CORROSION Introduction Corrosion is defined as the destructive
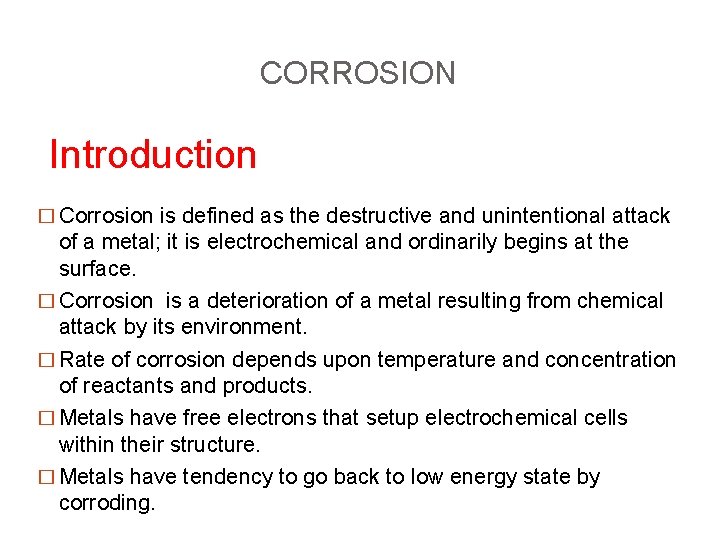
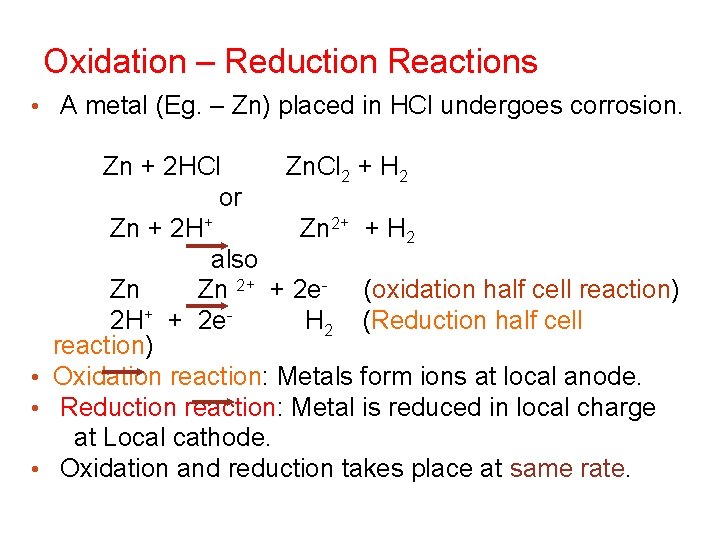
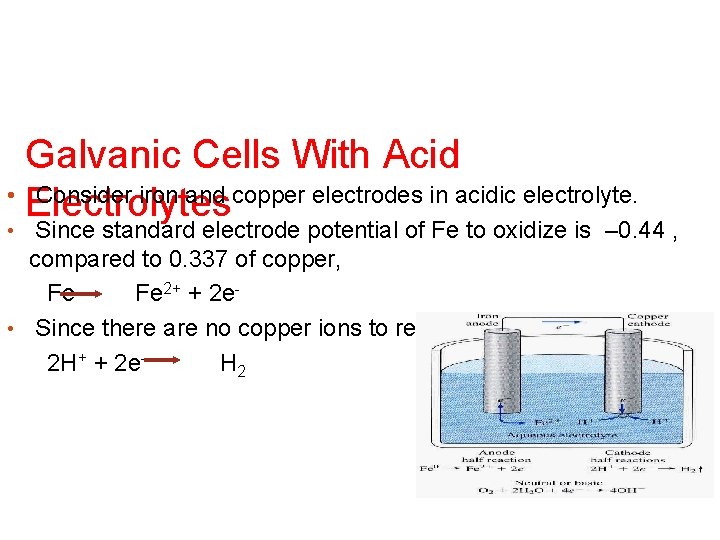
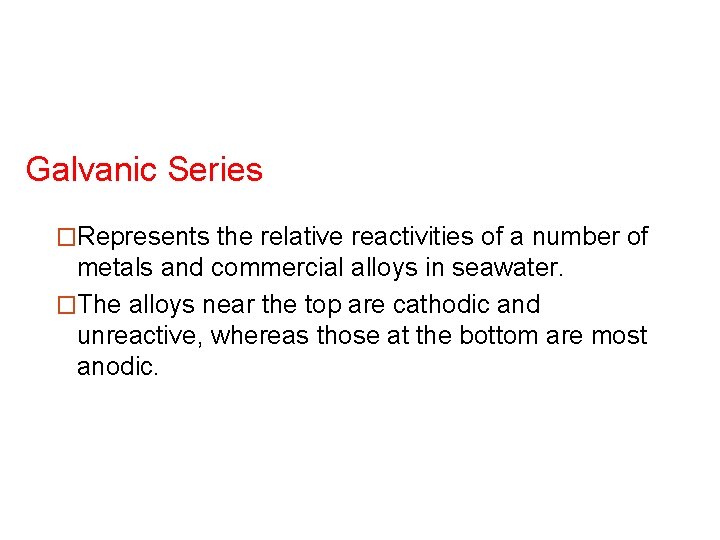
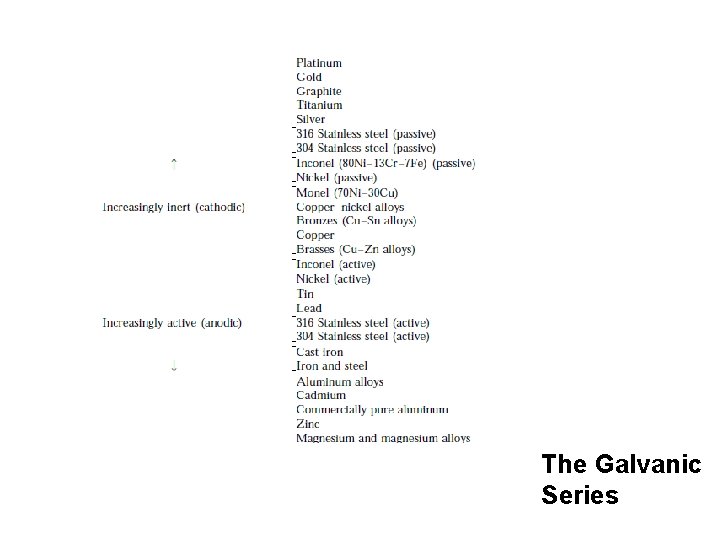
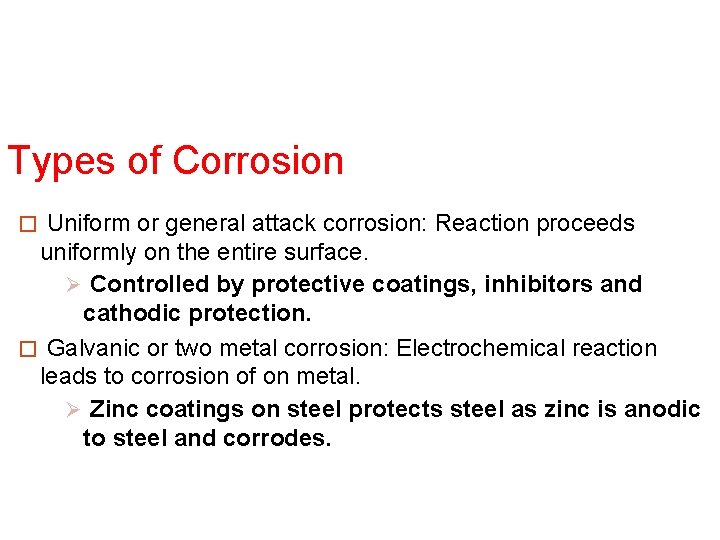
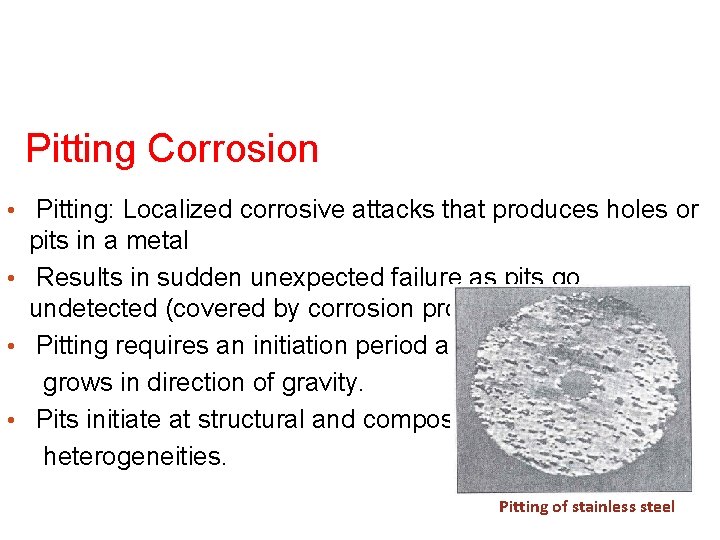
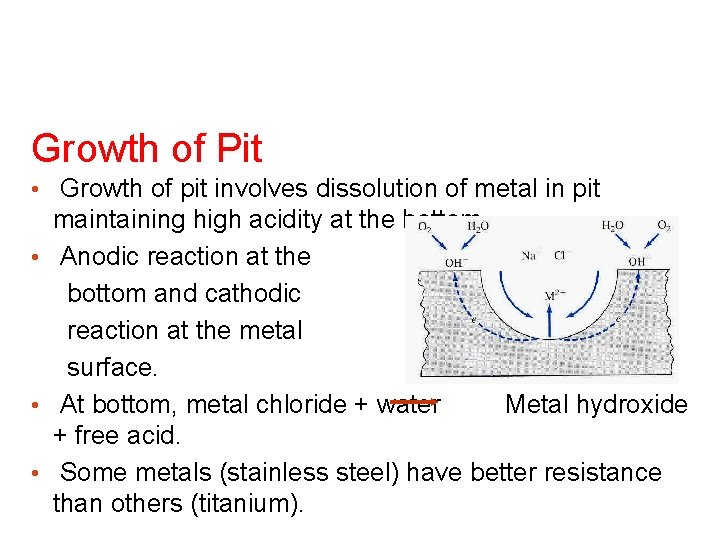
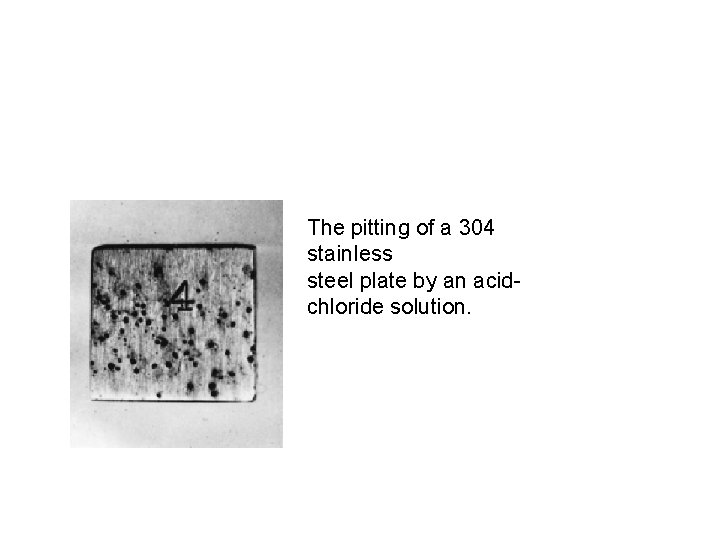
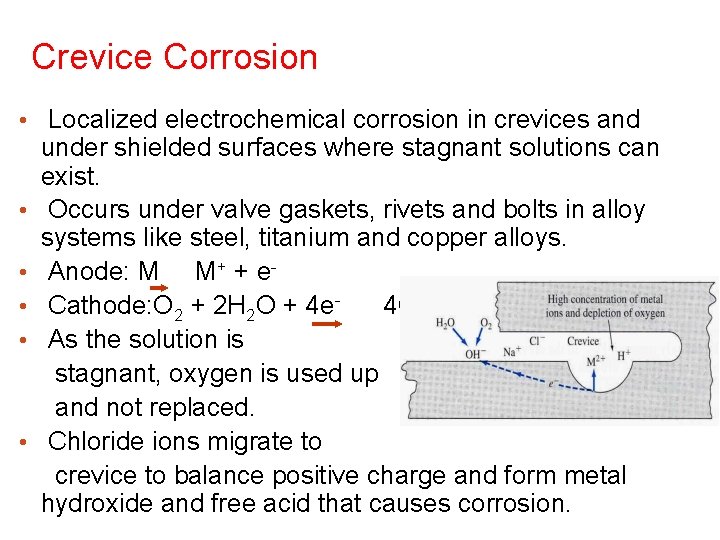
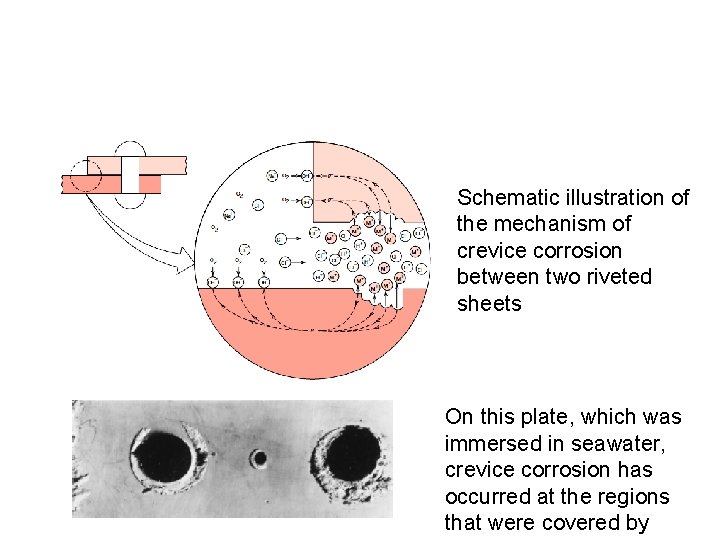
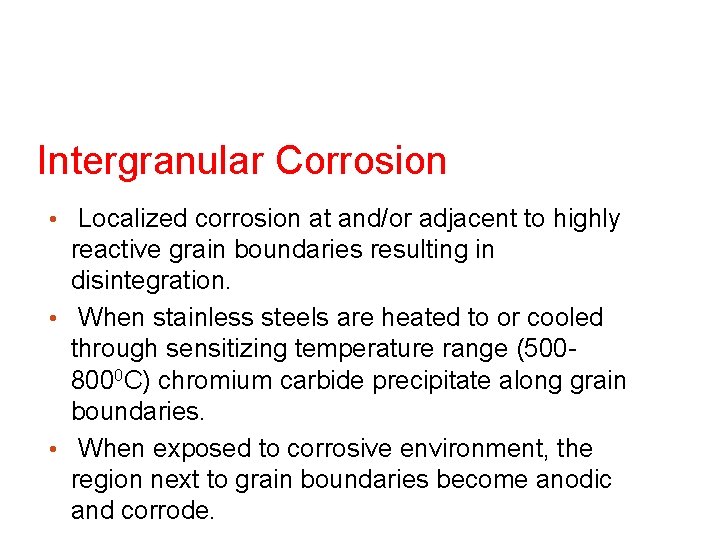
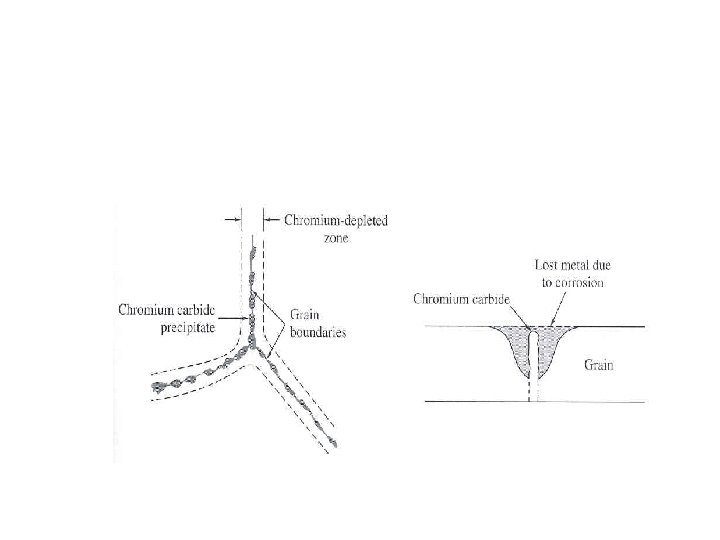
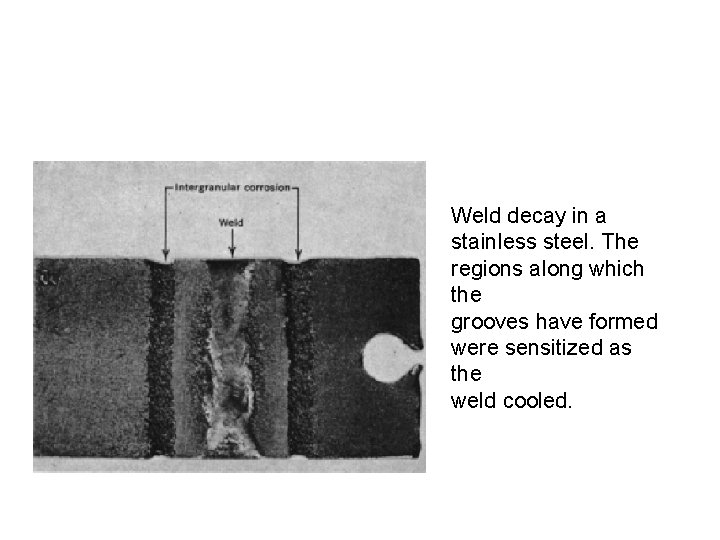
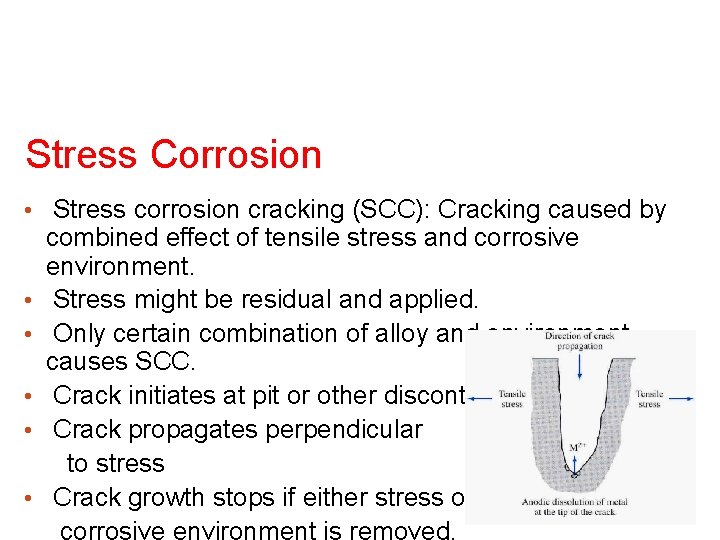
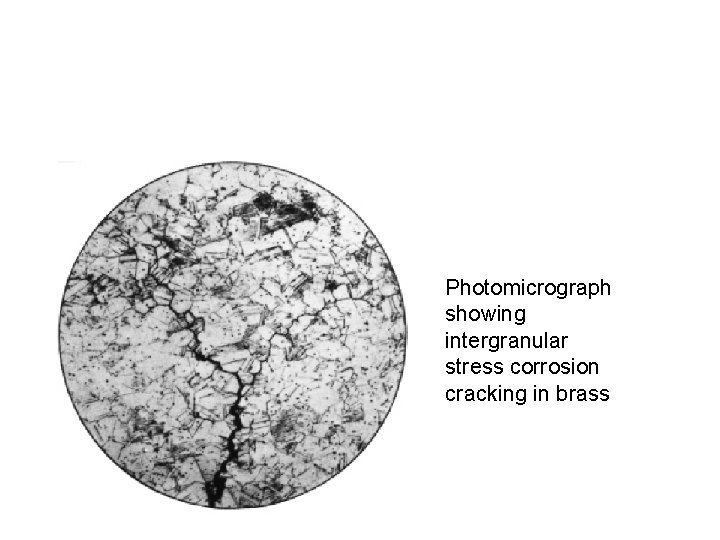
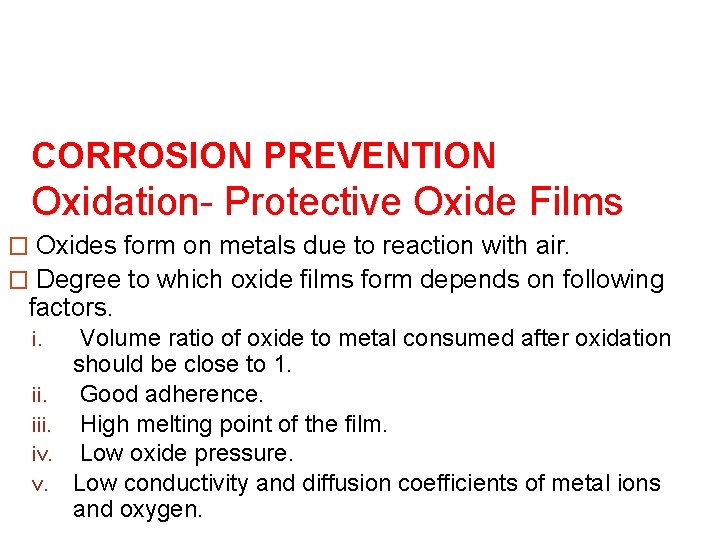
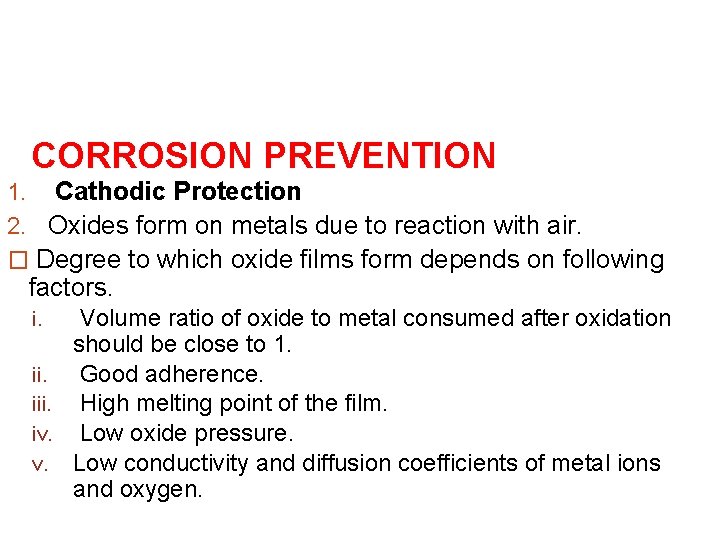
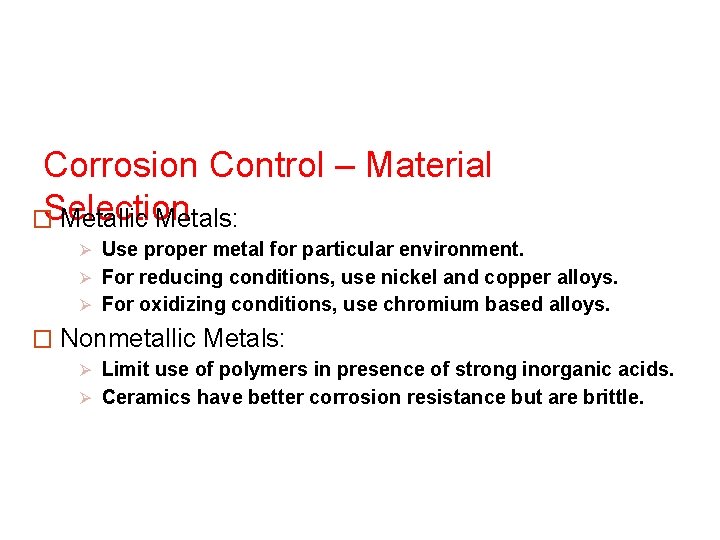
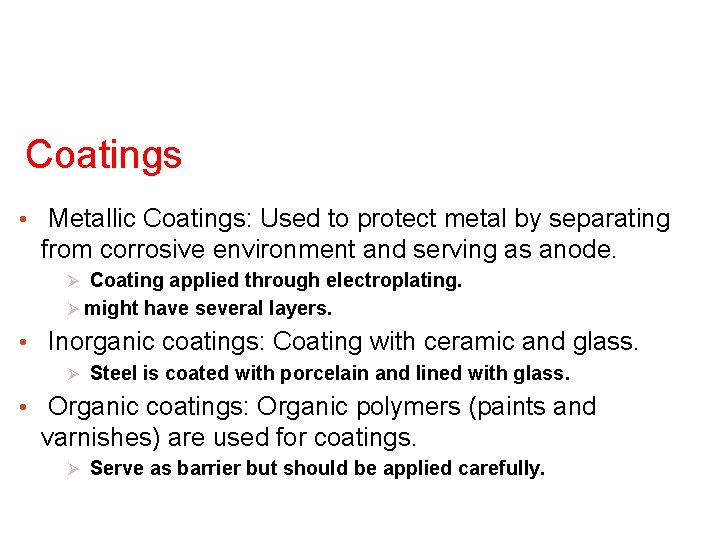
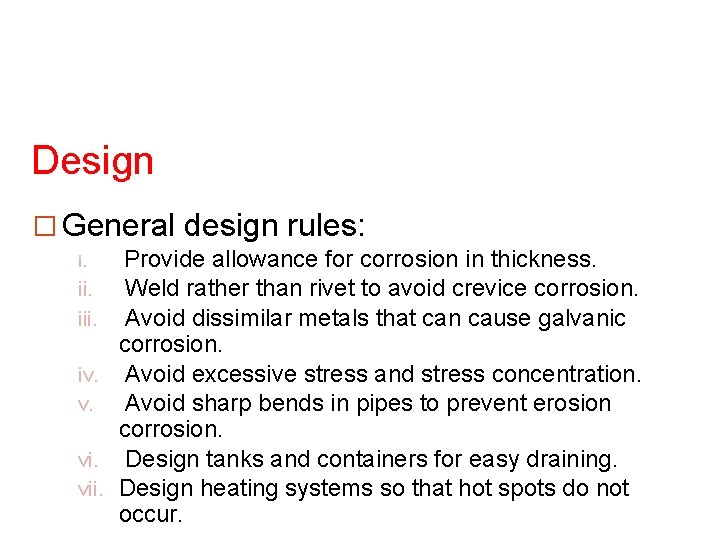
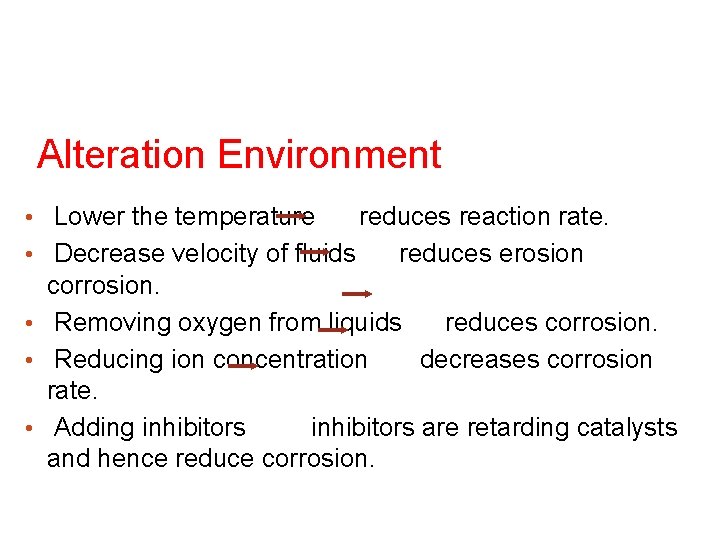
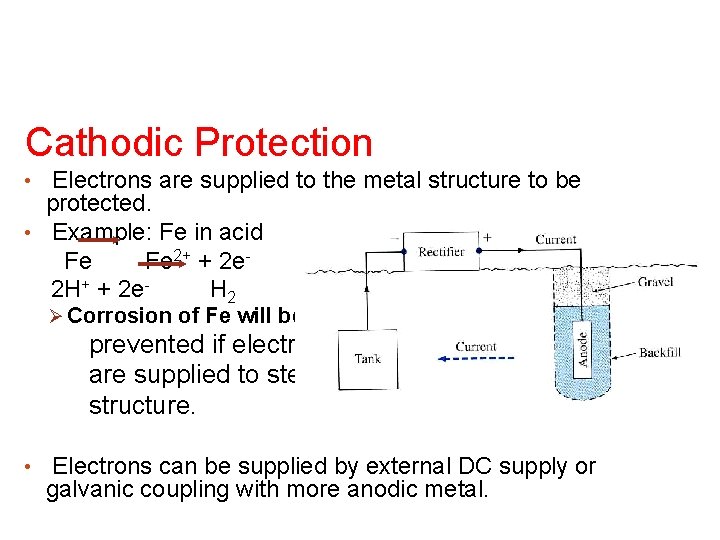
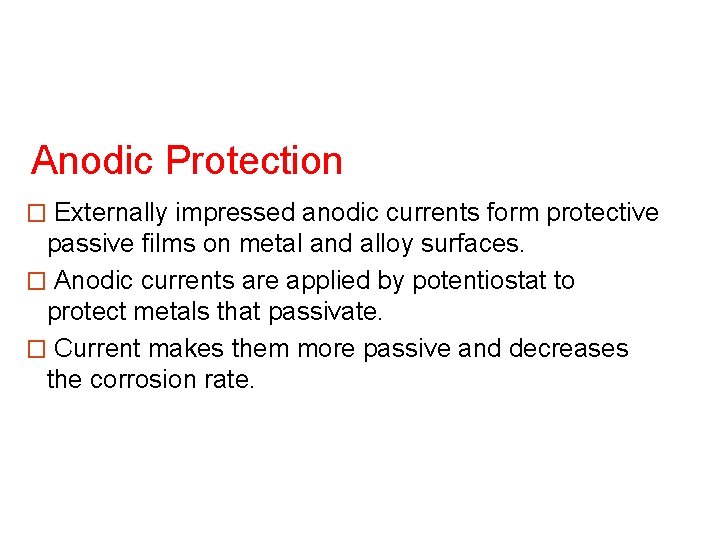
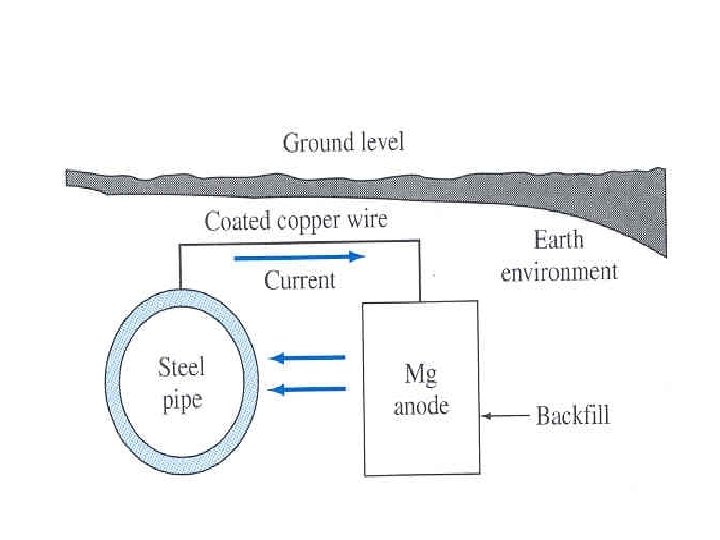
- Slides: 25
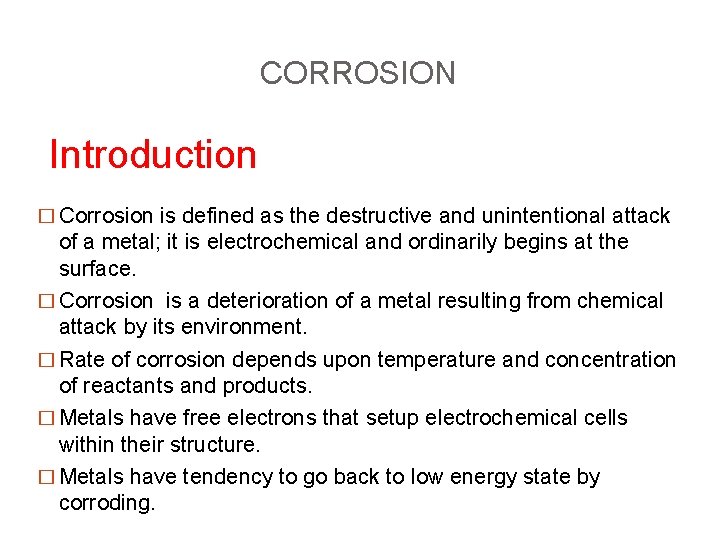
CORROSION Introduction � Corrosion is defined as the destructive and unintentional attack of a metal; it is electrochemical and ordinarily begins at the surface. � Corrosion is a deterioration of a metal resulting from chemical attack by its environment. � Rate of corrosion depends upon temperature and concentration of reactants and products. � Metals have free electrons that setup electrochemical cells within their structure. � Metals have tendency to go back to low energy state by corroding.
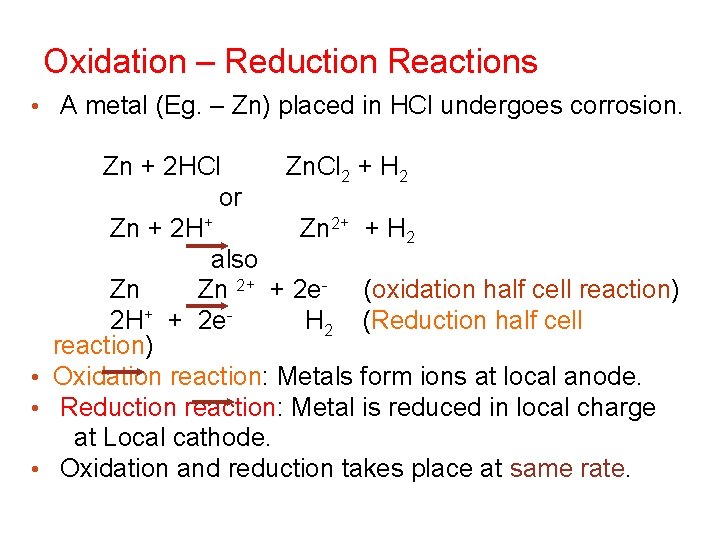
Oxidation – Reduction Reactions • A metal (Eg. – Zn) placed in HCl undergoes corrosion. Zn + 2 HCl Zn. Cl 2 + H 2 or Zn + 2 H+ Zn 2+ + H 2 also Zn Zn 2+ + 2 e- (oxidation half cell reaction) 2 H+ + 2 e. H 2 (Reduction half cell reaction) • Oxidation reaction: Metals form ions at local anode. • Reduction reaction: Metal is reduced in local charge at Local cathode. • Oxidation and reduction takes place at same rate.
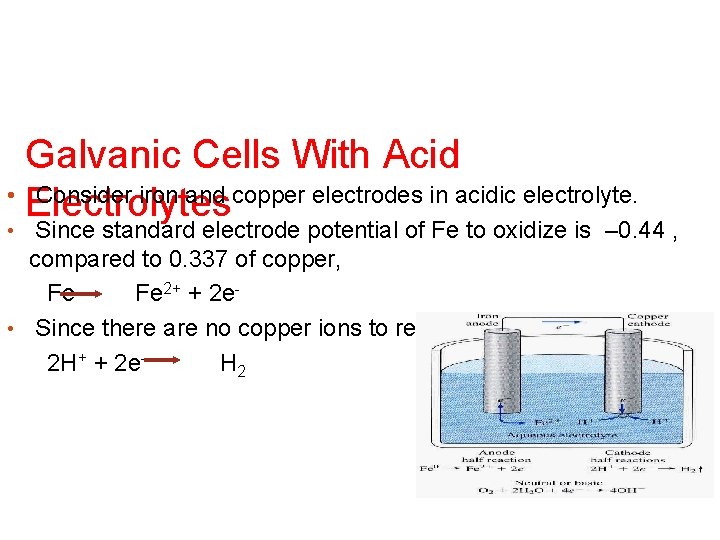
Galvanic Cells With Acid • Consider iron and copper electrodes in acidic electrolyte. Electrolytes Since standard electrode potential of Fe to oxidize is – 0. 44 , compared to 0. 337 of copper, Fe Fe 2+ + 2 e • Since there are no copper ions to reduce 2 H+ + 2 e. H 2 •
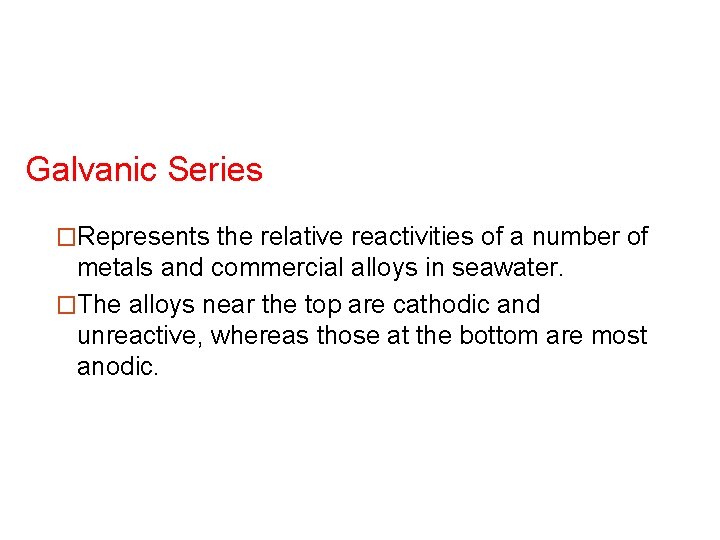
Galvanic Series �Represents the relative reactivities of a number of metals and commercial alloys in seawater. �The alloys near the top are cathodic and unreactive, whereas those at the bottom are most anodic.
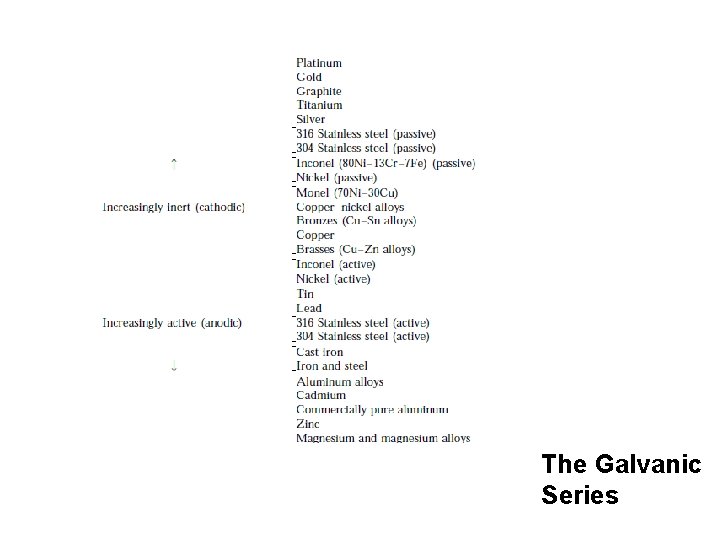
The Galvanic Series
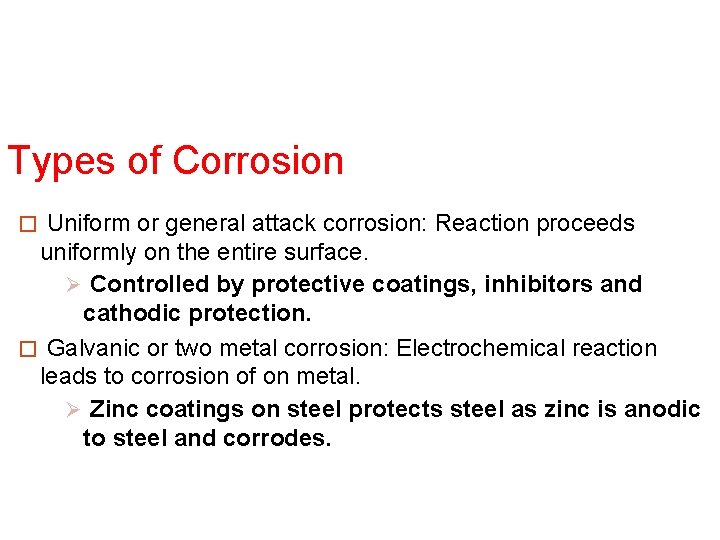
Types of Corrosion � Uniform or general attack corrosion: Reaction proceeds uniformly on the entire surface. Ø Controlled by protective coatings, inhibitors and cathodic protection. � Galvanic or two metal corrosion: Electrochemical reaction leads to corrosion of on metal. Ø Zinc coatings on steel protects steel as zinc is anodic to steel and corrodes.
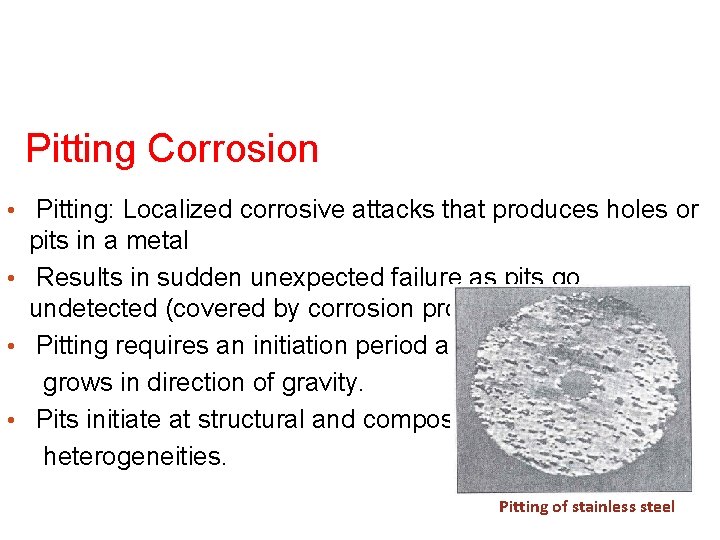
Pitting Corrosion • Pitting: Localized corrosive attacks that produces holes or pits in a metal • Results in sudden unexpected failure as pits go undetected (covered by corrosion products). • Pitting requires an initiation period and grows in direction of gravity. • Pits initiate at structural and compositional heterogeneities. Pitting of stainless steel
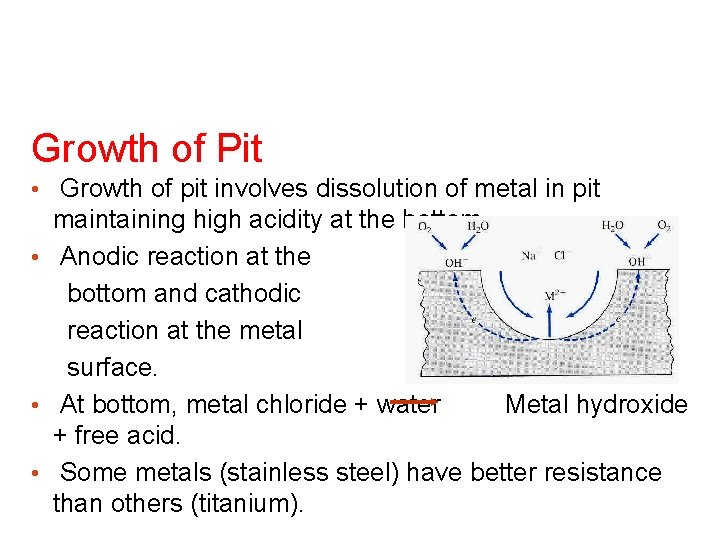
Growth of Pit • Growth of pit involves dissolution of metal in pit maintaining high acidity at the bottom. • Anodic reaction at the bottom and cathodic reaction at the metal surface. • At bottom, metal chloride + water Metal hydroxide + free acid. • Some metals (stainless steel) have better resistance than others (titanium).
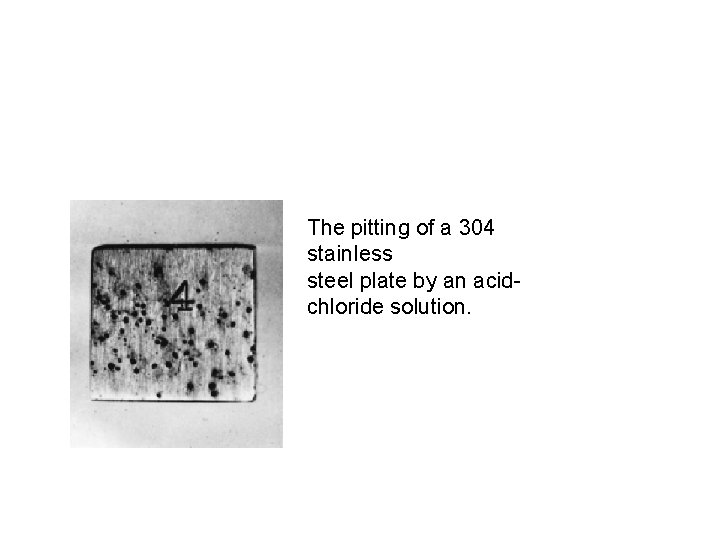
The pitting of a 304 stainless steel plate by an acidchloride solution.
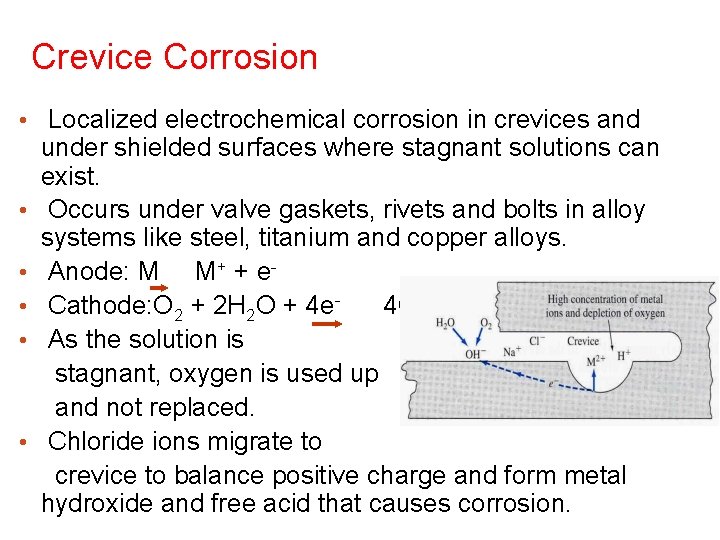
Crevice Corrosion • Localized electrochemical corrosion in crevices and • • • under shielded surfaces where stagnant solutions can exist. Occurs under valve gaskets, rivets and bolts in alloy systems like steel, titanium and copper alloys. Anode: M M+ + e. Cathode: O 2 + 2 H 2 O + 4 e 4 OHAs the solution is stagnant, oxygen is used up and not replaced. Chloride ions migrate to crevice to balance positive charge and form metal hydroxide and free acid that causes corrosion.
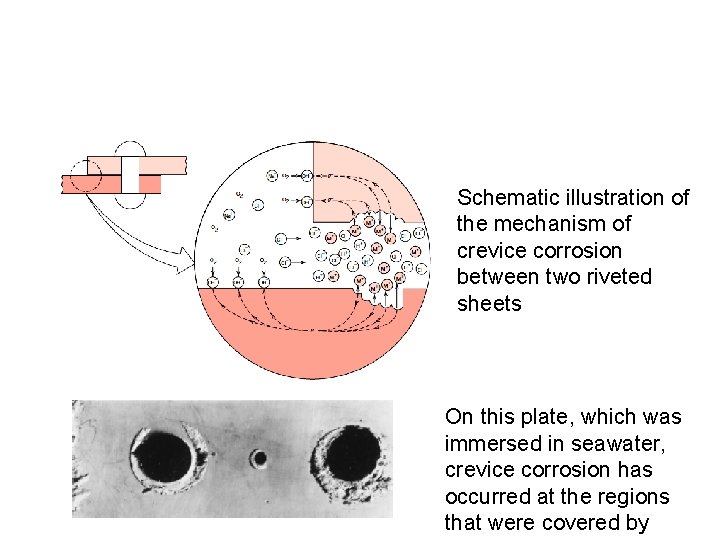
Schematic illustration of the mechanism of crevice corrosion between two riveted sheets On this plate, which was immersed in seawater, crevice corrosion has occurred at the regions that were covered by
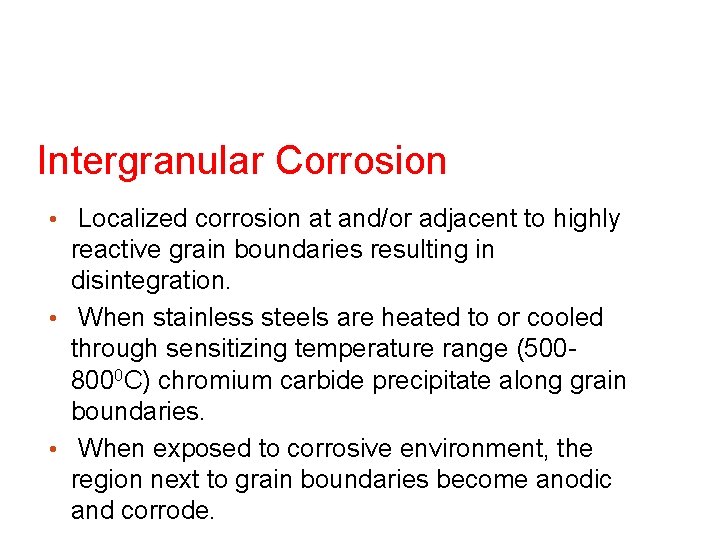
Intergranular Corrosion • Localized corrosion at and/or adjacent to highly reactive grain boundaries resulting in disintegration. • When stainless steels are heated to or cooled through sensitizing temperature range (5008000 C) chromium carbide precipitate along grain boundaries. • When exposed to corrosive environment, the region next to grain boundaries become anodic and corrode.
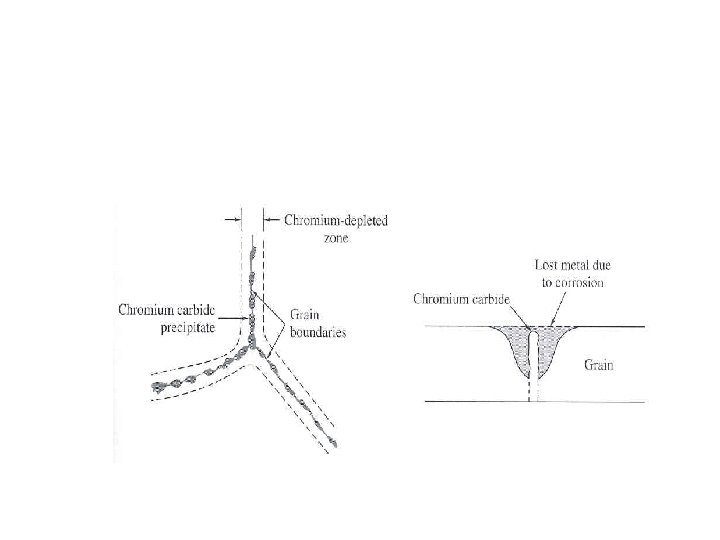
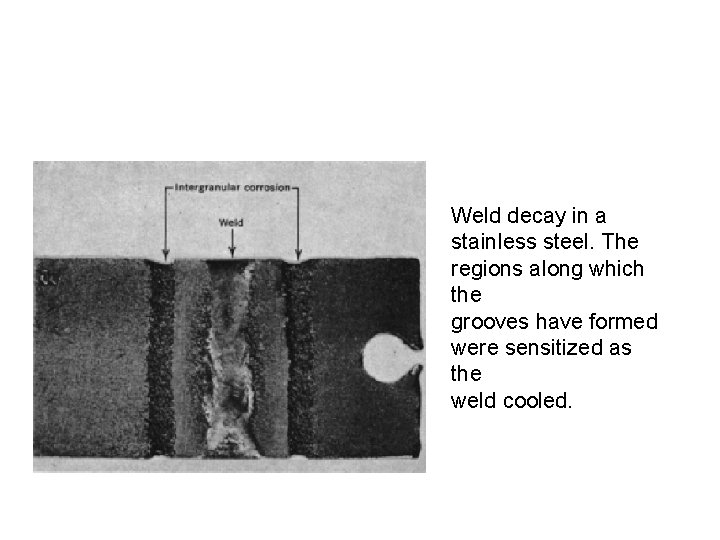
Weld decay in a stainless steel. The regions along which the grooves have formed were sensitized as the weld cooled.
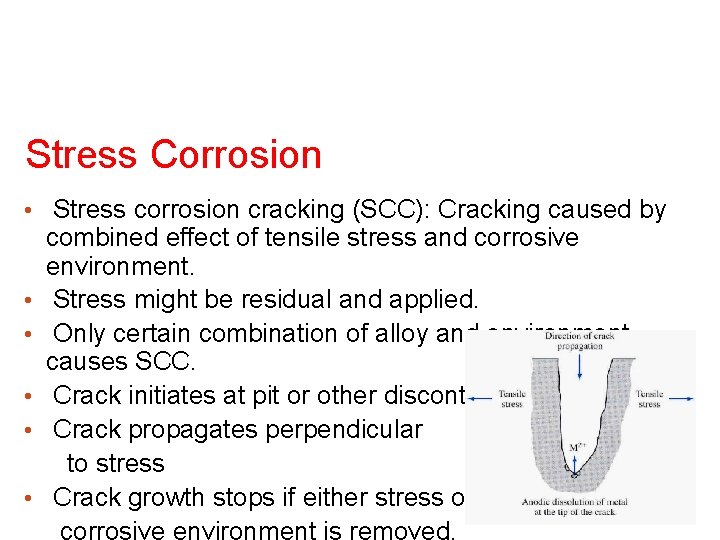
Stress Corrosion • Stress corrosion cracking (SCC): Cracking caused by • • • combined effect of tensile stress and corrosive environment. Stress might be residual and applied. Only certain combination of alloy and environment causes SCC. Crack initiates at pit or other discontinuity. Crack propagates perpendicular to stress Crack growth stops if either stress or corrosive environment is removed.
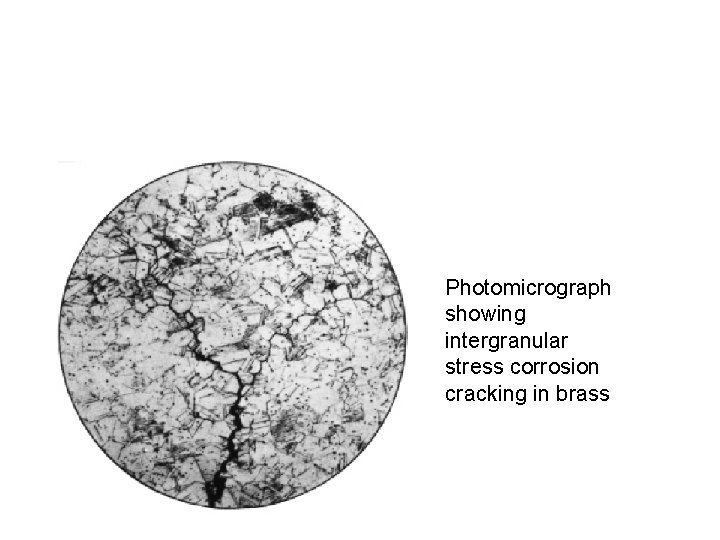
Photomicrograph showing intergranular stress corrosion cracking in brass
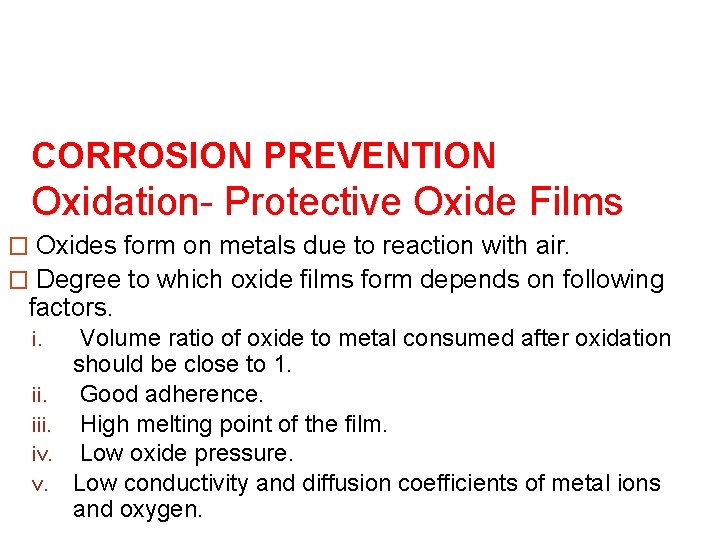
CORROSION PREVENTION Oxidation- Protective Oxide Films � Oxides form on metals due to reaction with air. � Degree to which oxide films form depends on following factors. Volume ratio of oxide to metal consumed after oxidation should be close to 1. ii. Good adherence. iii. High melting point of the film. iv. Low oxide pressure. v. Low conductivity and diffusion coefficients of metal ions and oxygen. i.
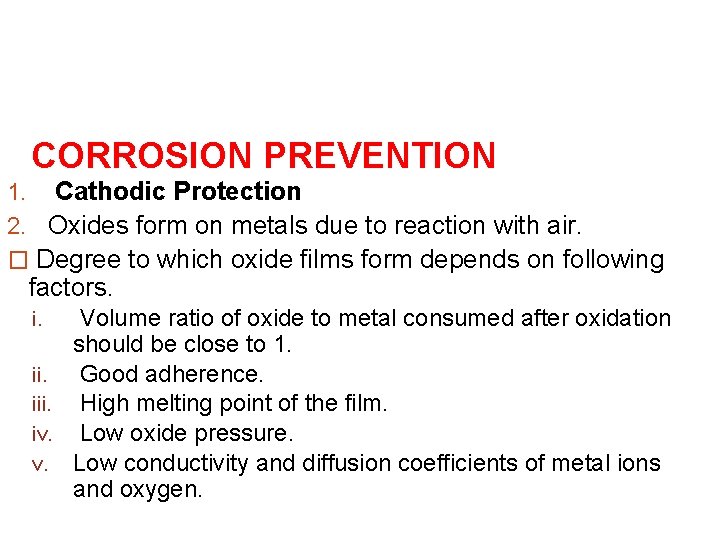
CORROSION PREVENTION 1. Cathodic Protection 2. Oxides form on metals due to reaction with air. � Degree to which oxide films form depends on following factors. Volume ratio of oxide to metal consumed after oxidation should be close to 1. ii. Good adherence. iii. High melting point of the film. iv. Low oxide pressure. v. Low conductivity and diffusion coefficients of metal ions and oxygen. i.
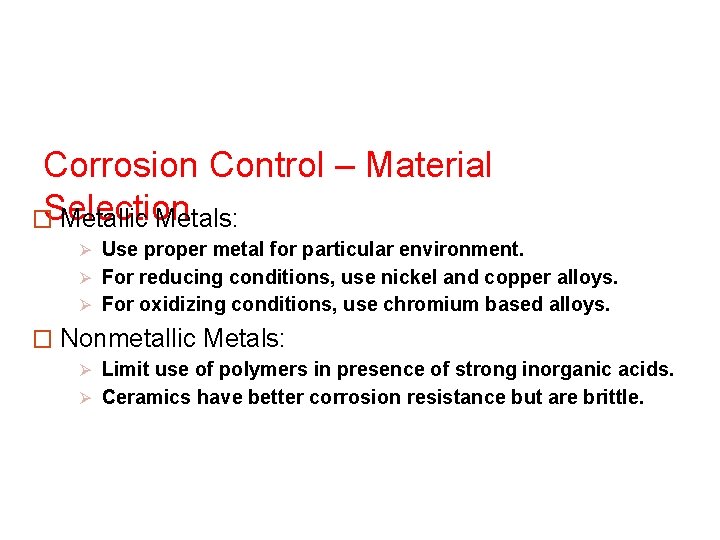
Corrosion Control – Material �Selection Metallic Metals: Ø Use proper metal for particular environment. Ø For reducing conditions, use nickel and copper alloys. Ø For oxidizing conditions, use chromium based alloys. � Nonmetallic Metals: Ø Limit use of polymers in presence of strong inorganic acids. Ø Ceramics have better corrosion resistance but are brittle.
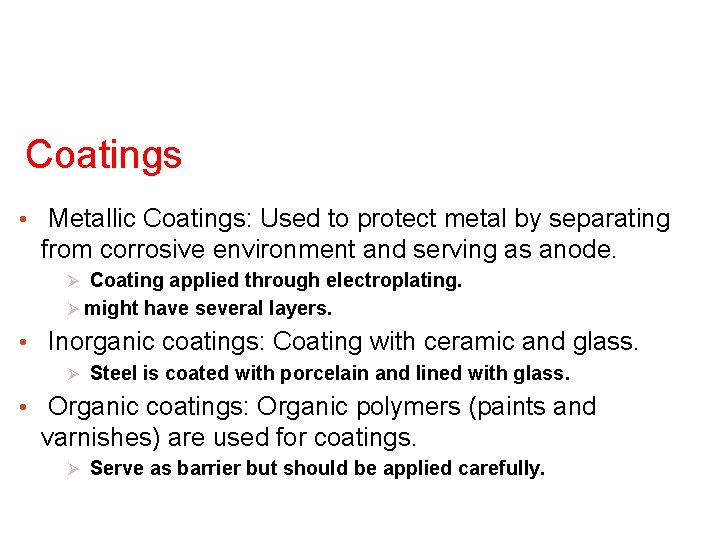
Coatings • Metallic Coatings: Used to protect metal by separating from corrosive environment and serving as anode. Ø Coating applied through electroplating. Ø might have several layers. • Inorganic coatings: Coating with ceramic and glass. Ø Steel is coated with porcelain and lined with glass. • Organic coatings: Organic polymers (paints and varnishes) are used for coatings. Ø Serve as barrier but should be applied carefully.
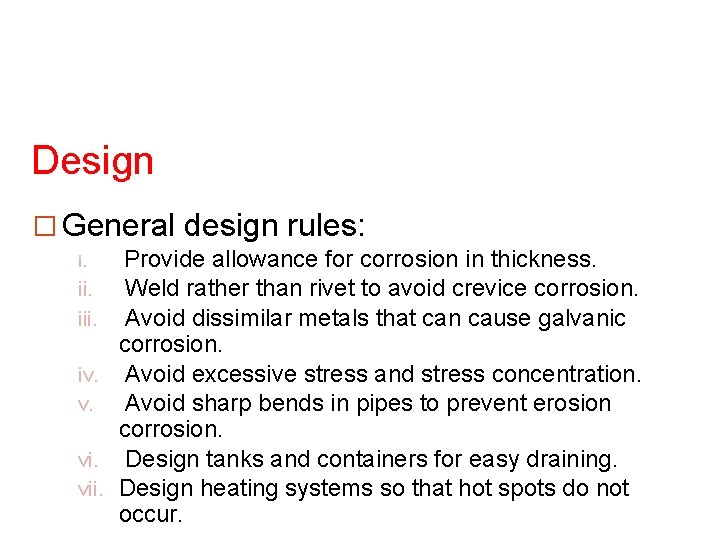
Design � General design rules: i. ii. iv. v. vii. Provide allowance for corrosion in thickness. Weld rather than rivet to avoid crevice corrosion. Avoid dissimilar metals that can cause galvanic corrosion. Avoid excessive stress and stress concentration. Avoid sharp bends in pipes to prevent erosion corrosion. Design tanks and containers for easy draining. Design heating systems so that hot spots do not occur.
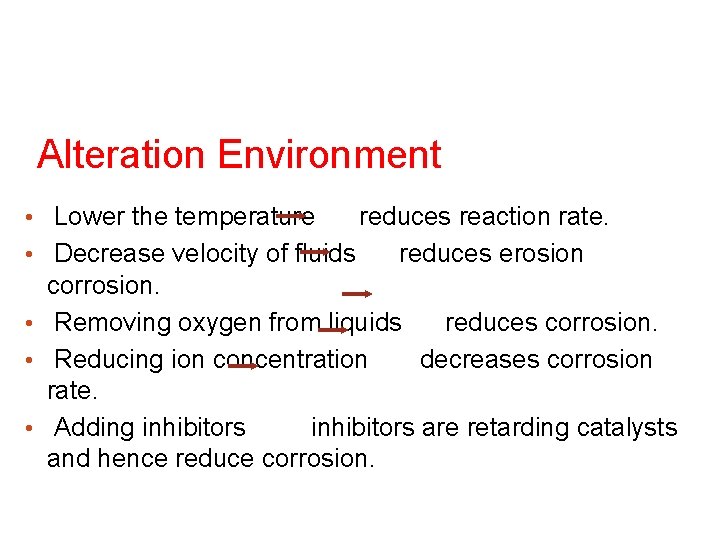
Alteration Environment • Lower the temperature • • reduces reaction rate. Decrease velocity of fluids reduces erosion corrosion. Removing oxygen from liquids reduces corrosion. Reducing ion concentration decreases corrosion rate. Adding inhibitors are retarding catalysts and hence reduce corrosion.
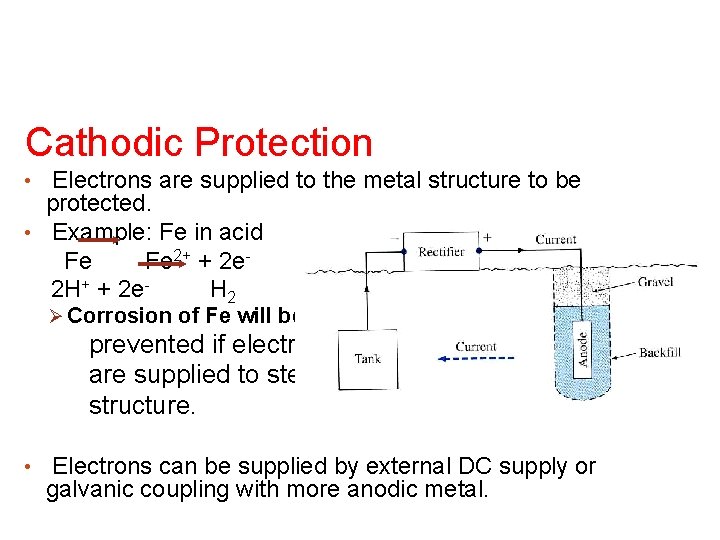
Cathodic Protection Electrons are supplied to the metal structure to be protected. • Example: Fe in acid Fe Fe 2+ + 2 e 2 H+ + 2 e. H 2 • Ø Corrosion of Fe will be prevented if electrons are supplied to steel structure. • Electrons can be supplied by external DC supply or galvanic coupling with more anodic metal.
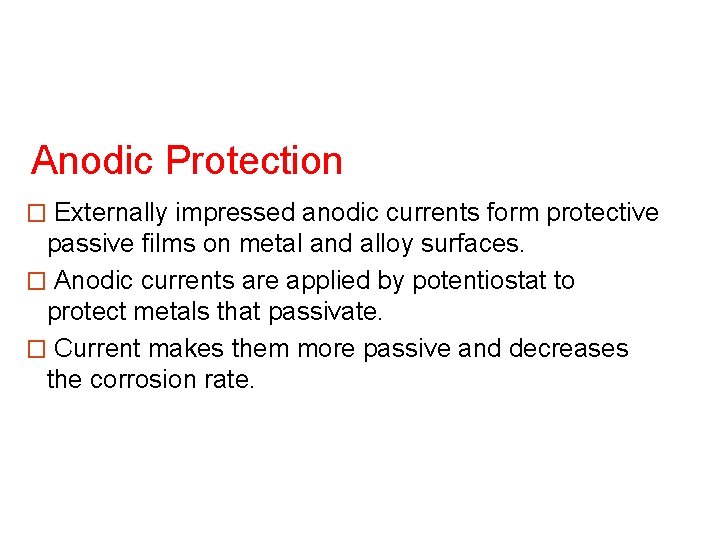
Anodic Protection � Externally impressed anodic currents form protective passive films on metal and alloy surfaces. � Anodic currents are applied by potentiostat to protect metals that passivate. � Current makes them more passive and decreases the corrosion rate.
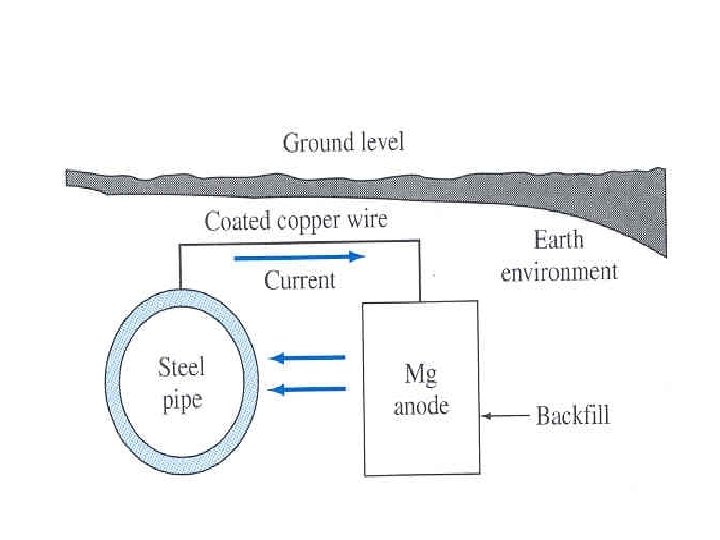
Differentiate between dry corrosion and wet corrosion
Differentiate between dry corrosion and wet corrosion
A collection of well defined objects is called
Introduction to software defined radio
Hình ảnh bộ gõ cơ thể búng tay
Slidetodoc
Bổ thể
Tỉ lệ cơ thể trẻ em
Voi kéo gỗ như thế nào
Tư thế worms-breton
Chúa sống lại
Các môn thể thao bắt đầu bằng tiếng nhảy
Thế nào là hệ số cao nhất
Các châu lục và đại dương trên thế giới
Công thức tính độ biến thiên đông lượng
Trời xanh đây là của chúng ta thể thơ
Mật thư anh em như thể tay chân
101012 bằng
Phản ứng thế ankan
Các châu lục và đại dương trên thế giới
Thơ thất ngôn tứ tuyệt đường luật
Quá trình desamine hóa có thể tạo ra
Một số thể thơ truyền thống
Cái miệng bé xinh thế chỉ nói điều hay thôi
Vẽ hình chiếu vuông góc của vật thể sau
Nguyên nhân của sự mỏi cơ sinh 8