THE ULTIMATE PERFORMANCE SPECIFICATION USING FEVE FLUOROPOLYMERS presented
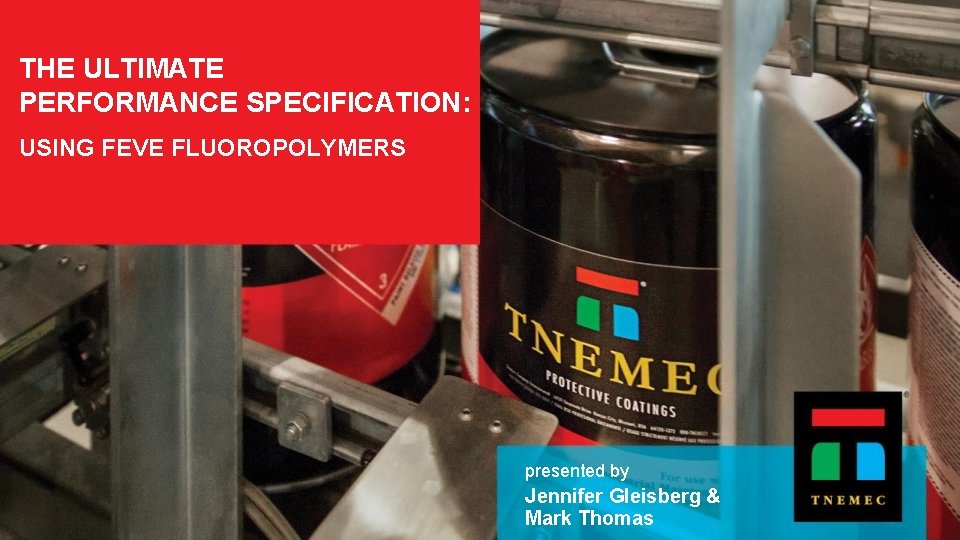
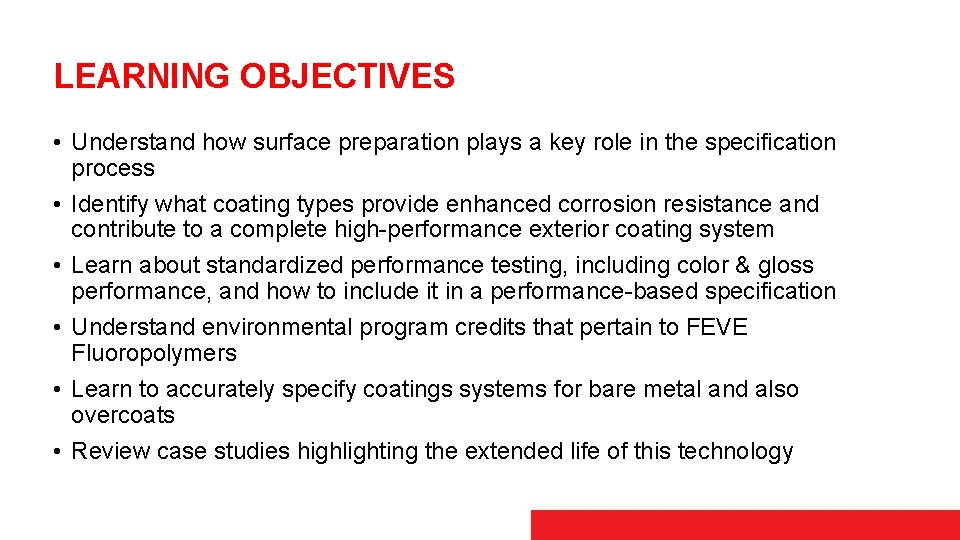
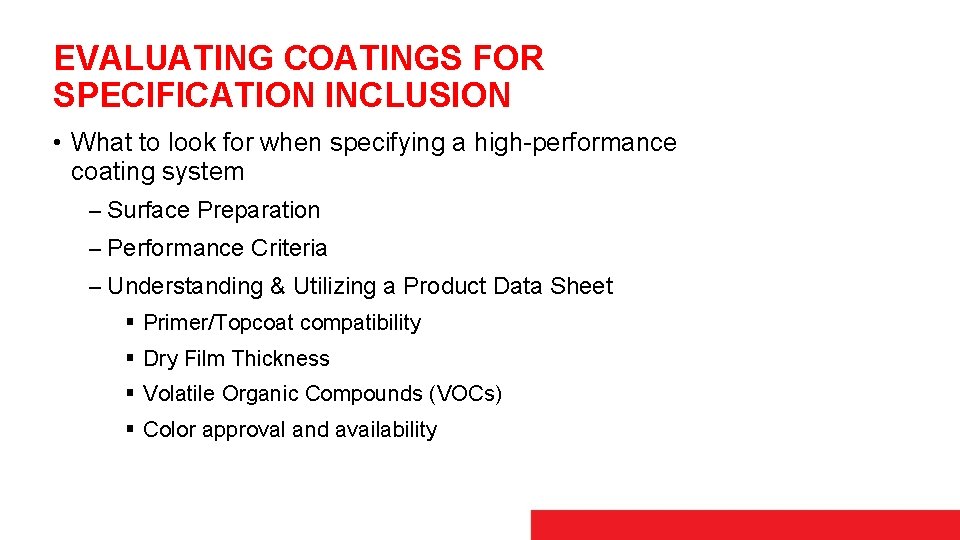
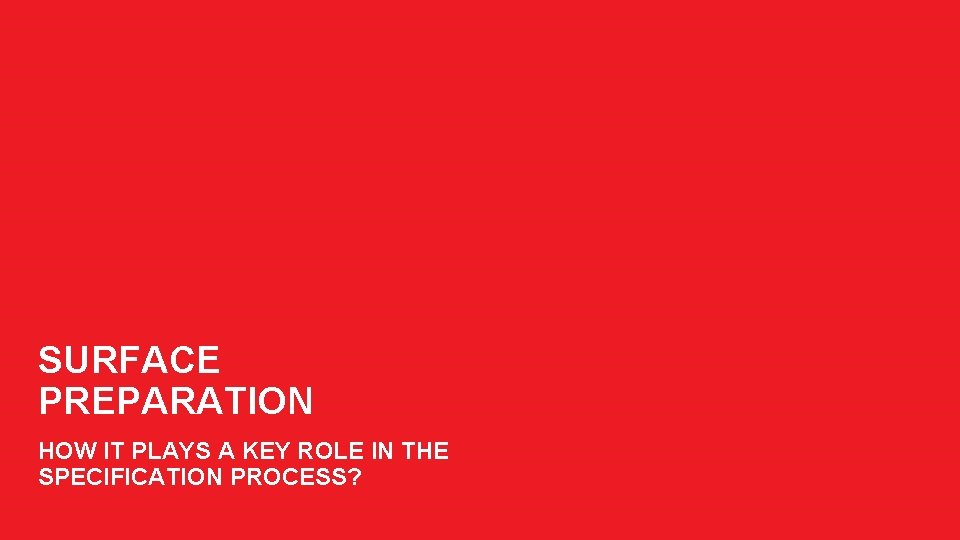
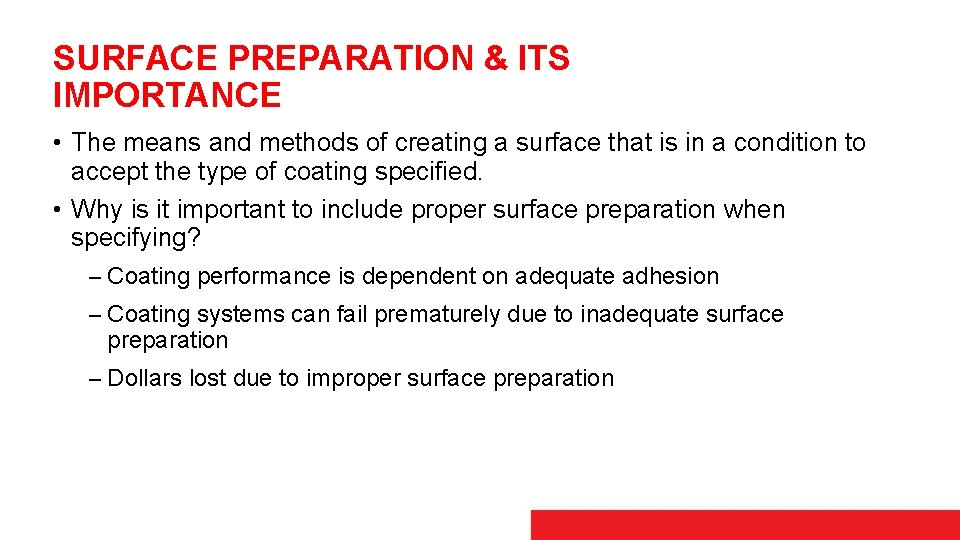

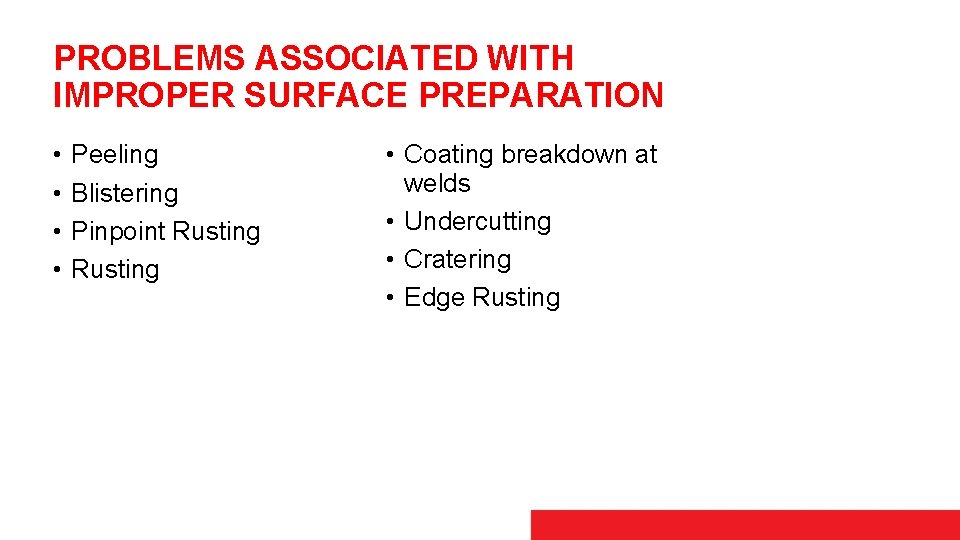
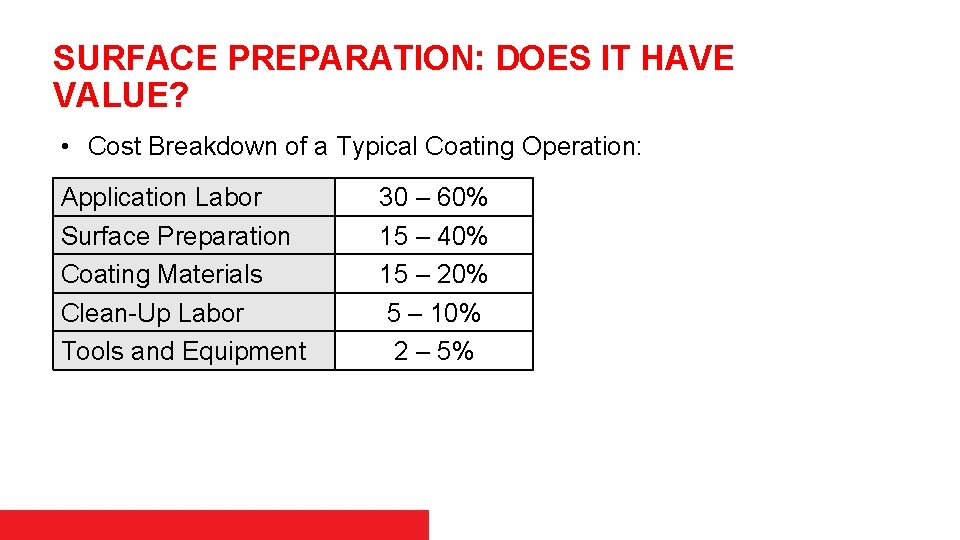
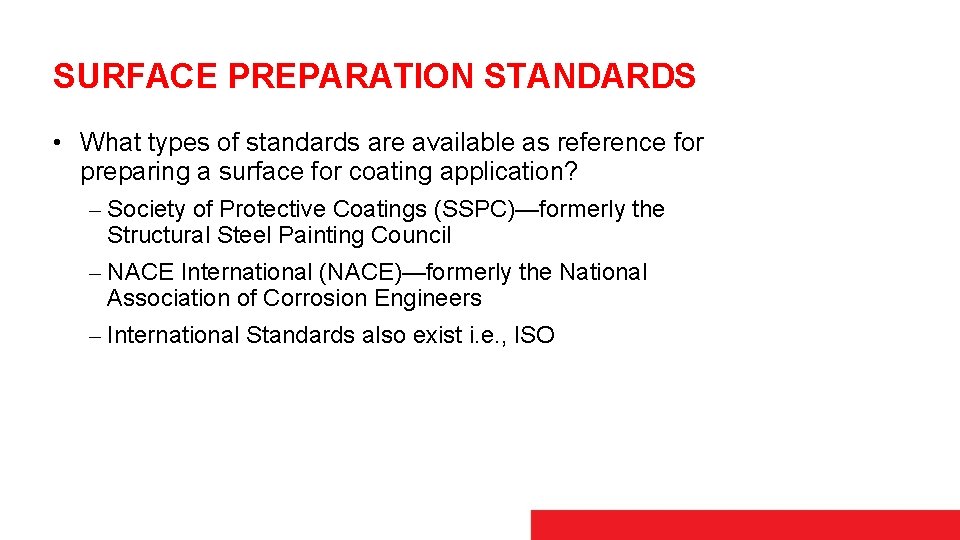
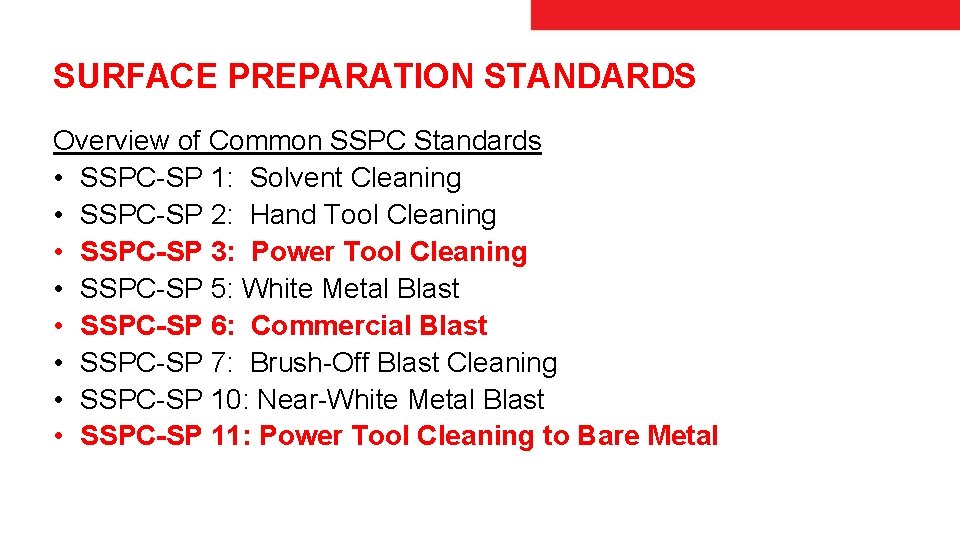
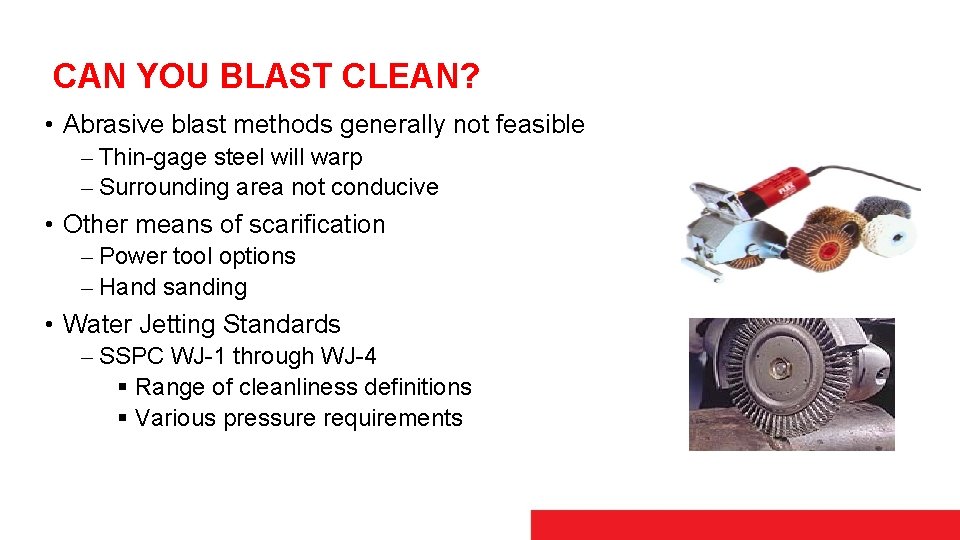
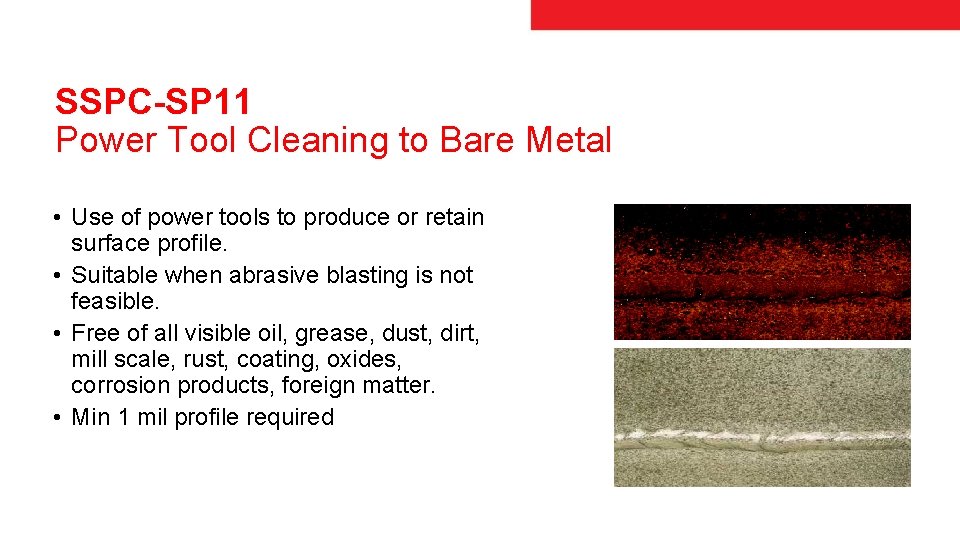
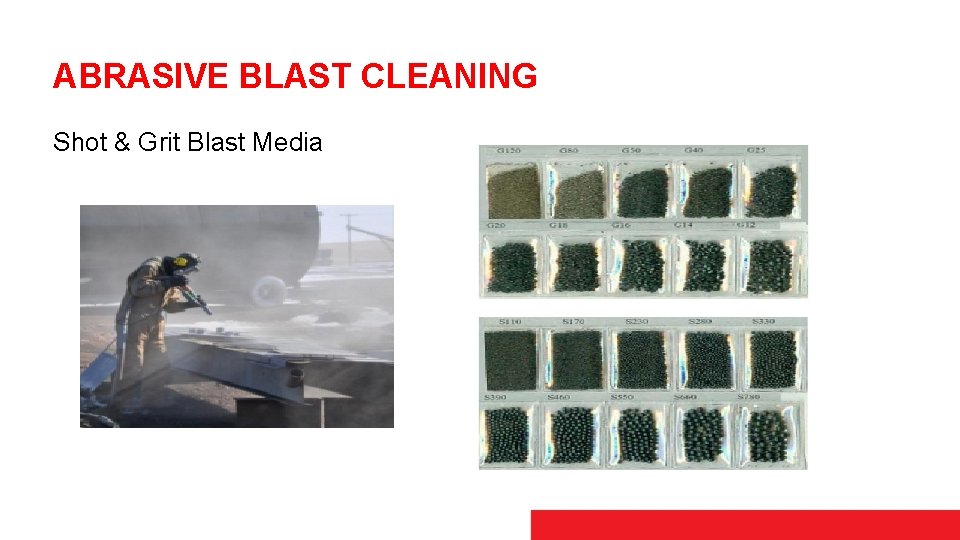
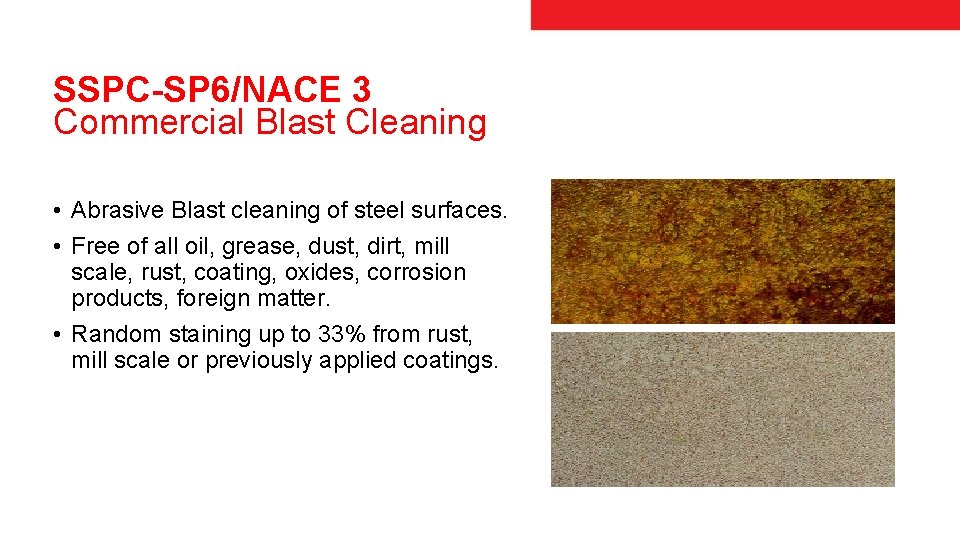
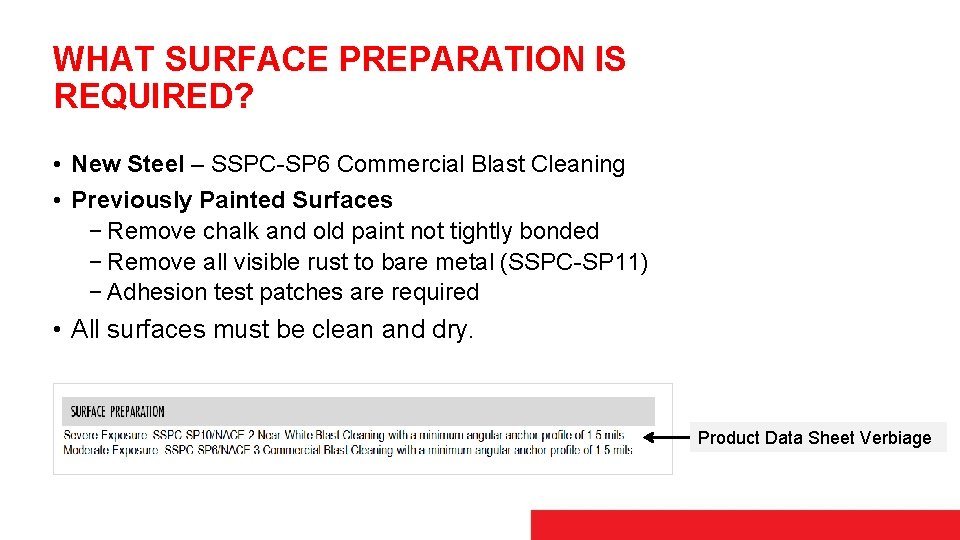
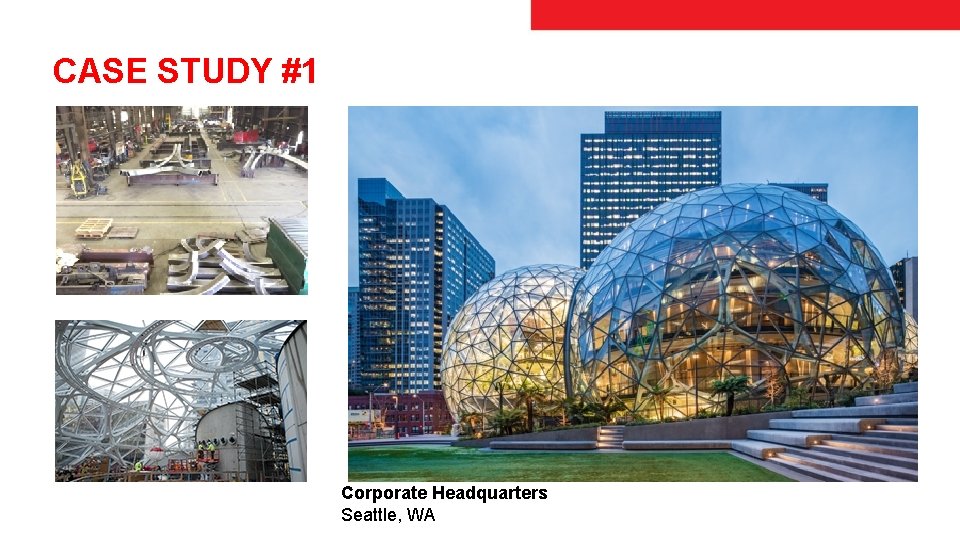
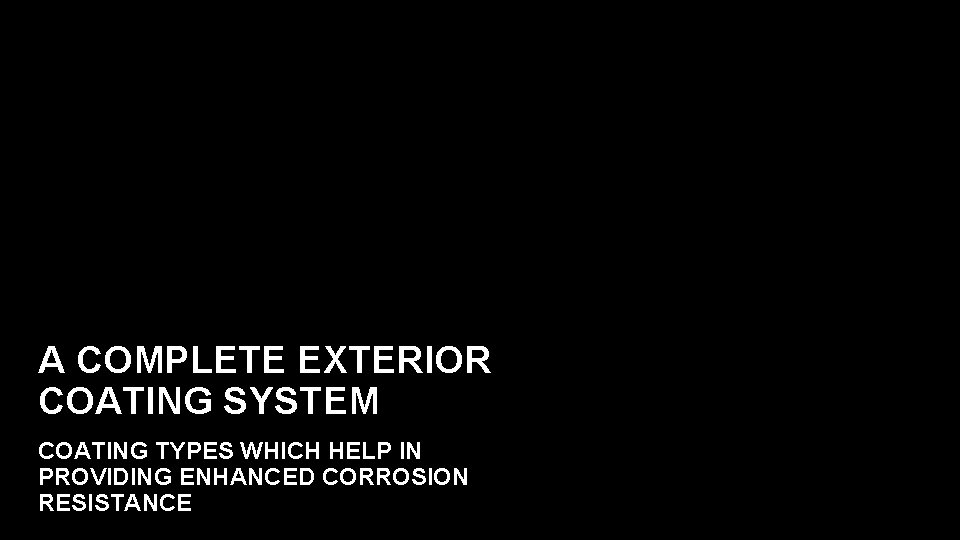
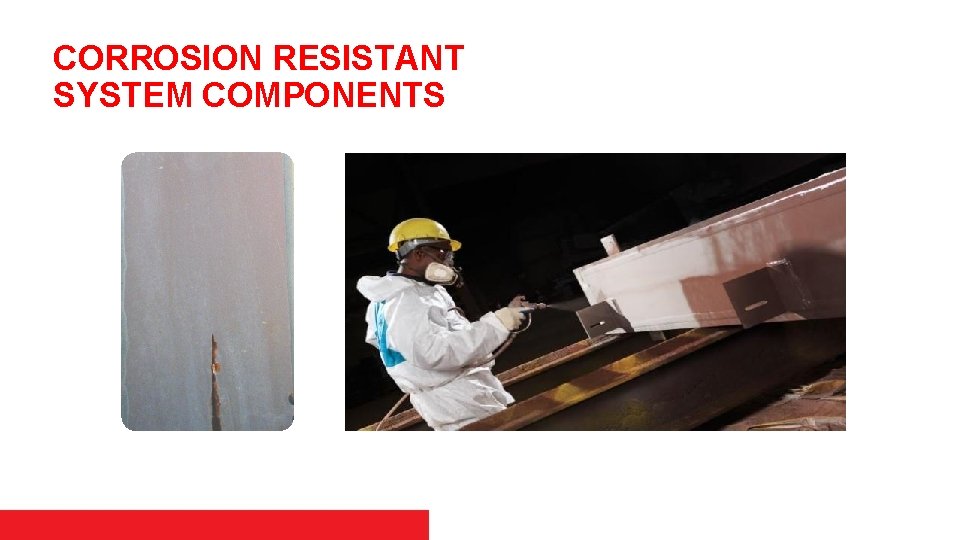
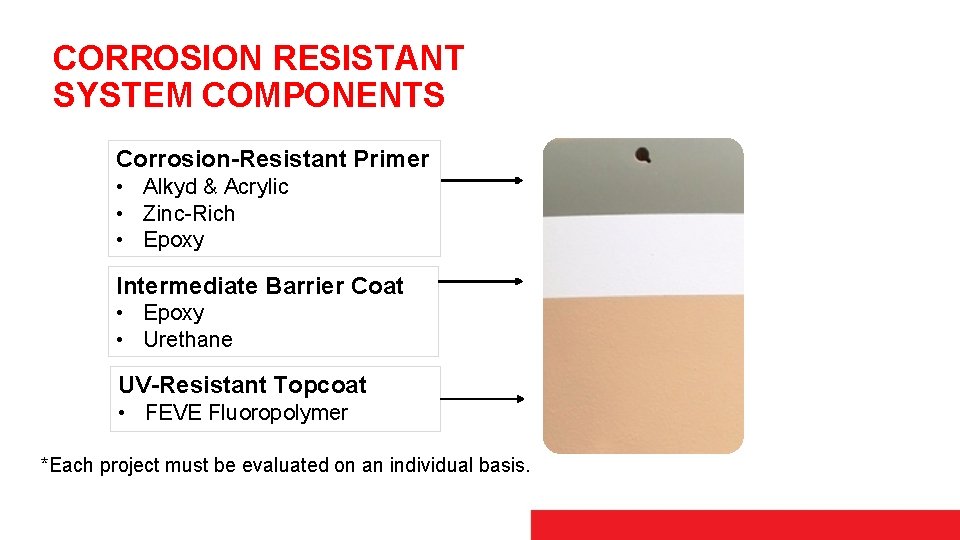
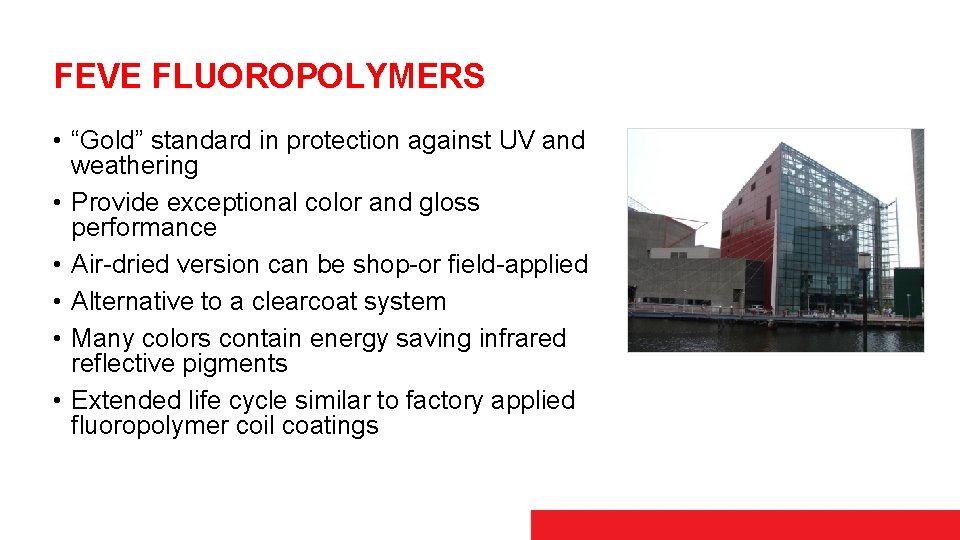
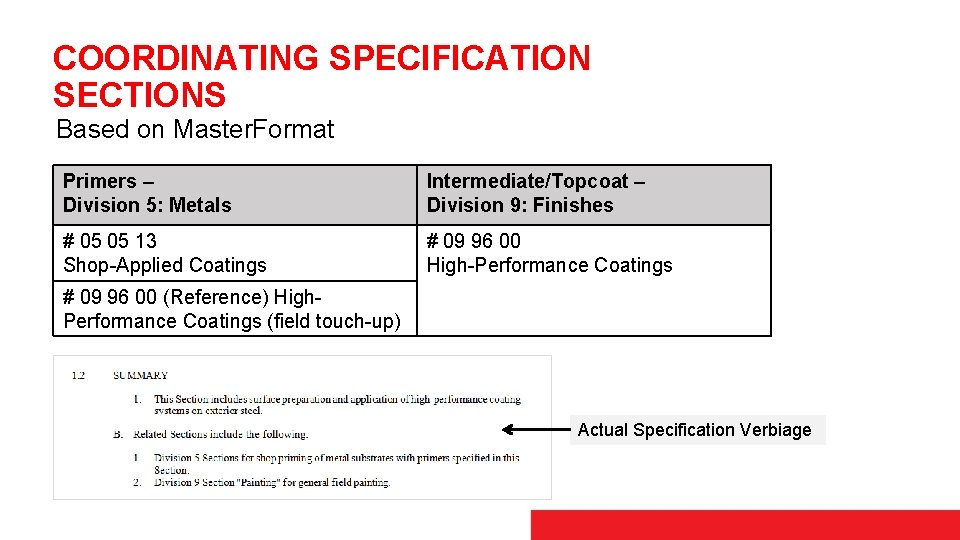
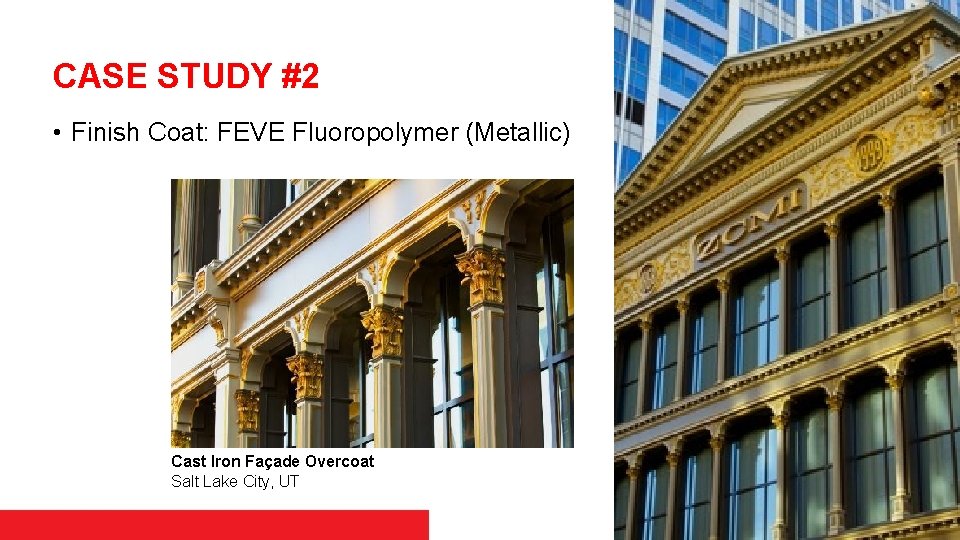
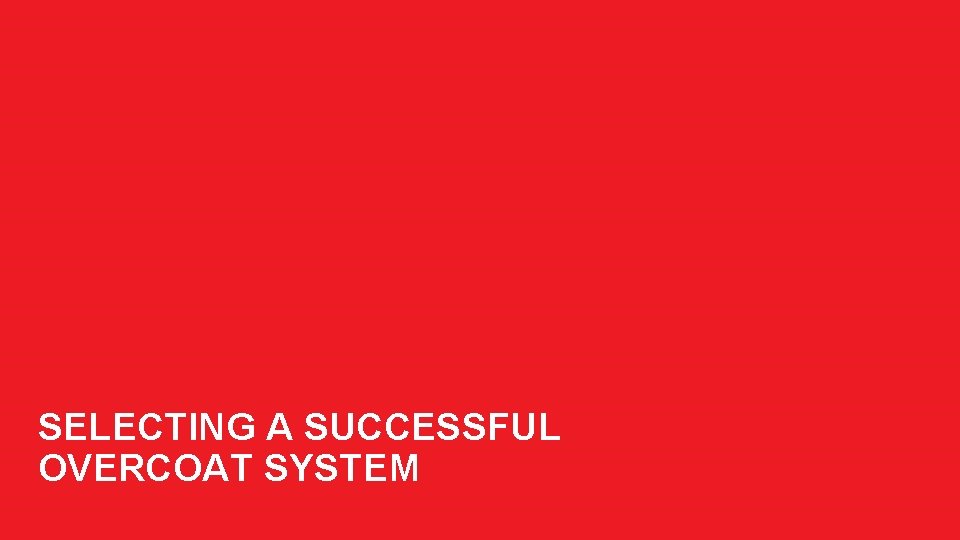
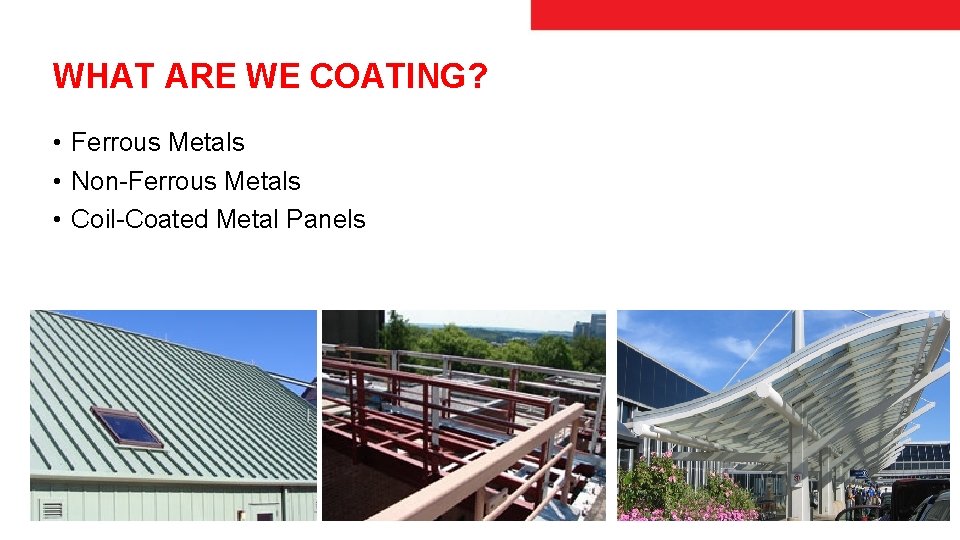
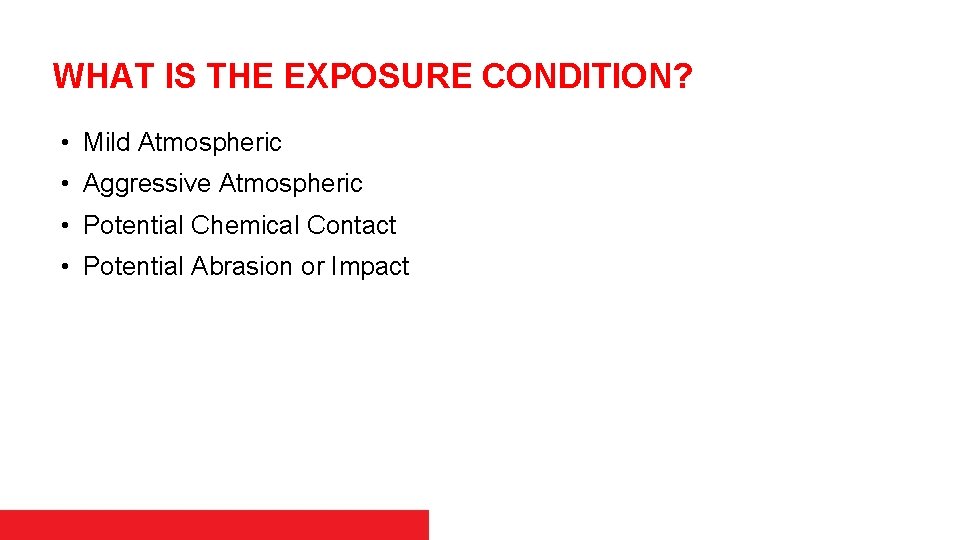
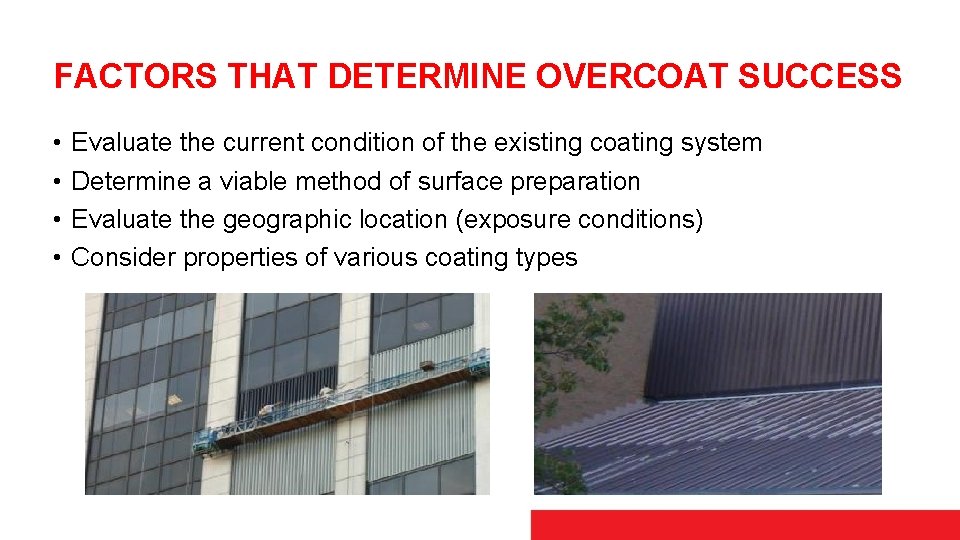
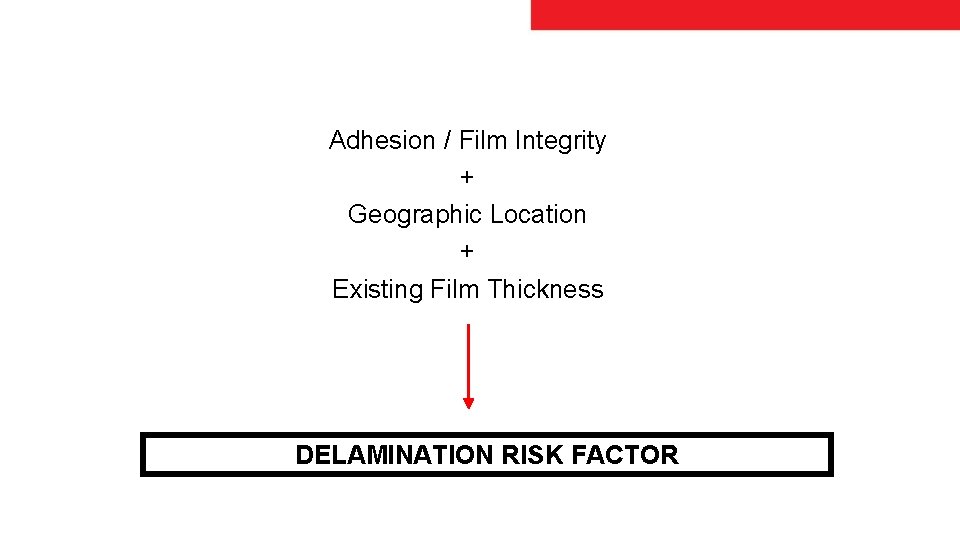
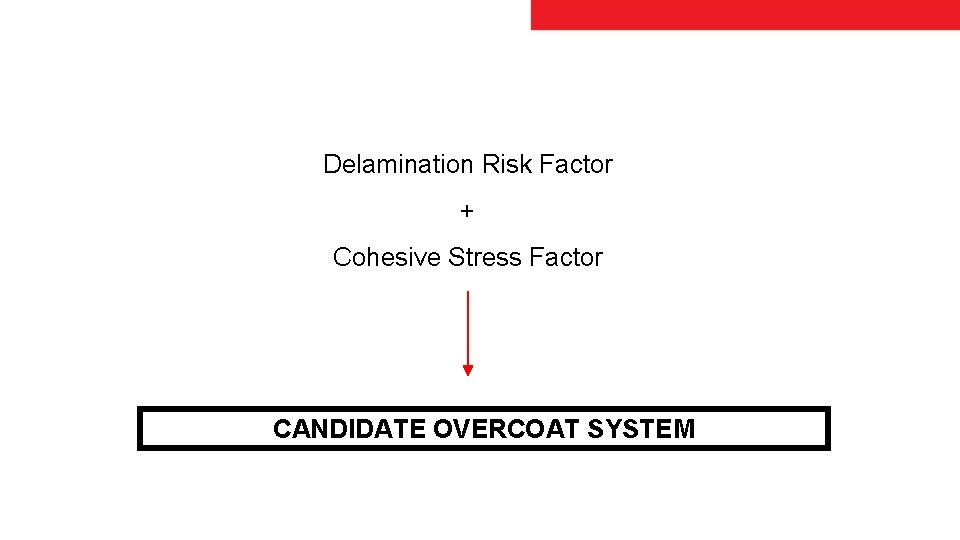
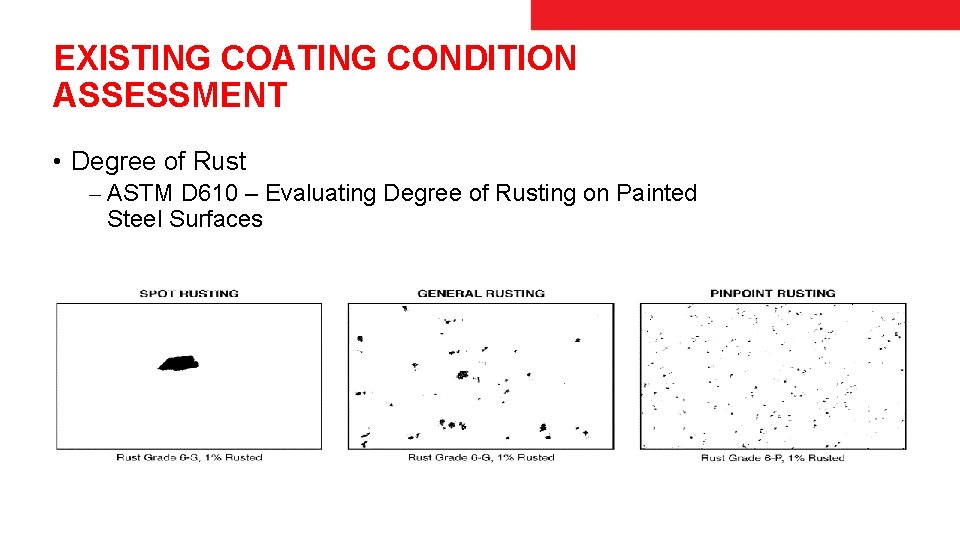
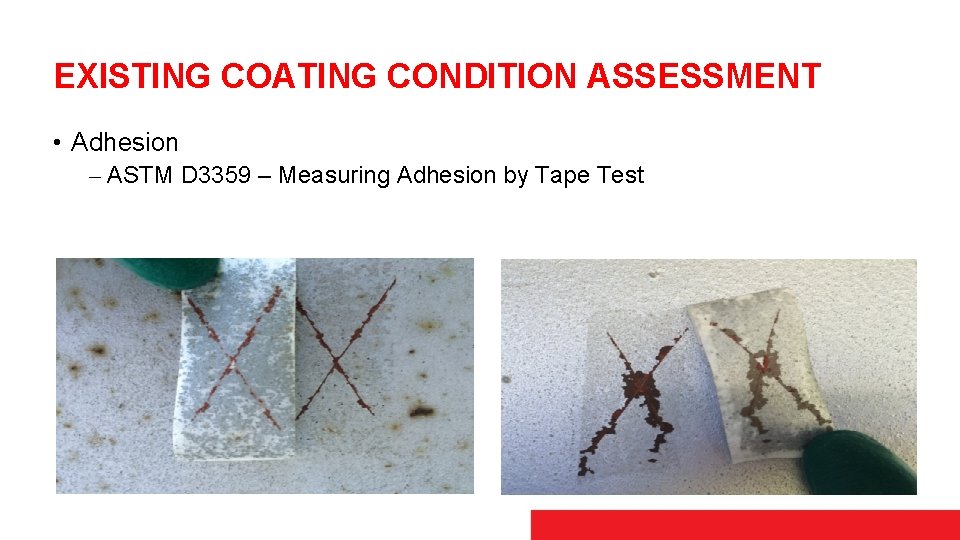
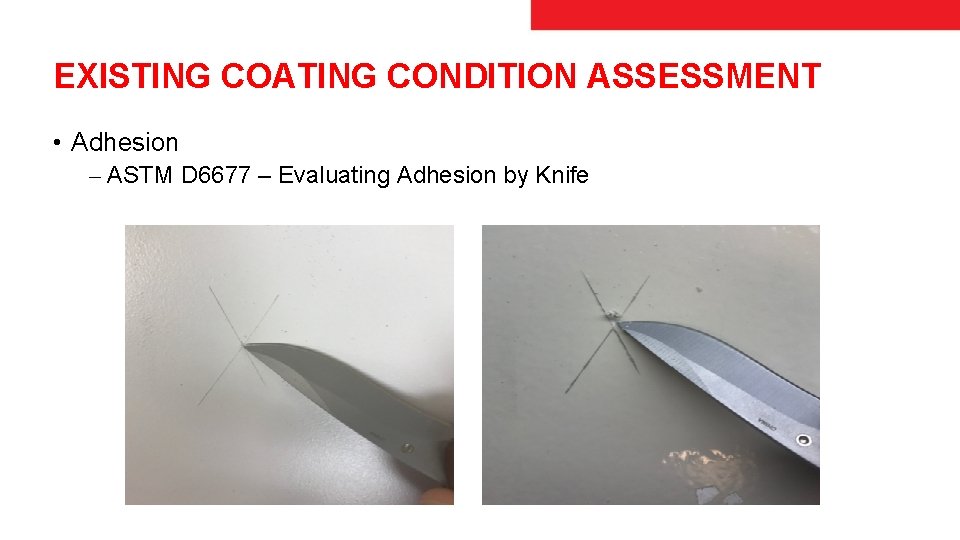
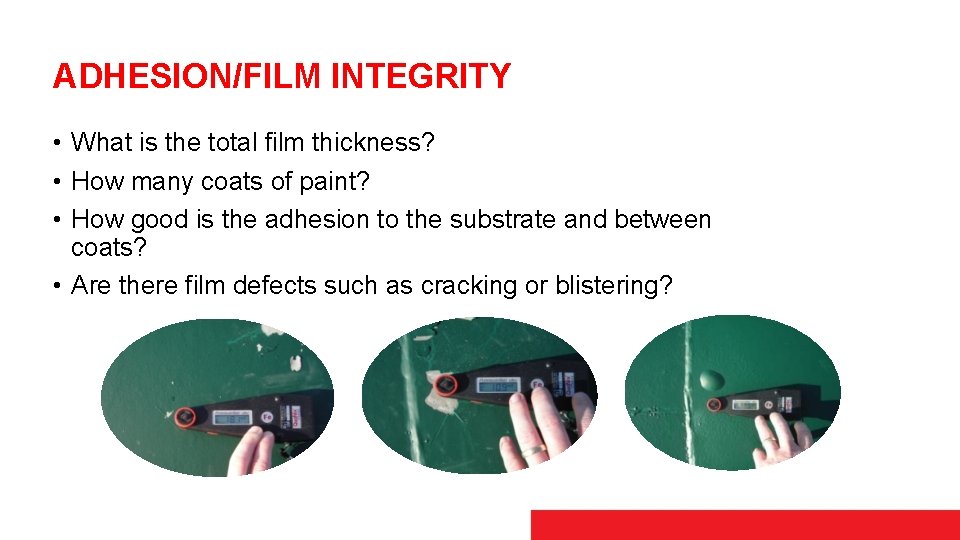
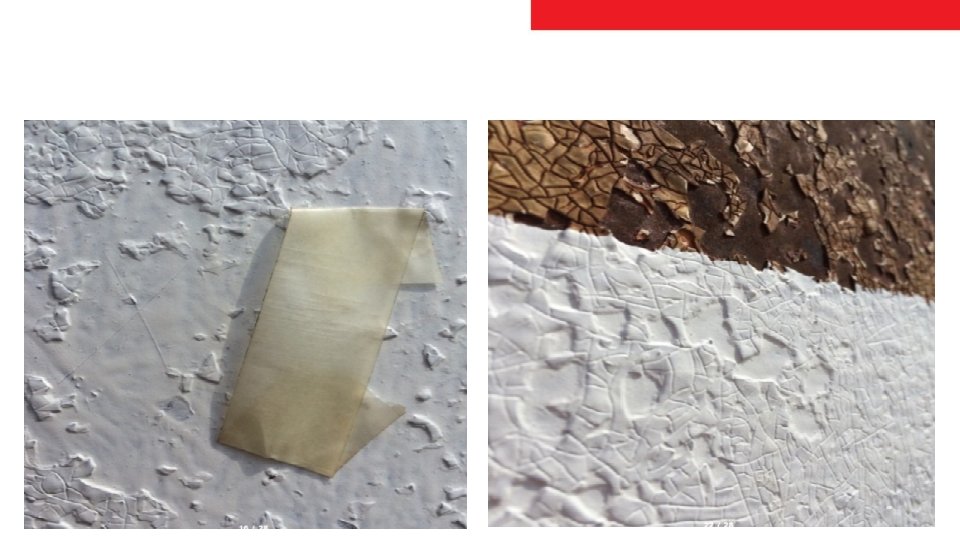
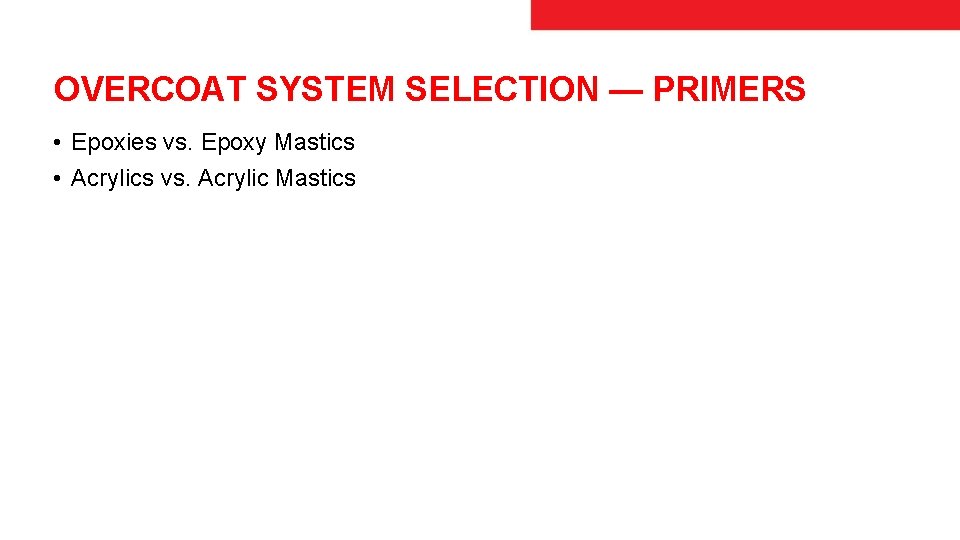
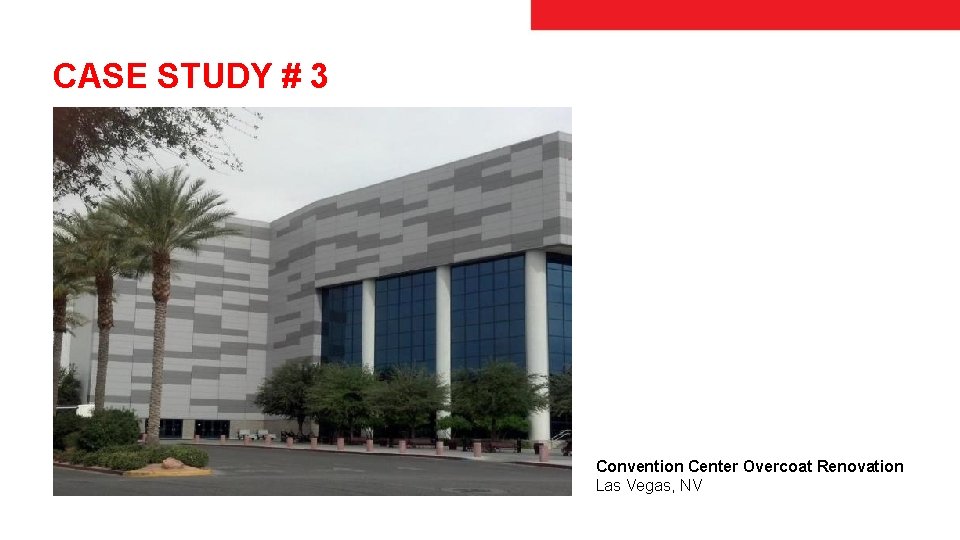
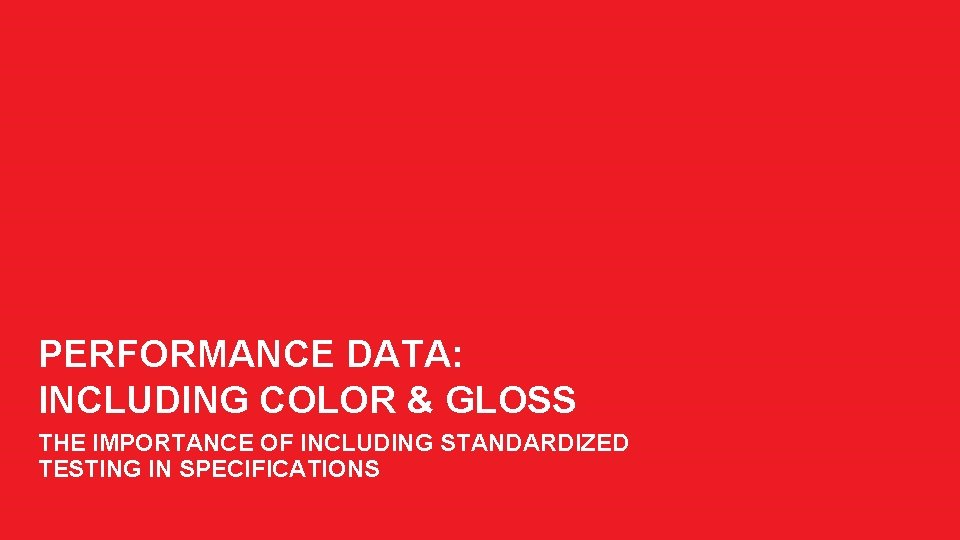
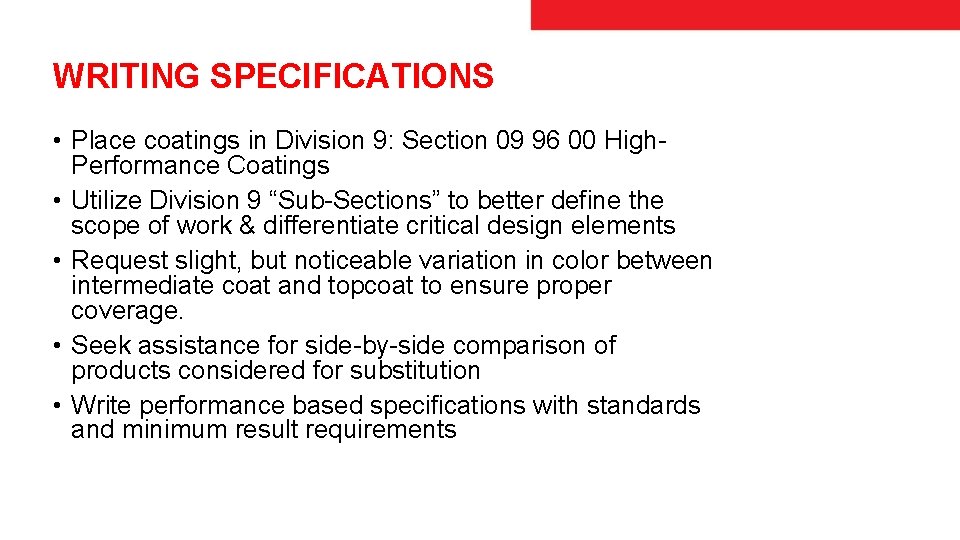
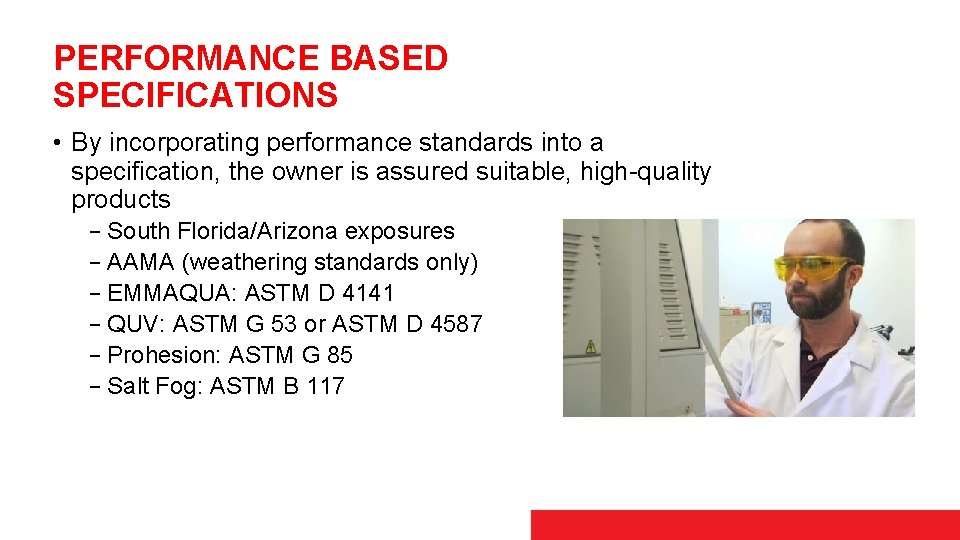
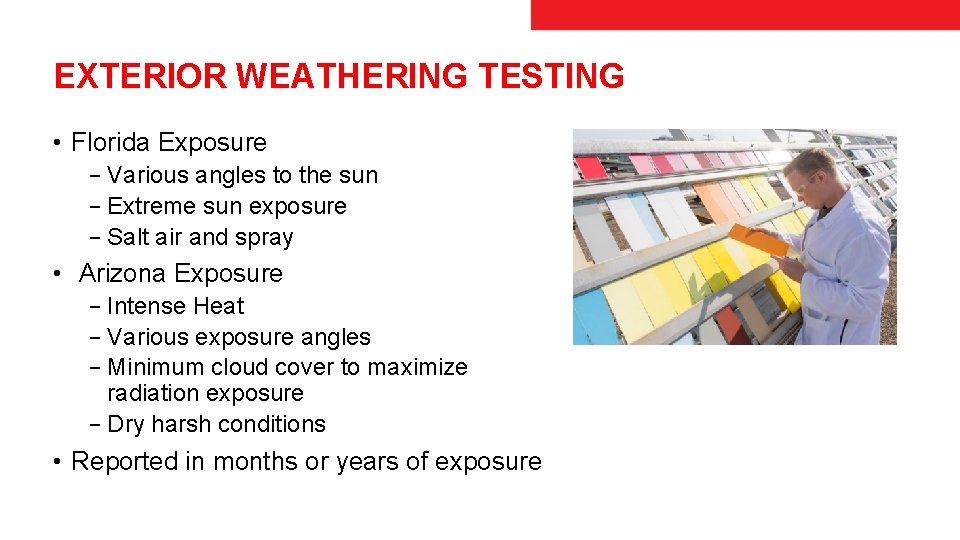
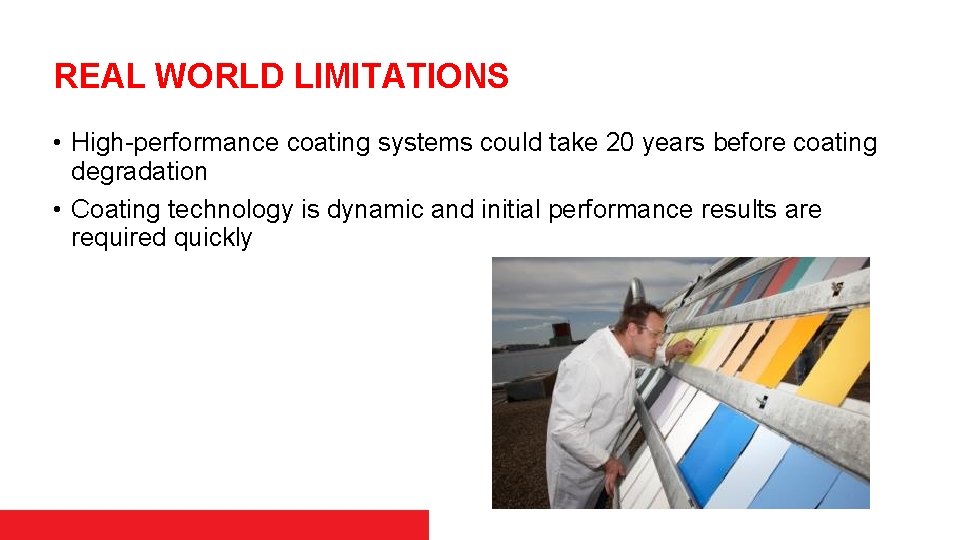
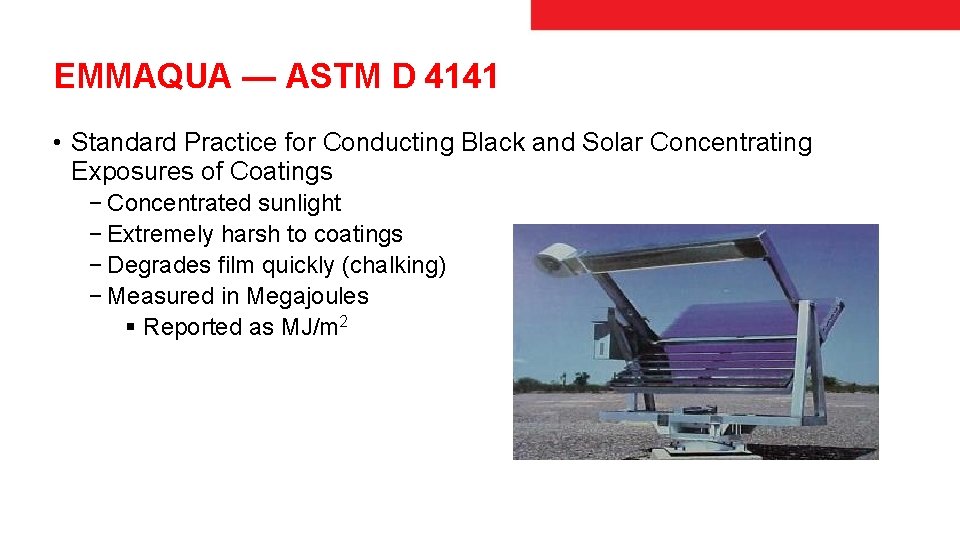
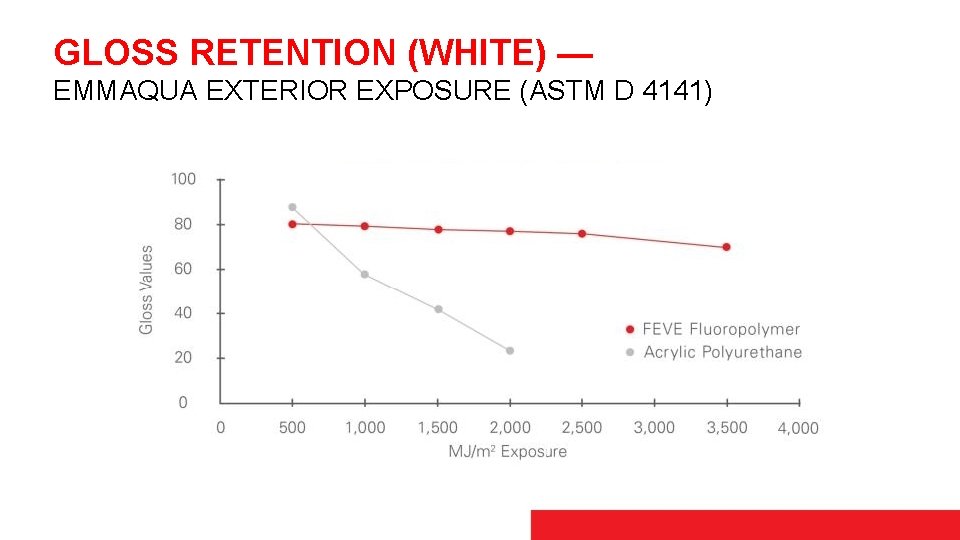

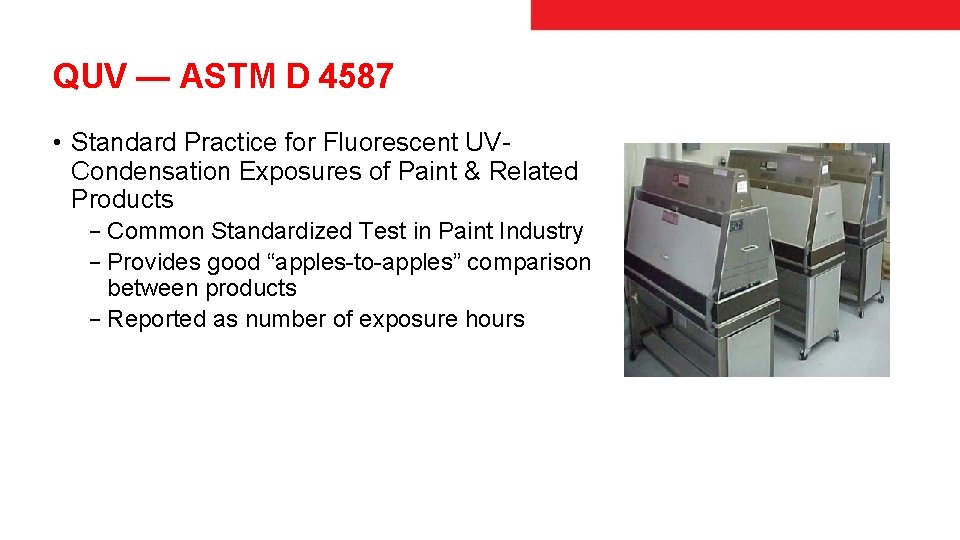
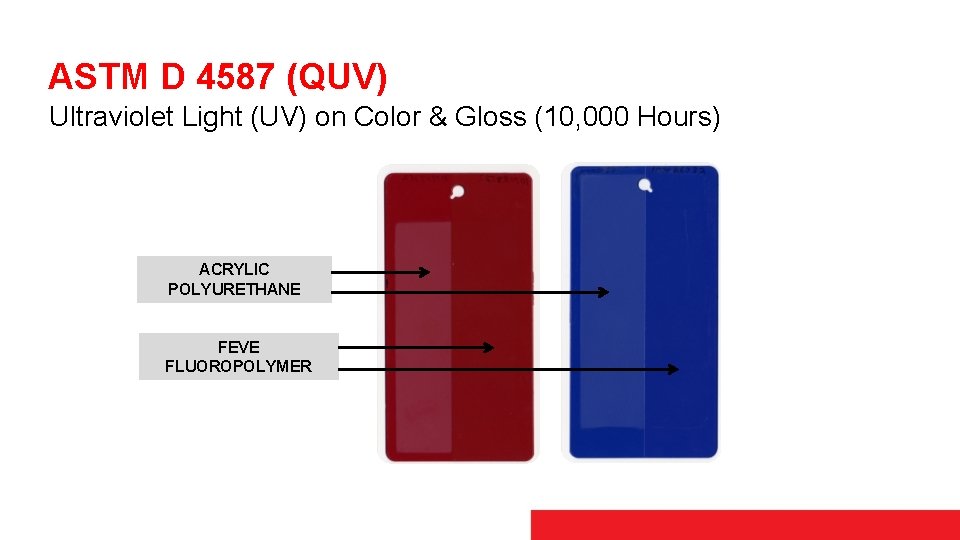
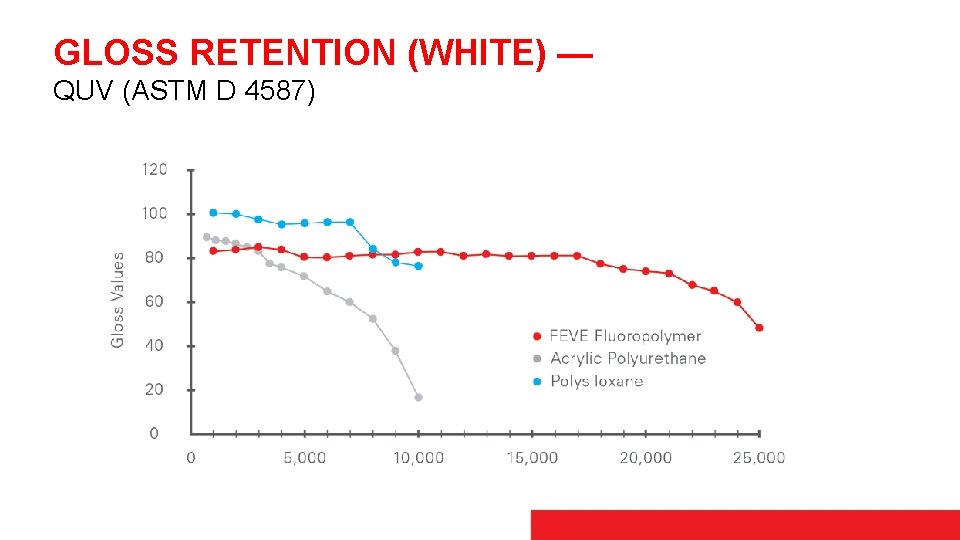
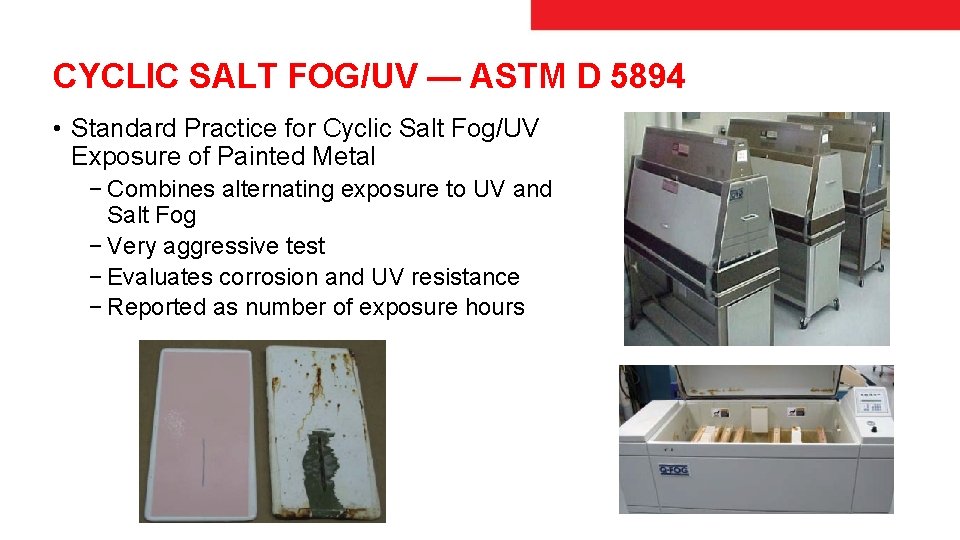
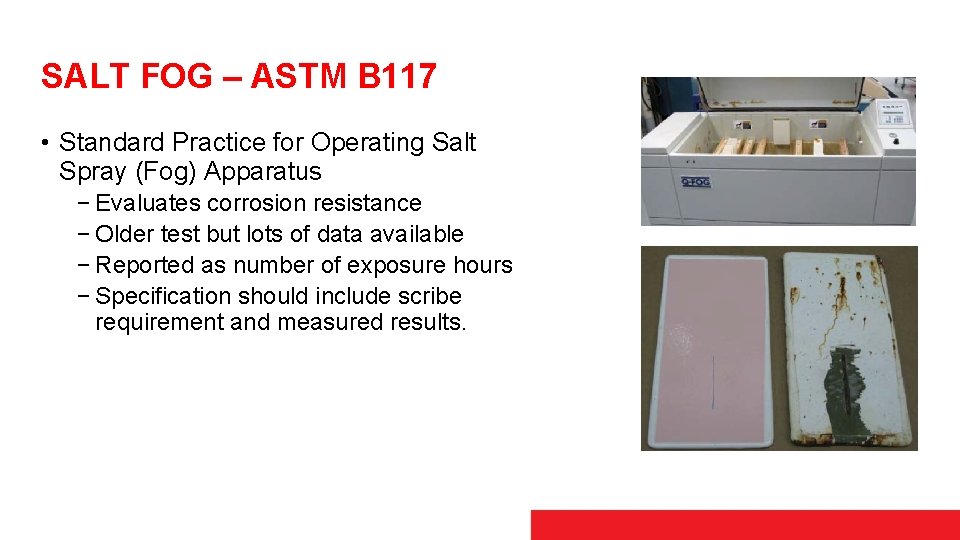
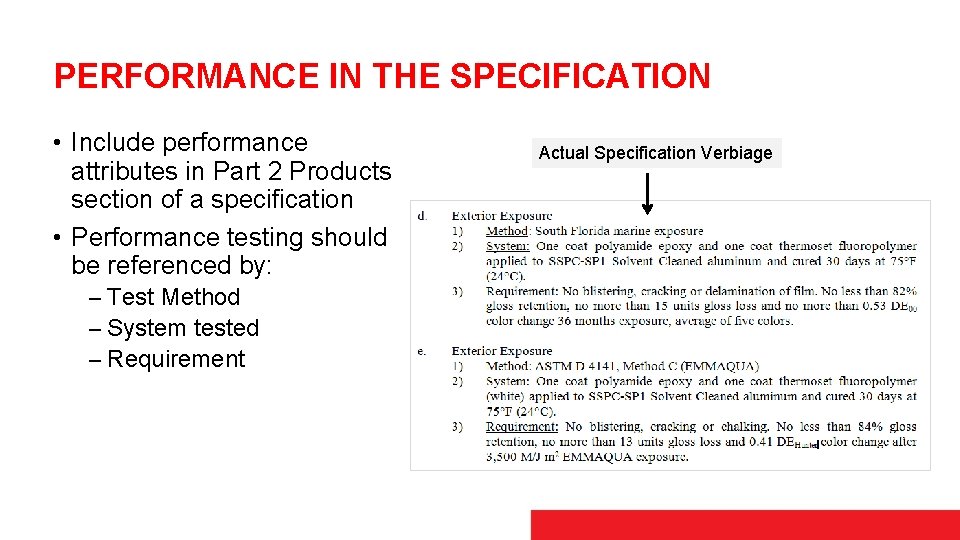
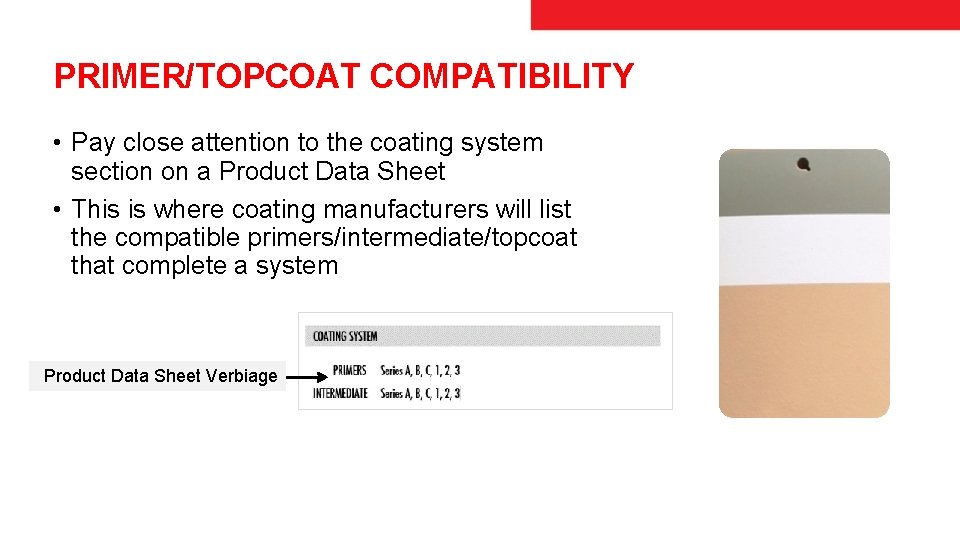
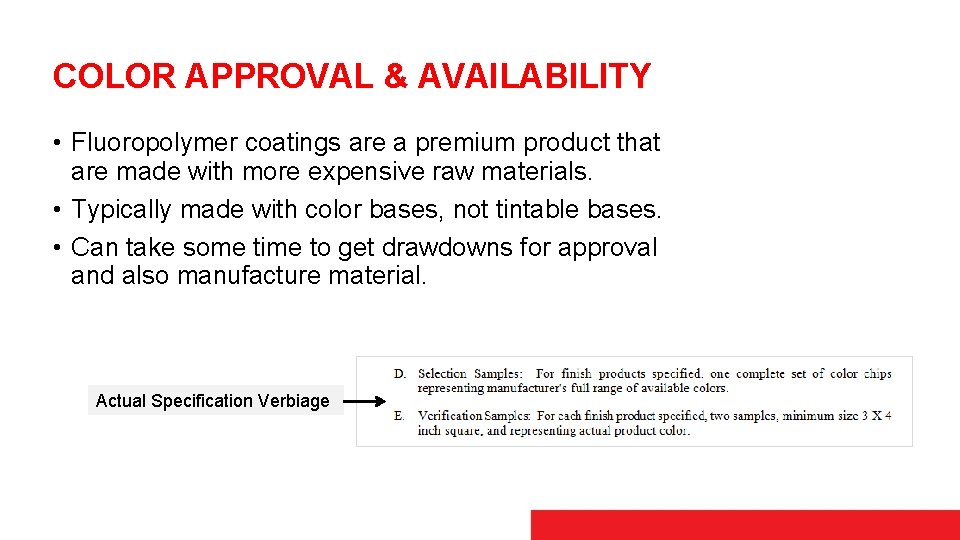
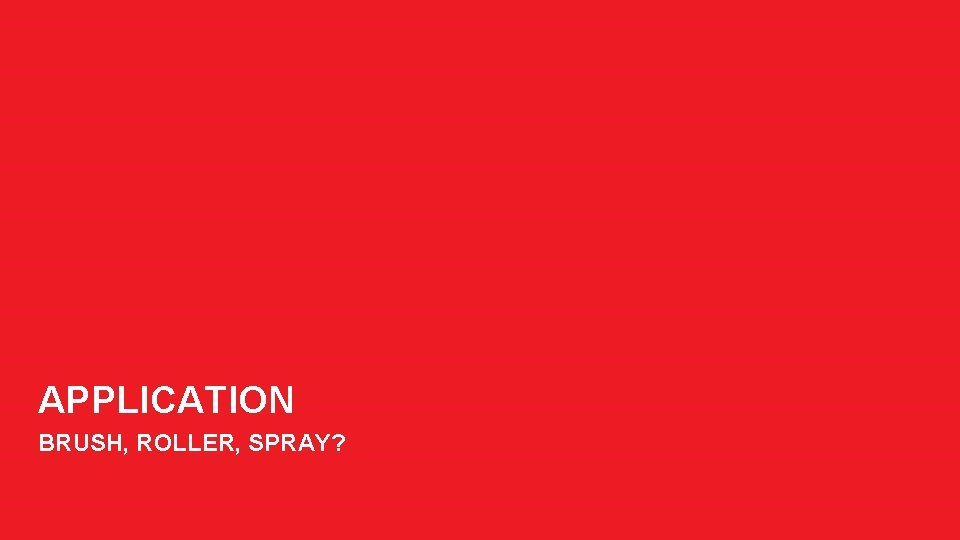
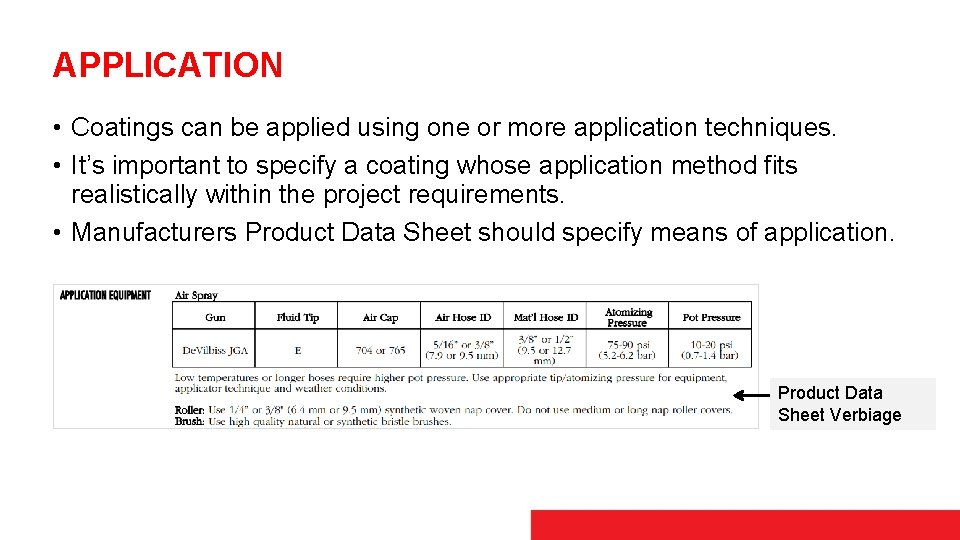
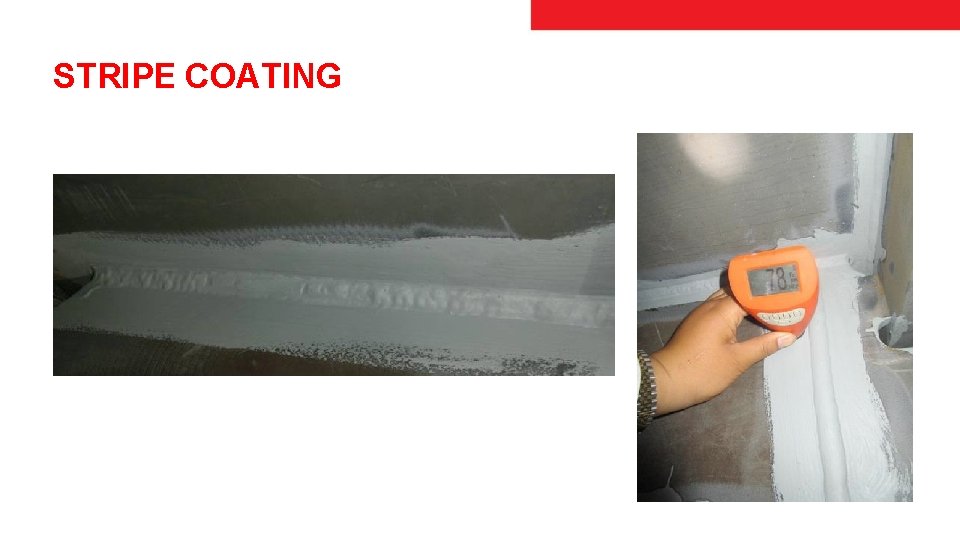
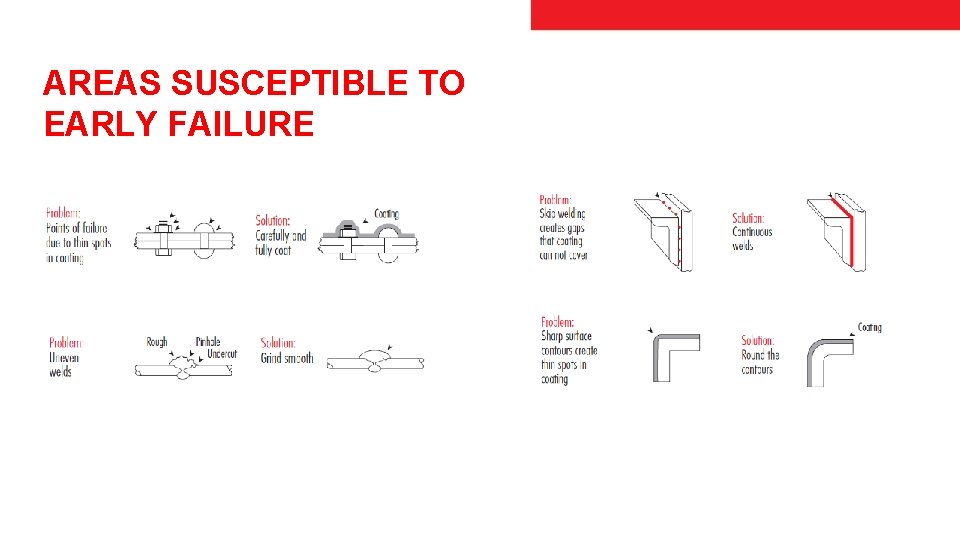
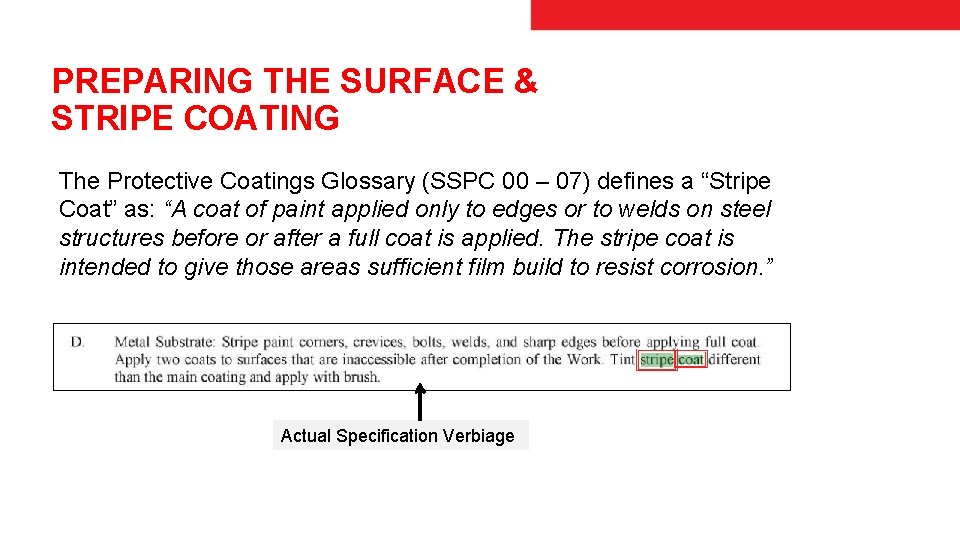
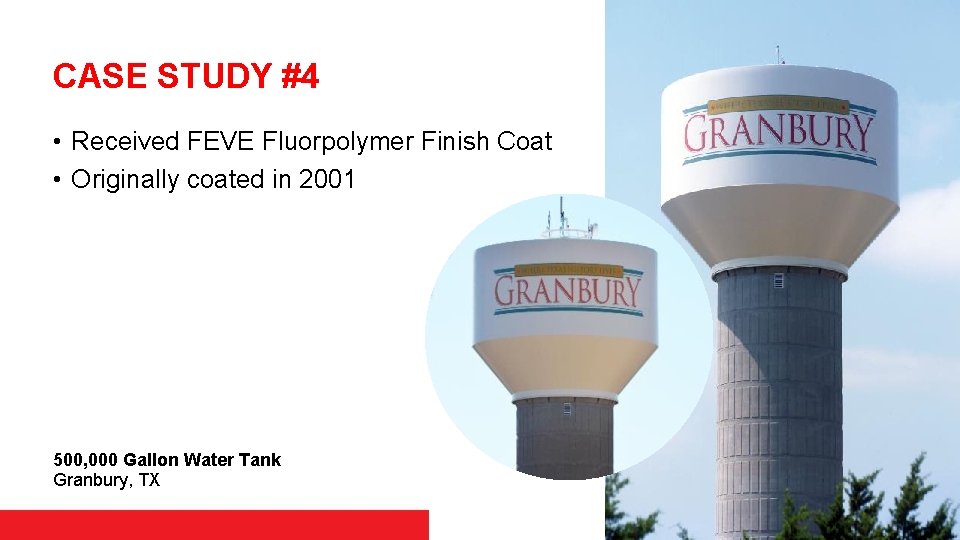
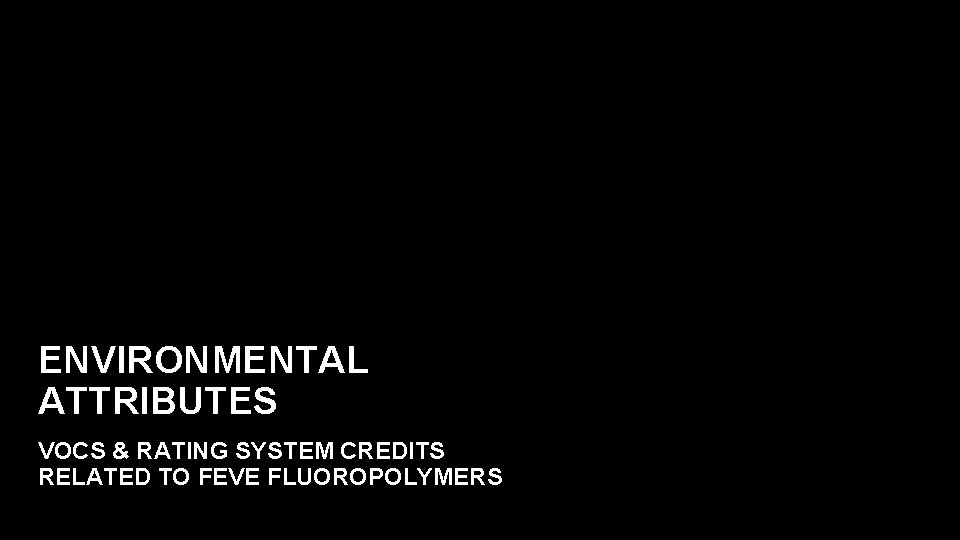
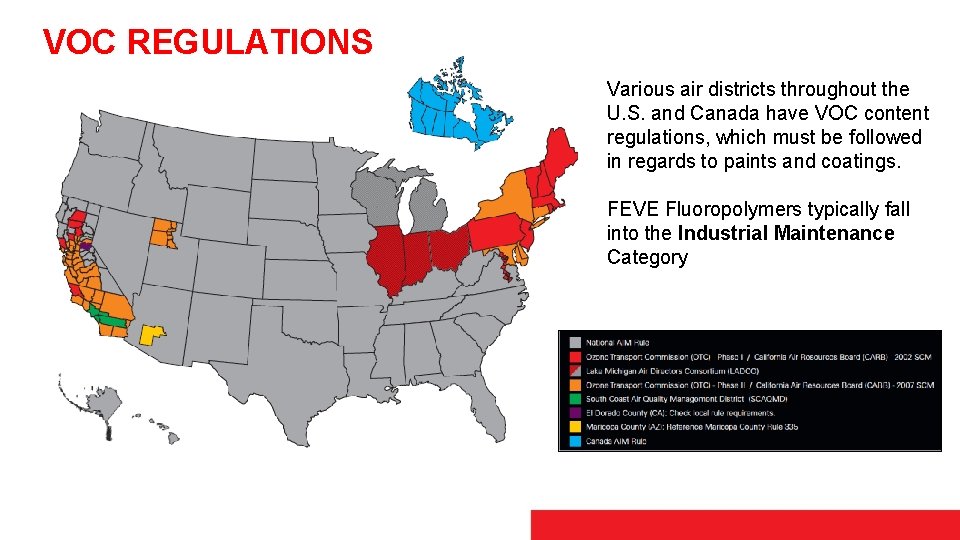
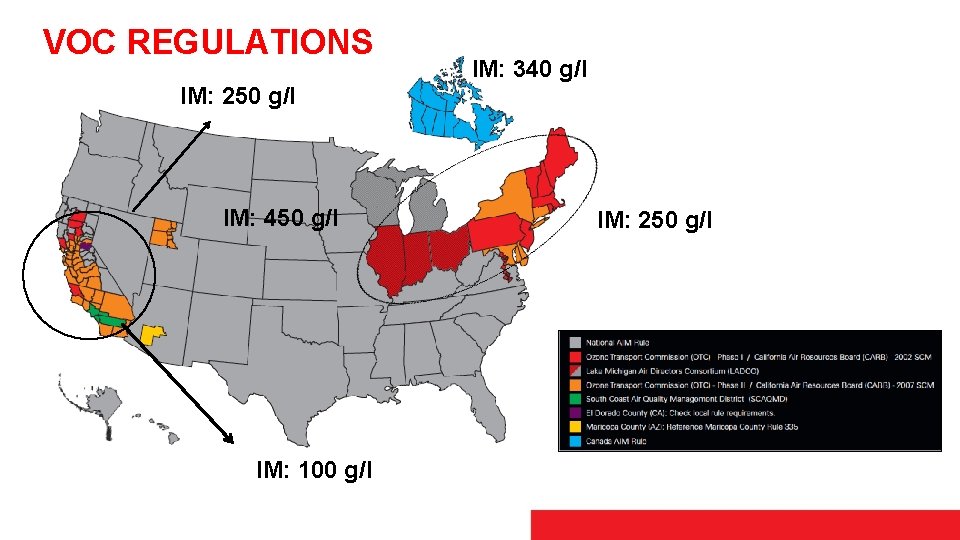
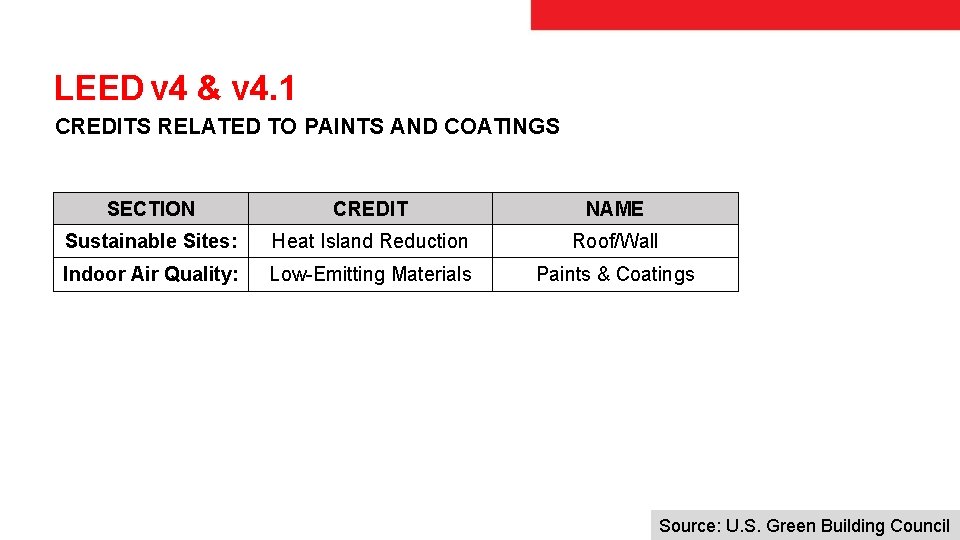
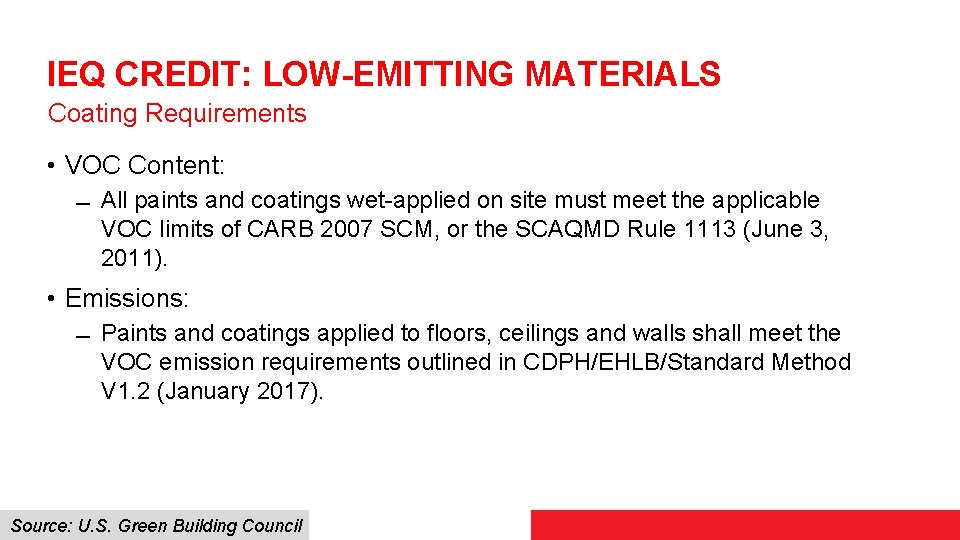
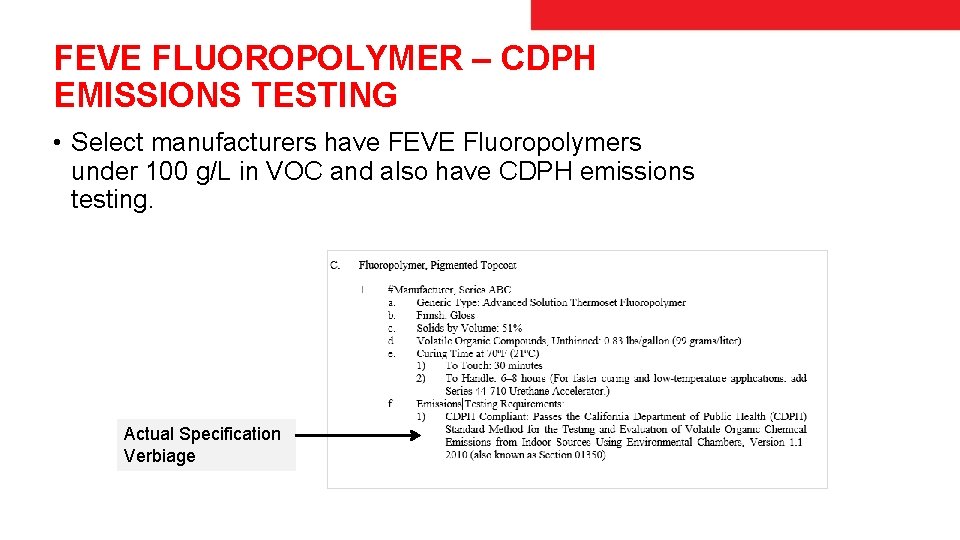
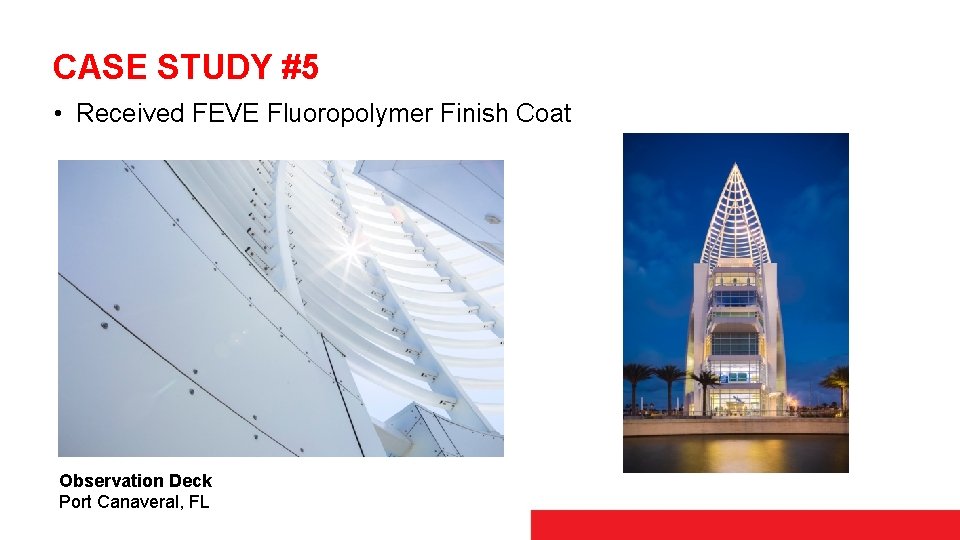
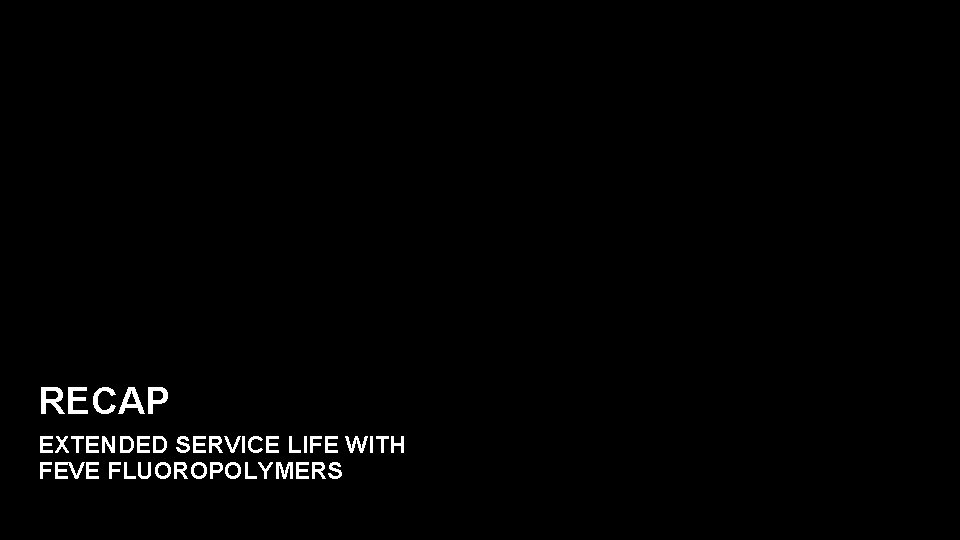
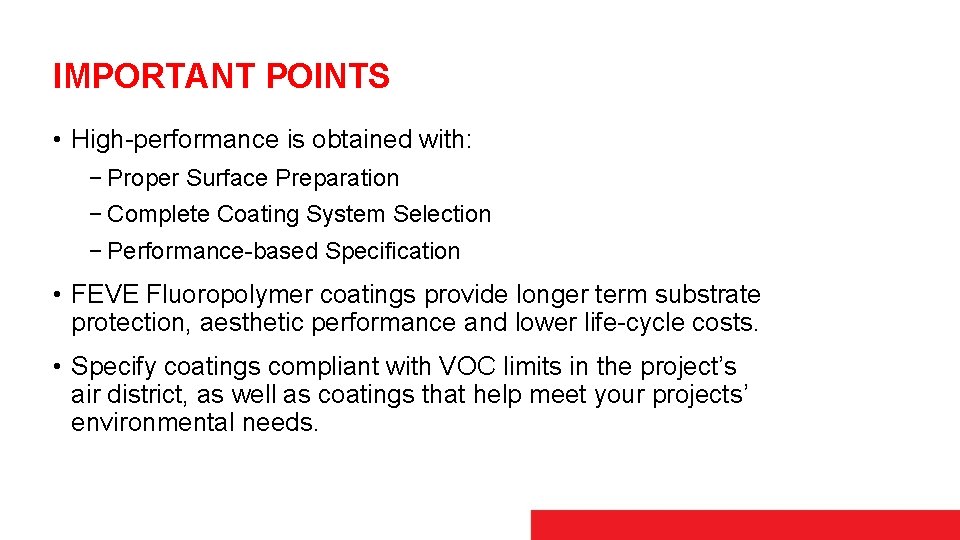
- Slides: 66
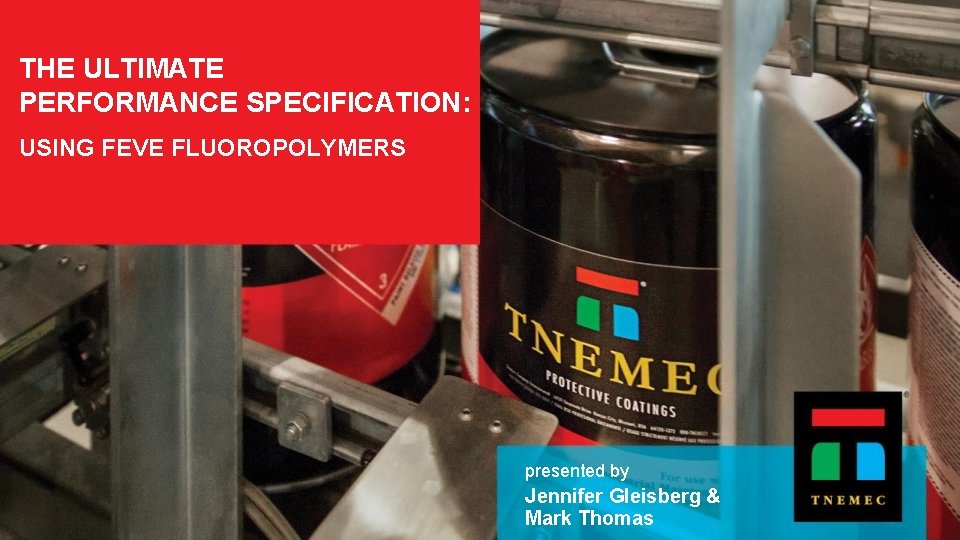
THE ULTIMATE PERFORMANCE SPECIFICATION: USING FEVE FLUOROPOLYMERS presented by Jennifer Gleisberg & Mark Thomas
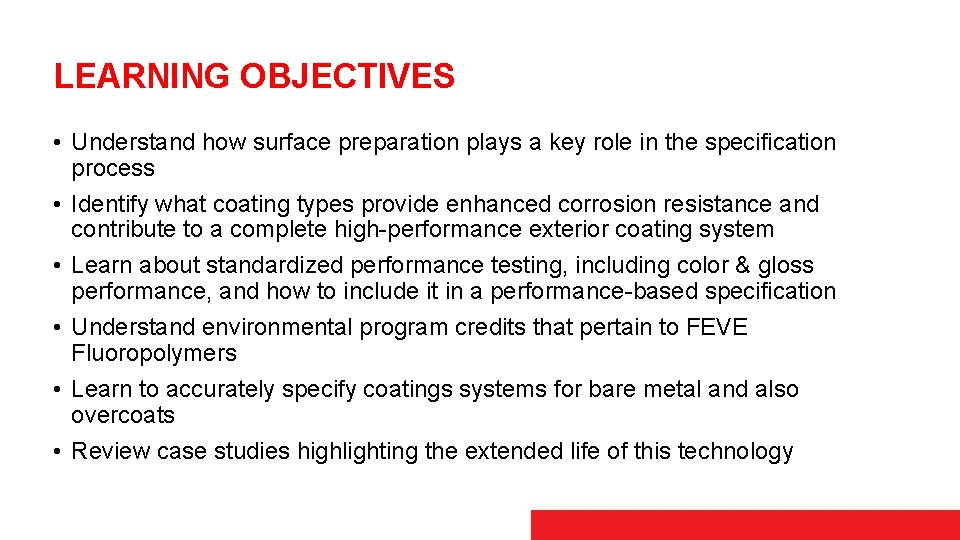
LEARNING OBJECTIVES • Understand how surface preparation plays a key role in the specification process • Identify what coating types provide enhanced corrosion resistance and contribute to a complete high-performance exterior coating system • Learn about standardized performance testing, including color & gloss performance, and how to include it in a performance-based specification • Understand environmental program credits that pertain to FEVE Fluoropolymers • Learn to accurately specify coatings systems for bare metal and also overcoats • Review case studies highlighting the extended life of this technology
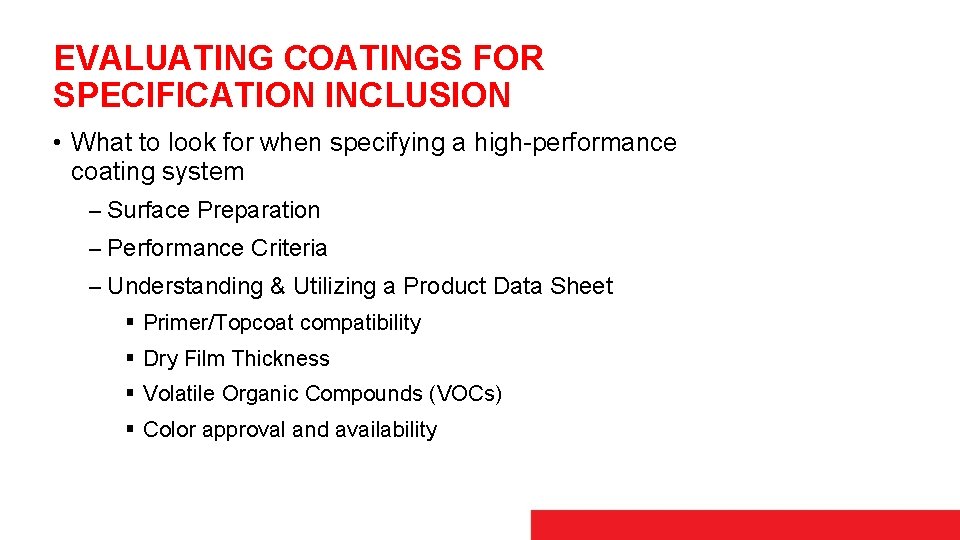
EVALUATING COATINGS FOR SPECIFICATION INCLUSION • What to look for when specifying a high-performance coating system ─ Surface Preparation ─ Performance Criteria ─ Understanding & Utilizing a Product Data Sheet § Primer/Topcoat compatibility § Dry Film Thickness § Volatile Organic Compounds (VOCs) § Color approval and availability
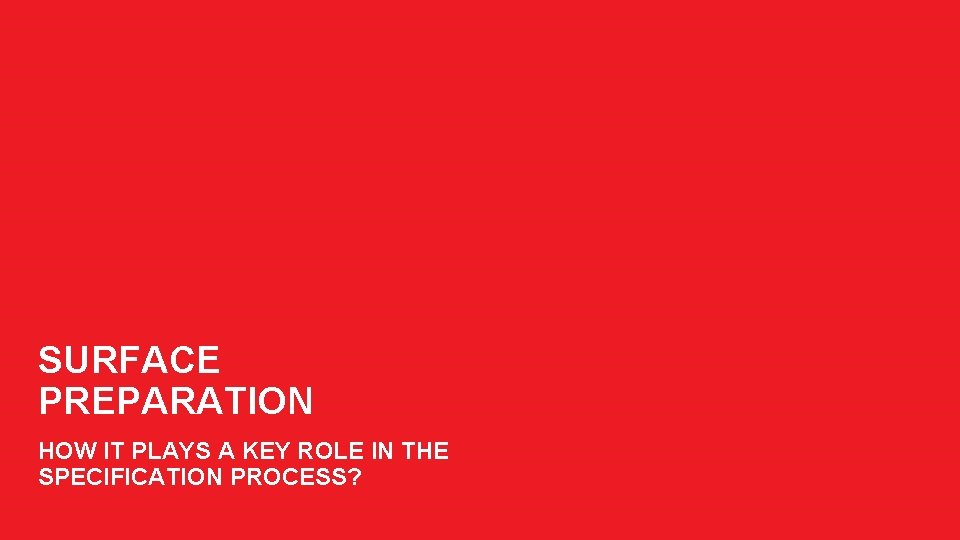
SURFACE PREPARATION HOW IT PLAYS A KEY ROLE IN THE SPECIFICATION PROCESS?
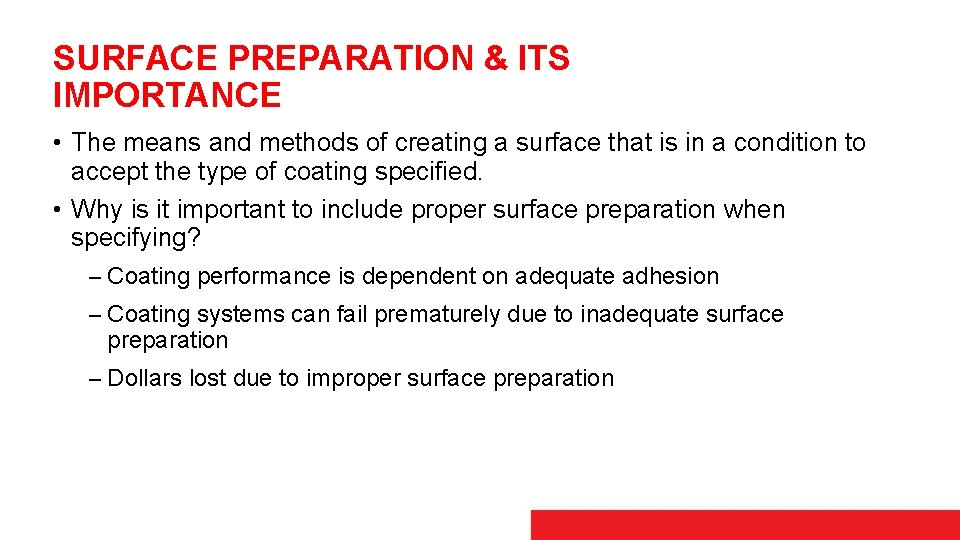
SURFACE PREPARATION & ITS IMPORTANCE • The means and methods of creating a surface that is in a condition to accept the type of coating specified. • Why is it important to include proper surface preparation when specifying? ─ Coating performance is dependent on adequate adhesion ─ Coating systems can fail prematurely due to inadequate surface preparation ─ Dollars lost due to improper surface preparation

THREE MAIN FACTORS THAT AFFECT COATING PERFORMANCE • Surface Preparation • Coating Selection • Application
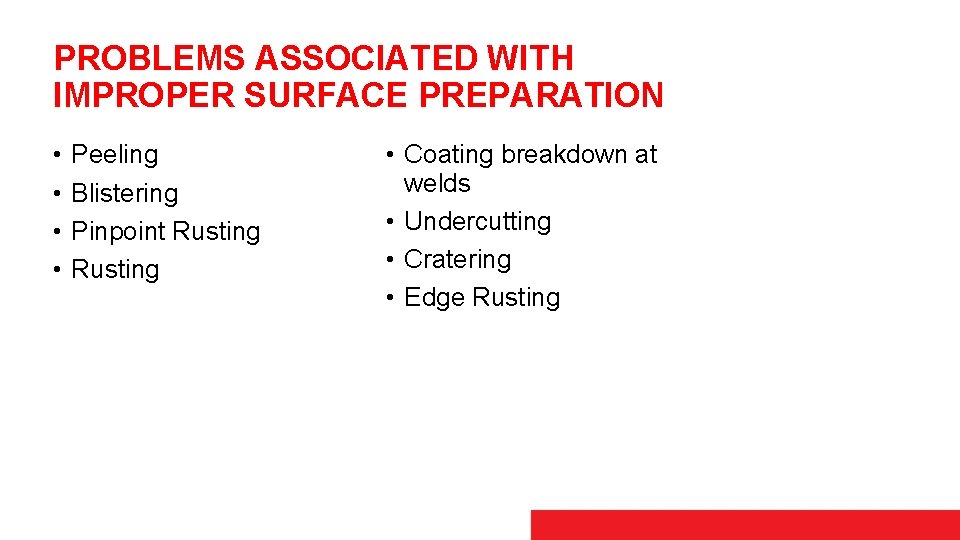
PROBLEMS ASSOCIATED WITH IMPROPER SURFACE PREPARATION • • Peeling Blistering Pinpoint Rusting • Coating breakdown at welds • Undercutting • Cratering • Edge Rusting
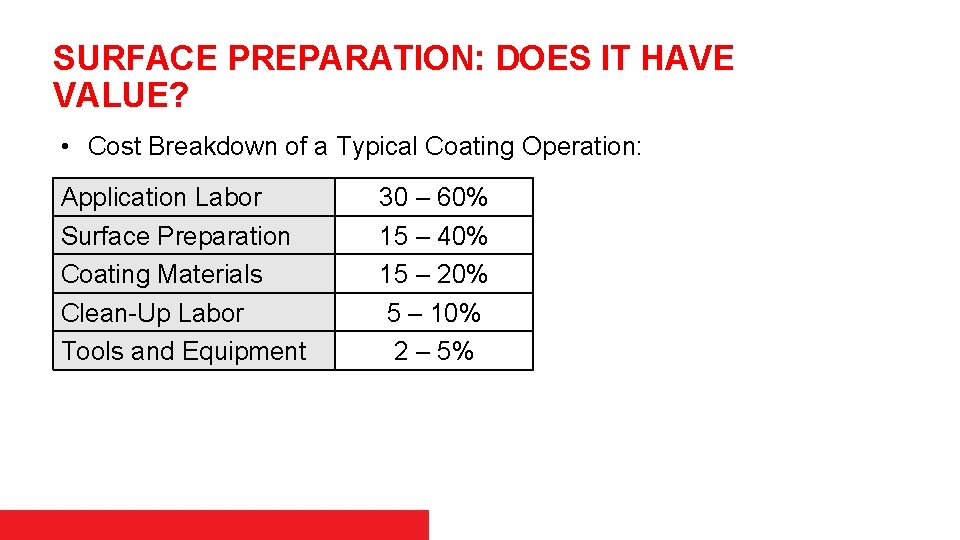
SURFACE PREPARATION: DOES IT HAVE VALUE? • Cost Breakdown of a Typical Coating Operation: Application Labor Surface Preparation Coating Materials Clean-Up Labor Tools and Equipment 30 – 60% 15 – 40% 15 – 20% 5 – 10% 2 – 5%
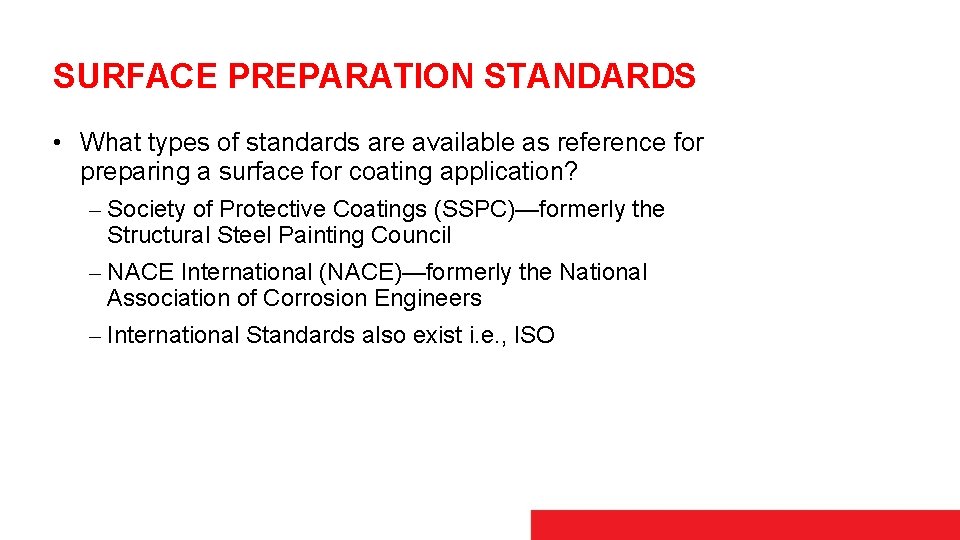
SURFACE PREPARATION STANDARDS • What types of standards are available as reference for preparing a surface for coating application? ⎼ Society of Protective Coatings (SSPC)—formerly the Structural Steel Painting Council ⎼ NACE International (NACE)—formerly the National Association of Corrosion Engineers ⎼ International Standards also exist i. e. , ISO
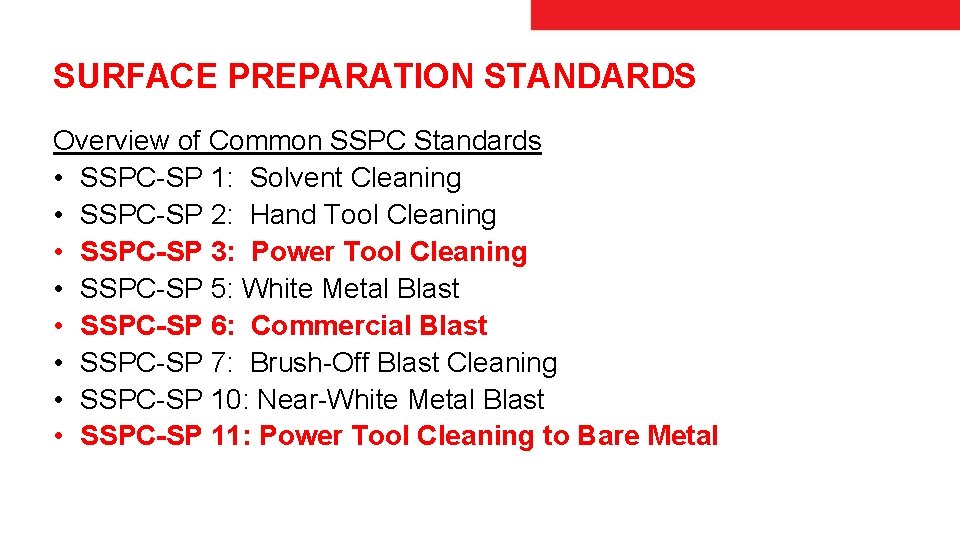
SURFACE PREPARATION STANDARDS Overview of Common SSPC Standards • SSPC-SP 1: Solvent Cleaning • SSPC-SP 2: Hand Tool Cleaning • SSPC-SP 3: Power Tool Cleaning • SSPC-SP 5: White Metal Blast • SSPC-SP 6: Commercial Blast • SSPC-SP 7: Brush-Off Blast Cleaning • SSPC-SP 10: Near-White Metal Blast • SSPC-SP 11: Power Tool Cleaning to Bare Metal
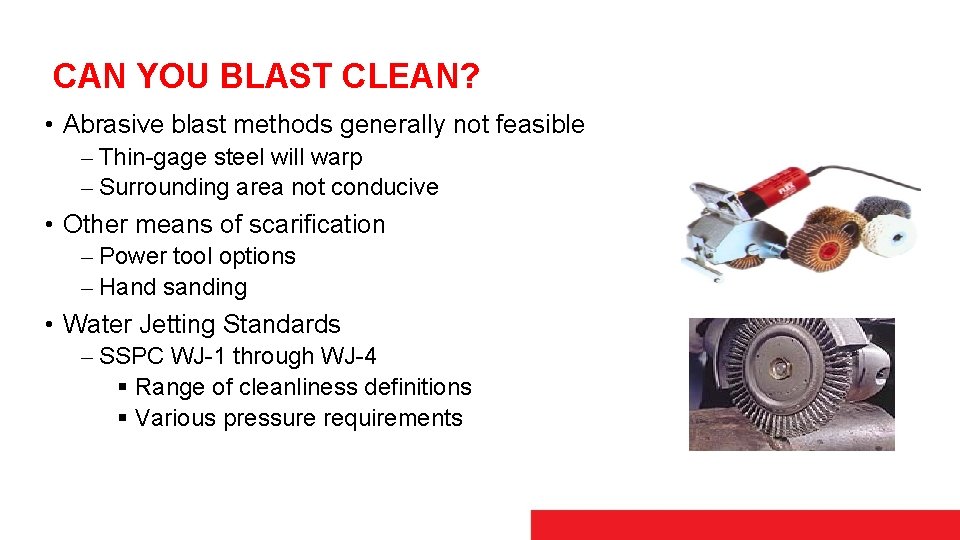
CAN YOU BLAST CLEAN? • Abrasive blast methods generally not feasible ⎼ Thin-gage steel will warp ⎼ Surrounding area not conducive • Other means of scarification ⎼ Power tool options ⎼ Hand sanding • Water Jetting Standards ⎼ SSPC WJ-1 through WJ-4 § Range of cleanliness definitions § Various pressure requirements
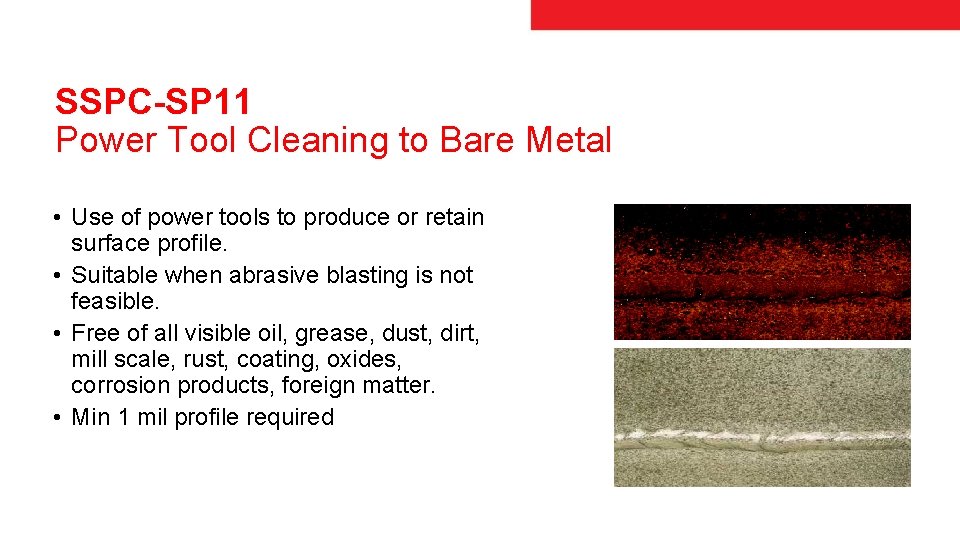
SSPC-SP 11 Power Tool Cleaning to Bare Metal • Use of power tools to produce or retain surface profile. • Suitable when abrasive blasting is not feasible. • Free of all visible oil, grease, dust, dirt, mill scale, rust, coating, oxides, corrosion products, foreign matter. • Min 1 mil profile required
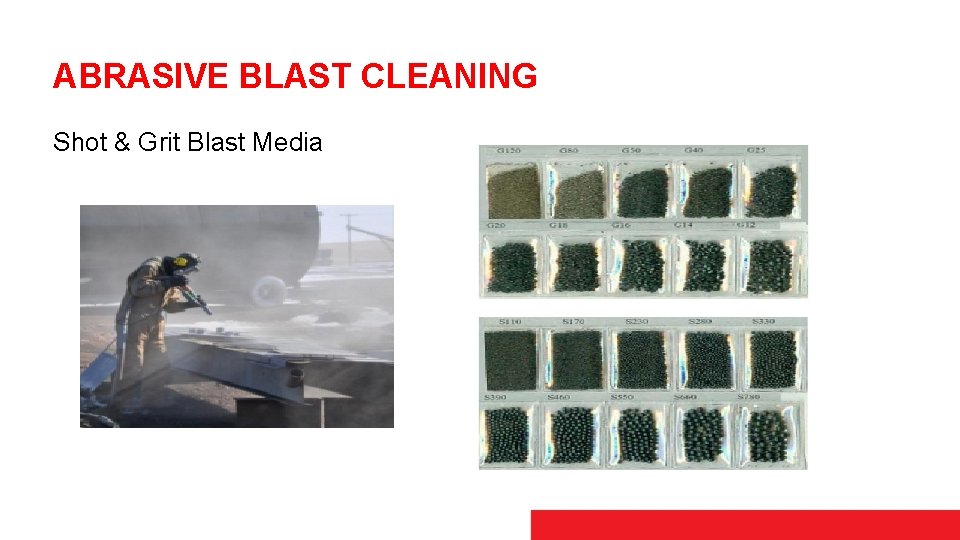
ABRASIVE BLAST CLEANING Shot & Grit Blast Media
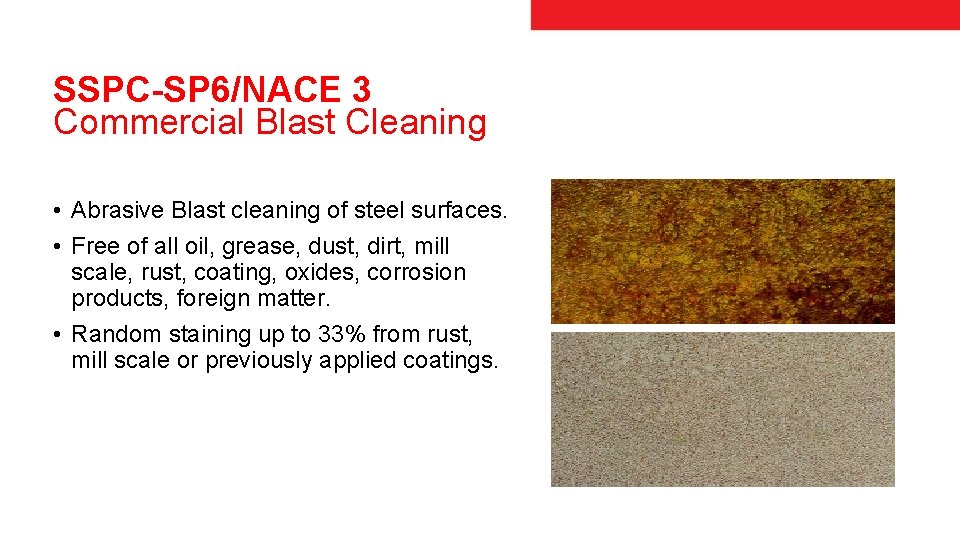
SSPC-SP 6/NACE 3 Commercial Blast Cleaning • Abrasive Blast cleaning of steel surfaces. • Free of all oil, grease, dust, dirt, mill scale, rust, coating, oxides, corrosion products, foreign matter. • Random staining up to 33% from rust, mill scale or previously applied coatings.
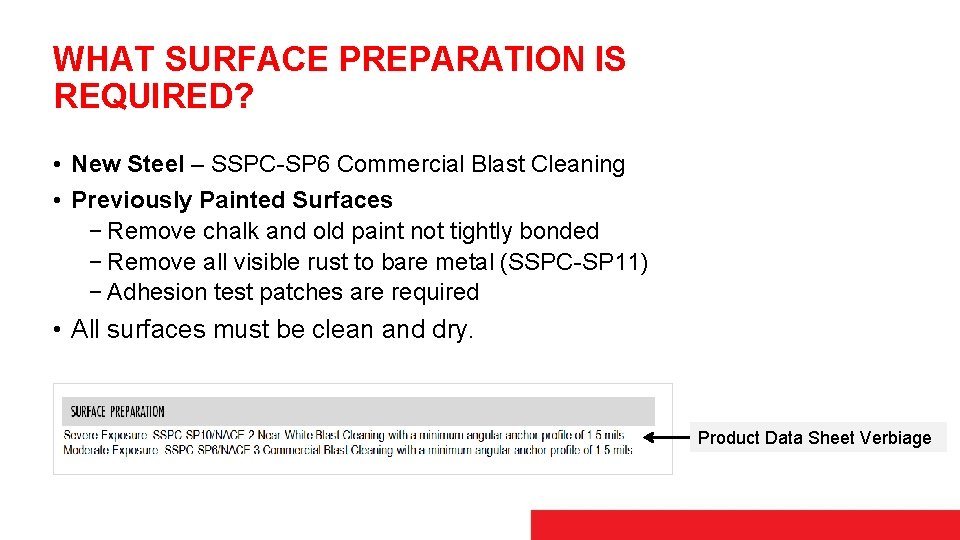
WHAT SURFACE PREPARATION IS REQUIRED? • New Steel – SSPC-SP 6 Commercial Blast Cleaning • Previously Painted Surfaces − Remove chalk and old paint not tightly bonded − Remove all visible rust to bare metal (SSPC-SP 11) − Adhesion test patches are required • All surfaces must be clean and dry. Product Data Sheet Verbiage
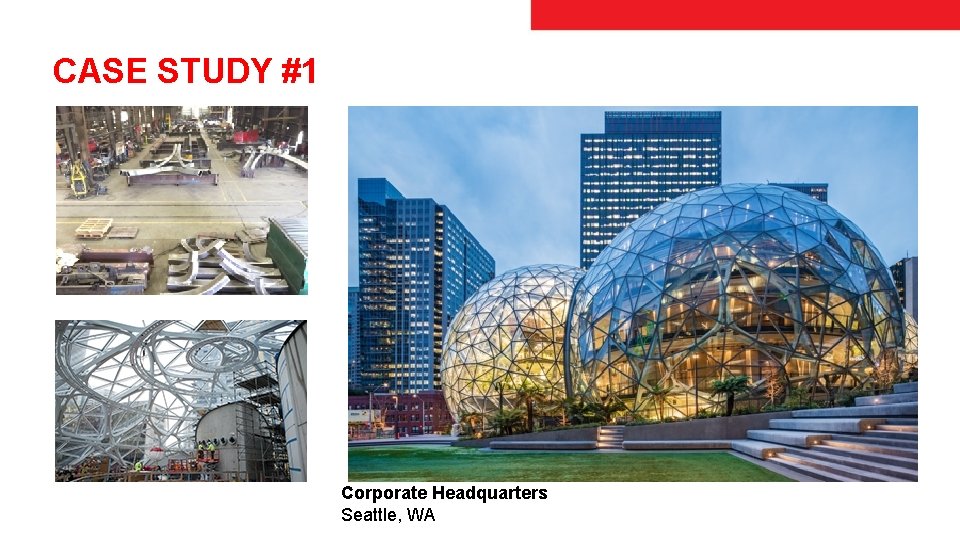
CASE STUDY #1 Corporate Headquarters Seattle, WA
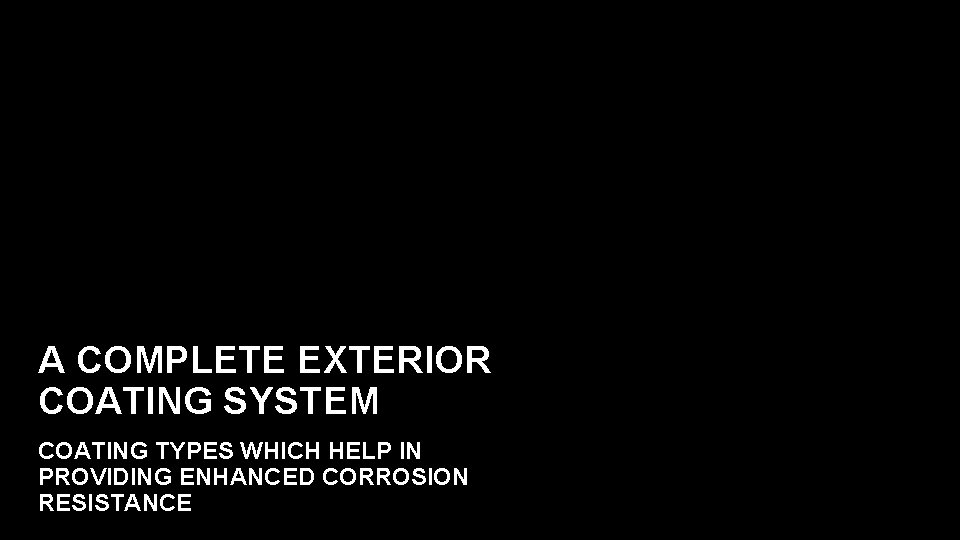
A COMPLETE EXTERIOR COATING SYSTEM COATING TYPES WHICH HELP IN PROVIDING ENHANCED CORROSION RESISTANCE
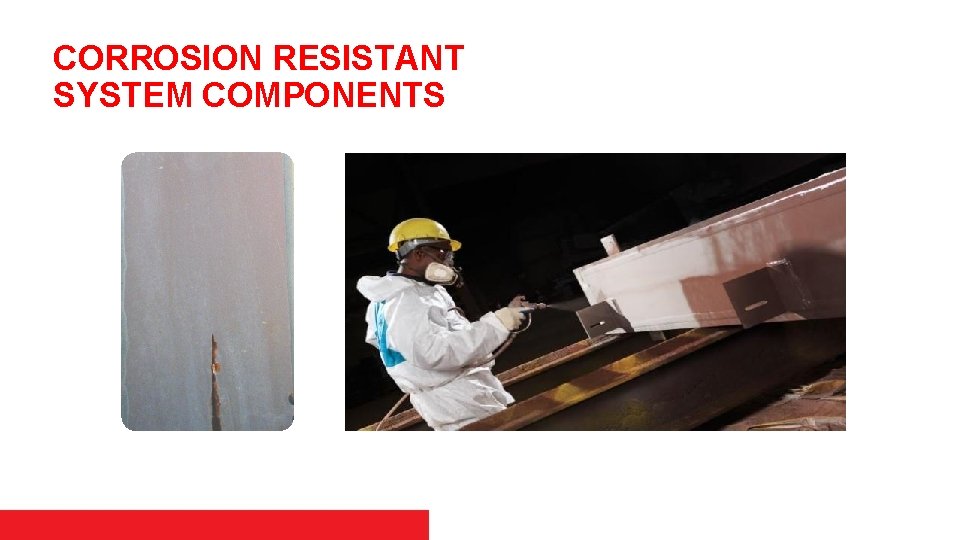
CORROSION RESISTANT SYSTEM COMPONENTS
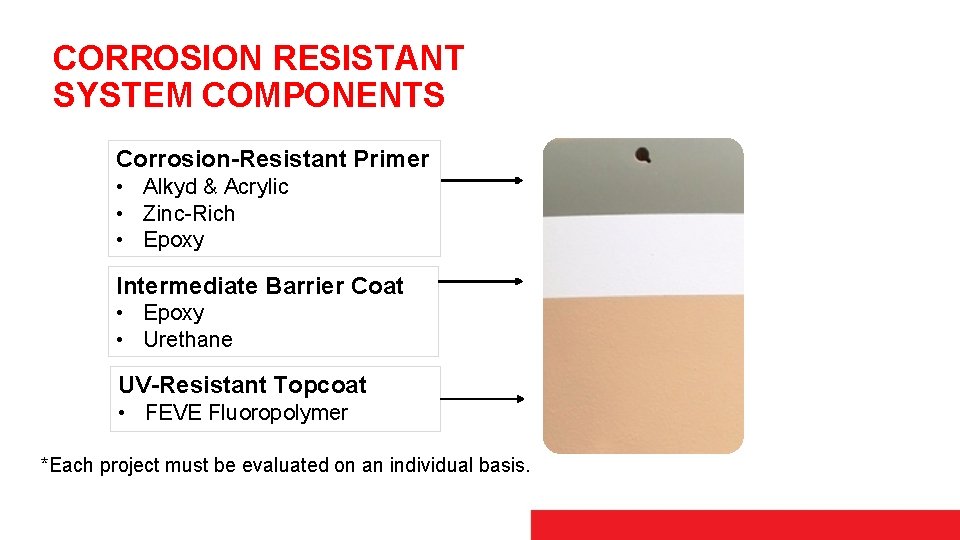
CORROSION RESISTANT SYSTEM COMPONENTS Corrosion-Resistant Primer • Alkyd & Acrylic • Zinc-Rich • Epoxy Intermediate Barrier Coat • Epoxy • Urethane UV-Resistant Topcoat • FEVE Fluoropolymer *Each project must be evaluated on an individual basis.
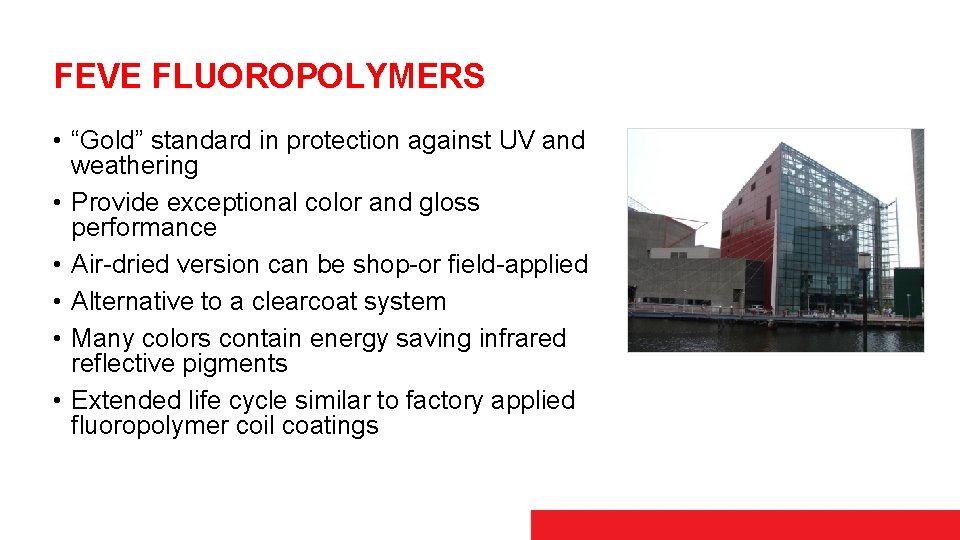
FEVE FLUOROPOLYMERS • “Gold” standard in protection against UV and weathering • Provide exceptional color and gloss performance • Air-dried version can be shop-or field-applied • Alternative to a clearcoat system • Many colors contain energy saving infrared reflective pigments • Extended life cycle similar to factory applied fluoropolymer coil coatings
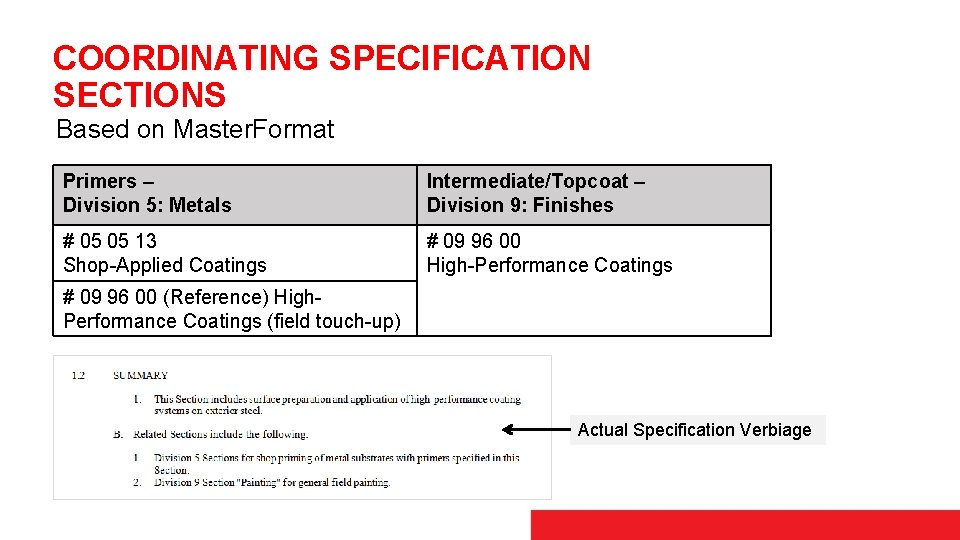
COORDINATING SPECIFICATION SECTIONS Based on Master. Format Primers – Division 5: Metals Intermediate/Topcoat – Division 9: Finishes # 05 05 13 Shop-Applied Coatings # 09 96 00 High-Performance Coatings # 09 96 00 (Reference) High. Performance Coatings (field touch-up) Actual Specification Verbiage
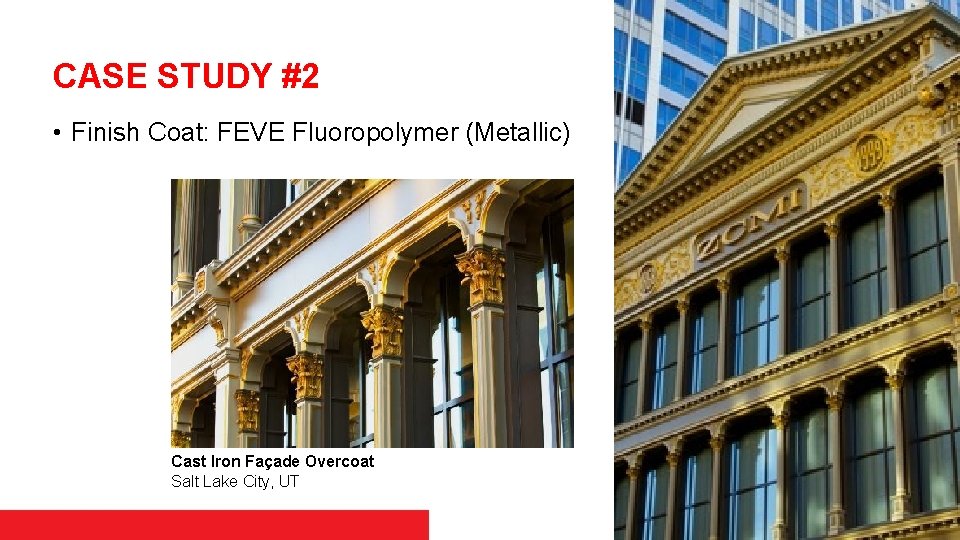
CASE STUDY #2 • Finish Coat: FEVE Fluoropolymer (Metallic) Cast Iron Façade Overcoat Salt Lake City, UT
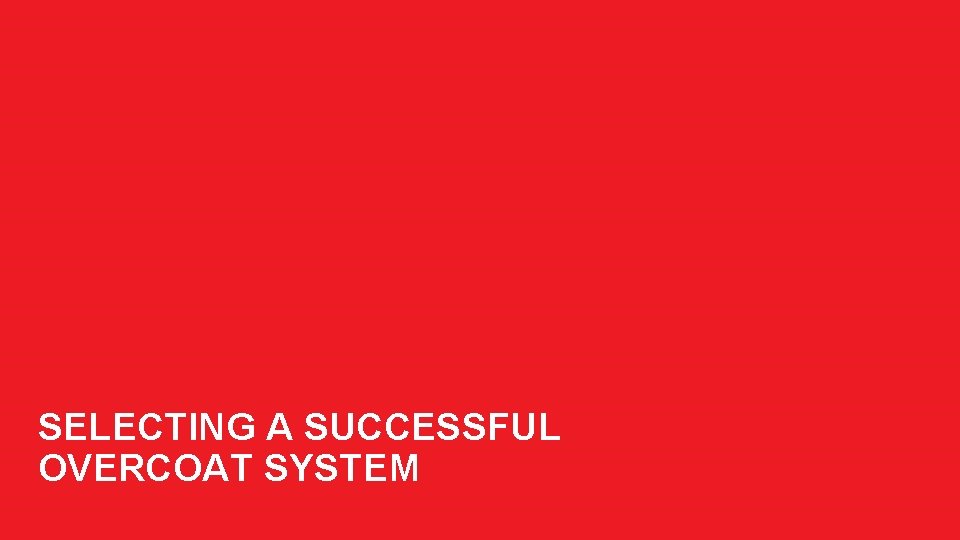
SELECTING A SUCCESSFUL OVERCOAT SYSTEM
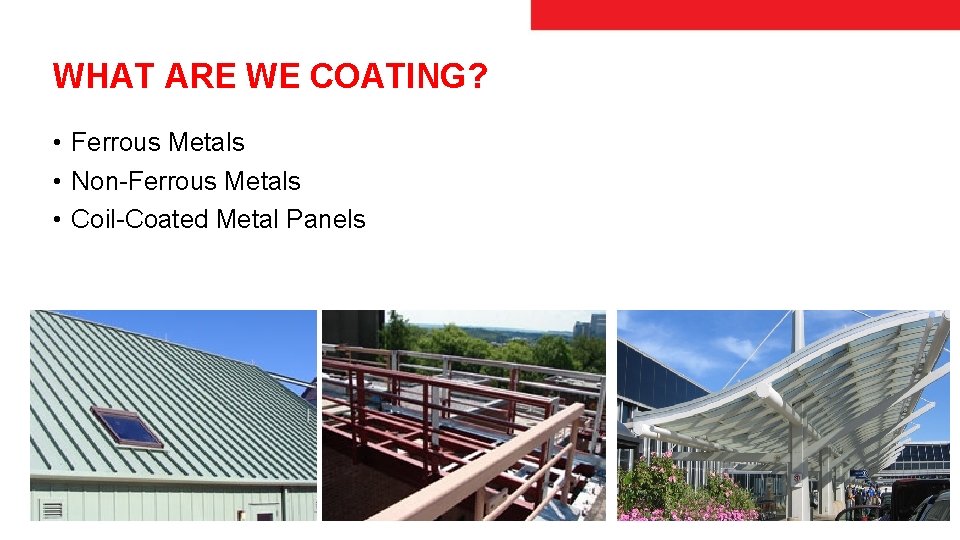
WHAT ARE WE COATING? • Ferrous Metals • Non-Ferrous Metals • Coil-Coated Metal Panels
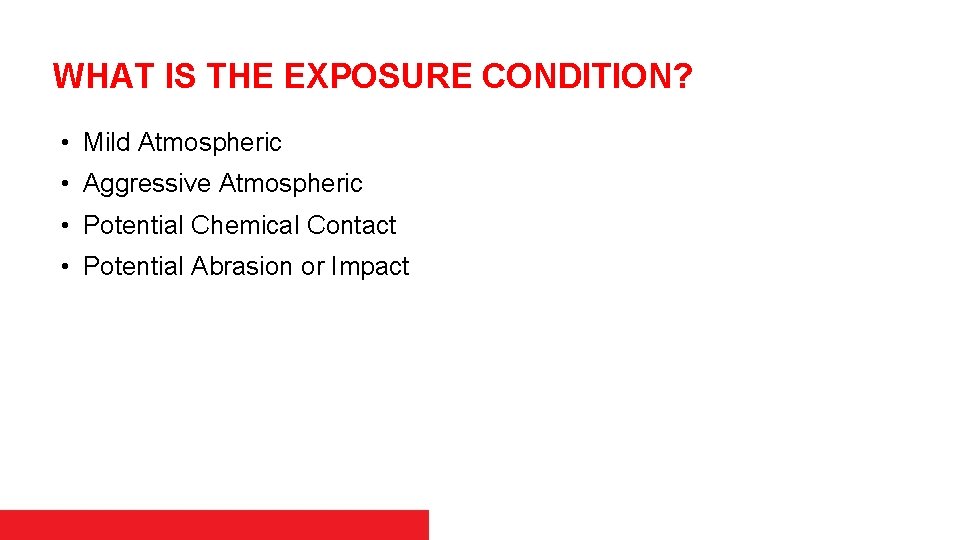
WHAT IS THE EXPOSURE CONDITION? • Mild Atmospheric • Aggressive Atmospheric • Potential Chemical Contact • Potential Abrasion or Impact
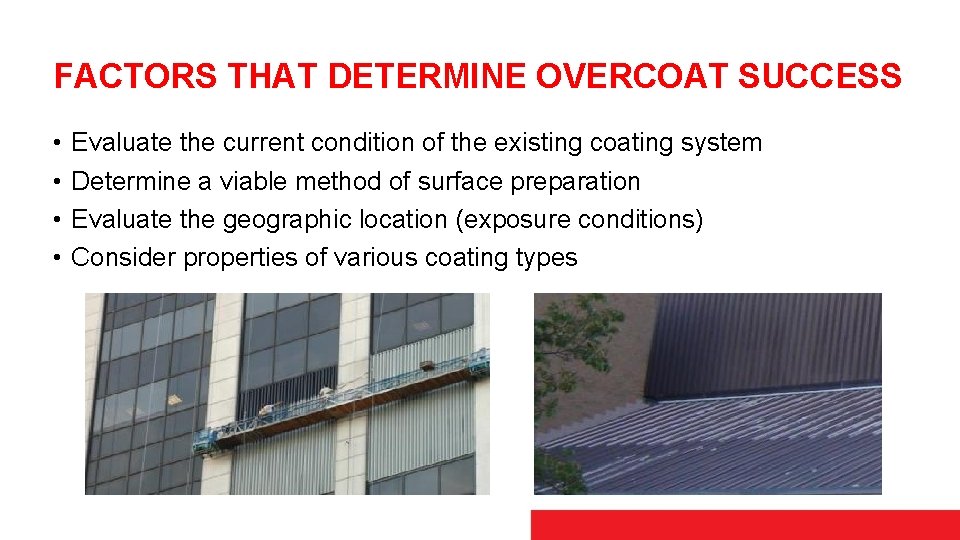
FACTORS THAT DETERMINE OVERCOAT SUCCESS • • Evaluate the current condition of the existing coating system Determine a viable method of surface preparation Evaluate the geographic location (exposure conditions) Consider properties of various coating types
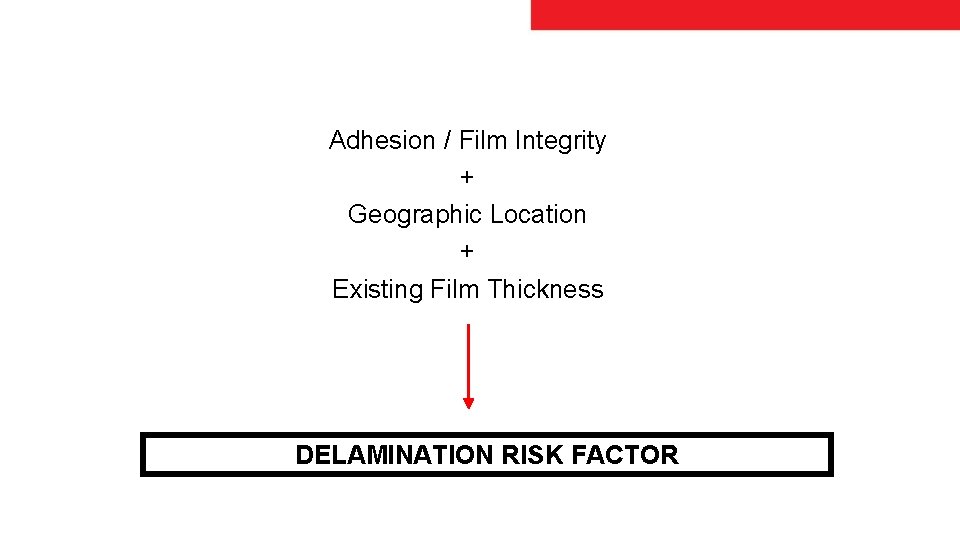
Adhesion / Film Integrity + Geographic Location + Existing Film Thickness DELAMINATION RISK FACTOR
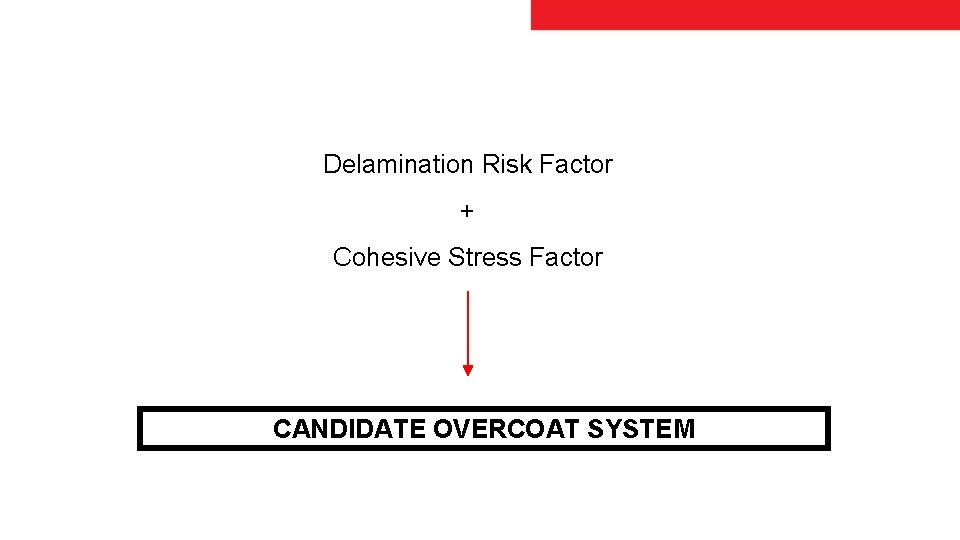
Delamination Risk Factor + Cohesive Stress Factor CANDIDATE OVERCOAT SYSTEM
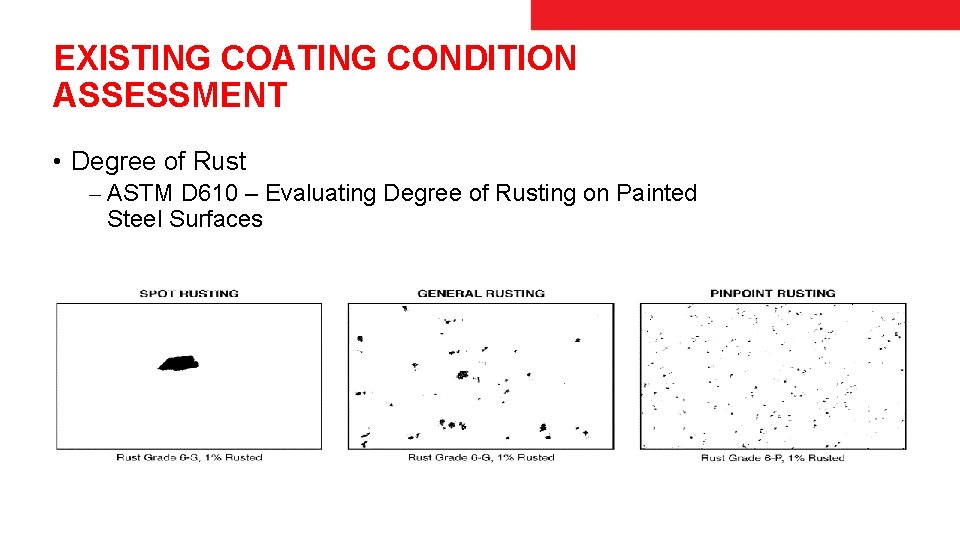
EXISTING COATING CONDITION ASSESSMENT • Degree of Rust ⎼ ASTM D 610 – Evaluating Degree of Rusting on Painted Steel Surfaces
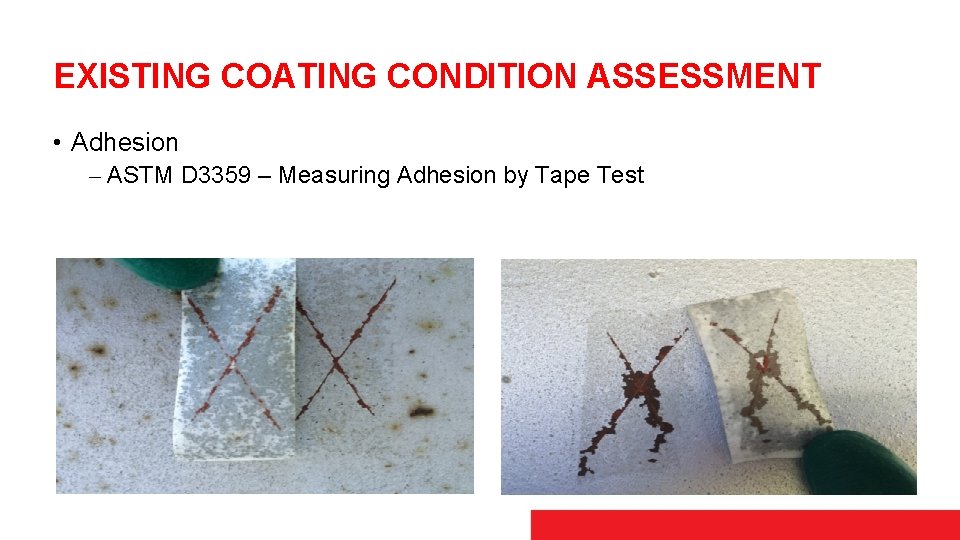
EXISTING COATING CONDITION ASSESSMENT • Adhesion ⎼ ASTM D 3359 – Measuring Adhesion by Tape Test
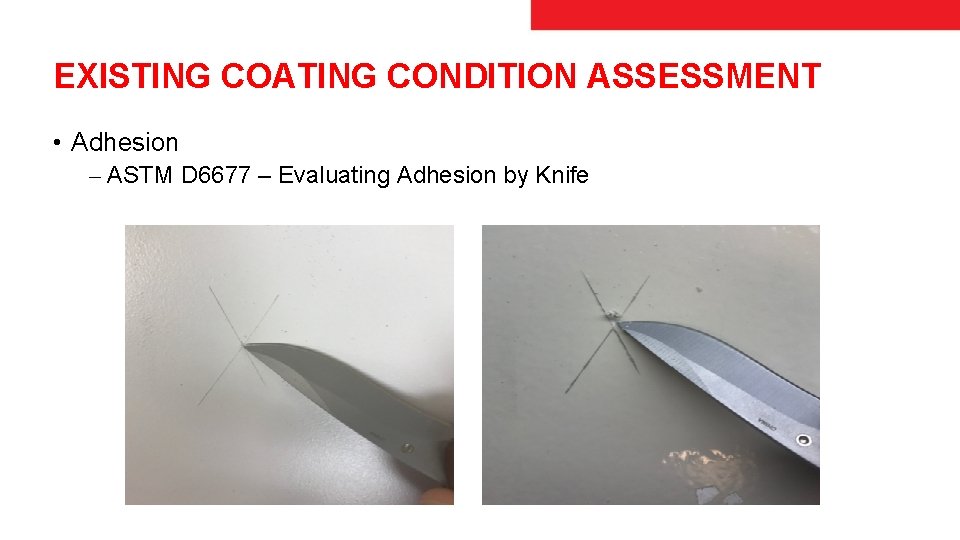
EXISTING COATING CONDITION ASSESSMENT • Adhesion ⎼ ASTM D 6677 – Evaluating Adhesion by Knife
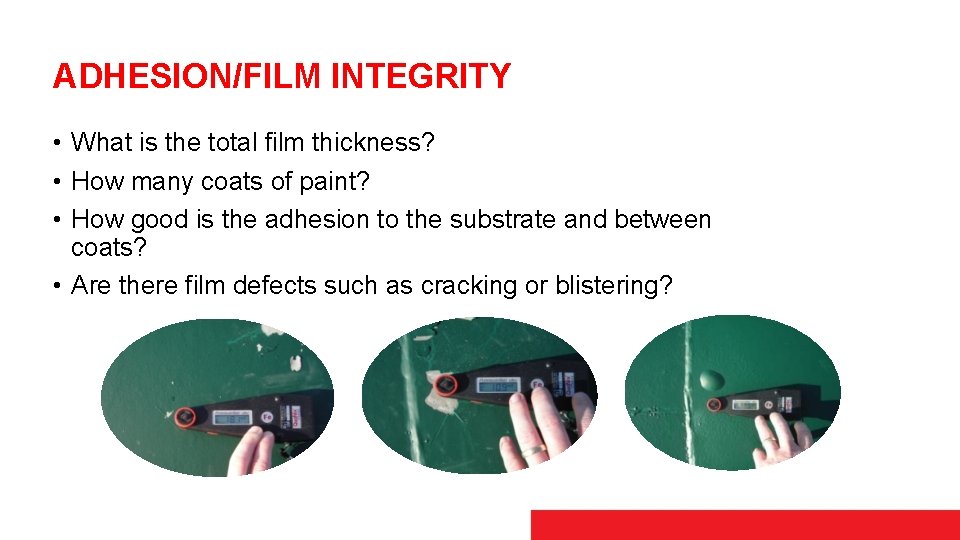
ADHESION/FILM INTEGRITY • What is the total film thickness? • How many coats of paint? • How good is the adhesion to the substrate and between coats? • Are there film defects such as cracking or blistering?
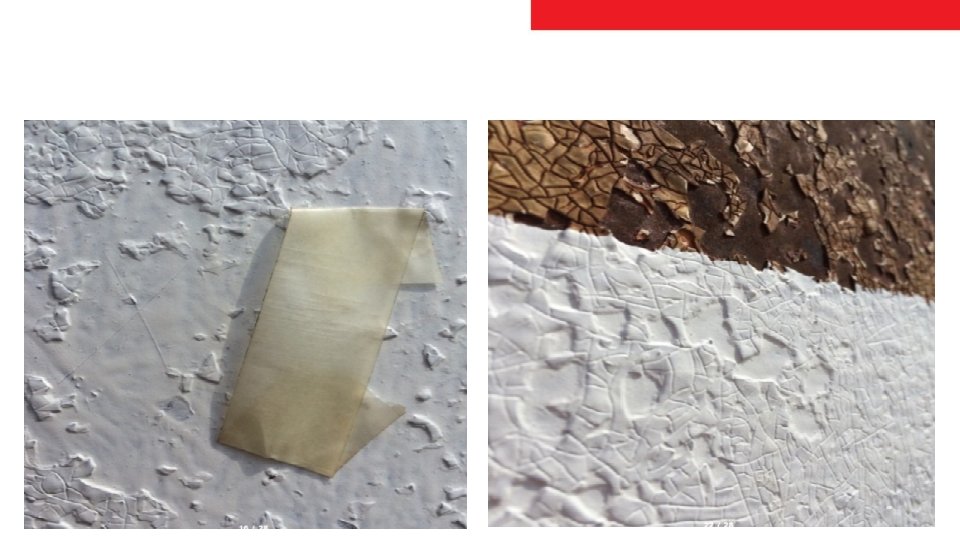
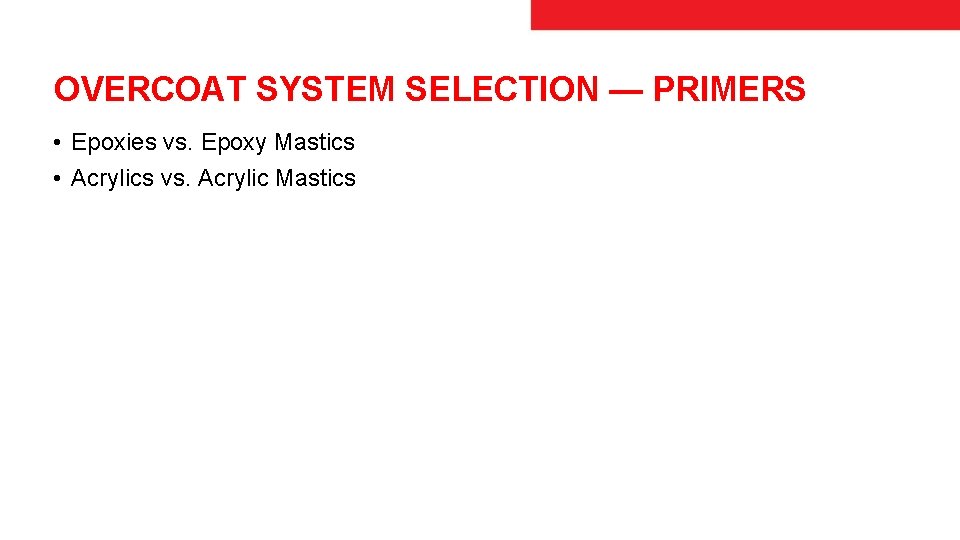
OVERCOAT SYSTEM SELECTION — PRIMERS • Epoxies vs. Epoxy Mastics • Acrylics vs. Acrylic Mastics
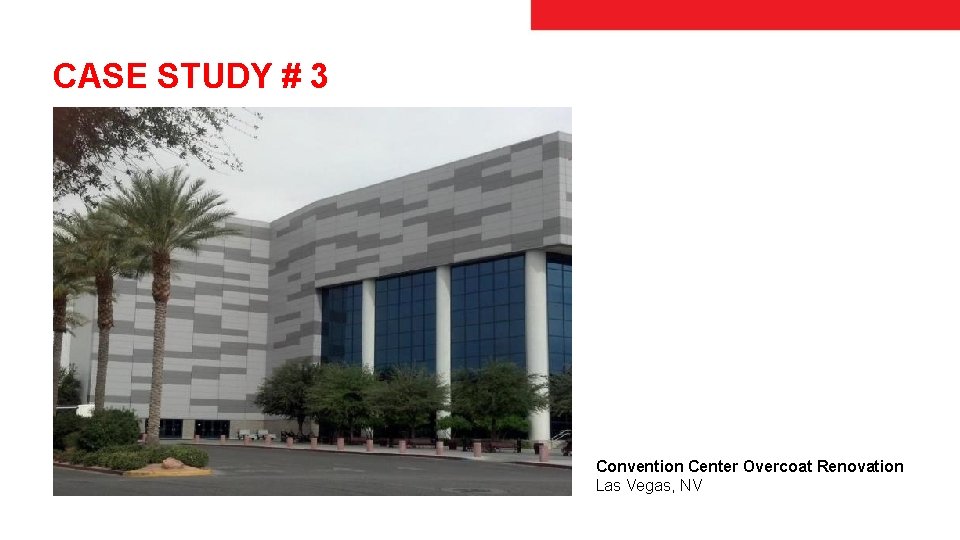
CASE STUDY # 3 Convention Center Overcoat Renovation Las Vegas, NV
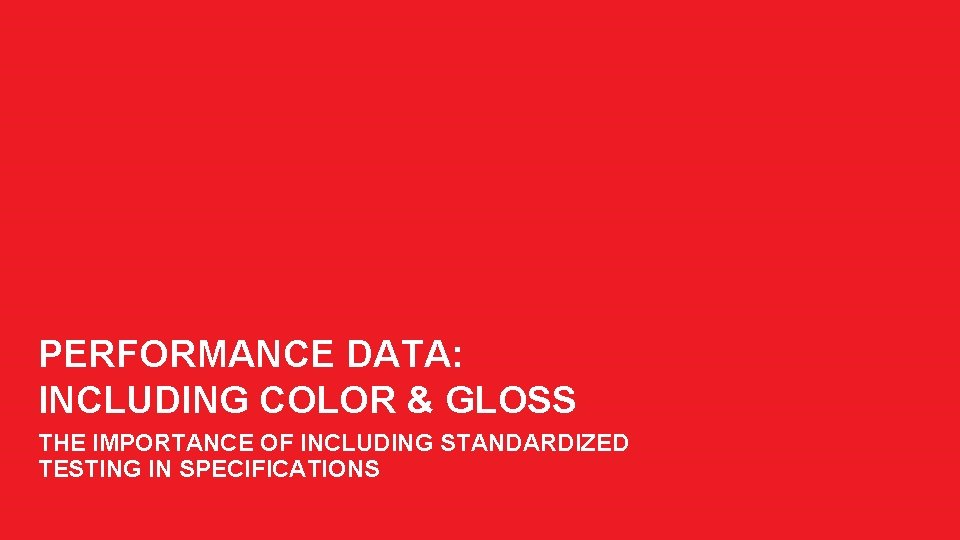
PERFORMANCE DATA: INCLUDING COLOR & GLOSS THE IMPORTANCE OF INCLUDING STANDARDIZED TESTING IN SPECIFICATIONS
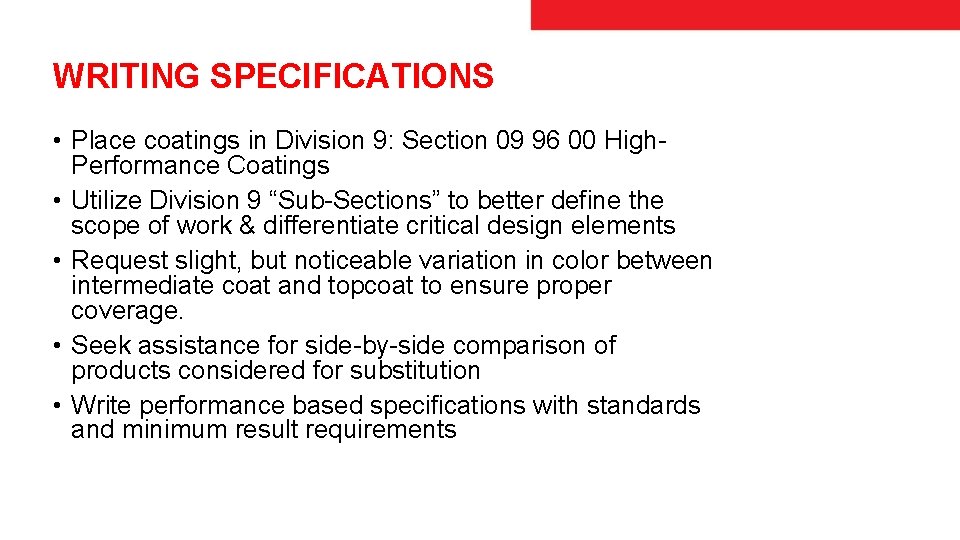
WRITING SPECIFICATIONS • Place coatings in Division 9: Section 09 96 00 High. Performance Coatings • Utilize Division 9 “Sub-Sections” to better define the scope of work & differentiate critical design elements • Request slight, but noticeable variation in color between intermediate coat and topcoat to ensure proper coverage. • Seek assistance for side-by-side comparison of products considered for substitution • Write performance based specifications with standards and minimum result requirements
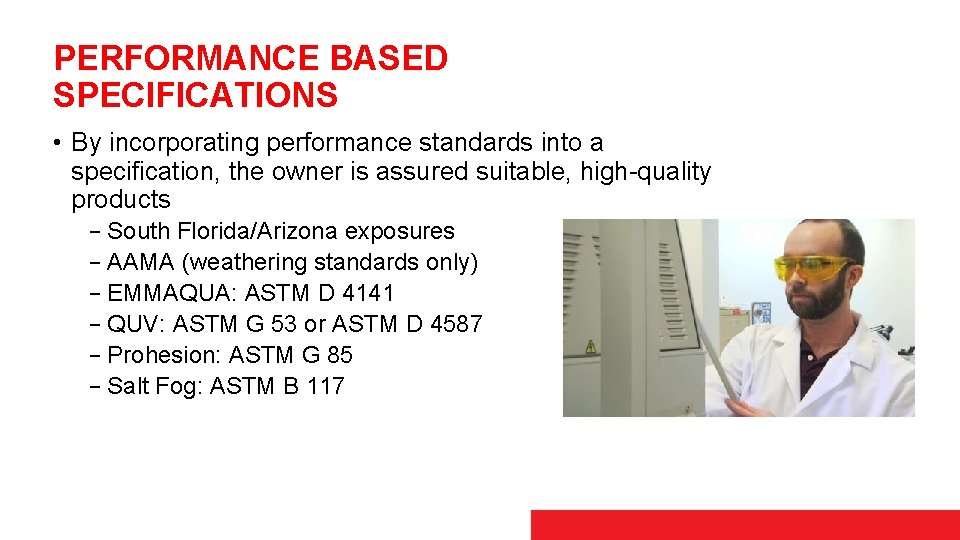
PERFORMANCE BASED SPECIFICATIONS • By incorporating performance standards into a specification, the owner is assured suitable, high-quality products − South Florida/Arizona exposures − AAMA (weathering standards only) − EMMAQUA: ASTM D 4141 − QUV: ASTM G 53 or ASTM D 4587 − Prohesion: ASTM G 85 − Salt Fog: ASTM B 117
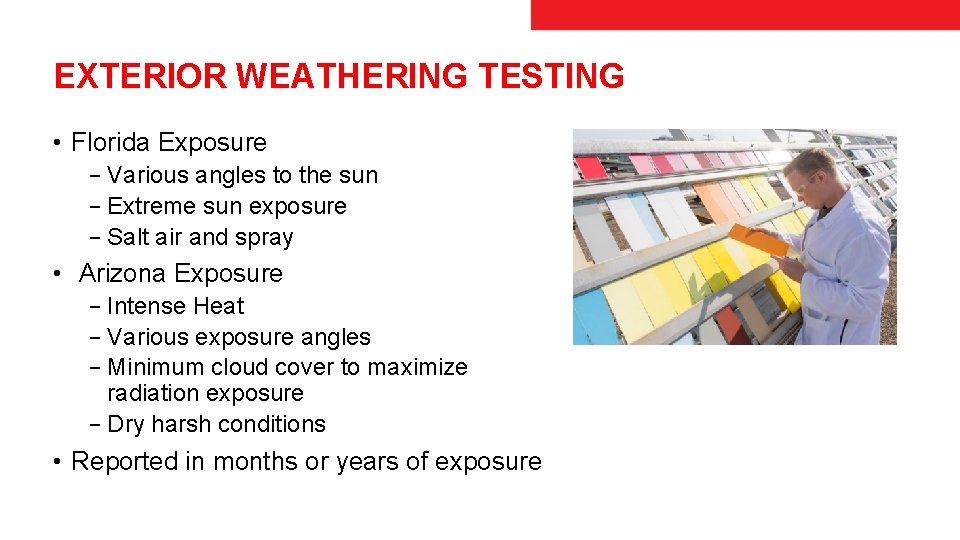
EXTERIOR WEATHERING TESTING • Florida Exposure − Various angles to the sun − Extreme sun exposure − Salt air and spray • Arizona Exposure − Intense Heat − Various exposure angles − Minimum cloud cover to maximize radiation exposure − Dry harsh conditions • Reported in months or years of exposure
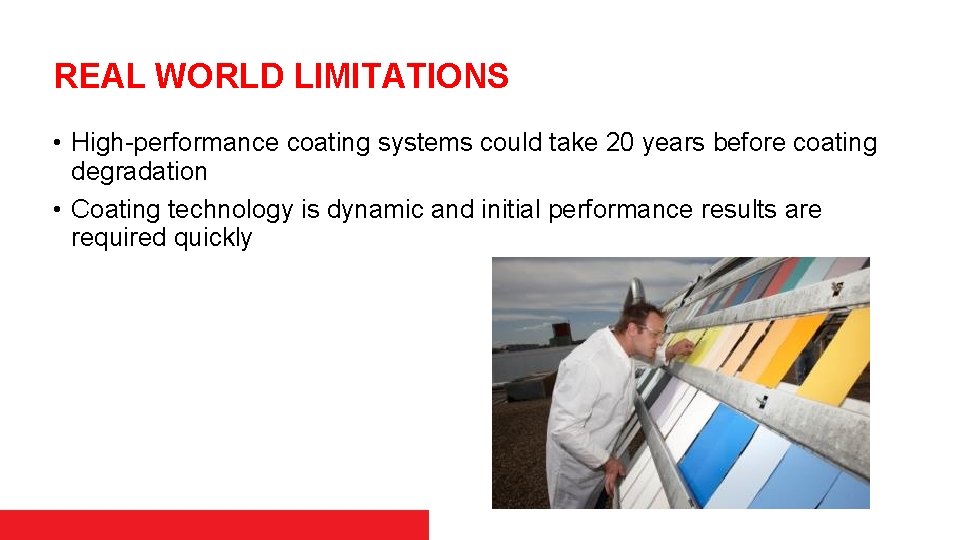
REAL WORLD LIMITATIONS • High-performance coating systems could take 20 years before coating degradation • Coating technology is dynamic and initial performance results are required quickly
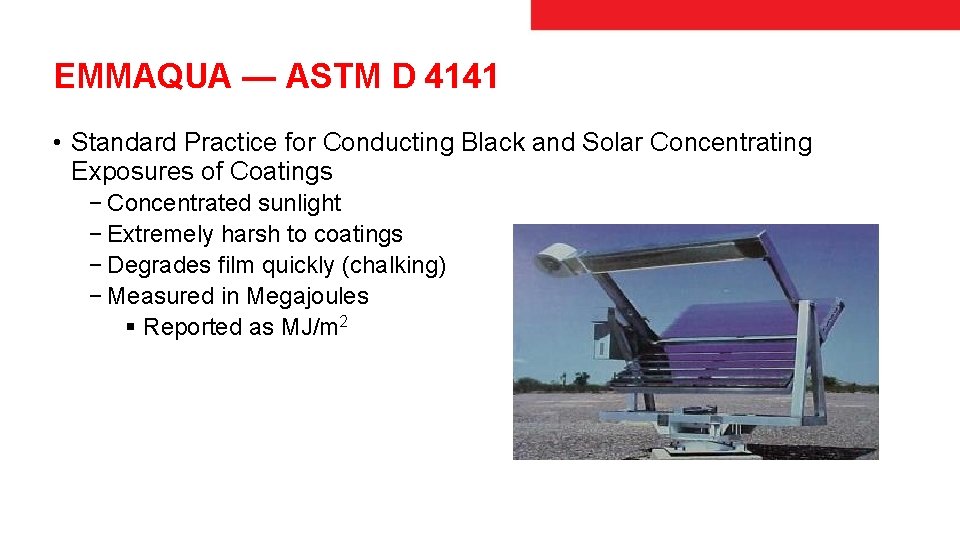
EMMAQUA — ASTM D 4141 • Standard Practice for Conducting Black and Solar Concentrating Exposures of Coatings − Concentrated sunlight − Extremely harsh to coatings − Degrades film quickly (chalking) − Measured in Megajoules § Reported as MJ/m 2
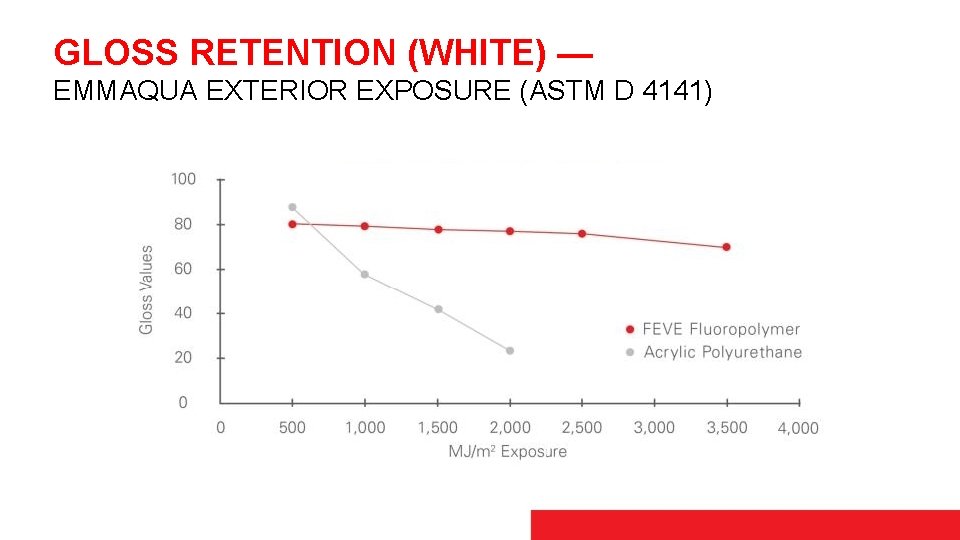
GLOSS RETENTION (WHITE) — EMMAQUA EXTERIOR EXPOSURE (ASTM D 4141)

COLOR CHANGE (WHITE) EMMAQUA EXTERIOR EXPOSURE (ASTM D 4141)
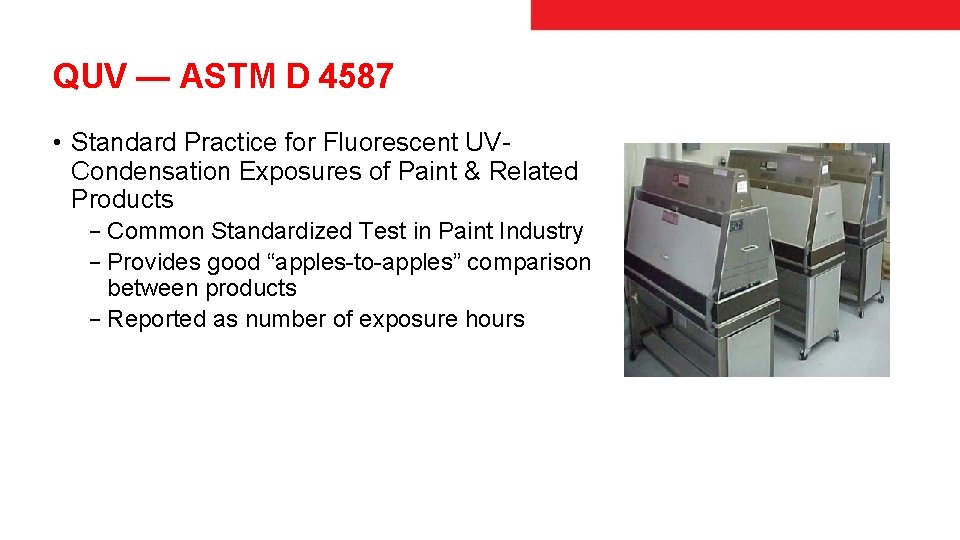
QUV — ASTM D 4587 • Standard Practice for Fluorescent UVCondensation Exposures of Paint & Related Products − Common Standardized Test in Paint Industry − Provides good “apples-to-apples” comparison between products − Reported as number of exposure hours
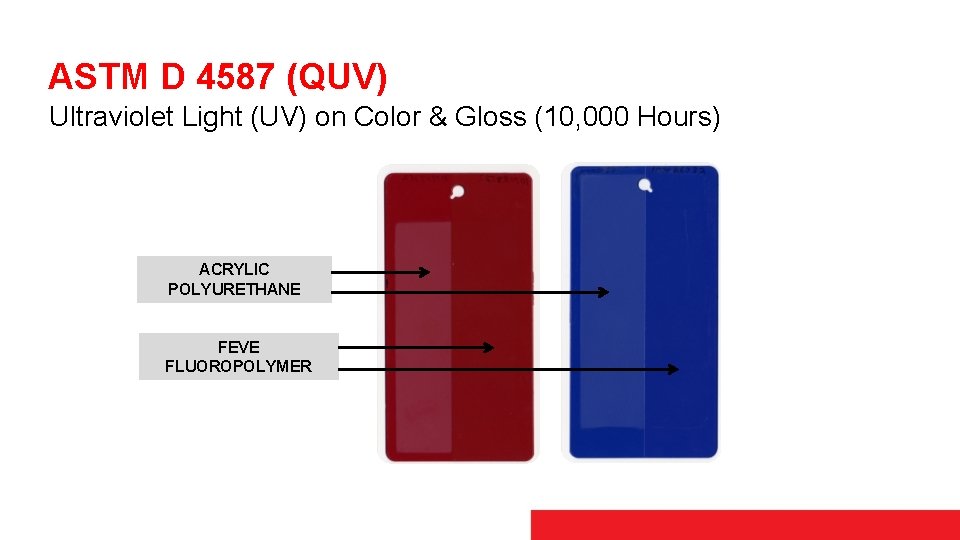
ASTM D 4587 (QUV) Ultraviolet Light (UV) on Color & Gloss (10, 000 Hours) ACRYLIC POLYURETHANE FEVE FLUOROPOLYMER
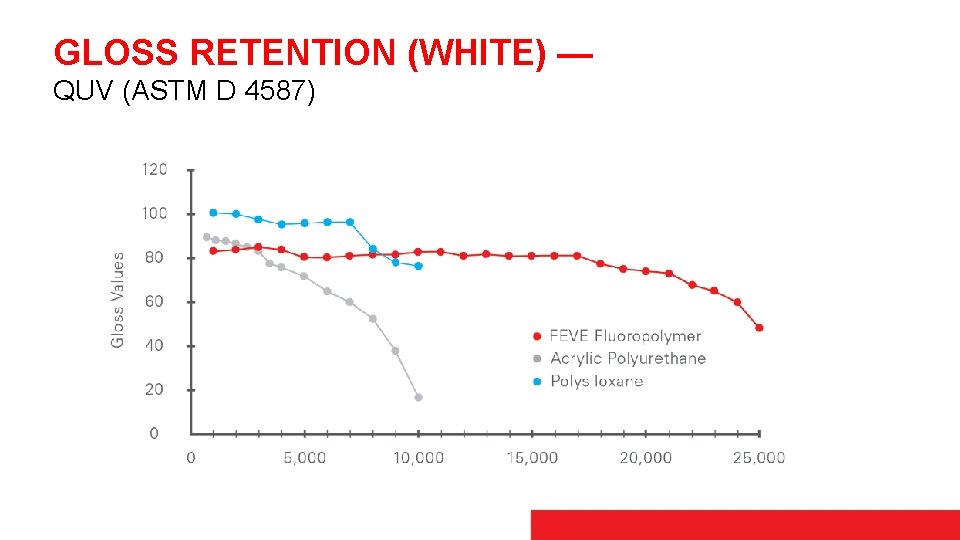
GLOSS RETENTION (WHITE) — QUV (ASTM D 4587)
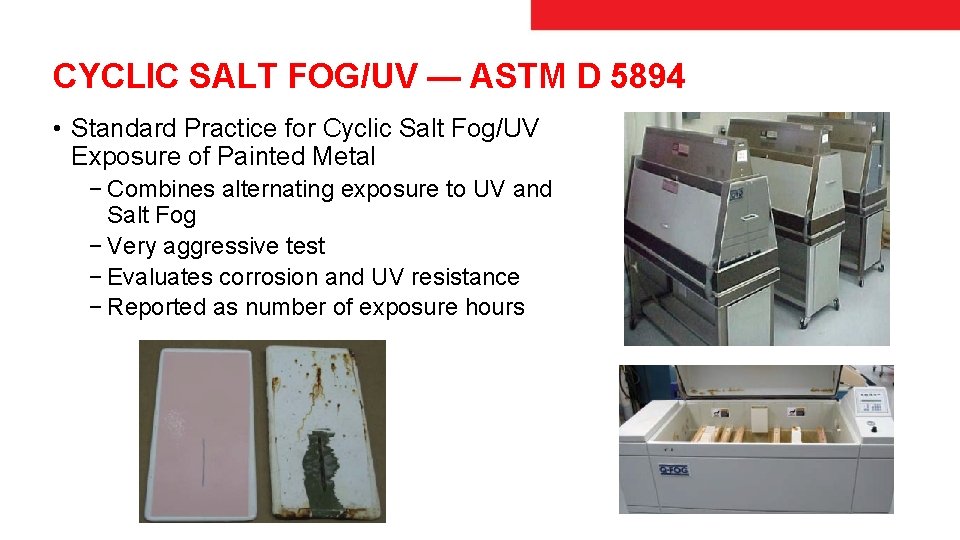
CYCLIC SALT FOG/UV — ASTM D 5894 • Standard Practice for Cyclic Salt Fog/UV Exposure of Painted Metal − Combines alternating exposure to UV and Salt Fog − Very aggressive test − Evaluates corrosion and UV resistance − Reported as number of exposure hours
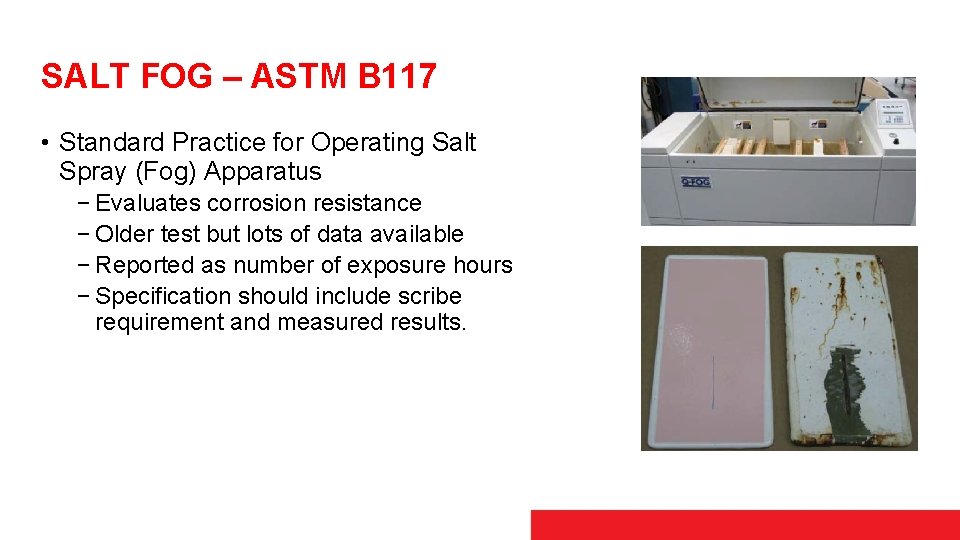
SALT FOG – ASTM B 117 • Standard Practice for Operating Salt Spray (Fog) Apparatus − Evaluates corrosion resistance − Older test but lots of data available − Reported as number of exposure hours − Specification should include scribe requirement and measured results.
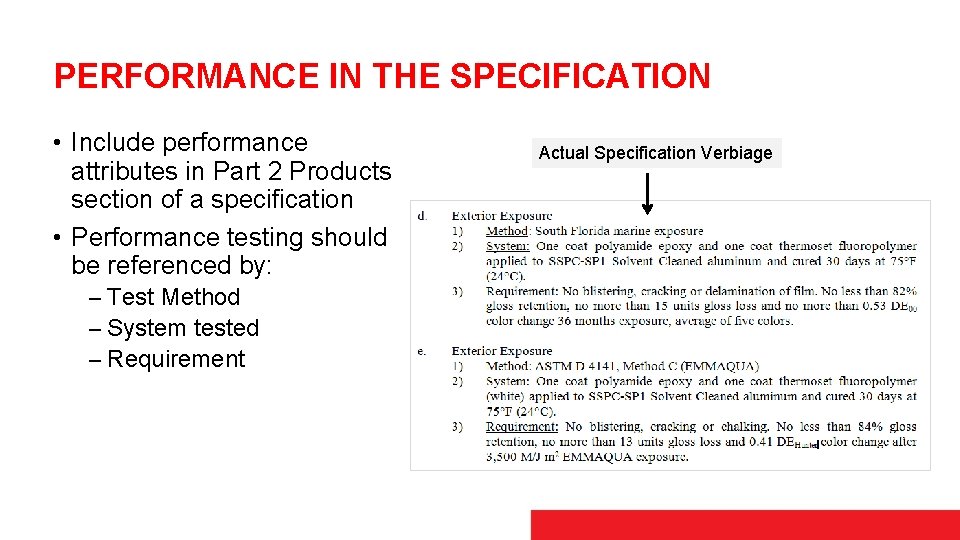
PERFORMANCE IN THE SPECIFICATION • Include performance attributes in Part 2 Products section of a specification • Performance testing should be referenced by: ─ Test Method ─ System tested ─ Requirement Actual Specification Verbiage
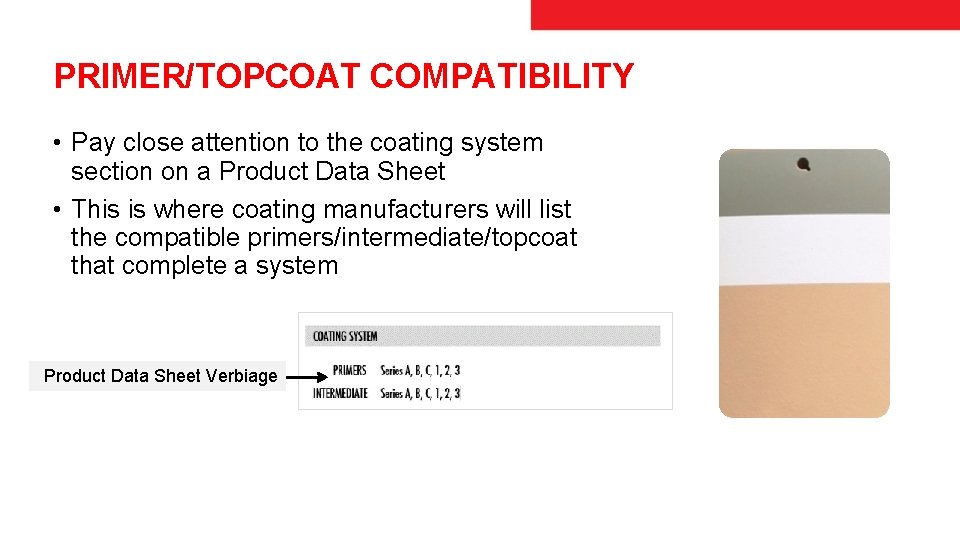
PRIMER/TOPCOAT COMPATIBILITY • Pay close attention to the coating system section on a Product Data Sheet • This is where coating manufacturers will list the compatible primers/intermediate/topcoat that complete a system Product Data Sheet Verbiage
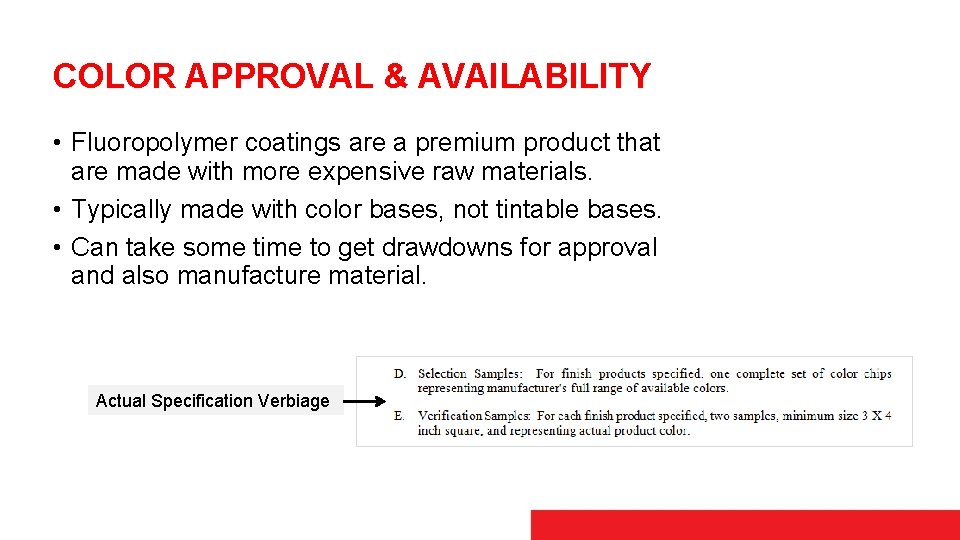
COLOR APPROVAL & AVAILABILITY • Fluoropolymer coatings are a premium product that are made with more expensive raw materials. • Typically made with color bases, not tintable bases. • Can take some time to get drawdowns for approval and also manufacture material. Actual Specification Verbiage
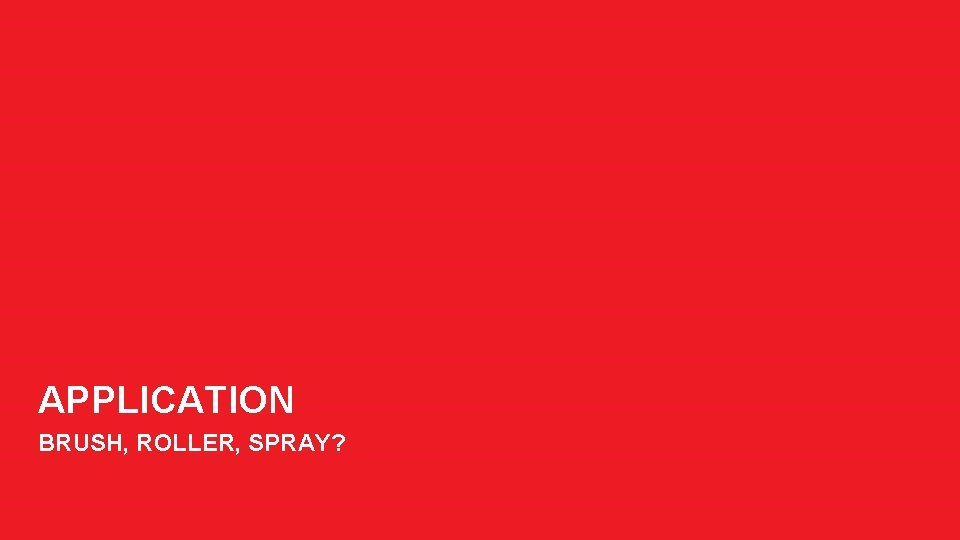
APPLICATION BRUSH, ROLLER, SPRAY?
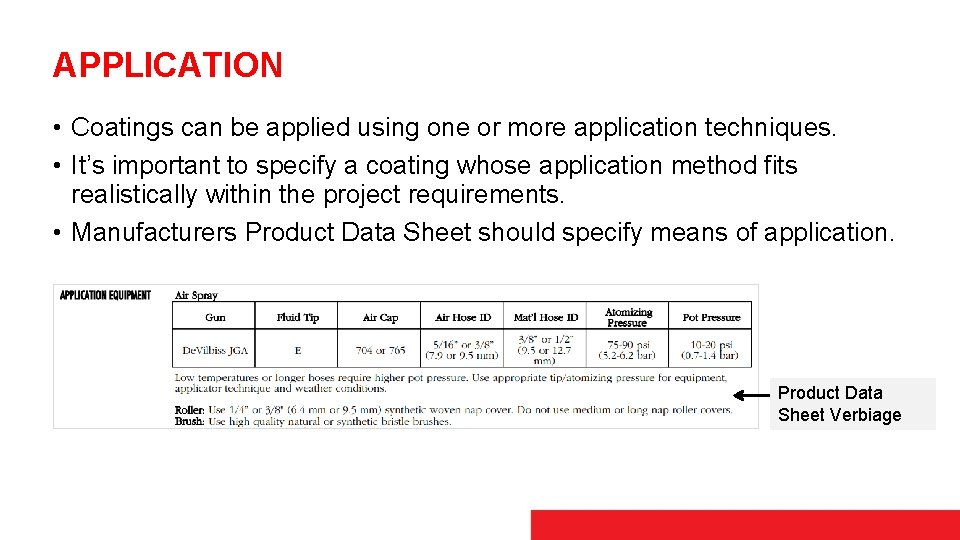
APPLICATION • Coatings can be applied using one or more application techniques. • It’s important to specify a coating whose application method fits realistically within the project requirements. • Manufacturers Product Data Sheet should specify means of application. Product Data Sheet Verbiage
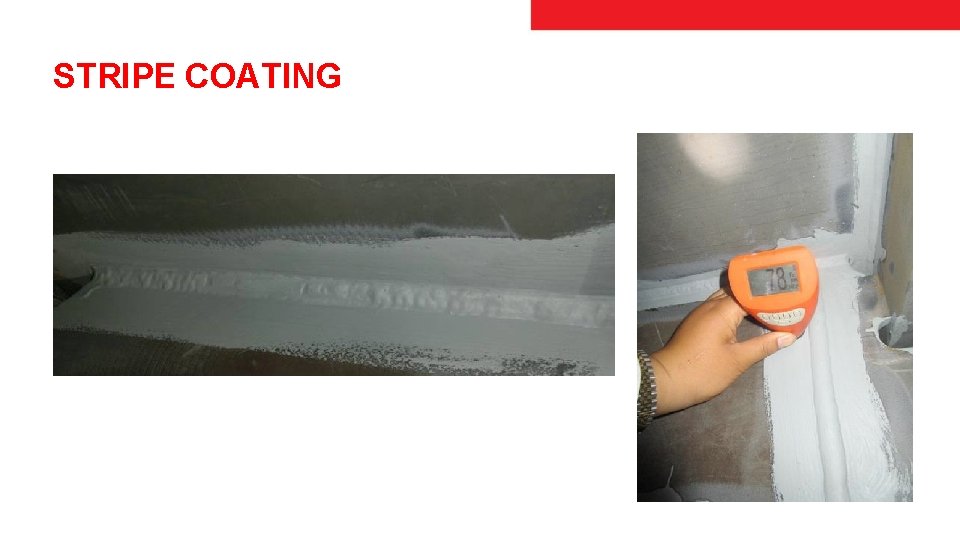
STRIPE COATING
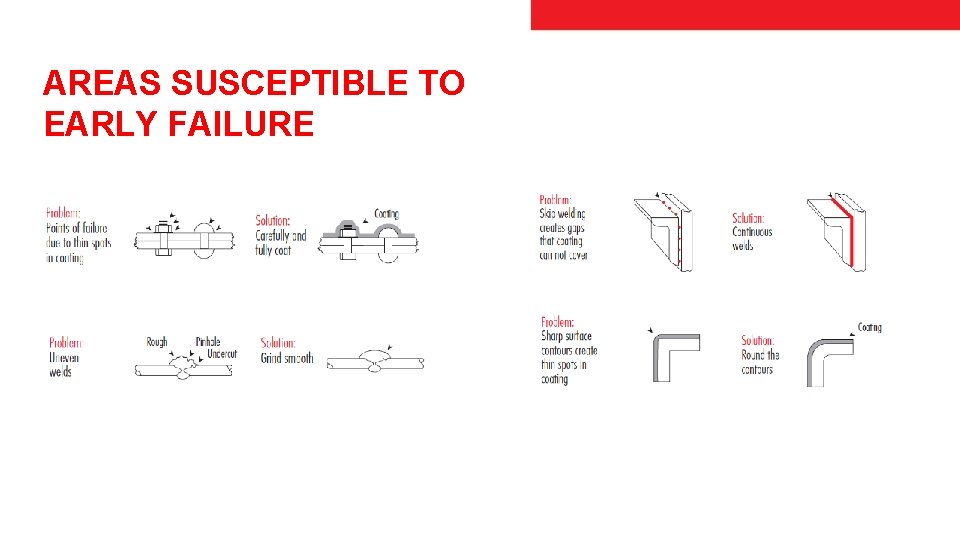
AREAS SUSCEPTIBLE TO EARLY FAILURE
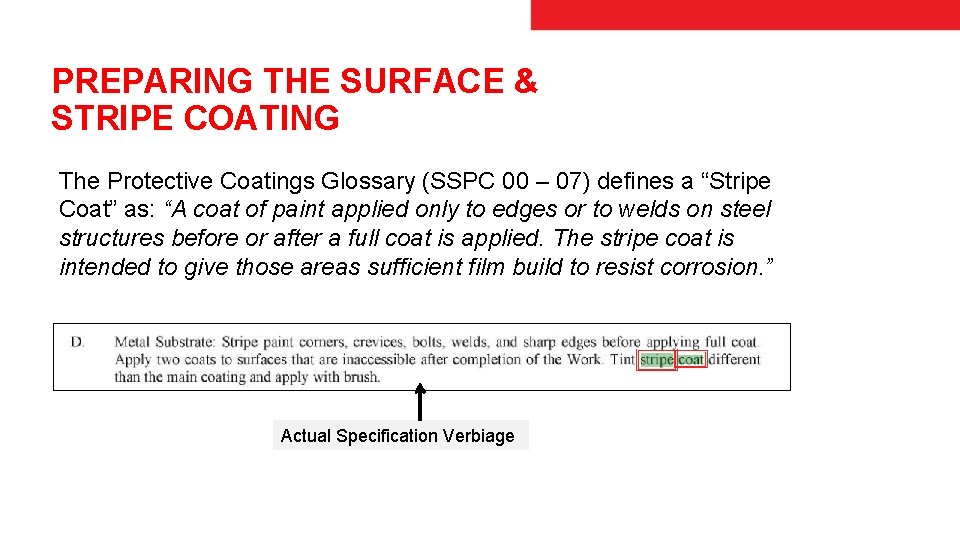
PREPARING THE SURFACE & STRIPE COATING The Protective Coatings Glossary (SSPC 00 – 07) defines a “Stripe Coat” as: “A coat of paint applied only to edges or to welds on steel structures before or after a full coat is applied. The stripe coat is intended to give those areas sufficient film build to resist corrosion. ” Actual Specification Verbiage
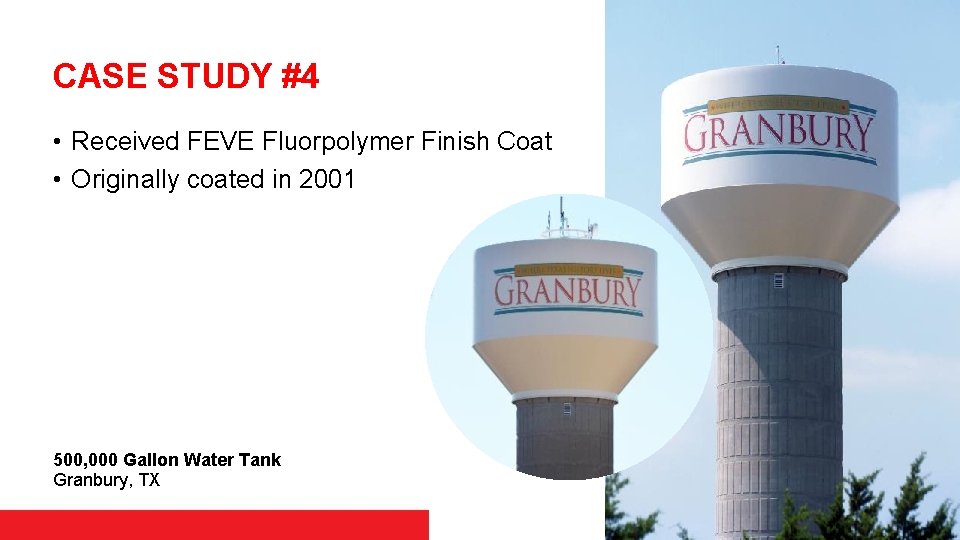
CASE STUDY #4 • Received FEVE Fluorpolymer Finish Coat • Originally coated in 2001 500, 000 Gallon Water Tank Granbury, TX
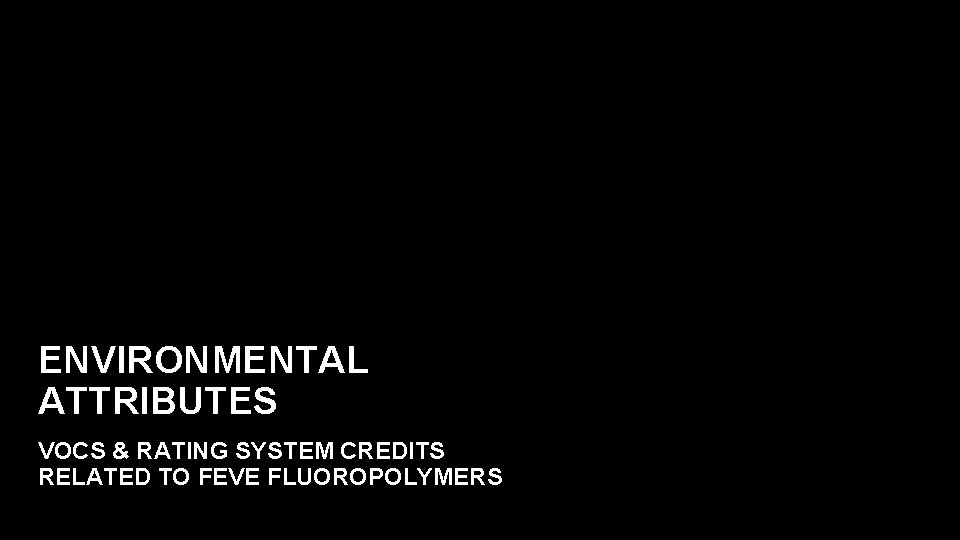
ENVIRONMENTAL ATTRIBUTES VOCS & RATING SYSTEM CREDITS RELATED TO FEVE FLUOROPOLYMERS
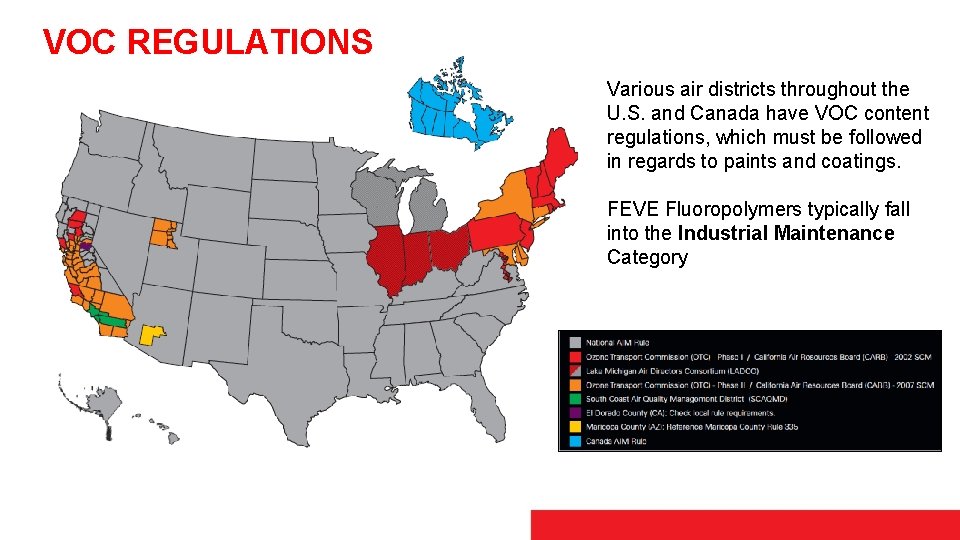
VOC REGULATIONS Various air districts throughout the U. S. and Canada have VOC content regulations, which must be followed in regards to paints and coatings. FEVE Fluoropolymers typically fall into the Industrial Maintenance Category
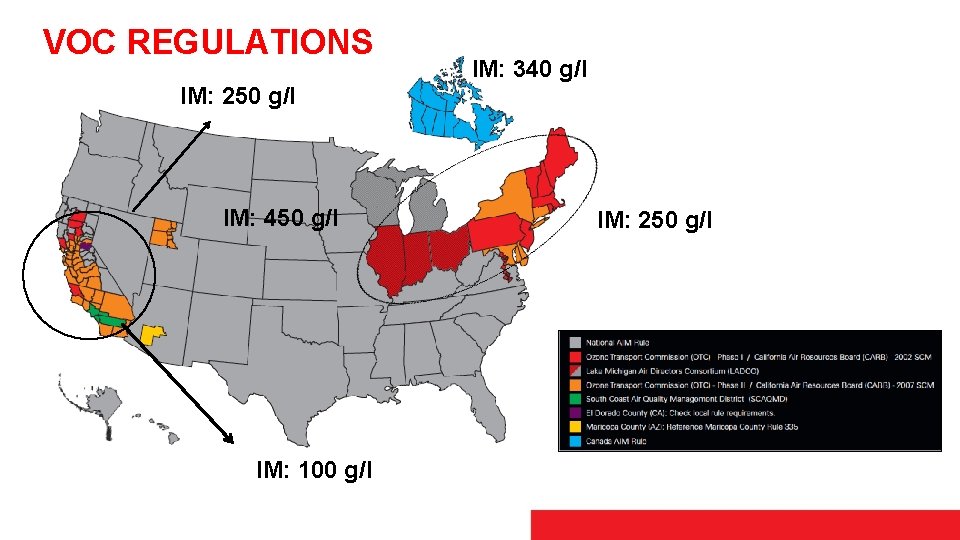
VOC REGULATIONS IM: 250 g/l IM: 450 g/l IM: 100 g/l IM: 340 g/l IM: 250 g/l
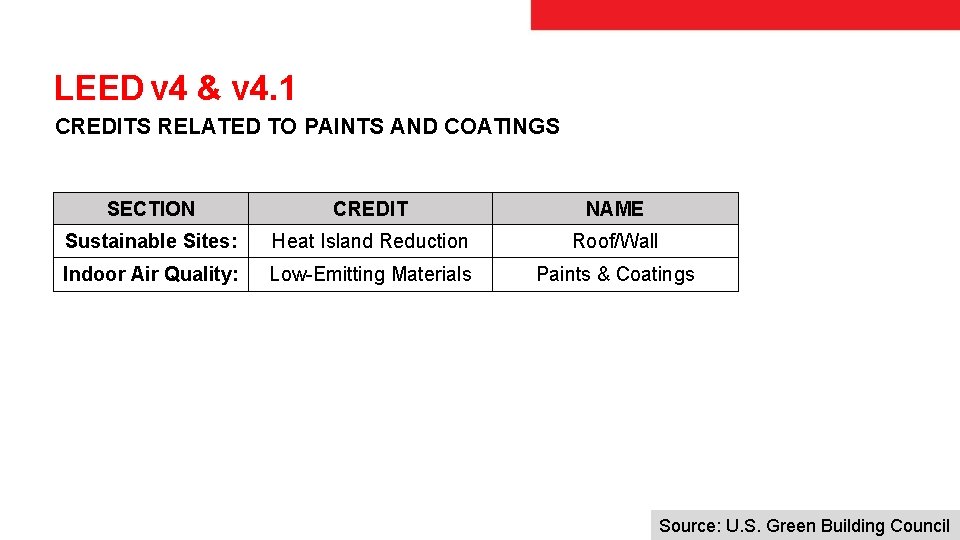
LEED v 4 & v 4. 1 CREDITS RELATED TO PAINTS AND COATINGS SECTION CREDIT NAME Sustainable Sites: Heat Island Reduction Roof/Wall Indoor Air Quality: Low-Emitting Materials Paints & Coatings Source: U. S. Green Building Council
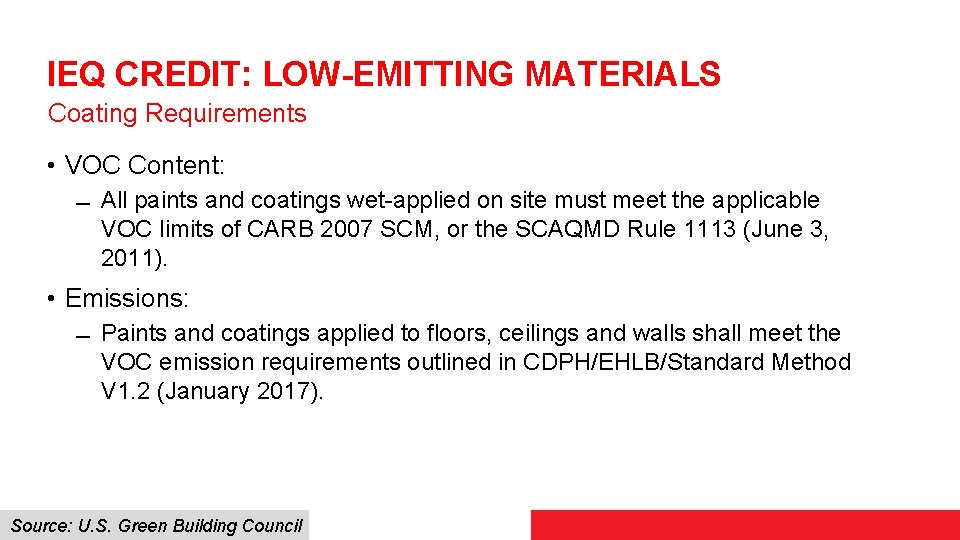
IEQ CREDIT: LOW-EMITTING MATERIALS Coating Requirements • VOC Content: All paints and coatings wet-applied on site must meet the applicable VOC limits of CARB 2007 SCM, or the SCAQMD Rule 1113 (June 3, 2011). • Emissions: Paints and coatings applied to floors, ceilings and walls shall meet the VOC emission requirements outlined in CDPH/EHLB/Standard Method V 1. 2 (January 2017). Source: U. S. Green Building Council
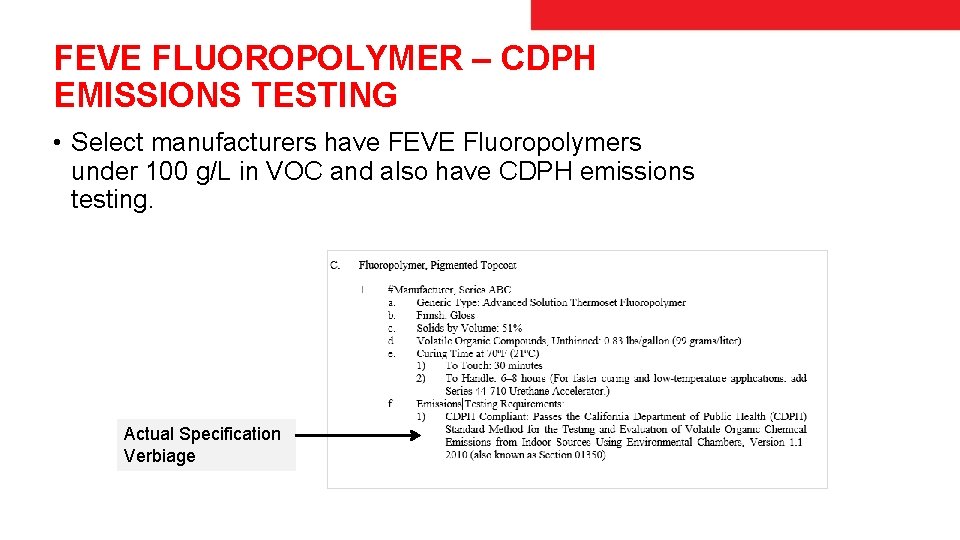
FEVE FLUOROPOLYMER – CDPH EMISSIONS TESTING • Select manufacturers have FEVE Fluoropolymers under 100 g/L in VOC and also have CDPH emissions testing. Actual Specification Verbiage
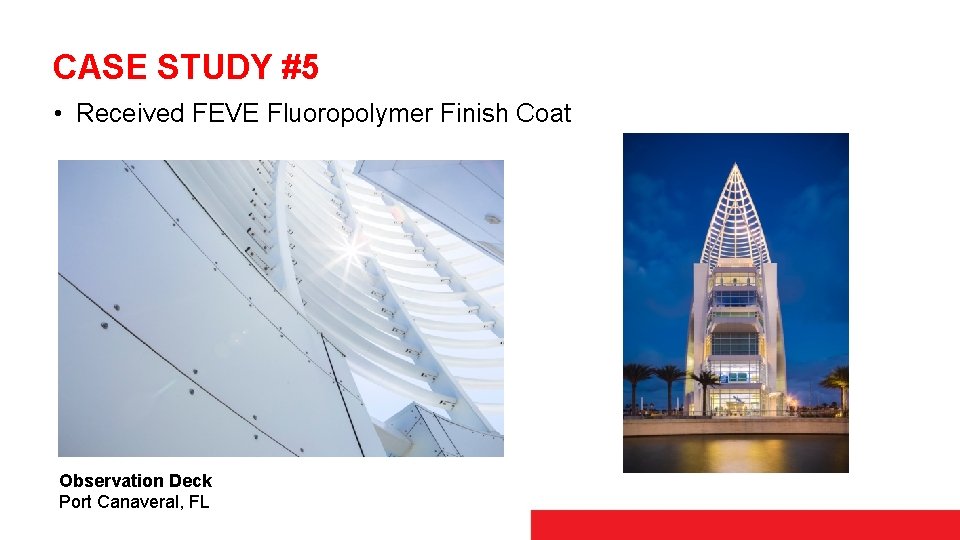
CASE STUDY #5 • Received FEVE Fluoropolymer Finish Coat Observation Deck Port Canaveral, FL
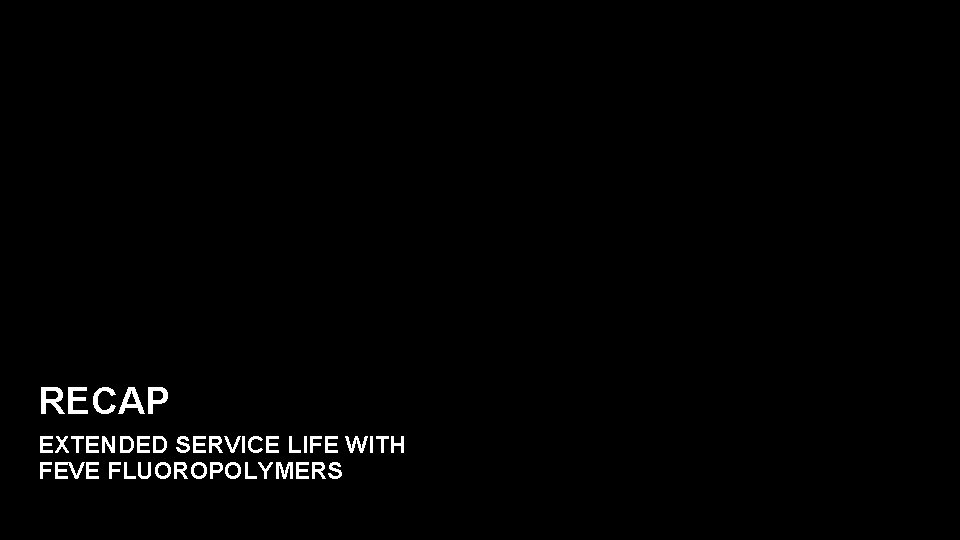
RECAP EXTENDED SERVICE LIFE WITH FEVE FLUOROPOLYMERS
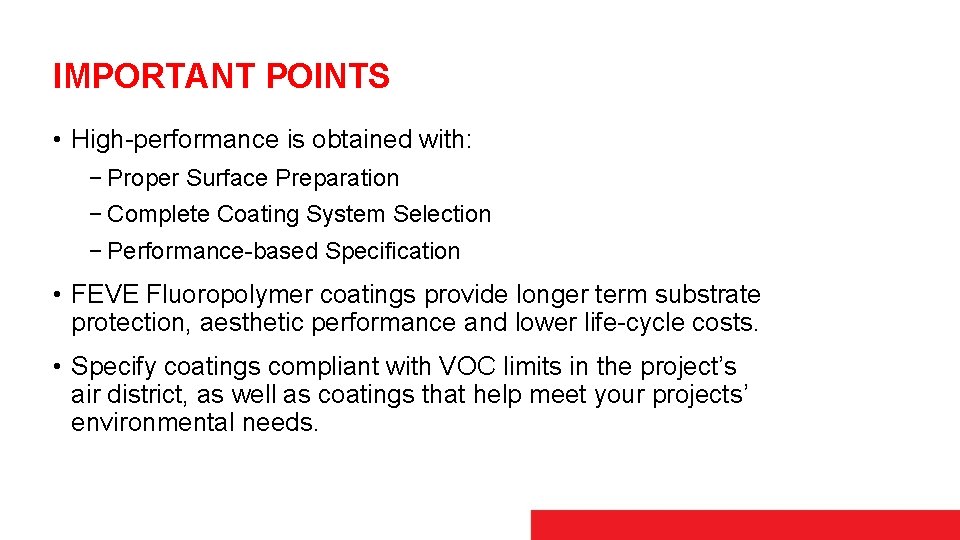
IMPORTANT POINTS • High-performance is obtained with: − Proper Surface Preparation − Complete Coating System Selection − Performance-based Specification • FEVE Fluoropolymer coatings provide longer term substrate protection, aesthetic performance and lower life-cycle costs. • Specify coatings compliant with VOC limits in the project’s air district, as well as coatings that help meet your projects’ environmental needs.
Feve resin
Feve resin
Upper specification limit and lower specification limit
Natural variations operations management
Minimum navigation performance specification
What is banner headline in newspaper
Presenter title
Jekyll and hyde quotes about setting
Romeo and juilet themes
Identify a key term used in both passages
Name of the presenter
How is power presented in ozymandias
Jerome bruner cognitive theory
Hyde as an outsider
Talisman presented
Topic, main idea and supporting details examples
How is the power of nature presented in the prelude
Technological design steps
Bob cratchit quotes
Text
What type of conics is presented in a tilted glass of water
My last duchess and ozymandias
Prism is presented with
Examples of cause and effect text structure
Introduction to drafting
How are the events in the text presented
Proudly presented to
Macbeth act 5 scene 5 she should have died hereafter
Macbeth act 1 scene 5 quotes
How are disposals of plant assets accounted for
As presented below
Identify the following polygons
Nnn1996
Edexcel igcse english language young and dyslexic
Presented sy
The kitchen presented by
Professionally presented
Family feud presented by
When a melodic idea is used as a building block
How it's made presented by
Plant assets natural resources and intangible assets
Hình ảnh bộ gõ cơ thể búng tay
Lp html
Bổ thể
Tỉ lệ cơ thể trẻ em
Voi kéo gỗ như thế nào
Chụp tư thế worms-breton
Bài hát chúa yêu trần thế alleluia
Môn thể thao bắt đầu bằng chữ đua
Thế nào là hệ số cao nhất
Các châu lục và đại dương trên thế giới
Cong thức tính động năng
Trời xanh đây là của chúng ta thể thơ
Mật thư tọa độ 5x5
Làm thế nào để 102-1=99
Phản ứng thế ankan
Các châu lục và đại dương trên thế giới
Thơ thất ngôn tứ tuyệt đường luật
Quá trình desamine hóa có thể tạo ra
Một số thể thơ truyền thống
Cái miệng nó xinh thế
Vẽ hình chiếu vuông góc của vật thể sau
Thế nào là sự mỏi cơ
đặc điểm cơ thể của người tối cổ
Thế nào là giọng cùng tên? *
Vẽ hình chiếu đứng bằng cạnh của vật thể
Fecboak