Lecture 14 Wires Outline q Introduction q Interconnect
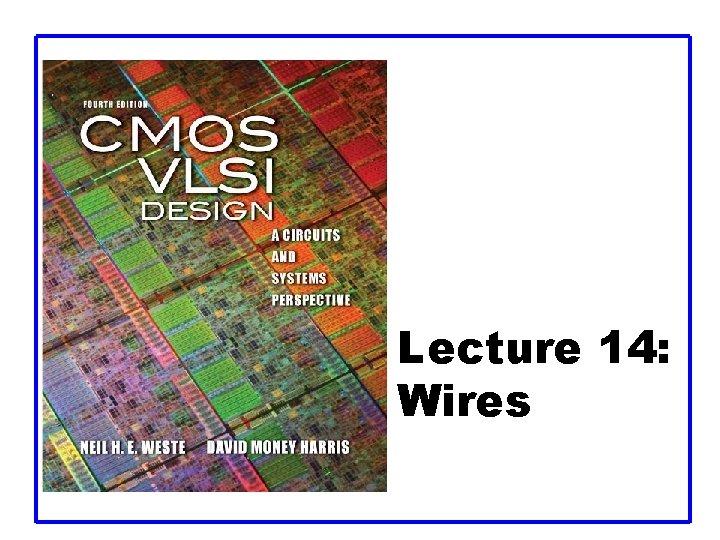
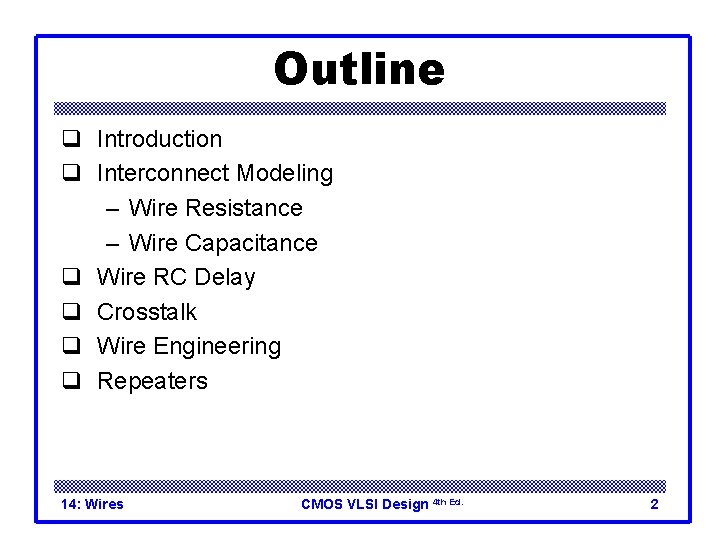
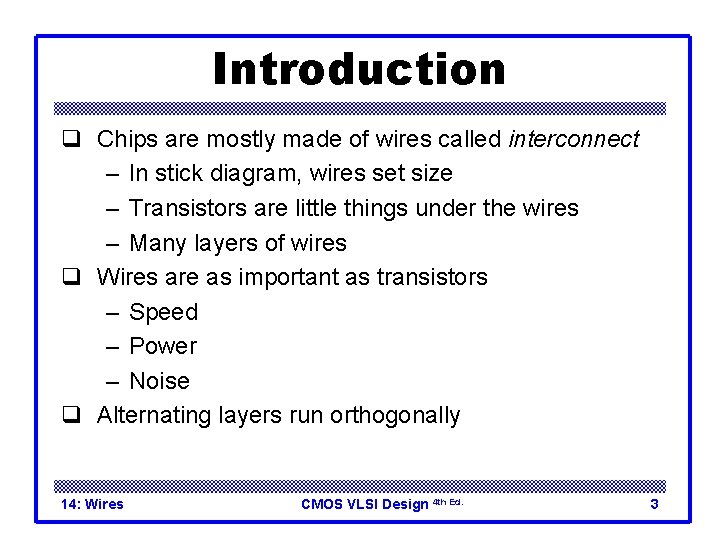
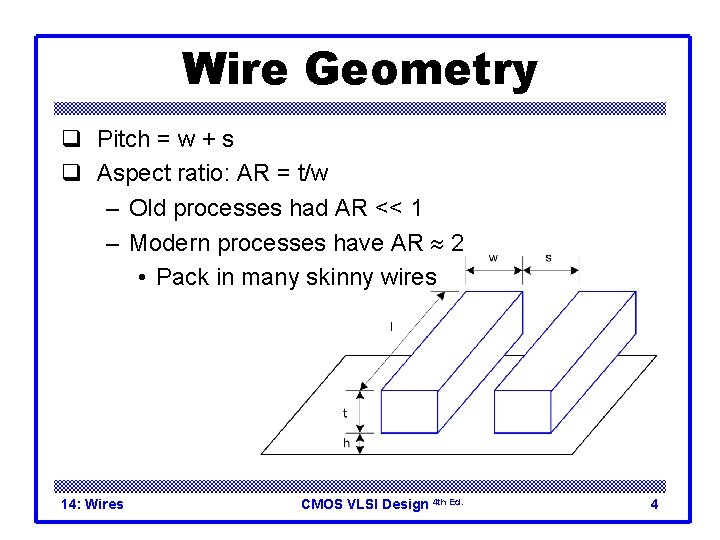
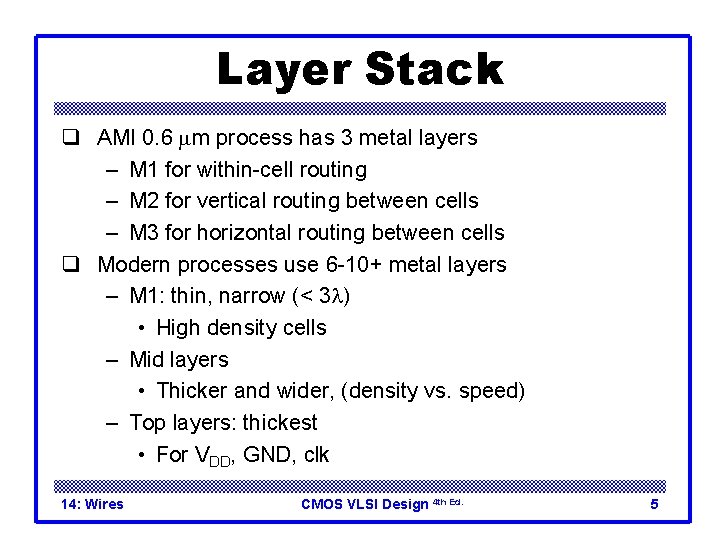
![Example Intel 90 nm Stack Intel 45 nm Stack [Thompson 02] 14: Wires [Moon Example Intel 90 nm Stack Intel 45 nm Stack [Thompson 02] 14: Wires [Moon](https://slidetodoc.com/presentation_image_h/902ff1d811adb49f92ff0eaf2594cc6b/image-6.jpg)
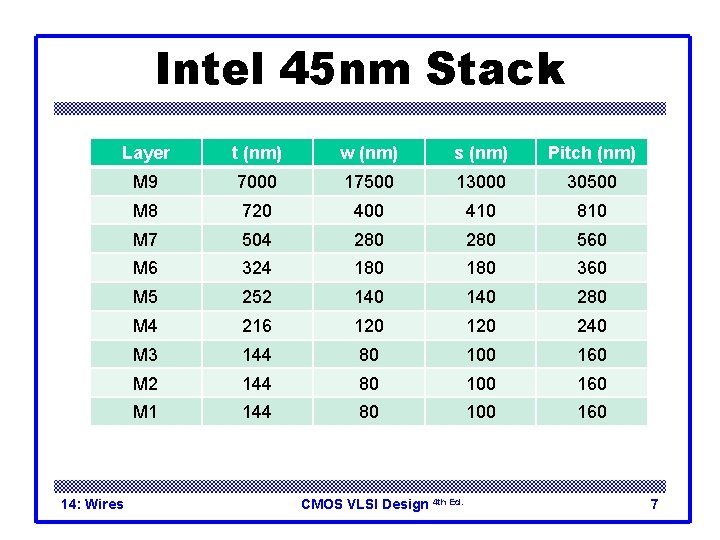
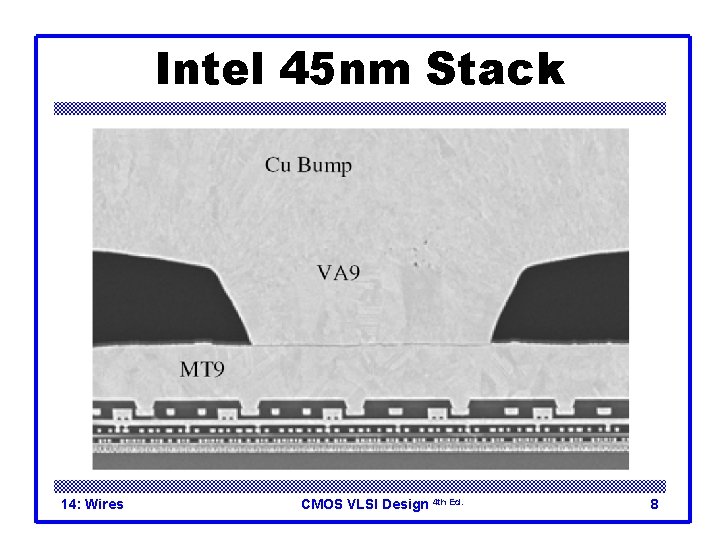
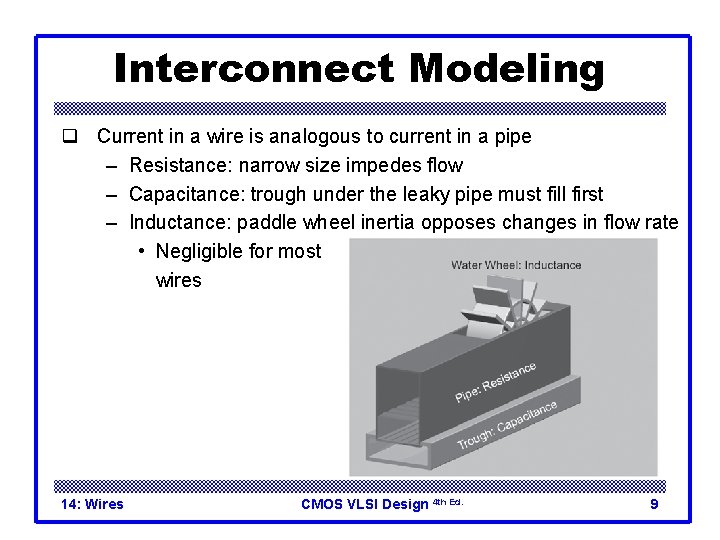
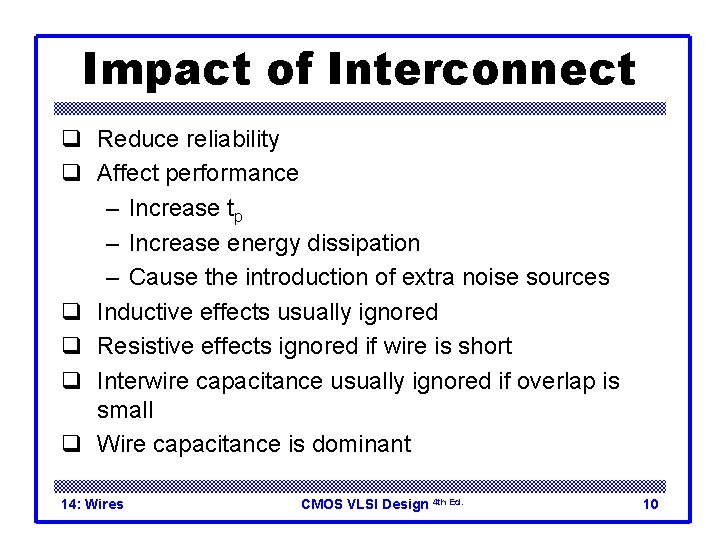
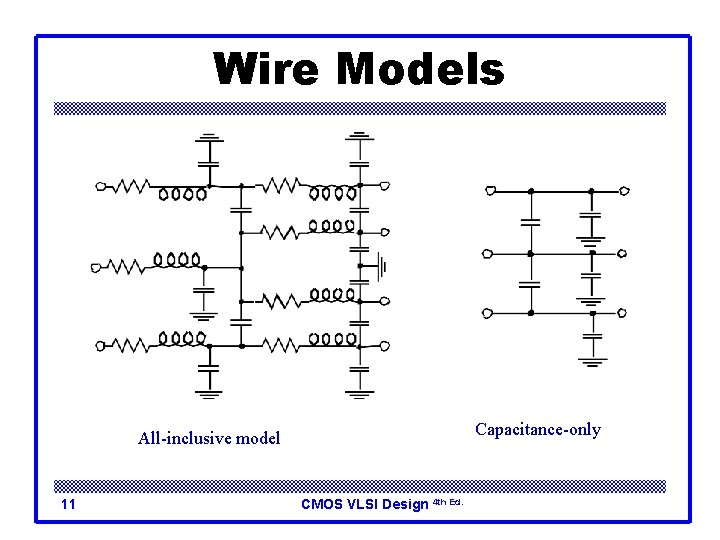
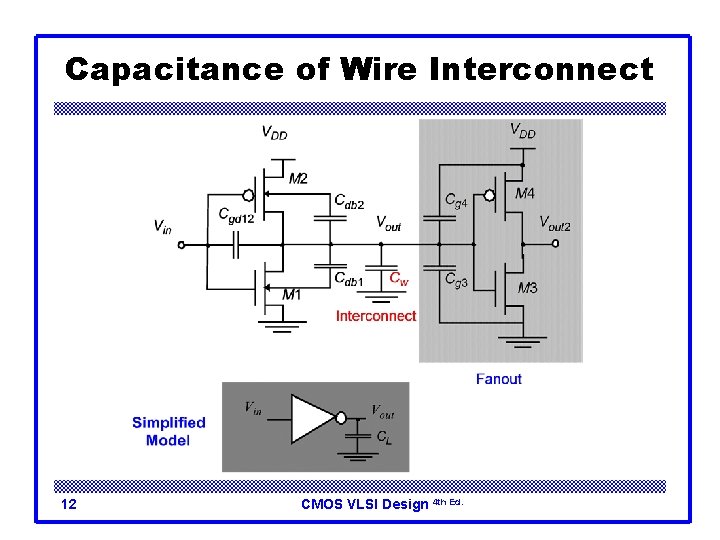
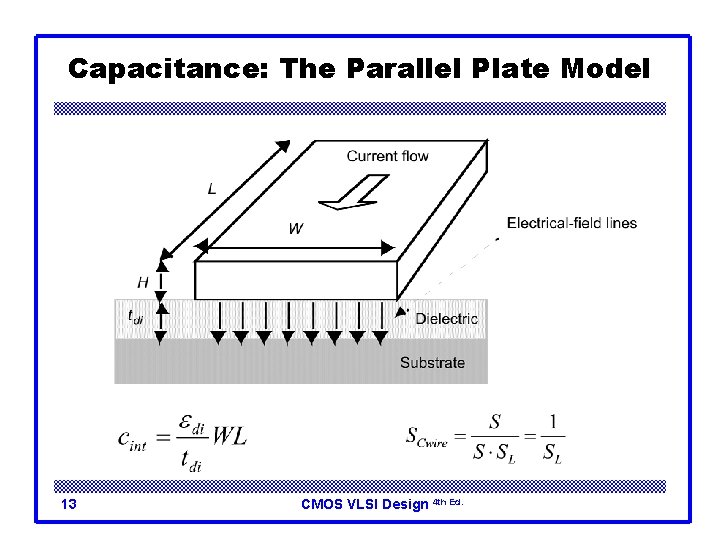
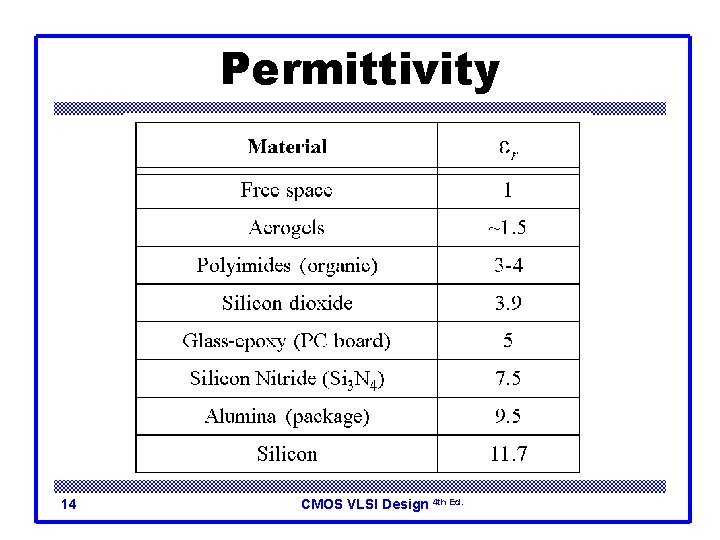
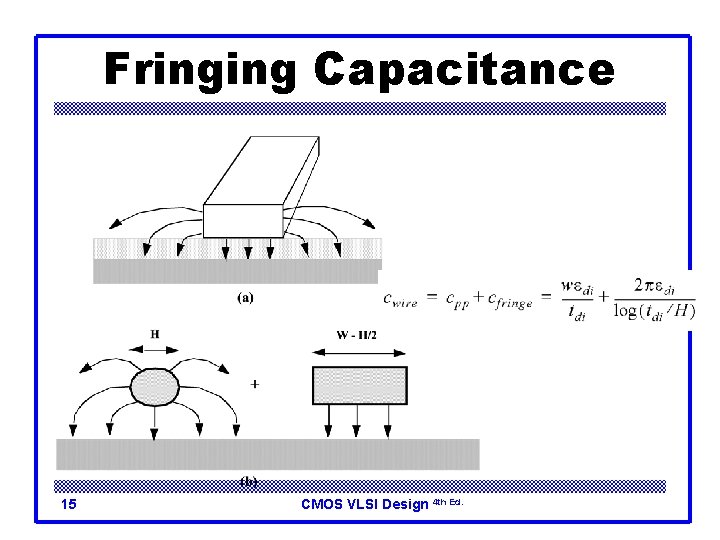
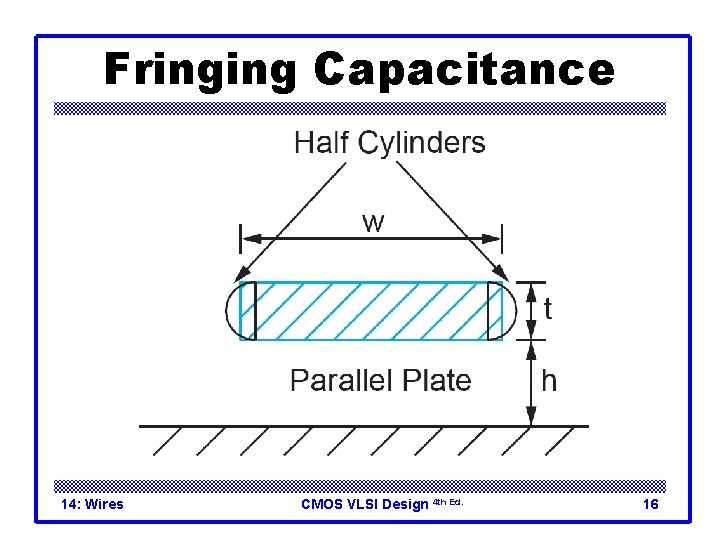
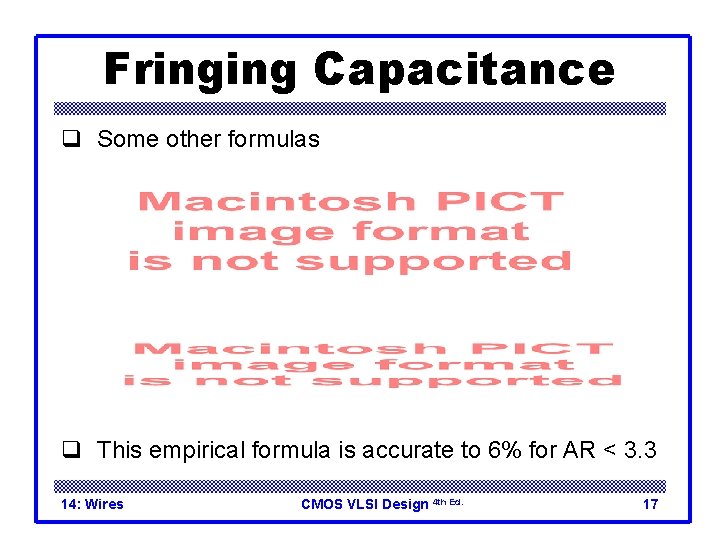
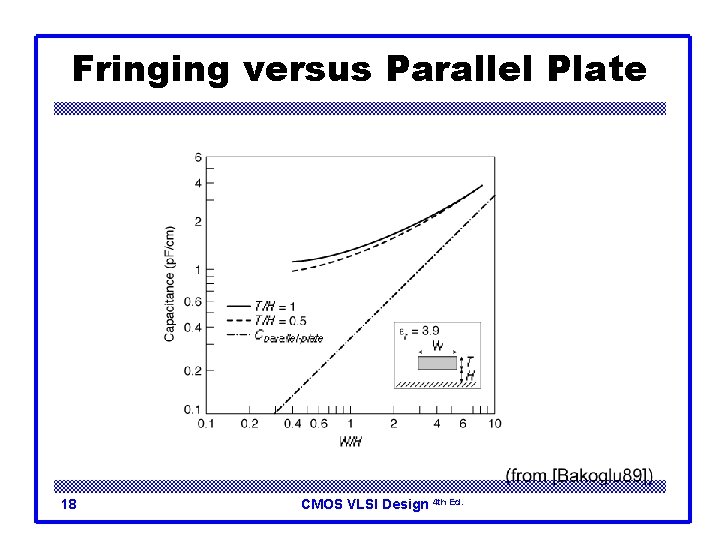
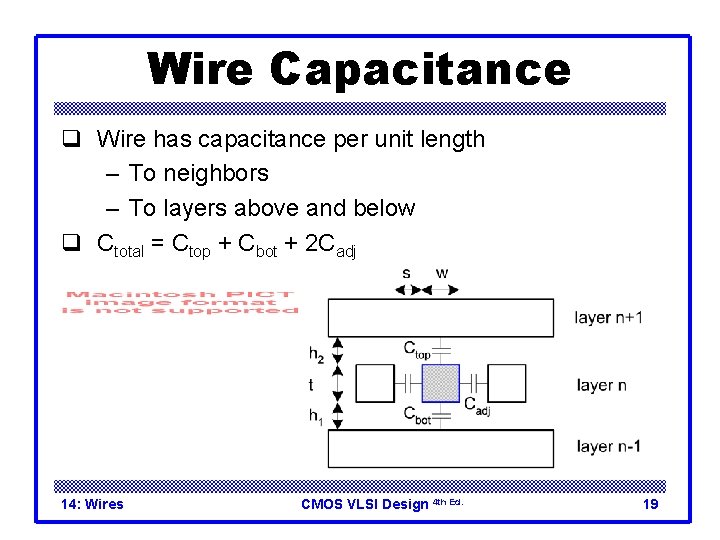
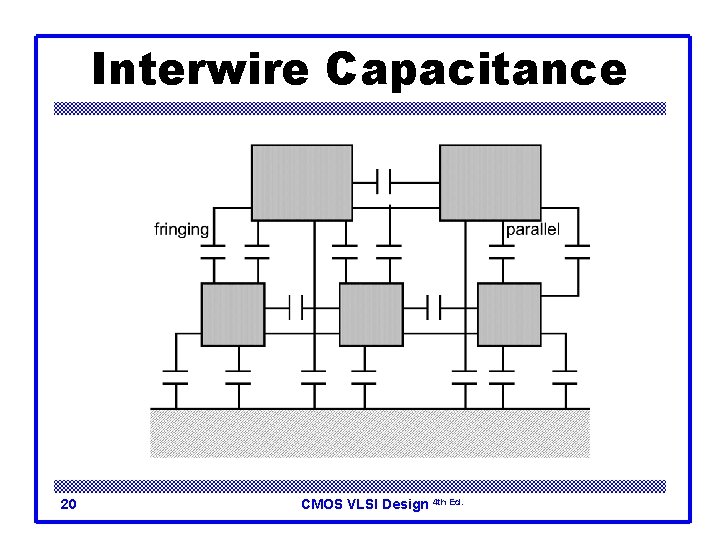
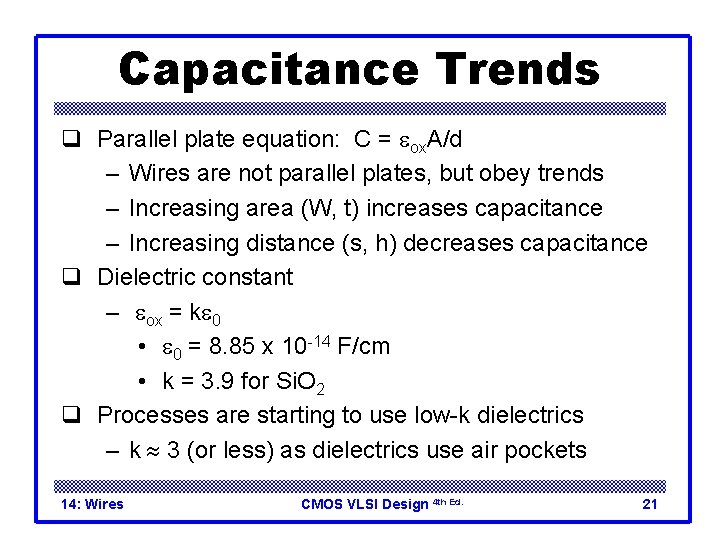
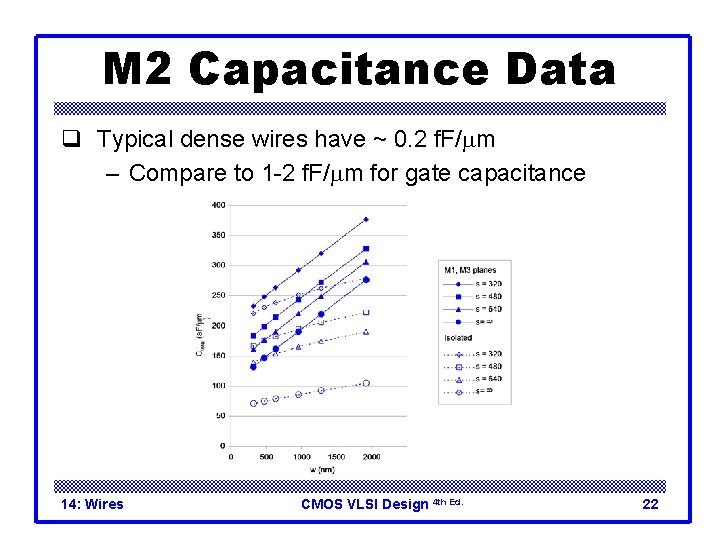
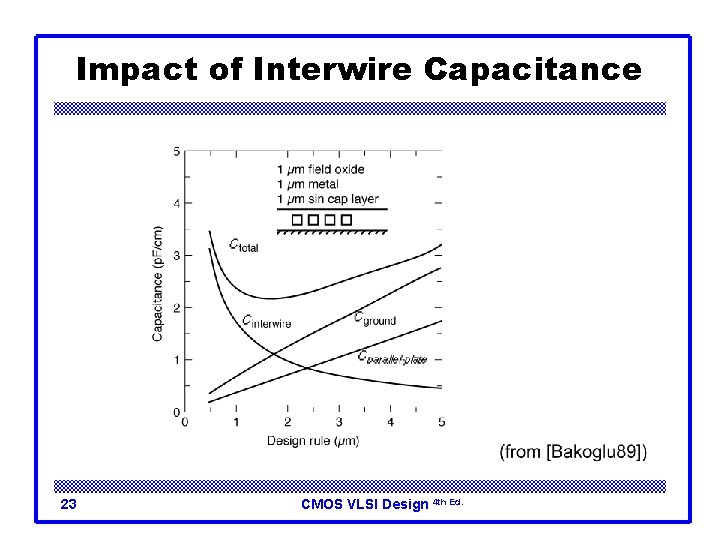
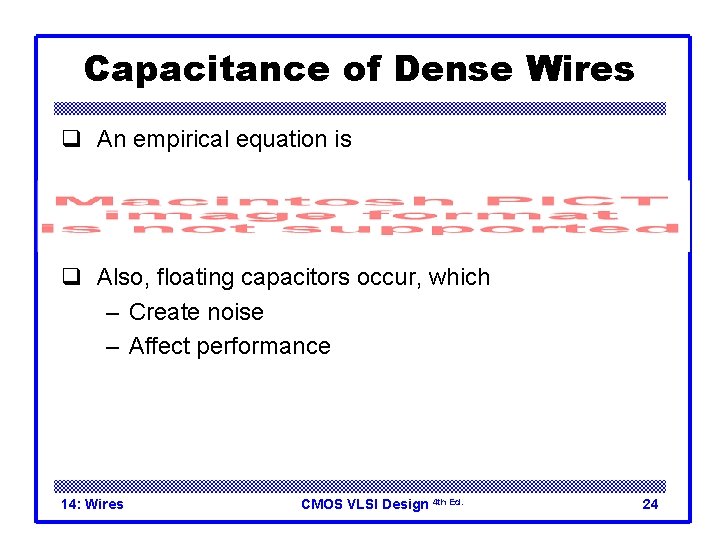
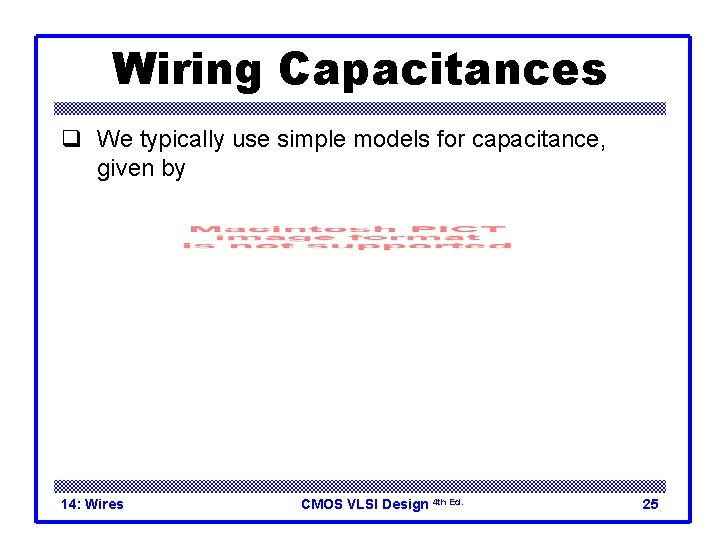
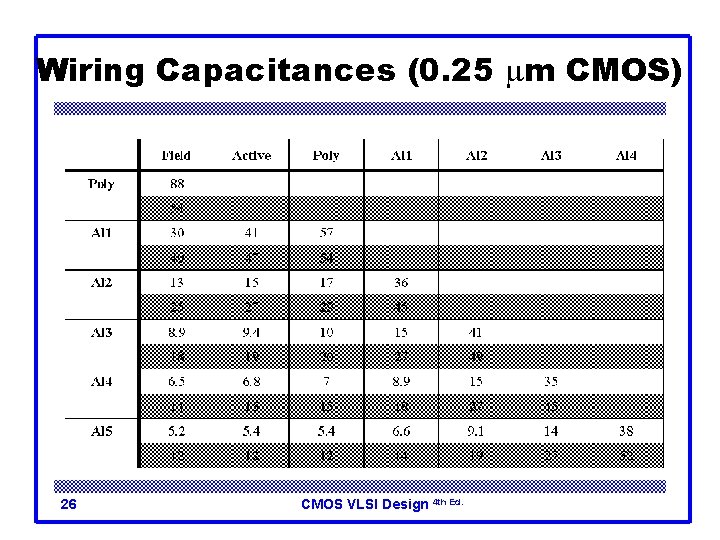
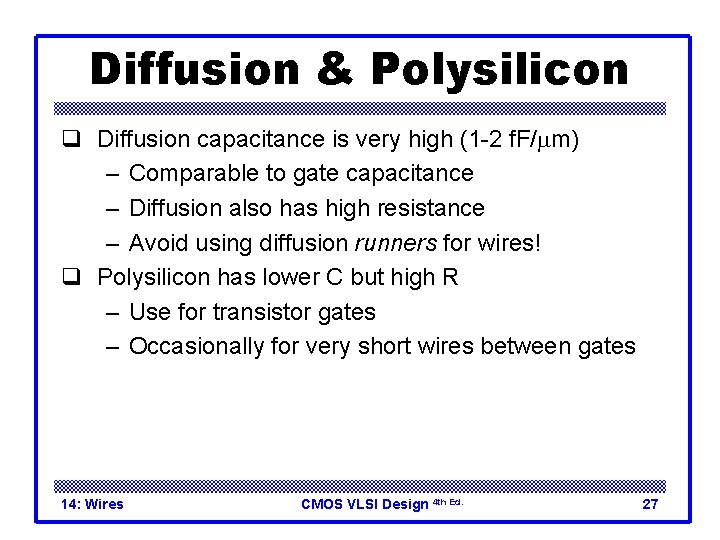
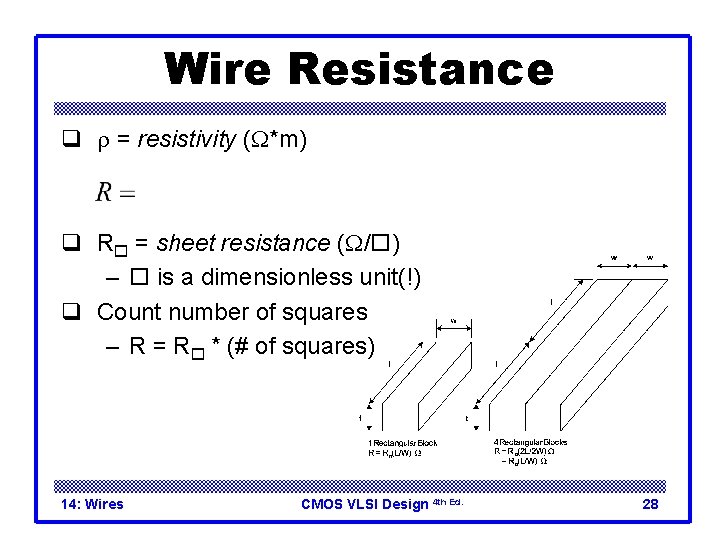

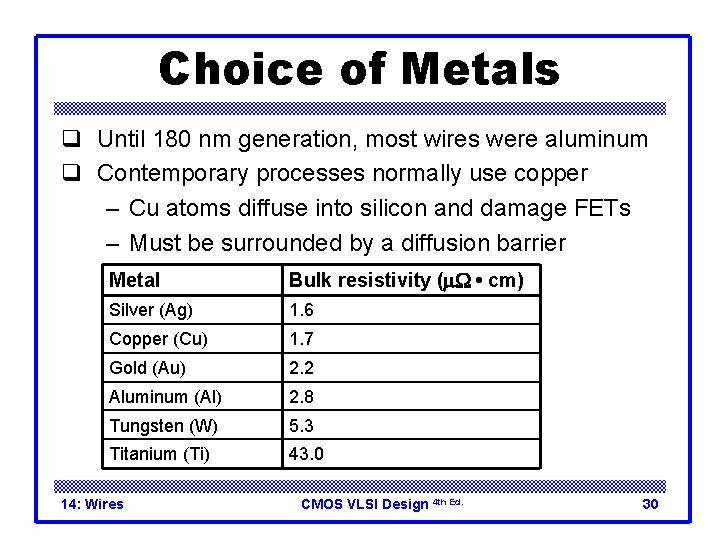
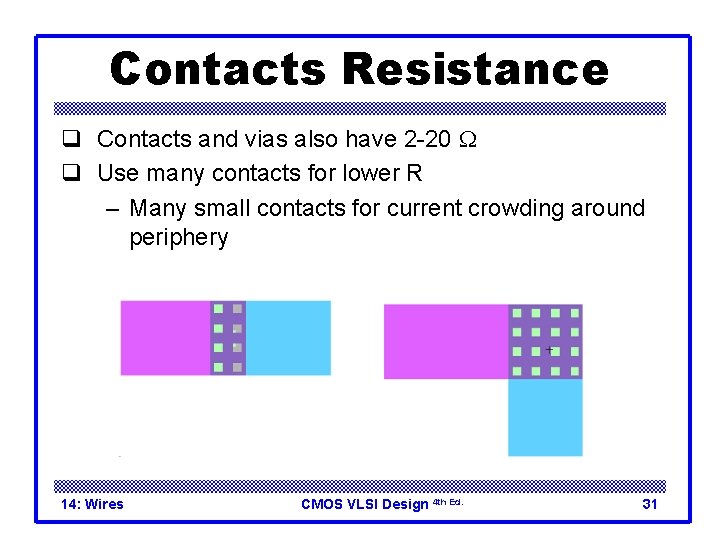
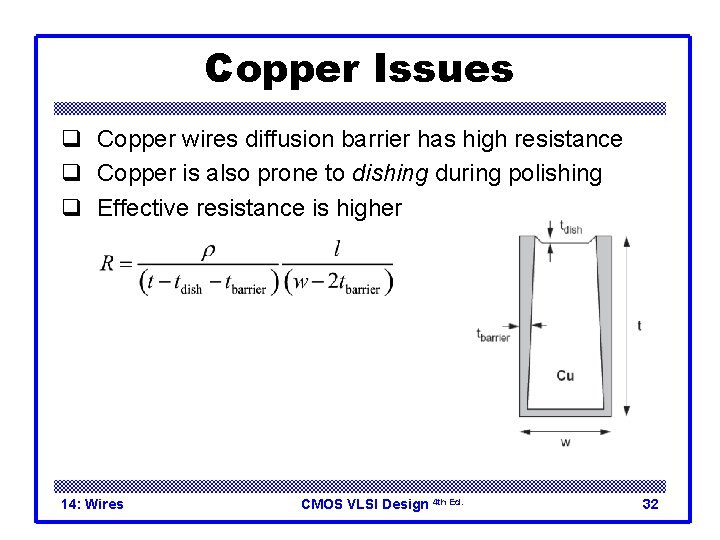
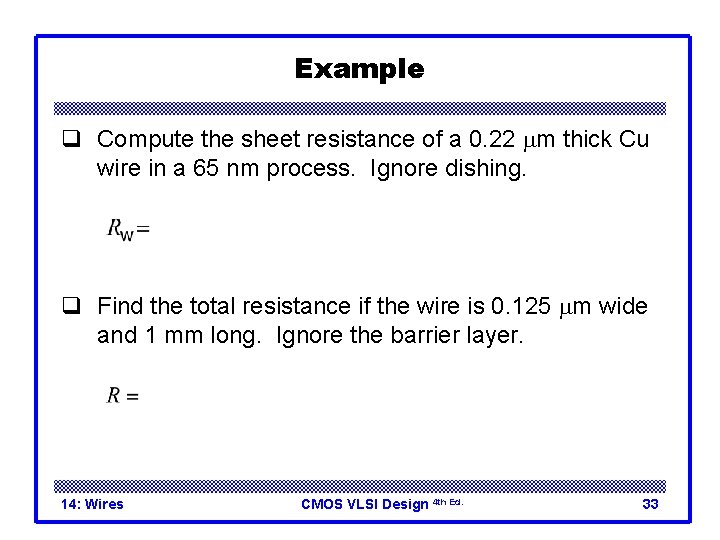
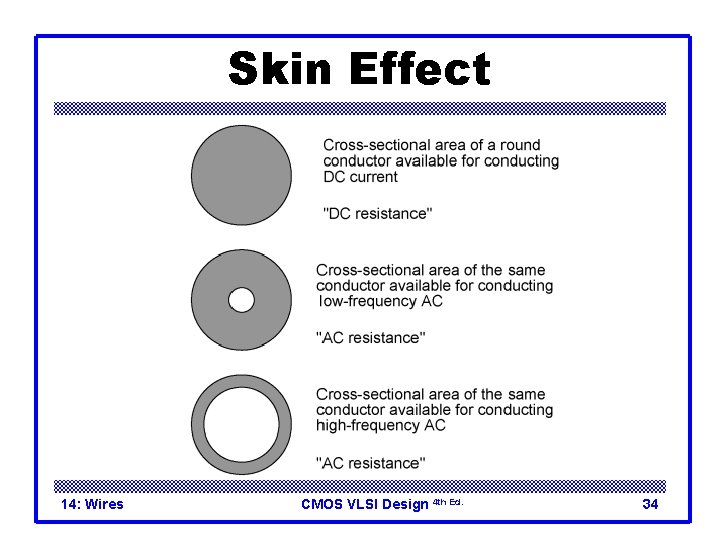
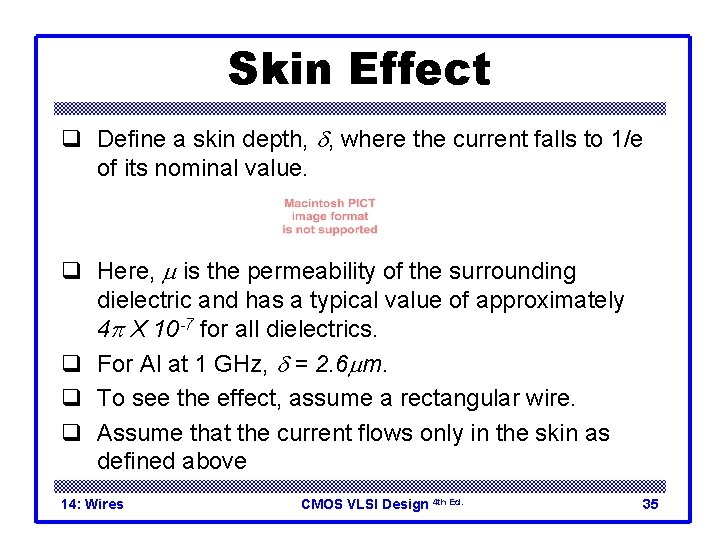
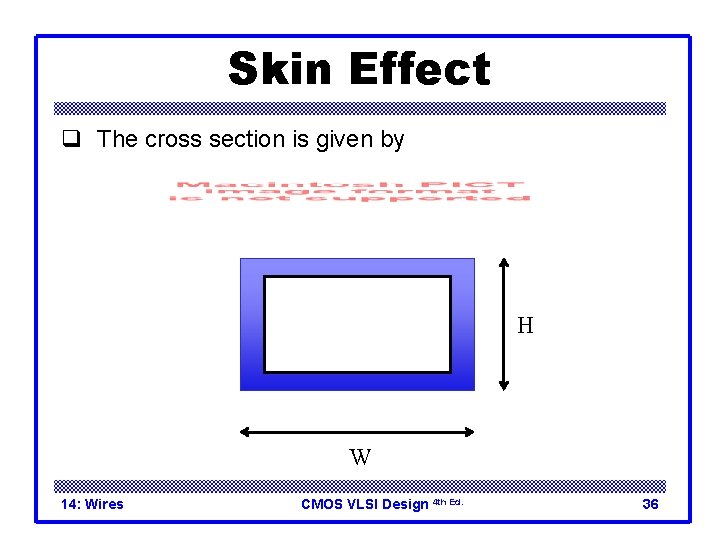
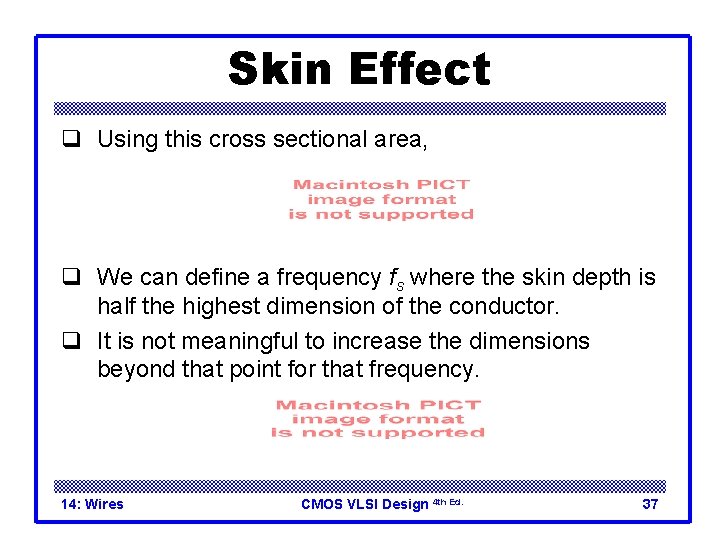
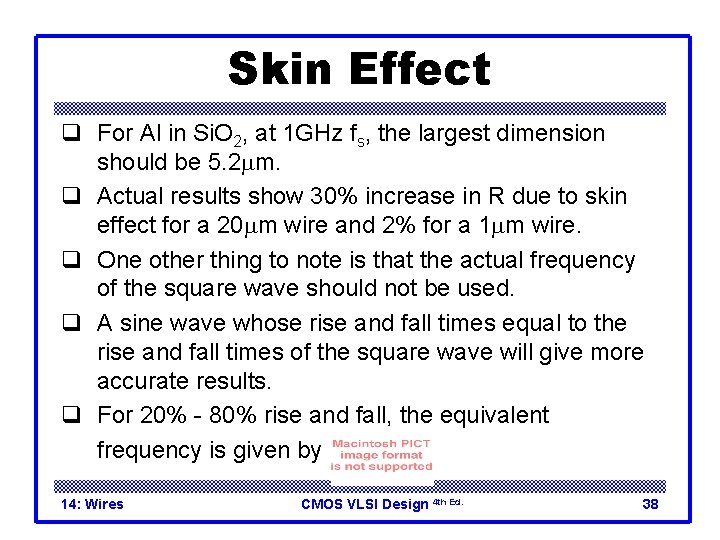
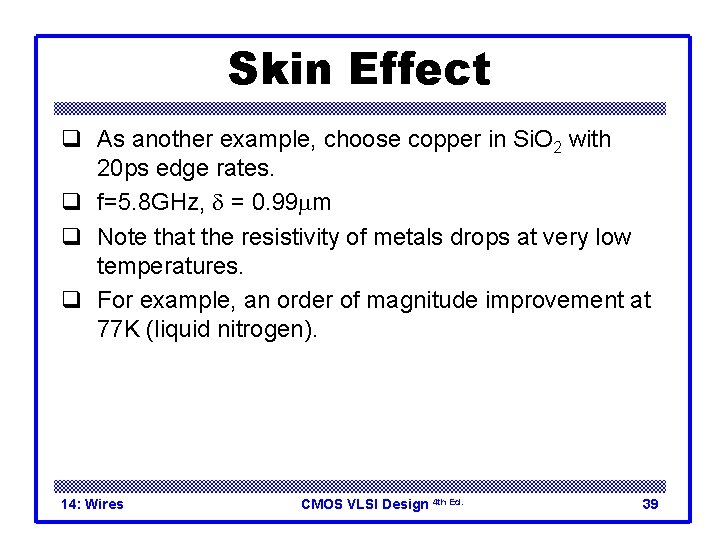
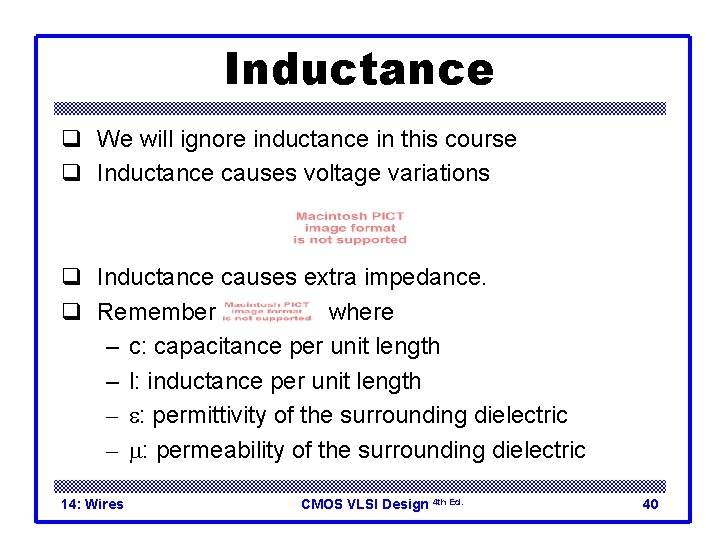
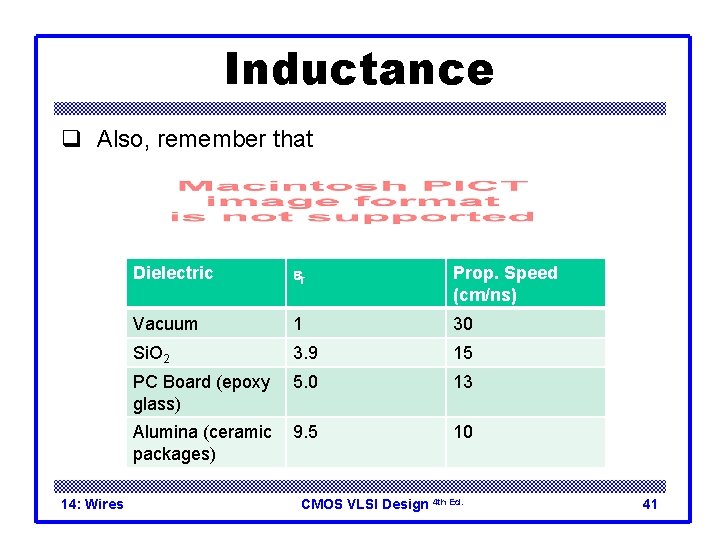
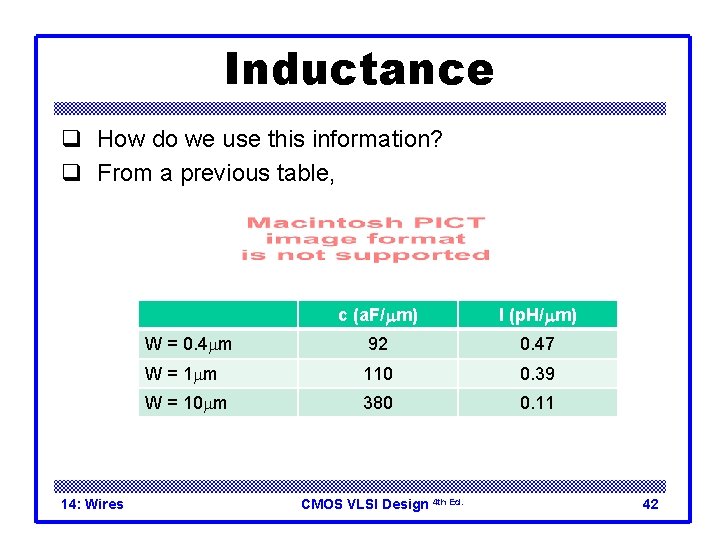
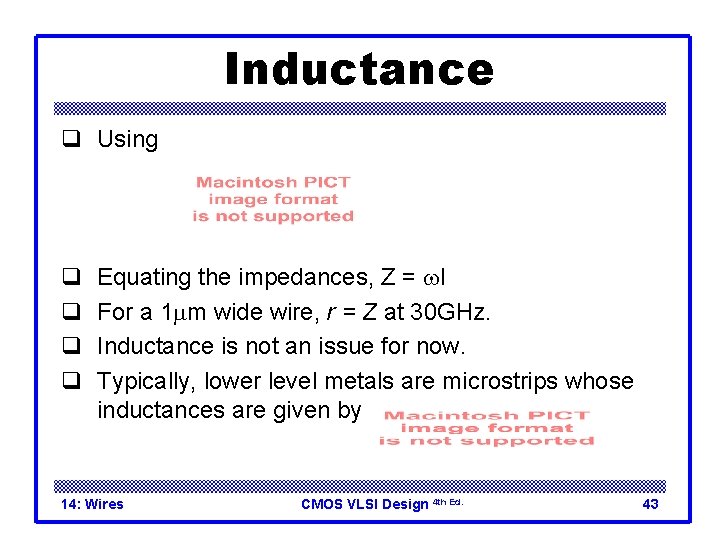
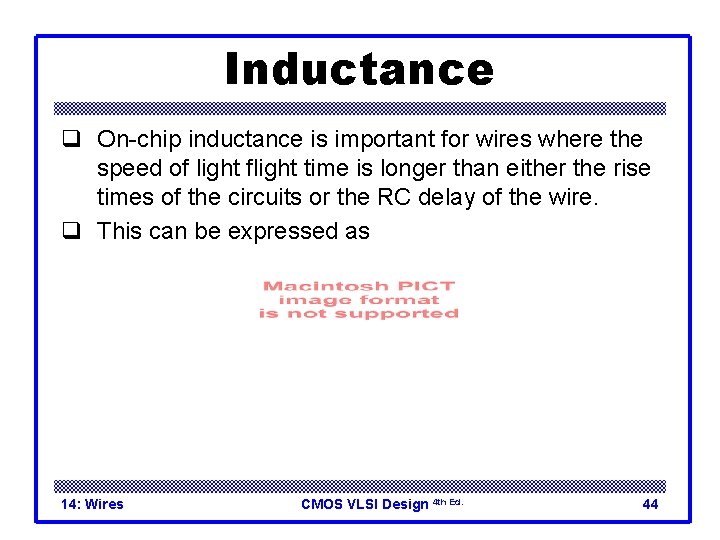
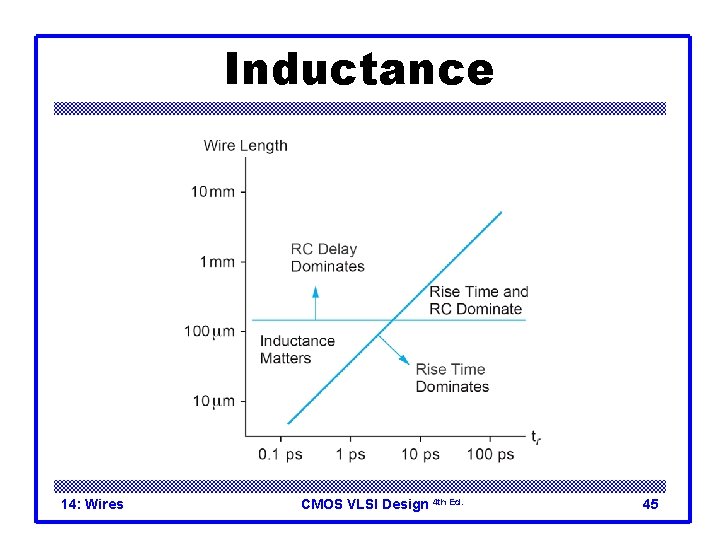
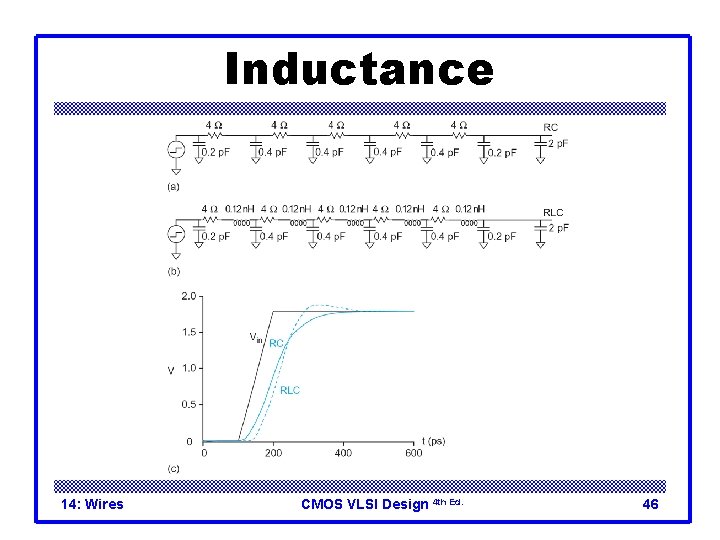
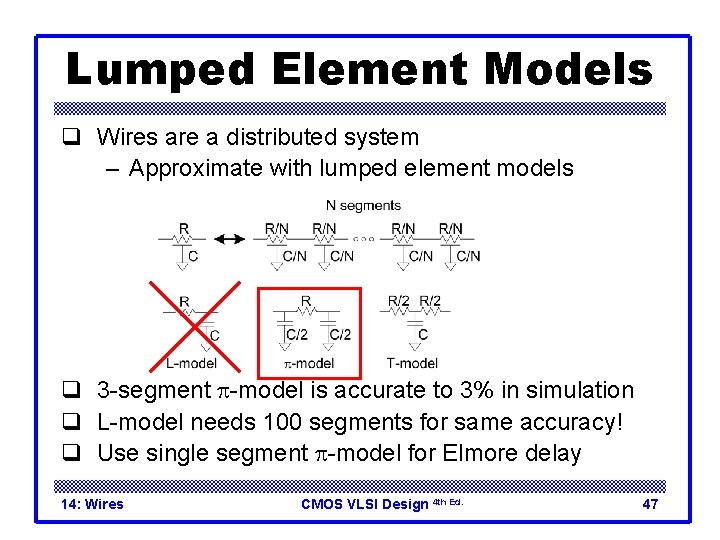
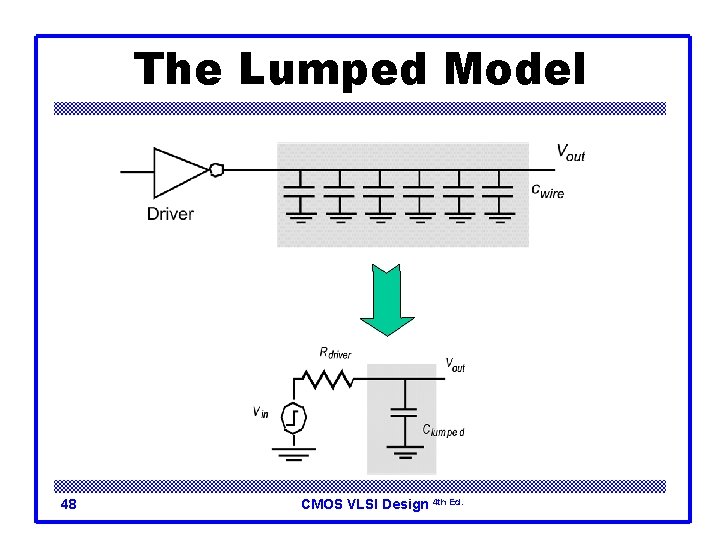
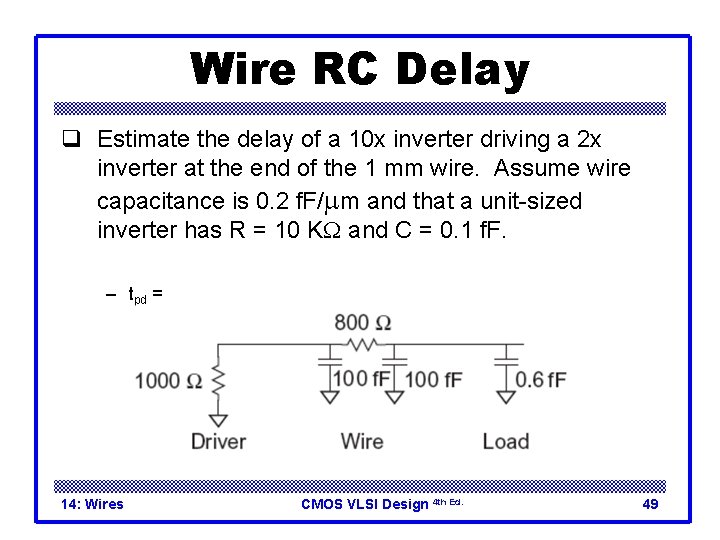
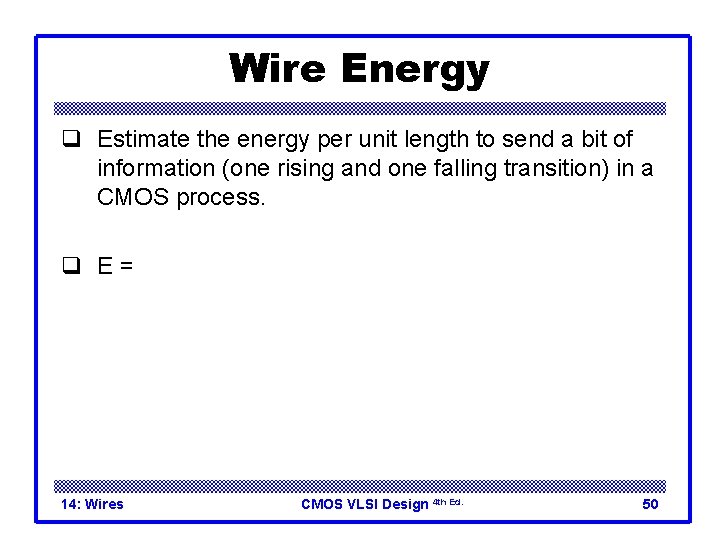
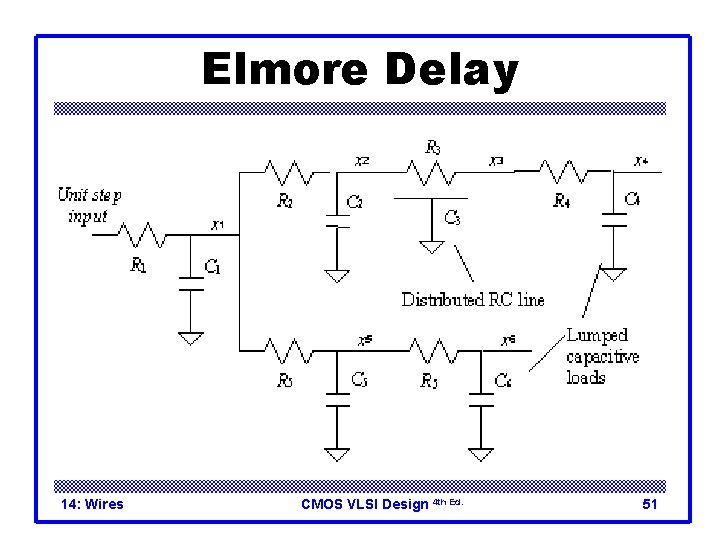
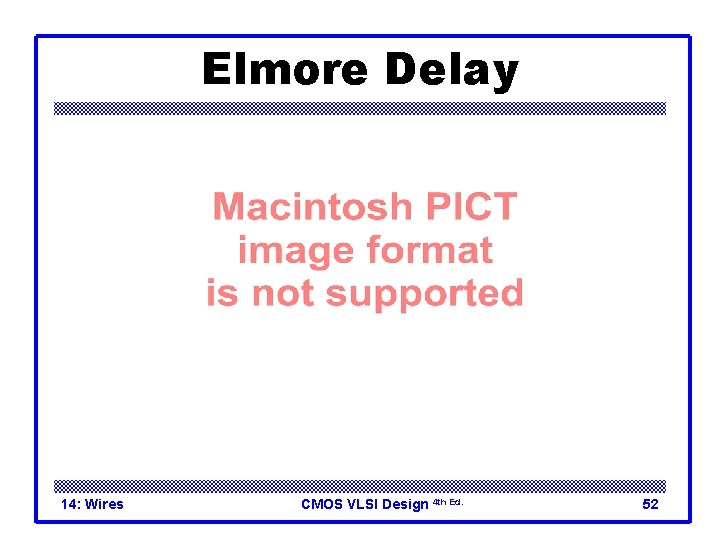
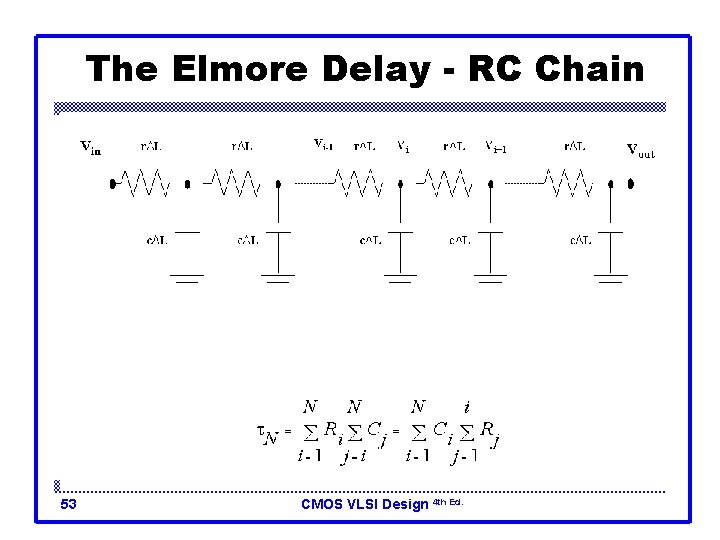
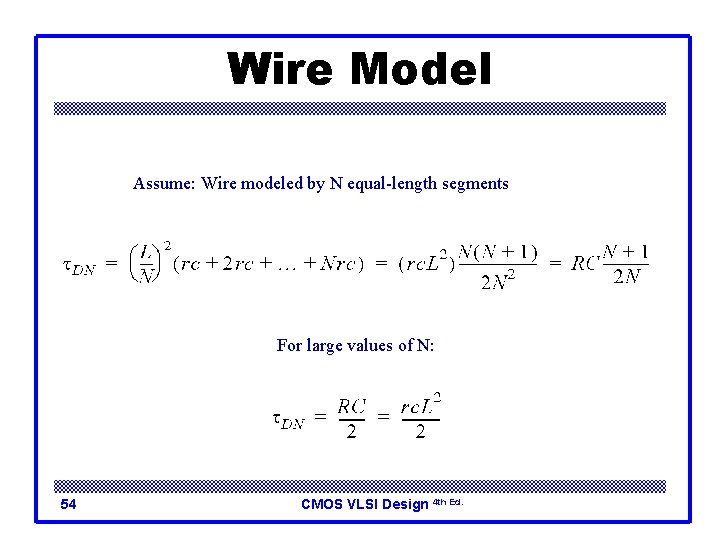
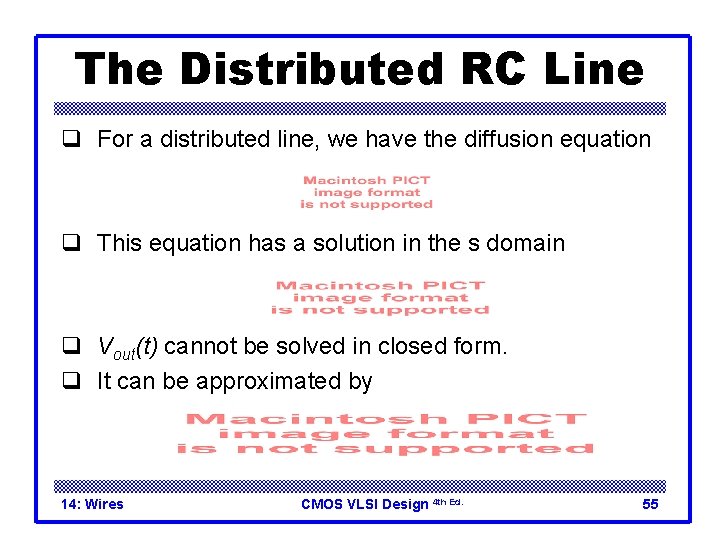
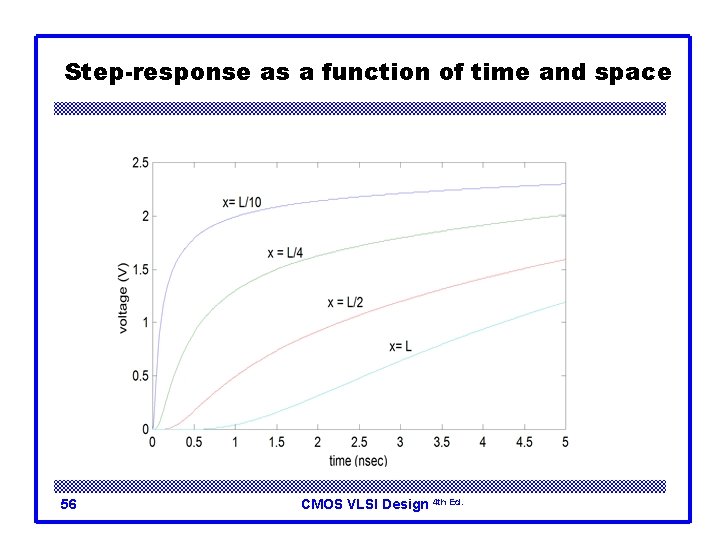
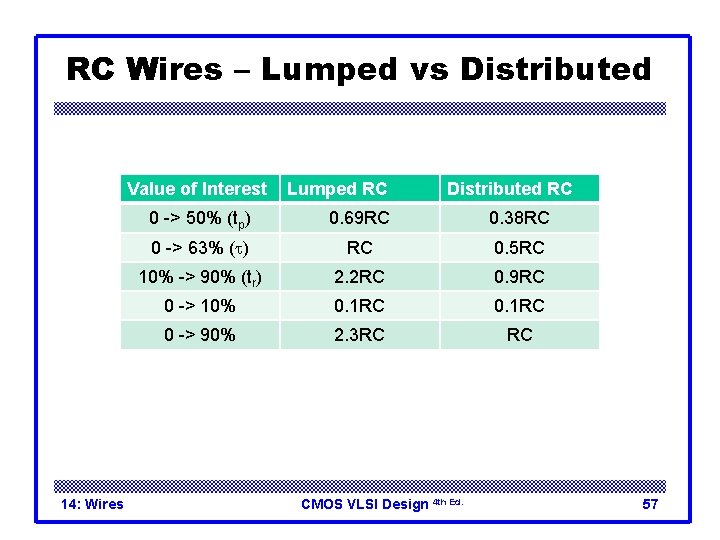
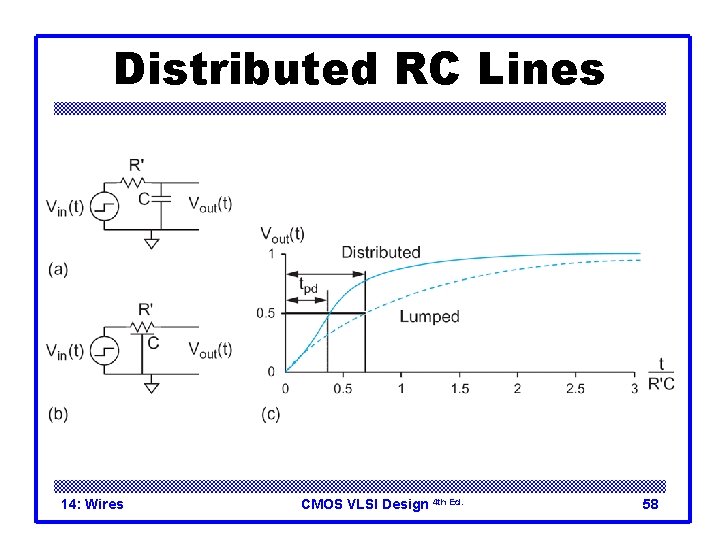
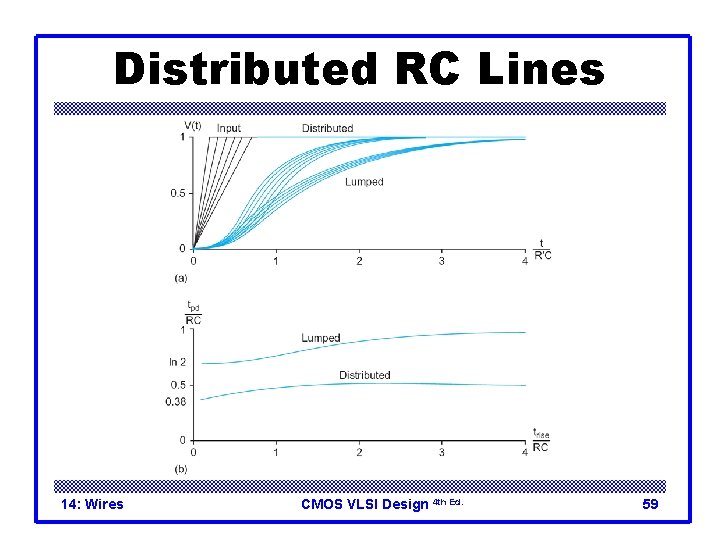
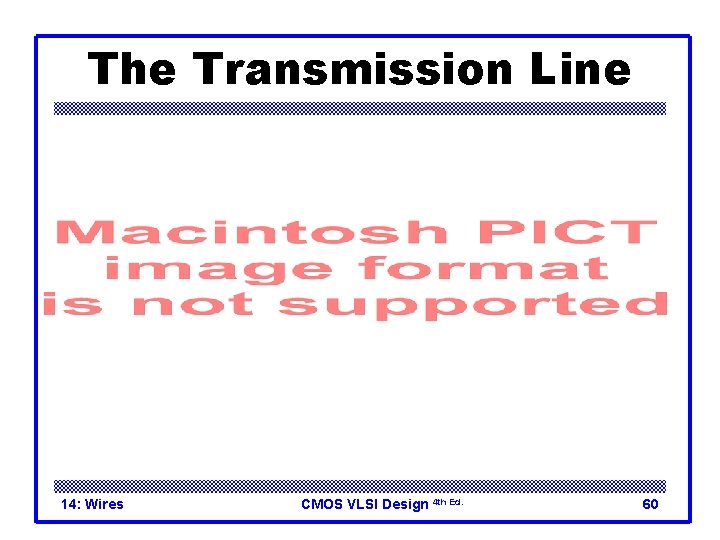
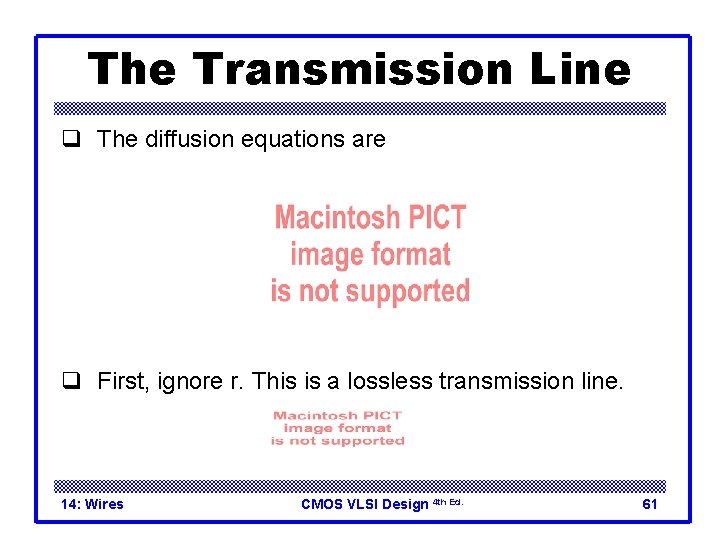
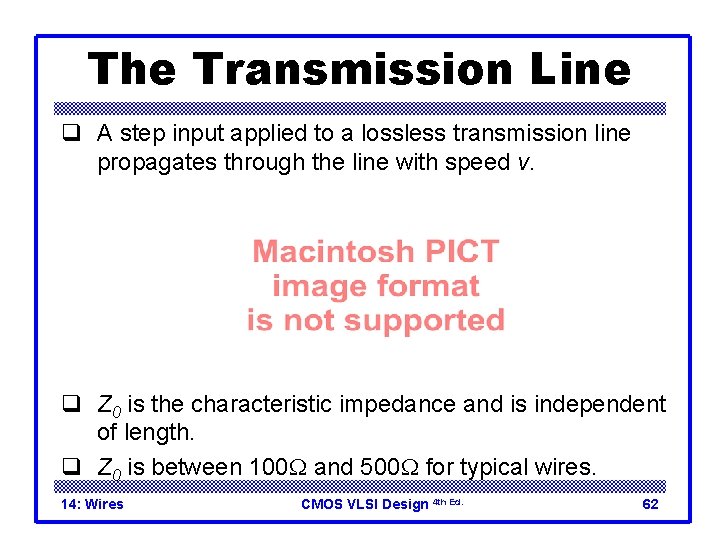
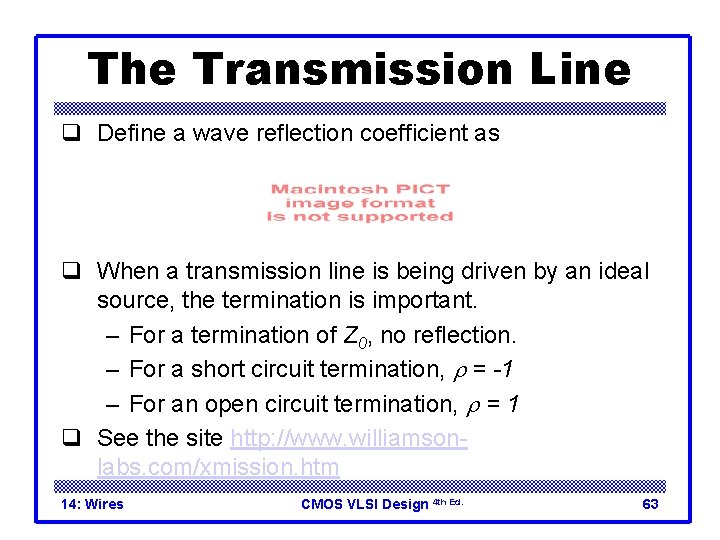
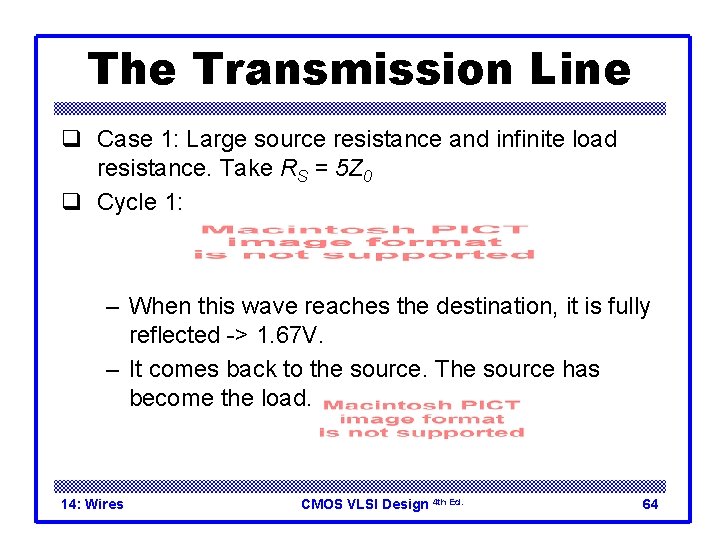
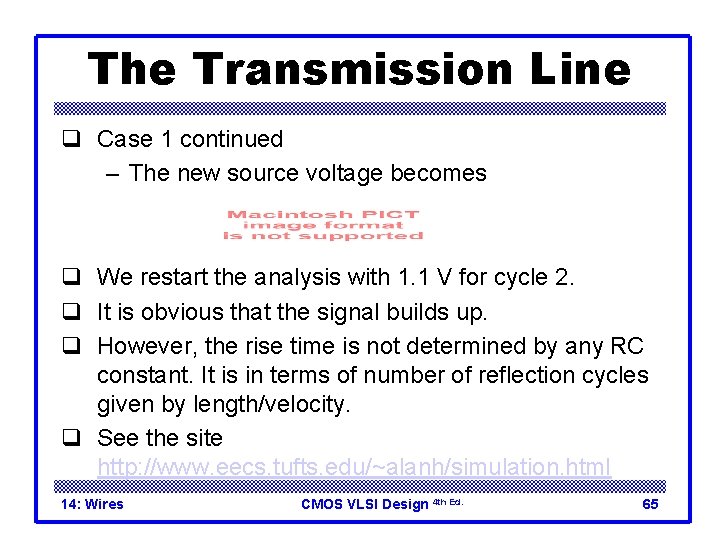
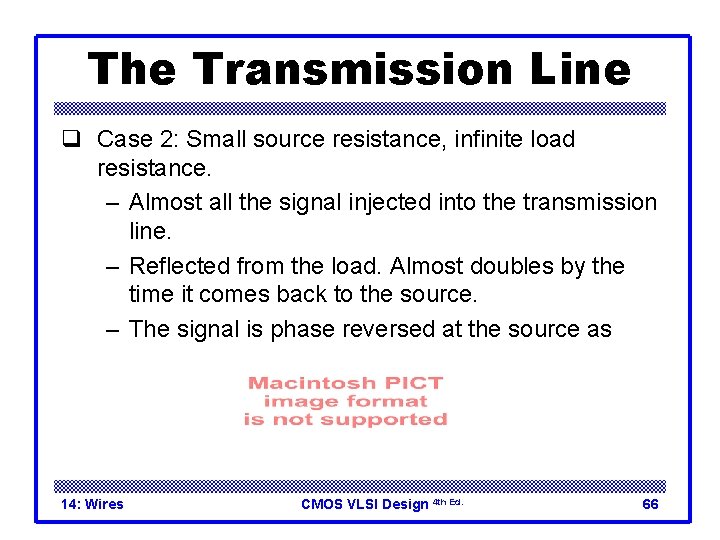
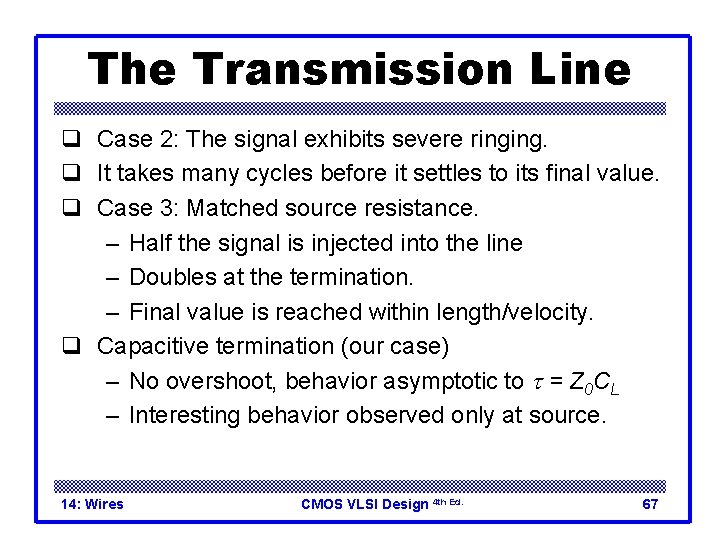
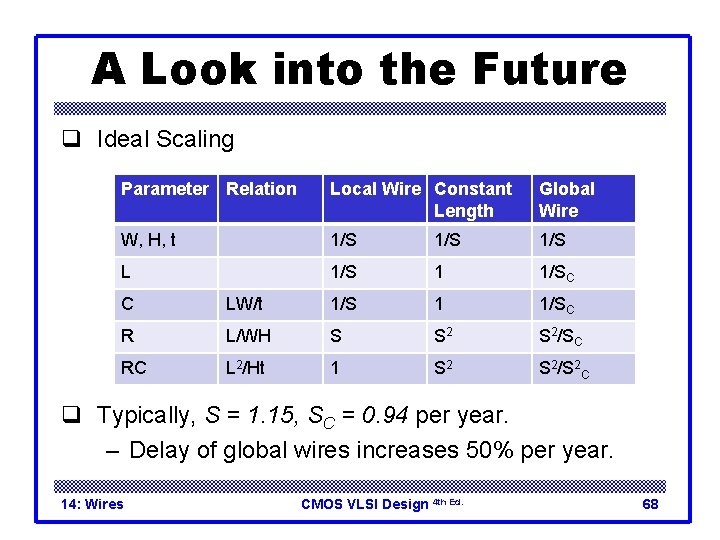
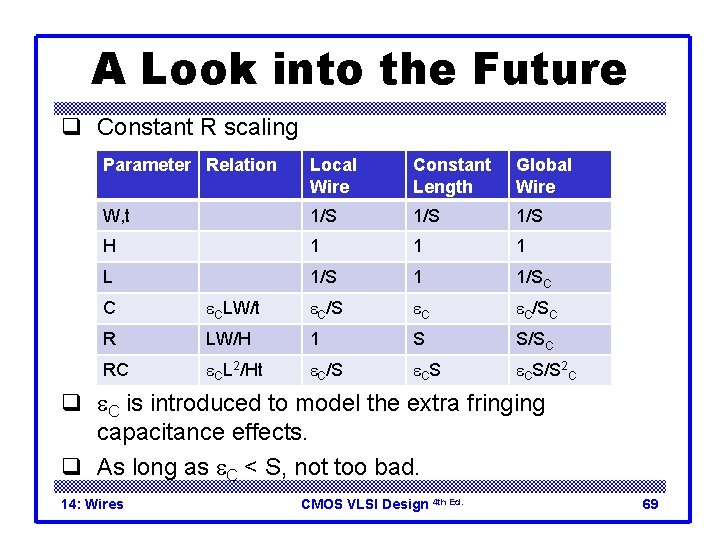
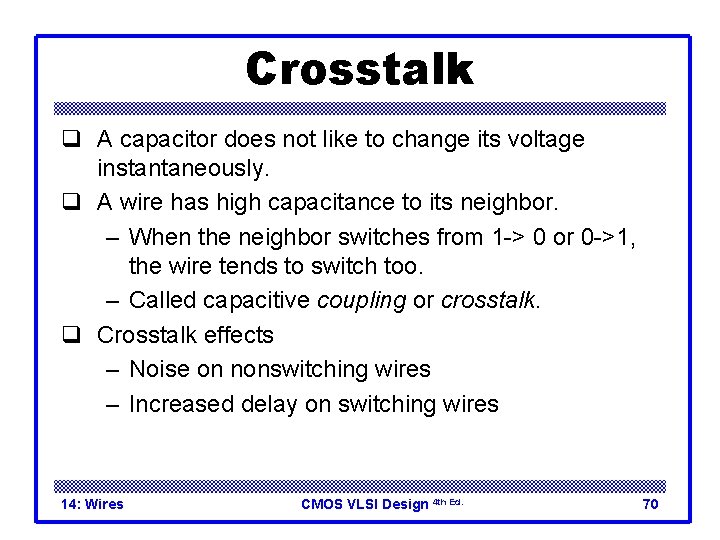
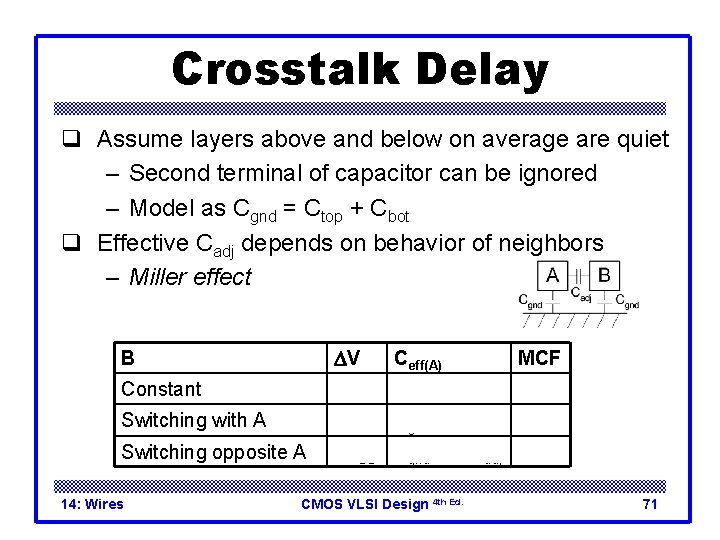
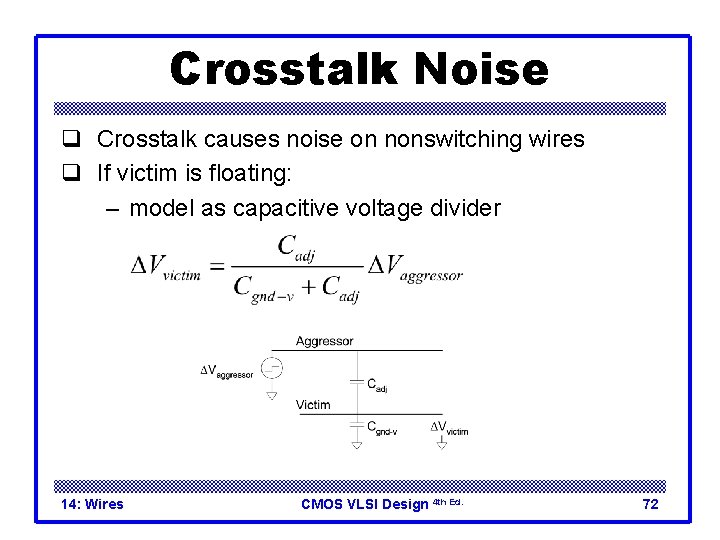
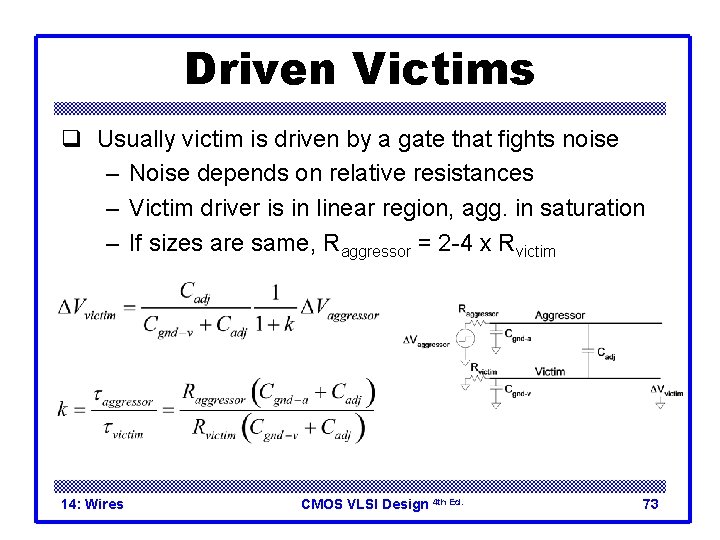
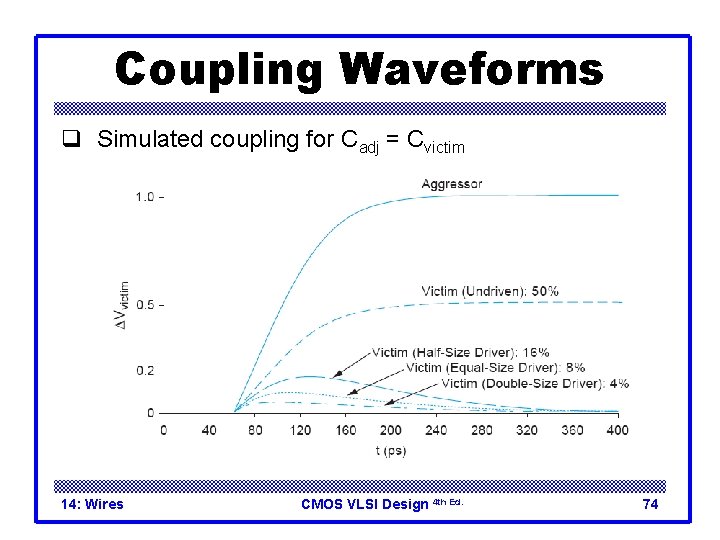
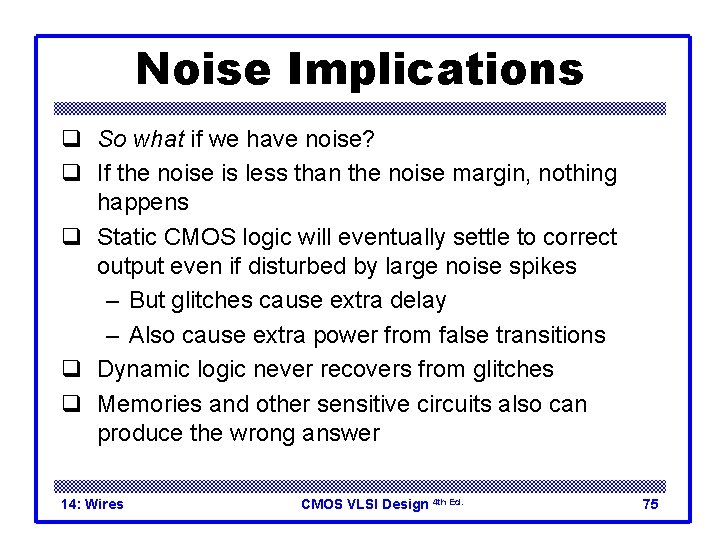
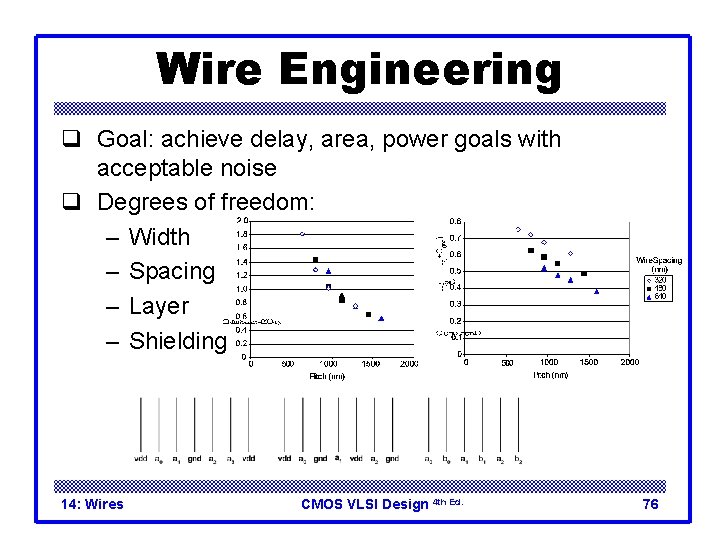
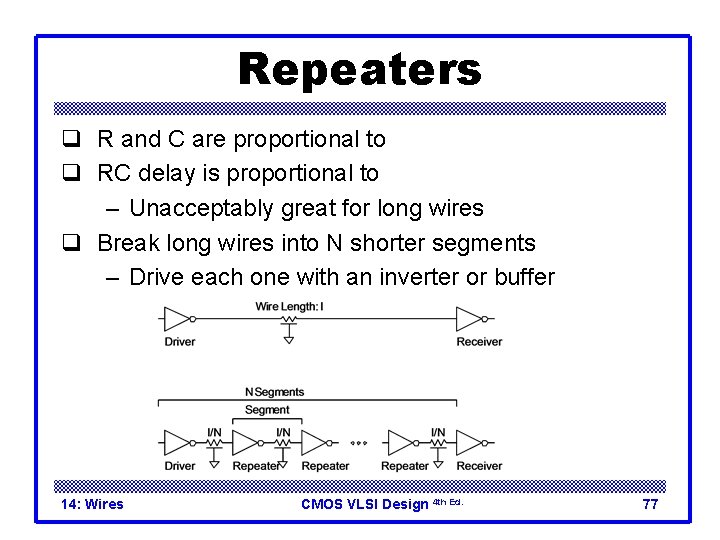
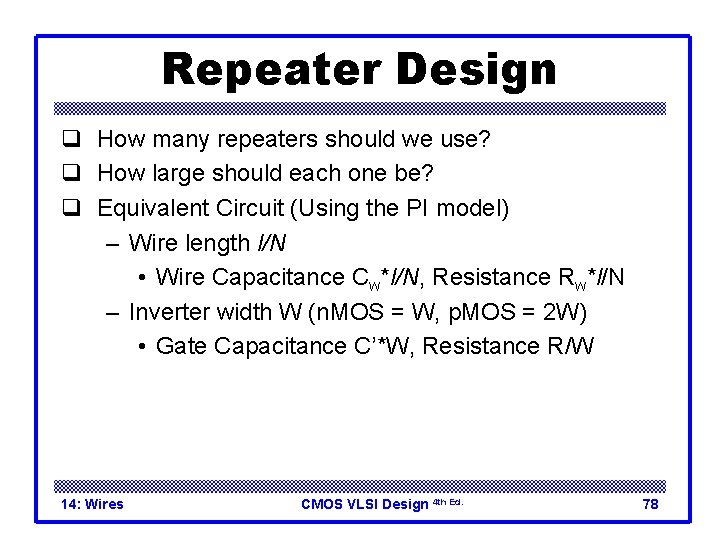
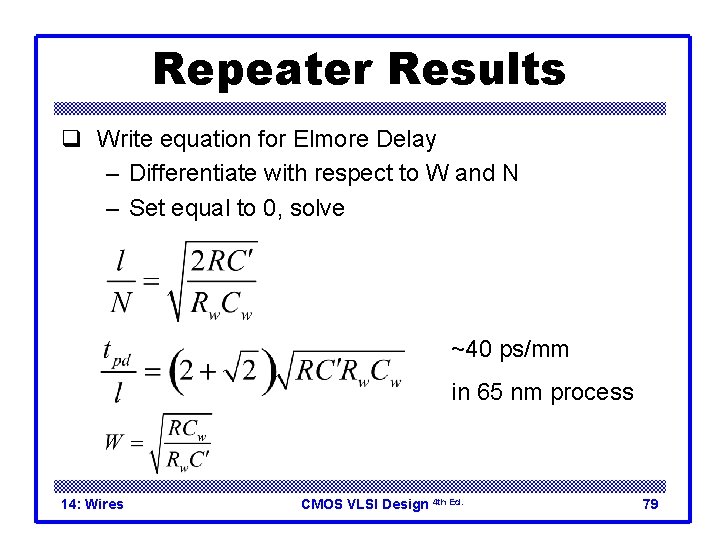
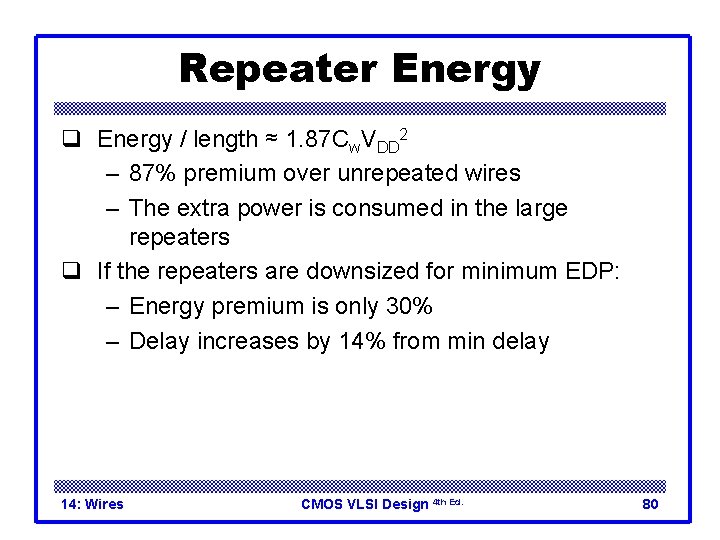
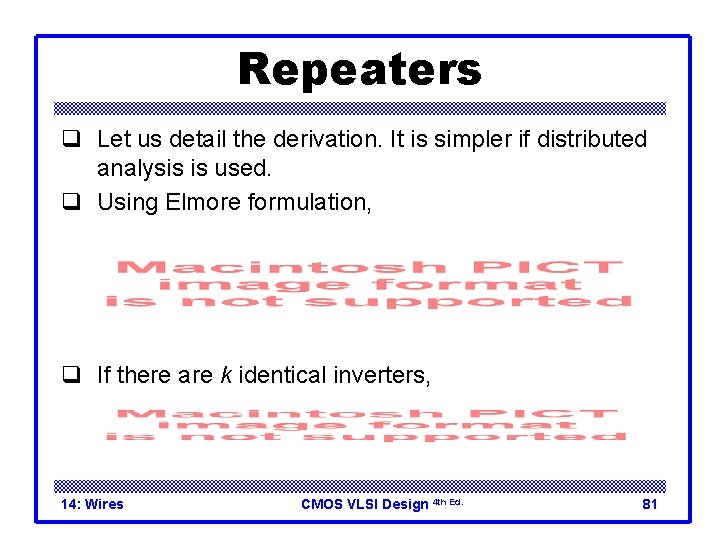
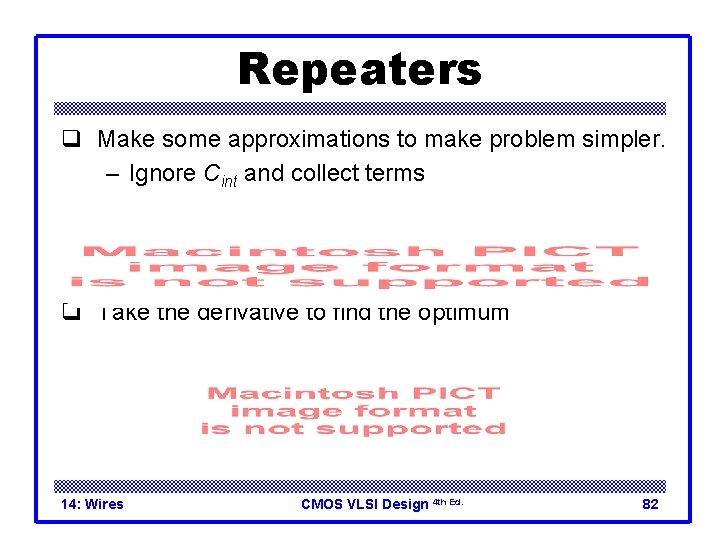
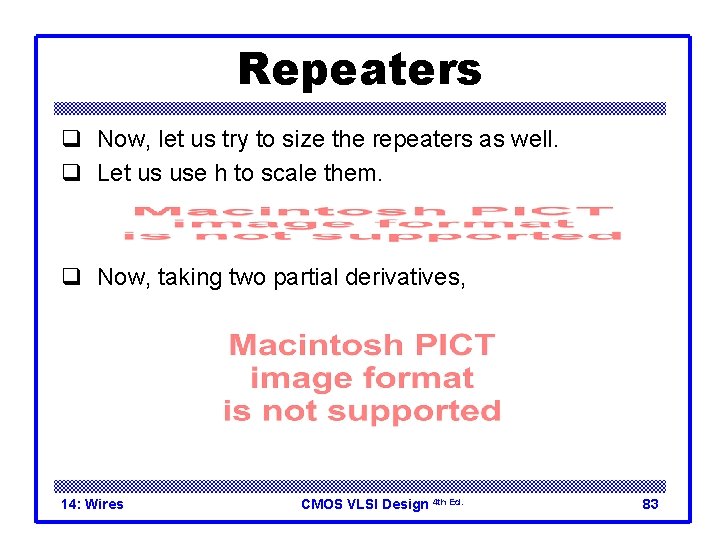
- Slides: 83
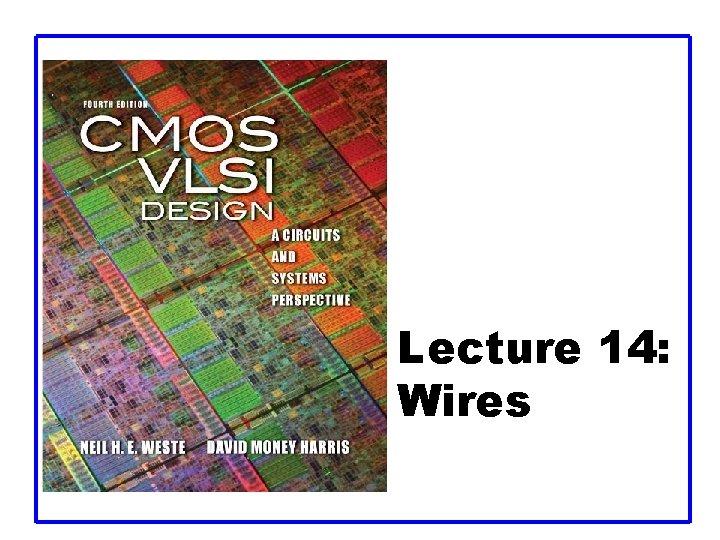
Lecture 14: Wires
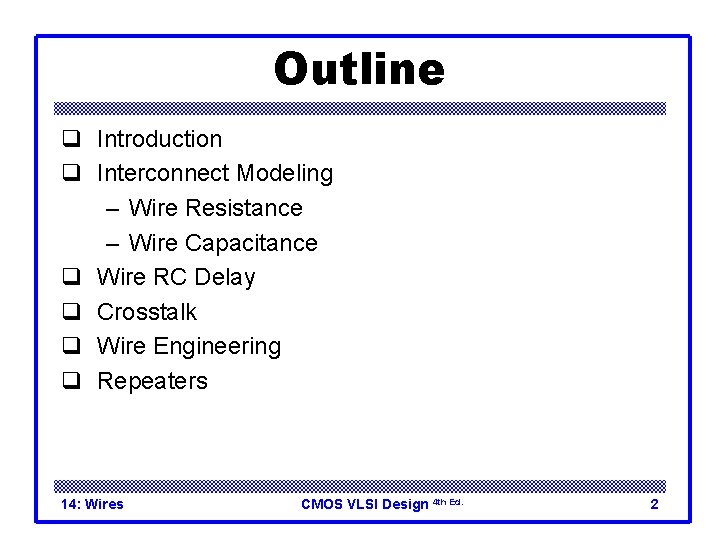
Outline q Introduction q Interconnect Modeling – Wire Resistance – Wire Capacitance q Wire RC Delay q Crosstalk q Wire Engineering q Repeaters 14: Wires CMOS VLSI Design 4 th Ed. 2
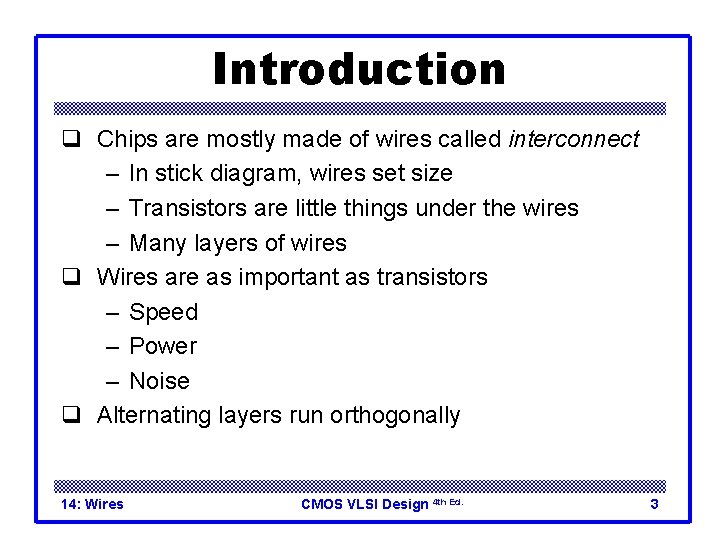
Introduction q Chips are mostly made of wires called interconnect – In stick diagram, wires set size – Transistors are little things under the wires – Many layers of wires q Wires are as important as transistors – Speed – Power – Noise q Alternating layers run orthogonally 14: Wires CMOS VLSI Design 4 th Ed. 3
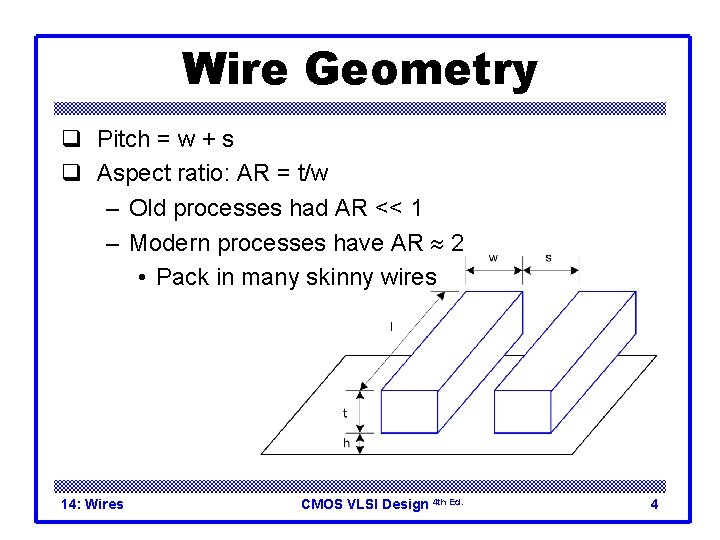
Wire Geometry q Pitch = w + s q Aspect ratio: AR = t/w – Old processes had AR << 1 – Modern processes have AR 2 • Pack in many skinny wires 14: Wires CMOS VLSI Design 4 th Ed. 4
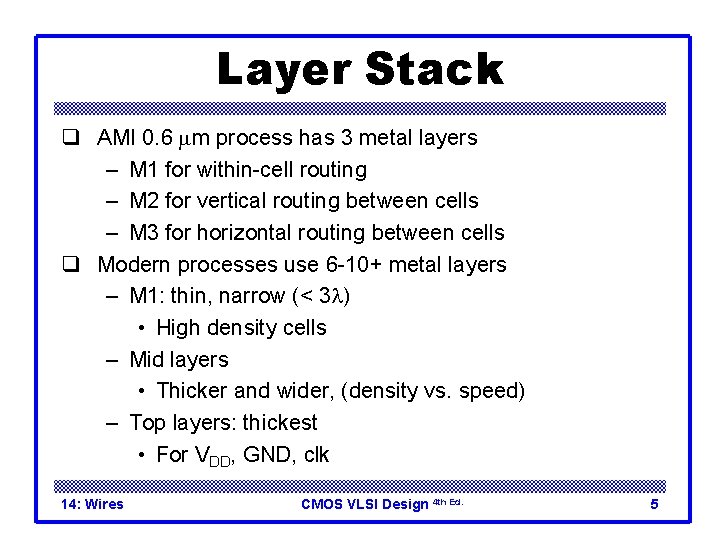
Layer Stack q AMI 0. 6 mm process has 3 metal layers – M 1 for within-cell routing – M 2 for vertical routing between cells – M 3 for horizontal routing between cells q Modern processes use 6 -10+ metal layers – M 1: thin, narrow (< 3 l) • High density cells – Mid layers • Thicker and wider, (density vs. speed) – Top layers: thickest • For VDD, GND, clk 14: Wires CMOS VLSI Design 4 th Ed. 5
![Example Intel 90 nm Stack Intel 45 nm Stack Thompson 02 14 Wires Moon Example Intel 90 nm Stack Intel 45 nm Stack [Thompson 02] 14: Wires [Moon](https://slidetodoc.com/presentation_image_h/902ff1d811adb49f92ff0eaf2594cc6b/image-6.jpg)
Example Intel 90 nm Stack Intel 45 nm Stack [Thompson 02] 14: Wires [Moon 08] CMOS VLSI Design 4 th Ed. 6
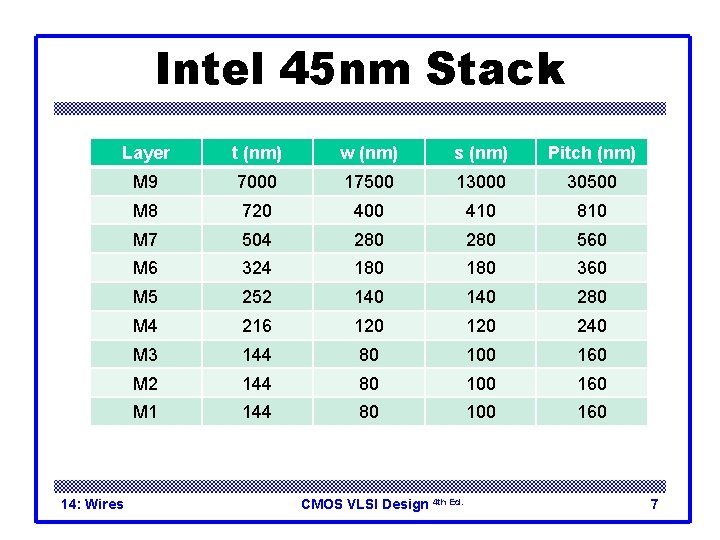
Intel 45 nm Stack Layer t (nm) w (nm) s (nm) Pitch (nm) M 9 7000 17500 13000 30500 M 8 720 400 410 810 M 7 504 280 560 M 6 324 180 360 M 5 252 140 280 M 4 216 120 240 M 3 144 80 100 160 M 2 144 80 100 160 M 1 144 80 100 160 14: Wires CMOS VLSI Design 4 th Ed. 7
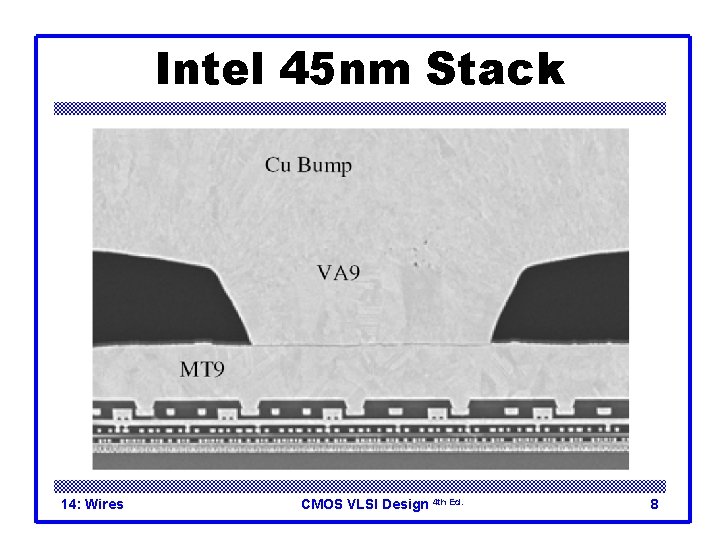
Intel 45 nm Stack 14: Wires CMOS VLSI Design 4 th Ed. 8
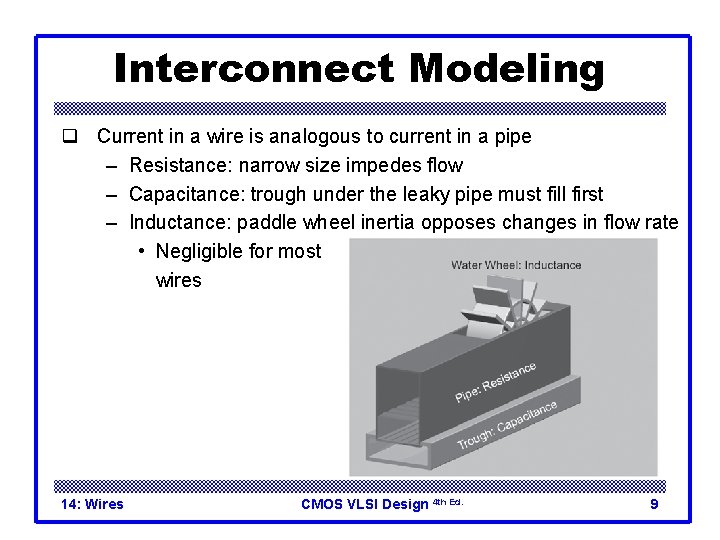
Interconnect Modeling q Current in a wire is analogous to current in a pipe – Resistance: narrow size impedes flow – Capacitance: trough under the leaky pipe must fill first – Inductance: paddle wheel inertia opposes changes in flow rate • Negligible for most wires 14: Wires CMOS VLSI Design 4 th Ed. 9
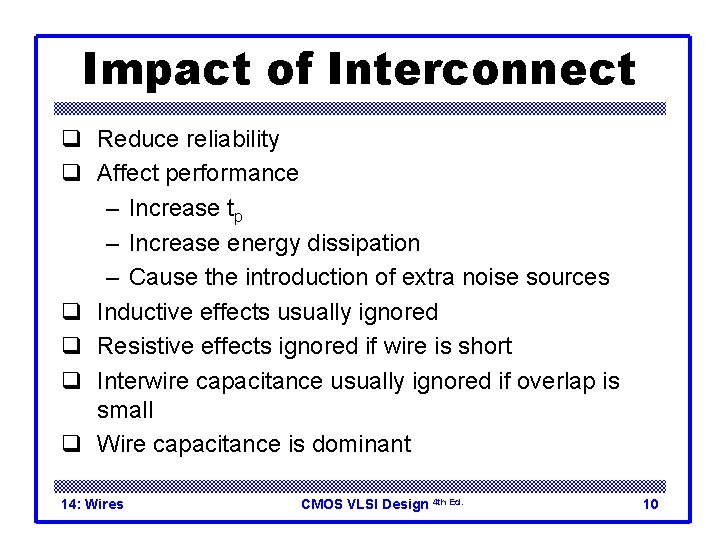
Impact of Interconnect q Reduce reliability q Affect performance – Increase tp – Increase energy dissipation – Cause the introduction of extra noise sources q Inductive effects usually ignored q Resistive effects ignored if wire is short q Interwire capacitance usually ignored if overlap is small q Wire capacitance is dominant 14: Wires CMOS VLSI Design 4 th Ed. 10
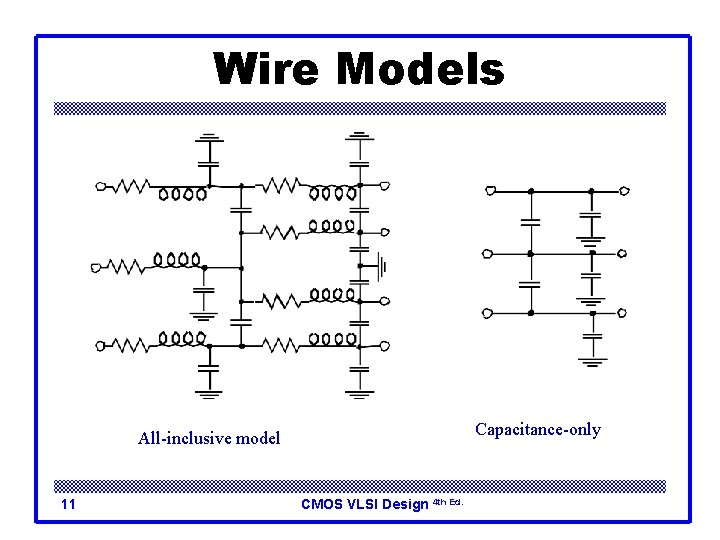
Wire Models Capacitance-only All-inclusive model 11 CMOS VLSI Design 4 th Ed.
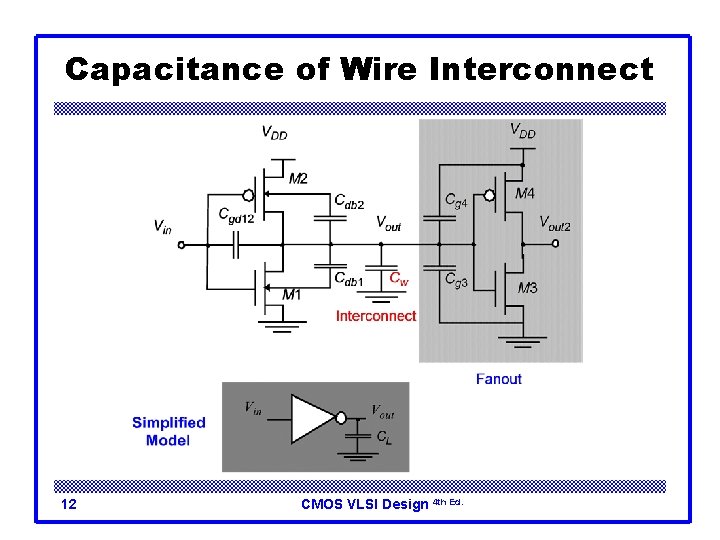
Capacitance of Wire Interconnect 12 CMOS VLSI Design 4 th Ed.
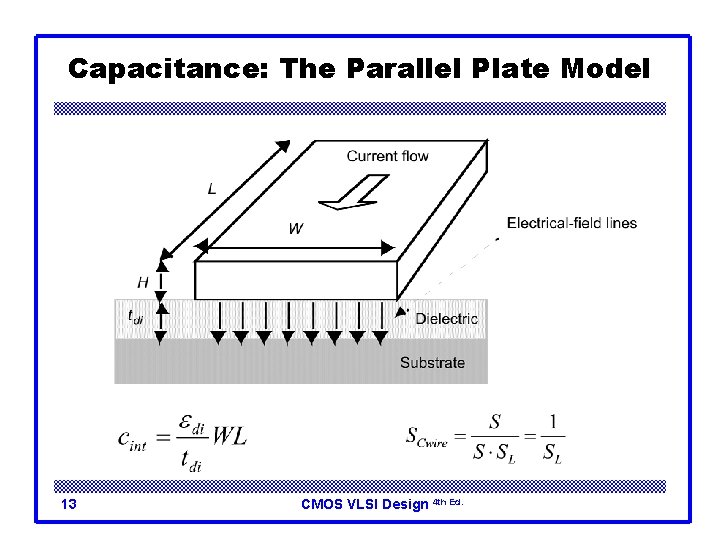
Capacitance: The Parallel Plate Model 13 CMOS VLSI Design 4 th Ed.
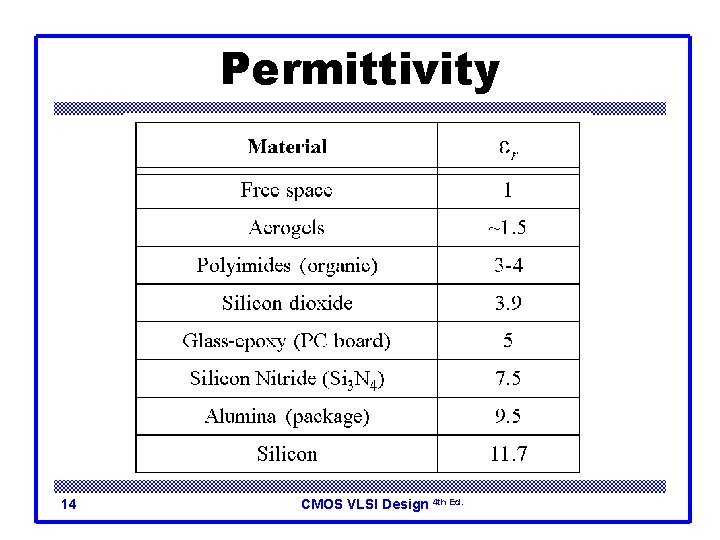
Permittivity 14 CMOS VLSI Design 4 th Ed.
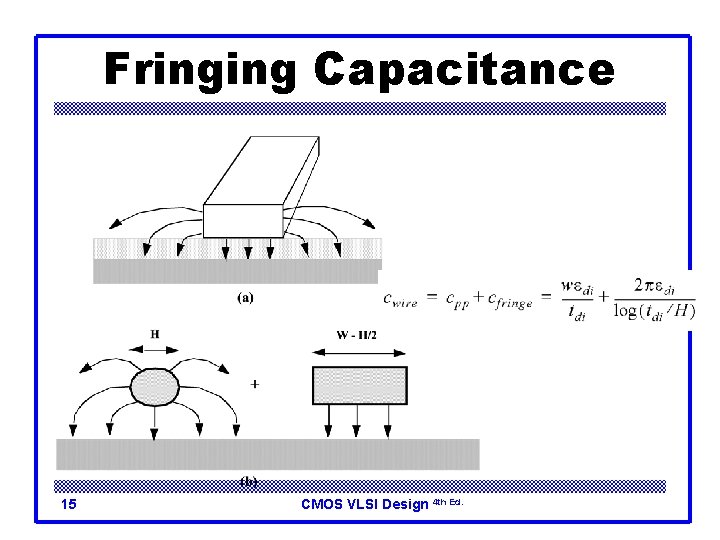
Fringing Capacitance 15 CMOS VLSI Design 4 th Ed.
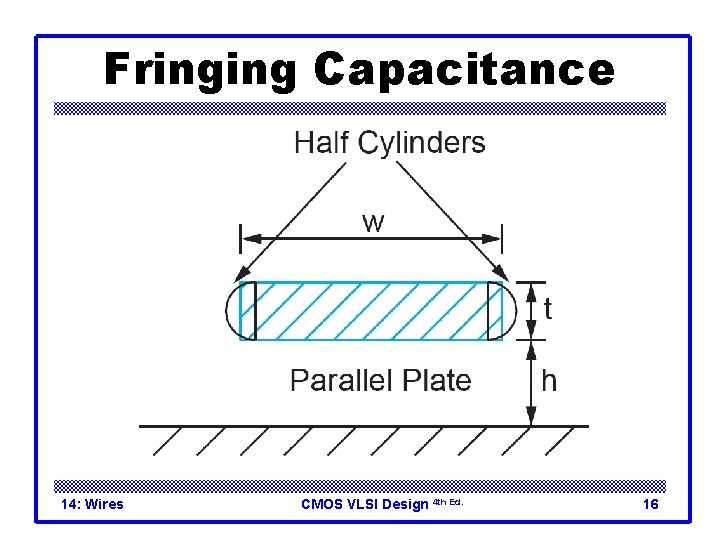
Fringing Capacitance 14: Wires CMOS VLSI Design 4 th Ed. 16
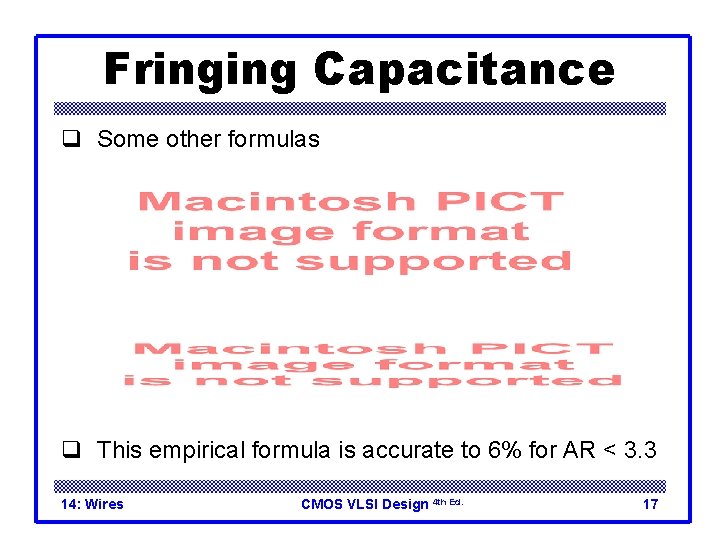
Fringing Capacitance q Some other formulas q This empirical formula is accurate to 6% for AR < 3. 3 14: Wires CMOS VLSI Design 4 th Ed. 17
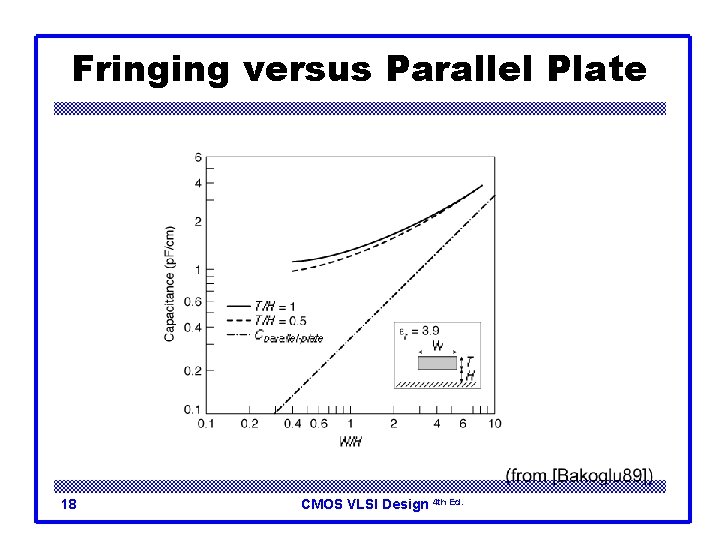
Fringing versus Parallel Plate 18 CMOS VLSI Design 4 th Ed.
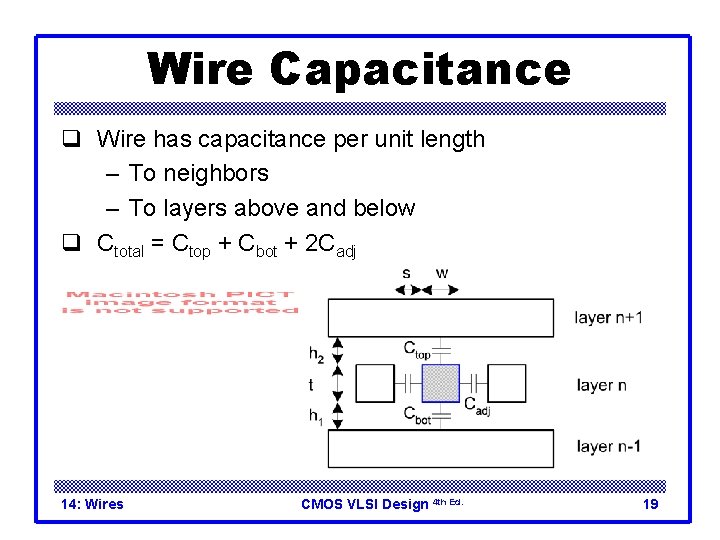
Wire Capacitance q Wire has capacitance per unit length – To neighbors – To layers above and below q Ctotal = Ctop + Cbot + 2 Cadj 14: Wires CMOS VLSI Design 4 th Ed. 19
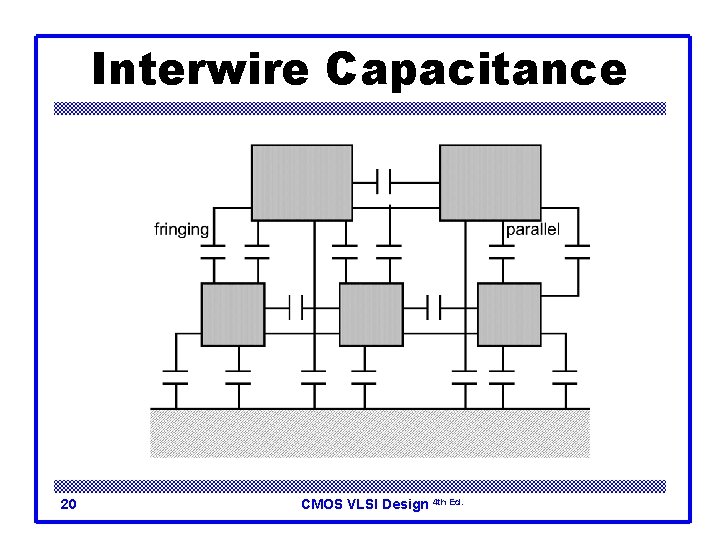
Interwire Capacitance 20 CMOS VLSI Design 4 th Ed.
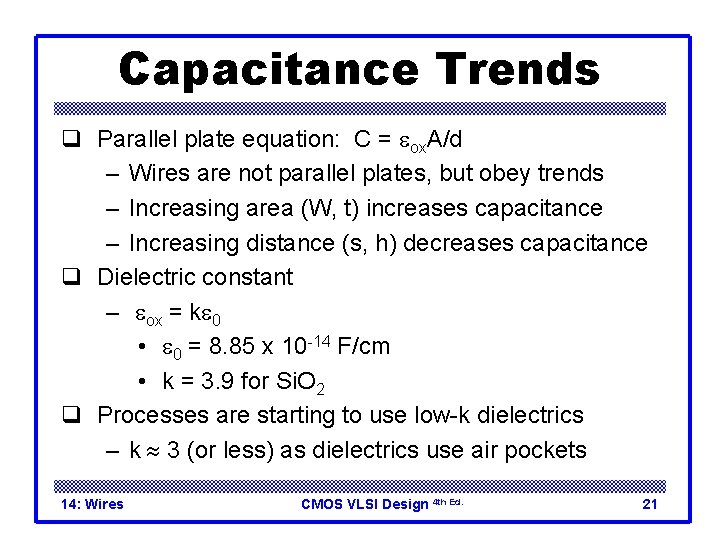
Capacitance Trends q Parallel plate equation: C = eox. A/d – Wires are not parallel plates, but obey trends – Increasing area (W, t) increases capacitance – Increasing distance (s, h) decreases capacitance q Dielectric constant – eox = ke 0 • e 0 = 8. 85 x 10 -14 F/cm • k = 3. 9 for Si. O 2 q Processes are starting to use low-k dielectrics – k 3 (or less) as dielectrics use air pockets 14: Wires CMOS VLSI Design 4 th Ed. 21
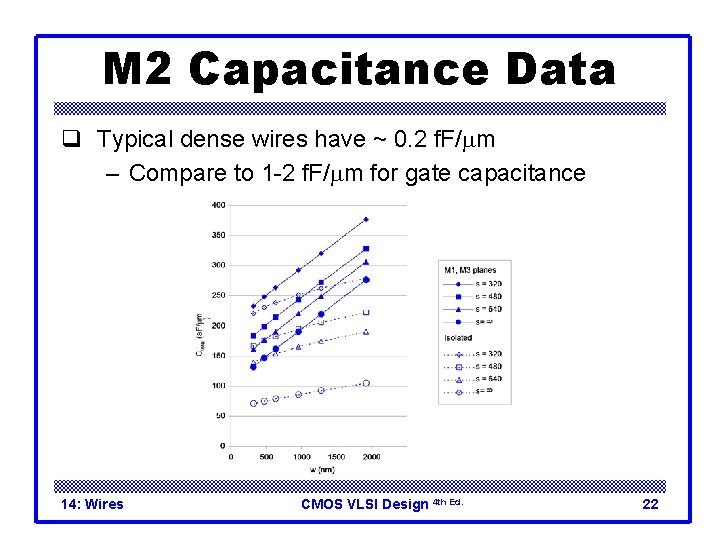
M 2 Capacitance Data q Typical dense wires have ~ 0. 2 f. F/mm – Compare to 1 -2 f. F/mm for gate capacitance 14: Wires CMOS VLSI Design 4 th Ed. 22
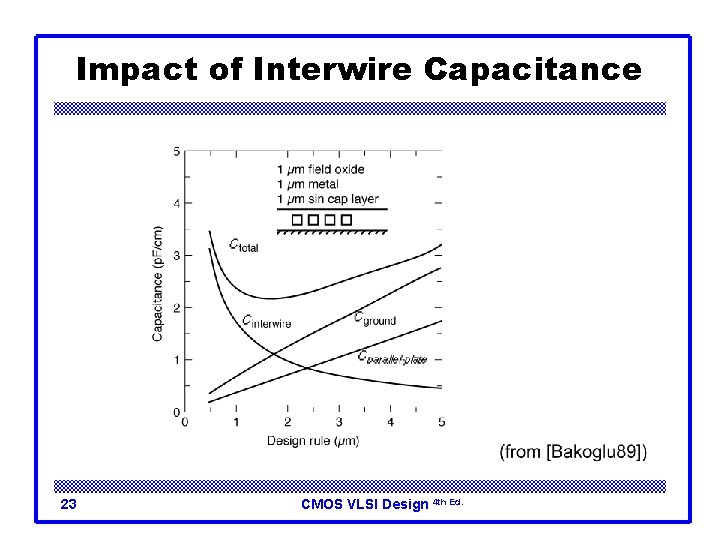
Impact of Interwire Capacitance 23 CMOS VLSI Design 4 th Ed.
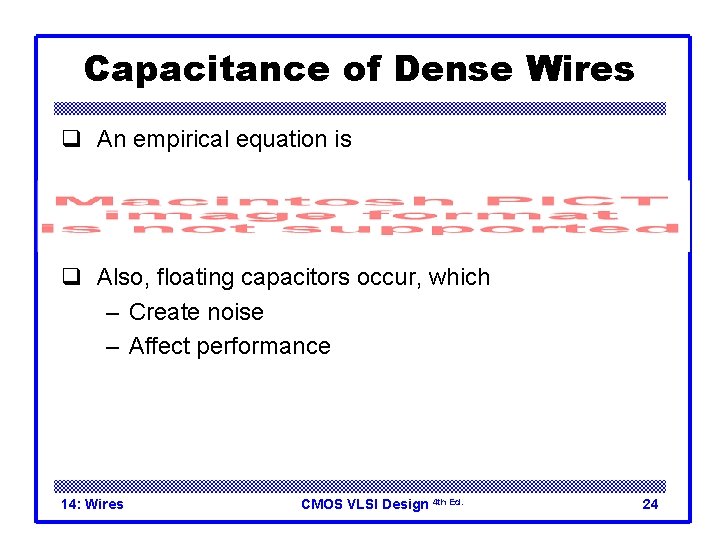
Capacitance of Dense Wires q An empirical equation is q Also, floating capacitors occur, which – Create noise – Affect performance 14: Wires CMOS VLSI Design 4 th Ed. 24
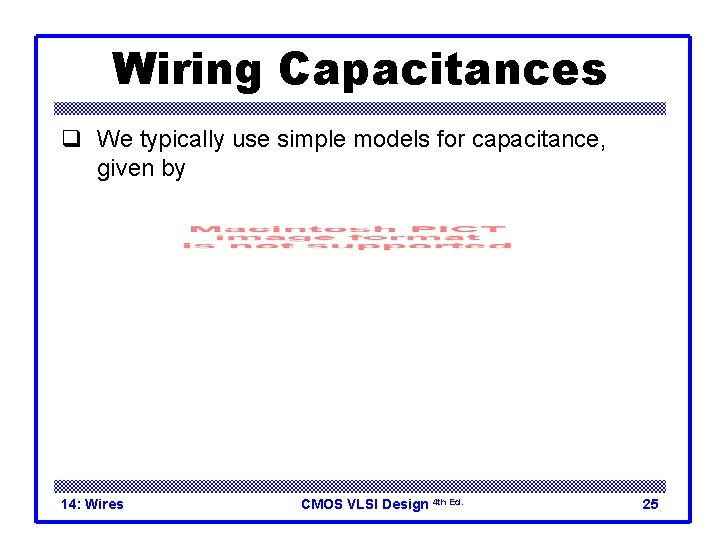
Wiring Capacitances q We typically use simple models for capacitance, given by 14: Wires CMOS VLSI Design 4 th Ed. 25
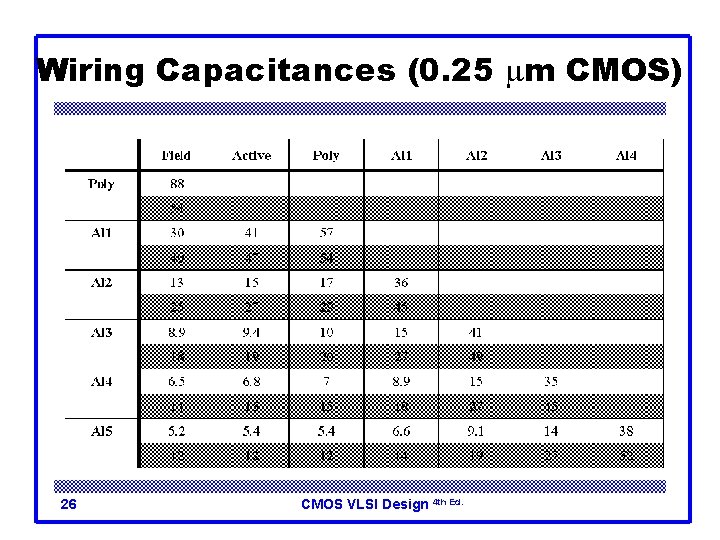
Wiring Capacitances (0. 25 mm CMOS) 26 CMOS VLSI Design 4 th Ed.
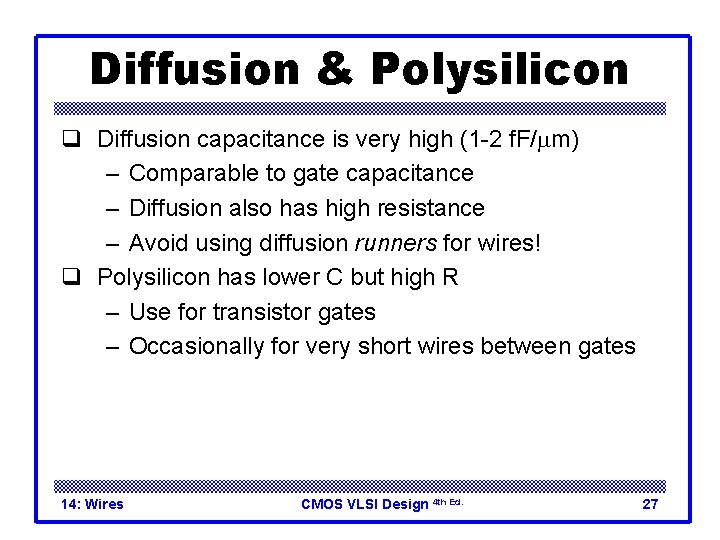
Diffusion & Polysilicon q Diffusion capacitance is very high (1 -2 f. F/mm) – Comparable to gate capacitance – Diffusion also has high resistance – Avoid using diffusion runners for wires! q Polysilicon has lower C but high R – Use for transistor gates – Occasionally for very short wires between gates 14: Wires CMOS VLSI Design 4 th Ed. 27
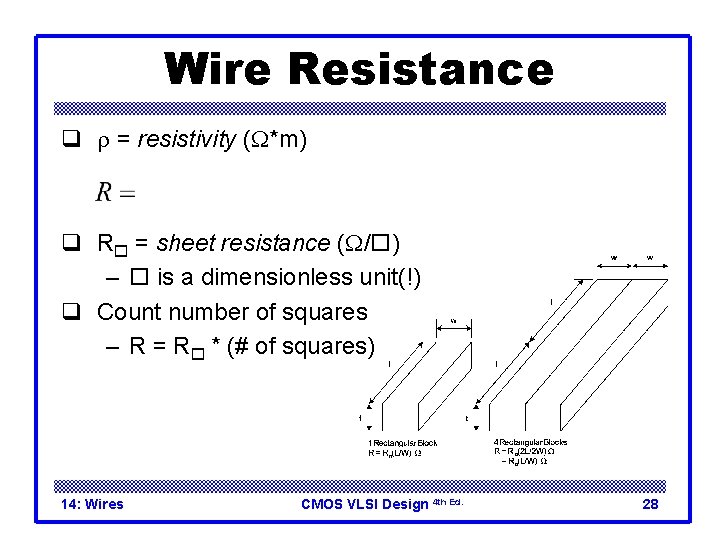
Wire Resistance q r = resistivity (W*m) q R = sheet resistance (W/ ) – is a dimensionless unit(!) q Count number of squares – R = R * (# of squares) 14: Wires CMOS VLSI Design 4 th Ed. 28

Sheet Resistance 29 CMOS VLSI Design 4 th Ed.
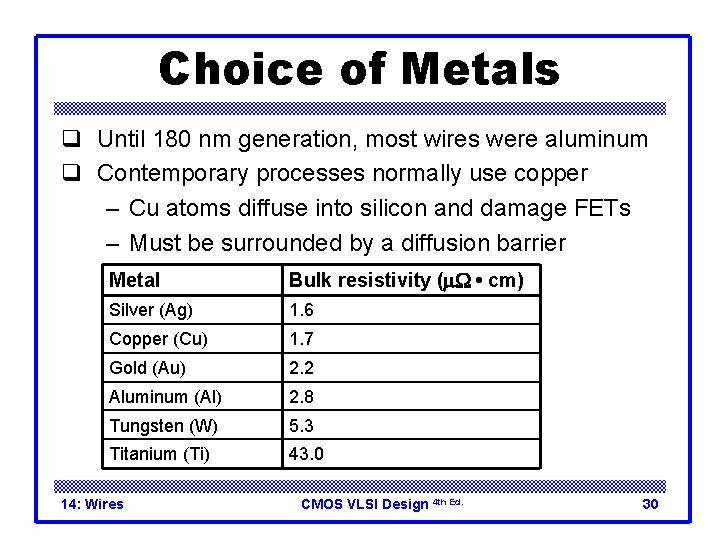
Choice of Metals q Until 180 nm generation, most wires were aluminum q Contemporary processes normally use copper – Cu atoms diffuse into silicon and damage FETs – Must be surrounded by a diffusion barrier Metal Bulk resistivity (m. W • cm) Silver (Ag) 1. 6 Copper (Cu) 1. 7 Gold (Au) 2. 2 Aluminum (Al) 2. 8 Tungsten (W) 5. 3 Titanium (Ti) 43. 0 14: Wires CMOS VLSI Design 4 th Ed. 30
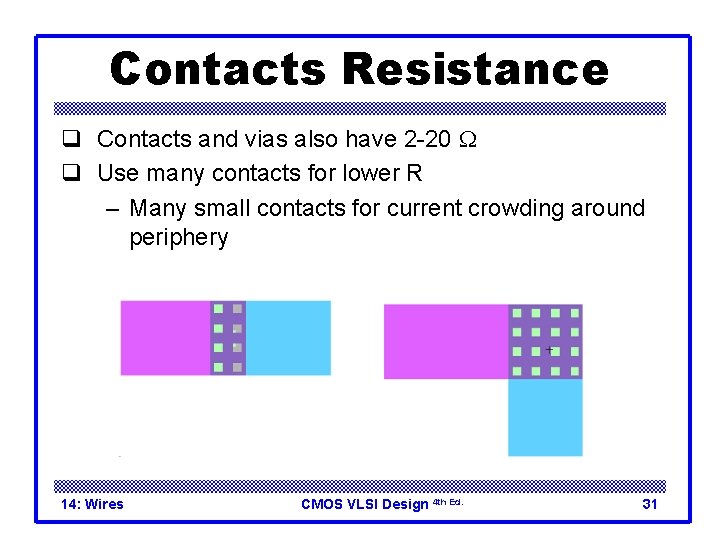
Contacts Resistance q Contacts and vias also have 2 -20 W q Use many contacts for lower R – Many small contacts for current crowding around periphery 14: Wires CMOS VLSI Design 4 th Ed. 31
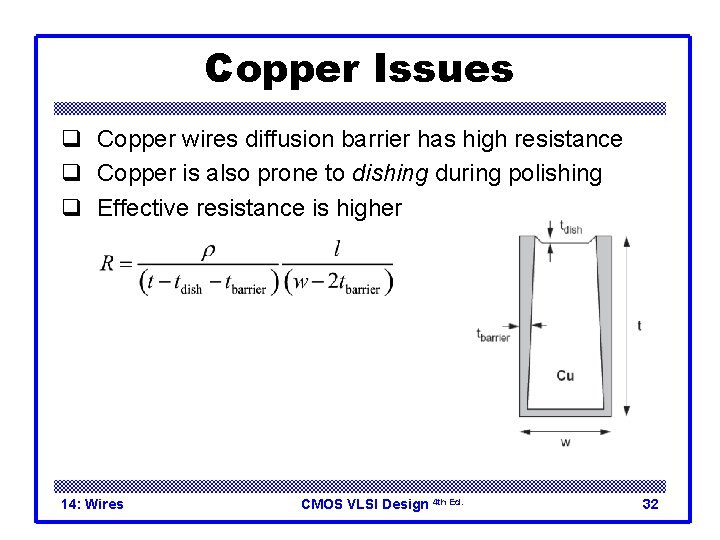
Copper Issues q Copper wires diffusion barrier has high resistance q Copper is also prone to dishing during polishing q Effective resistance is higher 14: Wires CMOS VLSI Design 4 th Ed. 32
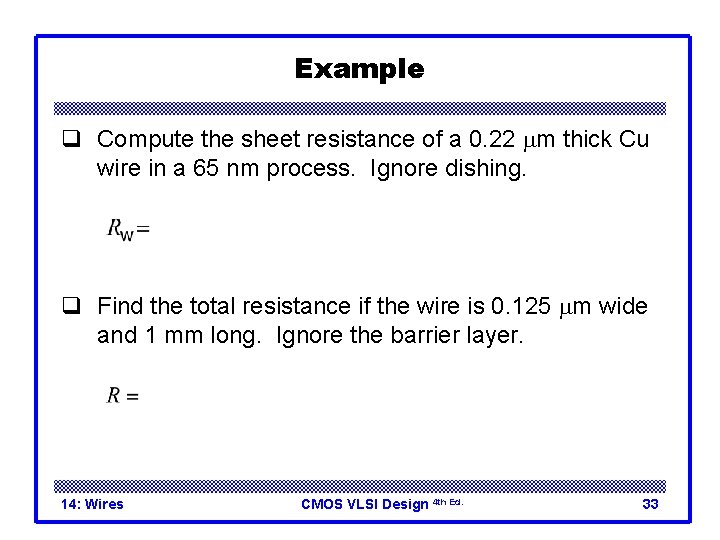
Example q Compute the sheet resistance of a 0. 22 mm thick Cu wire in a 65 nm process. Ignore dishing. q Find the total resistance if the wire is 0. 125 mm wide and 1 mm long. Ignore the barrier layer. 14: Wires CMOS VLSI Design 4 th Ed. 33
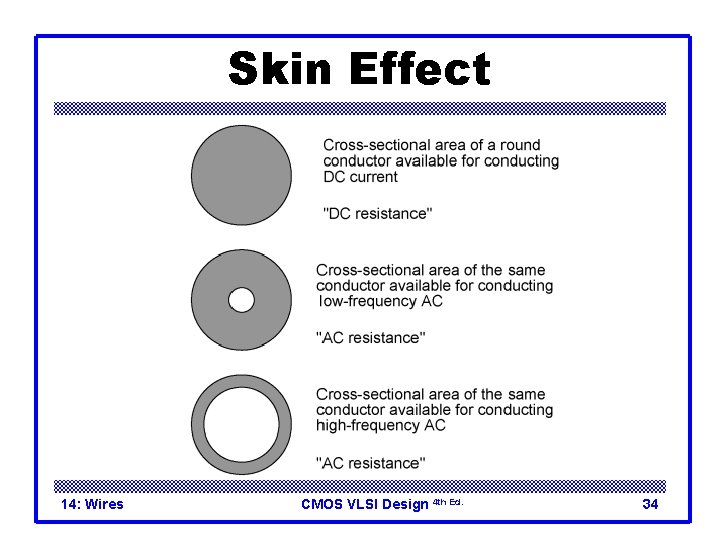
Skin Effect 14: Wires CMOS VLSI Design 4 th Ed. 34
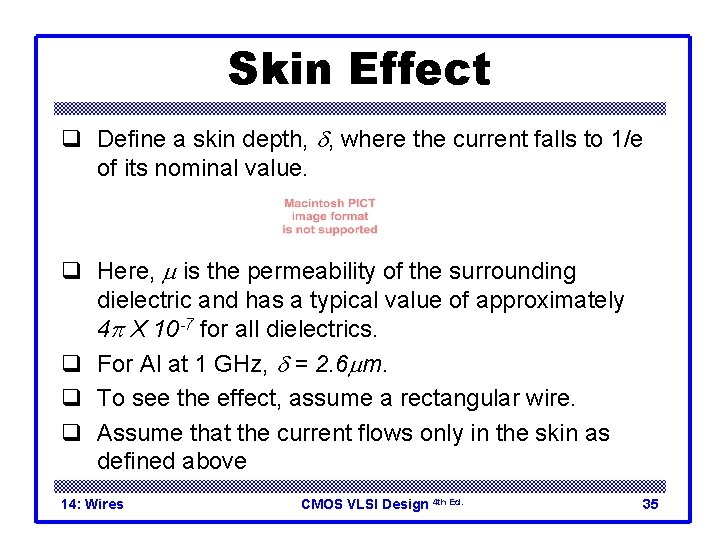
Skin Effect q Define a skin depth, d, where the current falls to 1/e of its nominal value. q Here, m is the permeability of the surrounding dielectric and has a typical value of approximately 4 p X 10 -7 for all dielectrics. q For Al at 1 GHz, d = 2. 6 mm. q To see the effect, assume a rectangular wire. q Assume that the current flows only in the skin as defined above 14: Wires CMOS VLSI Design 4 th Ed. 35
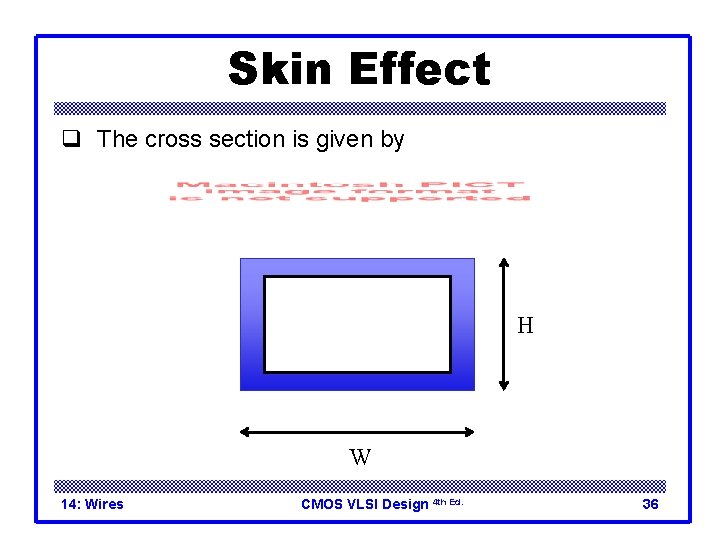
Skin Effect q The cross section is given by H W 14: Wires CMOS VLSI Design 4 th Ed. 36
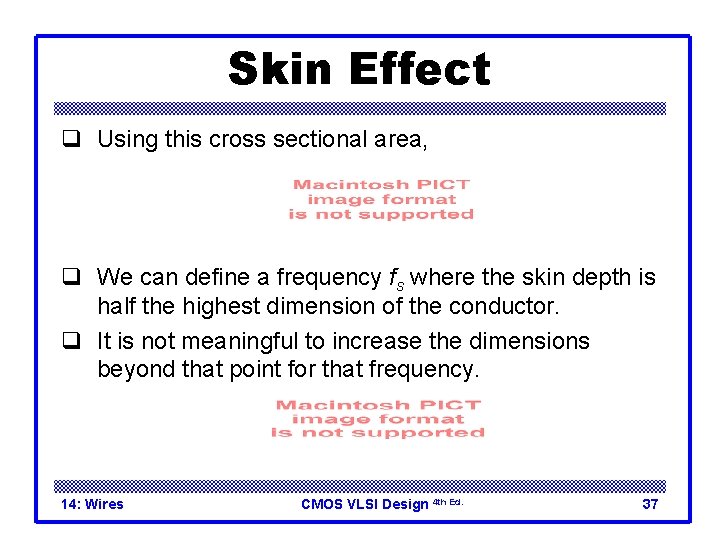
Skin Effect q Using this cross sectional area, q We can define a frequency fs where the skin depth is half the highest dimension of the conductor. q It is not meaningful to increase the dimensions beyond that point for that frequency. 14: Wires CMOS VLSI Design 4 th Ed. 37
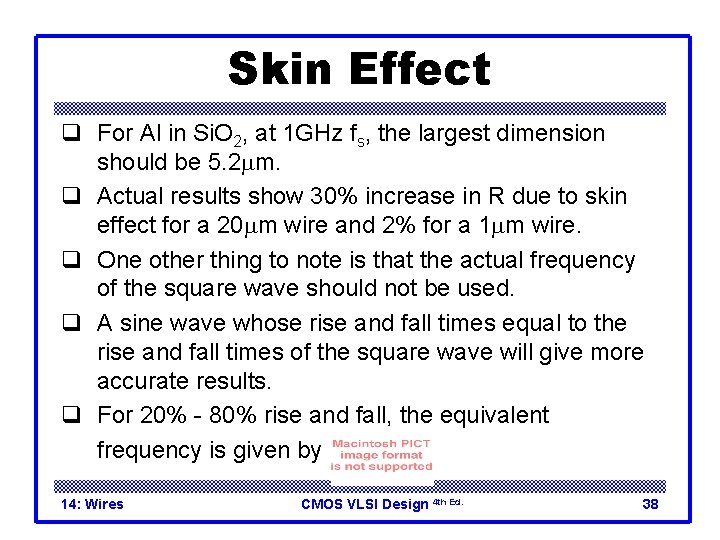
Skin Effect q For Al in Si. O 2, at 1 GHz fs, the largest dimension should be 5. 2 mm. q Actual results show 30% increase in R due to skin effect for a 20 mm wire and 2% for a 1 mm wire. q One other thing to note is that the actual frequency of the square wave should not be used. q A sine wave whose rise and fall times equal to the rise and fall times of the square wave will give more accurate results. q For 20% - 80% rise and fall, the equivalent frequency is given by 14: Wires CMOS VLSI Design 4 th Ed. 38
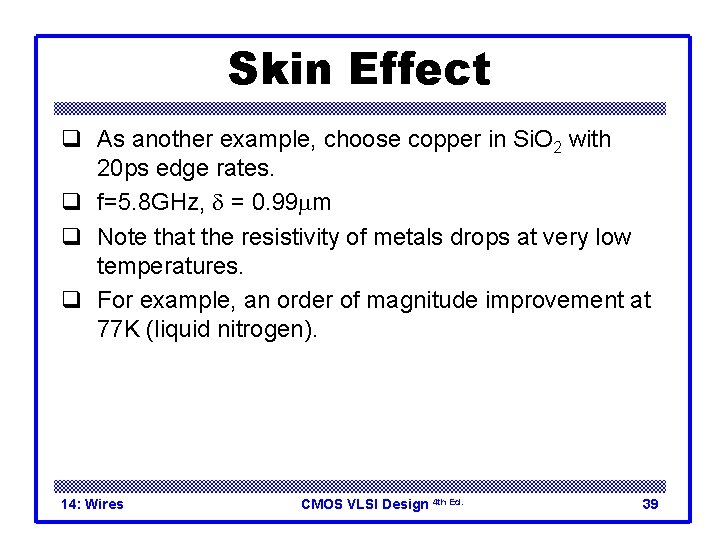
Skin Effect q As another example, choose copper in Si. O 2 with 20 ps edge rates. q f=5. 8 GHz, d = 0. 99 mm q Note that the resistivity of metals drops at very low temperatures. q For example, an order of magnitude improvement at 77 K (liquid nitrogen). 14: Wires CMOS VLSI Design 4 th Ed. 39
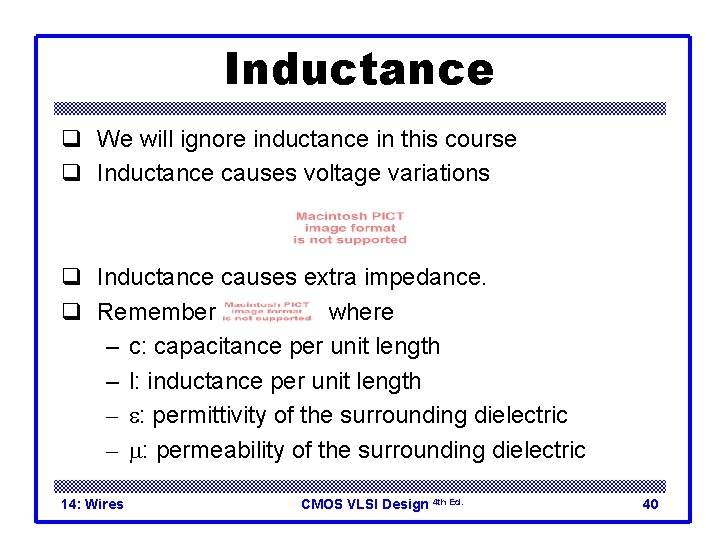
Inductance q We will ignore inductance in this course q Inductance causes voltage variations q Inductance causes extra impedance. q Remember where – c: capacitance per unit length – l: inductance per unit length – e: permittivity of the surrounding dielectric – m: permeability of the surrounding dielectric 14: Wires CMOS VLSI Design 4 th Ed. 40
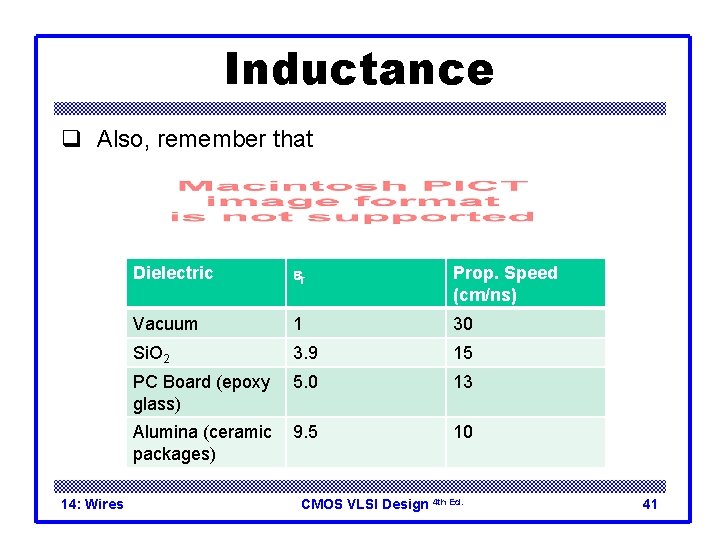
Inductance q Also, remember that 14: Wires Dielectric er Prop. Speed (cm/ns) Vacuum 1 30 Si. O 2 3. 9 15 PC Board (epoxy glass) 5. 0 13 Alumina (ceramic packages) 9. 5 10 CMOS VLSI Design 4 th Ed. 41
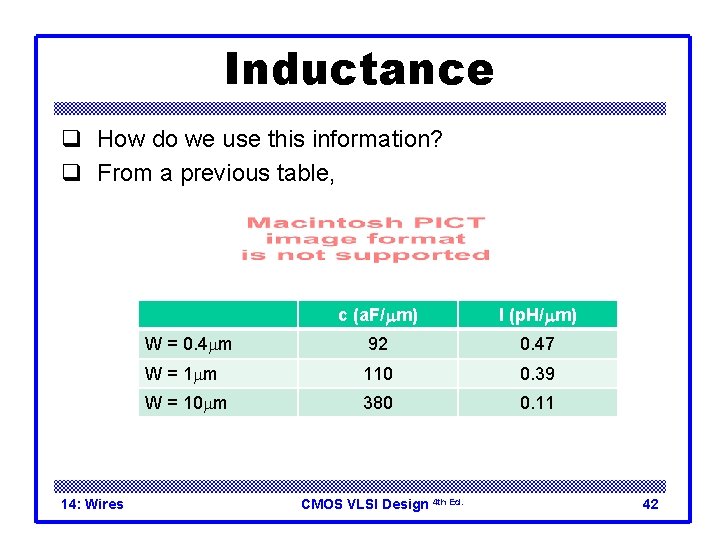
Inductance q How do we use this information? q From a previous table, 14: Wires c (a. F/mm) l (p. H/mm) W = 0. 4 mm 92 0. 47 W = 1 mm 110 0. 39 W = 10 mm 380 0. 11 CMOS VLSI Design 4 th Ed. 42
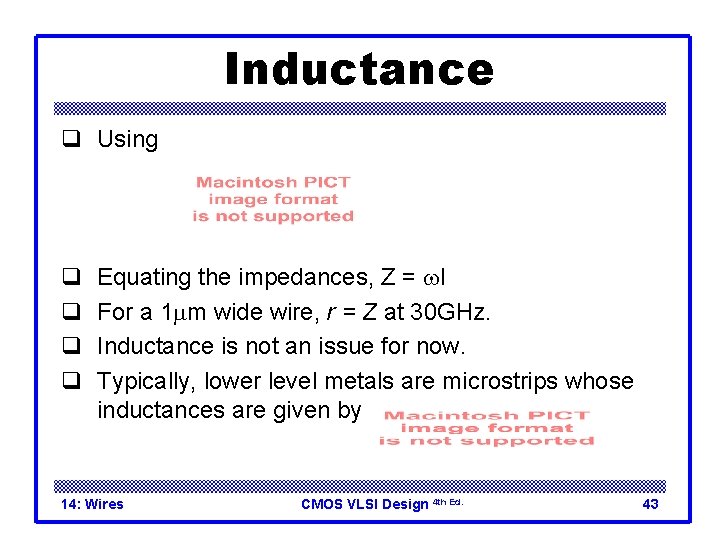
Inductance q Using q q Equating the impedances, Z = wl For a 1 mm wide wire, r = Z at 30 GHz. Inductance is not an issue for now. Typically, lower level metals are microstrips whose inductances are given by 14: Wires CMOS VLSI Design 4 th Ed. 43
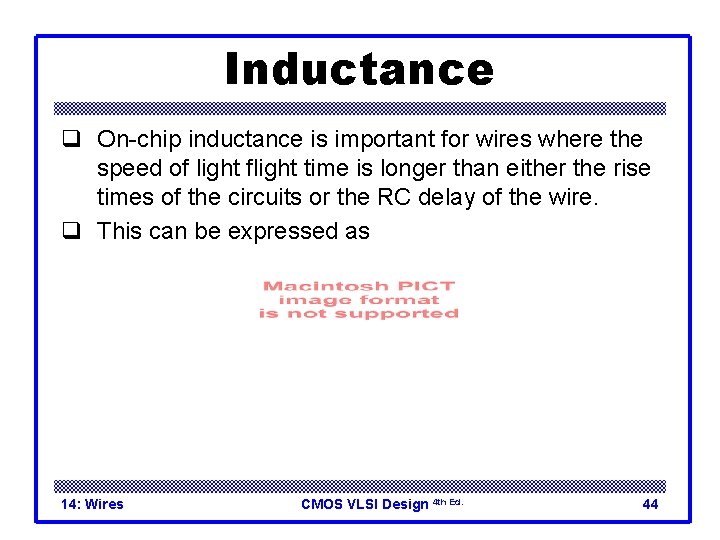
Inductance q On-chip inductance is important for wires where the speed of light flight time is longer than either the rise times of the circuits or the RC delay of the wire. q This can be expressed as 14: Wires CMOS VLSI Design 4 th Ed. 44
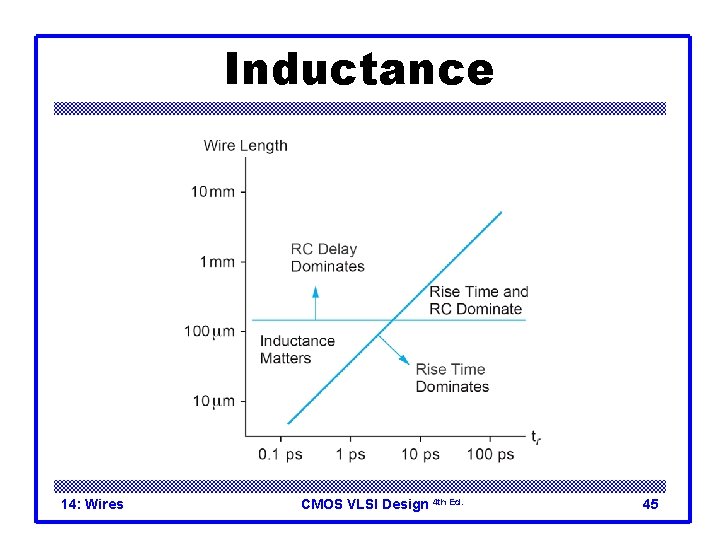
Inductance 14: Wires CMOS VLSI Design 4 th Ed. 45
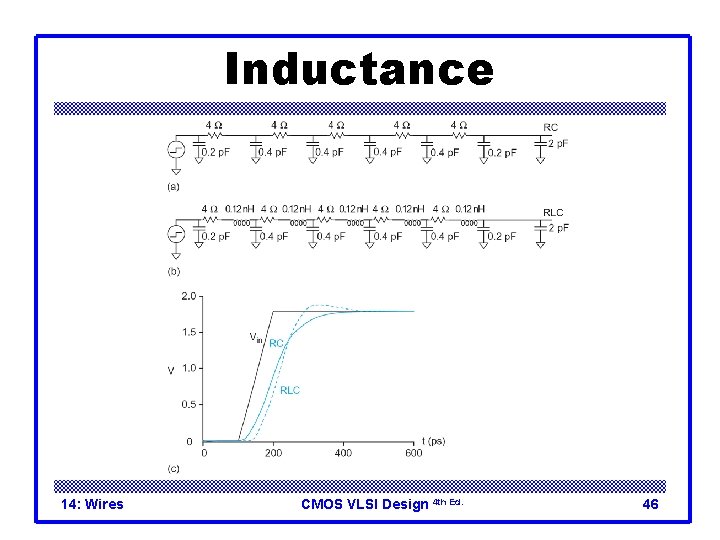
Inductance 14: Wires CMOS VLSI Design 4 th Ed. 46
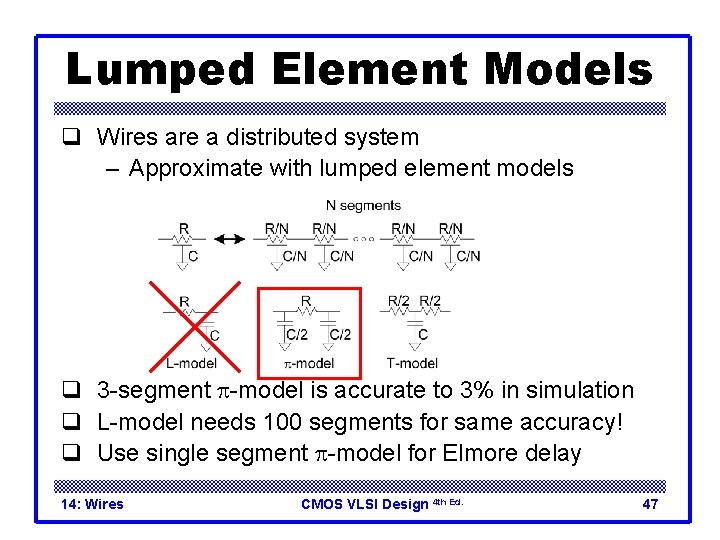
Lumped Element Models q Wires are a distributed system – Approximate with lumped element models q 3 -segment p-model is accurate to 3% in simulation q L-model needs 100 segments for same accuracy! q Use single segment p-model for Elmore delay 14: Wires CMOS VLSI Design 4 th Ed. 47
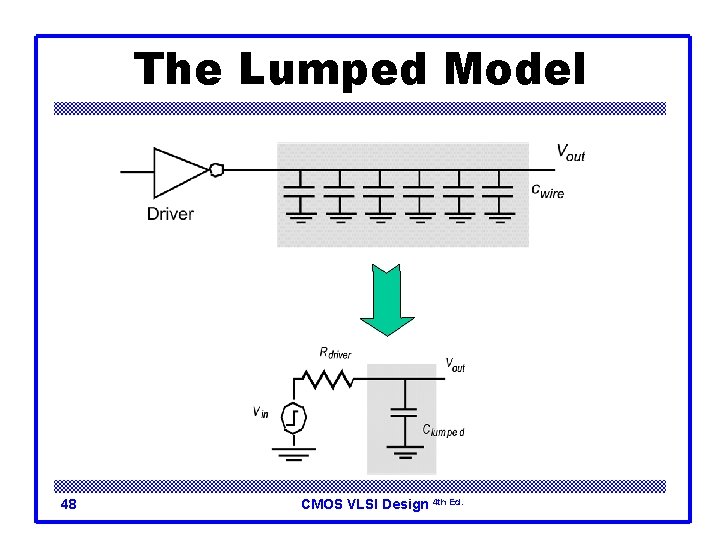
The Lumped Model 48 CMOS VLSI Design 4 th Ed.
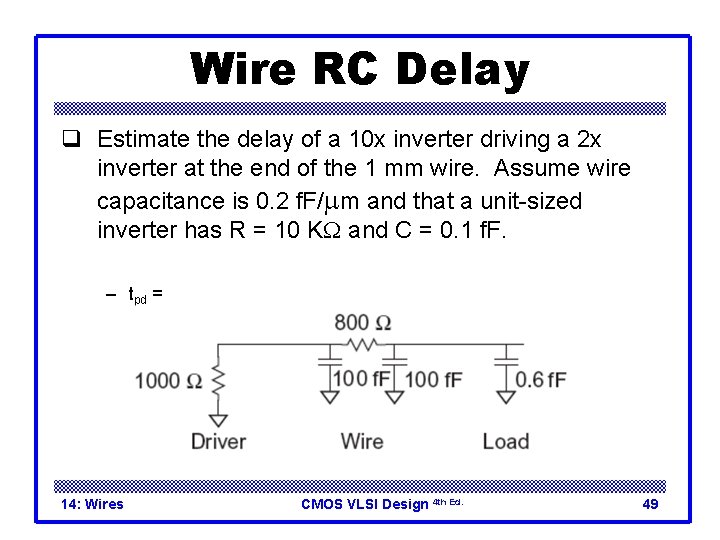
Wire RC Delay q Estimate the delay of a 10 x inverter driving a 2 x inverter at the end of the 1 mm wire. Assume wire capacitance is 0. 2 f. F/mm and that a unit-sized inverter has R = 10 KW and C = 0. 1 f. F. – tpd = (1000 W)(100 f. F) + (1000 + 800 W)(100 + 0. 6 f. F) = 281 ps 14: Wires CMOS VLSI Design 4 th Ed. 49
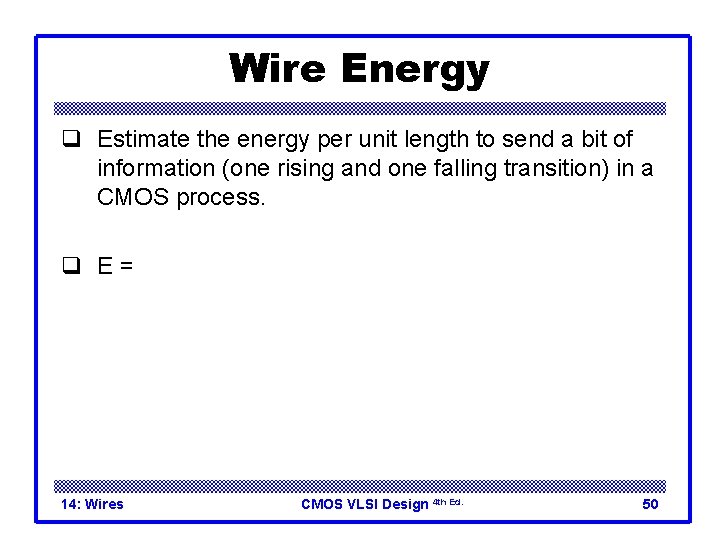
Wire Energy q Estimate the energy per unit length to send a bit of information (one rising and one falling transition) in a CMOS process. q E = (0. 2 p. F/mm)(1. 0 V)2 14: Wires = 0. 2 p. J/bit/mm = 0. 2 m. W/Gbps CMOS VLSI Design 4 th Ed. 50
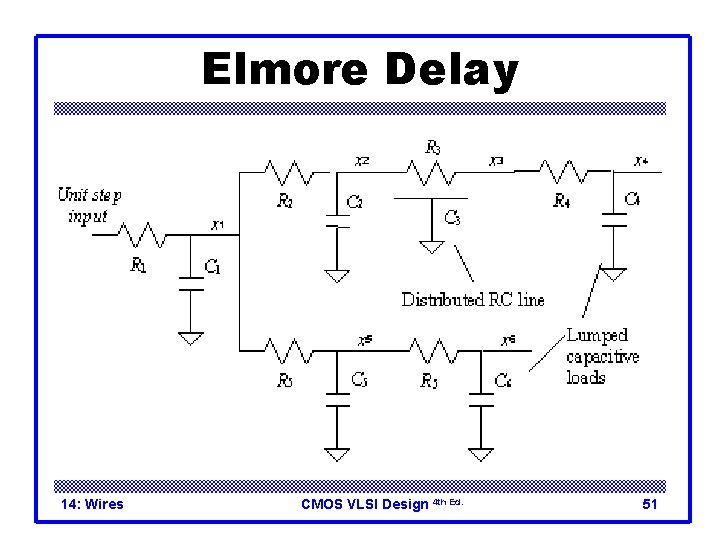
Elmore Delay 14: Wires CMOS VLSI Design 4 th Ed. 51
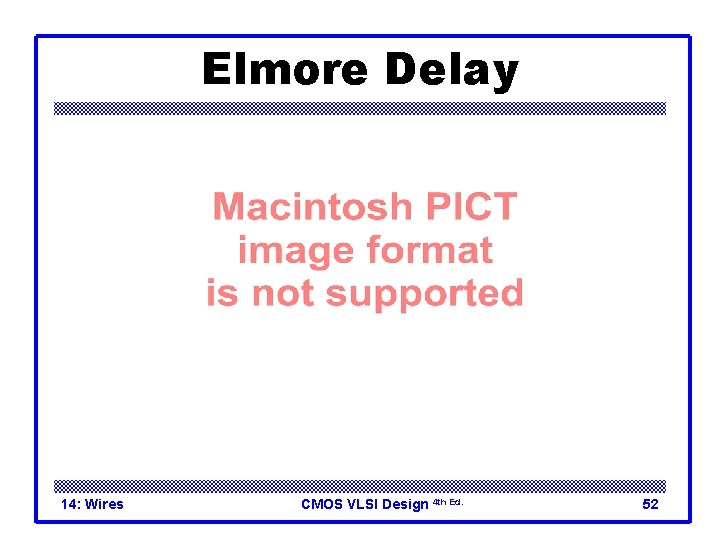
Elmore Delay 14: Wires CMOS VLSI Design 4 th Ed. 52
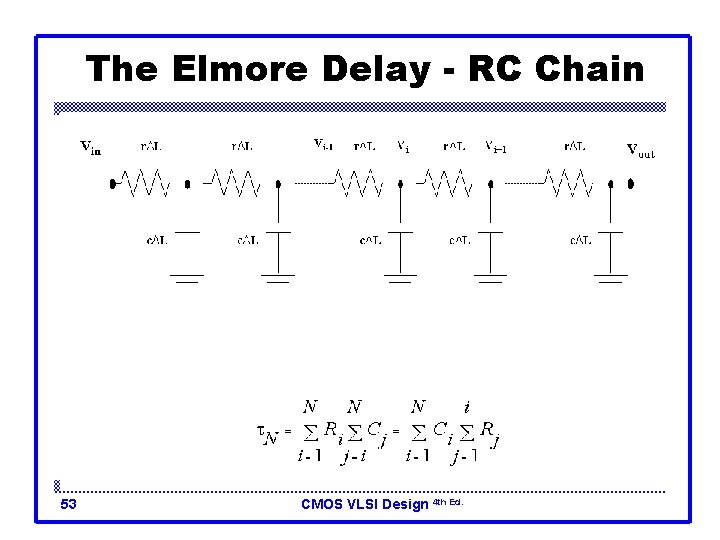
The Elmore Delay - RC Chain 53 CMOS VLSI Design 4 th Ed.
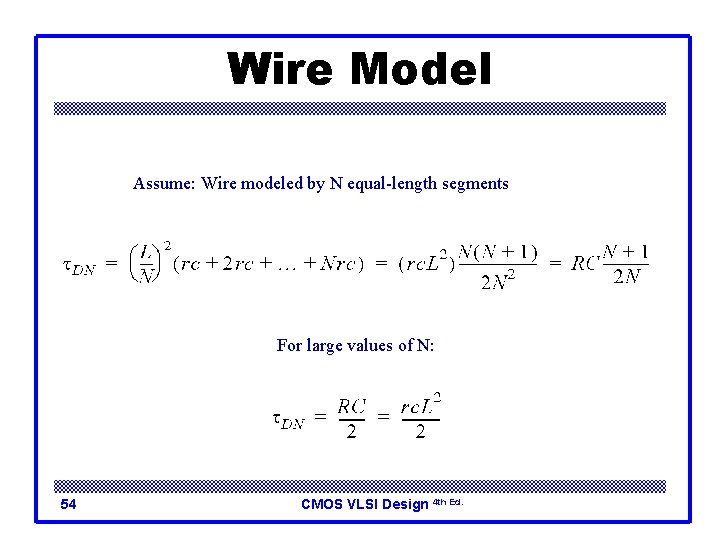
Wire Model Assume: Wire modeled by N equal-length segments For large values of N: 54 CMOS VLSI Design 4 th Ed.
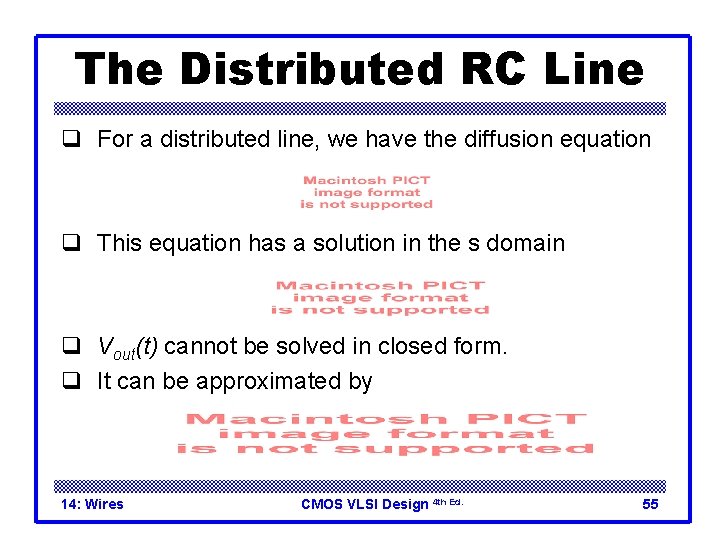
The Distributed RC Line q For a distributed line, we have the diffusion equation q This equation has a solution in the s domain q Vout(t) cannot be solved in closed form. q It can be approximated by 14: Wires CMOS VLSI Design 4 th Ed. 55
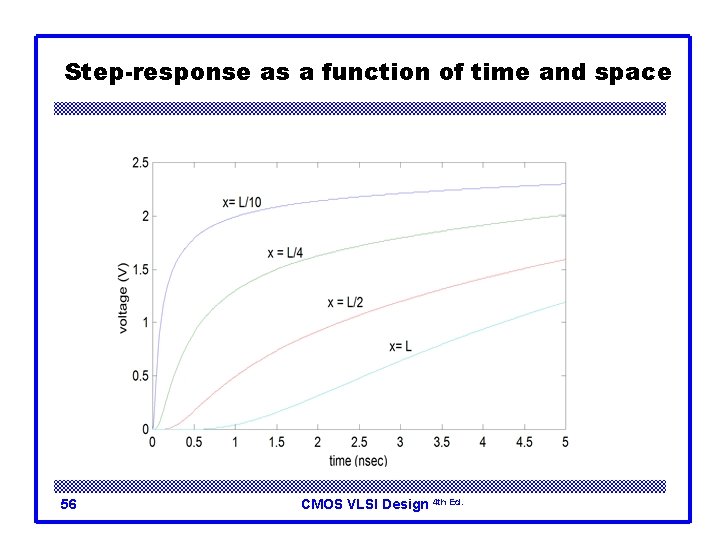
Step-response as a function of time and space 56 CMOS VLSI Design 4 th Ed.
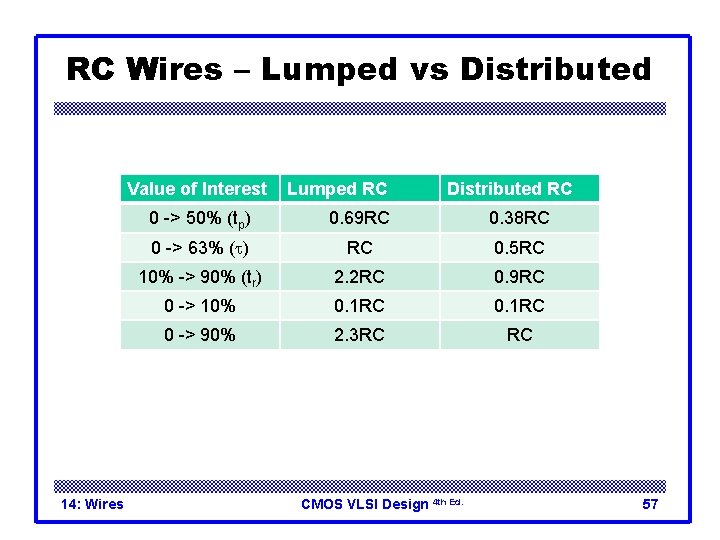
RC Wires – Lumped vs Distributed Value of Interest 14: Wires Lumped RC Distributed RC 0 -> 50% (tp) 0. 69 RC 0. 38 RC 0 -> 63% (t) RC 0. 5 RC 10% -> 90% (tr) 2. 2 RC 0. 9 RC 0 -> 10% 0. 1 RC 0 -> 90% 2. 3 RC RC CMOS VLSI Design 4 th Ed. 57
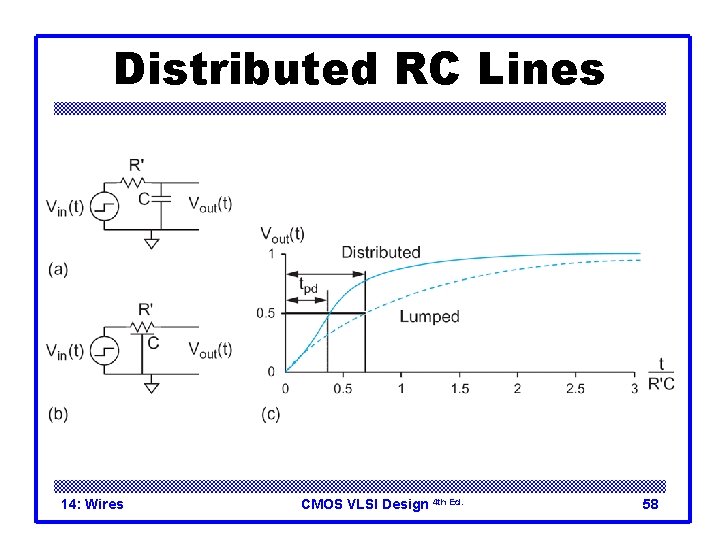
Distributed RC Lines 14: Wires CMOS VLSI Design 4 th Ed. 58
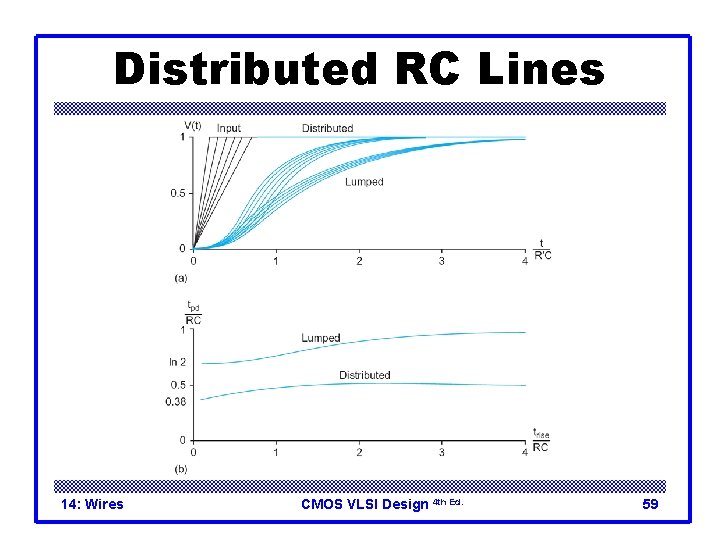
Distributed RC Lines 14: Wires CMOS VLSI Design 4 th Ed. 59
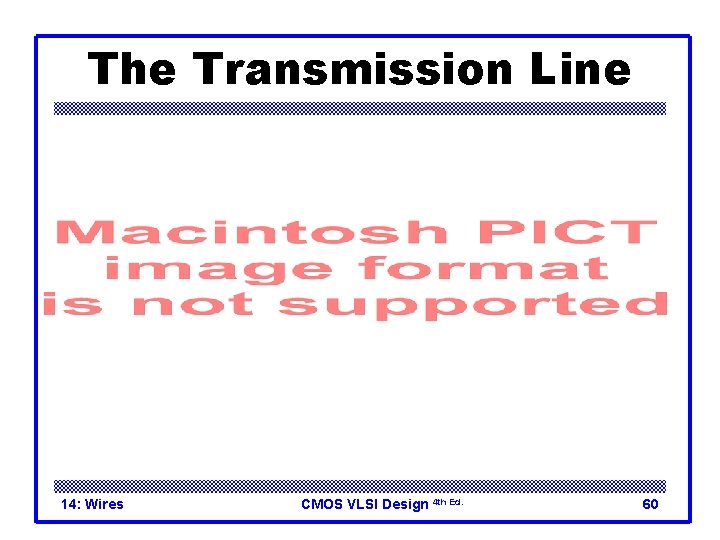
The Transmission Line 14: Wires CMOS VLSI Design 4 th Ed. 60
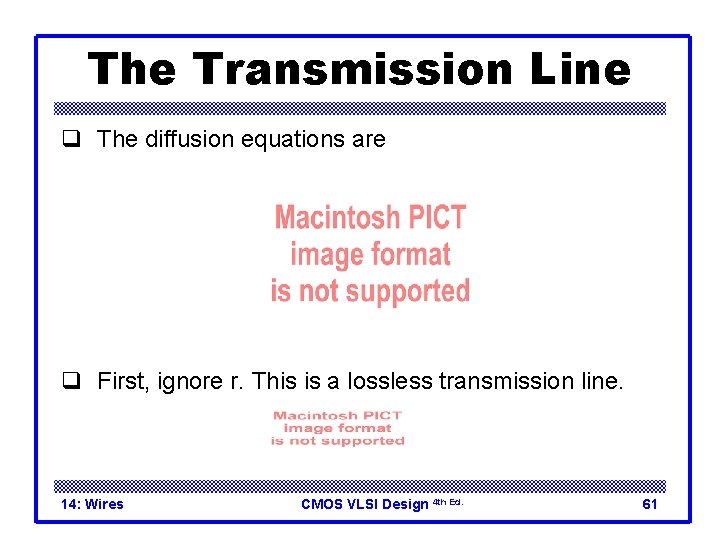
The Transmission Line q The diffusion equations are q First, ignore r. This is a lossless transmission line. 14: Wires CMOS VLSI Design 4 th Ed. 61
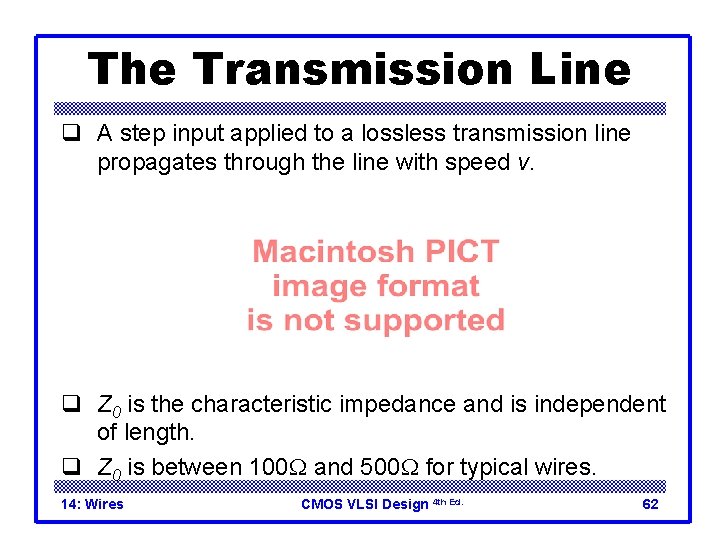
The Transmission Line q A step input applied to a lossless transmission line propagates through the line with speed v. q Z 0 is the characteristic impedance and is independent of length. q Z 0 is between 100 W and 500 W for typical wires. 14: Wires CMOS VLSI Design 4 th Ed. 62
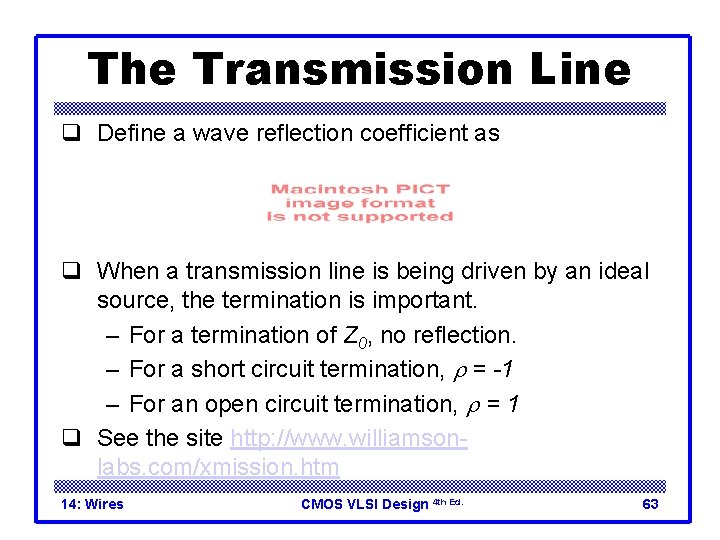
The Transmission Line q Define a wave reflection coefficient as q When a transmission line is being driven by an ideal source, the termination is important. – For a termination of Z 0, no reflection. – For a short circuit termination, r = -1 – For an open circuit termination, r = 1 q See the site http: //www. williamsonlabs. com/xmission. htm 14: Wires CMOS VLSI Design 4 th Ed. 63
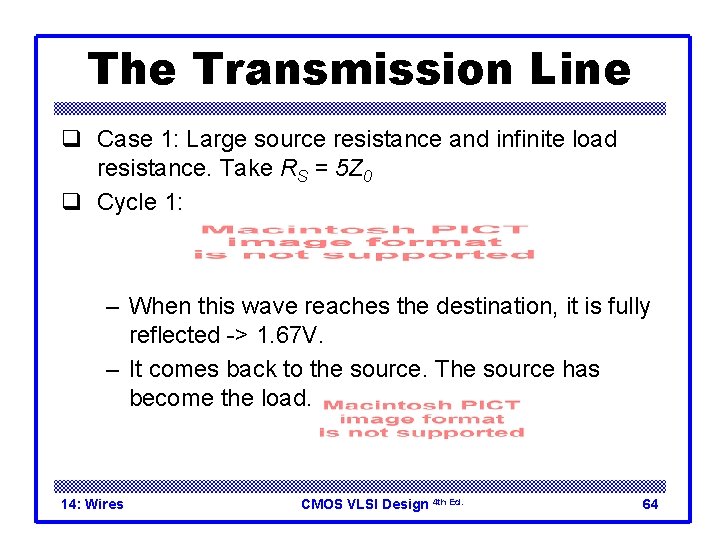
The Transmission Line q Case 1: Large source resistance and infinite load resistance. Take RS = 5 Z 0 q Cycle 1: – When this wave reaches the destination, it is fully reflected -> 1. 67 V. – It comes back to the source. The source has become the load. 14: Wires CMOS VLSI Design 4 th Ed. 64
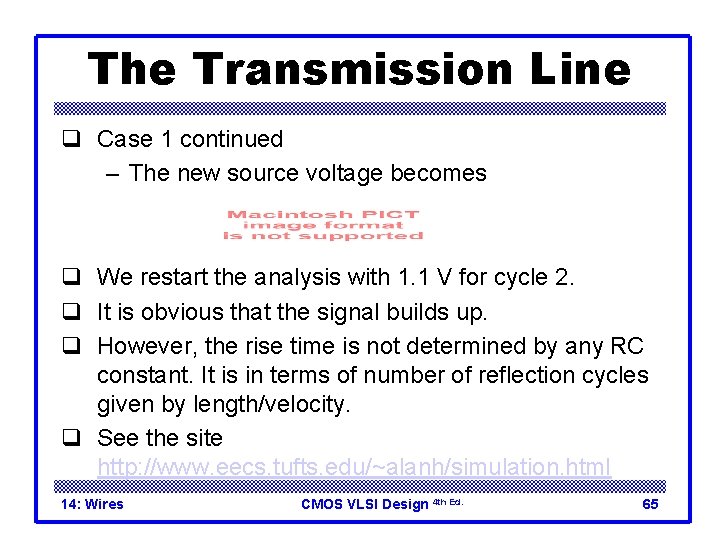
The Transmission Line q Case 1 continued – The new source voltage becomes q We restart the analysis with 1. 1 V for cycle 2. q It is obvious that the signal builds up. q However, the rise time is not determined by any RC constant. It is in terms of number of reflection cycles given by length/velocity. q See the site http: //www. eecs. tufts. edu/~alanh/simulation. html 14: Wires CMOS VLSI Design 4 th Ed. 65
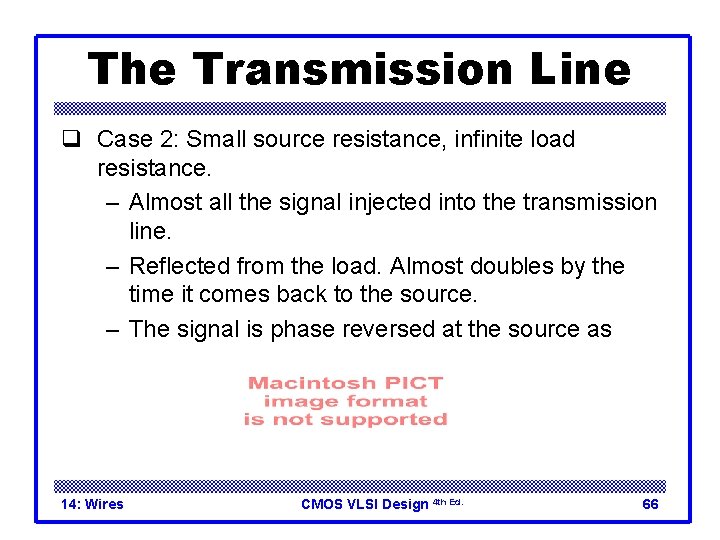
The Transmission Line q Case 2: Small source resistance, infinite load resistance. – Almost all the signal injected into the transmission line. – Reflected from the load. Almost doubles by the time it comes back to the source. – The signal is phase reversed at the source as 14: Wires CMOS VLSI Design 4 th Ed. 66
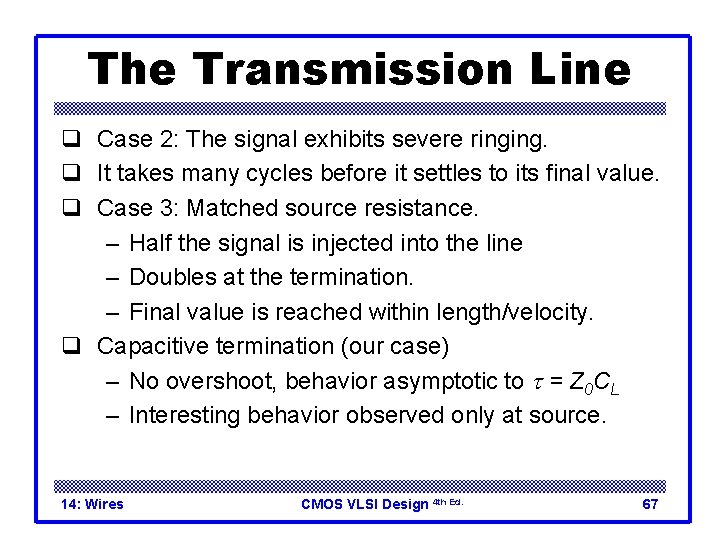
The Transmission Line q Case 2: The signal exhibits severe ringing. q It takes many cycles before it settles to its final value. q Case 3: Matched source resistance. – Half the signal is injected into the line – Doubles at the termination. – Final value is reached within length/velocity. q Capacitive termination (our case) – No overshoot, behavior asymptotic to t = Z 0 CL – Interesting behavior observed only at source. 14: Wires CMOS VLSI Design 4 th Ed. 67
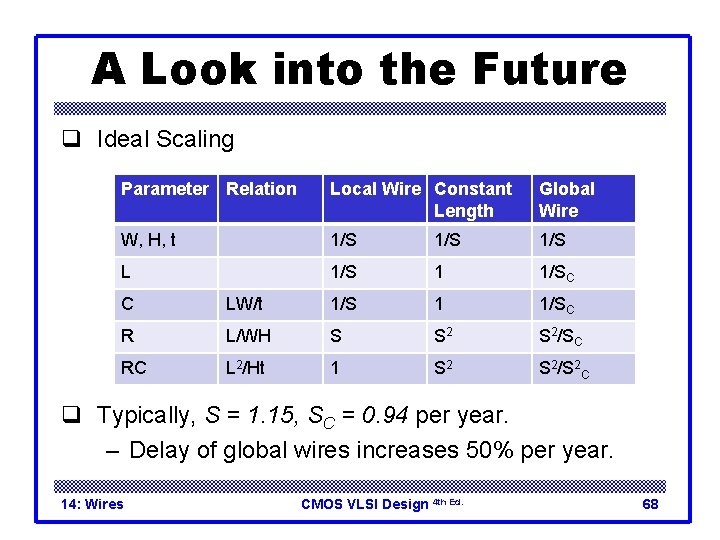
A Look into the Future q Ideal Scaling Parameter Relation Local Wire Constant Length Global Wire W, H, t 1/S 1/S L 1/S 1 1/SC C LW/t 1/S 1 1/SC R L/WH S S 2/SC RC L 2/Ht 1 S 2/S 2 C q Typically, S = 1. 15, SC = 0. 94 per year. – Delay of global wires increases 50% per year. 14: Wires CMOS VLSI Design 4 th Ed. 68
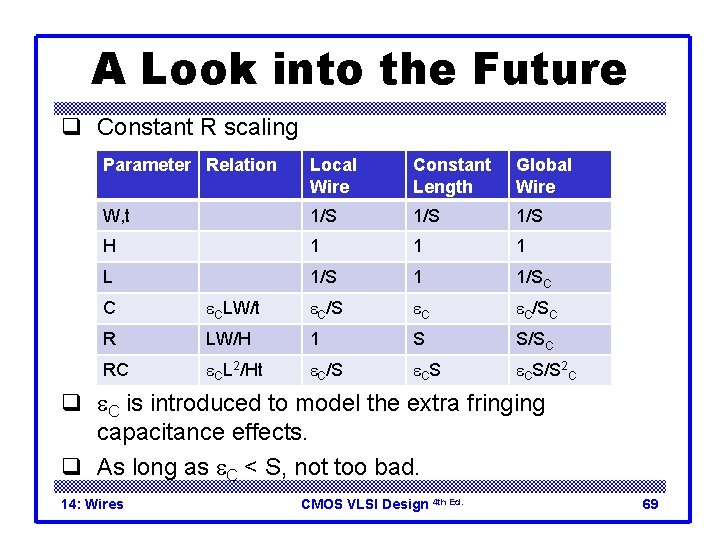
A Look into the Future q Constant R scaling Parameter Relation Local Wire Constant Length Global Wire W, t 1/S 1/S H 1 1 1 L 1/S 1 1/SC C e. CLW/t e. C/SC R LW/H 1 S S/SC RC e. CL 2/Ht e. C/S e. CS/S 2 C q e. C is introduced to model the extra fringing capacitance effects. q As long as e. C < S, not too bad. 14: Wires CMOS VLSI Design 4 th Ed. 69
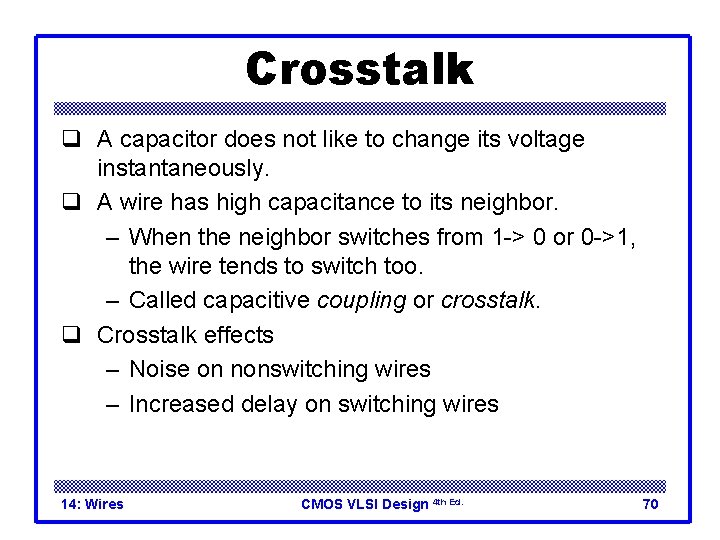
Crosstalk q A capacitor does not like to change its voltage instantaneously. q A wire has high capacitance to its neighbor. – When the neighbor switches from 1 -> 0 or 0 ->1, the wire tends to switch too. – Called capacitive coupling or crosstalk. q Crosstalk effects – Noise on nonswitching wires – Increased delay on switching wires 14: Wires CMOS VLSI Design 4 th Ed. 70
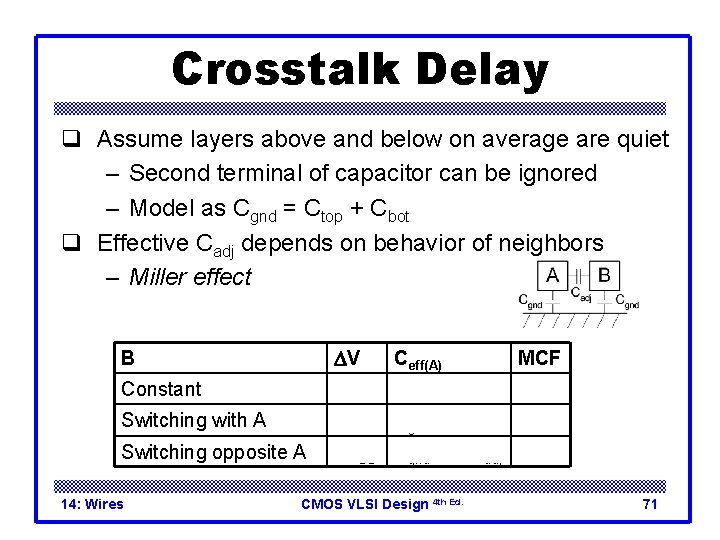
Crosstalk Delay q Assume layers above and below on average are quiet – Second terminal of capacitor can be ignored – Model as Cgnd = Ctop + Cbot q Effective Cadj depends on behavior of neighbors – Miller effect B DV Ceff(A) MCF Constant VDD Cgnd + Cadj 1 Switching with A 0 Cgnd 0 Switching opposite A 2 VDD Cgnd + 2 Cadj 2 14: Wires CMOS VLSI Design 4 th Ed. 71
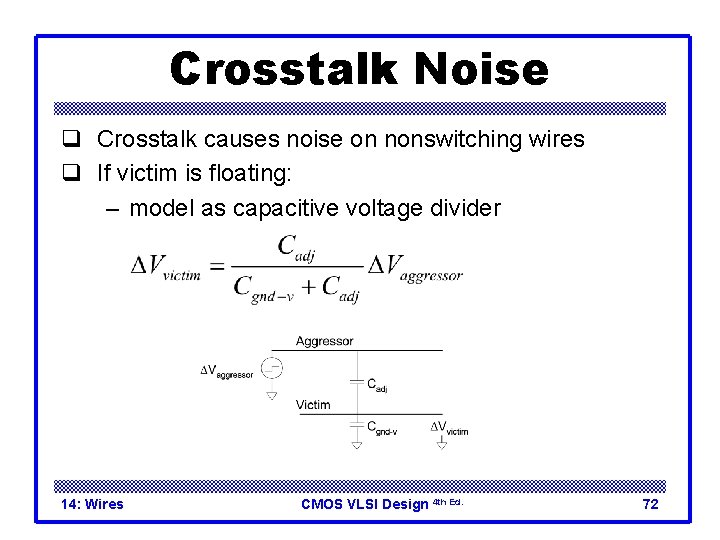
Crosstalk Noise q Crosstalk causes noise on nonswitching wires q If victim is floating: – model as capacitive voltage divider 14: Wires CMOS VLSI Design 4 th Ed. 72
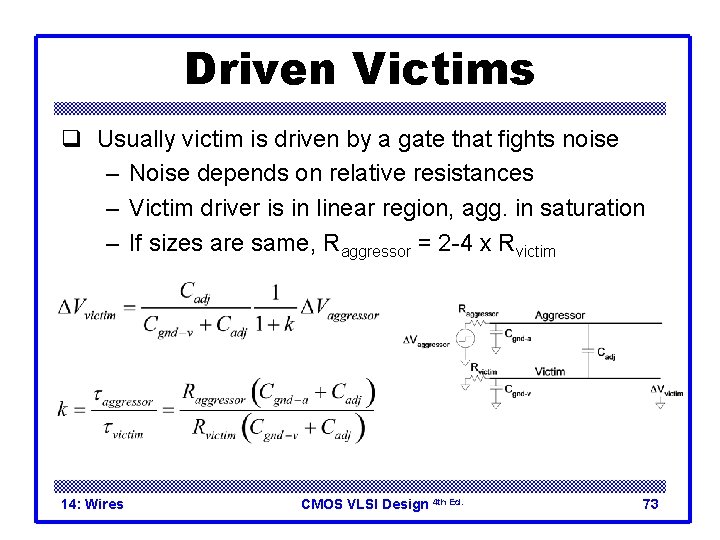
Driven Victims q Usually victim is driven by a gate that fights noise – Noise depends on relative resistances – Victim driver is in linear region, agg. in saturation – If sizes are same, Raggressor = 2 -4 x Rvictim 14: Wires CMOS VLSI Design 4 th Ed. 73
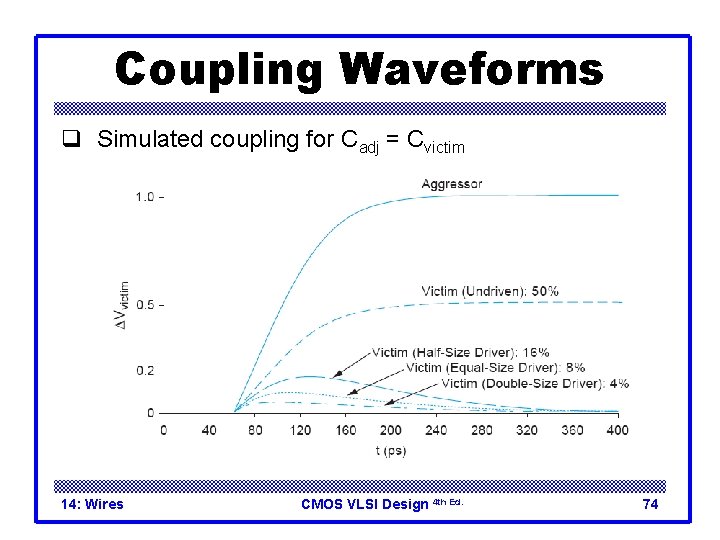
Coupling Waveforms q Simulated coupling for Cadj = Cvictim 14: Wires CMOS VLSI Design 4 th Ed. 74
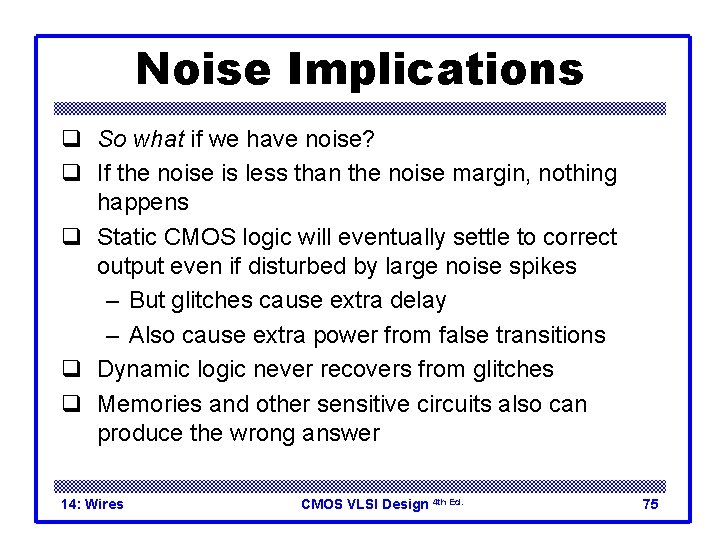
Noise Implications q So what if we have noise? q If the noise is less than the noise margin, nothing happens q Static CMOS logic will eventually settle to correct output even if disturbed by large noise spikes – But glitches cause extra delay – Also cause extra power from false transitions q Dynamic logic never recovers from glitches q Memories and other sensitive circuits also can produce the wrong answer 14: Wires CMOS VLSI Design 4 th Ed. 75
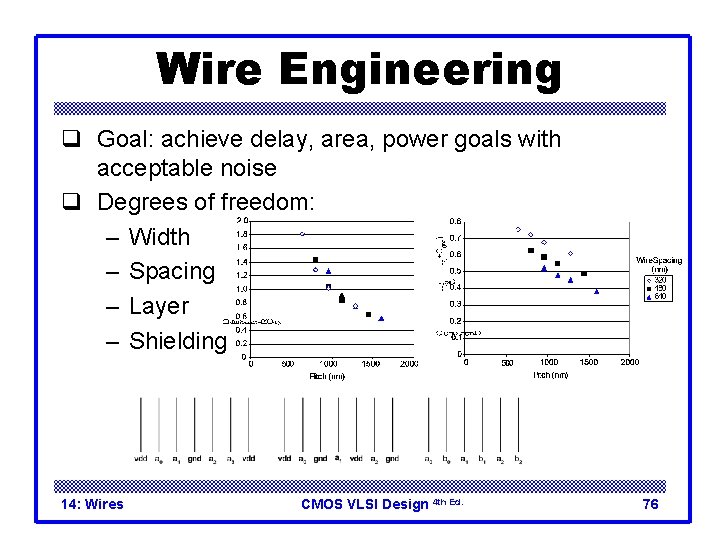
Wire Engineering q Goal: achieve delay, area, power goals with acceptable noise q Degrees of freedom: – Width – Spacing – Layer – Shielding 14: Wires CMOS VLSI Design 4 th Ed. 76
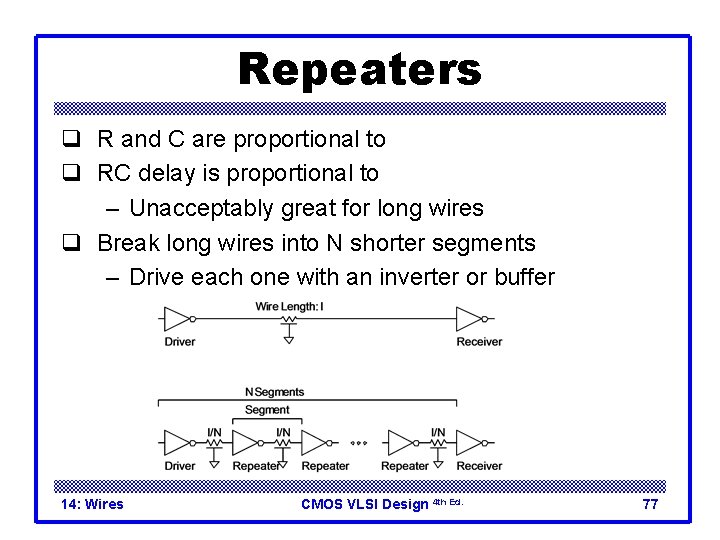
Repeaters q R and C are proportional to l q RC delay is proportional to l 2 – Unacceptably great for long wires q Break long wires into N shorter segments – Drive each one with an inverter or buffer 14: Wires CMOS VLSI Design 4 th Ed. 77
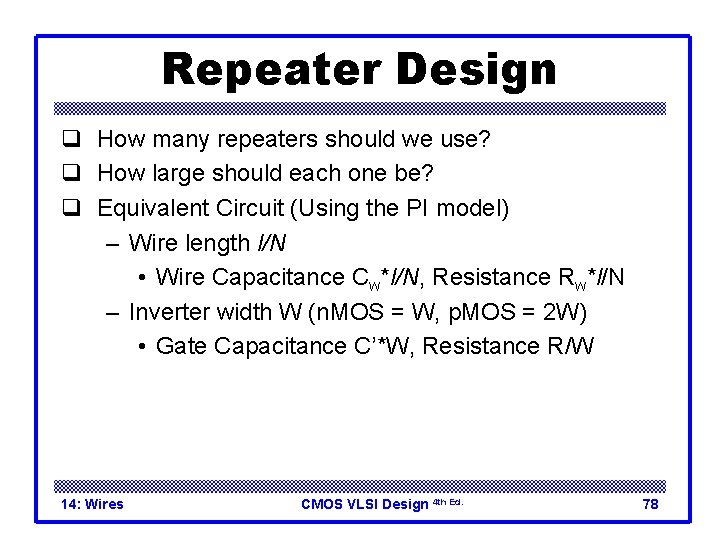
Repeater Design q How many repeaters should we use? q How large should each one be? q Equivalent Circuit (Using the PI model) – Wire length l/N • Wire Capacitance Cw*l/N, Resistance Rw*l/N – Inverter width W (n. MOS = W, p. MOS = 2 W) • Gate Capacitance C’*W, Resistance R/W 14: Wires CMOS VLSI Design 4 th Ed. 78
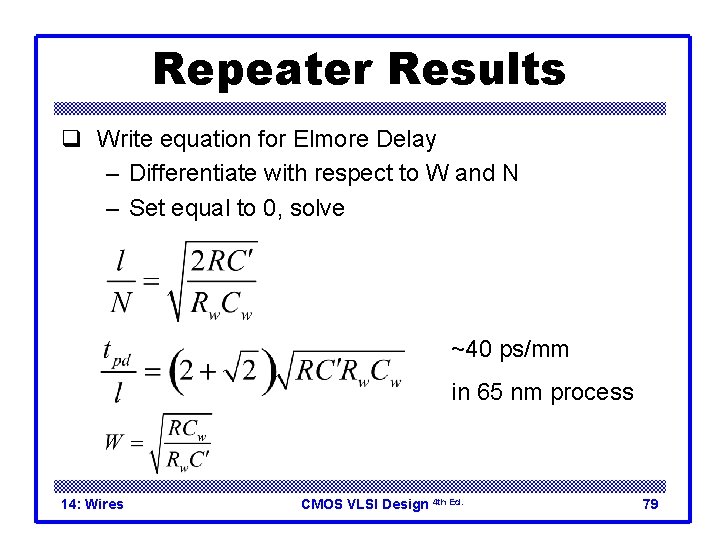
Repeater Results q Write equation for Elmore Delay – Differentiate with respect to W and N – Set equal to 0, solve ~40 ps/mm in 65 nm process 14: Wires CMOS VLSI Design 4 th Ed. 79
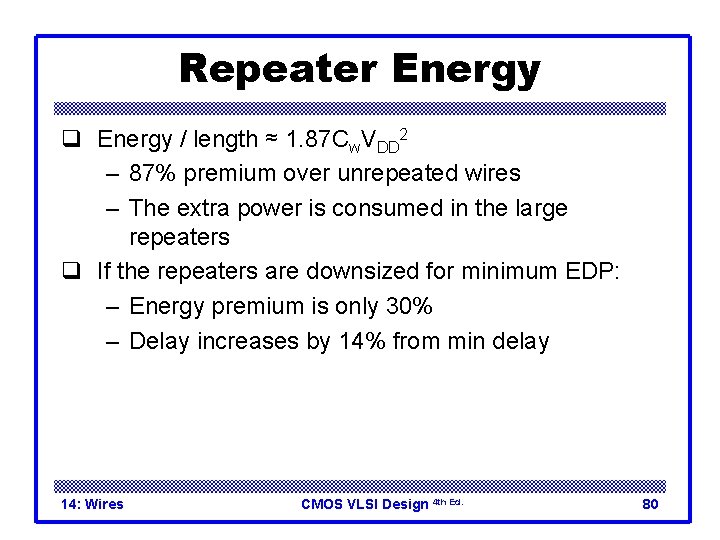
Repeater Energy q Energy / length ≈ 1. 87 Cw. VDD 2 – 87% premium over unrepeated wires – The extra power is consumed in the large repeaters q If the repeaters are downsized for minimum EDP: – Energy premium is only 30% – Delay increases by 14% from min delay 14: Wires CMOS VLSI Design 4 th Ed. 80
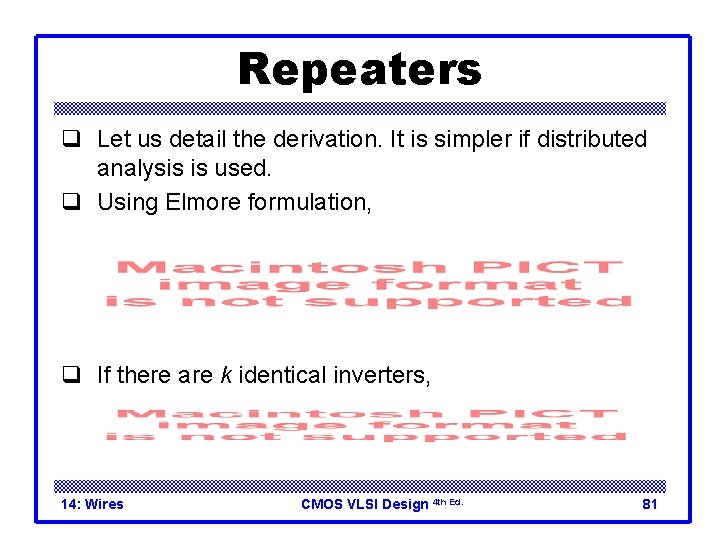
Repeaters q Let us detail the derivation. It is simpler if distributed analysis is used. q Using Elmore formulation, q If there are k identical inverters, 14: Wires CMOS VLSI Design 4 th Ed. 81
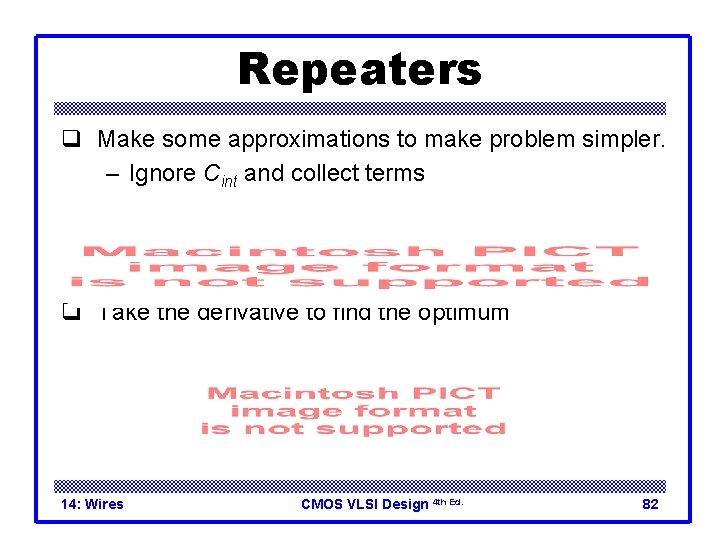
Repeaters q Make some approximations to make problem simpler. – Ignore Cint and collect terms q Take the derivative to find the optimum 14: Wires CMOS VLSI Design 4 th Ed. 82
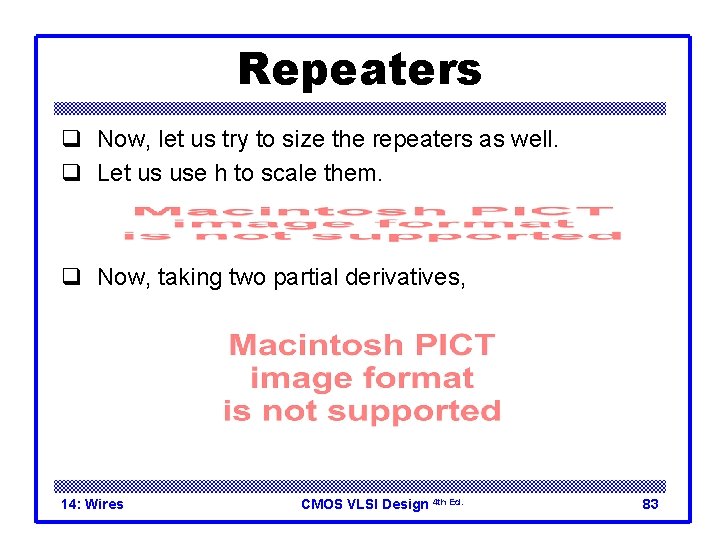
Repeaters q Now, let us try to size the repeaters as well. q Let us use h to scale them. q Now, taking two partial derivatives, 14: Wires CMOS VLSI Design 4 th Ed. 83
01:640:244 lecture notes - lecture 15: plat, idah, farad
Lecture outline example
Lecture outline example
Lecture outline example
Lecture outline meaning
Sip interconnect
Virtual protocol interconnect
Optical interconnect
Optical interconnect solutions
Butterfly network topology
Programmable asic
Bscs billing system
Cross building interconnect
Quick path interconnect
Wishbone fpga
Chet mehta
Dolphin interconnect
Open systems interconnect
High frequency interconnect
Interconnect
Interconnect
Dspx simulation suite
Flexible interconnect system
Interconnect
Ring interconnect
Lumerical interconnect
Sandwich paragraph example
Tripping over wires
5-1 reteach perpendicular and angle bisectors
A conductor suspended by two flexible wires
2 wires video entrance panels
Measure 45 minutes using 2 wires
What's the difference between an idiom and a hyperbole
Simple wire drawing
98 366
Electrical wiring materials
Doctrine of ultra vires in company law
Wires
Two parallel wires
Two parallel wires
Chapter 12 vectors and the geometry of space
A 100 lb weight hangs from two wires
Live and neutral wires
Opvoedbelasting
Plug wires diagram
Neutral earth live
Ideal wires
If 200 amperes flow from the positive terminal
Telegraph wires twisted pair
Ideal device
A conductor suspended by two flexible wires
Introduction to biochemistry lecture notes
Introduction to psychology lecture
Introduction to algorithms lecture notes
Conclusion paragraph outline
5 paragraph essay
Software engineering 1 course outline
Intro paragraph outline
Project procurement management lecture notes
Lecture about sport
Lecture on healthy lifestyle
Existentialism vs nihilism
Meaning of this
Randy pausch the last lecture summary
Tensorflow lecture
Theology proper lecture notes
Strategic management lecture
Geology lecture series
Social psychology lecture
In text citation for a lecture
Public sector accounting notes
Project management lecture notes doc
Practical design to eurocode 2
Magnetism
Physics 111 lecture notes
What is a harmonic wave in physics
Physical science lecture notes
Power system dynamics and stability lecture notes
Natural language processing
Microbial physiology and metabolism lecture notes
Mechatronics lecture notes / ppt
Ternology
Objectifs de lecture
Instruction de lecture