Separation Processes 2012 G P Towler UOP For
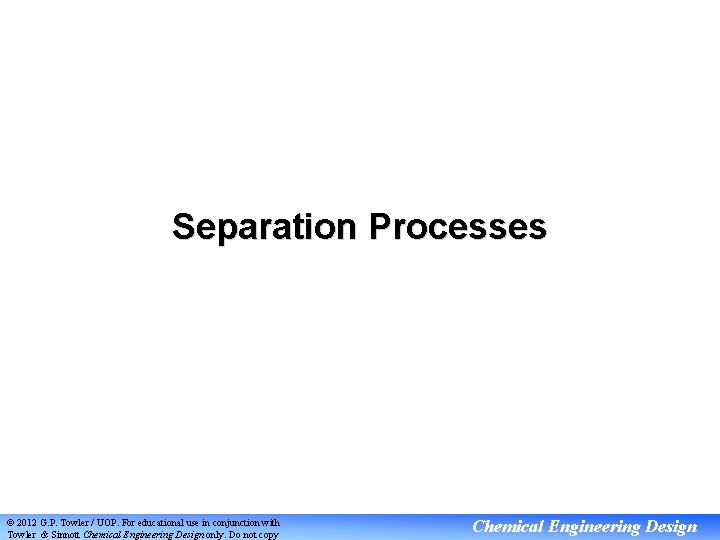
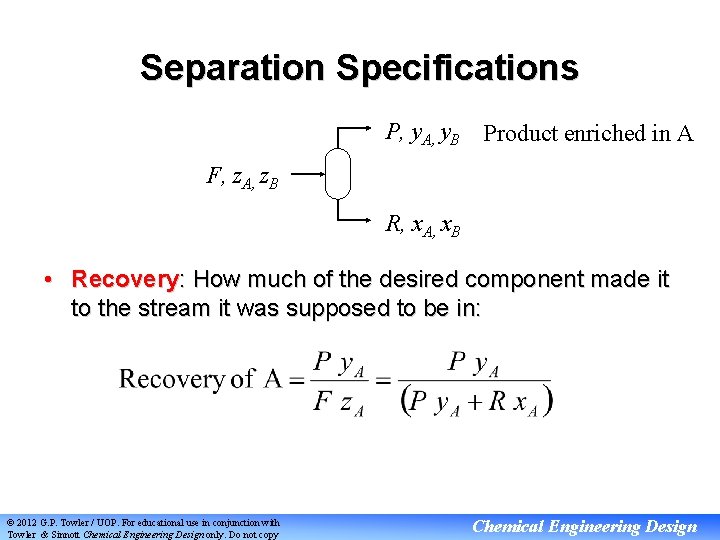
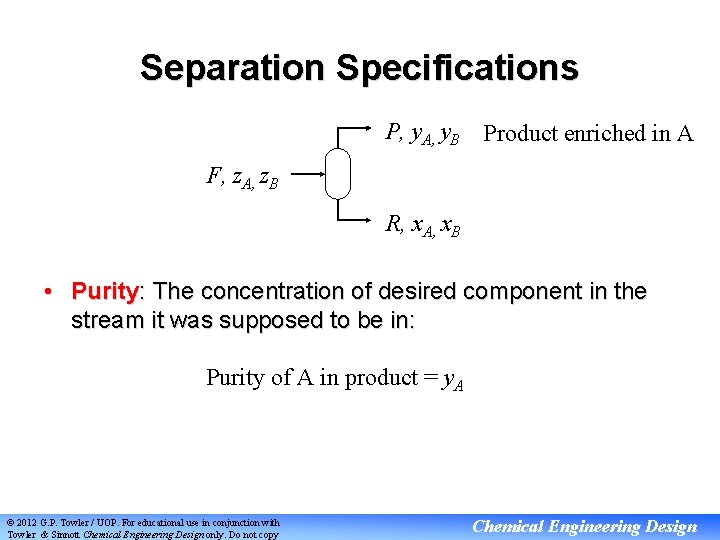
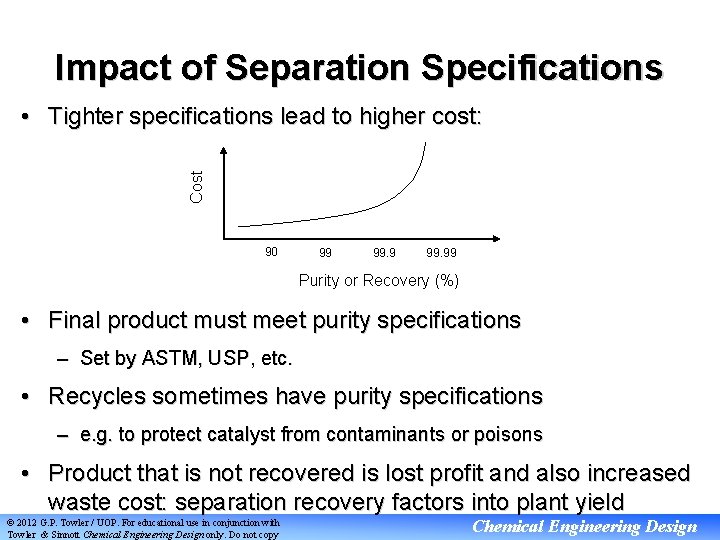
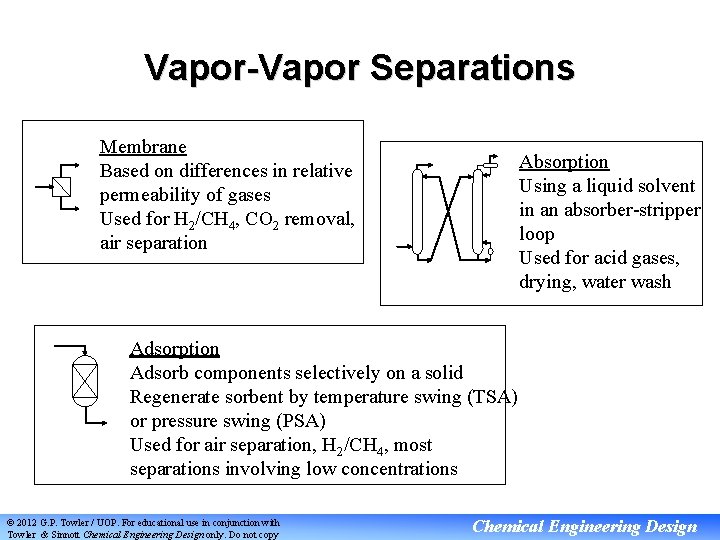
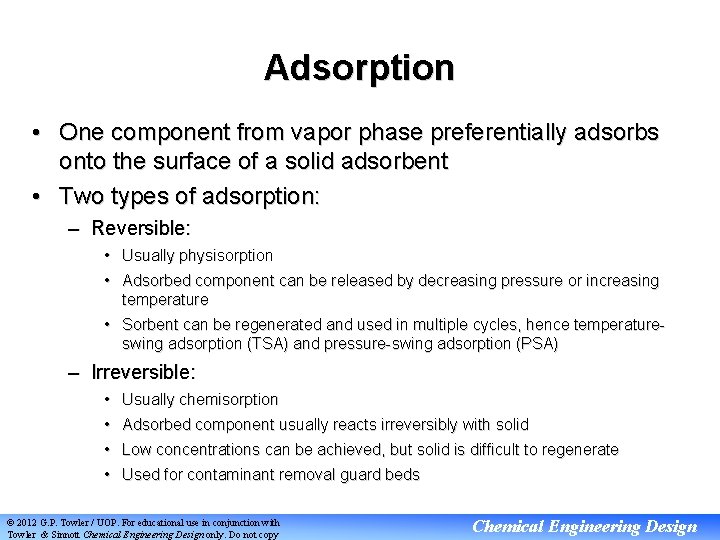
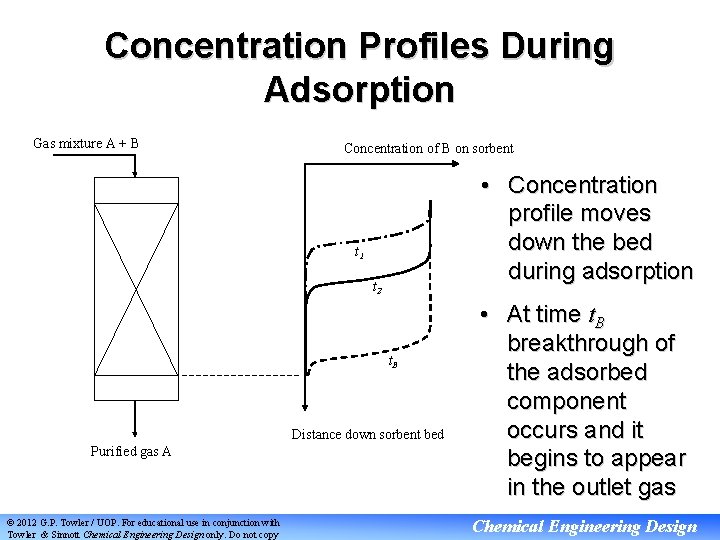
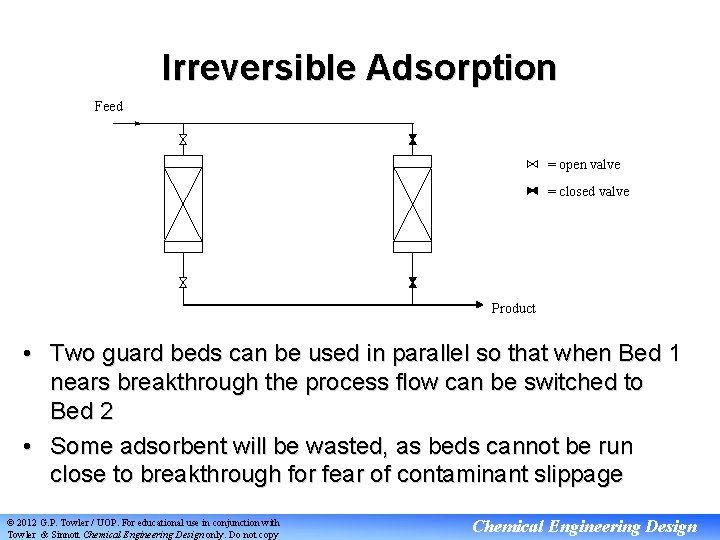
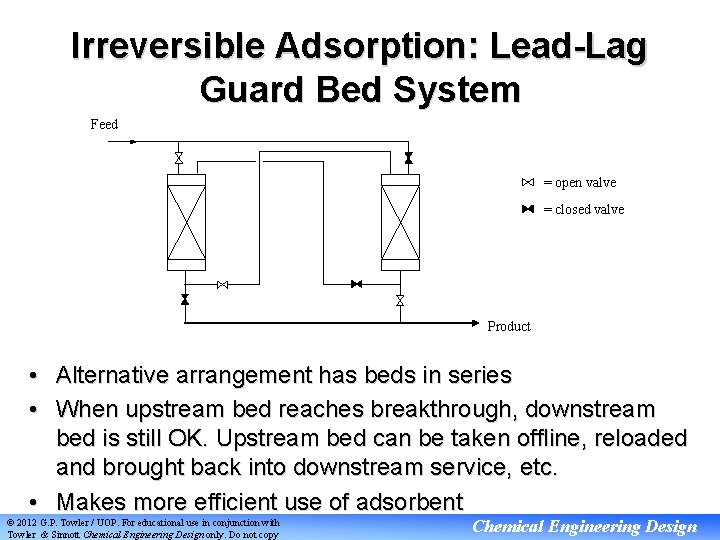
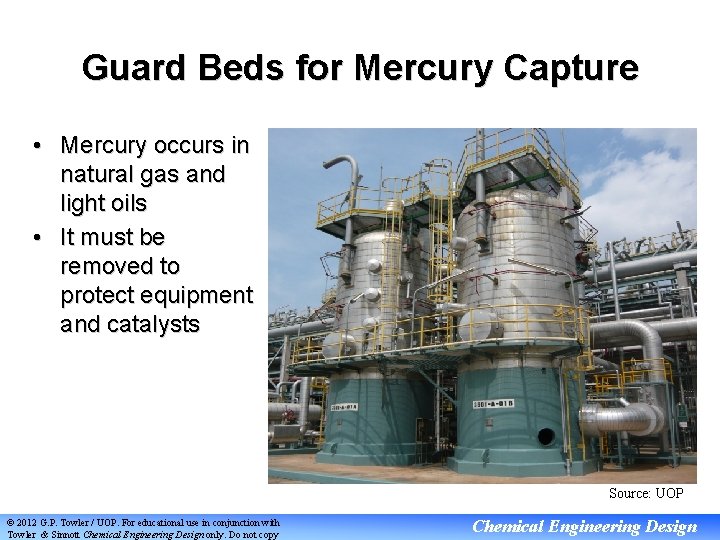
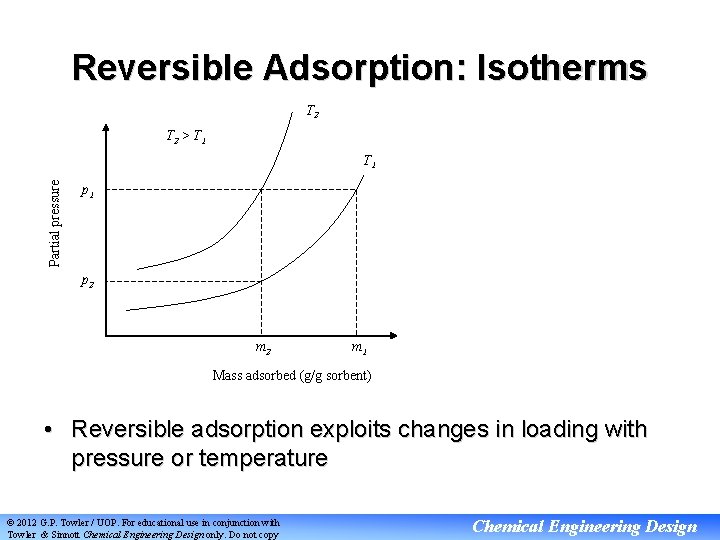
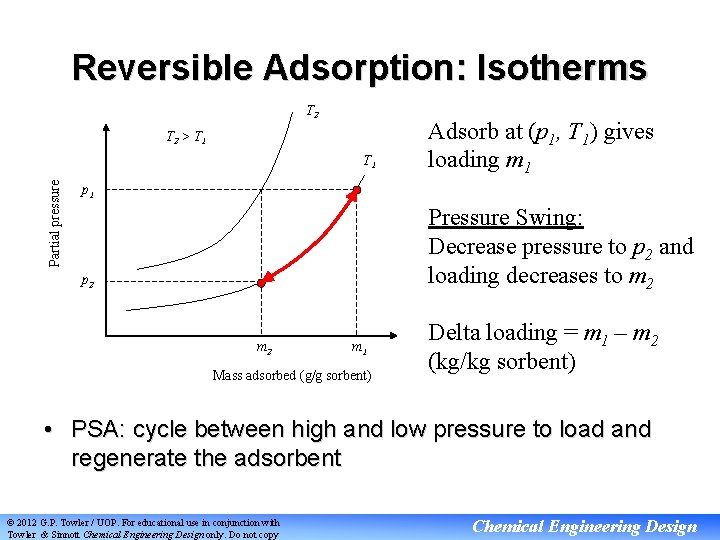
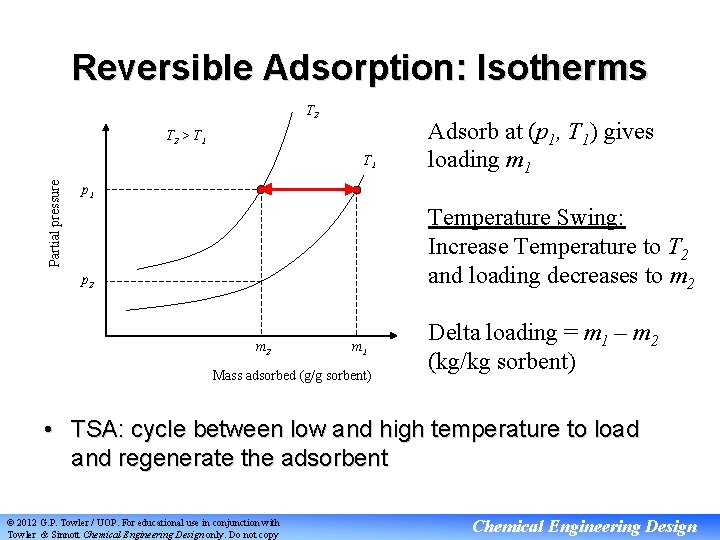
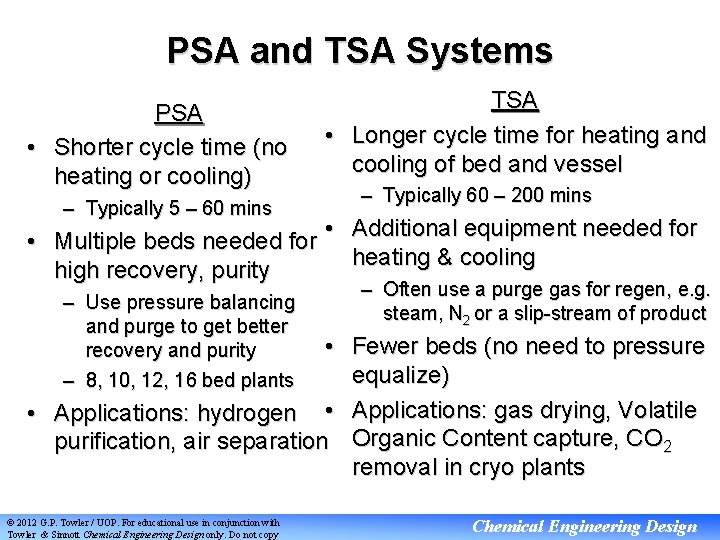
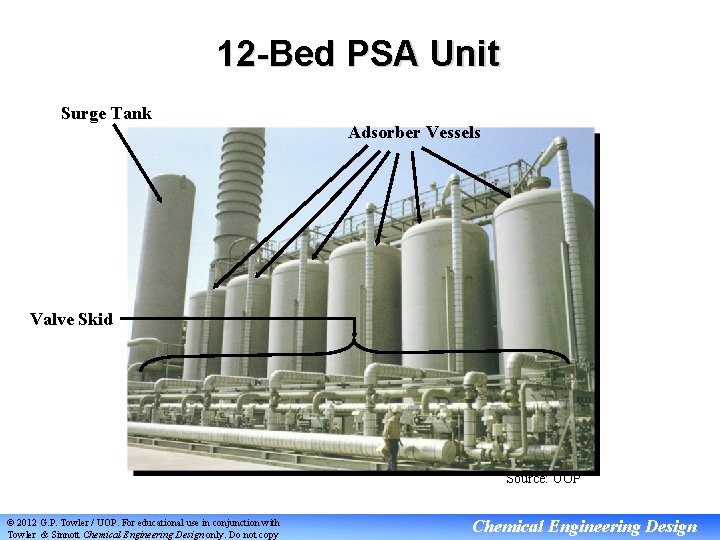
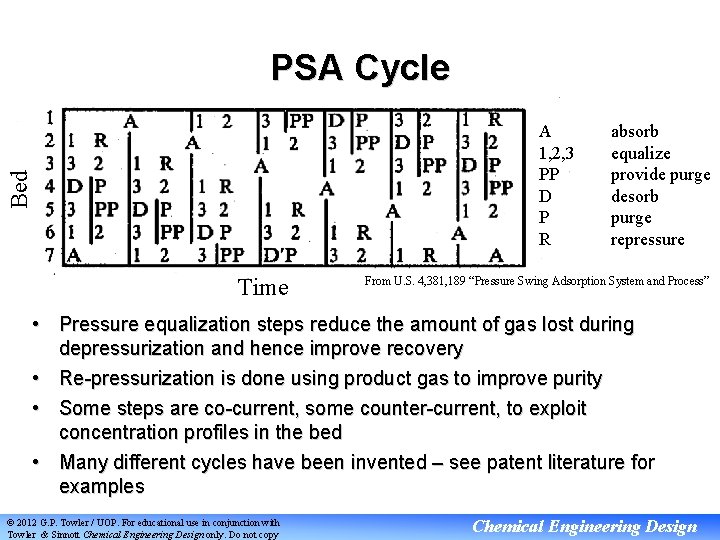
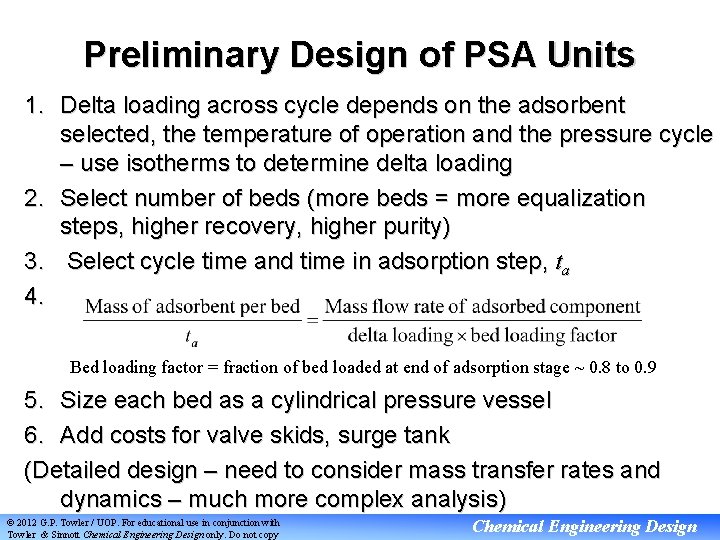
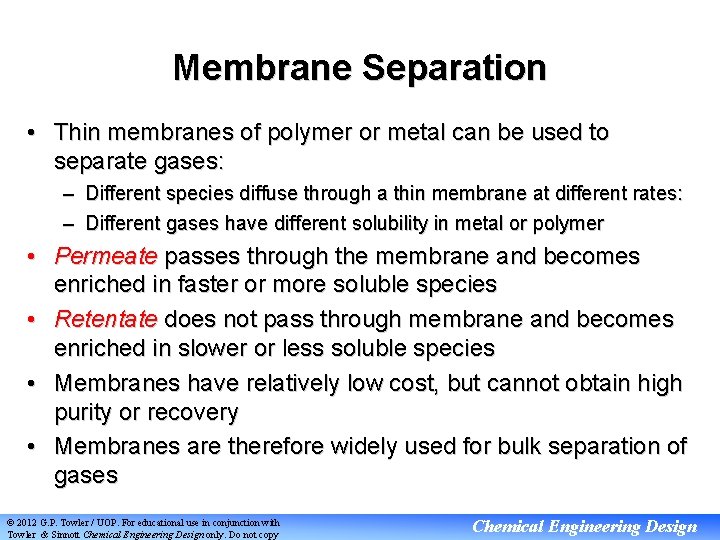
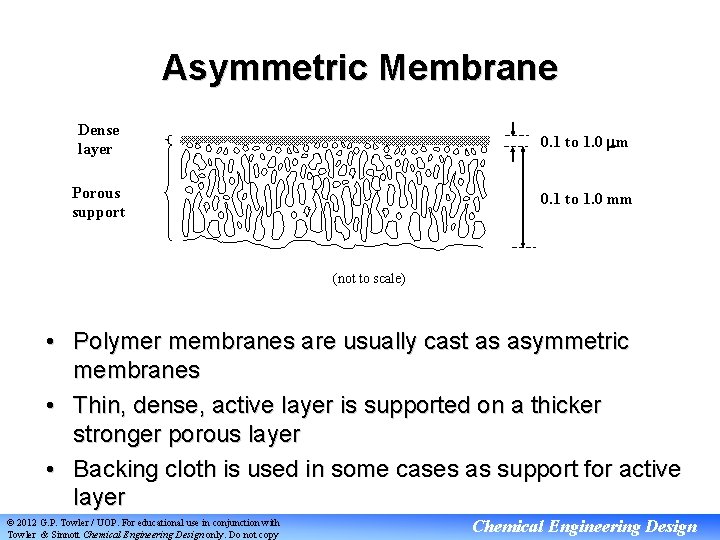
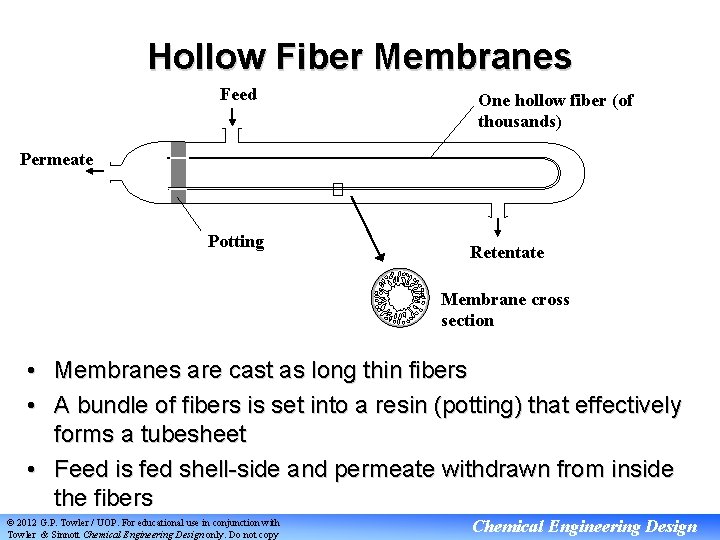
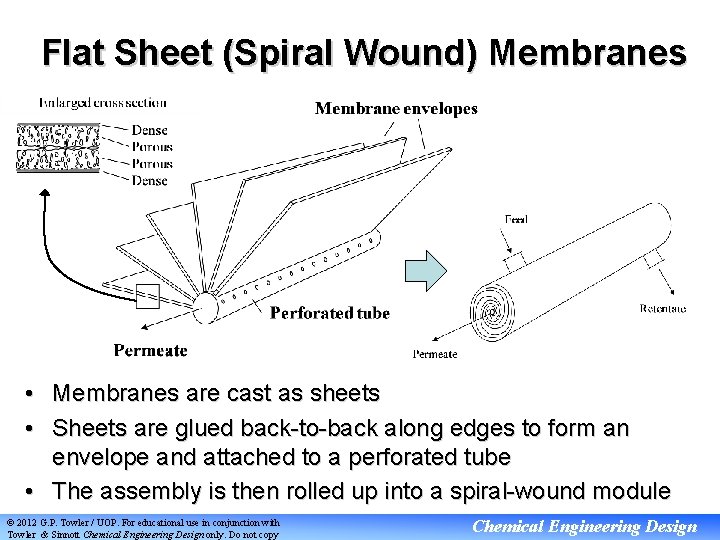
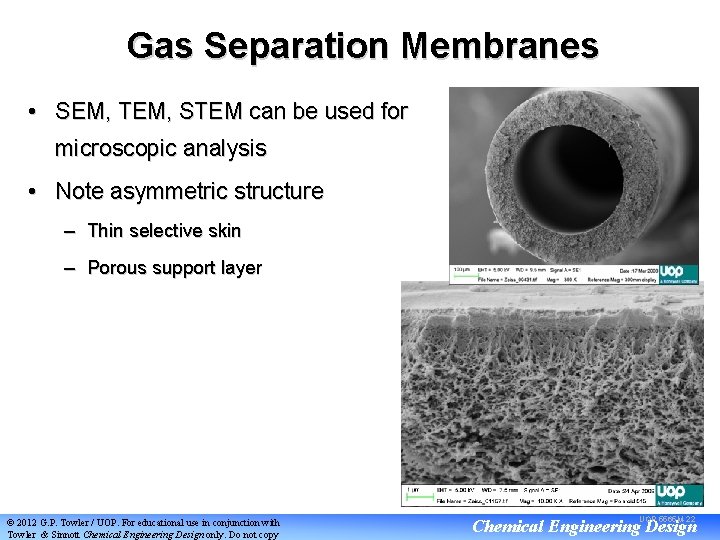
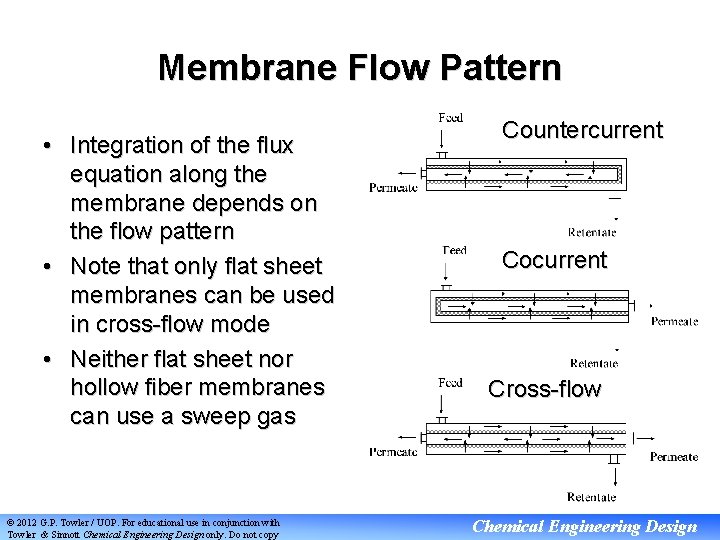
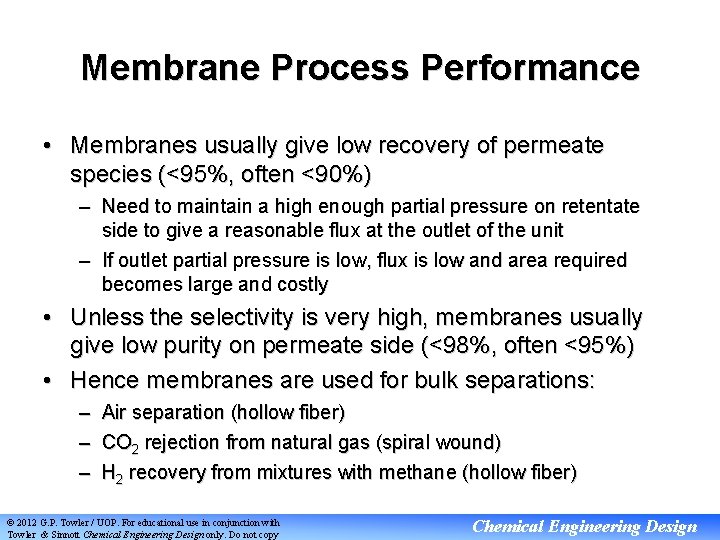
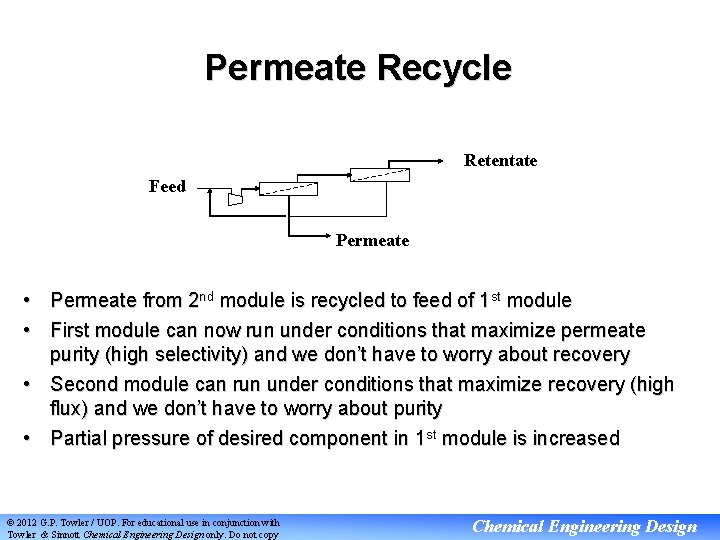
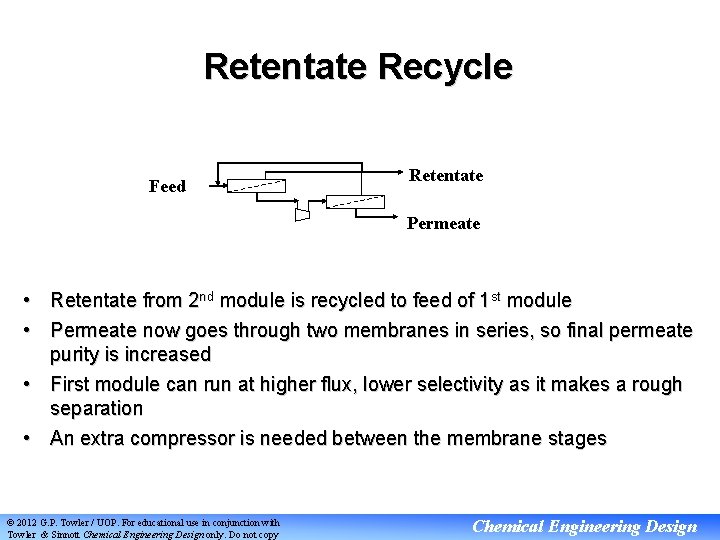
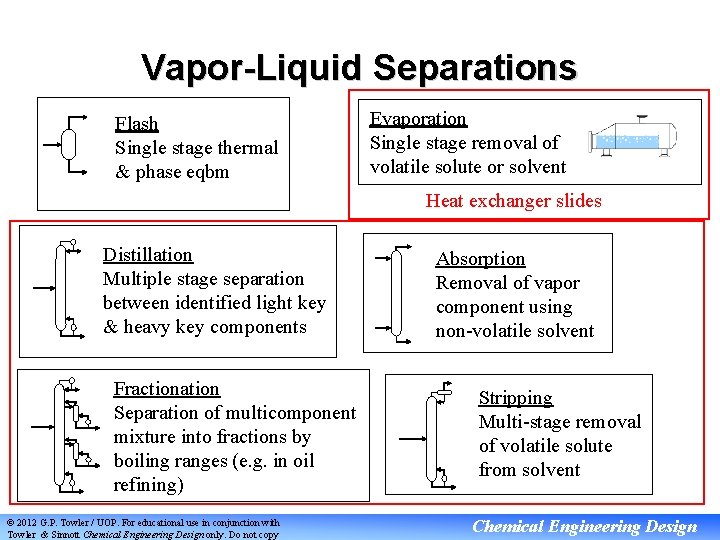
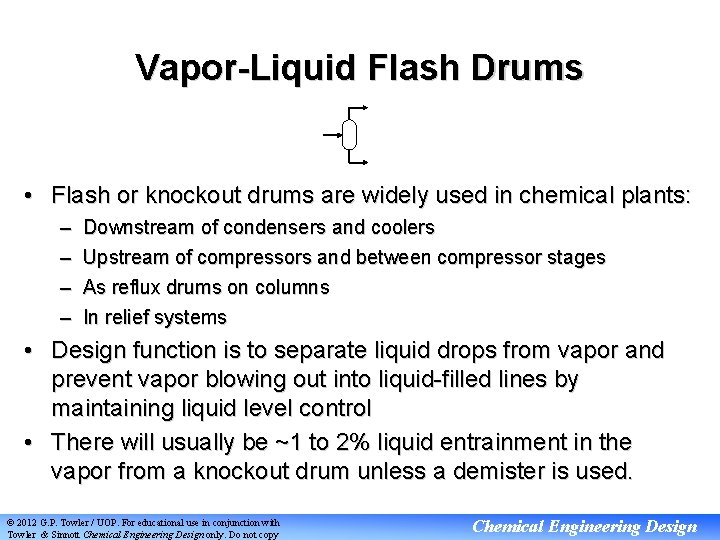
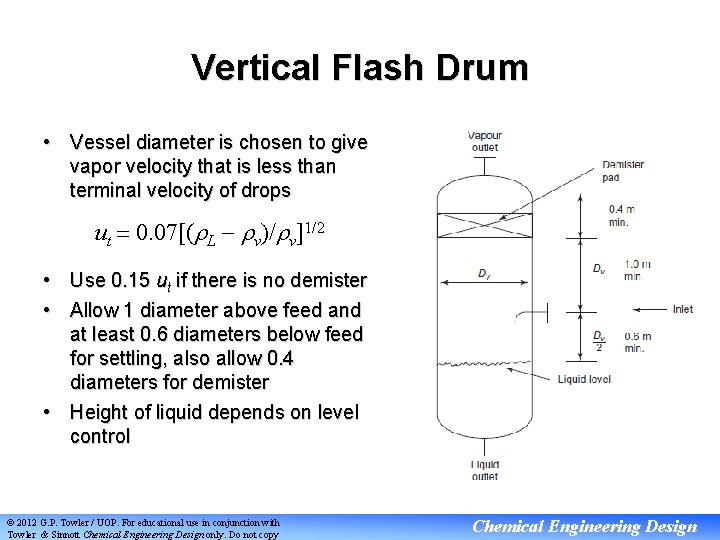
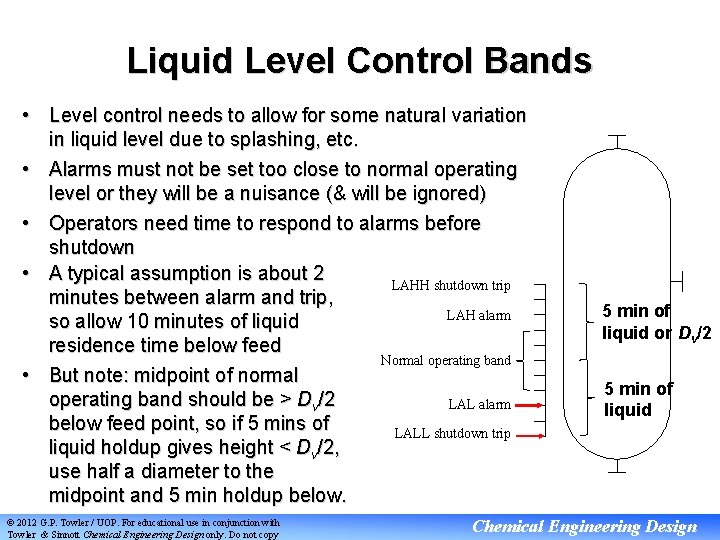
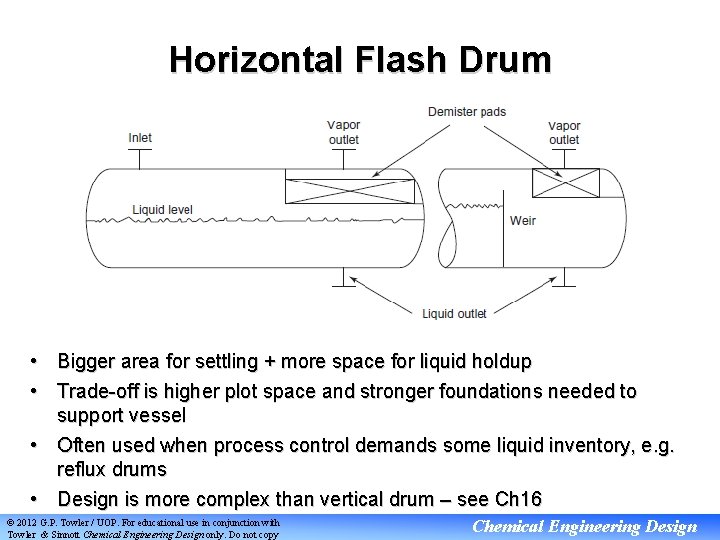
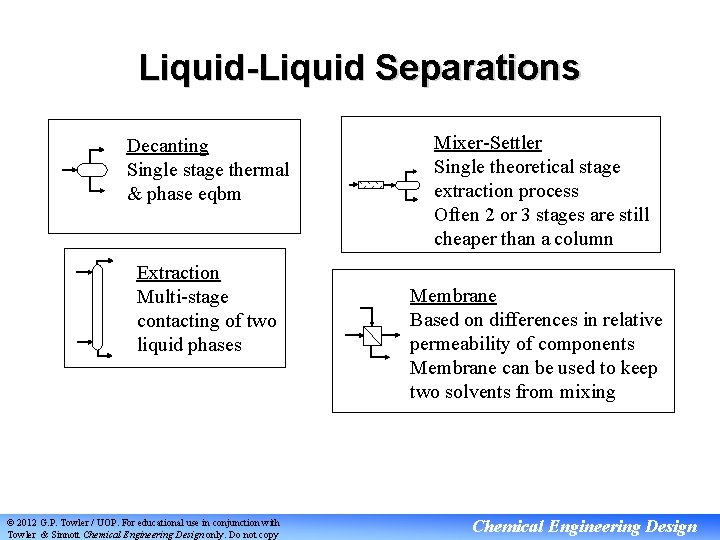
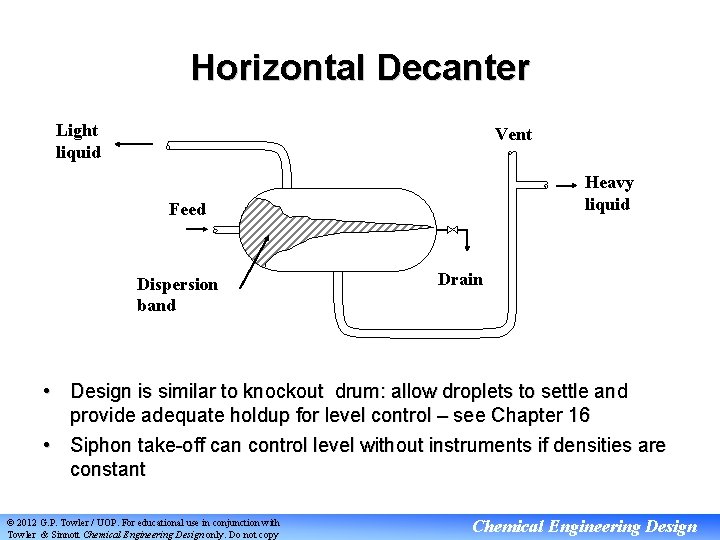
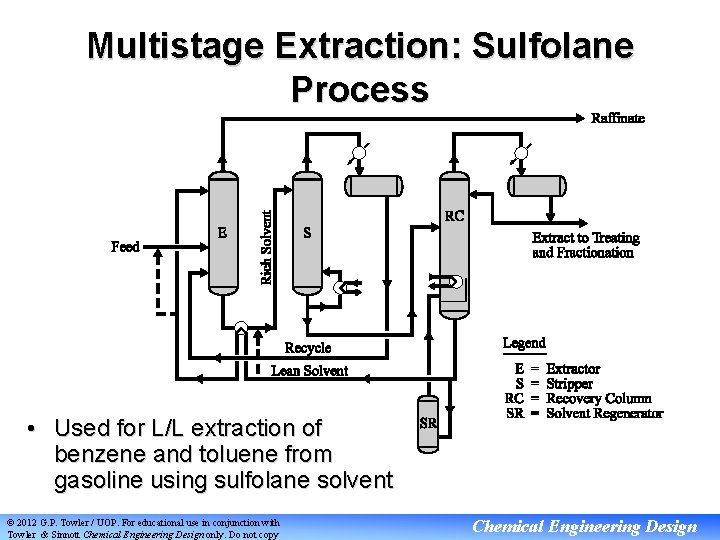
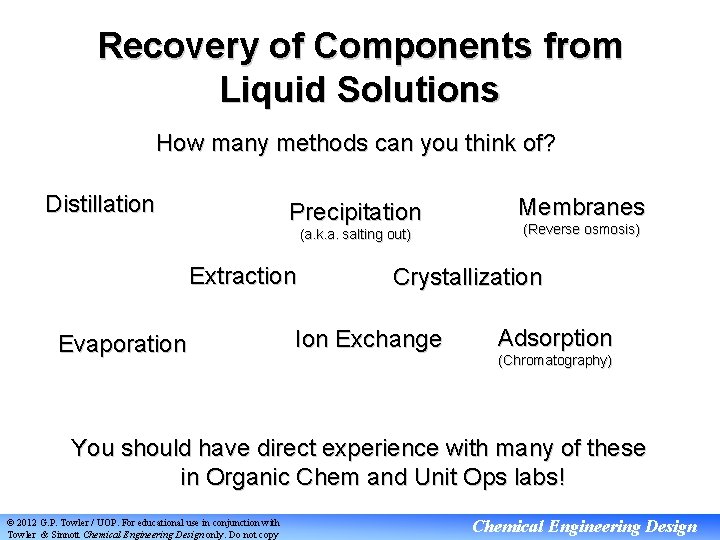
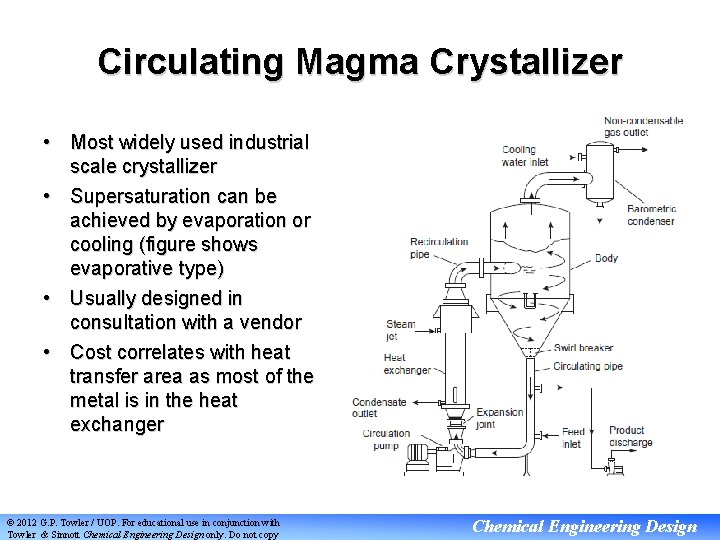
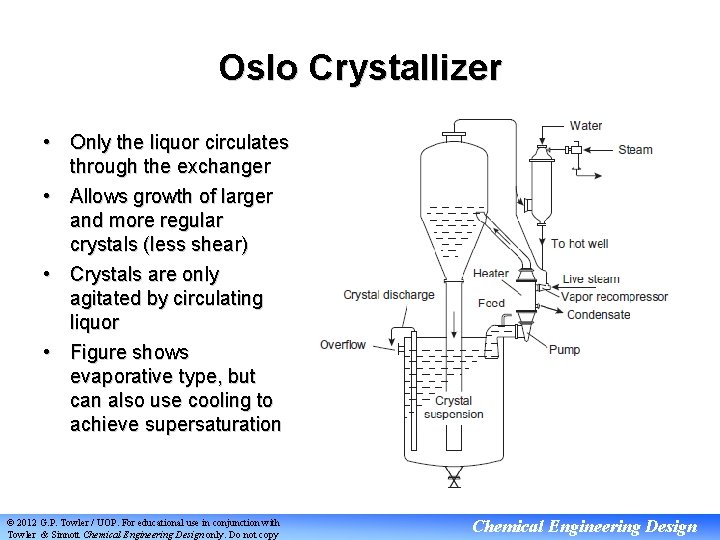
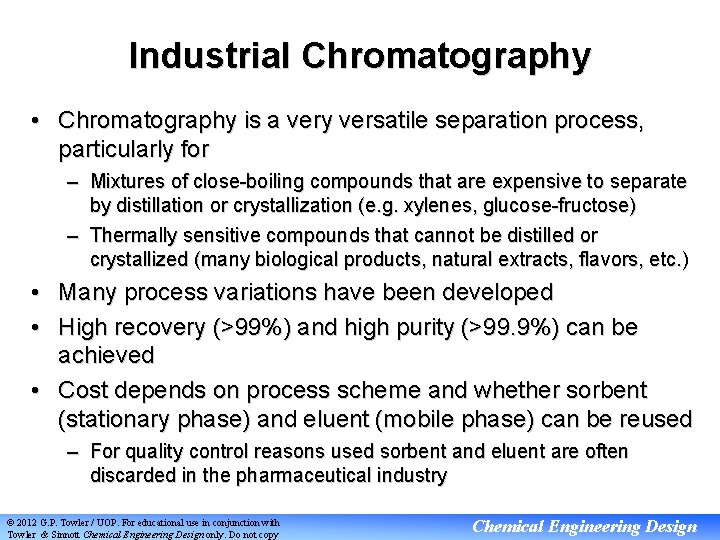
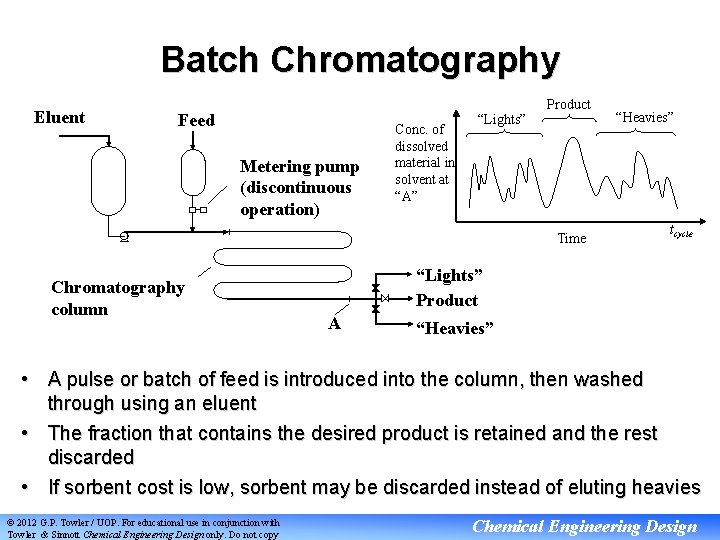
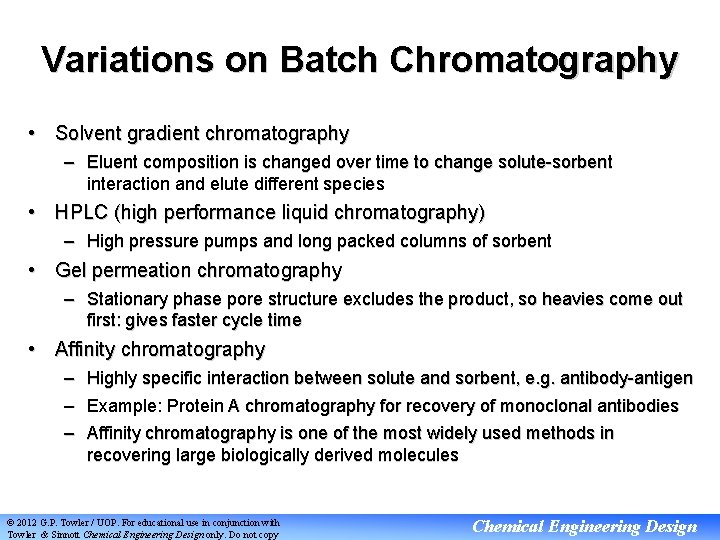
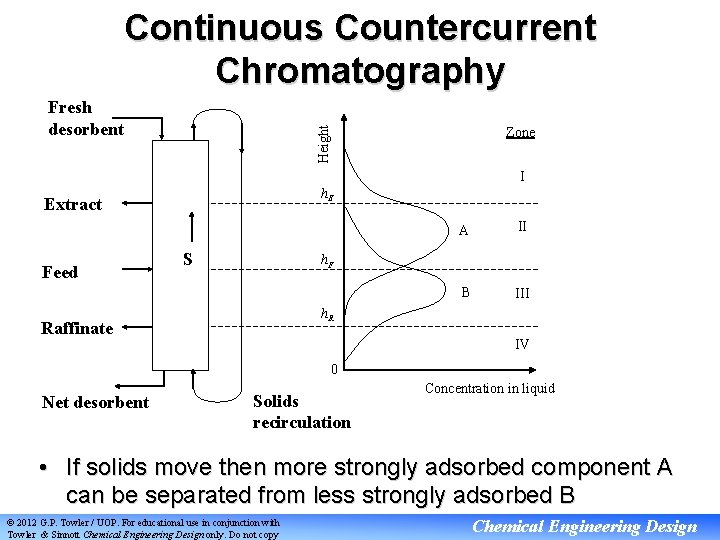
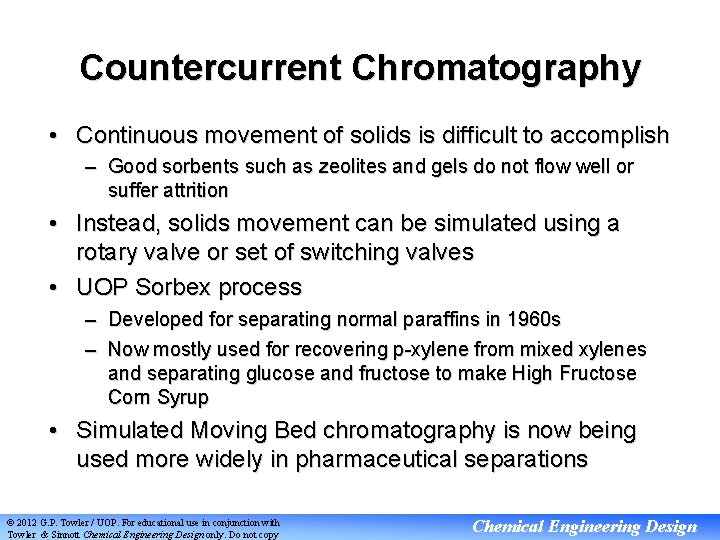
- Slides: 42
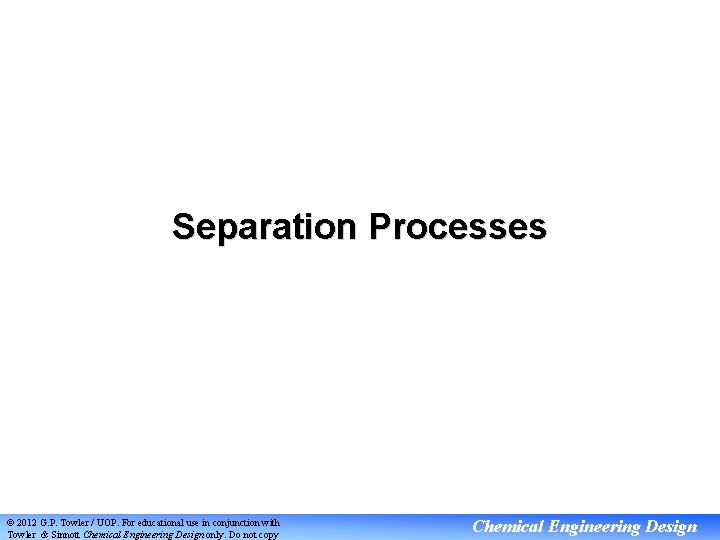
Separation Processes © 2012 G. P. Towler / UOP. For educational use in conjunction with Towler & Sinnott Chemical Engineering Design only. Do not copy Chemical Engineering Design
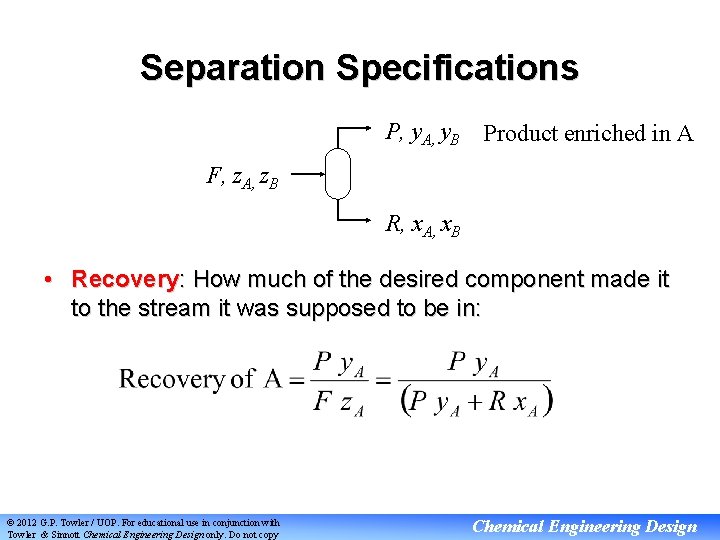
Separation Specifications P, y. A, y. B Product enriched in A F, z. A, z. B R, x. A, x. B • Recovery: How much of the desired component made it to the stream it was supposed to be in: © 2012 G. P. Towler / UOP. For educational use in conjunction with Towler & Sinnott Chemical Engineering Design only. Do not copy Chemical Engineering Design
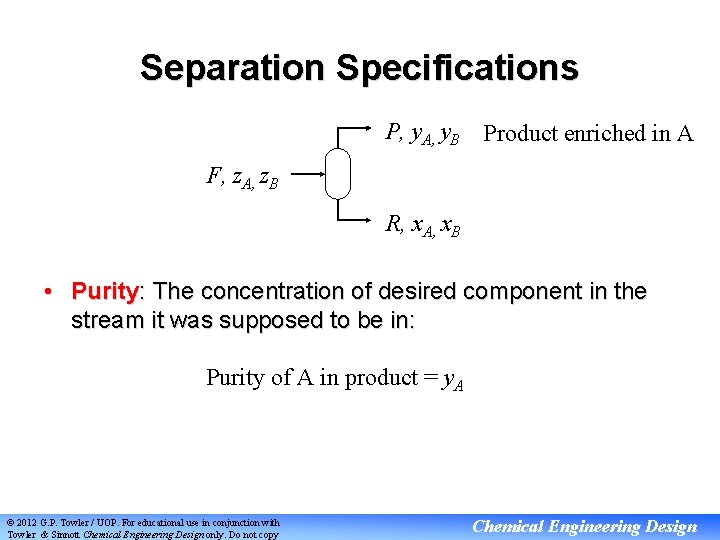
Separation Specifications P, y. A, y. B Product enriched in A F, z. A, z. B R, x. A, x. B • Purity: The concentration of desired component in the stream it was supposed to be in: Purity of A in product = y. A © 2012 G. P. Towler / UOP. For educational use in conjunction with Towler & Sinnott Chemical Engineering Design only. Do not copy Chemical Engineering Design
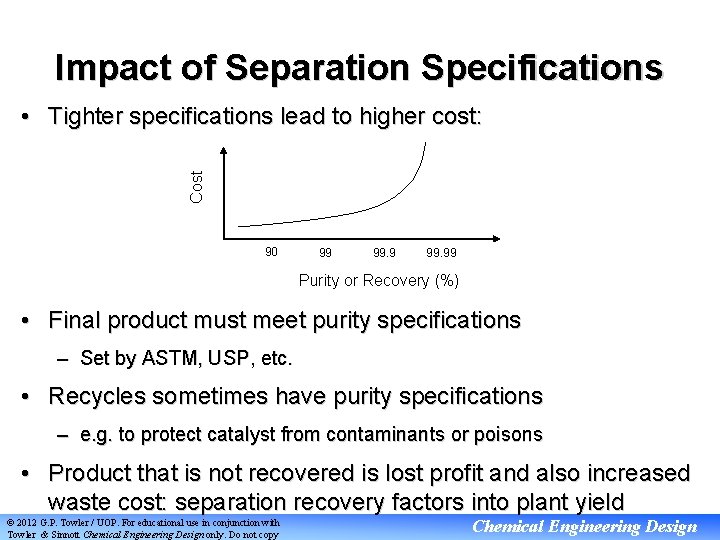
Impact of Separation Specifications Cost • Tighter specifications lead to higher cost: 90 99 99. 99 Purity or Recovery (%) • Final product must meet purity specifications – Set by ASTM, USP, etc. • Recycles sometimes have purity specifications – e. g. to protect catalyst from contaminants or poisons • Product that is not recovered is lost profit and also increased waste cost: separation recovery factors into plant yield © 2012 G. P. Towler / UOP. For educational use in conjunction with Towler & Sinnott Chemical Engineering Design only. Do not copy Chemical Engineering Design
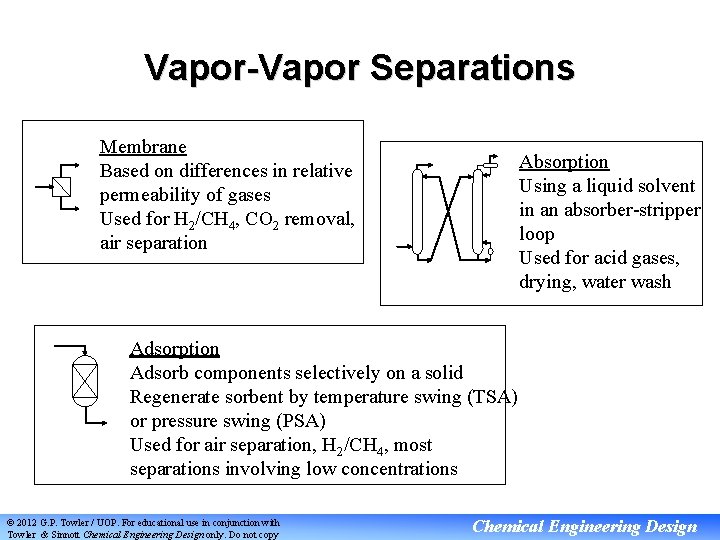
Vapor-Vapor Separations Membrane Based on differences in relative permeability of gases Used for H 2/CH 4, CO 2 removal, air separation Absorption Using a liquid solvent in an absorber-stripper loop Used for acid gases, drying, water wash Adsorption Adsorb components selectively on a solid Regenerate sorbent by temperature swing (TSA) or pressure swing (PSA) Used for air separation, H 2/CH 4, most separations involving low concentrations © 2012 G. P. Towler / UOP. For educational use in conjunction with Towler & Sinnott Chemical Engineering Design only. Do not copy Chemical Engineering Design
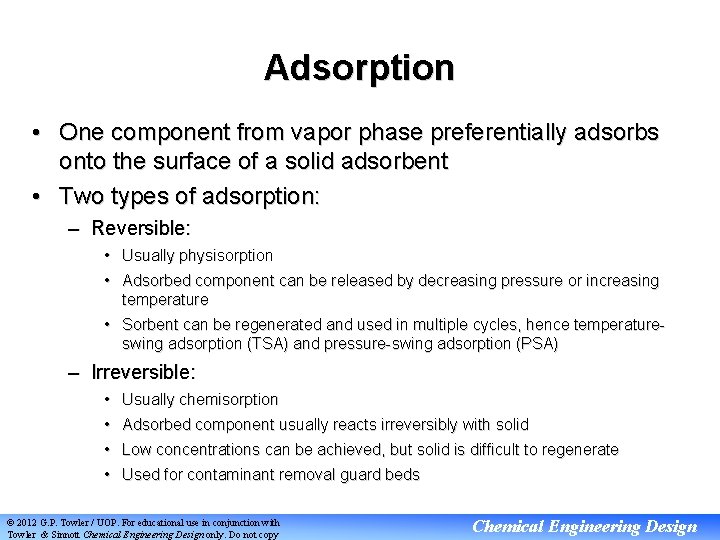
Adsorption • One component from vapor phase preferentially adsorbs onto the surface of a solid adsorbent • Two types of adsorption: – Reversible: • Usually physisorption • Adsorbed component can be released by decreasing pressure or increasing temperature • Sorbent can be regenerated and used in multiple cycles, hence temperatureswing adsorption (TSA) and pressure-swing adsorption (PSA) – Irreversible: • Usually chemisorption • Adsorbed component usually reacts irreversibly with solid • Low concentrations can be achieved, but solid is difficult to regenerate • Used for contaminant removal guard beds © 2012 G. P. Towler / UOP. For educational use in conjunction with Towler & Sinnott Chemical Engineering Design only. Do not copy Chemical Engineering Design
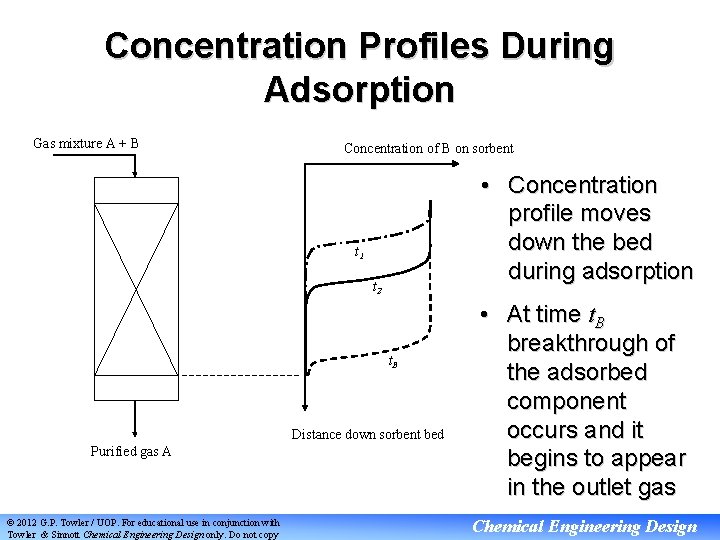
Concentration Profiles During Adsorption Gas mixture A + B Concentration of B on sorbent • Concentration profile moves down the bed during adsorption t 1 t 2 t. B Distance down sorbent bed Purified gas A © 2012 G. P. Towler / UOP. For educational use in conjunction with Towler & Sinnott Chemical Engineering Design only. Do not copy • At time t. B breakthrough of the adsorbed component occurs and it begins to appear in the outlet gas Chemical Engineering Design
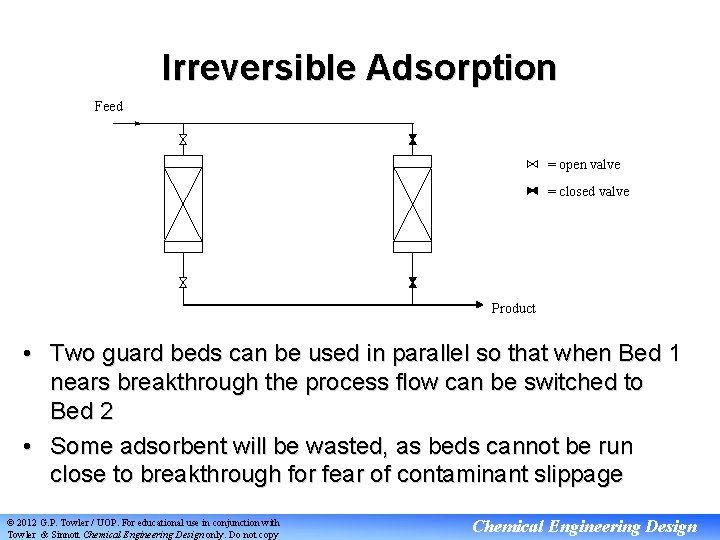
Irreversible Adsorption Feed = open valve = closed valve Product • Two guard beds can be used in parallel so that when Bed 1 nears breakthrough the process flow can be switched to Bed 2 • Some adsorbent will be wasted, as beds cannot be run close to breakthrough for fear of contaminant slippage © 2012 G. P. Towler / UOP. For educational use in conjunction with Towler & Sinnott Chemical Engineering Design only. Do not copy Chemical Engineering Design
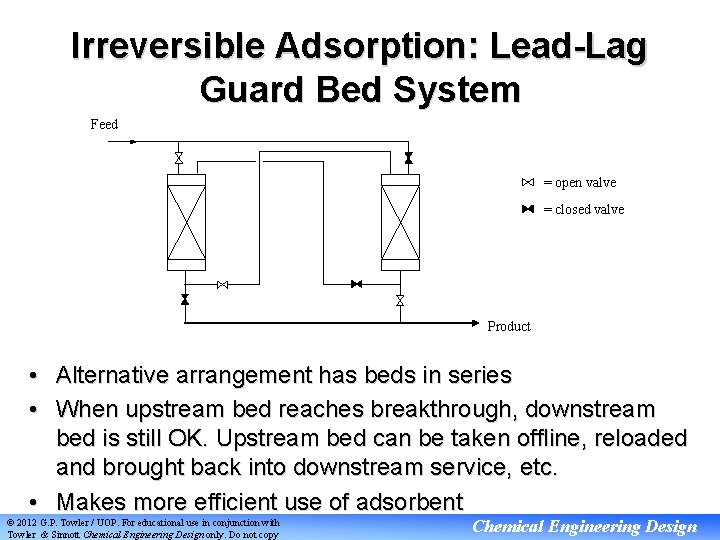
Irreversible Adsorption: Lead-Lag Guard Bed System Feed = open valve = closed valve Product • Alternative arrangement has beds in series • When upstream bed reaches breakthrough, downstream bed is still OK. Upstream bed can be taken offline, reloaded and brought back into downstream service, etc. • Makes more efficient use of adsorbent © 2012 G. P. Towler / UOP. For educational use in conjunction with Towler & Sinnott Chemical Engineering Design only. Do not copy Chemical Engineering Design
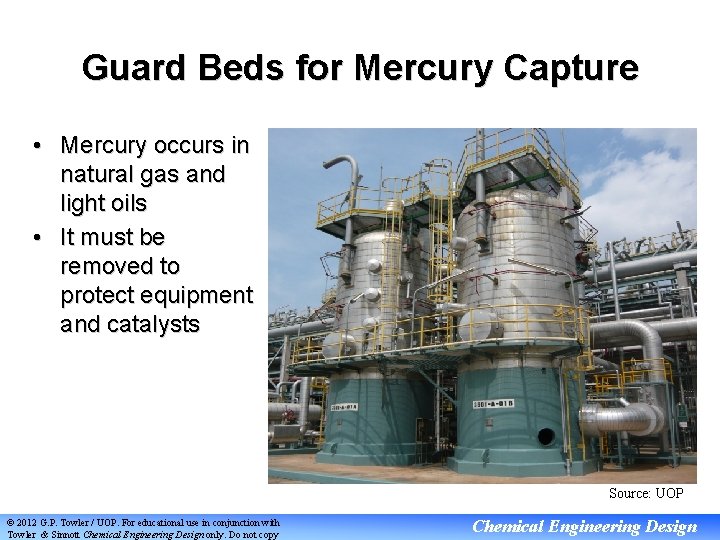
Guard Beds for Mercury Capture • Mercury occurs in natural gas and light oils • It must be removed to protect equipment and catalysts Source: UOP © 2012 G. P. Towler / UOP. For educational use in conjunction with Towler & Sinnott Chemical Engineering Design only. Do not copy Chemical Engineering Design
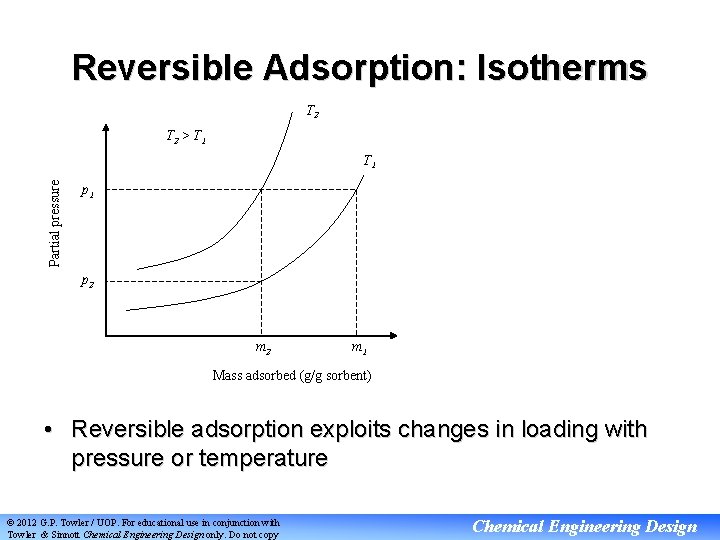
Reversible Adsorption: Isotherms T 2 > T 1 Partial pressure T 1 p 2 m 1 Mass adsorbed (g/g sorbent) • Reversible adsorption exploits changes in loading with pressure or temperature © 2012 G. P. Towler / UOP. For educational use in conjunction with Towler & Sinnott Chemical Engineering Design only. Do not copy Chemical Engineering Design
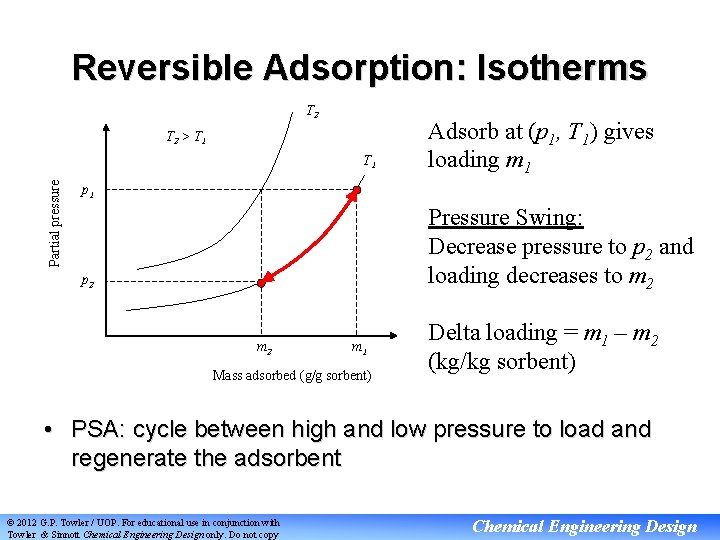
Reversible Adsorption: Isotherms T 2 > T 1 Partial pressure T 1 Adsorb at (p 1, T 1) gives loading m 1 p 1 Pressure Swing: Decrease pressure to p 2 and loading decreases to m 2 p 2 m 1 Mass adsorbed (g/g sorbent) Delta loading = m 1 – m 2 (kg/kg sorbent) • PSA: cycle between high and low pressure to load and regenerate the adsorbent © 2012 G. P. Towler / UOP. For educational use in conjunction with Towler & Sinnott Chemical Engineering Design only. Do not copy Chemical Engineering Design
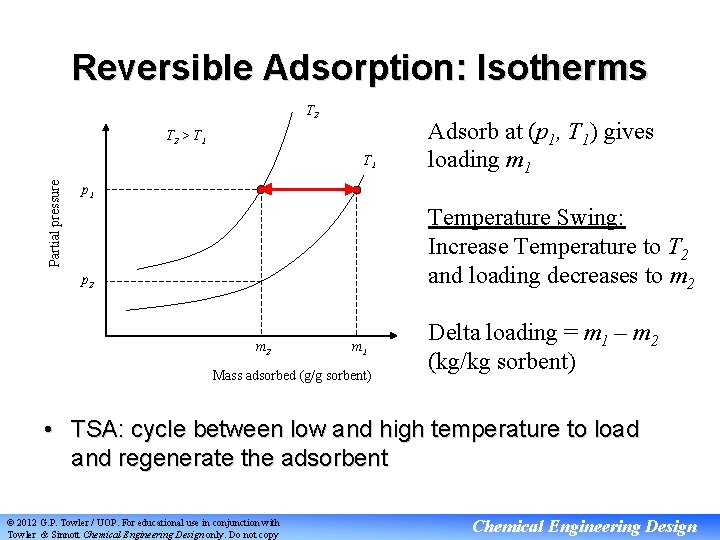
Reversible Adsorption: Isotherms T 2 > T 1 Partial pressure T 1 Adsorb at (p 1, T 1) gives loading m 1 p 1 Temperature Swing: Increase Temperature to T 2 and loading decreases to m 2 p 2 m 1 Mass adsorbed (g/g sorbent) Delta loading = m 1 – m 2 (kg/kg sorbent) • TSA: cycle between low and high temperature to load and regenerate the adsorbent © 2012 G. P. Towler / UOP. For educational use in conjunction with Towler & Sinnott Chemical Engineering Design only. Do not copy Chemical Engineering Design
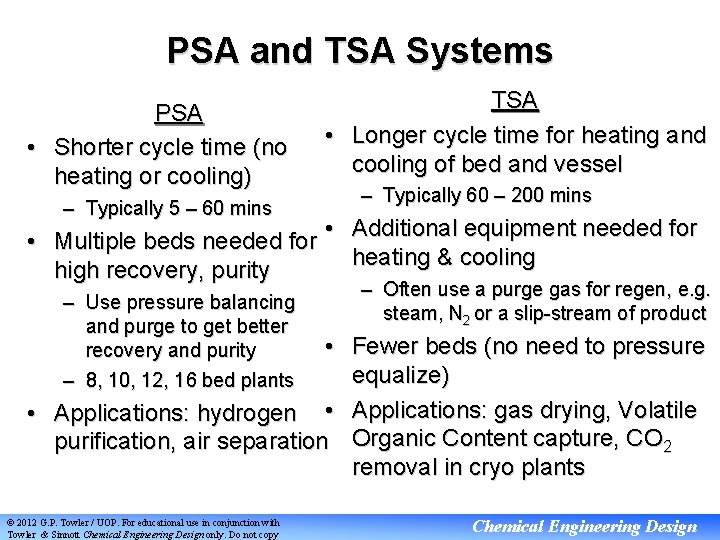
PSA and TSA Systems PSA • Shorter cycle time (no heating or cooling) – Typically 5 – 60 mins TSA • Longer cycle time for heating and cooling of bed and vessel – Typically 60 – 200 mins • Additional equipment needed for • Multiple beds needed for heating & cooling high recovery, purity – Use pressure balancing and purge to get better recovery and purity – 8, 10, 12, 16 bed plants – Often use a purge gas for regen, e. g. steam, N 2 or a slip-stream of product • Fewer beds (no need to pressure equalize) • Applications: hydrogen • Applications: gas drying, Volatile purification, air separation Organic Content capture, CO 2 removal in cryo plants © 2012 G. P. Towler / UOP. For educational use in conjunction with Towler & Sinnott Chemical Engineering Design only. Do not copy Chemical Engineering Design
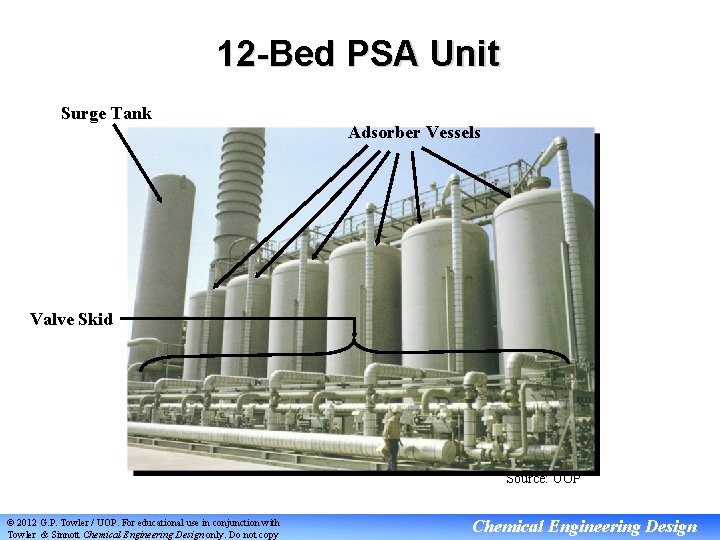
12 -Bed PSA Unit Surge Tank Adsorber Vessels Valve Skid Source: UOP © 2012 G. P. Towler / UOP. For educational use in conjunction with Towler & Sinnott Chemical Engineering Design only. Do not copy Chemical Engineering Design
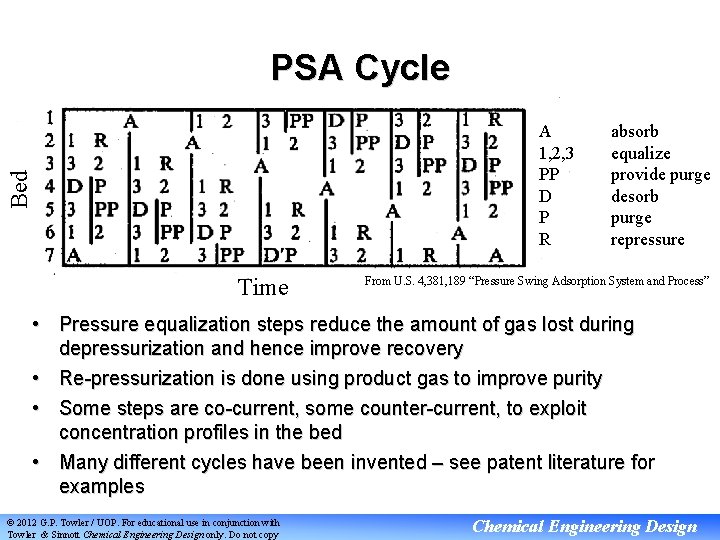
PSA Cycle Bed A 1, 2, 3 PP D P R Time absorb equalize provide purge desorb purge repressure From U. S. 4, 381, 189 “Pressure Swing Adsorption System and Process” • Pressure equalization steps reduce the amount of gas lost during depressurization and hence improve recovery • Re-pressurization is done using product gas to improve purity • Some steps are co-current, some counter-current, to exploit concentration profiles in the bed • Many different cycles have been invented – see patent literature for examples © 2012 G. P. Towler / UOP. For educational use in conjunction with Towler & Sinnott Chemical Engineering Design only. Do not copy Chemical Engineering Design
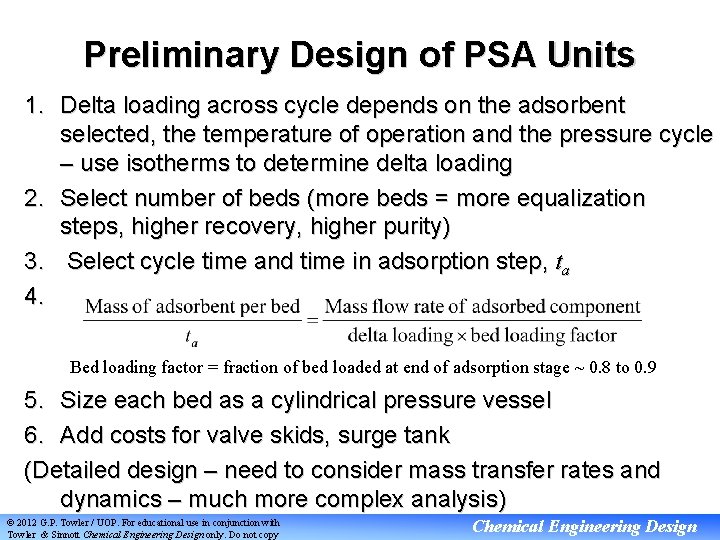
Preliminary Design of PSA Units 1. Delta loading across cycle depends on the adsorbent selected, the temperature of operation and the pressure cycle – use isotherms to determine delta loading 2. Select number of beds (more beds = more equalization steps, higher recovery, higher purity) 3. Select cycle time and time in adsorption step, ta 4. Bed loading factor = fraction of bed loaded at end of adsorption stage ~ 0. 8 to 0. 9 5. Size each bed as a cylindrical pressure vessel 6. Add costs for valve skids, surge tank (Detailed design – need to consider mass transfer rates and dynamics – much more complex analysis) © 2012 G. P. Towler / UOP. For educational use in conjunction with Towler & Sinnott Chemical Engineering Design only. Do not copy Chemical Engineering Design
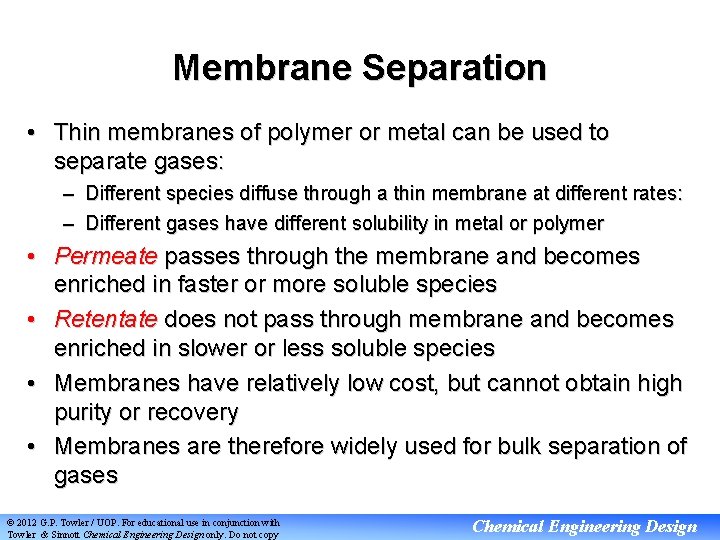
Membrane Separation • Thin membranes of polymer or metal can be used to separate gases: – Different species diffuse through a thin membrane at different rates: – Different gases have different solubility in metal or polymer • Permeate passes through the membrane and becomes enriched in faster or more soluble species • Retentate does not pass through membrane and becomes enriched in slower or less soluble species • Membranes have relatively low cost, but cannot obtain high purity or recovery • Membranes are therefore widely used for bulk separation of gases © 2012 G. P. Towler / UOP. For educational use in conjunction with Towler & Sinnott Chemical Engineering Design only. Do not copy Chemical Engineering Design
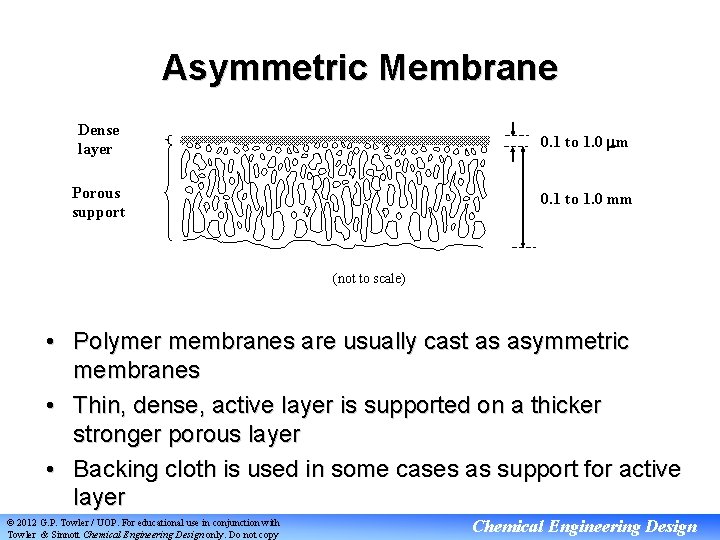
Asymmetric Membrane Dense layer 0. 1 to 1. 0 m Porous support 0. 1 to 1. 0 mm (not to scale) • Polymer membranes are usually cast as asymmetric membranes • Thin, dense, active layer is supported on a thicker stronger porous layer • Backing cloth is used in some cases as support for active layer © 2012 G. P. Towler / UOP. For educational use in conjunction with Towler & Sinnott Chemical Engineering Design only. Do not copy Chemical Engineering Design
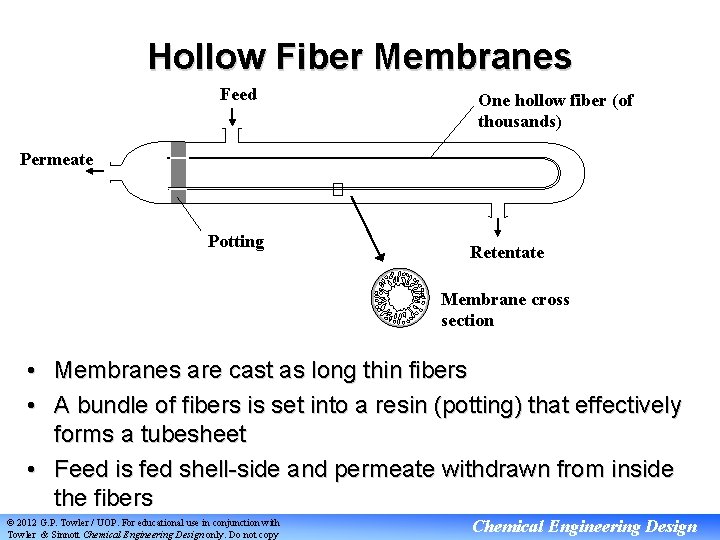
Hollow Fiber Membranes Feed One hollow fiber (of thousands) Permeate Potting Retentate Membrane cross section • Membranes are cast as long thin fibers • A bundle of fibers is set into a resin (potting) that effectively forms a tubesheet • Feed is fed shell-side and permeate withdrawn from inside the fibers © 2012 G. P. Towler / UOP. For educational use in conjunction with Towler & Sinnott Chemical Engineering Design only. Do not copy Chemical Engineering Design
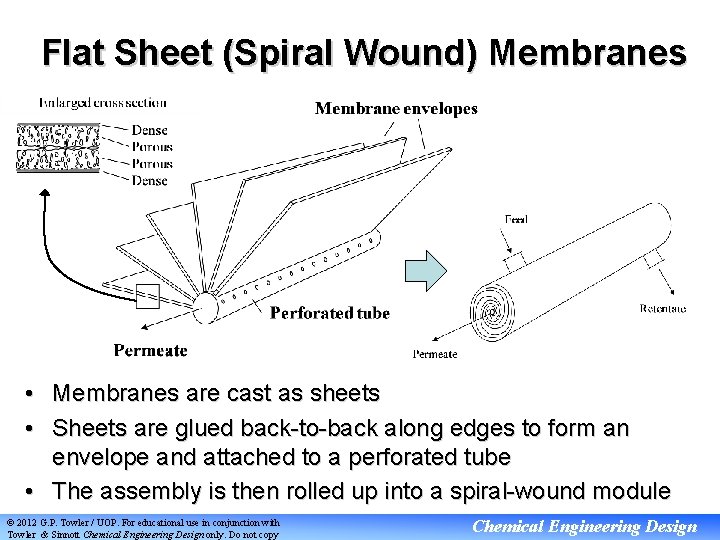
Flat Sheet (Spiral Wound) Membranes • Membranes are cast as sheets • Sheets are glued back-to-back along edges to form an envelope and attached to a perforated tube • The assembly is then rolled up into a spiral-wound module © 2012 G. P. Towler / UOP. For educational use in conjunction with Towler & Sinnott Chemical Engineering Design only. Do not copy Chemical Engineering Design
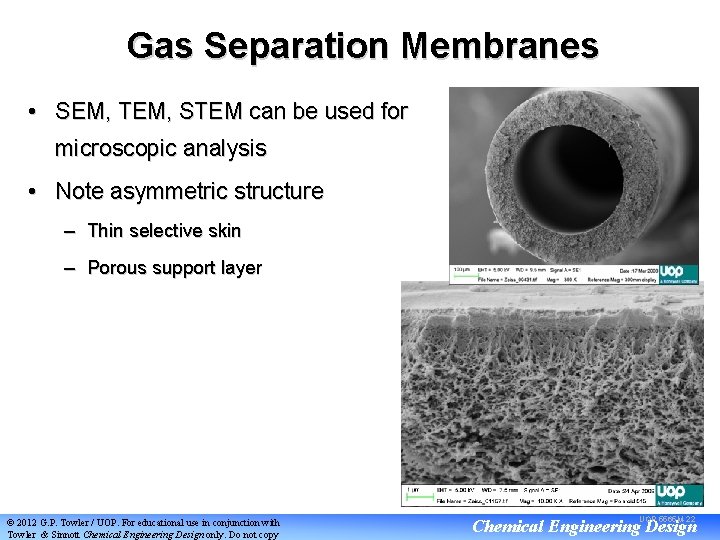
Gas Separation Membranes • SEM, TEM, STEM can be used for microscopic analysis • Note asymmetric structure – Thin selective skin – Porous support layer © 2012 G. P. Towler / UOP. For educational use in conjunction with Towler & Sinnott Chemical Engineering Design only. Do not copy UOP 5565 M-22 Chemical Engineering Design
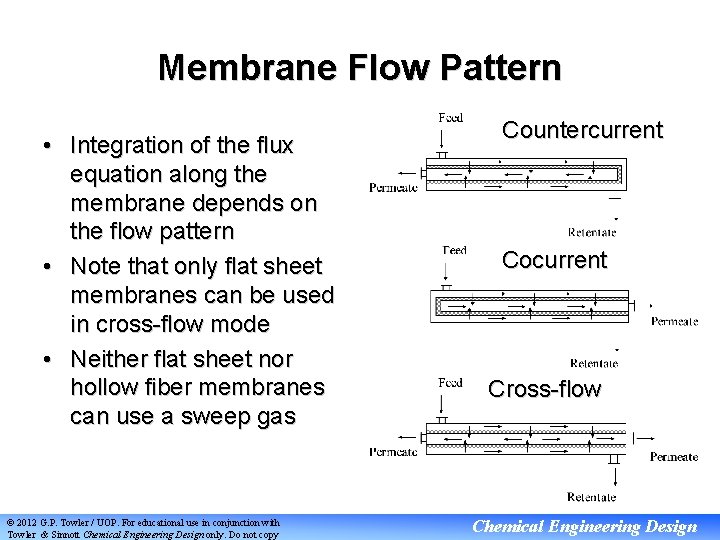
Membrane Flow Pattern • Integration of the flux equation along the membrane depends on the flow pattern • Note that only flat sheet membranes can be used in cross-flow mode • Neither flat sheet nor hollow fiber membranes can use a sweep gas © 2012 G. P. Towler / UOP. For educational use in conjunction with Towler & Sinnott Chemical Engineering Design only. Do not copy Countercurrent Cocurrent Cross-flow Chemical Engineering Design
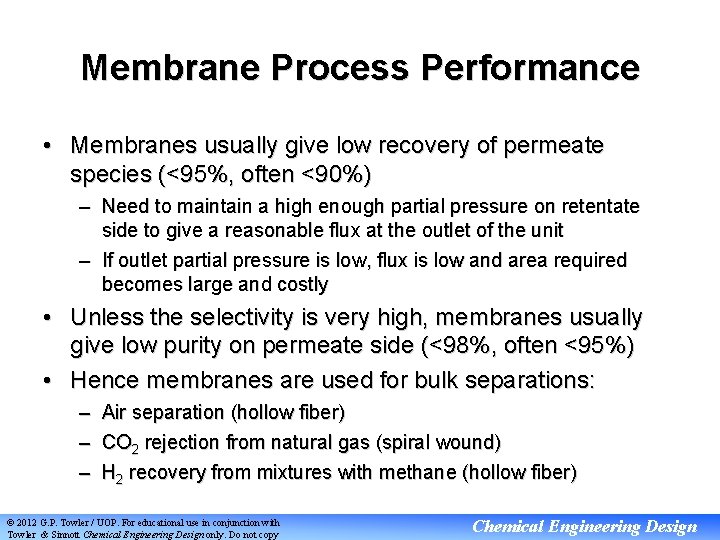
Membrane Process Performance • Membranes usually give low recovery of permeate species (<95%, often <90%) – Need to maintain a high enough partial pressure on retentate side to give a reasonable flux at the outlet of the unit – If outlet partial pressure is low, flux is low and area required becomes large and costly • Unless the selectivity is very high, membranes usually give low purity on permeate side (<98%, often <95%) • Hence membranes are used for bulk separations: – Air separation (hollow fiber) – CO 2 rejection from natural gas (spiral wound) – H 2 recovery from mixtures with methane (hollow fiber) © 2012 G. P. Towler / UOP. For educational use in conjunction with Towler & Sinnott Chemical Engineering Design only. Do not copy Chemical Engineering Design
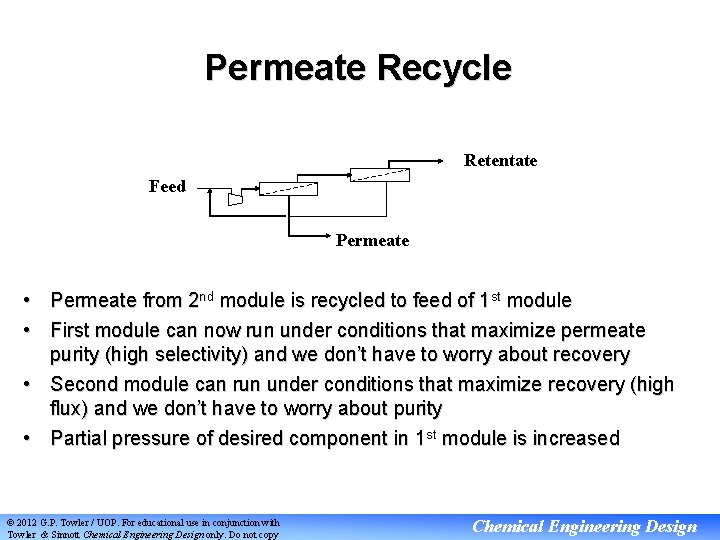
Permeate Recycle Retentate Feed Permeate • Permeate from 2 nd module is recycled to feed of 1 st module • First module can now run under conditions that maximize permeate purity (high selectivity) and we don’t have to worry about recovery • Second module can run under conditions that maximize recovery (high flux) and we don’t have to worry about purity • Partial pressure of desired component in 1 st module is increased © 2012 G. P. Towler / UOP. For educational use in conjunction with Towler & Sinnott Chemical Engineering Design only. Do not copy Chemical Engineering Design
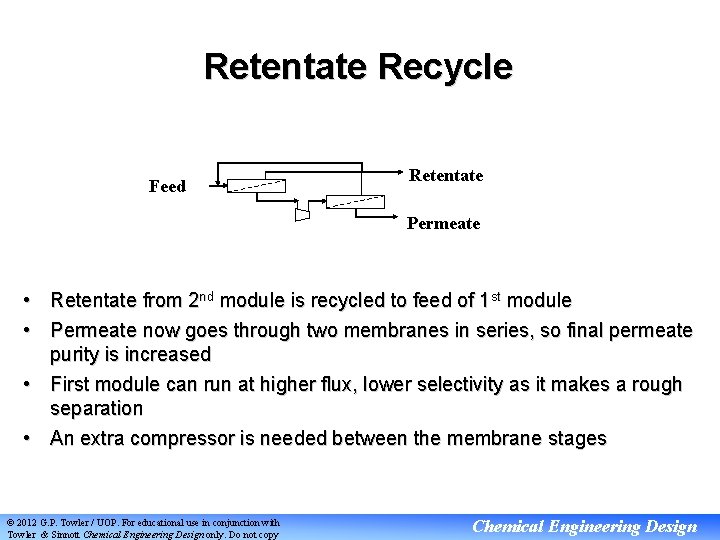
Retentate Recycle Feed Retentate Permeate • Retentate from 2 nd module is recycled to feed of 1 st module • Permeate now goes through two membranes in series, so final permeate purity is increased • First module can run at higher flux, lower selectivity as it makes a rough separation • An extra compressor is needed between the membrane stages © 2012 G. P. Towler / UOP. For educational use in conjunction with Towler & Sinnott Chemical Engineering Design only. Do not copy Chemical Engineering Design
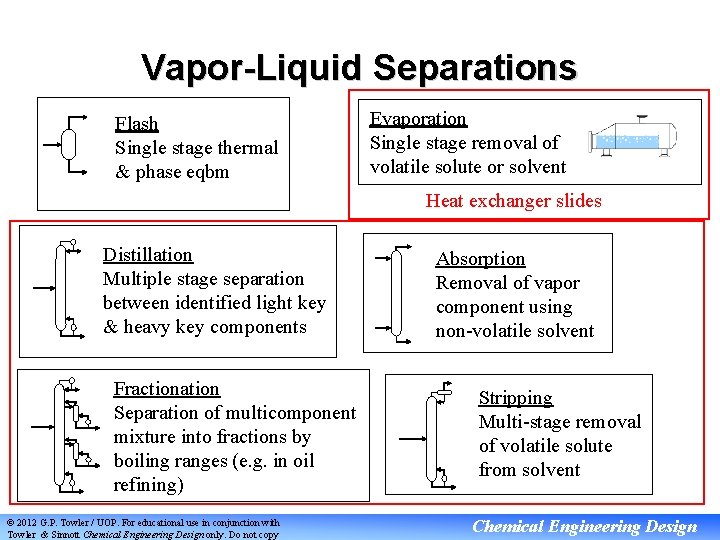
Vapor-Liquid Separations Flash Single stage thermal & phase eqbm Evaporation Single stage removal of volatile solute or solvent Heat exchanger slides Distillation Multiple stage separation between identified light key & heavy key components Fractionation Separation of multicomponent mixture into fractions by boiling ranges (e. g. in oil refining) © 2012 G. P. Towler / UOP. For educational use in conjunction with Towler & Sinnott Chemical Engineering Design only. Do not copy Absorption Removal of vapor component using non-volatile solvent Stripping Multi-stage removal of volatile solute from solvent Chemical Engineering Design
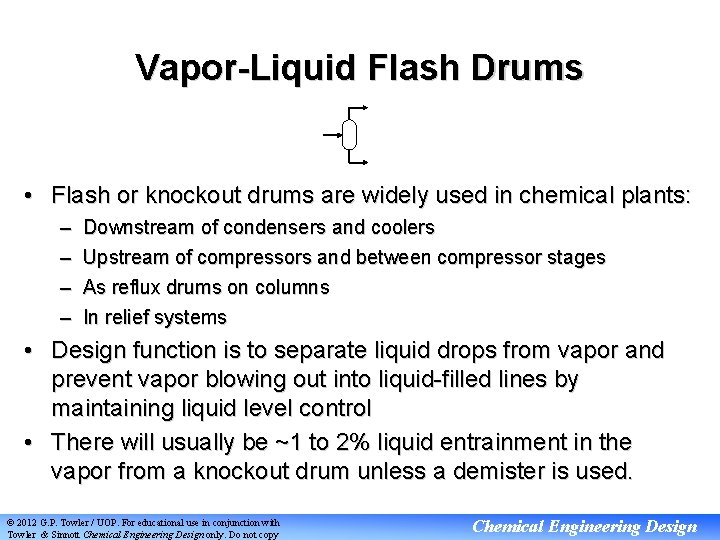
Vapor-Liquid Flash Drums • Flash or knockout drums are widely used in chemical plants: – – Downstream of condensers and coolers Upstream of compressors and between compressor stages As reflux drums on columns In relief systems • Design function is to separate liquid drops from vapor and prevent vapor blowing out into liquid-filled lines by maintaining liquid level control • There will usually be ~1 to 2% liquid entrainment in the vapor from a knockout drum unless a demister is used. © 2012 G. P. Towler / UOP. For educational use in conjunction with Towler & Sinnott Chemical Engineering Design only. Do not copy Chemical Engineering Design
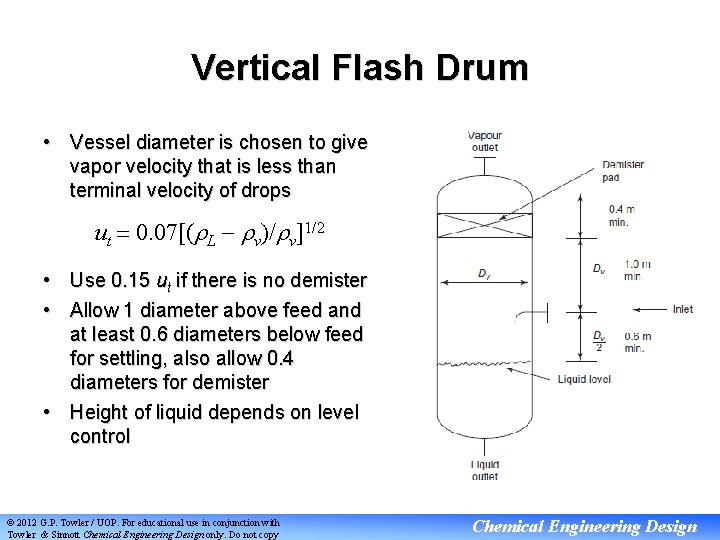
Vertical Flash Drum • Vessel diameter is chosen to give vapor velocity that is less than terminal velocity of drops ut 0. 07[( L v)/ v]1/2 • Use 0. 15 ut if there is no demister • Allow 1 diameter above feed and at least 0. 6 diameters below feed for settling, also allow 0. 4 diameters for demister • Height of liquid depends on level control © 2012 G. P. Towler / UOP. For educational use in conjunction with Towler & Sinnott Chemical Engineering Design only. Do not copy Chemical Engineering Design
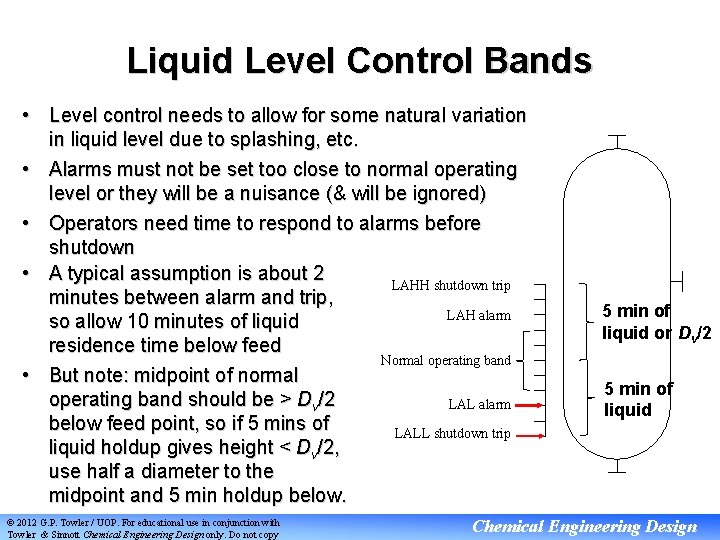
Liquid Level Control Bands • Level control needs to allow for some natural variation in liquid level due to splashing, etc. • Alarms must not be set too close to normal operating level or they will be a nuisance (& will be ignored) • Operators need time to respond to alarms before shutdown • A typical assumption is about 2 LAHH shutdown trip minutes between alarm and trip, LAH alarm so allow 10 minutes of liquid residence time below feed Normal operating band • But note: midpoint of normal operating band should be > Dv/2 LAL alarm below feed point, so if 5 mins of LALL shutdown trip liquid holdup gives height < Dv/2, use half a diameter to the midpoint and 5 min holdup below. © 2012 G. P. Towler / UOP. For educational use in conjunction with Towler & Sinnott Chemical Engineering Design only. Do not copy 5 min of liquid or Dv/2 5 min of liquid Chemical Engineering Design
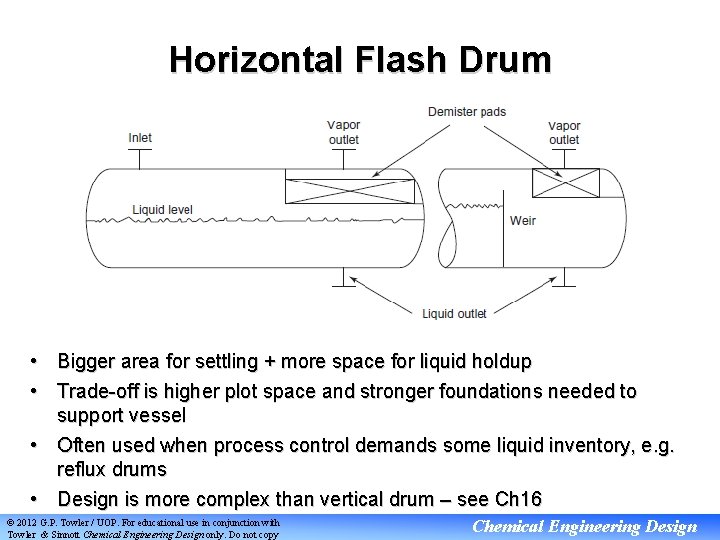
Horizontal Flash Drum • Bigger area for settling + more space for liquid holdup • Trade-off is higher plot space and stronger foundations needed to support vessel • Often used when process control demands some liquid inventory, e. g. reflux drums • Design is more complex than vertical drum – see Ch 16 © 2012 G. P. Towler / UOP. For educational use in conjunction with Towler & Sinnott Chemical Engineering Design only. Do not copy Chemical Engineering Design
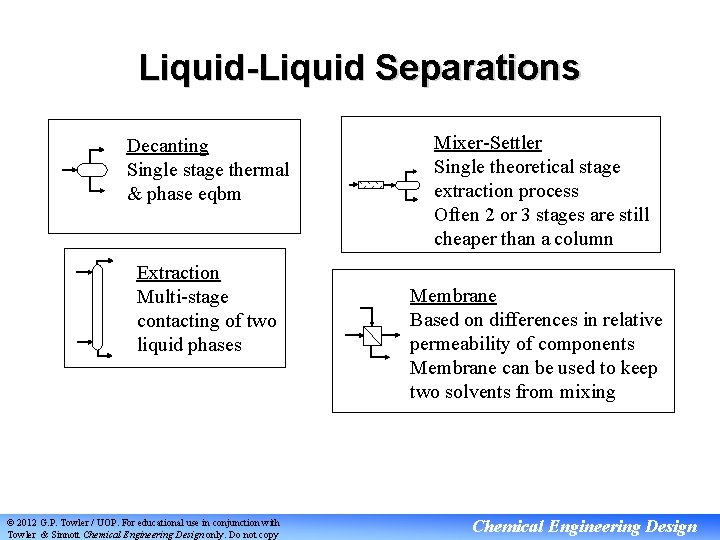
Liquid-Liquid Separations Decanting Single stage thermal & phase eqbm Extraction Multi-stage contacting of two liquid phases © 2012 G. P. Towler / UOP. For educational use in conjunction with Towler & Sinnott Chemical Engineering Design only. Do not copy Mixer-Settler Single theoretical stage extraction process Often 2 or 3 stages are still cheaper than a column Membrane Based on differences in relative permeability of components Membrane can be used to keep two solvents from mixing Chemical Engineering Design
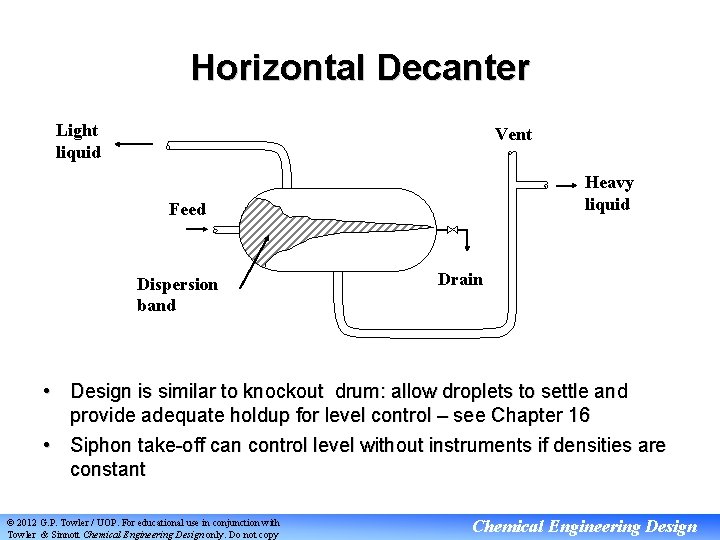
Horizontal Decanter Light liquid Vent Heavy liquid Feed Dispersion band Drain • Design is similar to knockout drum: allow droplets to settle and provide adequate holdup for level control – see Chapter 16 • Siphon take-off can control level without instruments if densities are constant © 2012 G. P. Towler / UOP. For educational use in conjunction with Towler & Sinnott Chemical Engineering Design only. Do not copy Chemical Engineering Design
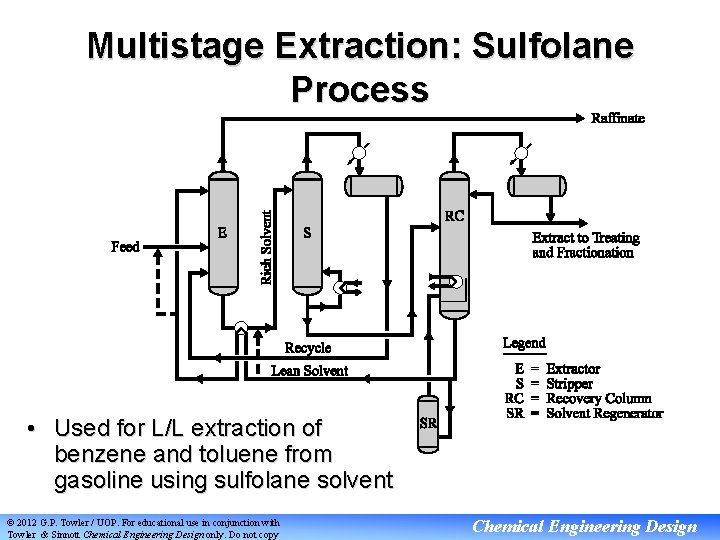
Multistage Extraction: Sulfolane Process • Used for L/L extraction of benzene and toluene from gasoline using sulfolane solvent © 2012 G. P. Towler / UOP. For educational use in conjunction with Towler & Sinnott Chemical Engineering Design only. Do not copy Chemical Engineering Design
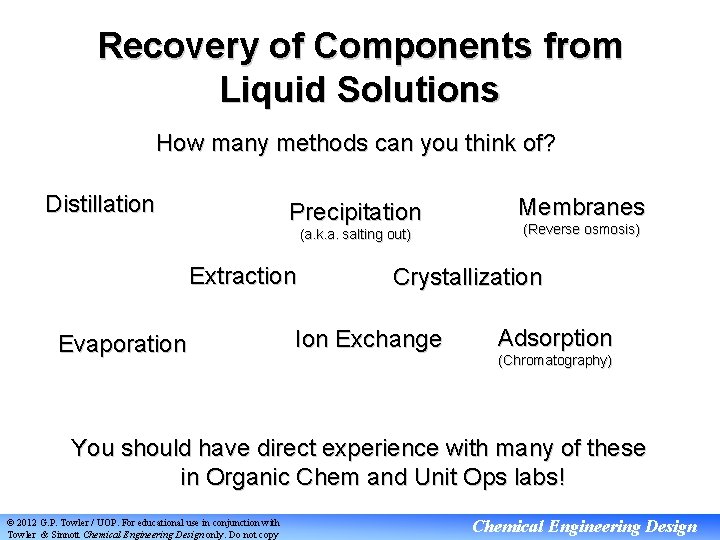
Recovery of Components from Liquid Solutions How many methods can you think of? Distillation Precipitation (a. k. a. salting out) Extraction Evaporation Membranes (Reverse osmosis) Crystallization Ion Exchange Adsorption (Chromatography) You should have direct experience with many of these in Organic Chem and Unit Ops labs! © 2012 G. P. Towler / UOP. For educational use in conjunction with Towler & Sinnott Chemical Engineering Design only. Do not copy Chemical Engineering Design
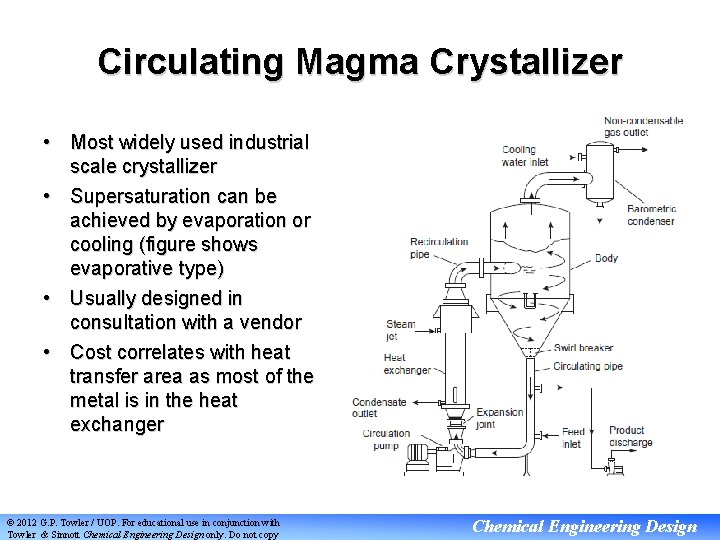
Circulating Magma Crystallizer • Most widely used industrial scale crystallizer • Supersaturation can be achieved by evaporation or cooling (figure shows evaporative type) • Usually designed in consultation with a vendor • Cost correlates with heat transfer area as most of the metal is in the heat exchanger © 2012 G. P. Towler / UOP. For educational use in conjunction with Towler & Sinnott Chemical Engineering Design only. Do not copy Chemical Engineering Design
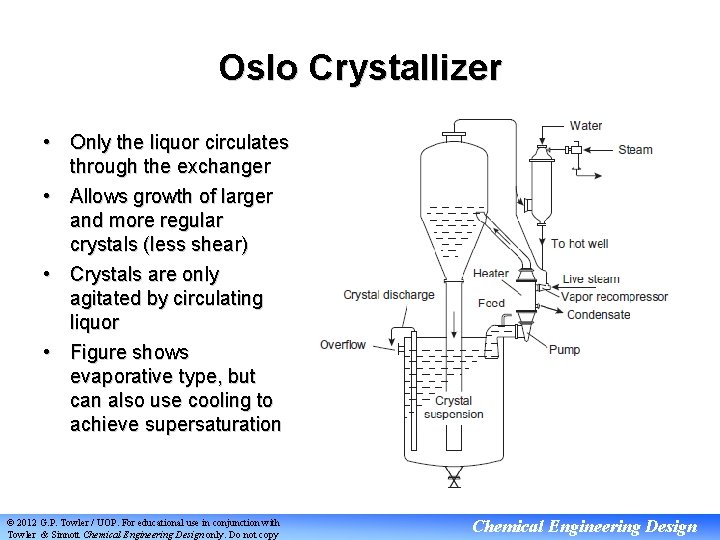
Oslo Crystallizer • Only the liquor circulates through the exchanger • Allows growth of larger and more regular crystals (less shear) • Crystals are only agitated by circulating liquor • Figure shows evaporative type, but can also use cooling to achieve supersaturation © 2012 G. P. Towler / UOP. For educational use in conjunction with Towler & Sinnott Chemical Engineering Design only. Do not copy Chemical Engineering Design
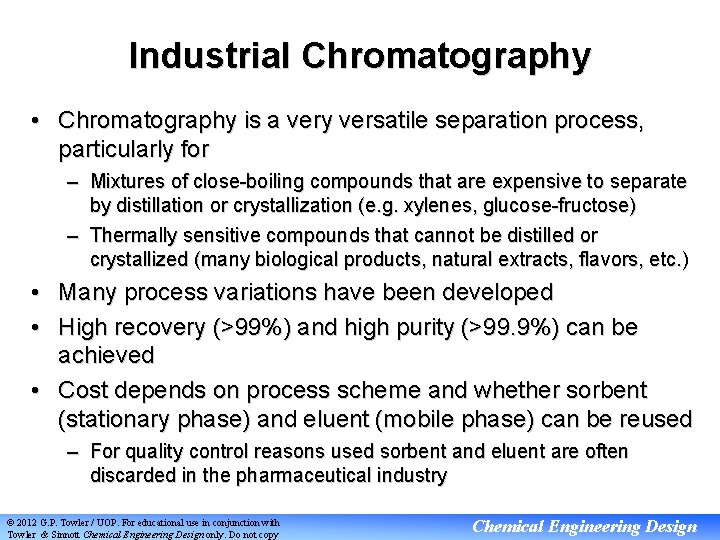
Industrial Chromatography • Chromatography is a very versatile separation process, particularly for – Mixtures of close-boiling compounds that are expensive to separate by distillation or crystallization (e. g. xylenes, glucose-fructose) – Thermally sensitive compounds that cannot be distilled or crystallized (many biological products, natural extracts, flavors, etc. ) • Many process variations have been developed • High recovery (>99%) and high purity (>99. 9%) can be achieved • Cost depends on process scheme and whether sorbent (stationary phase) and eluent (mobile phase) can be reused – For quality control reasons used sorbent and eluent are often discarded in the pharmaceutical industry © 2012 G. P. Towler / UOP. For educational use in conjunction with Towler & Sinnott Chemical Engineering Design only. Do not copy Chemical Engineering Design
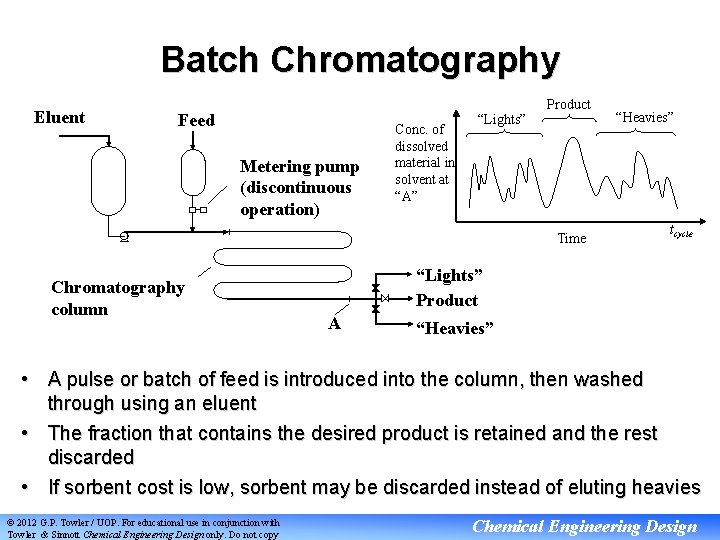
Batch Chromatography Eluent Feed Metering pump (discontinuous operation) Conc. of dissolved material in solvent at “A” “Lights” Product Time Chromatography column “Heavies” tcycle “Lights” Product A “Heavies” • A pulse or batch of feed is introduced into the column, then washed through using an eluent • The fraction that contains the desired product is retained and the rest discarded • If sorbent cost is low, sorbent may be discarded instead of eluting heavies © 2012 G. P. Towler / UOP. For educational use in conjunction with Towler & Sinnott Chemical Engineering Design only. Do not copy Chemical Engineering Design
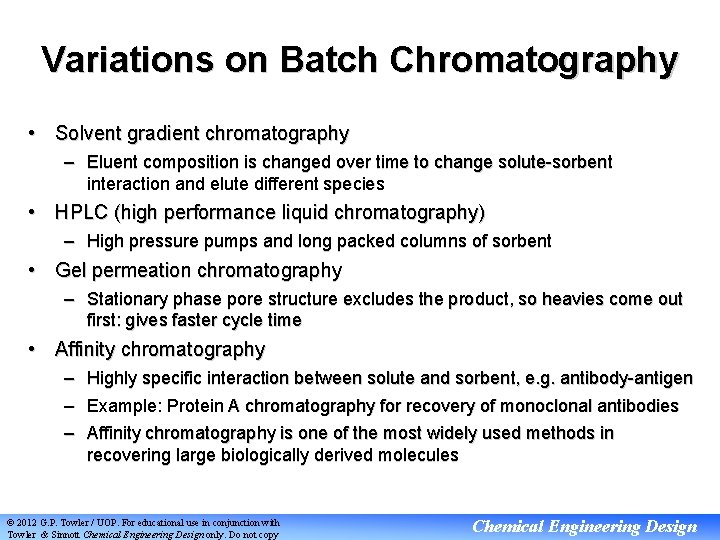
Variations on Batch Chromatography • Solvent gradient chromatography – Eluent composition is changed over time to change solute-sorbent interaction and elute different species • HPLC (high performance liquid chromatography) – High pressure pumps and long packed columns of sorbent • Gel permeation chromatography – Stationary phase pore structure excludes the product, so heavies come out first: gives faster cycle time • Affinity chromatography – – – Highly specific interaction between solute and sorbent, e. g. antibody-antigen Example: Protein A chromatography for recovery of monoclonal antibodies Affinity chromatography is one of the most widely used methods in recovering large biologically derived molecules © 2012 G. P. Towler / UOP. For educational use in conjunction with Towler & Sinnott Chemical Engineering Design only. Do not copy Chemical Engineering Design
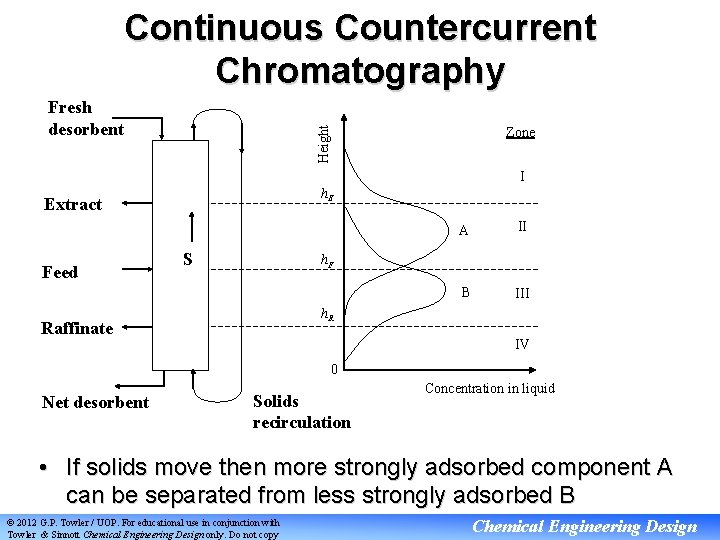
Continuous Countercurrent Chromatography Zone Height Fresh desorbent I h. E Extract Feed S A II B III h. F h. R Raffinate IV 0 Net desorbent Solids recirculation Concentration in liquid • If solids move then more strongly adsorbed component A can be separated from less strongly adsorbed B © 2012 G. P. Towler / UOP. For educational use in conjunction with Towler & Sinnott Chemical Engineering Design only. Do not copy Chemical Engineering Design
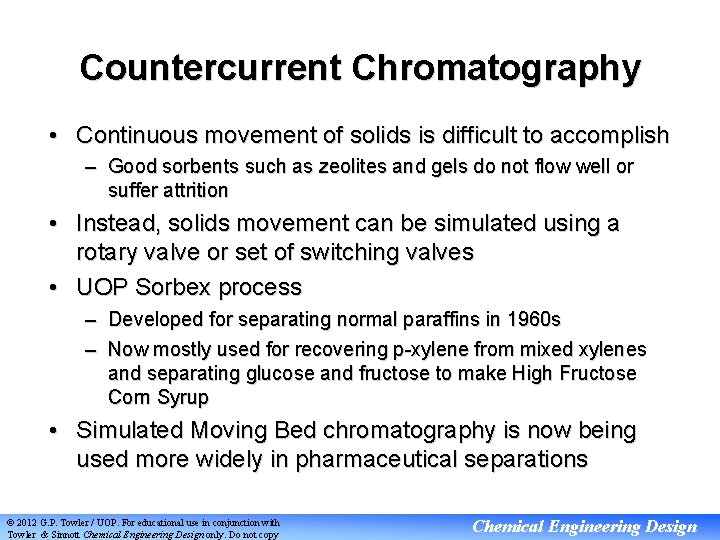
Countercurrent Chromatography • Continuous movement of solids is difficult to accomplish – Good sorbents such as zeolites and gels do not flow well or suffer attrition • Instead, solids movement can be simulated using a rotary valve or set of switching valves • UOP Sorbex process – Developed for separating normal paraffins in 1960 s – Now mostly used for recovering p-xylene from mixed xylenes and separating glucose and fructose to make High Fructose Corn Syrup • Simulated Moving Bed chromatography is now being used more widely in pharmaceutical separations © 2012 G. P. Towler / UOP. For educational use in conjunction with Towler & Sinnott Chemical Engineering Design only. Do not copy Chemical Engineering Design
Uop parking permit
Uop high flux tubing
Uop ecofining process flow diagram
Uop
Concurrent in os
Datorkunskap för nybörjare
Mantel som bars av kvinnor i antikens rom
Orubbliga rättigheter
Steg för steg rita
Förklara densitet för barn
Ministerstyre för och nackdelar
Jätte råtta
Kanaans land
Tack för att ni lyssnade bild
Tillitsbaserad ledning
Nyckelkompetenser för livslångt lärande
Sju för caesar
Upprepning i prosa
Modell för handledningsprocess
Stål för stötfångarsystem
Verktyg för automatisering av utbetalningar
Vishnuismen
Underlag för särskild löneskatt på pensionskostnader
Kolposkopi, px
I gullregnens månad
Boverket ka
Strategi för svensk viltförvaltning
Informationskartläggning
Stickprovsvarians
Tack för att ni har lyssnat
Klassificeringsstruktur för kommunala verksamheter
Ekologiskt fotavtryck
Cks
Läkarutlåtande för livränta
Påbyggnader för flakfordon
Tack för att ni lyssnade
Inköpsprocessen steg för steg
Egg för emanuel
Tack för att ni har lyssnat
Tidböcker
Rutin för avvikelsehantering
Var finns arvsanlagen
Formuö