AUTOMATION IN MANUFACTURING Foo Jin Hoe Ph D
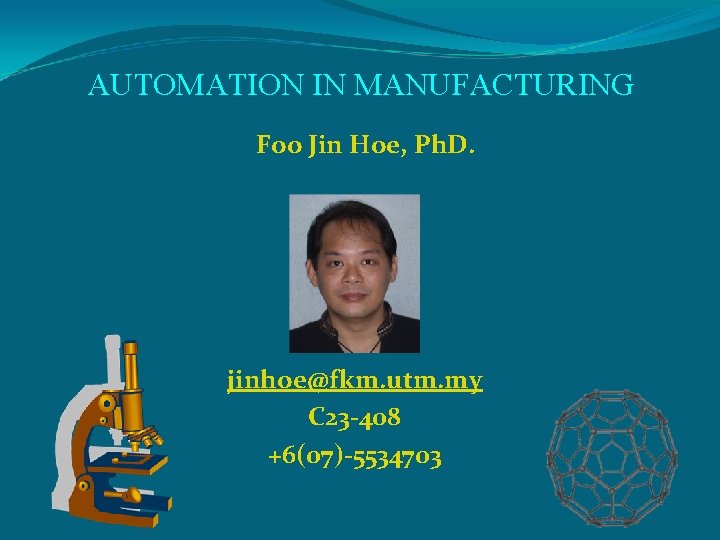
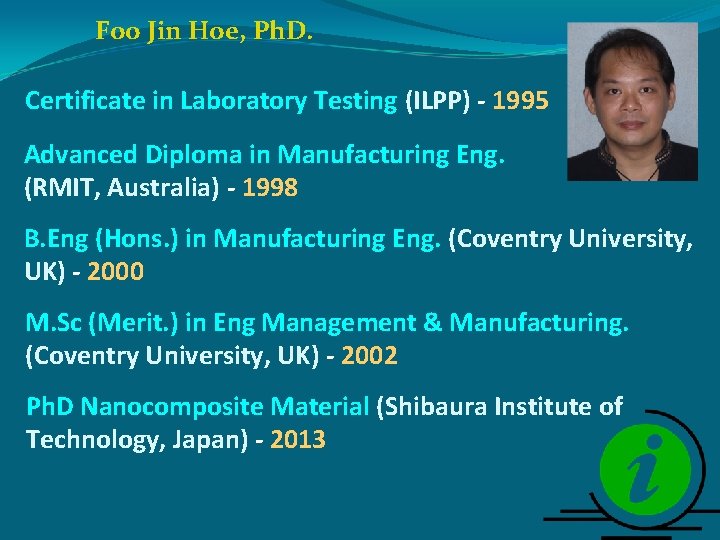
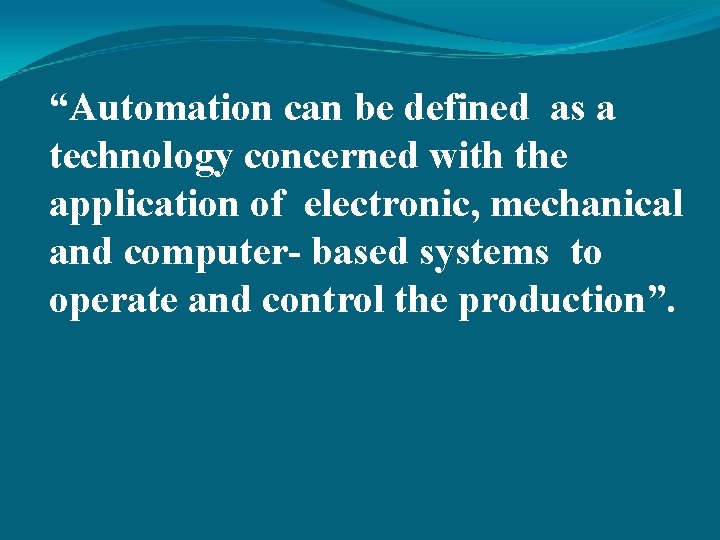
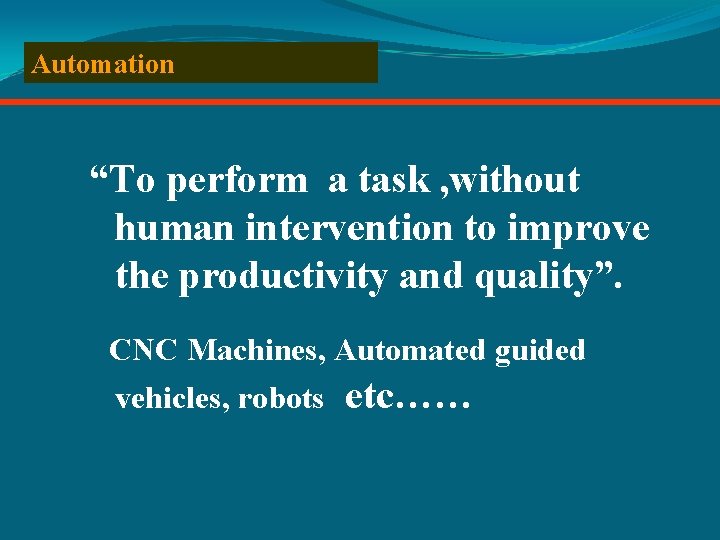
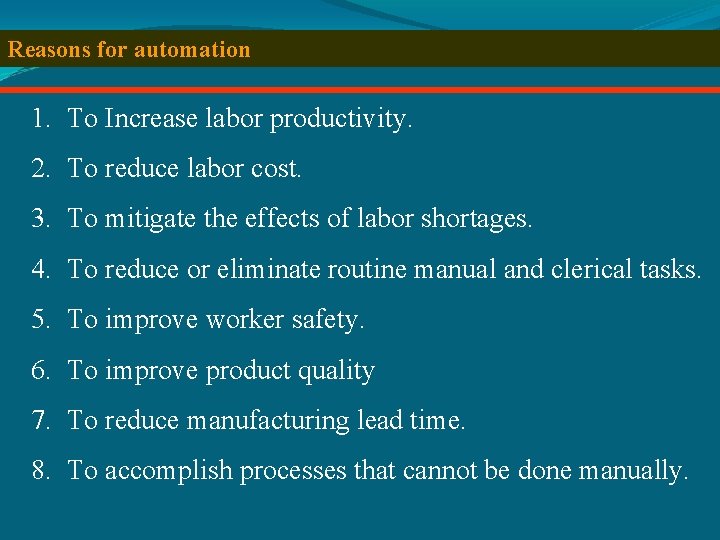
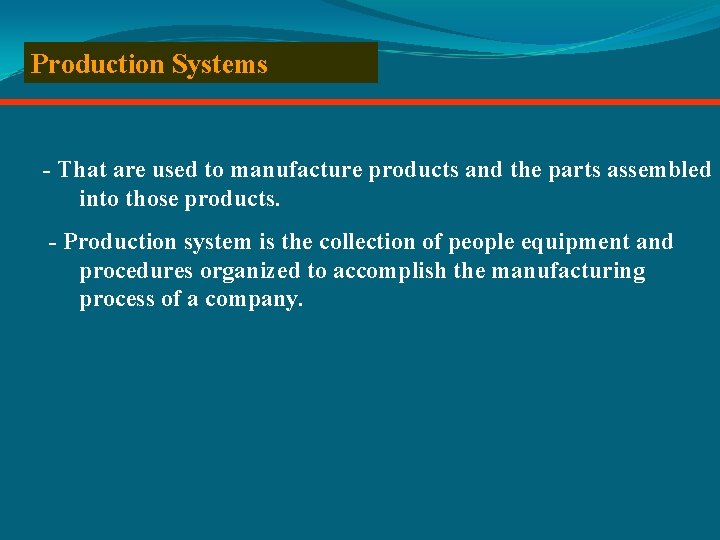
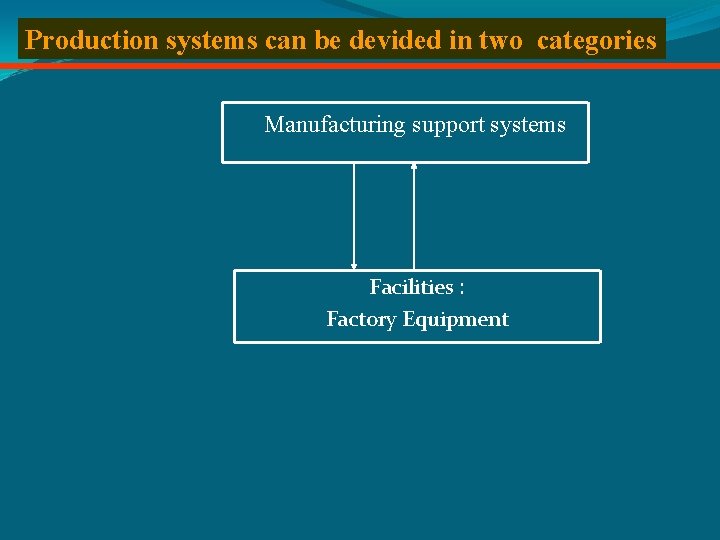
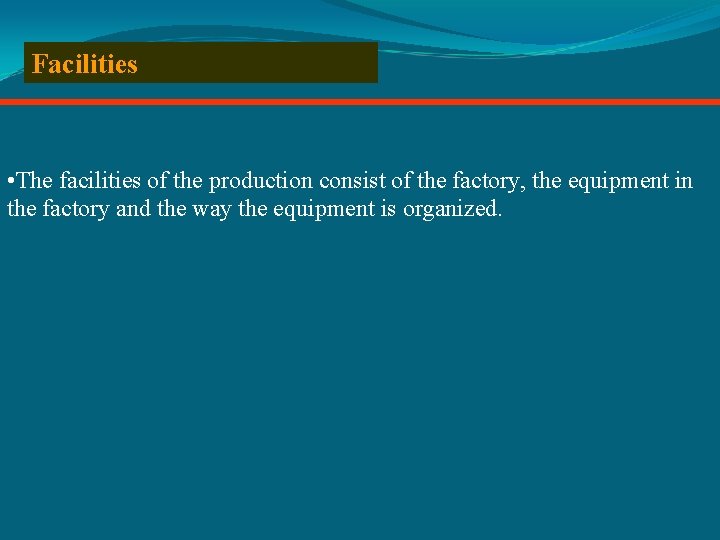
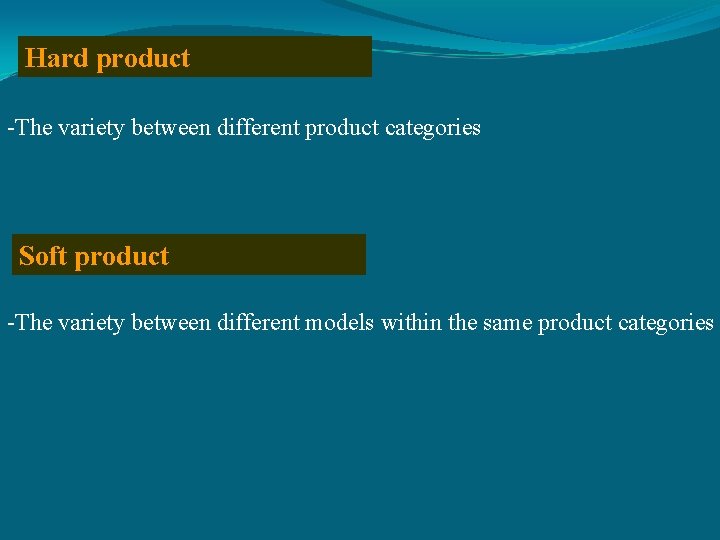
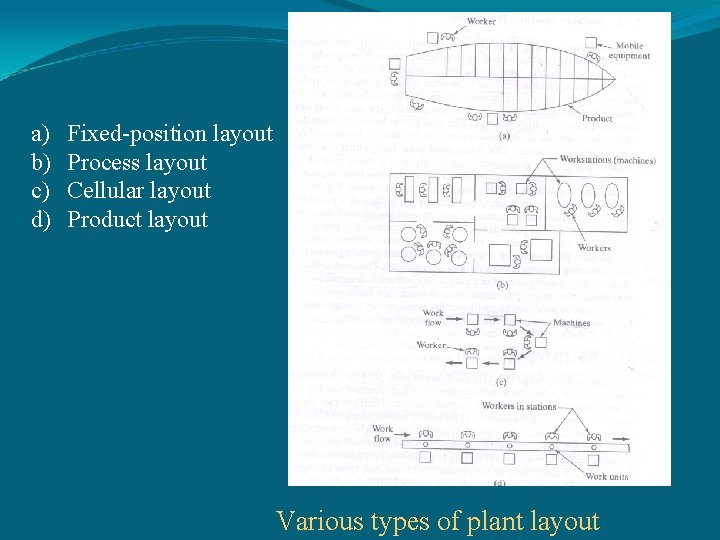
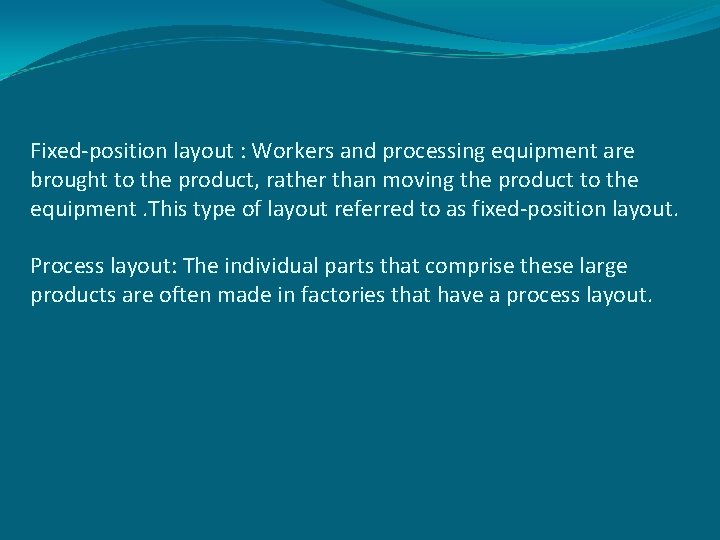
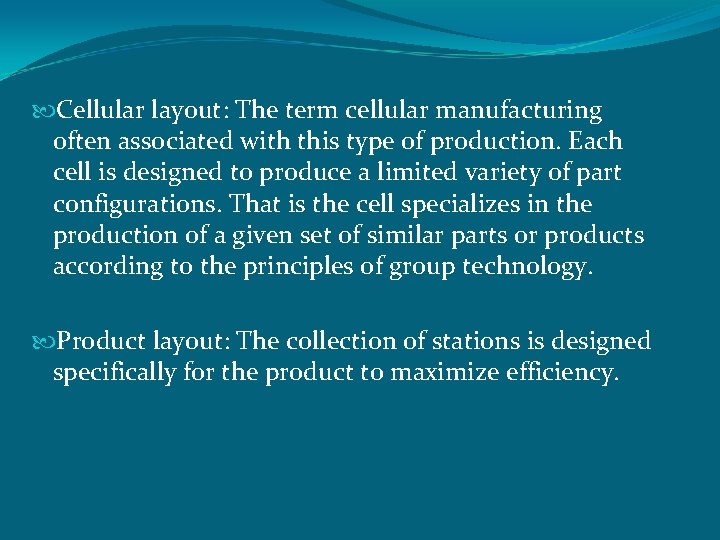
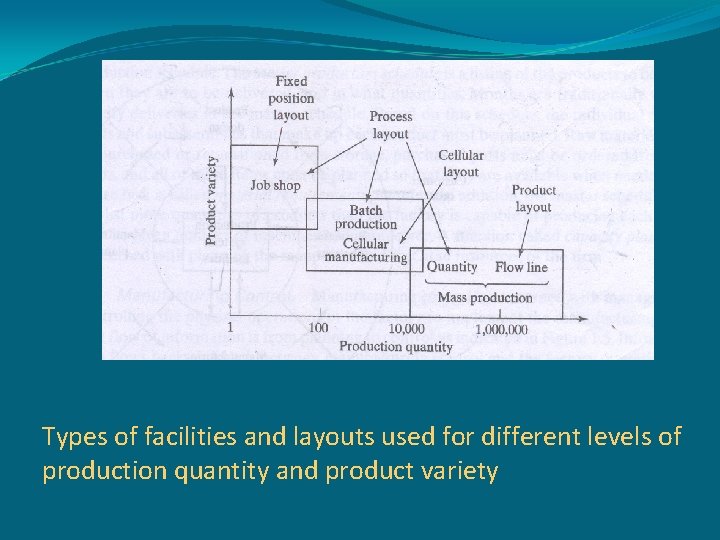
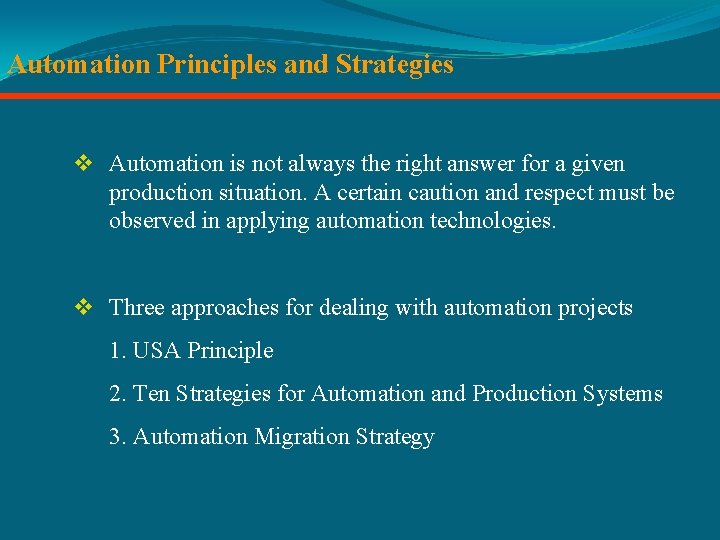
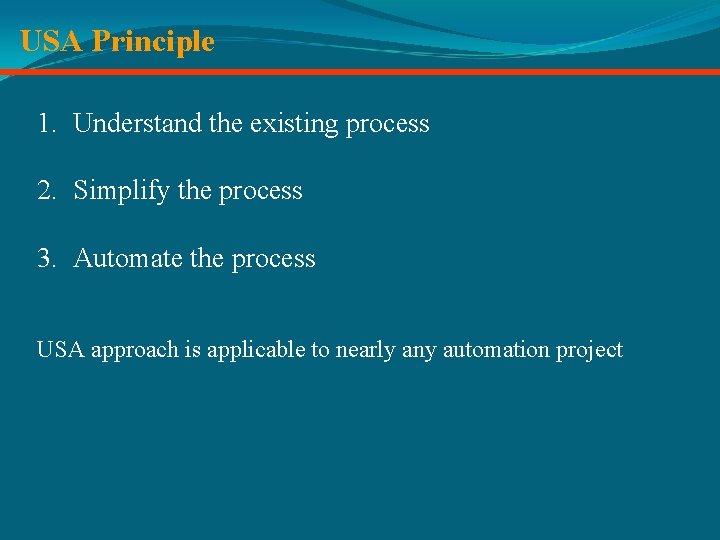
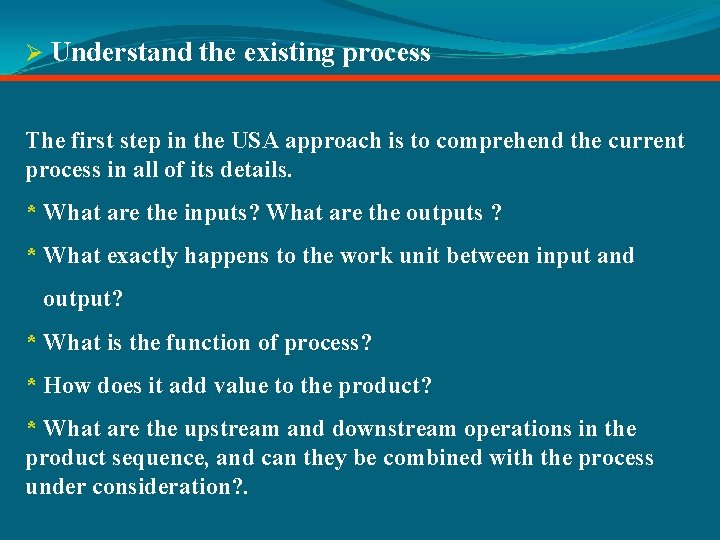
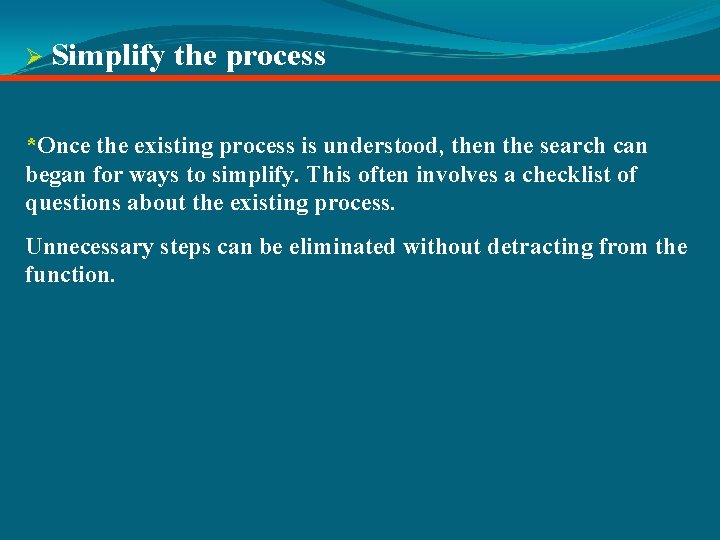
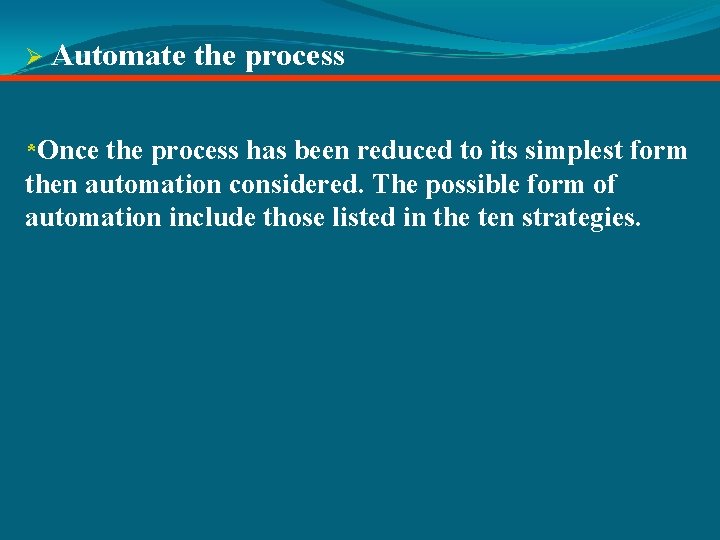
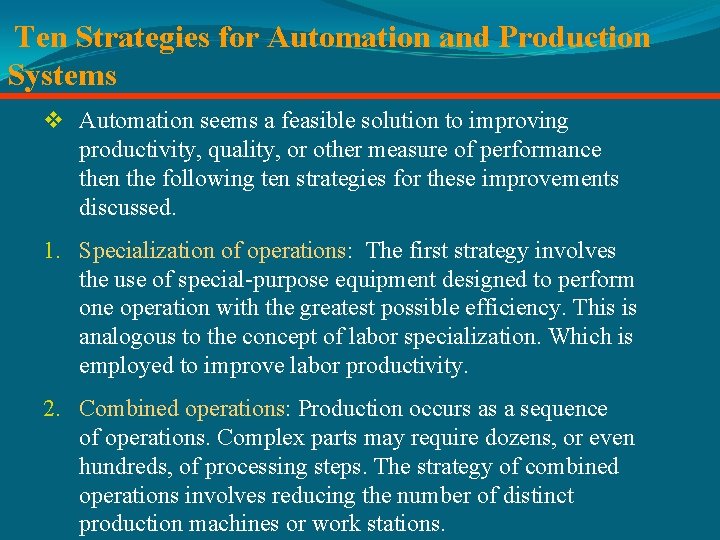
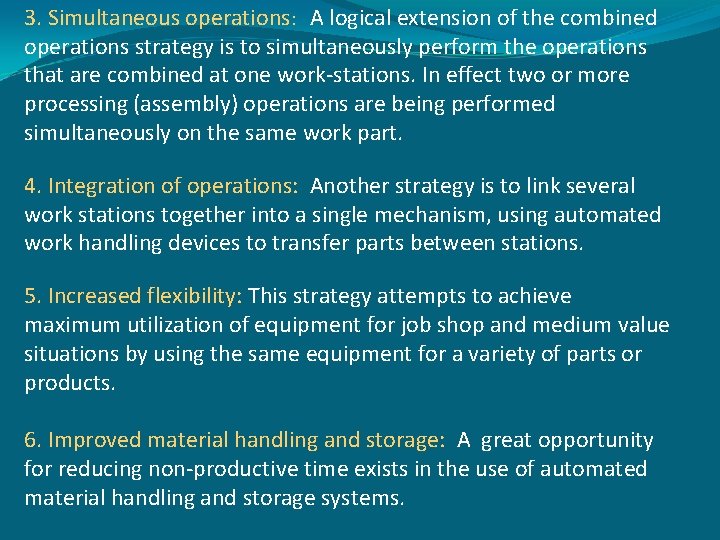
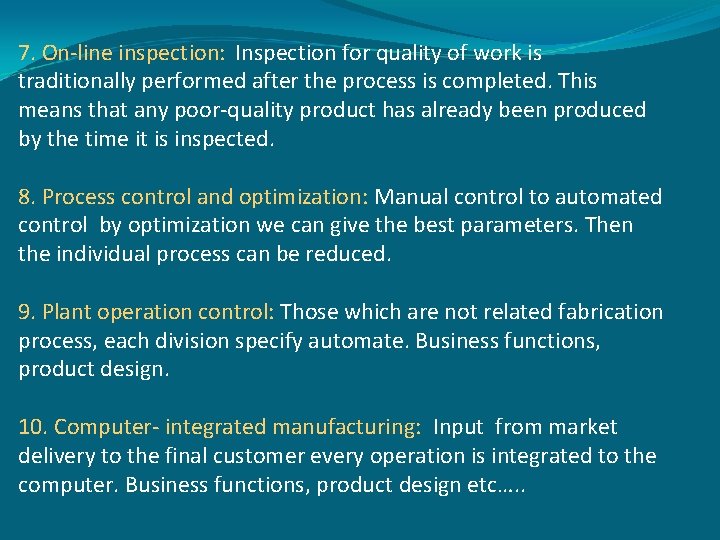
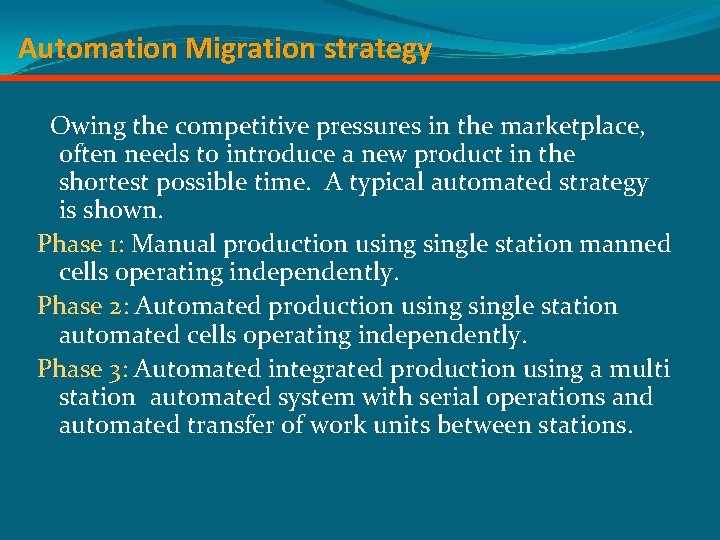

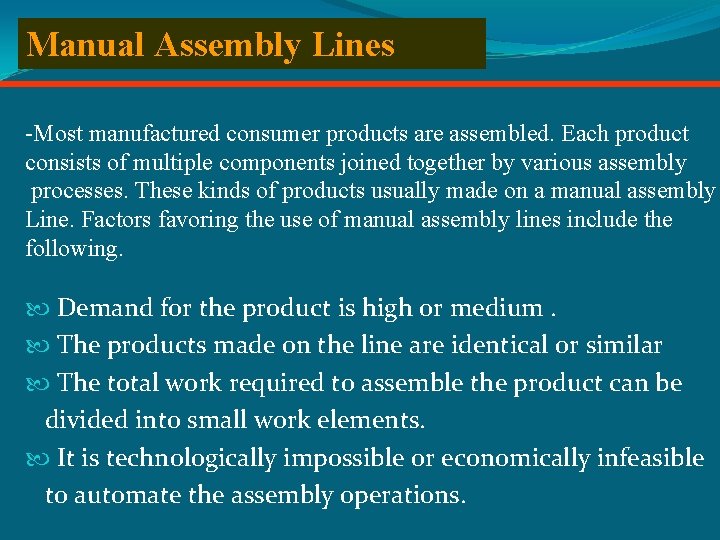
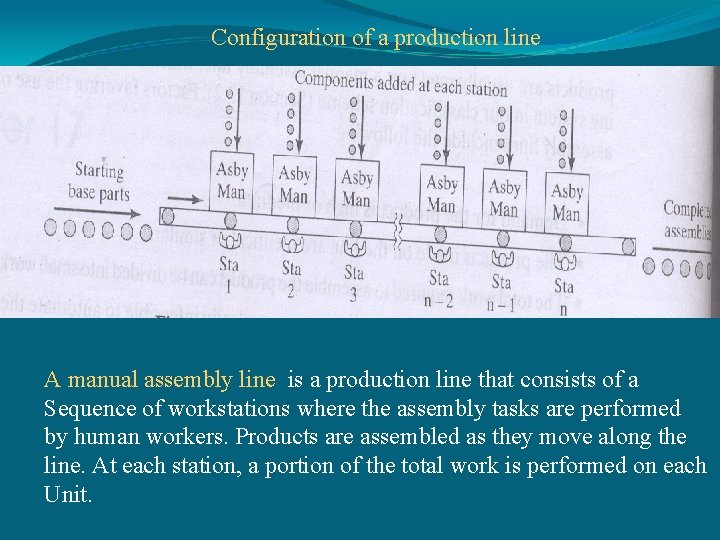
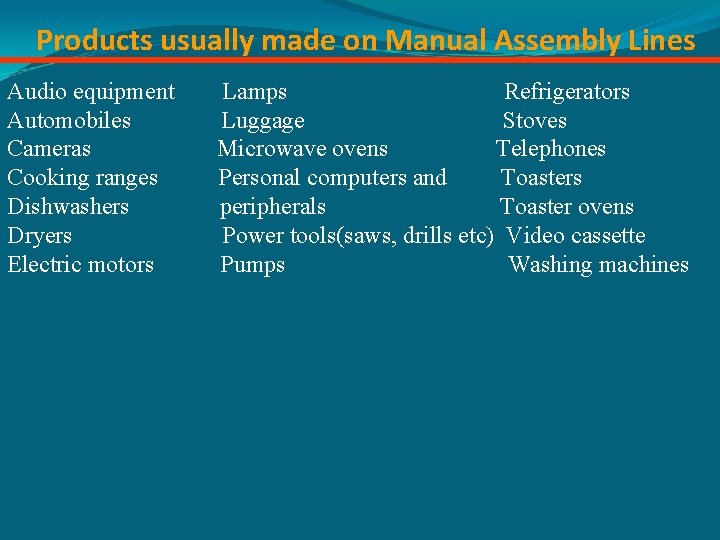
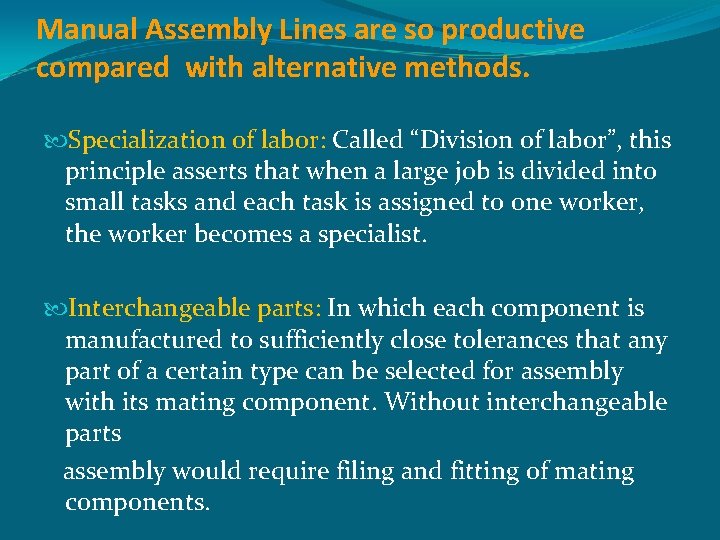
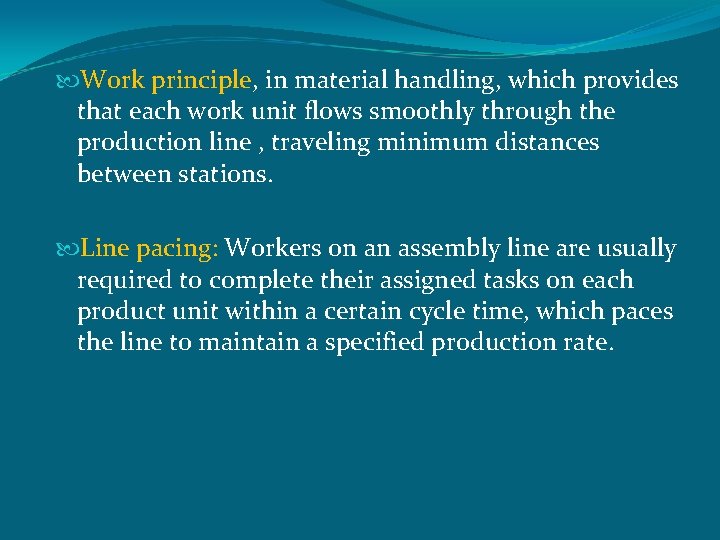
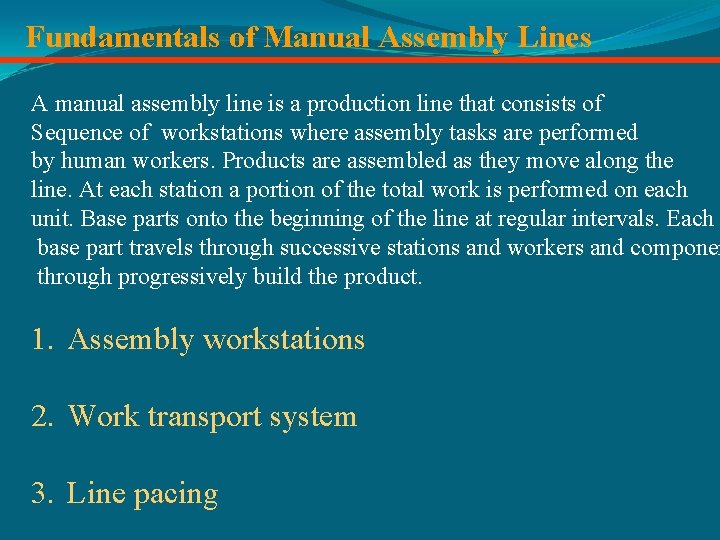
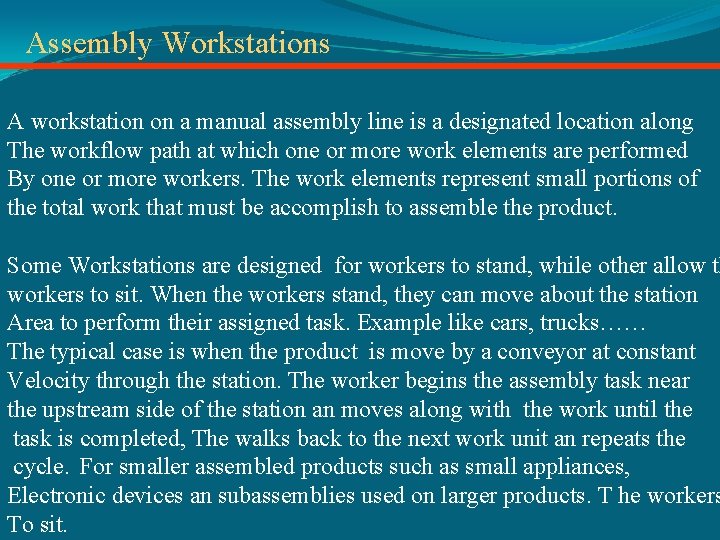
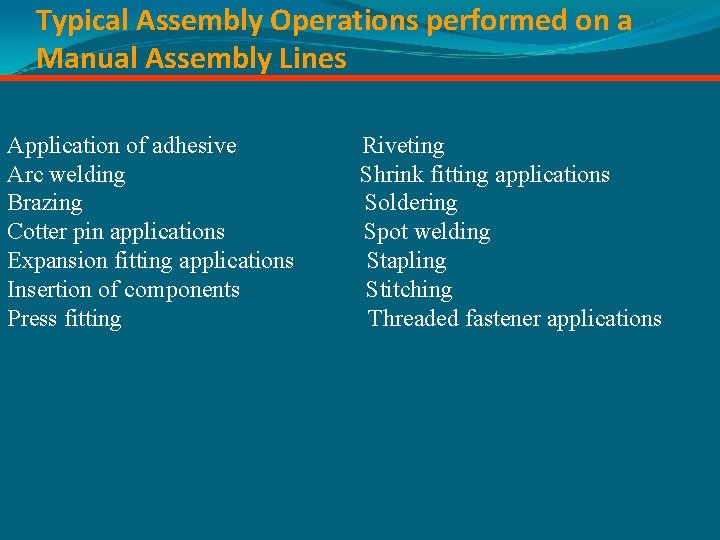
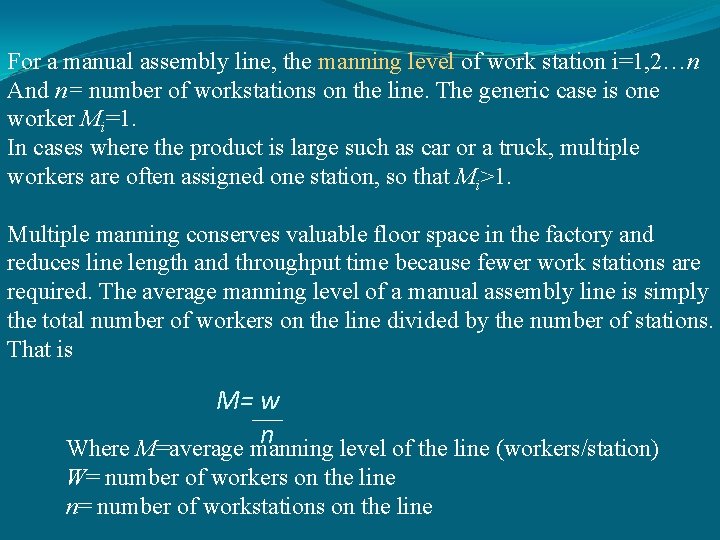
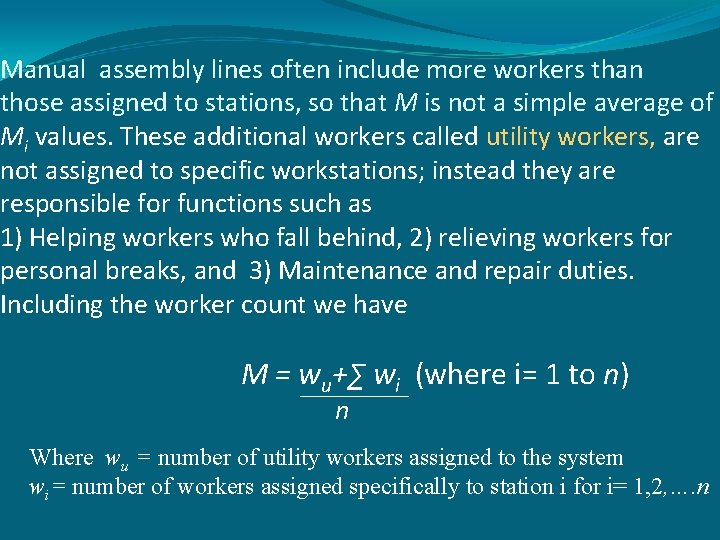
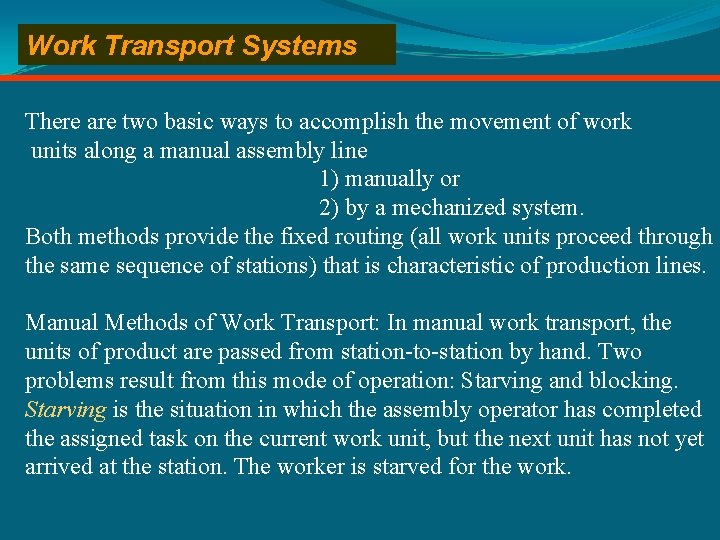
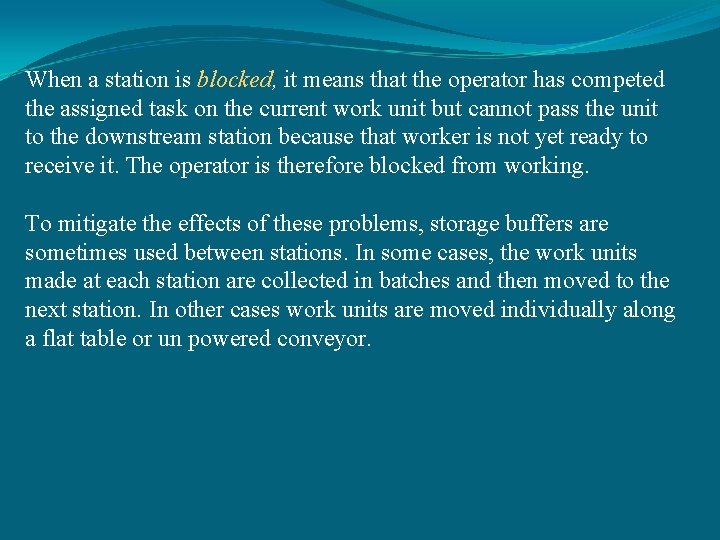
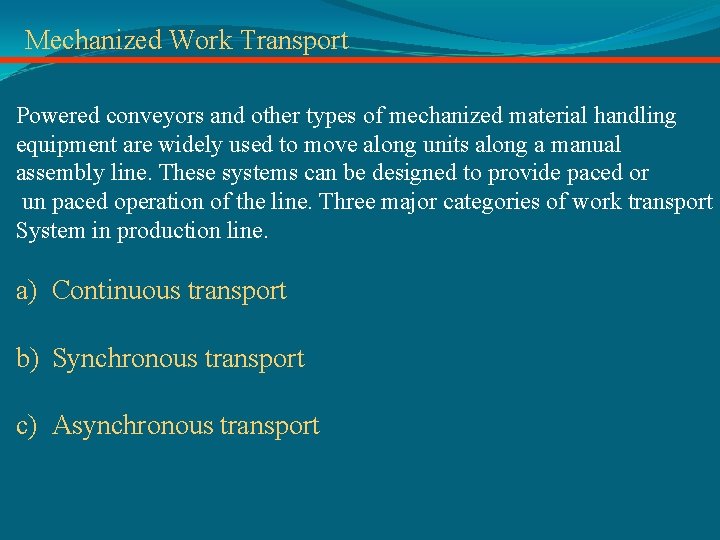
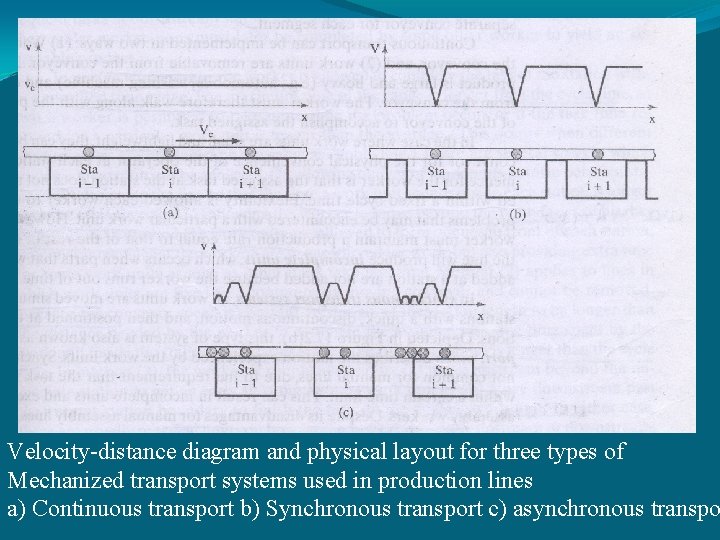
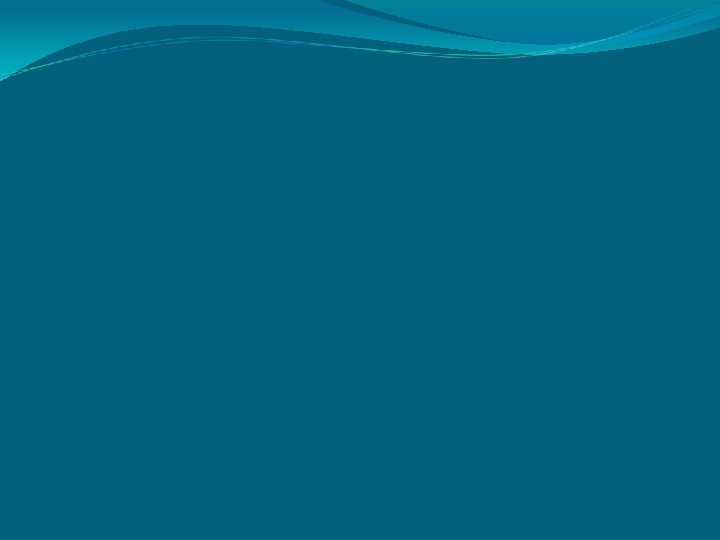
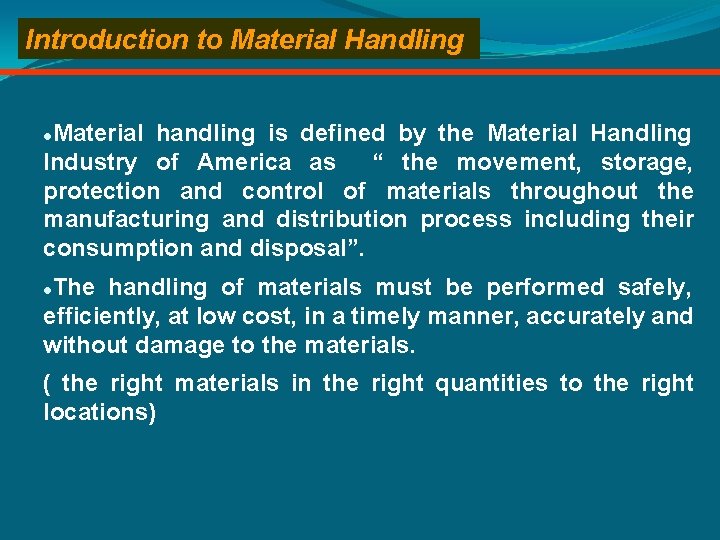
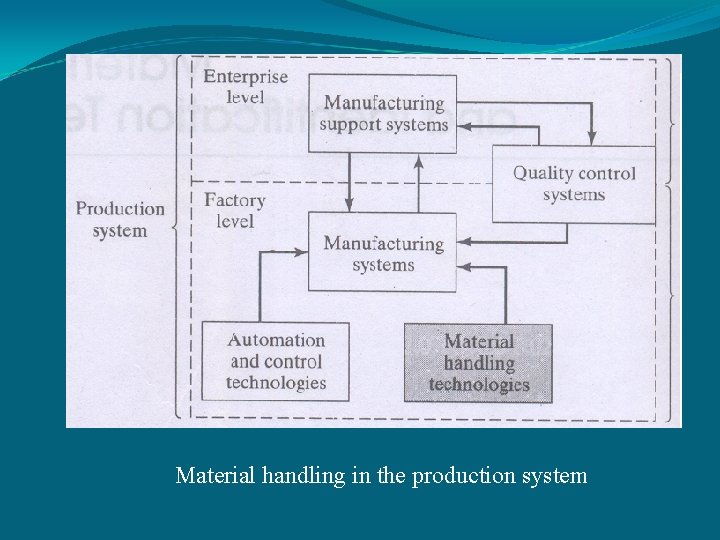
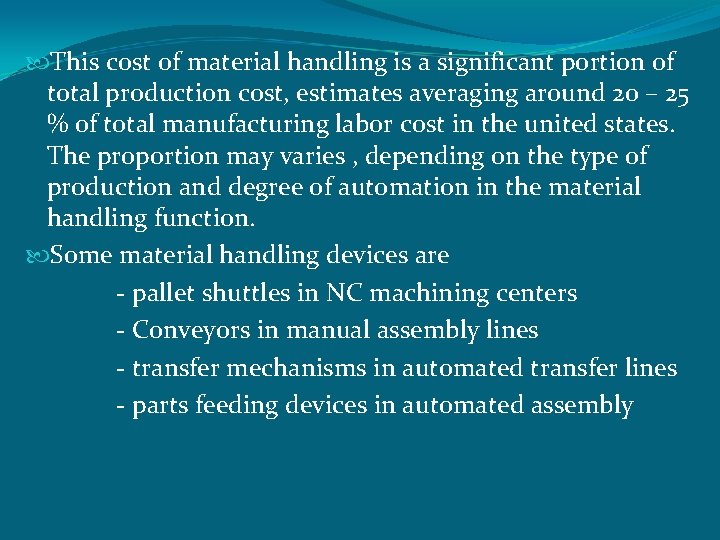
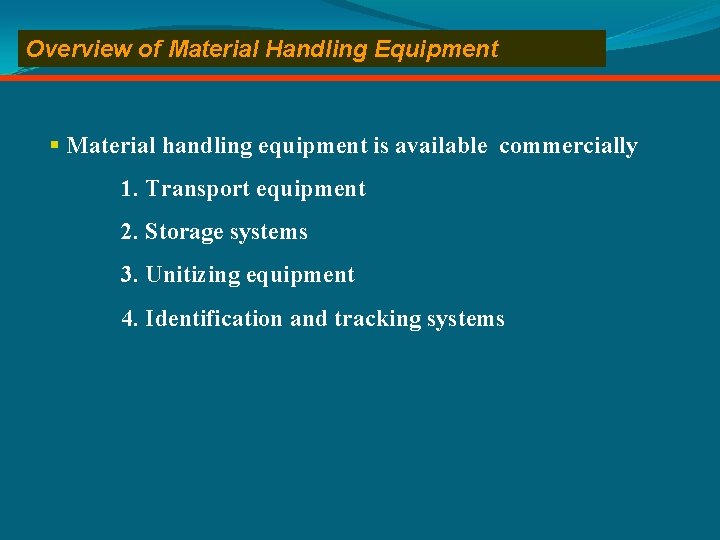
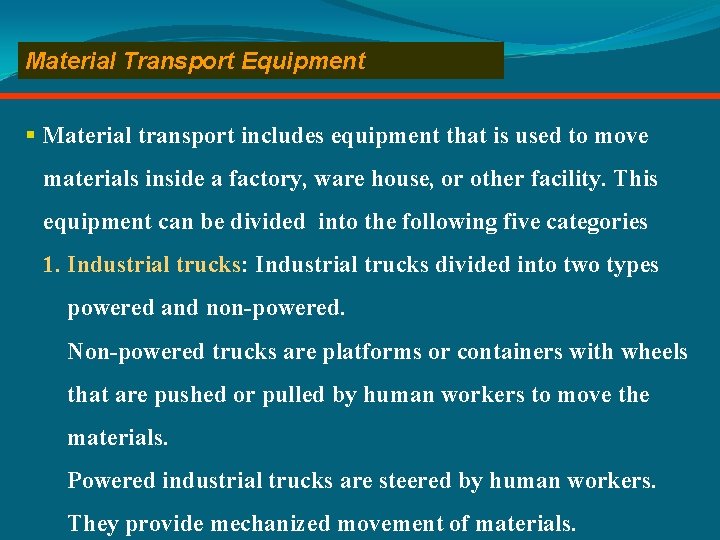
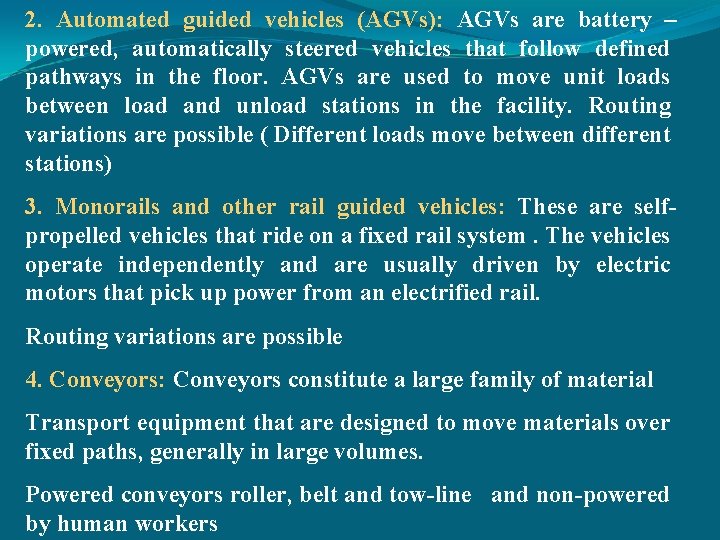
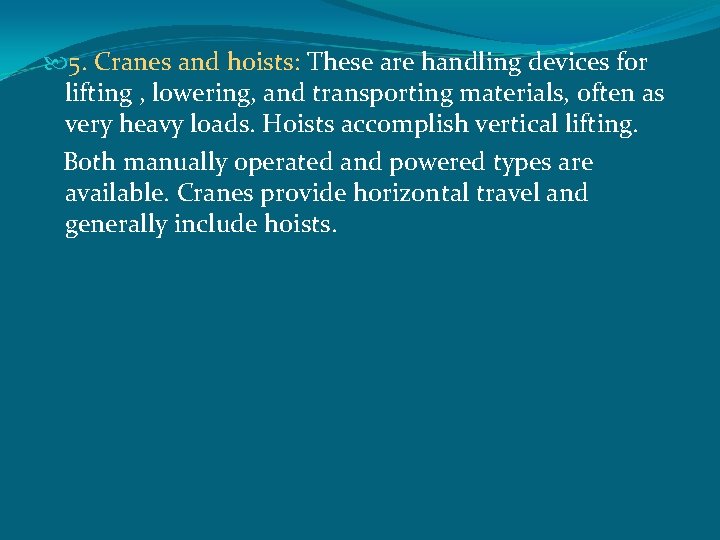
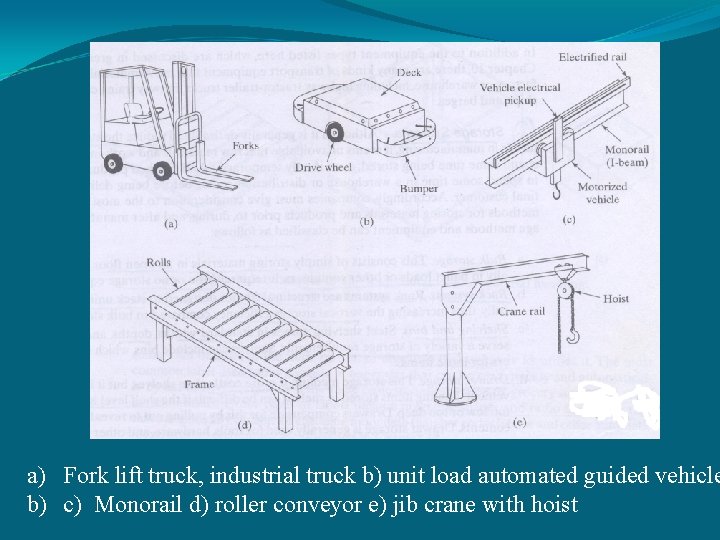
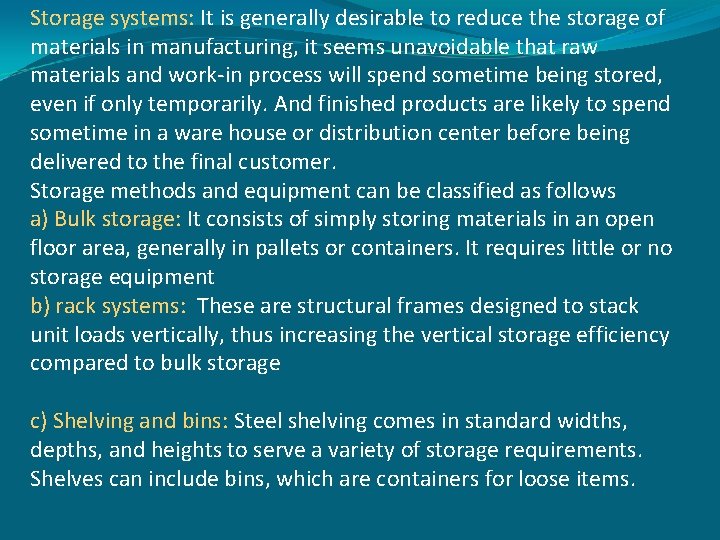
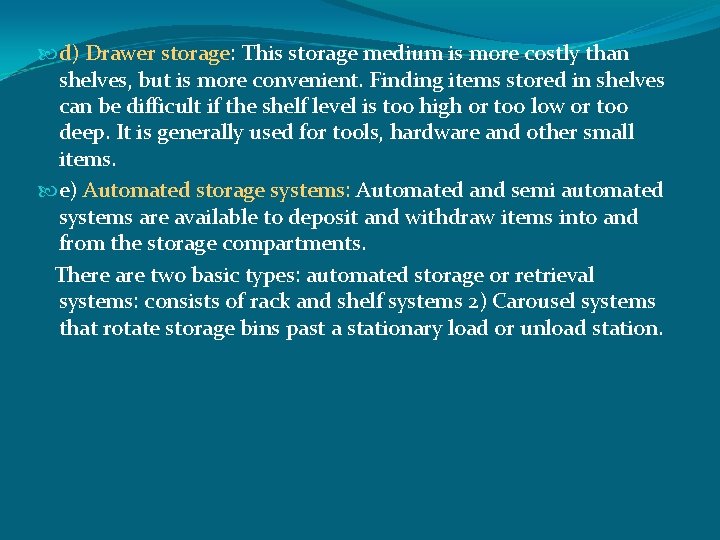
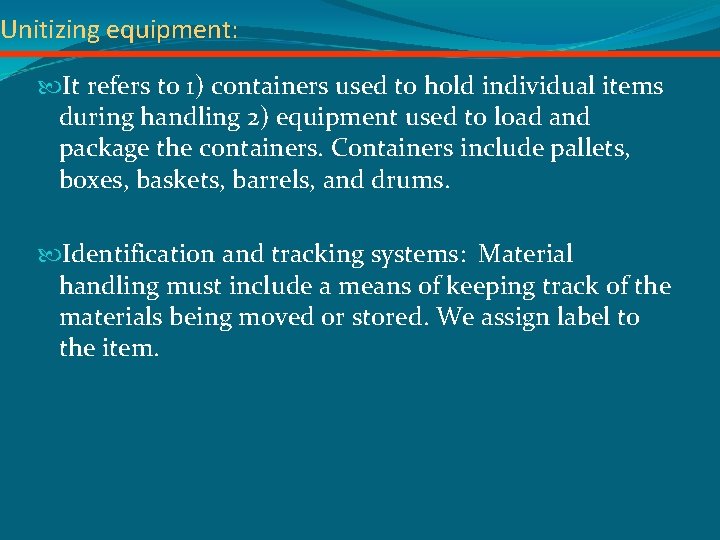
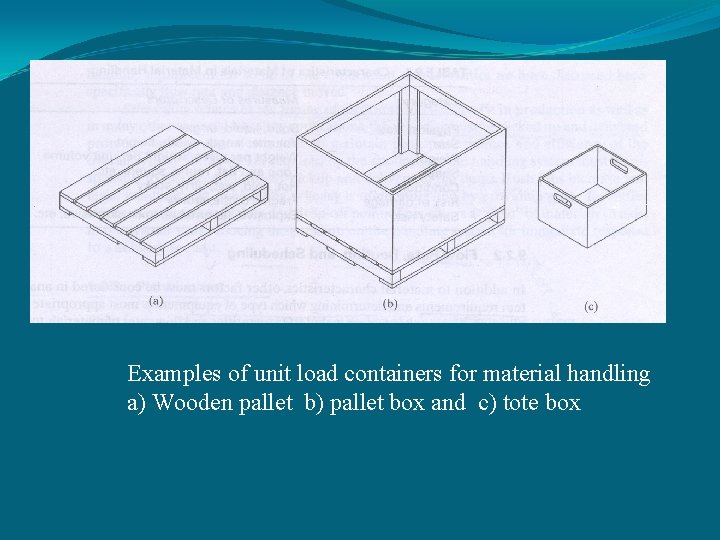
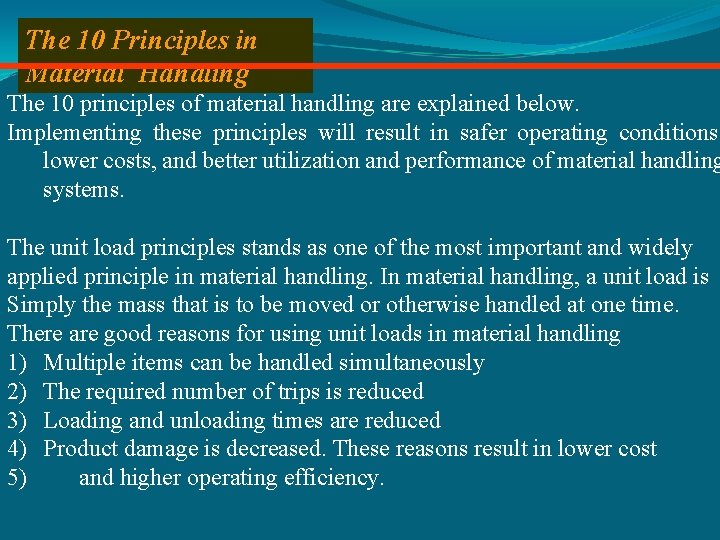
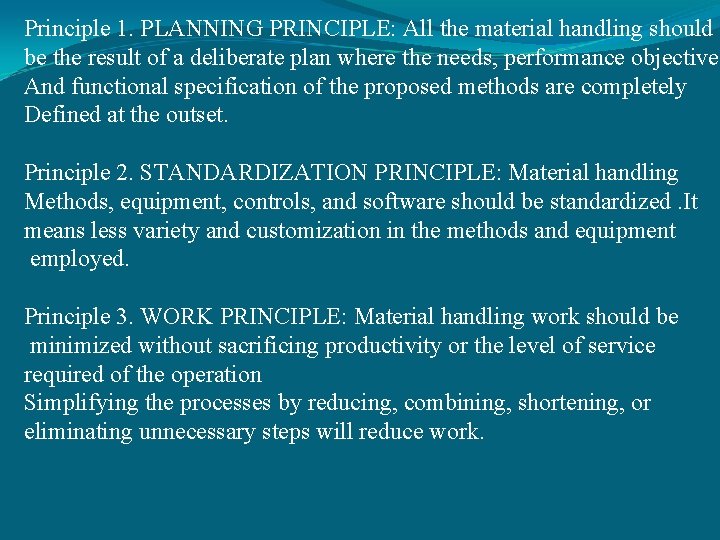
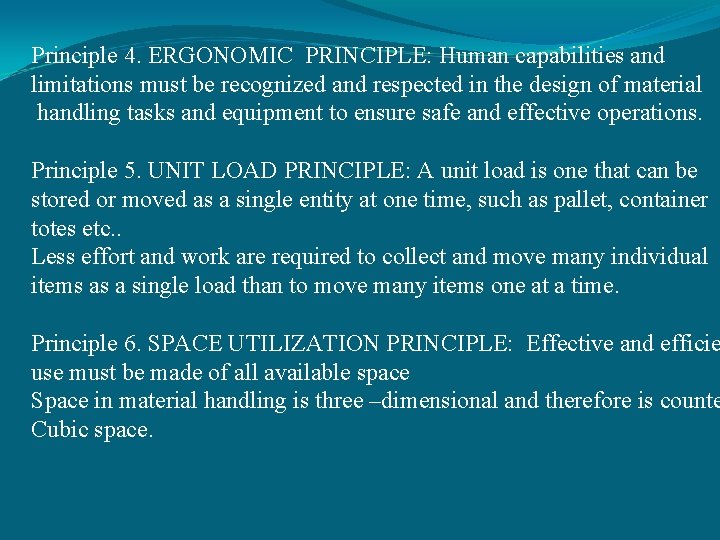
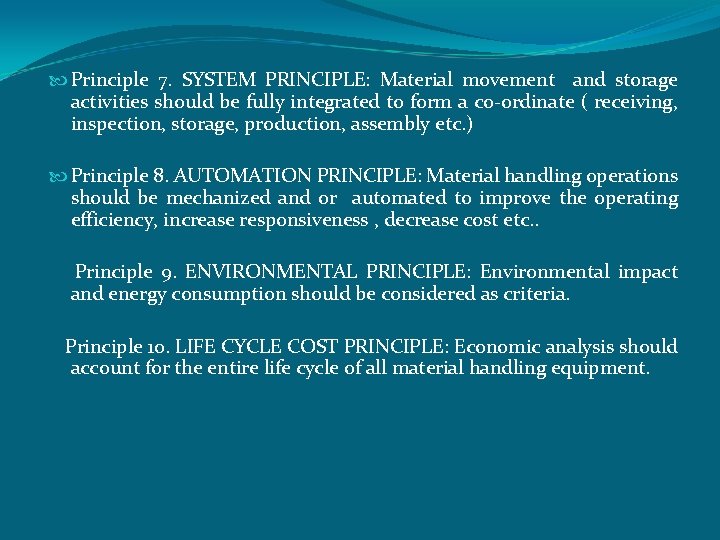
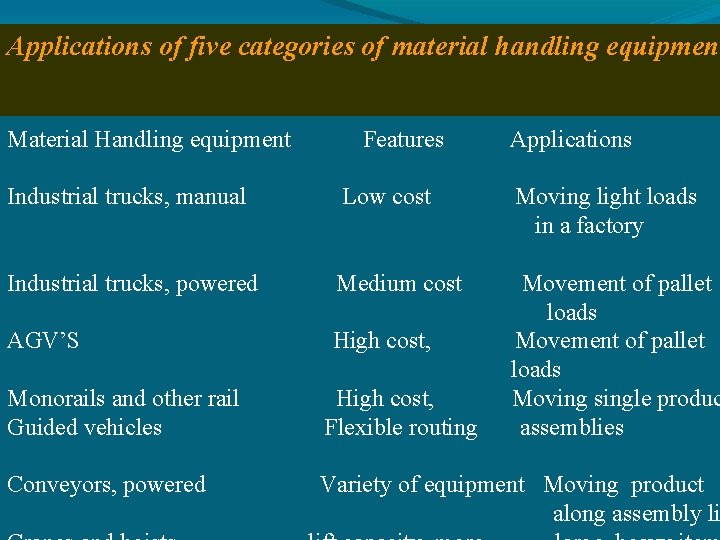
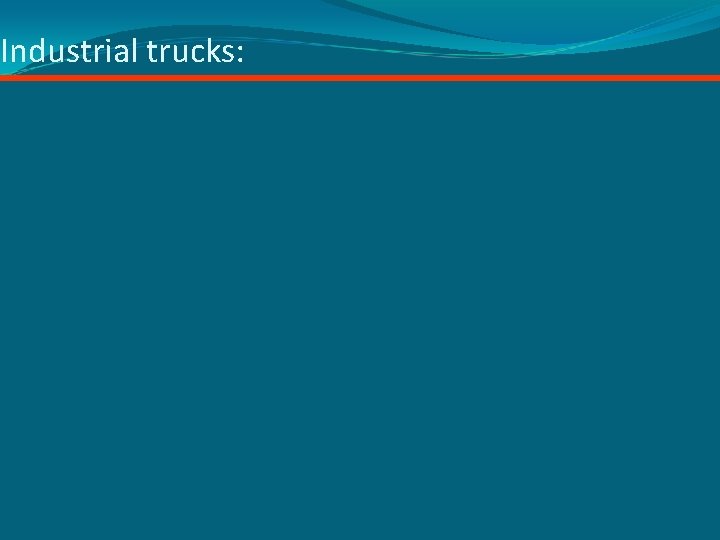
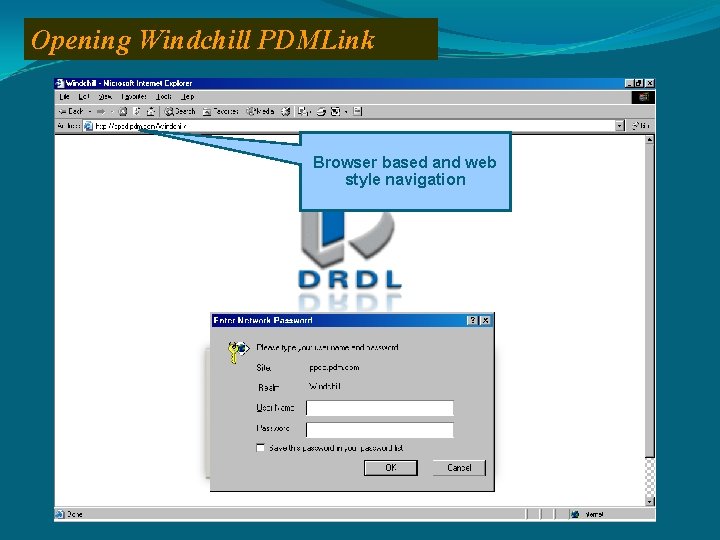
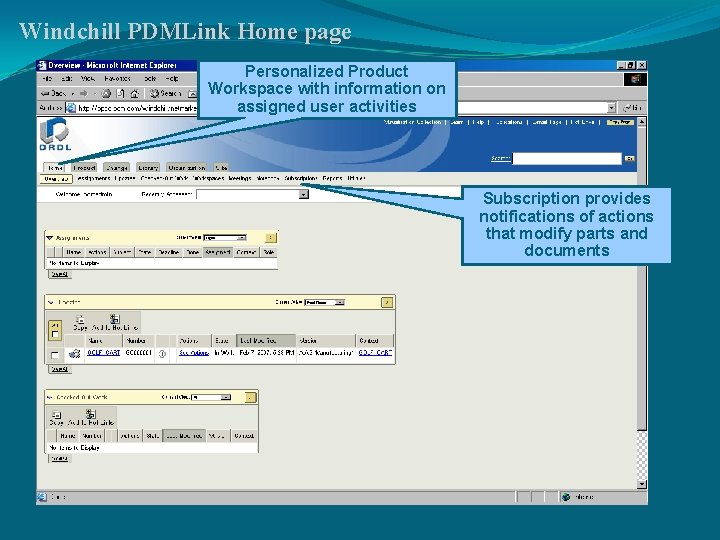
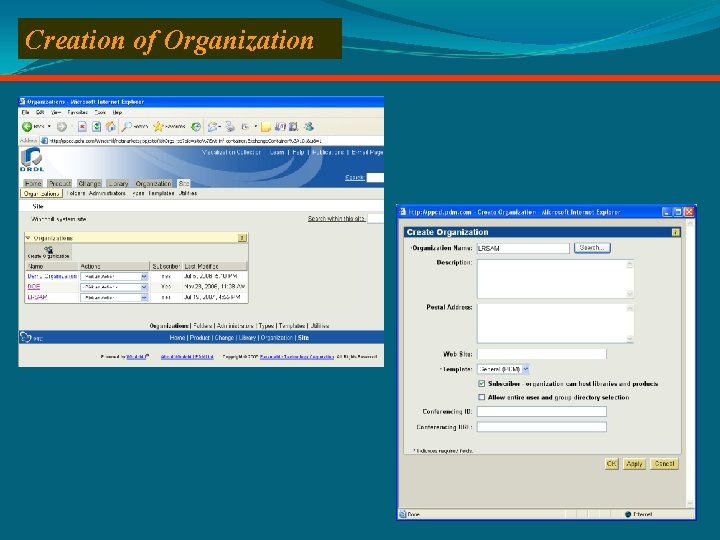
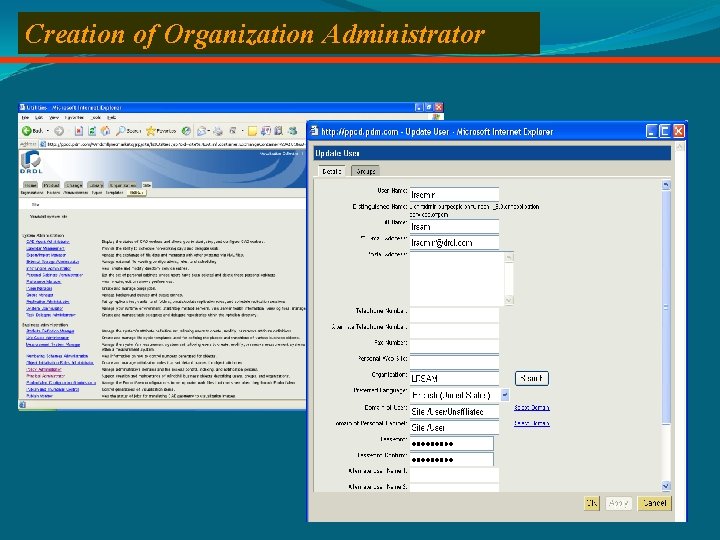
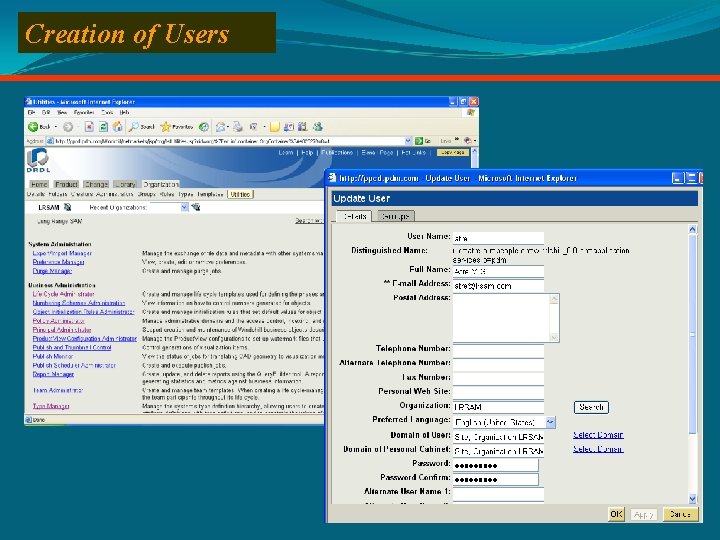
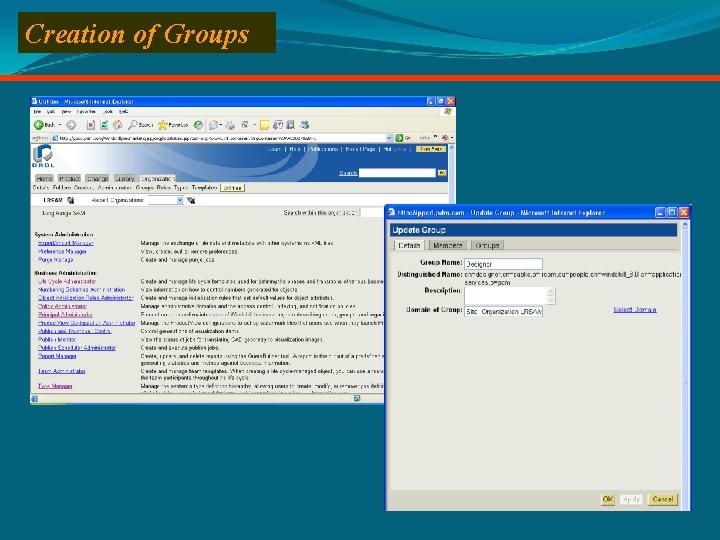
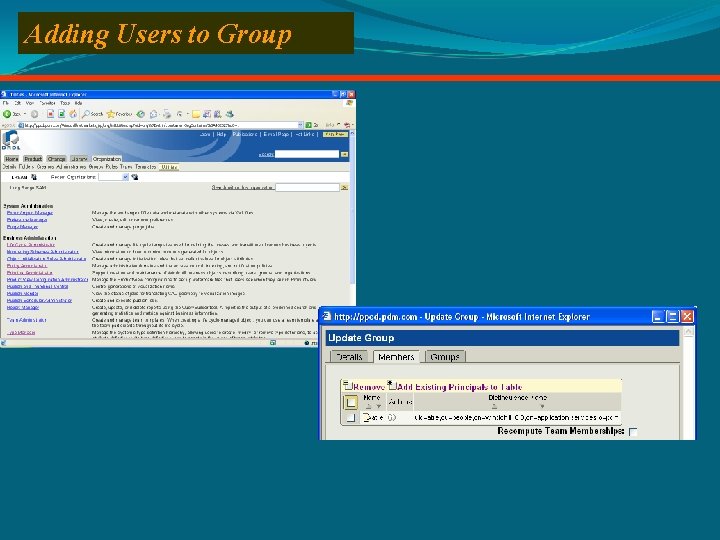
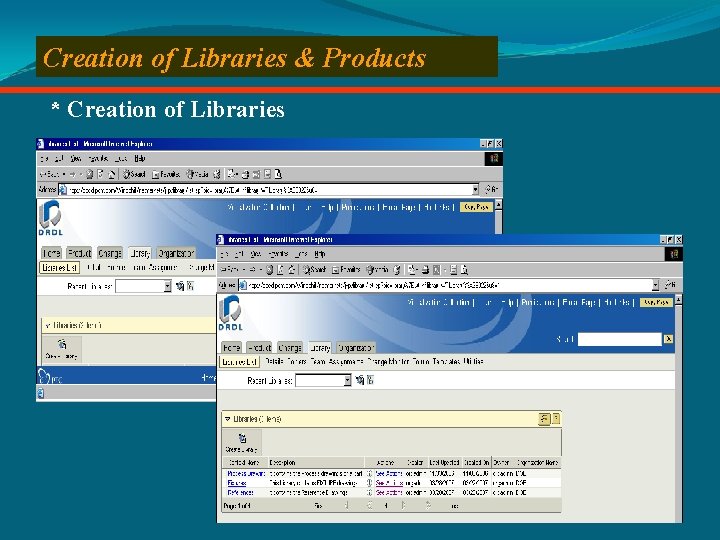
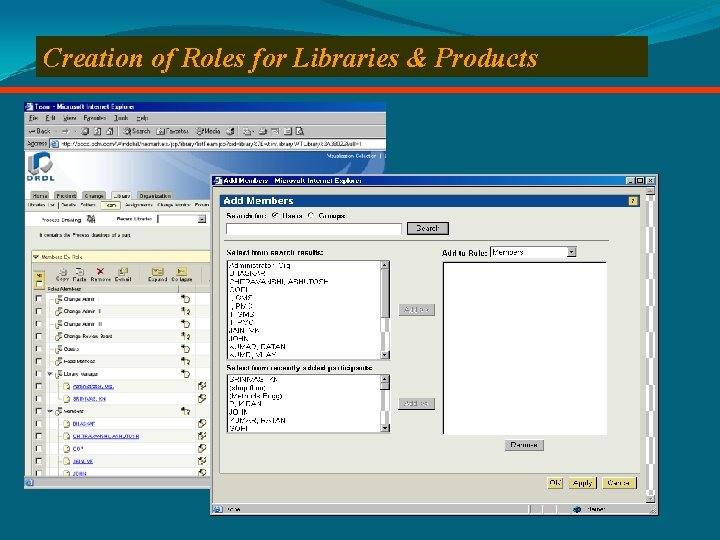
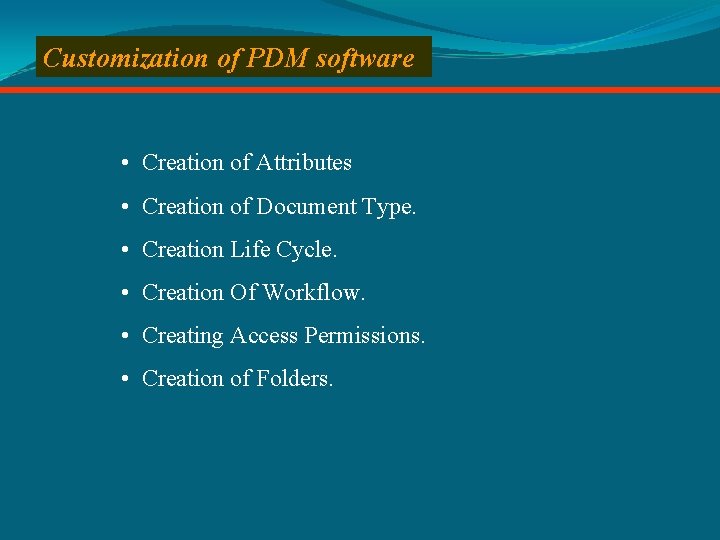
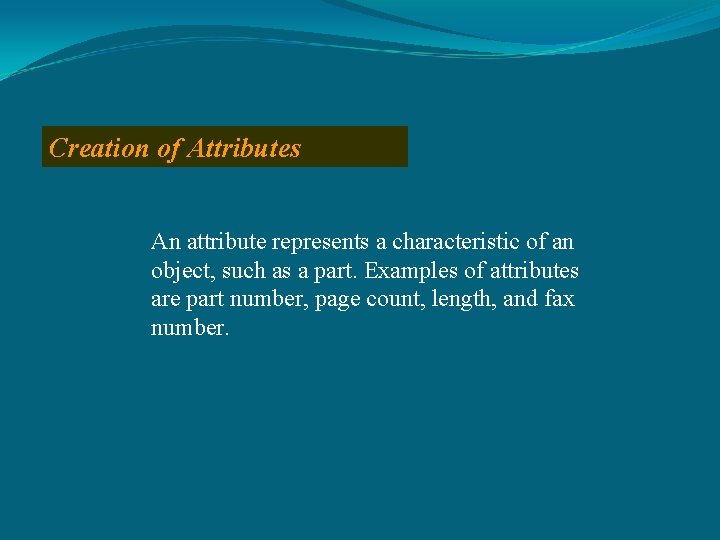
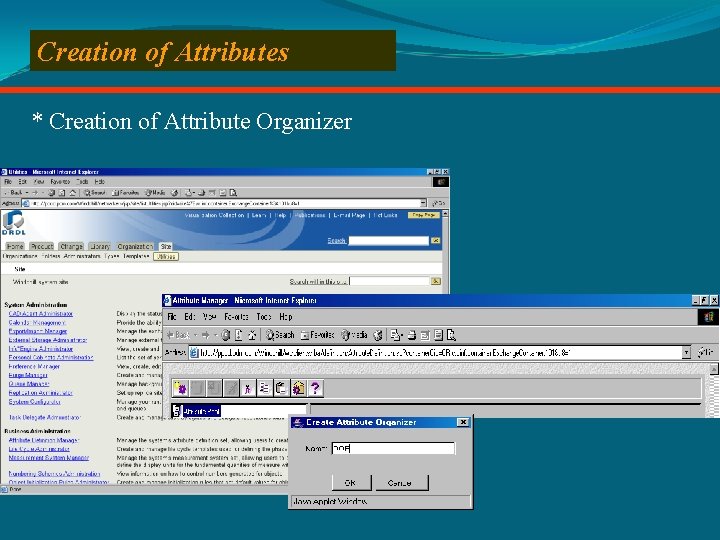
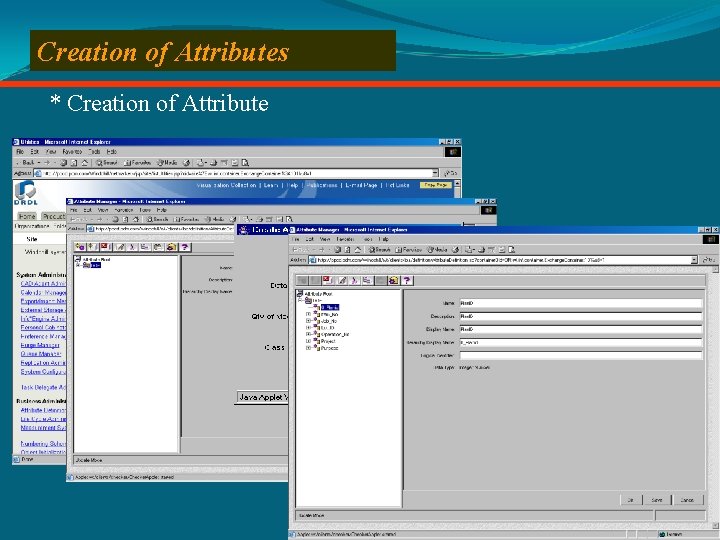
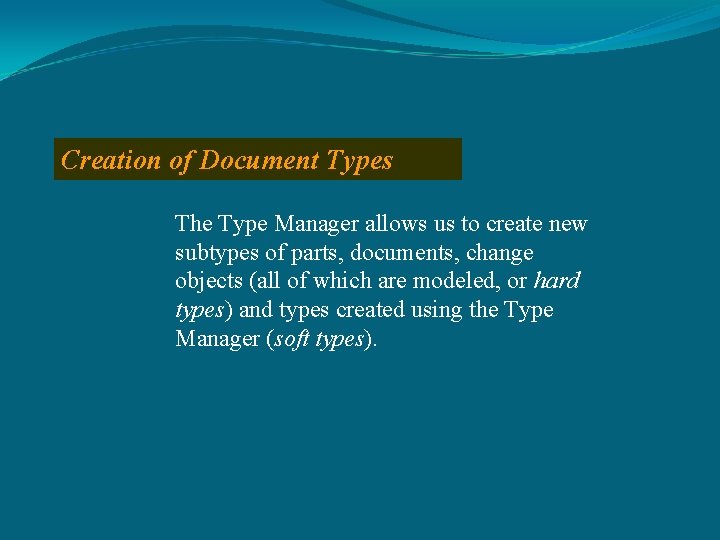
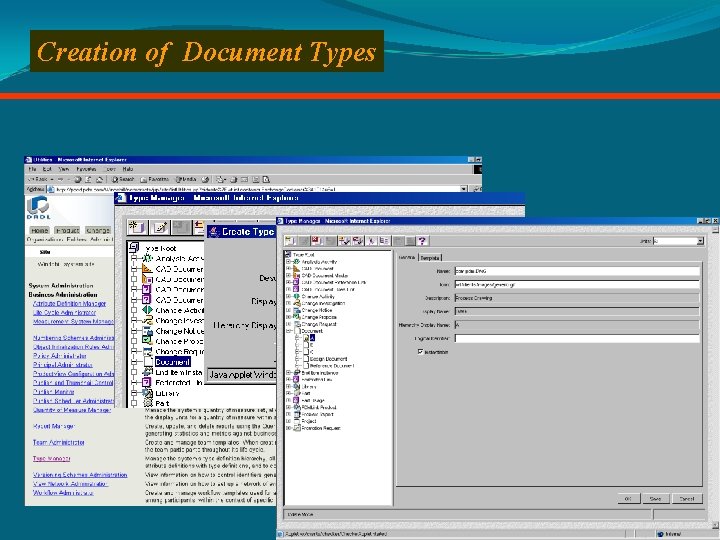
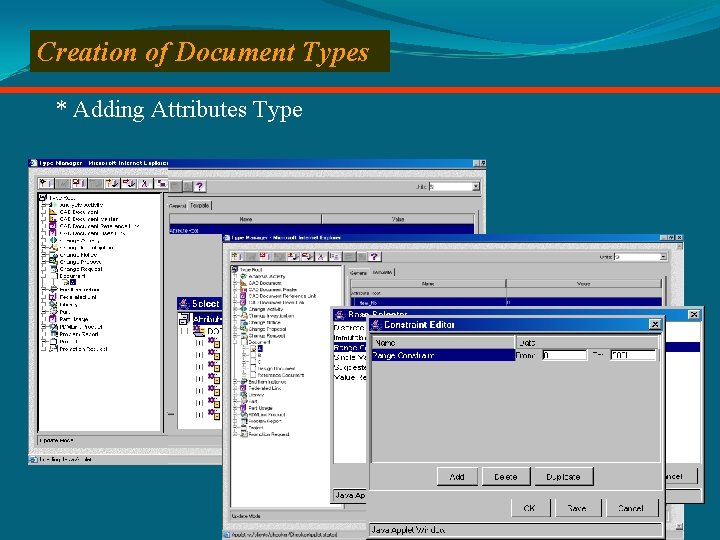
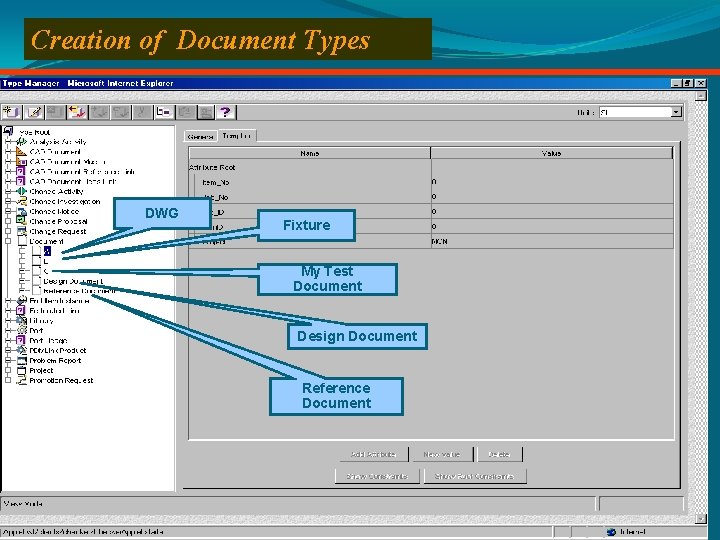
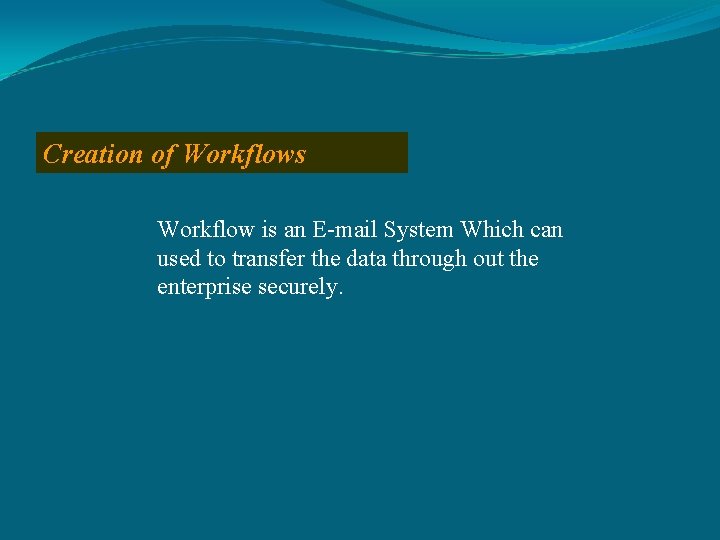
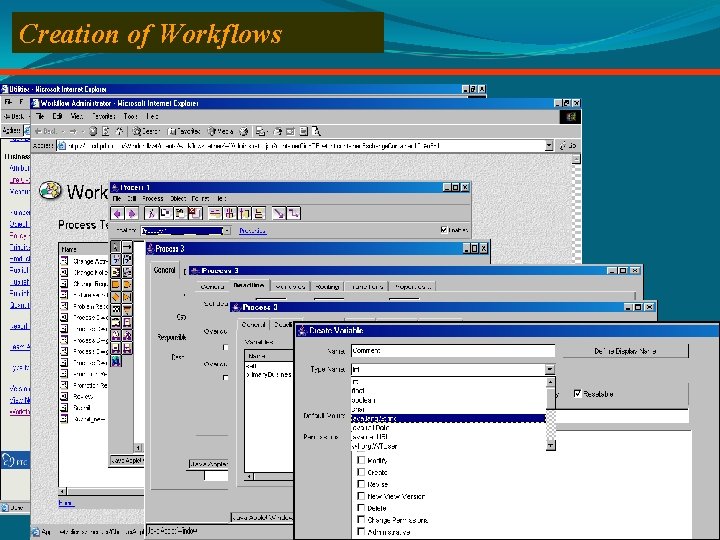
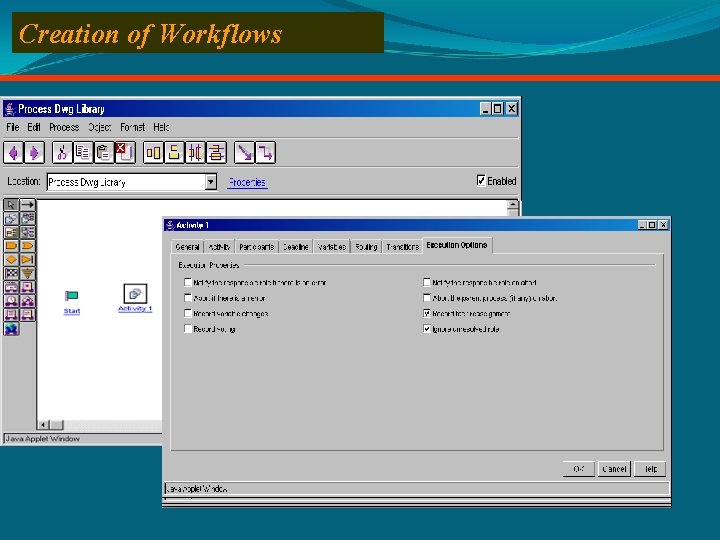
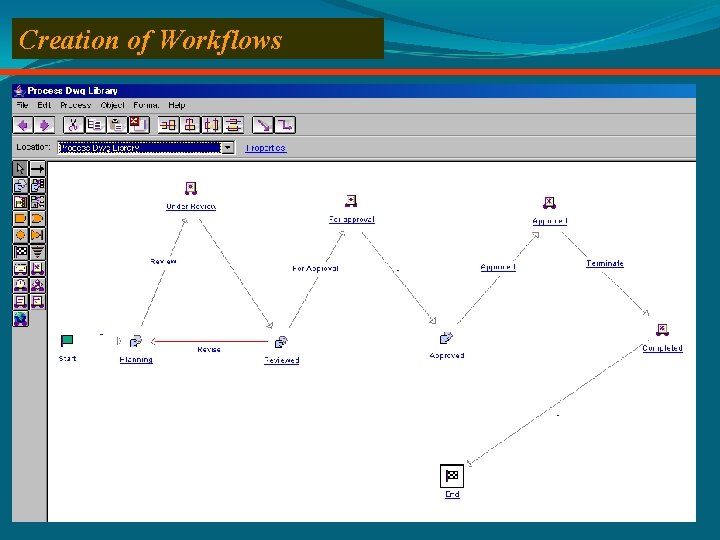
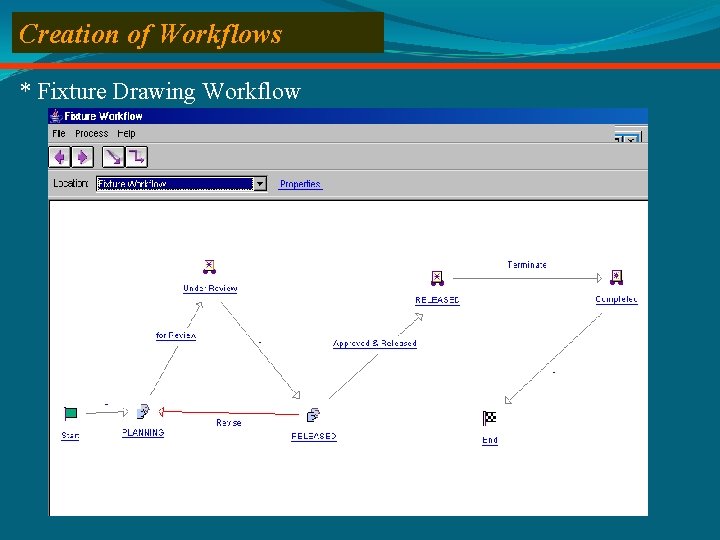
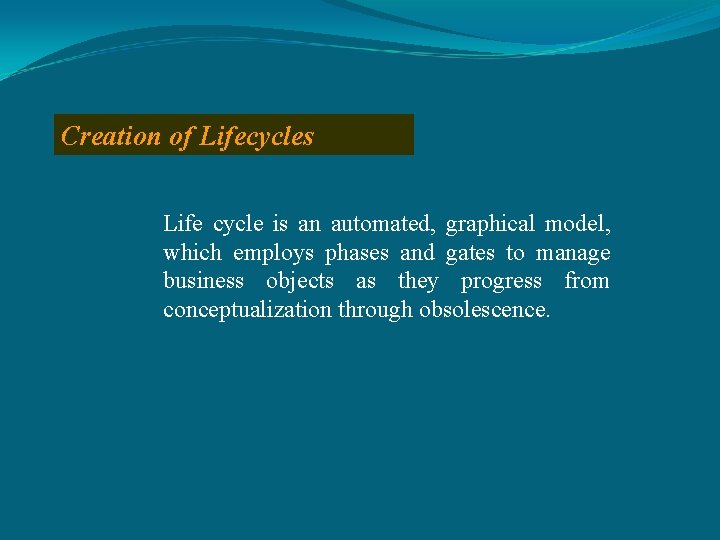
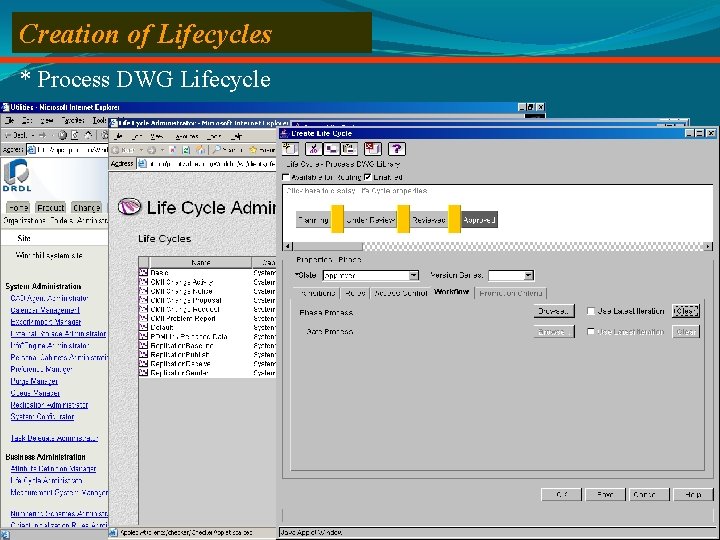
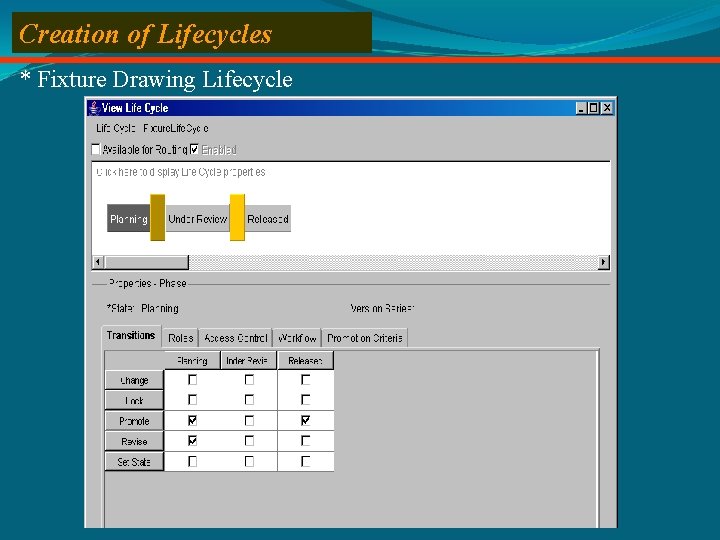
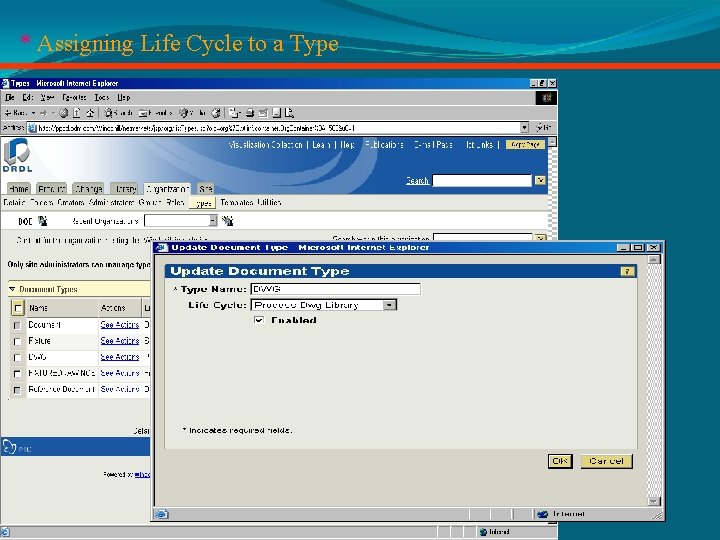
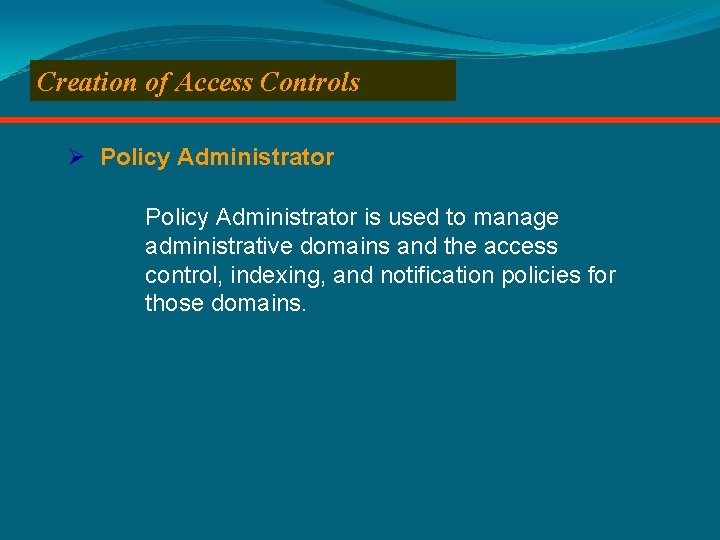
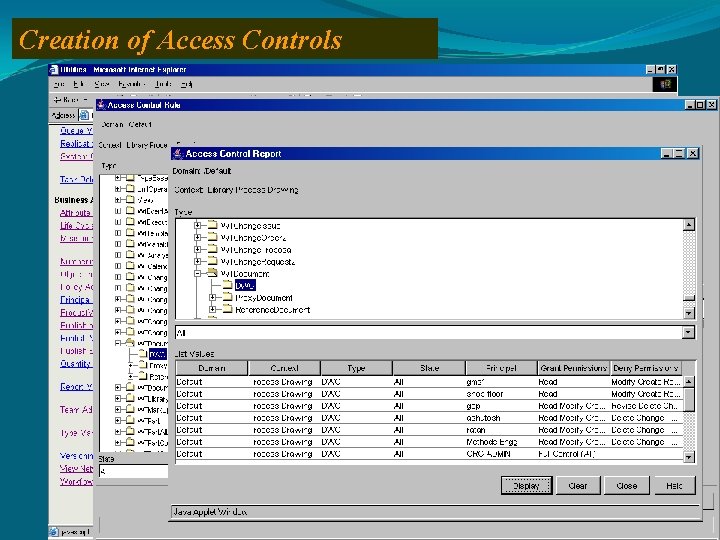
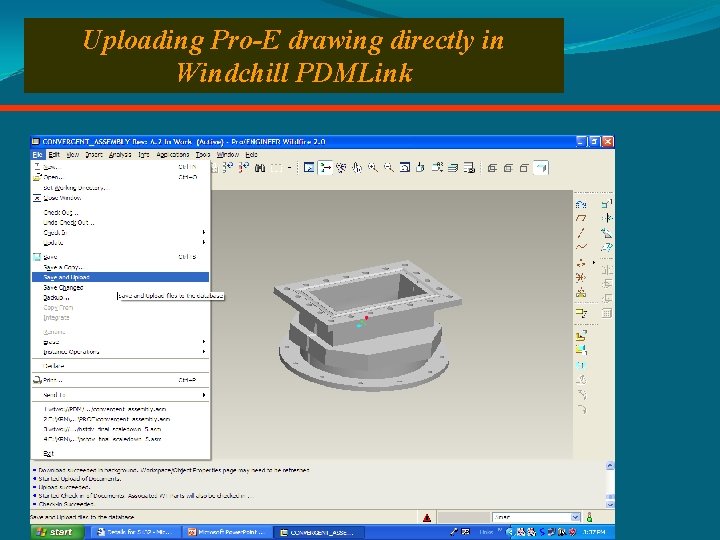
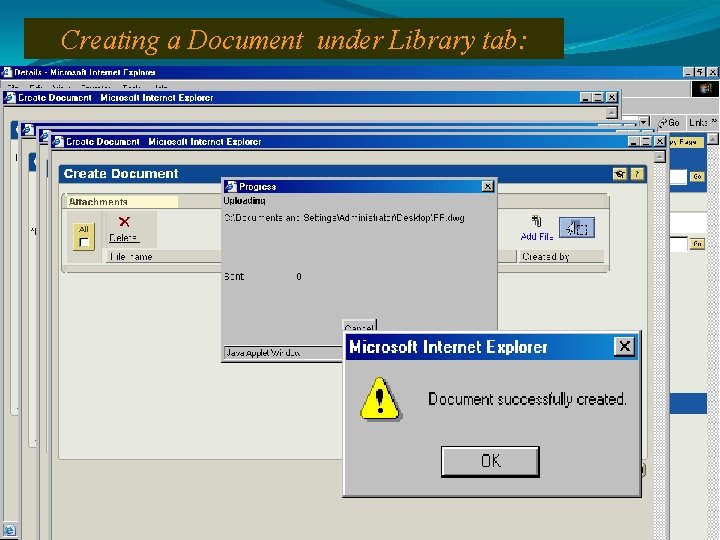
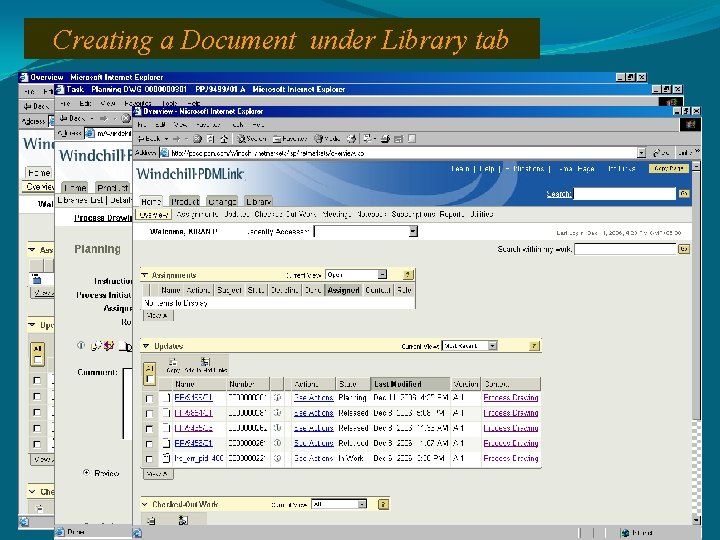
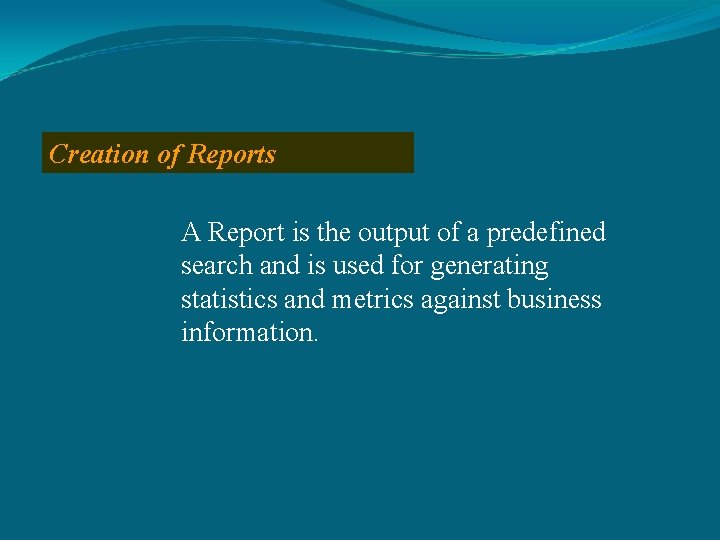
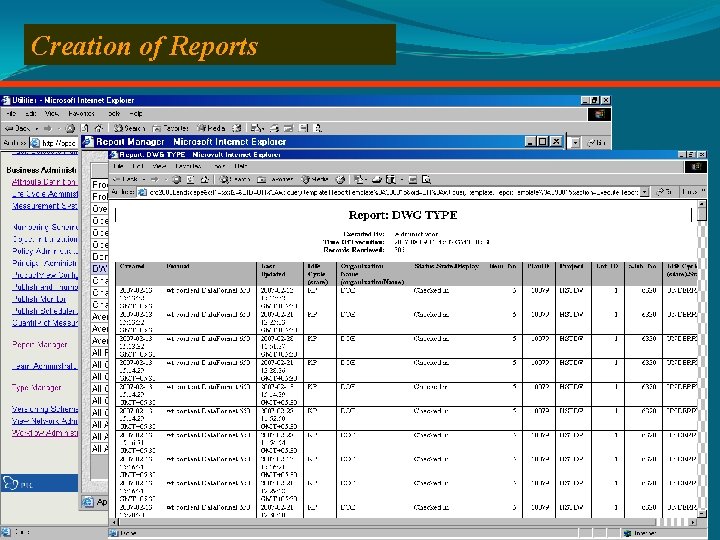
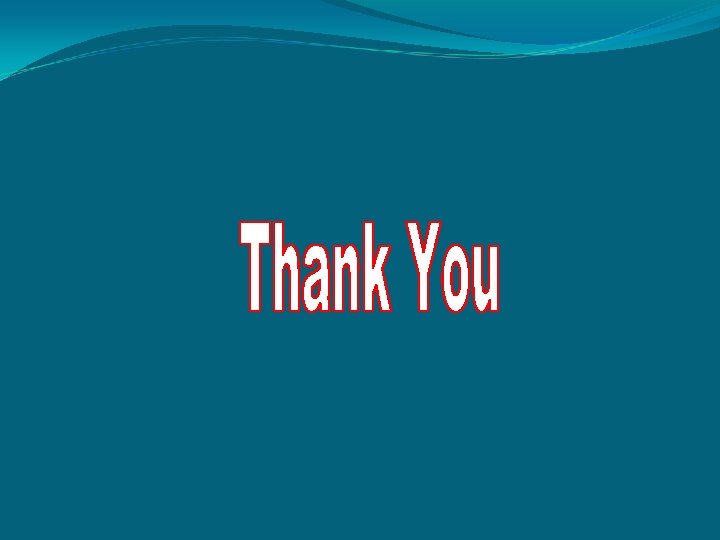
- Slides: 90
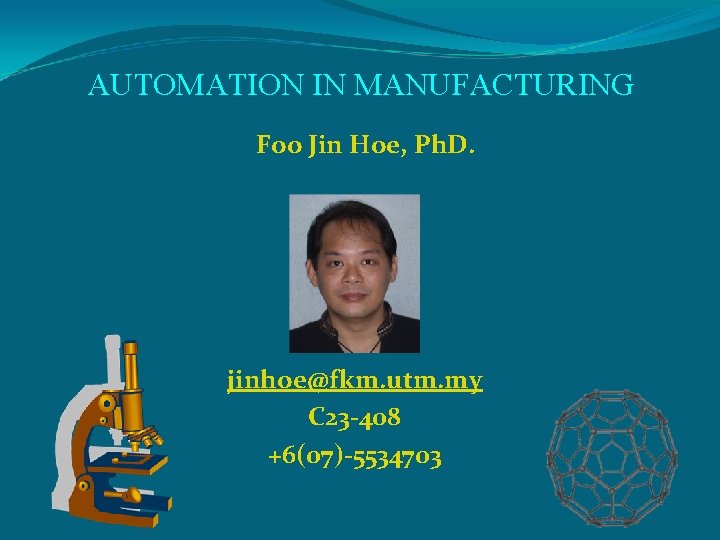
AUTOMATION IN MANUFACTURING Foo Jin Hoe, Ph. D. jinhoe@fkm. utm. my C 23 -408 +6(07)-5534703
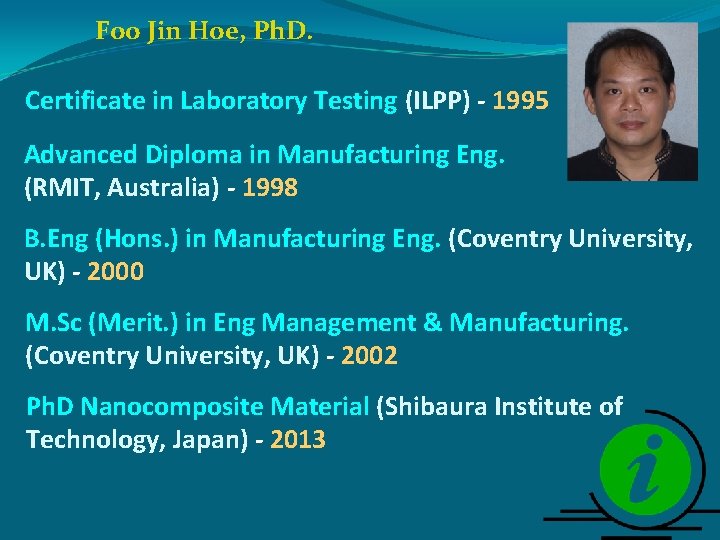
Foo Jin Hoe, Ph. D. Certificate in Laboratory Testing (ILPP) - 1995 Advanced Diploma in Manufacturing Eng. (RMIT, Australia) - 1998 B. Eng (Hons. ) in Manufacturing Eng. (Coventry University, UK) - 2000 M. Sc (Merit. ) in Eng Management & Manufacturing. (Coventry University, UK) - 2002 Ph. D Nanocomposite Material (Shibaura Institute of Technology, Japan) - 2013
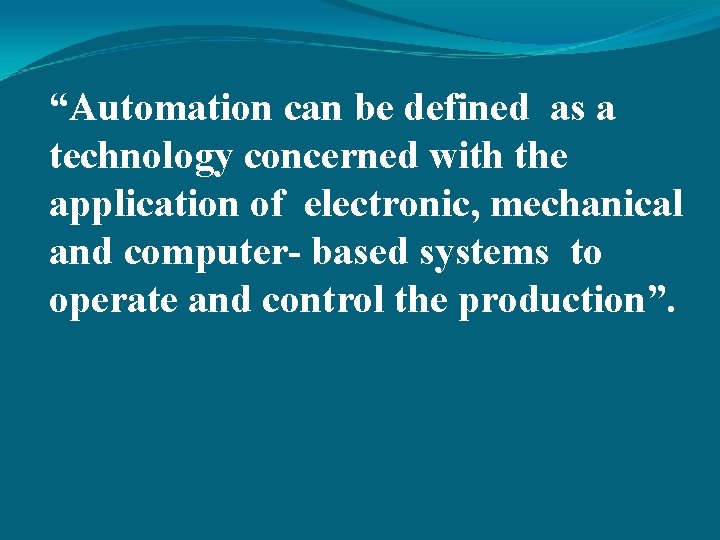
“Automation can be defined as a technology concerned with the application of electronic, mechanical and computer- based systems to operate and control the production”.
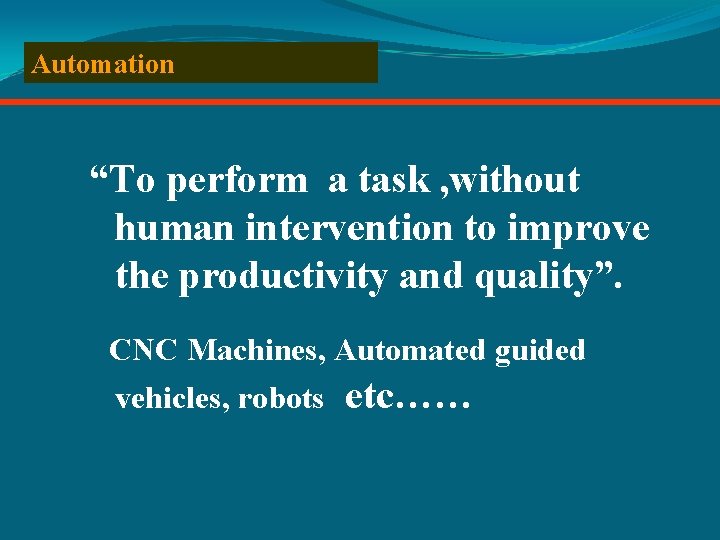
Automation “To perform a task , without human intervention to improve the productivity and quality”. CNC Machines, Automated guided vehicles, robots etc……
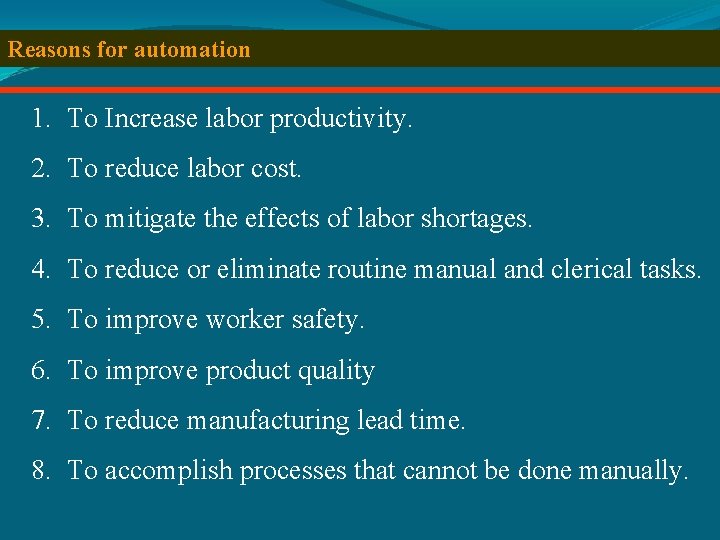
Reasons for automation 1. To Increase labor productivity. 2. To reduce labor cost. 3. To mitigate the effects of labor shortages. 4. To reduce or eliminate routine manual and clerical tasks. 5. To improve worker safety. 6. To improve product quality 7. To reduce manufacturing lead time. 8. To accomplish processes that cannot be done manually.
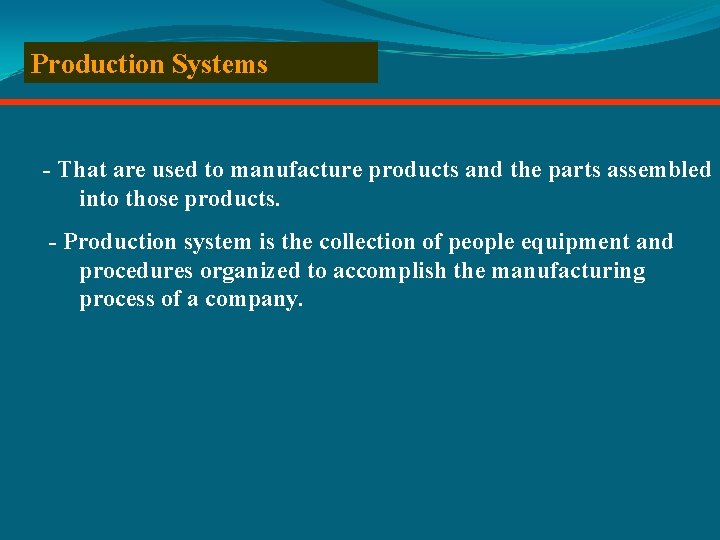
Production Systems - That are used to manufacture products and the parts assembled into those products. - Production system is the collection of people equipment and procedures organized to accomplish the manufacturing process of a company.
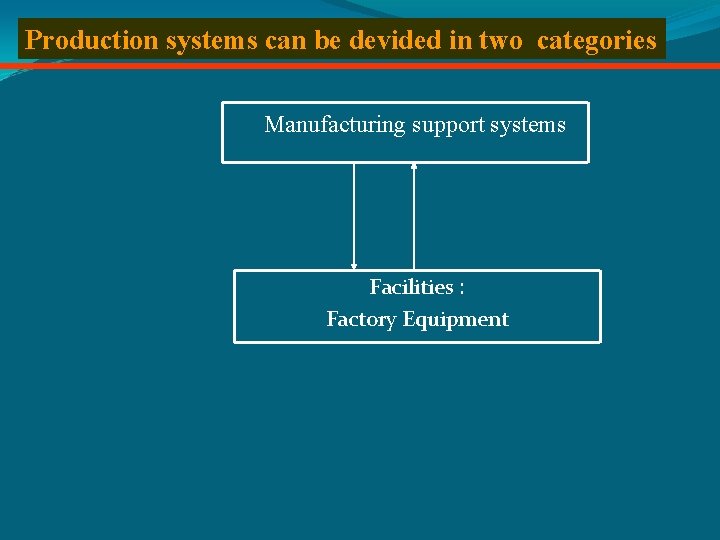
Production systems can be devided in two categories Manufacturing support systems Facilities : Factory Equipment
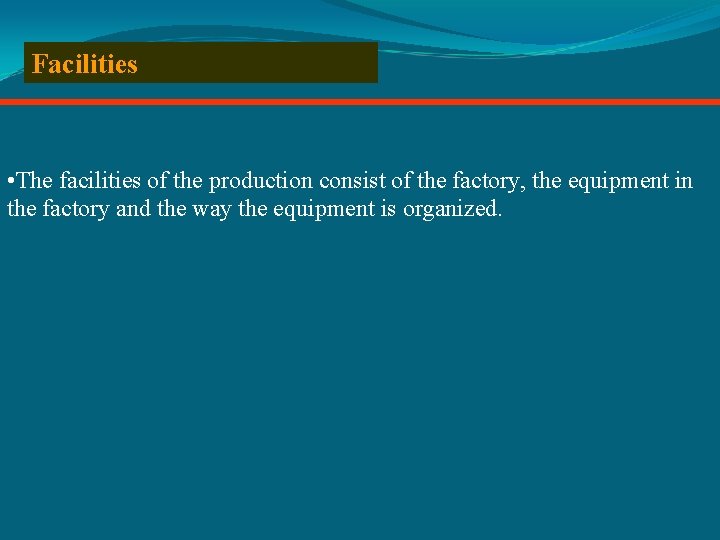
Facilities • The facilities of the production consist of the factory, the equipment in the factory and the way the equipment is organized.
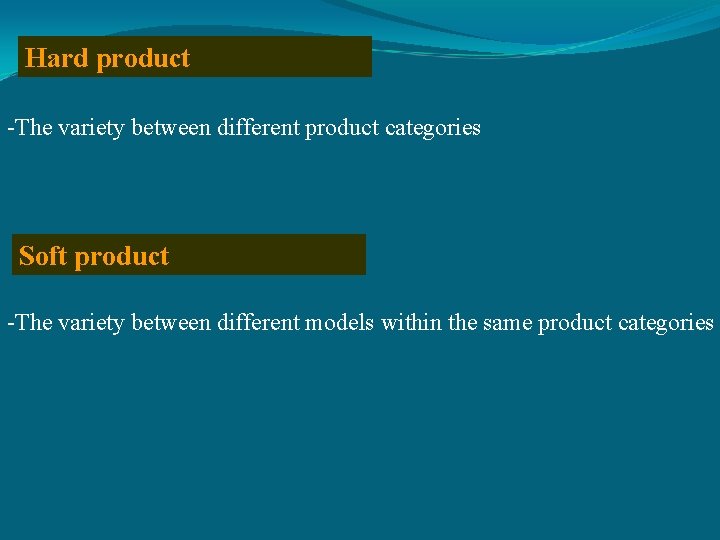
Hard product -The variety between different product categories Soft product -The variety between different models within the same product categories
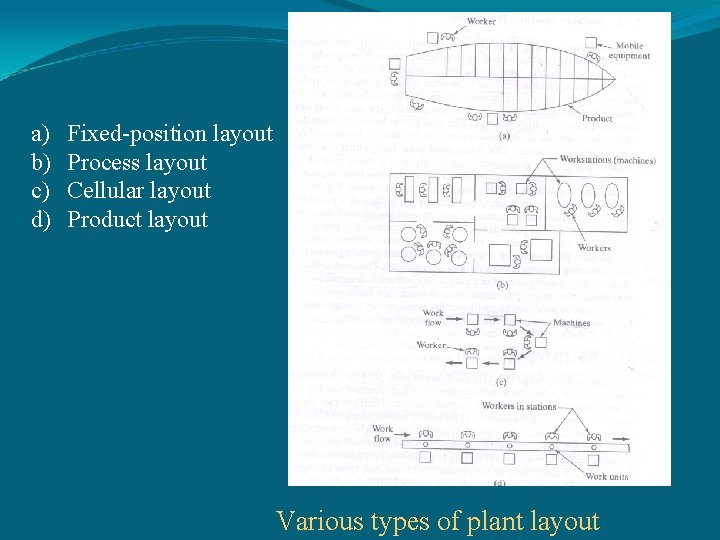
a) b) c) d) Fixed-position layout Process layout Cellular layout Product layout Various types of plant layout
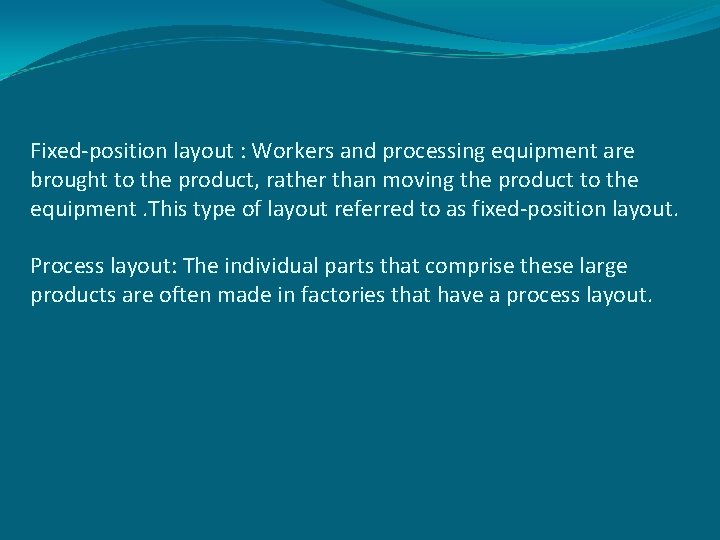
Fixed-position layout : Workers and processing equipment are brought to the product, rather than moving the product to the equipment. This type of layout referred to as fixed-position layout. Process layout: The individual parts that comprise these large products are often made in factories that have a process layout.
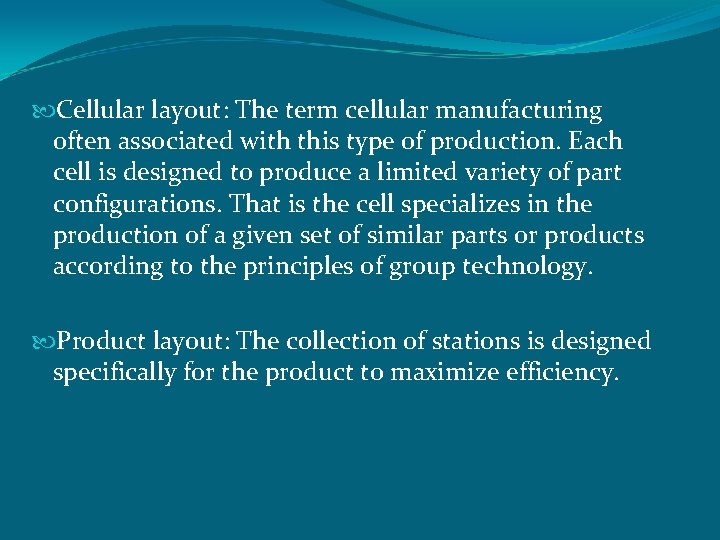
Cellular layout: The term cellular manufacturing often associated with this type of production. Each cell is designed to produce a limited variety of part configurations. That is the cell specializes in the production of a given set of similar parts or products according to the principles of group technology. Product layout: The collection of stations is designed specifically for the product to maximize efficiency.
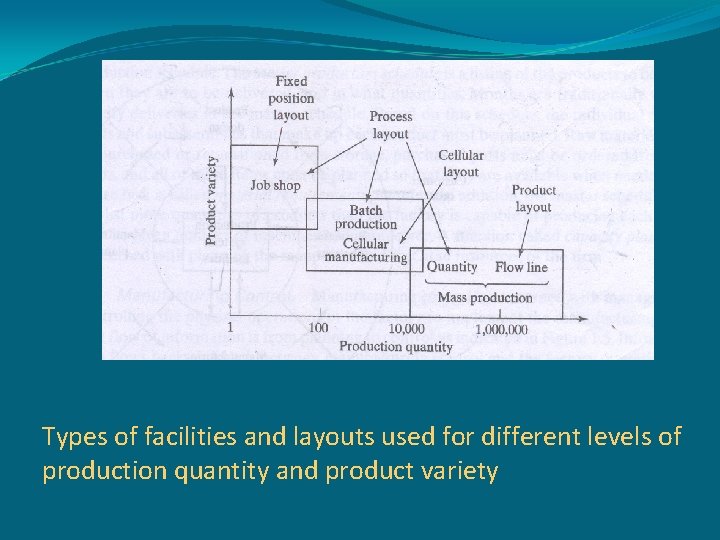
Types of facilities and layouts used for different levels of production quantity and product variety
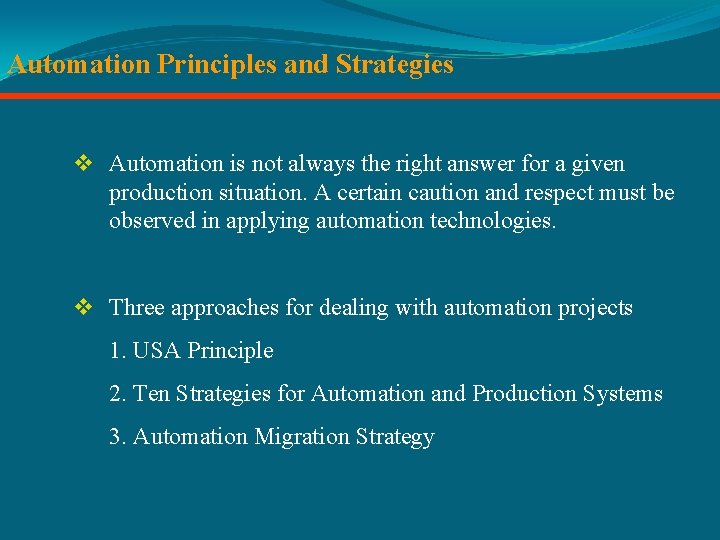
Automation Principles and Strategies v Automation is not always the right answer for a given production situation. A certain caution and respect must be observed in applying automation technologies. v Three approaches for dealing with automation projects 1. USA Principle 2. Ten Strategies for Automation and Production Systems 3. Automation Migration Strategy
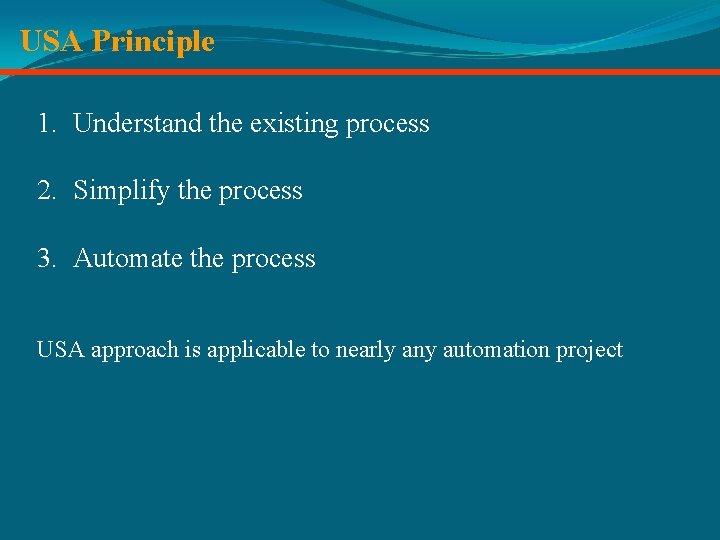
USA Principle 1. Understand the existing process 2. Simplify the process 3. Automate the process USA approach is applicable to nearly any automation project
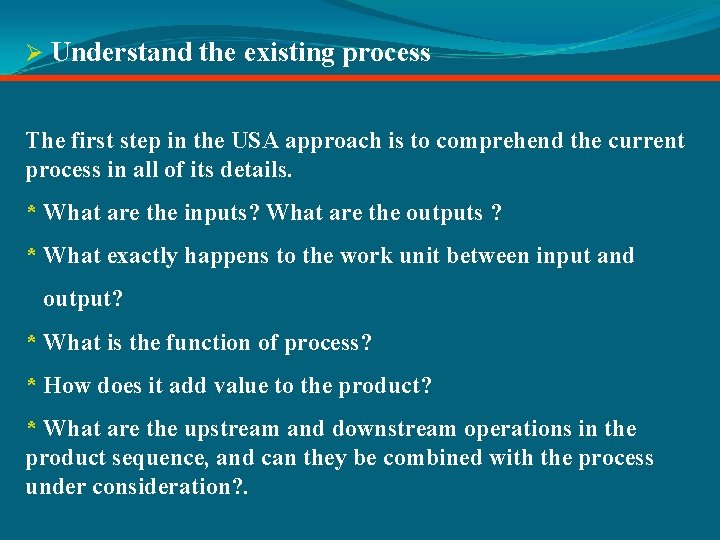
Ø Understand the existing process The first step in the USA approach is to comprehend the current process in all of its details. * What are the inputs? What are the outputs ? * What exactly happens to the work unit between input and output? * What is the function of process? * How does it add value to the product? * What are the upstream and downstream operations in the product sequence, and can they be combined with the process under consideration? .
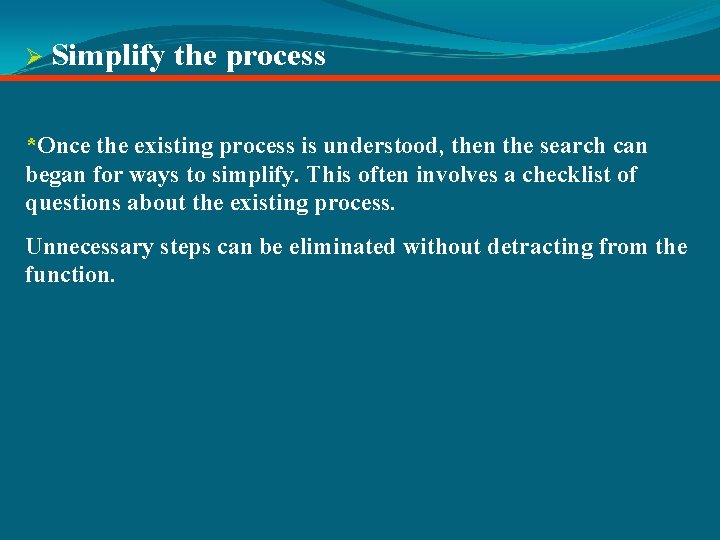
Ø Simplify the process *Once the existing process is understood, then the search can began for ways to simplify. This often involves a checklist of questions about the existing process. Unnecessary steps can be eliminated without detracting from the function.
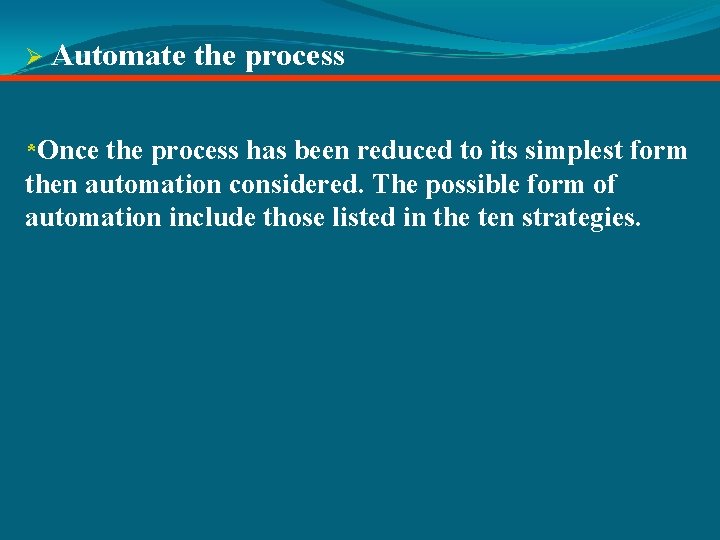
Ø Automate the process *Once the process has been reduced to its simplest form then automation considered. The possible form of automation include those listed in the ten strategies.
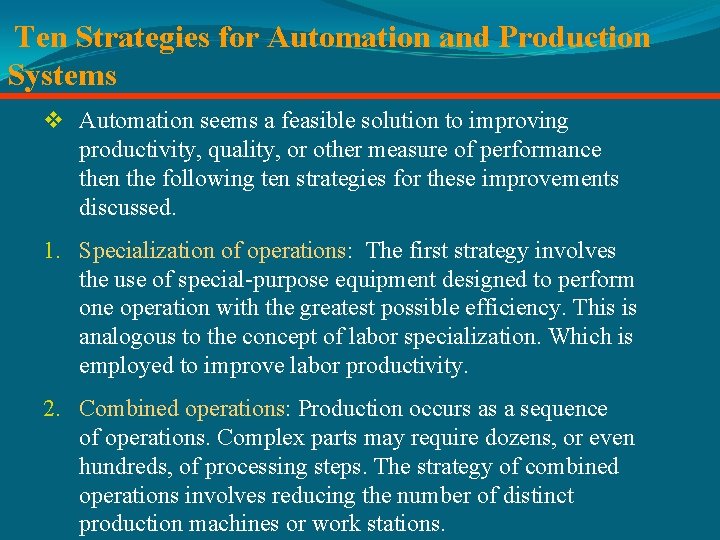
Ten Strategies for Automation and Production Systems v Automation seems a feasible solution to improving productivity, quality, or other measure of performance then the following ten strategies for these improvements discussed. 1. Specialization of operations: The first strategy involves the use of special-purpose equipment designed to perform one operation with the greatest possible efficiency. This is analogous to the concept of labor specialization. Which is employed to improve labor productivity. 2. Combined operations: Production occurs as a sequence of operations. Complex parts may require dozens, or even hundreds, of processing steps. The strategy of combined operations involves reducing the number of distinct production machines or work stations.
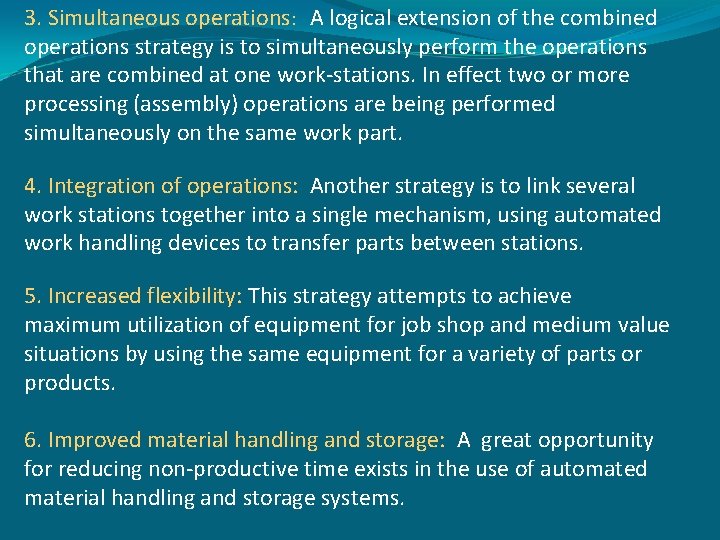
3. Simultaneous operations: A logical extension of the combined operations strategy is to simultaneously perform the operations that are combined at one work-stations. In effect two or more processing (assembly) operations are being performed simultaneously on the same work part. 4. Integration of operations: Another strategy is to link several work stations together into a single mechanism, using automated work handling devices to transfer parts between stations. 5. Increased flexibility: This strategy attempts to achieve maximum utilization of equipment for job shop and medium value situations by using the same equipment for a variety of parts or products. 6. Improved material handling and storage: A great opportunity for reducing non-productive time exists in the use of automated material handling and storage systems.
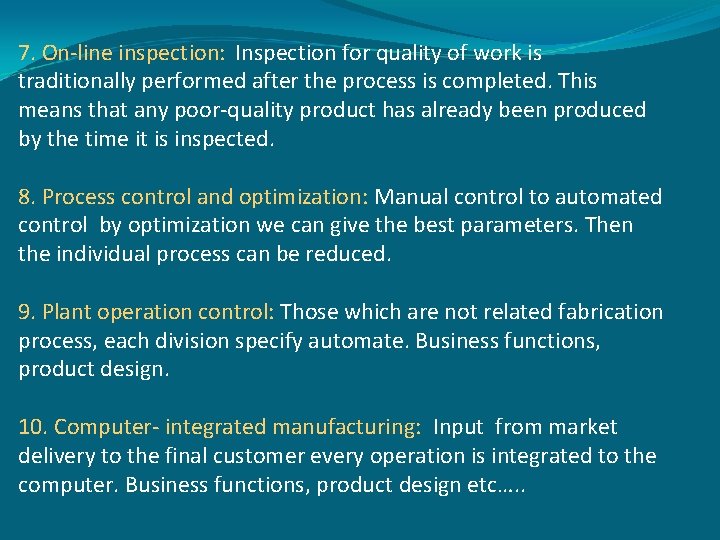
7. On-line inspection: Inspection for quality of work is traditionally performed after the process is completed. This means that any poor-quality product has already been produced by the time it is inspected. 8. Process control and optimization: Manual control to automated control by optimization we can give the best parameters. Then the individual process can be reduced. 9. Plant operation control: Those which are not related fabrication process, each division specify automate. Business functions, product design. 10. Computer- integrated manufacturing: Input from market delivery to the final customer every operation is integrated to the computer. Business functions, product design etc…. .
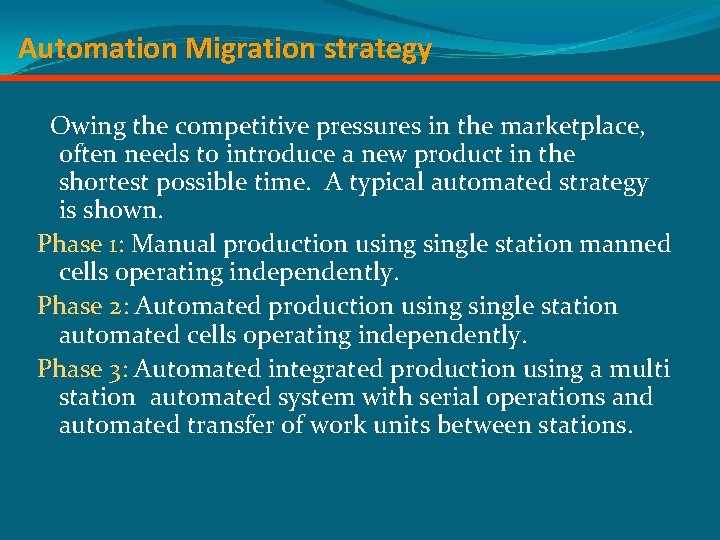
Automation Migration strategy Owing the competitive pressures in the marketplace, often needs to introduce a new product in the shortest possible time. A typical automated strategy is shown. Phase 1: Manual production usingle station manned cells operating independently. Phase 2: Automated production usingle station automated cells operating independently. Phase 3: Automated integrated production using a multi station automated system with serial operations and automated transfer of work units between stations.

A typical automation migration strategy
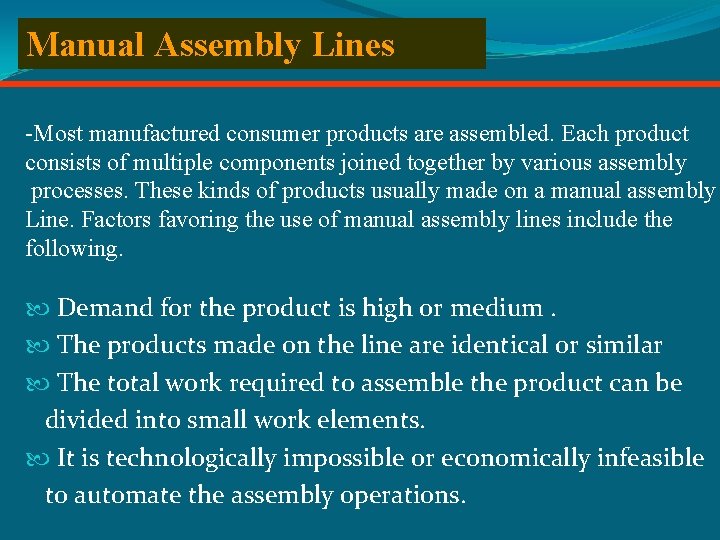
Manual Assembly Lines -Most manufactured consumer products are assembled. Each product consists of multiple components joined together by various assembly processes. These kinds of products usually made on a manual assembly Line. Factors favoring the use of manual assembly lines include the following. Demand for the product is high or medium. The products made on the line are identical or similar The total work required to assemble the product can be divided into small work elements. It is technologically impossible or economically infeasible to automate the assembly operations.
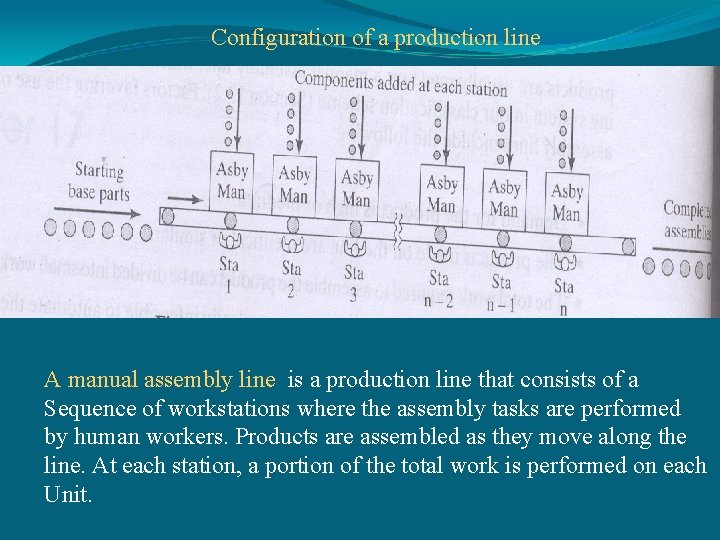
Configuration of a production line A manual assembly line is a production line that consists of a Sequence of workstations where the assembly tasks are performed by human workers. Products are assembled as they move along the line. At each station, a portion of the total work is performed on each Unit.
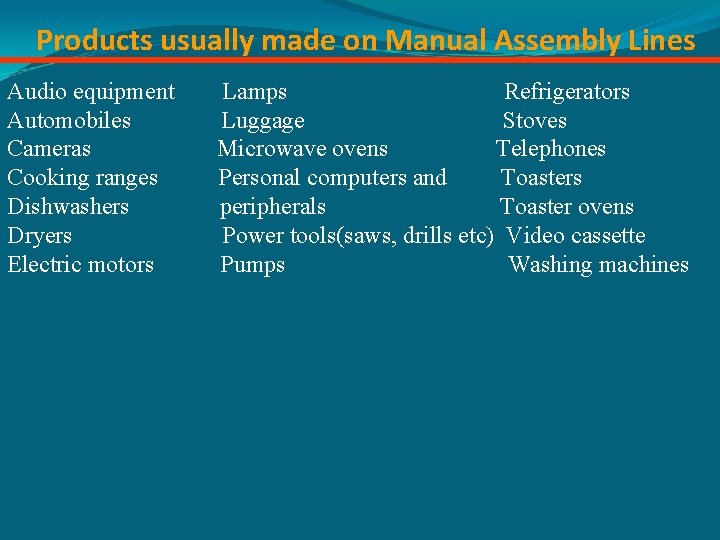
Products usually made on Manual Assembly Lines Audio equipment Automobiles Cameras Cooking ranges Dishwashers Dryers Electric motors Lamps Refrigerators Luggage Stoves Microwave ovens Telephones Personal computers and Toasters peripherals Toaster ovens Power tools(saws, drills etc) Video cassette Pumps Washing machines
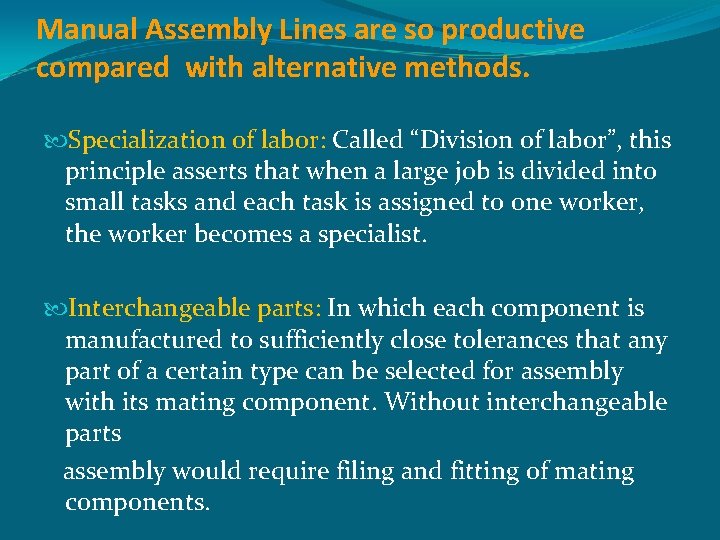
Manual Assembly Lines are so productive compared with alternative methods. Specialization of labor: Called “Division of labor”, this principle asserts that when a large job is divided into small tasks and each task is assigned to one worker, the worker becomes a specialist. Interchangeable parts: In which each component is manufactured to sufficiently close tolerances that any part of a certain type can be selected for assembly with its mating component. Without interchangeable parts assembly would require filing and fitting of mating components.
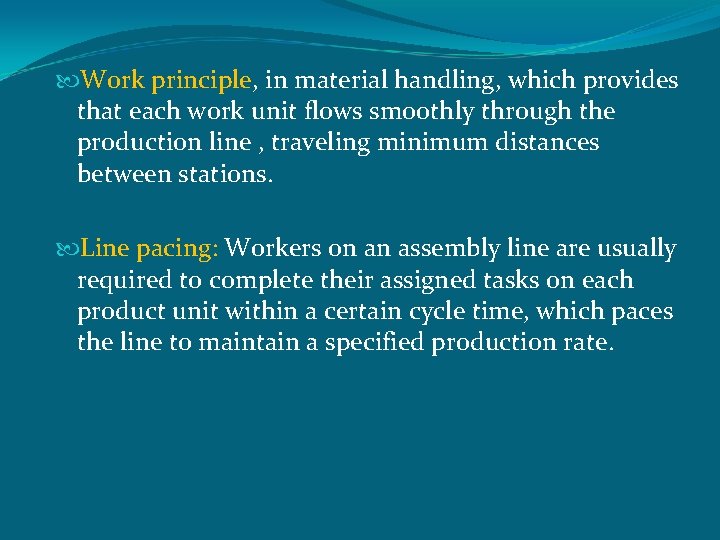
Work principle, in material handling, which provides that each work unit flows smoothly through the production line , traveling minimum distances between stations. Line pacing: Workers on an assembly line are usually required to complete their assigned tasks on each product unit within a certain cycle time, which paces the line to maintain a specified production rate.
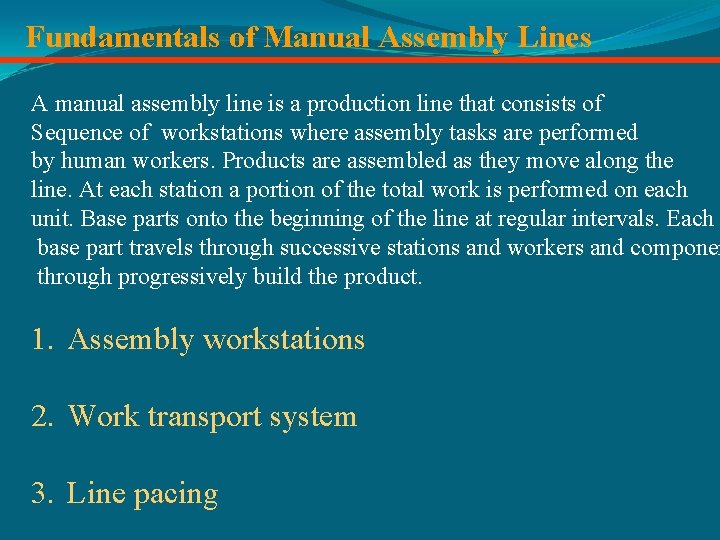
Fundamentals of Manual Assembly Lines A manual assembly line is a production line that consists of Sequence of workstations where assembly tasks are performed by human workers. Products are assembled as they move along the line. At each station a portion of the total work is performed on each unit. Base parts onto the beginning of the line at regular intervals. Each base part travels through successive stations and workers and componen through progressively build the product. 1. Assembly workstations 2. Work transport system 3. Line pacing
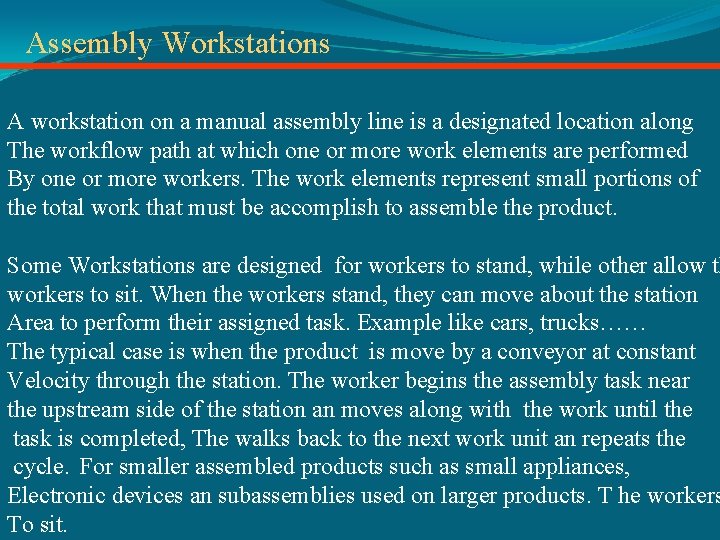
Assembly Workstations A workstation on a manual assembly line is a designated location along The workflow path at which one or more work elements are performed By one or more workers. The work elements represent small portions of the total work that must be accomplish to assemble the product. Some Workstations are designed for workers to stand, while other allow th workers to sit. When the workers stand, they can move about the station Area to perform their assigned task. Example like cars, trucks…… The typical case is when the product is move by a conveyor at constant Velocity through the station. The worker begins the assembly task near the upstream side of the station an moves along with the work until the task is completed, The walks back to the next work unit an repeats the cycle. For smaller assembled products such as small appliances, Electronic devices an subassemblies used on larger products. T he workers To sit.
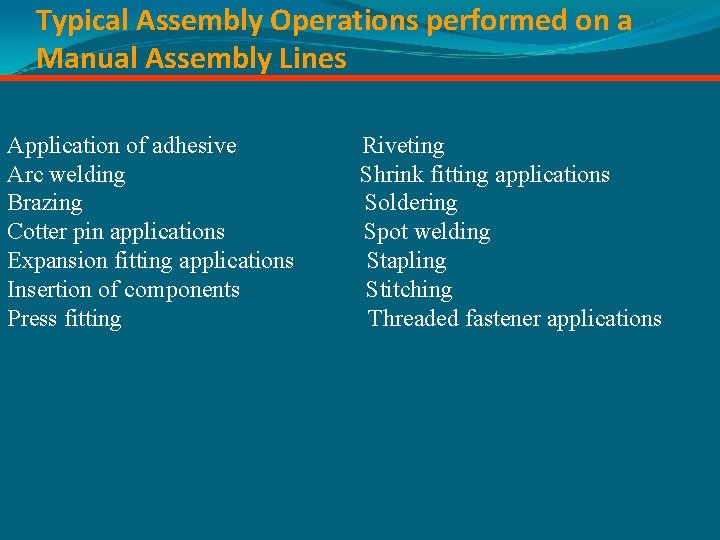
Typical Assembly Operations performed on a Manual Assembly Lines Application of adhesive Arc welding Brazing Cotter pin applications Expansion fitting applications Insertion of components Press fitting Riveting Shrink fitting applications Soldering Spot welding Stapling Stitching Threaded fastener applications
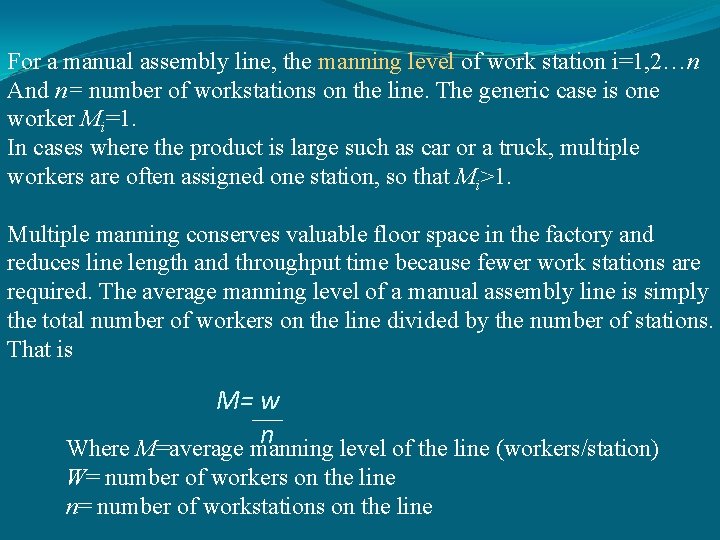
For a manual assembly line, the manning level of work station i=1, 2…n And n= number of workstations on the line. The generic case is one worker Mi=1. In cases where the product is large such as car or a truck, multiple workers are often assigned one station, so that Mi>1. Multiple manning conserves valuable floor space in the factory and reduces line length and throughput time because fewer work stations are required. The average manning level of a manual assembly line is simply the total number of workers on the line divided by the number of stations. That is M= w n Where M=average manning level of the line (workers/station) W= number of workers on the line n= number of workstations on the line
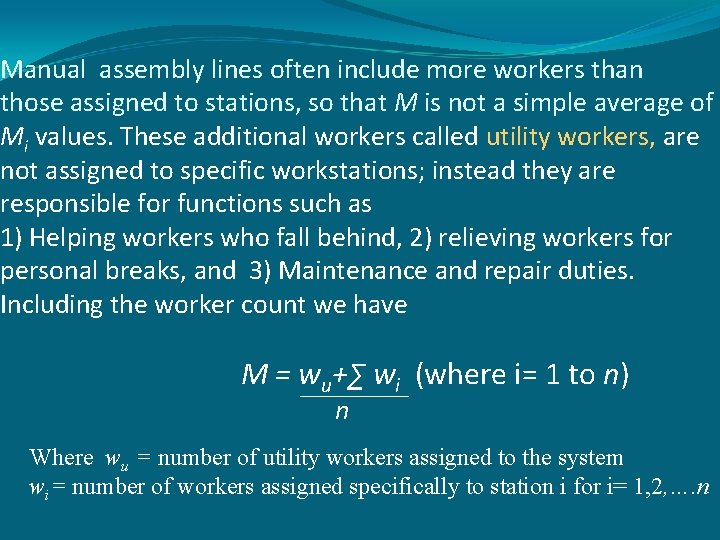
Manual assembly lines often include more workers than those assigned to stations, so that M is not a simple average of Mi values. These additional workers called utility workers, are not assigned to specific workstations; instead they are responsible for functions such as 1) Helping workers who fall behind, 2) relieving workers for personal breaks, and 3) Maintenance and repair duties. Including the worker count we have M = wu+∑ wi (where i= 1 to n) n Where wu = number of utility workers assigned to the system wi= number of workers assigned specifically to station i for i= 1, 2, …. n
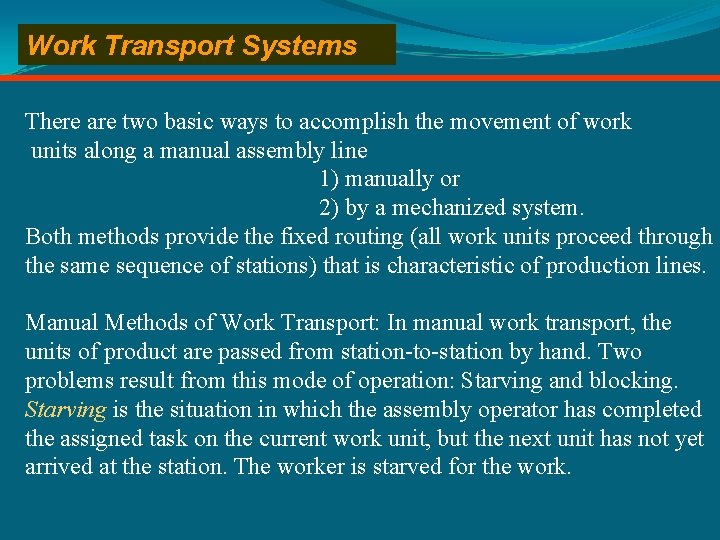
Work Transport Systems There are two basic ways to accomplish the movement of work units along a manual assembly line 1) manually or 2) by a mechanized system. Both methods provide the fixed routing (all work units proceed through the same sequence of stations) that is characteristic of production lines. Manual Methods of Work Transport: In manual work transport, the units of product are passed from station-to-station by hand. Two problems result from this mode of operation: Starving and blocking. Starving is the situation in which the assembly operator has completed the assigned task on the current work unit, but the next unit has not yet arrived at the station. The worker is starved for the work.
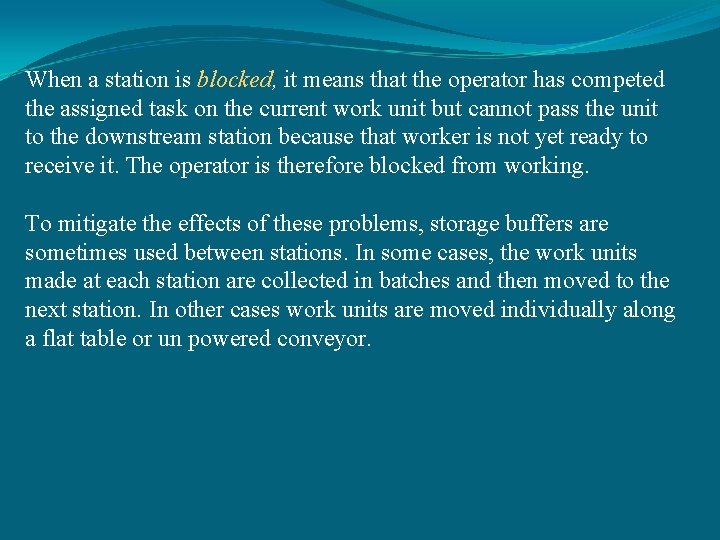
When a station is blocked, it means that the operator has competed the assigned task on the current work unit but cannot pass the unit to the downstream station because that worker is not yet ready to receive it. The operator is therefore blocked from working. To mitigate the effects of these problems, storage buffers are sometimes used between stations. In some cases, the work units made at each station are collected in batches and then moved to the next station. In other cases work units are moved individually along a flat table or un powered conveyor.
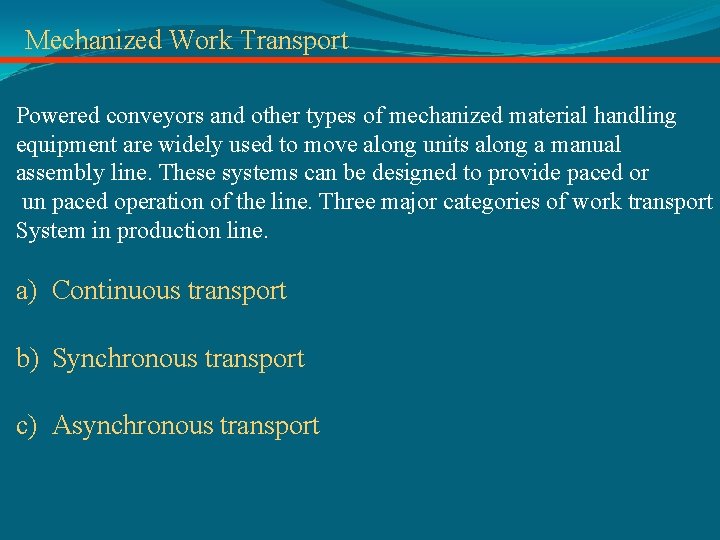
Mechanized Work Transport Powered conveyors and other types of mechanized material handling equipment are widely used to move along units along a manual assembly line. These systems can be designed to provide paced or un paced operation of the line. Three major categories of work transport System in production line. a) Continuous transport b) Synchronous transport c) Asynchronous transport
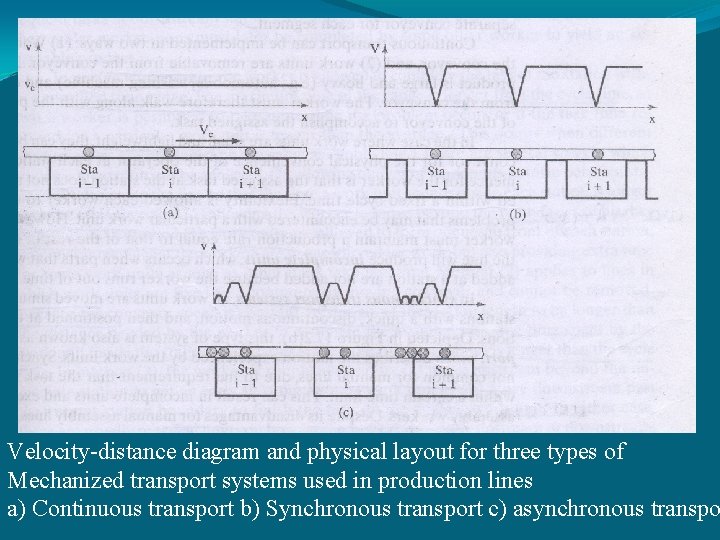
Velocity-distance diagram and physical layout for three types of Mechanized transport systems used in production lines a) Continuous transport b) Synchronous transport c) asynchronous transpo
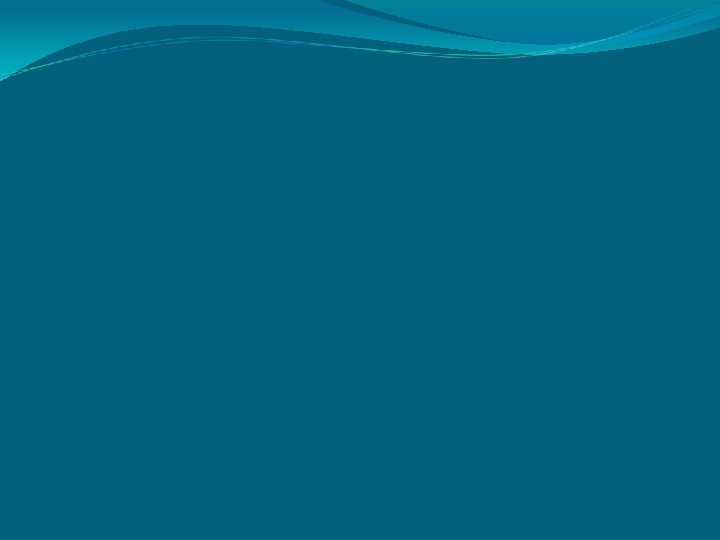
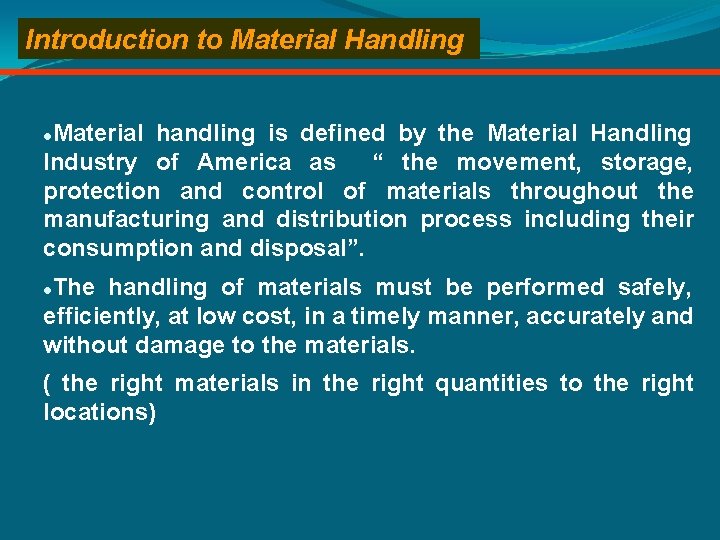
Introduction to Material Handling Material handling is defined by the Material Handling Industry of America as “ the movement, storage, protection and control of materials throughout the manufacturing and distribution process including their consumption and disposal”. l The handling of materials must be performed safely, efficiently, at low cost, in a timely manner, accurately and without damage to the materials. l ( the right materials in the right quantities to the right locations)
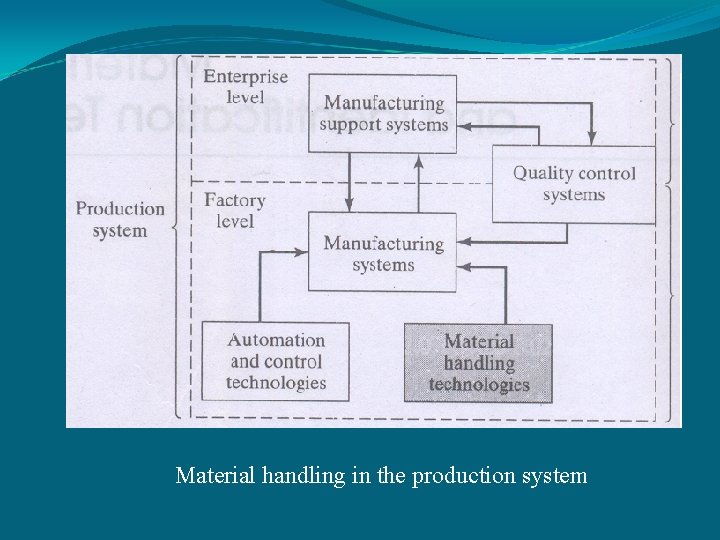
Material handling in the production system
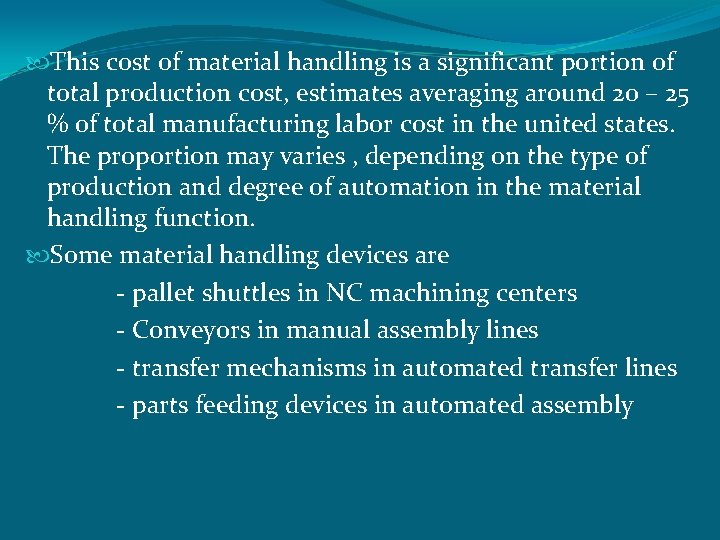
This cost of material handling is a significant portion of total production cost, estimates averaging around 20 – 25 % of total manufacturing labor cost in the united states. The proportion may varies , depending on the type of production and degree of automation in the material handling function. Some material handling devices are - pallet shuttles in NC machining centers - Conveyors in manual assembly lines - transfer mechanisms in automated transfer lines - parts feeding devices in automated assembly
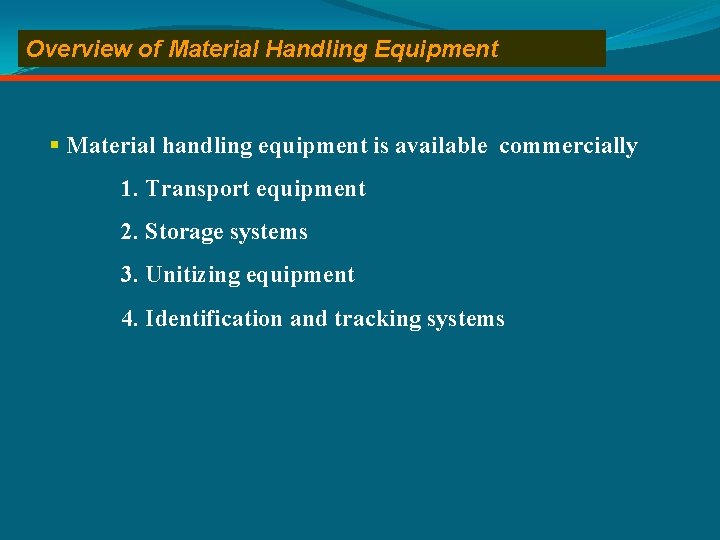
Overview of Material Handling Equipment § Material handling equipment is available commercially 1. Transport equipment 2. Storage systems 3. Unitizing equipment 4. Identification and tracking systems
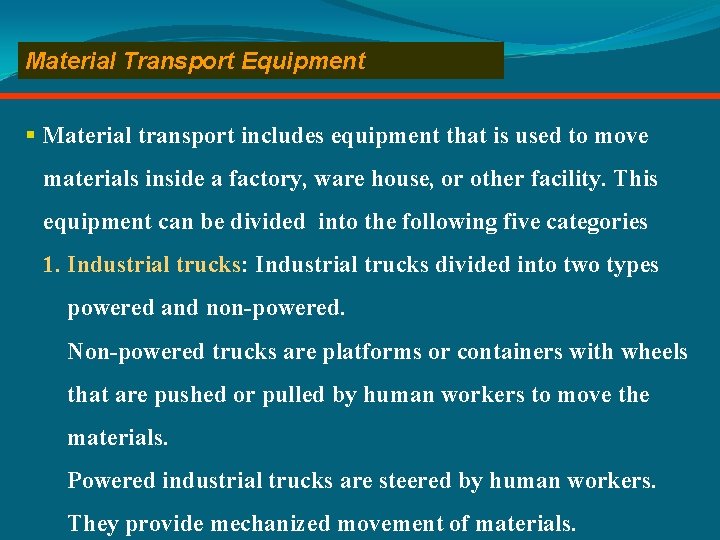
Material Transport Equipment § Material transport includes equipment that is used to move materials inside a factory, ware house, or other facility. This equipment can be divided into the following five categories 1. Industrial trucks: Industrial trucks divided into two types powered and non-powered. Non-powered trucks are platforms or containers with wheels that are pushed or pulled by human workers to move the materials. Powered industrial trucks are steered by human workers. They provide mechanized movement of materials.
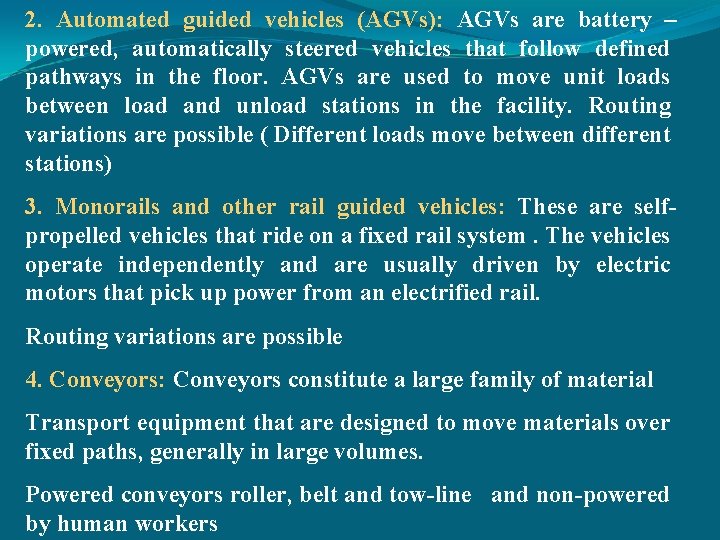
2. Automated guided vehicles (AGVs): AGVs are battery – powered, automatically steered vehicles that follow defined pathways in the floor. AGVs are used to move unit loads between load and unload stations in the facility. Routing variations are possible ( Different loads move between different stations) 3. Monorails and other rail guided vehicles: These are selfpropelled vehicles that ride on a fixed rail system. The vehicles operate independently and are usually driven by electric motors that pick up power from an electrified rail. Routing variations are possible 4. Conveyors: Conveyors constitute a large family of material Transport equipment that are designed to move materials over fixed paths, generally in large volumes. Powered conveyors roller, belt and tow-line and non-powered by human workers
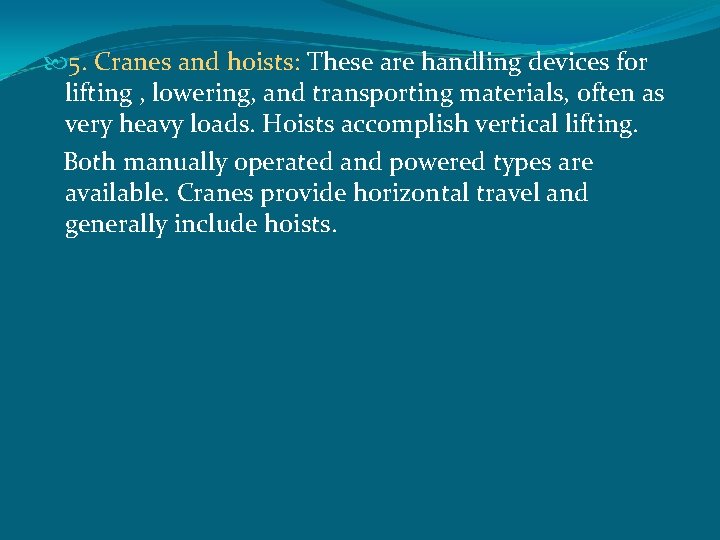
5. Cranes and hoists: These are handling devices for lifting , lowering, and transporting materials, often as very heavy loads. Hoists accomplish vertical lifting. Both manually operated and powered types are available. Cranes provide horizontal travel and generally include hoists.
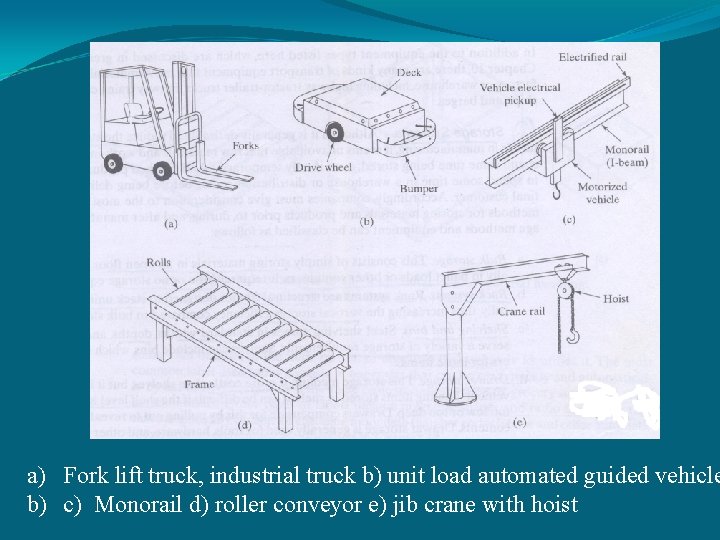
a) Fork lift truck, industrial truck b) unit load automated guided vehicle b) c) Monorail d) roller conveyor e) jib crane with hoist
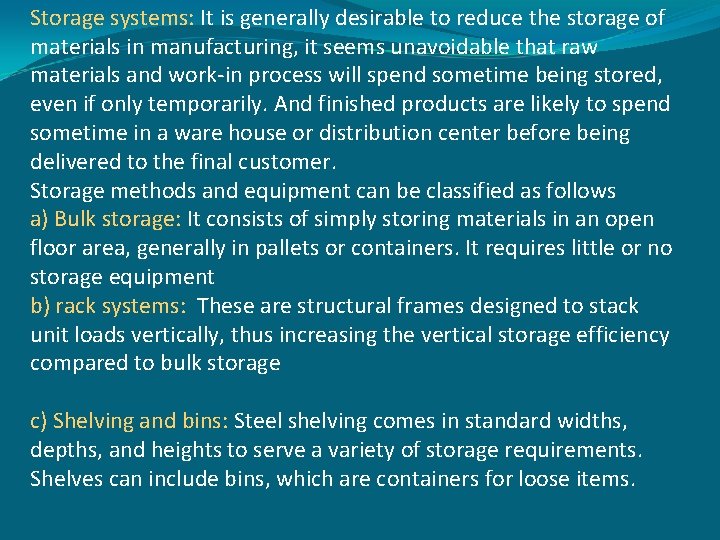
Storage systems: It is generally desirable to reduce the storage of materials in manufacturing, it seems unavoidable that raw materials and work-in process will spend sometime being stored, even if only temporarily. And finished products are likely to spend sometime in a ware house or distribution center before being delivered to the final customer. Storage methods and equipment can be classified as follows a) Bulk storage: It consists of simply storing materials in an open floor area, generally in pallets or containers. It requires little or no storage equipment b) rack systems: These are structural frames designed to stack unit loads vertically, thus increasing the vertical storage efficiency compared to bulk storage c) Shelving and bins: Steel shelving comes in standard widths, depths, and heights to serve a variety of storage requirements. Shelves can include bins, which are containers for loose items.
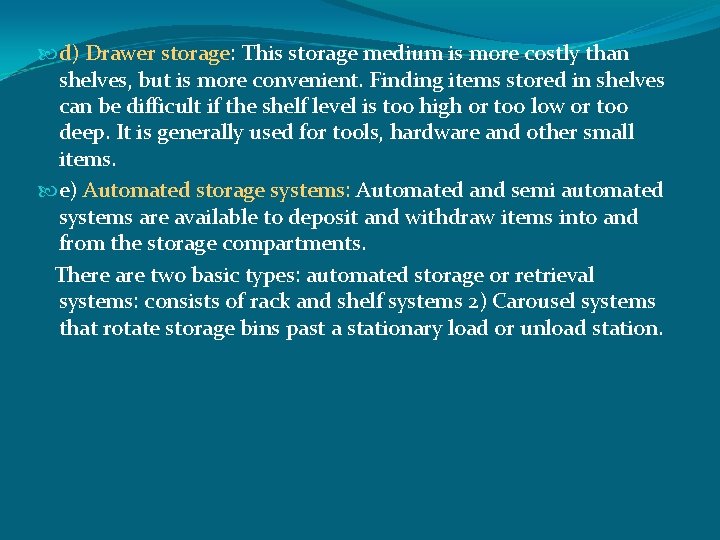
d) Drawer storage: This storage medium is more costly than shelves, but is more convenient. Finding items stored in shelves can be difficult if the shelf level is too high or too low or too deep. It is generally used for tools, hardware and other small items. e) Automated storage systems: Automated and semi automated systems are available to deposit and withdraw items into and from the storage compartments. There are two basic types: automated storage or retrieval systems: consists of rack and shelf systems 2) Carousel systems that rotate storage bins past a stationary load or unload station.
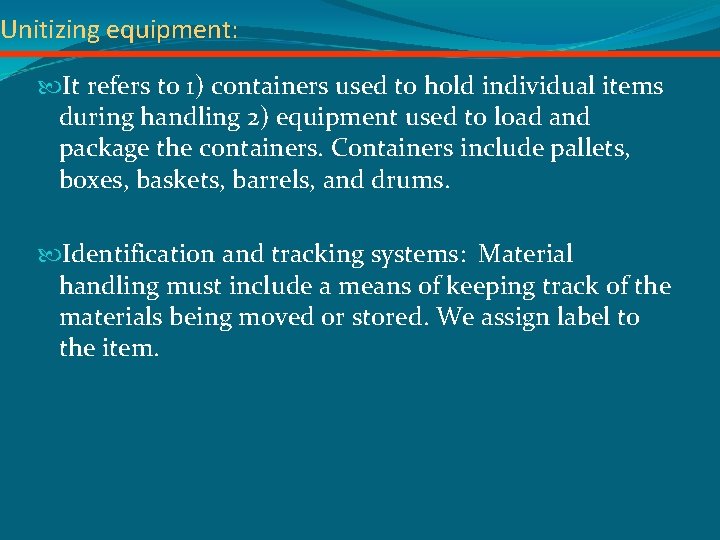
Unitizing equipment: It refers to 1) containers used to hold individual items during handling 2) equipment used to load and package the containers. Containers include pallets, boxes, baskets, barrels, and drums. Identification and tracking systems: Material handling must include a means of keeping track of the materials being moved or stored. We assign label to the item.
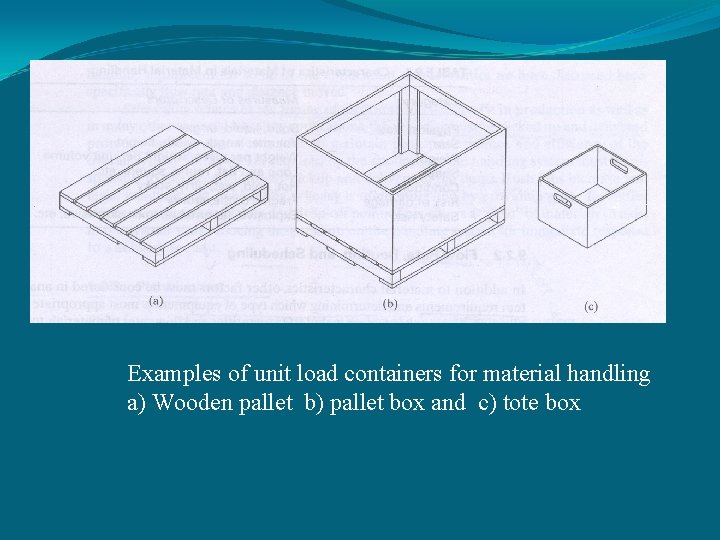
Examples of unit load containers for material handling a) Wooden pallet b) pallet box and c) tote box
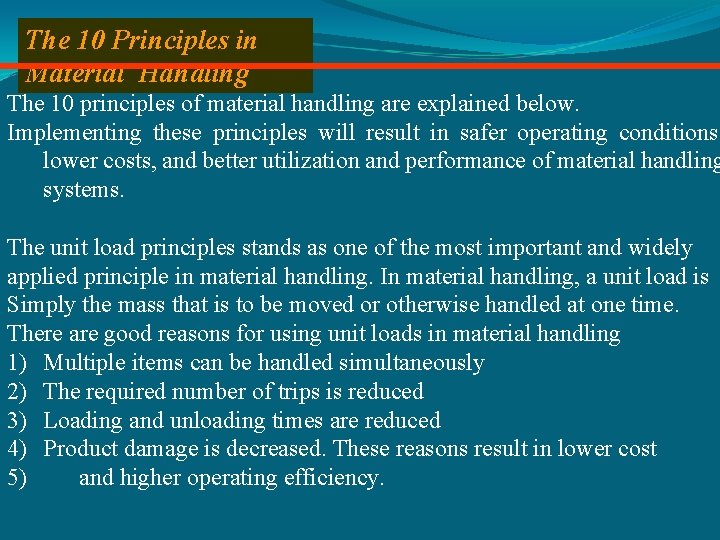
The 10 Principles in Material Handling The 10 principles of material handling are explained below. Implementing these principles will result in safer operating conditions, lower costs, and better utilization and performance of material handling systems. The unit load principles stands as one of the most important and widely applied principle in material handling. In material handling, a unit load is Simply the mass that is to be moved or otherwise handled at one time. There are good reasons for using unit loads in material handling 1) Multiple items can be handled simultaneously 2) The required number of trips is reduced 3) Loading and unloading times are reduced 4) Product damage is decreased. These reasons result in lower cost 5) and higher operating efficiency.
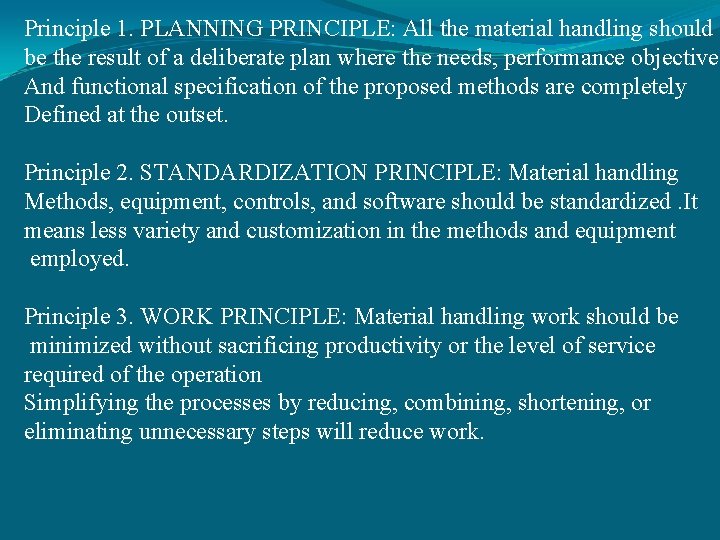
Principle 1. PLANNING PRINCIPLE: All the material handling should be the result of a deliberate plan where the needs, performance objectives And functional specification of the proposed methods are completely Defined at the outset. Principle 2. STANDARDIZATION PRINCIPLE: Material handling Methods, equipment, controls, and software should be standardized. It means less variety and customization in the methods and equipment employed. Principle 3. WORK PRINCIPLE: Material handling work should be minimized without sacrificing productivity or the level of service required of the operation Simplifying the processes by reducing, combining, shortening, or eliminating unnecessary steps will reduce work.
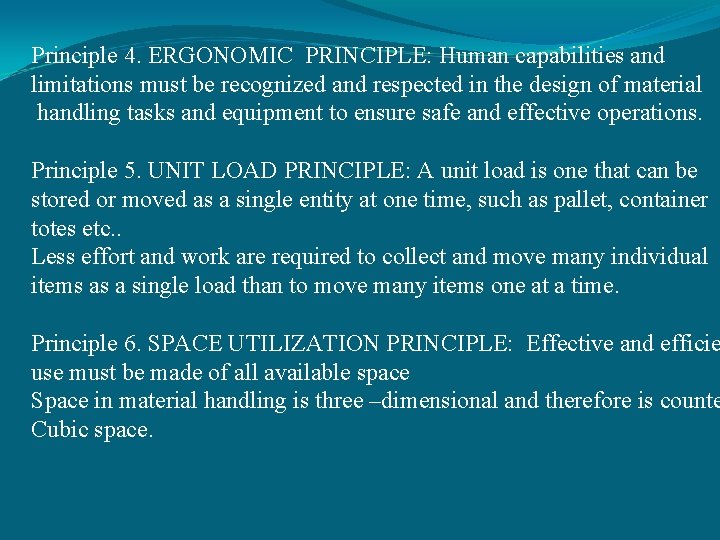
Principle 4. ERGONOMIC PRINCIPLE: Human capabilities and limitations must be recognized and respected in the design of material handling tasks and equipment to ensure safe and effective operations. Principle 5. UNIT LOAD PRINCIPLE: A unit load is one that can be stored or moved as a single entity at one time, such as pallet, container totes etc. . Less effort and work are required to collect and move many individual items as a single load than to move many items one at a time. Principle 6. SPACE UTILIZATION PRINCIPLE: Effective and efficie use must be made of all available space Space in material handling is three –dimensional and therefore is counte Cubic space.
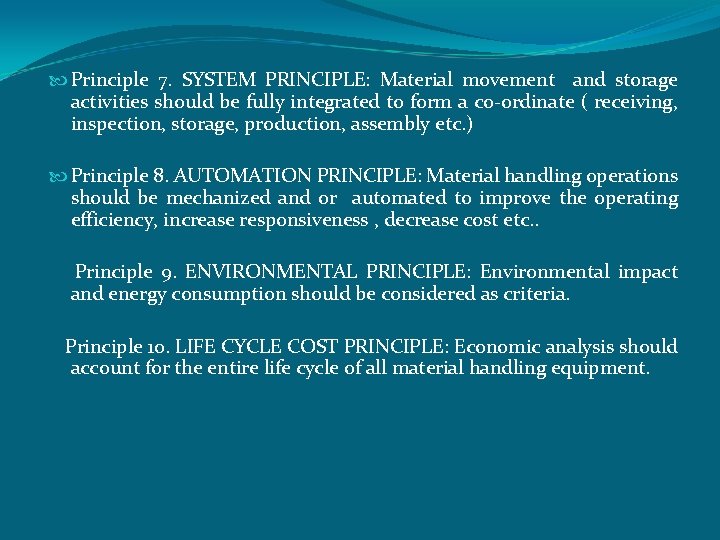
Principle 7. SYSTEM PRINCIPLE: Material movement and storage activities should be fully integrated to form a co-ordinate ( receiving, inspection, storage, production, assembly etc. ) Principle 8. AUTOMATION PRINCIPLE: Material handling operations should be mechanized and or automated to improve the operating efficiency, increase responsiveness , decrease cost etc. . Principle 9. ENVIRONMENTAL PRINCIPLE: Environmental impact and energy consumption should be considered as criteria. Principle 10. LIFE CYCLE COST PRINCIPLE: Economic analysis should account for the entire life cycle of all material handling equipment.
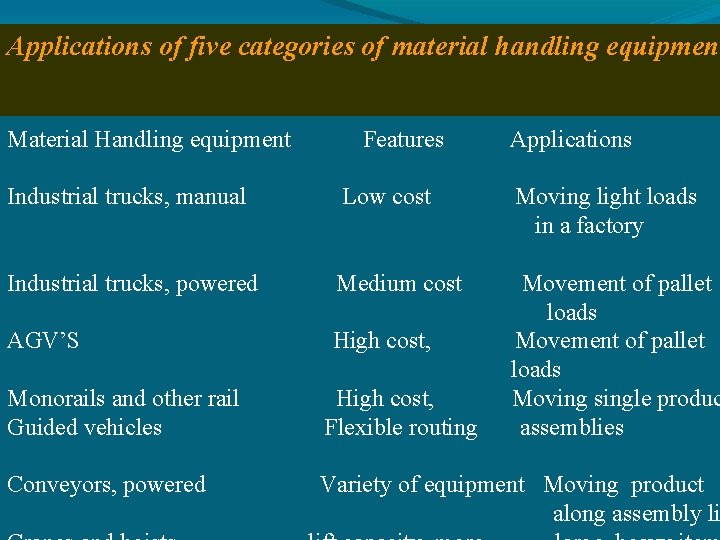
Applications of five categories of material handling equipment Material Handling equipment Features Applications Industrial trucks, manual Low cost Moving light loads in a factory Industrial trucks, powered Medium cost AGV’S High cost, Movement of pallet loads Moving single produc assemblies Monorails and other rail Guided vehicles High cost, Flexible routing Conveyors, powered Variety of equipment Moving product along assembly li
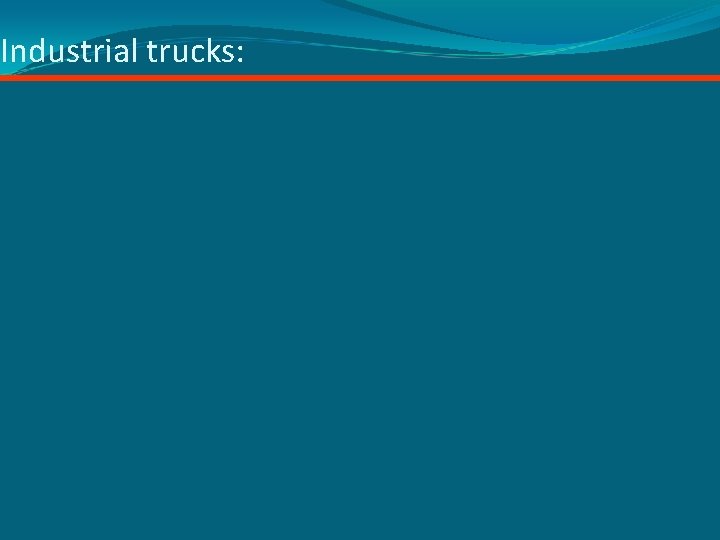
Industrial trucks:
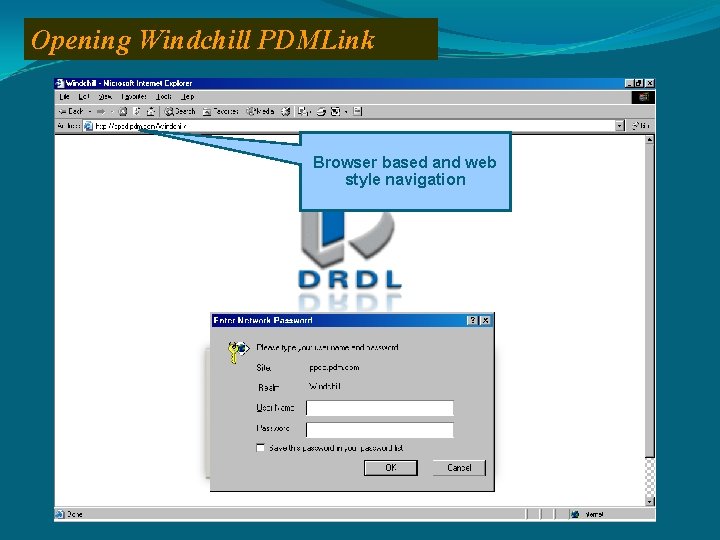
Opening Windchill PDMLink Browser based and web style navigation
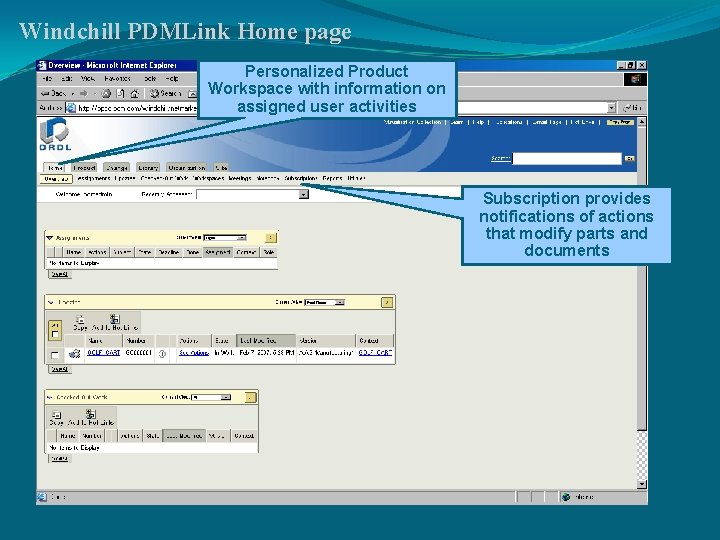
Windchill PDMLink Home page Personalized Product Workspace with information on assigned user activities Subscription provides notifications of actions that modify parts and documents
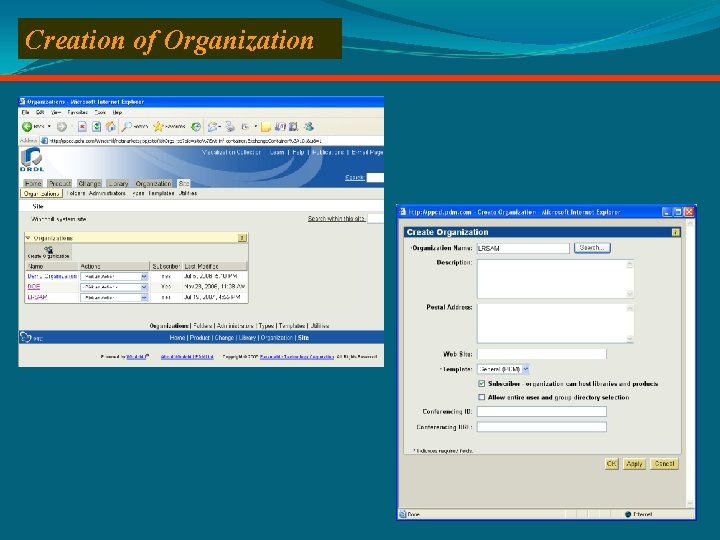
Creation of Organization
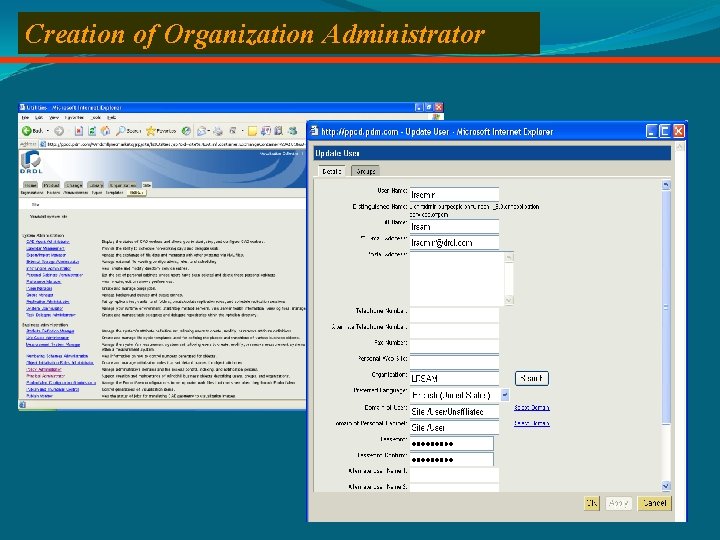
Creation of Organization Administrator
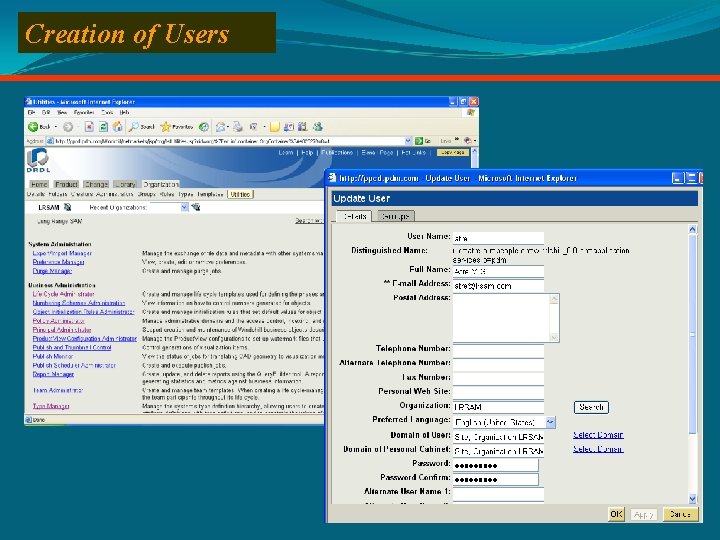
Creation of Users
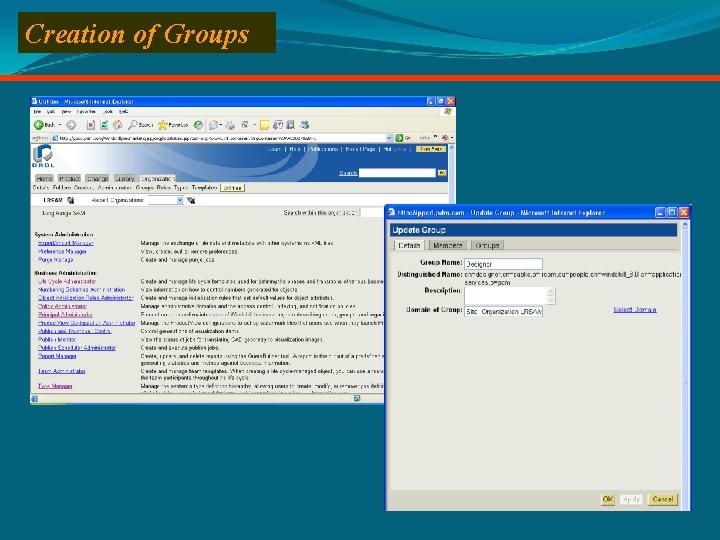
Creation of Groups
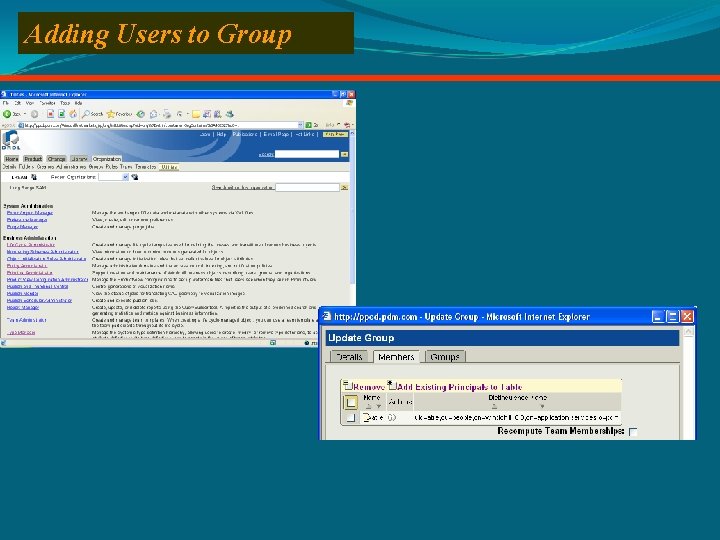
Adding Users to Group
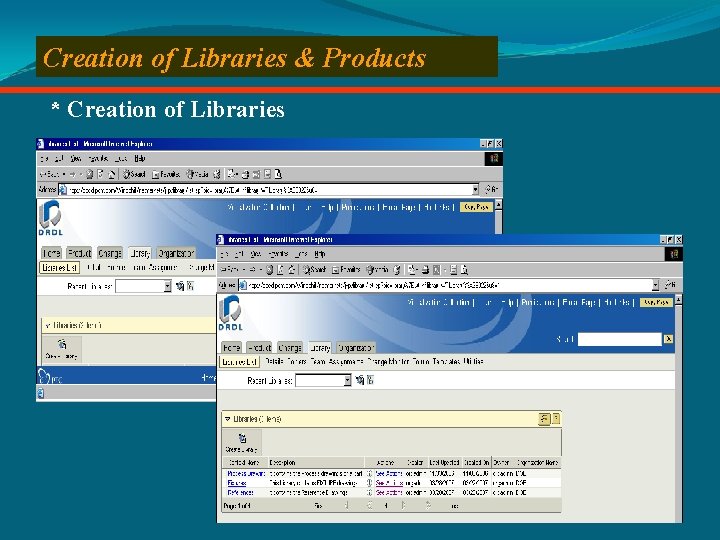
Creation of Libraries & Products * Creation of Libraries
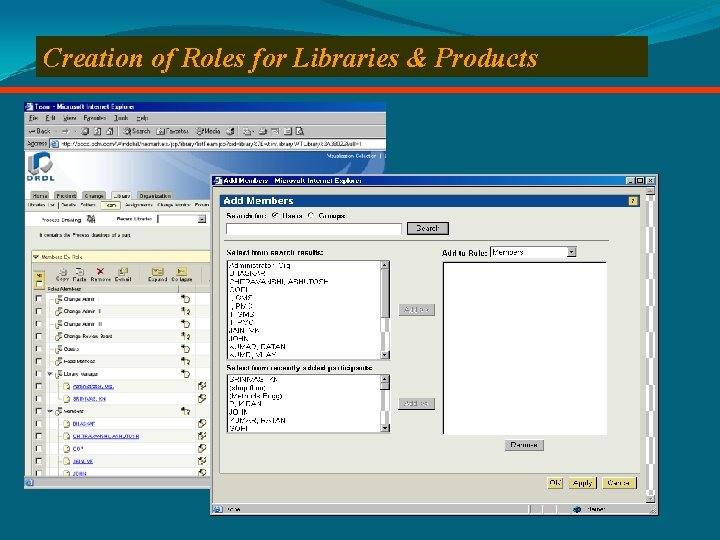
Creation of Roles for Libraries & Products
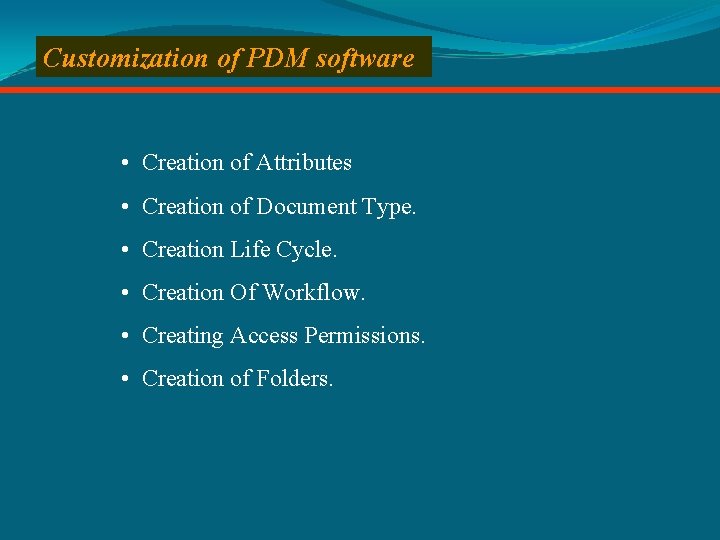
Customization of PDM software • Creation of Attributes • Creation of Document Type. • Creation Life Cycle. • Creation Of Workflow. • Creating Access Permissions. • Creation of Folders.
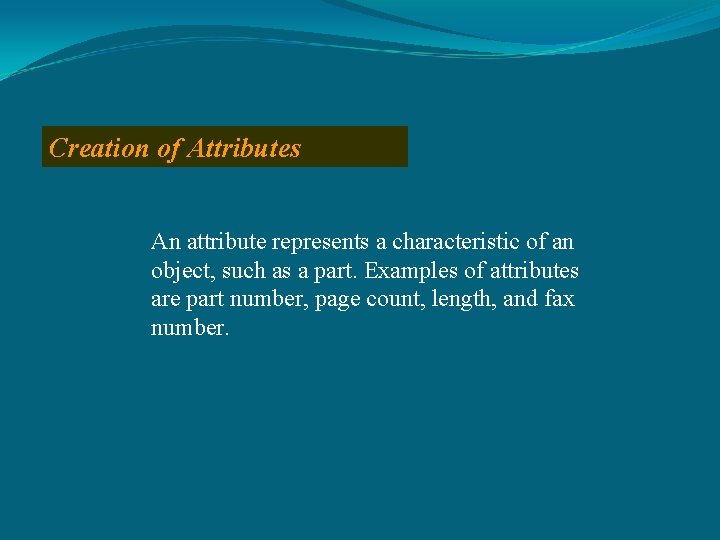
Creation of Attributes An attribute represents a characteristic of an object, such as a part. Examples of attributes are part number, page count, length, and fax number.
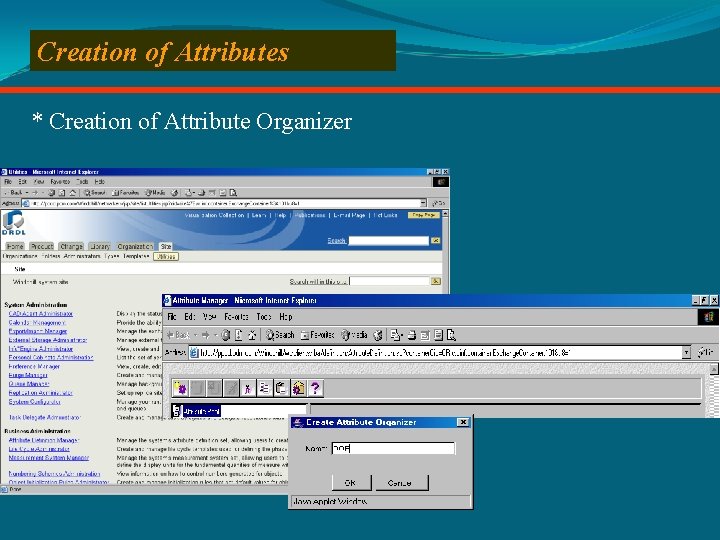
Creation of Attributes * Creation of Attribute Organizer
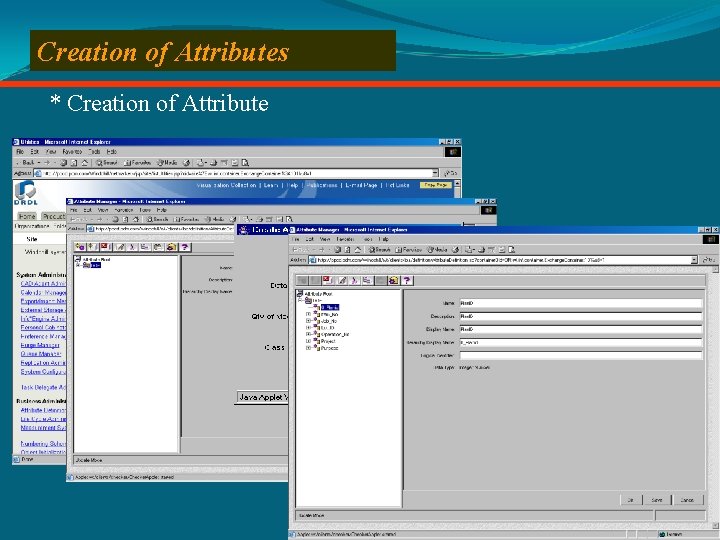
Creation of Attributes * Creation of Attribute
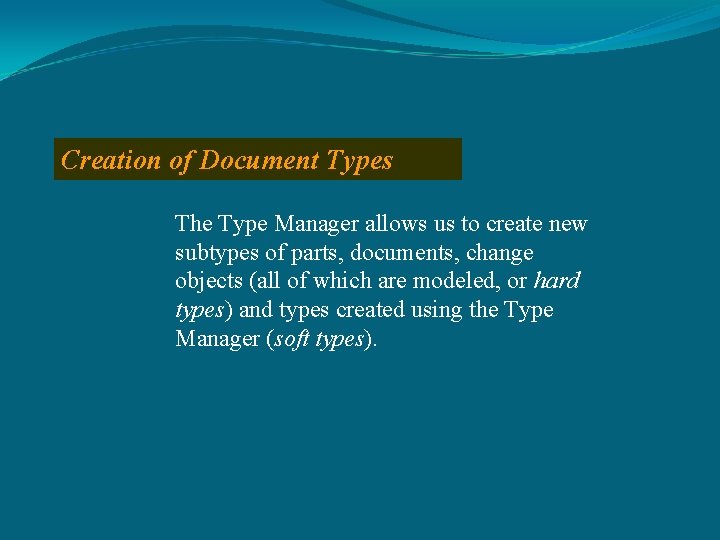
Creation of Document Types The Type Manager allows us to create new subtypes of parts, documents, change objects (all of which are modeled, or hard types) and types created using the Type Manager (soft types).
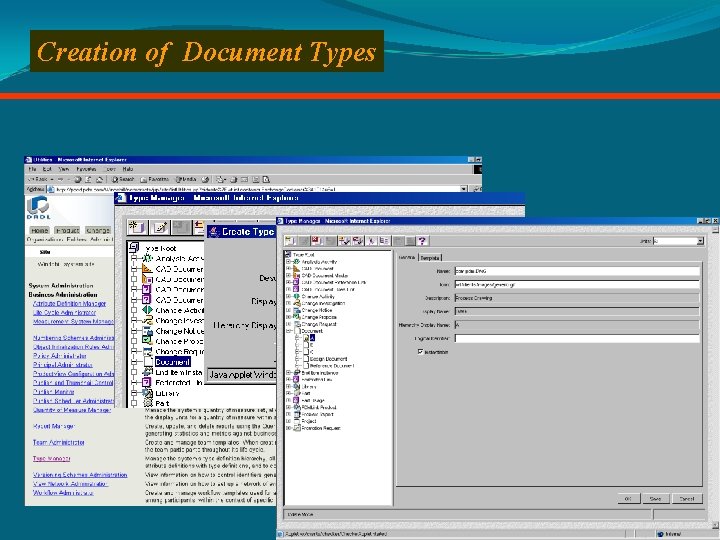
Creation of Document Types
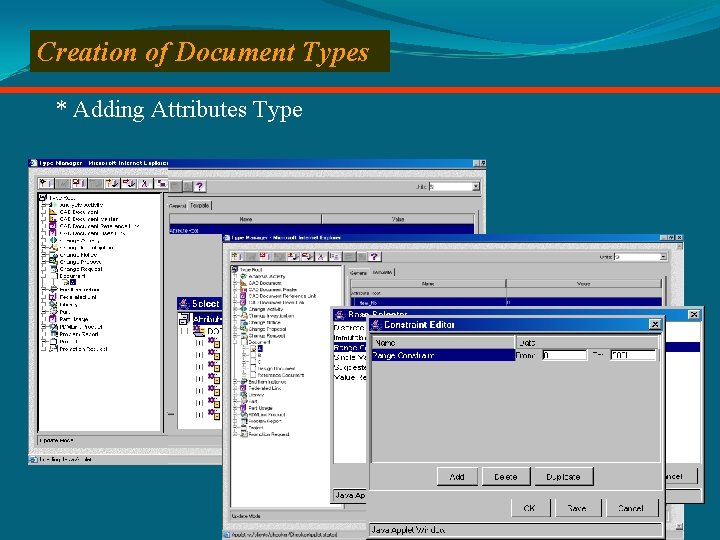
Creation of Document Types * Adding Attributes Type
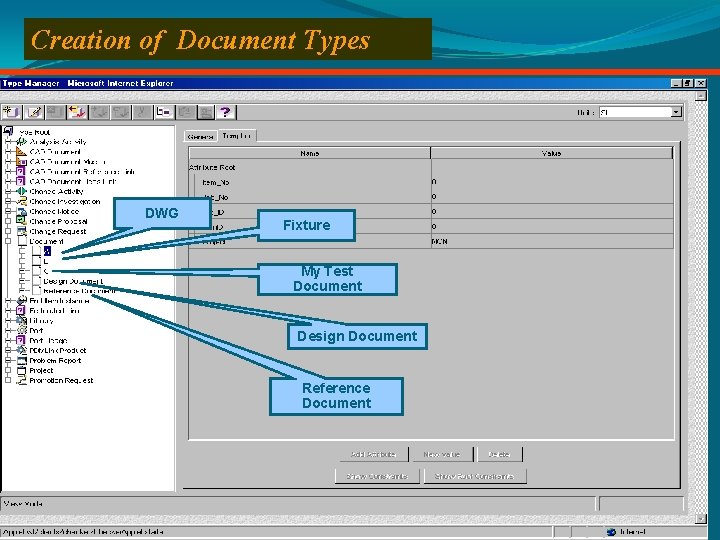
Creation of Document Types DWG Fixture My Test Document Design Document Reference Document
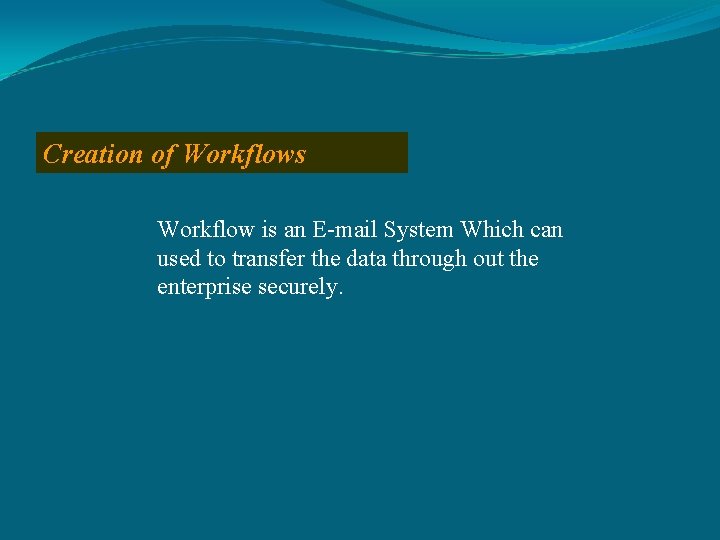
Creation of Workflows Workflow is an E-mail System Which can used to transfer the data through out the enterprise securely.
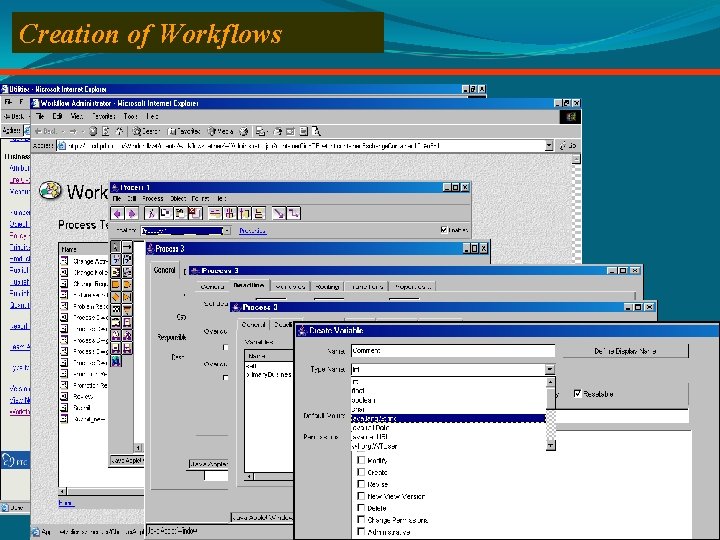
Creation of Workflows
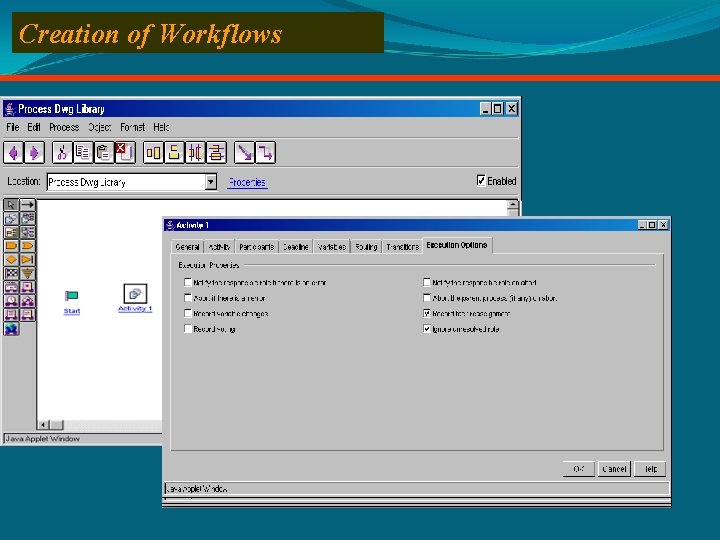
Creation of Workflows
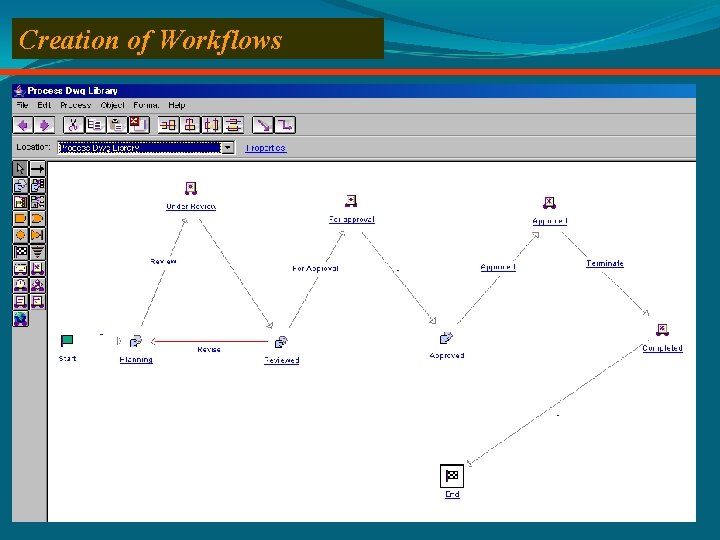
Creation of Workflows
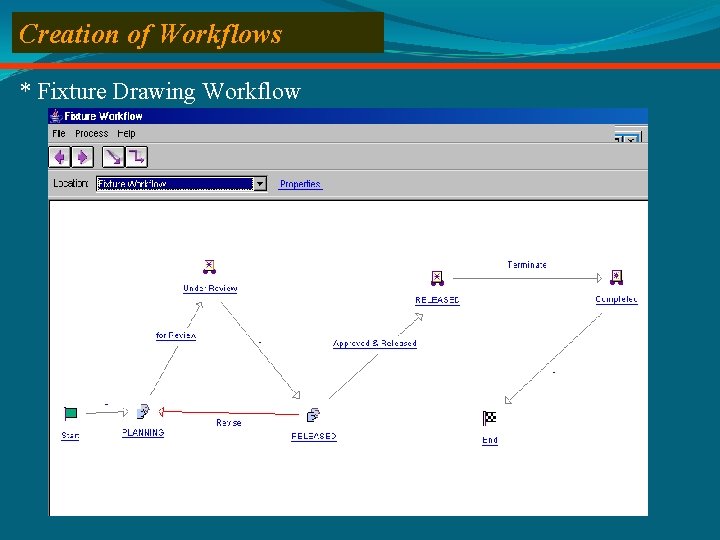
Creation of Workflows * Fixture Drawing Workflow
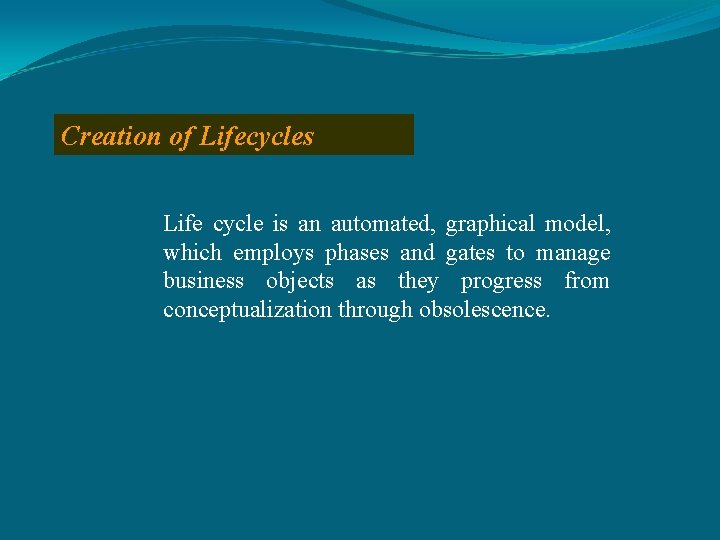
Creation of Lifecycles Life cycle is an automated, graphical model, which employs phases and gates to manage business objects as they progress from conceptualization through obsolescence.
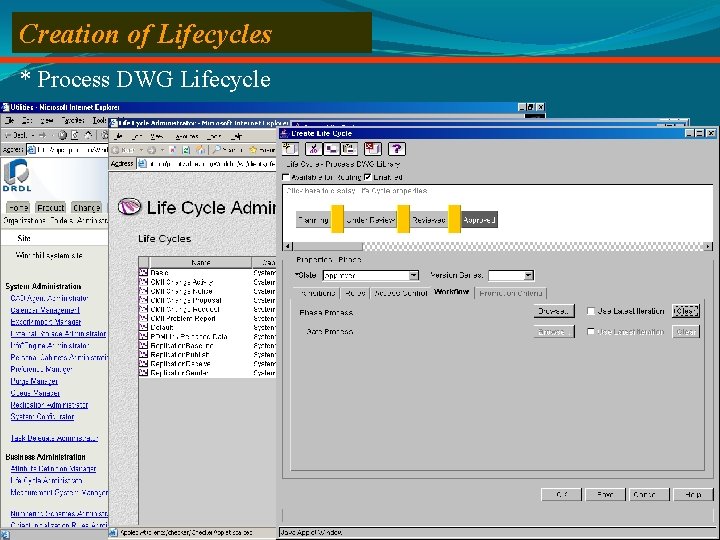
Creation of Lifecycles * Process DWG Lifecycle
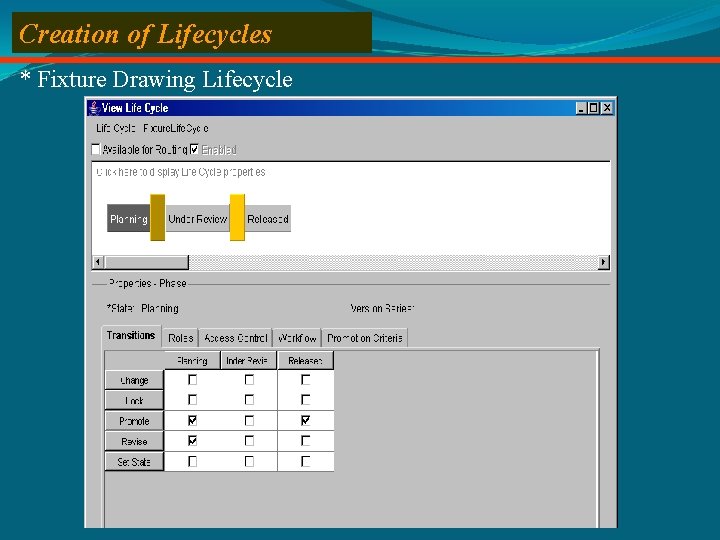
Creation of Lifecycles * Fixture Drawing Lifecycle
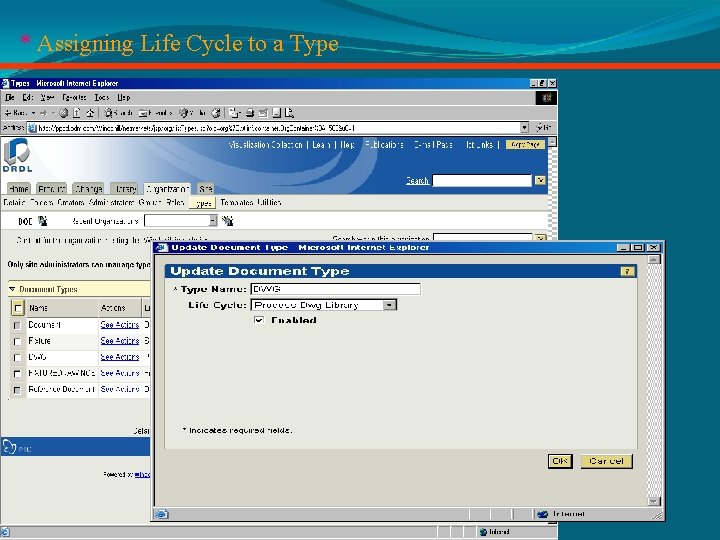
* Assigning Life Cycle to a Type
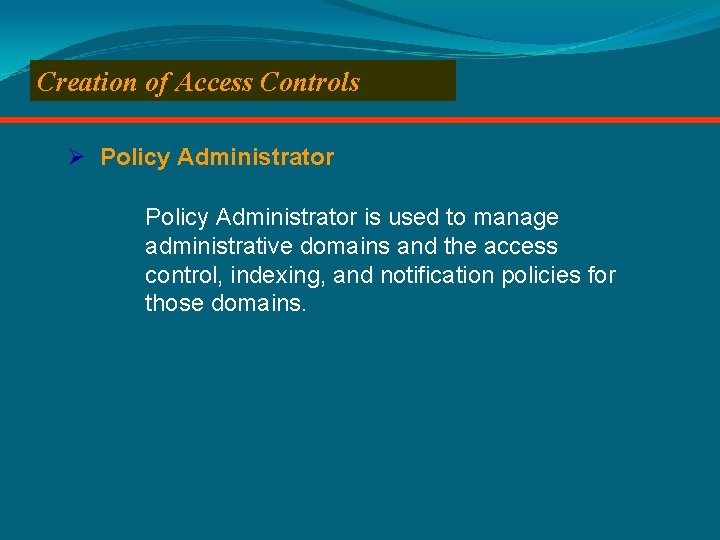
Creation of Access Controls Ø Policy Administrator is used to manage administrative domains and the access control, indexing, and notification policies for those domains.
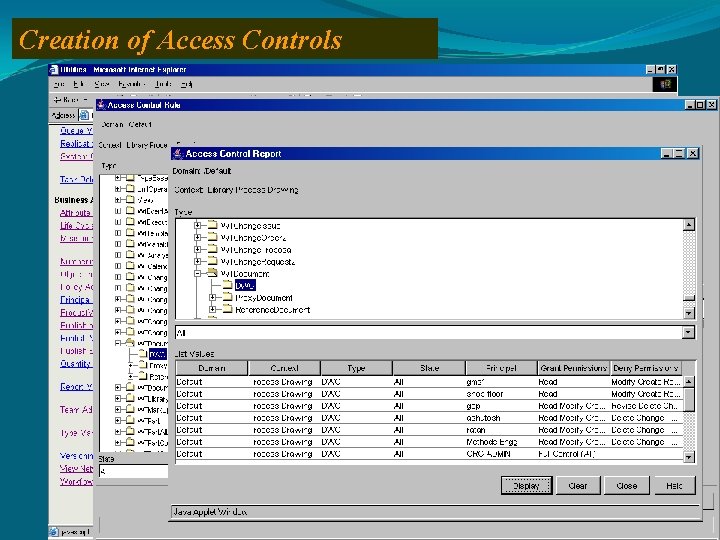
Creation of Access Controls
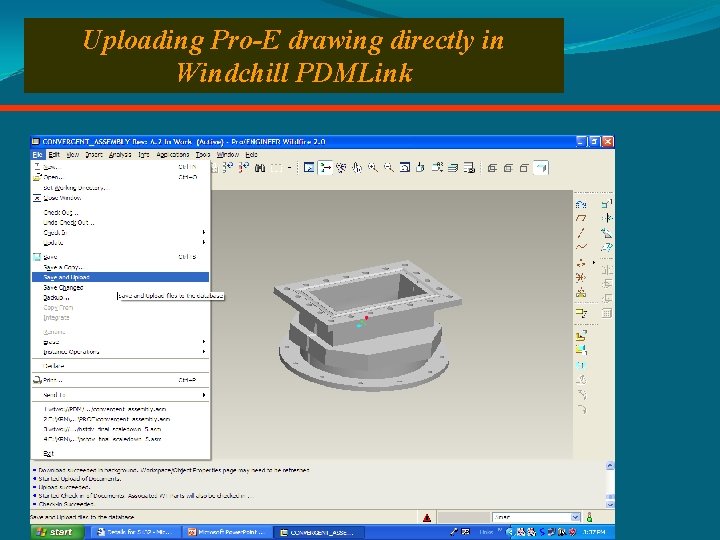
Uploading Pro-E drawing directly in Windchill PDMLink
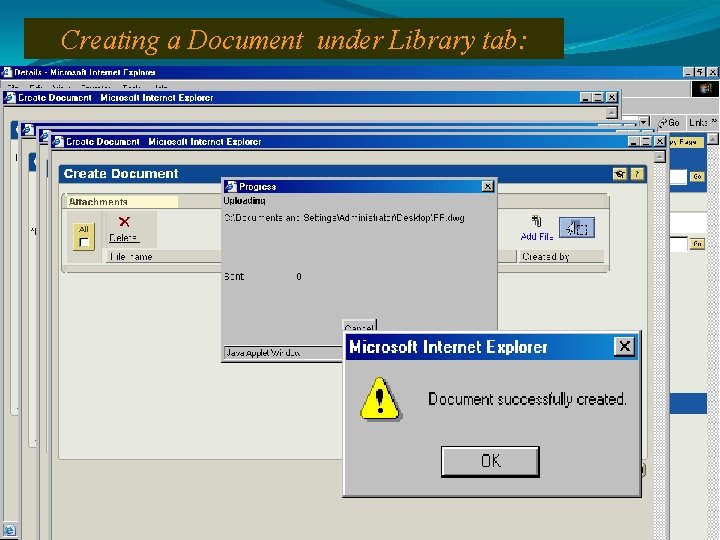
Creating a Document under Library tab:
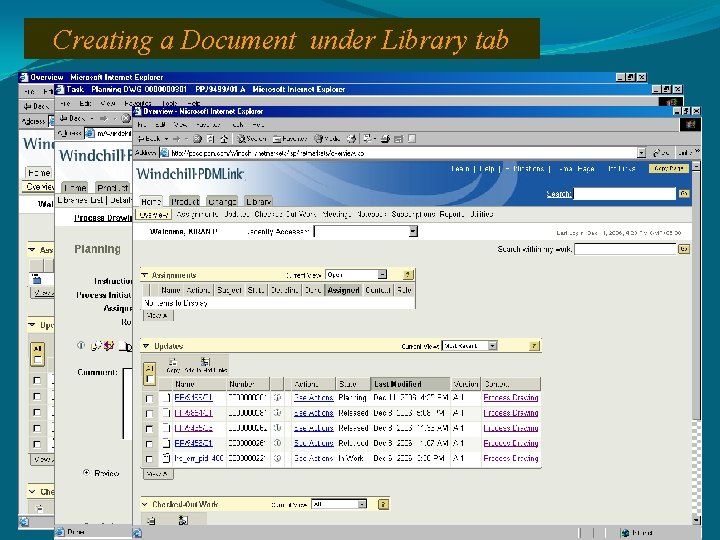
Creating a Document under Library tab
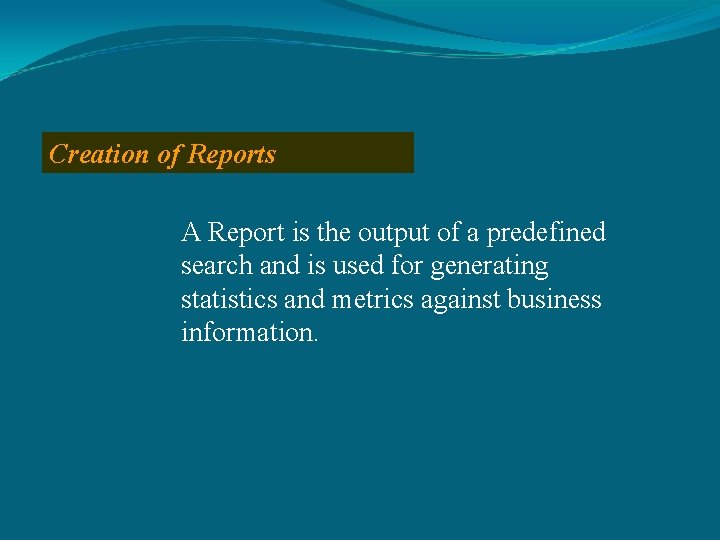
Creation of Reports A Report is the output of a predefined search and is used for generating statistics and metrics against business information.
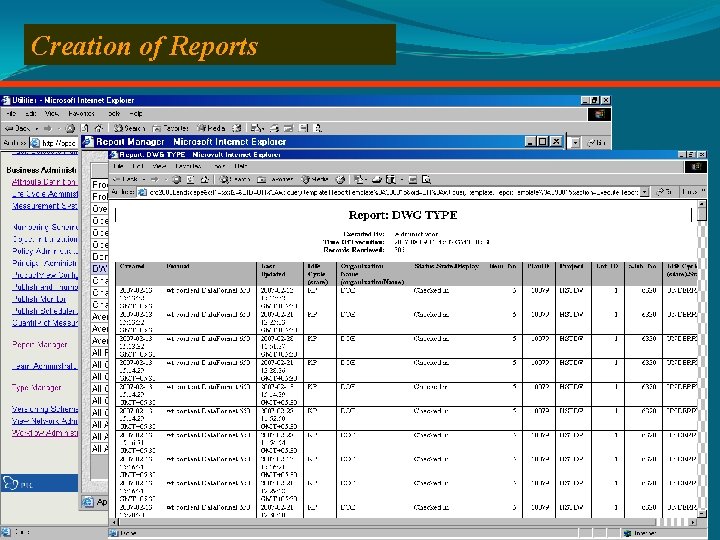
Creation of Reports
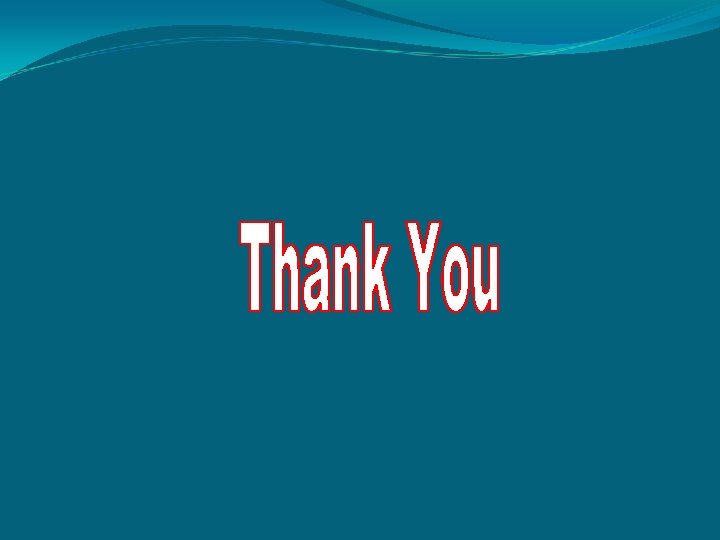
Hoe sneller hoe beter
Gelijknamige breuk
Job costing definition
Manufacturing cost vs non manufacturing cost
Manufacturing cost vs non manufacturing cost
Manufacturing cost vs non manufacturing cost
Additive manufacturing steps
Ipv foo
Ipv foo
Spring foo
Interface myinterface int foo(int x)
Def foo(n)
Foo joon liang
Interface foo int k=0
Define:foo
Class a void foo() throws exception
Foo
Joo hee jin
Jin kwan ho
Aqa a level psychology specification
Ibig sabihin ng sining
Dong nao jin
Plvi
David jin caltech
Proworx
Jin ji du li
Jin pc template
"hong jin pai"
Jin-yi yu
Liu xiang
Jingshan primary
Jin won lee
Jin tpn
Yandi jin
Belle jin
Zuo tian shi ji yue ji hao
Shengmin jin
American born chinese transformer
Eujin goh
Laura hope chaffey college
Sonu hyang hui
Jin ling cigarettes
Ruoming jin
Unsur manusia
Jin frame data
Jin-fa lee
Min jin ha
Dummynet
Dr. jin-ichi sasaki
Jin koda
Dxn dato' dr. lim siow jin
Xiao hongchi poisoned blood therapy
Hoe ziet een kip eruit
Hoe heet dit
Aadrijkskunde
Onderdelen boom
Elektrische katrollen en takels
Hoe maak ik een gedicht
Kanarie eieren
Hoe werkt een mondharmonica
Hoe heet dit
Spreukbeurt
Stappenplan zinsdelen
Intensiewe vorm van ryp
Voorbeeld informele brief
Reactiewarmte
Lijdende zin en bedrijvende zin
Inleiding voorbeeld stageverslag
Hoe teken je een loodlijn
Toolboxmeeting betekenis
Hoe ontstaat een trend
Functie gewrichtssmeer
Plaatsbepaling op aarde
Mazouttank overpompen
Pedagogische driehoek
Hoe maak mens
Brown paper sessie kleuren
Hoe
Weerklank 359
Verschil hypocentrum en epicentrum
Intracutaan injecteren betekenis
Hoe vind je het lijdend voorwerp
Hoe dept
Klein seminarie hoogstraten smartschool
Wie heeft volleybal bedacht
Vraaglijn en aanbodlijn tekenen
Burs classification
Seed drill jethro tull
Hoe herken je de inleiding van een tekst
Beschouwing
Hoe schrijf je een abstract