Lunar Settlement Transportation and Exploration Program LSTEP Kayvan
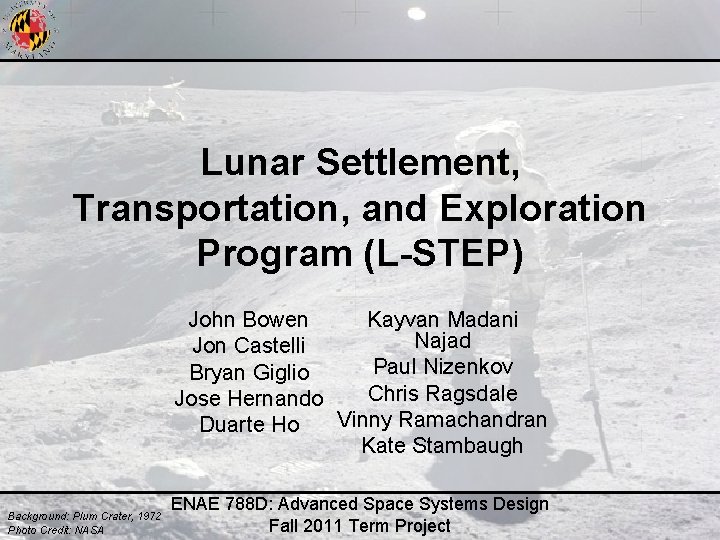
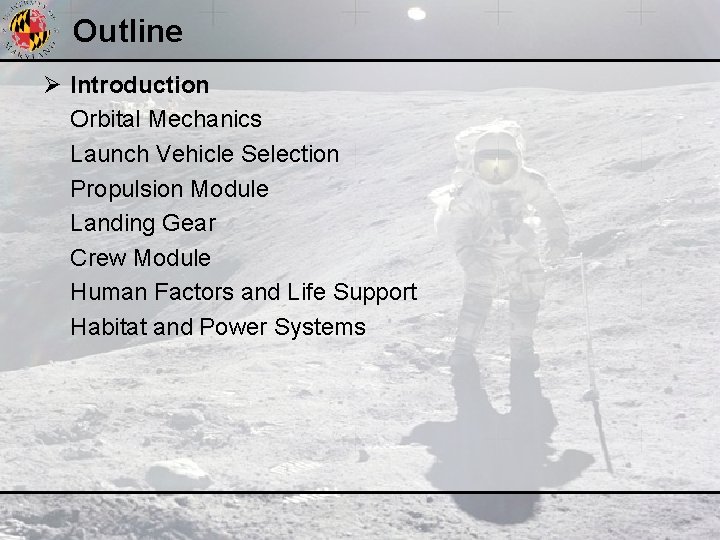
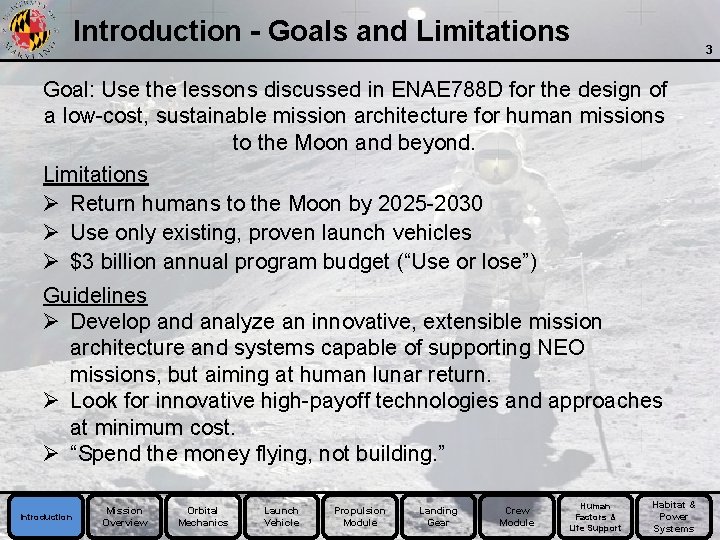
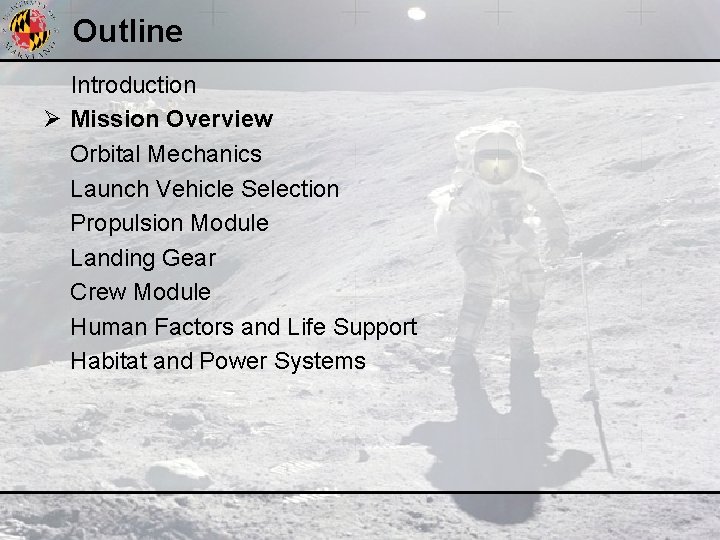
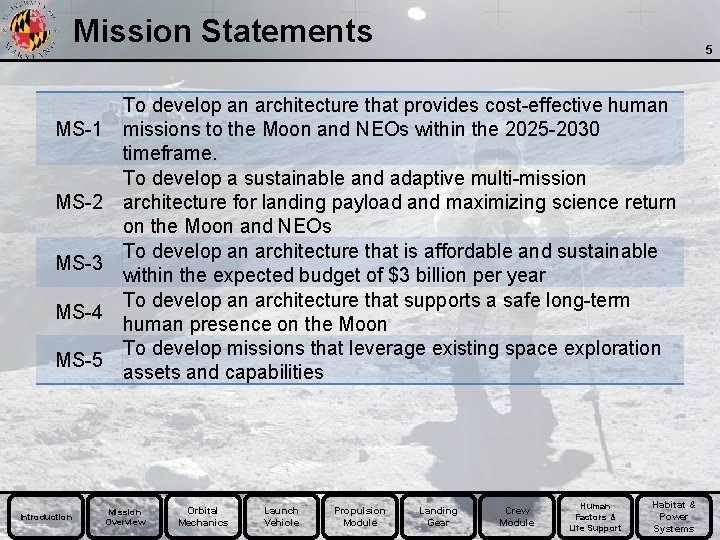

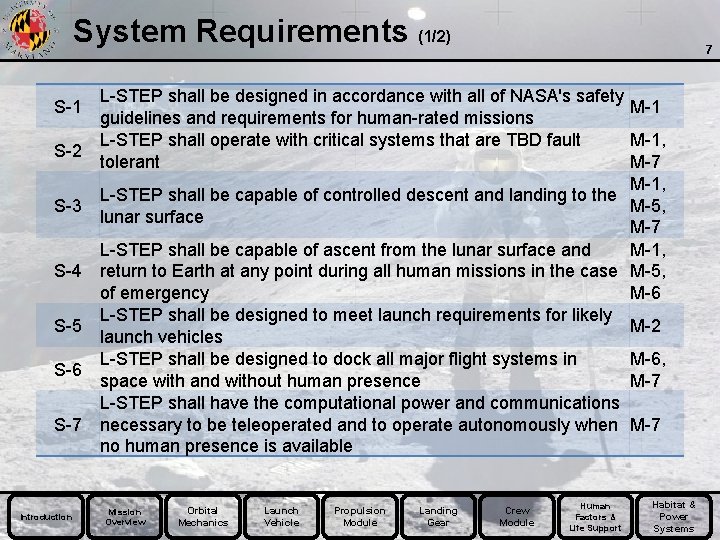
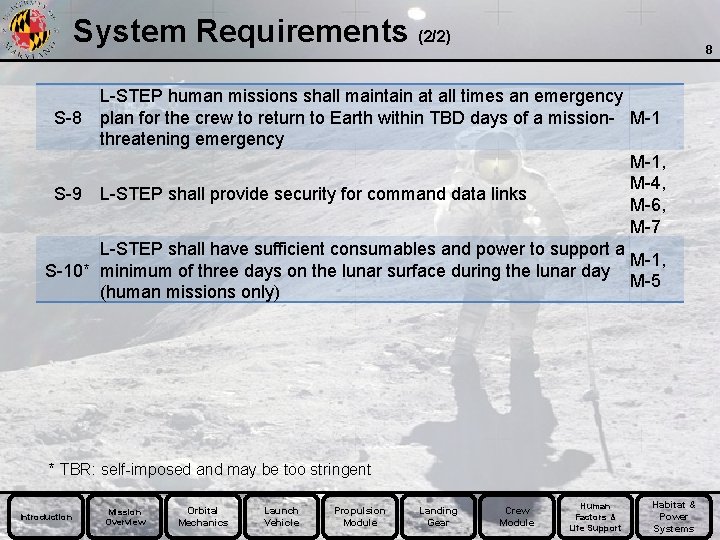
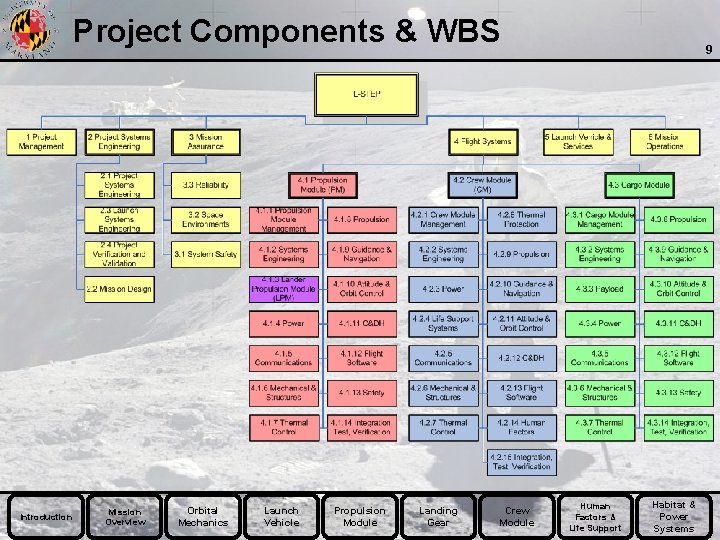
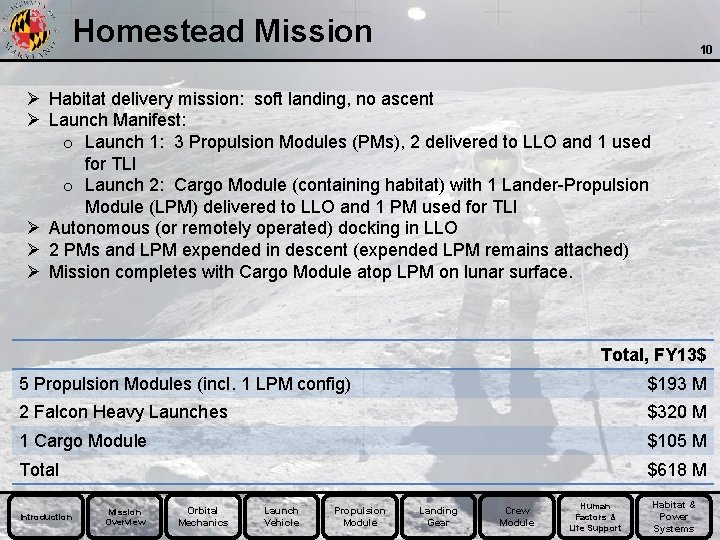
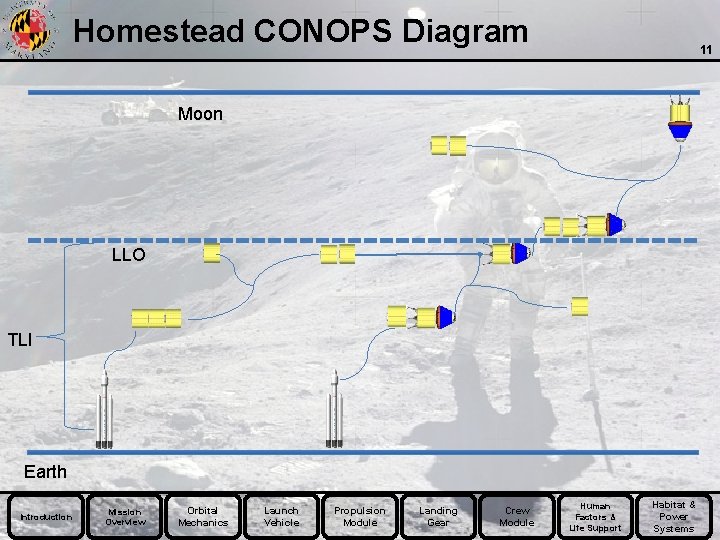
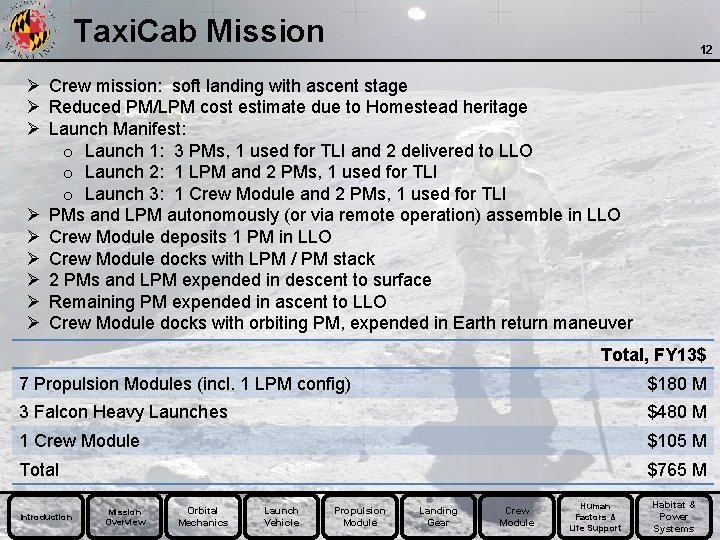
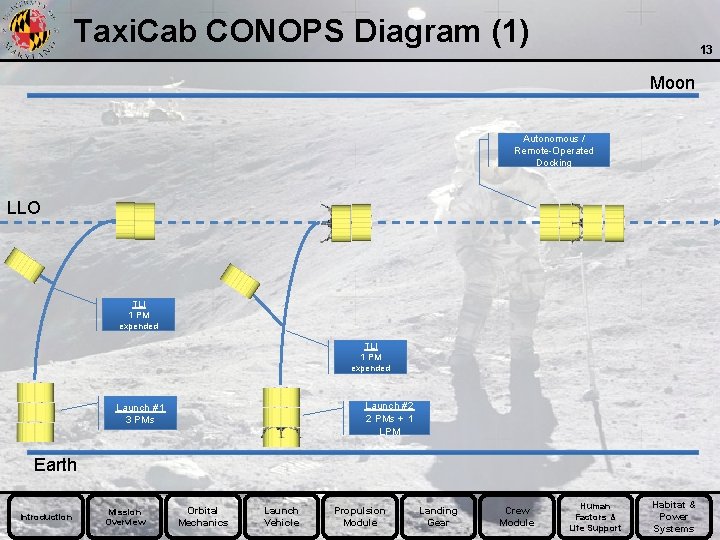
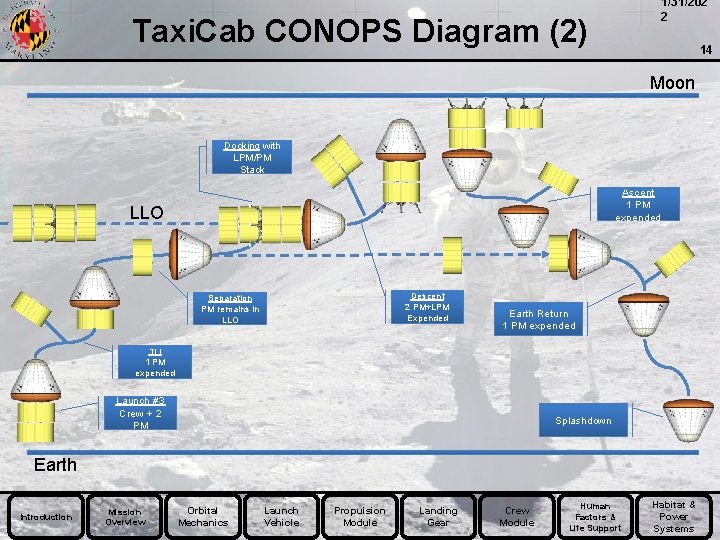
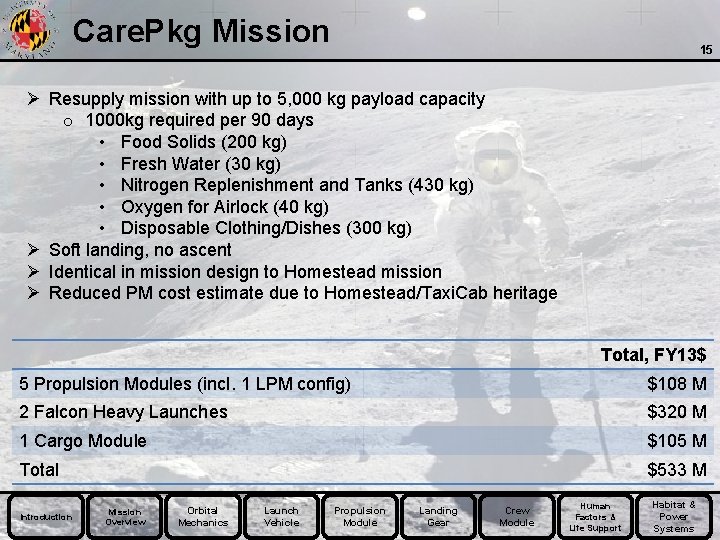
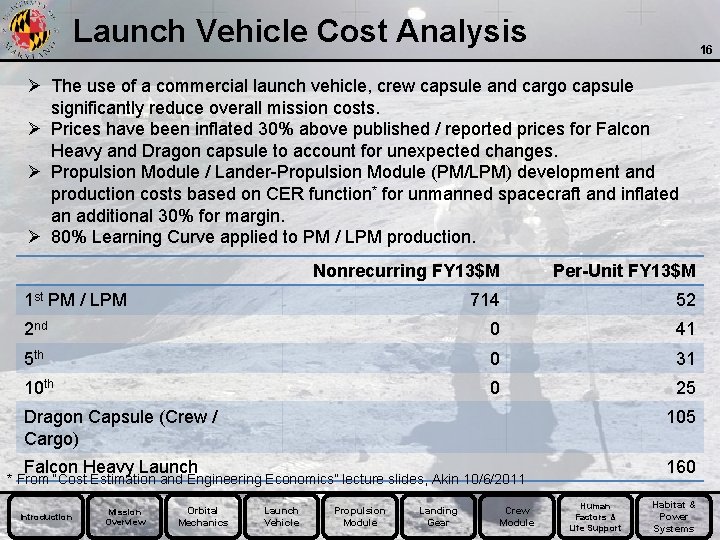
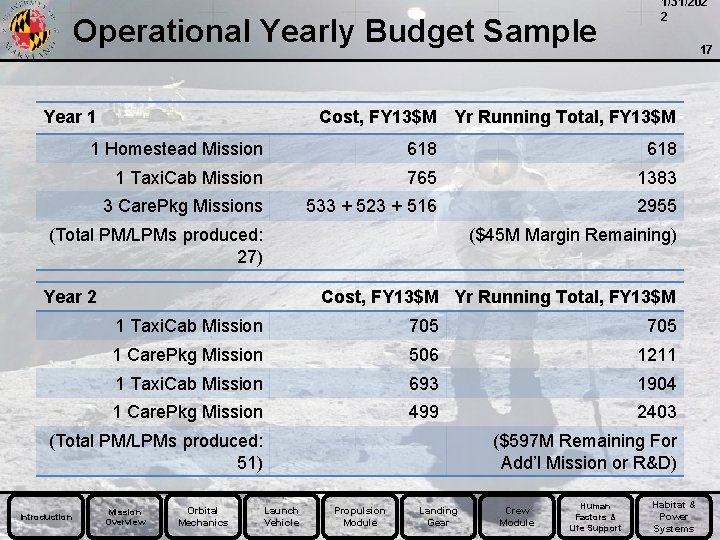
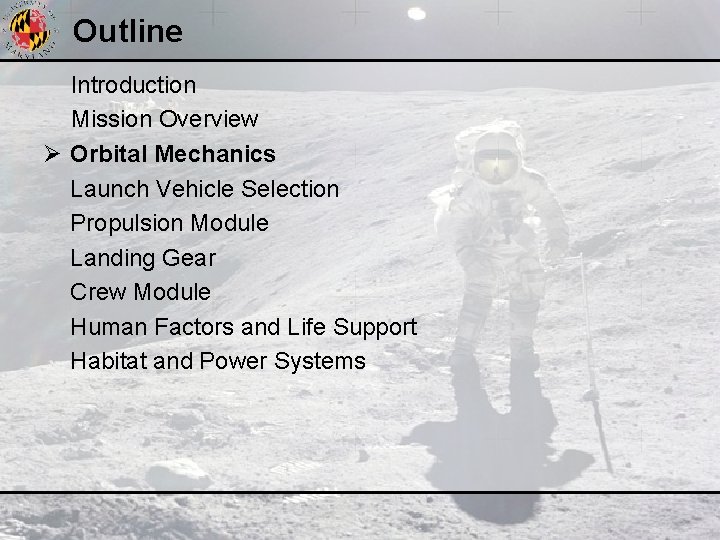
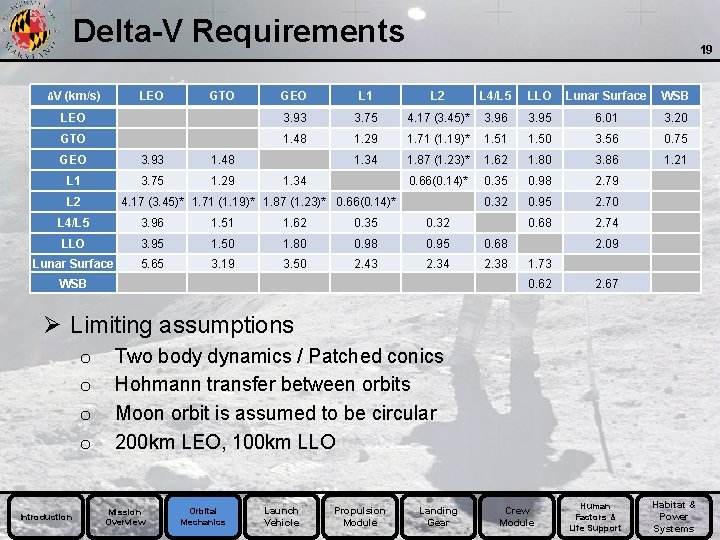
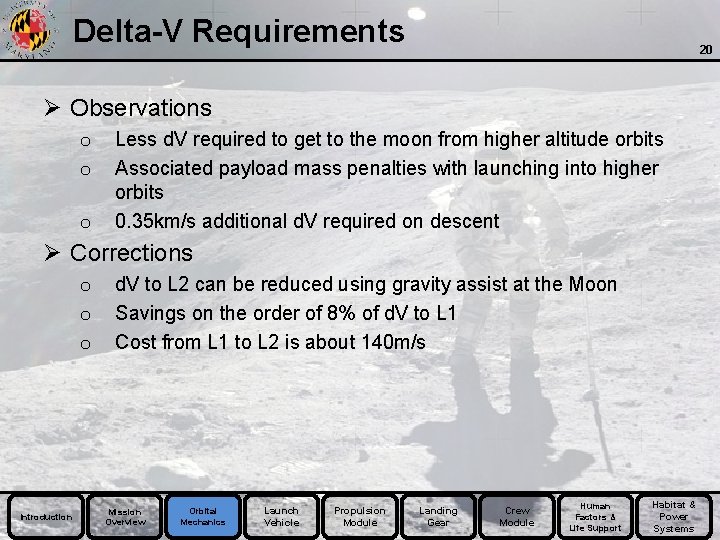
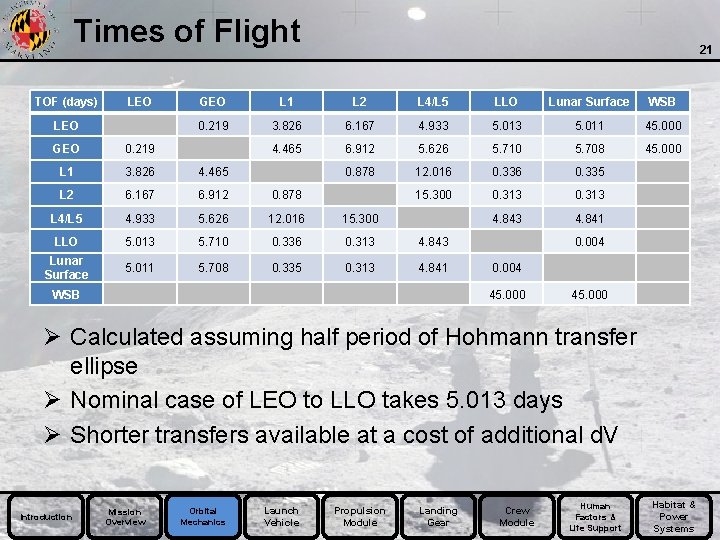
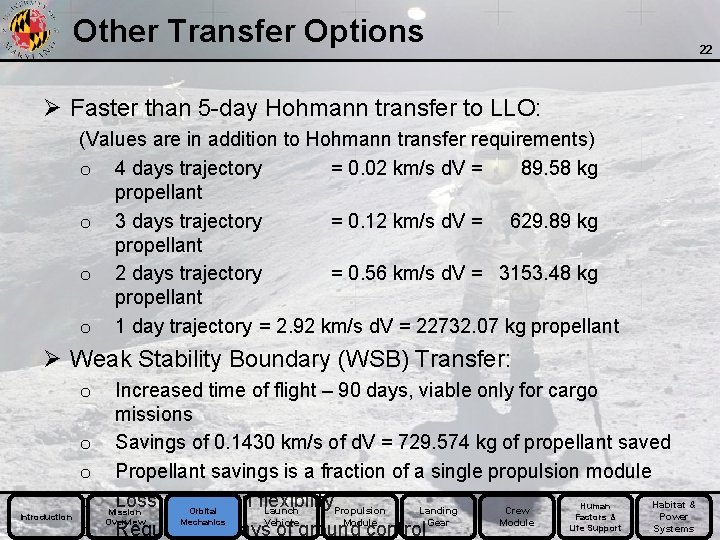
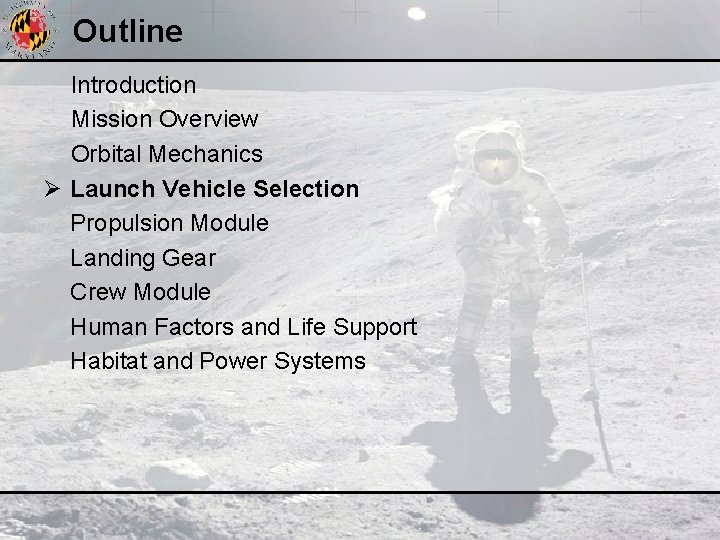
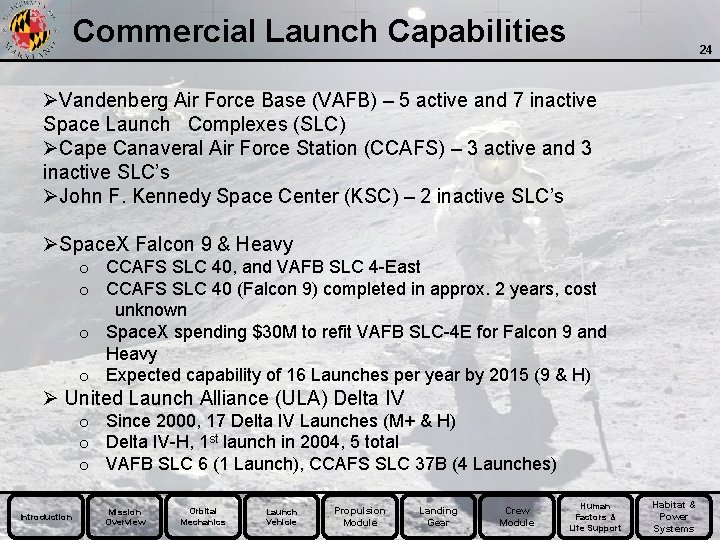
![Payload Capabilities 25 Delta IV Heavy Falcon Heavy Mass Limits to LEO [kg] 22, Payload Capabilities 25 Delta IV Heavy Falcon Heavy Mass Limits to LEO [kg] 22,](https://slidetodoc.com/presentation_image_h2/9b83375e0ef3e844c37a8446a76f7ea9/image-25.jpg)
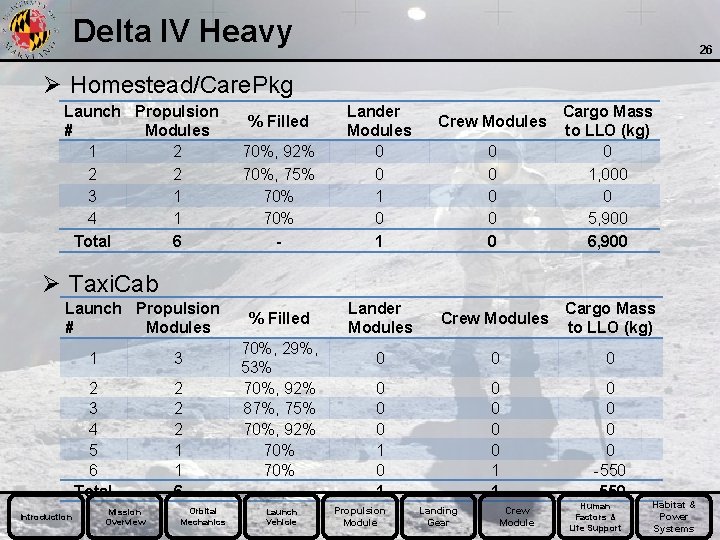
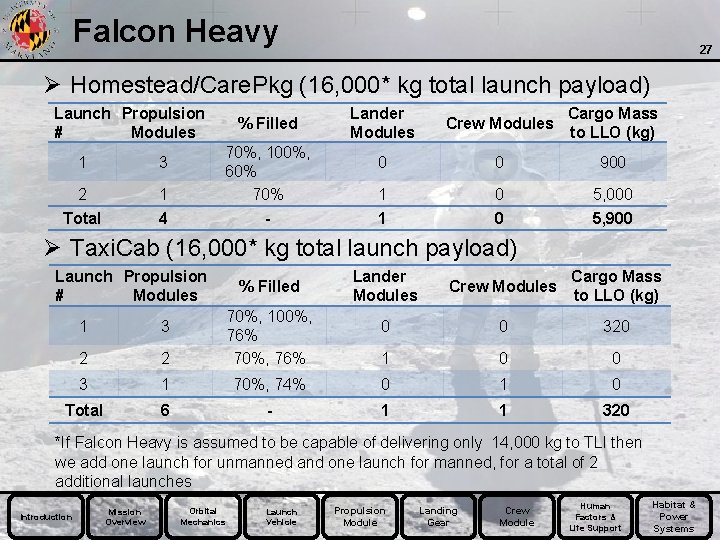
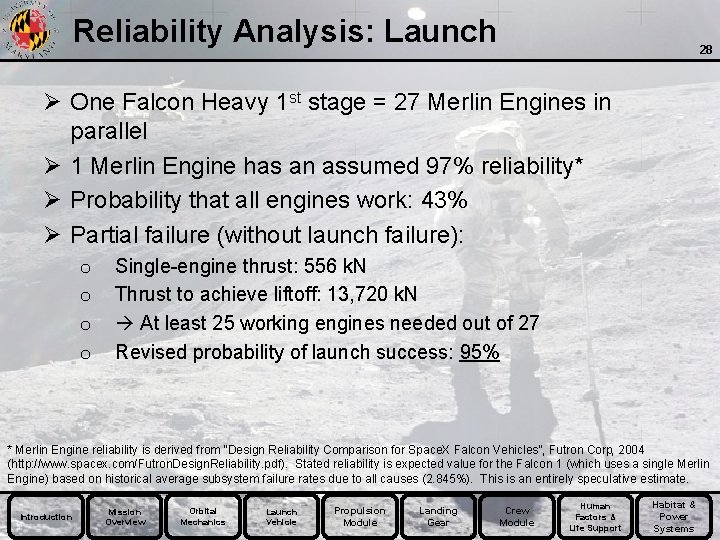
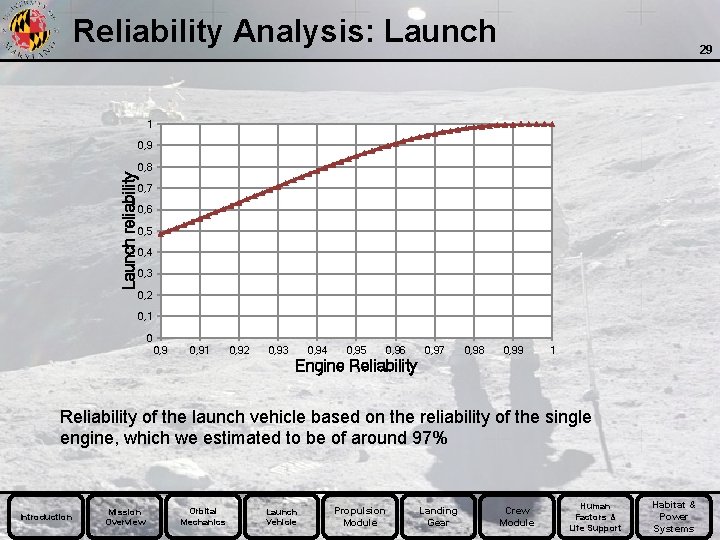
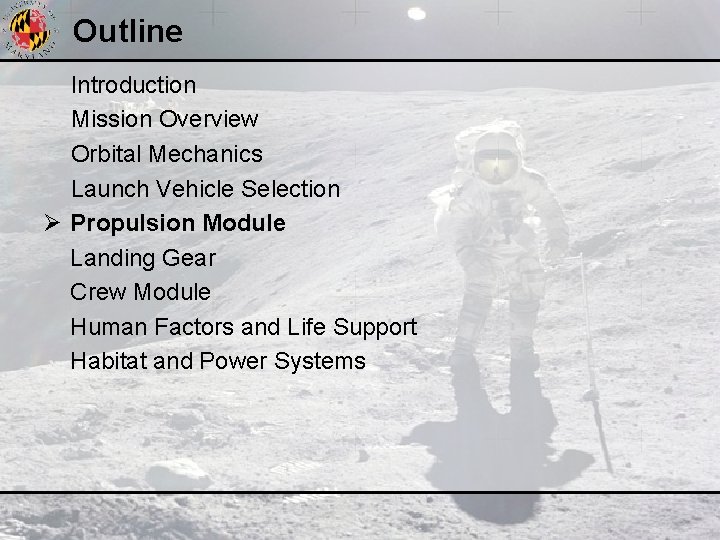
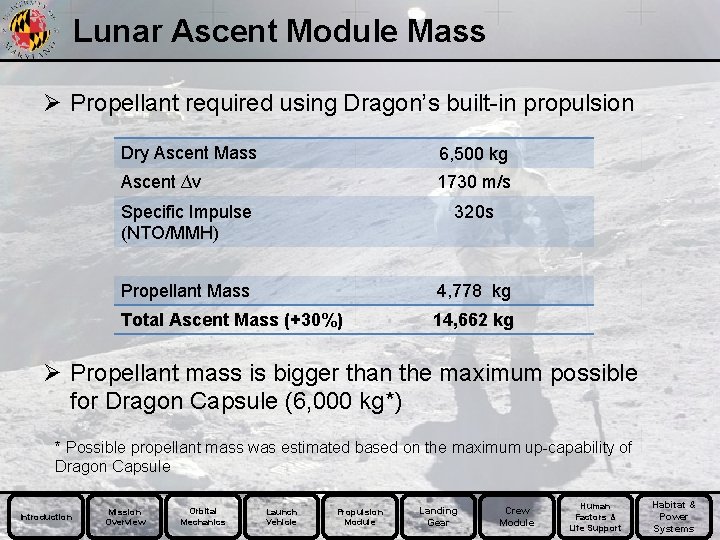
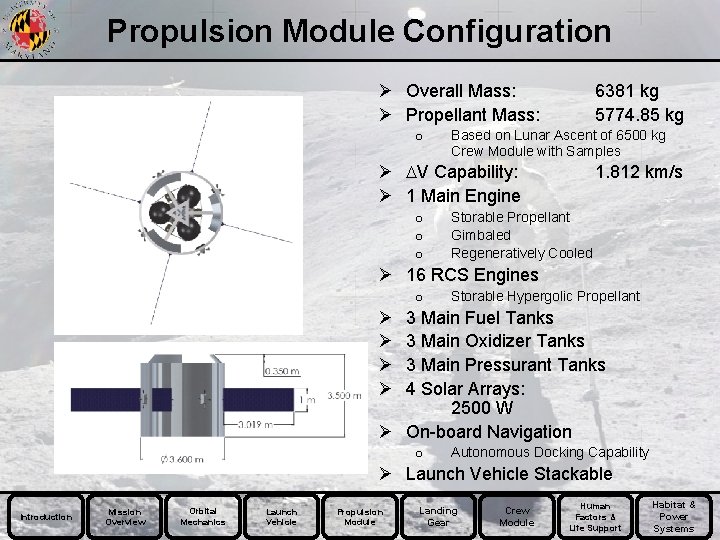
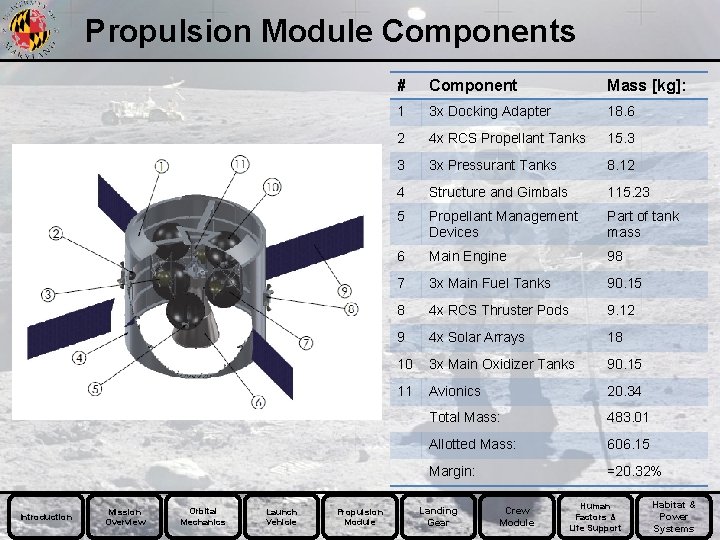
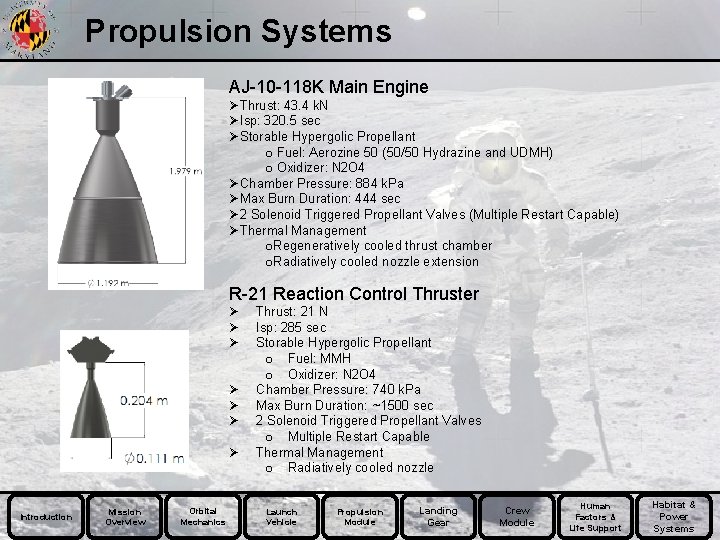
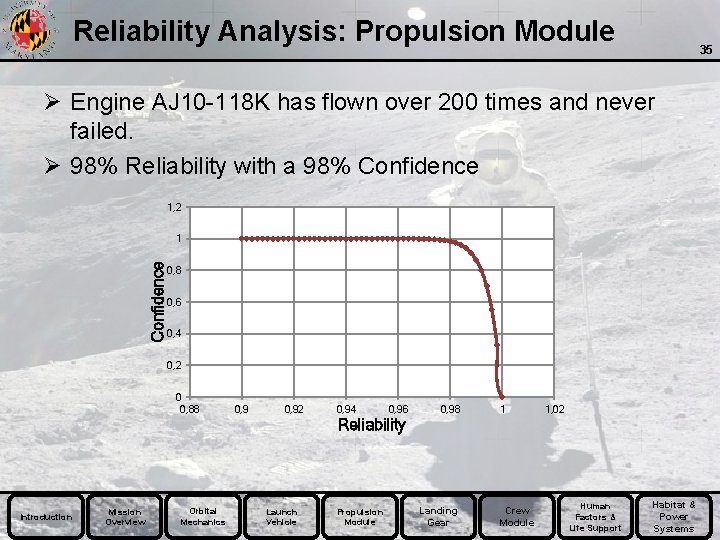
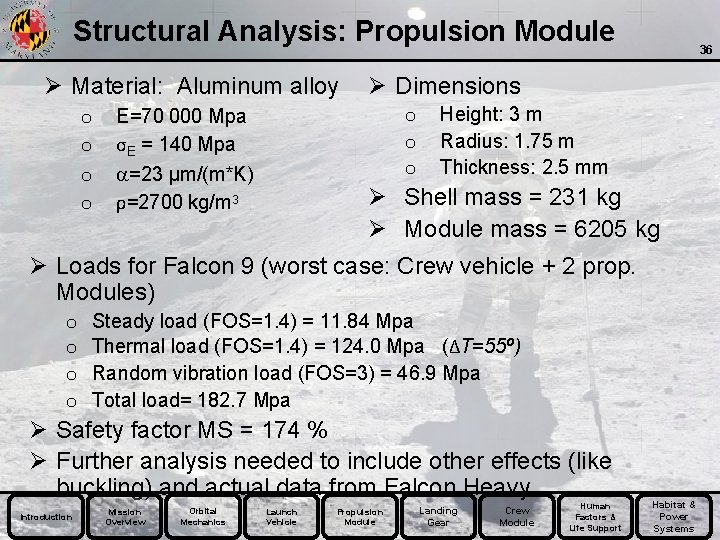
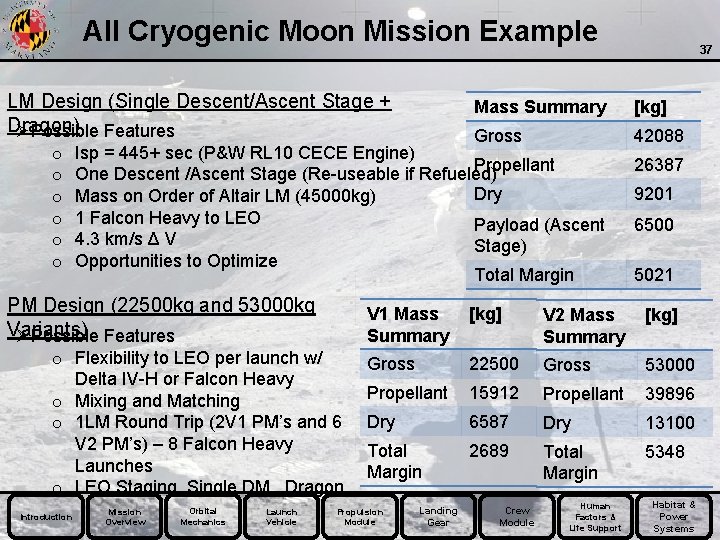
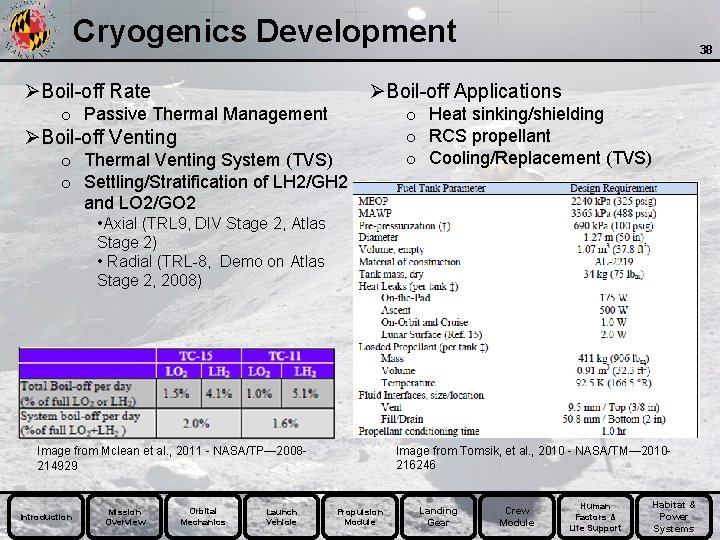
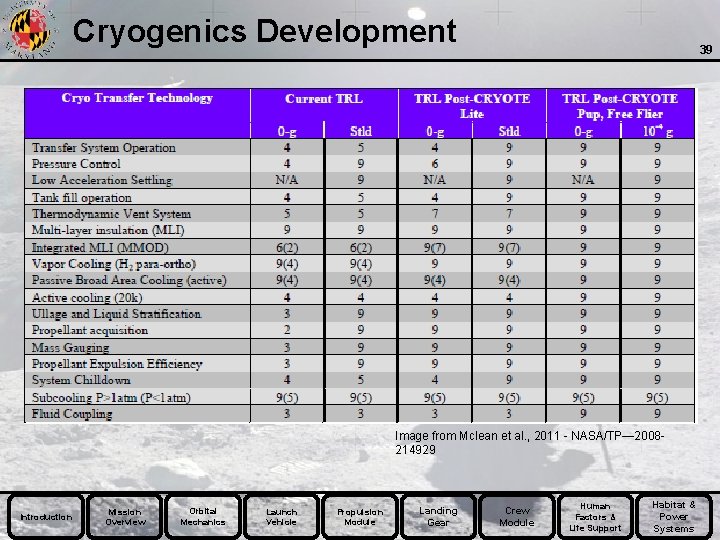
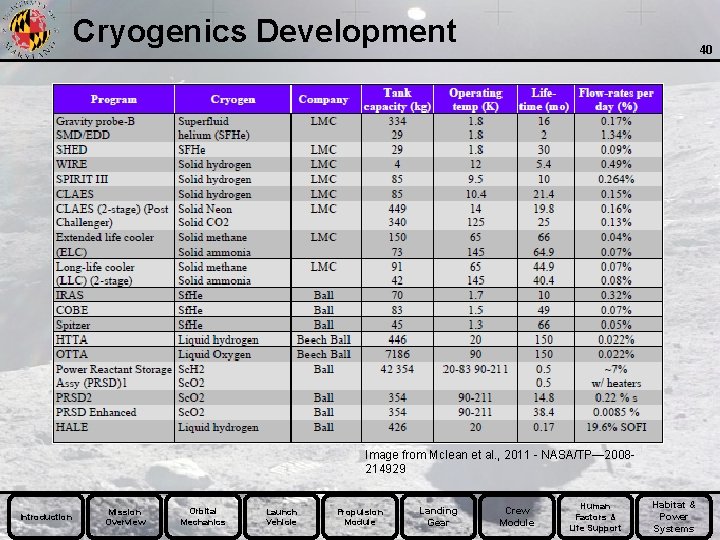
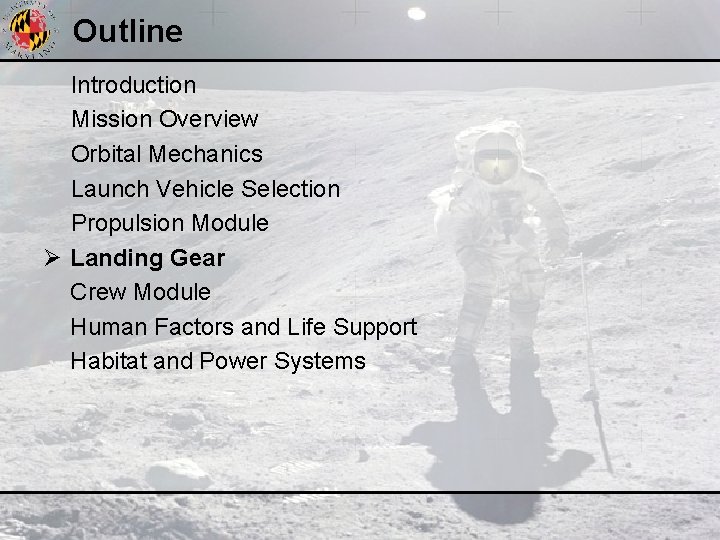
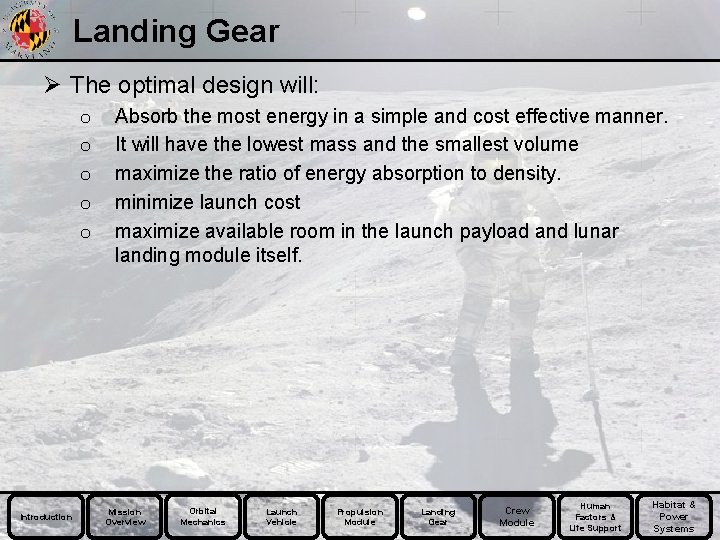
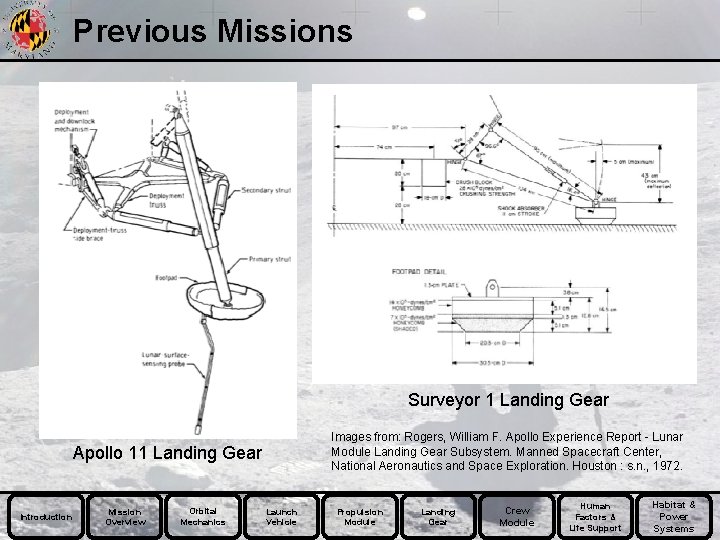
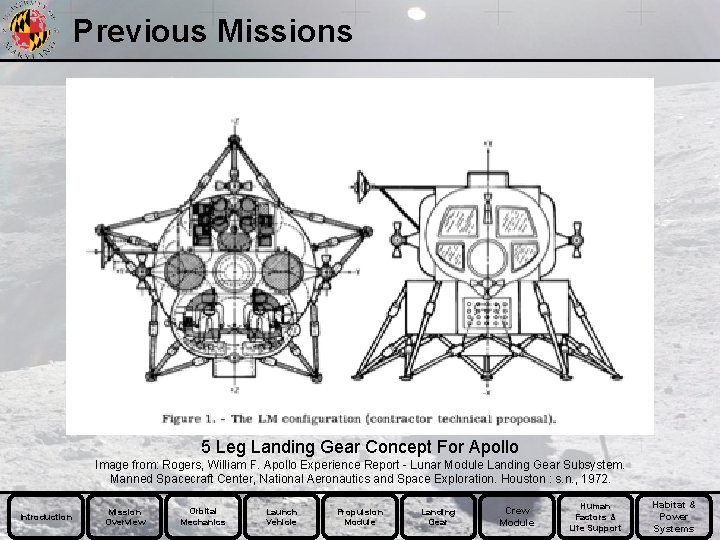
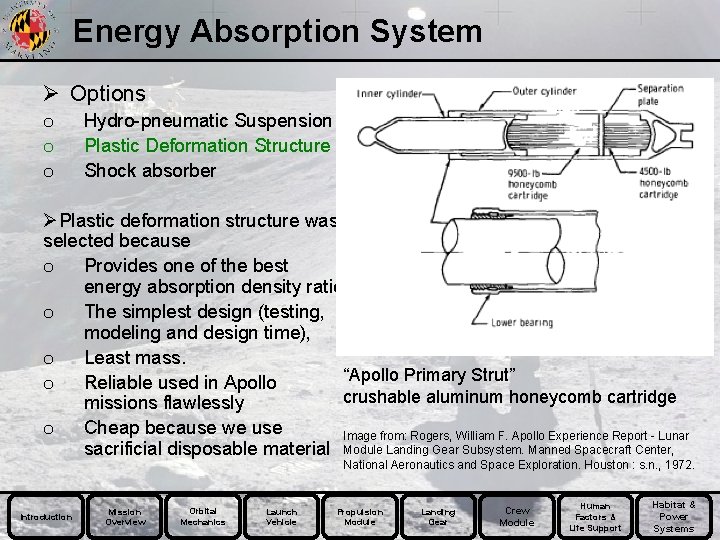
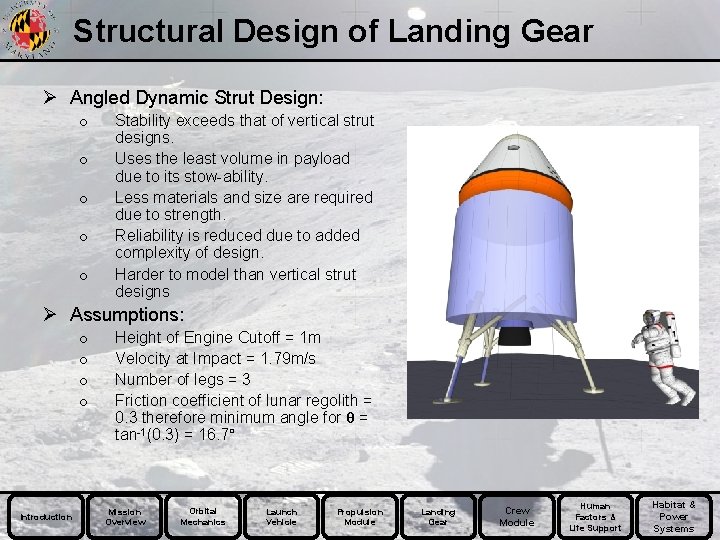
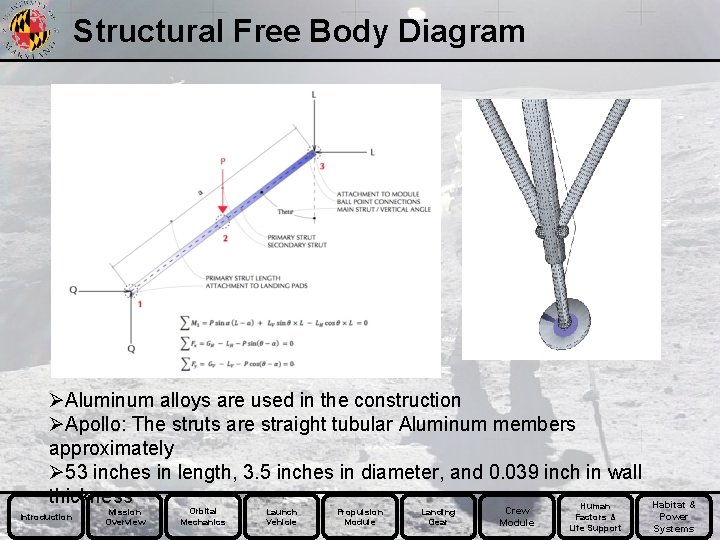
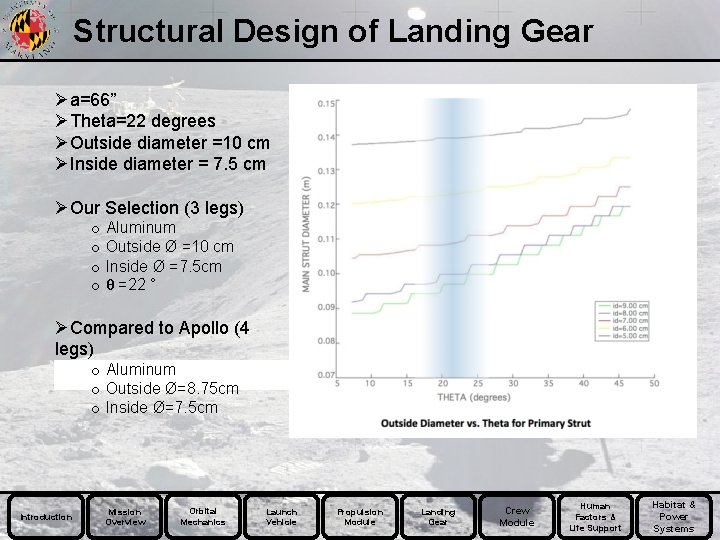
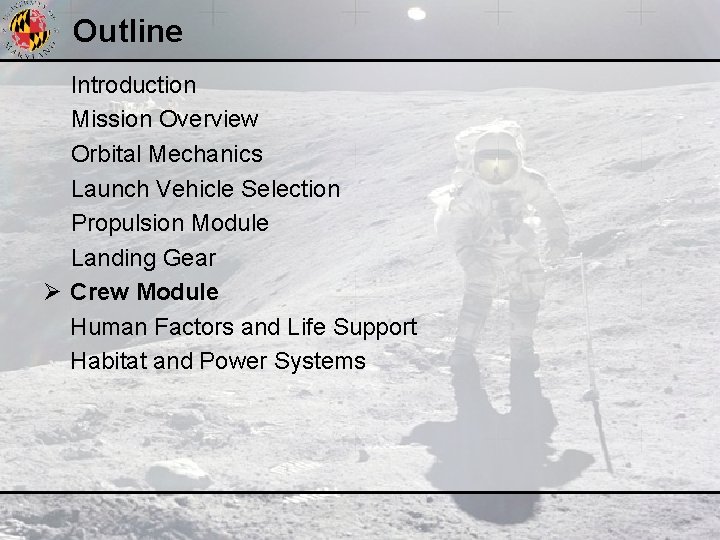
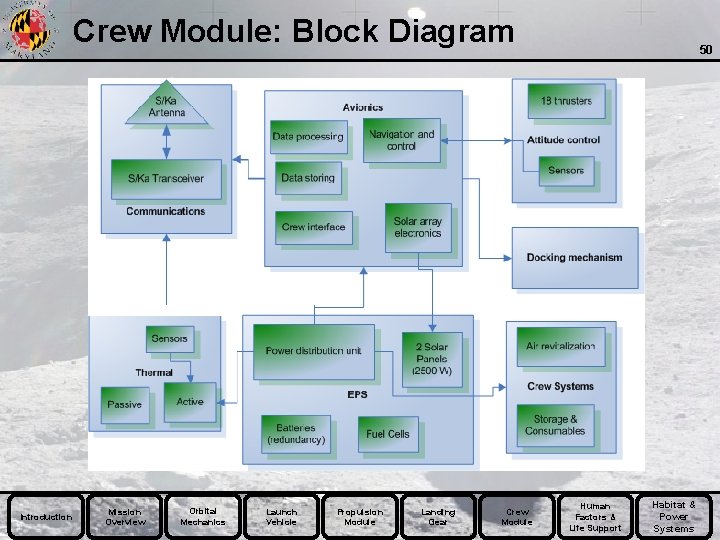
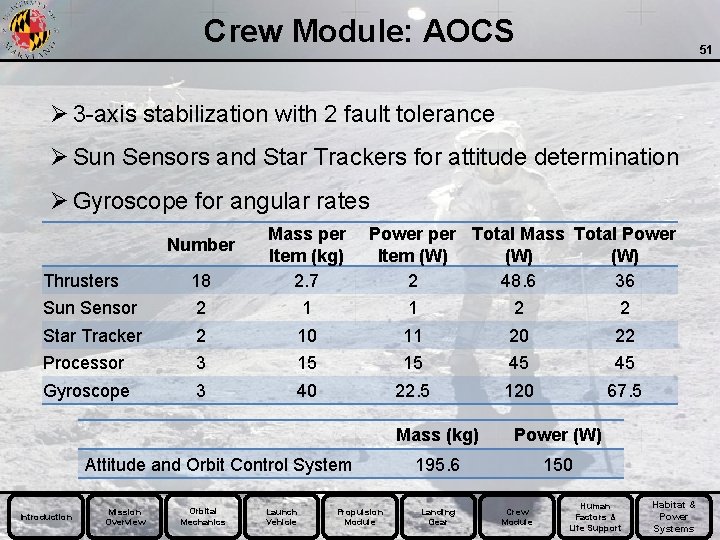
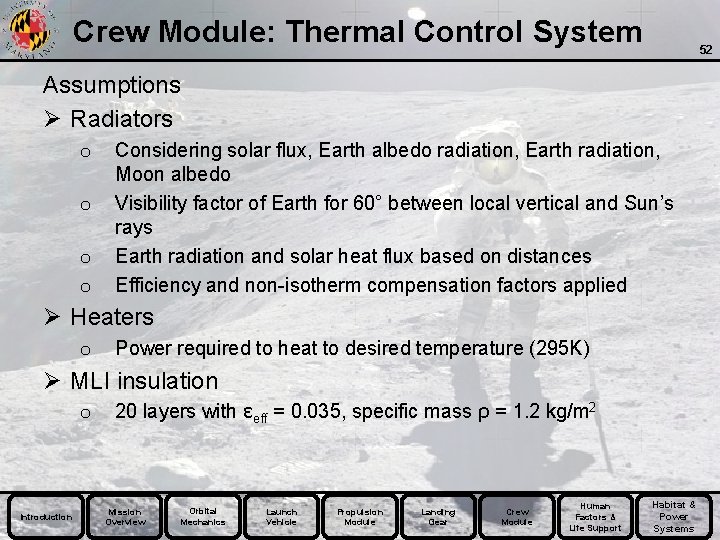
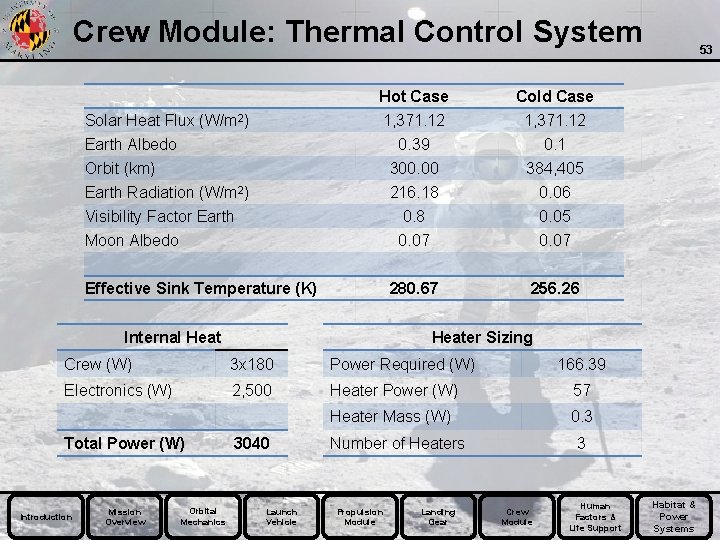
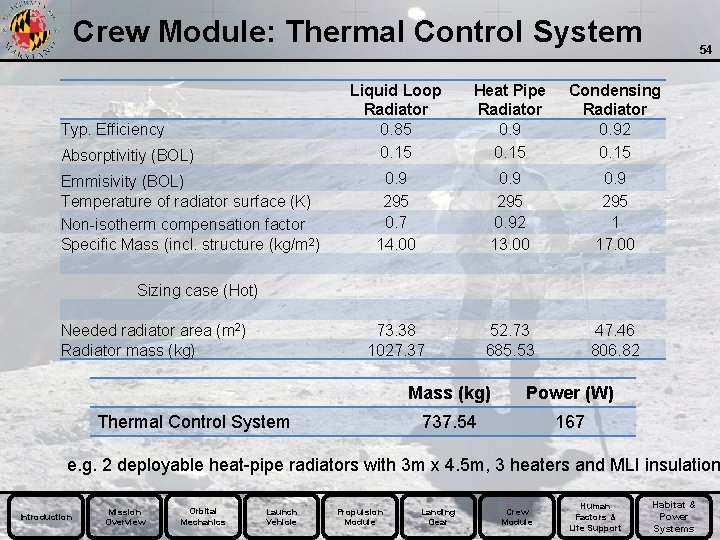
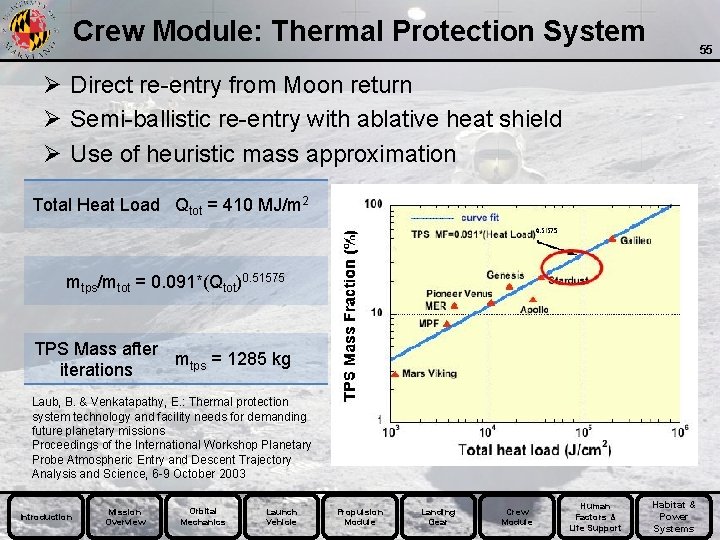
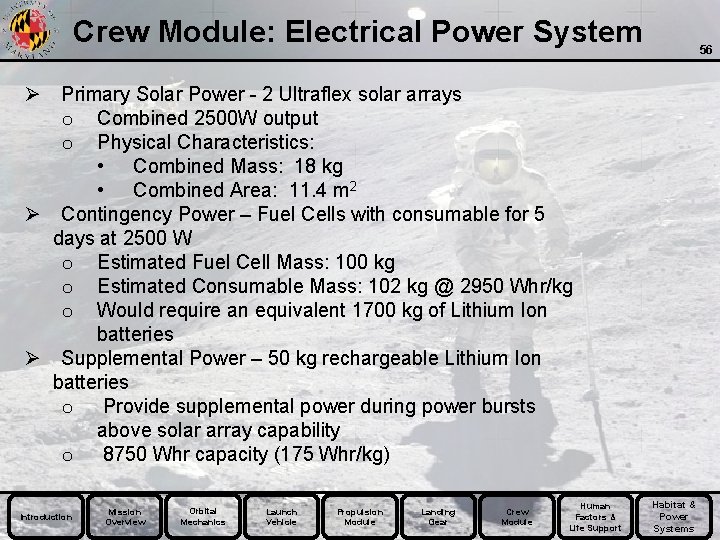
![Crew Module: Mass Budget Mass [kg] AOCS TCS Structure Avionics ECLSS EPS Communication TPS Crew Module: Mass Budget Mass [kg] AOCS TCS Structure Avionics ECLSS EPS Communication TPS](https://slidetodoc.com/presentation_image_h2/9b83375e0ef3e844c37a8446a76f7ea9/image-57.jpg)
![Crew Module: Power Budget Power [W] % of Total Power with Margin [W] 150 Crew Module: Power Budget Power [W] % of Total Power with Margin [W] 150](https://slidetodoc.com/presentation_image_h2/9b83375e0ef3e844c37a8446a76f7ea9/image-58.jpg)
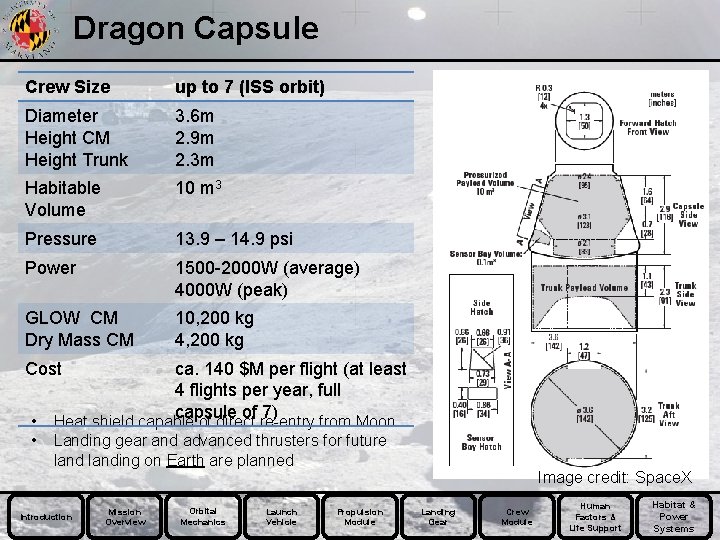
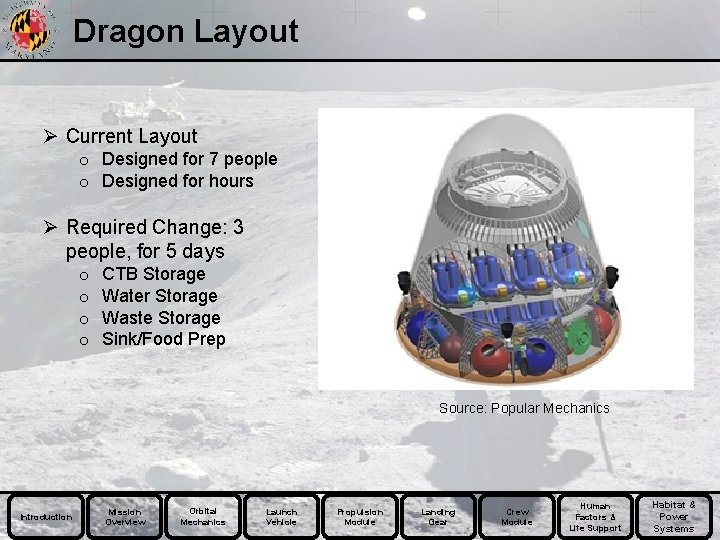
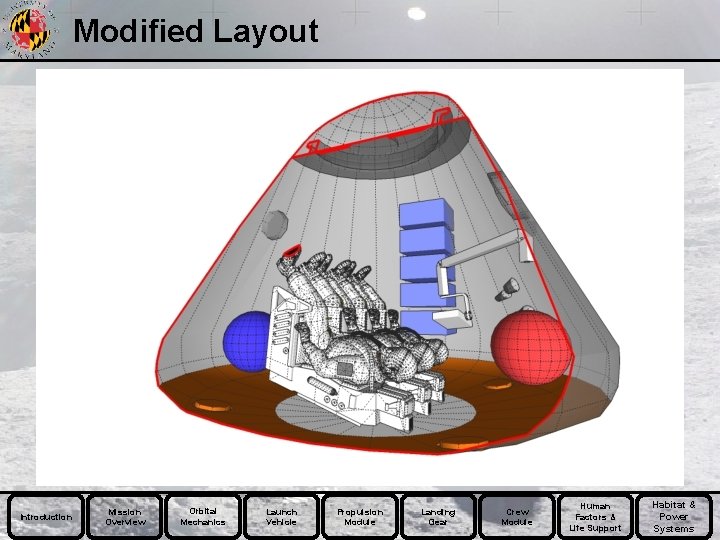
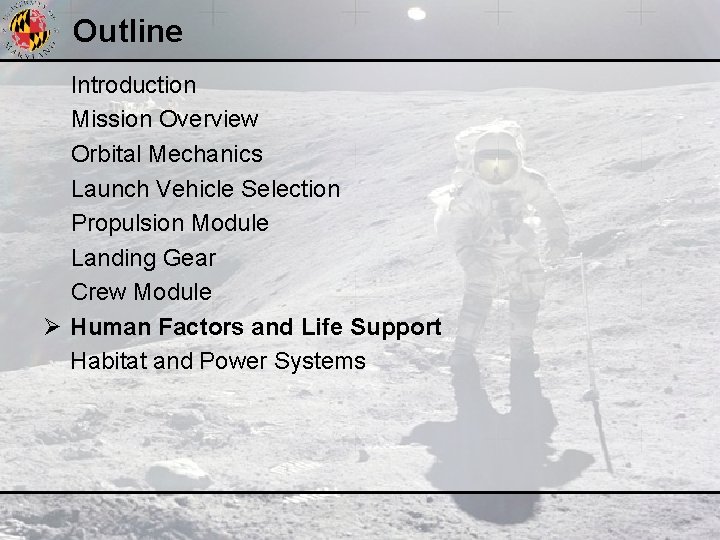
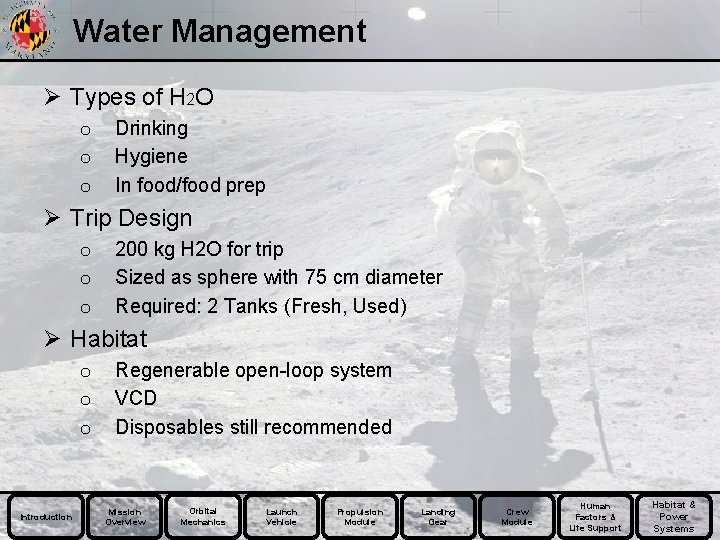
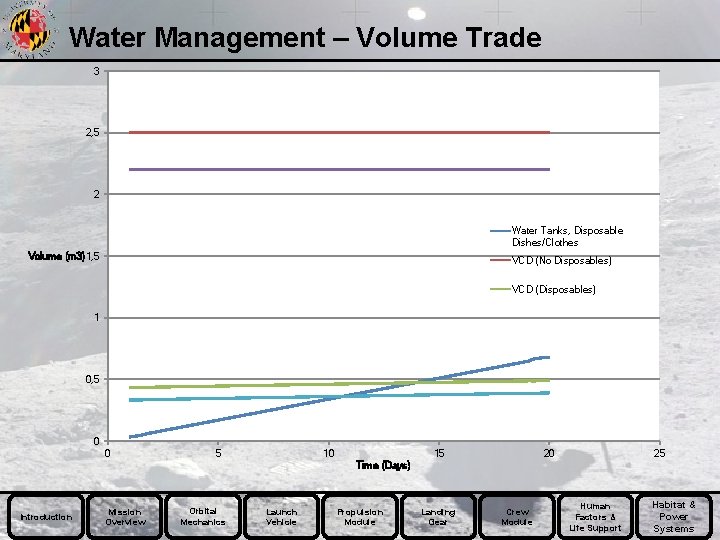
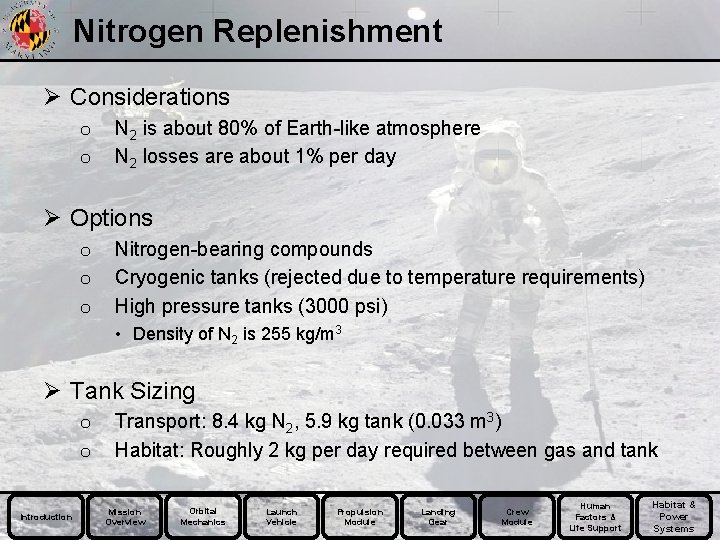
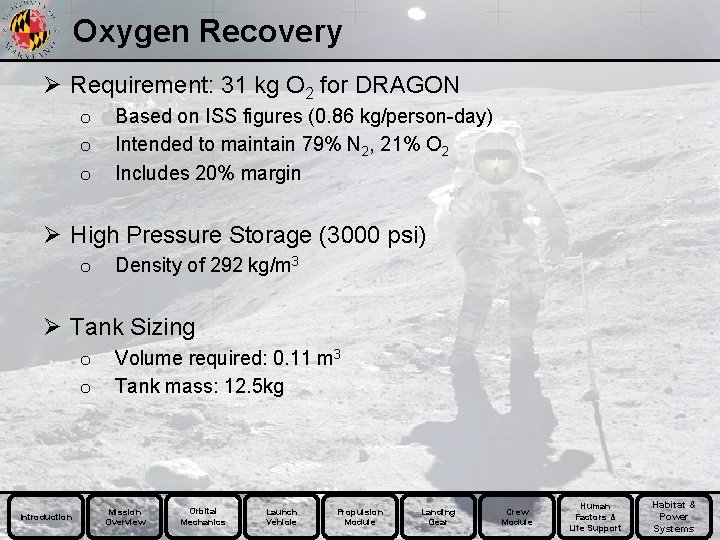
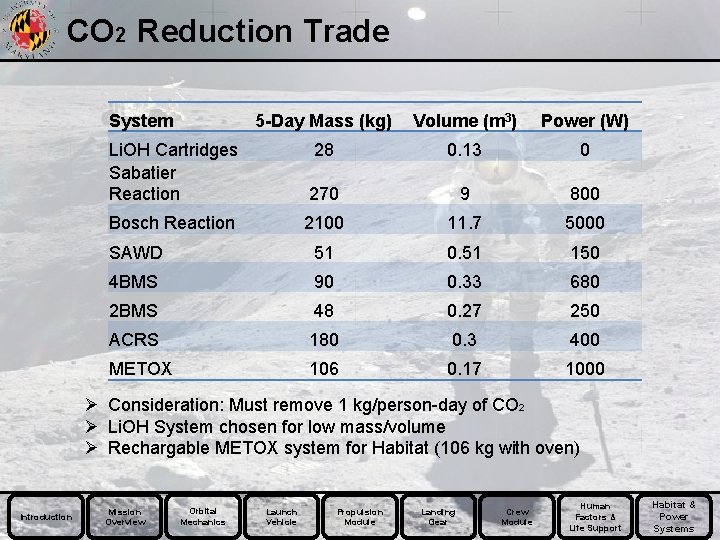
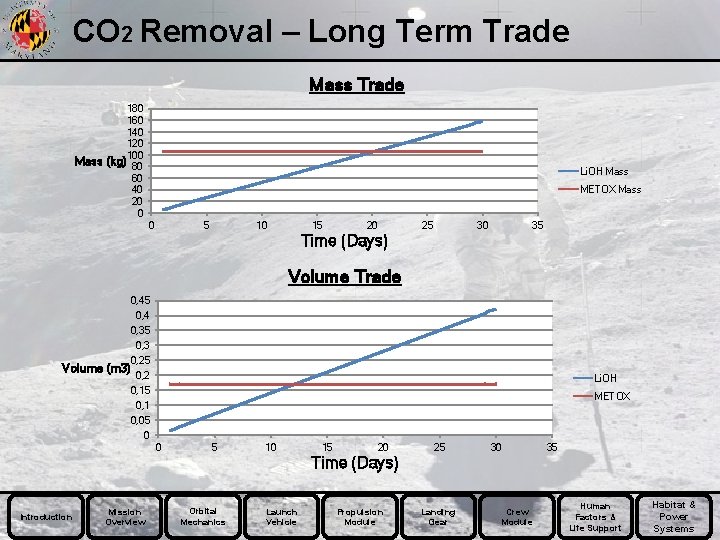
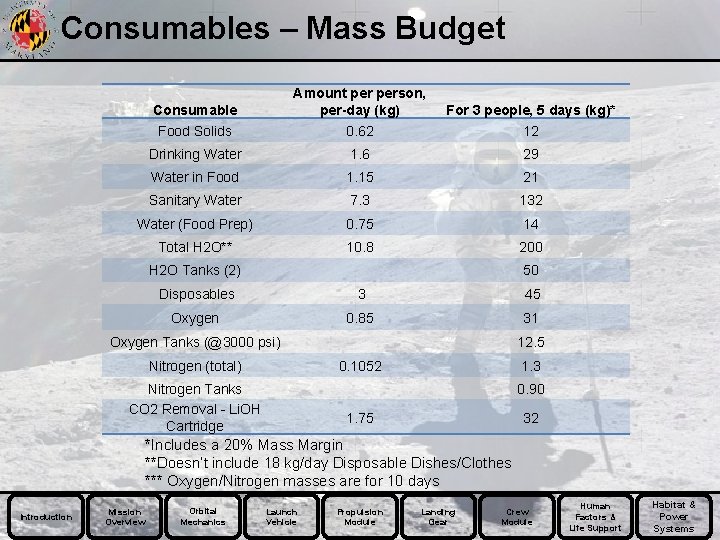
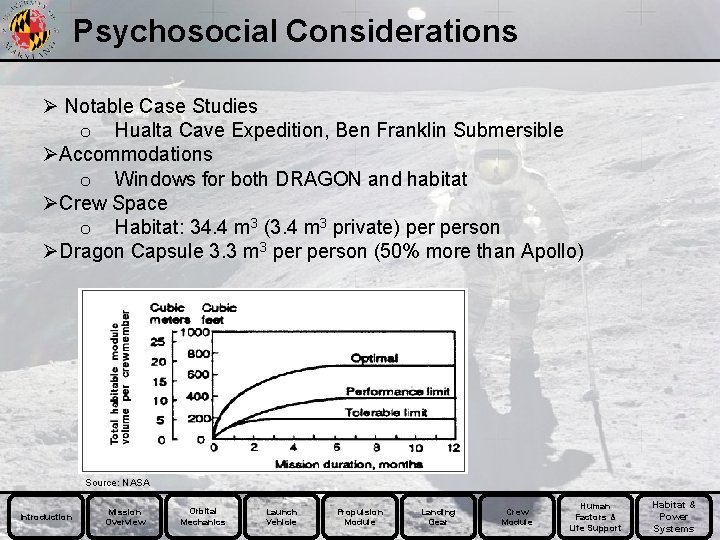
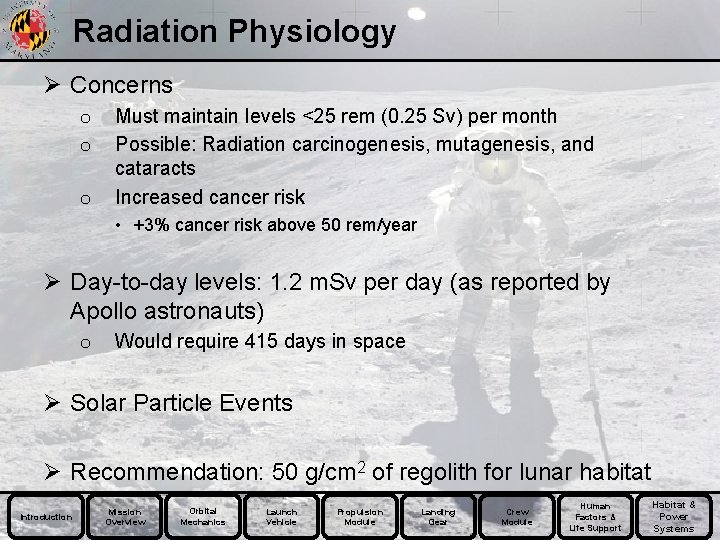
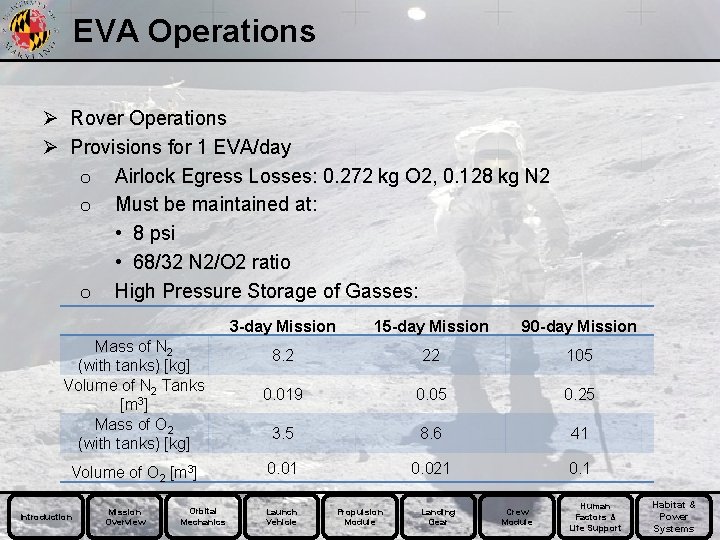
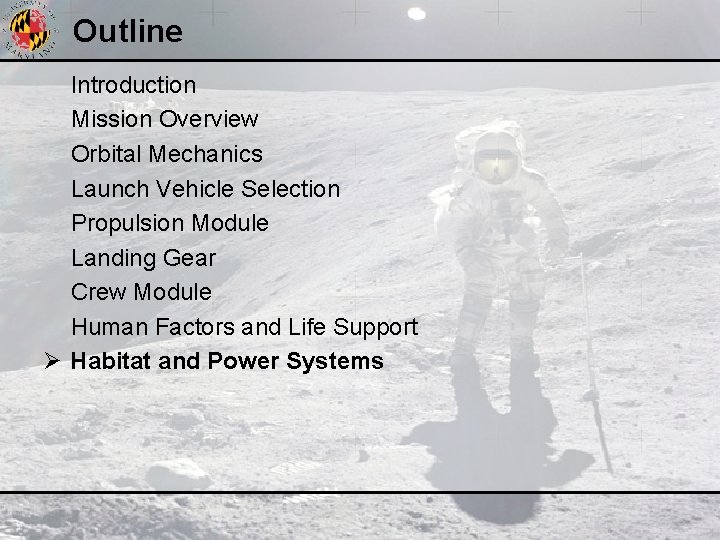
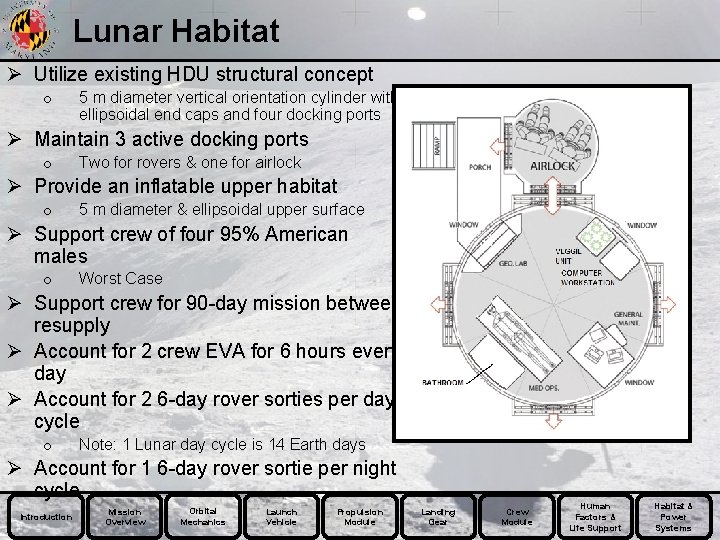
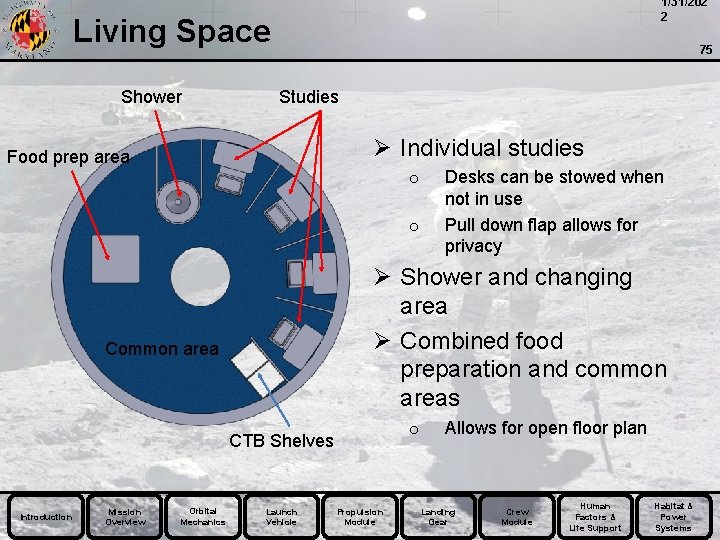
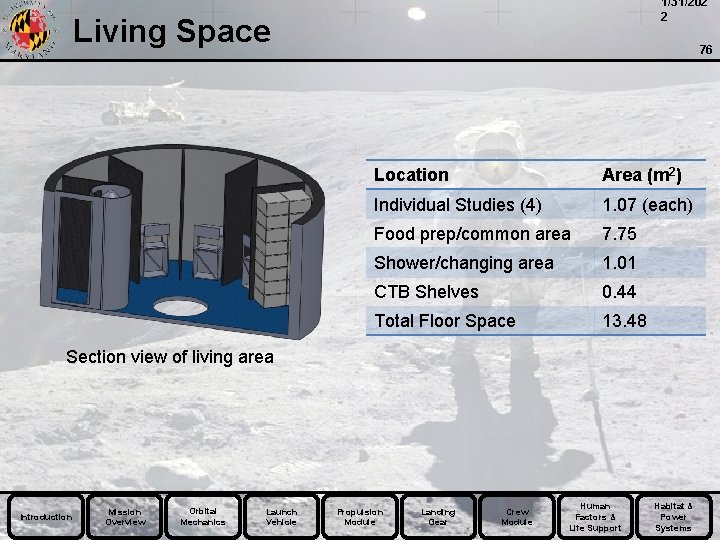
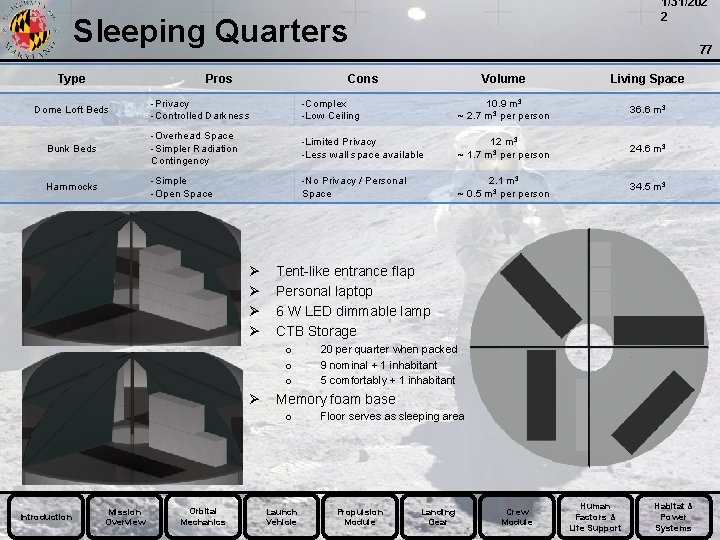
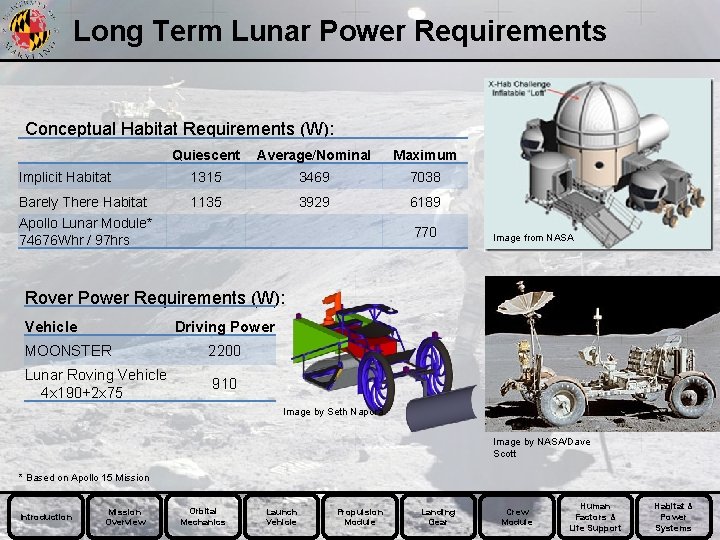
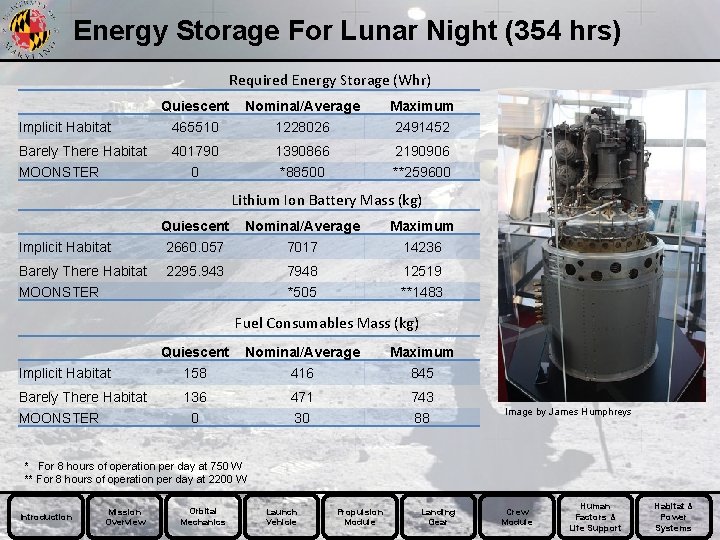
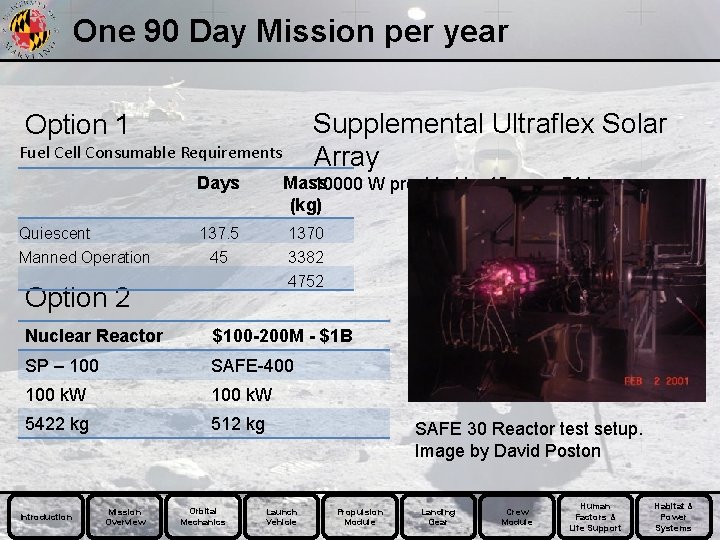
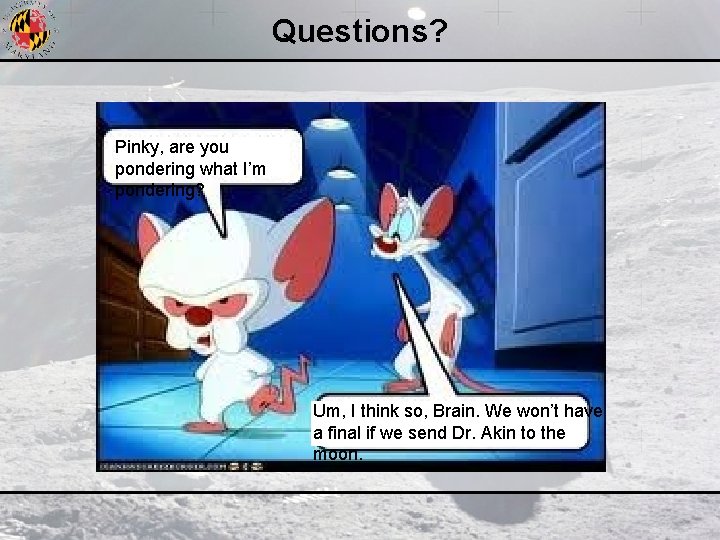
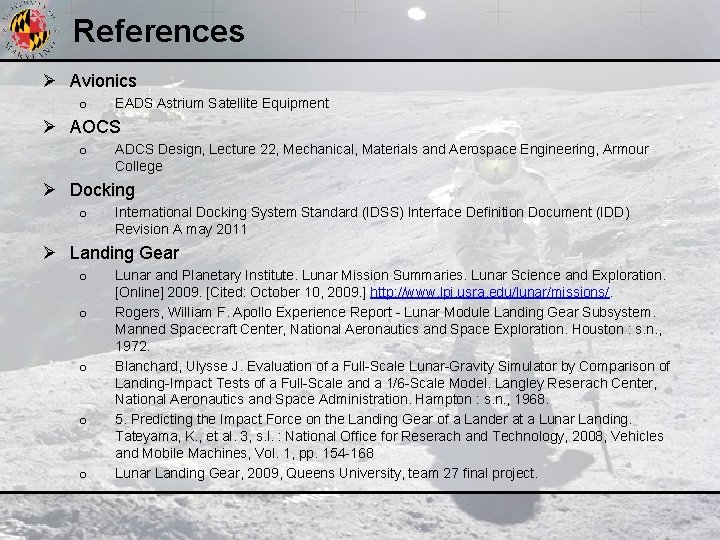
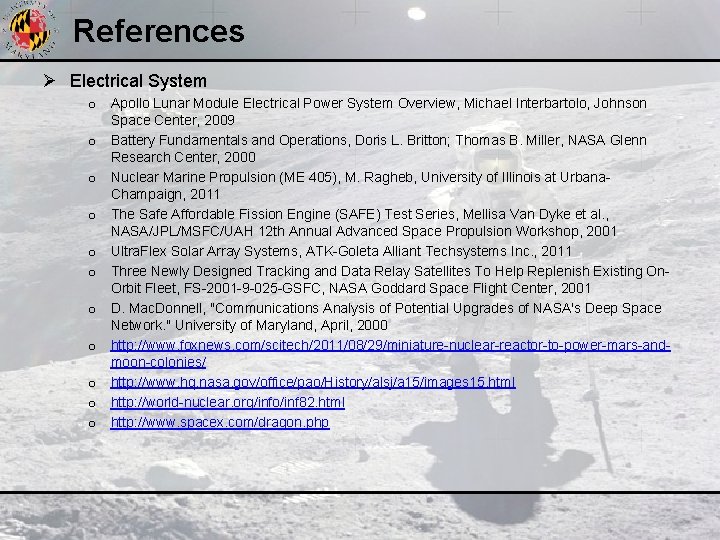
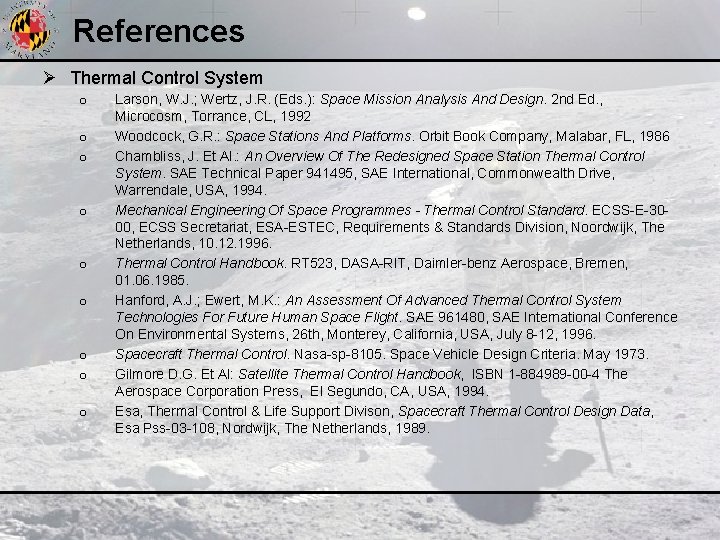
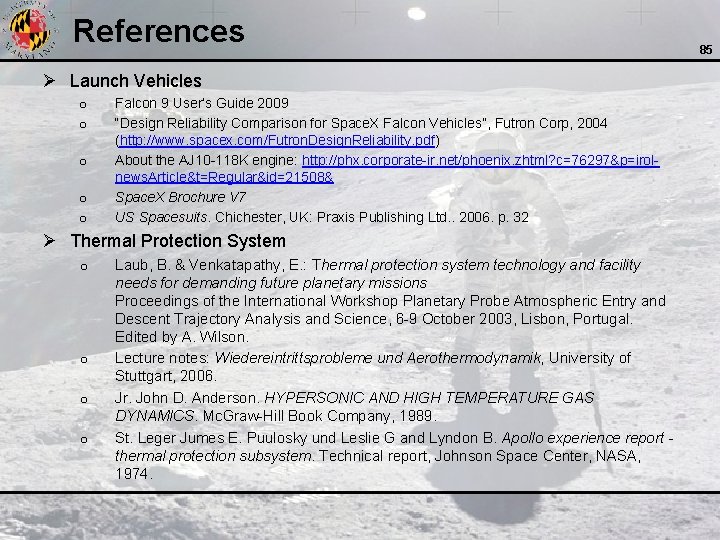
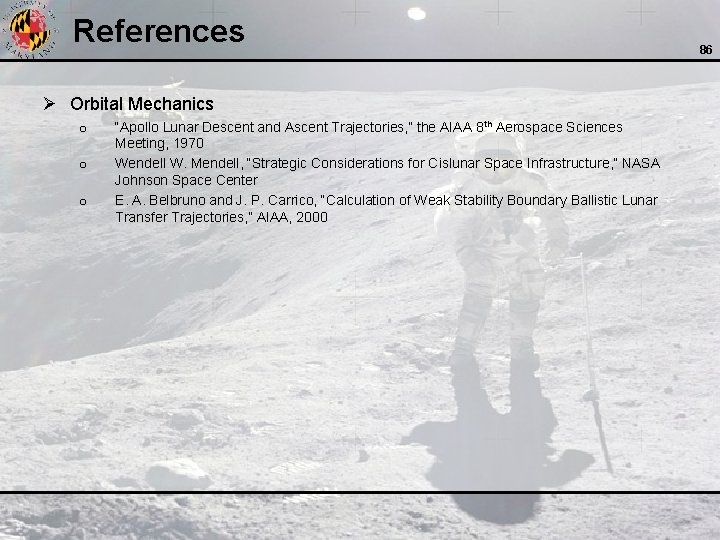
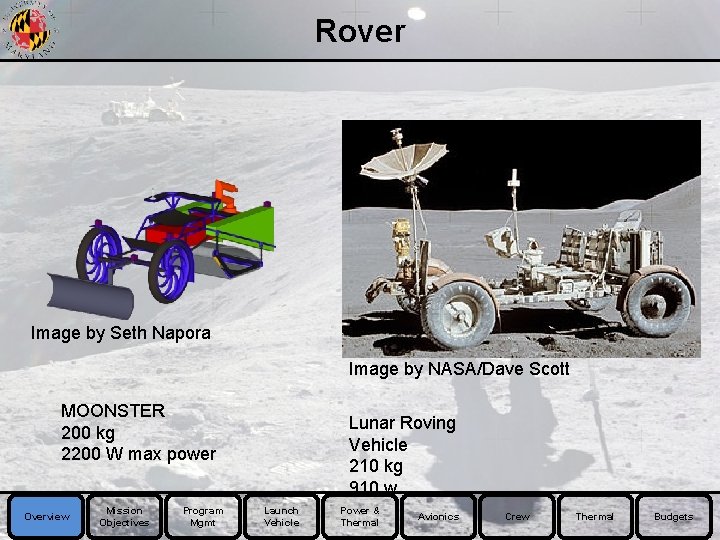
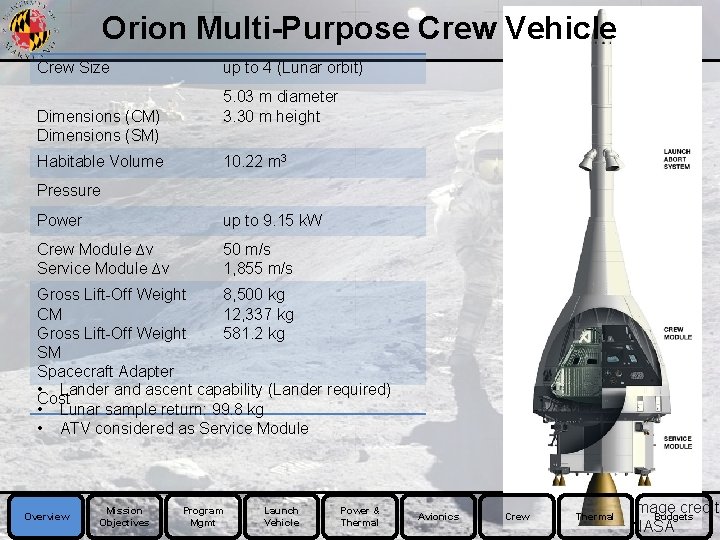
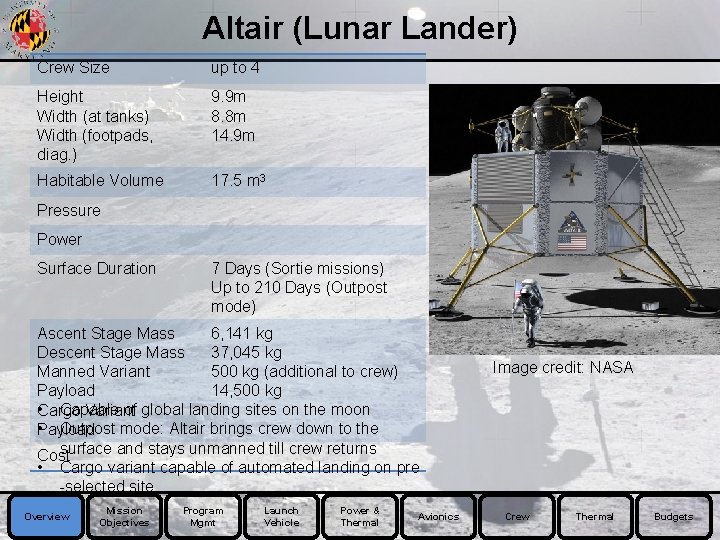
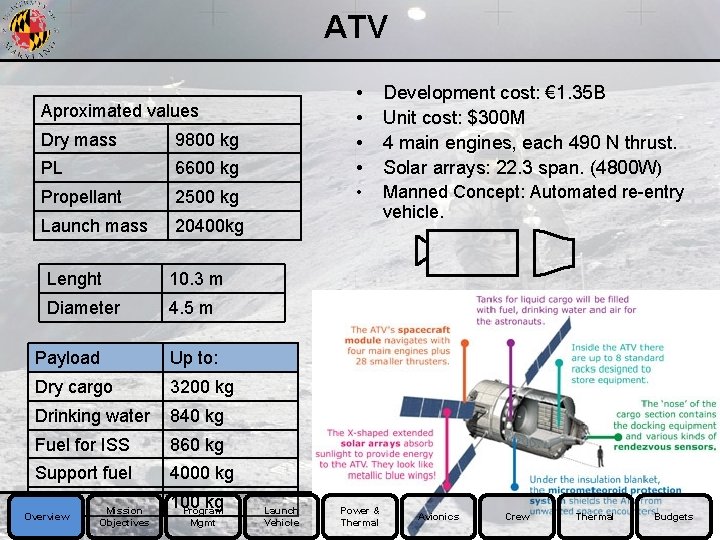
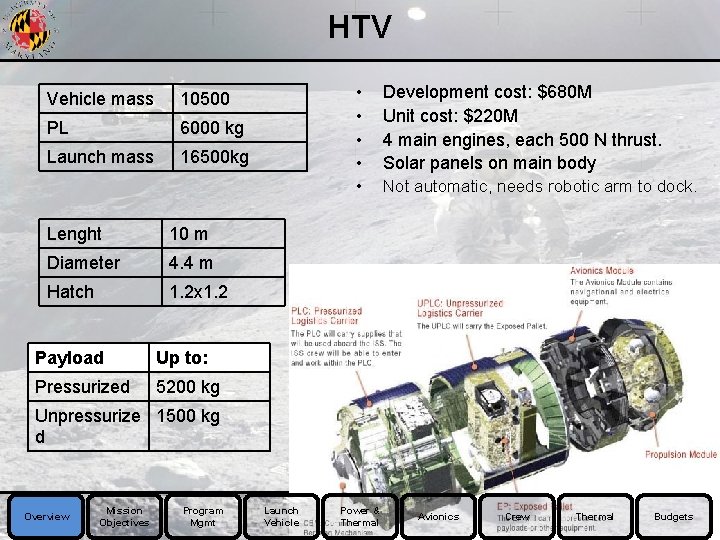
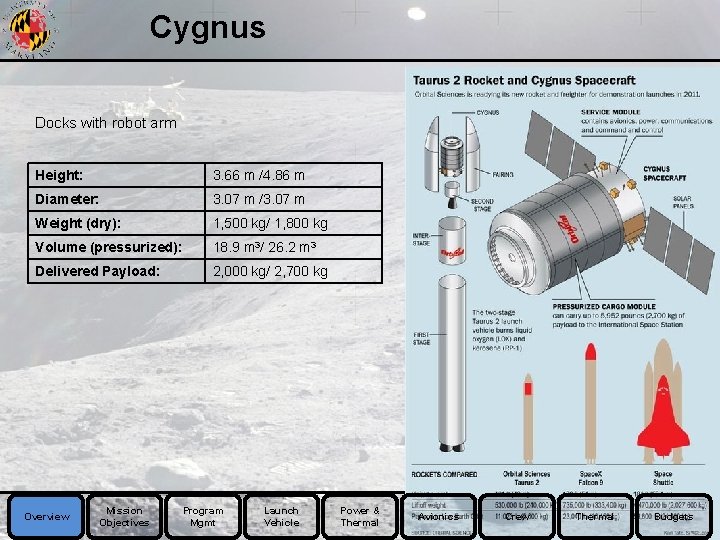
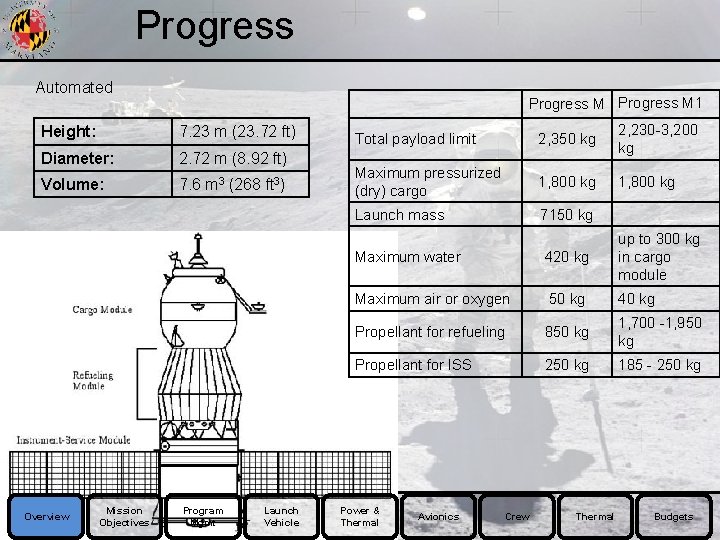
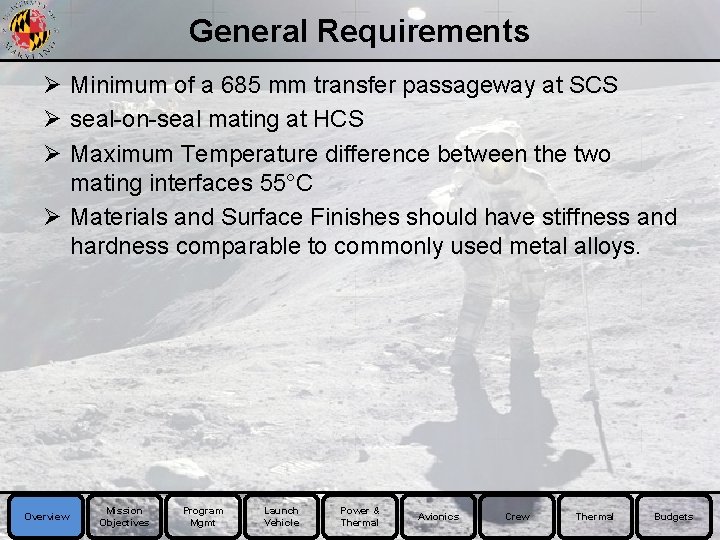
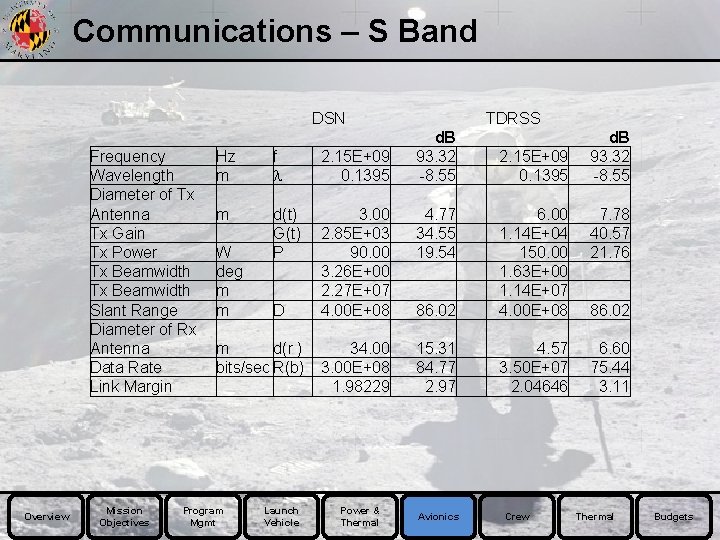
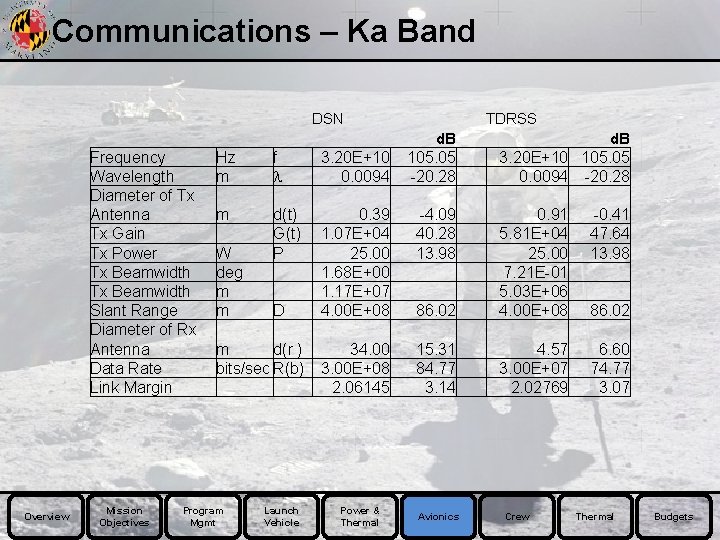
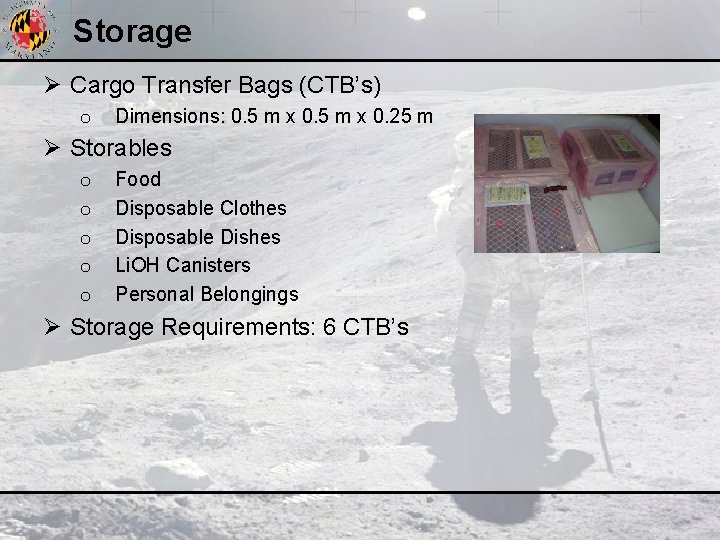
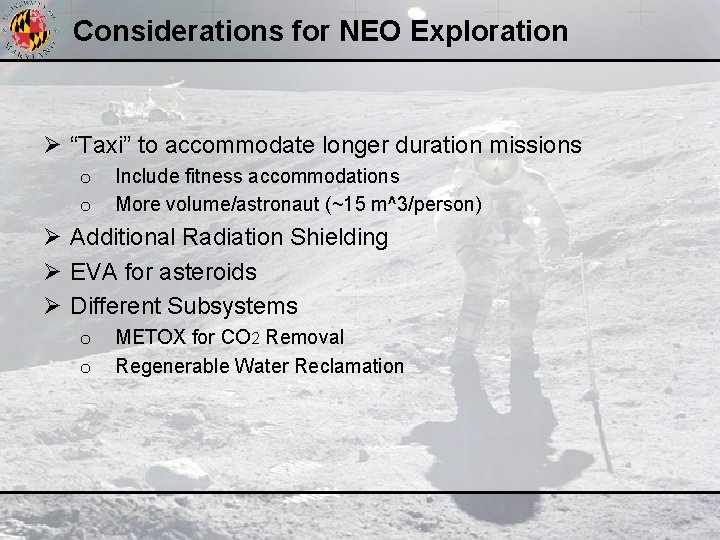
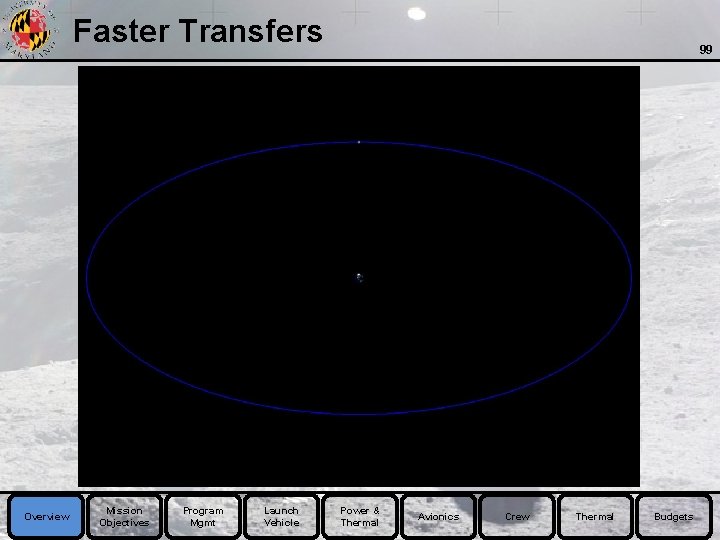
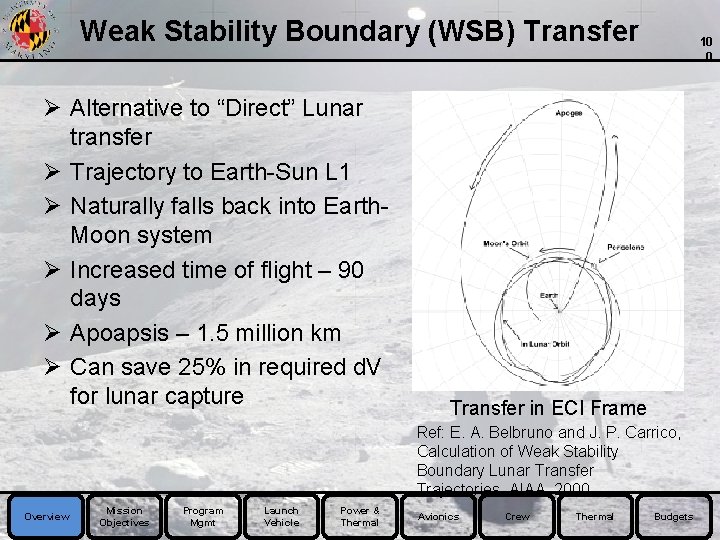
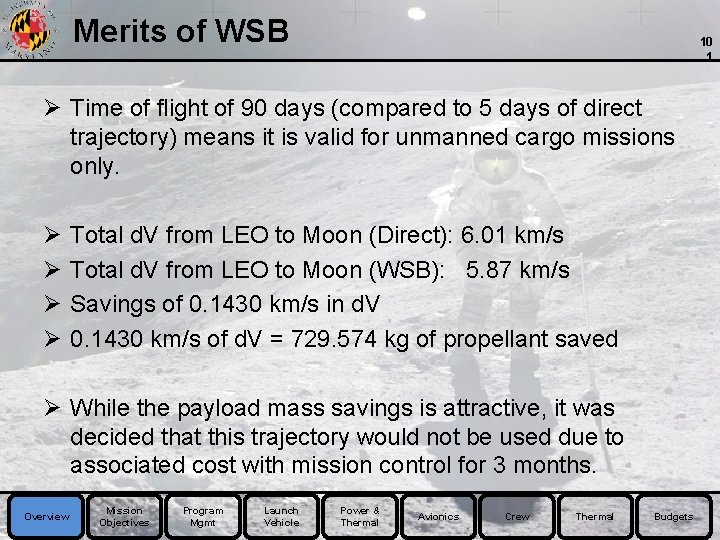
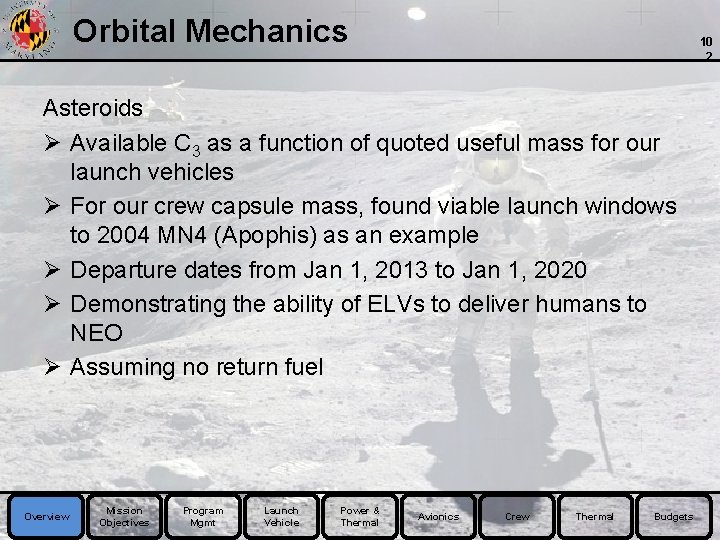
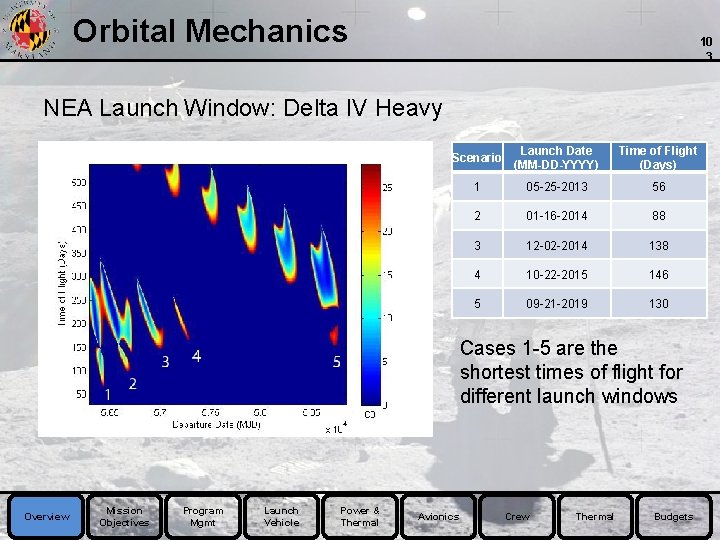
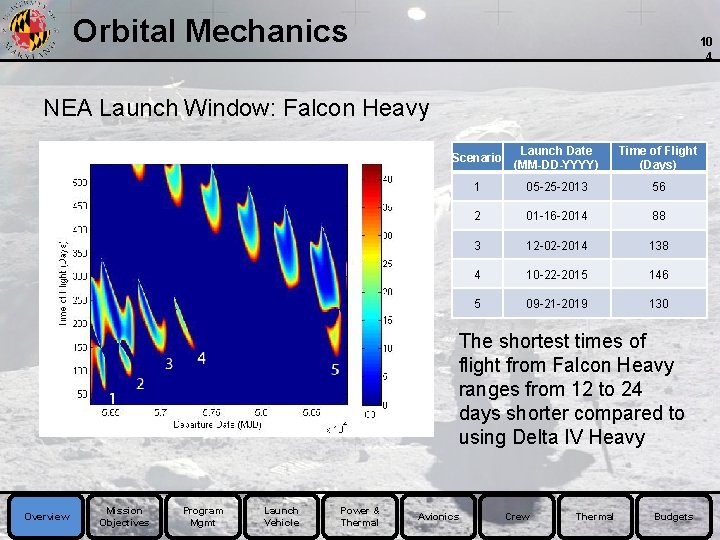
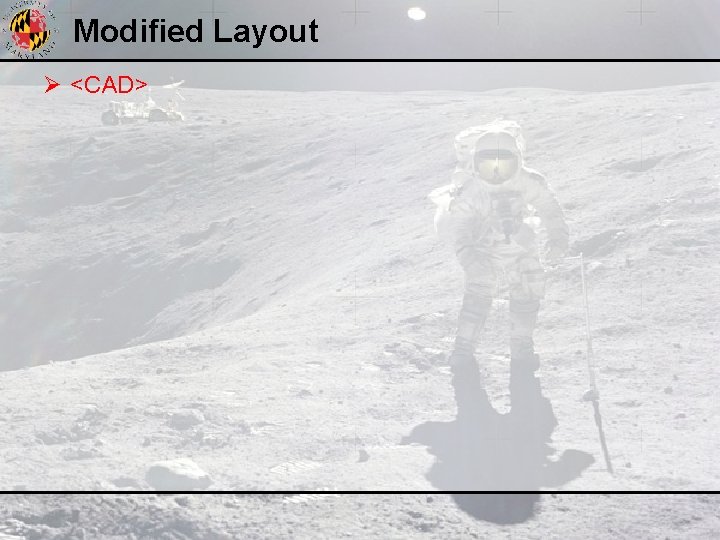
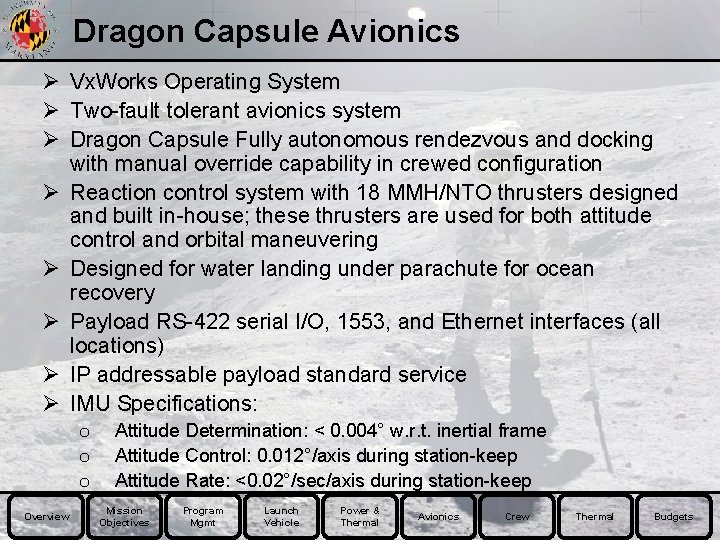
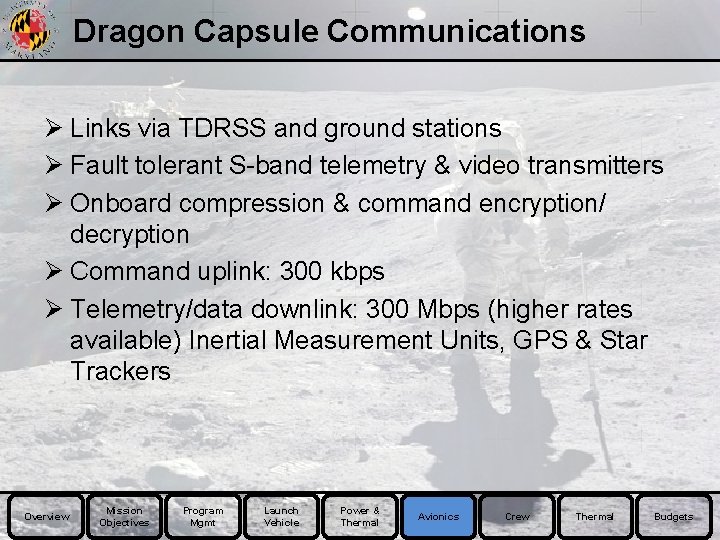
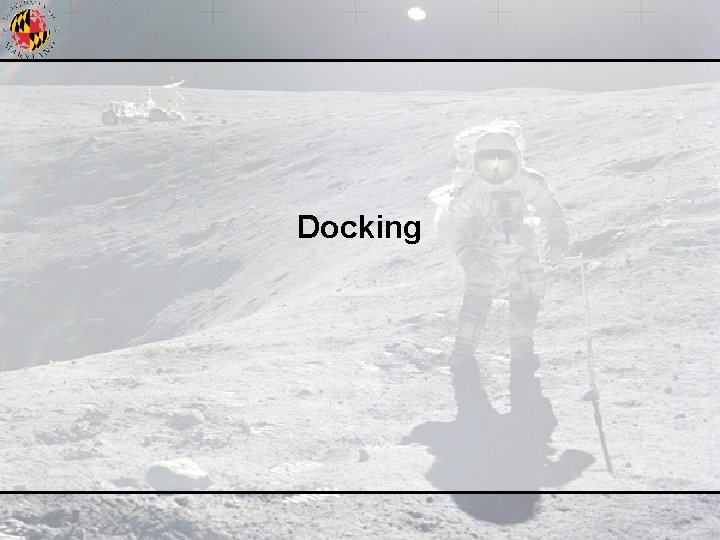
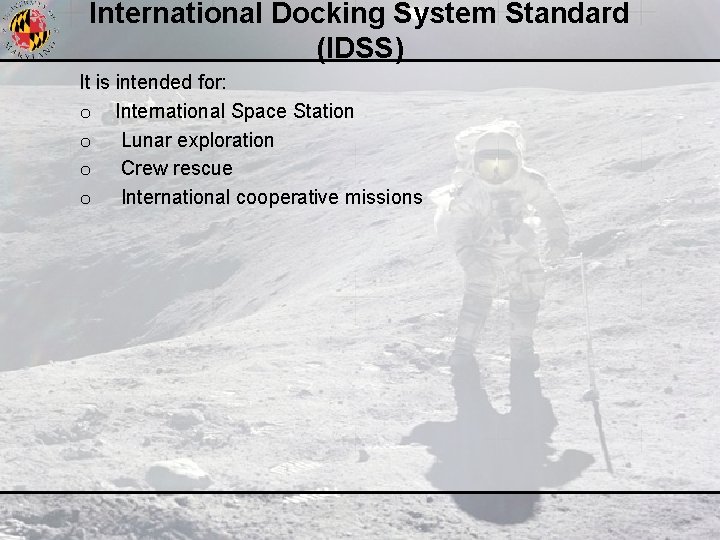
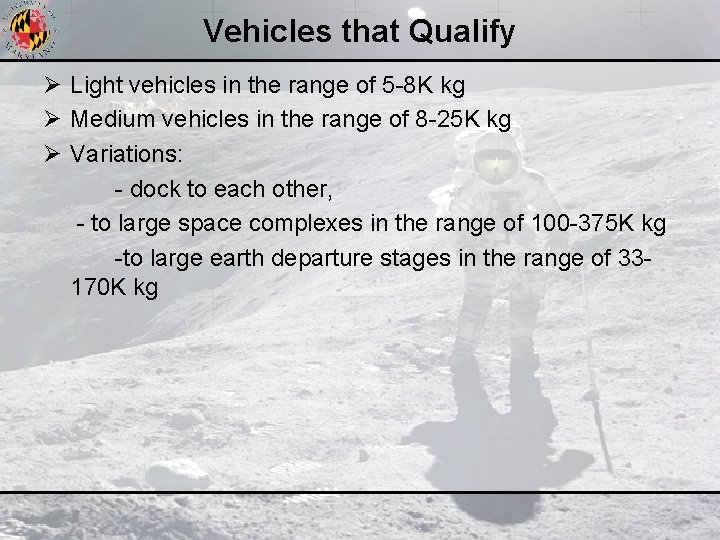
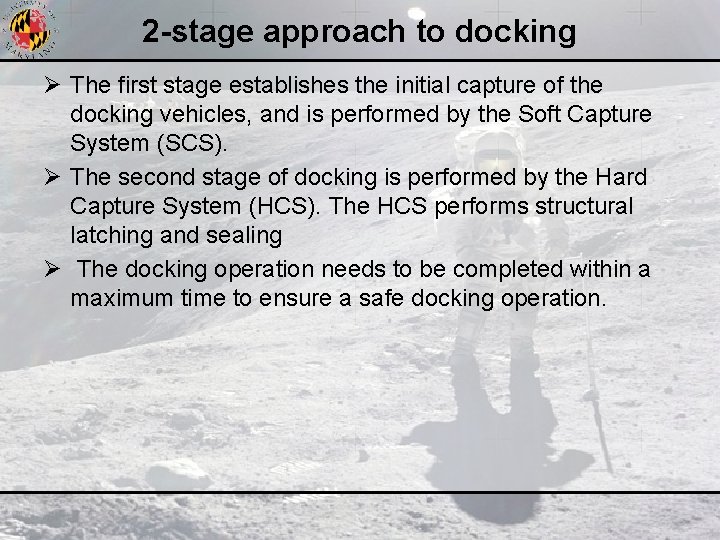
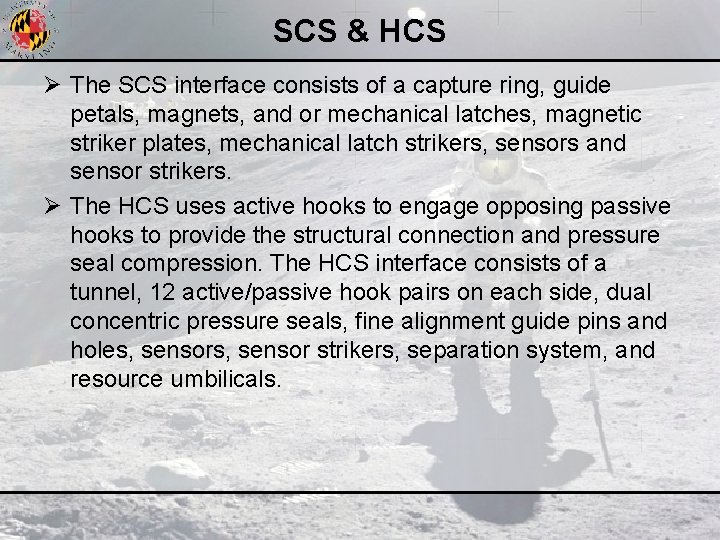
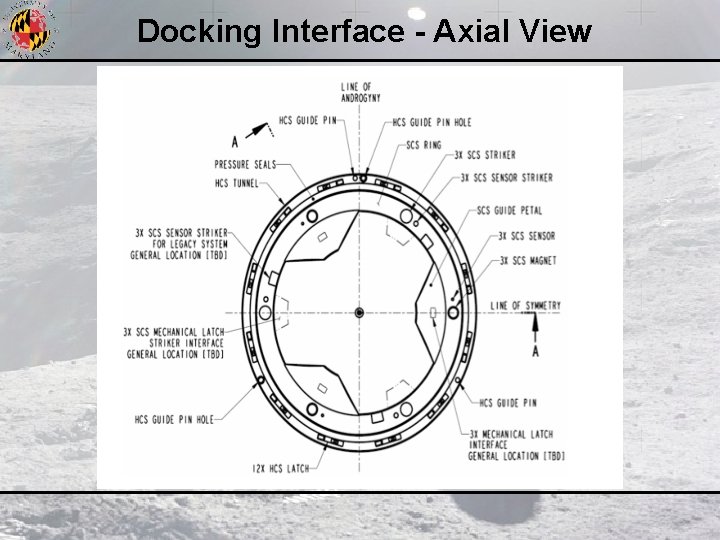
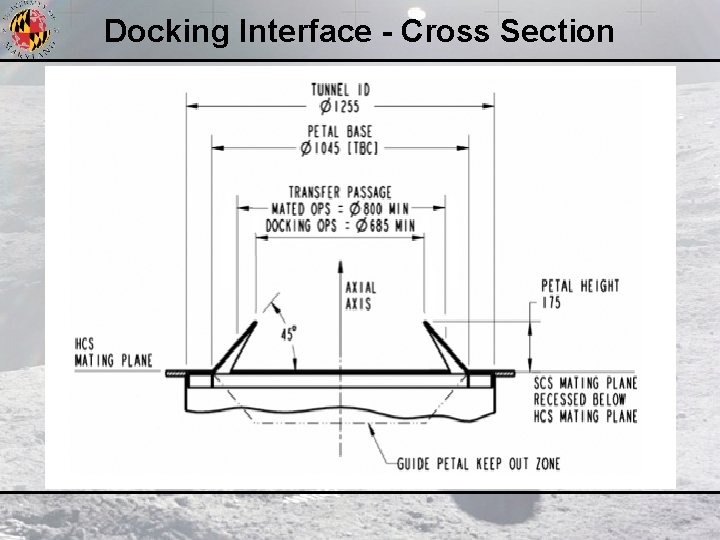
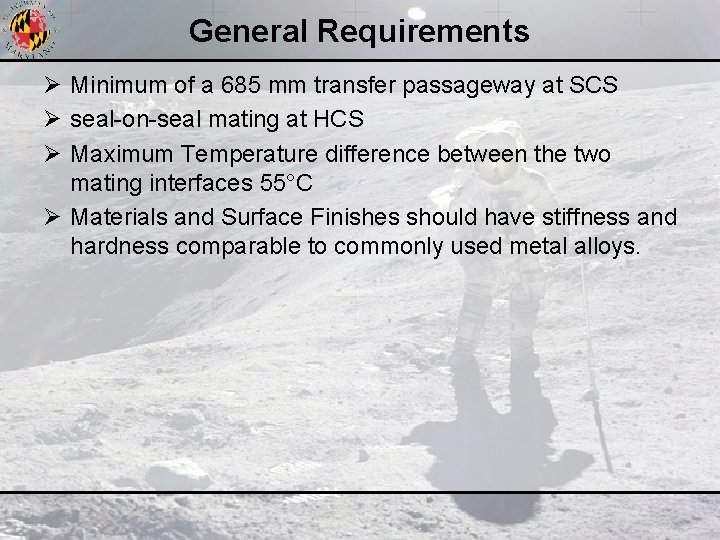
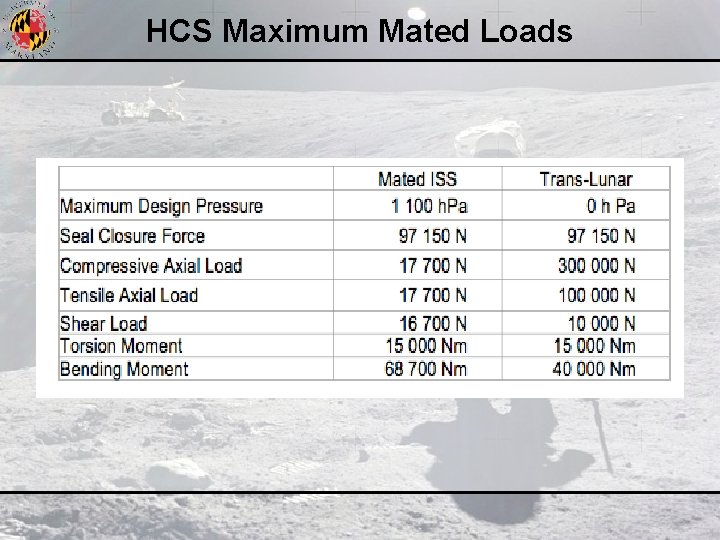
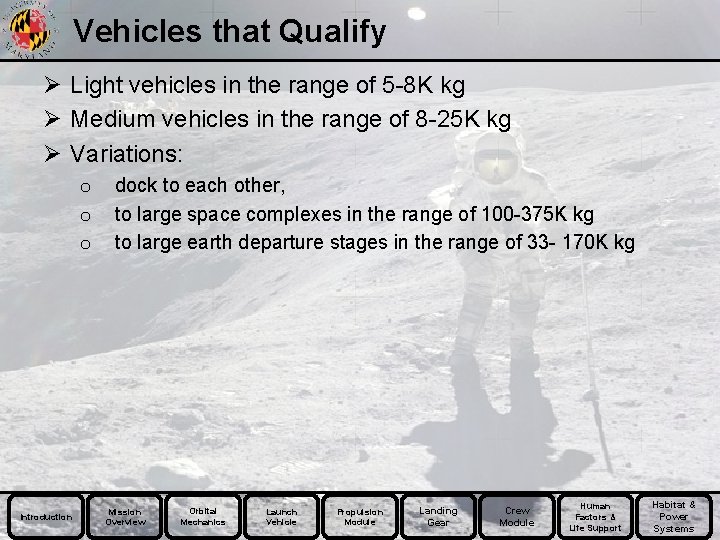
- Slides: 117
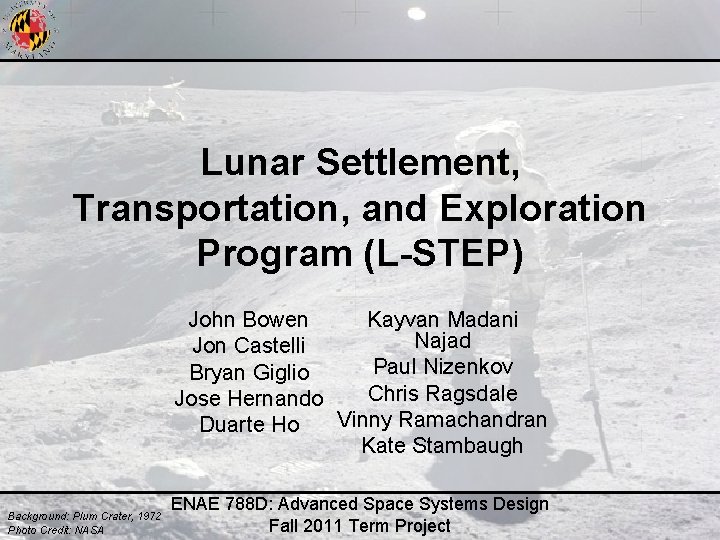
Lunar Settlement, Transportation, and Exploration Program (L-STEP) Kayvan Madani John Bowen Najad Jon Castelli Paul Nizenkov Bryan Giglio Chris Ragsdale Jose Hernando Vinny Ramachandran Duarte Ho Kate Stambaugh Background: Plum Crater, 1972 Photo Credit: NASA ENAE 788 D: Advanced Space Systems Design Fall 2011 Term Project
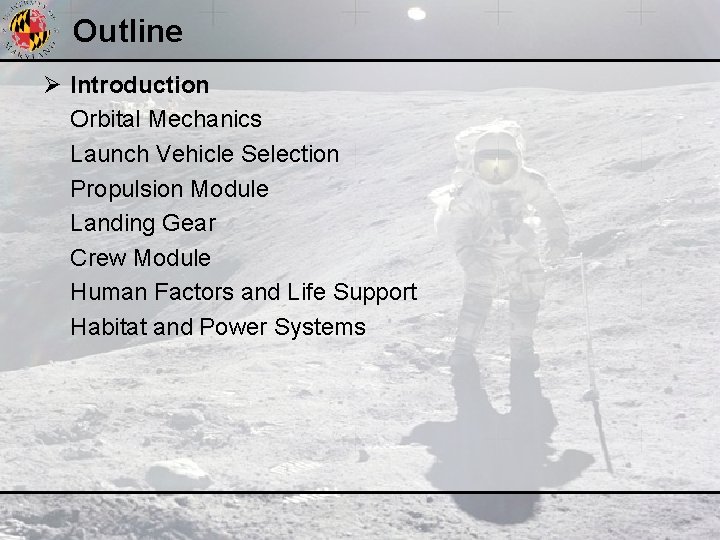
Outline Ø Introduction Orbital Mechanics Launch Vehicle Selection Propulsion Module Landing Gear Crew Module Human Factors and Life Support Habitat and Power Systems
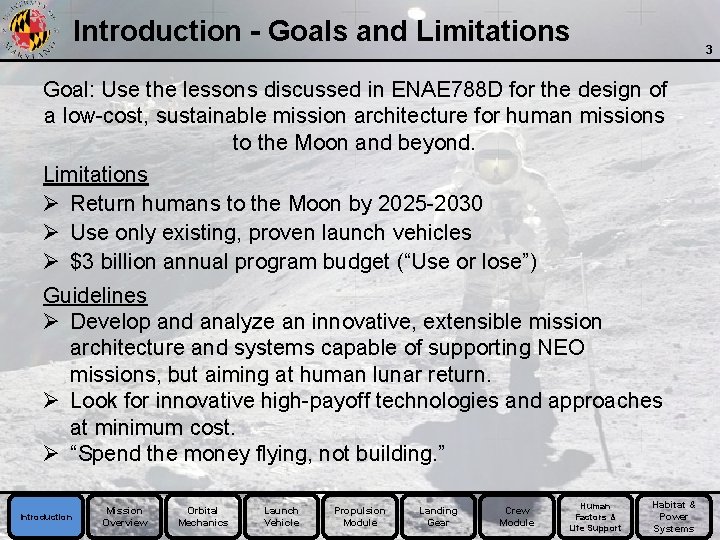
Introduction - Goals and Limitations 3 Goal: Use the lessons discussed in ENAE 788 D for the design of a low-cost, sustainable mission architecture for human missions to the Moon and beyond. Limitations Ø Return humans to the Moon by 2025 -2030 Ø Use only existing, proven launch vehicles Ø $3 billion annual program budget (“Use or lose”) Guidelines Ø Develop and analyze an innovative, extensible mission architecture and systems capable of supporting NEO missions, but aiming at human lunar return. Ø Look for innovative high-payoff technologies and approaches at minimum cost. Ø “Spend the money flying, not building. ” Introduction Mission Overview Orbital Mechanics Launch Vehicle Propulsion Module Landing Gear Crew Module Human Factors & Life Support Habitat & Power Systems
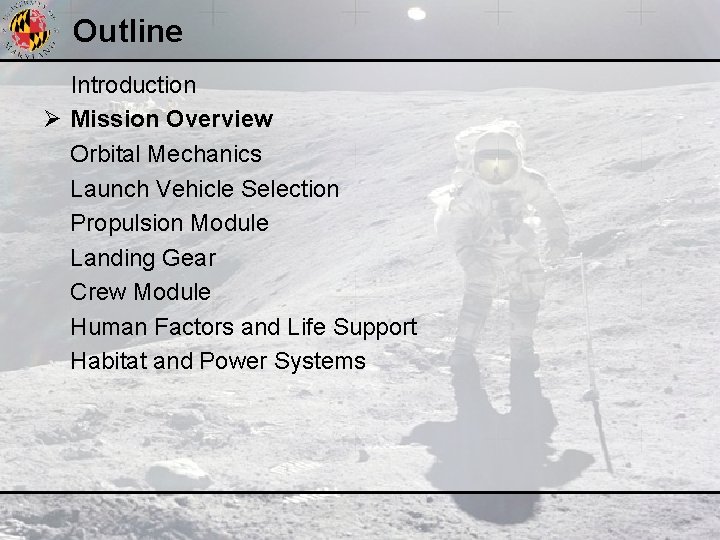
Outline Introduction Ø Mission Overview Orbital Mechanics Launch Vehicle Selection Propulsion Module Landing Gear Crew Module Human Factors and Life Support Habitat and Power Systems
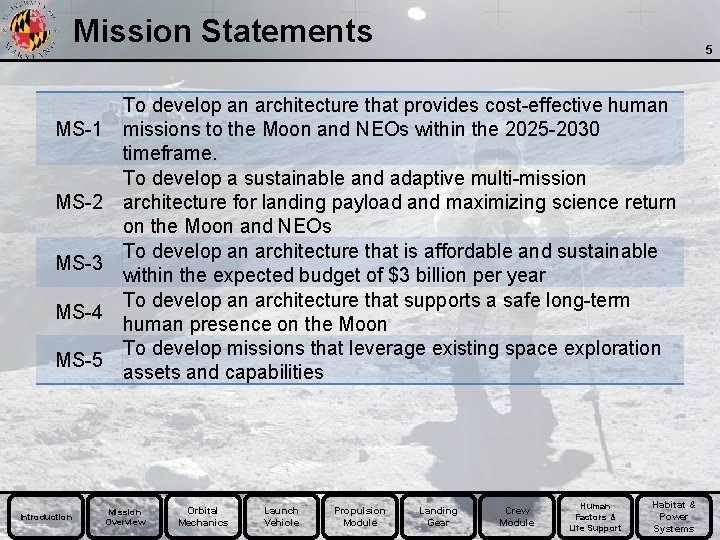
Mission Statements MS-1 MS-2 MS-3 MS-4 MS-5 Introduction 5 To develop an architecture that provides cost-effective human missions to the Moon and NEOs within the 2025 -2030 timeframe. To develop a sustainable and adaptive multi-mission architecture for landing payload and maximizing science return on the Moon and NEOs To develop an architecture that is affordable and sustainable within the expected budget of $3 billion per year To develop an architecture that supports a safe long-term human presence on the Moon To develop missions that leverage existing space exploration assets and capabilities Mission Overview Orbital Mechanics Launch Vehicle Propulsion Module Landing Gear Crew Module Human Factors & Life Support Habitat & Power Systems

Mission Requirements 6 L-STEP shall be capable of sending humans to the surface MS-1, of the Moon and returning them safely to Earth MS-4 L-STEP shall be designed to launch missions using only M-2 MS-5 existing launch vehicle systems L-STEP shall not exceed $3 billion per year in M-3 development, launch, and mission (including resupply) MS-3 costs L-STEP shall be designed to accommodate modular M-4 MS-2 science instrument and payload packages L-STEP shall be designed to support lunar surface MS-2, M-5 operation missions of increasing duration MS-4 L-STEP shall be designed to transport humans in planned MS-1, M-6* human-rated exploration vehicles (e. g. Dragon, MPCV, MS-4, Soyuz) MS-5 L-STEP shall be capable of teleoperated and limited when no human presence is MS-2 *M-7 TBR: autonomous self-imposed andoperations may be too stringent available M-1 Introduction Mission Overview Orbital Mechanics Launch Vehicle Propulsion Module Landing Gear Crew Module Human Factors & Life Support Habitat & Power Systems
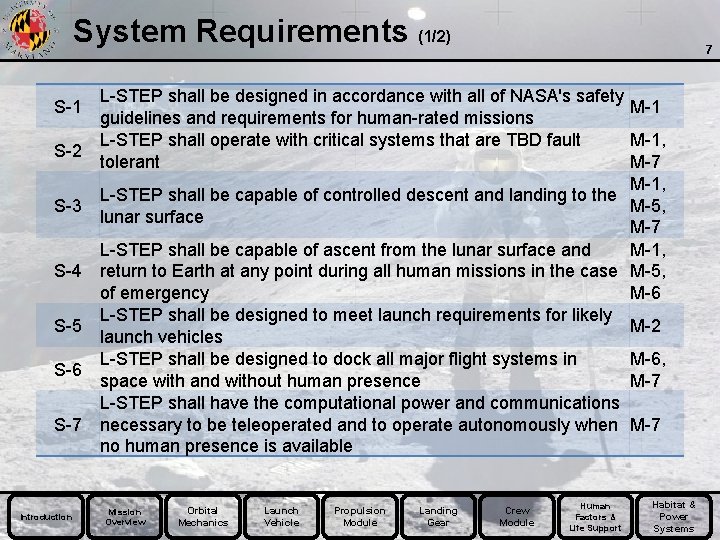
System Requirements (1/2) S-1 S-2 S-3 S-4 S-5 S-6 S-7 Introduction 7 L-STEP shall be designed in accordance with all of NASA's safety M-1 guidelines and requirements for human-rated missions L-STEP shall operate with critical systems that are TBD fault M-1, tolerant M-7 M-1, L-STEP shall be capable of controlled descent and landing to the M-5, lunar surface M-7 L-STEP shall be capable of ascent from the lunar surface and M-1, return to Earth at any point during all human missions in the case M-5, of emergency M-6 L-STEP shall be designed to meet launch requirements for likely M-2 launch vehicles L-STEP shall be designed to dock all major flight systems in M-6, space with and without human presence M-7 L-STEP shall have the computational power and communications necessary to be teleoperated and to operate autonomously when M-7 no human presence is available Mission Overview Orbital Mechanics Launch Vehicle Propulsion Module Landing Gear Crew Module Human Factors & Life Support Habitat & Power Systems
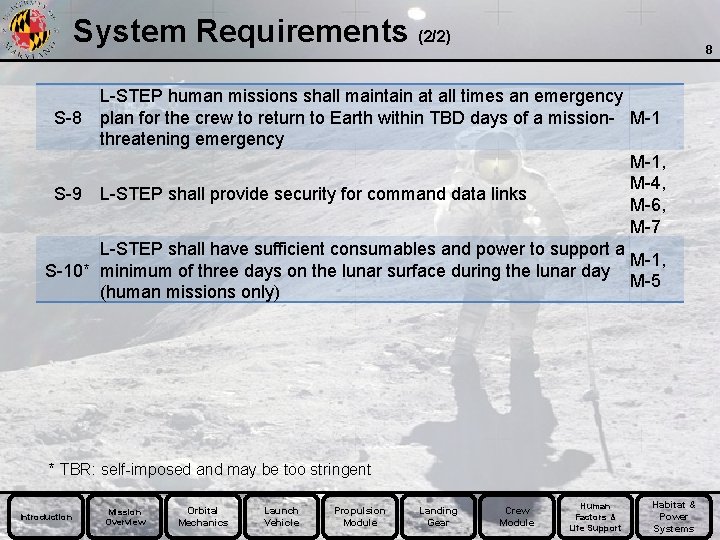
System Requirements (2/2) 8 L-STEP human missions shall maintain at all times an emergency S-8 plan for the crew to return to Earth within TBD days of a mission- M-1 threatening emergency M-1, M-4, S-9 L-STEP shall provide security for command data links M-6, M-7 L-STEP shall have sufficient consumables and power to support a M-1, S-10* minimum of three days on the lunar surface during the lunar day M-5 (human missions only) * TBR: self-imposed and may be too stringent Introduction Mission Overview Orbital Mechanics Launch Vehicle Propulsion Module Landing Gear Crew Module Human Factors & Life Support Habitat & Power Systems
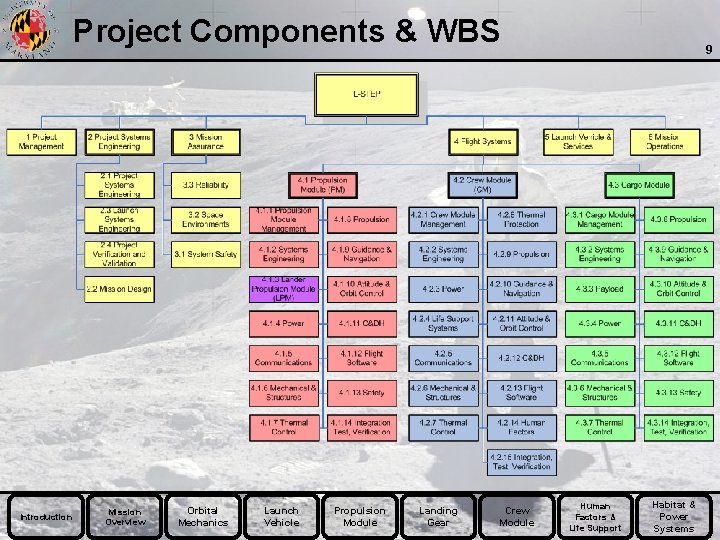
Project Components & WBS Introduction Mission Overview Orbital Mechanics Launch Vehicle Propulsion Module Landing Gear Crew Module 9 Human Factors & Life Support Habitat & Power Systems
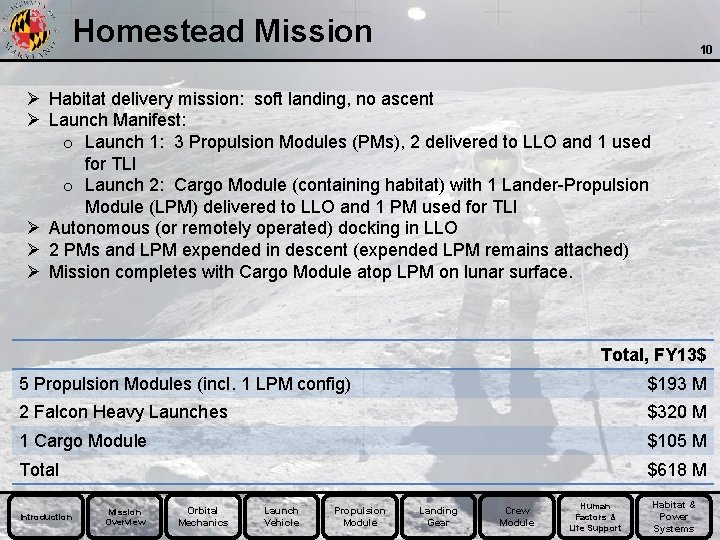
Homestead Mission 10 Ø Habitat delivery mission: soft landing, no ascent Ø Launch Manifest: o Launch 1: 3 Propulsion Modules (PMs), 2 delivered to LLO and 1 used for TLI o Launch 2: Cargo Module (containing habitat) with 1 Lander-Propulsion Module (LPM) delivered to LLO and 1 PM used for TLI Ø Autonomous (or remotely operated) docking in LLO Ø 2 PMs and LPM expended in descent (expended LPM remains attached) Ø Mission completes with Cargo Module atop LPM on lunar surface. Total, FY 13$ 5 Propulsion Modules (incl. 1 LPM config) $193 M 2 Falcon Heavy Launches $320 M 1 Cargo Module $105 M Total $618 M Introduction Mission Overview Orbital Mechanics Launch Vehicle Propulsion Module Landing Gear Crew Module Human Factors & Life Support Habitat & Power Systems
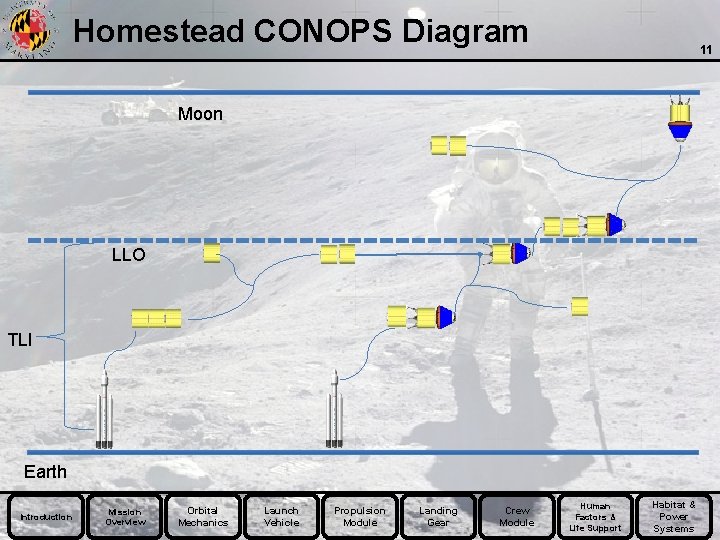
Homestead CONOPS Diagram 11 Moon LLO TLI Earth Introduction Mission Overview Orbital Mechanics Launch Vehicle Propulsion Module Landing Gear Crew Module Human Factors & Life Support Habitat & Power Systems
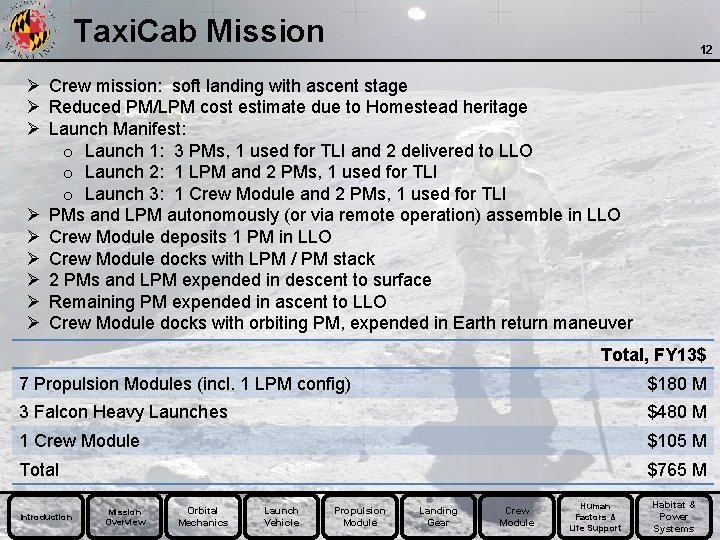
Taxi. Cab Mission 12 Ø Crew mission: soft landing with ascent stage Ø Reduced PM/LPM cost estimate due to Homestead heritage Ø Launch Manifest: o Launch 1: 3 PMs, 1 used for TLI and 2 delivered to LLO o Launch 2: 1 LPM and 2 PMs, 1 used for TLI o Launch 3: 1 Crew Module and 2 PMs, 1 used for TLI Ø PMs and LPM autonomously (or via remote operation) assemble in LLO Ø Crew Module deposits 1 PM in LLO Ø Crew Module docks with LPM / PM stack Ø 2 PMs and LPM expended in descent to surface Ø Remaining PM expended in ascent to LLO Ø Crew Module docks with orbiting PM, expended in Earth return maneuver Total, FY 13$ 7 Propulsion Modules (incl. 1 LPM config) $180 M 3 Falcon Heavy Launches $480 M 1 Crew Module $105 M Total $765 M Introduction Mission Overview Orbital Mechanics Launch Vehicle Propulsion Module Landing Gear Crew Module Human Factors & Life Support Habitat & Power Systems
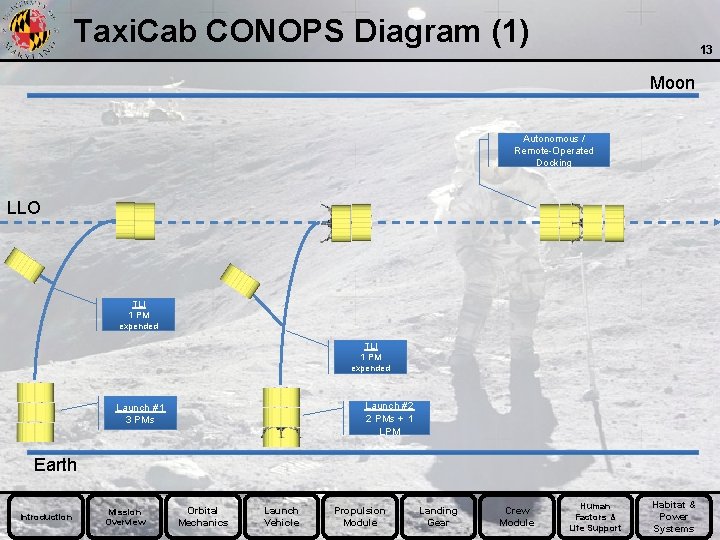
Taxi. Cab CONOPS Diagram (1) 13 Moon Autonomous / Remote-Operated Docking LLO TLI 1 PM expended Launch #2 2 PMs + 1 LPM Launch #1 3 PMs Earth Introduction Mission Overview Orbital Mechanics Launch Vehicle Propulsion Module Landing Gear Crew Module Human Factors & Life Support Habitat & Power Systems
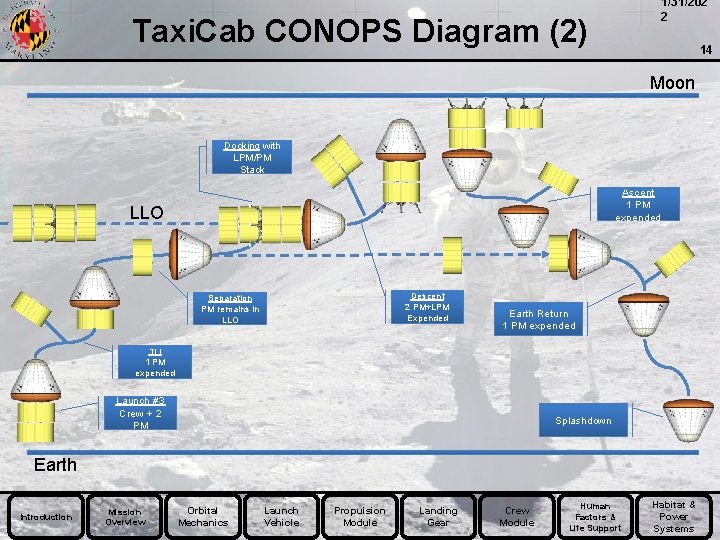
1/31/202 2 Taxi. Cab CONOPS Diagram (2) 14 Moon Docking with LPM/PM Stack Ascent 1 PM expended LLO Descent 2 PM+LPM Expended Separation PM remains in LLO Earth Return 1 PM expended TLI 1 PM expended Launch #3 Crew + 2 PM Splashdown Earth Introduction Mission Overview Orbital Mechanics Launch Vehicle Propulsion Module Landing Gear Crew Module Human Factors & Life Support Habitat & Power Systems
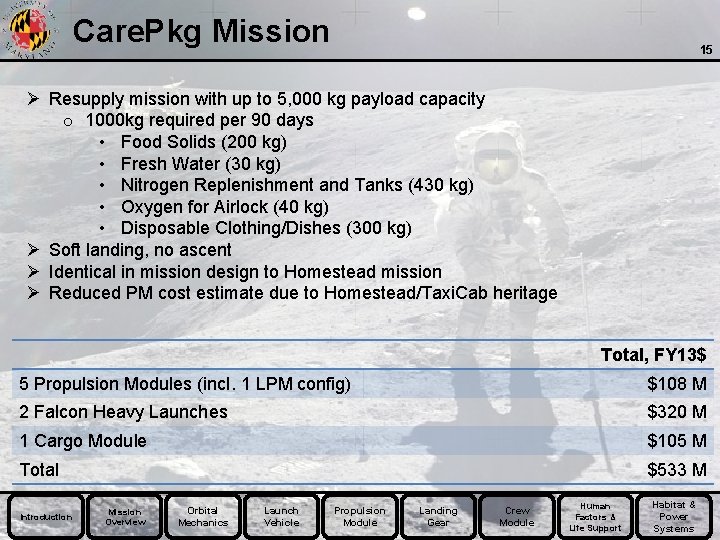
Care. Pkg Mission 15 Ø Resupply mission with up to 5, 000 kg payload capacity o 1000 kg required per 90 days • Food Solids (200 kg) • Fresh Water (30 kg) • Nitrogen Replenishment and Tanks (430 kg) • Oxygen for Airlock (40 kg) • Disposable Clothing/Dishes (300 kg) Ø Soft landing, no ascent Ø Identical in mission design to Homestead mission Ø Reduced PM cost estimate due to Homestead/Taxi. Cab heritage Total, FY 13$ 5 Propulsion Modules (incl. 1 LPM config) $108 M 2 Falcon Heavy Launches $320 M 1 Cargo Module $105 M Total $533 M Introduction Mission Overview Orbital Mechanics Launch Vehicle Propulsion Module Landing Gear Crew Module Human Factors & Life Support Habitat & Power Systems
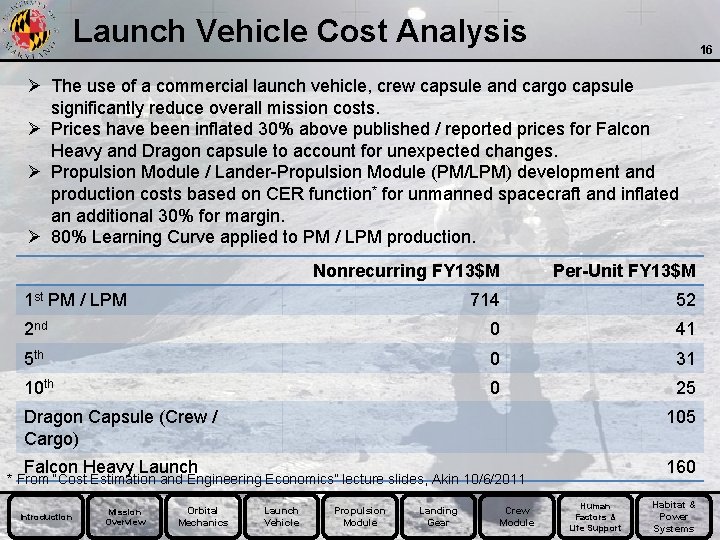
Launch Vehicle Cost Analysis 16 Ø The use of a commercial launch vehicle, crew capsule and cargo capsule significantly reduce overall mission costs. Ø Prices have been inflated 30% above published / reported prices for Falcon Heavy and Dragon capsule to account for unexpected changes. Ø Propulsion Module / Lander-Propulsion Module (PM/LPM) development and production costs based on CER function* for unmanned spacecraft and inflated an additional 30% for margin. Ø 80% Learning Curve applied to PM / LPM production. Nonrecurring FY 13$M Per-Unit FY 13$M 714 52 2 nd 0 41 5 th 0 31 10 th 0 25 1 st PM / LPM Dragon Capsule (Crew / Cargo) 105 Falcon Heavy Launch 160 * From “Cost Estimation and Engineering Economics” lecture slides, Akin 10/6/2011 Introduction Mission Overview Orbital Mechanics Launch Vehicle Propulsion Module Landing Gear Crew Module Human Factors & Life Support Habitat & Power Systems
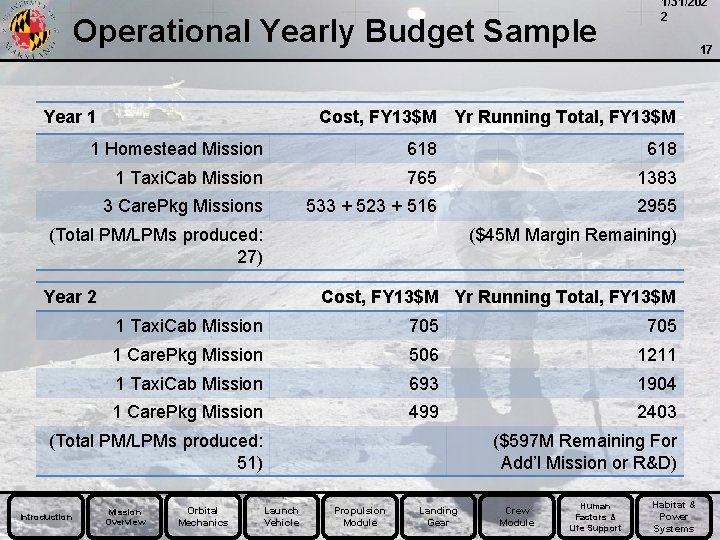
Operational Yearly Budget Sample Year 1 17 Cost, FY 13$M Yr Running Total, FY 13$M 1 Homestead Mission 618 1 Taxi. Cab Mission 765 1383 3 Care. Pkg Missions 533 + 523 + 516 2955 (Total PM/LPMs produced: 27) ($45 M Margin Remaining) Year 2 Cost, FY 13$M Yr Running Total, FY 13$M 1 Taxi. Cab Mission 705 1 Care. Pkg Mission 506 1211 1 Taxi. Cab Mission 693 1904 1 Care. Pkg Mission 499 2403 (Total PM/LPMs produced: 51) Introduction 1/31/202 2 Mission Overview Orbital Mechanics ($597 M Remaining For Add’l Mission or R&D) Launch Vehicle Propulsion Module Landing Gear Crew Module Human Factors & Life Support Habitat & Power Systems
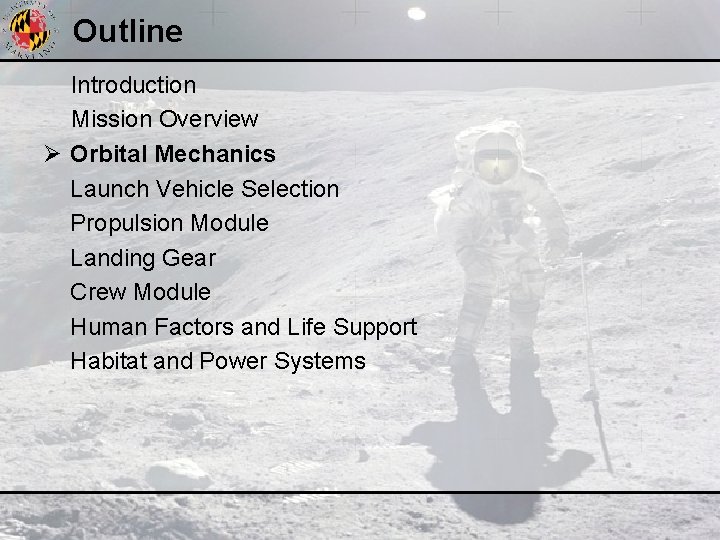
Outline Introduction Mission Overview Ø Orbital Mechanics Launch Vehicle Selection Propulsion Module Landing Gear Crew Module Human Factors and Life Support Habitat and Power Systems
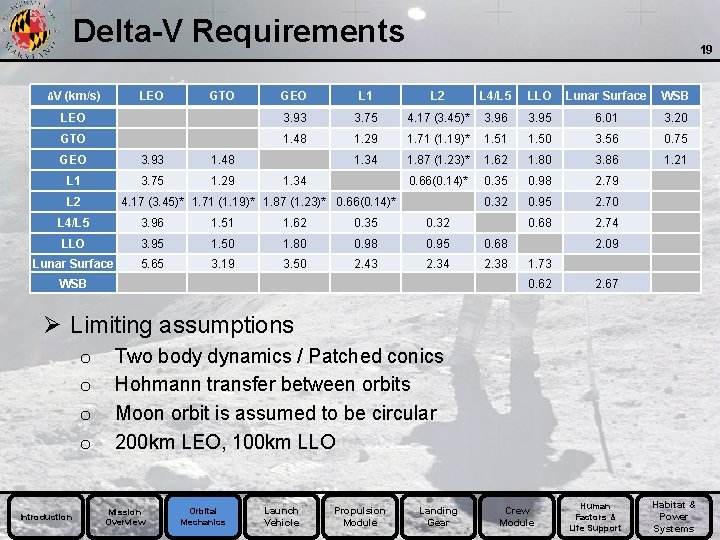
Delta-V Requirements ΔV (km/s) LEO GTO 19 GEO L 1 L 2 L 4/L 5 LLO Lunar Surface WSB LEO 3. 93 3. 75 4. 17 (3. 45)* 3. 96 3. 95 6. 01 3. 20 GTO 1. 48 1. 29 1. 71 (1. 19)* 1. 51 1. 50 3. 56 0. 75 1. 34 1. 87 (1. 23)* 1. 62 1. 80 3. 86 1. 21 0. 66(0. 14)* 0. 35 0. 98 2. 79 0. 32 0. 95 2. 70 0. 68 2. 74 GEO 3. 93 1. 48 L 1 3. 75 1. 29 L 2 1. 34 4. 17 (3. 45)* 1. 71 (1. 19)* 1. 87 (1. 23)* 0. 66(0. 14)* L 4/L 5 3. 96 1. 51 1. 62 0. 35 0. 32 LLO 3. 95 1. 50 1. 80 0. 98 0. 95 0. 68 Lunar Surface 5. 65 3. 19 3. 50 2. 43 2. 34 2. 38 WSB 2. 09 1. 73 0. 62 2. 67 Ø Limiting assumptions o o Introduction Two body dynamics / Patched conics Hohmann transfer between orbits Moon orbit is assumed to be circular 200 km LEO, 100 km LLO Mission Overview Orbital Mechanics Launch Vehicle Propulsion Module Landing Gear Crew Module Human Factors & Life Support Habitat & Power Systems
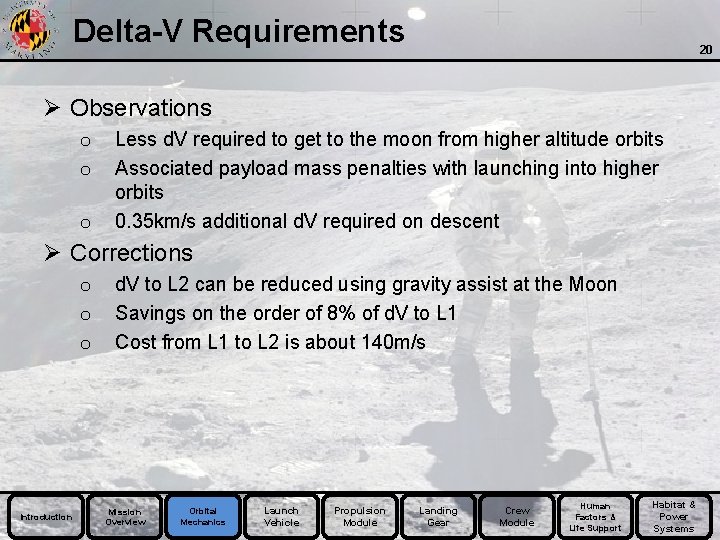
Delta-V Requirements 20 Ø Observations o o o Less d. V required to get to the moon from higher altitude orbits Associated payload mass penalties with launching into higher orbits 0. 35 km/s additional d. V required on descent Ø Corrections o o o Introduction d. V to L 2 can be reduced using gravity assist at the Moon Savings on the order of 8% of d. V to L 1 Cost from L 1 to L 2 is about 140 m/s Mission Overview Orbital Mechanics Launch Vehicle Propulsion Module Landing Gear Crew Module Human Factors & Life Support Habitat & Power Systems
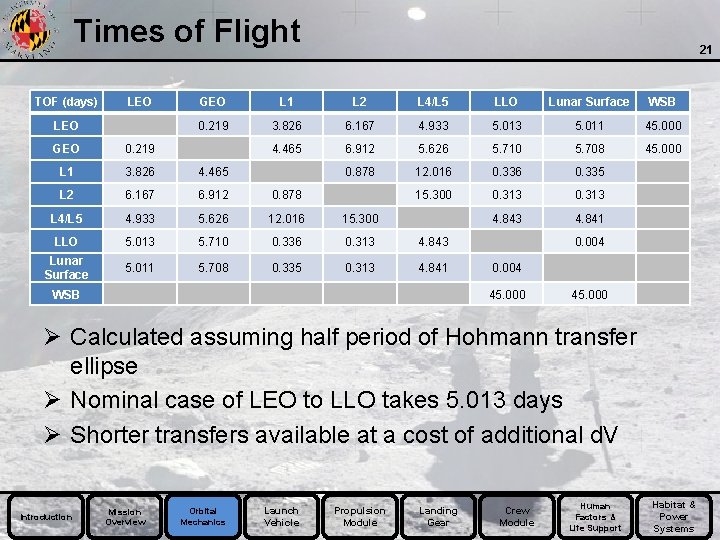
Times of Flight TOF (days) LEO 21 GEO L 1 L 2 L 4/L 5 LLO Lunar Surface WSB 0. 219 3. 826 6. 167 4. 933 5. 011 45. 000 4. 465 6. 912 5. 626 5. 710 5. 708 45. 000 0. 878 12. 016 0. 335 15. 300 0. 313 4. 843 4. 841 GEO 0. 219 L 1 3. 826 4. 465 L 2 6. 167 6. 912 0. 878 L 4/L 5 4. 933 5. 626 12. 016 15. 300 LLO 5. 013 5. 710 0. 336 0. 313 4. 843 Lunar Surface 5. 011 5. 708 0. 335 0. 313 4. 841 WSB 0. 004 45. 000 Ø Calculated assuming half period of Hohmann transfer ellipse Ø Nominal case of LEO to LLO takes 5. 013 days Ø Shorter transfers available at a cost of additional d. V Introduction Mission Overview Orbital Mechanics Launch Vehicle Propulsion Module Landing Gear Crew Module Human Factors & Life Support Habitat & Power Systems
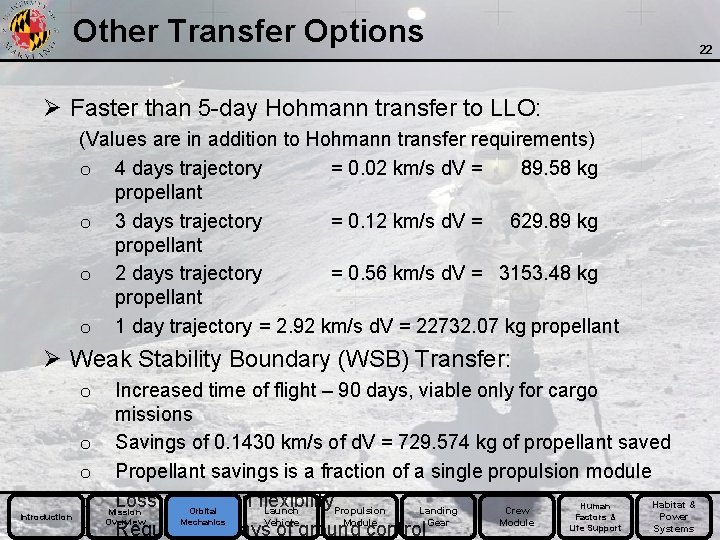
Other Transfer Options Ø Faster than 5 -day Hohmann transfer to LLO: (Values are in addition to Hohmann transfer requirements) o 4 days trajectory = 0. 02 km/s d. V = 89. 58 kg propellant o 3 days trajectory = 0. 12 km/s d. V = 629. 89 kg propellant o 2 days trajectory = 0. 56 km/s d. V = 3153. 48 kg propellant o 1 day trajectory = 2. 92 km/s d. V = 22732. 07 kg propellant Ø Weak Stability Boundary (WSB) Transfer: o Introduction o o Increased time of flight – 90 days, viable only for cargo missions Savings of 0. 1430 km/s of d. V = 729. 574 kg of propellant saved Propellant savings is a fraction of a single propulsion module Loss of mission flexibility Habitat & Human Orbital Launch Propulsion Landing Crew Mission Factors & Power Mechanics Overview Module Life Support Systems Requires 90 days. Vehicle of ground control Gear 22
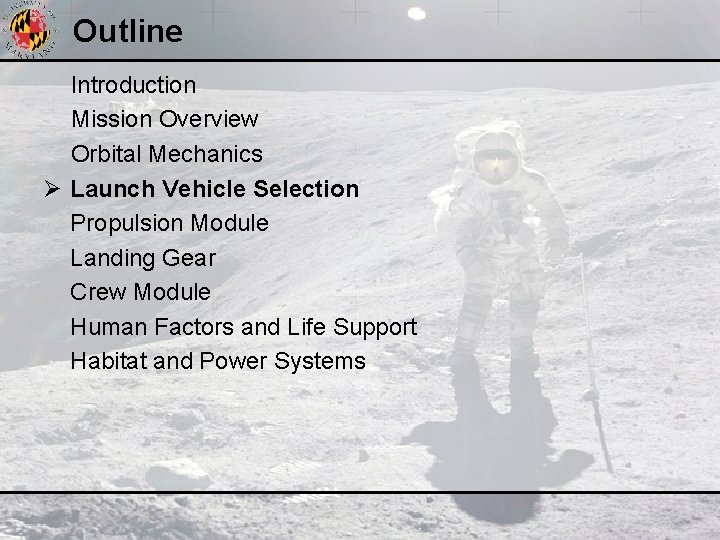
Outline Introduction Mission Overview Orbital Mechanics Ø Launch Vehicle Selection Propulsion Module Landing Gear Crew Module Human Factors and Life Support Habitat and Power Systems
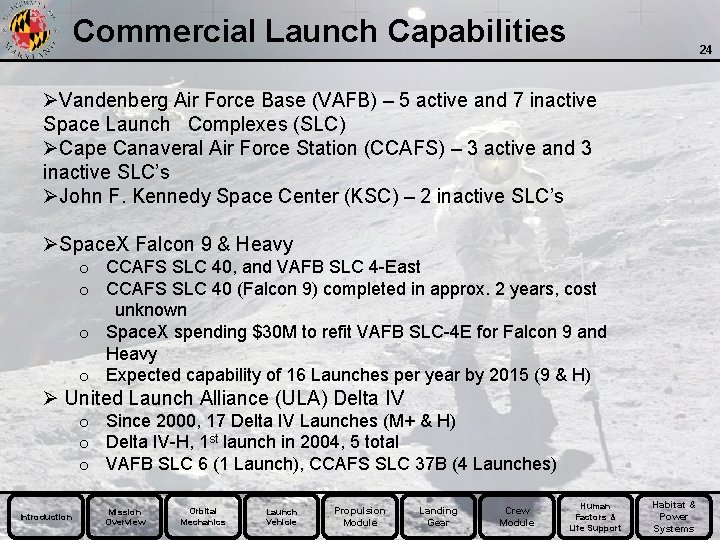
Commercial Launch Capabilities 24 ØVandenberg Air Force Base (VAFB) – 5 active and 7 inactive Space Launch Complexes (SLC) ØCape Canaveral Air Force Station (CCAFS) – 3 active and 3 inactive SLC’s ØJohn F. Kennedy Space Center (KSC) – 2 inactive SLC’s ØSpace. X Falcon 9 & Heavy o CCAFS SLC 40, and VAFB SLC 4 -East o CCAFS SLC 40 (Falcon 9) completed in approx. 2 years, cost unknown o Space. X spending $30 M to refit VAFB SLC-4 E for Falcon 9 and Heavy o Expected capability of 16 Launches per year by 2015 (9 & H) Ø United Launch Alliance (ULA) Delta IV o Since 2000, 17 Delta IV Launches (M+ & H) o Delta IV-H, 1 st launch in 2004, 5 total o VAFB SLC 6 (1 Launch), CCAFS SLC 37 B (4 Launches) Introduction Mission Overview Orbital Mechanics Launch Vehicle Propulsion Module Landing Gear Crew Module Human Factors & Life Support Habitat & Power Systems
![Payload Capabilities 25 Delta IV Heavy Falcon Heavy Mass Limits to LEO kg 22 Payload Capabilities 25 Delta IV Heavy Falcon Heavy Mass Limits to LEO [kg] 22,](https://slidetodoc.com/presentation_image_h2/9b83375e0ef3e844c37a8446a76f7ea9/image-25.jpg)
Payload Capabilities 25 Delta IV Heavy Falcon Heavy Mass Limits to LEO [kg] 22, 500 53, 000 Mass Limit to TLI [kg] 10, 600 16, 000 Fairing Length [m] 13. 761 + 6. 053 6. 60 + 4. 80 Fairing Diameter [m] 5. 080 5. 200 Ref: Delta IV Heavy Payload Users Guide Introduction Mission Overview Orbital Mechanics Launch Vehicle Ref: Falcon 9 Payload Users Guide Propulsion Module Landing Gear Crew Module Human Factors & Life Support Habitat & Power Systems
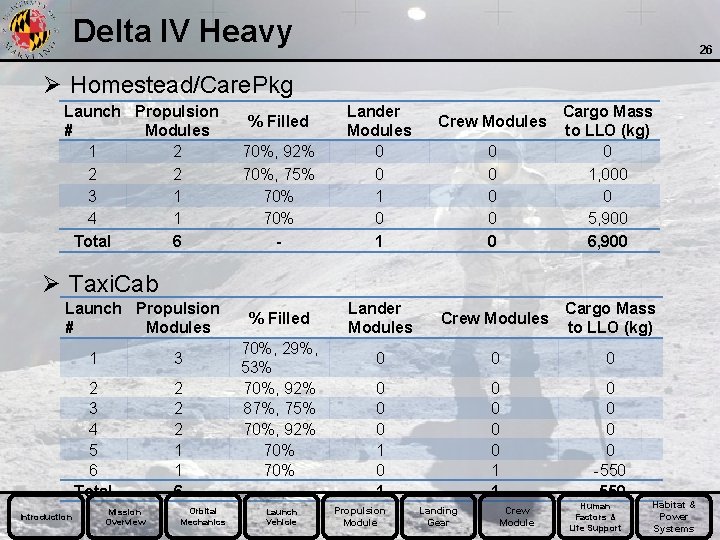
Delta IV Heavy 26 Ø Homestead/Care. Pkg Launch Propulsion # Modules 1 2 2 2 3 1 4 1 Total 6 % Filled 70%, 92% 70%, 75% 70% - Lander Modules 0 0 1 Crew Modules 0 0 0 Cargo Mass to LLO (kg) 0 1, 000 0 5, 900 6, 900 Ø Taxi. Cab Launch Propulsion # Modules Introduction 1 3 2 3 4 5 6 Total 2 2 2 1 1 6 Mission Overview Orbital Mechanics % Filled 70%, 29%, 53% 70%, 92% 87%, 75% 70%, 92% 70% Launch Vehicle Lander Modules Crew Modules Cargo Mass to LLO (kg) 0 0 0 1 0 0 0 0 1 1 0 0 -550 Propulsion Module Landing Gear Crew Module Human Factors & Life Support Habitat & Power Systems
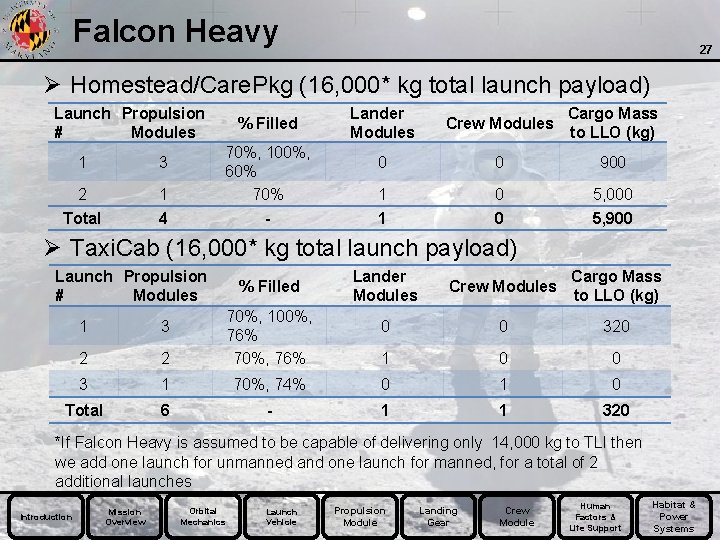
Falcon Heavy 27 Ø Homestead/Care. Pkg (16, 000* kg total launch payload) Launch Propulsion # Modules % Filled 1 3 2 1 70%, 100%, 60% 70% Total 4 - Lander Modules Crew Modules Cargo Mass to LLO (kg) 0 0 900 1 0 5, 000 1 0 5, 900 Ø Taxi. Cab (16, 000* kg total launch payload) Launch Propulsion # Modules % Filled Lander Modules Crew Modules Cargo Mass to LLO (kg) 0 0 320 1 0 0 1 3 2 2 70%, 100%, 76% 70%, 76% 3 1 70%, 74% 0 1 0 Total 6 - 1 1 320 *If Falcon Heavy is assumed to be capable of delivering only 14, 000 kg to TLI then we add one launch for unmanned and one launch for manned, for a total of 2 additional launches Introduction Mission Overview Orbital Mechanics Launch Vehicle Propulsion Module Landing Gear Crew Module Human Factors & Life Support Habitat & Power Systems
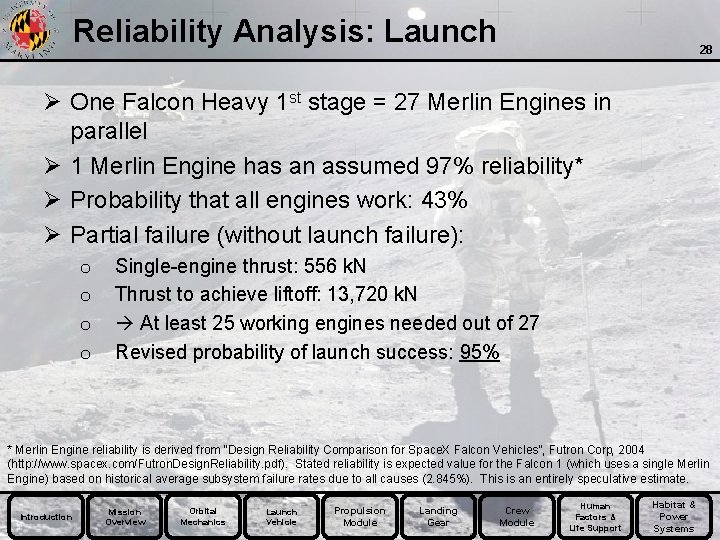
Reliability Analysis: Launch 28 Ø One Falcon Heavy 1 st stage = 27 Merlin Engines in parallel Ø 1 Merlin Engine has an assumed 97% reliability* Ø Probability that all engines work: 43% Ø Partial failure (without launch failure): o o Single-engine thrust: 556 k. N Thrust to achieve liftoff: 13, 720 k. N At least 25 working engines needed out of 27 Revised probability of launch success: 95% * Merlin Engine reliability is derived from “Design Reliability Comparison for Space. X Falcon Vehicles”, Futron Corp, 2004 (http: //www. spacex. com/Futron. Design. Reliability. pdf). Stated reliability is expected value for the Falcon 1 (which uses a single Merlin Engine) based on historical average subsystem failure rates due to all causes (2. 845%). This is an entirely speculative estimate. Introduction Mission Overview Orbital Mechanics Launch Vehicle Propulsion Module Landing Gear Crew Module Human Factors & Life Support Habitat & Power Systems
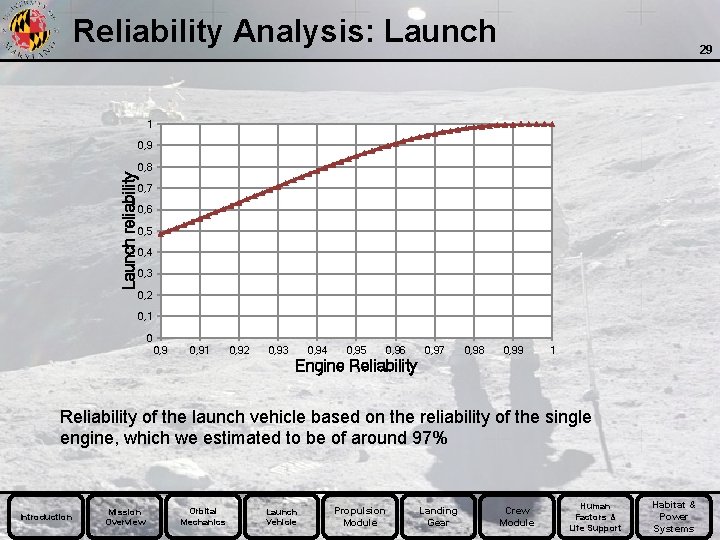
Reliability Analysis: Launch 29 1 Launch reliability 0, 9 0, 8 0, 7 0, 6 0, 5 0, 4 0, 3 0, 2 0, 1 0 0, 91 0, 92 0, 93 0, 94 0, 95 0, 96 0, 97 0, 98 0, 99 1 Engine Reliability of the launch vehicle based on the reliability of the single engine, which we estimated to be of around 97% Introduction Mission Overview Orbital Mechanics Launch Vehicle Propulsion Module Landing Gear Crew Module Human Factors & Life Support Habitat & Power Systems
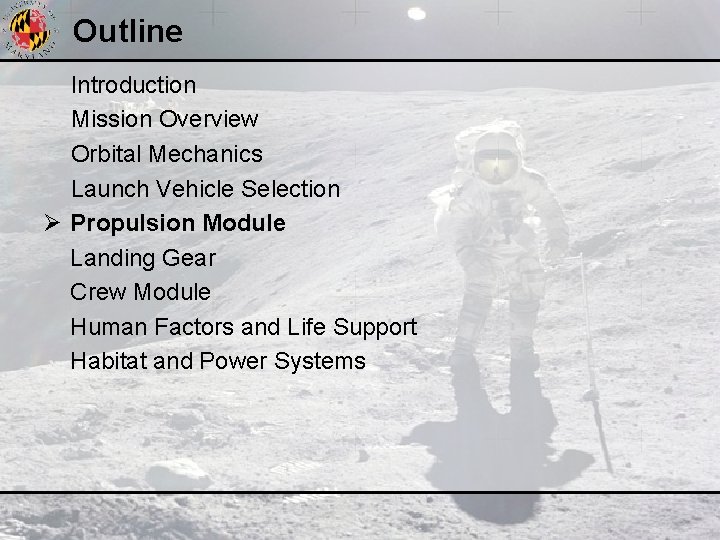
Outline Introduction Mission Overview Orbital Mechanics Launch Vehicle Selection Ø Propulsion Module Landing Gear Crew Module Human Factors and Life Support Habitat and Power Systems
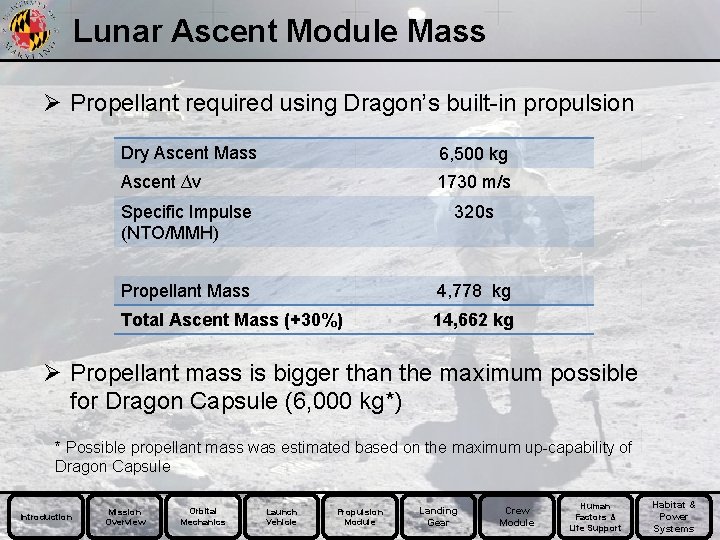
Lunar Ascent Module Mass Ø Propellant required using Dragon’s built-in propulsion Dry Ascent Mass 6, 500 kg Ascent ∆v 1730 m/s Specific Impulse (NTO/MMH) 320 s Propellant Mass 4, 778 kg Total Ascent Mass (+30%) 14, 662 kg Ø Propellant mass is bigger than the maximum possible for Dragon Capsule (6, 000 kg*) * Possible propellant mass was estimated based on the maximum up-capability of Dragon Capsule Introduction Mission Overview Orbital Mechanics Launch Vehicle Propulsion Module Landing Gear Crew Module Human Factors & Life Support Habitat & Power Systems
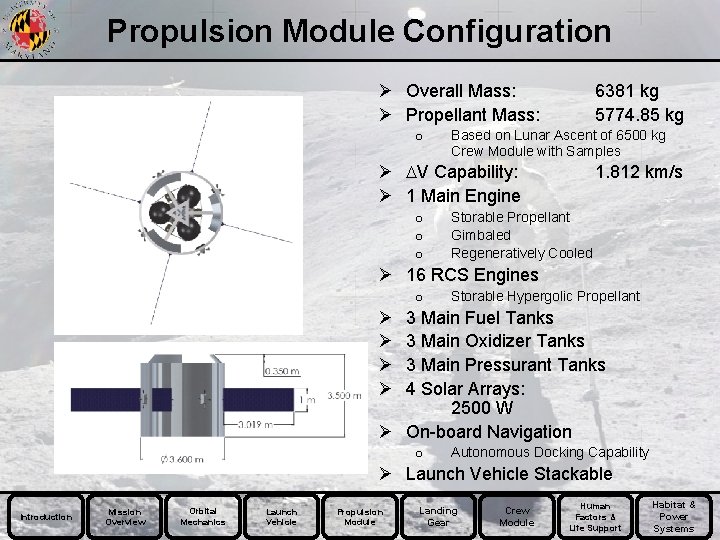
Propulsion Module Configuration Ø Overall Mass: Ø Propellant Mass: o 6381 kg 5774. 85 kg Based on Lunar Ascent of 6500 kg Crew Module with Samples Ø V Capability: Ø 1 Main Engine o o o 1. 812 km/s Storable Propellant Gimbaled Regeneratively Cooled Ø 16 RCS Engines o Storable Hypergolic Propellant Ø Ø 3 Main Fuel Tanks 3 Main Oxidizer Tanks 3 Main Pressurant Tanks 4 Solar Arrays: 2500 W Ø On-board Navigation o Autonomous Docking Capability Ø Launch Vehicle Stackable Introduction Mission Overview Orbital Mechanics Launch Vehicle Propulsion Module Landing Gear Crew Module Human Factors & Life Support Habitat & Power Systems
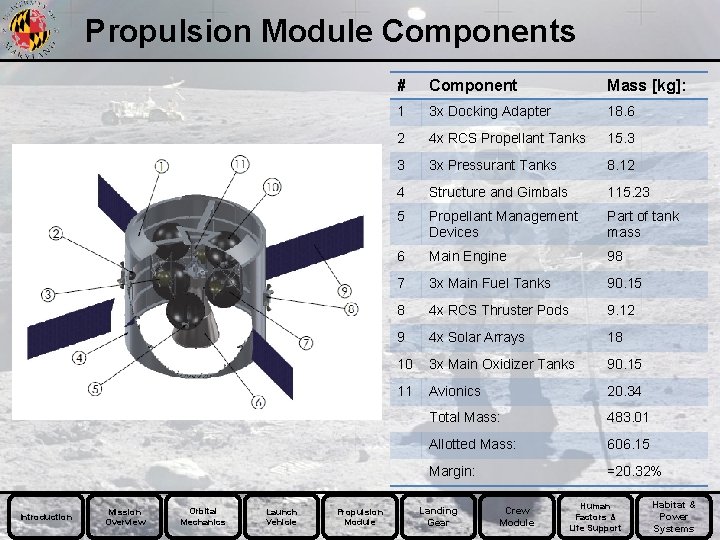
Propulsion Module Components Introduction Mission Overview Orbital Mechanics Launch Vehicle Propulsion Module # Component Mass [kg]: 1 3 x Docking Adapter 18. 6 2 4 x RCS Propellant Tanks 15. 3 3 3 x Pressurant Tanks 8. 12 4 Structure and Gimbals 115. 23 5 Propellant Management Devices Part of tank mass 6 Main Engine 98 7 3 x Main Fuel Tanks 90. 15 8 4 x RCS Thruster Pods 9. 12 9 4 x Solar Arrays 18 10 3 x Main Oxidizer Tanks 90. 15 11 Avionics 20. 34 Total Mass: 483. 01 Allotted Mass: 606. 15 Margin: =20. 32% Landing Gear Crew Module Human Factors & Life Support Habitat & Power Systems
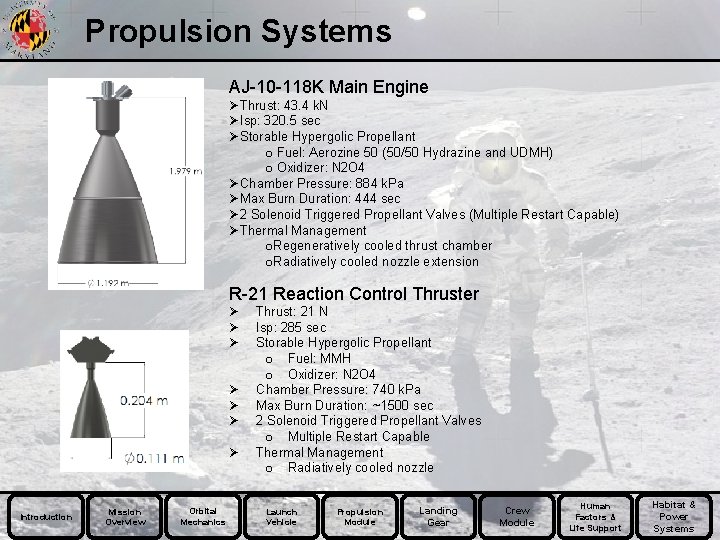
Propulsion Systems AJ-10 -118 K Main Engine ØThrust: 43. 4 k. N ØIsp: 320. 5 sec ØStorable Hypergolic Propellant o Fuel: Aerozine 50 (50/50 Hydrazine and UDMH) o Oxidizer: N 2 O 4 ØChamber Pressure: 884 k. Pa ØMax Burn Duration: 444 sec Ø 2 Solenoid Triggered Propellant Valves (Multiple Restart Capable) ØThermal Management o. Regeneratively cooled thrust chamber o. Radiatively cooled nozzle extension R-21 Reaction Control Thruster Ø Ø Ø Ø Introduction Mission Overview Orbital Mechanics Thrust: 21 N Isp: 285 sec Storable Hypergolic Propellant o Fuel: MMH o Oxidizer: N 2 O 4 Chamber Pressure: 740 k. Pa Max Burn Duration: ~1500 sec 2 Solenoid Triggered Propellant Valves o Multiple Restart Capable Thermal Management o Radiatively cooled nozzle Launch Vehicle Propulsion Module Landing Gear Crew Module Human Factors & Life Support Habitat & Power Systems
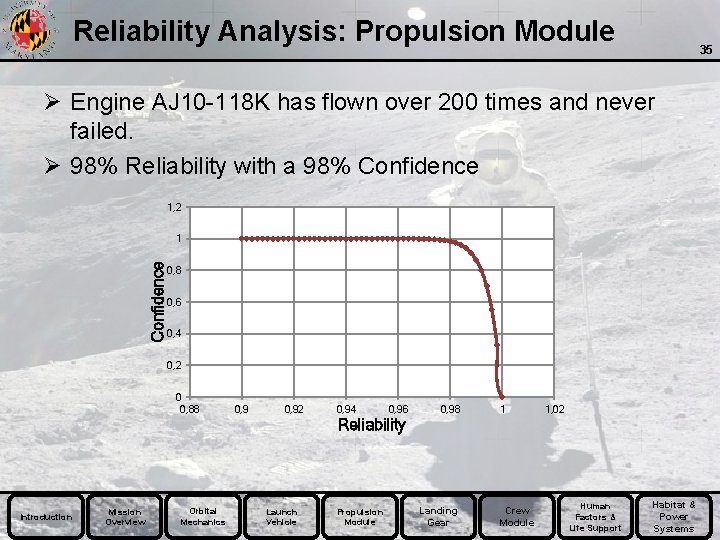
Reliability Analysis: Propulsion Module 35 Ø Engine AJ 10 -118 K has flown over 200 times and never failed. Ø 98% Reliability with a 98% Confidence 1, 2 Confidence 1 0, 8 0, 6 0, 4 0, 2 0 0, 88 0, 92 0, 94 0, 96 0, 98 1 1, 02 Reliability Introduction Mission Overview Orbital Mechanics Launch Vehicle Propulsion Module Landing Gear Crew Module Human Factors & Life Support Habitat & Power Systems
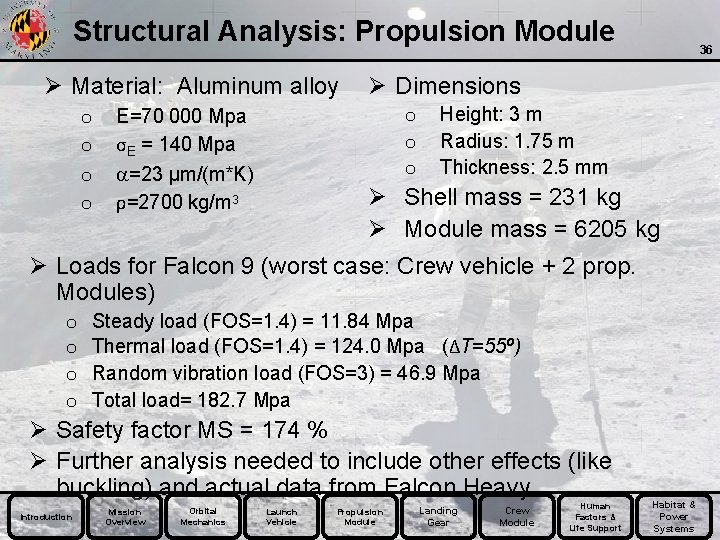
Structural Analysis: Propulsion Module Ø Material: Aluminum alloy o o Ø Dimensions o o o E=70 000 Mpa σE = 140 Mpa =23 µm/(m*K) ρ=2700 kg/m 3 36 Height: 3 m Radius: 1. 75 m Thickness: 2. 5 mm Ø Shell mass = 231 kg Ø Module mass = 6205 kg Ø Loads for Falcon 9 (worst case: Crew vehicle + 2 prop. Modules) o o Steady load (FOS=1. 4) = 11. 84 Mpa Thermal load (FOS=1. 4) = 124. 0 Mpa (ΔT=55º) Random vibration load (FOS=3) = 46. 9 Mpa Total load= 182. 7 Mpa Ø Safety factor MS = 174 % Ø Further analysis needed to include other effects (like buckling) and actual data from Falcon Heavy. Introduction Mission Overview Orbital Mechanics Launch Vehicle Propulsion Module Landing Gear Crew Module Human Factors & Life Support Habitat & Power Systems
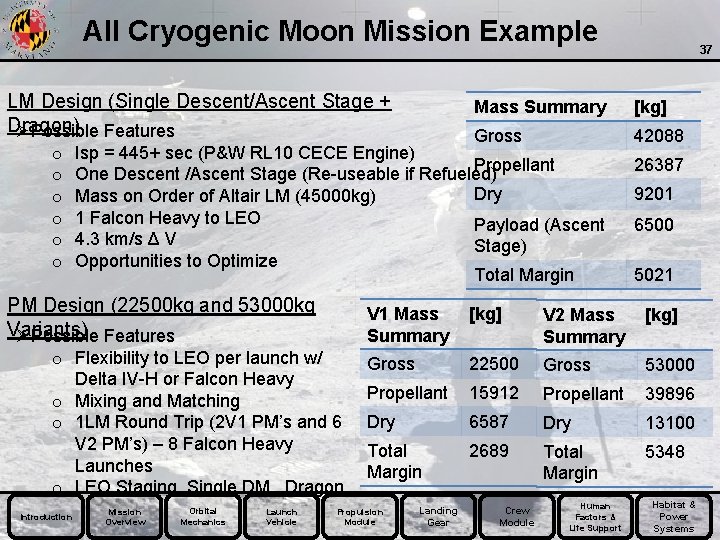
All Cryogenic Moon Mission Example LM Design (Single Descent/Ascent Stage + Dragon) ØPossible Features o o o o Flexibility to LEO per launch w/ Delta IV-H or Falcon Heavy o Mixing and Matching o 1 LM Round Trip (2 V 1 PM’s and 6 V 2 PM’s) – 8 Falcon Heavy Launches o LEO Staging, Single DM, Dragon Introduction Mass Summary [kg] Gross 42088 Isp = 445+ sec (P&W RL 10 CECE Engine) Propellant One Descent /Ascent Stage (Re-useable if Refueled) Dry Mass on Order of Altair LM (45000 kg) 1 Falcon Heavy to LEO Payload (Ascent 4. 3 km/s Δ V Stage) Opportunities to Optimize Total Margin PM Design (22500 kg and 53000 kg Variants) ØPossible Features Mission Overview Orbital Mechanics Launch Vehicle 37 26387 9201 6500 5021 V 1 Mass Summary [kg] V 2 Mass Summary [kg] Gross 22500 Gross 53000 Propellant 15912 Propellant 39896 Dry 6587 Dry 13100 Total Margin 2689 Total Margin 5348 Propulsion Module Landing Gear Crew Module Human Factors & Life Support Habitat & Power Systems
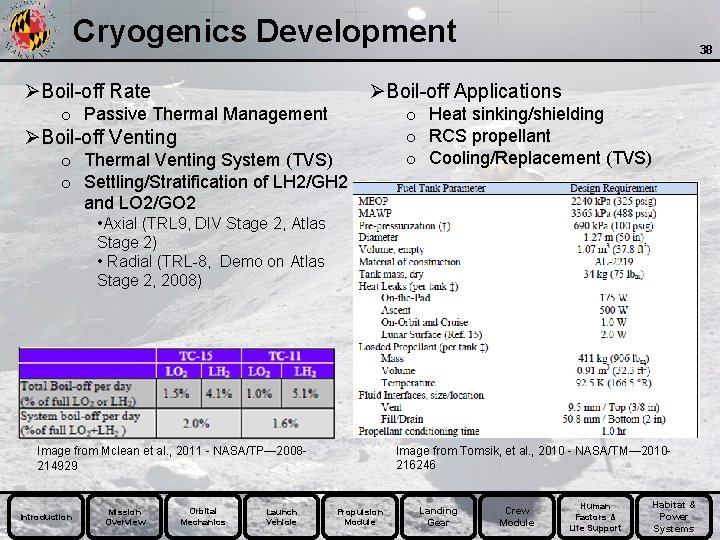
Cryogenics Development ØBoil-off Rate 38 ØBoil-off Applications o Passive Thermal Management ØBoil-off Venting o Thermal Venting System (TVS) o Settling/Stratification of LH 2/GH 2 and LO 2/GO 2 o Heat sinking/shielding o RCS propellant o Cooling/Replacement (TVS) • Axial (TRL 9, DIV Stage 2, Atlas Stage 2) • Radial (TRL-8, Demo on Atlas Stage 2, 2008) Image from Tomsik, et al. , 2010 - NASA/TM— 2010216246 Image from Mclean et al. , 2011 - NASA/TP— 2008214929 Introduction Mission Overview Orbital Mechanics Launch Vehicle Propulsion Module Landing Gear Crew Module Human Factors & Life Support Habitat & Power Systems
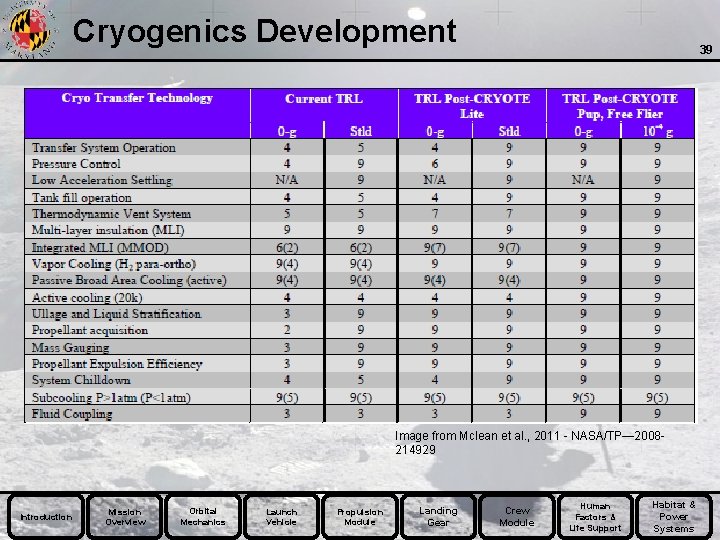
Cryogenics Development 39 Image from Mclean et al. , 2011 - NASA/TP— 2008214929 Introduction Mission Overview Orbital Mechanics Launch Vehicle Propulsion Module Landing Gear Crew Module Human Factors & Life Support Habitat & Power Systems
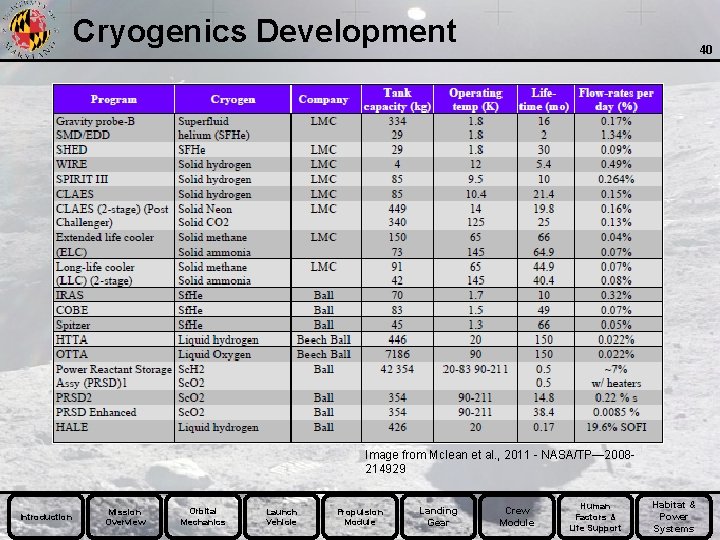
Cryogenics Development 40 Image from Mclean et al. , 2011 - NASA/TP— 2008214929 Introduction Mission Overview Orbital Mechanics Launch Vehicle Propulsion Module Landing Gear Crew Module Human Factors & Life Support Habitat & Power Systems
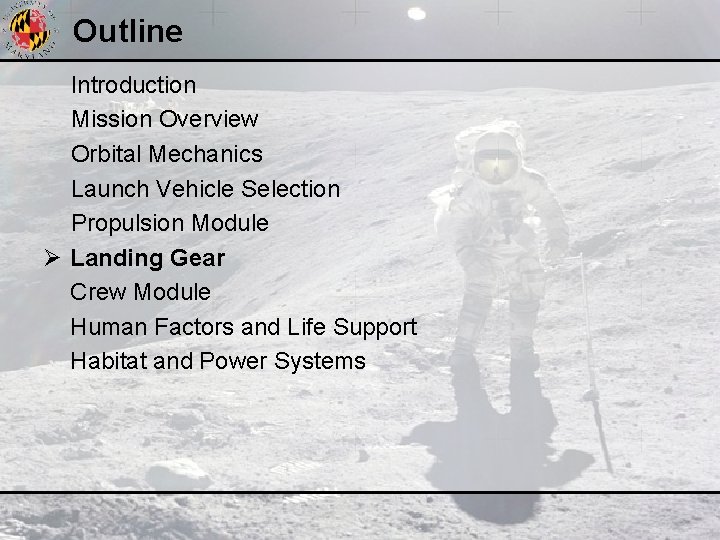
Outline Introduction Mission Overview Orbital Mechanics Launch Vehicle Selection Propulsion Module Ø Landing Gear Crew Module Human Factors and Life Support Habitat and Power Systems
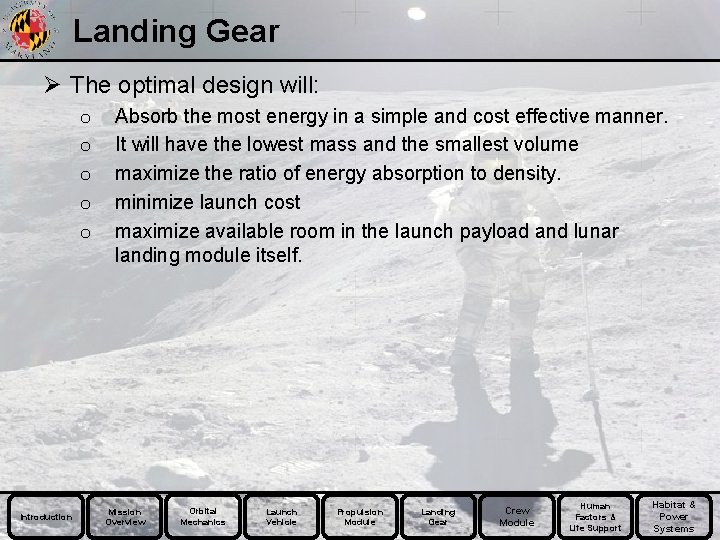
Landing Gear Ø The optimal design will: o o o Introduction Absorb the most energy in a simple and cost effective manner. It will have the lowest mass and the smallest volume maximize the ratio of energy absorption to density. minimize launch cost maximize available room in the launch payload and lunar landing module itself. Mission Overview Orbital Mechanics Launch Vehicle Propulsion Module Landing Gear Crew Module Human Factors & Life Support Habitat & Power Systems
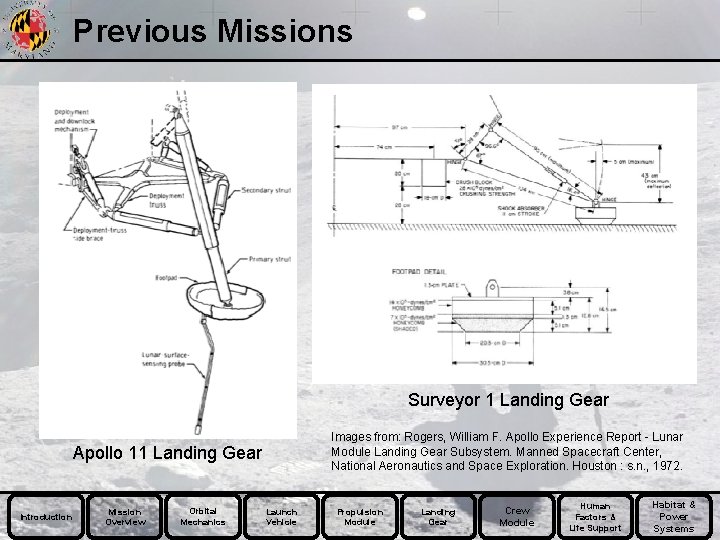
Previous Missions Surveyor 1 Landing Gear Images from: Rogers, William F. Apollo Experience Report - Lunar Module Landing Gear Subsystem. Manned Spacecraft Center, National Aeronautics and Space Exploration. Houston : s. n. , 1972. Apollo 11 Landing Gear Introduction Mission Overview Orbital Mechanics Launch Vehicle Propulsion Module Landing Gear Crew Module Human Factors & Life Support Habitat & Power Systems
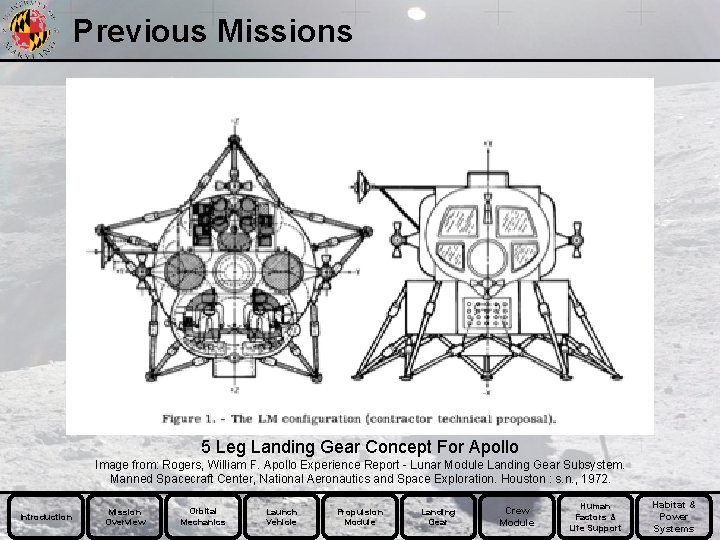
Previous Missions 5 Leg Landing Gear Concept For Apollo Image from: Rogers, William F. Apollo Experience Report - Lunar Module Landing Gear Subsystem. Manned Spacecraft Center, National Aeronautics and Space Exploration. Houston : s. n. , 1972. Introduction Mission Overview Orbital Mechanics Launch Vehicle Propulsion Module Landing Gear Crew Module Human Factors & Life Support Habitat & Power Systems
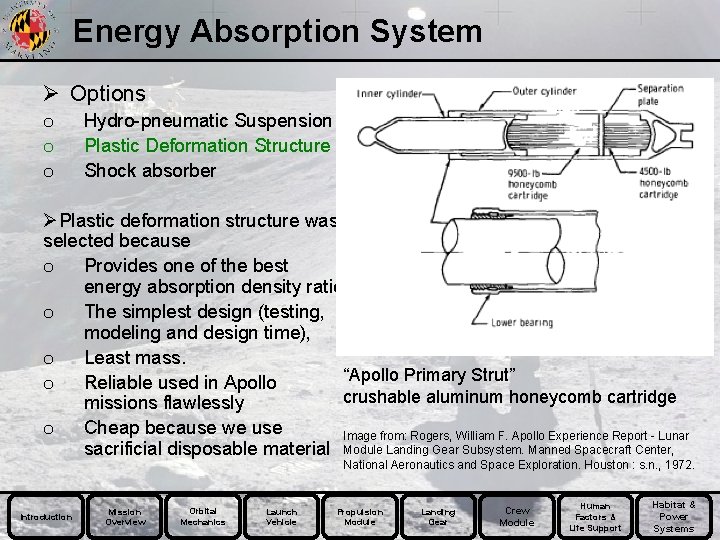
Energy Absorption System Ø Options o o o Hydro-pneumatic Suspension Plastic Deformation Structure Shock absorber ØPlastic deformation structure was selected because o Provides one of the best energy absorption density ratio o The simplest design (testing, modeling and design time), o Least mass. “Apollo Primary Strut” o Reliable used in Apollo crushable aluminum honeycomb cartridge missions flawlessly o Cheap because we use Image from: Rogers, William F. Apollo Experience Report - Lunar sacrificial disposable material Module Landing Gear Subsystem. Manned Spacecraft Center, National Aeronautics and Space Exploration. Houston : s. n. , 1972. Introduction Mission Overview Orbital Mechanics Launch Vehicle Propulsion Module Landing Gear Crew Module Human Factors & Life Support Habitat & Power Systems
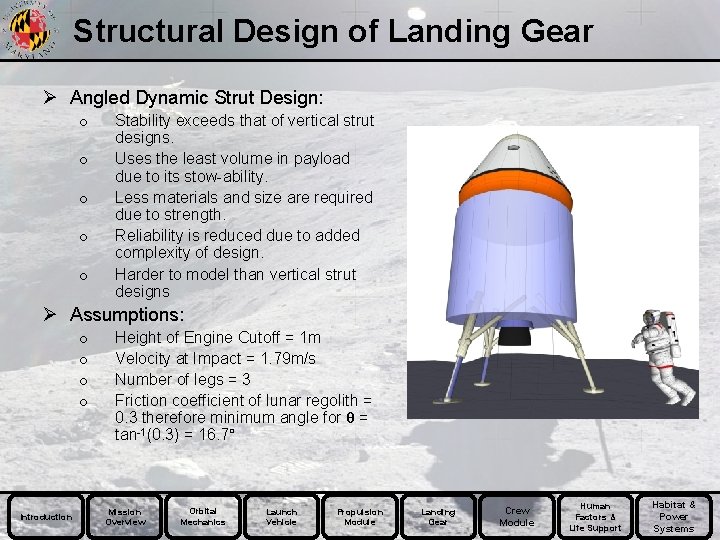
Structural Design of Landing Gear Ø Angled Dynamic Strut Design: o o o Stability exceeds that of vertical strut designs. Uses the least volume in payload due to its stow-ability. Less materials and size are required due to strength. Reliability is reduced due to added complexity of design. Harder to model than vertical strut designs Ø Assumptions: o o Introduction Height of Engine Cutoff = 1 m Velocity at Impact = 1. 79 m/s Number of legs = 3 Friction coefficient of lunar regolith = 0. 3 therefore minimum angle for θ = tan-1(0. 3) = 16. 7° Mission Overview Orbital Mechanics Launch Vehicle Propulsion Module Landing Gear Crew Module Human Factors & Life Support Habitat & Power Systems
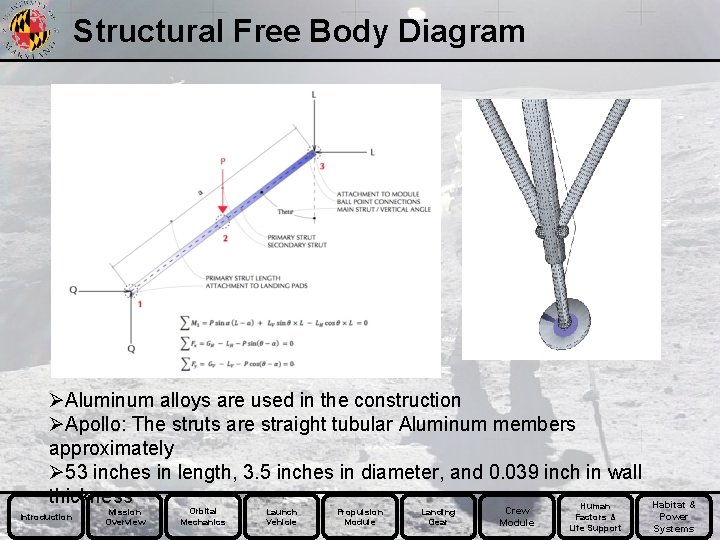
Structural Free Body Diagram ØAluminum alloys are used in the construction ØApollo: The struts are straight tubular Aluminum members approximately Ø 53 inches in length, 3. 5 inches in diameter, and 0. 039 inch in wall thickness Human Introduction Mission Overview Orbital Mechanics Launch Vehicle Propulsion Module Landing Gear Crew Module Factors & Life Support Habitat & Power Systems
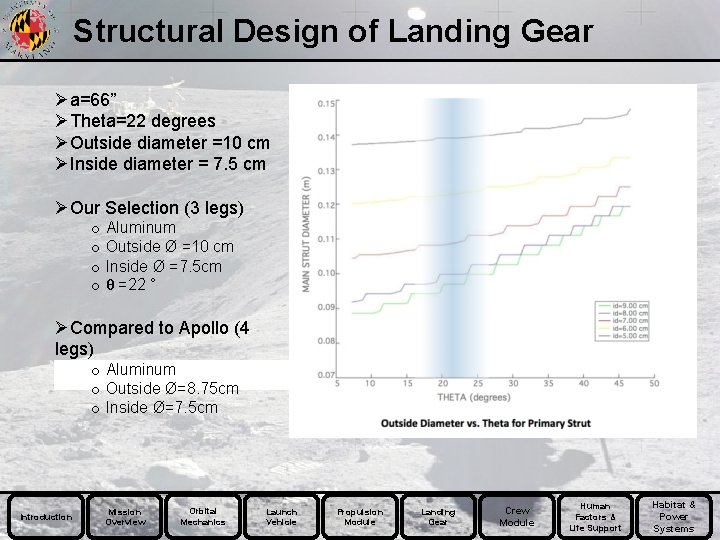
Structural Design of Landing Gear Øa=66” ØTheta=22 degrees ØOutside diameter =10 cm ØInside diameter = 7. 5 cm ØOur Selection (3 legs) o Aluminum o Outside Ø =10 cm o Inside Ø =7. 5 cm o θ =22 ° ØCompared to Apollo (4 legs) o Aluminum o Outside Ø=8. 75 cm o Inside Ø=7. 5 cm Introduction Mission Overview Orbital Mechanics Launch Vehicle Propulsion Module Landing Gear Crew Module Human Factors & Life Support Habitat & Power Systems
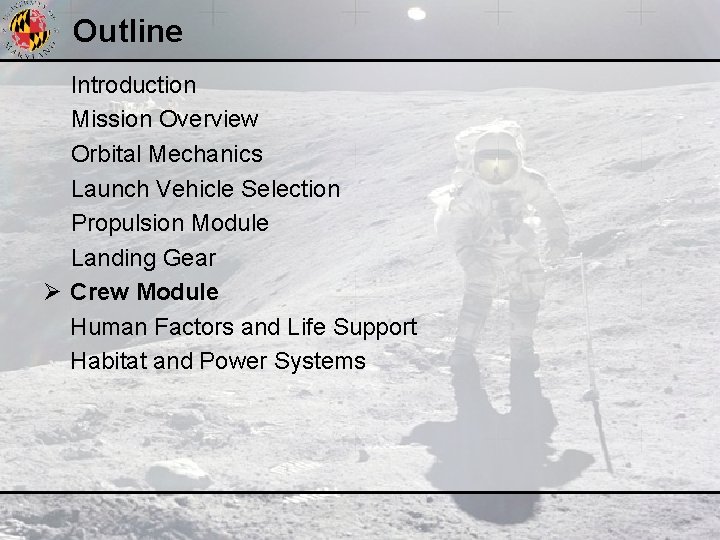
Outline Introduction Mission Overview Orbital Mechanics Launch Vehicle Selection Propulsion Module Landing Gear Ø Crew Module Human Factors and Life Support Habitat and Power Systems
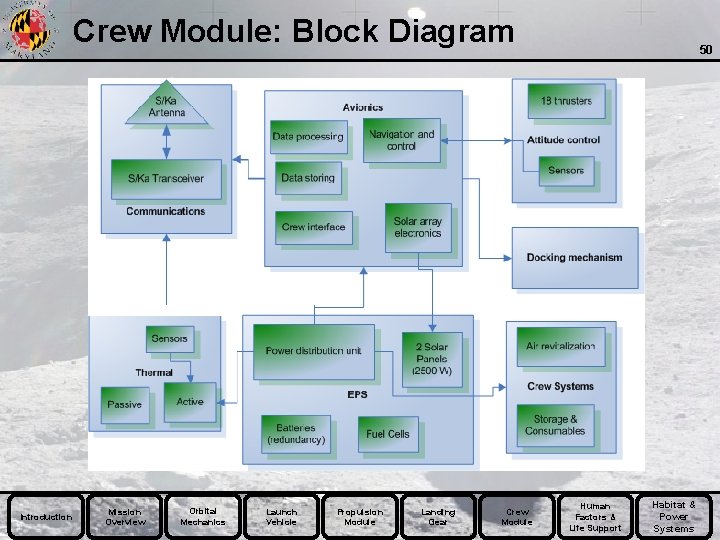
Crew Module: Block Diagram Introduction Mission Overview Orbital Mechanics Launch Vehicle Propulsion Module Landing Gear Crew Module 50 Human Factors & Life Support Habitat & Power Systems
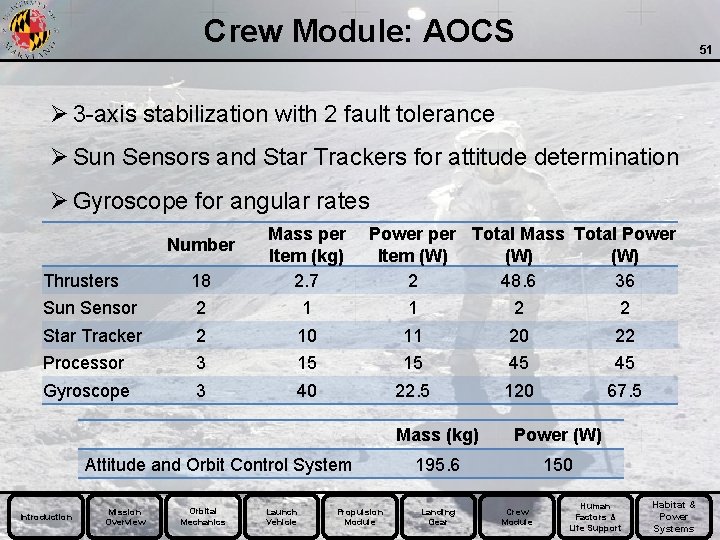
Crew Module: AOCS 51 Ø 3 -axis stabilization with 2 fault tolerance Ø Sun Sensors and Star Trackers for attitude determination Ø Gyroscope for angular rates Thrusters 18 Mass per Item (kg) 2. 7 Sun Sensor 2 1 1 2 2 Star Tracker 2 10 11 20 22 Processor 3 15 15 45 45 Gyroscope 3 40 22. 5 120 67. 5 Number Power per Total Mass Total Power Item (W) (W) 2 48. 6 36 Attitude and Orbit Control System Introduction Mission Overview Orbital Mechanics Launch Vehicle Propulsion Module Mass (kg) Power (W) 195. 6 150 Landing Gear Crew Module Human Factors & Life Support Habitat & Power Systems
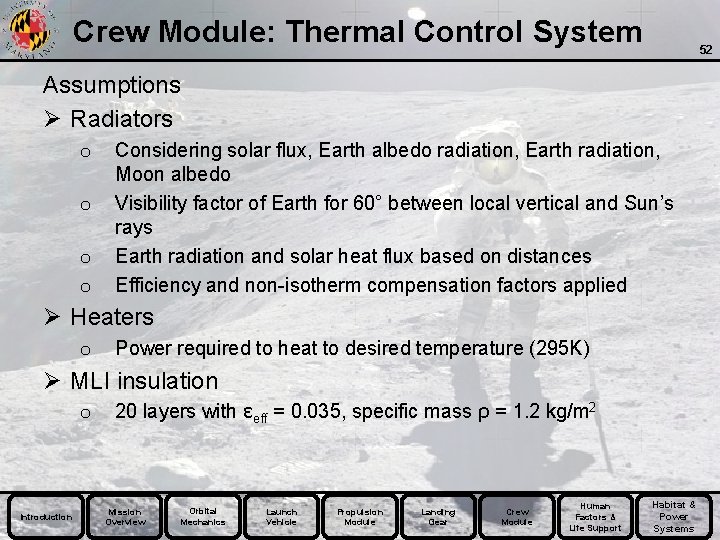
Crew Module: Thermal Control System 52 Assumptions Ø Radiators o o Considering solar flux, Earth albedo radiation, Earth radiation, Moon albedo Visibility factor of Earth for 60° between local vertical and Sun’s rays Earth radiation and solar heat flux based on distances Efficiency and non-isotherm compensation factors applied Ø Heaters o Power required to heat to desired temperature (295 K) Ø MLI insulation o Introduction 20 layers with εeff = 0. 035, specific mass ρ = 1. 2 kg/m 2 Mission Overview Orbital Mechanics Launch Vehicle Propulsion Module Landing Gear Crew Module Human Factors & Life Support Habitat & Power Systems
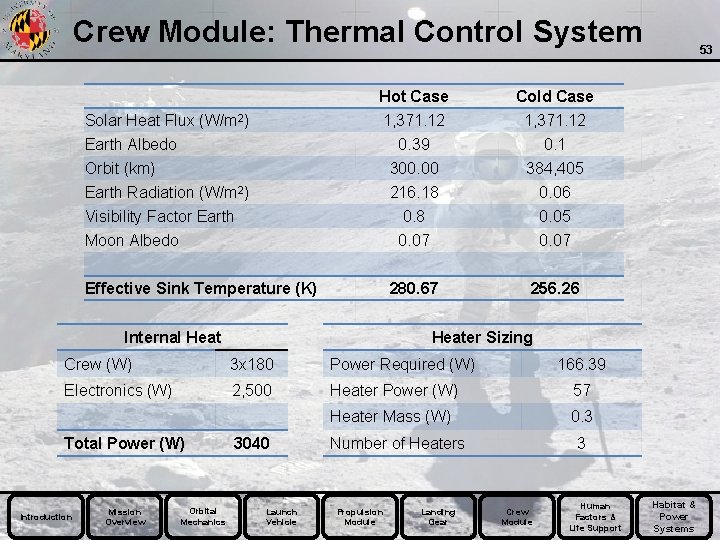
Crew Module: Thermal Control System Solar Heat Flux (W/m 2) Earth Albedo Orbit (km) Earth Radiation (W/m 2) Visibility Factor Earth Moon Albedo Hot Case 1, 371. 12 0. 39 300. 00 216. 18 0. 07 Cold Case 1, 371. 12 0. 1 384, 405 0. 06 0. 05 0. 07 280. 67 256. 26 Effective Sink Temperature (K) Internal Heater Sizing Crew (W) 3 x 180 Power Required (W) Electronics (W) 2, 500 Heater Power (W) 57 Heater Mass (W) 0. 3 Total Power (W) Introduction Mission Overview Orbital Mechanics 53 3040 Launch Vehicle 166. 39 Number of Heaters Propulsion Module Landing Gear 3 Crew Module Human Factors & Life Support Habitat & Power Systems
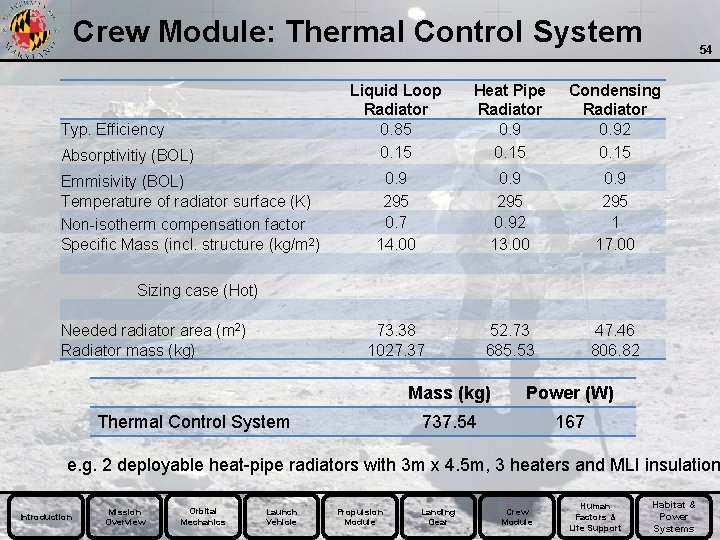
Crew Module: Thermal Control System Typ. Efficiency Absorptivitiy (BOL) Emmisivity (BOL) Temperature of radiator surface (K) Non-isotherm compensation factor Specific Mass (incl. structure (kg/m 2) 54 Liquid Loop Radiator 0. 85 0. 15 Heat Pipe Radiator 0. 9 0. 15 Condensing Radiator 0. 92 0. 15 0. 9 295 0. 7 14. 00 0. 9 295 0. 92 13. 00 0. 9 295 1 17. 00 73. 38 1027. 37 52. 73 685. 53 47. 46 806. 82 Sizing case (Hot) Needed radiator area (m 2) Radiator mass (kg) Thermal Control System Mass (kg) Power (W) 737. 54 167 e. g. 2 deployable heat-pipe radiators with 3 m x 4. 5 m, 3 heaters and MLI insulation Introduction Mission Overview Orbital Mechanics Launch Vehicle Propulsion Module Landing Gear Crew Module Human Factors & Life Support Habitat & Power Systems
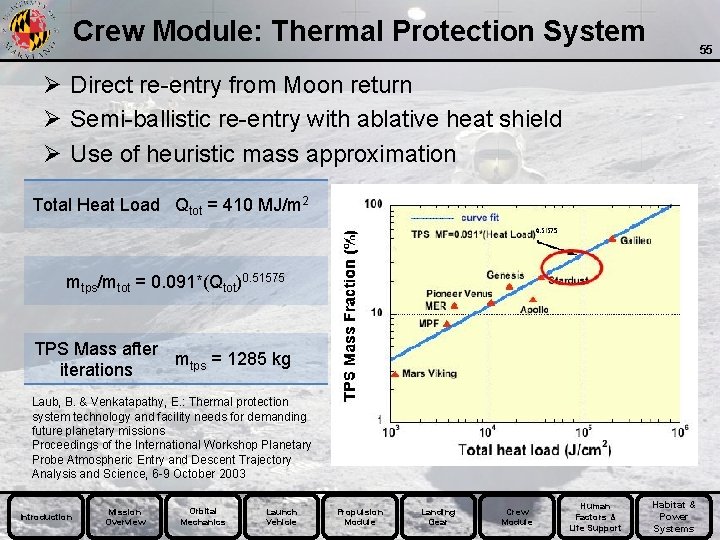
Crew Module: Thermal Protection System 55 Ø Direct re-entry from Moon return Ø Semi-ballistic re-entry with ablative heat shield Ø Use of heuristic mass approximation Total Heat Load Qtot = 410 MJ/m 2 mtps/mtot = 0. 091*(Qtot)0. 51575 TPS Mass after mtps = 1285 kg iterations Laub, B. & Venkatapathy, E. : Thermal protection system technology and facility needs for demanding future planetary missions Proceedings of the International Workshop Planetary Probe Atmospheric Entry and Descent Trajectory Analysis and Science, 6 -9 October 2003 Introduction Mission Overview Orbital Mechanics Launch Vehicle Propulsion Module Landing Gear Crew Module Human Factors & Life Support Habitat & Power Systems
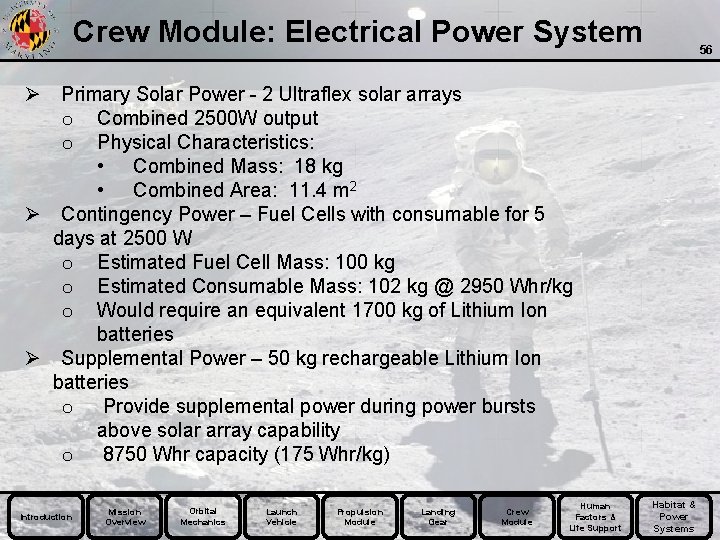
Crew Module: Electrical Power System 56 Ø Primary Solar Power - 2 Ultraflex solar arrays o Combined 2500 W output o Physical Characteristics: • Combined Mass: 18 kg • Combined Area: 11. 4 m 2 Ø Contingency Power – Fuel Cells with consumable for 5 days at 2500 W o Estimated Fuel Cell Mass: 100 kg o Estimated Consumable Mass: 102 kg @ 2950 Whr/kg o Would require an equivalent 1700 kg of Lithium Ion batteries Ø Supplemental Power – 50 kg rechargeable Lithium Ion batteries o Provide supplemental power during power bursts above solar array capability o 8750 Whr capacity (175 Whr/kg) Introduction Mission Overview Orbital Mechanics Launch Vehicle Propulsion Module Landing Gear Crew Module Human Factors & Life Support Habitat & Power Systems
![Crew Module Mass Budget Mass kg AOCS TCS Structure Avionics ECLSS EPS Communication TPS Crew Module: Mass Budget Mass [kg] AOCS TCS Structure Avionics ECLSS EPS Communication TPS](https://slidetodoc.com/presentation_image_h2/9b83375e0ef3e844c37a8446a76f7ea9/image-57.jpg)
Crew Module: Mass Budget Mass [kg] AOCS TCS Structure Avionics ECLSS EPS Communication TPS 195. 6 735. 75 1180 255. 39 600 270. 00 22. 75 1285. 10 Subsystem Margin Total Dry Mass (kg) 30% 4544. 59 Margin Total Dry Mass with Margin (kg) Introduction Mission Overview Orbital Mechanics % of Total 4% 16% 26% 6% 13% 6% 1% 28% 57 Mass with Margin [kg] 254. 28 956. 47 1534. 00 332. 01 780. 00 351. 00 29. 58 1670. 63 30% 5907. 96 Launch Vehicle Propulsion Module Landing Gear Crew Module Human Factors & Life Support Habitat & Power Systems
![Crew Module Power Budget Power W of Total Power with Margin W 150 Crew Module: Power Budget Power [W] % of Total Power with Margin [W] 150](https://slidetodoc.com/presentation_image_h2/9b83375e0ef3e844c37a8446a76f7ea9/image-58.jpg)
Crew Module: Power Budget Power [W] % of Total Power with Margin [W] 150 10% 195. 00 167. 00 11% 217. 10 Avionics 300 17% 390. 00 ECLSS 650 44% 845. 00 Communication 250 17% 325. 00 Subsystem Margin 30% AOCS Total Power (W) 1517. 00 Margin Total Power with Margin (W) Introduction 58 Mission Overview Orbital Mechanics 30% 1972. 10 Launch Vehicle Propulsion Module Landing Gear Crew Module Human Factors & Life Support Habitat & Power Systems
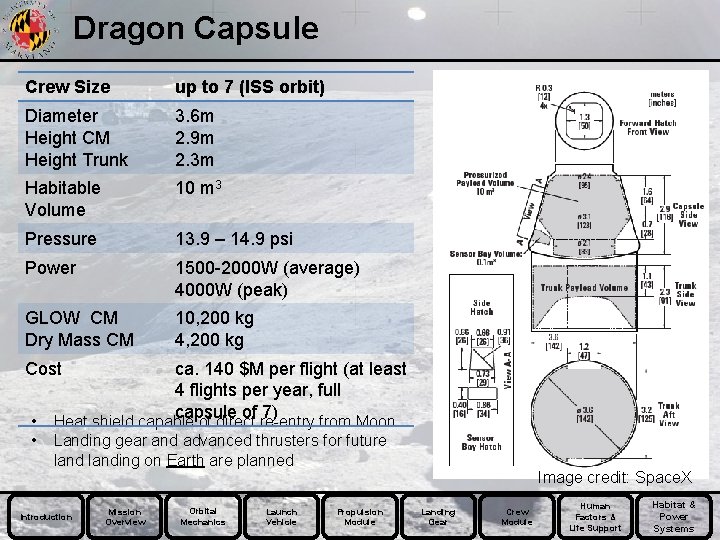
Dragon Capsule Crew Size up to 7 (ISS orbit) Diameter Height CM Height Trunk 3. 6 m 2. 9 m 2. 3 m Habitable Volume 10 m 3 Pressure 13. 9 – 14. 9 psi Power 1500 -2000 W (average) 4000 W (peak) GLOW CM Dry Mass CM 10, 200 kg 4, 200 kg Cost ca. 140 $M per flight (at least 4 flights per year, full capsule of 7) • • Heat shield capable of direct re-entry from Moon Landing gear and advanced thrusters for future landing on Earth are planned Introduction Mission Overview Orbital Mechanics Launch Vehicle Propulsion Module Image credit: Space. X Landing Gear Crew Module Human Factors & Life Support Habitat & Power Systems
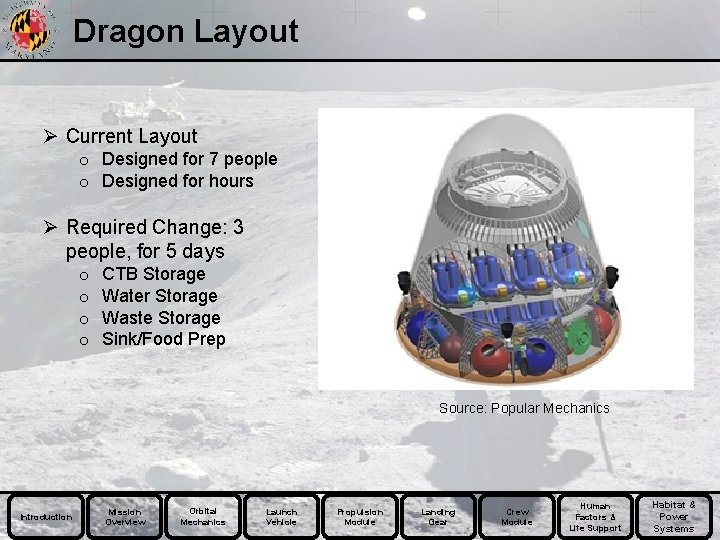
Dragon Layout Ø Current Layout o Designed for 7 people o Designed for hours Ø Required Change: 3 people, for 5 days o o CTB Storage Water Storage Waste Storage Sink/Food Prep Source: Popular Mechanics Introduction Mission Overview Orbital Mechanics Launch Vehicle Propulsion Module Landing Gear Crew Module Human Factors & Life Support Habitat & Power Systems
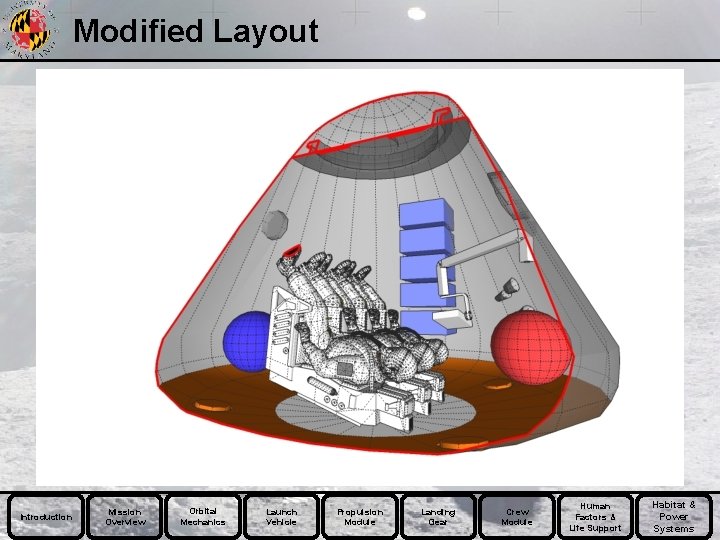
Modified Layout Introduction Mission Overview Orbital Mechanics Launch Vehicle Propulsion Module Landing Gear Crew Module Human Factors & Life Support Habitat & Power Systems
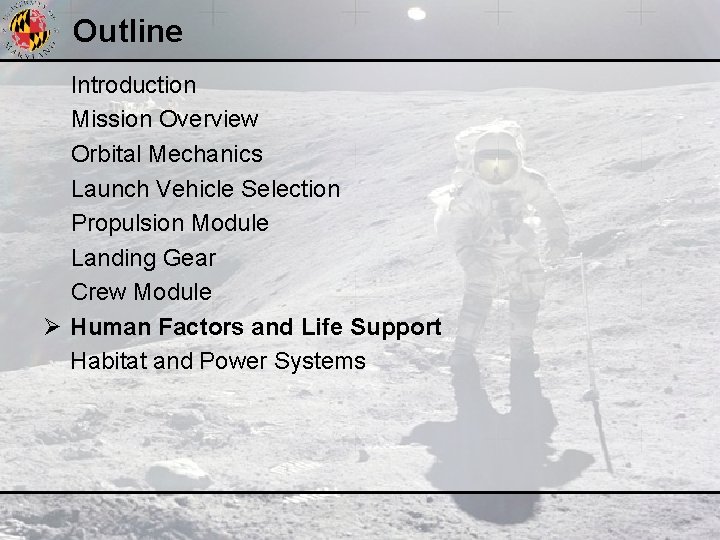
Outline Introduction Mission Overview Orbital Mechanics Launch Vehicle Selection Propulsion Module Landing Gear Crew Module Ø Human Factors and Life Support Habitat and Power Systems
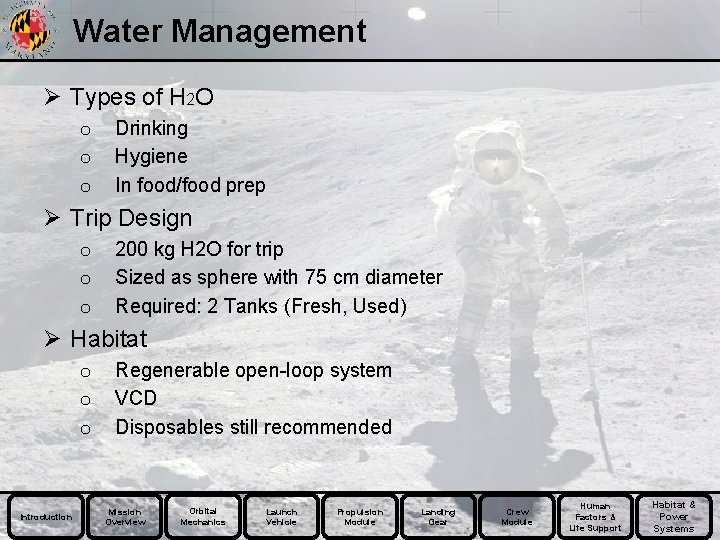
Water Management Ø Types of H 2 O o o o Drinking Hygiene In food/food prep Ø Trip Design o o o 200 kg H 2 O for trip Sized as sphere with 75 cm diameter Required: 2 Tanks (Fresh, Used) Ø Habitat o o o Introduction Regenerable open-loop system VCD Disposables still recommended Mission Overview Orbital Mechanics Launch Vehicle Propulsion Module Landing Gear Crew Module Human Factors & Life Support Habitat & Power Systems
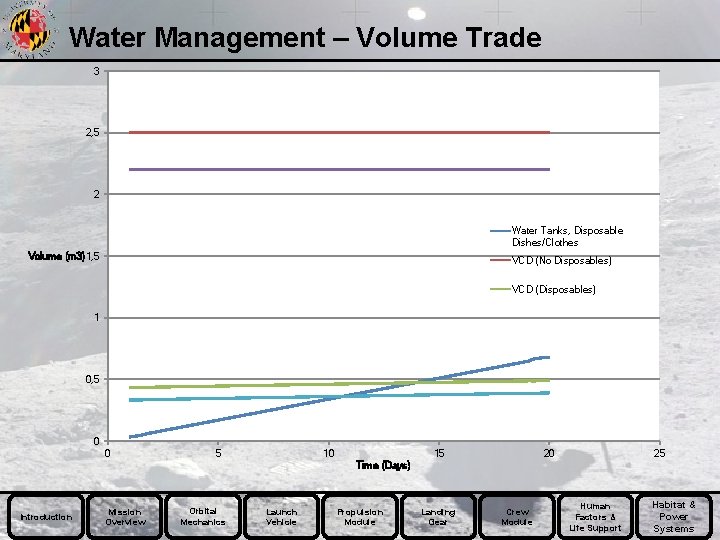
Water Management – Volume Trade 3 2, 5 2 Water Tanks, Disposable Dishes/Clothes Volume (m 3)1, 5 VCD (No Disposables) VCD (Disposables) 1 0, 5 0 0 5 10 15 20 25 Time (Days) Introduction Mission Overview Orbital Mechanics Launch Vehicle Propulsion Module Landing Gear Crew Module Human Factors & Life Support Habitat & Power Systems
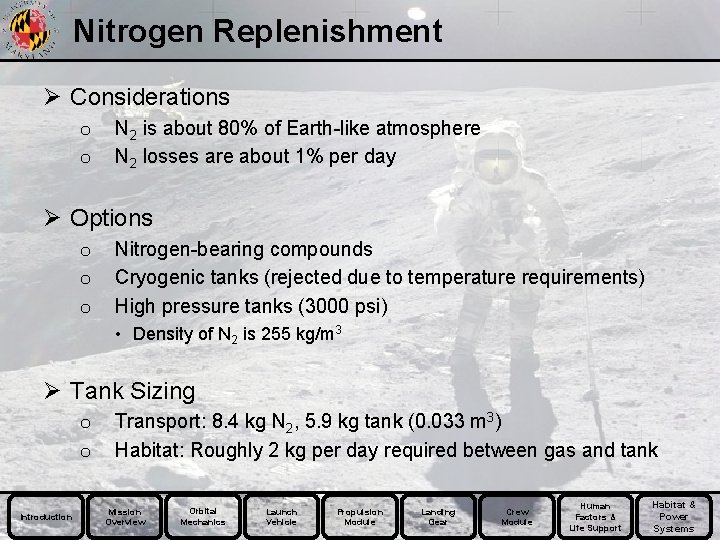
Nitrogen Replenishment Ø Considerations o o N 2 is about 80% of Earth-like atmosphere N 2 losses are about 1% per day Ø Options o o o Nitrogen-bearing compounds Cryogenic tanks (rejected due to temperature requirements) High pressure tanks (3000 psi) • Density of N 2 is 255 kg/m 3 Ø Tank Sizing o o Introduction Transport: 8. 4 kg N 2, 5. 9 kg tank (0. 033 m 3) Habitat: Roughly 2 kg per day required between gas and tank Mission Overview Orbital Mechanics Launch Vehicle Propulsion Module Landing Gear Crew Module Human Factors & Life Support Habitat & Power Systems
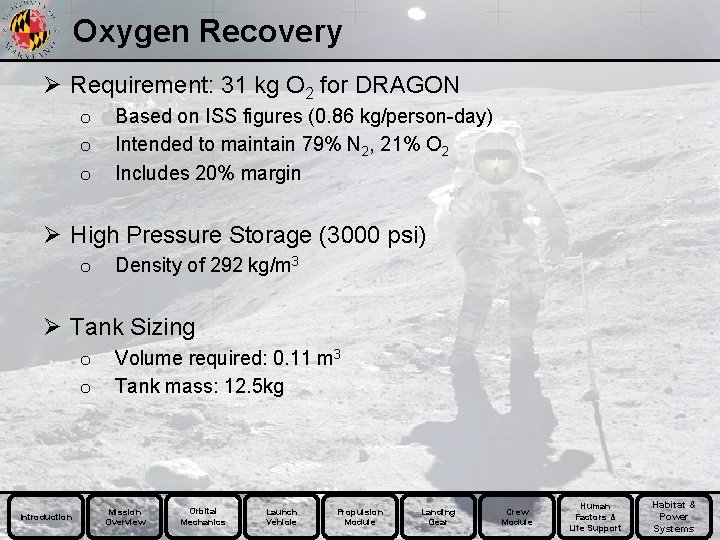
Oxygen Recovery Ø Requirement: 31 kg O 2 for DRAGON o o o Based on ISS figures (0. 86 kg/person-day) Intended to maintain 79% N 2, 21% O 2 Includes 20% margin Ø High Pressure Storage (3000 psi) o Density of 292 kg/m 3 Ø Tank Sizing o o Introduction Volume required: 0. 11 m 3 Tank mass: 12. 5 kg Mission Overview Orbital Mechanics Launch Vehicle Propulsion Module Landing Gear Crew Module Human Factors & Life Support Habitat & Power Systems
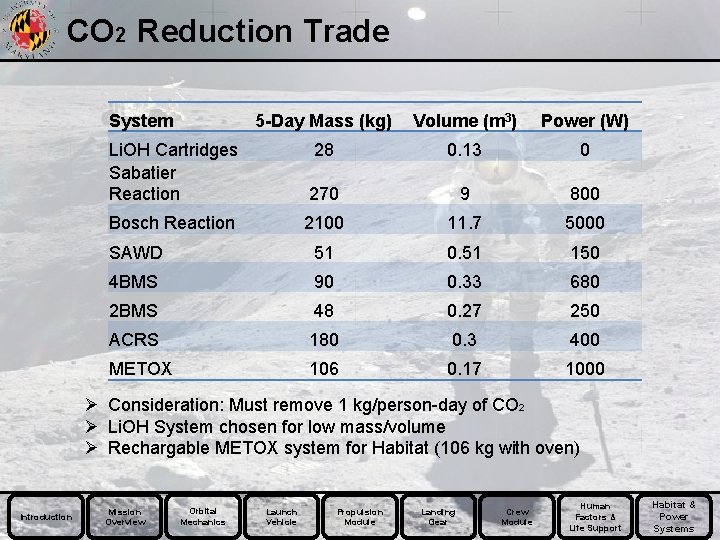
CO 2 Reduction Trade System 5 -Day Mass (kg) Volume (m 3) Power (W) Li. OH Cartridges Sabatier Reaction 28 0. 13 0 270 9 800 Bosch Reaction 2100 11. 7 5000 SAWD 51 0. 51 150 4 BMS 90 0. 33 680 2 BMS 48 0. 27 250 ACRS 180 0. 3 400 METOX 106 0. 17 1000 Ø Consideration: Must remove 1 kg/person-day of CO 2 Ø Li. OH System chosen for low mass/volume Ø Rechargable METOX system for Habitat (106 kg with oven) Introduction Mission Overview Orbital Mechanics Launch Vehicle Propulsion Module Landing Gear Crew Module Human Factors & Life Support Habitat & Power Systems
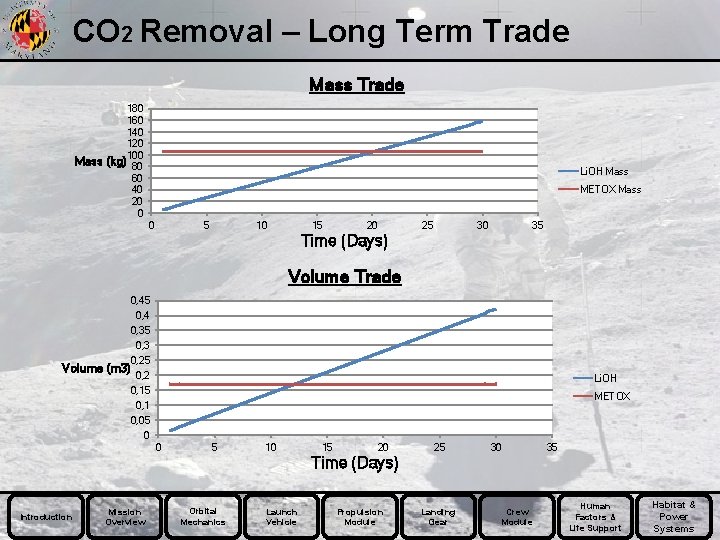
CO 2 Removal – Long Term Trade Mass 180 160 140 120 100 (kg) 80 60 40 20 0 Li. OH Mass METOX Mass 0 5 10 15 20 25 30 35 Time (Days) Volume Trade Volume 0, 45 0, 4 0, 35 0, 3 0, 25 (m 3) 0, 2 0, 15 0, 1 0, 05 0 Li. OH METOX 0 5 10 15 20 25 30 35 Time (Days) Introduction Mission Overview Orbital Mechanics Launch Vehicle Propulsion Module Landing Gear Crew Module Human Factors & Life Support Habitat & Power Systems
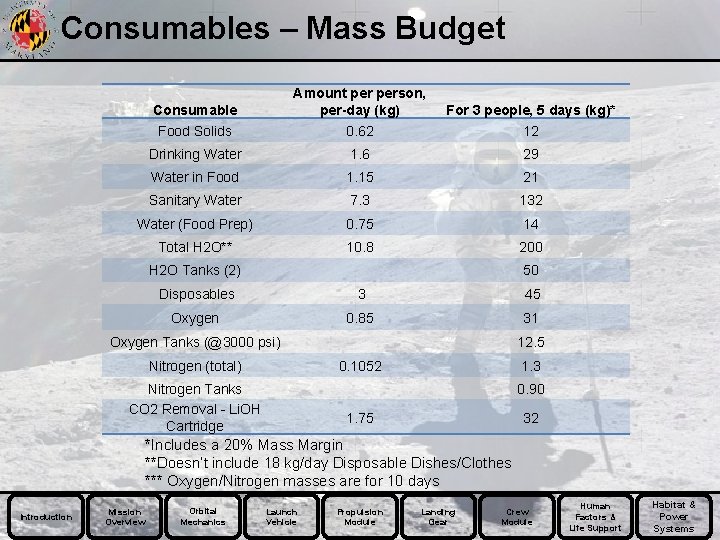
Consumables – Mass Budget Consumable Food Solids Amount person, per-day (kg) 0. 62 For 3 people, 5 days (kg)* 12 Drinking Water 1. 6 29 Water in Food 1. 15 21 Sanitary Water 7. 3 132 Water (Food Prep) 0. 75 14 Total H 2 O** 10. 8 200 H 2 O Tanks (2) 50 Disposables 3 45 Oxygen 0. 85 31 Oxygen Tanks (@3000 psi) Nitrogen (total) 12. 5 0. 1052 Nitrogen Tanks CO 2 Removal - Li. OH Cartridge 1. 3 0. 90 1. 75 32 *Includes a 20% Mass Margin **Doesn’t include 18 kg/day Disposable Dishes/Clothes *** Oxygen/Nitrogen masses are for 10 days Introduction Mission Overview Orbital Mechanics Launch Vehicle Propulsion Module Landing Gear Crew Module Human Factors & Life Support Habitat & Power Systems
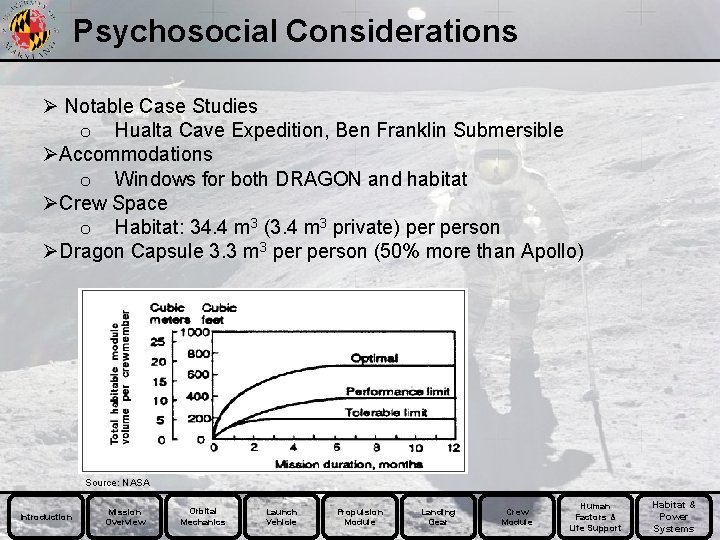
Psychosocial Considerations Ø Notable Case Studies o Hualta Cave Expedition, Ben Franklin Submersible ØAccommodations o Windows for both DRAGON and habitat ØCrew Space o Habitat: 34. 4 m 3 (3. 4 m 3 private) person ØDragon Capsule 3. 3 m 3 person (50% more than Apollo) Source: NASA Introduction Mission Overview Orbital Mechanics Launch Vehicle Propulsion Module Landing Gear Crew Module Human Factors & Life Support Habitat & Power Systems
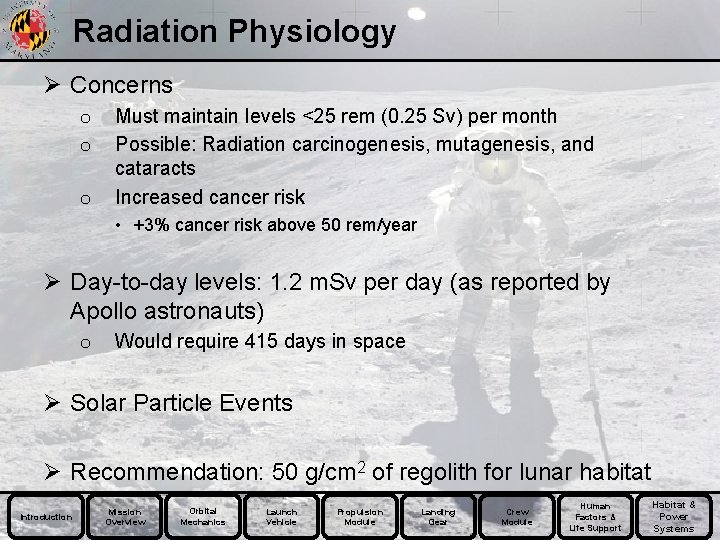
Radiation Physiology Ø Concerns o o o Must maintain levels <25 rem (0. 25 Sv) per month Possible: Radiation carcinogenesis, mutagenesis, and cataracts Increased cancer risk • +3% cancer risk above 50 rem/year Ø Day-to-day levels: 1. 2 m. Sv per day (as reported by Apollo astronauts) o Would require 415 days in space Ø Solar Particle Events Ø Recommendation: 50 g/cm 2 of regolith for lunar habitat Introduction Mission Overview Orbital Mechanics Launch Vehicle Propulsion Module Landing Gear Crew Module Human Factors & Life Support Habitat & Power Systems
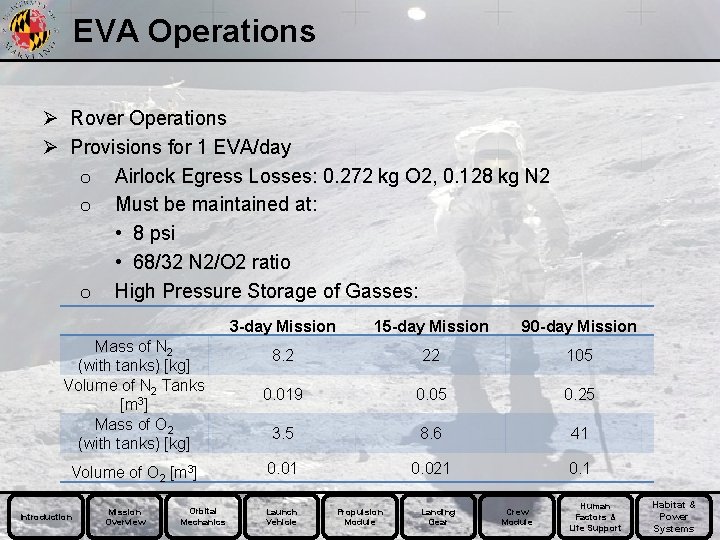
EVA Operations Ø Rover Operations Ø Provisions for 1 EVA/day o Airlock Egress Losses: 0. 272 kg O 2, 0. 128 kg N 2 o Must be maintained at: • 8 psi • 68/32 N 2/O 2 ratio o High Pressure Storage of Gasses: 3 -day Mission 15 -day Mission 90 -day Mission Mass of N 2 (with tanks) [kg] Volume of N 2 Tanks [m 3] Mass of O 2 (with tanks) [kg] 8. 2 22 105 0. 019 0. 05 0. 25 3. 5 8. 6 41 Volume of O 2 [m 3] 0. 01 0. 021 0. 1 Introduction Mission Overview Orbital Mechanics Launch Vehicle Propulsion Module Landing Gear Crew Module Human Factors & Life Support Habitat & Power Systems
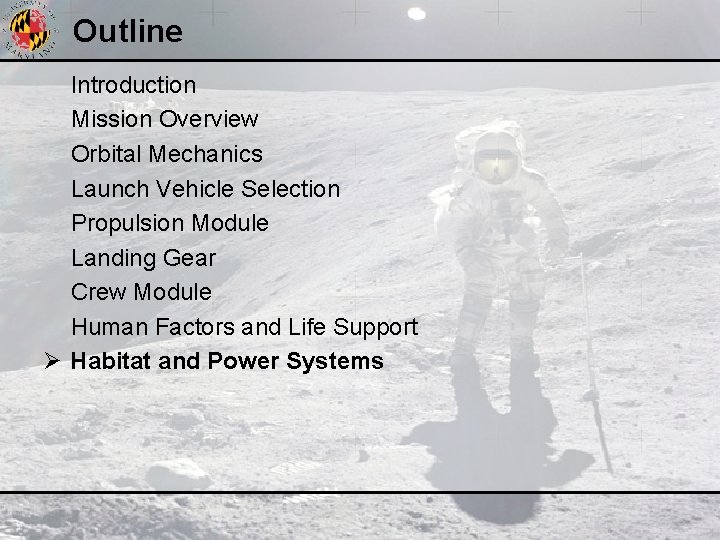
Outline Introduction Mission Overview Orbital Mechanics Launch Vehicle Selection Propulsion Module Landing Gear Crew Module Human Factors and Life Support Ø Habitat and Power Systems
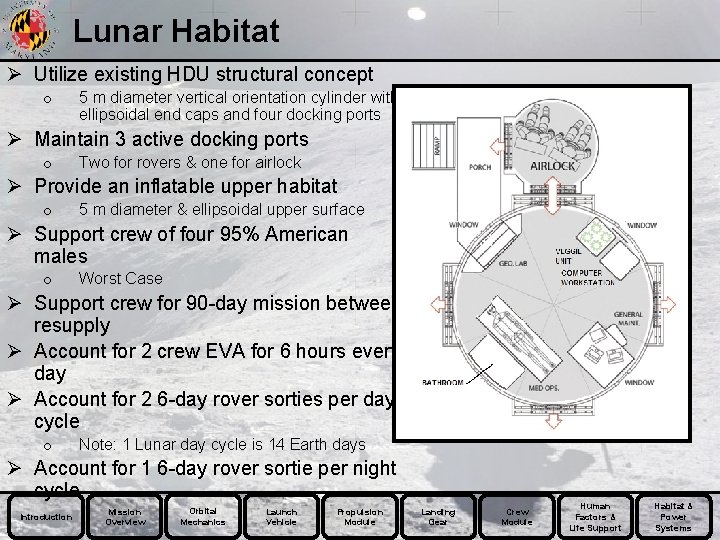
Lunar Habitat Ø Utilize existing HDU structural concept o 5 m diameter vertical orientation cylinder with ellipsoidal end caps and four docking ports Ø Maintain 3 active docking ports o Two for rovers & one for airlock Ø Provide an inflatable upper habitat o 5 m diameter & ellipsoidal upper surface Ø Support crew of four 95% American males o Worst Case Ø Support crew for 90 -day mission between resupply Ø Account for 2 crew EVA for 6 hours every day Ø Account for 2 6 -day rover sorties per day cycle o Note: 1 Lunar day cycle is 14 Earth days Ø Account for 1 6 -day rover sortie per night cycle Introduction Mission Overview Orbital Mechanics Launch Vehicle Propulsion Module Landing Gear Crew Module Human Factors & Life Support Habitat & Power Systems
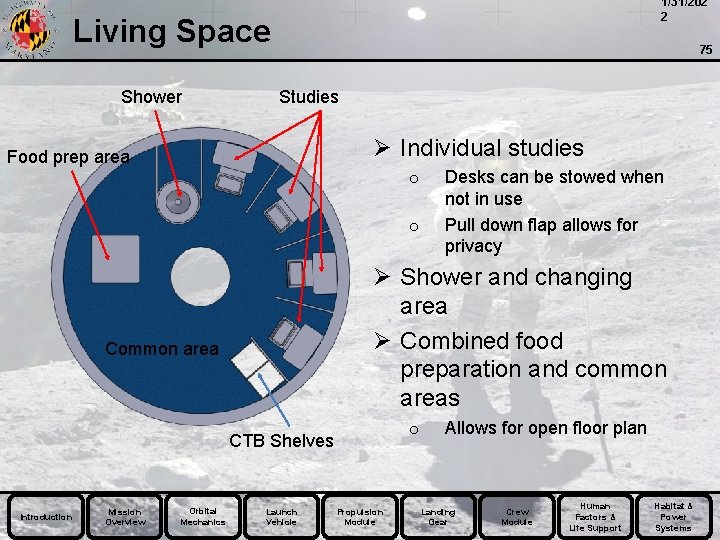
1/31/202 2 Living Space Shower 75 Studies Ø Individual studies Food prep area o o Ø Shower and changing area Ø Combined food preparation and common areas Common area o CTB Shelves Introduction Mission Overview Orbital Mechanics Desks can be stowed when not in use Pull down flap allows for privacy Launch Vehicle Propulsion Module Allows for open floor plan Landing Gear Crew Module Human Factors & Life Support Habitat & Power Systems
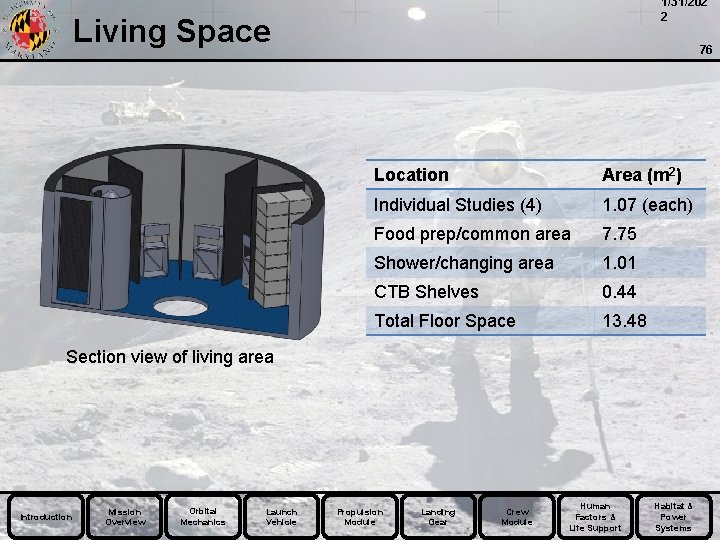
1/31/202 2 Living Space 76 Location Area (m 2) Individual Studies (4) 1. 07 (each) Food prep/common area 7. 75 Shower/changing area 1. 01 CTB Shelves 0. 44 Total Floor Space 13. 48 Section view of living area Introduction Mission Overview Orbital Mechanics Launch Vehicle Propulsion Module Landing Gear Crew Module Human Factors & Life Support Habitat & Power Systems
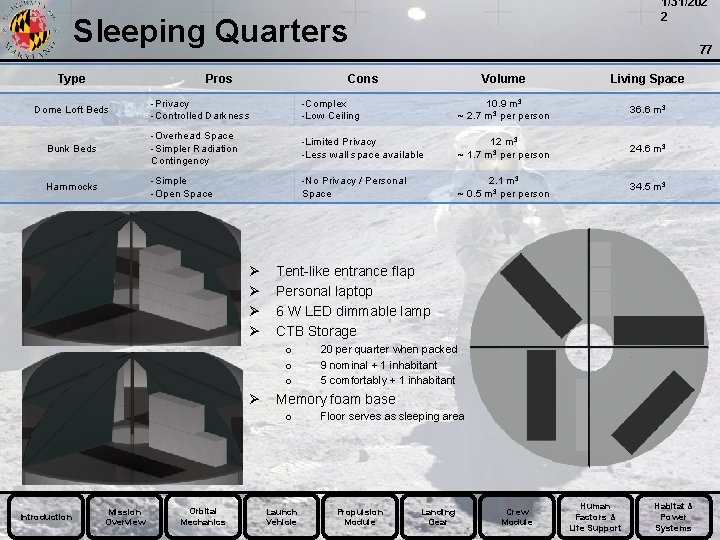
1/31/202 2 Sleeping Quarters Type Pros 77 Cons Volume Living Space -Privacy -Controlled Darkness -Complex -Low Ceiling 10. 9 m 3 ~ 2. 7 m 3 person 36. 6 m 3 Bunk Beds -Overhead Space -Simpler Radiation Contingency -Limited Privacy -Less wall space available 12 m 3 ~ 1. 7 m 3 person 24. 6 m 3 Hammocks -Simple -Open Space -No Privacy / Personal Space 2. 1 m 3 ~ 0. 5 m 3 person 34. 5 m 3 Dome Loft Beds Ø Ø Tent-like entrance flap Personal laptop 6 W LED dimmable lamp CTB Storage o o o Ø Memory foam base o Introduction Mission Overview Orbital Mechanics 20 per quarter when packed 9 nominal + 1 inhabitant 5 comfortably + 1 inhabitant Launch Vehicle Floor serves as sleeping area Propulsion Module Landing Gear Crew Module Human Factors & Life Support Habitat & Power Systems
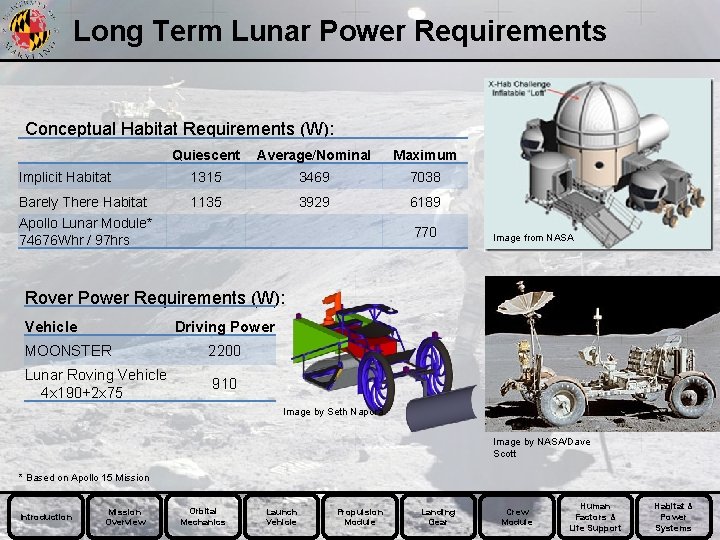
Long Term Lunar Power Requirements Conceptual Habitat Requirements (W): Quiescent Average/Nominal Maximum Implicit Habitat 1315 3469 7038 Barely There Habitat 1135 3929 6189 Apollo Lunar Module* 74676 Whr / 97 hrs 770 Image from NASA Rover Power Requirements (W): Vehicle Driving Power MOONSTER 2200 Lunar Roving Vehicle 4 x 190+2 x 75 910 Image by Seth Napora Image by NASA/Dave Scott * Based on Apollo 15 Mission Introduction Mission Overview Orbital Mechanics Launch Vehicle Propulsion Module Landing Gear Crew Module Human Factors & Life Support Habitat & Power Systems
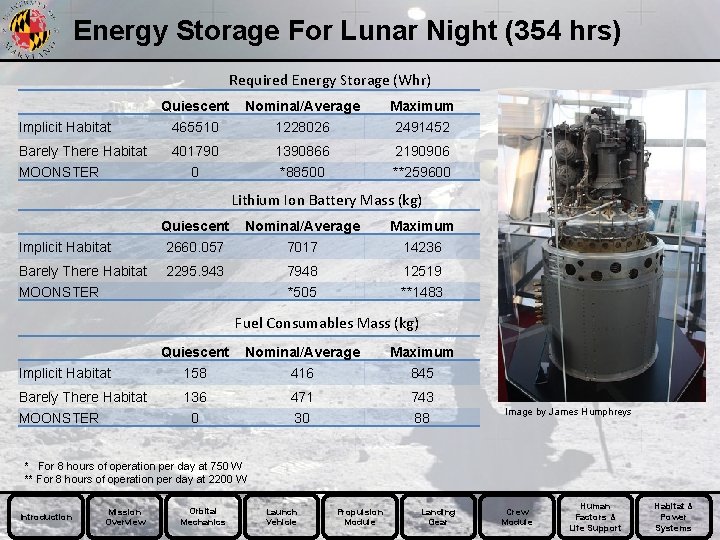
Energy Storage For Lunar Night (354 hrs) Required Energy Storage (Whr) Implicit Habitat Barely There Habitat MOONSTER Quiescent 465510 Nominal/Average 1228026 Maximum 2491452 401790 0 1390866 *88500 2190906 **259600 Lithium Ion Battery Mass (kg) Implicit Habitat Barely There Habitat MOONSTER Quiescent 2660. 057 Nominal/Average 7017 Maximum 14236 2295. 943 7948 *505 12519 **1483 Fuel Consumables Mass (kg) Implicit Habitat Barely There Habitat MOONSTER Quiescent 158 Nominal/Average 416 Maximum 845 136 0 471 30 743 88 Image by James Humphreys * For 8 hours of operation per day at 750 W ** For 8 hours of operation per day at 2200 W Introduction Mission Overview Orbital Mechanics Launch Vehicle Propulsion Module Landing Gear Crew Module Human Factors & Life Support Habitat & Power Systems
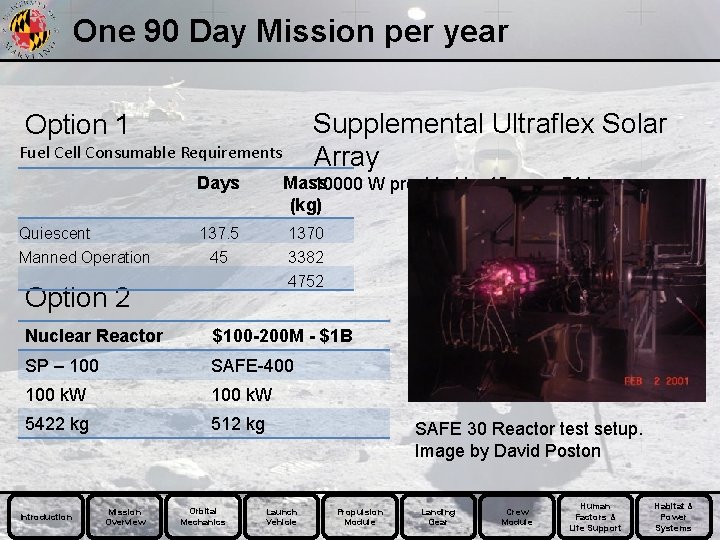
One 90 Day Mission per year Supplemental Ultraflex Solar Array Option 1 Fuel Cell Consumable Requirements Quiescent Manned Operation Days Mass 10000 W provided by 45 sq m, 71 kg array (kg) 137. 5 45 1370 3382 4752 Option 2 Nuclear Reactor $100 -200 M - $1 B SP – 100 SAFE-400 100 k. W 5422 kg 512 kg Introduction Mission Overview Orbital Mechanics SAFE 30 Reactor test setup. Image by David Poston Launch Vehicle Propulsion Module Landing Gear Crew Module Human Factors & Life Support Habitat & Power Systems
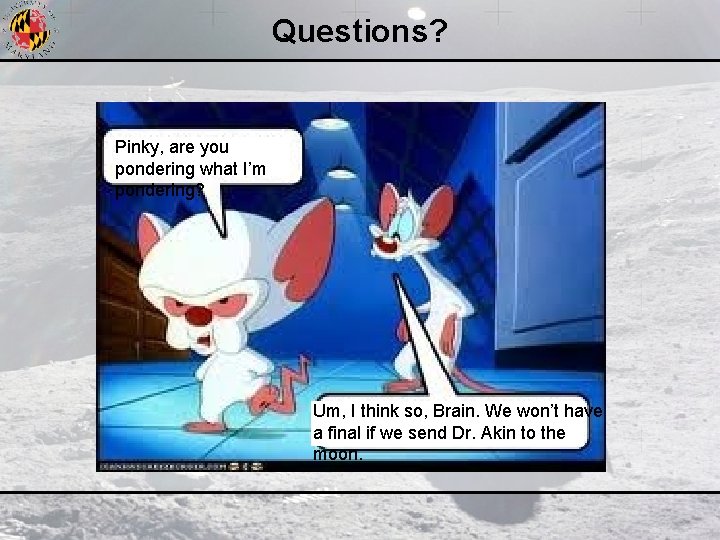
Questions? Pinky, are you pondering what I’m pondering? Um, I think so, Brain. We won’t have a final if we send Dr. Akin to the moon.
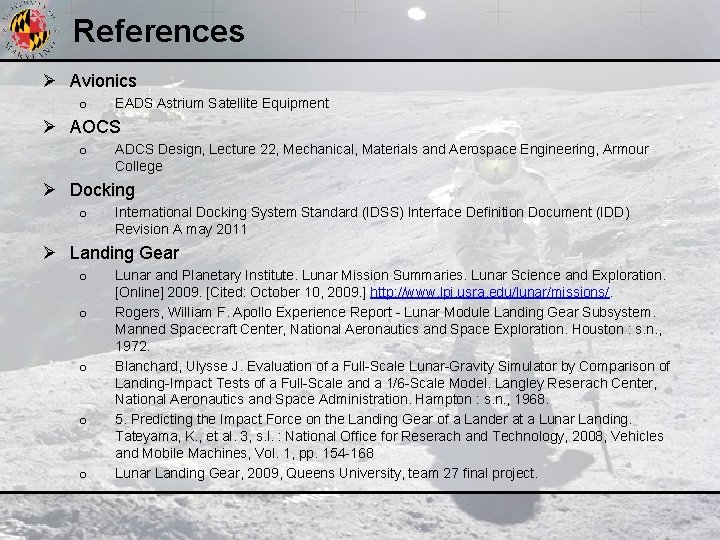
References Ø Avionics o EADS Astrium Satellite Equipment Ø AOCS o ADCS Design, Lecture 22, Mechanical, Materials and Aerospace Engineering, Armour College Ø Docking o International Docking System Standard (IDSS) Interface Definition Document (IDD) Revision A may 2011 Ø Landing Gear o o o Lunar and Planetary Institute. Lunar Mission Summaries. Lunar Science and Exploration. [Online] 2009. [Cited: October 10, 2009. ] http: //www. lpi. usra. edu/lunar/missions/. Rogers, William F. Apollo Experience Report - Lunar Module Landing Gear Subsystem. Manned Spacecraft Center, National Aeronautics and Space Exploration. Houston : s. n. , 1972. Blanchard, Ulysse J. Evaluation of a Full-Scale Lunar-Gravity Simulator by Comparison of Landing-Impact Tests of a Full-Scale and a 1/6 -Scale Model. Langley Reserach Center, National Aeronautics and Space Administration. Hampton : s. n. , 1968. 5. Predicting the Impact Force on the Landing Gear of a Lander at a Lunar Landing. Tateyama, K. , et al. 3, s. l. : National Office for Reserach and Technology, 2008, Vehicles and Mobile Machines, Vol. 1, pp. 154 -168 Lunar Landing Gear, 2009, Queens University, team 27 final project.
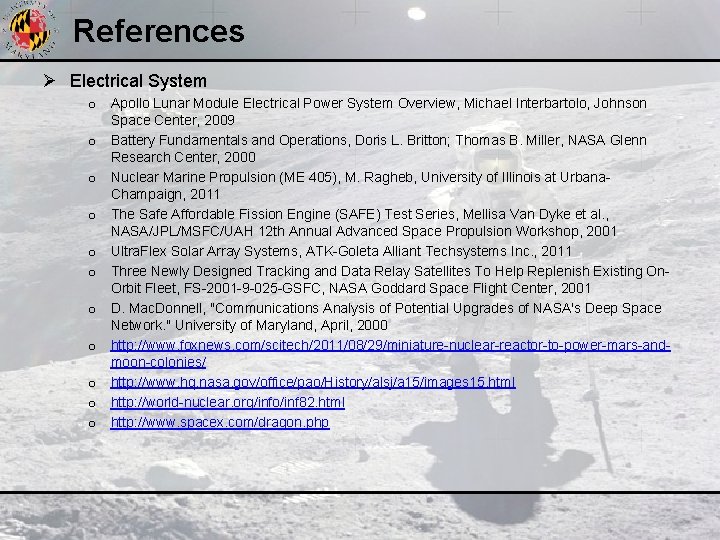
References Ø Electrical System o Apollo Lunar Module Electrical Power System Overview, Michael Interbartolo, Johnson Space Center, 2009 o Battery Fundamentals and Operations, Doris L. Britton; Thomas B. Miller, NASA Glenn Research Center, 2000 o Nuclear Marine Propulsion (ME 405), M. Ragheb, University of Illinois at Urbana. Champaign, 2011 o The Safe Affordable Fission Engine (SAFE) Test Series, Mellisa Van Dyke et al. , NASA/JPL/MSFC/UAH 12 th Annual Advanced Space Propulsion Workshop, 2001 o Ultra. Flex Solar Array Systems, ATK-Goleta Alliant Techsystems Inc. , 2011 o Three Newly Designed Tracking and Data Relay Satellites To Help Replenish Existing On. Orbit Fleet, FS-2001 -9 -025 -GSFC, NASA Goddard Space Flight Center, 2001 o D. Mac. Donnell, "Communications Analysis of Potential Upgrades of NASA's Deep Space Network. " University of Maryland, April, 2000 o http: //www. foxnews. com/scitech/2011/08/29/miniature-nuclear-reactor-to-power-mars-andmoon-colonies/ o http: //www. hq. nasa. gov/office/pao/History/alsj/a 15/images 15. html o http: //world-nuclear. org/info/inf 82. html o http: //www. spacex. com/dragon. php
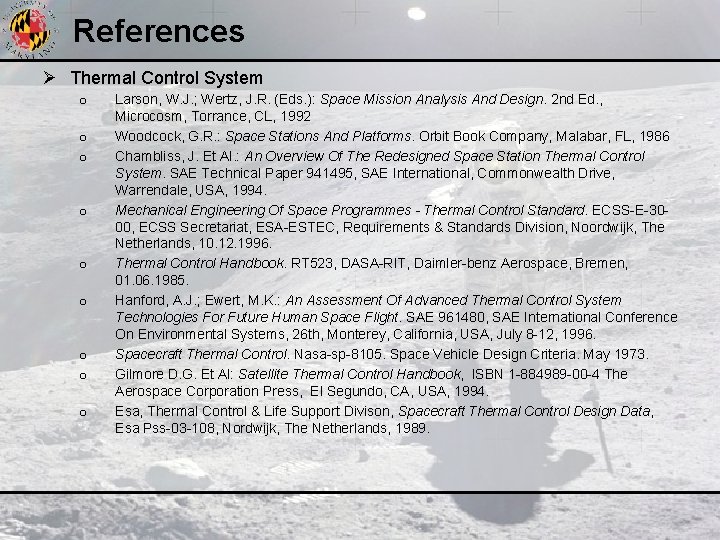
References Ø Thermal Control System o o o o o Larson, W. J. ; Wertz, J. R. (Eds. ): Space Mission Analysis And Design. 2 nd Ed. , Microcosm, Torrance, CL, 1992 Woodcock, G. R. : Space Stations And Platforms. Orbit Book Company, Malabar, FL, 1986 Chambliss, J. Et Al. : An Overview Of The Redesigned Space Station Thermal Control System. SAE Technical Paper 941495, SAE International, Commonwealth Drive, Warrendale, USA, 1994. Mechanical Engineering Of Space Programmes - Thermal Control Standard. ECSS-E-3000, ECSS Secretariat, ESA-ESTEC, Requirements & Standards Division, Noordwijk, The Netherlands, 10. 12. 1996. Thermal Control Handbook. RT 523, DASA-RIT, Daimler-benz Aerospace, Bremen, 01. 06. 1985. Hanford, A. J. ; Ewert, M. K. : An Assessment Of Advanced Thermal Control System Technologies For Future Human Space Flight. SAE 961480, SAE International Conference On Environmental Systems, 26 th, Monterey, California, USA, July 8 -12, 1996. Spacecraft Thermal Control. Nasa-sp-8105. Space Vehicle Design Criteria. May 1973. Gilmore D. G. Et Al: Satellite Thermal Control Handbook, ISBN 1 -884989 -00 -4 The Aerospace Corporation Press, El Segundo, CA, USA, 1994. Esa, Thermal Control & Life Support Divison, Spacecraft Thermal Control Design Data, Esa Pss-03 -108, Nordwijk, The Netherlands, 1989.
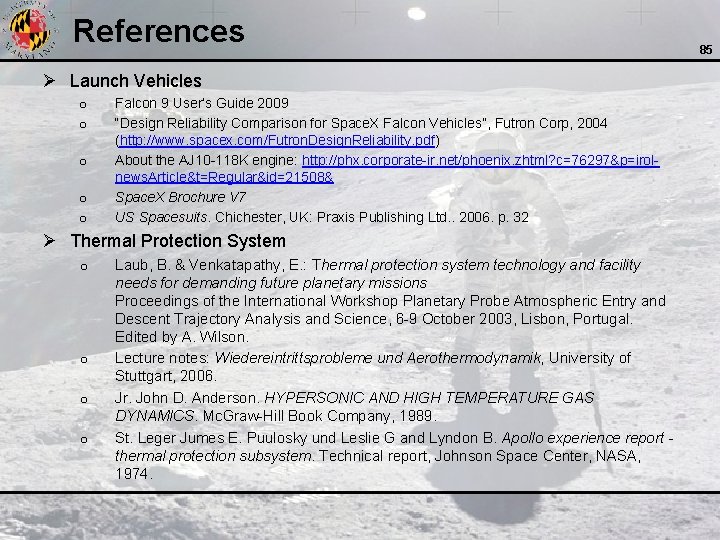
References Ø Launch Vehicles o o o Falcon 9 User’s Guide 2009 “Design Reliability Comparison for Space. X Falcon Vehicles”, Futron Corp, 2004 (http: //www. spacex. com/Futron. Design. Reliability. pdf) About the AJ 10 -118 K engine: http: //phx. corporate-ir. net/phoenix. zhtml? c=76297&p=irolnews. Article&t=Regular&id=21508& Space. X Brochure V 7 US Spacesuits. Chichester, UK: Praxis Publishing Ltd. . 2006. p. 32 Ø Thermal Protection System o o Laub, B. & Venkatapathy, E. : Thermal protection system technology and facility needs for demanding future planetary missions Proceedings of the International Workshop Planetary Probe Atmospheric Entry and Descent Trajectory Analysis and Science, 6 -9 October 2003, Lisbon, Portugal. Edited by A. Wilson. Lecture notes: Wiedereintrittsprobleme und Aerothermodynamik, University of Stuttgart, 2006. Jr. John D. Anderson. HYPERSONIC AND HIGH TEMPERATURE GAS DYNAMICS. Mc. Graw-Hill Book Company, 1989. St. Leger Jumes E. Puulosky und Leslie G and Lyndon B. Apollo experience report thermal protection subsystem. Technical report, Johnson Space Center, NASA, 1974. 85
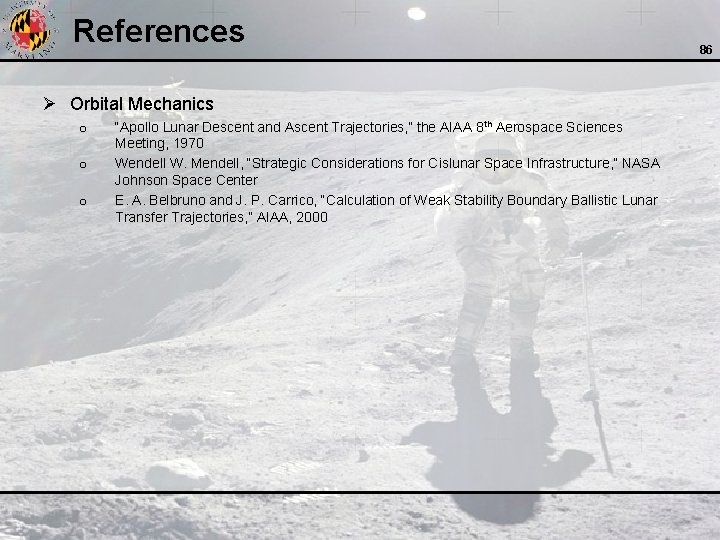
References Ø Orbital Mechanics o o o “Apollo Lunar Descent and Ascent Trajectories, ” the AIAA 8 th Aerospace Sciences Meeting, 1970 Wendell W. Mendell, “Strategic Considerations for Cislunar Space Infrastructure, ” NASA Johnson Space Center E. A. Belbruno and J. P. Carrico, “Calculation of Weak Stability Boundary Ballistic Lunar Transfer Trajectories, ” AIAA, 2000 86
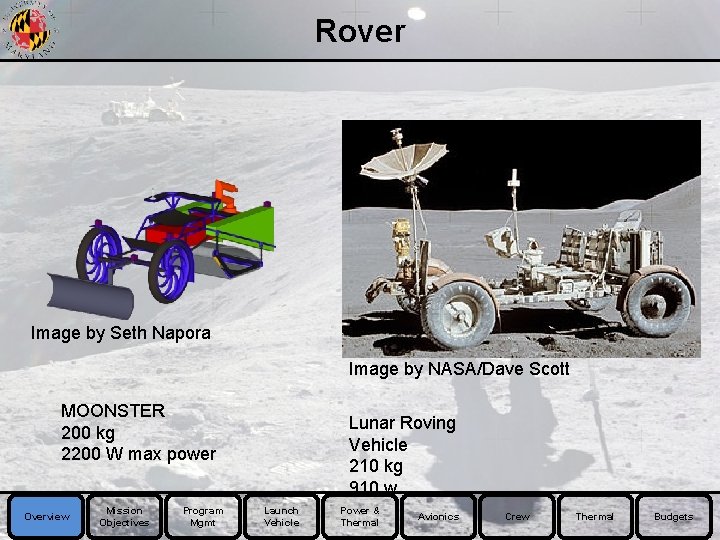
Rover Image by Seth Napora Image by NASA/Dave Scott MOONSTER 200 kg 2200 W max power Overview Mission Objectives Program Mgmt Lunar Roving Vehicle 210 kg 910 w Launch Vehicle Power & Thermal Avionics Crew Thermal Budgets
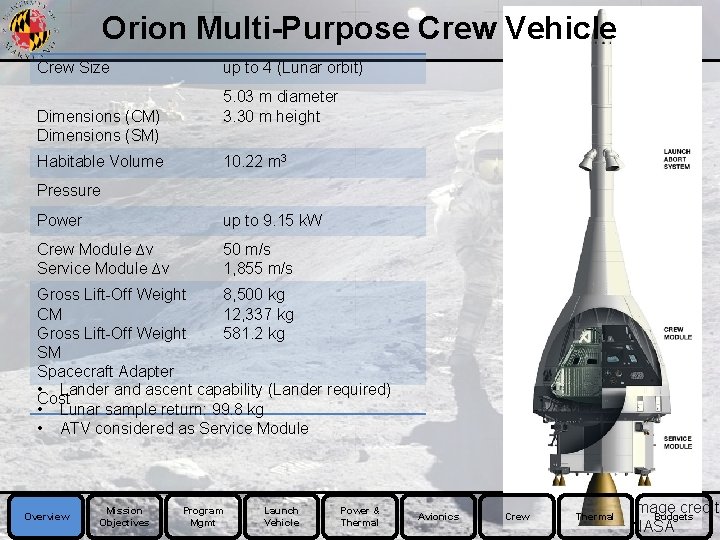
Orion Multi-Purpose Crew Vehicle Crew Size Dimensions (CM) Dimensions (SM) Habitable Volume up to 4 (Lunar orbit) 5. 03 m diameter 3. 30 m height 10. 22 m 3 Pressure Power up to 9. 15 k. W Crew Module ∆v Service Module ∆v 50 m/s 1, 855 m/s Gross Lift-Off Weight 8, 500 kg CM 12, 337 kg Gross Lift-Off Weight 581. 2 kg SM Spacecraft Adapter • Lander and ascent capability (Lander required) Cost • Lunar sample return: 99. 8 kg • ATV considered as Service Module Overview Mission Objectives Program Mgmt Launch Vehicle Power & Thermal Avionics Crew Thermal Image credit: Budgets NASA
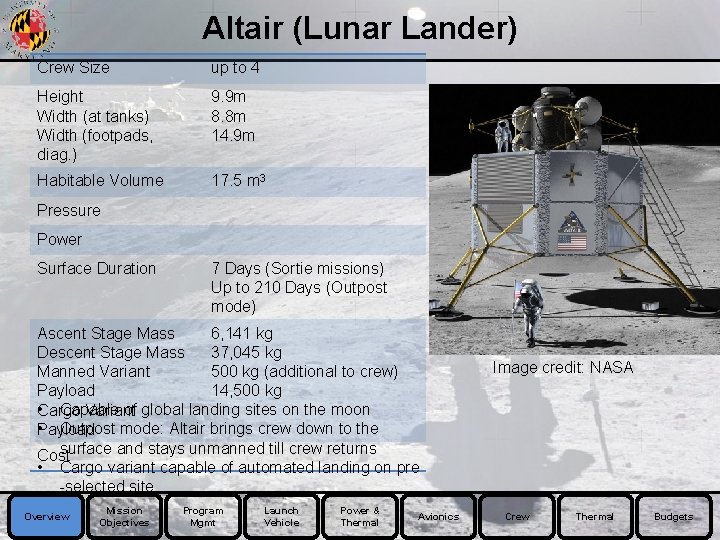
Altair (Lunar Lander) Crew Size up to 4 Height Width (at tanks) Width (footpads, diag. ) 9. 9 m 8. 8 m 14. 9 m Habitable Volume 17. 5 m 3 Pressure Power Surface Duration 7 Days (Sortie missions) Up to 210 Days (Outpost mode) Ascent Stage Mass 6, 141 kg Descent Stage Mass 37, 045 kg Manned Variant 500 kg (additional to crew) Payload 14, 500 kg • Cargo Capable of global landing sites on the moon Variant • Payload Outpost mode: Altair brings crew down to the surface and stays unmanned till crew returns Cost • Cargo variant capable of automated landing on pre -selected site Overview Mission Objectives Program Mgmt Launch Vehicle Power & Thermal Avionics Image credit: NASA Crew Thermal Budgets
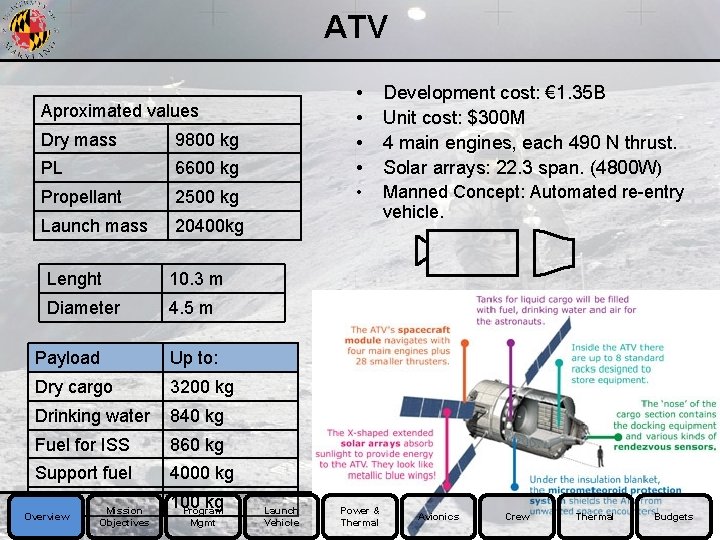
ATV Dry mass 9800 kg PL 6600 kg • • Propellant 2500 kg • Launch mass 20400 kg Aproximated values Lenght 10. 3 m Diameter 4. 5 m Payload Up to: Dry cargo 3200 kg Drinking water 840 kg Fuel for ISS 860 kg Support fuel 4000 kg Air 100 kg Program Overview Mission Objectives Mgmt Launch Vehicle Power & Thermal Development cost: € 1. 35 B Unit cost: $300 M 4 main engines, each 490 N thrust. Solar arrays: 22. 3 span. (4800 W) Manned Concept: Automated re-entry vehicle. Avionics Crew Thermal Budgets
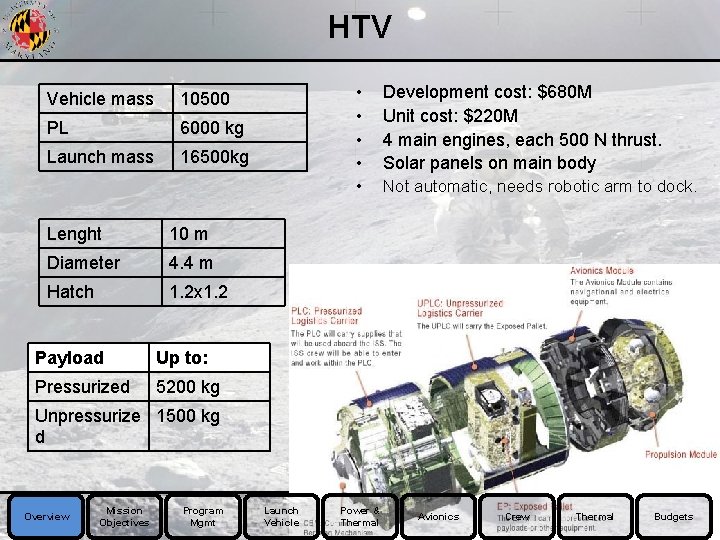
HTV Vehicle mass 10500 PL 6000 kg Launch mass 16500 kg Lenght 10 m Diameter 4. 4 m Hatch 1. 2 x 1. 2 Payload Up to: Pressurized 5200 kg • • Development cost: $680 M Unit cost: $220 M 4 main engines, each 500 N thrust. Solar panels on main body • Not automatic, needs robotic arm to dock. Unpressurize 1500 kg d Overview Mission Objectives Program Mgmt Launch Vehicle Power & Thermal Avionics Crew Thermal Budgets
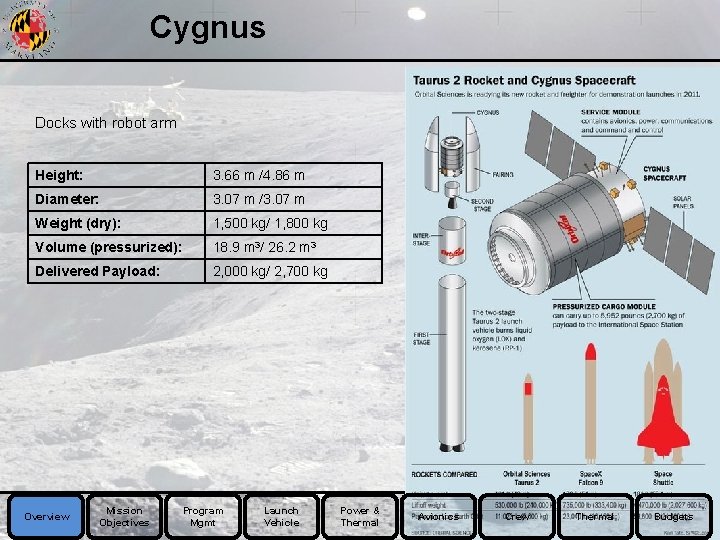
Cygnus Docks with robot arm Height: 3. 66 m /4. 86 m Diameter: 3. 07 m /3. 07 m Weight (dry): 1, 500 kg/ 1, 800 kg Volume (pressurized): 18. 9 m 3/ 26. 2 m 3 Delivered Payload: 2, 000 kg/ 2, 700 kg Overview Mission Objectives Program Mgmt Launch Vehicle Power & Thermal Avionics Crew Thermal Budgets
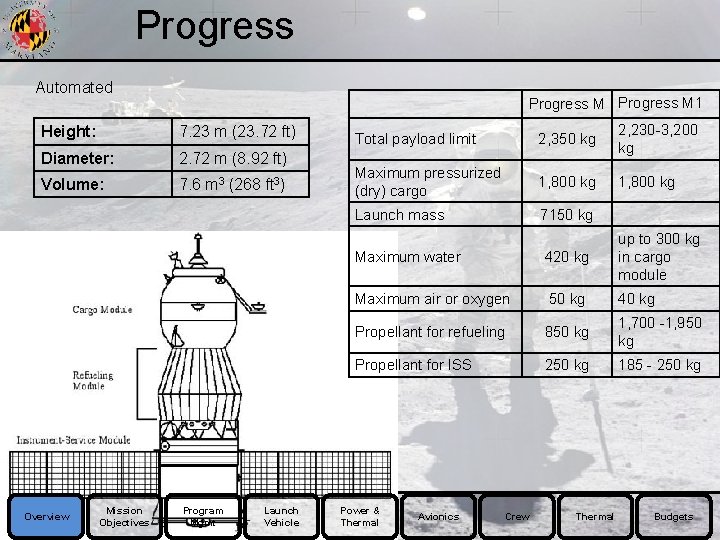
Progress Automated Progress M 1 Height: 7. 23 m (23. 72 ft) Diameter: 2. 72 m (8. 92 ft) Volume: 7. 6 m 3 (268 ft 3) Overview Mission Objectives Program Mgmt Launch Vehicle Total payload limit 2, 350 kg 2, 230 -3, 200 kg Maximum pressurized (dry) cargo 1, 800 kg Launch mass 7150 kg Maximum water 420 kg up to 300 kg in cargo module Maximum air or oxygen 50 kg 40 kg Propellant for refueling 850 kg 1, 700 -1, 950 kg Propellant for ISS 250 kg 185 - 250 kg Power & Thermal Avionics Crew Thermal Budgets
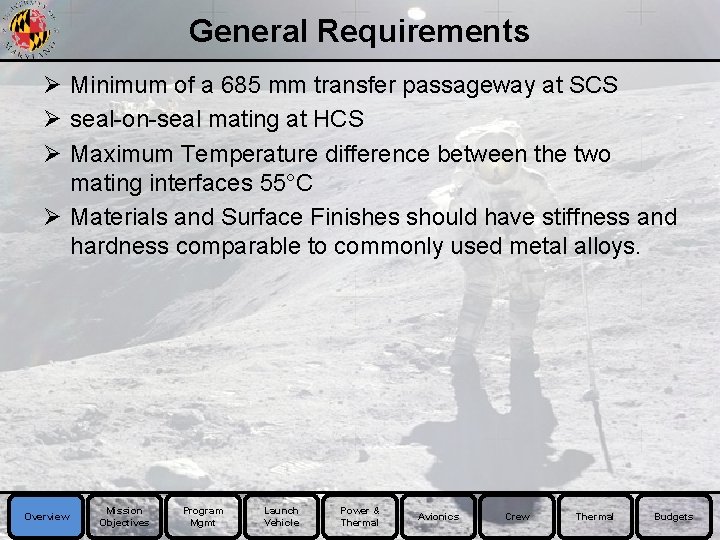
General Requirements Ø Minimum of a 685 mm transfer passageway at SCS Ø seal-on-seal mating at HCS Ø Maximum Temperature difference between the two mating interfaces 55°C Ø Materials and Surface Finishes should have stiffness and hardness comparable to commonly used metal alloys. Overview Mission Objectives Program Mgmt Launch Vehicle Power & Thermal Avionics Crew Thermal Budgets
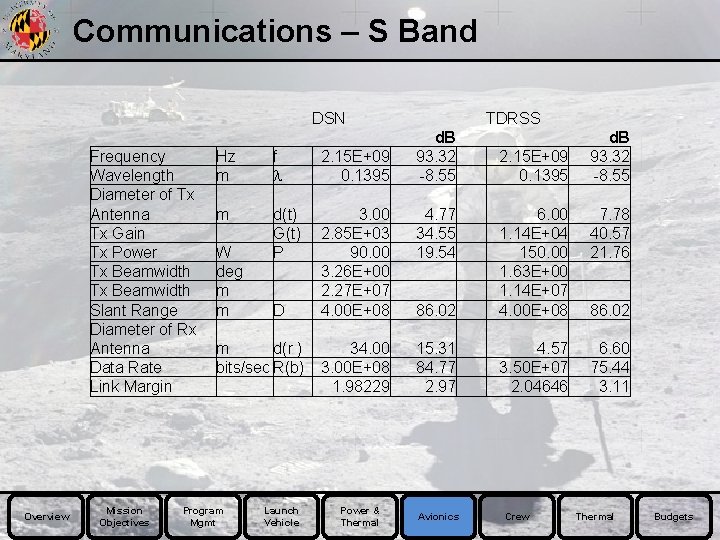
Communications – S Band DSN Frequency Wavelength Diameter of Tx Antenna Tx Gain Tx Power Tx Beamwidth Slant Range Diameter of Rx Antenna Data Rate Link Margin Overview Mission Objectives TDRSS d. B 93. 32 -8. 55 Hz m f l 2. 15 E+09 0. 1395 m d(t) G(t) P 3. 00 2. 85 E+03 90. 00 3. 26 E+00 2. 27 E+07 4. 00 E+08 4. 77 34. 55 19. 54 34. 00 3. 00 E+08 1. 98229 W deg m m D m d(r ) bits/sec R(b) Program Mgmt Launch Vehicle Power & Thermal 2. 15 E+09 0. 1395 d. B 93. 32 -8. 55 7. 78 40. 57 21. 76 86. 02 6. 00 1. 14 E+04 150. 00 1. 63 E+00 1. 14 E+07 4. 00 E+08 15. 31 84. 77 2. 97 4. 57 3. 50 E+07 2. 04646 6. 60 75. 44 3. 11 Avionics Crew 86. 02 Thermal Budgets
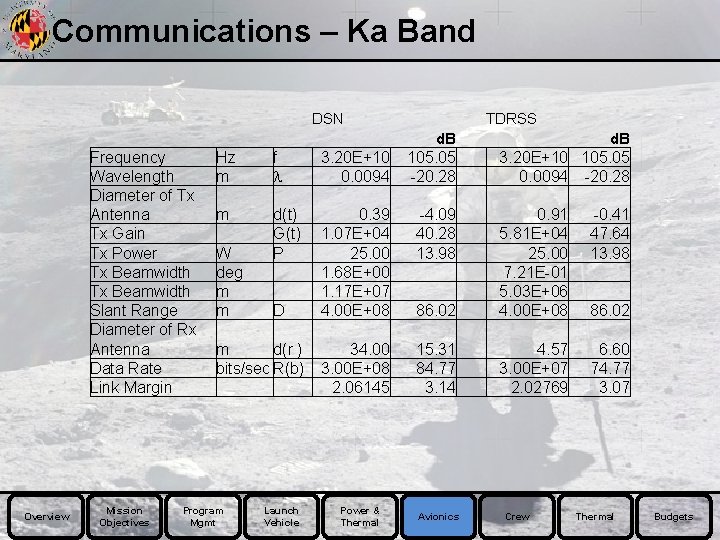
Communications – Ka Band DSN Frequency Wavelength Diameter of Tx Antenna Tx Gain Tx Power Tx Beamwidth Slant Range Diameter of Rx Antenna Data Rate Link Margin Overview Mission Objectives TDRSS d. B 3. 20 E+10 105. 05 0. 0094 -20. 28 Hz m f l 3. 20 E+10 0. 0094 105. 05 -20. 28 m d(t) G(t) P 0. 39 1. 07 E+04 25. 00 1. 68 E+00 1. 17 E+07 4. 00 E+08 -4. 09 40. 28 13. 98 34. 00 3. 00 E+08 2. 06145 W deg m m D m d(r ) bits/sec R(b) Program Mgmt Launch Vehicle Power & Thermal -0. 41 47. 64 13. 98 86. 02 0. 91 5. 81 E+04 25. 00 7. 21 E-01 5. 03 E+06 4. 00 E+08 15. 31 84. 77 3. 14 4. 57 3. 00 E+07 2. 02769 6. 60 74. 77 3. 07 Avionics Crew 86. 02 Thermal Budgets
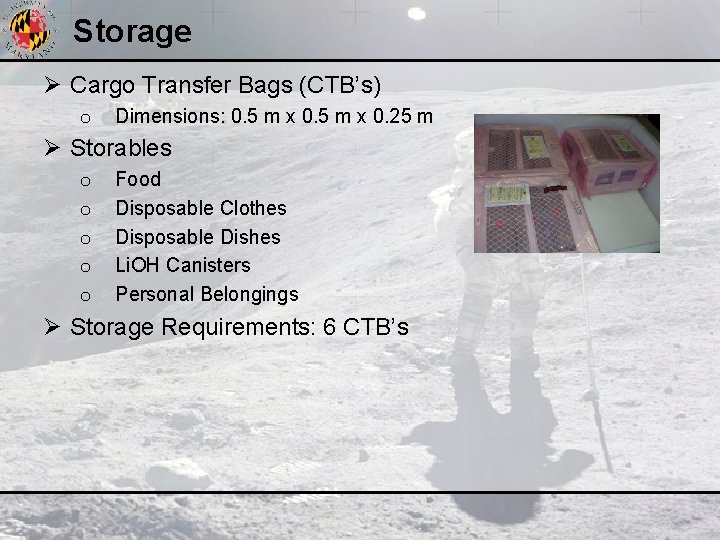
Storage Ø Cargo Transfer Bags (CTB’s) o Dimensions: 0. 5 m x 0. 25 m Ø Storables o o o Food Disposable Clothes Disposable Dishes Li. OH Canisters Personal Belongings Ø Storage Requirements: 6 CTB’s
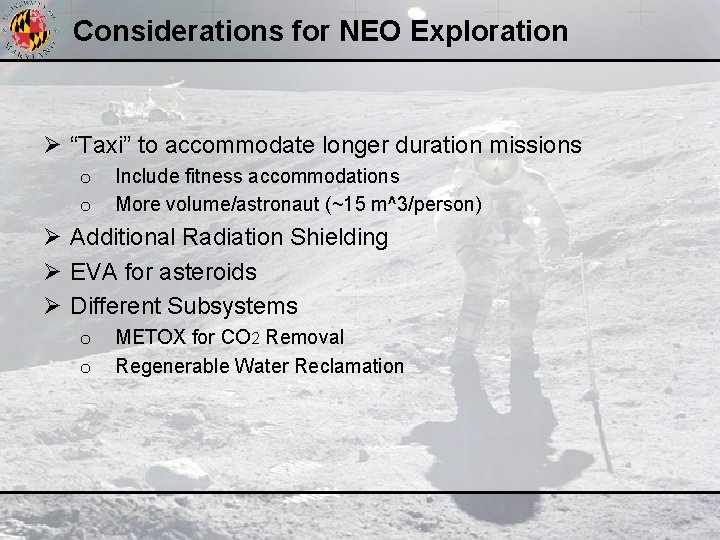
Considerations for NEO Exploration Ø “Taxi” to accommodate longer duration missions o o Include fitness accommodations More volume/astronaut (~15 m^3/person) Ø Additional Radiation Shielding Ø EVA for asteroids Ø Different Subsystems o o METOX for CO 2 Removal Regenerable Water Reclamation
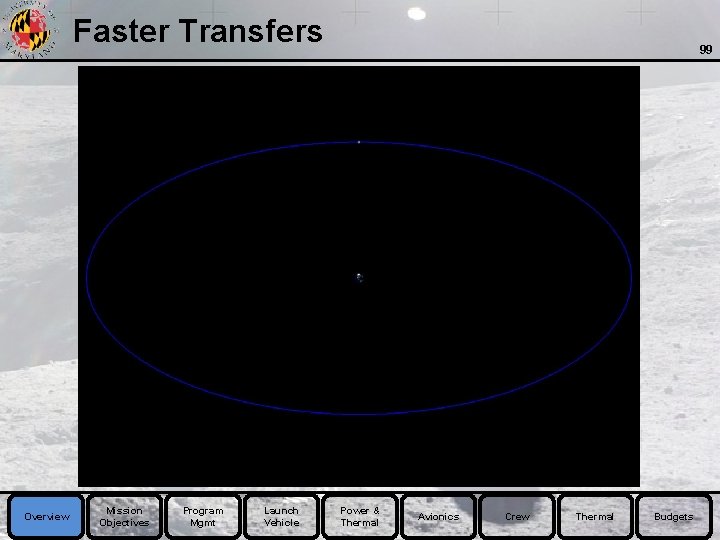
Faster Transfers Overview Mission Objectives Program Mgmt Launch Vehicle 99 Power & Thermal Avionics Crew Thermal Budgets
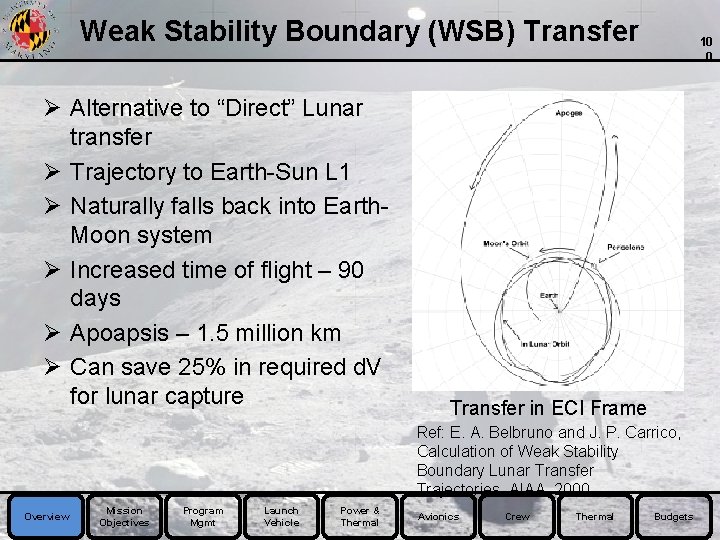
Weak Stability Boundary (WSB) Transfer Ø Alternative to “Direct” Lunar transfer Ø Trajectory to Earth-Sun L 1 Ø Naturally falls back into Earth. Moon system Ø Increased time of flight – 90 days Ø Apoapsis – 1. 5 million km Ø Can save 25% in required d. V for lunar capture 10 0 Transfer in ECI Frame Ref: E. A. Belbruno and J. P. Carrico, Calculation of Weak Stability Boundary Lunar Transfer Trajectories, AIAA, 2000 Overview Mission Objectives Program Mgmt Launch Vehicle Power & Thermal Avionics Crew Thermal Budgets
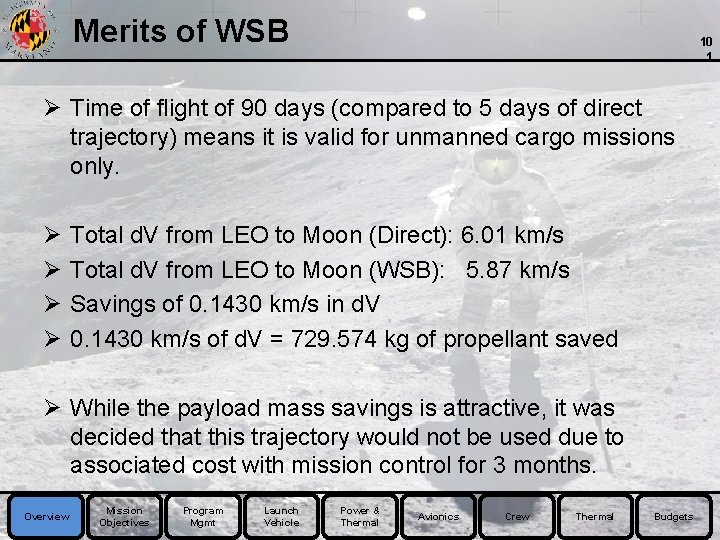
Merits of WSB 10 1 Ø Time of flight of 90 days (compared to 5 days of direct trajectory) means it is valid for unmanned cargo missions only. Ø Ø Total d. V from LEO to Moon (Direct): 6. 01 km/s Total d. V from LEO to Moon (WSB): 5. 87 km/s Savings of 0. 1430 km/s in d. V 0. 1430 km/s of d. V = 729. 574 kg of propellant saved Ø While the payload mass savings is attractive, it was decided that this trajectory would not be used due to associated cost with mission control for 3 months. Overview Mission Objectives Program Mgmt Launch Vehicle Power & Thermal Avionics Crew Thermal Budgets
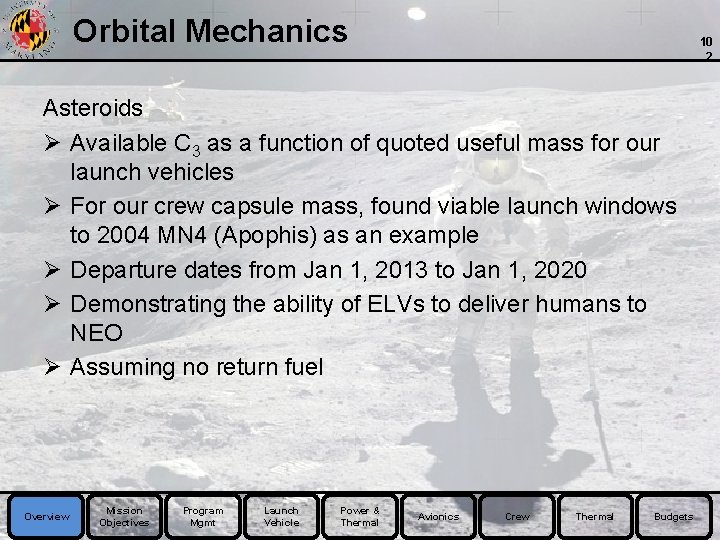
Orbital Mechanics 10 2 Asteroids Ø Available C 3 as a function of quoted useful mass for our launch vehicles Ø For our crew capsule mass, found viable launch windows to 2004 MN 4 (Apophis) as an example Ø Departure dates from Jan 1, 2013 to Jan 1, 2020 Ø Demonstrating the ability of ELVs to deliver humans to NEO Ø Assuming no return fuel Overview Mission Objectives Program Mgmt Launch Vehicle Power & Thermal Avionics Crew Thermal Budgets
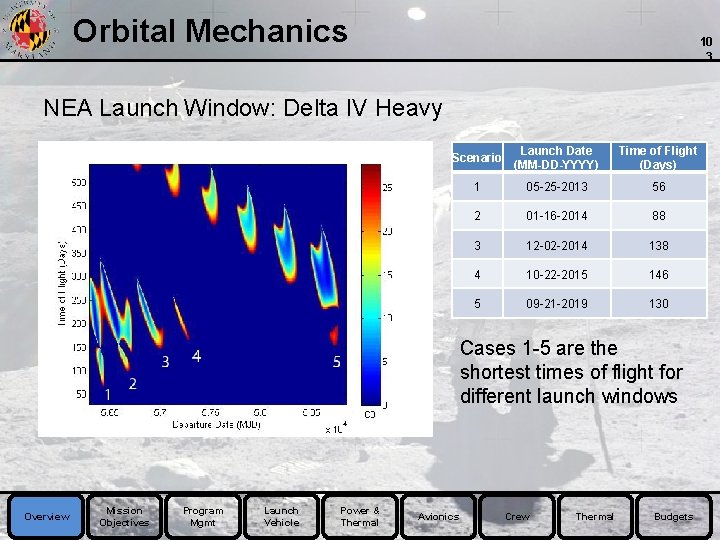
Orbital Mechanics 10 3 NEA Launch Window: Delta IV Heavy Scenario Launch Date (MM-DD-YYYY) Time of Flight (Days) 1 05 -25 -2013 56 2 01 -16 -2014 88 3 12 -02 -2014 138 4 10 -22 -2015 146 5 09 -21 -2019 130 Cases 1 -5 are the shortest times of flight for different launch windows Overview Mission Objectives Program Mgmt Launch Vehicle Power & Thermal Avionics Crew Thermal Budgets
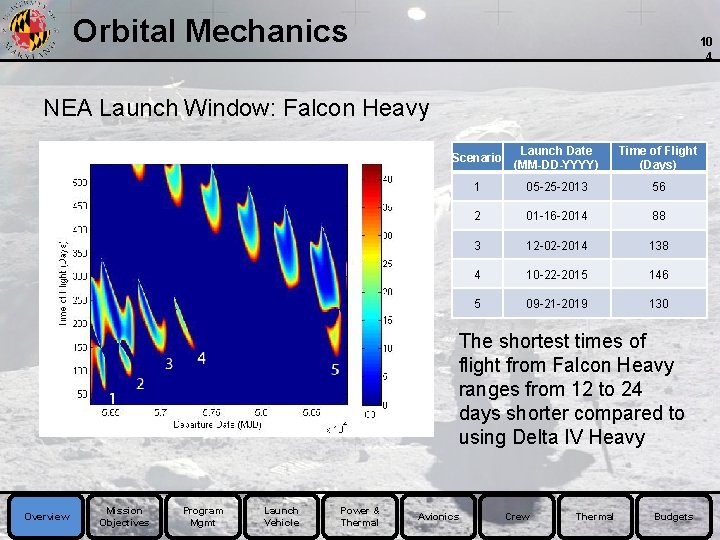
Orbital Mechanics 10 4 NEA Launch Window: Falcon Heavy Scenario Launch Date (MM-DD-YYYY) Time of Flight (Days) 1 05 -25 -2013 56 2 01 -16 -2014 88 3 12 -02 -2014 138 4 10 -22 -2015 146 5 09 -21 -2019 130 The shortest times of flight from Falcon Heavy ranges from 12 to 24 days shorter compared to using Delta IV Heavy Overview Mission Objectives Program Mgmt Launch Vehicle Power & Thermal Avionics Crew Thermal Budgets
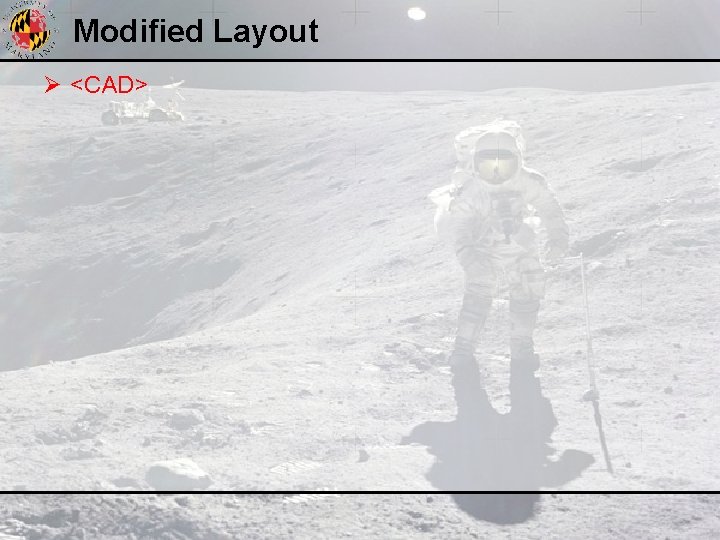
Modified Layout Ø <CAD>
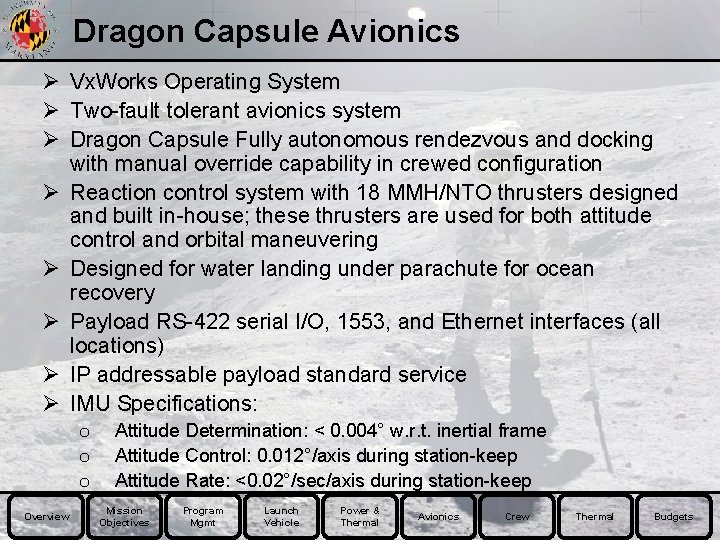
Dragon Capsule Avionics Ø Vx. Works Operating System Ø Two-fault tolerant avionics system Ø Dragon Capsule Fully autonomous rendezvous and docking with manual override capability in crewed configuration Ø Reaction control system with 18 MMH/NTO thrusters designed and built in-house; these thrusters are used for both attitude control and orbital maneuvering Ø Designed for water landing under parachute for ocean recovery Ø Payload RS-422 serial I/O, 1553, and Ethernet interfaces (all locations) Ø IP addressable payload standard service Ø IMU Specifications: o o o Overview Attitude Determination: < 0. 004° w. r. t. inertial frame Attitude Control: 0. 012°/axis during station-keep Attitude Rate: <0. 02°/sec/axis during station-keep Mission Objectives Program Mgmt Launch Vehicle Power & Thermal Avionics Crew Thermal Budgets
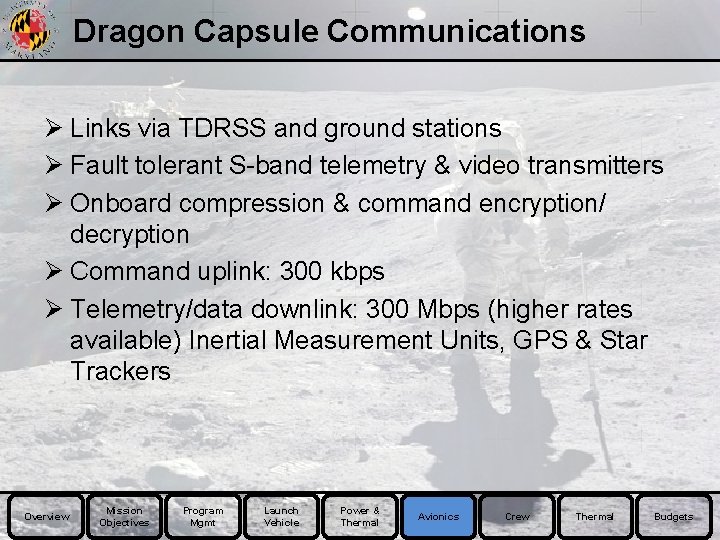
Dragon Capsule Communications Ø Links via TDRSS and ground stations Ø Fault tolerant S-band telemetry & video transmitters Ø Onboard compression & command encryption/ decryption Ø Command uplink: 300 kbps Ø Telemetry/data downlink: 300 Mbps (higher rates available) Inertial Measurement Units, GPS & Star Trackers Overview Mission Objectives Program Mgmt Launch Vehicle Power & Thermal Avionics Crew Thermal Budgets
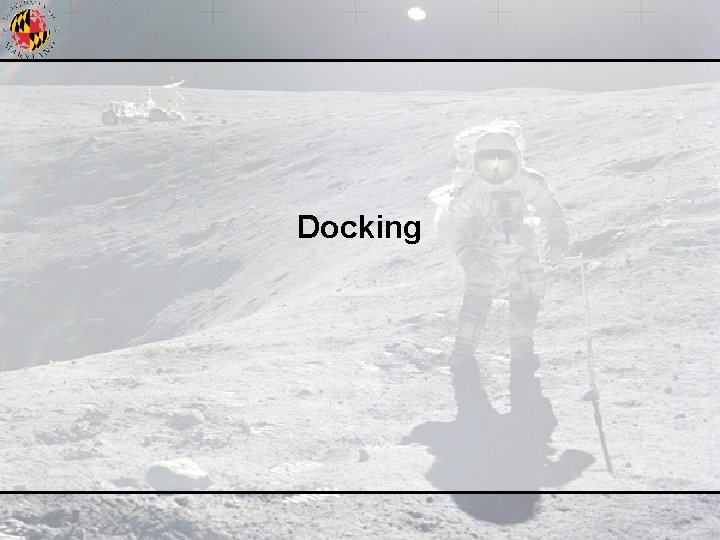
Docking
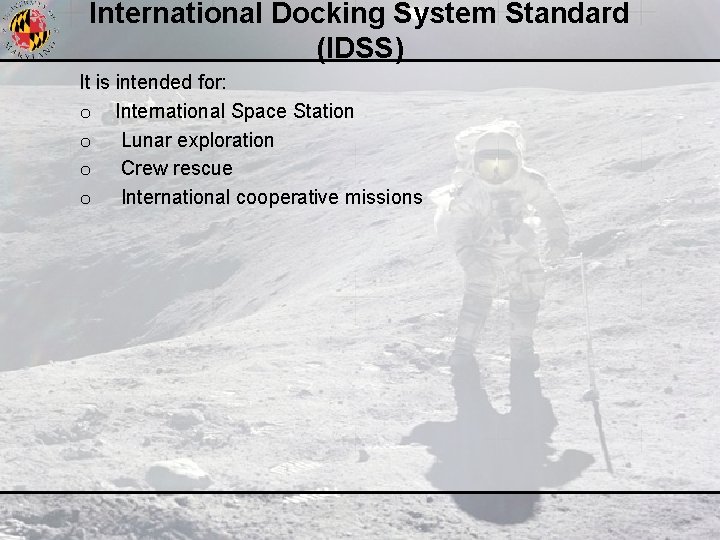
International Docking System Standard (IDSS) It is intended for: o International Space Station o Lunar exploration o Crew rescue o International cooperative missions
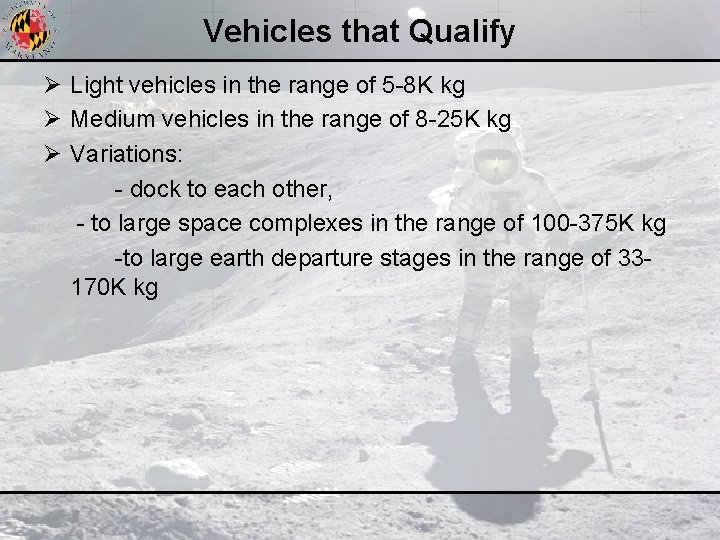
Vehicles that Qualify Ø Light vehicles in the range of 5 -8 K kg Ø Medium vehicles in the range of 8 -25 K kg Ø Variations: - dock to each other, - to large space complexes in the range of 100 -375 K kg -to large earth departure stages in the range of 33170 K kg
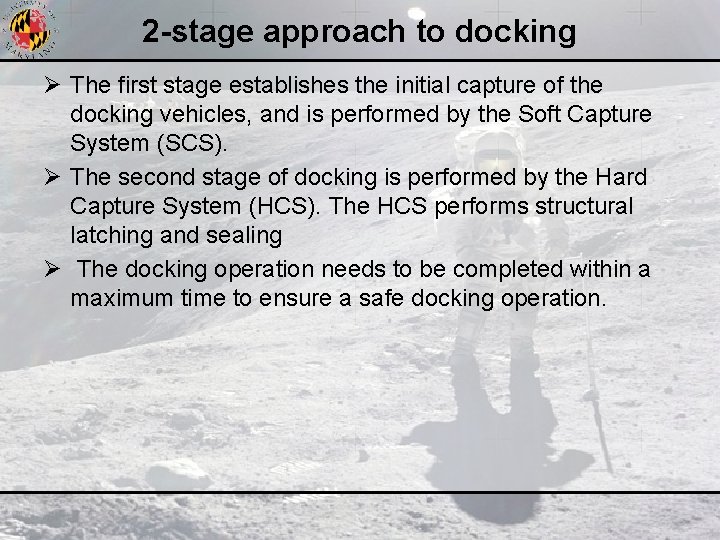
2 -stage approach to docking Ø The first stage establishes the initial capture of the docking vehicles, and is performed by the Soft Capture System (SCS). Ø The second stage of docking is performed by the Hard Capture System (HCS). The HCS performs structural latching and sealing Ø The docking operation needs to be completed within a maximum time to ensure a safe docking operation.
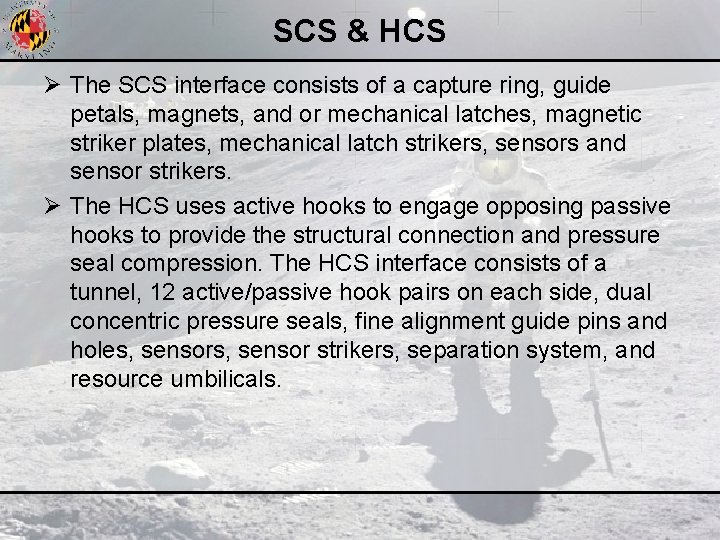
SCS & HCS Ø The SCS interface consists of a capture ring, guide petals, magnets, and or mechanical latches, magnetic striker plates, mechanical latch strikers, sensors and sensor strikers. Ø The HCS uses active hooks to engage opposing passive hooks to provide the structural connection and pressure seal compression. The HCS interface consists of a tunnel, 12 active/passive hook pairs on each side, dual concentric pressure seals, fine alignment guide pins and holes, sensor strikers, separation system, and resource umbilicals.
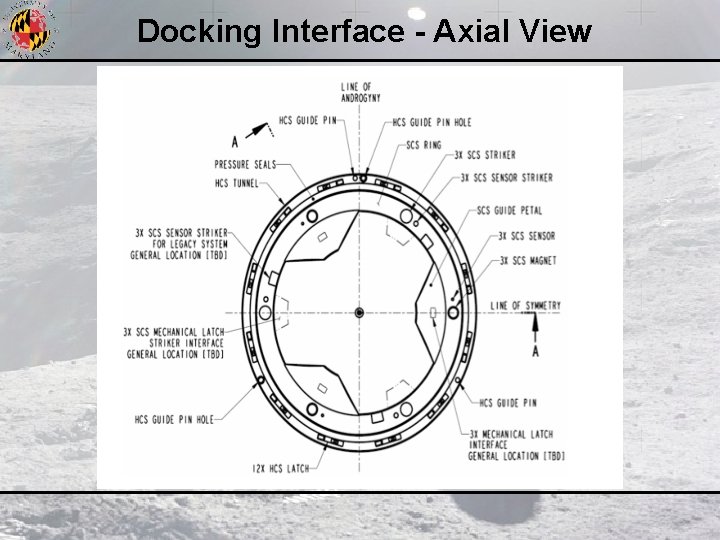
Docking Interface - Axial View
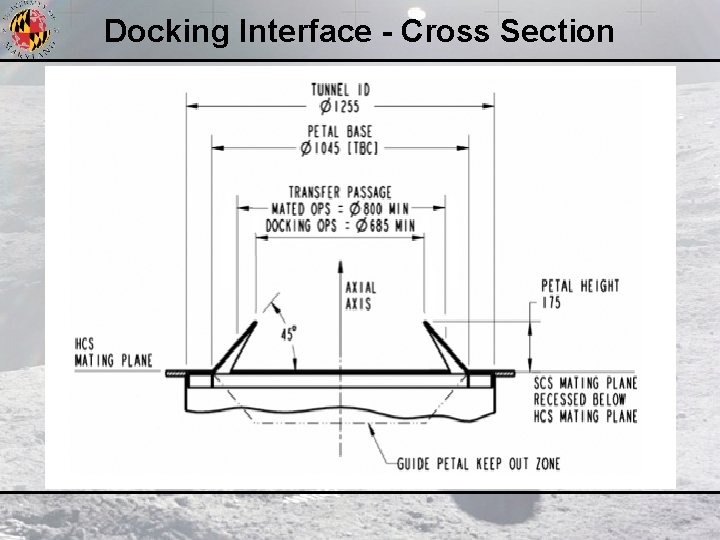
Docking Interface - Cross Section
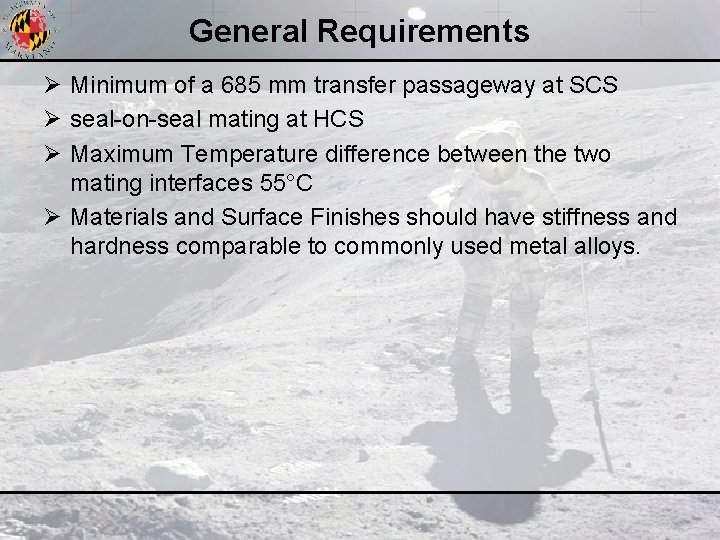
General Requirements Ø Minimum of a 685 mm transfer passageway at SCS Ø seal-on-seal mating at HCS Ø Maximum Temperature difference between the two mating interfaces 55°C Ø Materials and Surface Finishes should have stiffness and hardness comparable to commonly used metal alloys.
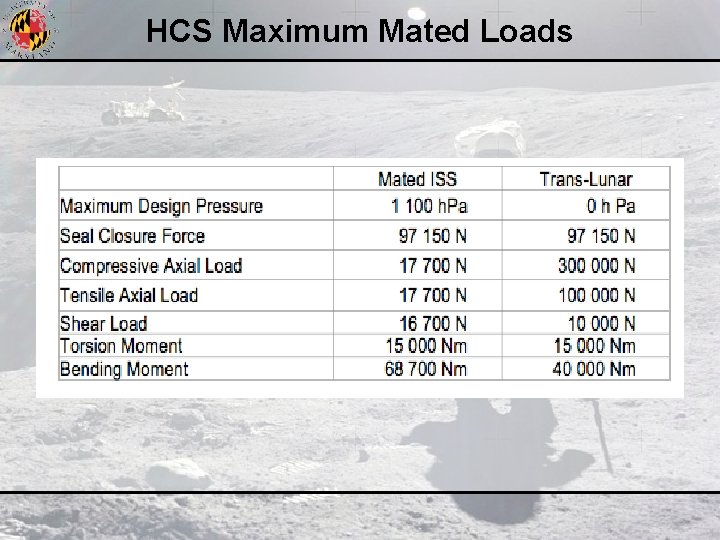
HCS Maximum Mated Loads
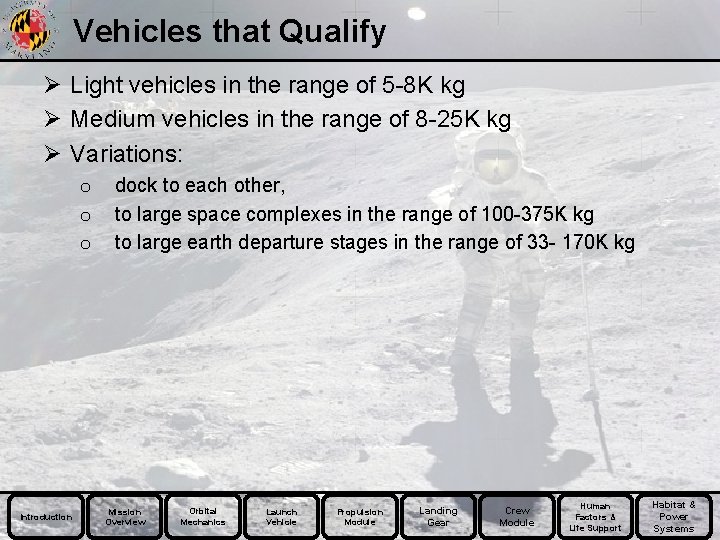
Vehicles that Qualify Ø Light vehicles in the range of 5 -8 K kg Ø Medium vehicles in the range of 8 -25 K kg Ø Variations: o o o Introduction dock to each other, to large space complexes in the range of 100 -375 K kg to large earth departure stages in the range of 33 - 170 K kg Mission Overview Orbital Mechanics Launch Vehicle Propulsion Module Landing Gear Crew Module Human Factors & Life Support Habitat & Power Systems
Exploration cloze notes 1
Lunar precursor robotic program
Asvabprogram access code
Asvab career exploration program for high school students
Mars exploration program analysis group
Exoplanet exploration program
Nonemergency medical transportation
Army mass transportation benefit program
Difference between solar and lunar eclipse
Differentiate between lunar eclipse and solar eclipse
Tides and eclipses
Association of lunar and planetary observers
The dark inner portion of the shadow cone
Lunar solar exo
Whats the lunar cycle
Lunar regolith definition
Lunar ice cube
Lunar eclipse israel
Moon stats
Pontaj electronic
Carl sagan lunar eclipse
What was the sumerian calendar based on
Lunar laser ranging retroreflector array
Whats a natural satellite
Busek bit-3
300 solar years to lunar years
Coronary sinus
Sky light allsearchlights.com
Lunar 1996
New year jeopardy
Lunar legend festival riddles
Lunar
Lunar
Lunar survival activity
Lunar
Lunar
Obs ahi
Iaaras real name
Solar eclipse chapter 10
Lunar
Inst-154
Hymen
Lunar
A lunar excursion module weighs 1500 kg
Lunar security
What is the moon made out of
Lunar
Ruth bruno
Partial lunar eclipse
Lunar eclipse moon phase
Movement on the moon
Lunar orbital plane
Dua for lunar eclipse in islam
Lunar system
Eclipse penumbral
The two eclipses
Pamayanang naitatag ng sumer
Lunaf.com 14.01.2004
Lunar new year quiz
Calendario lunar 219
Advantage of clustered settlement
Linear settlement pattern
Grade 12 geography settlement
Clearing and settlement
Sensys easy pay
Payment and settlement system in sri lanka
Payment and settlement system in sri lanka
Payment and settlement system in sri lanka
Lesson 2 settlement culture and government of the colonies
Trading and settlement code
Payment gateway license in bangladesh
Geography and the settlement of greece
Confederated salish and kootenai tribes settlement
Transportation and assignment problems and solutions
Hungarian algorithm worksheet
Robotics webquest
Expansion exploration and encounters
The three g's (gold god glory)
Presidential elections exploration and announcement
Early european exploration and colonization resulted in -
Exploration and evaluation assets
Guided reading activity 13-1 exploration and expansion
Mineral exploration and mining active reading
The age of exploration outcome china and japan's reactions
The age of exploration outcome china and japan's reactions
Unit 2 exploration and georgia colonization
“god, glory, gold”
An age of exploration and isolation
1-6 midpoint and distance in the coordinate plane
Causes and effects of european exploration
Spanish exploration and conquest apush
Explorations in creative reading and writing
Exploration and discovery where ideas come from
Exploration and exploitation in organizational learning
Exploration and discovery
Unit 1 exploration and colonization
Astromaterials research and exploration science
Chapter 19 an age of exploration and isolation
Explain god gold and glory
Sequential program and an event-driven program?
Linear settlement pattern
What is settlement patterns
Settlement hierarchy pyramid
Long lots of southern quebec
Pompey's eastern settlement
Define squatter settlement
What was the first permanent english settlement
Why did raffles choose singapore as a trading port
Recompression index
Wto dispute settlement mechanism
Dispute settlement mechanism meaning
Coefficient of volume compressibility formula
Elizabethan settlement
Disturbunce
Rural settlement patterns
The west settlement of the last frontier
Settlement hierarchy pyramid
Threshold ap human geography