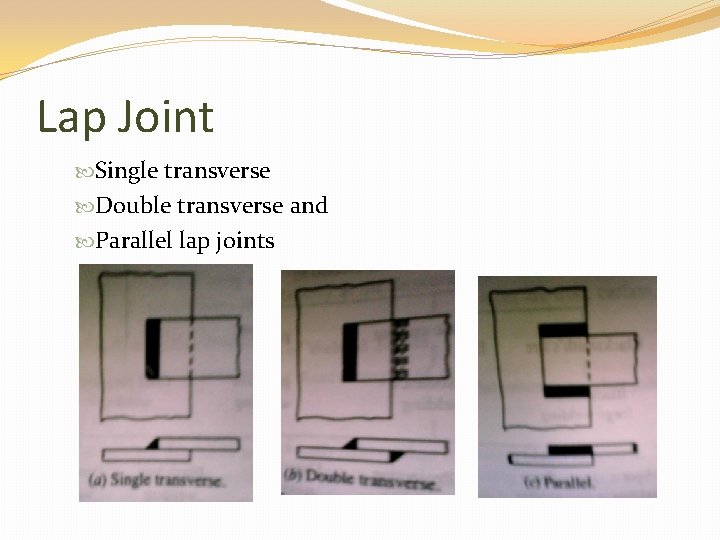
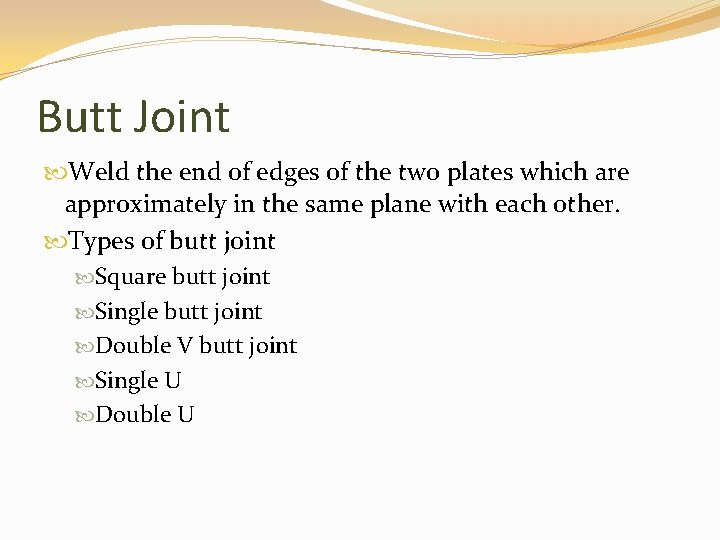
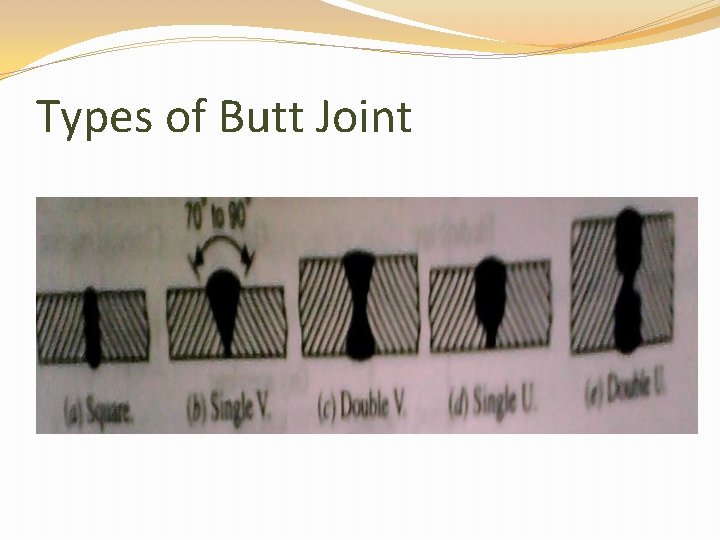
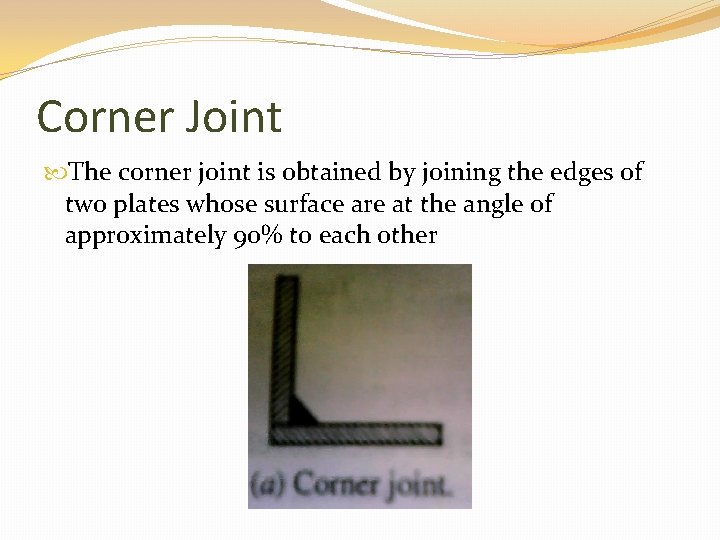
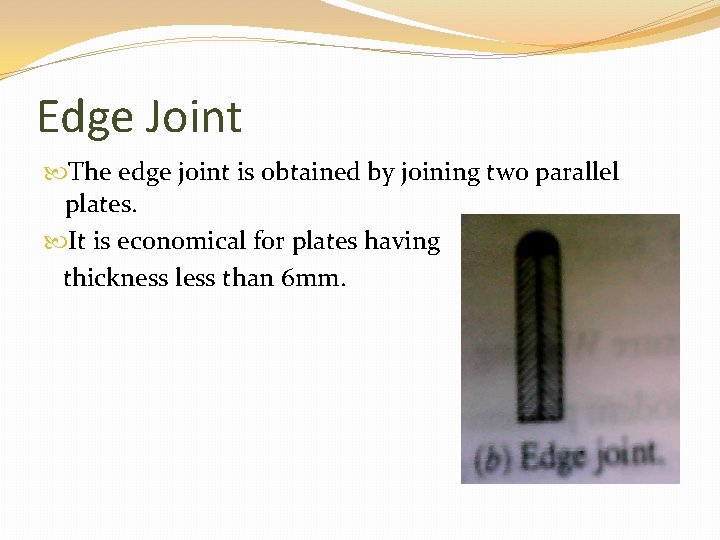
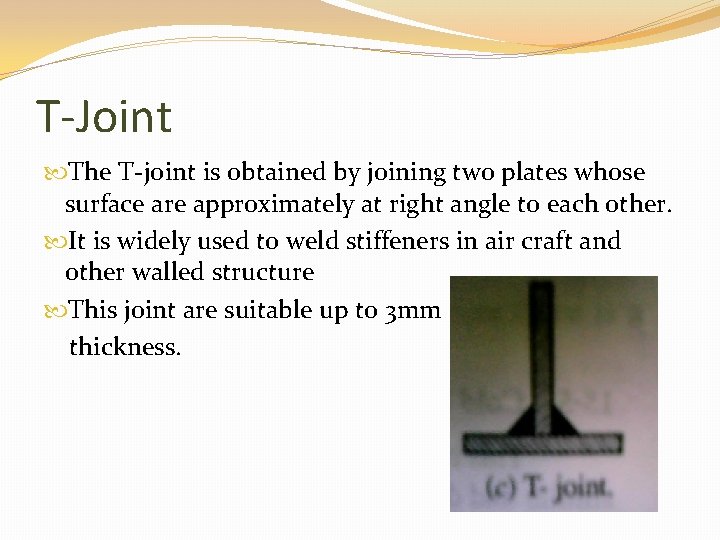
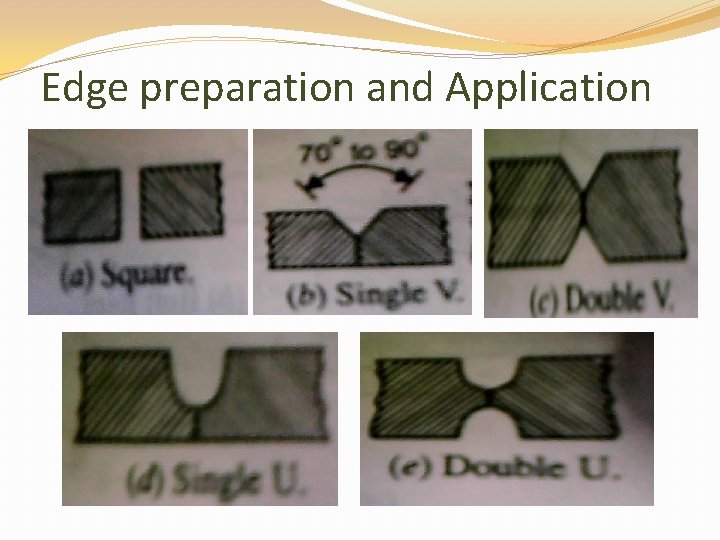

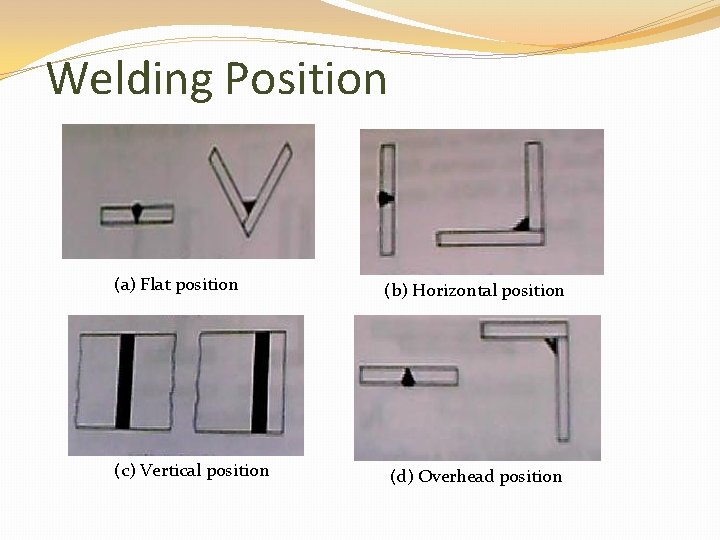
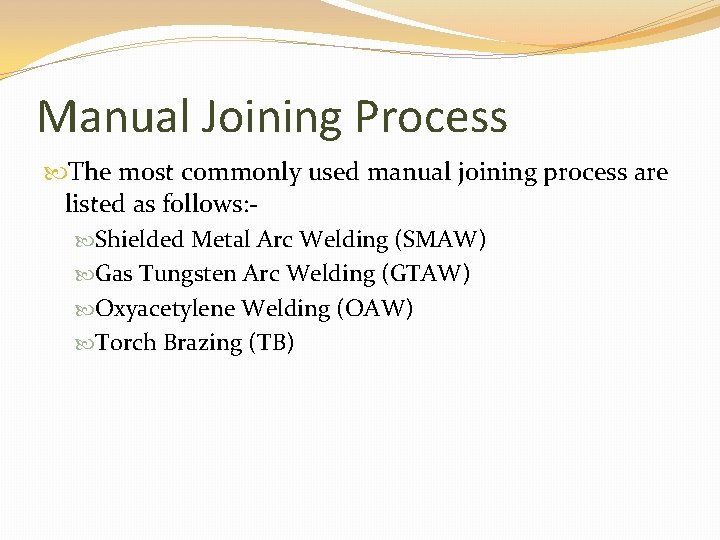
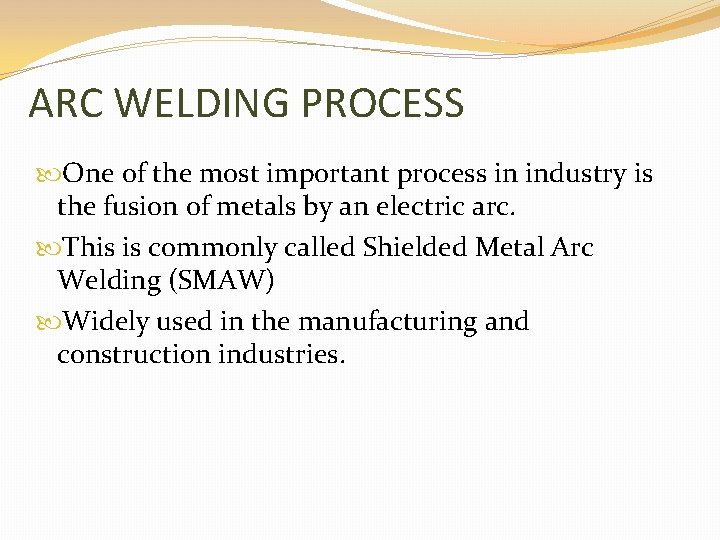
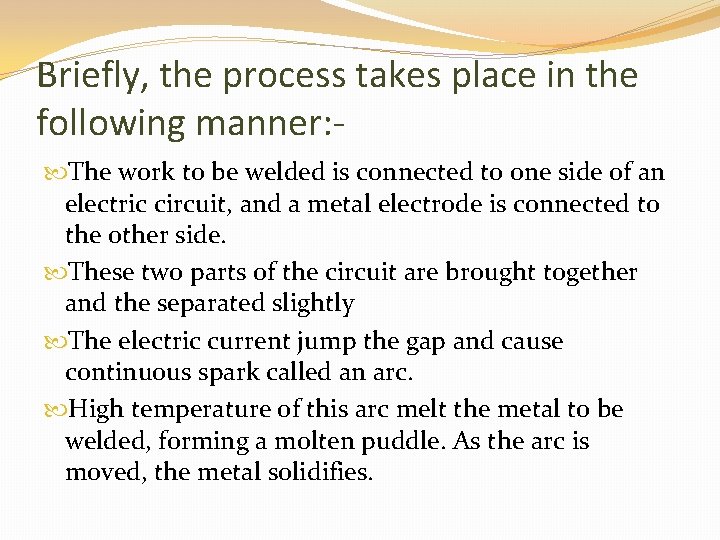
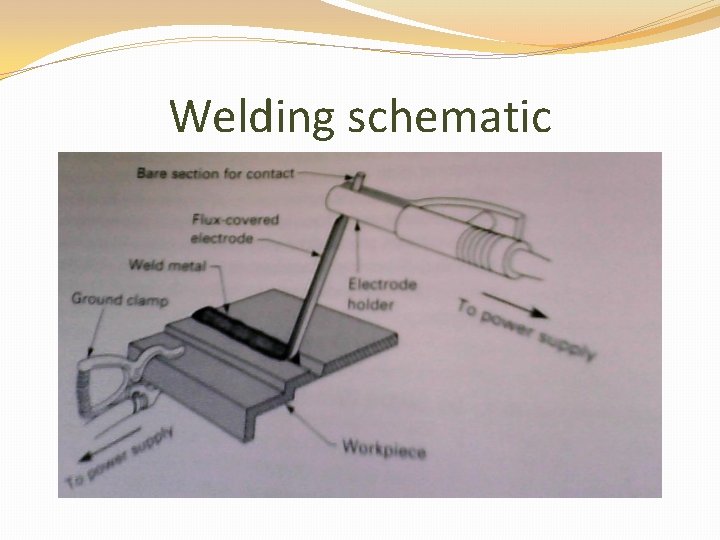
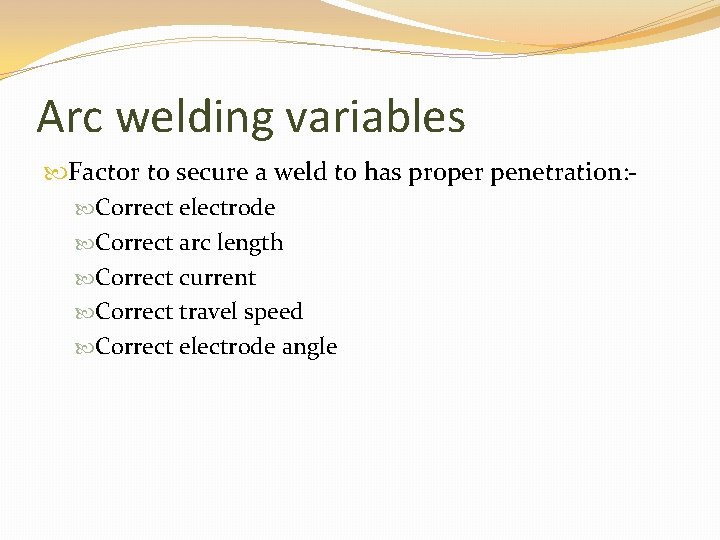
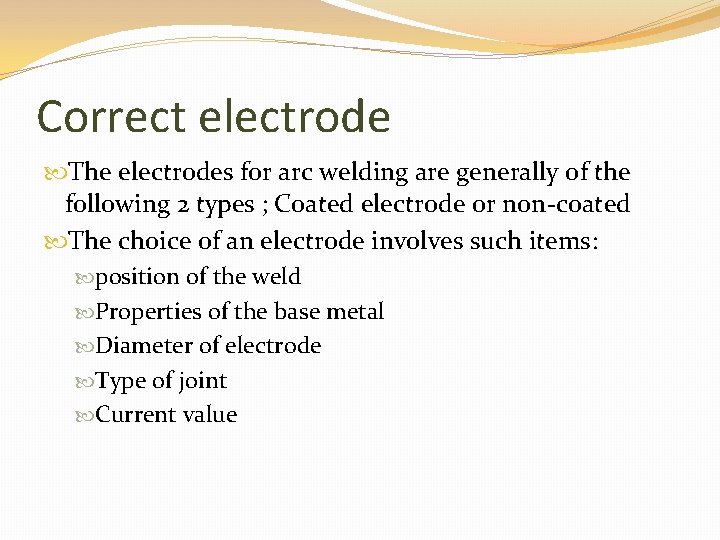
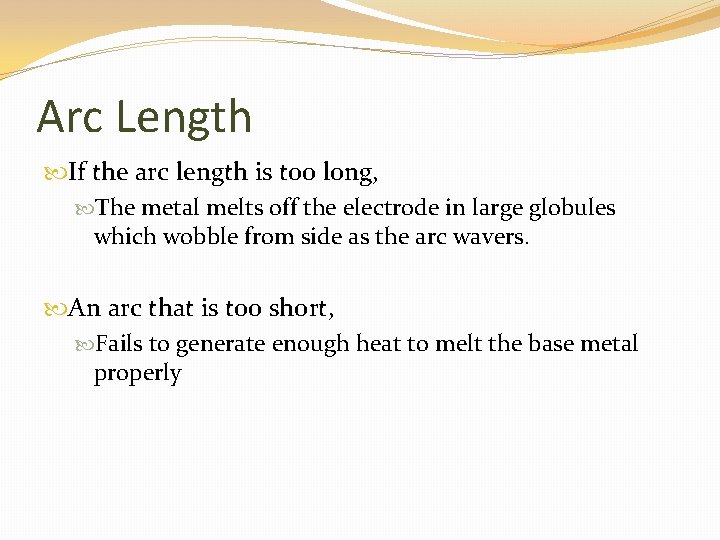
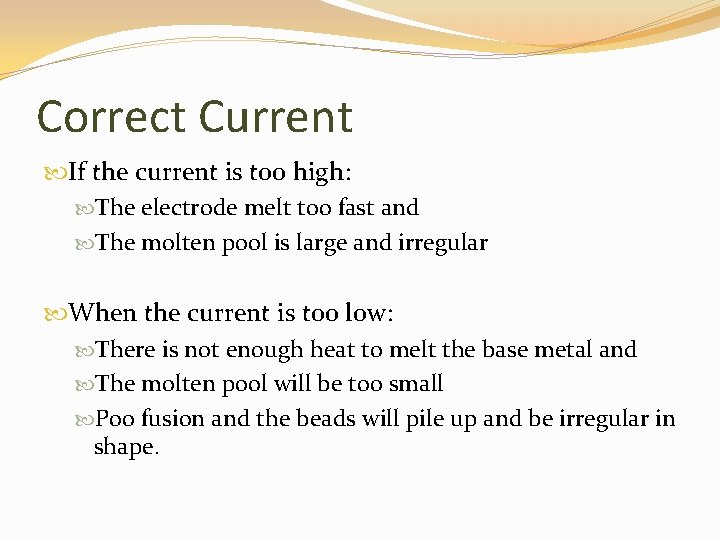
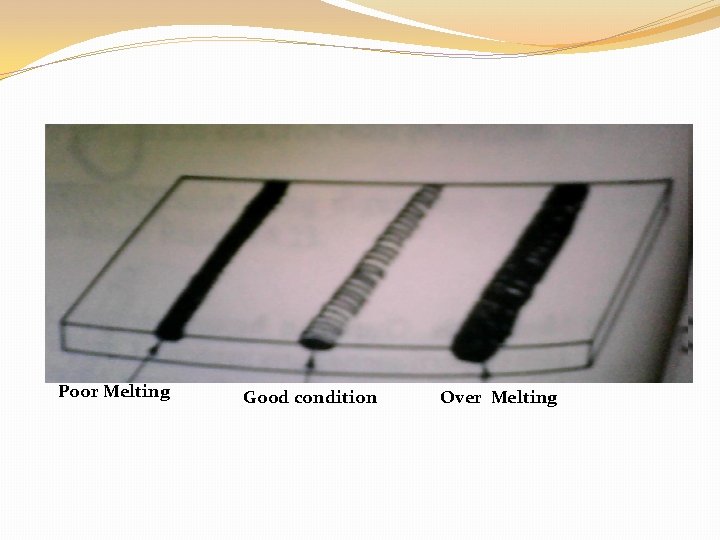
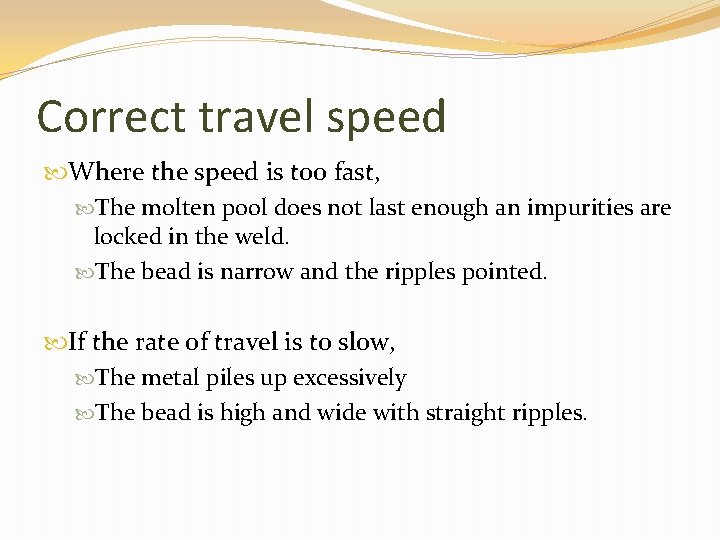
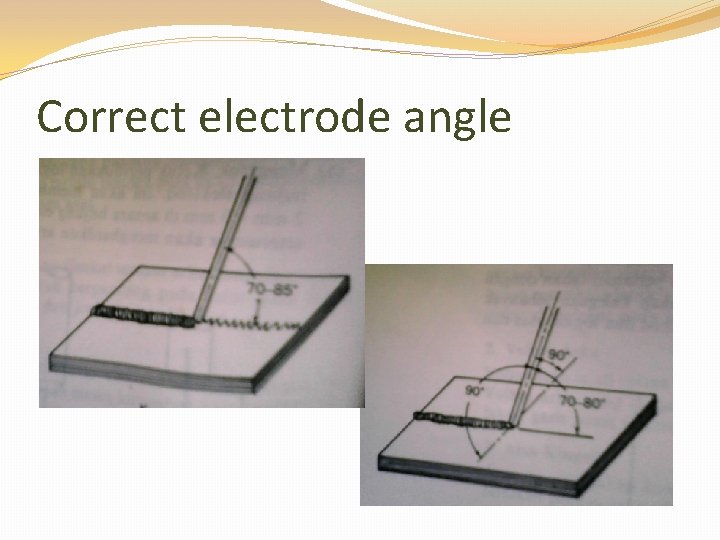
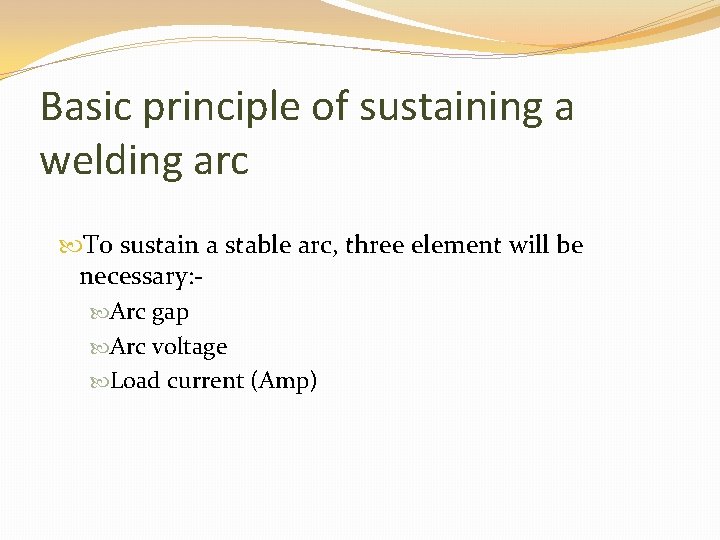
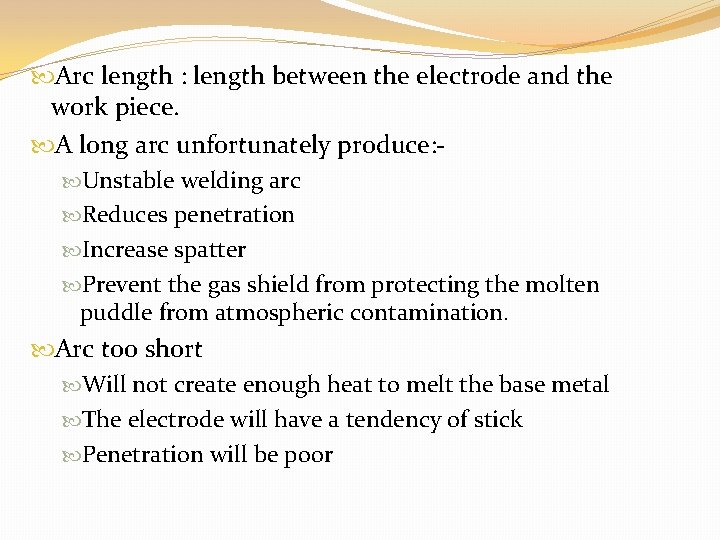
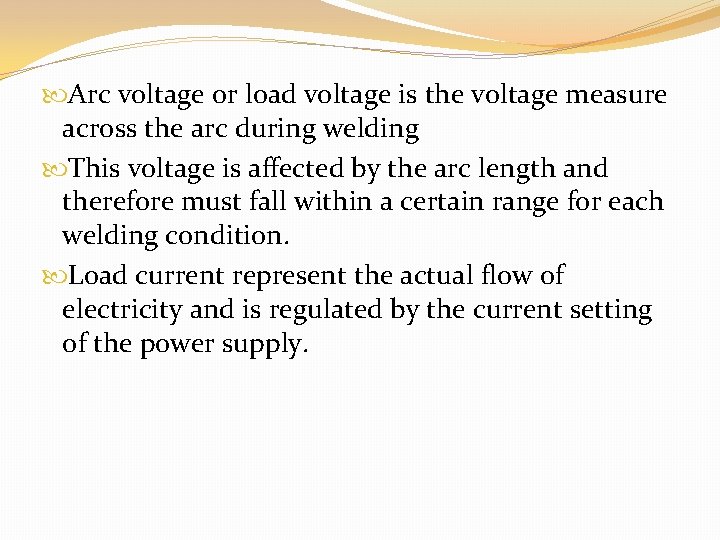
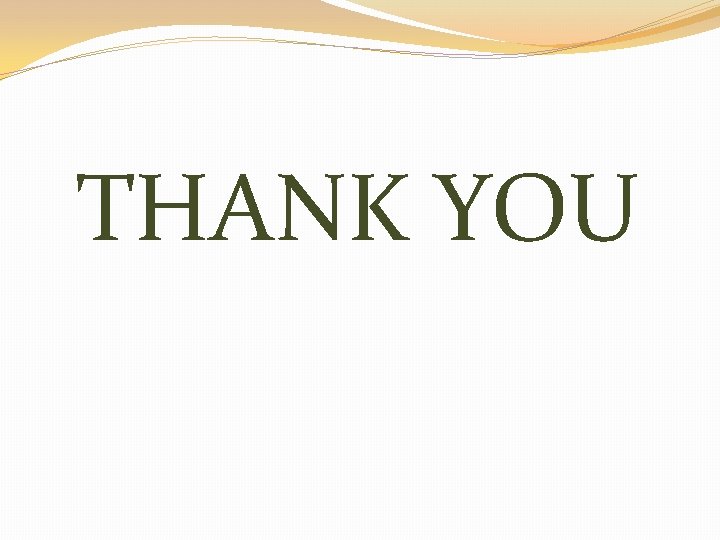
- Slides: 32
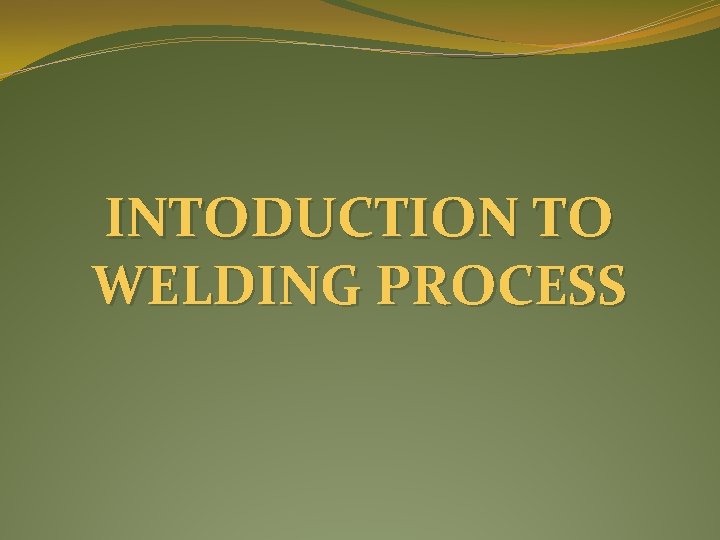
INTODUCTION TO WELDING PROCESS
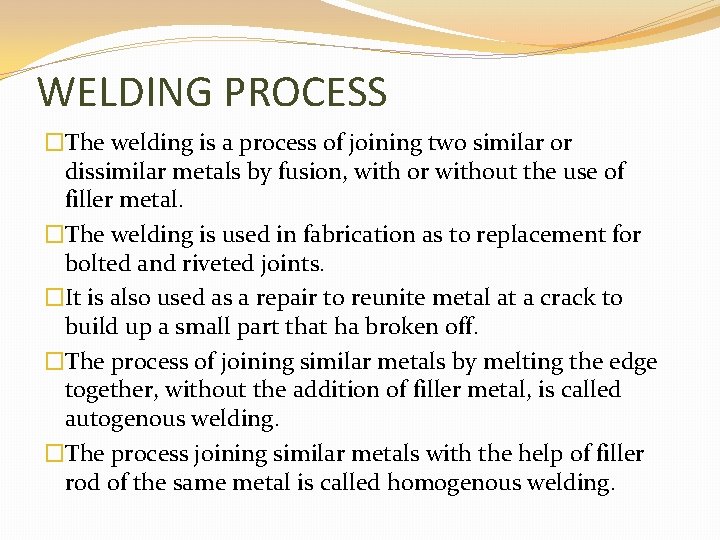
WELDING PROCESS �The welding is a process of joining two similar or dissimilar metals by fusion, with or without the use of filler metal. �The welding is used in fabrication as to replacement for bolted and riveted joints. �It is also used as a repair to reunite metal at a crack to build up a small part that ha broken off. �The process of joining similar metals by melting the edge together, without the addition of filler metal, is called autogenous welding. �The process joining similar metals with the help of filler rod of the same metal is called homogenous welding.
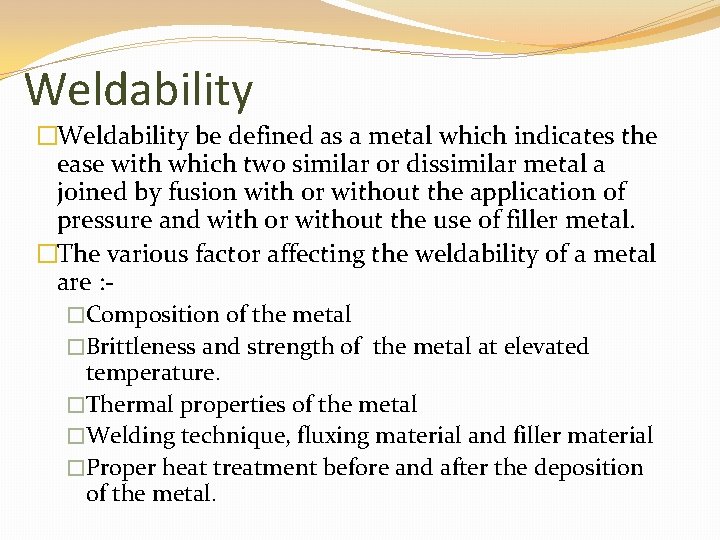
Weldability �Weldability be defined as a metal which indicates the ease with which two similar or dissimilar metal a joined by fusion with or without the application of pressure and with or without the use of filler metal. �The various factor affecting the weldability of a metal are : �Composition of the metal �Brittleness and strength of the metal at elevated temperature. �Thermal properties of the metal �Welding technique, fluxing material and filler material �Proper heat treatment before and after the deposition of the metal.
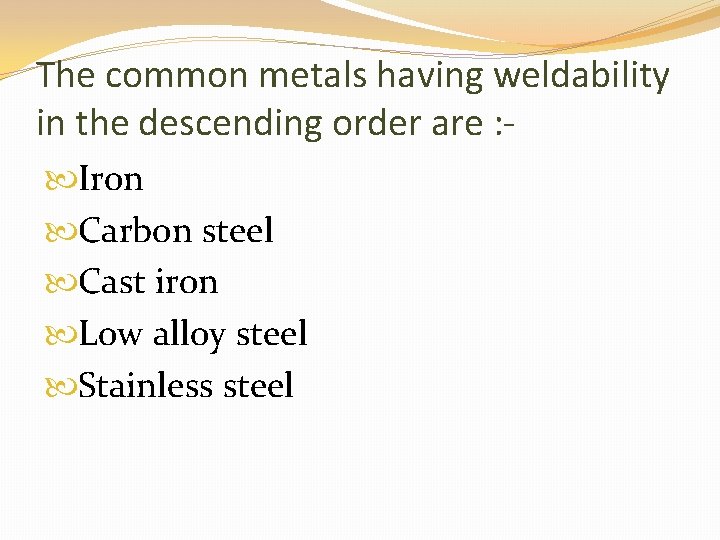
The common metals having weldability in the descending order are : Iron Carbon steel Cast iron Low alloy steel Stainless steel
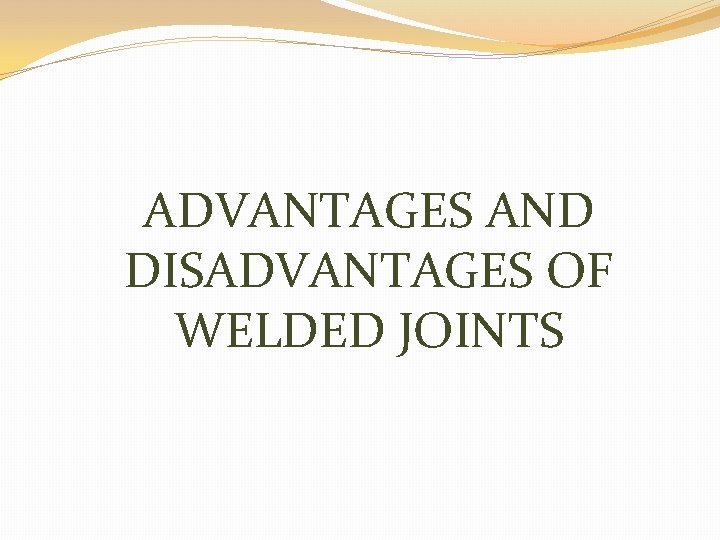
ADVANTAGES AND DISADVANTAGES OF WELDED JOINTS
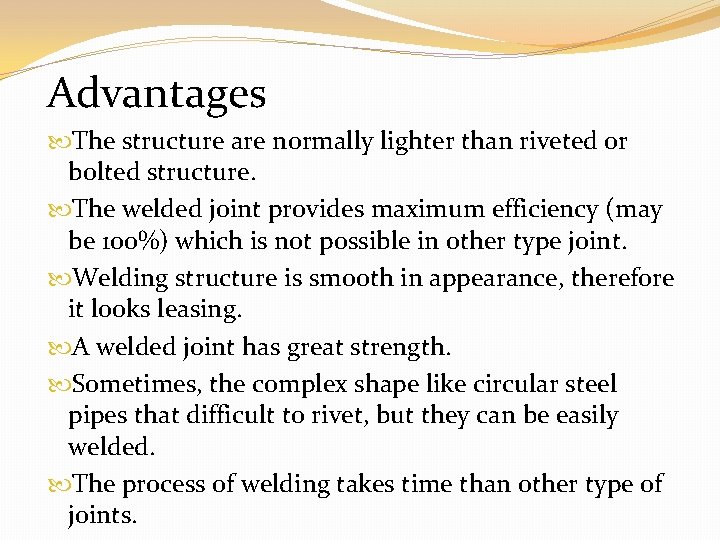
Advantages The structure are normally lighter than riveted or bolted structure. The welded joint provides maximum efficiency (may be 100%) which is not possible in other type joint. Welding structure is smooth in appearance, therefore it looks leasing. A welded joint has great strength. Sometimes, the complex shape like circular steel pipes that difficult to rivet, but they can be easily welded. The process of welding takes time than other type of joints.
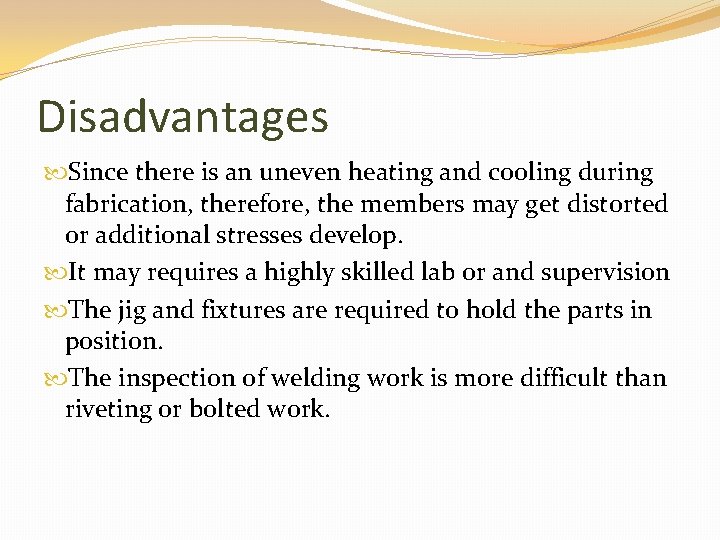
Disadvantages Since there is an uneven heating and cooling during fabrication, therefore, the members may get distorted or additional stresses develop. It may requires a highly skilled lab or and supervision The jig and fixtures are required to hold the parts in position. The inspection of welding work is more difficult than riveting or bolted work.
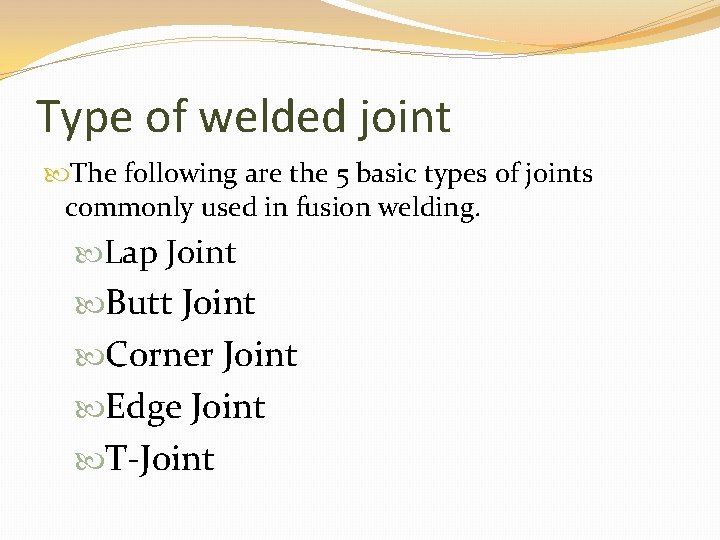
Type of welded joint The following are the 5 basic types of joints commonly used in fusion welding. Lap Joint Butt Joint Corner Joint Edge Joint T-Joint
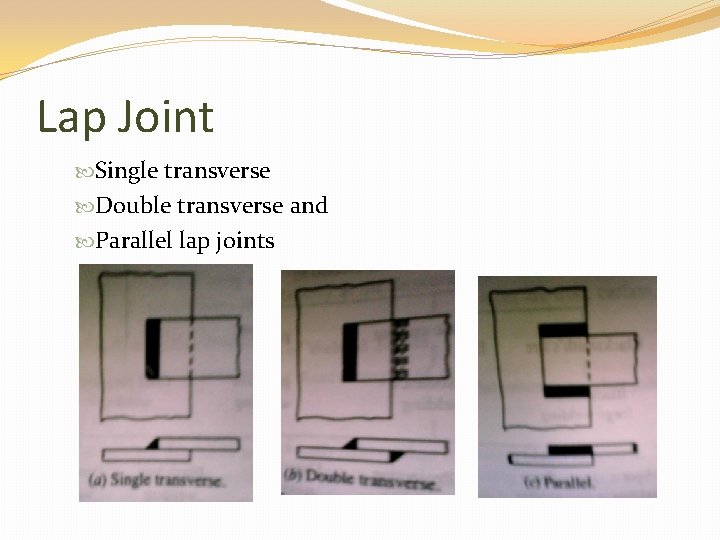
Lap Joint Single transverse Double transverse and Parallel lap joints
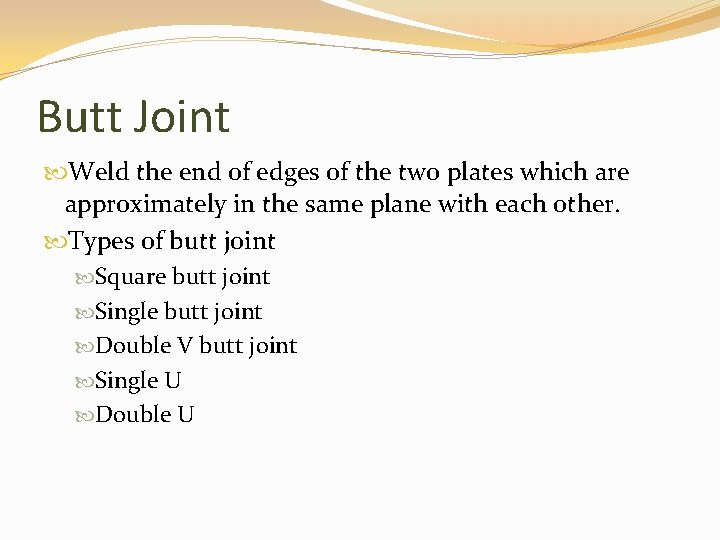
Butt Joint Weld the end of edges of the two plates which are approximately in the same plane with each other. Types of butt joint Square butt joint Single butt joint Double V butt joint Single U Double U
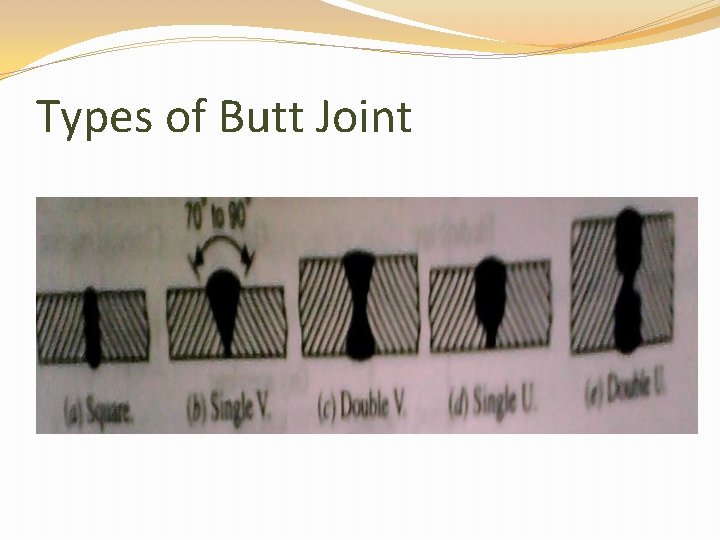
Types of Butt Joint
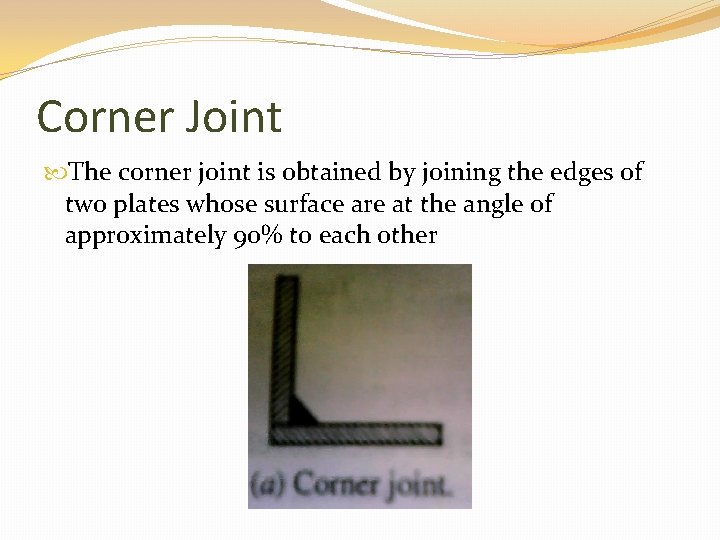
Corner Joint The corner joint is obtained by joining the edges of two plates whose surface are at the angle of approximately 90% to each other
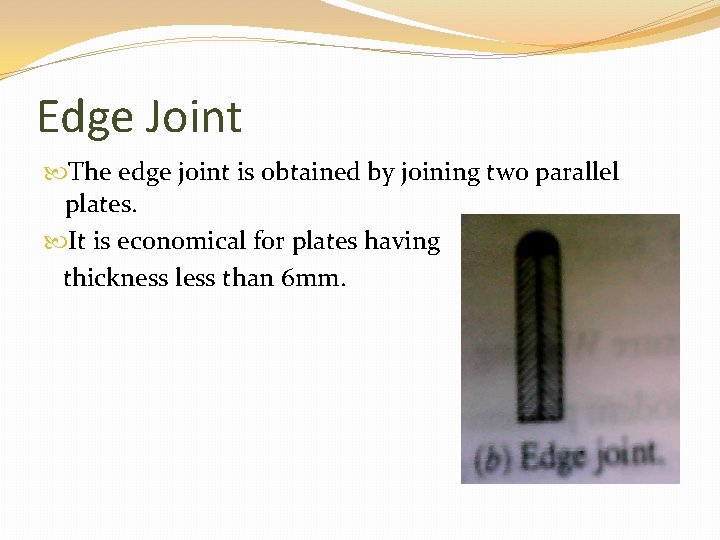
Edge Joint The edge joint is obtained by joining two parallel plates. It is economical for plates having thickness less than 6 mm.
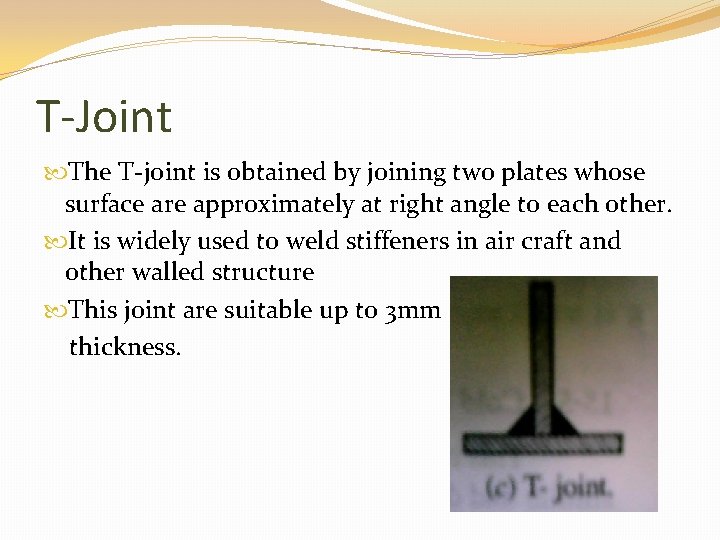
T-Joint The T-joint is obtained by joining two plates whose surface are approximately at right angle to each other. It is widely used to weld stiffeners in air craft and other walled structure This joint are suitable up to 3 mm thickness.
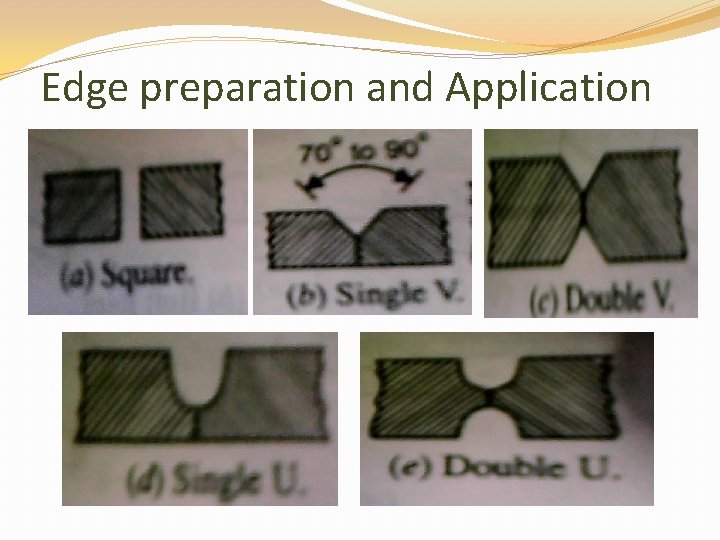
Edge preparation and Application

Welding Position The welding position are classified as follows: Flat Position Horizontal position Vertical position
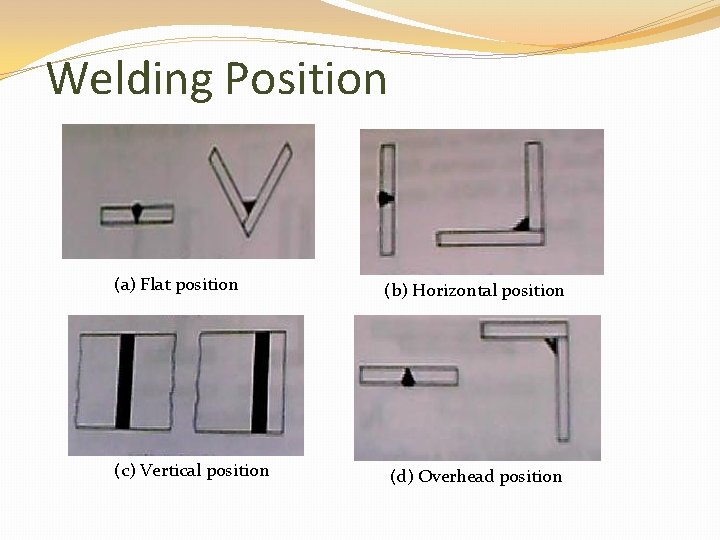
Welding Position (a) Flat position (c) Vertical position (b) Horizontal position (d) Overhead position
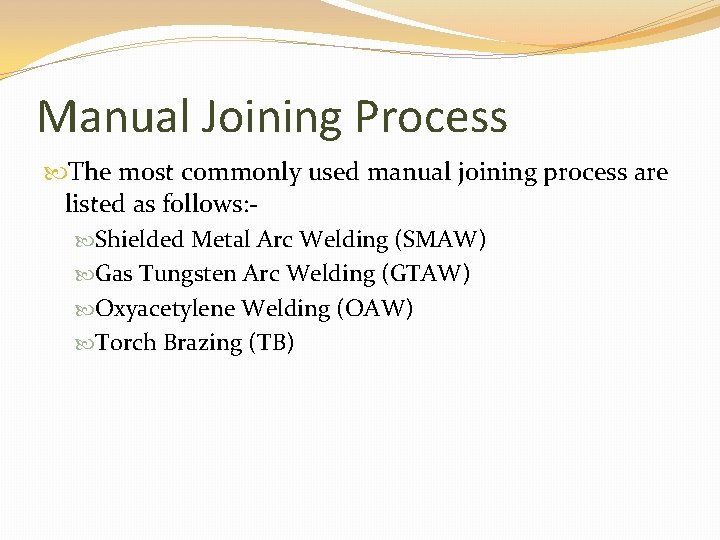
Manual Joining Process The most commonly used manual joining process are listed as follows: Shielded Metal Arc Welding (SMAW) Gas Tungsten Arc Welding (GTAW) Oxyacetylene Welding (OAW) Torch Brazing (TB)
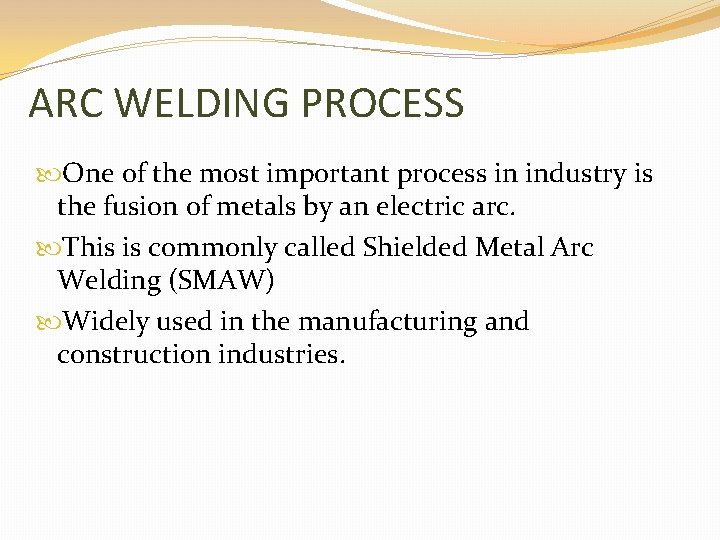
ARC WELDING PROCESS One of the most important process in industry is the fusion of metals by an electric arc. This is commonly called Shielded Metal Arc Welding (SMAW) Widely used in the manufacturing and construction industries.
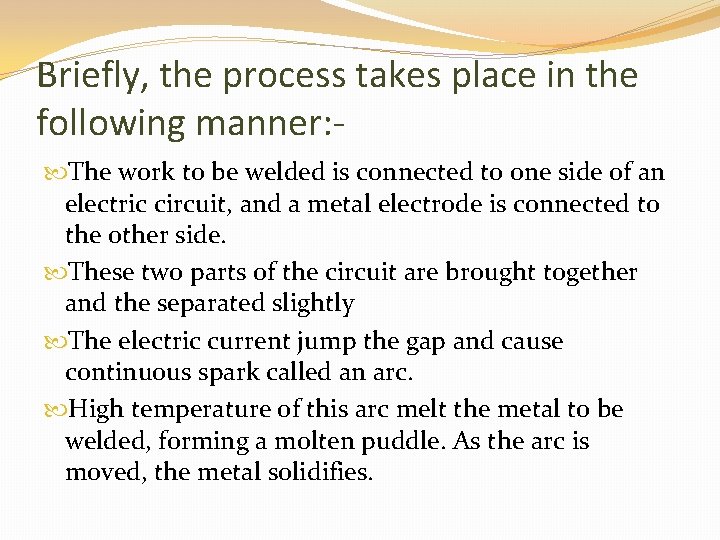
Briefly, the process takes place in the following manner: The work to be welded is connected to one side of an electric circuit, and a metal electrode is connected to the other side. These two parts of the circuit are brought together and the separated slightly The electric current jump the gap and cause continuous spark called an arc. High temperature of this arc melt the metal to be welded, forming a molten puddle. As the arc is moved, the metal solidifies.
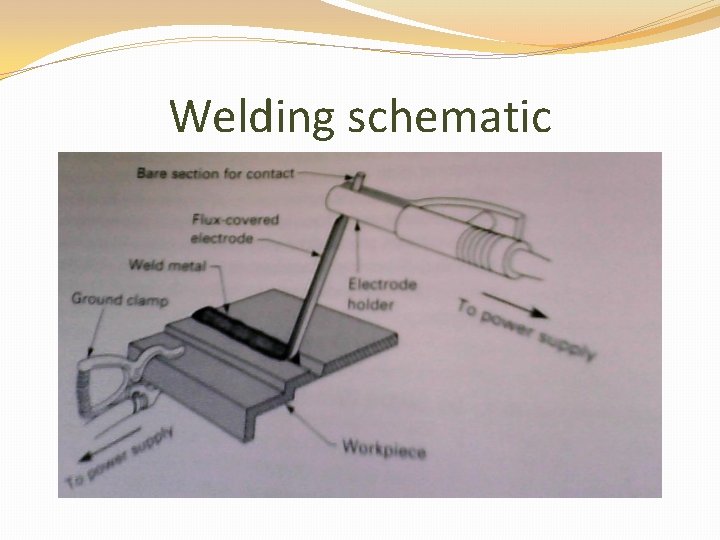
Welding schematic
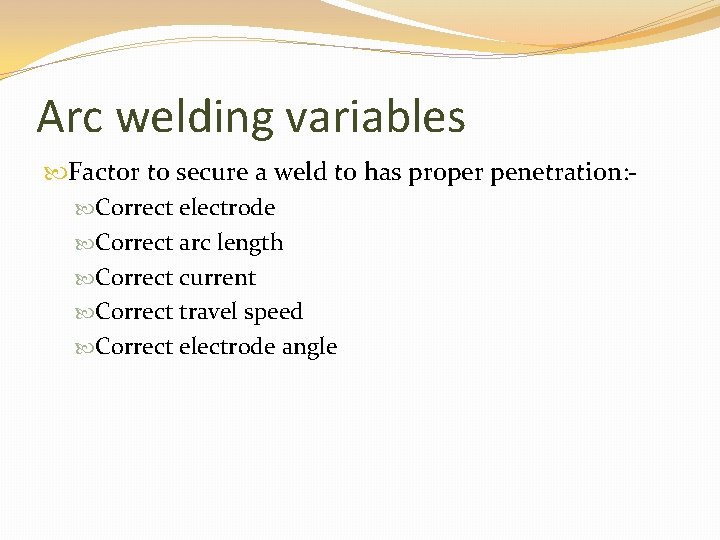
Arc welding variables Factor to secure a weld to has proper penetration: Correct electrode Correct arc length Correct current Correct travel speed Correct electrode angle
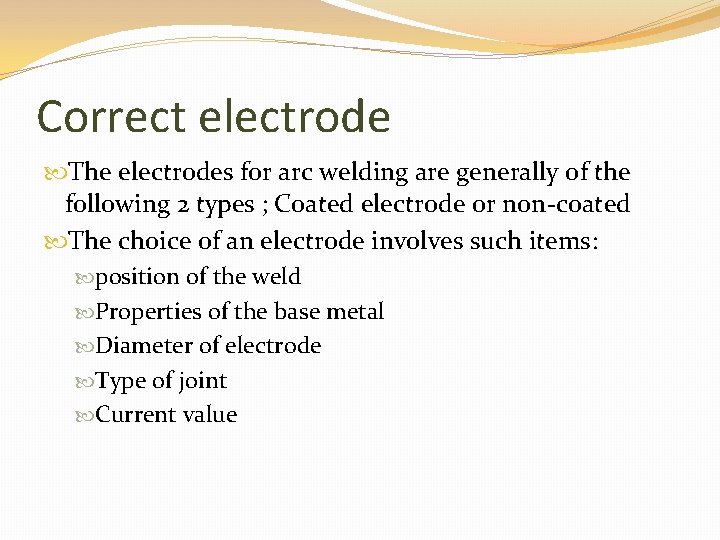
Correct electrode The electrodes for arc welding are generally of the following 2 types ; Coated electrode or non-coated The choice of an electrode involves such items: position of the weld Properties of the base metal Diameter of electrode Type of joint Current value
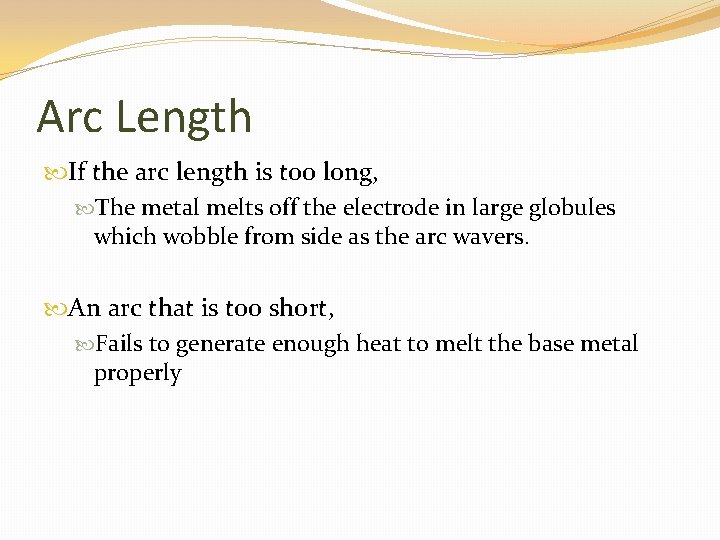
Arc Length If the arc length is too long, The metal melts off the electrode in large globules which wobble from side as the arc wavers. An arc that is too short, Fails to generate enough heat to melt the base metal properly
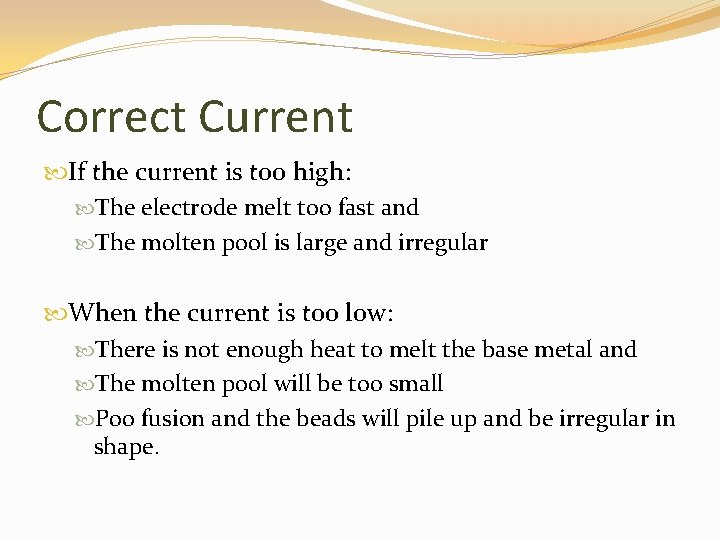
Correct Current If the current is too high: The electrode melt too fast and The molten pool is large and irregular When the current is too low: There is not enough heat to melt the base metal and The molten pool will be too small Poo fusion and the beads will pile up and be irregular in shape.
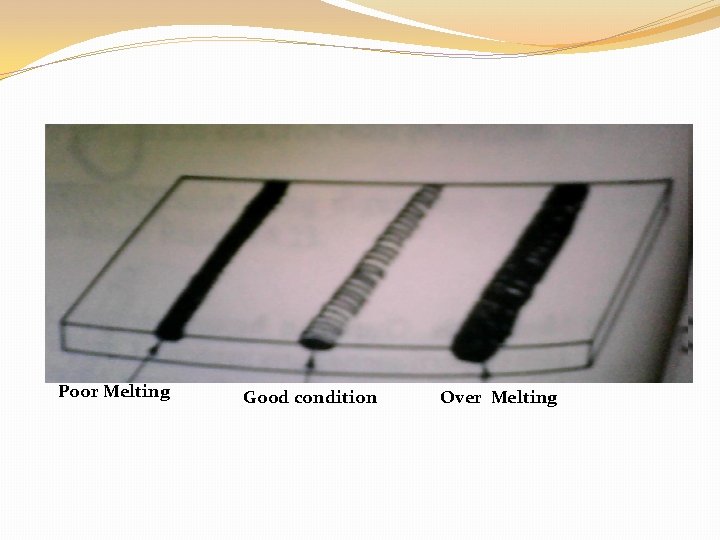
Poor Melting Good condition Over Melting
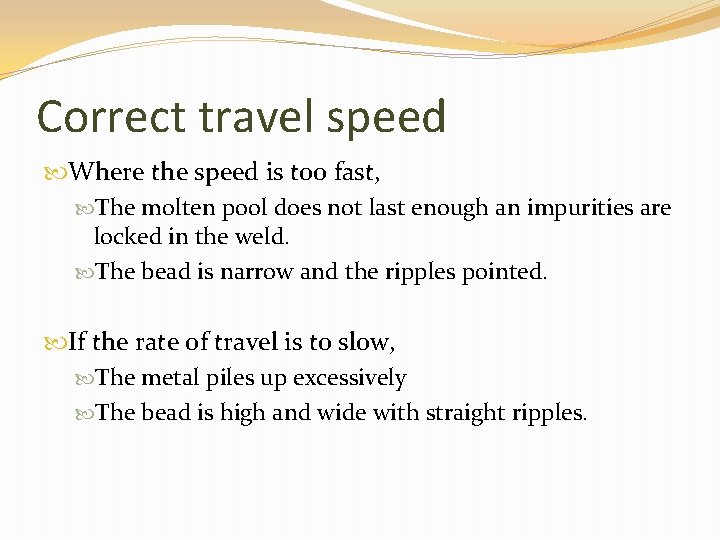
Correct travel speed Where the speed is too fast, The molten pool does not last enough an impurities are locked in the weld. The bead is narrow and the ripples pointed. If the rate of travel is to slow, The metal piles up excessively The bead is high and wide with straight ripples.
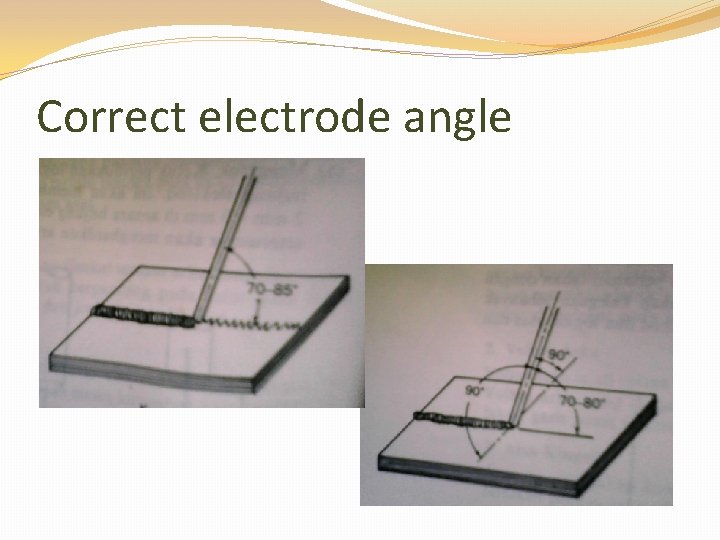
Correct electrode angle
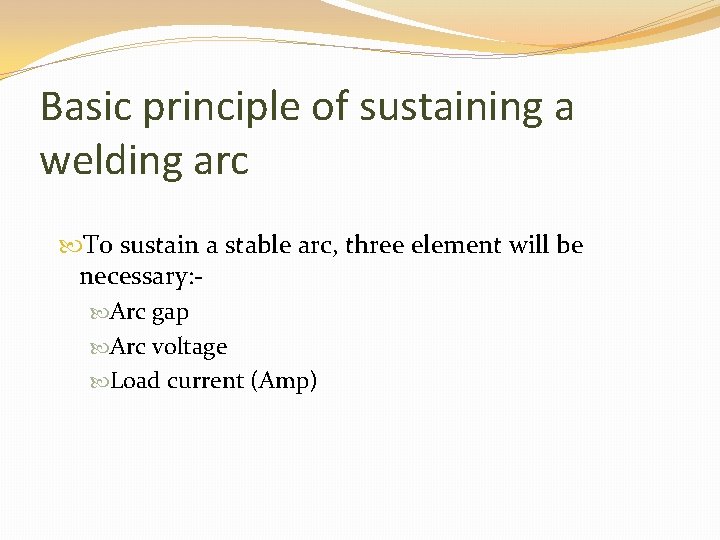
Basic principle of sustaining a welding arc To sustain a stable arc, three element will be necessary: Arc gap Arc voltage Load current (Amp)
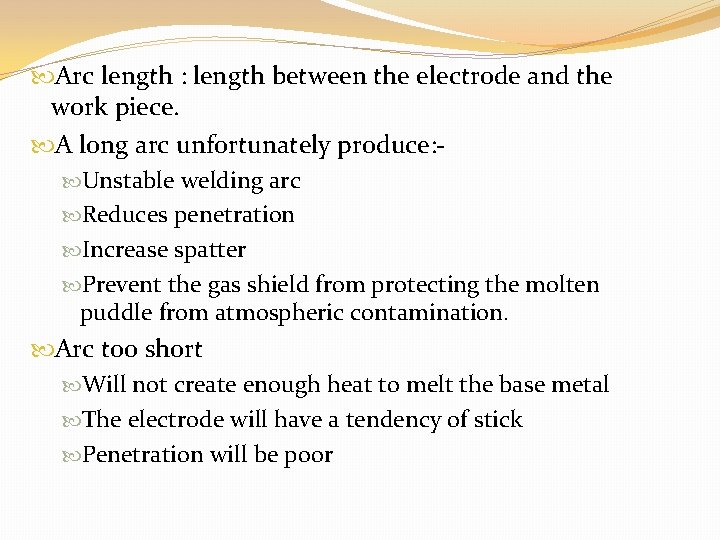
Arc length : length between the electrode and the work piece. A long arc unfortunately produce: Unstable welding arc Reduces penetration Increase spatter Prevent the gas shield from protecting the molten puddle from atmospheric contamination. Arc too short Will not create enough heat to melt the base metal The electrode will have a tendency of stick Penetration will be poor
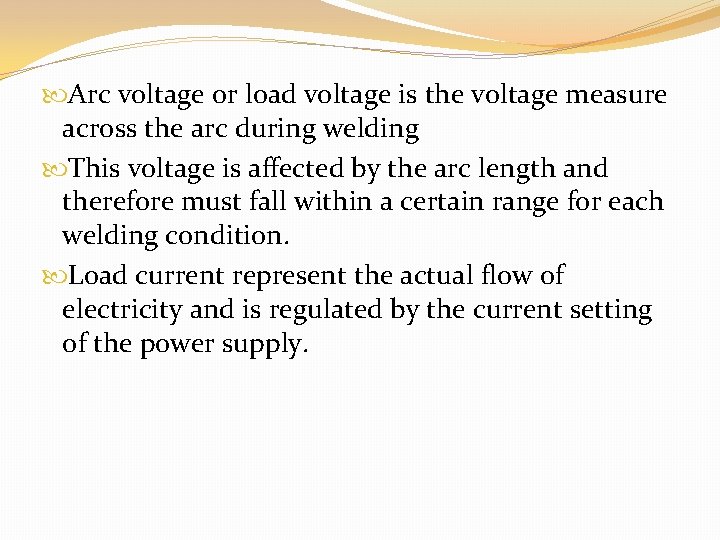
Arc voltage or load voltage is the voltage measure across the arc during welding This voltage is affected by the arc length and therefore must fall within a certain range for each welding condition. Load current represent the actual flow of electricity and is regulated by the current setting of the power supply.
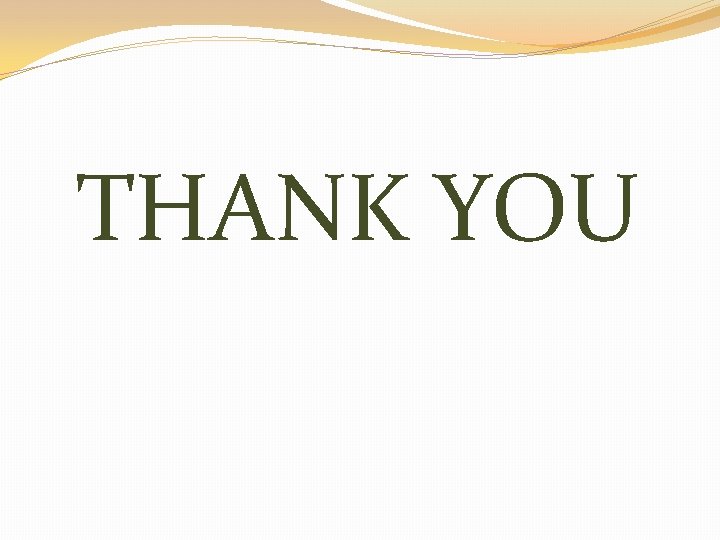
THANK YOU
Mig welding process
Hát kết hợp bộ gõ cơ thể
Ng-html
Bổ thể
Tỉ lệ cơ thể trẻ em
Voi kéo gỗ như thế nào
Tư thế worms-breton
Alleluia hat len nguoi oi
Các môn thể thao bắt đầu bằng từ đua
Thế nào là hệ số cao nhất
Các châu lục và đại dương trên thế giới
Công thức tính thế năng
Trời xanh đây là của chúng ta thể thơ
Mật thư anh em như thể tay chân
Phép trừ bù
Phản ứng thế ankan
Các châu lục và đại dương trên thế giới
Thơ thất ngôn tứ tuyệt đường luật
Quá trình desamine hóa có thể tạo ra
Một số thể thơ truyền thống
Bàn tay mà dây bẩn
Vẽ hình chiếu vuông góc của vật thể sau
Biện pháp chống mỏi cơ
đặc điểm cơ thể của người tối cổ
Thế nào là giọng cùng tên? *
Vẽ hình chiếu đứng bằng cạnh của vật thể
Tia chieu sa te
Thẻ vin
đại từ thay thế
điện thế nghỉ
Tư thế ngồi viết
Diễn thế sinh thái là
Các loại đột biến cấu trúc nhiễm sắc thể