Methods and Work Measurement Lecture 4 The General
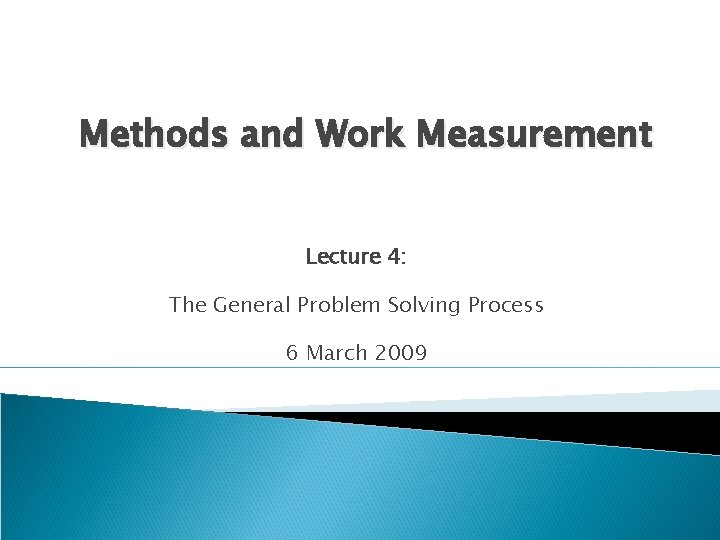
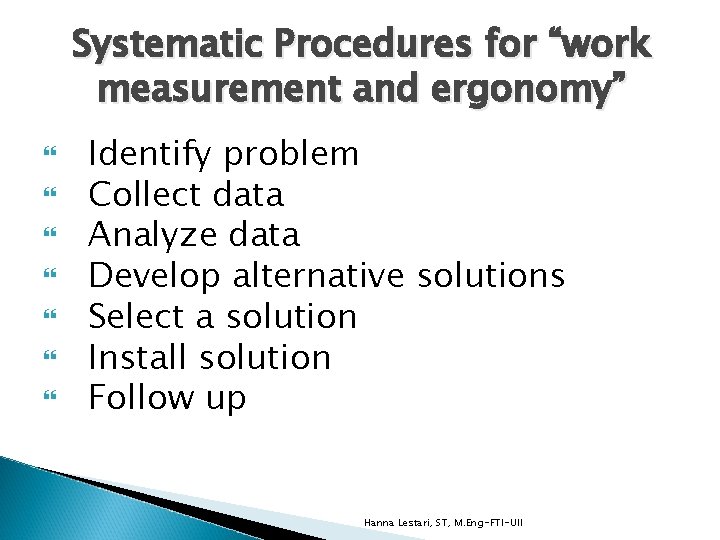
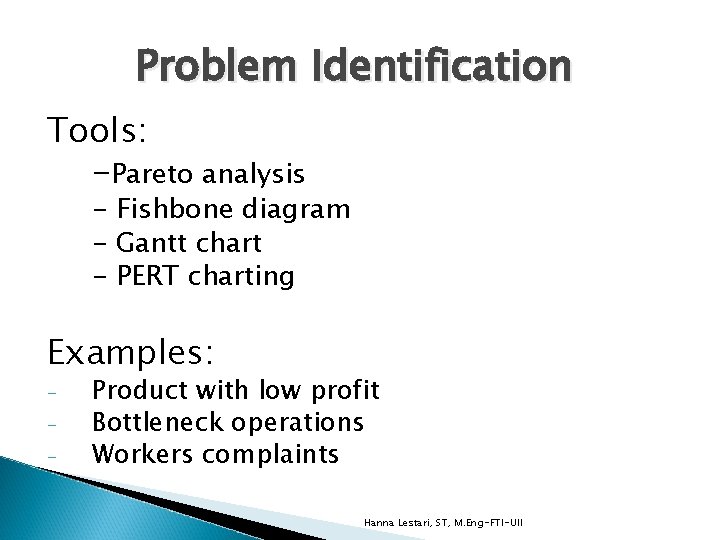
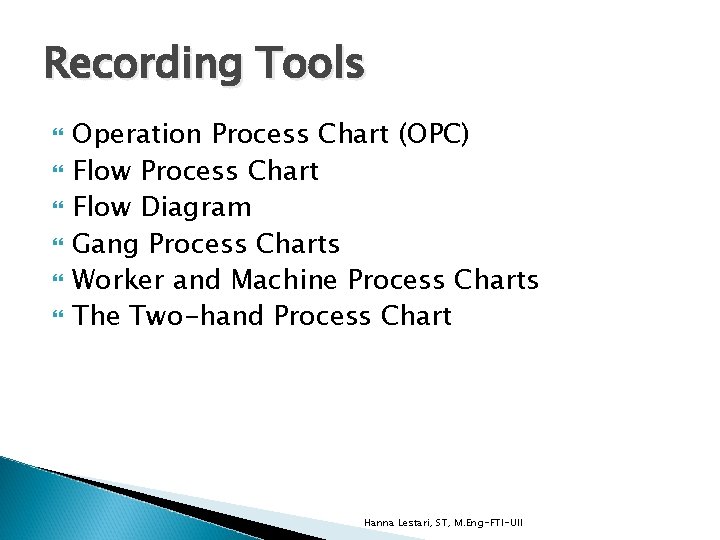
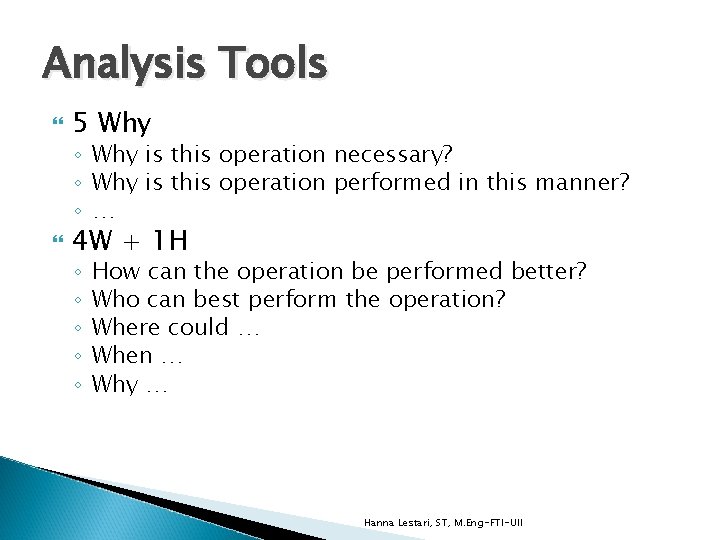
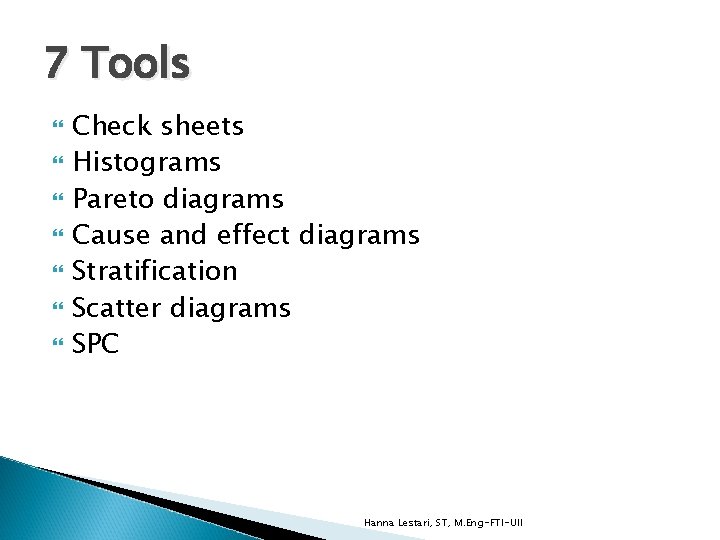
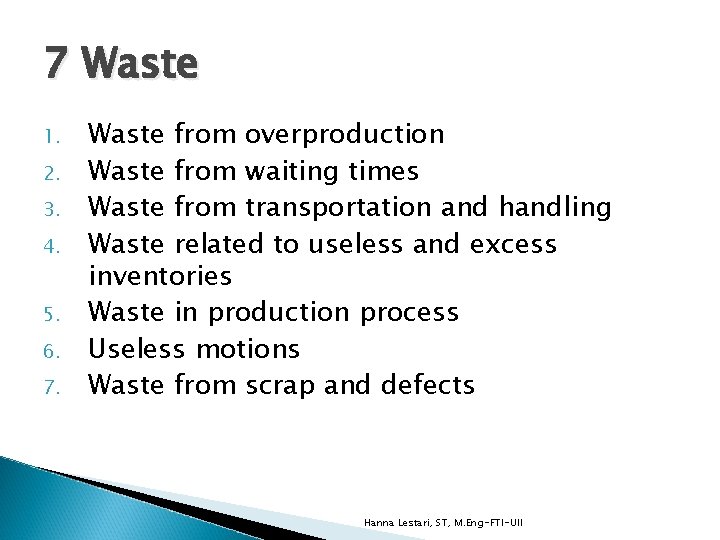
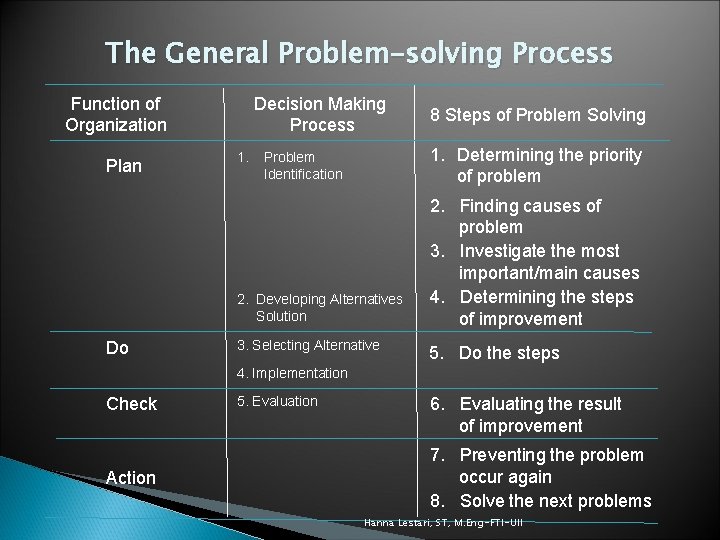
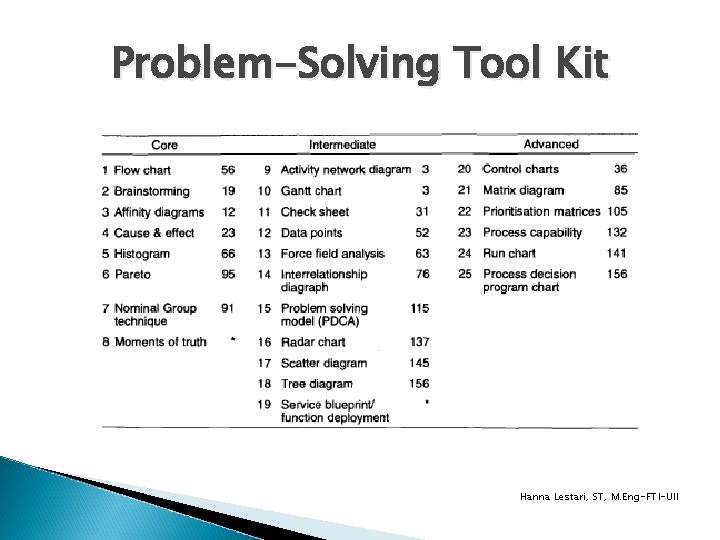
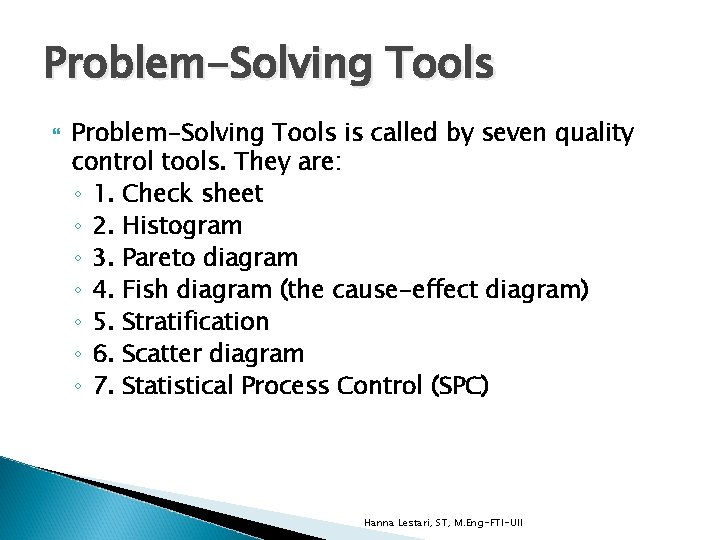
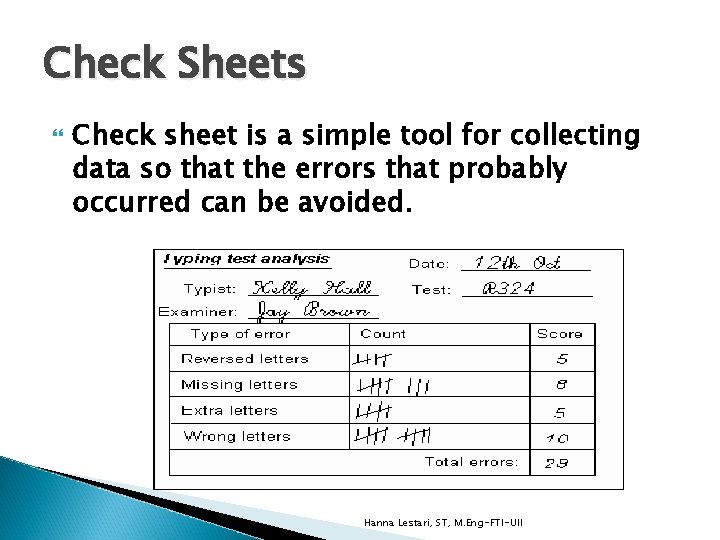
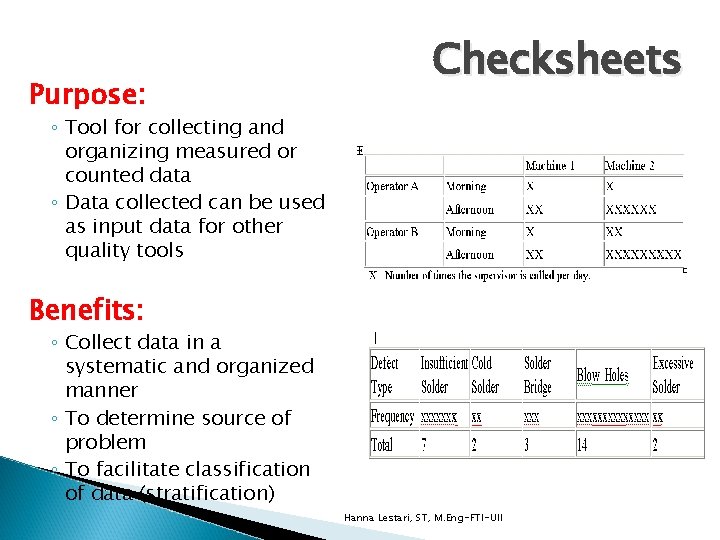
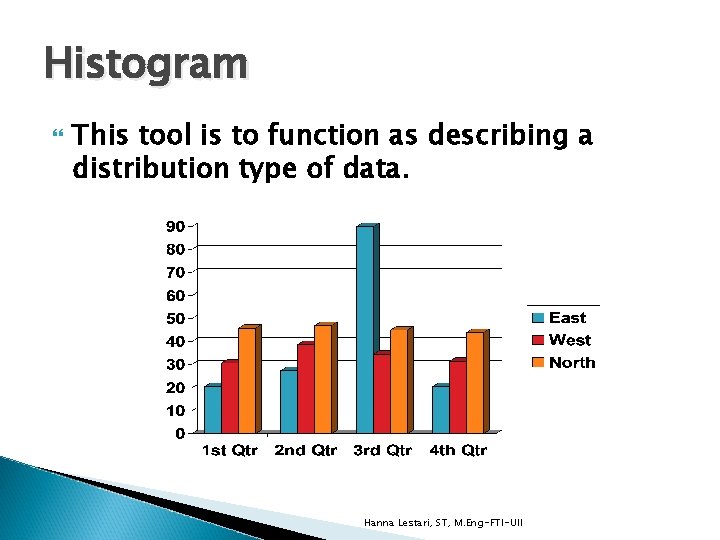
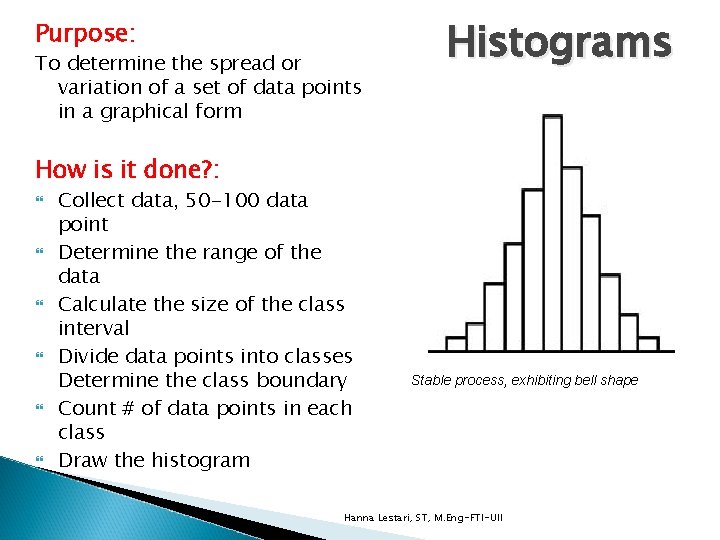
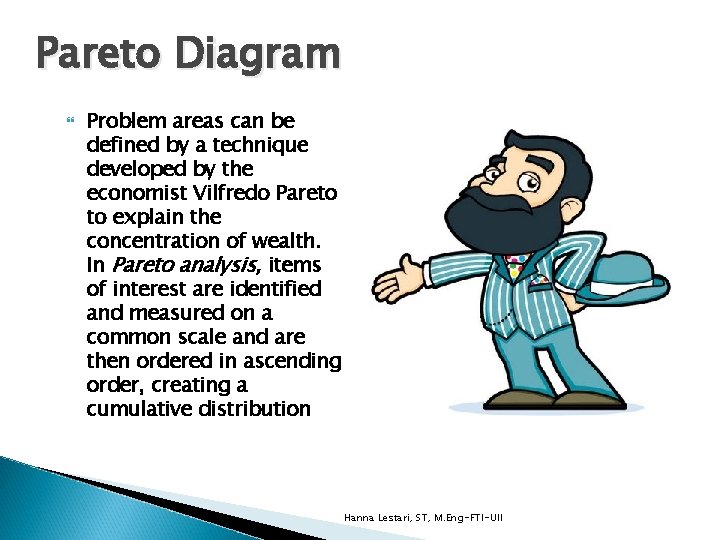
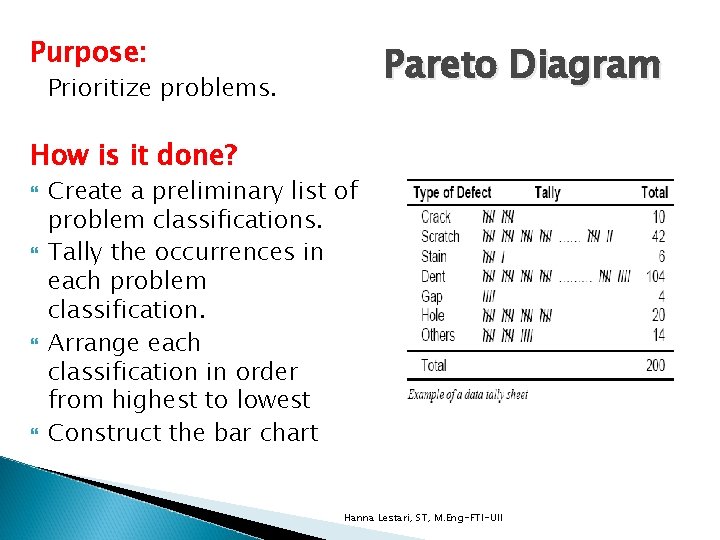
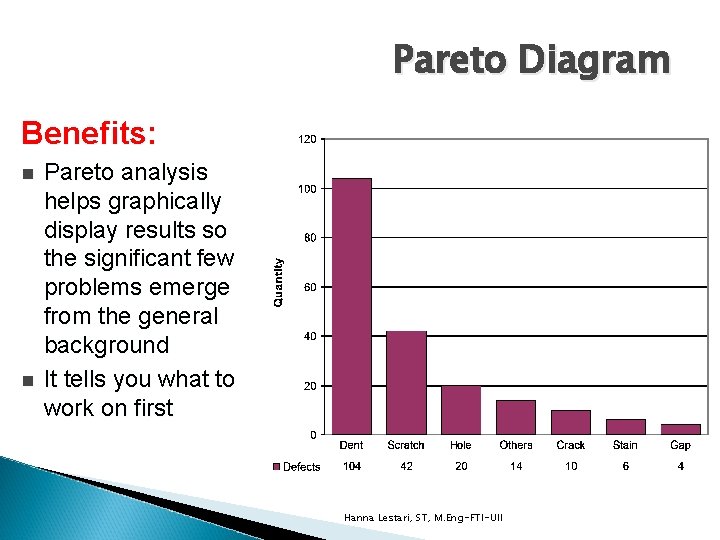
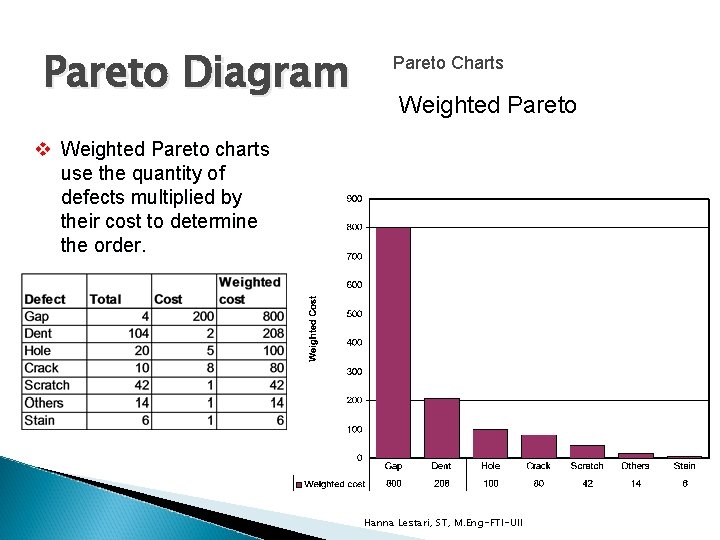
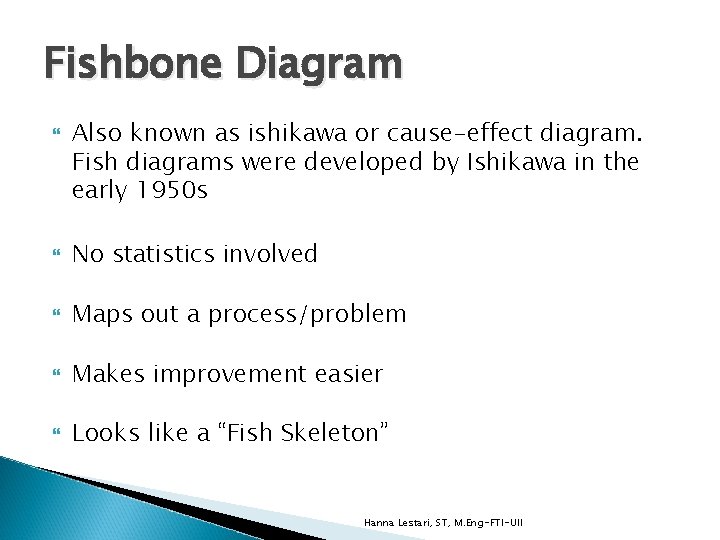
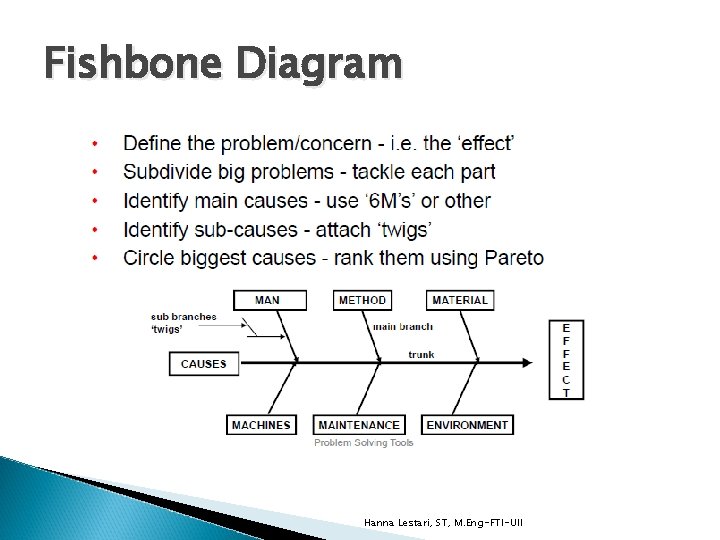
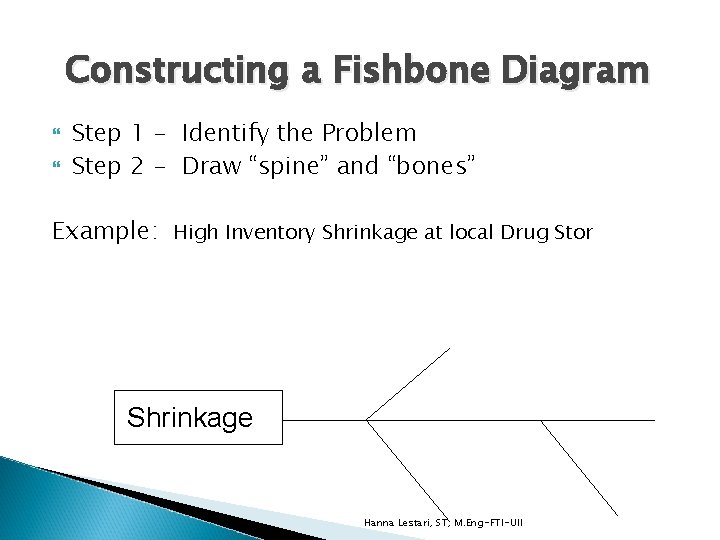
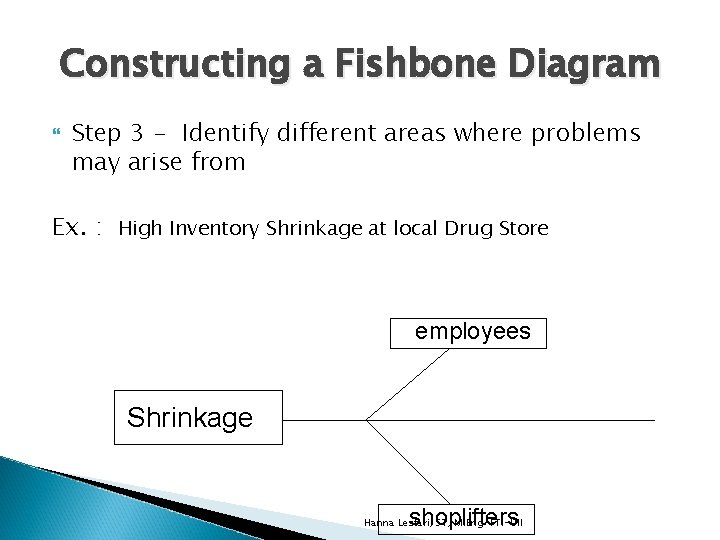
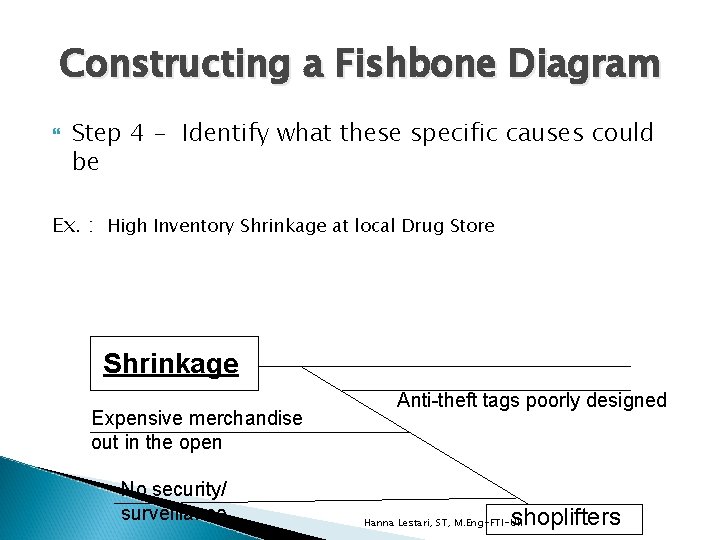
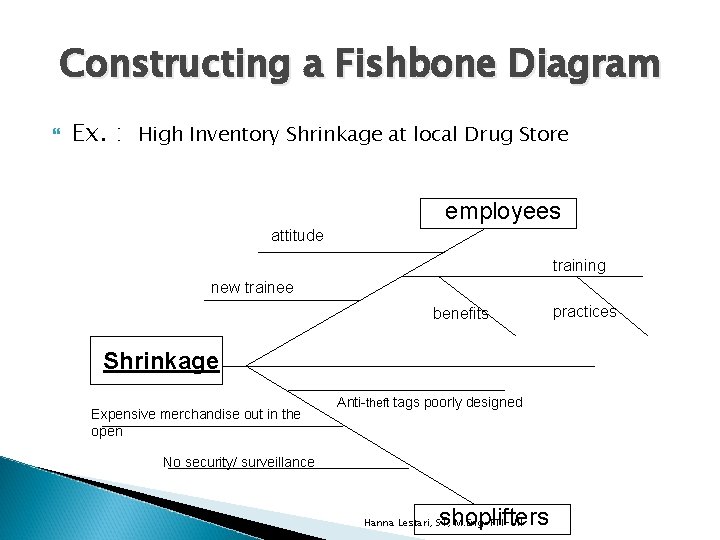
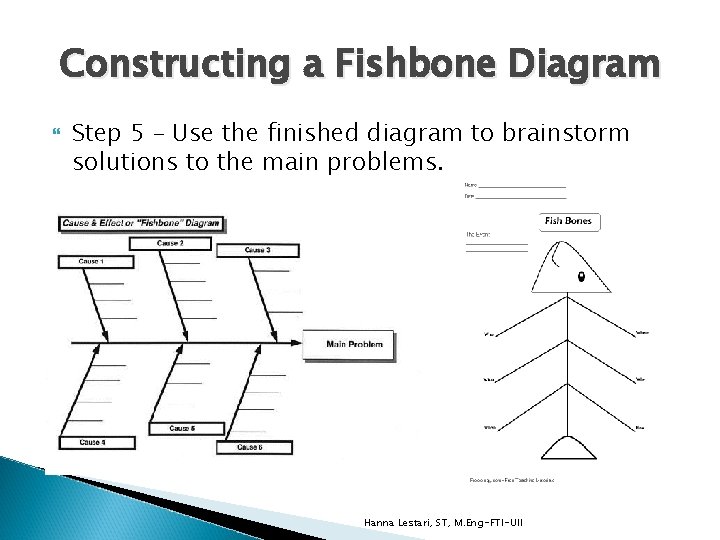
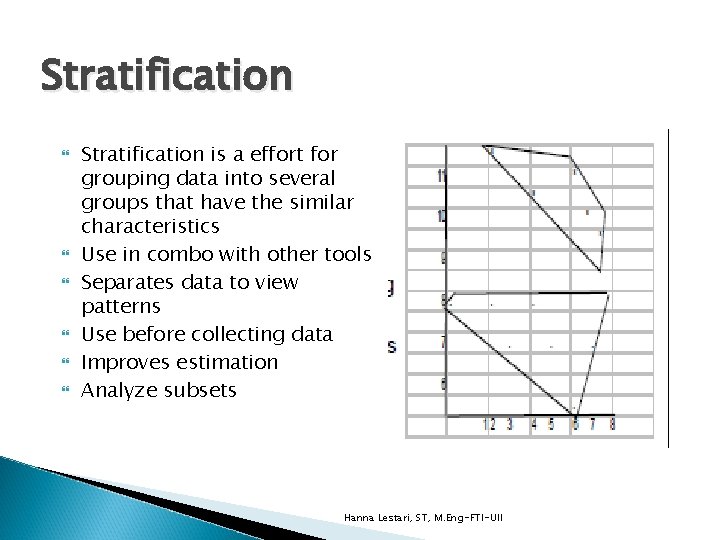
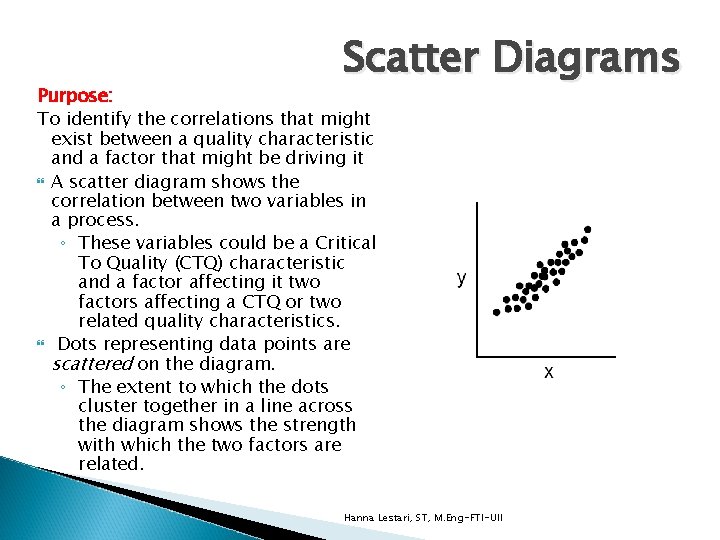
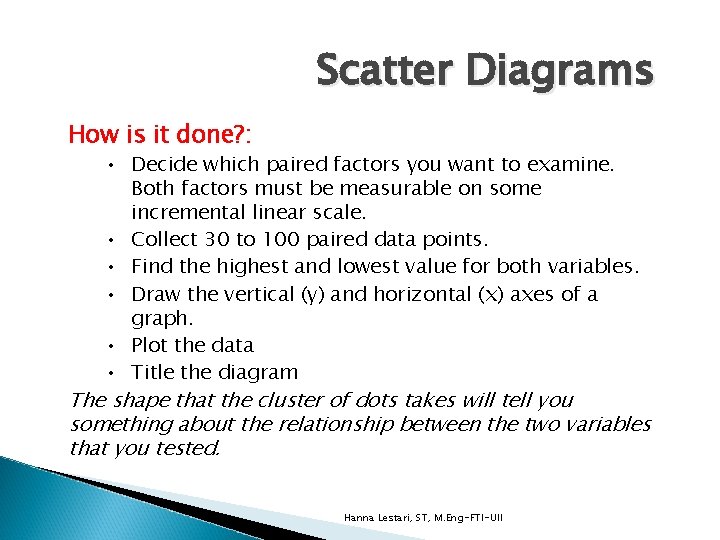
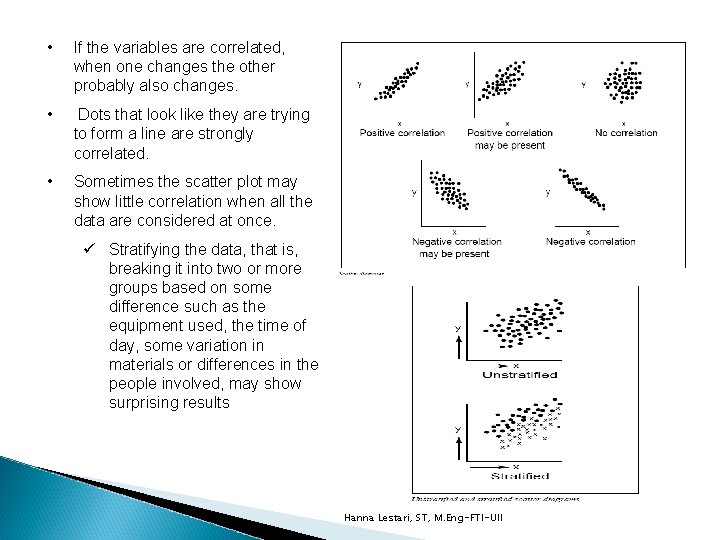
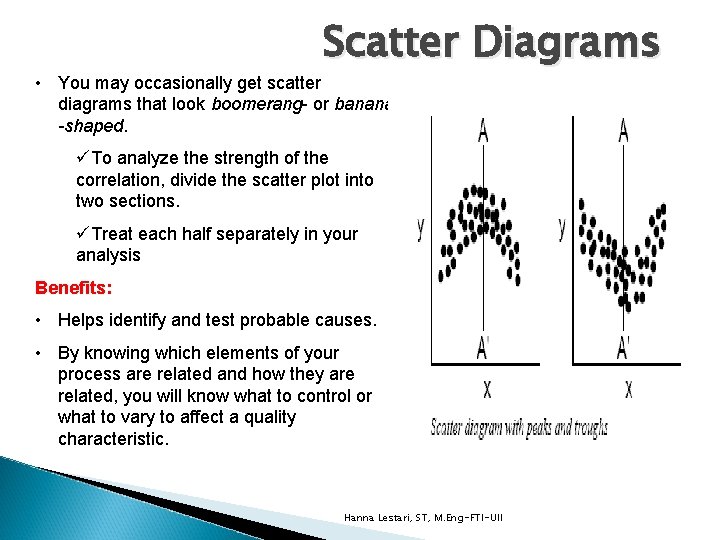
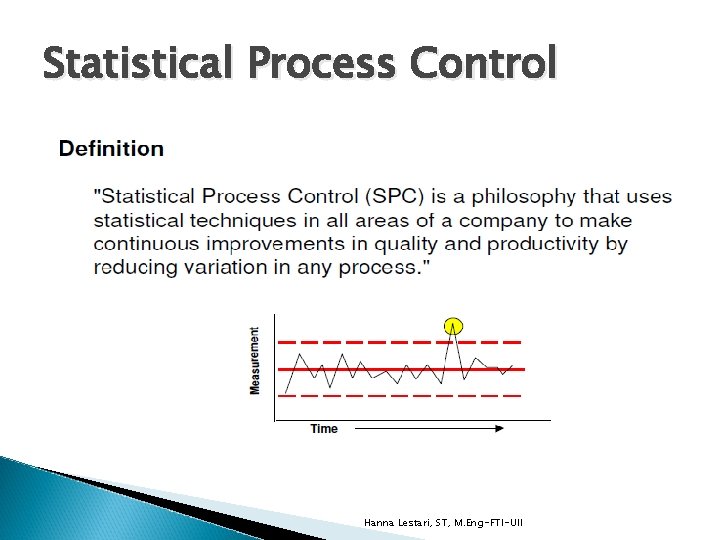
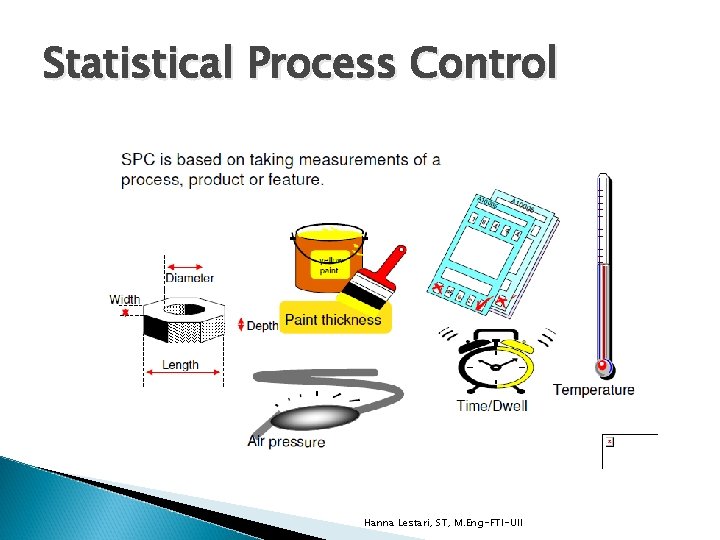
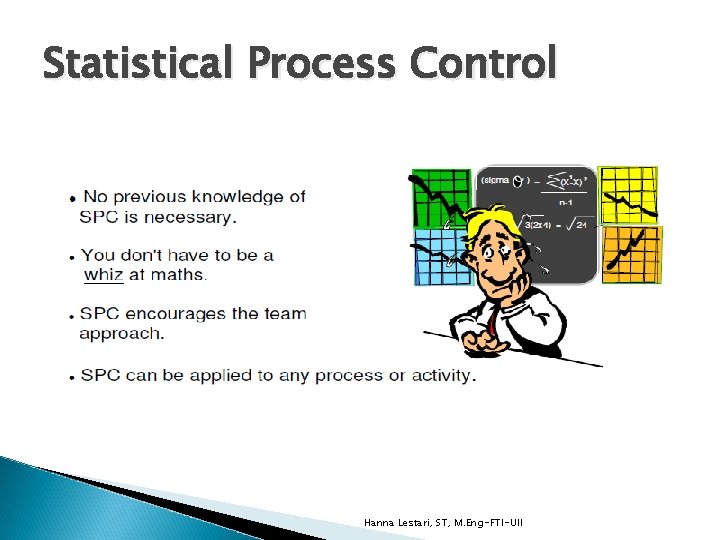
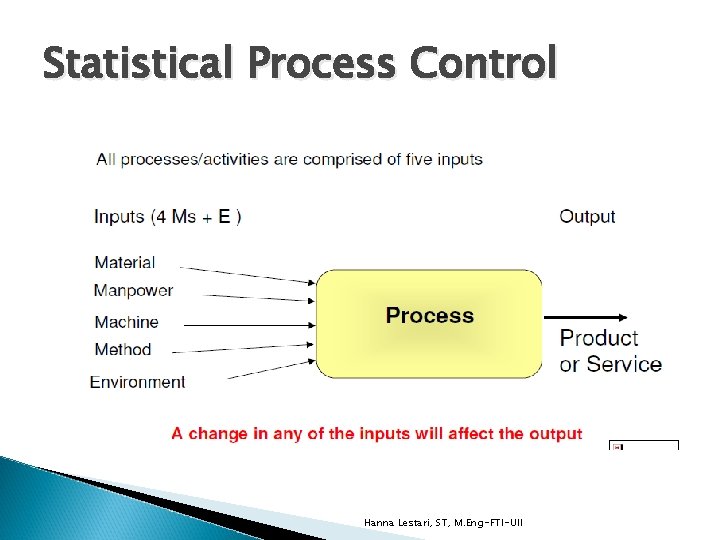
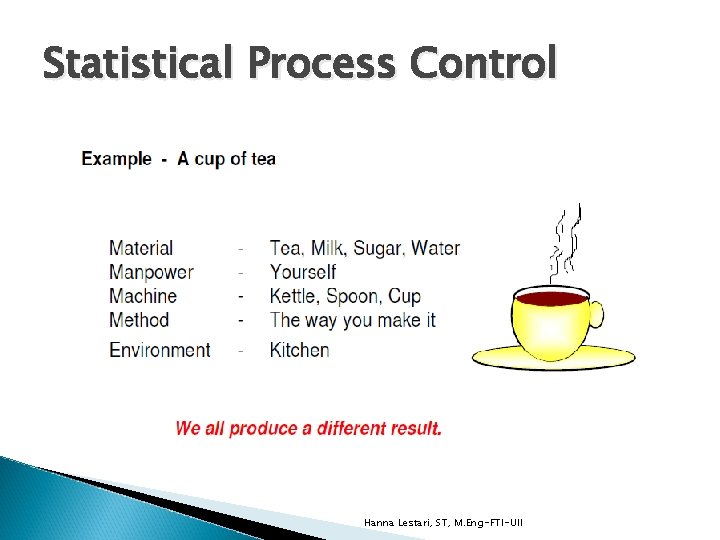
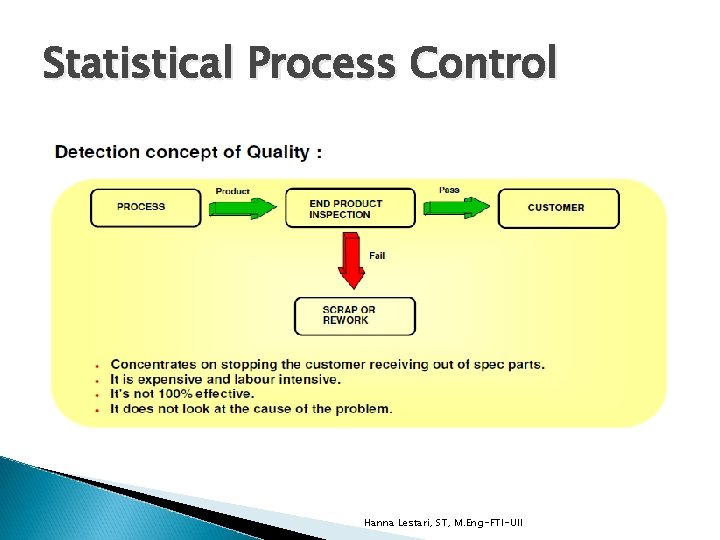
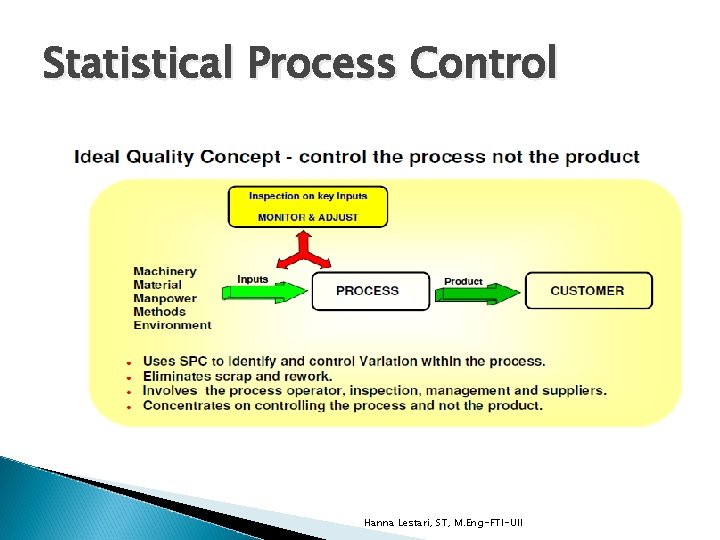
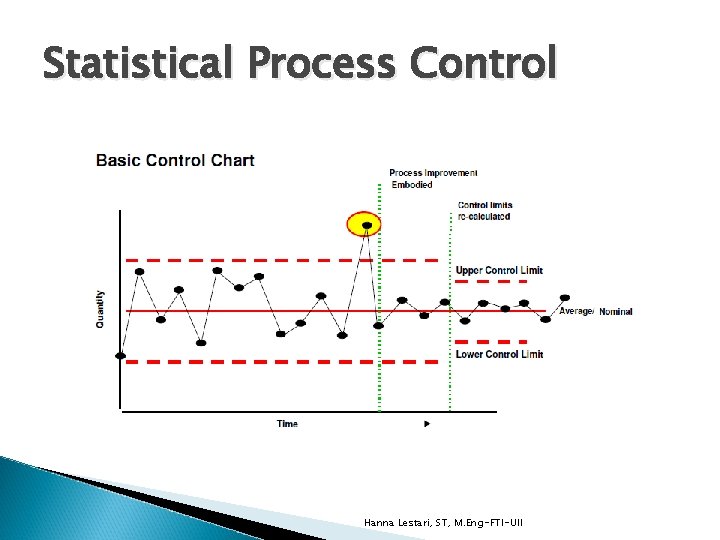
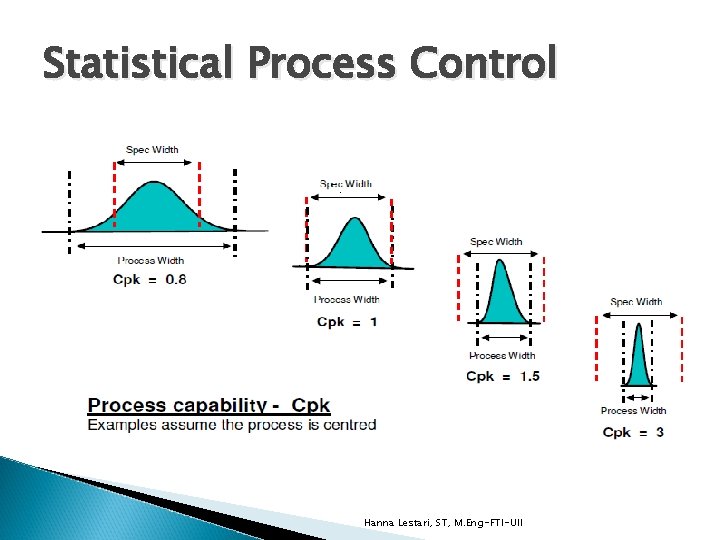
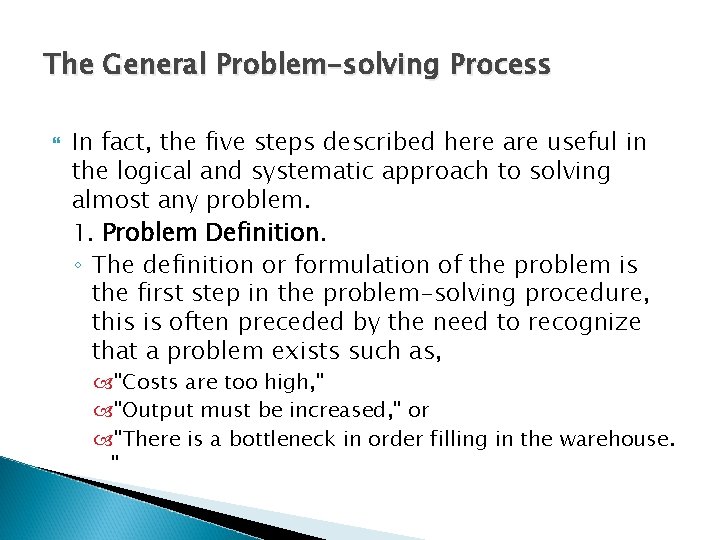
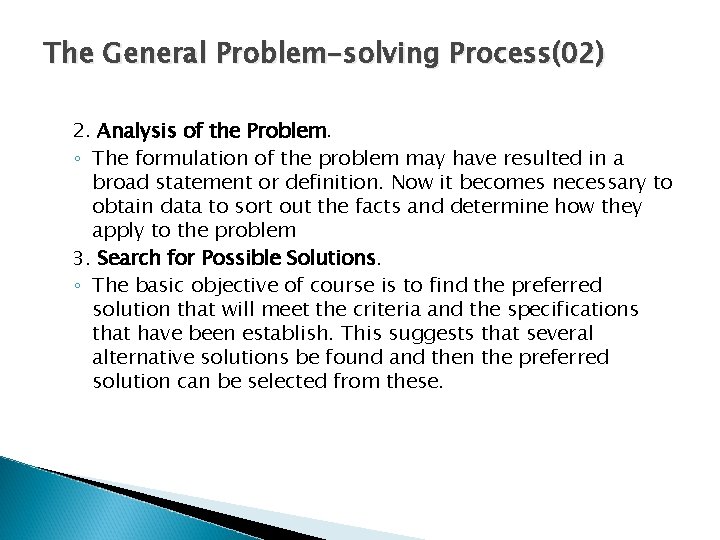
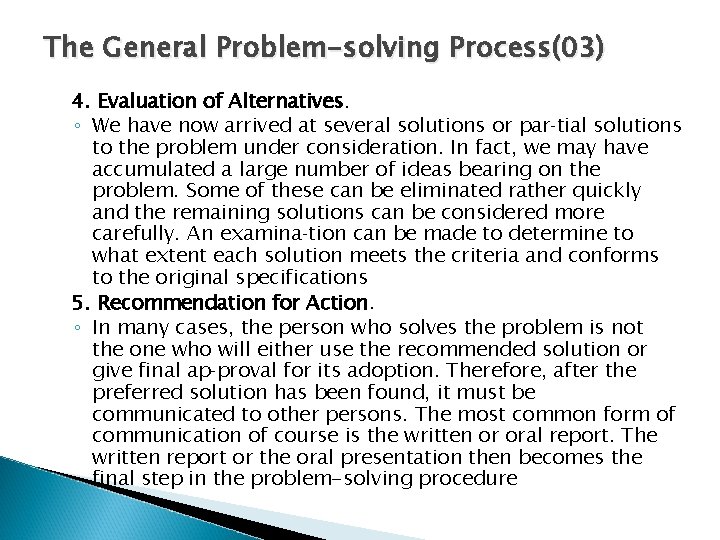
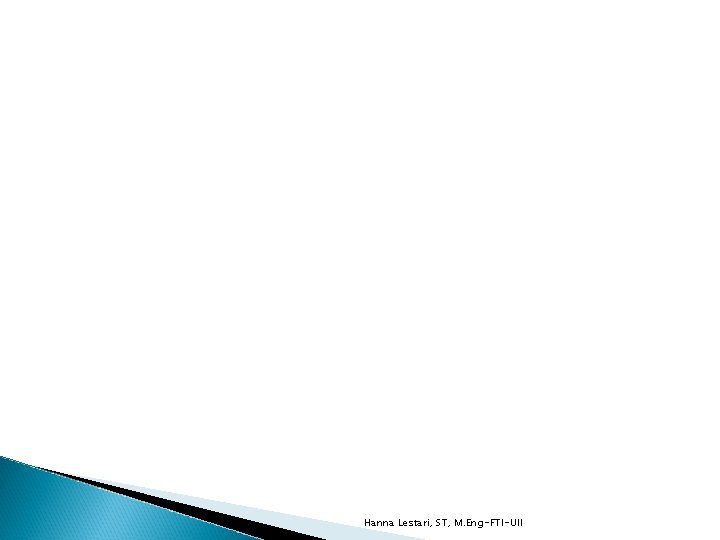
- Slides: 43
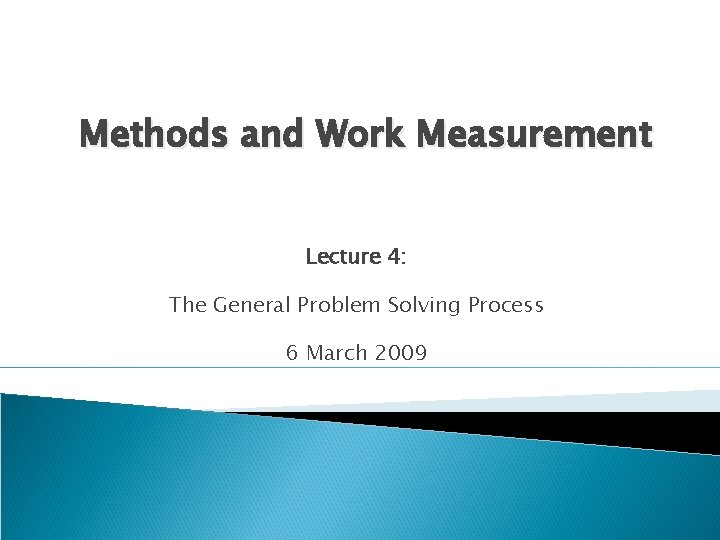
Methods and Work Measurement Lecture 4: The General Problem Solving Process 6 March 2009
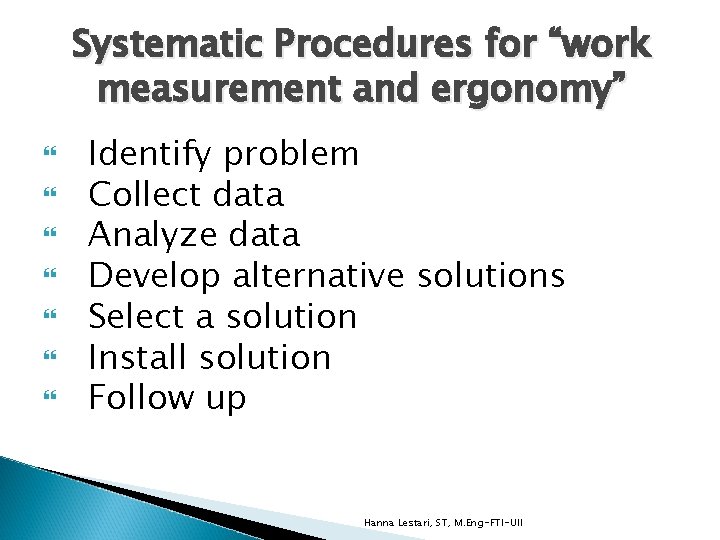
Systematic Procedures for “work measurement and ergonomy” Identify problem Collect data Analyze data Develop alternative solutions Select a solution Install solution Follow up Hanna Lestari, ST, M. Eng-FTI-UII
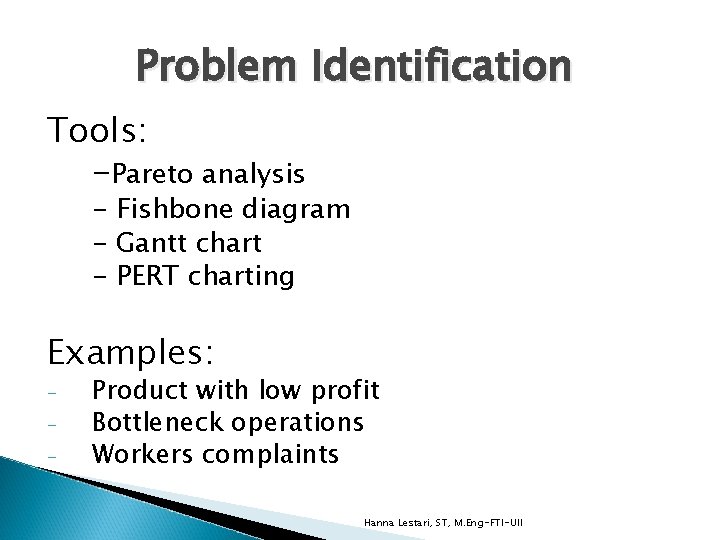
Problem Identification Tools: -Pareto analysis - Fishbone diagram - Gantt chart - PERT charting Examples: - Product with low profit Bottleneck operations Workers complaints Hanna Lestari, ST, M. Eng-FTI-UII
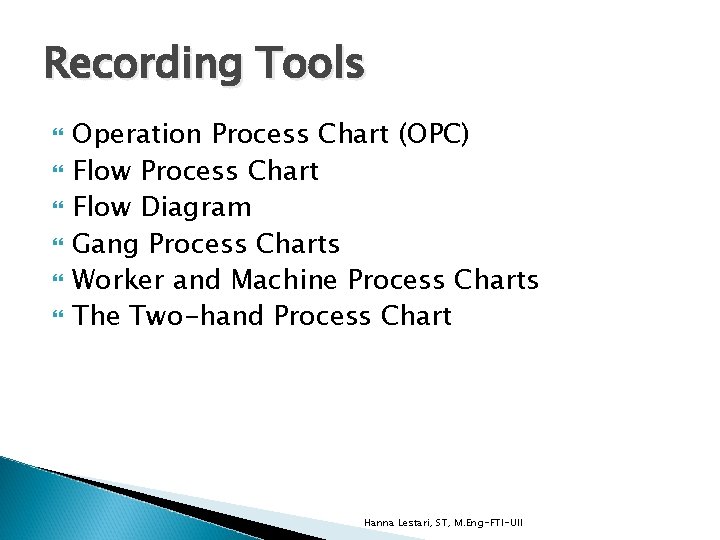
Recording Tools Operation Process Chart (OPC) Flow Process Chart Flow Diagram Gang Process Charts Worker and Machine Process Charts The Two-hand Process Chart Hanna Lestari, ST, M. Eng-FTI-UII
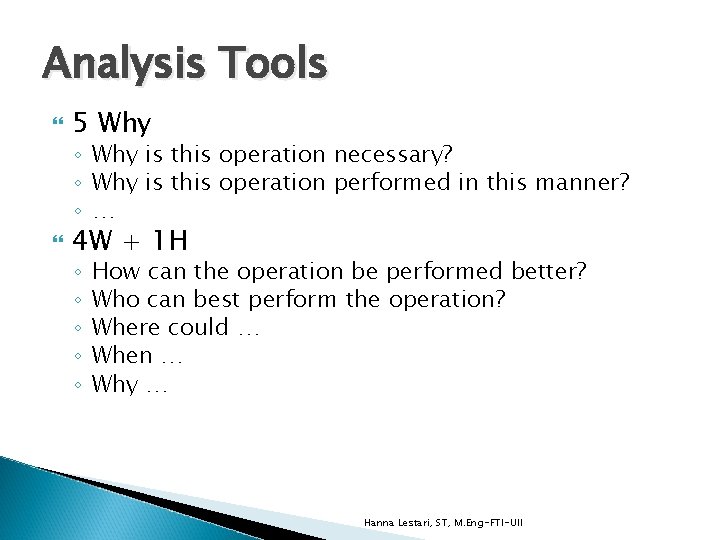
Analysis Tools 5 Why ◦ Why is this operation necessary? ◦ Why is this operation performed in this manner? ◦ … 4 W + 1 H ◦ ◦ ◦ How can the operation be performed better? Who can best perform the operation? Where could … When … Why … Hanna Lestari, ST, M. Eng-FTI-UII
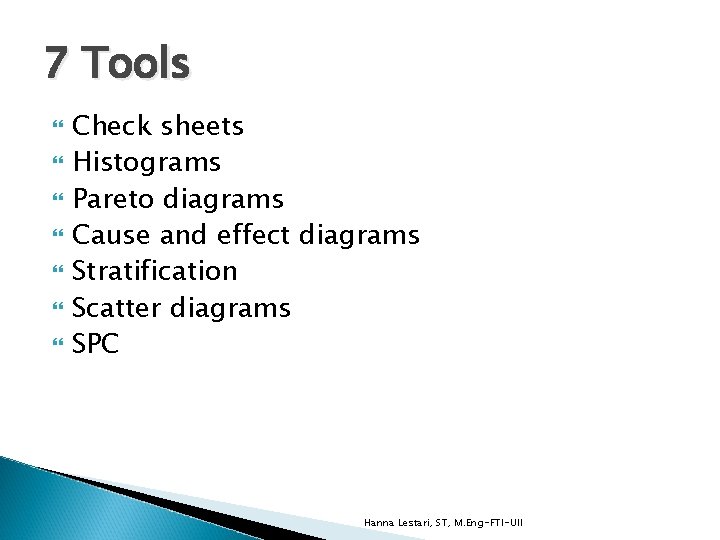
7 Tools Check sheets Histograms Pareto diagrams Cause and effect diagrams Stratification Scatter diagrams SPC Hanna Lestari, ST, M. Eng-FTI-UII
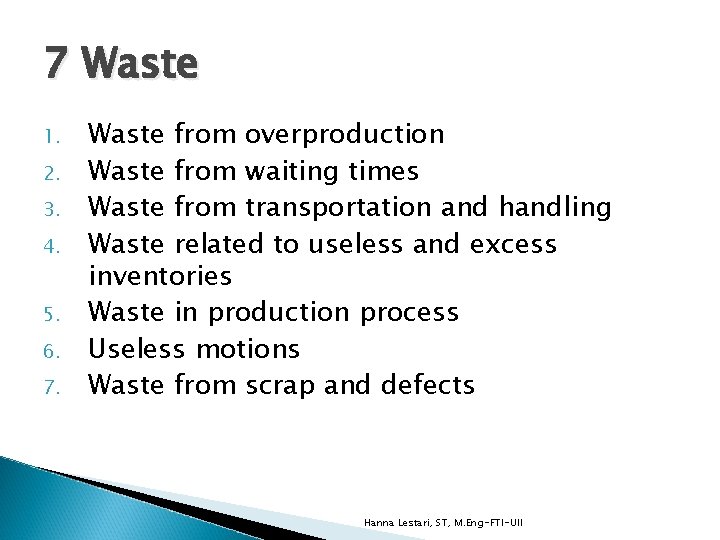
7 Waste 1. 2. 3. 4. 5. 6. 7. Waste from overproduction Waste from waiting times Waste from transportation and handling Waste related to useless and excess inventories Waste in production process Useless motions Waste from scrap and defects Hanna Lestari, ST, M. Eng-FTI-UII
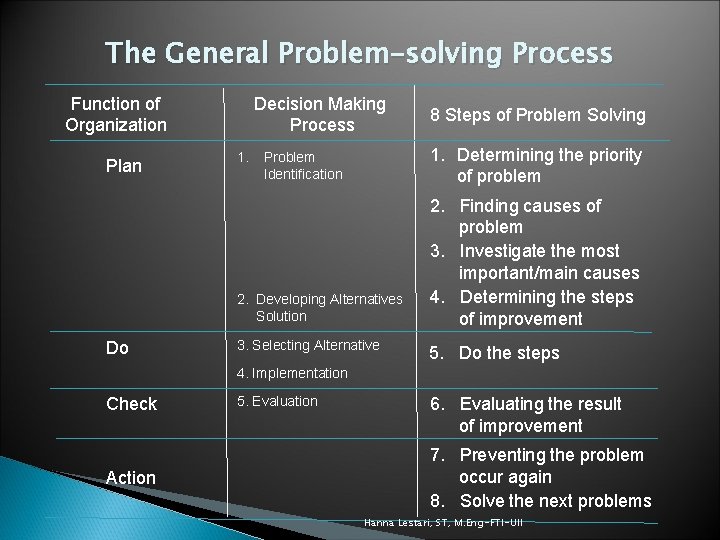
The General Problem-solving Process Function of Organization Plan Decision Making Process 1. Determining the priority of problem Problem Identification 2. Developing Alternatives Solution Do 8 Steps of Problem Solving 3. Selecting Alternative 2. Finding causes of problem 3. Investigate the most important/main causes 4. Determining the steps of improvement 5. Do the steps 4. Implementation Check Action 5. Evaluation 6. Evaluating the result of improvement 7. Preventing the problem occur again 8. Solve the next problems Hanna Lestari, ST, M. Eng-FTI-UII
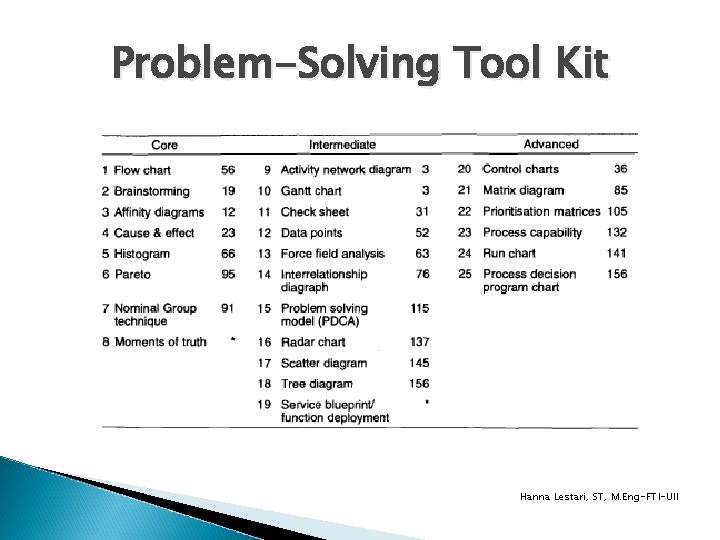
Problem-Solving Tool Kit Hanna Lestari, ST, M. Eng-FTI-UII
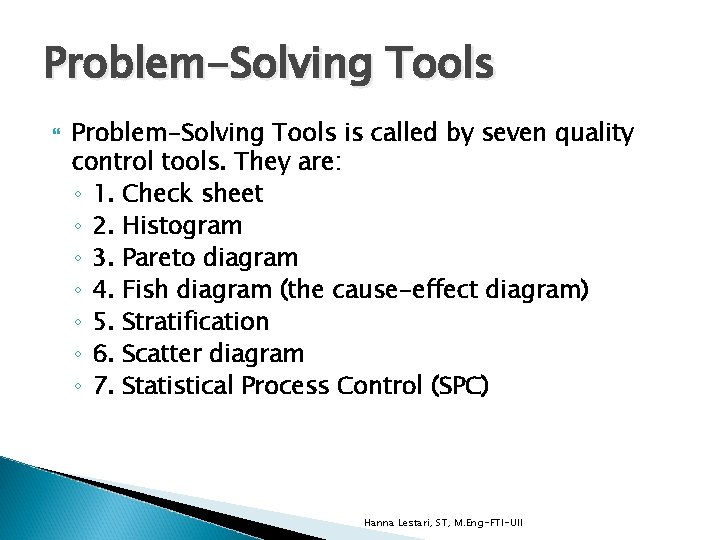
Problem-Solving Tools is called by seven quality control tools. They are: ◦ 1. Check sheet ◦ 2. Histogram ◦ 3. Pareto diagram ◦ 4. Fish diagram (the cause-effect diagram) ◦ 5. Stratification ◦ 6. Scatter diagram ◦ 7. Statistical Process Control (SPC) Hanna Lestari, ST, M. Eng-FTI-UII
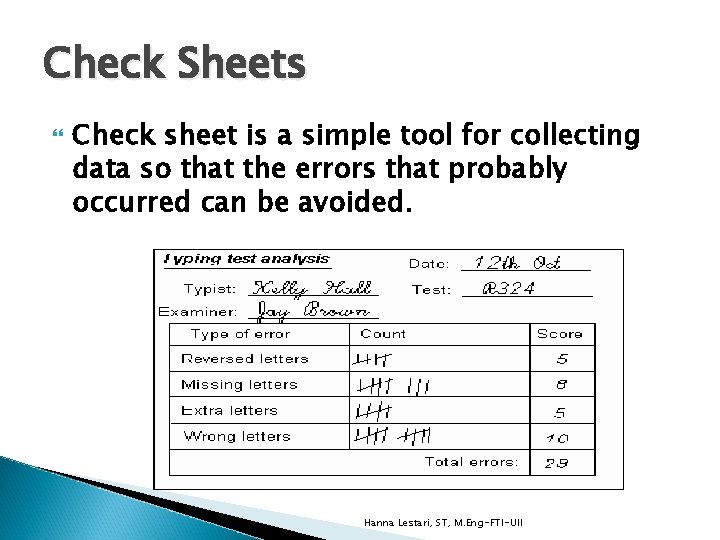
Check Sheets Check sheet is a simple tool for collecting data so that the errors that probably occurred can be avoided. Hanna Lestari, ST, M. Eng-FTI-UII
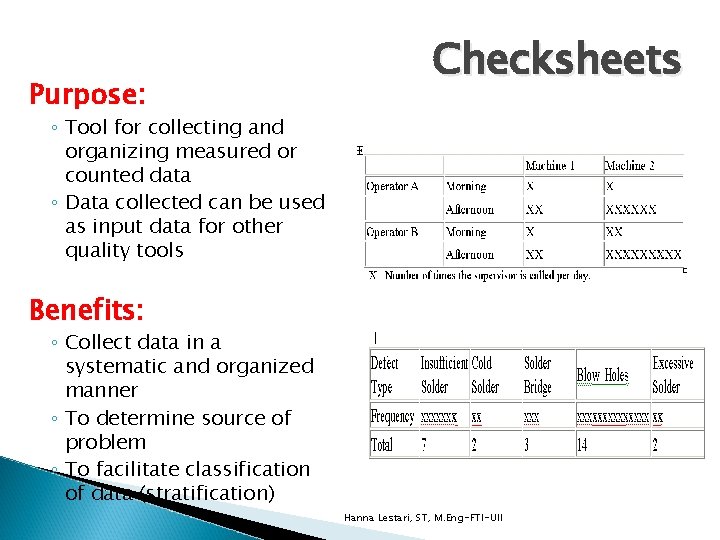
Purpose: Checksheets ◦ Tool for collecting and organizing measured or counted data ◦ Data collected can be used as input data for other quality tools Benefits: ◦ Collect data in a systematic and organized manner ◦ To determine source of problem ◦ To facilitate classification of data (stratification) Hanna Lestari, ST, M. Eng-FTI-UII
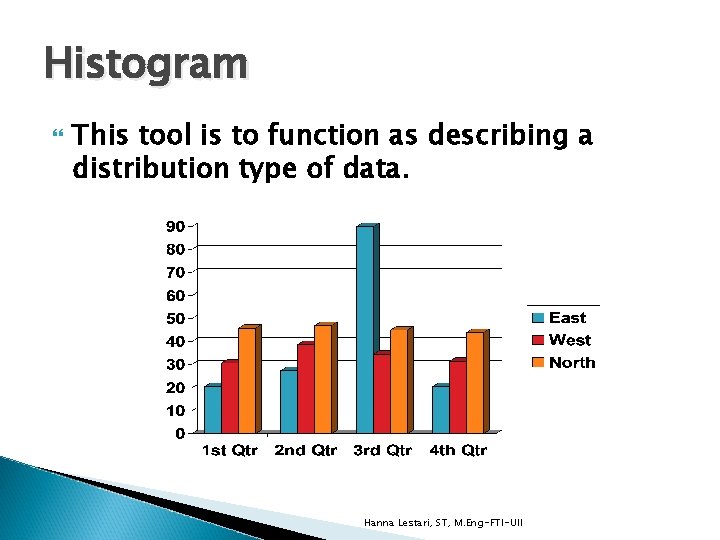
Histogram This tool is to function as describing a distribution type of data. Hanna Lestari, ST, M. Eng-FTI-UII
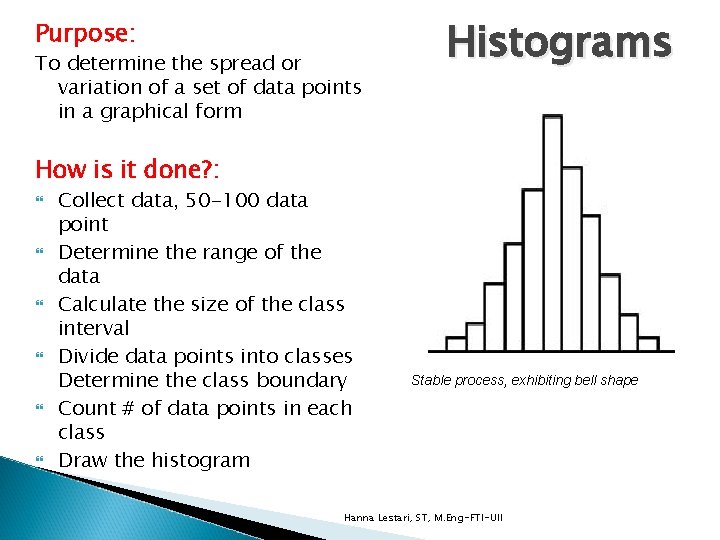
Purpose: To determine the spread or variation of a set of data points in a graphical form Histograms How is it done? : Collect data, 50 -100 data point Determine the range of the data Calculate the size of the class interval Divide data points into classes Determine the class boundary Count # of data points in each class Draw the histogram Stable process, exhibiting bell shape Hanna Lestari, ST, M. Eng-FTI-UII
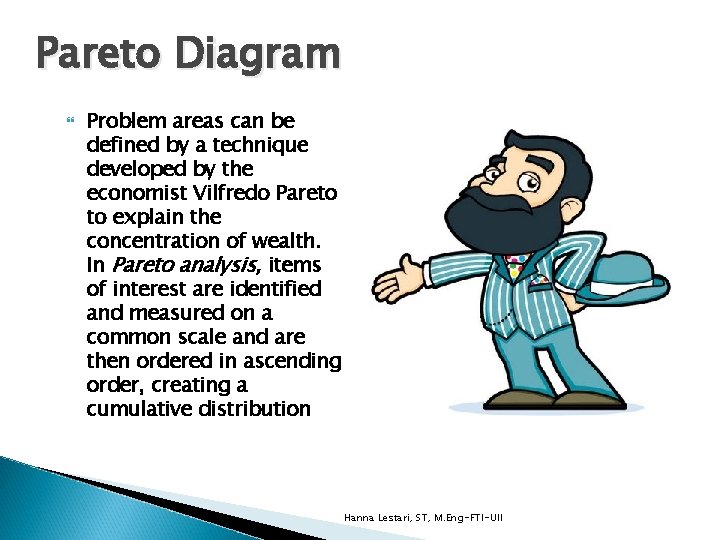
Pareto Diagram Problem areas can be defined by a technique developed by the economist Vilfredo Pareto to explain the concentration of wealth. In Pareto analysis, items of interest are identified and measured on a common scale and are then ordered in ascending order, creating a cumulative distribution Hanna Lestari, ST, M. Eng-FTI-UII
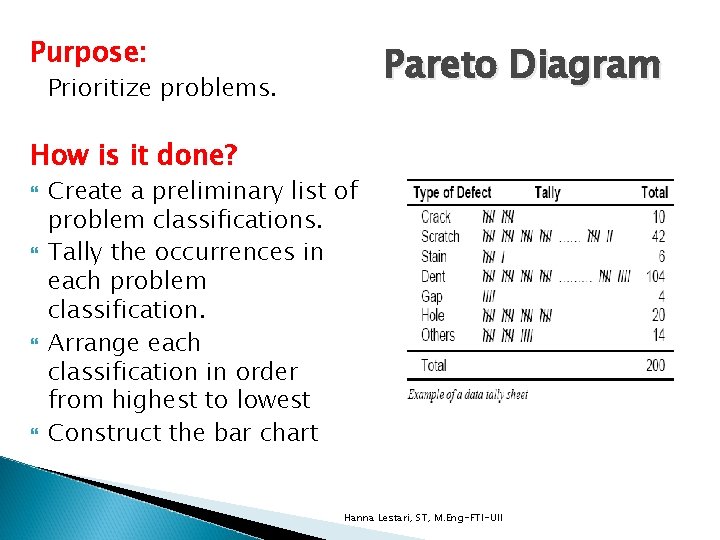
Purpose: Pareto Diagram Prioritize problems. How is it done? Create a preliminary list of problem classifications. Tally the occurrences in each problem classification. Arrange each classification in order from highest to lowest Construct the bar chart Hanna Lestari, ST, M. Eng-FTI-UII
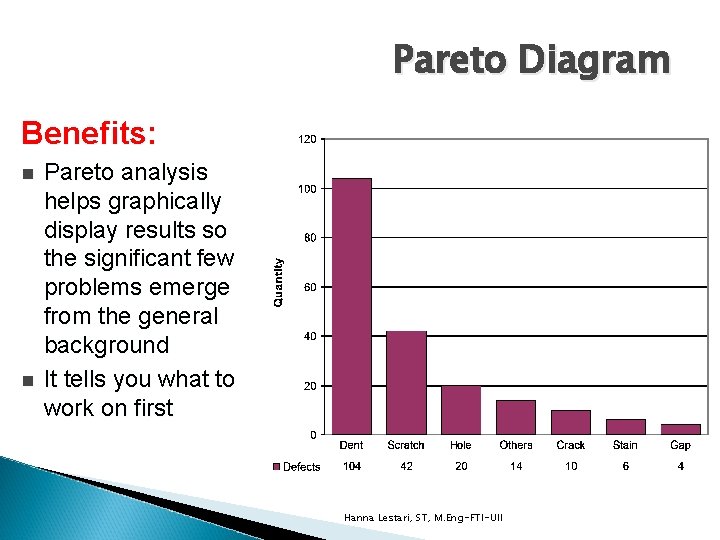
Pareto Diagram Benefits: n n Pareto analysis helps graphically display results so the significant few problems emerge from the general background It tells you what to work on first Hanna Lestari, ST, M. Eng-FTI-UII
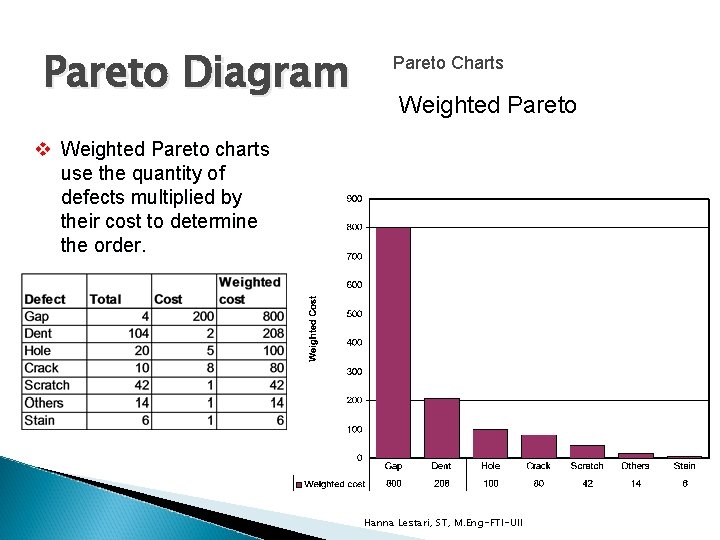
Pareto Diagram Pareto Charts Weighted Pareto v Weighted Pareto charts use the quantity of defects multiplied by their cost to determine the order. Hanna Lestari, ST, M. Eng-FTI-UII
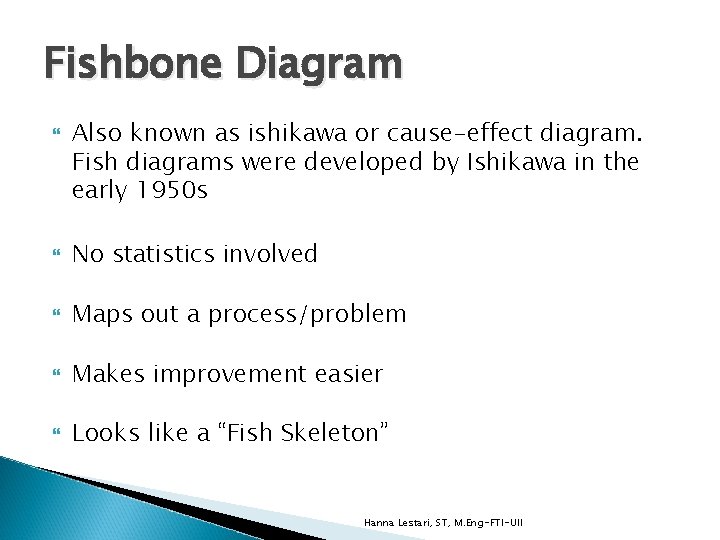
Fishbone Diagram Also known as ishikawa or cause-effect diagram. Fish diagrams were developed by Ishikawa in the early 1950 s No statistics involved Maps out a process/problem Makes improvement easier Looks like a “Fish Skeleton” Hanna Lestari, ST, M. Eng-FTI-UII
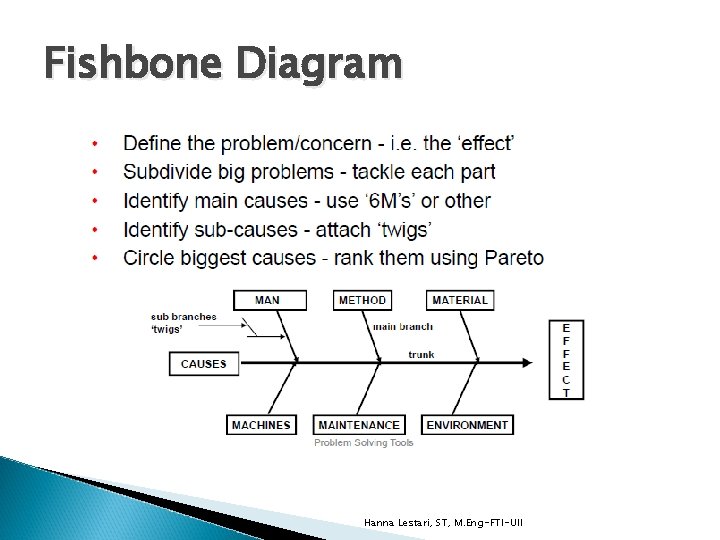
Fishbone Diagram Hanna Lestari, ST, M. Eng-FTI-UII
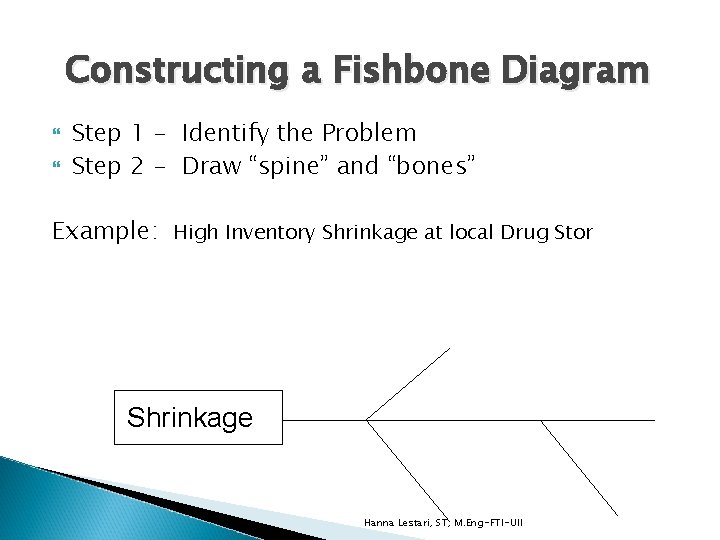
Constructing a Fishbone Diagram Step 1 - Identify the Problem Step 2 - Draw “spine” and “bones” Example: High Inventory Shrinkage at local Drug Stor Shrinkage Hanna Lestari, ST, M. Eng-FTI-UII
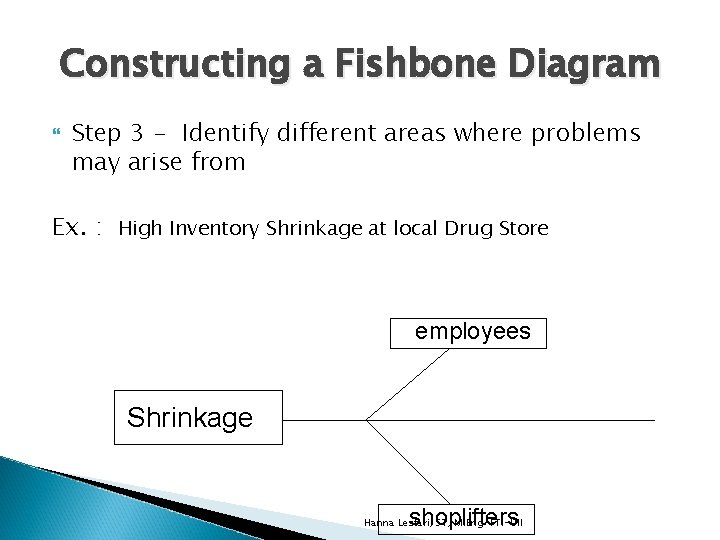
Constructing a Fishbone Diagram Step 3 - Identify different areas where problems may arise from Ex. : High Inventory Shrinkage at local Drug Store employees Shrinkage shoplifters Hanna Lestari, ST, M. Eng-FTI-UII
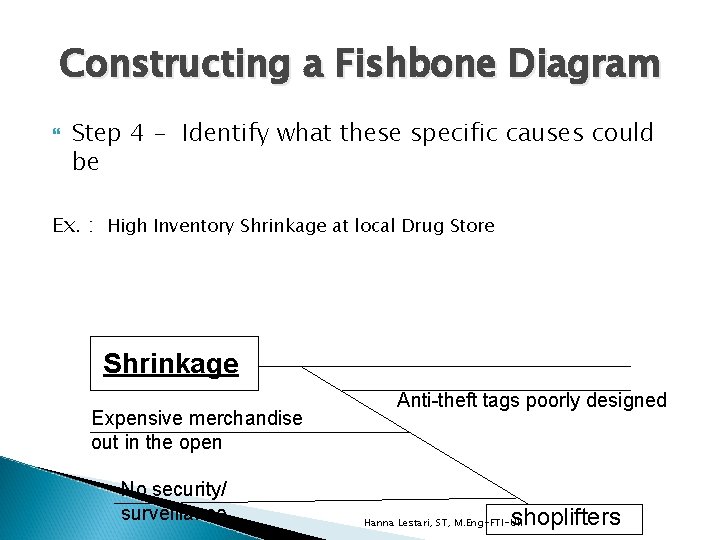
Constructing a Fishbone Diagram Step 4 - Identify what these specific causes could be Ex. : High Inventory Shrinkage at local Drug Store Shrinkage Expensive merchandise out in the open No security/ surveillance Anti-theft tags poorly designed shoplifters Hanna Lestari, ST, M. Eng-FTI-UII
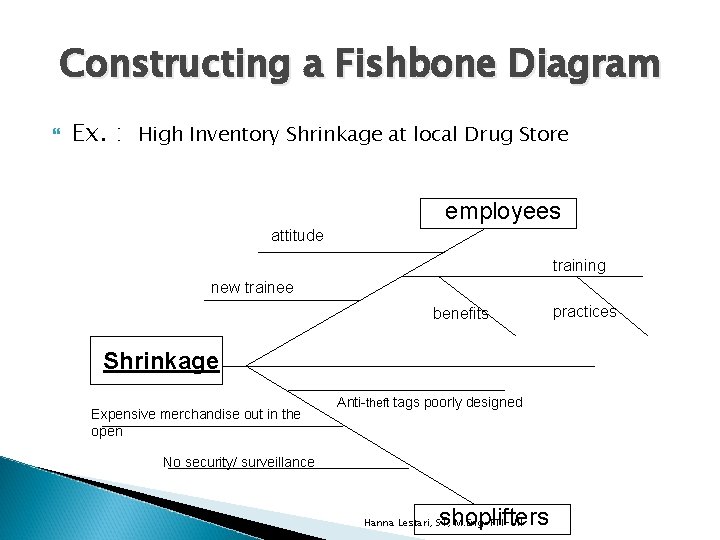
Constructing a Fishbone Diagram Ex. : High Inventory Shrinkage at local Drug Store employees attitude training new trainee benefits Shrinkage Expensive merchandise out in the open Anti-theft tags poorly designed No security/ surveillance shoplifters Hanna Lestari, ST, M. Eng-FTI-UII practices
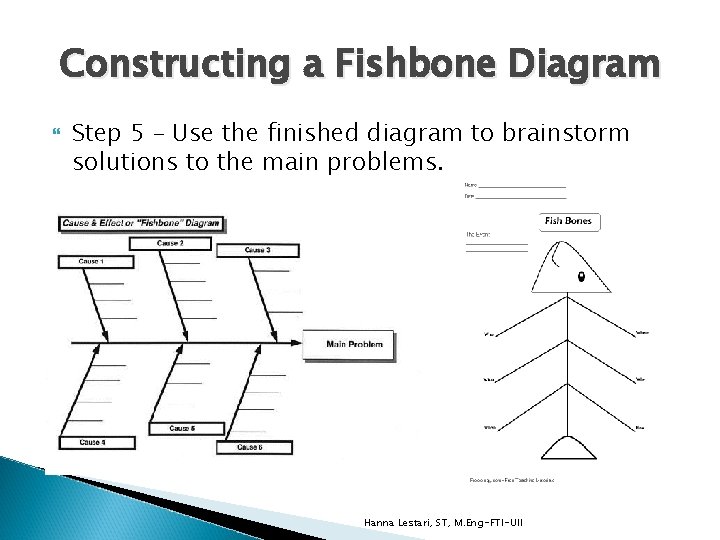
Constructing a Fishbone Diagram Step 5 – Use the finished diagram to brainstorm solutions to the main problems. Hanna Lestari, ST, M. Eng-FTI-UII
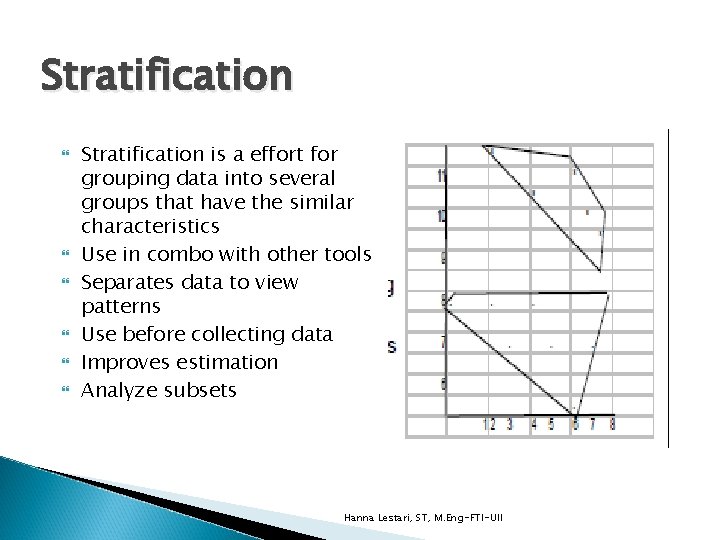
Stratification Stratification is a effort for grouping data into several groups that have the similar characteristics Use in combo with other tools Separates data to view patterns Use before collecting data Improves estimation Analyze subsets Hanna Lestari, ST, M. Eng-FTI-UII
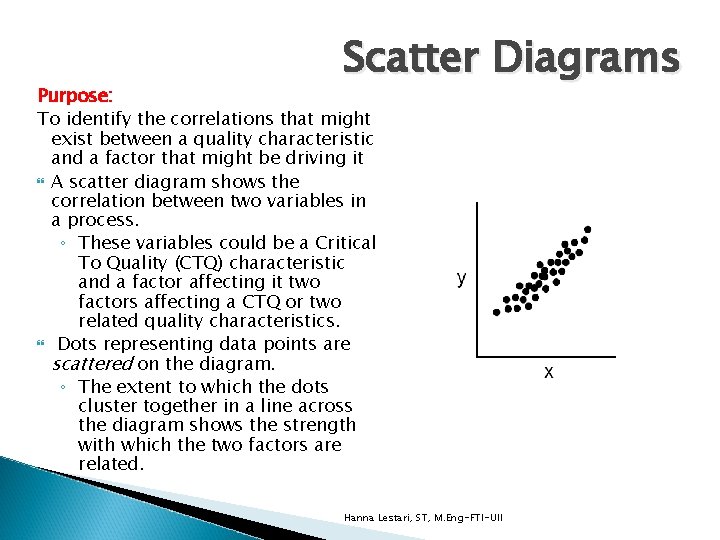
Scatter Diagrams Purpose: To identify the correlations that might exist between a quality characteristic and a factor that might be driving it A scatter diagram shows the correlation between two variables in a process. ◦ These variables could be a Critical To Quality (CTQ) characteristic and a factor affecting it two factors affecting a CTQ or two related quality characteristics. Dots representing data points are scattered on the diagram. ◦ The extent to which the dots cluster together in a line across the diagram shows the strength with which the two factors are related. Hanna Lestari, ST, M. Eng-FTI-UII
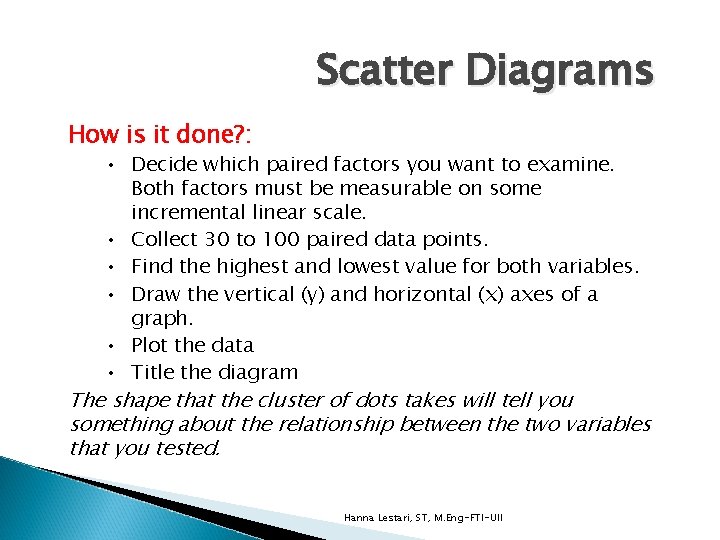
Scatter Diagrams How is it done? : • Decide which paired factors you want to examine. Both factors must be measurable on some incremental linear scale. • Collect 30 to 100 paired data points. • Find the highest and lowest value for both variables. • Draw the vertical (y) and horizontal (x) axes of a graph. • Plot the data • Title the diagram The shape that the cluster of dots takes will tell you something about the relationship between the two variables that you tested. Hanna Lestari, ST, M. Eng-FTI-UII
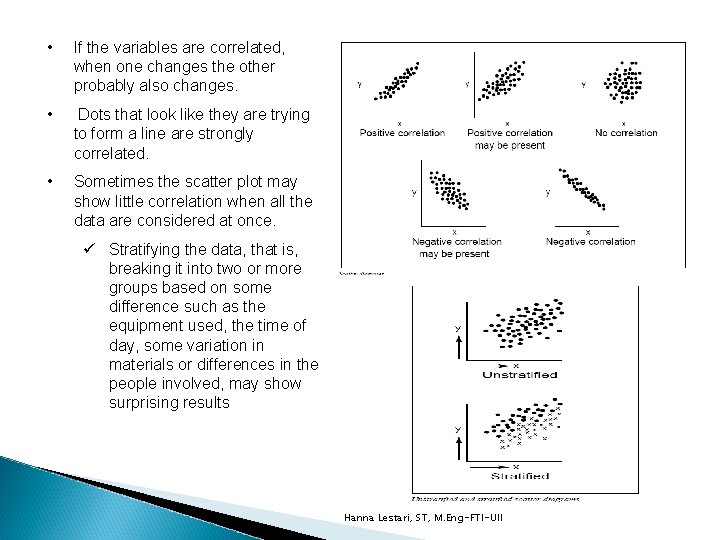
• If the variables are correlated, when one changes the other probably also changes. • Dots that look like they are trying to form a line are strongly correlated. • Sometimes the scatter plot may show little correlation when all the data are considered at once. Scatter Diagrams ü Stratifying the data, that is, breaking it into two or more groups based on some difference such as the equipment used, the time of day, some variation in materials or differences in the people involved, may show surprising results Hanna Lestari, ST, M. Eng-FTI-UII
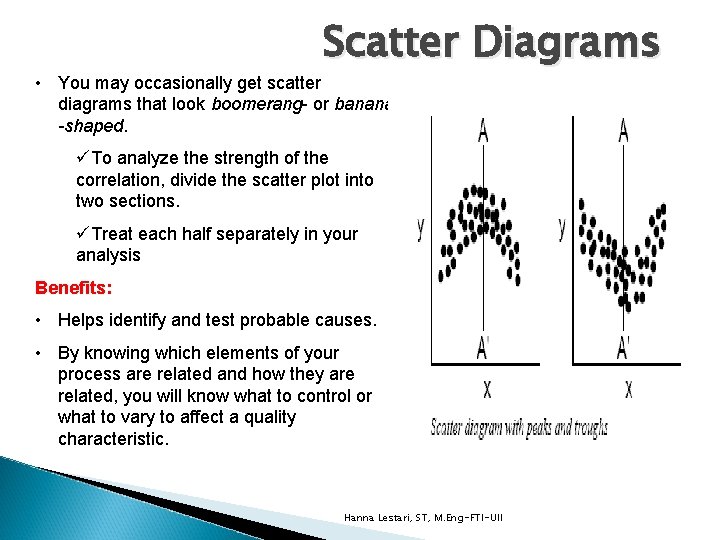
Scatter Diagrams • You may occasionally get scatter diagrams that look boomerang- or banana -shaped. üTo analyze the strength of the correlation, divide the scatter plot into two sections. üTreat each half separately in your analysis Benefits: • Helps identify and test probable causes. • By knowing which elements of your process are related and how they are related, you will know what to control or what to vary to affect a quality characteristic. Hanna Lestari, ST, M. Eng-FTI-UII
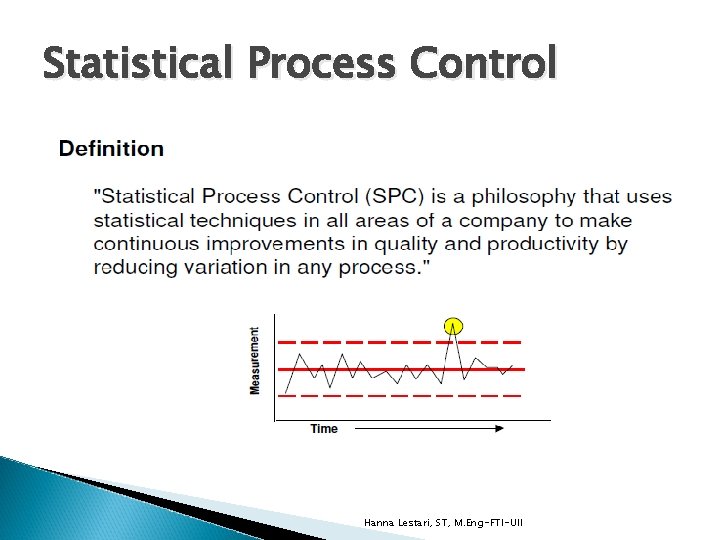
Statistical Process Control Hanna Lestari, ST, M. Eng-FTI-UII
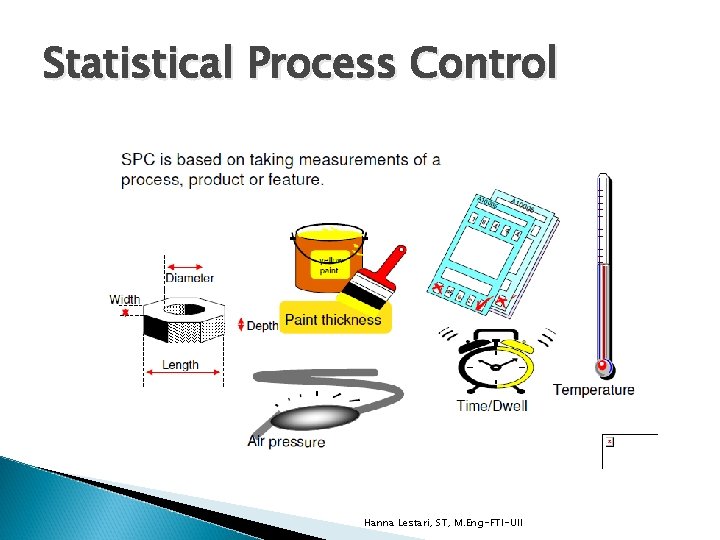
Statistical Process Control Hanna Lestari, ST, M. Eng-FTI-UII
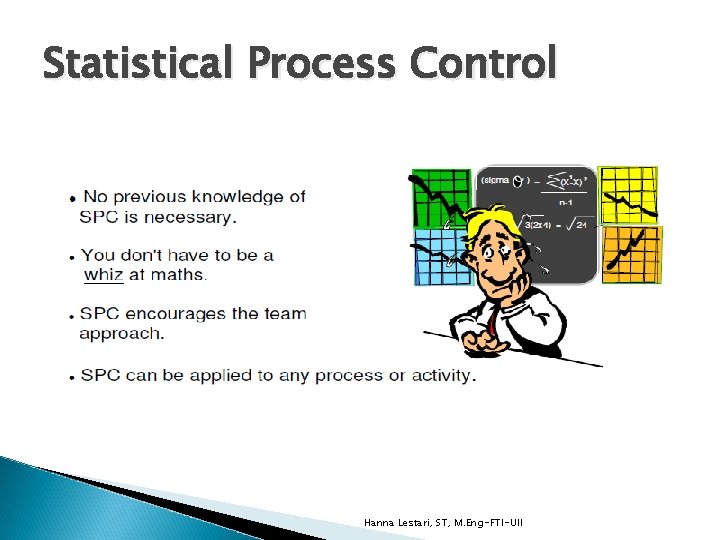
Statistical Process Control Hanna Lestari, ST, M. Eng-FTI-UII
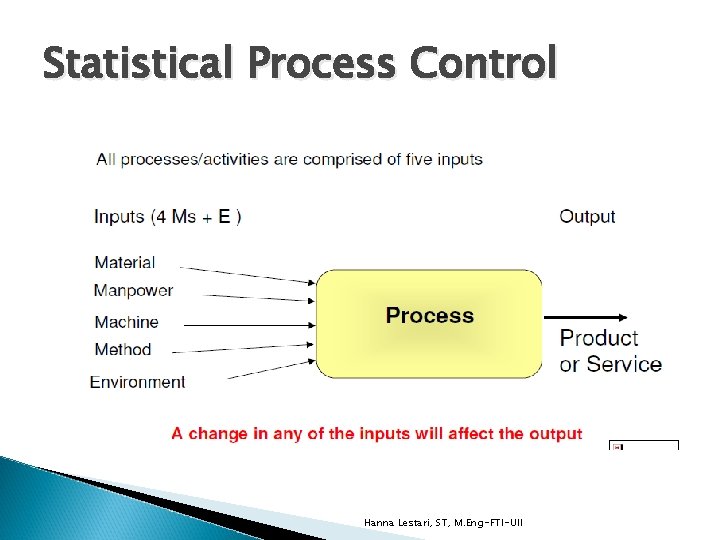
Statistical Process Control Hanna Lestari, ST, M. Eng-FTI-UII
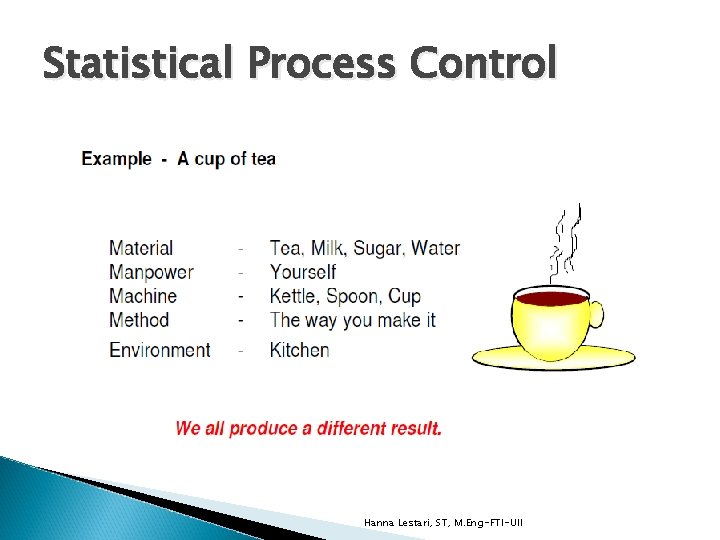
Statistical Process Control Hanna Lestari, ST, M. Eng-FTI-UII
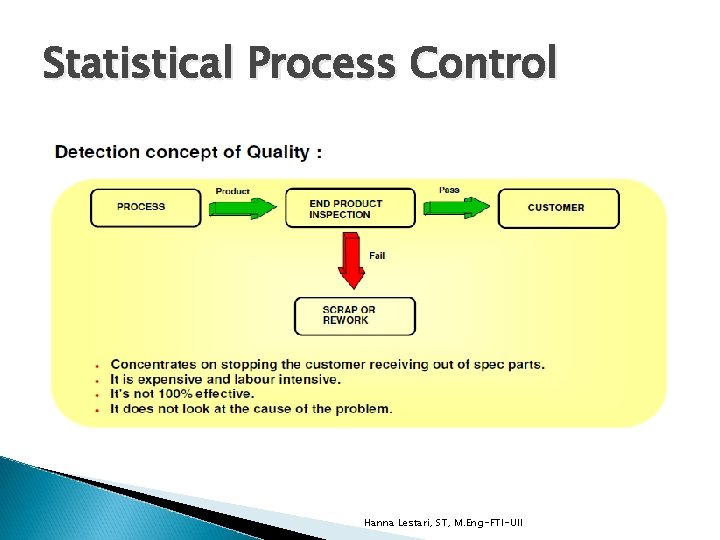
Statistical Process Control Hanna Lestari, ST, M. Eng-FTI-UII
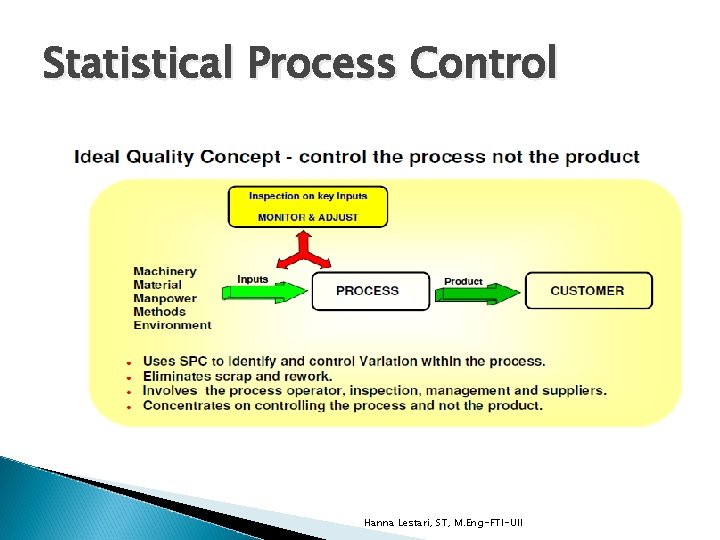
Statistical Process Control Hanna Lestari, ST, M. Eng-FTI-UII
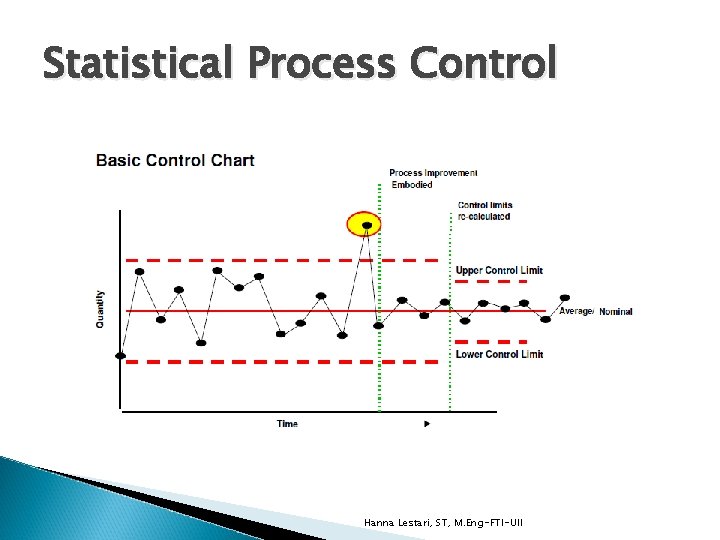
Statistical Process Control Hanna Lestari, ST, M. Eng-FTI-UII
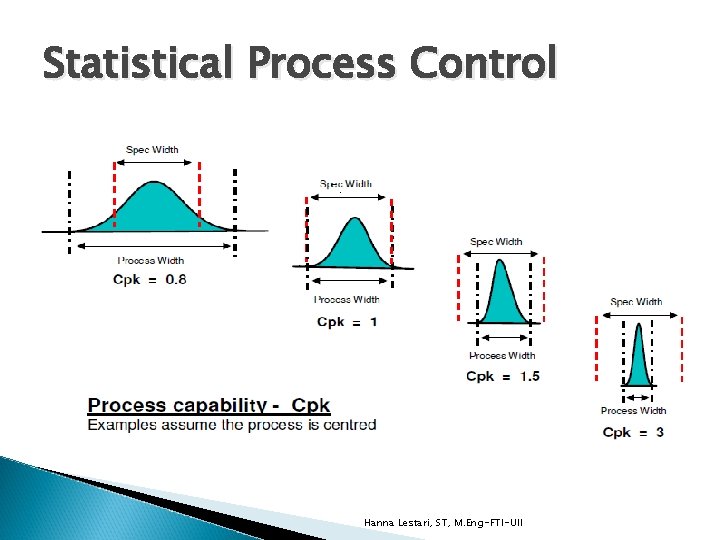
Statistical Process Control Hanna Lestari, ST, M. Eng-FTI-UII
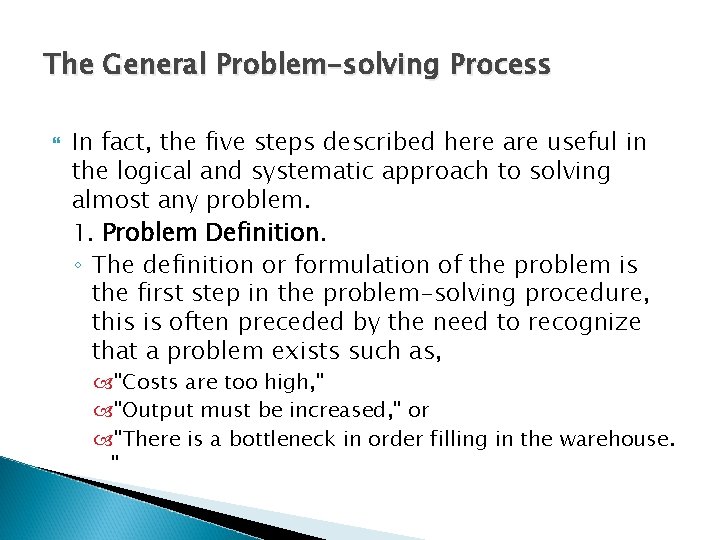
The General Problem-solving Process In fact, the five steps described here are useful in the logical and systematic approach to solving almost any problem. 1. Problem Definition. ◦ The definition or formulation of the problem is the first step in the problem-solving procedure, this is often preceded by the need to recognize that a problem exists such as, "Costs are too high, " "Output must be increased, " or "There is a bottleneck in order filling in the warehouse. "
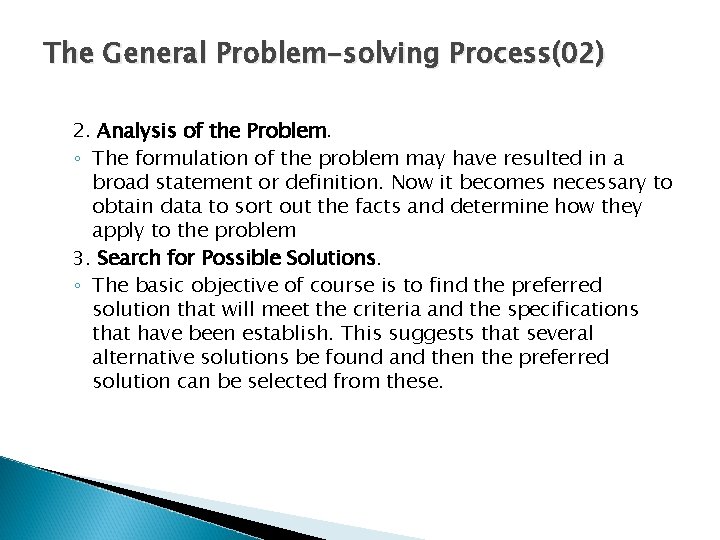
The General Problem-solving Process(02) 2. Analysis of the Problem. ◦ The formulation of the problem may have resulted in a broad statement or definition. Now it becomes necessary to obtain data to sort out the facts and determine how they apply to the problem 3. Search for Possible Solutions. ◦ The basic objective of course is to find the preferred solution that will meet the criteria and the specifications that have been establish. This suggests that several alternative solutions be found and then the preferred solution can be selected from these.
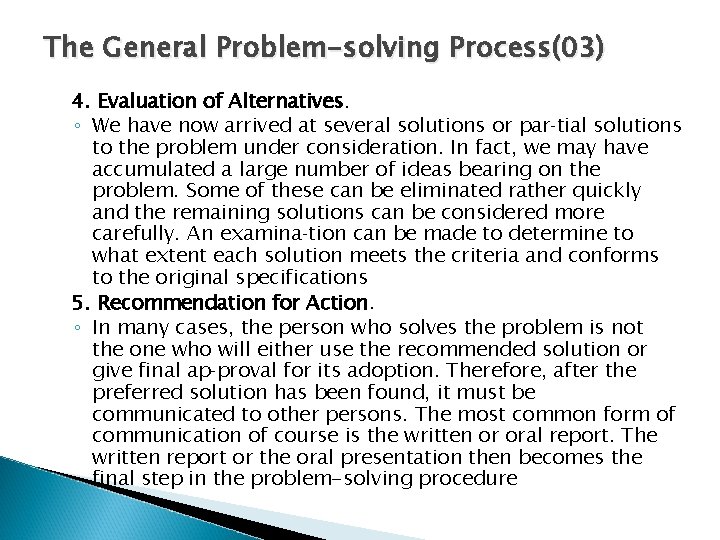
The General Problem-solving Process(03) 4. Evaluation of Alternatives. ◦ We have now arrived at several solutions or par tial solutions to the problem under consideration. In fact, we may have accumulated a large number of ideas bearing on the problem. Some of these can be eliminated rather quickly and the remaining solutions can be considered more carefully. An examina tion can be made to determine to what extent each solution meets the criteria and conforms to the original specifications 5. Recommendation for Action. ◦ In many cases, the person who solves the problem is not the one who will either use the recommended solution or give final ap proval for its adoption. Therefore, after the preferred solution has been found, it must be communicated to other persons. The most common form of communication of course is the written or oral report. The written report or the oral presentation then becomes the final step in the problem-solving procedure
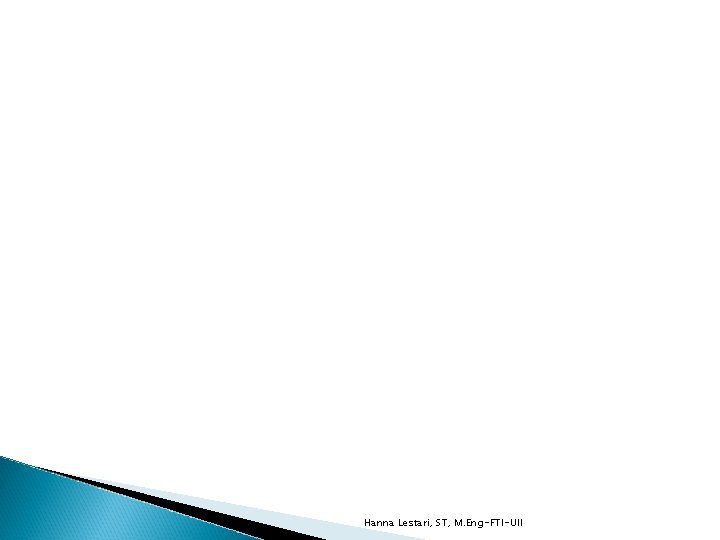
Hanna Lestari, ST, M. Eng-FTI-UII
01:640:244 lecture notes - lecture 15: plat, idah, farad
Transport phenomena lecture notes ppt
Body structure general survey
Normal pediatric vitals by age
Amoxicillin
Color of cyanmethemoglobin
Hook type level measurement
Mean arterial pressure formula
Butterflies pinwheels and wallpaper
Direct wax pattern technique
Wormhost chest worm locations
General medicine lecture
General parasitology lecture notes
Work design and measurement
Cara mengukur standar desain pekerjaan
Work design and measurement
Job design and work measurement
General physics 1 measurements
Work measurement steps
Section 4 review physical science
Methods in social work
Hát kết hợp bộ gõ cơ thể
Frameset trong html5
Bổ thể
Tỉ lệ cơ thể trẻ em
Gấu đi như thế nào
Thang điểm glasgow
Alleluia hat len nguoi oi
Môn thể thao bắt đầu bằng từ đua
Thế nào là hệ số cao nhất
Các châu lục và đại dương trên thế giới
Công thức tính thế năng
Trời xanh đây là của chúng ta thể thơ
Cách giải mật thư tọa độ
Phép trừ bù
độ dài liên kết
Các châu lục và đại dương trên thế giới
Thể thơ truyền thống
Quá trình desamine hóa có thể tạo ra
Một số thể thơ truyền thống
Cái miệng bé xinh thế chỉ nói điều hay thôi
Vẽ hình chiếu vuông góc của vật thể sau
Thế nào là sự mỏi cơ
đặc điểm cơ thể của người tối cổ