Surface Energy and Surface Cleaning 1 Thermodynamics of
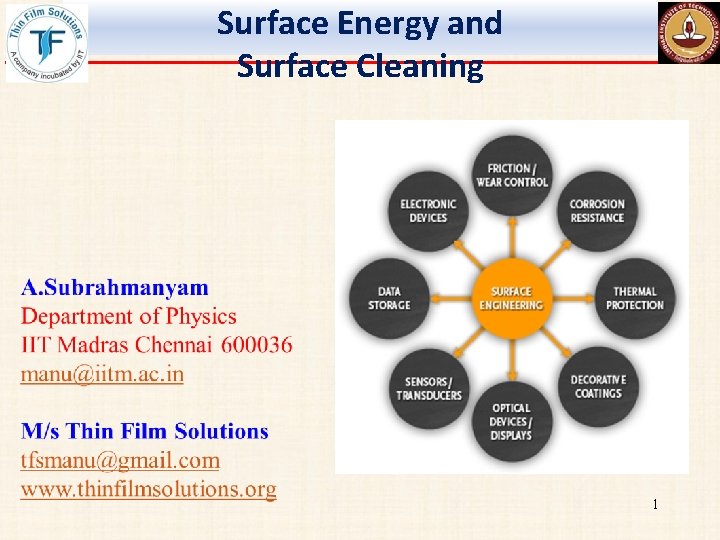
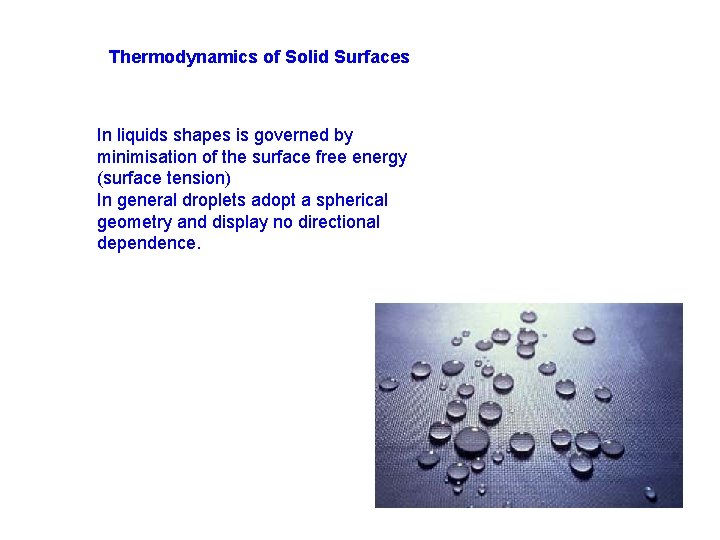
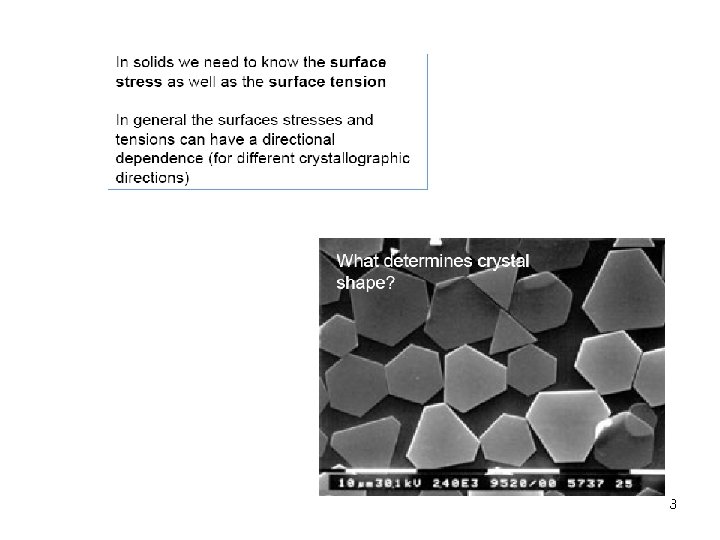
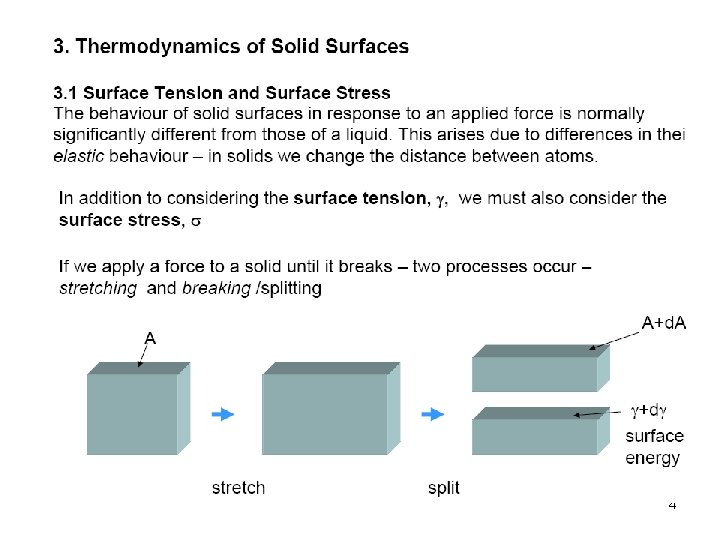
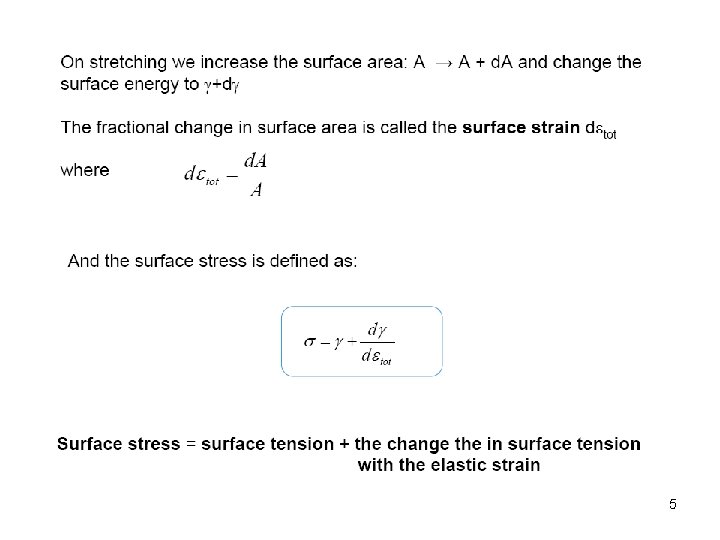
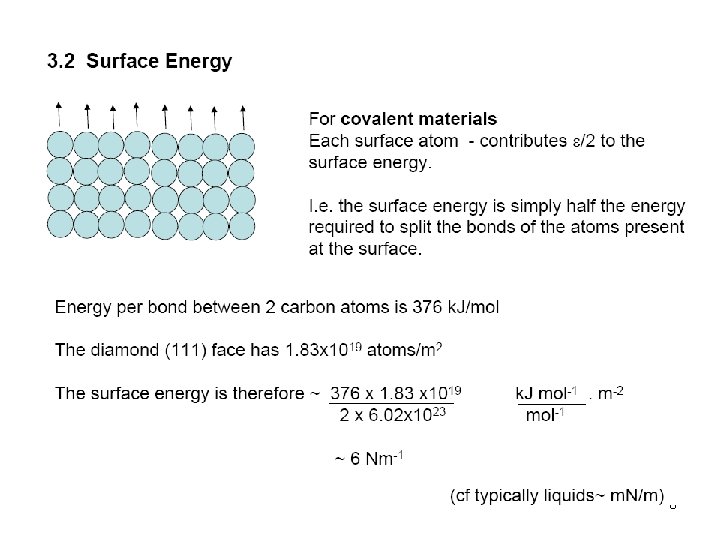
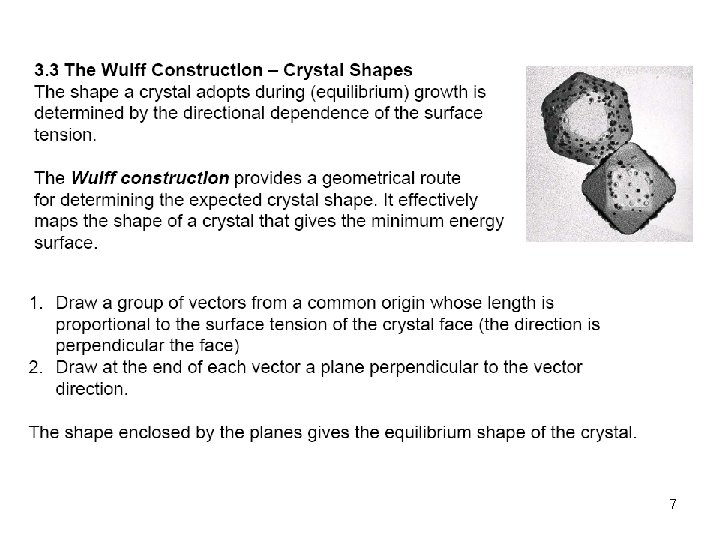
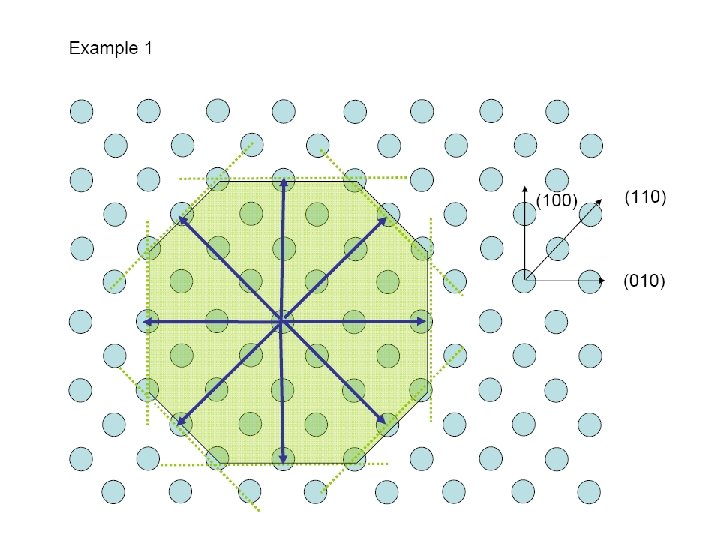
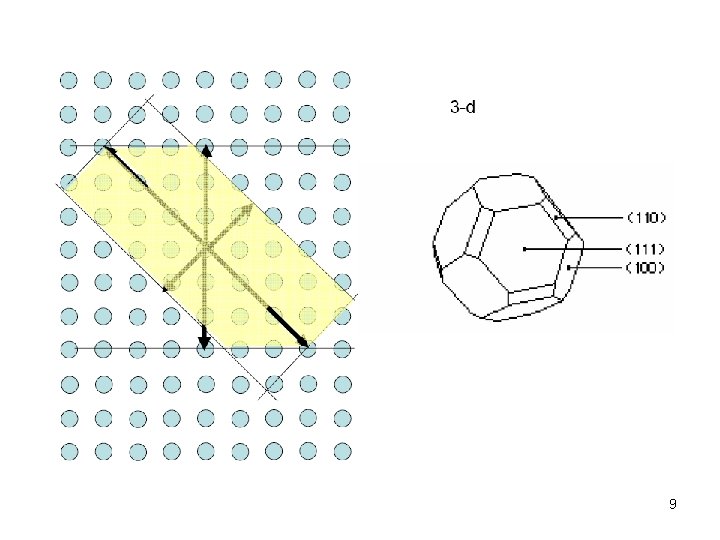
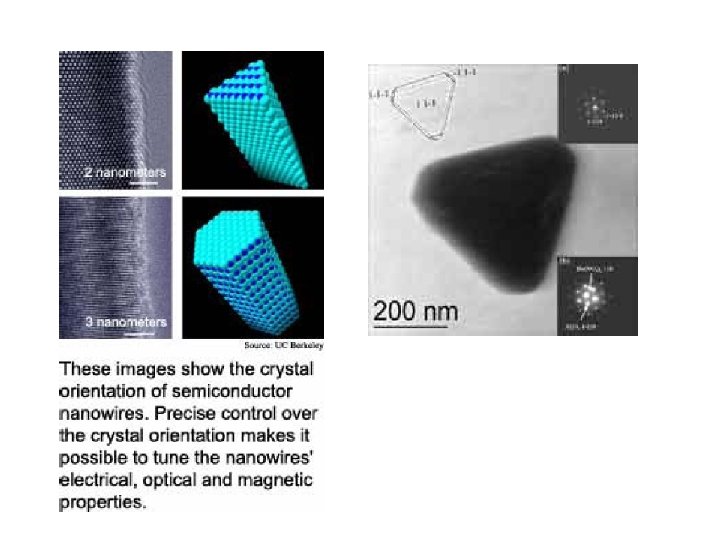
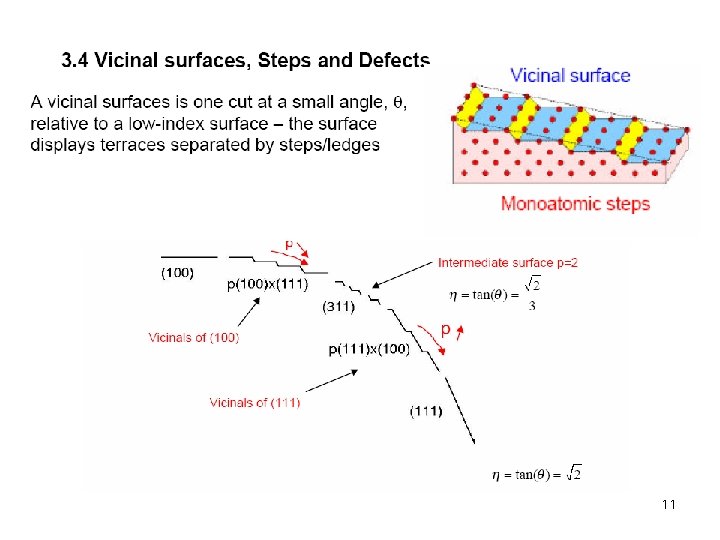
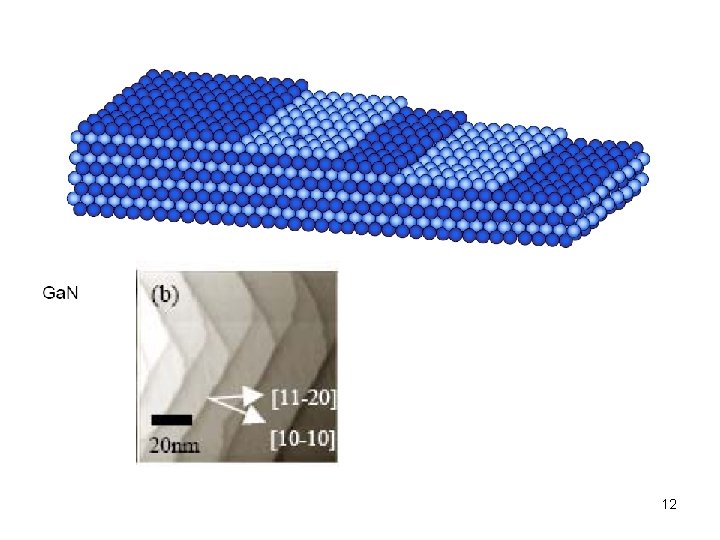
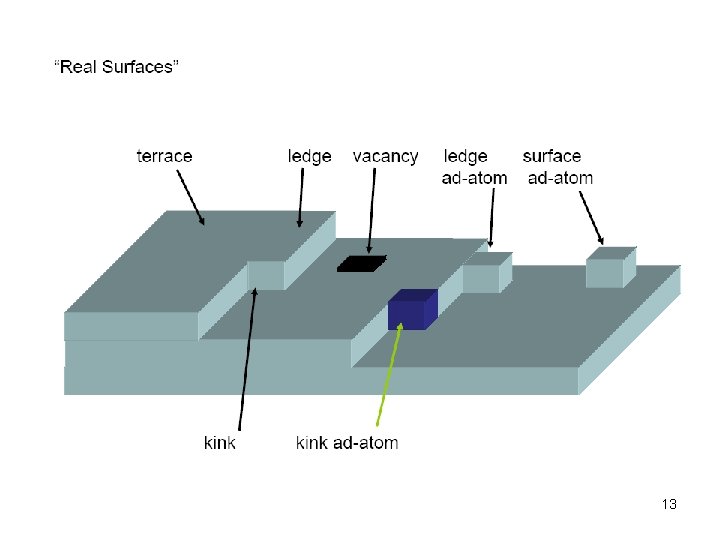
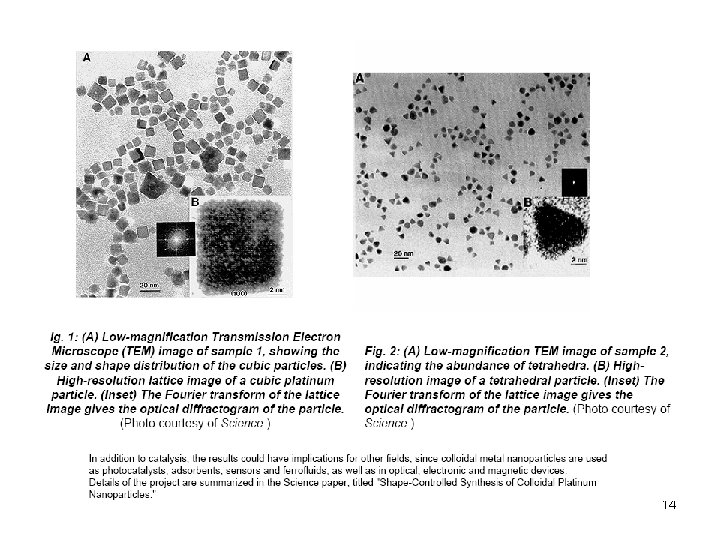
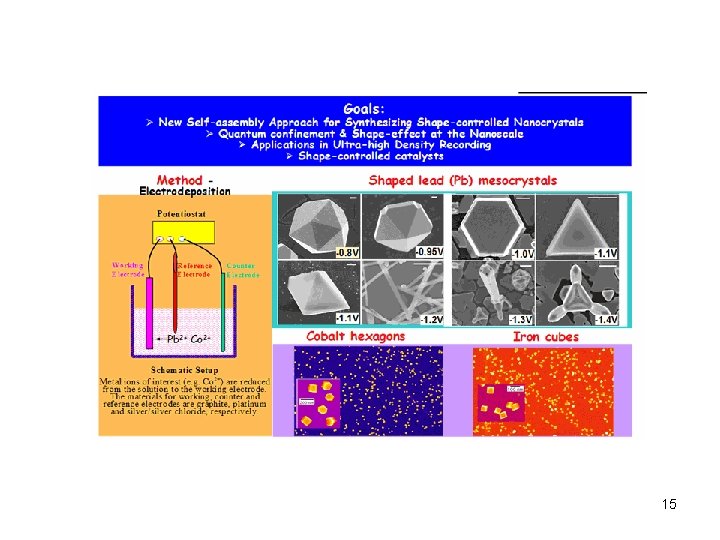
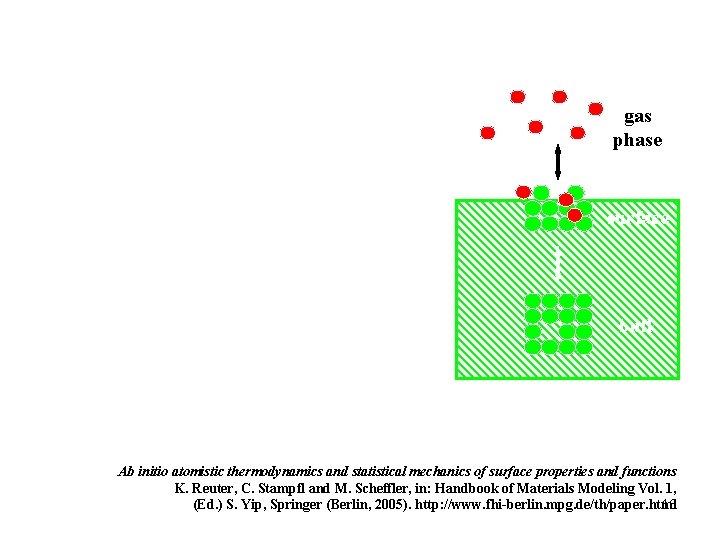
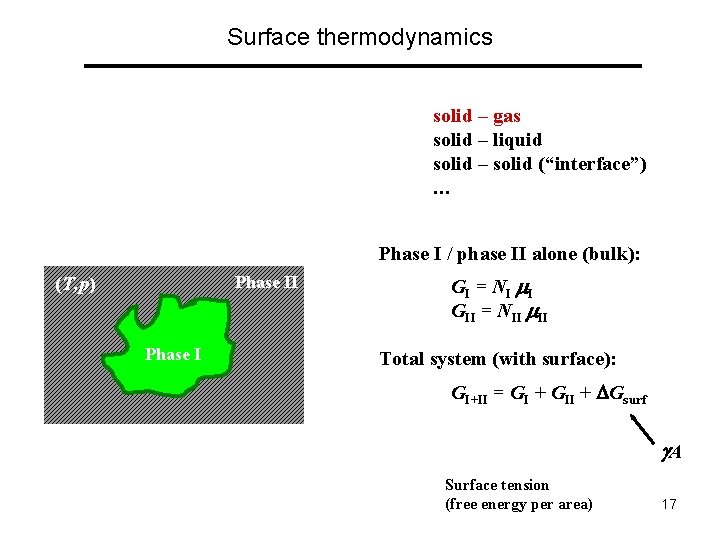
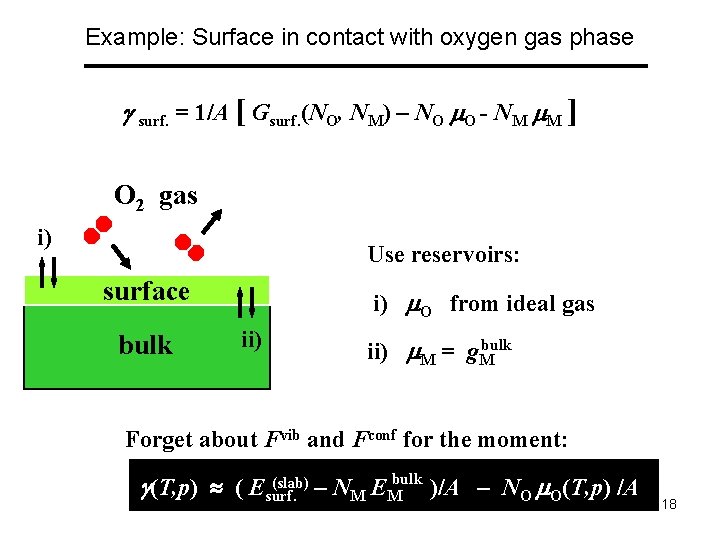
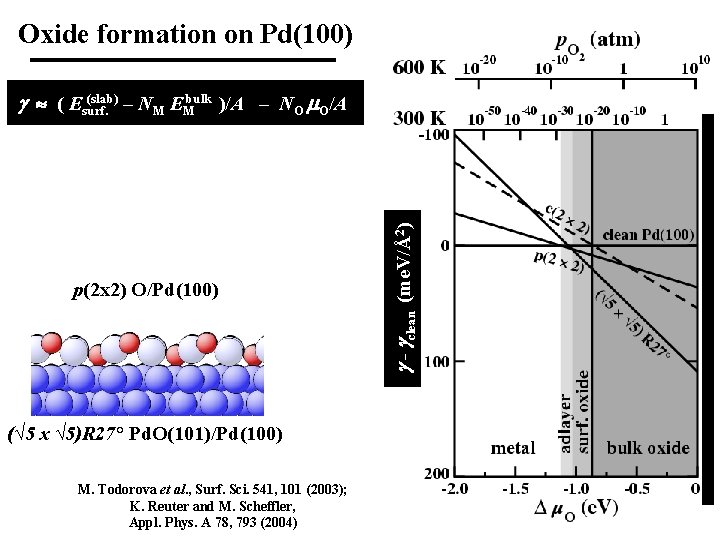
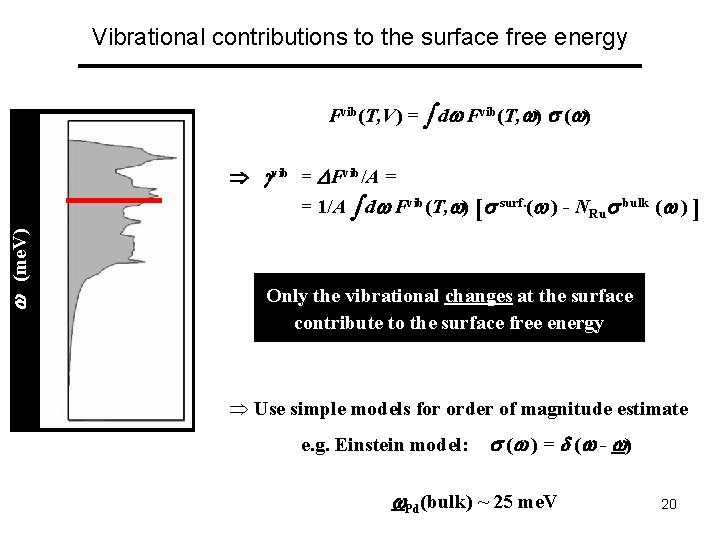
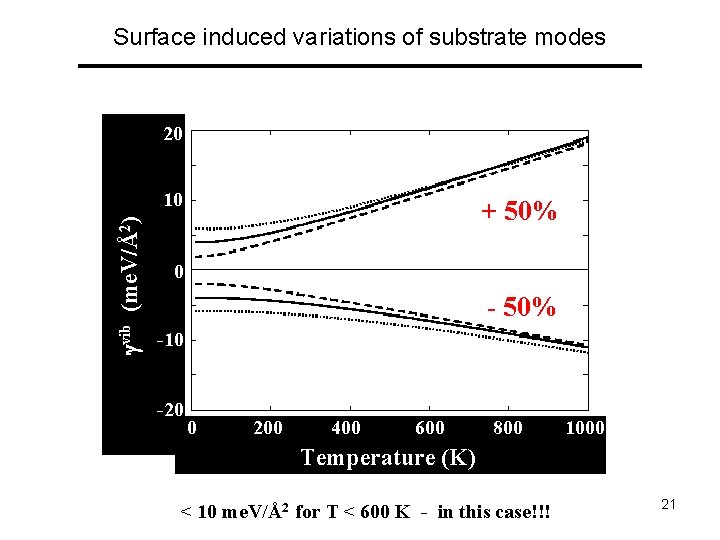
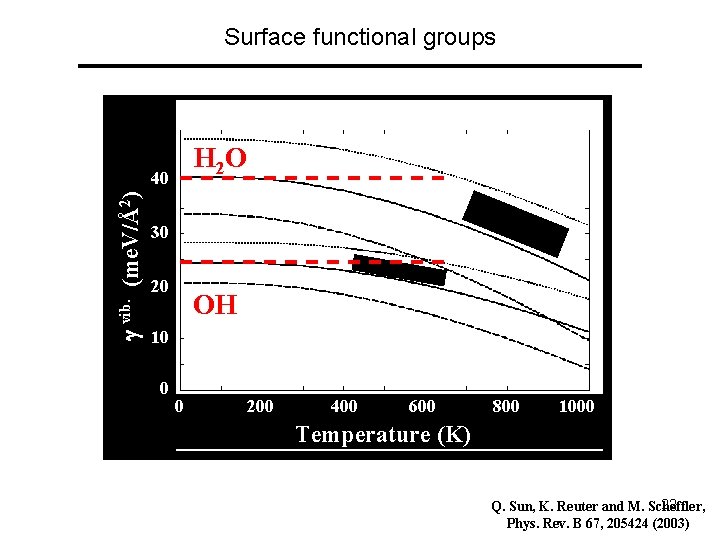
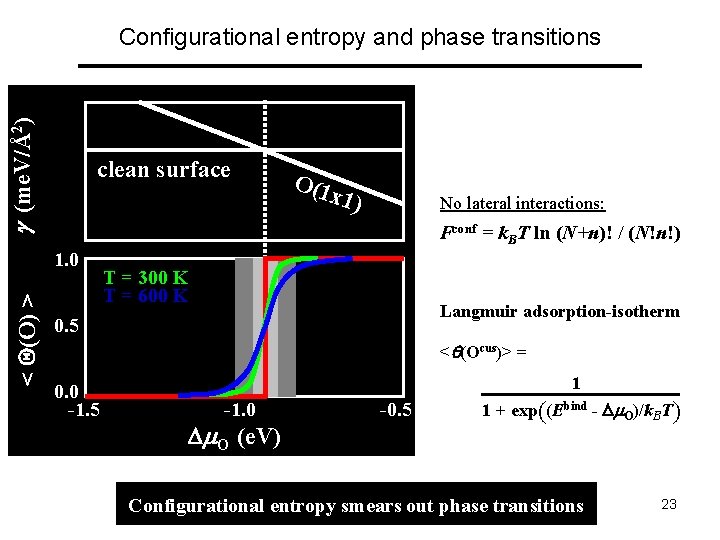
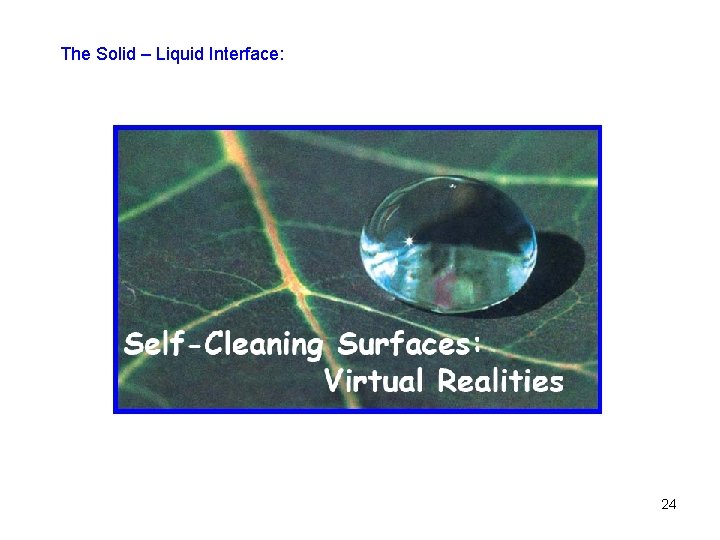
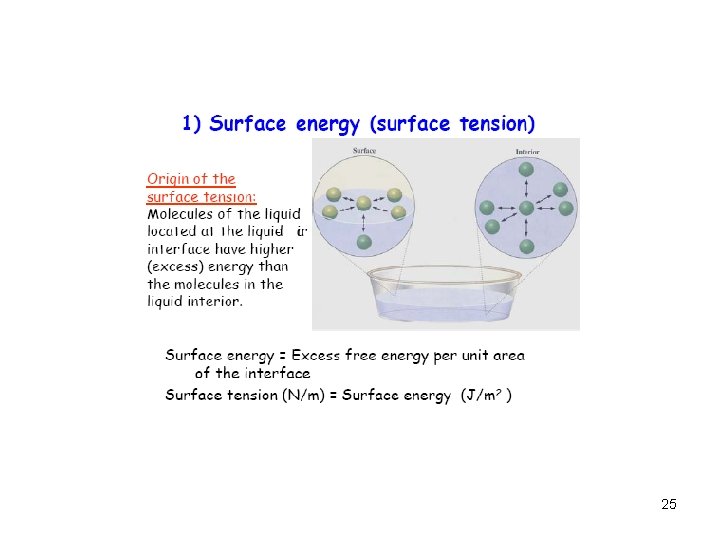
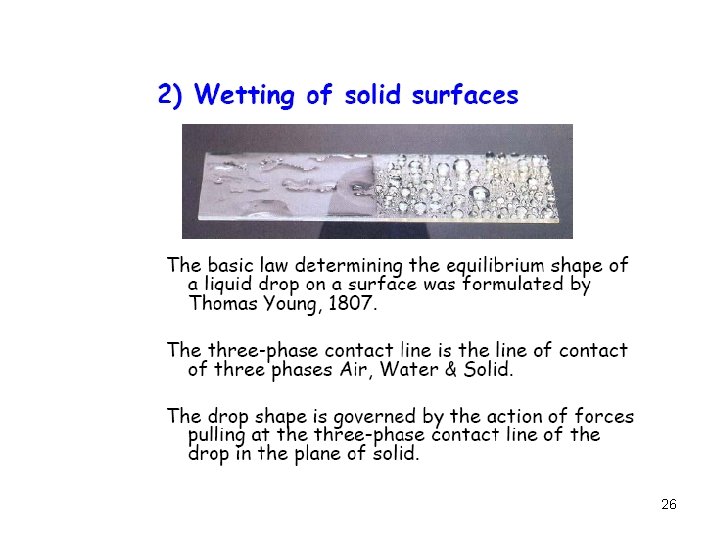
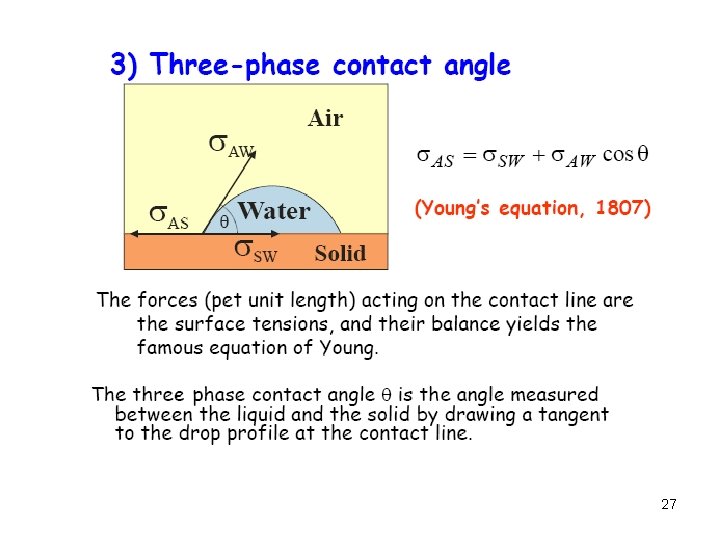
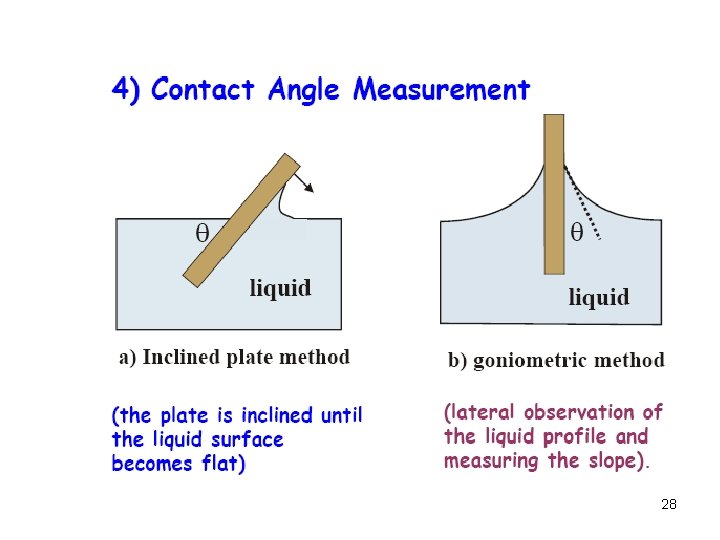
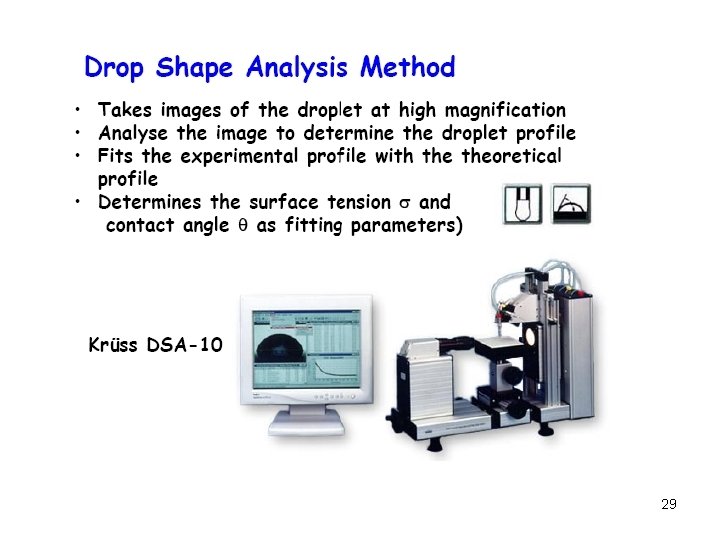
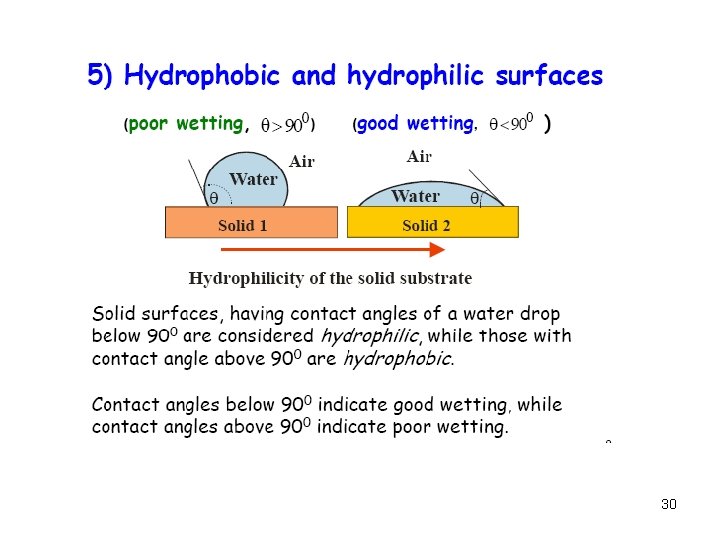
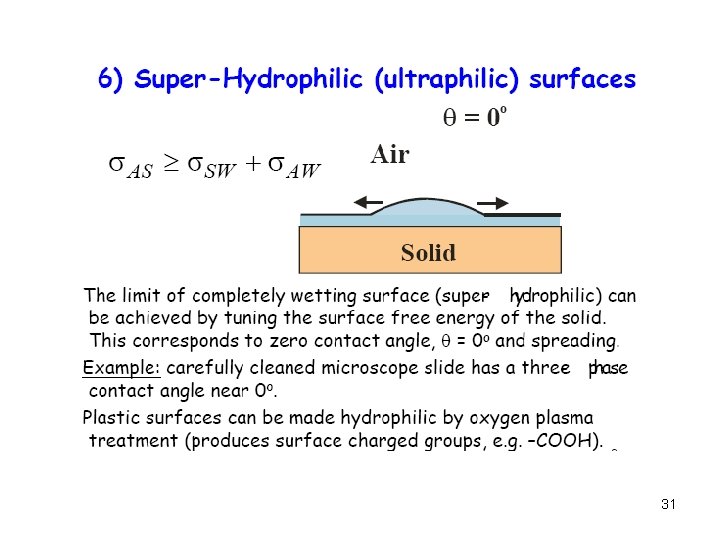
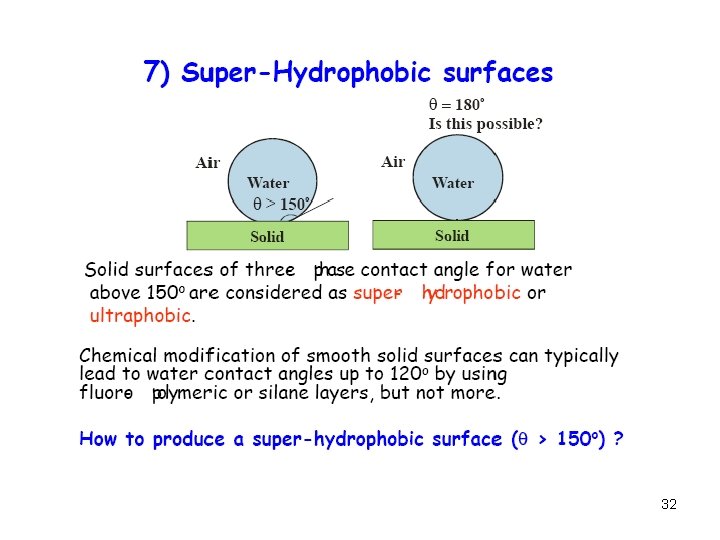
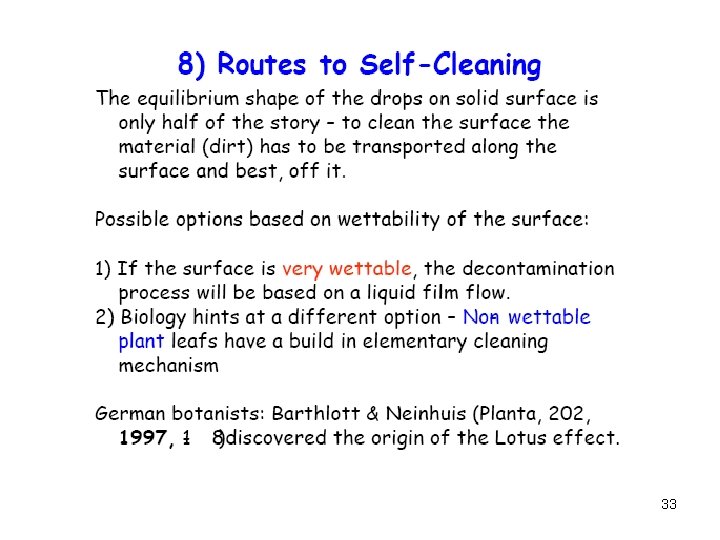
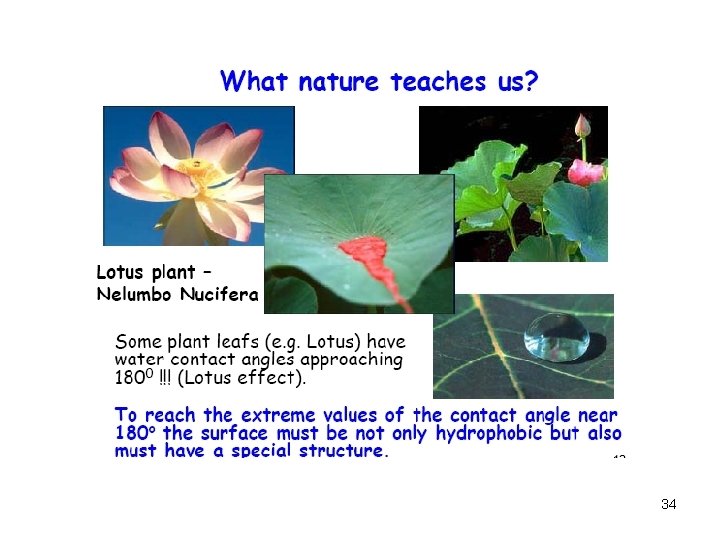
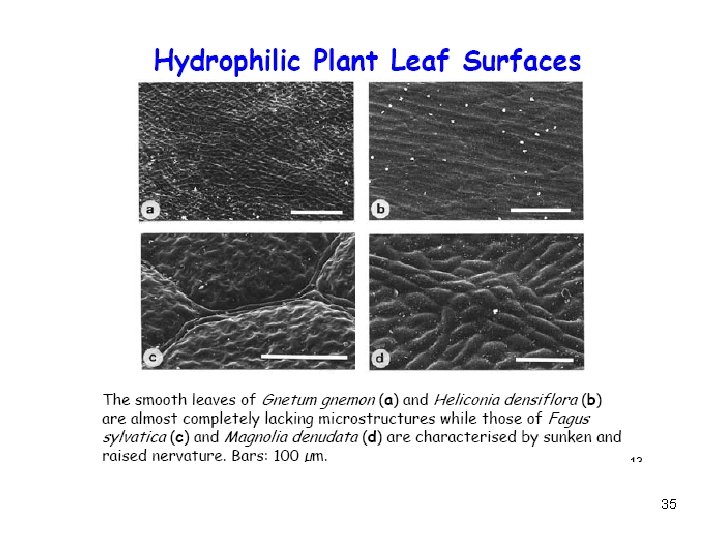
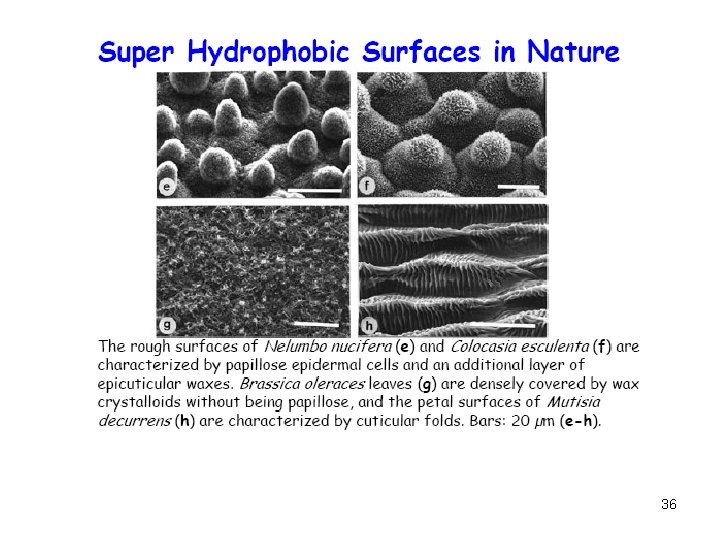
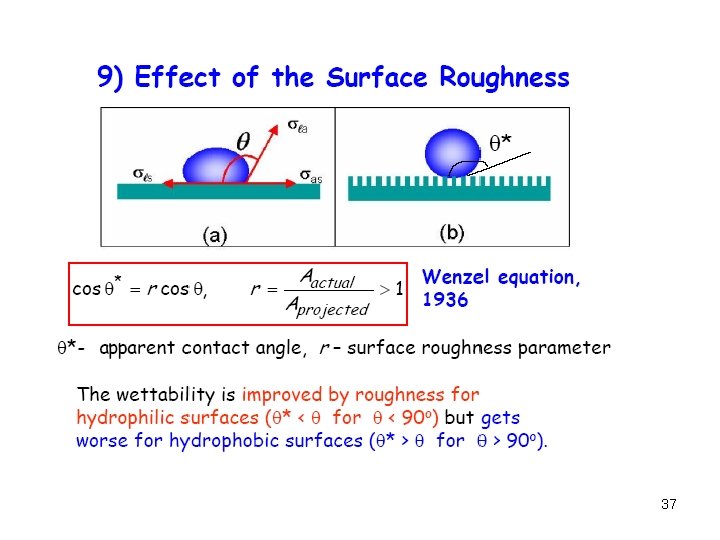
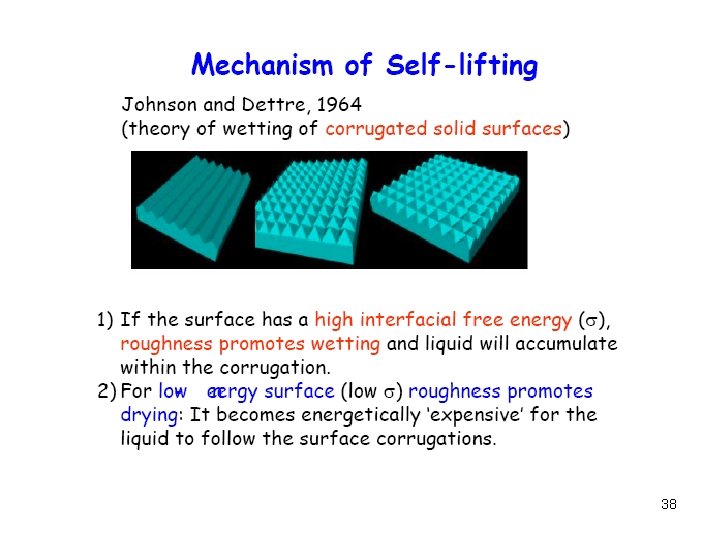
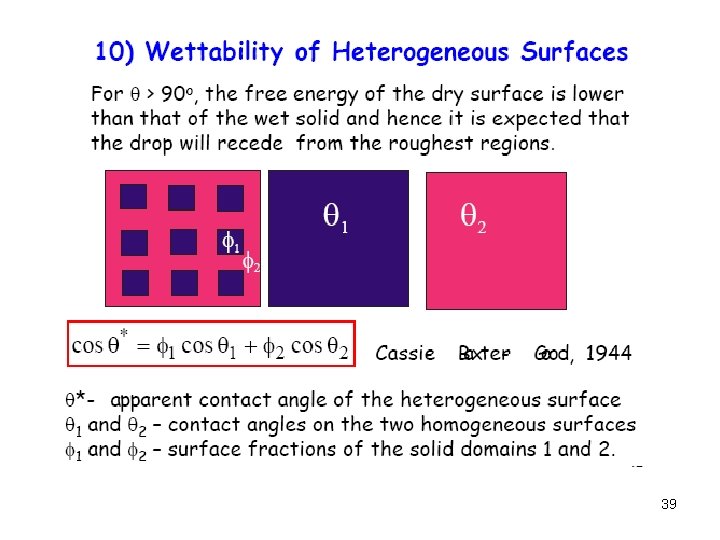
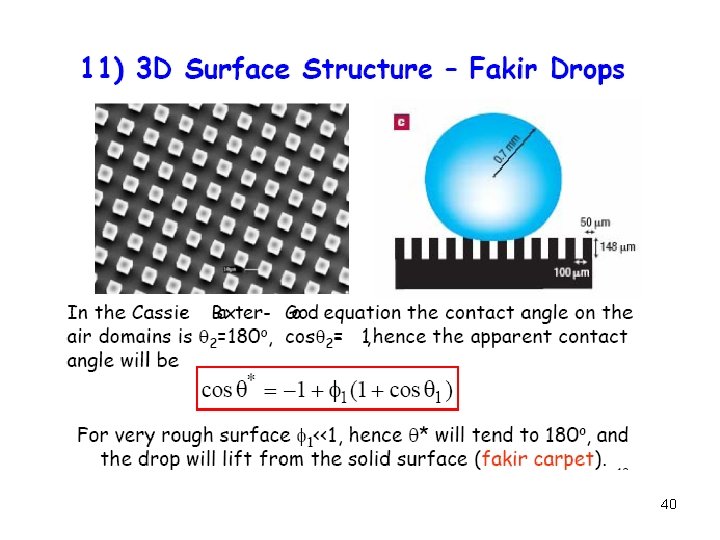
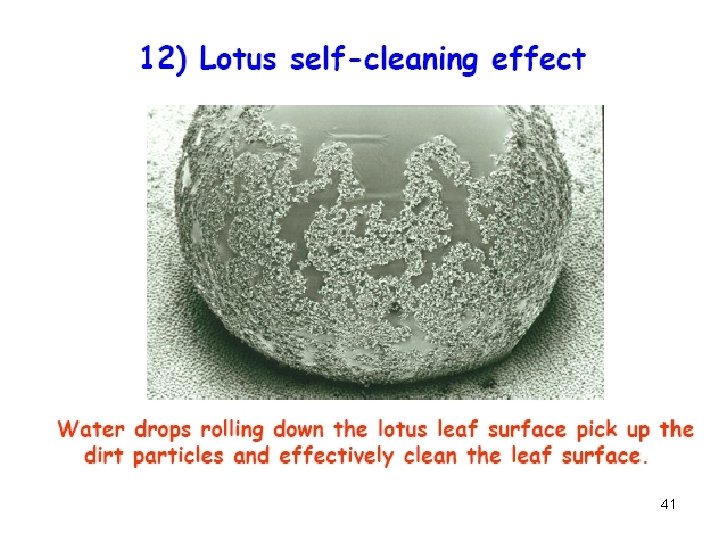
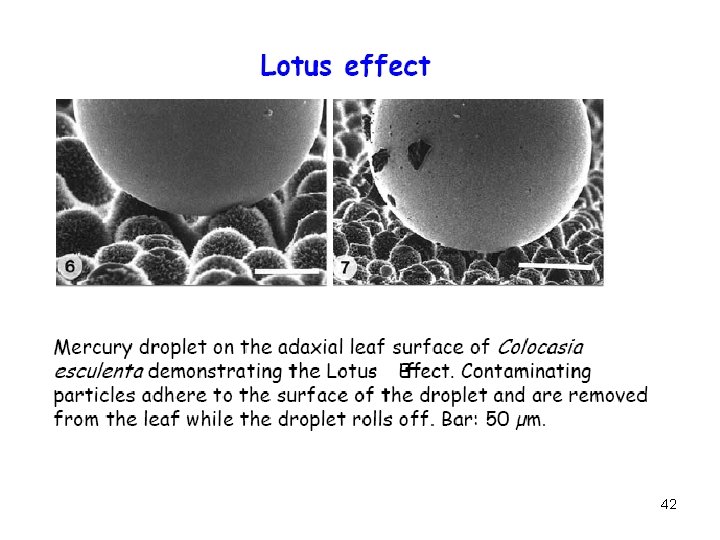
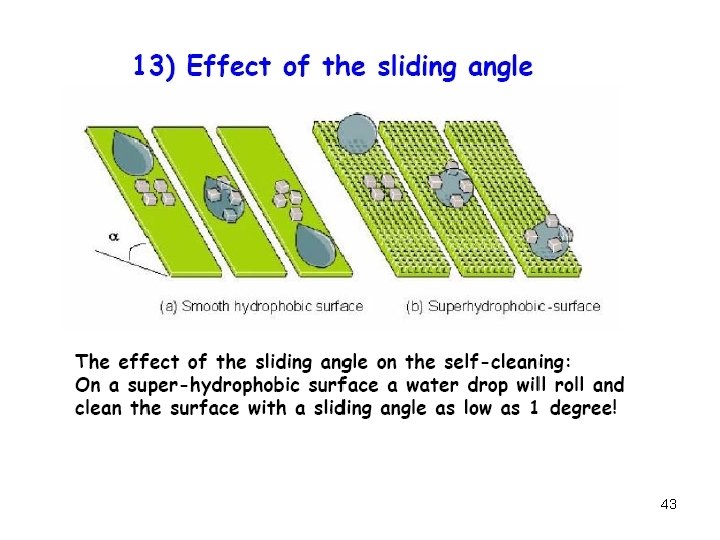
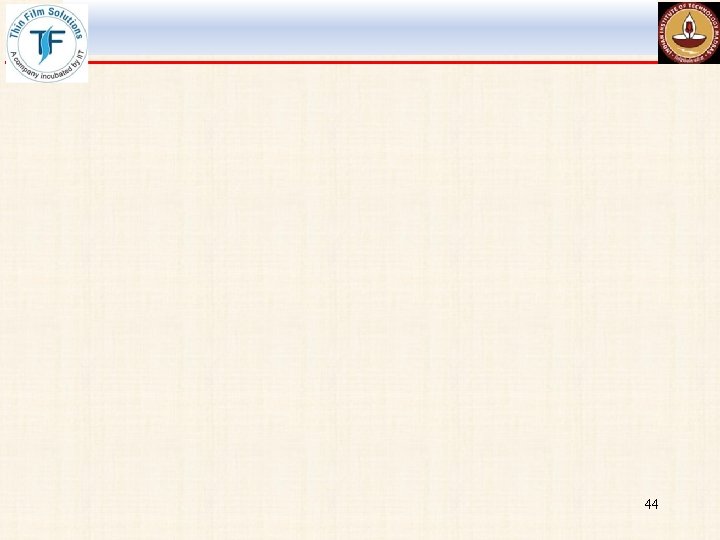
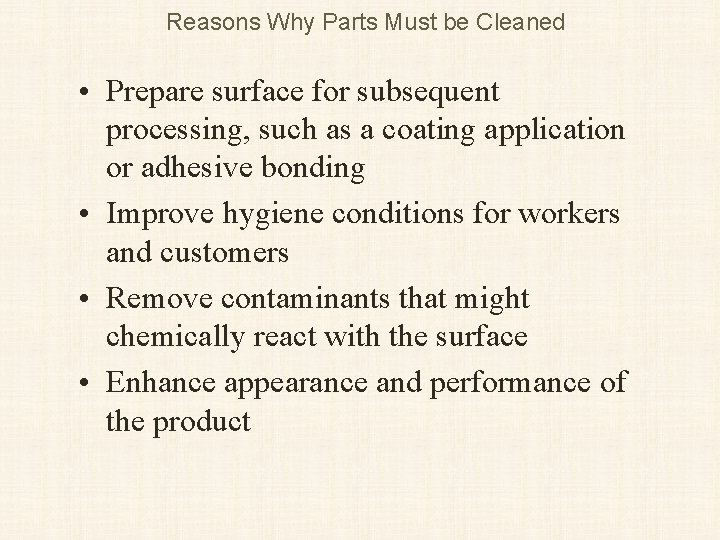
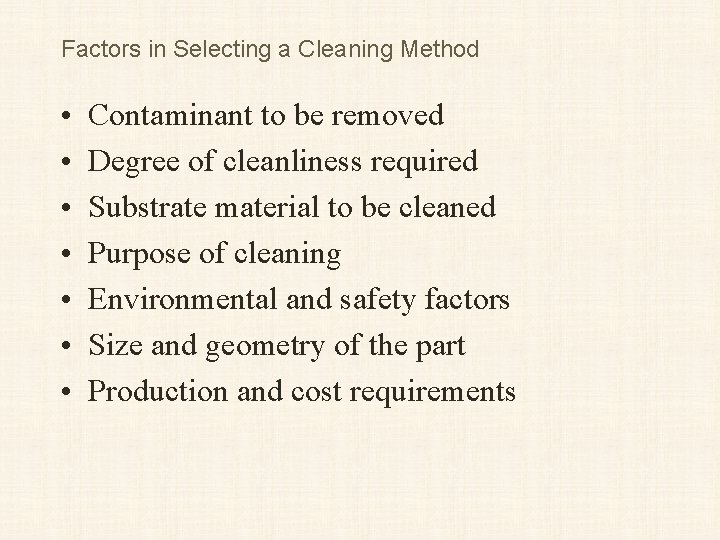
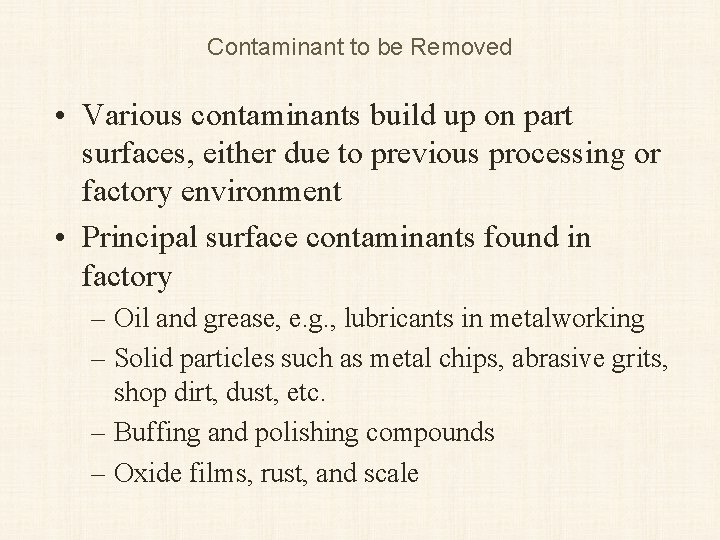
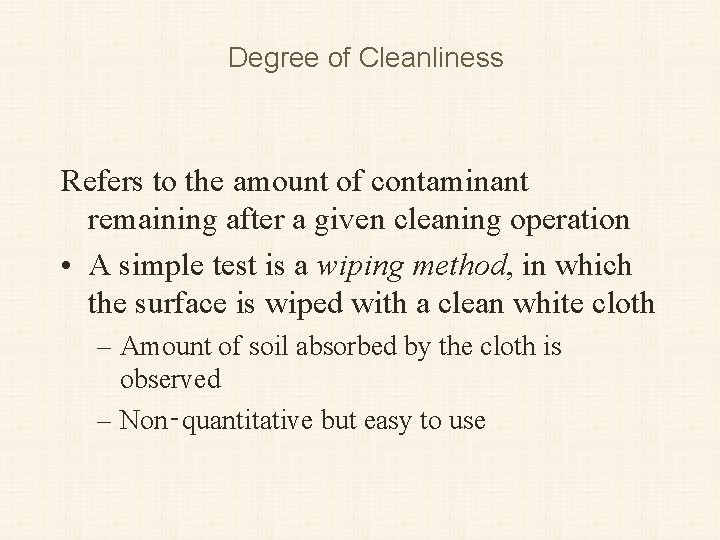
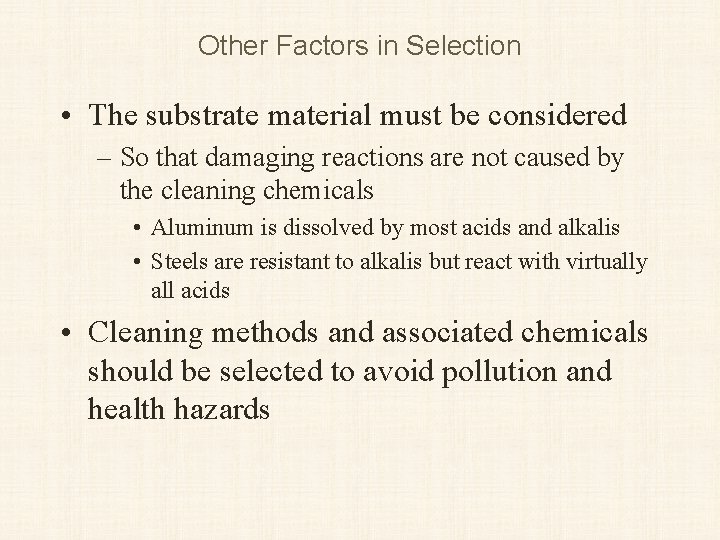
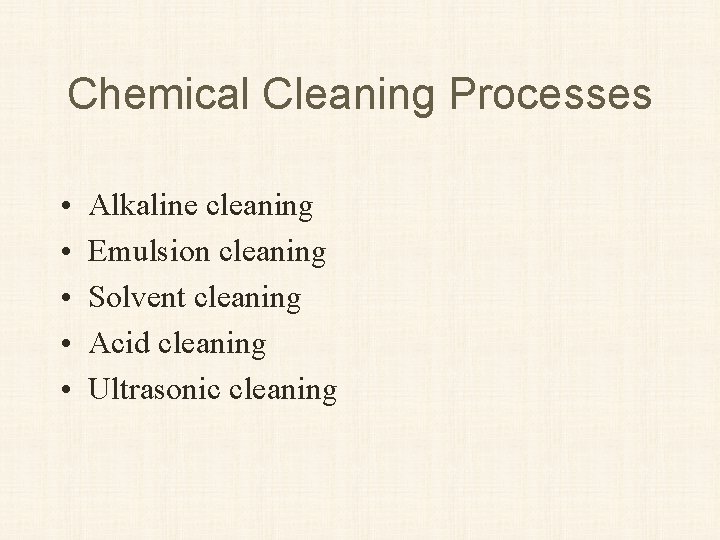
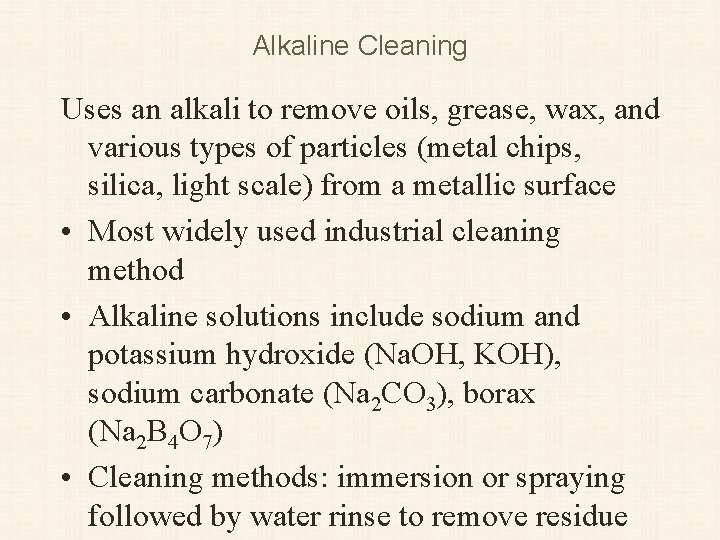
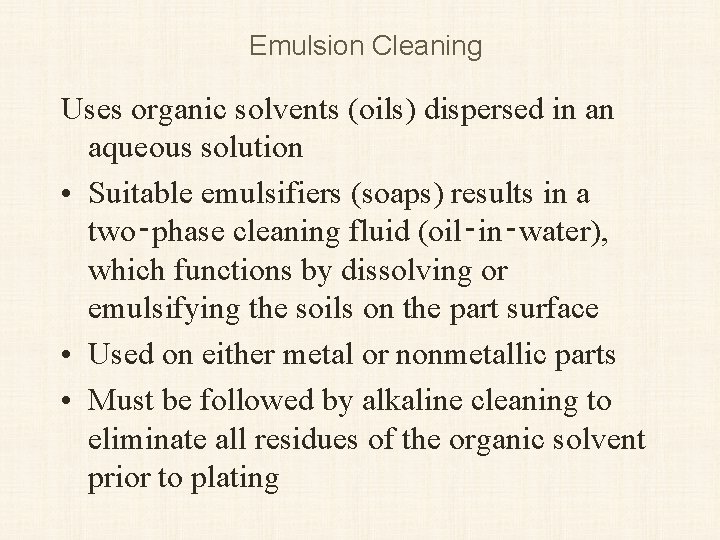
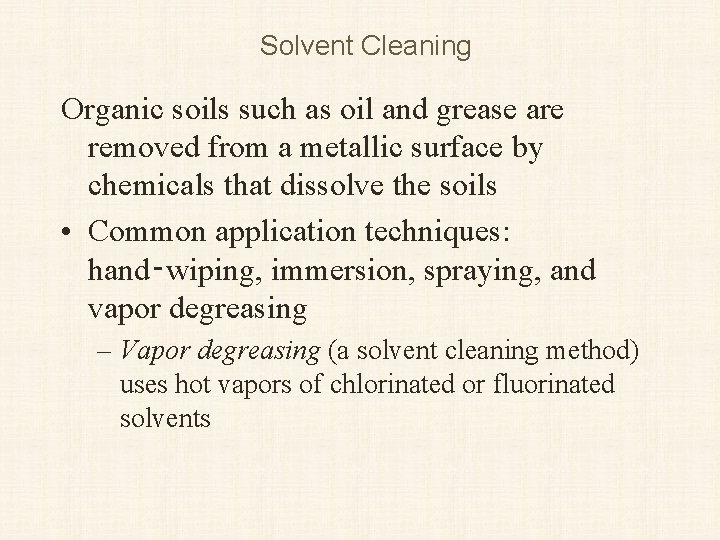
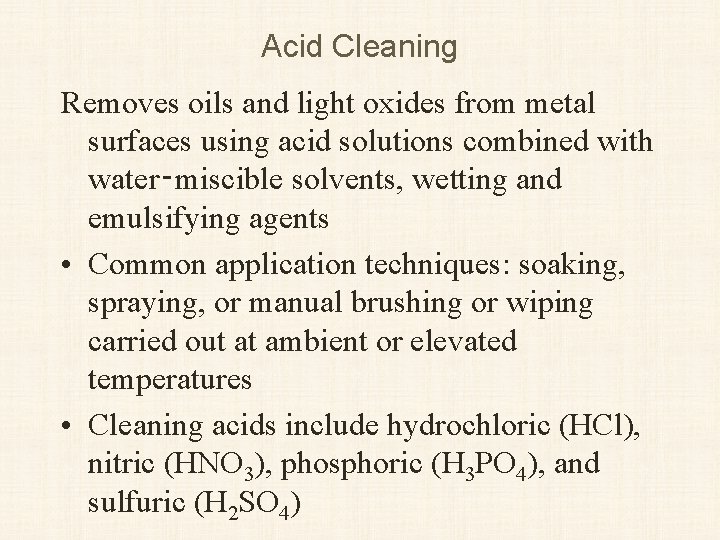
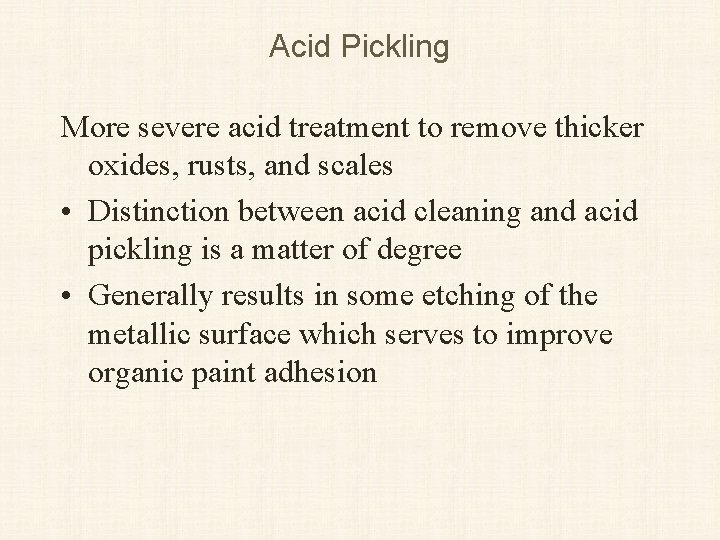
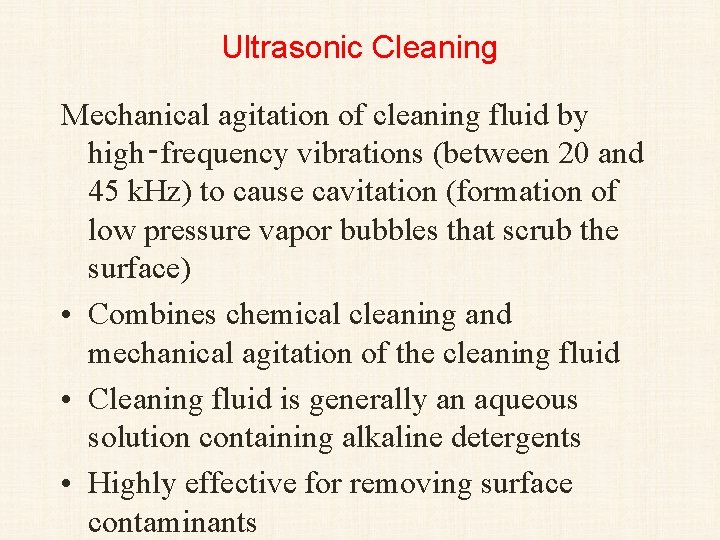
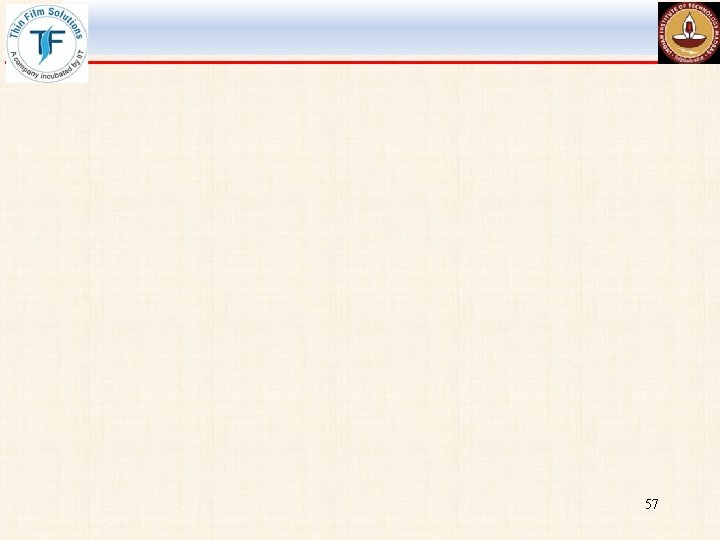
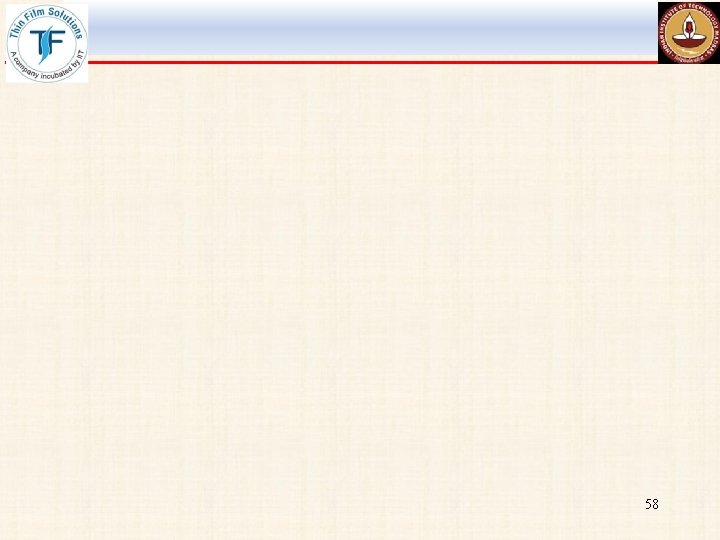
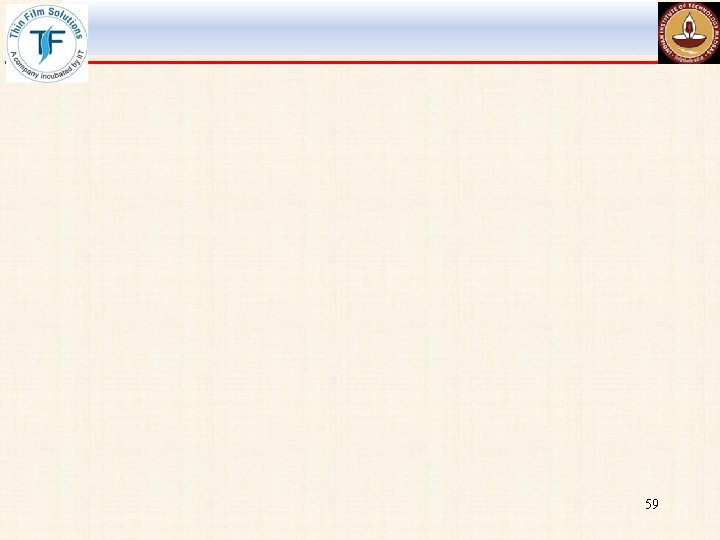
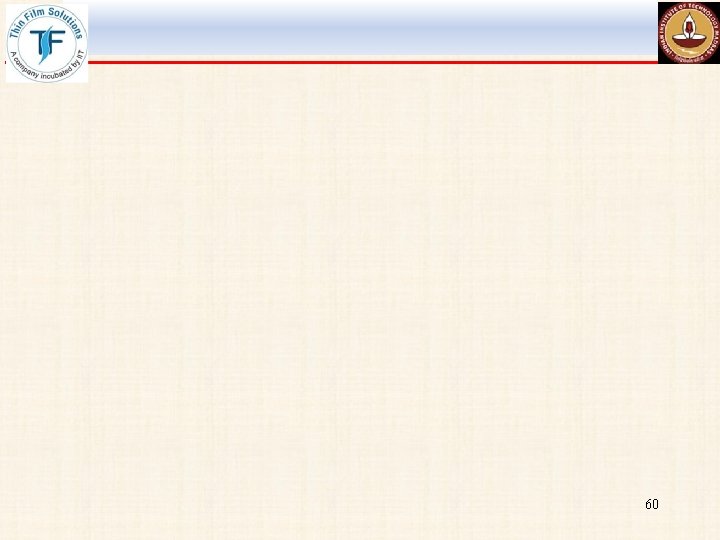
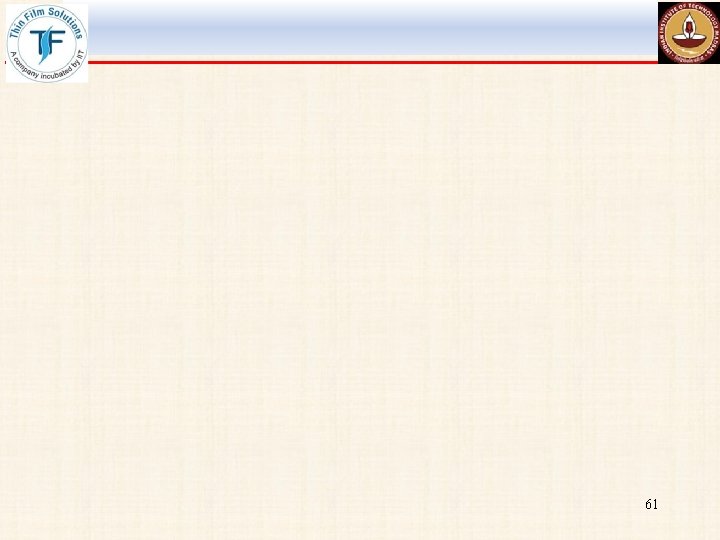
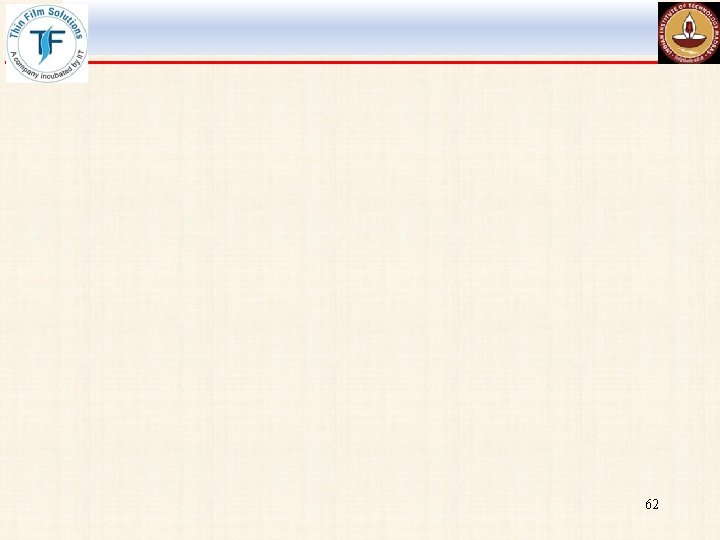
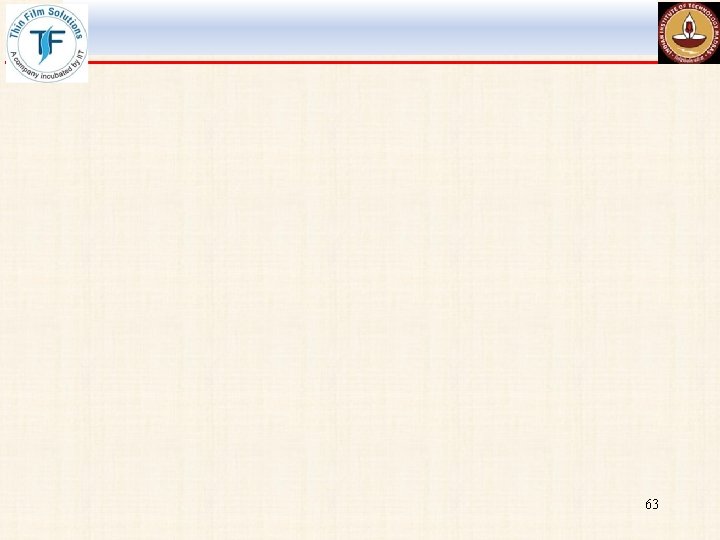
- Slides: 63
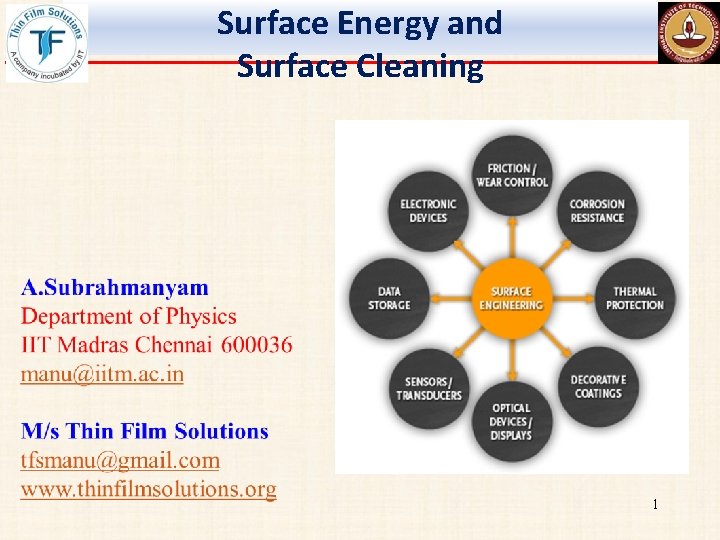
Surface Energy and Surface Cleaning 1
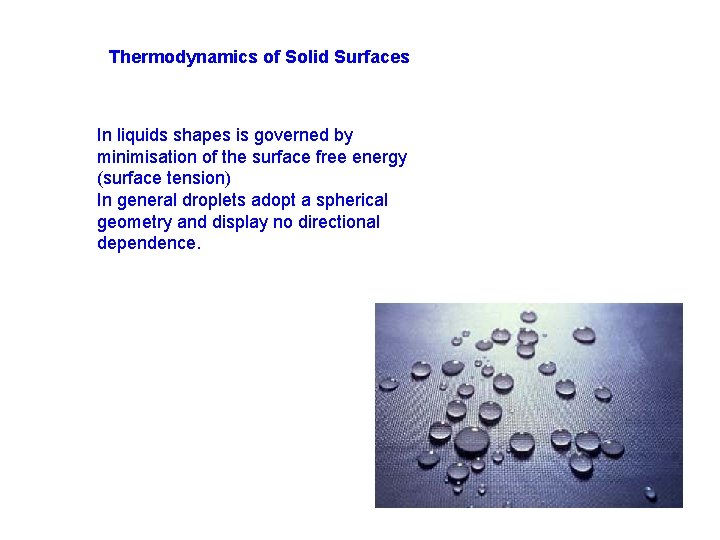
Thermodynamics of Solid Surfaces In liquids shapes is governed by minimisation of the surface free energy (surface tension) In general droplets adopt a spherical geometry and display no directional dependence. 2
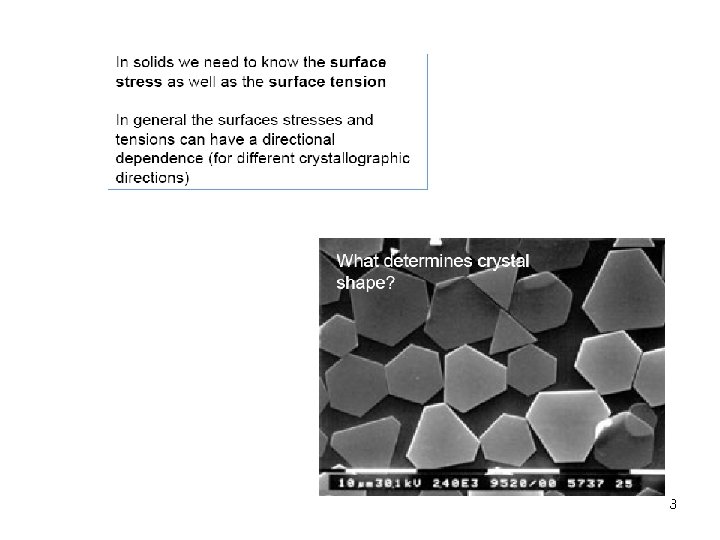
3
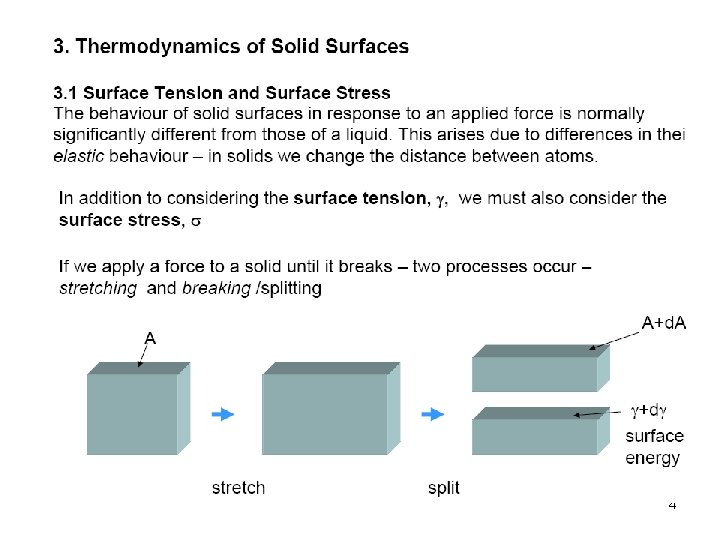
4
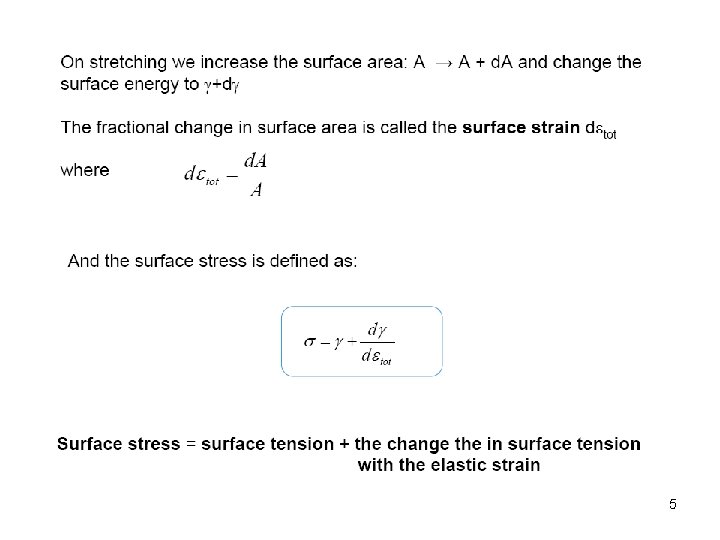
5
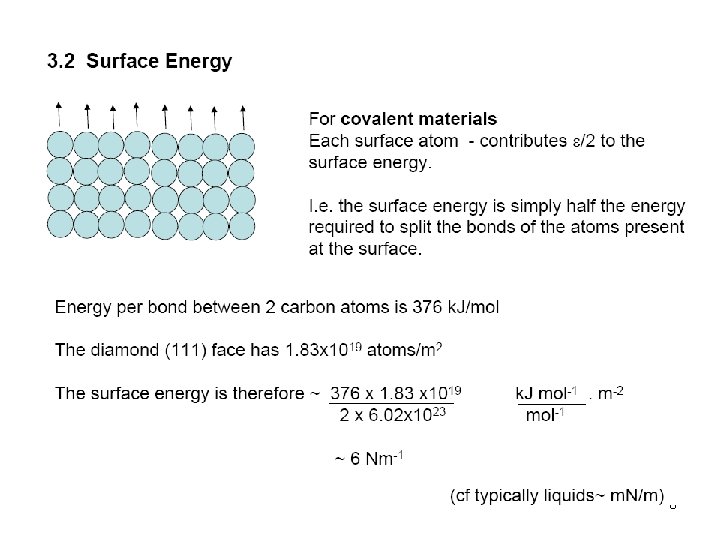
6
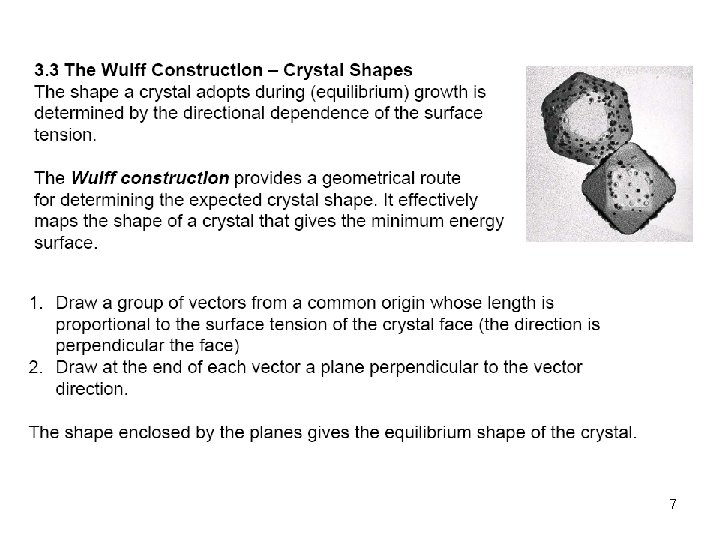
7
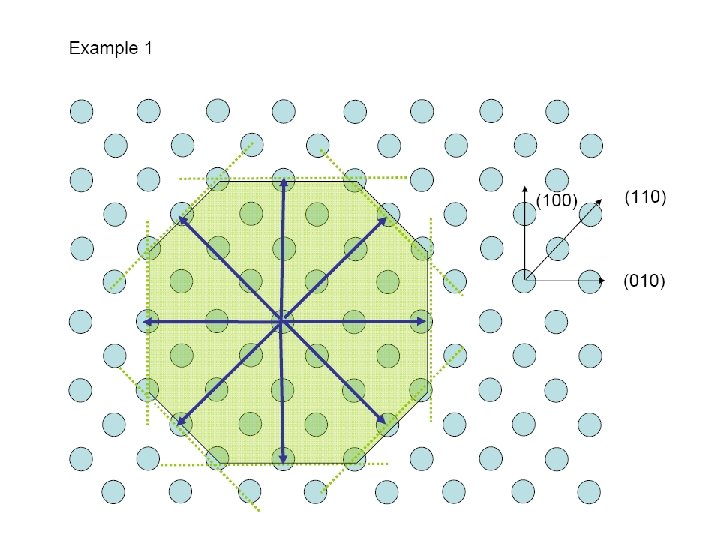
8
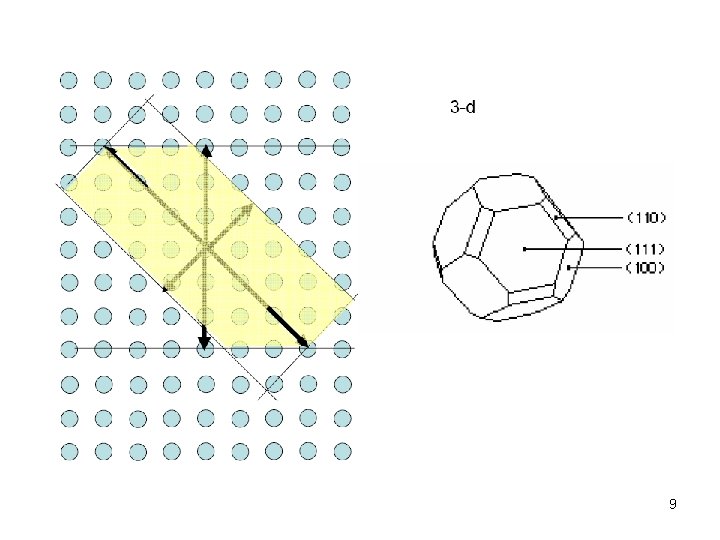
9
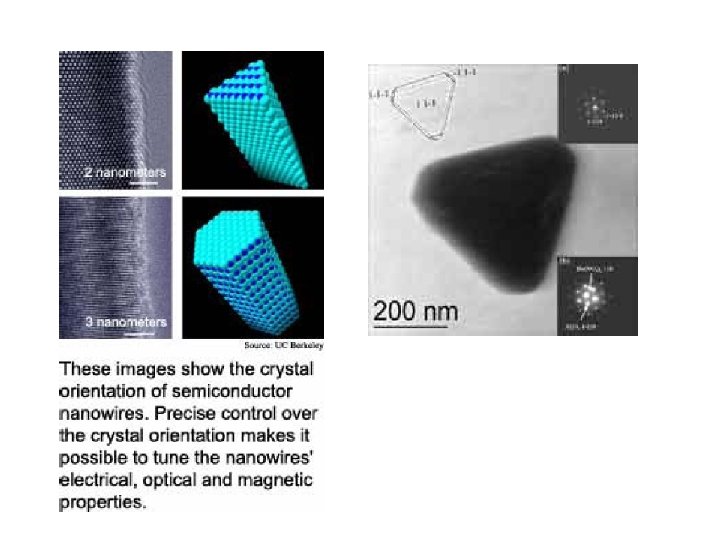
10
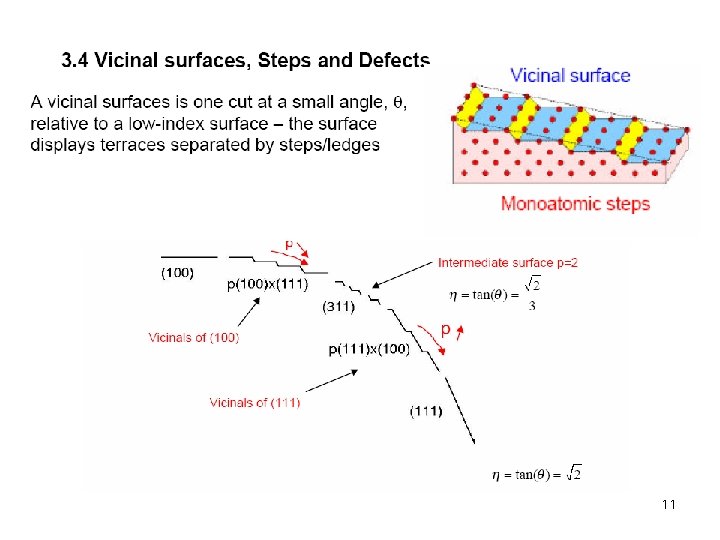
11
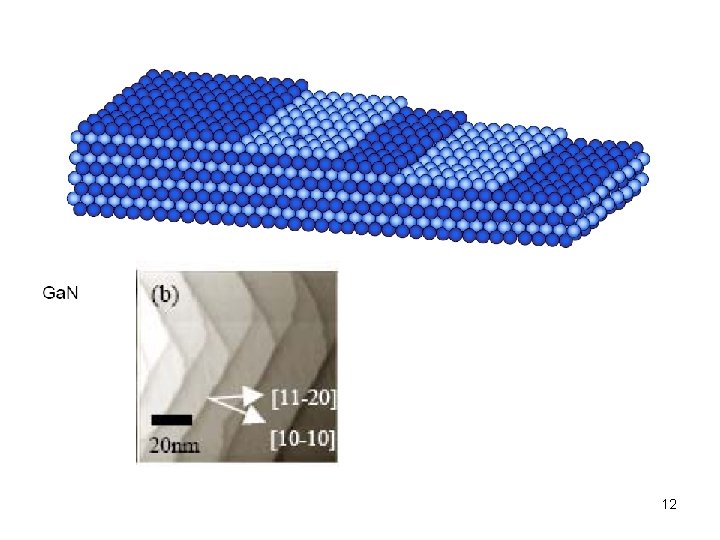
12
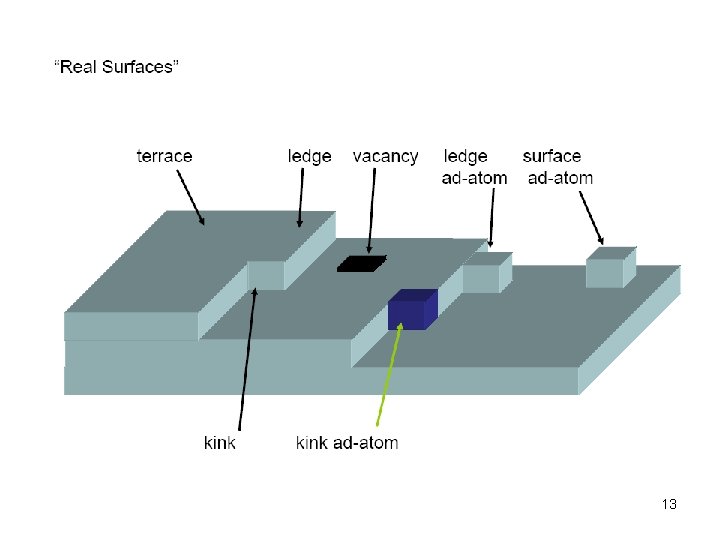
13
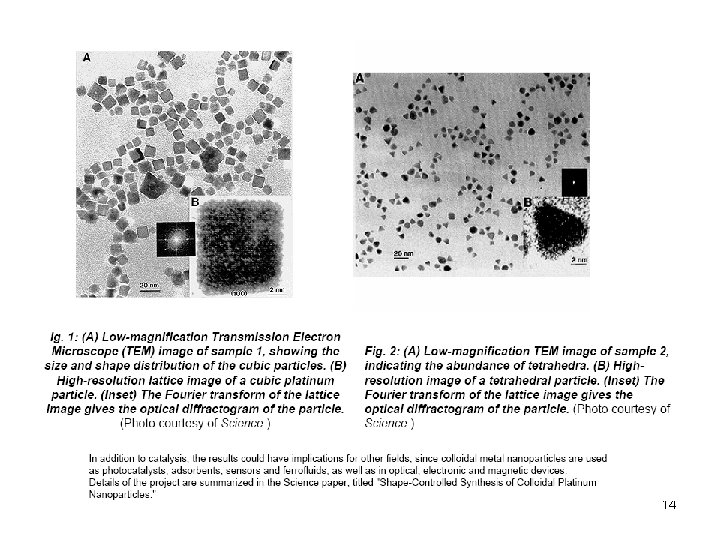
14
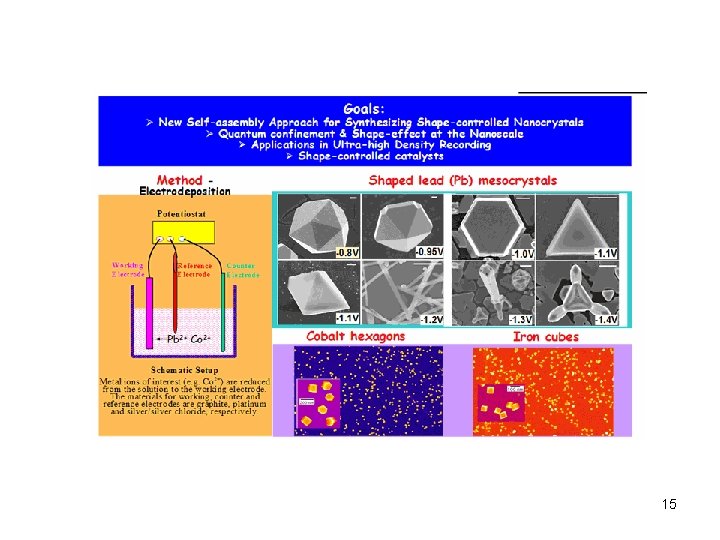
15
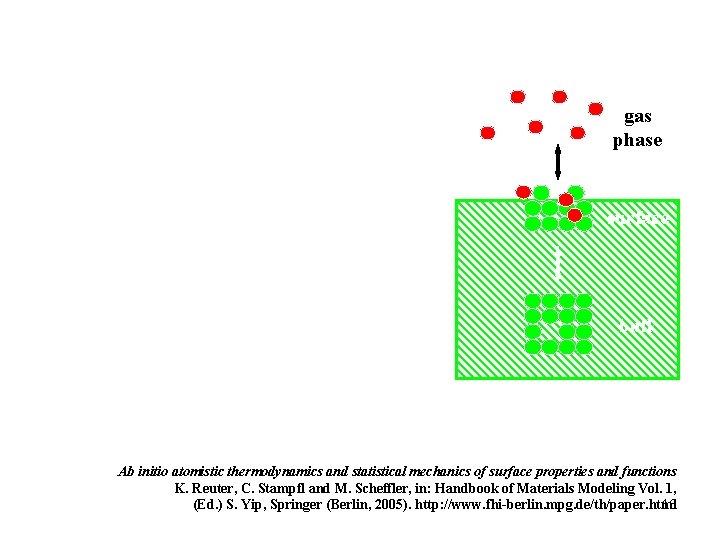
gas phase surface bulk Ab initio atomistic thermodynamics and statistical mechanics of surface properties and functions K. Reuter, C. Stampfl and M. Scheffler, in: Handbook of Materials Modeling Vol. 1, 16 (Ed. ) S. Yip, Springer (Berlin, 2005). http: //www. fhi-berlin. mpg. de/th/paper. html
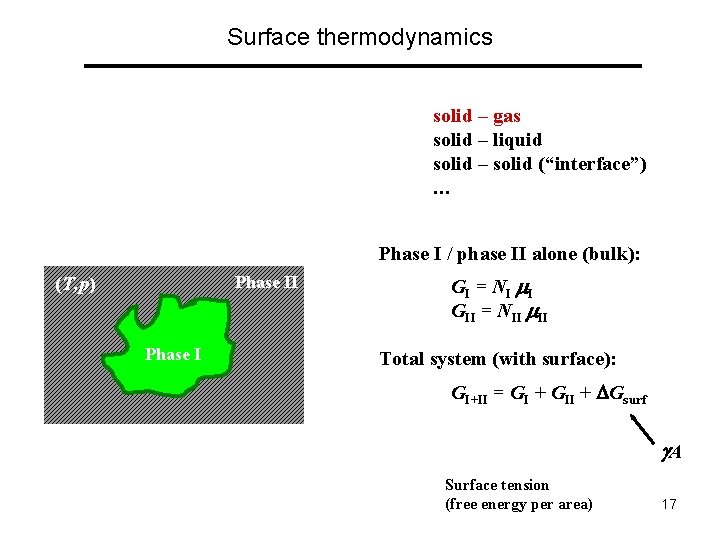
Surface thermodynamics solid – gas solid – liquid solid – solid (“interface”) … A surface can never be alone: there always “two sides” to it !!! Phase I / phase II alone (bulk): Phase II (T, p) Phase I GI = NI I GII = NII II Total system (with surface): GI+II = GI + GII + Gsurf A = 1/A ( GI+II - i Ni i ) Surface tension (free energy per area) 17
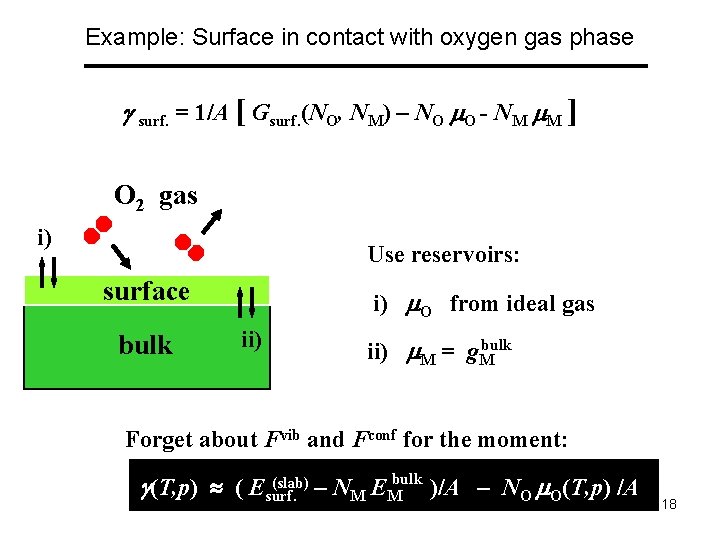
Example: Surface in contact with oxygen gas phase surf. = 1/A [ Gsurf. (NO, NM) – NO O - NM M ] O 2 gas i) Use reservoirs: surface bulk i) O from ideal gas ii) bulk ii) M = g. M Forget about Fvib and Fconf for the moment: (slab) – N E bulk )/A – N (T, p) /A (T, p) ( Esurf. M M O O 18
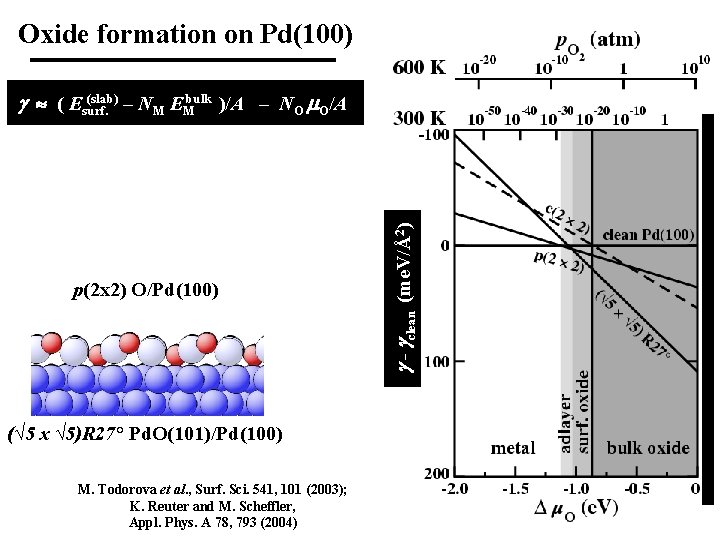
Oxide formation on Pd(100) p(2 x 2) O/Pd(100) - clean (me. V/Å2) (slab) ( Esurf. – NM EMbulk )/A – NO O/A (√ 5 x √ 5)R 27° Pd. O(101)/Pd(100) M. Todorova et al. , Surf. Sci. 541, 101 (2003); K. Reuter and M. Scheffler, Appl. Phys. A 78, 793 (2004) 19
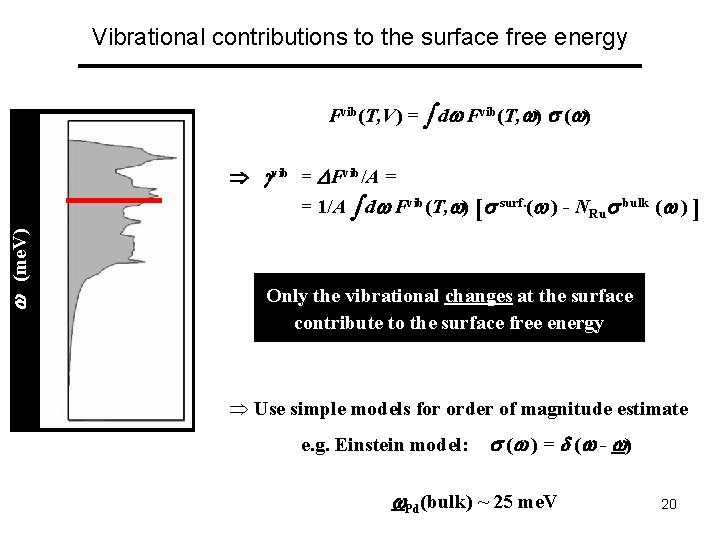
Vibrational contributions to the surface free energy Fvib(T, V) = d Fvib(T, ) ( ) 30 vib = Fvib/A = (me. V) = 1/A d Fvib(T, ) [ surf. ( ) - NRu bulk ( ) ] 20 Only the vibrational changes at the surface contribute to the surface free energy 10 0 Pd bulk Þ Use simple models for order of magnitude estimate e. g. Einstein model: ( ) = ( - ) Pd(bulk) ~ 25 me. V 20
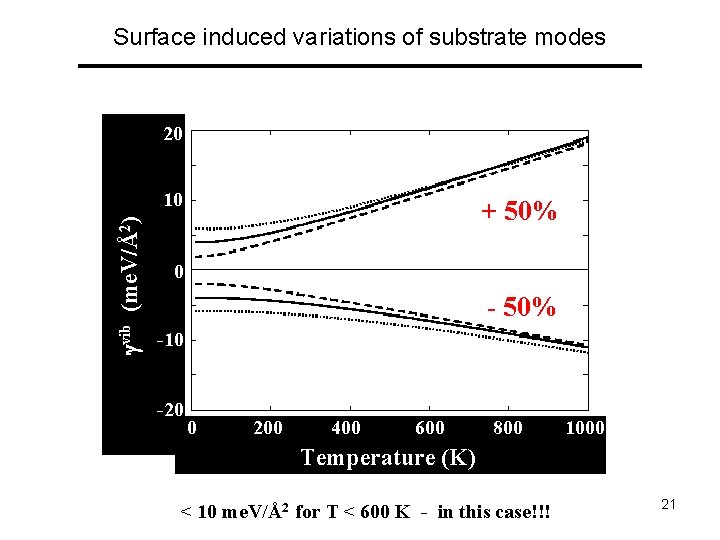
Surface induced variations of substrate modes 20 vib (me. V/Å2) 10 + 50% 0 - 50% -10 -20 0 200 400 600 800 1000 Temperature (K) < 10 me. V/Å2 for T < 600 K - in this case!!! 21
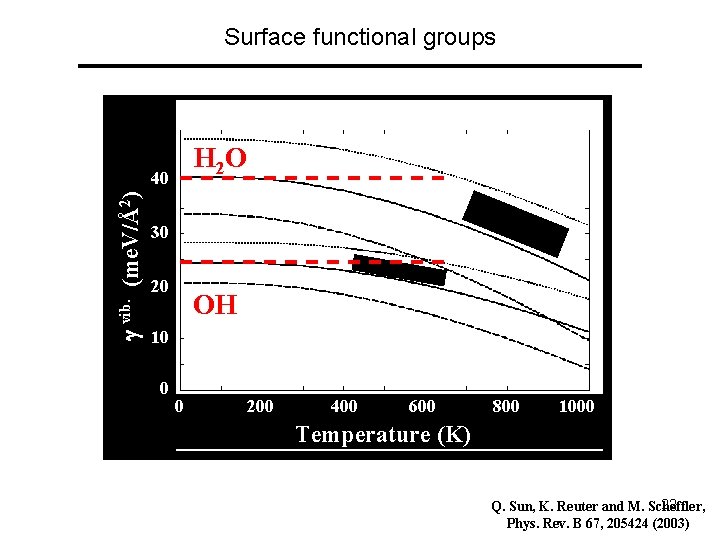
Surface functional groups H 2 O vib. (me. V/Å2) 40 30 20 OH 10 0 0 200 400 600 800 1000 Temperature (K) 22 Q. Sun, K. Reuter and M. Scheffler, Phys. Rev. B 67, 205424 (2003)
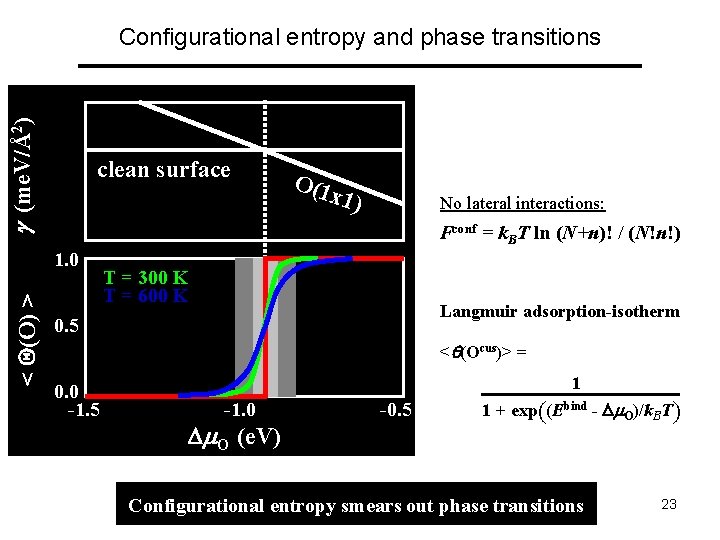
(me. V/Å2) Configurational entropy and phase transitions clean surface x 1) No lateral interactions: Fconf = k. BT ln (N+n)! / (N!n!) 1. 0 < (O) > O(1 T = 300 K T = 600 K Langmuir adsorption-isotherm 0. 5 < (Ocus)> = 0. 0 -1. 5 1 -1. 0 O (e. V) -0. 5 1 + exp((Ebind - O)/k. BT) Configurational entropy smears out phase transitions 23
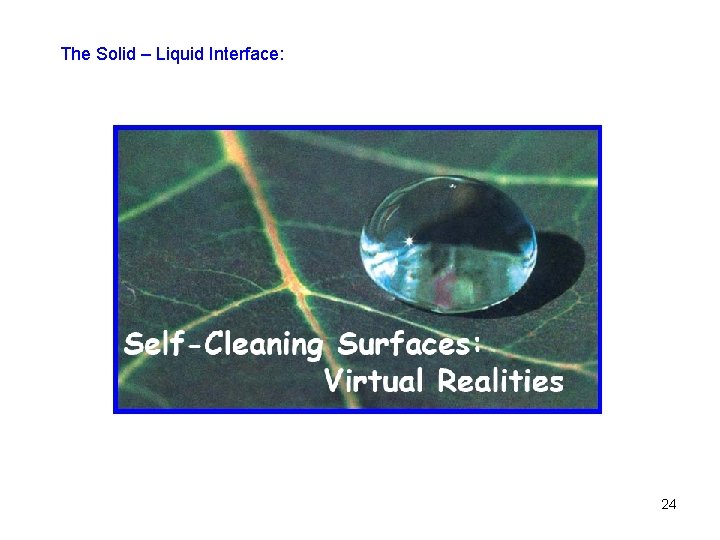
The Solid – Liquid Interface: 24
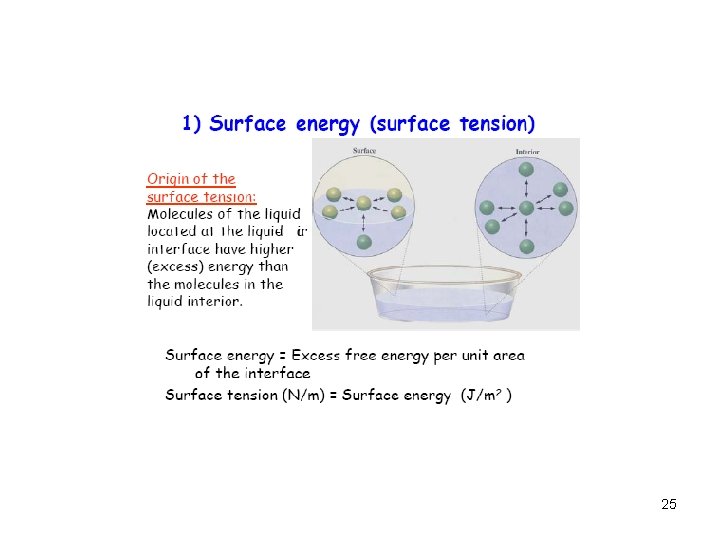
25
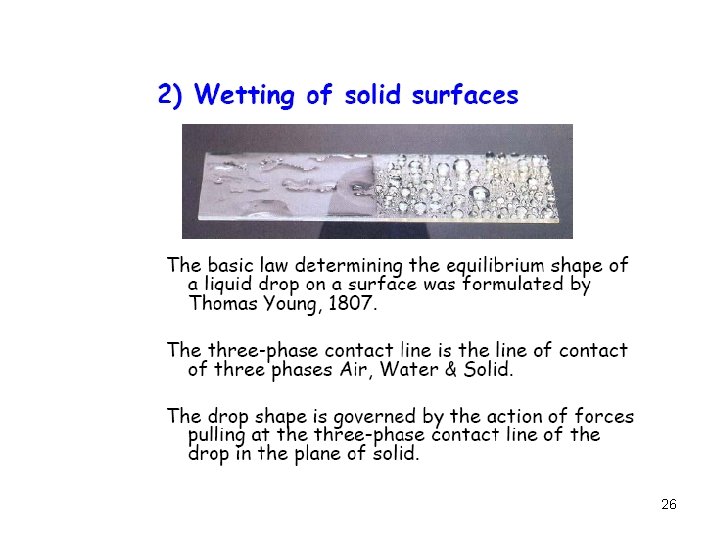
26
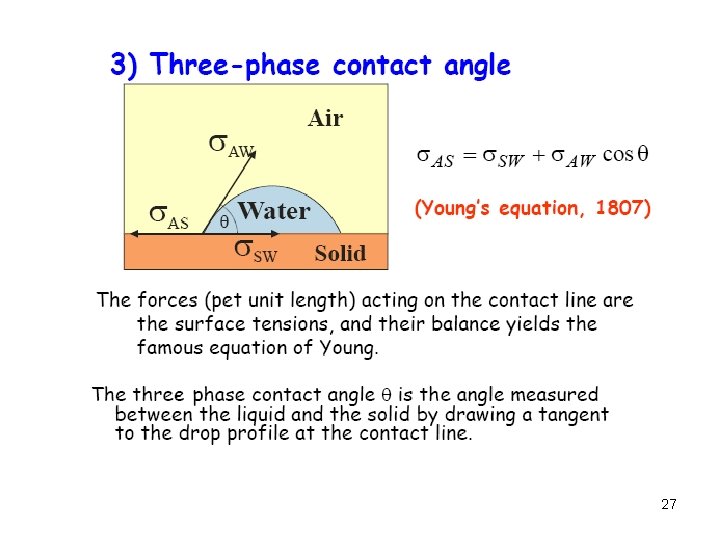
27
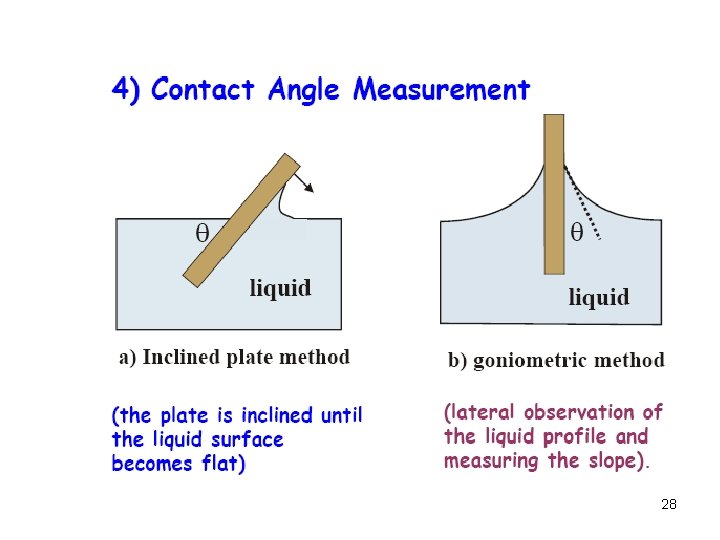
28
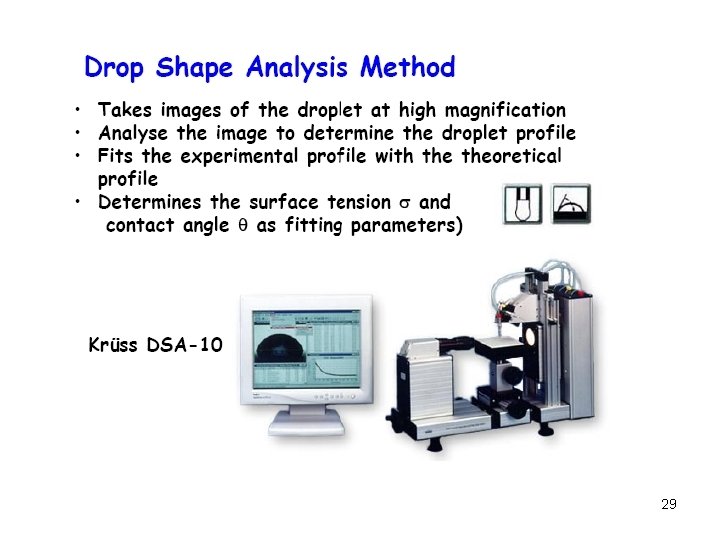
29
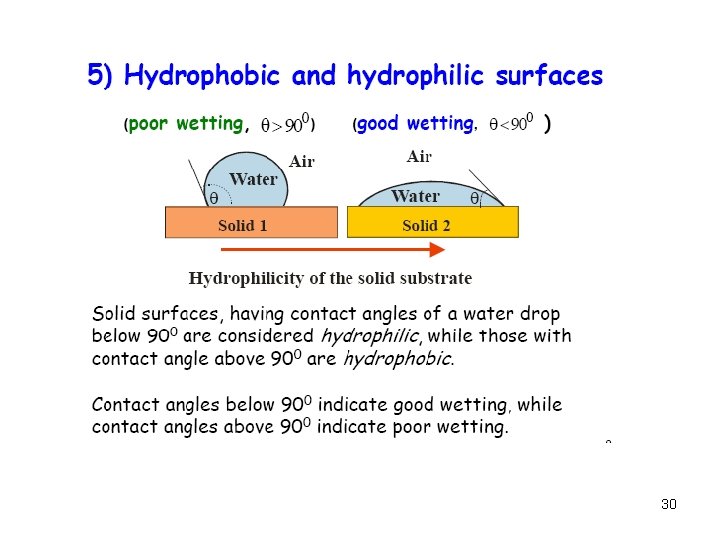
30
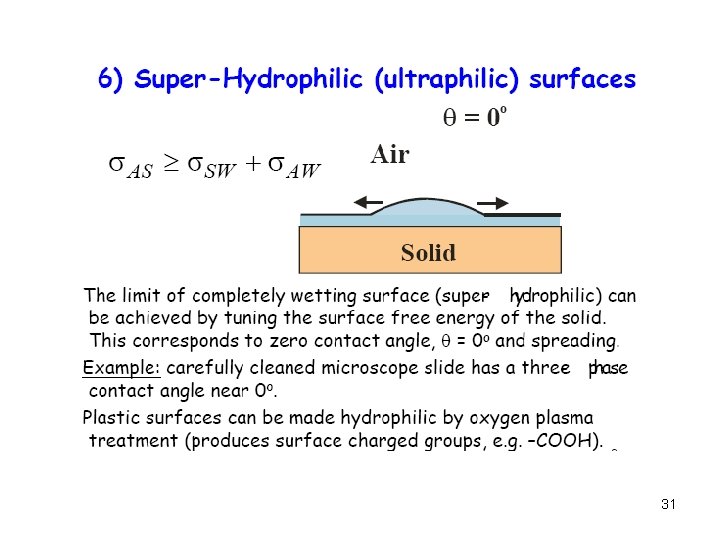
31
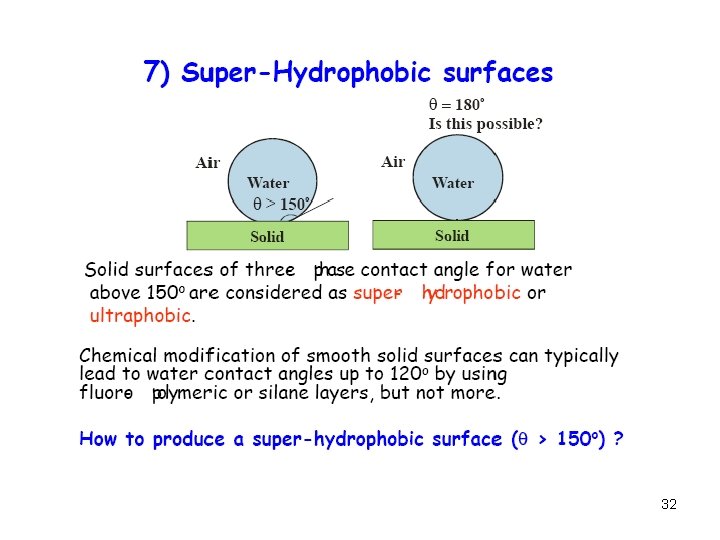
32
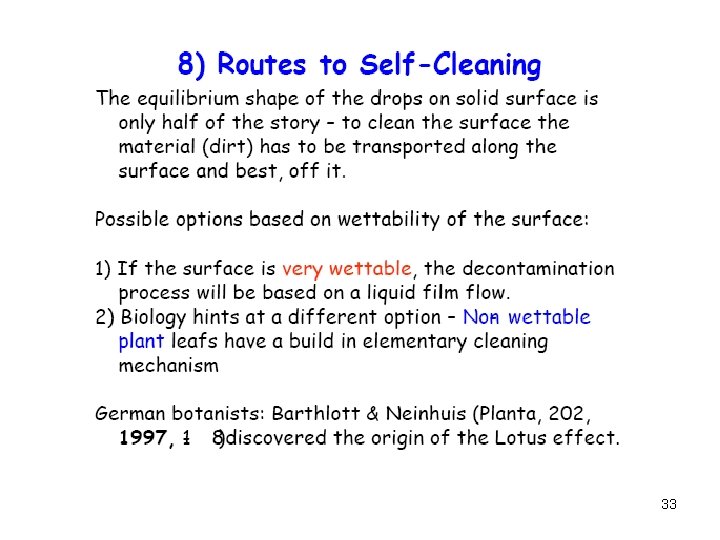
33
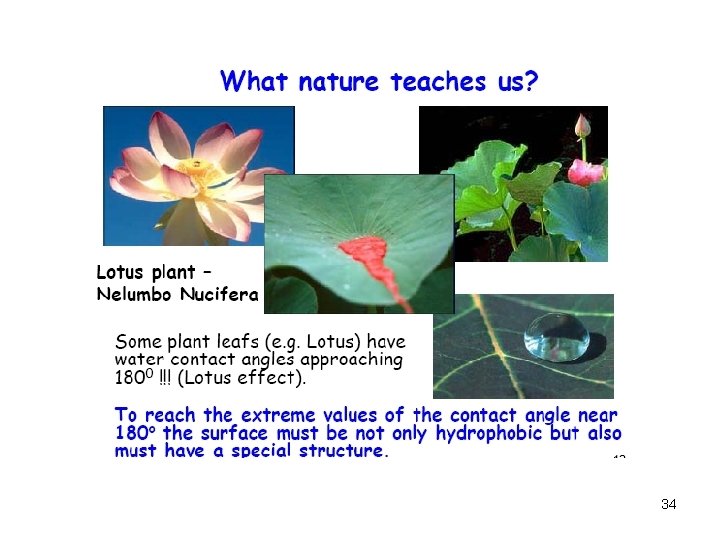
34
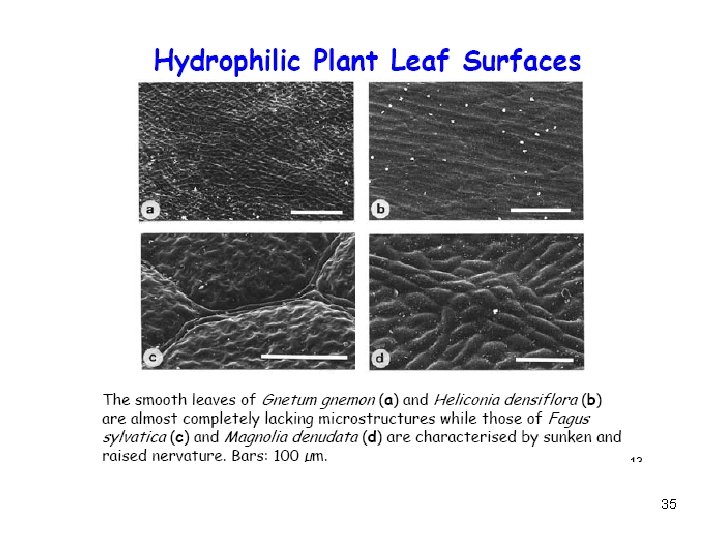
35
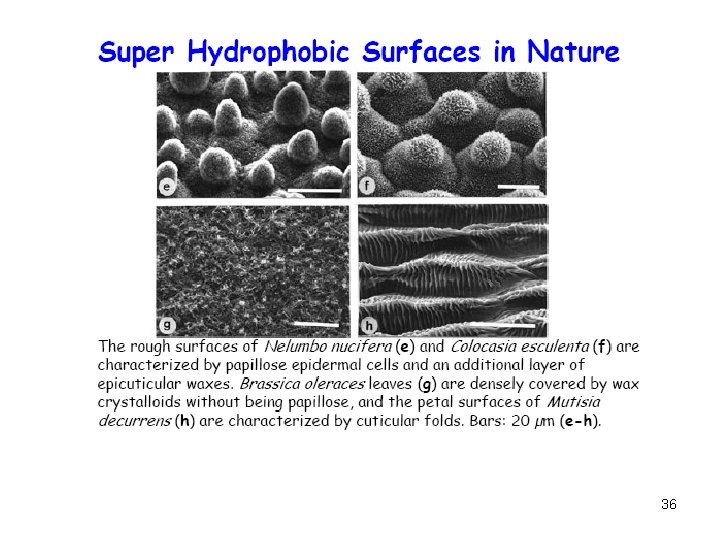
36
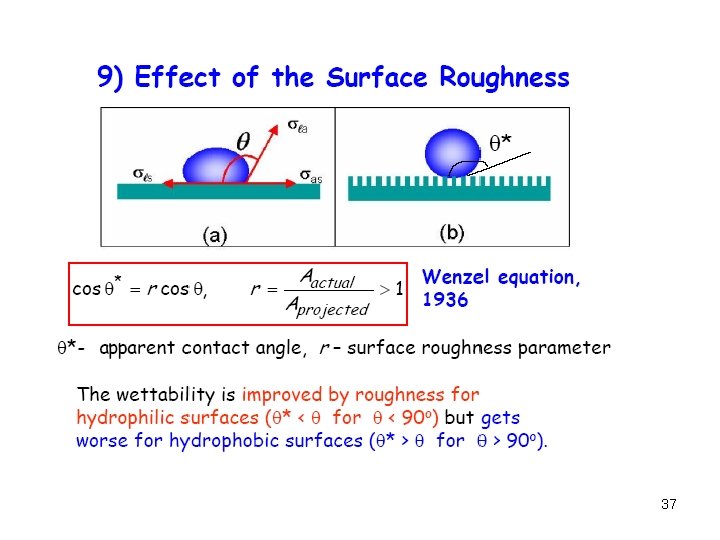
37
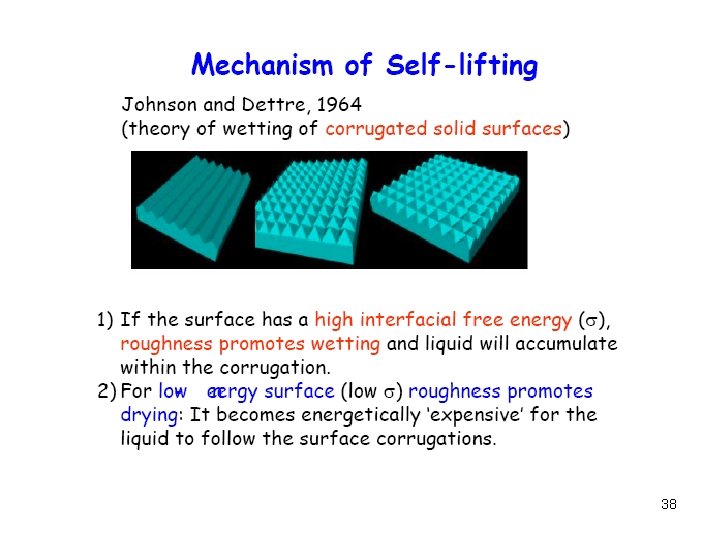
38
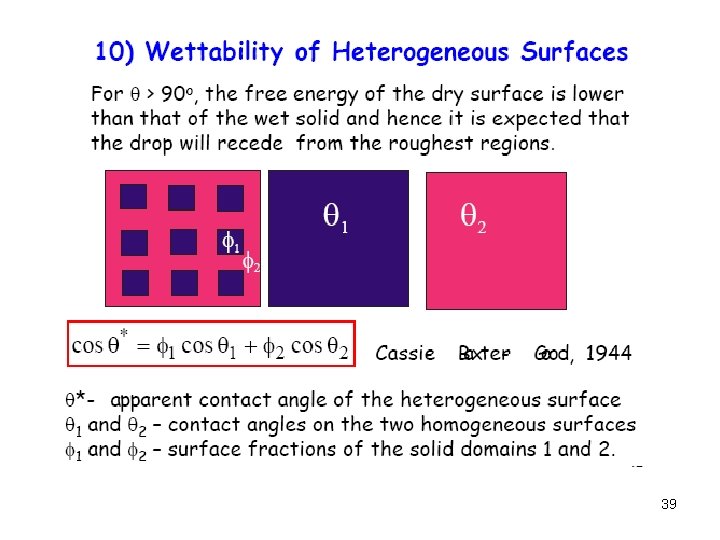
39
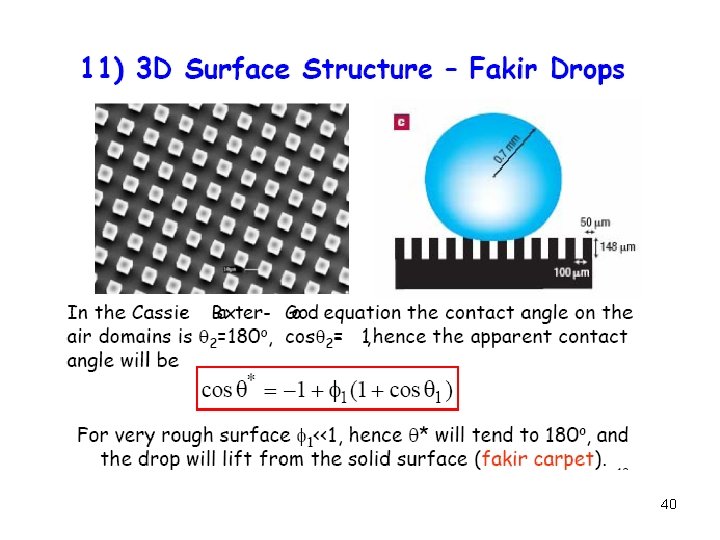
40
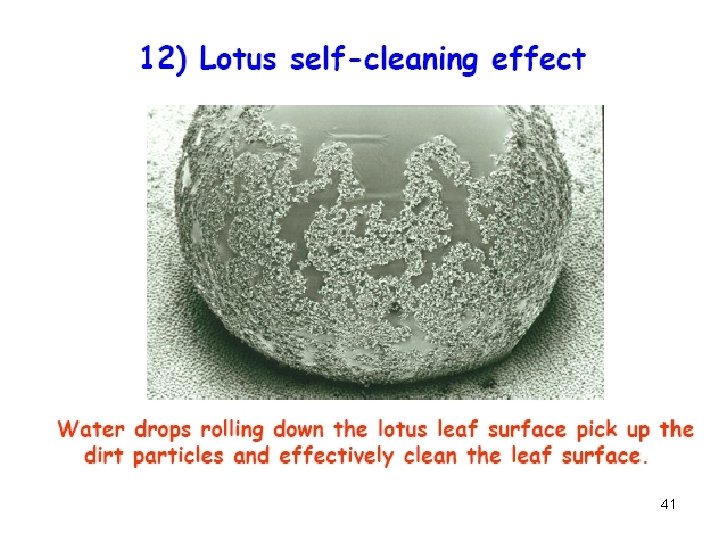
41
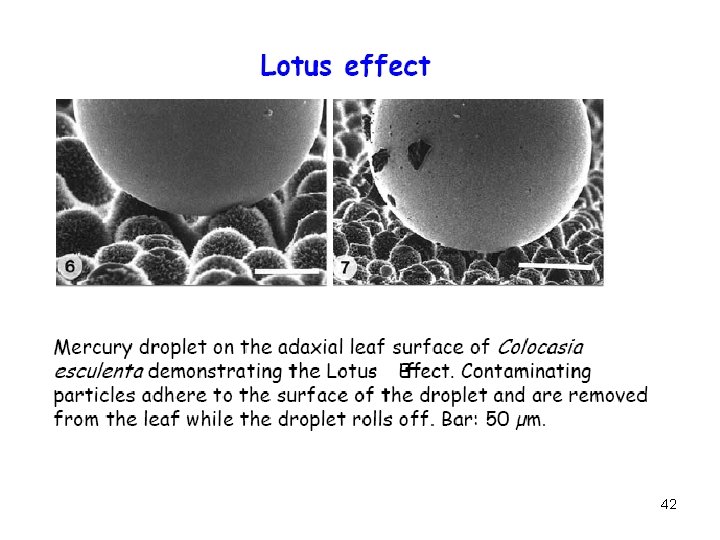
42
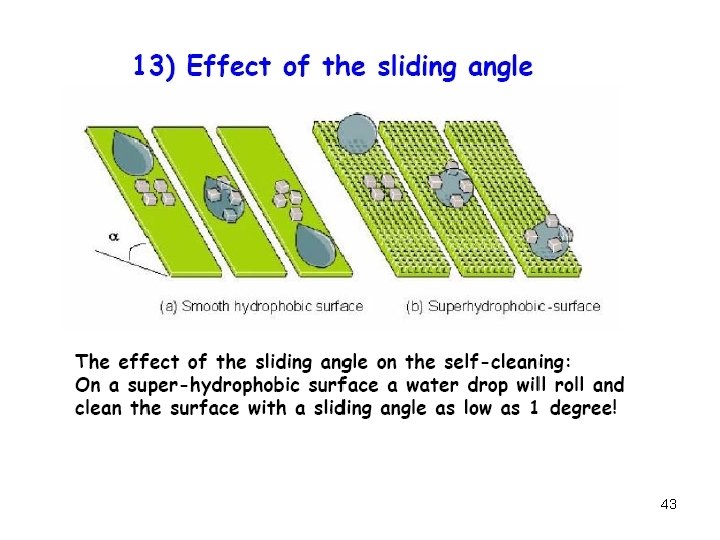
43
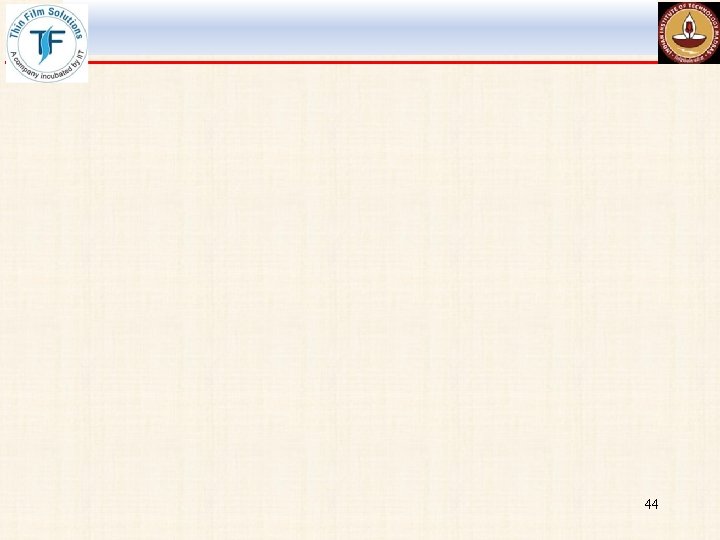
44
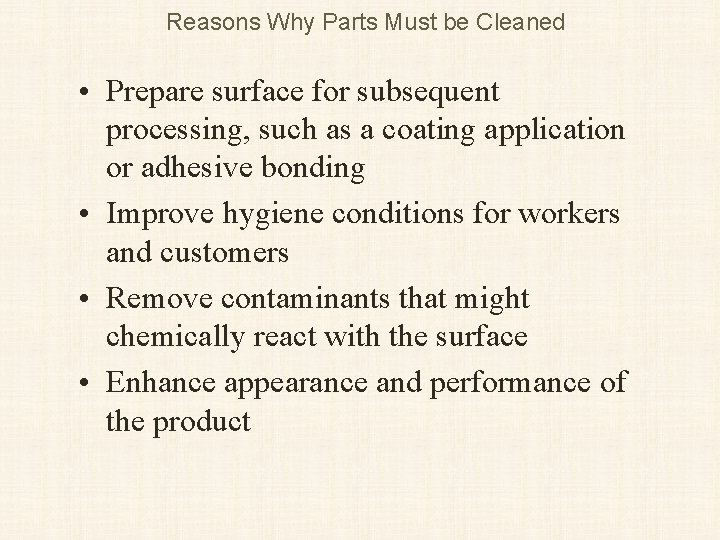
Reasons Why Parts Must be Cleaned • Prepare surface for subsequent processing, such as a coating application or adhesive bonding • Improve hygiene conditions for workers and customers • Remove contaminants that might chemically react with the surface • Enhance appearance and performance of the product
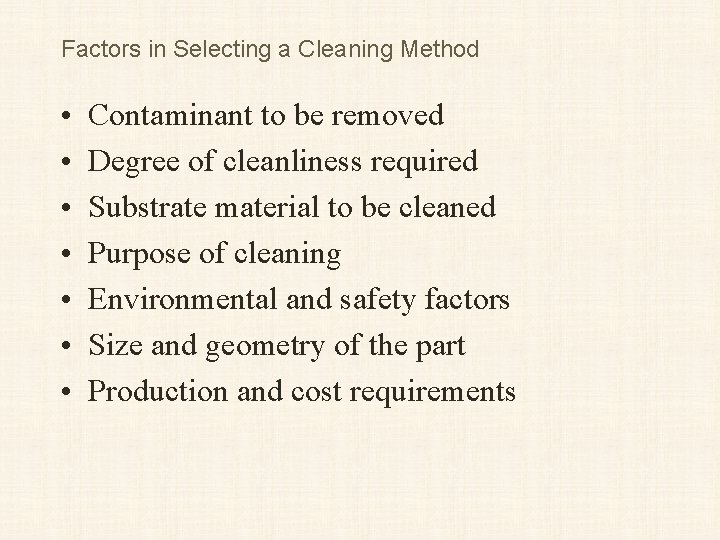
Factors in Selecting a Cleaning Method • • Contaminant to be removed Degree of cleanliness required Substrate material to be cleaned Purpose of cleaning Environmental and safety factors Size and geometry of the part Production and cost requirements
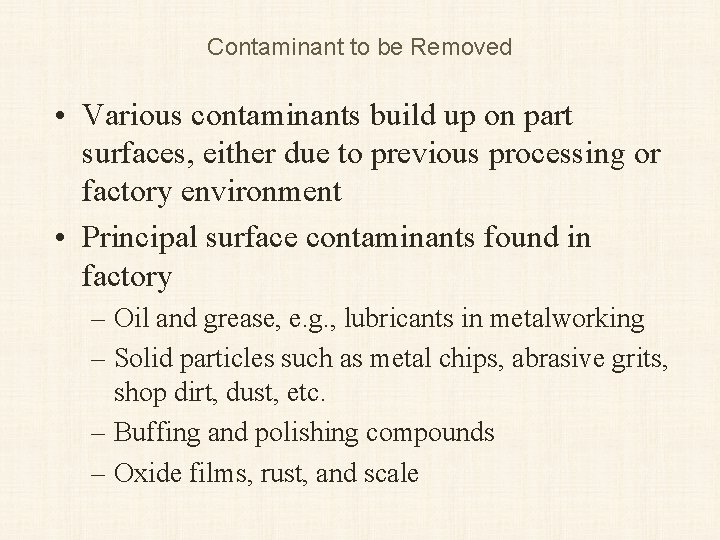
Contaminant to be Removed • Various contaminants build up on part surfaces, either due to previous processing or factory environment • Principal surface contaminants found in factory – Oil and grease, e. g. , lubricants in metalworking – Solid particles such as metal chips, abrasive grits, shop dirt, dust, etc. – Buffing and polishing compounds – Oxide films, rust, and scale
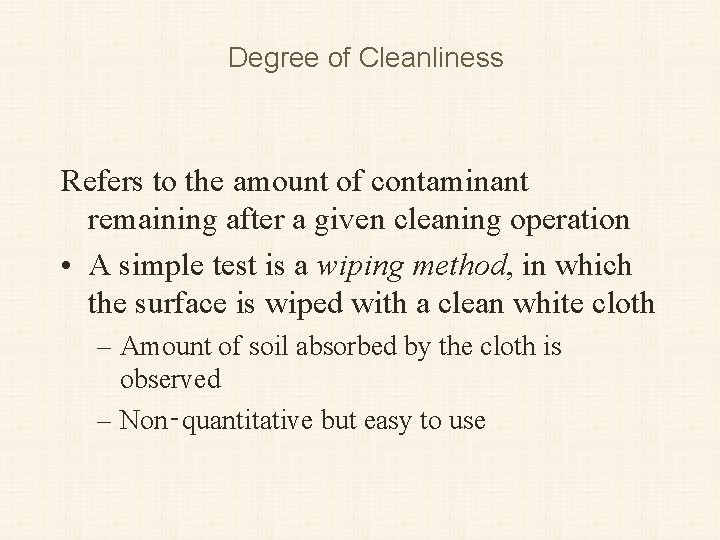
Degree of Cleanliness Refers to the amount of contaminant remaining after a given cleaning operation • A simple test is a wiping method, in which the surface is wiped with a clean white cloth – Amount of soil absorbed by the cloth is observed – Non‑quantitative but easy to use
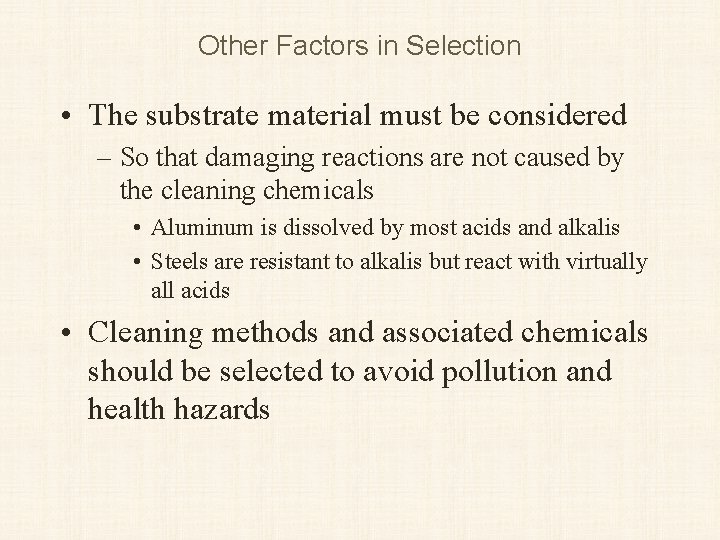
Other Factors in Selection • The substrate material must be considered – So that damaging reactions are not caused by the cleaning chemicals • Aluminum is dissolved by most acids and alkalis • Steels are resistant to alkalis but react with virtually all acids • Cleaning methods and associated chemicals should be selected to avoid pollution and health hazards
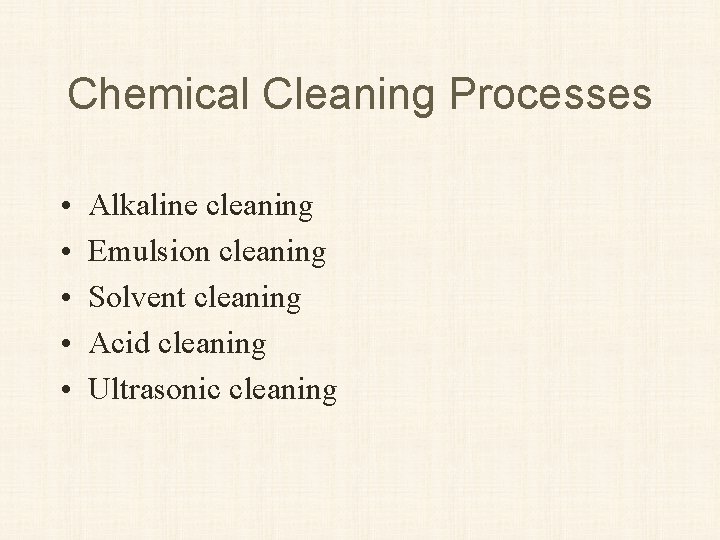
Chemical Cleaning Processes • • • Alkaline cleaning Emulsion cleaning Solvent cleaning Acid cleaning Ultrasonic cleaning
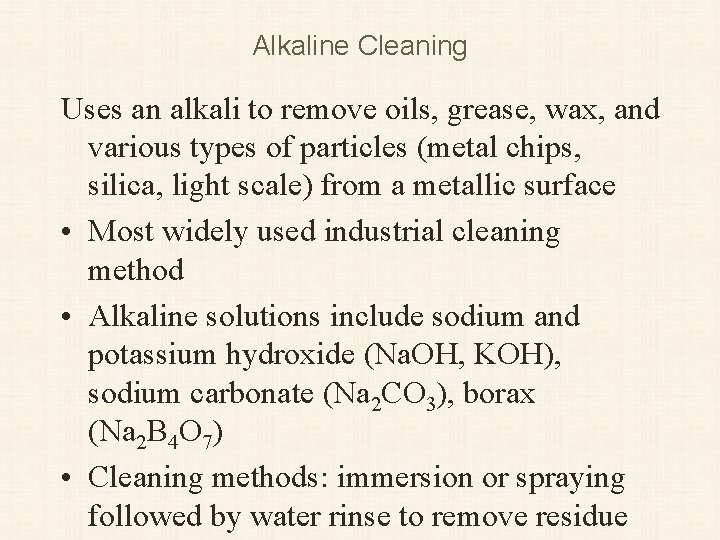
Alkaline Cleaning Uses an alkali to remove oils, grease, wax, and various types of particles (metal chips, silica, light scale) from a metallic surface • Most widely used industrial cleaning method • Alkaline solutions include sodium and potassium hydroxide (Na. OH, KOH), sodium carbonate (Na 2 CO 3), borax (Na 2 B 4 O 7) • Cleaning methods: immersion or spraying followed by water rinse to remove residue
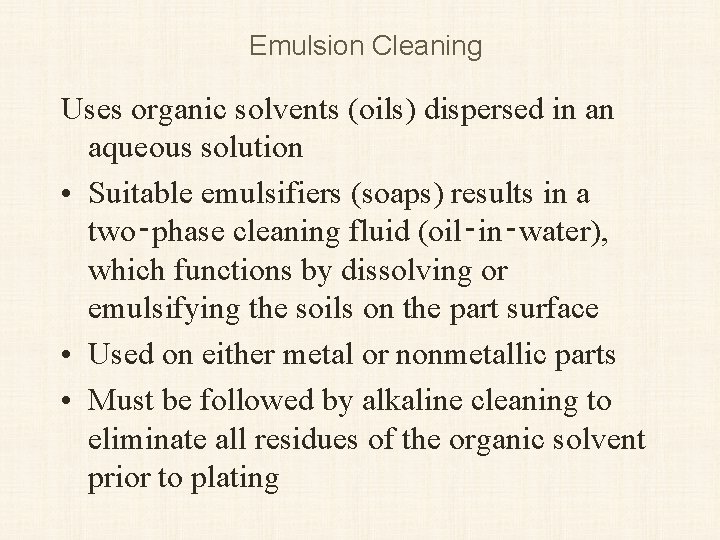
Emulsion Cleaning Uses organic solvents (oils) dispersed in an aqueous solution • Suitable emulsifiers (soaps) results in a two‑phase cleaning fluid (oil‑in‑water), which functions by dissolving or emulsifying the soils on the part surface • Used on either metal or nonmetallic parts • Must be followed by alkaline cleaning to eliminate all residues of the organic solvent prior to plating
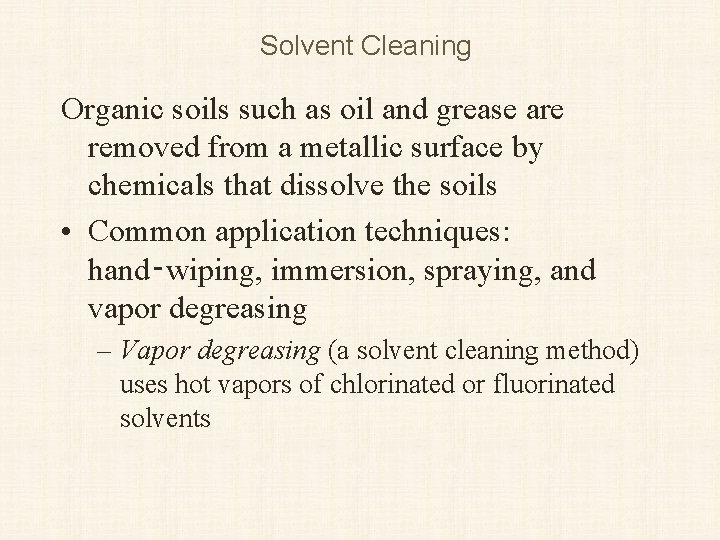
Solvent Cleaning Organic soils such as oil and grease are removed from a metallic surface by chemicals that dissolve the soils • Common application techniques: hand‑wiping, immersion, spraying, and vapor degreasing – Vapor degreasing (a solvent cleaning method) uses hot vapors of chlorinated or fluorinated solvents
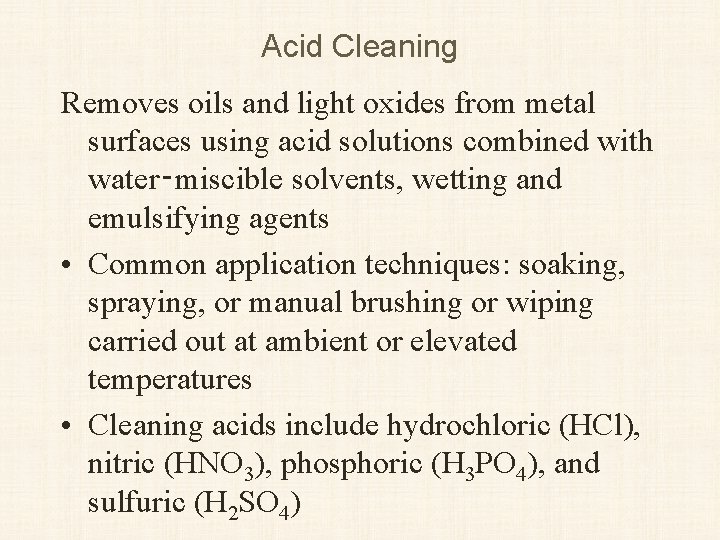
Acid Cleaning Removes oils and light oxides from metal surfaces using acid solutions combined with water‑miscible solvents, wetting and emulsifying agents • Common application techniques: soaking, spraying, or manual brushing or wiping carried out at ambient or elevated temperatures • Cleaning acids include hydrochloric (HCl), nitric (HNO 3), phosphoric (H 3 PO 4), and sulfuric (H 2 SO 4)
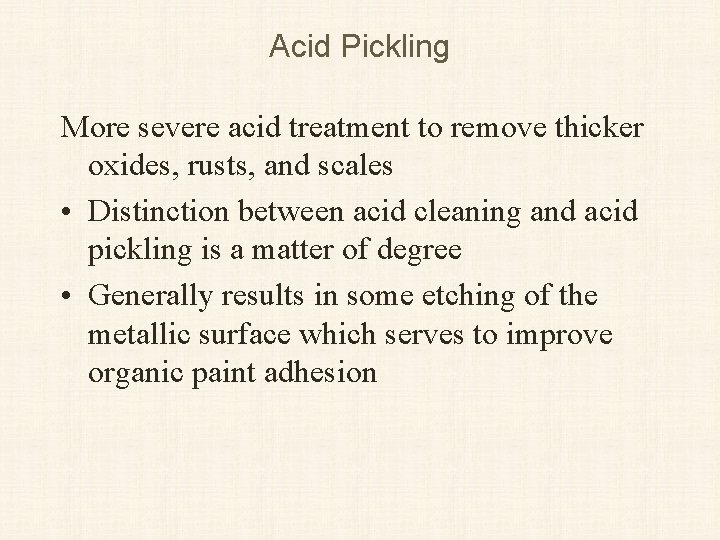
Acid Pickling More severe acid treatment to remove thicker oxides, rusts, and scales • Distinction between acid cleaning and acid pickling is a matter of degree • Generally results in some etching of the metallic surface which serves to improve organic paint adhesion
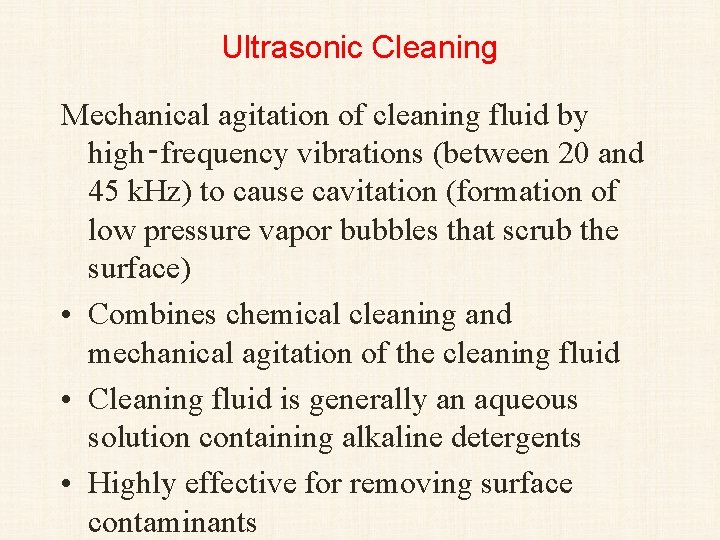
Ultrasonic Cleaning Mechanical agitation of cleaning fluid by high‑frequency vibrations (between 20 and 45 k. Hz) to cause cavitation (formation of low pressure vapor bubbles that scrub the surface) • Combines chemical cleaning and mechanical agitation of the cleaning fluid • Cleaning fluid is generally an aqueous solution containing alkaline detergents • Highly effective for removing surface contaminants
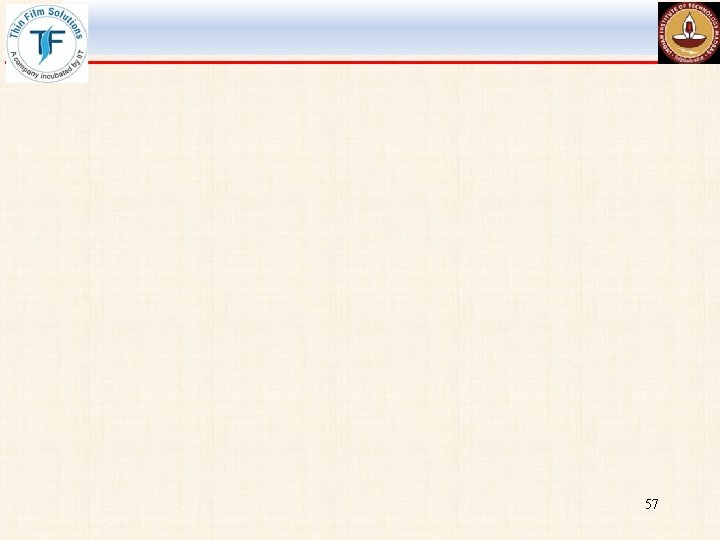
57
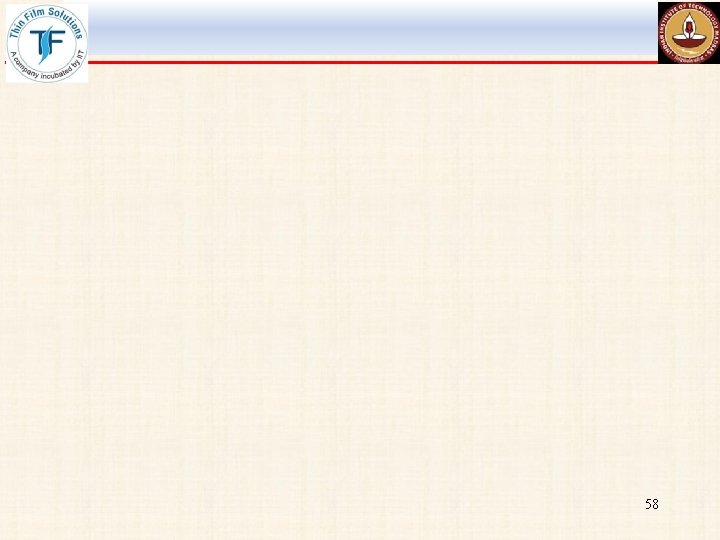
58
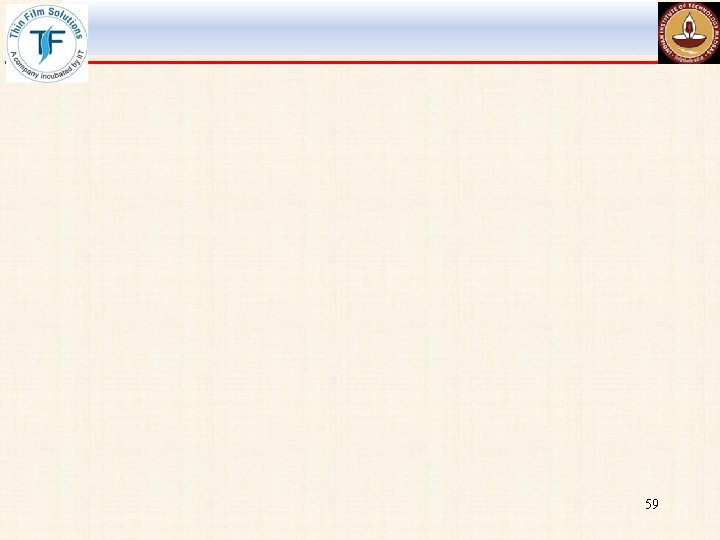
59
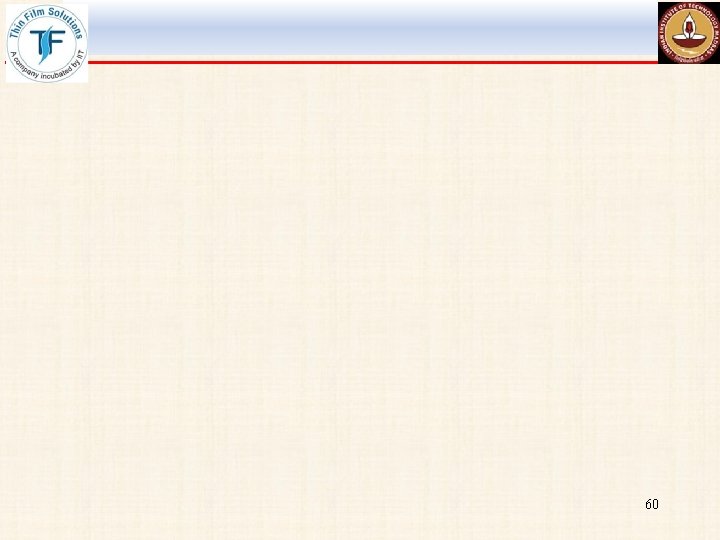
60
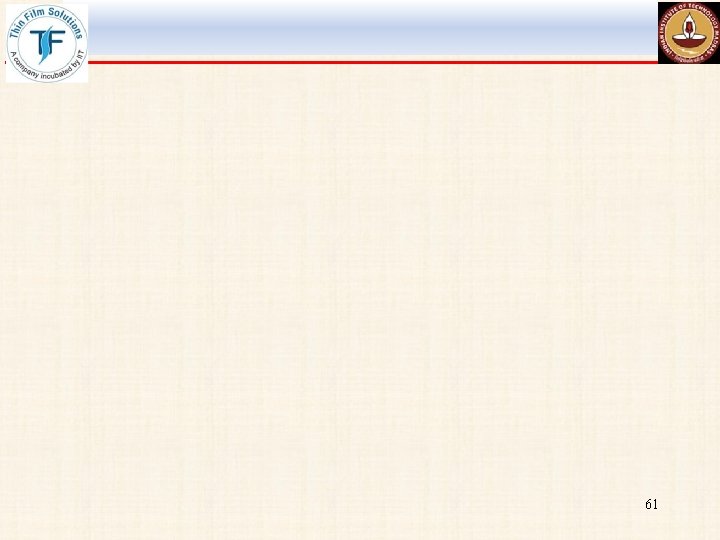
61
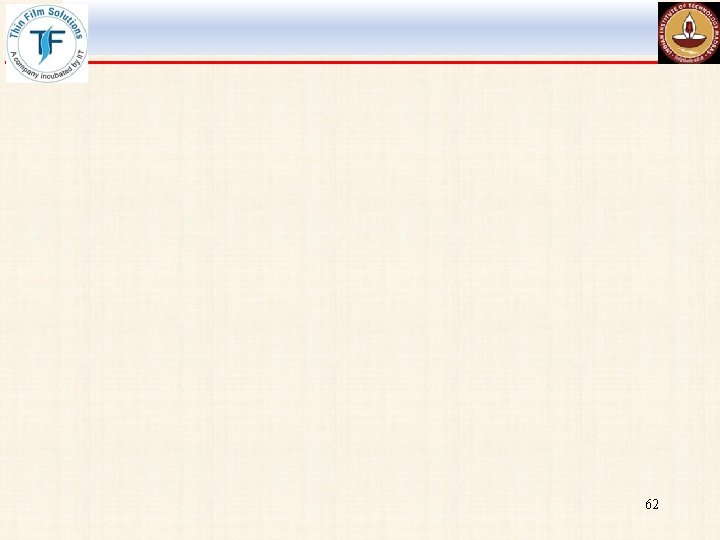
62
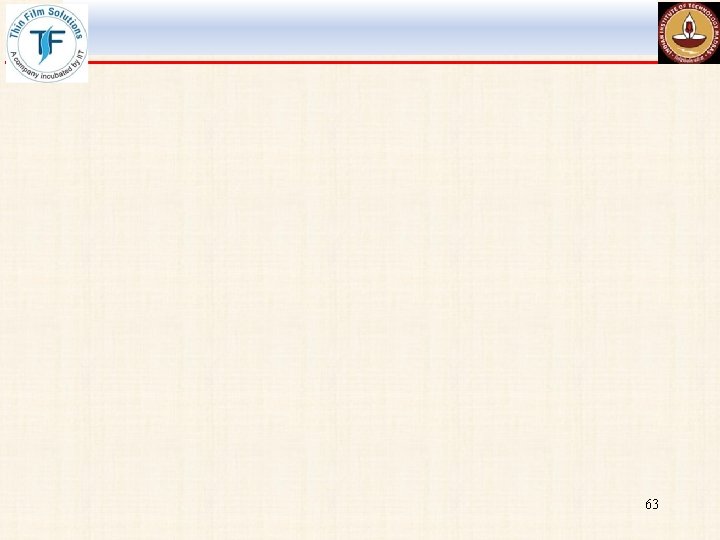
63
Energy energy transfer and general energy analysis
Energy energy transfer and general energy analysis
Entropy equation
Nozzle and diffuser
What is internal energy
1st law of thermodynamics
First law of td
Internal energy formula thermodynamics
Formula thermal energy
Data quality and data cleaning an overview
Clean public areas facilities and equipment
Things we use to clean utensils
What is the definition of sanitizing servsafe
Data quality and data cleaning an overview
Data quality and data cleaning an overview
Etl in data cleaning and preprocessing stands for
Cleaning and sanitation manual for breweries
Importance of cleaning kitchen premises and equipment
Cleaning the tides of san diego and tijuana
Wet curved surface area
Surface area vs area
Thermodynamics by cengel and boles
Introduction and basic concepts of thermodynamics
Irreversible process in thermodynamics
Thermodynamics introduction and basic concepts
Thermodynamics enthalpy of reaction and hess's law
Non spontaneous process
Extensive properties in thermodynamics
Thermodynamics and statistical mechanics
Thermodynamics and statistical mechanics
Difference between open and closed system
Heat capacity is state or path function
Tru count air clutch parts diagram
Power tool cleaning
Standard cost operating statement
Sedimclean water tank cleaning machine
What are three types of hazards that make food unsafe
Pengolahan data editing, coding processing cleaning
Pt among kampung rambutan
Hospital patient room cleaning procedures
Cleaning methods
Language
Fifth labor of hercules
Negative feedback loop
Cleanscape cleaning services dublin
Objectives of cleaning program
Waste container
Gene eat dinner when his friend called
Particle removal wet etch filters
Usp 797 laminar flow hood cleaning
Intensive cleaner for stainless steel exhaust system
Woodard cleaning
Potter's tool is data cleaning tool
Operating room cleaning procedures
Relational agent in ai
Pictures of unsafe dented cans
Data cleaning in stata
Planche v colburn 1831
Cleaning speech
Delatexing meaning
Orifice cleaning tool
Four cleaning agents
Chapter 15:2 bioterrorism
Which organelle prepares proteins for specific jobs