DEPARTMENT OF MECHANICAL ENGINEERING Aligarh Muslim University Aligarh
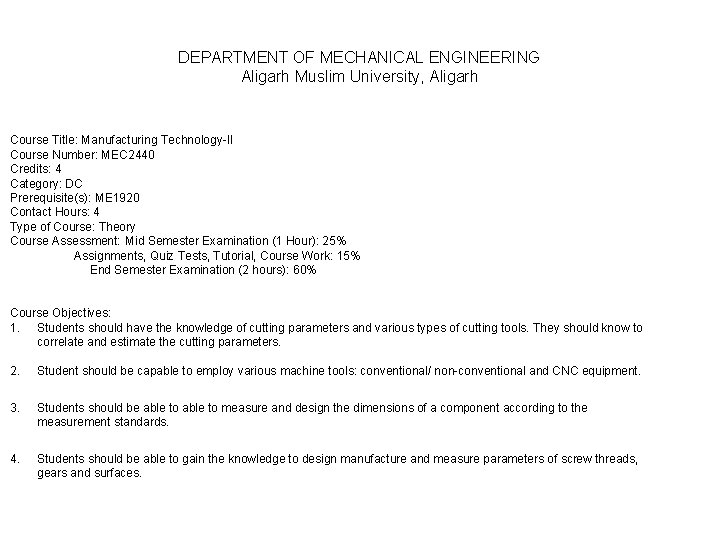
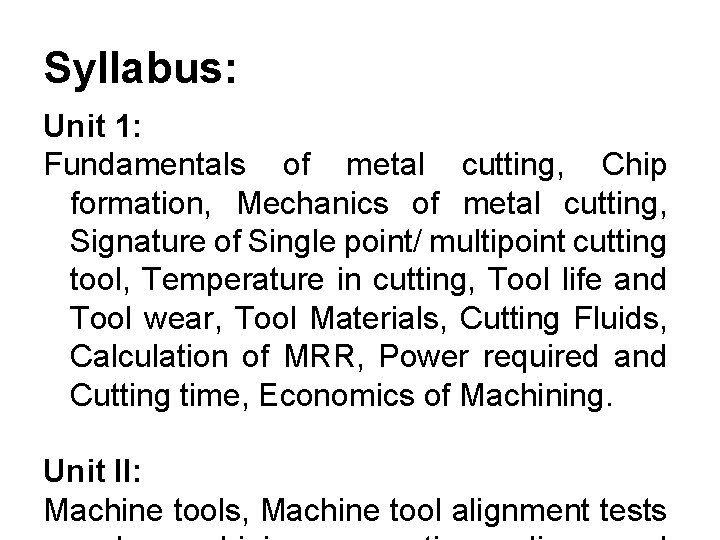

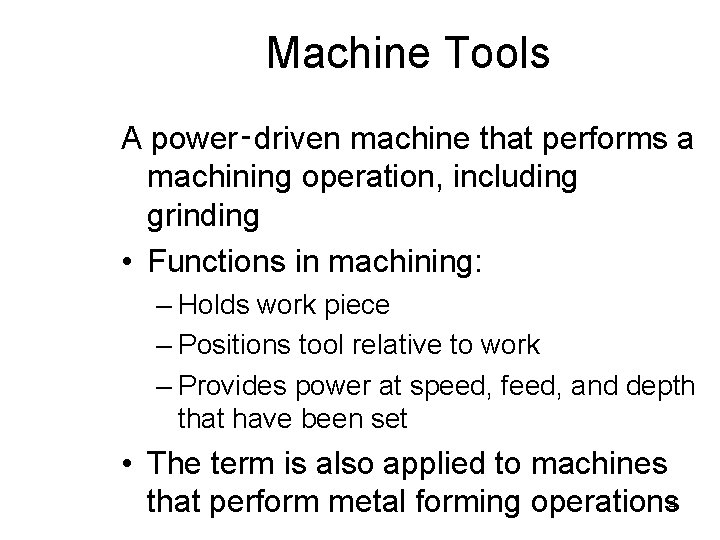

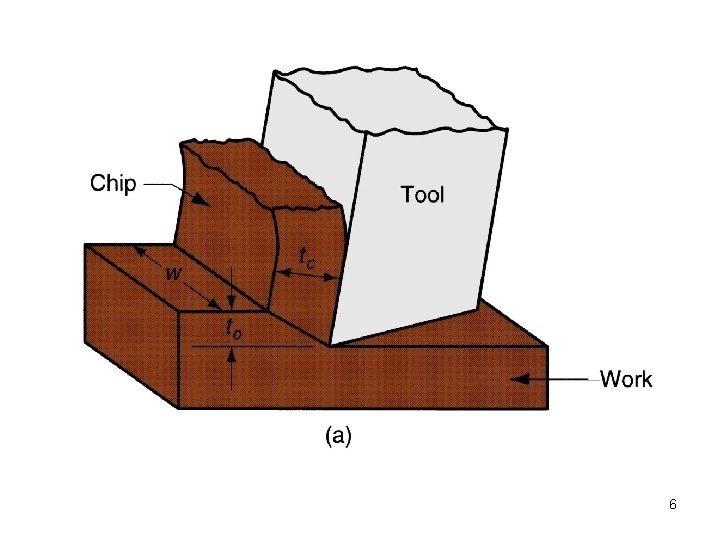
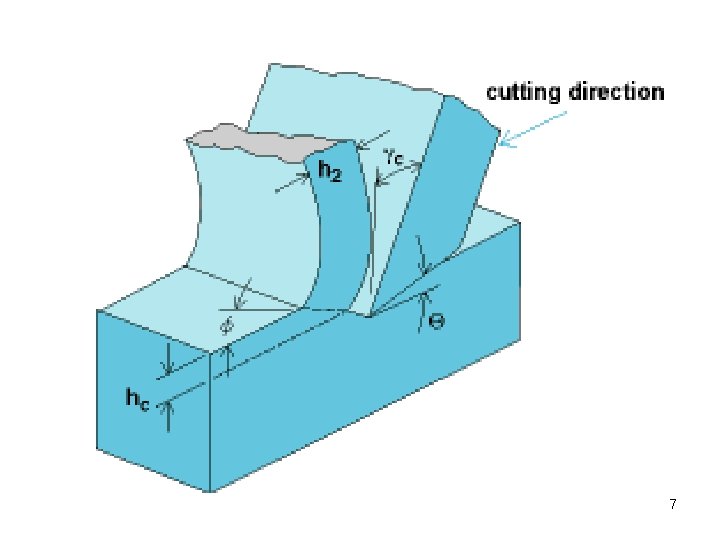
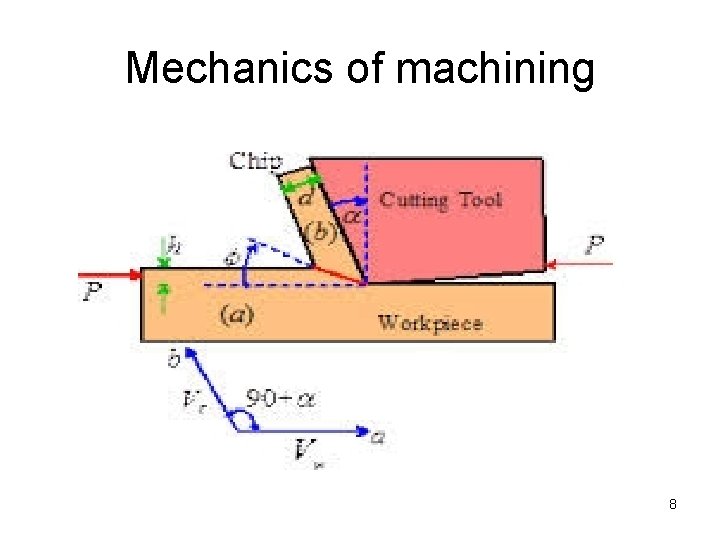
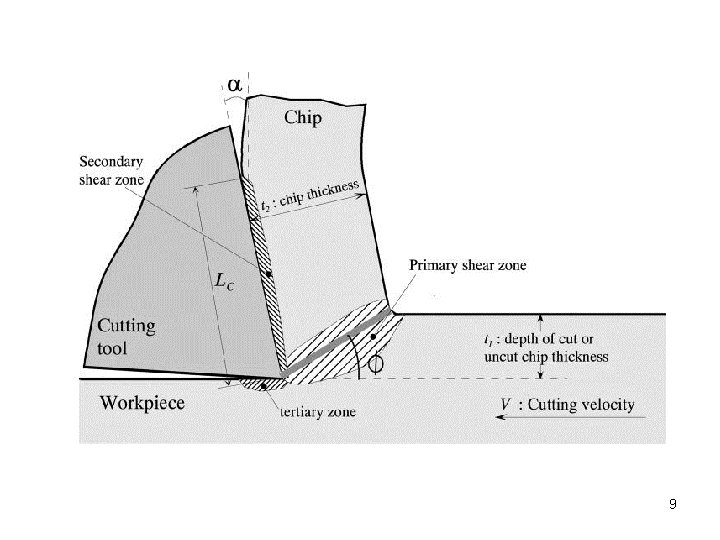
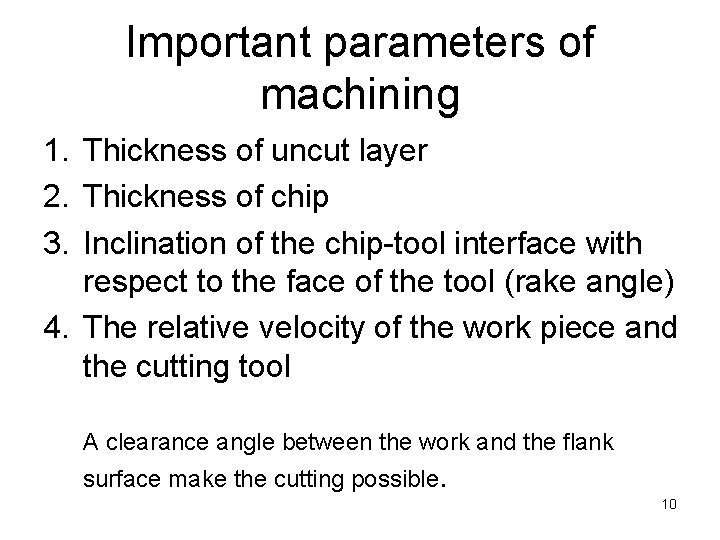
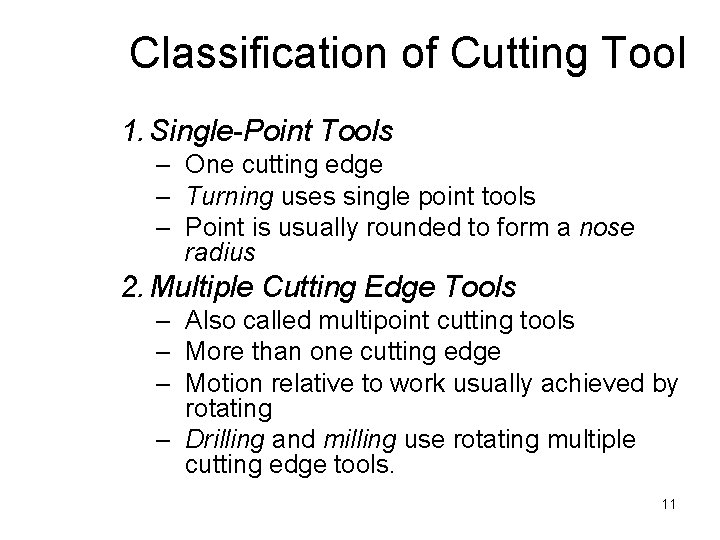
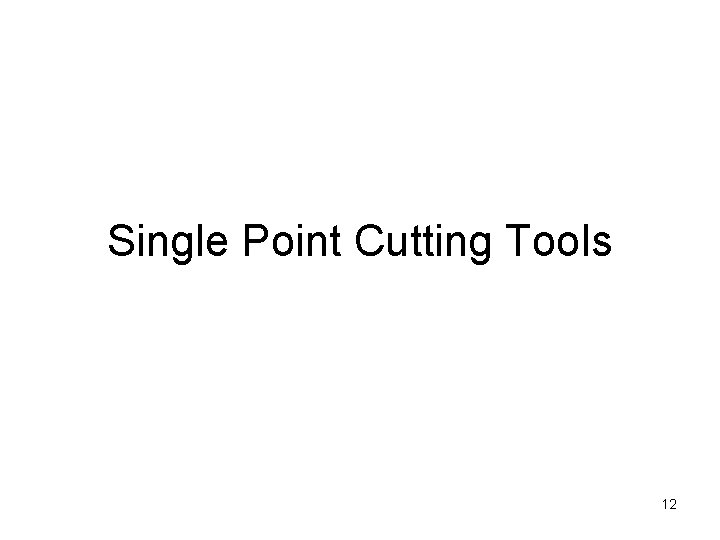
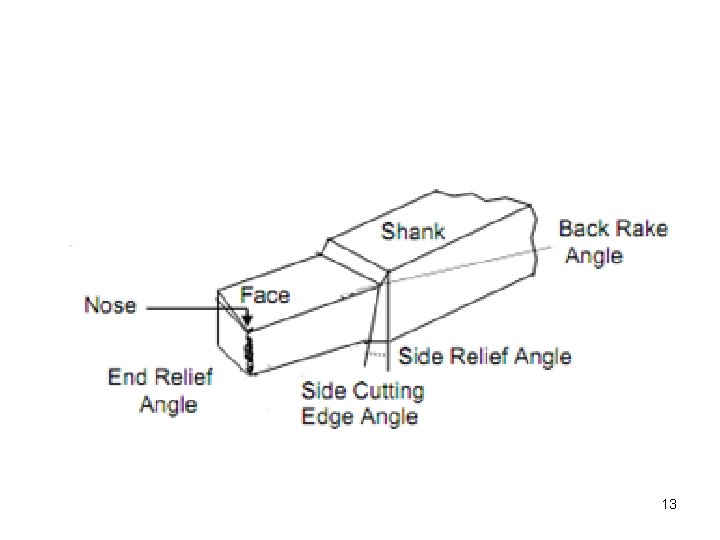
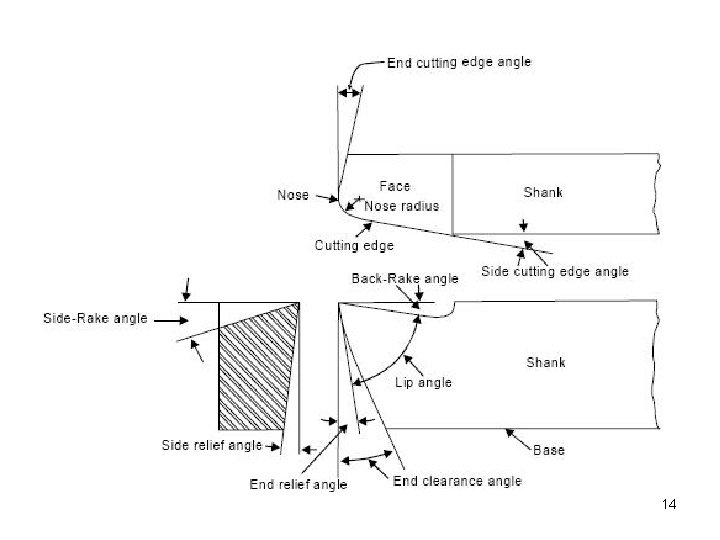
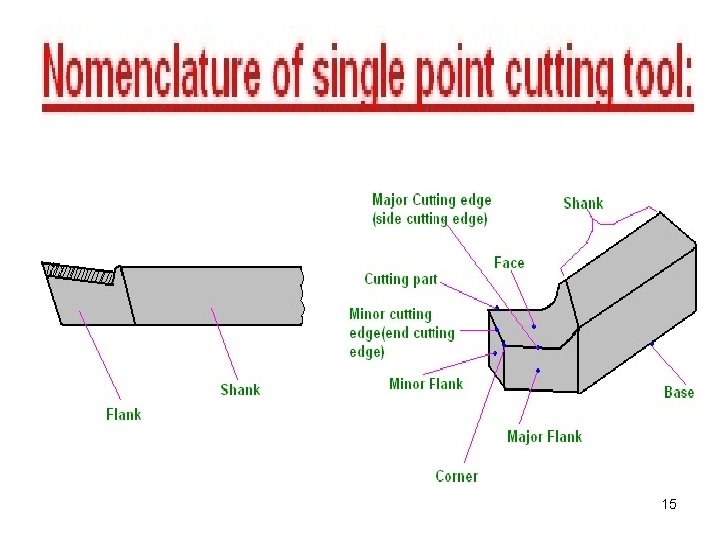
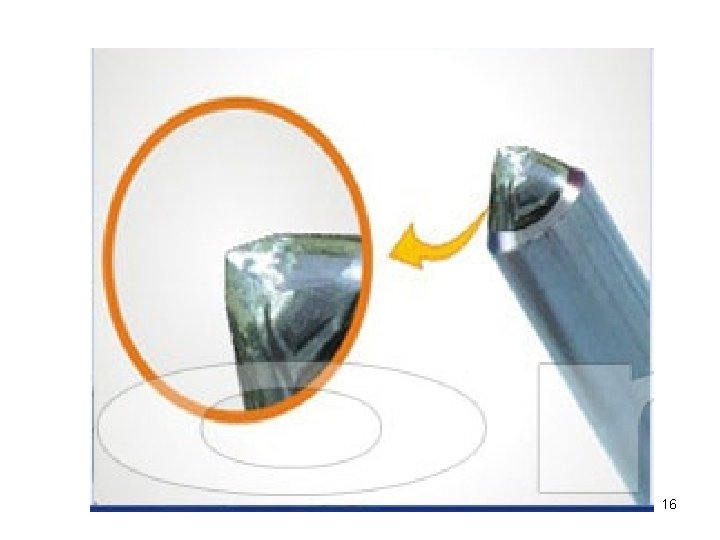
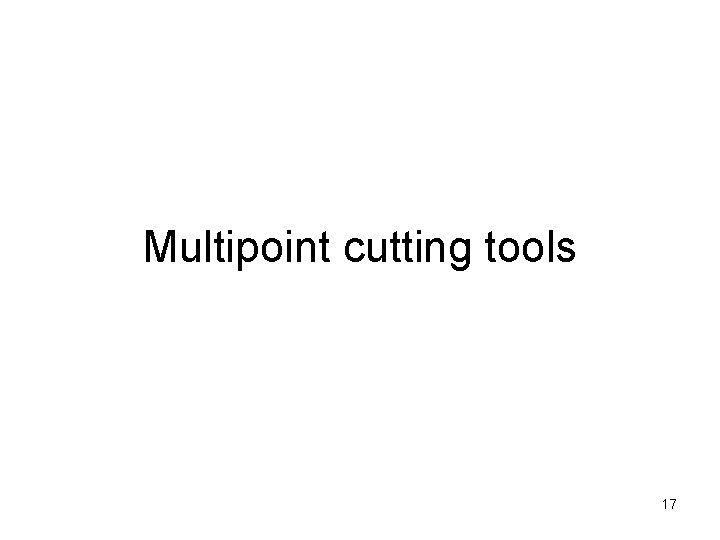
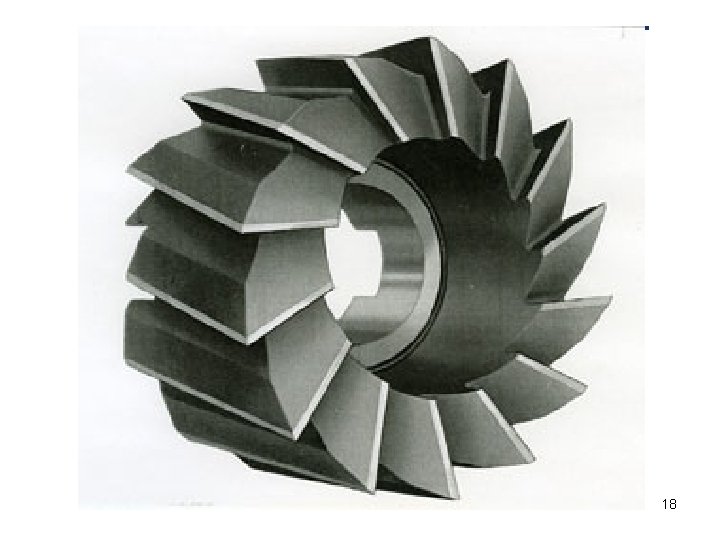
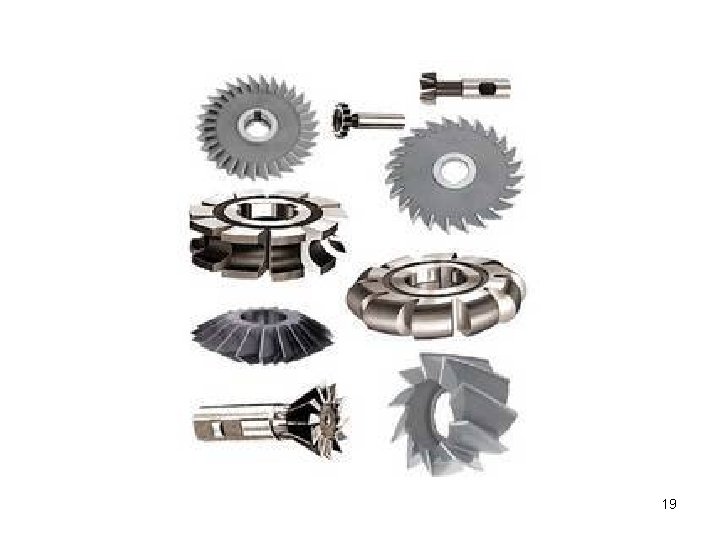
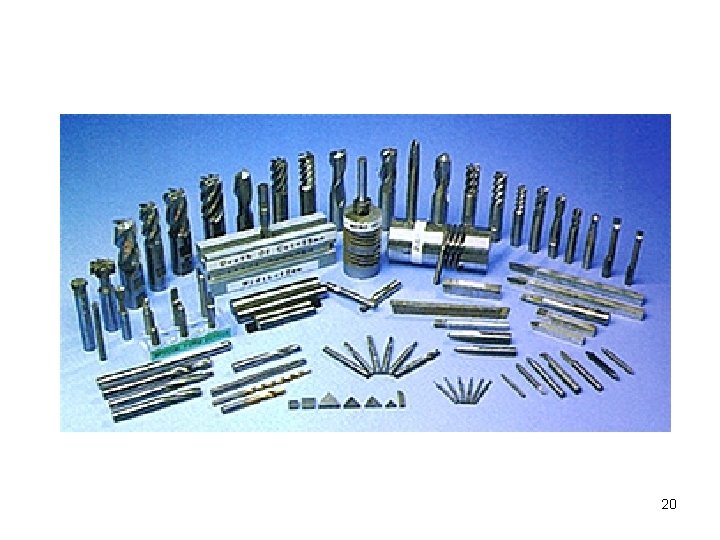
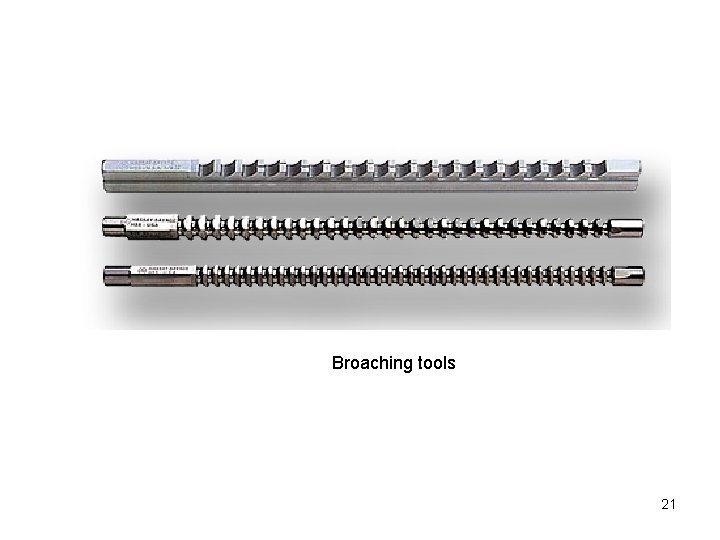
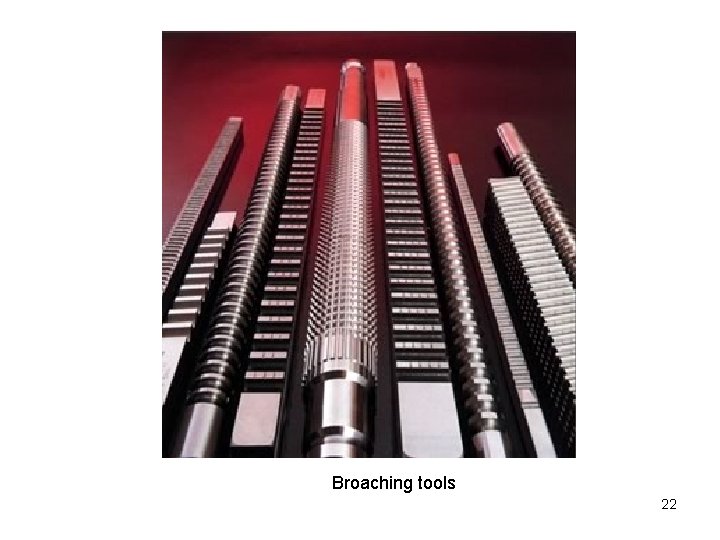
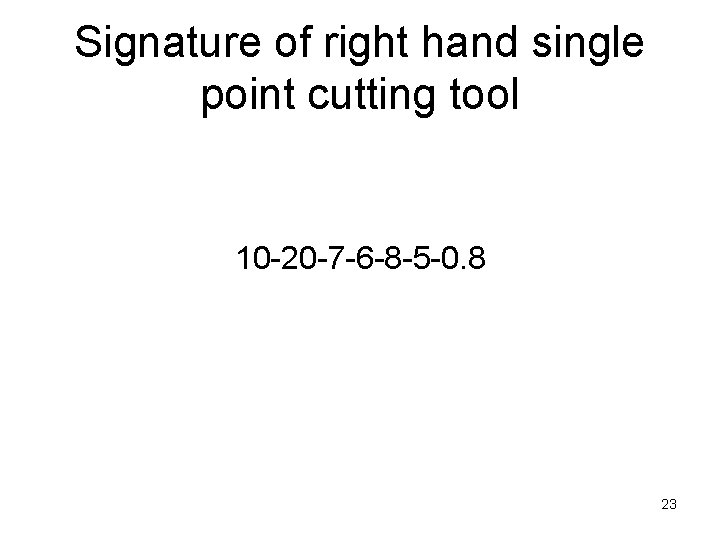
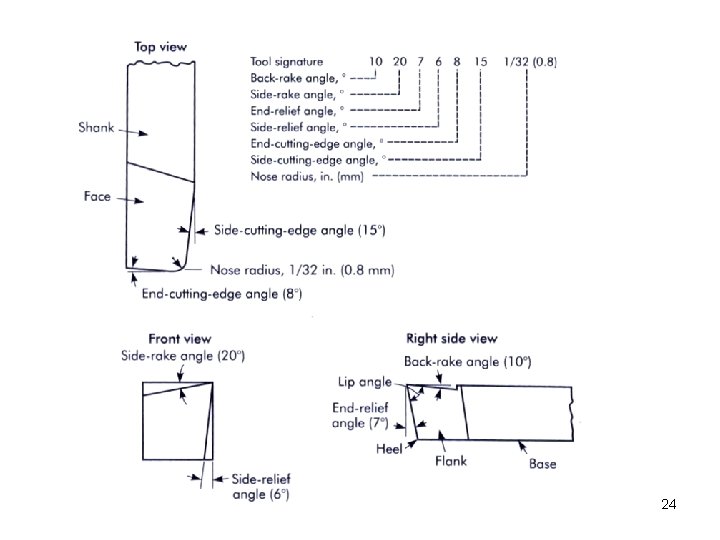
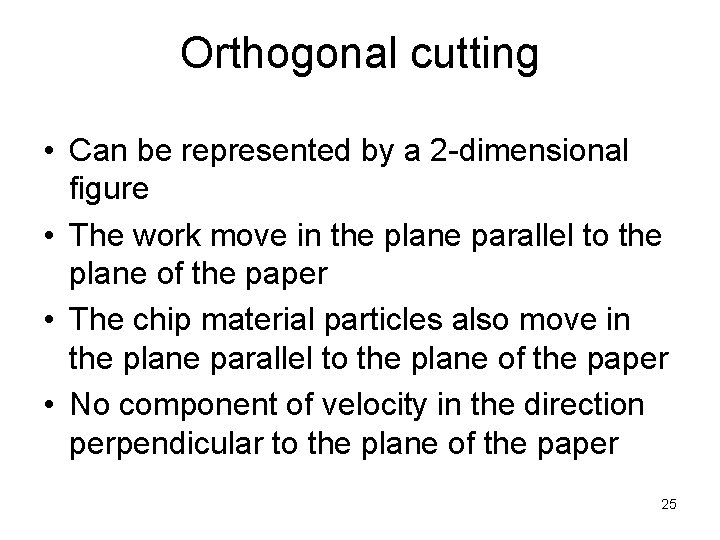

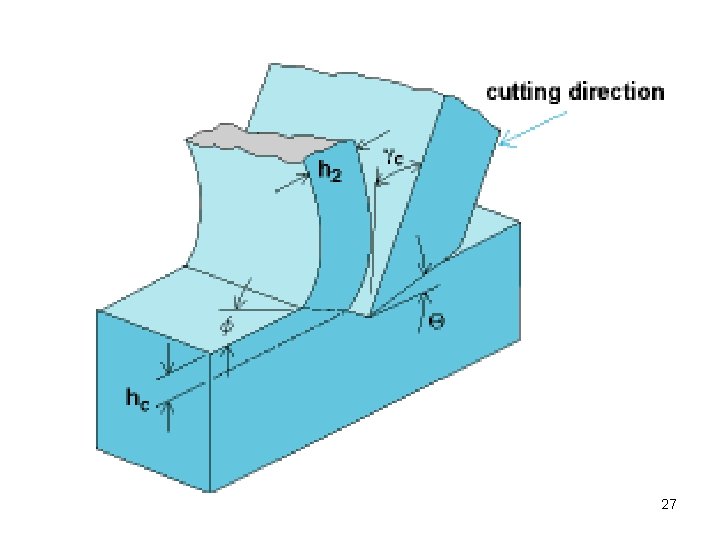
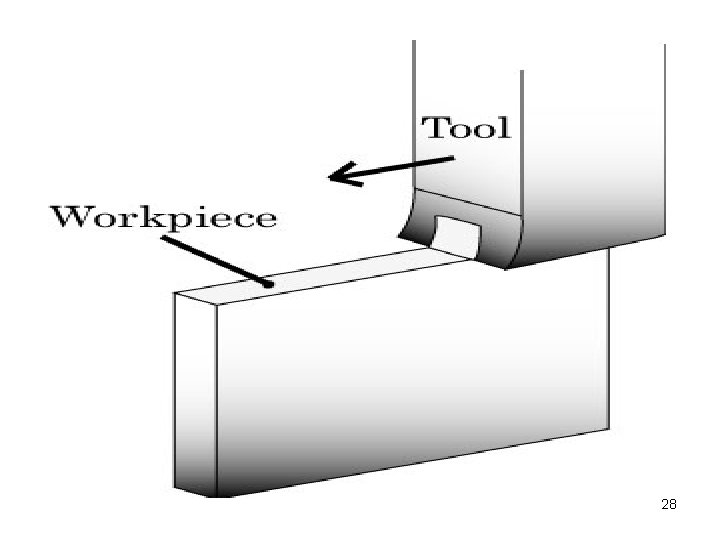
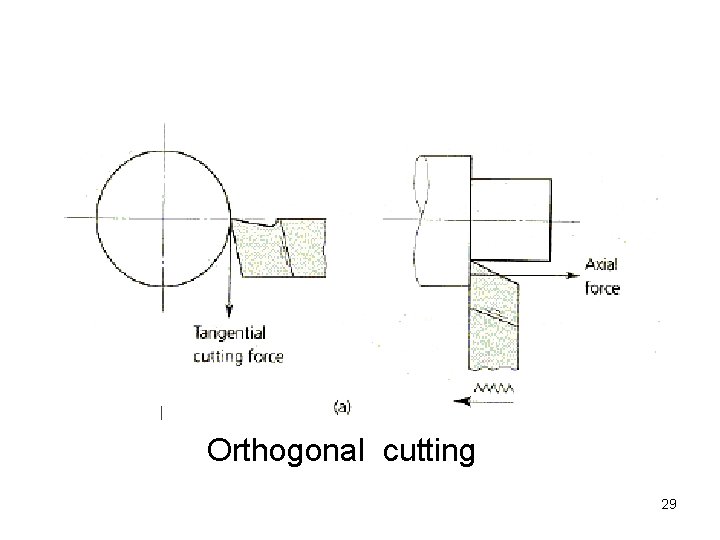
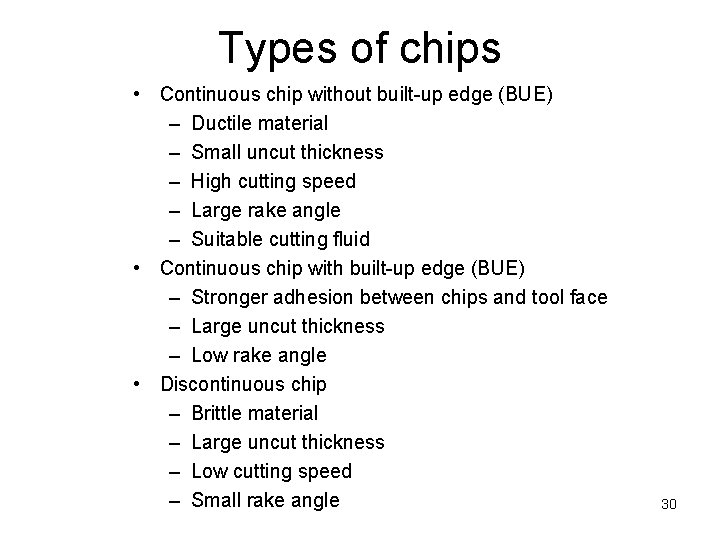
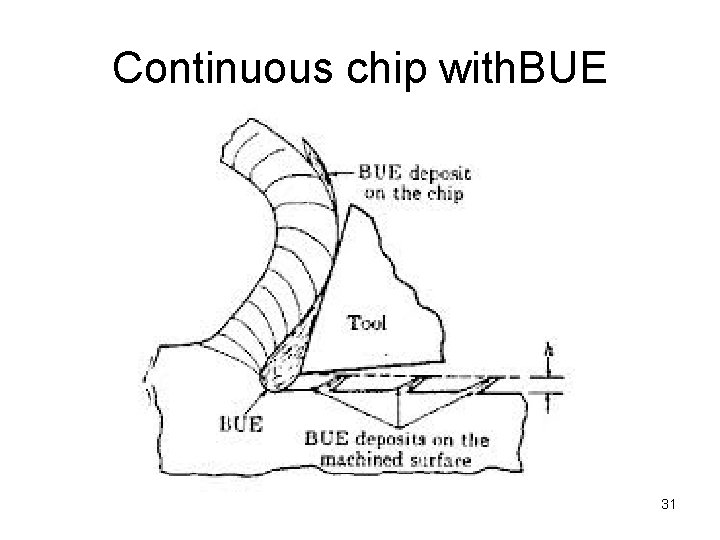
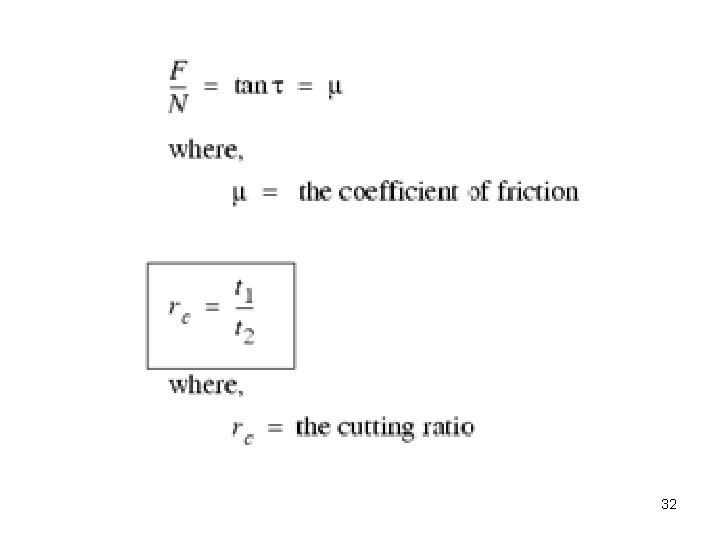
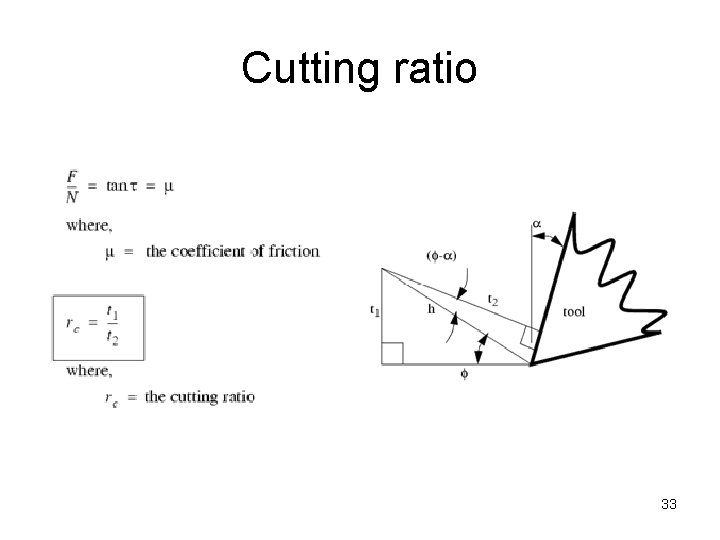
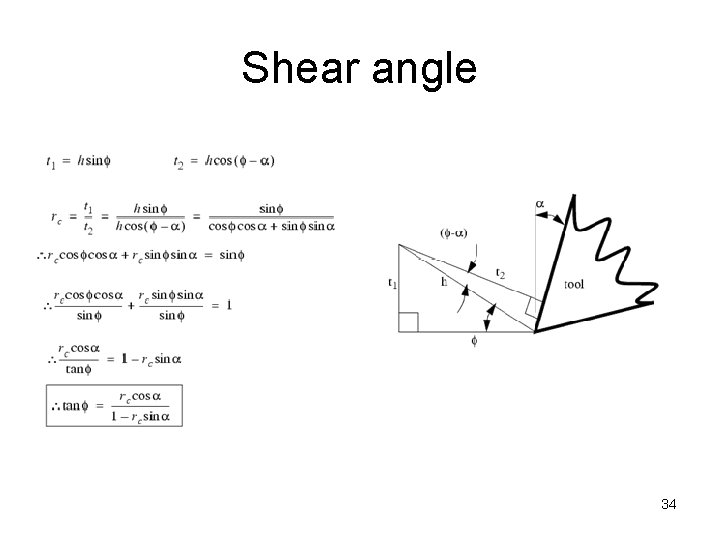
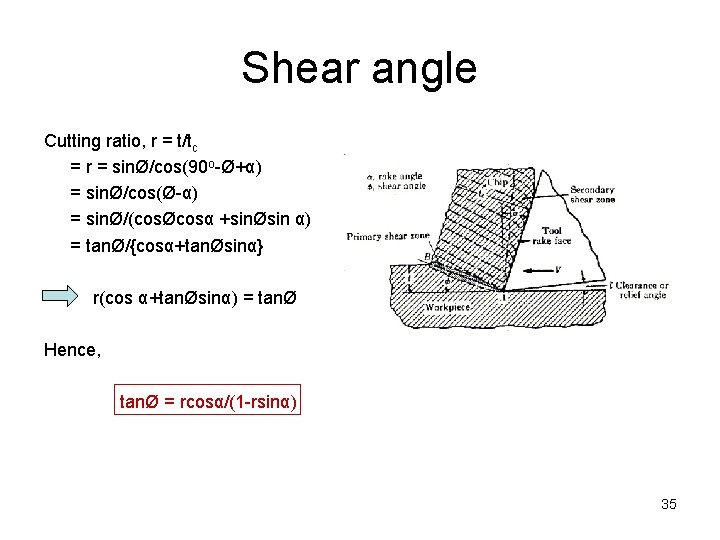
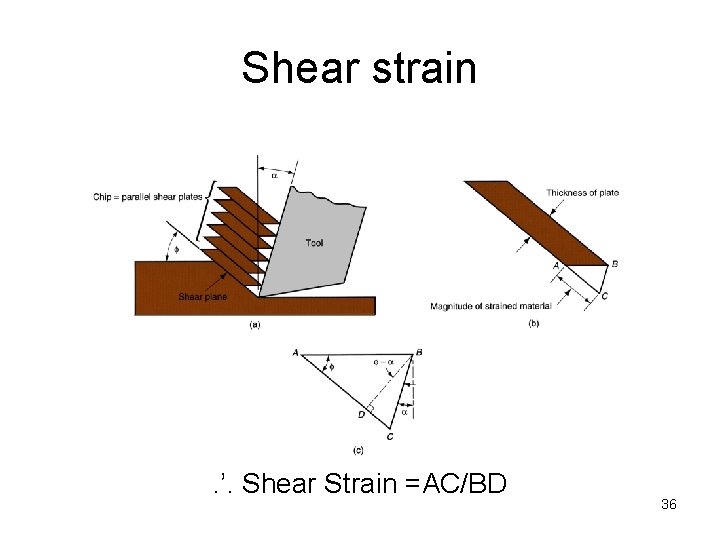
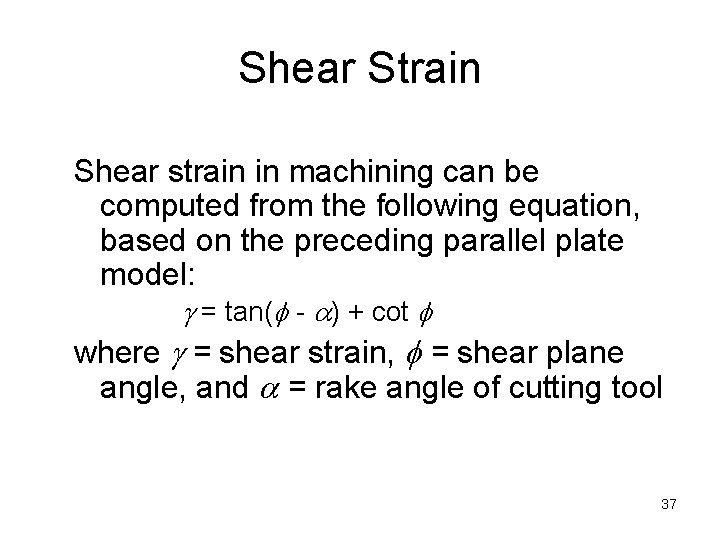
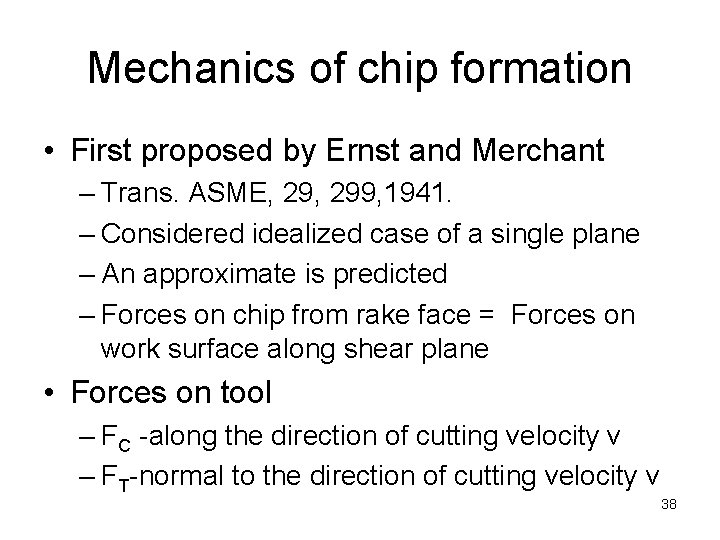
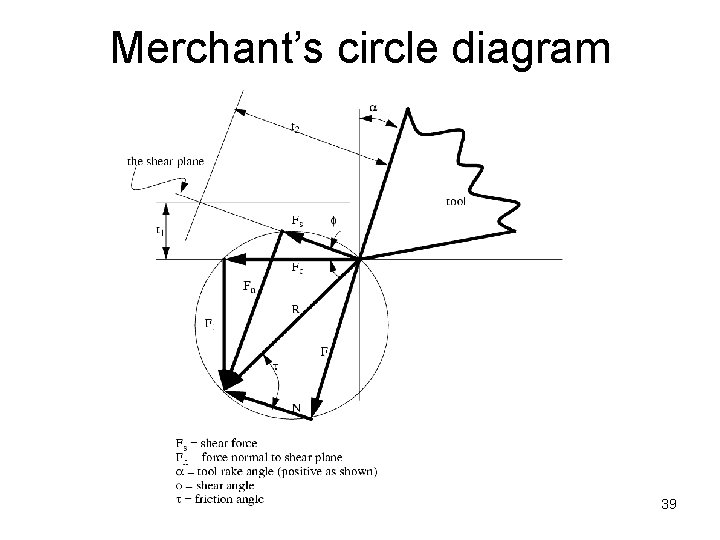
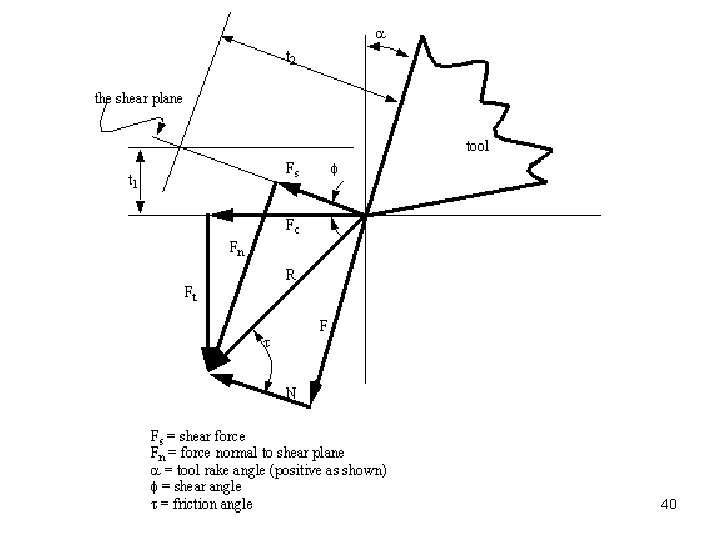
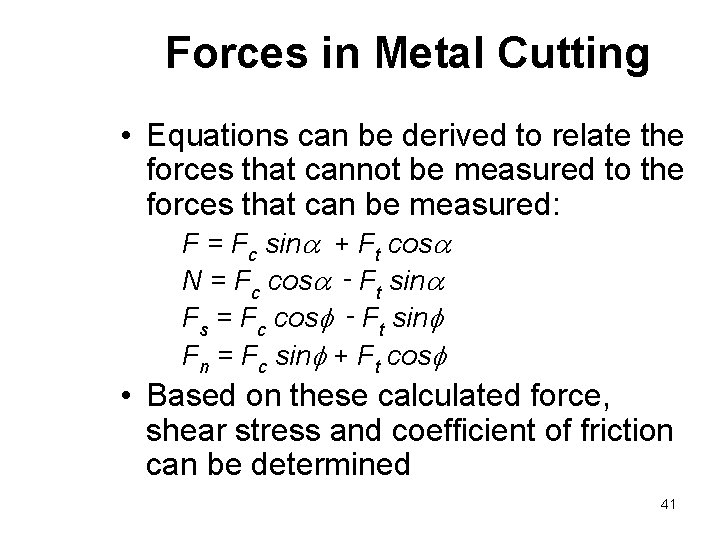
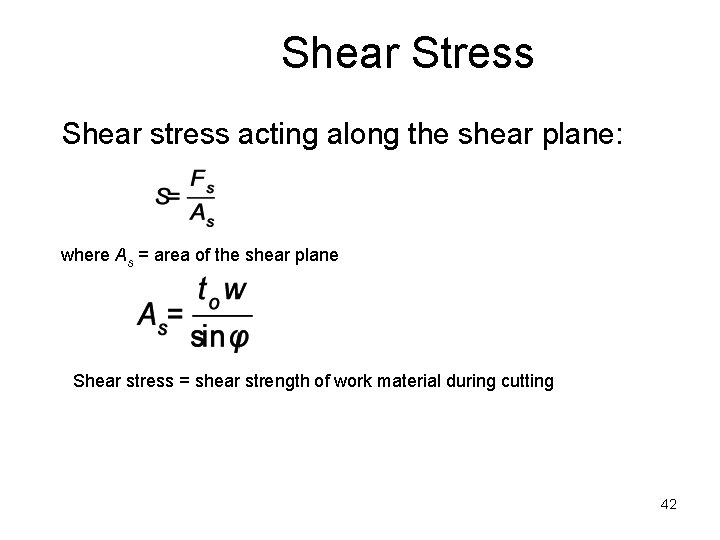
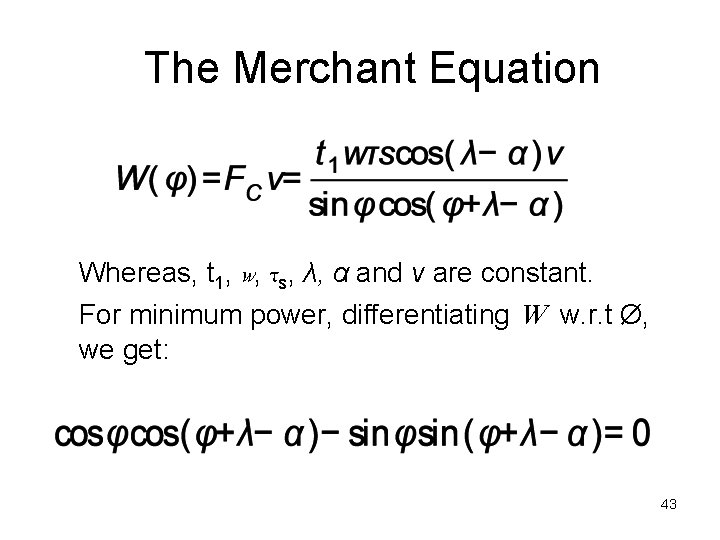
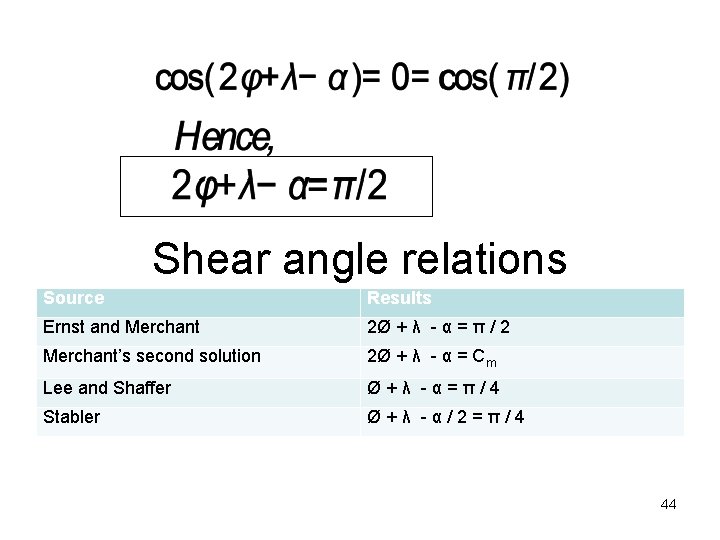
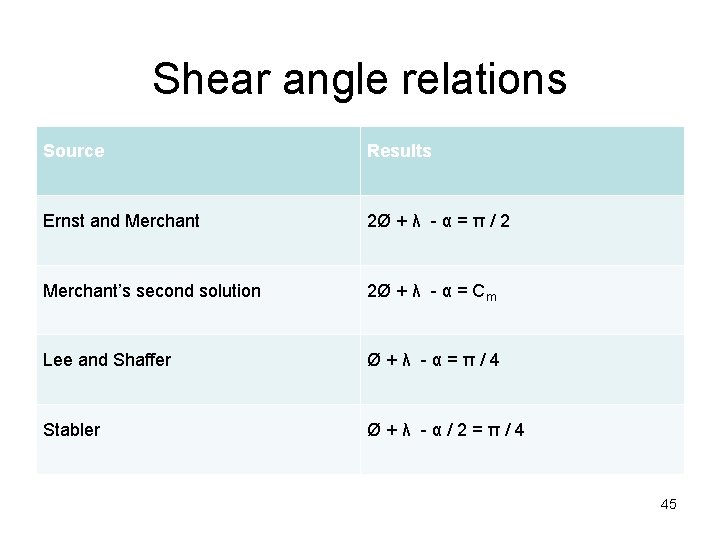
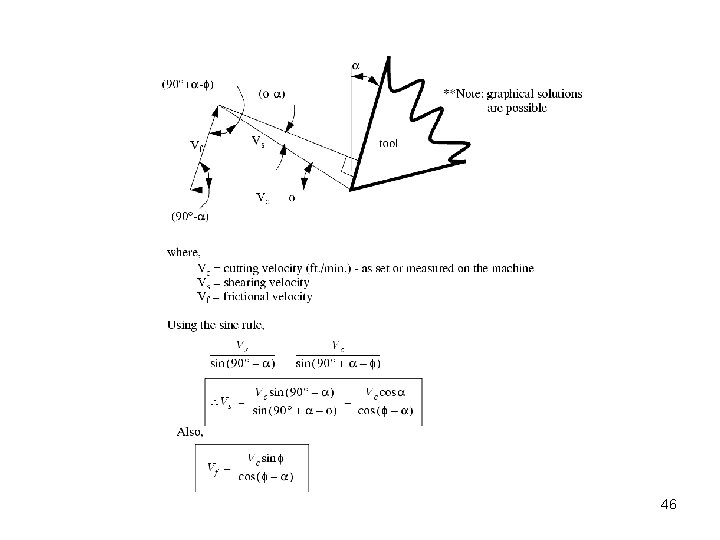
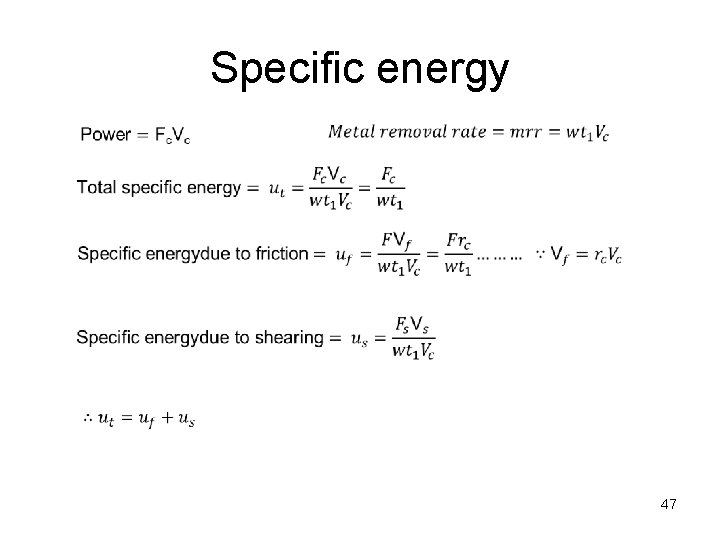
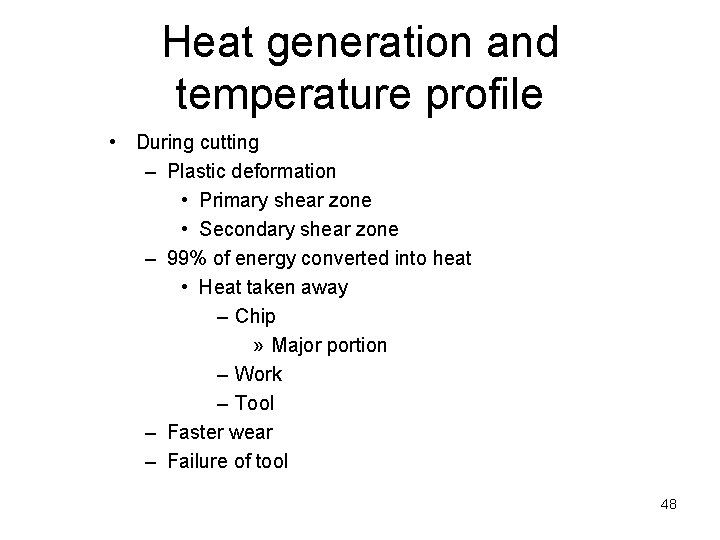
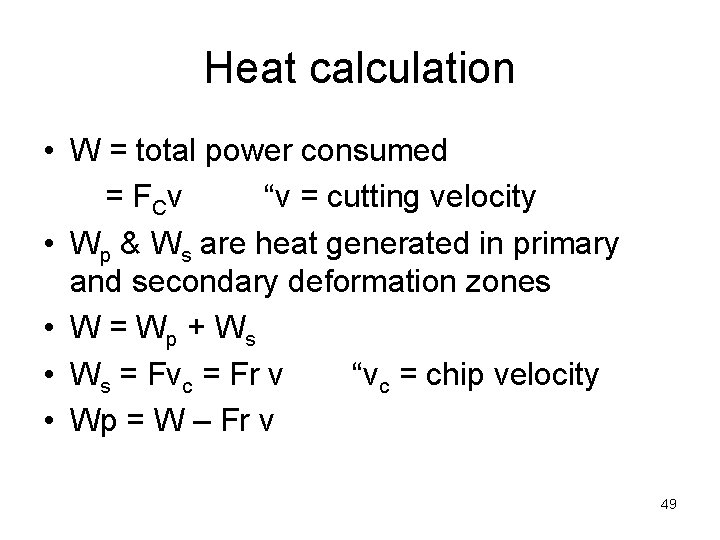
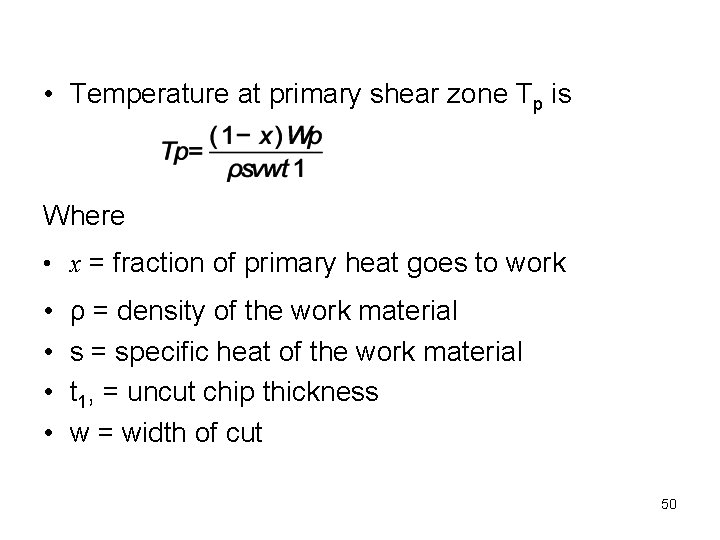
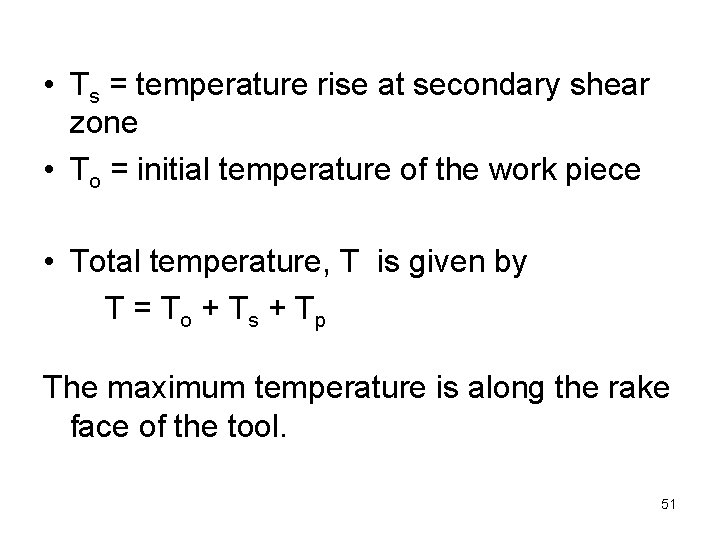
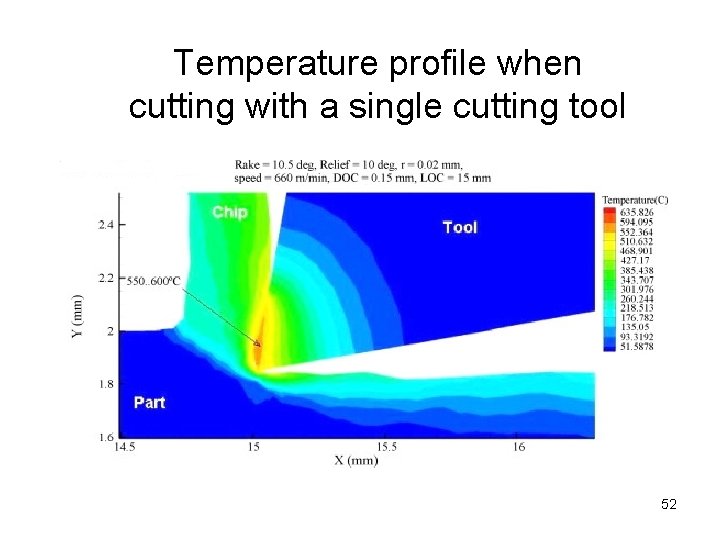
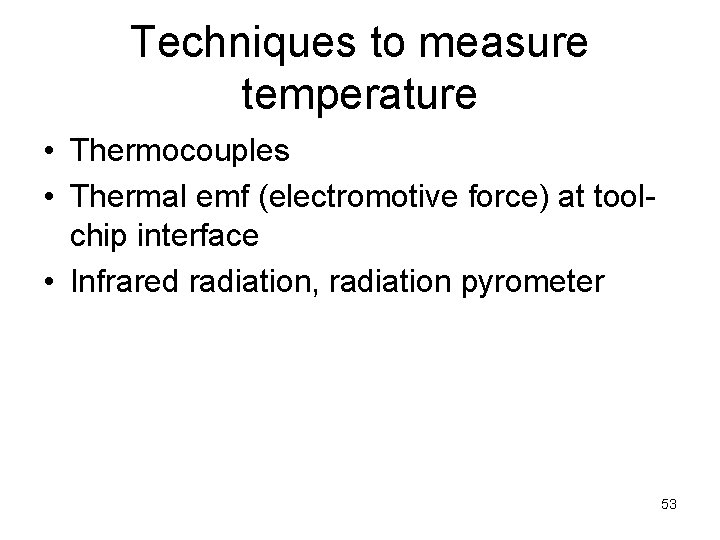
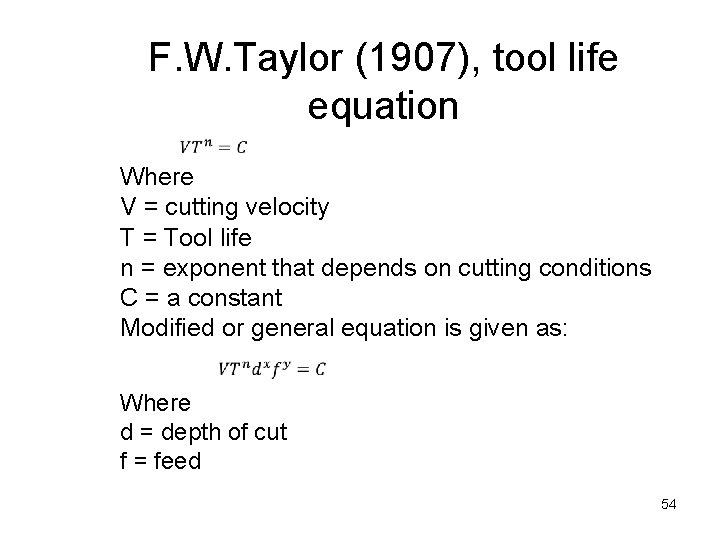
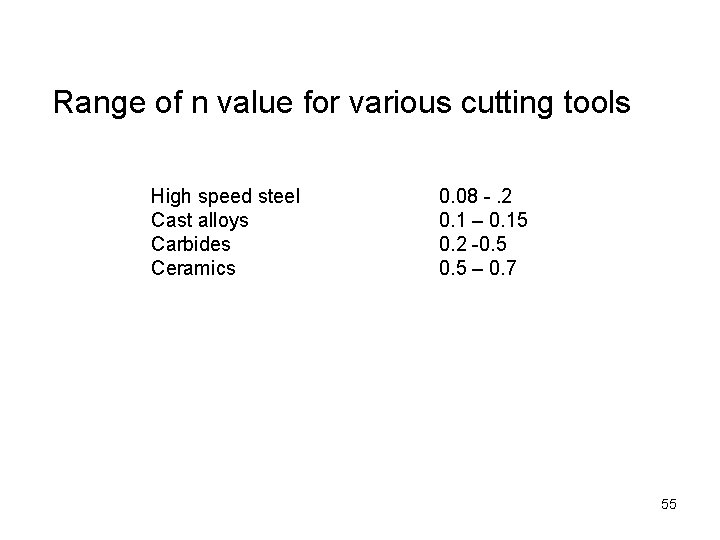
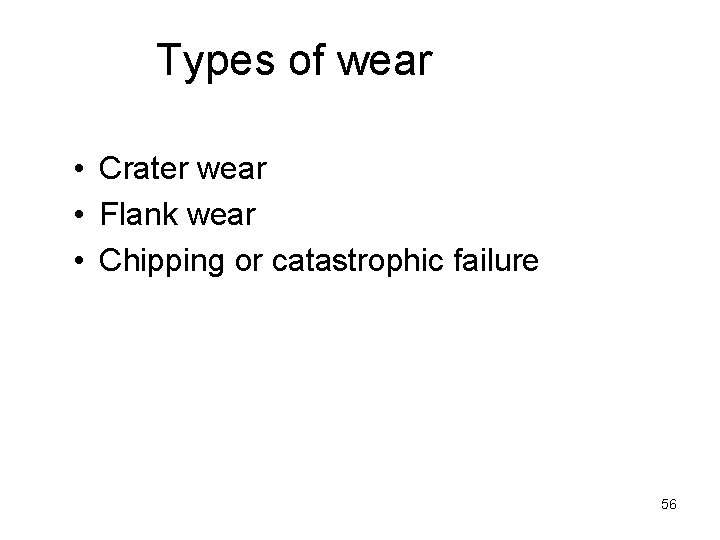
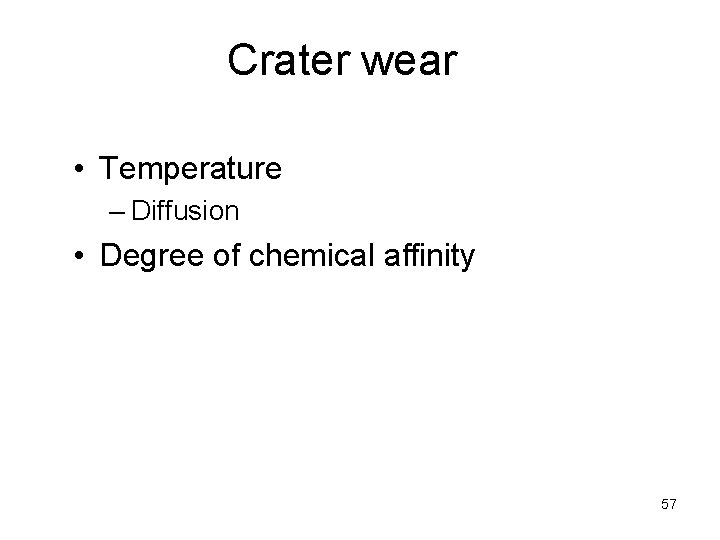
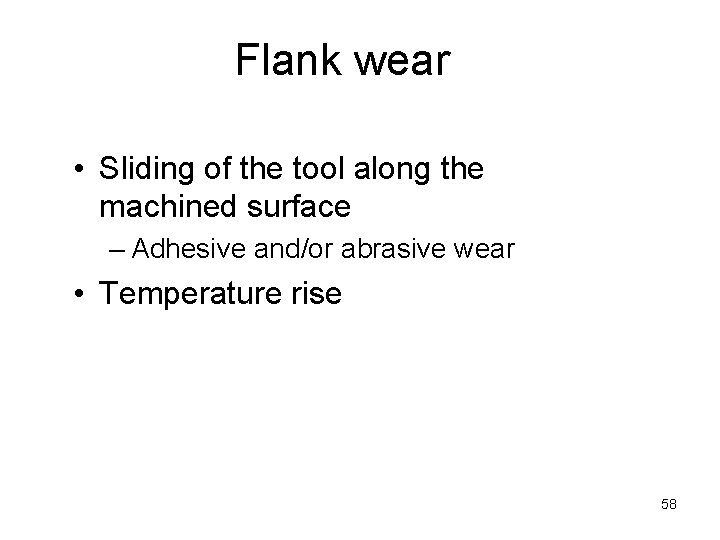
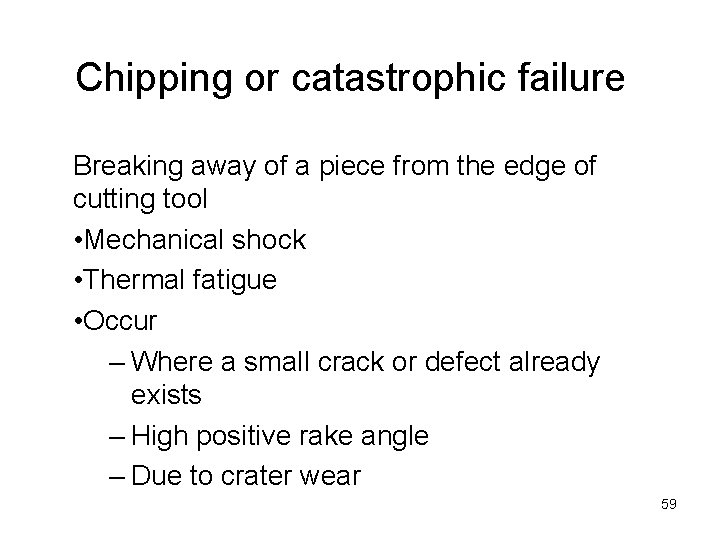
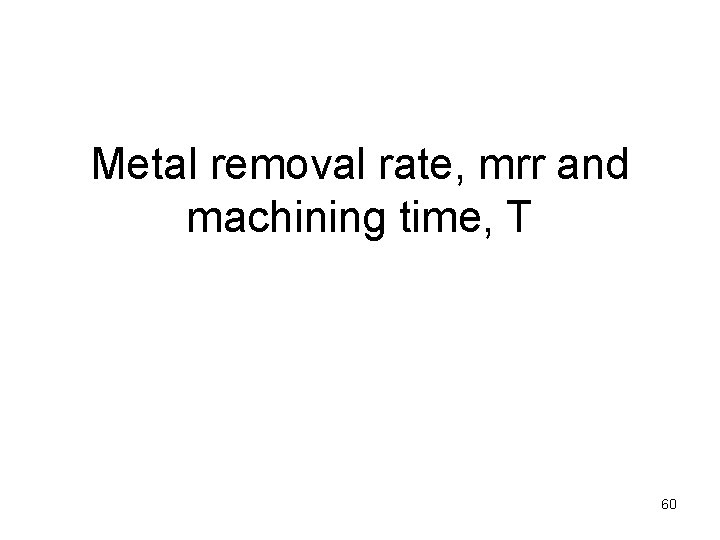
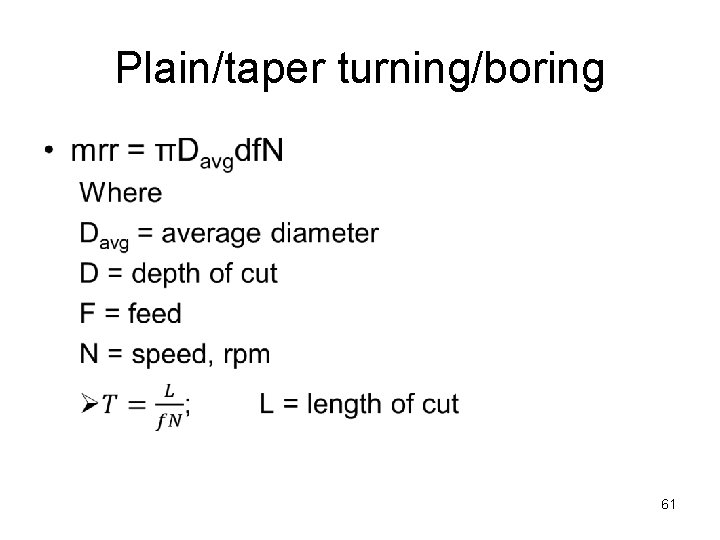
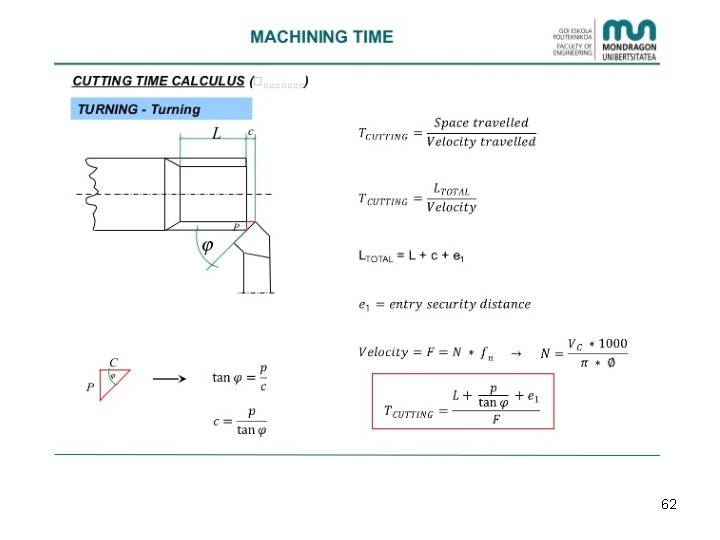
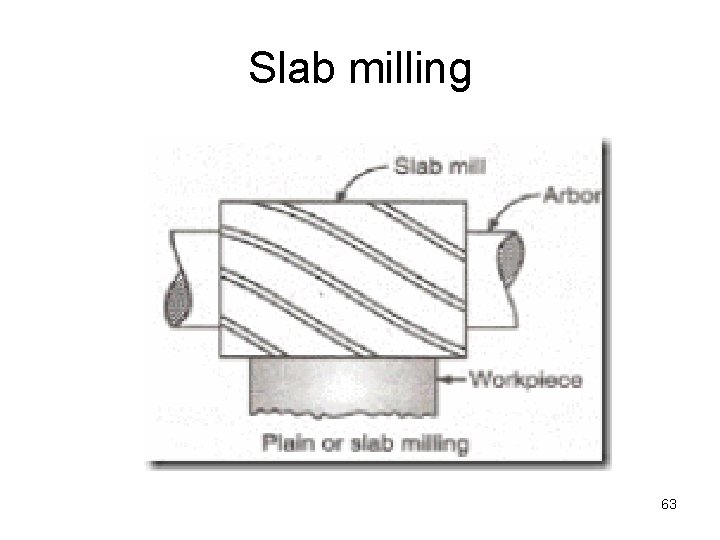
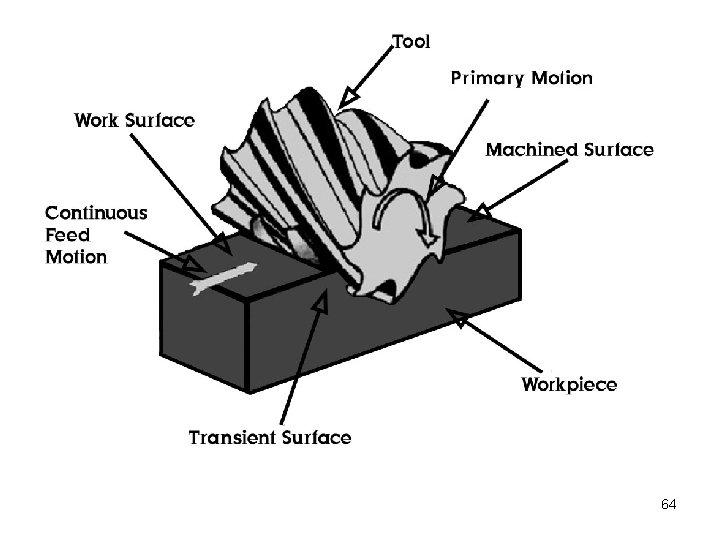
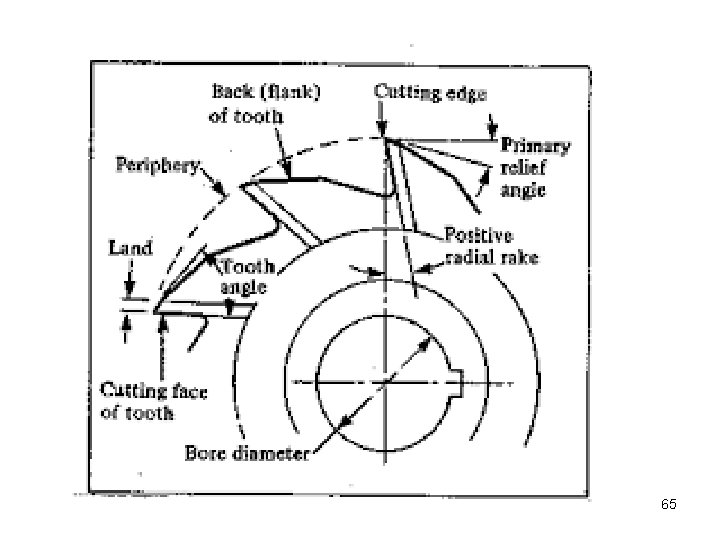
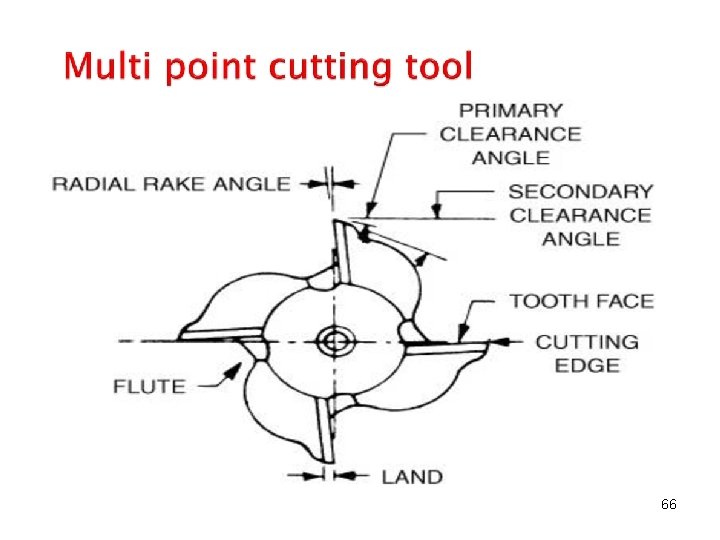
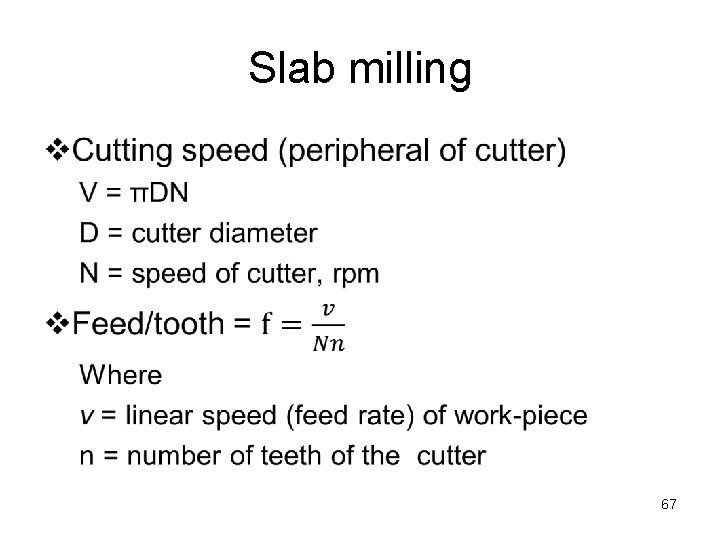
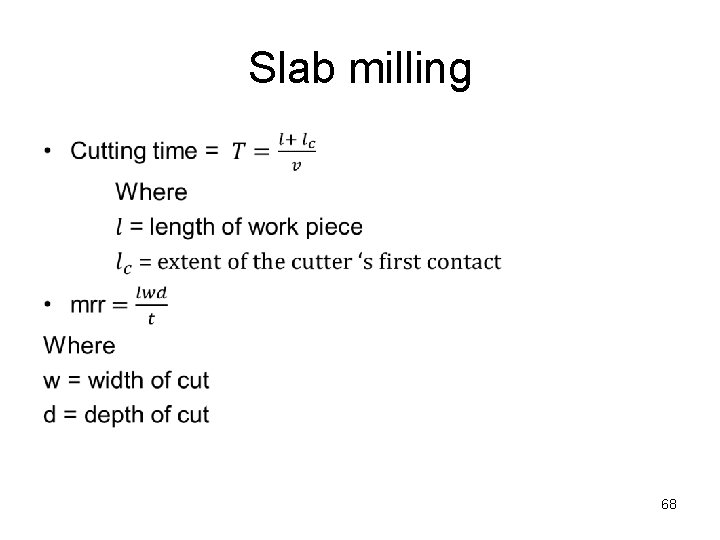
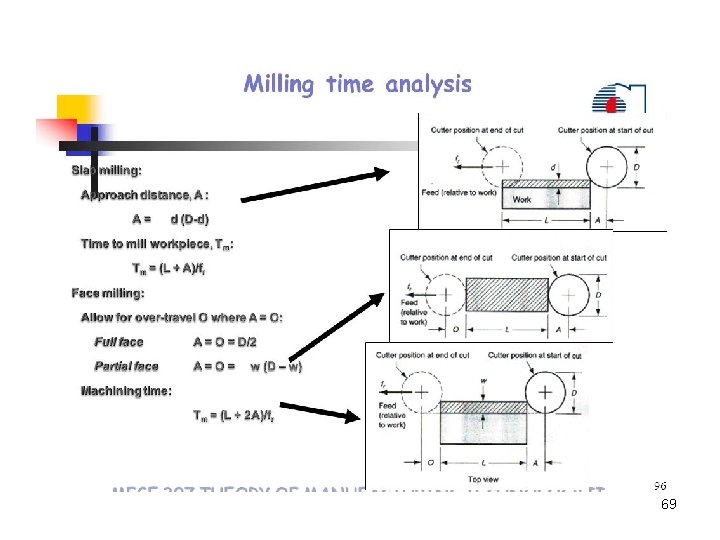
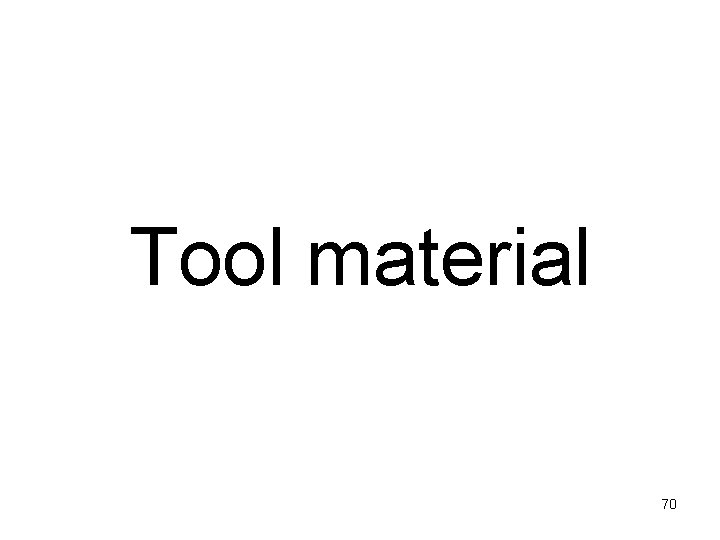
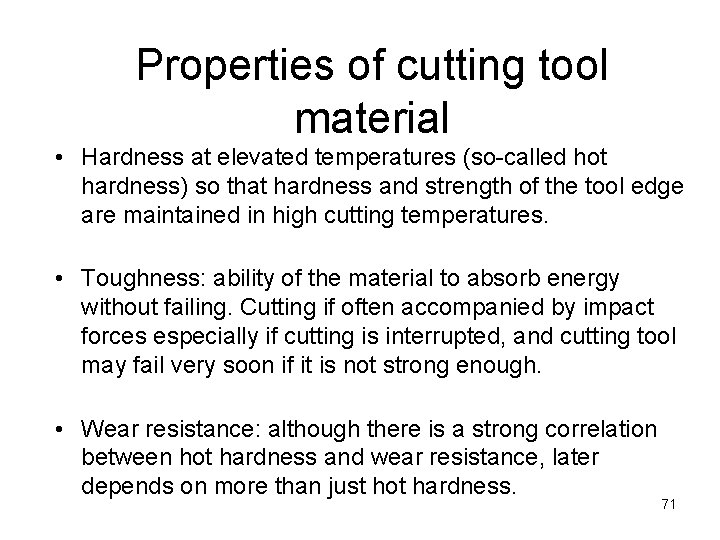
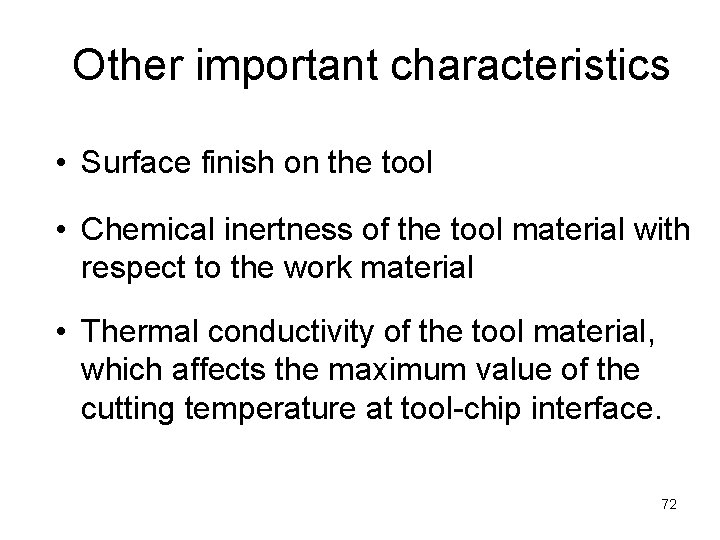
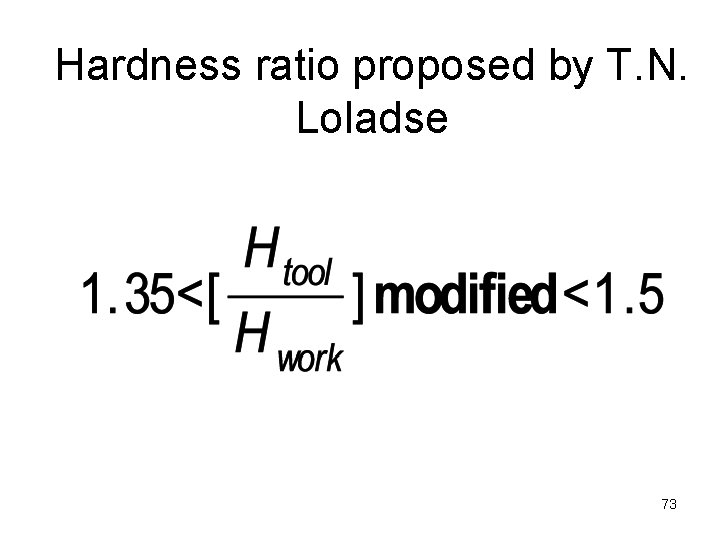
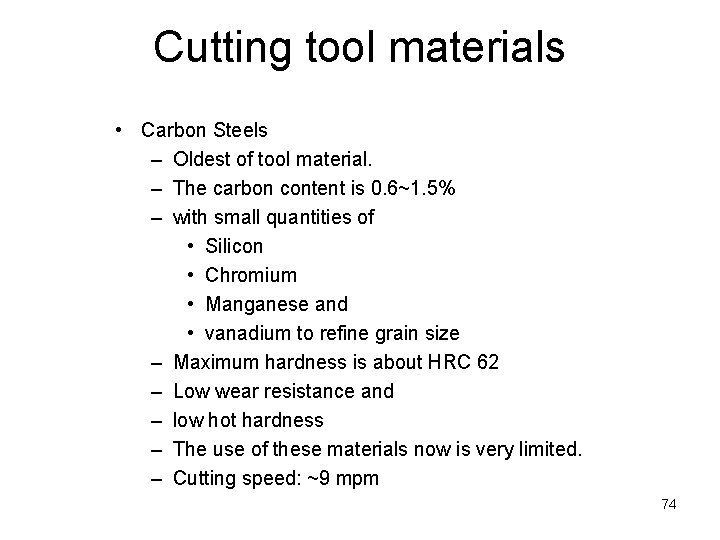
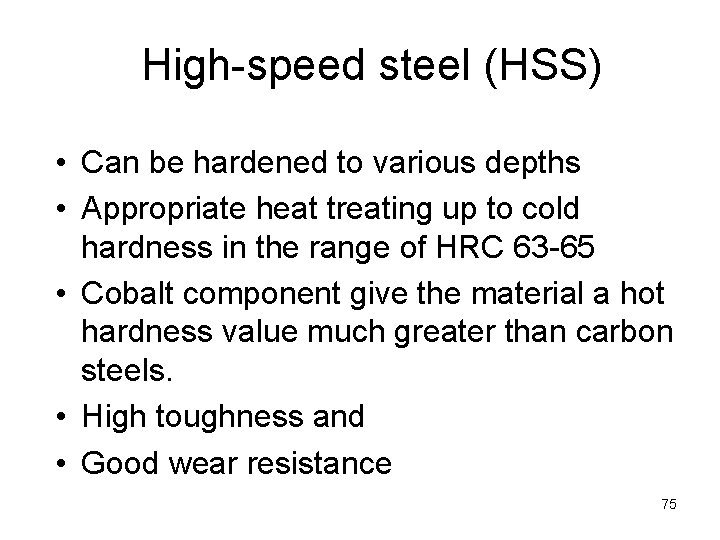
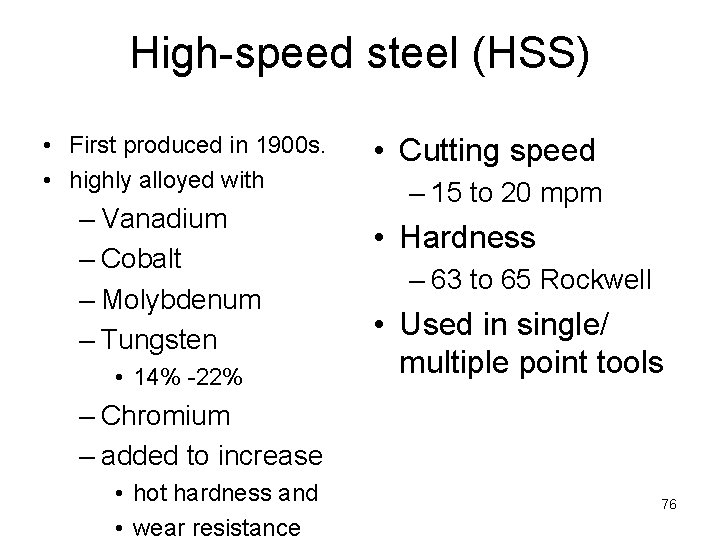
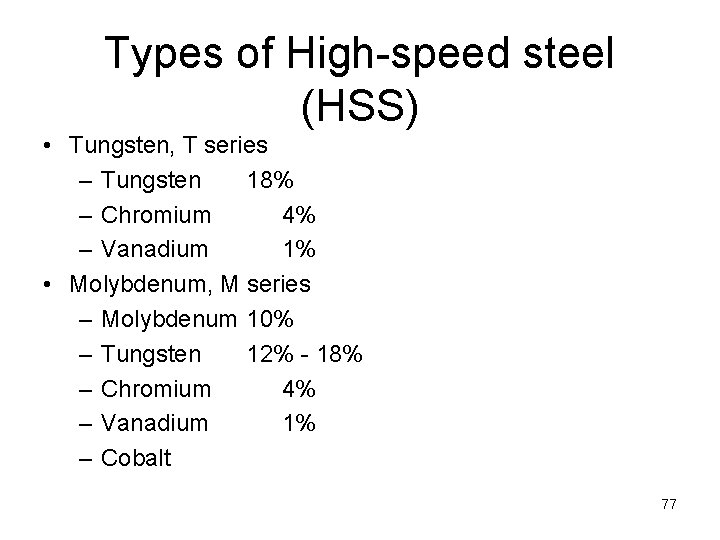
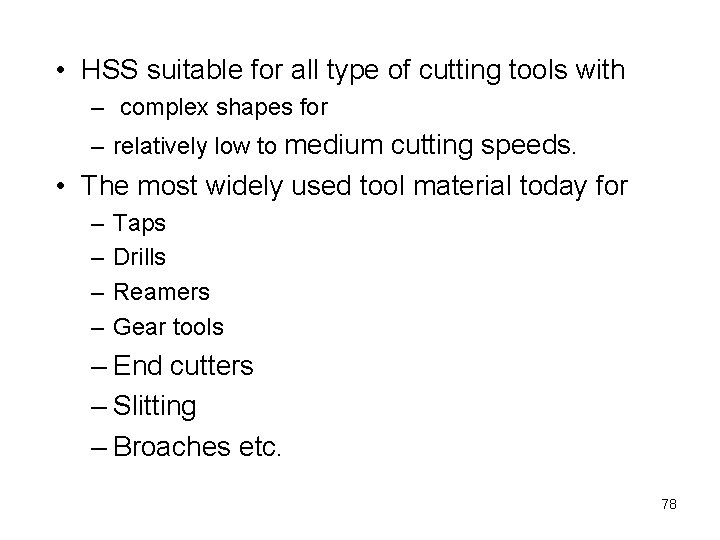
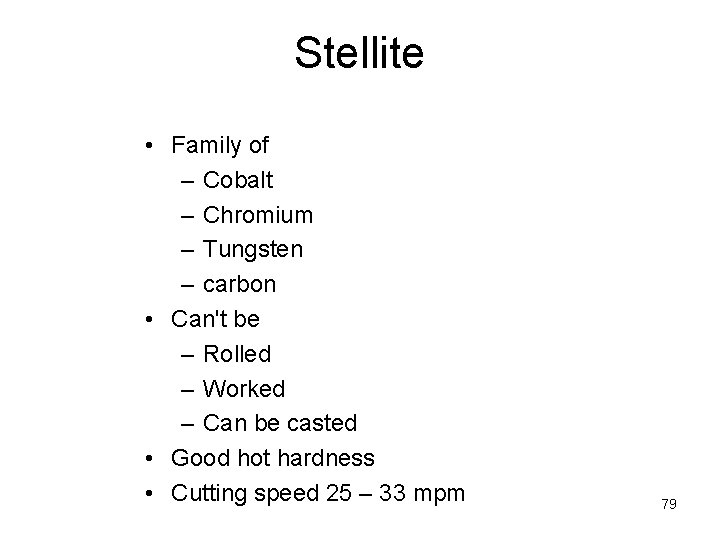
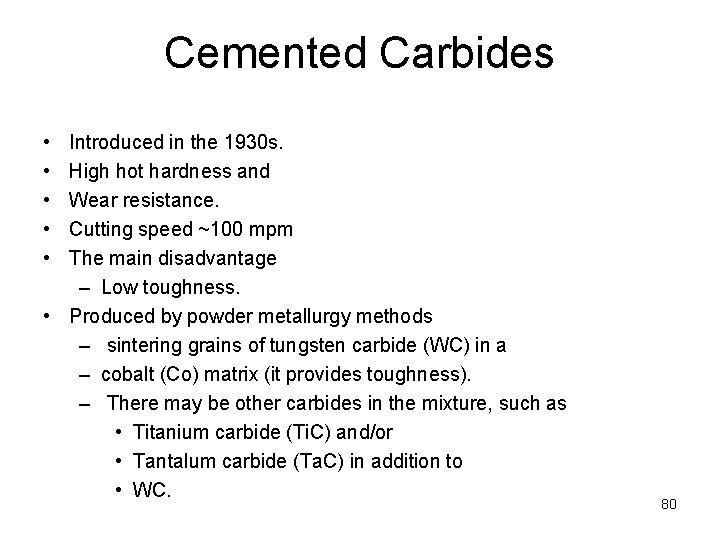
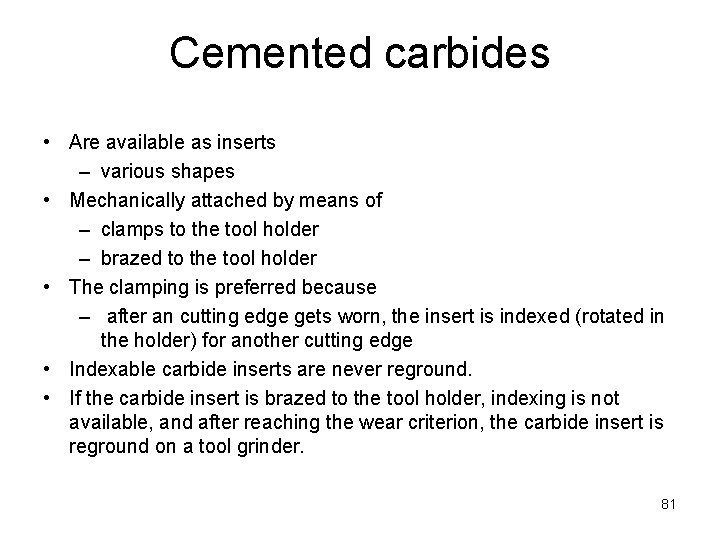
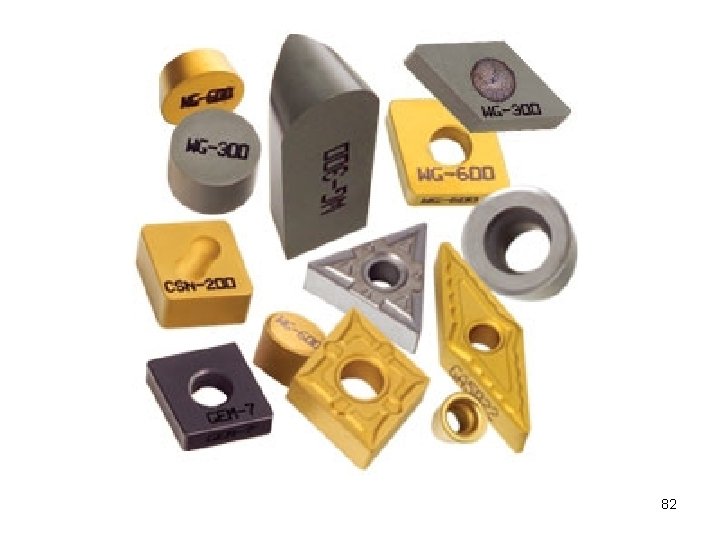
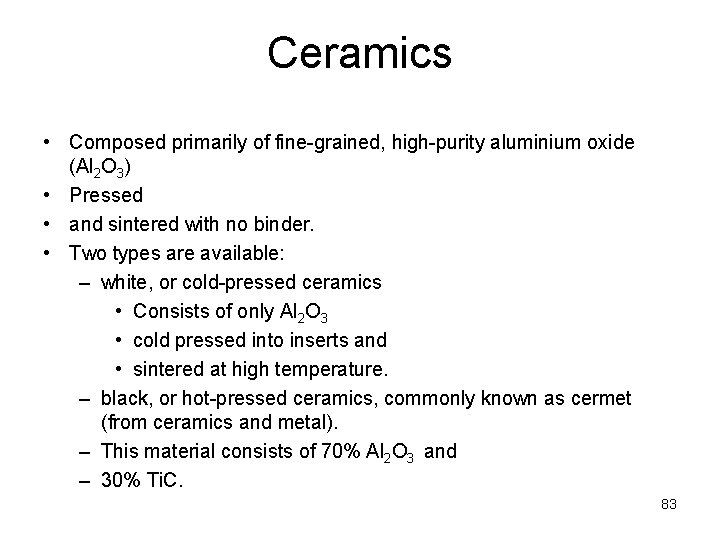
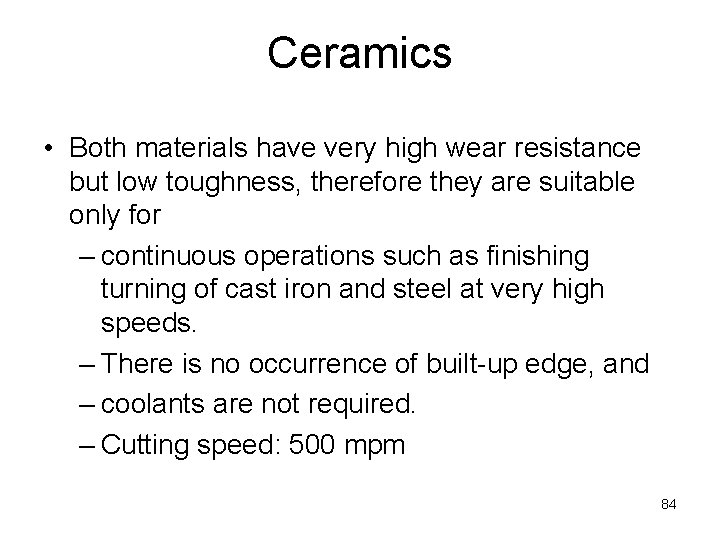
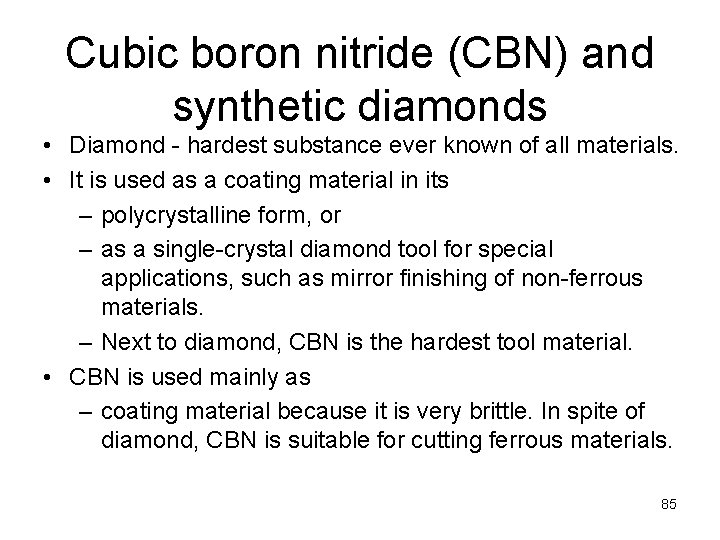
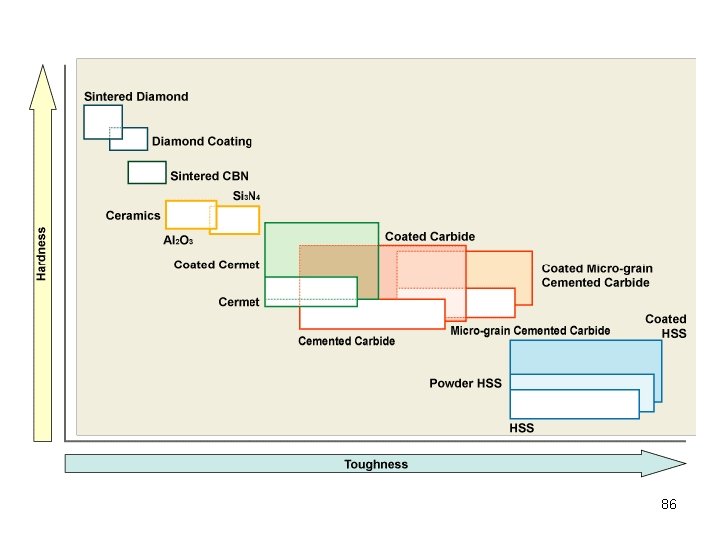
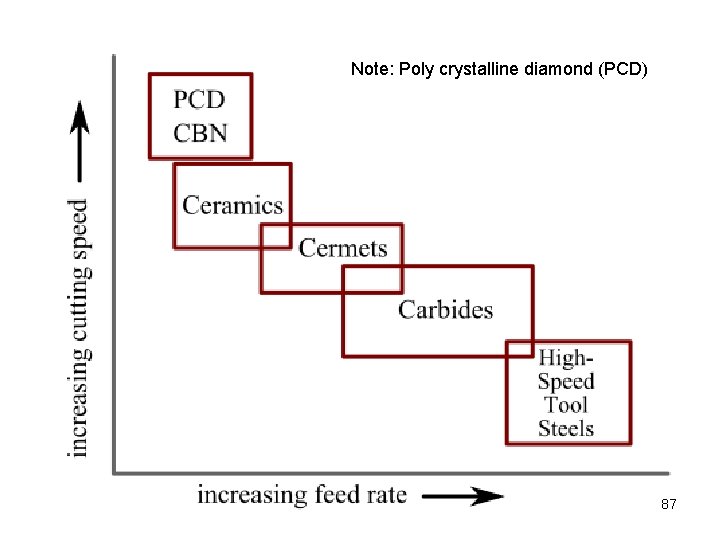
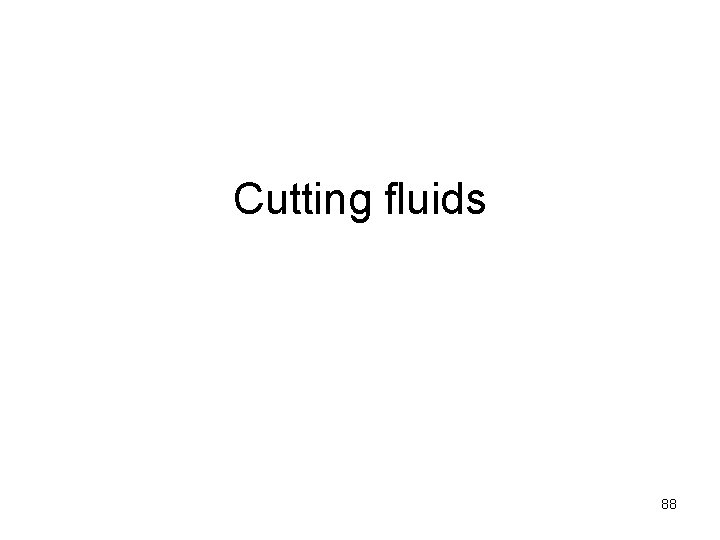
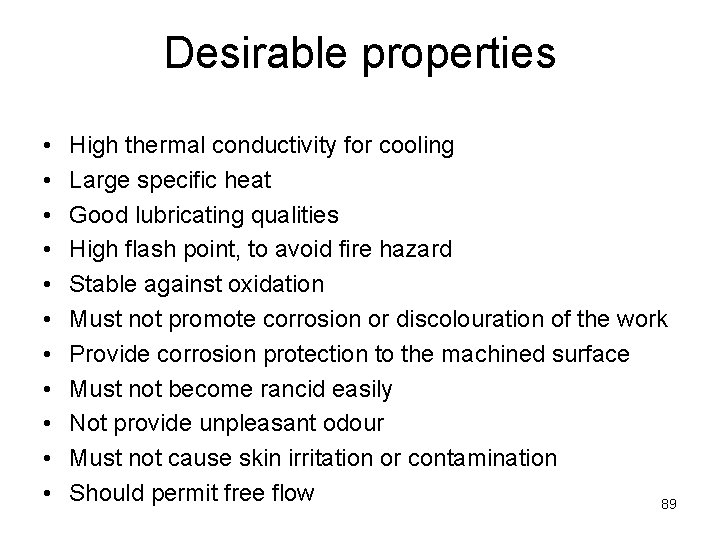
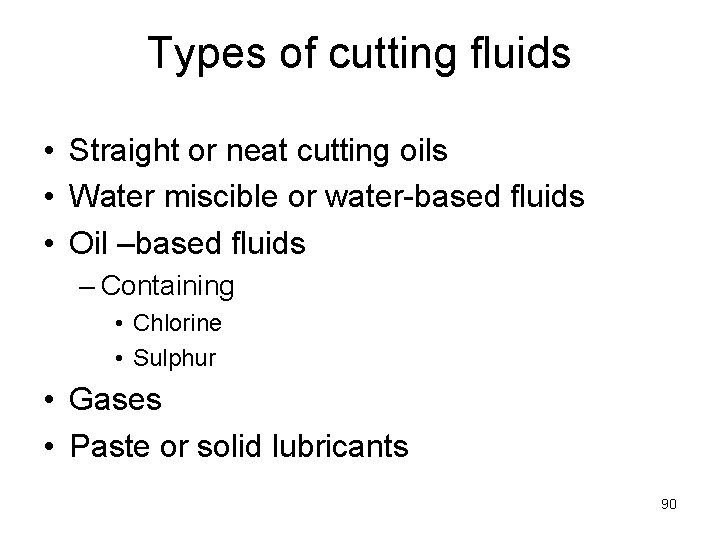
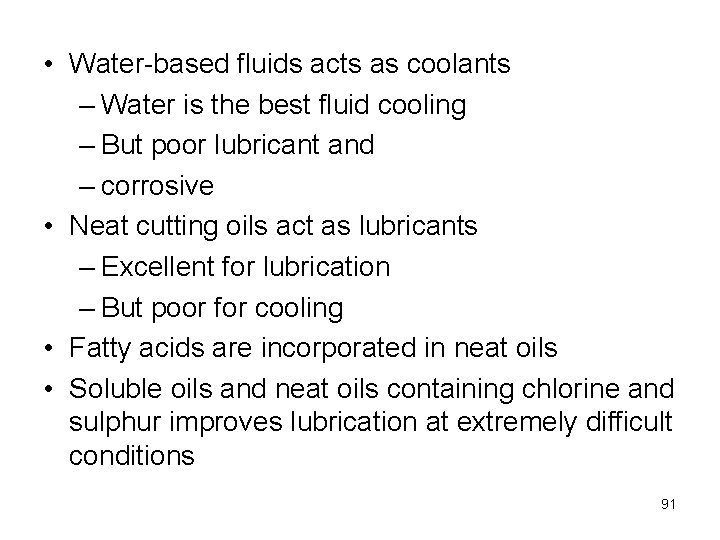
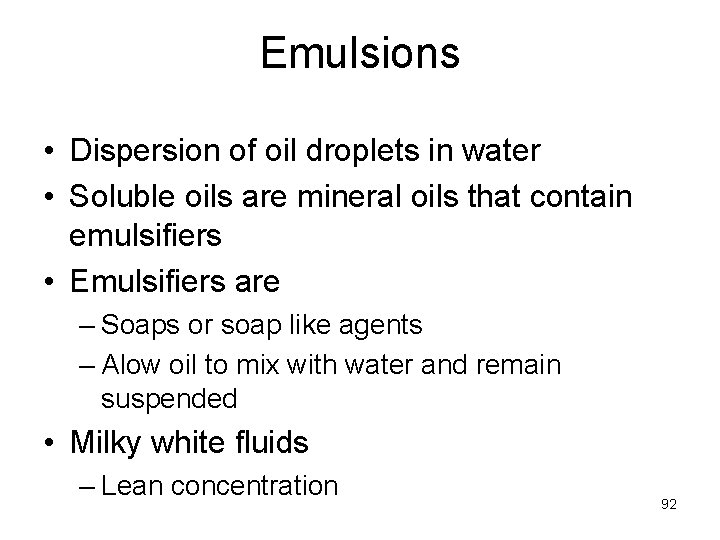
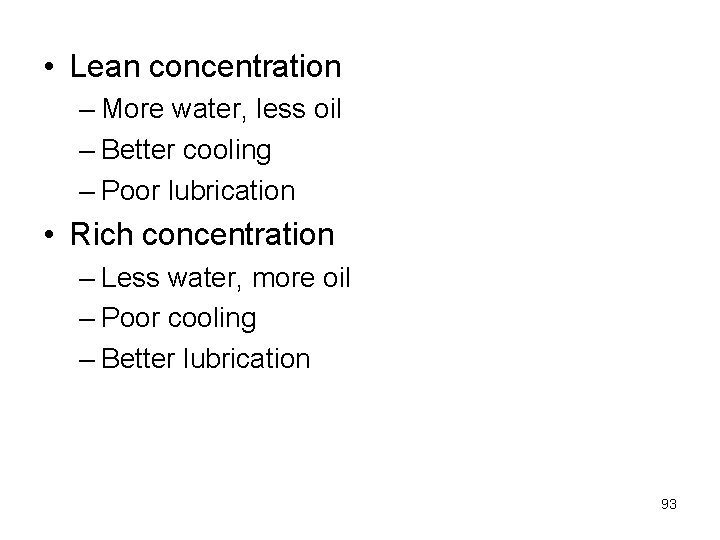
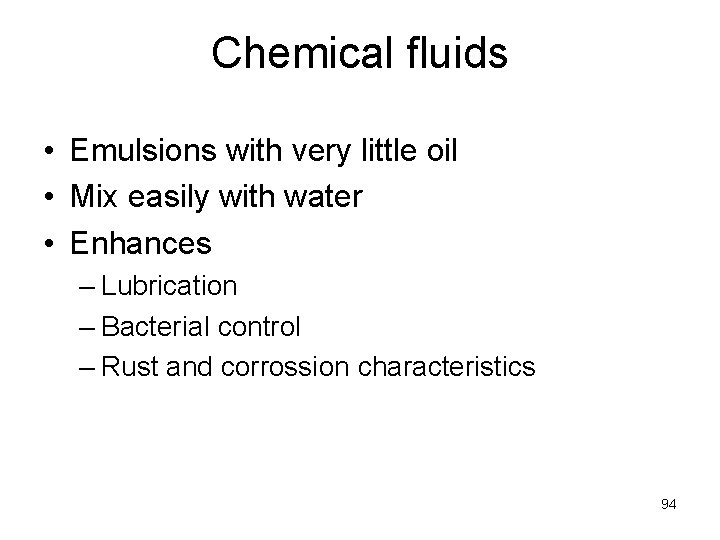
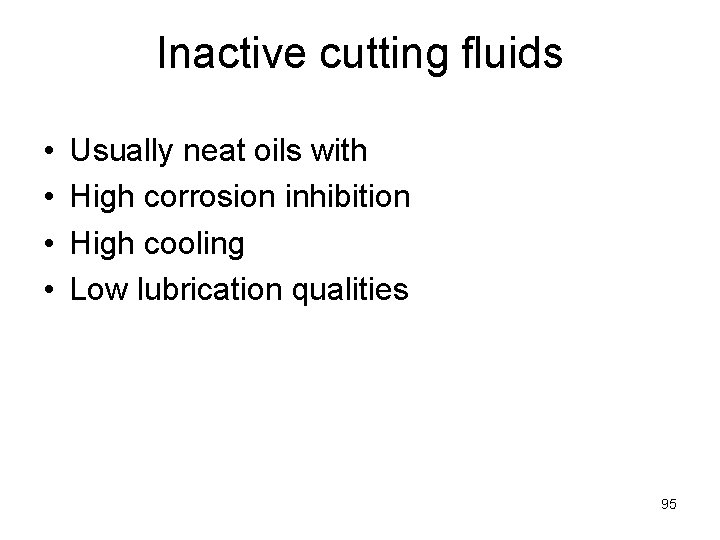
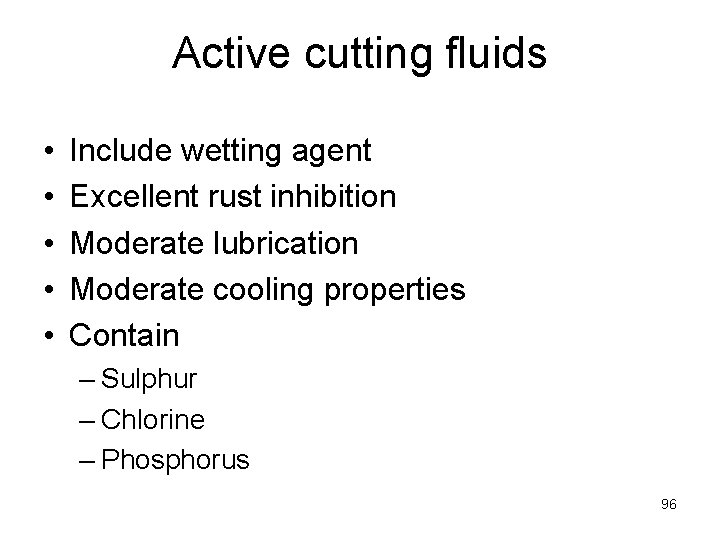
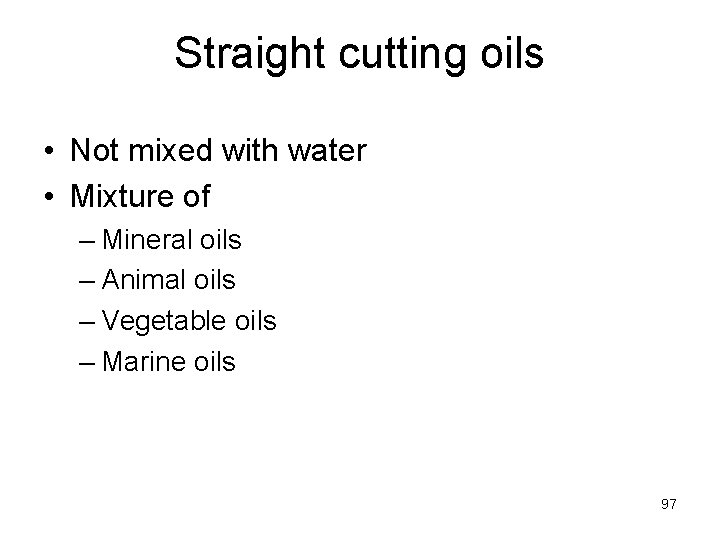
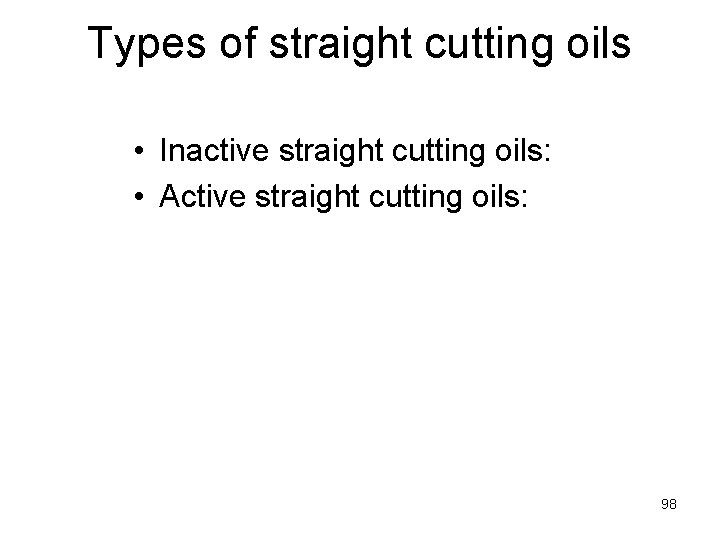
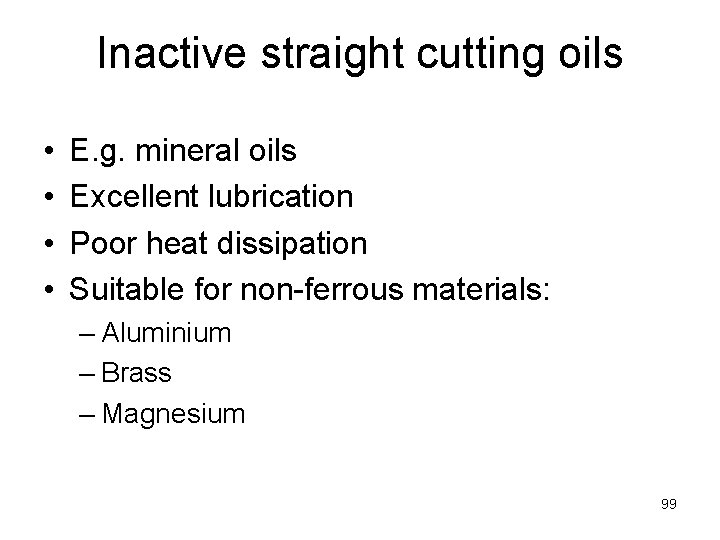
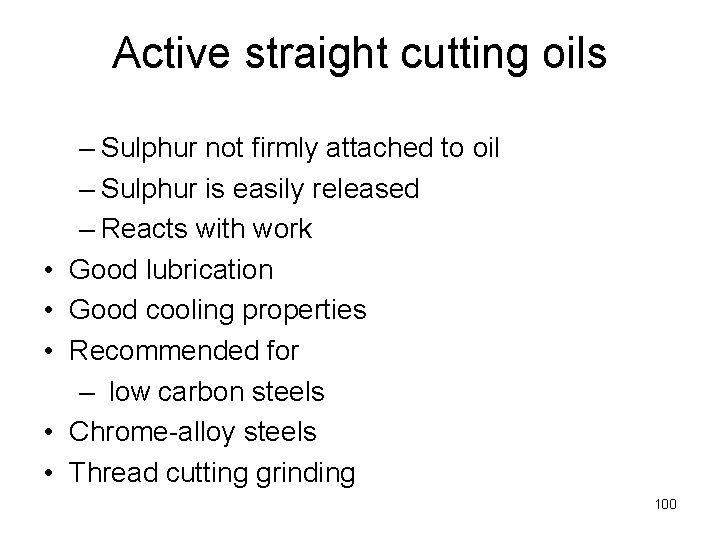
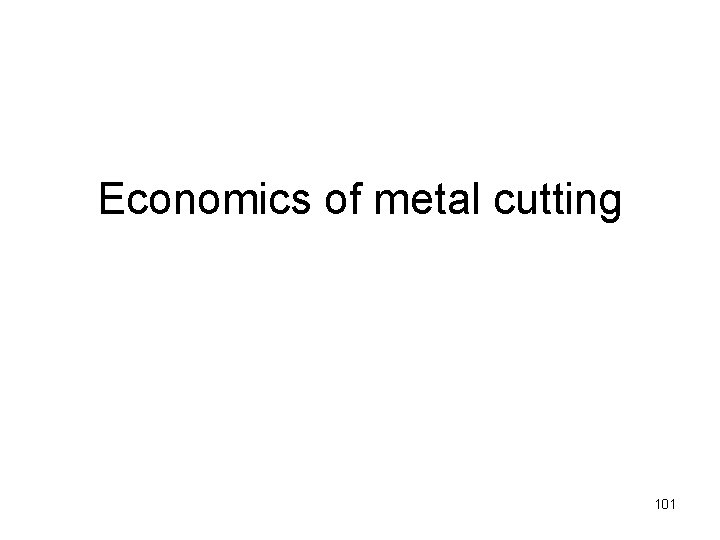
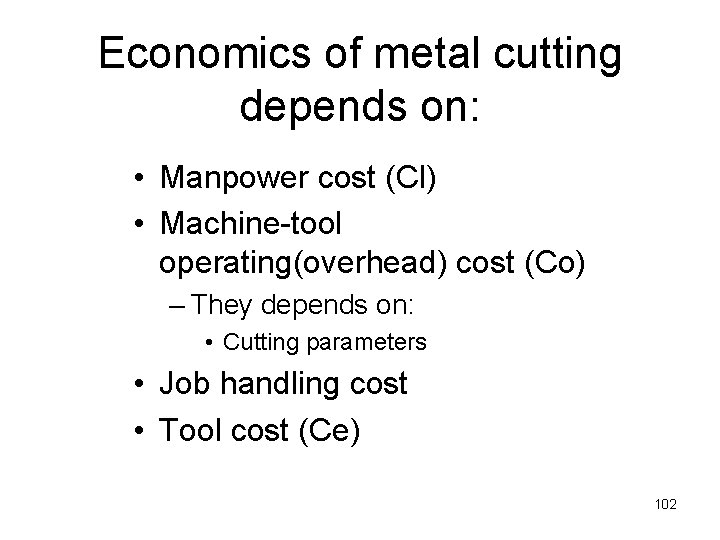
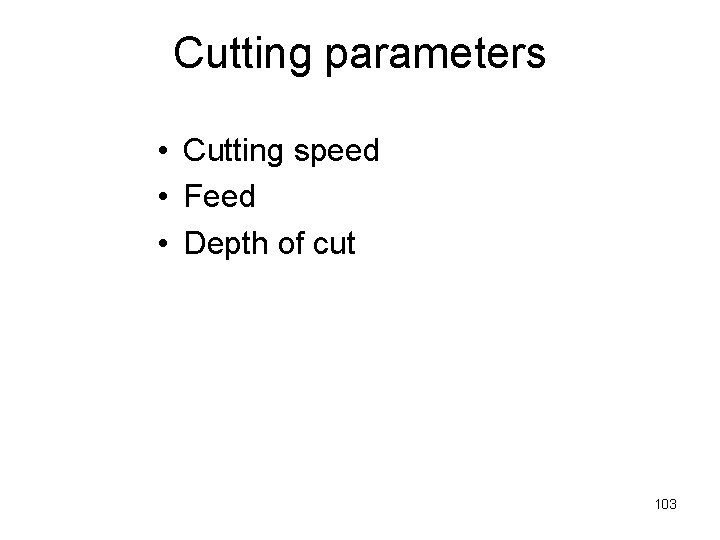
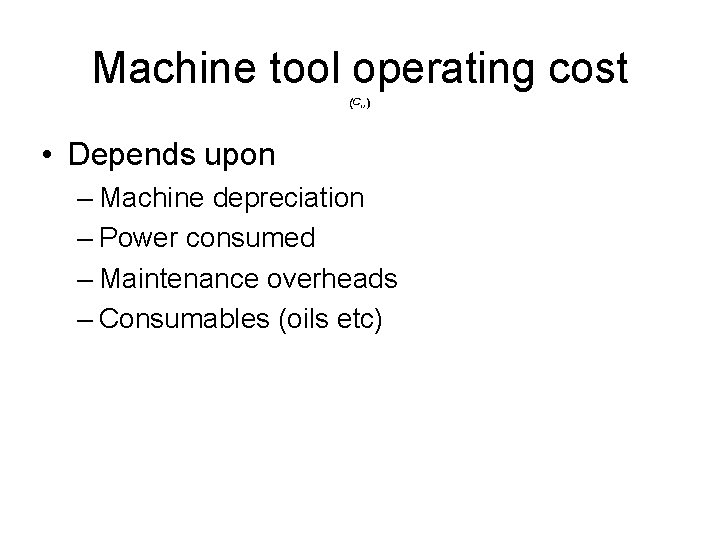
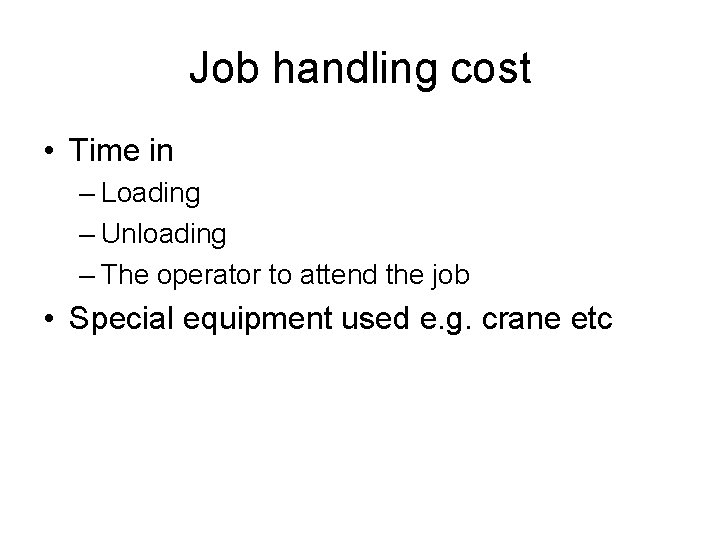
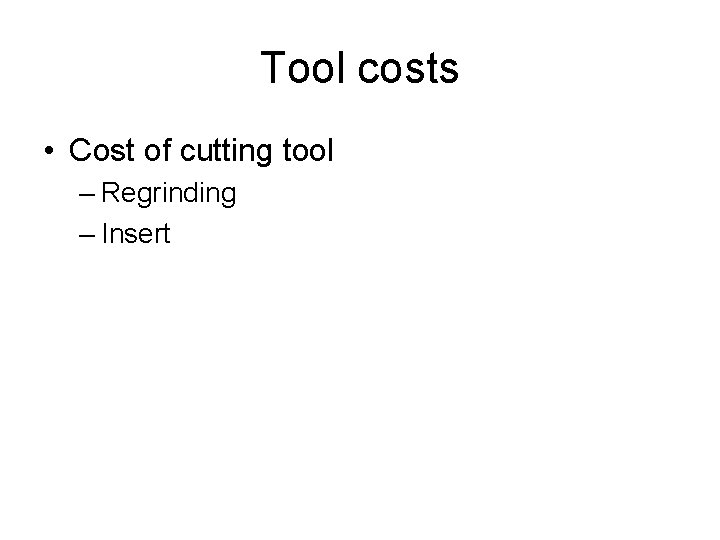
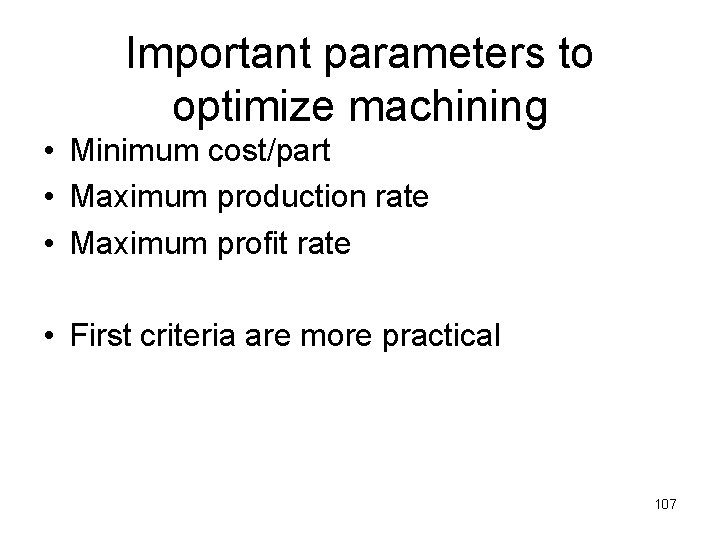
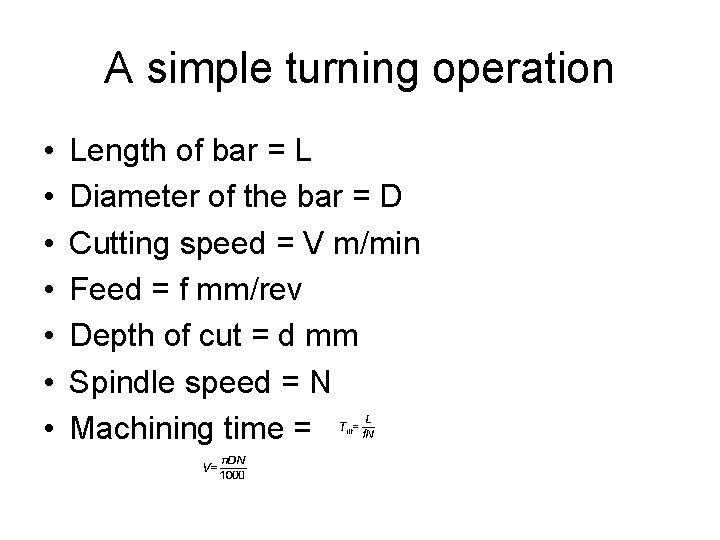
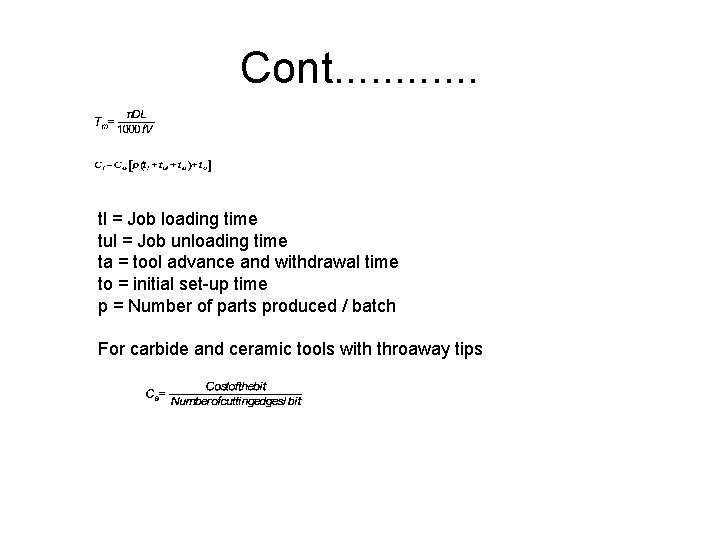
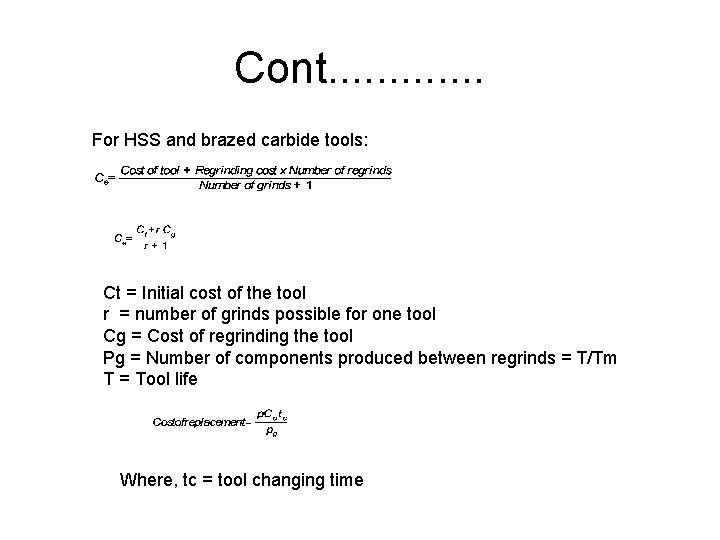
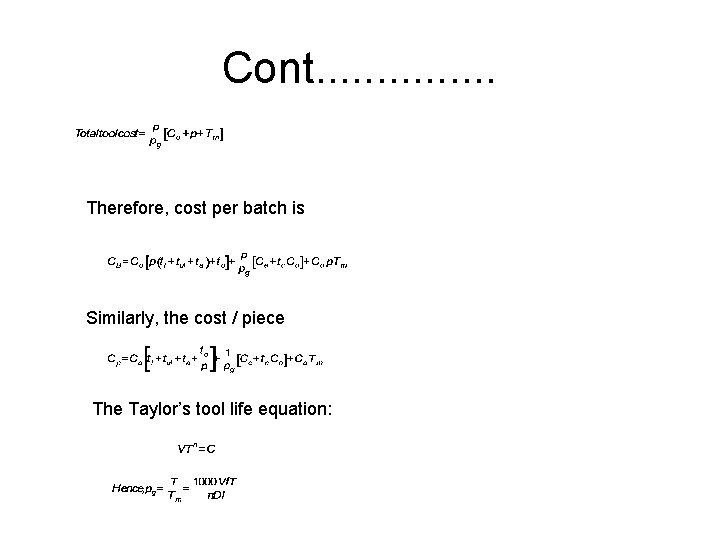
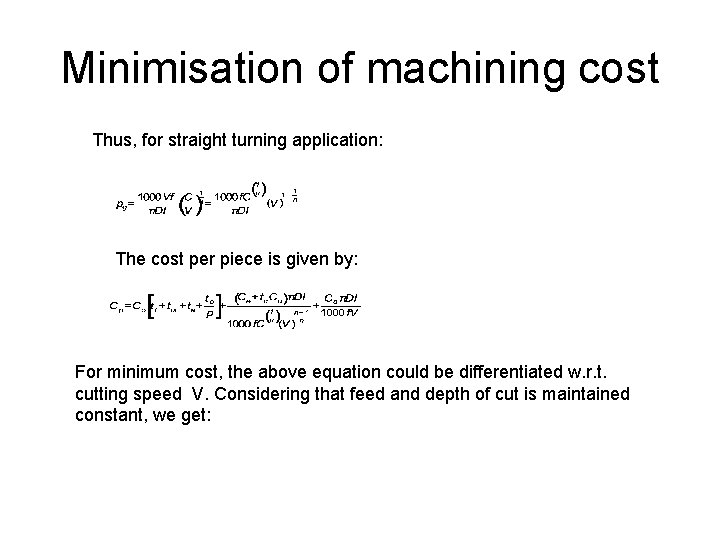
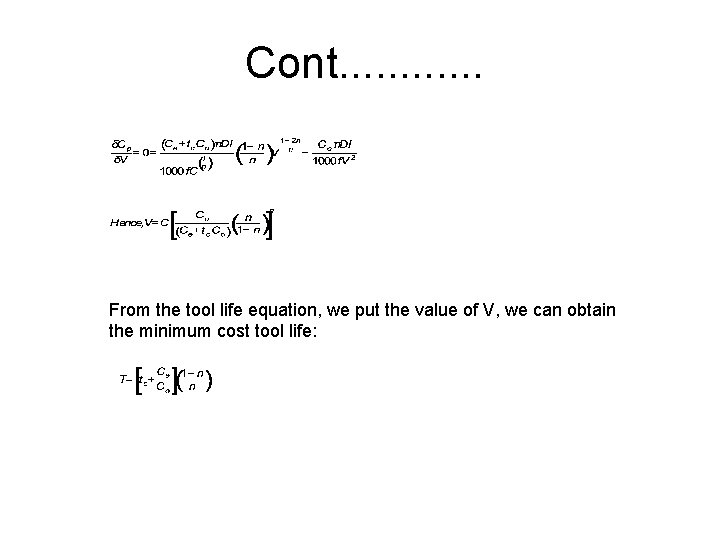
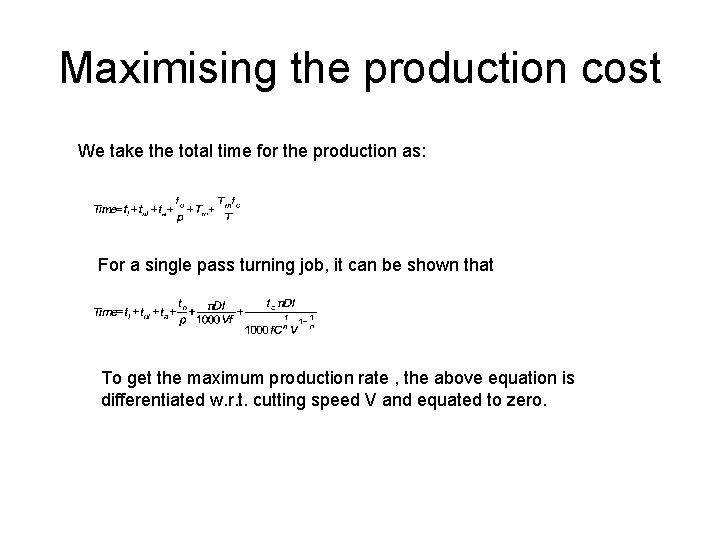
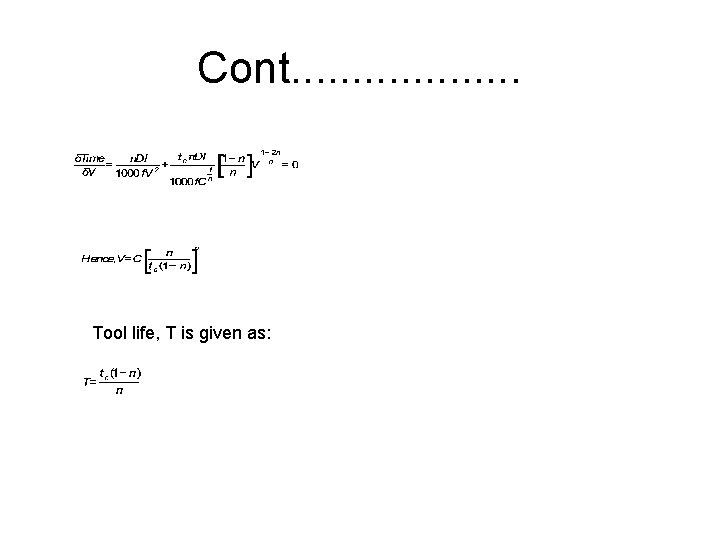
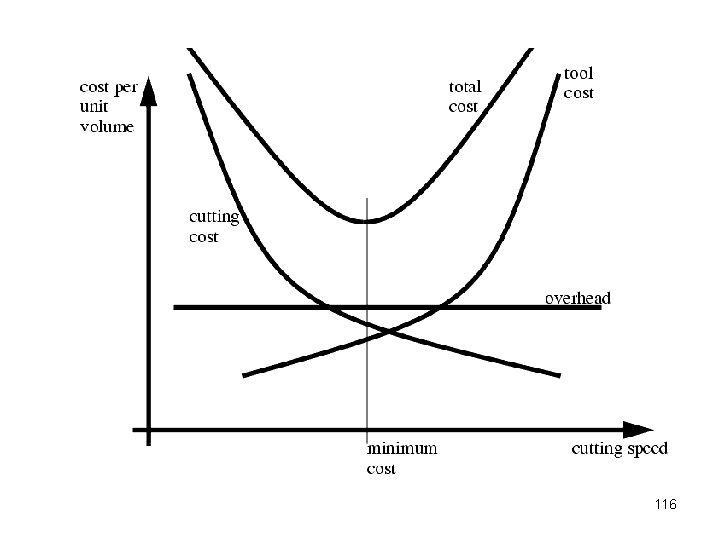
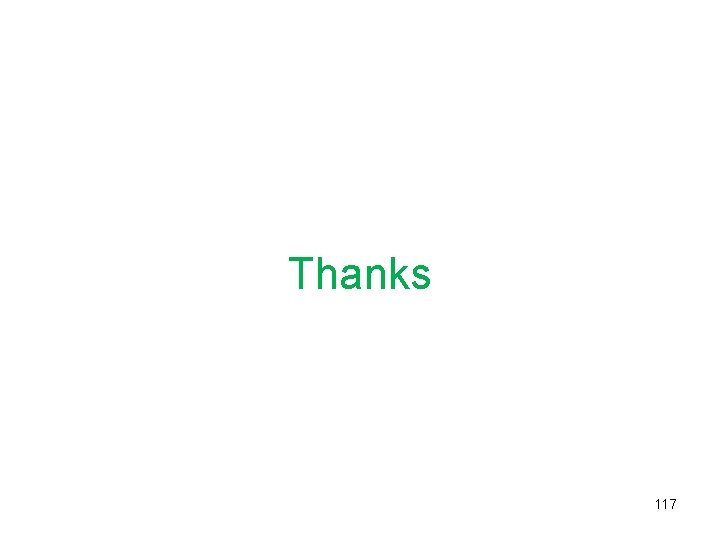
- Slides: 117
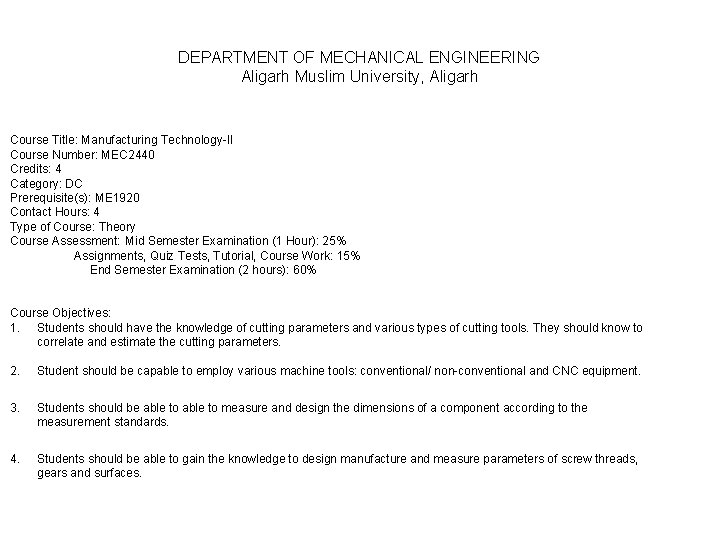
DEPARTMENT OF MECHANICAL ENGINEERING Aligarh Muslim University, Aligarh Course Title: Manufacturing Technology-II Course Number: MEC 2440 Credits: 4 Category: DC Prerequisite(s): ME 1920 Contact Hours: 4 Type of Course: Theory Course Assessment: Mid Semester Examination (1 Hour): 25% Assignments, Quiz Tests, Tutorial, Course Work: 15% End Semester Examination (2 hours): 60% Course Objectives: 1. Students should have the knowledge of cutting parameters and various types of cutting tools. They should know to correlate and estimate the cutting parameters. 2. Student should be capable to employ various machine tools: conventional/ non-conventional and CNC equipment. 3. Students should be able to measure and design the dimensions of a component according to the measurement standards. 4. Students should be able to gain the knowledge to design manufacture and measure parameters of screw threads, gears and surfaces.
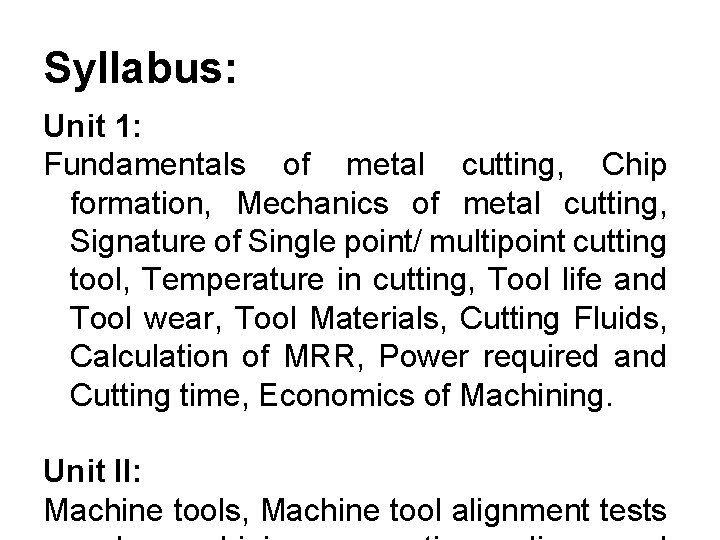
Syllabus: Unit 1: Fundamentals of metal cutting, Chip formation, Mechanics of metal cutting, Signature of Single point/ multipoint cutting tool, Temperature in cutting, Tool life and Tool wear, Tool Materials, Cutting Fluids, Calculation of MRR, Power required and Cutting time, Economics of Machining. Unit II: Machine tools, Machine tool alignment tests

Machining processes
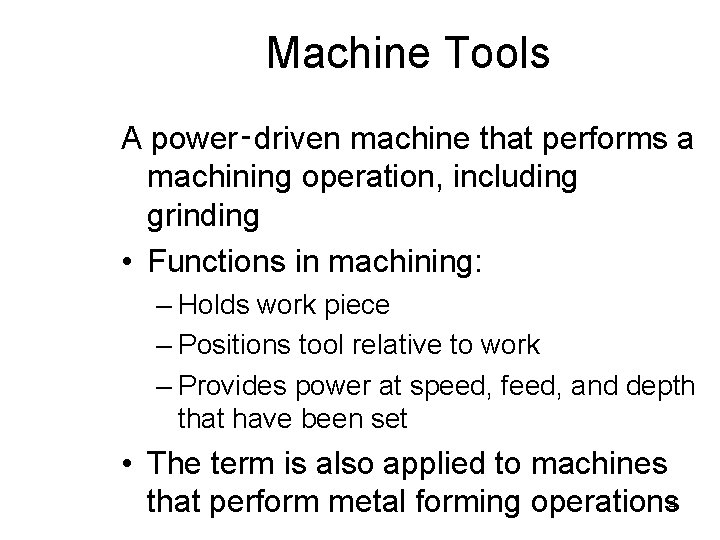
Machine Tools A power‑driven machine that performs a machining operation, including grinding • Functions in machining: – Holds work piece – Positions tool relative to work – Provides power at speed, feed, and depth that have been set • The term is also applied to machines that perform metal forming operations 4

5
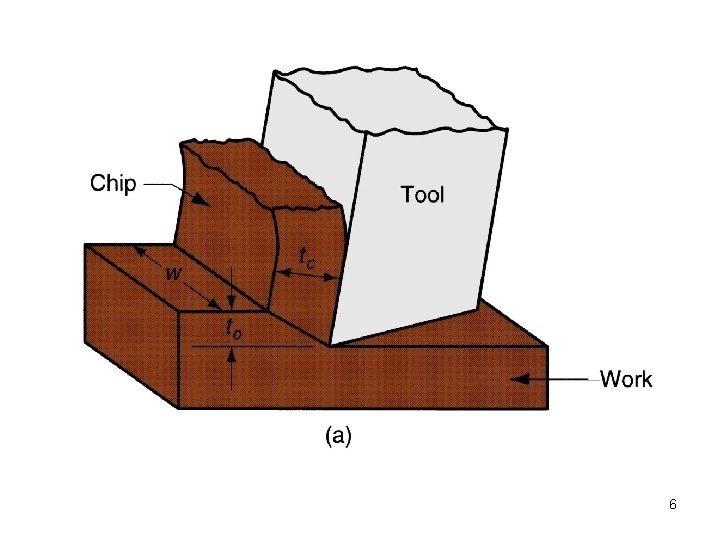
6
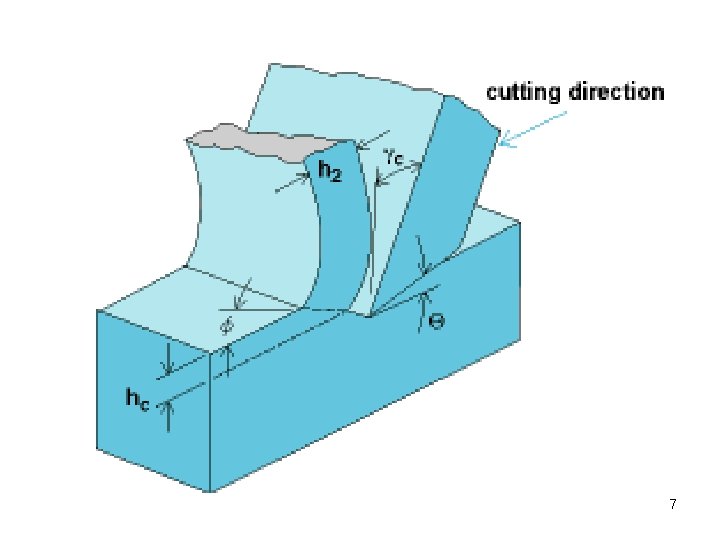
7
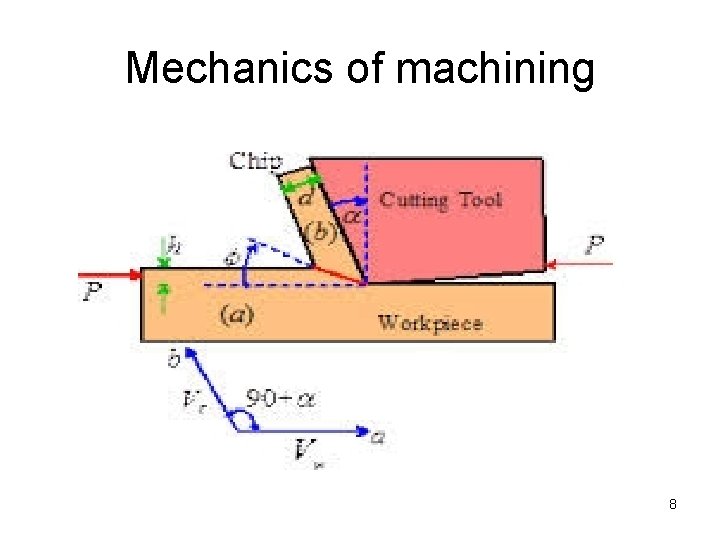
Mechanics of machining 8
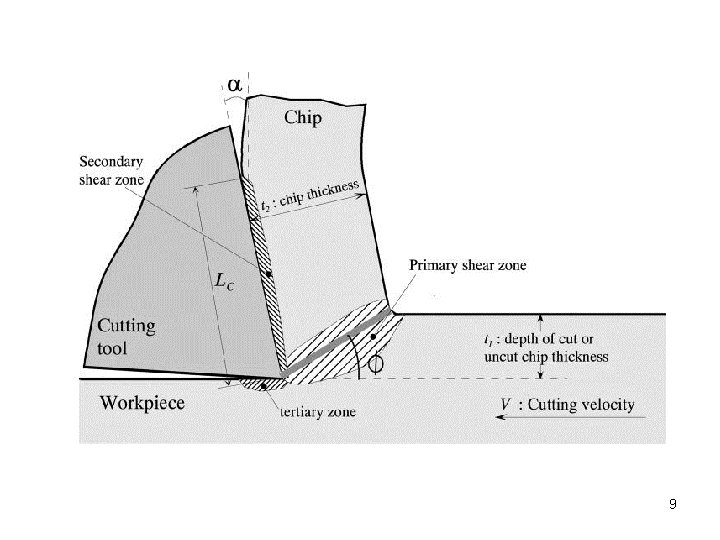
9
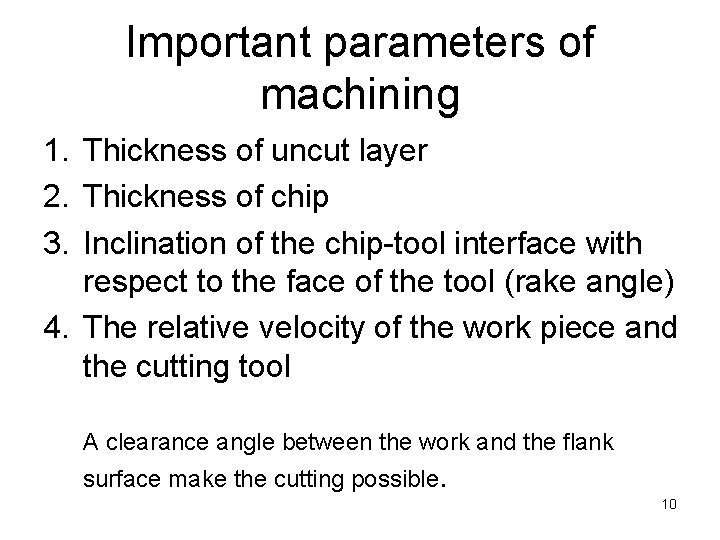
Important parameters of machining 1. Thickness of uncut layer 2. Thickness of chip 3. Inclination of the chip-tool interface with respect to the face of the tool (rake angle) 4. The relative velocity of the work piece and the cutting tool A clearance angle between the work and the flank surface make the cutting possible. 10
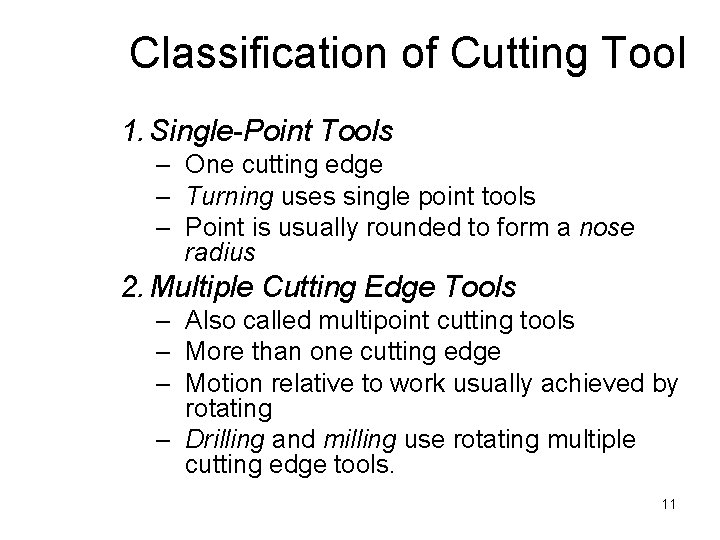
Classification of Cutting Tool 1. Single-Point Tools – One cutting edge – Turning uses single point tools – Point is usually rounded to form a nose radius 2. Multiple Cutting Edge Tools – Also called multipoint cutting tools – More than one cutting edge – Motion relative to work usually achieved by rotating – Drilling and milling use rotating multiple cutting edge tools. 11
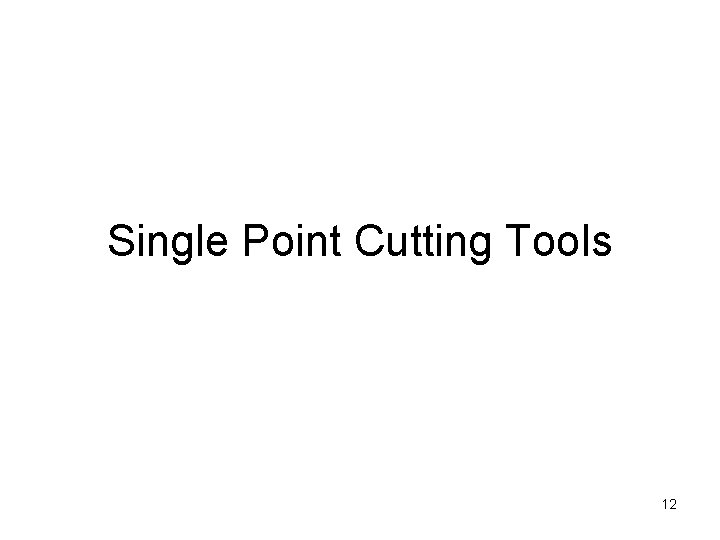
Single Point Cutting Tools 12
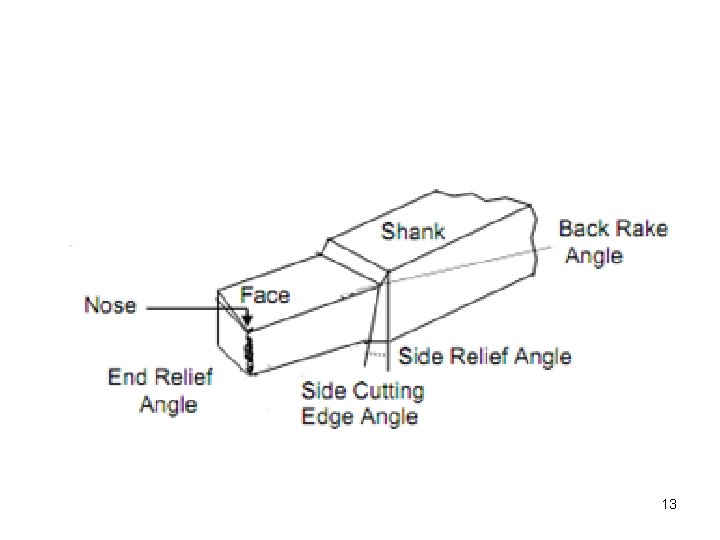
13
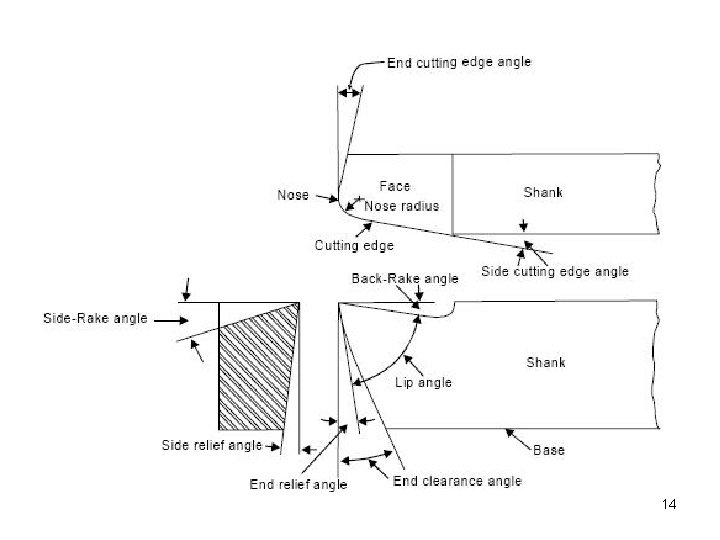
14
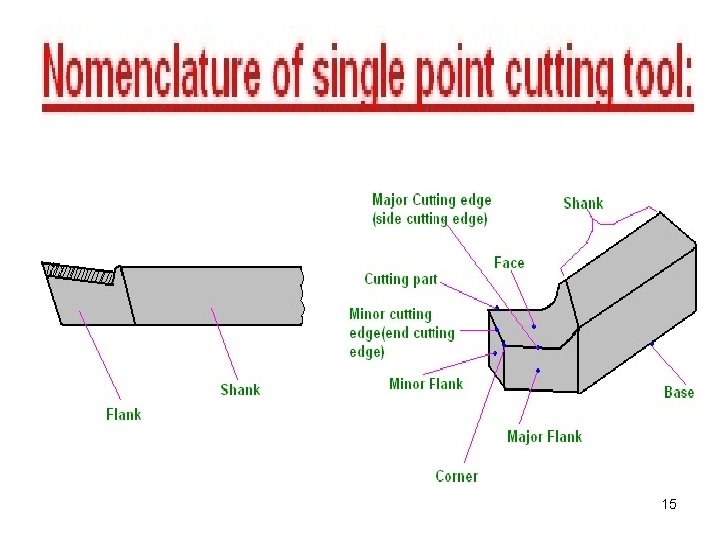
15
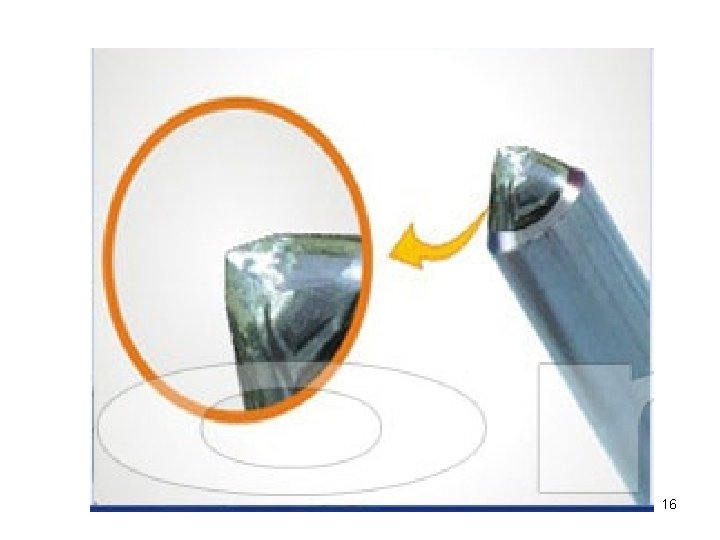
16
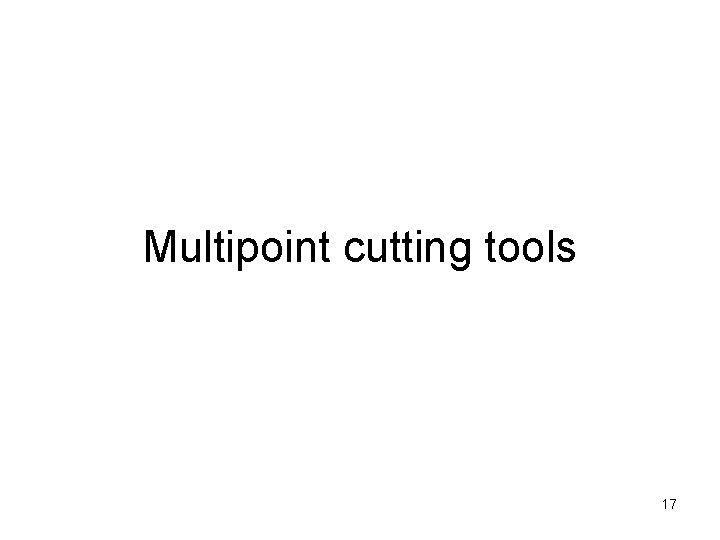
Multipoint cutting tools 17
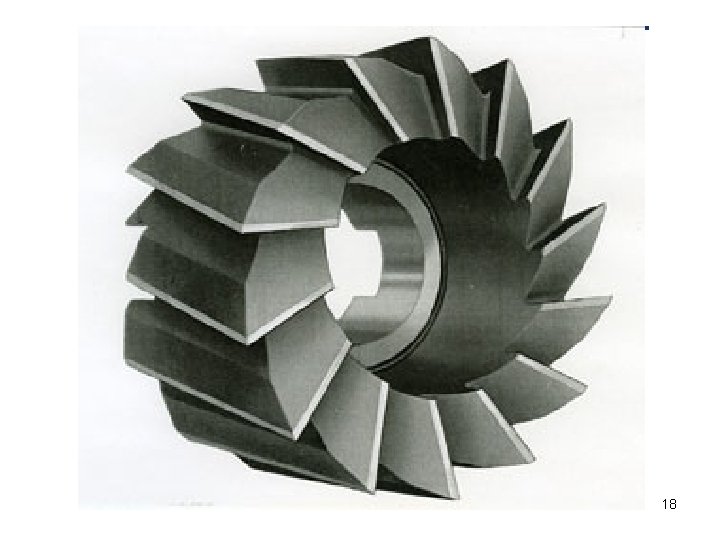
18
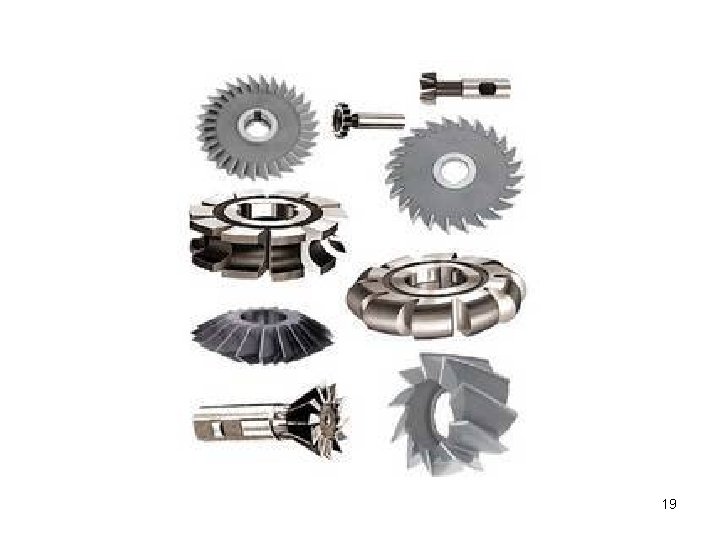
19
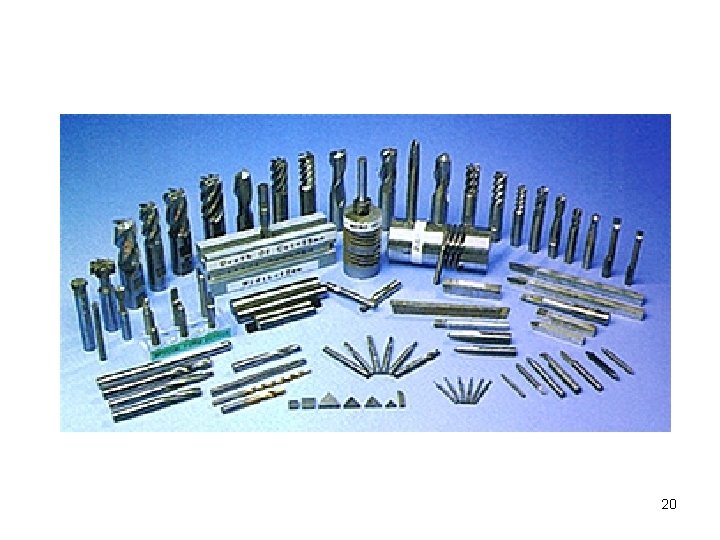
20
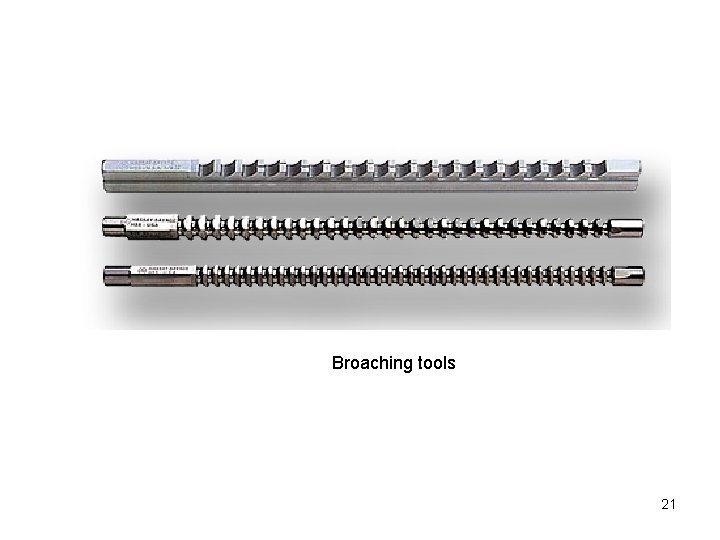
Broaching tools 21
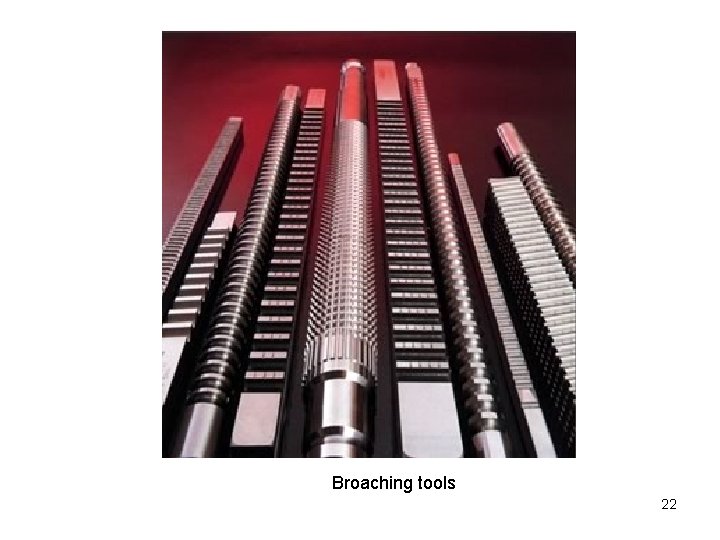
Broaching tools 22
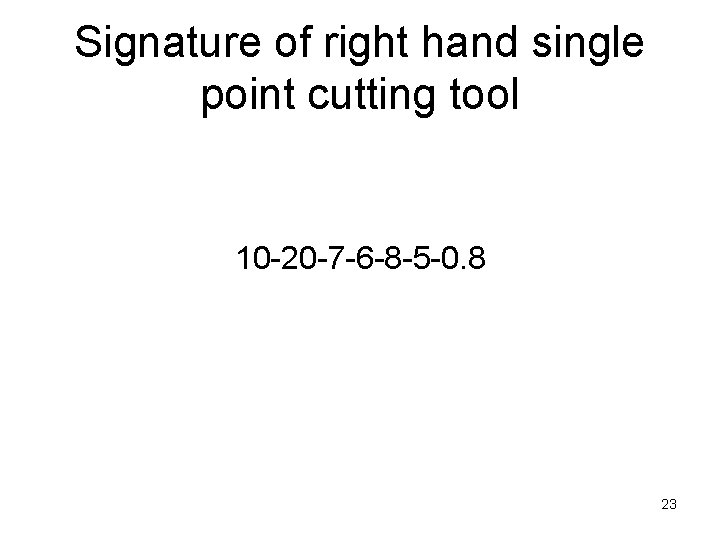
Signature of right hand single point cutting tool 10 -20 -7 -6 -8 -5 -0. 8 23
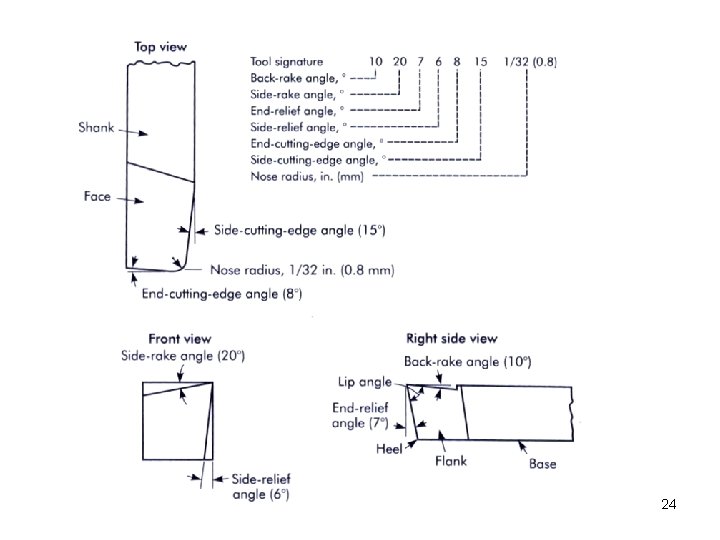
24
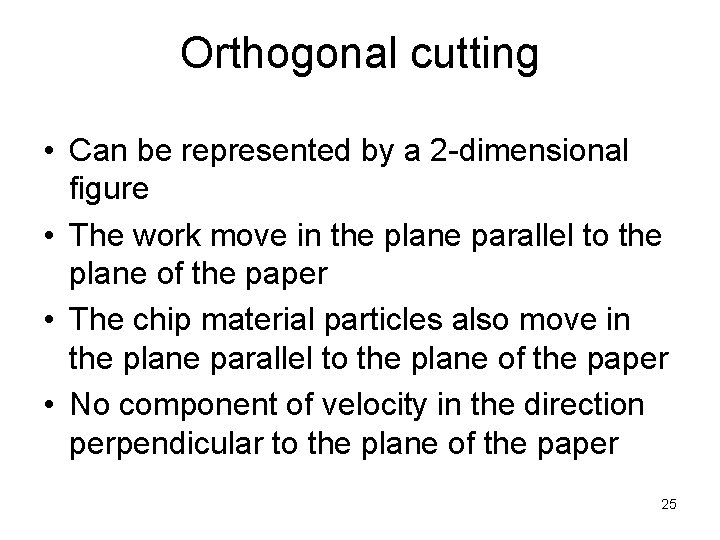
Orthogonal cutting • Can be represented by a 2 -dimensional figure • The work move in the plane parallel to the plane of the paper • The chip material particles also move in the plane parallel to the plane of the paper • No component of velocity in the direction perpendicular to the plane of the paper 25

Orthogonal Cutting Model A simplified 2 -D model of machining that describes the mechanics of machining fairly accurately Figure ‑ Orthogonal cutting: (a) as a three‑dimensional process 26
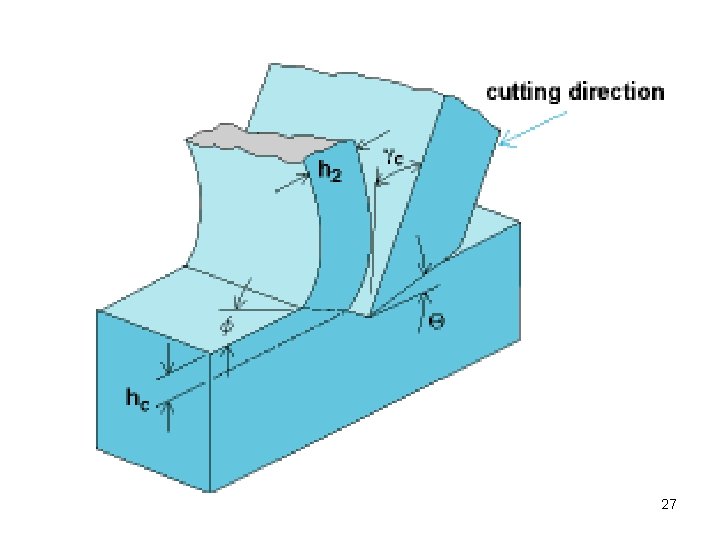
27
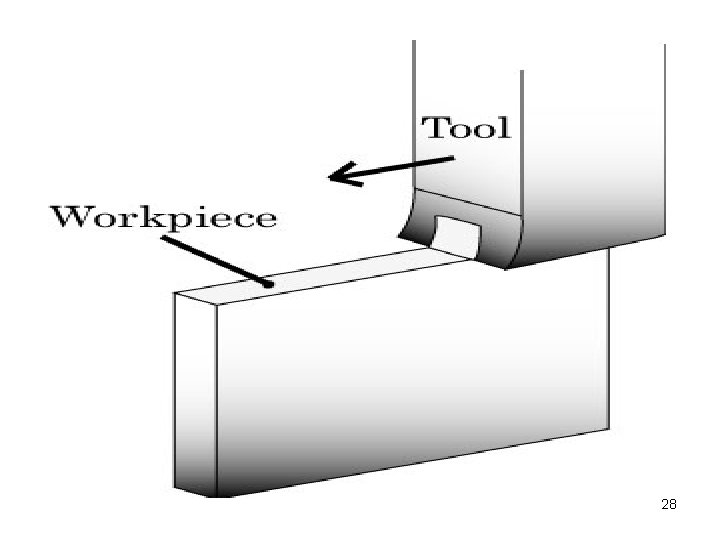
28
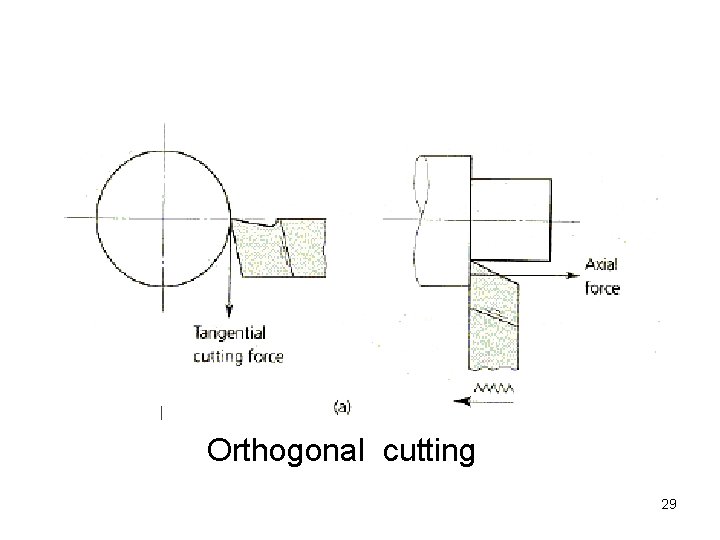
Orthogonal cutting 29
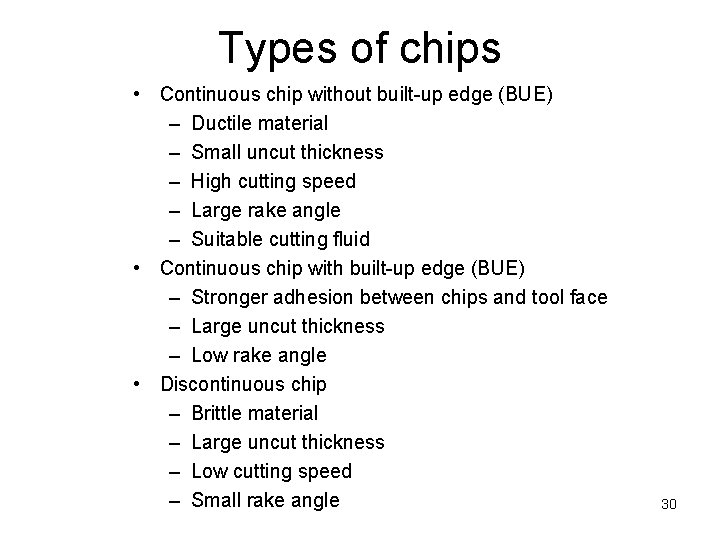
Types of chips • Continuous chip without built-up edge (BUE) – Ductile material – Small uncut thickness – High cutting speed – Large rake angle – Suitable cutting fluid • Continuous chip with built-up edge (BUE) – Stronger adhesion between chips and tool face – Large uncut thickness – Low rake angle • Discontinuous chip – Brittle material – Large uncut thickness – Low cutting speed – Small rake angle 30
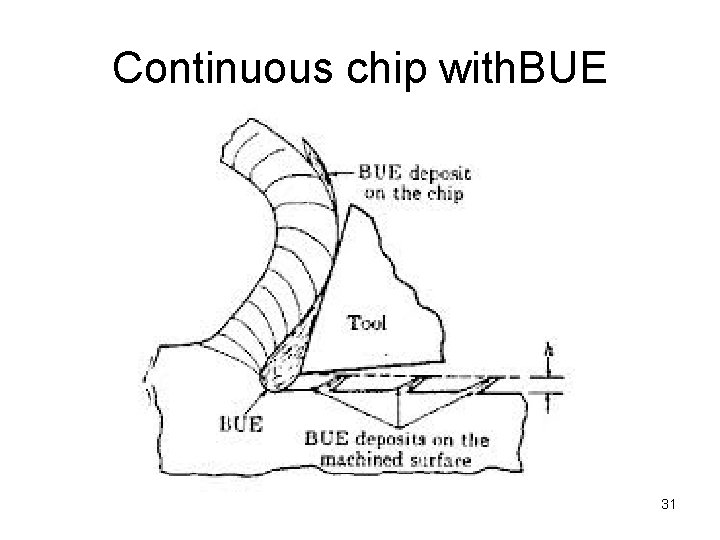
Continuous chip with. BUE 31
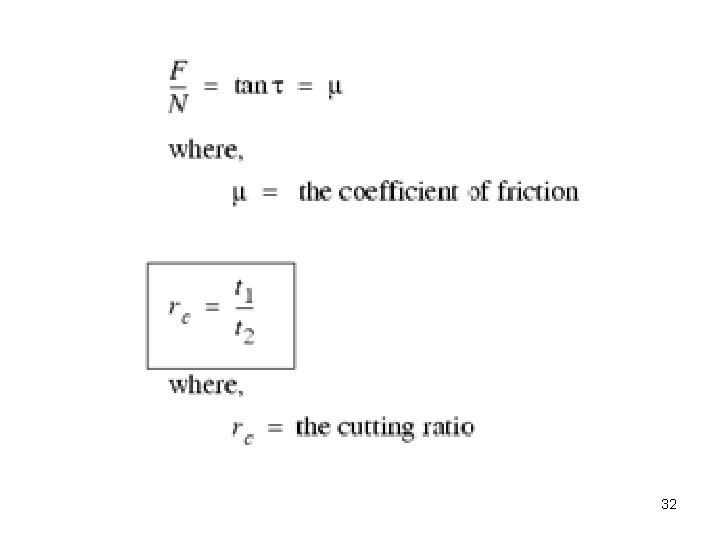
32
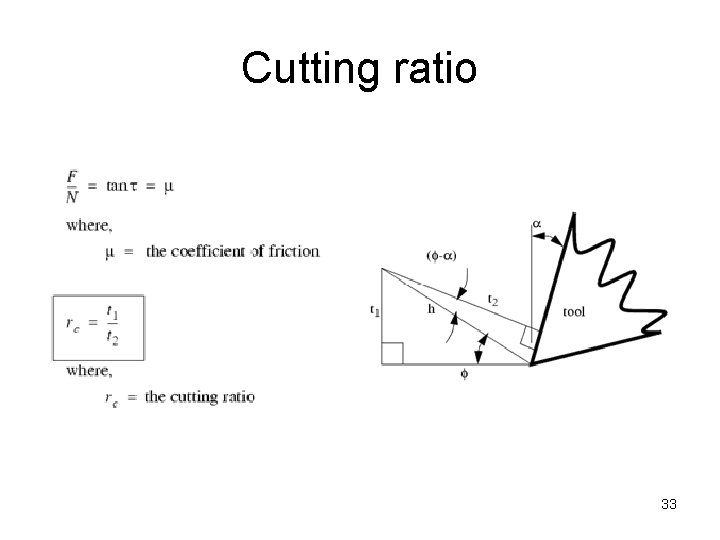
Cutting ratio 33
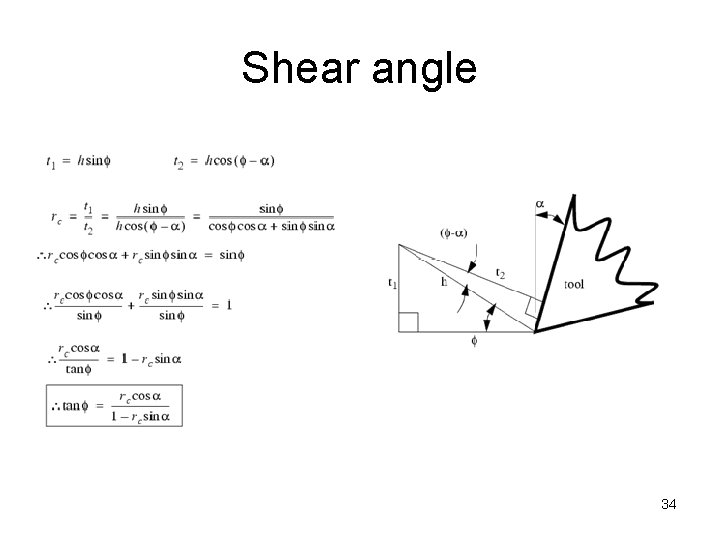
Shear angle 34
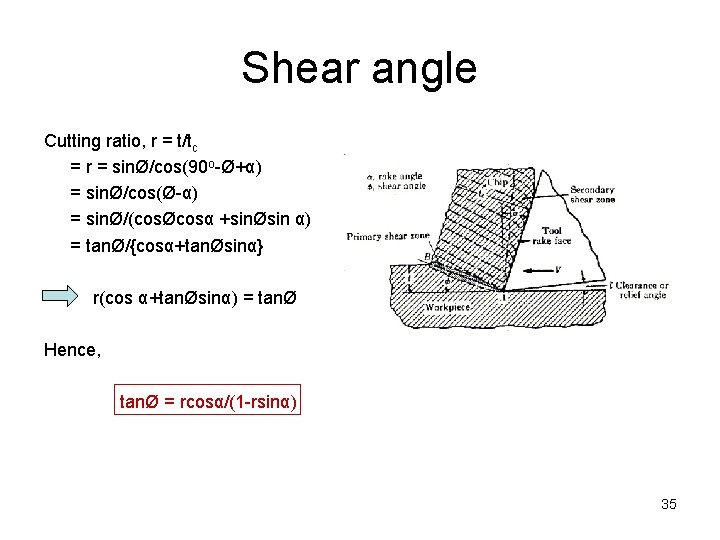
Shear angle Cutting ratio, r = t/tc = r = sinØ/cos(90 o-Ø+α) = sinØ/cos(Ø-α) = sinØ/(cosØcosα +sinØsin α) = tanØ/{cosα+tanØsinα} r(cos α+tanØsinα) = tanØ Hence, tanØ = rcosα/(1 -rsinα) 35
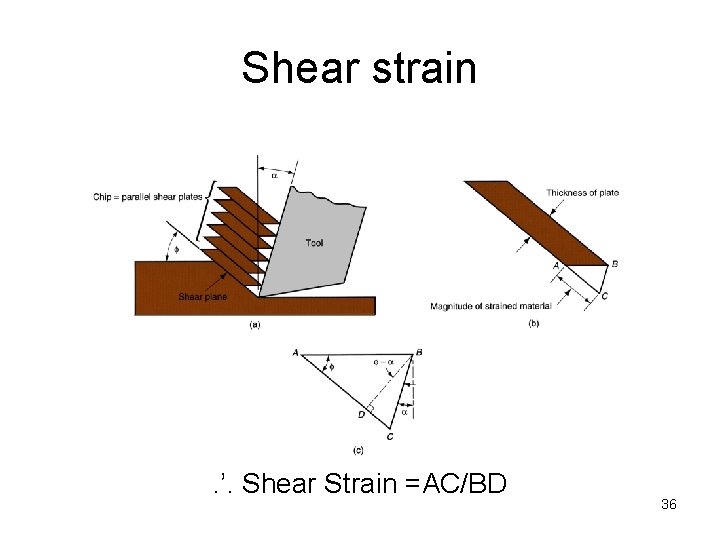
Shear strain . ’. Shear Strain =AC/BD 36
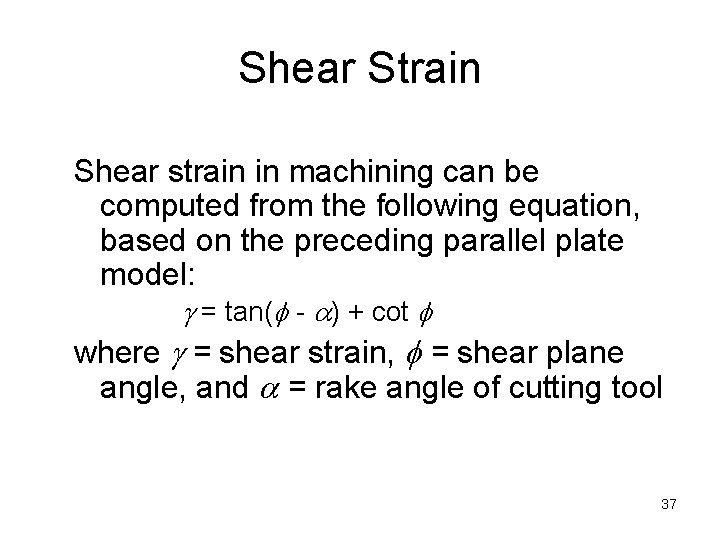
Shear Strain Shear strain in machining can be computed from the following equation, based on the preceding parallel plate model: = tan( - ) + cot where = shear strain, = shear plane angle, and = rake angle of cutting tool 37
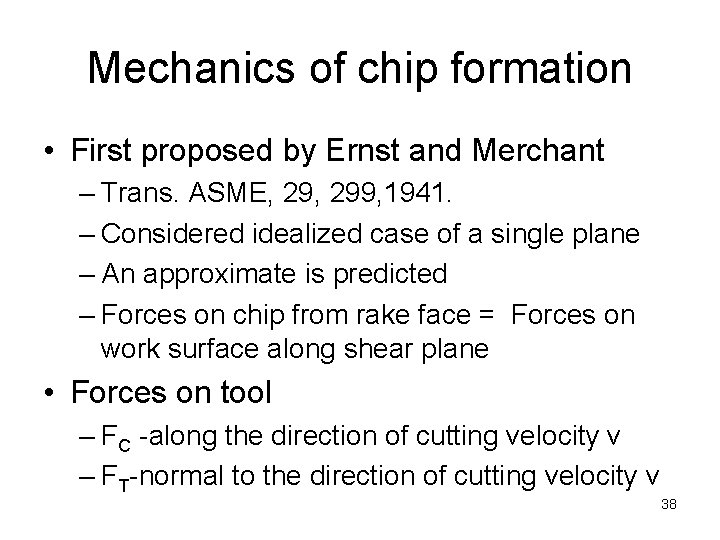
Mechanics of chip formation • First proposed by Ernst and Merchant – Trans. ASME, 299, 1941. – Considered idealized case of a single plane – An approximate is predicted – Forces on chip from rake face = Forces on work surface along shear plane • Forces on tool – FC -along the direction of cutting velocity v – FT-normal to the direction of cutting velocity v 38
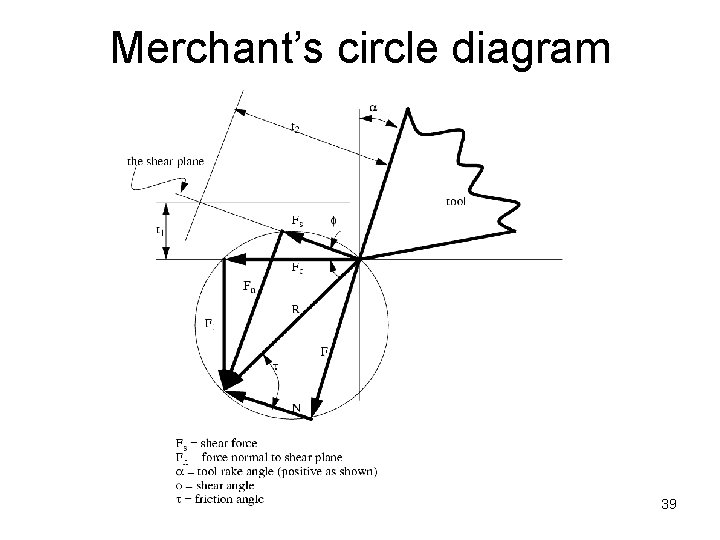
Merchant’s circle diagram 39
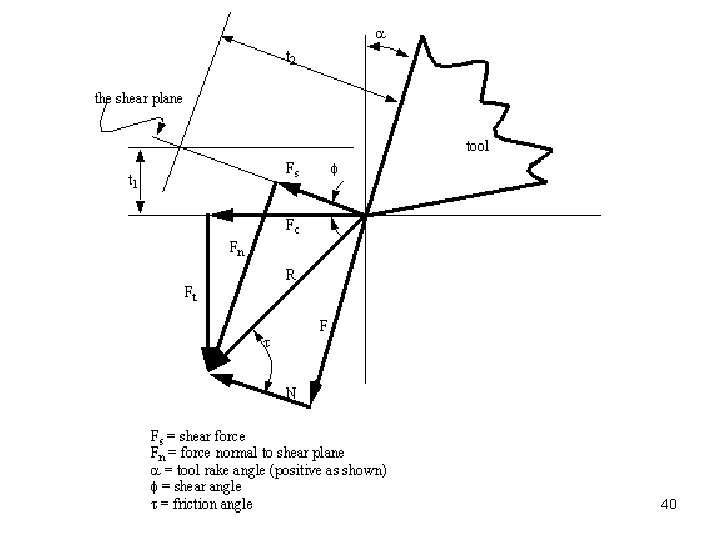
40
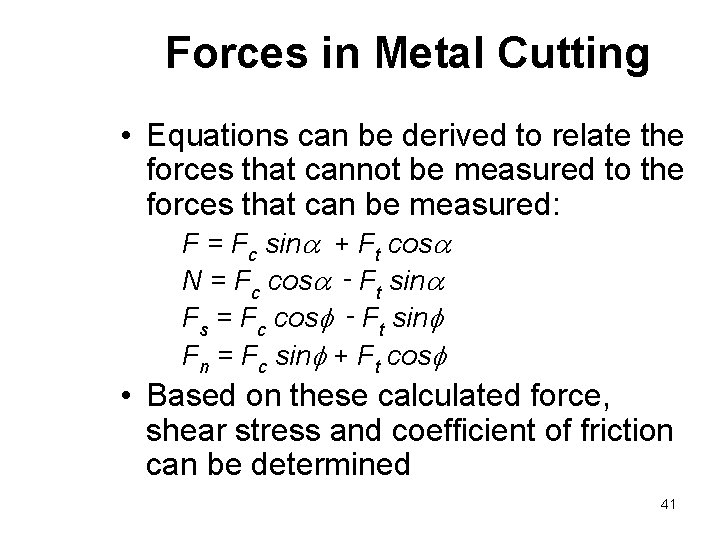
Forces in Metal Cutting • Equations can be derived to relate the forces that cannot be measured to the forces that can be measured: F = Fc sin + Ft cos N = Fc cos ‑ Ft sin Fs = Fc cos ‑ Ft sin Fn = Fc sin + Ft cos • Based on these calculated force, shear stress and coefficient of friction can be determined 41
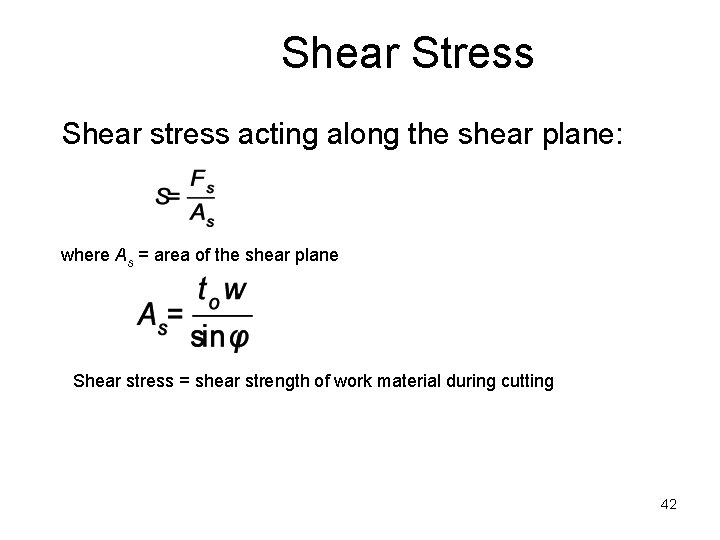
Shear Stress Shear stress acting along the shear plane: where As = area of the shear plane Shear stress = shear strength of work material during cutting 42
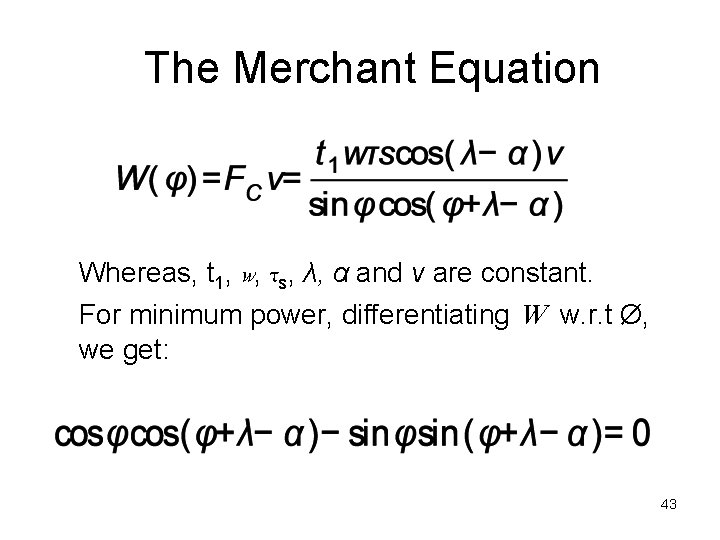
The Merchant Equation Whereas, t 1, w, τs, λ, α and v are constant. For minimum power, differentiating W w. r. t Ø, we get: 43
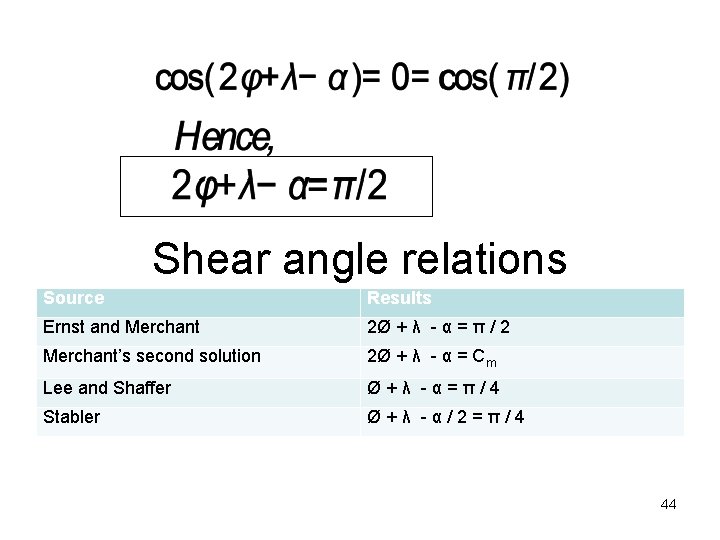
Shear angle relations Source Results Ernst and Merchant 2Ø + λ - α = π / 2 Merchant’s second solution 2Ø + λ - α = Cm Lee and Shaffer Ø+λ -α=π/4 Stabler Ø+λ -α/2=π/4 44
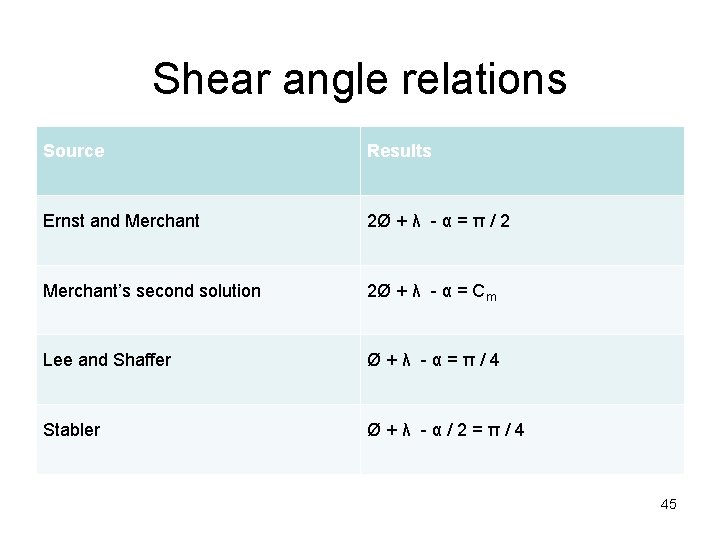
Shear angle relations Source Results Ernst and Merchant 2Ø + λ - α = π / 2 Merchant’s second solution 2Ø + λ - α = Cm Lee and Shaffer Ø+λ -α=π/4 Stabler Ø+λ -α/2=π/4 45
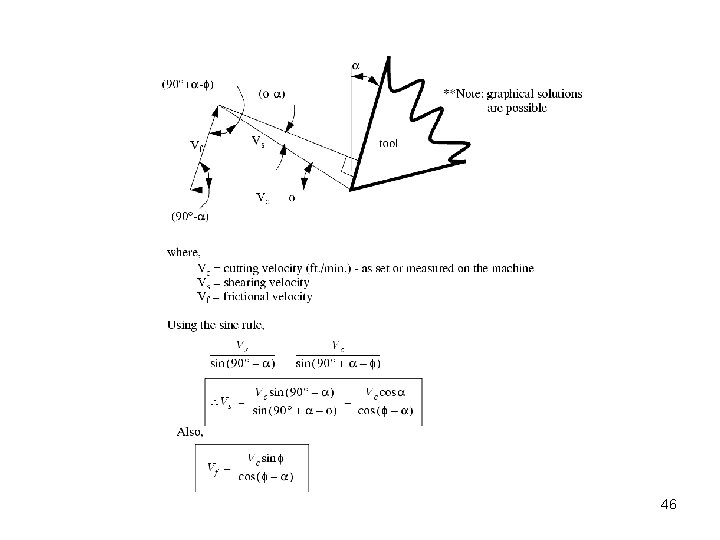
46
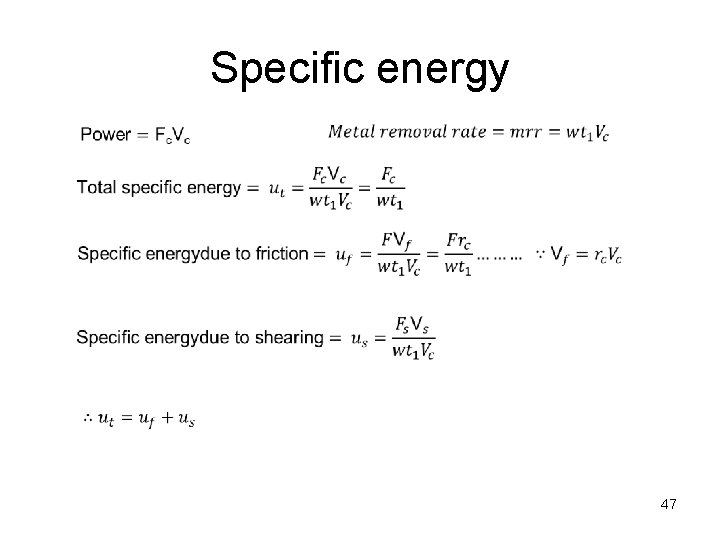
Specific energy 47
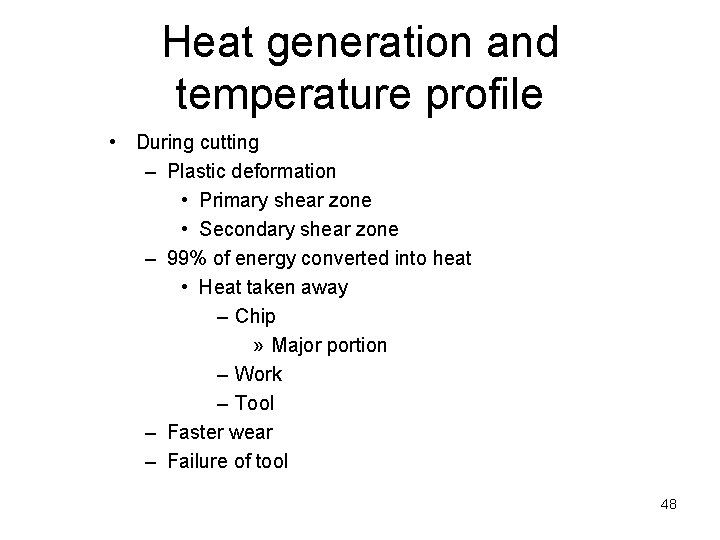
Heat generation and temperature profile • During cutting – Plastic deformation • Primary shear zone • Secondary shear zone – 99% of energy converted into heat • Heat taken away – Chip » Major portion – Work – Tool – Faster wear – Failure of tool 48
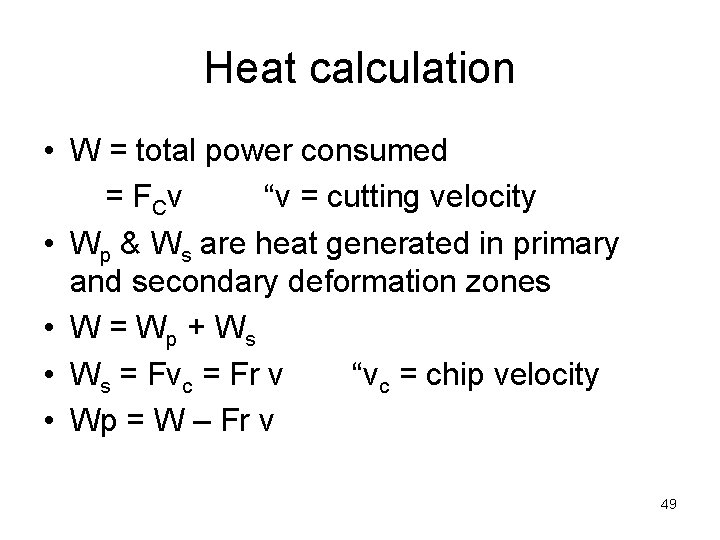
Heat calculation • W = total power consumed = F Cv “v = cutting velocity • Wp & Ws are heat generated in primary and secondary deformation zones • W = Wp + Ws • Ws = Fvc = Fr v “vc = chip velocity • Wp = W – Fr v 49
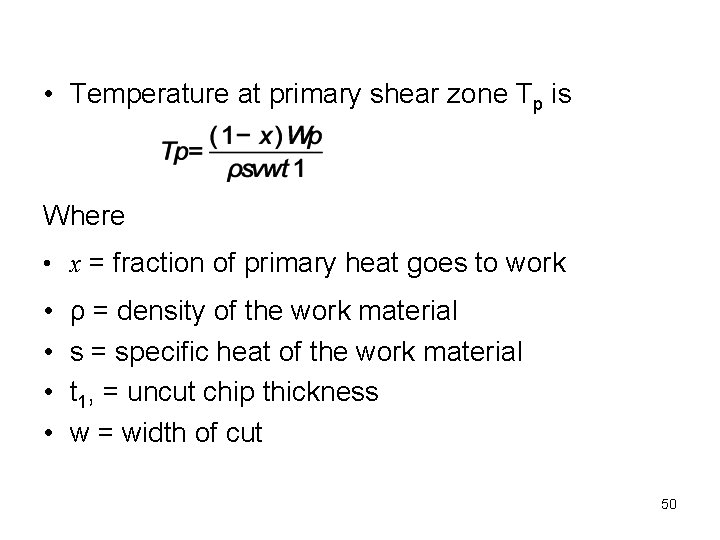
• Temperature at primary shear zone Tp is Where • x = fraction of primary heat goes to work • • ρ = density of the work material s = specific heat of the work material t 1, = uncut chip thickness w = width of cut 50
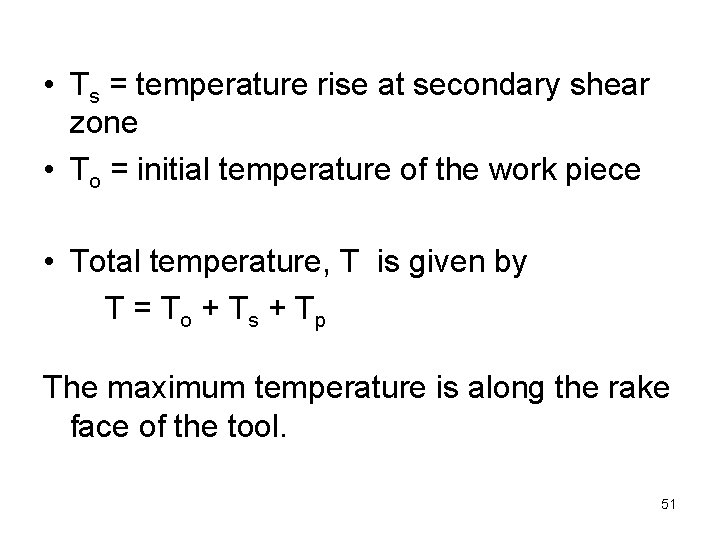
• Ts = temperature rise at secondary shear zone • To = initial temperature of the work piece • Total temperature, T is given by T = To + Ts + Tp The maximum temperature is along the rake face of the tool. 51
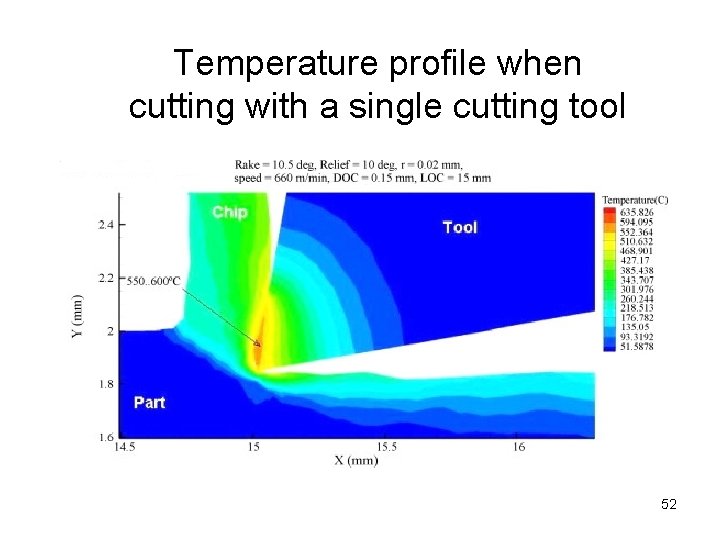
Temperature profile when cutting with a single cutting tool 52
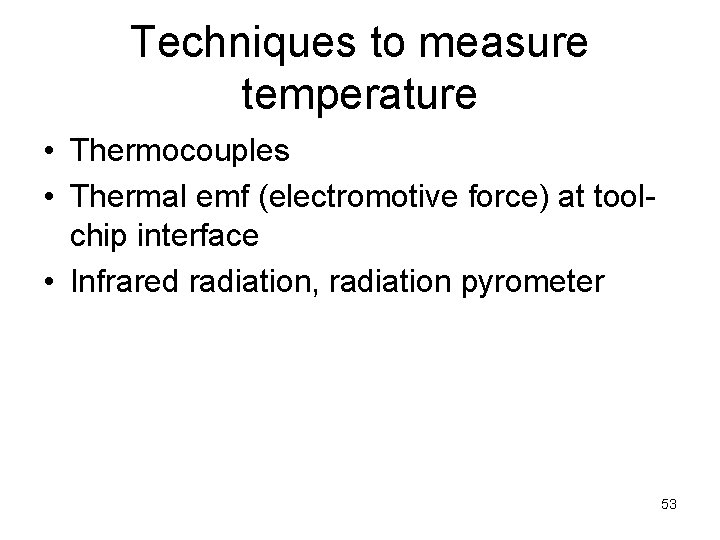
Techniques to measure temperature • Thermocouples • Thermal emf (electromotive force) at toolchip interface • Infrared radiation, radiation pyrometer 53
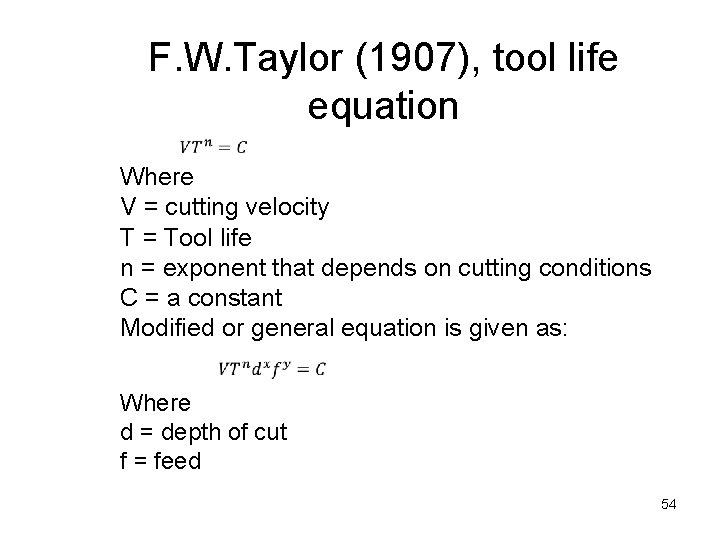
F. W. Taylor (1907), tool life equation Where V = cutting velocity T = Tool life n = exponent that depends on cutting conditions C = a constant Modified or general equation is given as: Where d = depth of cut f = feed 54
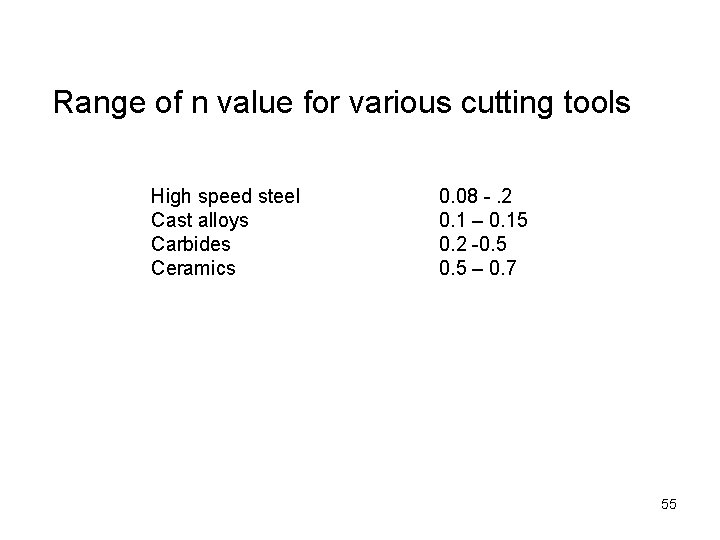
Range of n value for various cutting tools High speed steel Cast alloys Carbides Ceramics 0. 08 -. 2 0. 1 – 0. 15 0. 2 -0. 5 – 0. 7 55
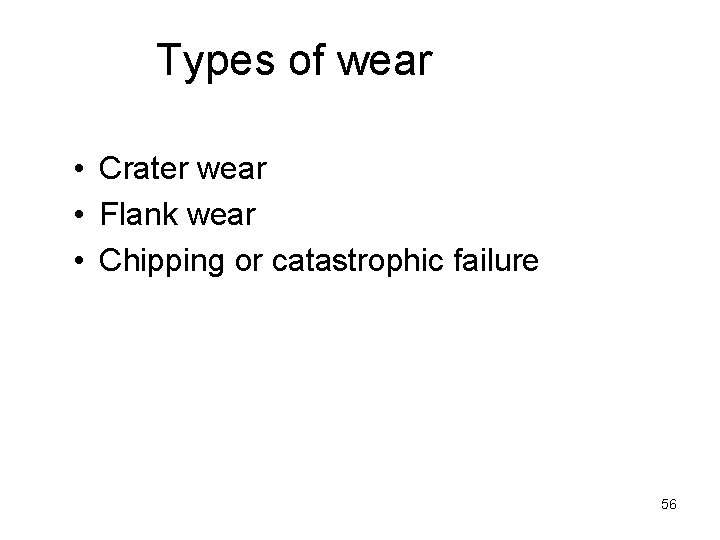
Types of wear • Crater wear • Flank wear • Chipping or catastrophic failure 56
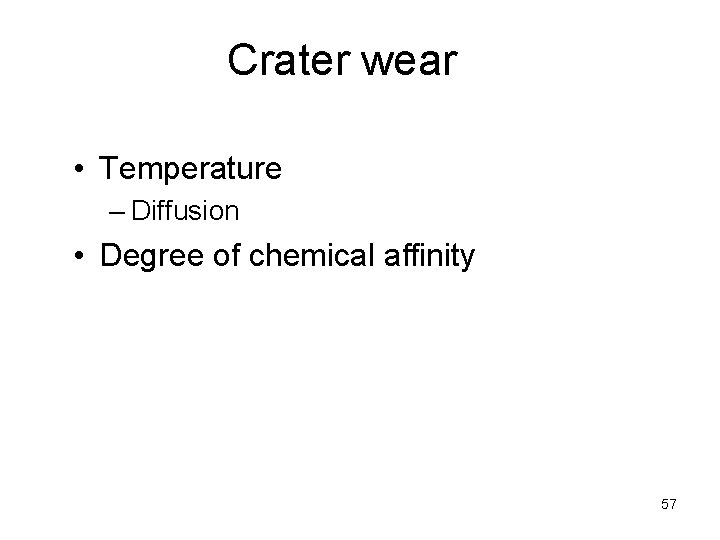
Crater wear • Temperature – Diffusion • Degree of chemical affinity 57
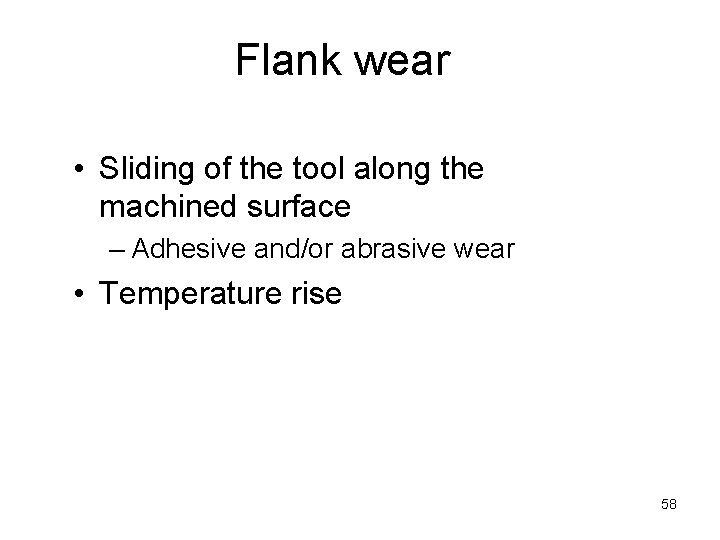
Flank wear • Sliding of the tool along the machined surface – Adhesive and/or abrasive wear • Temperature rise 58
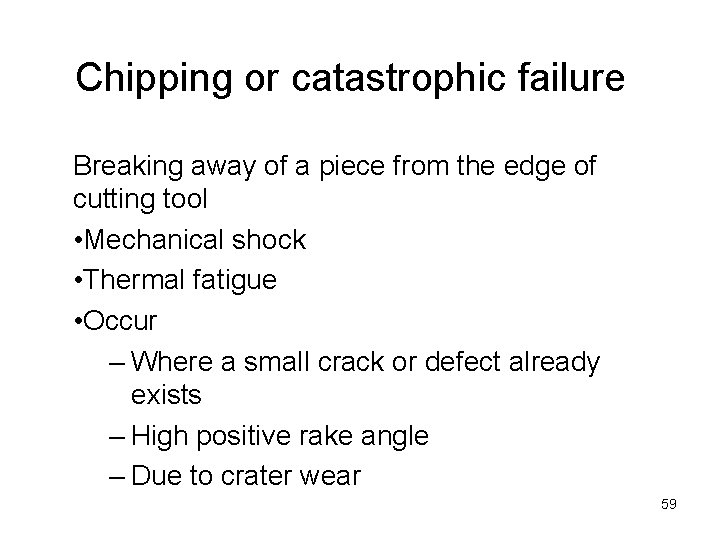
Chipping or catastrophic failure Breaking away of a piece from the edge of cutting tool • Mechanical shock • Thermal fatigue • Occur – Where a small crack or defect already exists – High positive rake angle – Due to crater wear 59
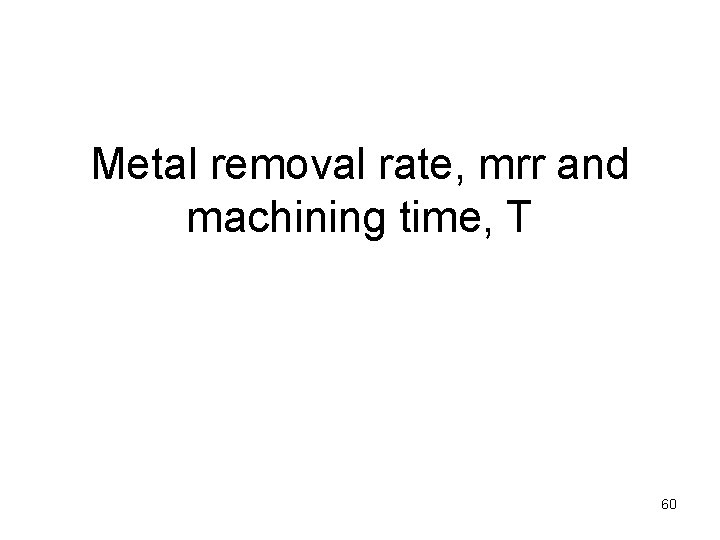
Metal removal rate, mrr and machining time, T 60
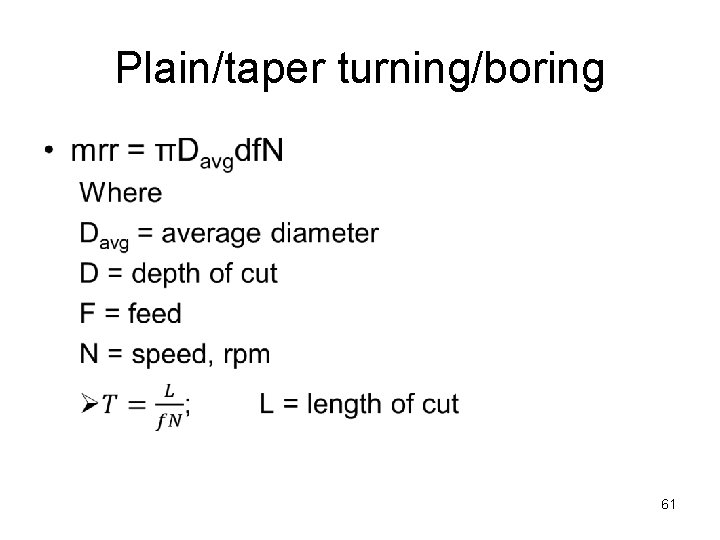
Plain/taper turning/boring 61
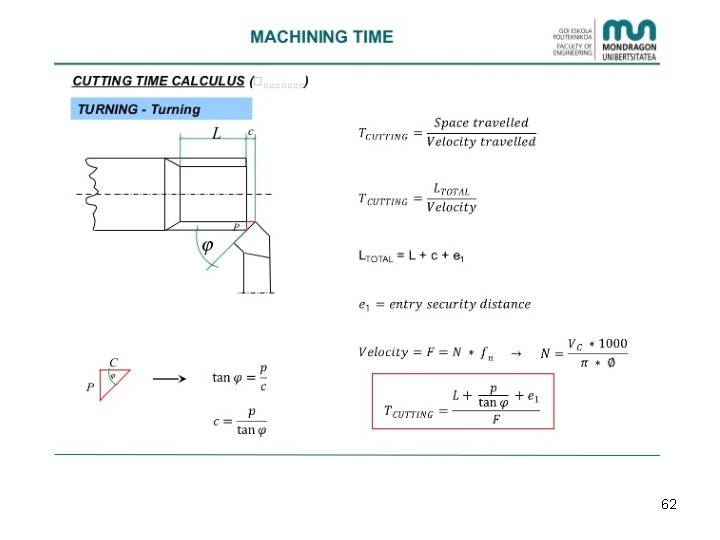
62
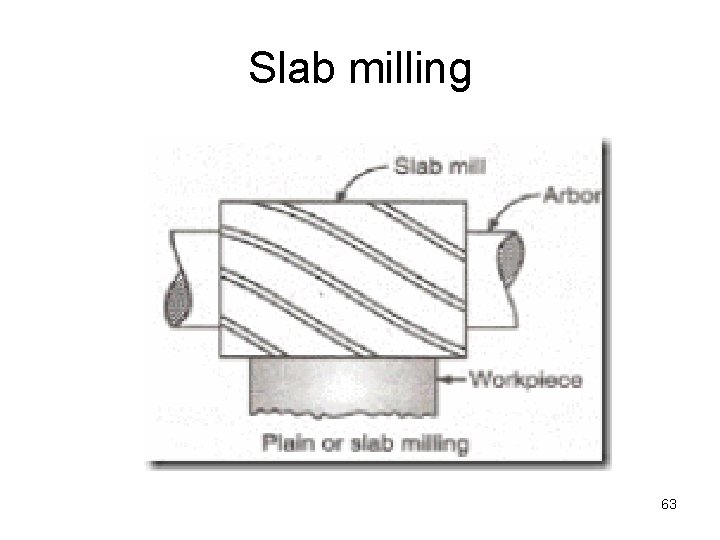
Slab milling 63
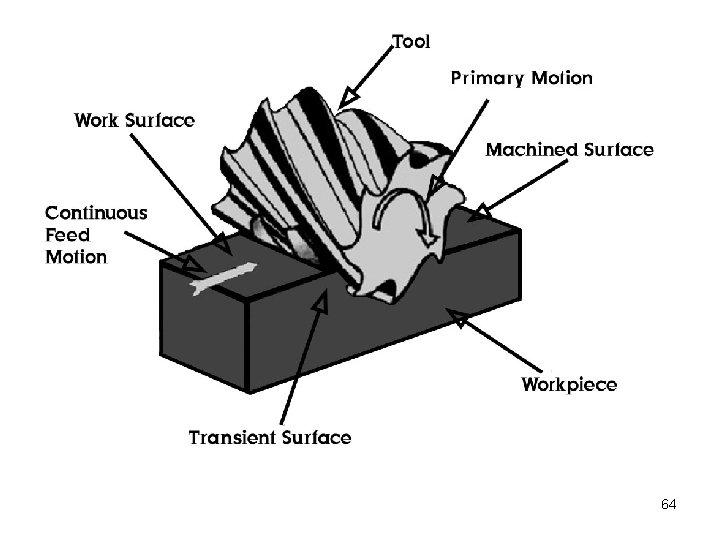
64
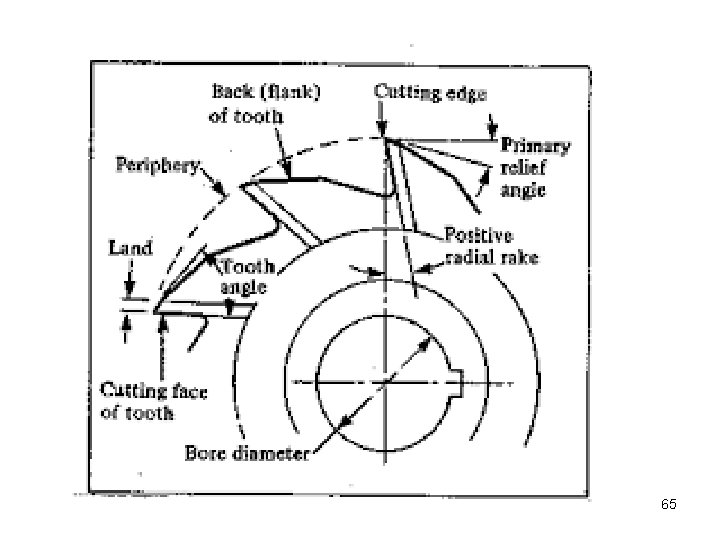
65
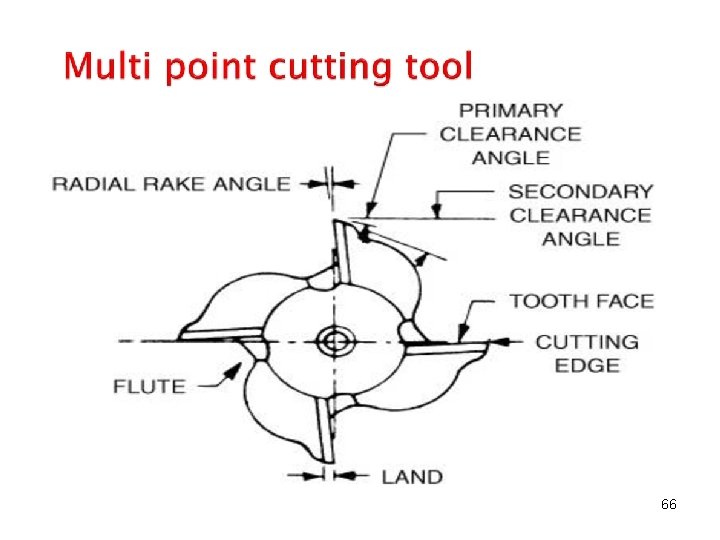
66
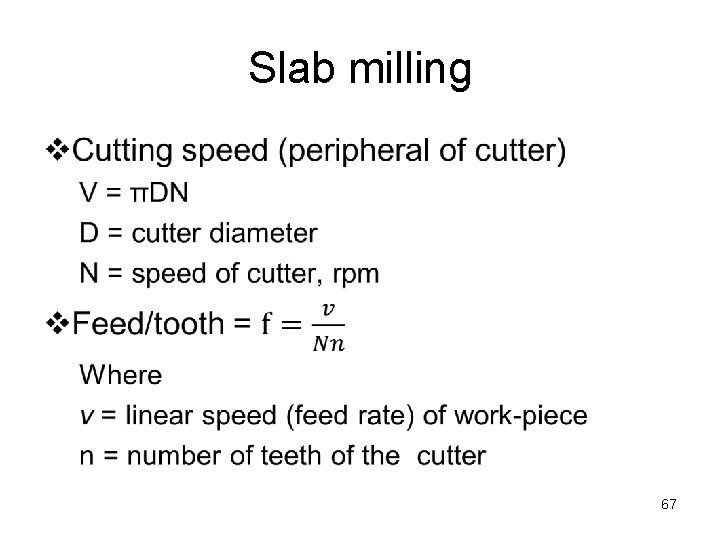
Slab milling 67
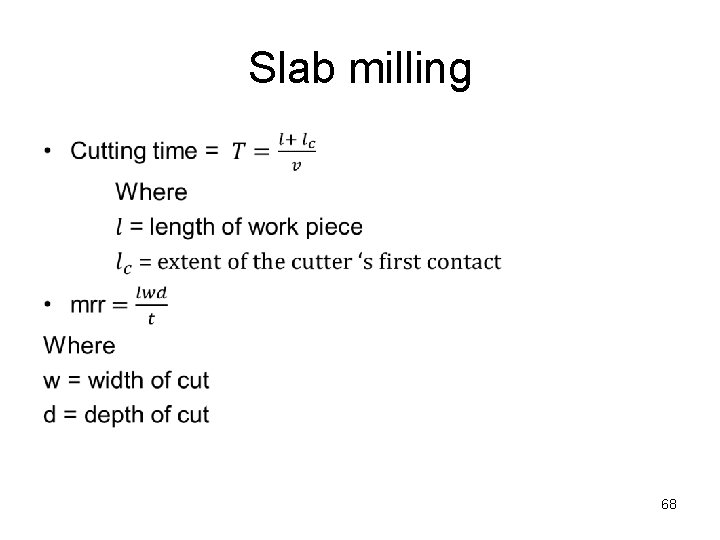
Slab milling 68
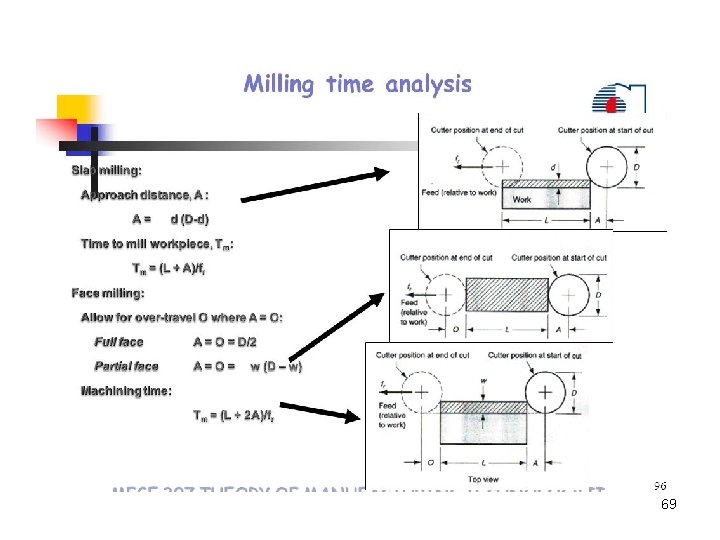
69
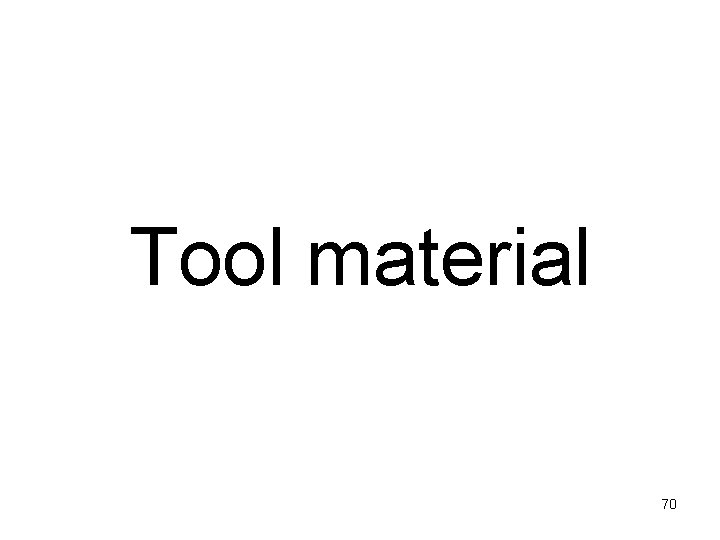
Tool material 70
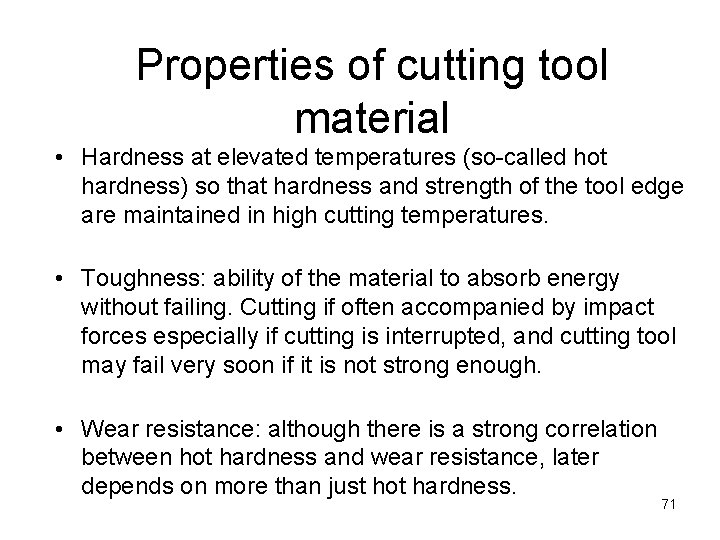
Properties of cutting tool material • Hardness at elevated temperatures (so-called hot hardness) so that hardness and strength of the tool edge are maintained in high cutting temperatures. • Toughness: ability of the material to absorb energy without failing. Cutting if often accompanied by impact forces especially if cutting is interrupted, and cutting tool may fail very soon if it is not strong enough. • Wear resistance: although there is a strong correlation between hot hardness and wear resistance, later depends on more than just hot hardness. 71
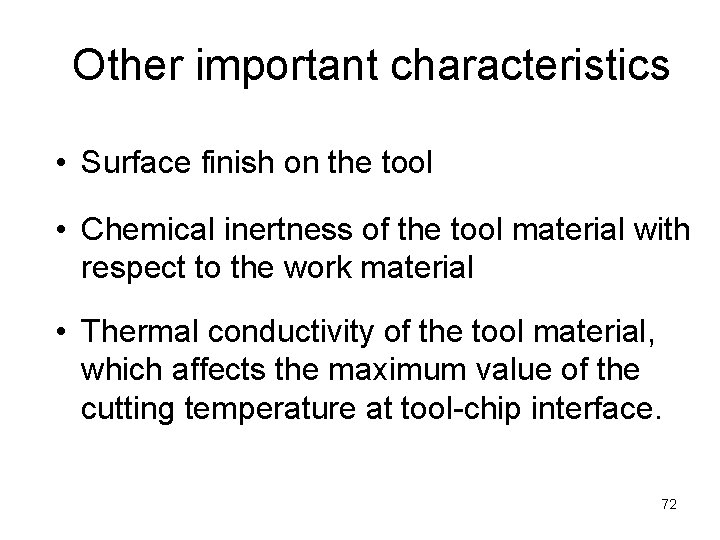
Other important characteristics • Surface finish on the tool • Chemical inertness of the tool material with respect to the work material • Thermal conductivity of the tool material, which affects the maximum value of the cutting temperature at tool-chip interface. 72
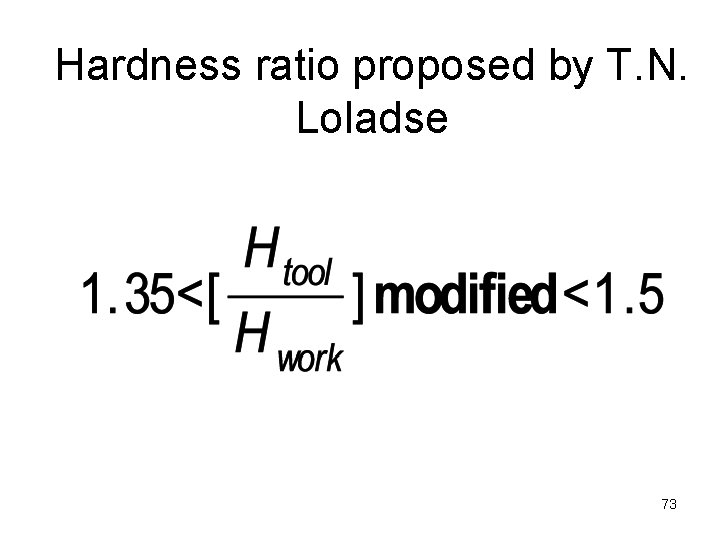
Hardness ratio proposed by T. N. Loladse 73
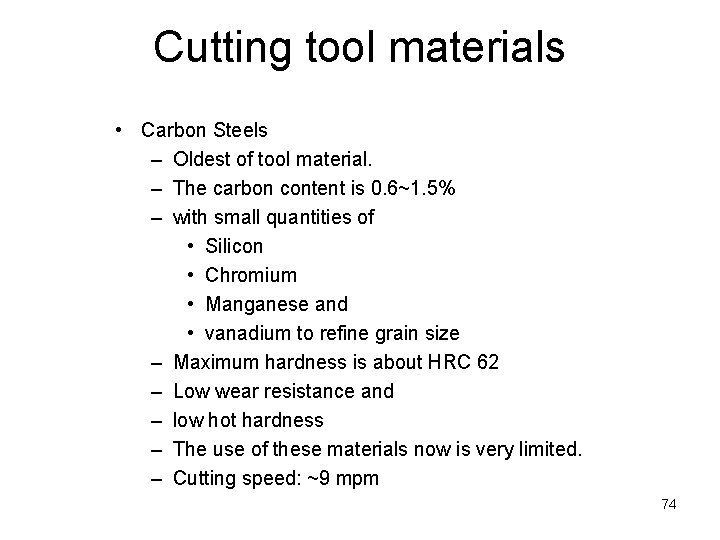
Cutting tool materials • Carbon Steels – Oldest of tool material. – The carbon content is 0. 6~1. 5% – with small quantities of • Silicon • Chromium • Manganese and • vanadium to refine grain size – Maximum hardness is about HRC 62 – Low wear resistance and – low hot hardness – The use of these materials now is very limited. – Cutting speed: ~9 mpm 74
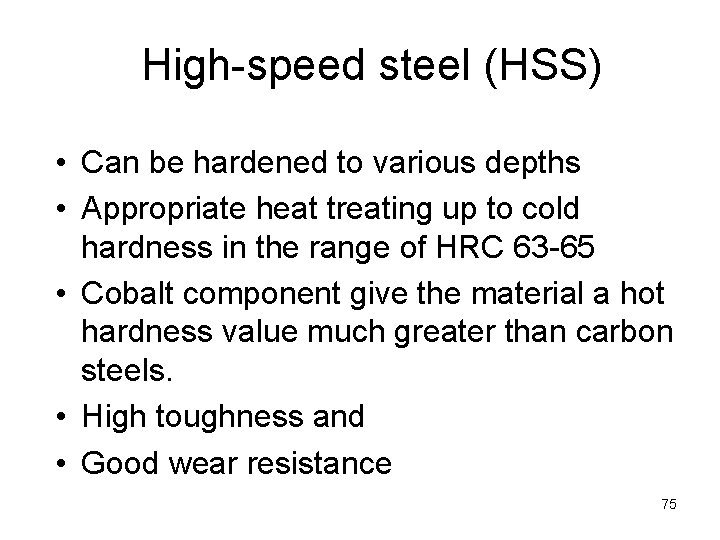
High-speed steel (HSS) • Can be hardened to various depths • Appropriate heat treating up to cold hardness in the range of HRC 63 -65 • Cobalt component give the material a hot hardness value much greater than carbon steels. • High toughness and • Good wear resistance 75
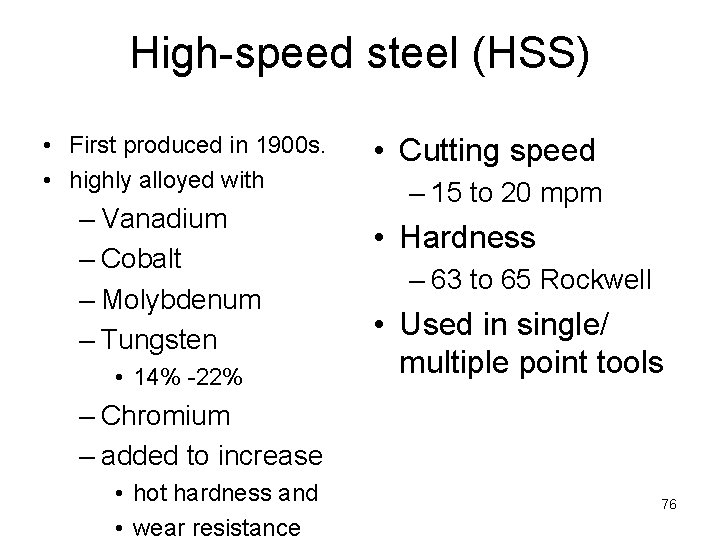
High-speed steel (HSS) • First produced in 1900 s. • highly alloyed with – Vanadium – Cobalt – Molybdenum – Tungsten • 14% -22% • Cutting speed – 15 to 20 mpm • Hardness – 63 to 65 Rockwell • Used in single/ multiple point tools – Chromium – added to increase • hot hardness and • wear resistance 76
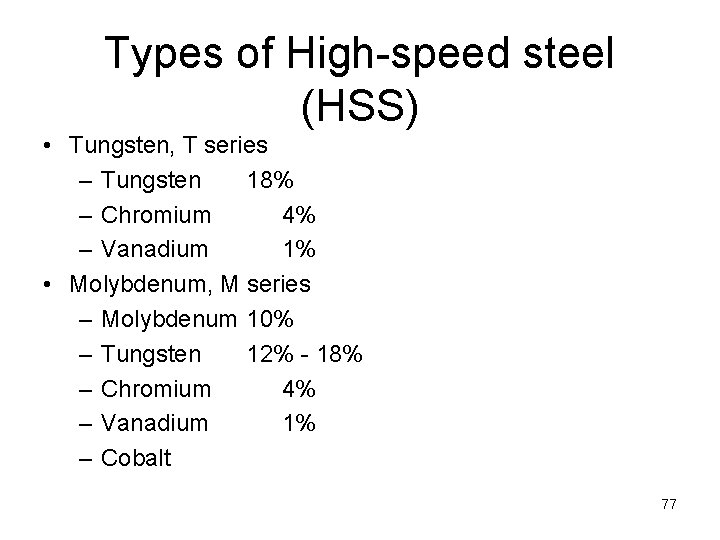
Types of High-speed steel (HSS) • Tungsten, T series – Tungsten 18% – Chromium 4% – Vanadium 1% • Molybdenum, M series – Molybdenum 10% – Tungsten 12% - 18% – Chromium 4% – Vanadium 1% – Cobalt 77
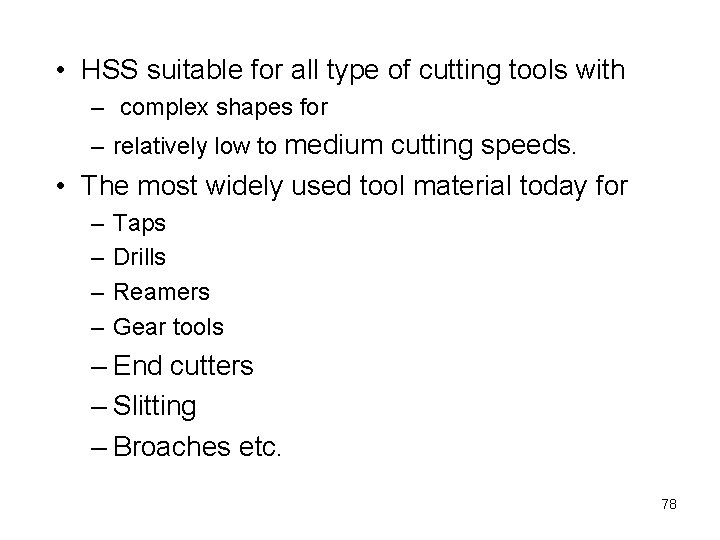
• HSS suitable for all type of cutting tools with – complex shapes for – relatively low to medium cutting speeds. • The most widely used tool material today for – – Taps Drills Reamers Gear tools – End cutters – Slitting – Broaches etc. 78
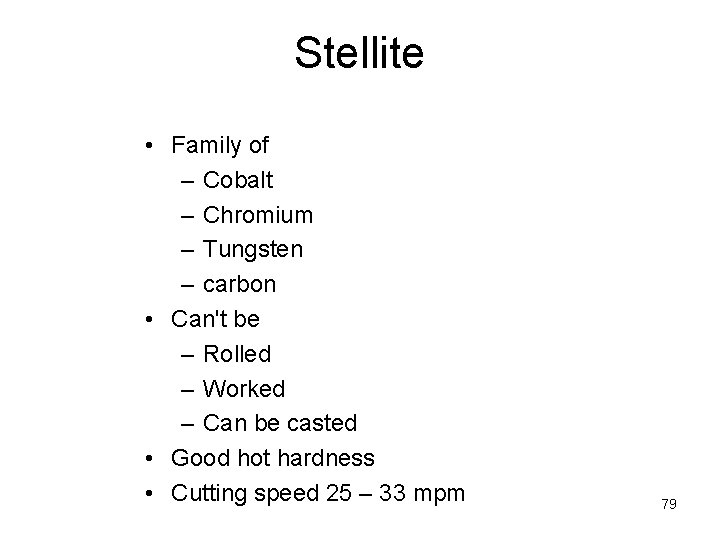
Stellite • Family of – Cobalt – Chromium – Tungsten – carbon • Can't be – Rolled – Worked – Can be casted • Good hot hardness • Cutting speed 25 – 33 mpm 79
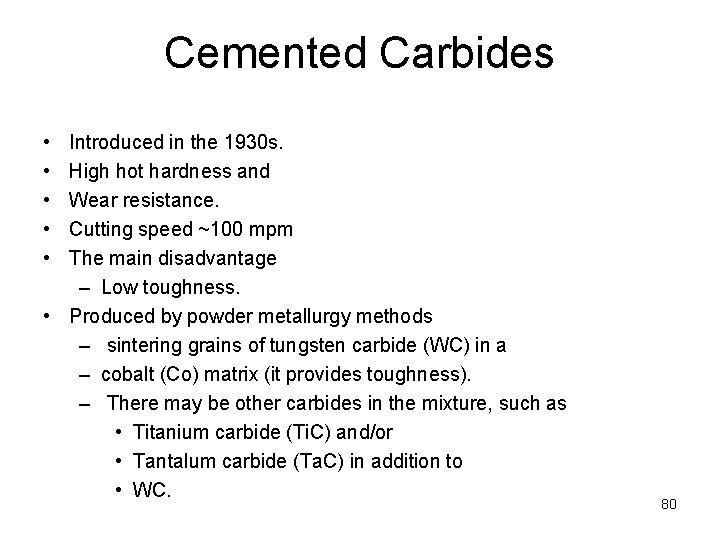
Cemented Carbides • • • Introduced in the 1930 s. High hot hardness and Wear resistance. Cutting speed ~100 mpm The main disadvantage – Low toughness. • Produced by powder metallurgy methods – sintering grains of tungsten carbide (WC) in a – cobalt (Co) matrix (it provides toughness). – There may be other carbides in the mixture, such as • Titanium carbide (Ti. C) and/or • Tantalum carbide (Ta. C) in addition to • WC. 80
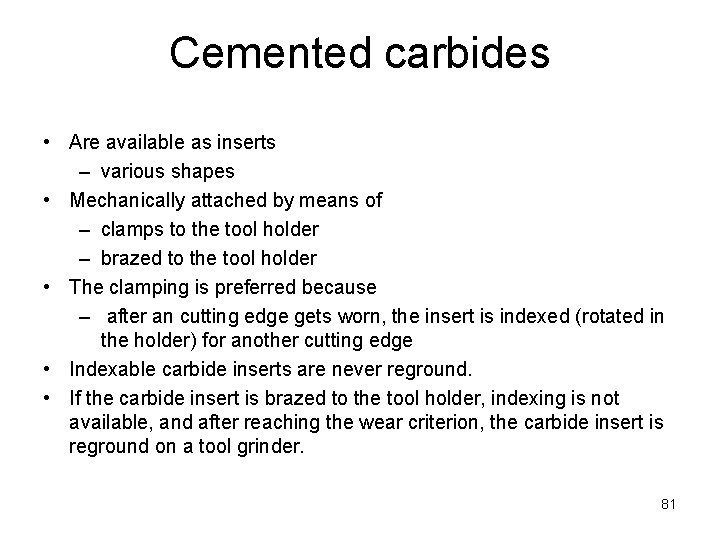
Cemented carbides • Are available as inserts – various shapes • Mechanically attached by means of – clamps to the tool holder – brazed to the tool holder • The clamping is preferred because – after an cutting edge gets worn, the insert is indexed (rotated in the holder) for another cutting edge • Indexable carbide inserts are never reground. • If the carbide insert is brazed to the tool holder, indexing is not available, and after reaching the wear criterion, the carbide insert is reground on a tool grinder. 81
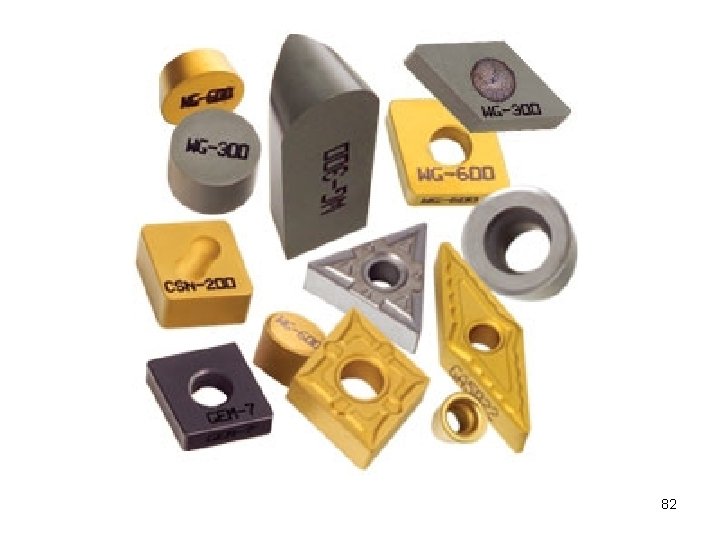
82
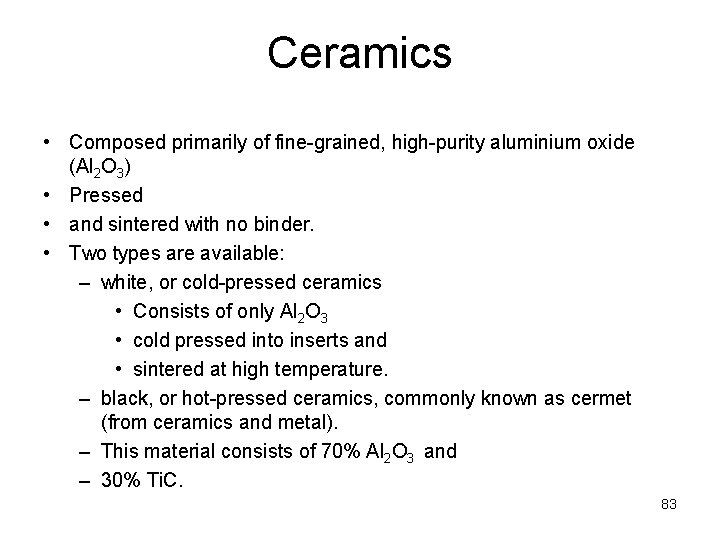
Ceramics • Composed primarily of fine-grained, high-purity aluminium oxide (Al 2 O 3) • Pressed • and sintered with no binder. • Two types are available: – white, or cold-pressed ceramics • Consists of only Al 2 O 3 • cold pressed into inserts and • sintered at high temperature. – black, or hot-pressed ceramics, commonly known as cermet (from ceramics and metal). – This material consists of 70% Al 2 O 3 and – 30% Ti. C. 83
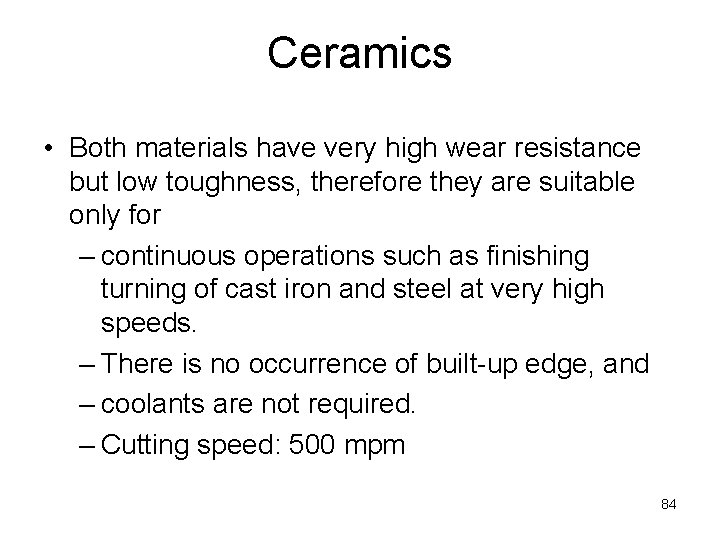
Ceramics • Both materials have very high wear resistance but low toughness, therefore they are suitable only for – continuous operations such as finishing turning of cast iron and steel at very high speeds. – There is no occurrence of built-up edge, and – coolants are not required. – Cutting speed: 500 mpm 84
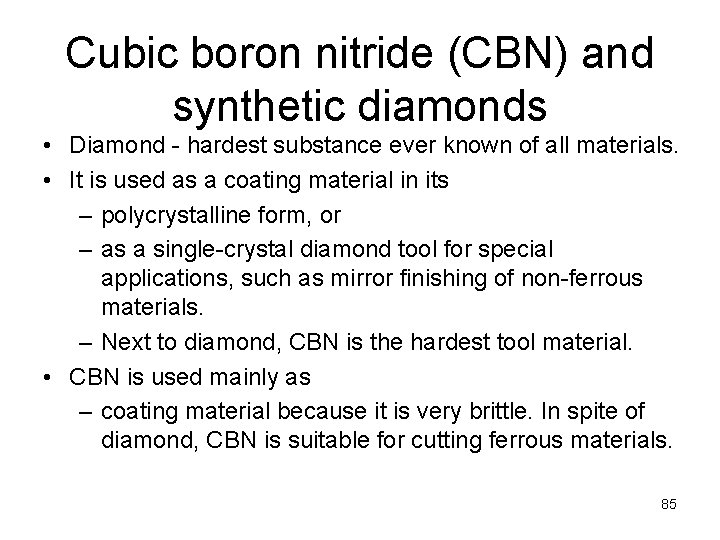
Cubic boron nitride (CBN) and synthetic diamonds • Diamond - hardest substance ever known of all materials. • It is used as a coating material in its – polycrystalline form, or – as a single-crystal diamond tool for special applications, such as mirror finishing of non-ferrous materials. – Next to diamond, CBN is the hardest tool material. • CBN is used mainly as – coating material because it is very brittle. In spite of diamond, CBN is suitable for cutting ferrous materials. 85
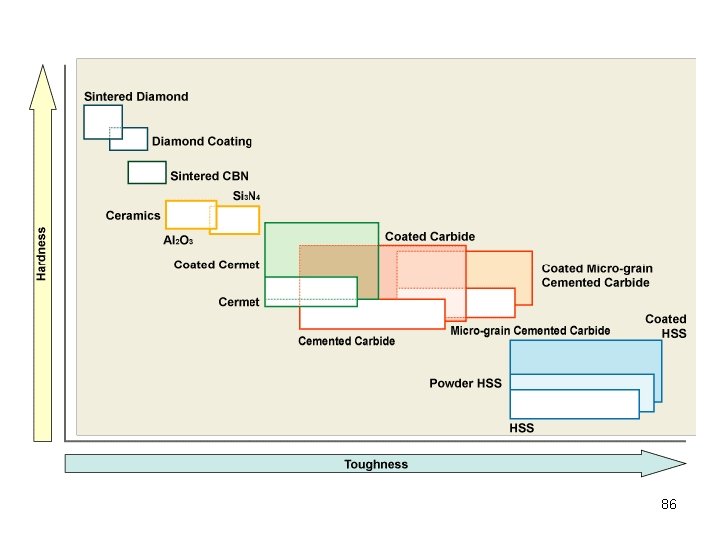
86
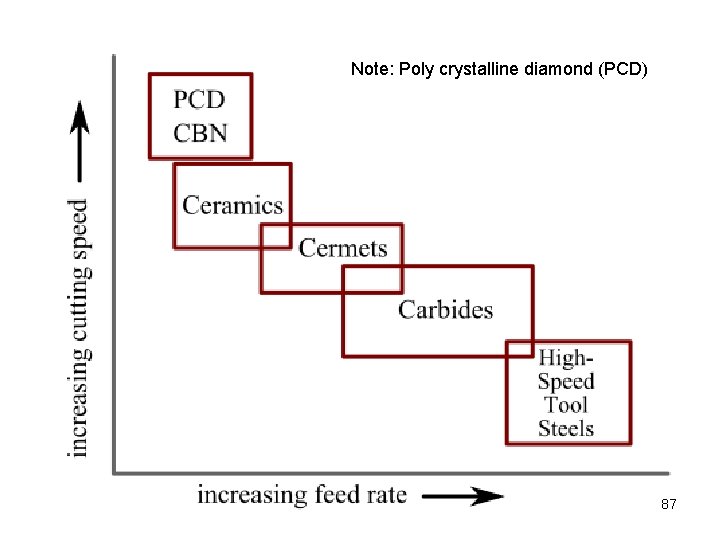
Note: Poly crystalline diamond (PCD) 87
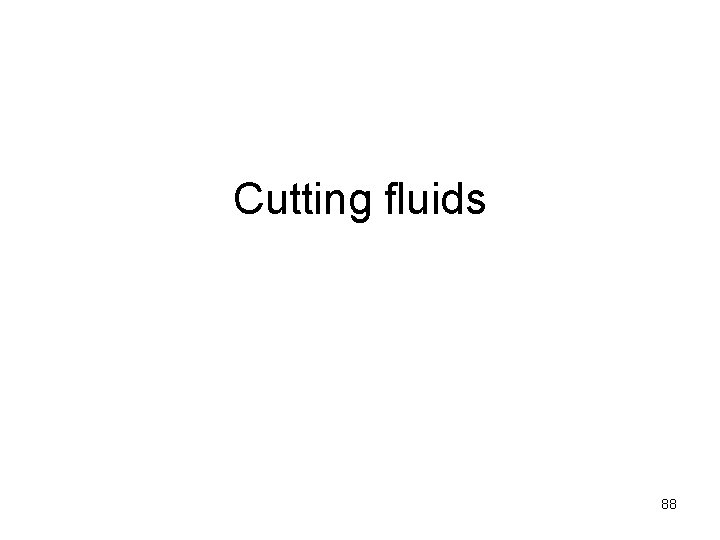
Cutting fluids 88
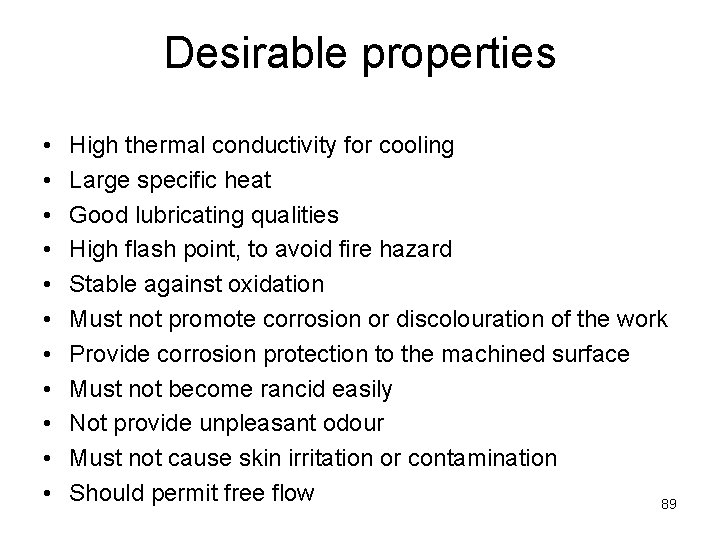
Desirable properties • • • High thermal conductivity for cooling Large specific heat Good lubricating qualities High flash point, to avoid fire hazard Stable against oxidation Must not promote corrosion or discolouration of the work Provide corrosion protection to the machined surface Must not become rancid easily Not provide unpleasant odour Must not cause skin irritation or contamination Should permit free flow 89
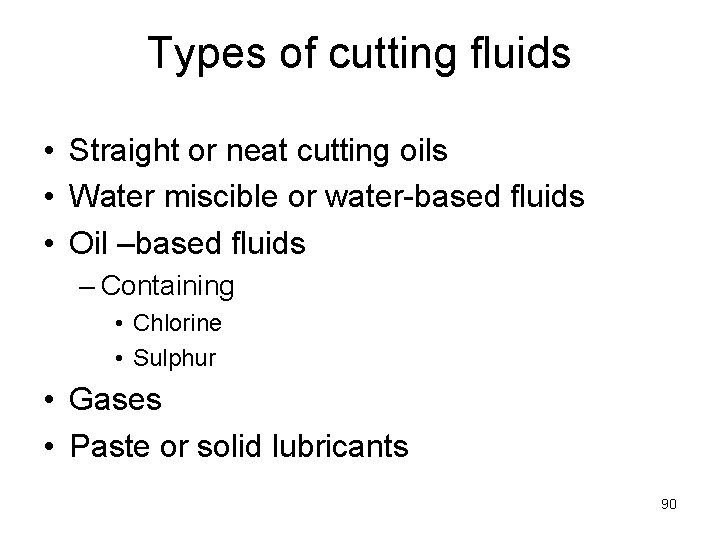
Types of cutting fluids • Straight or neat cutting oils • Water miscible or water-based fluids • Oil –based fluids – Containing • Chlorine • Sulphur • Gases • Paste or solid lubricants 90
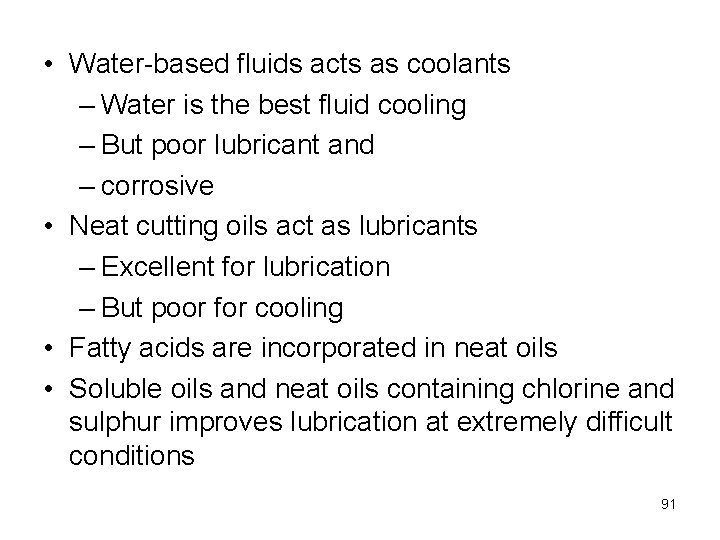
• Water-based fluids acts as coolants – Water is the best fluid cooling – But poor lubricant and – corrosive • Neat cutting oils act as lubricants – Excellent for lubrication – But poor for cooling • Fatty acids are incorporated in neat oils • Soluble oils and neat oils containing chlorine and sulphur improves lubrication at extremely difficult conditions 91
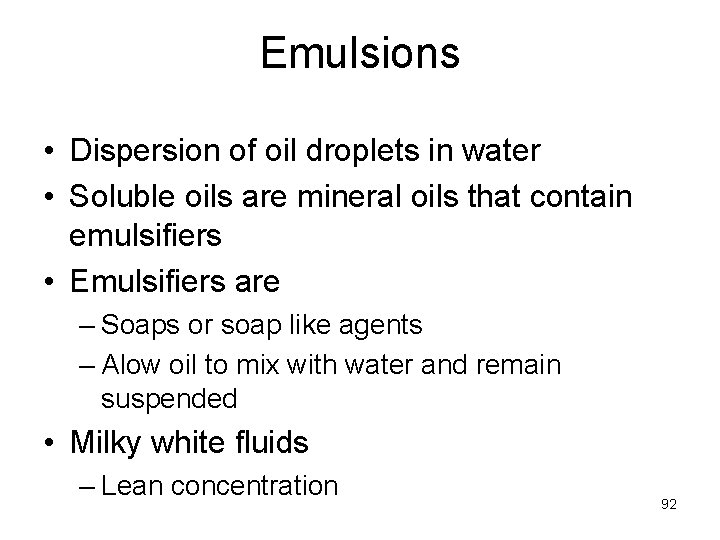
Emulsions • Dispersion of oil droplets in water • Soluble oils are mineral oils that contain emulsifiers • Emulsifiers are – Soaps or soap like agents – Alow oil to mix with water and remain suspended • Milky white fluids – Lean concentration 92
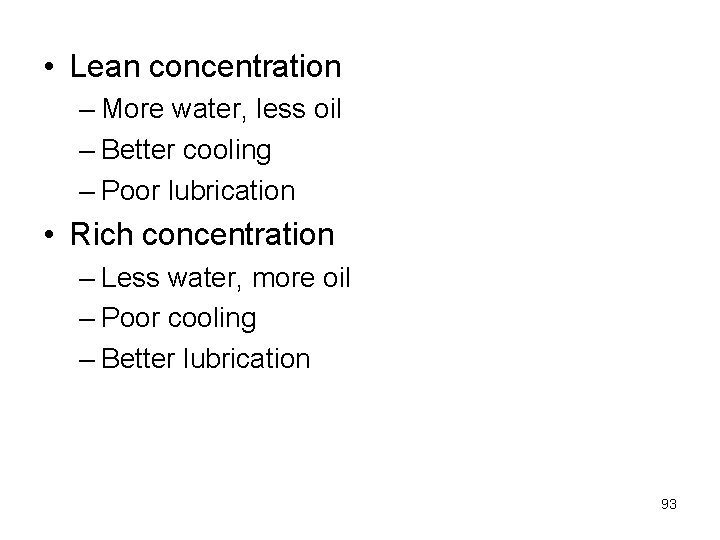
• Lean concentration – More water, less oil – Better cooling – Poor lubrication • Rich concentration – Less water, more oil – Poor cooling – Better lubrication 93
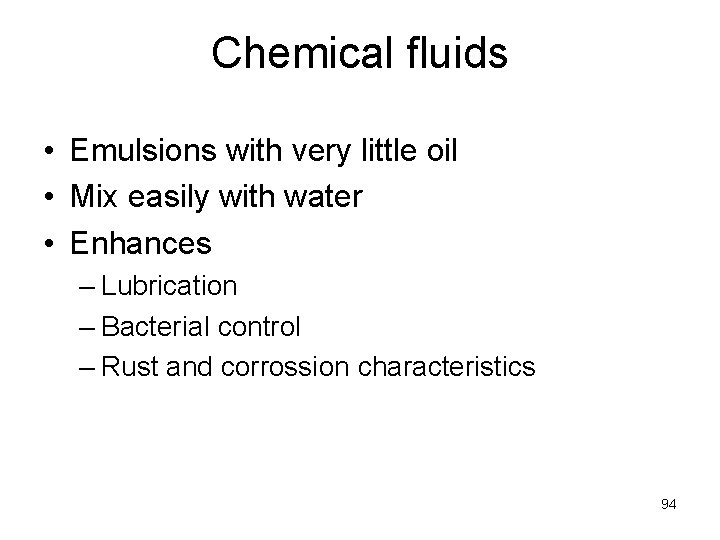
Chemical fluids • Emulsions with very little oil • Mix easily with water • Enhances – Lubrication – Bacterial control – Rust and corrossion characteristics 94
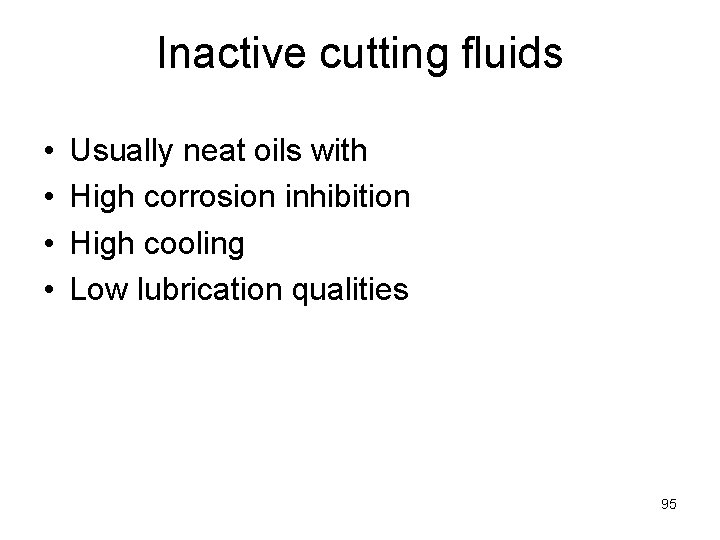
Inactive cutting fluids • • Usually neat oils with High corrosion inhibition High cooling Low lubrication qualities 95
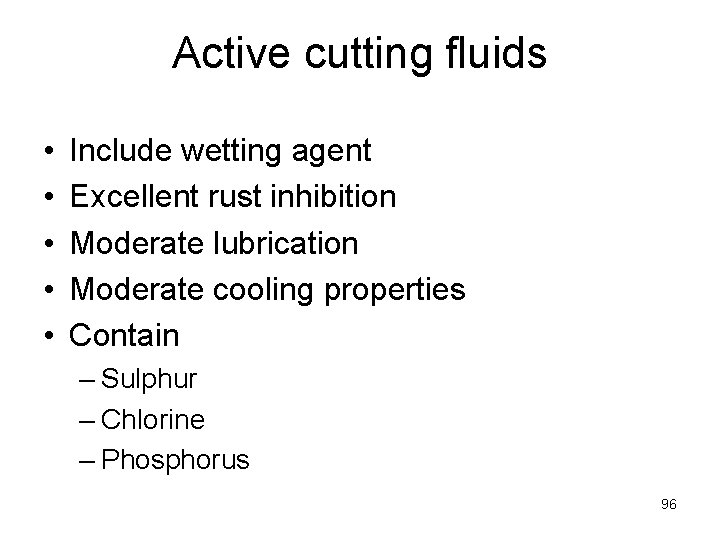
Active cutting fluids • • • Include wetting agent Excellent rust inhibition Moderate lubrication Moderate cooling properties Contain – Sulphur – Chlorine – Phosphorus 96
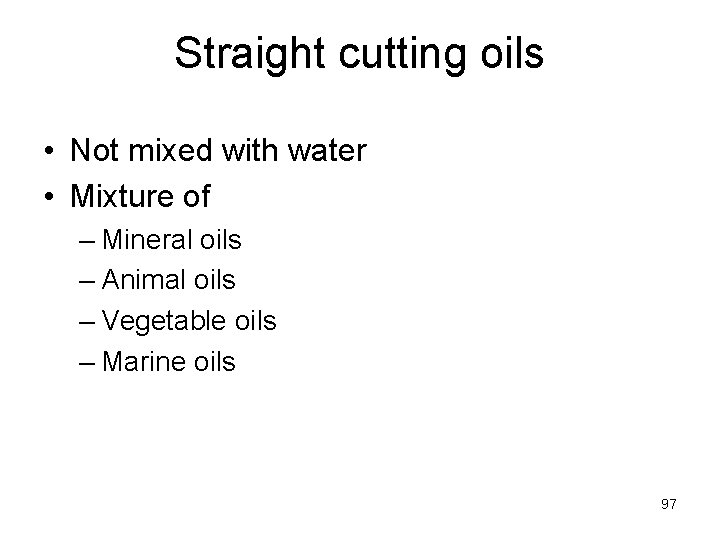
Straight cutting oils • Not mixed with water • Mixture of – Mineral oils – Animal oils – Vegetable oils – Marine oils 97
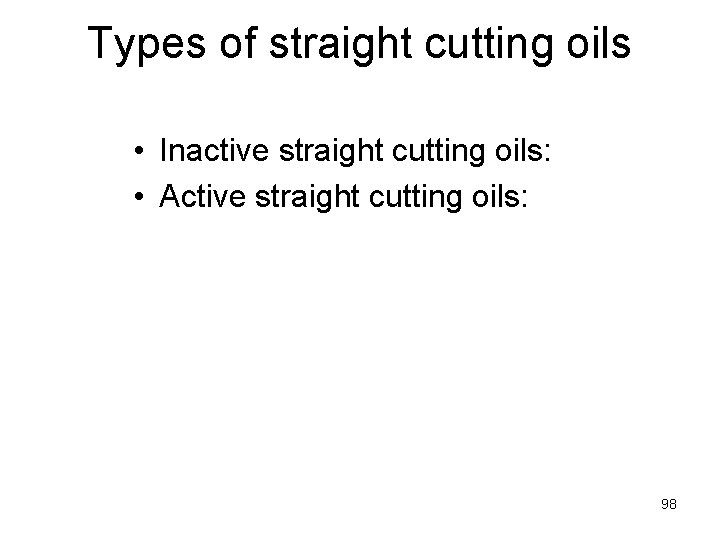
Types of straight cutting oils • Inactive straight cutting oils: • Active straight cutting oils: 98
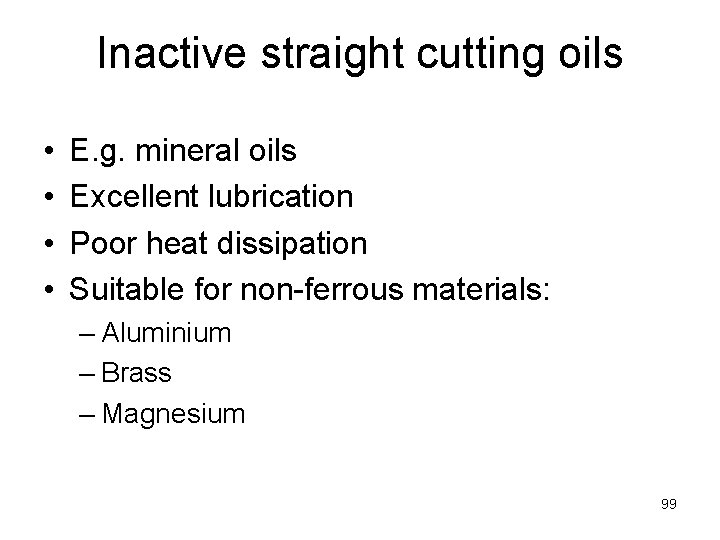
Inactive straight cutting oils • • E. g. mineral oils Excellent lubrication Poor heat dissipation Suitable for non-ferrous materials: – Aluminium – Brass – Magnesium 99
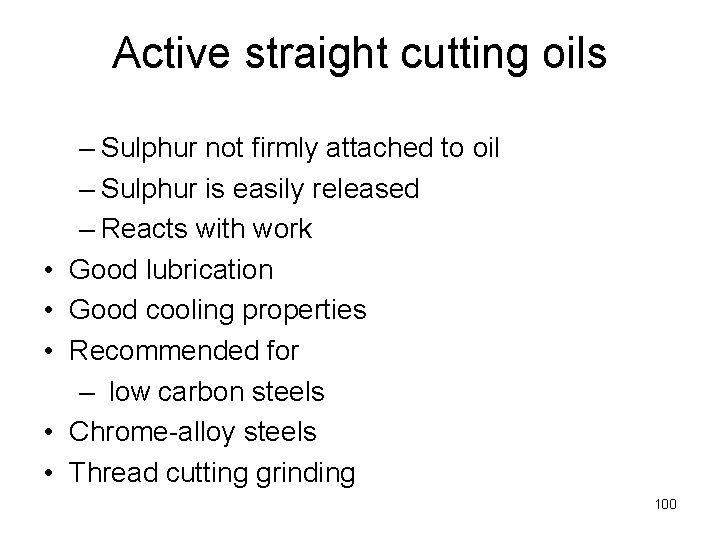
Active straight cutting oils • • • – Sulphur not firmly attached to oil – Sulphur is easily released – Reacts with work Good lubrication Good cooling properties Recommended for – low carbon steels Chrome-alloy steels Thread cutting grinding 100
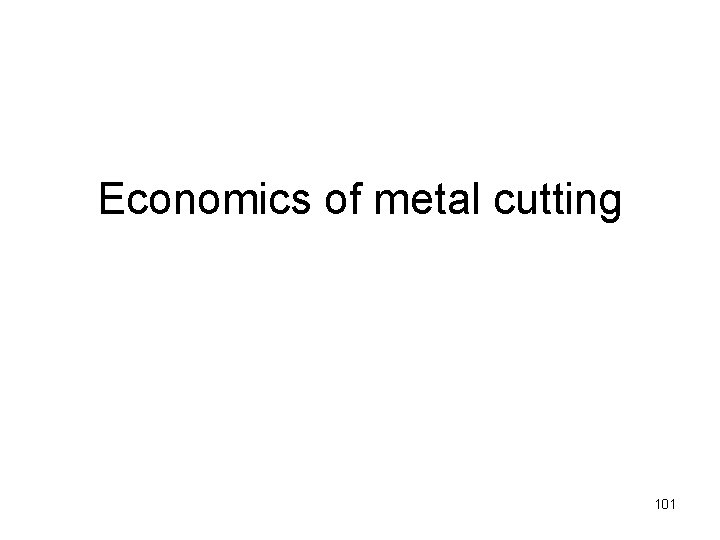
Economics of metal cutting 101
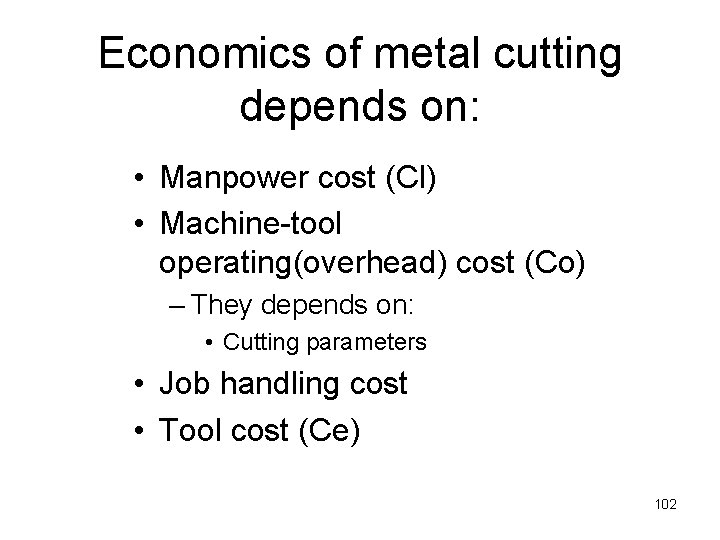
Economics of metal cutting depends on: • Manpower cost (Cl) • Machine-tool operating(overhead) cost (Co) – They depends on: • Cutting parameters • Job handling cost • Tool cost (Ce) 102
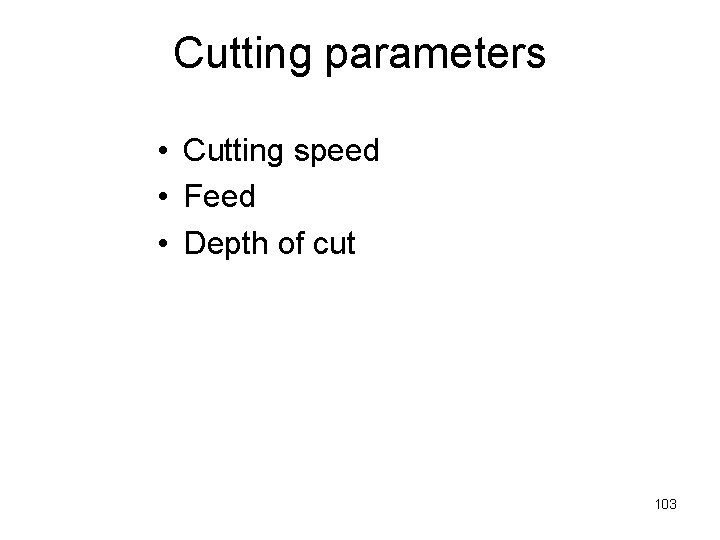
Cutting parameters • Cutting speed • Feed • Depth of cut 103
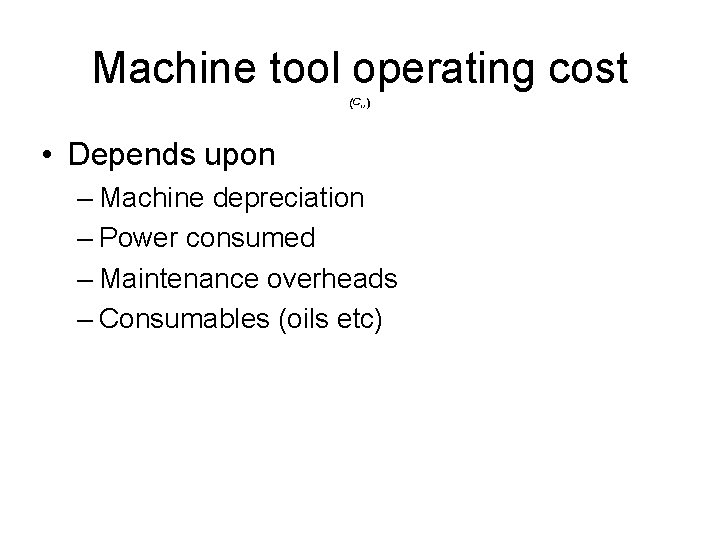
Machine tool operating cost • Depends upon – Machine depreciation – Power consumed – Maintenance overheads – Consumables (oils etc)
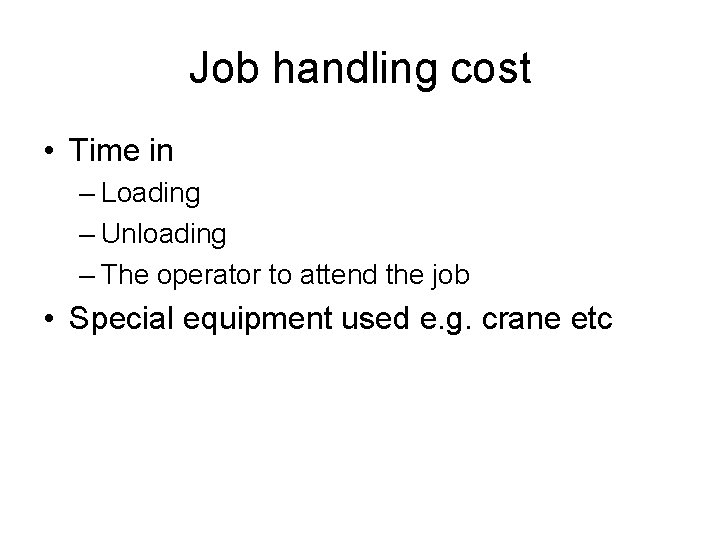
Job handling cost • Time in – Loading – Unloading – The operator to attend the job • Special equipment used e. g. crane etc
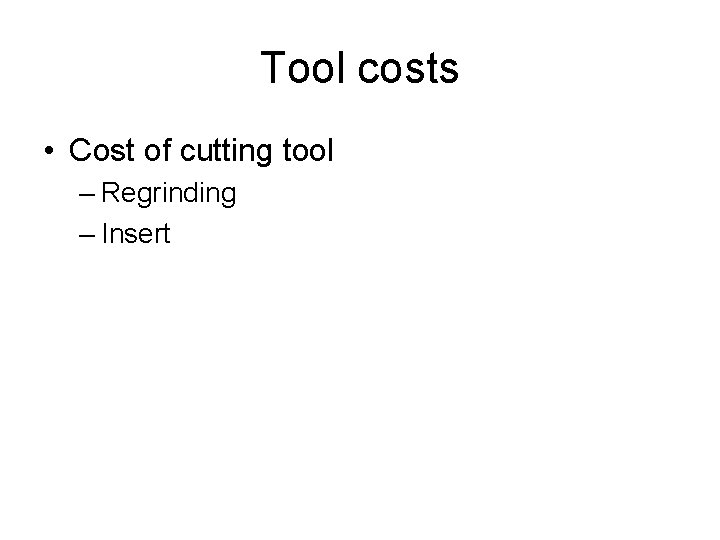
Tool costs • Cost of cutting tool – Regrinding – Insert
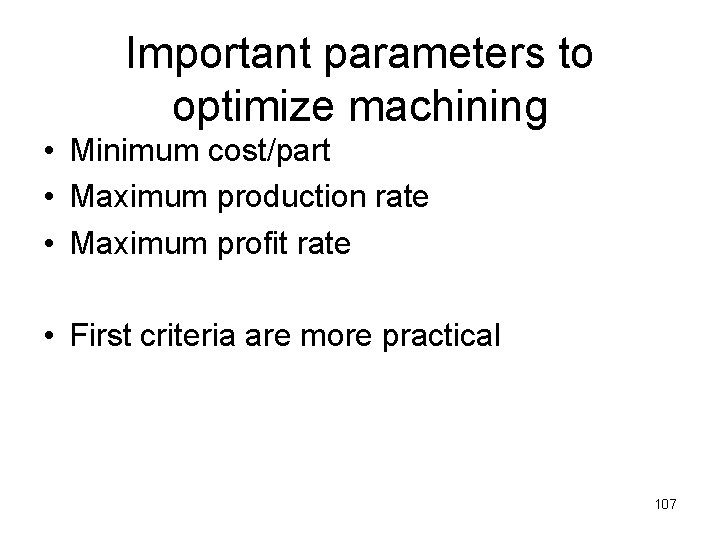
Important parameters to optimize machining • Minimum cost/part • Maximum production rate • Maximum profit rate • First criteria are more practical 107
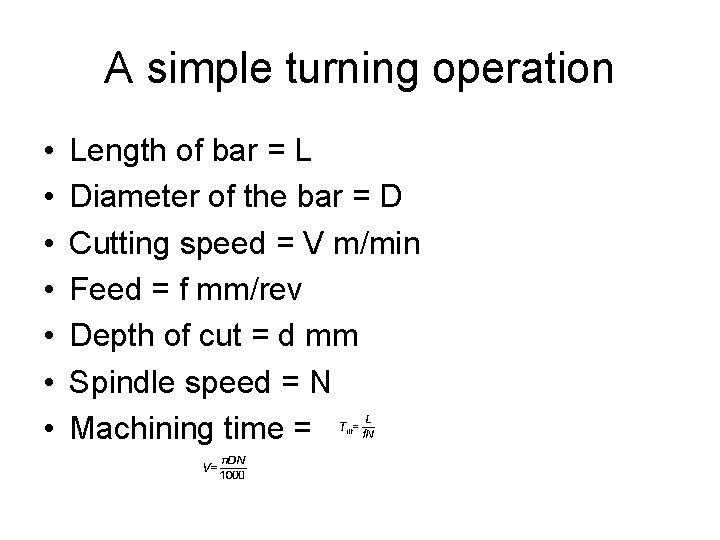
A simple turning operation • • Length of bar = L Diameter of the bar = D Cutting speed = V m/min Feed = f mm/rev Depth of cut = d mm Spindle speed = N Machining time =
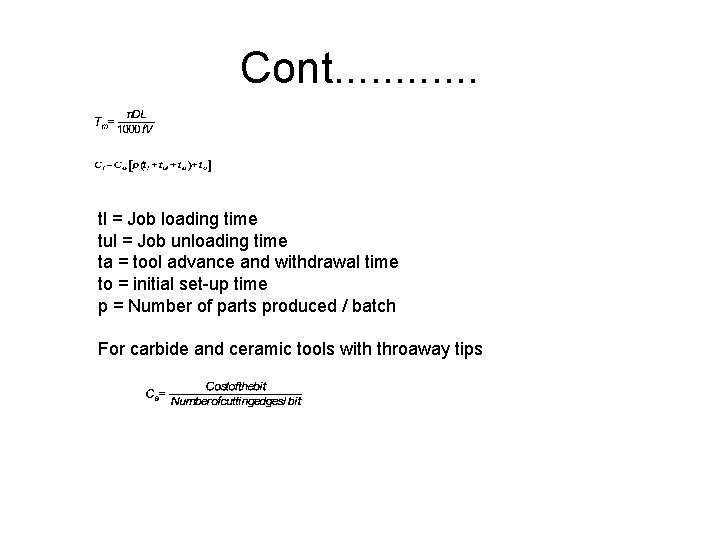
Cont. . . tl = Job loading time tul = Job unloading time ta = tool advance and withdrawal time to = initial set-up time p = Number of parts produced / batch For carbide and ceramic tools with throaway tips
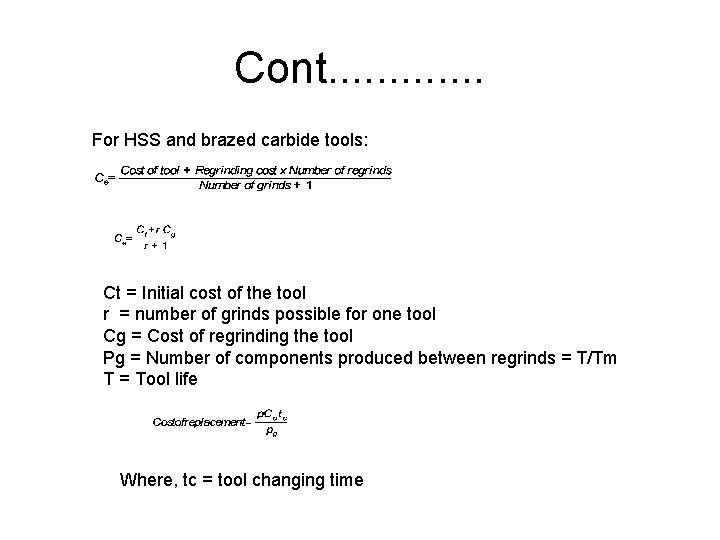
Cont. . . For HSS and brazed carbide tools: Ct = Initial cost of the tool r = number of grinds possible for one tool Cg = Cost of regrinding the tool Pg = Number of components produced between regrinds = T/Tm T = Tool life Where, tc = tool changing time
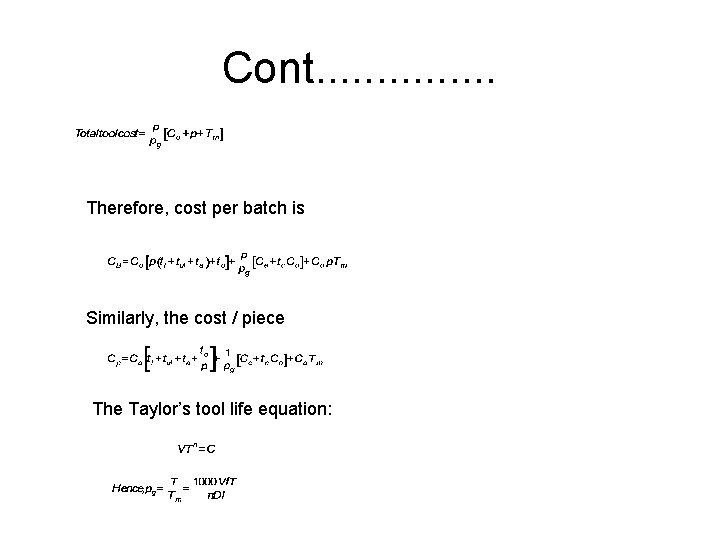
Cont. . . . Therefore, cost per batch is Similarly, the cost / piece The Taylor’s tool life equation:
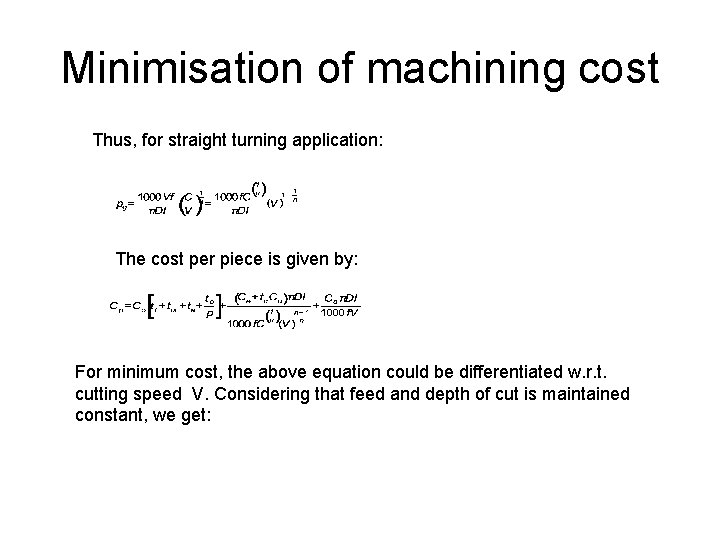
Minimisation of machining cost Thus, for straight turning application: The cost per piece is given by: For minimum cost, the above equation could be differentiated w. r. t. cutting speed V. Considering that feed and depth of cut is maintained constant, we get:
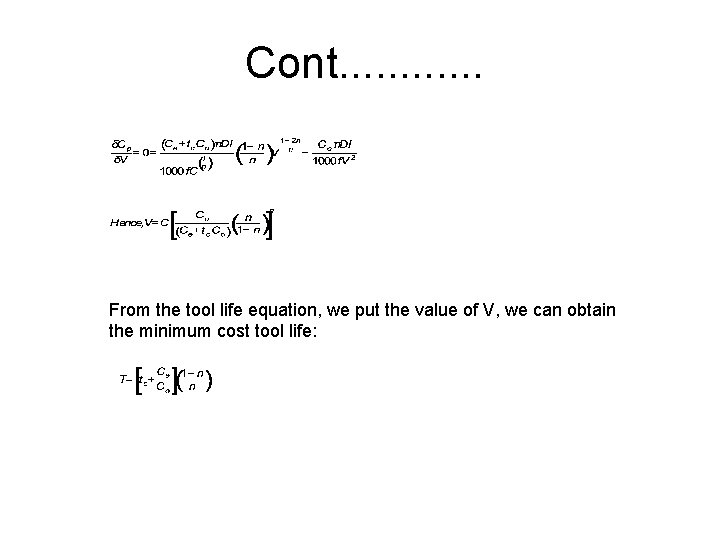
Cont. . . From the tool life equation, we put the value of V, we can obtain the minimum cost tool life:
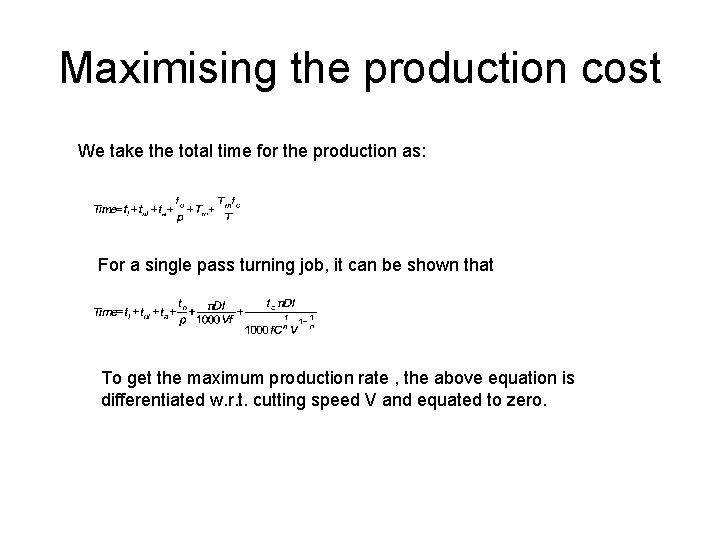
Maximising the production cost We take the total time for the production as: For a single pass turning job, it can be shown that To get the maximum production rate , the above equation is differentiated w. r. t. cutting speed V and equated to zero.
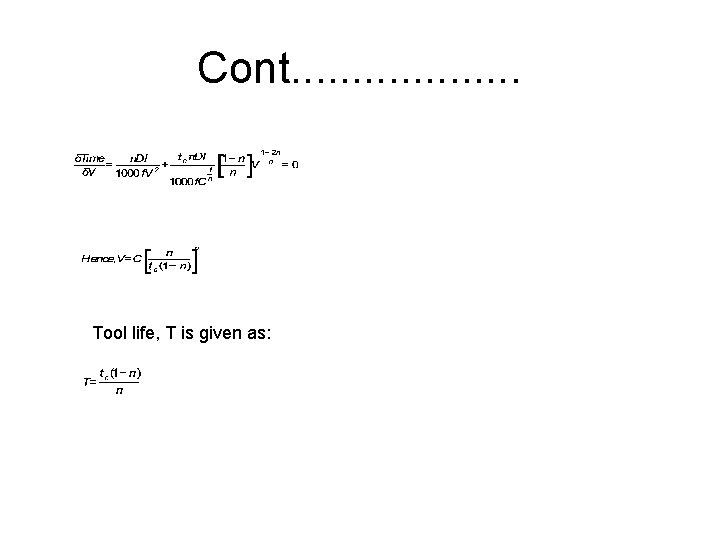
Cont. . . . . Tool life, T is given as:
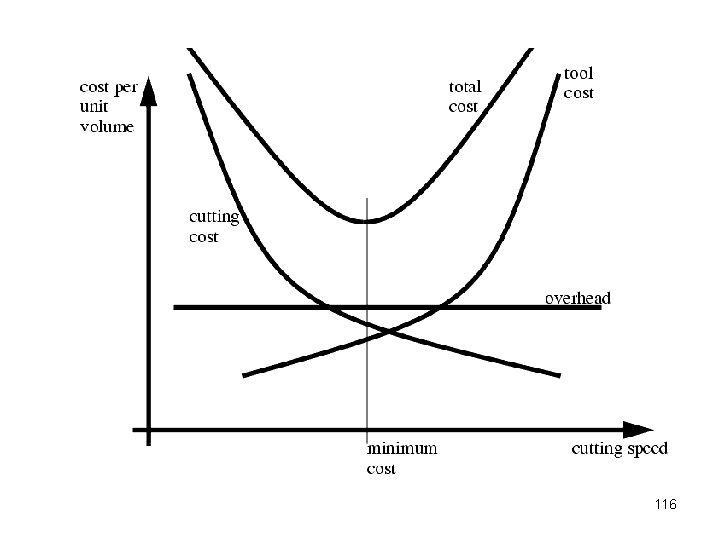
116
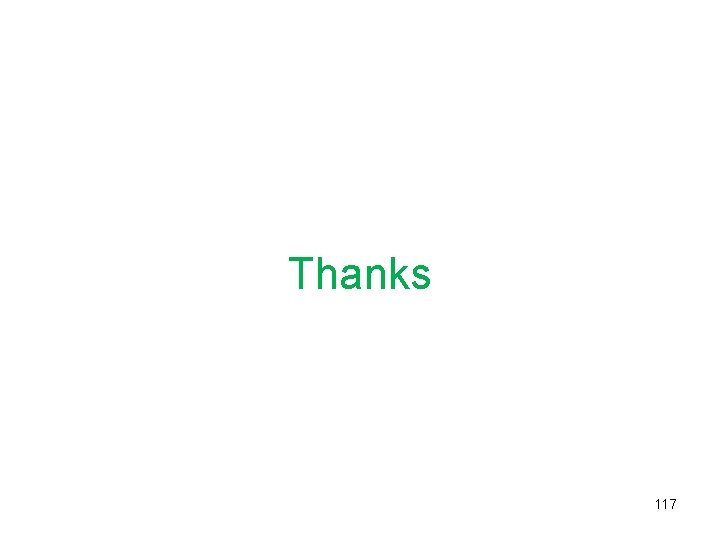
Thanks 117
Aligarh muslim university orientation programme
Ytu erasmus
Sjsu mechanical engineering
King saud university mechanical engineering
Czech technical university mechanical engineering
American university mechanical engineering
American university mechanical engineering
Yale university mechanical engineering
University of florida mechanical engineering
Tel aviv university mechanical engineering
Concordia university mechanical engineering
Faculty of mechanical engineering thammasat university
Department of information engineering university of padova
Department of information engineering university of padova
University of sargodha engineering department
Jnmc hospital aligarh
Sir syed ahmed khan father name
Actual mechanical advantage vs ideal mechanical advantage
Mechanical engineering rit
Nps mechanical engineering
Mechanical engineering usf flowchart
Specialcourseinfo
Importance of machine design
Statics centroid
Mechanical engineering presentation
Drawing chapter 1
Utwente lisa
Mechanical engineering uwaterloo
Oregon state mecop
Mechanical engineering design book
Mcpsmd pdo
Basic mechanical engineering syllabus
Clarkson university aeronautical engineering
Stevens institute of technology mechanical engineering
Backstop mechanical engineering
Jungwoo mechanical engineering
Vcu mechanical engineering
Mechanical engineering course
Mechanical engineering course
Minimum number of teeth
Roller chain
Mechanical engineering programming
Mechanical engineering
Mechanical engineering
Mechanical engineering
Mechanical control system
Mechanical engineering design
Stevens institute of technology mechanical engineering
Isolation routing
Liang zhu umbc
Motion transformation systems
Mathcad mechanical engineering library
Ethical issues in mechanical engineering
Automotive prime movers
Rit withdraw from class
Tamu meen advising
Rov lighting
Backstop mechanical engineering
Electrical engineering department
Hotel engineering department
City of houston design manual
What is kpi in engineering
Tum
Material science iit delhi
University of bridgeport computer science
Bridgeport university computer science
Computer engineering department
Ucla electrical engineering department
Department of law university of jammu
Department of geology university of dhaka
University of padova psychology
University of bridgeport it department
Iowa state math department
Sputonik
Texas state psychology program
Manipal university chemistry department
Syracuse university psychology department
Jackson state university finance department
Columbia university department of computer science
Michigan state university physics
Columbia university cs department
Claudia arrighi
Biggest muslim empire
Chapter 18: the muslim world expands answer key
How were efforts to westernize problematic
Mawlid proof
Epiko ng mindanao indarapatra at sulayman
Salubong panitikan
Muslim social pyramid
Why was polo a popular sport among wealthy muslims?
Chapter 27 section 3 european claim muslim lands
Chapter 27 section 3 european claim muslim lands
Simpsons muslim episode
When muslim came to india
Muslim aqiqah ceremony
How muslim came to india
Chapter 11 section 3 european claim muslim lands
Lenasia muslim association
Muslim housing services
Ano ang pinakaunang estadong naitatag sa kanlurang africa?
Powerpoint template islamic
Europeans claim muslim lands
Muslim specialist hospital zaria
Muslim innovations and adaptations
Chapter 10 the muslim world
Chapter 10 section 2 building a muslim empire
Chapter 2 the muslim world expands
Muslim freedom fighters name
Religion
Muslim saladin retakes jerusalem
Masjid
Why do muslims fast
All india muslim league 1906
All india muslim league 1906
Hukum syirkah
Conclusion of jammu and kashmir
Muslim women's quarters
European claims in muslim regions