Unit 3 Metal Joining processes TYPES OF JOINING
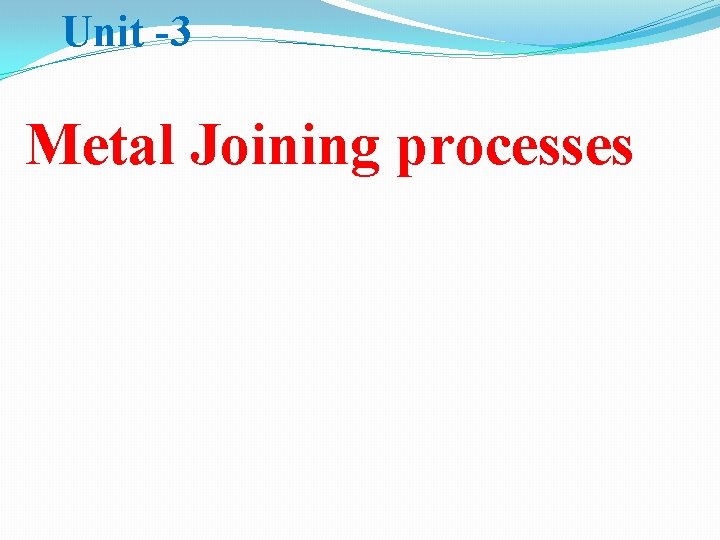
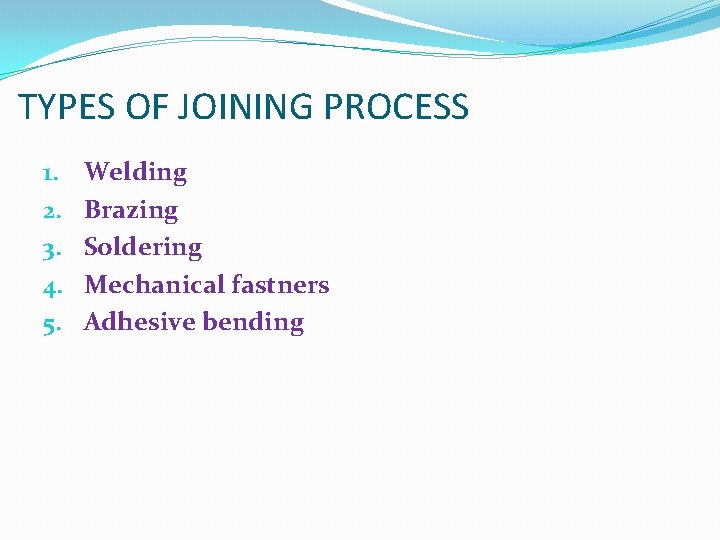
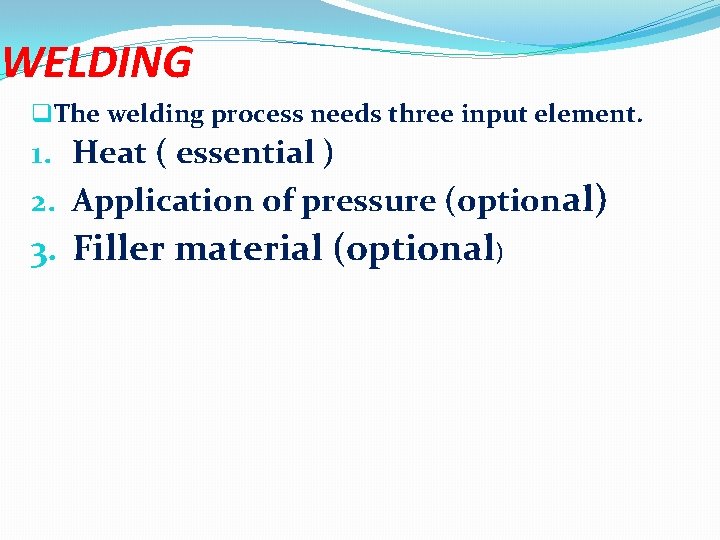
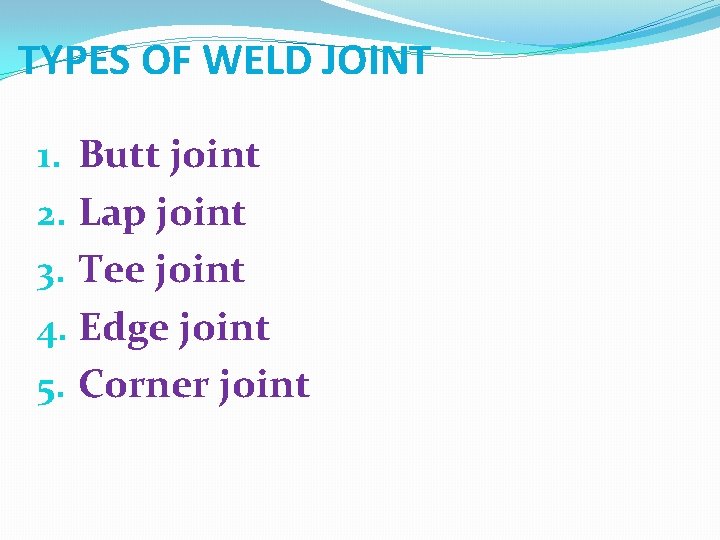
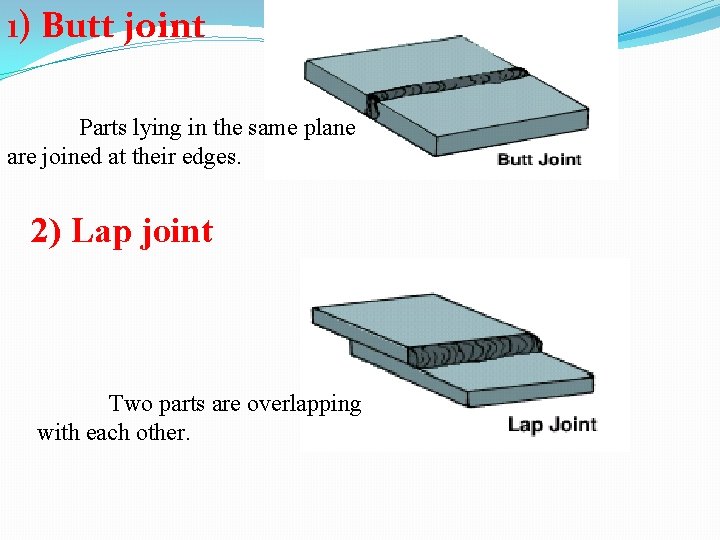
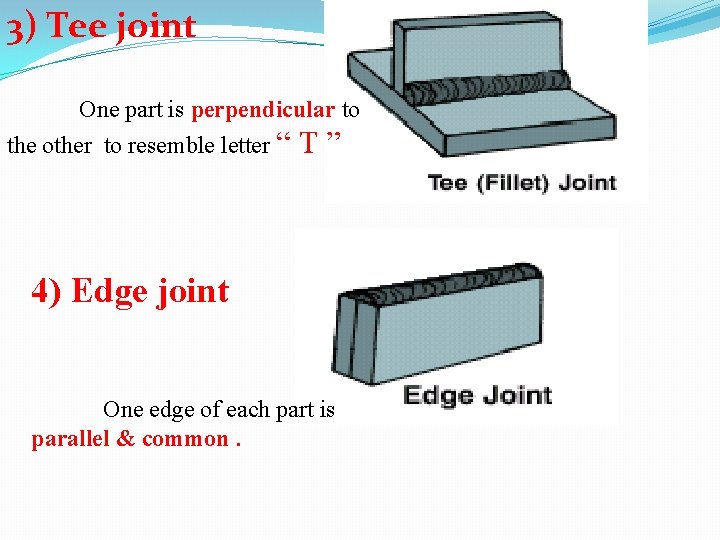
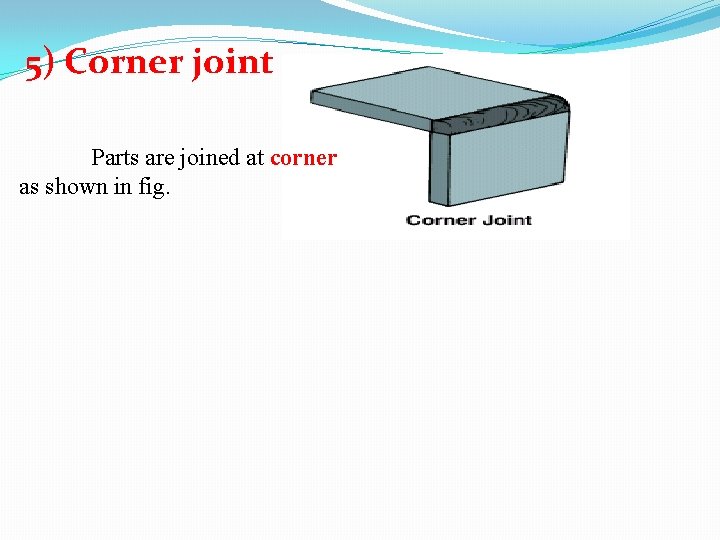
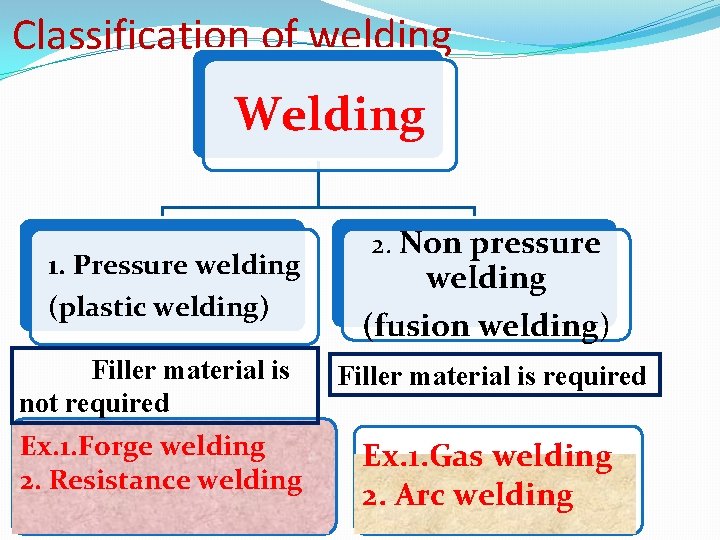
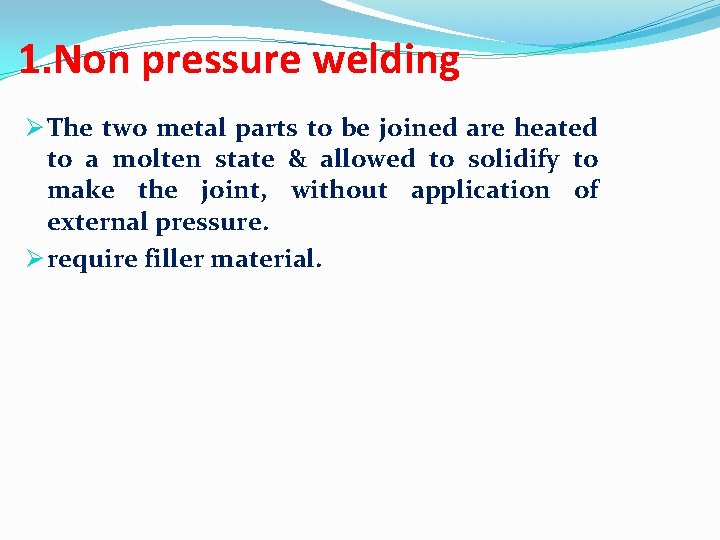
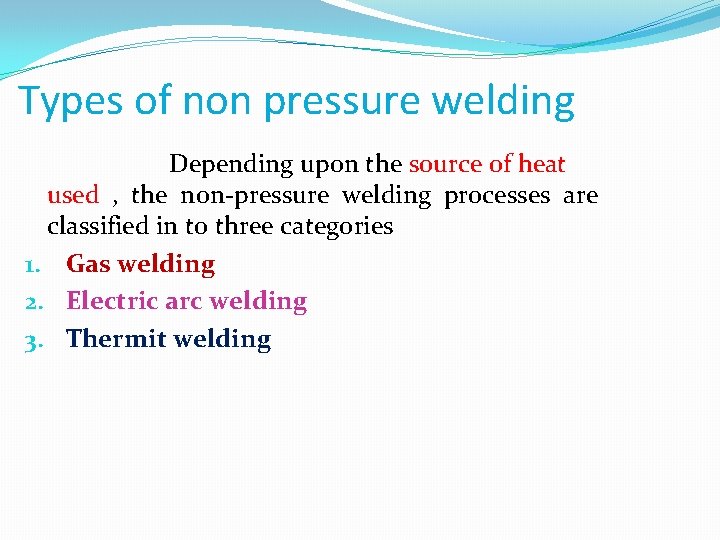
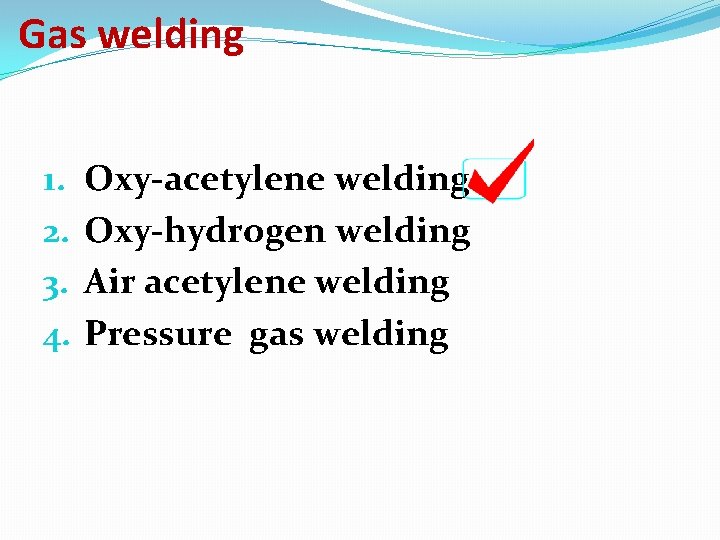
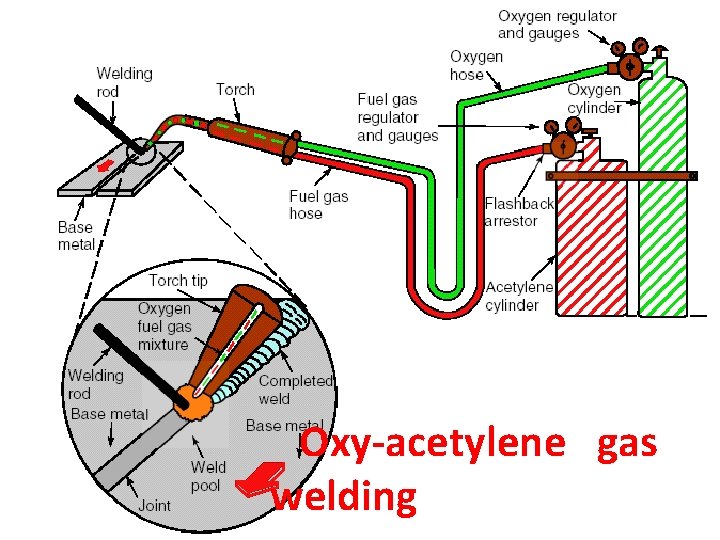
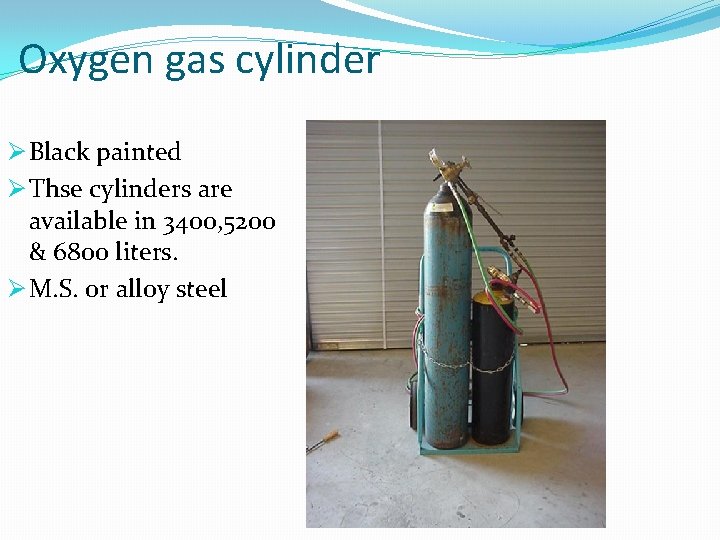
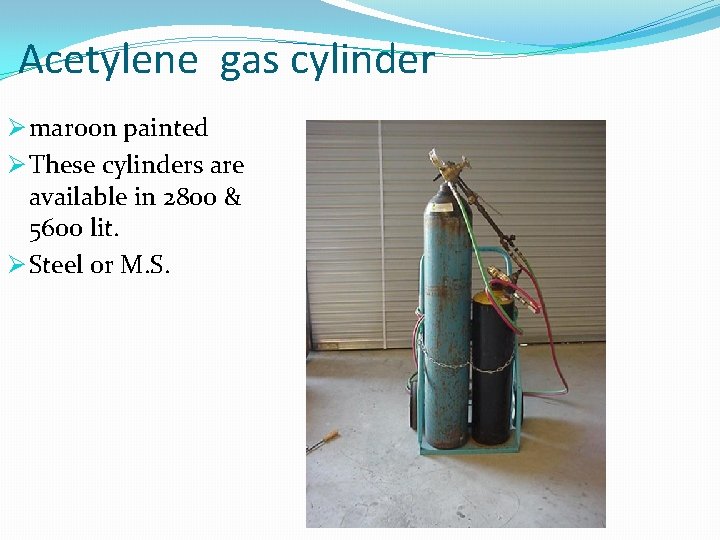
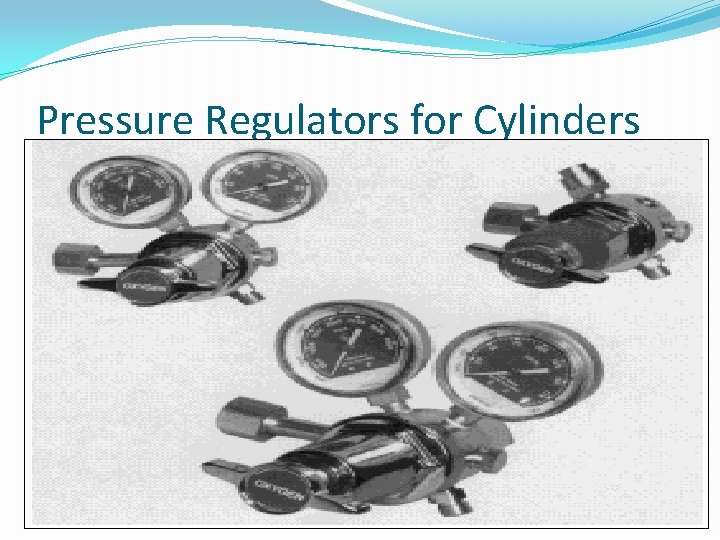
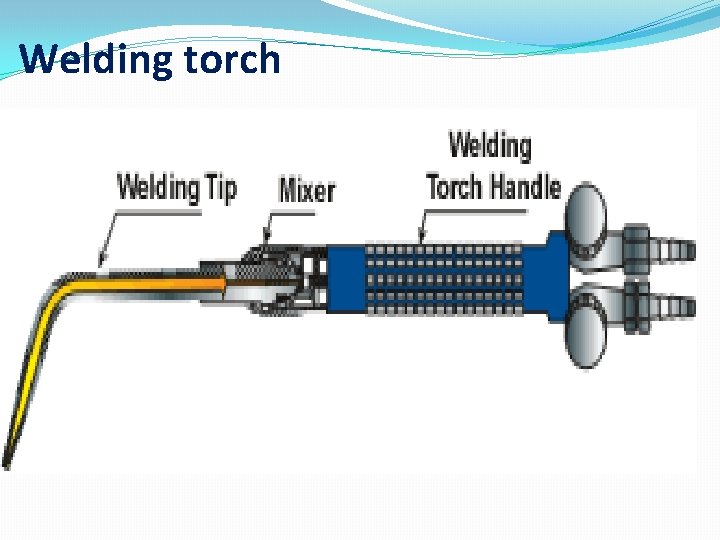
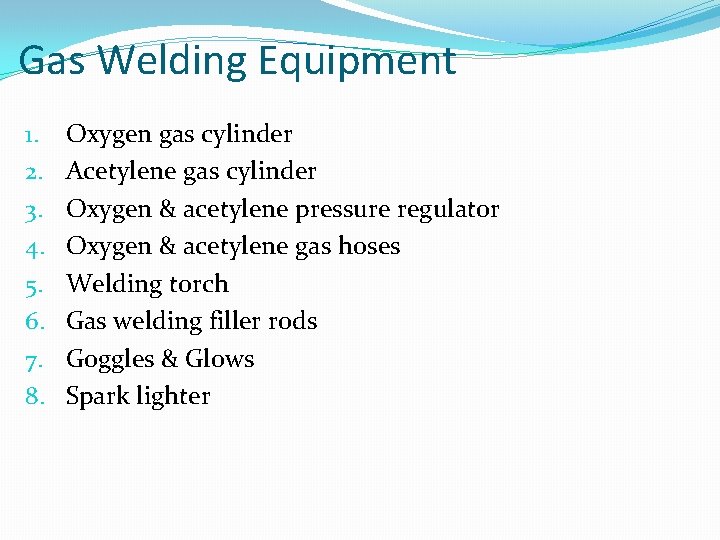
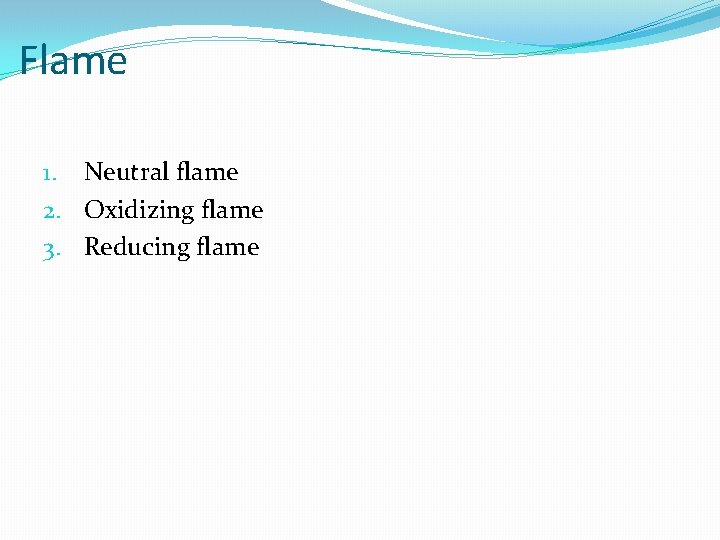
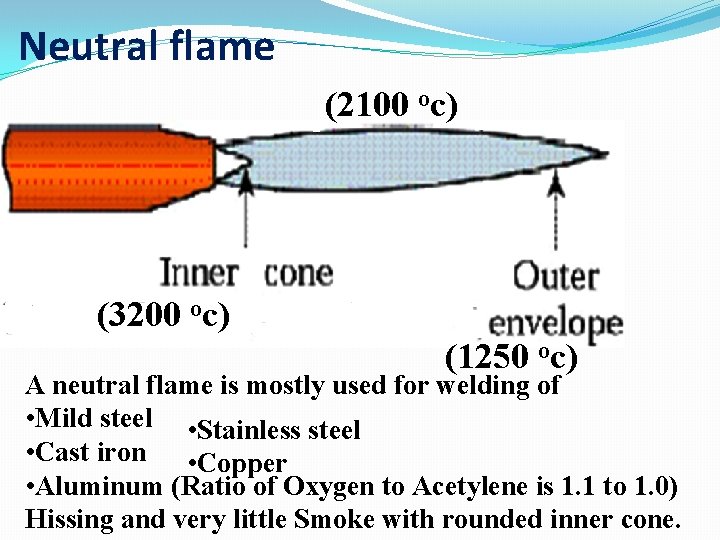

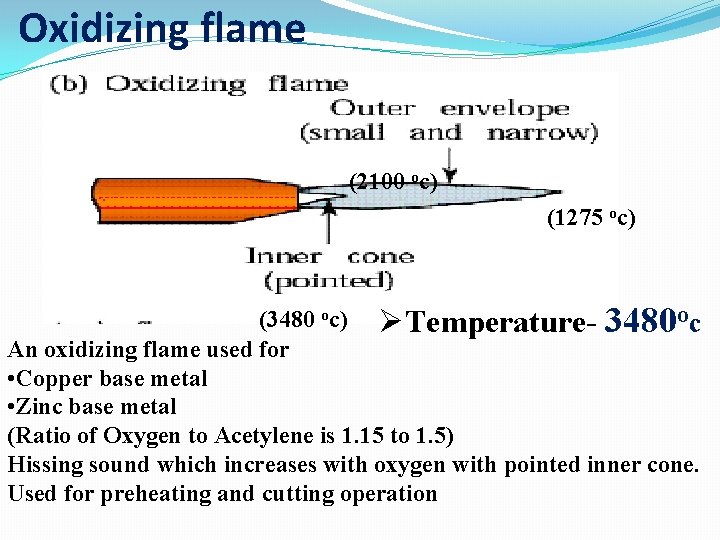
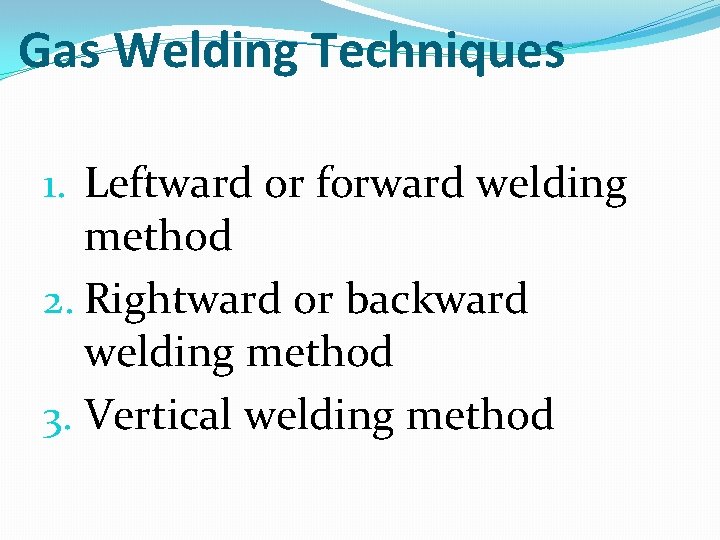
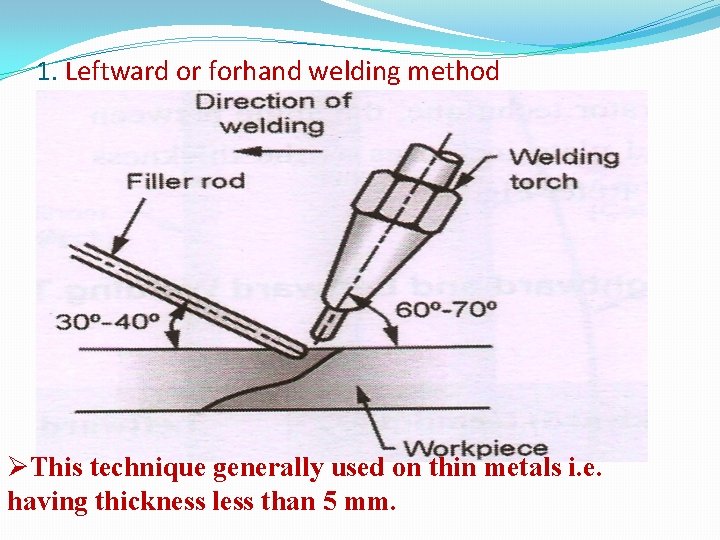
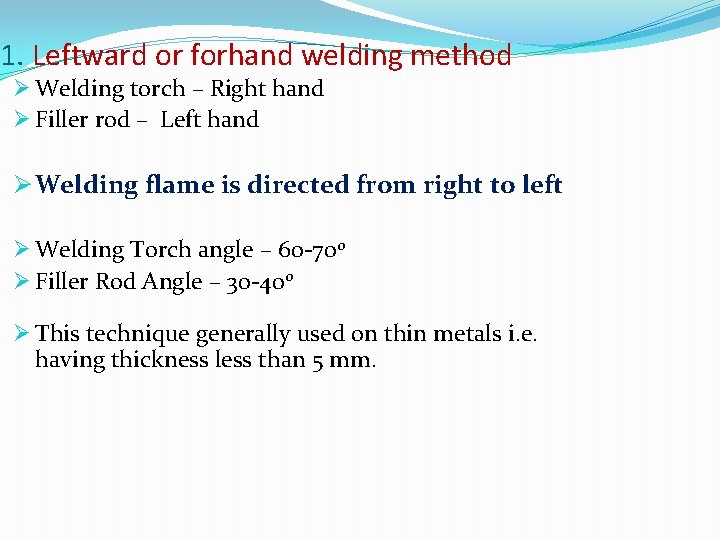
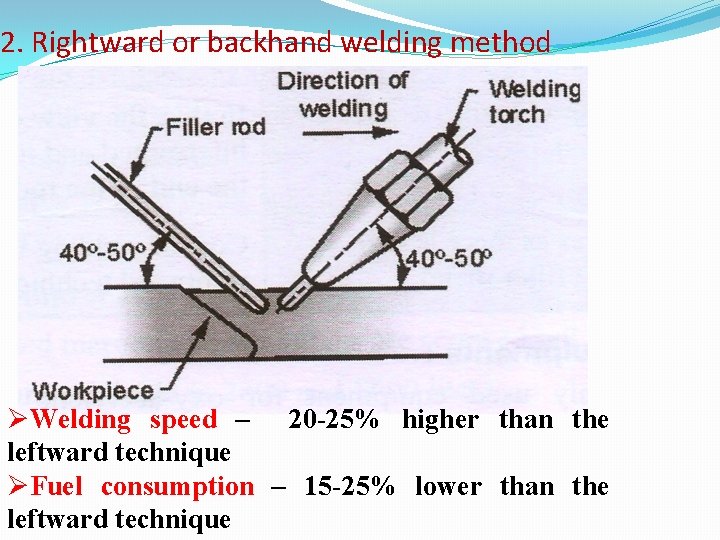
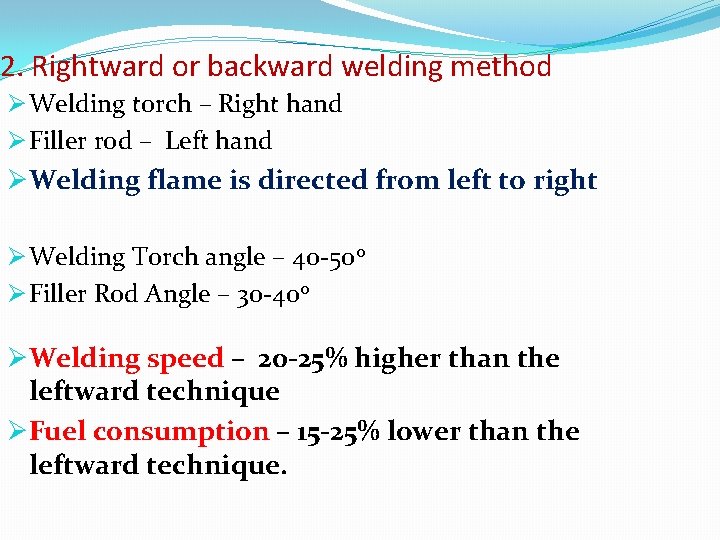
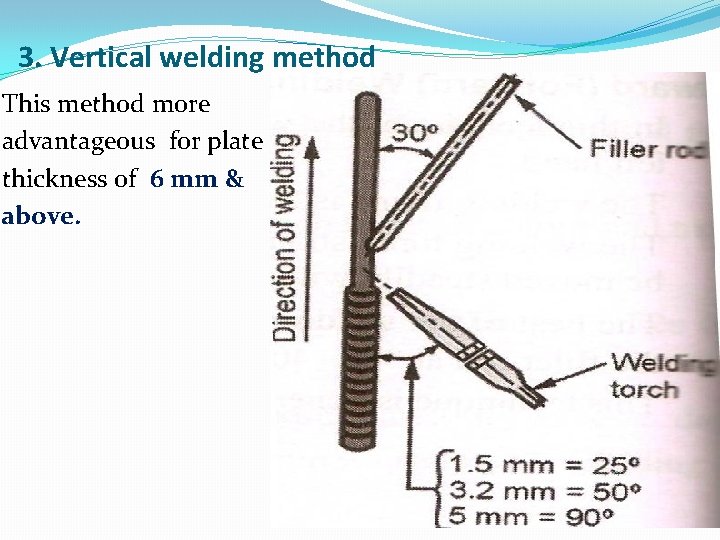
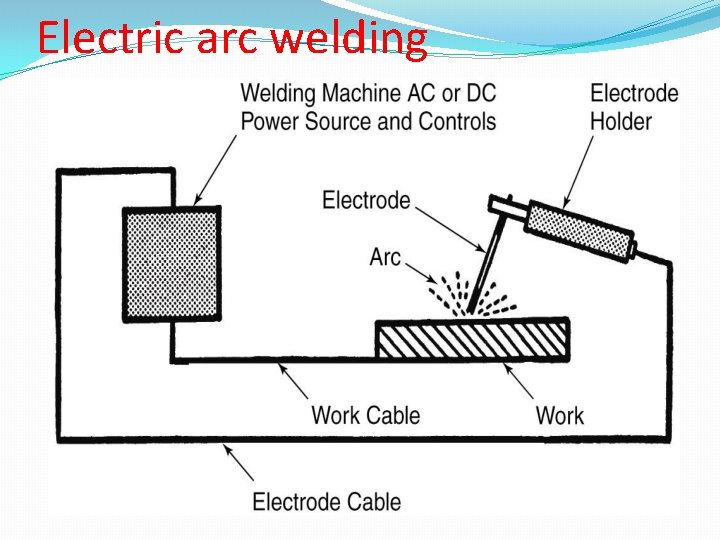
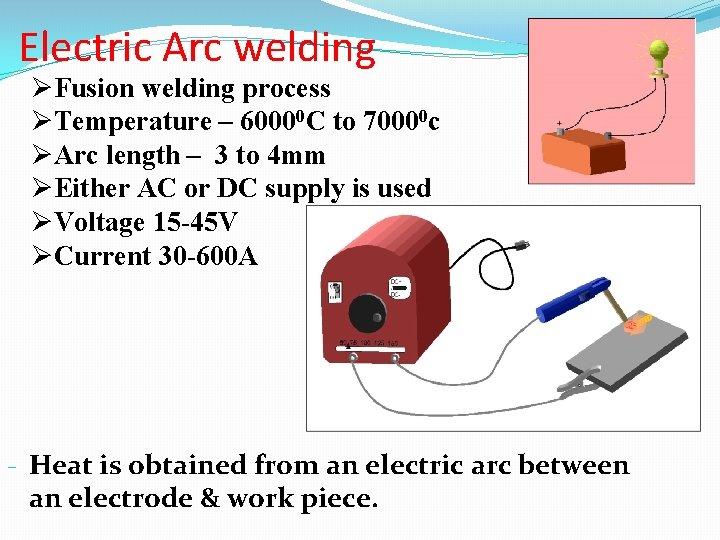
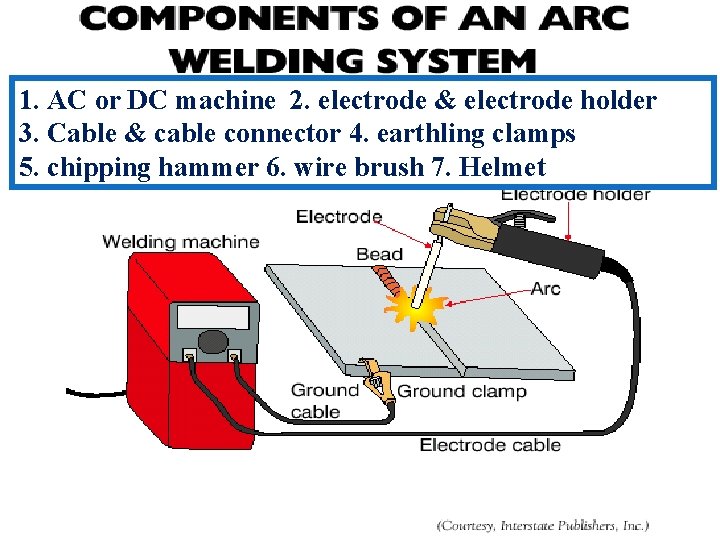
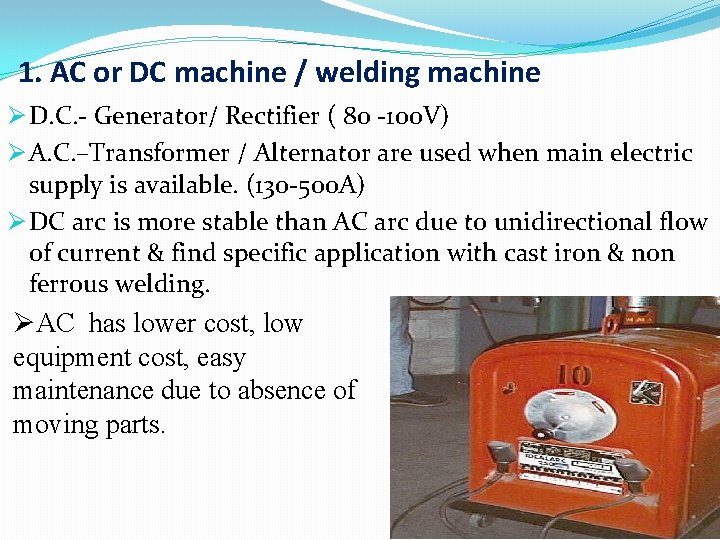
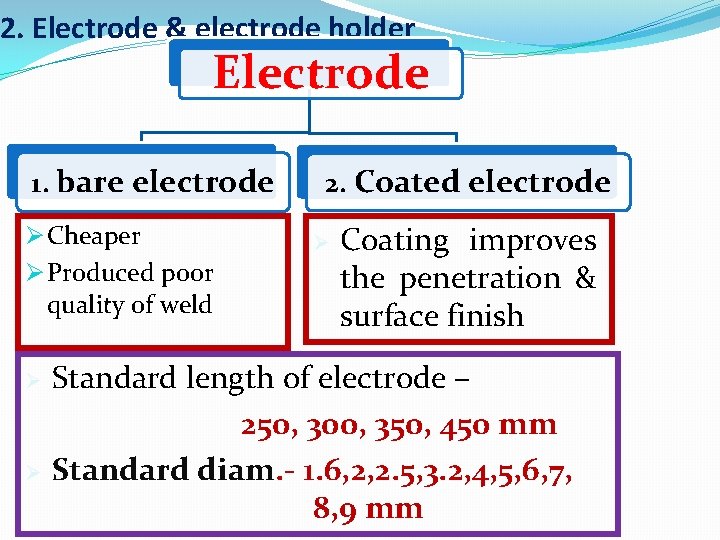
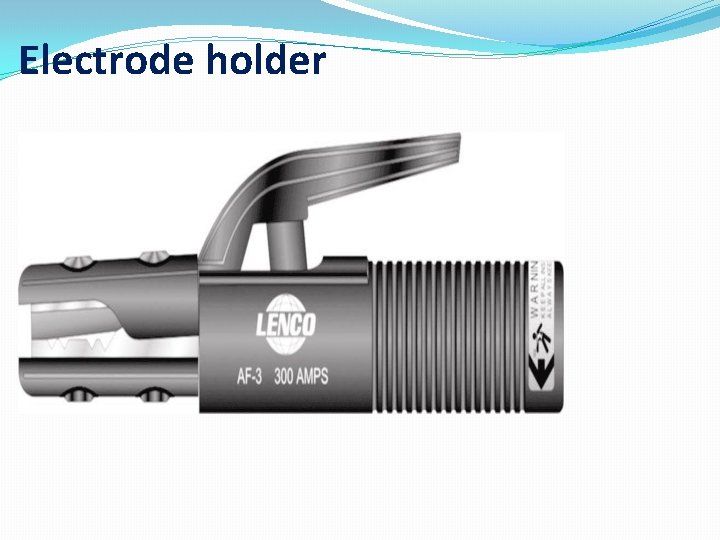
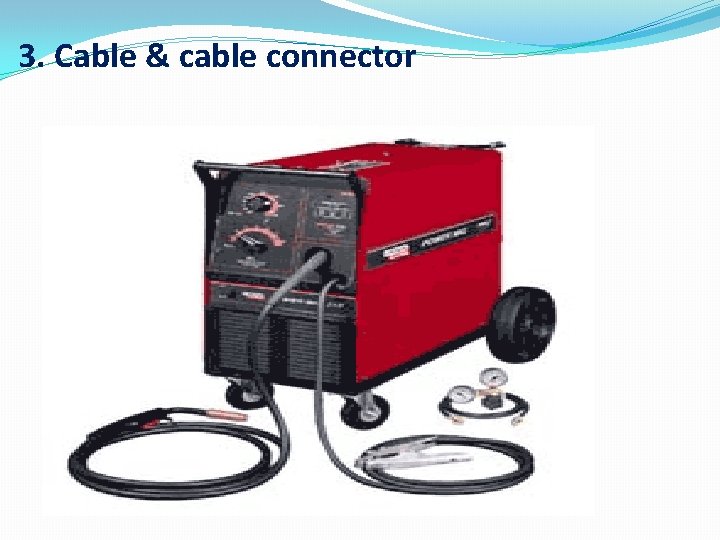
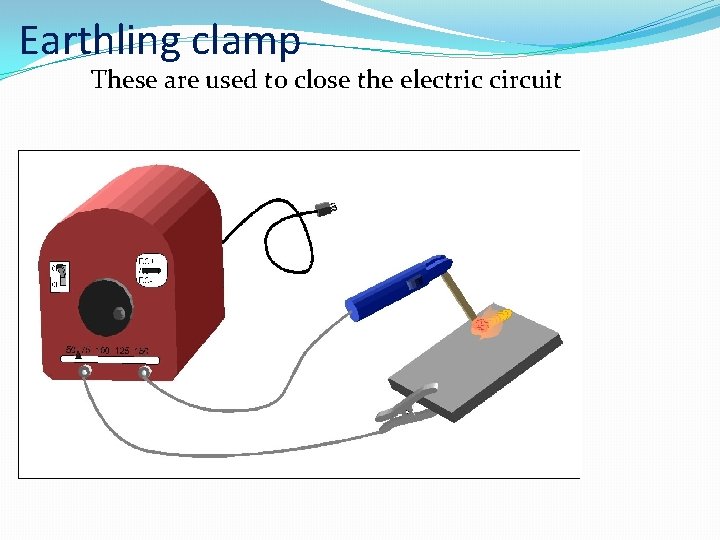
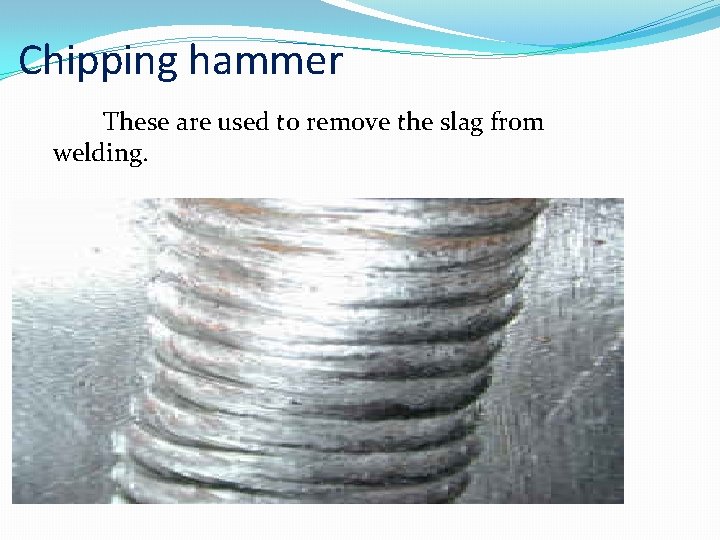
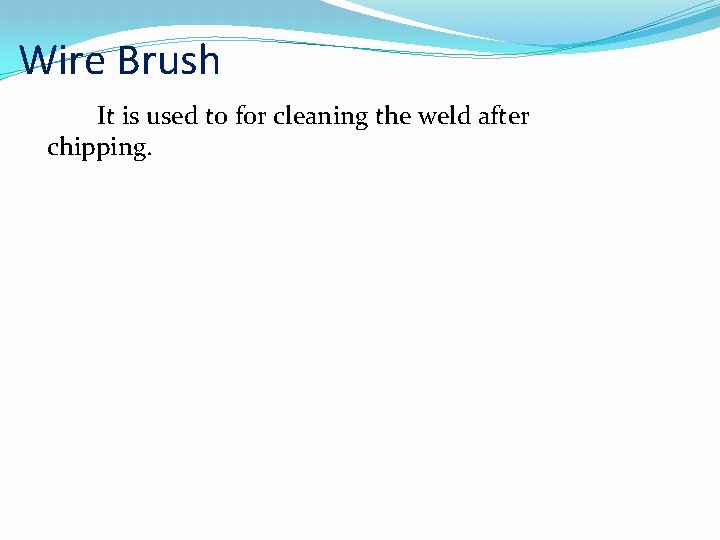
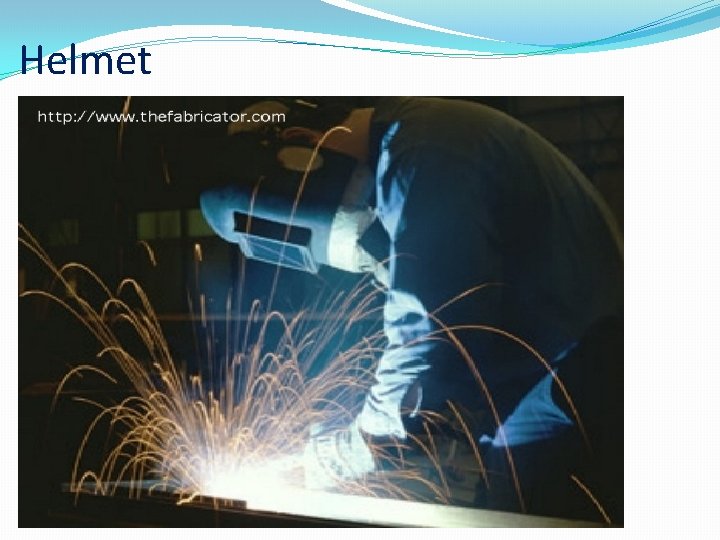
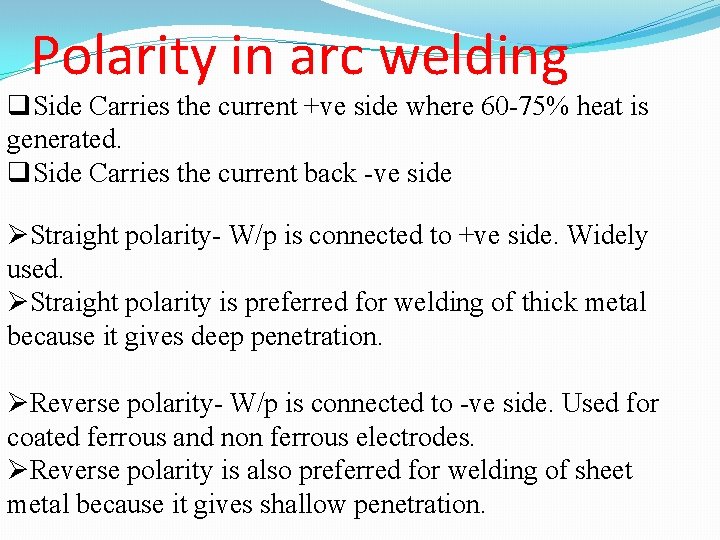
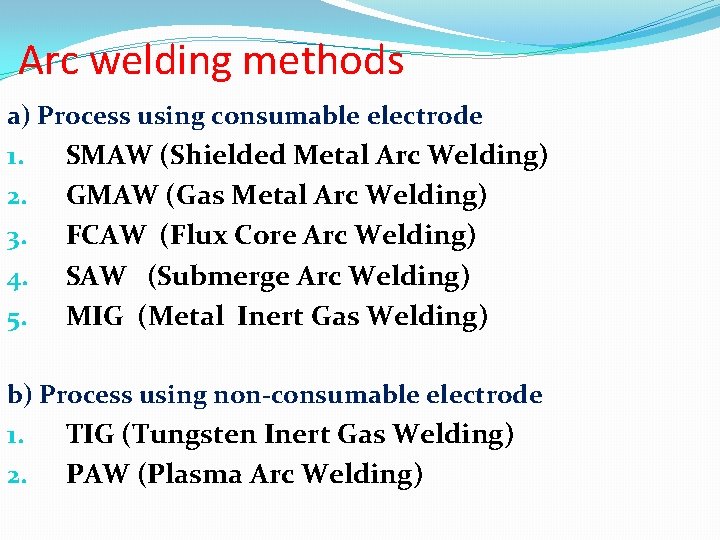
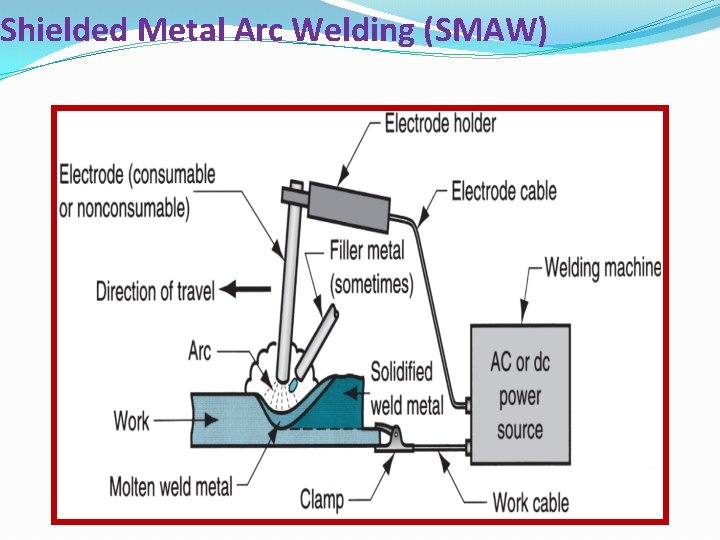
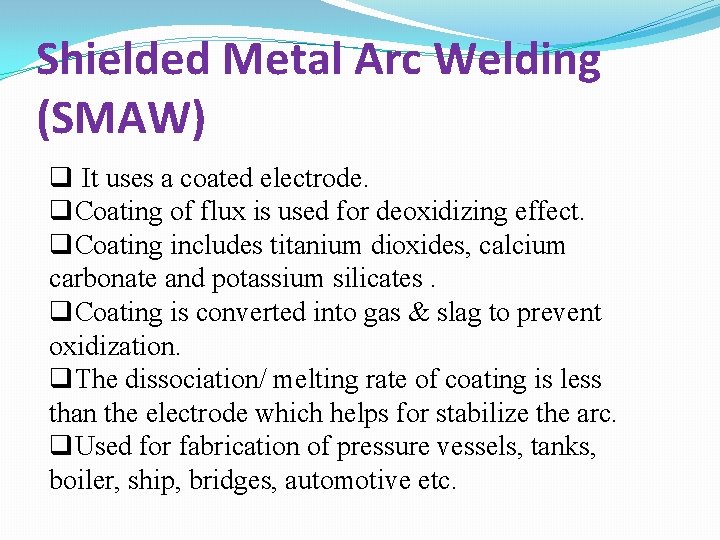
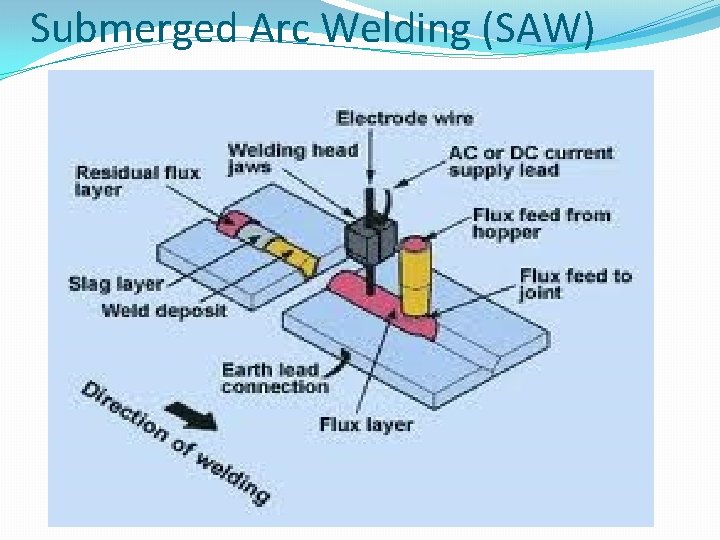
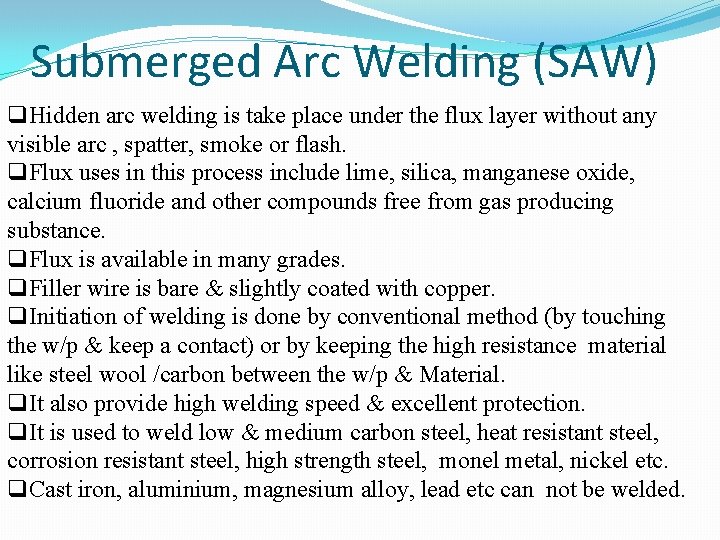
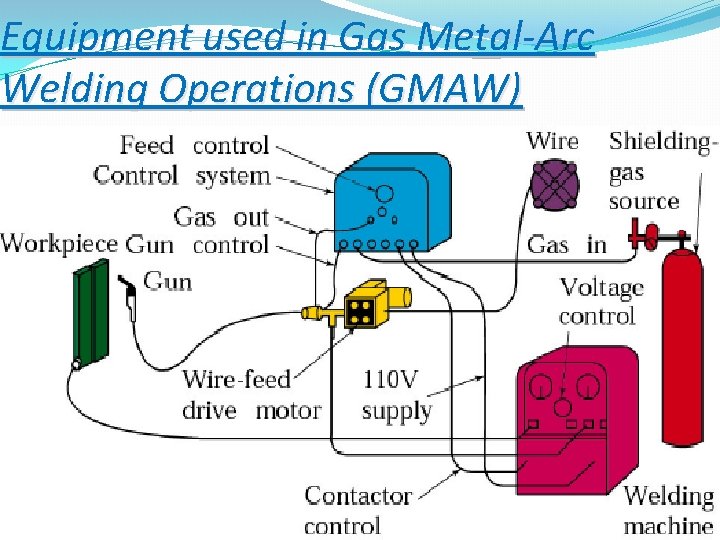
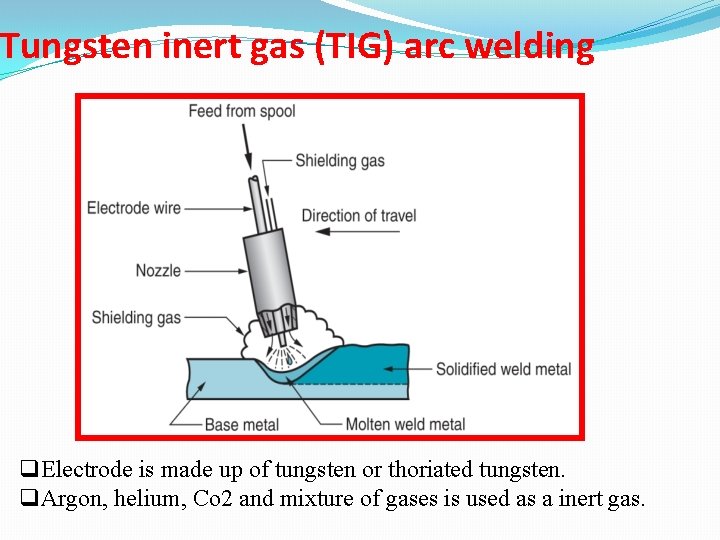
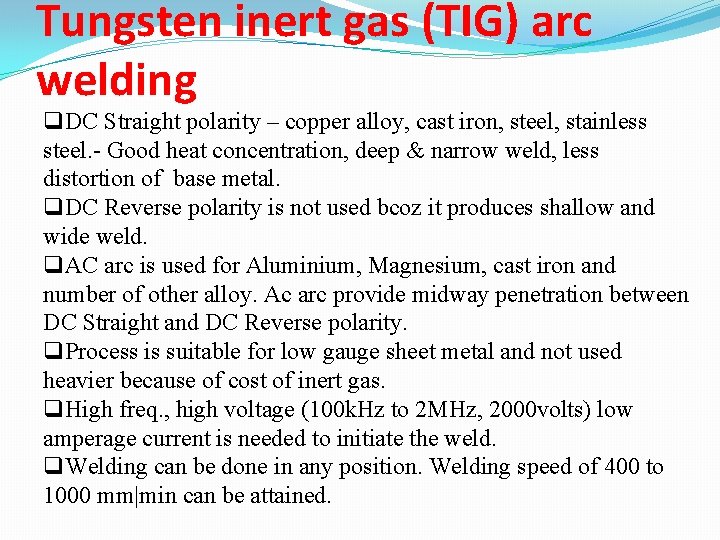
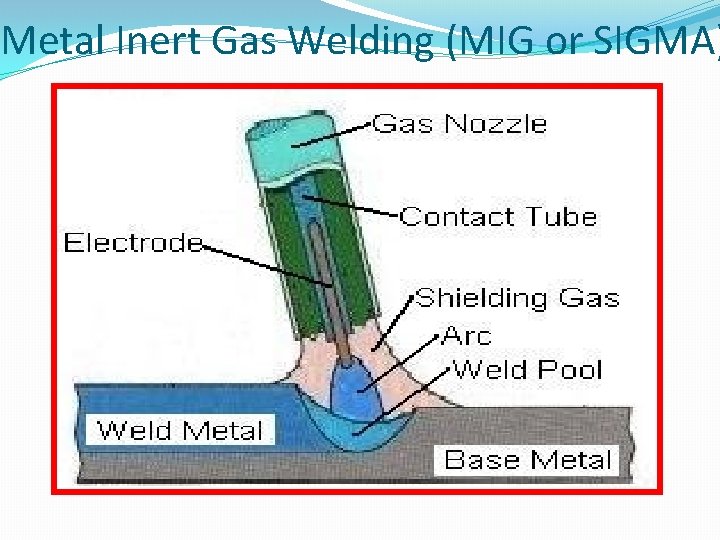
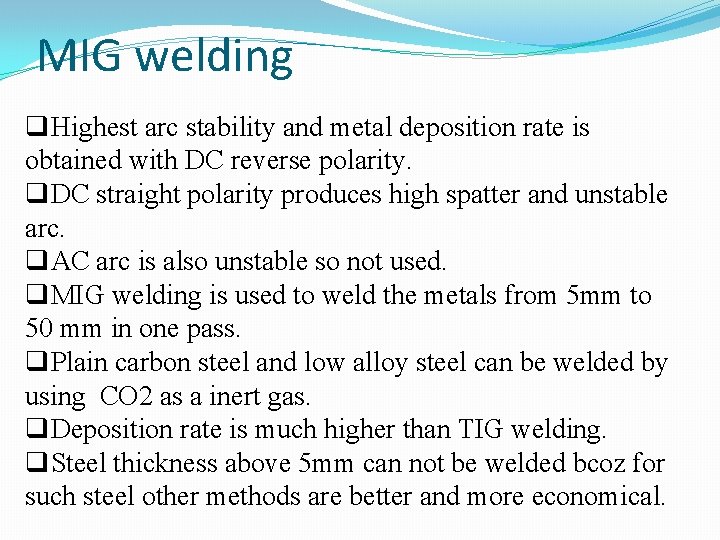
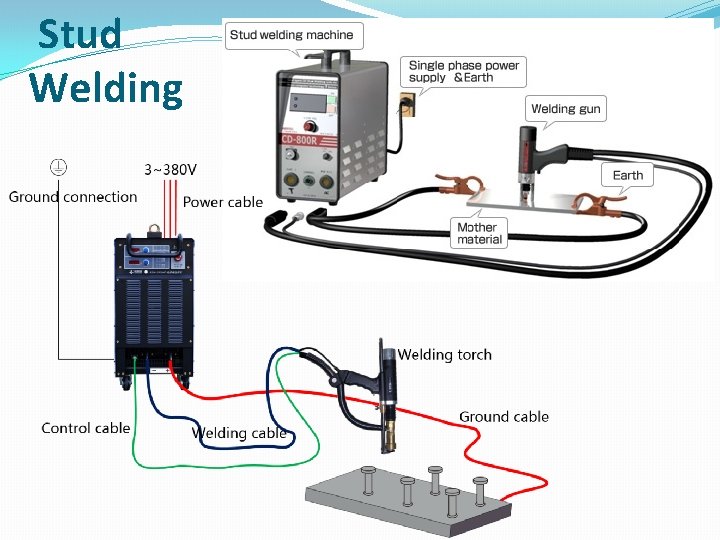
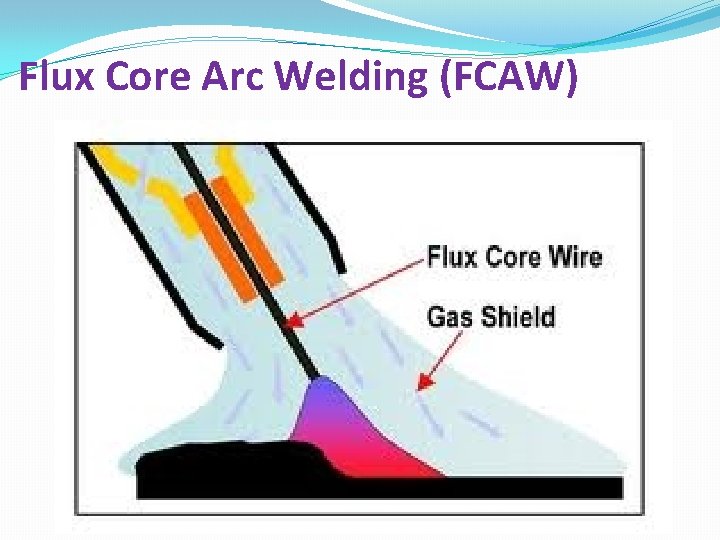
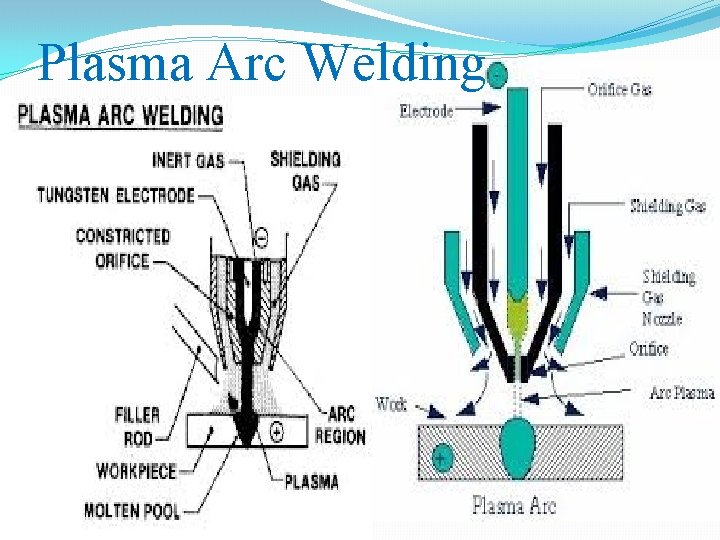
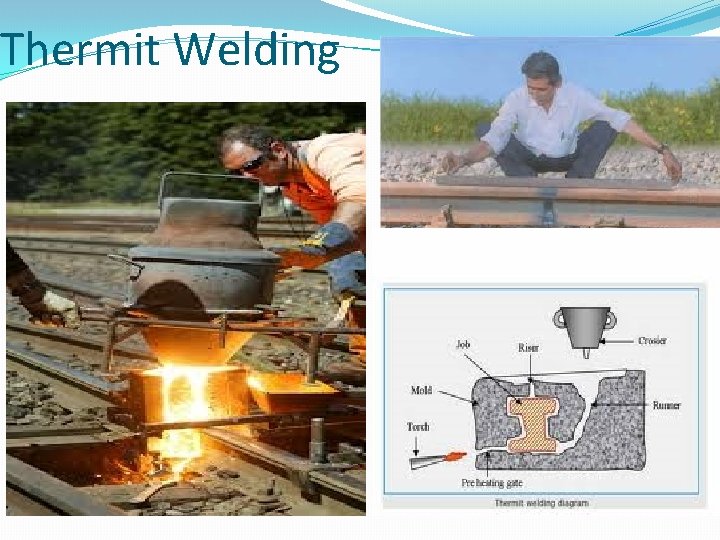
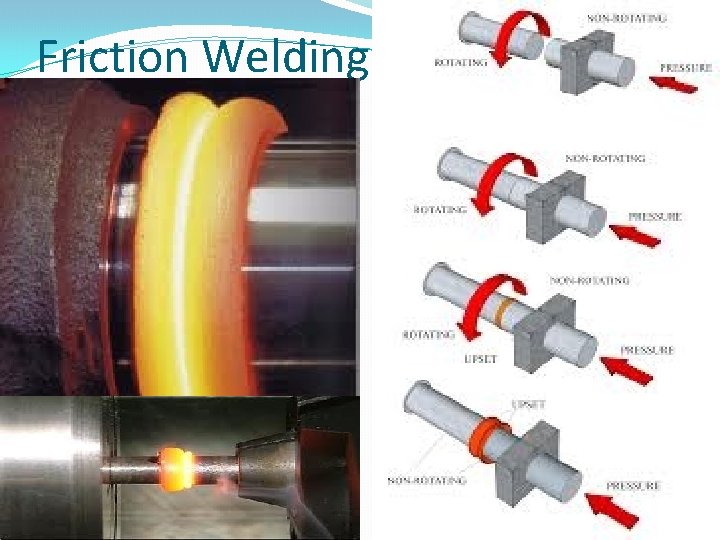
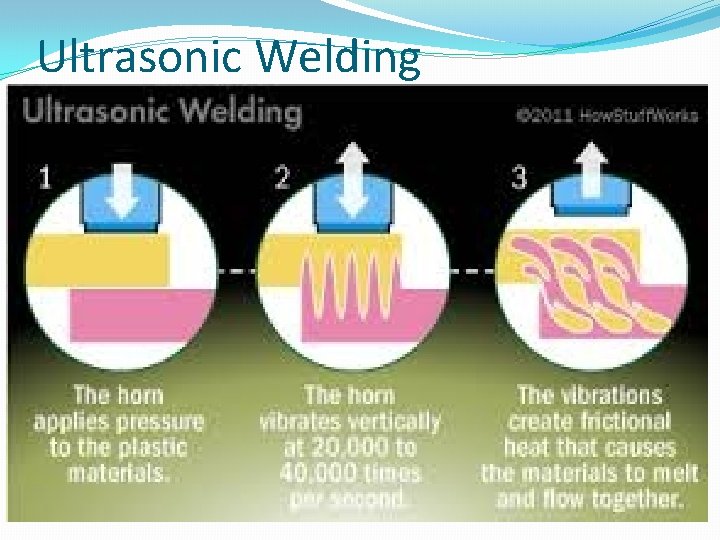
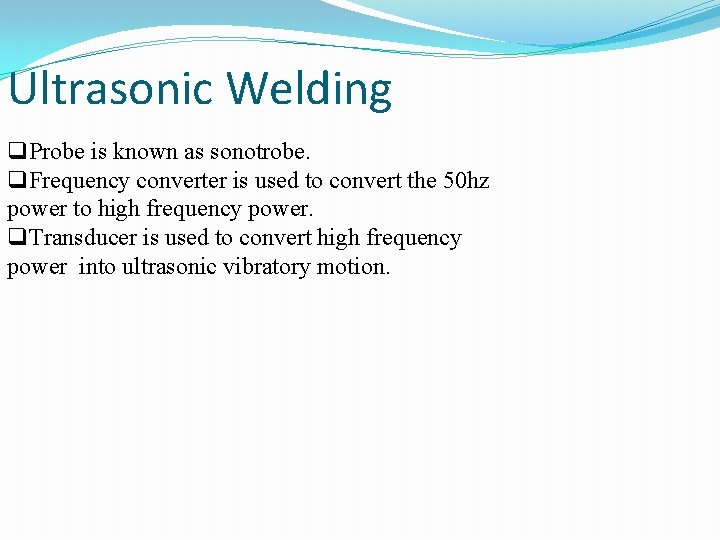
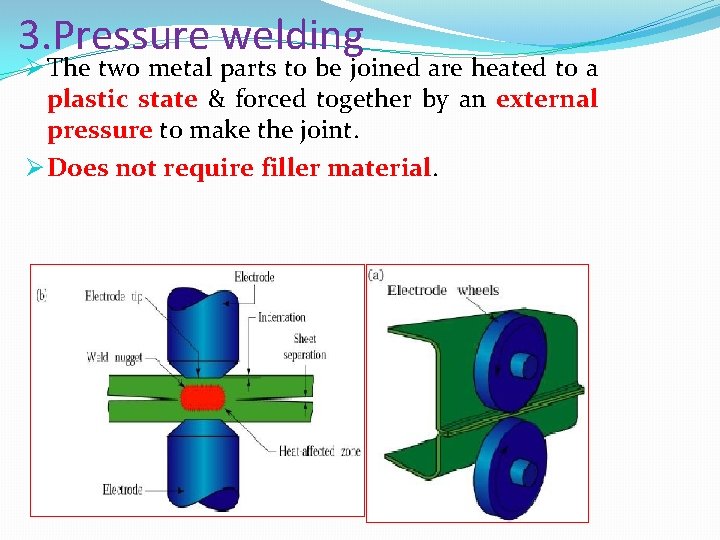
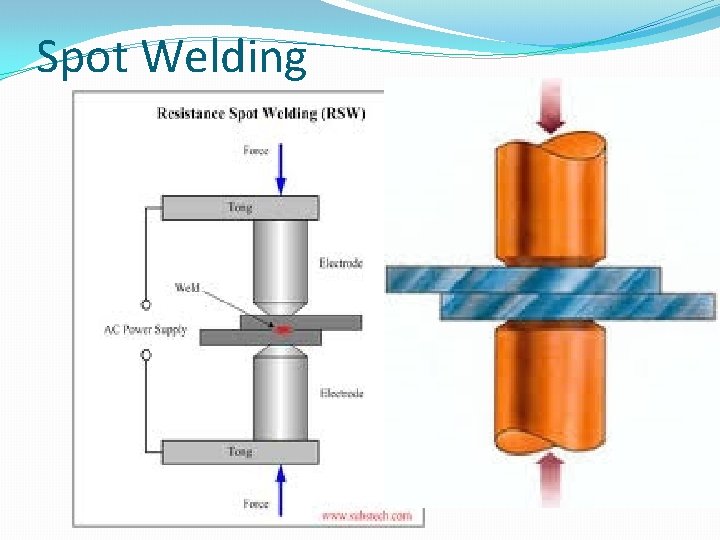
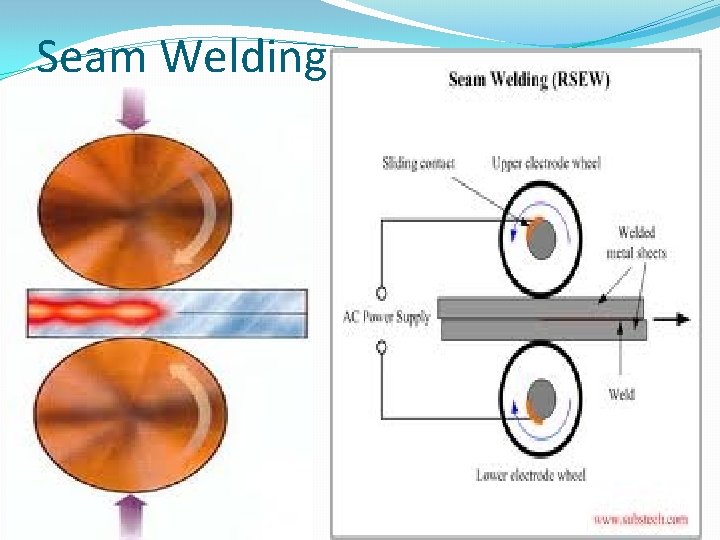
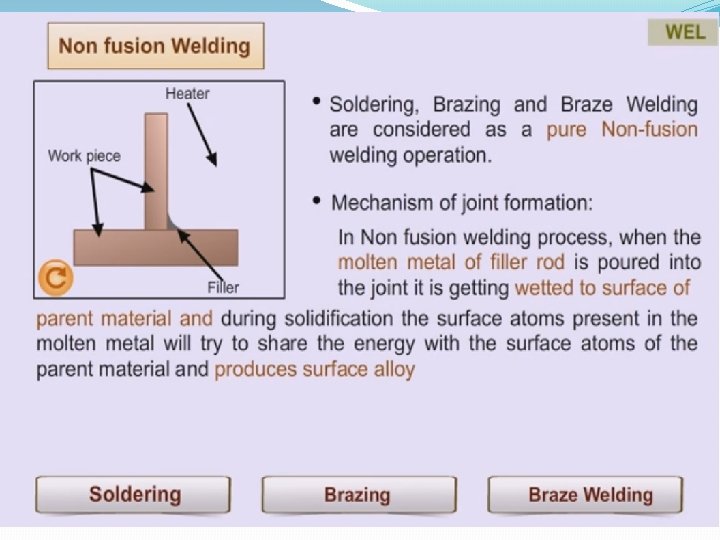

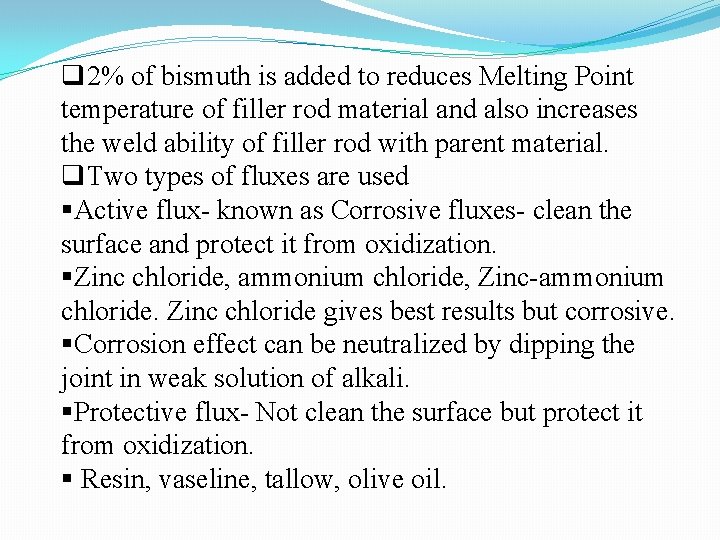
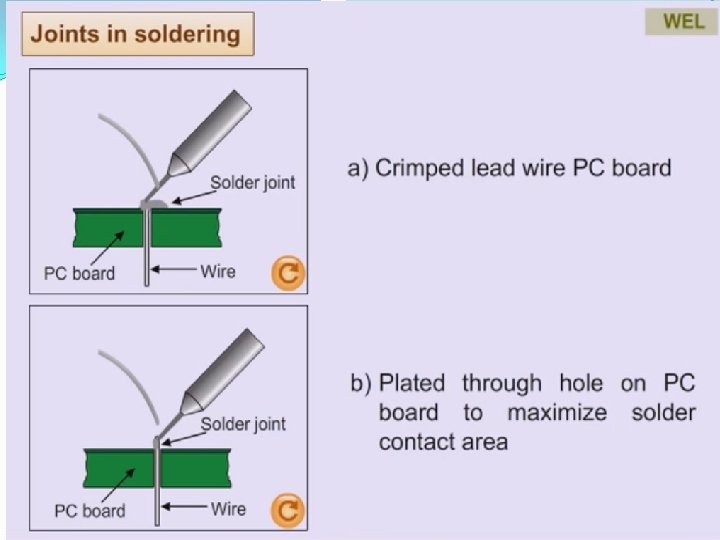
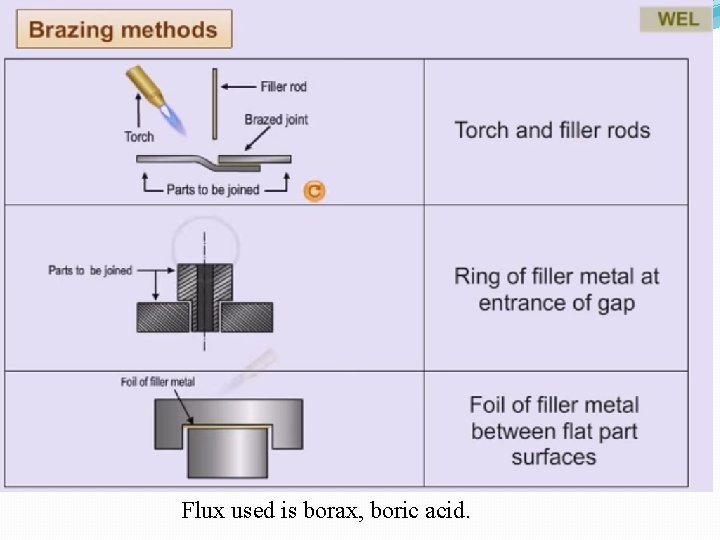
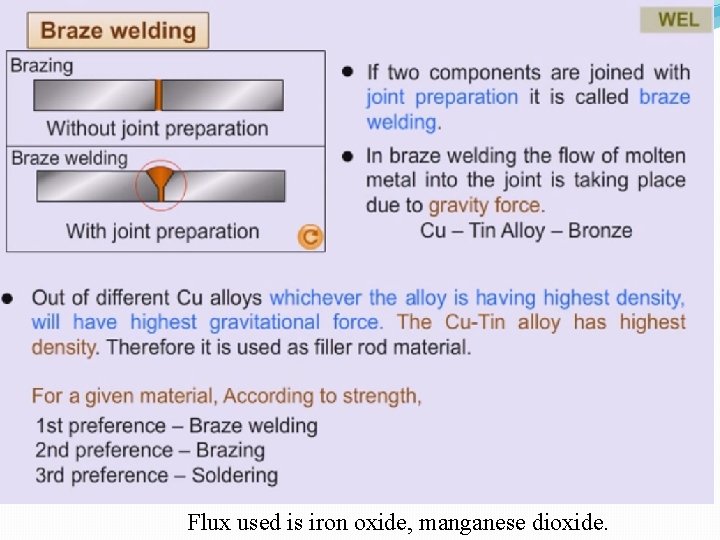
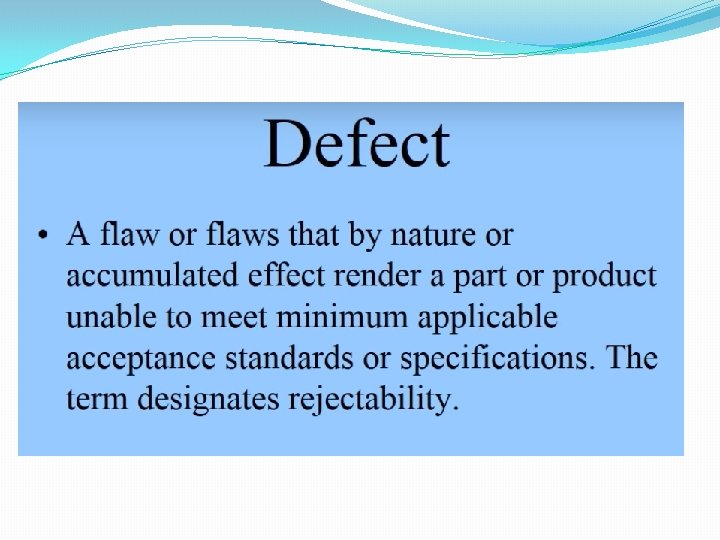
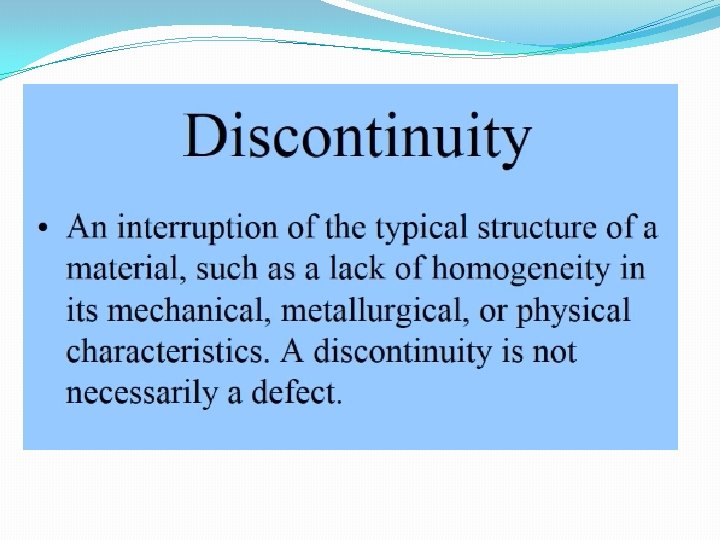
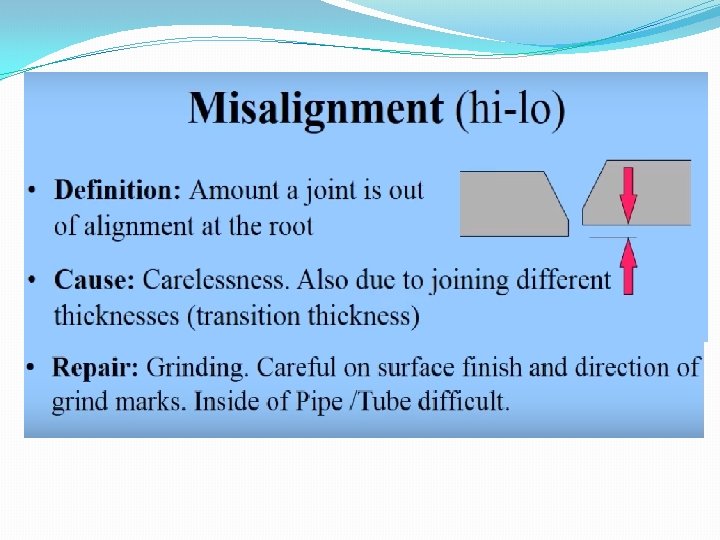
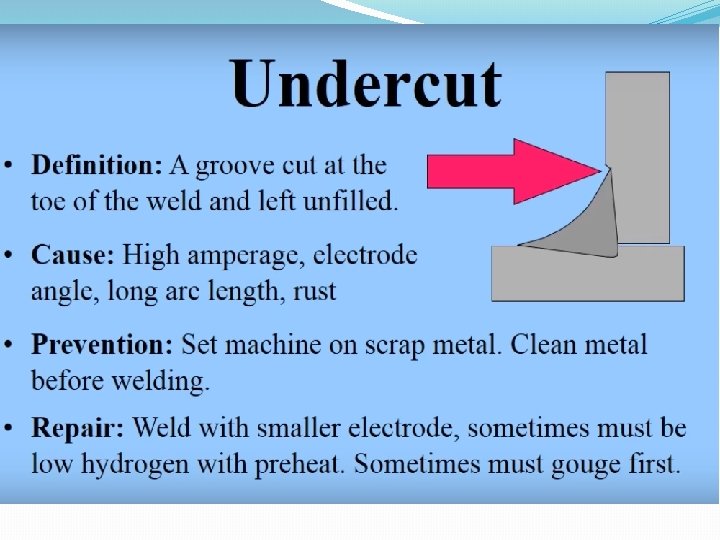
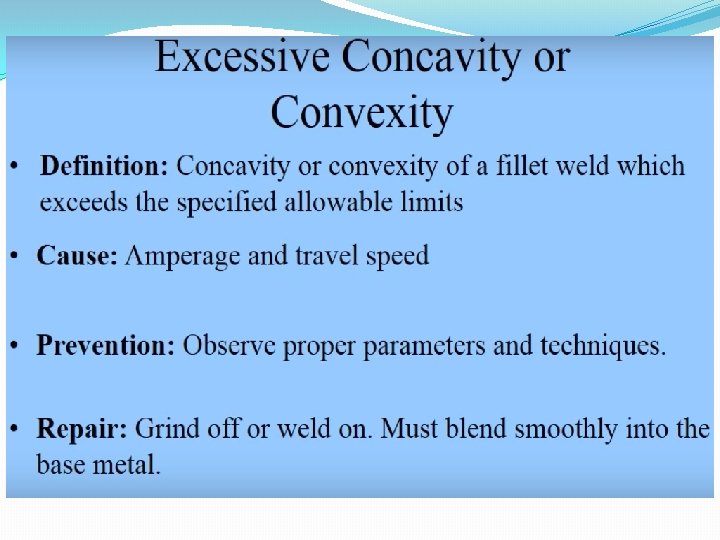
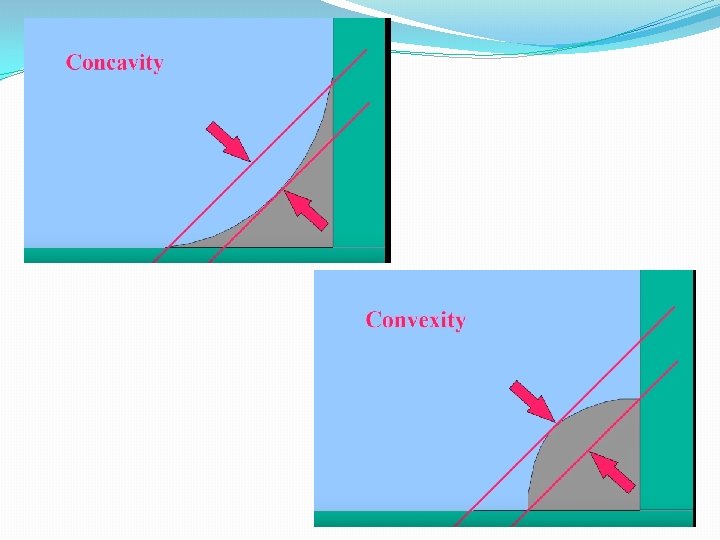
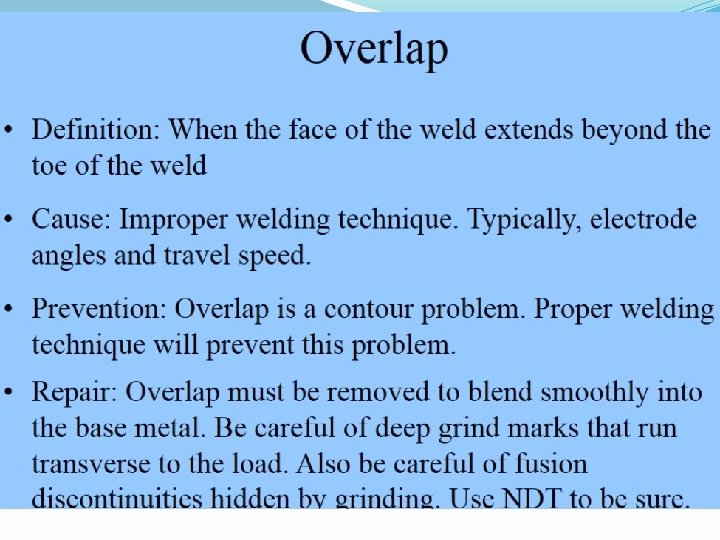
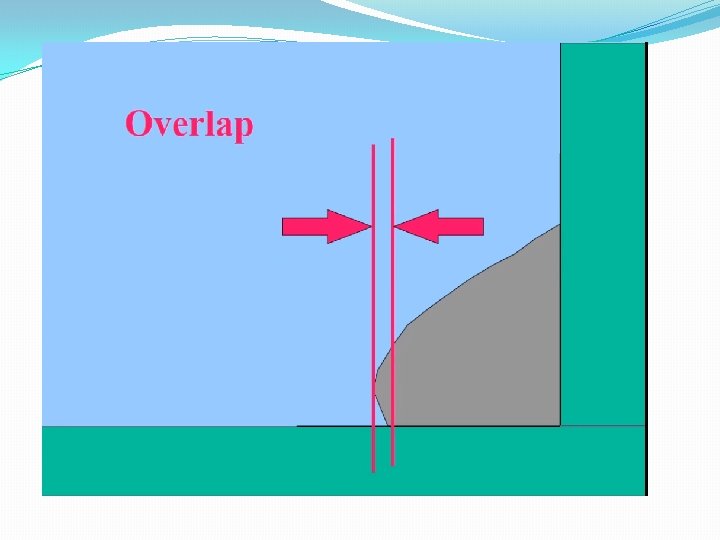
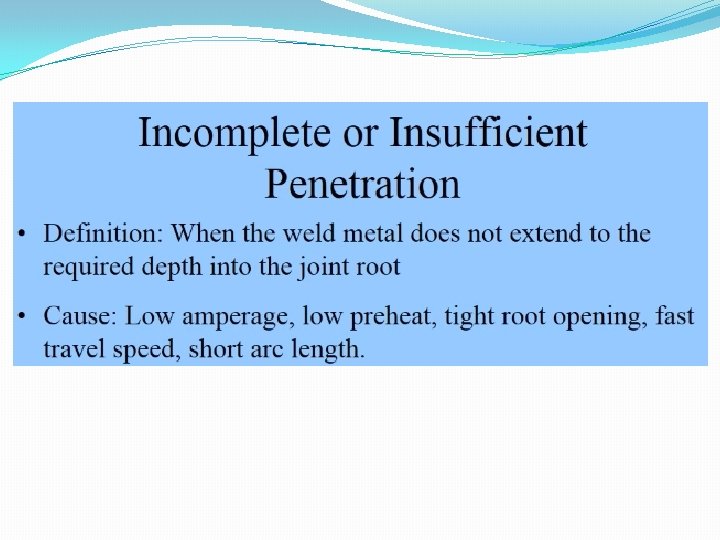
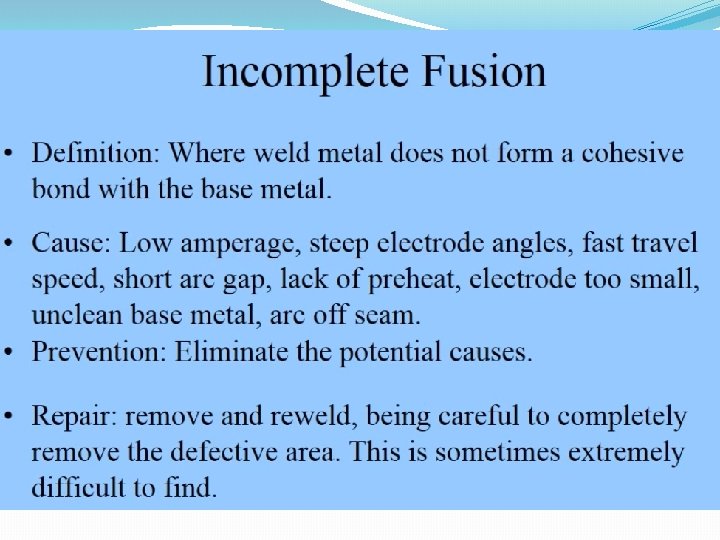
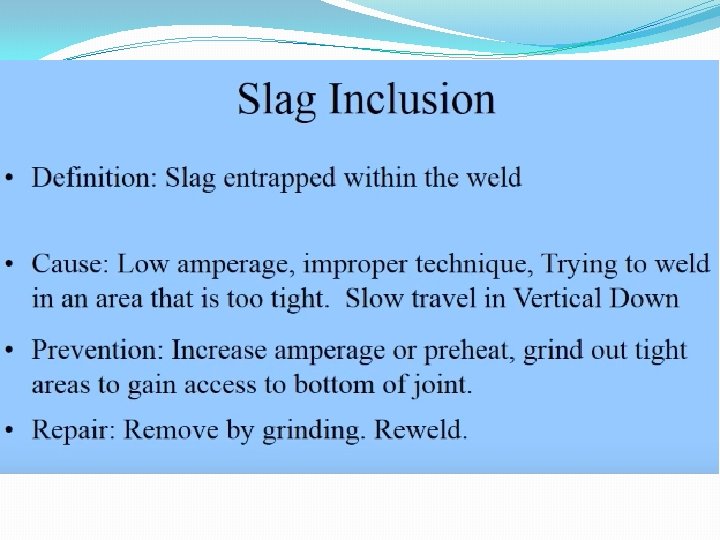
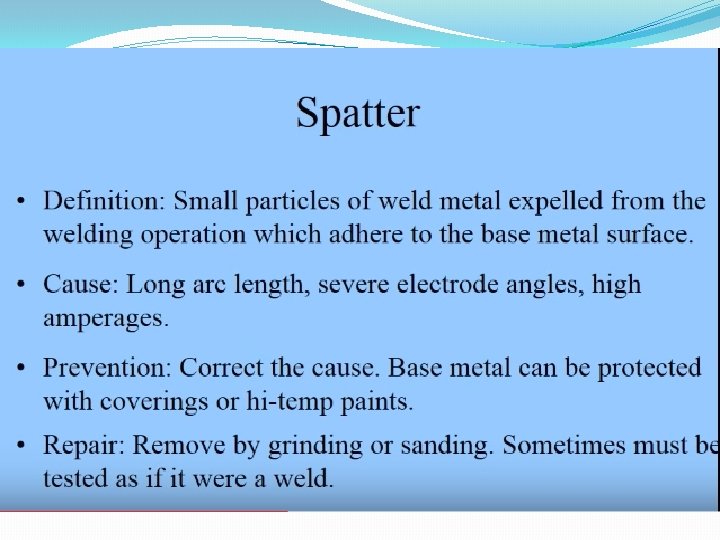
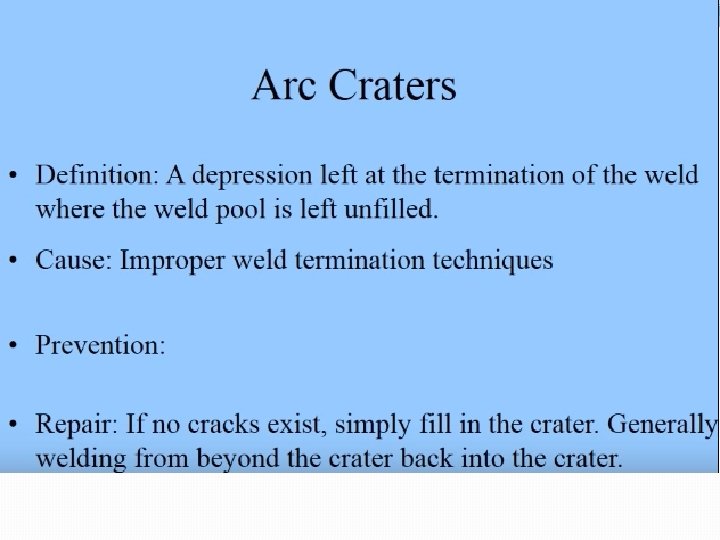
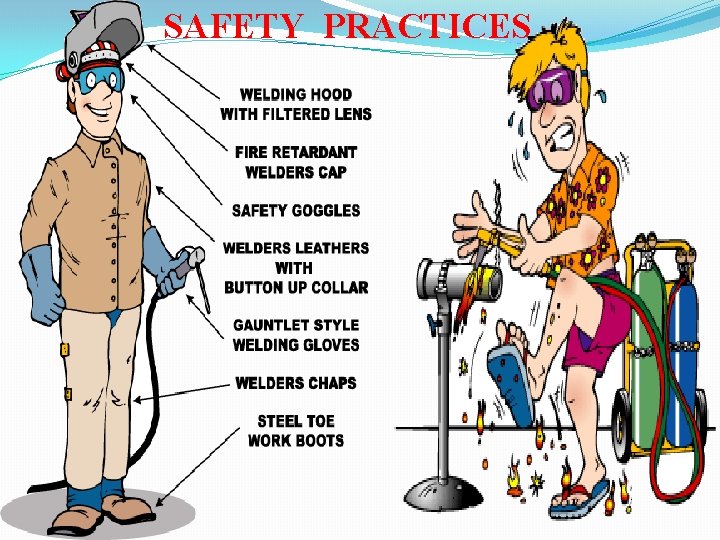
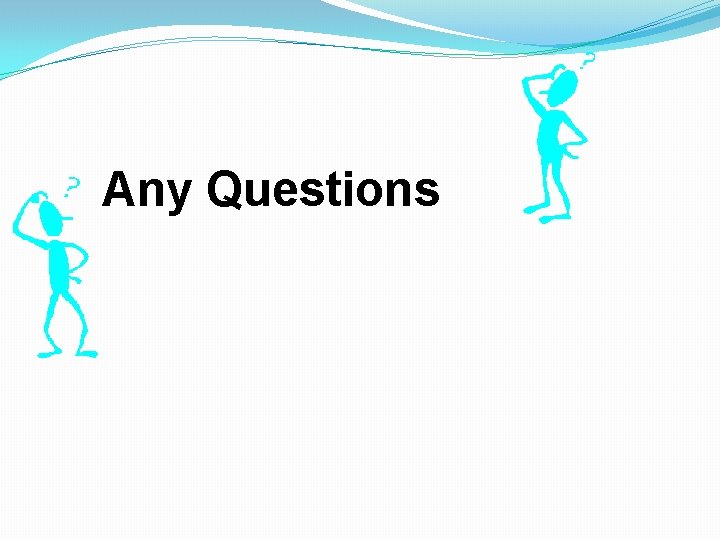
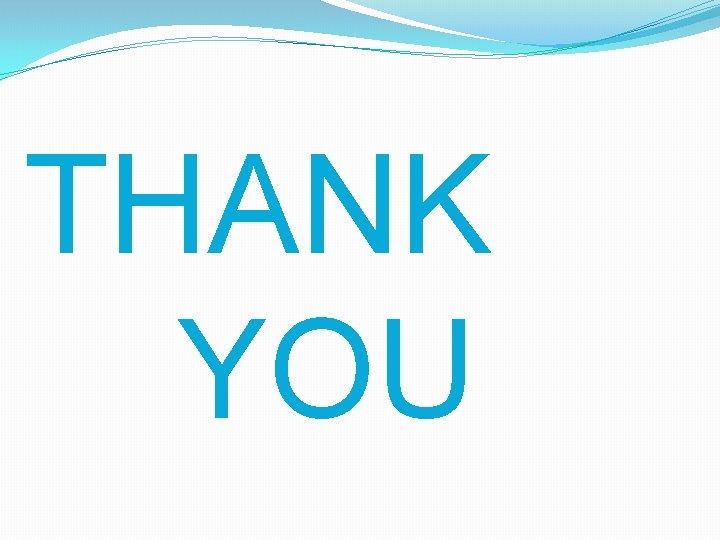
- Slides: 81
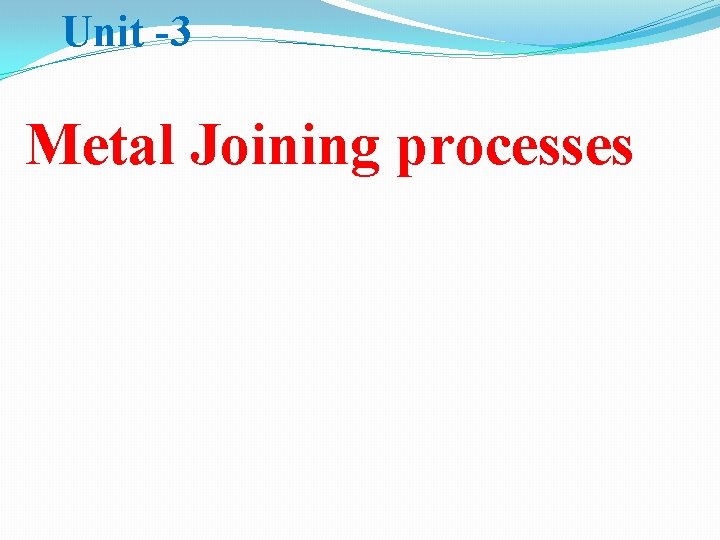
Unit -3 Metal Joining processes
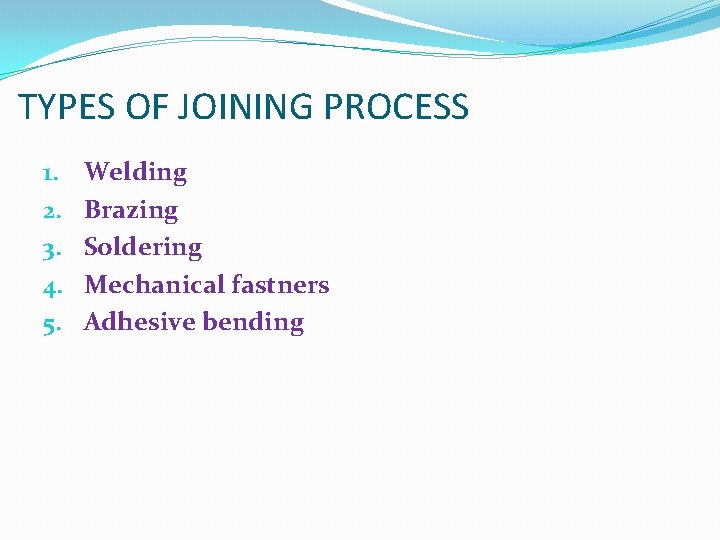
TYPES OF JOINING PROCESS 1. 2. 3. 4. 5. Welding Brazing Soldering Mechanical fastners Adhesive bending
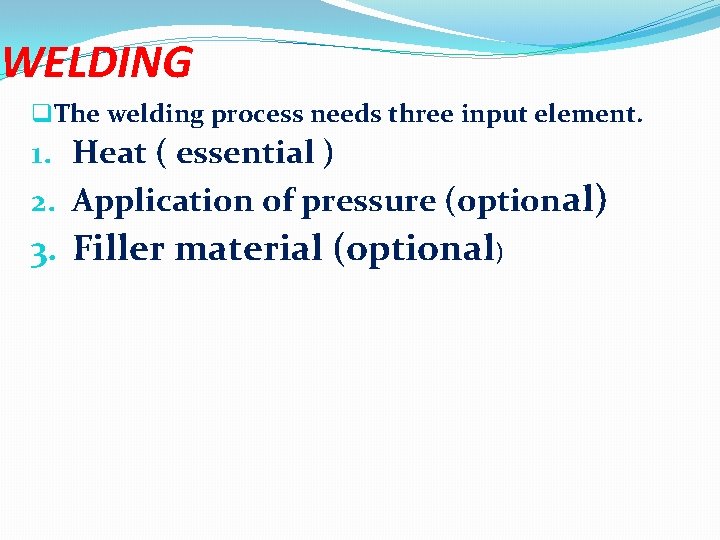
WELDING q. The welding process needs three input element. 1. Heat ( essential ) 2. Application of pressure (optional) 3. Filler material (optional)
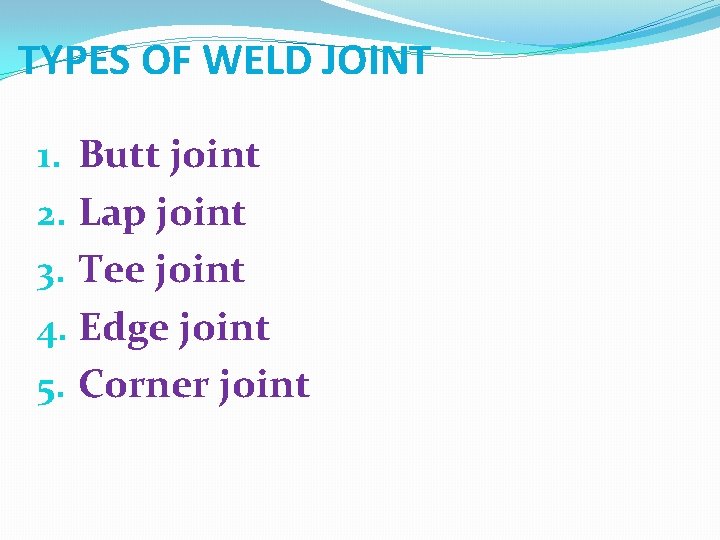
TYPES OF WELD JOINT 1. Butt joint 2. Lap joint 3. Tee joint 4. Edge joint 5. Corner joint
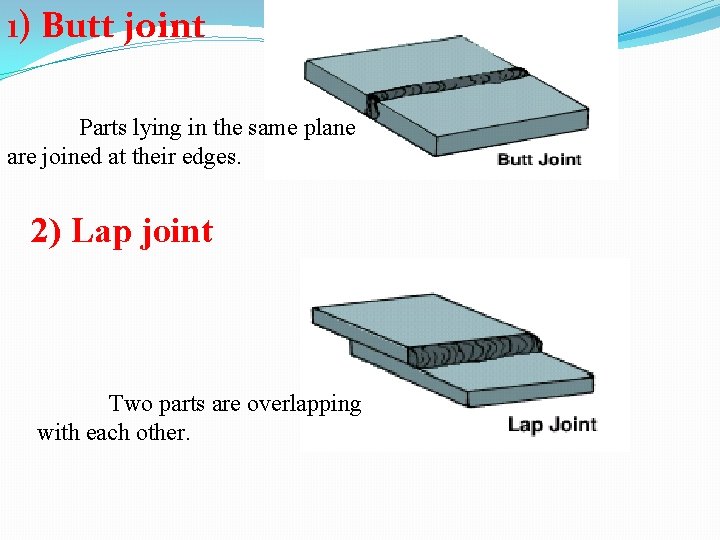
1) Butt joint Parts lying in the same plane are joined at their edges. 2) Lap joint Two parts are overlapping with each other.
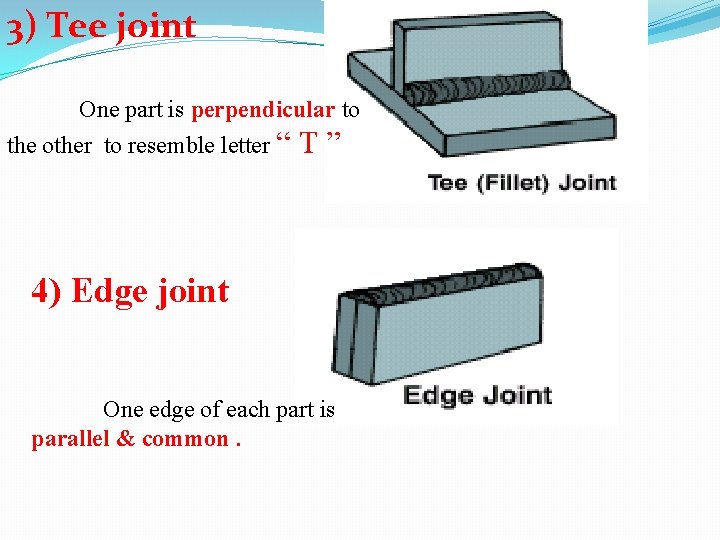
3) Tee joint One part is perpendicular to the other to resemble letter “ T” 4) Edge joint One edge of each part is parallel & common.
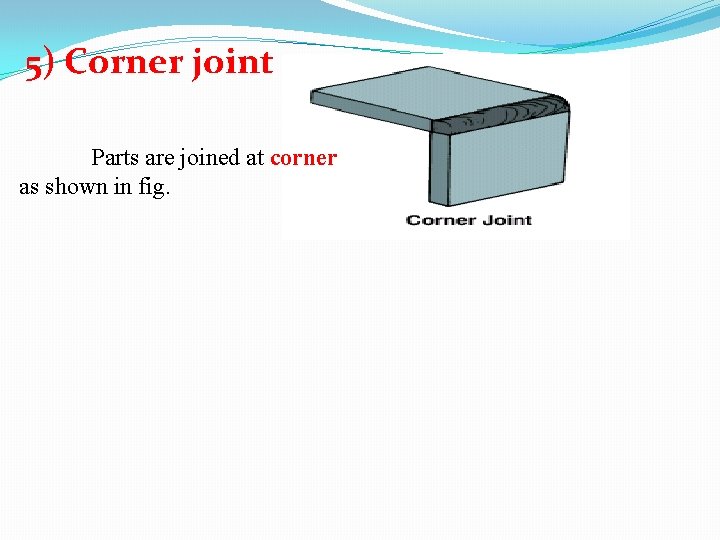
5) Corner joint Parts are joined at corner as shown in fig.
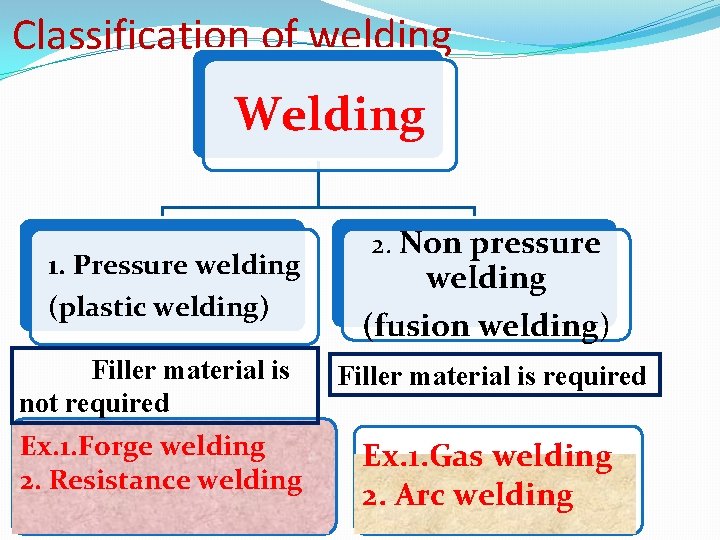
Classification of welding Welding 1. Pressure welding (plastic welding) 2. Non pressure welding (fusion welding) Filler material is not required Filler material is required Ex. 1. Forge welding 2. Resistance welding Ex. 1. Gas welding 2. Arc welding
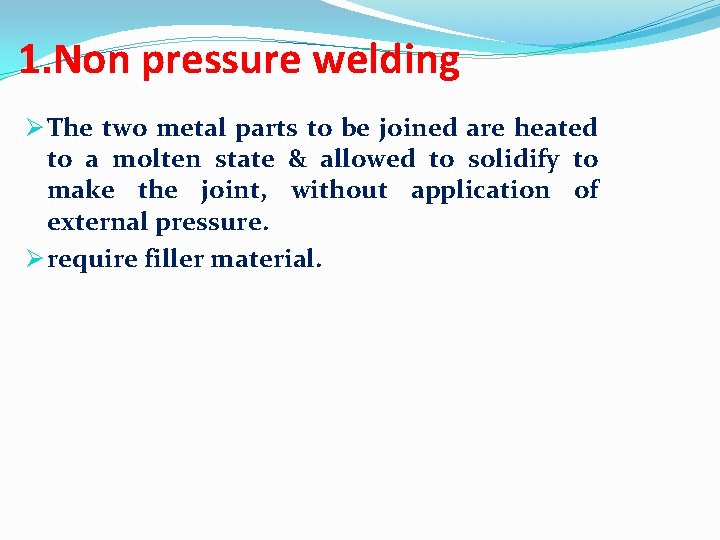
1. Non pressure welding Ø The two metal parts to be joined are heated to a molten state & allowed to solidify to make the joint, without application of external pressure. Ø require filler material.
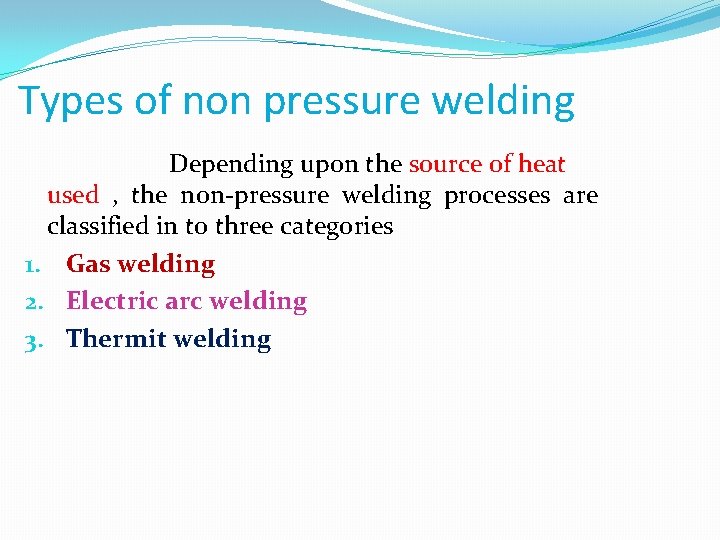
Types of non pressure welding Depending upon the source of heat used , the non-pressure welding processes are classified in to three categories 1. Gas welding 2. Electric arc welding 3. Thermit welding
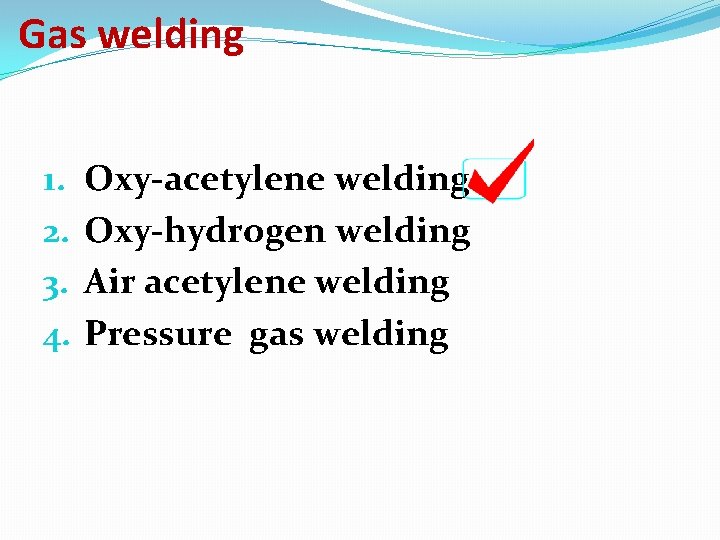
Gas welding 1. 2. 3. 4. Oxy-acetylene welding Oxy-hydrogen welding Air acetylene welding Pressure gas welding
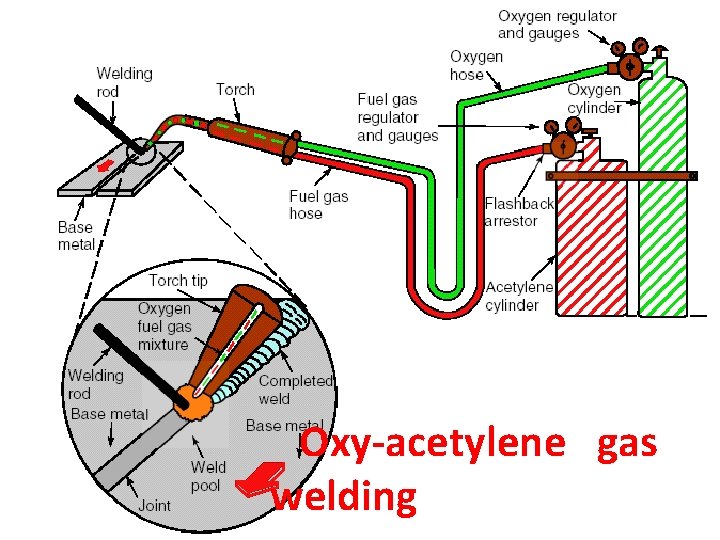
Oxy-acetylene gas welding
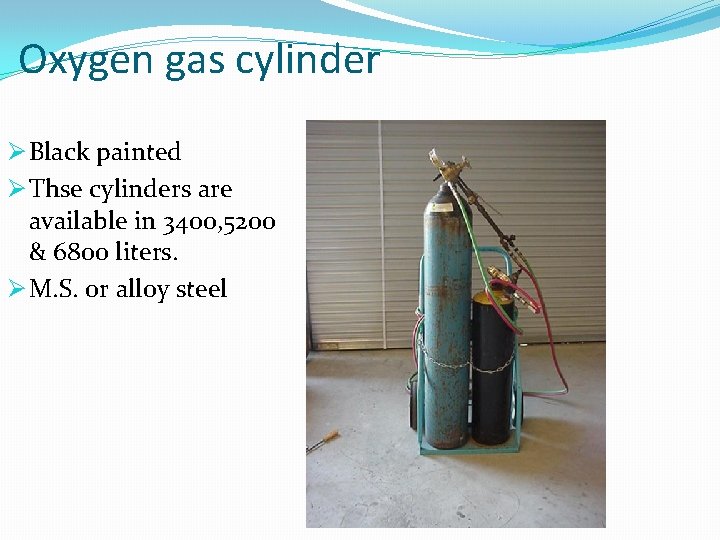
Oxygen gas cylinder Ø Black painted Ø Thse cylinders are available in 3400, 5200 & 6800 liters. Ø M. S. or alloy steel
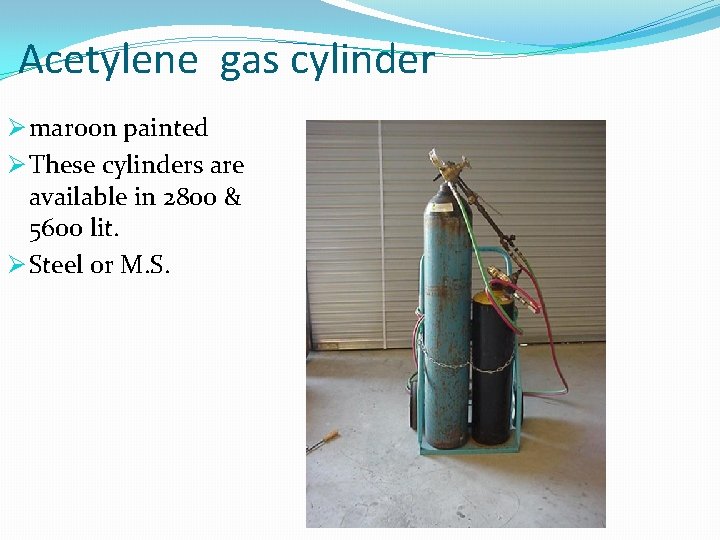
Acetylene gas cylinder Ø maroon painted Ø These cylinders are available in 2800 & 5600 lit. Ø Steel or M. S.
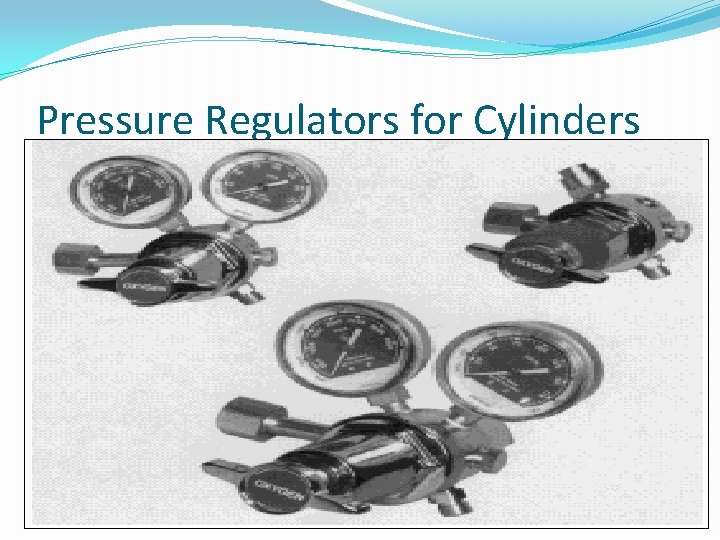
Pressure Regulators for Cylinders
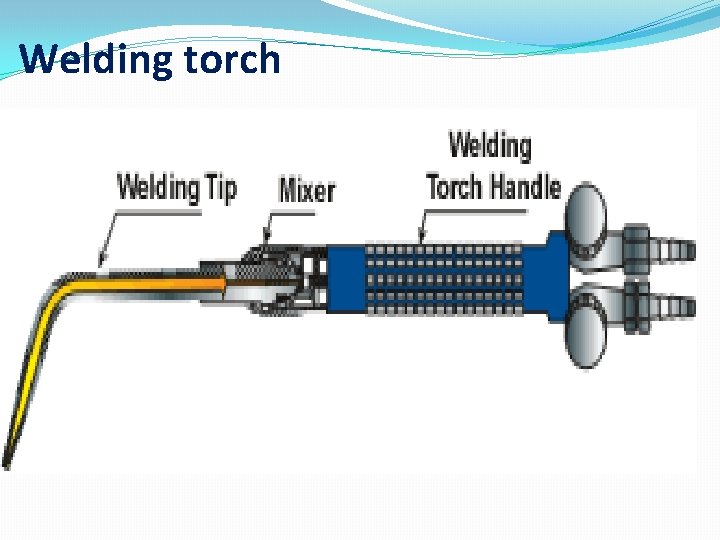
Welding torch
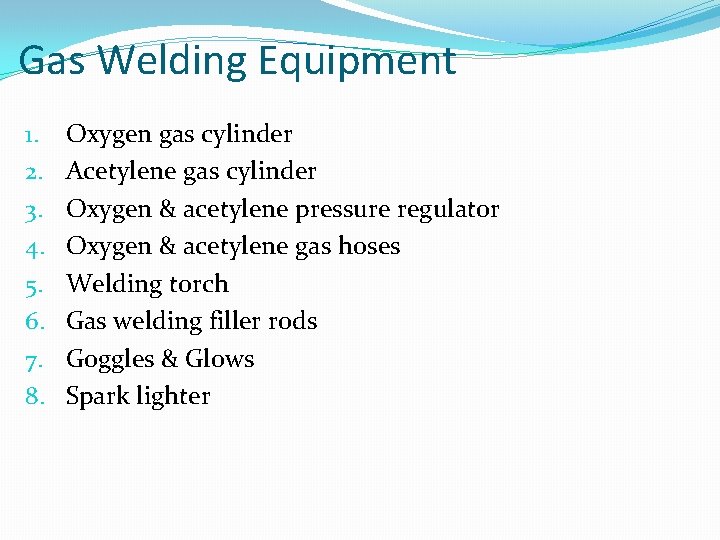
Gas Welding Equipment 1. 2. 3. 4. 5. 6. 7. 8. Oxygen gas cylinder Acetylene gas cylinder Oxygen & acetylene pressure regulator Oxygen & acetylene gas hoses Welding torch Gas welding filler rods Goggles & Glows Spark lighter
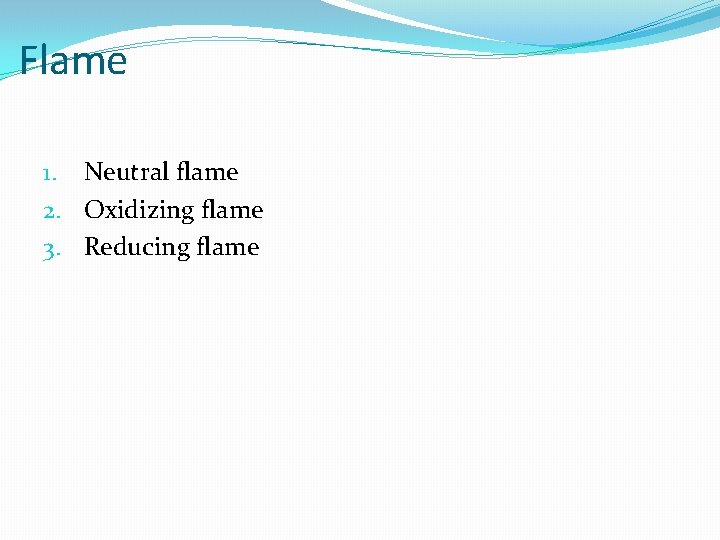
Flame 1. Neutral flame 2. Oxidizing flame 3. Reducing flame
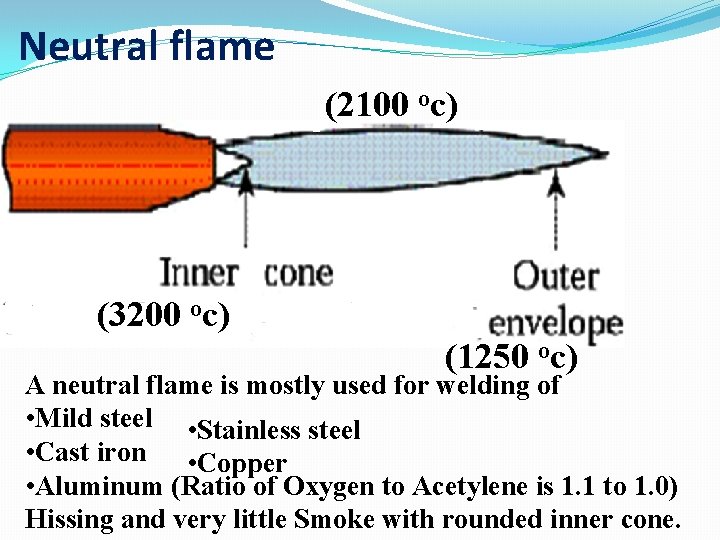
Neutral flame (2100 oc) (3200 oc) (1250 oc) A neutral flame is mostly used for welding of • Mild steel • Stainless steel • Cast iron • Copper • Aluminum (Ratio of Oxygen to Acetylene is 1. 1 to 1. 0) Hissing and very little Smoke with rounded inner cone.

Reducing flame (carburizing flame ) (2500 oc) (2740 oc) (1250 oc) Temperature – 2740 oc This flame generally used for welding for • Low alloy steel rods to increase welding speed. • Non ferrous metal, Monel metal, Nickel, Alloy steel • High carbon steel • (Ratio of Oxygen to Acetylene is 0. 85 to 0. 95) • Free carbon helps to reduces the period of heating thus increases welding speed.
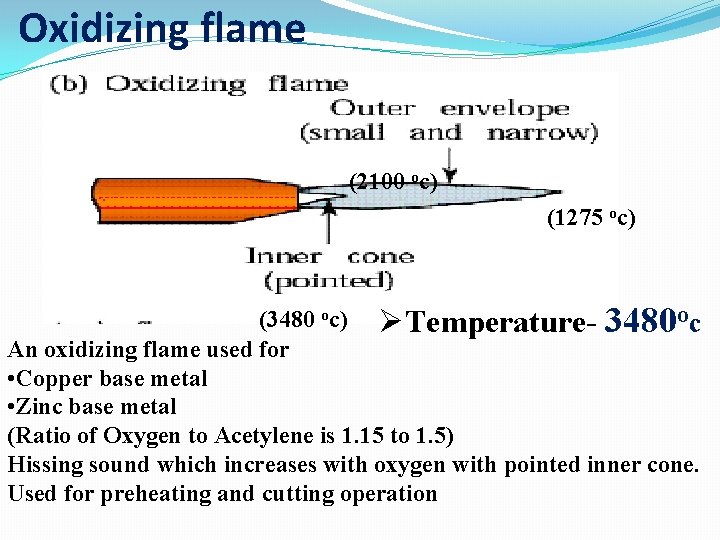
Oxidizing flame (2100 oc) (1275 oc) (3480 oc) ØTemperature- 3480 oc An oxidizing flame used for • Copper base metal • Zinc base metal (Ratio of Oxygen to Acetylene is 1. 15 to 1. 5) Hissing sound which increases with oxygen with pointed inner cone. Used for preheating and cutting operation
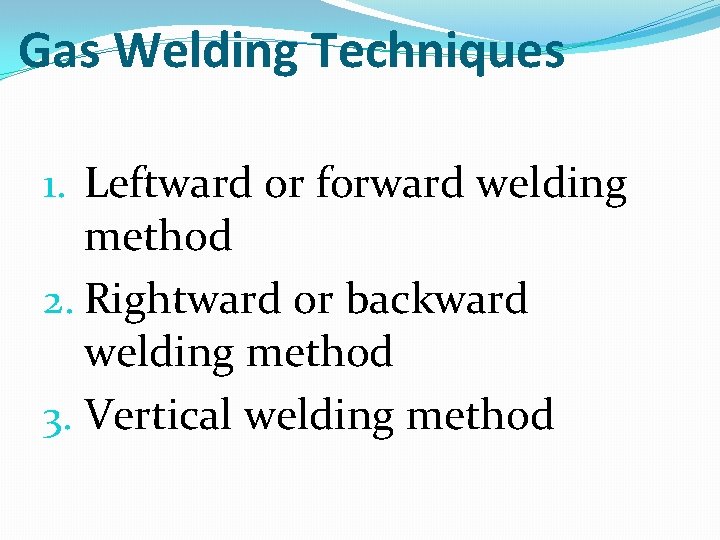
Gas Welding Techniques 1. Leftward or forward welding method 2. Rightward or backward welding method 3. Vertical welding method
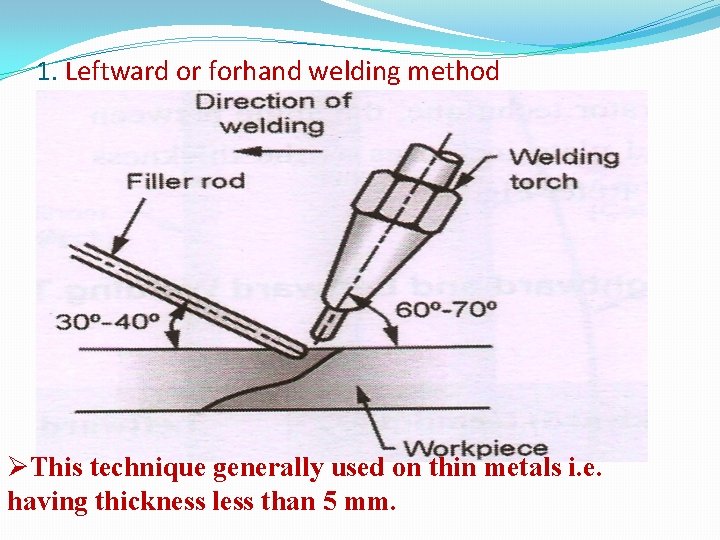
1. Leftward or forhand welding method ØThis technique generally used on thin metals i. e. having thickness less than 5 mm.
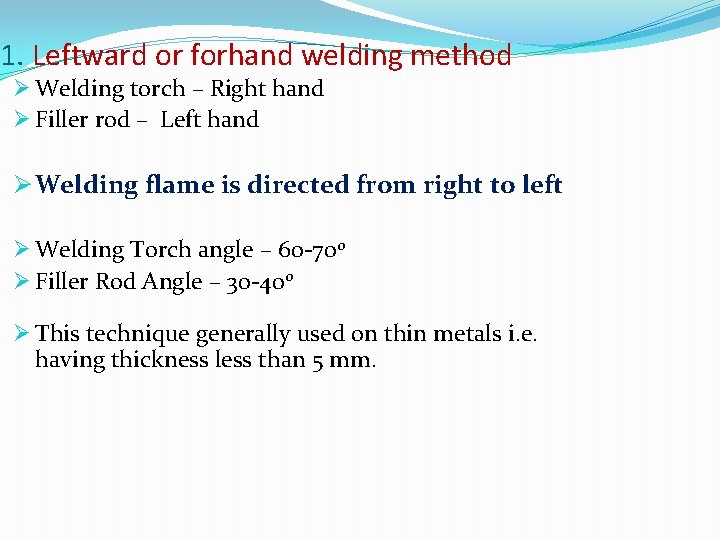
1. Leftward or forhand welding method Ø Welding torch – Right hand Ø Filler rod – Left hand Ø Welding flame is directed from right to left Ø Welding Torch angle – 60 -700 Ø Filler Rod Angle – 30 -400 Ø This technique generally used on thin metals i. e. having thickness less than 5 mm.
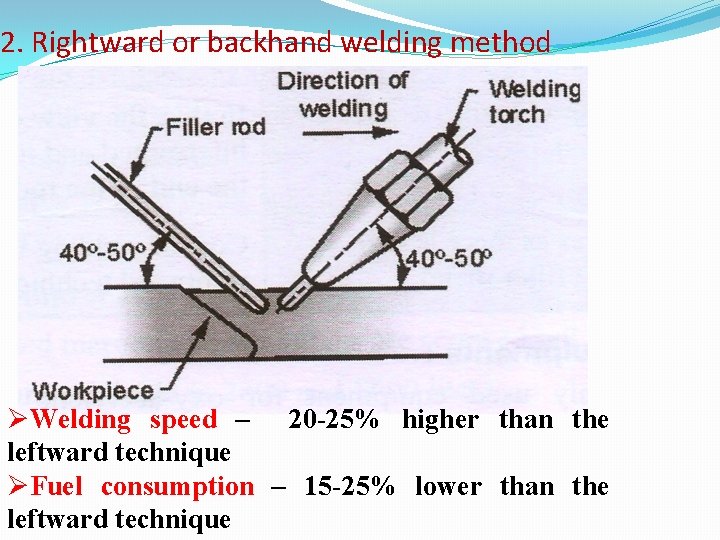
2. Rightward or backhand welding method ØWelding speed – 20 -25% higher than the leftward technique ØFuel consumption – 15 -25% lower than the leftward technique
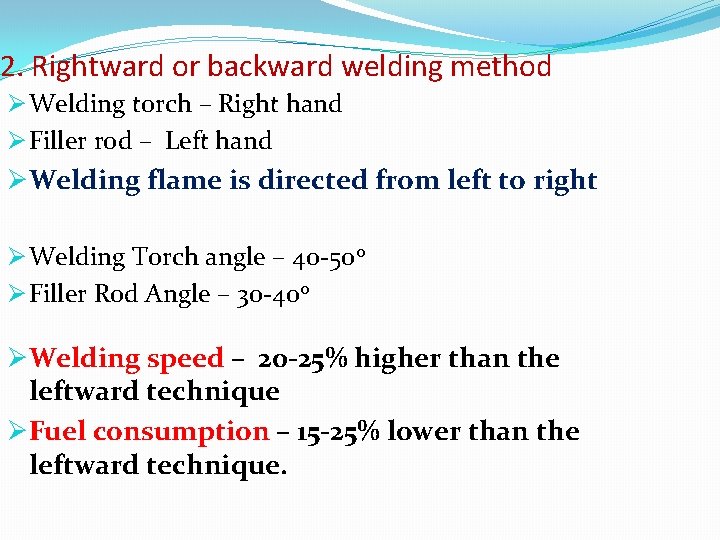
2. Rightward or backward welding method Ø Welding torch – Right hand Ø Filler rod – Left hand ØWelding flame is directed from left to right Ø Welding Torch angle – 40 -500 Ø Filler Rod Angle – 30 -400 ØWelding speed – 20 -25% higher than the leftward technique ØFuel consumption – 15 -25% lower than the leftward technique.
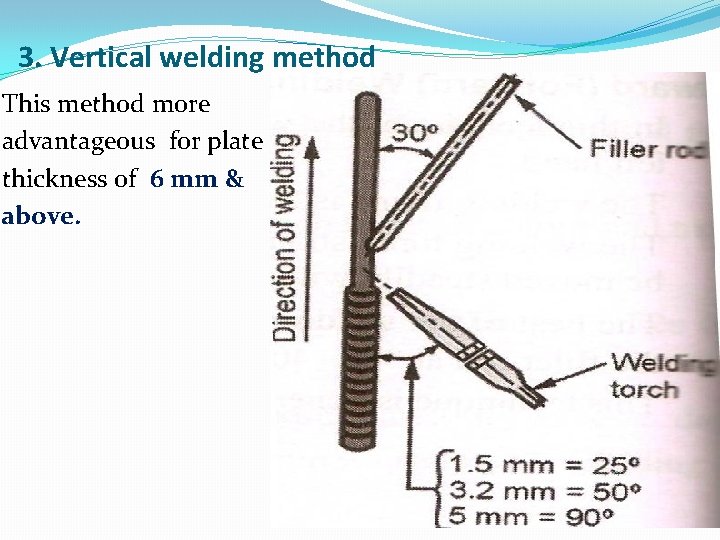
3. Vertical welding method This method more advantageous for plate thickness of 6 mm & above.
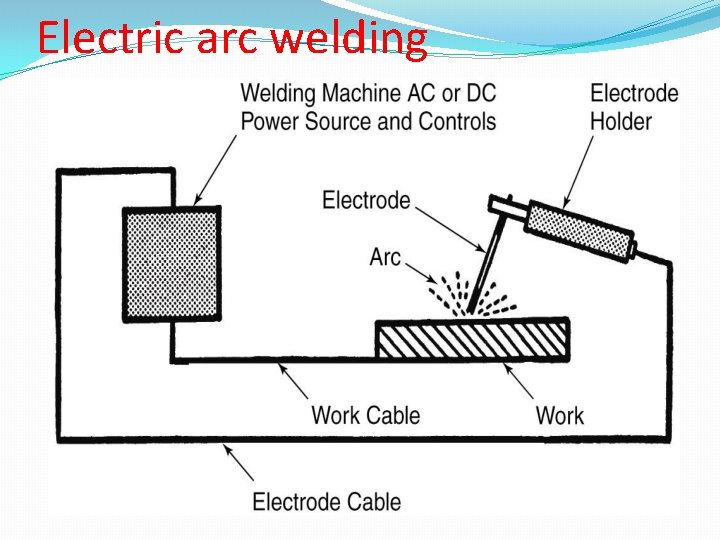
Electric arc welding
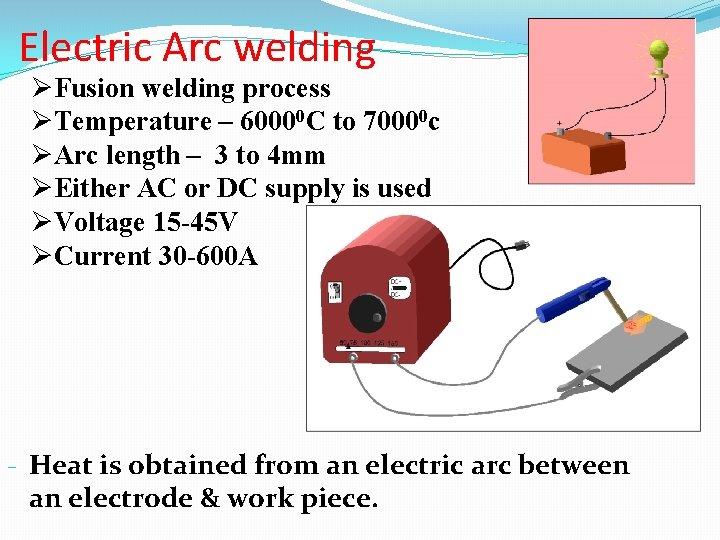
Electric Arc welding ØFusion welding process ØTemperature – 60000 C to 70000 c ØArc length – 3 to 4 mm ØEither AC or DC supply is used ØVoltage 15 -45 V ØCurrent 30 -600 A - Heat is obtained from an electric arc between an electrode & work piece.
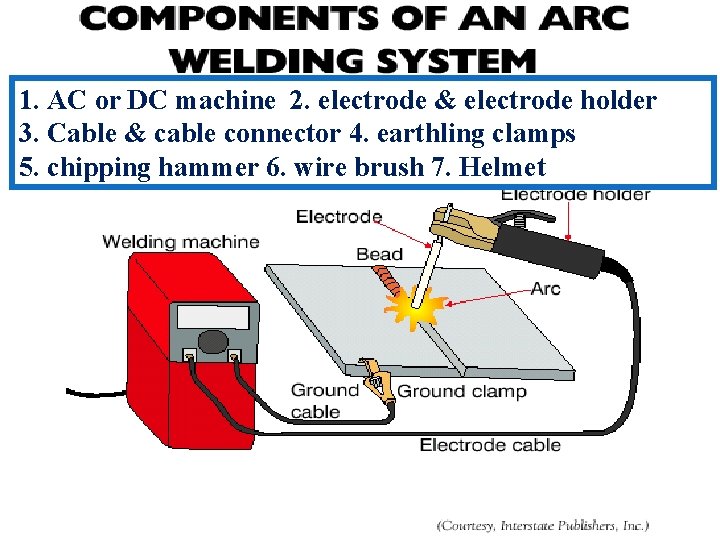
1. AC or DC machine 2. electrode & electrode holder 3. Cable & cable connector 4. earthling clamps 5. chipping hammer 6. wire brush 7. Helmet
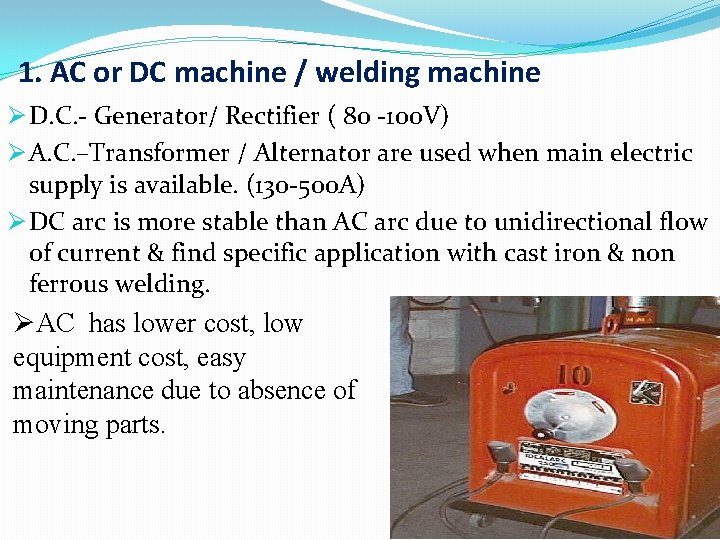
1. AC or DC machine / welding machine Ø D. C. - Generator/ Rectifier ( 80 -100 V) Ø A. C. –Transformer / Alternator are used when main electric supply is available. (130 -500 A) Ø DC arc is more stable than AC arc due to unidirectional flow of current & find specific application with cast iron & non ferrous welding. ØAC has lower cost, low equipment cost, easy maintenance due to absence of moving parts.
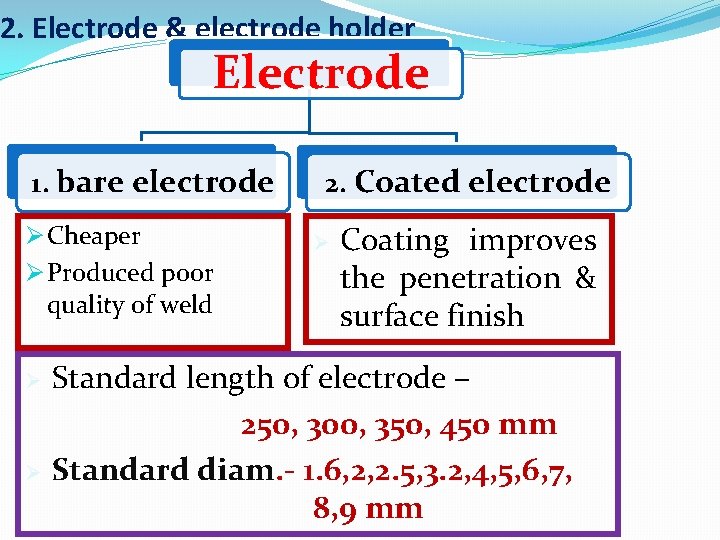
2. Electrode & electrode holder Electrode 1. bare electrode Ø Cheaper Ø Produced poor quality of weld Ø Ø 2. Coated electrode Ø Coating improves the penetration & surface finish Standard length of electrode – 250, 300, 350, 450 mm Standard diam. - 1. 6, 2, 2. 5, 3. 2, 4, 5, 6, 7, 8, 9 mm
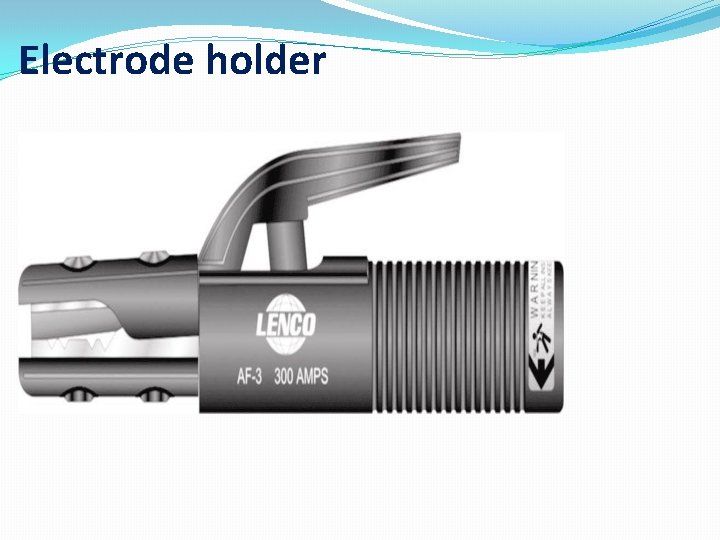
Electrode holder
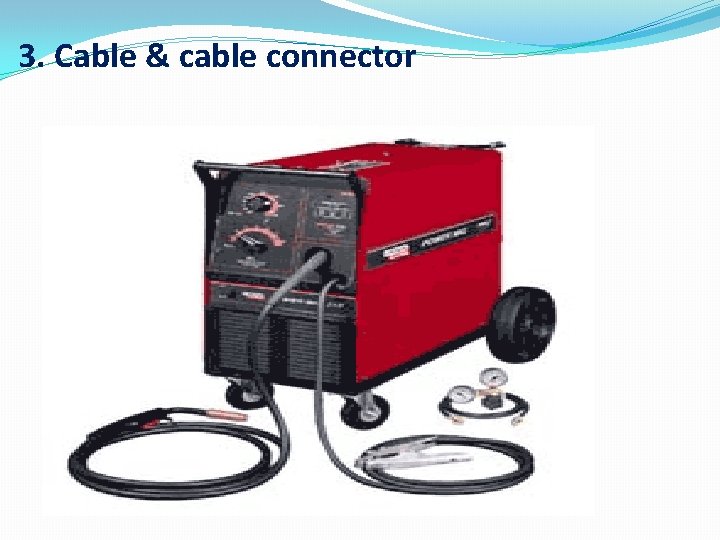
3. Cable & cable connector
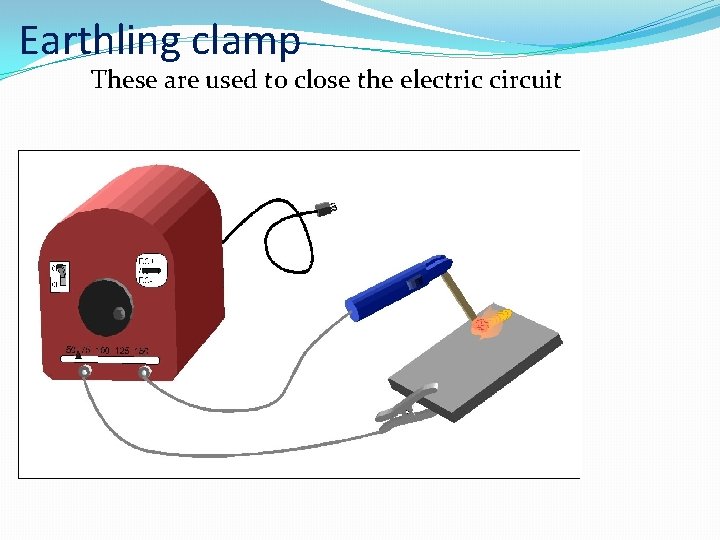
Earthling clamp These are used to close the electric circuit
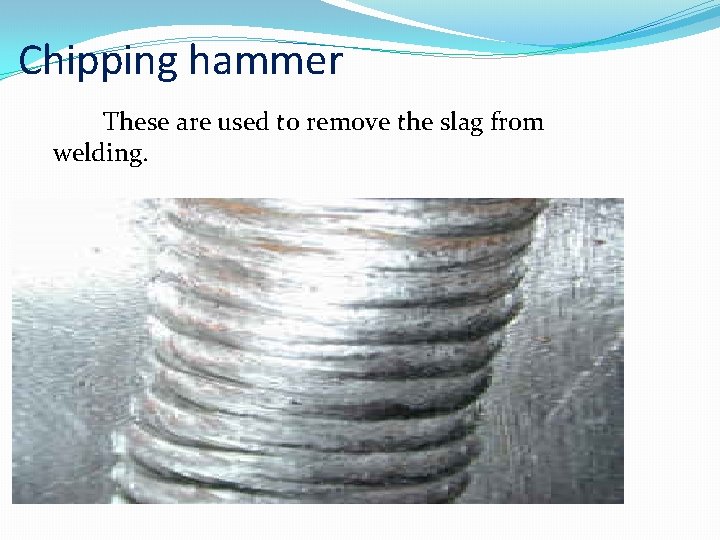
Chipping hammer These are used to remove the slag from welding.
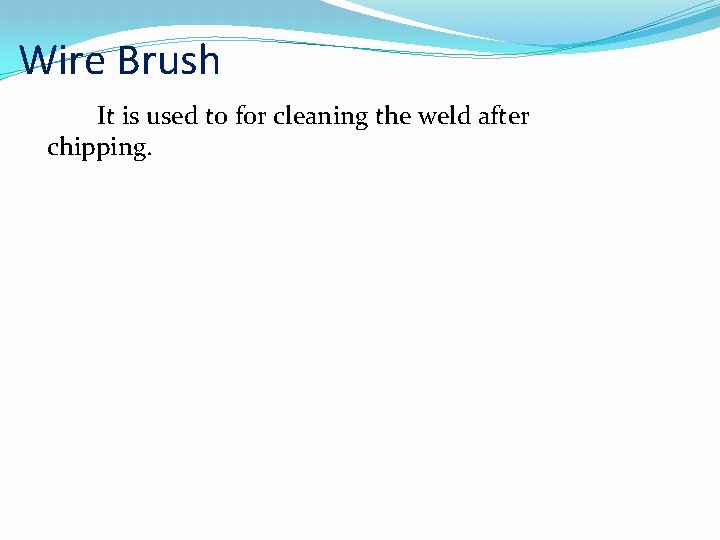
Wire Brush It is used to for cleaning the weld after chipping.
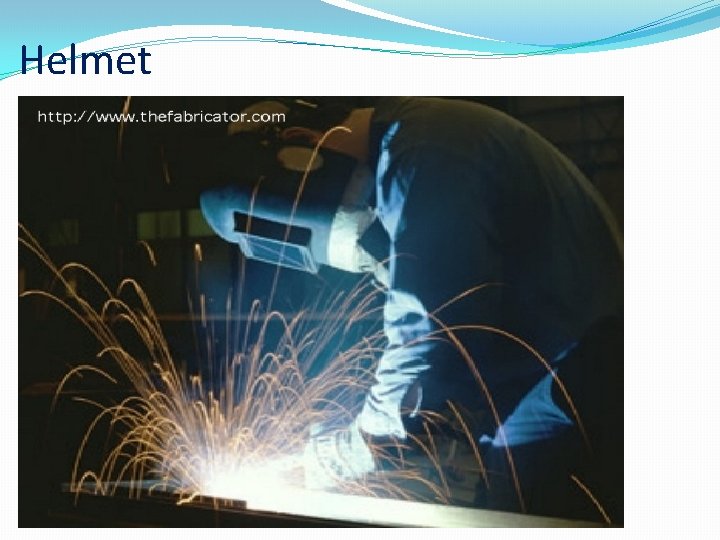
Helmet
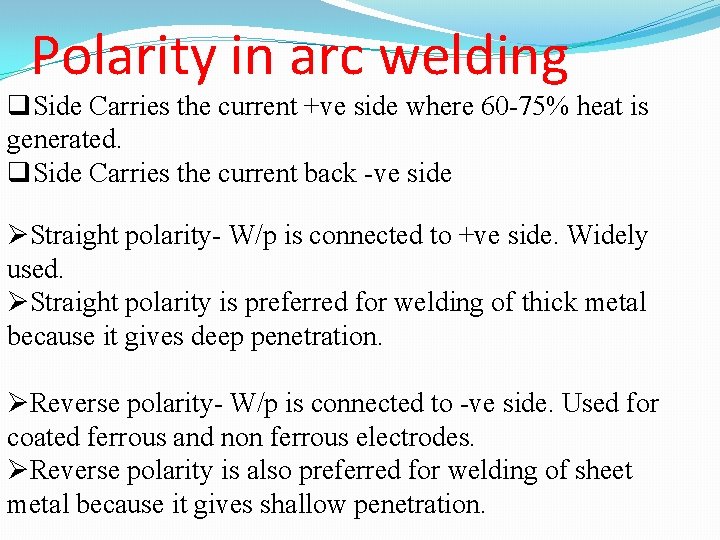
Polarity in arc welding q. Side Carries the current +ve side where 60 -75% heat is generated. q. Side Carries the current back -ve side ØStraight polarity- W/p is connected to +ve side. Widely used. ØStraight polarity is preferred for welding of thick metal because it gives deep penetration. ØReverse polarity- W/p is connected to -ve side. Used for coated ferrous and non ferrous electrodes. ØReverse polarity is also preferred for welding of sheet metal because it gives shallow penetration.
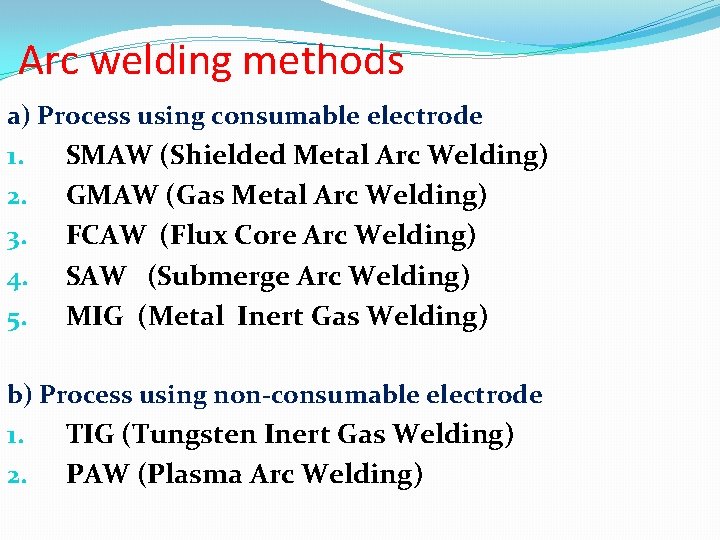
Arc welding methods a) Process using consumable electrode 1. 2. 3. 4. 5. SMAW (Shielded Metal Arc Welding) GMAW (Gas Metal Arc Welding) FCAW (Flux Core Arc Welding) SAW (Submerge Arc Welding) MIG (Metal Inert Gas Welding) b) Process using non-consumable electrode 1. 2. TIG (Tungsten Inert Gas Welding) PAW (Plasma Arc Welding)
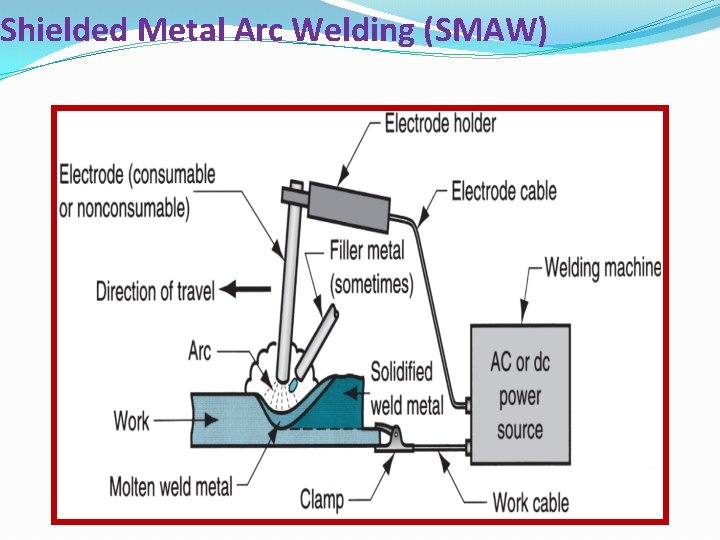
Shielded Metal Arc Welding (SMAW)
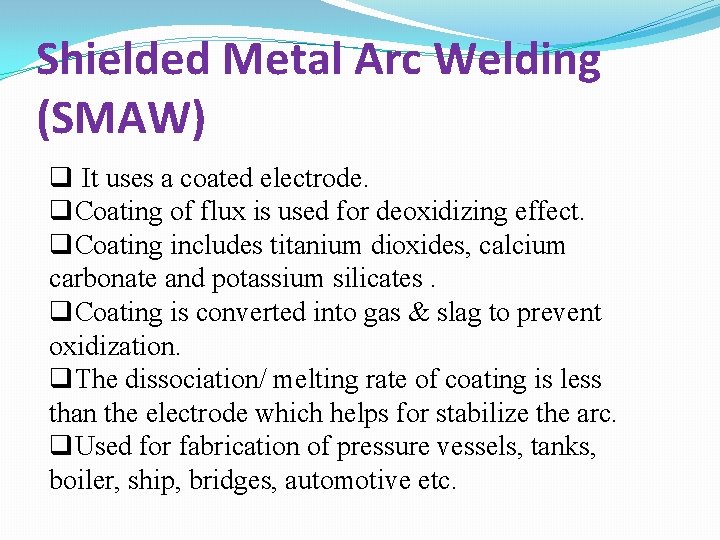
Shielded Metal Arc Welding (SMAW) q It uses a coated electrode. q. Coating of flux is used for deoxidizing effect. q. Coating includes titanium dioxides, calcium carbonate and potassium silicates. q. Coating is converted into gas & slag to prevent oxidization. q. The dissociation/ melting rate of coating is less than the electrode which helps for stabilize the arc. q. Used for fabrication of pressure vessels, tanks, boiler, ship, bridges, automotive etc.
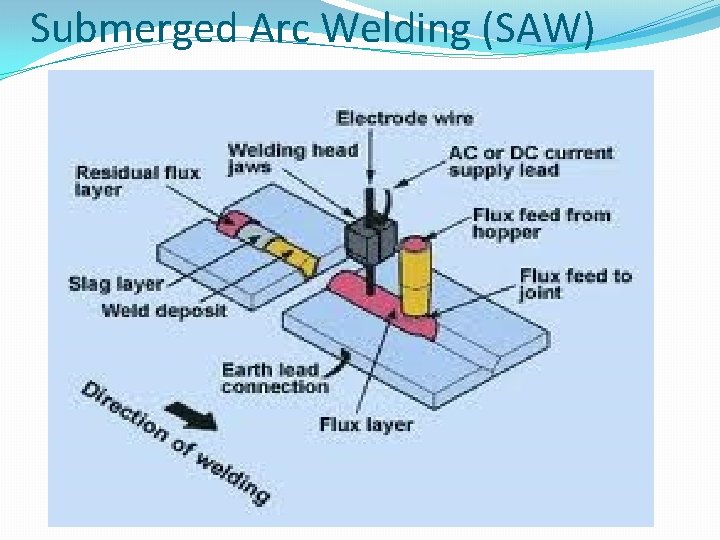
Submerged Arc Welding (SAW)
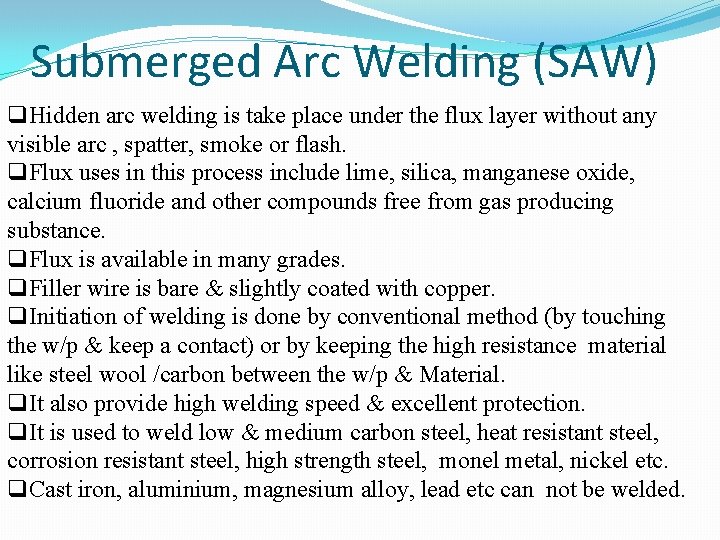
Submerged Arc Welding (SAW) q. Hidden arc welding is take place under the flux layer without any visible arc , spatter, smoke or flash. q. Flux uses in this process include lime, silica, manganese oxide, calcium fluoride and other compounds free from gas producing substance. q. Flux is available in many grades. q. Filler wire is bare & slightly coated with copper. q. Initiation of welding is done by conventional method (by touching the w/p & keep a contact) or by keeping the high resistance material like steel wool /carbon between the w/p & Material. q. It also provide high welding speed & excellent protection. q. It is used to weld low & medium carbon steel, heat resistant steel, corrosion resistant steel, high strength steel, monel metal, nickel etc. q. Cast iron, aluminium, magnesium alloy, lead etc can not be welded.
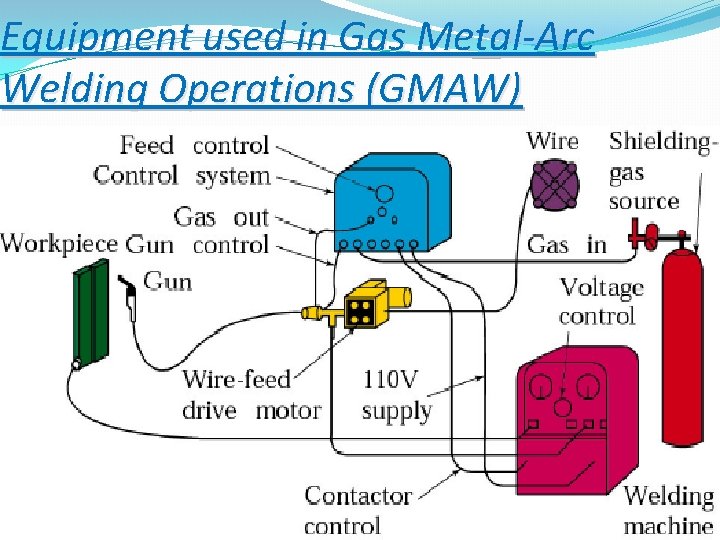
Equipment used in Gas Metal-Arc Welding Operations (GMAW)
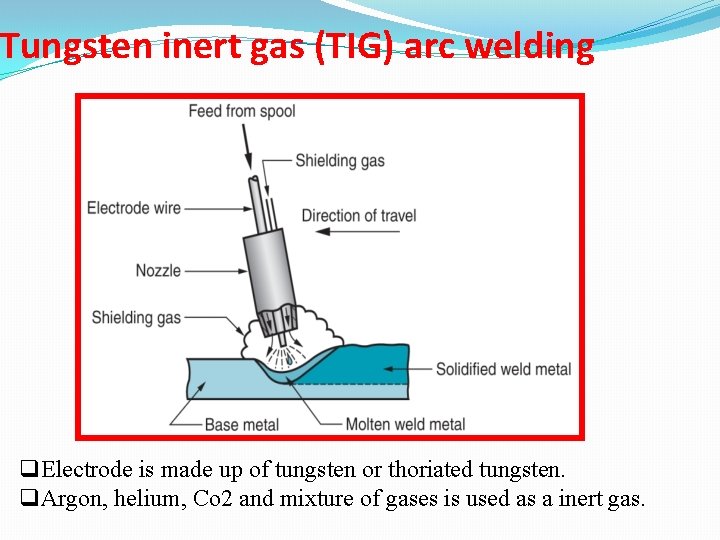
Tungsten inert gas (TIG) arc welding q. Electrode is made up of tungsten or thoriated tungsten. q. Argon, helium, Co 2 and mixture of gases is used as a inert gas.
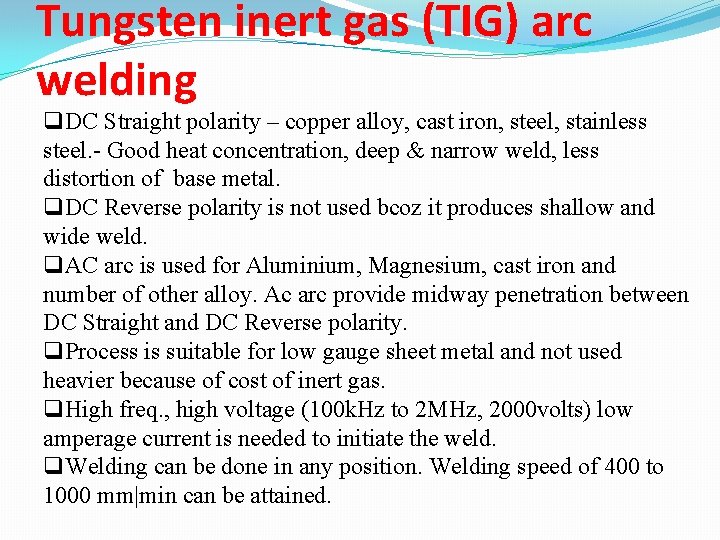
Tungsten inert gas (TIG) arc welding q. DC Straight polarity – copper alloy, cast iron, steel, stainless steel. - Good heat concentration, deep & narrow weld, less distortion of base metal. q. DC Reverse polarity is not used bcoz it produces shallow and wide weld. q. AC arc is used for Aluminium, Magnesium, cast iron and number of other alloy. Ac arc provide midway penetration between DC Straight and DC Reverse polarity. q. Process is suitable for low gauge sheet metal and not used heavier because of cost of inert gas. q. High freq. , high voltage (100 k. Hz to 2 MHz, 2000 volts) low amperage current is needed to initiate the weld. q. Welding can be done in any position. Welding speed of 400 to 1000 mm|min can be attained.
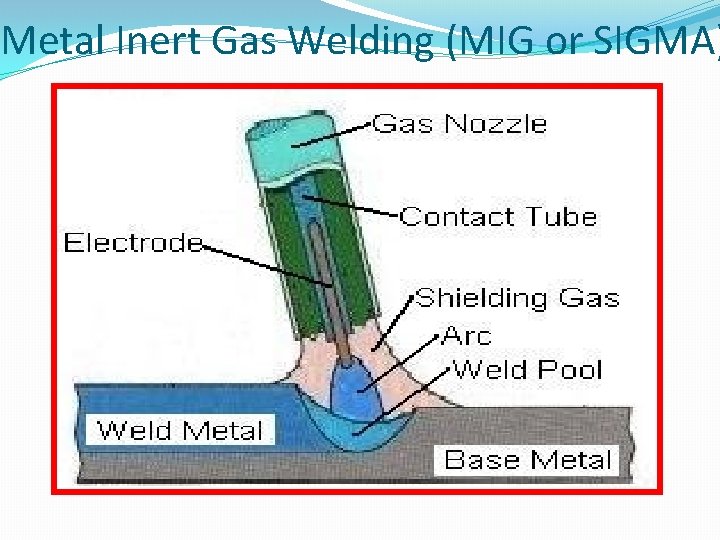
Metal Inert Gas Welding (MIG or SIGMA)
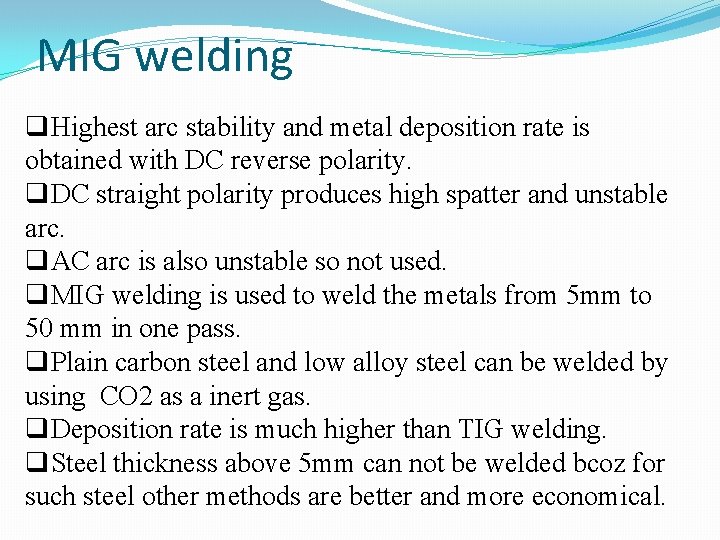
MIG welding q. Highest arc stability and metal deposition rate is obtained with DC reverse polarity. q. DC straight polarity produces high spatter and unstable arc. q. AC arc is also unstable so not used. q. MIG welding is used to weld the metals from 5 mm to 50 mm in one pass. q. Plain carbon steel and low alloy steel can be welded by using CO 2 as a inert gas. q. Deposition rate is much higher than TIG welding. q. Steel thickness above 5 mm can not be welded bcoz for such steel other methods are better and more economical.
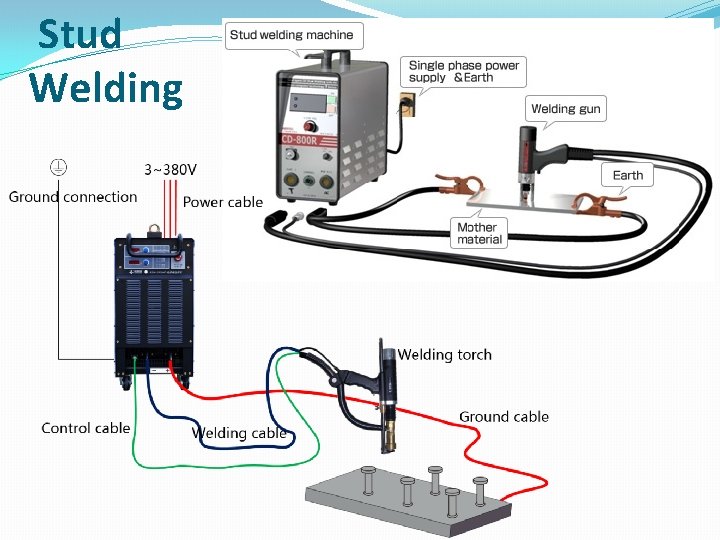
Stud Welding
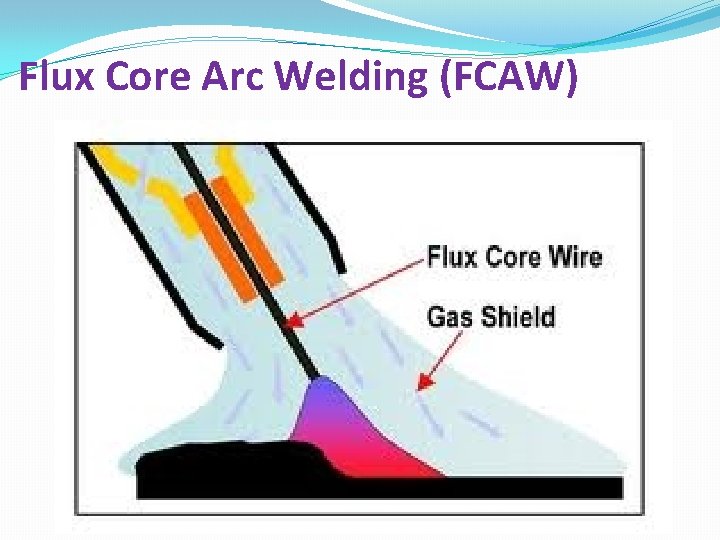
Flux Core Arc Welding (FCAW)
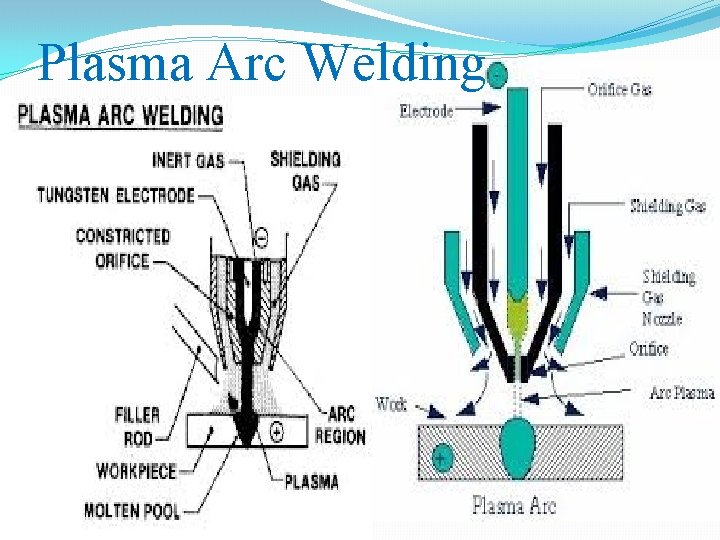
Plasma Arc Welding
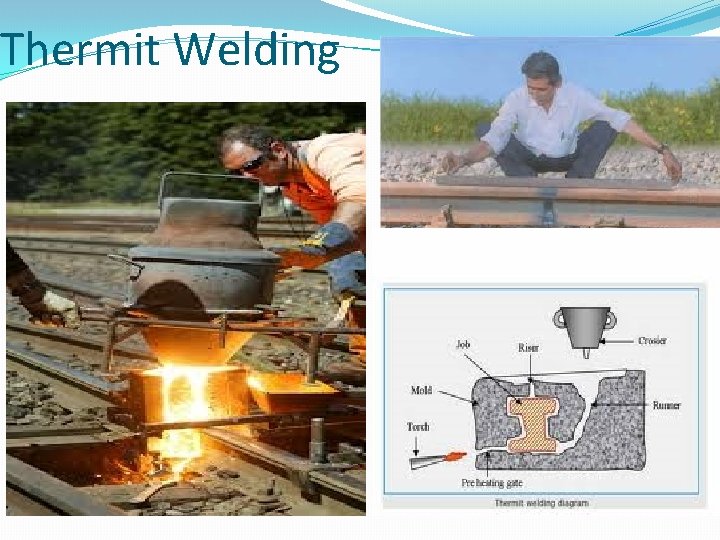
Thermit Welding
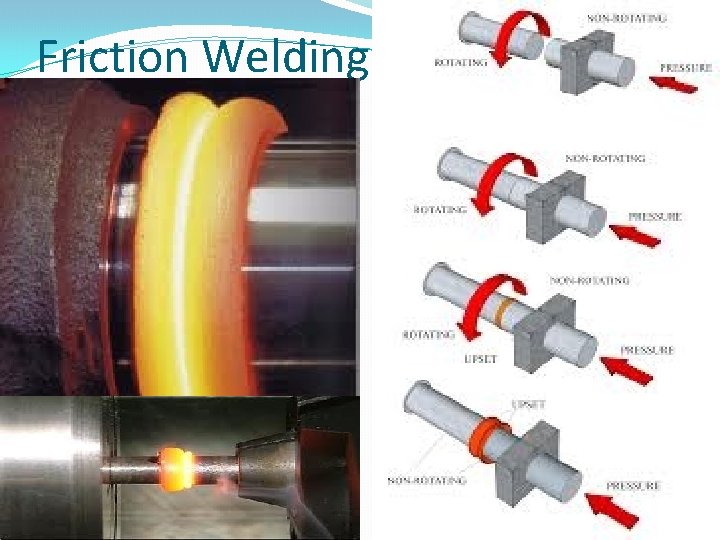
Friction Welding
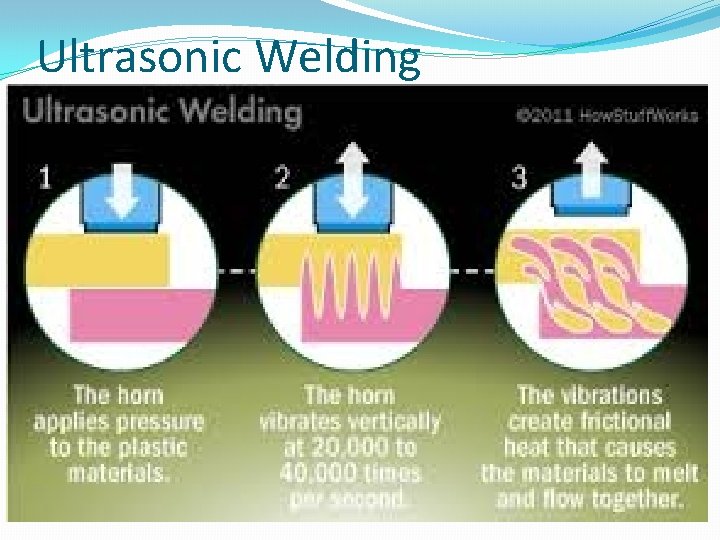
Ultrasonic Welding
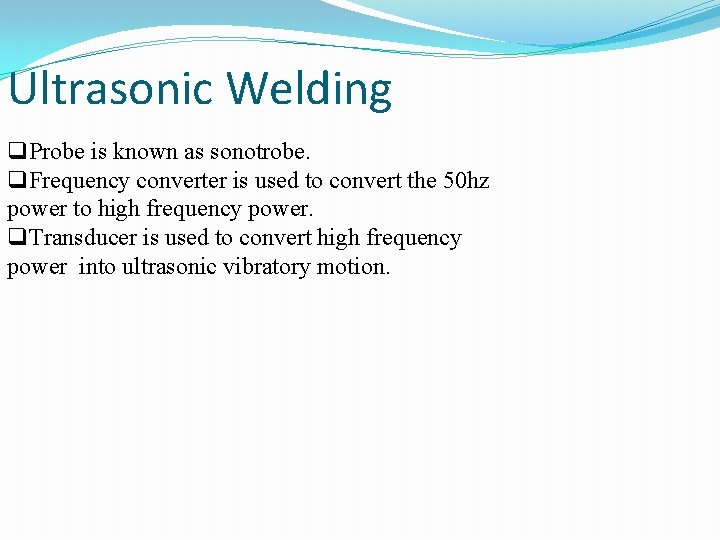
Ultrasonic Welding q. Probe is known as sonotrobe. q. Frequency converter is used to convert the 50 hz power to high frequency power. q. Transducer is used to convert high frequency power into ultrasonic vibratory motion.
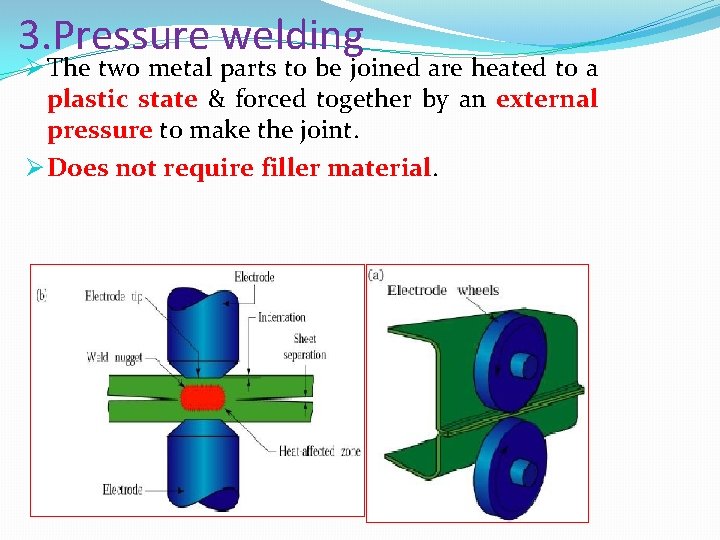
3. Pressure welding Ø The two metal parts to be joined are heated to a plastic state & forced together by an external pressure to make the joint. Ø Does not require filler material.
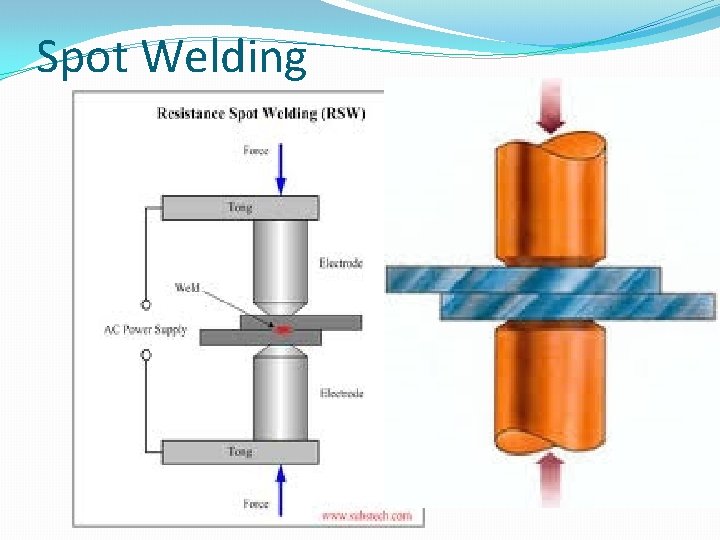
Spot Welding
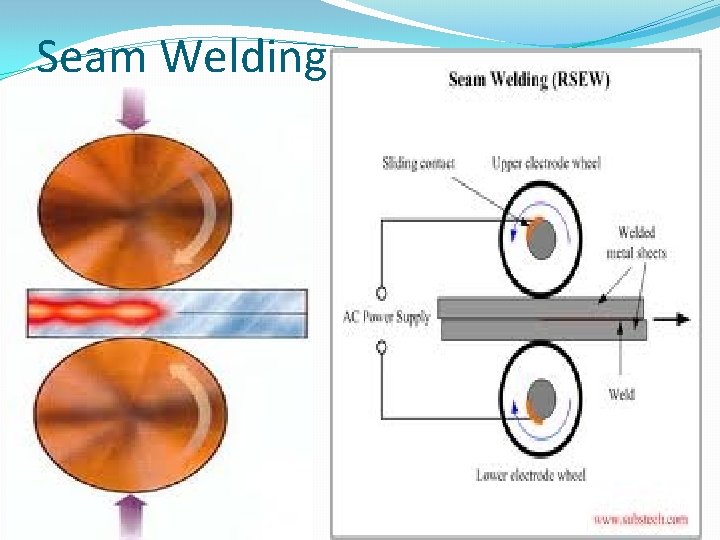
Seam Welding
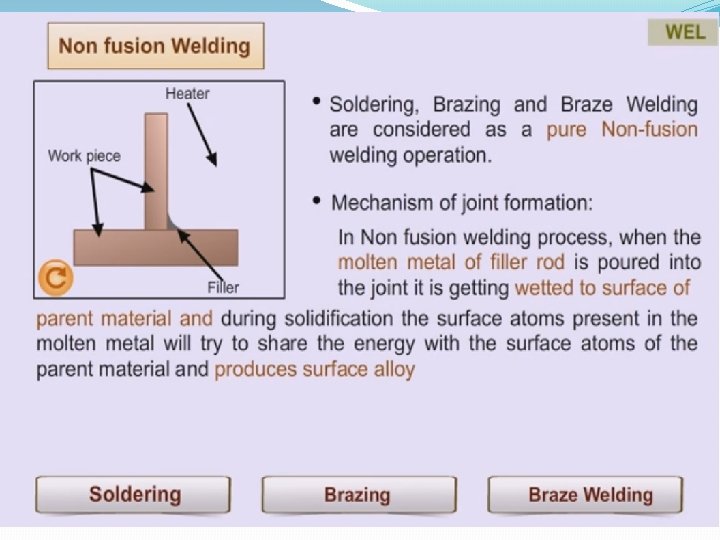

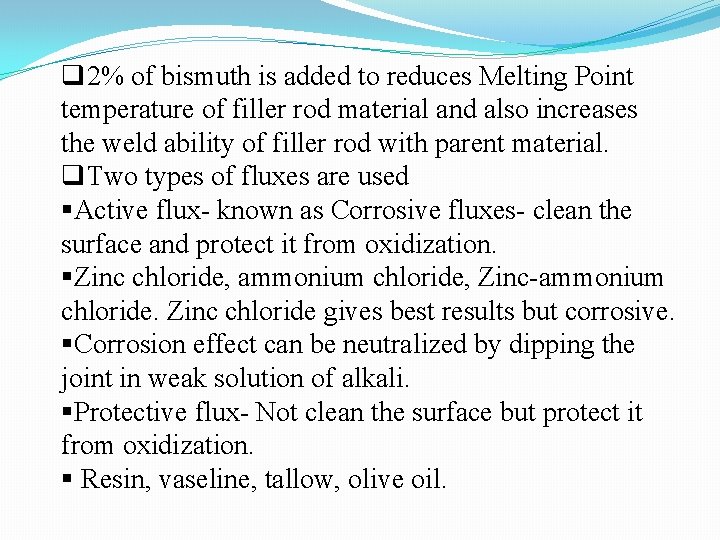
q 2% of bismuth is added to reduces Melting Point temperature of filler rod material and also increases the weld ability of filler rod with parent material. q. Two types of fluxes are used §Active flux- known as Corrosive fluxes- clean the surface and protect it from oxidization. §Zinc chloride, ammonium chloride, Zinc-ammonium chloride. Zinc chloride gives best results but corrosive. §Corrosion effect can be neutralized by dipping the joint in weak solution of alkali. §Protective flux- Not clean the surface but protect it from oxidization. § Resin, vaseline, tallow, olive oil.
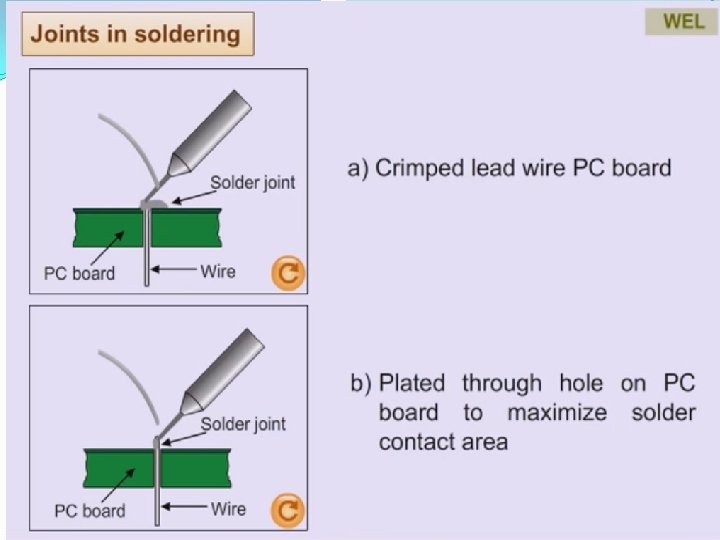
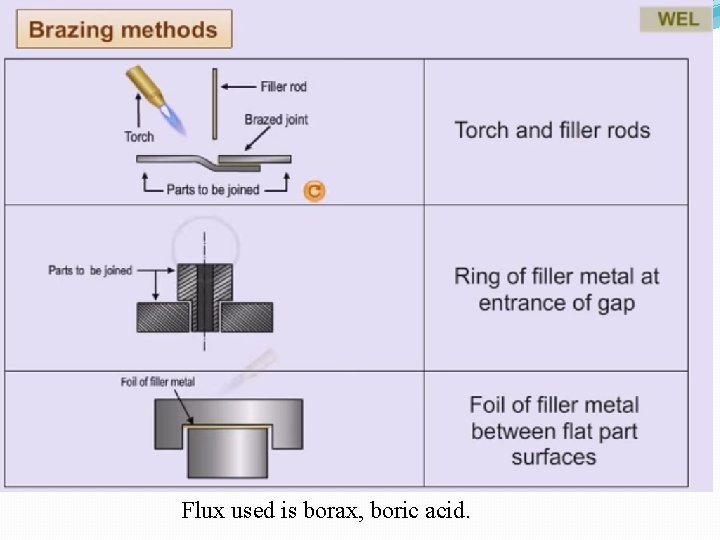
Flux used is borax, boric acid.
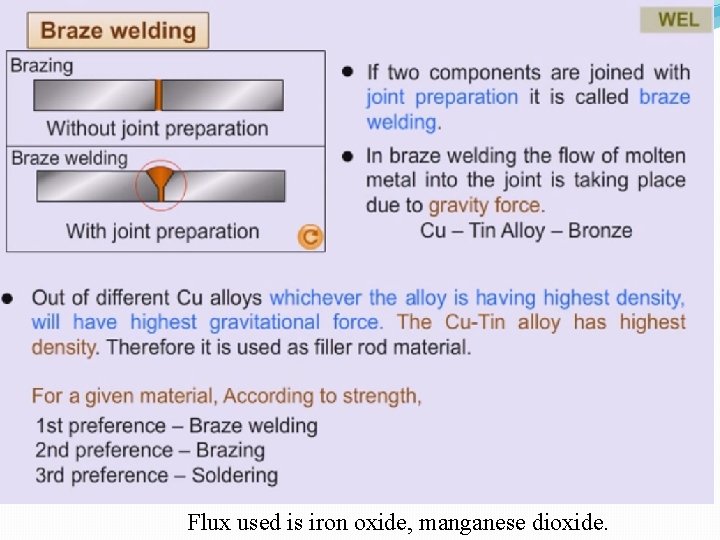
Flux used is iron oxide, manganese dioxide.
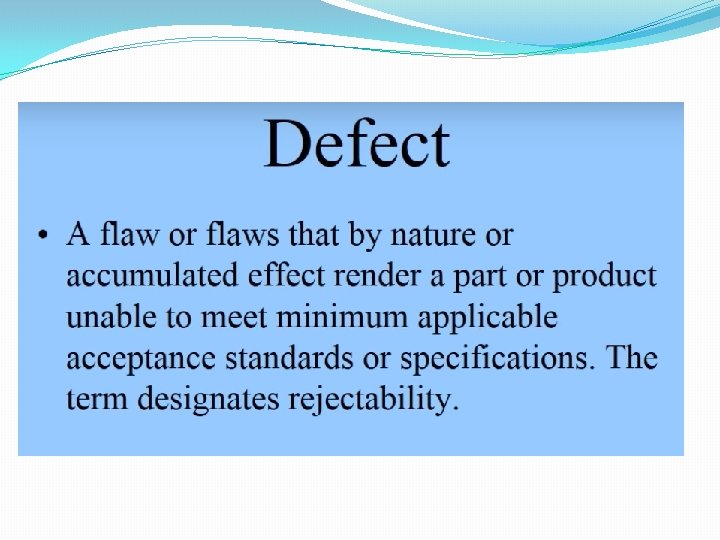
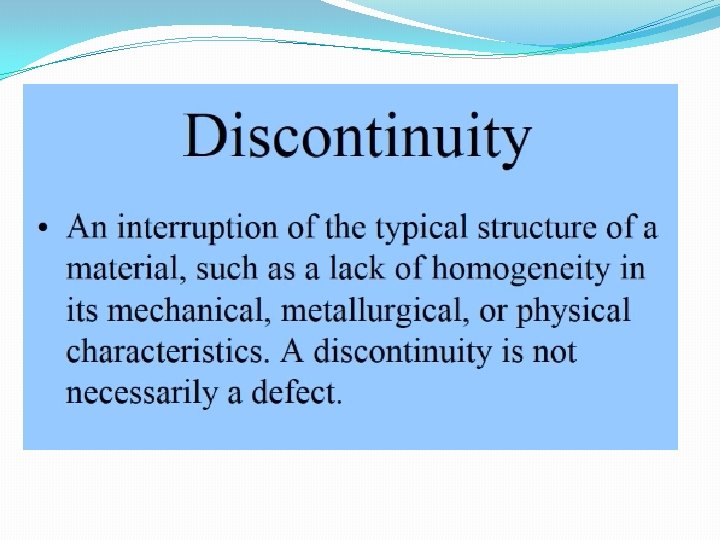
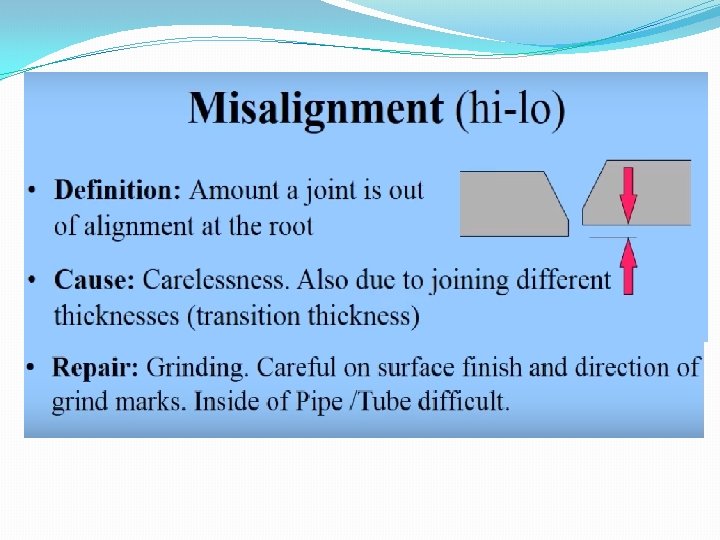
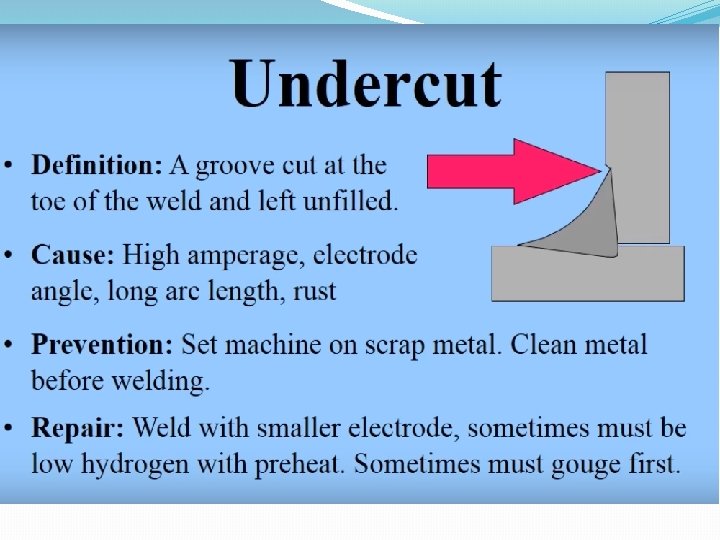
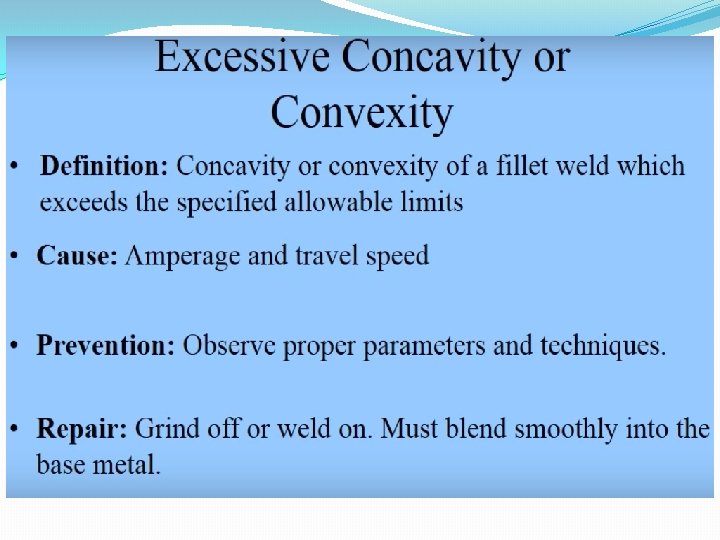
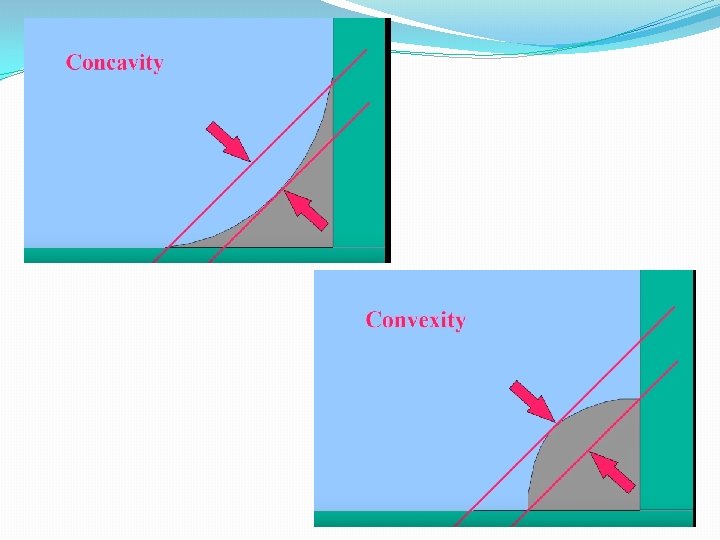
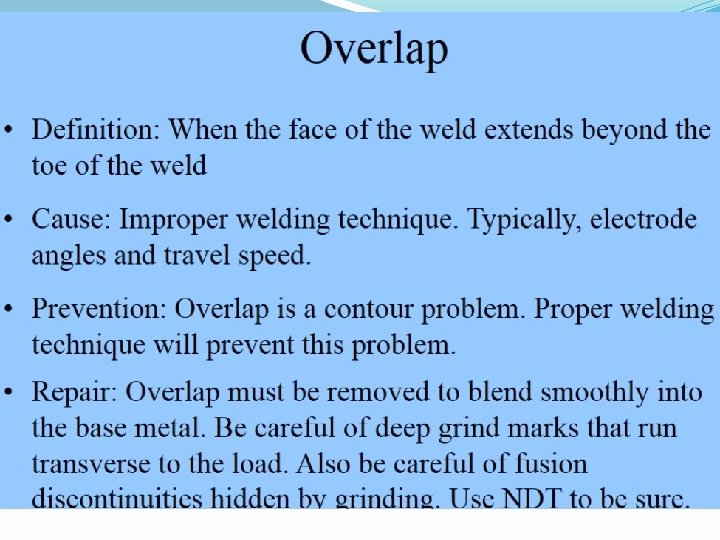
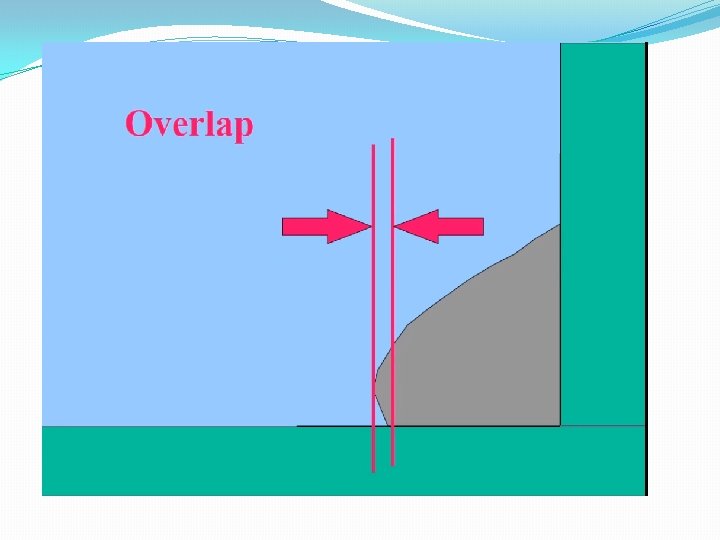
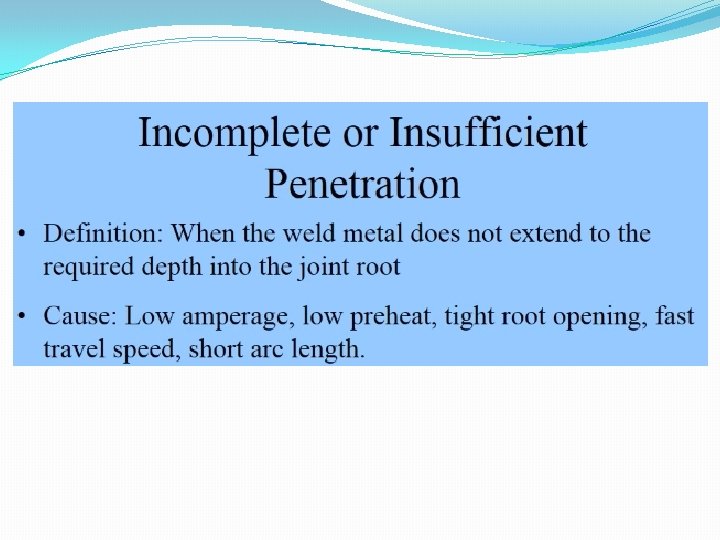
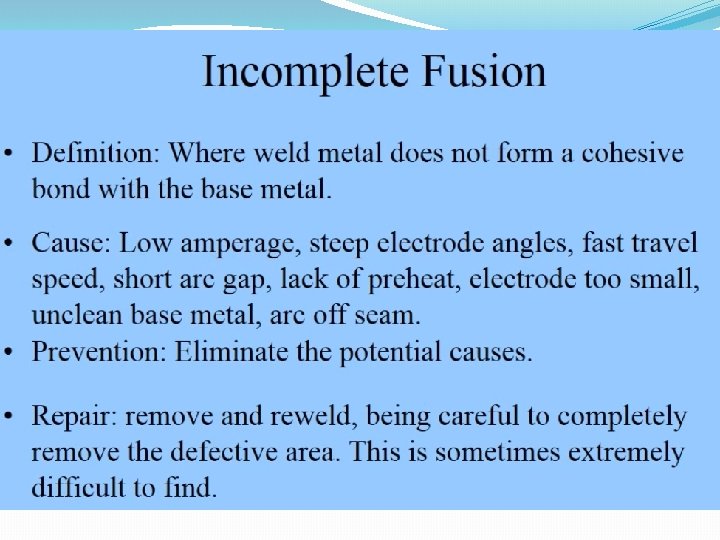
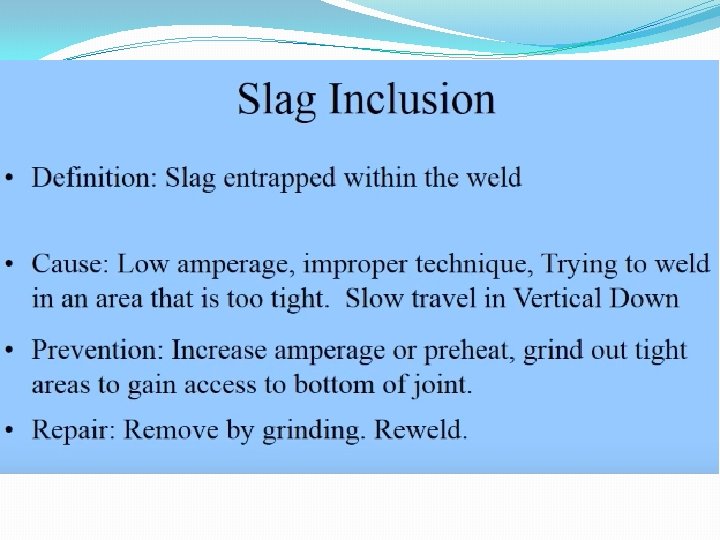
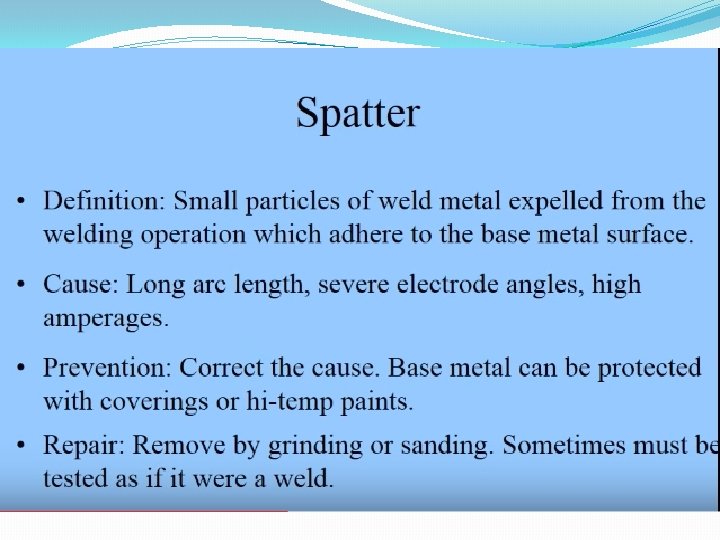
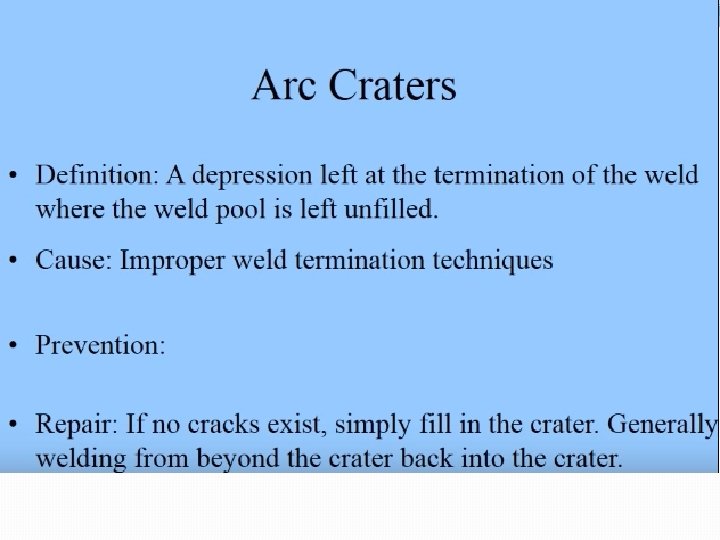
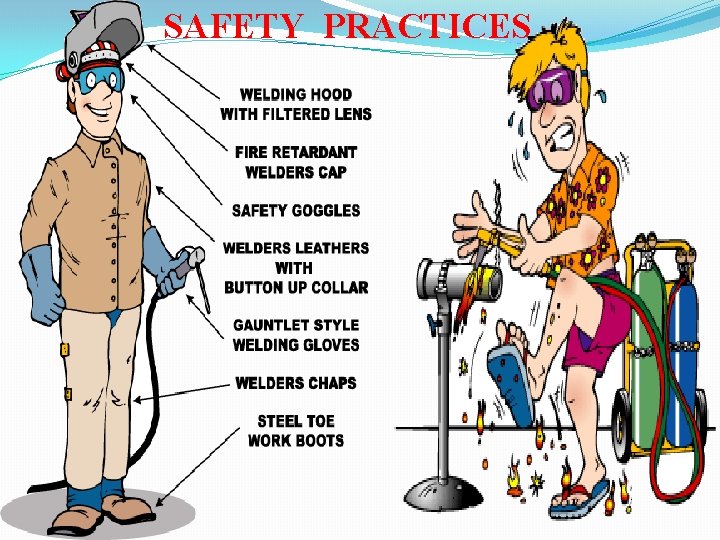
SAFETY PRACTICES
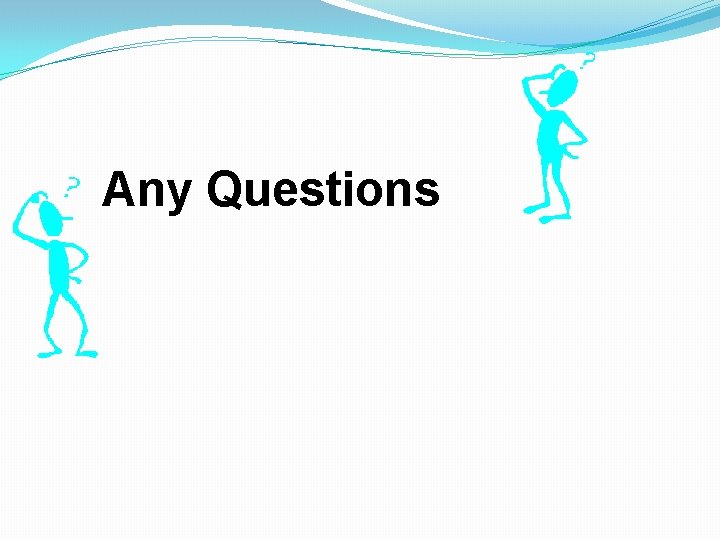
Any Questions
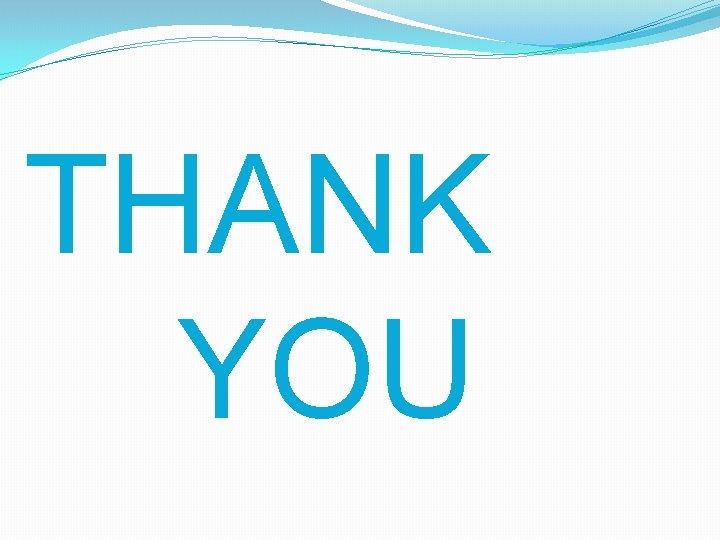
THANK YOU
Mechanical fastening
Types of temporary joint
Concurrent in os
Difference between bulk deformation and sheet metal forming
Conduction and convection venn diagram
Metals and non metals
Difference between metal oxides and non metal oxides
Melting point of diamond
Hot nwell
Nonmetals uses
Substances
Metals react with nonmetals to form ionic compounds by
P
Metal and non metal definition
Características de los metales de la tabla periódica
Examples of non metal
Hidrgeno
Permanent joining
Unit 10, unit 10 review tests, unit 10 general test
10 types of morphological processes
Paned down
Seam sheet metal
Truncated cylinder development
Traditional wood joints
Mcsr joining time rules in marathi
Welding disadvantages
Welcome and thank you for joining us
Welcome and thank you for joining us
Reproductive system vocabulary
Rafsanjani-soga secondary school images
Group dynamics in organisational behaviour
Joining word
Proses penyambungan
Reasons for joining groups in organisational behaviour
Subordinating conjunctions example
Dlle sws project report
Imaginary line joining points of equal elevation
Cardboard canoe template
Thank you for joining our webinar
Joining together as a team to improve the quality
What is a ctso and what are the benefits of joining
Subordinating.conjunction
Joining clauses
Thank you for joining the webinar
Join sentences using relative pronoun
Joining a mat
Process of joining two metals
Welcome thanks for joining us
Joining clauses with if and when
Join with relative clause
Mechanical joining methods
Join
Fccla human scavenger hunt answers
Joining us today
Thank you for joining us good evening
Thank you for joining us good evening
Non-homologous end joining
An imaginary line joining the points of equal elevation
Nuclear institute membership
Thank you for joining us today
Joining means
Neighbor-joining method
Keva joining
Joining manufacturing process definition
Joining grammar
Joining grammar
Chemical joining
Benefits of joining fccla
Joining together group theory and group skills
You are on a three lane motorway towing a trailer
Itrcs
Welcome thanks for joining us
Metode pembiayaan semi langsung
Right triangle trigonometry examples
English unit conversions
Unit test unit test review algebra 2
Contoh kebutuhan mengitung unit cos unit kerja rekam medis
Unit process and unit operation
Difference between unit process and unit operation
Setiap unit akuntansi dianggap sebagai unit yang mandiri
Proximal processes
Coinage in morphology