Welding Welding Content Soldering Brazing Welding Gas welding
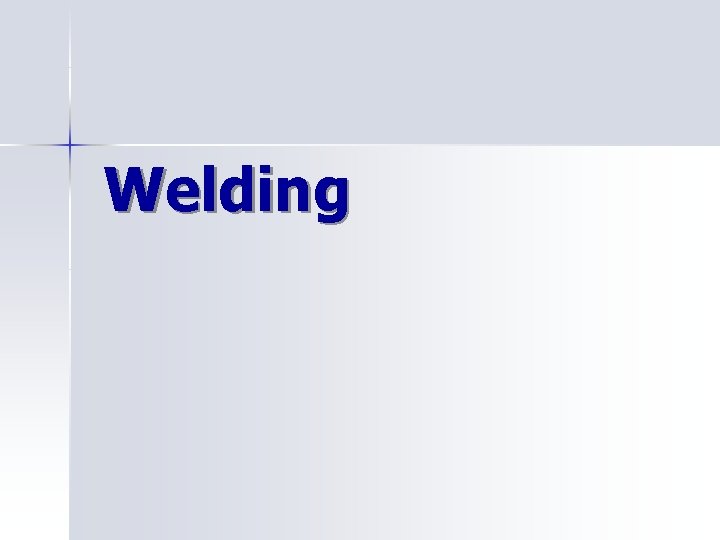
Welding
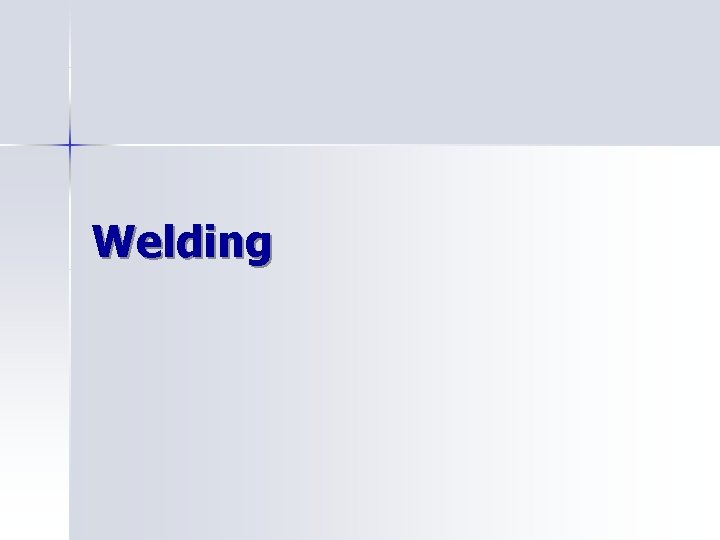
Welding
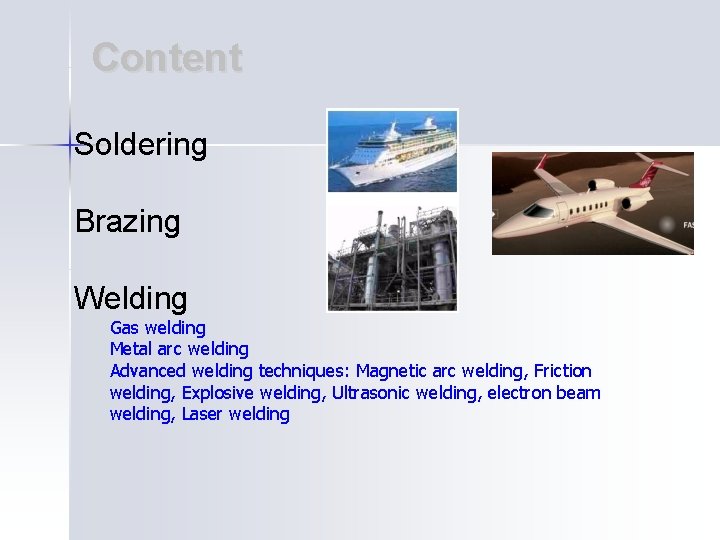
Content Soldering Brazing Welding Gas welding Metal arc welding Advanced welding techniques: Magnetic arc welding, Friction welding, Explosive welding, Ultrasonic welding, electron beam welding, Laser welding
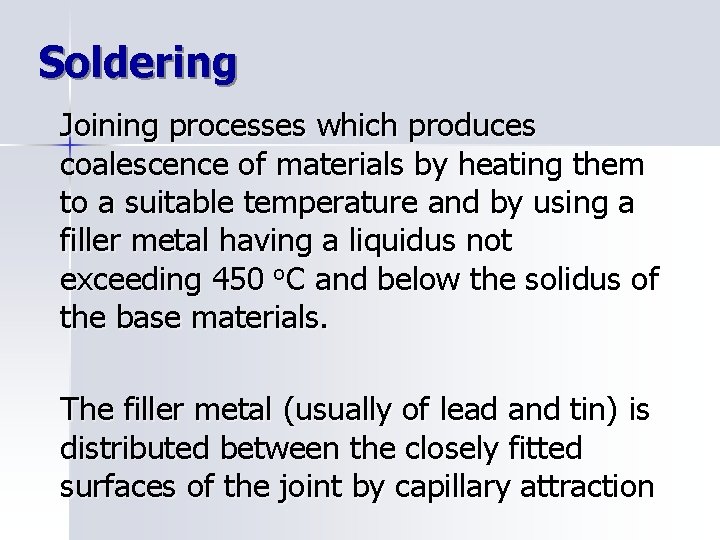
Soldering Joining processes which produces coalescence of materials by heating them to a suitable temperature and by using a filler metal having a liquidus not exceeding 450 o. C and below the solidus of the base materials. The filler metal (usually of lead and tin) is distributed between the closely fitted surfaces of the joint by capillary attraction
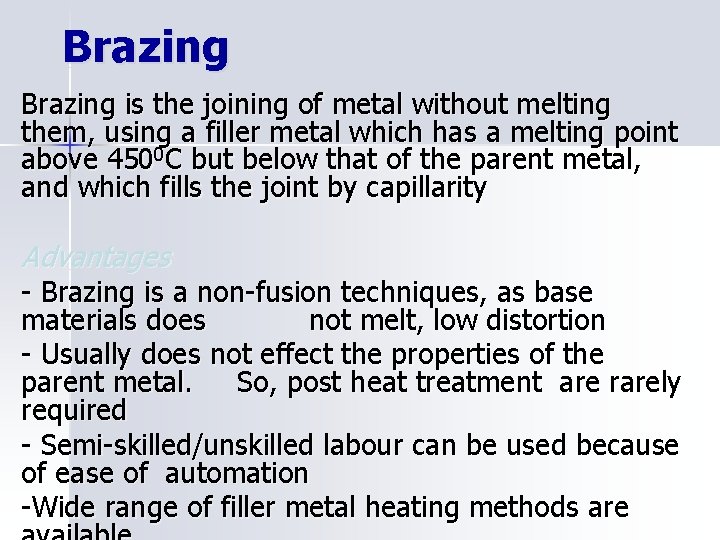
Brazing is the joining of metal without melting them, using a filler metal which has a melting point above 4500 C but below that of the parent metal, and which fills the joint by capillarity Advantages - Brazing is a non-fusion techniques, as base materials does not melt, low distortion - Usually does not effect the properties of the parent metal. So, post heat treatment are rarely required - Semi-skilled/unskilled labour can be used because of ease of automation -Wide range of filler metal heating methods are
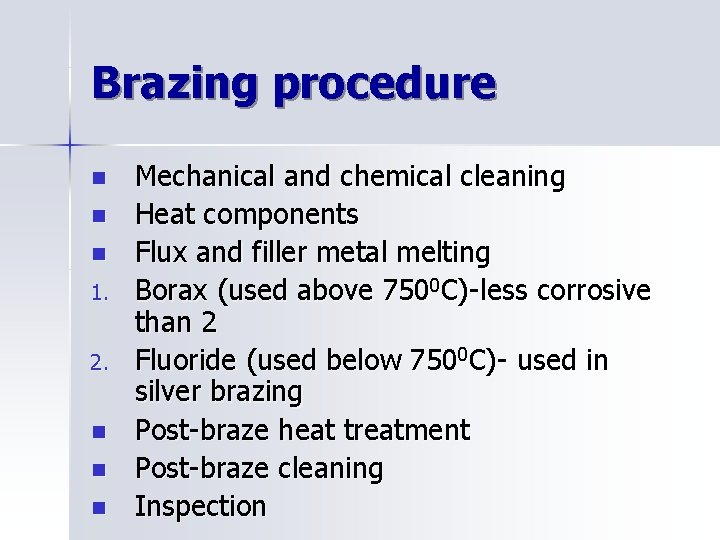
Brazing procedure n n n 1. 2. n n n Mechanical and chemical cleaning Heat components Flux and filler metal melting Borax (used above 7500 C)-less corrosive than 2 Fluoride (used below 7500 C)- used in silver brazing Post-braze heat treatment Post-braze cleaning Inspection

Disadvantages or Difficulties n n The nature of the braze component is complex. The most important consideration as regards strength is the continuity of the bond, which can vary from 0 -100%, as it is dependent on the ability of the brass metal to wet the surfaces of the gap In general, liquid braze metals will not wet, clean unfilmed surfaces unless (a) the liquid metal is intersoluble with the base (parent) metal (b) the liquid and solid metal react to form an intermetallic compounds
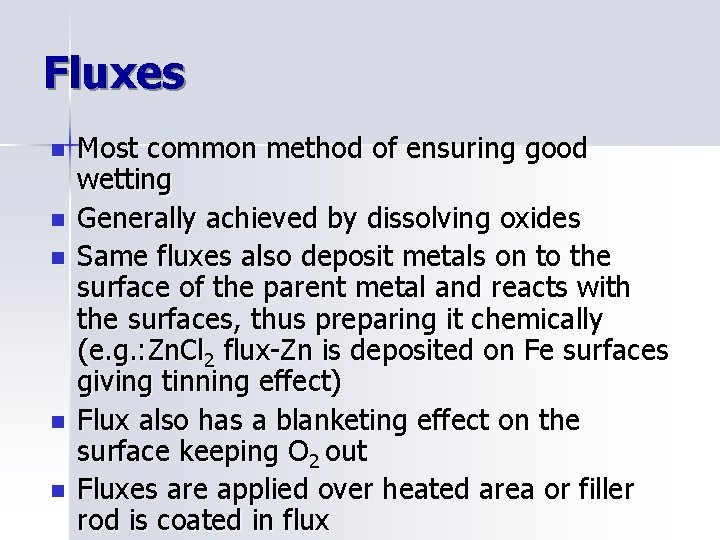
Fluxes n n n Most common method of ensuring good wetting Generally achieved by dissolving oxides Same fluxes also deposit metals on to the surface of the parent metal and reacts with the surfaces, thus preparing it chemically (e. g. : Zn. Cl 2 flux-Zn is deposited on Fe surfaces giving tinning effect) Flux also has a blanketing effect on the surface keeping O 2 out Fluxes are applied over heated area or filler rod is coated in flux

Brazing Induction heating Inductor is placed close to the parts to be brazed. In most cases the coil surrounds the components. A high frequency current in the inductor induces a heating current in the work piece. The brazing cycle can be precisely controlled using timing equipment built into the HF generator. Advantage of induction heating Rapid and uniform heat-rate Can be used in inert atmosphere or in vacuum Good heating techniques for high quality Mostly used for steel components
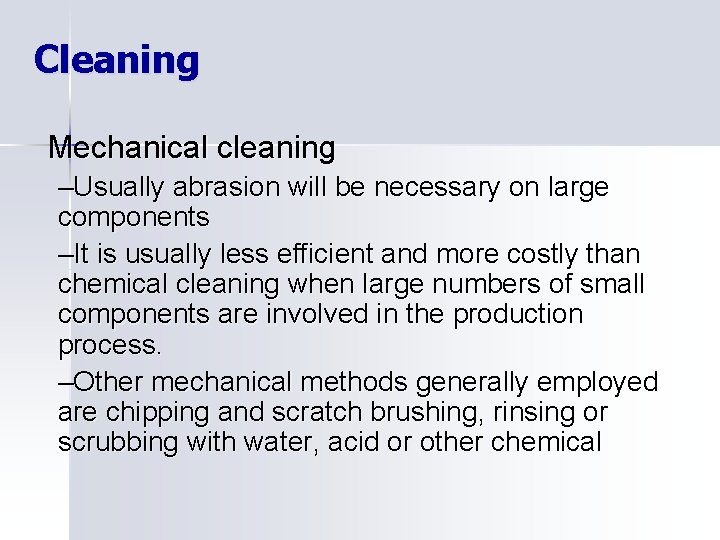
Cleaning Mechanical cleaning –Usually abrasion will be necessary on large components –It is usually less efficient and more costly than chemical cleaning when large numbers of small components are involved in the production process. –Other mechanical methods generally employed are chipping and scratch brushing, rinsing or scrubbing with water, acid or other chemical
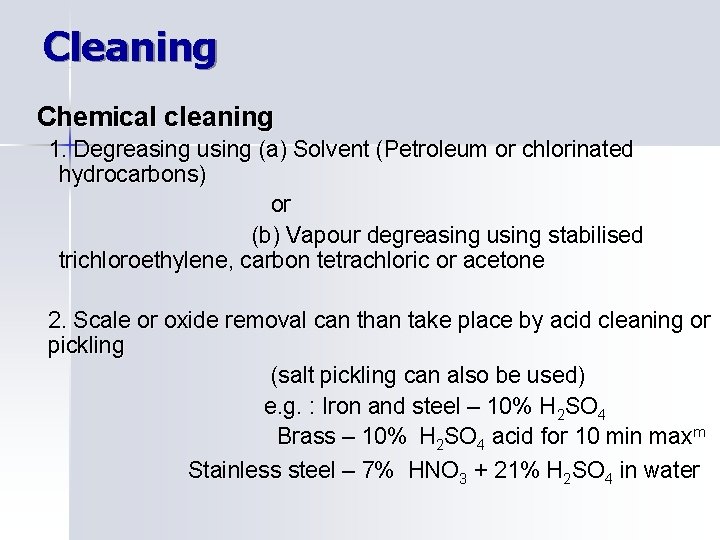
Cleaning Chemical cleaning 1. Degreasing using (a) Solvent (Petroleum or chlorinated hydrocarbons) or (b) Vapour degreasing using stabilised trichloroethylene, carbon tetrachloric or acetone 2. Scale or oxide removal can than take place by acid cleaning or pickling (salt pickling can also be used) e. g. : Iron and steel – 10% H 2 SO 4 Brass – 10% H 2 SO 4 acid for 10 min maxm Stainless steel – 7% HNO 3 + 21% H 2 SO 4 in water
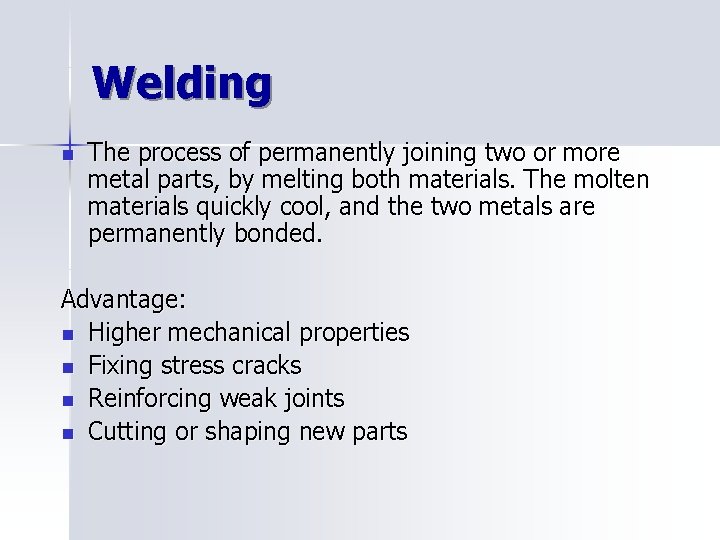
Welding n The process of permanently joining two or more metal parts, by melting both materials. The molten materials quickly cool, and the two metals are permanently bonded. Advantage: n Higher mechanical properties n Fixing stress cracks n Reinforcing weak joints n Cutting or shaping new parts
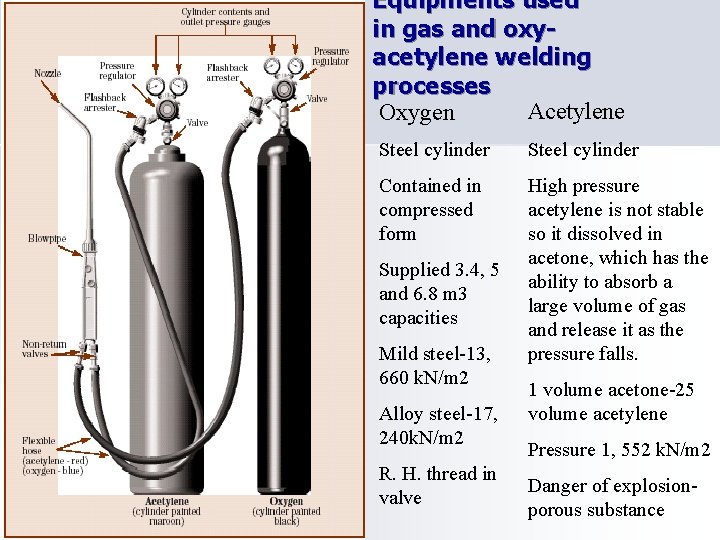
Equipments used in gas and oxyacetylene welding processes Acetylene Oxygen Steel cylinder Contained in compressed form High pressure acetylene is not stable so it dissolved in acetone, which has the ability to absorb a large volume of gas and release it as the pressure falls. Supplied 3. 4, 5 and 6. 8 m 3 capacities Mild steel-13, 660 k. N/m 2 Alloy steel-17, 240 k. N/m 2 R. H. thread in valve 1 volume acetone-25 volume acetylene Pressure 1, 552 k. N/m 2 Danger of explosionporous substance
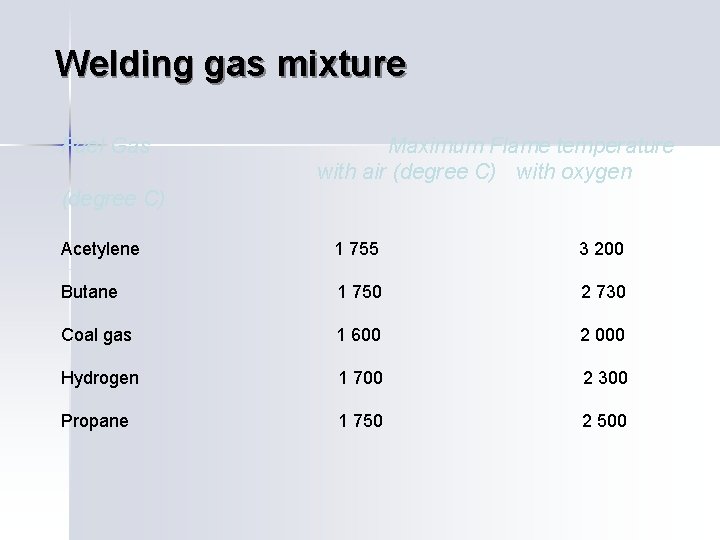
Welding gas mixture Fuel Gas Maximum Flame temperature with air (degree C) with oxygen (degree C) Acetylene 1 755 3 200 Butane 1 750 2 730 Coal gas 1 600 2 000 Hydrogen 1 700 2 300 Propane 1 750 2 500
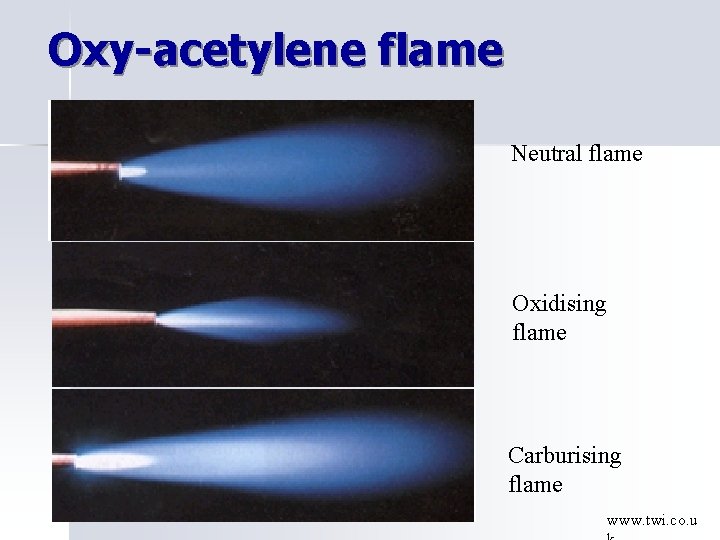
Oxy-acetylene flame Neutral flame Oxidising flame Carburising flame www. twi. co. u
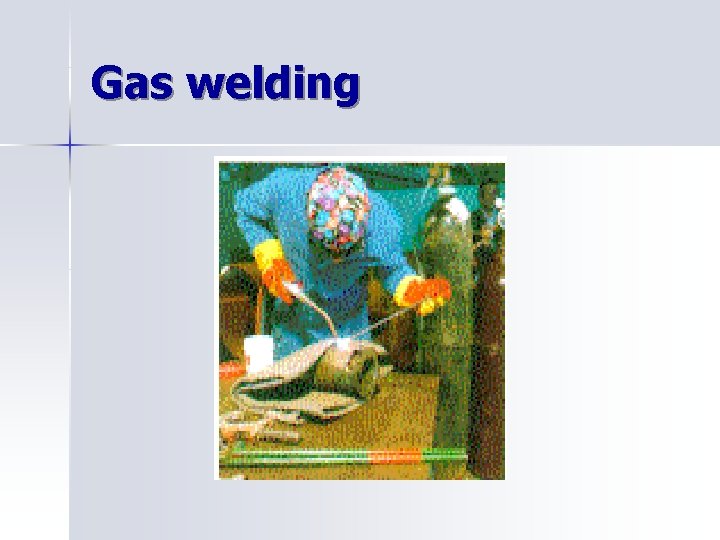
Gas welding
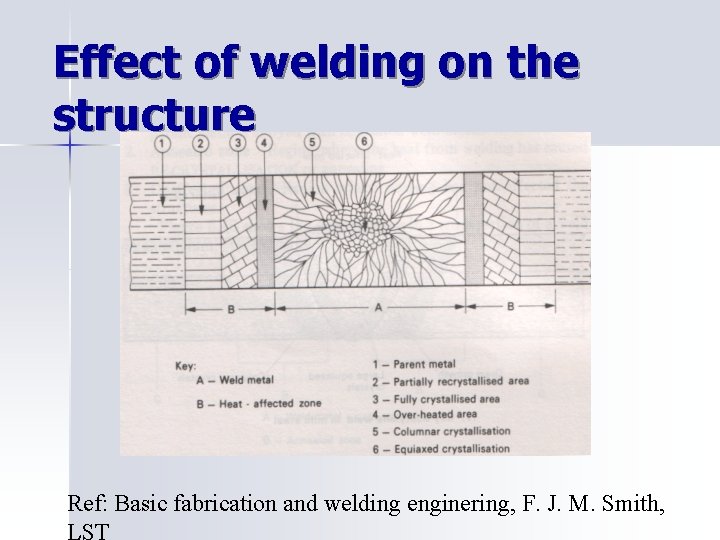
Effect of welding on the structure Ref: Basic fabrication and welding enginering, F. J. M. Smith, LST
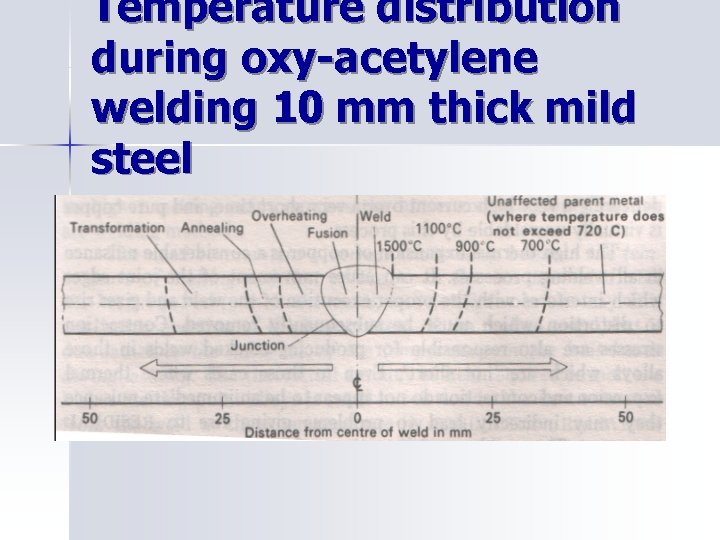
Temperature distribution during oxy-acetylene welding 10 mm thick mild steel
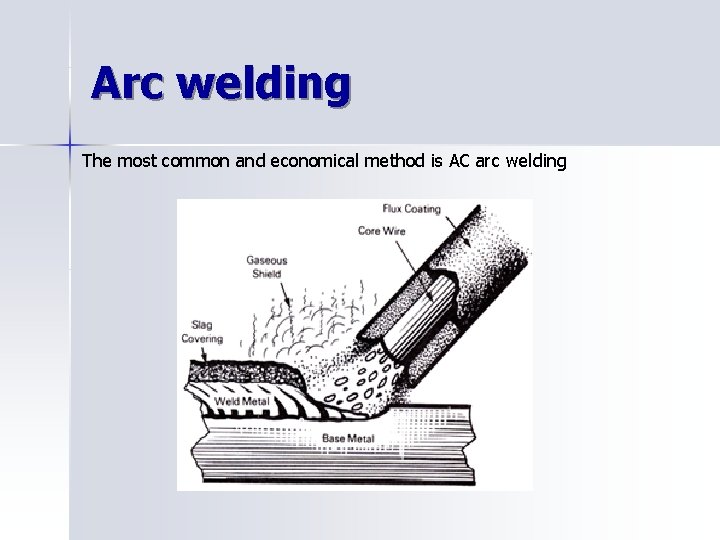
Arc welding The most common and economical method is AC arc welding
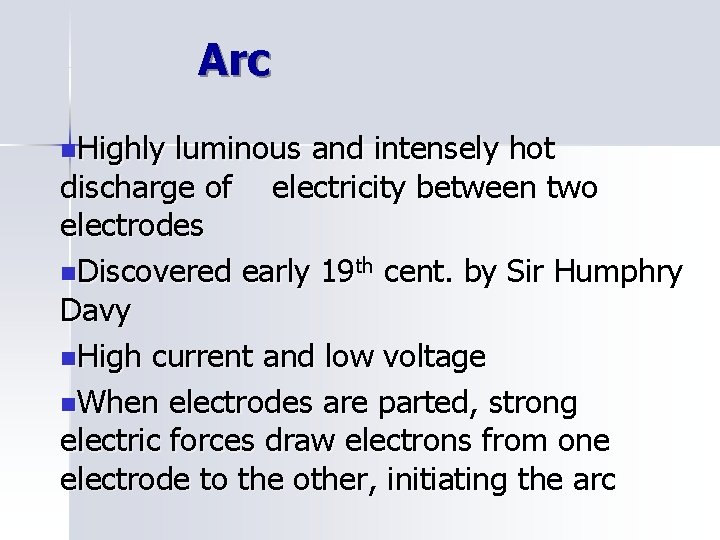
Arc n. Highly luminous and intensely hot discharge of electricity between two electrodes n. Discovered early 19 th cent. by Sir Humphry Davy n. High current and low voltage n. When electrodes are parted, strong electric forces draw electrons from one electrode to the other, initiating the arc
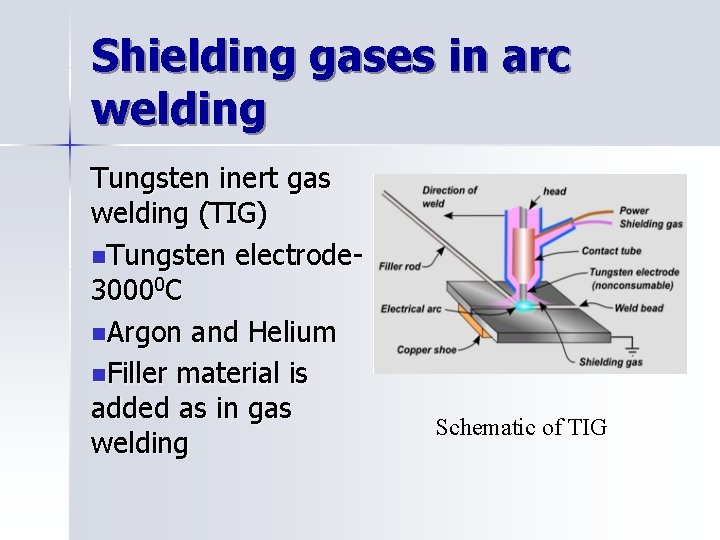
Shielding gases in arc welding Tungsten inert gas welding (TIG) n. Tungsten electrode 30000 C n. Argon and Helium n. Filler material is added as in gas welding Schematic of TIG
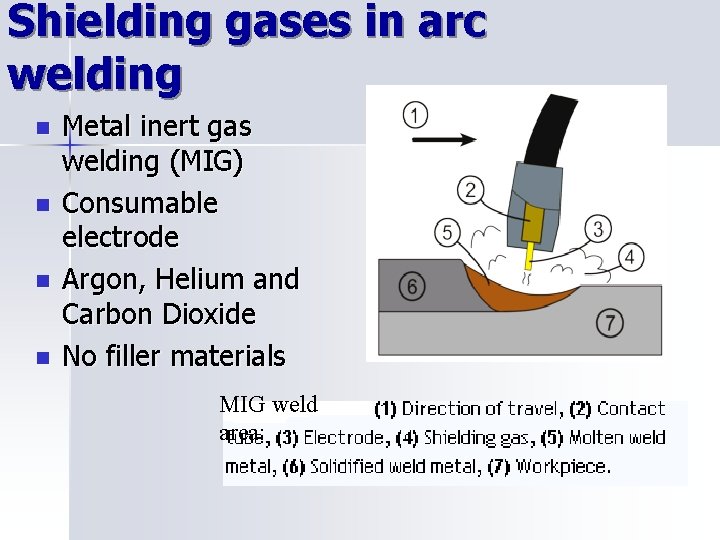
Shielding gases in arc welding n n Metal inert gas welding (MIG) Consumable electrode Argon, Helium and Carbon Dioxide No filler materials MIG weld area:
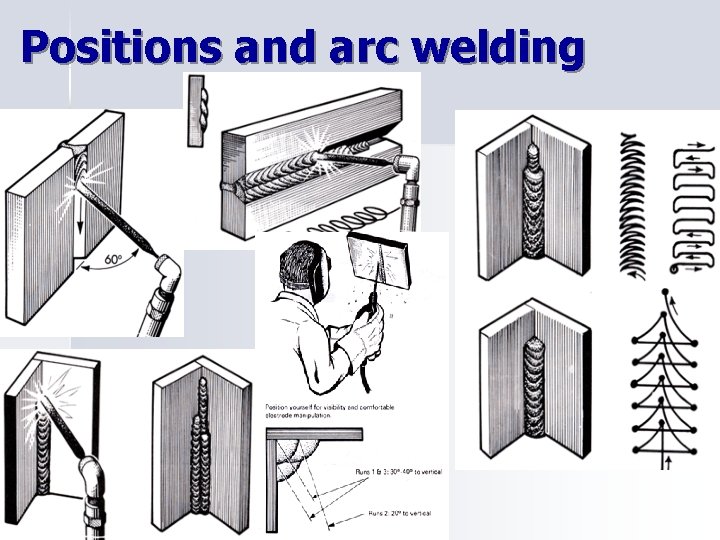
Positions and arc welding
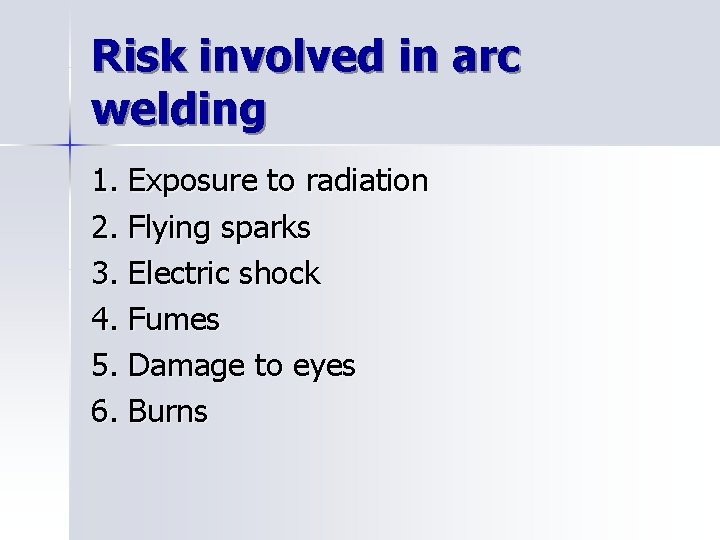
Risk involved in arc welding 1. Exposure to radiation 2. Flying sparks 3. Electric shock 4. Fumes 5. Damage to eyes 6. Burns
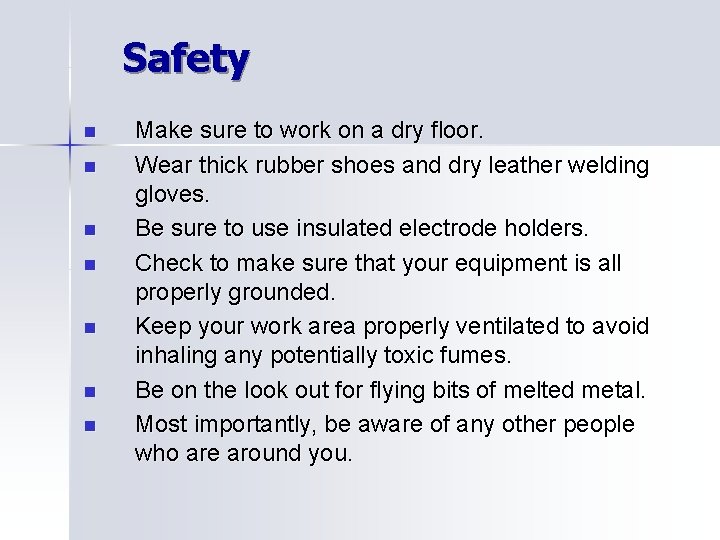
Safety n n n n Make sure to work on a dry floor. Wear thick rubber shoes and dry leather welding gloves. Be sure to use insulated electrode holders. Check to make sure that your equipment is all properly grounded. Keep your work area properly ventilated to avoid inhaling any potentially toxic fumes. Be on the look out for flying bits of melted metal. Most importantly, be aware of any other people who are around you.
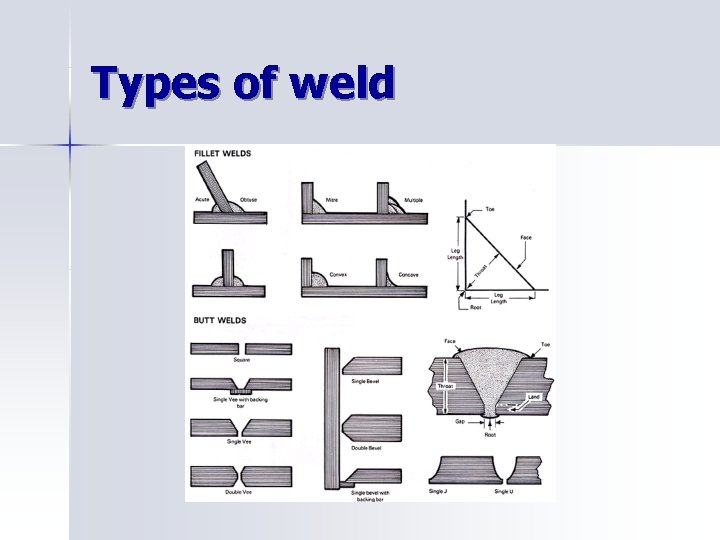
Types of weld
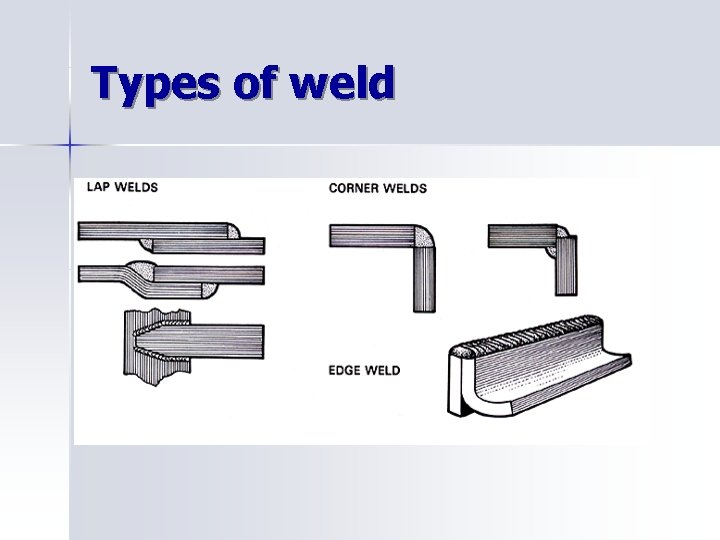
Types of weld
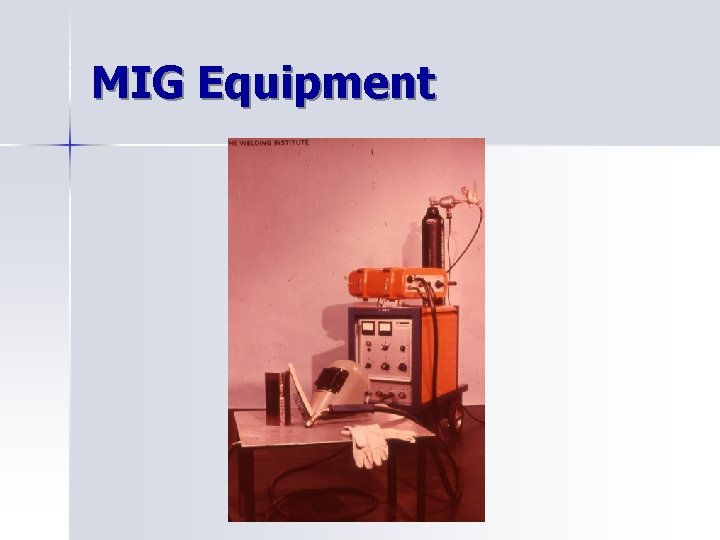
MIG Equipment
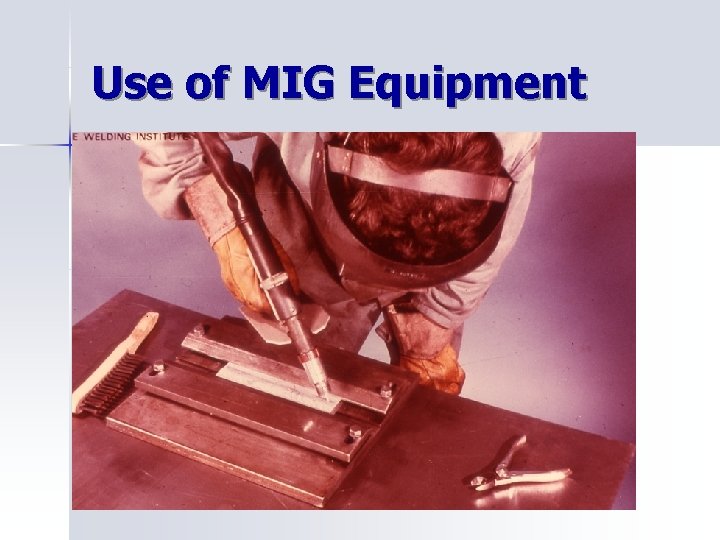
Use of MIG Equipment
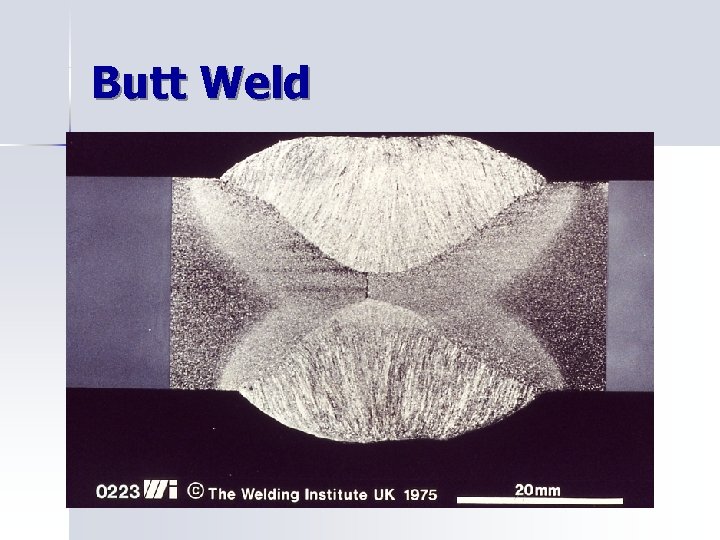
Butt Weld
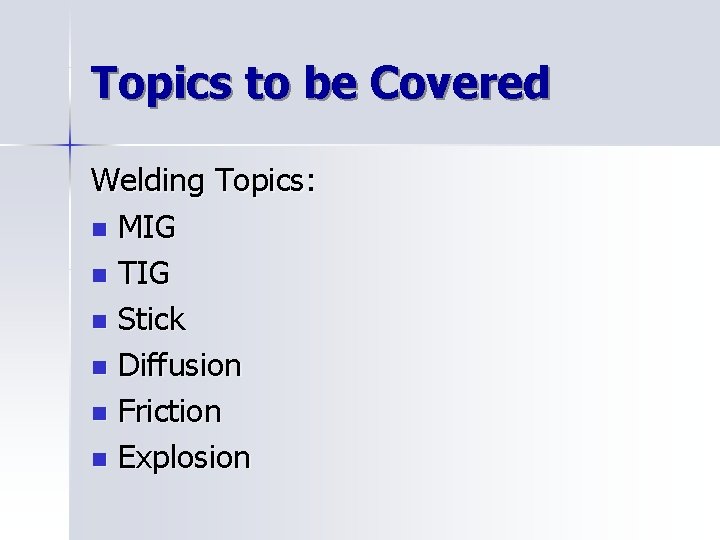
Topics to be Covered Welding Topics: n MIG n TIG n Stick n Diffusion n Friction n Explosion
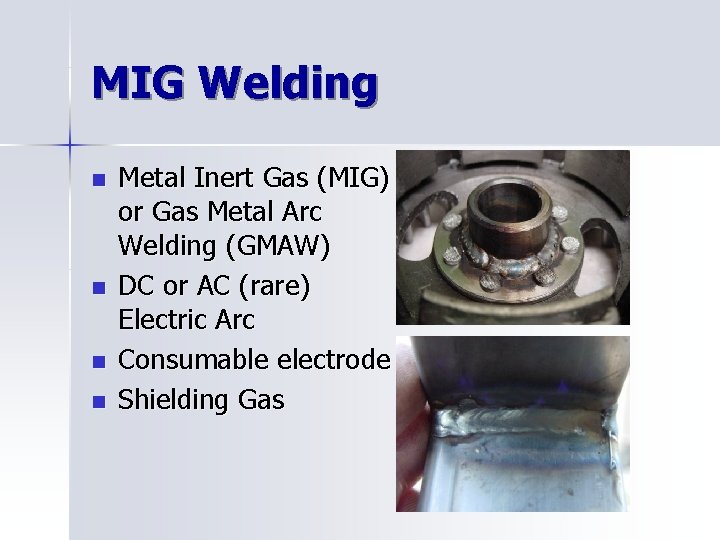
MIG Welding n n Metal Inert Gas (MIG) or Gas Metal Arc Welding (GMAW) DC or AC (rare) Electric Arc Consumable electrode Shielding Gas
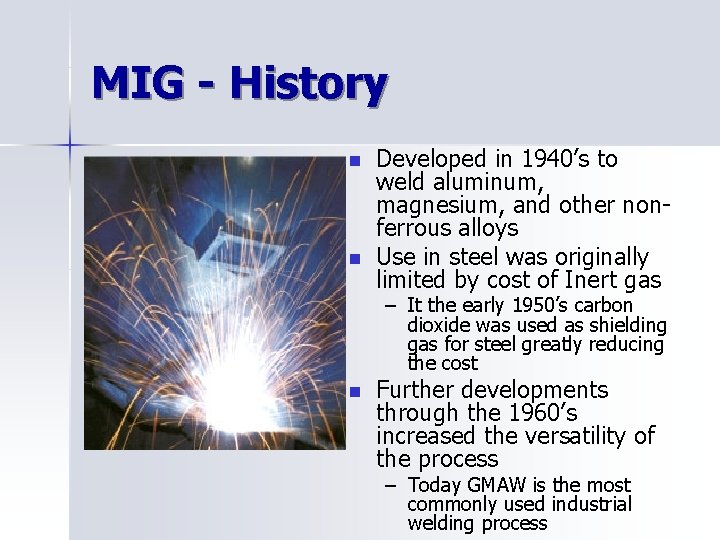
MIG - History n n Developed in 1940’s to weld aluminum, magnesium, and other nonferrous alloys Use in steel was originally limited by cost of Inert gas – It the early 1950’s carbon dioxide was used as shielding gas for steel greatly reducing the cost n Further developments through the 1960’s increased the versatility of the process – Today GMAW is the most commonly used industrial welding process
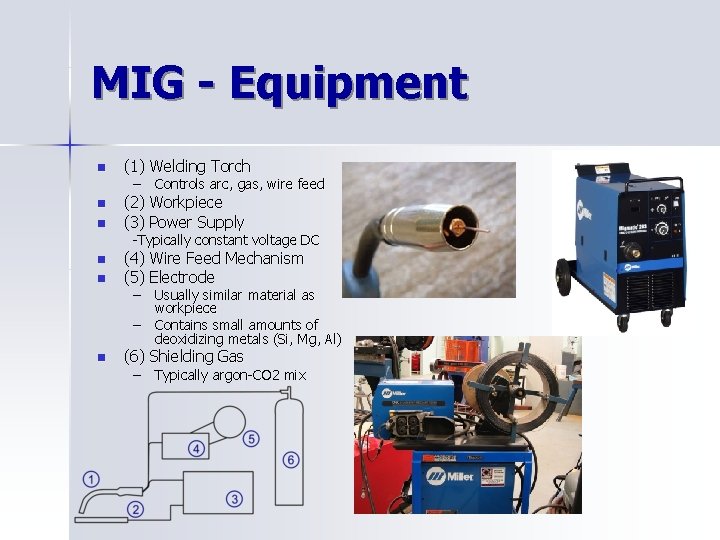
MIG - Equipment n (1) Welding Torch n (2) Workpiece (3) Power Supply n – Controls arc, gas, wire feed -Typically constant voltage DC n (4) Wire Feed Mechanism (5) Electrode n (6) Shielding Gas n – Usually similar material as workpiece – Contains small amounts of deoxidizing metals (Si, Mg, Al) – Typically argon-CO 2 mix
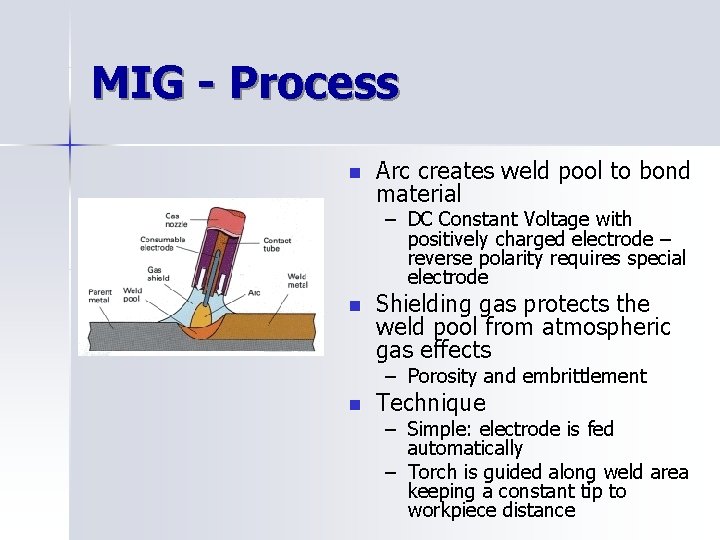
MIG - Process n Arc creates weld pool to bond material – DC Constant Voltage with positively charged electrode – reverse polarity requires special electrode n Shielding gas protects the weld pool from atmospheric gas effects – Porosity and embrittlement n Technique – Simple: electrode is fed automatically – Torch is guided along weld area keeping a constant tip to workpiece distance
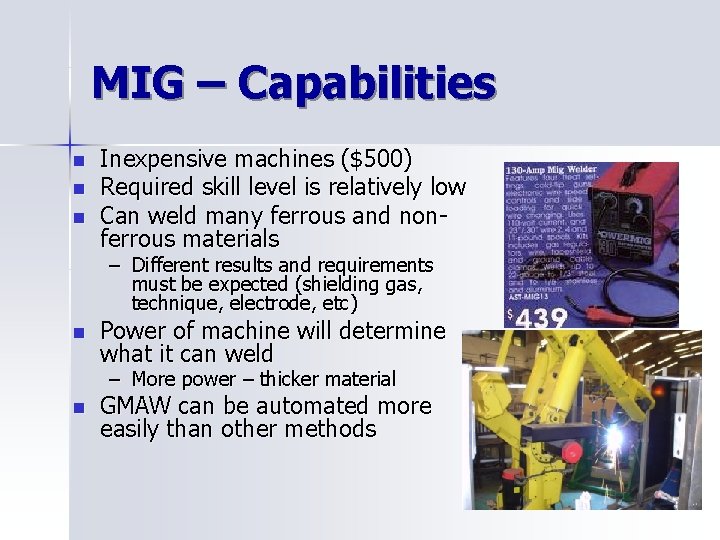
MIG – Capabilities n n n Inexpensive machines ($500) Required skill level is relatively low Can weld many ferrous and nonferrous materials – Different results and requirements must be expected (shielding gas, technique, electrode, etc) n Power of machine will determine what it can weld – More power – thicker material n GMAW can be automated more easily than other methods
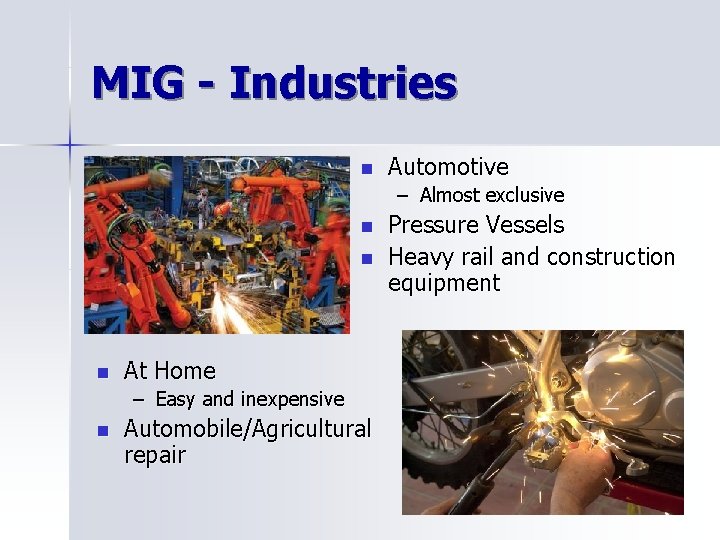
MIG - Industries n Automotive – Almost exclusive n n n At Home – Easy and inexpensive n Automobile/Agricultural repair Pressure Vessels Heavy rail and construction equipment
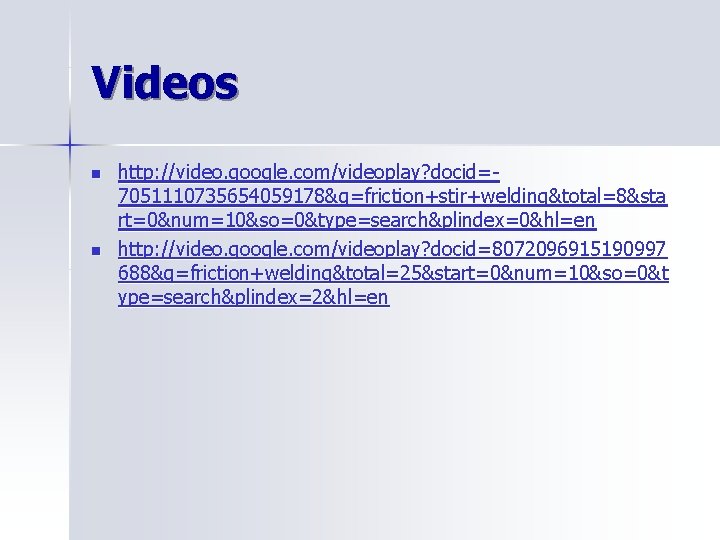
Videos n n http: //video. google. com/videoplay? docid=7051110735654059178&q=friction+stir+welding&total=8&sta rt=0&num=10&so=0&type=search&plindex=0&hl=en http: //video. google. com/videoplay? docid=8072096915190997 688&q=friction+welding&total=25&start=0&num=10&so=0&t ype=search&plindex=2&hl=en
- Slides: 38