IGC Code IMOs International Gas Carrier Code is
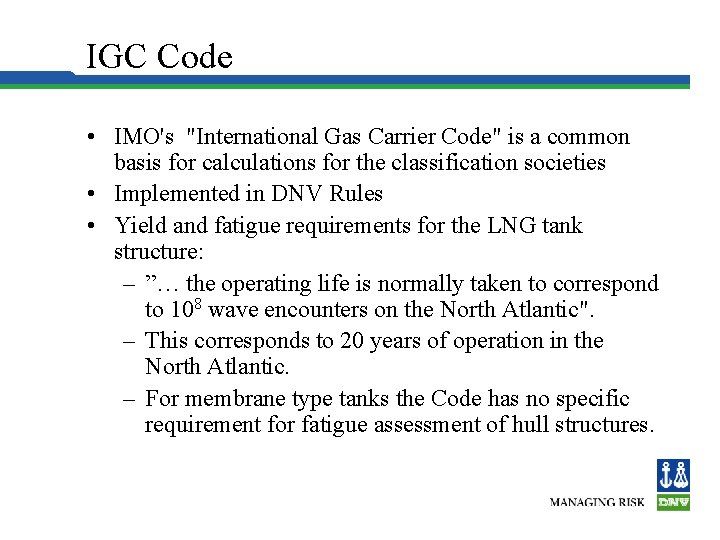
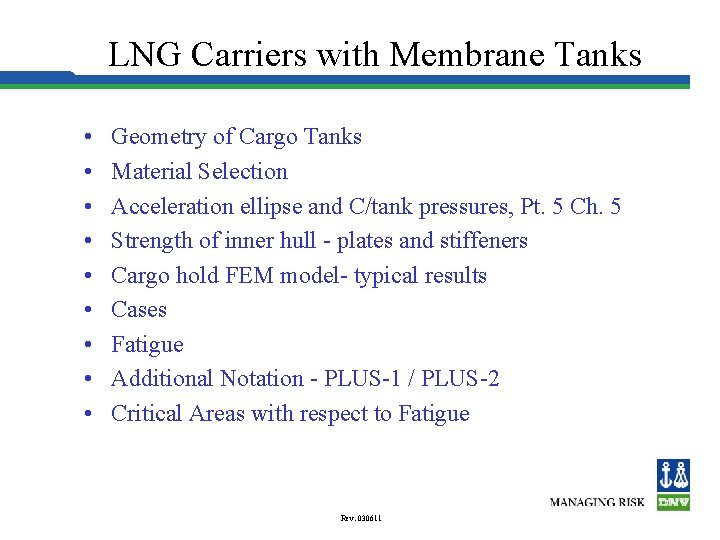
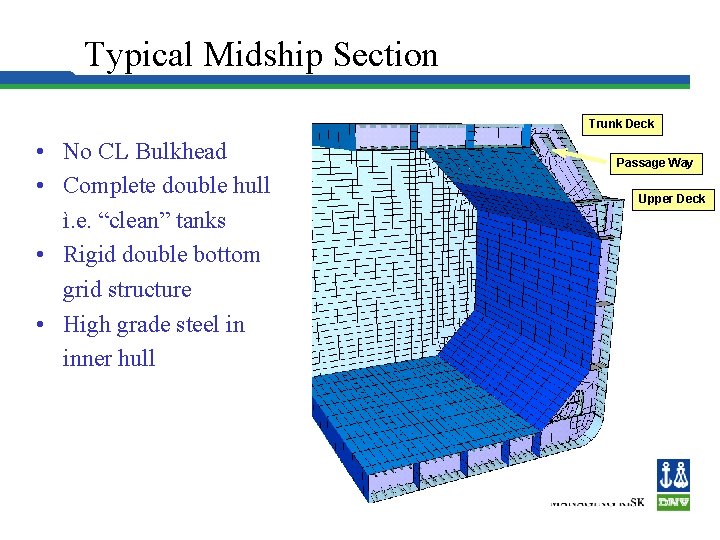
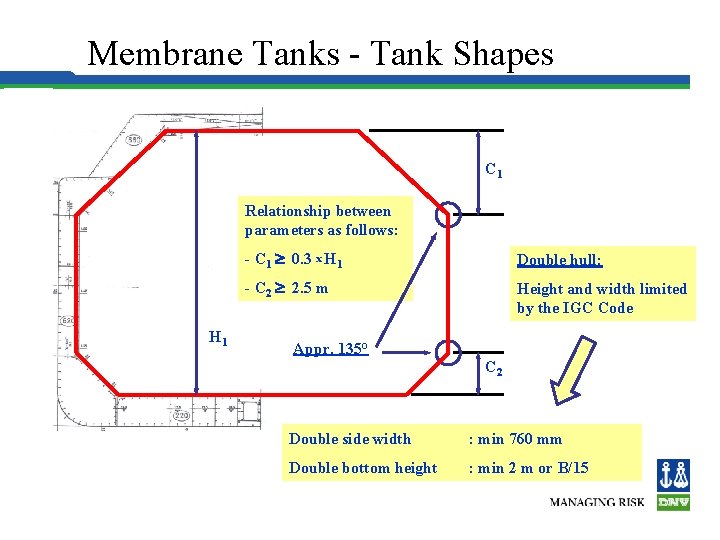
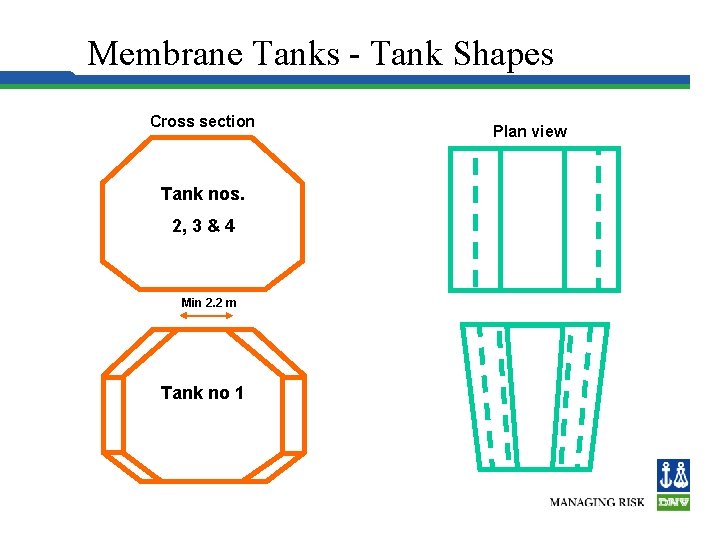
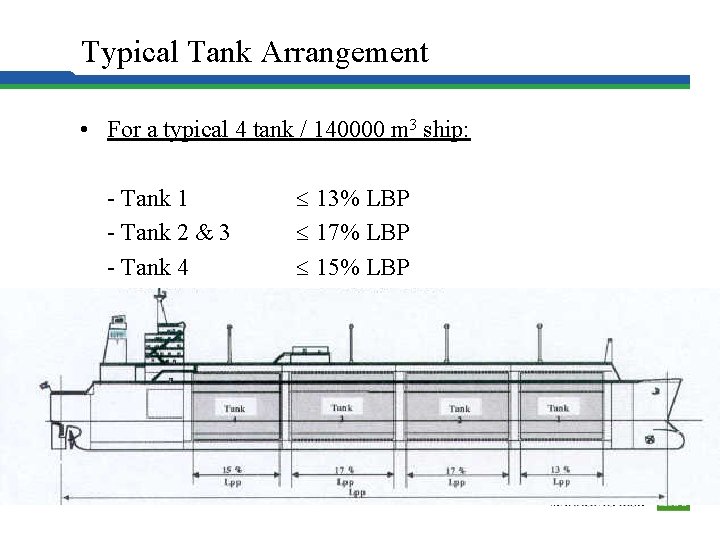
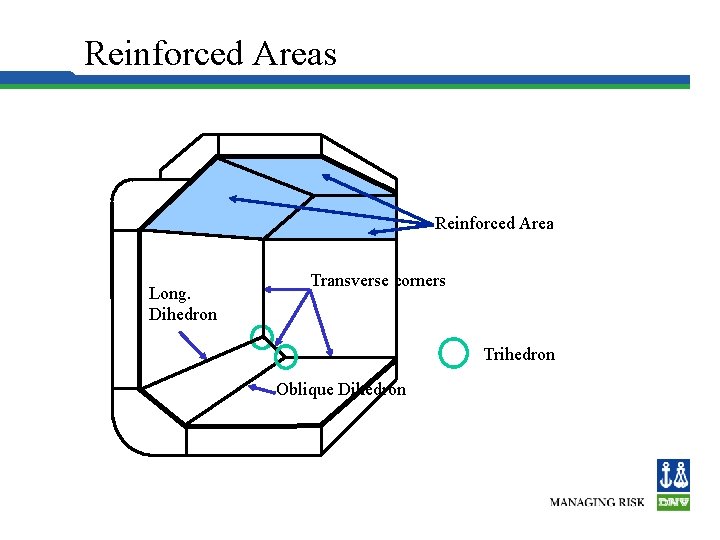
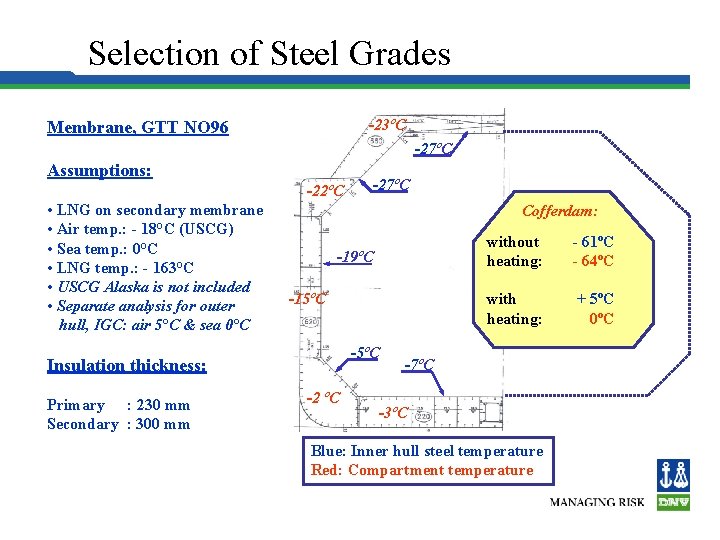
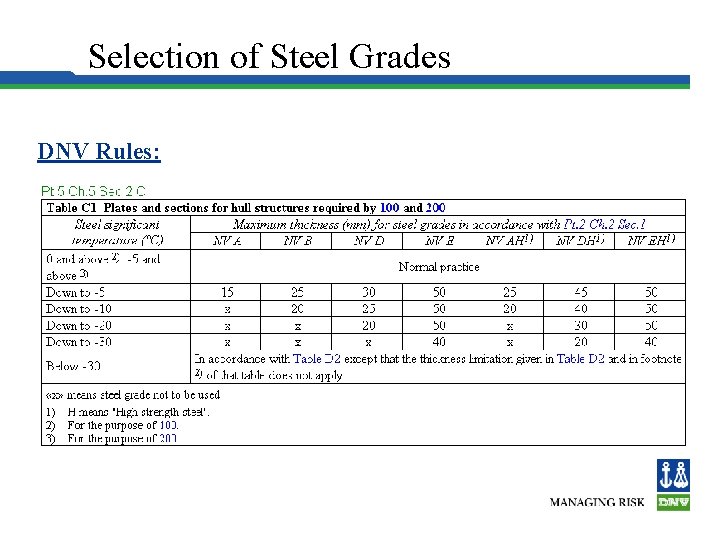
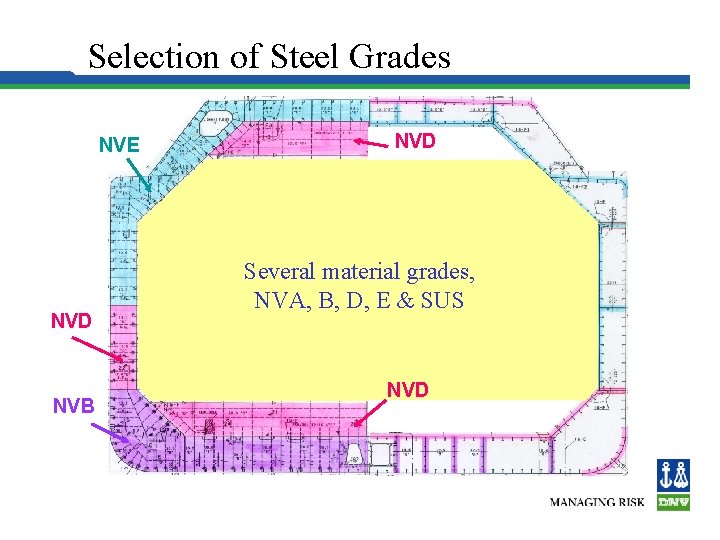
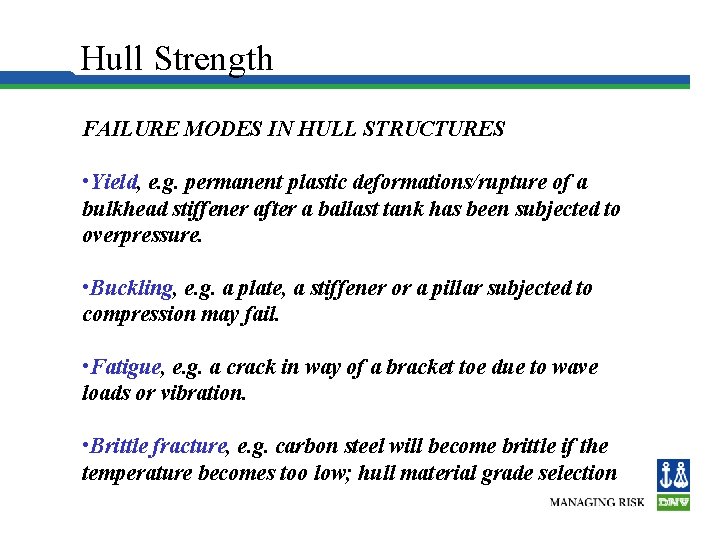
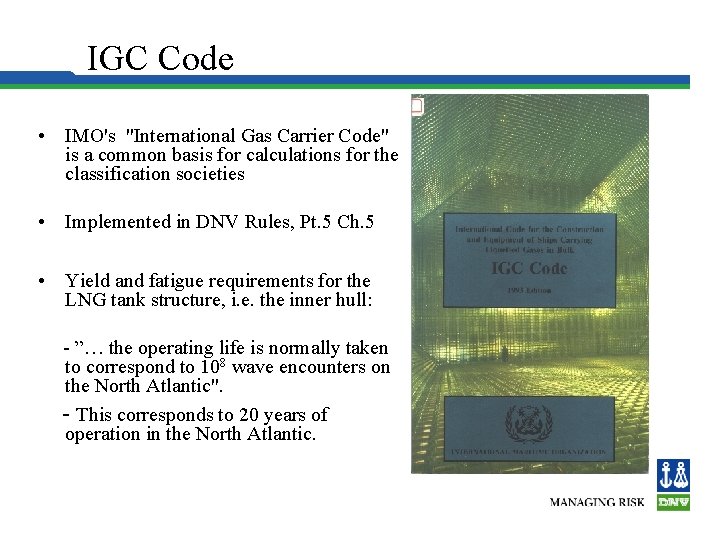
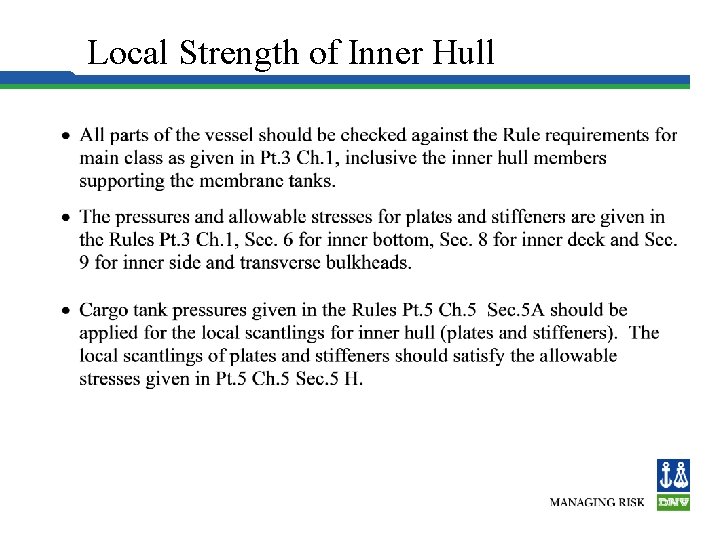
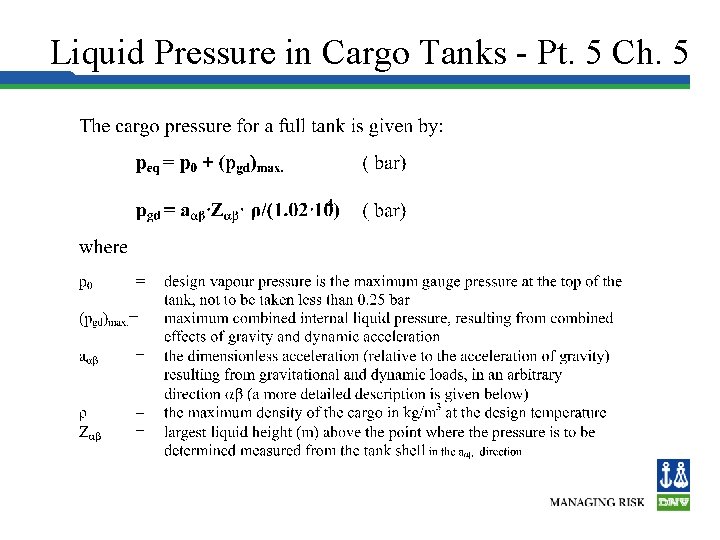
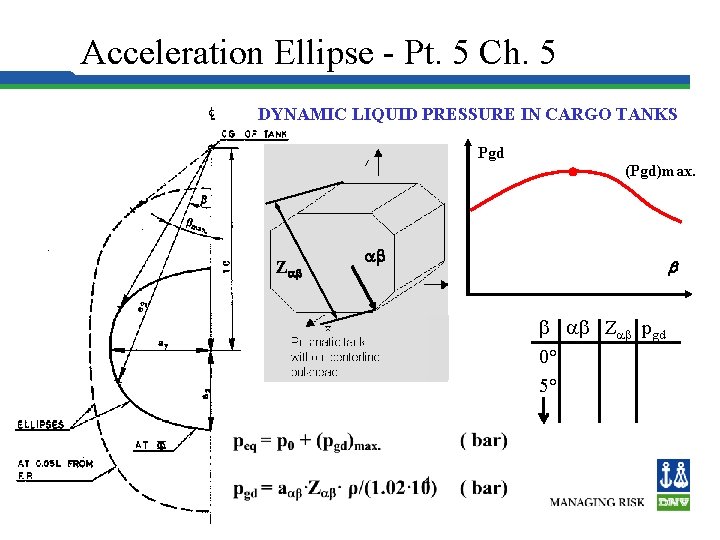
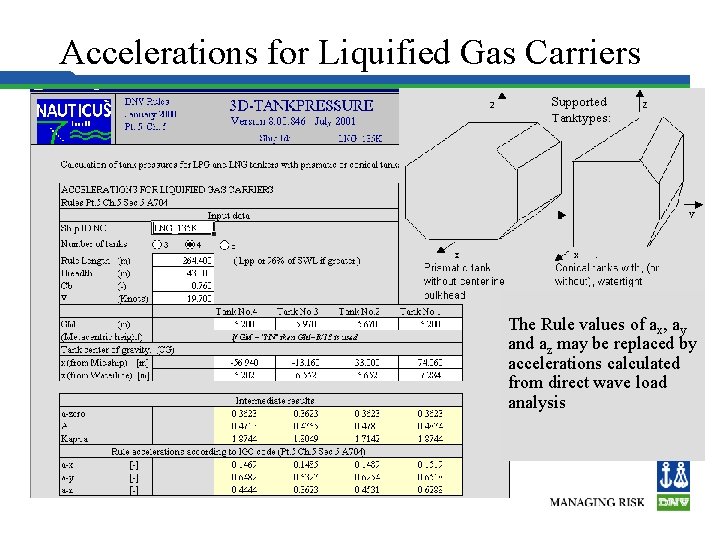
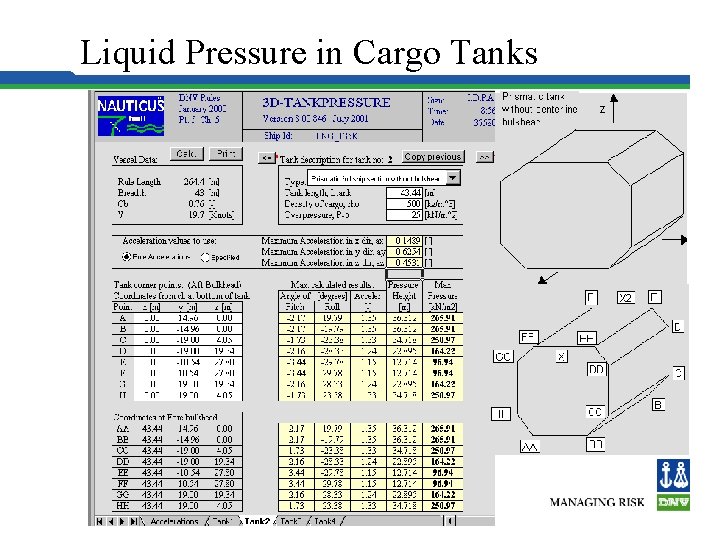
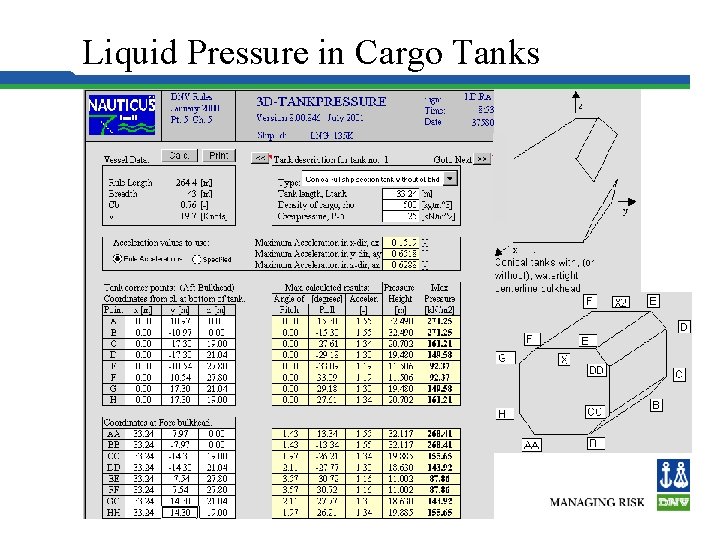
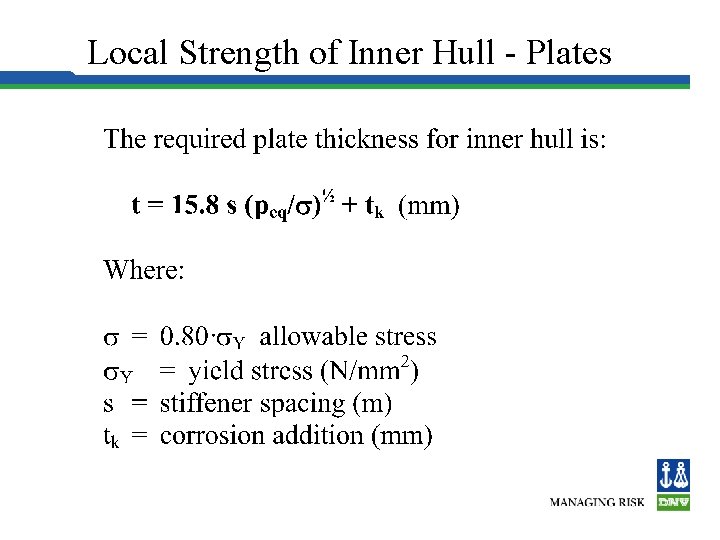
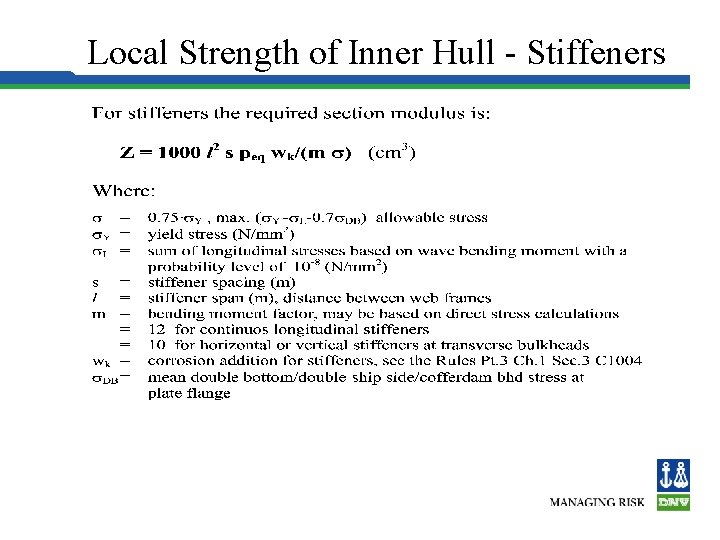
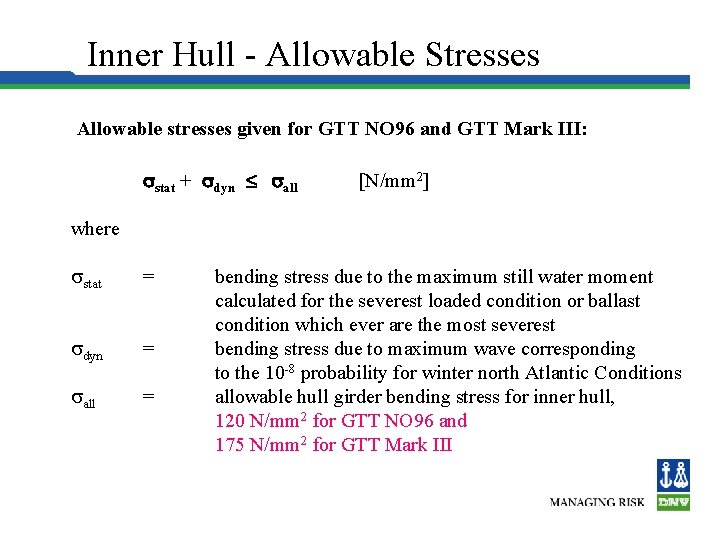
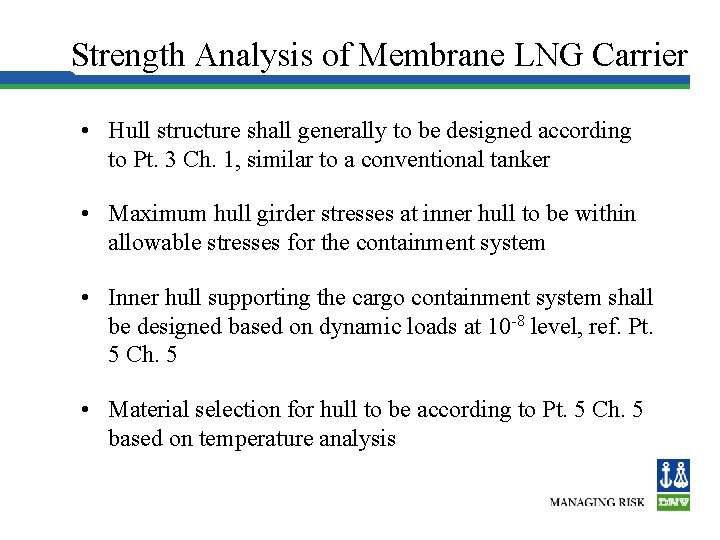
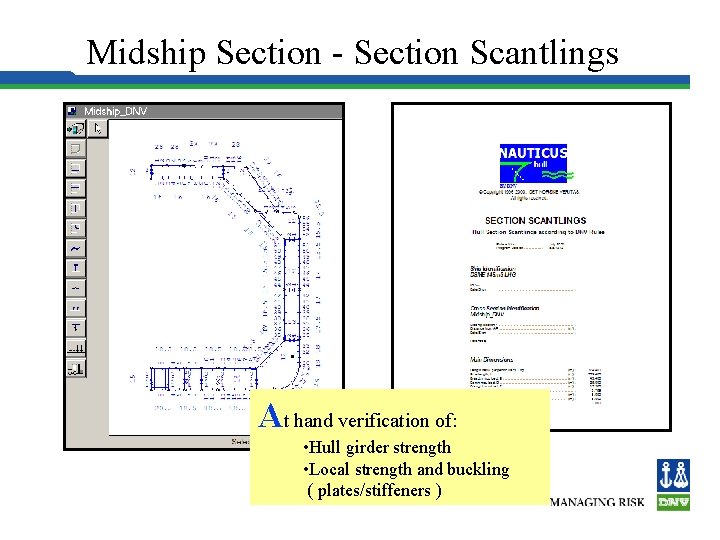
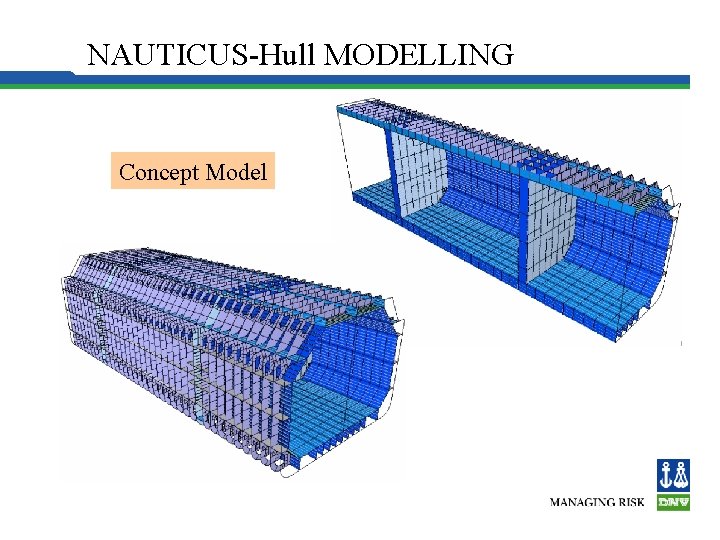

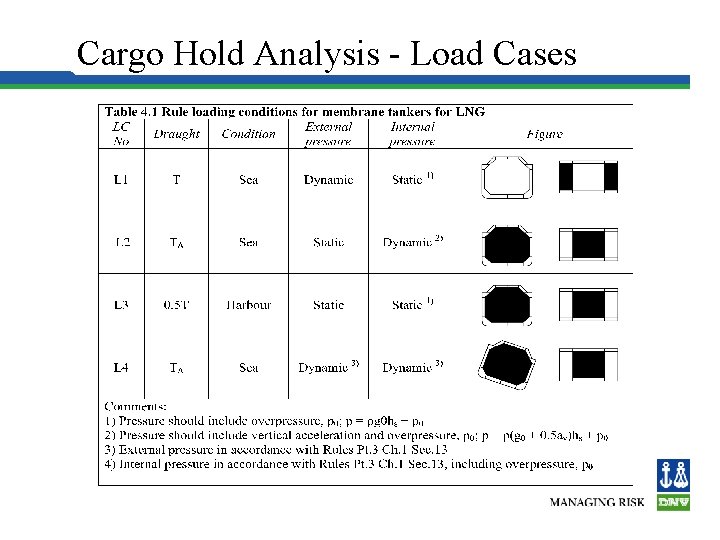
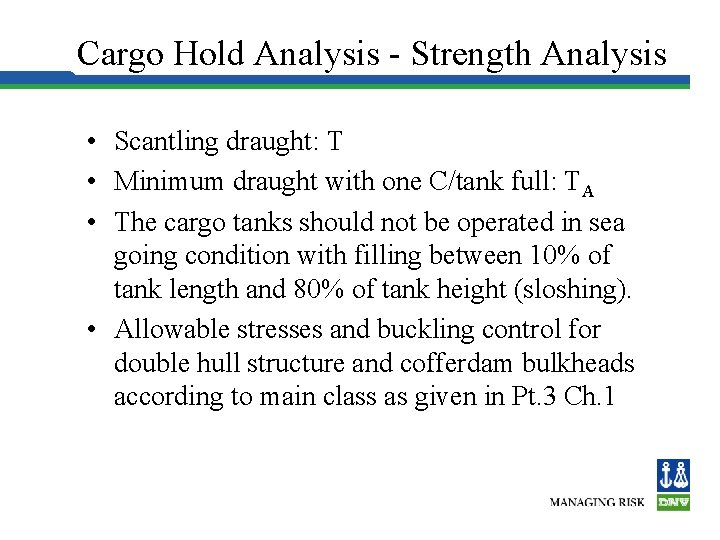
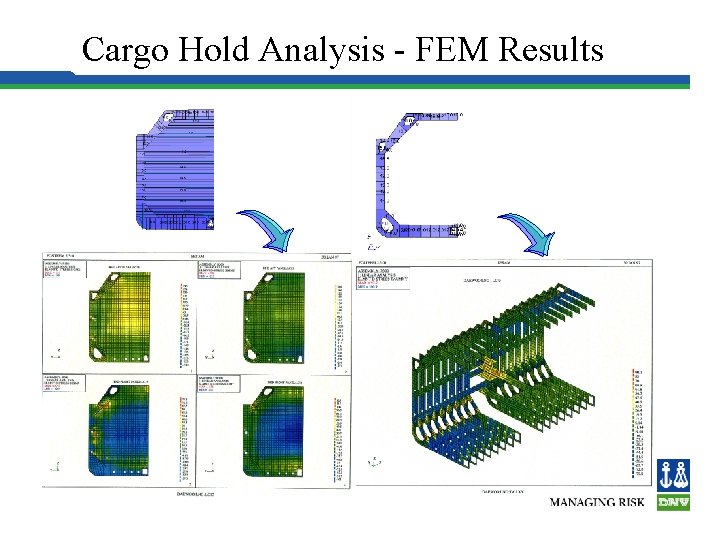
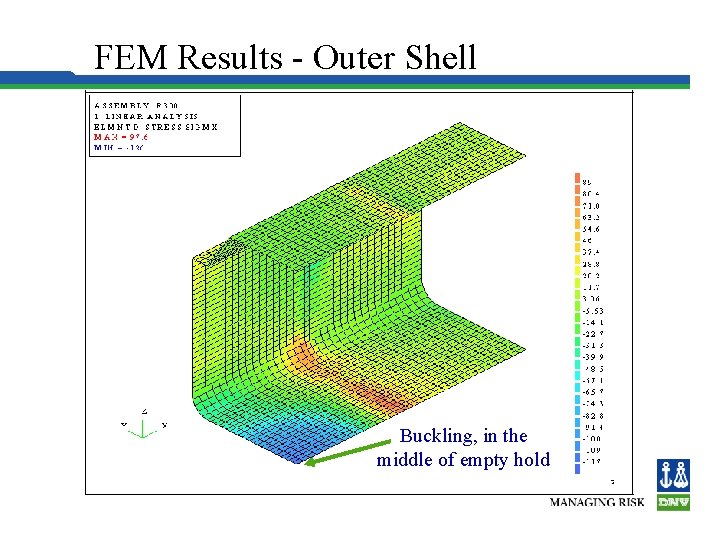
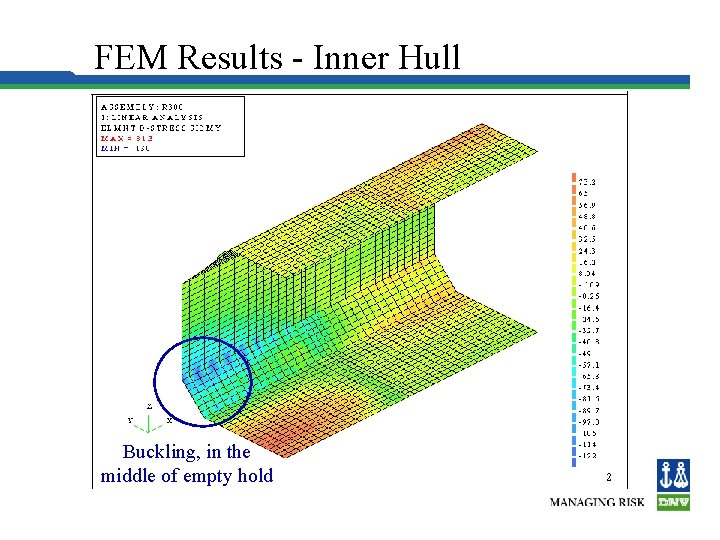

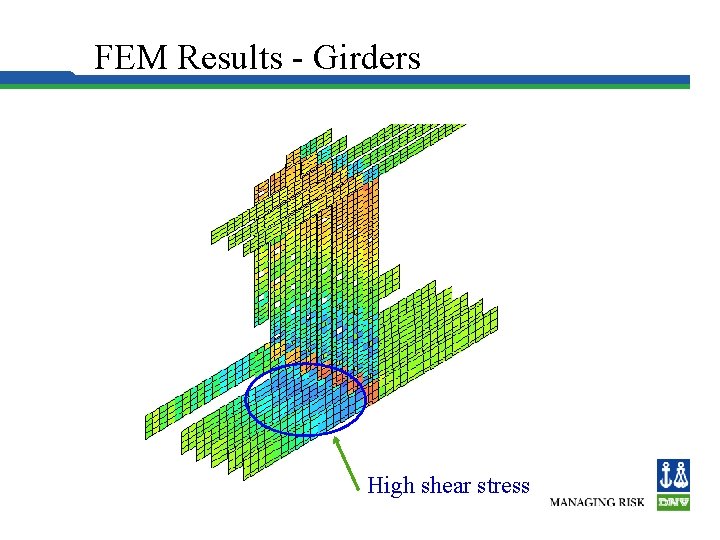
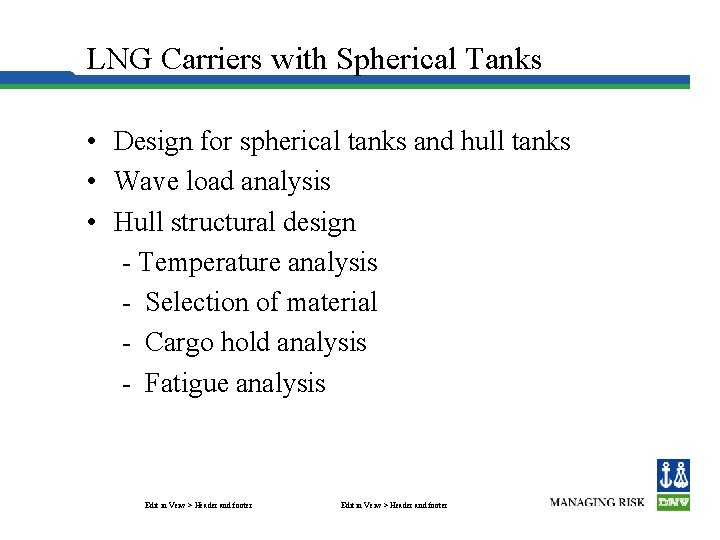
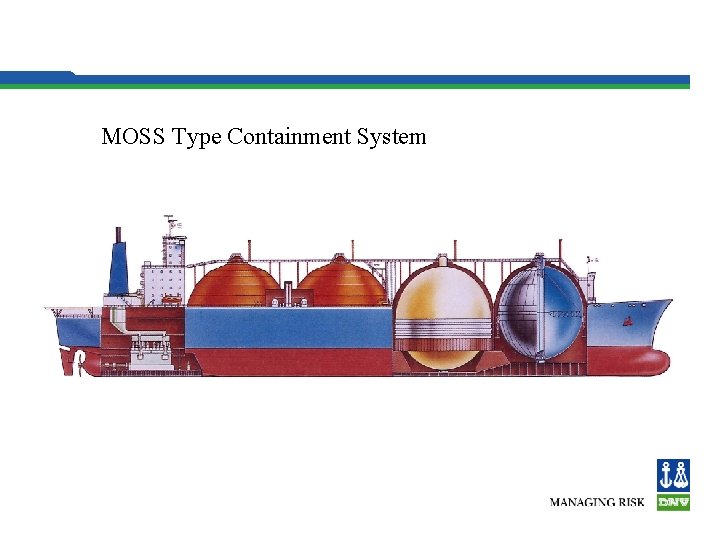
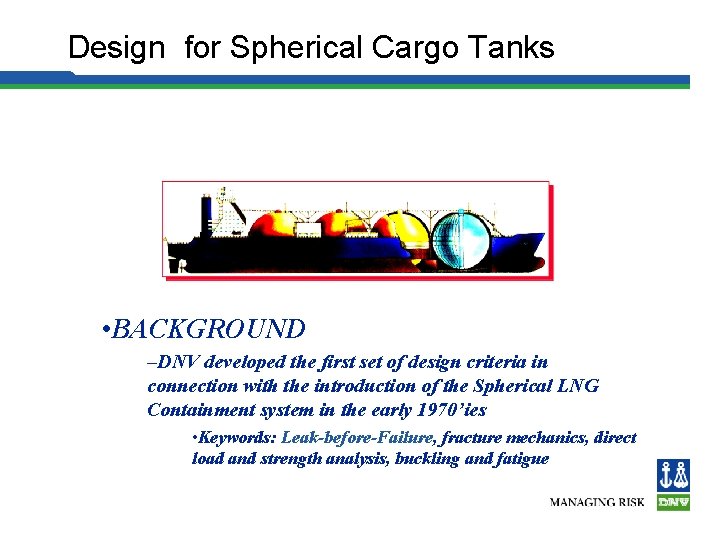
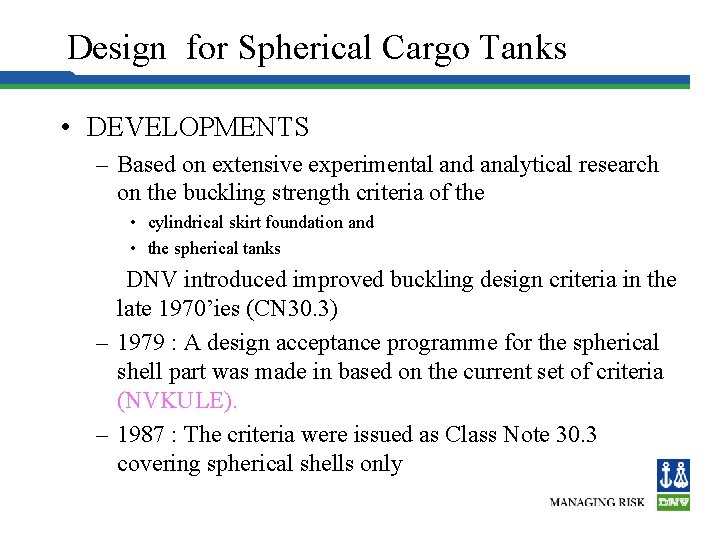
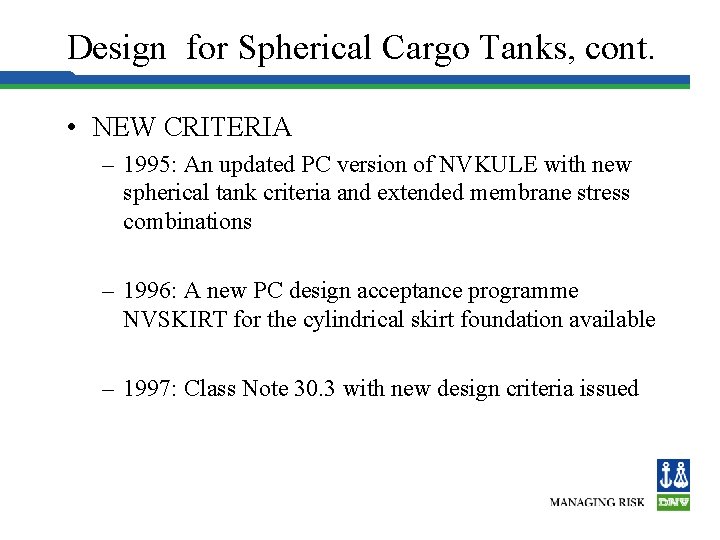
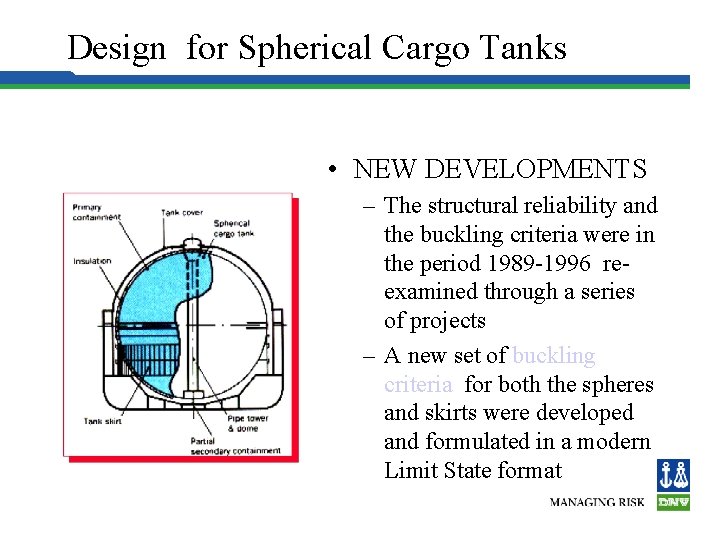
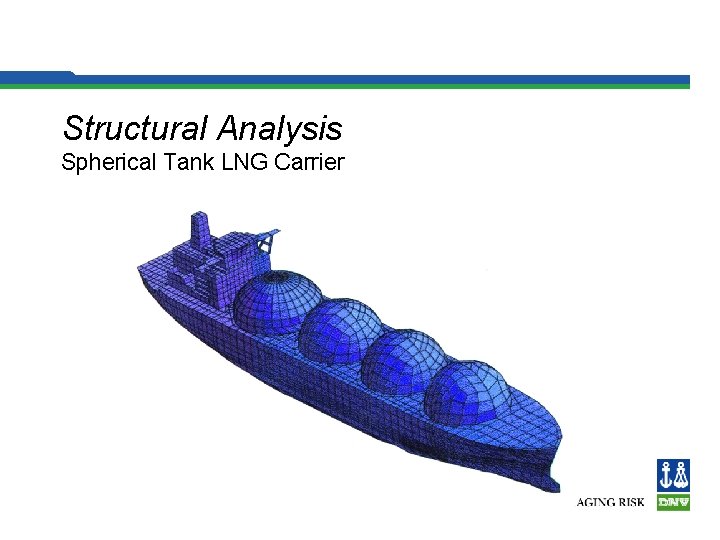
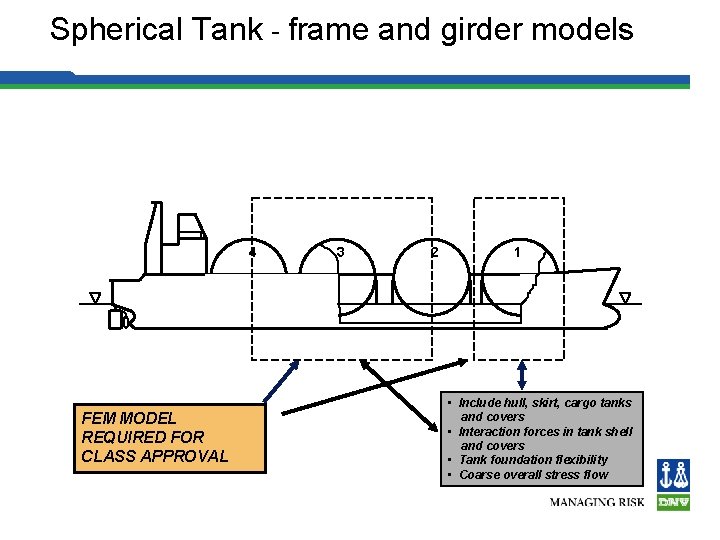
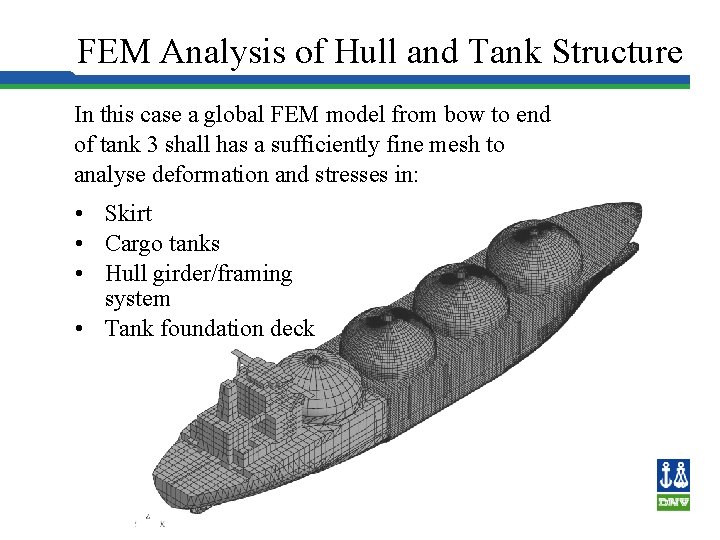
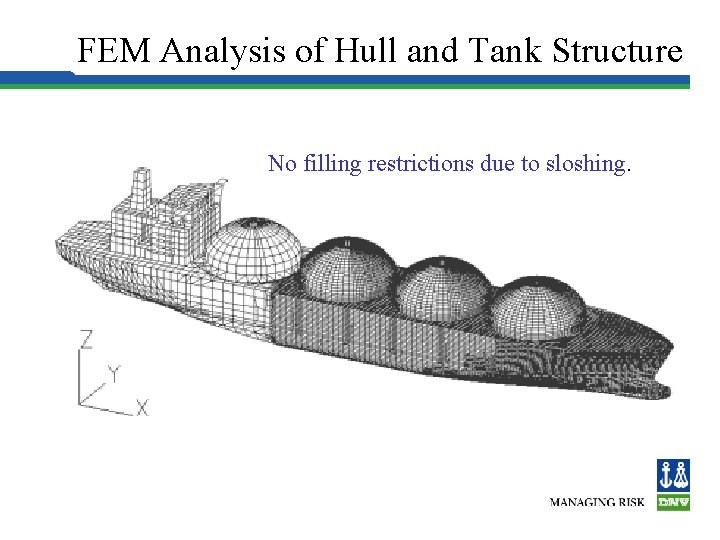
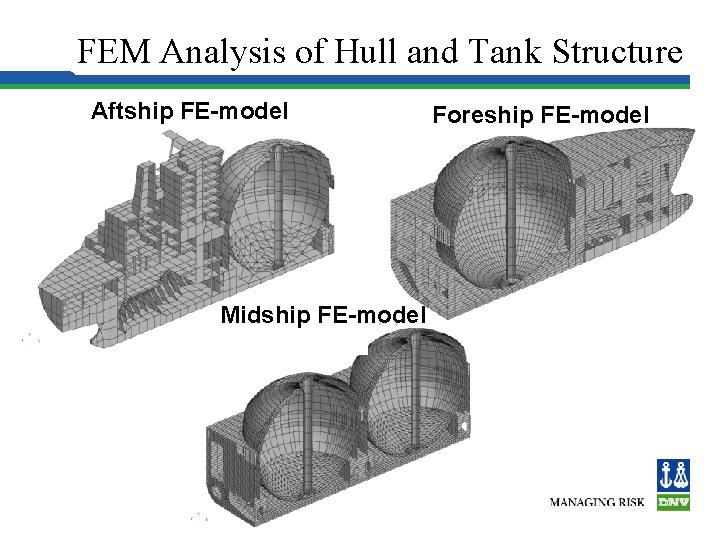
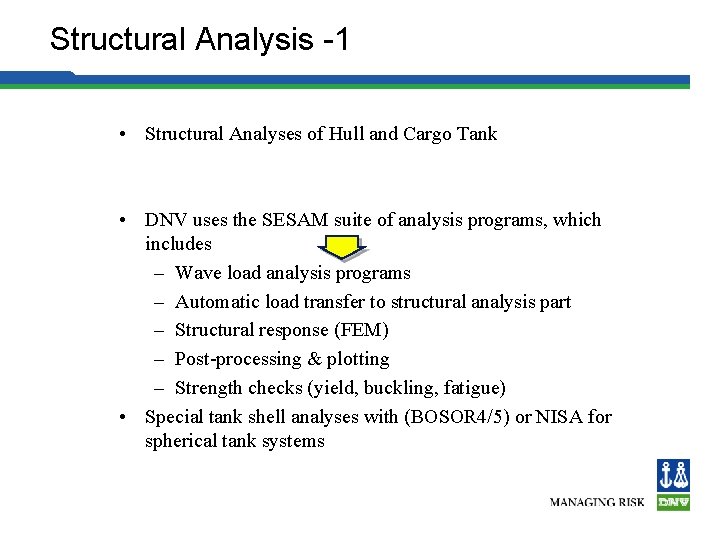
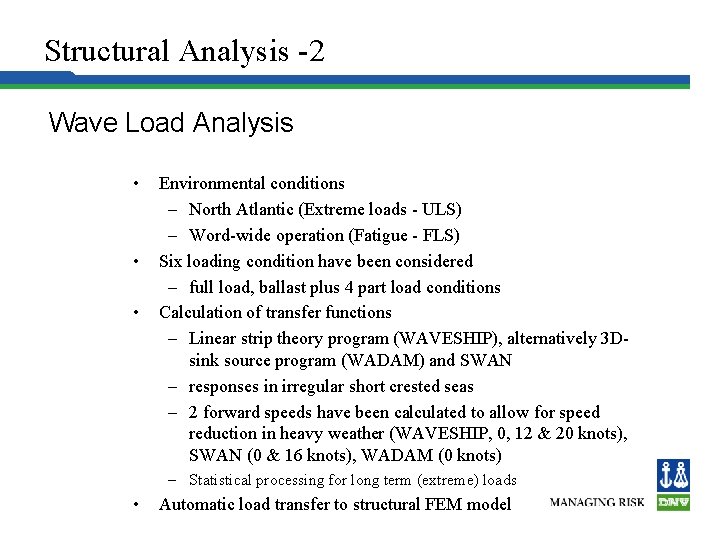
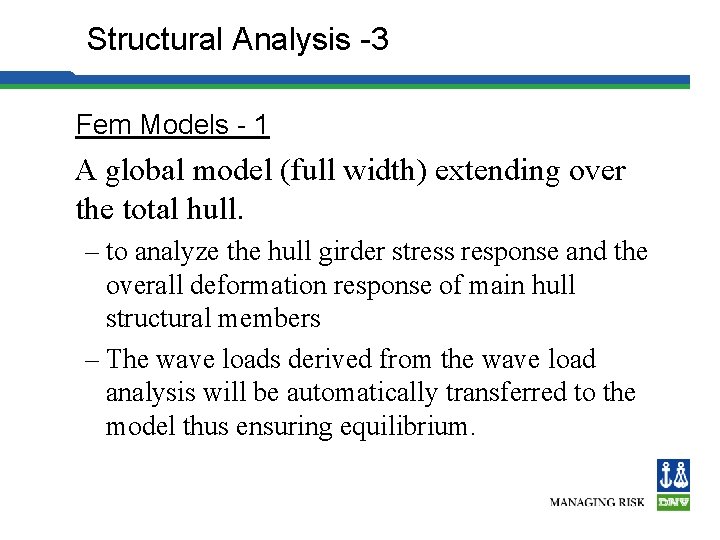
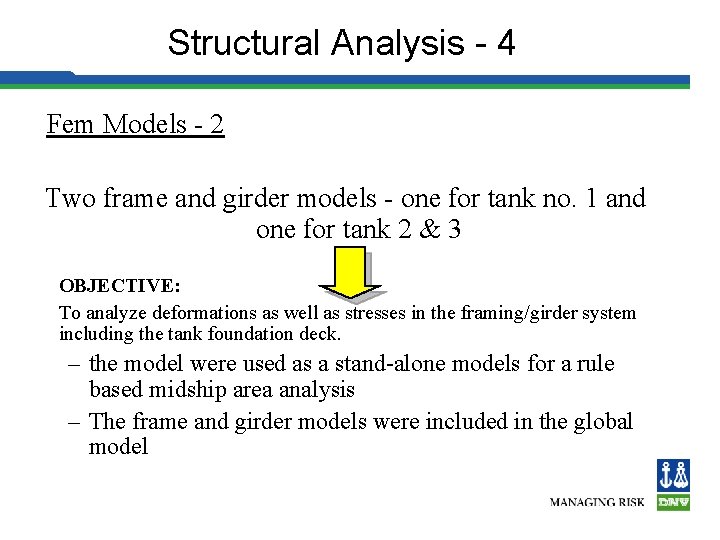
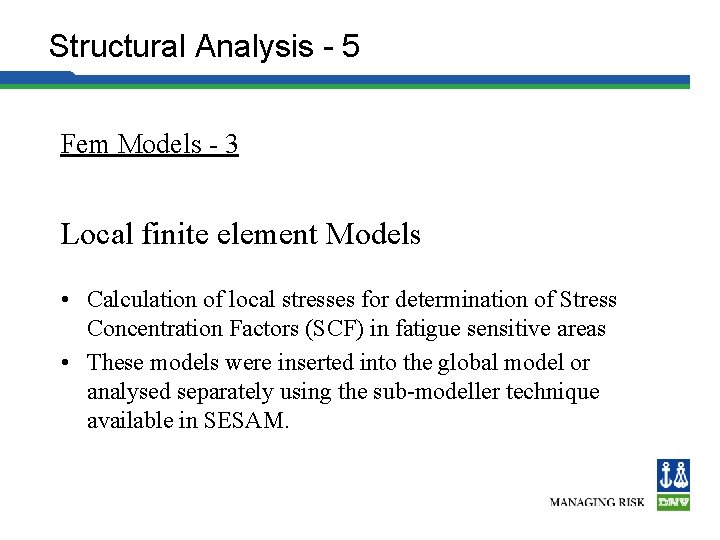
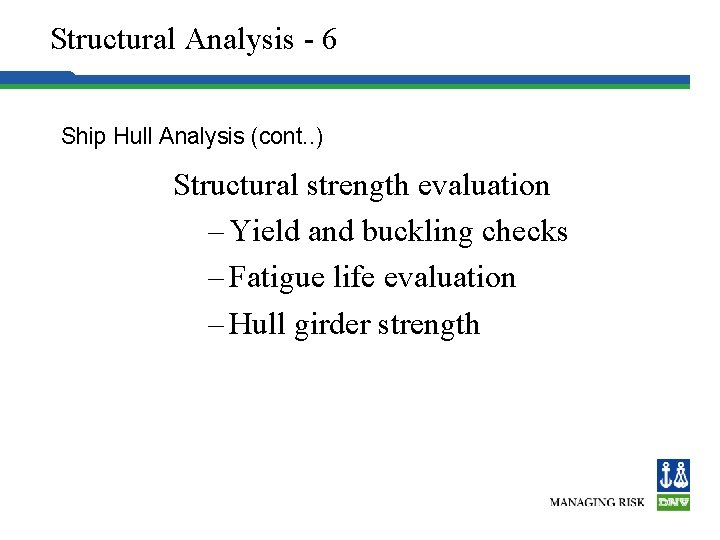
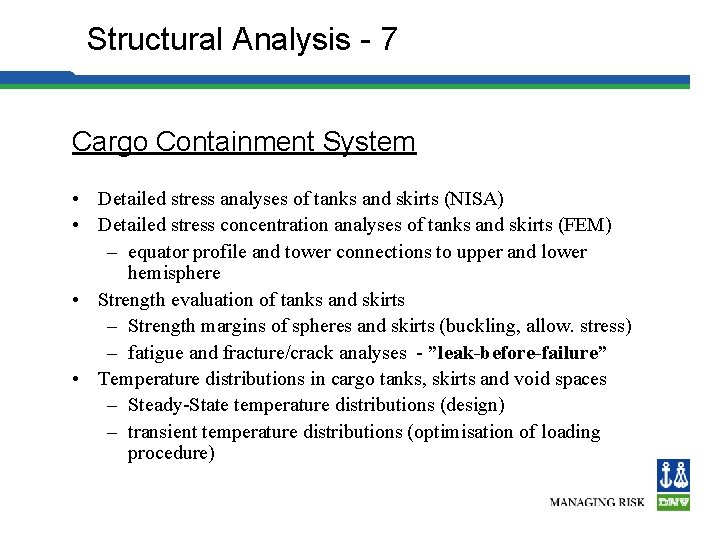
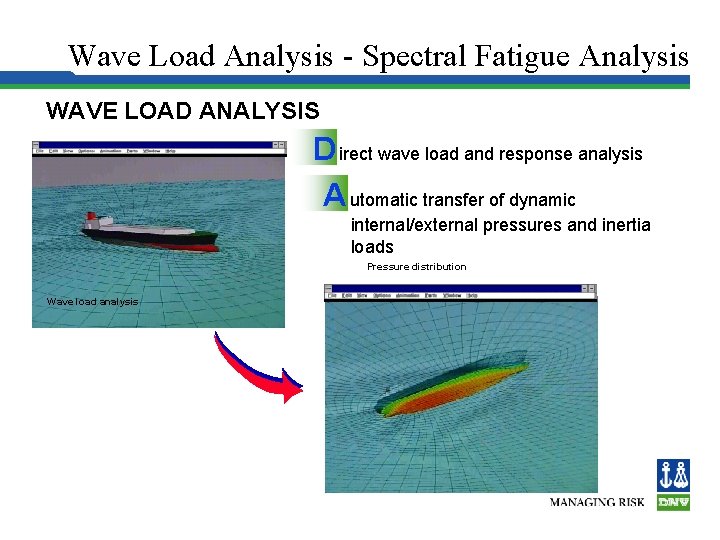
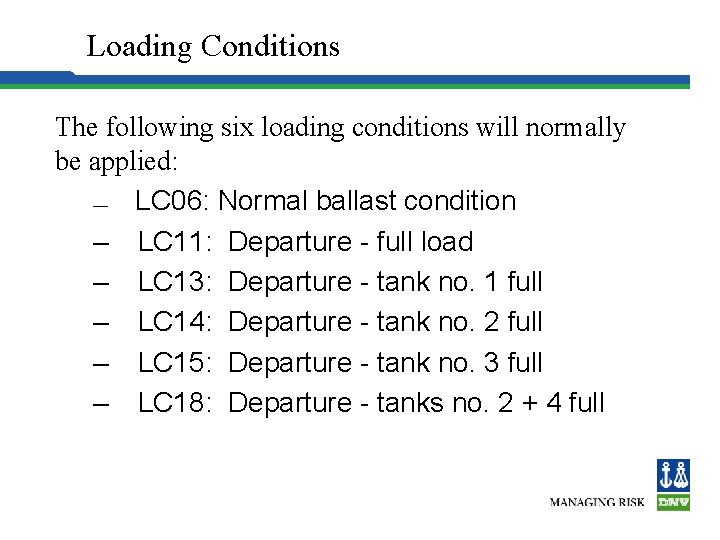
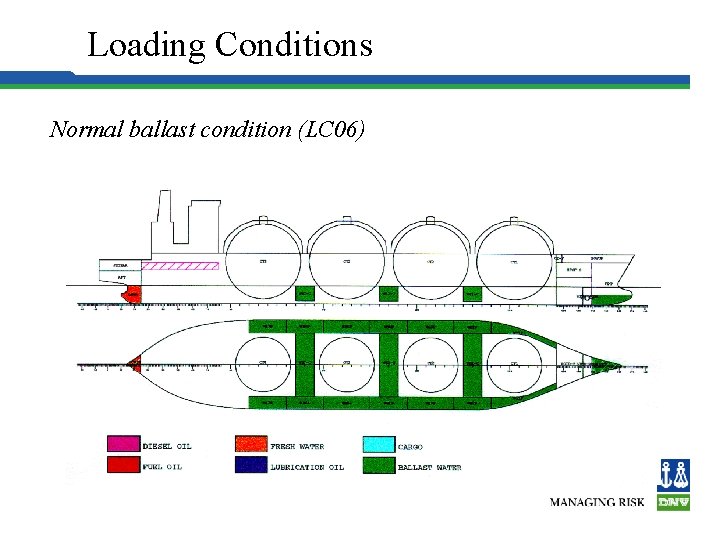
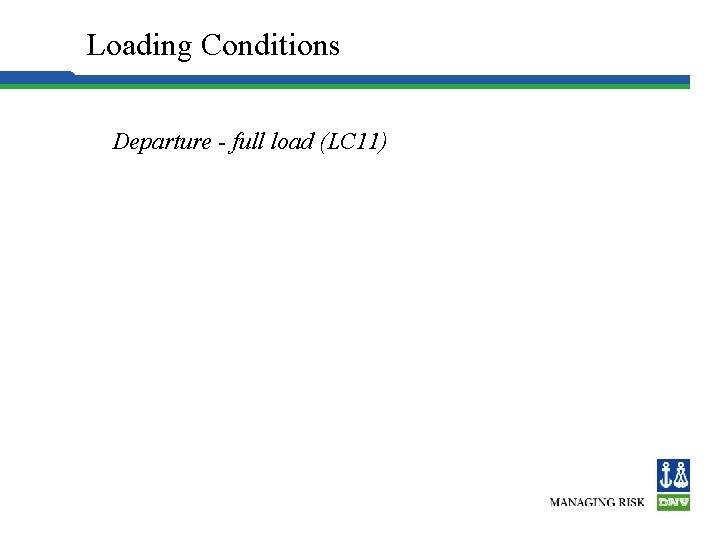
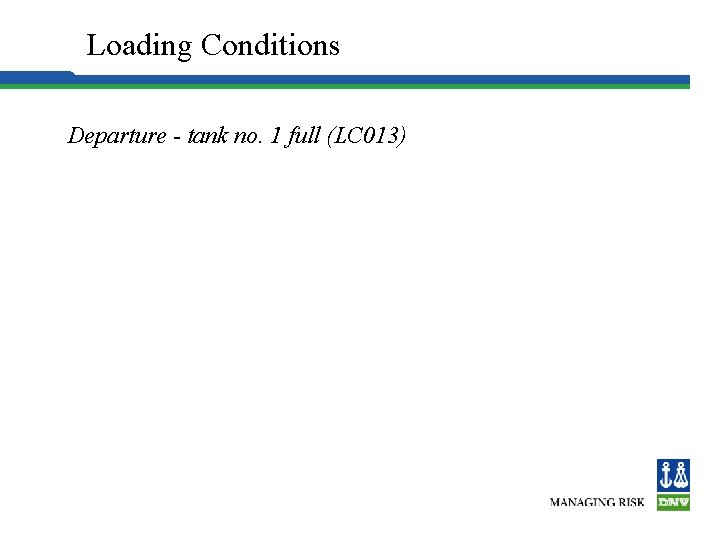
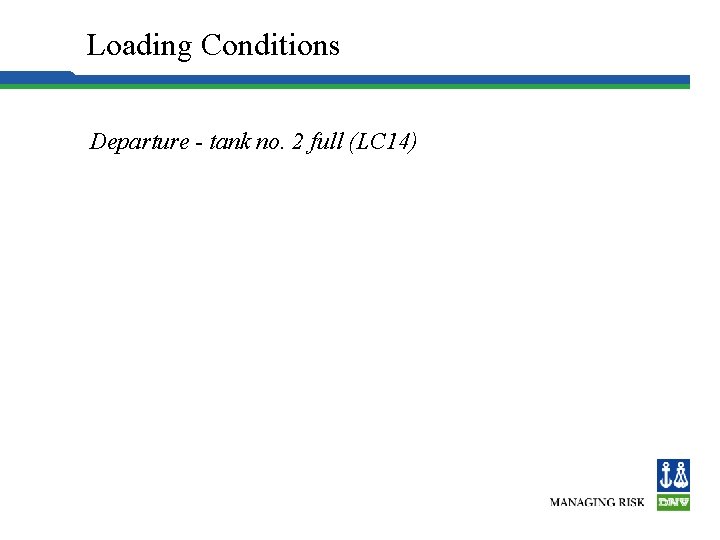
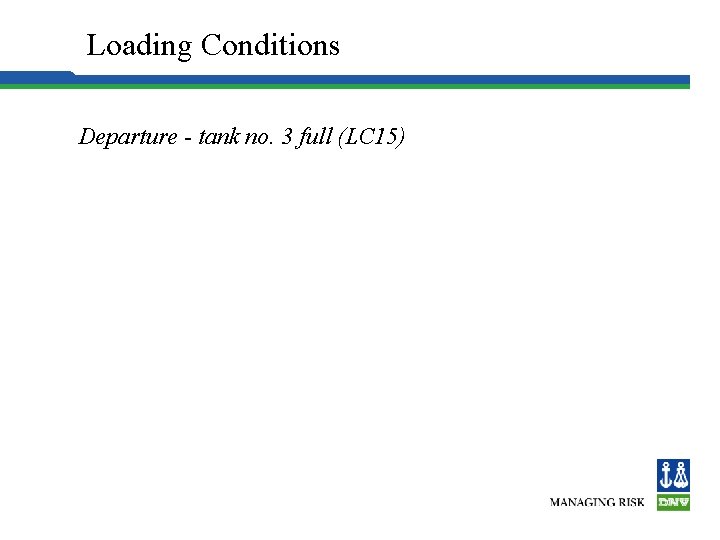
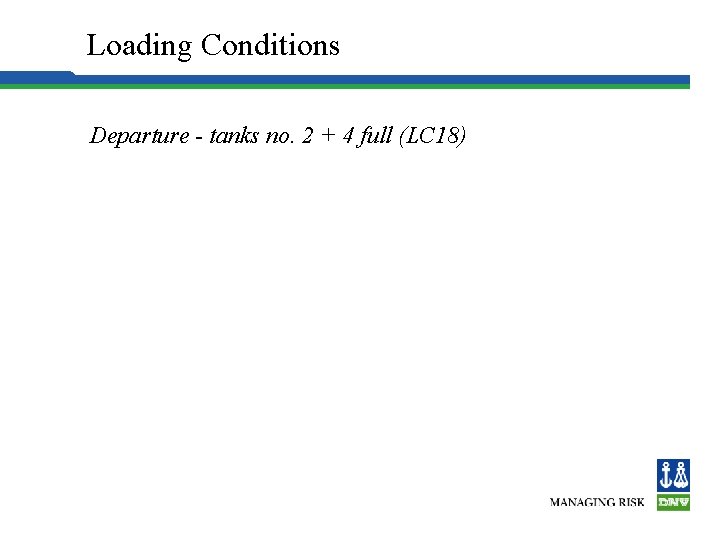
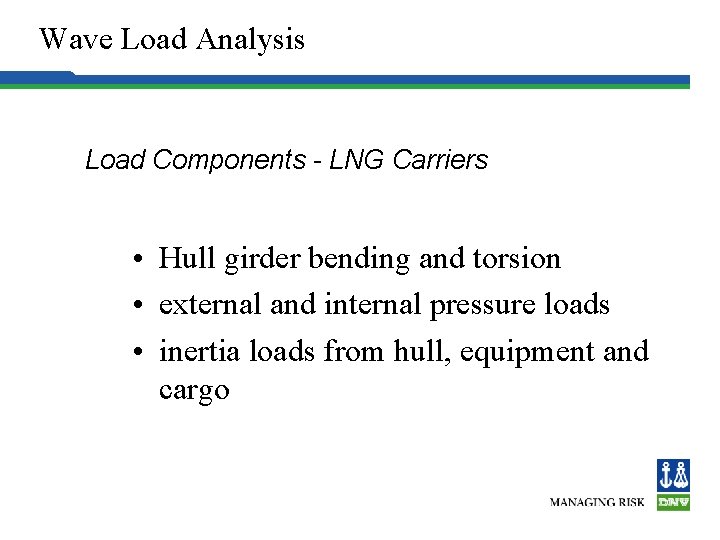
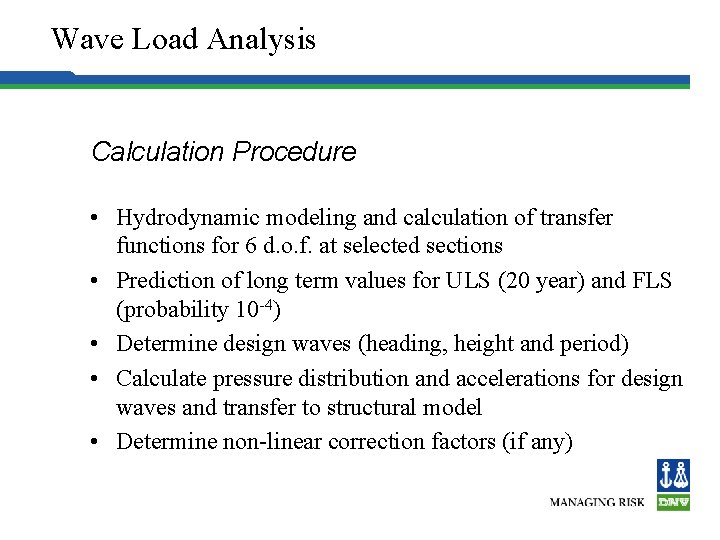
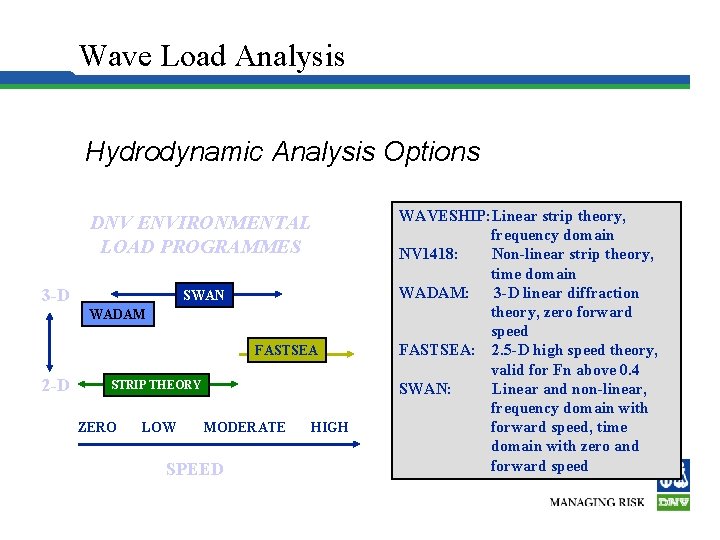
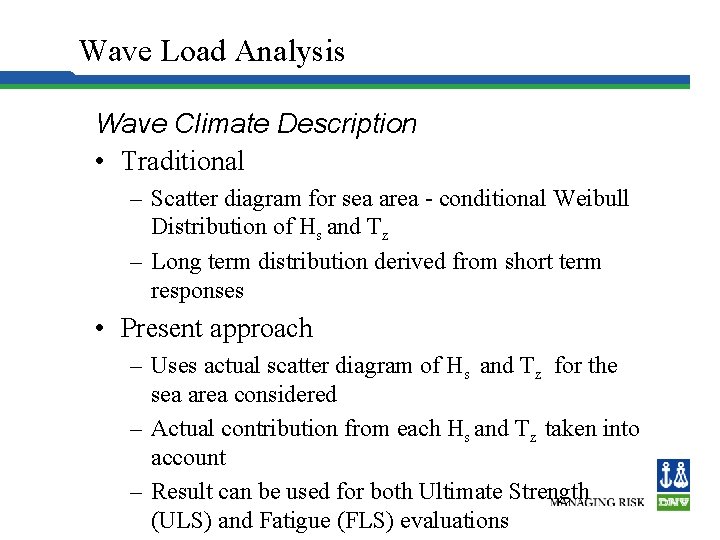
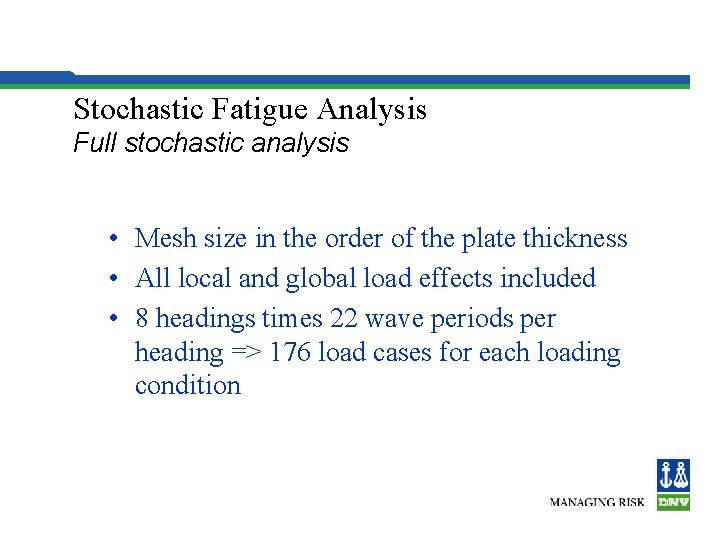
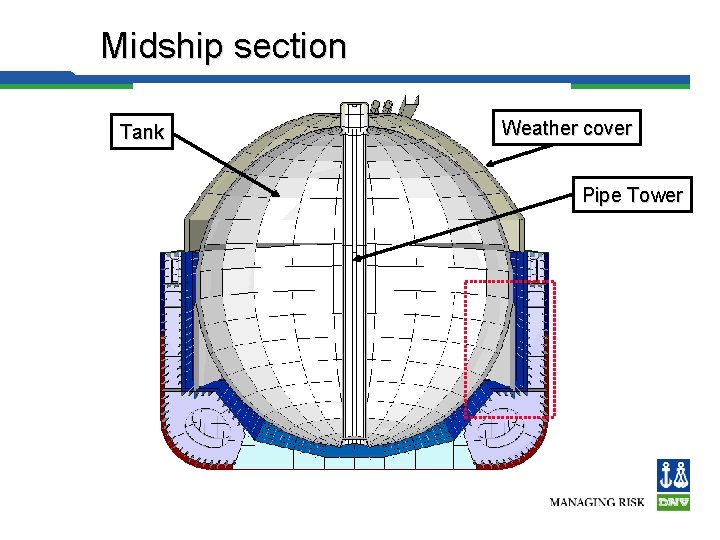
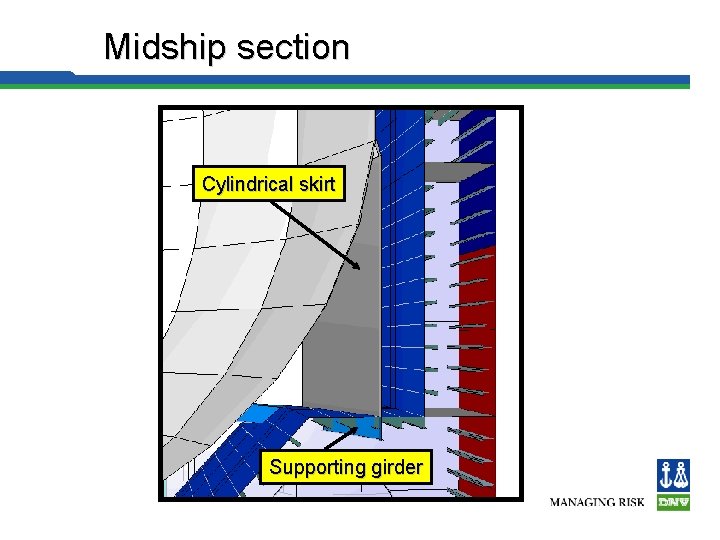
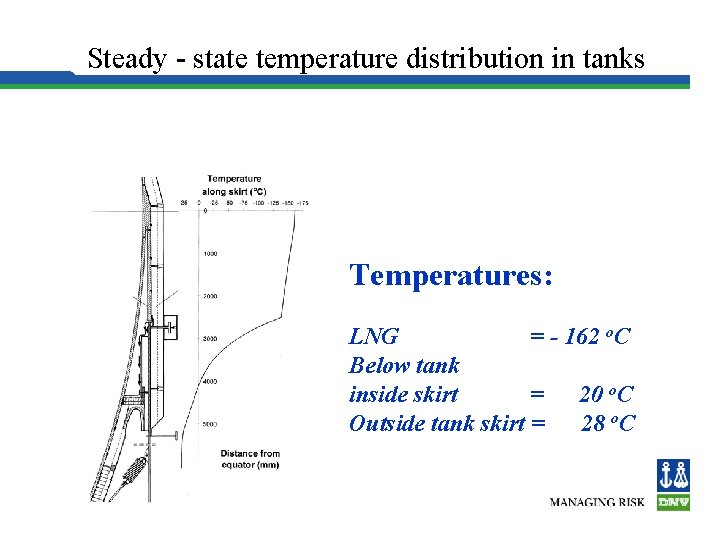
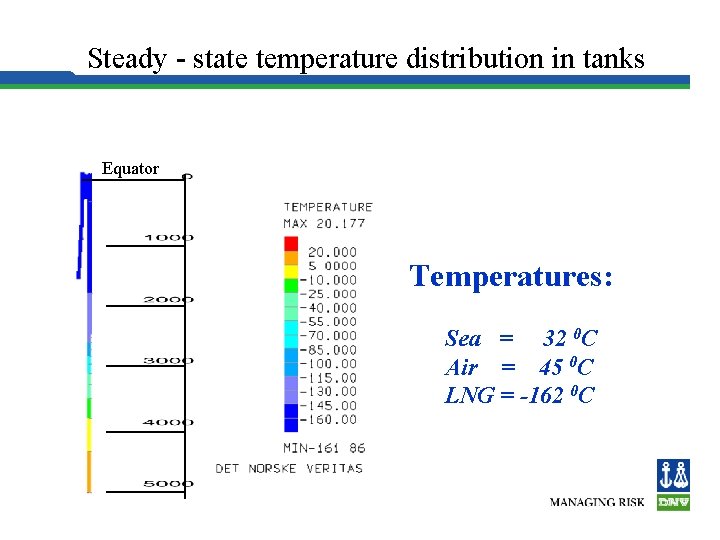
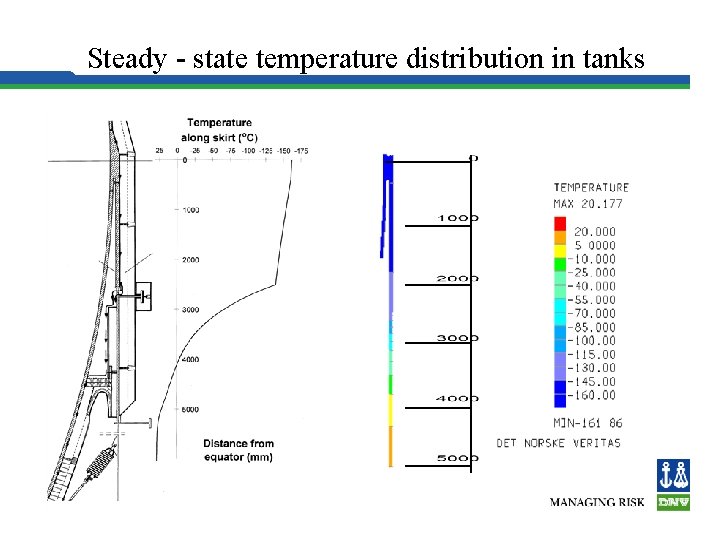
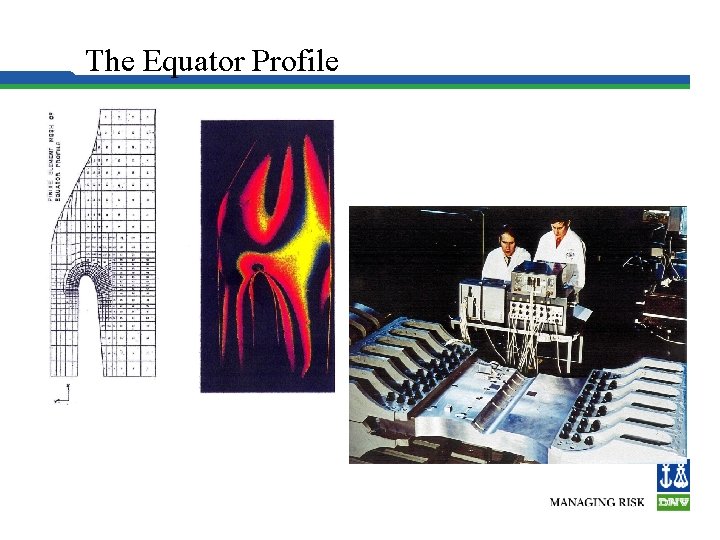
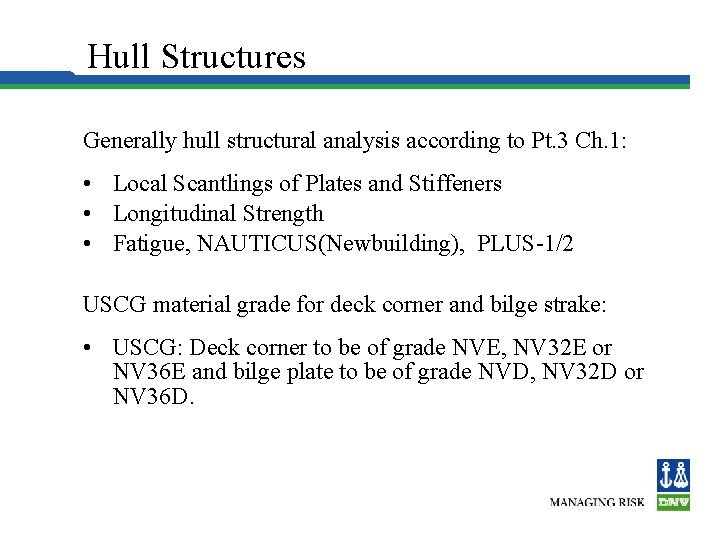
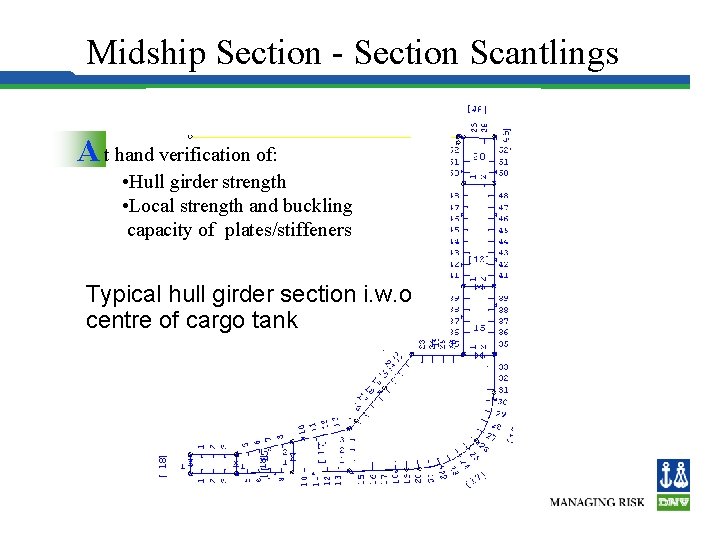
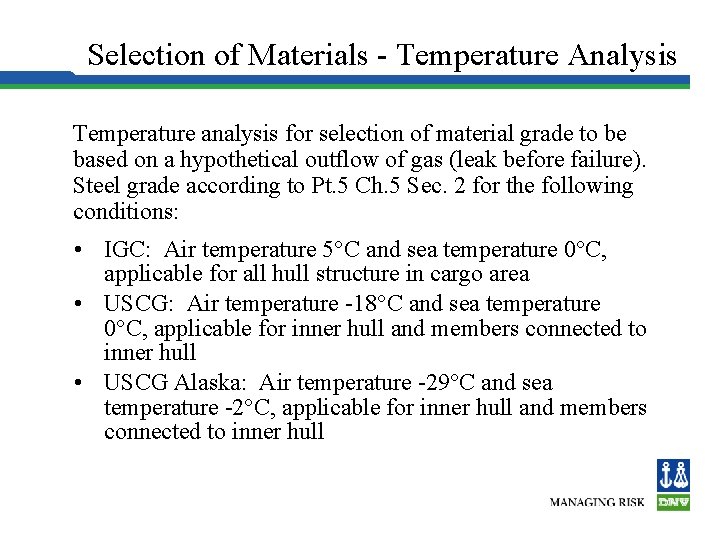
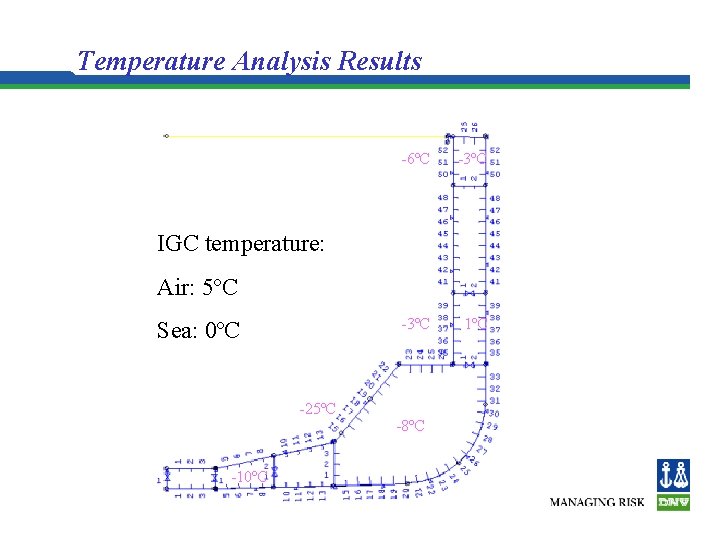
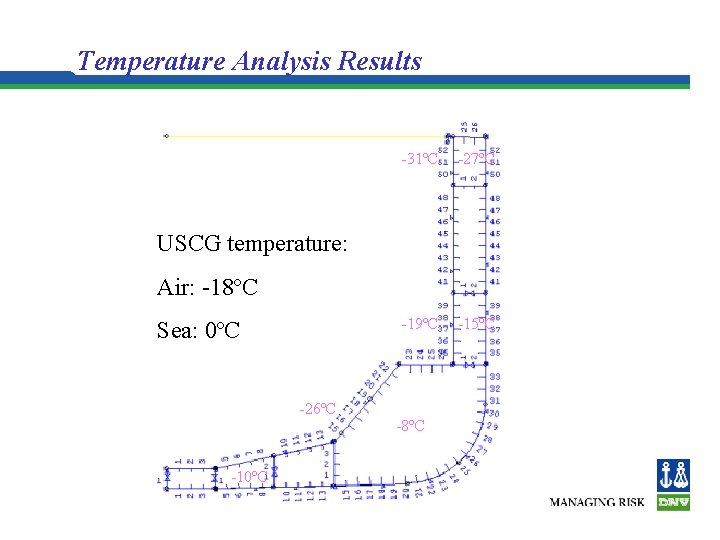
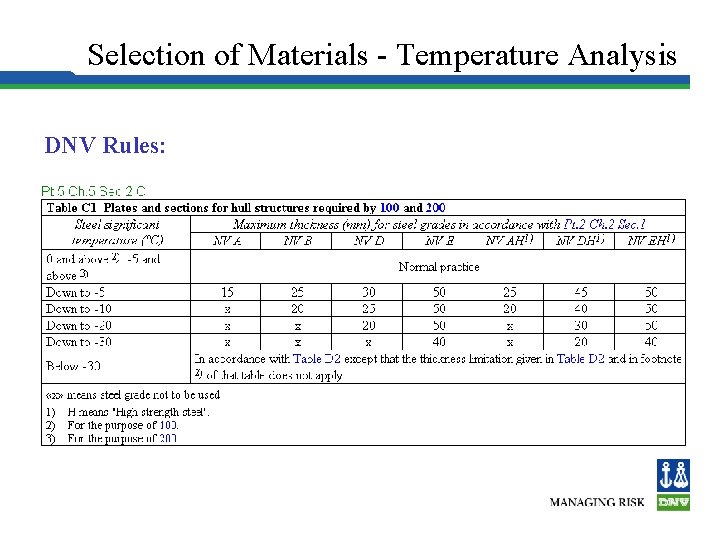
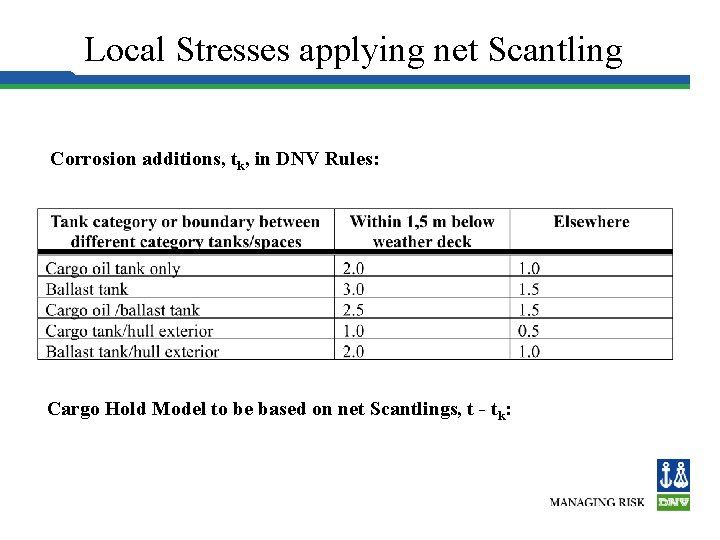
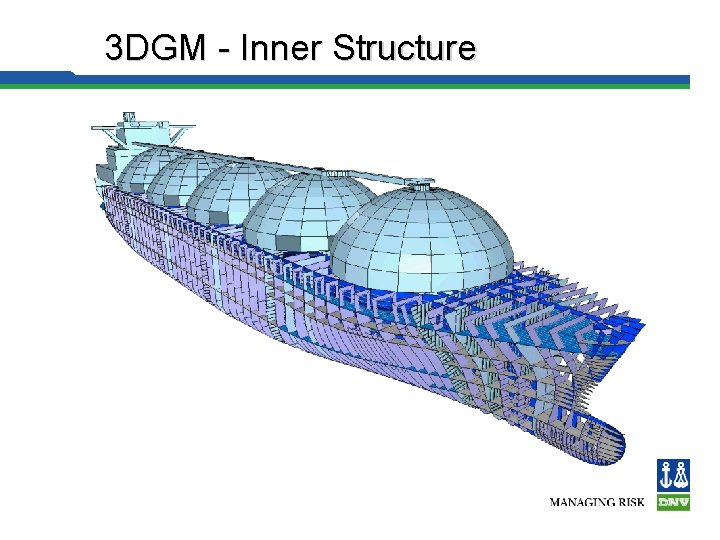
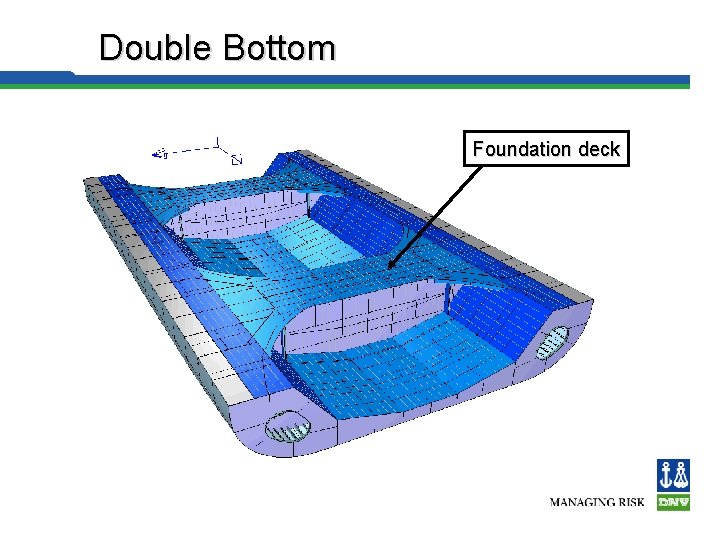
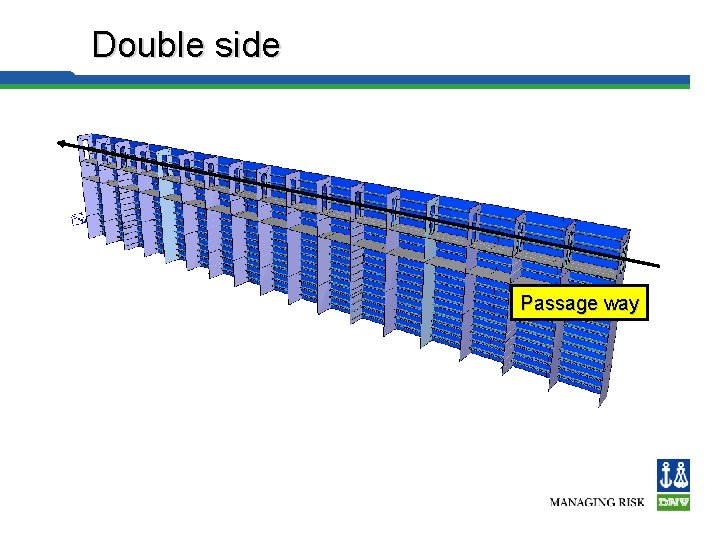

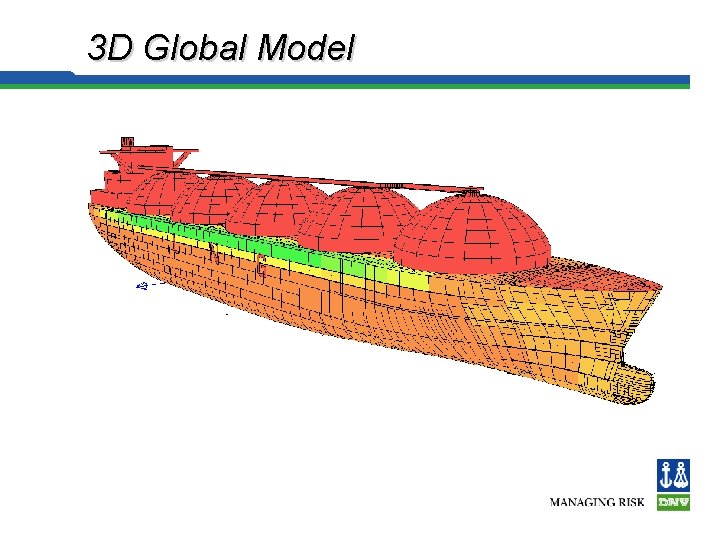
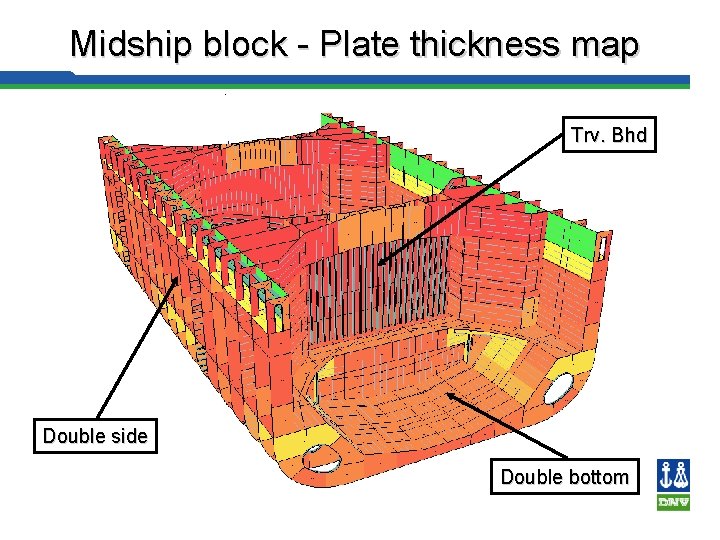
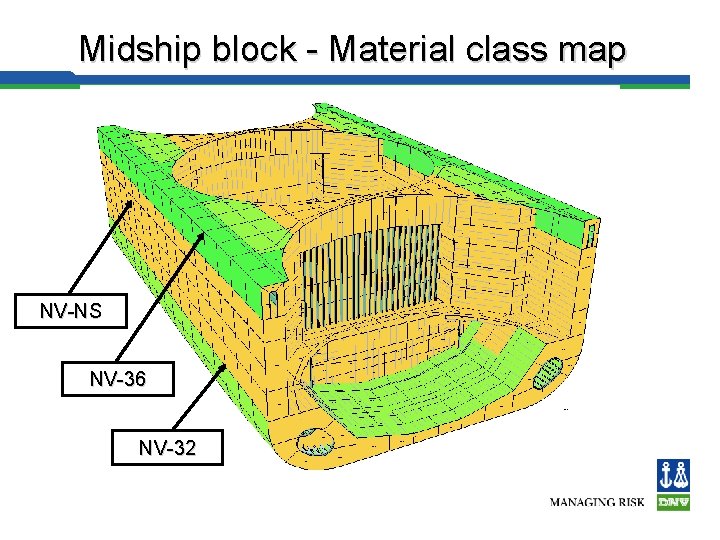
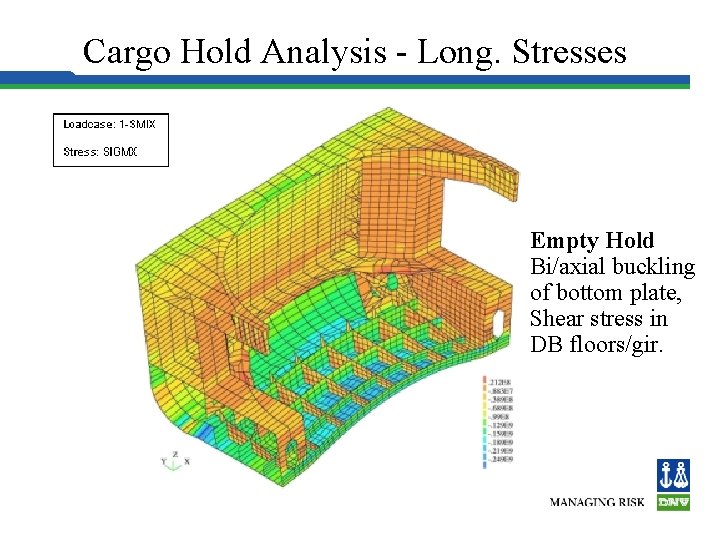
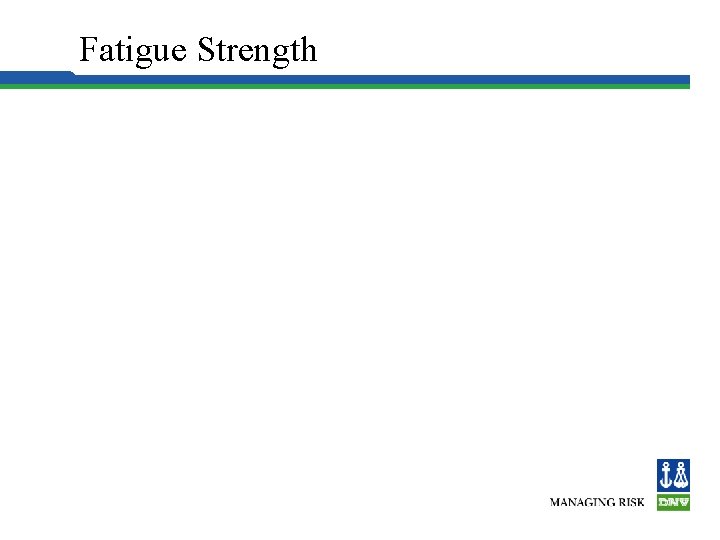
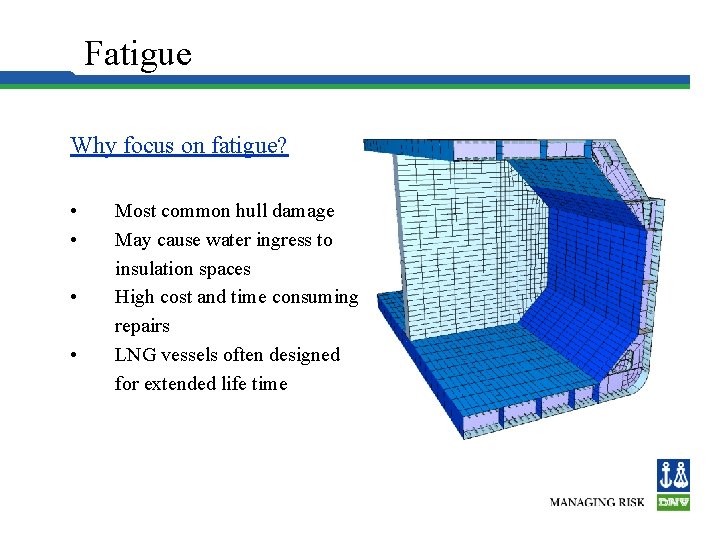
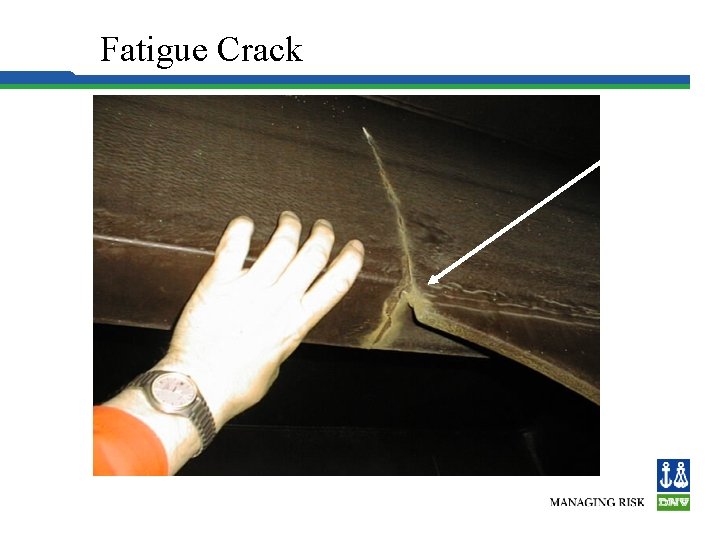
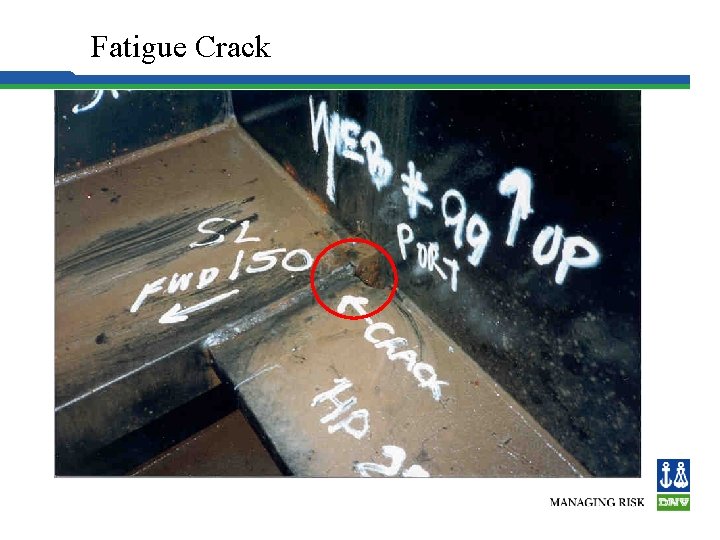
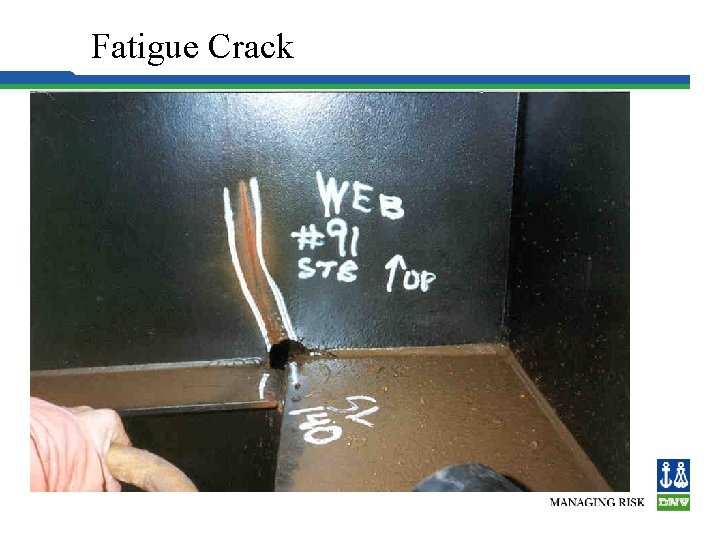
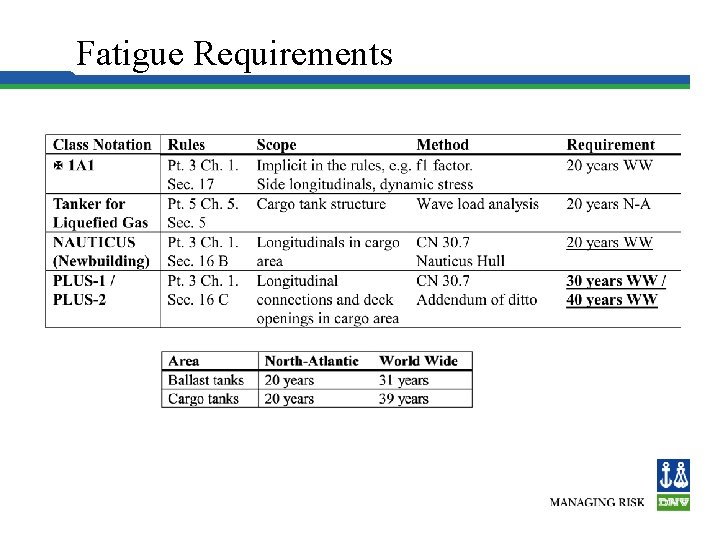
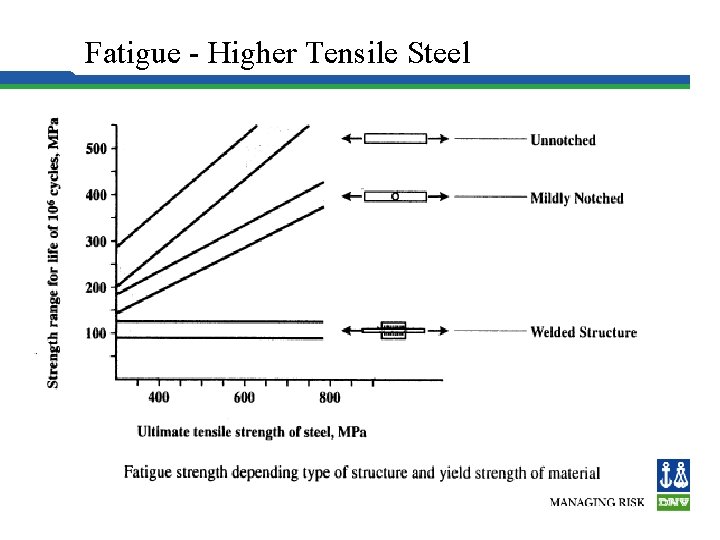
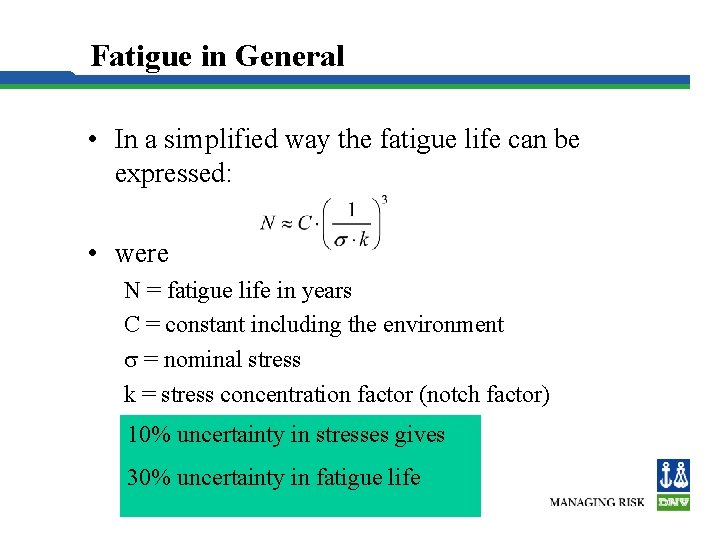
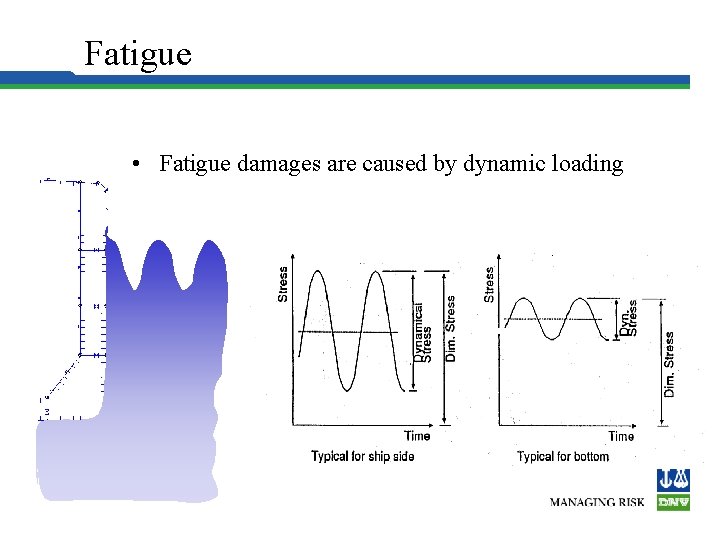
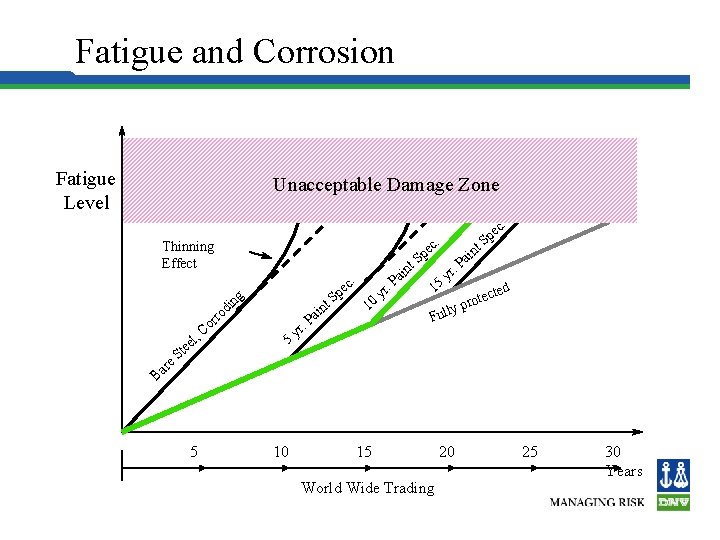
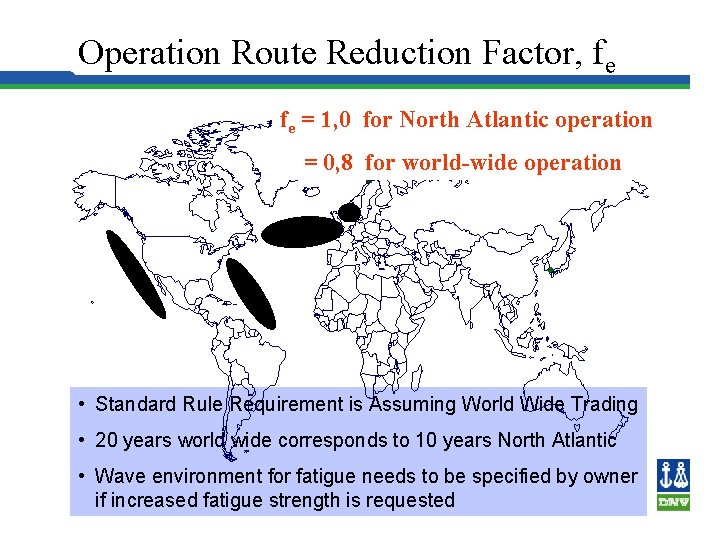
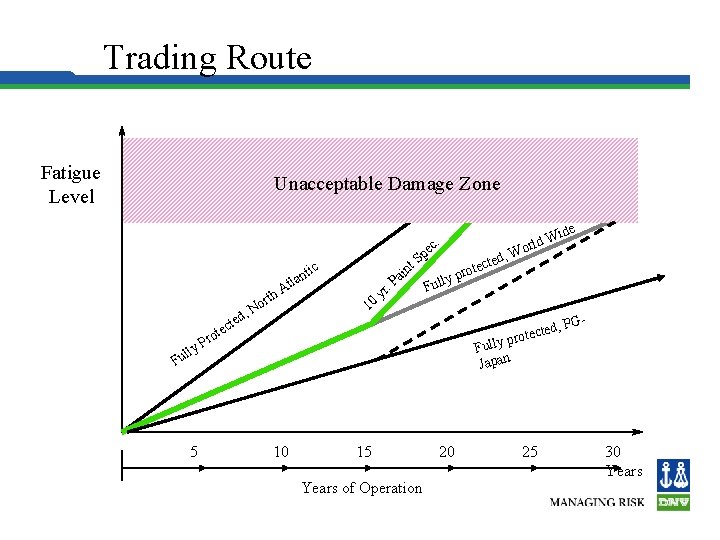
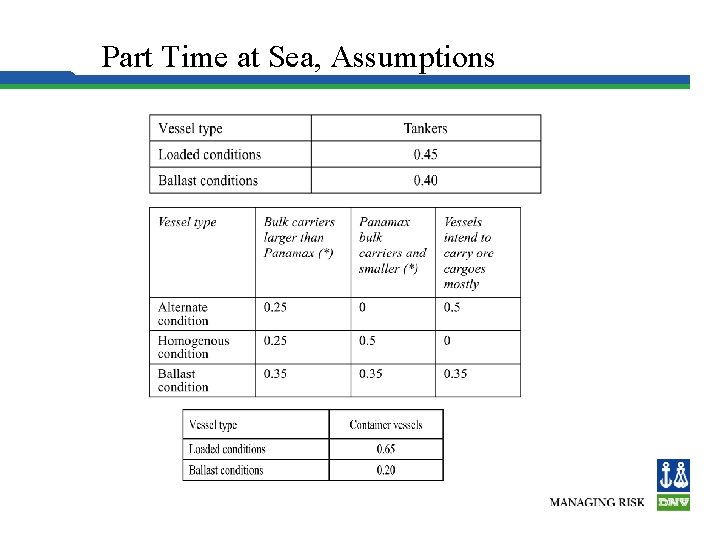
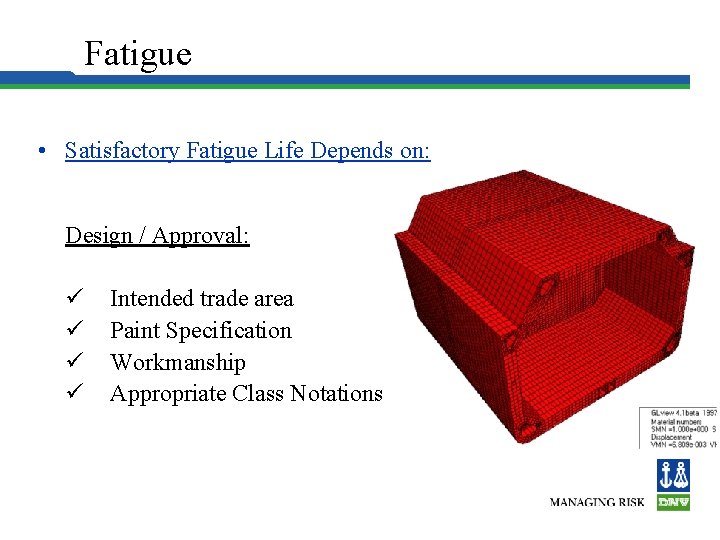
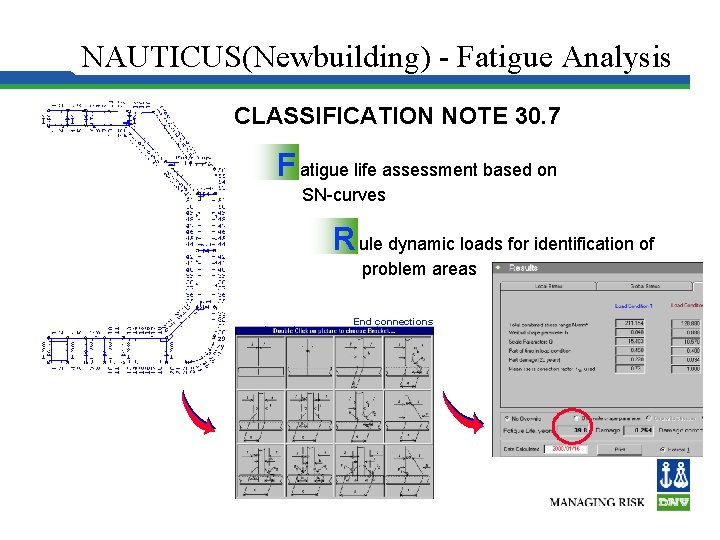
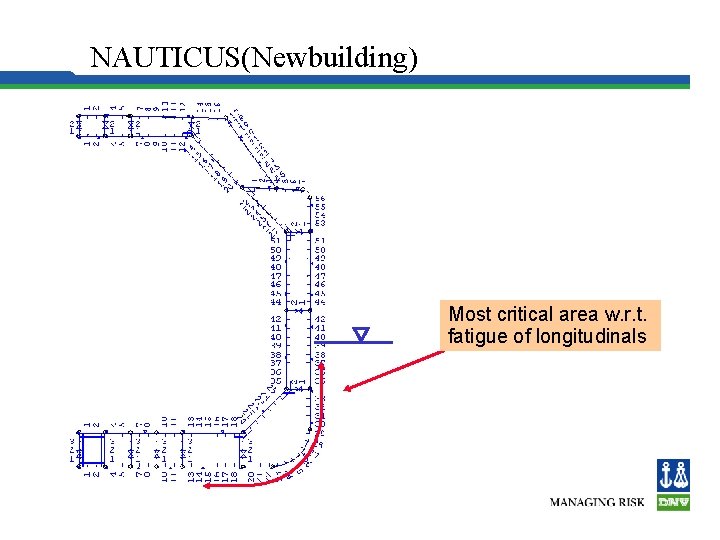
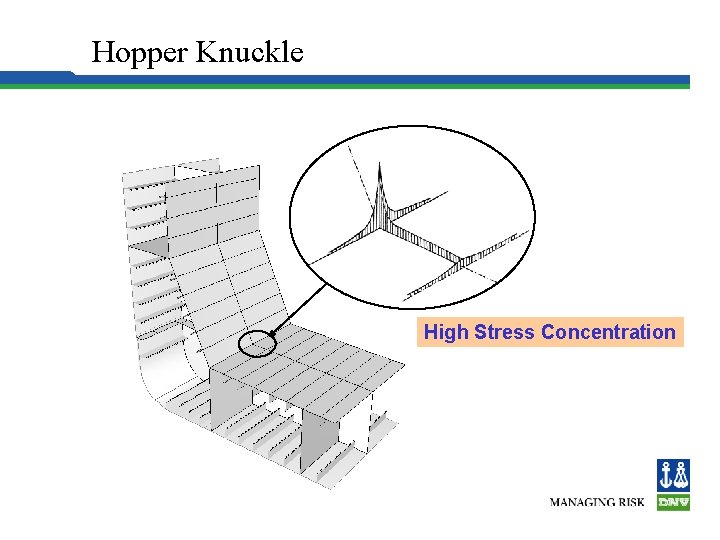
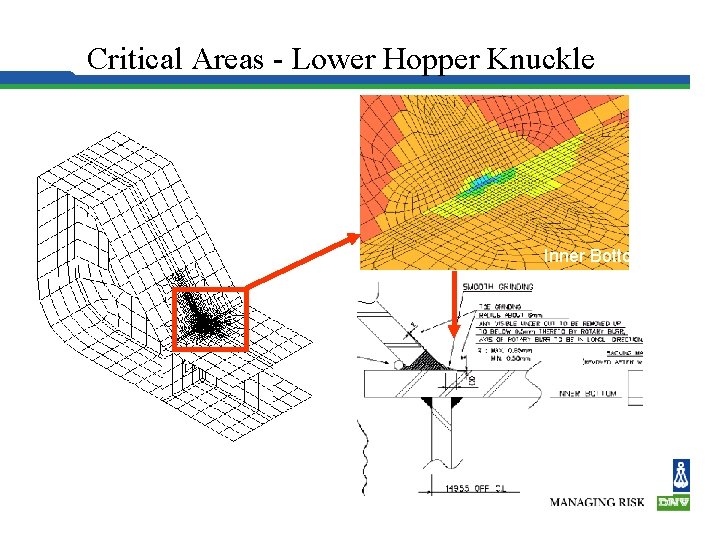
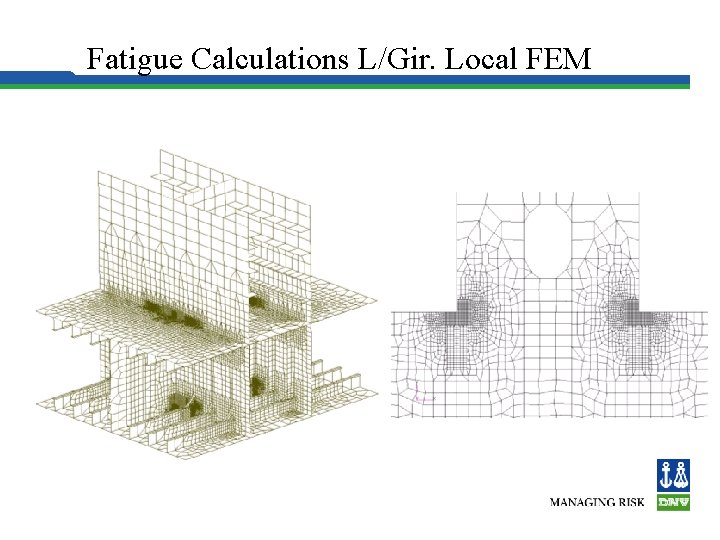
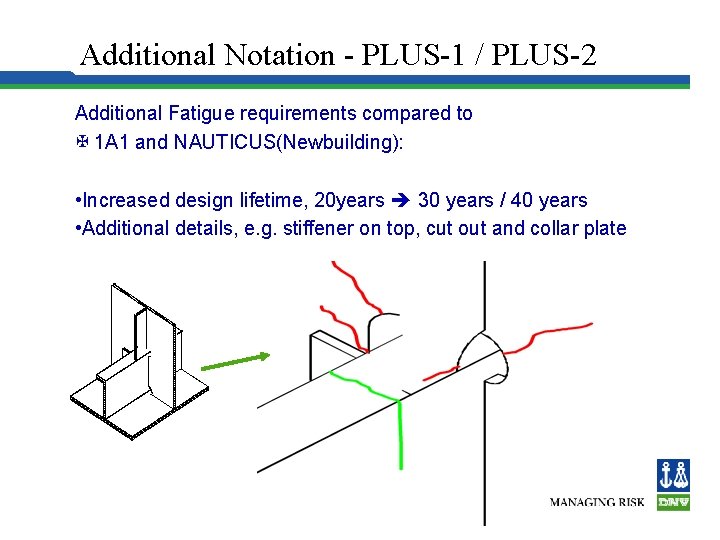
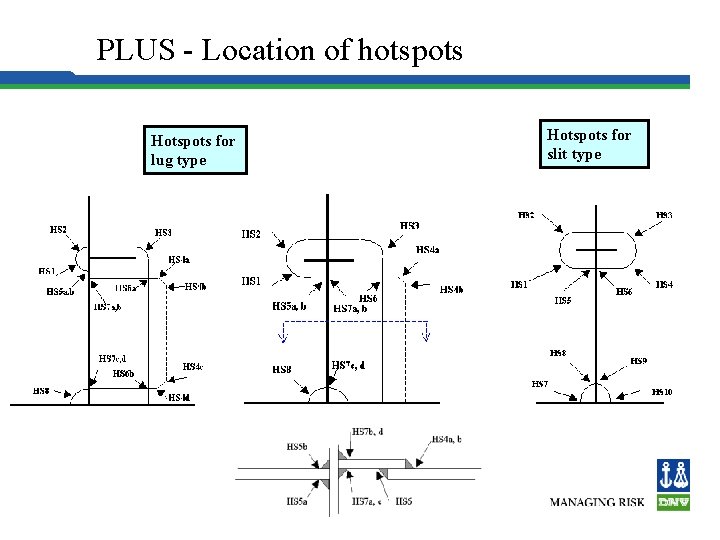
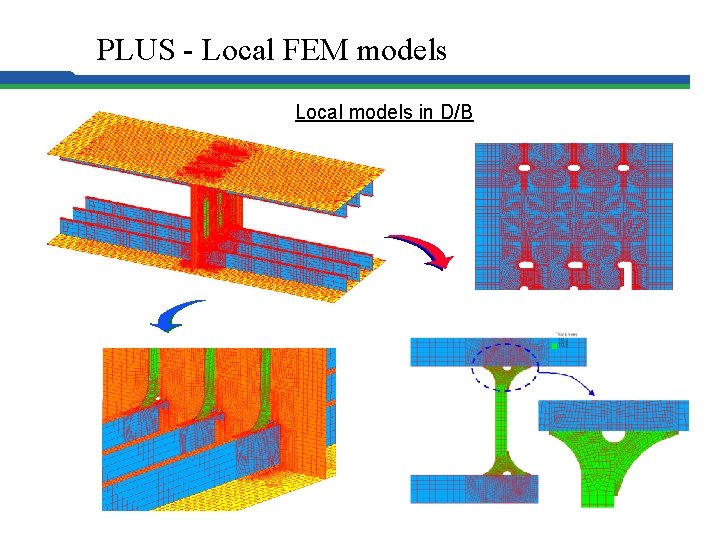
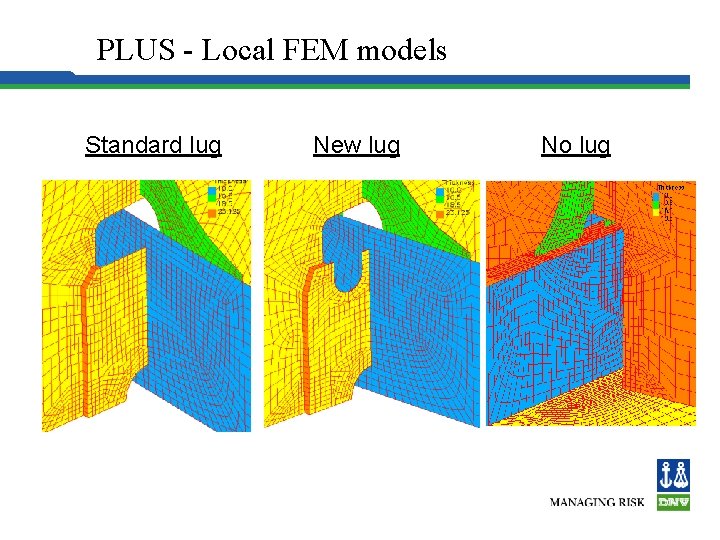
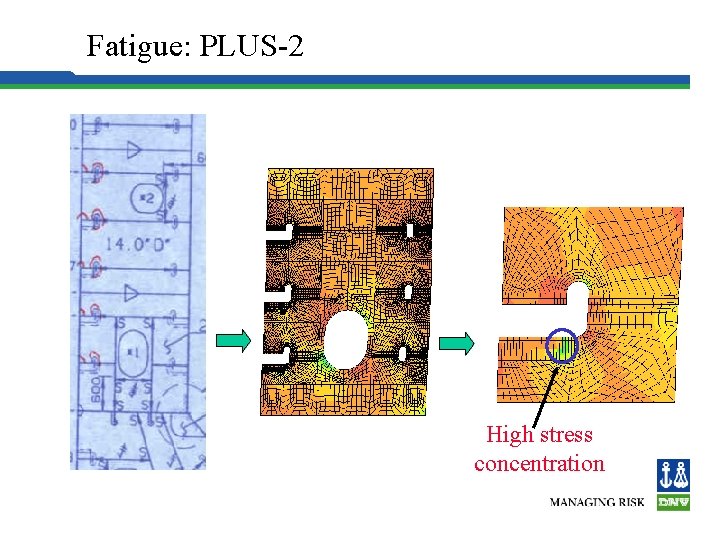
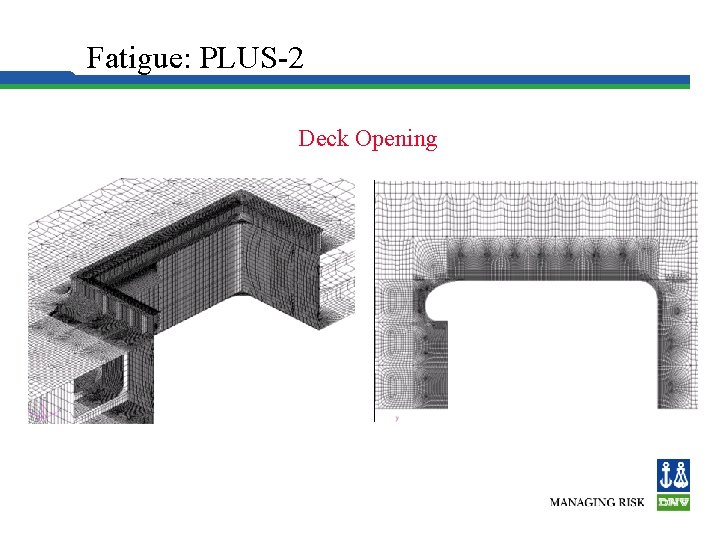
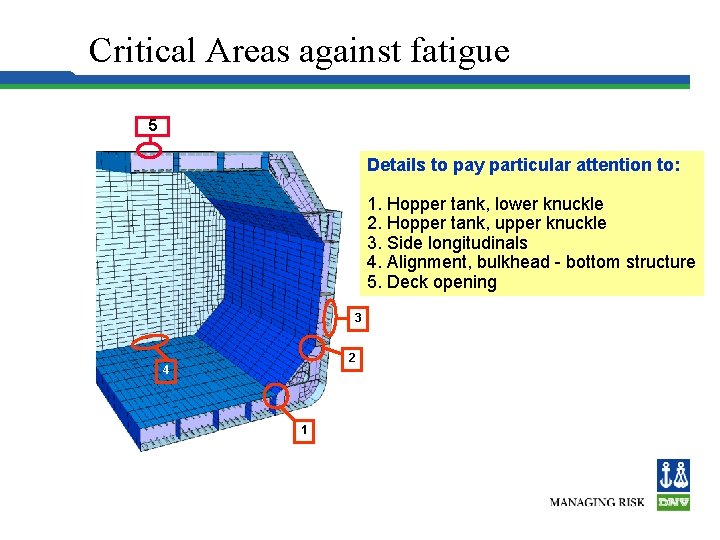
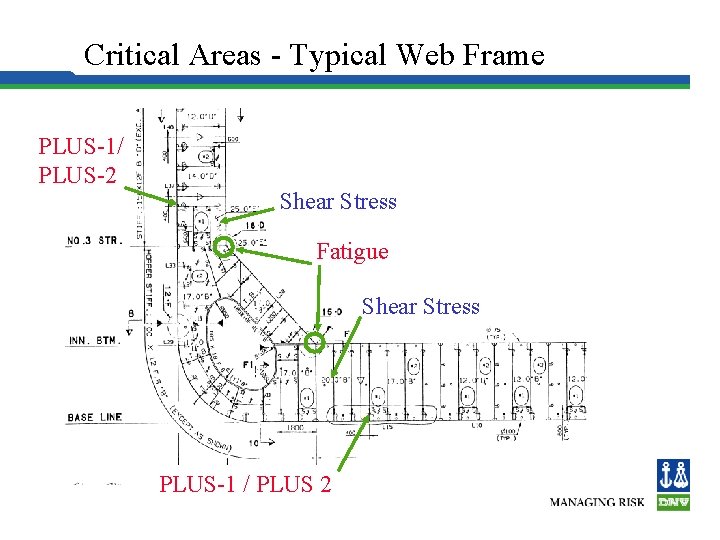
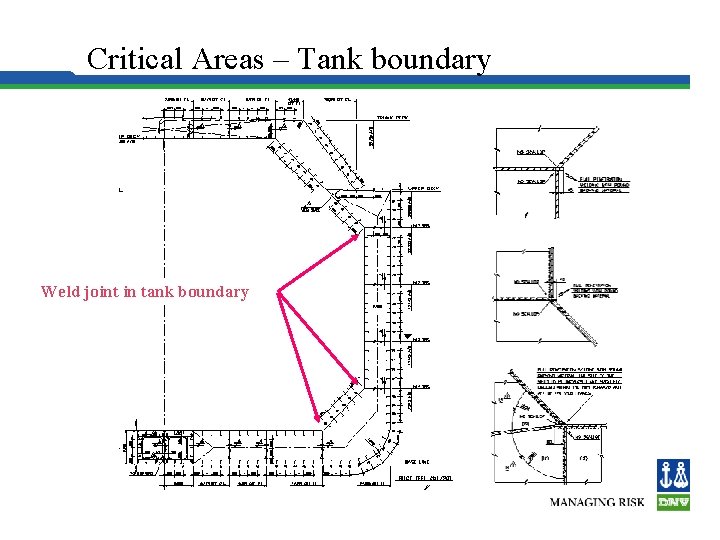
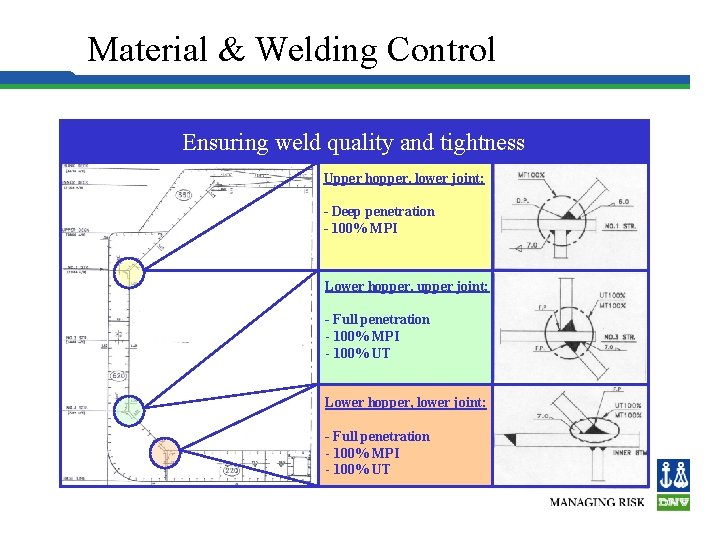
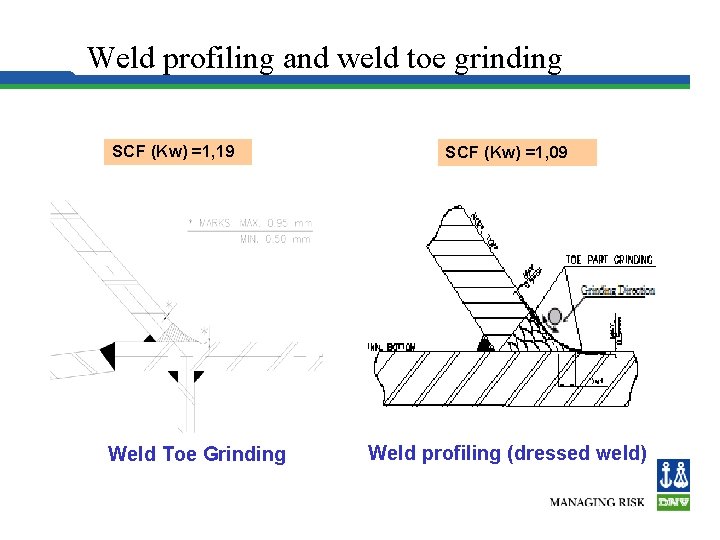
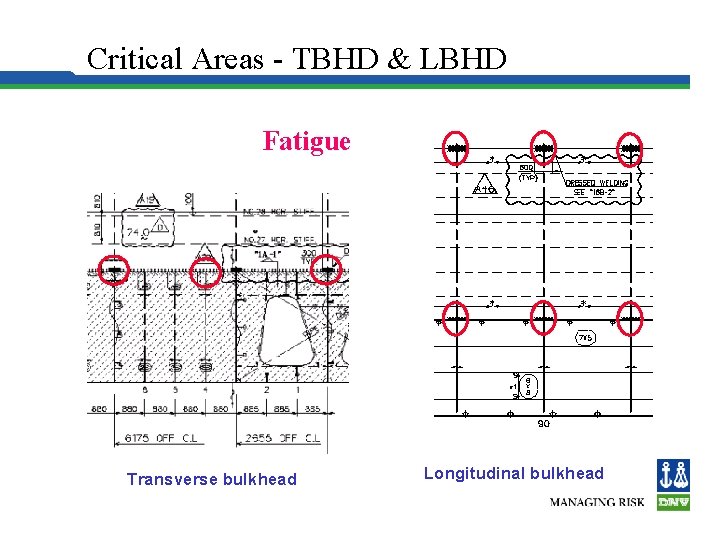
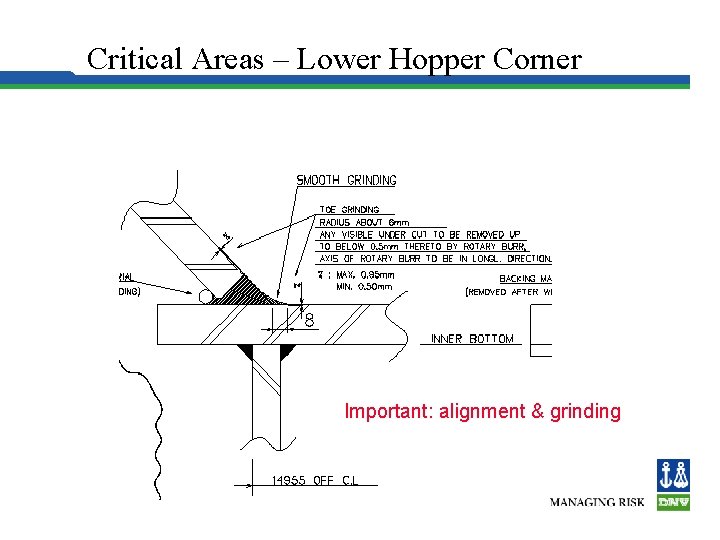
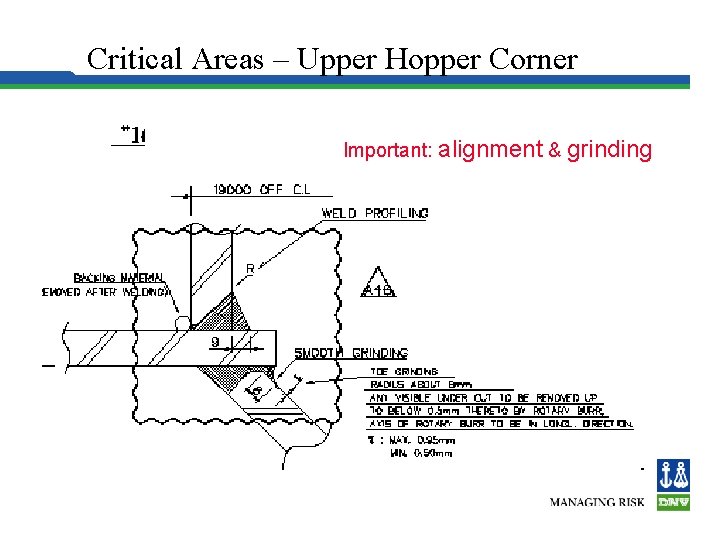
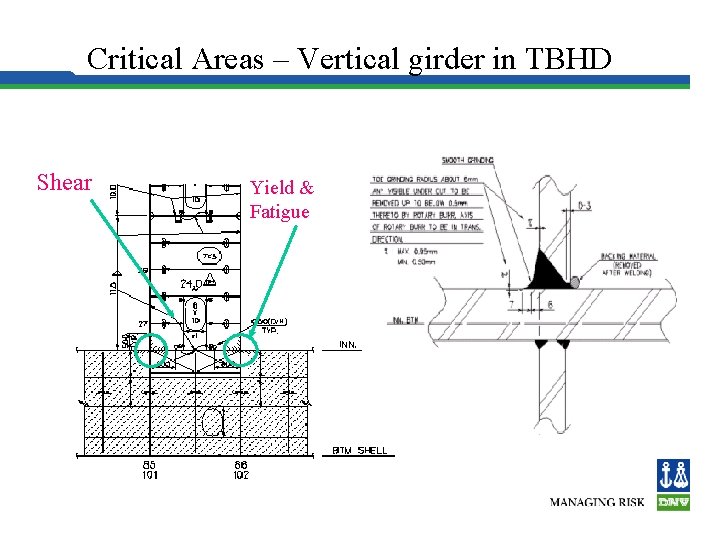
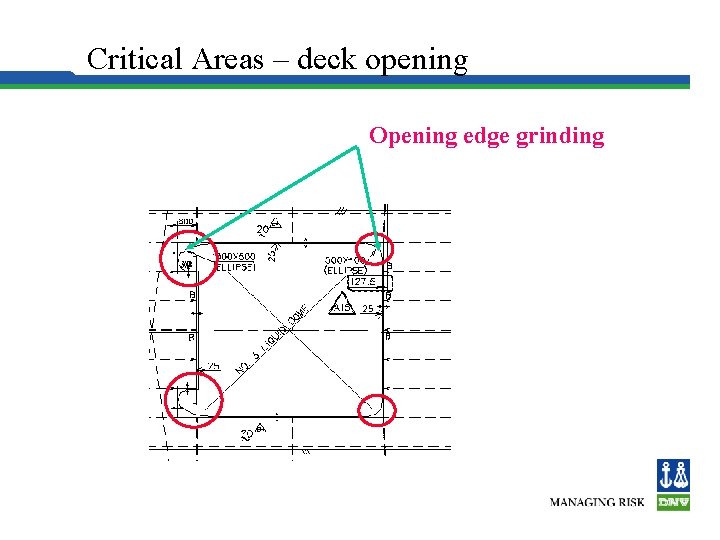
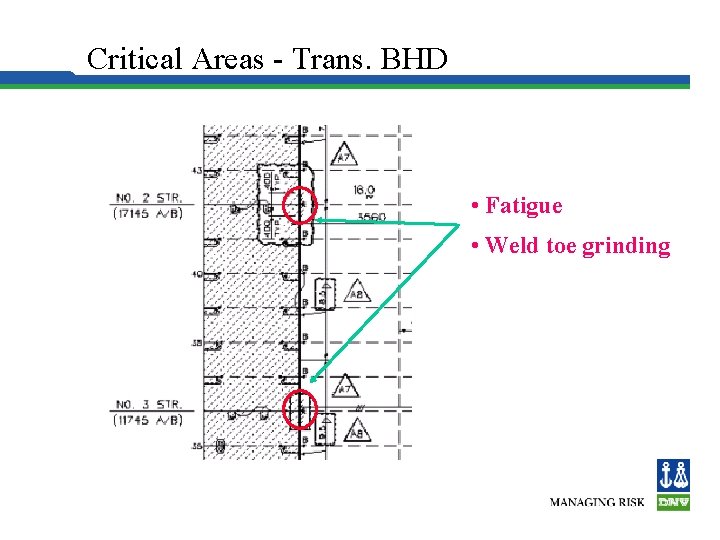
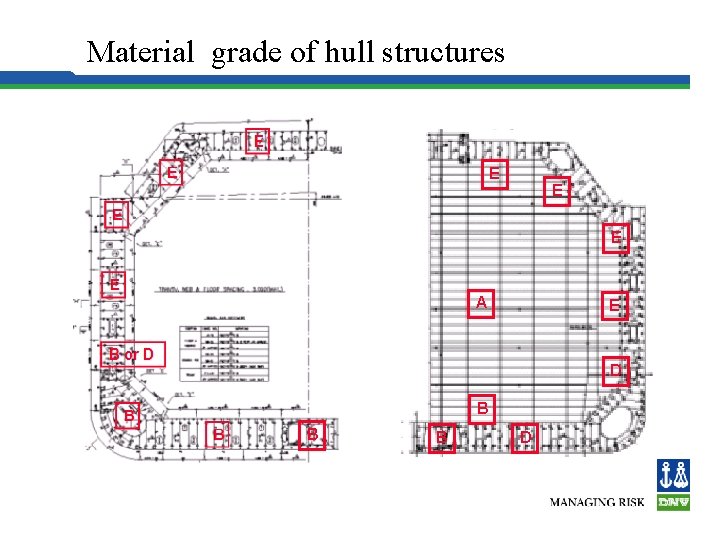
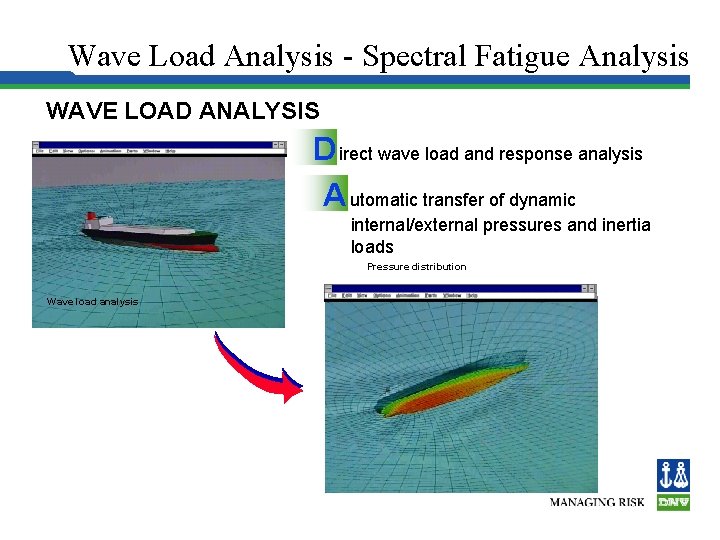
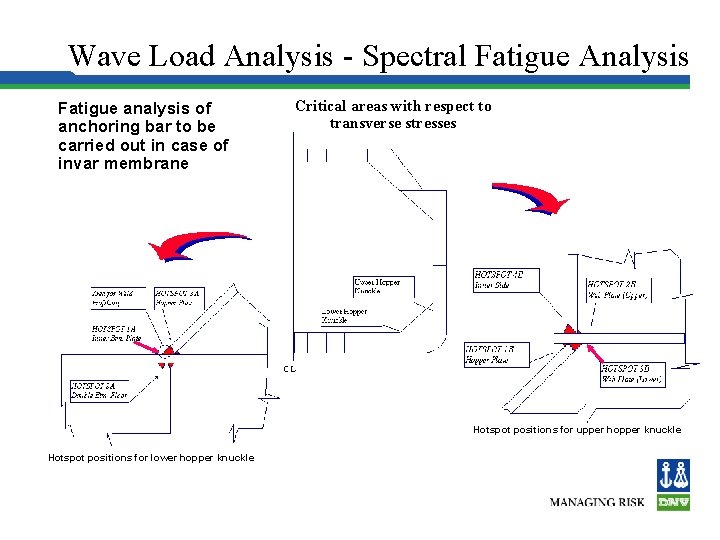
- Slides: 123
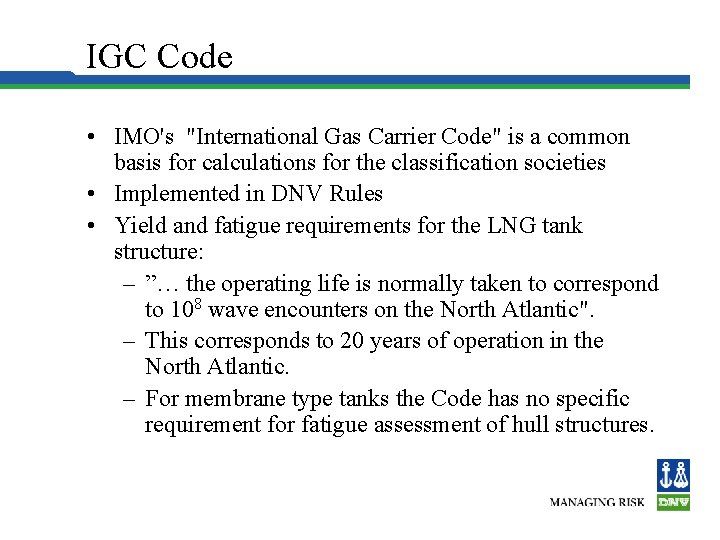
IGC Code • IMO's "International Gas Carrier Code" is a common basis for calculations for the classification societies • Implemented in DNV Rules • Yield and fatigue requirements for the LNG tank structure: – ”… the operating life is normally taken to correspond to 108 wave encounters on the North Atlantic". – This corresponds to 20 years of operation in the North Atlantic. – For membrane type tanks the Code has no specific requirement for fatigue assessment of hull structures.
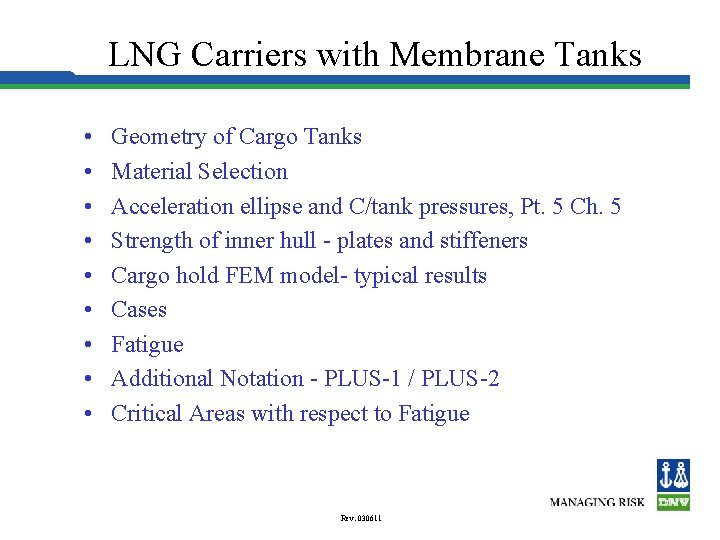
LNG Carriers with Membrane Tanks • • • Geometry of Cargo Tanks Material Selection Acceleration ellipse and C/tank pressures, Pt. 5 Ch. 5 Strength of inner hull - plates and stiffeners Cargo hold FEM model- typical results Cases Fatigue Additional Notation - PLUS-1 / PLUS-2 Critical Areas with respect to Fatigue Rev. 030611
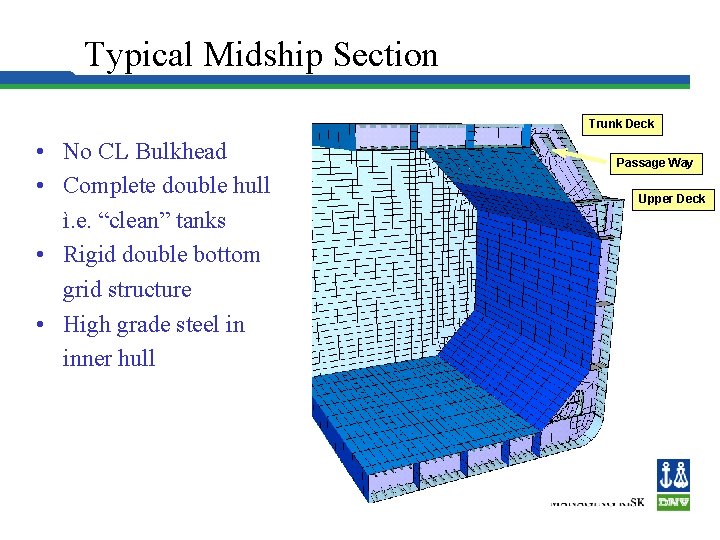
Typical Midship Section Trunk Deck • No CL Bulkhead • Complete double hull ì. e. “clean” tanks • Rigid double bottom grid structure • High grade steel in inner hull Passage Way Upper Deck
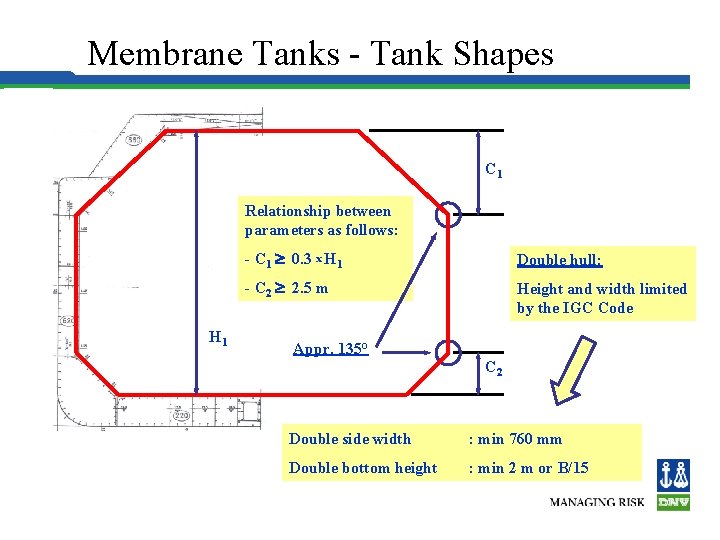
Hull Structure Membrane Tanks - Tank Shapes C 1 Relationship between parameters as follows: H 1 - C 1 0. 3 x H 1 Double hull: - C 2 2. 5 m Height and width limited by the IGC Code Appr. 135° C 2 Double side width : min 760 mm Double bottom height : min 2 m or B/15
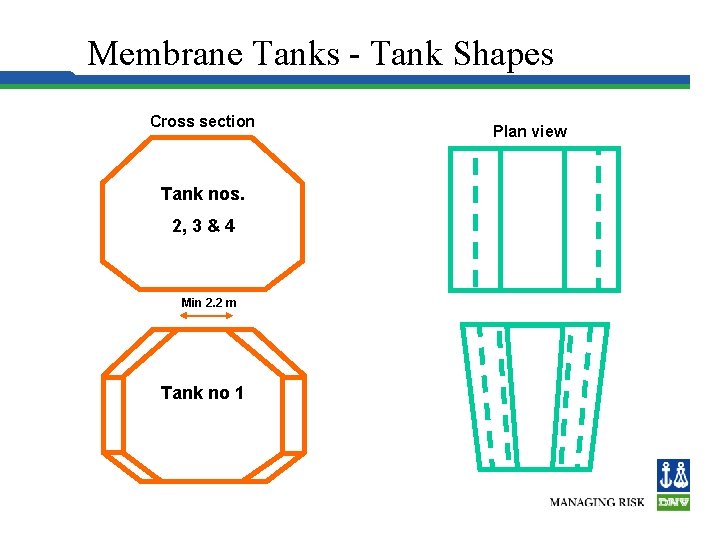
Hull Structure Membrane Tanks - Tank Shapes Cross section Tank nos. 2, 3 & 4 Min 2. 2 m Tank no 1 Plan view
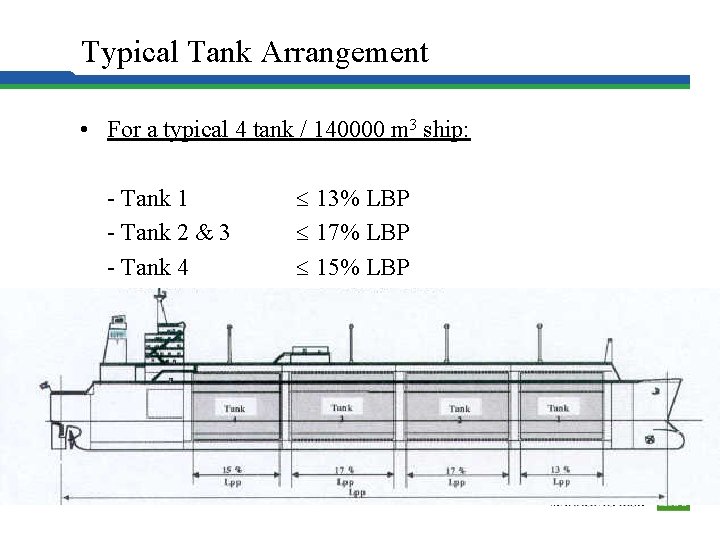
Hull Structure Typical Tank Arrangement • For a typical 4 tank / 140000 m 3 ship: - Tank 1 - Tank 2 & 3 - Tank 4 13% LBP 17% LBP 15% LBP
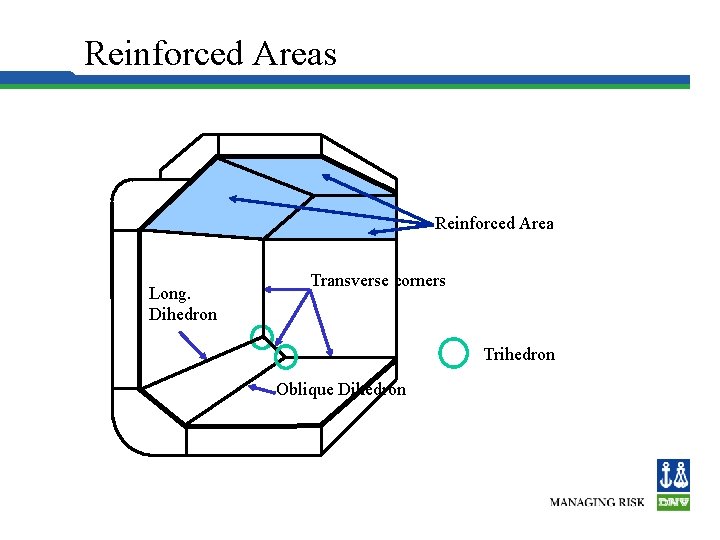
Hull Structure Reinforced Areas Reinforced Area Long. Dihedron Transverse corners Trihedron Oblique Dihedron
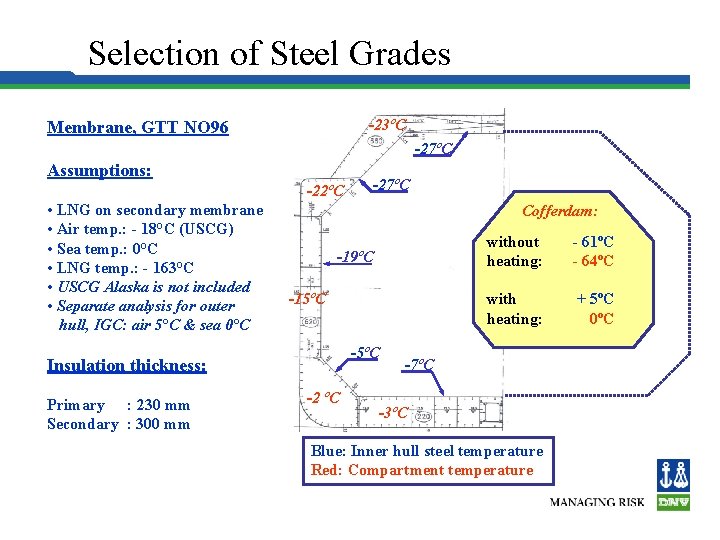
Selection of Steel Grades -23ºC Membrane, GTT NO 96 -27ºC Assumptions: -22ºC • LNG on secondary membrane • Air temp. : - 18°C (USCG) • Sea temp. : 0°C • LNG temp. : - 163°C • USCG Alaska is not included • Separate analysis for outer hull, IGC: air 5°C & sea 0°C Cofferdam: -19ºC -15ºC -5ºC Insulation thickness: Primary : 230 mm Secondary : 300 mm -27ºC -2 ºC without heating: - 61ºC - 64ºC with heating: + 5ºC 0ºC -7ºC -3ºC Blue: Inner hull steel temperature Red: Compartment temperature
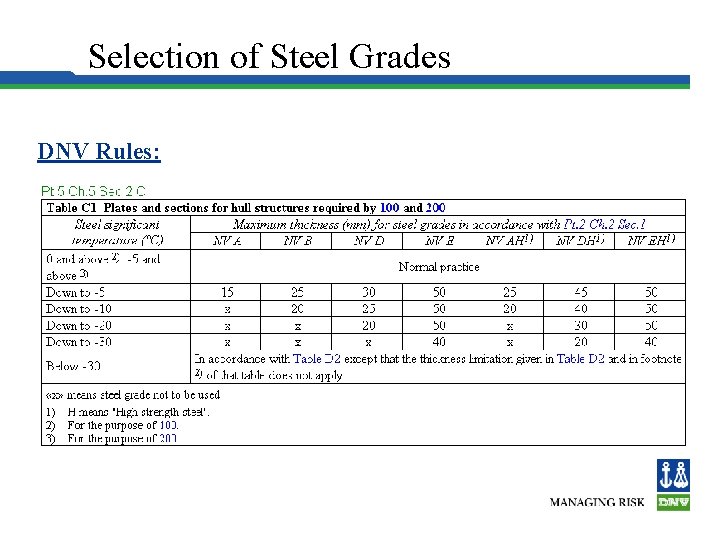
Selection of Steel Grades DNV Rules:
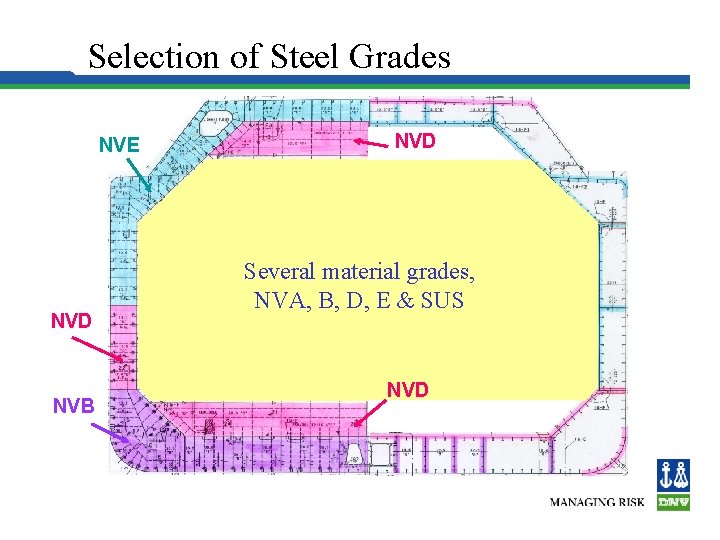
Selection of Steel Grades NVE NVD NVB NVD Several material grades, NVA, B, D, E & SUS NVD
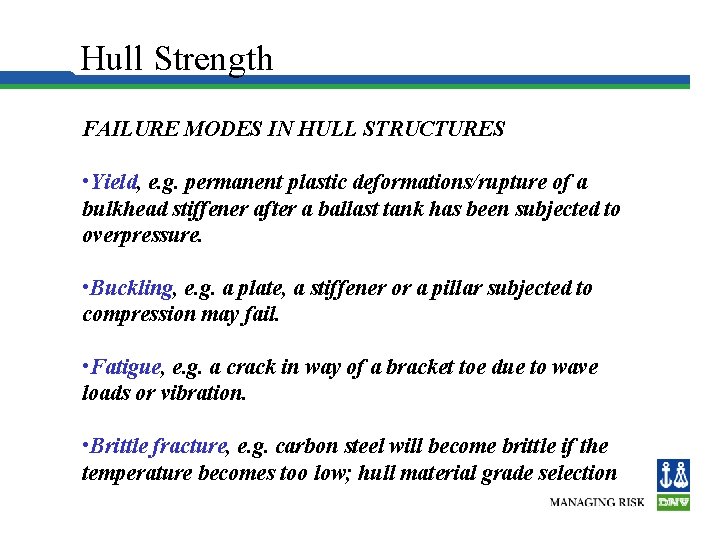
Hull Strength FAILURE MODES IN HULL STRUCTURES • Yield, e. g. permanent plastic deformations/rupture of a bulkhead stiffener after a ballast tank has been subjected to overpressure. • Buckling, e. g. a plate, a stiffener or a pillar subjected to compression may fail. • Fatigue, e. g. a crack in way of a bracket toe due to wave loads or vibration. • Brittle fracture, e. g. carbon steel will become brittle if the temperature becomes too low; hull material grade selection
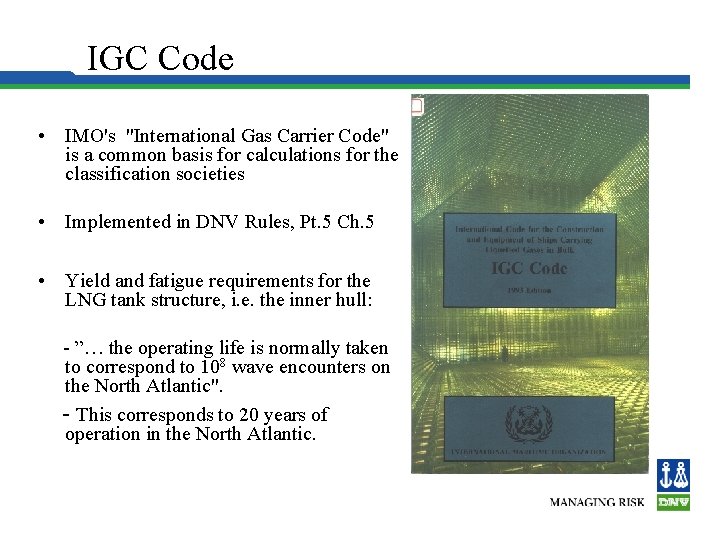
IGC Code • IMO's "International Gas Carrier Code" is a common basis for calculations for the classification societies • Implemented in DNV Rules, Pt. 5 Ch. 5 • Yield and fatigue requirements for the LNG tank structure, i. e. the inner hull: - ”… the operating life is normally taken to correspond to 108 wave encounters on the North Atlantic". - This corresponds to 20 years of operation in the North Atlantic.
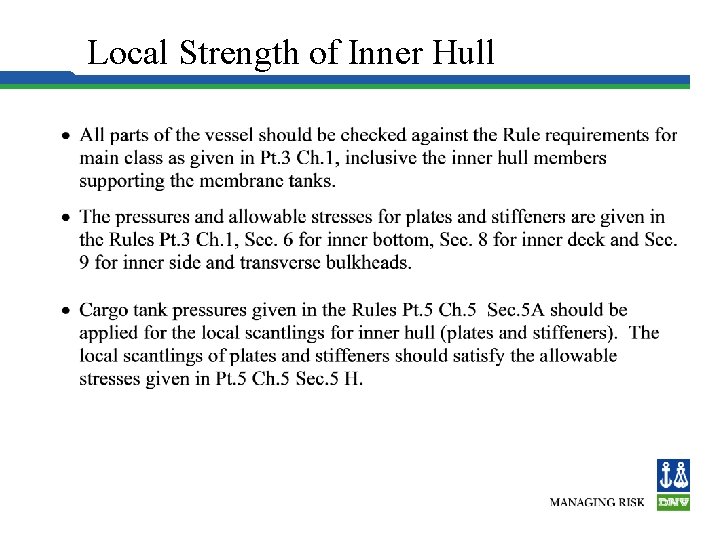
Local Strength of Inner Hull
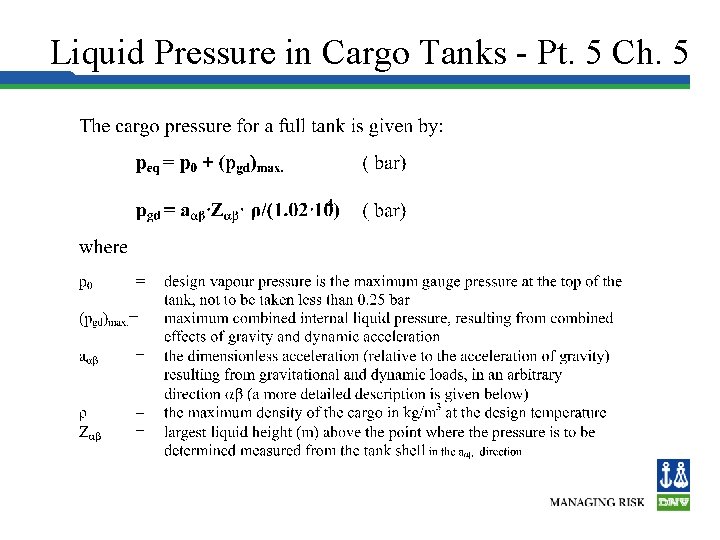
Liquid Pressure in Cargo Tanks - Pt. 5 Ch. 5
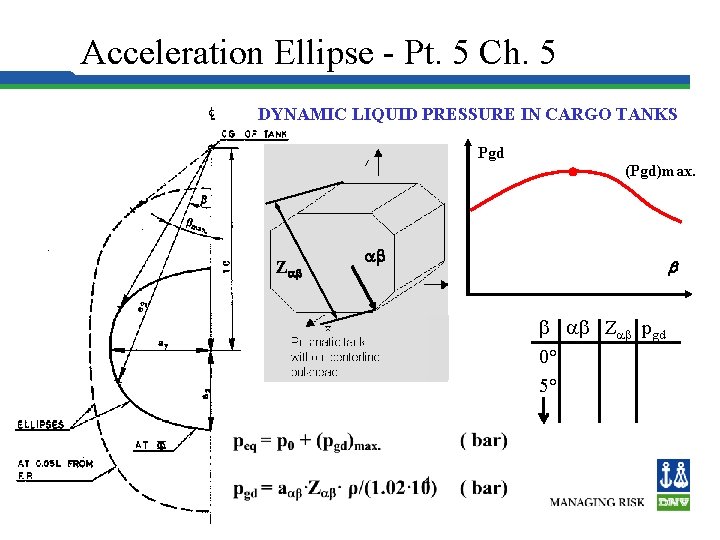
Acceleration Ellipse - Pt. 5 Ch. 5 DYNAMIC LIQUID PRESSURE IN CARGO TANKS Pgd (Pgd)max. Z pgd 0° 5°
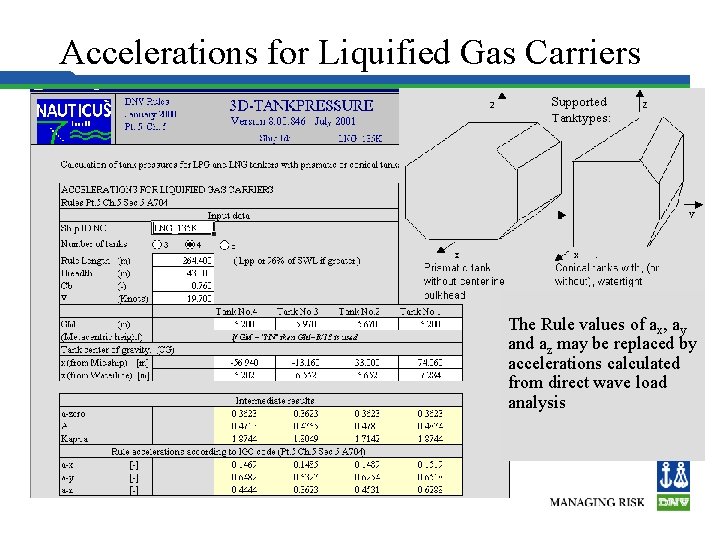
Accelerations for Liquified Gas Carriers The Rule values of ax, ay and az may be replaced by accelerations calculated from direct wave load analysis
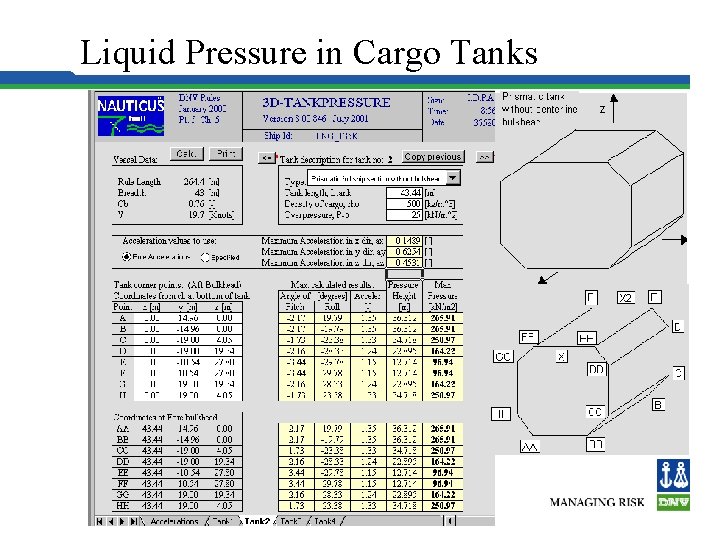
Liquid Pressure in Cargo Tanks
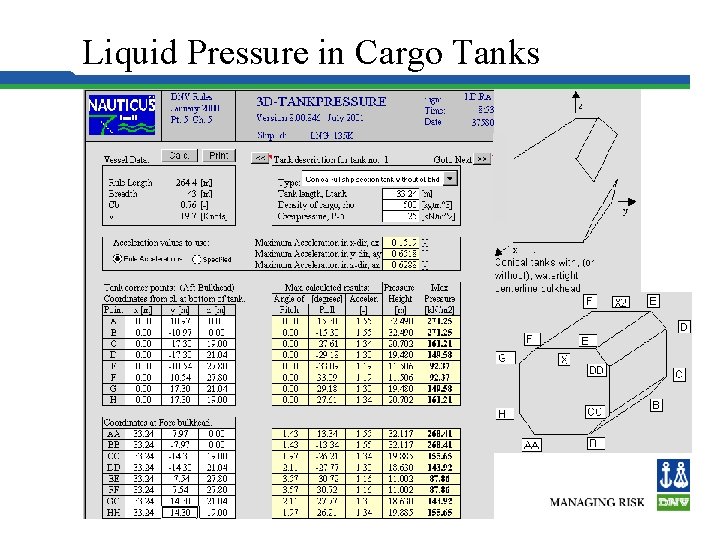
Liquid Pressure in Cargo Tanks
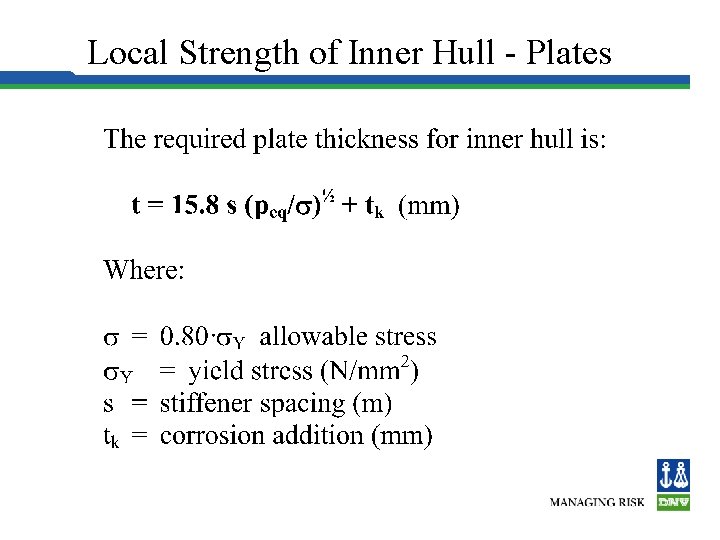
Local Strength of Inner Hull - Plates
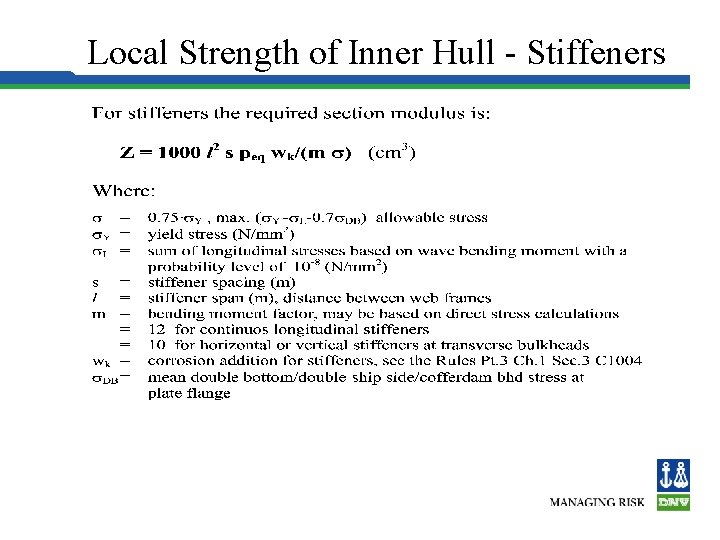
Local Strength of Inner Hull - Stiffeners
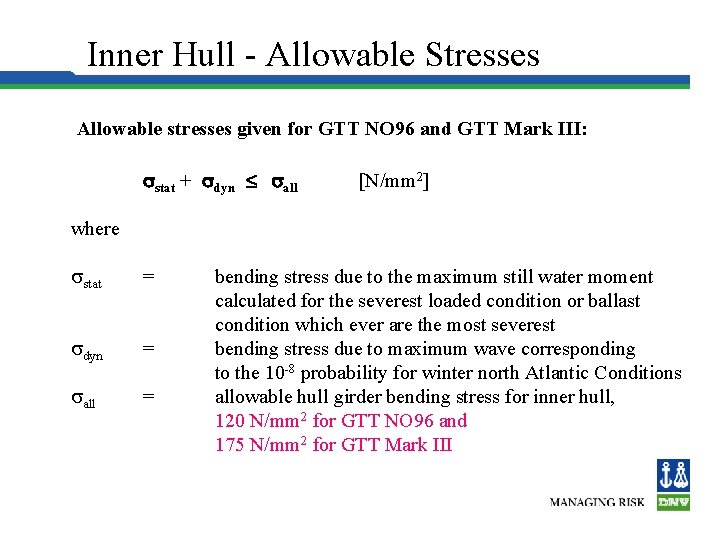
Inner Hull - Allowable Stresses Allowable stresses given for GTT NO 96 and GTT Mark III: stat + dyn all [N/mm 2] where stat = dyn = all = bending stress due to the maximum still water moment calculated for the severest loaded condition or ballast condition which ever are the most severest bending stress due to maximum wave corresponding to the 10 -8 probability for winter north Atlantic Conditions allowable hull girder bending stress for inner hull, 120 N/mm 2 for GTT NO 96 and 175 N/mm 2 for GTT Mark III
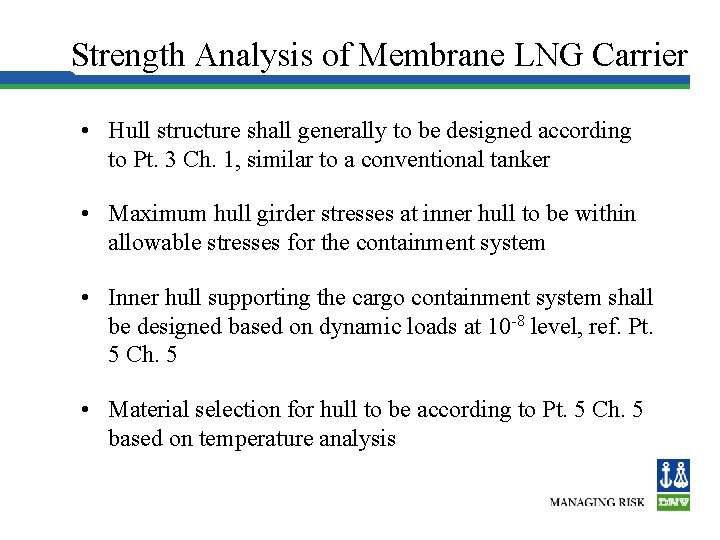
Strength Analysis of Membrane LNG Carrier • Hull structure shall generally to be designed according to Pt. 3 Ch. 1, similar to a conventional tanker • Maximum hull girder stresses at inner hull to be within allowable stresses for the containment system • Inner hull supporting the cargo containment system shall be designed based on dynamic loads at 10 -8 level, ref. Pt. 5 Ch. 5 • Material selection for hull to be according to Pt. 5 Ch. 5 based on temperature analysis
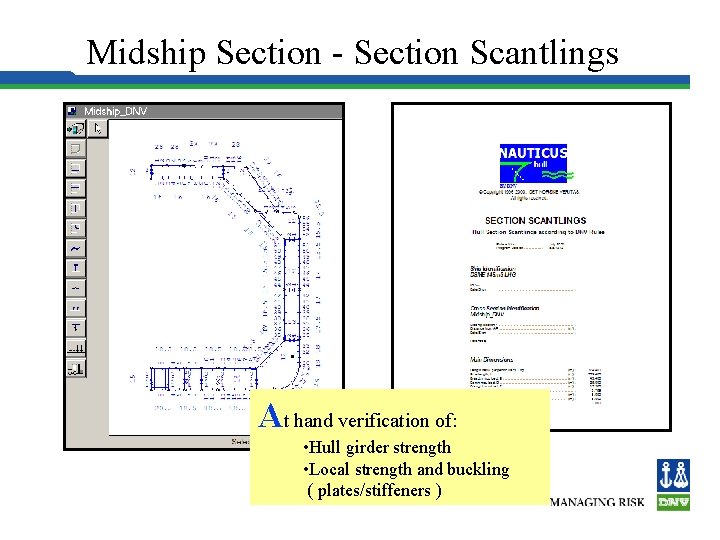
Midship Section - Section Scantlings At hand verification of: • Hull girder strength • Local strength and buckling ( plates/stiffeners )
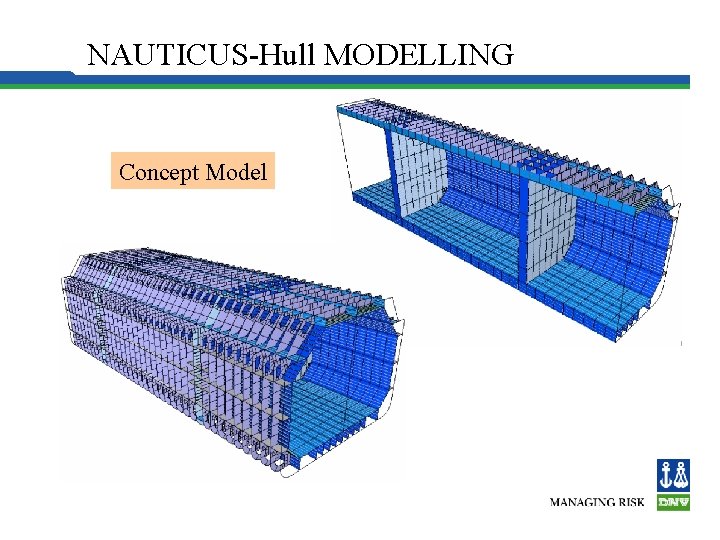
NAUTICUS-Hull MODELLING Concept Model

Cargo Hold Analysis - FEM Model Concept Model FEM Results
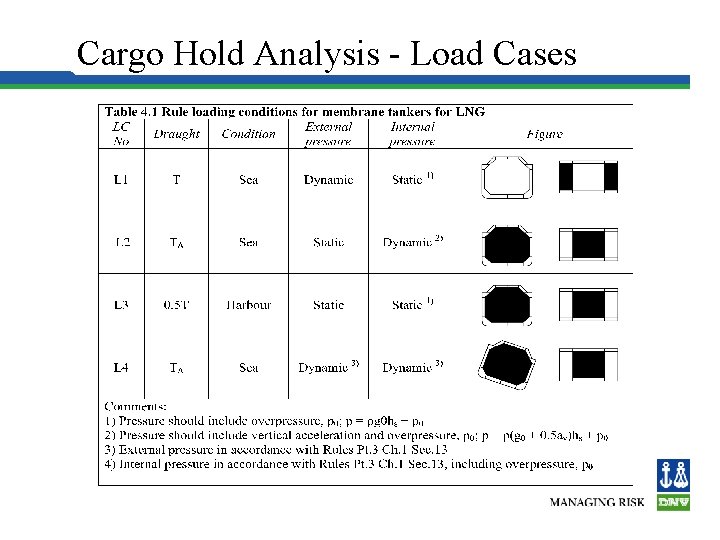
Cargo Hold Analysis - Load Cases
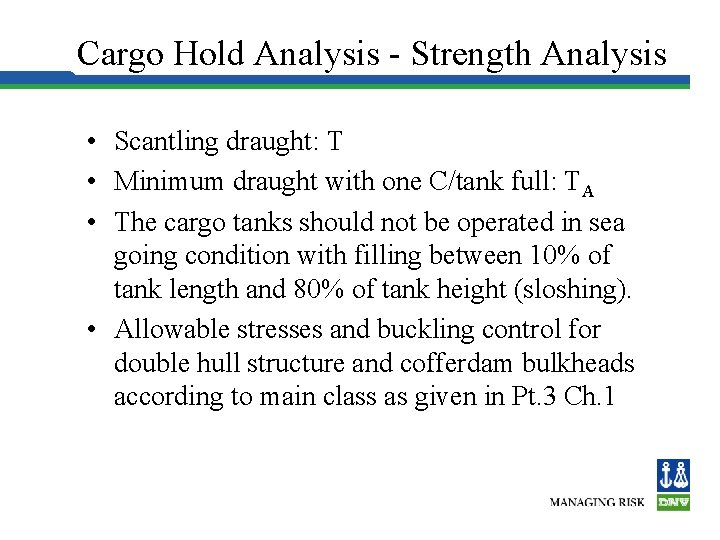
Cargo Hold Analysis - Strength Analysis • Scantling draught: T • Minimum draught with one C/tank full: TA • The cargo tanks should not be operated in sea going condition with filling between 10% of tank length and 80% of tank height (sloshing). • Allowable stresses and buckling control for double hull structure and cofferdam bulkheads according to main class as given in Pt. 3 Ch. 1
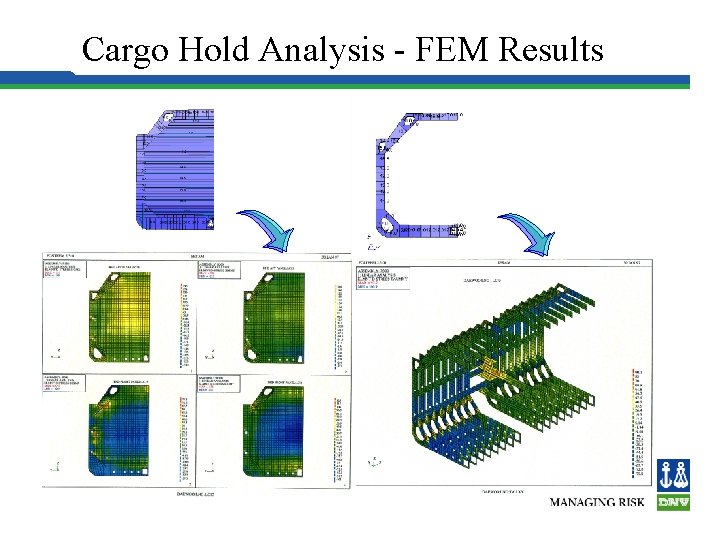
Cargo Hold Analysis - FEM Results
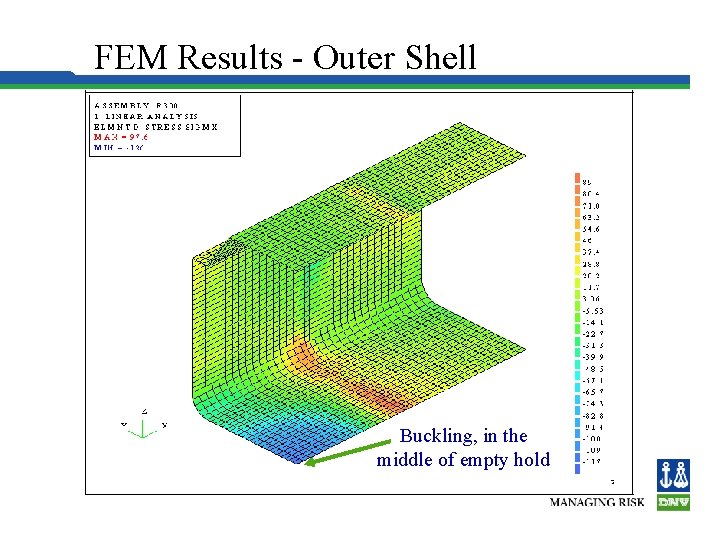
FEM Results - Outer Shell Buckling, in the middle of empty hold
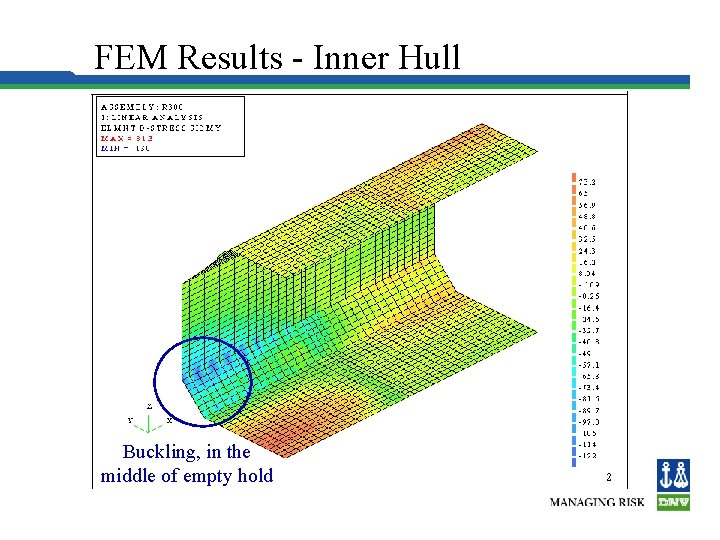
FEM Results - Inner Hull Buckling, in the middle of empty hold

FEM Results - Transverse Bulkhead Buckling, in way of full hold, compression both horizontally and vertically
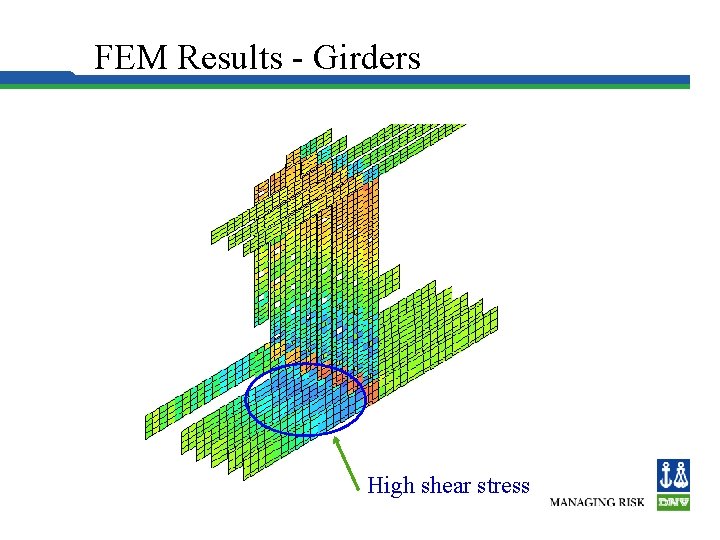
FEM Results - Girders High shear stress
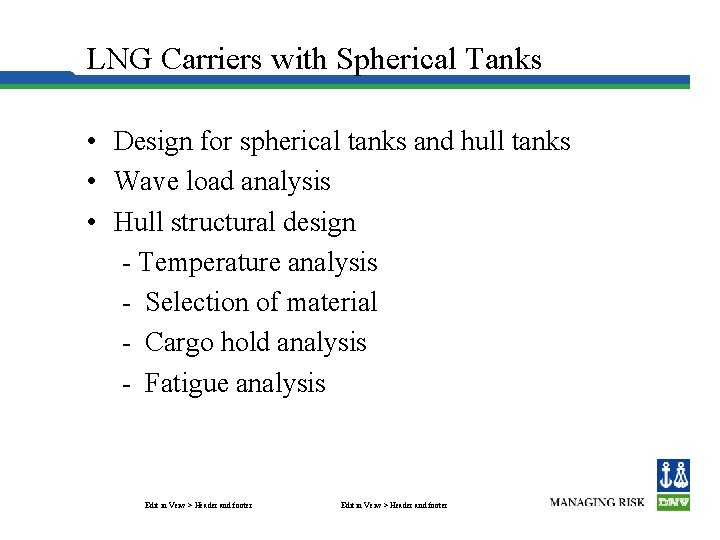
LNG Carriers with Spherical Tanks • Design for spherical tanks and hull tanks • Wave load analysis • Hull structural design - Temperature analysis - Selection of material - Cargo hold analysis - Fatigue analysis Edit in Veiw > Header and footer
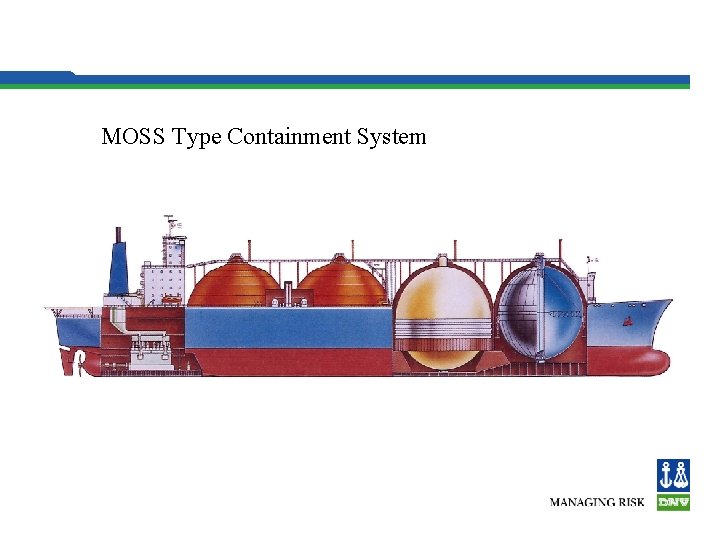
MOSS Type Containment System
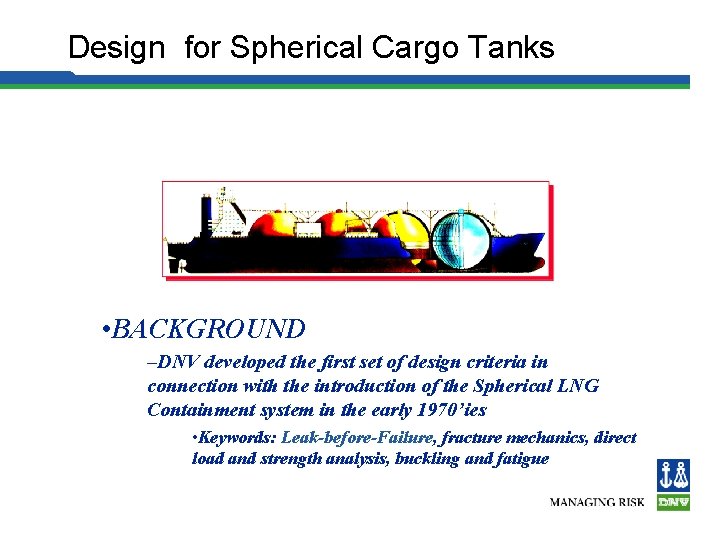
Design for Spherical Cargo Tanks • BACKGROUND –DNV developed the first set of design criteria in connection with the introduction of the Spherical LNG Containment system in the early 1970’ies • Keywords: Leak-before-Failure, fracture mechanics, direct load and strength analysis, buckling and fatigue
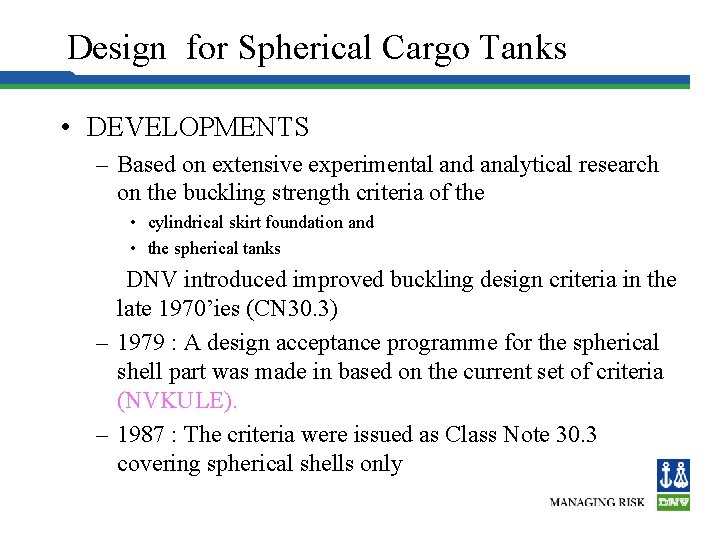
Design for Spherical Cargo Tanks • DEVELOPMENTS – Based on extensive experimental and analytical research on the buckling strength criteria of the • cylindrical skirt foundation and • the spherical tanks DNV introduced improved buckling design criteria in the late 1970’ies (CN 30. 3) – 1979 : A design acceptance programme for the spherical shell part was made in based on the current set of criteria (NVKULE). – 1987 : The criteria were issued as Class Note 30. 3 covering spherical shells only
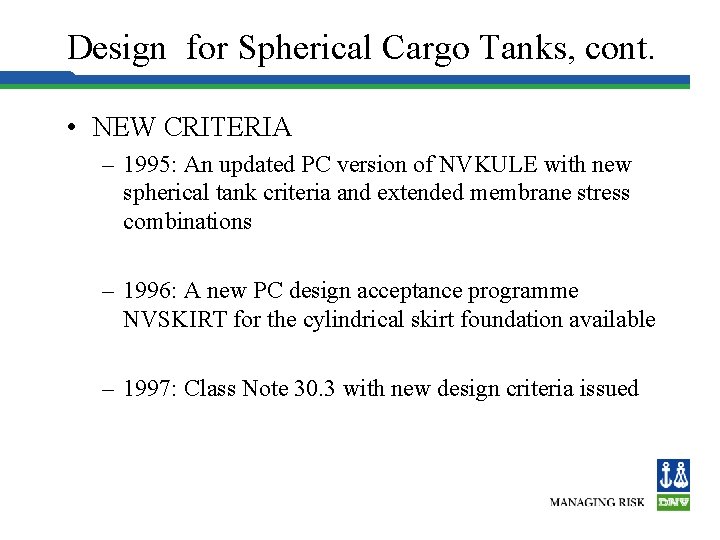
Design for Spherical Cargo Tanks, cont. • NEW CRITERIA – 1995: An updated PC version of NVKULE with new spherical tank criteria and extended membrane stress combinations – 1996: A new PC design acceptance programme NVSKIRT for the cylindrical skirt foundation available – 1997: Class Note 30. 3 with new design criteria issued
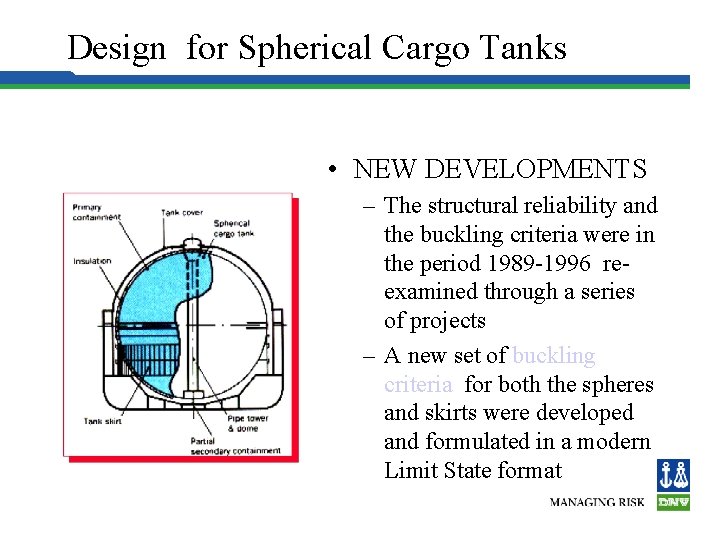
Design for Spherical Cargo Tanks • NEW DEVELOPMENTS – The structural reliability and the buckling criteria were in the period 1989 -1996 reexamined through a series of projects – A new set of buckling criteria for both the spheres and skirts were developed and formulated in a modern Limit State format
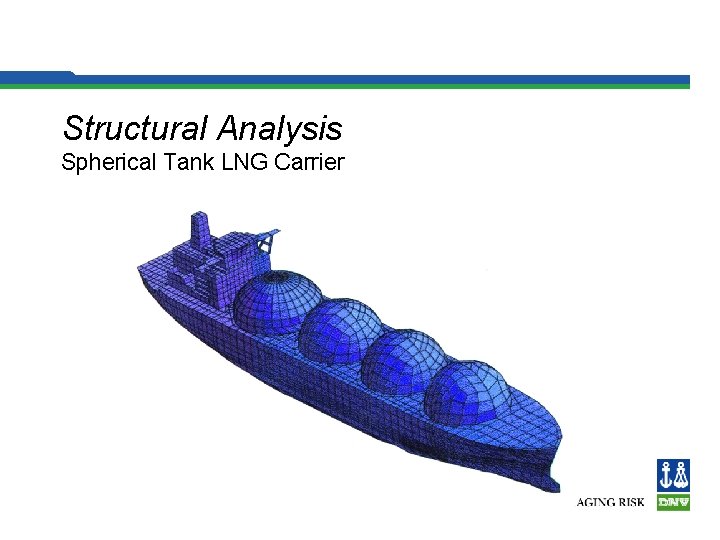
Structural Analysis Spherical Tank LNG Carrier
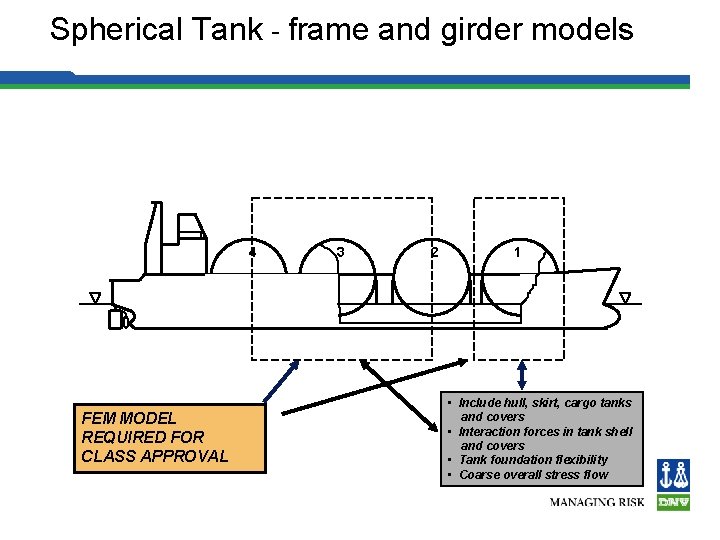
Spherical Tank - frame and girder models 4 FEM MODEL REQUIRED FOR CLASS APPROVAL 3 2 1 • Include hull, skirt, cargo tanks and covers • Interaction forces in tank shell and covers • Tank foundation flexibility • Coarse overall stress flow
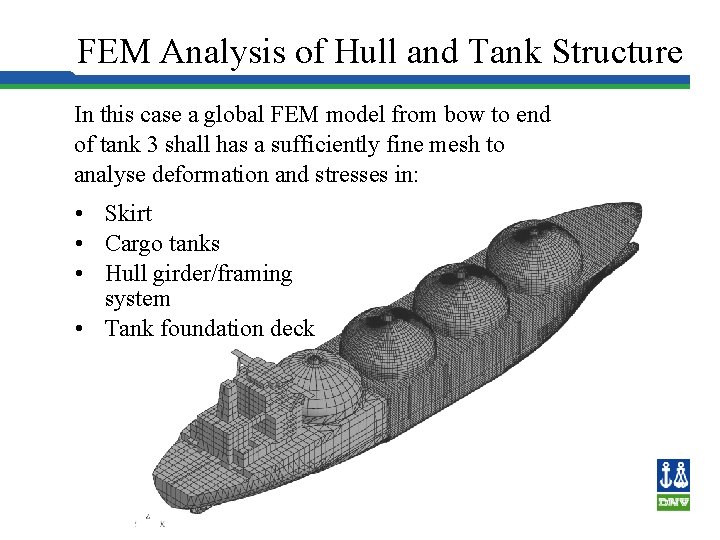
FEM Analysis of Hull and Tank Structure In this case a global FEM model from bow to end of tank 3 shall has a sufficiently fine mesh to analyse deformation and stresses in: • Skirt • Cargo tanks • Hull girder/framing system • Tank foundation deck
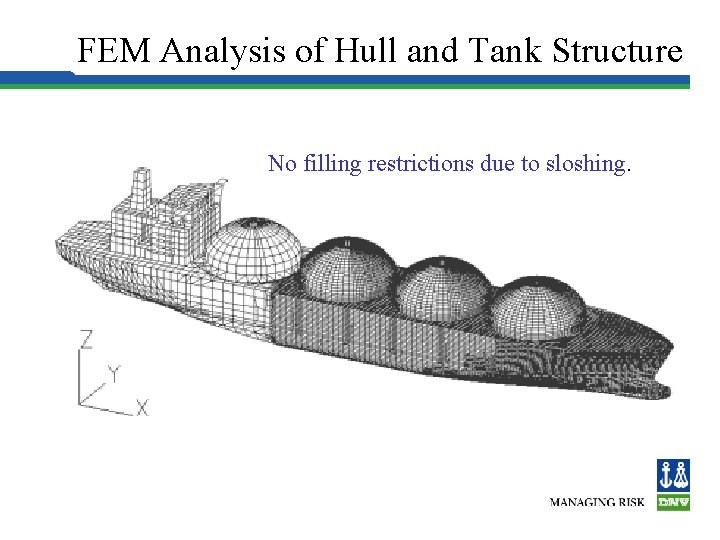
FEM Analysis of Hull and Tank Structure No filling restrictions due to sloshing.
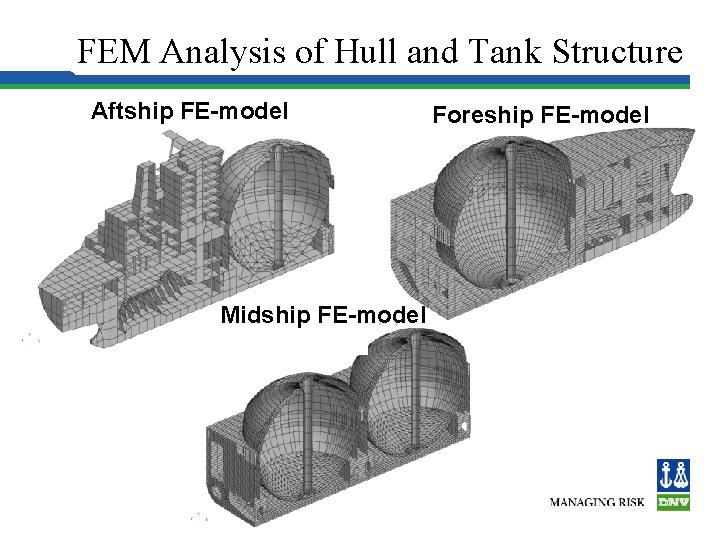
FEM Analysis of Hull and Tank Structure Aftship FE-model Midship FE-model Foreship FE-model
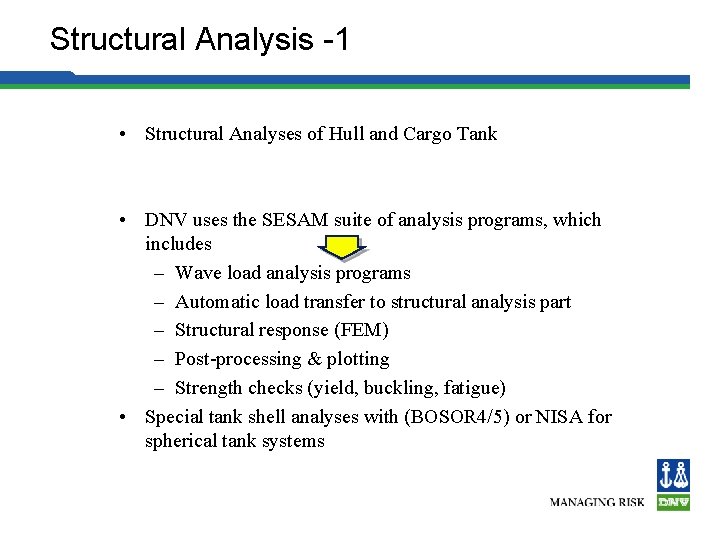
Structural Analysis -1 • Structural Analyses of Hull and Cargo Tank • DNV uses the SESAM suite of analysis programs, which includes – Wave load analysis programs – Automatic load transfer to structural analysis part – Structural response (FEM) – Post-processing & plotting – Strength checks (yield, buckling, fatigue) • Special tank shell analyses with (BOSOR 4/5) or NISA for spherical tank systems
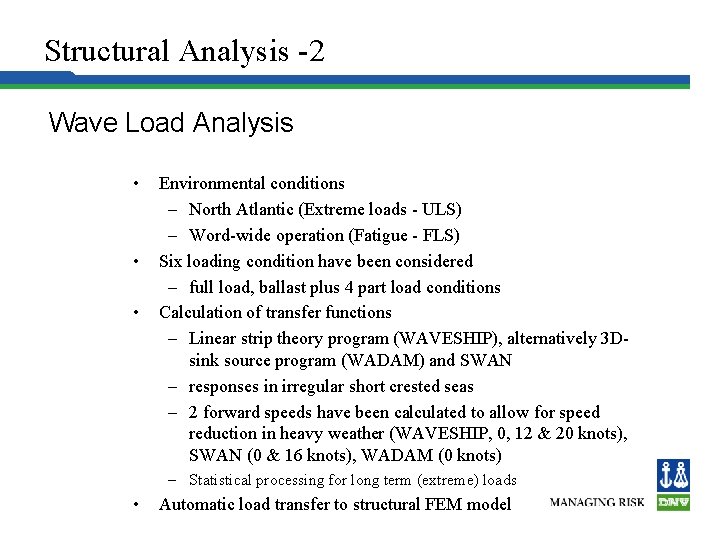
Structural Analysis -2 Wave Load Analysis • • • Environmental conditions – North Atlantic (Extreme loads - ULS) – Word-wide operation (Fatigue - FLS) Six loading condition have been considered – full load, ballast plus 4 part load conditions Calculation of transfer functions – Linear strip theory program (WAVESHIP), alternatively 3 Dsink source program (WADAM) and SWAN – responses in irregular short crested seas – 2 forward speeds have been calculated to allow for speed reduction in heavy weather (WAVESHIP, 0, 12 & 20 knots), SWAN (0 & 16 knots), WADAM (0 knots) – Statistical processing for long term (extreme) loads • Automatic load transfer to structural FEM model
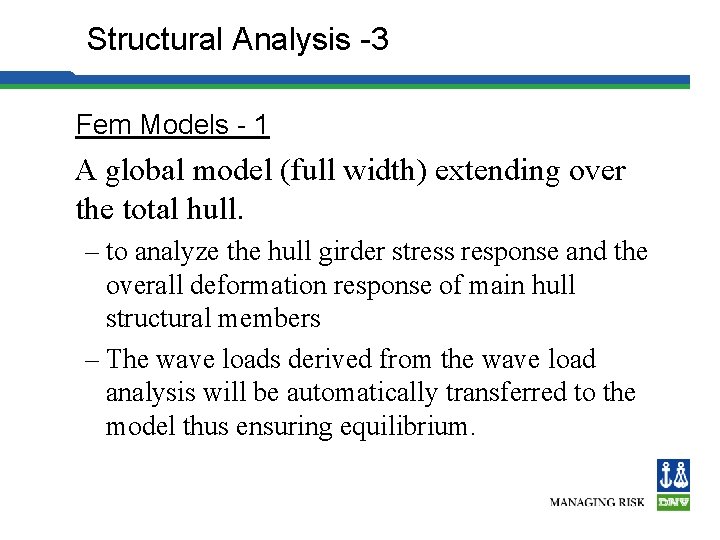
Structural Analysis -3 Fem Models - 1 A global model (full width) extending over the total hull. – to analyze the hull girder stress response and the overall deformation response of main hull structural members – The wave loads derived from the wave load analysis will be automatically transferred to the model thus ensuring equilibrium.
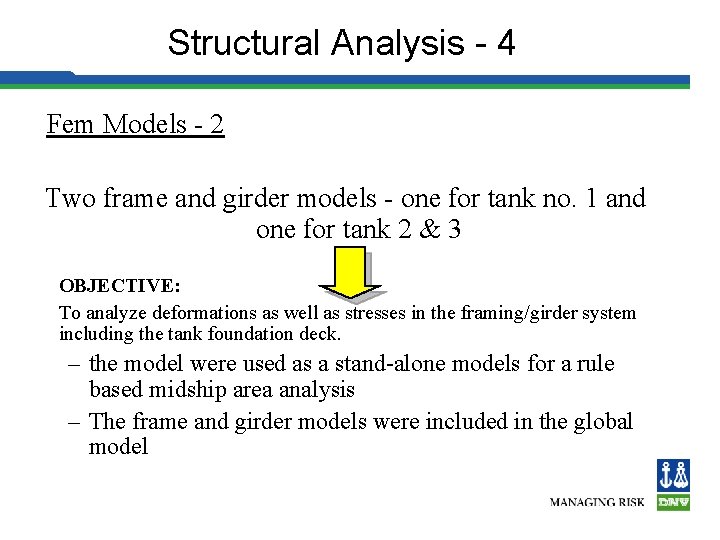
Structural Analysis - 4 Fem Models - 2 Two frame and girder models - one for tank no. 1 and one for tank 2 & 3 OBJECTIVE: To analyze deformations as well as stresses in the framing/girder system including the tank foundation deck. – the model were used as a stand-alone models for a rule based midship area analysis – The frame and girder models were included in the global model
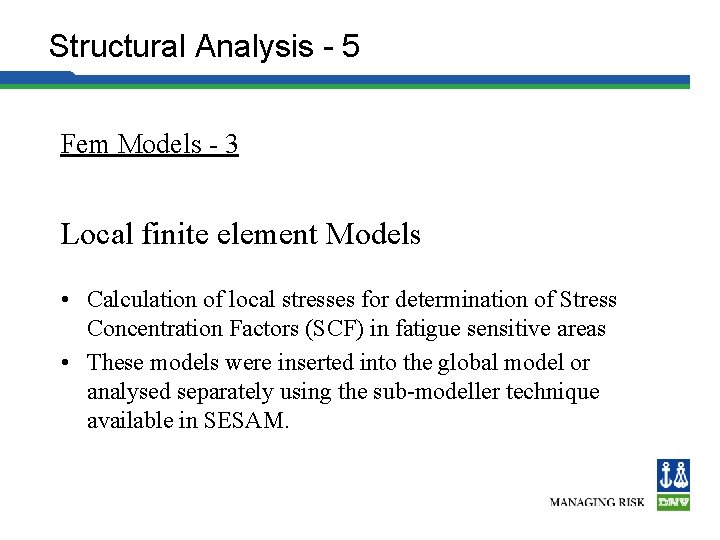
Structural Analysis - 5 Fem Models - 3 Local finite element Models • Calculation of local stresses for determination of Stress Concentration Factors (SCF) in fatigue sensitive areas • These models were inserted into the global model or analysed separately using the sub-modeller technique available in SESAM.
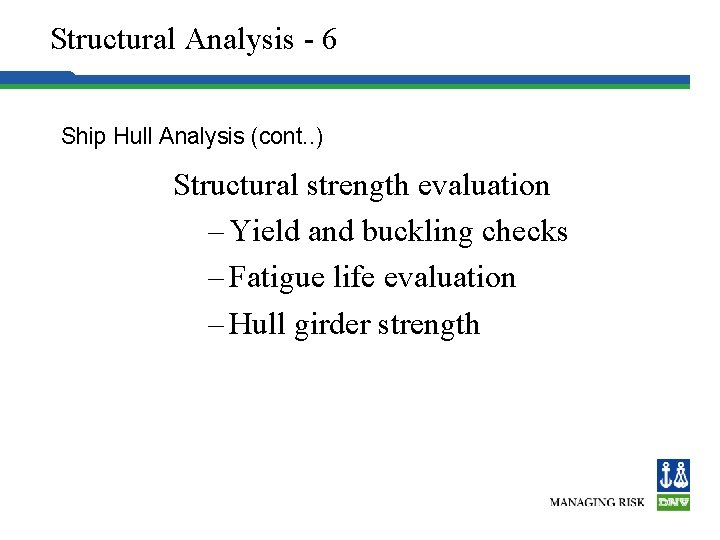
Structural Analysis - 6 Ship Hull Analysis (cont. . ) Structural strength evaluation – Yield and buckling checks – Fatigue life evaluation – Hull girder strength
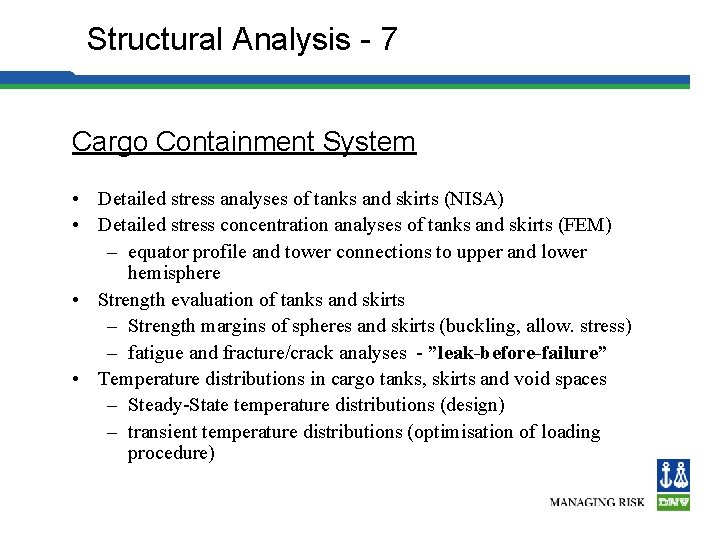
Structural Analysis - 7 Cargo Containment System • Detailed stress analyses of tanks and skirts (NISA) • Detailed stress concentration analyses of tanks and skirts (FEM) – equator profile and tower connections to upper and lower hemisphere • Strength evaluation of tanks and skirts – Strength margins of spheres and skirts (buckling, allow. stress) – fatigue and fracture/crack analyses - ”leak-before-failure” • Temperature distributions in cargo tanks, skirts and void spaces – Steady-State temperature distributions (design) – transient temperature distributions (optimisation of loading procedure)
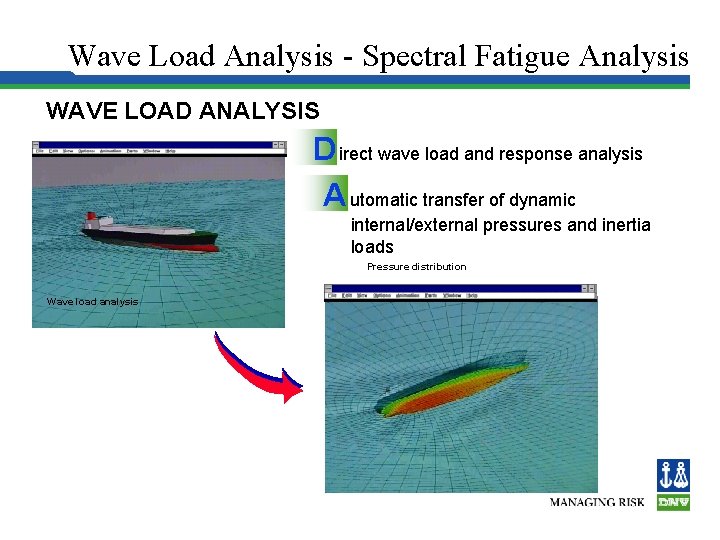
Wave Load Analysis - Spectral Fatigue Analysis WAVE LOAD ANALYSIS D irect wave load and response analysis A utomatic transfer of dynamic internal/external pressures and inertia loads Pressure distribution Wave load analysis
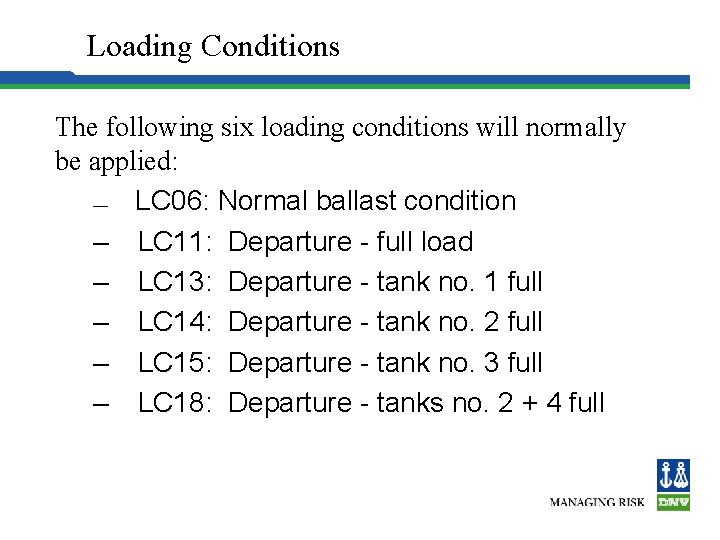
Loading Conditions The following six loading conditions will normally be applied: — LC 06: Normal ballast condition – LC 11: Departure - full load – LC 13: Departure - tank no. 1 full – LC 14: Departure - tank no. 2 full – LC 15: Departure - tank no. 3 full – LC 18: Departure - tanks no. 2 + 4 full
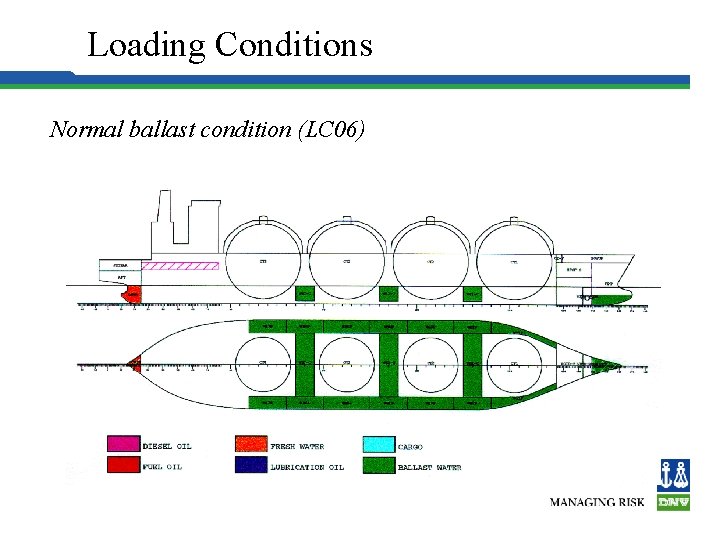
Loading Conditions Normal ballast condition (LC 06)
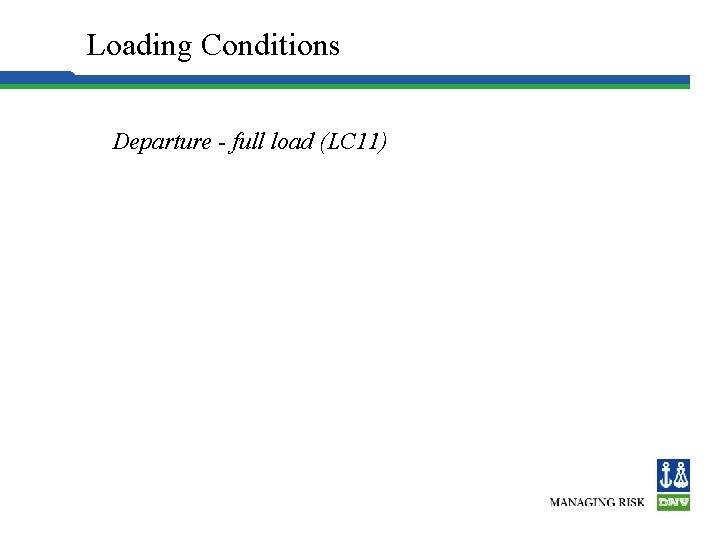
Loading Conditions Departure - full load (LC 11)
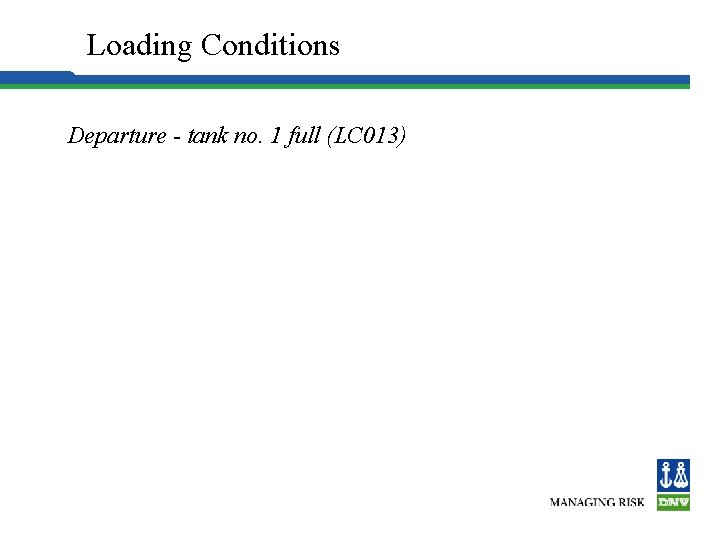
Loading Conditions Departure - tank no. 1 full (LC 013)
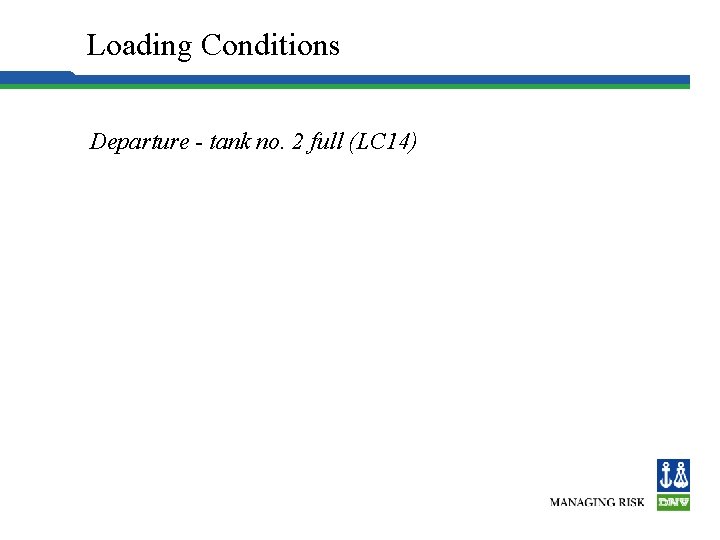
Loading Conditions Departure - tank no. 2 full (LC 14)
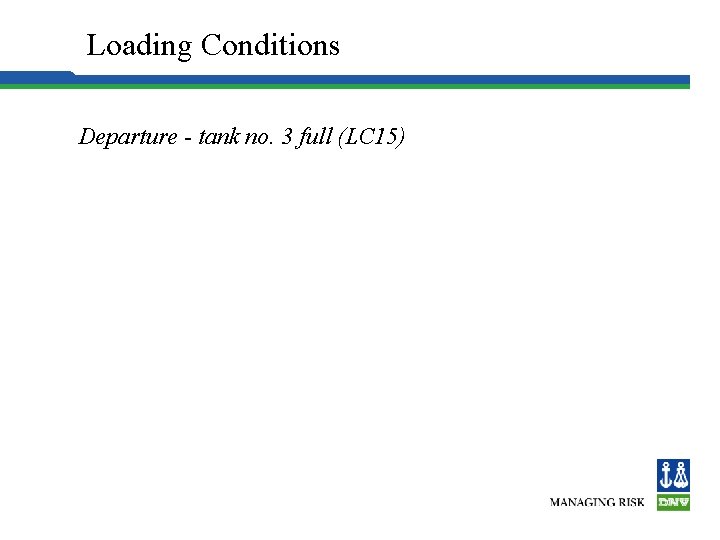
Loading Conditions Departure - tank no. 3 full (LC 15)
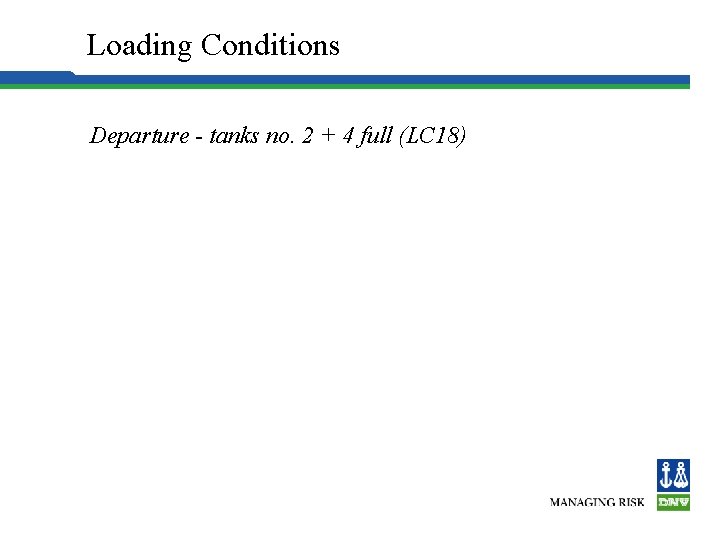
Loading Conditions Departure - tanks no. 2 + 4 full (LC 18)
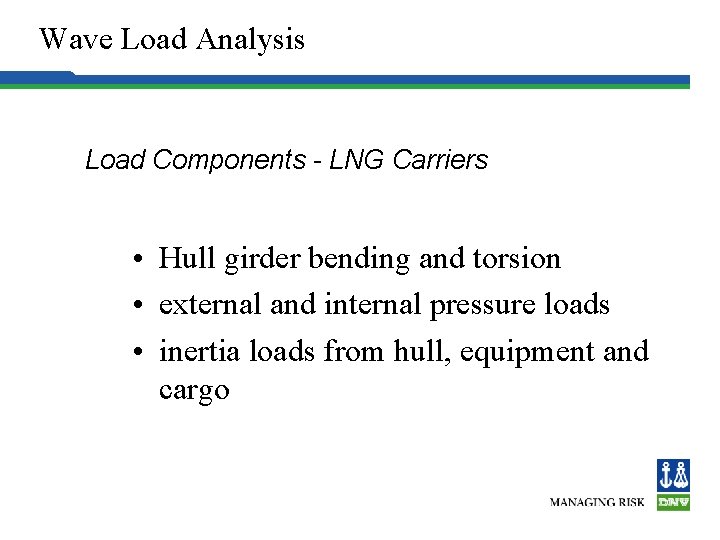
Wave Load Analysis Load Components - LNG Carriers • Hull girder bending and torsion • external and internal pressure loads • inertia loads from hull, equipment and cargo
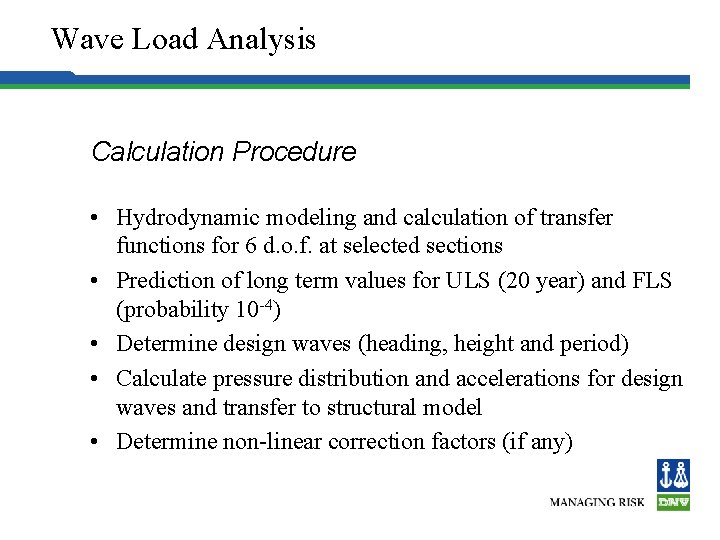
Wave Load Analysis Calculation Procedure • Hydrodynamic modeling and calculation of transfer functions for 6 d. o. f. at selected sections • Prediction of long term values for ULS (20 year) and FLS (probability 10 -4) • Determine design waves (heading, height and period) • Calculate pressure distribution and accelerations for design waves and transfer to structural model • Determine non-linear correction factors (if any)
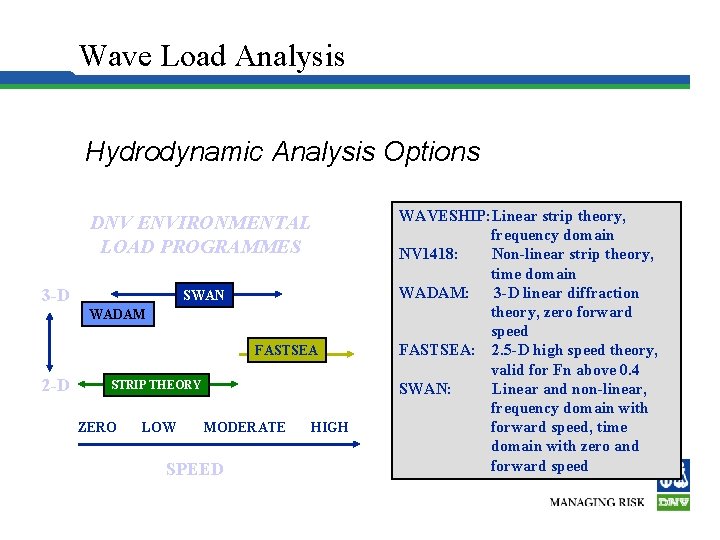
Wave Load Analysis Hydrodynamic Analysis Options DNV ENVIRONMENTAL LOAD PROGRAMMES 3 -D SWAN WADAM FASTSEA 2 -D STRIP THEORY ZERO LOW MODERATE SPEED HIGH WAVESHIP: Linear strip theory, frequency domain NV 1418: Non-linear strip theory, time domain WADAM: 3 -D linear diffraction theory, zero forward speed FASTSEA: 2. 5 -D high speed theory, valid for Fn above 0. 4 SWAN: Linear and non-linear, frequency domain with forward speed, time domain with zero and forward speed
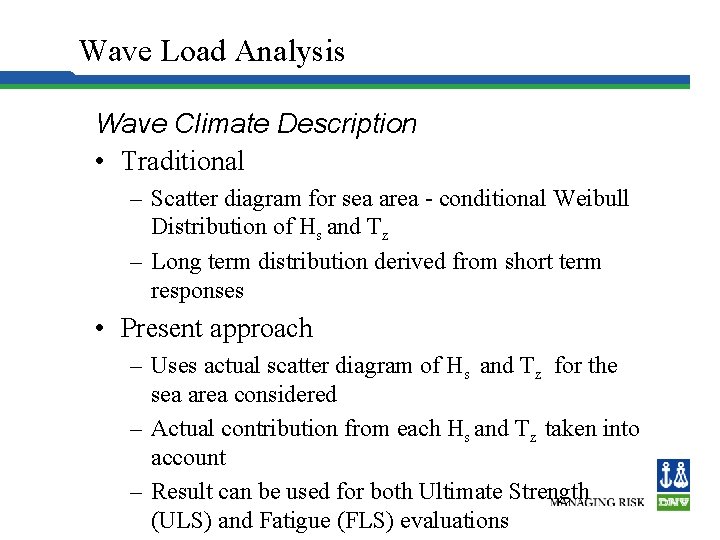
Wave Load Analysis Wave Climate Description • Traditional – Scatter diagram for sea area - conditional Weibull Distribution of Hs and Tz – Long term distribution derived from short term responses • Present approach – Uses actual scatter diagram of Hs and Tz for the sea area considered – Actual contribution from each Hs and Tz taken into account – Result can be used for both Ultimate Strength (ULS) and Fatigue (FLS) evaluations
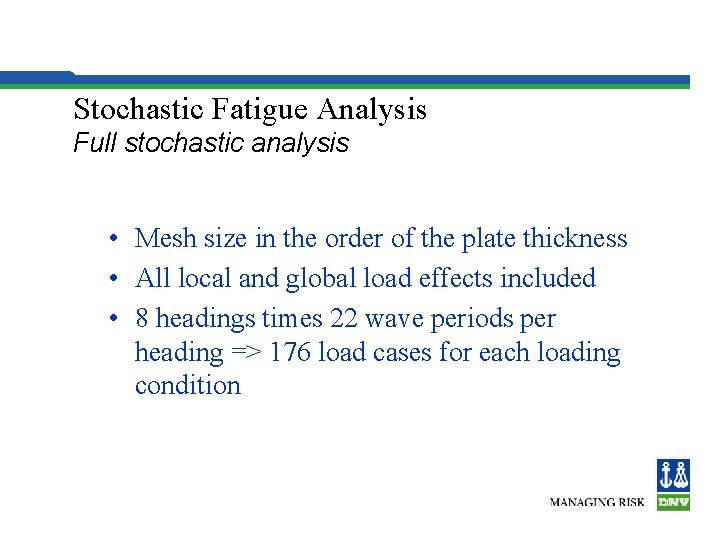
Stochastic Fatigue Analysis Full stochastic analysis • Mesh size in the order of the plate thickness • All local and global load effects included • 8 headings times 22 wave periods per heading => 176 load cases for each loading condition
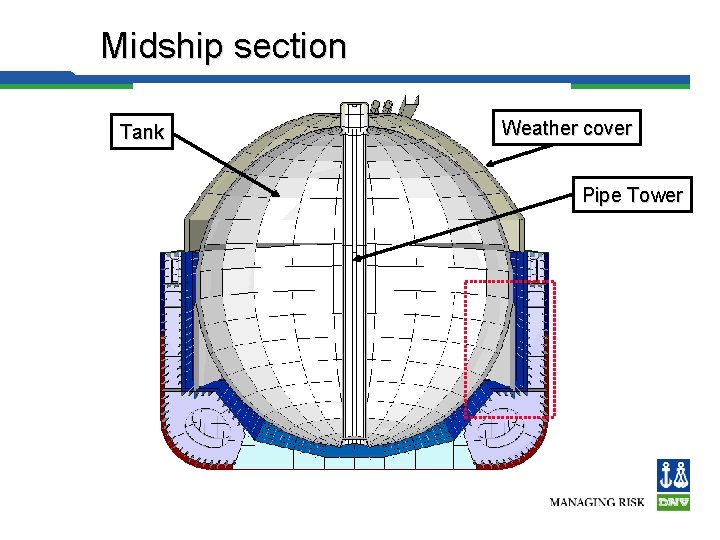
Midship section Tank Weather cover Pipe Tower
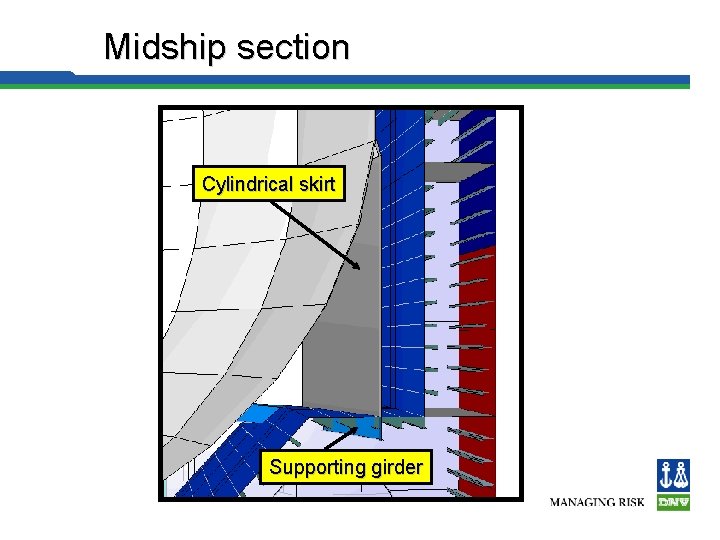
Midship section Cylindrical skirt Supporting girder
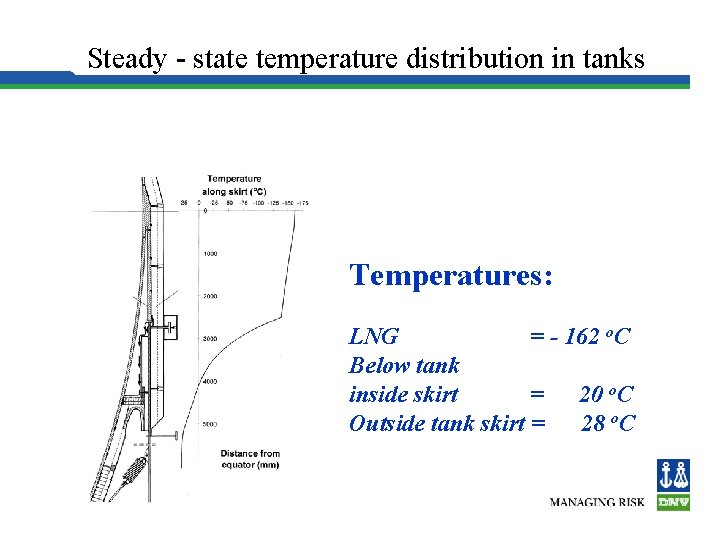
Steady - state temperature distribution in tanks Temperatures: LNG = - 162 o. C Below tank inside skirt = 20 o. C Outside tank skirt = 28 o. C
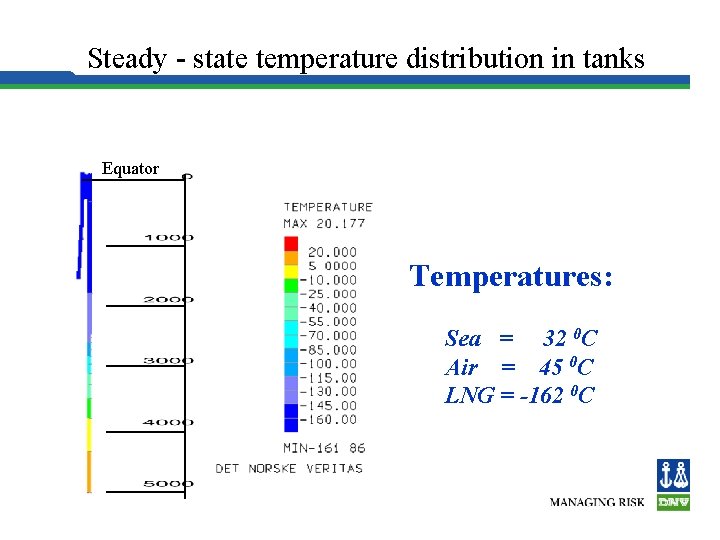
Steady - state temperature distribution in tanks Equator Temperatures: Sea = 32 0 C Air = 45 0 C LNG = -162 0 C
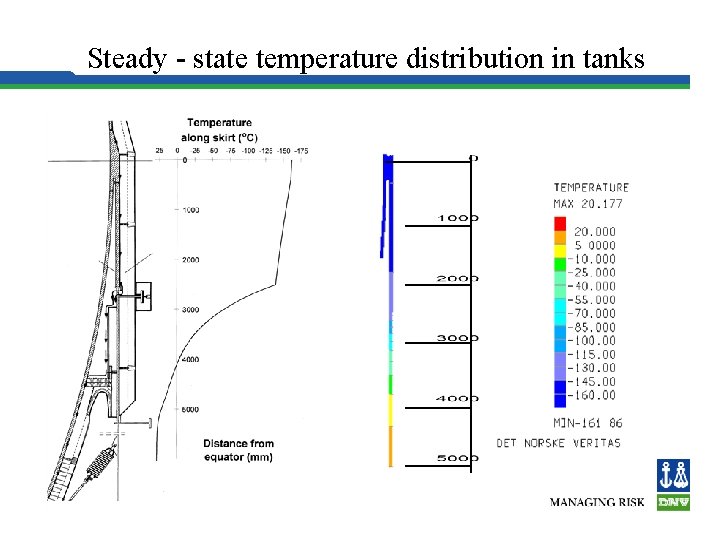
Steady - state temperature distribution in tanks
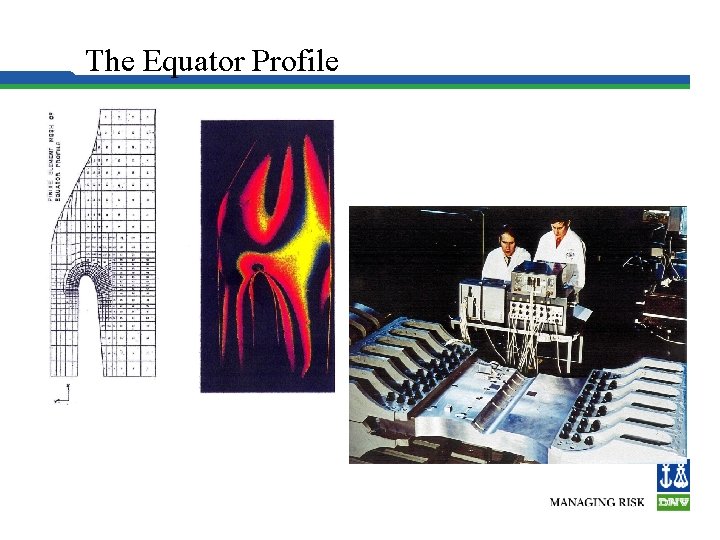
The Equator Profile
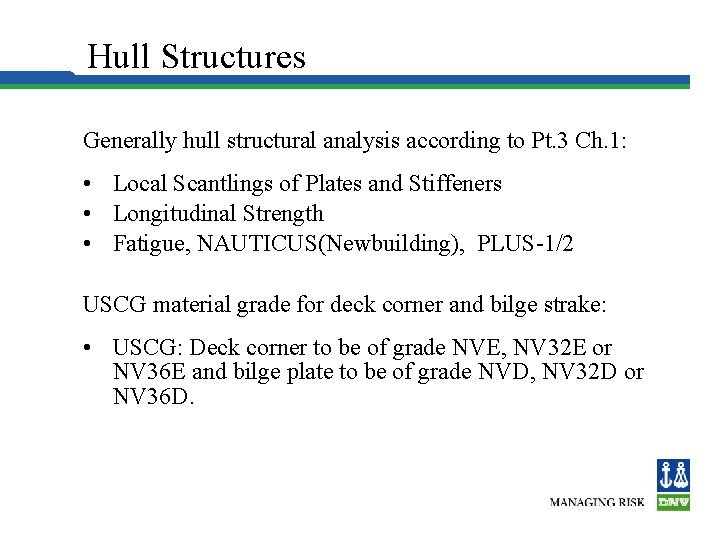
Hull Structures Generally hull structural analysis according to Pt. 3 Ch. 1: • Local Scantlings of Plates and Stiffeners • Longitudinal Strength • Fatigue, NAUTICUS(Newbuilding), PLUS-1/2 USCG material grade for deck corner and bilge strake: • USCG: Deck corner to be of grade NVE, NV 32 E or NV 36 E and bilge plate to be of grade NVD, NV 32 D or NV 36 D.
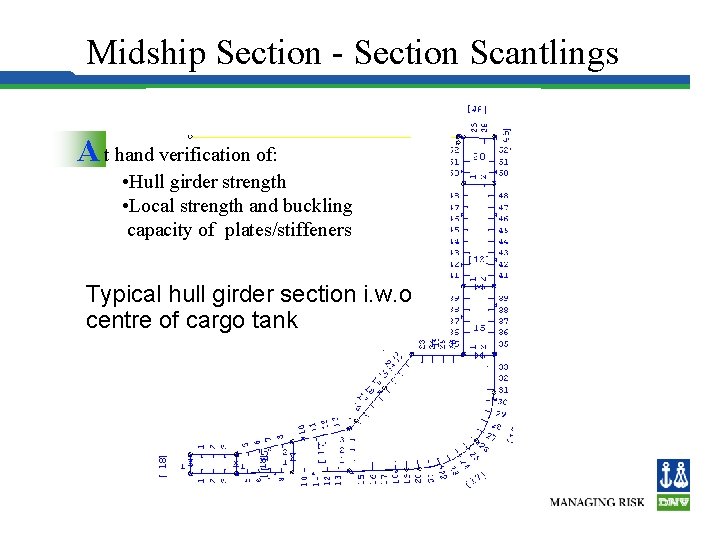
Midship Section - Section Scantlings A t hand verification of: • Hull girder strength • Local strength and buckling capacity of plates/stiffeners Typical hull girder section i. w. o. centre of cargo tank
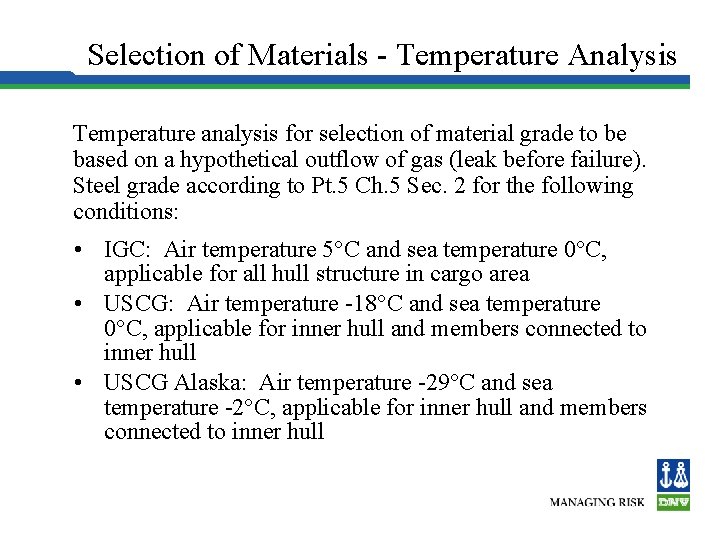
Selection of Materials - Temperature Analysis Temperature analysis for selection of material grade to be based on a hypothetical outflow of gas (leak before failure). Steel grade according to Pt. 5 Ch. 5 Sec. 2 for the following conditions: • IGC: Air temperature 5°C and sea temperature 0°C, applicable for all hull structure in cargo area • USCG: Air temperature -18°C and sea temperature 0°C, applicable for inner hull and members connected to inner hull • USCG Alaska: Air temperature -29°C and sea temperature -2°C, applicable for inner hull and members connected to inner hull
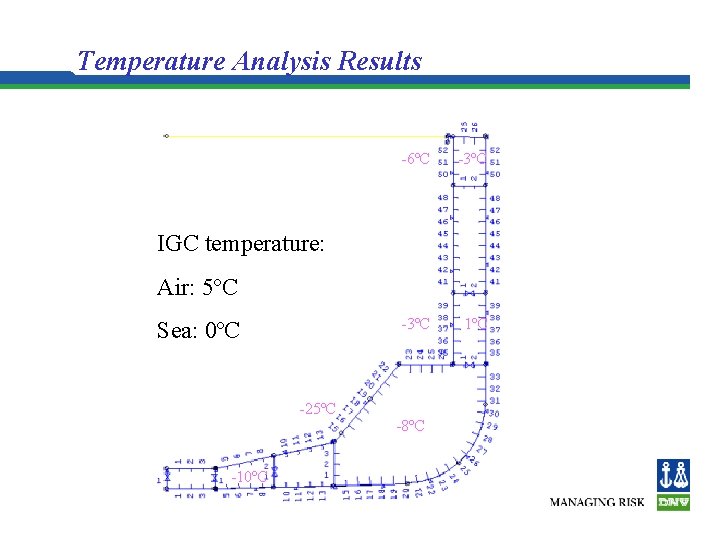
Temperature Analysis Results -6ºC -3ºC 1ºC IGC temperature: Air: 5ºC Sea: 0ºC -25ºC -10ºC -8ºC
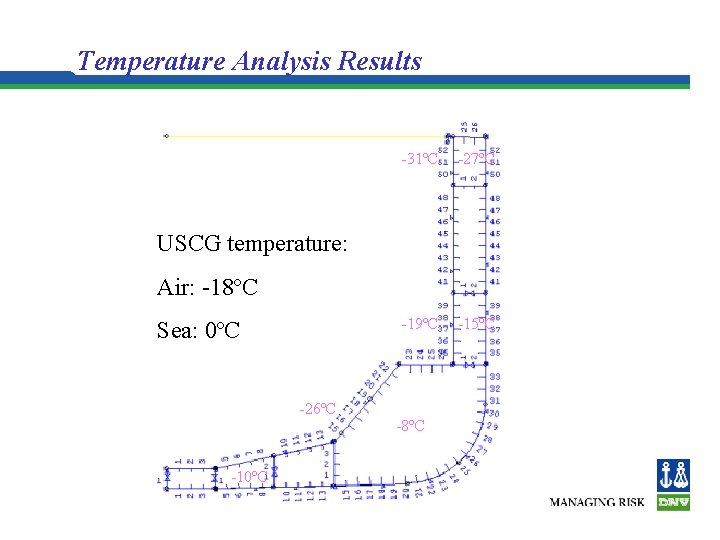
Temperature Analysis Results -31ºC -27ºC -19ºC -15ºC USCG temperature: Air: -18ºC Sea: 0ºC -26ºC -10ºC -8ºC
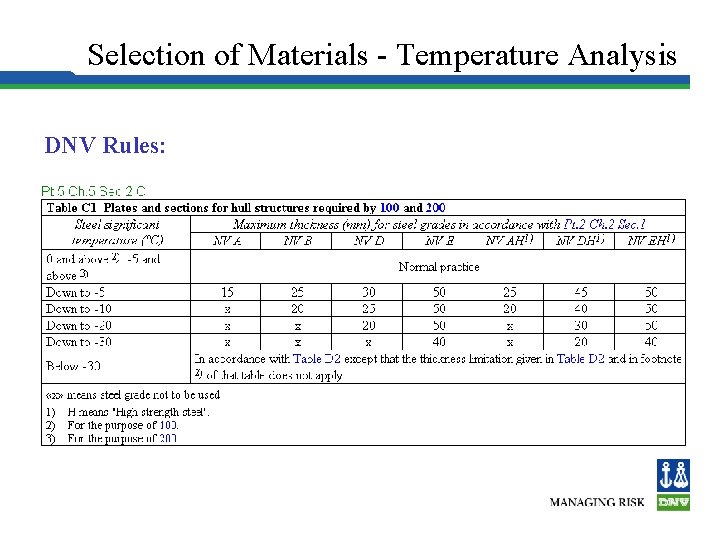
Selection of Materials - Temperature Analysis DNV Rules:
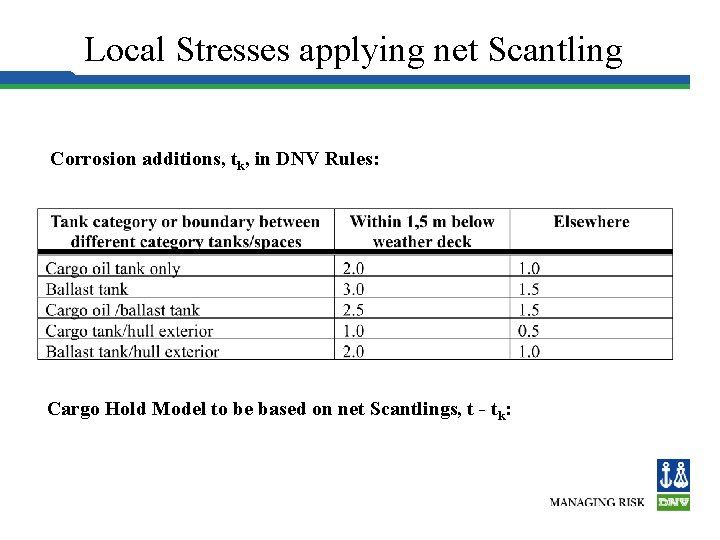
Local Stresses applying net Scantling Corrosion additions, tk, in DNV Rules: Cargo Hold Model to be based on net Scantlings, t - tk:
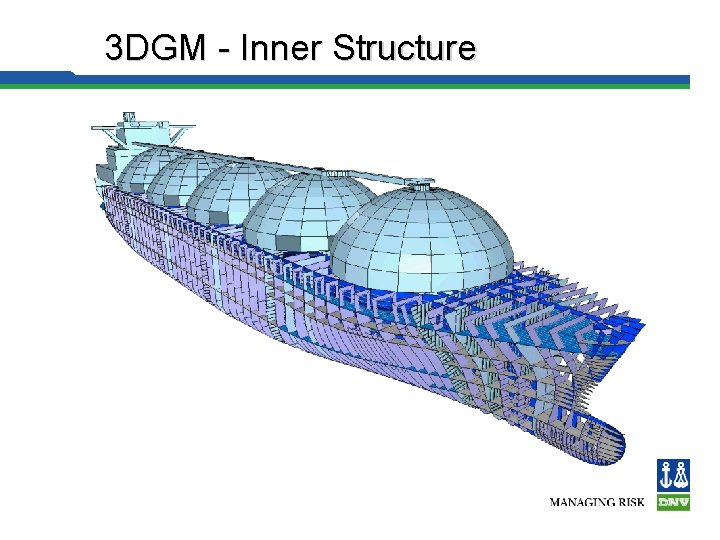
3 DGM - Inner Structure
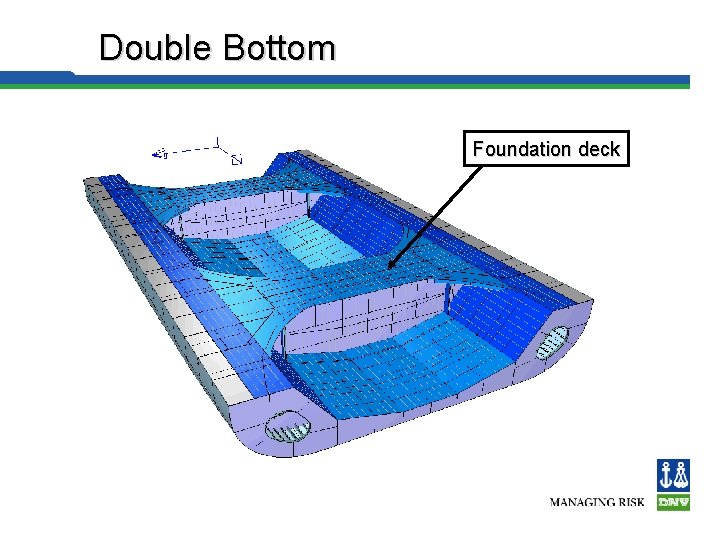
Double Bottom Foundation deck
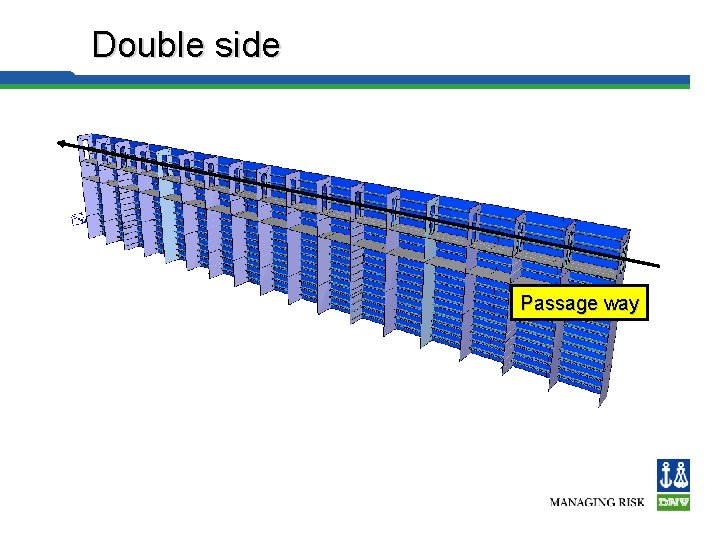
Double side Passage way

Transverse bulkhead Upper stool Single skin trv. bhd
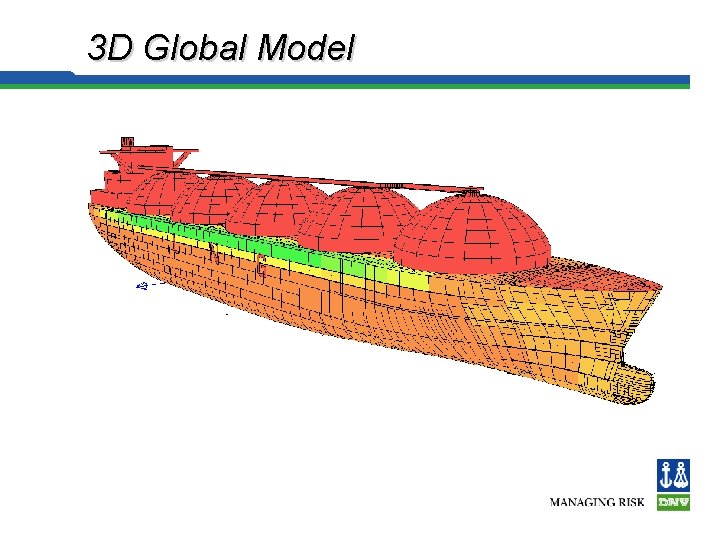
3 D Global Model
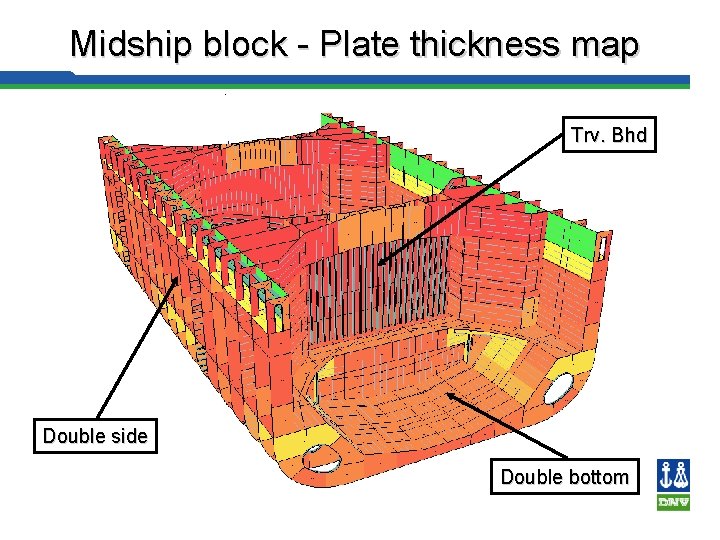
Midship block - Plate thickness map Trv. Bhd Double side Double bottom
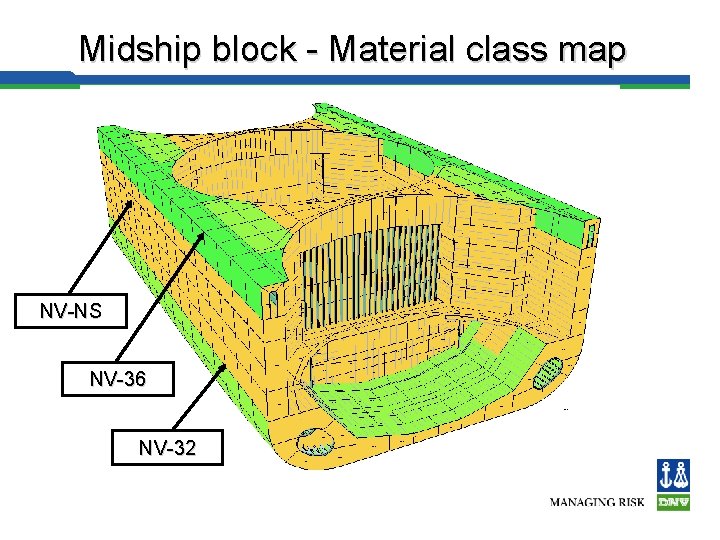
Midship block - Material class map NV-NS NV-36 NV-32
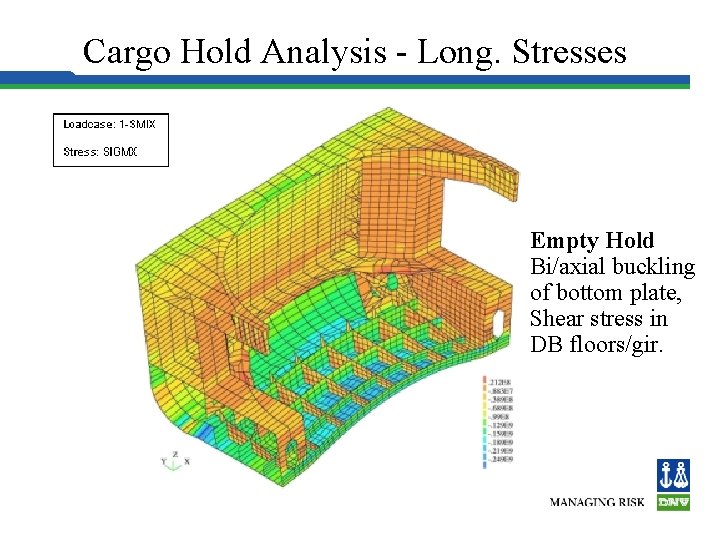
Cargo Hold Analysis - Long. Stresses Empty Hold Bi/axial buckling of bottom plate, Shear stress in DB floors/gir.
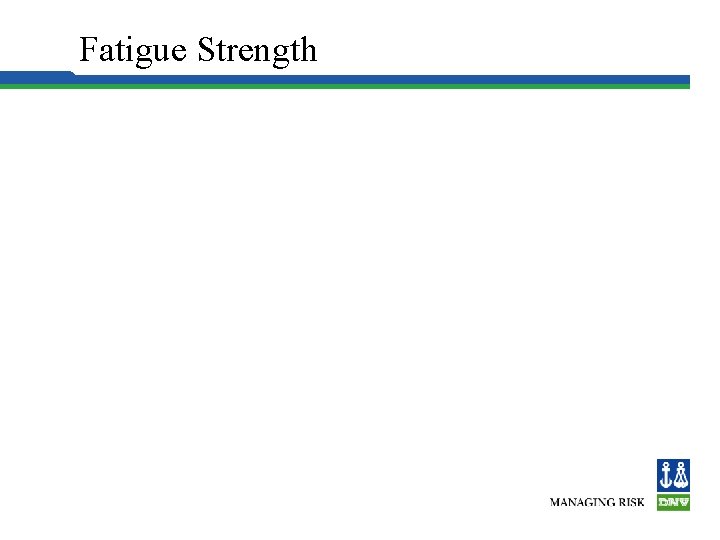
Fatigue Strength
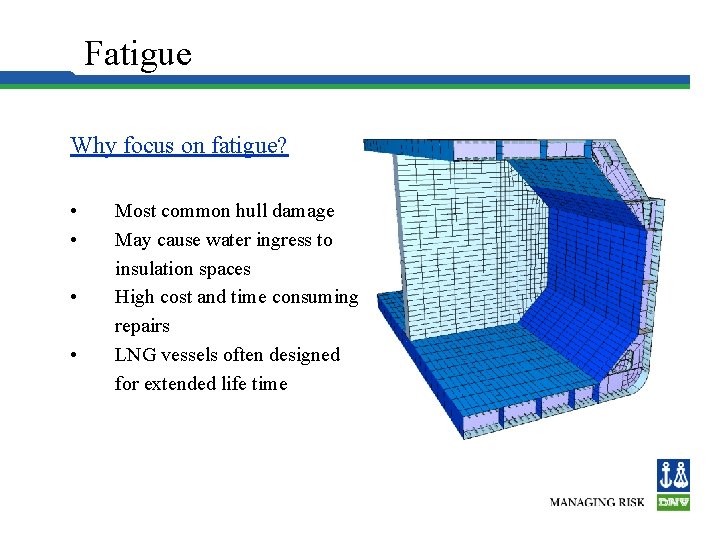
Hull Structure Fatigue Why focus on fatigue? • • Most common hull damage May cause water ingress to insulation spaces High cost and time consuming repairs LNG vessels often designed for extended life time
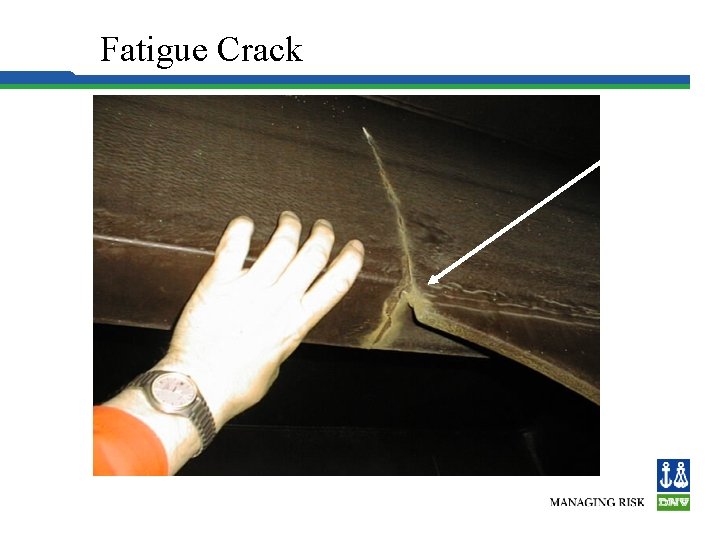
Fatigue Crack
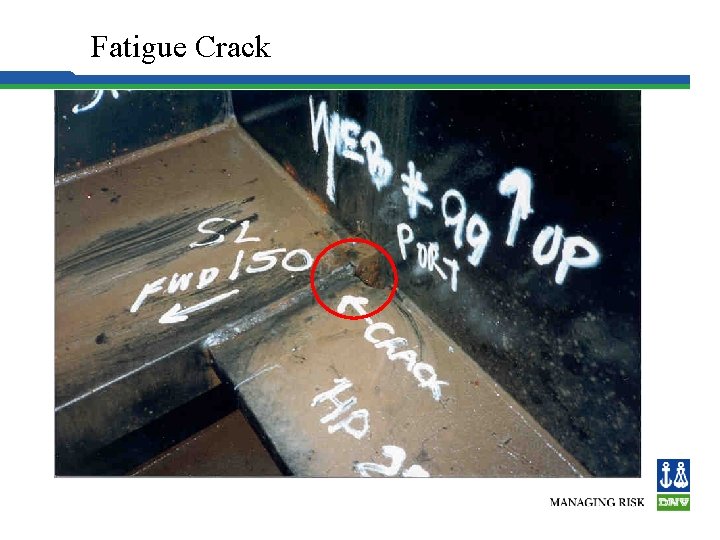
Fatigue Crack
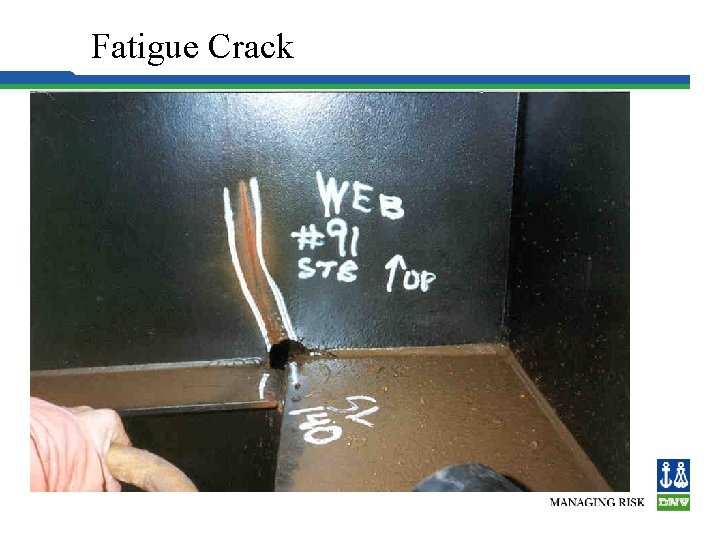
Fatigue Crack
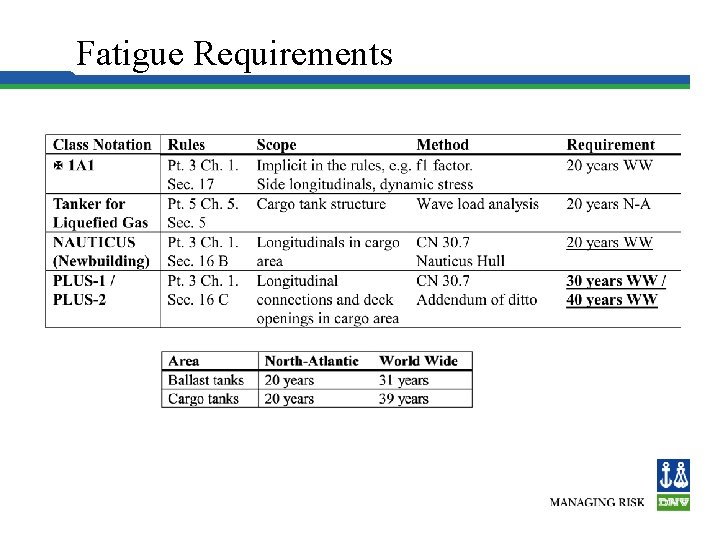
Fatigue Requirements
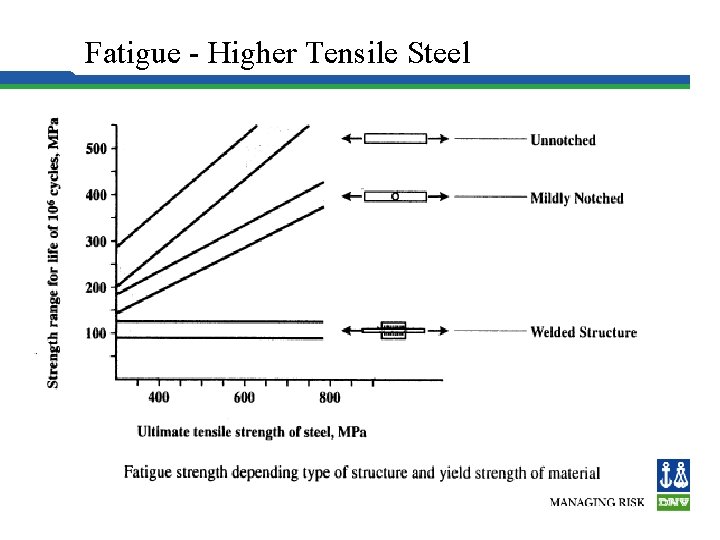
Fatigue - Higher Tensile Steel
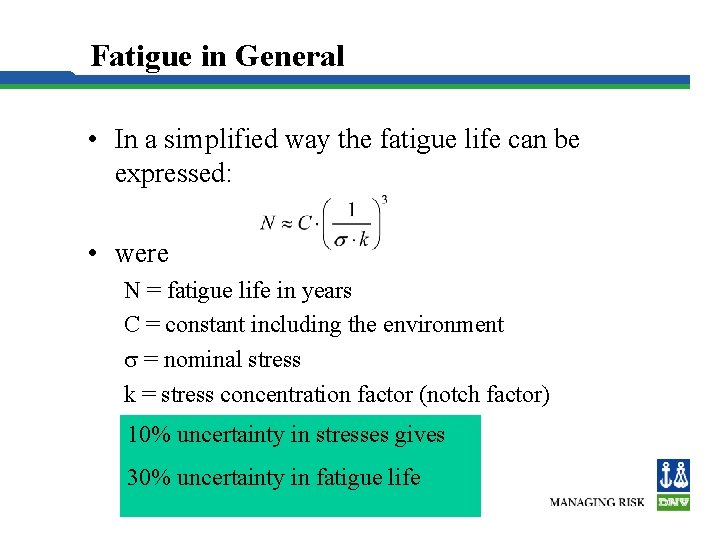
Fatigue in General • In a simplified way the fatigue life can be expressed: • were N = fatigue life in years C = constant including the environment = nominal stress k = stress concentration factor (notch factor) 10% uncertainty in stresses gives 30% uncertainty in fatigue life
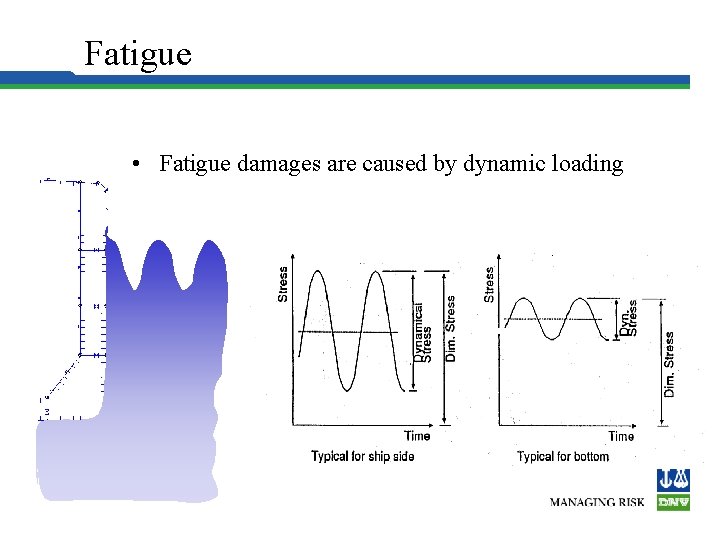
Hull Structure Fatigue • Fatigue damages are caused by dynamic loading
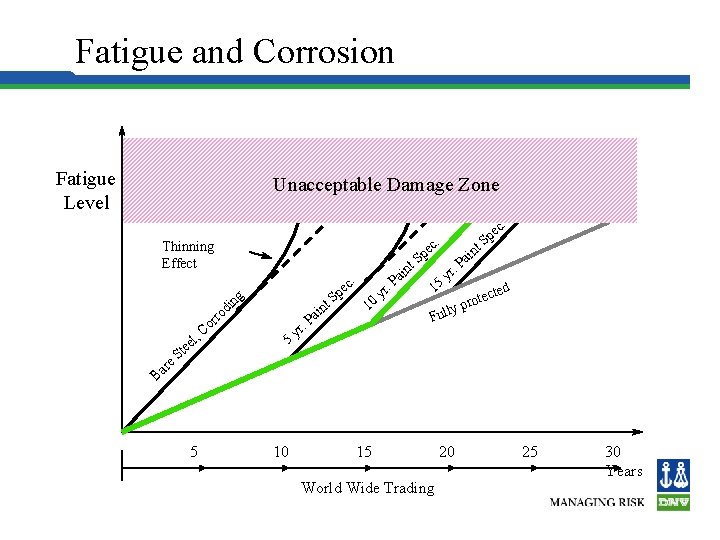
Fatigue and Corrosion Fatigue Level Unacceptable Damage Zone c. Thinning Effect c. g in , el re a B e St 5 d ro r Co t t 5 10 . yr in Pa e Sp 15 c. e p t. S ain . P yr cted ote y pr Full 15 World Wide Trading 20 25 30 Years
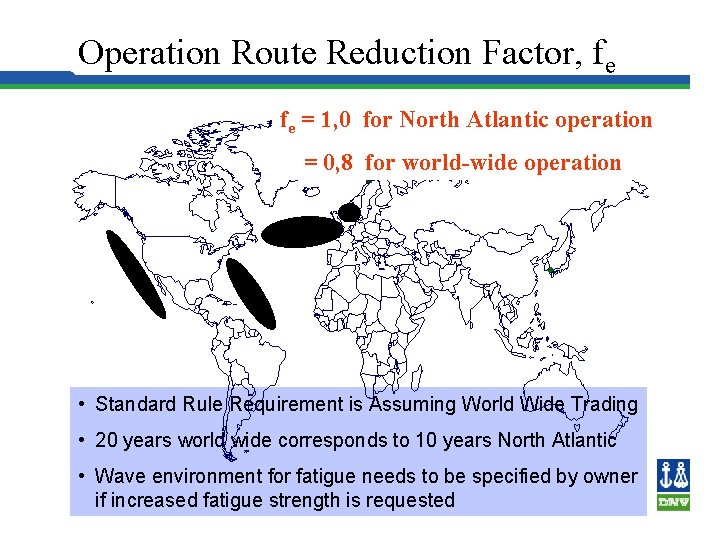
Operation Route Reduction Factor, fe fe = 1, 0 for North Atlantic operation = 0, 8 for world-wide operation • Standard Rule Requirement is Assuming World Wide Trading • 20 years world wide corresponds to 10 years North Atlantic • Wave environment for fatigue needs to be specified by owner if increased fatigue strength is requested
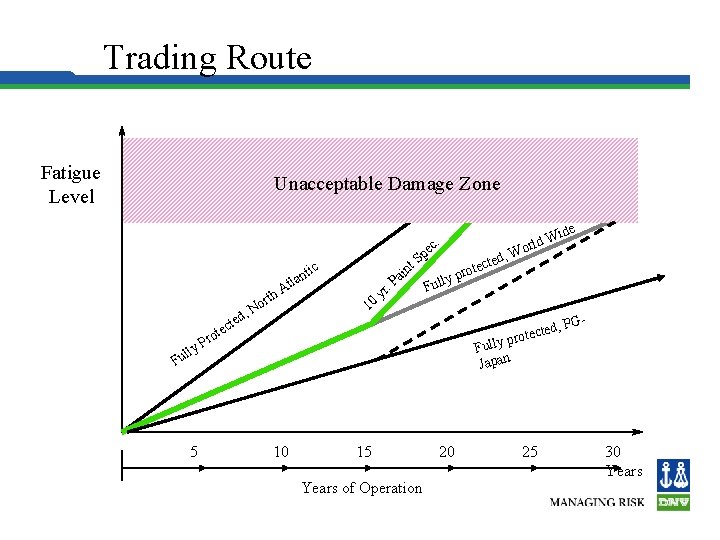
Trading Route Fatigue Level Unacceptable Damage Zone te tec lly Fu 5 d, rt No S nt ai n tla 10 P r. y W orld d, W p tic h. A ide . ec cte rote yp Full Ged, P t c e t pro Pro Fully Japan 10 15 Years of Operation 20 25 30 Years
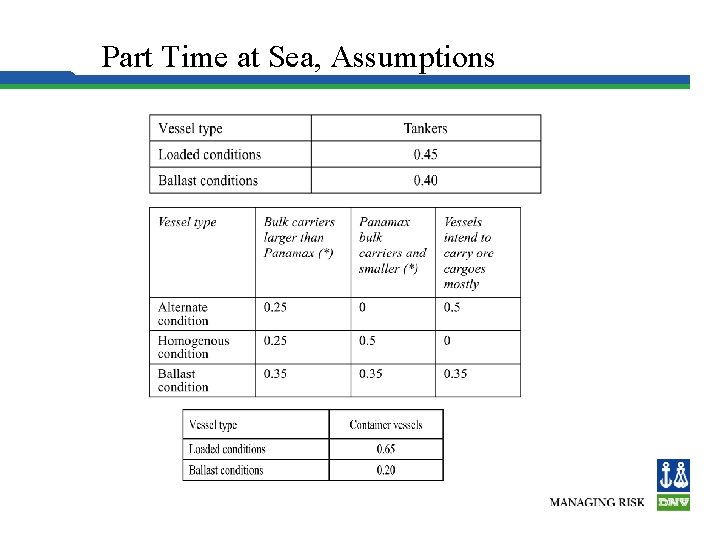
Part Time at Sea, Assumptions
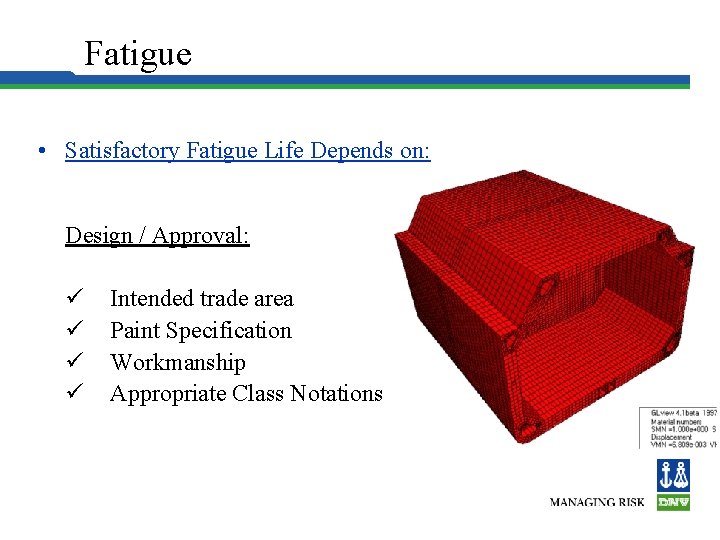
Hull Structure Fatigue • Satisfactory Fatigue Life Depends on: Design / Approval: Intended trade area Paint Specification Workmanship Appropriate Class Notations
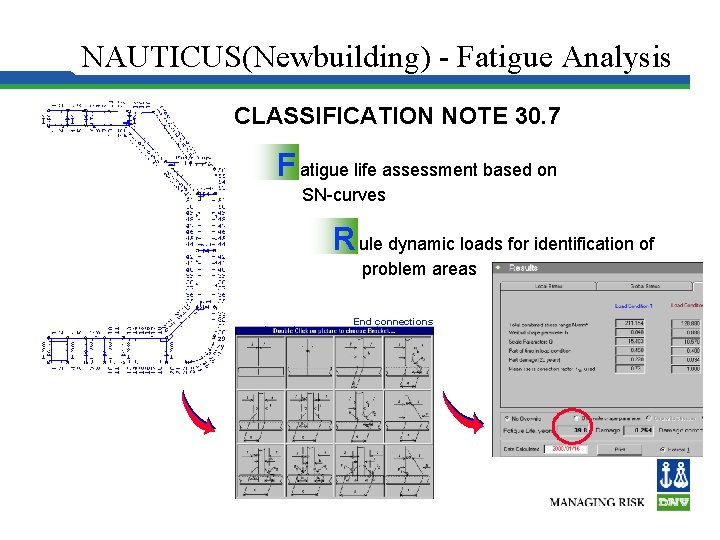
NAUTICUS(Newbuilding) - Fatigue Analysis CLASSIFICATION NOTE 30. 7 F atigue life assessment based on SN-curves R ule dynamic loads for identification of posproblem areas End connections
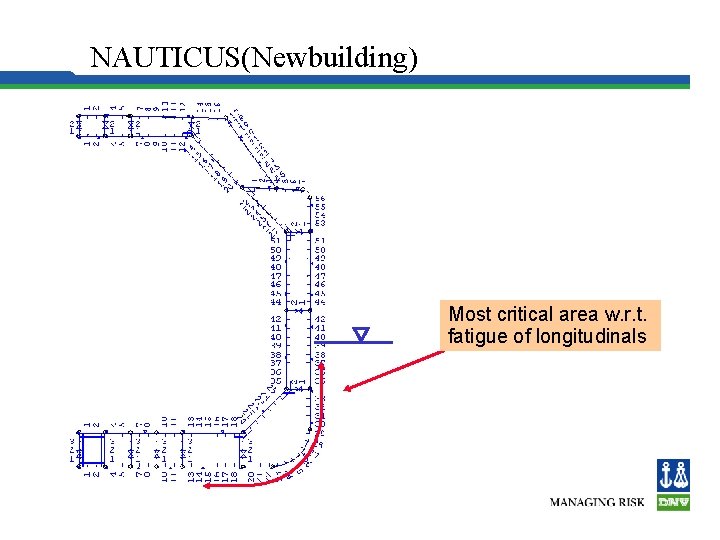
NAUTICUS(Newbuilding) Most critical area w. r. t. fatigue of longitudinals
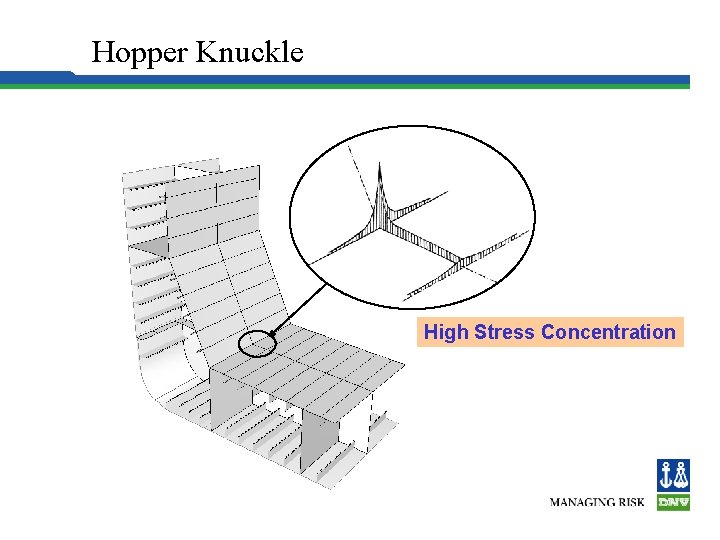
Hopper Knuckle High Stress Concentration
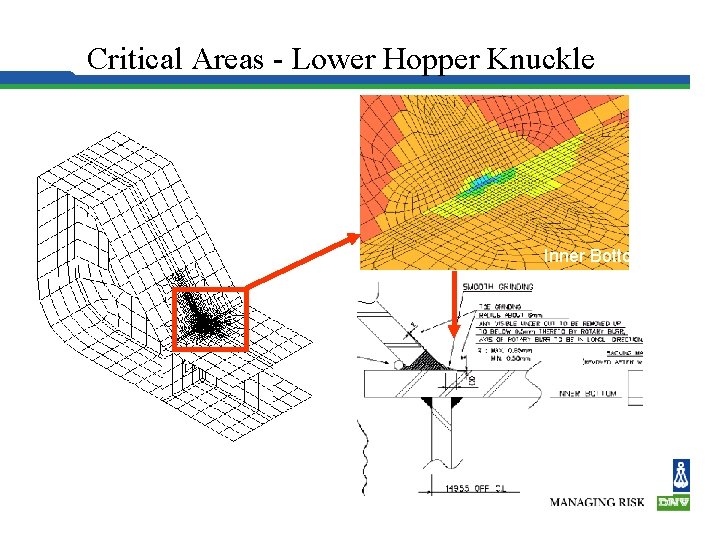
Hull Structure Critical Areas - Lower Hopper Knuckle Inner Bottom
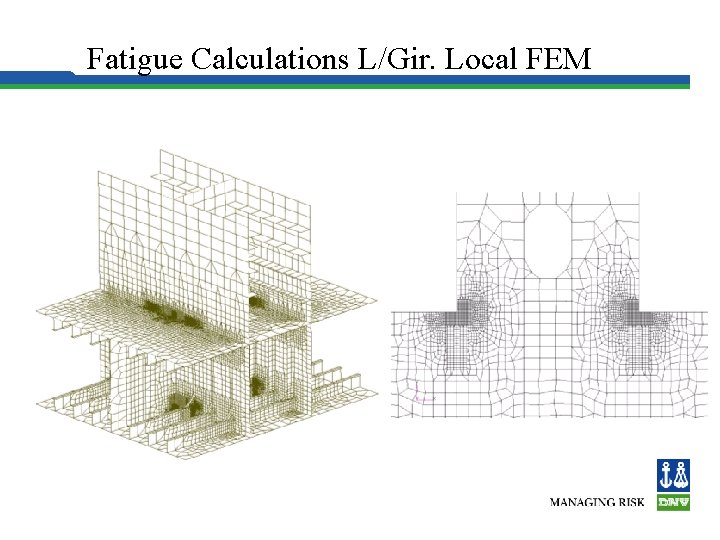
Fatigue Calculations L/Gir. Local FEM
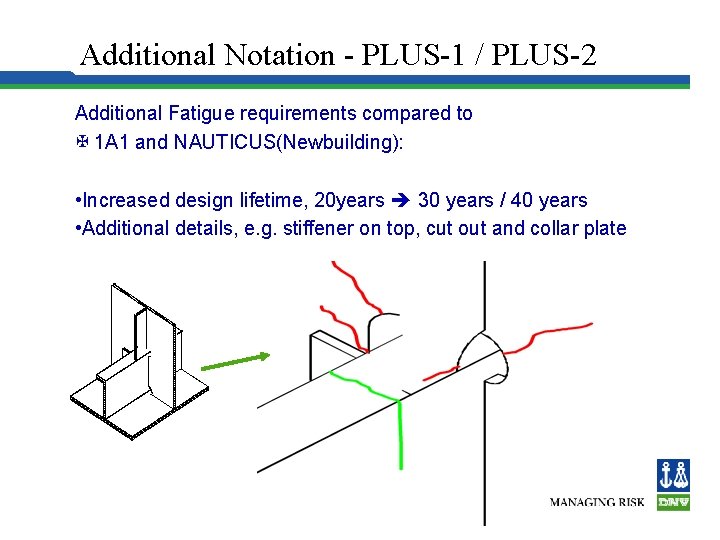
Additional Notation - PLUS-1 / PLUS-2 Additional Fatigue requirements compared to 1 A 1 and NAUTICUS(Newbuilding): • Increased design lifetime, 20 years 30 years / 40 years • Additional details, e. g. stiffener on top, cut out and collar plate
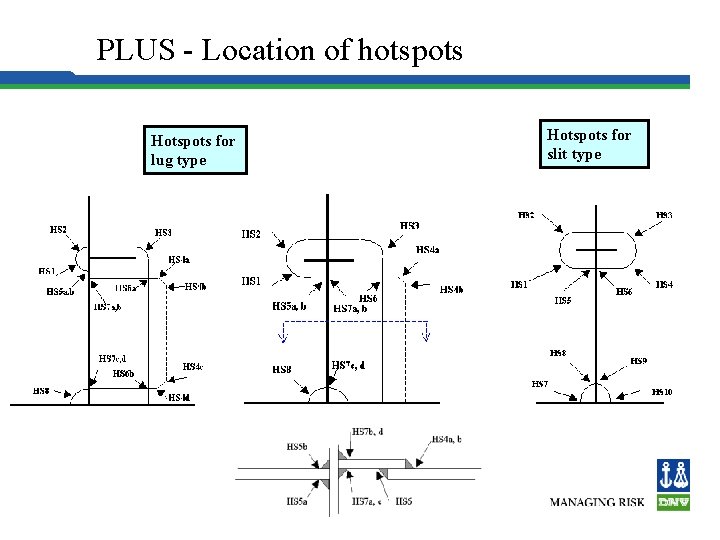
PLUS - Location of hotspots Hotspots for lug type Hotspots for slit type
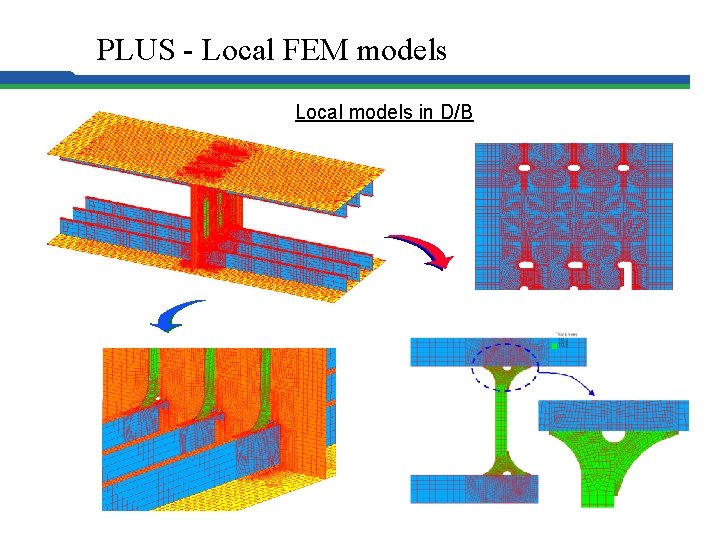
PLUS - Local FEM models Local models in D/B
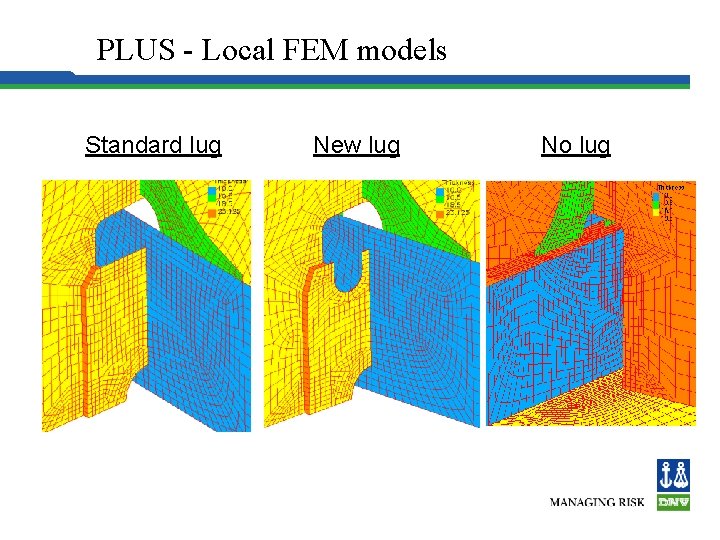
PLUS - Local FEM models Standard lug New lug No lug
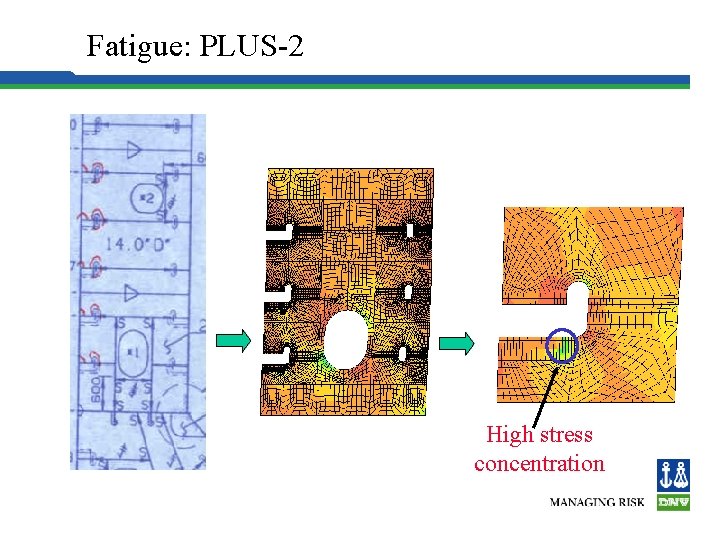
Hull Structure Fatigue: PLUS-2 High stress concentration
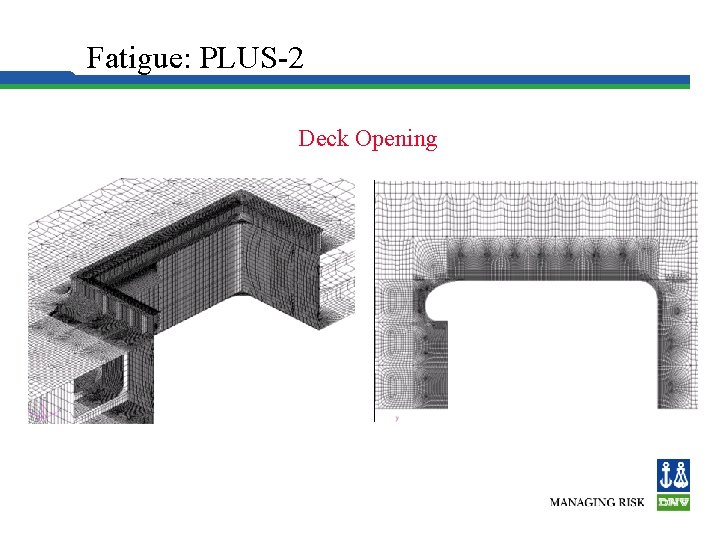
Hull Structure Fatigue: PLUS-2 Deck Opening
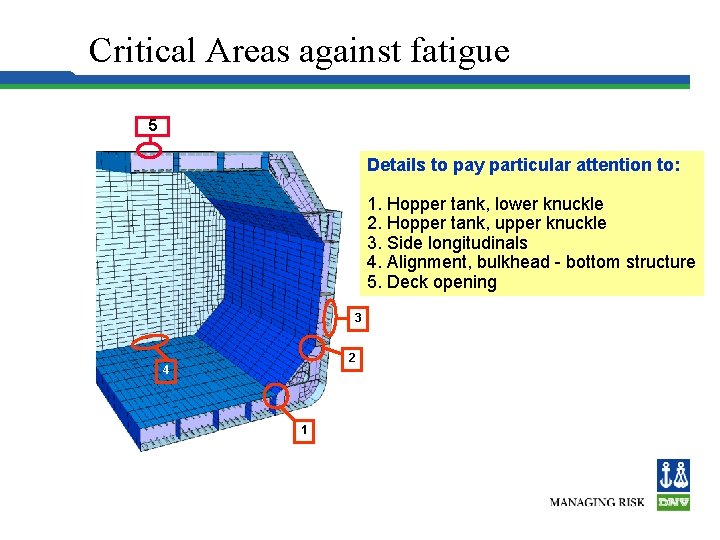
Hull Structure Critical Areas against fatigue 5 Details to pay particular attention to: 1. Hopper tank, lower knuckle 2. Hopper tank, upper knuckle 3. Side longitudinals 4. Alignment, bulkhead - bottom structure 5. Deck opening 3 2 4 1
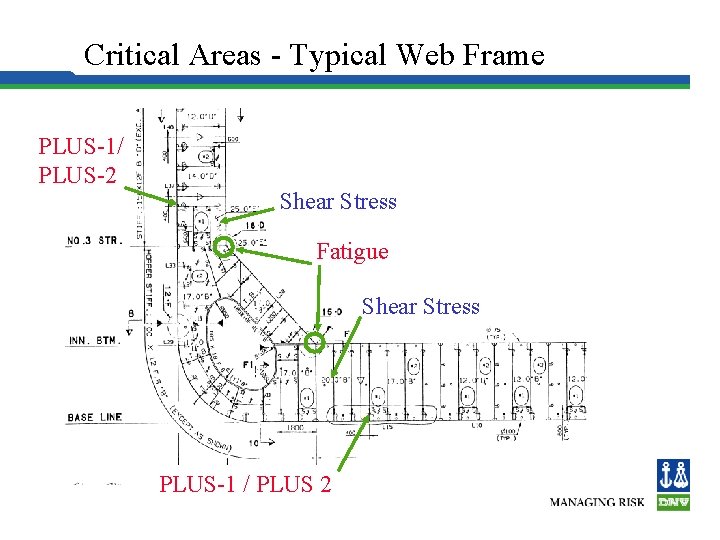
Critical Areas - Typical Web Frame PLUS-1/ PLUS-2 Shear Stress Fatigue Shear Stress PLUS-1 / PLUS 2
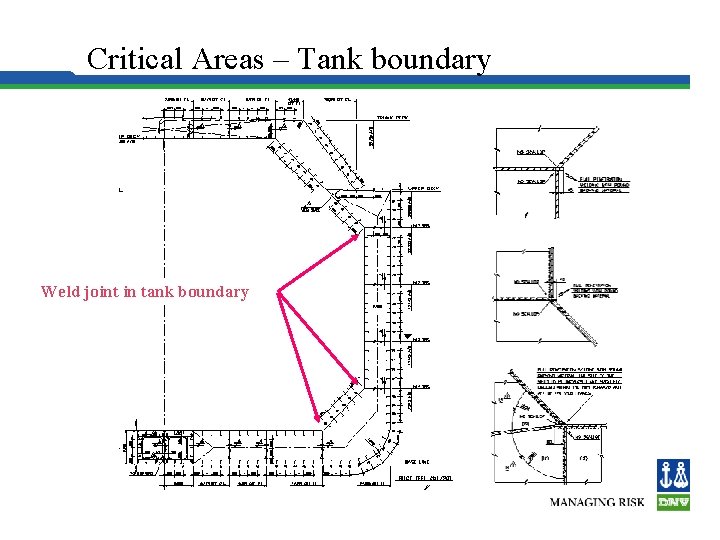
Critical Areas – Tank boundary Weld joint in tank boundary
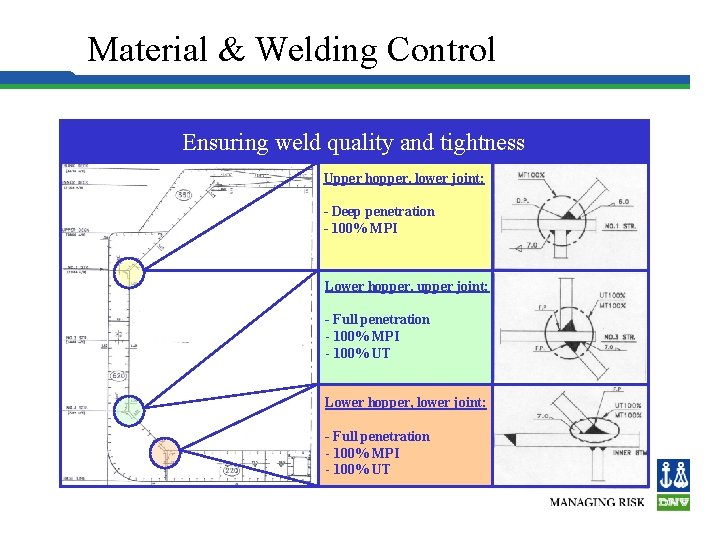
Material & Welding Control Ensuring weld quality and tightness Upper hopper, lower joint: - Deep penetration - 100% MPI Lower hopper, upper joint: - Full penetration - 100% MPI - 100% UT Lower hopper, lower joint: - Full penetration - 100% MPI - 100% UT
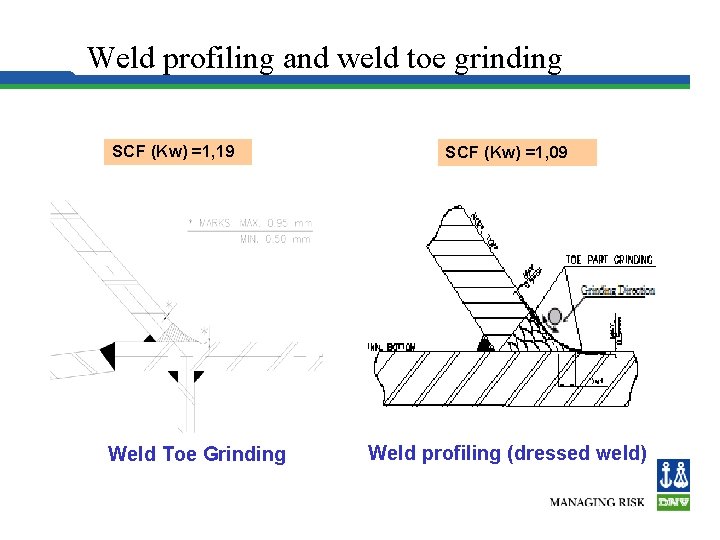
Weld profiling and weld toe grinding SCF (Kw) =1, 19 Weld Toe Grinding SCF (Kw) =1, 09 Weld profiling (dressed weld)
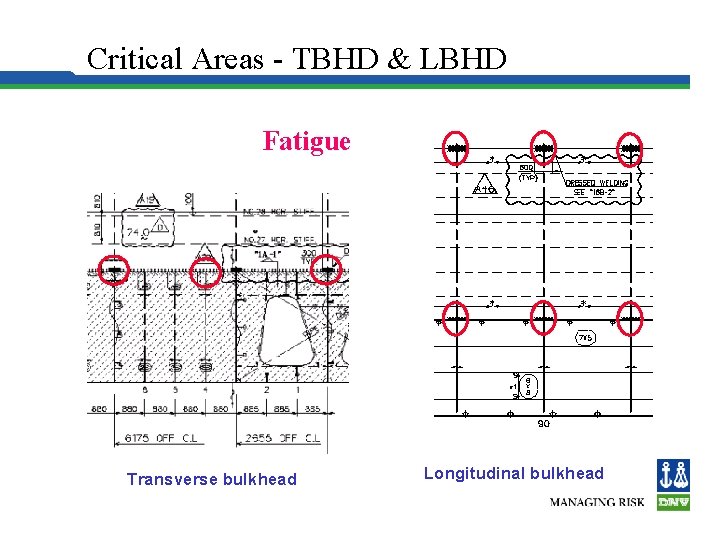
Critical Areas - TBHD & LBHD Fatigue Transverse bulkhead Longitudinal bulkhead
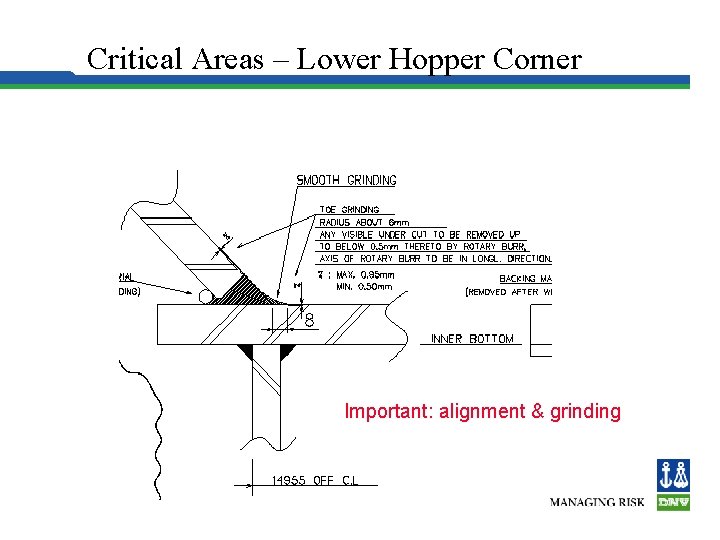
Critical Areas – Lower Hopper Corner Important: alignment & grinding
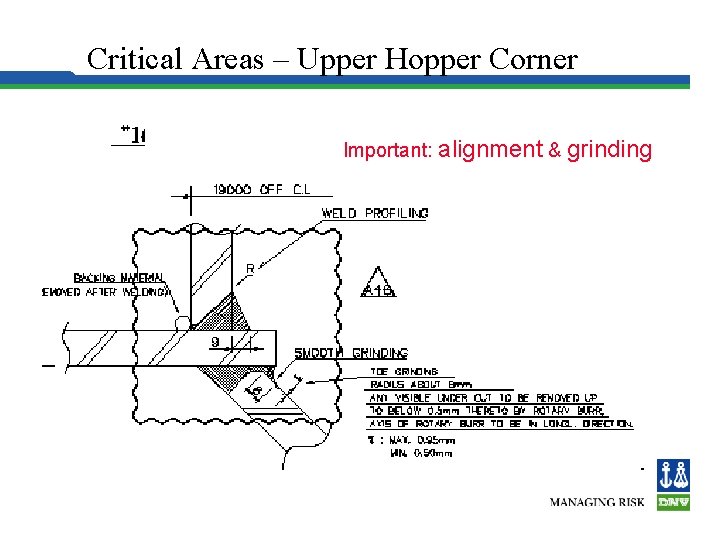
Critical Areas – Upper Hopper Corner Important: && grinding Important: alignment grinding
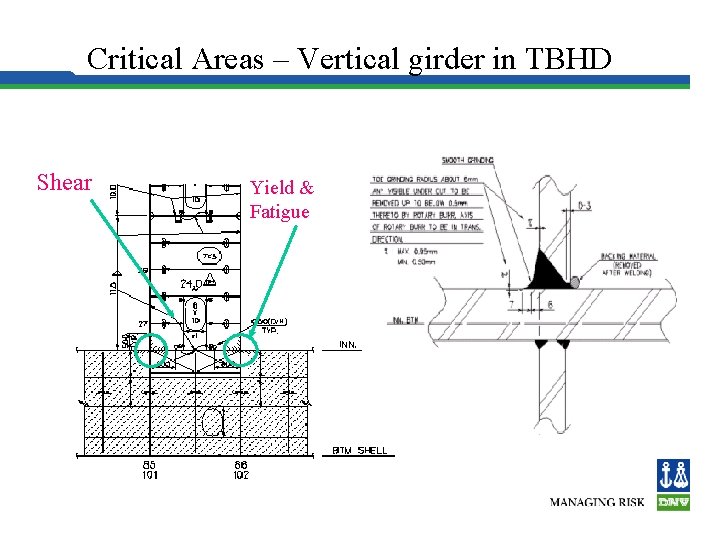
Critical Areas – Vertical girder in TBHD Shear Yield & Fatigue
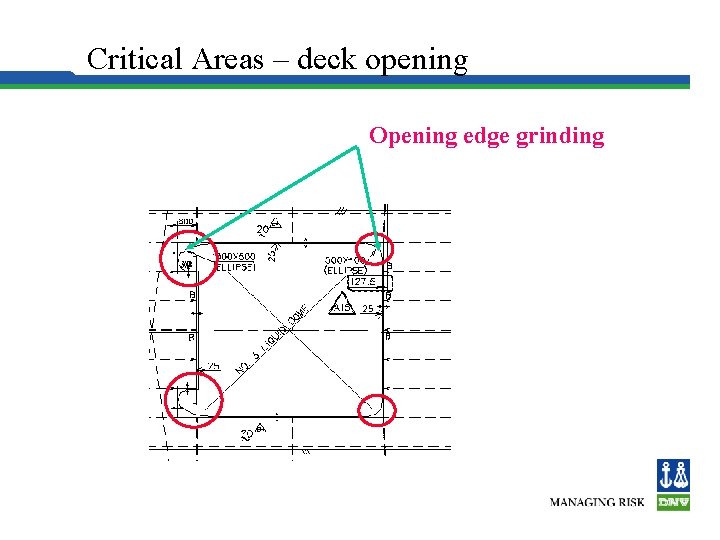
Critical Areas – deck opening Opening edge grinding
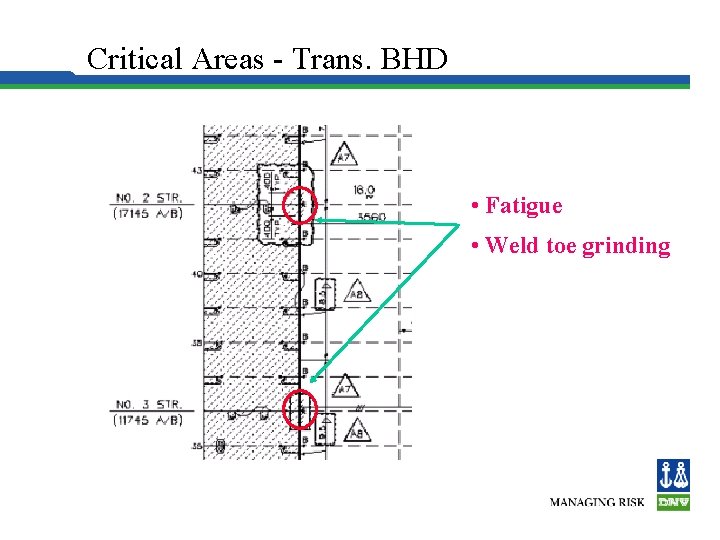
Critical Areas - Trans. BHD • Fatigue • Weld toe grinding
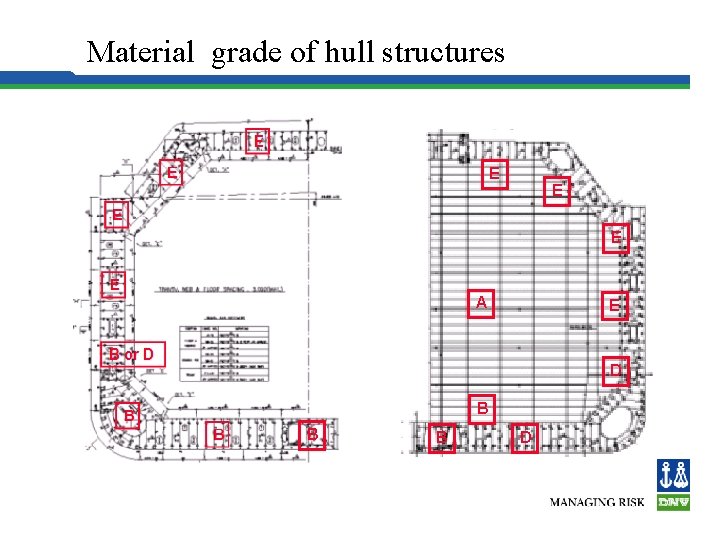
Hull Structure Material grade of hull structures E E E A E D B B B D
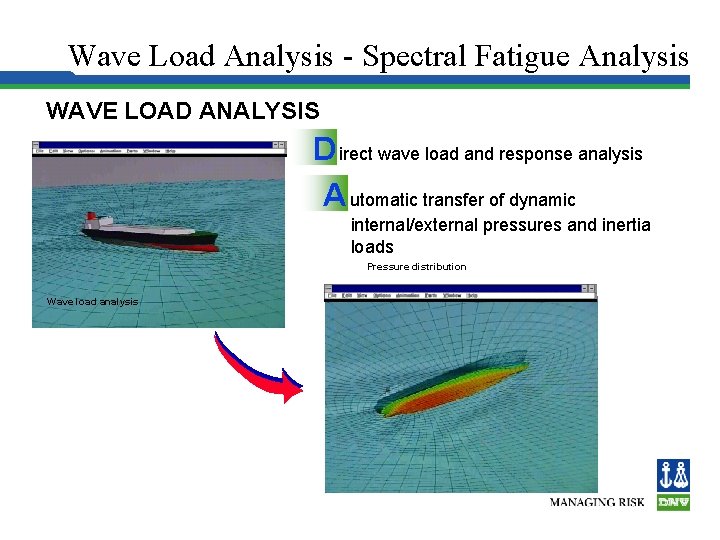
Wave Load Analysis - Spectral Fatigue Analysis WAVE LOAD ANALYSIS D irect wave load and response analysis A utomatic transfer of dynamic internal/external pressures and inertia loads Pressure distribution Wave load analysis
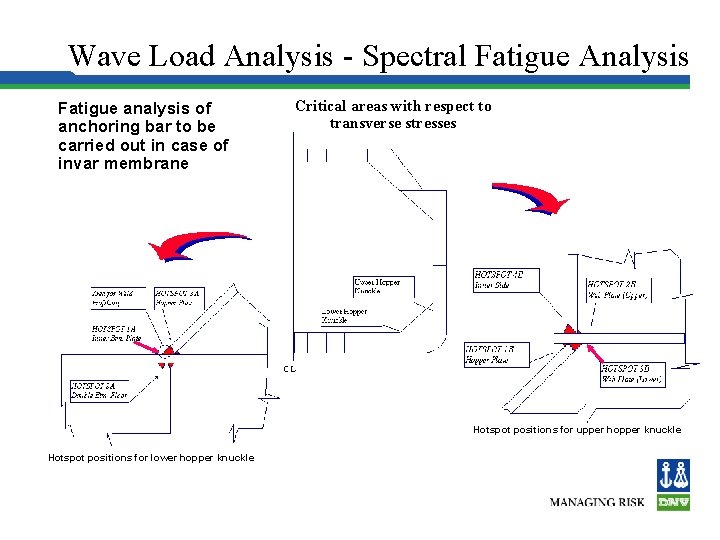
Wave Load Analysis - Spectral Fatigue Analysis Fatigue analysis of anchoring bar to be carried out in case of invar membrane Critical areas with respect to transverse stresses Hotspot positions for upper hopper knuckle Hotspot positions for lower hopper knuckle
International gas carrier code
Rentas exentas del igc según art. 54 n° 3 lir
Robyn fiori
Imos landing page
Netcdf ninja
Pseudo reduced specific volume
Imaginary gas
Differences between ideal gas and real gas
Computational fluid dynamics
Gas leaked in bhopal gas tragedy
Gas leaked in bhopal gas tragedy
Volume molare
Flue gas desulfurisation gas filter
Poisonous gas leaked in bhopal gas tragedy
Difference between ideal gas and real gas
Hukum laju terintegrasi
Gas exchange key events in gas exchange
Busceral
"databank"
"leads international" "international marketing"
Carrier to noise ratio
Tonicity
Channel vs carrier proteins
Hudrops
Distributor storage with customer pickup
Kinds of chromosomal mutations
Carrier ethernet security
Robertsonian translocation 14 21
Que es una regla cardinal de seguridad
Punnett square for color blindness
Chapter 7 extending mendelian genetics
Carrier to noise ratio
Hot carrier 효과
Fermi energy formula
Continuity equation in semiconductor
Npn and pnp transistor difference
Otcl carrier
Number blocks
Rr x rr
Motor carrier compliance division
Heterozygous b blood type
Real content and carrier content in esp
Intrinsic carrier concentration
Motor carrier safety assistance program
For unsaturated air the value of dpt is
Partial non hunting gearset
For an am dsbfc modulator with a carrier frequency
Hierarchy
Intrinsic semiconductor carrier concentration
Band gaps of semiconductors
Transcellular diffusion
Cell membrane function
Carrier transport phenomena
Microwave technologies for carrier ethernet services
Carrier ccn
Carrier in bpo
Bulk carrier booklet
Safer fmcsa company snapshot
Virtual carrier sensing
Transporte
Fmcsr 396
Ucr registration ga
Carrier concentration in intrinsic semiconductor
Carrier concentration in intrinsic semiconductor
Illustrative content
Unmodulated carrier power formula
Universal energy carrier
Gluon force carrier
Why schottky diode is called hot carrier diode
Safersys snapshot
Carrier bid optimization
Modot motor carrier services
Velazquez water carrier of seville
Fmcsa login portal
Carrier selection determinants
Aircraft carrier catapult acceleration
Plastic leaded chip carrier
Csma cd
My carrier resources
My carrier resources
Carrier fmc4
Carrier power formula
Design options for a distribution network
Contoh data carrier adalah
Intra arterial route advantages and disadvantages
Carrier farrag method of graduation
The pedigree below tracks the presence of attached earlobes
Carrier aggregation
Retail storage with customer pickup
Pnp minority carrier distribution
Hapten carrier
Ef-ei semiconductor
Echinococcus granulosus sketchy
Unified carrier registration nc
Retail storage with customer pickup
Delivery gas png
Modot motor carrier express
Carrier envelope phase
Scalability matrix
Landstar carrier packet
Freightline carrier systems
Ethernet code b
Modot motor carrier express
Carrier comfort network
One wilshire meet me room
Landstar carrier setup packet
Florida building code gas piping
Nfpa chapter 5
Morse code speed record
International food code
Tableau de classification des bactéries
International council of nurses code of ethics
Code élaboré code restreint
Managed code unmanaged code
Apa itu assembler
Difference between source code and machine code
What is linguistic repertoire
Order of bases in dna
Alveolar gas equation
What happens to gas when the temperature decreases
Alicia milner
Height of cylinder gas
A luminous ball of gas
Gas and liquid solution example