GAS WELDING INTRODUCTION Gas welding is a fusion
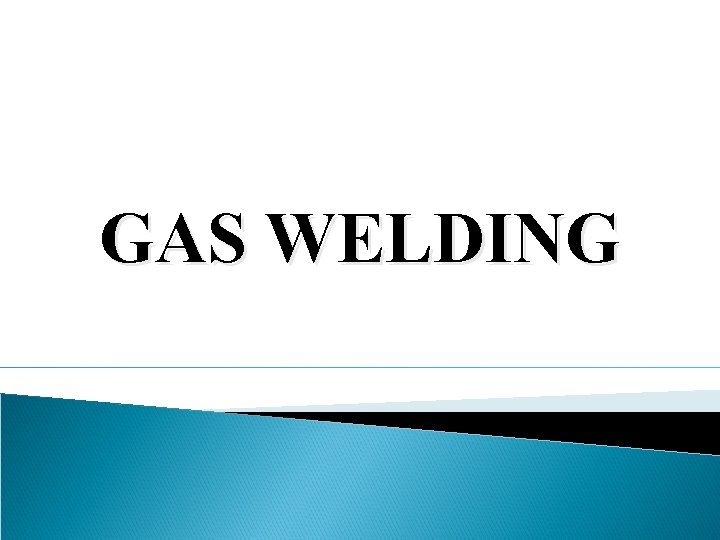
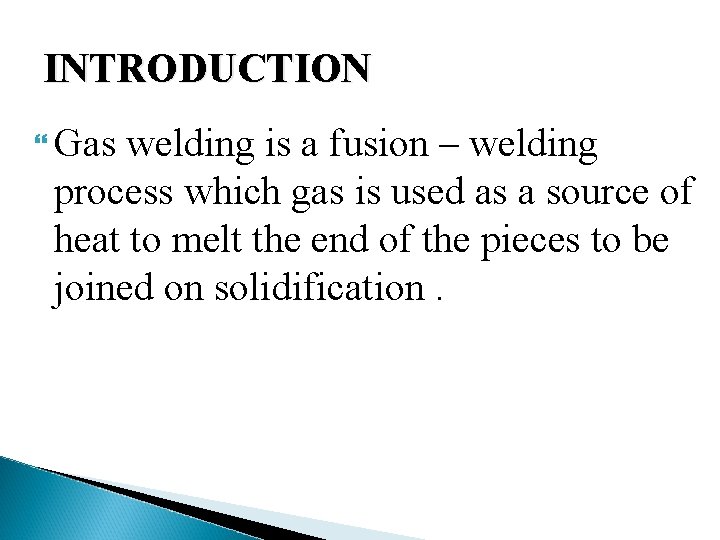
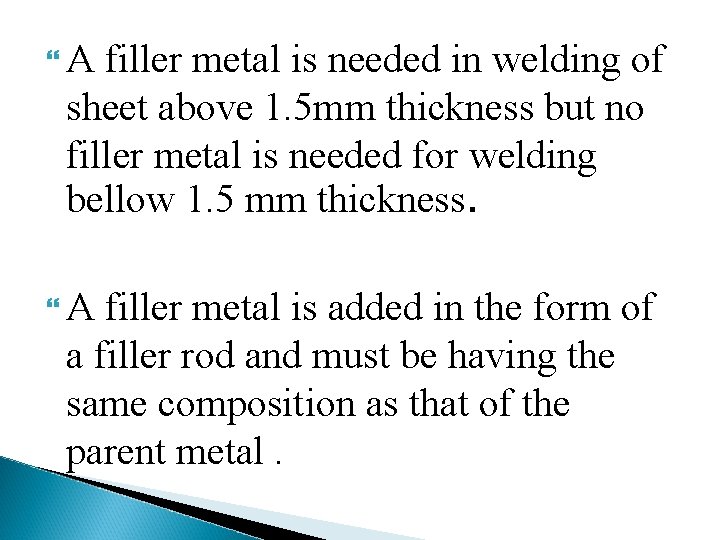
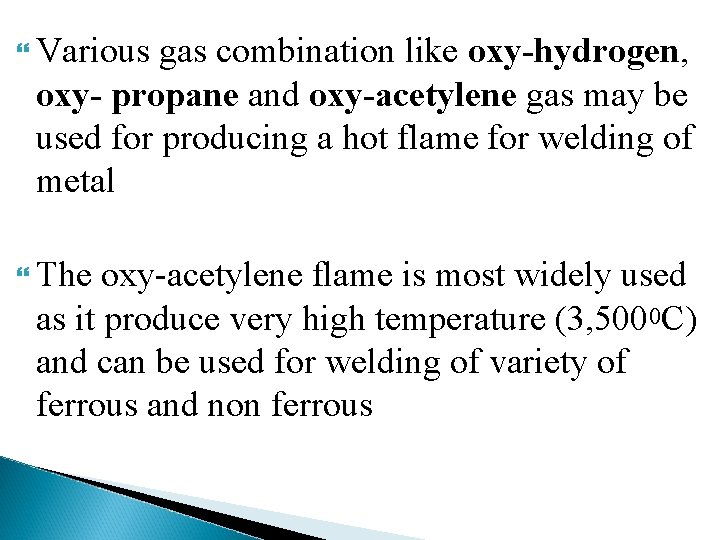
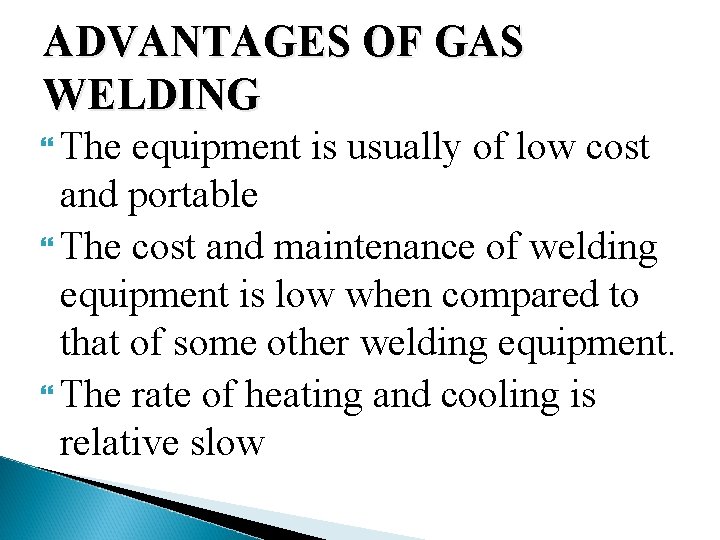
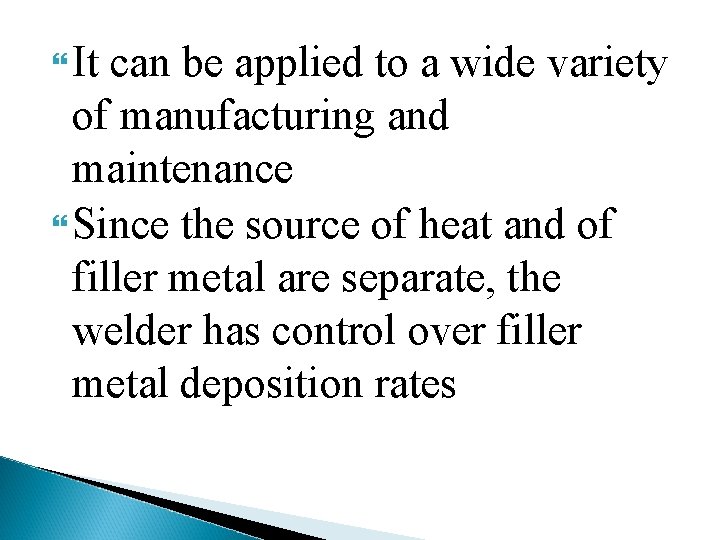
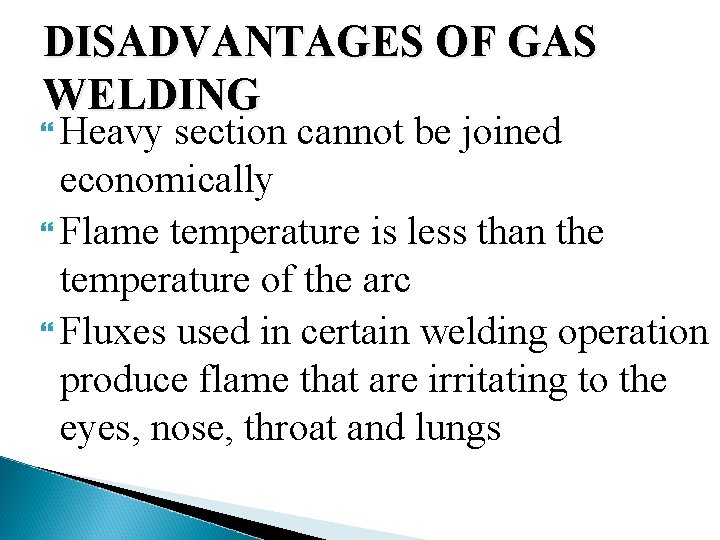
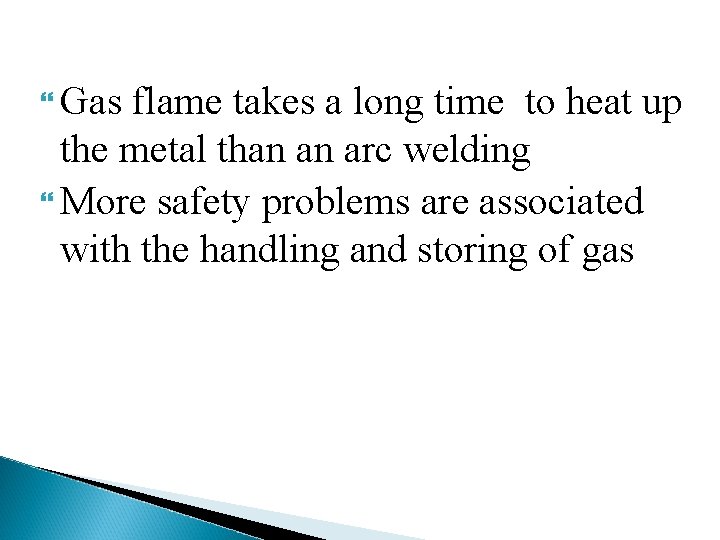
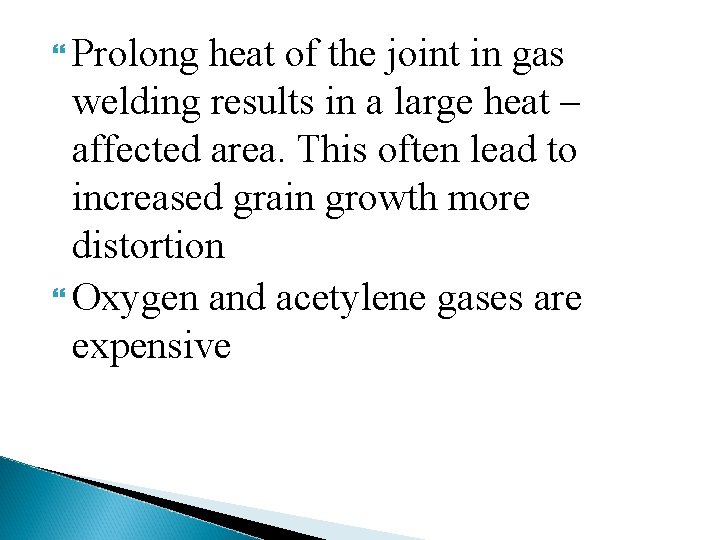
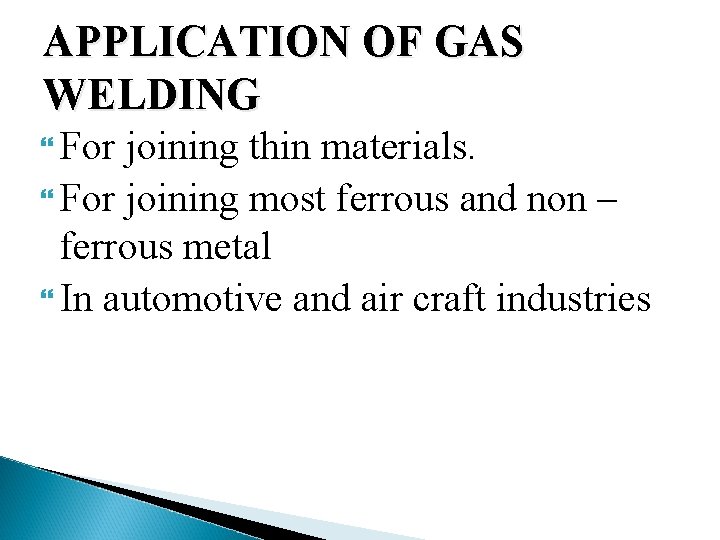
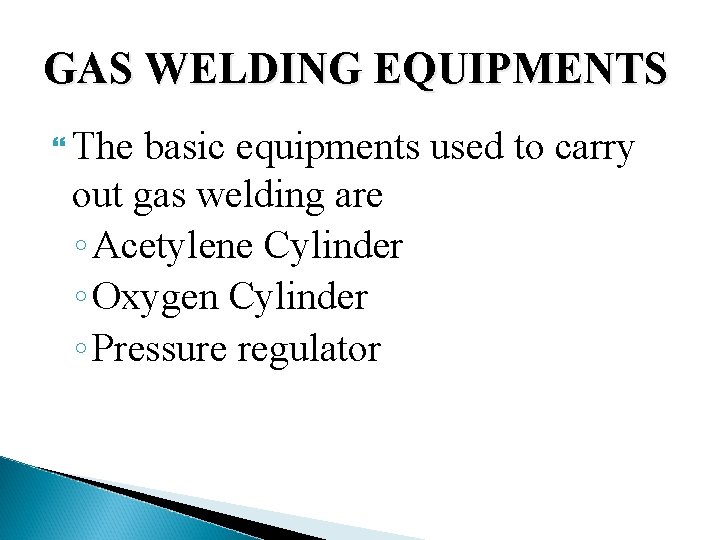
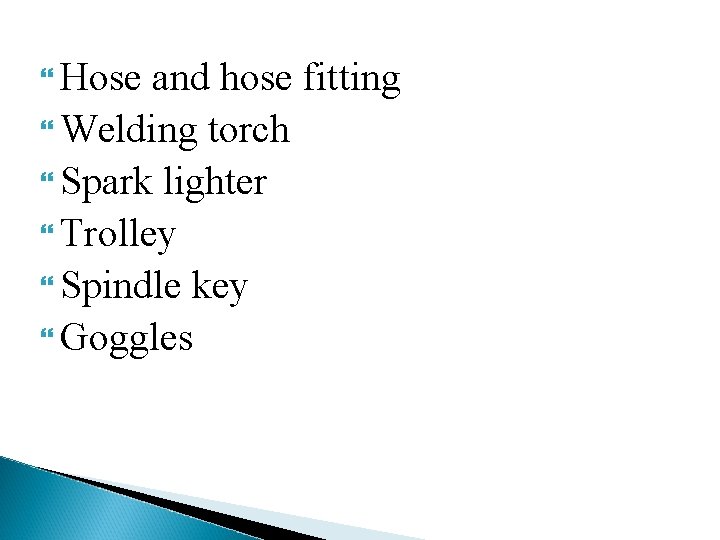
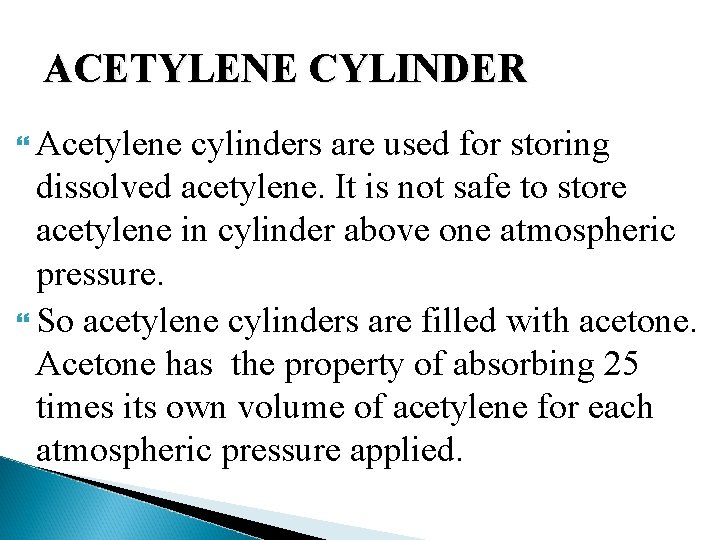
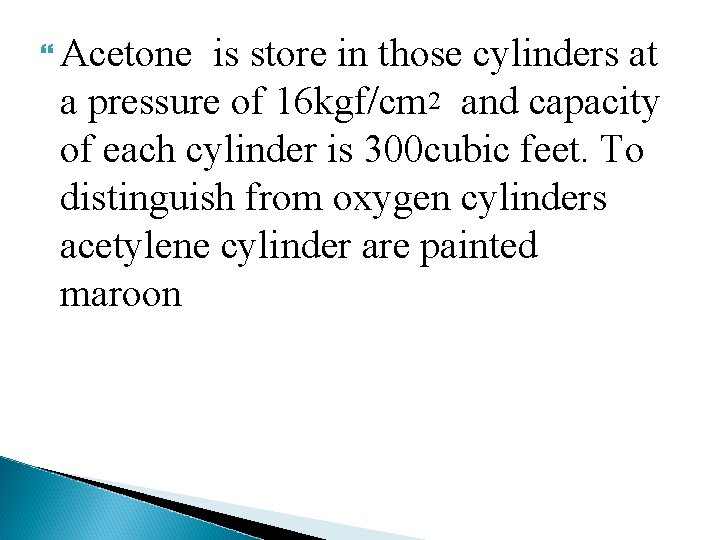
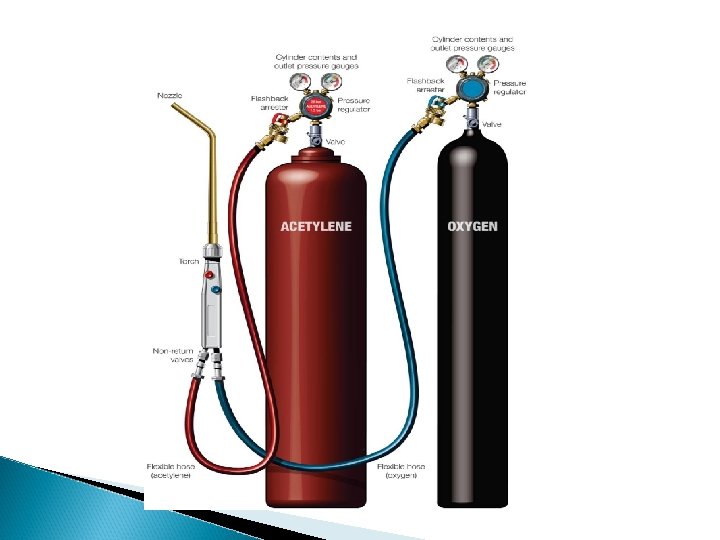
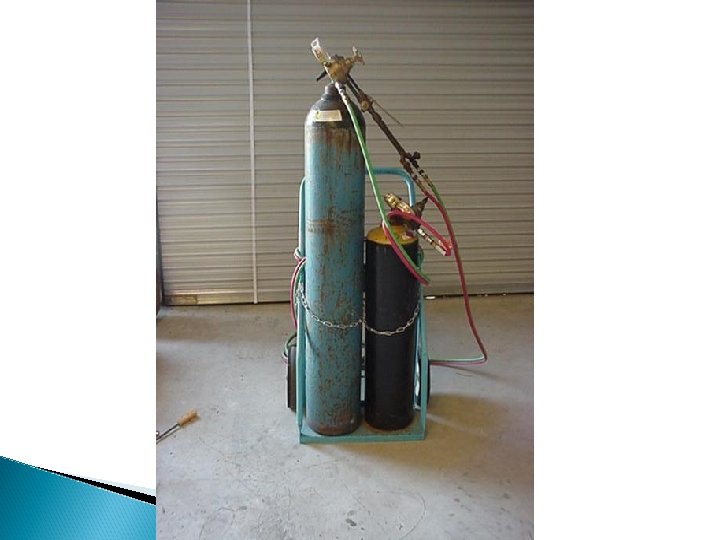
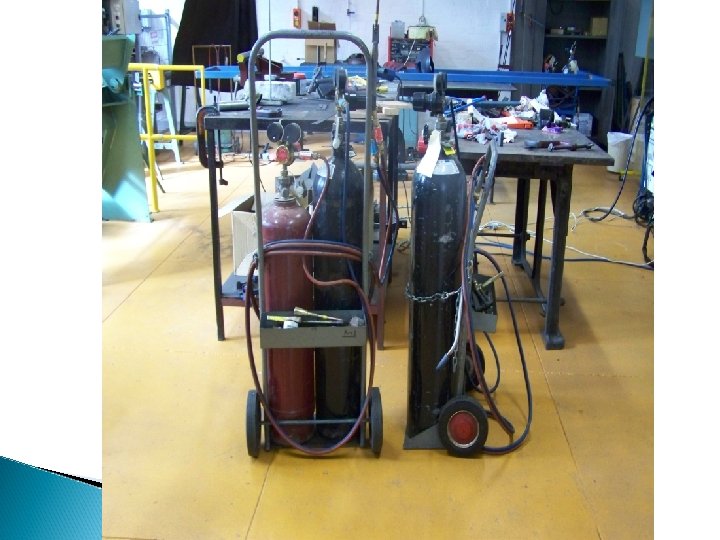
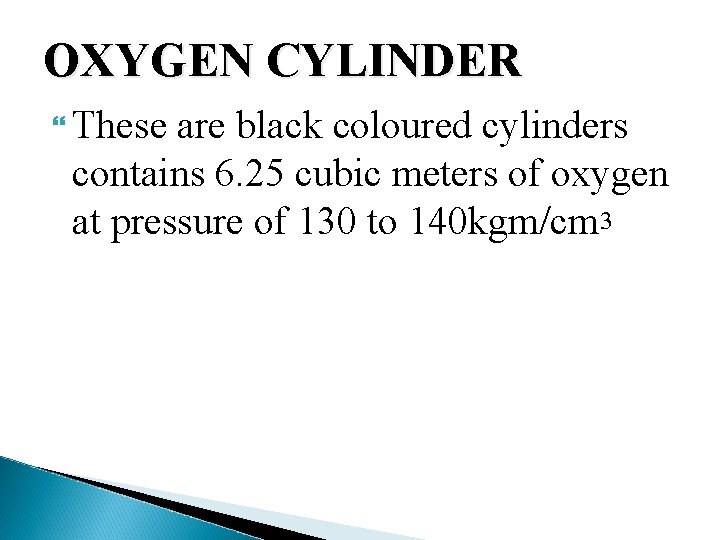
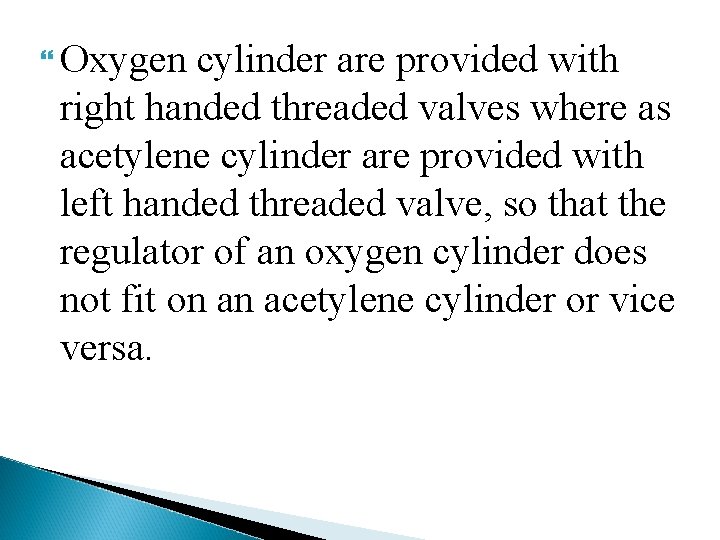

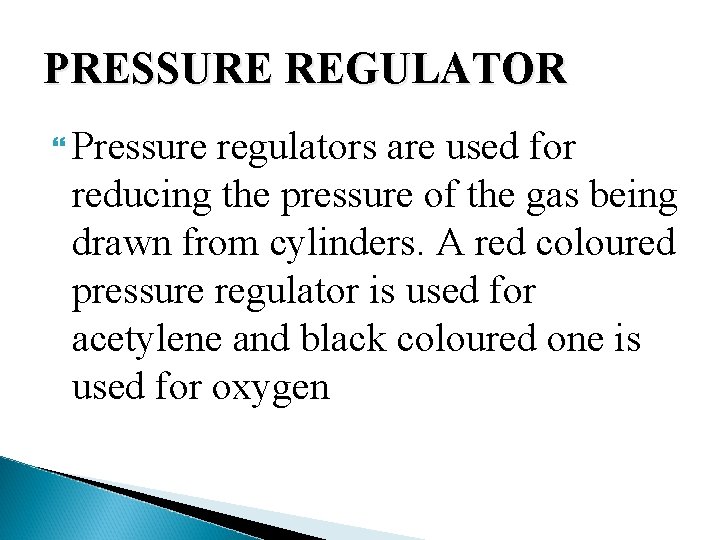
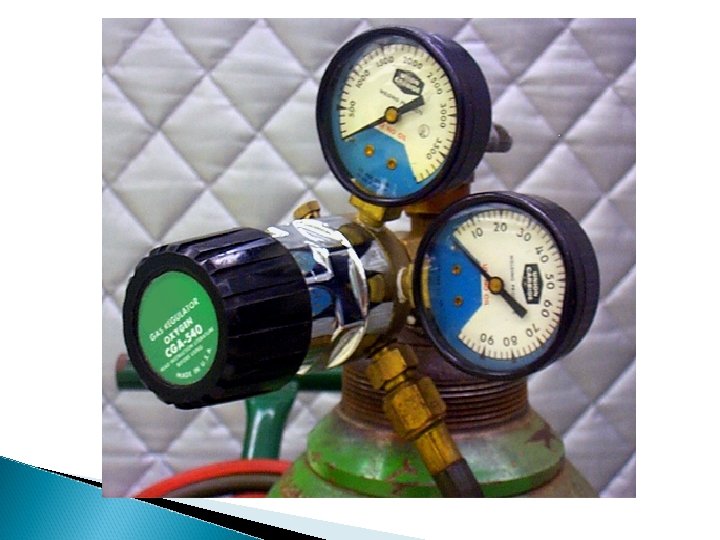
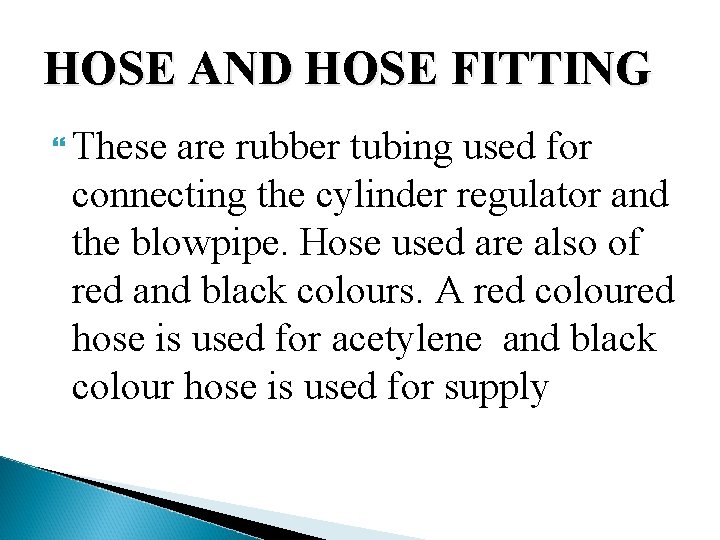
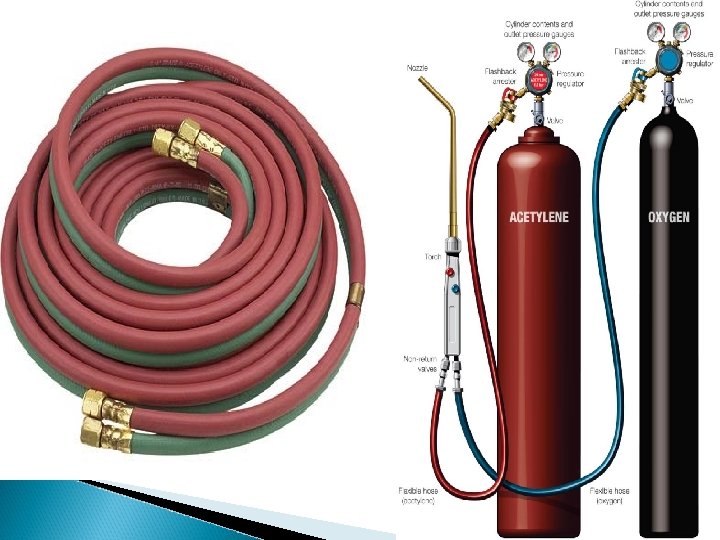
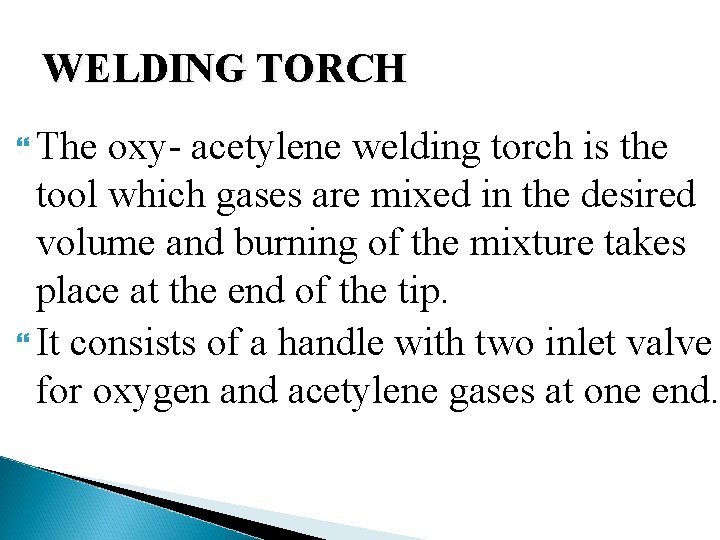
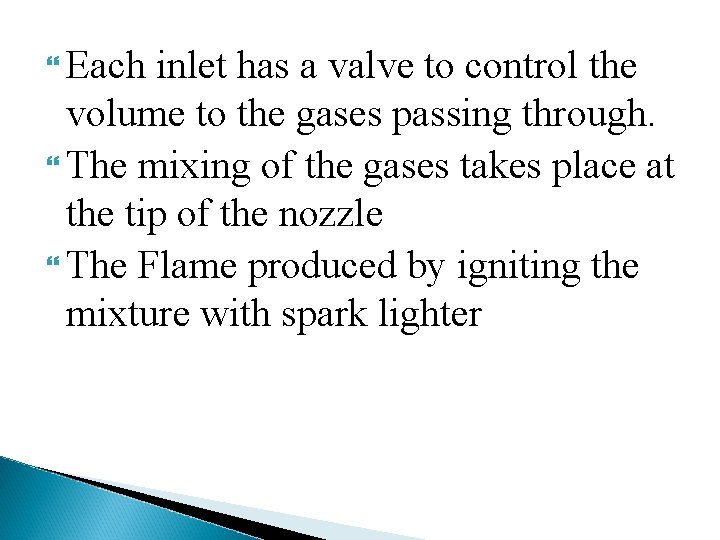
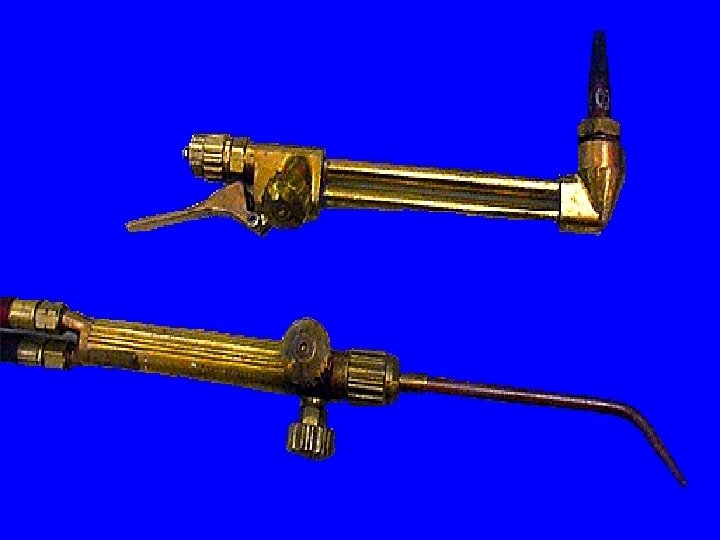
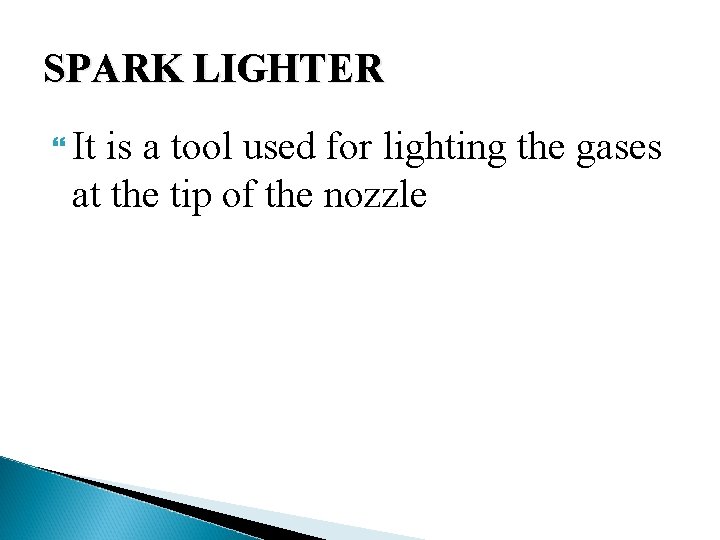
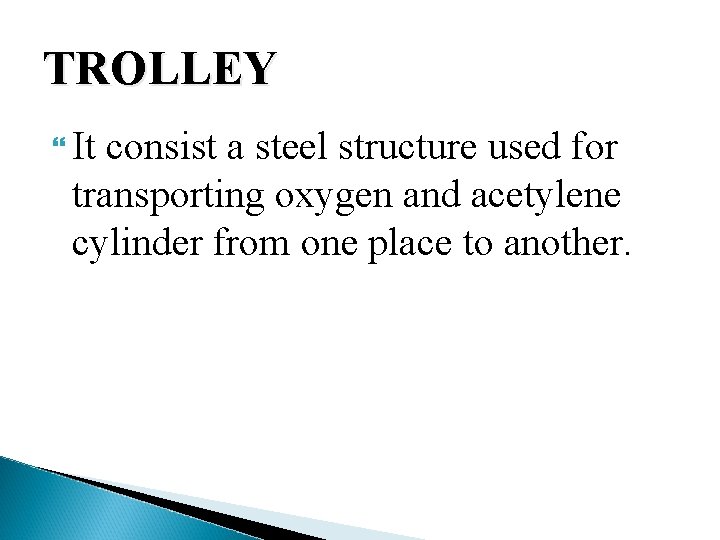
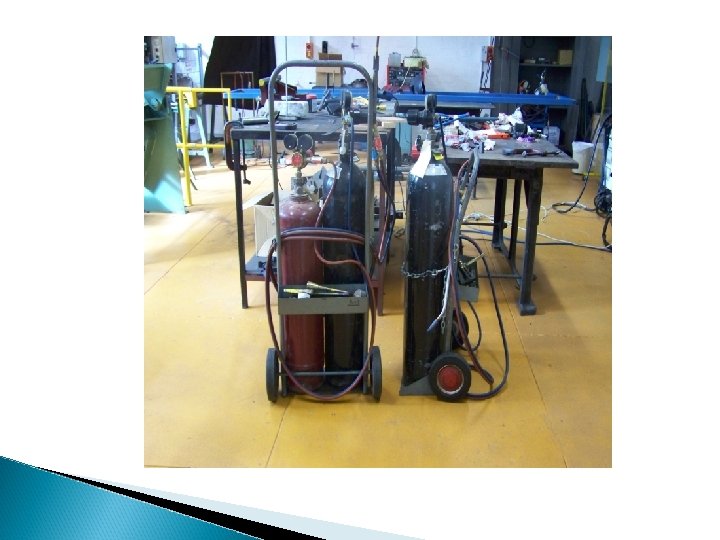
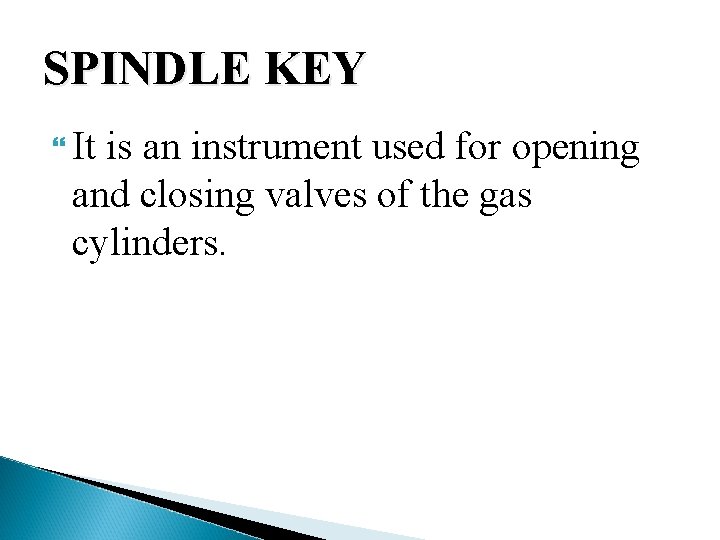
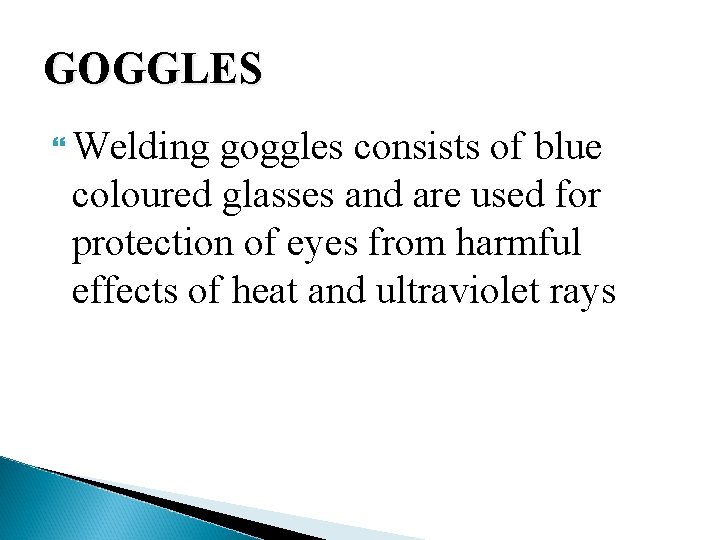
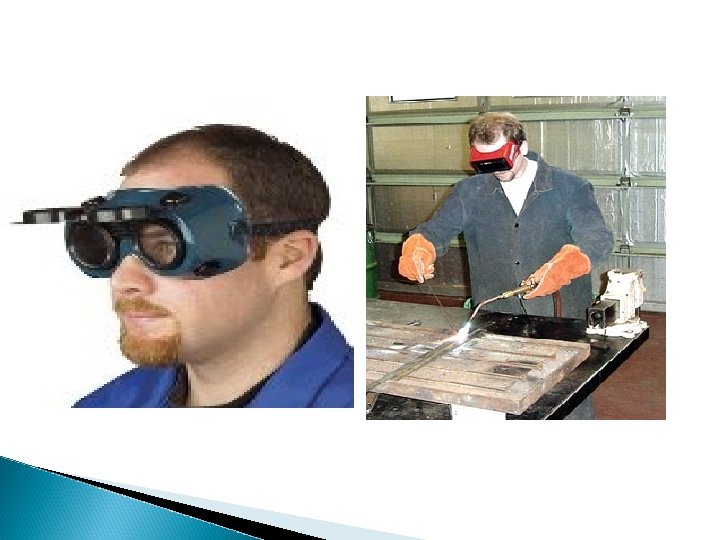
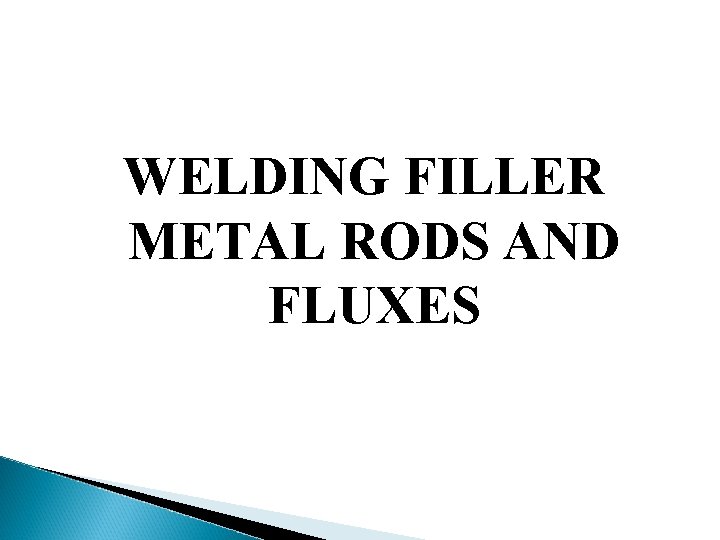
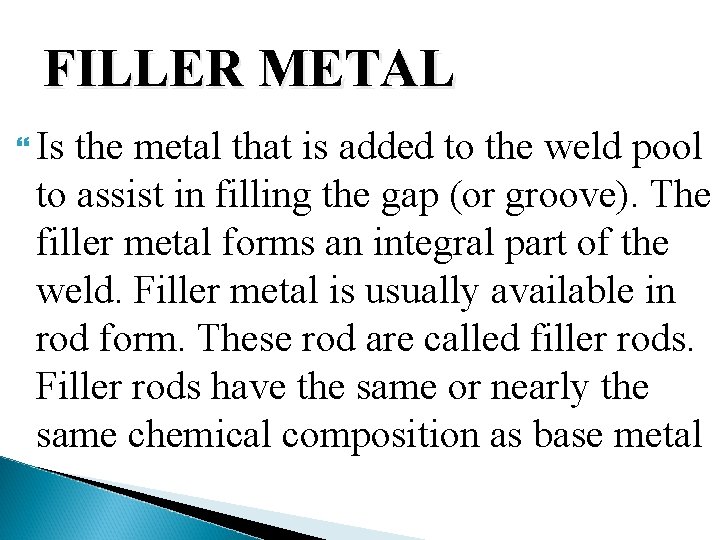
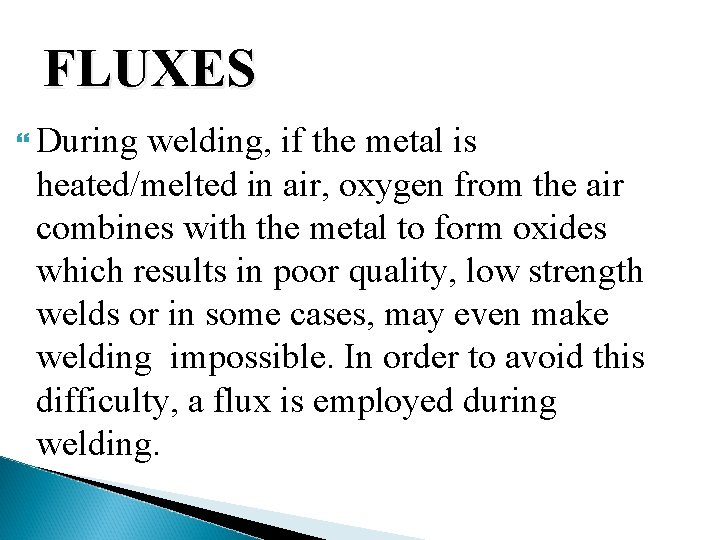
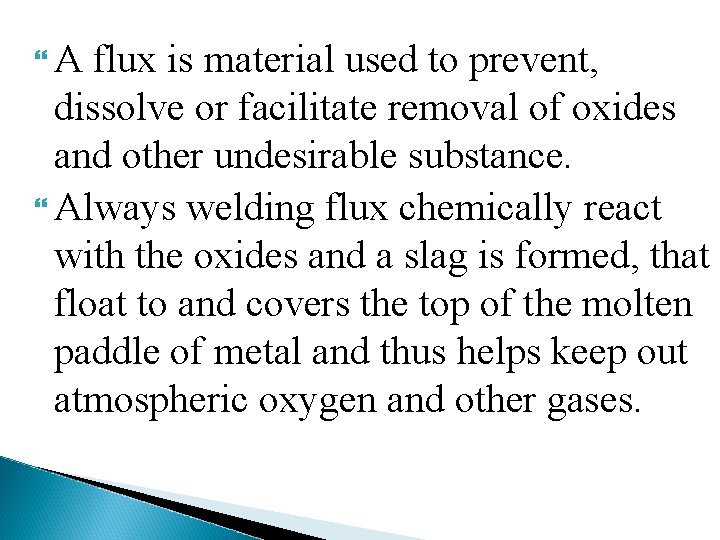
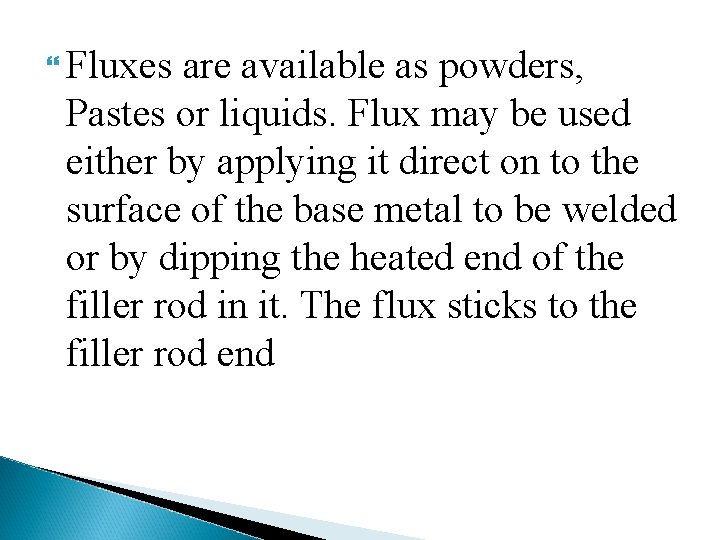
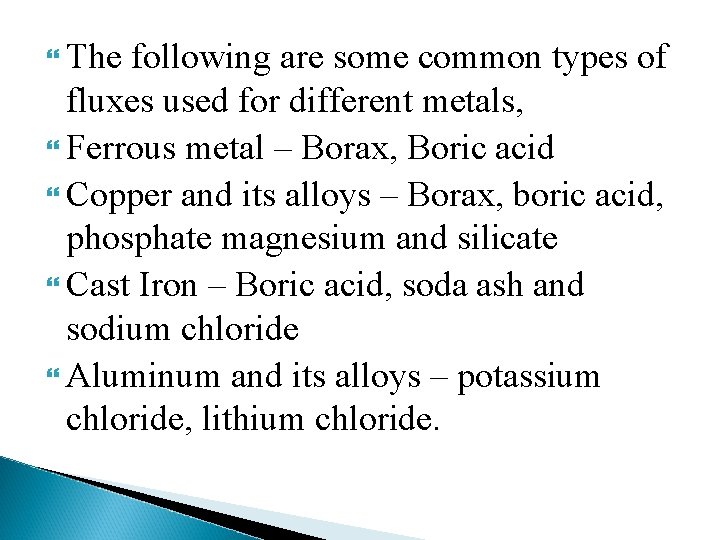
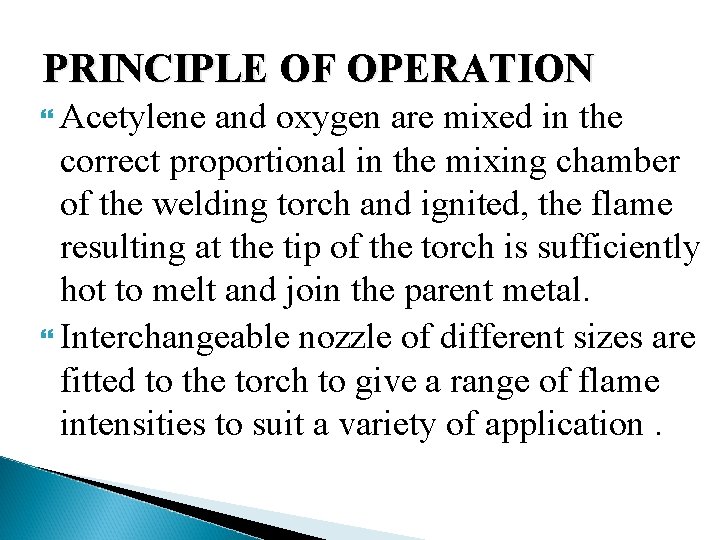
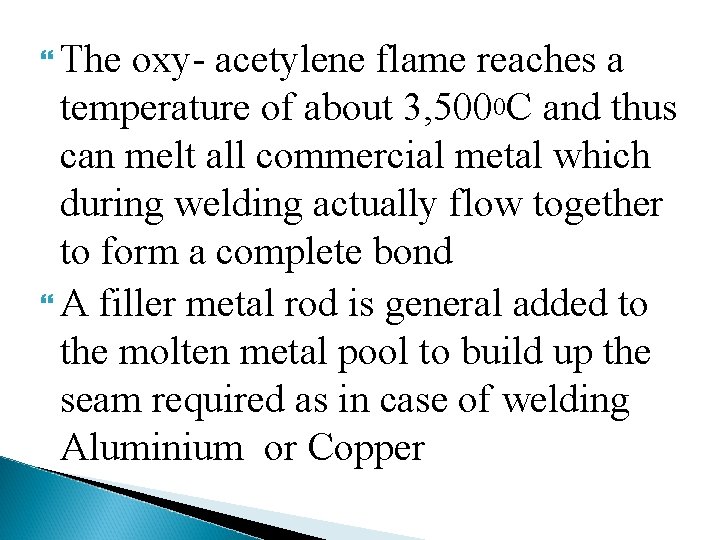
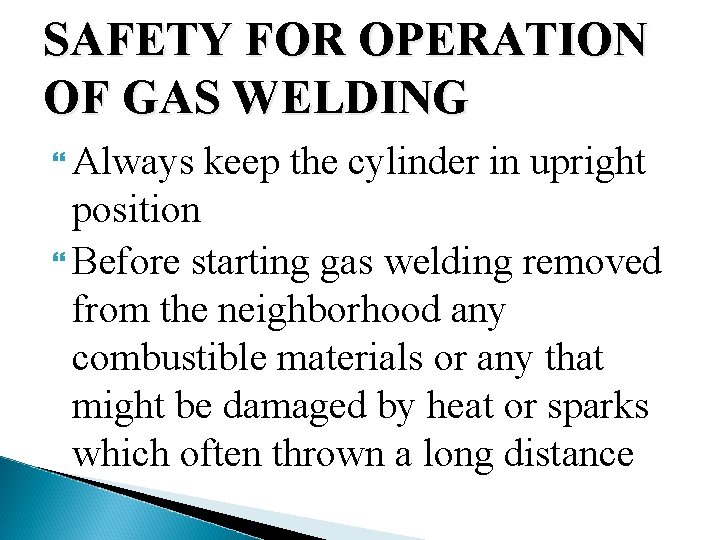
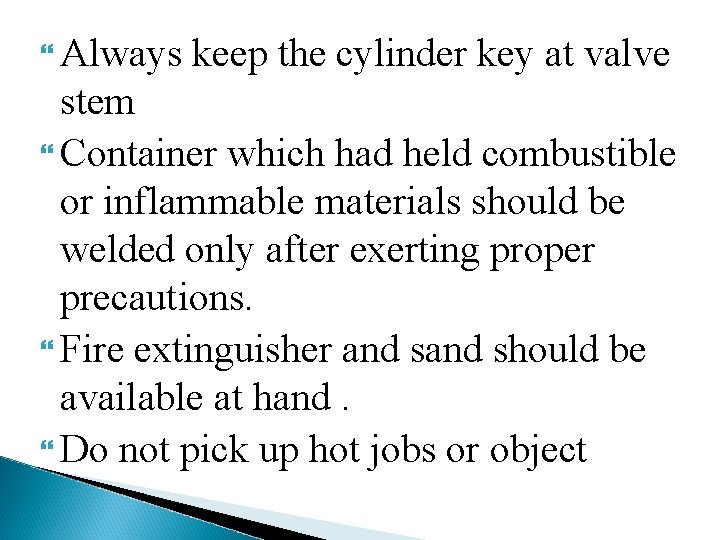
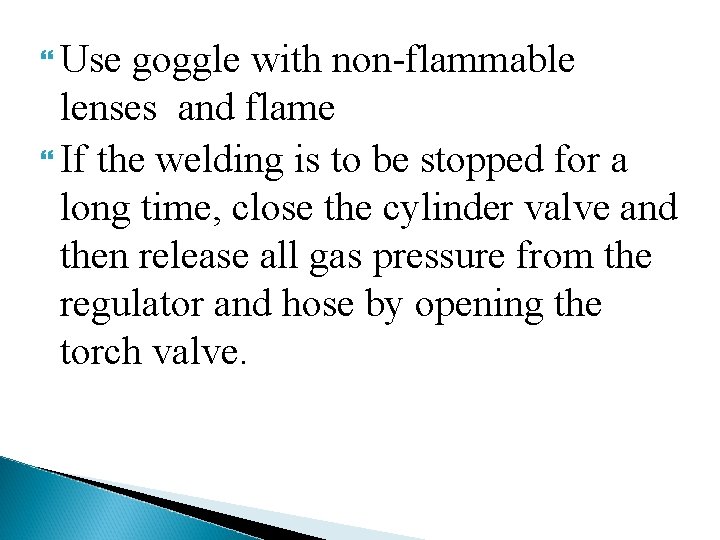
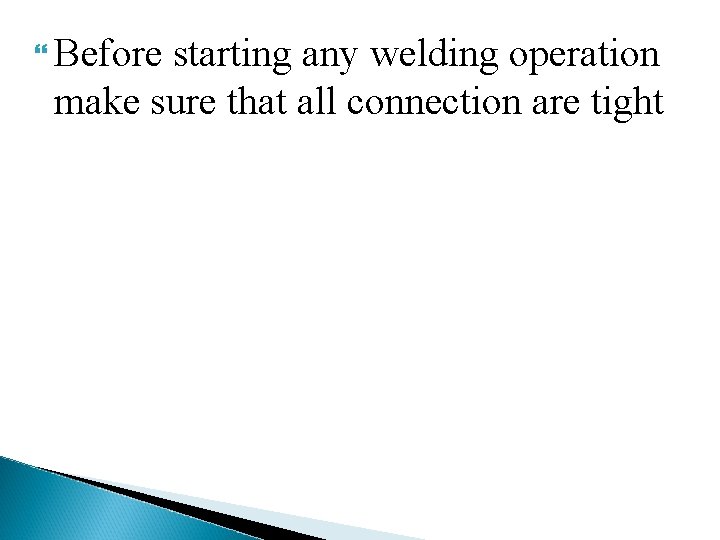
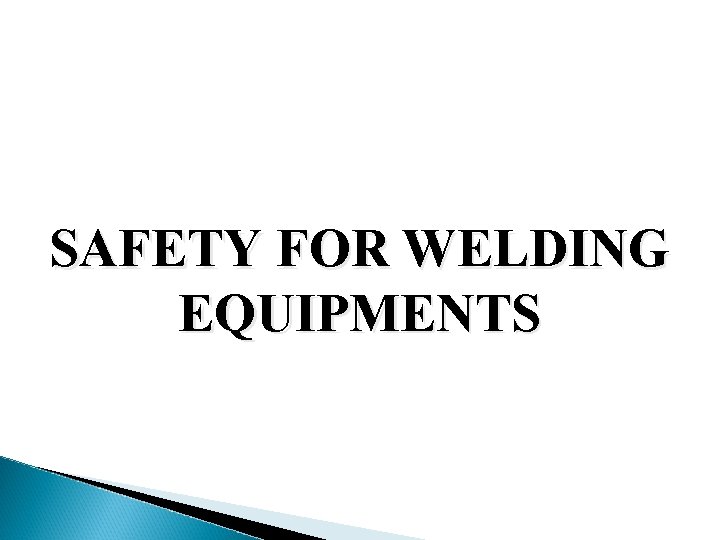

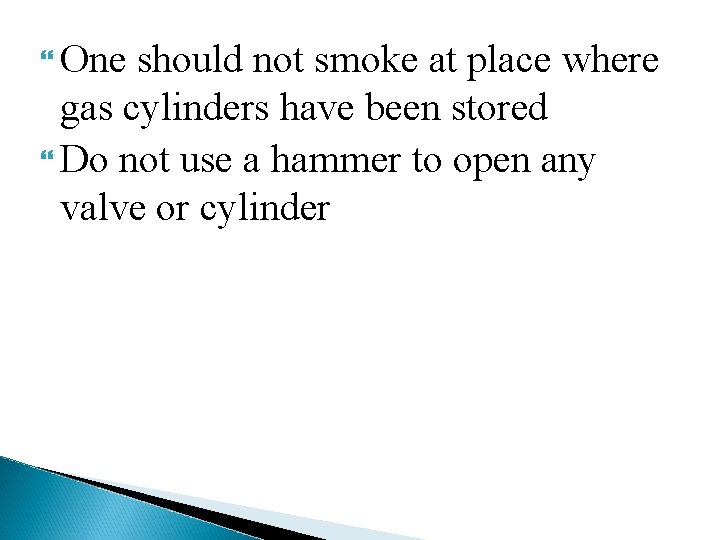
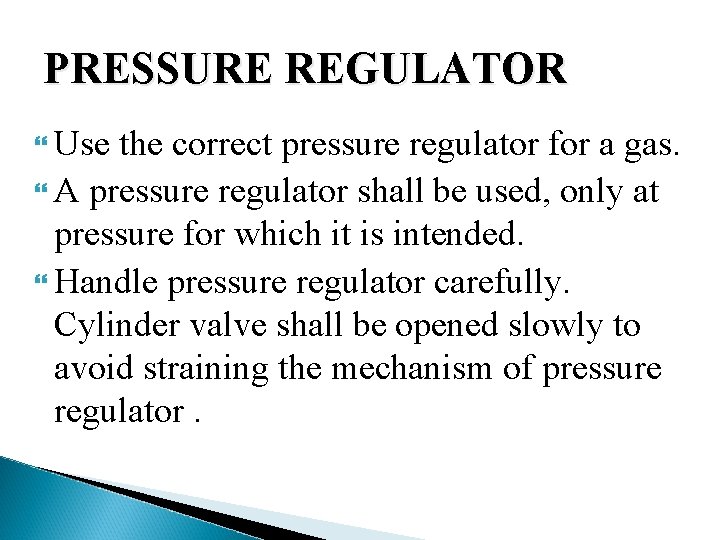
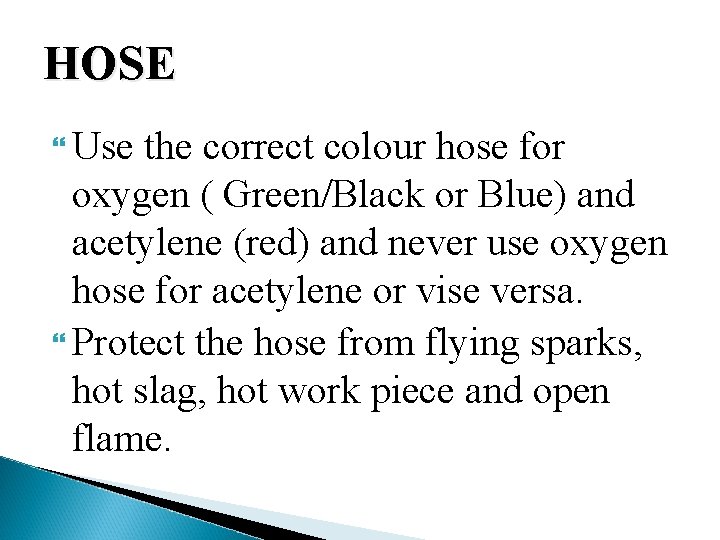
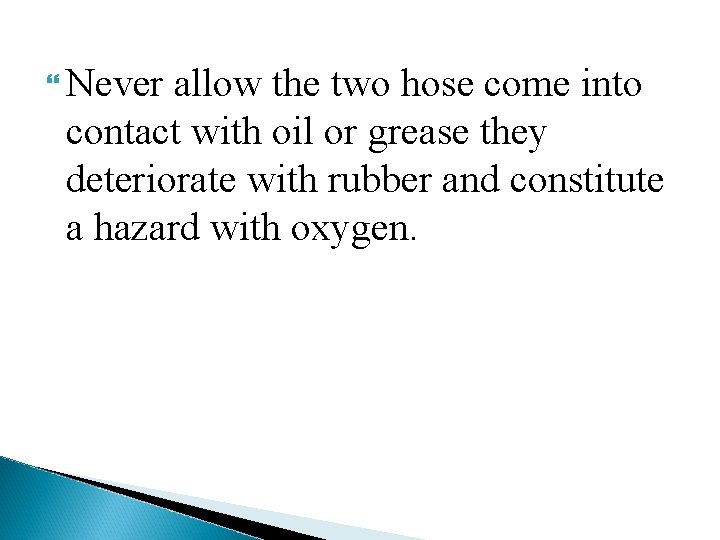
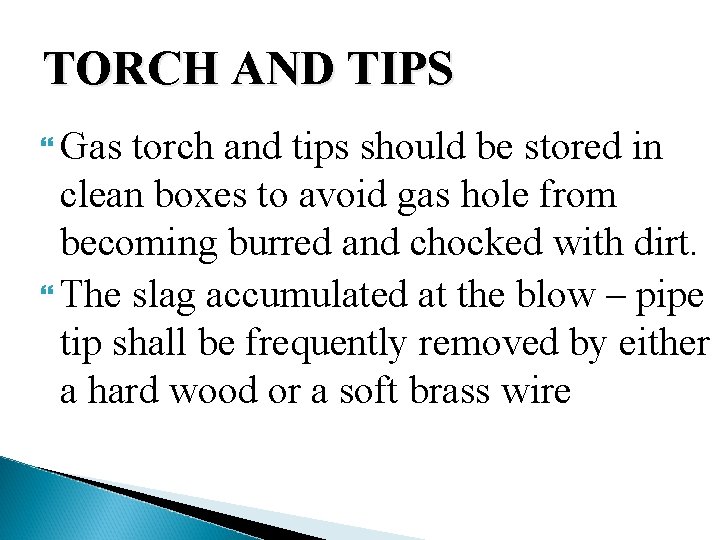
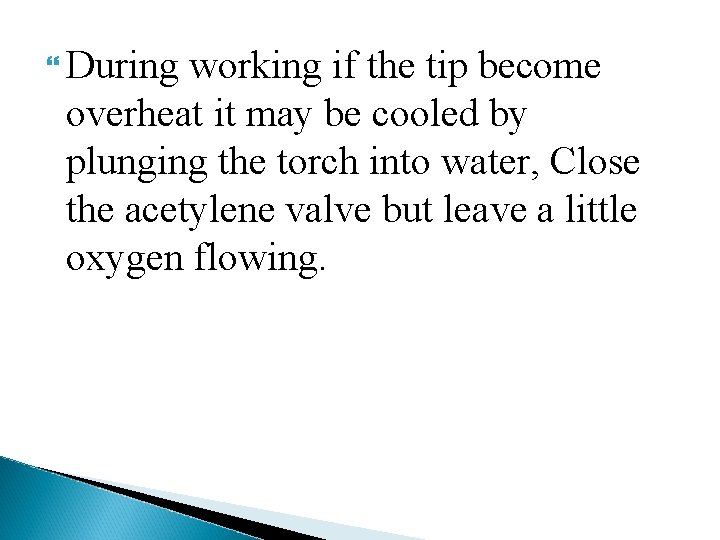
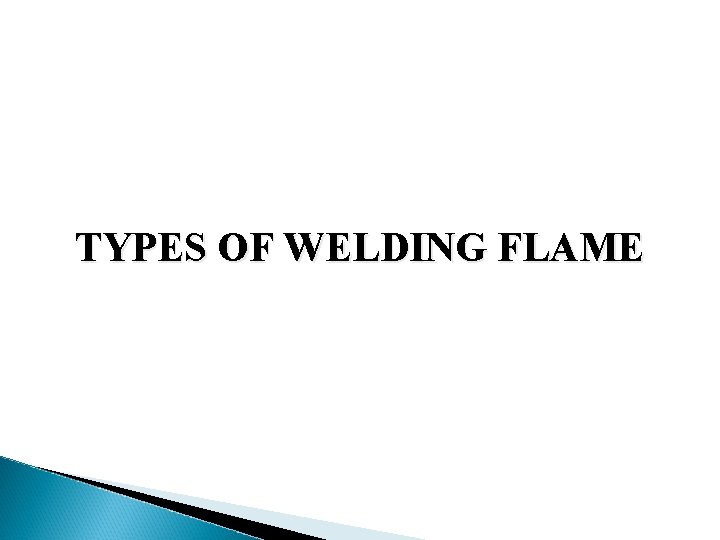
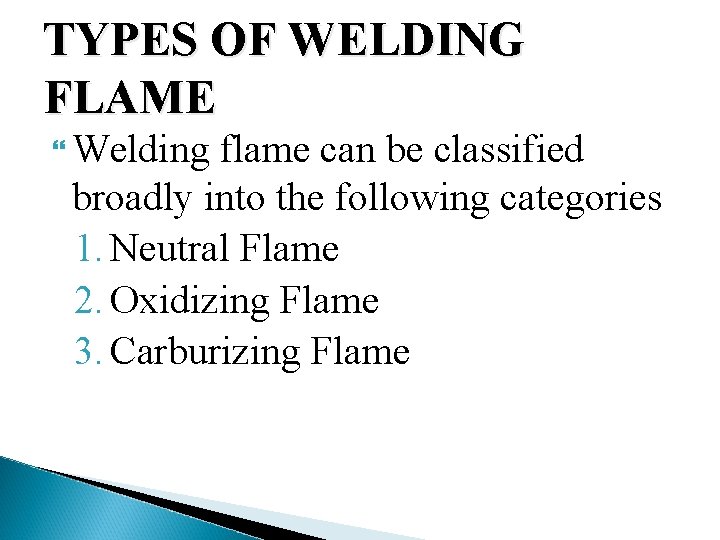
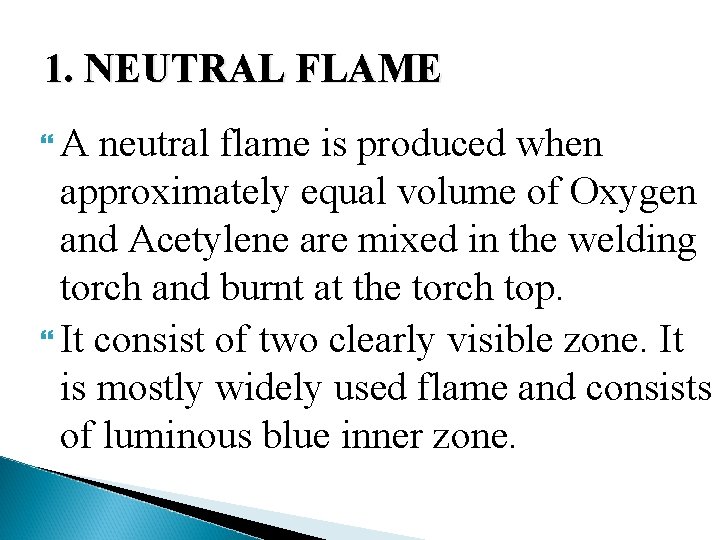
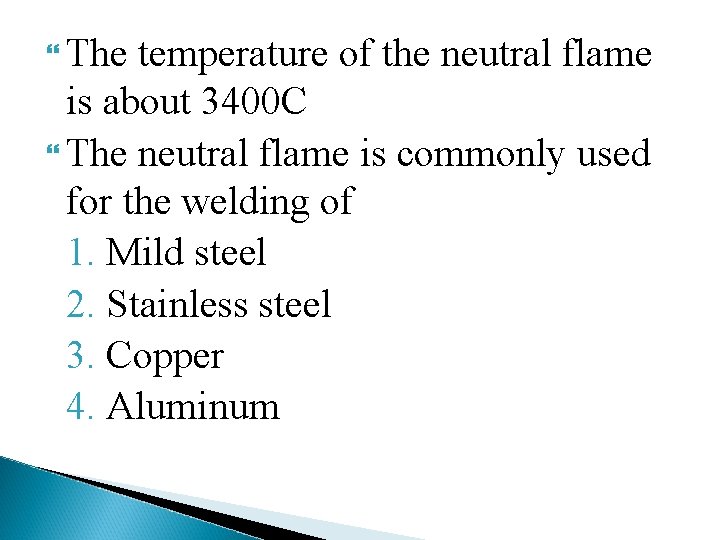
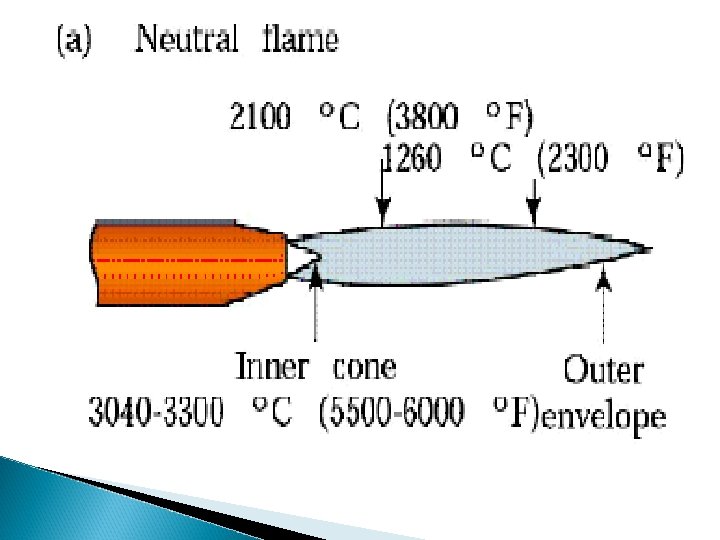
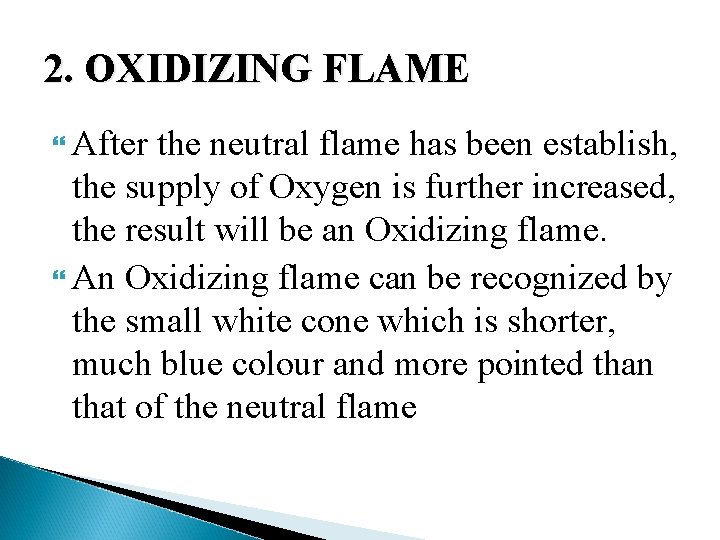
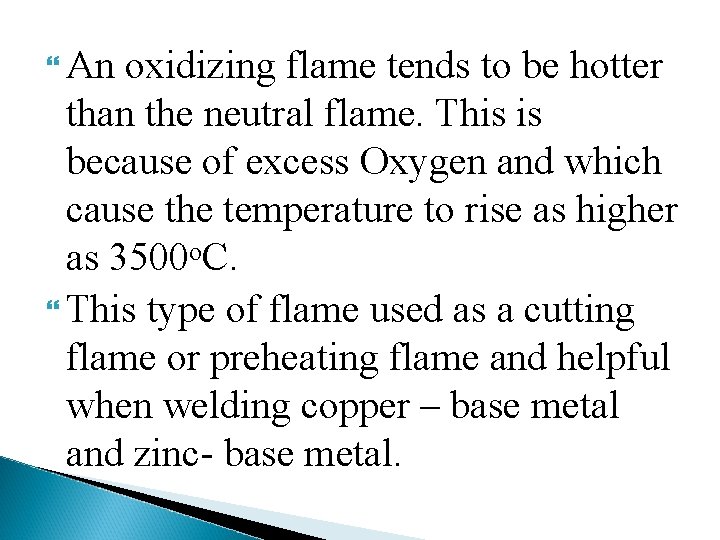
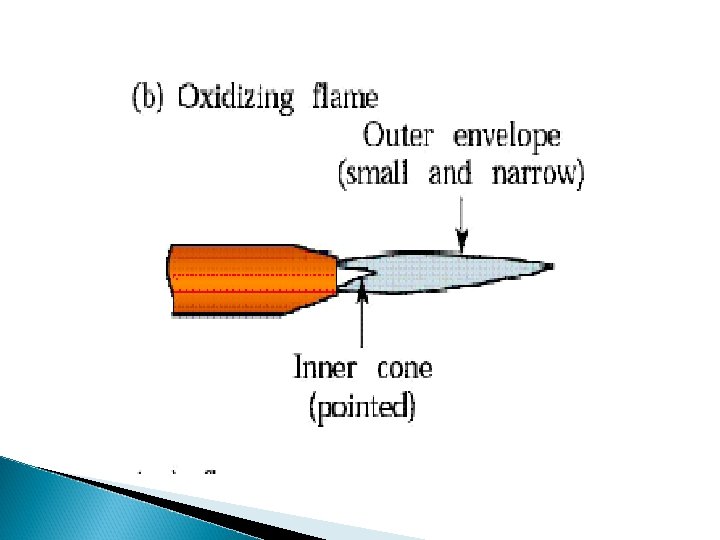
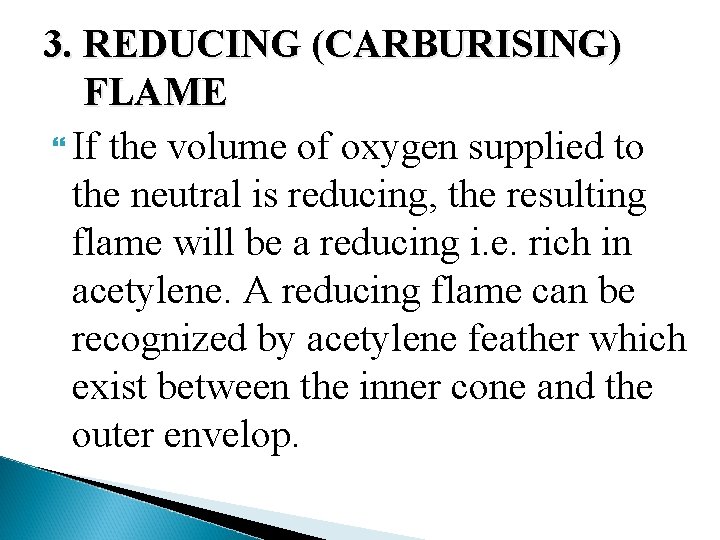
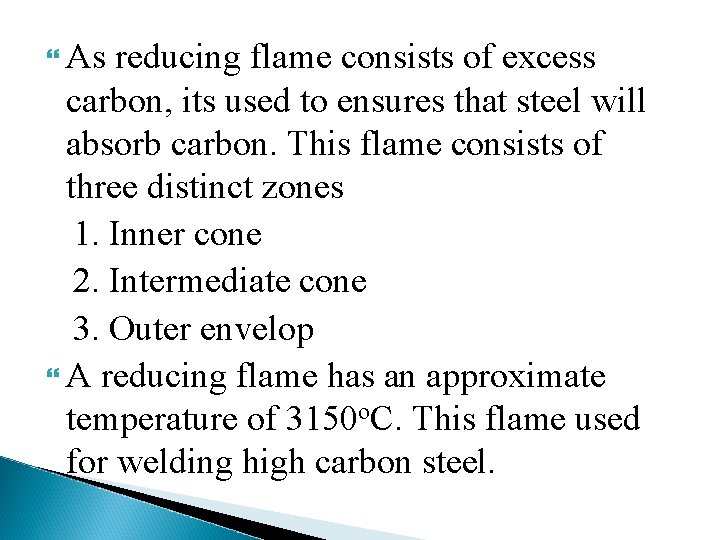
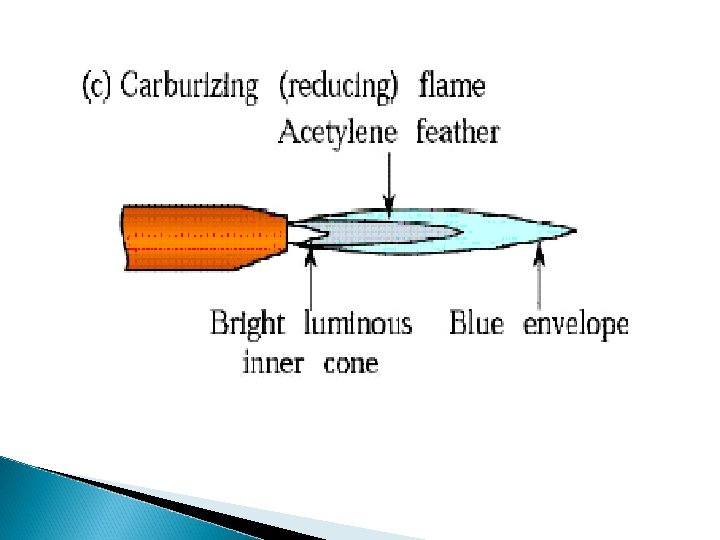
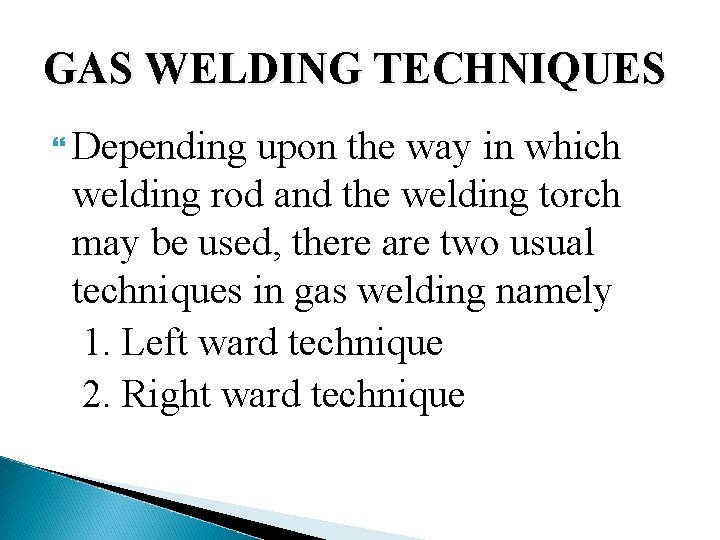
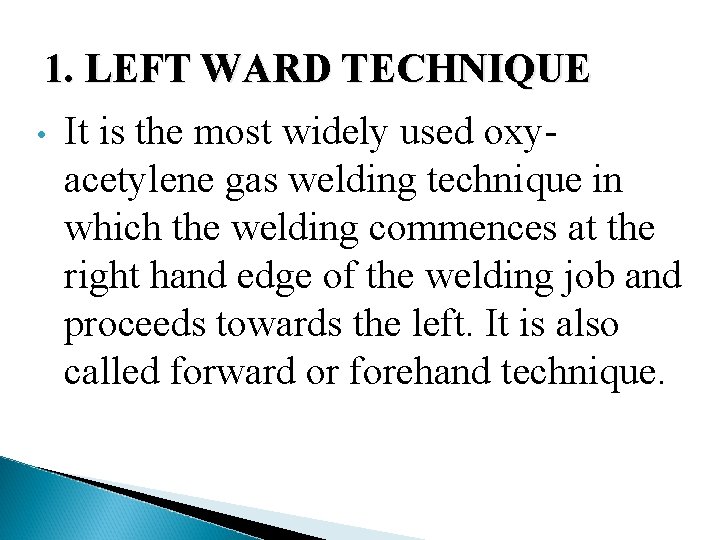
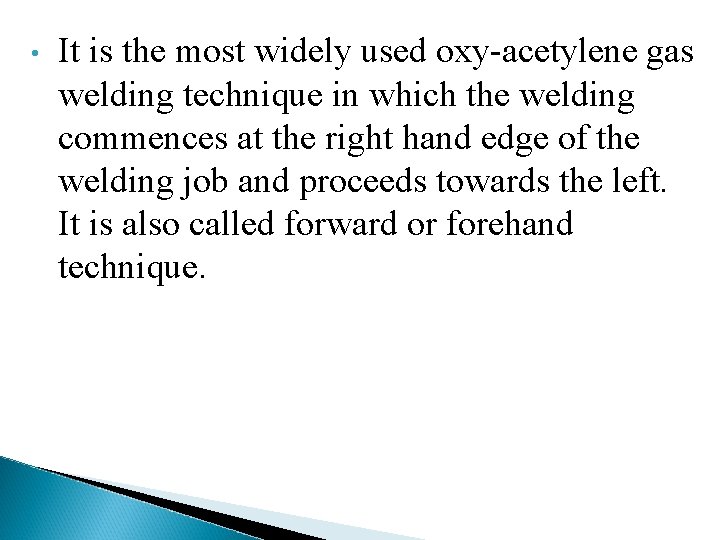
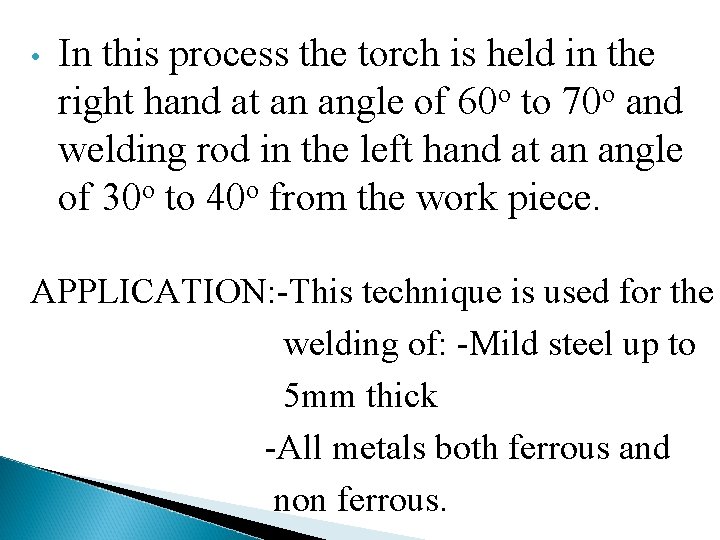
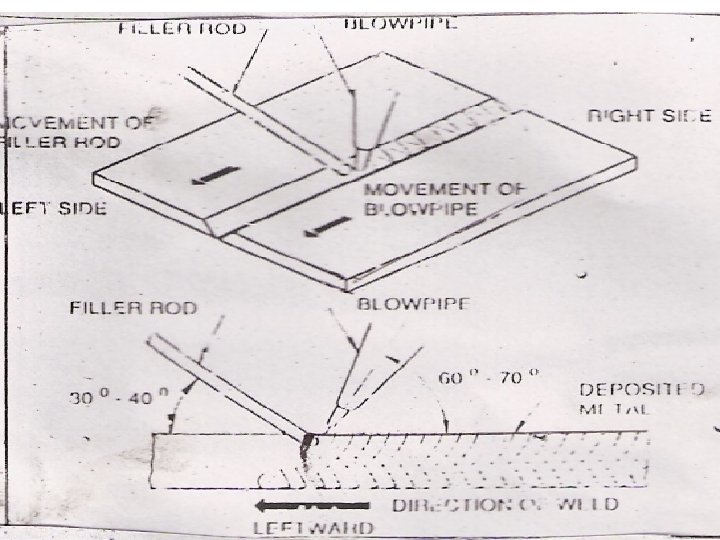

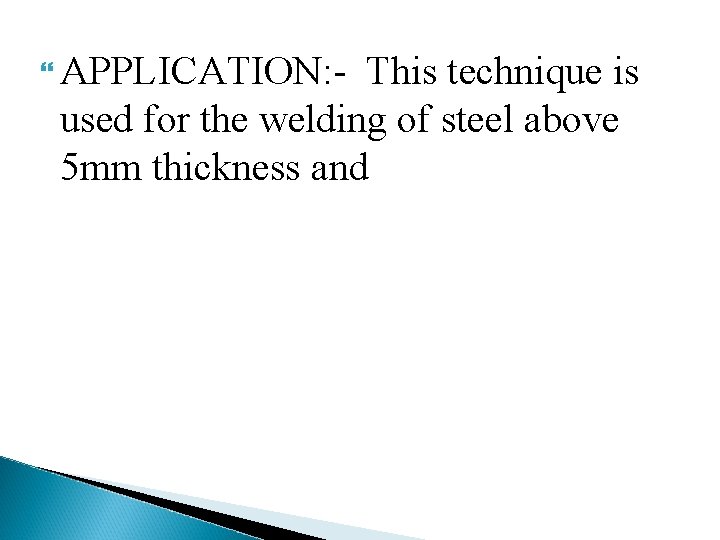
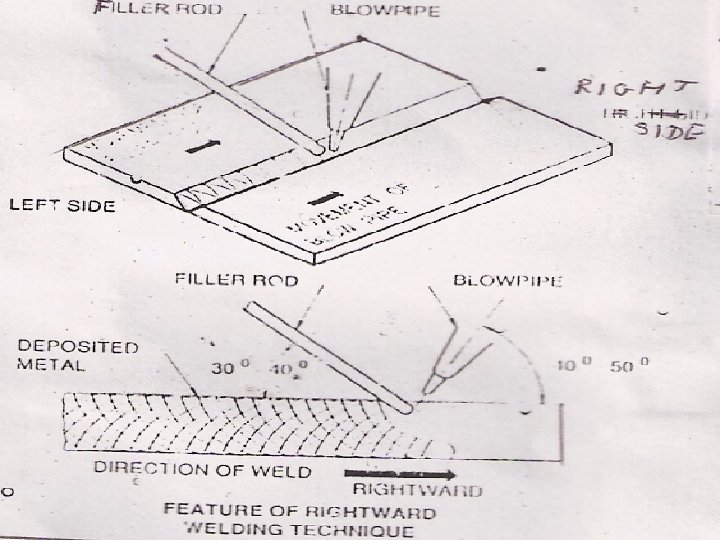
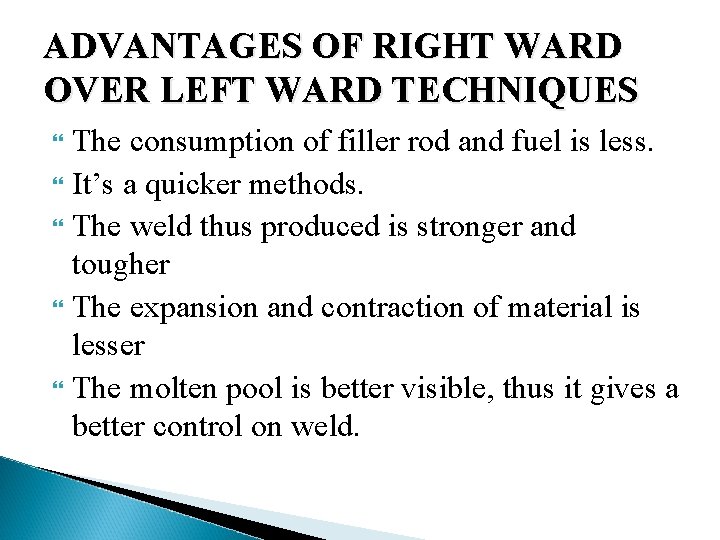
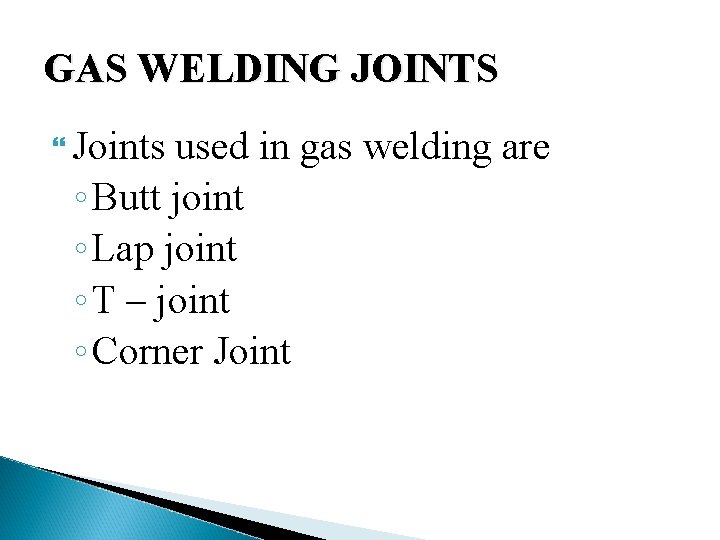
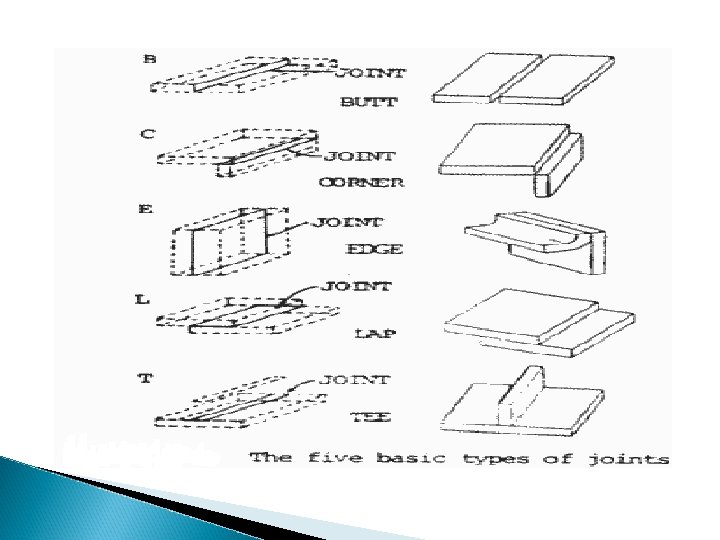
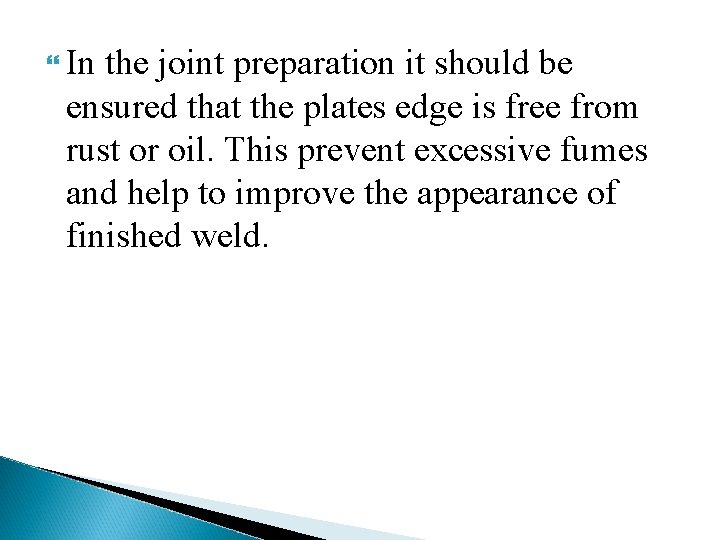
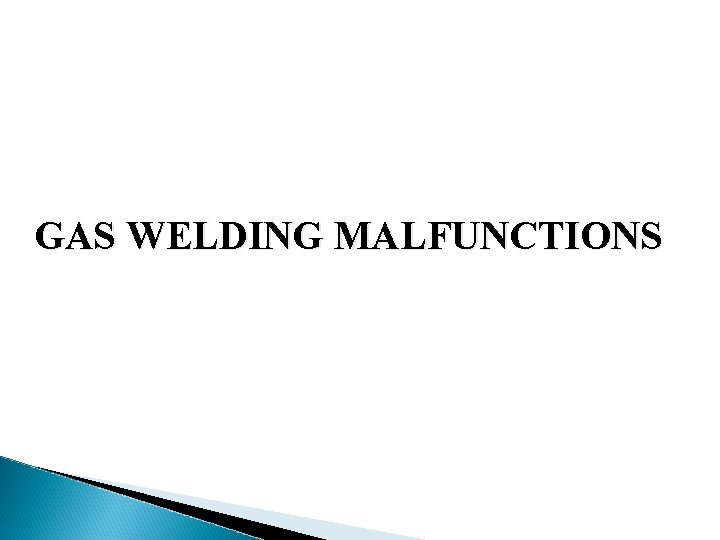
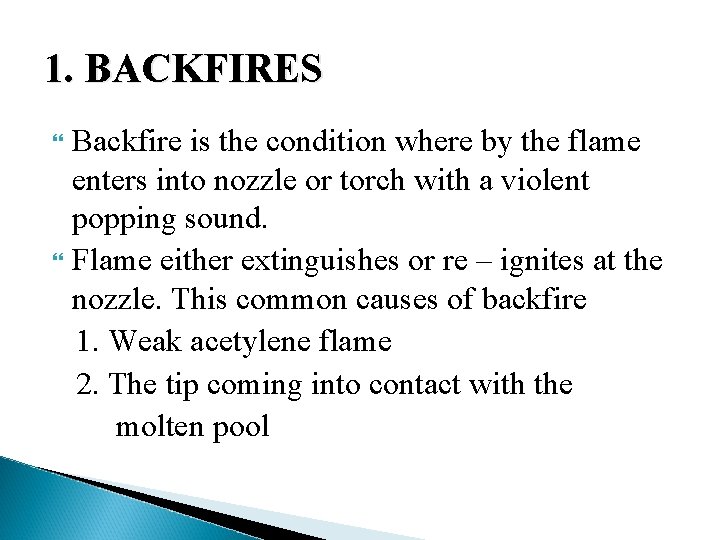
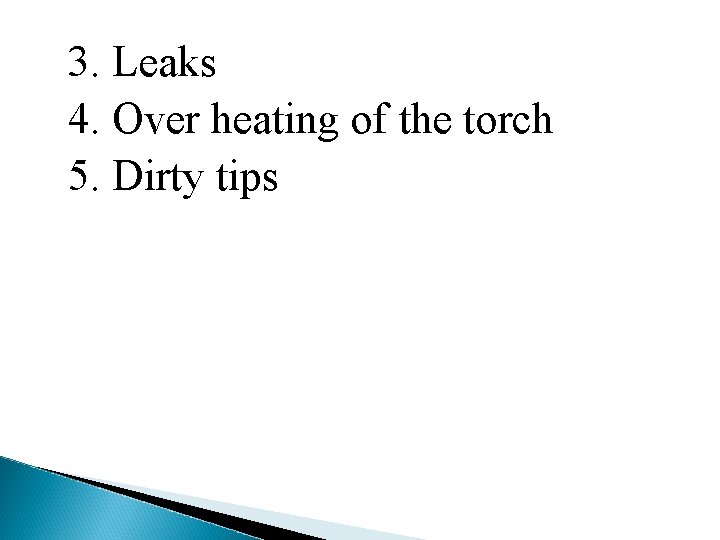
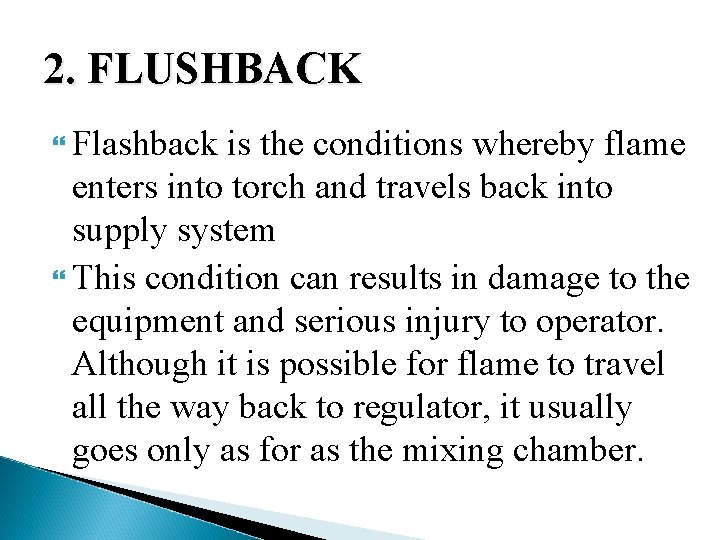
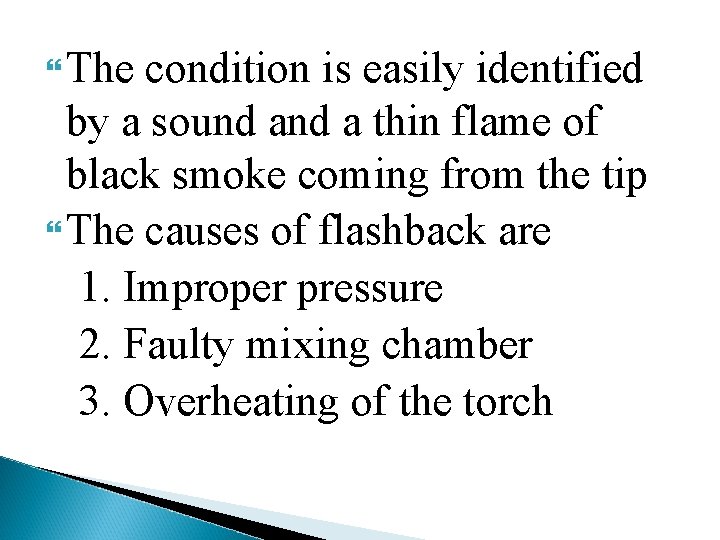
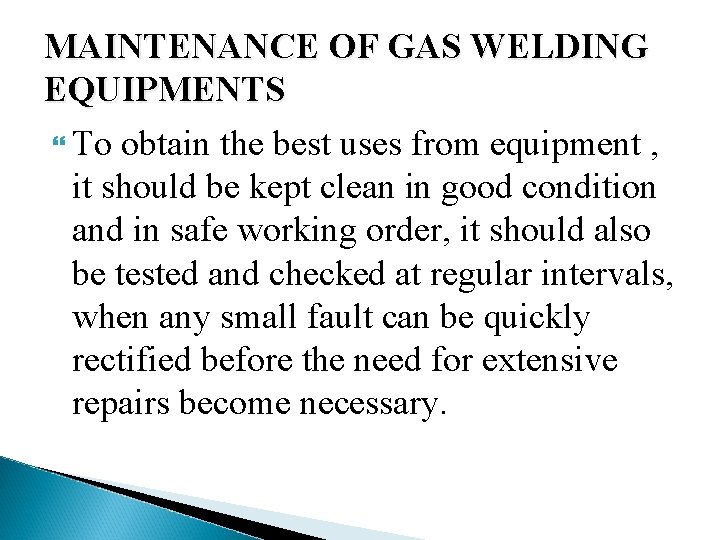
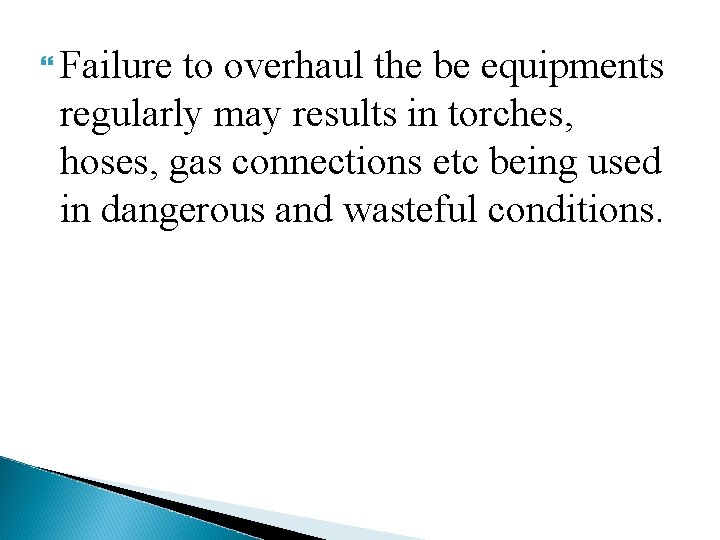
- Slides: 83
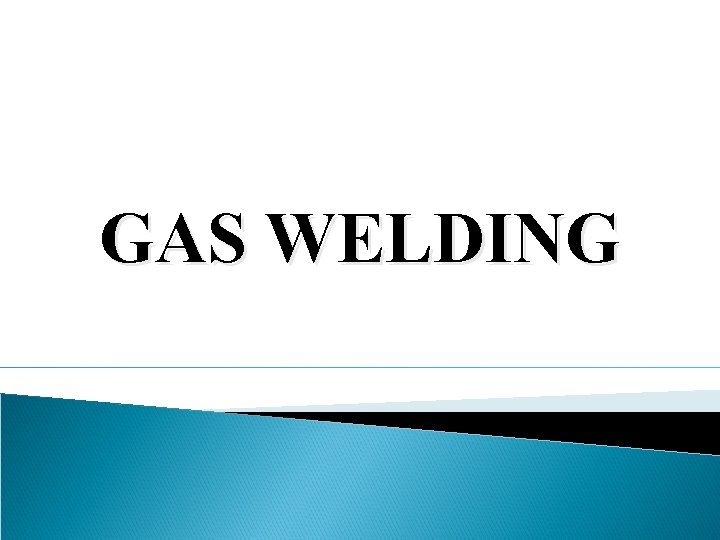
GAS WELDING
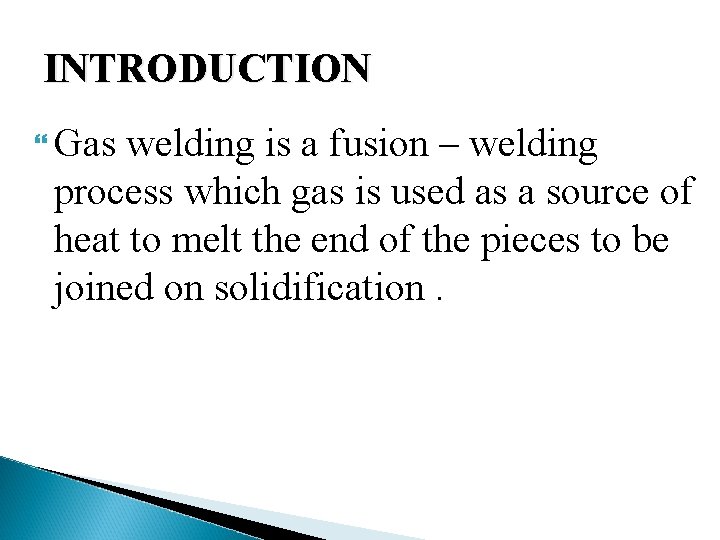
INTRODUCTION Gas welding is a fusion – welding process which gas is used as a source of heat to melt the end of the pieces to be joined on solidification.
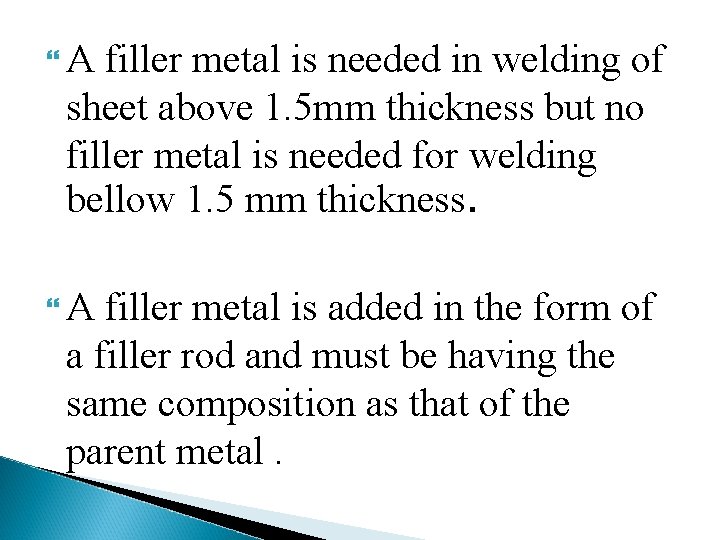
A filler metal is needed in welding of sheet above 1. 5 mm thickness but no filler metal is needed for welding bellow 1. 5 mm thickness. A filler metal is added in the form of a filler rod and must be having the same composition as that of the parent metal.
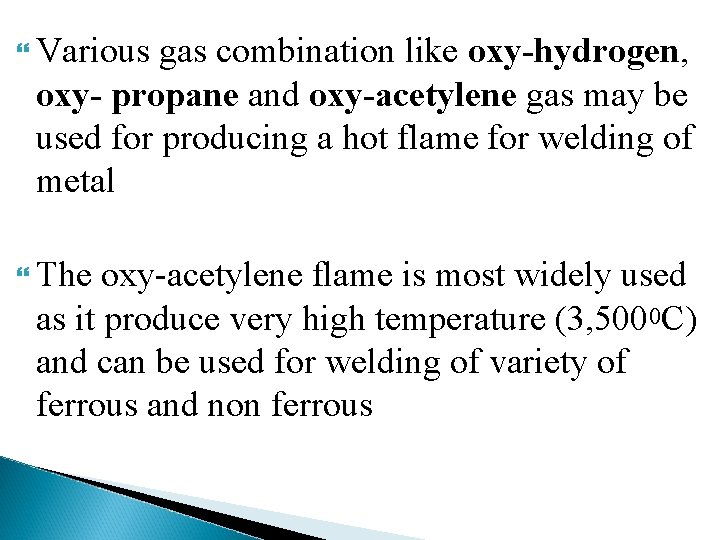
Various gas combination like oxy-hydrogen, oxy- propane and oxy-acetylene gas may be used for producing a hot flame for welding of metal The oxy-acetylene flame is most widely used as it produce very high temperature (3, 5000 C) and can be used for welding of variety of ferrous and non ferrous
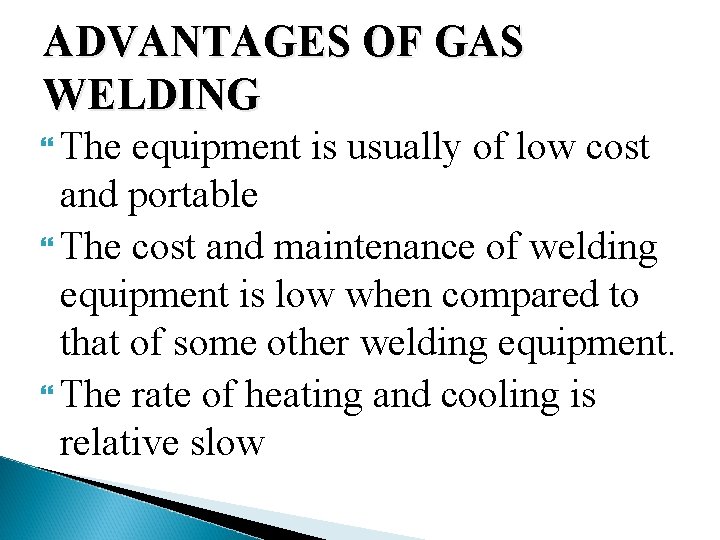
ADVANTAGES OF GAS WELDING The equipment is usually of low cost and portable The cost and maintenance of welding equipment is low when compared to that of some other welding equipment. The rate of heating and cooling is relative slow
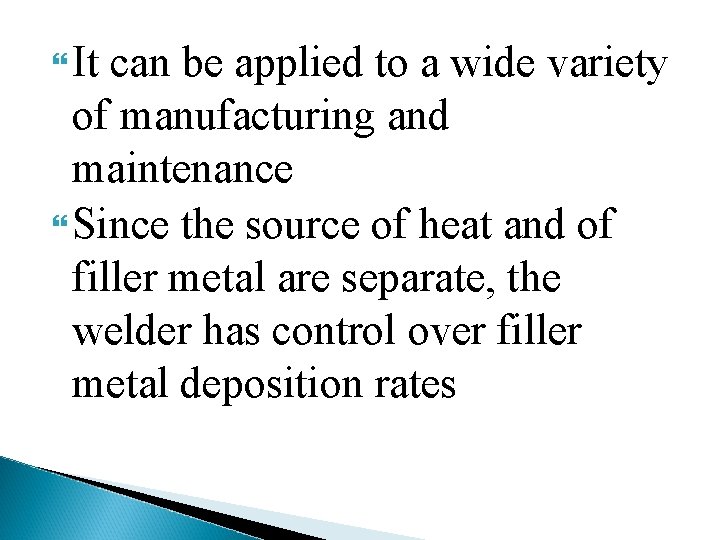
It can be applied to a wide variety of manufacturing and maintenance Since the source of heat and of filler metal are separate, the welder has control over filler metal deposition rates
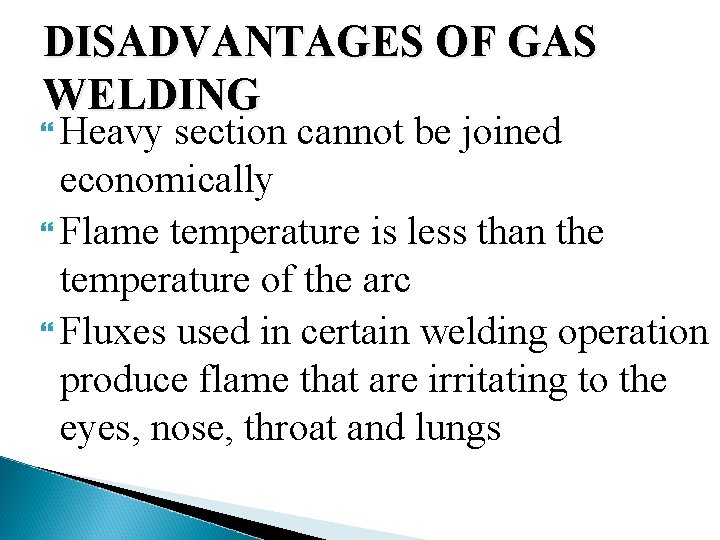
DISADVANTAGES OF GAS WELDING Heavy section cannot be joined economically Flame temperature is less than the temperature of the arc Fluxes used in certain welding operation produce flame that are irritating to the eyes, nose, throat and lungs
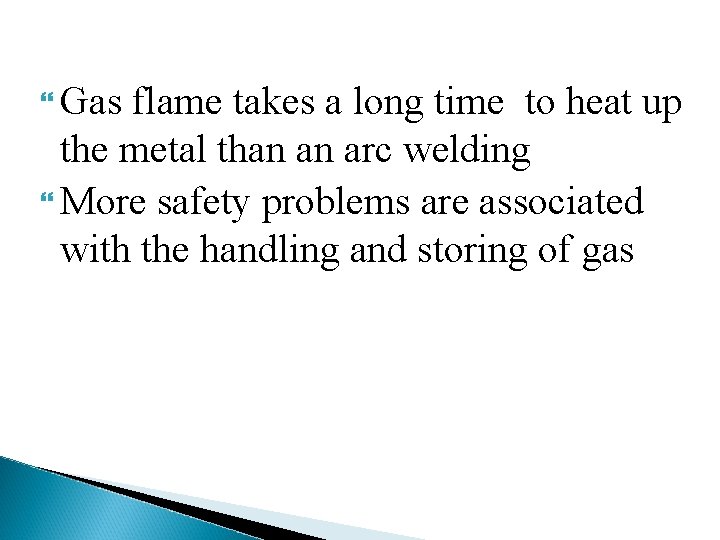
Gas flame takes a long time to heat up the metal than an arc welding More safety problems are associated with the handling and storing of gas
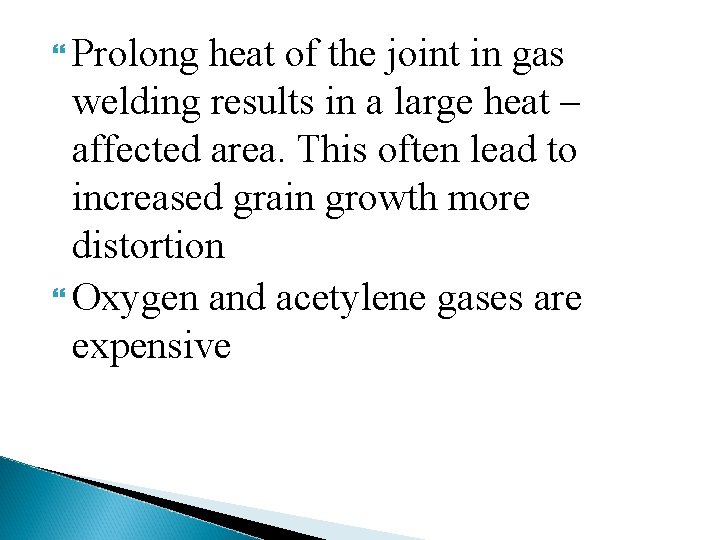
Prolong heat of the joint in gas welding results in a large heat – affected area. This often lead to increased grain growth more distortion Oxygen and acetylene gases are expensive
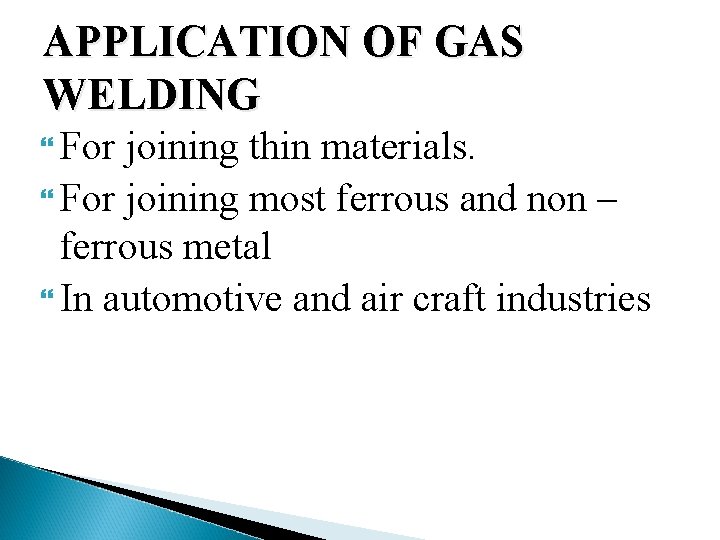
APPLICATION OF GAS WELDING For joining thin materials. For joining most ferrous and non – ferrous metal In automotive and air craft industries
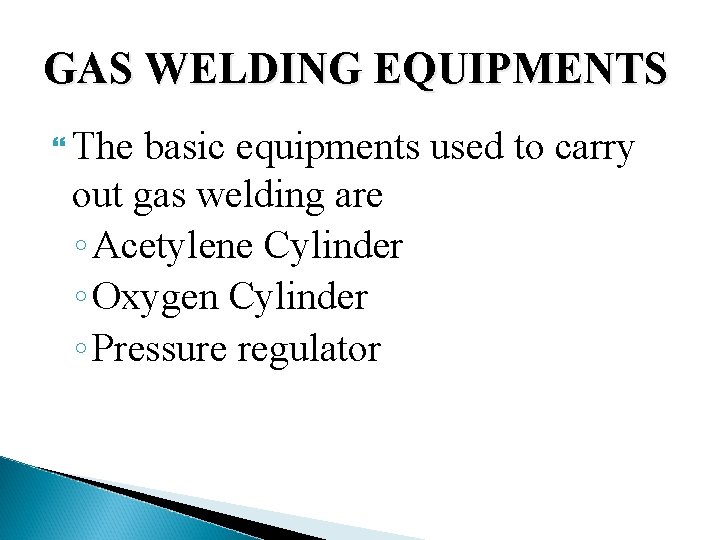
GAS WELDING EQUIPMENTS The basic equipments used to carry out gas welding are ◦ Acetylene Cylinder ◦ Oxygen Cylinder ◦ Pressure regulator
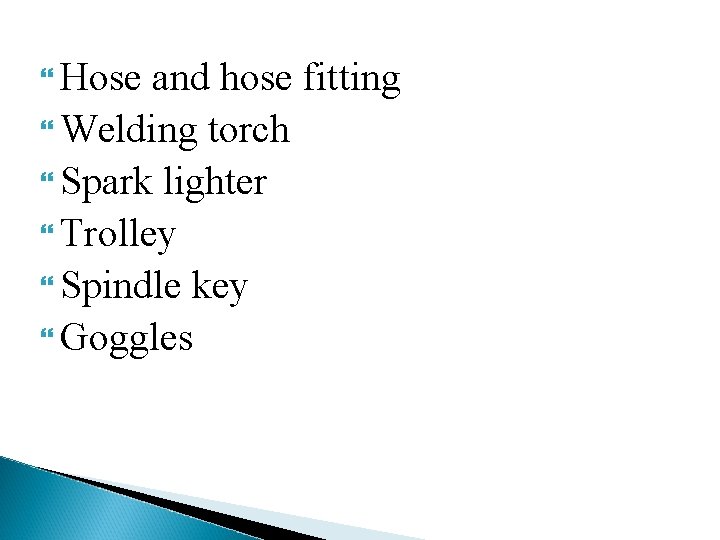
Hose and hose fitting Welding torch Spark lighter Trolley Spindle key Goggles
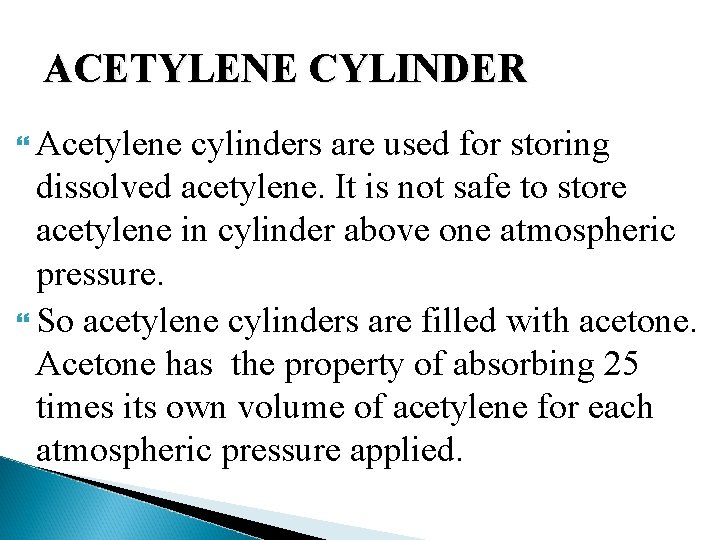
ACETYLENE CYLINDER Acetylene cylinders are used for storing dissolved acetylene. It is not safe to store acetylene in cylinder above one atmospheric pressure. So acetylene cylinders are filled with acetone. Acetone has the property of absorbing 25 times its own volume of acetylene for each atmospheric pressure applied.
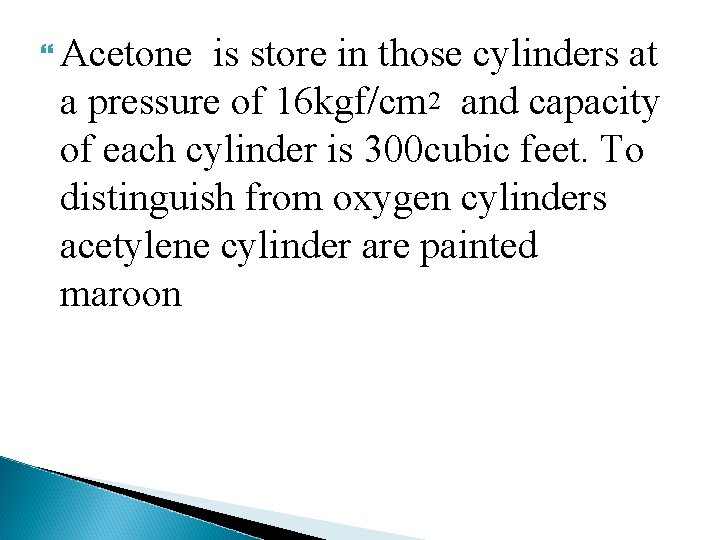
Acetone is store in those cylinders at a pressure of 16 kgf/cm 2 and capacity of each cylinder is 300 cubic feet. To distinguish from oxygen cylinders acetylene cylinder are painted maroon
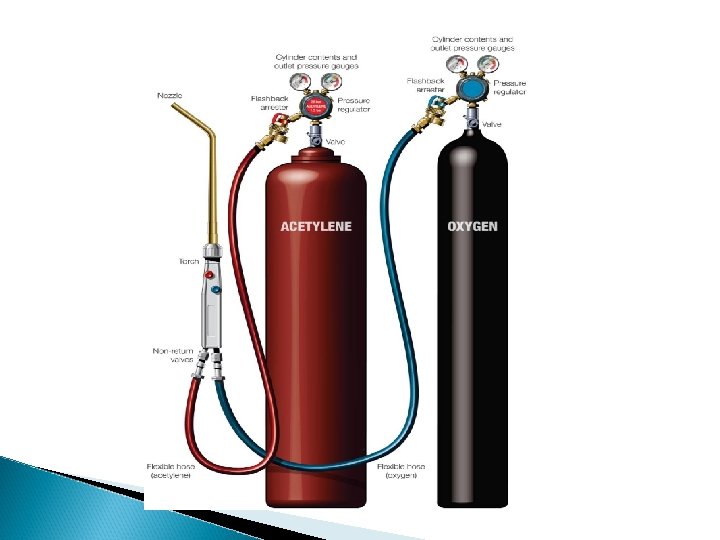
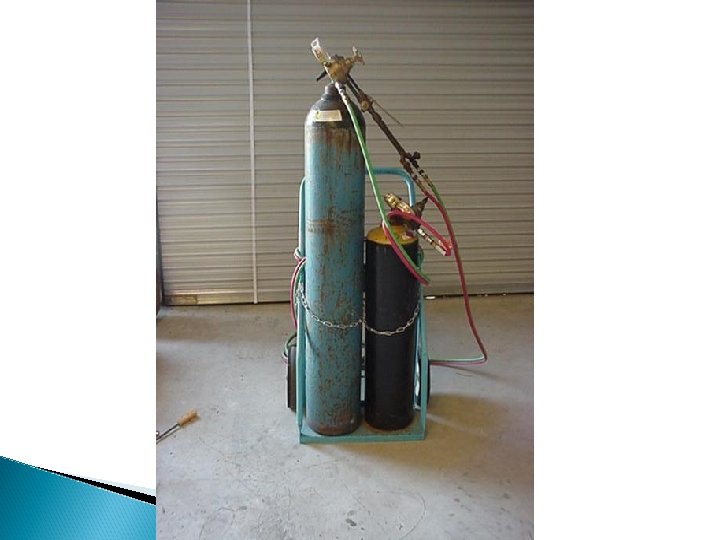
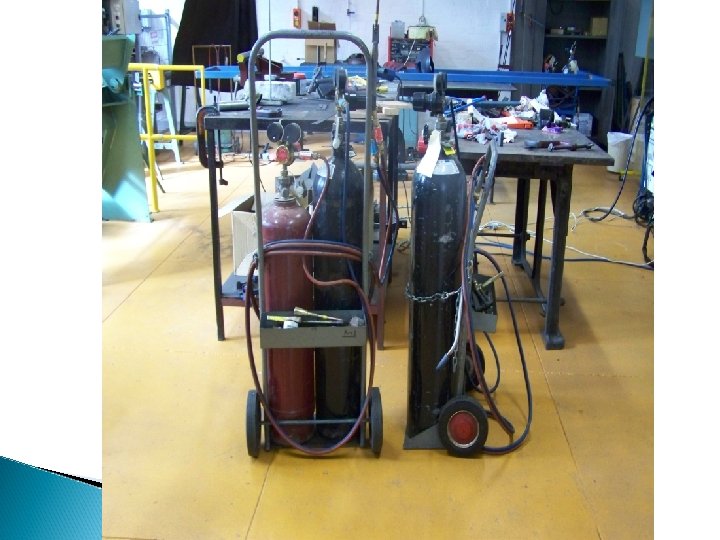
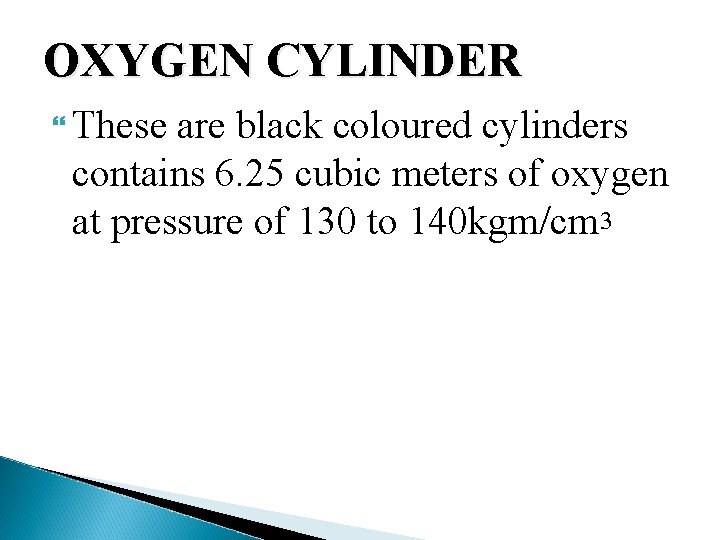
OXYGEN CYLINDER These are black coloured cylinders contains 6. 25 cubic meters of oxygen at pressure of 130 to 140 kgm/cm 3
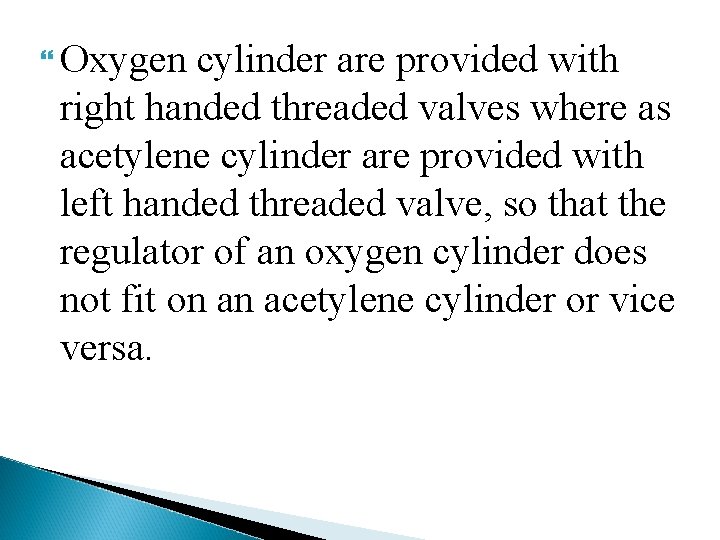
Oxygen cylinder are provided with right handed threaded valves where as acetylene cylinder are provided with left handed threaded valve, so that the regulator of an oxygen cylinder does not fit on an acetylene cylinder or vice versa.

To check against any explosion or accident , oxygen cylinders are also fitted with safety valve
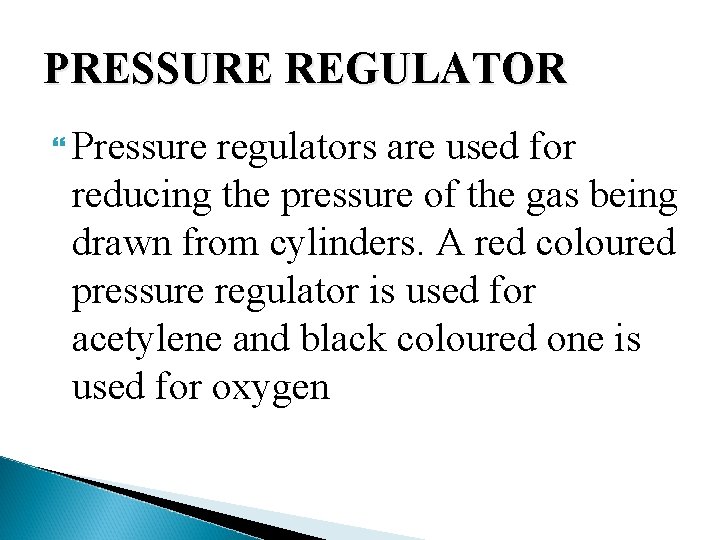
PRESSURE REGULATOR Pressure regulators are used for reducing the pressure of the gas being drawn from cylinders. A red coloured pressure regulator is used for acetylene and black coloured one is used for oxygen
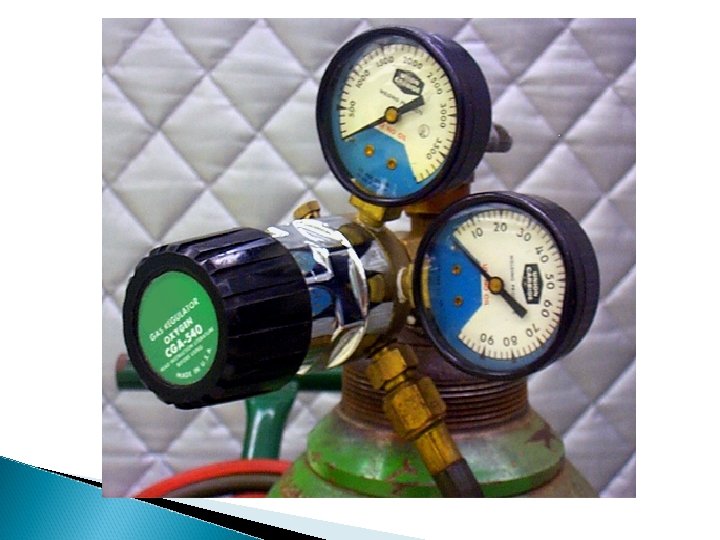
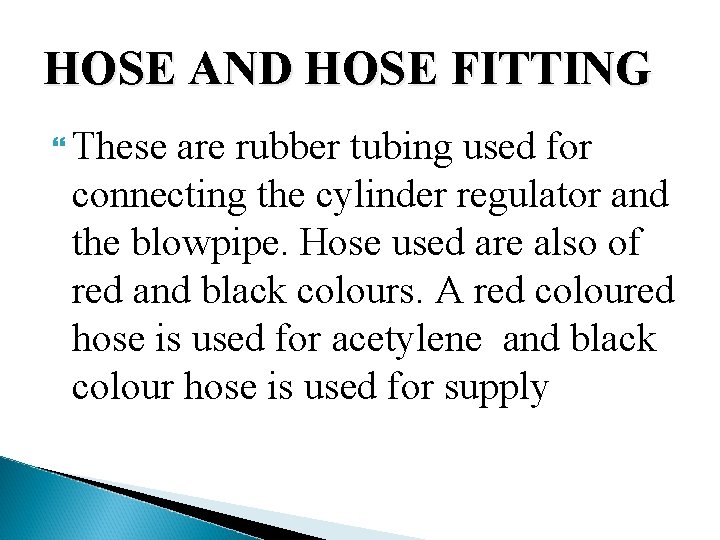
HOSE AND HOSE FITTING These are rubber tubing used for connecting the cylinder regulator and the blowpipe. Hose used are also of red and black colours. A red coloured hose is used for acetylene and black colour hose is used for supply
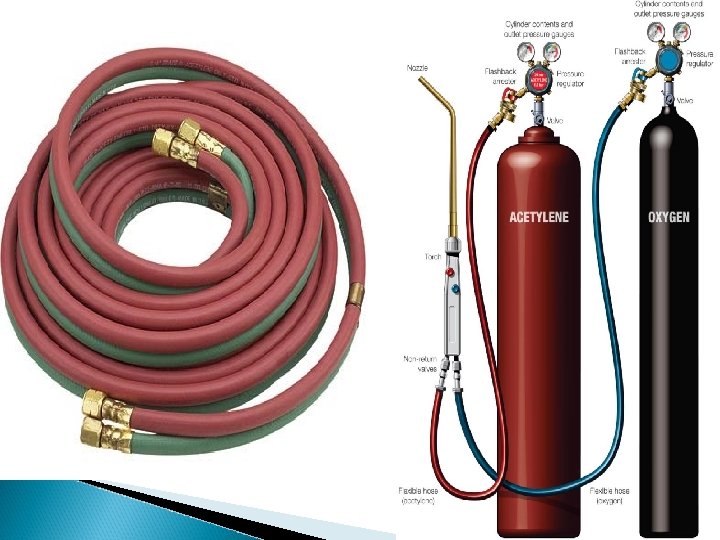
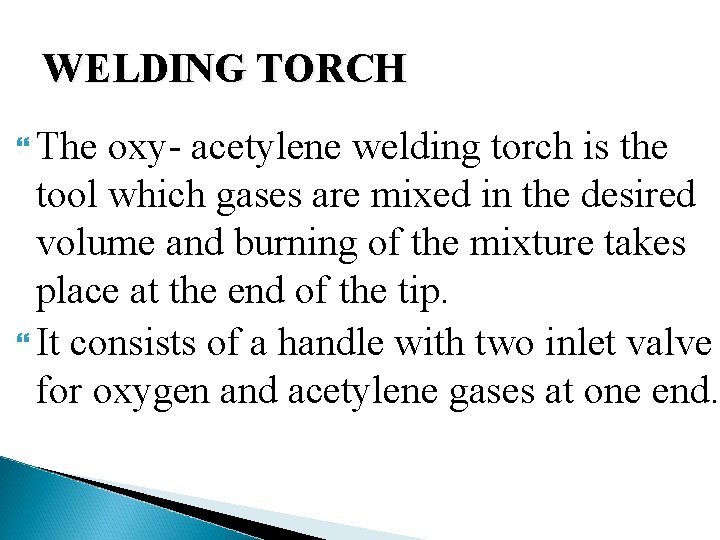
WELDING TORCH The oxy- acetylene welding torch is the tool which gases are mixed in the desired volume and burning of the mixture takes place at the end of the tip. It consists of a handle with two inlet valve for oxygen and acetylene gases at one end.
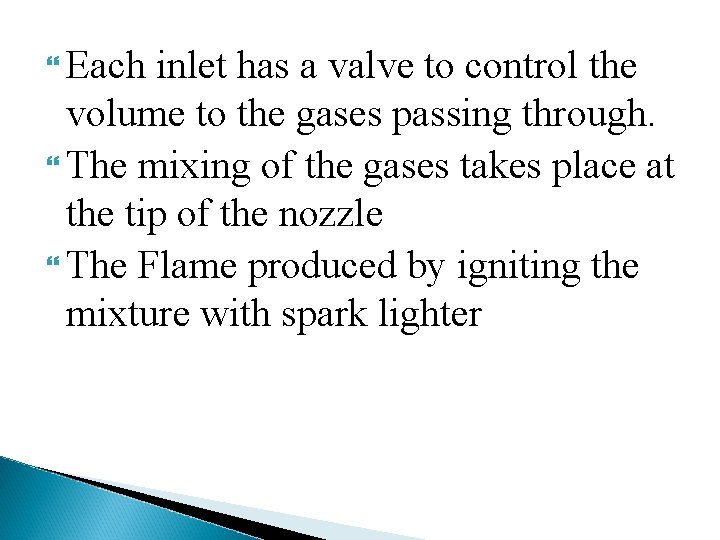
Each inlet has a valve to control the volume to the gases passing through. The mixing of the gases takes place at the tip of the nozzle The Flame produced by igniting the mixture with spark lighter
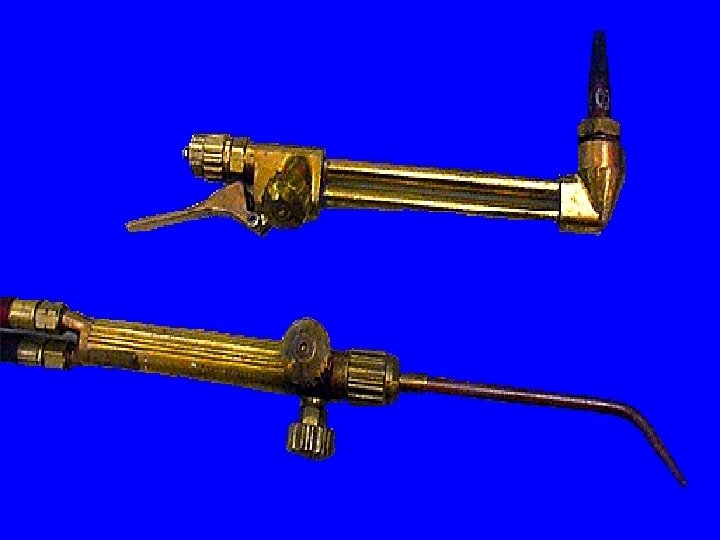
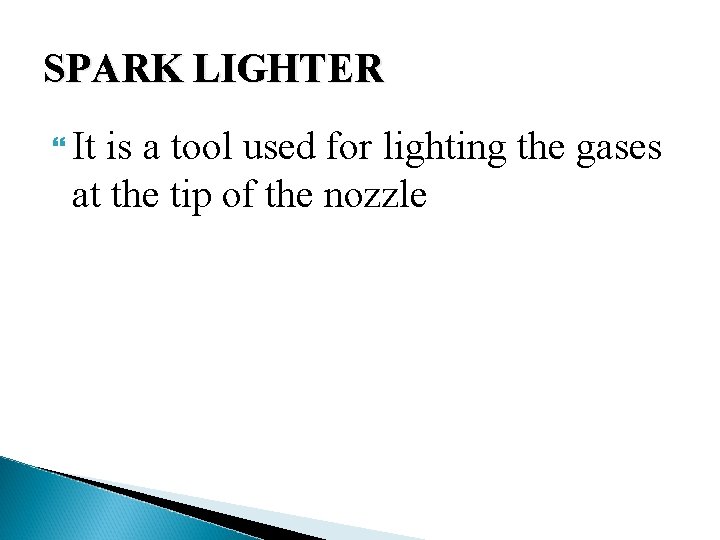
SPARK LIGHTER It is a tool used for lighting the gases at the tip of the nozzle
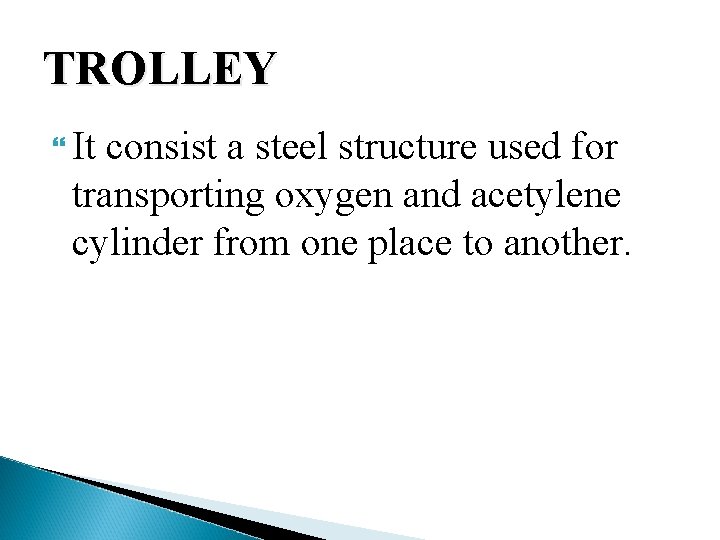
TROLLEY It consist a steel structure used for transporting oxygen and acetylene cylinder from one place to another.
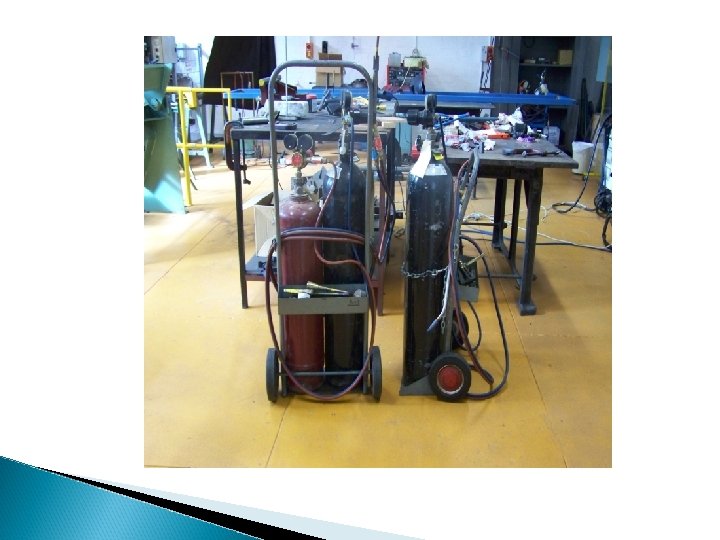
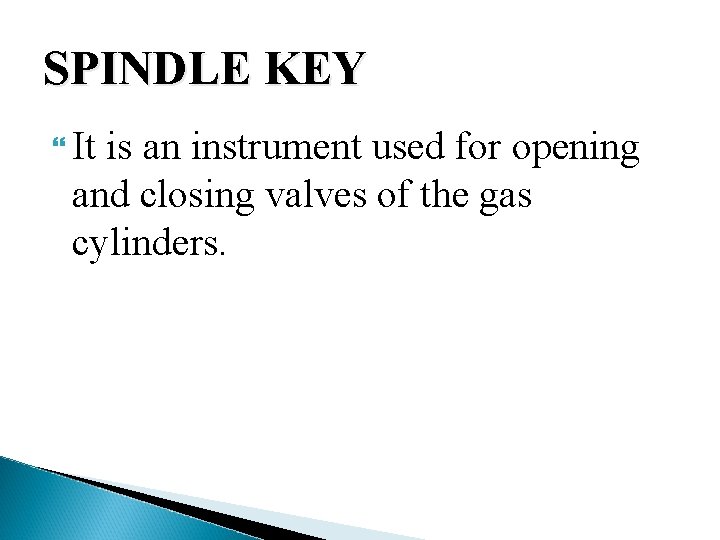
SPINDLE KEY It is an instrument used for opening and closing valves of the gas cylinders.
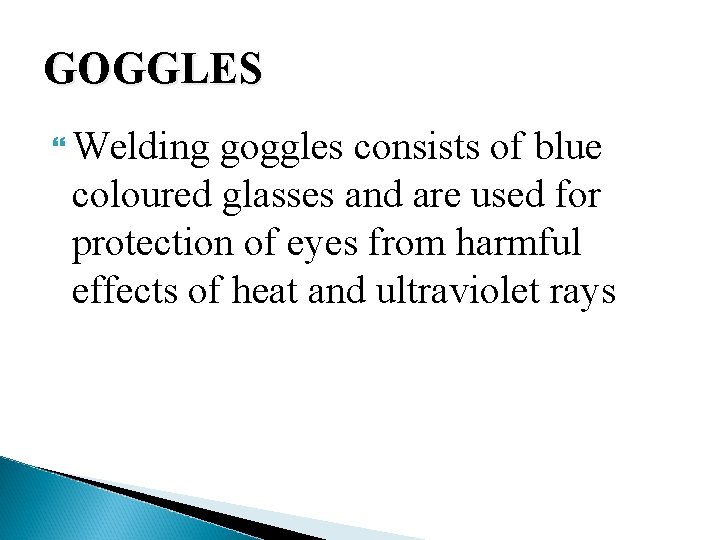
GOGGLES Welding goggles consists of blue coloured glasses and are used for protection of eyes from harmful effects of heat and ultraviolet rays
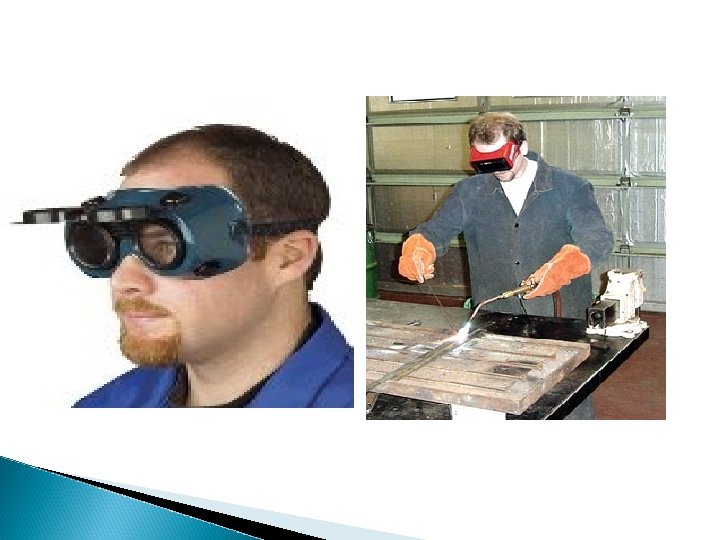
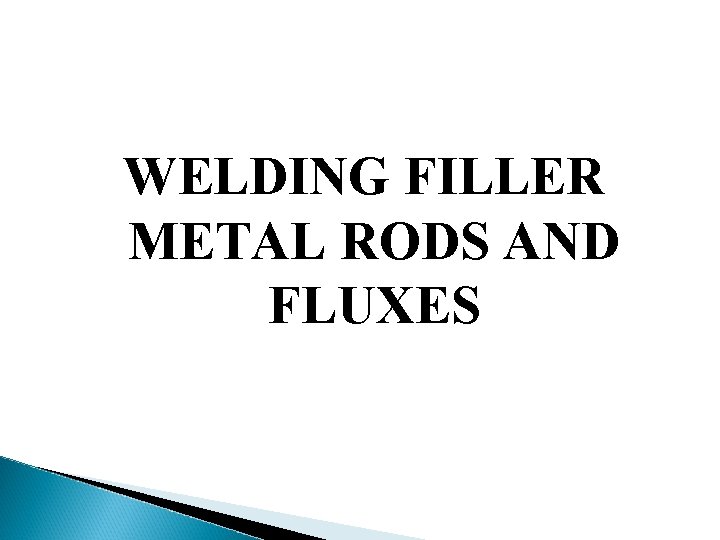
WELDING FILLER METAL RODS AND FLUXES
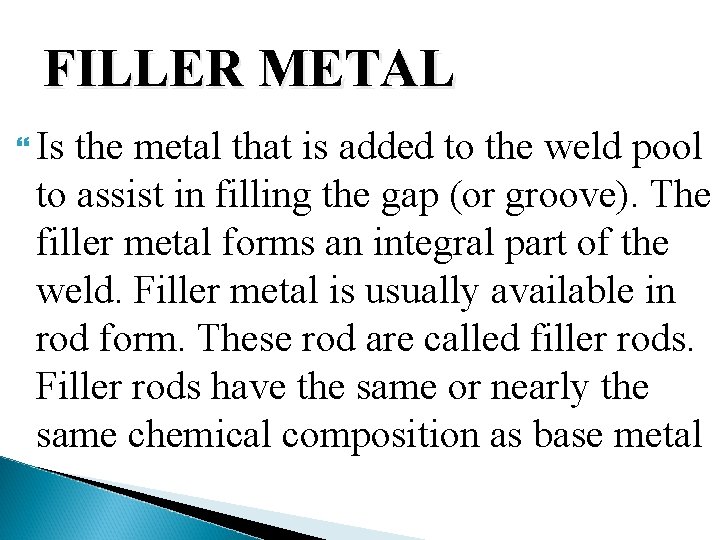
FILLER METAL Is the metal that is added to the weld pool to assist in filling the gap (or groove). The filler metal forms an integral part of the weld. Filler metal is usually available in rod form. These rod are called filler rods. Filler rods have the same or nearly the same chemical composition as base metal
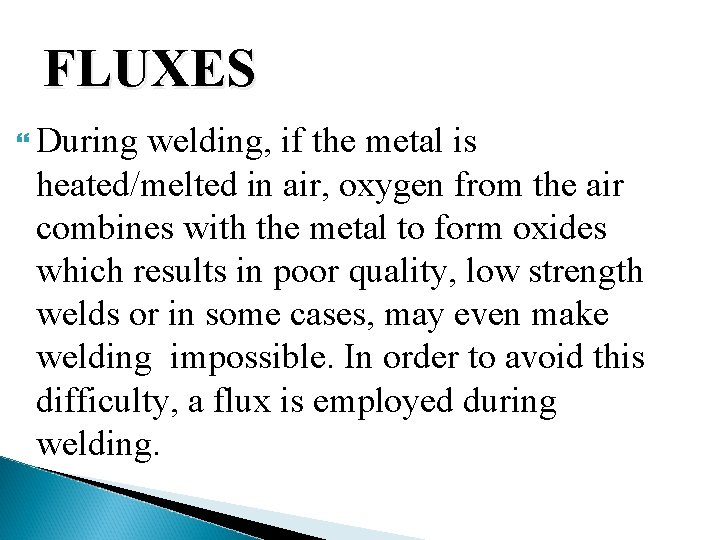
FLUXES During welding, if the metal is heated/melted in air, oxygen from the air combines with the metal to form oxides which results in poor quality, low strength welds or in some cases, may even make welding impossible. In order to avoid this difficulty, a flux is employed during welding.
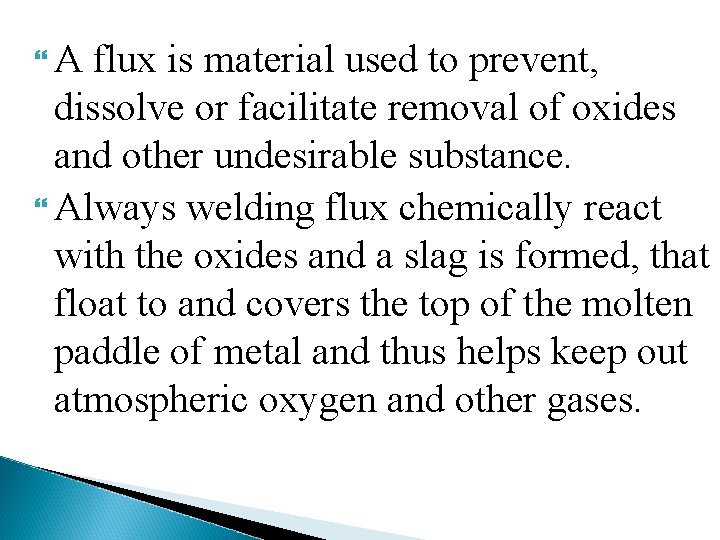
A flux is material used to prevent, dissolve or facilitate removal of oxides and other undesirable substance. Always welding flux chemically react with the oxides and a slag is formed, that float to and covers the top of the molten paddle of metal and thus helps keep out atmospheric oxygen and other gases.
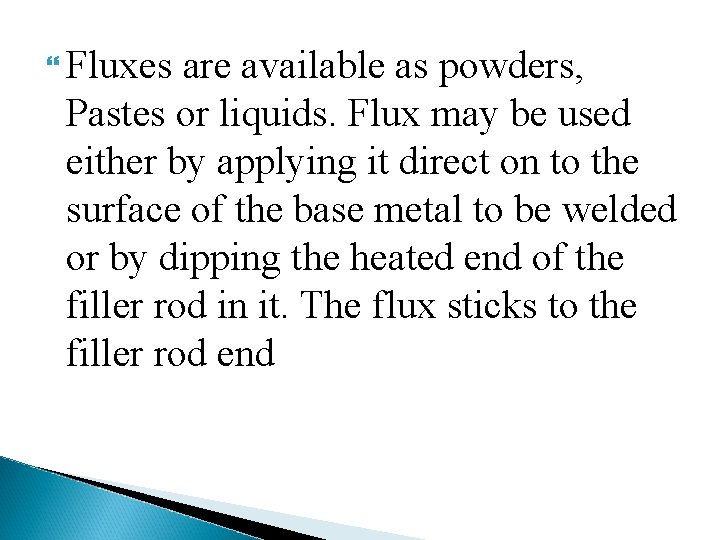
Fluxes are available as powders, Pastes or liquids. Flux may be used either by applying it direct on to the surface of the base metal to be welded or by dipping the heated end of the filler rod in it. The flux sticks to the filler rod end
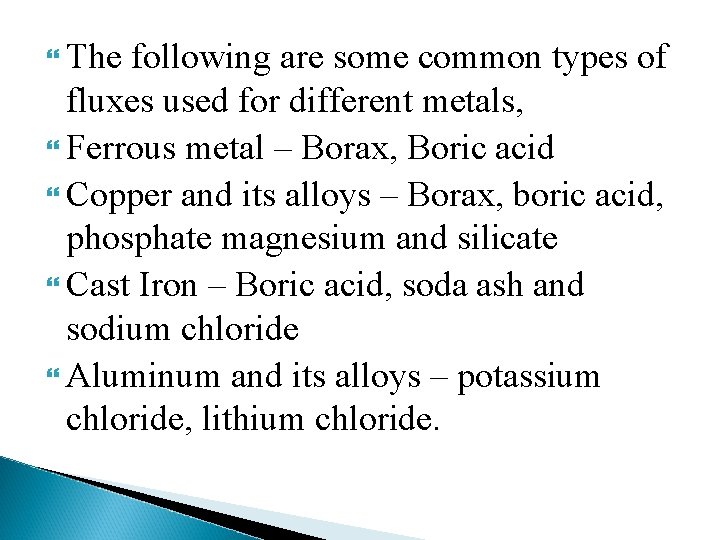
The following are some common types of fluxes used for different metals, Ferrous metal – Borax, Boric acid Copper and its alloys – Borax, boric acid, phosphate magnesium and silicate Cast Iron – Boric acid, soda ash and sodium chloride Aluminum and its alloys – potassium chloride, lithium chloride.
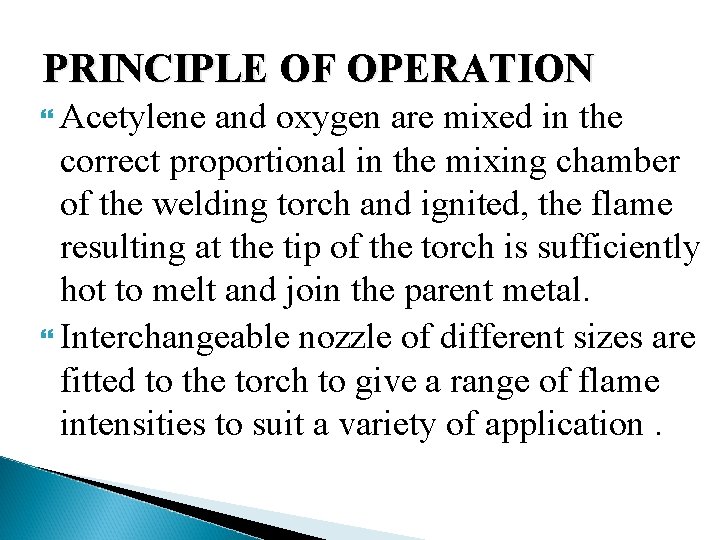
PRINCIPLE OF OPERATION Acetylene and oxygen are mixed in the correct proportional in the mixing chamber of the welding torch and ignited, the flame resulting at the tip of the torch is sufficiently hot to melt and join the parent metal. Interchangeable nozzle of different sizes are fitted to the torch to give a range of flame intensities to suit a variety of application.
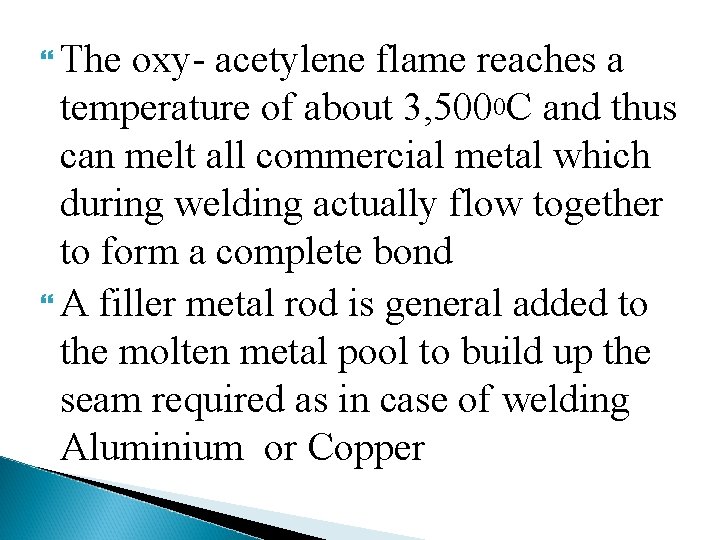
The oxy- acetylene flame reaches a temperature of about 3, 5000 C and thus can melt all commercial metal which during welding actually flow together to form a complete bond A filler metal rod is general added to the molten metal pool to build up the seam required as in case of welding Aluminium or Copper
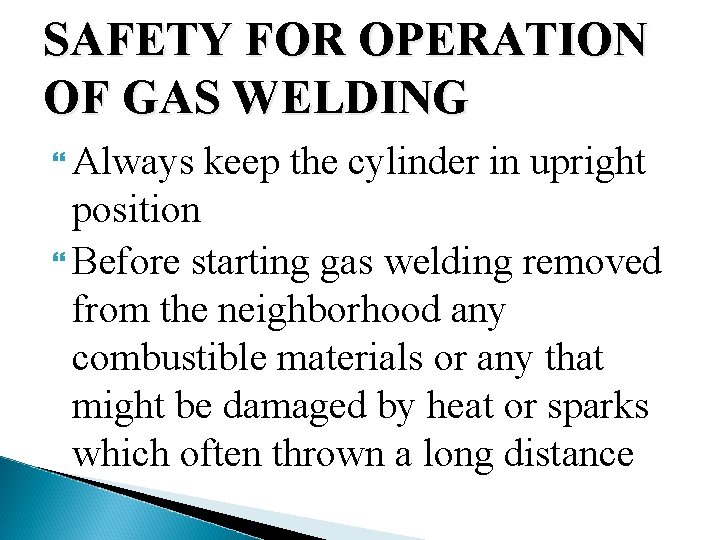
SAFETY FOR OPERATION OF GAS WELDING Always keep the cylinder in upright position Before starting gas welding removed from the neighborhood any combustible materials or any that might be damaged by heat or sparks which often thrown a long distance
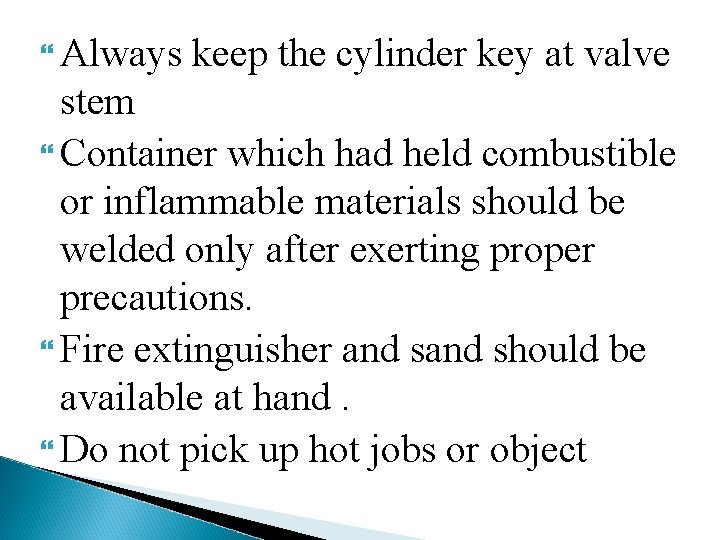
Always keep the cylinder key at valve stem Container which had held combustible or inflammable materials should be welded only after exerting proper precautions. Fire extinguisher and should be available at hand. Do not pick up hot jobs or object
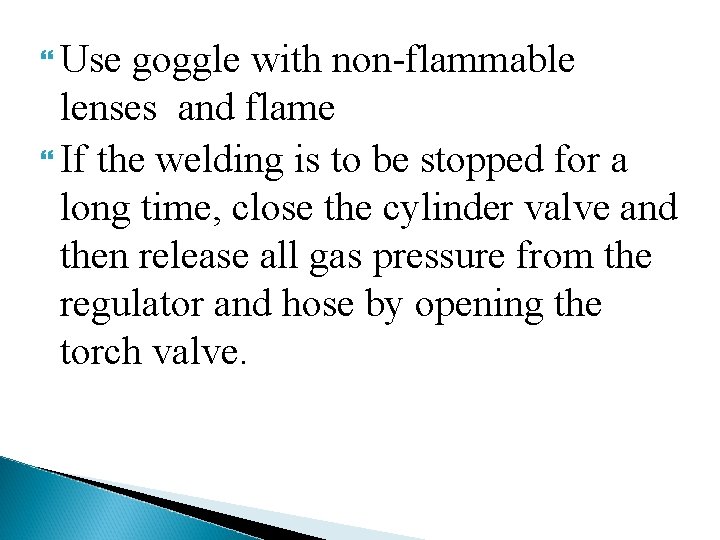
Use goggle with non-flammable lenses and flame If the welding is to be stopped for a long time, close the cylinder valve and then release all gas pressure from the regulator and hose by opening the torch valve.
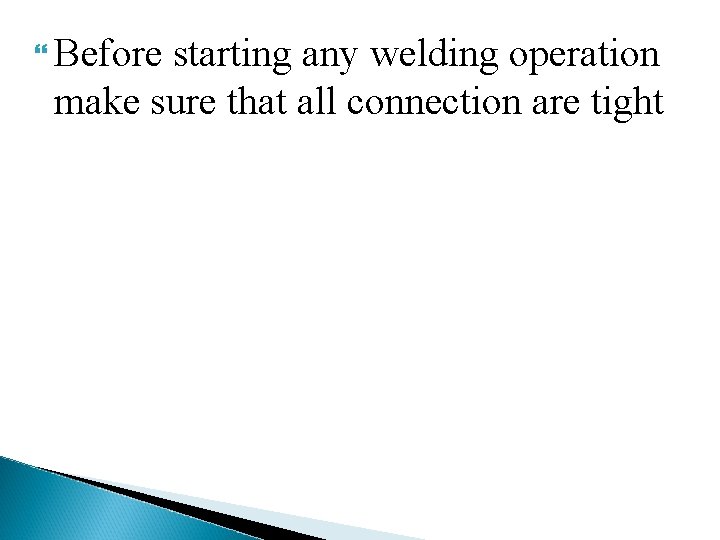
Before starting any welding operation make sure that all connection are tight
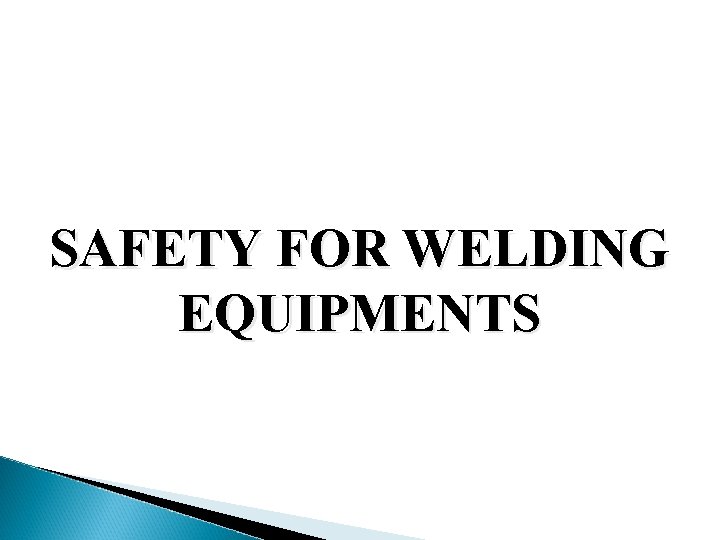
SAFETY FOR WELDING EQUIPMENTS

GAS CYLINDERS Gas cylinder must be prevented from sharp impact with one another or with the ground. Cylinders should not be exposed to welding. Cylinders should be stored in a well protected well ventilated, well away from highly combustible materials such as oil.
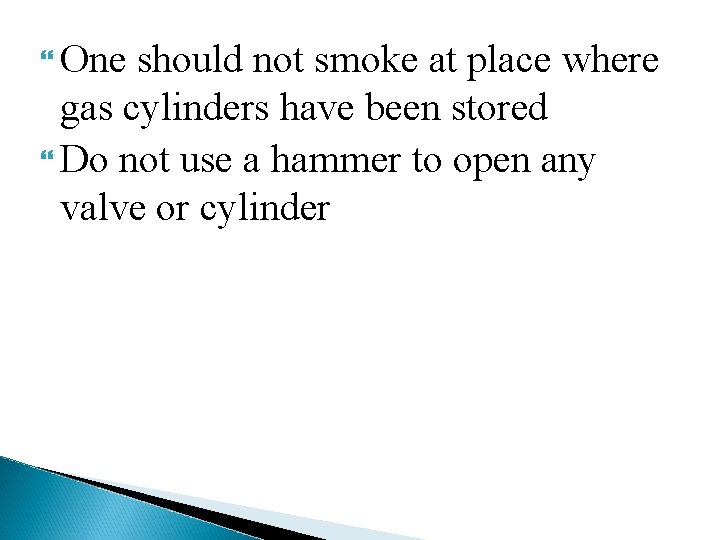
One should not smoke at place where gas cylinders have been stored Do not use a hammer to open any valve or cylinder
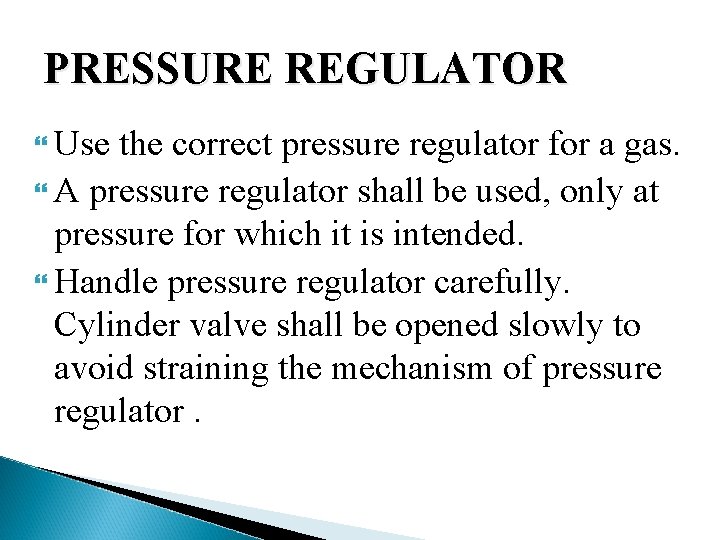
PRESSURE REGULATOR Use the correct pressure regulator for a gas. A pressure regulator shall be used, only at pressure for which it is intended. Handle pressure regulator carefully. Cylinder valve shall be opened slowly to avoid straining the mechanism of pressure regulator.
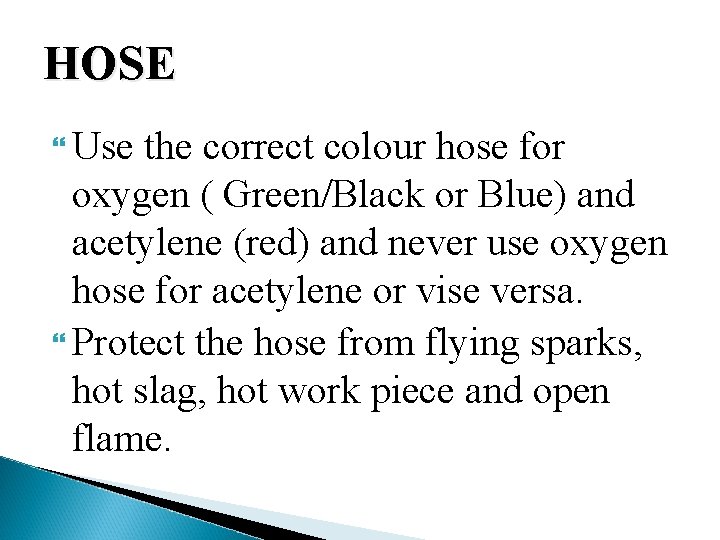
HOSE Use the correct colour hose for oxygen ( Green/Black or Blue) and acetylene (red) and never use oxygen hose for acetylene or vise versa. Protect the hose from flying sparks, hot slag, hot work piece and open flame.
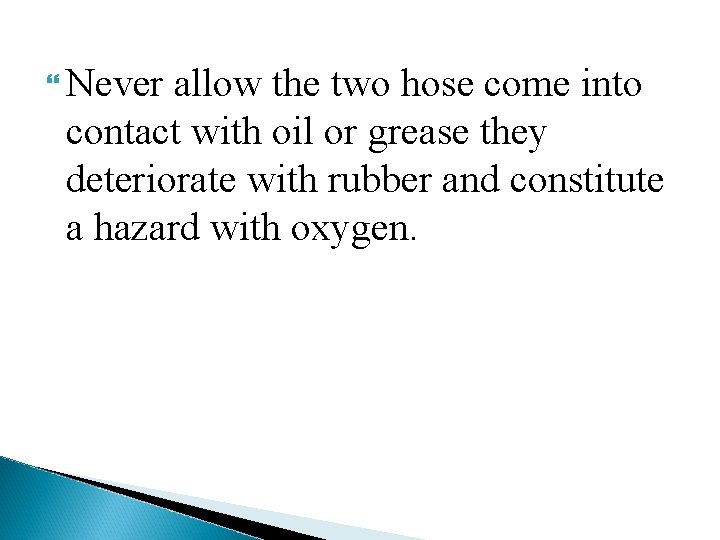
Never allow the two hose come into contact with oil or grease they deteriorate with rubber and constitute a hazard with oxygen.
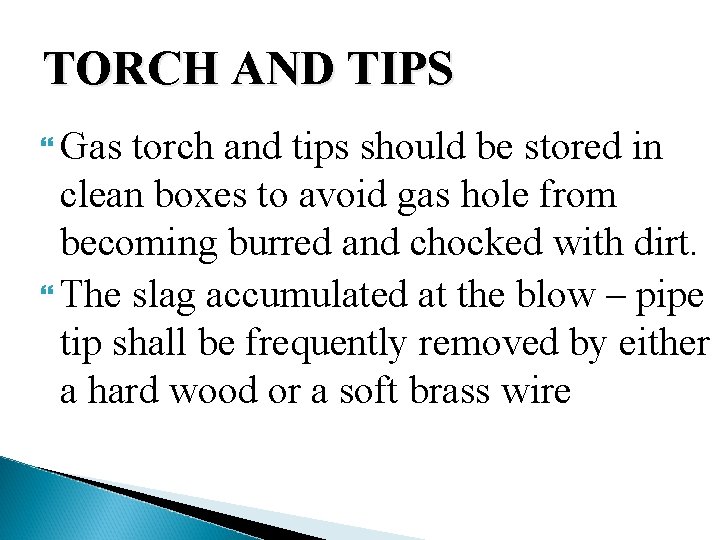
TORCH AND TIPS Gas torch and tips should be stored in clean boxes to avoid gas hole from becoming burred and chocked with dirt. The slag accumulated at the blow – pipe tip shall be frequently removed by either a hard wood or a soft brass wire
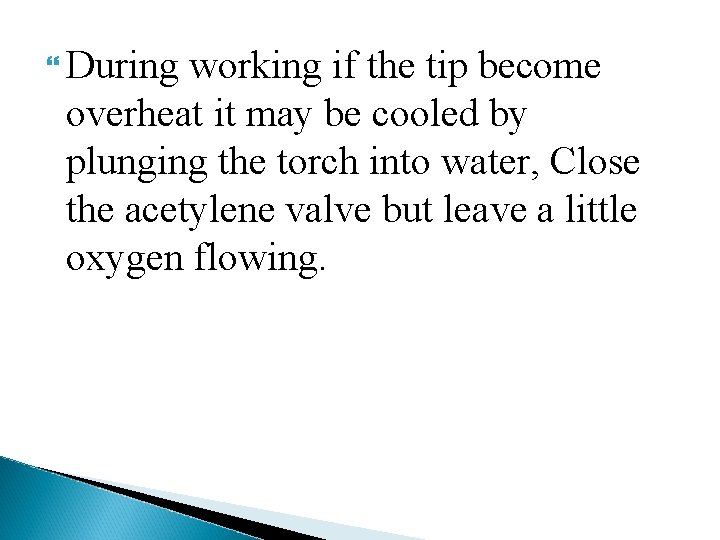
During working if the tip become overheat it may be cooled by plunging the torch into water, Close the acetylene valve but leave a little oxygen flowing.
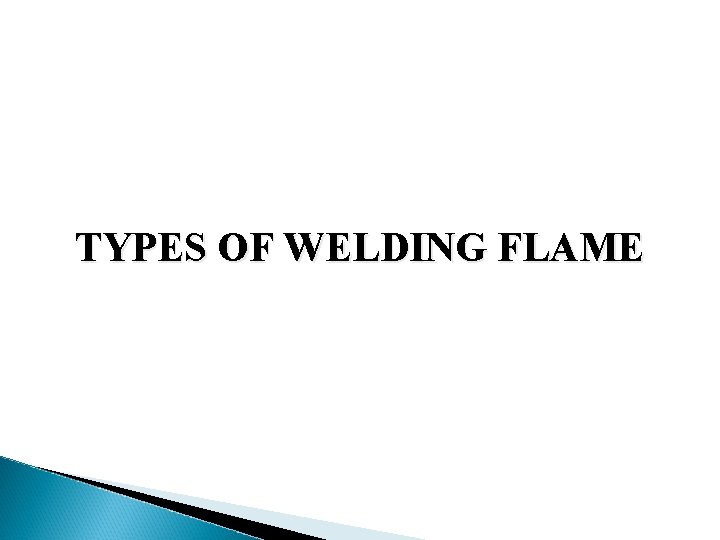
TYPES OF WELDING FLAME
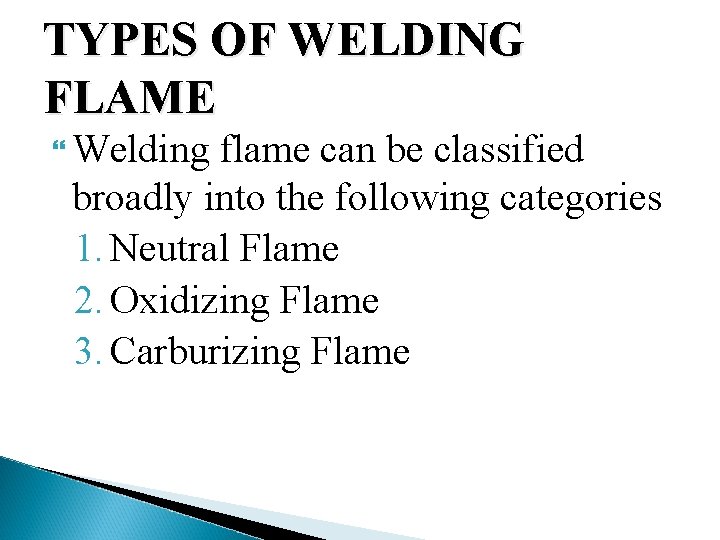
TYPES OF WELDING FLAME Welding flame can be classified broadly into the following categories 1. Neutral Flame 2. Oxidizing Flame 3. Carburizing Flame
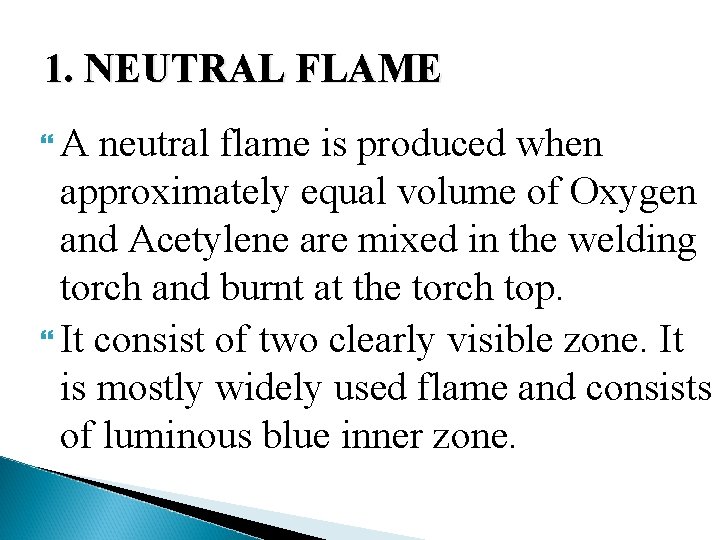
1. NEUTRAL FLAME A neutral flame is produced when approximately equal volume of Oxygen and Acetylene are mixed in the welding torch and burnt at the torch top. It consist of two clearly visible zone. It is mostly widely used flame and consists of luminous blue inner zone.
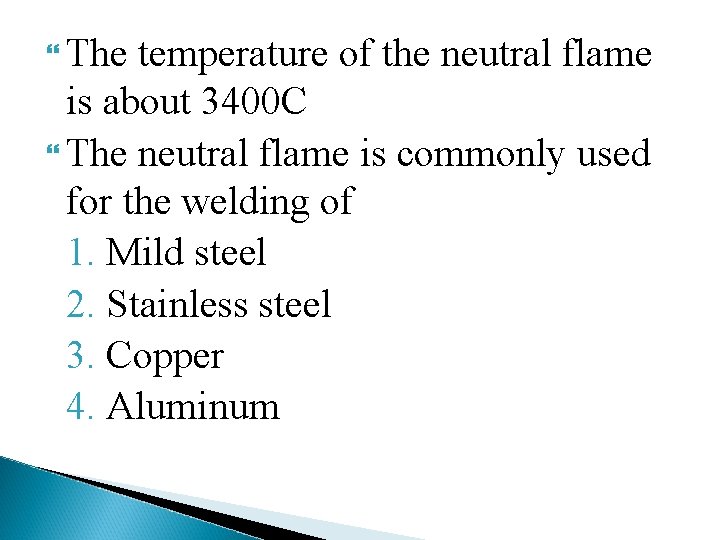
The temperature of the neutral flame is about 3400 C The neutral flame is commonly used for the welding of 1. Mild steel 2. Stainless steel 3. Copper 4. Aluminum
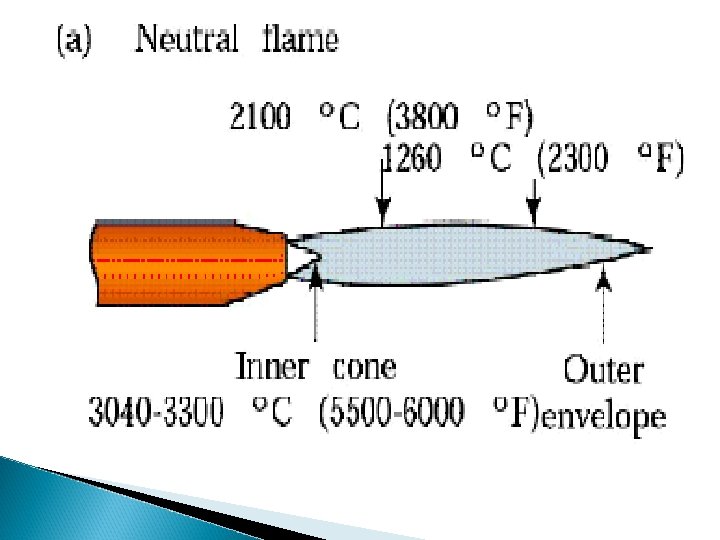
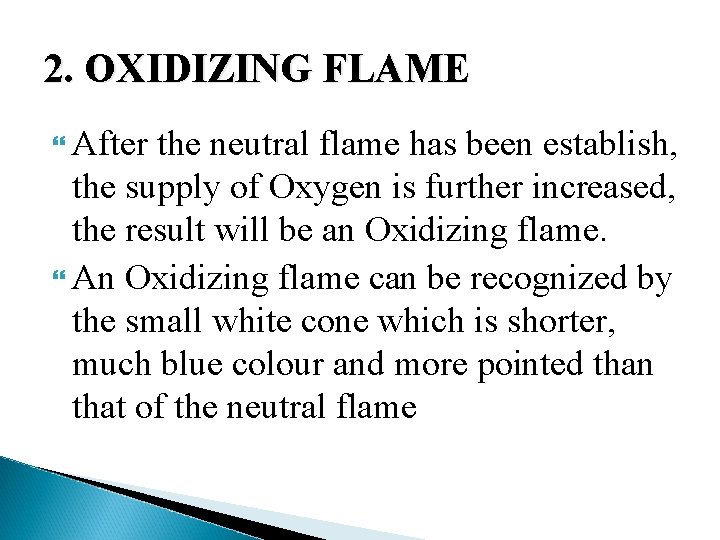
2. OXIDIZING FLAME After the neutral flame has been establish, the supply of Oxygen is further increased, the result will be an Oxidizing flame. An Oxidizing flame can be recognized by the small white cone which is shorter, much blue colour and more pointed than that of the neutral flame
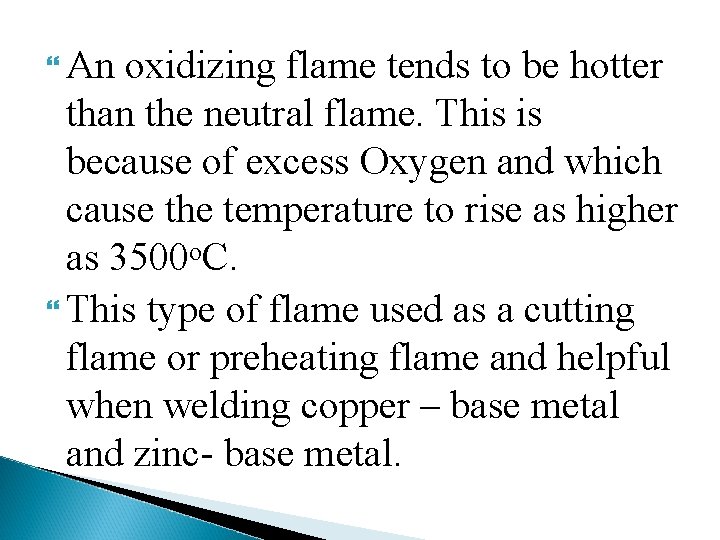
An oxidizing flame tends to be hotter than the neutral flame. This is because of excess Oxygen and which cause the temperature to rise as higher as 3500 o. C. This type of flame used as a cutting flame or preheating flame and helpful when welding copper – base metal and zinc- base metal.
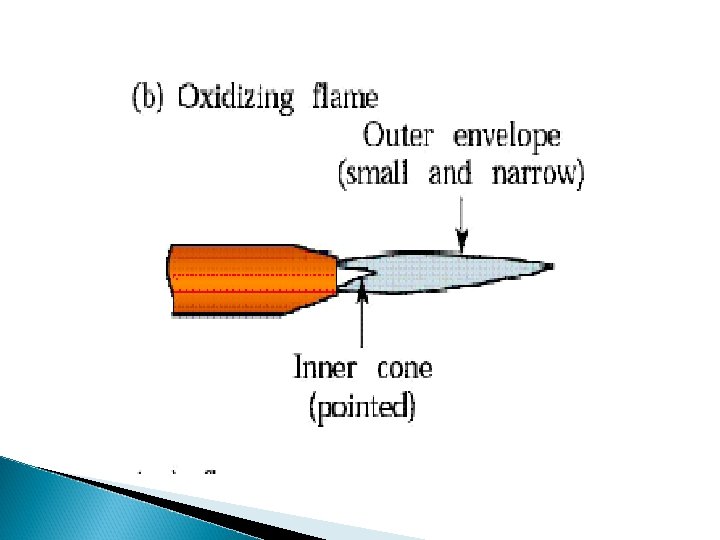
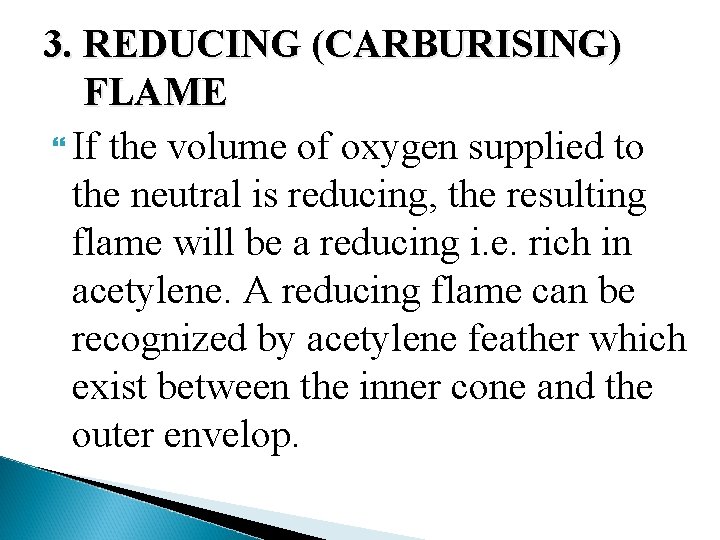
3. REDUCING (CARBURISING) FLAME If the volume of oxygen supplied to the neutral is reducing, the resulting flame will be a reducing i. e. rich in acetylene. A reducing flame can be recognized by acetylene feather which exist between the inner cone and the outer envelop.
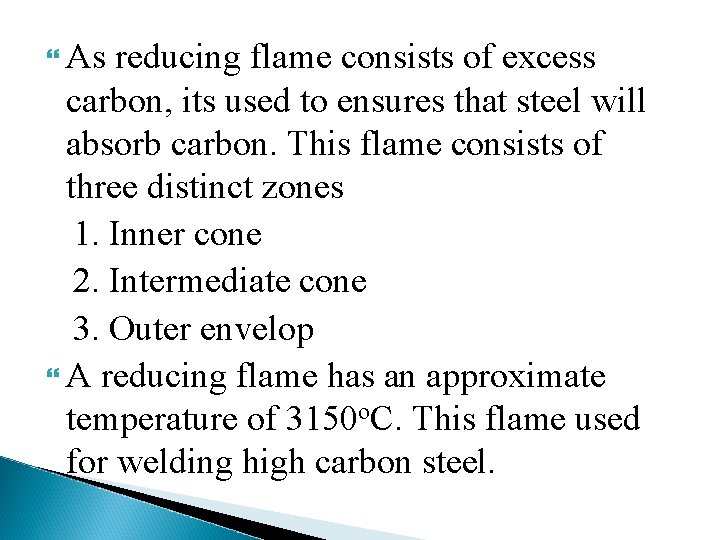
As reducing flame consists of excess carbon, its used to ensures that steel will absorb carbon. This flame consists of three distinct zones 1. Inner cone 2. Intermediate cone 3. Outer envelop A reducing flame has an approximate temperature of 3150 o. C. This flame used for welding high carbon steel.
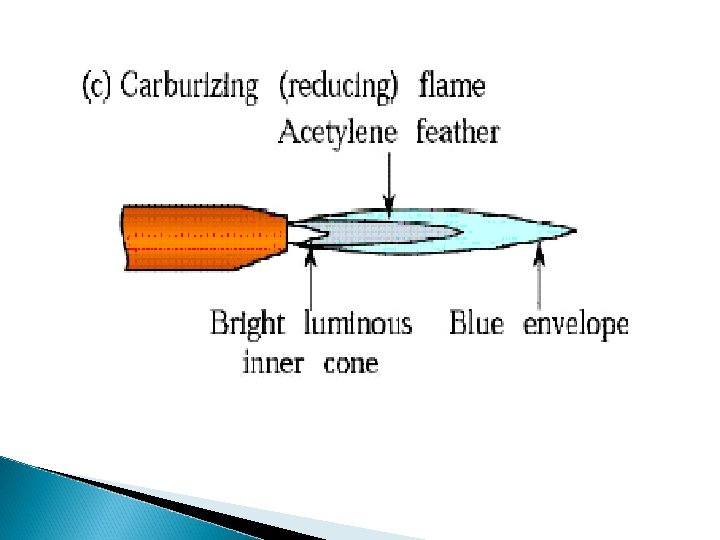
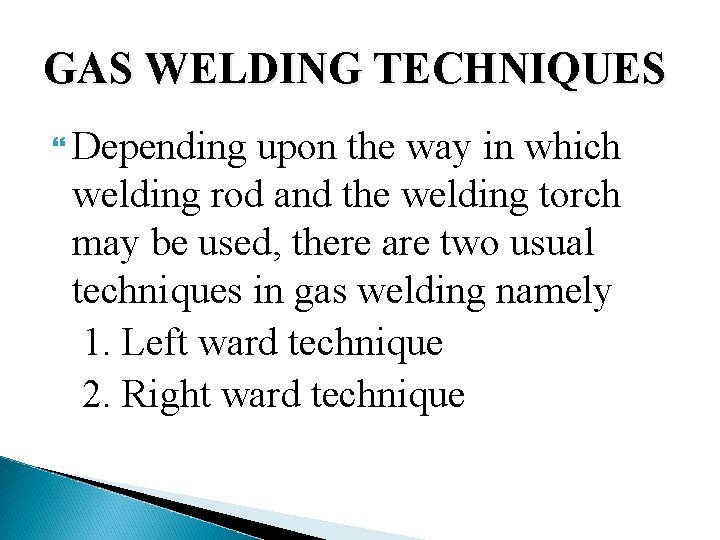
GAS WELDING TECHNIQUES Depending upon the way in which welding rod and the welding torch may be used, there are two usual techniques in gas welding namely 1. Left ward technique 2. Right ward technique
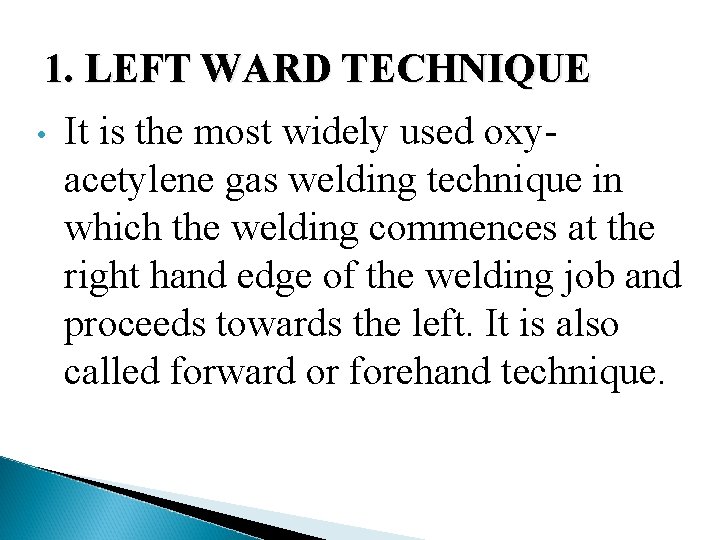
1. LEFT WARD TECHNIQUE • It is the most widely used oxyacetylene gas welding technique in which the welding commences at the right hand edge of the welding job and proceeds towards the left. It is also called forward or forehand technique.
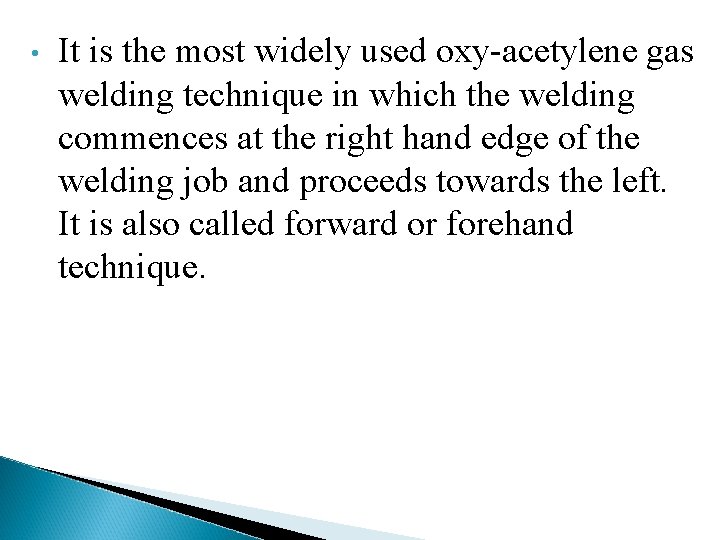
• It is the most widely used oxy-acetylene gas welding technique in which the welding commences at the right hand edge of the welding job and proceeds towards the left. It is also called forward or forehand technique.
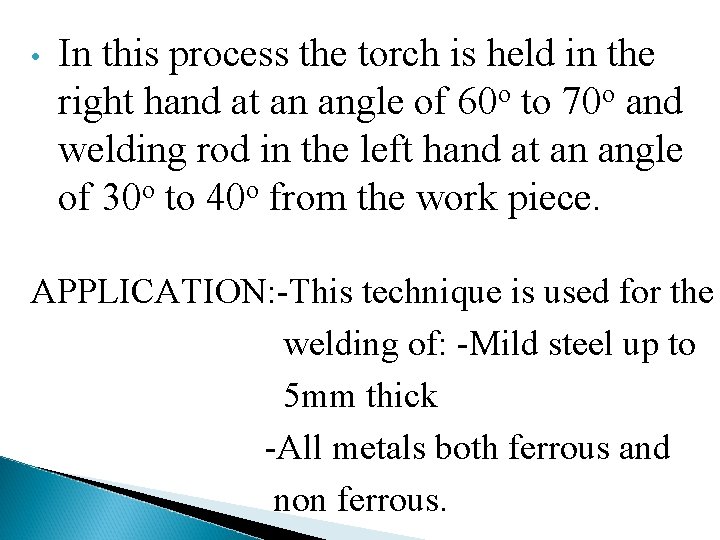
• In this process the torch is held in the right hand at an angle of 60 o to 70 o and welding rod in the left hand at an angle of 30 o to 40 o from the work piece. APPLICATION: -This technique is used for the welding of: -Mild steel up to 5 mm thick -All metals both ferrous and non ferrous.
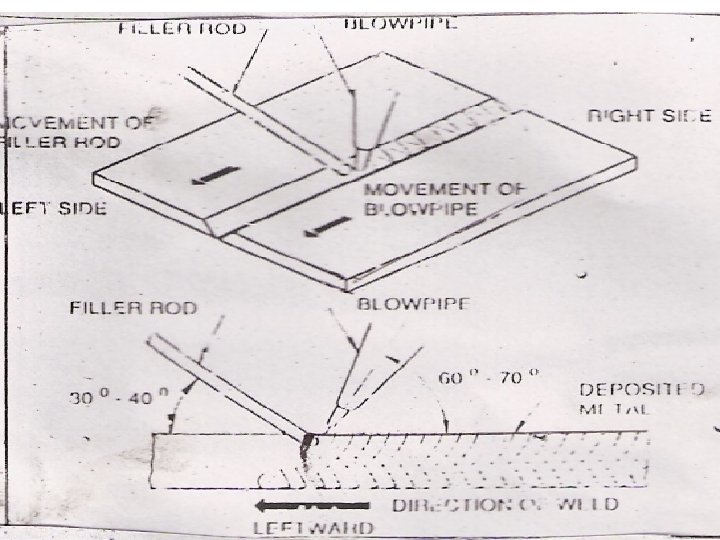

2. RIGHT WARD TECHNIQUE It differ from left ward welding in the direction of movement of the torch. In this system the torch moves from left to right. The torch is held in the right hand at an angle of 40 o to 50 o and the filler rod in the left hand at an angle of 30 o to 40 o
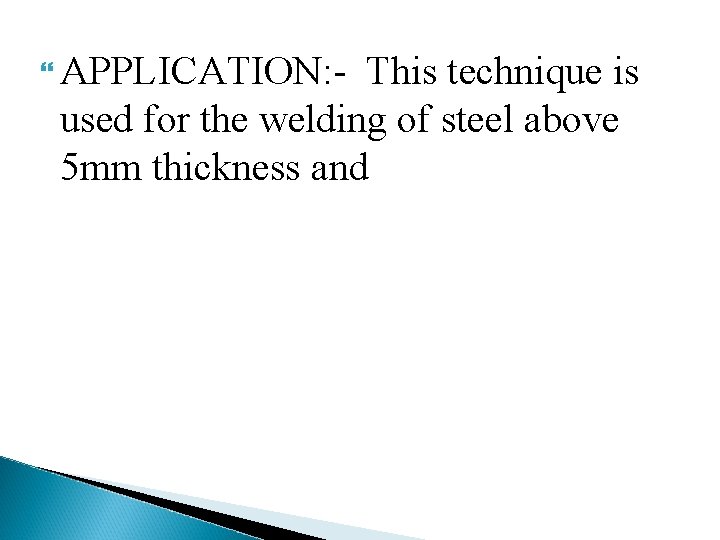
APPLICATION: - This technique is used for the welding of steel above 5 mm thickness and
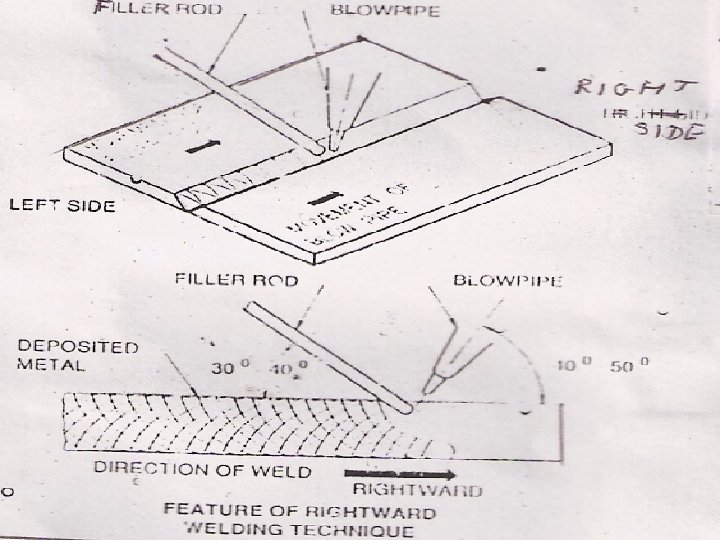
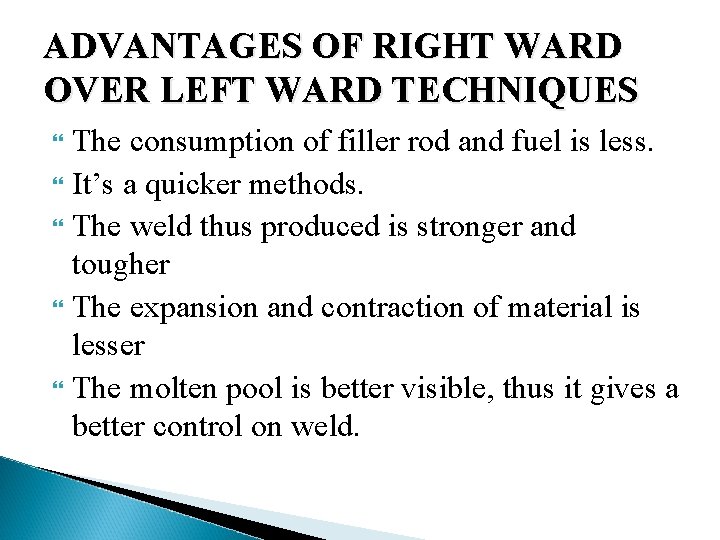
ADVANTAGES OF RIGHT WARD OVER LEFT WARD TECHNIQUES The consumption of filler rod and fuel is less. It’s a quicker methods. The weld thus produced is stronger and tougher The expansion and contraction of material is lesser The molten pool is better visible, thus it gives a better control on weld.
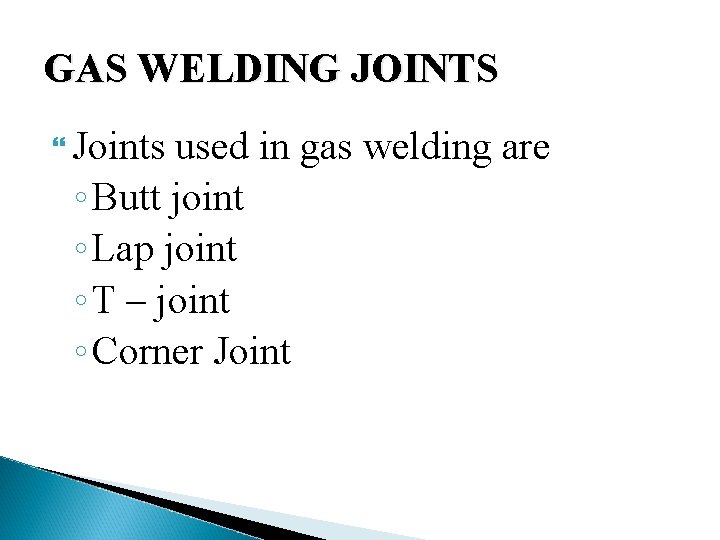
GAS WELDING JOINTS Joints used in gas welding are ◦ Butt joint ◦ Lap joint ◦ T – joint ◦ Corner Joint
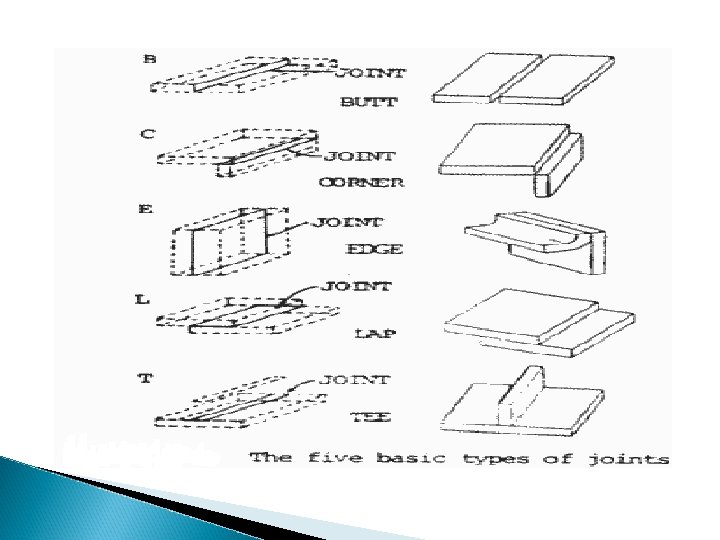
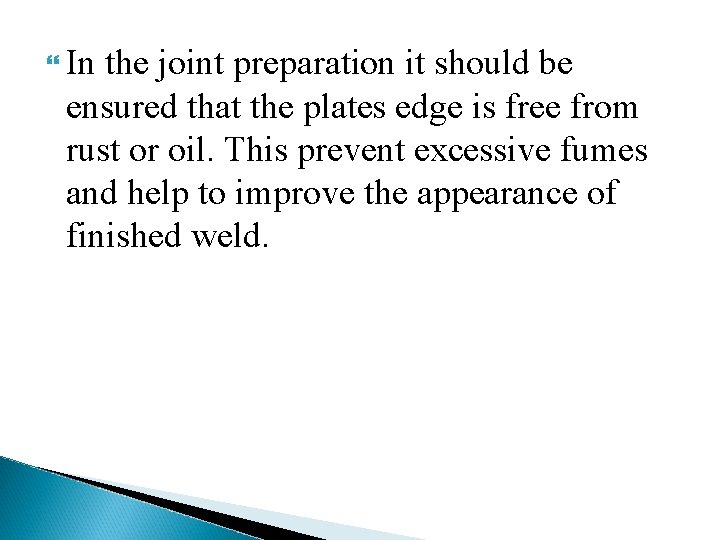
In the joint preparation it should be ensured that the plates edge is free from rust or oil. This prevent excessive fumes and help to improve the appearance of finished weld.
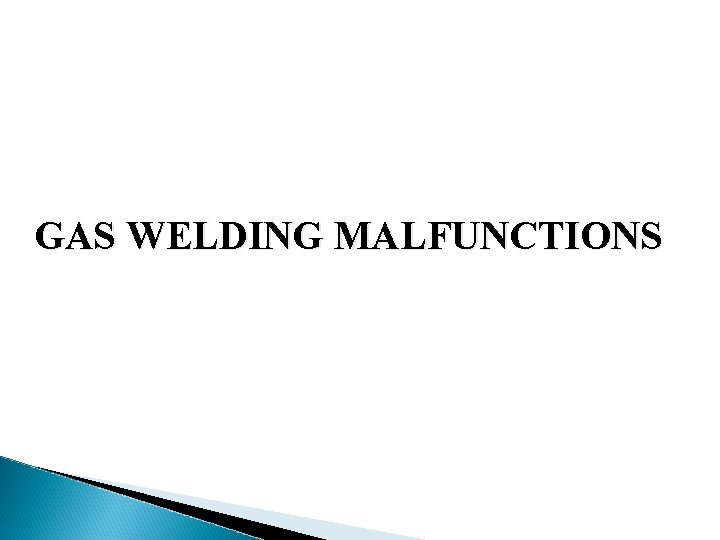
GAS WELDING MALFUNCTIONS
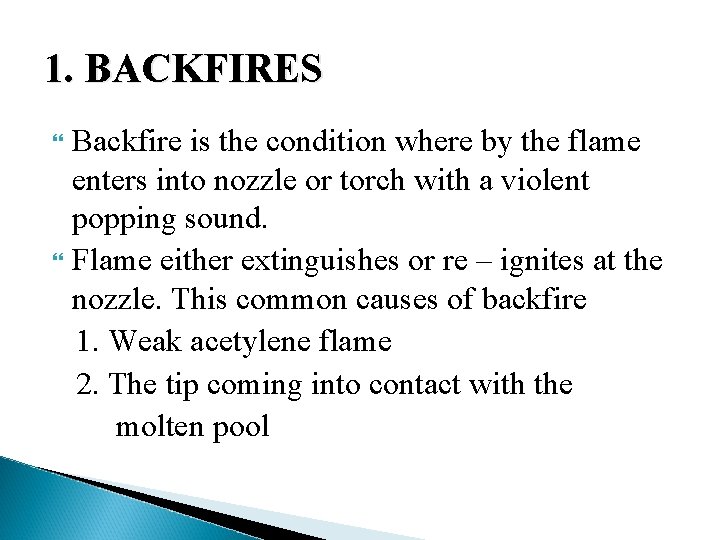
1. BACKFIRES Backfire is the condition where by the flame enters into nozzle or torch with a violent popping sound. Flame either extinguishes or re – ignites at the nozzle. This common causes of backfire 1. Weak acetylene flame 2. The tip coming into contact with the molten pool
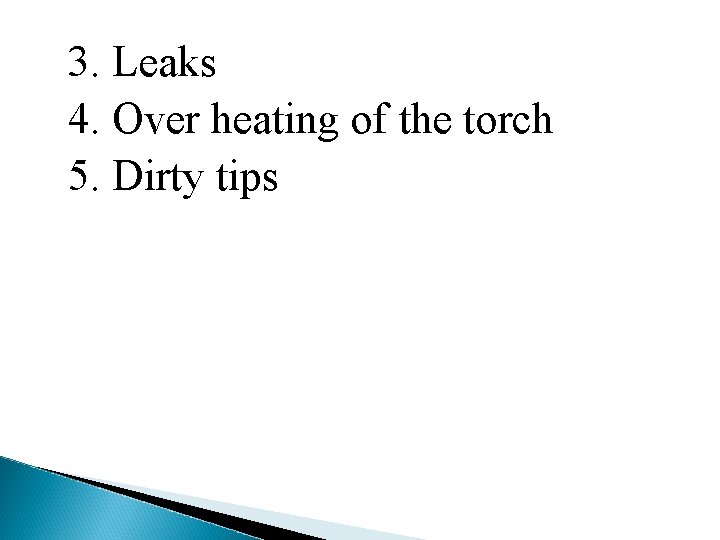
3. Leaks 4. Over heating of the torch 5. Dirty tips
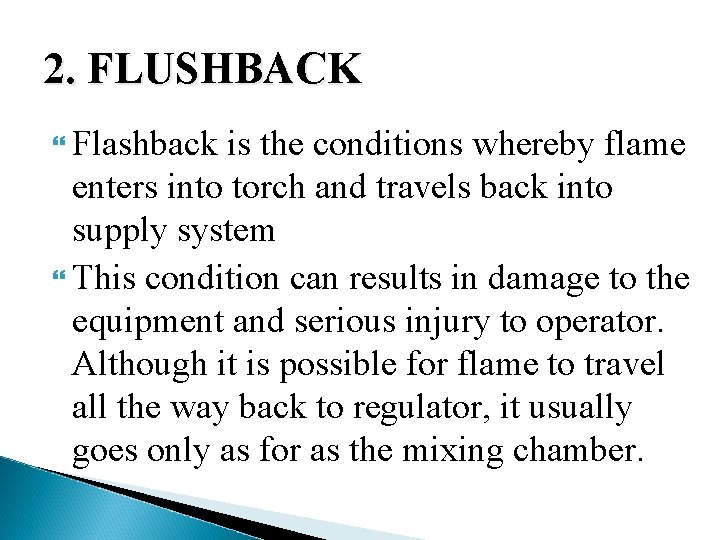
2. FLUSHBACK Flashback is the conditions whereby flame enters into torch and travels back into supply system This condition can results in damage to the equipment and serious injury to operator. Although it is possible for flame to travel all the way back to regulator, it usually goes only as for as the mixing chamber.
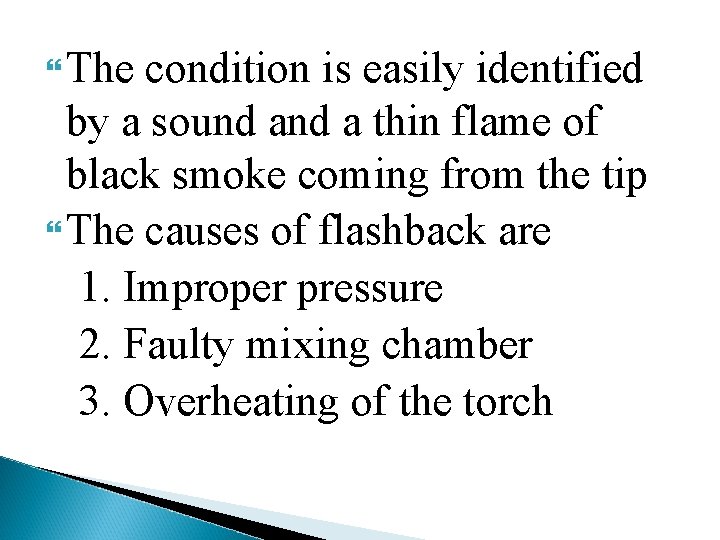
The condition is easily identified by a sound a thin flame of black smoke coming from the tip The causes of flashback are 1. Improper pressure 2. Faulty mixing chamber 3. Overheating of the torch
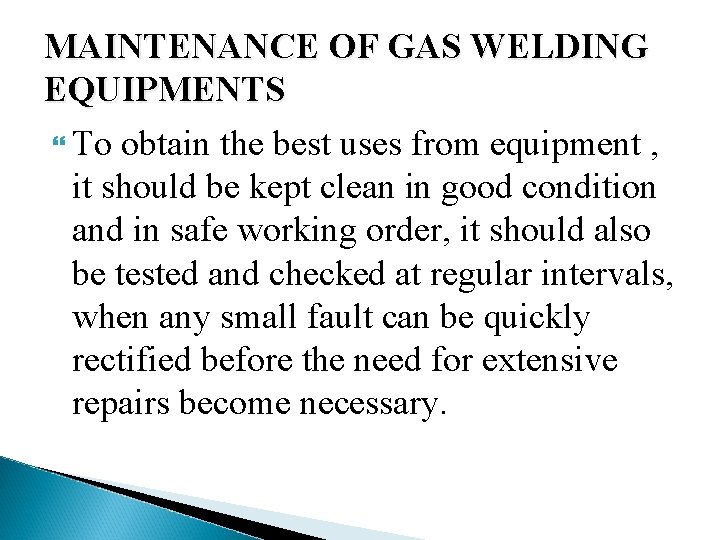
MAINTENANCE OF GAS WELDING EQUIPMENTS To obtain the best uses from equipment , it should be kept clean in good condition and in safe working order, it should also be tested and checked at regular intervals, when any small fault can be quickly rectified before the need for extensive repairs become necessary.
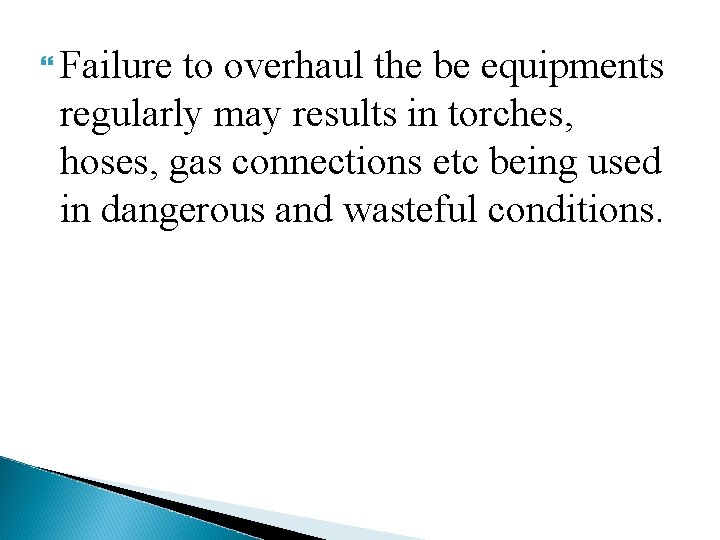
Failure to overhaul the be equipments regularly may results in torches, hoses, gas connections etc being used in dangerous and wasteful conditions.
Rmd welding
Gas welding techniques
Acetylene welding definition
Introduction of gas welding
Introduction of gas welding
Introduction of gas welding
Fusion welding definition
Draglines welding definition
Casting forming and welding mcq
Fusion arc welding
Fusion welding process
Science fusion online
Chapter 3 joint design and welding terms
Tungsten inert gas welding
Chapter 2 welding safety quiz
Welding robot introduction
Gas welding conclusion
Tig welding definition
Describe what a lap joint is in oxy fuel welding.
Gas shielded arc welding
Gas welding
Gas welding safety tips
Introduction to smaw
Chapter 1 introduction to welding
Ideal gas vs perfect gas
Imaginary gas
Gas law
Computational fluid dynamics
Bhopal gas tragedy causes
Gas leaked in bhopal gas tragedy
Gas reale e gas ideale
Flue gas desulfurisation gas filter
Poisonous gas leaked in bhopal gas tragedy
Difference between ideal gas and real gas
Kinetika kimia
Gas exchange key events in gas exchange
[email protected]
Introduction of gas turbine
Gas chromatography
Fission and fusion similarities
Advanced fusion systems llc
Tri fusion java
Propiedades del xenón
Operator fusion deep learning
Unit of latent heat
First somatic hybrid in plant was obtained by
Smart fusion pole
Smart fusion pole
Uranium nuclear fission
Fusion por descompresion
Pyroelectric fusion ppt
Ointment preparation by fusion method
Protoplast fusion
Cache fusion
Are nuclear power plants fission or fusion
Nuclear fission and fusion similarities
Nucluar fusion
Rectangle real life examples
Sectionneur porte fusible symbole
1 mol
Effervescent granules examples
Fusion liberal conservadora
Inertial confinement fusion lasers
Fusion table layer
Fusion medical staffing llc
Fusion inspector
Fusioncompute huawei
Fission and fusion similarities
Scad fusion360
Venn diagram nuclear fission and fusion
Fission vs fusion
Fission vs fusion nuclear
Fusion figura fondo
6 phase changes
Direct fusion drive
Endocitosis
Fission vs fusion
Fusion blanket
Nuclear fusion radiation
Enthalpy of fusion
Epiphyseal fusion
Development of binocular single vision
Blair fusion
Fission vs fusion energy output