ANTRC 170V3 Training Unit 4 Operations Operations Overview
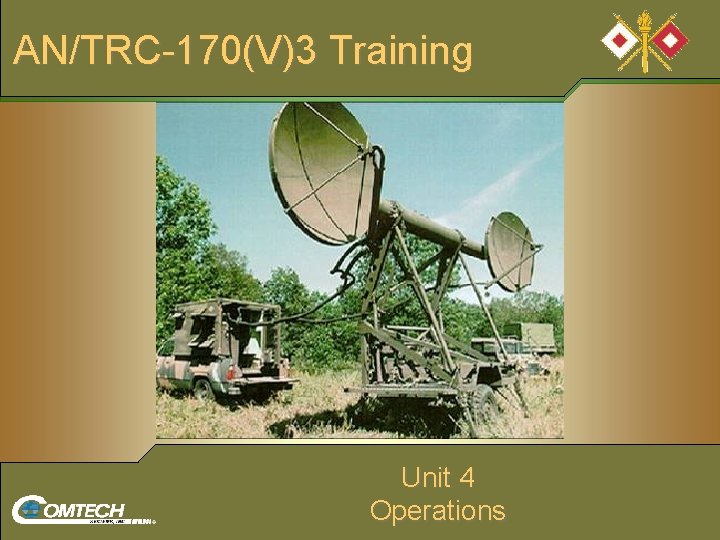
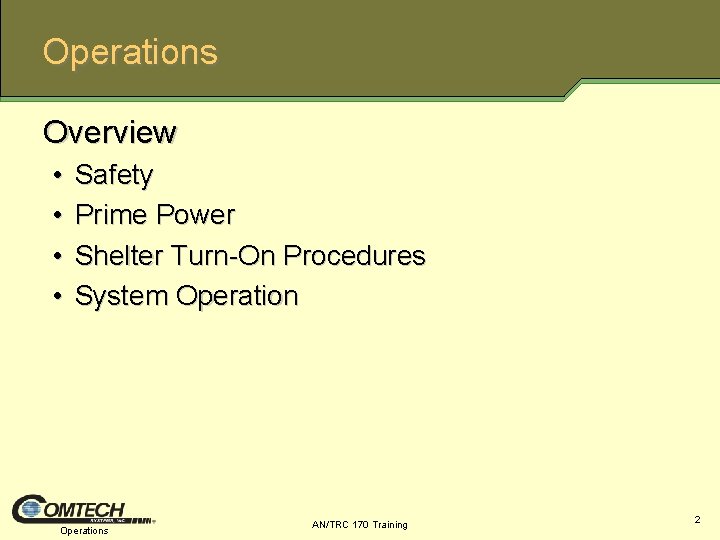


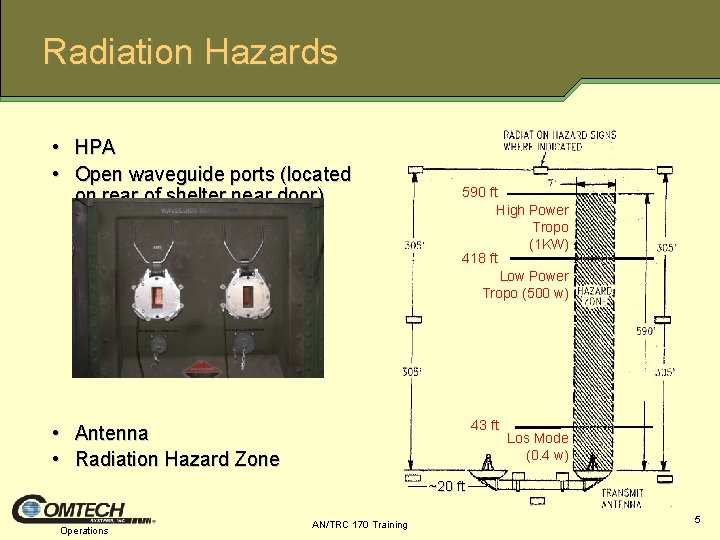
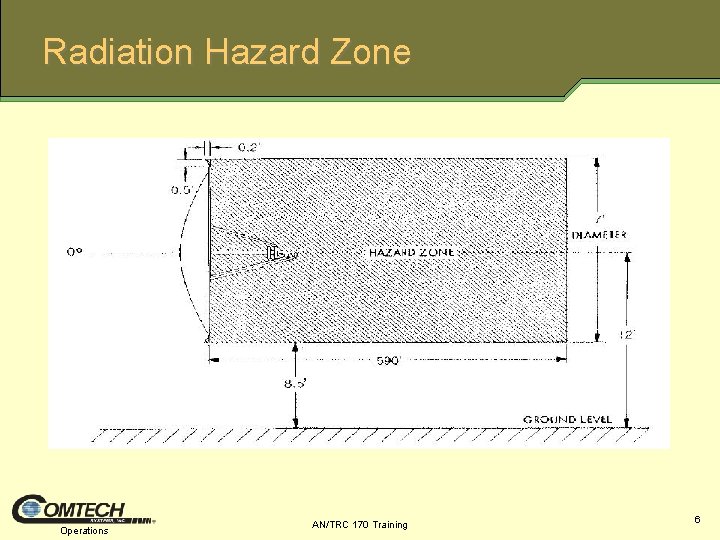
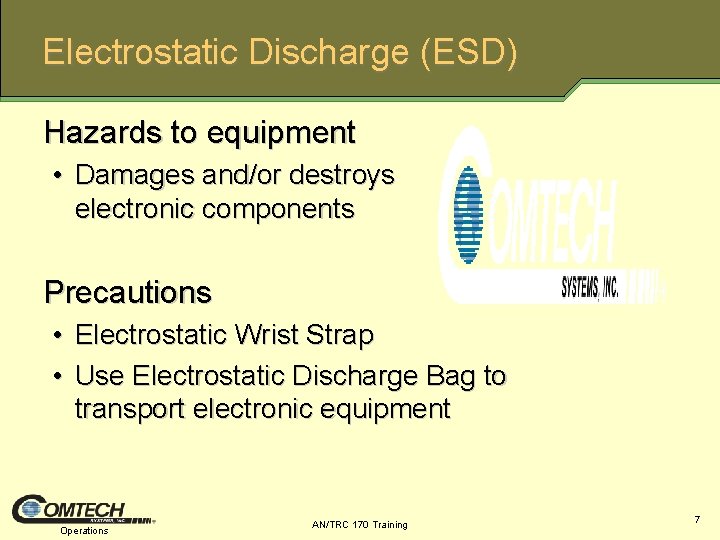
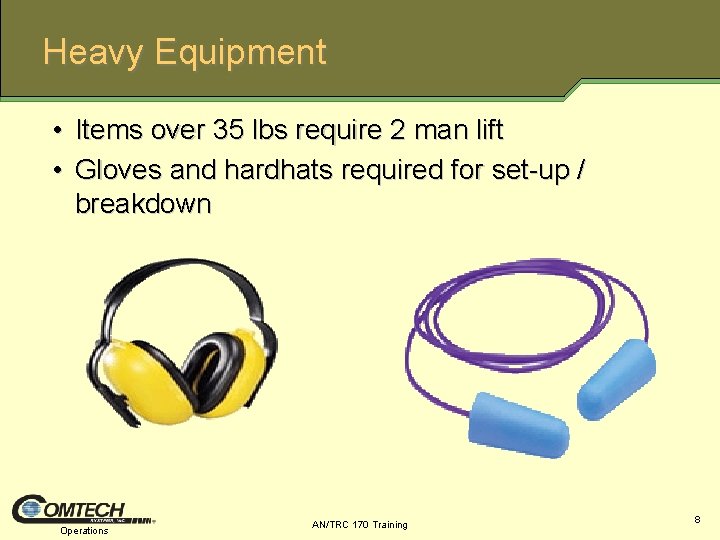
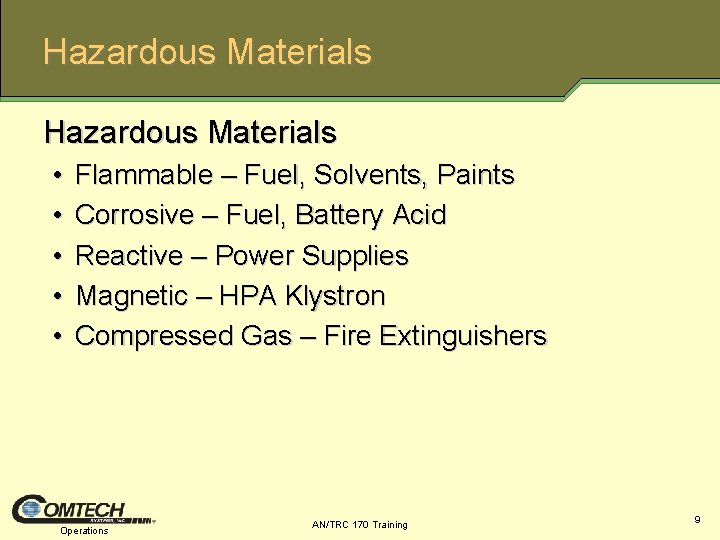
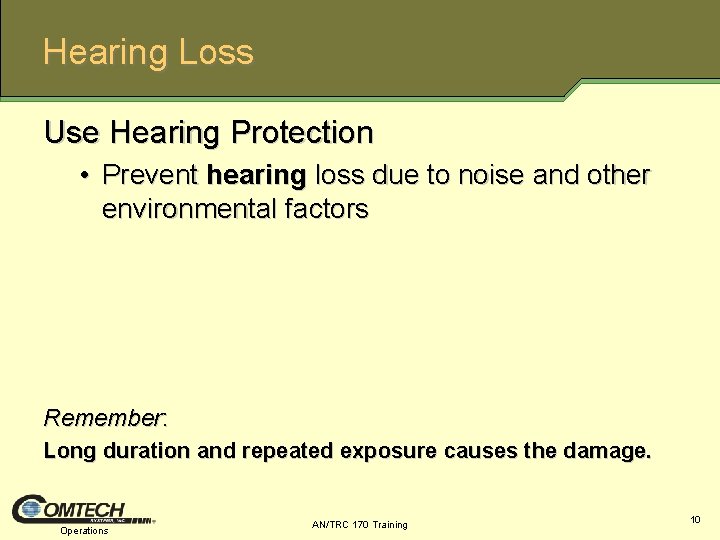
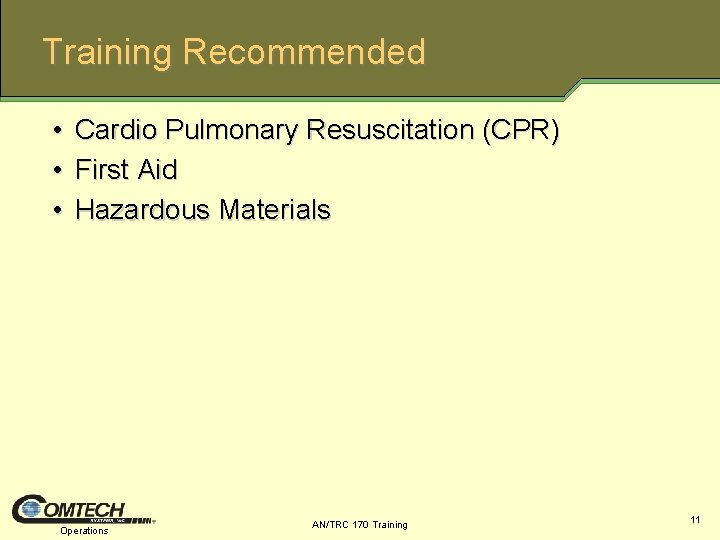
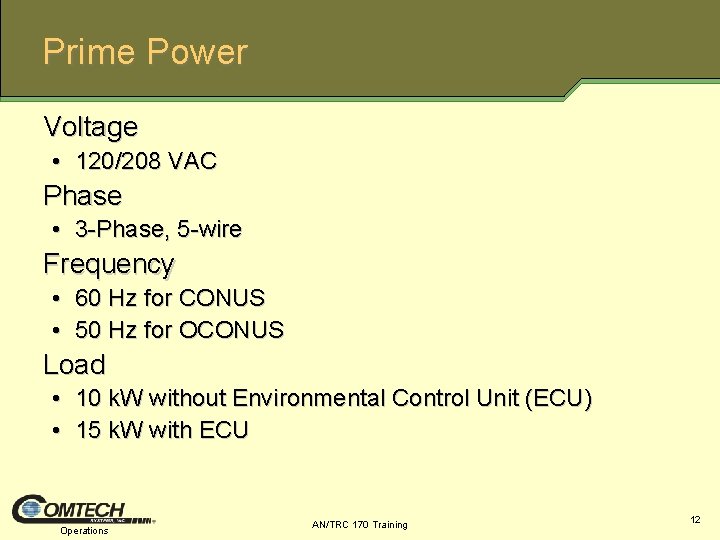
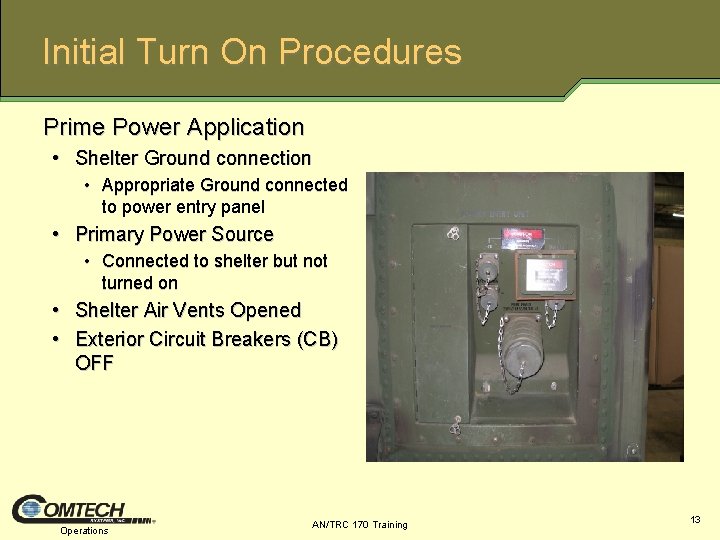
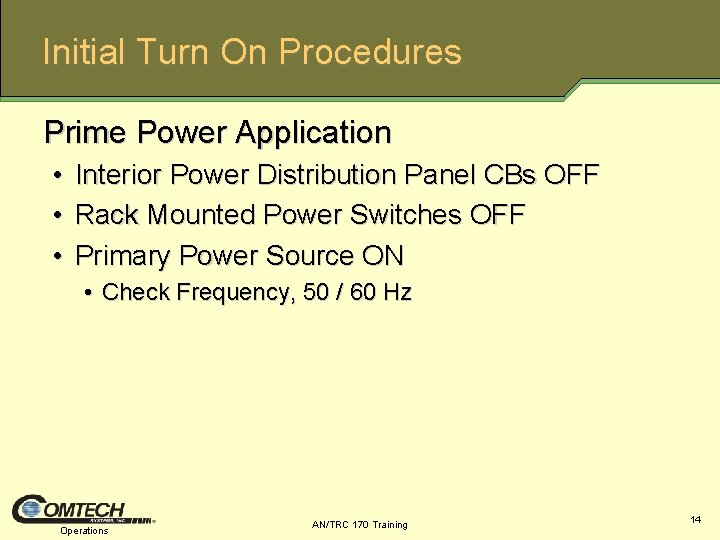
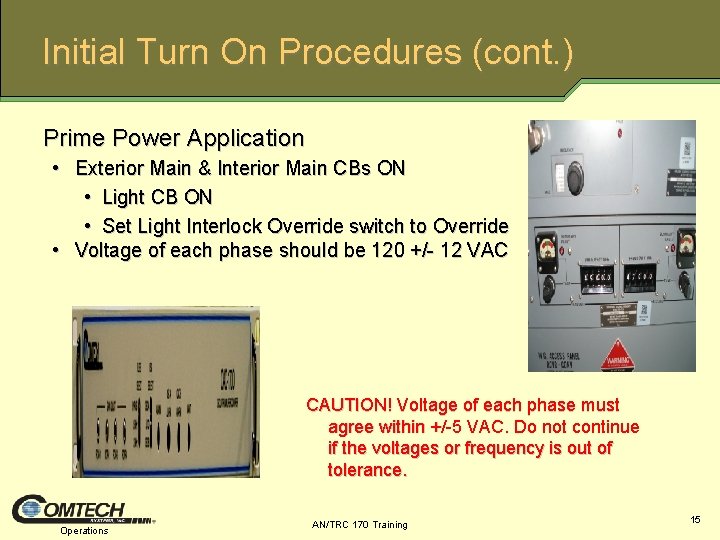
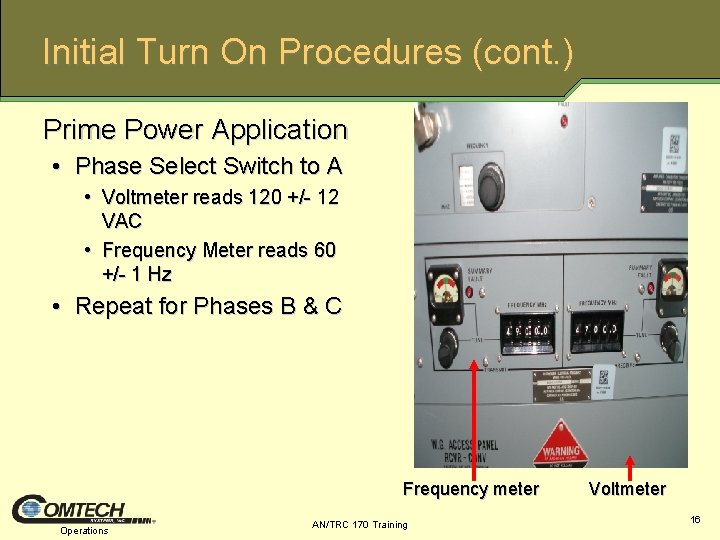
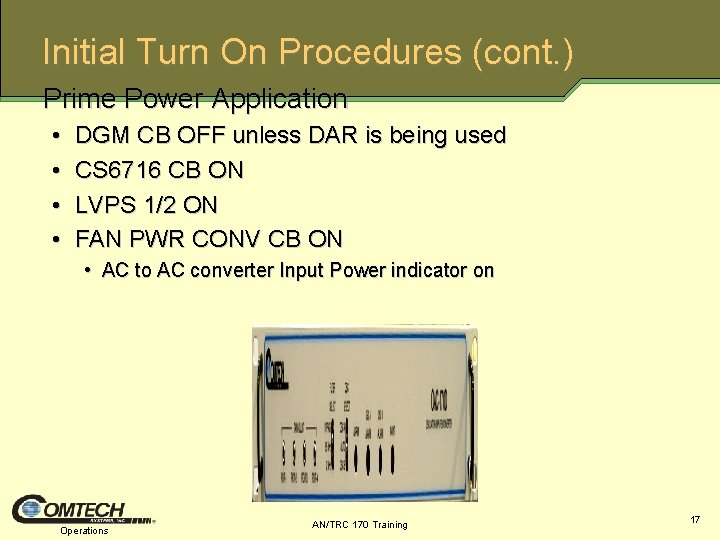
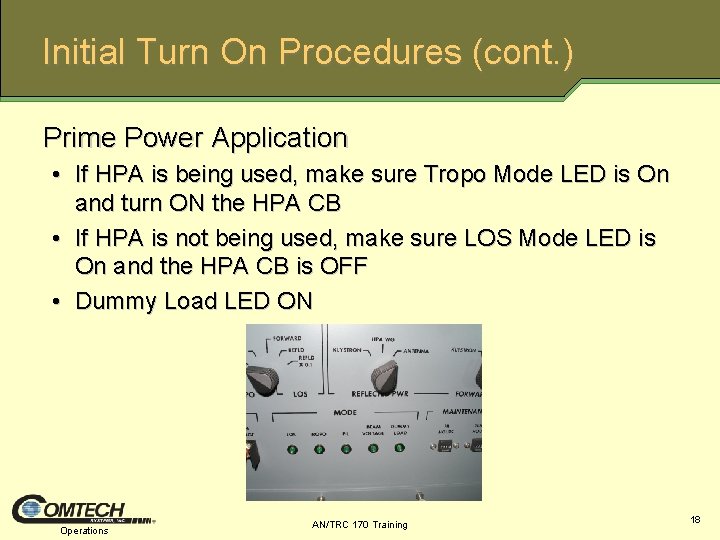
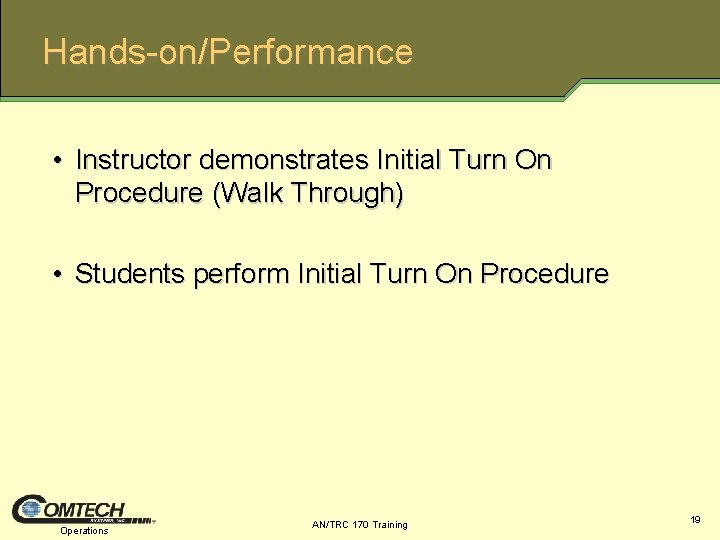
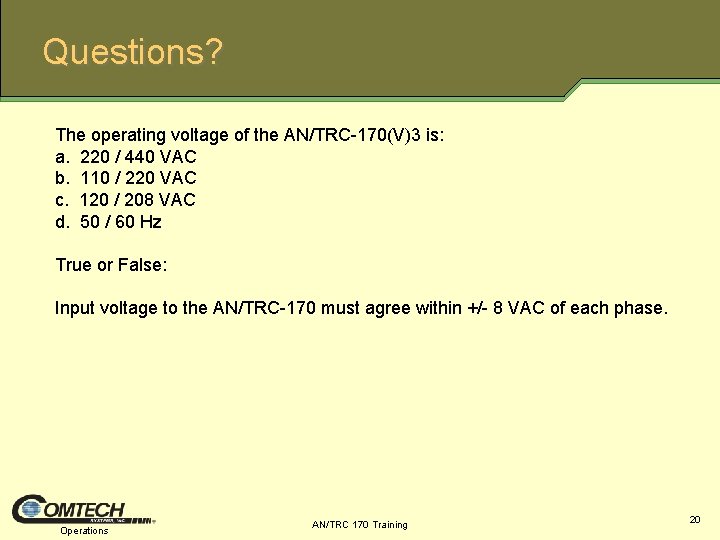
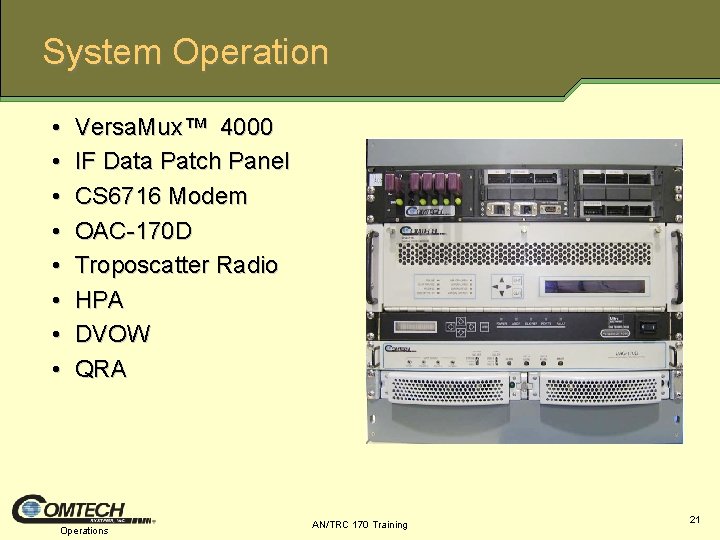
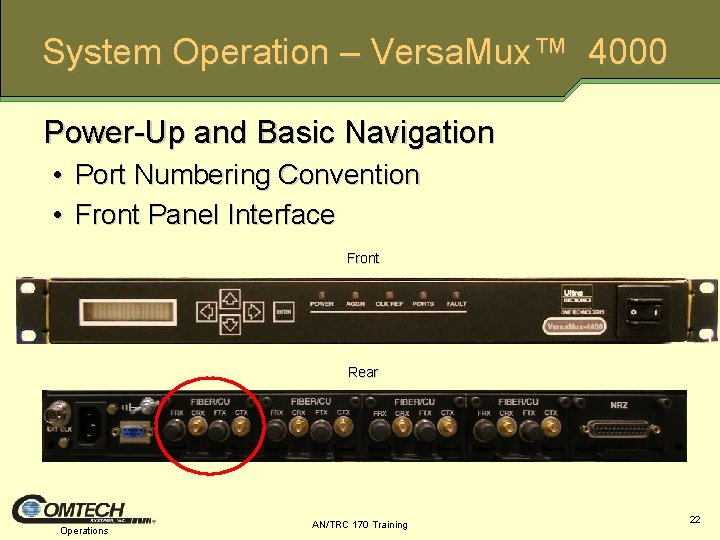
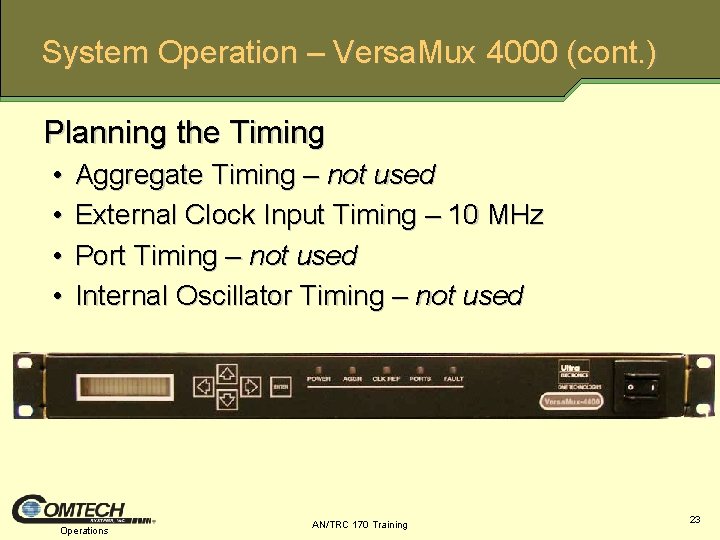
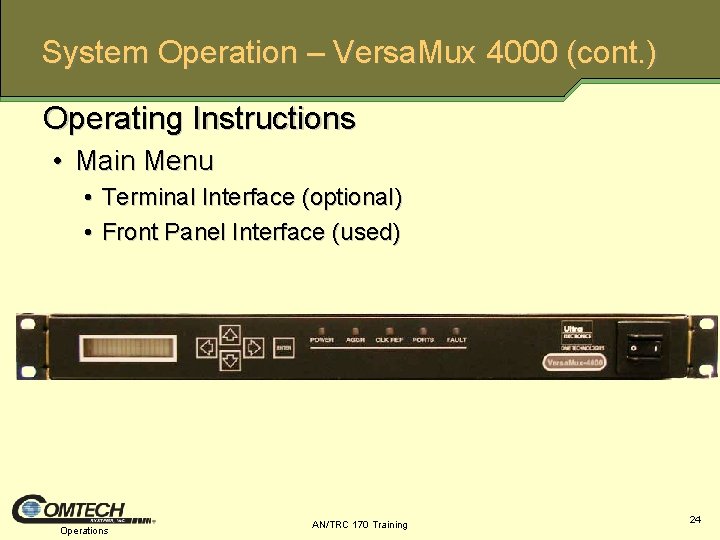
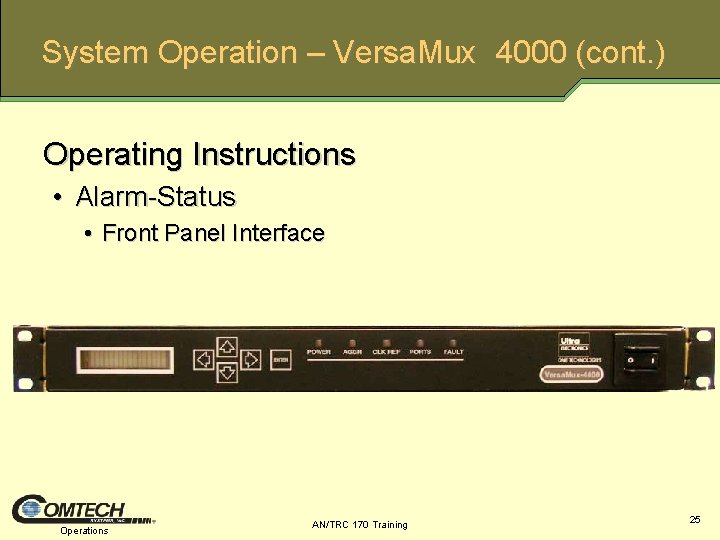
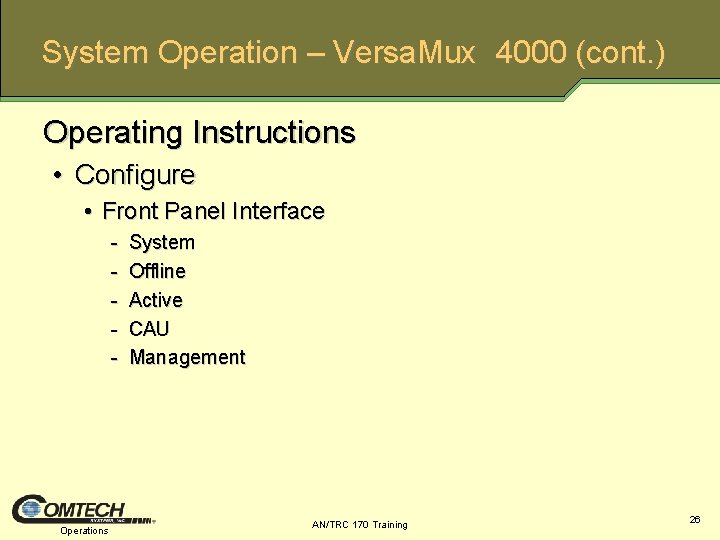
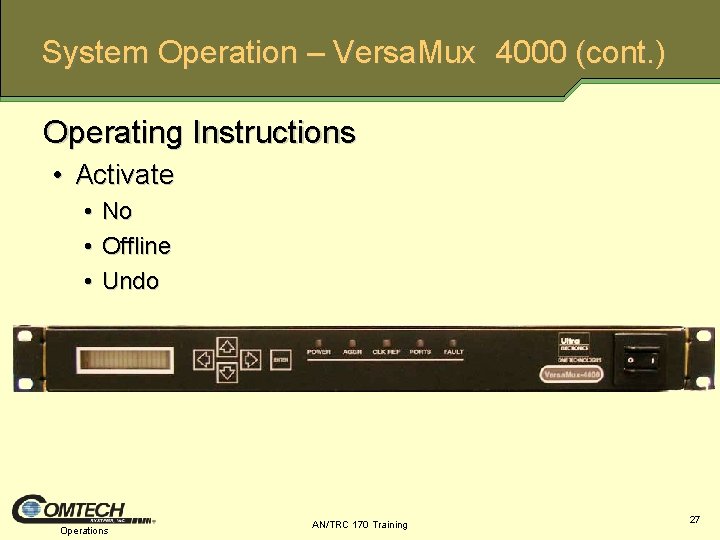
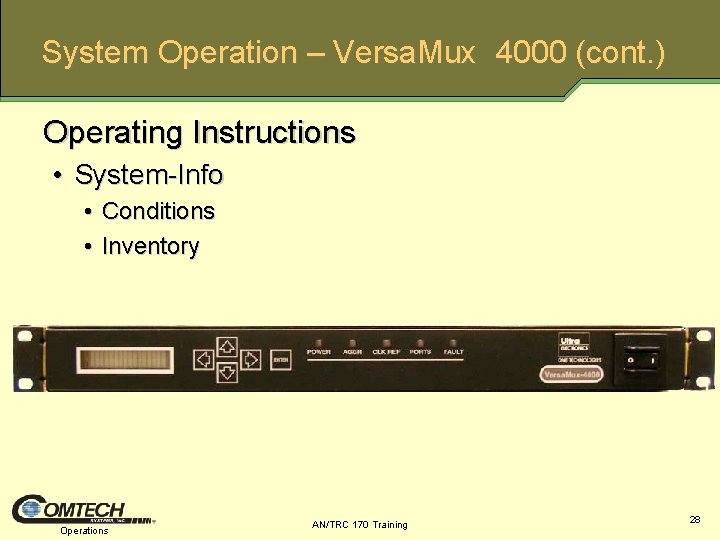
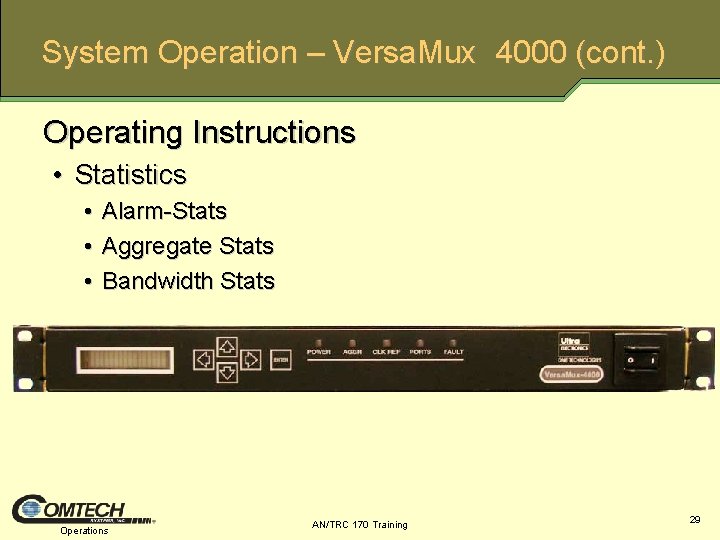
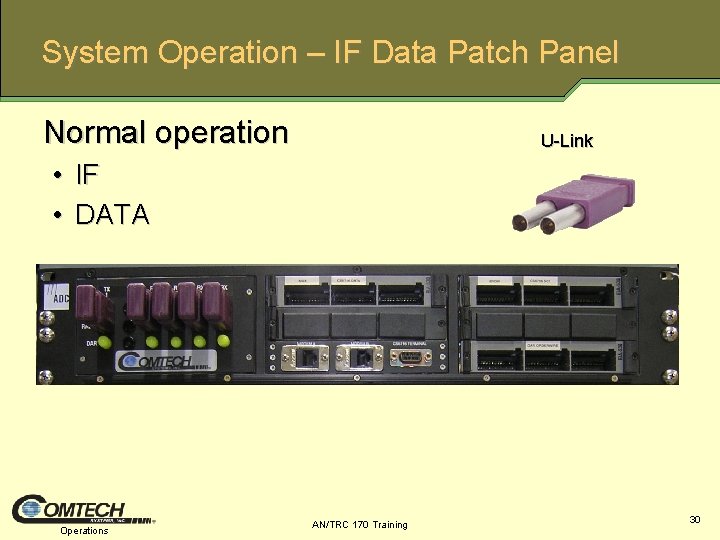
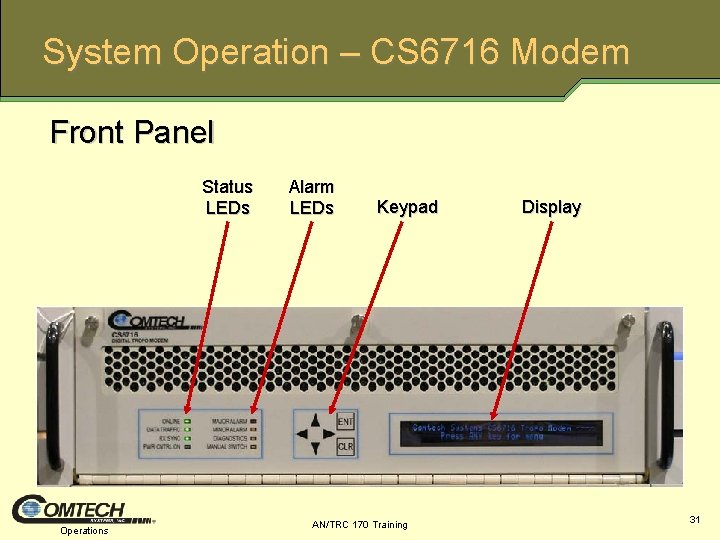
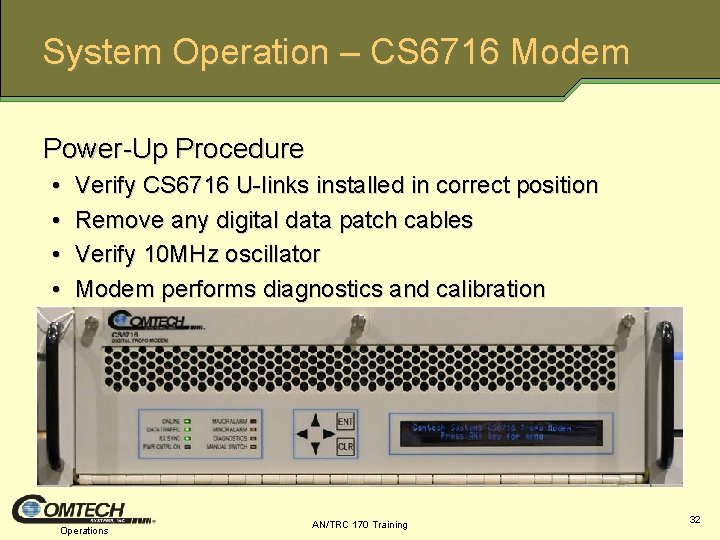
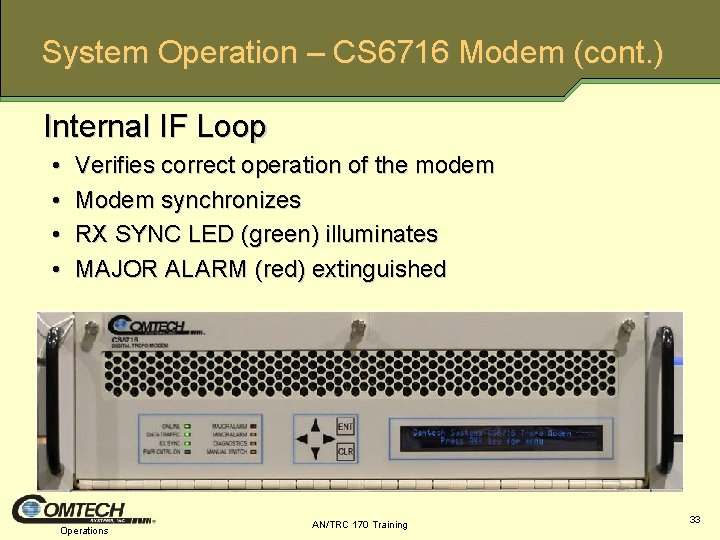
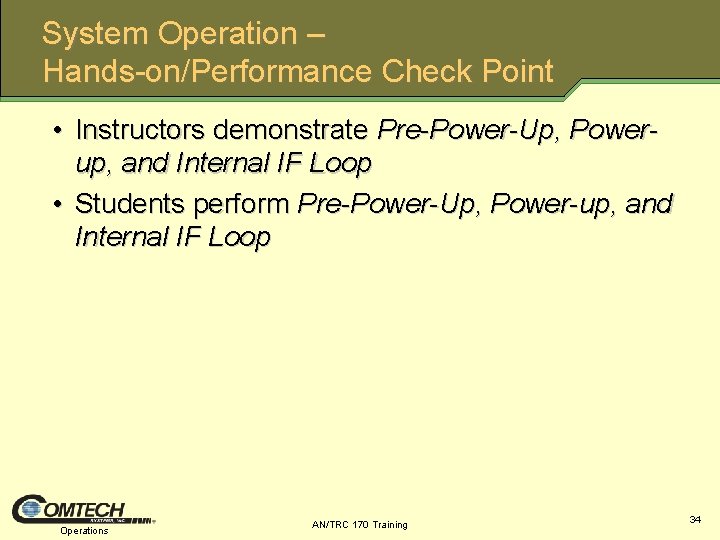
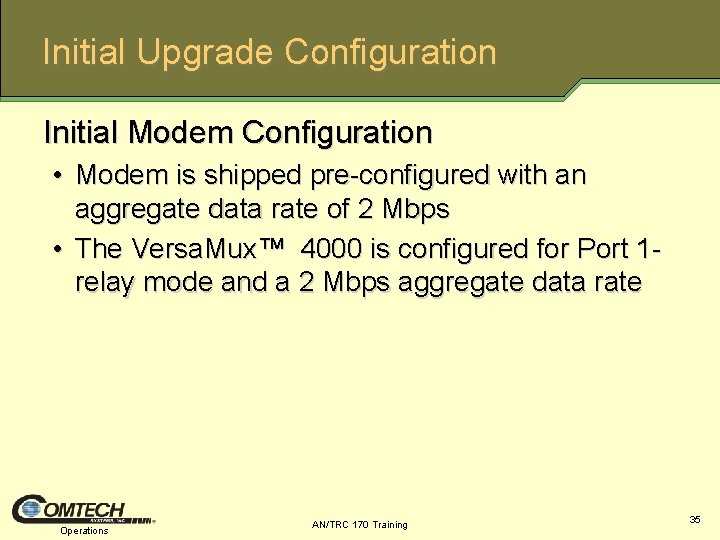
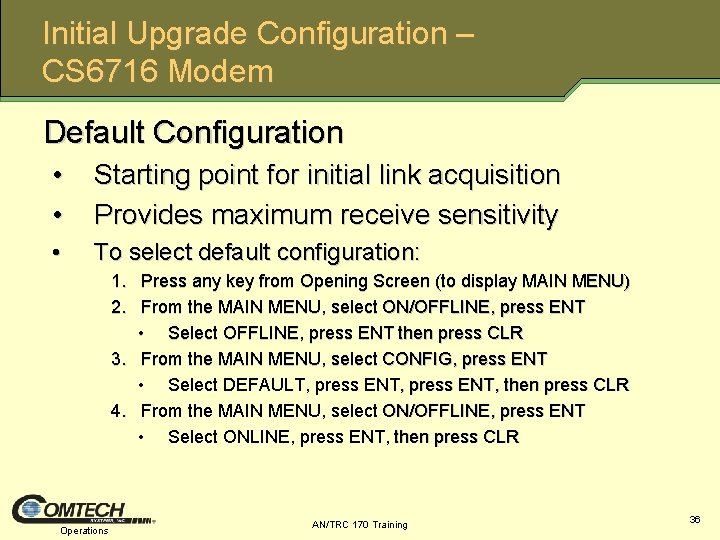
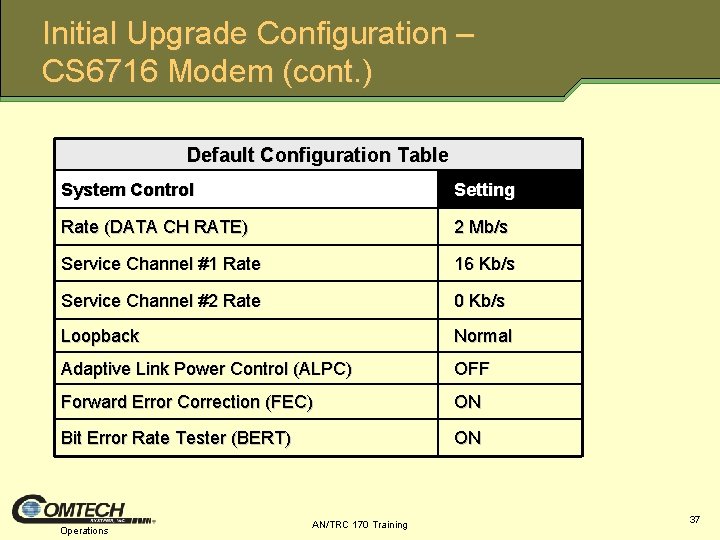
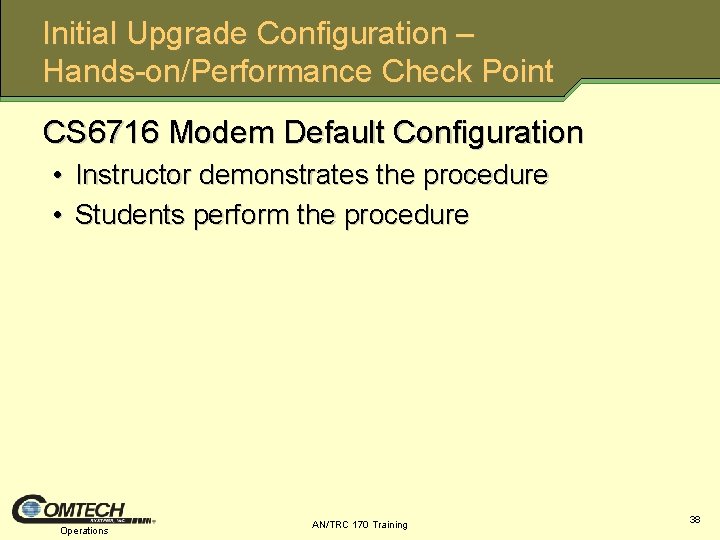
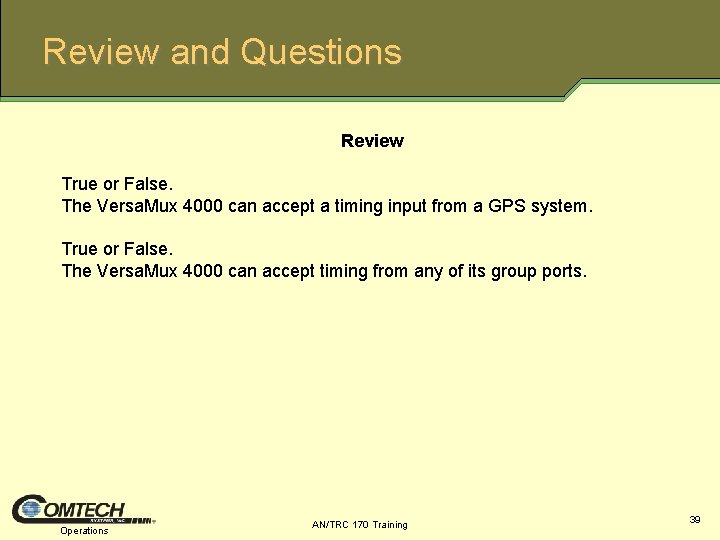
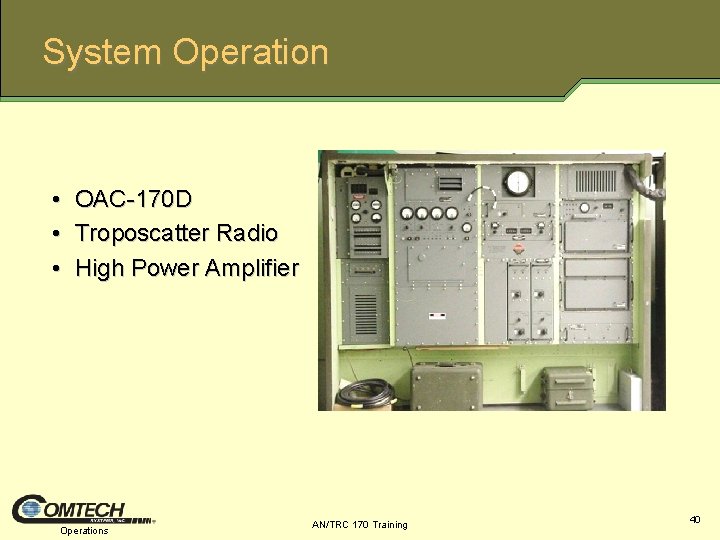

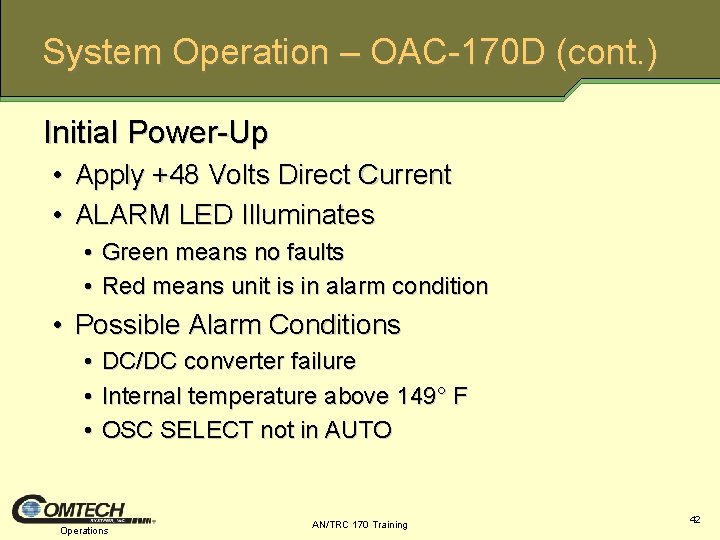
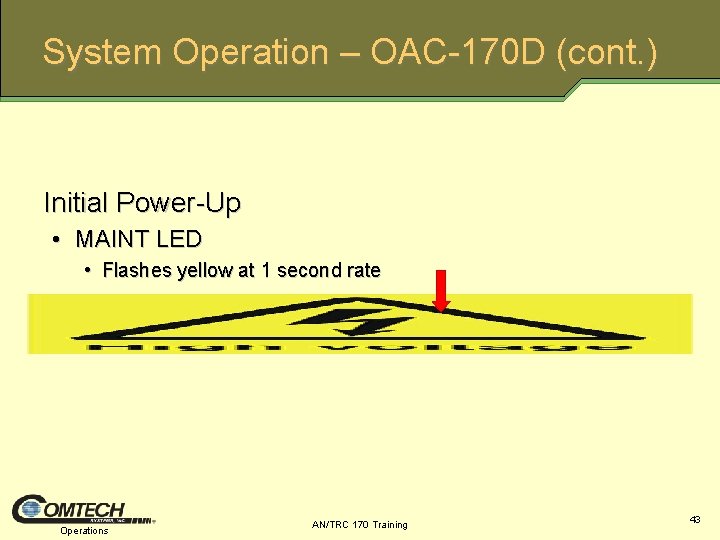
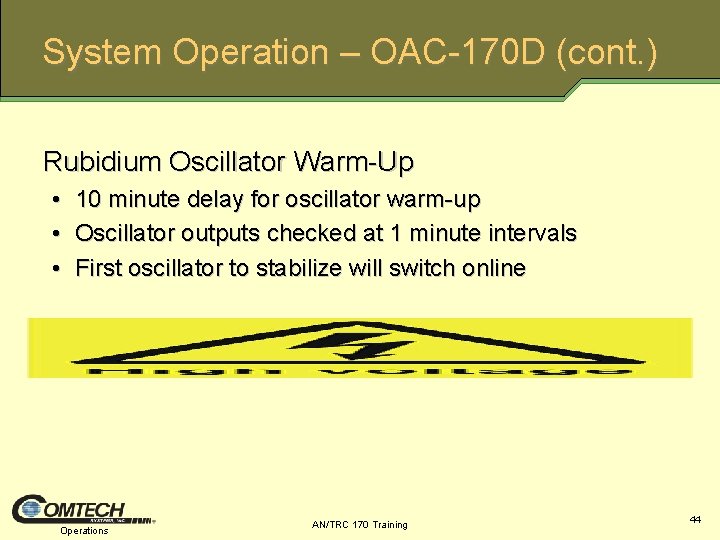
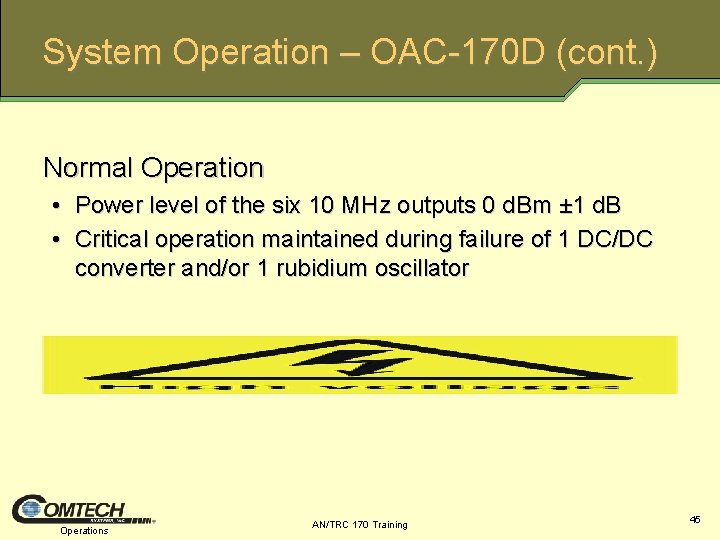
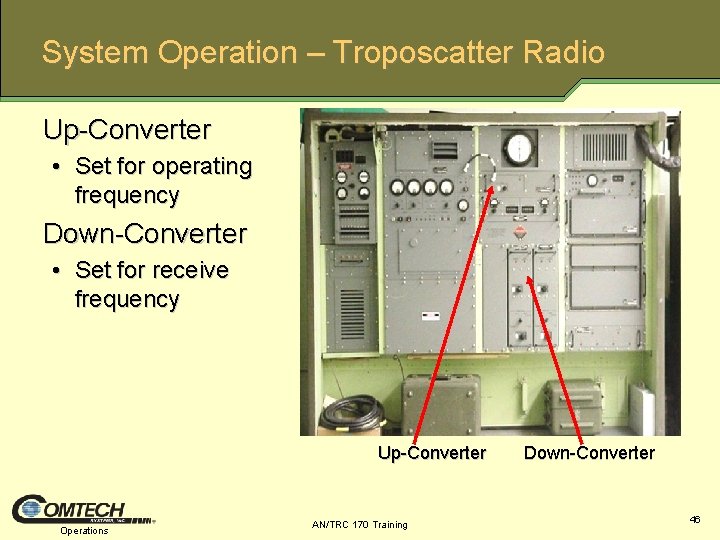
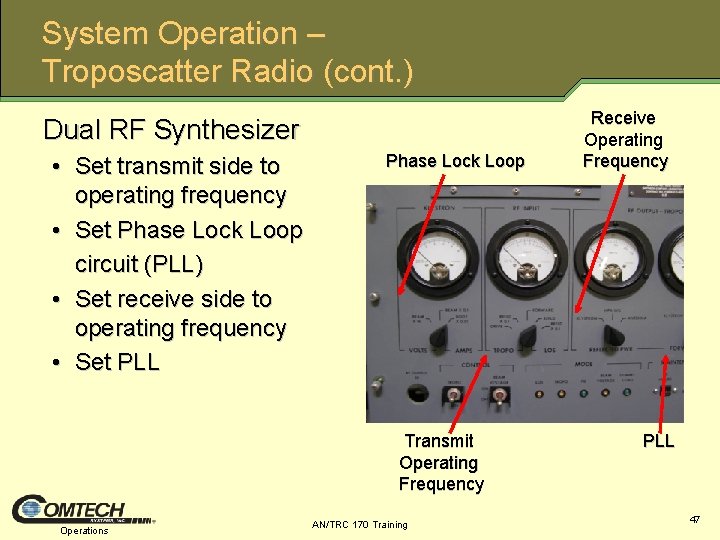
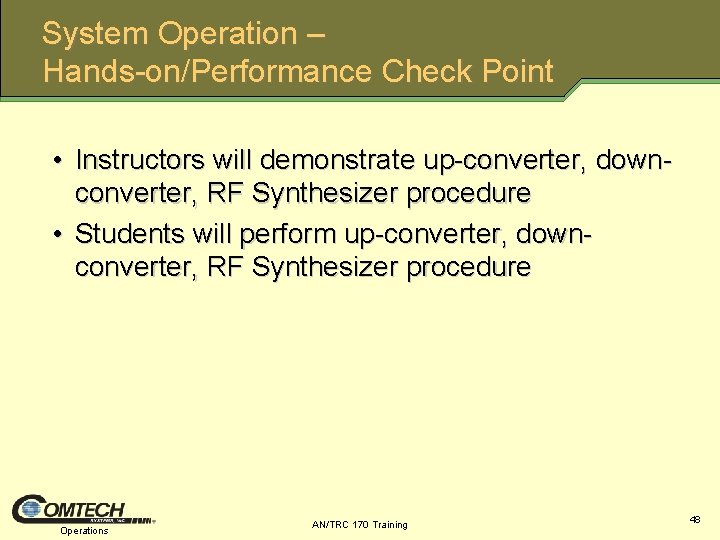
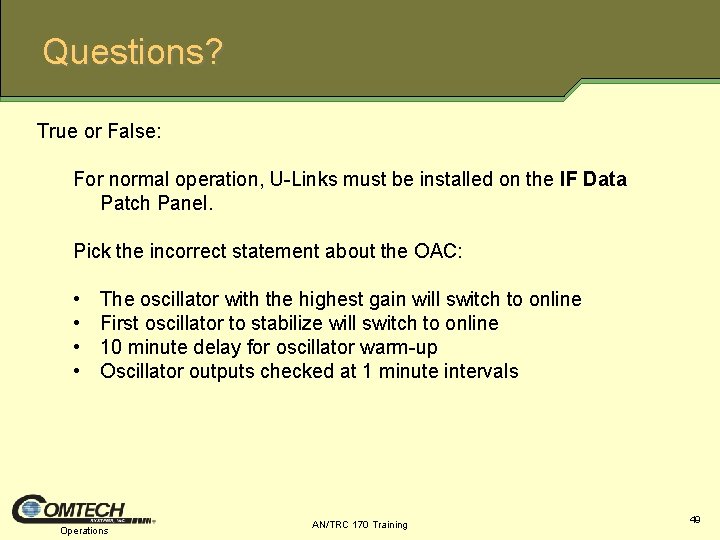
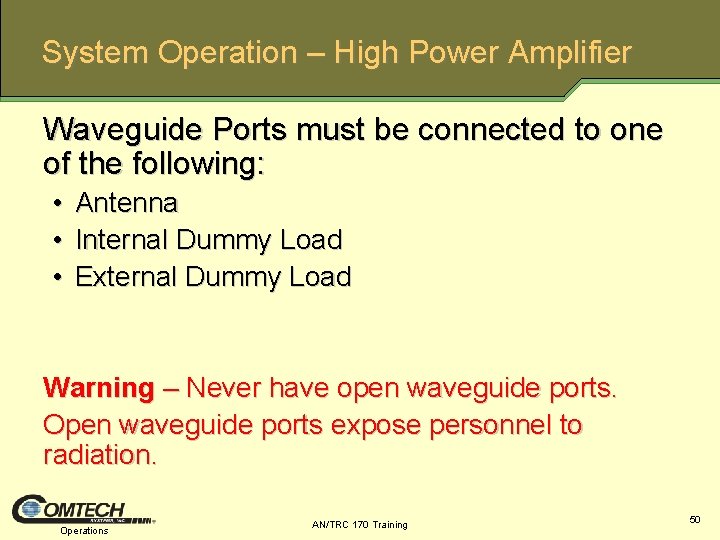
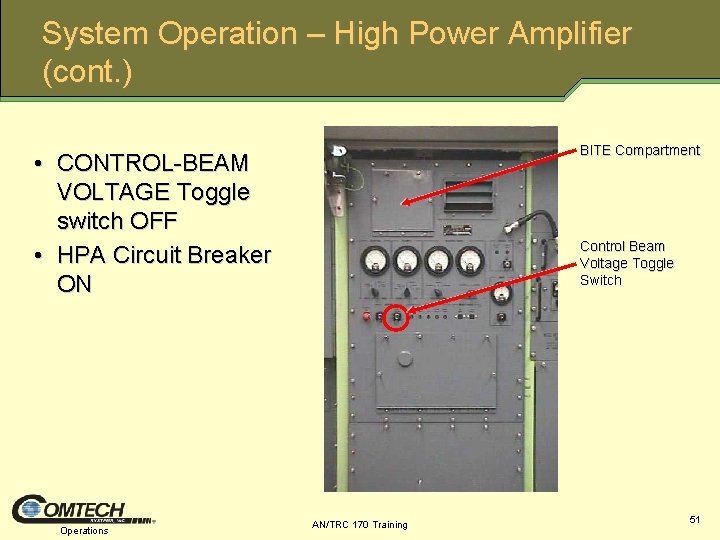
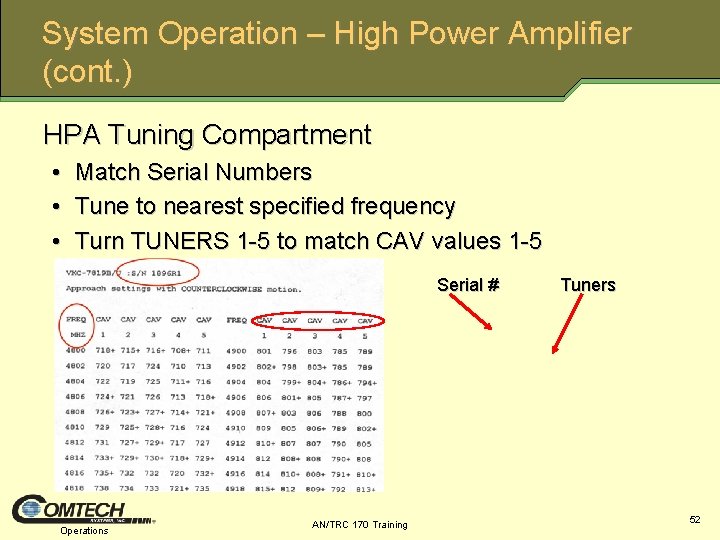
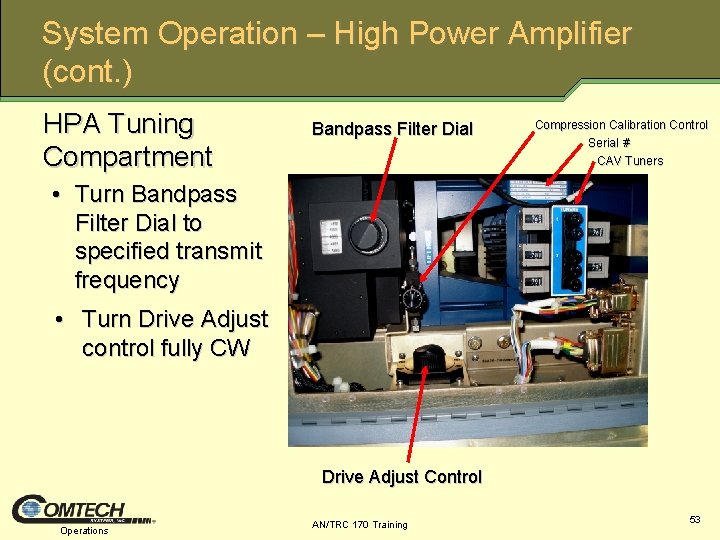
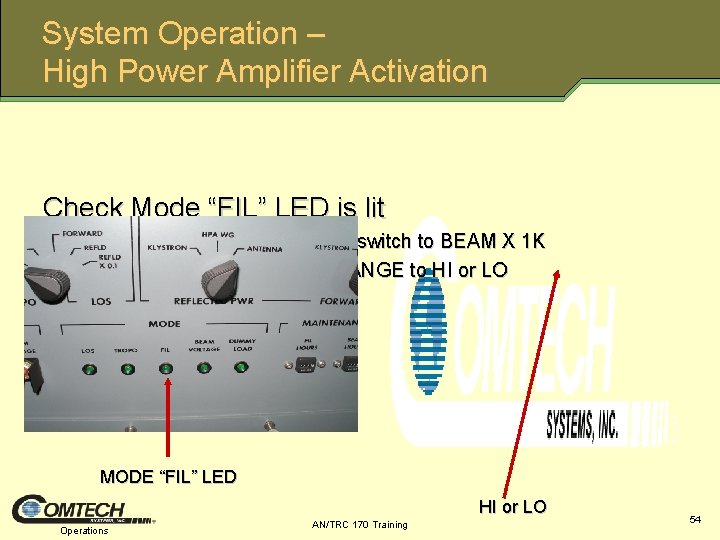
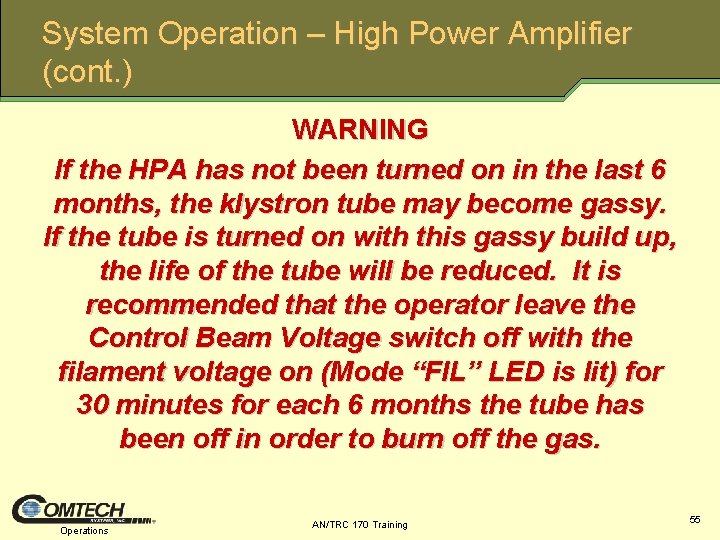
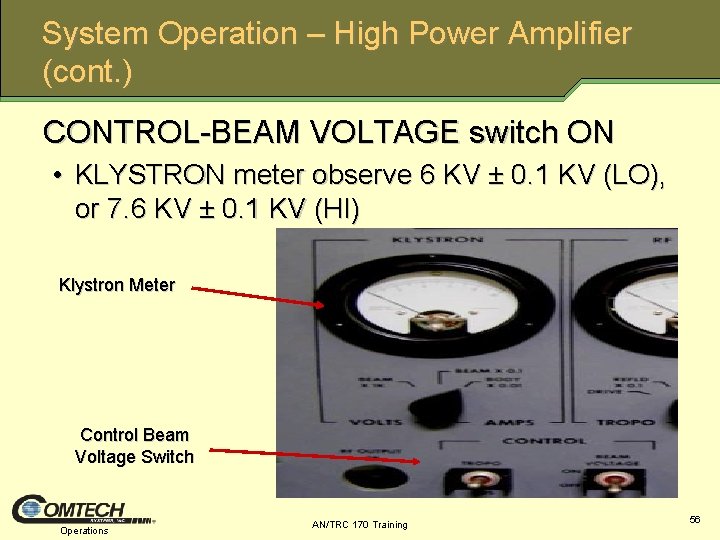
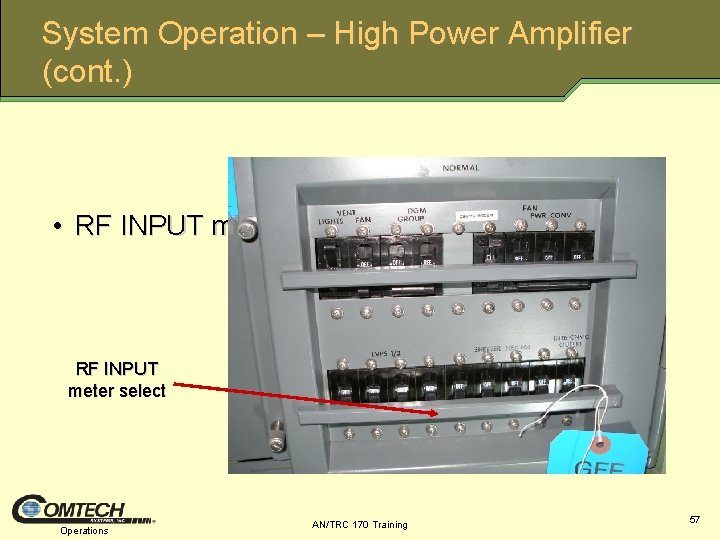
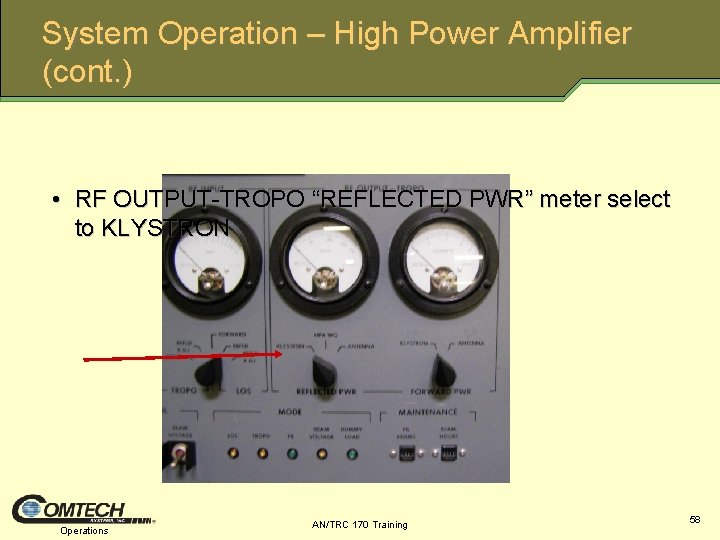
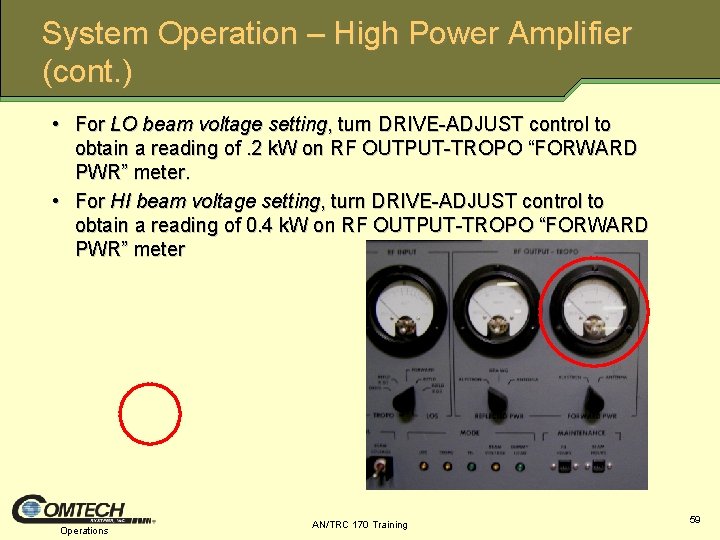

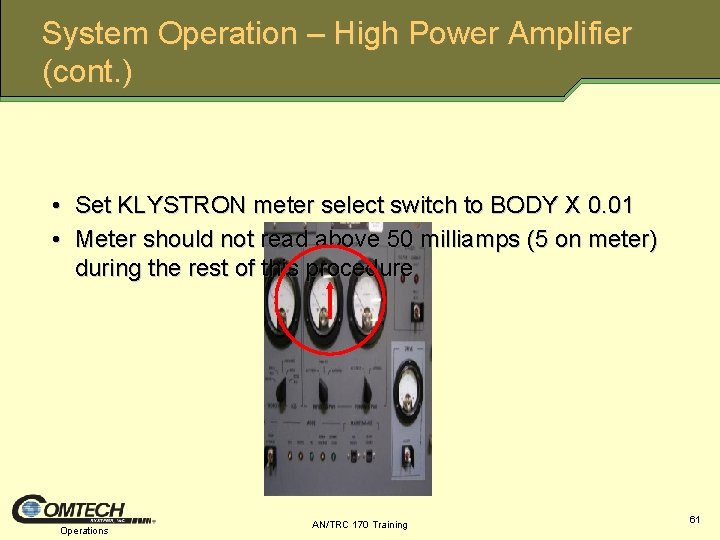
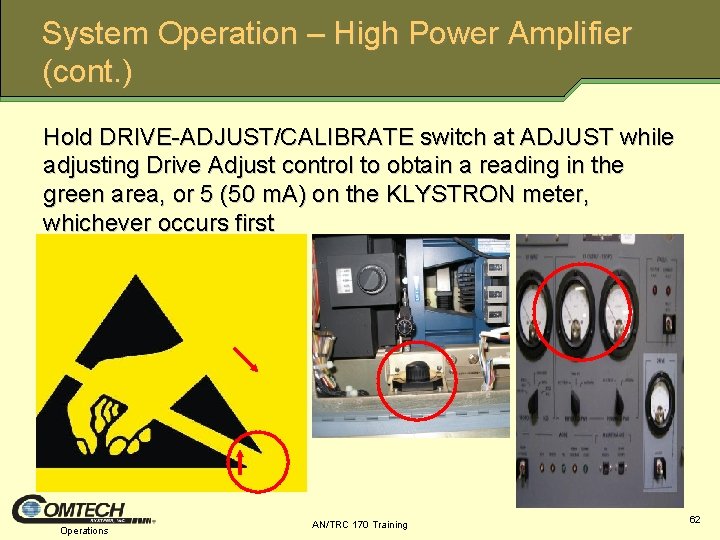
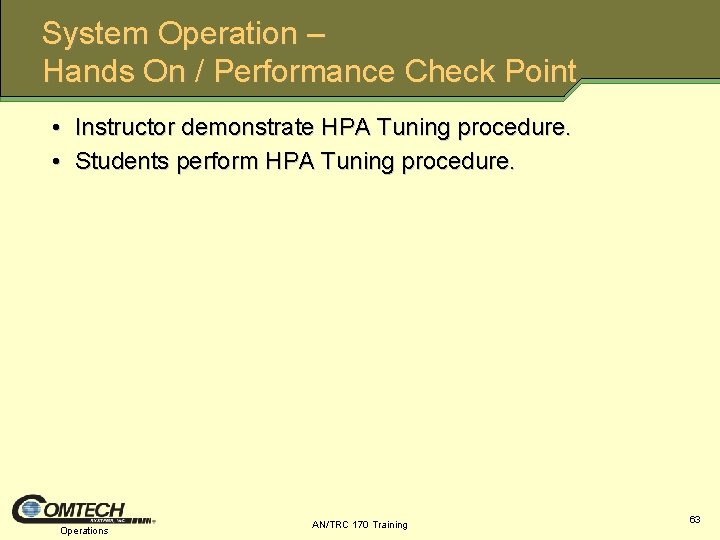
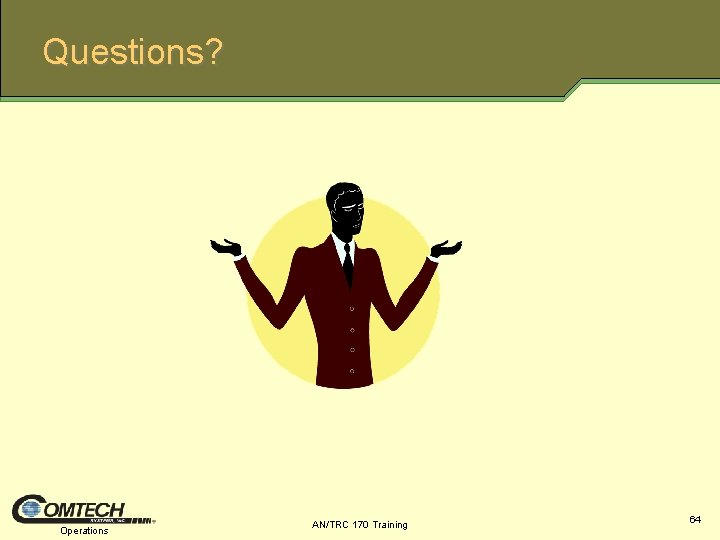
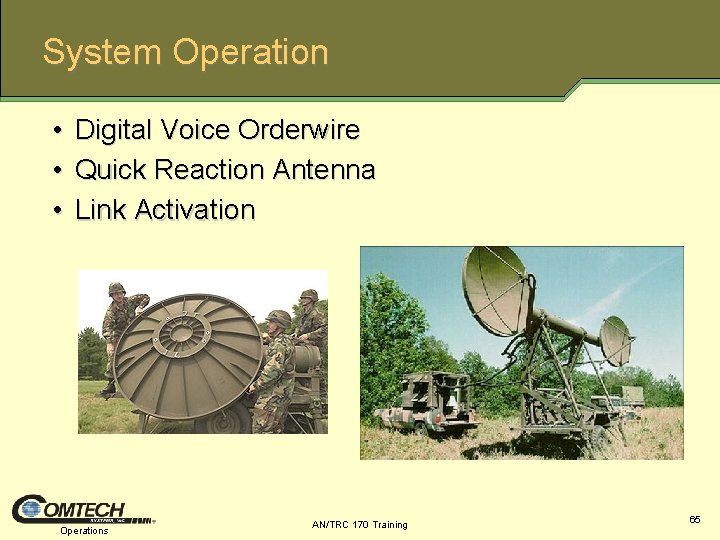
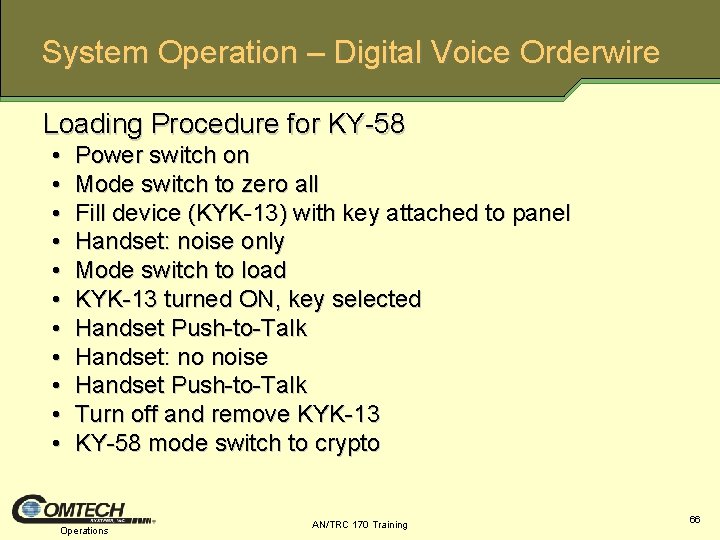
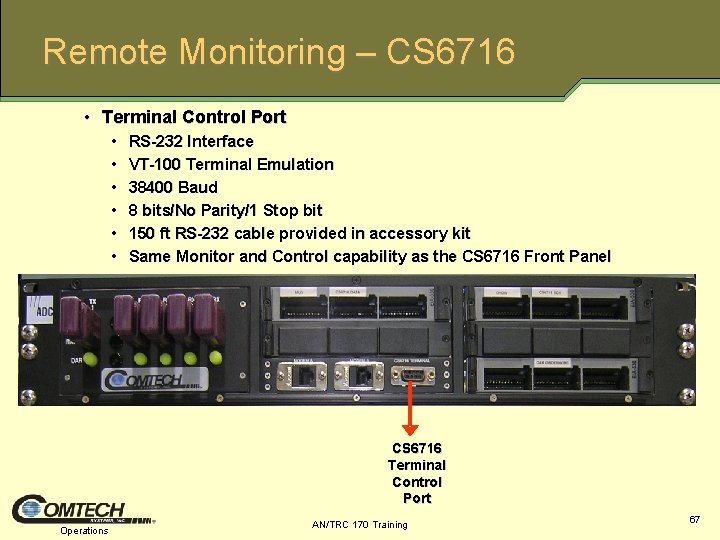
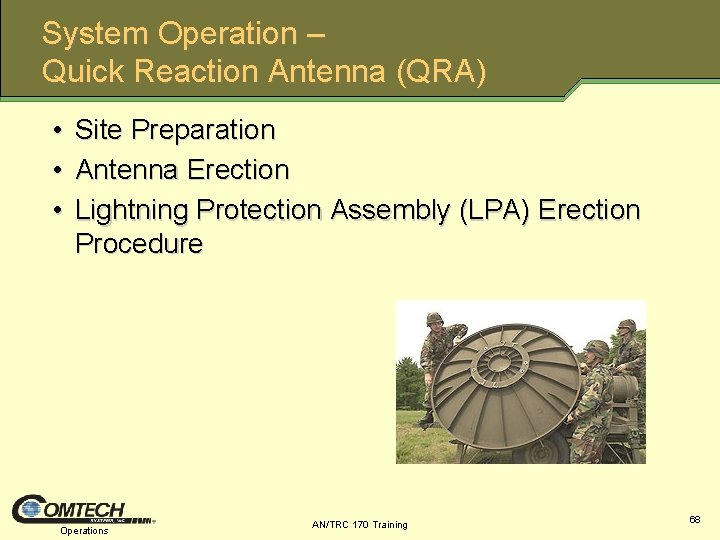
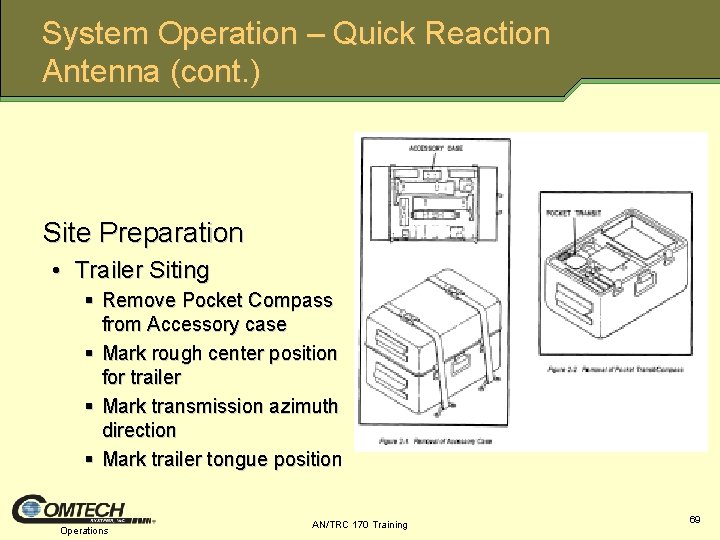
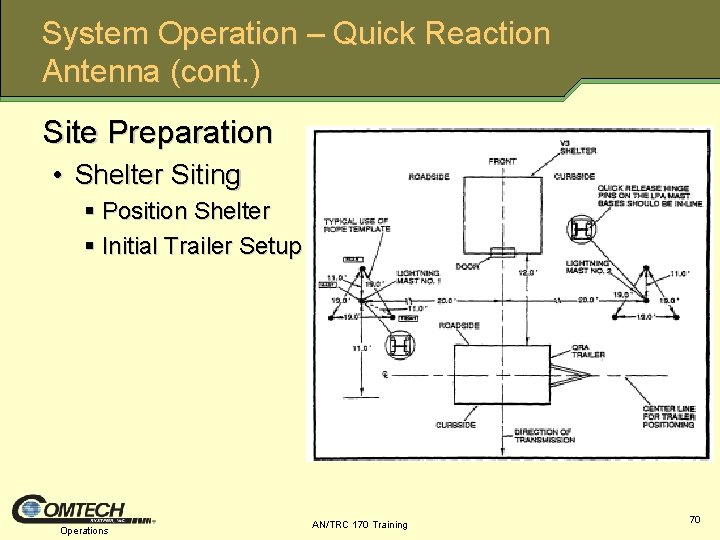
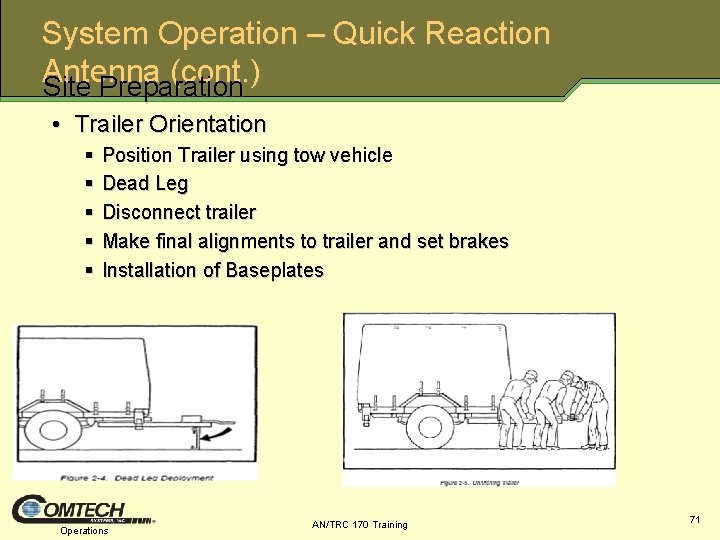
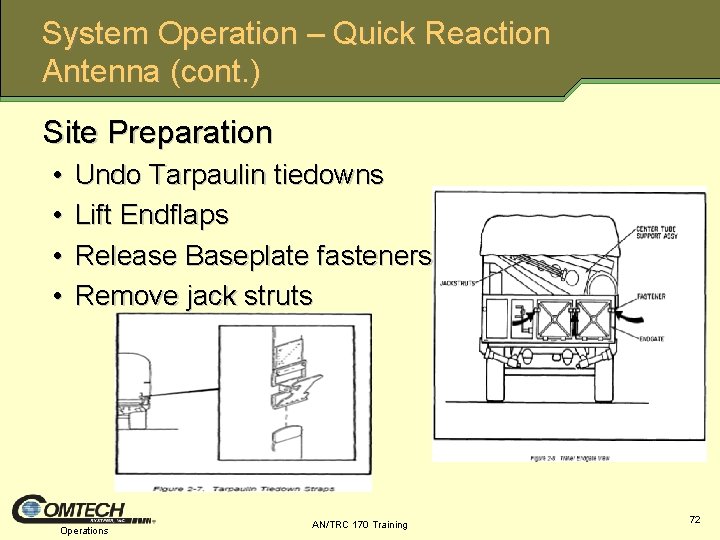
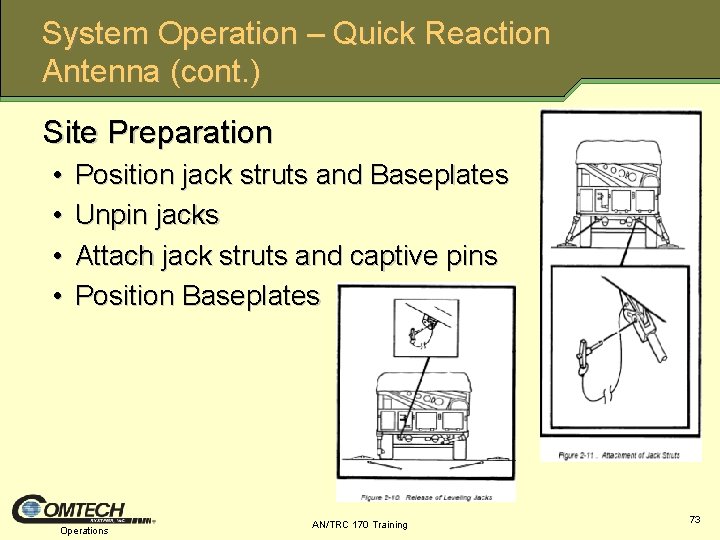
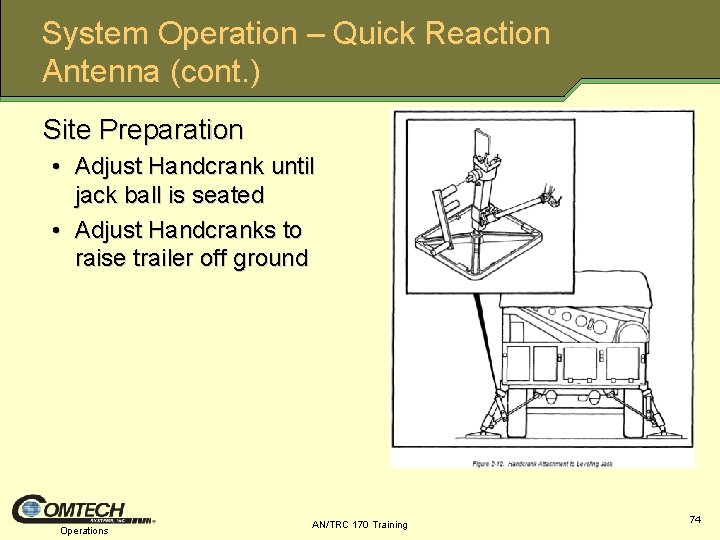
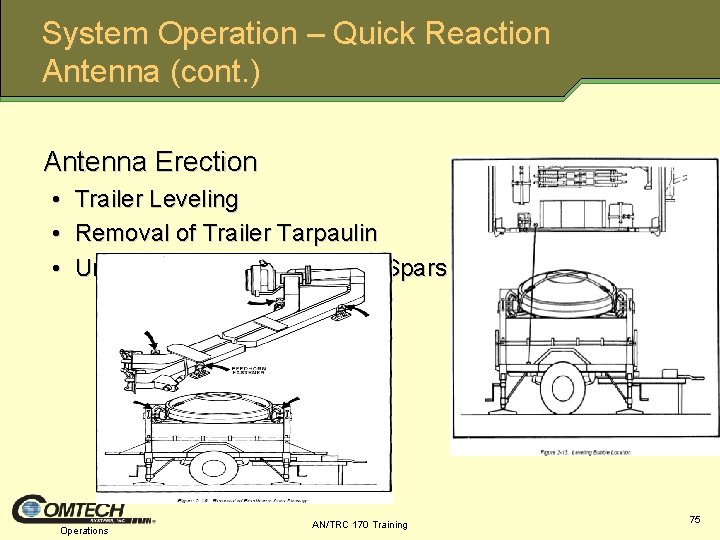
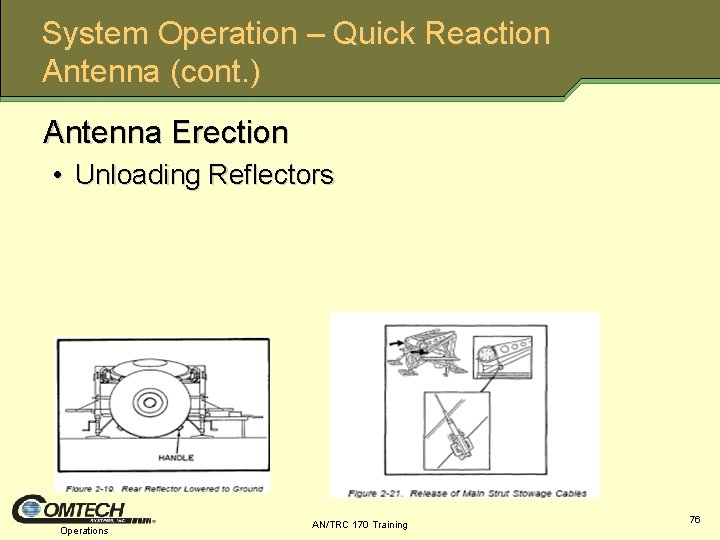
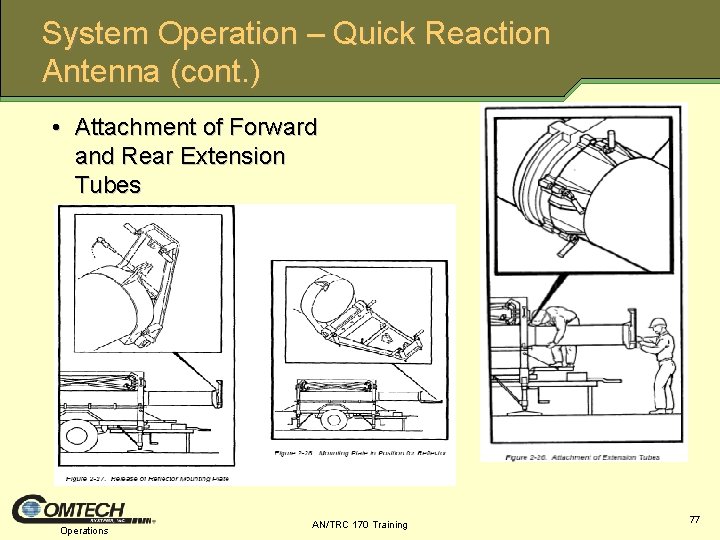
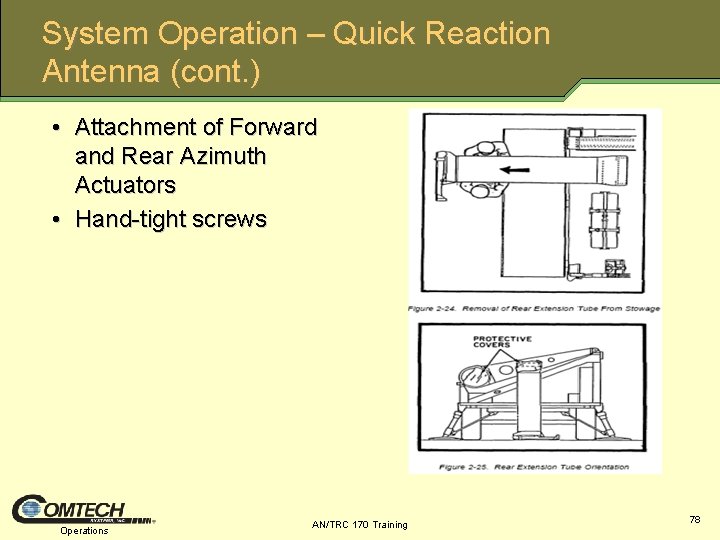
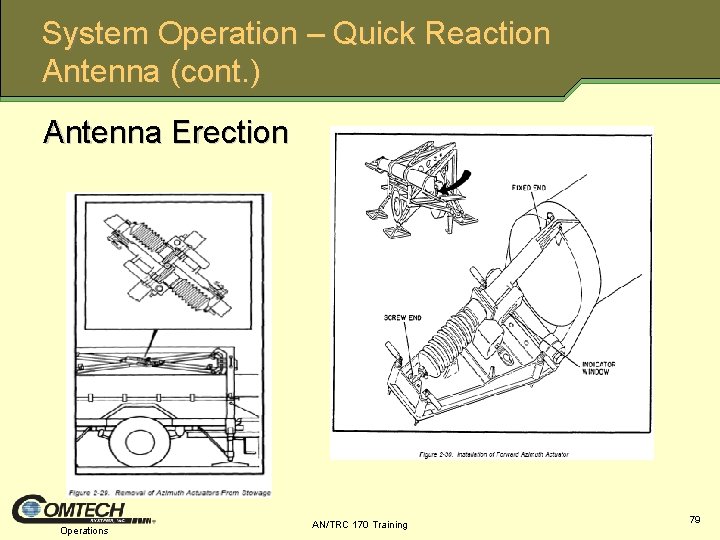
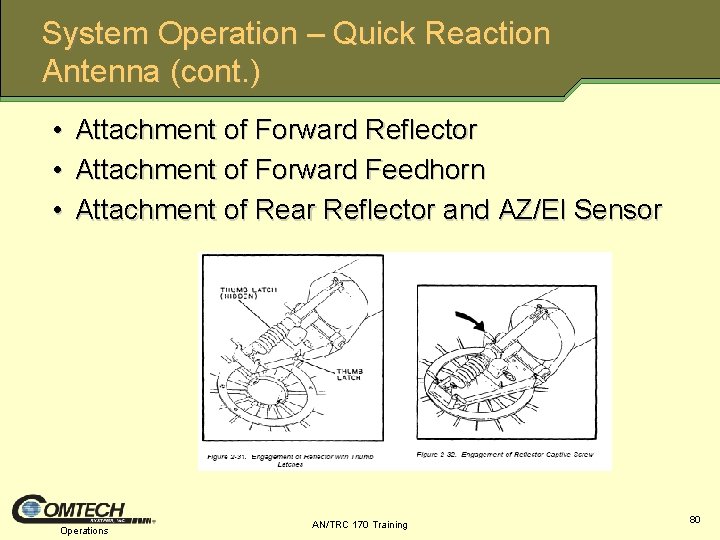
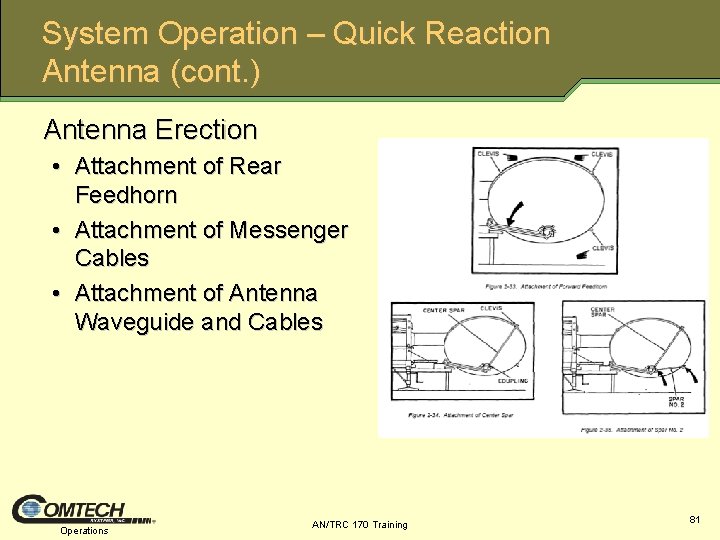
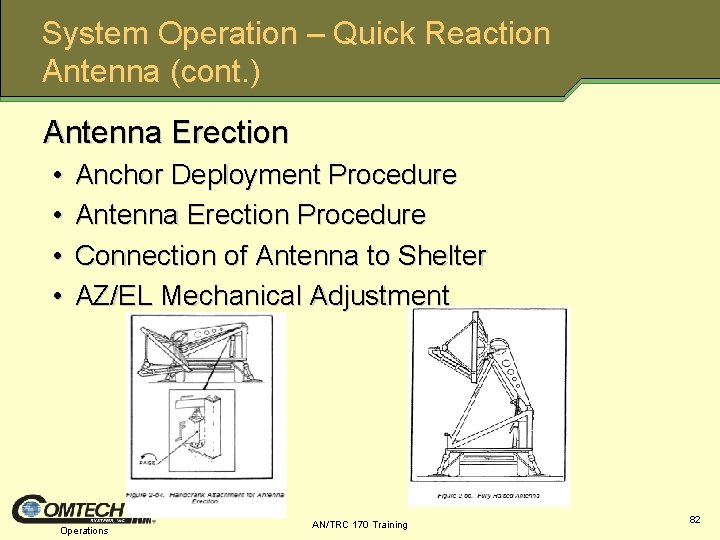
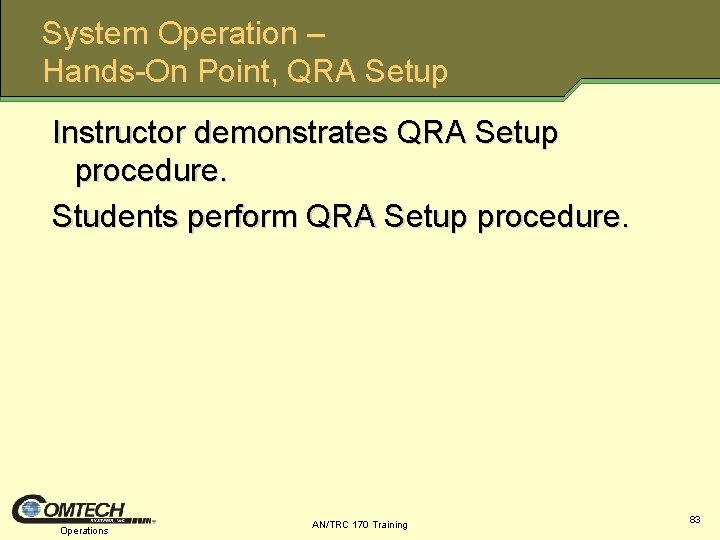
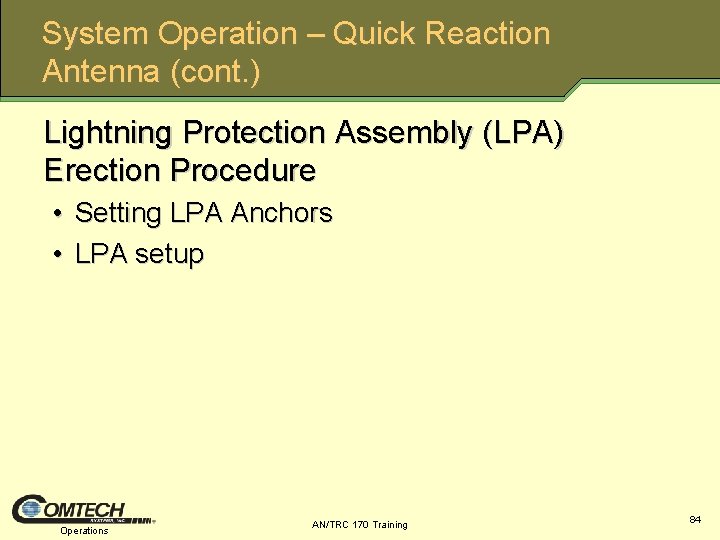
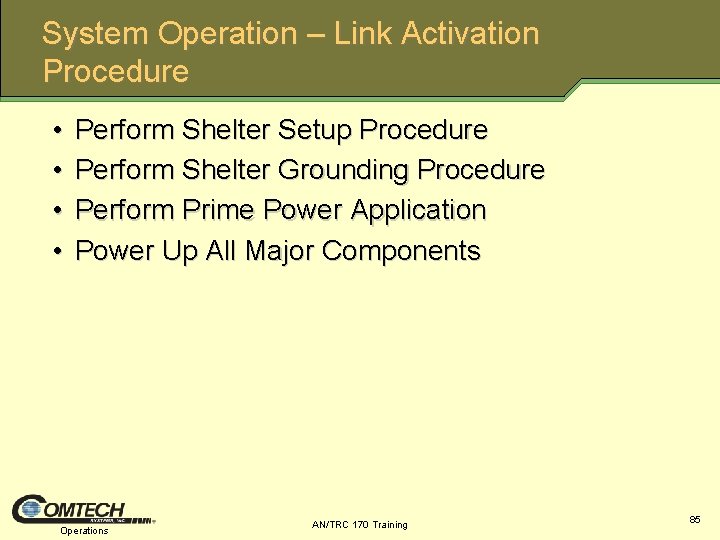
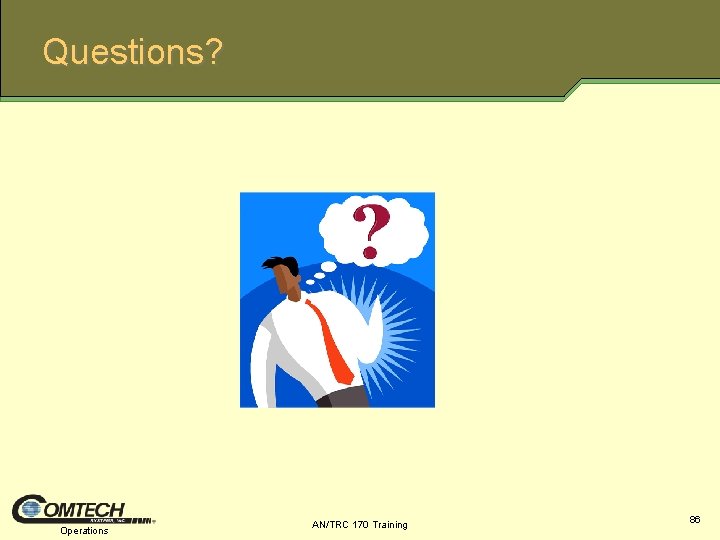
- Slides: 86
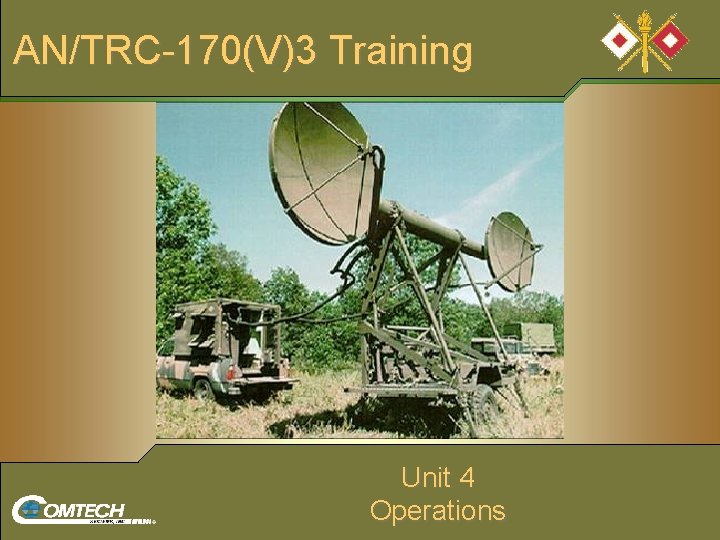
AN/TRC 170(V)3 Training Unit 4 Operations
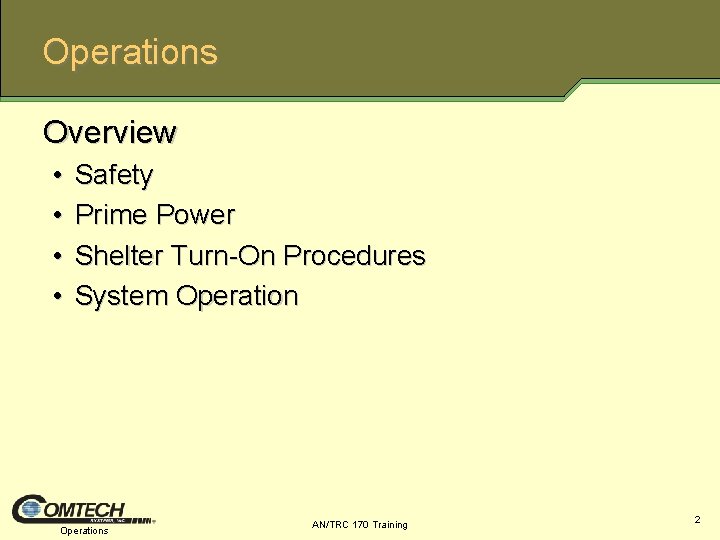
Operations Overview • • Safety Prime Power Shelter Turn On Procedures System Operations AN/TRC 170 Training 2

Safety Concerns • • High Voltage Radiation Hazards Electro Static Discharge (ESD) Heavy Equipment Hazardous Materials Hearing Loss Training required Operations AN/TRC 170 Training 3

Personnel Hazards These hazards can cause serious injury or death to personnel: • • • High Voltage Radiation High Voltage sources Operations AN/TRC 170 Training 4
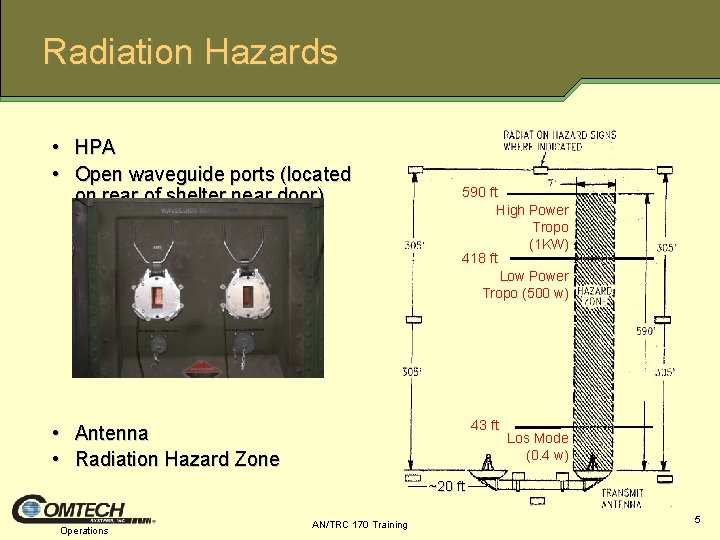
Radiation Hazards • HPA • Open waveguide ports (located on rear of shelter near door) 590 ft High Power Tropo (1 KW) 418 ft Low Power Tropo (500 w) 43 ft • Antenna • Radiation Hazard Zone Los Mode (0. 4 w) ~20 ft Operations AN/TRC 170 Training 5
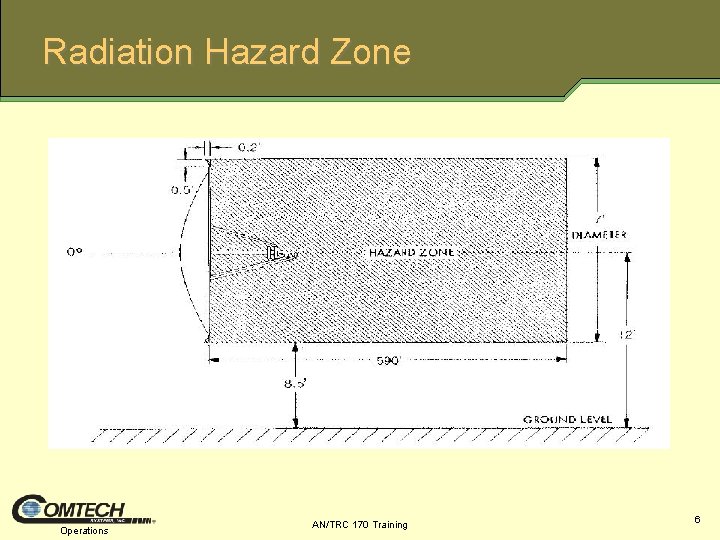
Radiation Hazard Zone Operations AN/TRC 170 Training 6
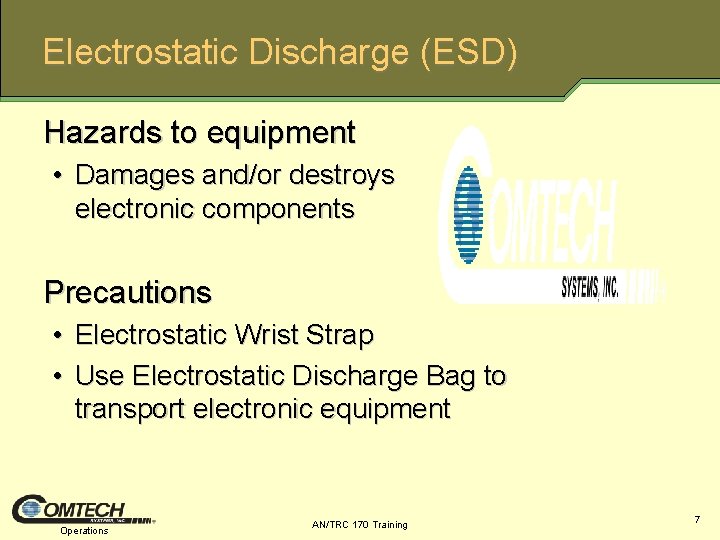
Electrostatic Discharge (ESD) Hazards to equipment • Damages and/or destroys electronic components Precautions • Electrostatic Wrist Strap • Use Electrostatic Discharge Bag to transport electronic equipment Operations AN/TRC 170 Training 7
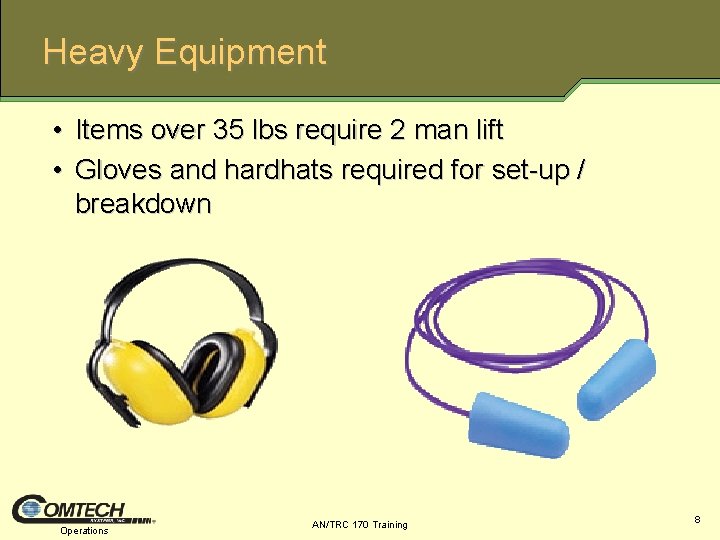
Heavy Equipment • Items over 35 lbs require 2 man lift • Gloves and hardhats required for set up / breakdown Operations AN/TRC 170 Training 8
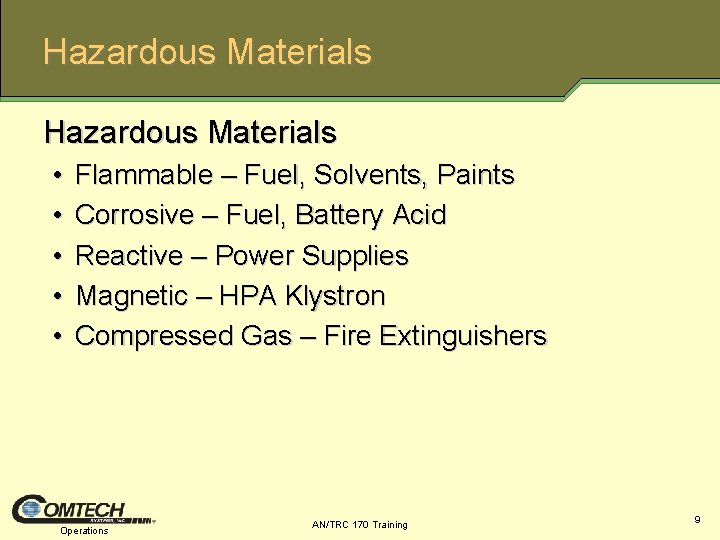
Hazardous Materials • • • Flammable – Fuel, Solvents, Paints Corrosive – Fuel, Battery Acid Reactive – Power Supplies Magnetic – HPA Klystron Compressed Gas – Fire Extinguishers Operations AN/TRC 170 Training 9
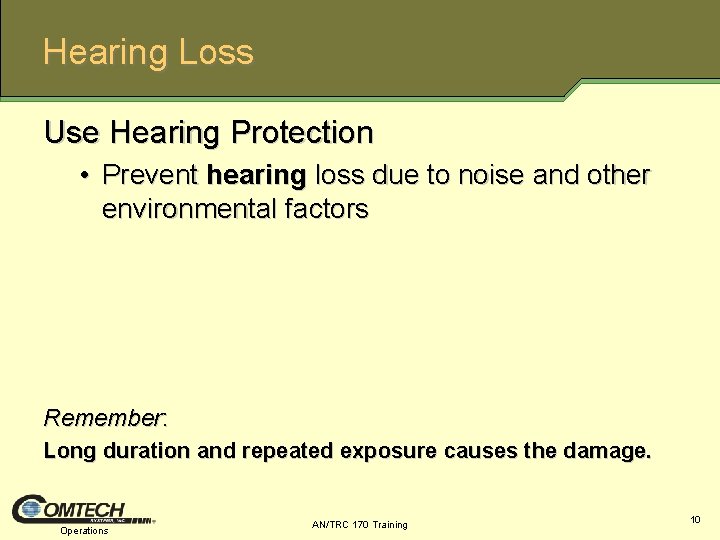
Hearing Loss Use Hearing Protection • Prevent hearing loss due to noise and other environmental factors Remember: Long duration and repeated exposure causes the damage. Operations AN/TRC 170 Training 10
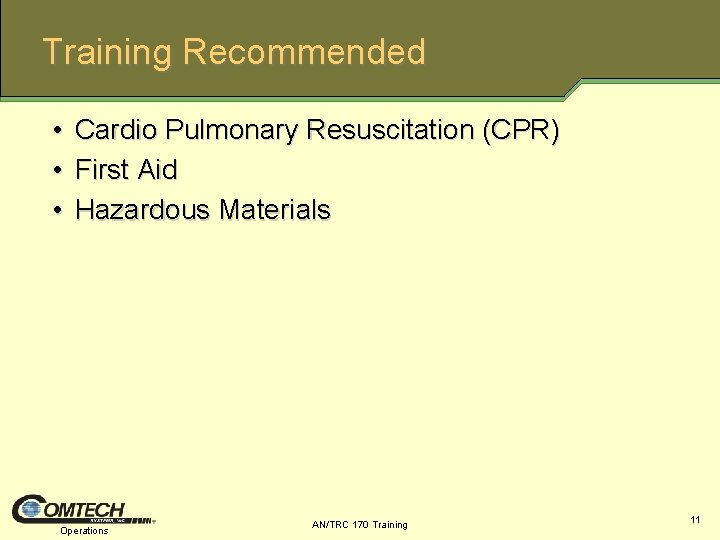
Training Recommended • • • Cardio Pulmonary Resuscitation (CPR) First Aid Hazardous Materials Operations AN/TRC 170 Training 11
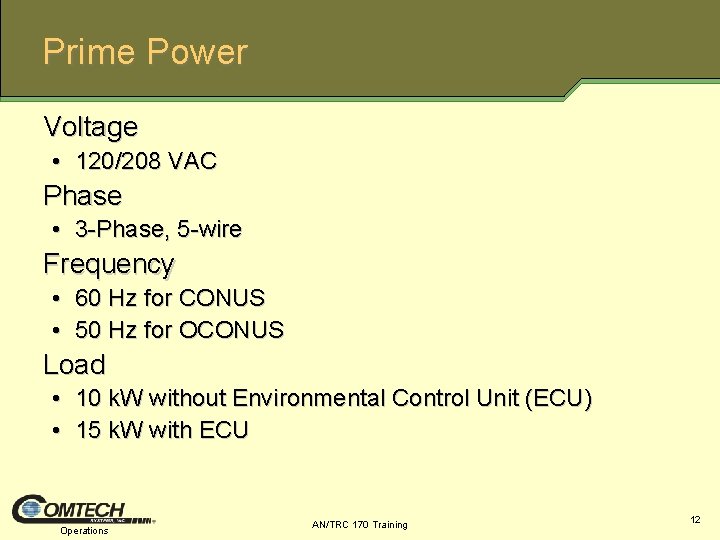
Prime Power Voltage • 120/208 VAC Phase • 3 Phase, 5 wire Frequency • 60 Hz for CONUS • 50 Hz for OCONUS Load • 10 k. W without Environmental Control Unit (ECU) • 15 k. W with ECU Operations AN/TRC 170 Training 12
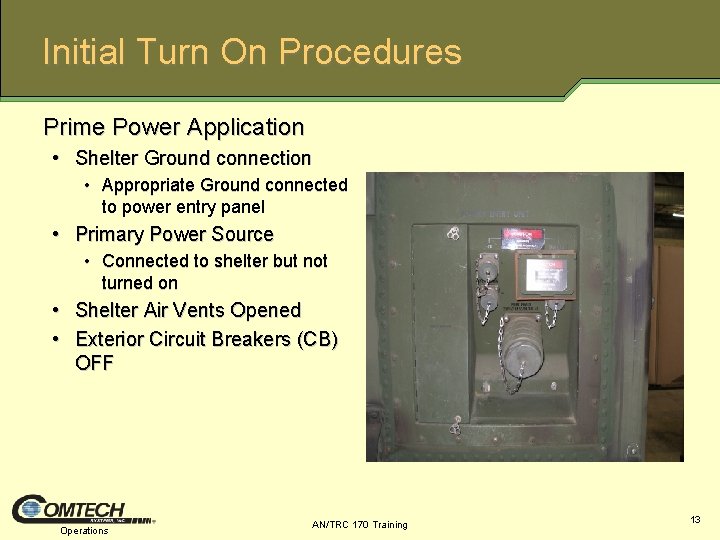
Initial Turn On Procedures Prime Power Application • Shelter Ground connection • Appropriate Ground connected to power entry panel • Primary Power Source • Connected to shelter but not turned on • Shelter Air Vents Opened • Exterior Circuit Breakers (CB) OFF Operations AN/TRC 170 Training 13
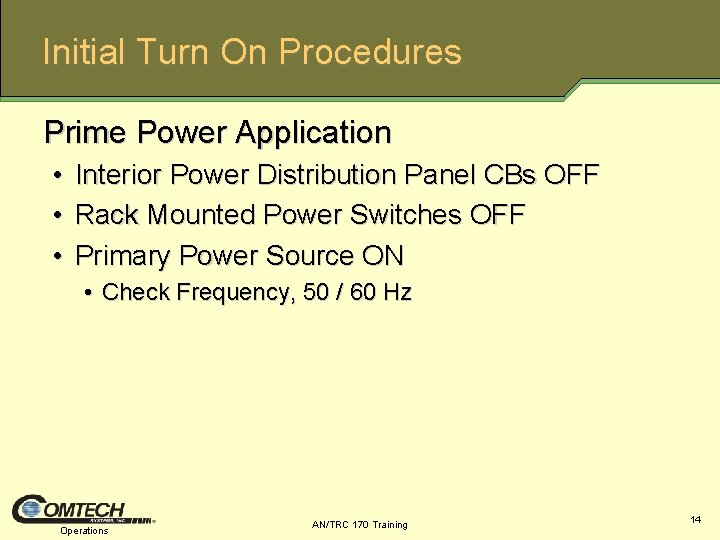
Initial Turn On Procedures Prime Power Application • • • Interior Power Distribution Panel CBs OFF Rack Mounted Power Switches OFF Primary Power Source ON • Check Frequency, 50 / 60 Hz Operations AN/TRC 170 Training 14
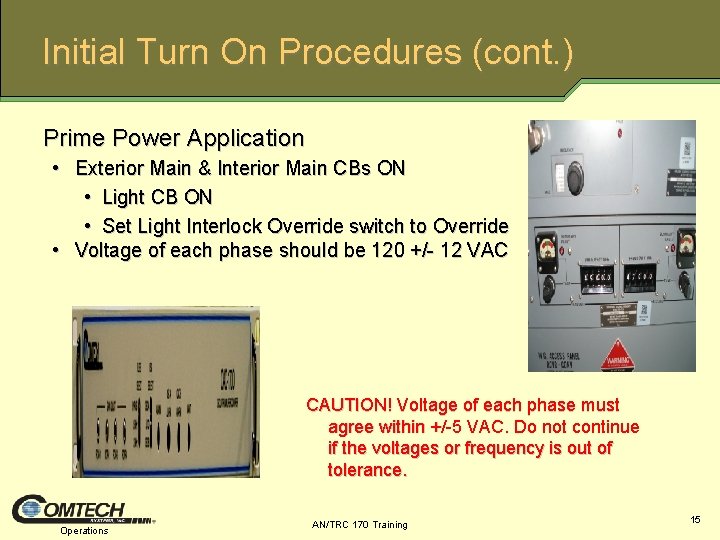
Initial Turn On Procedures (cont. ) Prime Power Application • Exterior Main & Interior Main CBs ON • Light CB ON • Set Light Interlock Override switch to Override • Voltage of each phase should be 120 +/ 12 VAC CAUTION! Voltage of each phase must agree within +/ 5 VAC. Do not continue if the voltages or frequency is out of tolerance. Operations AN/TRC 170 Training 15
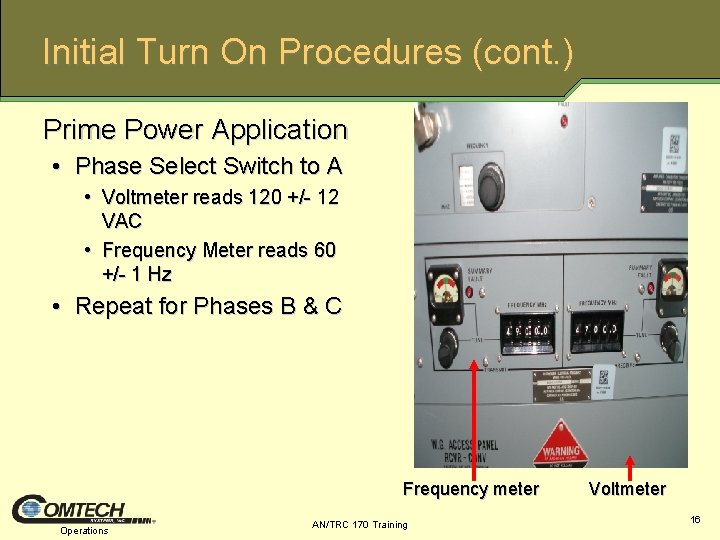
Initial Turn On Procedures (cont. ) Prime Power Application • Phase Select Switch to A • Voltmeter reads 120 +/ 12 VAC • Frequency Meter reads 60 +/ 1 Hz • Repeat for Phases B & C Frequency meter Operations AN/TRC 170 Training Voltmeter 16
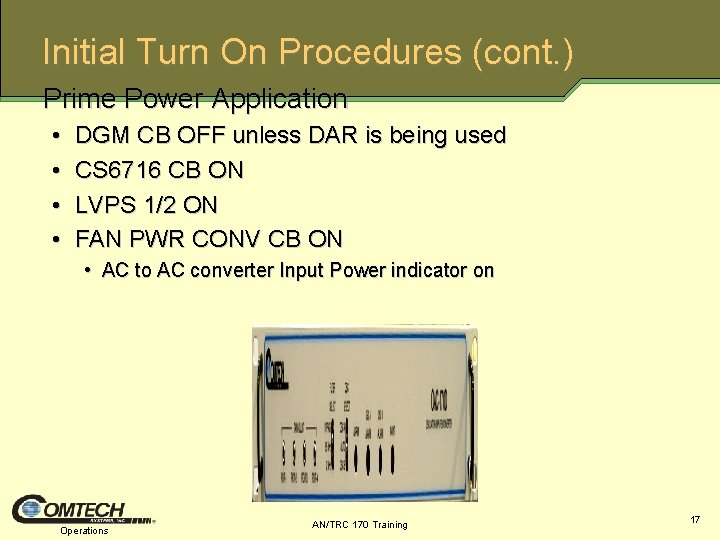
Initial Turn On Procedures (cont. ) Prime Power Application • • DGM CB OFF unless DAR is being used CS 6716 CB ON LVPS 1/2 ON FAN PWR CONV CB ON • AC to AC converter Input Power indicator on Operations AN/TRC 170 Training 17
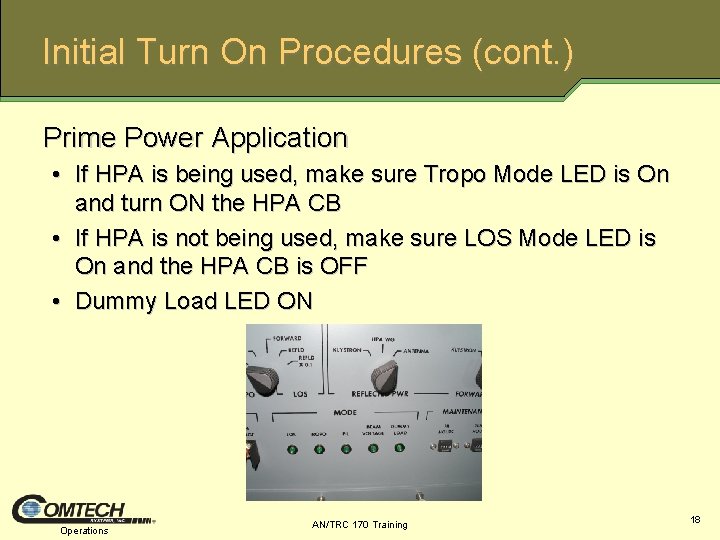
Initial Turn On Procedures (cont. ) Prime Power Application • If HPA is being used, make sure Tropo Mode LED is On and turn ON the HPA CB • If HPA is not being used, make sure LOS Mode LED is On and the HPA CB is OFF • Dummy Load LED ON Operations AN/TRC 170 Training 18
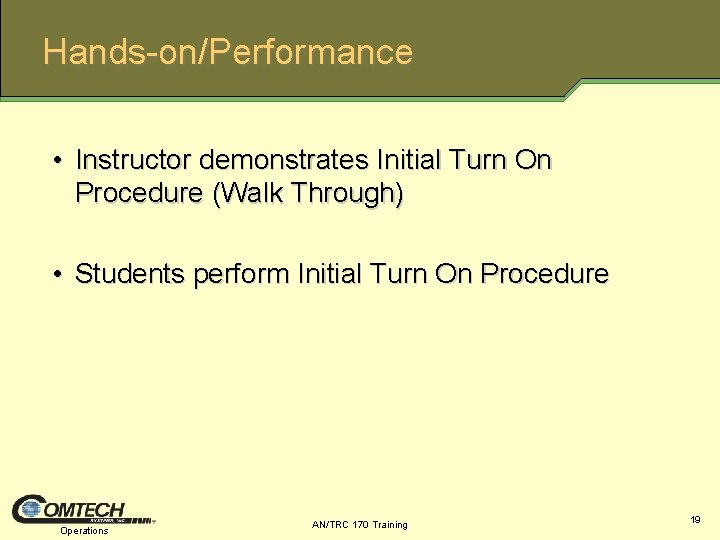
Hands on/Performance • Instructor demonstrates Initial Turn On Procedure (Walk Through) • Students perform Initial Turn On Procedure Operations AN/TRC 170 Training 19
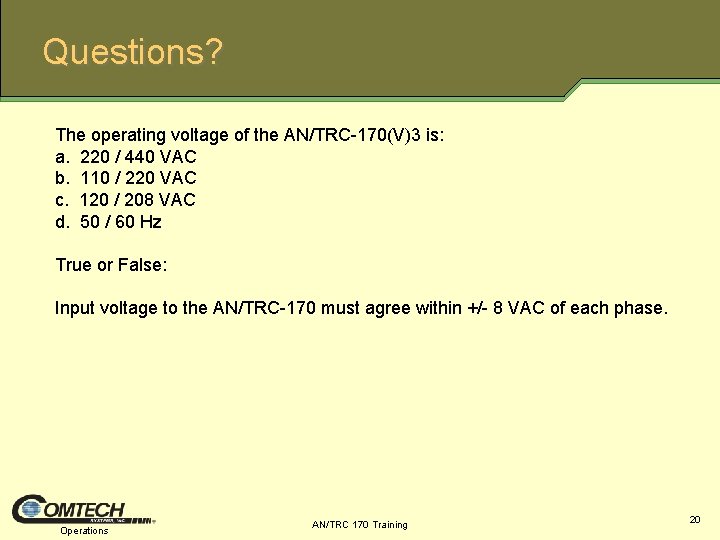
Questions? The operating voltage of the AN/TRC 170(V)3 is: a. 220 / 440 VAC b. 110 / 220 VAC c. 120 / 208 VAC d. 50 / 60 Hz True or False: Input voltage to the AN/TRC 170 must agree within +/ 8 VAC of each phase. Operations AN/TRC 170 Training 20
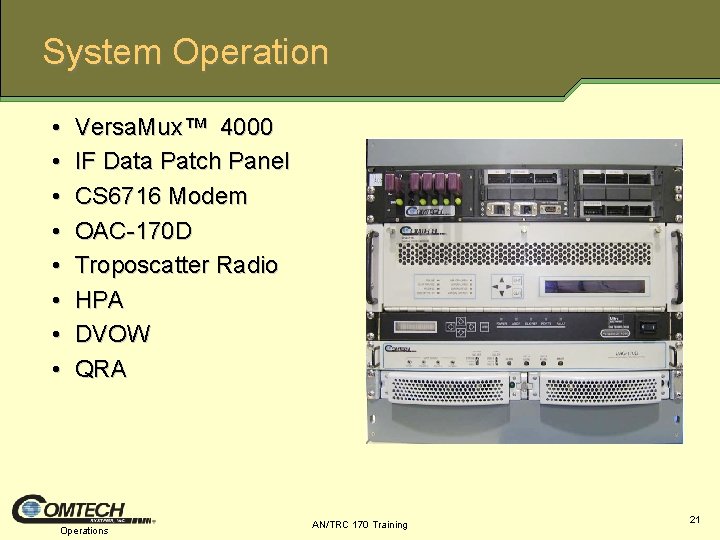
System Operation • • Versa. Mux™ 4000 IF Data Patch Panel CS 6716 Modem OAC 170 D Troposcatter Radio HPA DVOW QRA Operations AN/TRC 170 Training 21
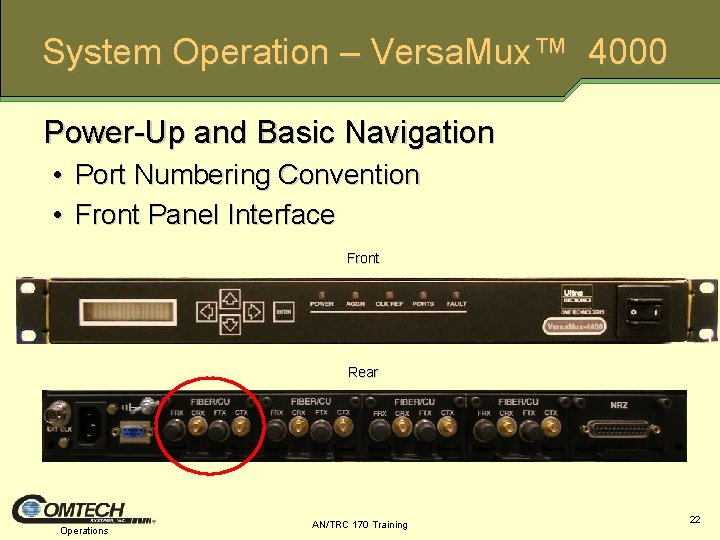
System Operation – Versa. Mux™ 4000 Power Up and Basic Navigation • Port Numbering Convention • Front Panel Interface Front Rear Operations AN/TRC 170 Training 22
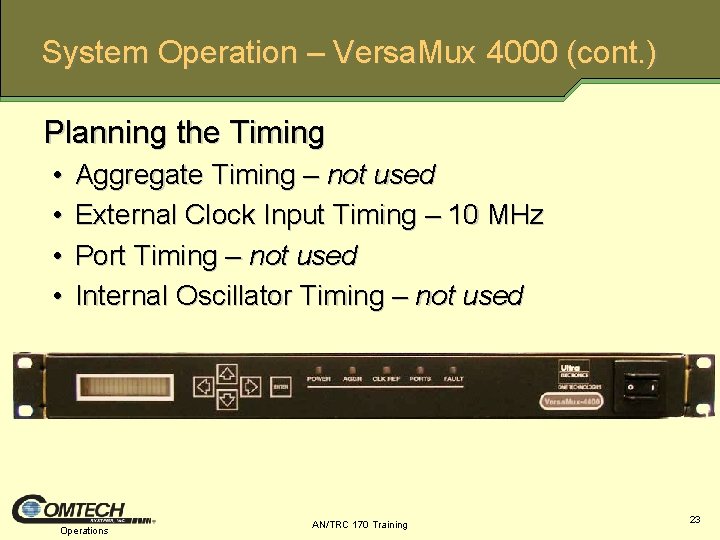
System Operation – Versa. Mux 4000 (cont. ) Planning the Timing • • Aggregate Timing – not used External Clock Input Timing – 10 MHz Port Timing – not used Internal Oscillator Timing – not used Operations AN/TRC 170 Training 23
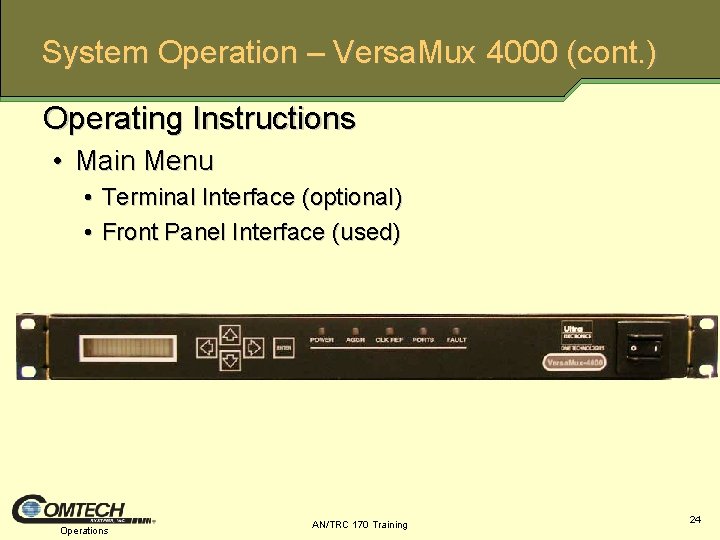
System Operation – Versa. Mux 4000 (cont. ) Operating Instructions • Main Menu • Terminal Interface (optional) • Front Panel Interface (used) Operations AN/TRC 170 Training 24
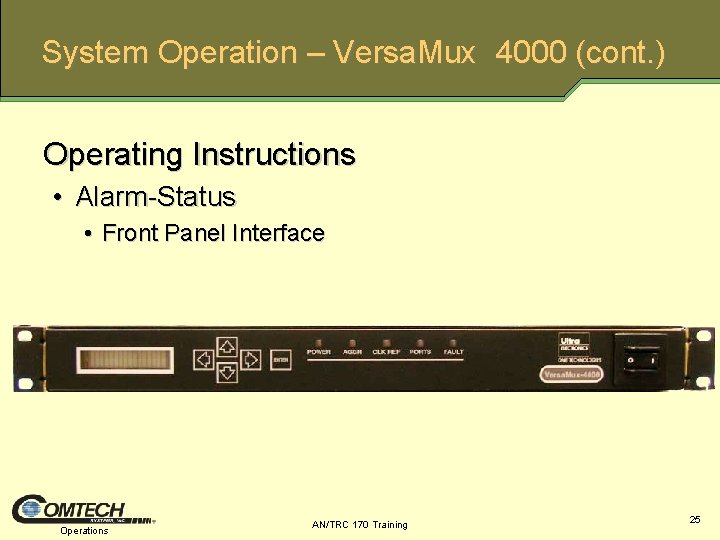
System Operation – Versa. Mux 4000 (cont. ) Operating Instructions • Alarm Status • Front Panel Interface Operations AN/TRC 170 Training 25
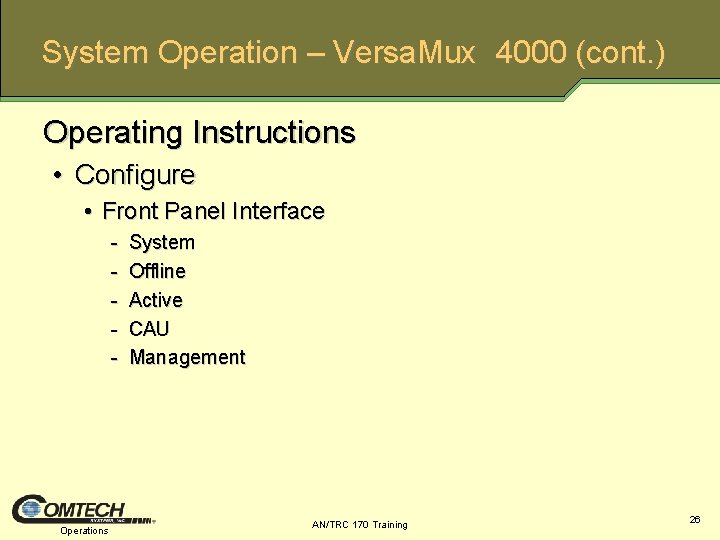
System Operation – Versa. Mux 4000 (cont. ) Operating Instructions • Configure • Front Panel Interface Operations System Offline Active CAU Management AN/TRC 170 Training 26
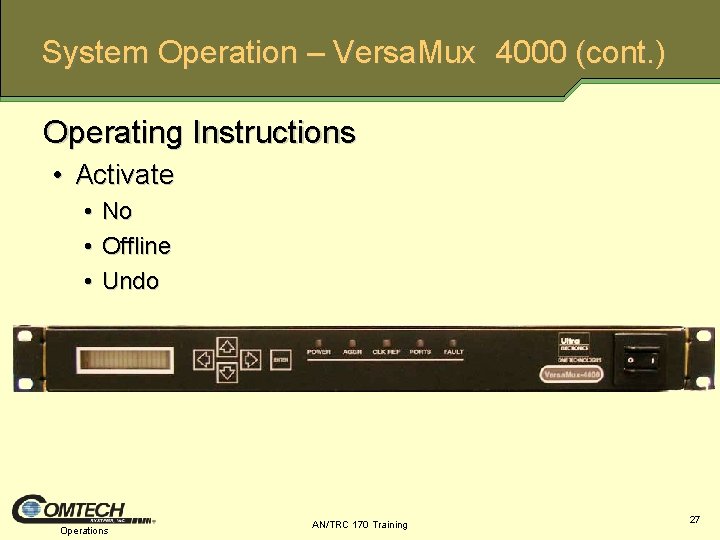
System Operation – Versa. Mux 4000 (cont. ) Operating Instructions • Activate • • • No Offline Undo Operations AN/TRC 170 Training 27
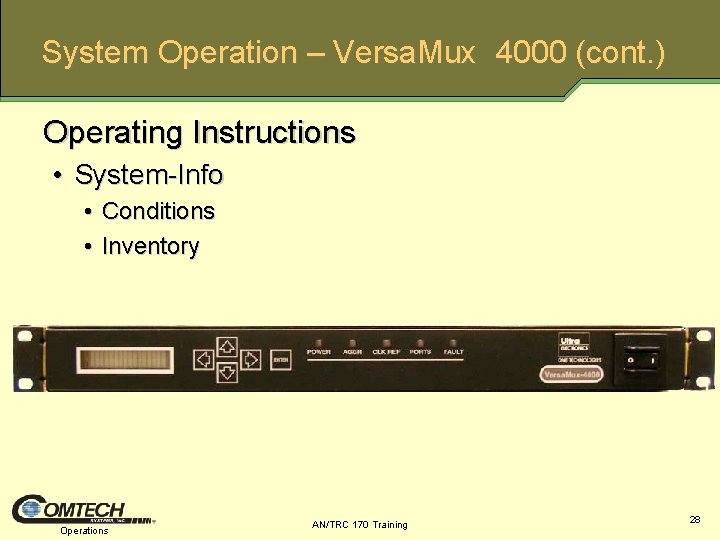
System Operation – Versa. Mux 4000 (cont. ) Operating Instructions • System Info • Conditions • Inventory Operations AN/TRC 170 Training 28
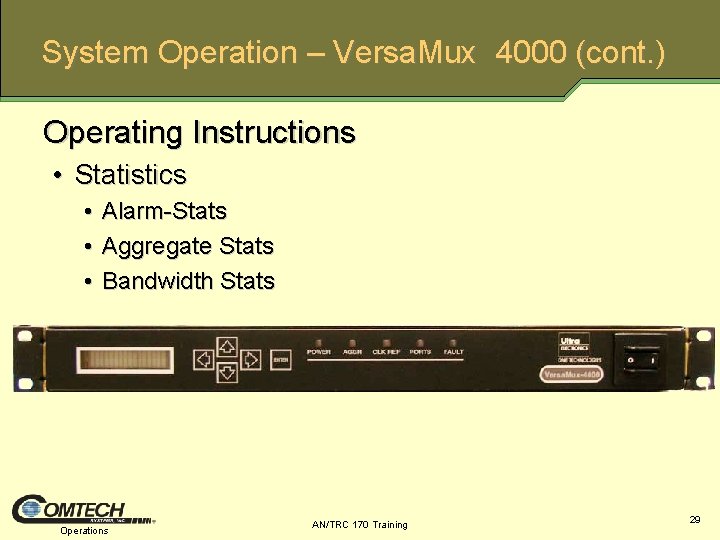
System Operation – Versa. Mux 4000 (cont. ) Operating Instructions • Statistics • • • Alarm Stats Aggregate Stats Bandwidth Stats Operations AN/TRC 170 Training 29
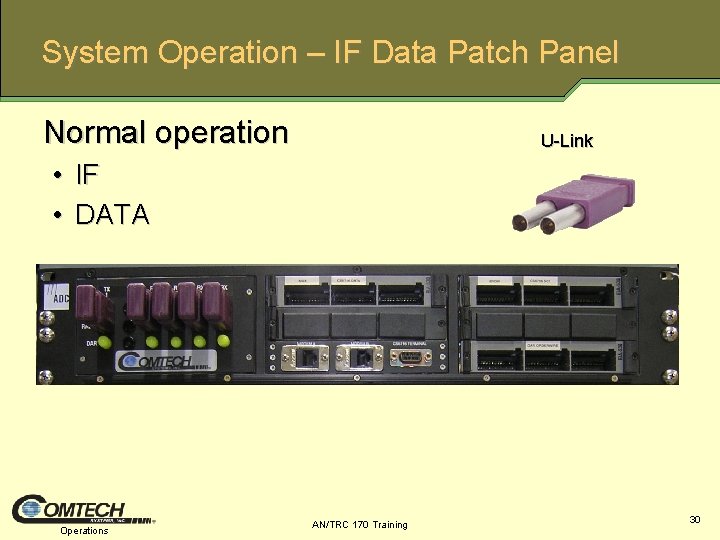
System Operation – IF Data Patch Panel Normal operation U Link • IF • DATA Operations AN/TRC 170 Training 30
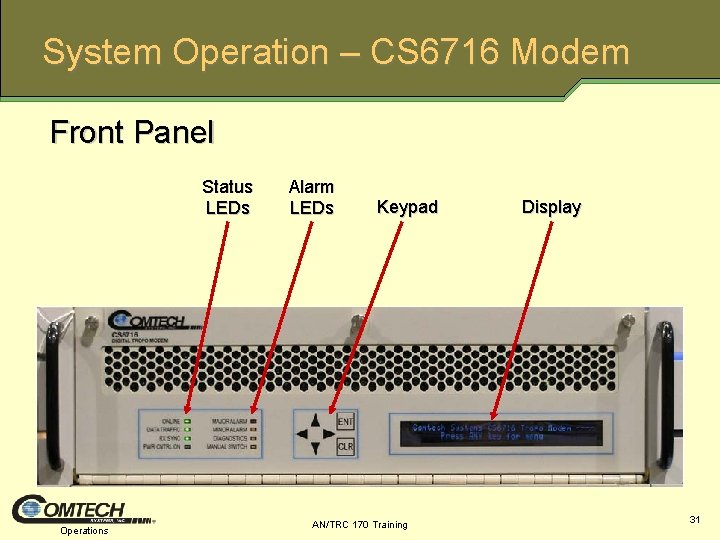
System Operation – CS 6716 Modem Front Panel Status LEDs Operations Alarm LEDs Keypad AN/TRC 170 Training Display 31
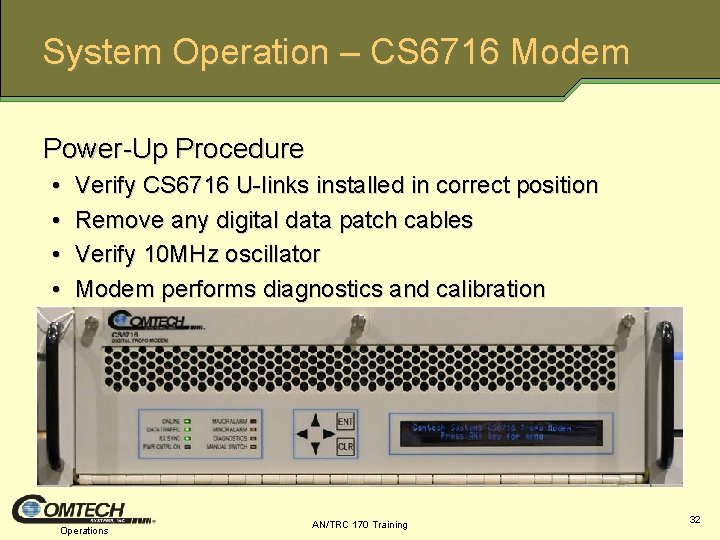
System Operation – CS 6716 Modem Power Up Procedure • • Verify CS 6716 U links installed in correct position Remove any digital data patch cables Verify 10 MHz oscillator Modem performs diagnostics and calibration Operations AN/TRC 170 Training 32
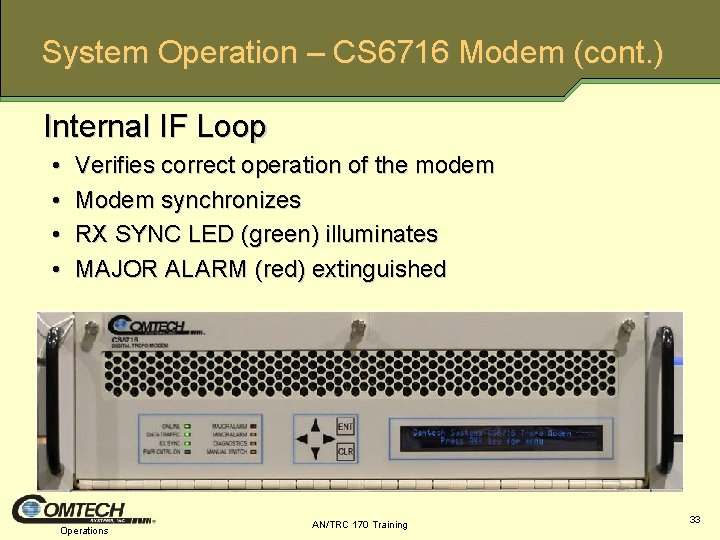
System Operation – CS 6716 Modem (cont. ) Internal IF Loop • • Verifies correct operation of the modem Modem synchronizes RX SYNC LED (green) illuminates MAJOR ALARM (red) extinguished Operations AN/TRC 170 Training 33
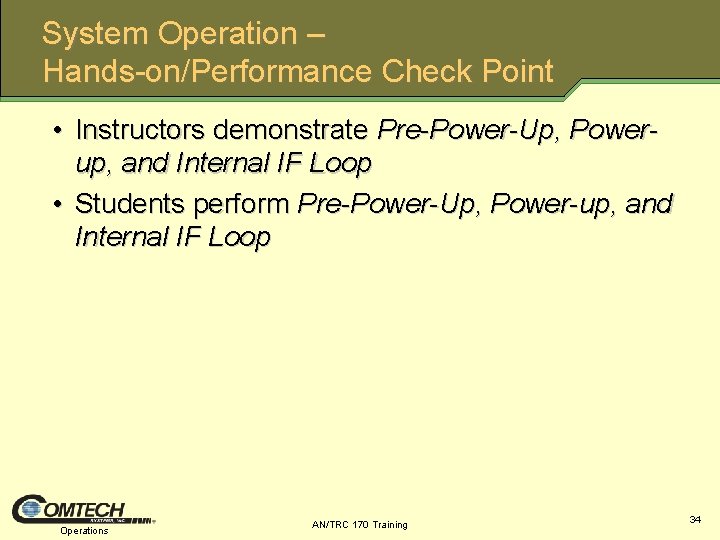
System Operation – Hands on/Performance Check Point • Instructors demonstrate Pre-Power-Up, Powerup, and Internal IF Loop • Students perform Pre-Power-Up, Power-up, and Internal IF Loop Operations AN/TRC 170 Training 34
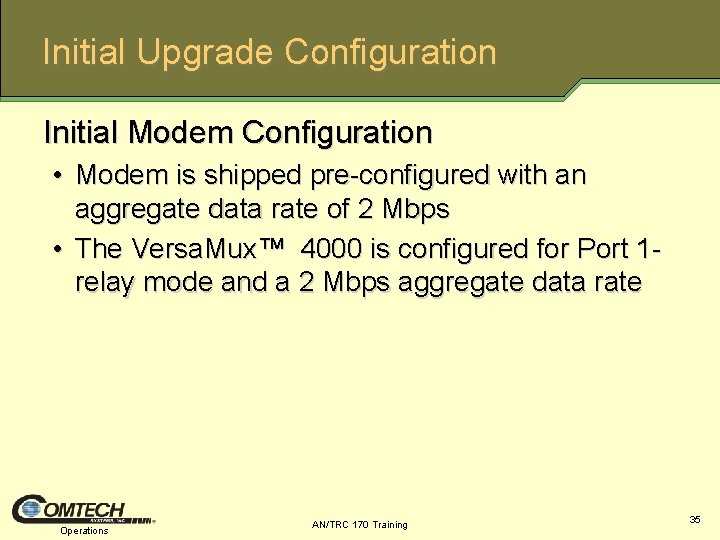
Initial Upgrade Configuration Initial Modem Configuration • Modem is shipped pre configured with an aggregate data rate of 2 Mbps • The Versa. Mux™ 4000 is configured for Port 1 relay mode and a 2 Mbps aggregate data rate Operations AN/TRC 170 Training 35
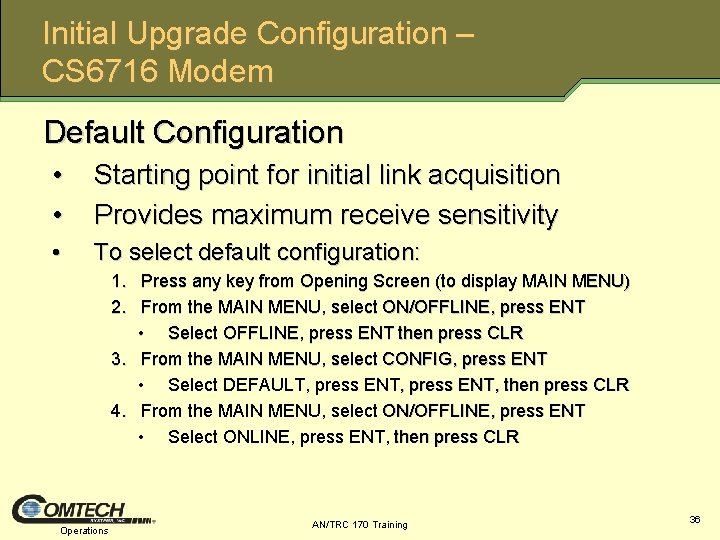
Initial Upgrade Configuration – CS 6716 Modem Default Configuration • • Starting point for initial link acquisition Provides maximum receive sensitivity • To select default configuration: 1. Press any key from Opening Screen (to display MAIN MENU) 2. From the MAIN MENU, select ON/OFFLINE, press ENT • Select OFFLINE, press ENT then press CLR 3. From the MAIN MENU, select CONFIG, press ENT • Select DEFAULT, press ENT, then press CLR 4. From the MAIN MENU, select ON/OFFLINE, press ENT • Select ONLINE, press ENT, then press CLR Operations AN/TRC 170 Training 36
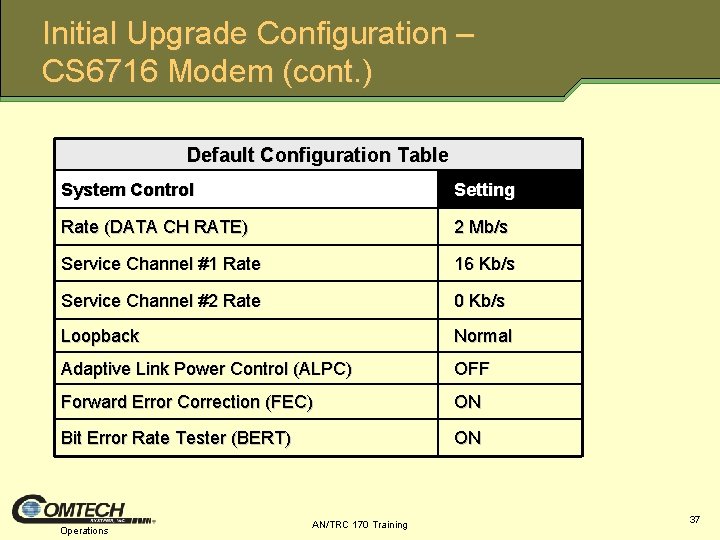
Initial Upgrade Configuration – CS 6716 Modem (cont. ) Default Configuration Table System Control Setting Rate (DATA CH RATE) 2 Mb/s Service Channel #1 Rate 16 Kb/s Service Channel #2 Rate 0 Kb/s Loopback Normal Adaptive Link Power Control (ALPC) OFF Forward Error Correction (FEC) ON Bit Error Rate Tester (BERT) ON Operations AN/TRC 170 Training 37
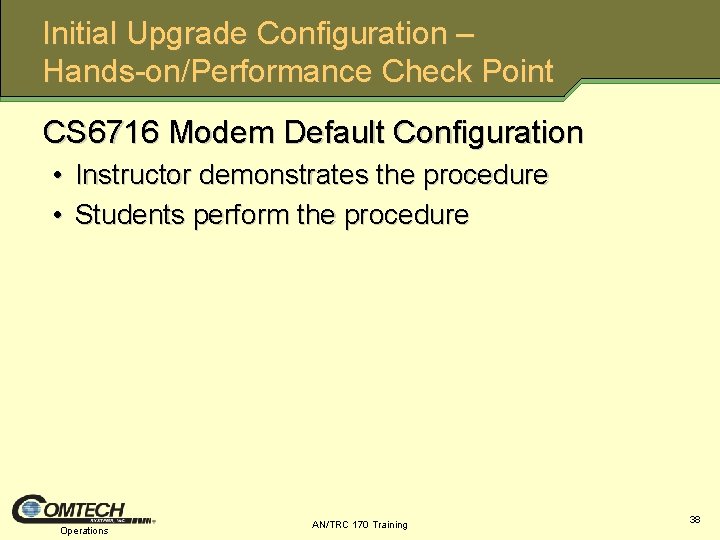
Initial Upgrade Configuration – Hands on/Performance Check Point CS 6716 Modem Default Configuration • Instructor demonstrates the procedure • Students perform the procedure Operations AN/TRC 170 Training 38
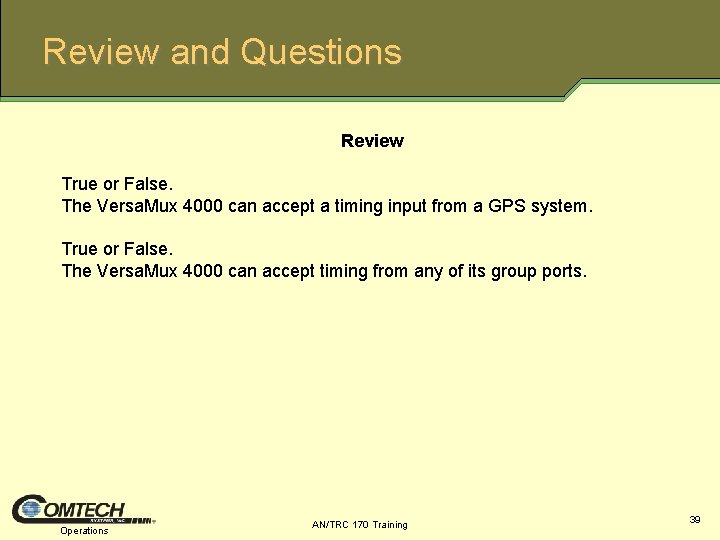
Review and Questions Review True or False. The Versa. Mux 4000 can accept a timing input from a GPS system. True or False. The Versa. Mux 4000 can accept timing from any of its group ports. Operations AN/TRC 170 Training 39
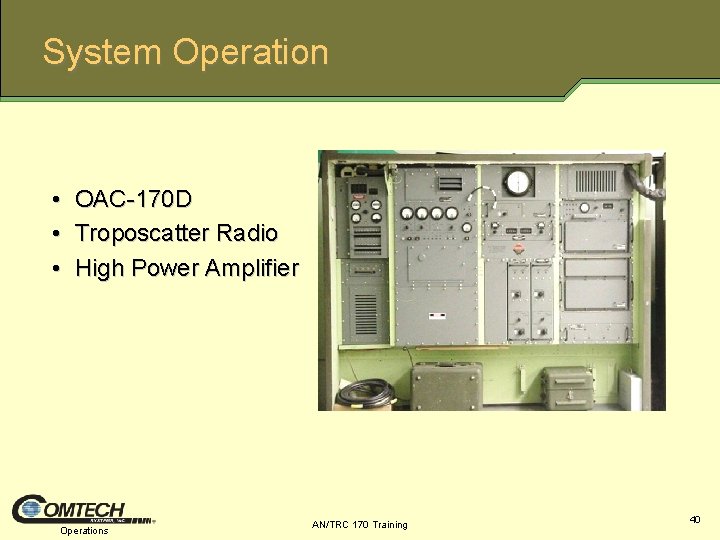
System Operation • • • OAC 170 D Troposcatter Radio High Power Amplifier Operations AN/TRC 170 Training 40

System Operation – OAC 170 D Pre Power Up Procedure • Set FILTER SELECT switch to desired bandwidth • Set OSC SELECT to AUTO Operations AN/TRC 170 Training 41
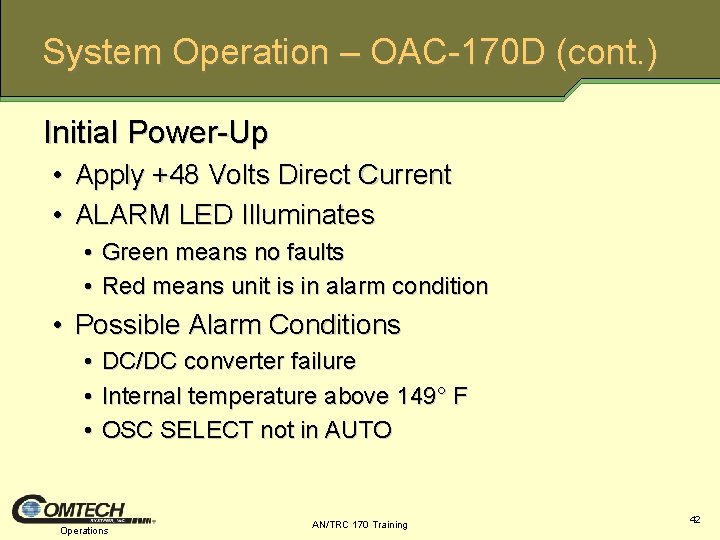
System Operation – OAC 170 D (cont. ) Initial Power Up • Apply +48 Volts Direct Current • ALARM LED Illuminates • Green means no faults • Red means unit is in alarm condition • Possible Alarm Conditions • • • DC/DC converter failure Internal temperature above 149° F OSC SELECT not in AUTO Operations AN/TRC 170 Training 42
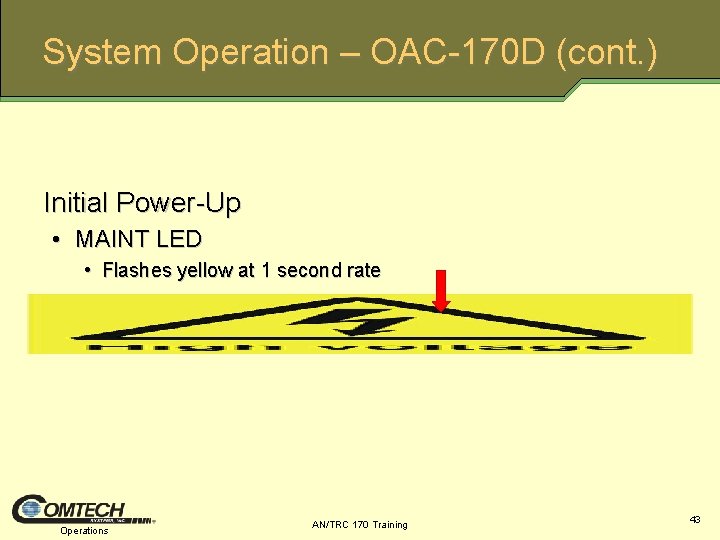
System Operation – OAC 170 D (cont. ) Initial Power Up • MAINT LED • Flashes yellow at 1 second rate Operations AN/TRC 170 Training 43
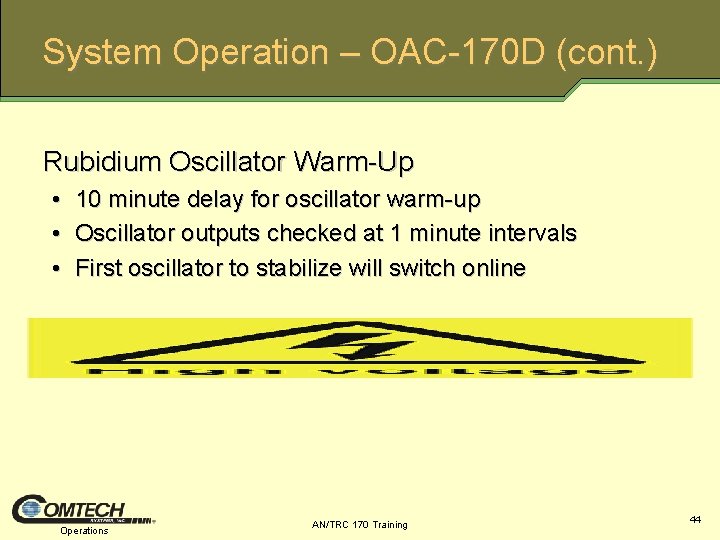
System Operation – OAC 170 D (cont. ) Rubidium Oscillator Warm Up • • • 10 minute delay for oscillator warm up Oscillator outputs checked at 1 minute intervals First oscillator to stabilize will switch online Operations AN/TRC 170 Training 44
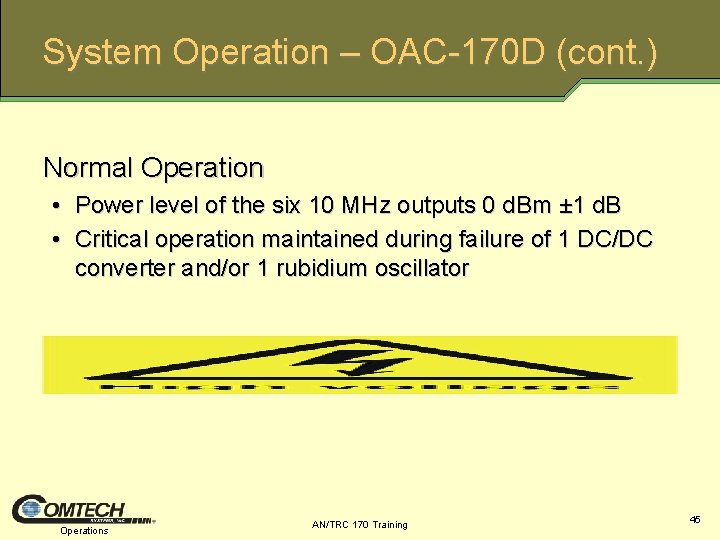
System Operation – OAC 170 D (cont. ) Normal Operation • Power level of the six 10 MHz outputs 0 d. Bm ± 1 d. B • Critical operation maintained during failure of 1 DC/DC converter and/or 1 rubidium oscillator Operations AN/TRC 170 Training 45
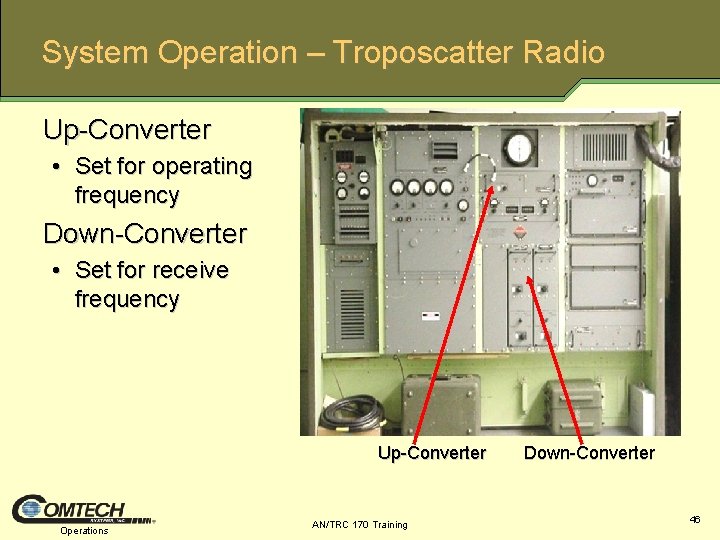
System Operation – Troposcatter Radio Up Converter • Set for operating frequency Down Converter • Set for receive frequency Up Converter Operations AN/TRC 170 Training Down Converter 46
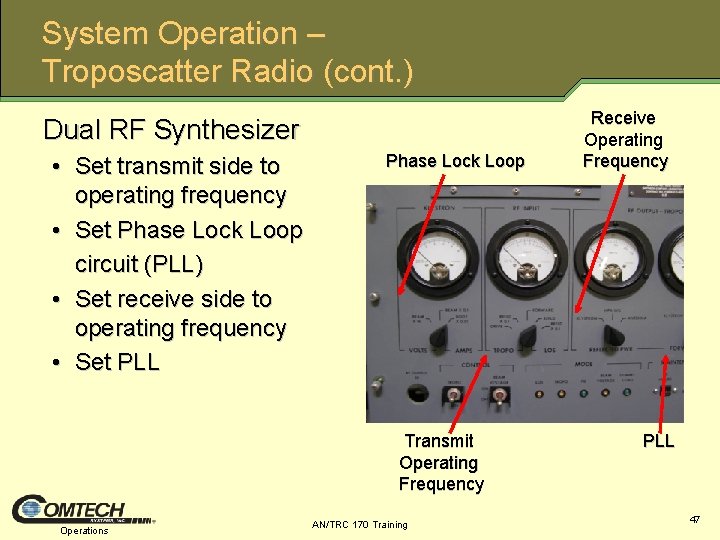
System Operation – Troposcatter Radio (cont. ) Dual RF Synthesizer • Set transmit side to operating frequency • Set Phase Lock Loop circuit (PLL) • Set receive side to operating frequency • Set PLL Phase Lock Loop Transmit Operating Frequency Operations AN/TRC 170 Training Receive Operating Frequency PLL 47
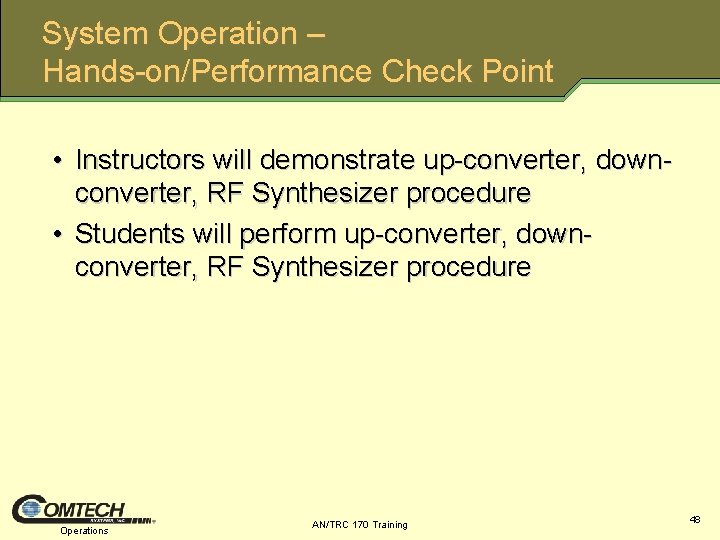
System Operation – Hands on/Performance Check Point • Instructors will demonstrate up converter, down converter, RF Synthesizer procedure • Students will perform up converter, down converter, RF Synthesizer procedure Operations AN/TRC 170 Training 48
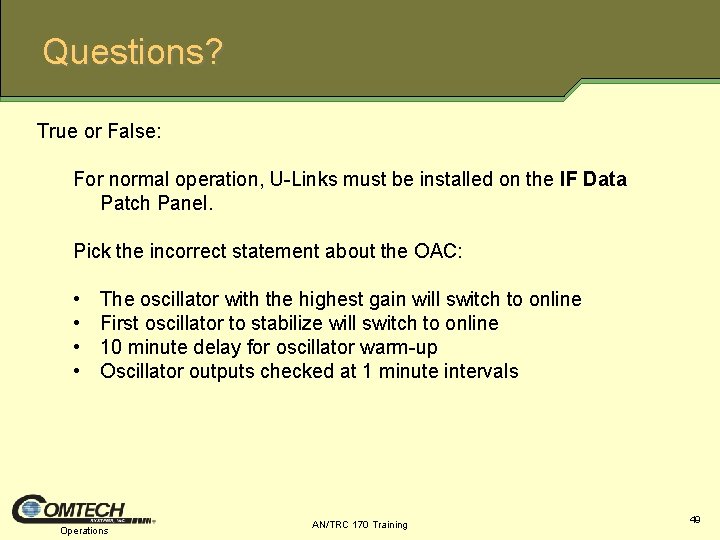
Questions? True or False: For normal operation, U Links must be installed on the IF Data Patch Panel. Pick the incorrect statement about the OAC: • • The oscillator with the highest gain will switch to online First oscillator to stabilize will switch to online 10 minute delay for oscillator warm up Oscillator outputs checked at 1 minute intervals Operations AN/TRC 170 Training 49
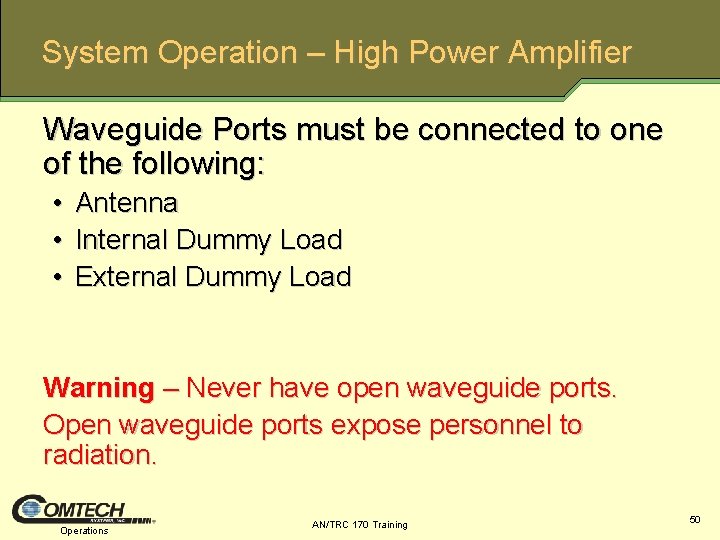
System Operation – High Power Amplifier Waveguide Ports must be connected to one of the following: • • • Antenna Internal Dummy Load External Dummy Load Warning – Never have open waveguide ports. Open waveguide ports expose personnel to radiation. Operations AN/TRC 170 Training 50
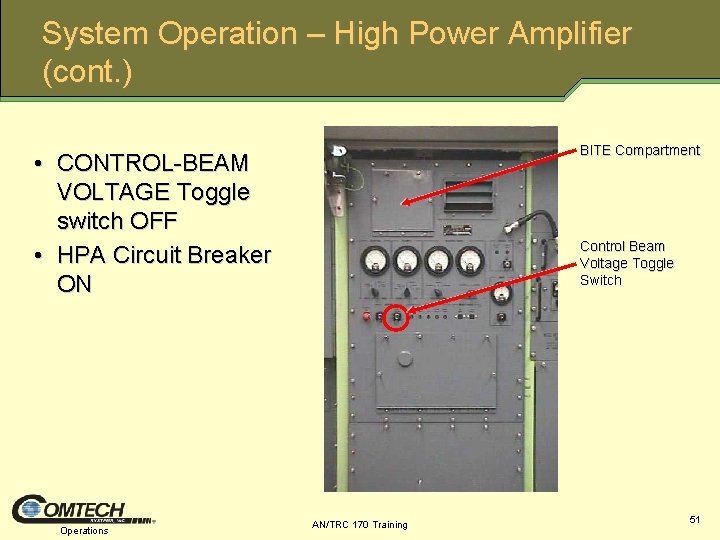
System Operation – High Power Amplifier (cont. ) BITE Compartment • CONTROL BEAM VOLTAGE Toggle switch OFF • HPA Circuit Breaker ON Operations Control Beam Voltage Toggle Switch AN/TRC 170 Training 51
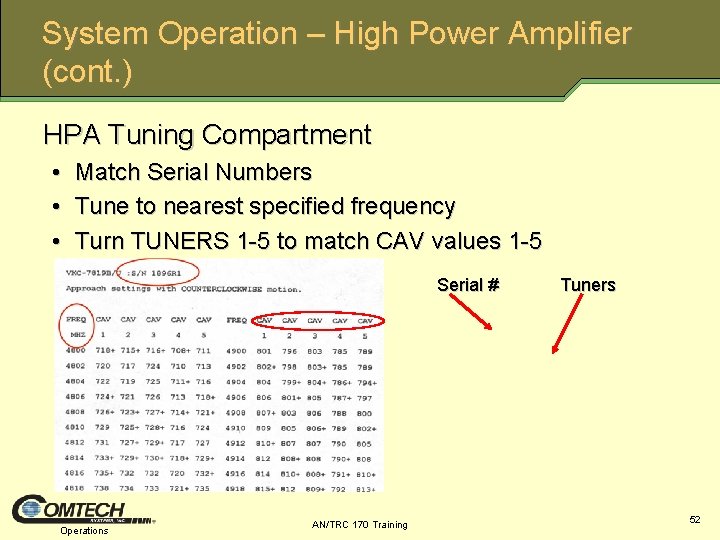
System Operation – High Power Amplifier (cont. ) HPA Tuning Compartment • • • Match Serial Numbers Tune to nearest specified frequency Turn TUNERS 1 5 to match CAV values 1 5 Serial # Operations AN/TRC 170 Training Tuners 52
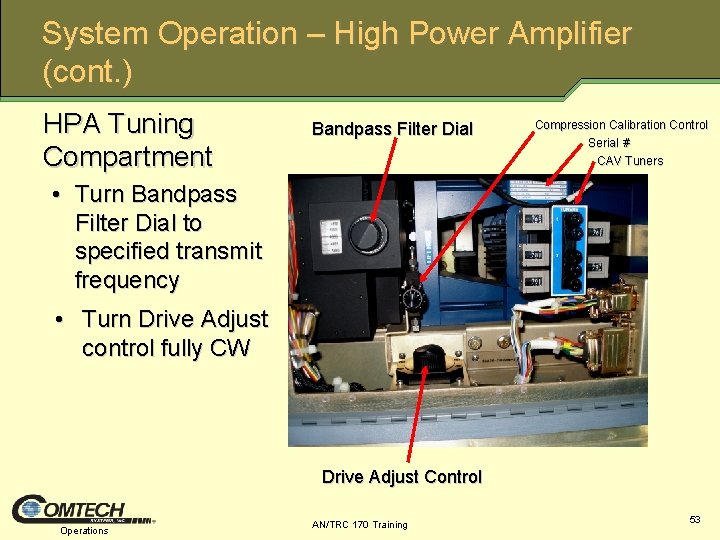
System Operation – High Power Amplifier (cont. ) HPA Tuning Compartment Bandpass Filter Dial Compression Calibration Control Serial # CAV Tuners • Turn Bandpass Filter Dial to specified transmit frequency • Turn Drive Adjust control fully CW Drive Adjust Control Operations AN/TRC 170 Training 53
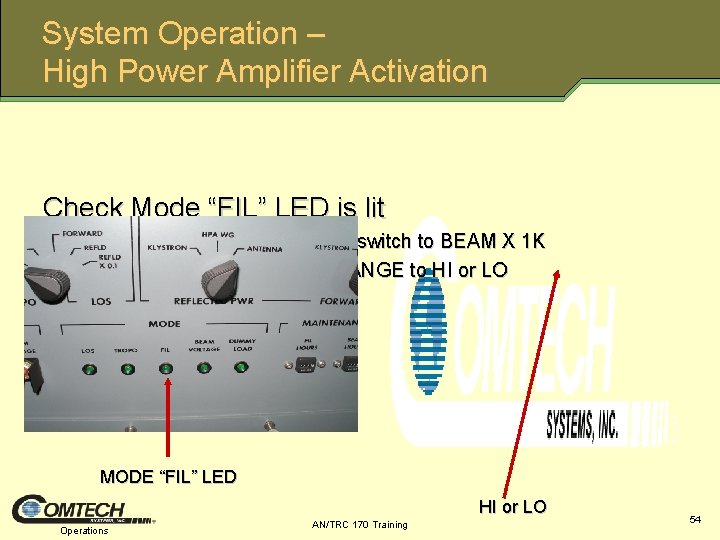
System Operation – High Power Amplifier Activation Check Mode “FIL” LED is lit • Move KLYSTRON meter select switch to BEAM X 1 K • BITE compartment panel set RANGE to HI or LO MODE “FIL” LED HI or LO Operations AN/TRC 170 Training 54
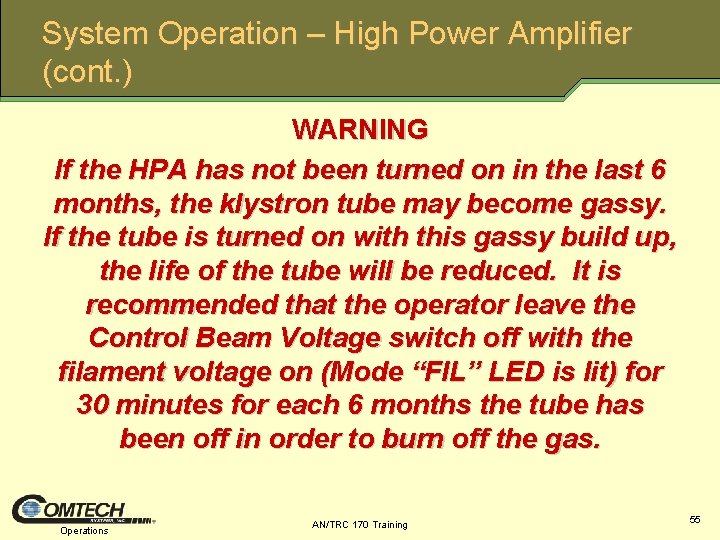
System Operation – High Power Amplifier (cont. ) WARNING If the HPA has not been turned on in the last 6 months, the klystron tube may become gassy. If the tube is turned on with this gassy build up, the life of the tube will be reduced. It is recommended that the operator leave the Control Beam Voltage switch off with the filament voltage on (Mode “FIL” LED is lit) for 30 minutes for each 6 months the tube has been off in order to burn off the gas. Operations AN/TRC 170 Training 55
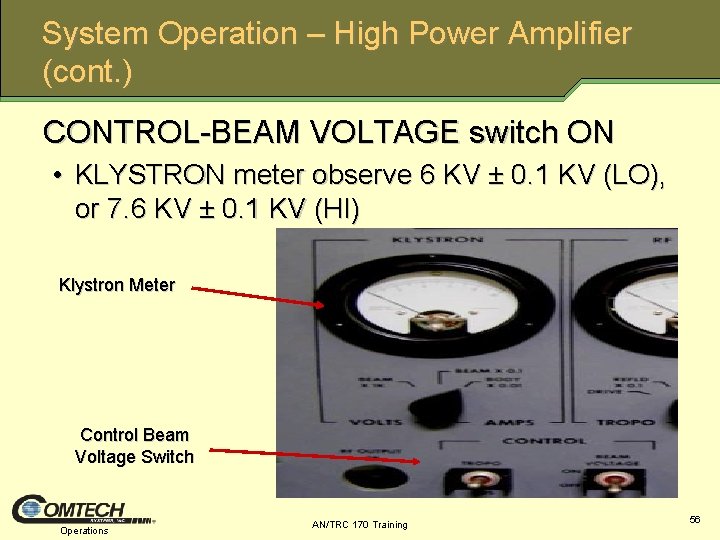
System Operation – High Power Amplifier (cont. ) CONTROL BEAM VOLTAGE switch ON • KLYSTRON meter observe 6 KV ± 0. 1 KV (LO), or 7. 6 KV ± 0. 1 KV (HI) Klystron Meter Control Beam Voltage Switch Operations AN/TRC 170 Training 56
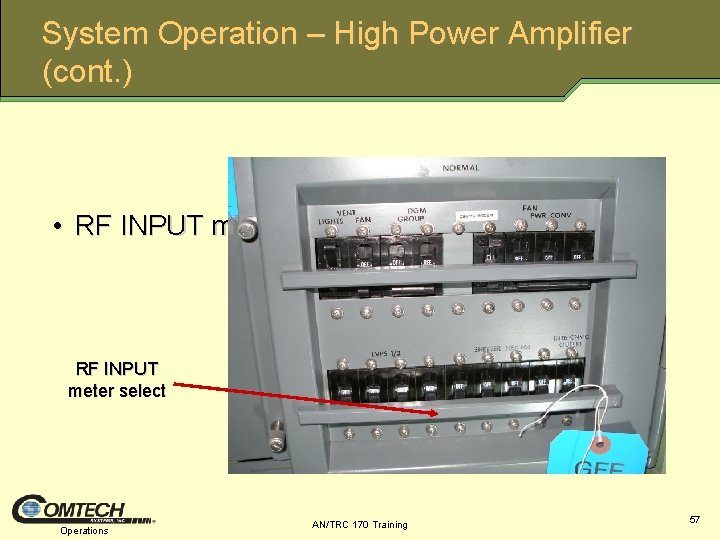
System Operation – High Power Amplifier (cont. ) • RF INPUT meter select to DRIVE RF INPUT meter select Operations AN/TRC 170 Training 57
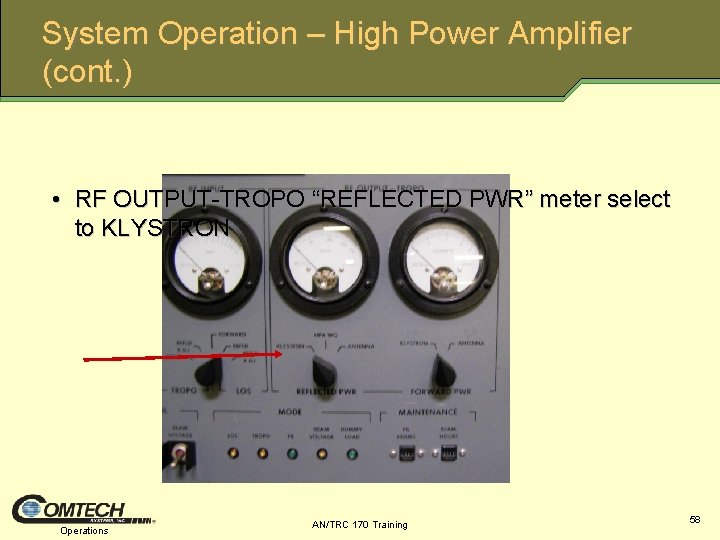
System Operation – High Power Amplifier (cont. ) • RF OUTPUT TROPO “REFLECTED PWR” meter select to KLYSTRON Operations AN/TRC 170 Training 58
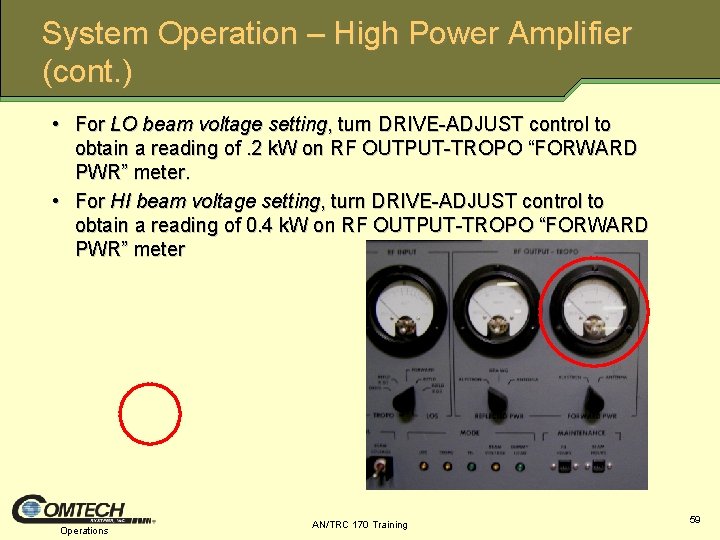
System Operation – High Power Amplifier (cont. ) • For LO beam voltage setting, turn DRIVE ADJUST control to obtain a reading of. 2 k. W on RF OUTPUT TROPO “FORWARD PWR” meter. • For HI beam voltage setting, turn DRIVE ADJUST control to obtain a reading of 0. 4 k. W on RF OUTPUT TROPO “FORWARD PWR” meter Operations AN/TRC 170 Training 59

System Operation – High Power Amplifier (cont. ) Hold DRIVE ADJUST/CALIBRATE switch in CALIBRATE, and adjust compression calibration control to obtain DRIVE meter reading in green area Compression Calibration Control Drive Meter & Calibrate Switch Operations AN/TRC 170 Training 60
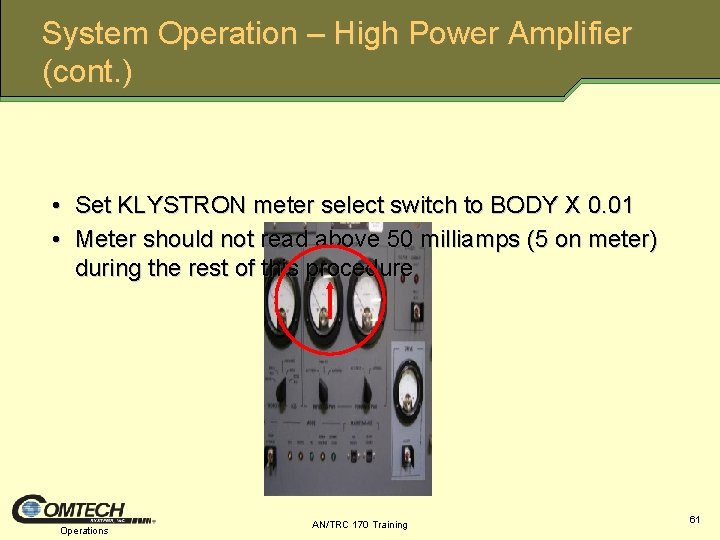
System Operation – High Power Amplifier (cont. ) • Set KLYSTRON meter select switch to BODY X 0. 01 • Meter should not read above 50 milliamps (5 on meter) during the rest of this procedure Operations AN/TRC 170 Training 61
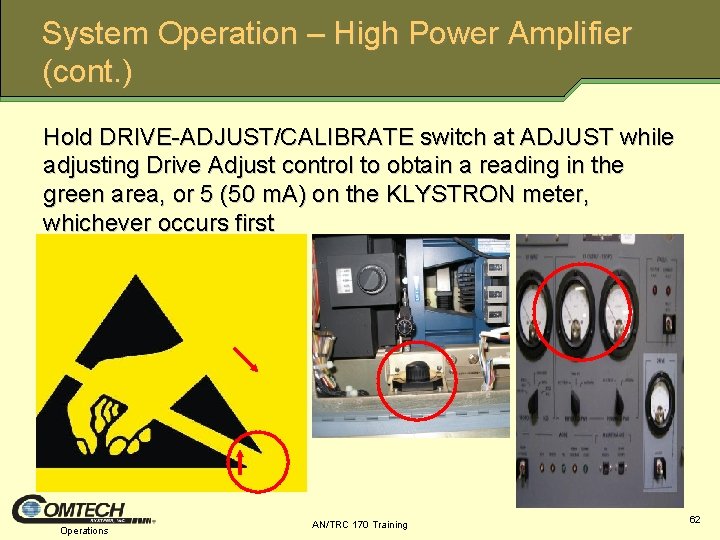
System Operation – High Power Amplifier (cont. ) Hold DRIVE ADJUST/CALIBRATE switch at ADJUST while adjusting Drive Adjust control to obtain a reading in the green area, or 5 (50 m. A) on the KLYSTRON meter, whichever occurs first Operations AN/TRC 170 Training 62
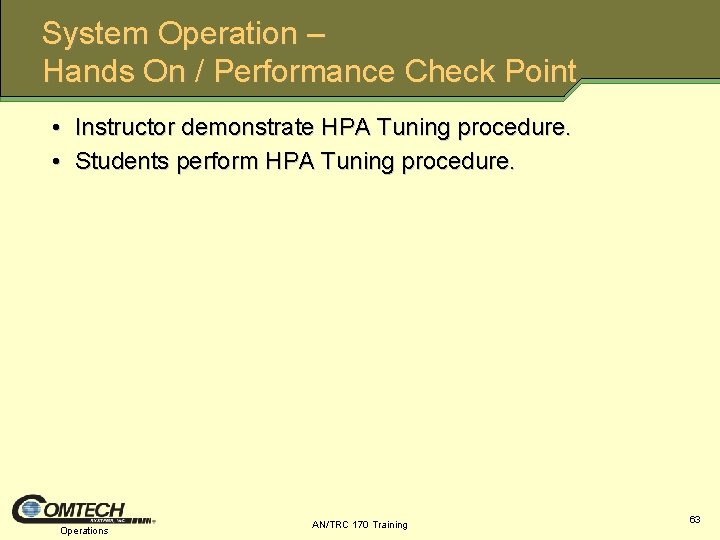
System Operation – Hands On / Performance Check Point • Instructor demonstrate HPA Tuning procedure. • Students perform HPA Tuning procedure. Operations AN/TRC 170 Training 63
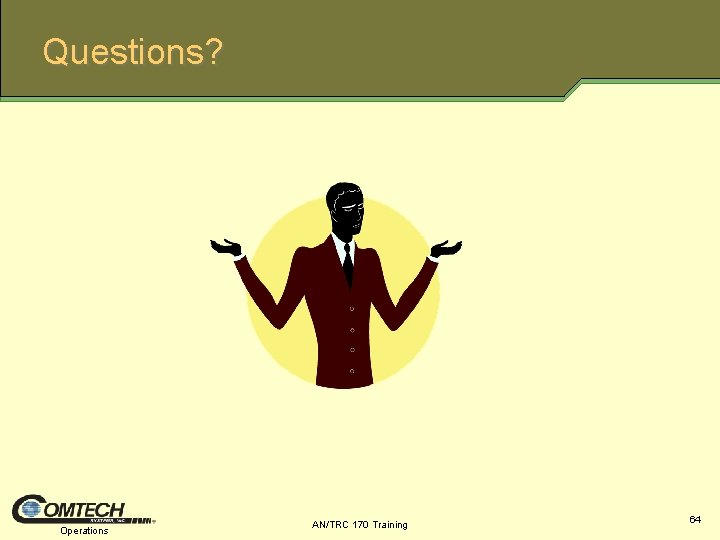
Questions? Operations AN/TRC 170 Training 64
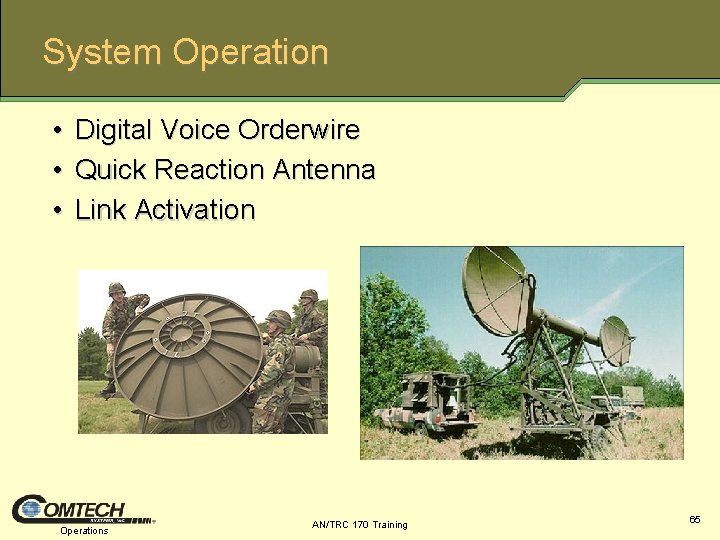
System Operation • • • Digital Voice Orderwire Quick Reaction Antenna Link Activation Operations AN/TRC 170 Training 65
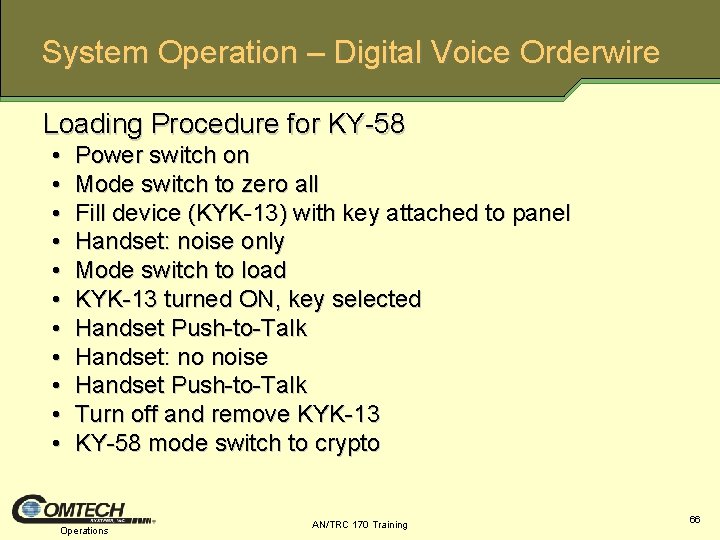
System Operation – Digital Voice Orderwire Loading Procedure for KY 58 • • • Power switch on Mode switch to zero all Fill device (KYK 13) with key attached to panel Handset: noise only Mode switch to load KYK 13 turned ON, key selected Handset Push to Talk Handset: no noise Handset Push to Talk Turn off and remove KYK 13 KY 58 mode switch to crypto Operations AN/TRC 170 Training 66
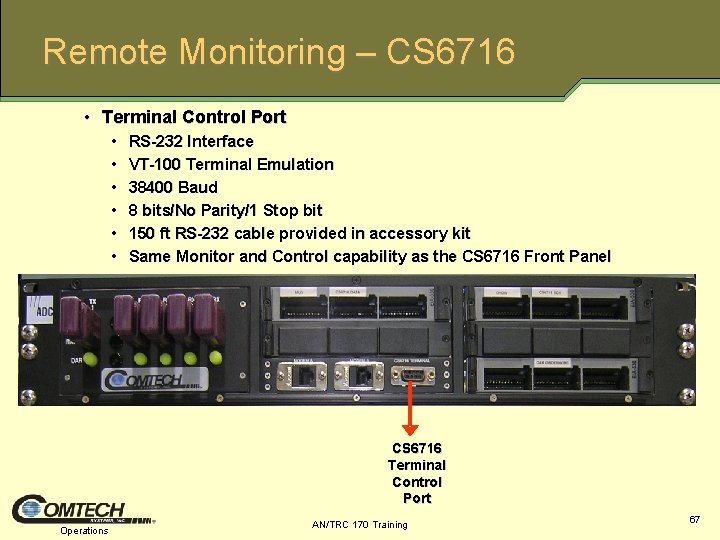
Remote Monitoring – CS 6716 • Terminal Control Port • • • RS-232 Interface VT-100 Terminal Emulation 38400 Baud 8 bits/No Parity/1 Stop bit 150 ft RS-232 cable provided in accessory kit Same Monitor and Control capability as the CS 6716 Front Panel CS 6716 Terminal Control Port Operations AN/TRC 170 Training 67
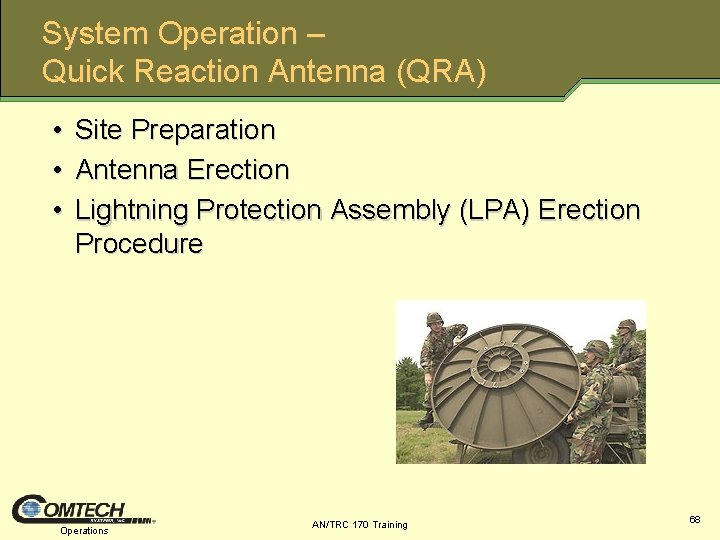
System Operation – Quick Reaction Antenna (QRA) • • • Site Preparation Antenna Erection Lightning Protection Assembly (LPA) Erection Procedure Operations AN/TRC 170 Training 68
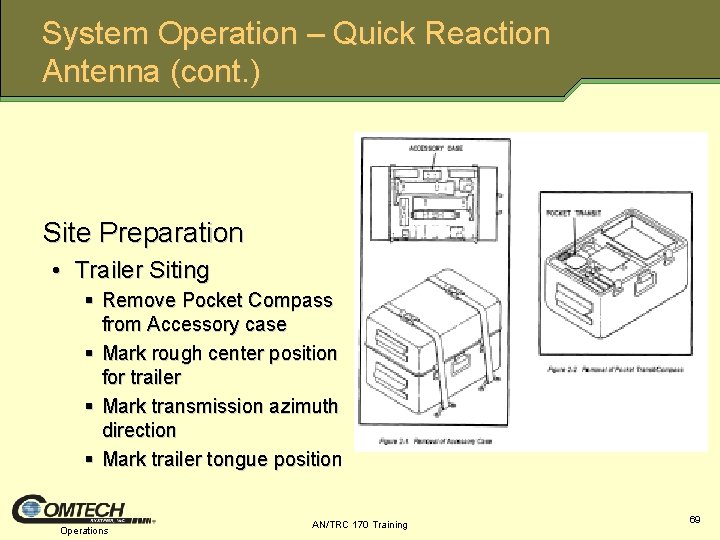
System Operation – Quick Reaction Antenna (cont. ) Site Preparation • Trailer Siting § Remove Pocket Compass from Accessory case § Mark rough center position for trailer § Mark transmission azimuth direction § Mark trailer tongue position Operations AN/TRC 170 Training 69
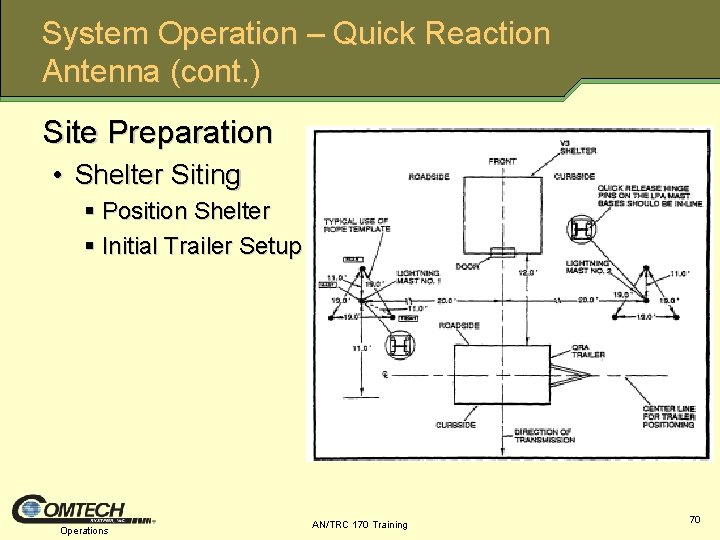
System Operation – Quick Reaction Antenna (cont. ) Site Preparation • Shelter Siting § Position Shelter § Initial Trailer Setup Operations AN/TRC 170 Training 70
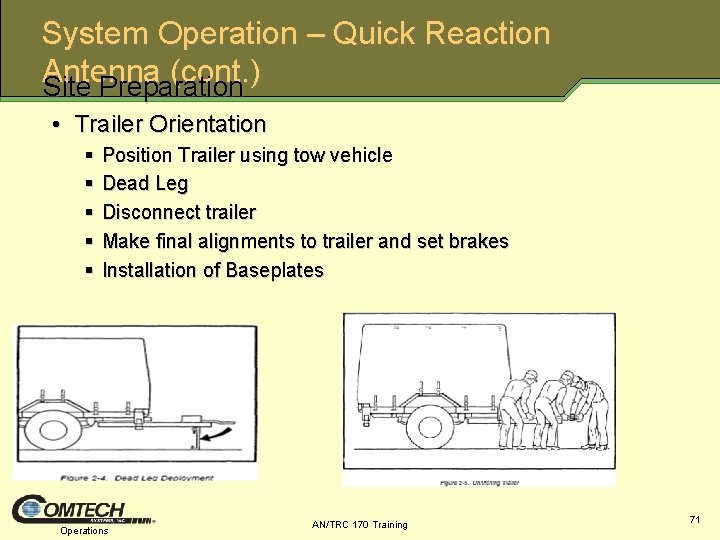
System Operation – Quick Reaction Antenna (cont. ) Site Preparation • Trailer Orientation § § § Position Trailer using tow vehicle Dead Leg Disconnect trailer Make final alignments to trailer and set brakes Installation of Baseplates Operations AN/TRC 170 Training 71
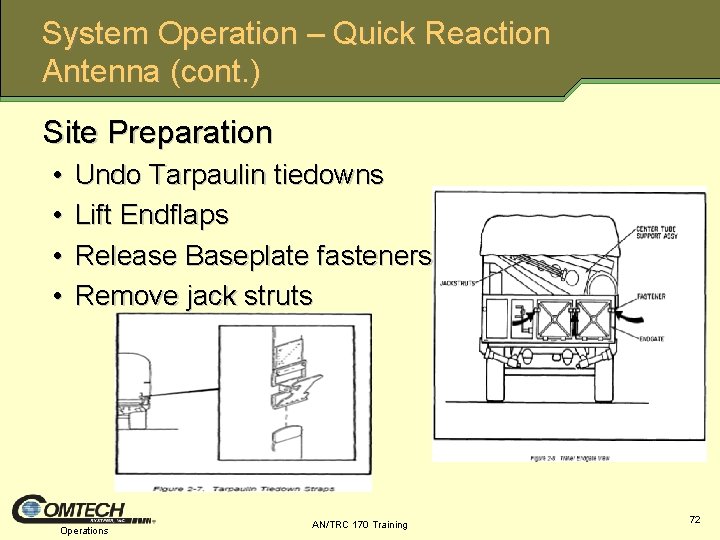
System Operation – Quick Reaction Antenna (cont. ) Site Preparation • • Undo Tarpaulin tiedowns Lift Endflaps Release Baseplate fasteners Remove jack struts Operations AN/TRC 170 Training 72
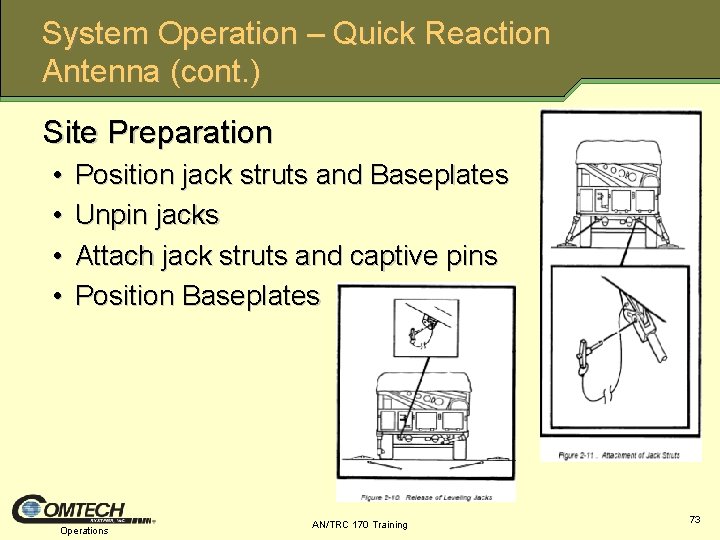
System Operation – Quick Reaction Antenna (cont. ) Site Preparation • • Position jack struts and Baseplates Unpin jacks Attach jack struts and captive pins Position Baseplates Operations AN/TRC 170 Training 73
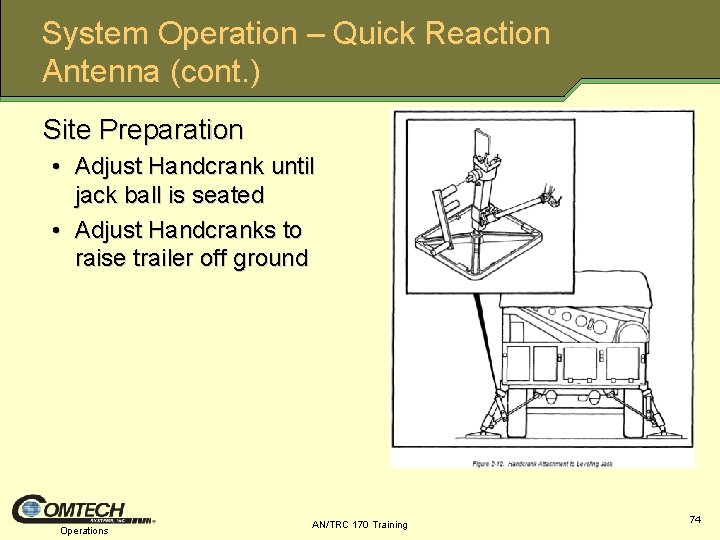
System Operation – Quick Reaction Antenna (cont. ) Site Preparation • Adjust Handcrank until jack ball is seated • Adjust Handcranks to raise trailer off ground Operations AN/TRC 170 Training 74
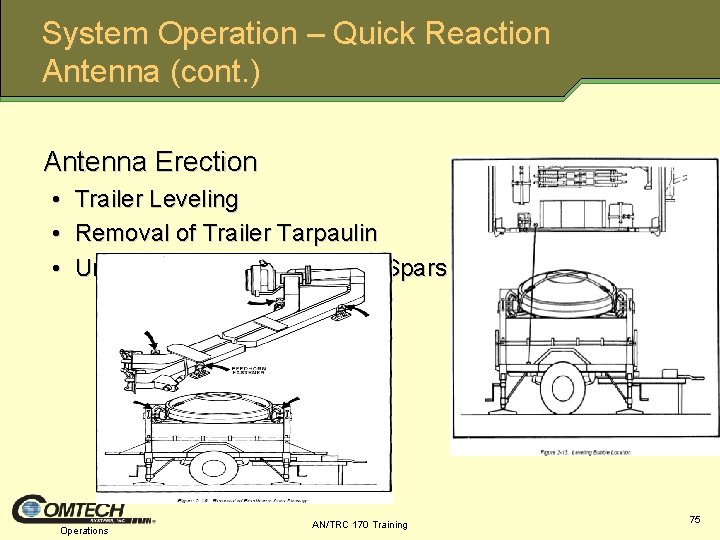
System Operation – Quick Reaction Antenna (cont. ) Antenna Erection • • • Trailer Leveling Removal of Trailer Tarpaulin Unloading of Feedhorns and Spars Operations AN/TRC 170 Training 75
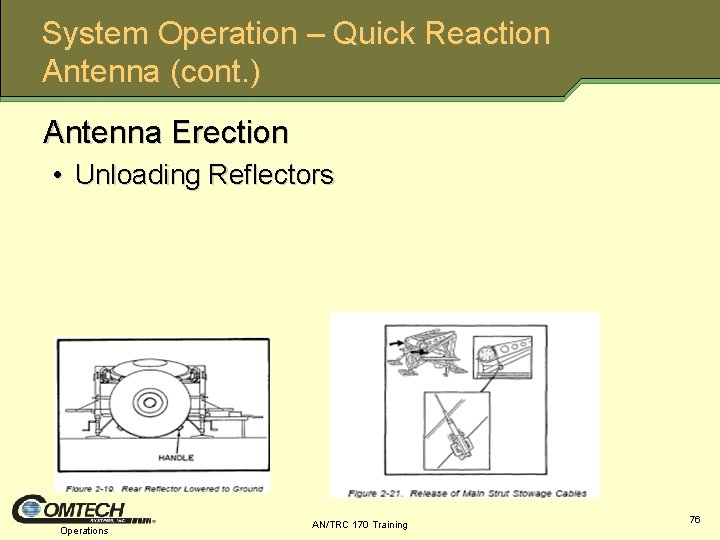
System Operation – Quick Reaction Antenna (cont. ) Antenna Erection • Unloading Reflectors Operations AN/TRC 170 Training 76
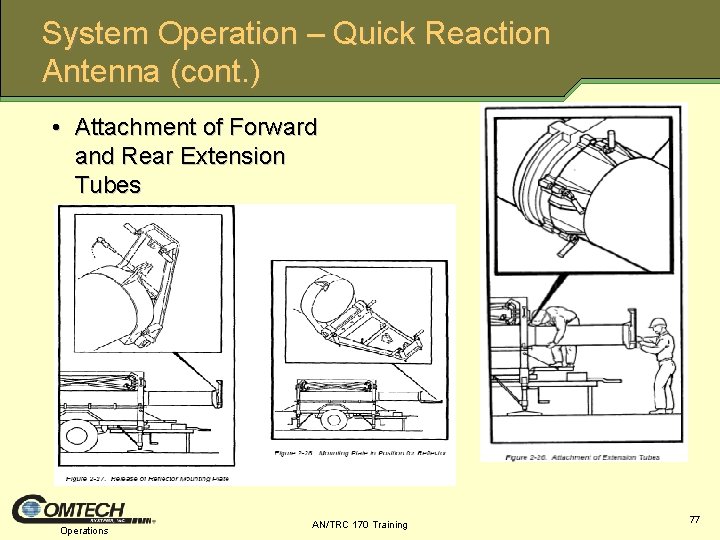
System Operation – Quick Reaction Antenna (cont. ) • Attachment of Forward and Rear Extension Tubes Operations AN/TRC 170 Training 77
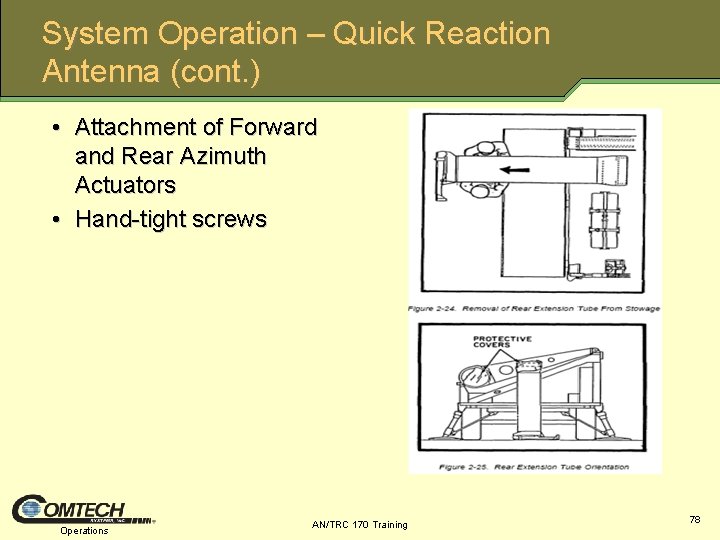
System Operation – Quick Reaction Antenna (cont. ) • Attachment of Forward and Rear Azimuth Actuators • Hand tight screws Operations AN/TRC 170 Training 78
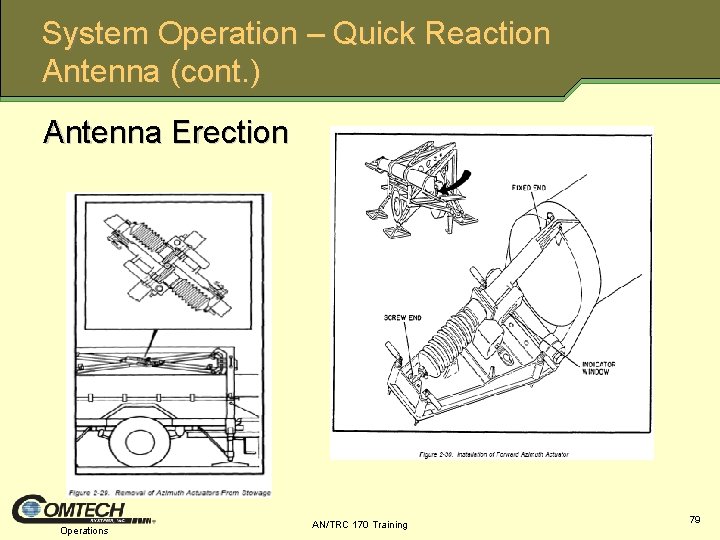
System Operation – Quick Reaction Antenna (cont. ) Antenna Erection Operations AN/TRC 170 Training 79
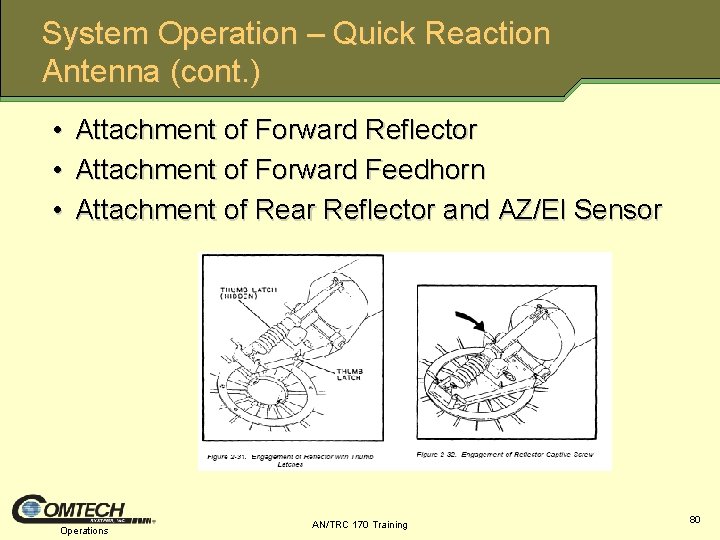
System Operation – Quick Reaction Antenna (cont. ) • • • Attachment of Forward Reflector Attachment of Forward Feedhorn Attachment of Rear Reflector and AZ/El Sensor Operations AN/TRC 170 Training 80
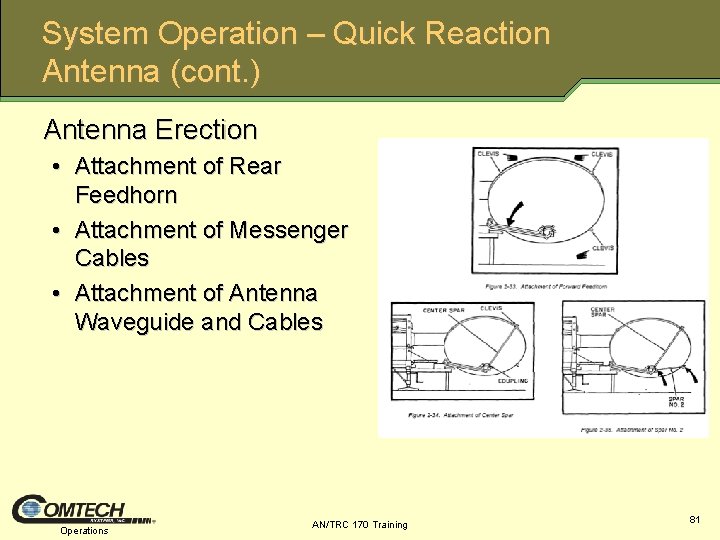
System Operation – Quick Reaction Antenna (cont. ) Antenna Erection • Attachment of Rear Feedhorn • Attachment of Messenger Cables • Attachment of Antenna Waveguide and Cables Operations AN/TRC 170 Training 81
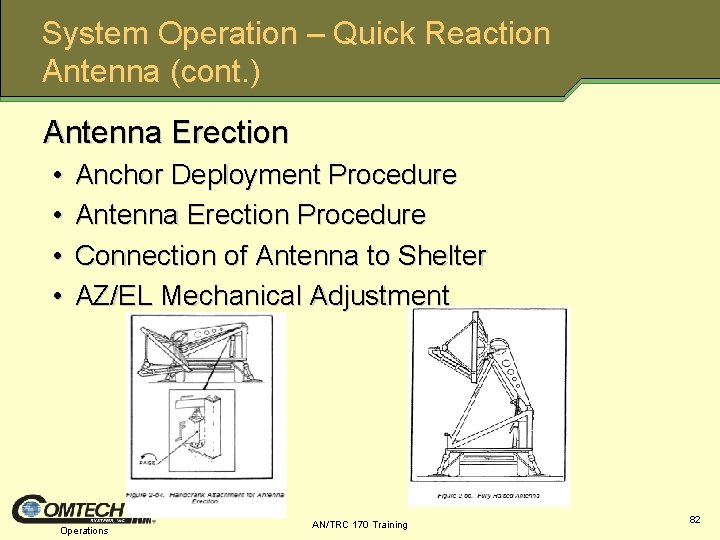
System Operation – Quick Reaction Antenna (cont. ) Antenna Erection • • Anchor Deployment Procedure Antenna Erection Procedure Connection of Antenna to Shelter AZ/EL Mechanical Adjustment Operations AN/TRC 170 Training 82
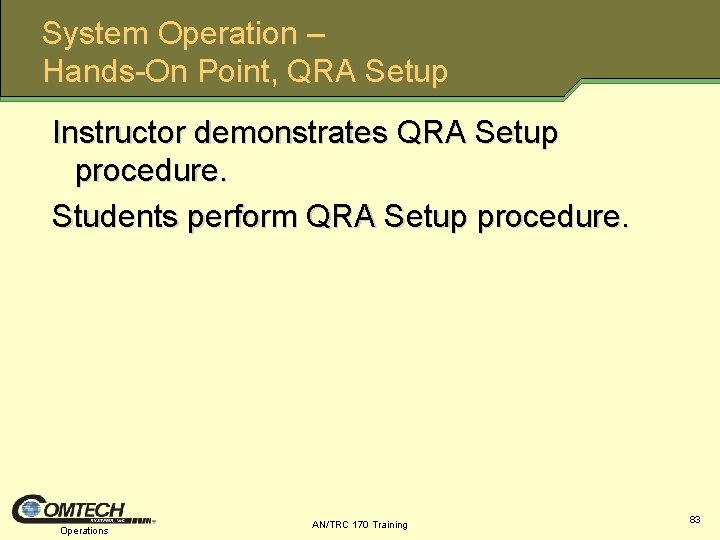
System Operation – Hands On Point, QRA Setup Instructor demonstrates QRA Setup procedure. Students perform QRA Setup procedure. Operations AN/TRC 170 Training 83
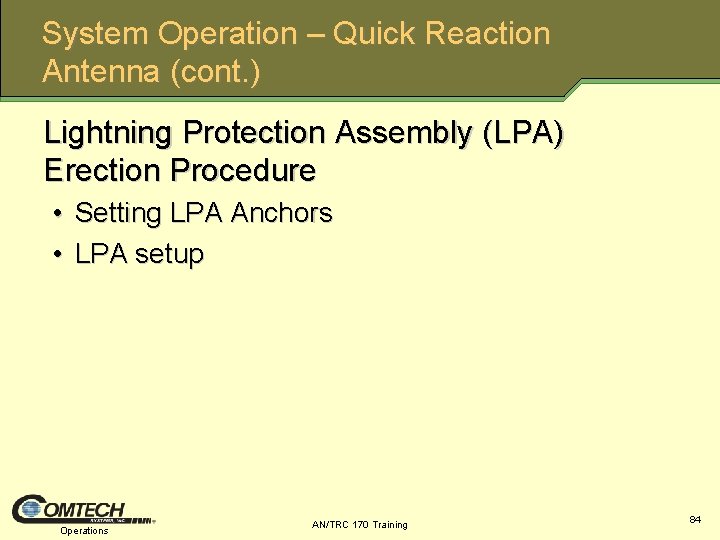
System Operation – Quick Reaction Antenna (cont. ) Lightning Protection Assembly (LPA) Erection Procedure • Setting LPA Anchors • LPA setup Operations AN/TRC 170 Training 84
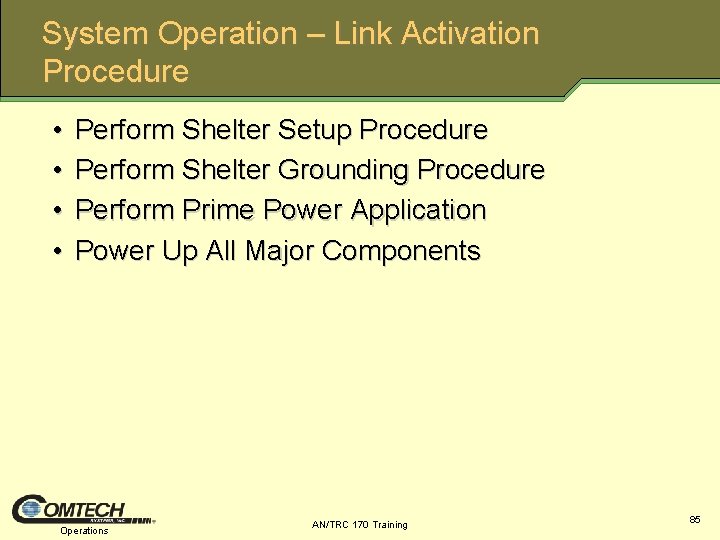
System Operation – Link Activation Procedure • • Perform Shelter Setup Procedure Perform Shelter Grounding Procedure Perform Prime Power Application Power Up All Major Components Operations AN/TRC 170 Training 85
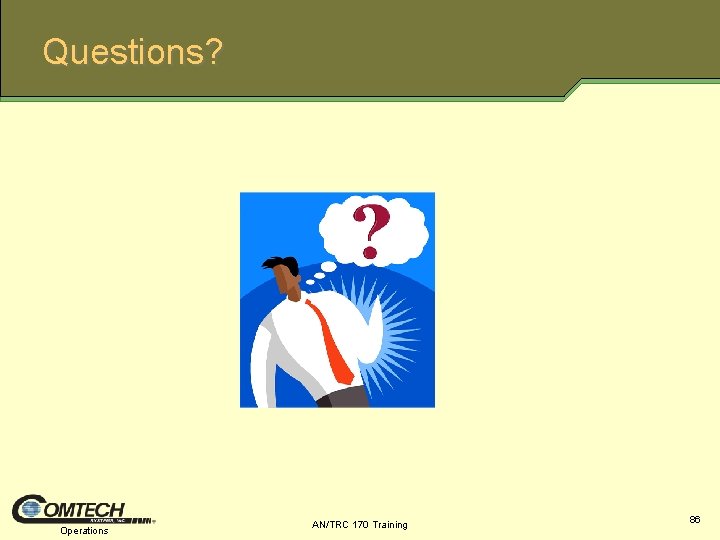
Questions? Operations AN/TRC 170 Training 86
Antrc
Overview of airport operations
Informal email example to a friend
Unit 6 review questions
Joint special operations medical training center
Training is expensive without training it is more expensive
Perbedaan on the job training dan off the job training
Aggression replacement training facilitator training
Grading of food
Unit operations
Unit operations
Unit operations in food processing
Virgin unit 22
Unit 20 hospitality operations in travel and tourism
Classification of unit operations in food processing
5 principles of training
Www stands for world wide web
Maximo work order priority
Universal modeling language
Uml overview
Retail vertical
Figure 12-1 provides an overview of the lymphatic vessels
Pulmonary circuit
Texas public school finance overview
Walmart company introduction
Stylistic overview of architecture
Sa sd
Spring framework overview
Nagios tactical overview
Market overview managed file transfer solutions
Nfv vs sdn
Sbic program
Sap pb00
Ariba registration process
Safe overview
Rfid technology overview
Review paper introduction
Virusmax
Title project example
Overview of the major systemic arteries
Is abstract a summary
Solvency ii pillar iii
Physical media storage
Example of nursing process
Marcus scheuren
Ospf overview
Architecture review template
Oedipus the king episode 2 summary
Show ip cache flow
Overview on the national tuberculosis elimination program
Mpls overview
Azure blob storage price
Master data services overview
Overview of cellular respiration
Overview of aerobic respiration
Overview of cellular respiration
Cellular respiration
Transformer overview
Kaizen prioritization
Itil brief overview
Iptv technology overview
Overview of mobile computing
Microprocessor overview
Kfc company
Moritz zimmermann sap
Huawei company information
Early years learning framework overview
Erp system introduction
Master data services overview
Data quality and data cleaning an overview
Cuda overview
Counterfeit electronic components an overview
Content management system features
Introduction to accounting software
Generations overview
Java collections overview
Dr korson
8-2 photosynthesis an overview
Emt chapter 24 trauma overview
Overview of the major systemic arteries
Group of carbon
Emt chapter 14 medical overview
Overview of the major systemic arteries
Overview of badminton
Overview of government accounting
Industry analysis of apple
Apple company history and background