MANUFACTURING SYSTEMS AND AUTOMATION CHAPTER 10 DR SHALIZA
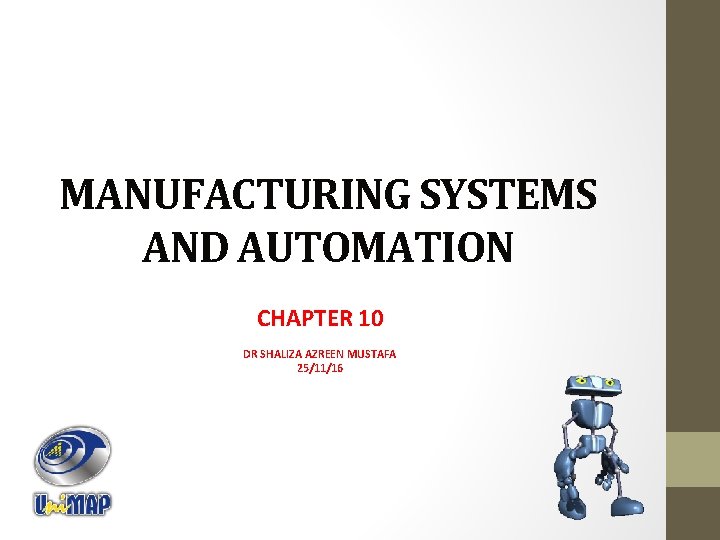
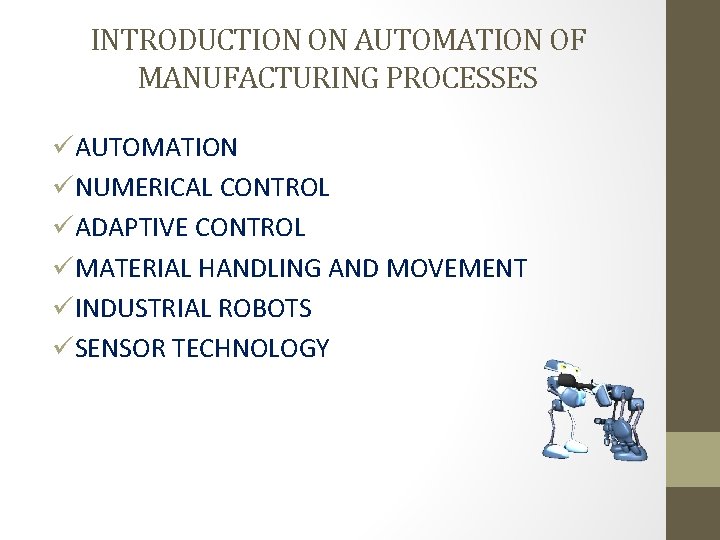
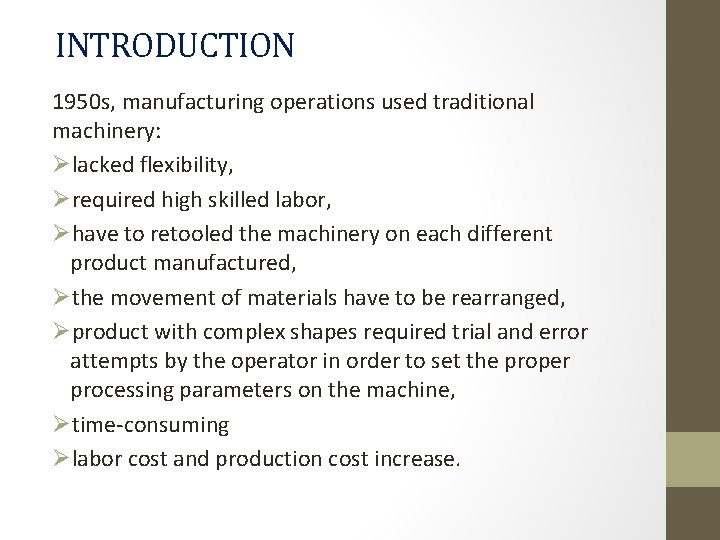
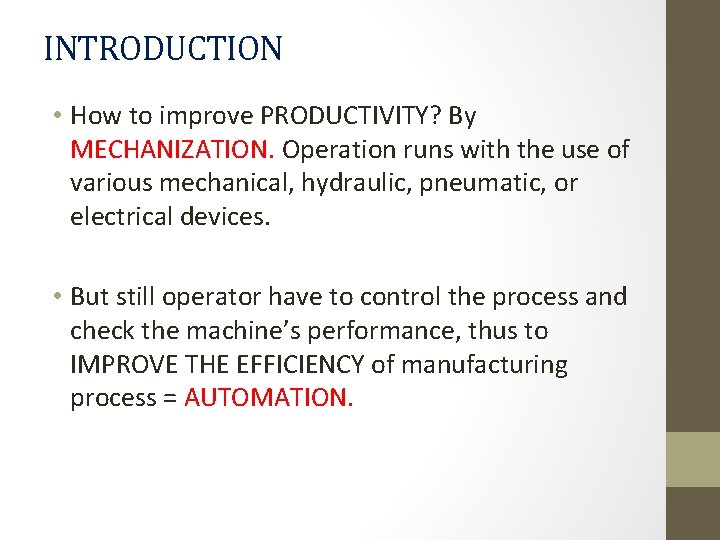
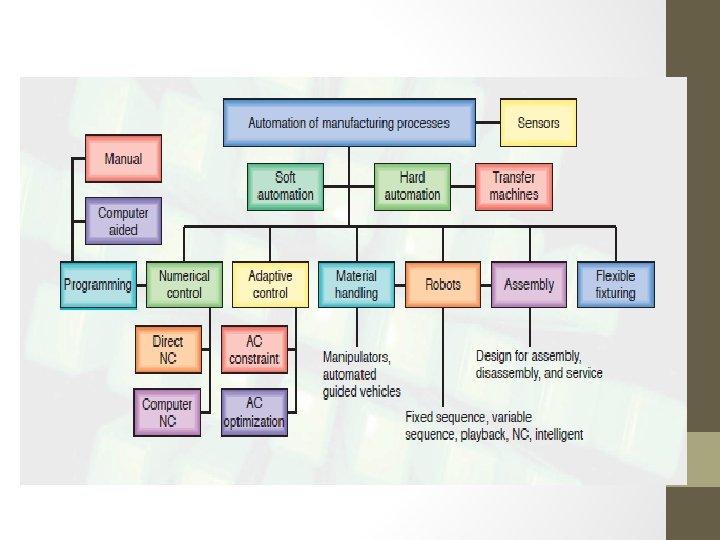
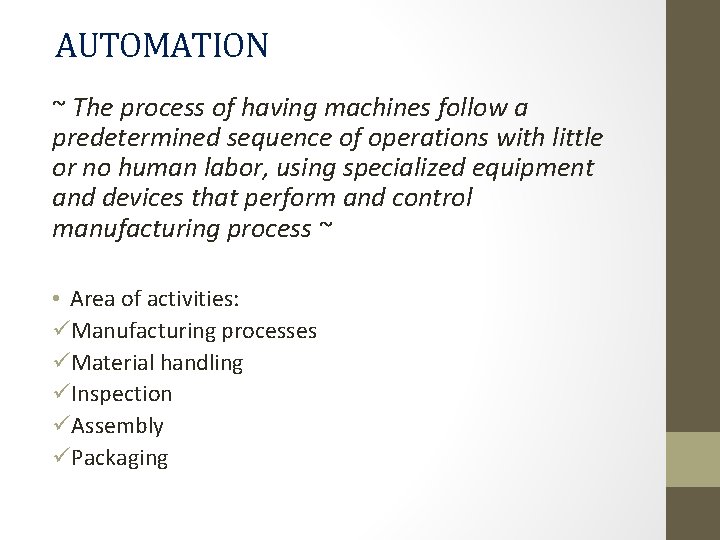
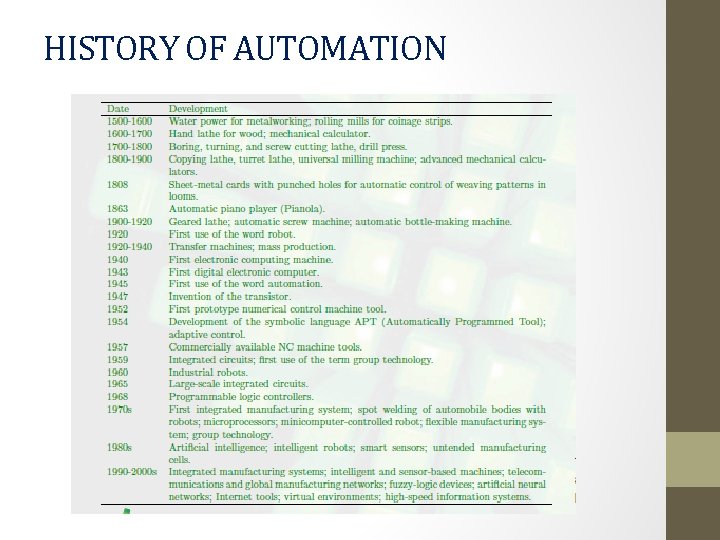
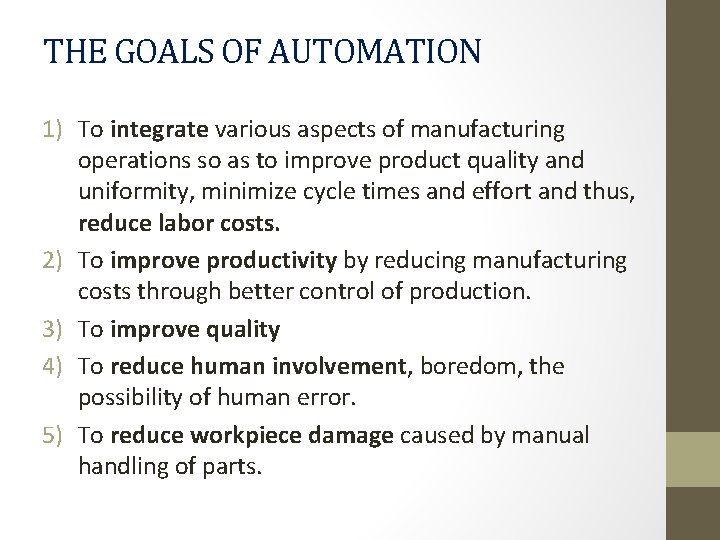
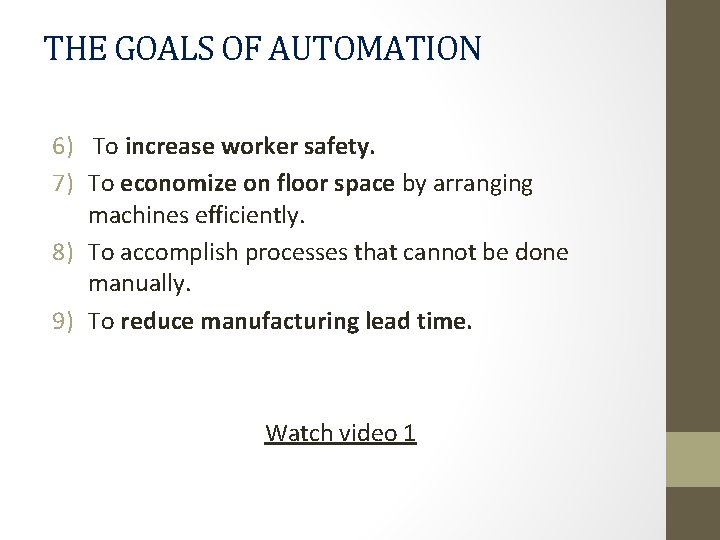
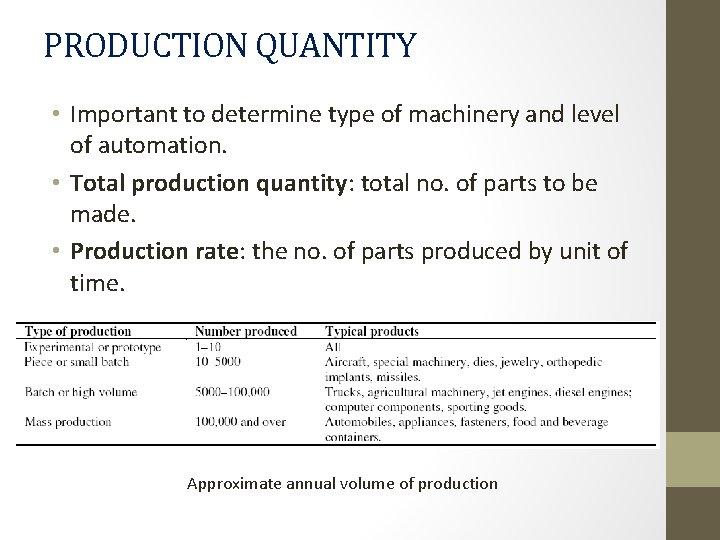
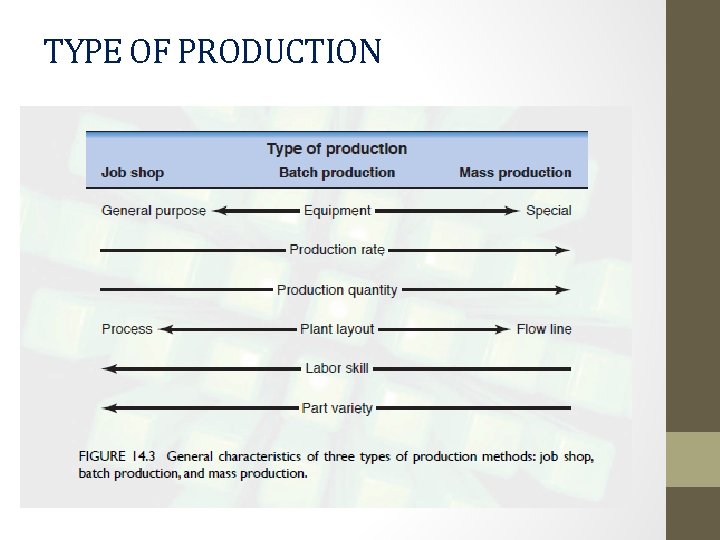
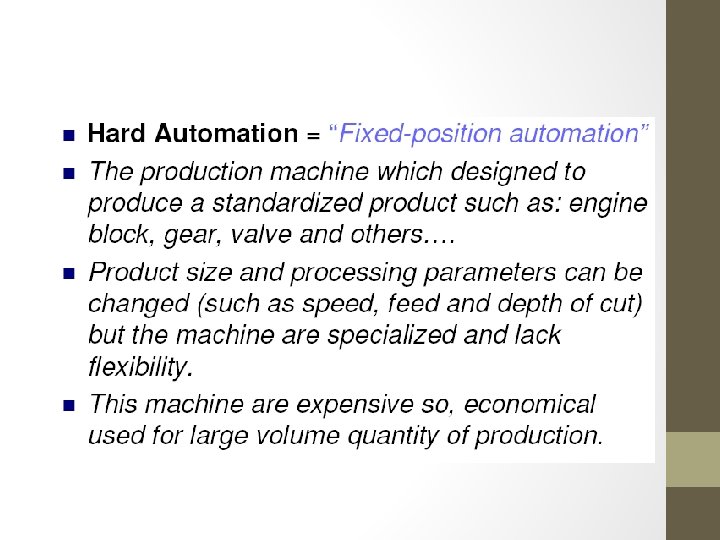
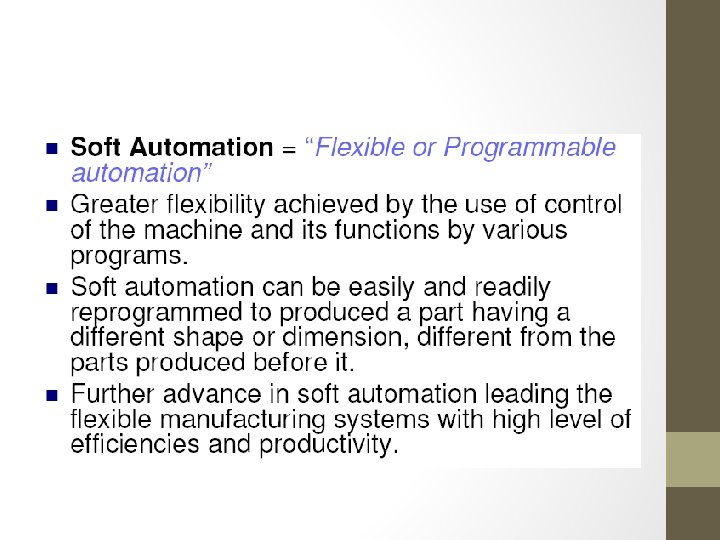
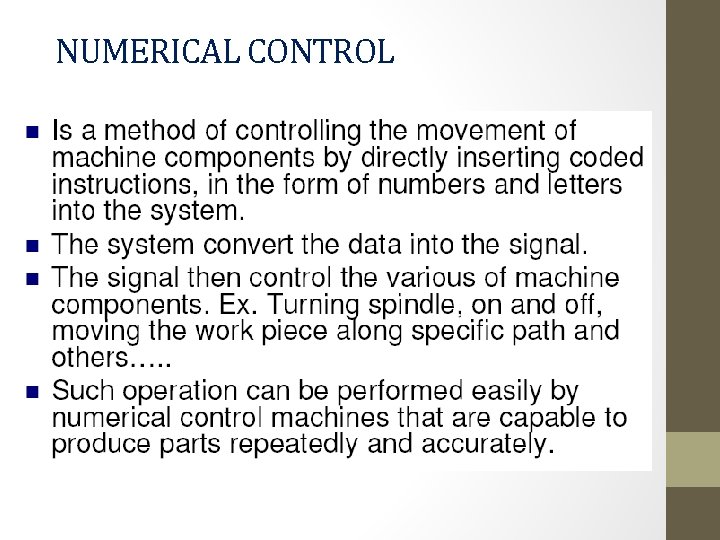
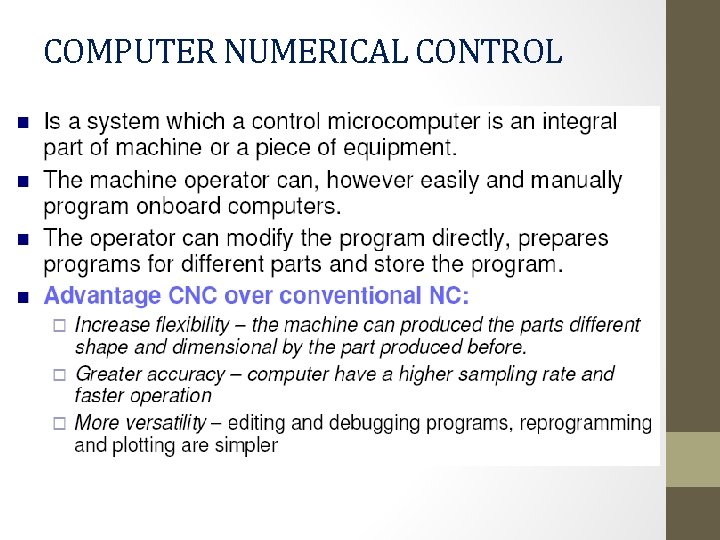
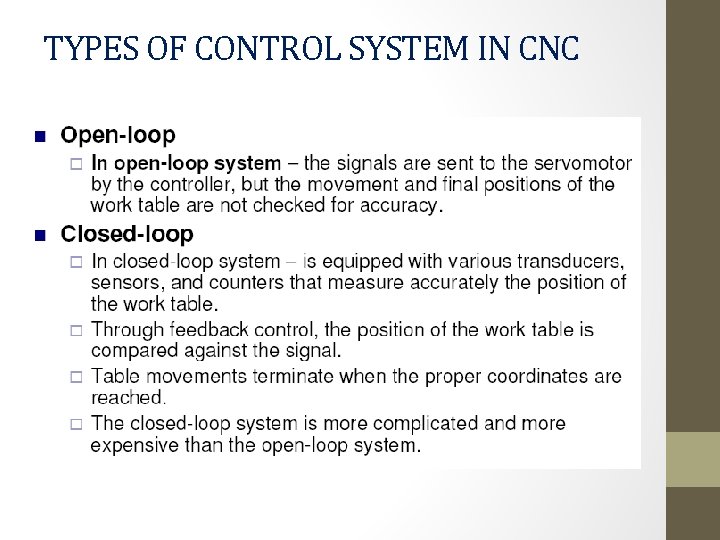
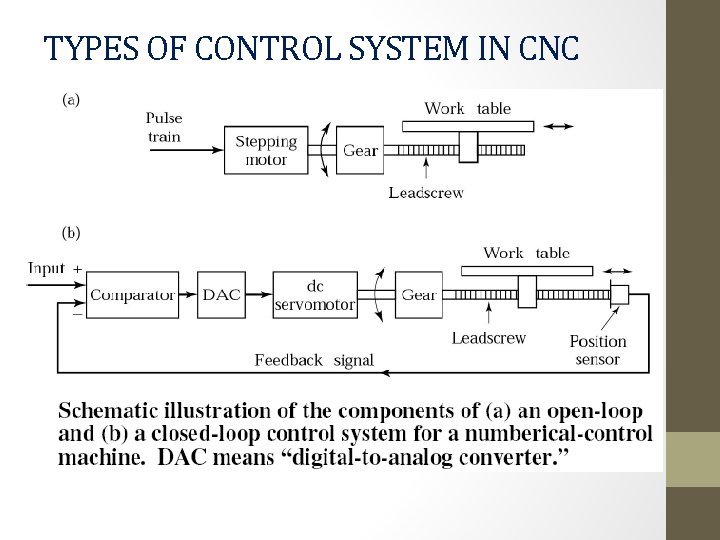
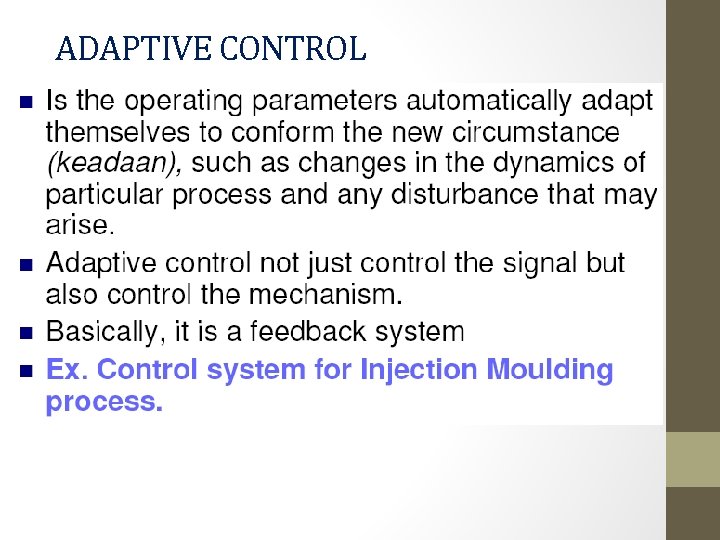
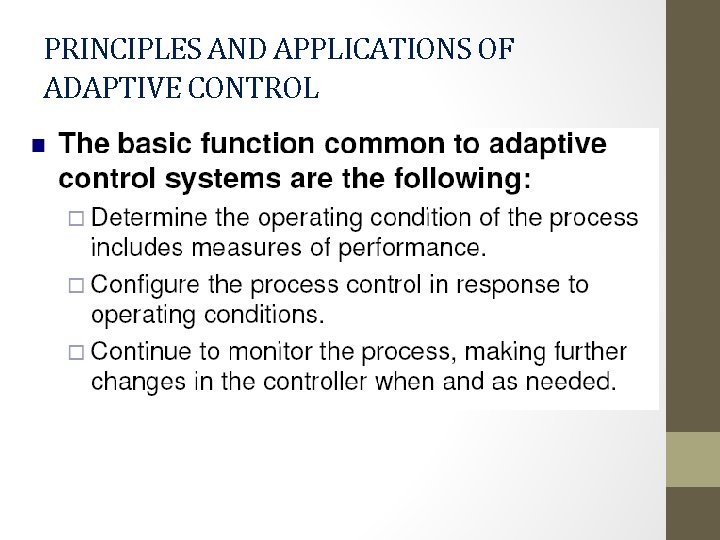
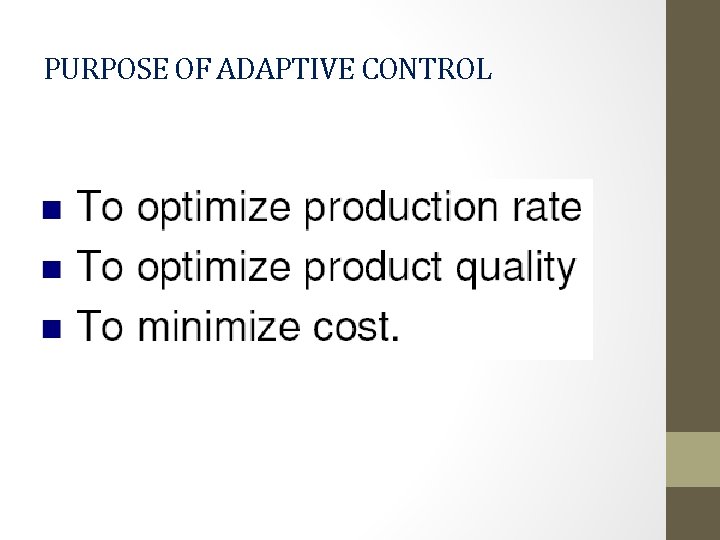
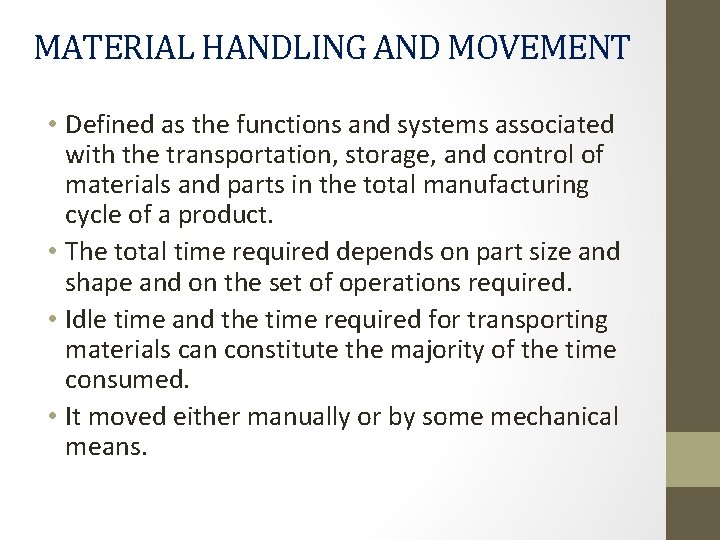
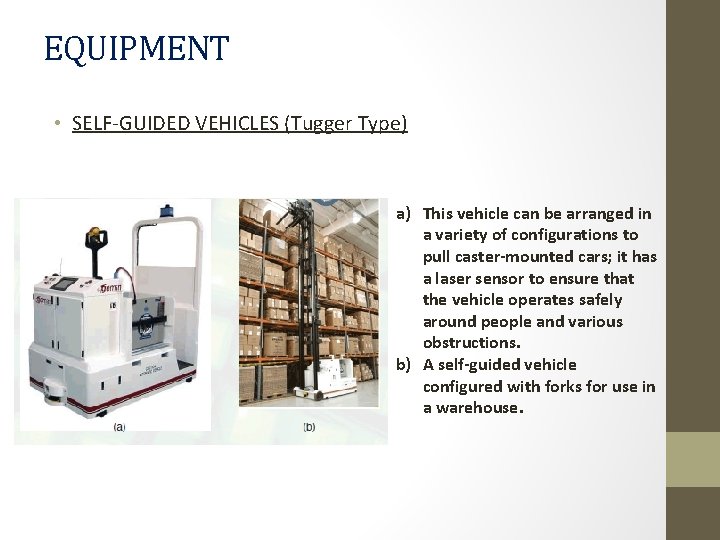

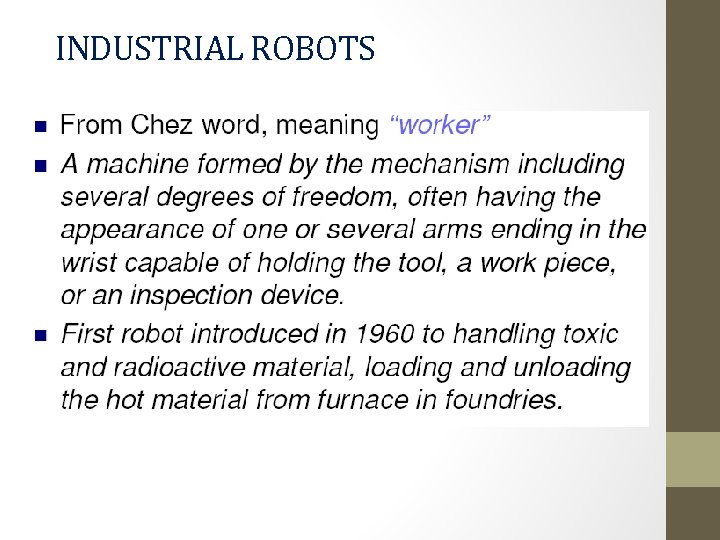
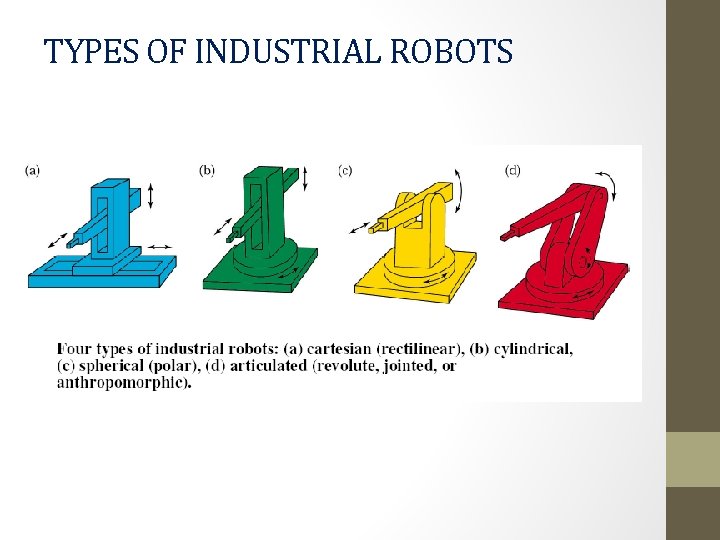

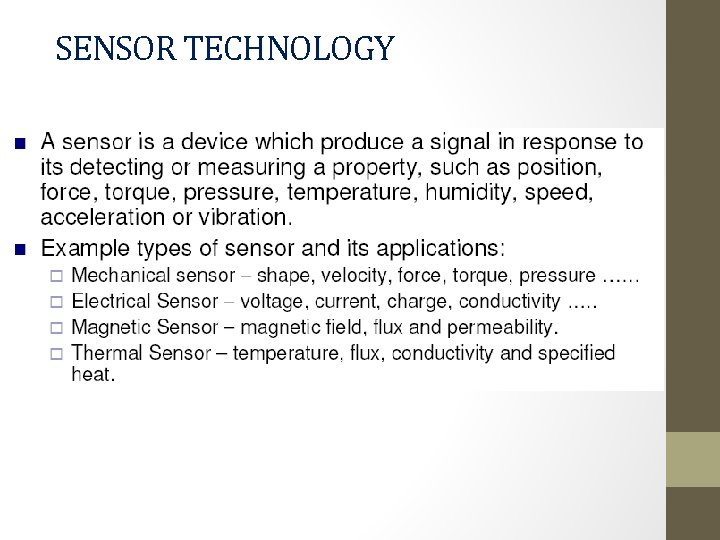
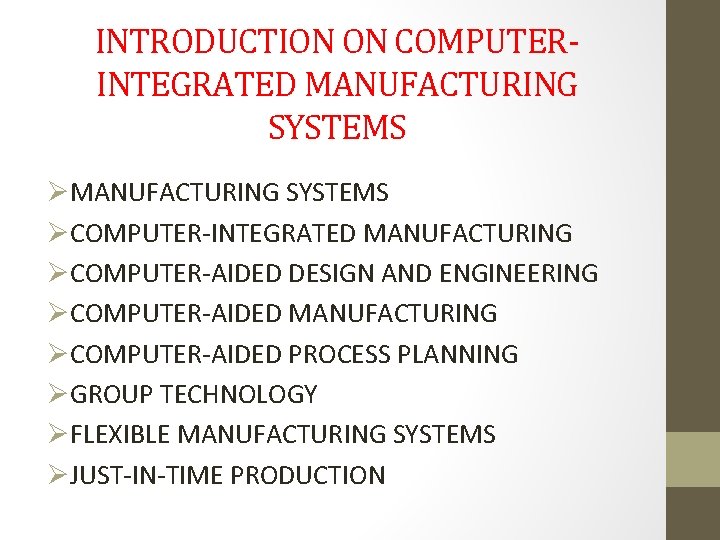
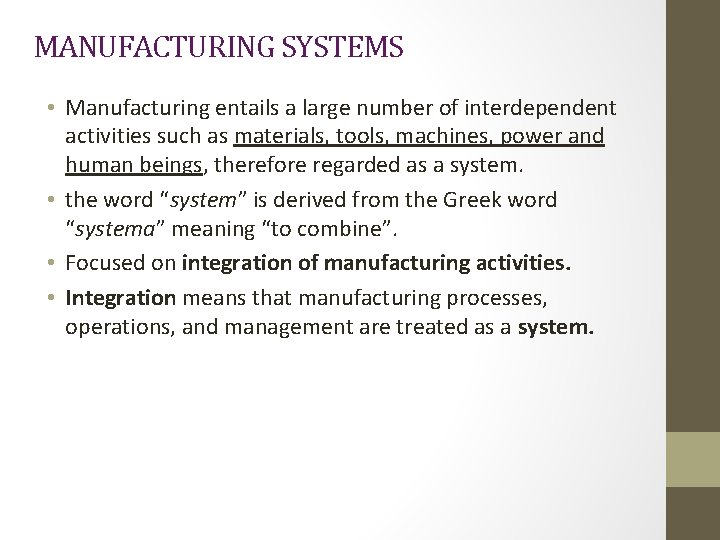
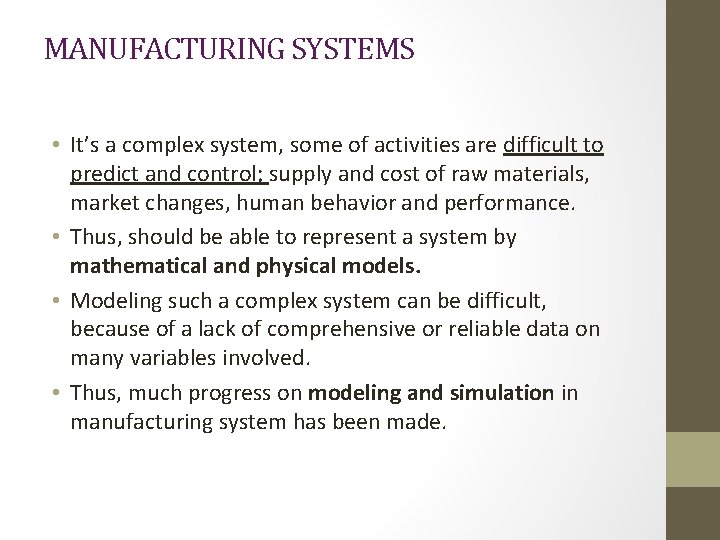
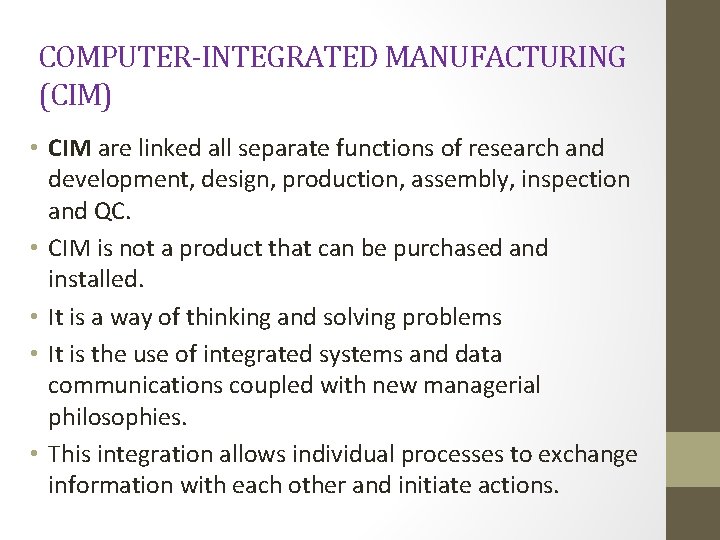
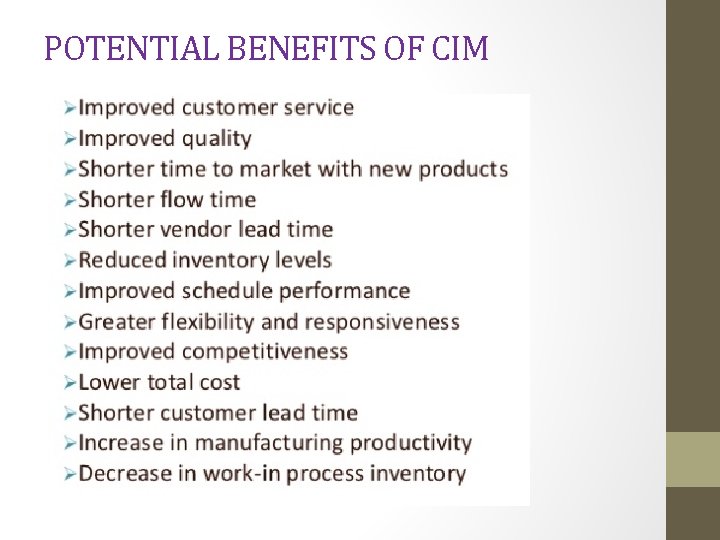
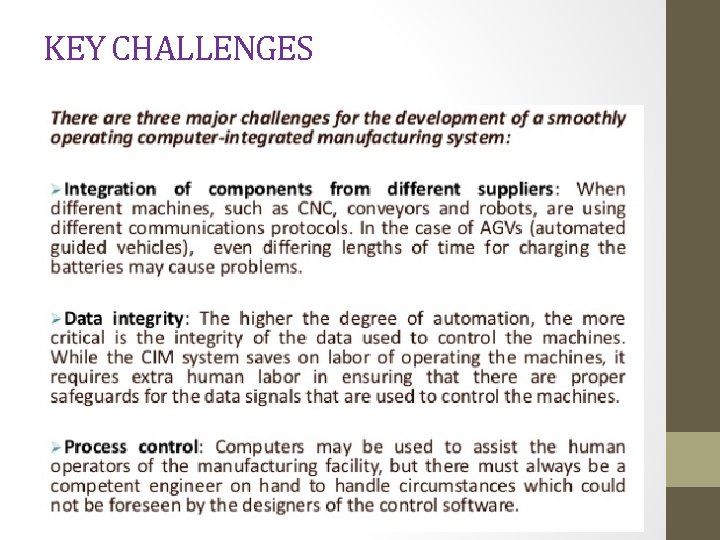
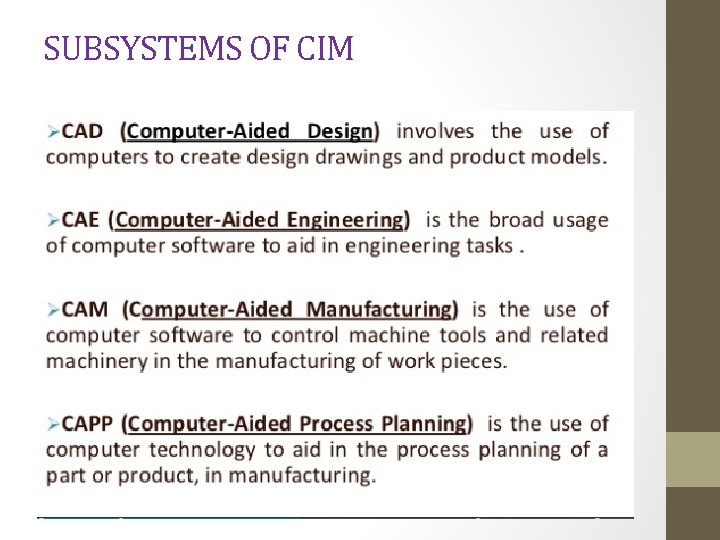
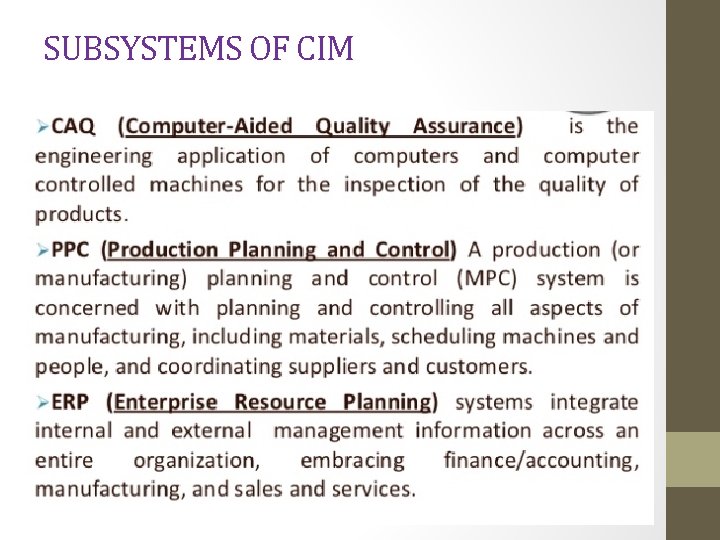
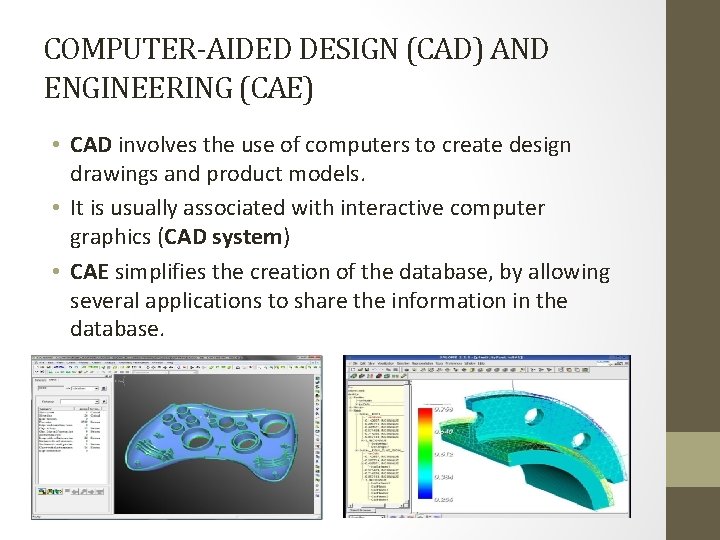
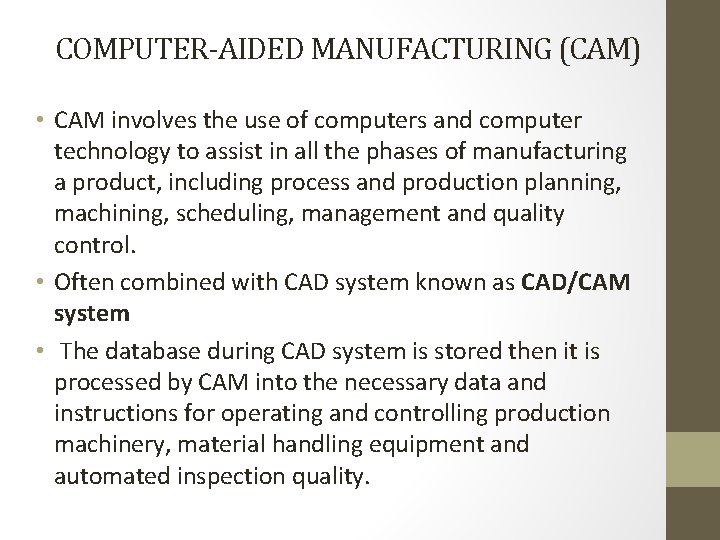
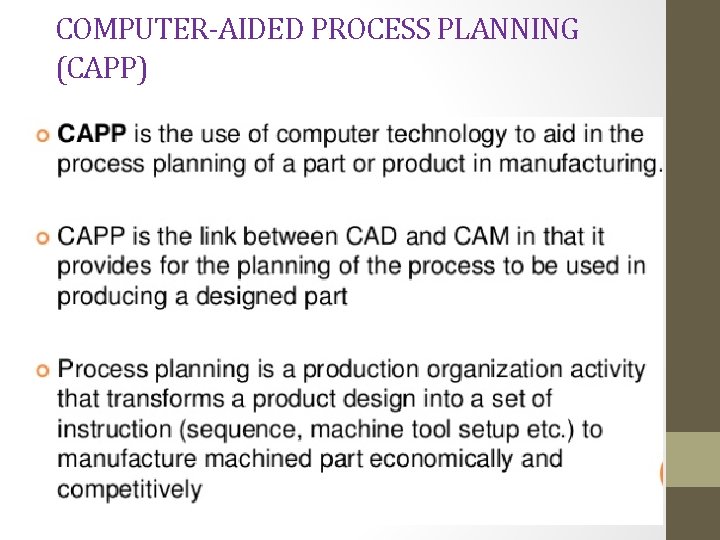
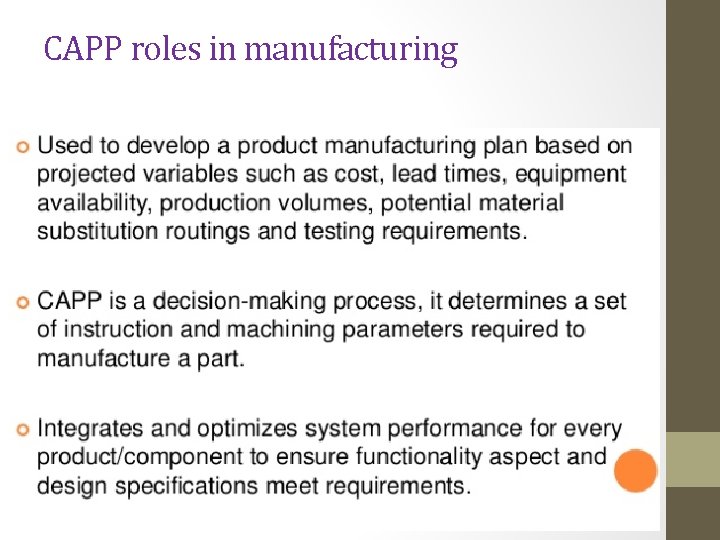
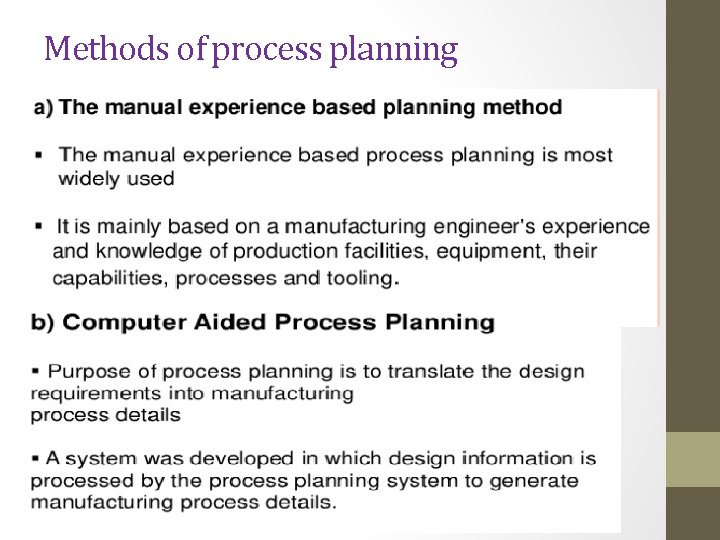
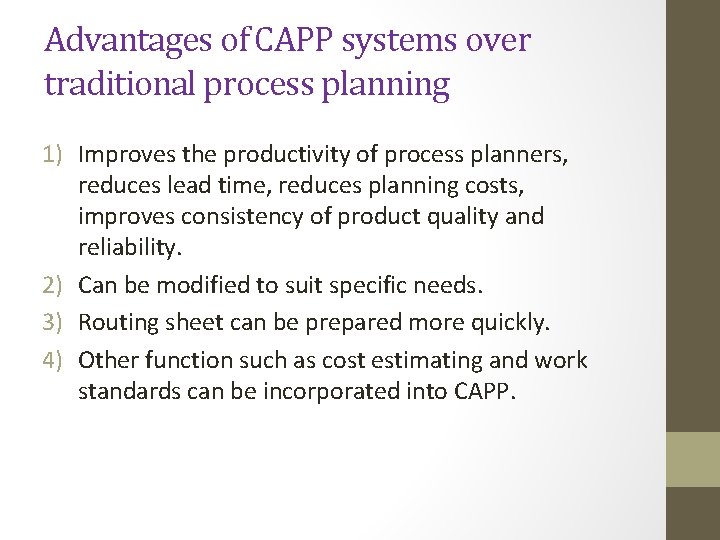
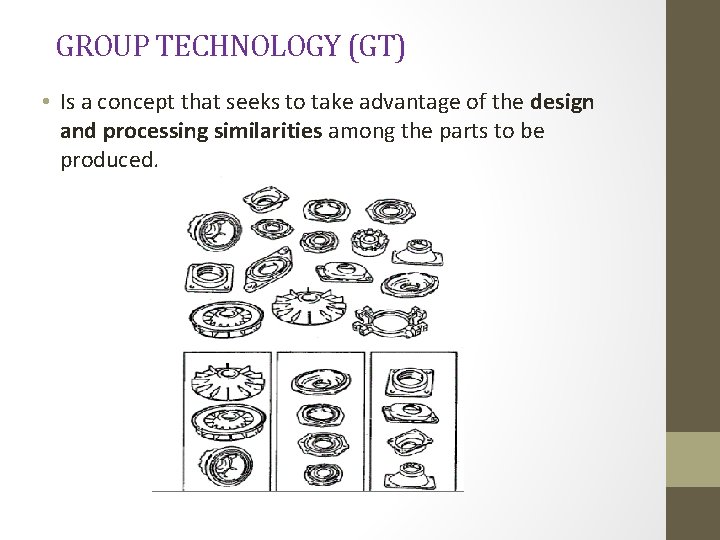
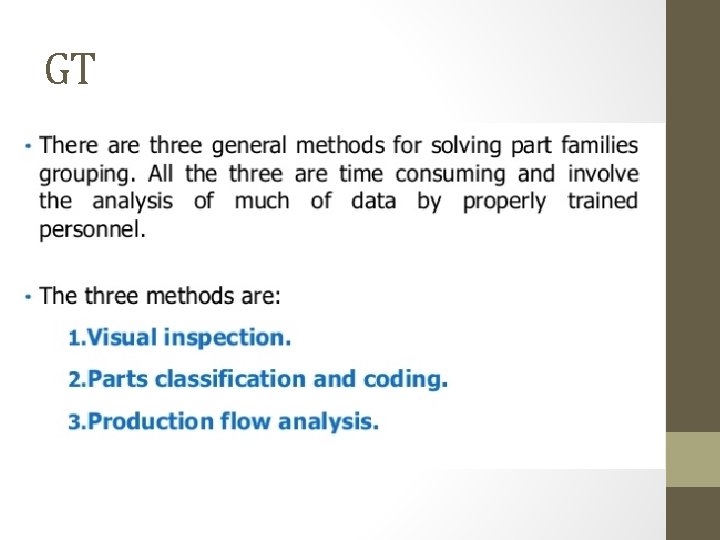
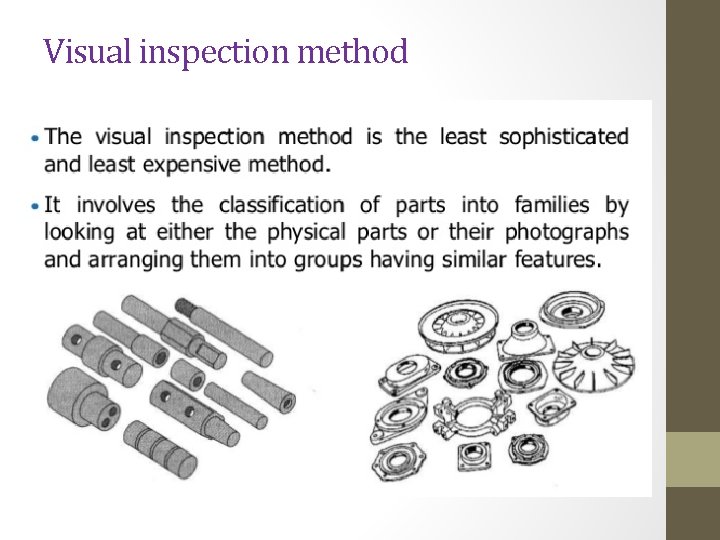
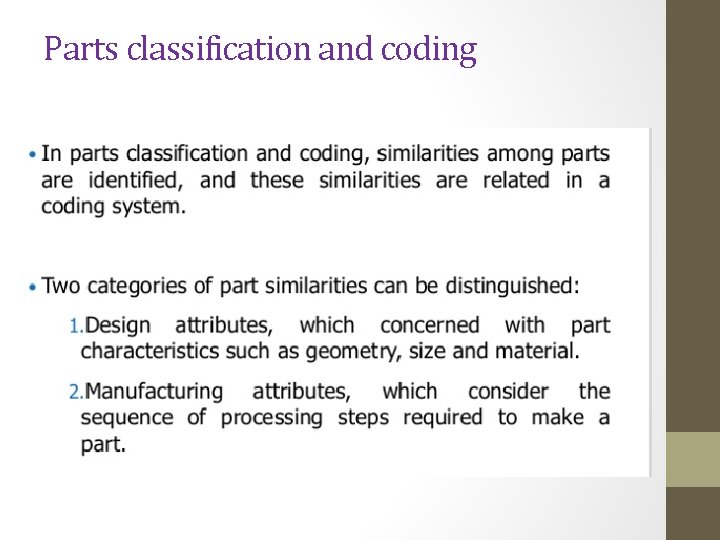

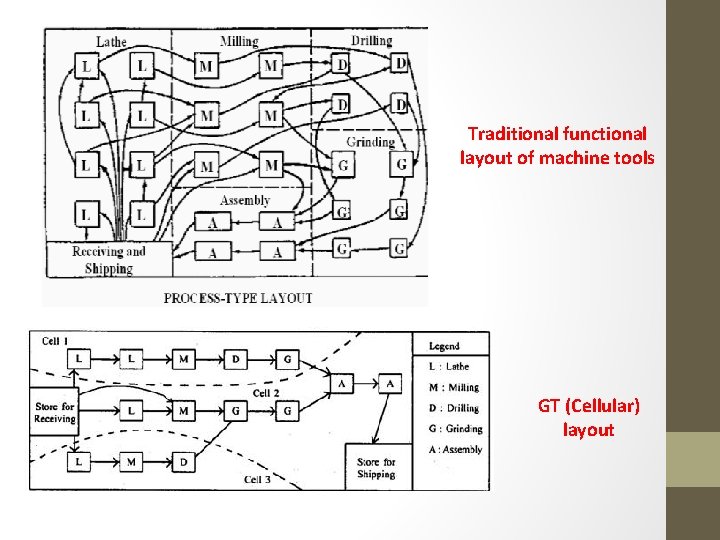
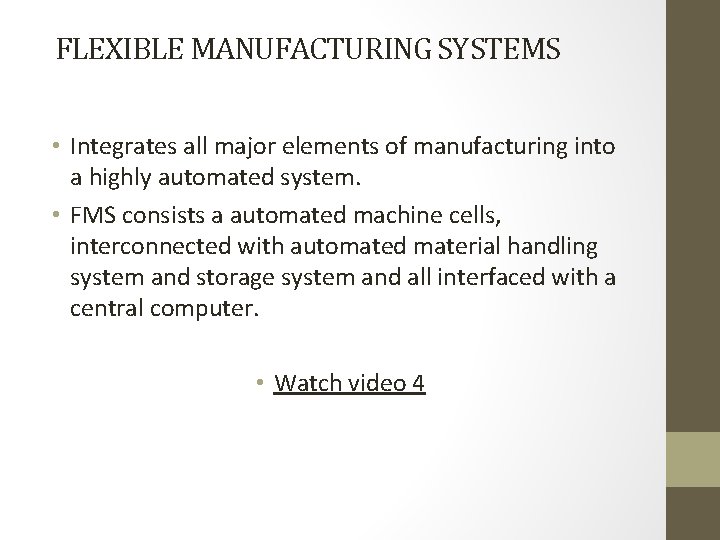
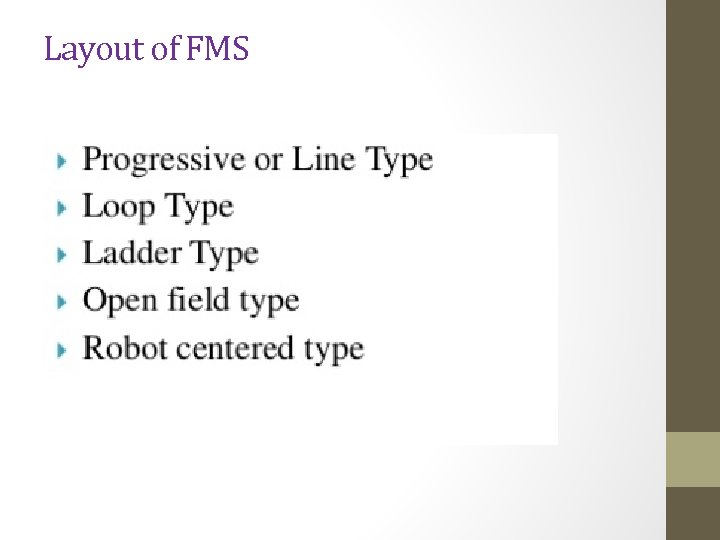
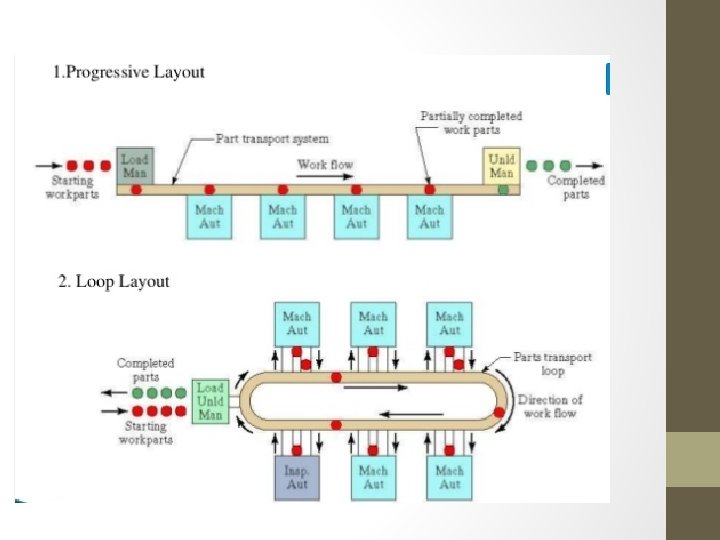

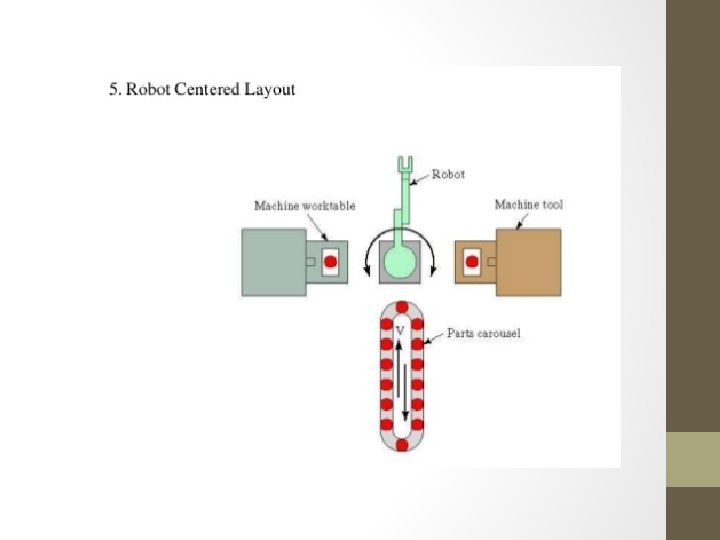
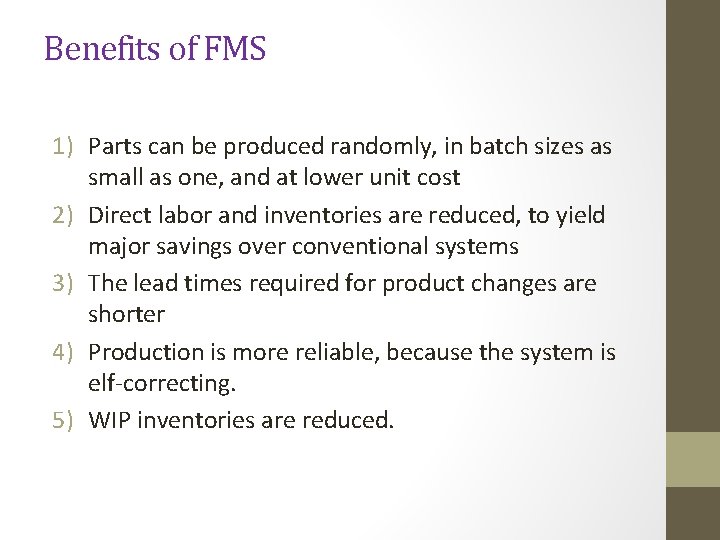
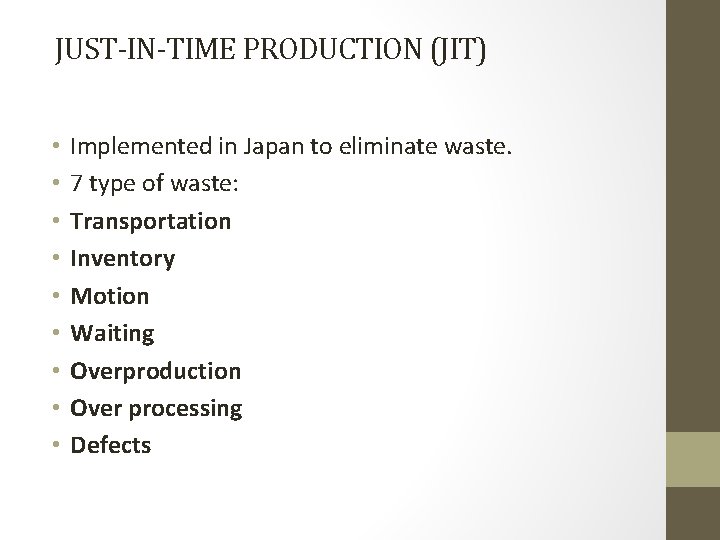
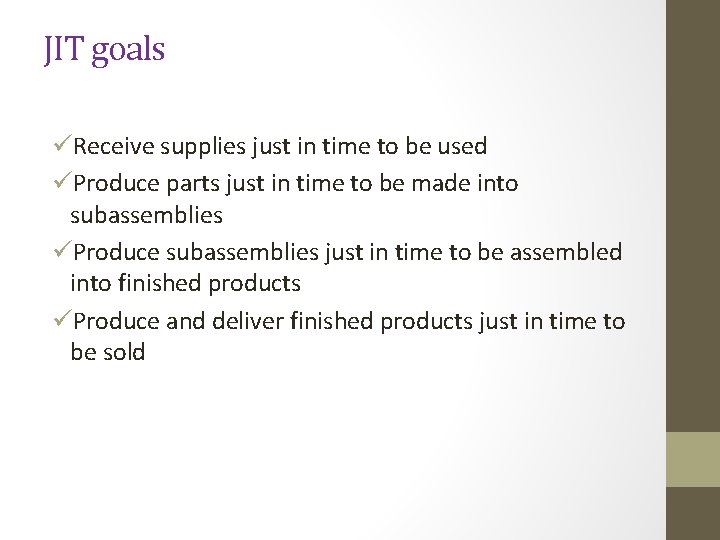
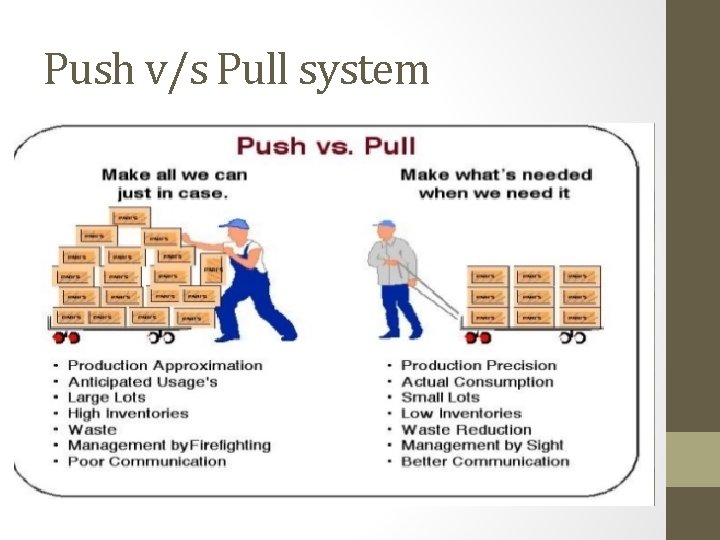
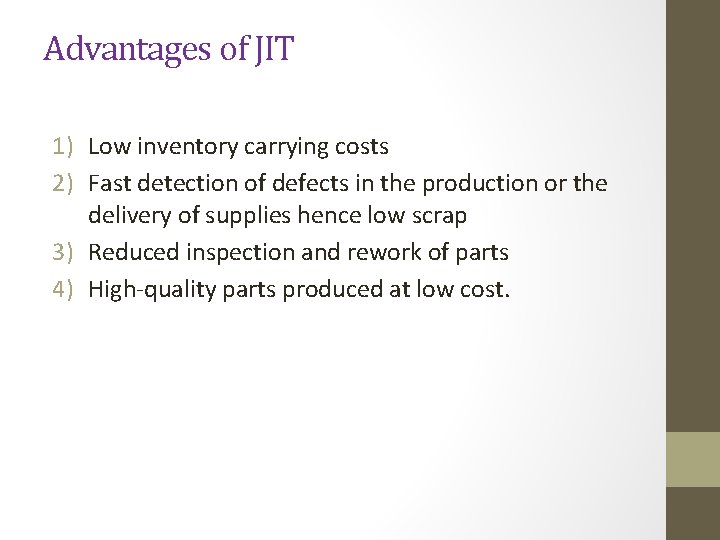
- Slides: 57
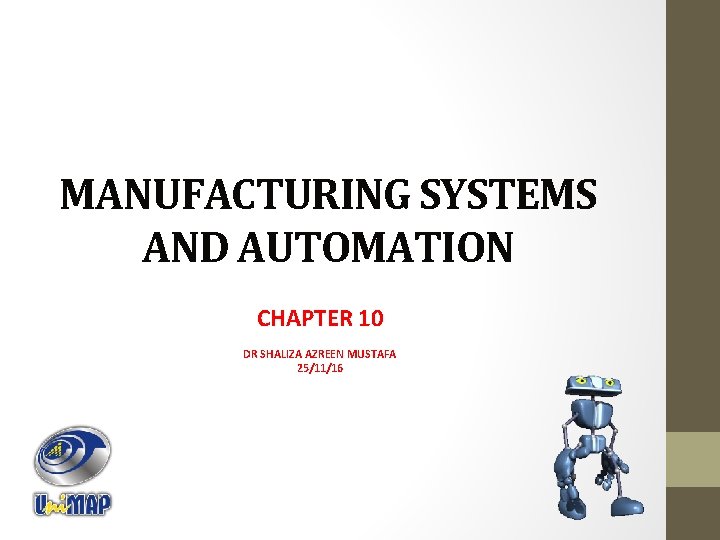
MANUFACTURING SYSTEMS AND AUTOMATION CHAPTER 10 DR SHALIZA AZREEN MUSTAFA 25/11/16
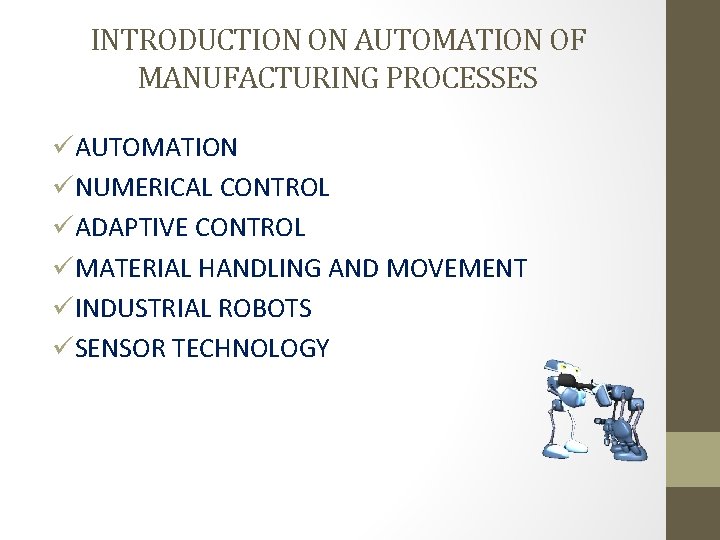
INTRODUCTION ON AUTOMATION OF MANUFACTURING PROCESSES üAUTOMATION üNUMERICAL CONTROL üADAPTIVE CONTROL üMATERIAL HANDLING AND MOVEMENT üINDUSTRIAL ROBOTS üSENSOR TECHNOLOGY
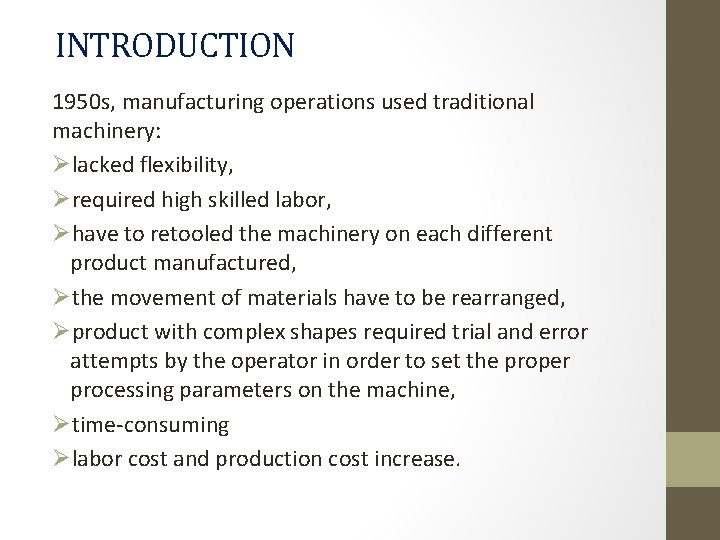
INTRODUCTION 1950 s, manufacturing operations used traditional machinery: Ølacked flexibility, Ørequired high skilled labor, Øhave to retooled the machinery on each different product manufactured, Øthe movement of materials have to be rearranged, Øproduct with complex shapes required trial and error attempts by the operator in order to set the proper processing parameters on the machine, Øtime-consuming Ølabor cost and production cost increase.
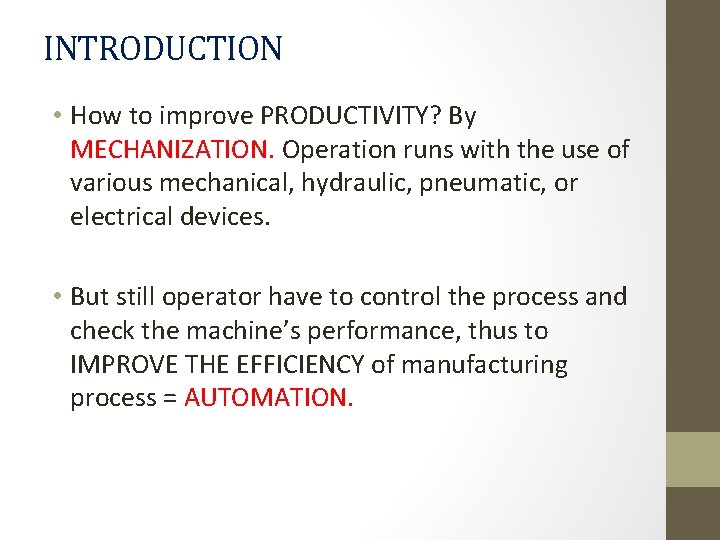
INTRODUCTION • How to improve PRODUCTIVITY? By MECHANIZATION. Operation runs with the use of various mechanical, hydraulic, pneumatic, or electrical devices. • But still operator have to control the process and check the machine’s performance, thus to IMPROVE THE EFFICIENCY of manufacturing process = AUTOMATION.
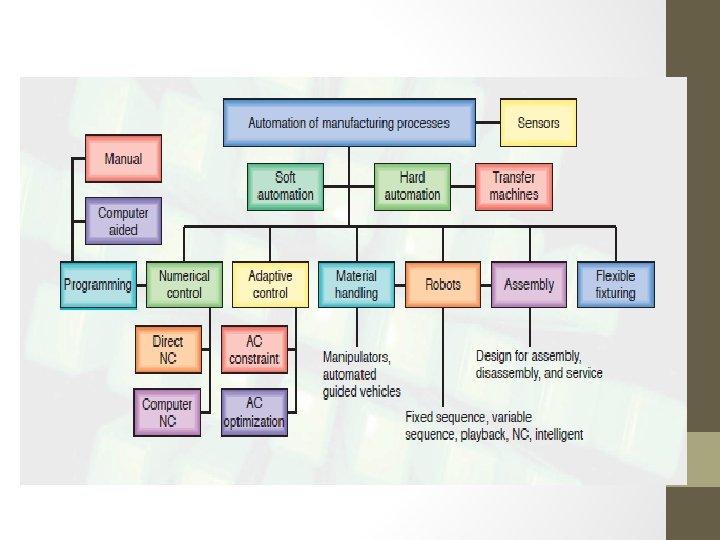
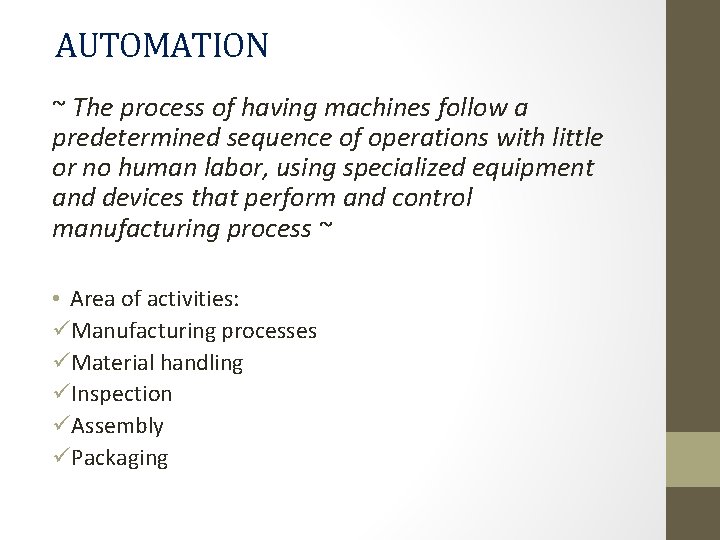
AUTOMATION ~ The process of having machines follow a predetermined sequence of operations with little or no human labor, using specialized equipment and devices that perform and control manufacturing process ~ • Area of activities: üManufacturing processes üMaterial handling üInspection üAssembly üPackaging
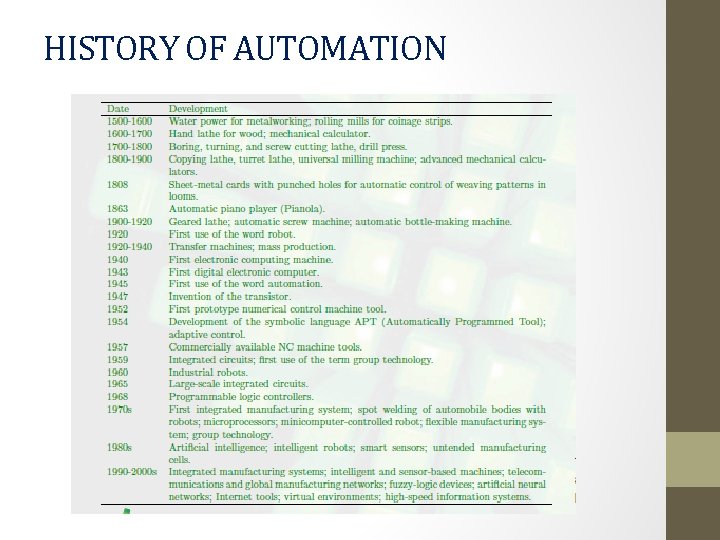
HISTORY OF AUTOMATION
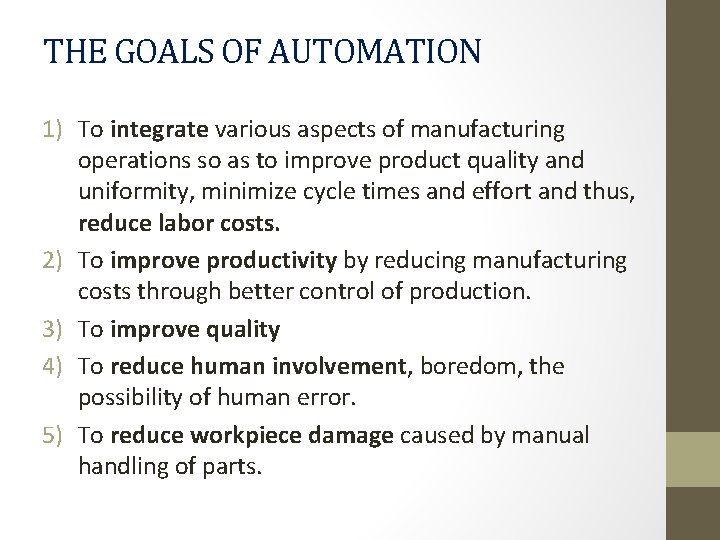
THE GOALS OF AUTOMATION 1) To integrate various aspects of manufacturing operations so as to improve product quality and uniformity, minimize cycle times and effort and thus, reduce labor costs. 2) To improve productivity by reducing manufacturing costs through better control of production. 3) To improve quality 4) To reduce human involvement, boredom, the possibility of human error. 5) To reduce workpiece damage caused by manual handling of parts.
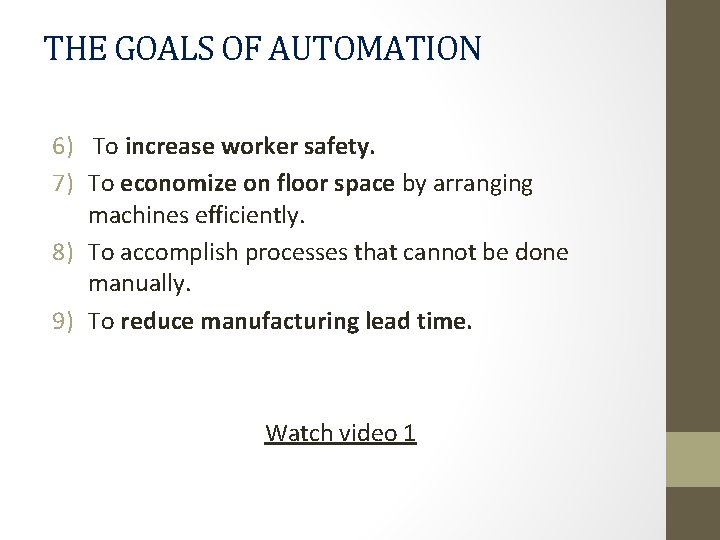
THE GOALS OF AUTOMATION 6) To increase worker safety. 7) To economize on floor space by arranging machines efficiently. 8) To accomplish processes that cannot be done manually. 9) To reduce manufacturing lead time. Watch video 1
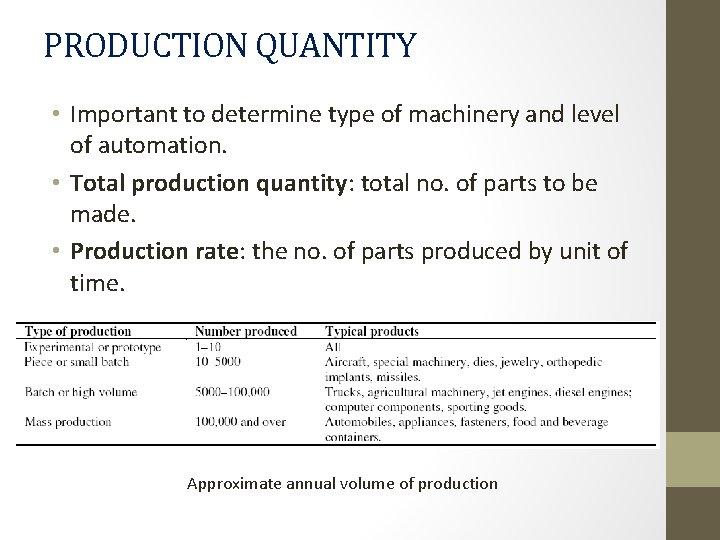
PRODUCTION QUANTITY • Important to determine type of machinery and level of automation. • Total production quantity: total no. of parts to be made. • Production rate: the no. of parts produced by unit of time. Approximate annual volume of production
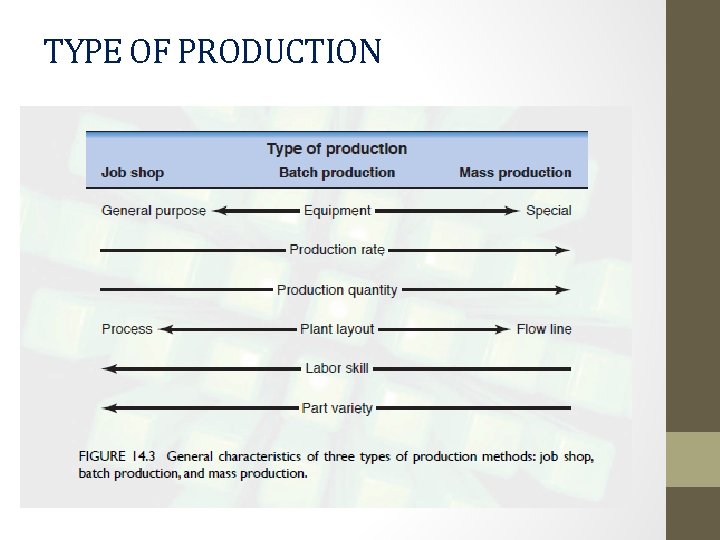
TYPE OF PRODUCTION
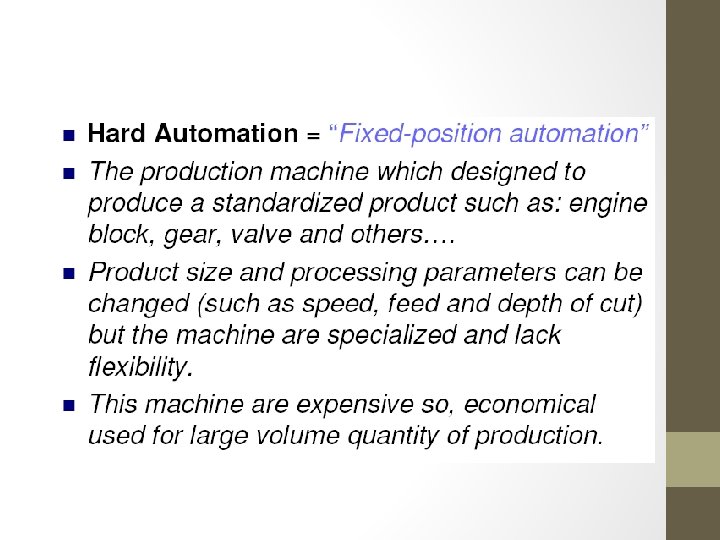
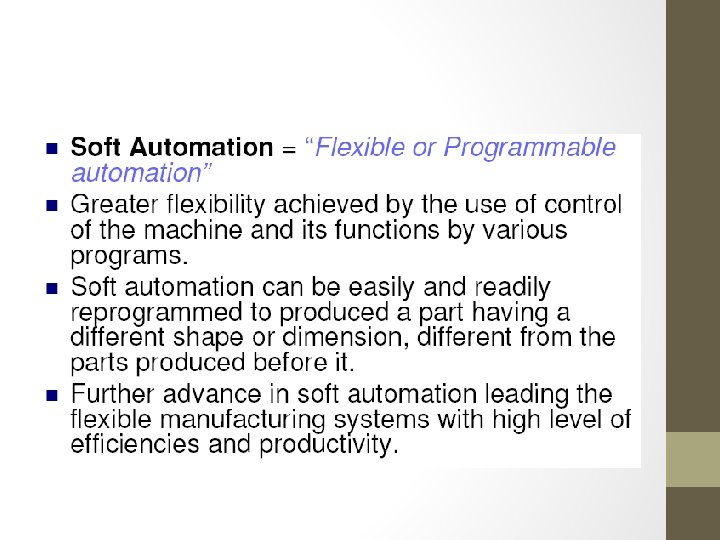
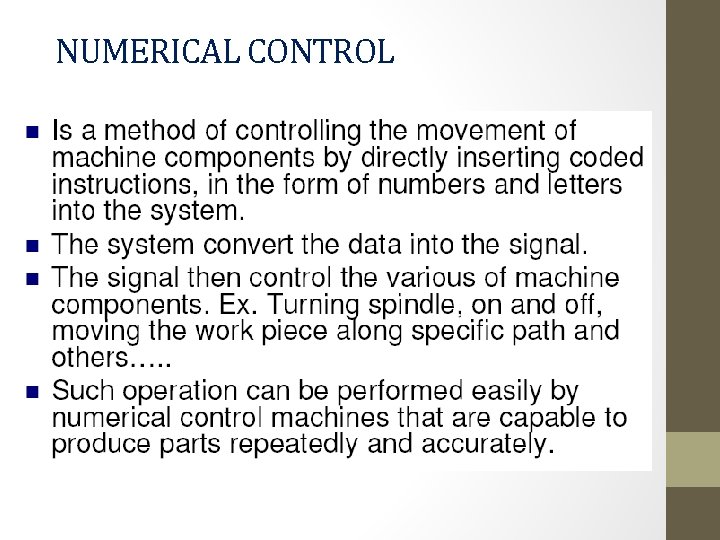
NUMERICAL CONTROL
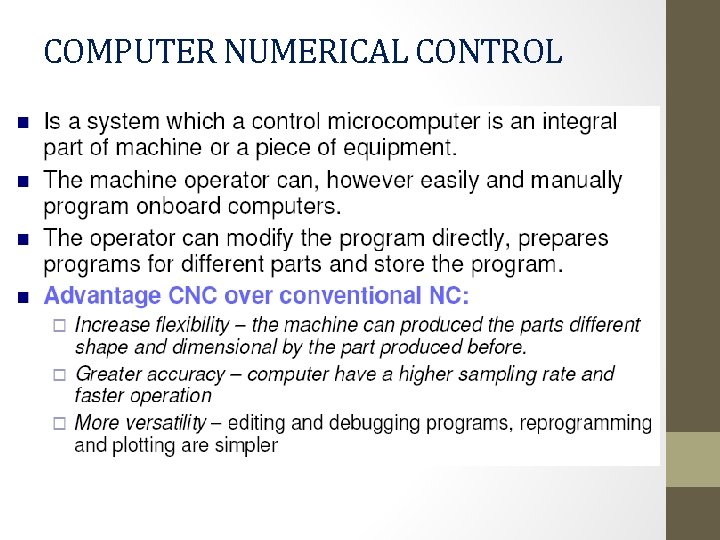
COMPUTER NUMERICAL CONTROL
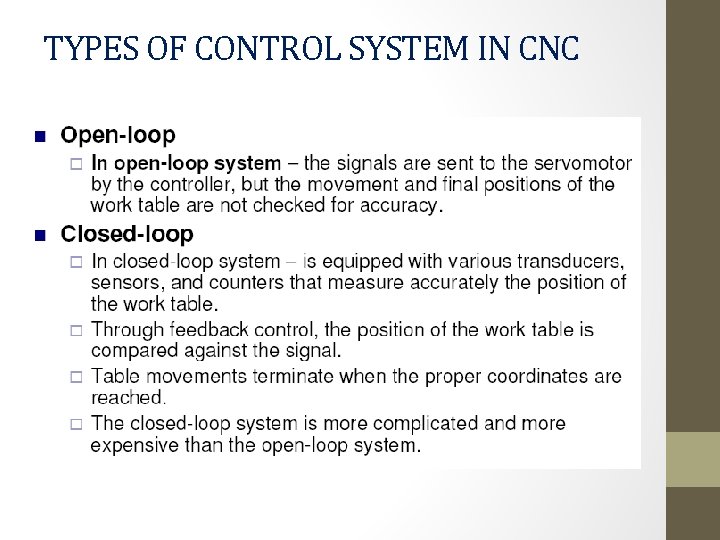
TYPES OF CONTROL SYSTEM IN CNC
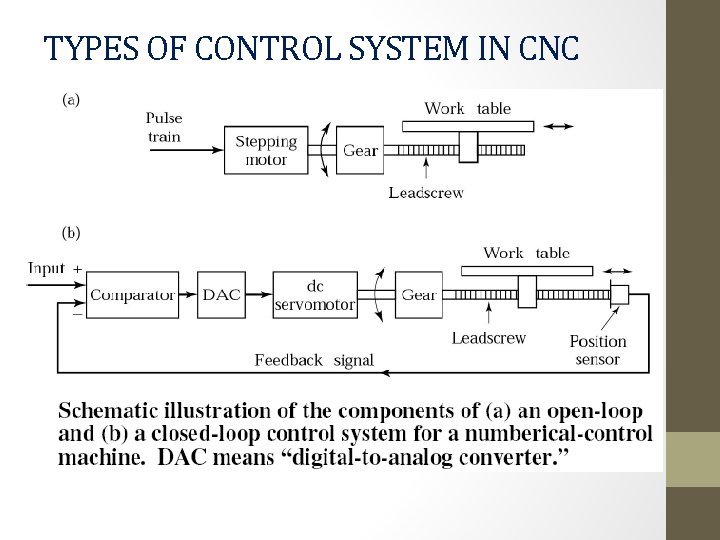
TYPES OF CONTROL SYSTEM IN CNC
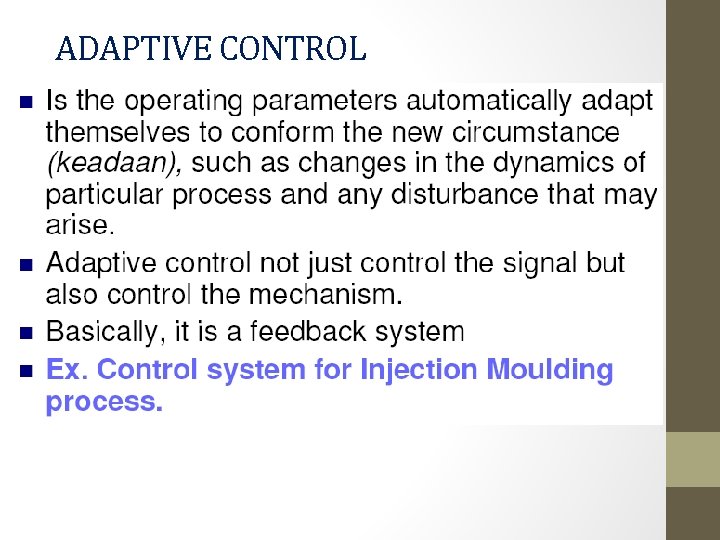
ADAPTIVE CONTROL
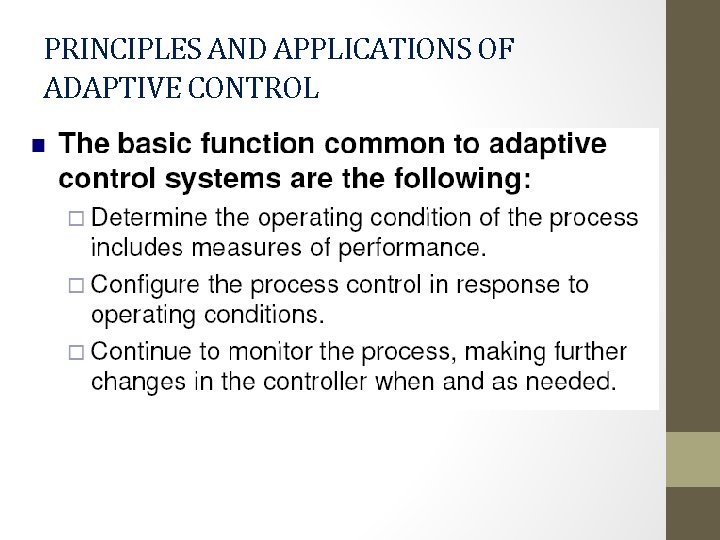
PRINCIPLES AND APPLICATIONS OF ADAPTIVE CONTROL
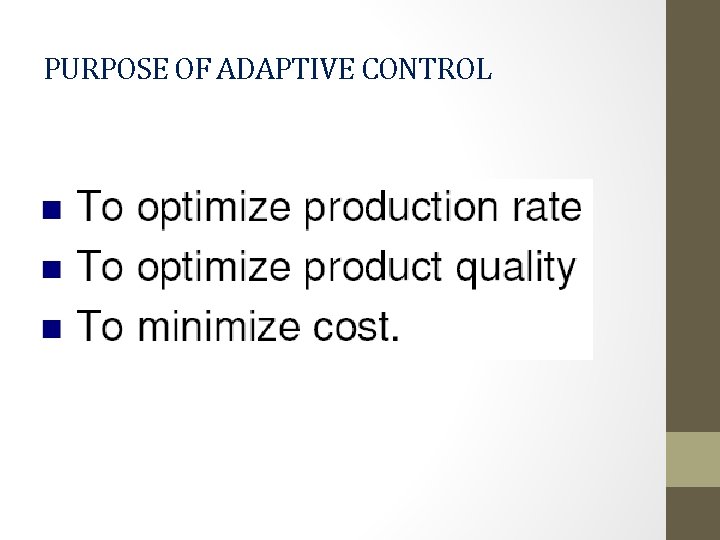
PURPOSE OF ADAPTIVE CONTROL
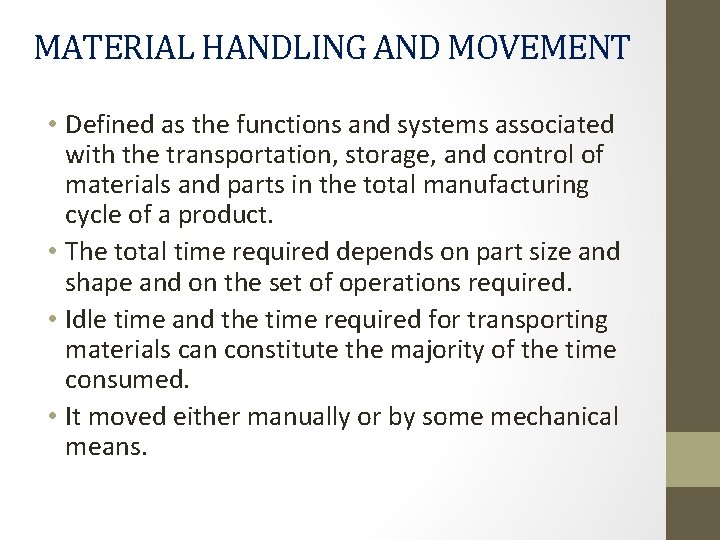
MATERIAL HANDLING AND MOVEMENT • Defined as the functions and systems associated with the transportation, storage, and control of materials and parts in the total manufacturing cycle of a product. • The total time required depends on part size and shape and on the set of operations required. • Idle time and the time required for transporting materials can constitute the majority of the time consumed. • It moved either manually or by some mechanical means.
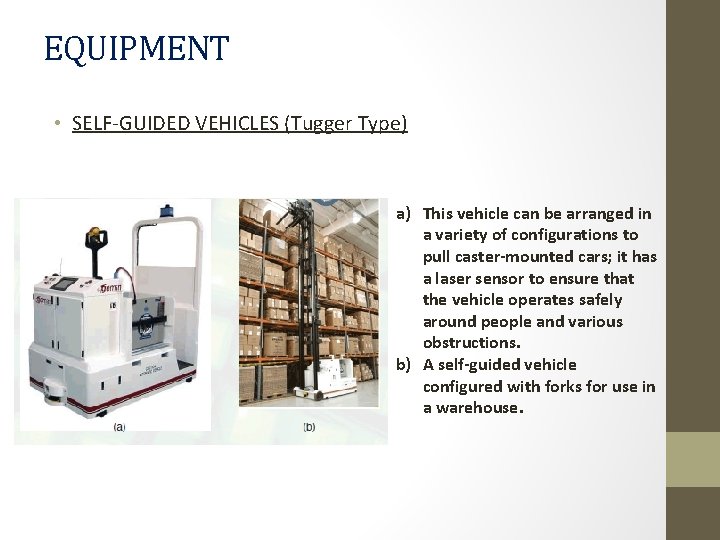
EQUIPMENT • SELF-GUIDED VEHICLES (Tugger Type) a) This vehicle can be arranged in a variety of configurations to pull caster-mounted cars; it has a laser sensor to ensure that the vehicle operates safely around people and various obstructions. b) A self-guided vehicle configured with forks for use in a warehouse.

EQUIPMENT AUTOMATED GUIDED VEHICLE (AGV) Watch video 2
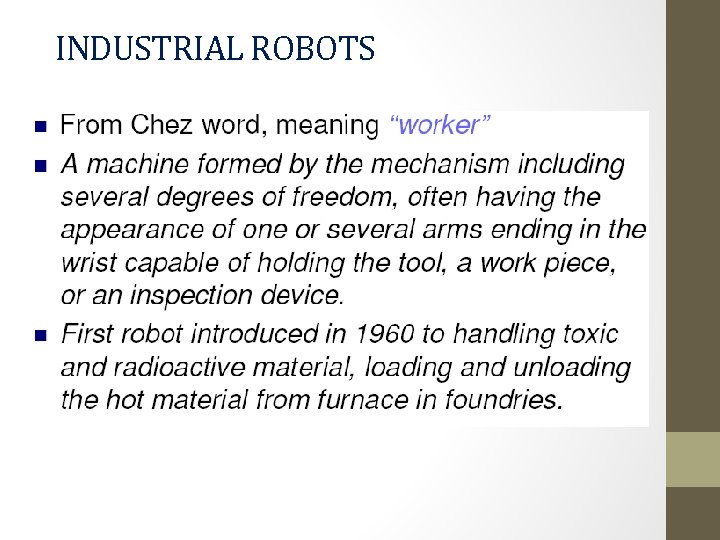
INDUSTRIAL ROBOTS
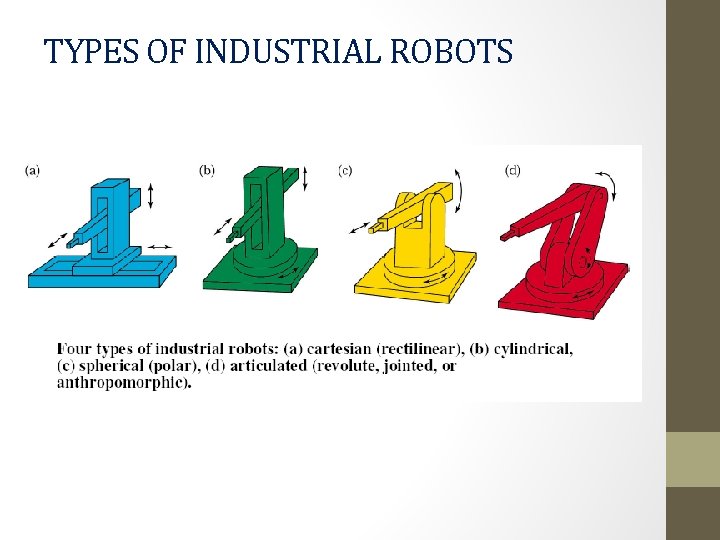
TYPES OF INDUSTRIAL ROBOTS

APPLICATION OF ROBOTS • • • Material handling Spot welding Spray painting Automated assembly is again very repetitive Inspection and gaging Applying adhesive and sealants grinding and polishing Watch video 3
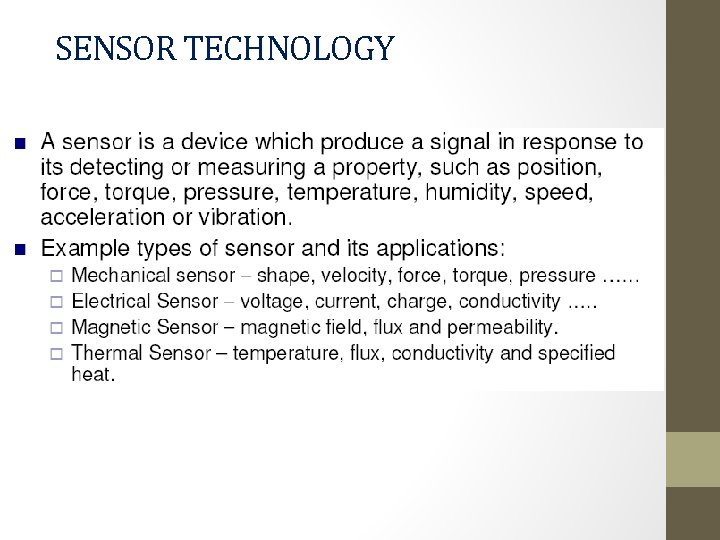
SENSOR TECHNOLOGY
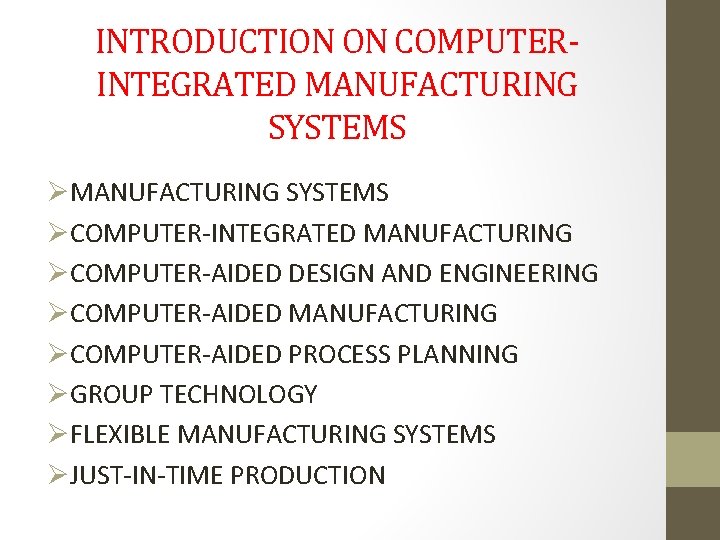
INTRODUCTION ON COMPUTERINTEGRATED MANUFACTURING SYSTEMS ØCOMPUTER-INTEGRATED MANUFACTURING ØCOMPUTER-AIDED DESIGN AND ENGINEERING ØCOMPUTER-AIDED MANUFACTURING ØCOMPUTER-AIDED PROCESS PLANNING ØGROUP TECHNOLOGY ØFLEXIBLE MANUFACTURING SYSTEMS ØJUST-IN-TIME PRODUCTION
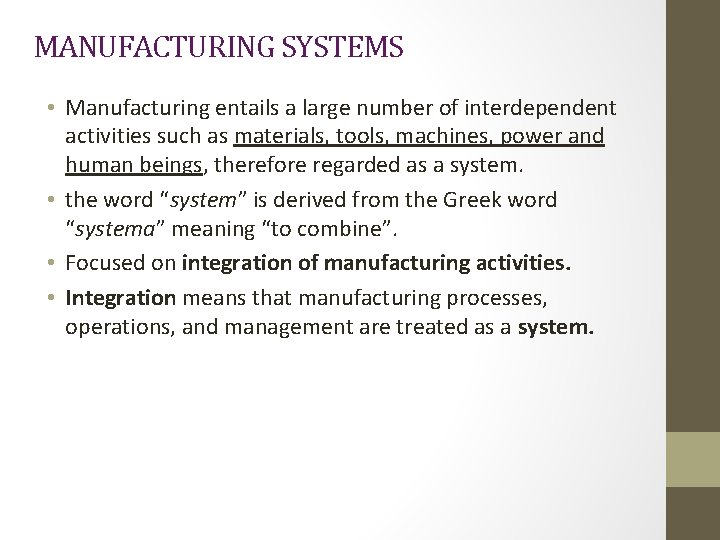
MANUFACTURING SYSTEMS • Manufacturing entails a large number of interdependent activities such as materials, tools, machines, power and human beings, therefore regarded as a system. • the word “system” is derived from the Greek word “systema” meaning “to combine”. • Focused on integration of manufacturing activities. • Integration means that manufacturing processes, operations, and management are treated as a system.
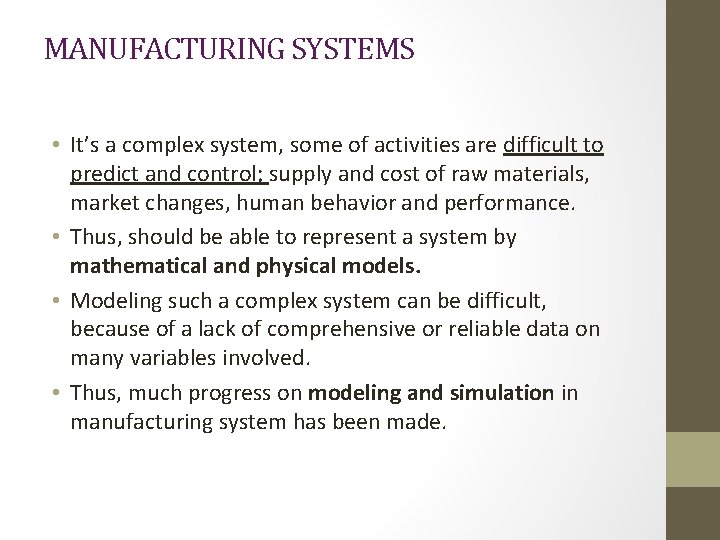
MANUFACTURING SYSTEMS • It’s a complex system, some of activities are difficult to predict and control; supply and cost of raw materials, market changes, human behavior and performance. • Thus, should be able to represent a system by mathematical and physical models. • Modeling such a complex system can be difficult, because of a lack of comprehensive or reliable data on many variables involved. • Thus, much progress on modeling and simulation in manufacturing system has been made.
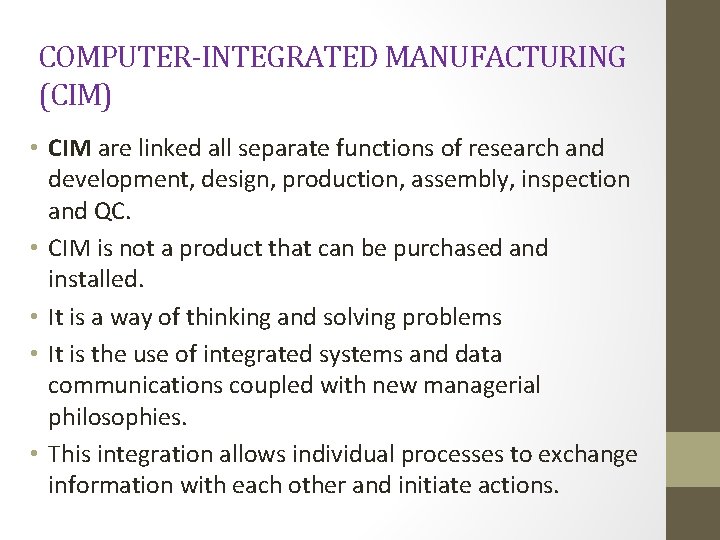
COMPUTER-INTEGRATED MANUFACTURING (CIM) • CIM are linked all separate functions of research and development, design, production, assembly, inspection and QC. • CIM is not a product that can be purchased and installed. • It is a way of thinking and solving problems • It is the use of integrated systems and data communications coupled with new managerial philosophies. • This integration allows individual processes to exchange information with each other and initiate actions.
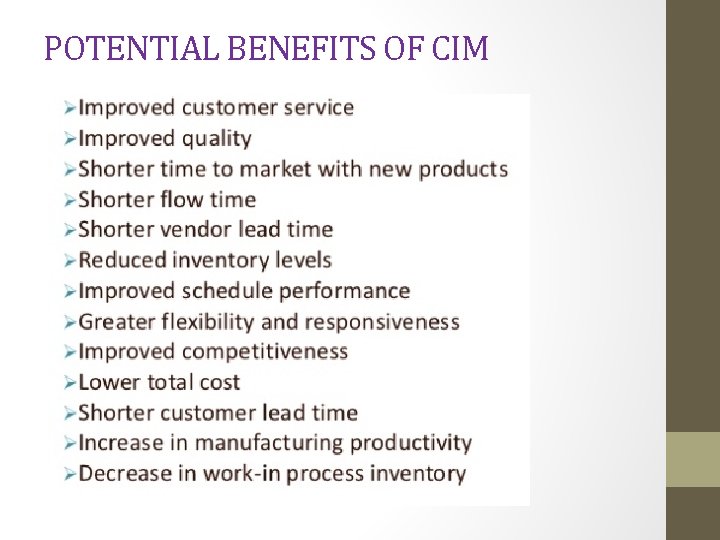
POTENTIAL BENEFITS OF CIM
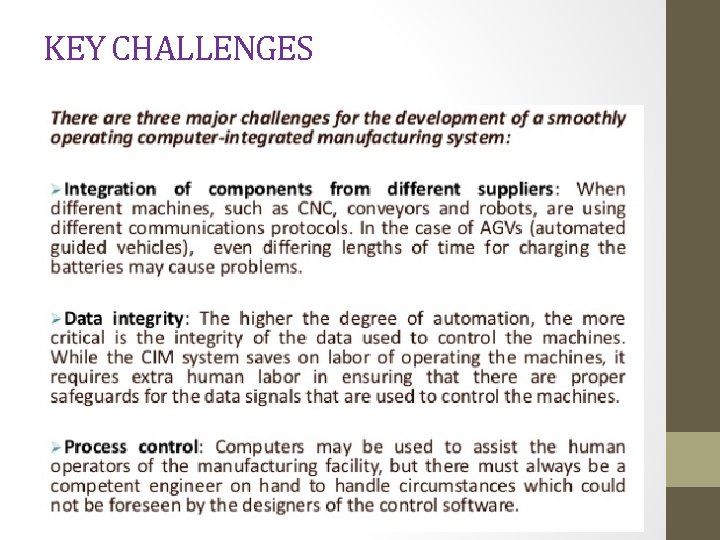
KEY CHALLENGES
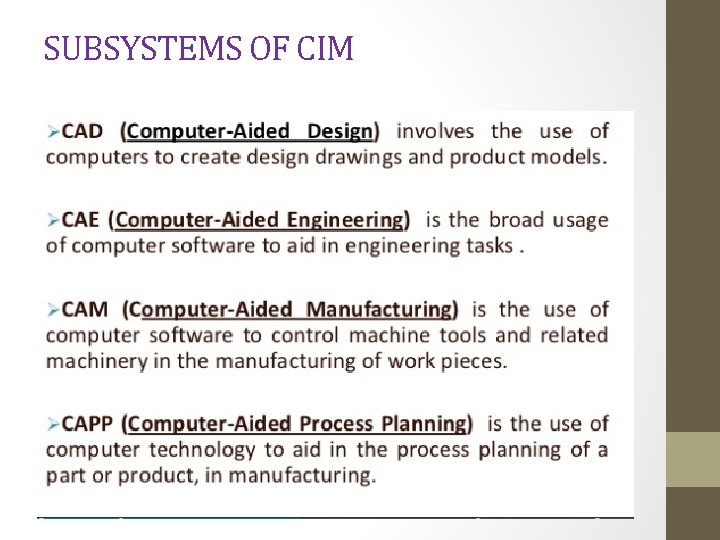
SUBSYSTEMS OF CIM
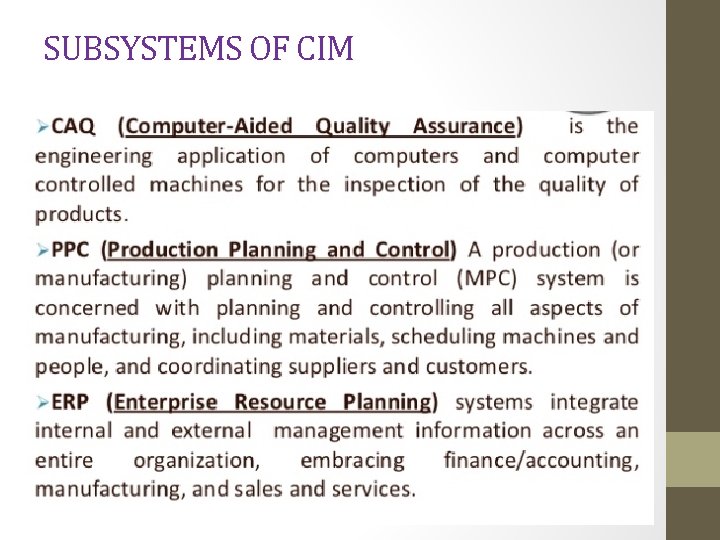
SUBSYSTEMS OF CIM
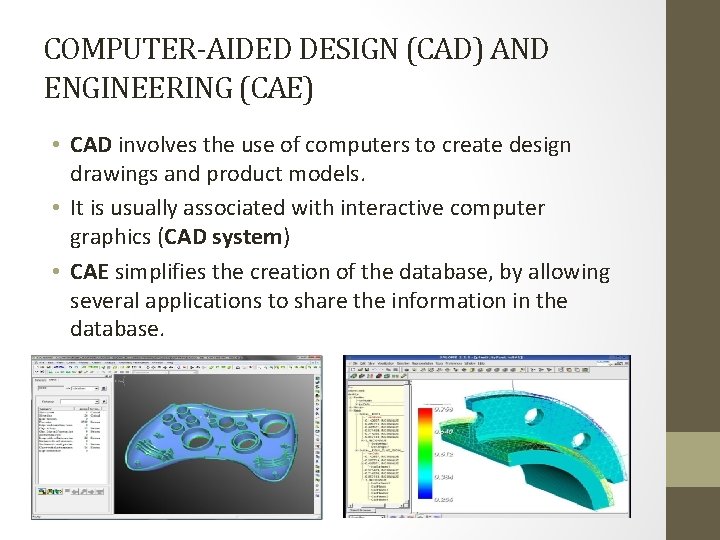
COMPUTER-AIDED DESIGN (CAD) AND ENGINEERING (CAE) • CAD involves the use of computers to create design drawings and product models. • It is usually associated with interactive computer graphics (CAD system) • CAE simplifies the creation of the database, by allowing several applications to share the information in the database.
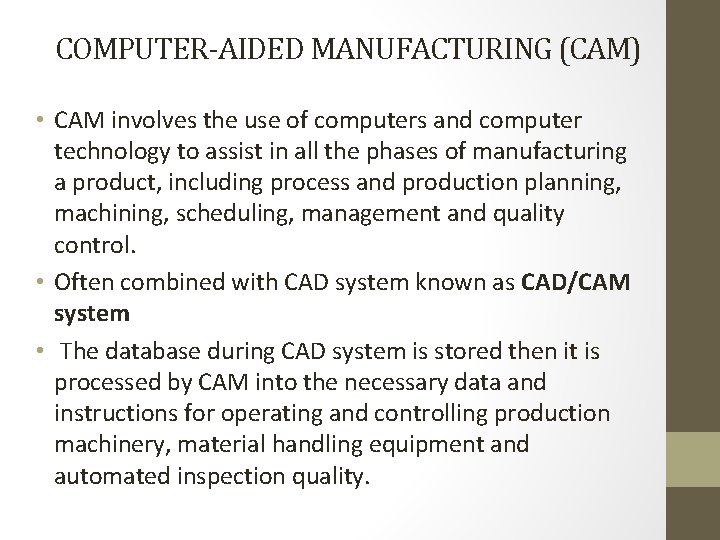
COMPUTER-AIDED MANUFACTURING (CAM) • CAM involves the use of computers and computer technology to assist in all the phases of manufacturing a product, including process and production planning, machining, scheduling, management and quality control. • Often combined with CAD system known as CAD/CAM system • The database during CAD system is stored then it is processed by CAM into the necessary data and instructions for operating and controlling production machinery, material handling equipment and automated inspection quality.
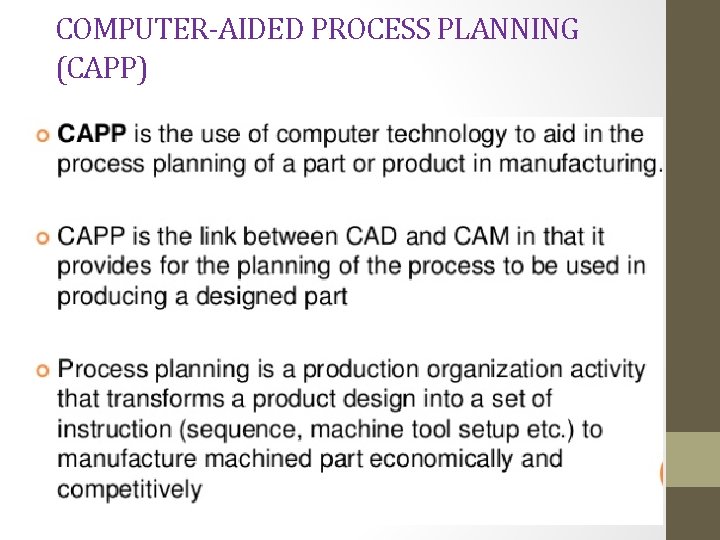
COMPUTER-AIDED PROCESS PLANNING (CAPP)
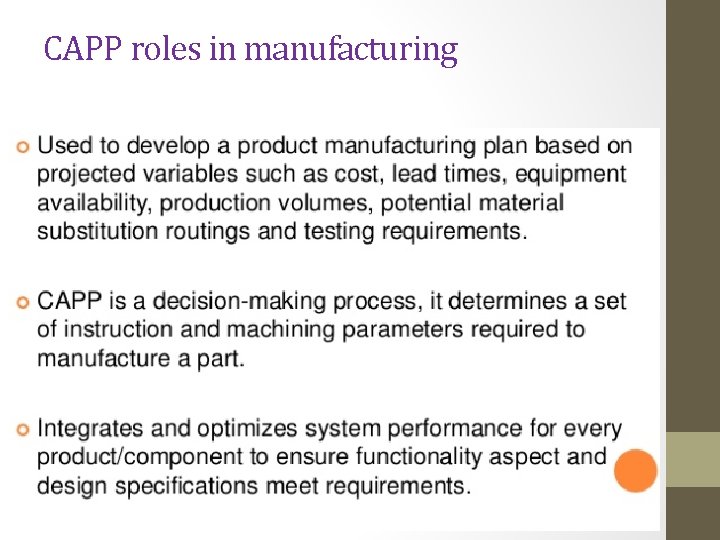
CAPP roles in manufacturing
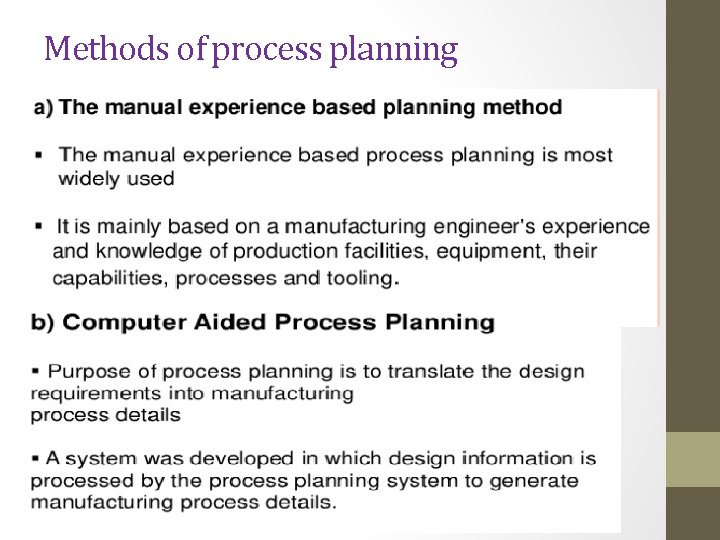
Methods of process planning
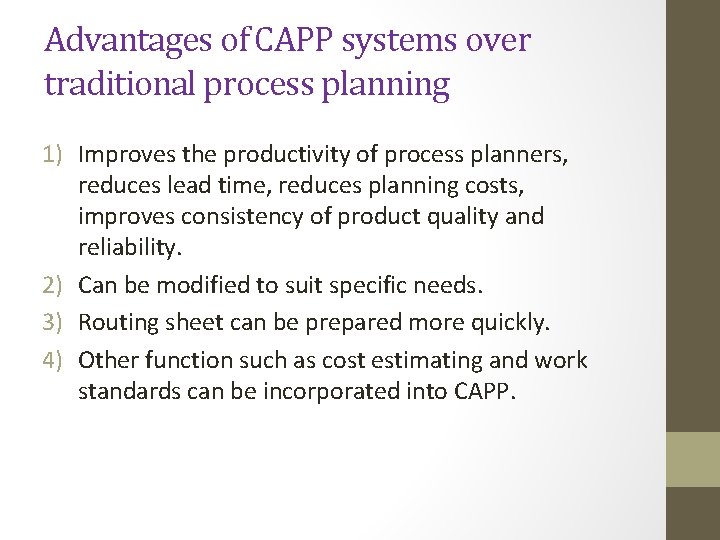
Advantages of CAPP systems over traditional process planning 1) Improves the productivity of process planners, reduces lead time, reduces planning costs, improves consistency of product quality and reliability. 2) Can be modified to suit specific needs. 3) Routing sheet can be prepared more quickly. 4) Other function such as cost estimating and work standards can be incorporated into CAPP.
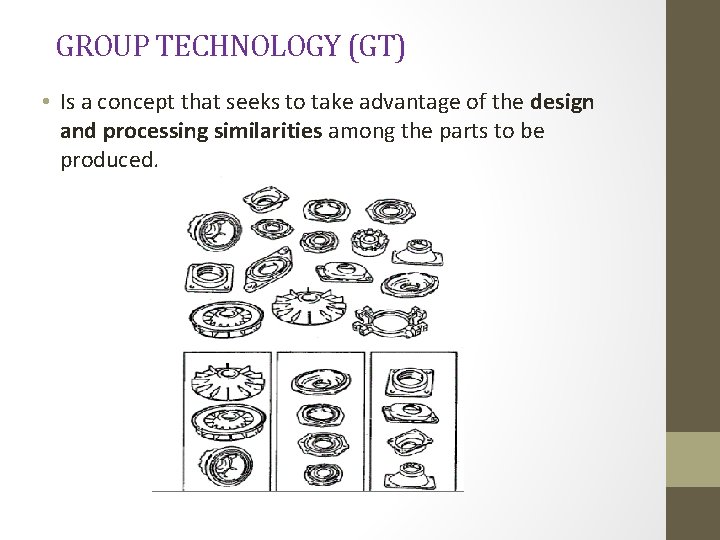
GROUP TECHNOLOGY (GT) • Is a concept that seeks to take advantage of the design and processing similarities among the parts to be produced.
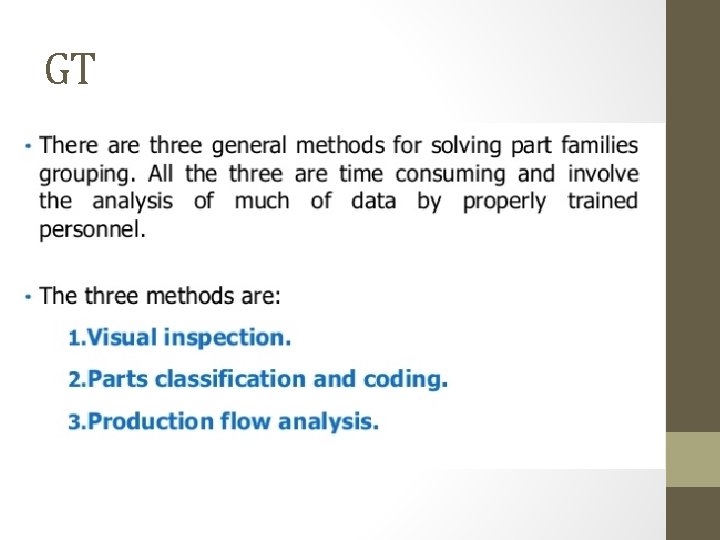
GT
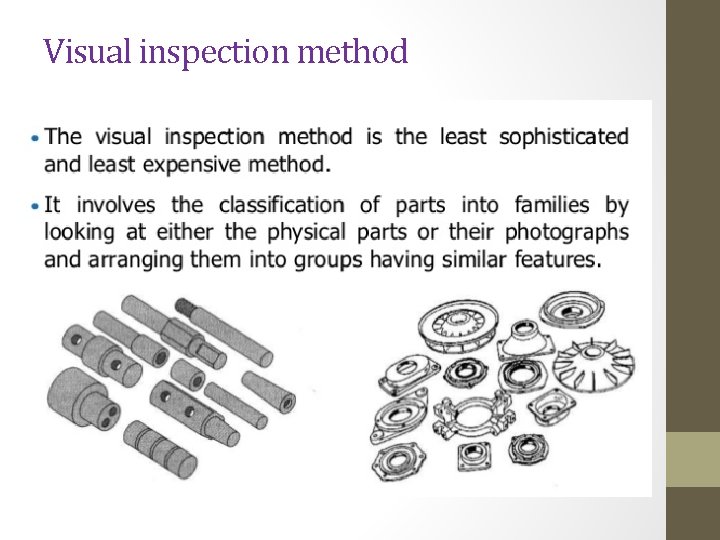
Visual inspection method
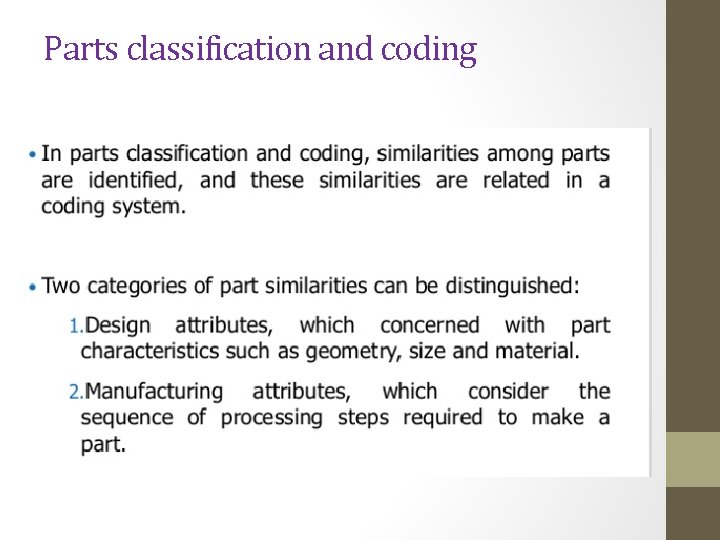
Parts classification and coding

Production flow analysis
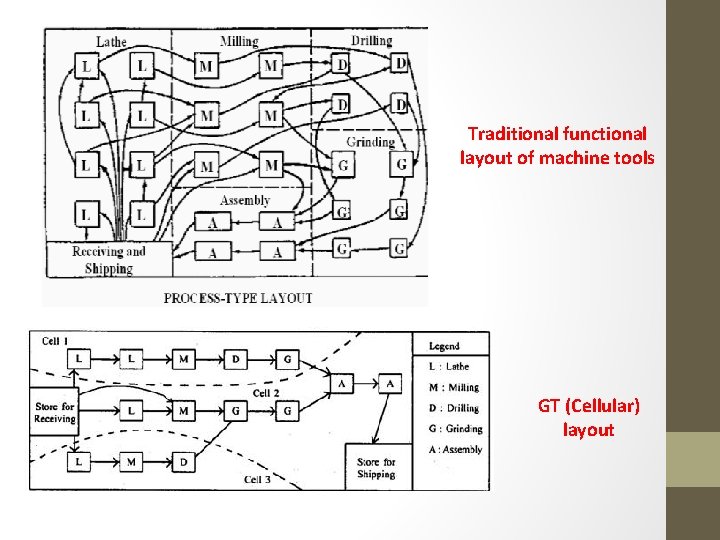
Traditional functional layout of machine tools GT (Cellular) layout
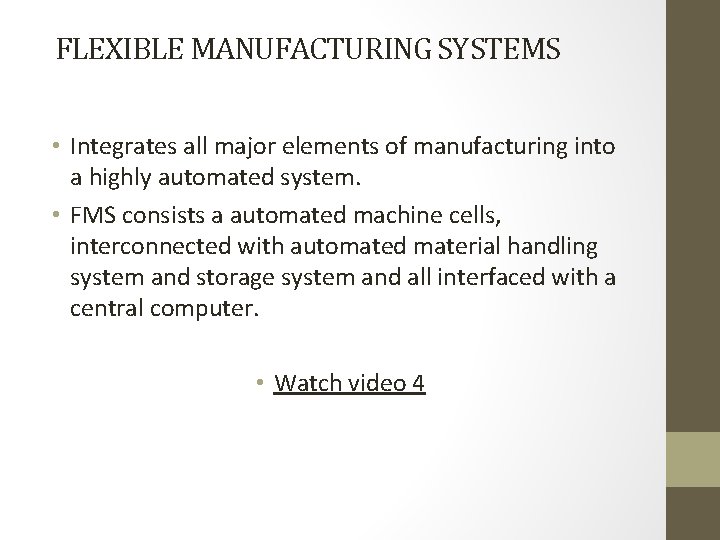
FLEXIBLE MANUFACTURING SYSTEMS • Integrates all major elements of manufacturing into a highly automated system. • FMS consists a automated machine cells, interconnected with automated material handling system and storage system and all interfaced with a central computer. • Watch video 4
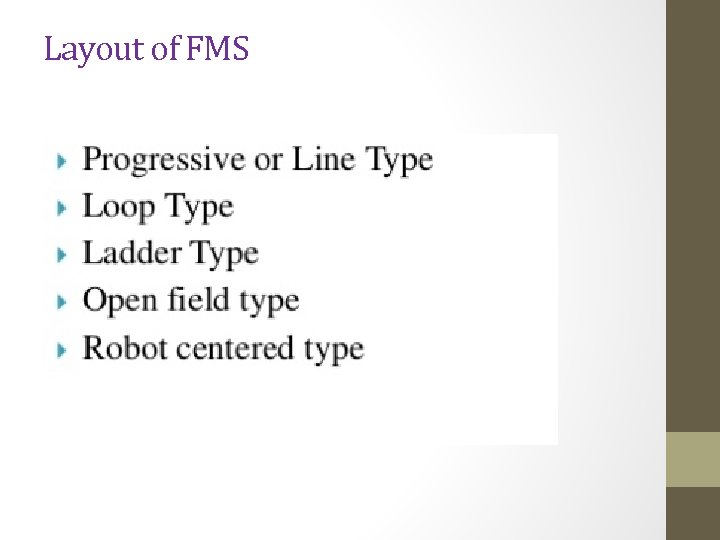
Layout of FMS
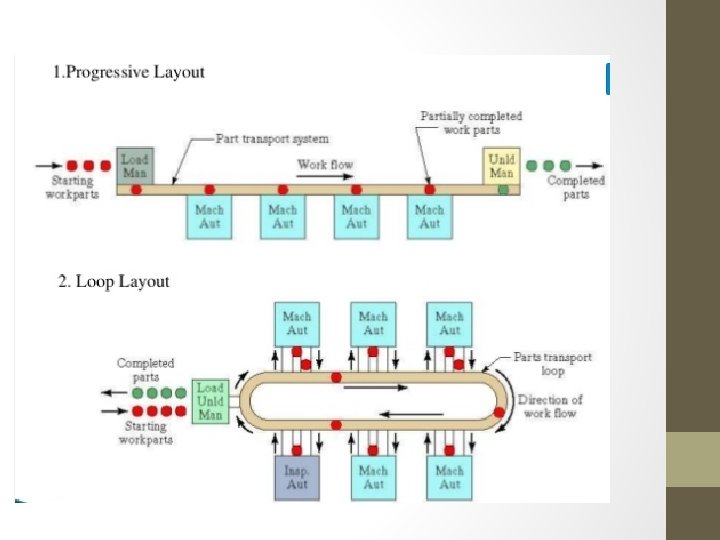

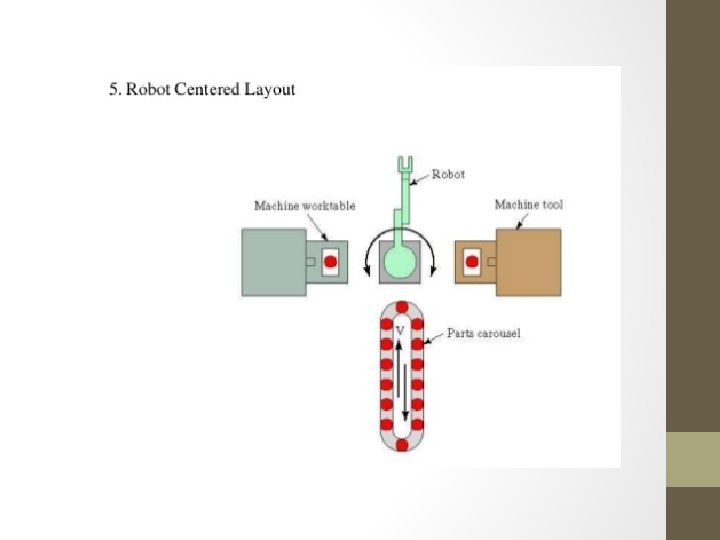
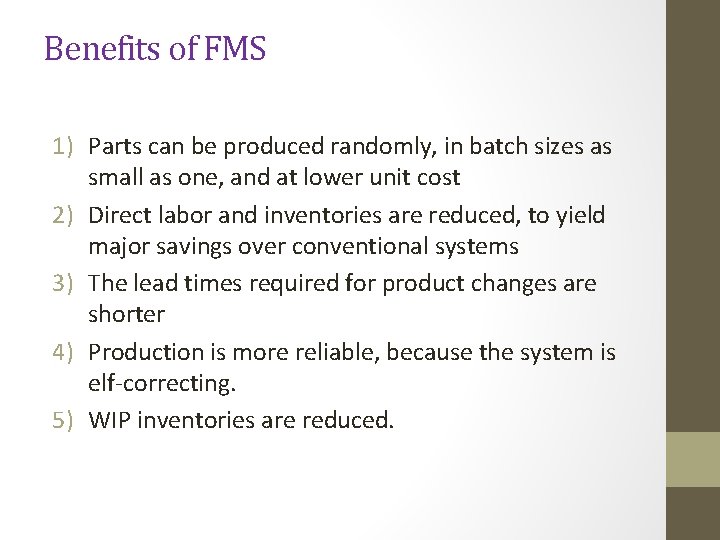
Benefits of FMS 1) Parts can be produced randomly, in batch sizes as small as one, and at lower unit cost 2) Direct labor and inventories are reduced, to yield major savings over conventional systems 3) The lead times required for product changes are shorter 4) Production is more reliable, because the system is elf-correcting. 5) WIP inventories are reduced.
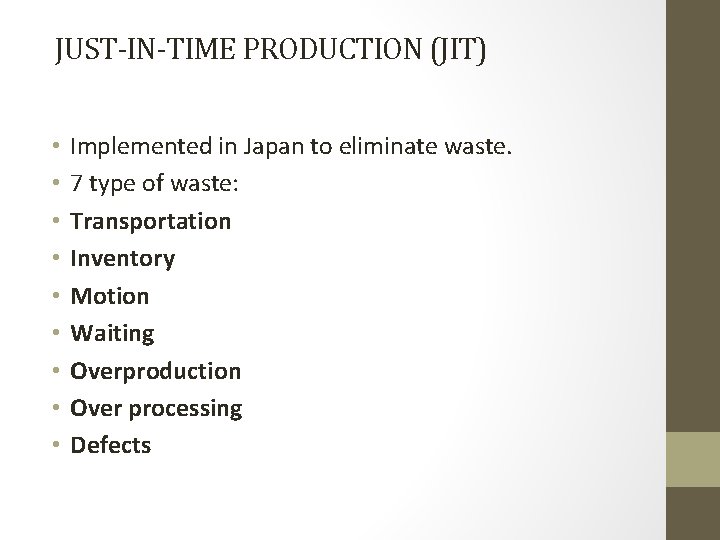
JUST-IN-TIME PRODUCTION (JIT) • • • Implemented in Japan to eliminate waste. 7 type of waste: Transportation Inventory Motion Waiting Overproduction Over processing Defects
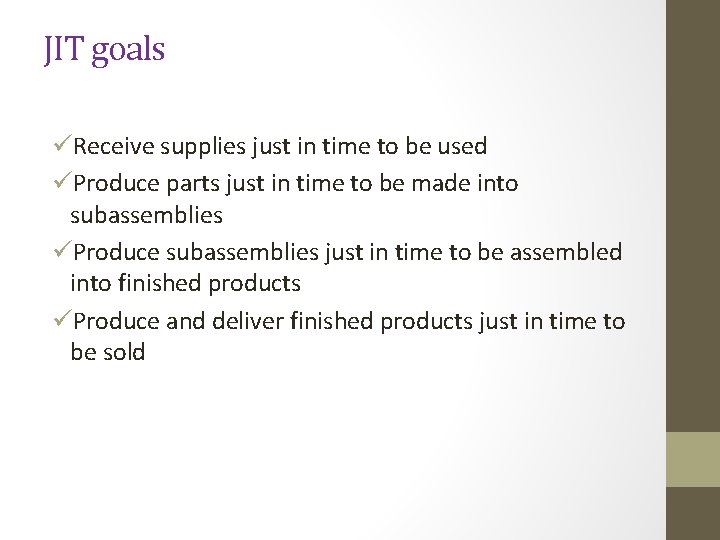
JIT goals üReceive supplies just in time to be used üProduce parts just in time to be made into subassemblies üProduce subassemblies just in time to be assembled into finished products üProduce and deliver finished products just in time to be sold
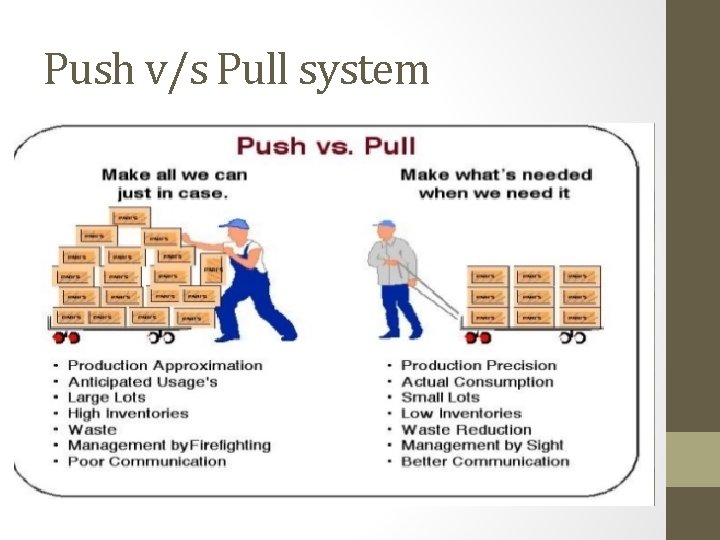
Push v/s Pull system
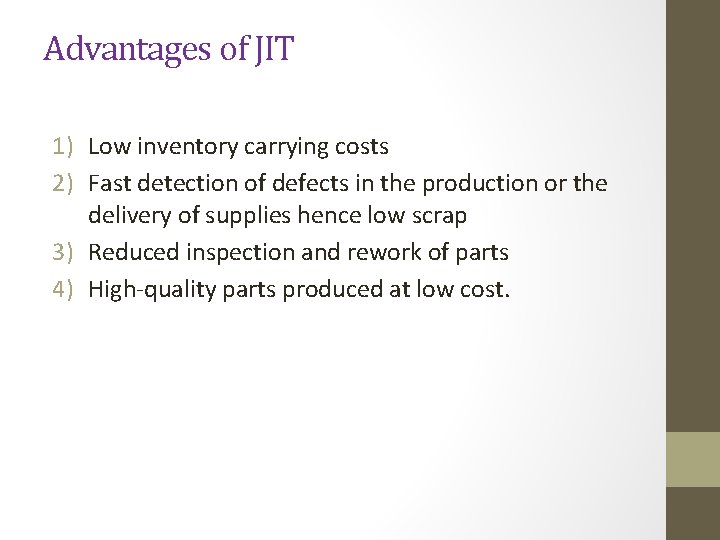
Advantages of JIT 1) Low inventory carrying costs 2) Fast detection of defects in the production or the delivery of supplies hence low scrap 3) Reduced inspection and rework of parts 4) High-quality parts produced at low cost.
Manufacturing cost vs non manufacturing cost
Manufacturing cost vs non manufacturing cost
Controllable costs
Manufacturing cost vs non manufacturing cost
Additive manufacturing steps
Manufacturing systems modeling and analysis
Office automation system (oas) adalah
Beihang
Cadet automation systems
Design automation for embedded systems
Poc informatics
Cadet automation systems
Industrial automation systems
P&id
Comecer isolator
Briefing automation systems
Computer control of manufacturing systems
Opitz coding system
Introduction to manufacturing systems
Decision support systems and intelligent systems
Chapter 24 the immune and lymphatic systems and cancer
Lymph diagram
Principles of complex systems for systems engineering
Embedded systems vs cyber physical systems
Engineering elegant systems: theory of systems engineering
Siemens energy automation
Extract transform and load automation
"sensor wafer" and "manufacturing"
Benefits of ict in design and manufacturing
Jit and lean operations
"klatencor" and "support"
Manufacturing and service technologies
Manufacturing planning and control
Manufacturing models and metrics
Similarities of merchandising and manufacturing
Wood manufacturing and finishing
Difference between manufacturing and service operations
Group technology and cellular manufacturing
Minnesota mining and manufacturing post-it
Managing service and manufacturing operations
Managing service and manufacturing operations
Global manufacturing and supply chain management
Comparing merchandising and manufacturing activities
Cmc chemistry manufacturing and controls
Air force research laboratory logo
What is subtractive modeling
Synchronous manufacturing
Chapter 28 human systems and homeostasis
Signals and systems oppenheim solutions chapter 5
Lower court
Chapter 2 economic systems and decision making
Chapter 38 digestive and excretory systems
Section 39-4 fertilization and development
Chapter 36 skeletal muscular and integumentary systems
Chapter 33 circulatory and respiratory systems
Chapter 2 economic systems and decision making
Chapter 15 water and aqueous systems answer key
Water and aqueous systems chapter 15 answers