LAN 0106081197 18320 507 CONFIDENTIAL Sample Kickoff Meeting
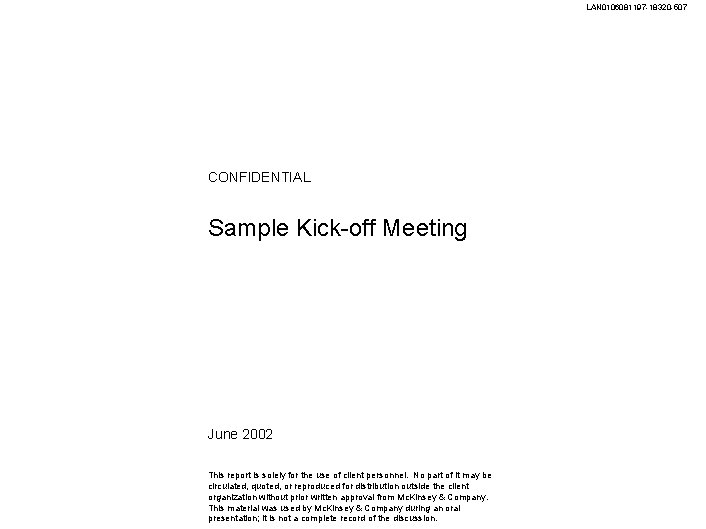
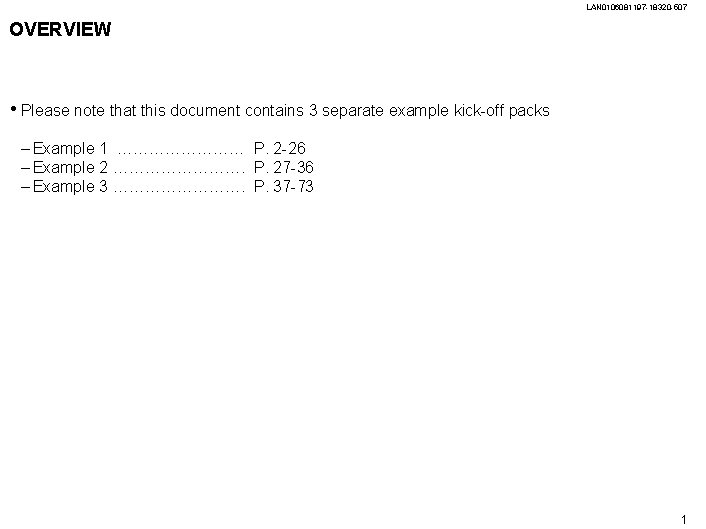

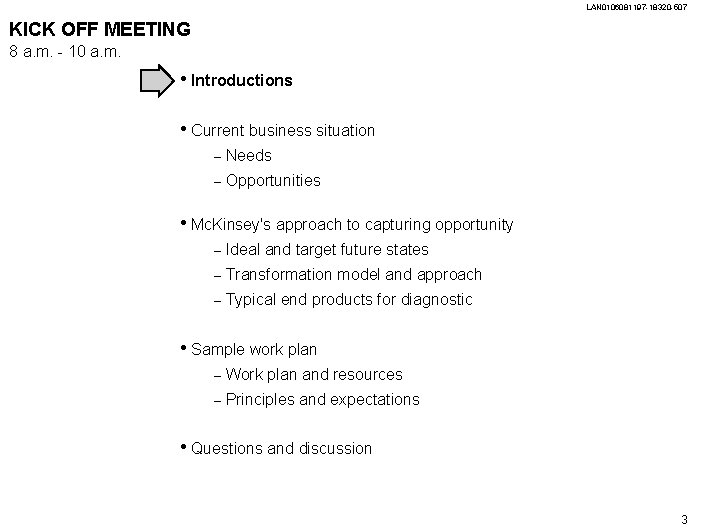
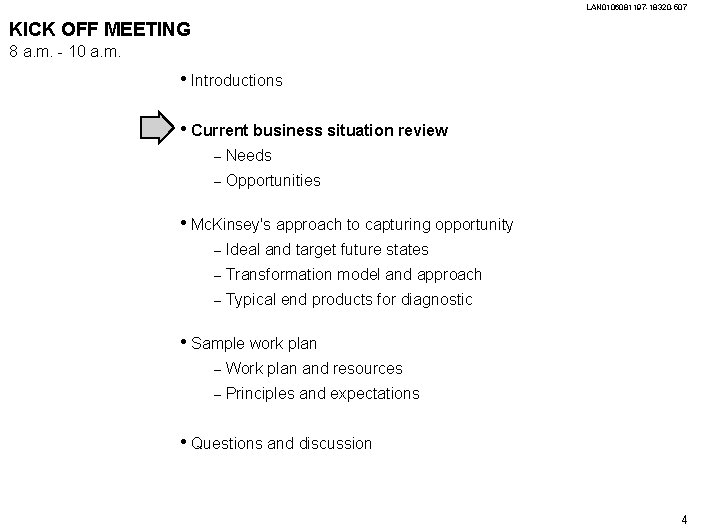
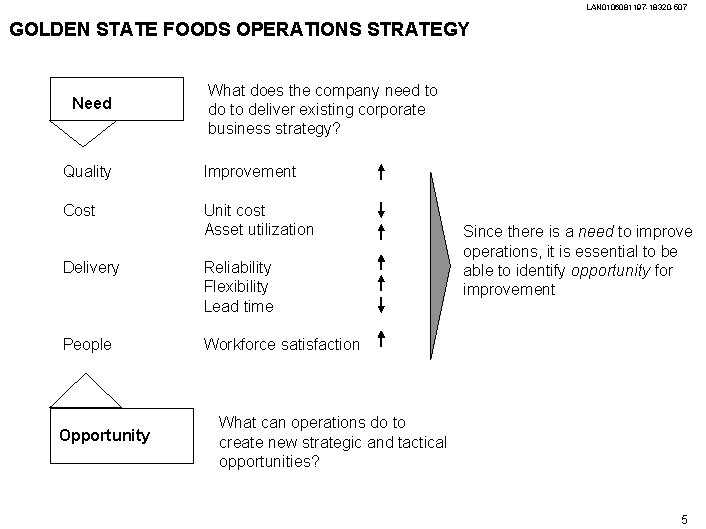
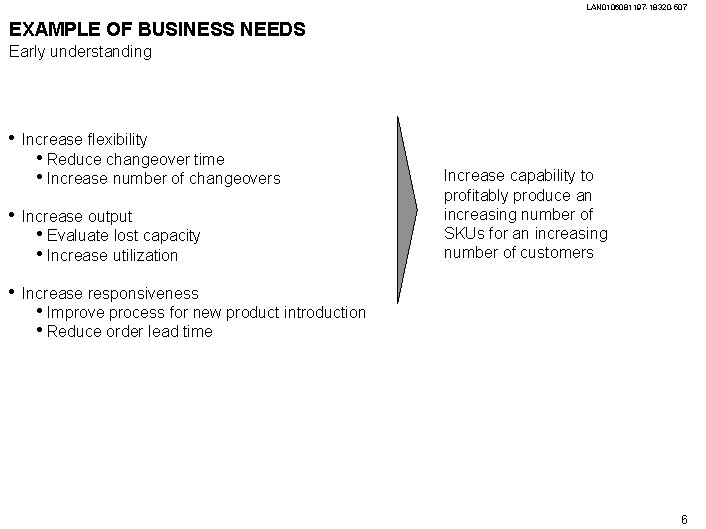
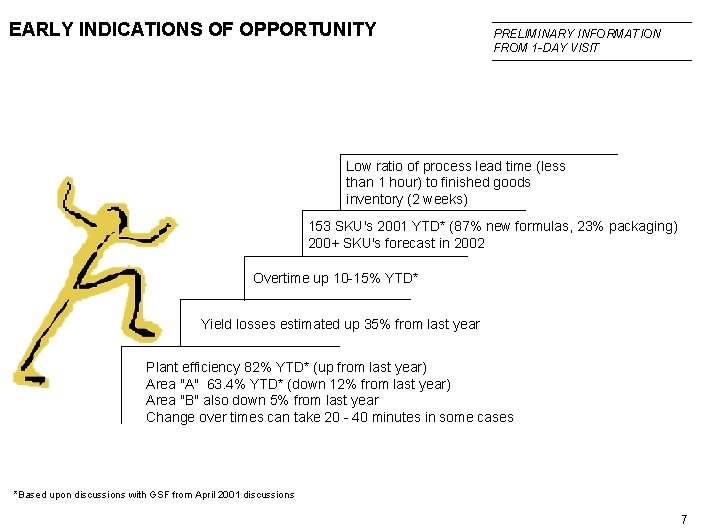
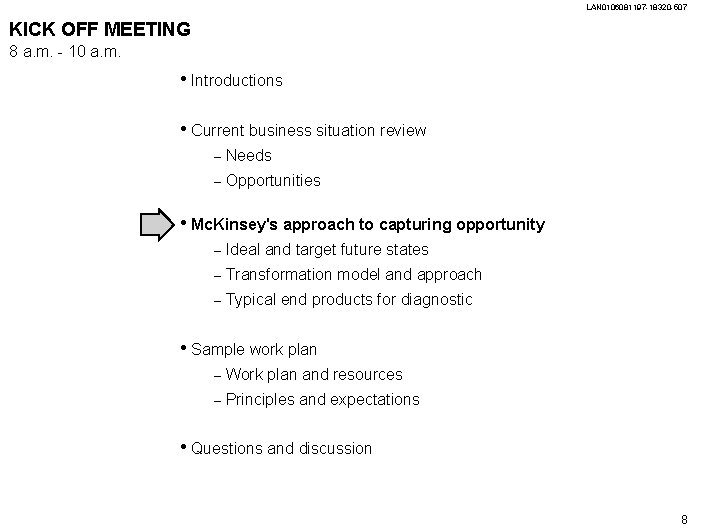
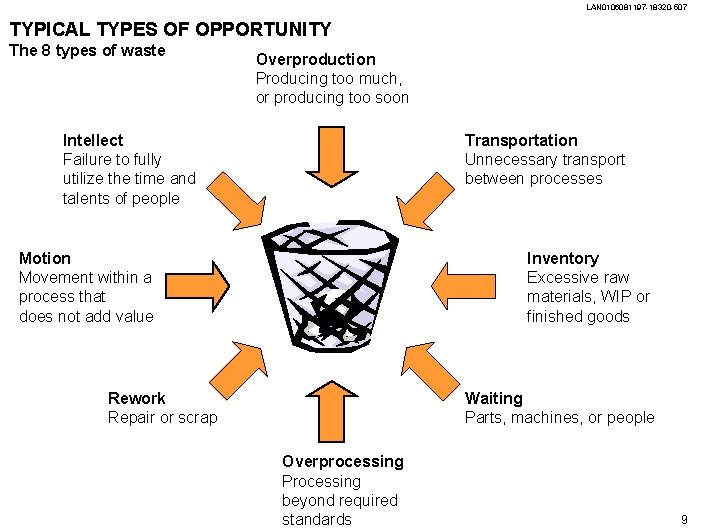
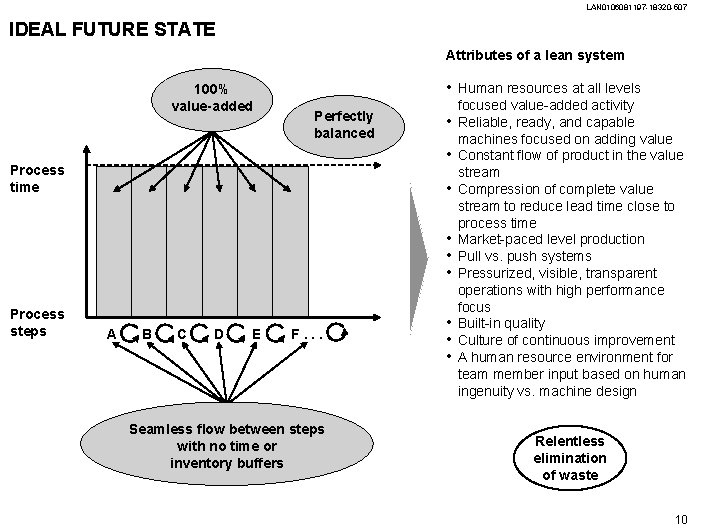
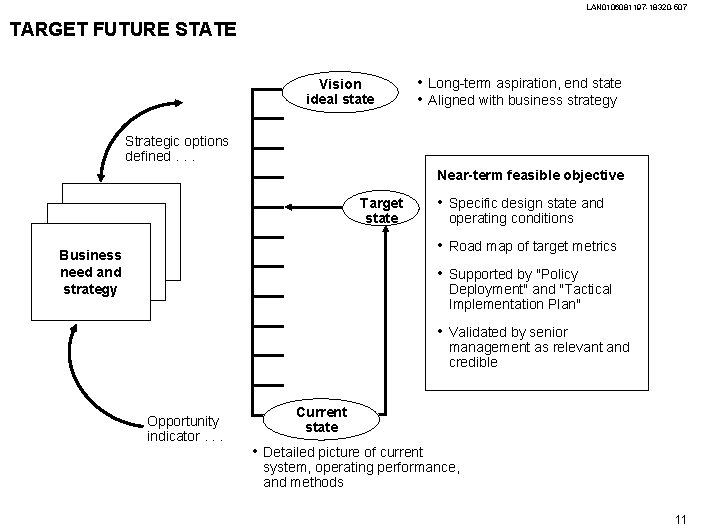
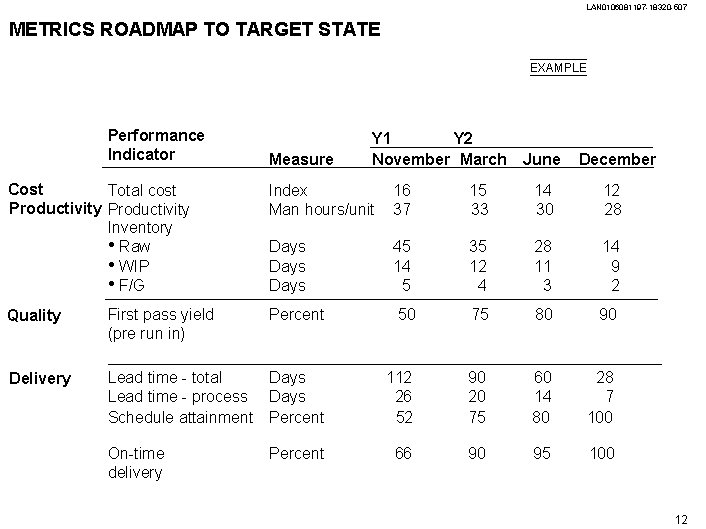
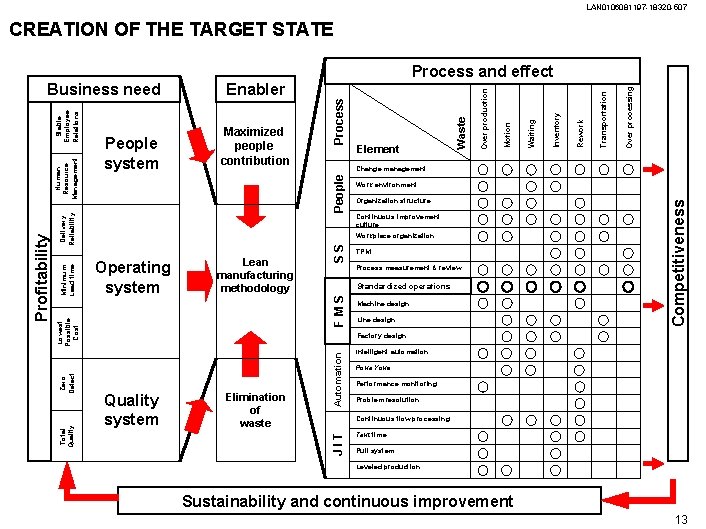
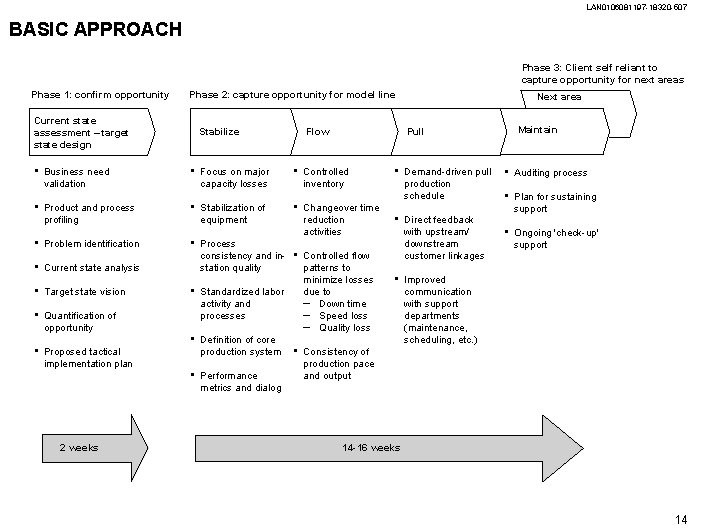
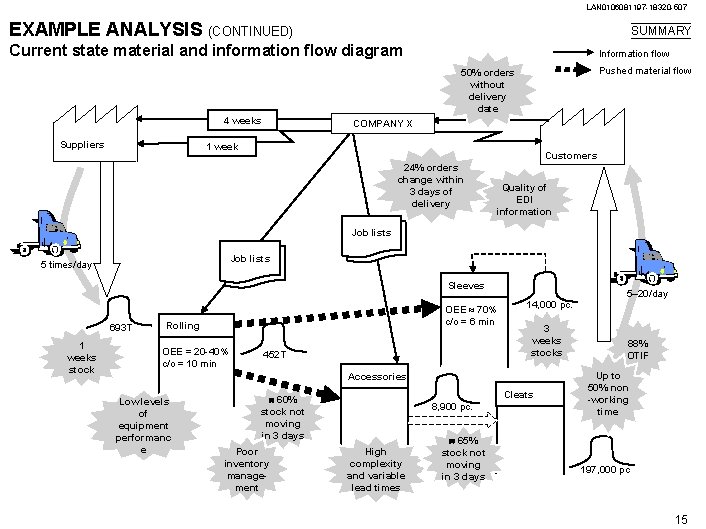
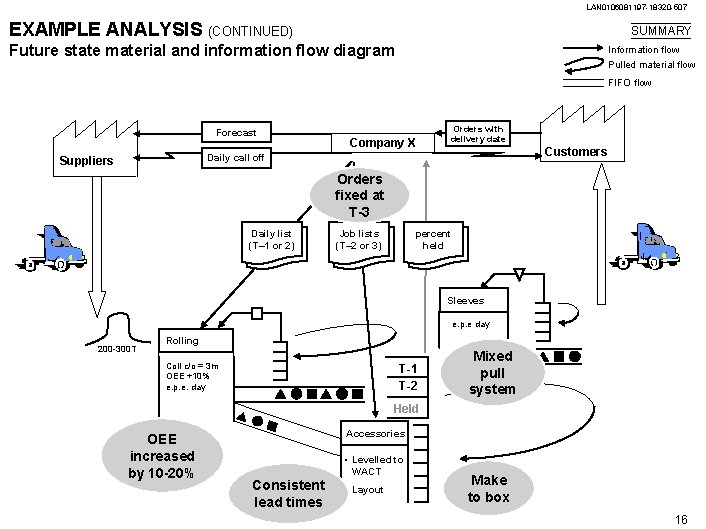
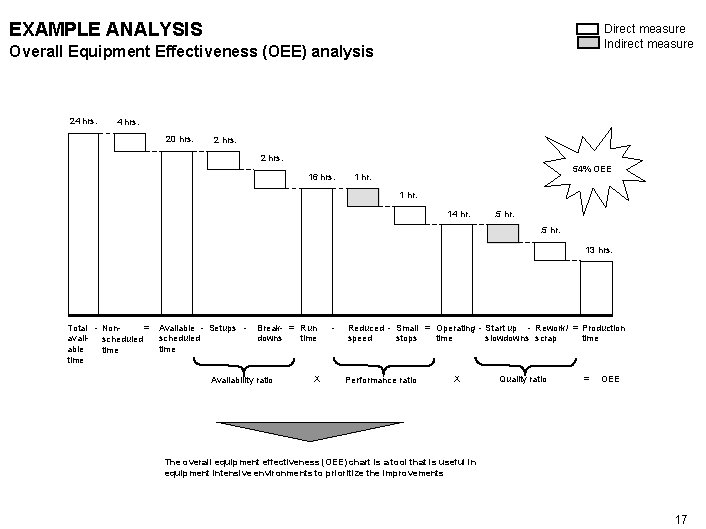
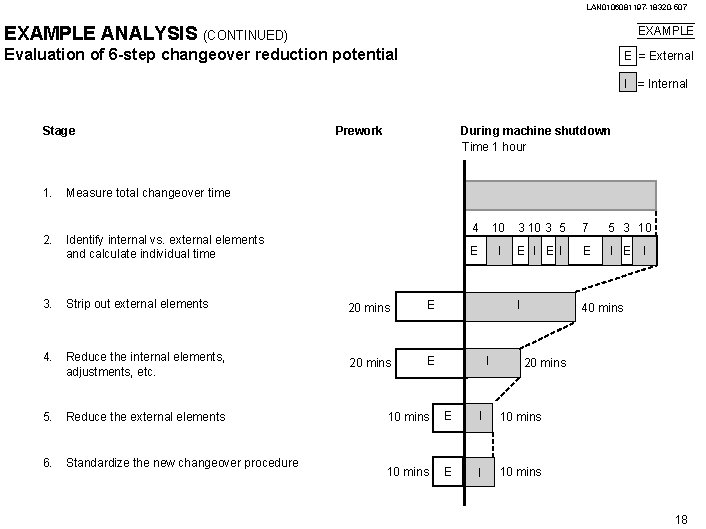
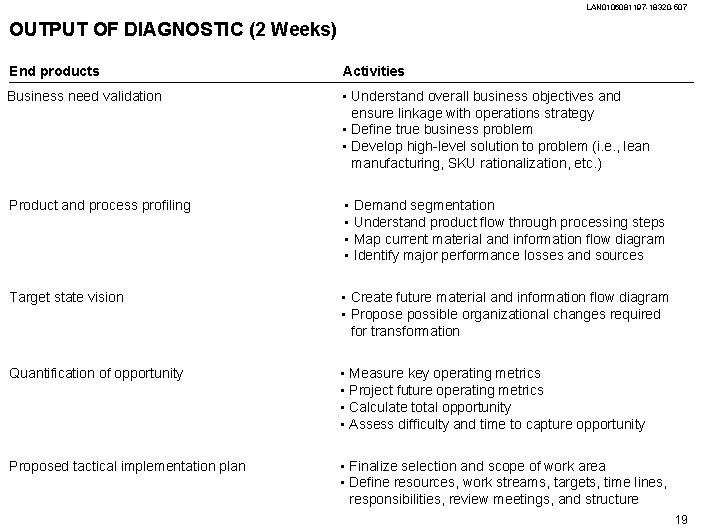
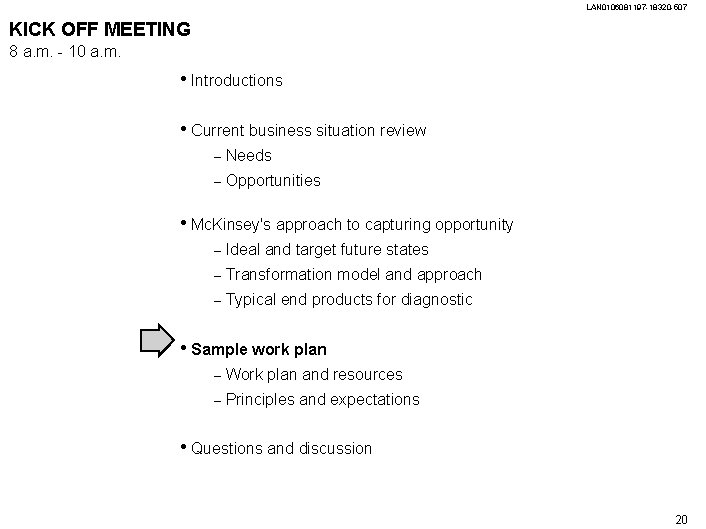
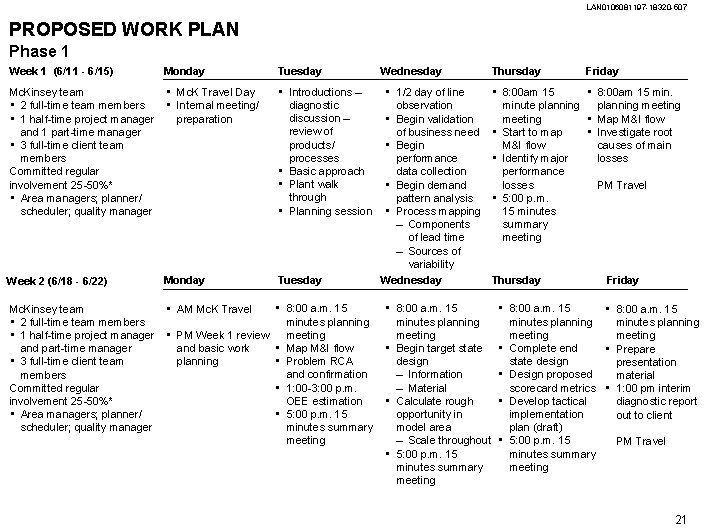
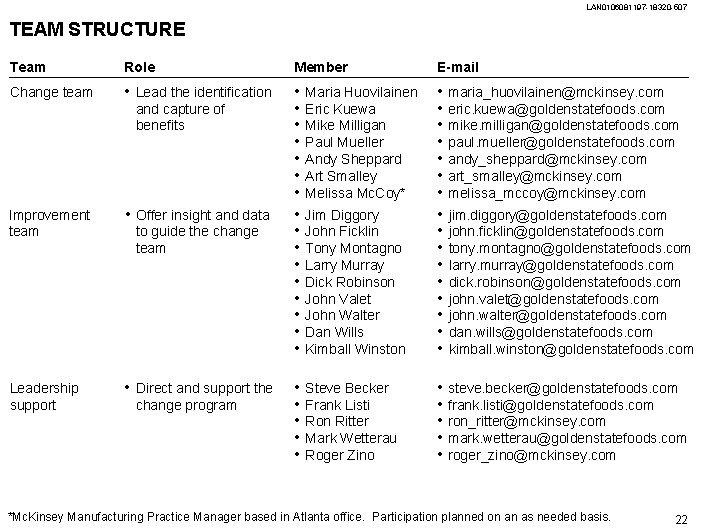
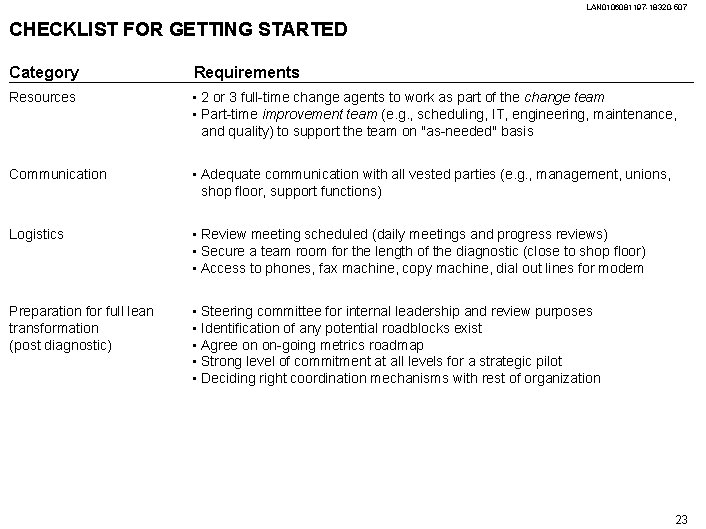
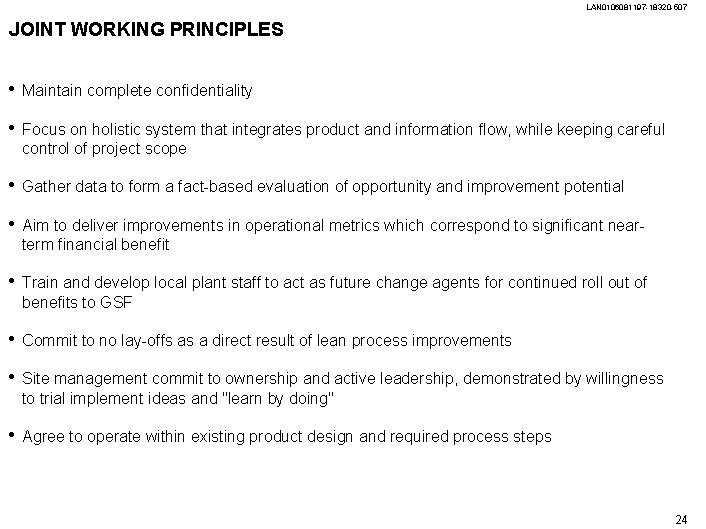
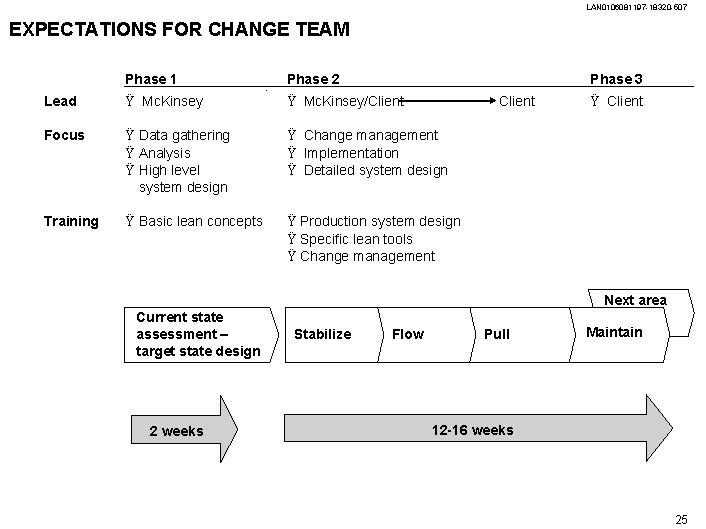
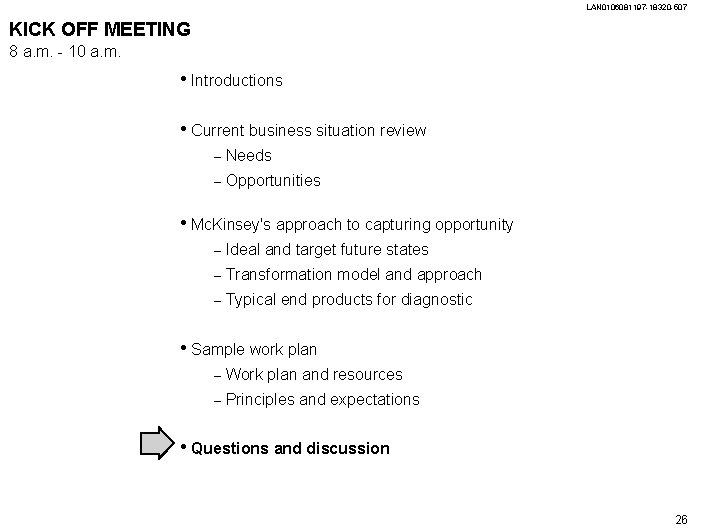
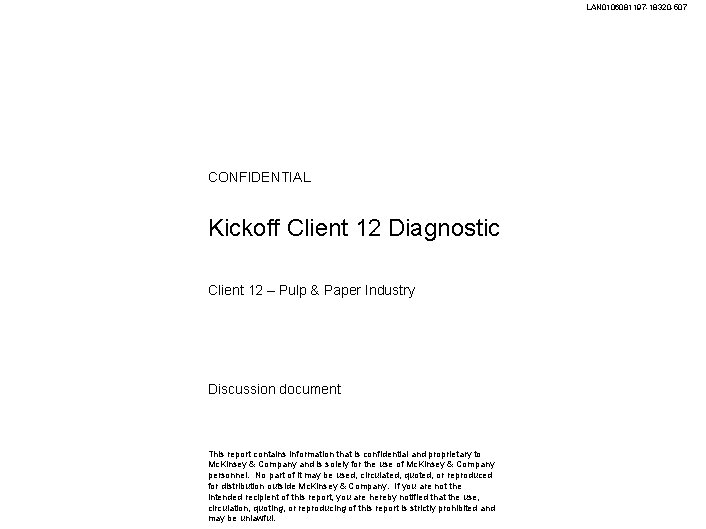
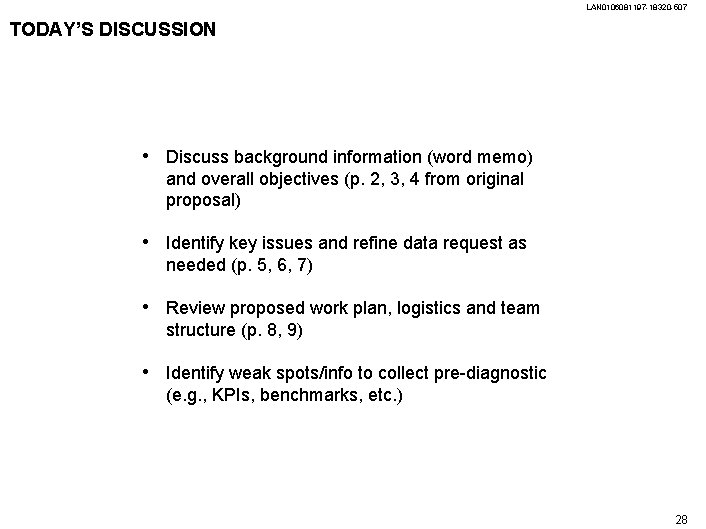
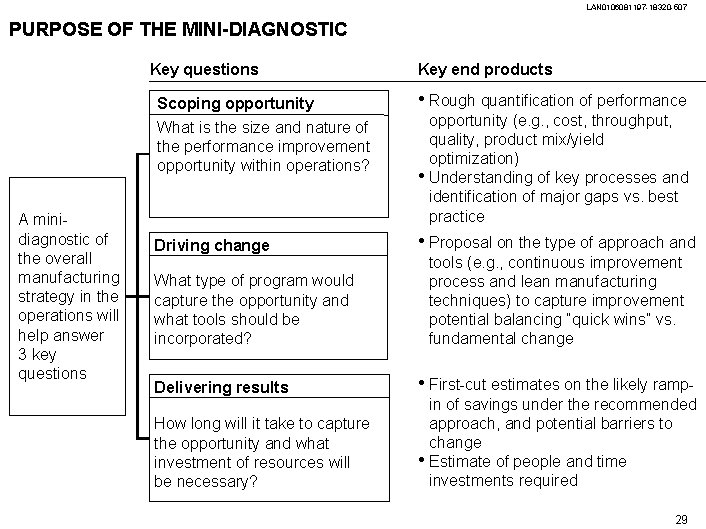

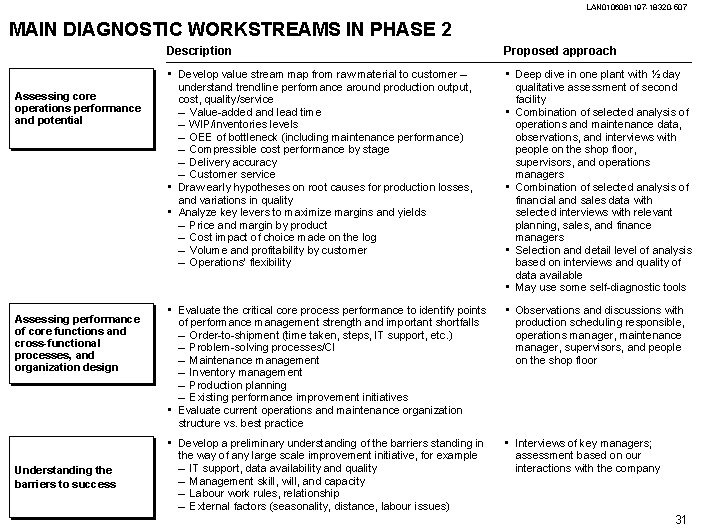
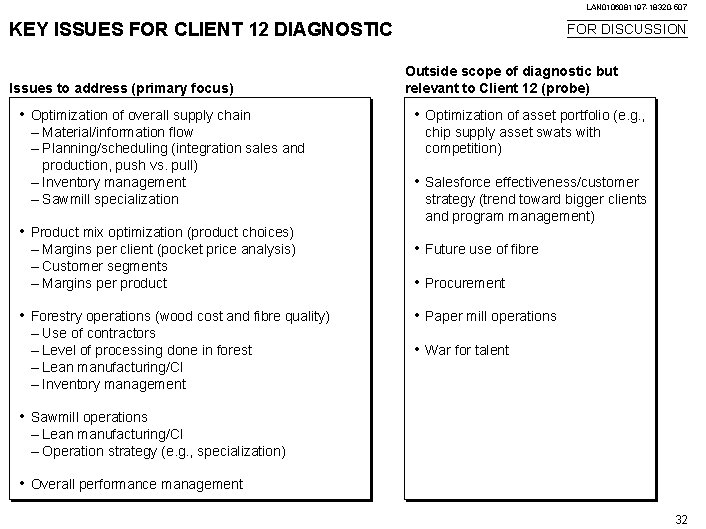
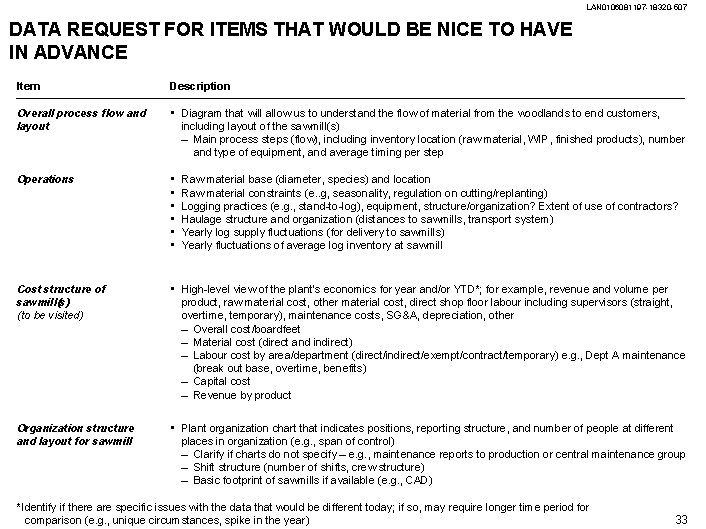
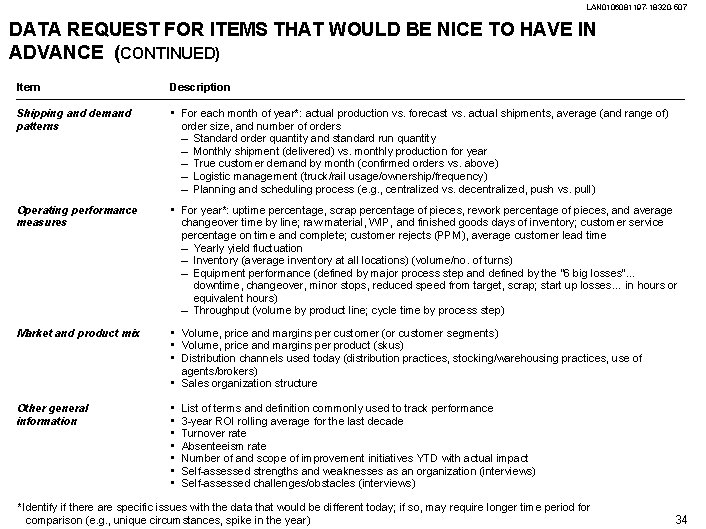
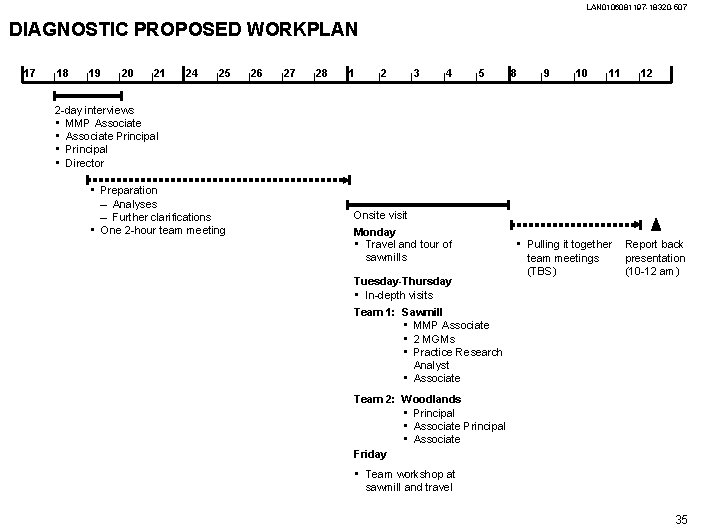
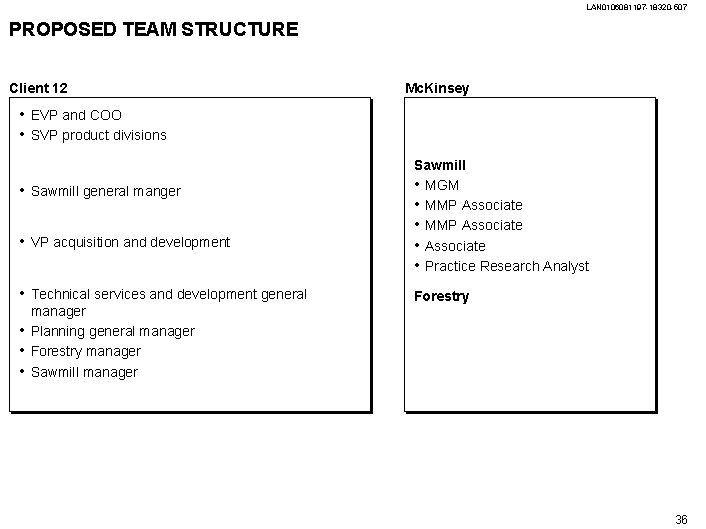
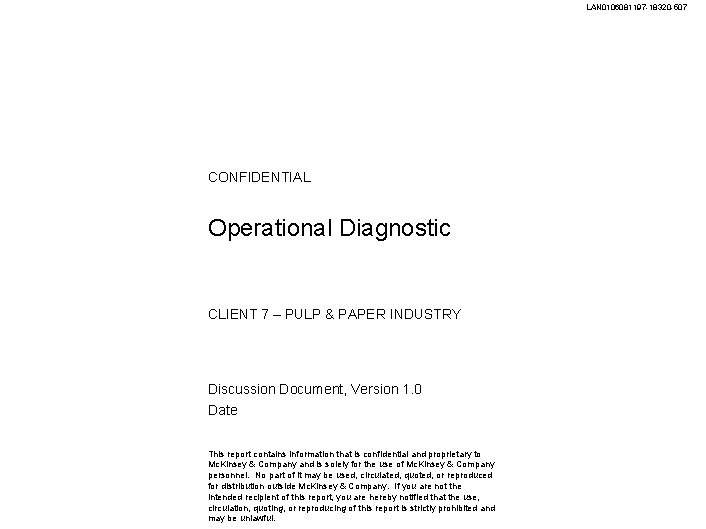
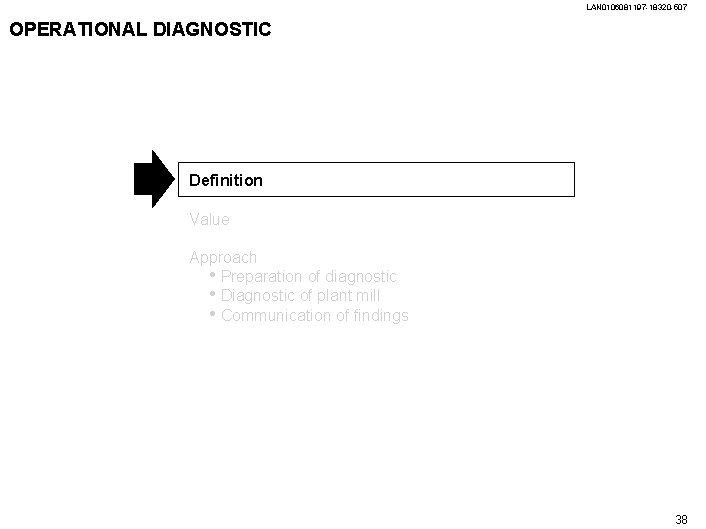
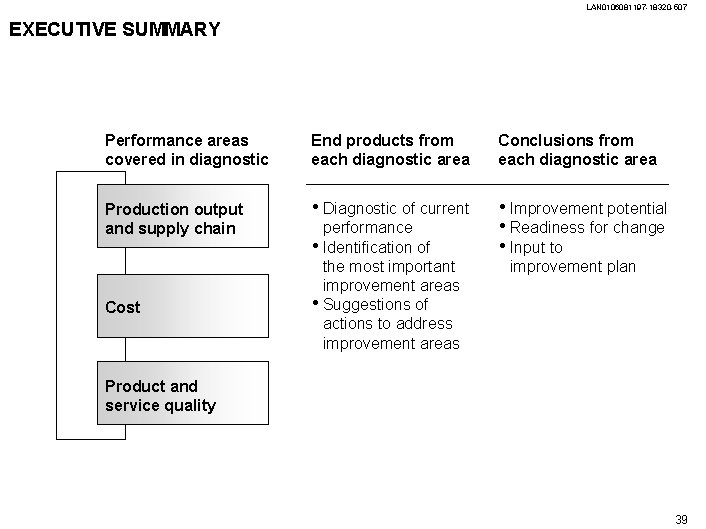
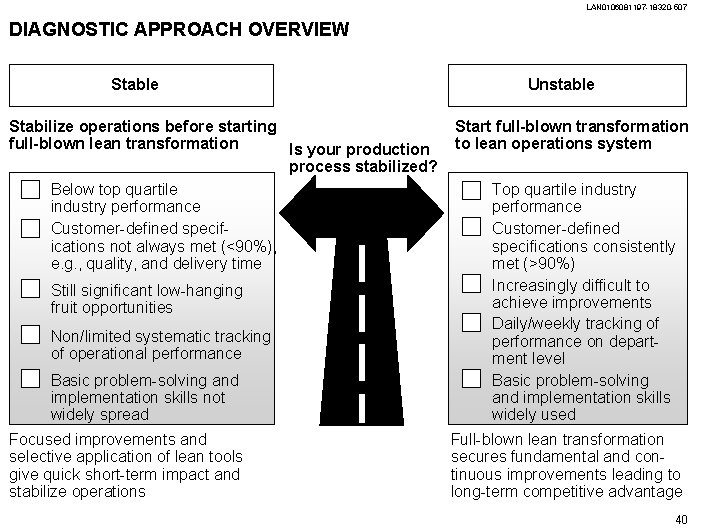
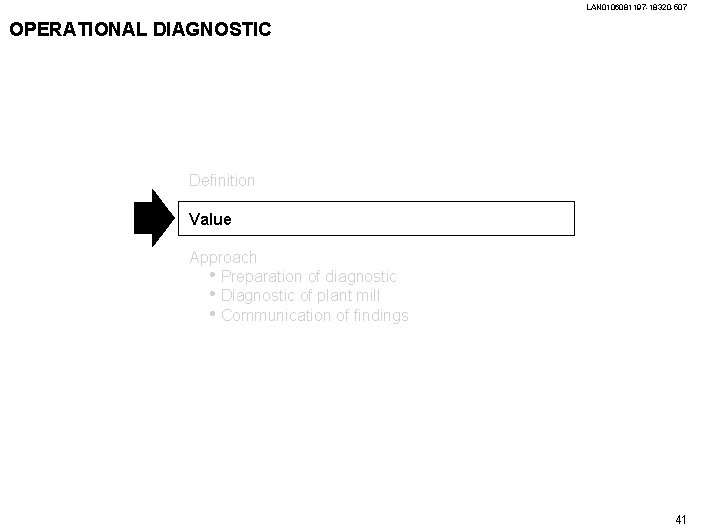
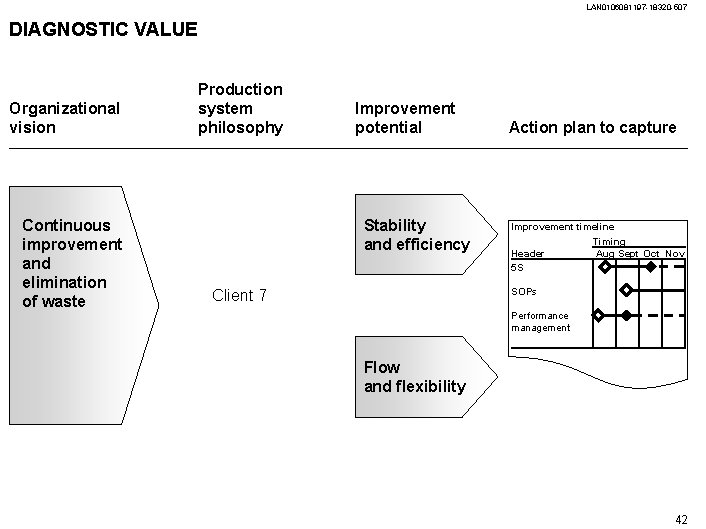
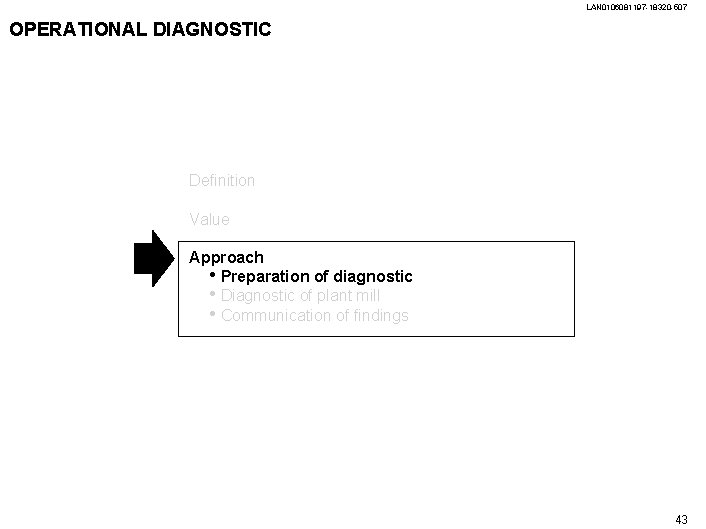
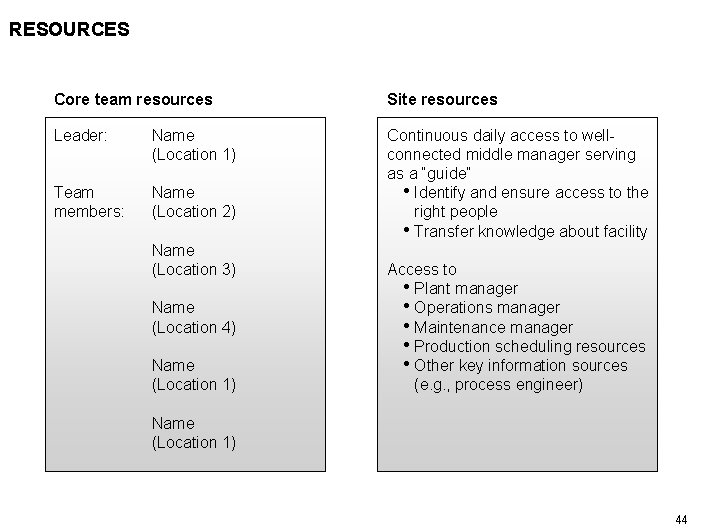

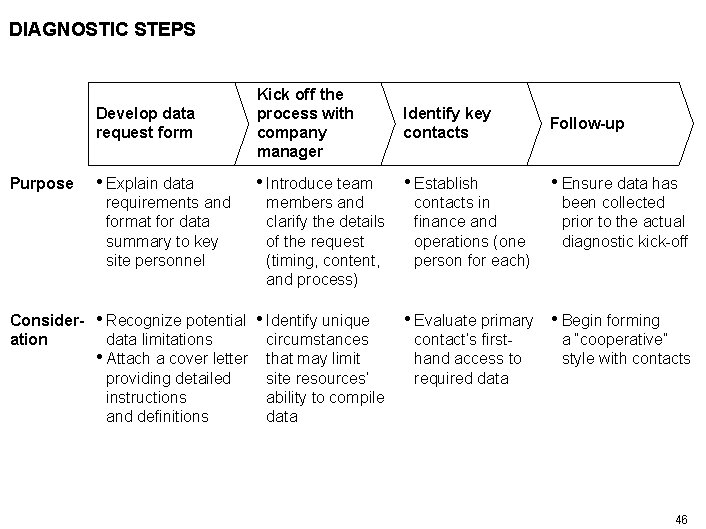
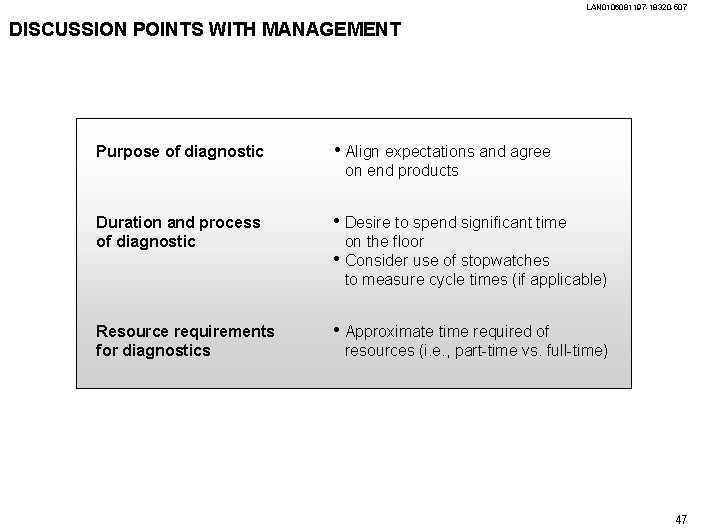
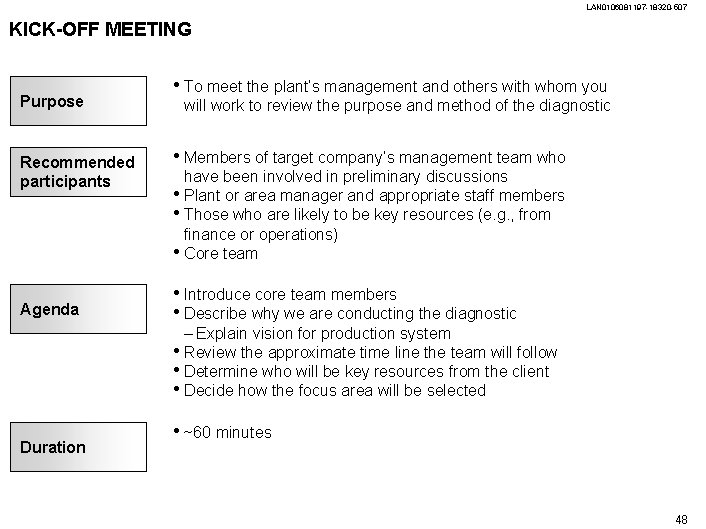
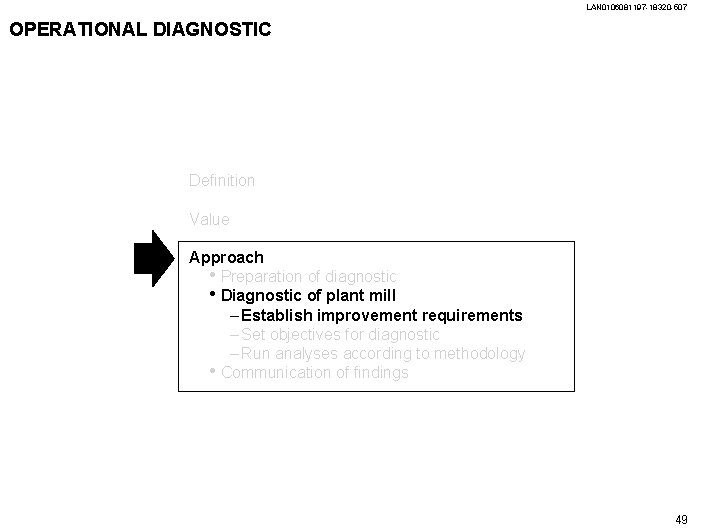
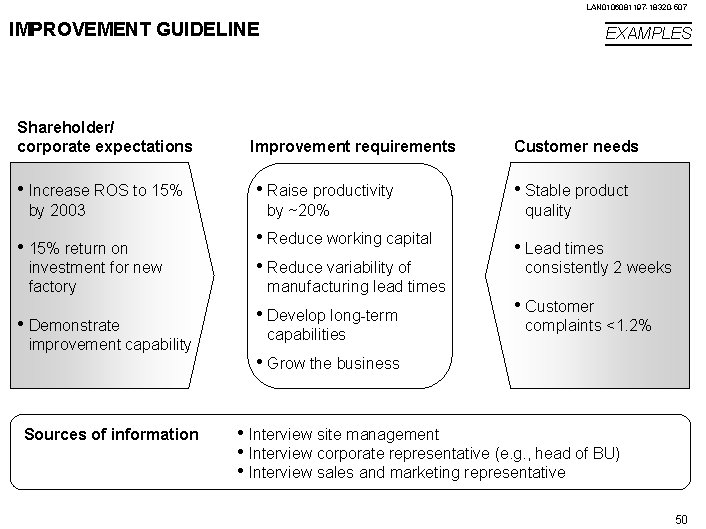
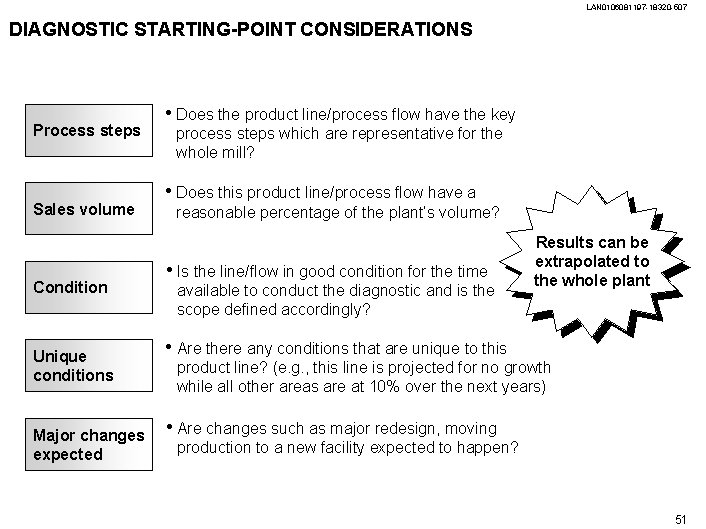
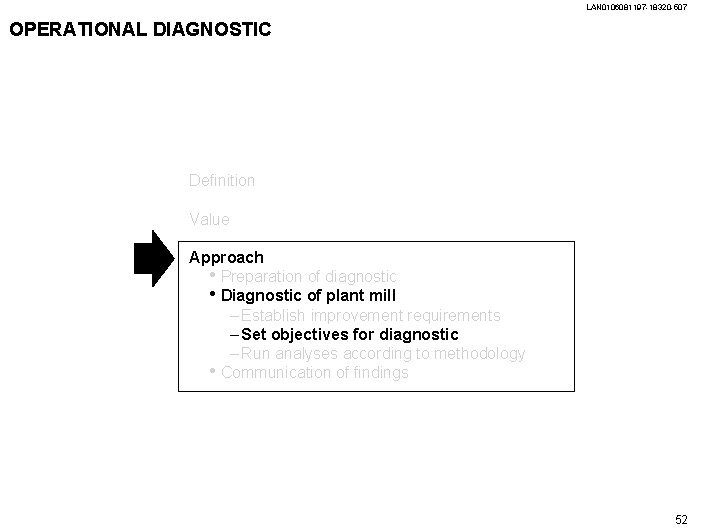
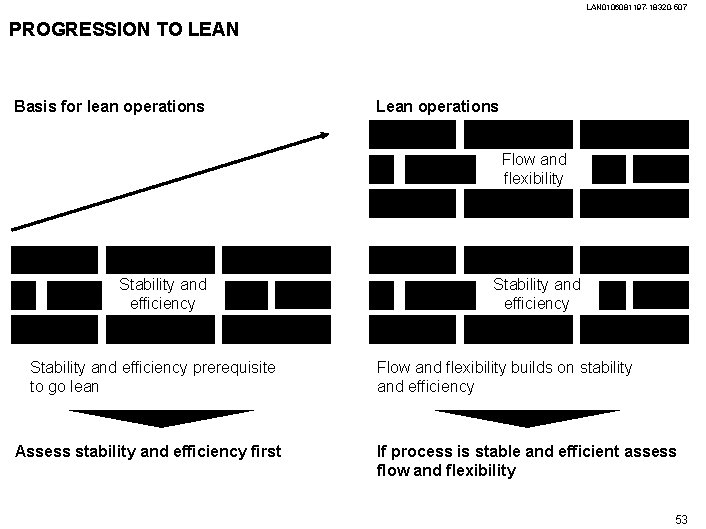
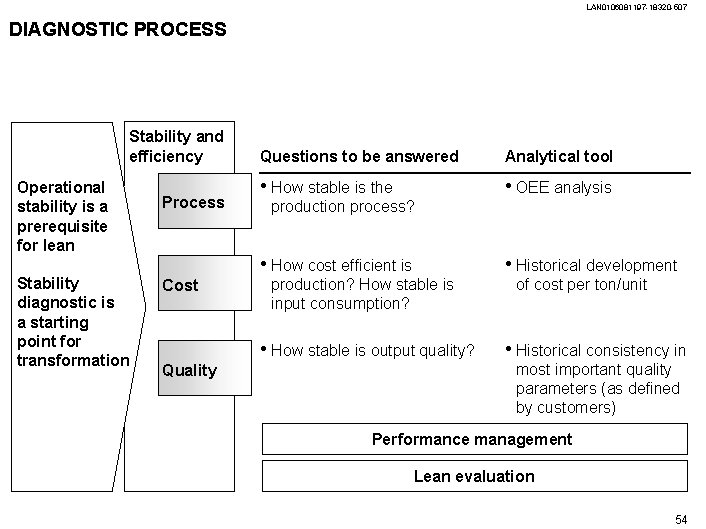
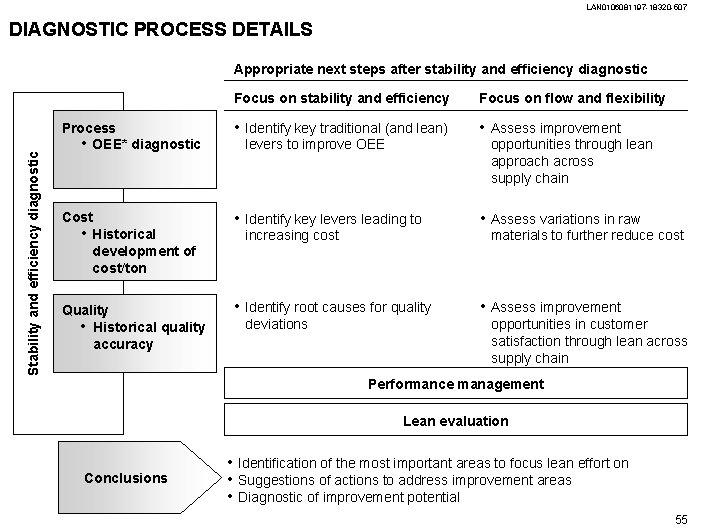
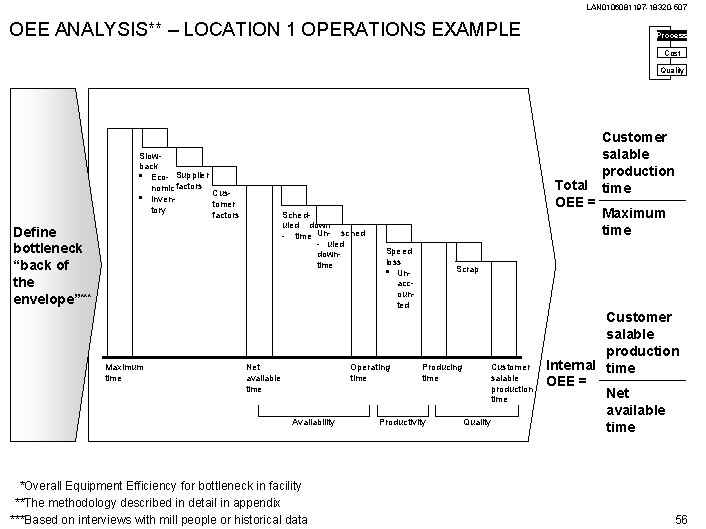
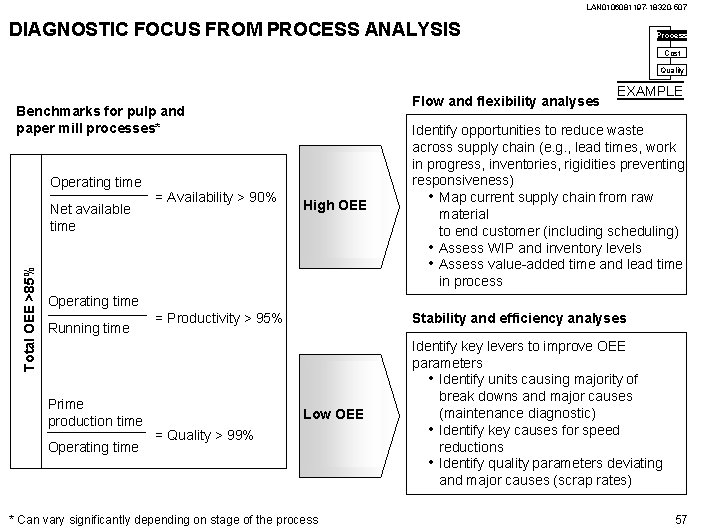
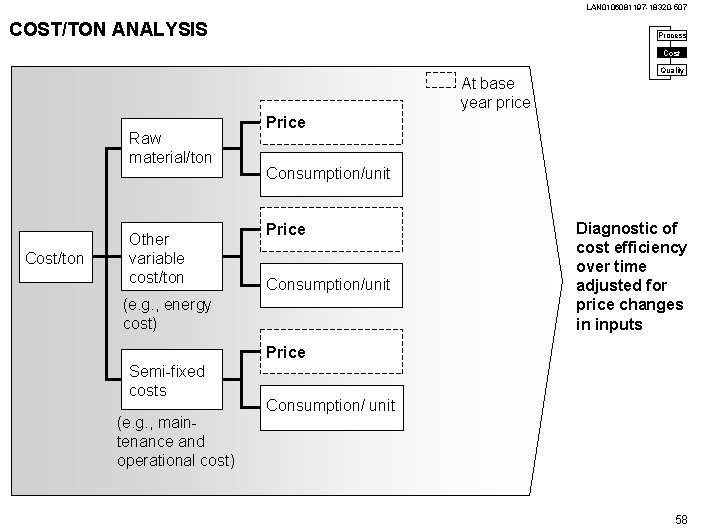
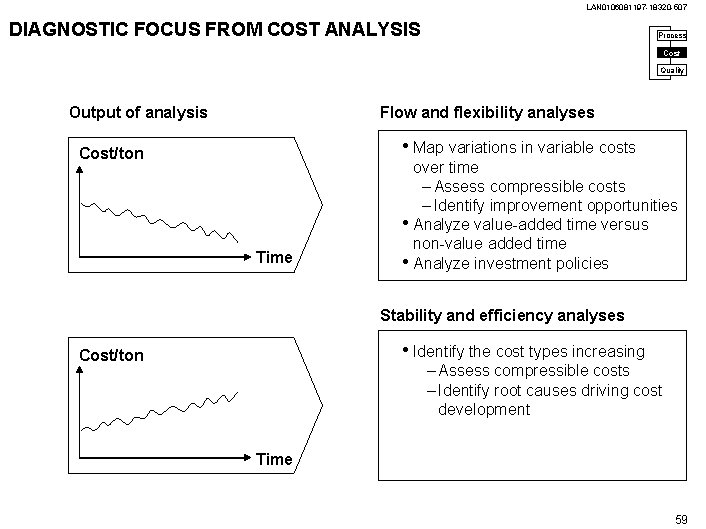
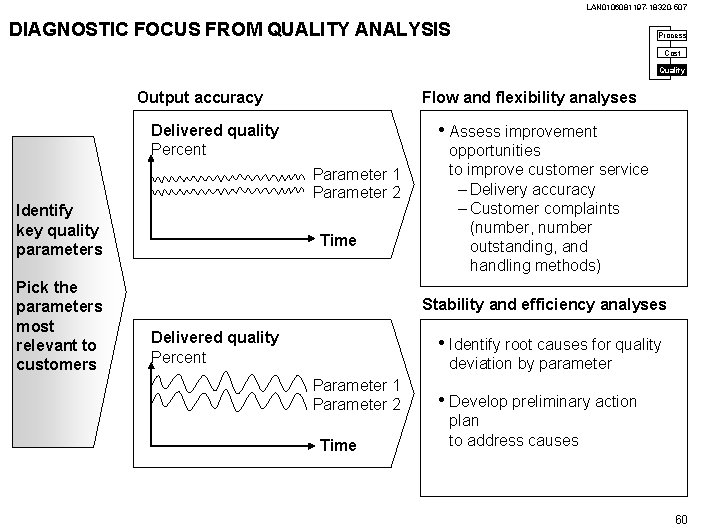
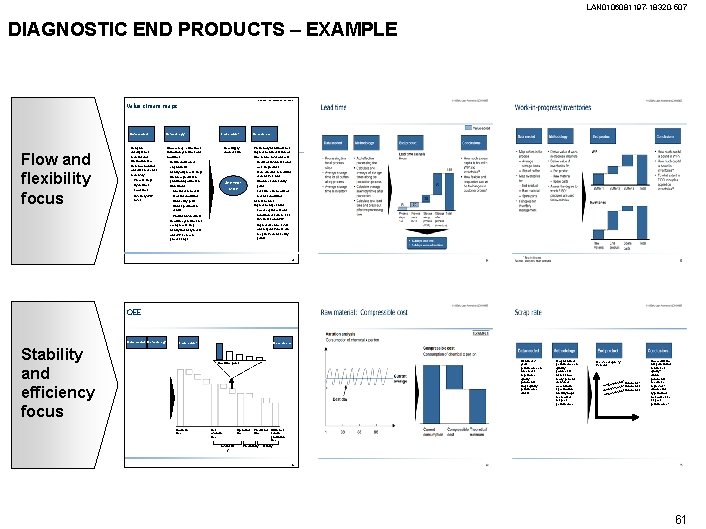
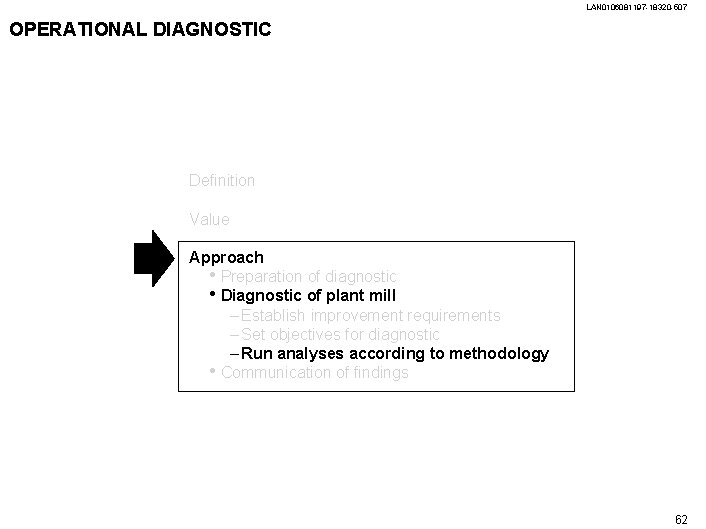
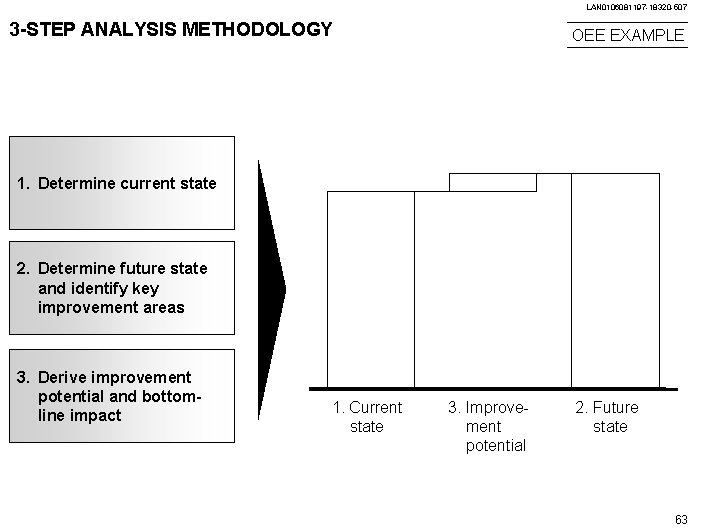
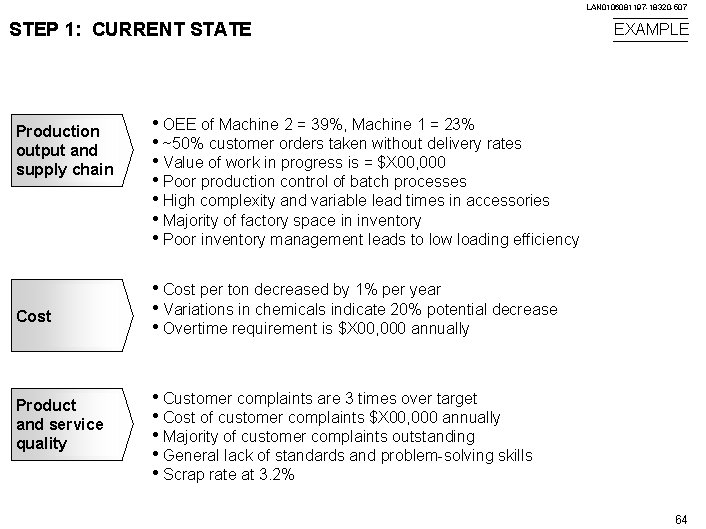
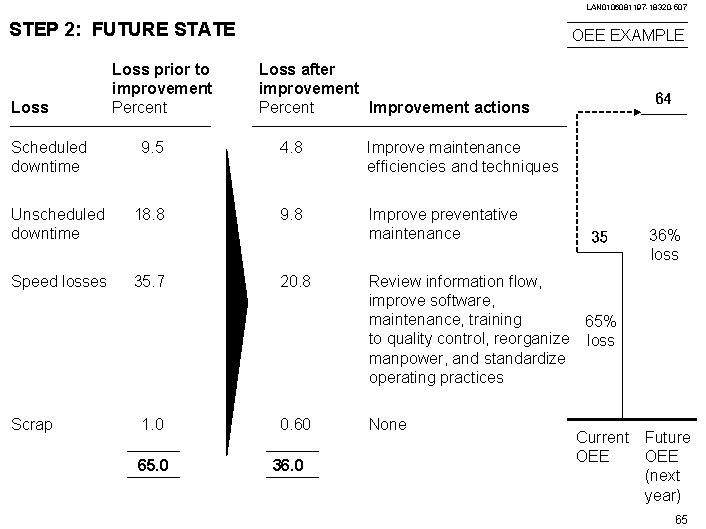
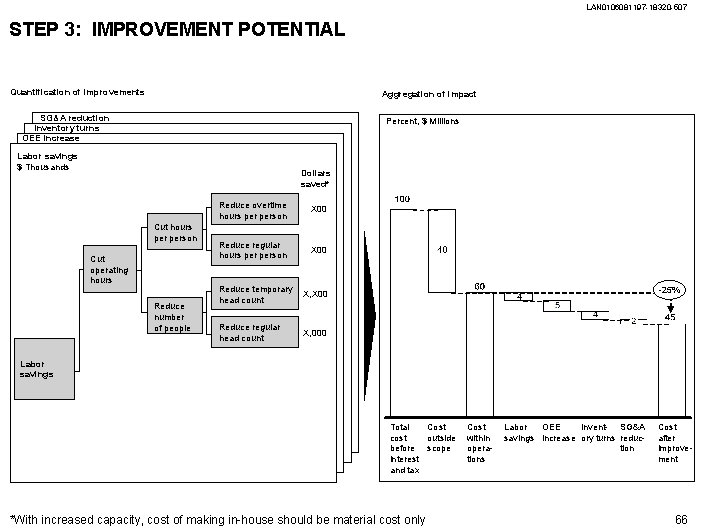
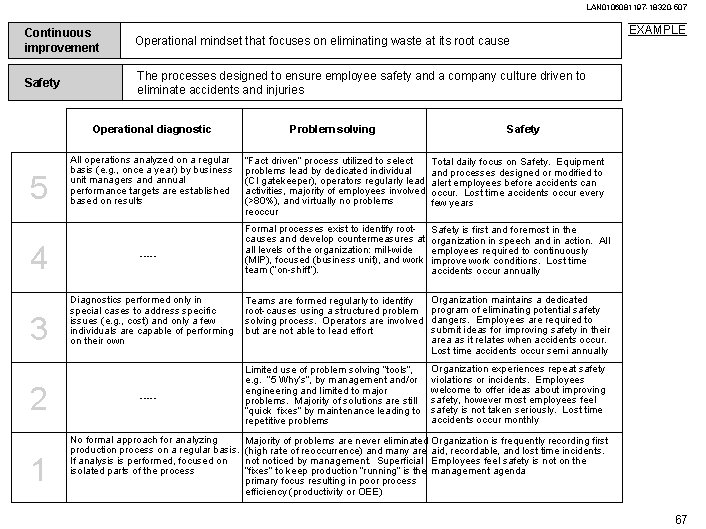
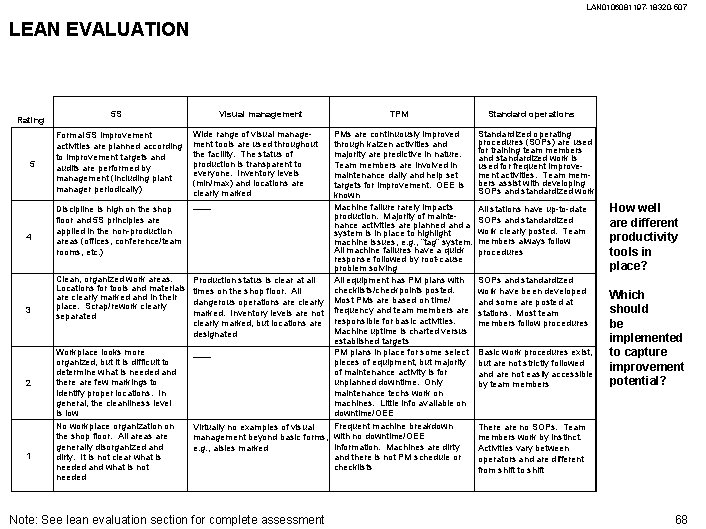
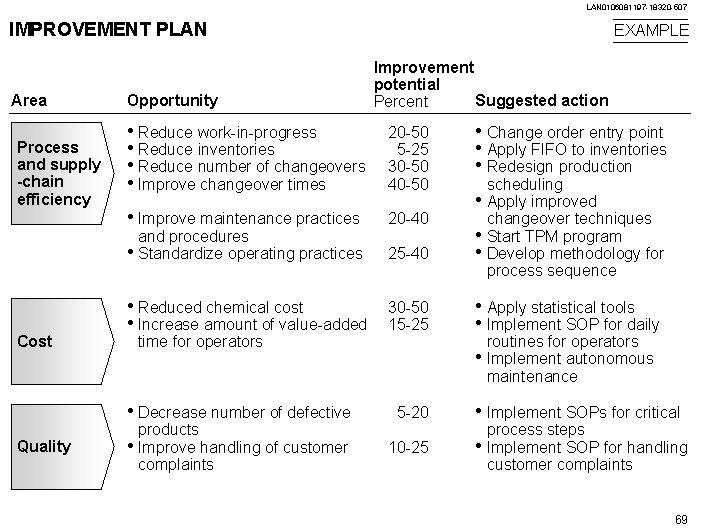
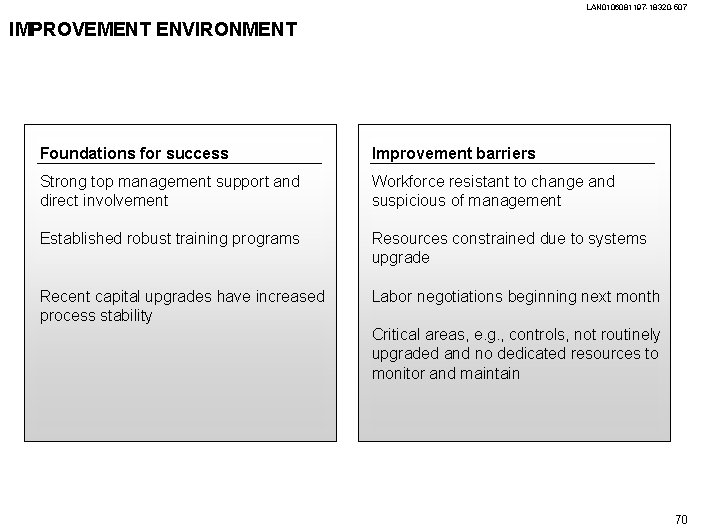
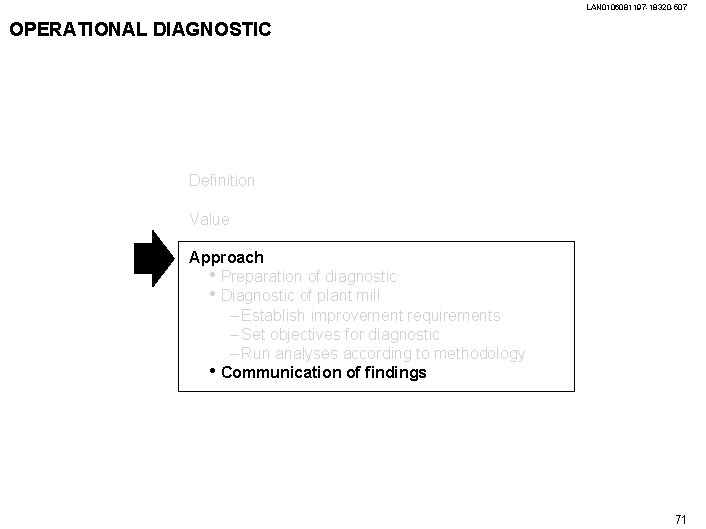
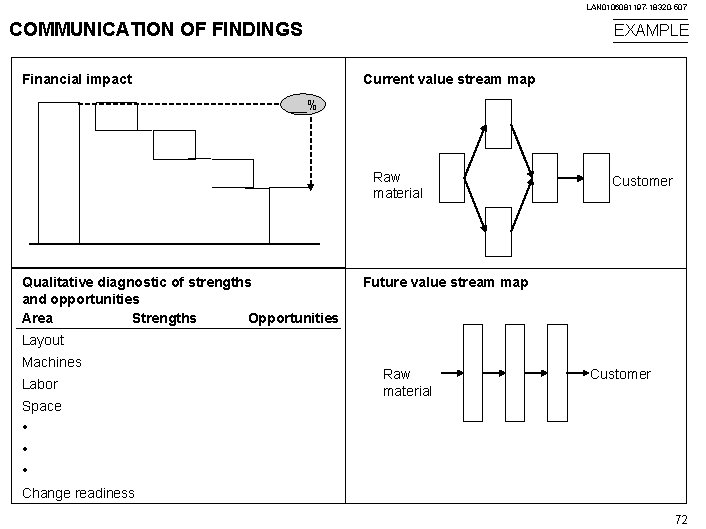
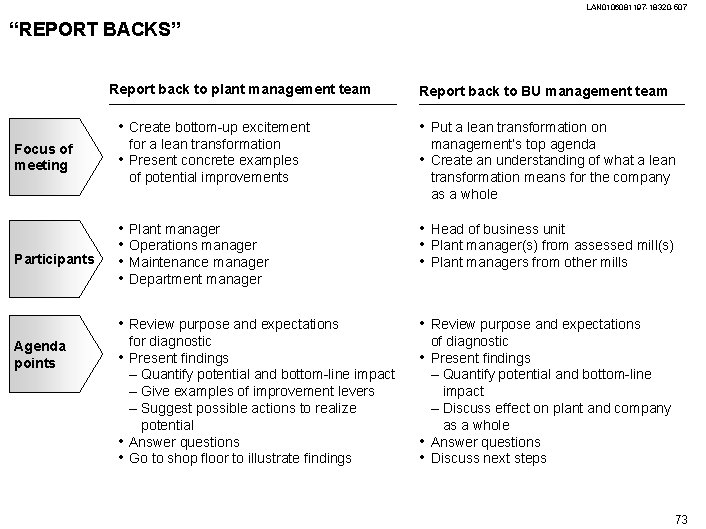
- Slides: 74
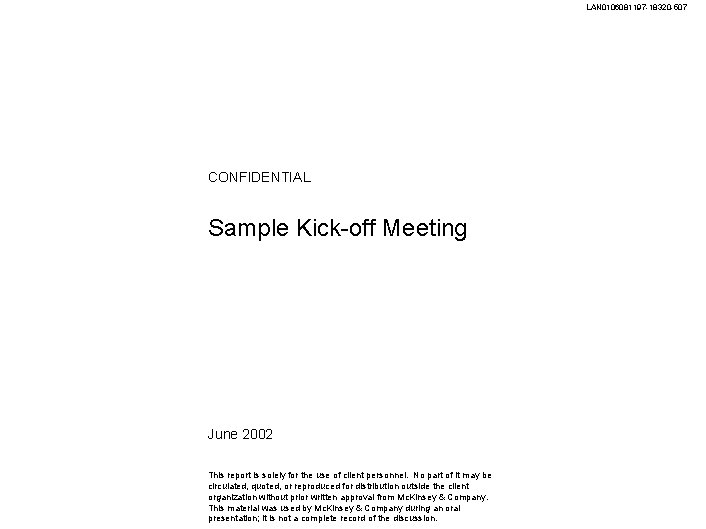
LAN 0106081197 -18320 -507 CONFIDENTIAL Sample Kick-off Meeting June 2002 This report is solely for the use of client personnel. No part of it may be circulated, quoted, or reproduced for distribution outside the client organization without prior written approval from Mc. Kinsey & Company. This material was used by Mc. Kinsey & Company during an oral presentation; it is not a complete record of the discussion.
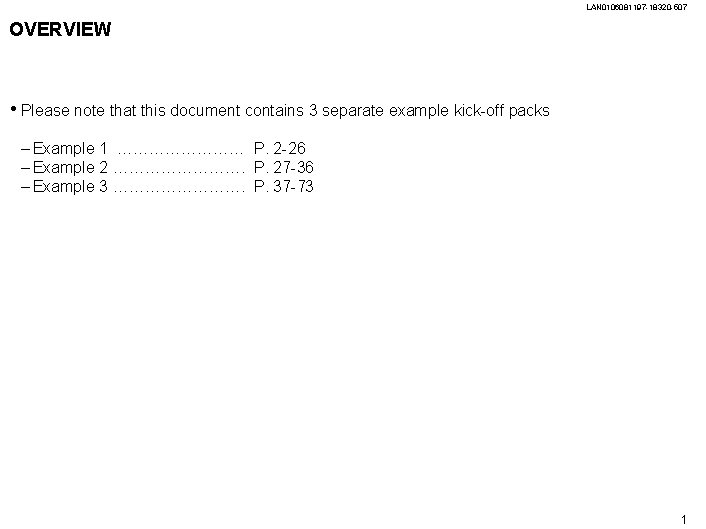
LAN 0106081197 -18320 -507 OVERVIEW • Please note that this document contains 3 separate example kick-off packs – Example 1 ………… P. 2 -26 – Example 2 …………. P. 27 -36 – Example 3 …………. P. 37 -73 1

LAN 0106081197 -18320 -507 KICK OFF MEETING AGENDA 8 a. m. - 10 a. m. • Introductions • Current business situation review – Needs – Opportunities • Mc. Kinsey's approach to capturing opportunity – Ideal and target future states – Transformation model and approach – Typical end products for 2 week diagnostic • Sample work plan – Work plan and resources – Principles and expectations • Questions and discussion 2
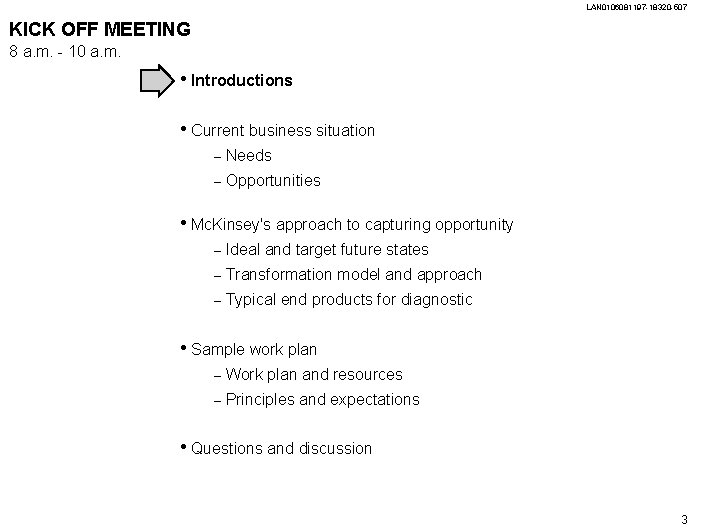
LAN 0106081197 -18320 -507 KICK OFF MEETING 8 a. m. - 10 a. m. • Introductions • Current business situation – Needs – Opportunities • Mc. Kinsey's approach to capturing opportunity – Ideal and target future states – Transformation model and approach – Typical end products for diagnostic • Sample work plan – Work plan and resources – Principles and expectations • Questions and discussion 3
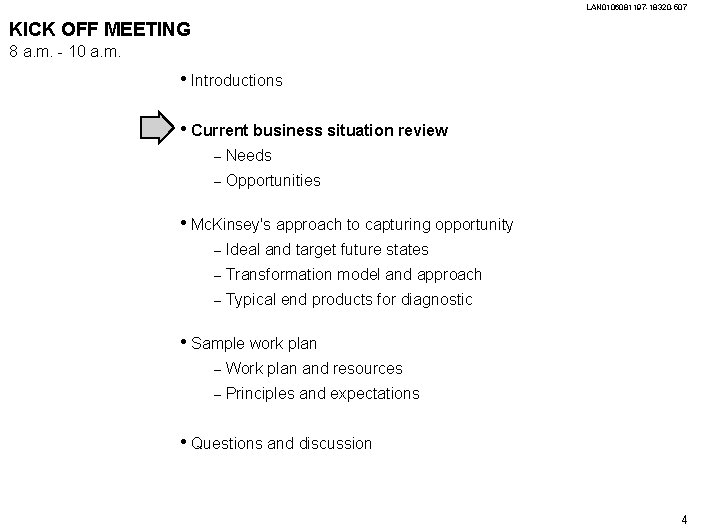
LAN 0106081197 -18320 -507 KICK OFF MEETING 8 a. m. - 10 a. m. • Introductions • Current business situation review – Needs – Opportunities • Mc. Kinsey's approach to capturing opportunity – Ideal and target future states – Transformation model and approach – Typical end products for diagnostic • Sample work plan – Work plan and resources – Principles and expectations • Questions and discussion 4
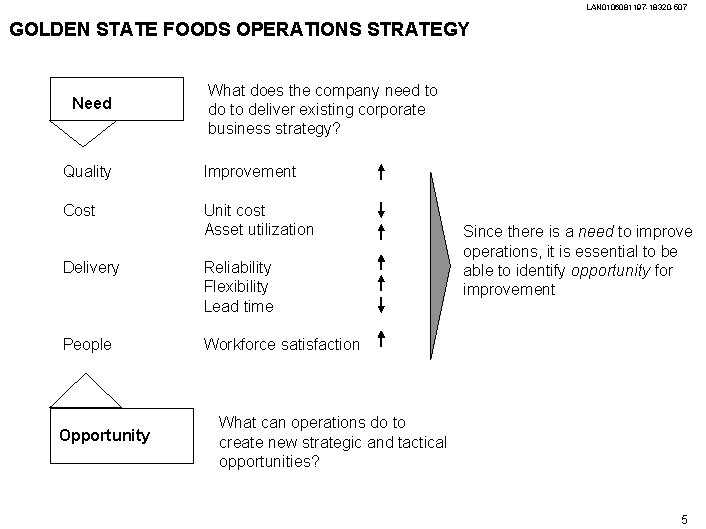
LAN 0106081197 -18320 -507 GOLDEN STATE FOODS OPERATIONS STRATEGY Need What does the company need to do to deliver existing corporate business strategy? Quality Improvement Cost Unit cost Asset utilization Delivery Reliability Flexibility Lead time People Workforce satisfaction Opportunity Since there is a need to improve operations, it is essential to be able to identify opportunity for improvement What can operations do to create new strategic and tactical opportunities? 5
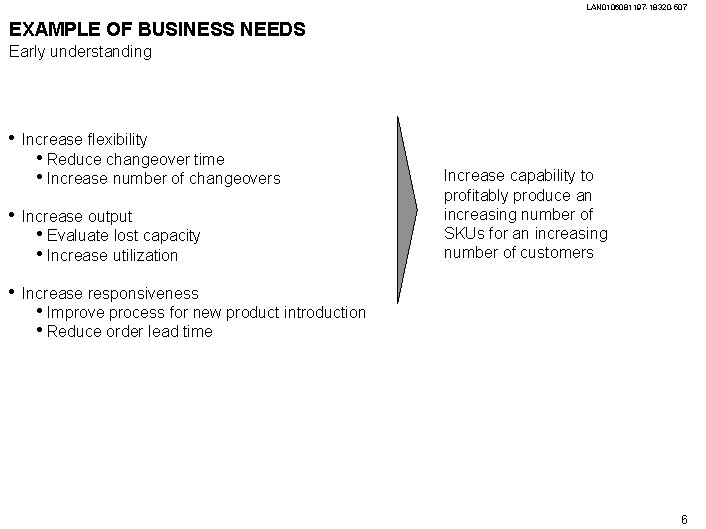
LAN 0106081197 -18320 -507 EXAMPLE OF BUSINESS NEEDS Early understanding • Increase flexibility • Reduce changeover time • Increase number of changeovers • Increase output • Evaluate lost capacity • Increase utilization Increase capability to profitably produce an increasing number of SKUs for an increasing number of customers • Increase responsiveness • Improve process for new product introduction • Reduce order lead time 6
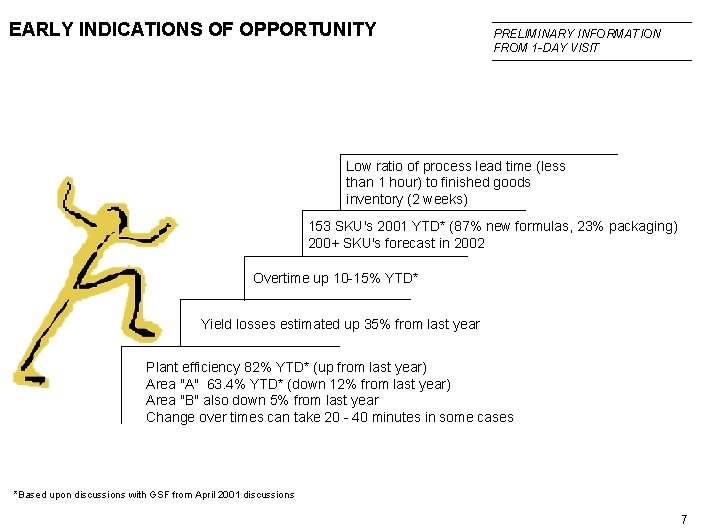
EARLY INDICATIONS OF OPPORTUNITY PRELIMINARY INFORMATION FROM 1 -DAY VISIT Low ratio of process lead time (less than 1 hour) to finished goods inventory (2 weeks) 153 SKU's 2001 YTD* (87% new formulas, 23% packaging) 200+ SKU's forecast in 2002 Overtime up 10 -15% YTD* Yield losses estimated up 35% from last year Plant efficiency 82% YTD* (up from last year) Area "A" 63. 4% YTD* (down 12% from last year) Area "B" also down 5% from last year Change over times can take 20 - 40 minutes in some cases *Based upon discussions with GSF from April 2001 discussions 7
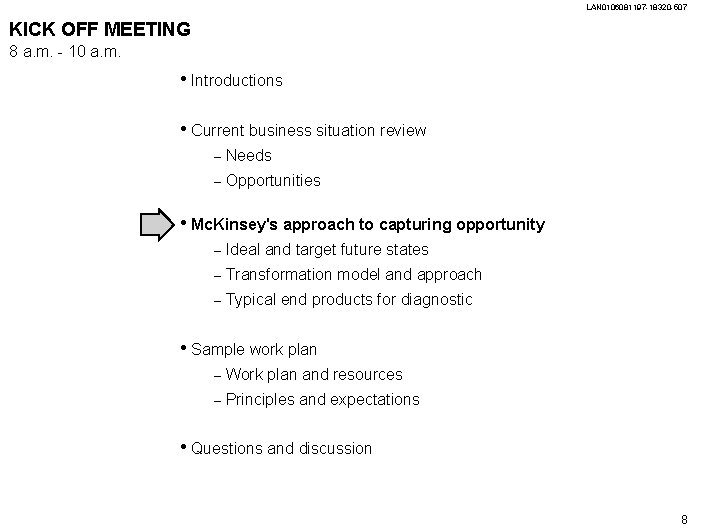
LAN 0106081197 -18320 -507 KICK OFF MEETING 8 a. m. - 10 a. m. • Introductions • Current business situation review – Needs – Opportunities • Mc. Kinsey's approach to capturing opportunity – Ideal and target future states – Transformation model and approach – Typical end products for diagnostic • Sample work plan – Work plan and resources – Principles and expectations • Questions and discussion 8
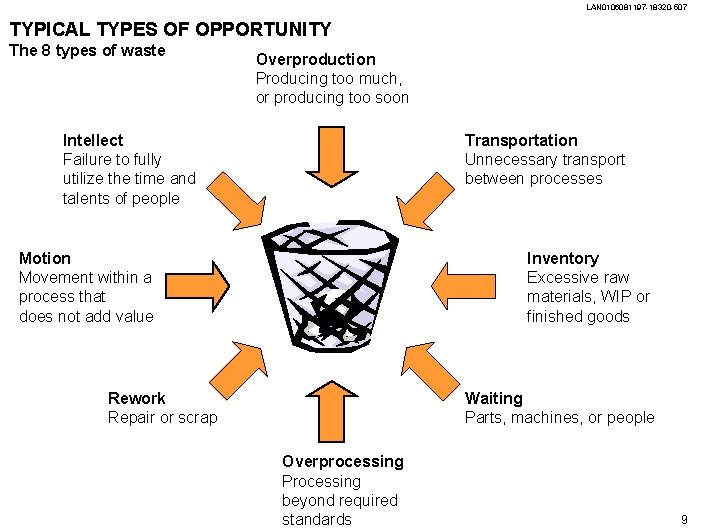
LAN 0106081197 -18320 -507 TYPICAL TYPES OF OPPORTUNITY The 8 types of waste Overproduction Producing too much, or producing too soon Intellect Failure to fully utilize the time and talents of people Transportation Unnecessary transport between processes Motion Movement within a process that does not add value Inventory Excessive raw materials, WIP or finished goods Rework Repair or scrap Source: Mc. Kinsey Waiting Parts, machines, or people Overprocessing Processing beyond required standards 9
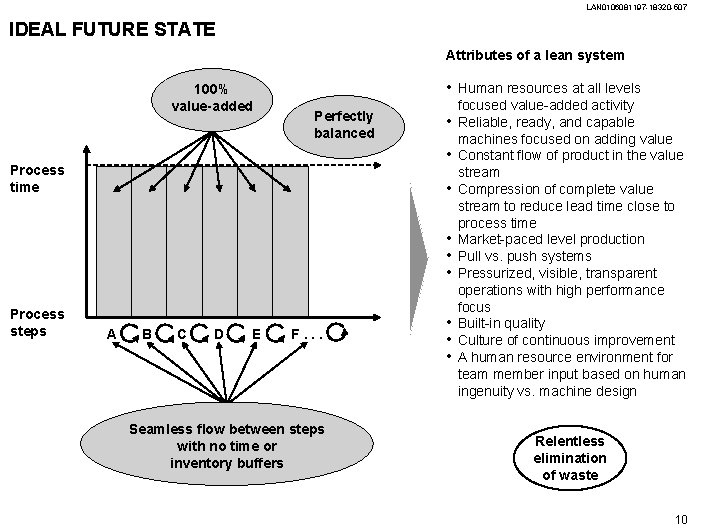
LAN 0106081197 -18320 -507 IDEAL FUTURE STATE Attributes of a lean system 100% value-added • Human resources at all levels Perfectly balanced • • Process time • • Process steps A B C D E F. . . Seamless flow between steps with no time or inventory buffers • • • focused value-added activity Reliable, ready, and capable machines focused on adding value Constant flow of product in the value stream Compression of complete value stream to reduce lead time close to process time Market-paced level production Pull vs. push systems Pressurized, visible, transparent operations with high performance focus Built-in quality Culture of continuous improvement A human resource environment for team member input based on human ingenuity vs. machine design Relentless elimination of waste 10
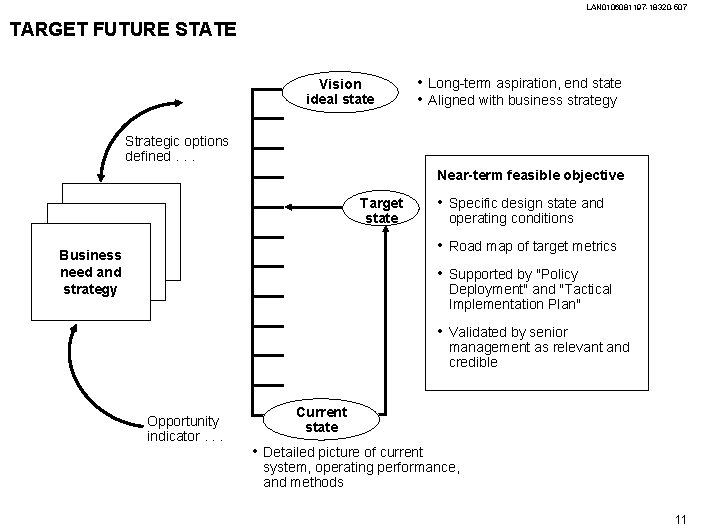
LAN 0106081197 -18320 -507 TARGET FUTURE STATE Vision ideal state • Long-term aspiration, end state • Aligned with business strategy Strategic options defined. . . Near-term feasible objective Target state • Specific design state and operating conditions • Road map of target metrics Business need and strategy • Supported by "Policy Deployment" and "Tactical Implementation Plan" • Validated by senior management as relevant and credible Opportunity indicator. . . Current state • Detailed picture of current system, operating performance, and methods 11
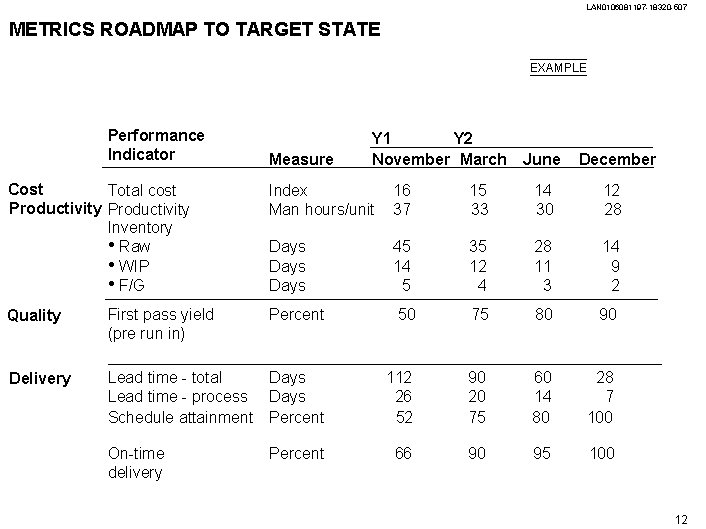
LAN 0106081197 -18320 -507 METRICS ROADMAP TO TARGET STATE EXAMPLE Performance Indicator Cost Total cost Productivity Inventory • Raw • WIP • F/G Measure Y 1 Y 2 November March June December Index Man hours/unit 16 37 15 33 14 30 12 28 Days 45 14 5 35 12 4 28 11 3 14 9 2 Quality First pass yield (pre run in) Percent 50 75 80 90 Delivery Lead time - total Days Lead time - process Days Schedule attainment Percent 112 26 52 90 20 75 60 14 80 28 7 100 66 90 95 100 On-time delivery Percent *Data based on two sample work days, assuming an average possible output of 7 to 8 units 12
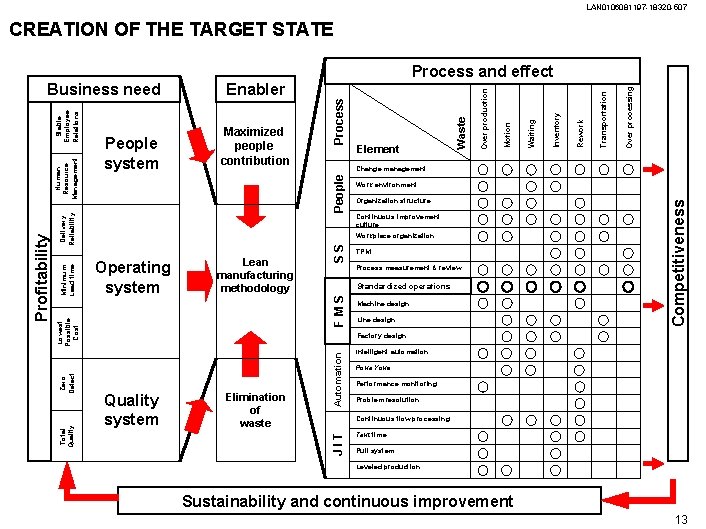
LAN 0106081197 -18320 -507 CREATION OF THE TARGET STATE Over processing Transportation Rework Work environment Organization structure Continuous improvement culture SS TPM Process measurement & review Standardized operations FMS Operating system Inventory Change management Workplace organization Lean manufacturing methodology Waiting Motion Waste Element Machine design Line design Competitiveness Delivery Reliability Factory design Elimination of waste Intelligent automation Poka Yoke Performance monitoring Problem resolution Continuous flow processing JIT Quality system Automation Minimum Lead time Process Maximized people contribution People system Enabler Lowest Possible Cost Zero Defect Total Quality Profitability Human Resource Management Stable Employee Relations Business need Over production Process and effect Takt time Pull system Leveled production Sustainability and continuous improvement 13
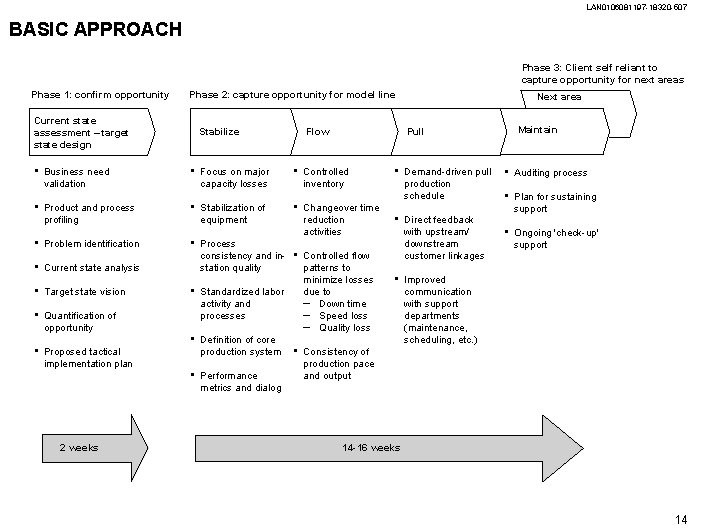
LAN 0106081197 -18320 -507 BASIC APPROACH Phase 3: Client self reliant to capture opportunity for next areas Phase 1: confirm opportunity Phase 2: capture opportunity for model line Current state assessment – target state design Stabilize Flow Business need validation • Focus on major capacity losses • Controlled inventory • Product and process profiling • Stabilization of equipment • • Problem identification • Changeover time reduction activities • Current state analysis • Target state vision • Quantification of opportunity • Proposed tactical implementation plan 2 weeks • Standardized labor activity and processes • Definition of core production system • Performance metrics and dialog • • Maintain Pull • Process consistency and instation quality Next area Controlled flow patterns to minimize losses due to – Down time – Speed loss – Quality loss • • • Demand-driven pull production schedule Direct feedback with upstream/ downstream customer linkages • Auditing process • Plan for sustaining support • Ongoing 'check-up' support Improved communication with support departments (maintenance, scheduling, etc. ) Consistency of production pace and output 14 -16 weeks 14
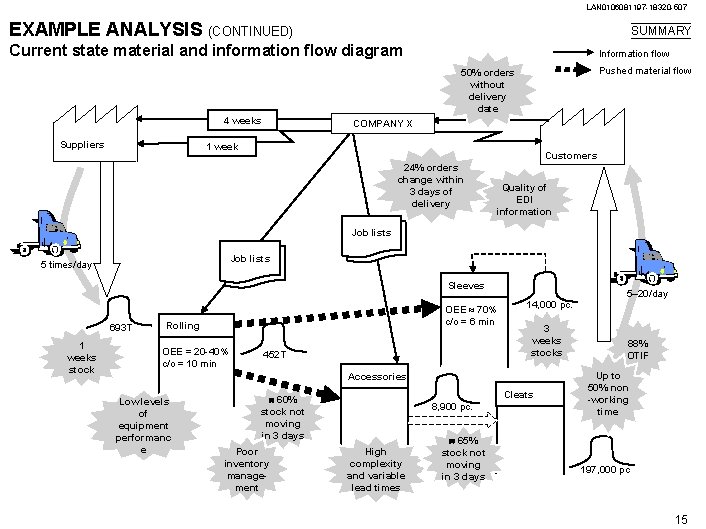
LAN 0106081197 -18320 -507 EXAMPLE ANALYSIS (CONTINUED) SUMMARY Current state material and information flow diagram Information flow Pushed material flow 50% orders without delivery date 4 weeks Suppliers COMPANY X 1 week Customers 24% orders change within 3 days of delivery Quality of EDI information Job lists 5 times/day Sleeves 693 T 1 weeks stock OEE 70% c/o = 6 min Rolling OEE = 20 -40% c/o = 10 min 452 T 14, 000 pc. 3 weeks stocks Accessories Low levels of equipment performanc e Cleats 60% stock not moving in 3 days Poor inventory management 8, 900 pc. High complexity and variable lead times 65% stock not moving in 3 days 5– 20/day 88% OTIF Up to 50% non -working time 197, 000 pc 15
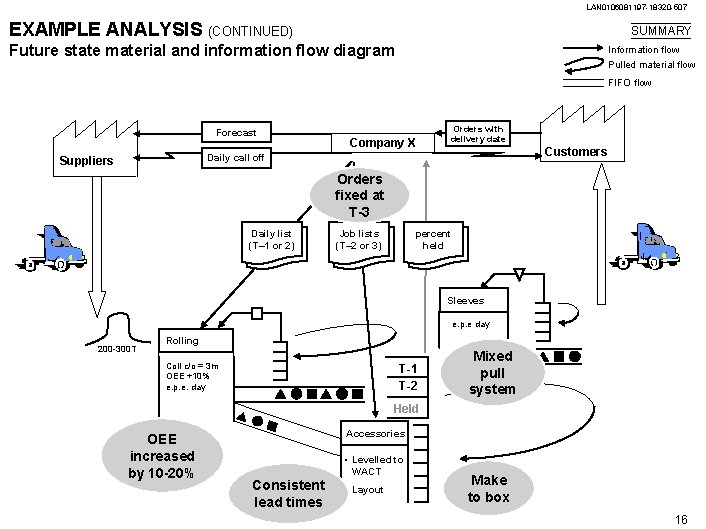
LAN 0106081197 -18320 -507 EXAMPLE ANALYSIS (CONTINUED) SUMMARY Future state material and information flow diagram Information flow Pulled material flow FIFO flow Forecast Company X Orders with delivery date Customers Daily call off Suppliers Orders fixed at T-3 Daily list (T– 1 or 2) Job lists (T– 2 or 3) percent held Sleeves e. p. e day 200 -300 T Rolling Coil c/o = 3 m OEE +10% e. p. e. day T-1 T-2 Mixed pull system Held OEE increased by 10 -20% Accessories • Levelled to WACT Consistent lead times • Layout Make to box 16
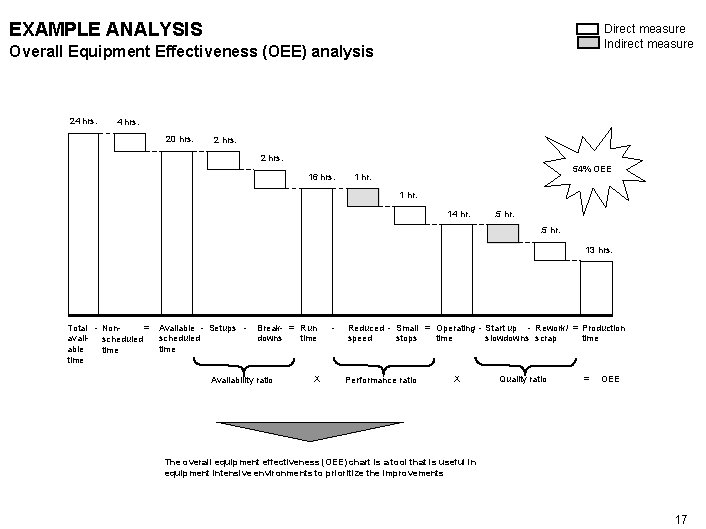
EXAMPLE ANALYSIS Direct measure Indirect measure Overall Equipment Effectiveness (OEE) analysis 24 hrs. 20 hrs. 2 hrs. 16 hrs. 54% OEE 1 hr. 14 hr. . 5 hr. 13 hrs. Total - Non= avail- scheduled able time Available - Setups scheduled time Break- = Run downs time Availability ratio X - Reduced - Small = Operating - Start up - Rework/ = Production speed stops time slowdowns scrap time Performance ratio X Quality ratio = OEE The overall equipment effectiveness (OEE) chart is a tool that is useful in equipment intensive environments to prioritize the improvements 17
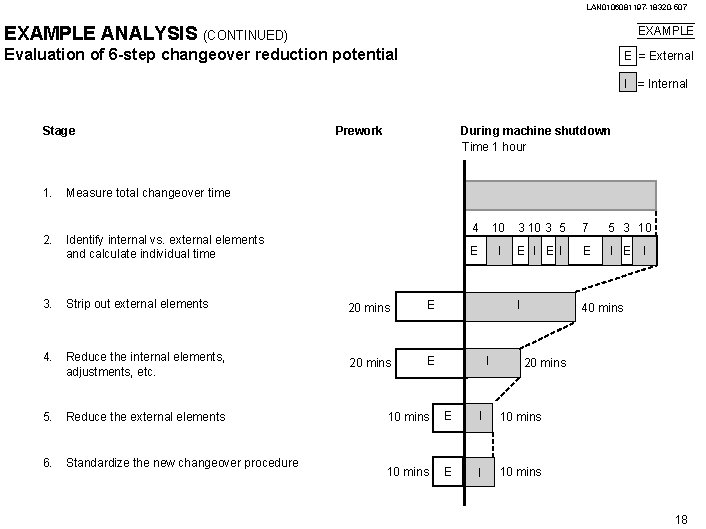
LAN 0106081197 -18320 -507 EXAMPLE ANALYSIS (CONTINUED) EXAMPLE Evaluation of 6 -step changeover reduction potential E = External I = Internal Stage Prework During machine shutdown Time 1 hour 1. Measure total changeover time 2. Identify internal vs. external elements and calculate individual time 3. Strip out external elements 20 mins E 4. Reduce the internal elements, adjustments, etc. 20 mins E 5. Reduce the external elements 6. Standardize the new changeover procedure 4 10 3 5 7 5 3 10 E I E I E I I 40 mins I 20 mins 10 mins E I 10 mins 18
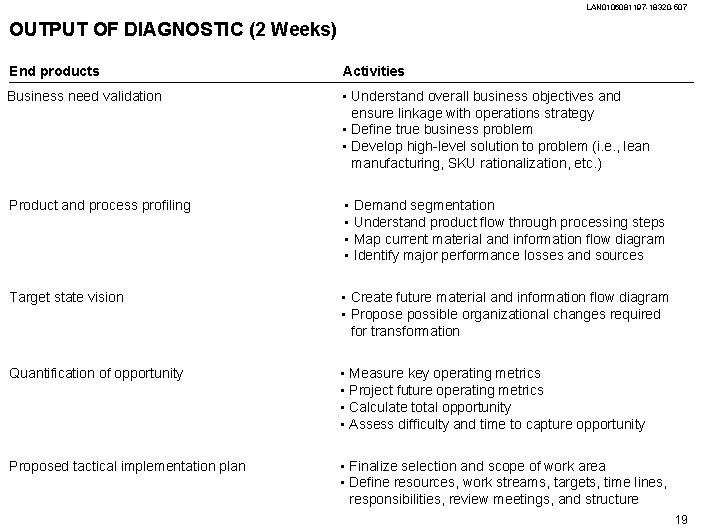
LAN 0106081197 -18320 -507 OUTPUT OF DIAGNOSTIC (2 Weeks) End products Activities Business need validation • Understand overall business objectives and ensure linkage with operations strategy • Define true business problem • Develop high-level solution to problem (i. e. , lean manufacturing, SKU rationalization, etc. ) Product and process profiling • Demand segmentation • Understand product flow through processing steps • Map current material and information flow diagram • Identify major performance losses and sources Target state vision • Create future material and information flow diagram • Propose possible organizational changes required for transformation Quantification of opportunity • Measure key operating metrics • Project future operating metrics • Calculate total opportunity • Assess difficulty and time to capture opportunity Proposed tactical implementation plan • Finalize selection and scope of work area • Define resources, work streams, targets, time lines, responsibilities, review meetings, and structure 19
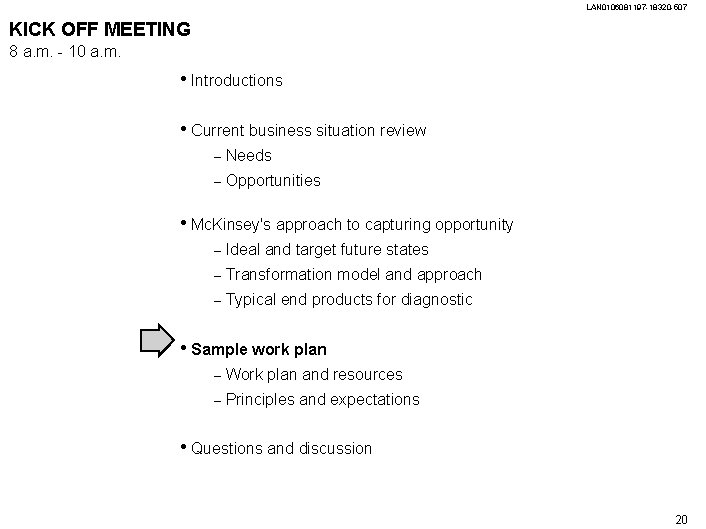
LAN 0106081197 -18320 -507 KICK OFF MEETING 8 a. m. - 10 a. m. • Introductions • Current business situation review – Needs – Opportunities • Mc. Kinsey's approach to capturing opportunity – Ideal and target future states – Transformation model and approach – Typical end products for diagnostic • Sample work plan – Work plan and resources – Principles and expectations • Questions and discussion 20
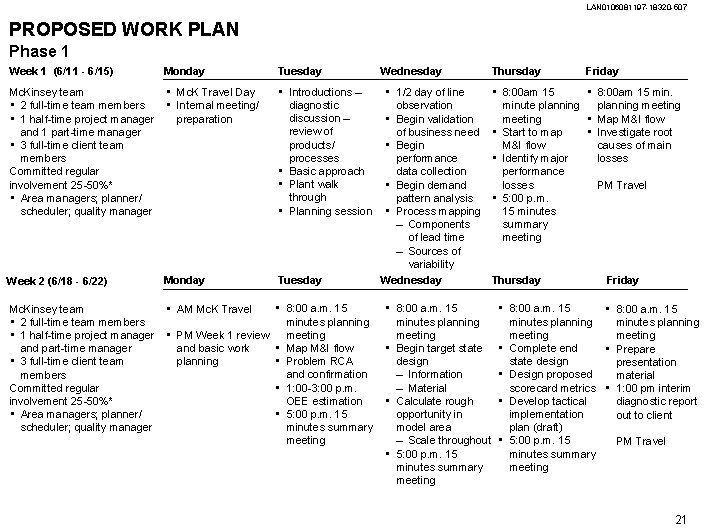
LAN 0106081197 -18320 -507 PROPOSED WORK PLAN Phase 1 Week 1 (6/11 - 6/15) Monday Tuesday Mc. Kinsey team • 2 full-time team members • 1 half-time project manager and 1 part-time manager • 3 full-time client team members Committed regular involvement 25 -50%* • Area managers; planner/ scheduler; quality manager • Mc. K Travel Day • Internal meeting/ • Introductions – Week 2 (6/18 - 6/22) Monday Tuesday Mc. Kinsey team • 2 full-time team members • 1 half-time project manager and part-time manager • 3 full-time client team members Committed regular involvement 25 -50%* • Area managers; planner/ scheduler; quality manager • AM Mc. K Travel • 8: 00 a. m. 15 preparation • • PM Week 1 review and basic work planning • • diagnostic discussion – review of products/ processes Basic approach Plant walk through Planning session minutes planning meeting Map M&I flow Problem RCA and confirmation 1: 00 -3: 00 p. m. OEE estimation 5: 00 p. m. 15 minutes summary meeting Wednesday Thursday • 1/2 day of line Friday • 8: 00 am 15 • observation minute planning • Begin validation meeting • of business need • Start to map • • Begin M&I flow performance • Identify major data collection performance • Begin demand losses pattern analysis • 5: 00 p. m. • Process mapping 15 minutes – Components summary of lead time meeting – Sources of variability Wednesday Thursday • 8: 00 a. m. 15 • • • minutes planning meeting Begin target state design – Information – Material Calculate rough opportunity in model area – Scale throughout 5: 00 p. m. 15 minutes summary meeting 8: 00 am 15 min. planning meeting Map M&I flow Investigate root causes of main losses PM Travel • 8: 00 a. m. 15 • • minutes planning meeting Complete end state design Design proposed scorecard metrics Develop tactical implementation plan (draft) 5: 00 p. m. 15 minutes summary meeting Friday • 8: 00 a. m. 15 • • minutes planning meeting Prepare presentation material 1: 00 pm interim diagnostic report out to client PM Travel 21
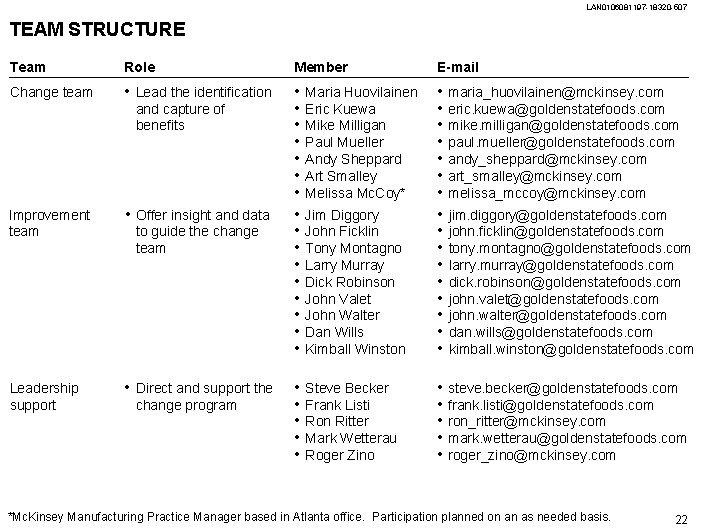
LAN 0106081197 -18320 -507 TEAM STRUCTURE Team Role Member E-mail Change team • Lead the identification • Maria Huovilainen • Eric Kuewa • Mike Milligan • Paul Mueller • Andy Sheppard • Art Smalley • Melissa Mc. Coy* • Jim Diggory • John Ficklin • Tony Montagno • Larry Murray • Dick Robinson • John Valet • John Walter • Dan Wills • Kimball Winston • maria_huovilainen@mckinsey. com • eric. kuewa@goldenstatefoods. com • mike. milligan@goldenstatefoods. com • paul. mueller@goldenstatefoods. com • andy_sheppard@mckinsey. com • art_smalley@mckinsey. com • melissa_mccoy@mckinsey. com • jim. diggory@goldenstatefoods. com • john. ficklin@goldenstatefoods. com • tony. montagno@goldenstatefoods. com • larry. murray@goldenstatefoods. com • dick. robinson@goldenstatefoods. com • john. valet@goldenstatefoods. com • john. walter@goldenstatefoods. com • dan. wills@goldenstatefoods. com • kimball. winston@goldenstatefoods. com and capture of benefits Improvement team • Offer insight and data Leadership support • Direct and support the • change program • • to guide the change team Steve Becker Frank Listi Ron Ritter Mark Wetterau Roger Zino • • • steve. becker@goldenstatefoods. com frank. listi@goldenstatefoods. com ron_ritter@mckinsey. com mark. wetterau@goldenstatefoods. com roger_zino@mckinsey. com *Mc. Kinsey Manufacturing Practice Manager based in Atlanta office. Participation planned on an as needed basis. 22
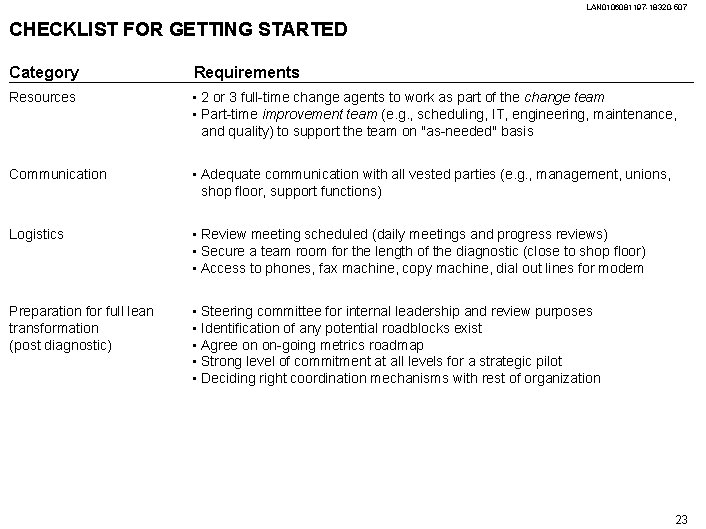
LAN 0106081197 -18320 -507 CHECKLIST FOR GETTING STARTED Category Requirements Resources • 2 or 3 full-time change agents to work as part of the change team • Part-time improvement team (e. g. , scheduling, IT, engineering, maintenance, and quality) to support the team on "as-needed" basis Communication • Adequate communication with all vested parties (e. g. , management, unions, shop floor, support functions) Logistics • Review meeting scheduled (daily meetings and progress reviews) • Secure a team room for the length of the diagnostic (close to shop floor) • Access to phones, fax machine, copy machine, dial out lines for modem Preparation for full lean transformation (post diagnostic) • Steering committee for internal leadership and review purposes • Identification of any potential roadblocks exist • Agree on on-going metrics roadmap • Strong level of commitment at all levels for a strategic pilot • Deciding right coordination mechanisms with rest of organization 23
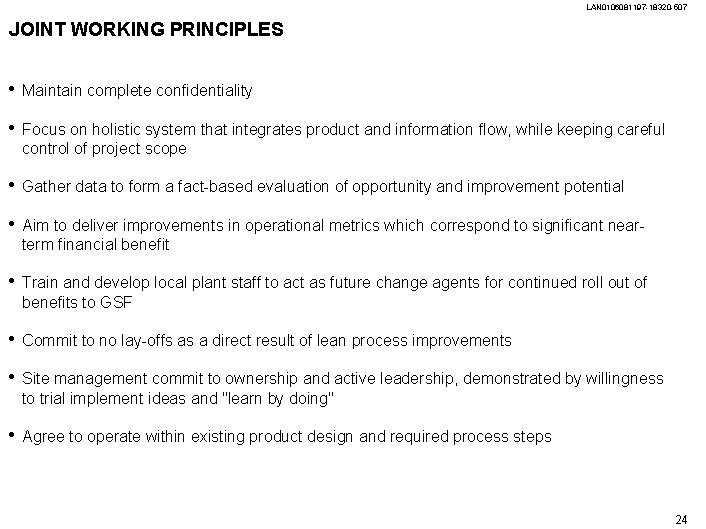
LAN 0106081197 -18320 -507 JOINT WORKING PRINCIPLES • Maintain complete confidentiality • Focus on holistic system that integrates product and information flow, while keeping careful control of project scope • Gather data to form a fact-based evaluation of opportunity and improvement potential • Aim to deliver improvements in operational metrics which correspond to significant nearterm financial benefit • Train and develop local plant staff to act as future change agents for continued roll out of benefits to GSF • Commit to no lay-offs as a direct result of lean process improvements • Site management commit to ownership and active leadership, demonstrated by willingness to trial implement ideas and "learn by doing" • Agree to operate within existing product design and required process steps 24
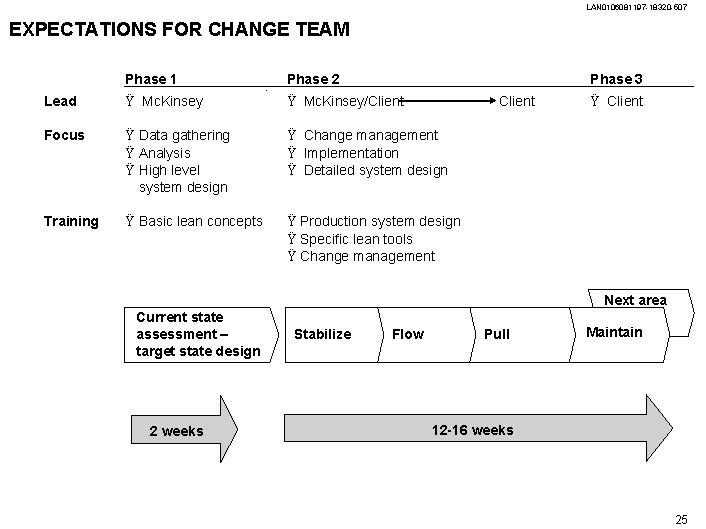
LAN 0106081197 -18320 -507 EXPECTATIONS FOR CHANGE TEAM Lead Focus Training Phase 1 Phase 2 Mc. Kinsey Ÿ Ÿ Data gathering Ÿ Analysis Ÿ High level system design Ÿ Basic lean concepts Ÿ Ÿ Ÿ Ÿ Phase 3 Mc. Kinsey/Client Change management Implementation Detailed system design Ÿ Production system design Ÿ Specific lean tools Ÿ Change management Client Ÿ Next area Current state assessment – target state design 2 weeks Stabilize Flow Pull Maintain 12 -16 weeks 25
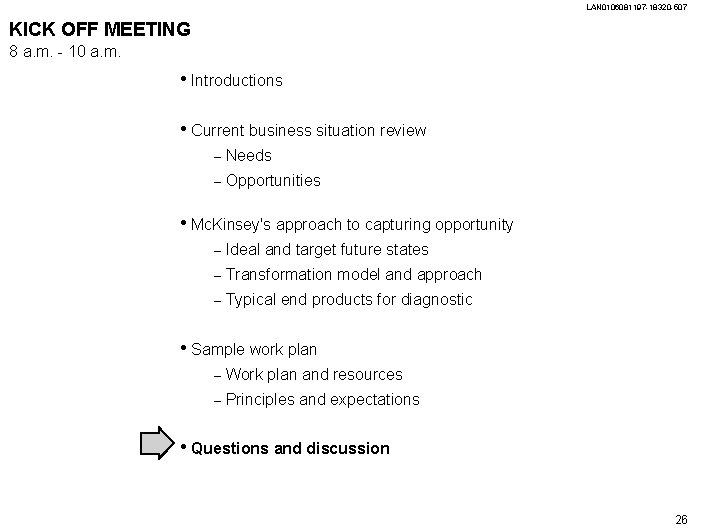
LAN 0106081197 -18320 -507 KICK OFF MEETING 8 a. m. - 10 a. m. • Introductions • Current business situation review – Needs – Opportunities • Mc. Kinsey's approach to capturing opportunity – Ideal and target future states – Transformation model and approach – Typical end products for diagnostic • Sample work plan – Work plan and resources – Principles and expectations • Questions and discussion 26
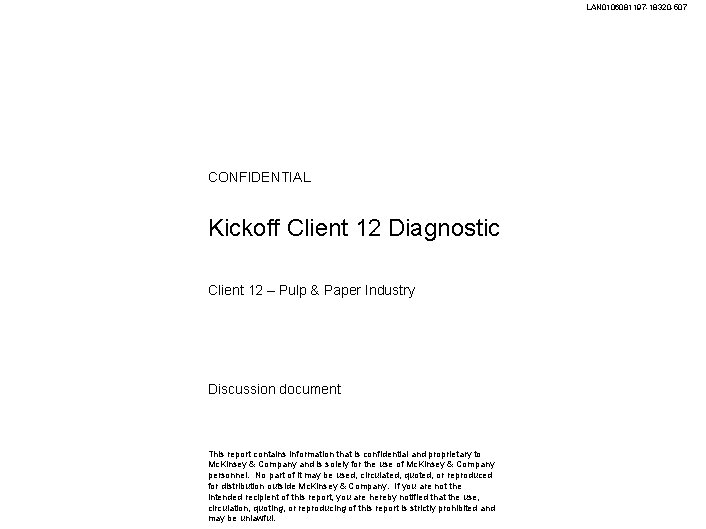
LAN 0106081197 -18320 -507 CONFIDENTIAL Kickoff Client 12 Diagnostic Client 12 – Pulp & Paper Industry Discussion document This report contains information that is confidential and proprietary to Mc. Kinsey & Company and is solely for the use of Mc. Kinsey & Company personnel. No part of it may be used, circulated, quoted, or reproduced for distribution outside Mc. Kinsey & Company. If you are not the intended recipient of this report, you are hereby notified that the use, circulation, quoting, or reproducing of this report is strictly prohibited and may be unlawful.
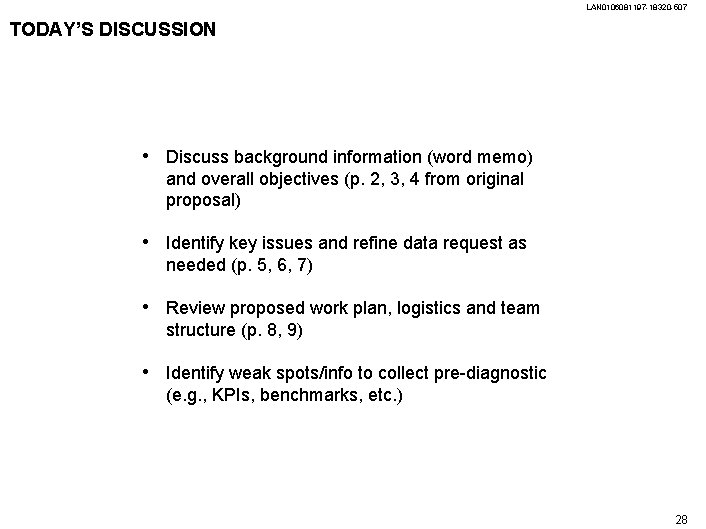
LAN 0106081197 -18320 -507 TODAY’S DISCUSSION • Discuss background information (word memo) and overall objectives (p. 2, 3, 4 from original proposal) • Identify key issues and refine data request as needed (p. 5, 6, 7) • Review proposed work plan, logistics and team structure (p. 8, 9) • Identify weak spots/info to collect pre-diagnostic (e. g. , KPIs, benchmarks, etc. ) 28
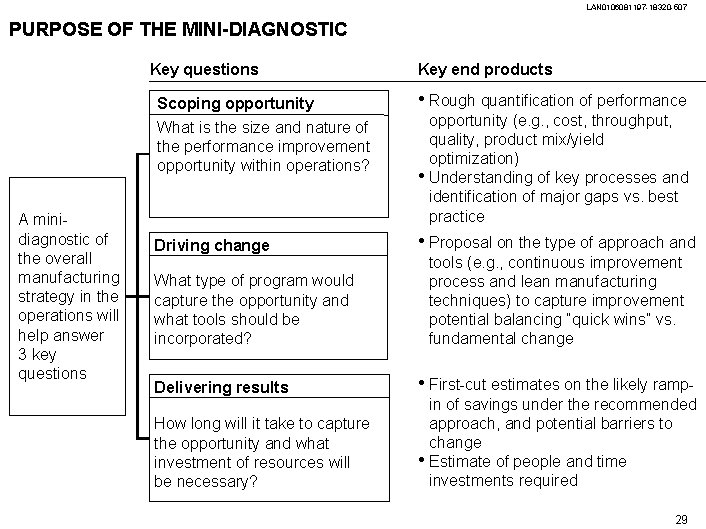
LAN 0106081197 -18320 -507 PURPOSE OF THE MINI-DIAGNOSTIC Key questions A minidiagnostic of the overall manufacturing strategy in the operations will help answer 3 key questions Key end products Scoping opportunity What is the size and nature of the performance improvement opportunity within operations? • Rough quantification of performance Driving change • Proposal on the type of approach and What type of program would capture the opportunity and what tools should be incorporated? Delivering results How long will it take to capture the opportunity and what investment of resources will be necessary? opportunity (e. g. , cost, throughput, quality, product mix/yield optimization) • Understanding of key processes and identification of major gaps vs. best practice tools (e. g. , continuous improvement process and lean manufacturing techniques) to capture improvement potential balancing “quick wins” vs. fundamental change • First-cut estimates on the likely rampin of savings under the recommended approach, and potential barriers to change • Estimate of people and time investments required 29

LAN 0106081197 -18320 -507 PROPOSED APPROACH: 10 -DAY DIAGNOSTIC PROCESS Phase 1 Phase 2 Phase 3 Data request and preparation On-site observations and analysis Synthesis and presentation Day (-10) - 2 • Gather data (as much as possible) • • prior to on-site visit to maximize value of visit (data request sent in advance with some minor discussions to clarify data) Conduct 1 -2 -day visit at head office to review – The organization – Product mix and flows from woodlands to customers and key decisions drivers (e. g. , margins by grade, needs and profitability of customer segments) – Corporate decision processes influencing operations – e. g. , production planning process – Unique conditions at facilities to visit Hold introductory discussions with key managers to refine approach and identify improvement hypotheses 5 days • Visit, observe, and conduct • analysis of the operation(s) across 3 areas – Operations performance and potential (cost, throughput, quality, material flow, etc. ) – Core process performance (order-to-ship, maintenance management, CI, etc. ) and organizational design – Barriers to success Identify major improvement areas 3 days Synthesize the results of the effort • Rough estimate of size and nature of the opportunity • How to capture it and where to start • Perspective on resource requirements and barriers to success • High-level estimate on ramp-in of savings for a well-executed program 30
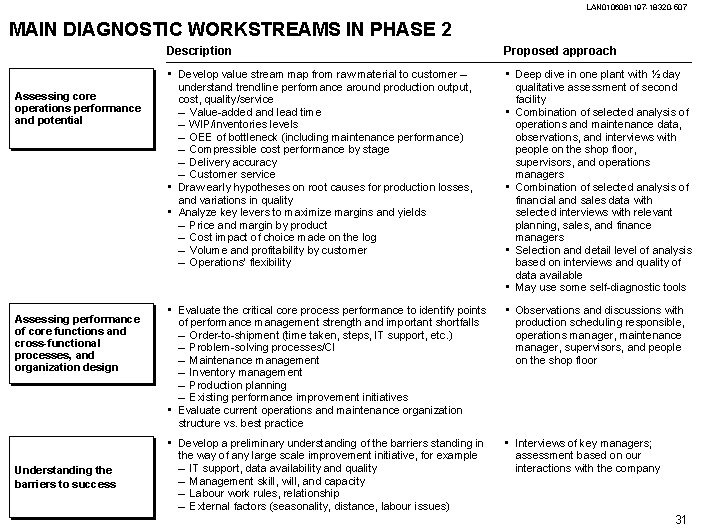
LAN 0106081197 -18320 -507 MAIN DIAGNOSTIC WORKSTREAMS IN PHASE 2 Description Proposed approach • Develop value stream map from raw material to customer – • Deep dive in one plant with ½ day Assessing core operations performance and potential • • understand trendline performance around production output, cost, quality/service – Value-added and lead time – WIP/inventories levels – OEE of bottleneck (including maintenance performance) – Compressible cost performance by stage – Delivery accuracy – Customer service Draw early hypotheses on root causes for production losses, and variations in quality Analyze key levers to maximize margins and yields – Price and margin by product – Cost impact of choice made on the log – Volume and profitability by customer – Operations’ flexibility • • Assessing performance of core functions and cross-functional processes, and organization design • Evaluate the critical core process performance to identify points • of performance management strength and important shortfalls – Order-to-shipment (time taken, steps, IT support, etc. ) – Problem-solving processes/CI – Maintenance management – Inventory management – Production planning – Existing performance improvement initiatives Evaluate current operations and maintenance organization structure vs. best practice • Develop a preliminary understanding of the barriers standing in Understanding the barriers to success the way of any large scale improvement initiative, for example – IT support, data availability and quality – Management skill, will, and capacity – Labour work rules, relationship – External factors (seasonality, distance, labour issues) qualitative assessment of second facility Combination of selected analysis of operations and maintenance data, observations, and interviews with people on the shop floor, supervisors, and operations managers Combination of selected analysis of financial and sales data with selected interviews with relevant planning, sales, and finance managers Selection and detail level of analysis based on interviews and quality of data available May use some self-diagnostic tools • Observations and discussions with production scheduling responsible, operations manager, maintenance manager, supervisors, and people on the shop floor • Interviews of key managers; assessment based on our interactions with the company 31
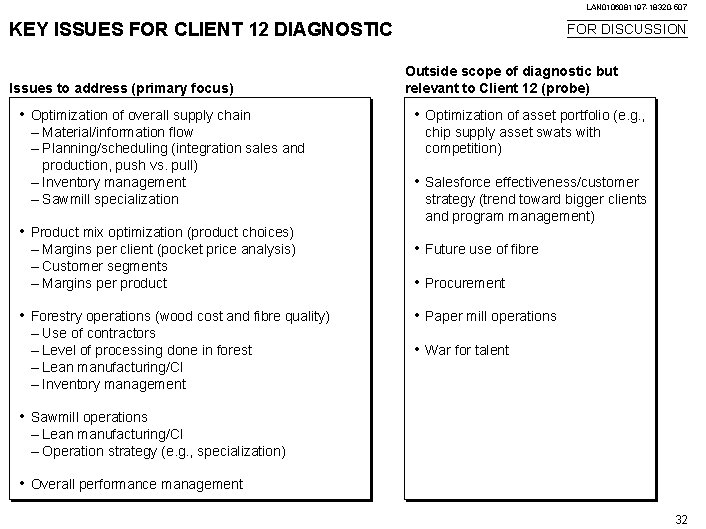
LAN 0106081197 -18320 -507 KEY ISSUES FOR CLIENT 12 DIAGNOSTIC Issues to address (primary focus) • Optimization of overall supply chain – Material/information flow – Planning/scheduling (integration sales and production, push vs. pull) – Inventory management – Sawmill specialization • Product mix optimization (product choices) – Margins per client (pocket price analysis) – Customer segments – Margins per product • Forestry operations (wood cost and fibre quality) – Use of contractors – Level of processing done in forest – Lean manufacturing/CI – Inventory management FOR DISCUSSION Outside scope of diagnostic but relevant to Client 12 (probe) • Optimization of asset portfolio (e. g. , chip supply asset swats with competition) • Salesforce effectiveness/customer strategy (trend toward bigger clients and program management) • Future use of fibre • Procurement • Paper mill operations • War for talent • Sawmill operations – Lean manufacturing/CI – Operation strategy (e. g. , specialization) • Overall performance management 32
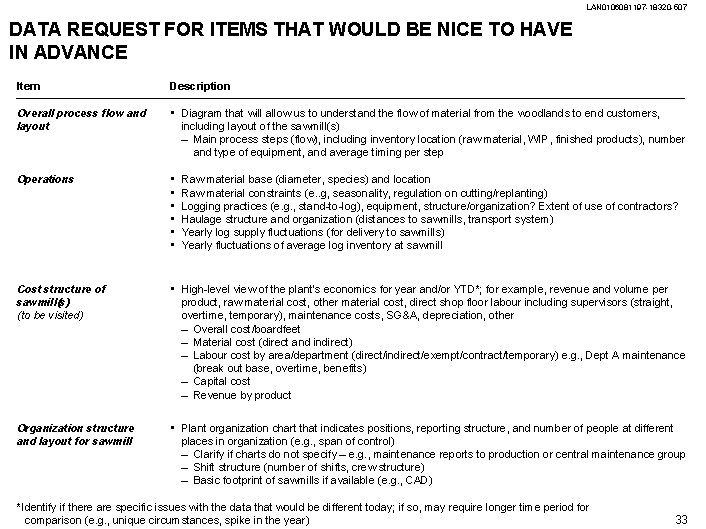
LAN 0106081197 -18320 -507 DATA REQUEST FOR ITEMS THAT WOULD BE NICE TO HAVE IN ADVANCE Item Description Overall process flow and layout • Diagram that will allow us to understand the flow of material from the woodlands to end customers, Operations • • • Cost structure of sawmill(s) (to be visited) • High-level view of the plant’s economics for year and/or YTD*; for example, revenue and volume per Organization structure and layout for sawmill • Plant organization chart that indicates positions, reporting structure, and number of people at different including layout of the sawmill(s) – Main process steps (flow), including inventory location (raw material, WIP, finished products), number and type of equipment, and average timing per step Raw material base (diameter, species) and location Raw material constraints (e. . g, seasonality, regulation on cutting/replanting) Logging practices (e. g. , stand-to-log), equipment, structure/organization? Extent of use of contractors? Haulage structure and organization (distances to sawmills, transport system) Yearly log supply fluctuations (for delivery to sawmills) Yearly fluctuations of average log inventory at sawmill product, raw material cost, other material cost, direct shop floor labour including supervisors (straight, overtime, temporary), maintenance costs, SG&A, depreciation, other – Overall cost/boardfeet – Material cost (direct and indirect) – Labour cost by area/department (direct/indirect/exempt/contract/temporary) e. g. , Dept A maintenance (break out base, overtime, benefits) – Capital cost – Revenue by product places in organization (e. g. , span of control) – Clarify if charts do not specify – e. g. , maintenance reports to production or central maintenance group – Shift structure (number of shifts, crew structure) – Basic footprint of sawmills if available (e. g. , CAD) *Identify if there are specific issues with the data that would be different today; if so, may require longer time period for comparison (e. g. , unique circumstances, spike in the year) 33
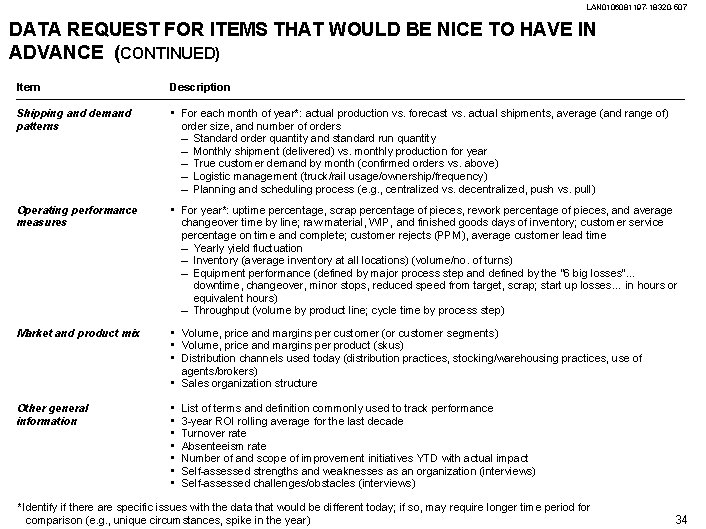
LAN 0106081197 -18320 -507 DATA REQUEST FOR ITEMS THAT WOULD BE NICE TO HAVE IN ADVANCE (CONTINUED) Item Description Shipping and demand patterns • For each month of year*: actual production vs. forecast vs. actual shipments, average (and range of) Operating performance measures • For year*: uptime percentage, scrap percentage of pieces, rework percentage of pieces, and average Market and product mix • Volume, price and margins per customer (or customer segments) • Volume, price and margins per product (skus) • Distribution channels used today (distribution practices, stocking/warehousing practices, use of order size, and number of orders – Standard order quantity and standard run quantity – Monthly shipment (delivered) vs. monthly production for year – True customer demand by month (confirmed orders vs. above) – Logistic management (truck/rail usage/ownership/frequency) – Planning and scheduling process (e. g. , centralized vs. decentralized, push vs. pull) changeover time by line; raw material, WIP, and finished goods days of inventory; customer service percentage on time and complete; customer rejects (PPM), average customer lead time – Yearly yield fluctuation – Inventory (average inventory at all locations) (volume/no. of turns) – Equipment performance (defined by major process step and defined by the “ 6 big losses”… downtime, changeover, minor stops, reduced speed from target, scrap; start up losses… in hours or equivalent hours) – Throughput (volume by product line; cycle time by process step) agents/brokers) • Sales organization structure Other general information • • List of terms and definition commonly used to track performance 3 -year ROI rolling average for the last decade Turnover rate Absenteeism rate Number of and scope of improvement initiatives YTD with actual impact Self-assessed strengths and weaknesses as an organization (interviews) Self-assessed challenges/obstacles (interviews) *Identify if there are specific issues with the data that would be different today; if so, may require longer time period for comparison (e. g. , unique circumstances, spike in the year) 34
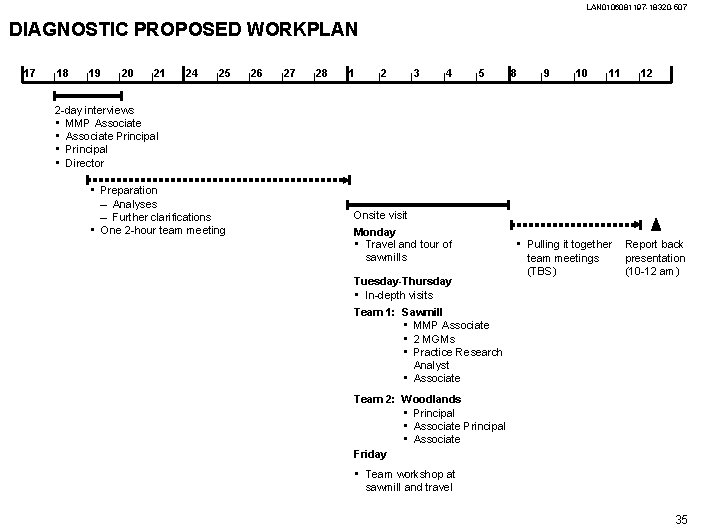
LAN 0106081197 -18320 -507 DIAGNOSTIC PROPOSED WORKPLAN 17 18 19 20 21 24 25 26 27 28 1 2 3 4 5 8 9 10 11 12 2 -day interviews • MMP Associate • Associate Principal • Director • Preparation – Analyses – Further clarifications • One 2 -hour team meeting Onsite visit Monday • Travel and tour of sawmills Tuesday-Thursday • In-depth visits • Pulling it together Report back team meetings (TBS) presentation (10 -12 am) Team 1: Sawmill • MMP Associate • 2 MGMs • Practice Research Analyst • Associate Team 2: Woodlands • Principal • Associate Friday • Team workshop at sawmill and travel 35
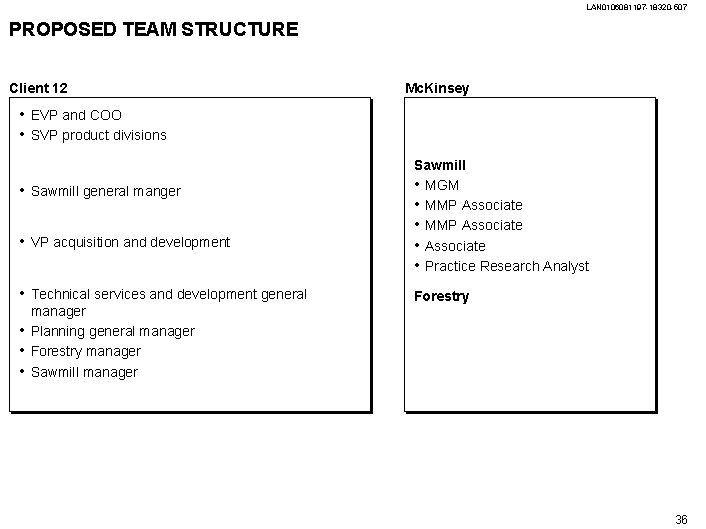
LAN 0106081197 -18320 -507 PROPOSED TEAM STRUCTURE Client 12 Mc. Kinsey • EVP and COO • SVP product divisions • Sawmill general manger • VP acquisition and development • Technical services and development general • • • manager Planning general manager Forestry manager Sawmill • MGM • MMP Associate • Practice Research Analyst Forestry 36
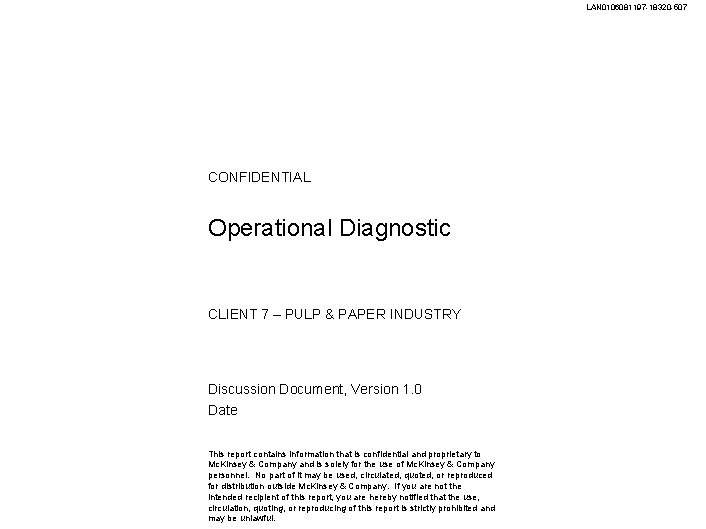
LAN 0106081197 -18320 -507 CONFIDENTIAL Operational Diagnostic CLIENT 7 – PULP & PAPER INDUSTRY Discussion Document, Version 1. 0 Date This report contains information that is confidential and proprietary to Mc. Kinsey & Company and is solely for the use of Mc. Kinsey & Company personnel. No part of it may be used, circulated, quoted, or reproduced for distribution outside Mc. Kinsey & Company. If you are not the intended recipient of this report, you are hereby notified that the use, circulation, quoting, or reproducing of this report is strictly prohibited and may be unlawful.
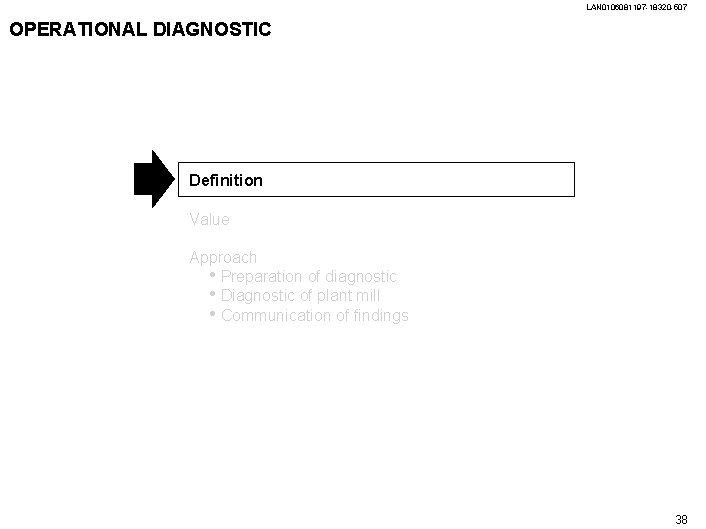
LAN 0106081197 -18320 -507 OPERATIONAL DIAGNOSTIC Definition Value Approach • Preparation of diagnostic • Diagnostic of plant mill • Communication of findings 38
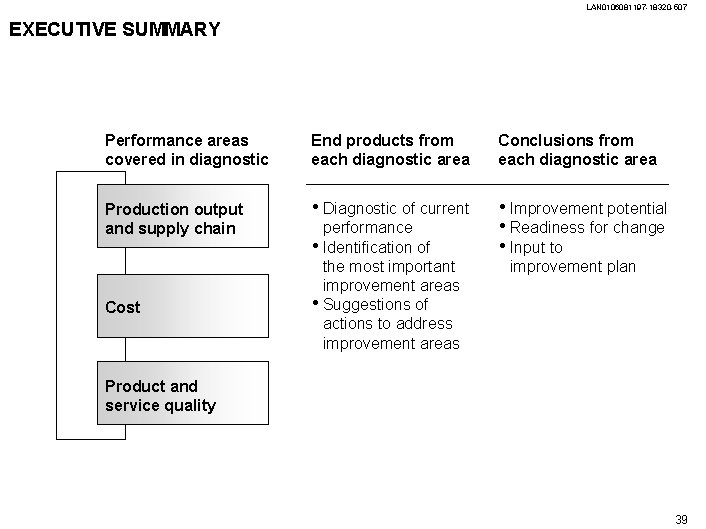
LAN 0106081197 -18320 -507 EXECUTIVE SUMMARY Performance areas covered in diagnostic End products from each diagnostic area Conclusions from each diagnostic area Production output and supply chain • Diagnostic of current • Improvement potential • Readiness for change • Input to Cost performance • Identification of the most important improvement areas • Suggestions of actions to address improvement areas improvement plan Product and service quality 39
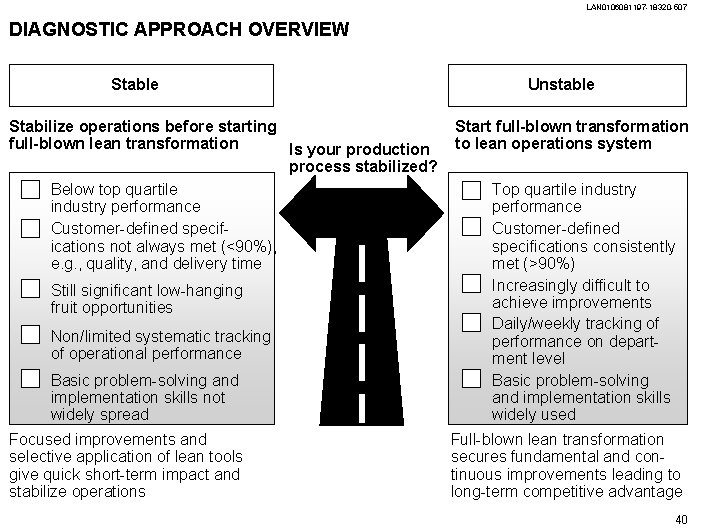
LAN 0106081197 -18320 -507 DIAGNOSTIC APPROACH OVERVIEW Stable Stabilize operations before starting full-blown lean transformation Is your production process stabilized? Below top quartile industry performance Customer-defined specifications not always met (<90%), e. g. , quality, and delivery time Still significant low-hanging fruit opportunities Non/limited systematic tracking of operational performance Basic problem-solving and implementation skills not widely spread Focused improvements and selective application of lean tools give quick short-term impact and stabilize operations Unstable Start full-blown transformation to lean operations system Top quartile industry performance Customer-defined specifications consistently met (>90%) Increasingly difficult to achieve improvements Daily/weekly tracking of performance on department level Basic problem-solving and implementation skills widely used Full-blown lean transformation secures fundamental and continuous improvements leading to long-term competitive advantage 40
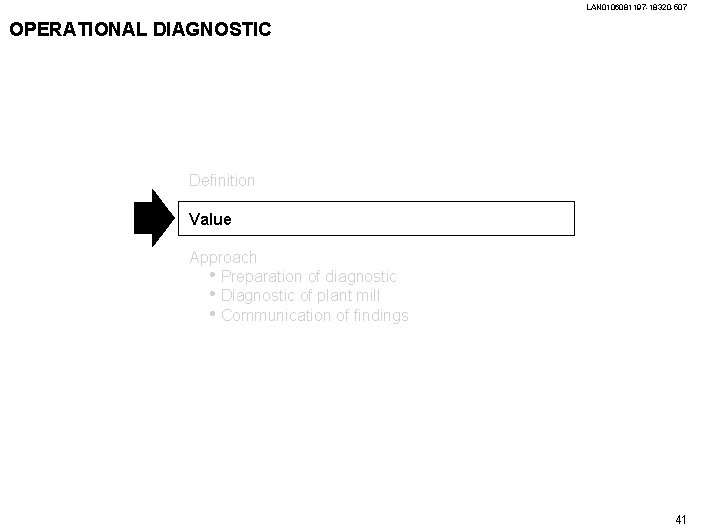
LAN 0106081197 -18320 -507 OPERATIONAL DIAGNOSTIC Definition Value Approach • Preparation of diagnostic • Diagnostic of plant mill • Communication of findings 41
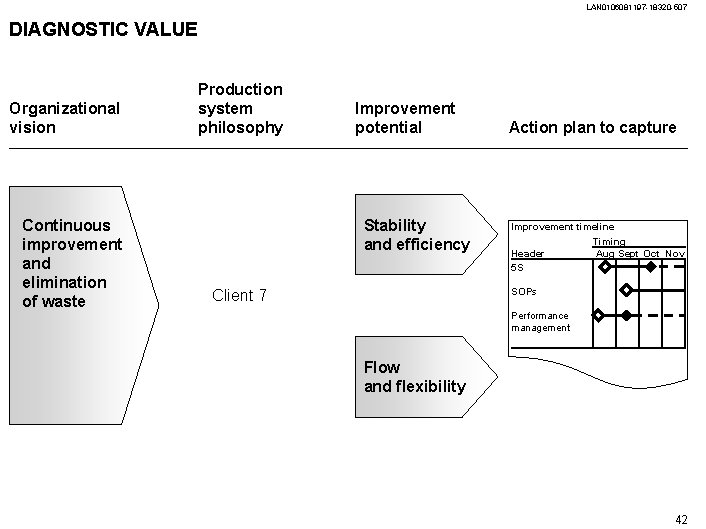
LAN 0106081197 -18320 -507 DIAGNOSTIC VALUE Organizational vision Continuous improvement and elimination of waste Production system philosophy Improvement potential Stability and efficiency Action plan to capture Improvement timeline Header 5 S Timing Aug Sept Oct Nov SOPs Client 7 Performance management Flow and flexibility 42
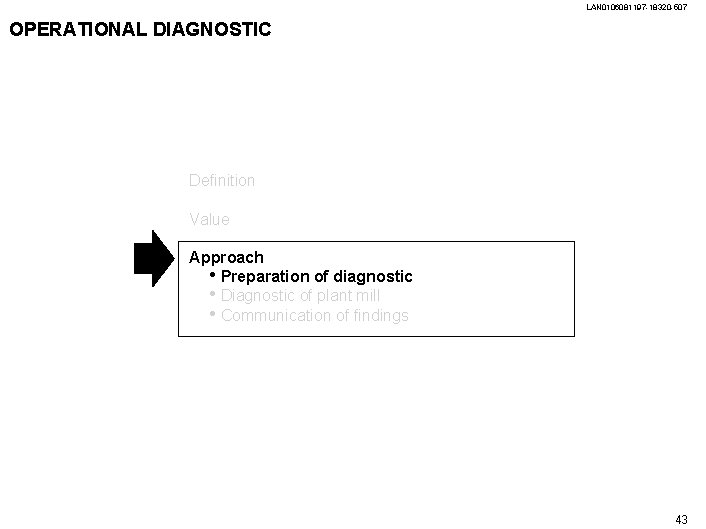
LAN 0106081197 -18320 -507 OPERATIONAL DIAGNOSTIC Definition Value Approach • Preparation of diagnostic • Diagnostic of plant mill • Communication of findings 43
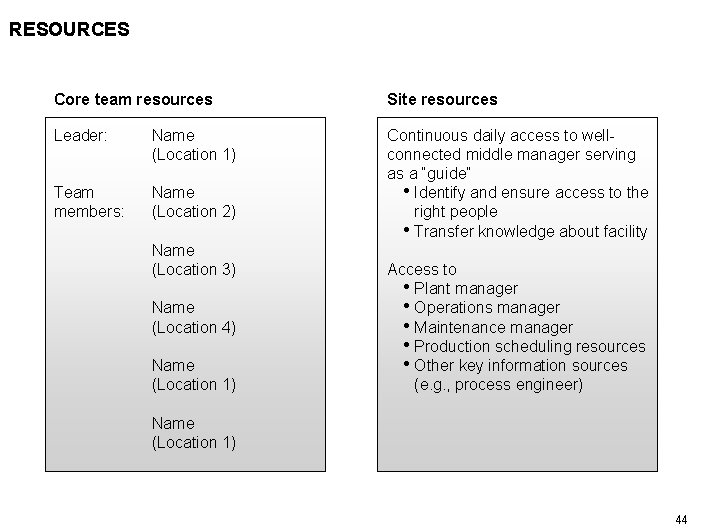
RESOURCES Core team resources Site resources Leader: Name (Location 1) Team members: Name (Location 2) Continuous daily access to wellconnected middle manager serving as a “guide” • Identify and ensure access to the right people • Transfer knowledge about facility Name (Location 3) Name (Location 4) Name (Location 1) Access to • Plant manager • Operations manager • Maintenance manager • Production scheduling resources • Other key information sources (e. g. , process engineer) Name (Location 1) 44

DIAGNOSTIC PROCESS Activities Day (-10) – 0 Day 1– 5 Day 10 Prepare diagnostic Perform diagnostic Communicate findings • Gather data prior to • Run analyses • Incorporate diagnostic start • Hold introductory discussions with plant manager • Hold kick-off meeting with management and other key resources – Determine current state – Define future state – Quantify impact diagnostic results into key communications for – Senior management – Entire site – Area of focus (e. g. , pulp mill) 45
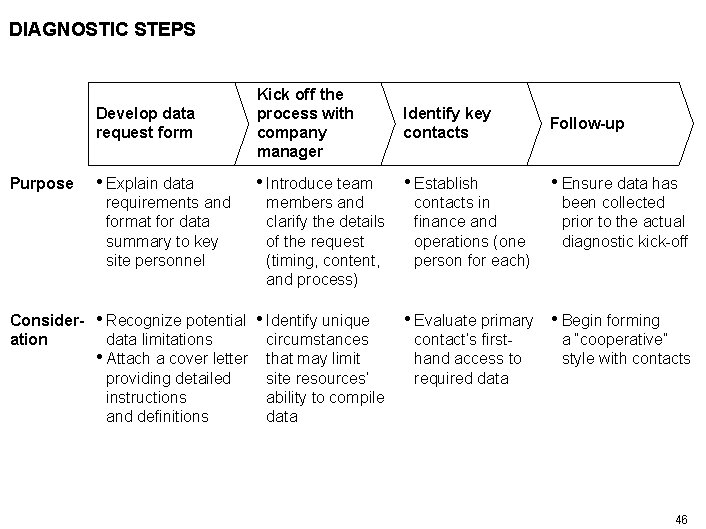
DIAGNOSTIC STEPS Purpose Develop data request form Kick off the process with company manager Identify key contacts Follow-up • Explain data • Introduce team • Establish • Ensure data has requirements and format for data summary to key site personnel Consideration members and clarify the details of the request (timing, content, and process) • Recognize potential • Identify unique data limitations • Attach a cover letter providing detailed instructions and definitions circumstances that may limit site resources’ ability to compile data contacts in finance and operations (one person for each) been collected prior to the actual diagnostic kick-off • Evaluate primary • Begin forming contact’s firsthand access to required data a “cooperative” style with contacts 46
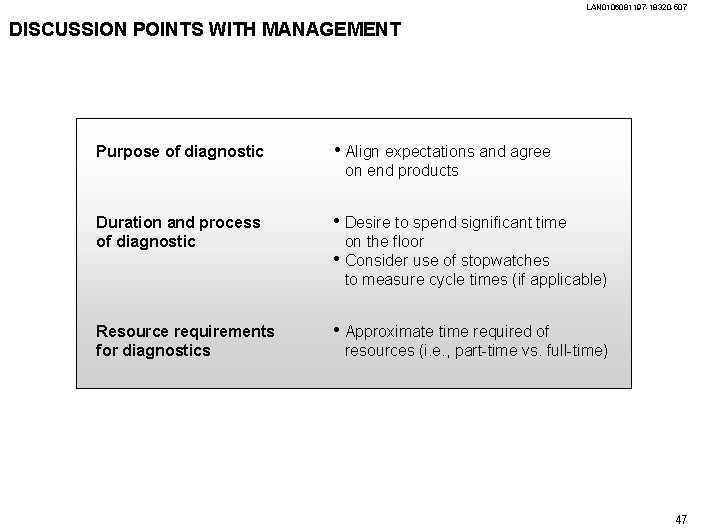
LAN 0106081197 -18320 -507 DISCUSSION POINTS WITH MANAGEMENT Purpose of diagnostic • Align expectations and agree on end products Duration and process of diagnostic • Desire to spend significant time Resource requirements for diagnostics • Approximate time required of on the floor • Consider use of stopwatches to measure cycle times (if applicable) resources (i. e. , part-time vs. full-time) 47
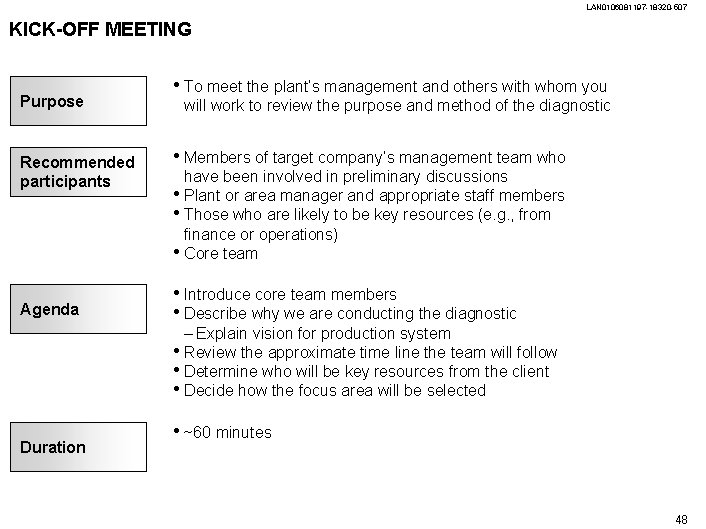
LAN 0106081197 -18320 -507 KICK-OFF MEETING Purpose Recommended participants Agenda • To meet the plant’s management and others with whom you will work to review the purpose and method of the diagnostic • Members of target company’s management team who have been involved in preliminary discussions • Plant or area manager and appropriate staff members • Those who are likely to be key resources (e. g. , from finance or operations) • Core team • Introduce core team members • Describe why we are conducting the diagnostic – Explain vision for production system • Review the approximate time line the team will follow • Determine who will be key resources from the client • Decide how the focus area will be selected Duration • ~60 minutes 48
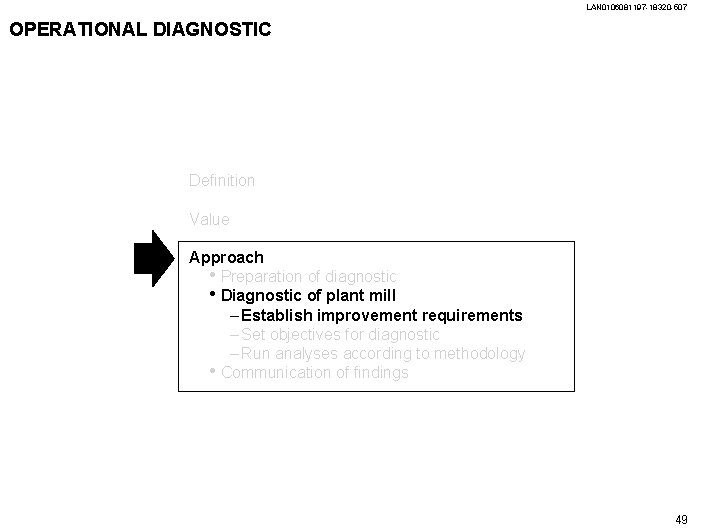
LAN 0106081197 -18320 -507 OPERATIONAL DIAGNOSTIC Definition Value Approach • Preparation of diagnostic • Diagnostic of plant mill – Establish improvement requirements – Set objectives for diagnostic – Run analyses according to methodology • Communication of findings 49
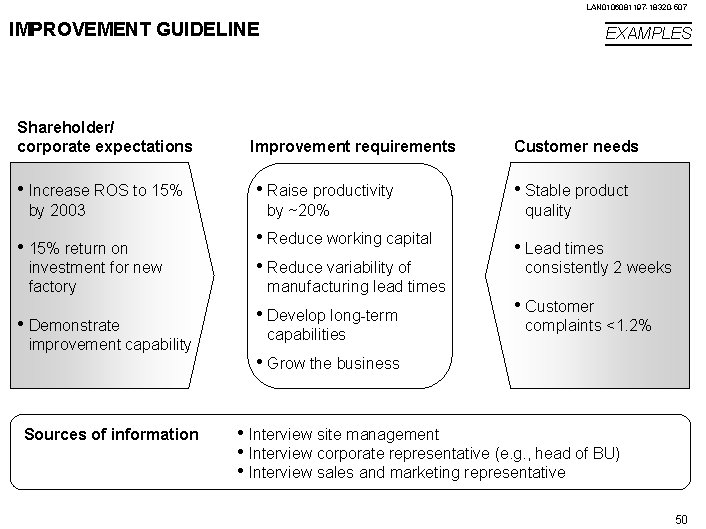
LAN 0106081197 -18320 -507 IMPROVEMENT GUIDELINE Shareholder/ corporate expectations • Increase ROS to 15% by 2003 • 15% return on investment for new factory • Demonstrate improvement capability Sources of information EXAMPLES Improvement requirements • Raise productivity by ~20% • Reduce working capital • Reduce variability of manufacturing lead times • Develop long-term capabilities Customer needs • Stable product quality • Lead times consistently 2 weeks • Customer complaints <1. 2% • Grow the business • Interview site management • Interview corporate representative (e. g. , head of BU) • Interview sales and marketing representative 50
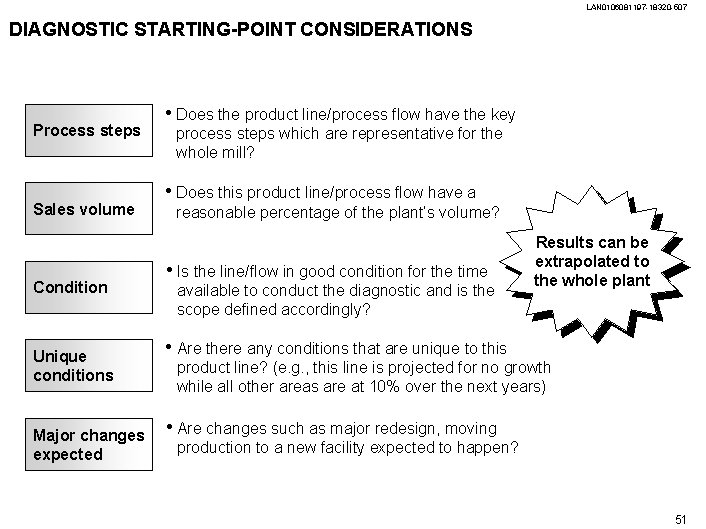
LAN 0106081197 -18320 -507 DIAGNOSTIC STARTING-POINT CONSIDERATIONS Process steps Sales volume Condition Unique conditions Major changes expected • Does the product line/process flow have the key process steps which are representative for the whole mill? • Does this product line/process flow have a reasonable percentage of the plant’s volume? • Is the line/flow in good condition for the time available to conduct the diagnostic and is the scope defined accordingly? Results can be extrapolated to the whole plant • Are there any conditions that are unique to this product line? (e. g. , this line is projected for no growth while all other areas are at 10% over the next years) • Are changes such as major redesign, moving production to a new facility expected to happen? 51
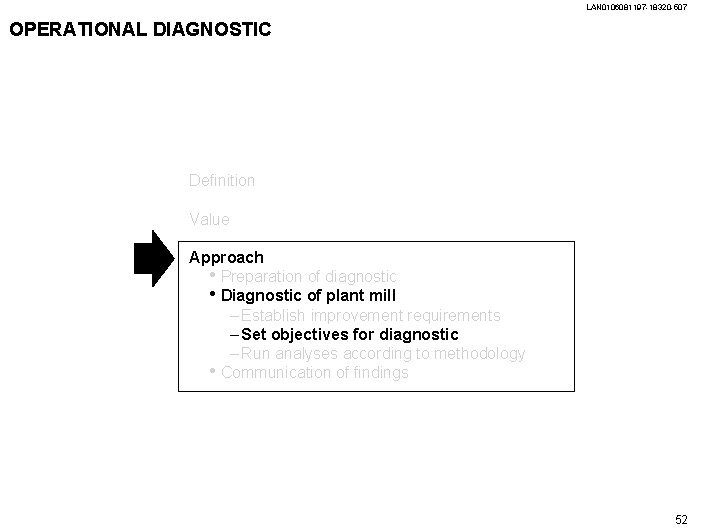
LAN 0106081197 -18320 -507 OPERATIONAL DIAGNOSTIC Definition Value Approach • Preparation of diagnostic • Diagnostic of plant mill – Establish improvement requirements – Set objectives for diagnostic – Run analyses according to methodology • Communication of findings 52
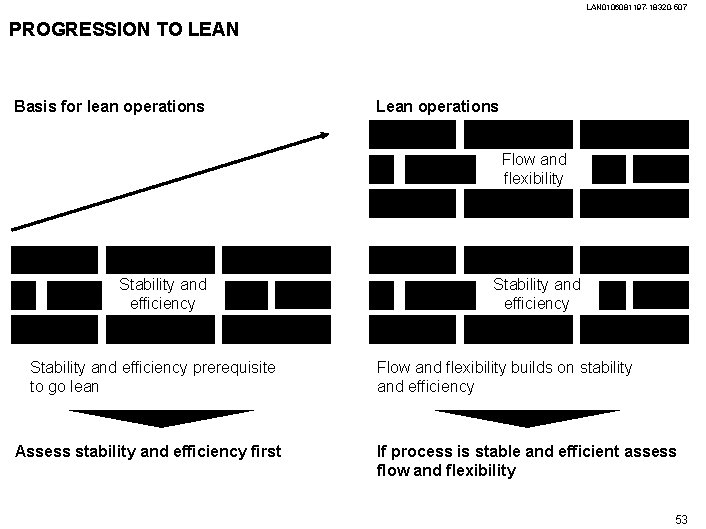
LAN 0106081197 -18320 -507 PROGRESSION TO LEAN Basis for lean operations Lean operations Flow and flexibility Stability and efficiency prerequisite to go lean Assess stability and efficiency first Stability and efficiency Flow and flexibility builds on stability and efficiency If process is stable and efficient assess flow and flexibility 53
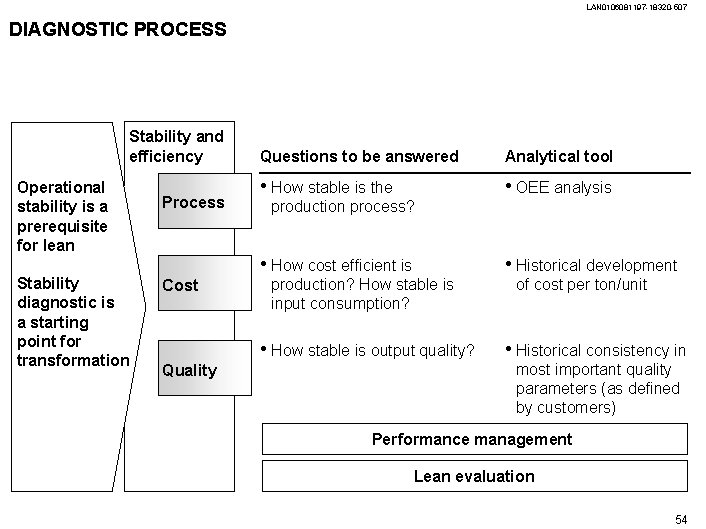
LAN 0106081197 -18320 -507 DIAGNOSTIC PROCESS Stability and efficiency Operational stability is a prerequisite for lean Stability diagnostic is a starting point for transformation Process Questions to be answered Analytical tool • How stable is the • OEE analysis production process? • How cost efficient is Cost production? How stable is input consumption? • How stable is output quality? Quality • Historical development of cost per ton/unit • Historical consistency in most important quality parameters (as defined by customers) Performance management Lean evaluation 54
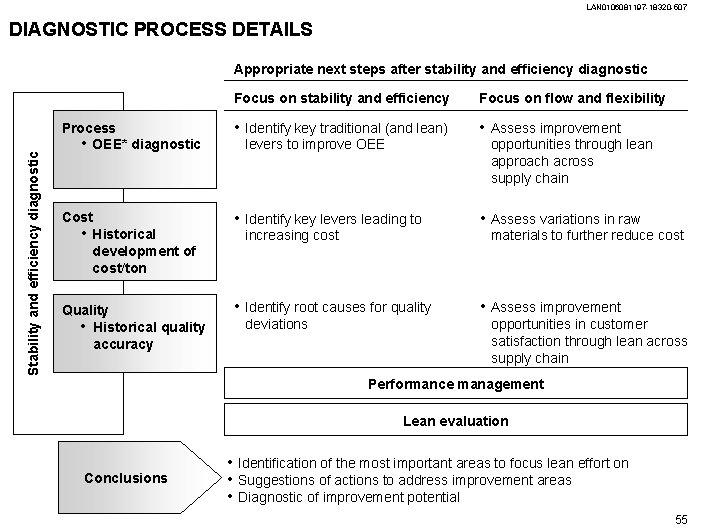
LAN 0106081197 -18320 -507 DIAGNOSTIC PROCESS DETAILS Stability and efficiency diagnostic Appropriate next steps after stability and efficiency diagnostic Focus on stability and efficiency Focus on flow and flexibility Process • OEE* diagnostic • Identify key traditional (and lean) • Assess improvement Cost • Historical development of cost/ton • Identify key levers leading to Quality • Historical quality accuracy • Identify root causes for quality levers to improve OEE opportunities through lean approach across supply chain increasing cost deviations • Assess variations in raw materials to further reduce cost • Assess improvement opportunities in customer satisfaction through lean across supply chain Performance management Lean evaluation Conclusions • Identification of the most important areas to focus lean effort on • Suggestions of actions to address improvement areas • Diagnostic of improvement potential 55
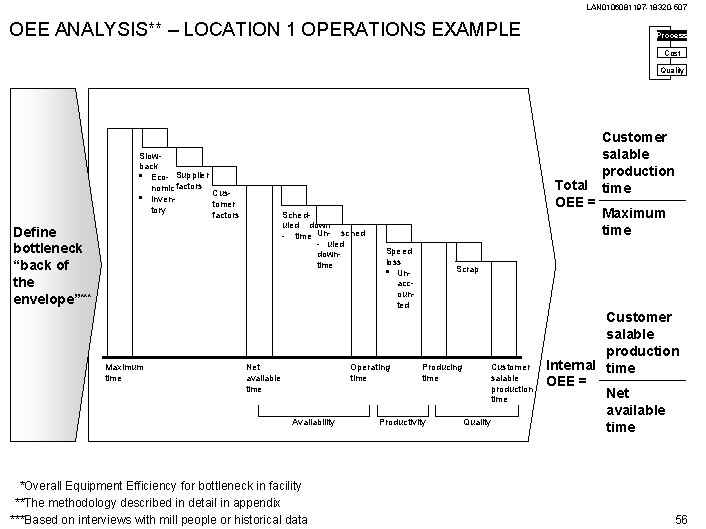
LAN 0106081197 -18320 -507 OEE ANALYSIS** – LOCATION 1 OPERATIONS EXAMPLE Process Cost Quality Slowback • Eco- Supplier nomic factors Cus • Inventomer tory factors Define bottleneck “back of the envelope”*** Maximum time Sched- uled down - time Un- sched - uled down- time Net available time Customer salable production Total time OEE = Maximum time Speed loss • Un- acc- oun- ted Operating time Availability *Overall Equipment Efficiency for bottleneck in facility **The methodology described in detail in appendix ***Based on interviews with mill people or historical data Scrap Producing time Productivity Customer salable production time Quality Customer salable production Internal time OEE = Net available time 56
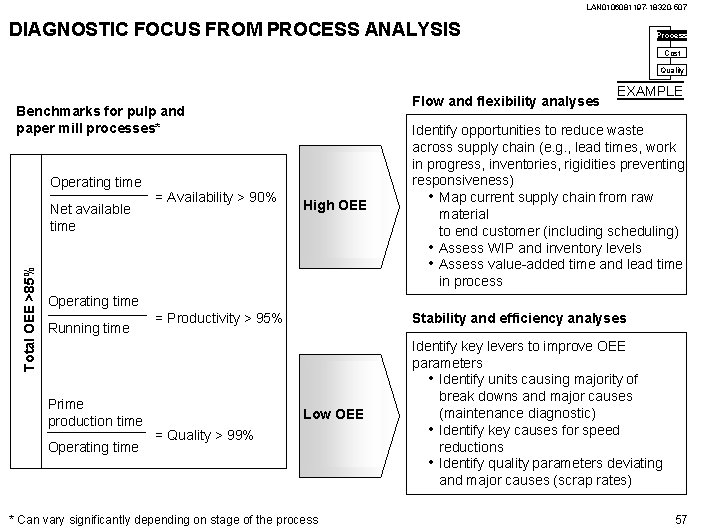
LAN 0106081197 -18320 -507 DIAGNOSTIC FOCUS FROM PROCESS ANALYSIS Process Cost Quality Flow and flexibility analyses Benchmarks for pulp and paper mill processes* Operating time Total OEE >85% Net available time = Availability > 90% High OEE EXAMPLE Identify opportunities to reduce waste across supply chain (e. g. , lead times, work in progress, inventories, rigidities preventing responsiveness) • Map current supply chain from raw material to end customer (including scheduling) • Assess WIP and inventory levels • Assess value-added time and lead time in process Operating time Running time Prime production time Operating time = Productivity > 95% Stability and efficiency analyses Low OEE = Quality > 99% * Can vary significantly depending on stage of the process Identify key levers to improve OEE parameters • Identify units causing majority of break downs and major causes (maintenance diagnostic) • Identify key causes for speed reductions • Identify quality parameters deviating and major causes (scrap rates) 57
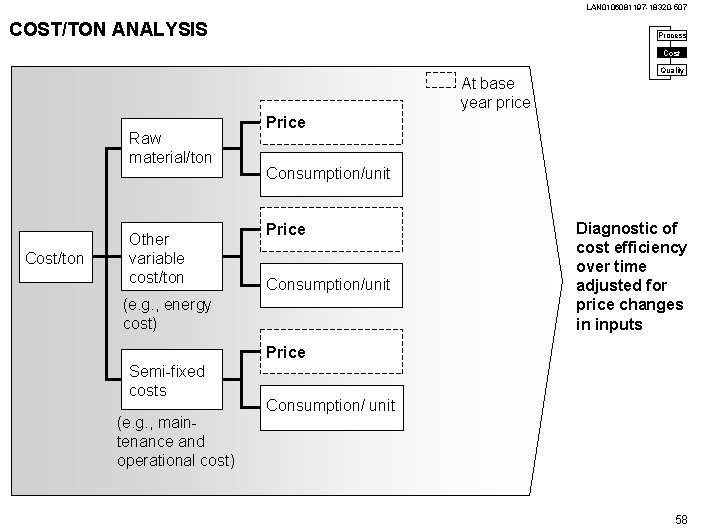
LAN 0106081197 -18320 -507 COST/TON ANALYSIS Process Cost At base year price Raw material/ton Cost/ton Other variable cost/ton Quality Price Consumption/unit (e. g. , energy cost) Diagnostic of cost efficiency over time adjusted for price changes in inputs Price Semi-fixed costs (e. g. , maintenance and operational cost) Consumption/ unit 58
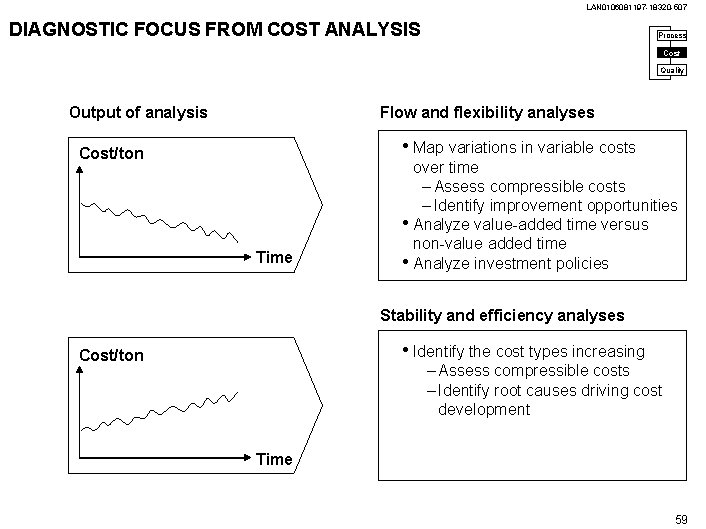
LAN 0106081197 -18320 -507 DIAGNOSTIC FOCUS FROM COST ANALYSIS Process Cost Quality Output of analysis Flow and flexibility analyses • Map variations in variable costs Cost/ton Time over time – Assess compressible costs – Identify improvement opportunities • Analyze value-added time versus non-value added time • Analyze investment policies Stability and efficiency analyses • Identify the cost types increasing Cost/ton – Assess compressible costs – Identify root causes driving cost development Time 59
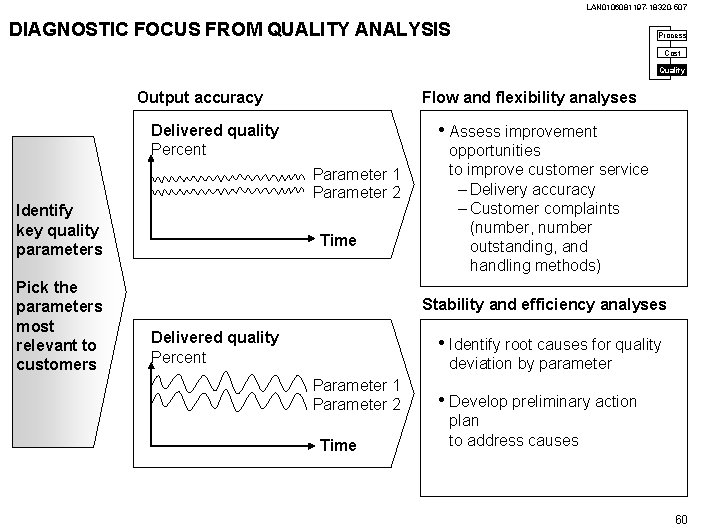
LAN 0106081197 -18320 -507 DIAGNOSTIC FOCUS FROM QUALITY ANALYSIS Process Cost Quality Output accuracy Flow and flexibility analyses • Assess improvement Delivered quality Percent Parameter 1 Parameter 2 Identify key quality parameters Pick the parameters most relevant to customers Time opportunities to improve customer service – Delivery accuracy – Customer complaints (number, number outstanding, and handling methods) Stability and efficiency analyses Delivered quality Percent • Identify root causes for quality deviation by parameter Parameter 1 Parameter 2 Time • Develop preliminary action plan to address causes 60
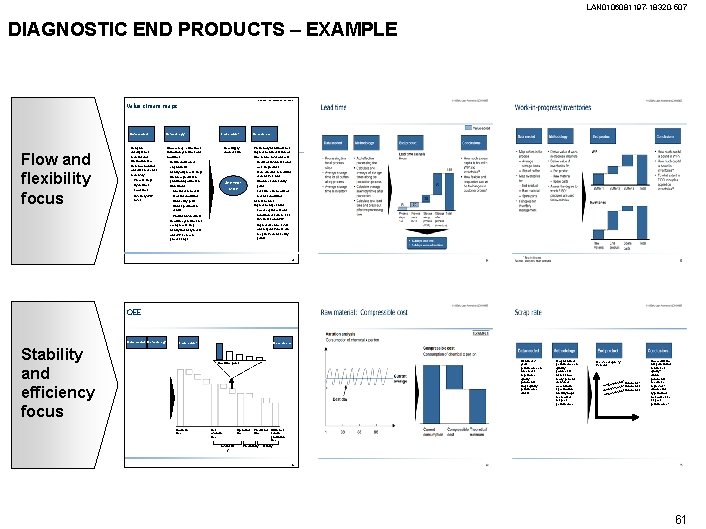
LAN 0106081197 -18320 -507 DIAGNOSTIC END PRODUCTS – EXAMPLE 010529 Ac-Lean Assessment-ZXH 954 GT Value stream maps Data needed • Flow and flexibility focus Complete description of Methodology • material and information flow from raw material and customer order to delivery – Process steps – Cycle times – Lead times – Inventory/WIP levels Draw a “map” of the flows indicating cycle times and End product • Conclusions • New supplychain design Preliminary identification of improvement levers in lead times time service level and cost – Rough draft based – Reduced inventories and on plant tour work-in progress – Identify all process steps – More effective scheduling (batch sizes, mix) – Interview production planning department to understand – Change of order entry point - See next slide • Amount of forecasts used in scheduling – Less use of forecasts as tool for scheduling • • Order entry point Assessment of improvement potential • Order specification details – Lower capital cost and handling cost due to less • Product mix decisions inventories and WIP – Measure cycle times for each process step – Improved service levels and responsiveness due – Identify inventory levels to optimized order entry points and WIP between process steps 40 OEE Data needed Methodology End product Stability and efficiency focus Conclusions • Downtime pareto • Maximum time Net available time Availabilit y Operating time Historical (1 year) performance on three most importance quality parameters Major quality performance drivers • Map historical • • performance on quality parameters Assess how many percent delivered according to specification Identify major root causes for poor performance • How well is the Delivered quality Percent mill performing in terms of quality? • Which Parameter 1 Parameter 2 Parameter 3 parameters need to be improved? • What could hypothetical root causes be for poor performance? Producing Customer time salable production time Productivity Quality 37 61
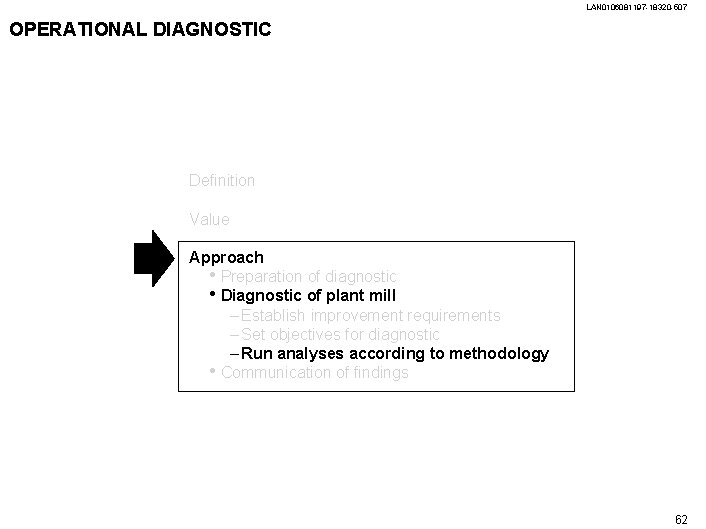
LAN 0106081197 -18320 -507 OPERATIONAL DIAGNOSTIC Definition Value Approach • Preparation of diagnostic • Diagnostic of plant mill – Establish improvement requirements – Set objectives for diagnostic – Run analyses according to methodology • Communication of findings 62
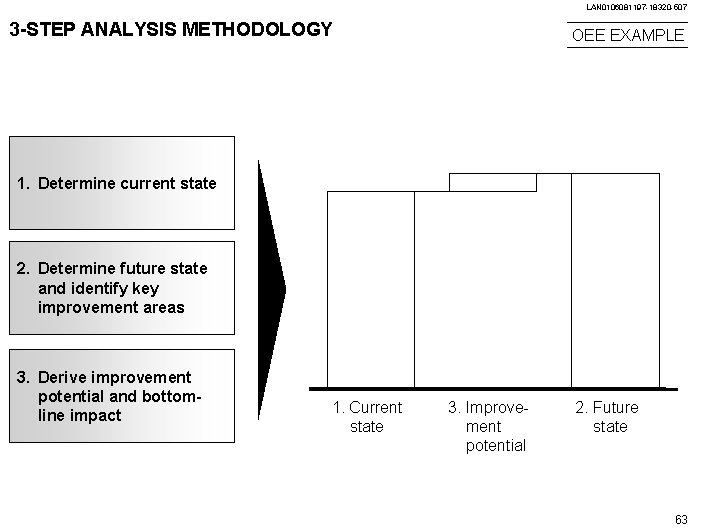
LAN 0106081197 -18320 -507 3 -STEP ANALYSIS METHODOLOGY OEE EXAMPLE 1. Determine current state 2. Determine future state and identify key improvement areas 3. Derive improvement potential and bottomline impact 1. Current state 3. Improvement potential 2. Future state 63
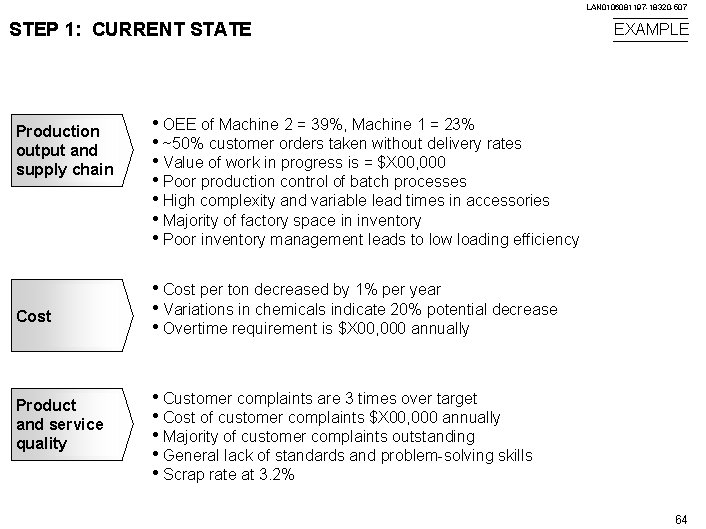
LAN 0106081197 -18320 -507 STEP 1: CURRENT STATE Production output and supply chain Cost Product and service quality EXAMPLE • OEE of Machine 2 = 39%, Machine 1 = 23% • ~50% customer orders taken without delivery rates • Value of work in progress is = $X 00, 000 • Poor production control of batch processes • High complexity and variable lead times in accessories • Majority of factory space in inventory • Poor inventory management leads to low loading efficiency • Cost per ton decreased by 1% per year • Variations in chemicals indicate 20% potential decrease • Overtime requirement is $X 00, 000 annually • Customer complaints are 3 times over target • Cost of customer complaints $X 00, 000 annually • Majority of customer complaints outstanding • General lack of standards and problem-solving skills • Scrap rate at 3. 2% 64
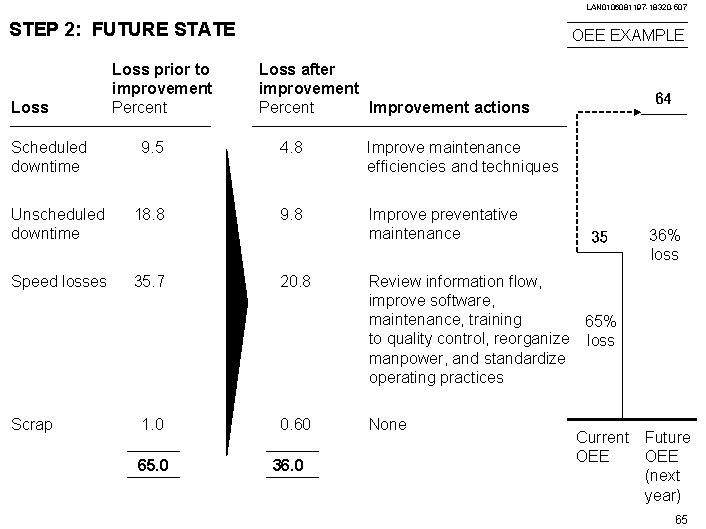
LAN 0106081197 -18320 -507 STEP 2: FUTURE STATE Loss Scheduled downtime Loss prior to improvement Percent OEE EXAMPLE Loss after improvement Percent Improvement actions 9. 5 4. 8 Improve maintenance efficiencies and techniques Unscheduled downtime 18. 8 9. 8 Improve preventative maintenance Speed losses 35. 7 20. 8 Review information flow, improve software, maintenance, training 65% to quality control, reorganize loss manpower, and standardize operating practices 1. 0 0. 60 None Scrap 65. 0 36% loss Current Future OEE (next year) 65
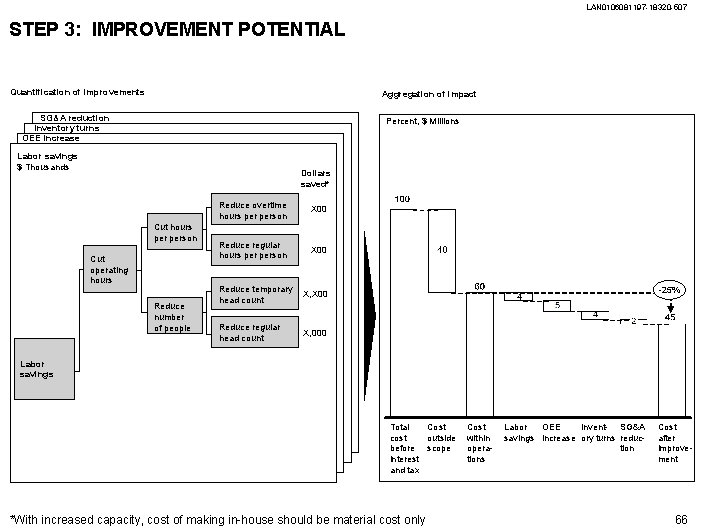
LAN 0106081197 -18320 -507 STEP 3: IMPROVEMENT POTENTIAL Quantification of improvements Aggregation of impact SG&A reduction Inventory turns OEE increase Percent, $ Millions Labor savings $ Thousands Dollars saved* Cut hours person Cut operating hours Reduce number of people Reduce overtime hours person X 00 Reduce regular hours person X 00 Reduce temporary X, X 00 head count Reduce regular head count -25% X, 000 Labor savings Total Cost cost outside before scope interest and tax *With increased capacity, cost of making in-house should be material cost only Cost within operations Labor OEE Invent- SG&A savings increase ory turns reduction Cost after improvement 66
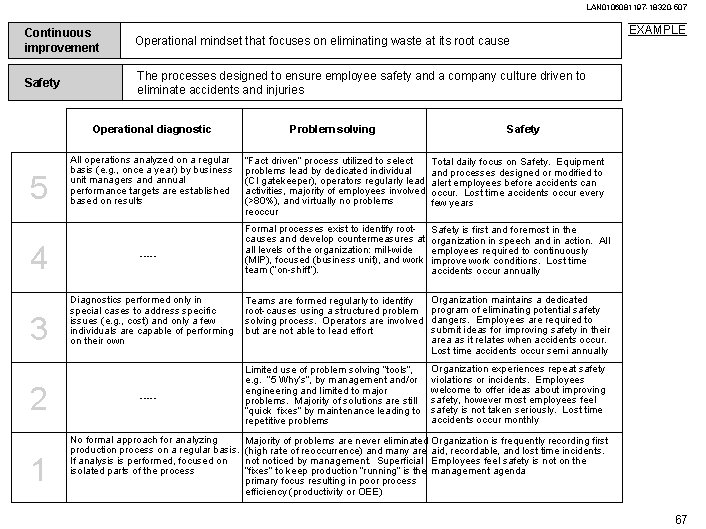
LAN 0106081197 -18320 -507 Continuous improvement Operational mindset that focuses on eliminating waste at its root cause Safety The processes designed to ensure employee safety and a company culture driven to eliminate accidents and injuries Operational diagnostic 5 4 3 2 1 All operations analyzed on a regular basis (e. g. , once a year) by business unit managers and annual performance targets are established based on results ----- Diagnostics performed only in special cases to address specific issues (e. g. , cost) and only a few individuals are capable of performing on their own ----- Problem solving EXAMPLE Safety “Fact driven” process utilized to select Total daily focus on Safety. Equipment problems lead by dedicated individual and processes designed or modified to (CI gatekeeper), operators regularly lead alert employees before accidents can activities, majority of employees involved occur. Lost time accidents occur every (>80%), and virtually no problems few years reoccur Formal processes exist to identify rootcauses and develop countermeasures at all levels of the organization: mill-wide (MIP), focused (business unit), and work team (“on-shift”). Safety is first and foremost in the organization in speech and in action. All employees required to continuously improve work conditions. Lost time accidents occur annually Teams are formed regularly to identify root-causes using a structured problem solving process. Operators are involved but are not able to lead effort Organization maintains a dedicated program of eliminating potential safety dangers. Employees are required to submit ideas for improving safety in their area as it relates when accidents occur. Lost time accidents occur semi annually Limited use of problem solving “tools”, e. g. “ 5 Why’s”, by management and/or engineering and limited to major problems. Majority of solutions are still “quick fixes” by maintenance leading to repetitive problems Organization experiences repeat safety violations or incidents. Employees welcome to offer ideas about improving safety, however most employees feel safety is not taken seriously. Lost time accidents occur monthly No formal approach for analyzing Majority of problems are never eliminated Organization is frequently recording first production process on a regular basis. (high rate of reoccurrence) and many are aid, recordable, and lost time incidents. If analysis is performed, focused on noticed by management. Superficial Employees feel safety is not on the isolated parts of the process “fixes” to keep production “running” is the management agenda primary focus resulting in poor process efficiency (productivity or OEE) 67
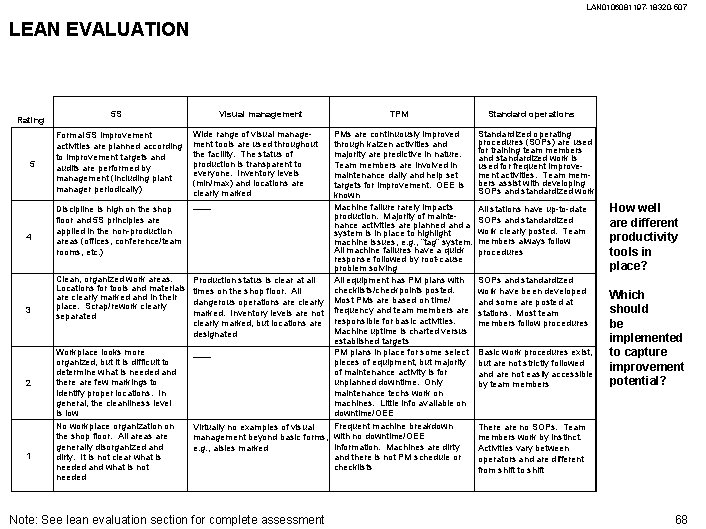
LAN 0106081197 -18320 -507 LEAN EVALUATION Rating 5 4 3 2 1 5 S Visual management TPM Standard operations PMs are continuously improved Standardized operating procedures (SOPs) are used through kaizen activities and majority are predictive in nature. for training team members and standardized work is Team members are involved in used for frequent improvement activities. Team memmaintenance daily and help set targets for improvement. OEE is bers assist with developing SOPs and standardized work known Machine failure rarely impacts Discipline is high on the shop —— All stations have up-to-date production. Majority of maintefloor and 5 S principles are SOPs and standardized nance activities are planned and a applied in the non-production work clearly posted. Team system is in place to highlight areas (offices, conference/team machine issues, e. g. , “tag” system. members always follow All machine failures have a quick procedures rooms, etc. ) response followed by root-cause problem solving Clean, organized work areas. All equipment has PM plans with SOPs and standardized Production status is clear at all Locations for tools and materials times on the shop floor. All checklists/checkpoints posted. work have been developed are clearly marked and in their dangerous operations are clearly Most PMs are based on time/ and some are posted at place. Scrap/rework clearly marked. Inventory levels are not frequency and team members are stations. Most team separated clearly marked, but locations are responsible for basic activities. members follow procedures Machine uptime is charted versus designated established targets Workplace looks more PM plans in place for some select Basic work procedures exist, —— organized, but it is difficult to pieces of equipment, but majority but are not strictly followed determine what is needed and of maintenance activity is for and are not easily accessible there are few markings to unplanned downtime. Only by team members identify proper locations. In maintenance techs work on general, the cleanliness level machines. Little info available on is low downtime/OEE No workplace organization on Frequent machine breakdown Virtually no examples of visual There are no SOPs. Team the shop floor. All areas are management beyond basic forms, with no downtime/OEE members work by instinct. generally disorganized and information. Machines are dirty e. g. , aisles marked Activities vary between dirty. It is not clear what is and there is not PM schedule or operators and are different needed and what is not checklists from shift to shift needed Formal 5 S improvement activities are planned according to improvement targets and audits are performed by management (including plant manager periodically) Wide range of visual management tools are used throughout the facility. The status of production is transparent to everyone. Inventory levels (min/max) and locations are clearly marked Note: See lean evaluation section for complete assessment How well are different productivity tools in place? Which should be implemented to capture improvement potential? 68
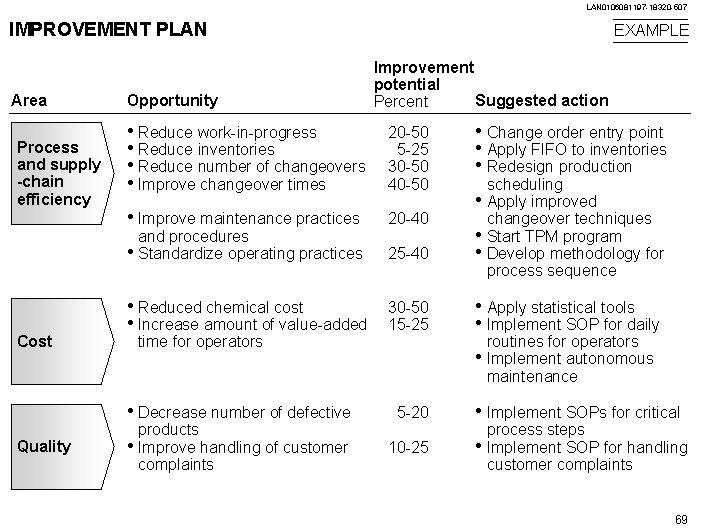
LAN 0106081197 -18320 -507 IMPROVEMENT PLAN Area Process and supply -chain efficiency Opportunity Quality Improvement potential Suggested action Percent • Reduce work-in-progress • Reduce inventories • Reduce number of changeovers • Improve changeover times 20 -50 5 -25 30 -50 40 -50 • Improve maintenance practices 20 -40 and procedures • Standardize operating practices Cost EXAMPLE 25 -40 • Change order entry point • Apply FIFO to inventories • Redesign production scheduling • Apply improved changeover techniques • Start TPM program • Develop methodology for process sequence • Reduced chemical cost 30 -50 • Increase amount of value-added 15 -25 • Apply statistical tools • Implement SOP for daily • Decrease number of defective • Implement SOPs for critical time for operators products • Improve handling of customer complaints 5 -20 10 -25 routines for operators • Implement autonomous maintenance process steps • Implement SOP for handling customer complaints 69
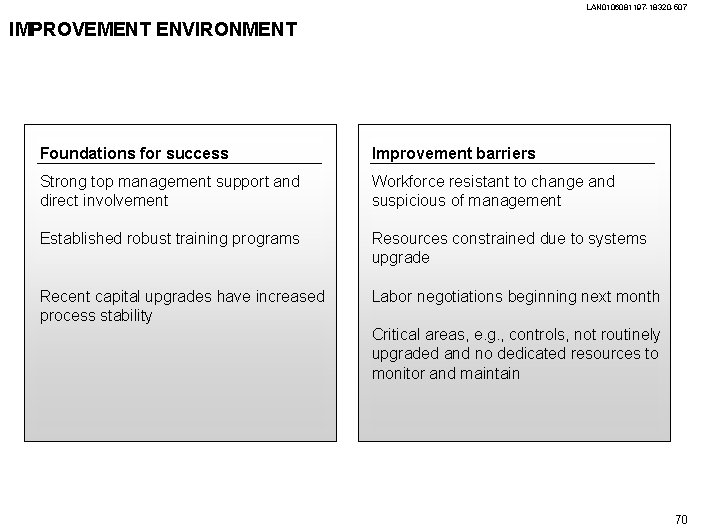
LAN 0106081197 -18320 -507 IMPROVEMENT ENVIRONMENT Foundations for success Improvement barriers Strong top management support and Workforce resistant to change and direct involvement suspicious of management Established robust training programs Resources constrained due to systems upgrade Recent capital upgrades have increased process stability Labor negotiations beginning next month Critical areas, e. g. , controls, not routinely upgraded and no dedicated resources to monitor and maintain 70
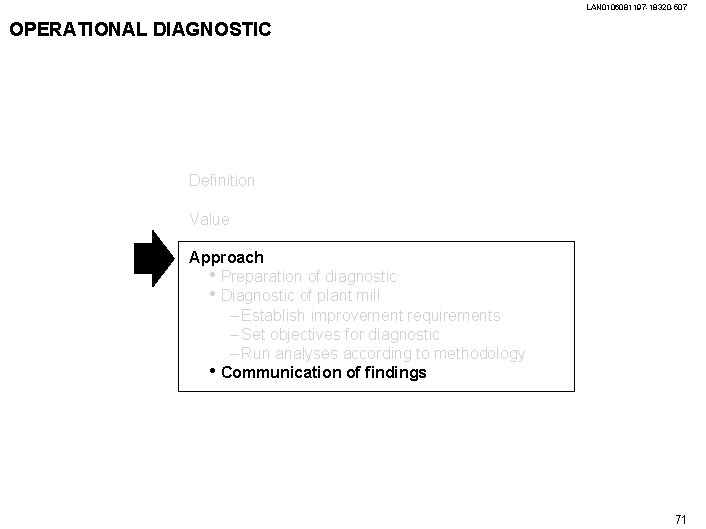
LAN 0106081197 -18320 -507 OPERATIONAL DIAGNOSTIC Definition Value Approach • Preparation of diagnostic • Diagnostic of plant mill – Establish improvement requirements – Set objectives for diagnostic – Run analyses according to methodology • Communication of findings 71
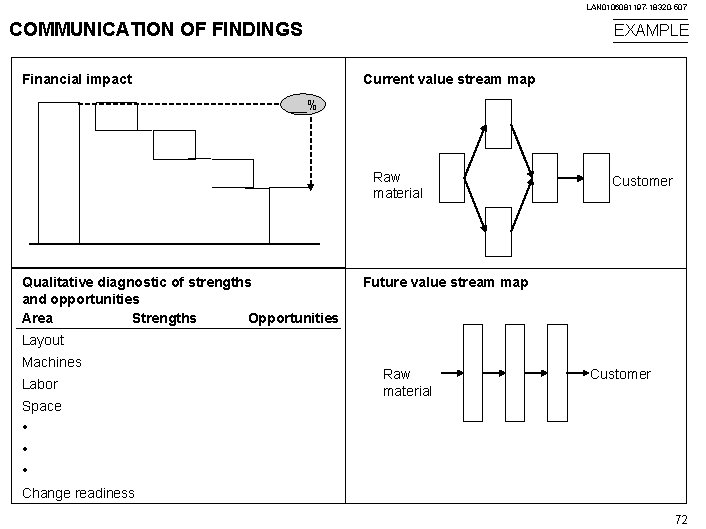
LAN 0106081197 -18320 -507 COMMUNICATION OF FINDINGS Financial impact EXAMPLE Current value stream map __% Raw material Qualitative diagnostic of strengths and opportunities Area Strengths Opportunities Customer Future value stream map Layout Machines Labor Space Raw material Customer • • • Change readiness 72
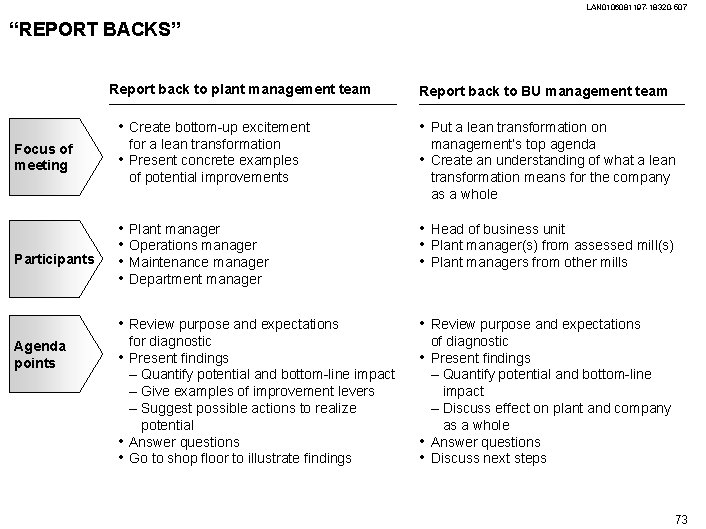
LAN 0106081197 -18320 -507 “REPORT BACKS” Report back to plant management team • Create bottom-up excitement Focus of meeting • for a lean transformation Present concrete examples of potential improvements Participants • • Plant manager Operations manager Maintenance manager Department manager • Review purpose and expectations Agenda points • • • for diagnostic Present findings – Quantify potential and bottom-line impact – Give examples of improvement levers – Suggest possible actions to realize potential Answer questions Go to shop floor to illustrate findings Report back to BU management team • Put a lean transformation on • management’s top agenda Create an understanding of what a lean transformation means for the company as a whole • Head of business unit • Plant manager(s) from assessed mill(s) • Plant managers from other mills • Review purpose and expectations • • • of diagnostic Present findings – Quantify potential and bottom-line impact – Discuss effect on plant and company as a whole Answer questions Discuss next steps 73
Project kickoff presentation
Uat kick off
Mentorship kickoff meeting
Proposal kickoff meeting agenda
Today meeting or today's meeting
Desain kerajinan
Agenda for mentoring session
Upc 2-513
Rocky glass
507 sqn
Uma pessoa empresta 80000 hoje para receber 507
Section 507 of the 2015 minnesota residential building code
Acute toxicity
507-802-380
Umh 507
Types of meeting
For today's meeting
What is meeting and types of meeting
Kickoff 168
Fast kickoff training code
Ava's kickoff
Uat kick off
Yellow report eic
Kickoff o que é
Kickoff projet
Kickoff drills
Project kick off meeting speech sample
Request to attend meeting sample
Notice is written in which language
Prayer for meeting
Sample prayer for meeting
Pre-meeting email
Closing speeches
Steering committee meeting agenda sample
Meeting rescheduled notice sample
Difference between cluster and stratified sampling
Merits and demerits of cluster sampling
Stratified sample vs cluster sample
Purposive sampling qualitative research
Uji t satu sampel
Volunteer sample vs convenience sample
Ncsbn clinical judgment measurement model
Rs br400s-jp
Nda phru,
Distribute images
Confidential internal use only
Evopro innovation kft
Dupixent
Confidential 資料
Confidential do not distribute
Confidential company profile
Hp confidential
This document contains confidential information
Confidential all rights reserved
Strictly confidential
Suranne jones strictly confidential
Confidential for internal use only
Confidential logistics company
Slot rf confidential
Confidential not for circulation
Not for distribution confidential
Intel confidential
Strictly confidential not for distribution
Confidential do not circulate
Remanent magnetization
Microsoft second internaluseonly distro
Azure secure enclave
Hp confidential
Nexty electronics corporation
Confidential
Tcs confidential
Company confidential singapore
Strictly private and confidential
Confidential renault
Notice of confidential info rule 2-420