MAL USULLER DKM Kalite Kontrol Kalite mamul zelliklerinin
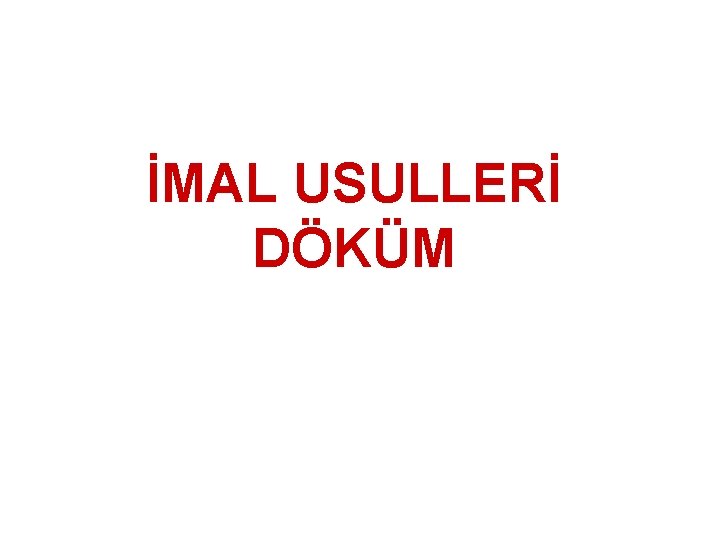
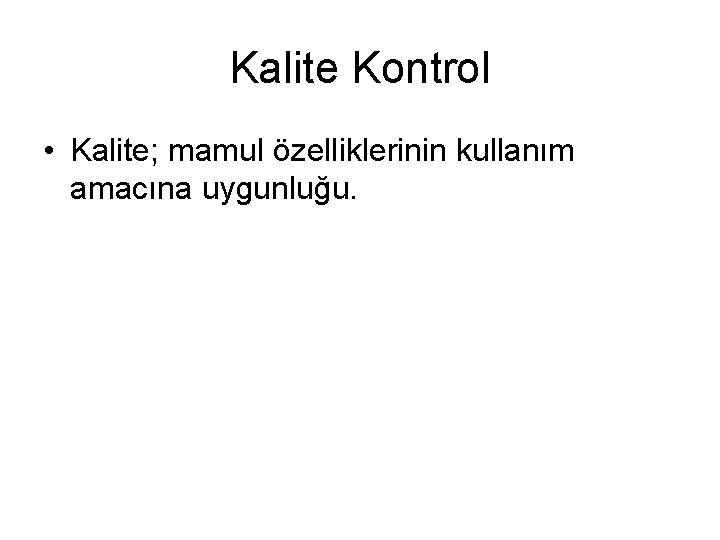
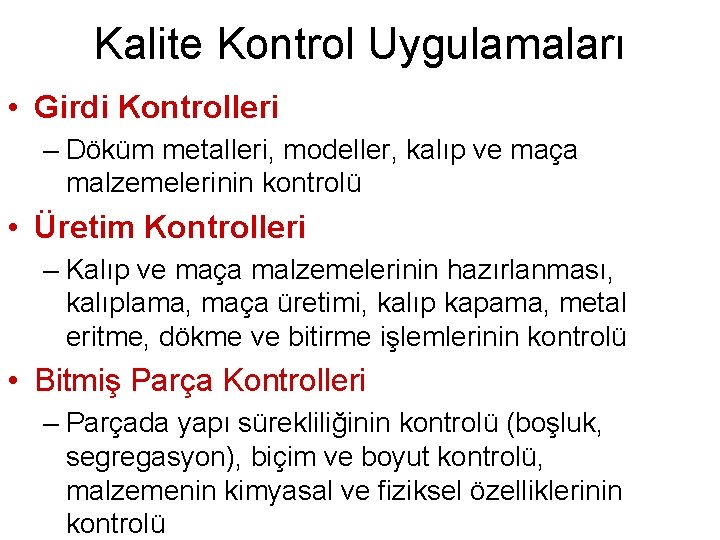
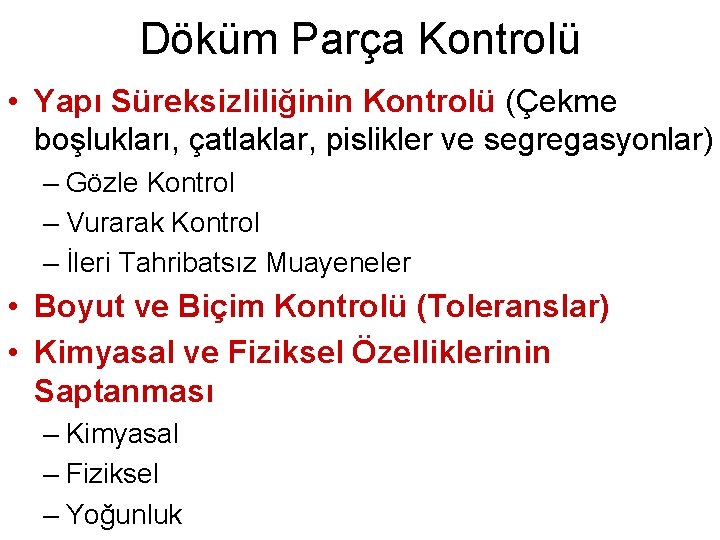
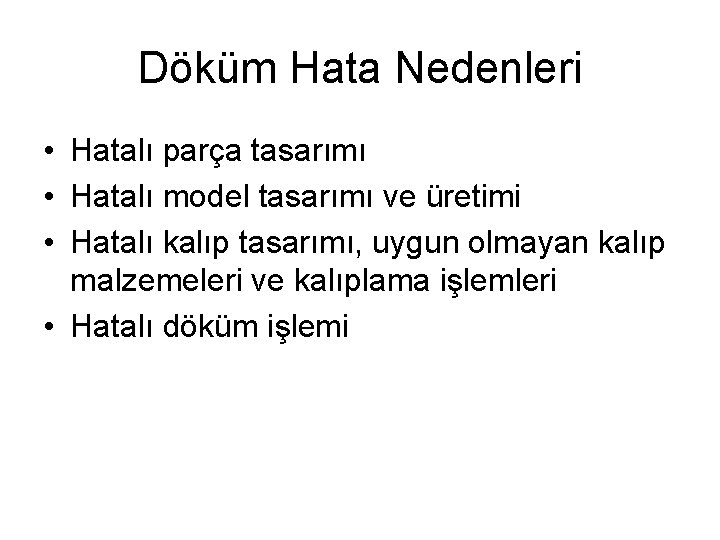
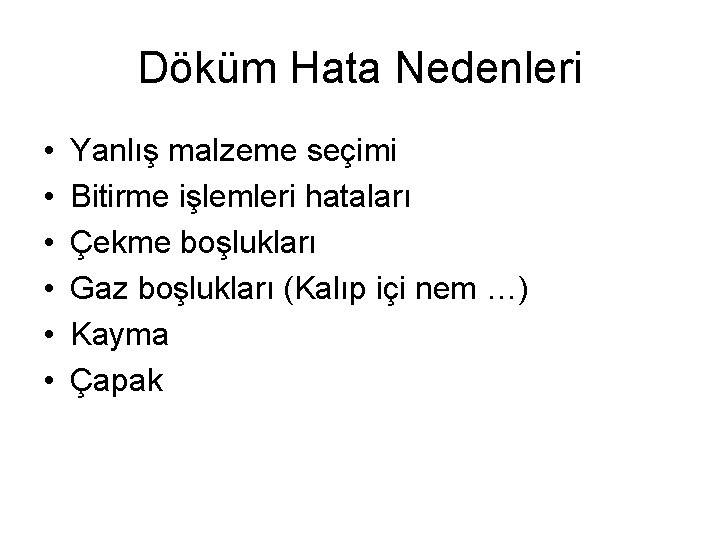
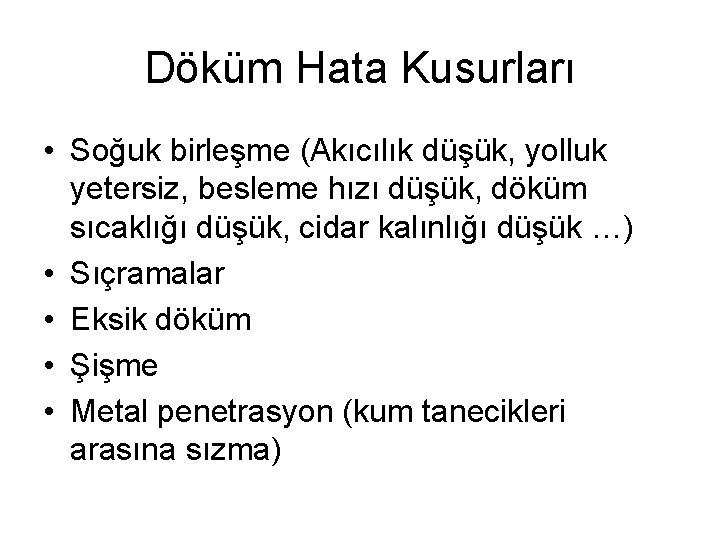
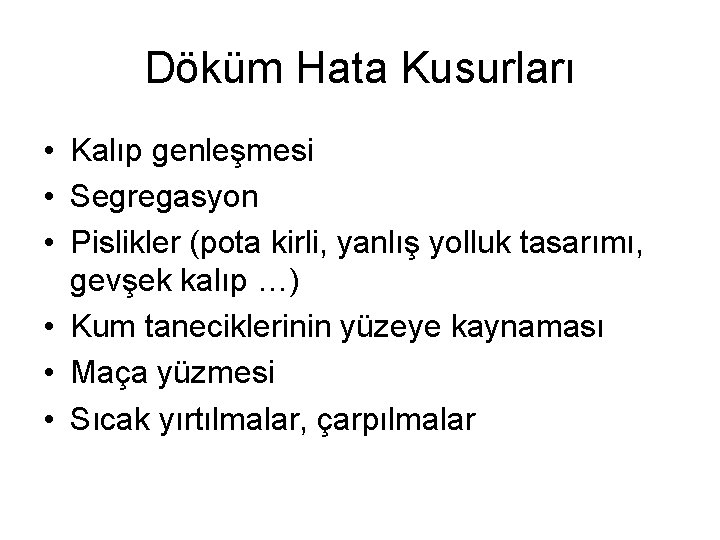
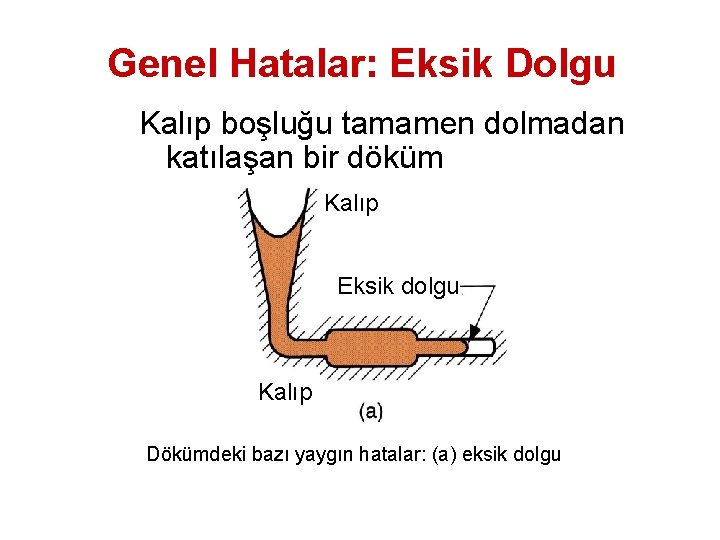
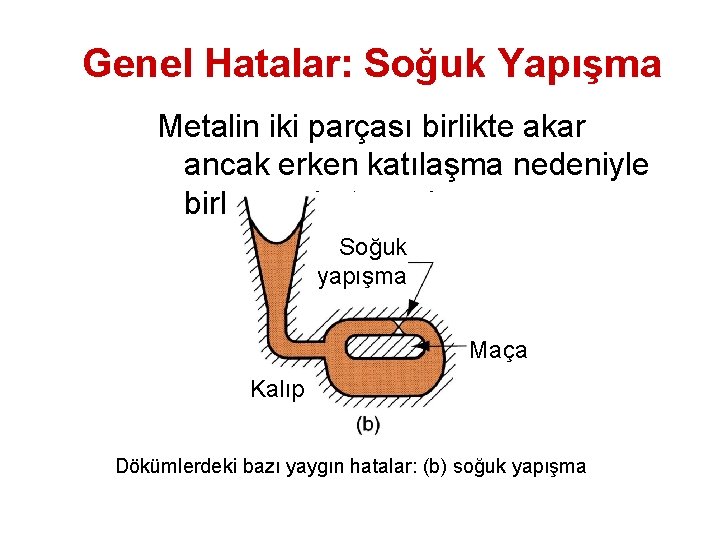
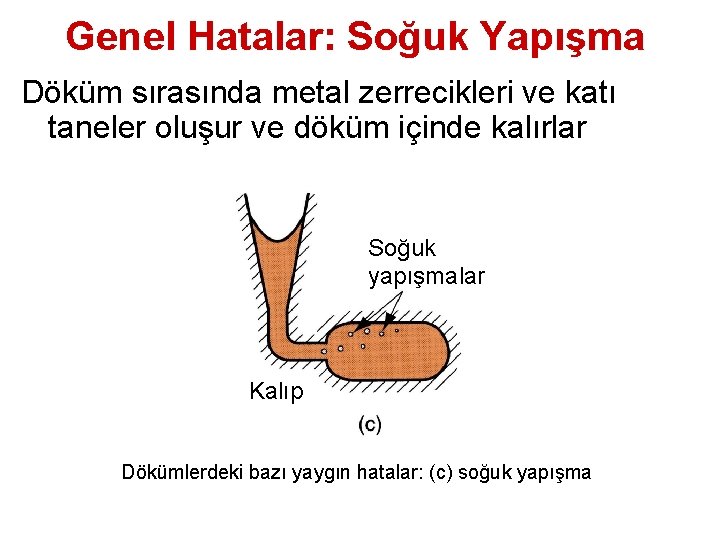
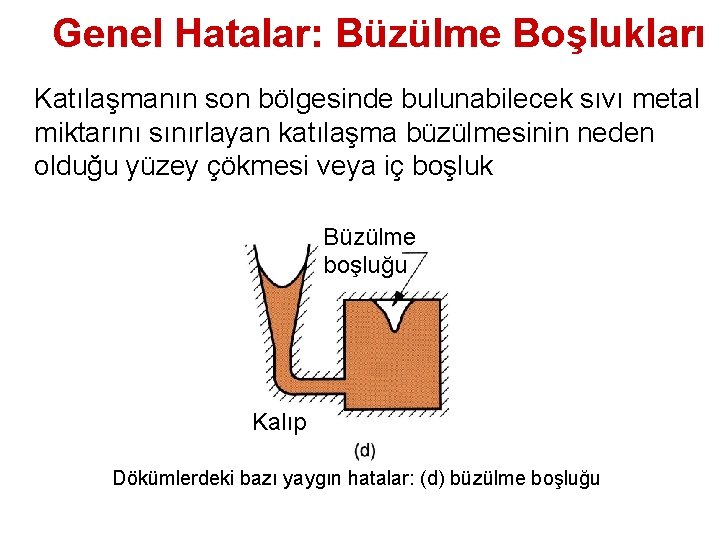
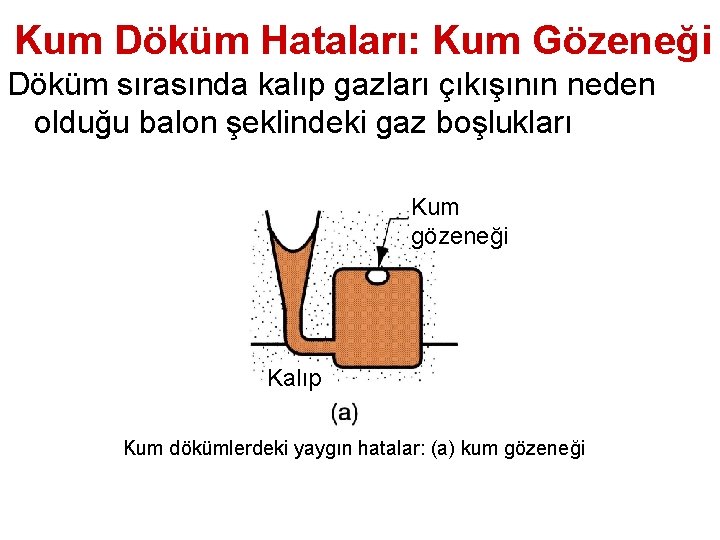
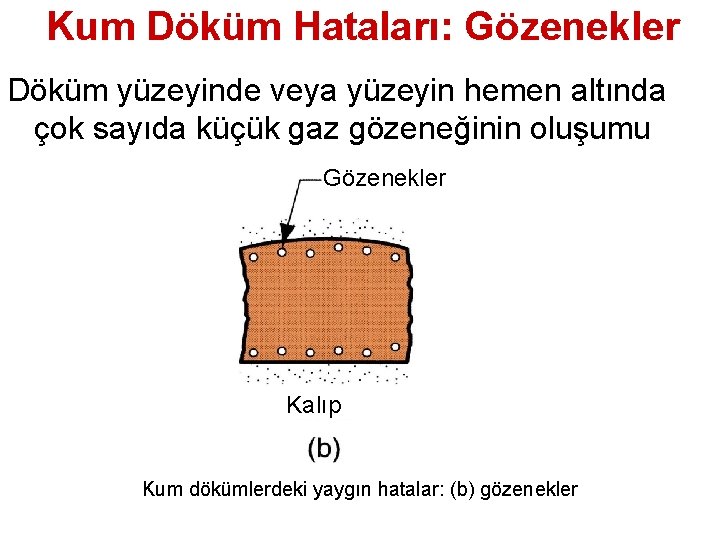
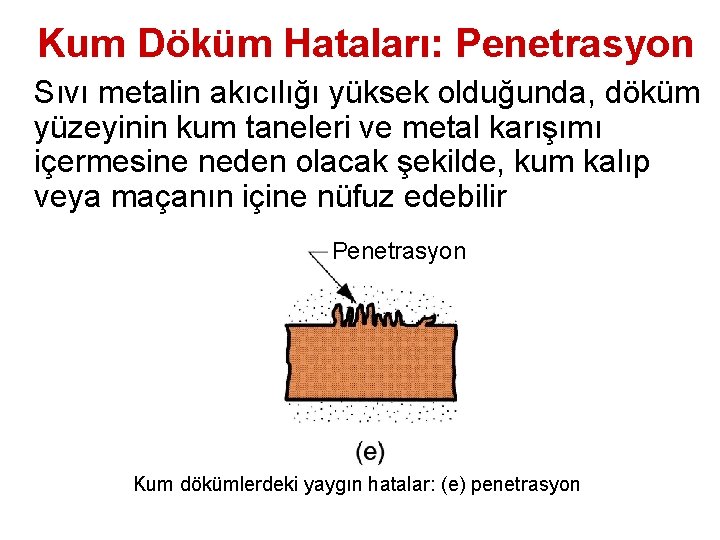
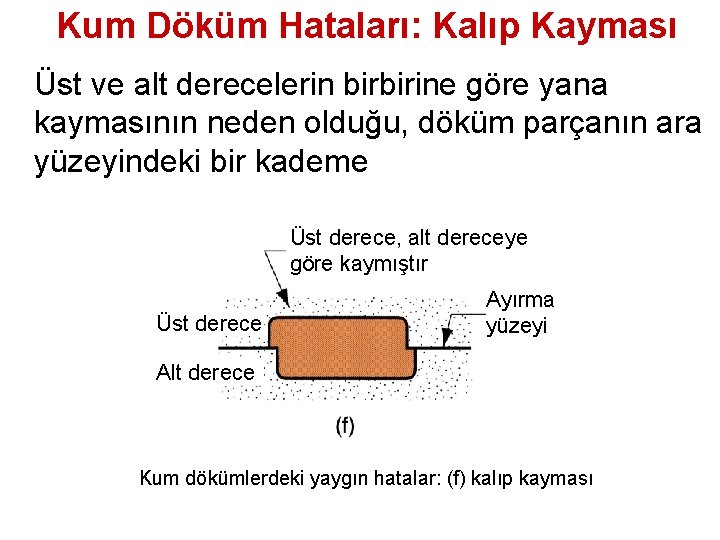
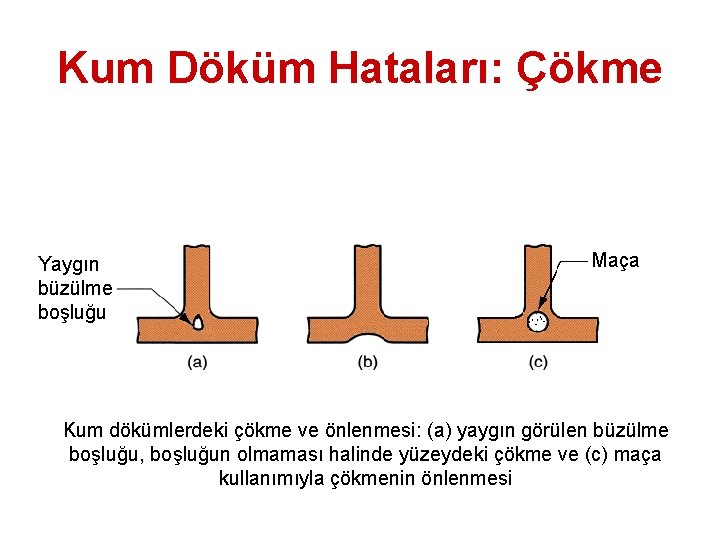
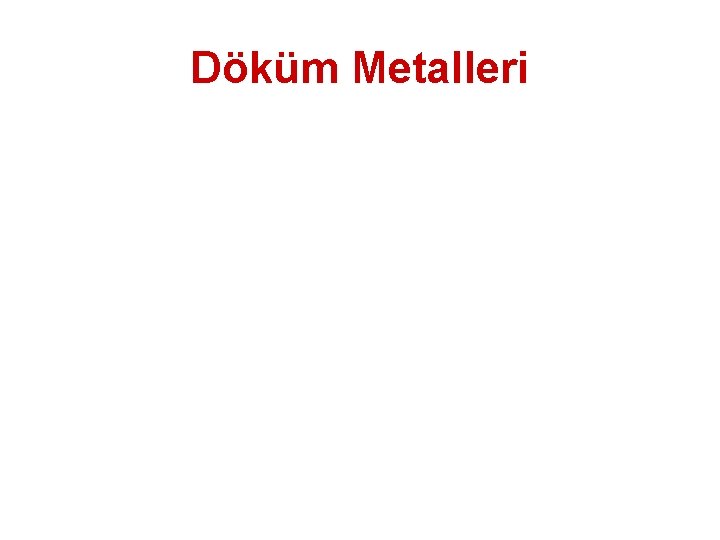
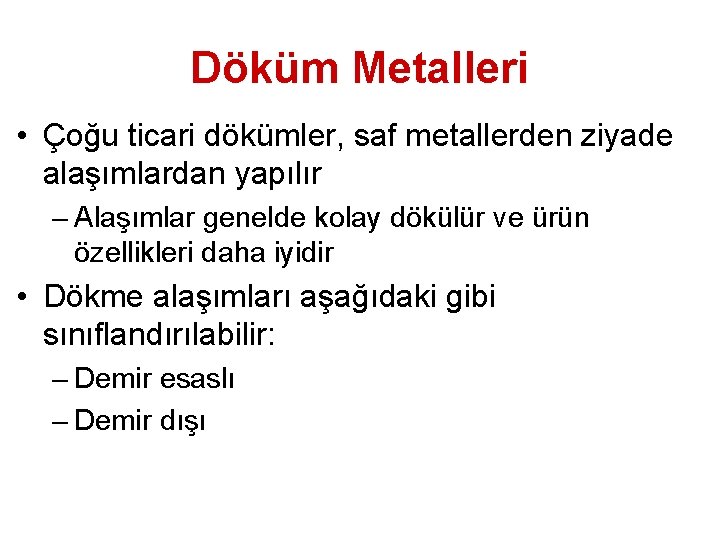
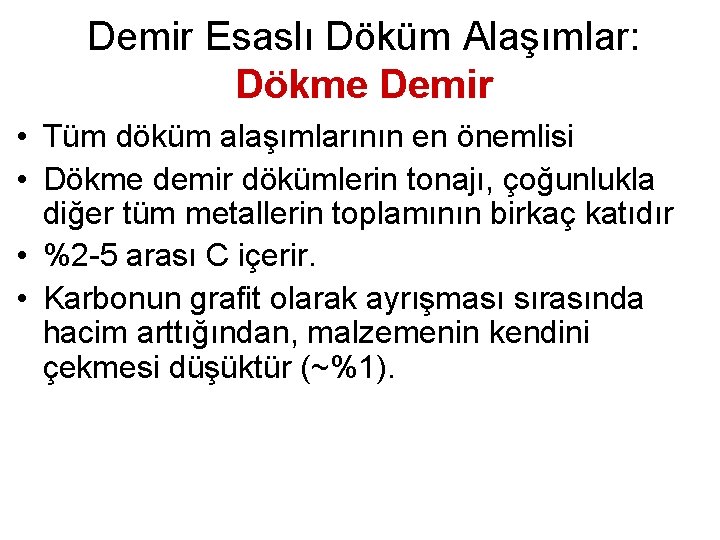
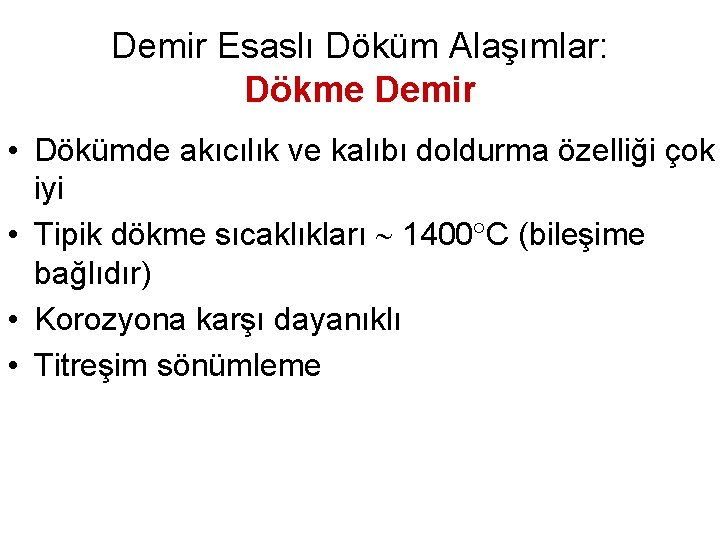
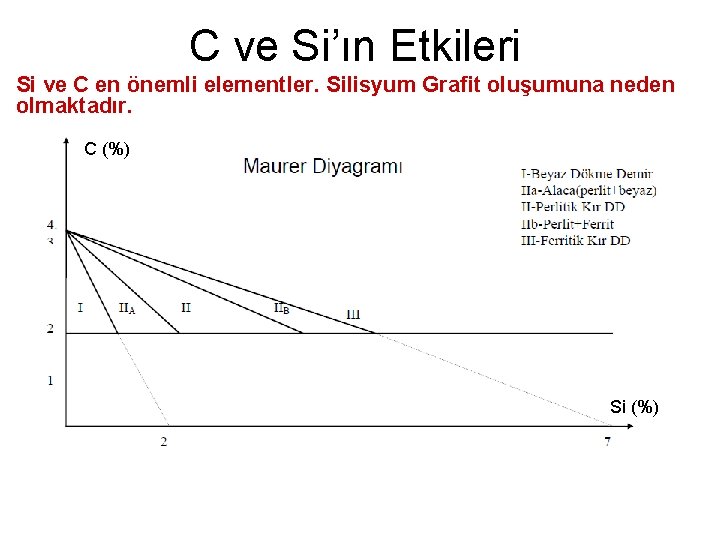
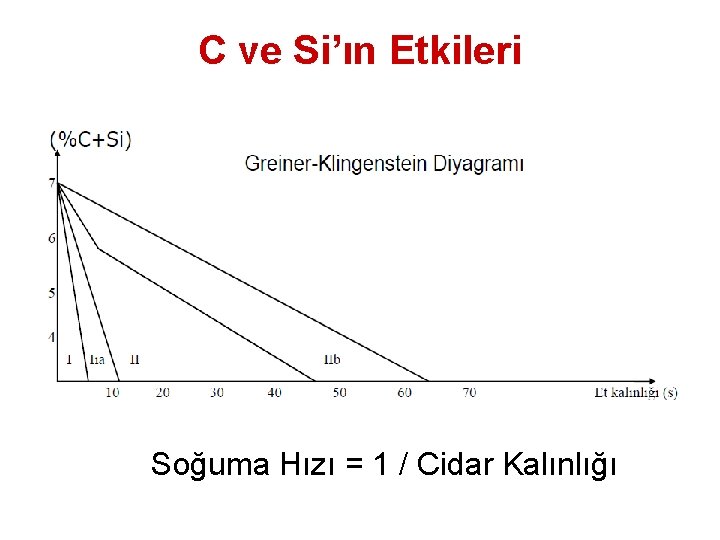
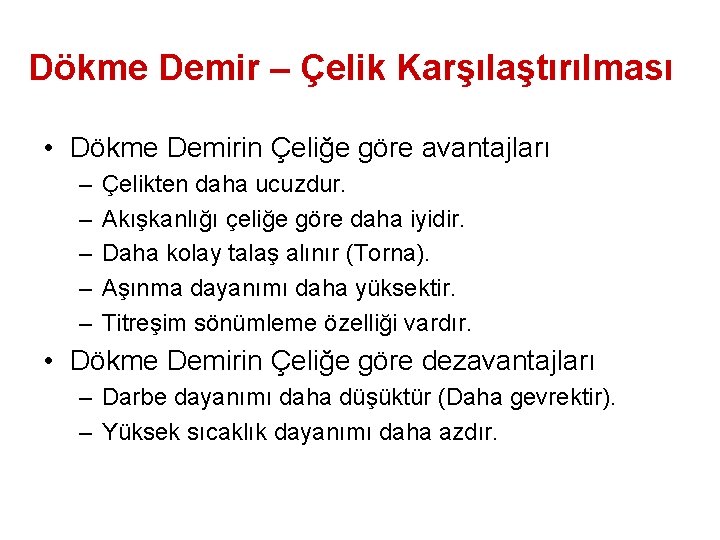
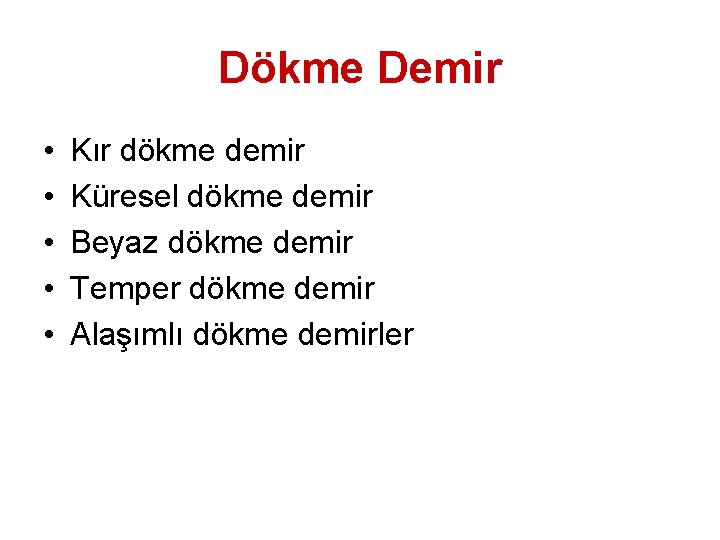
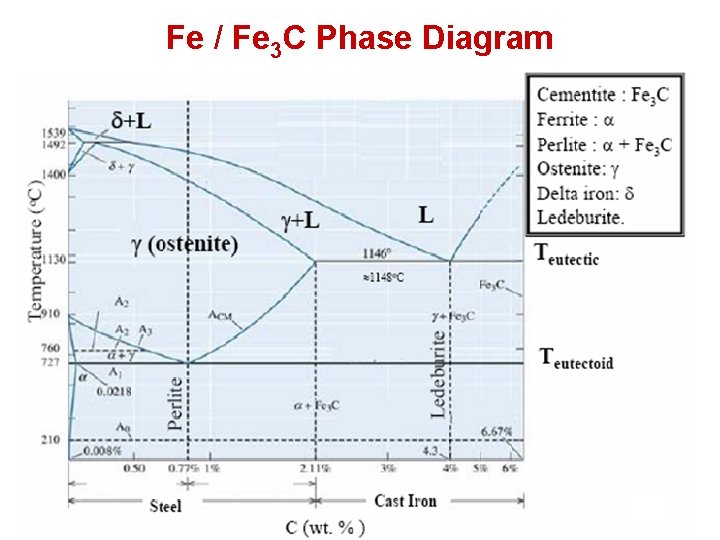
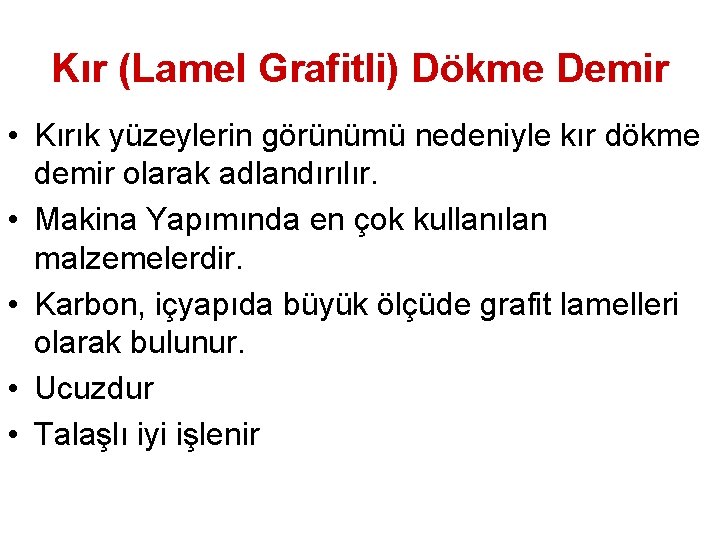

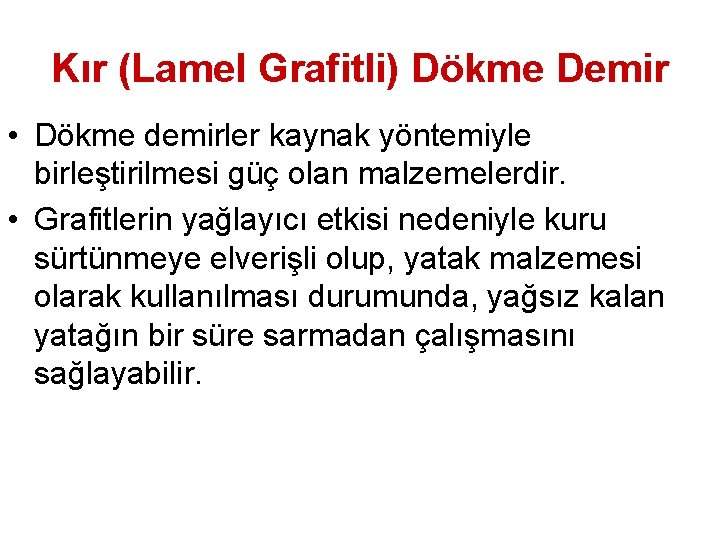
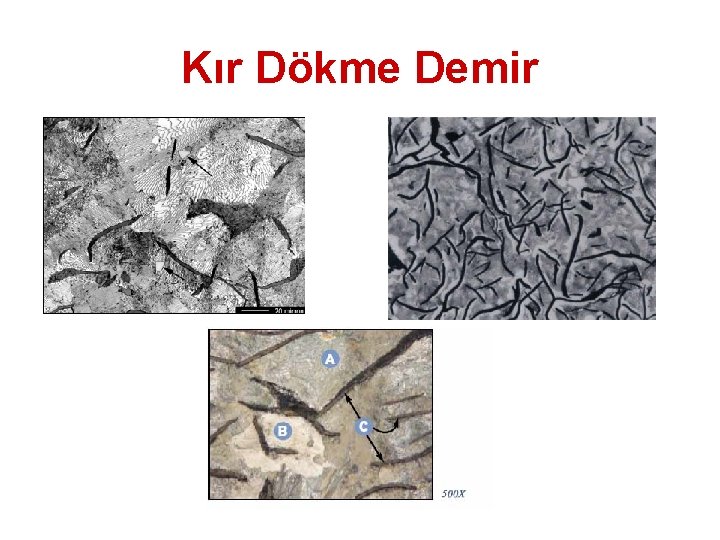
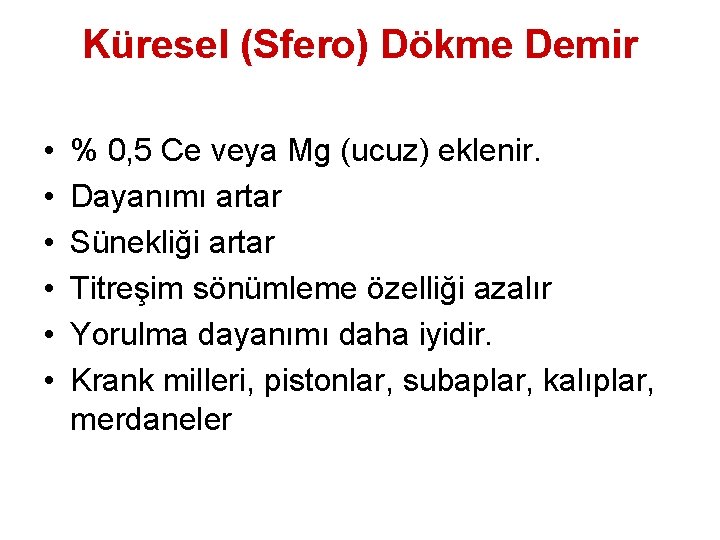

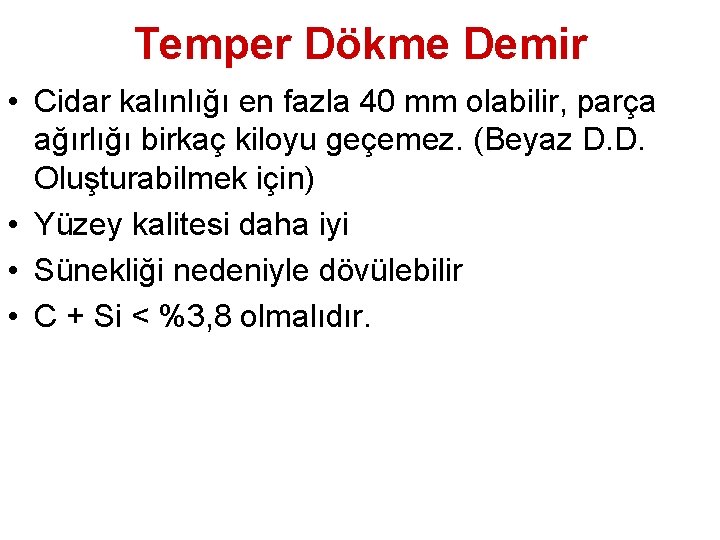
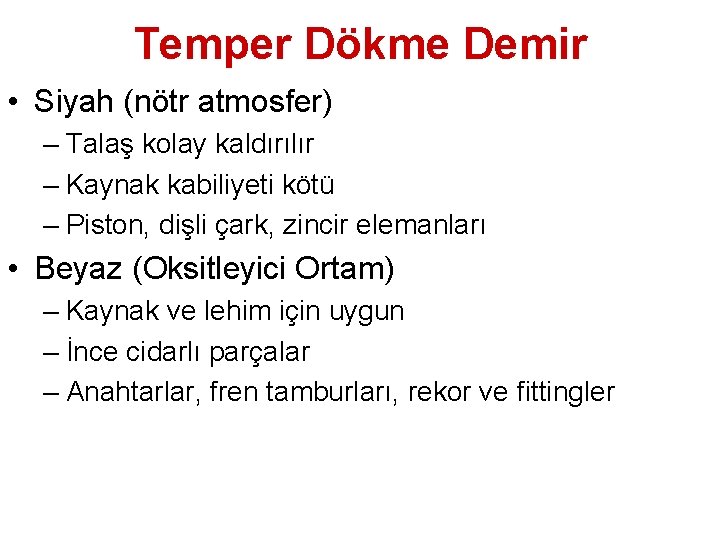
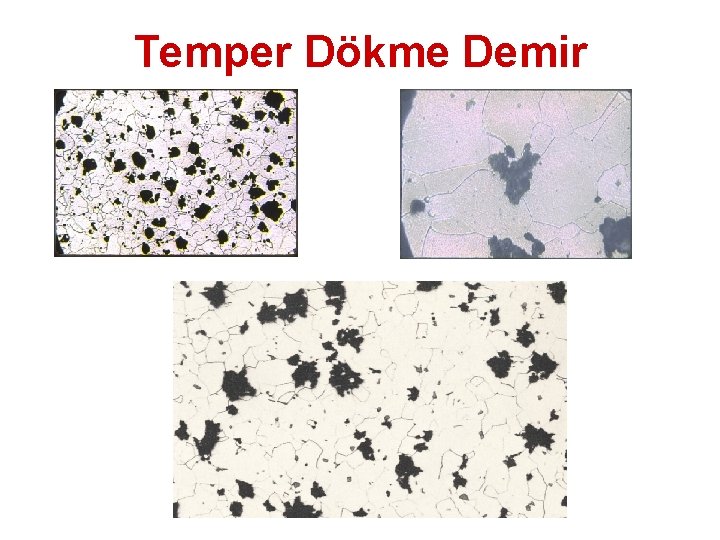
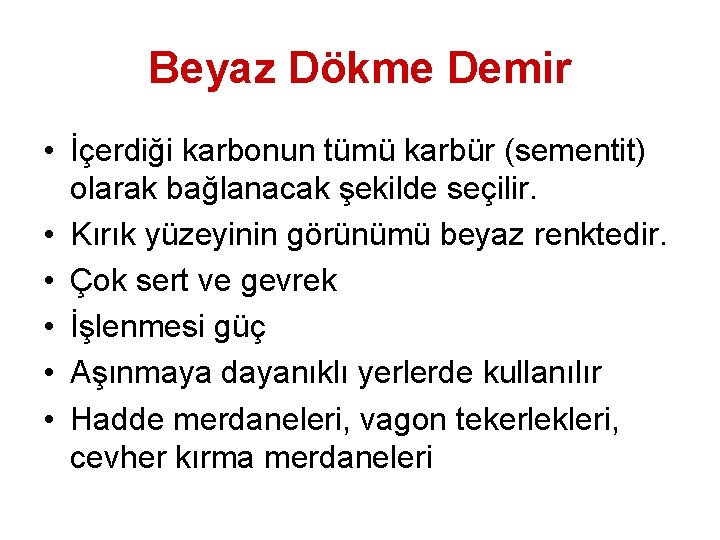
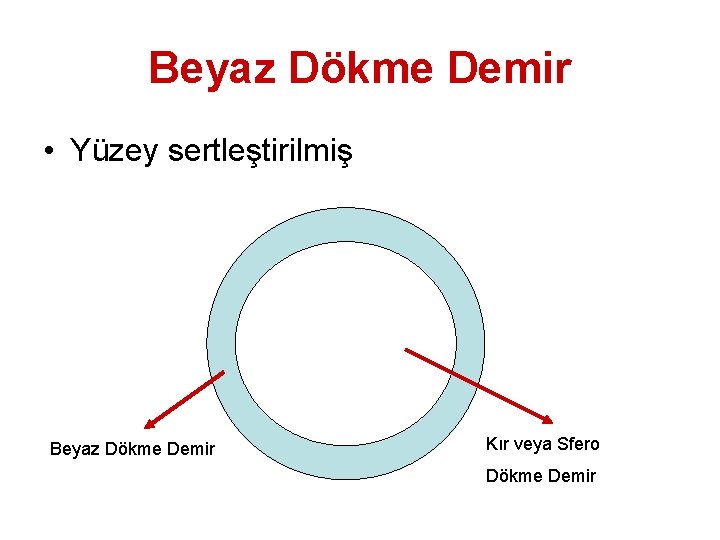
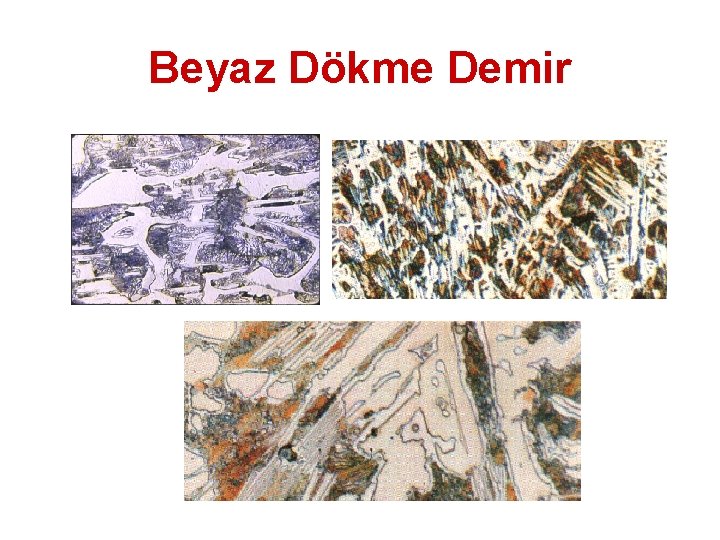
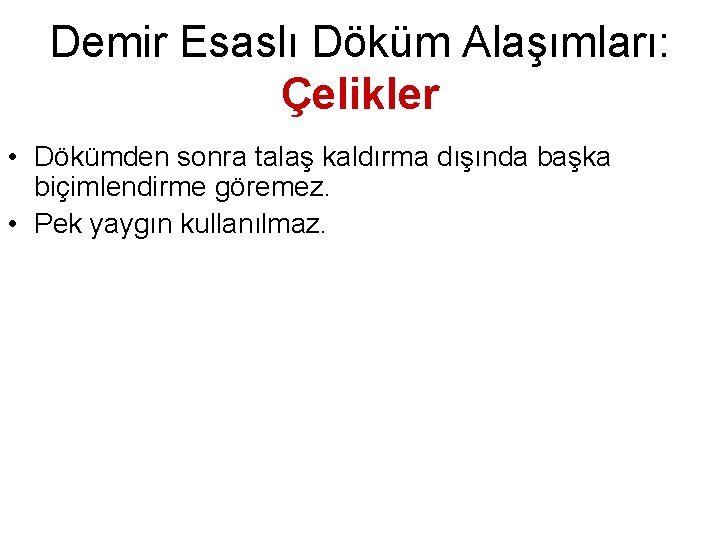
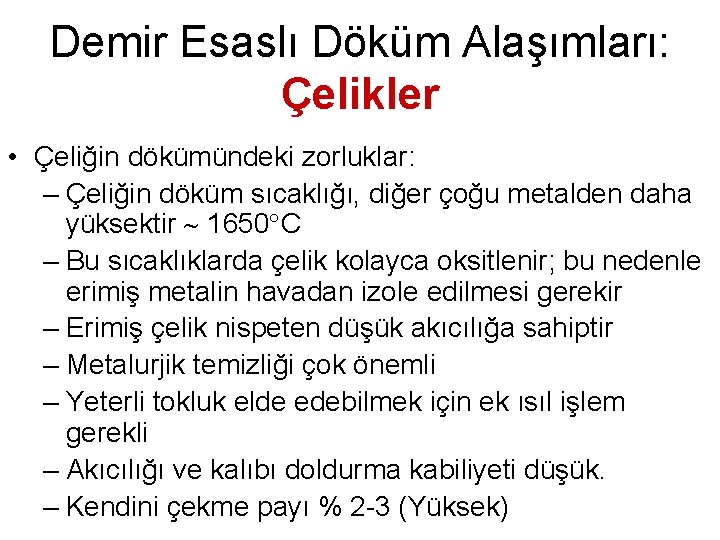
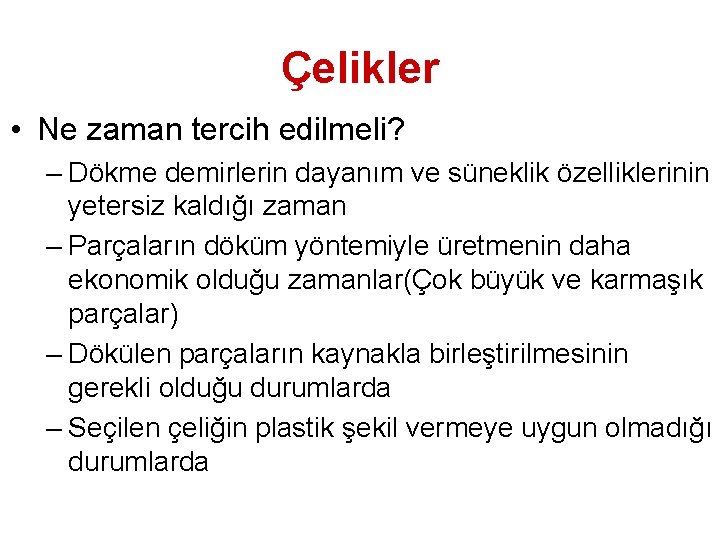
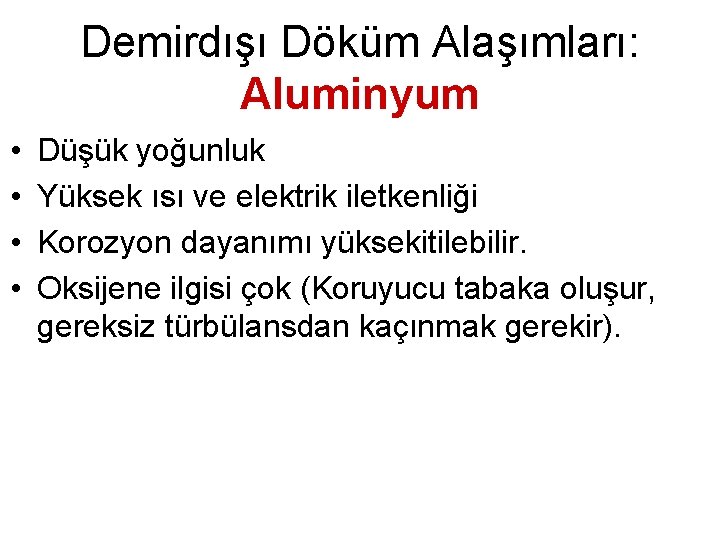
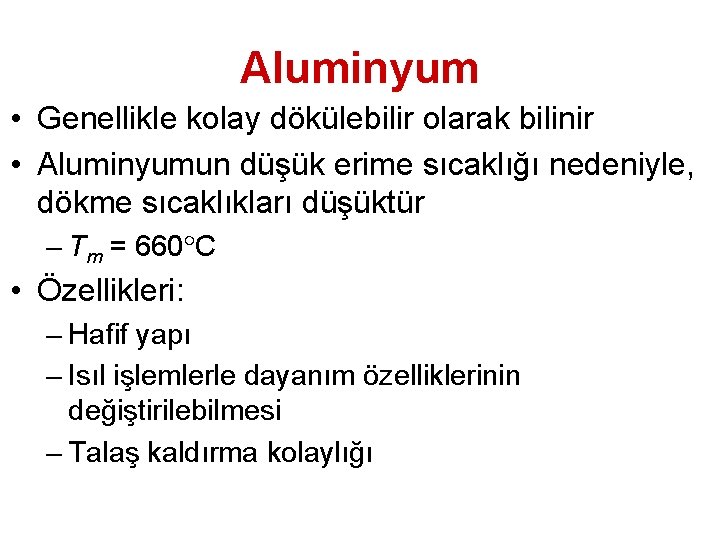
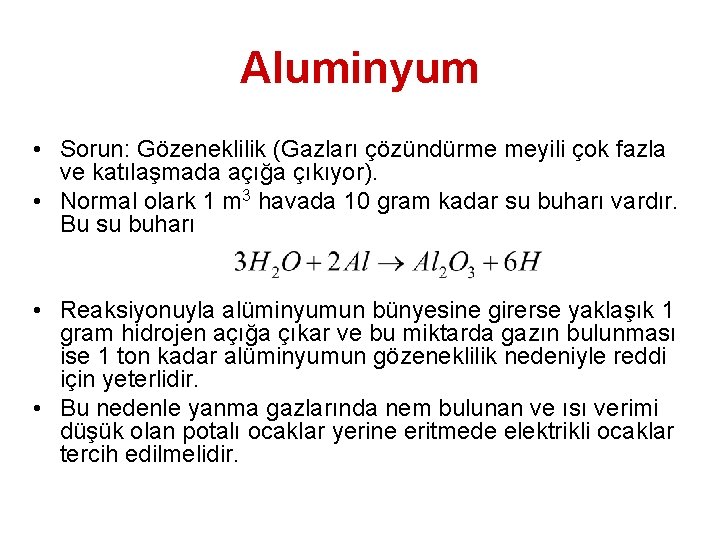
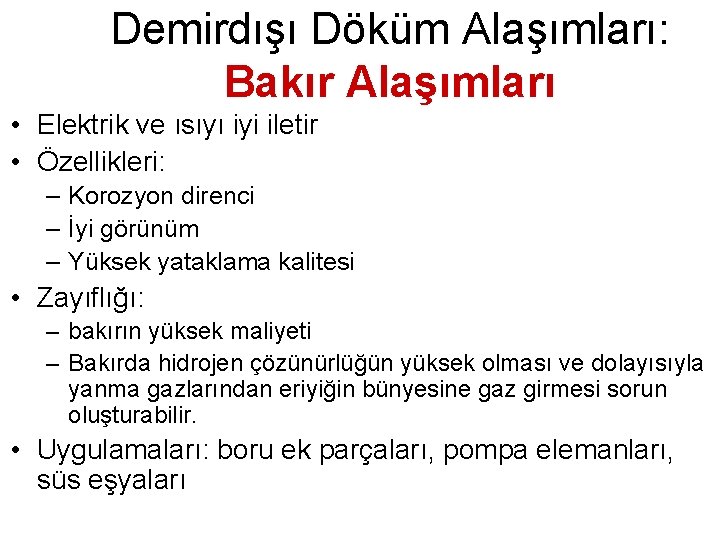
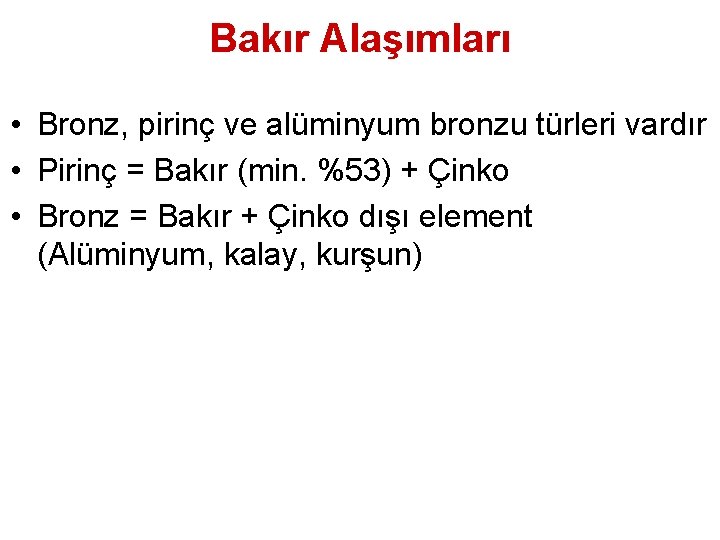
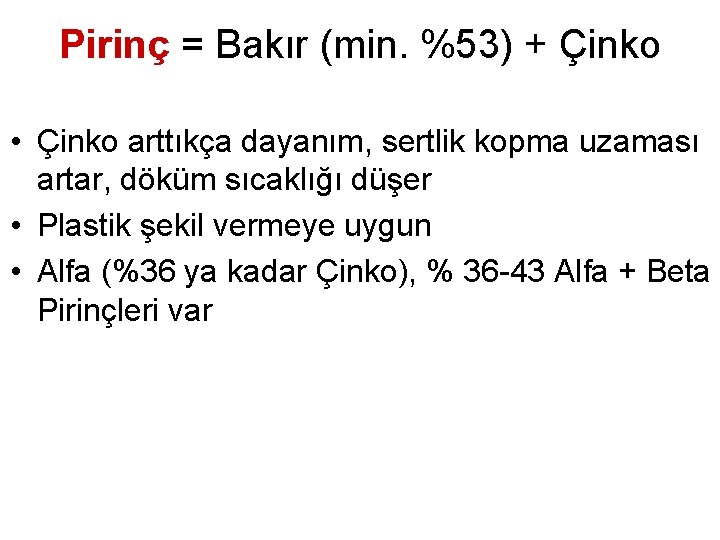
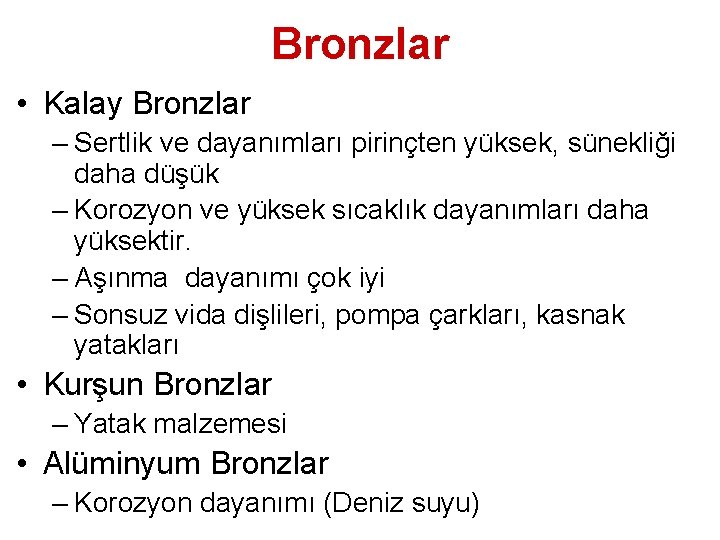
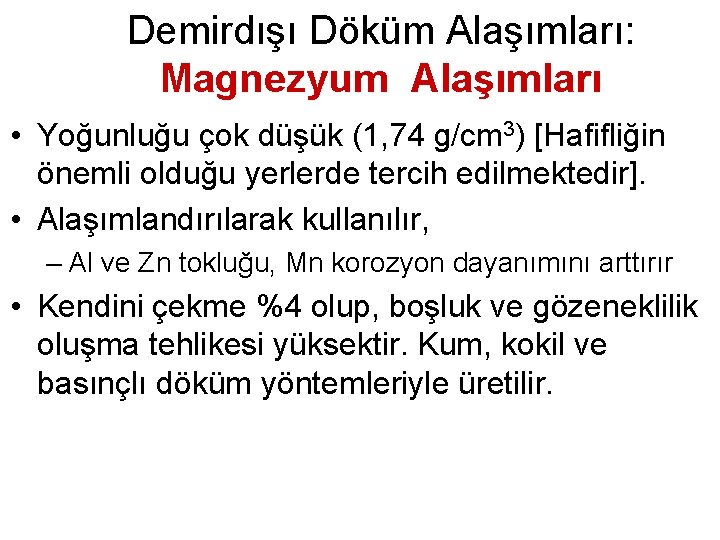
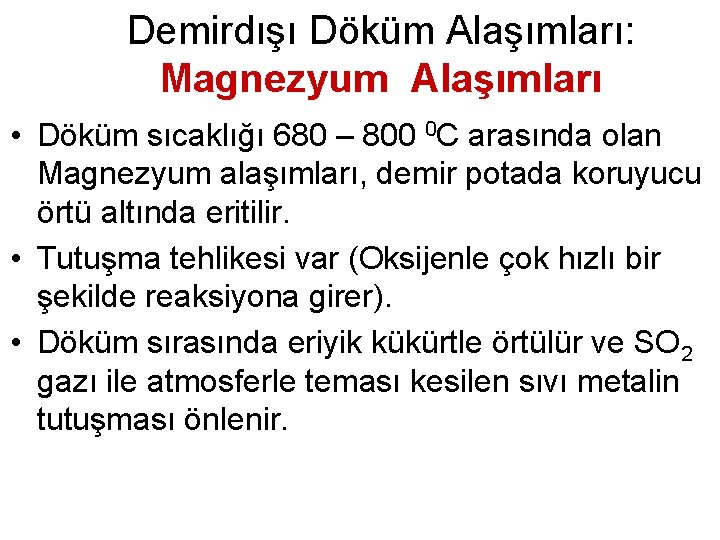
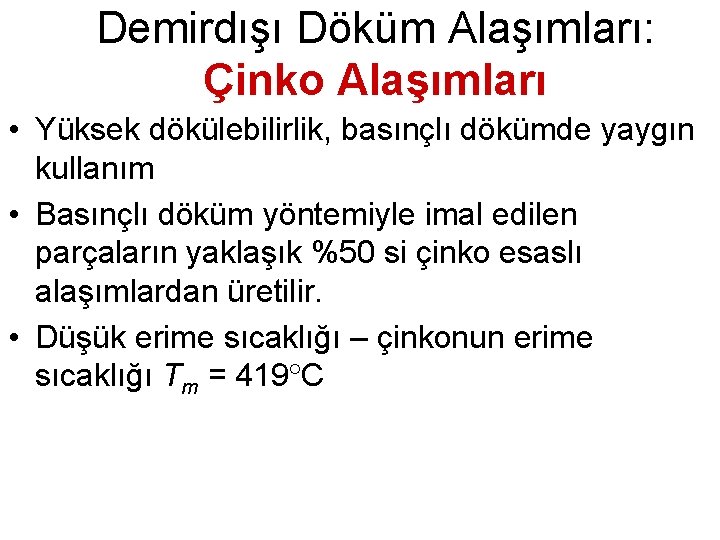
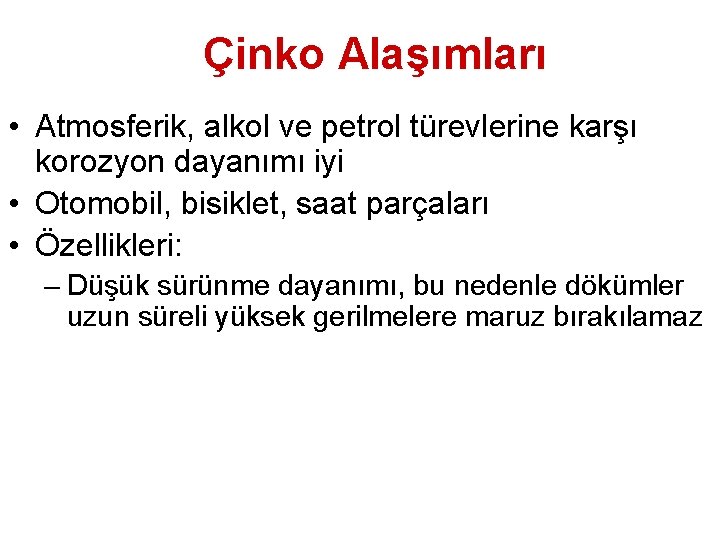
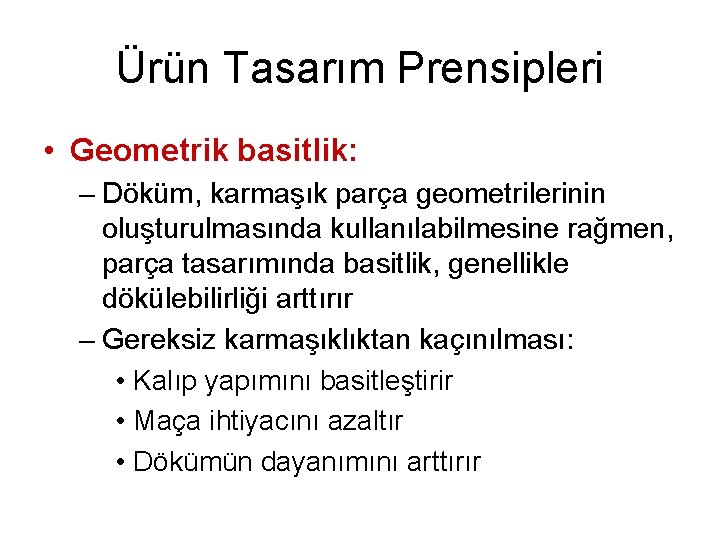
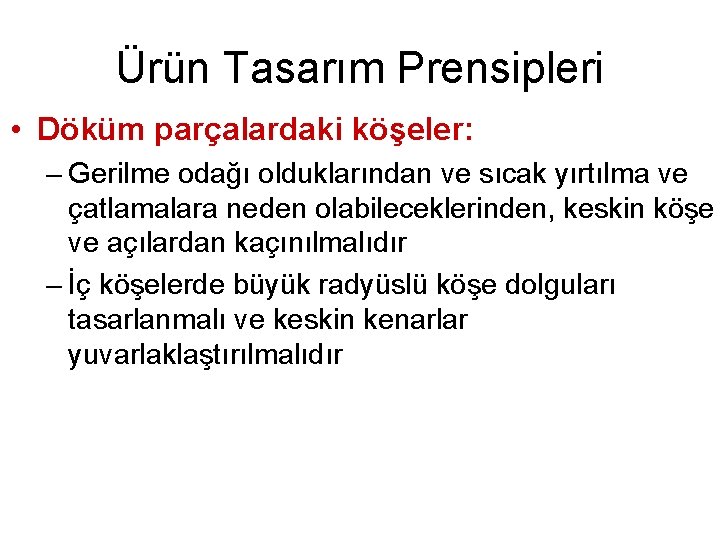
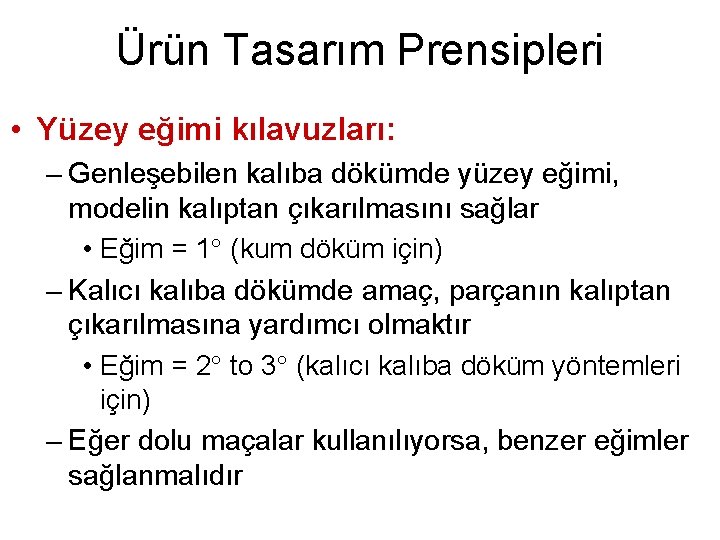
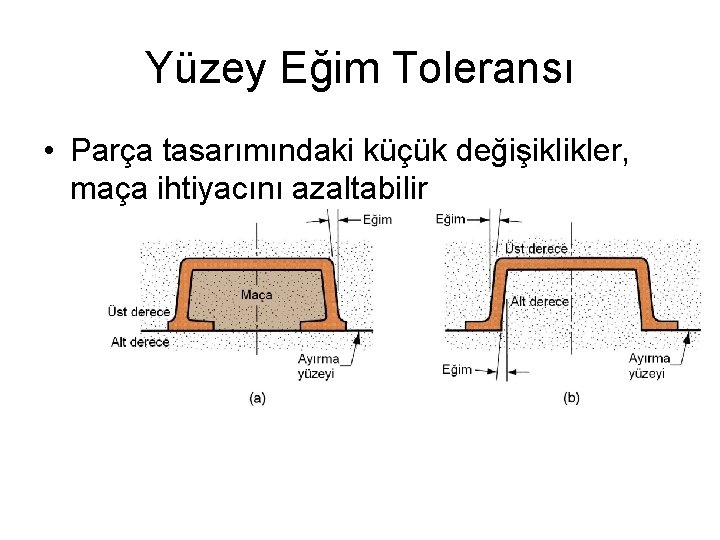
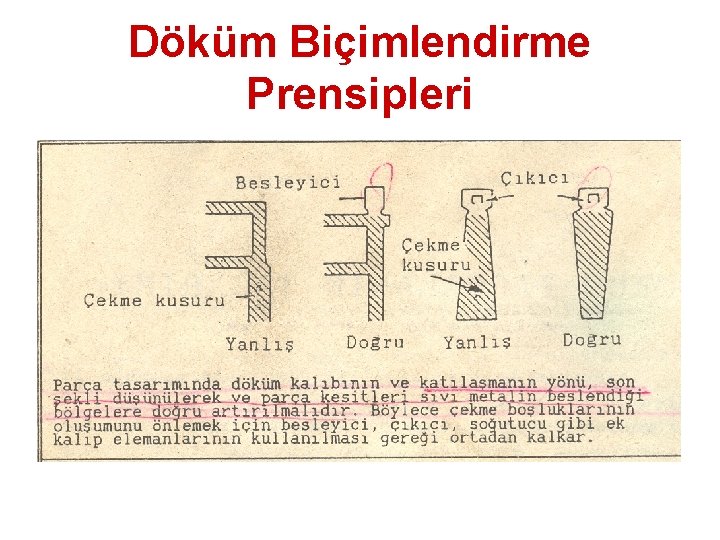
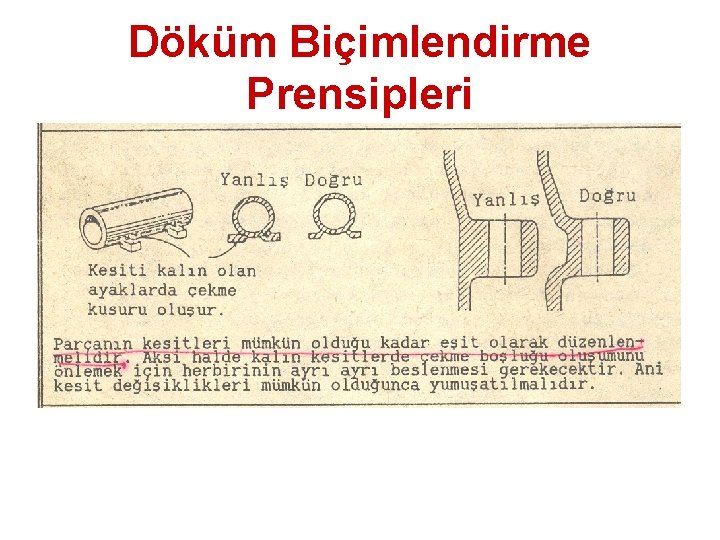
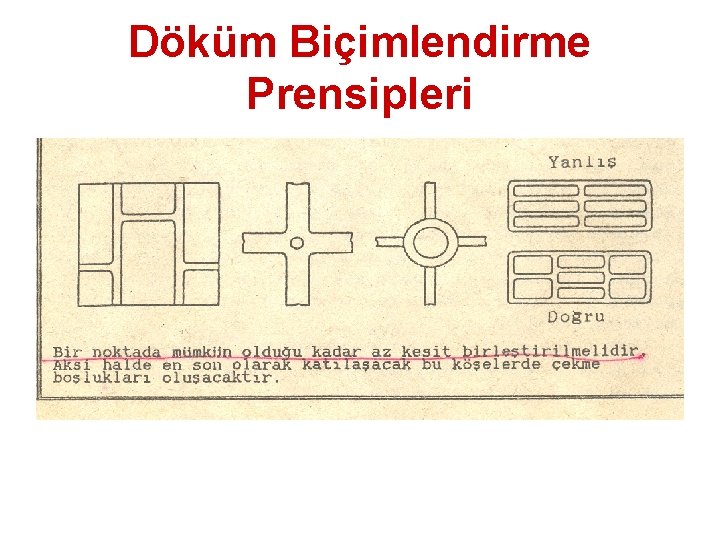
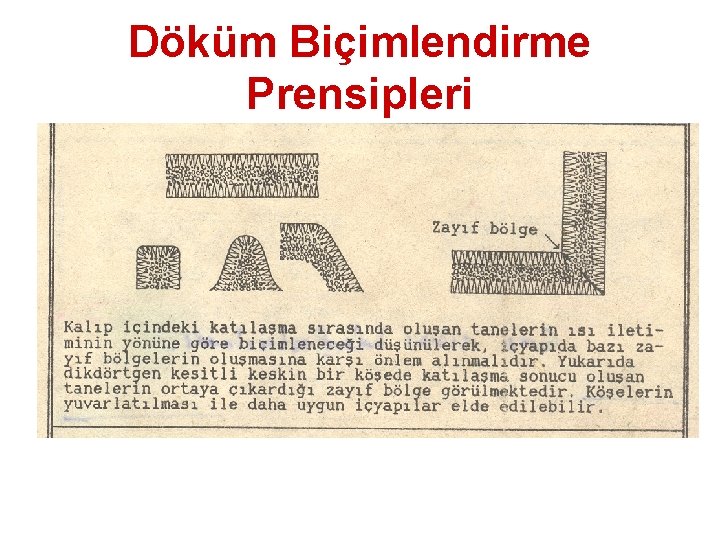
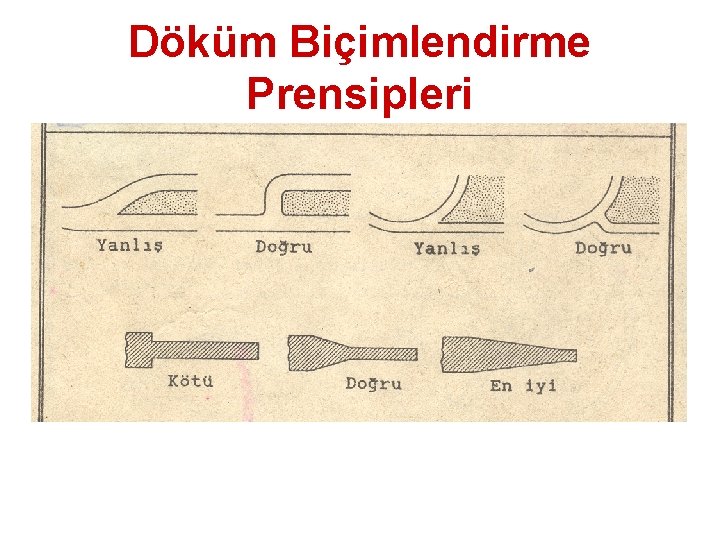
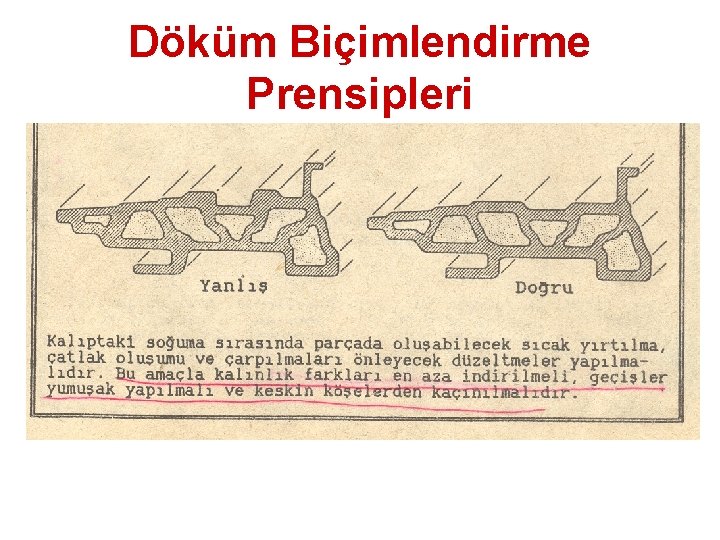
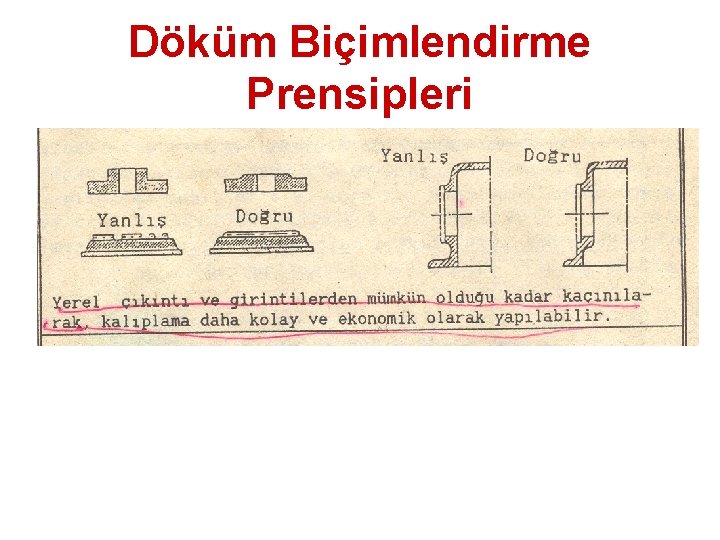
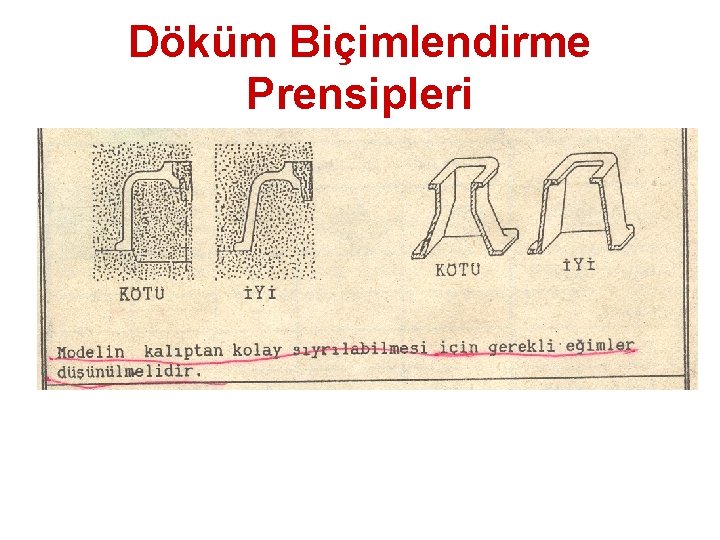
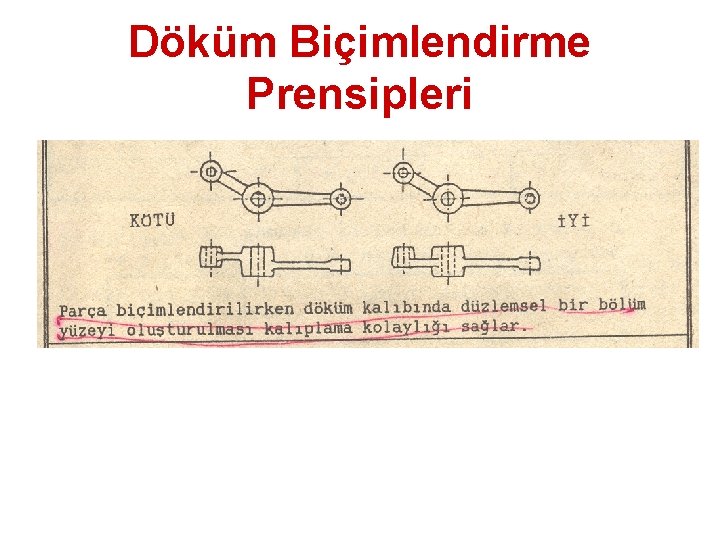
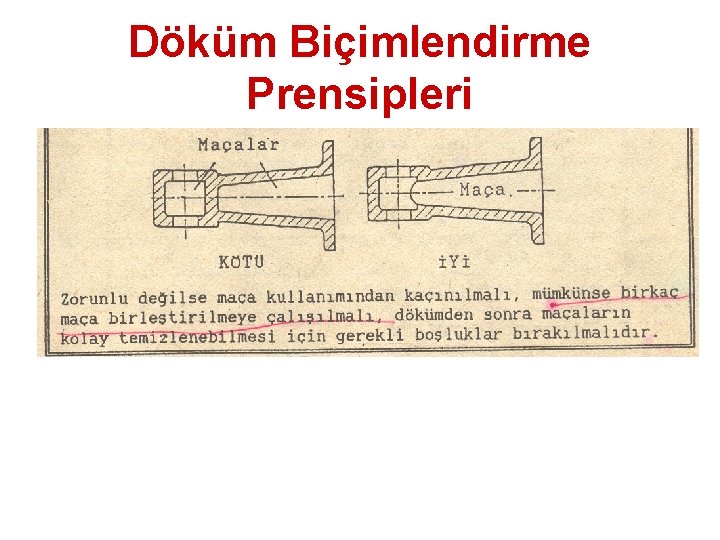
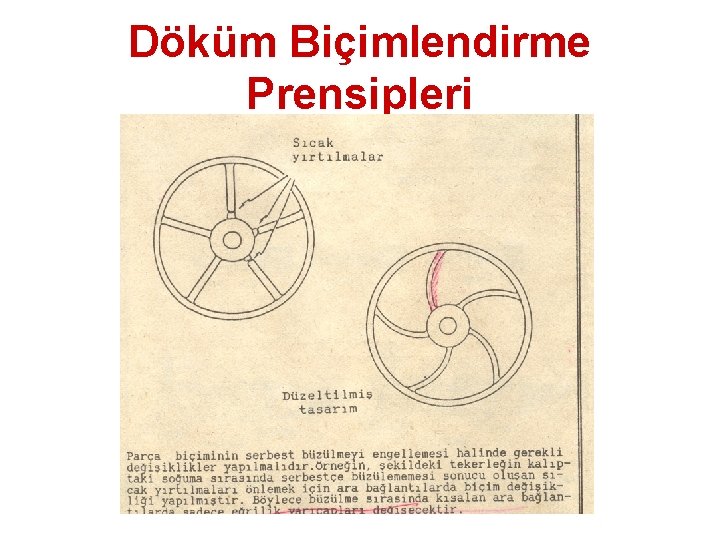
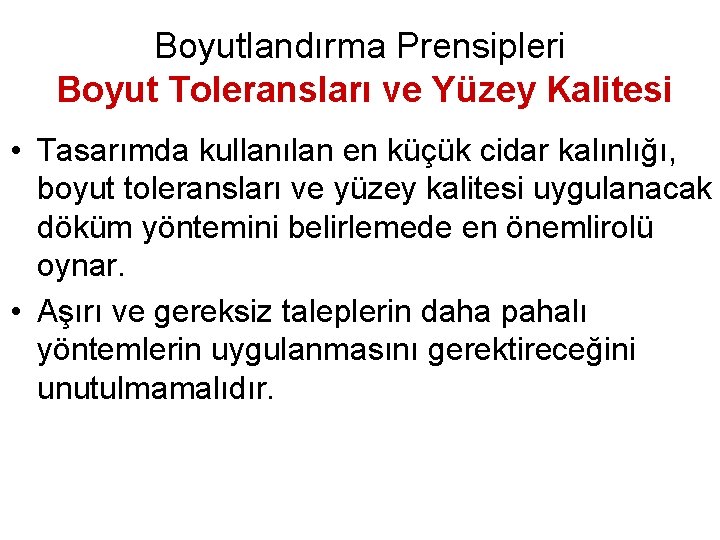
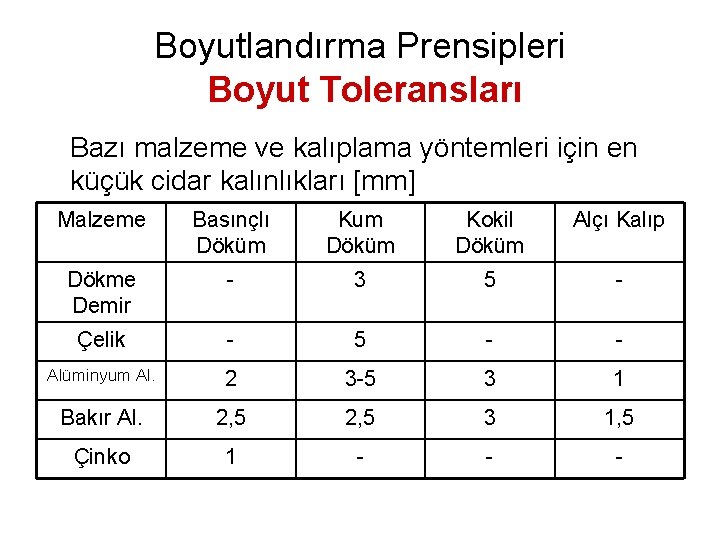
![Boyutlandırma Prensipleri Yüzey Kalitesi Bazı kalıplama yöntemleri için yüzey pürüzlülük değerleri [µm] Kalıplama Yöntemi Boyutlandırma Prensipleri Yüzey Kalitesi Bazı kalıplama yöntemleri için yüzey pürüzlülük değerleri [µm] Kalıplama Yöntemi](https://slidetodoc.com/presentation_image_h/761e36bea554940433692f270349680e/image-70.jpg)
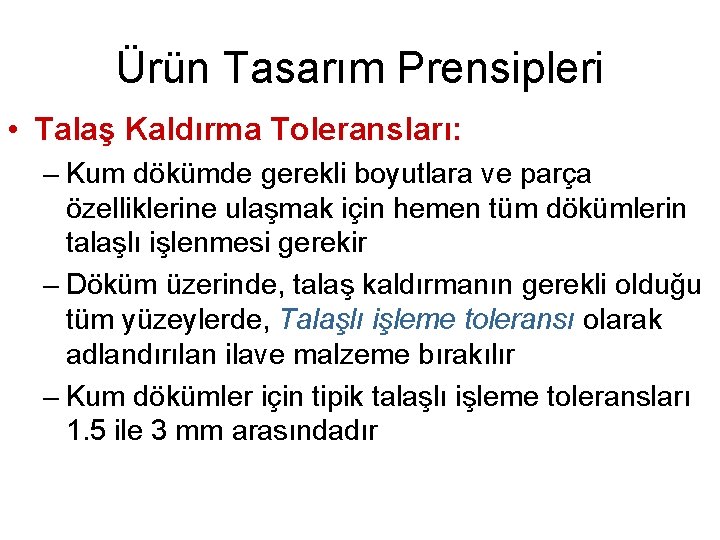
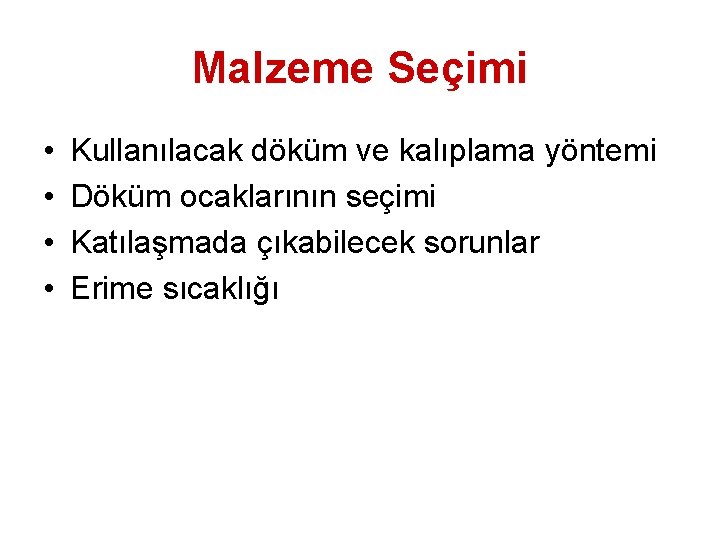
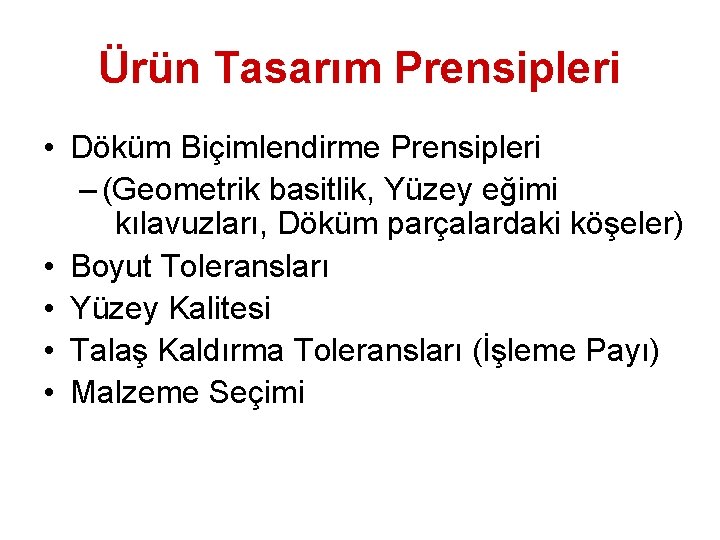
- Slides: 73
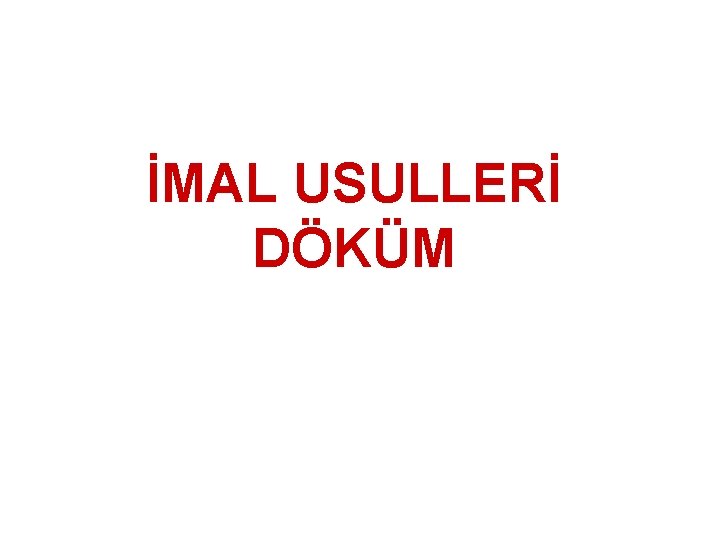
İMAL USULLERİ DÖKÜM
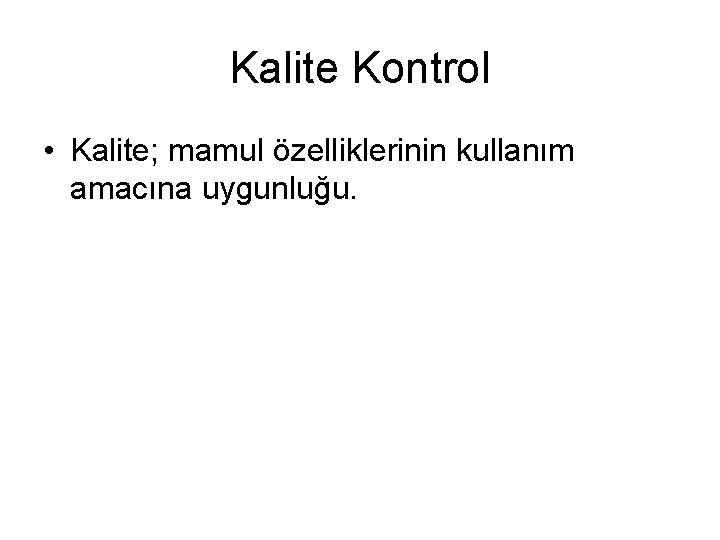
Kalite Kontrol • Kalite; mamul özelliklerinin kullanım amacına uygunluğu.
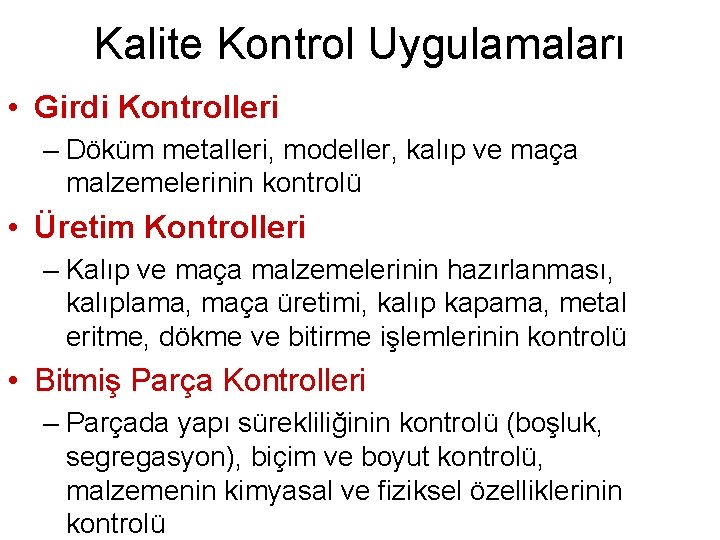
Kalite Kontrol Uygulamaları • Girdi Kontrolleri – Döküm metalleri, modeller, kalıp ve maça malzemelerinin kontrolü • Üretim Kontrolleri – Kalıp ve maça malzemelerinin hazırlanması, kalıplama, maça üretimi, kalıp kapama, metal eritme, dökme ve bitirme işlemlerinin kontrolü • Bitmiş Parça Kontrolleri – Parçada yapı sürekliliğinin kontrolü (boşluk, segregasyon), biçim ve boyut kontrolü, malzemenin kimyasal ve fiziksel özelliklerinin kontrolü
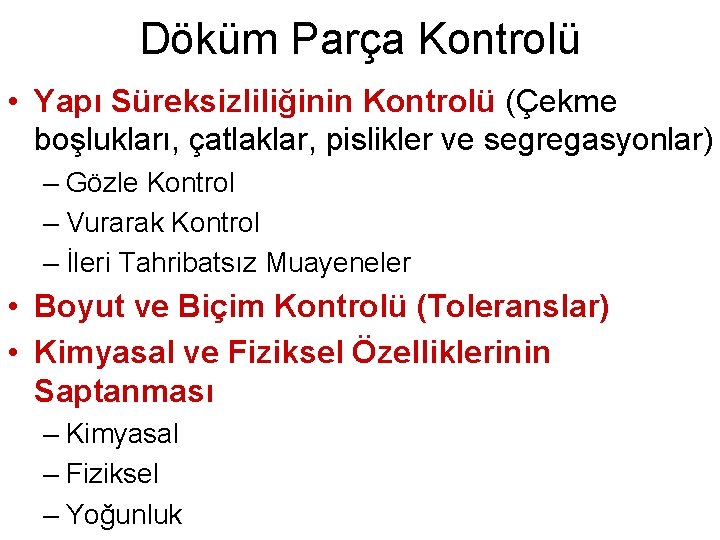
Döküm Parça Kontrolü • Yapı Süreksizliliğinin Kontrolü (Çekme boşlukları, çatlaklar, pislikler ve segregasyonlar) – Gözle Kontrol – Vurarak Kontrol – İleri Tahribatsız Muayeneler • Boyut ve Biçim Kontrolü (Toleranslar) • Kimyasal ve Fiziksel Özelliklerinin Saptanması – Kimyasal – Fiziksel – Yoğunluk
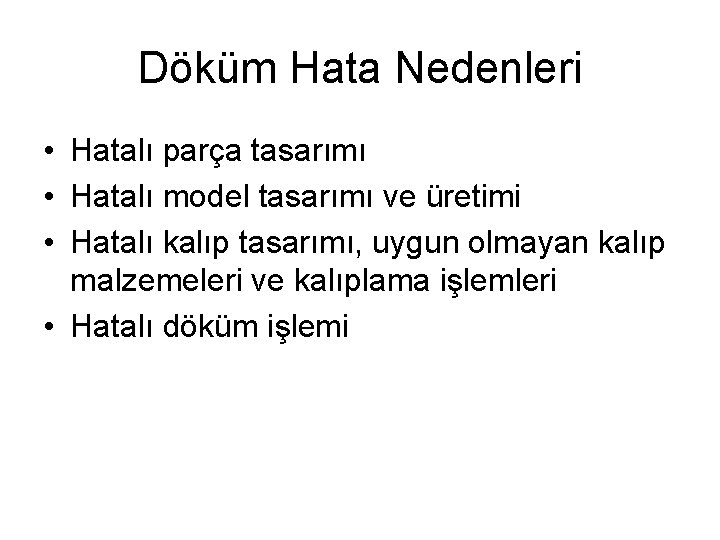
Döküm Hata Nedenleri • Hatalı parça tasarımı • Hatalı model tasarımı ve üretimi • Hatalı kalıp tasarımı, uygun olmayan kalıp malzemeleri ve kalıplama işlemleri • Hatalı döküm işlemi
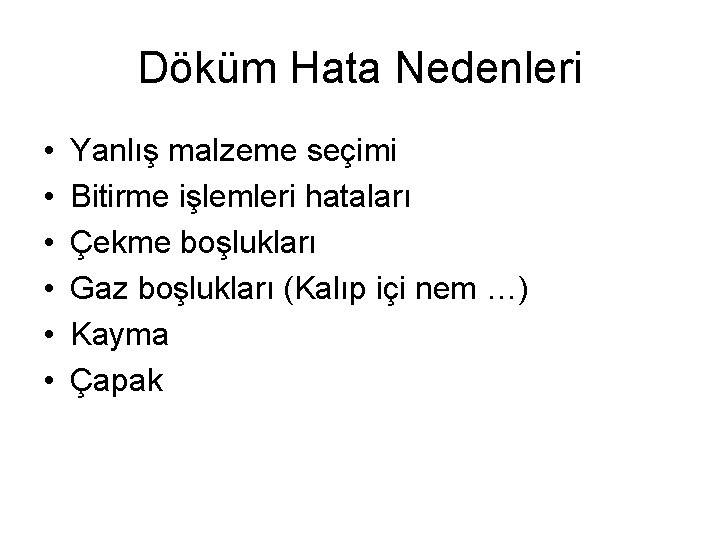
Döküm Hata Nedenleri • • • Yanlış malzeme seçimi Bitirme işlemleri hataları Çekme boşlukları Gaz boşlukları (Kalıp içi nem …) Kayma Çapak
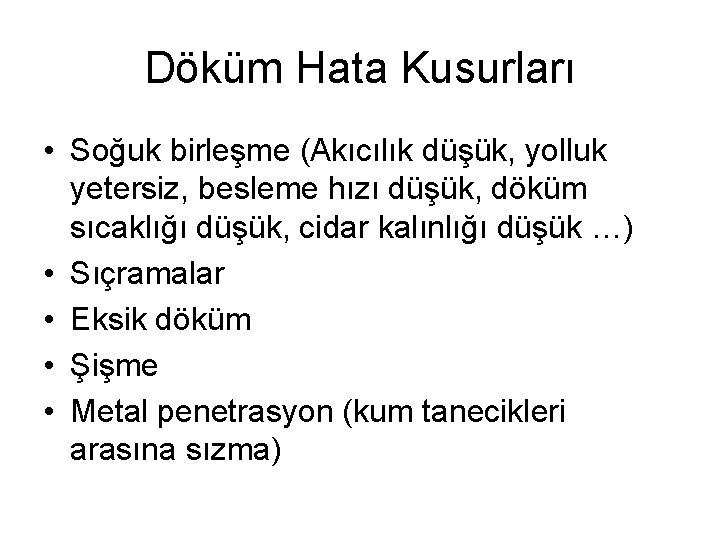
Döküm Hata Kusurları • Soğuk birleşme (Akıcılık düşük, yolluk yetersiz, besleme hızı düşük, döküm sıcaklığı düşük, cidar kalınlığı düşük …) • Sıçramalar • Eksik döküm • Şişme • Metal penetrasyon (kum tanecikleri arasına sızma)
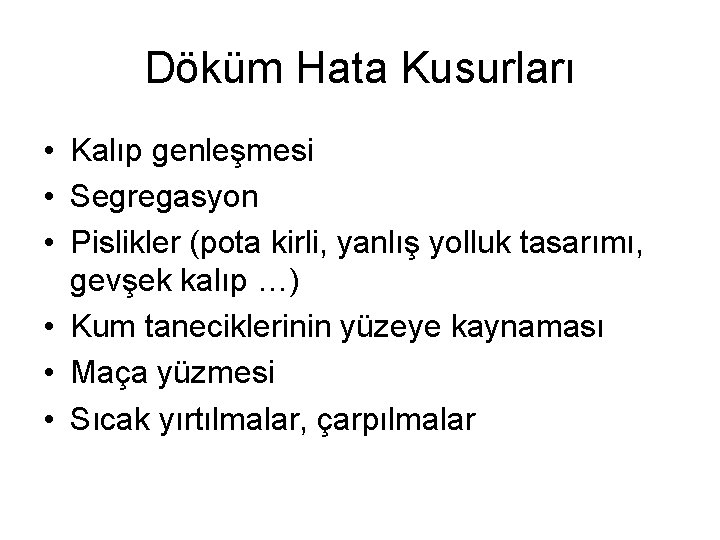
Döküm Hata Kusurları • Kalıp genleşmesi • Segregasyon • Pislikler (pota kirli, yanlış yolluk tasarımı, gevşek kalıp …) • Kum taneciklerinin yüzeye kaynaması • Maça yüzmesi • Sıcak yırtılmalar, çarpılmalar
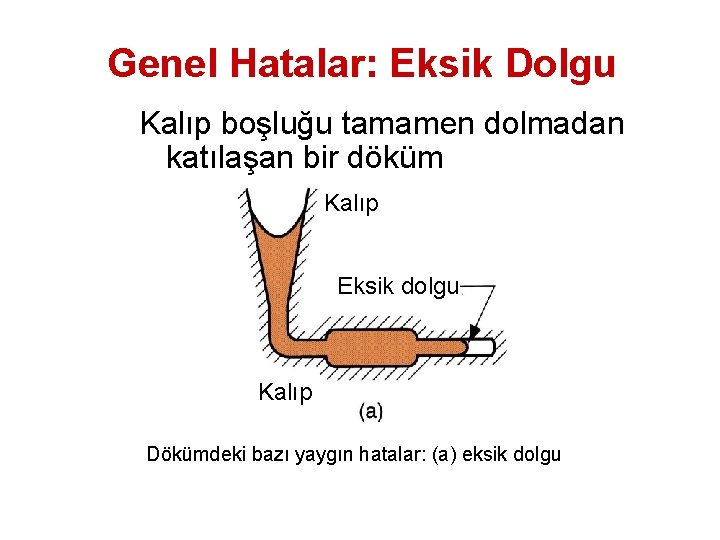
Genel Hatalar: Eksik Dolgu Kalıp boşluğu tamamen dolmadan katılaşan bir döküm Kalıp Eksik dolgu Kalıp Dökümdeki bazı yaygın hatalar: (a) eksik dolgu
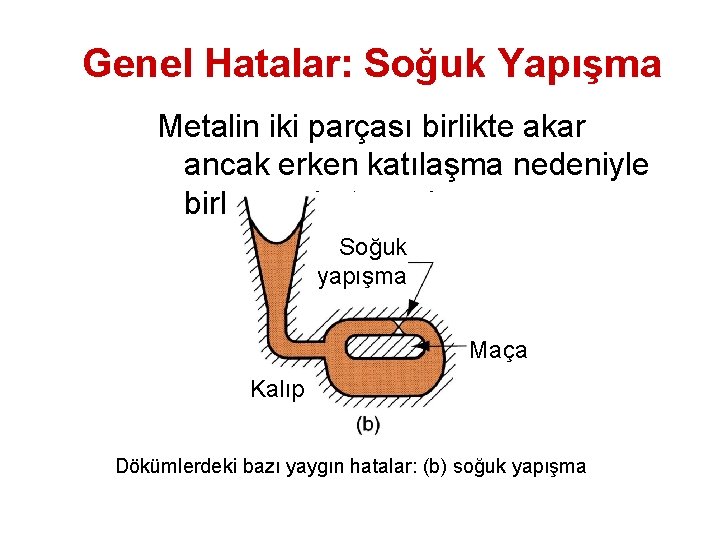
Genel Hatalar: Soğuk Yapışma Metalin iki parçası birlikte akar ancak erken katılaşma nedeniyle birleşme hatası oluşur Soğuk yapışma Maça Kalıp Dökümlerdeki bazı yaygın hatalar: (b) soğuk yapışma
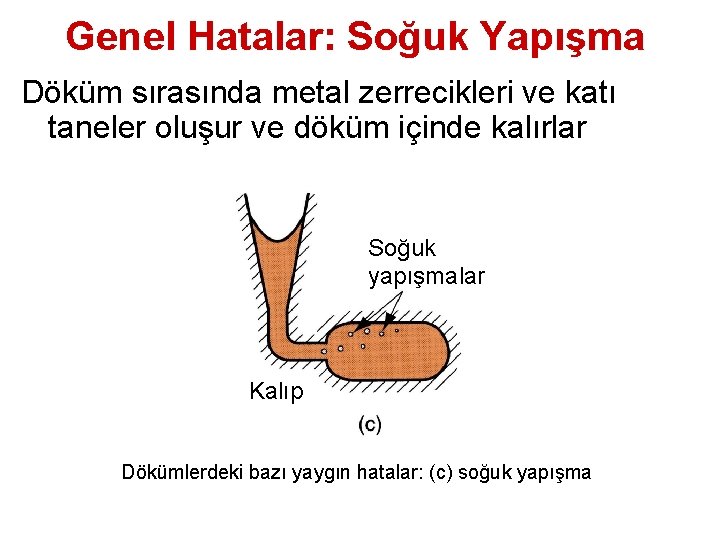
Genel Hatalar: Soğuk Yapışma Döküm sırasında metal zerrecikleri ve katı taneler oluşur ve döküm içinde kalırlar Soğuk yapışmalar Kalıp Dökümlerdeki bazı yaygın hatalar: (c) soğuk yapışma
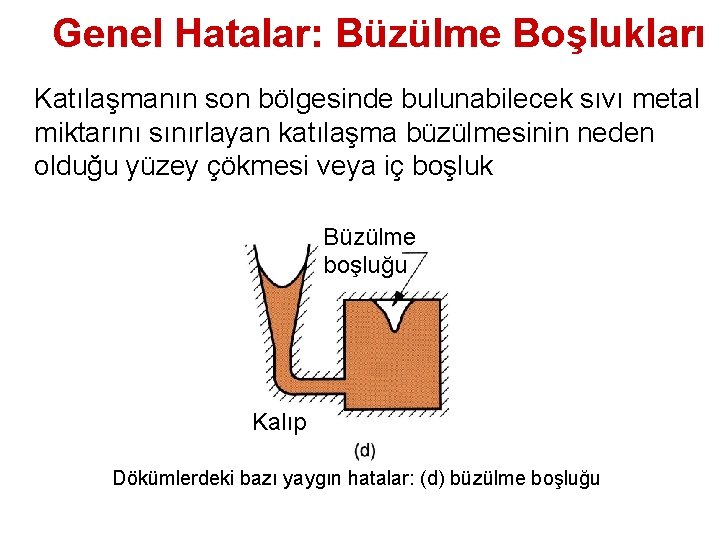
Genel Hatalar: Büzülme Boşlukları Katılaşmanın son bölgesinde bulunabilecek sıvı metal miktarını sınırlayan katılaşma büzülmesinin neden olduğu yüzey çökmesi veya iç boşluk Büzülme boşluğu Kalıp Dökümlerdeki bazı yaygın hatalar: (d) büzülme boşluğu
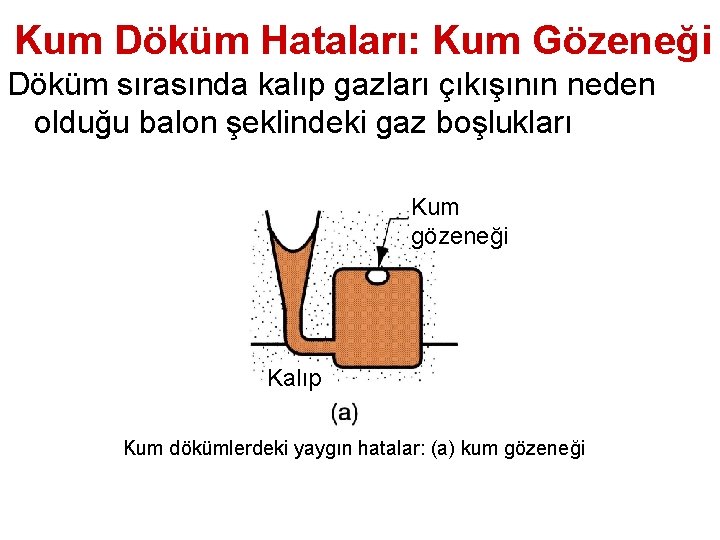
Kum Döküm Hataları: Kum Gözeneği Döküm sırasında kalıp gazları çıkışının neden olduğu balon şeklindeki gaz boşlukları Kum gözeneği Kalıp Kum dökümlerdeki yaygın hatalar: (a) kum gözeneği
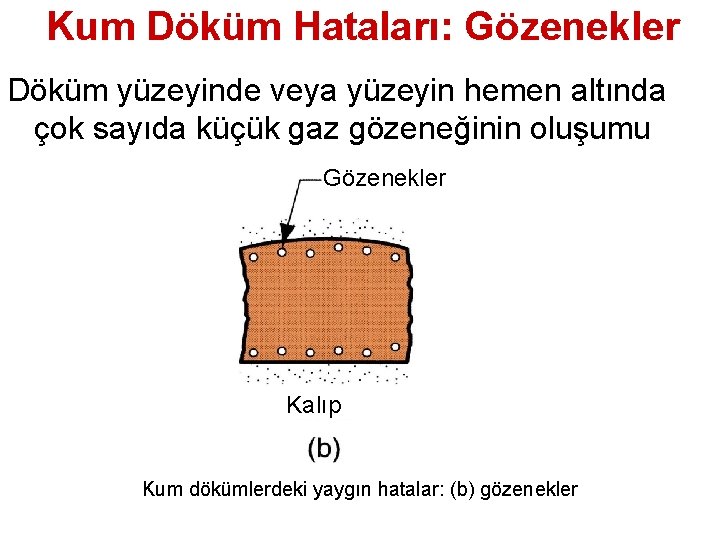
Kum Döküm Hataları: Gözenekler Döküm yüzeyinde veya yüzeyin hemen altında çok sayıda küçük gaz gözeneğinin oluşumu Gözenekler Kalıp Kum dökümlerdeki yaygın hatalar: (b) gözenekler
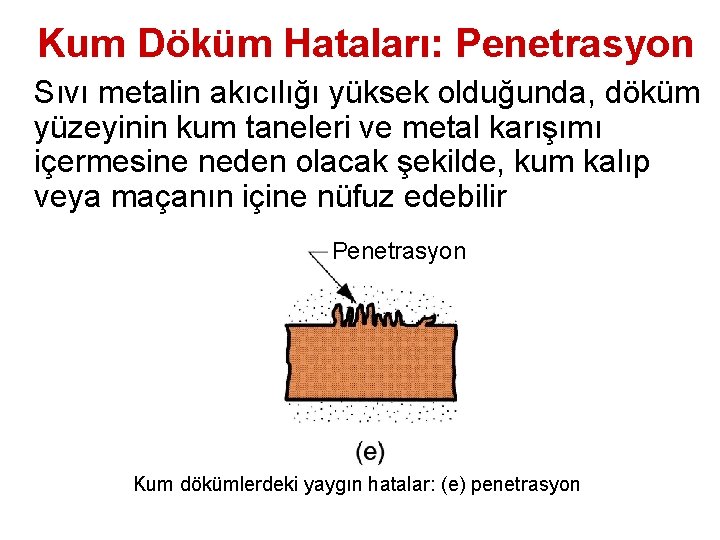
Kum Döküm Hataları: Penetrasyon Sıvı metalin akıcılığı yüksek olduğunda, döküm yüzeyinin kum taneleri ve metal karışımı içermesine neden olacak şekilde, kum kalıp veya maçanın içine nüfuz edebilir Penetrasyon Kum dökümlerdeki yaygın hatalar: (e) penetrasyon
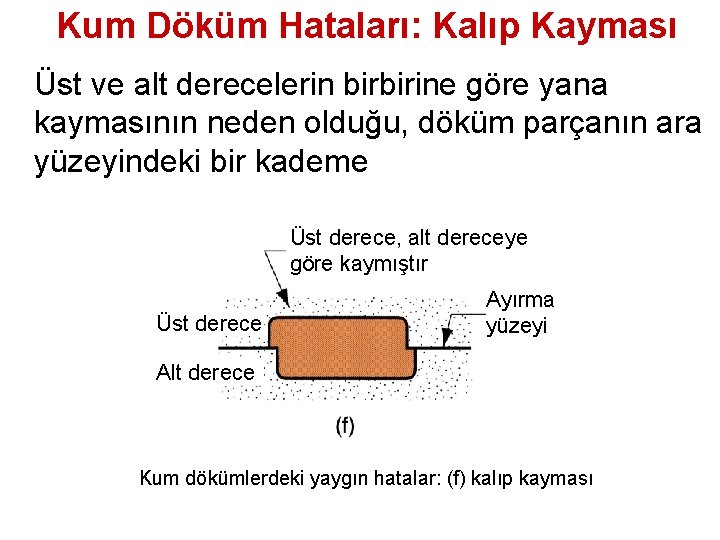
Kum Döküm Hataları: Kalıp Kayması Üst ve alt derecelerin birbirine göre yana kaymasının neden olduğu, döküm parçanın ara yüzeyindeki bir kademe Üst derece, alt dereceye göre kaymıştır Üst derece Ayırma yüzeyi Alt derece Kum dökümlerdeki yaygın hatalar: (f) kalıp kayması
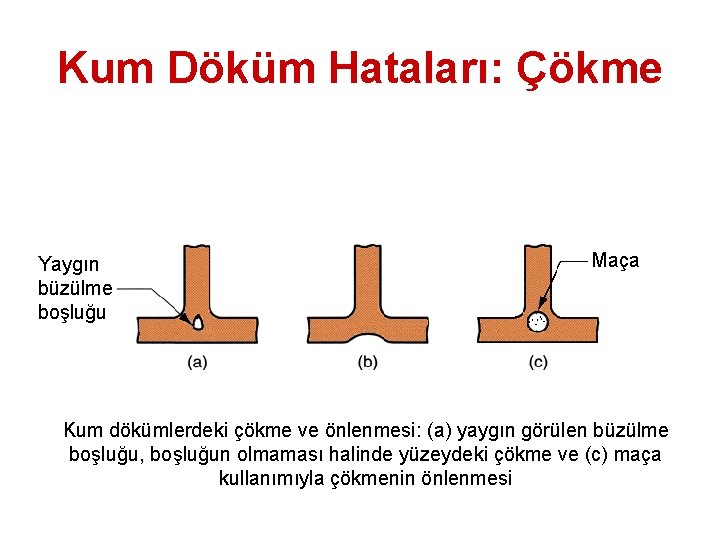
Kum Döküm Hataları: Çökme Yaygın büzülme boşluğu Maça Kum dökümlerdeki çökme ve önlenmesi: (a) yaygın görülen büzülme boşluğu, boşluğun olmaması halinde yüzeydeki çökme ve (c) maça kullanımıyla çökmenin önlenmesi
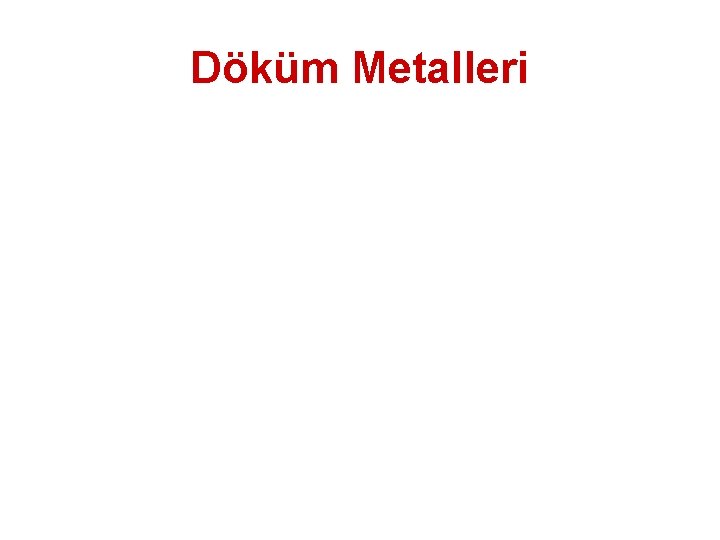
Döküm Metalleri
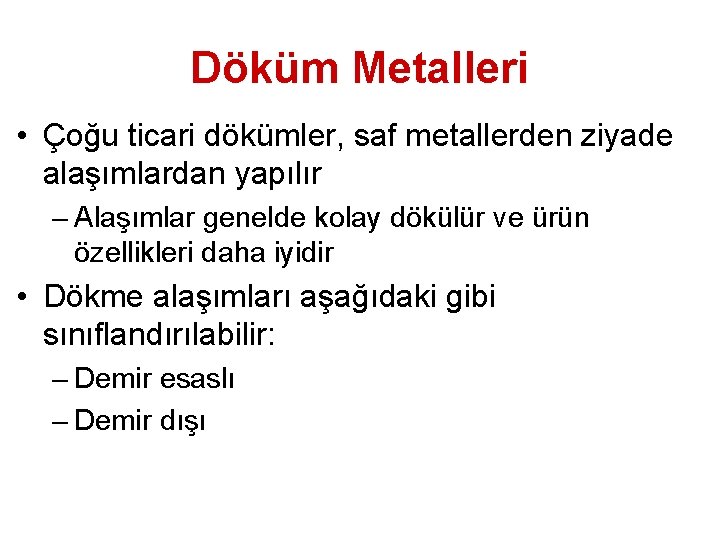
Döküm Metalleri • Çoğu ticari dökümler, saf metallerden ziyade alaşımlardan yapılır – Alaşımlar genelde kolay dökülür ve ürün özellikleri daha iyidir • Dökme alaşımları aşağıdaki gibi sınıflandırılabilir: – Demir esaslı – Demir dışı
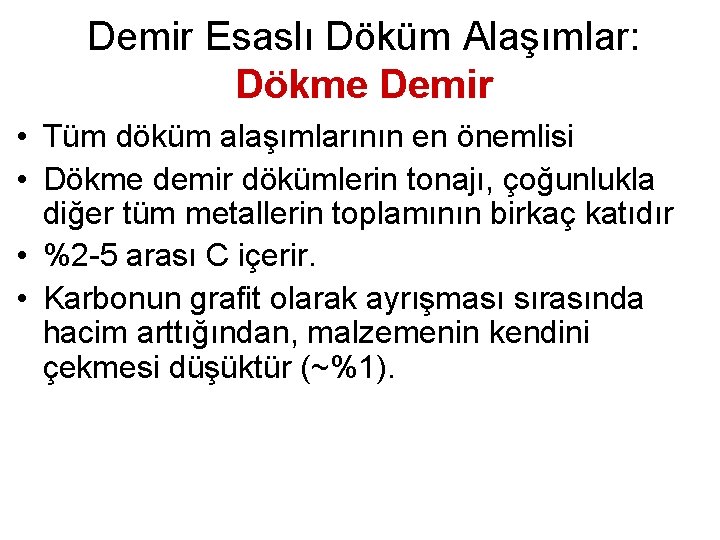
Demir Esaslı Döküm Alaşımlar: Dökme Demir • Tüm döküm alaşımlarının en önemlisi • Dökme demir dökümlerin tonajı, çoğunlukla diğer tüm metallerin toplamının birkaç katıdır • %2 -5 arası C içerir. • Karbonun grafit olarak ayrışması sırasında hacim arttığından, malzemenin kendini çekmesi düşüktür (~%1).
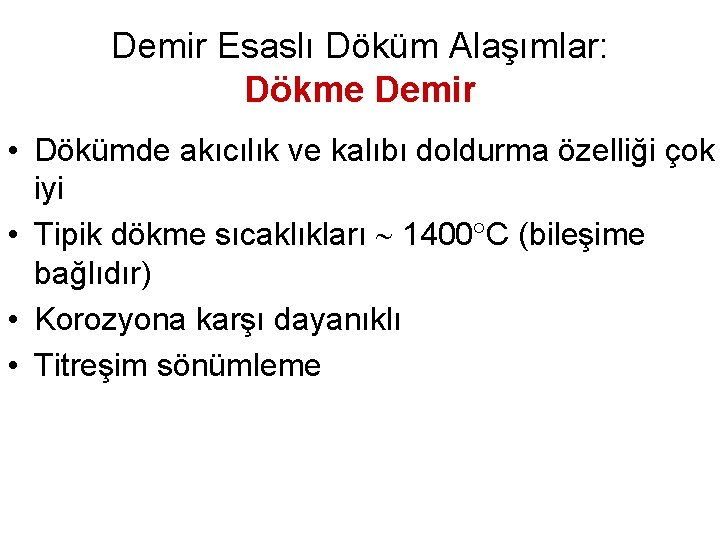
Demir Esaslı Döküm Alaşımlar: Dökme Demir • Dökümde akıcılık ve kalıbı doldurma özelliği çok iyi • Tipik dökme sıcaklıkları 1400 C (bileşime bağlıdır) • Korozyona karşı dayanıklı • Titreşim sönümleme
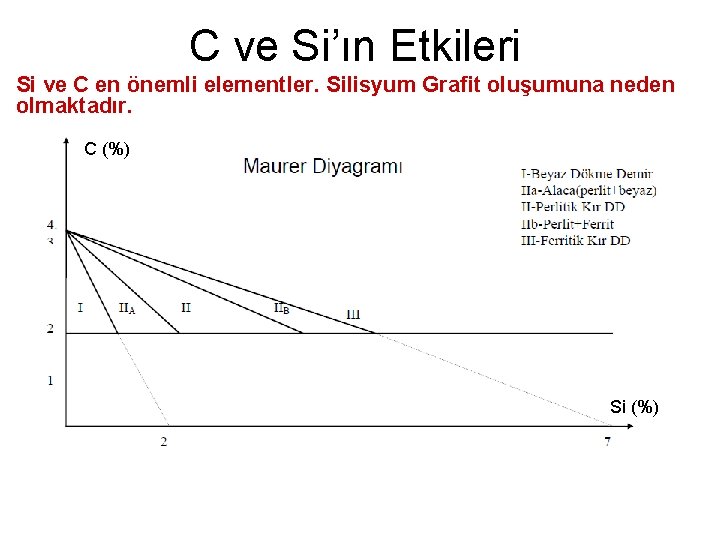
C ve Si’ın Etkileri Si ve C en önemli elementler. Silisyum Grafit oluşumuna neden olmaktadır. C (%) Si (%)
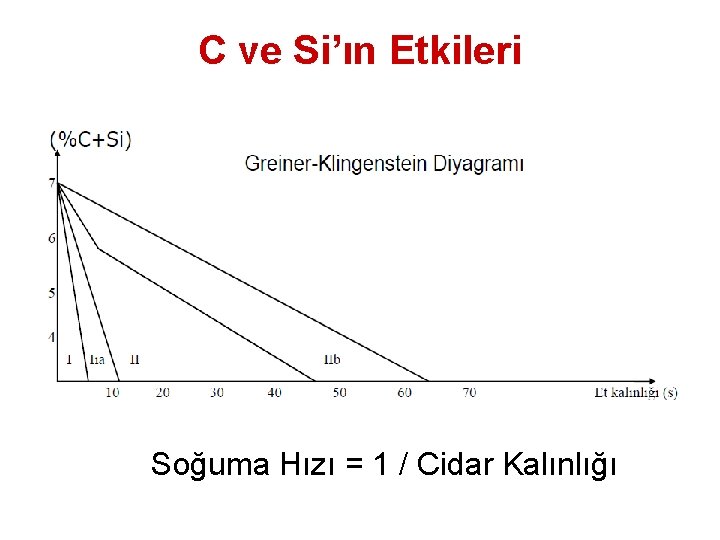
C ve Si’ın Etkileri Soğuma Hızı = 1 / Cidar Kalınlığı
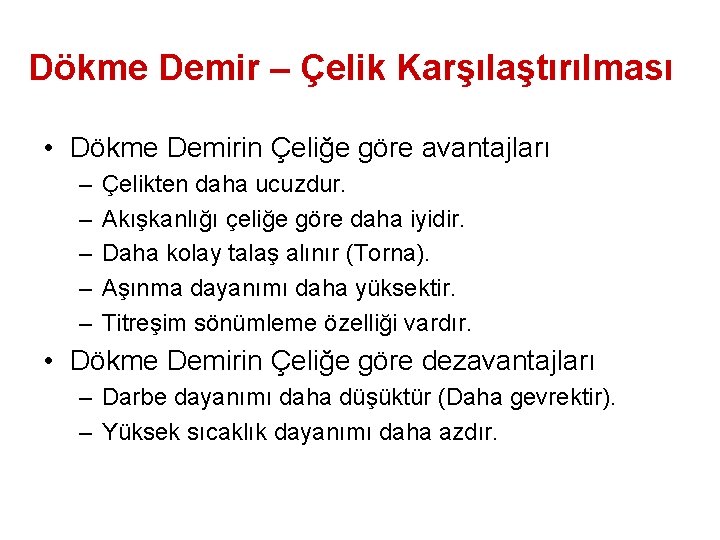
Dökme Demir – Çelik Karşılaştırılması • Dökme Demirin Çeliğe göre avantajları – – – Çelikten daha ucuzdur. Akışkanlığı çeliğe göre daha iyidir. Daha kolay talaş alınır (Torna). Aşınma dayanımı daha yüksektir. Titreşim sönümleme özelliği vardır. • Dökme Demirin Çeliğe göre dezavantajları – Darbe dayanımı daha düşüktür (Daha gevrektir). – Yüksek sıcaklık dayanımı daha azdır.
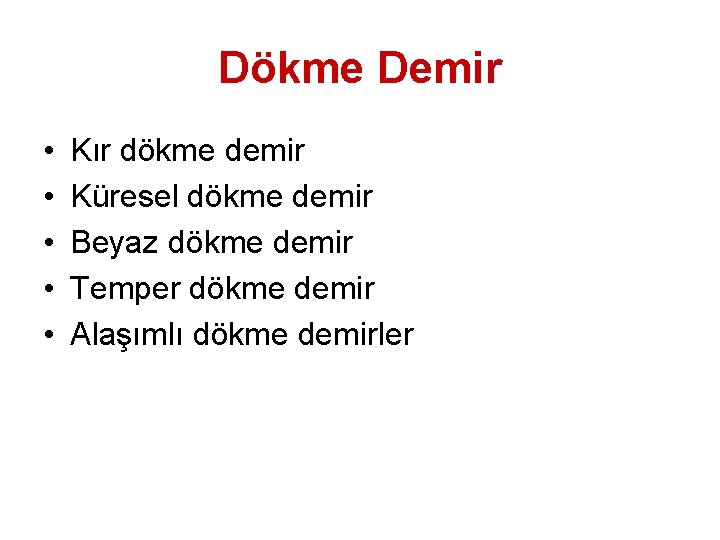
Dökme Demir • • • Kır dökme demir Küresel dökme demir Beyaz dökme demir Temper dökme demir Alaşımlı dökme demirler
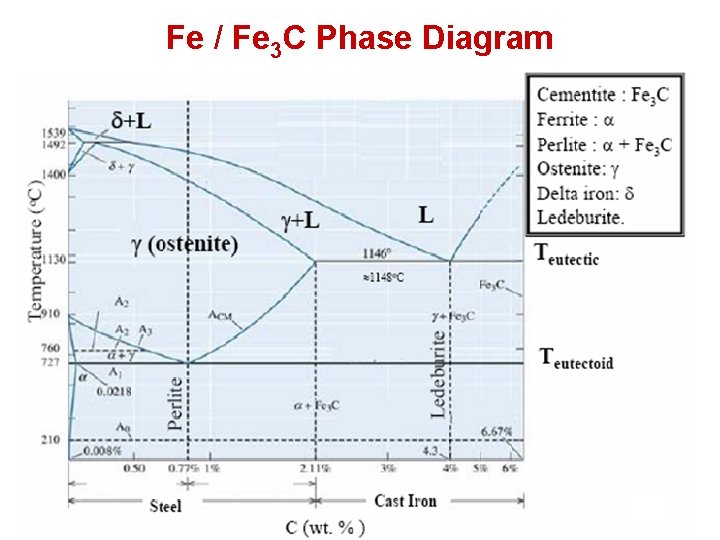
Fe / Fe 3 C Phase Diagram
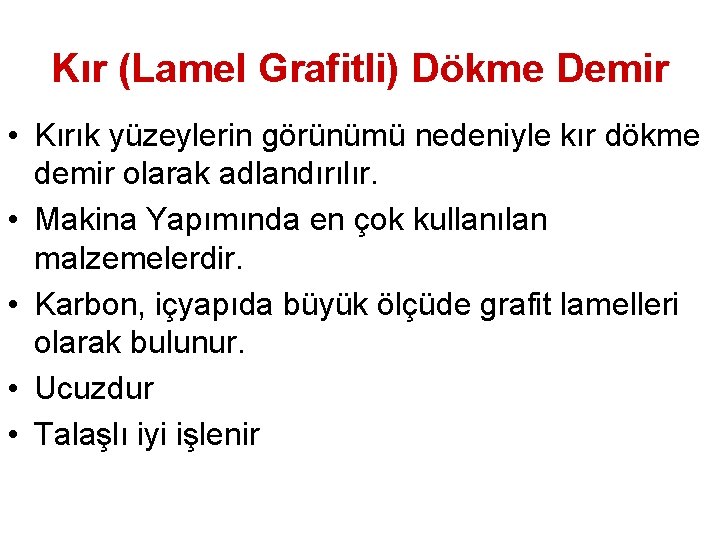
Kır (Lamel Grafitli) Dökme Demir • Kırık yüzeylerin görünümü nedeniyle kır dökme demir olarak adlandırılır. • Makina Yapımında en çok kullanılan malzemelerdir. • Karbon, içyapıda büyük ölçüde grafit lamelleri olarak bulunur. • Ucuzdur • Talaşlı iyi işlenir

Kır (Lamel Grafitli) Dökme Demir • Titreşim sönümler • Korozyona dayanıklı • Çentiğe duyarlı değil (İçyapıda grafirin bulunması, hem yük taşıyan kesiti küçülttüğünden, hem de çentik etkisi oluşturduğundan çekme dayanımını düşürür). • Makine Gövdeleri, dişli kutular, temel plakaları, yataklar (Basma) • Basma dayanımı, çekme dayanımının 3 -4 katıdır.
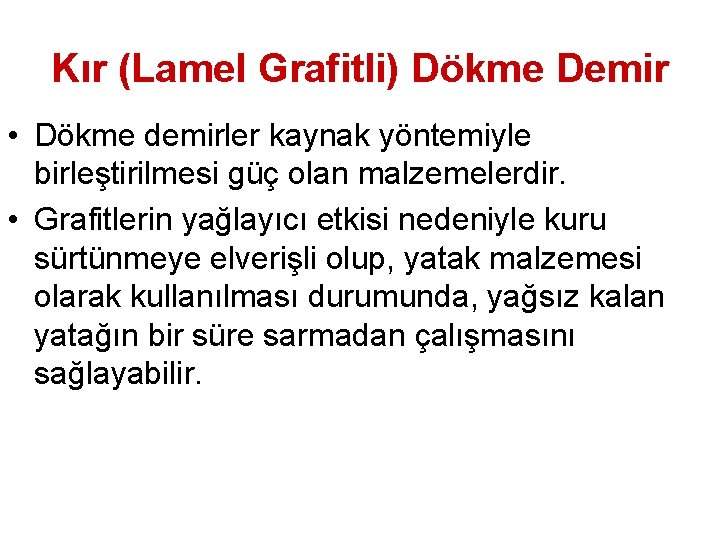
Kır (Lamel Grafitli) Dökme Demir • Dökme demirler kaynak yöntemiyle birleştirilmesi güç olan malzemelerdir. • Grafitlerin yağlayıcı etkisi nedeniyle kuru sürtünmeye elverişli olup, yatak malzemesi olarak kullanılması durumunda, yağsız kalan yatağın bir süre sarmadan çalışmasını sağlayabilir.
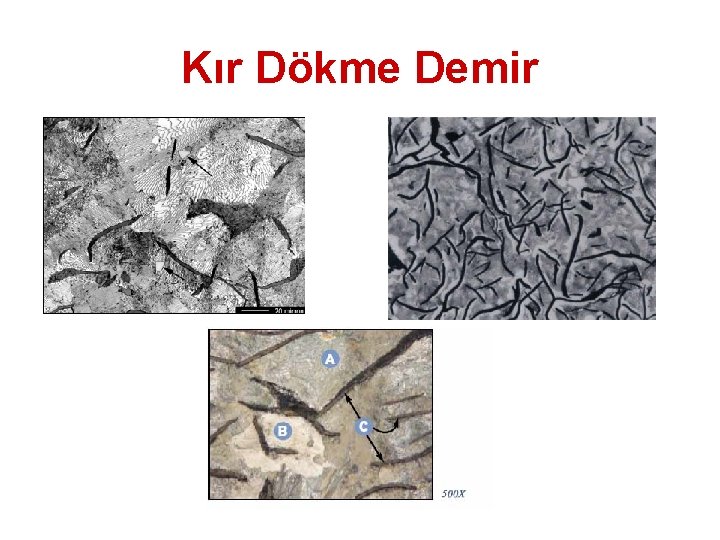
Kır Dökme Demir
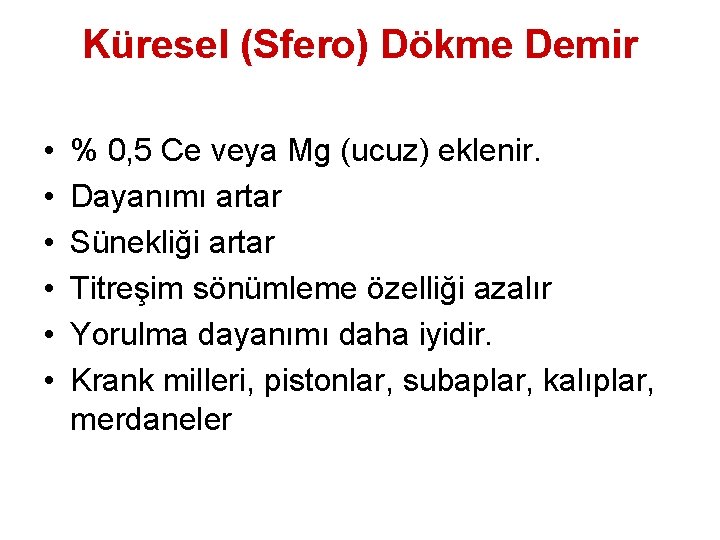
Küresel (Sfero) Dökme Demir • • • % 0, 5 Ce veya Mg (ucuz) eklenir. Dayanımı artar Sünekliği artar Titreşim sönümleme özelliği azalır Yorulma dayanımı daha iyidir. Krank milleri, pistonlar, subaplar, kalıplar, merdaneler

Küresel (Sfero) Dökme Demir
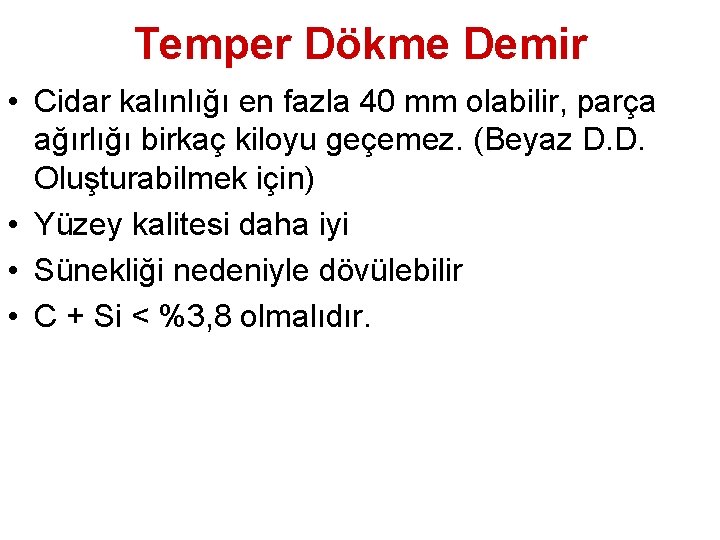
Temper Dökme Demir • Cidar kalınlığı en fazla 40 mm olabilir, parça ağırlığı birkaç kiloyu geçemez. (Beyaz D. D. Oluşturabilmek için) • Yüzey kalitesi daha iyi • Sünekliği nedeniyle dövülebilir • C + Si < %3, 8 olmalıdır.
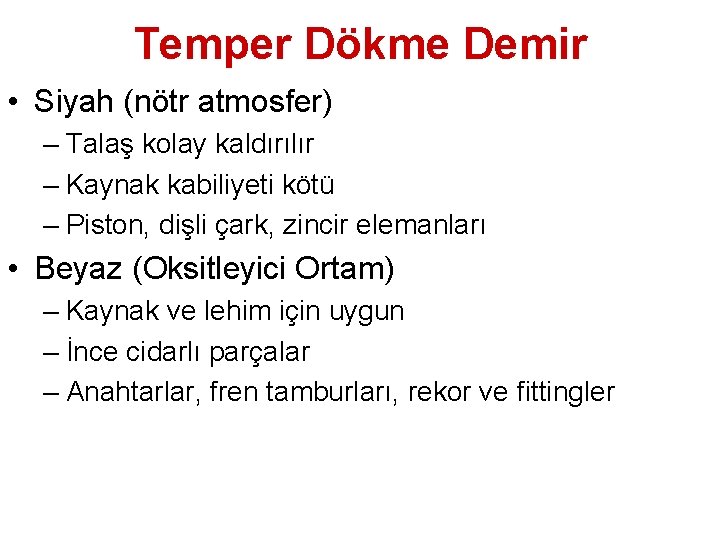
Temper Dökme Demir • Siyah (nötr atmosfer) – Talaş kolay kaldırılır – Kaynak kabiliyeti kötü – Piston, dişli çark, zincir elemanları • Beyaz (Oksitleyici Ortam) – Kaynak ve lehim için uygun – İnce cidarlı parçalar – Anahtarlar, fren tamburları, rekor ve fittingler
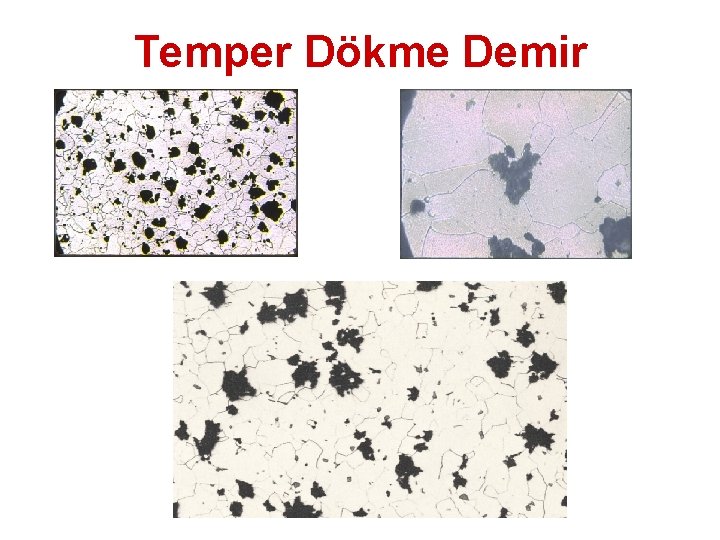
Temper Dökme Demir
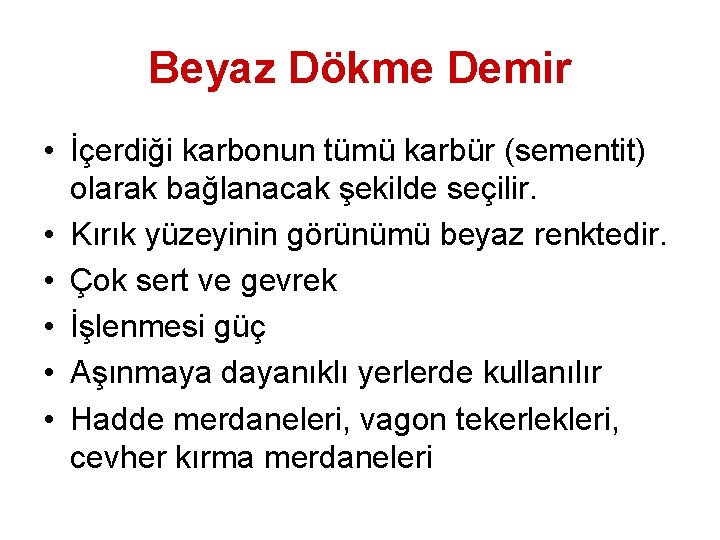
Beyaz Dökme Demir • İçerdiği karbonun tümü karbür (sementit) olarak bağlanacak şekilde seçilir. • Kırık yüzeyinin görünümü beyaz renktedir. • Çok sert ve gevrek • İşlenmesi güç • Aşınmaya dayanıklı yerlerde kullanılır • Hadde merdaneleri, vagon tekerlekleri, cevher kırma merdaneleri
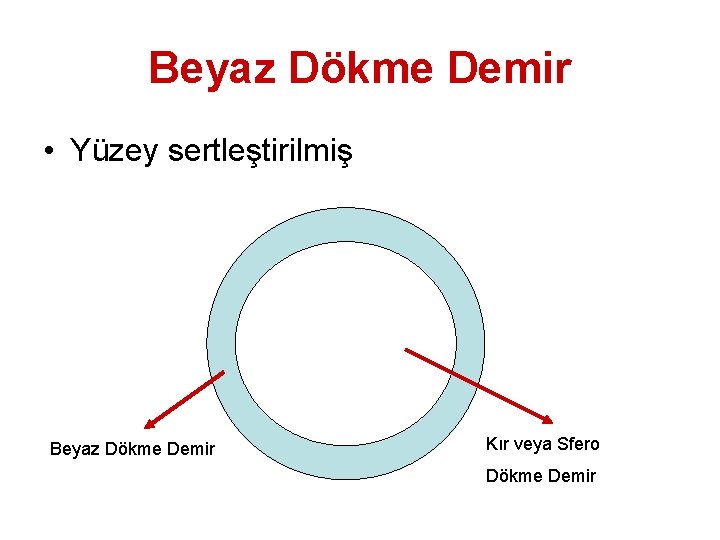
Beyaz Dökme Demir • Yüzey sertleştirilmiş Beyaz Dökme Demir Kır veya Sfero Dökme Demir
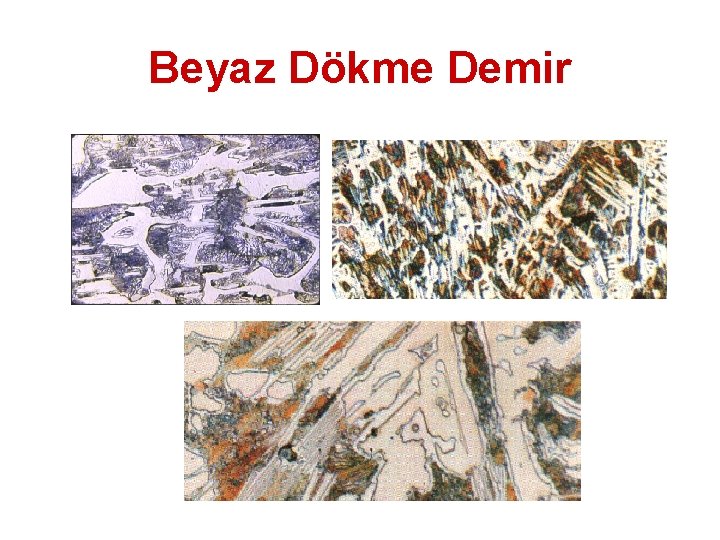
Beyaz Dökme Demir
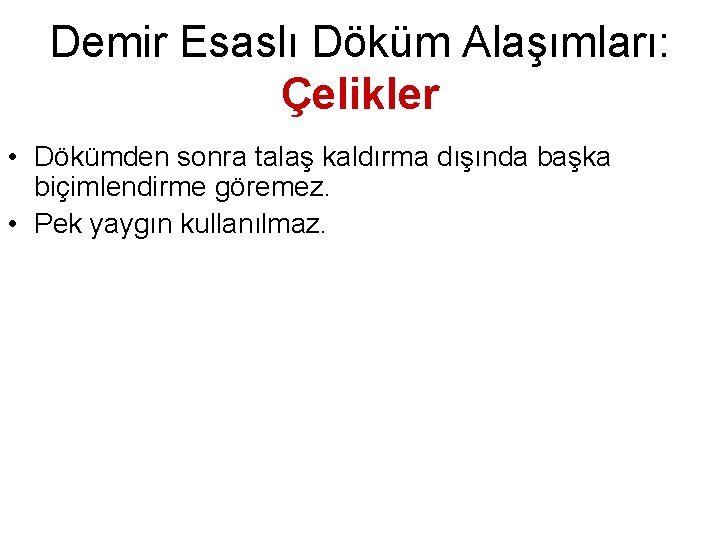
Demir Esaslı Döküm Alaşımları: Çelikler • Dökümden sonra talaş kaldırma dışında başka biçimlendirme göremez. • Pek yaygın kullanılmaz.
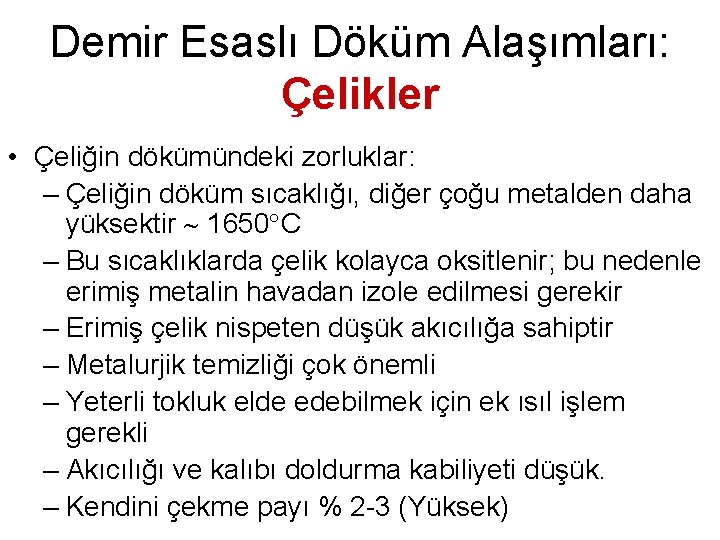
Demir Esaslı Döküm Alaşımları: Çelikler • Çeliğin dökümündeki zorluklar: – Çeliğin döküm sıcaklığı, diğer çoğu metalden daha yüksektir 1650 C – Bu sıcaklıklarda çelik kolayca oksitlenir; bu nedenle erimiş metalin havadan izole edilmesi gerekir – Erimiş çelik nispeten düşük akıcılığa sahiptir – Metalurjik temizliği çok önemli – Yeterli tokluk elde edebilmek için ek ısıl işlem gerekli – Akıcılığı ve kalıbı doldurma kabiliyeti düşük. – Kendini çekme payı % 2 -3 (Yüksek)
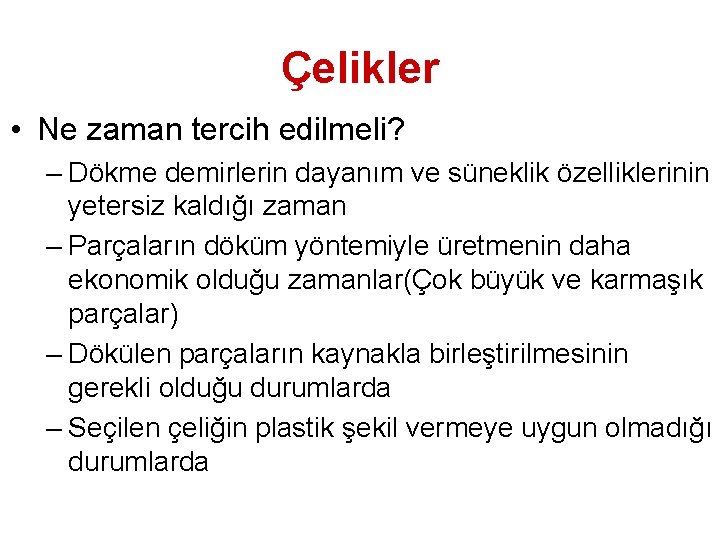
Çelikler • Ne zaman tercih edilmeli? – Dökme demirlerin dayanım ve süneklik özelliklerinin yetersiz kaldığı zaman – Parçaların döküm yöntemiyle üretmenin daha ekonomik olduğu zamanlar(Çok büyük ve karmaşık parçalar) – Dökülen parçaların kaynakla birleştirilmesinin gerekli olduğu durumlarda – Seçilen çeliğin plastik şekil vermeye uygun olmadığı durumlarda
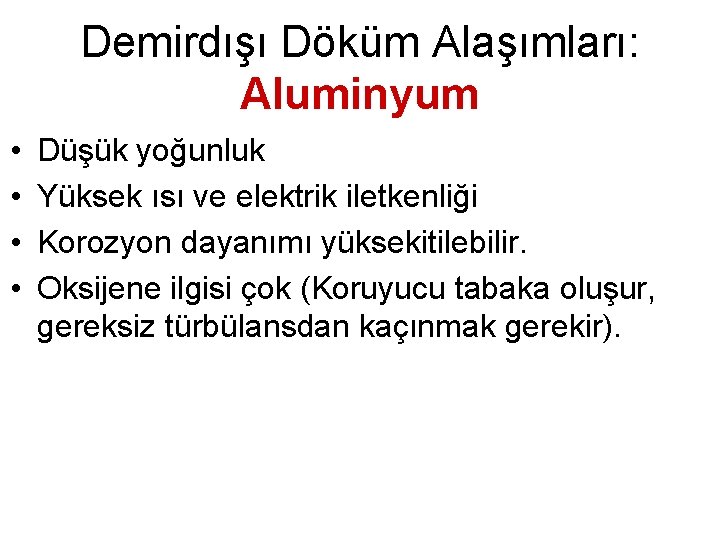
Demirdışı Döküm Alaşımları: Aluminyum • • Düşük yoğunluk Yüksek ısı ve elektrik iletkenliği Korozyon dayanımı yüksekitilebilir. Oksijene ilgisi çok (Koruyucu tabaka oluşur, gereksiz türbülansdan kaçınmak gerekir).
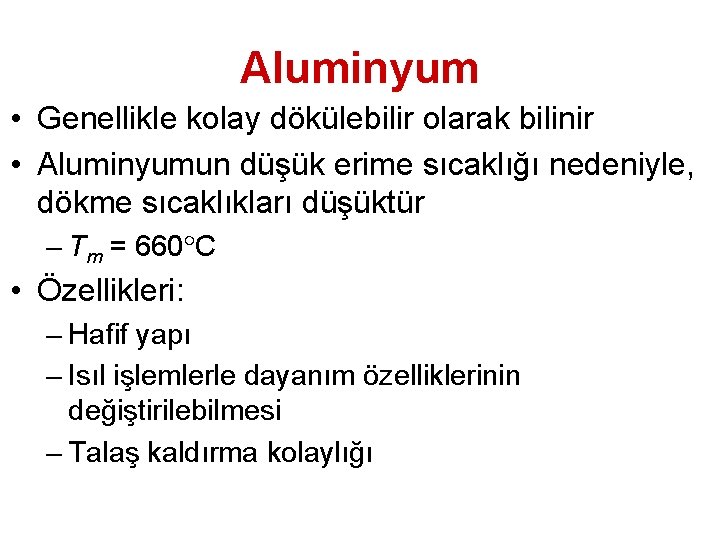
Aluminyum • Genellikle kolay dökülebilir olarak bilinir • Aluminyumun düşük erime sıcaklığı nedeniyle, dökme sıcaklıkları düşüktür – Tm = 660 C • Özellikleri: – Hafif yapı – Isıl işlemlerle dayanım özelliklerinin değiştirilebilmesi – Talaş kaldırma kolaylığı
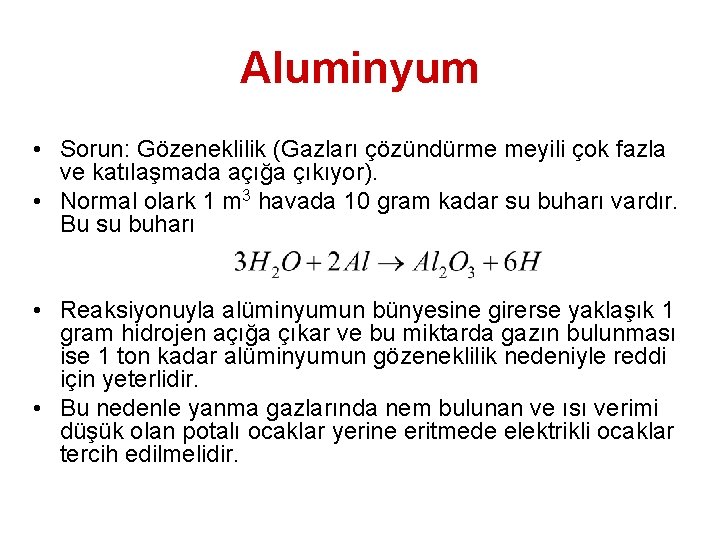
Aluminyum • Sorun: Gözeneklilik (Gazları çözündürme meyili çok fazla ve katılaşmada açığa çıkıyor). • Normal olark 1 m 3 havada 10 gram kadar su buharı vardır. Bu su buharı • Reaksiyonuyla alüminyumun bünyesine girerse yaklaşık 1 gram hidrojen açığa çıkar ve bu miktarda gazın bulunması ise 1 ton kadar alüminyumun gözeneklilik nedeniyle reddi için yeterlidir. • Bu nedenle yanma gazlarında nem bulunan ve ısı verimi düşük olan potalı ocaklar yerine eritmede elektrikli ocaklar tercih edilmelidir.
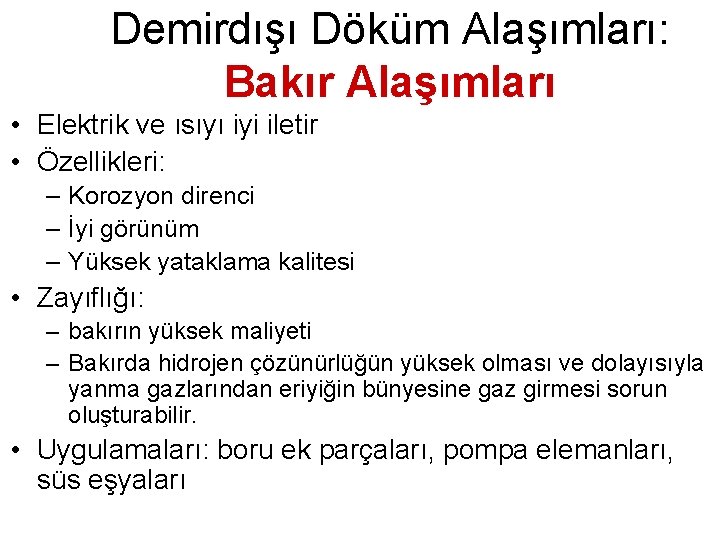
Demirdışı Döküm Alaşımları: Bakır Alaşımları • Elektrik ve ısıyı iyi iletir • Özellikleri: – Korozyon direnci – İyi görünüm – Yüksek yataklama kalitesi • Zayıflığı: – bakırın yüksek maliyeti – Bakırda hidrojen çözünürlüğün yüksek olması ve dolayısıyla yanma gazlarından eriyiğin bünyesine gaz girmesi sorun oluşturabilir. • Uygulamaları: boru ek parçaları, pompa elemanları, süs eşyaları
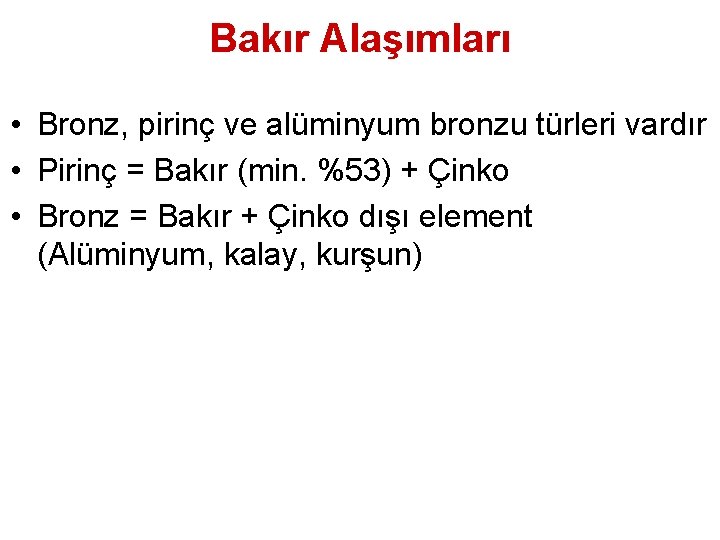
Bakır Alaşımları • Bronz, pirinç ve alüminyum bronzu türleri vardır • Pirinç = Bakır (min. %53) + Çinko • Bronz = Bakır + Çinko dışı element (Alüminyum, kalay, kurşun)
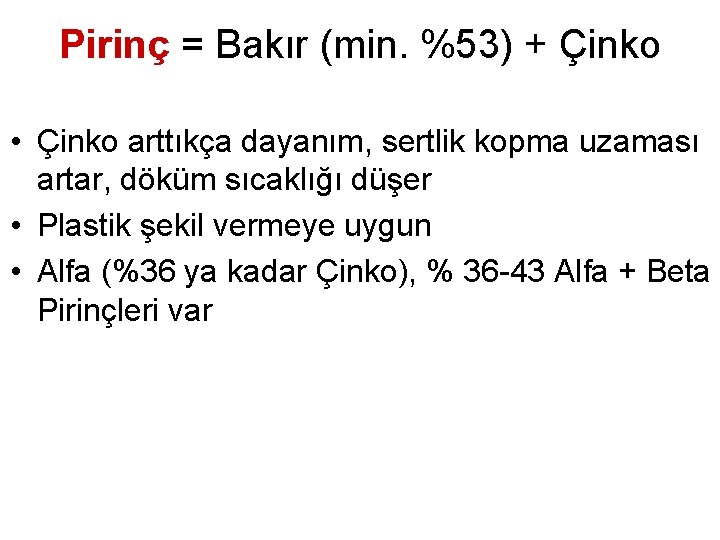
Pirinç = Bakır (min. %53) + Çinko • Çinko arttıkça dayanım, sertlik kopma uzaması artar, döküm sıcaklığı düşer • Plastik şekil vermeye uygun • Alfa (%36 ya kadar Çinko), % 36 -43 Alfa + Beta Pirinçleri var
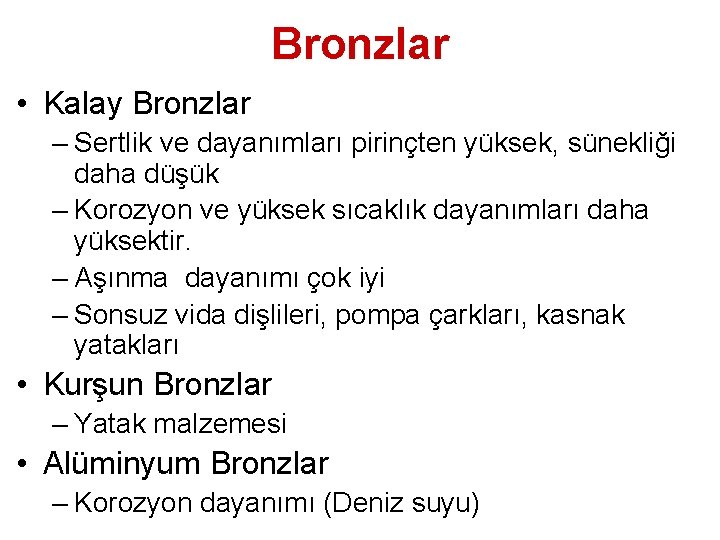
Bronzlar • Kalay Bronzlar – Sertlik ve dayanımları pirinçten yüksek, sünekliği daha düşük – Korozyon ve yüksek sıcaklık dayanımları daha yüksektir. – Aşınma dayanımı çok iyi – Sonsuz vida dişlileri, pompa çarkları, kasnak yatakları • Kurşun Bronzlar – Yatak malzemesi • Alüminyum Bronzlar – Korozyon dayanımı (Deniz suyu)
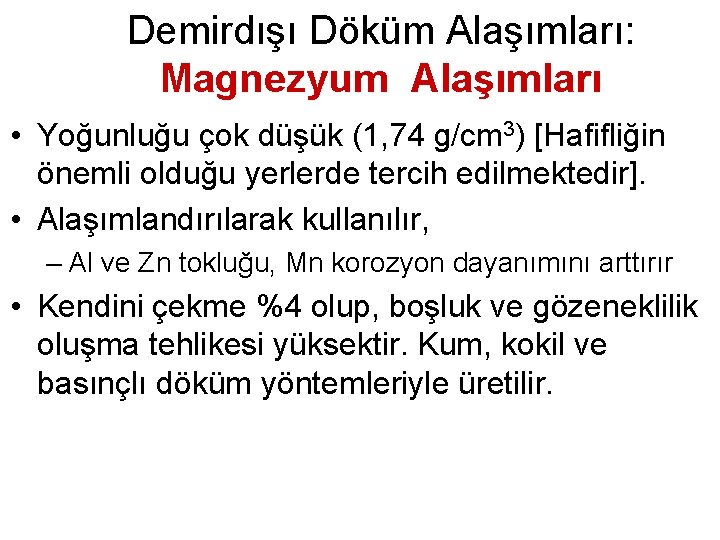
Demirdışı Döküm Alaşımları: Magnezyum Alaşımları • Yoğunluğu çok düşük (1, 74 g/cm 3) [Hafifliğin önemli olduğu yerlerde tercih edilmektedir]. • Alaşımlandırılarak kullanılır, – Al ve Zn tokluğu, Mn korozyon dayanımını arttırır • Kendini çekme %4 olup, boşluk ve gözeneklilik oluşma tehlikesi yüksektir. Kum, kokil ve basınçlı döküm yöntemleriyle üretilir.
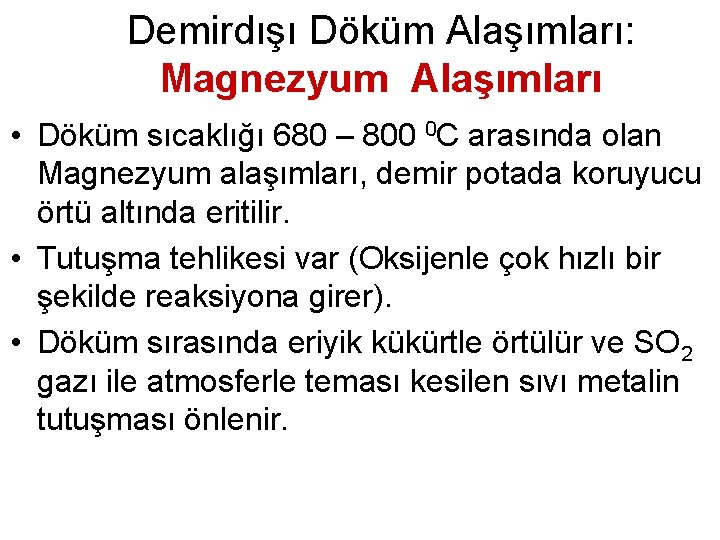
Demirdışı Döküm Alaşımları: Magnezyum Alaşımları • Döküm sıcaklığı 680 – 800 0 C arasında olan Magnezyum alaşımları, demir potada koruyucu örtü altında eritilir. • Tutuşma tehlikesi var (Oksijenle çok hızlı bir şekilde reaksiyona girer). • Döküm sırasında eriyik kükürtle örtülür ve SO 2 gazı ile atmosferle teması kesilen sıvı metalin tutuşması önlenir.
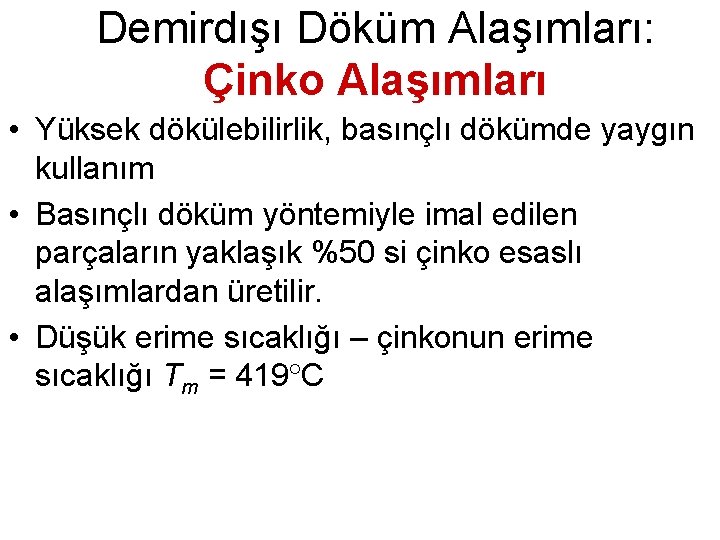
Demirdışı Döküm Alaşımları: Çinko Alaşımları • Yüksek dökülebilirlik, basınçlı dökümde yaygın kullanım • Basınçlı döküm yöntemiyle imal edilen parçaların yaklaşık %50 si çinko esaslı alaşımlardan üretilir. • Düşük erime sıcaklığı – çinkonun erime sıcaklığı Tm = 419 C
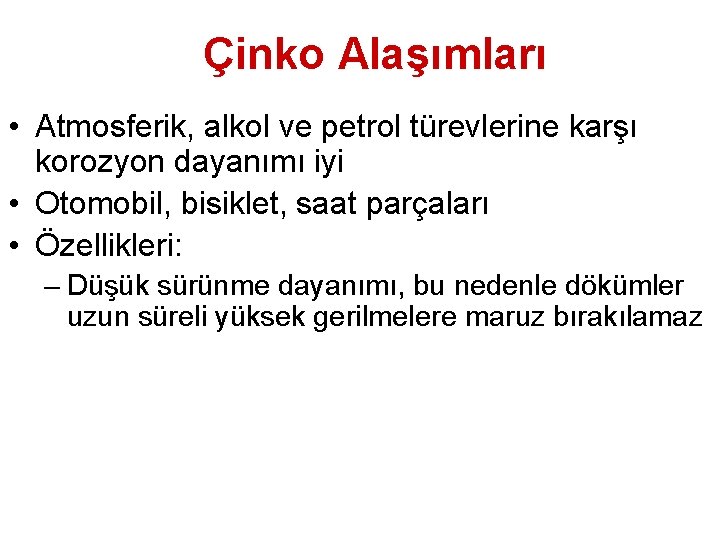
Çinko Alaşımları • Atmosferik, alkol ve petrol türevlerine karşı korozyon dayanımı iyi • Otomobil, bisiklet, saat parçaları • Özellikleri: – Düşük sürünme dayanımı, bu nedenle dökümler uzun süreli yüksek gerilmelere maruz bırakılamaz
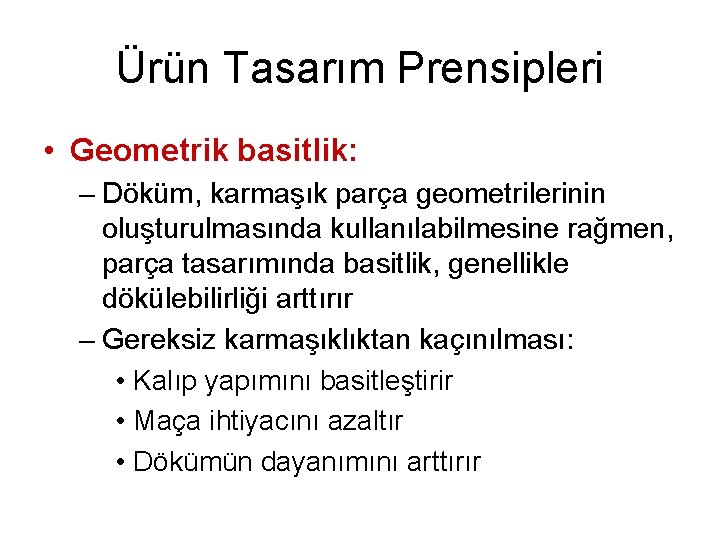
Ürün Tasarım Prensipleri • Geometrik basitlik: – Döküm, karmaşık parça geometrilerinin oluşturulmasında kullanılabilmesine rağmen, parça tasarımında basitlik, genellikle dökülebilirliği arttırır – Gereksiz karmaşıklıktan kaçınılması: • Kalıp yapımını basitleştirir • Maça ihtiyacını azaltır • Dökümün dayanımını arttırır
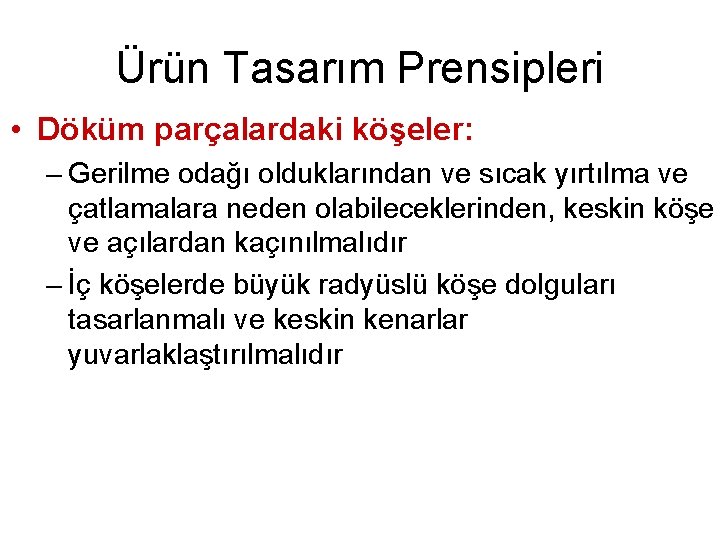
Ürün Tasarım Prensipleri • Döküm parçalardaki köşeler: – Gerilme odağı olduklarından ve sıcak yırtılma ve çatlamalara neden olabileceklerinden, keskin köşe ve açılardan kaçınılmalıdır – İç köşelerde büyük radyüslü köşe dolguları tasarlanmalı ve keskin kenarlar yuvarlaklaştırılmalıdır
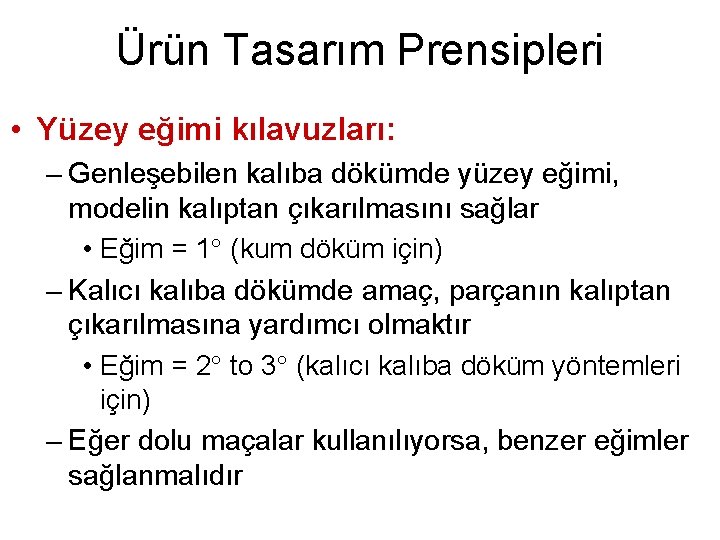
Ürün Tasarım Prensipleri • Yüzey eğimi kılavuzları: – Genleşebilen kalıba dökümde yüzey eğimi, modelin kalıptan çıkarılmasını sağlar • Eğim = 1 (kum döküm için) – Kalıcı kalıba dökümde amaç, parçanın kalıptan çıkarılmasına yardımcı olmaktır • Eğim = 2 to 3 (kalıcı kalıba döküm yöntemleri için) – Eğer dolu maçalar kullanılıyorsa, benzer eğimler sağlanmalıdır
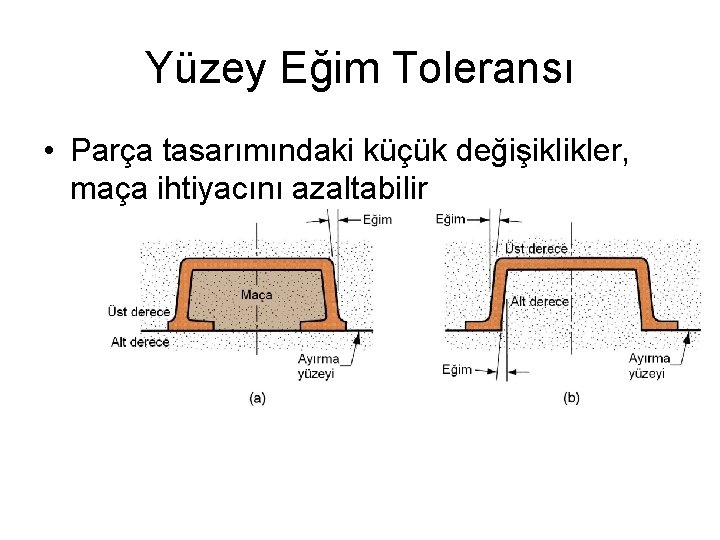
Yüzey Eğim Toleransı • Parça tasarımındaki küçük değişiklikler, maça ihtiyacını azaltabilir
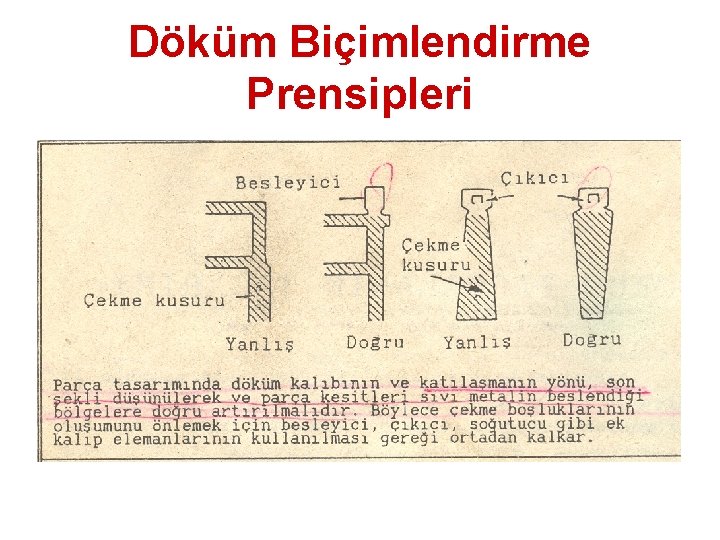
Döküm Biçimlendirme Prensipleri
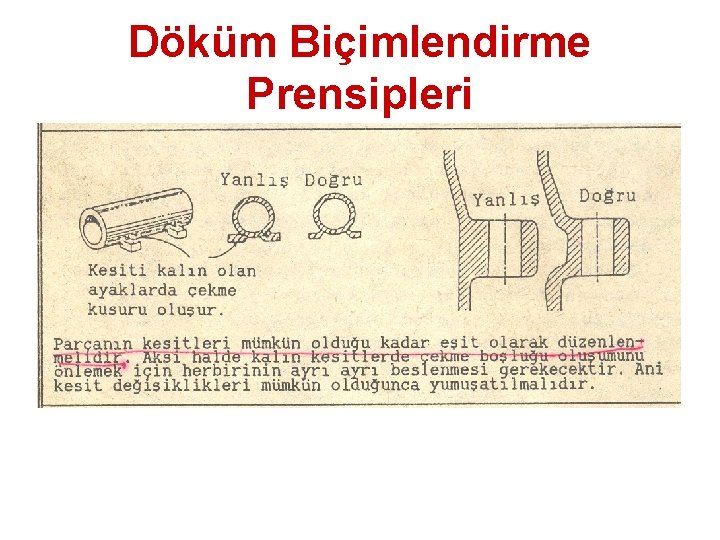
Döküm Biçimlendirme Prensipleri
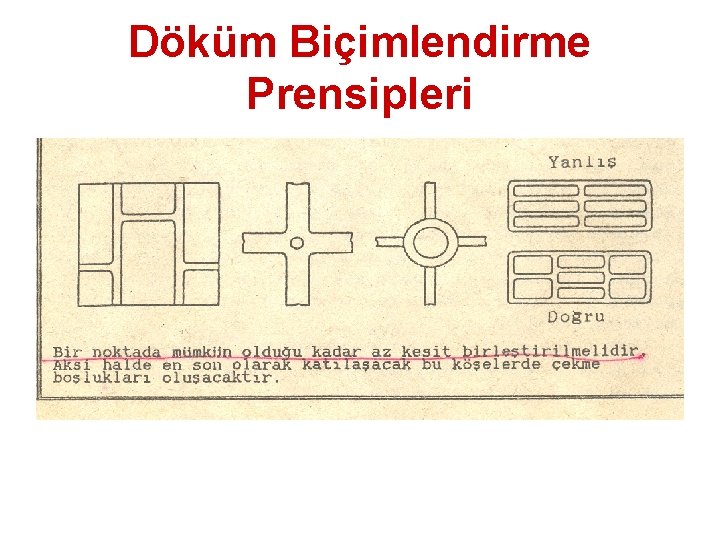
Döküm Biçimlendirme Prensipleri
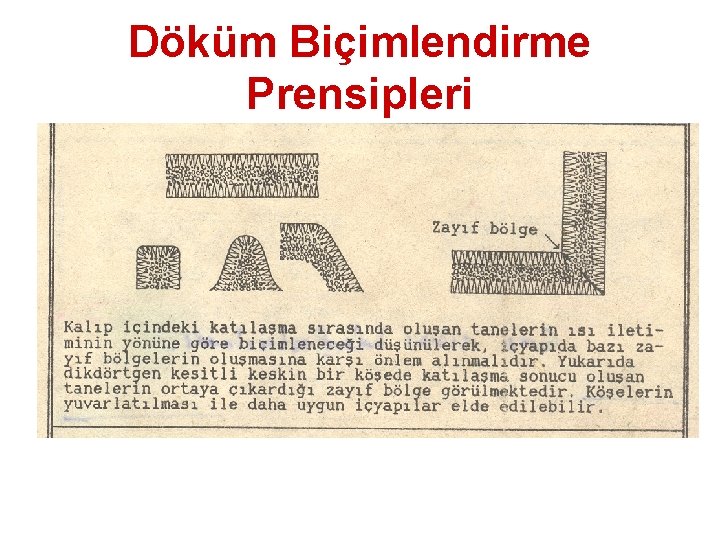
Döküm Biçimlendirme Prensipleri
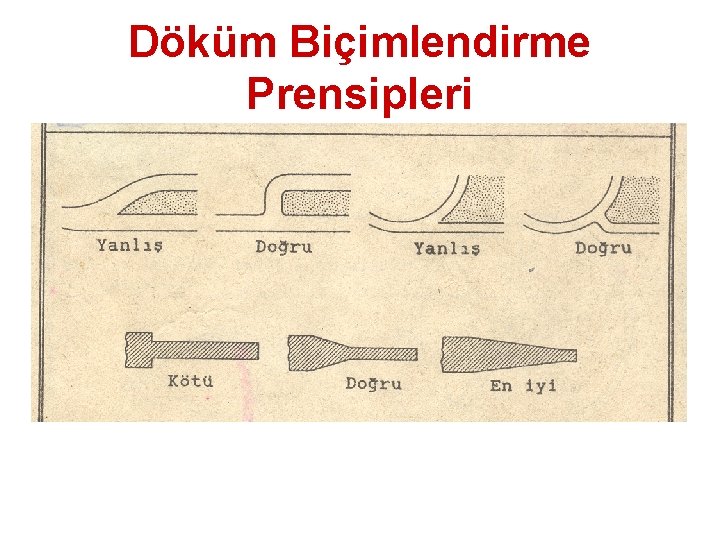
Döküm Biçimlendirme Prensipleri
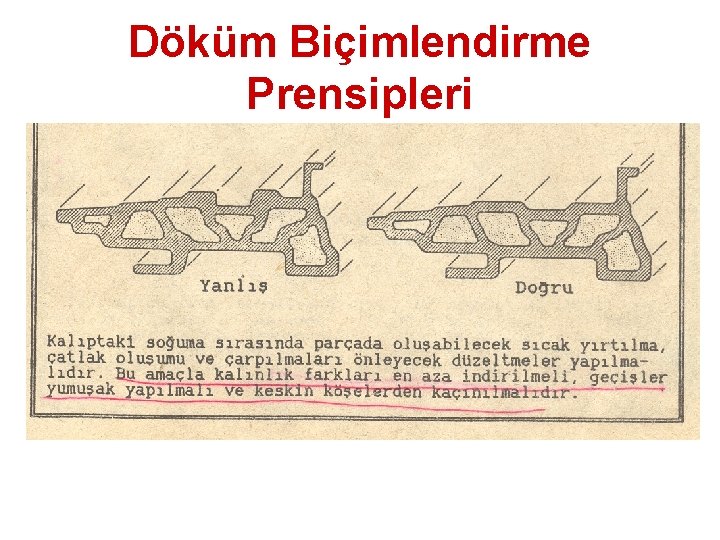
Döküm Biçimlendirme Prensipleri
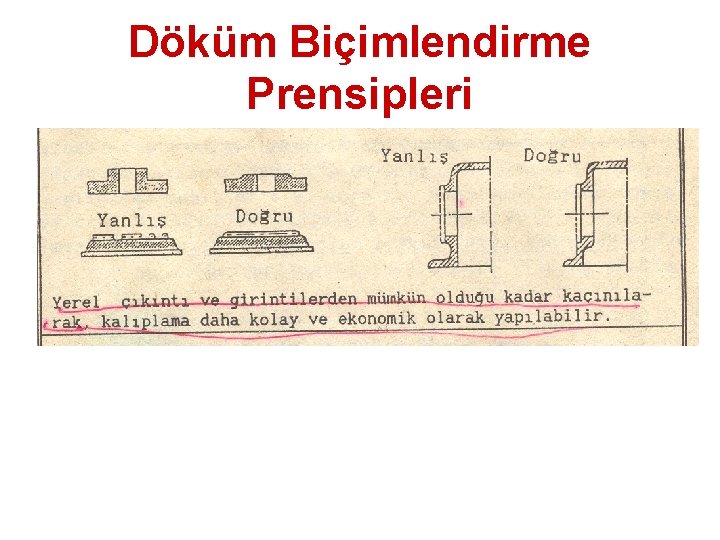
Döküm Biçimlendirme Prensipleri
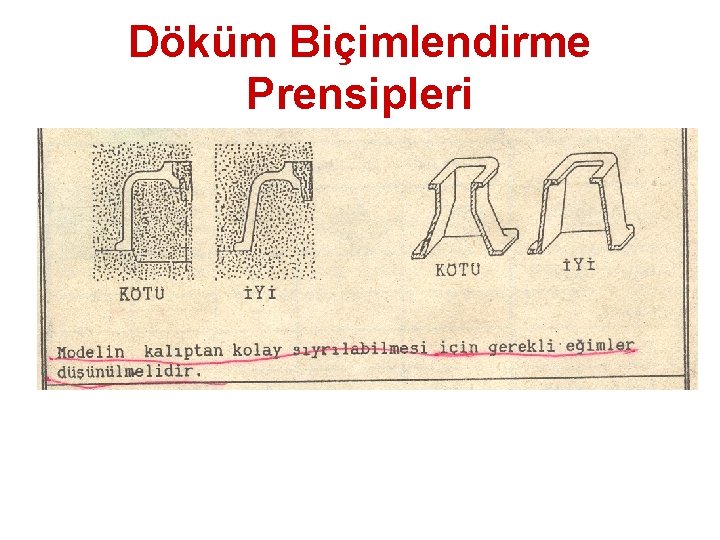
Döküm Biçimlendirme Prensipleri
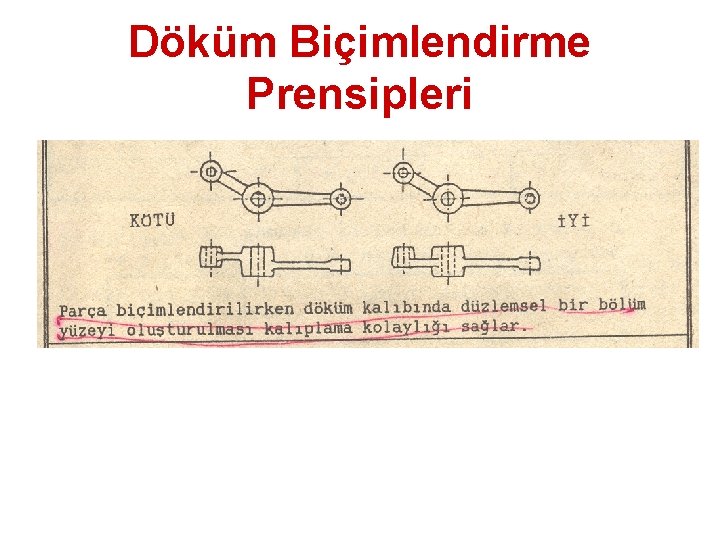
Döküm Biçimlendirme Prensipleri
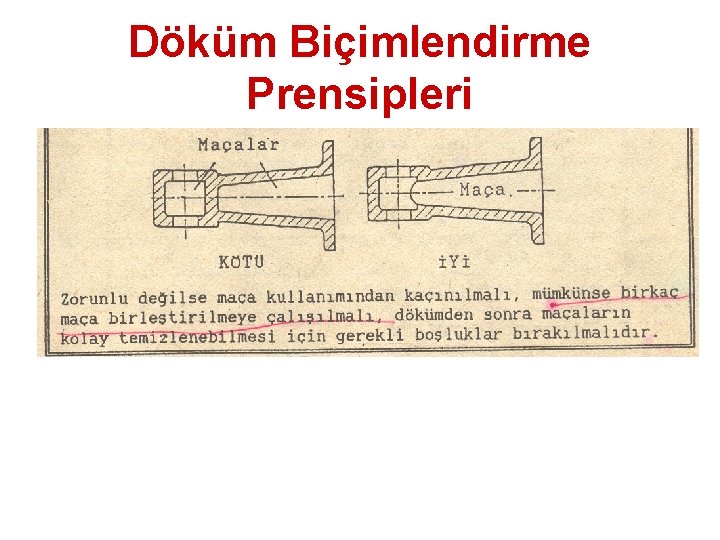
Döküm Biçimlendirme Prensipleri
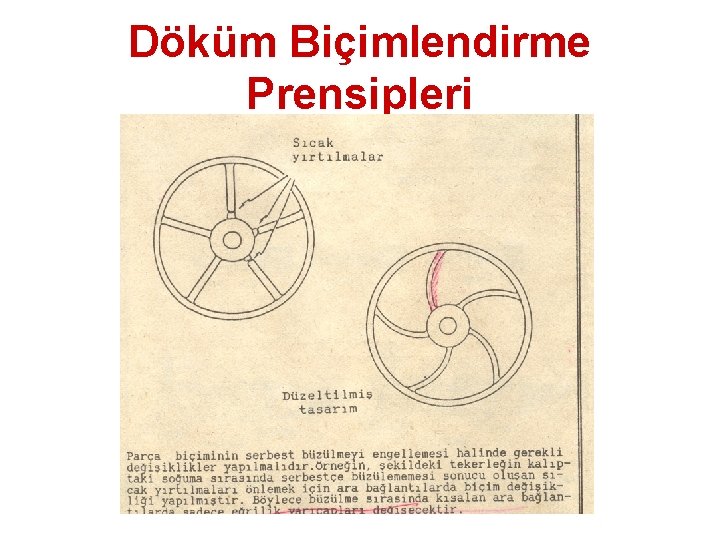
Döküm Biçimlendirme Prensipleri
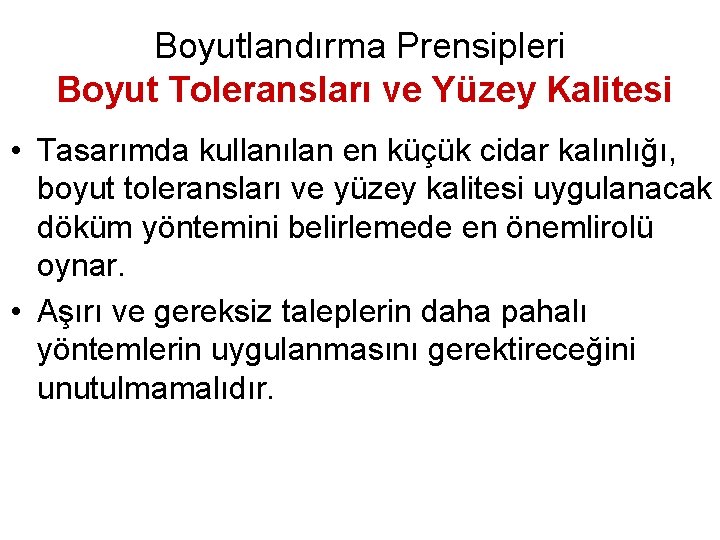
Boyutlandırma Prensipleri Boyut Toleransları ve Yüzey Kalitesi • Tasarımda kullanılan en küçük cidar kalınlığı, boyut toleransları ve yüzey kalitesi uygulanacak döküm yöntemini belirlemede en önemlirolü oynar. • Aşırı ve gereksiz taleplerin daha pahalı yöntemlerin uygulanmasını gerektireceğini unutulmamalıdır.
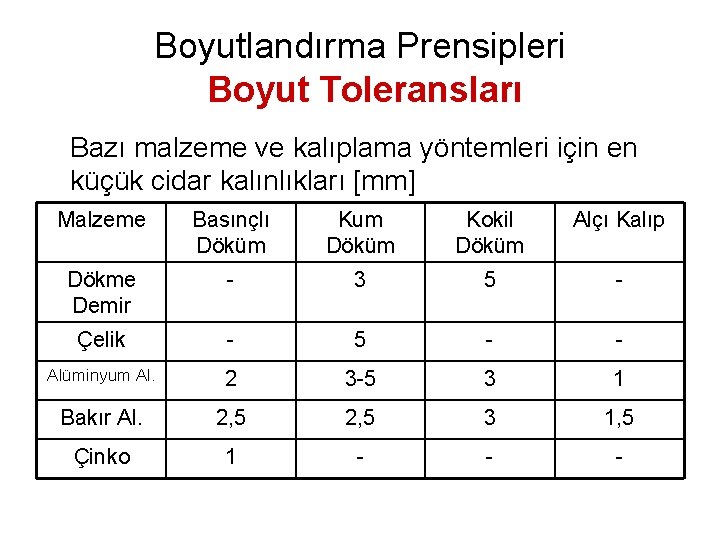
Boyutlandırma Prensipleri Boyut Toleransları Bazı malzeme ve kalıplama yöntemleri için en küçük cidar kalınlıkları [mm] Malzeme Basınçlı Döküm Kum Döküm Kokil Döküm Alçı Kalıp Dökme Demir - 3 5 - Çelik - 5 - - Alüminyum Al. 2 3 -5 3 1 Bakır Al. 2, 5 3 1, 5 Çinko 1 - - -
![Boyutlandırma Prensipleri Yüzey Kalitesi Bazı kalıplama yöntemleri için yüzey pürüzlülük değerleri µm Kalıplama Yöntemi Boyutlandırma Prensipleri Yüzey Kalitesi Bazı kalıplama yöntemleri için yüzey pürüzlülük değerleri [µm] Kalıplama Yöntemi](https://slidetodoc.com/presentation_image_h/761e36bea554940433692f270349680e/image-70.jpg)
Boyutlandırma Prensipleri Yüzey Kalitesi Bazı kalıplama yöntemleri için yüzey pürüzlülük değerleri [µm] Kalıplama Yöntemi Pürüzlülük [µm] Yaş Kum Kalıp 6 – 25 Özel Kum Kalıplar <6 Basınçlı Döküm 0, 5 – 3 Hassas Döküm 0, 4 – 1, 5 Alçı Kalıba Döküm 1
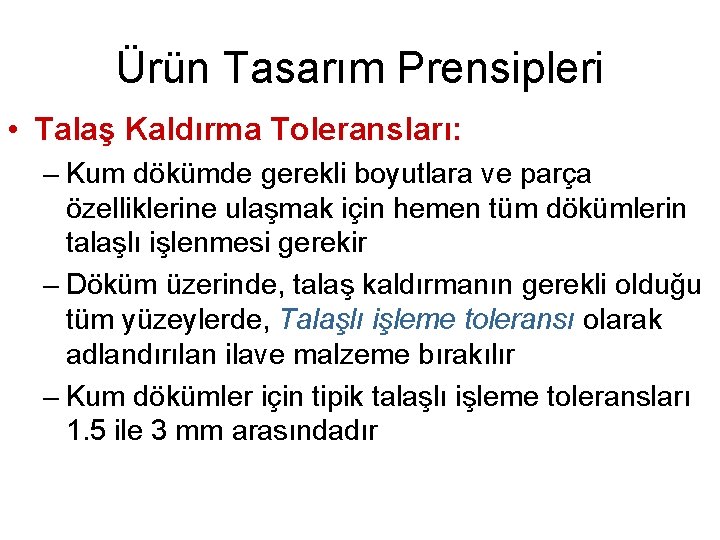
Ürün Tasarım Prensipleri • Talaş Kaldırma Toleransları: – Kum dökümde gerekli boyutlara ve parça özelliklerine ulaşmak için hemen tüm dökümlerin talaşlı işlenmesi gerekir – Döküm üzerinde, talaş kaldırmanın gerekli olduğu tüm yüzeylerde, Talaşlı işleme toleransı olarak adlandırılan ilave malzeme bırakılır – Kum dökümler için tipik talaşlı işleme toleransları 1. 5 ile 3 mm arasındadır
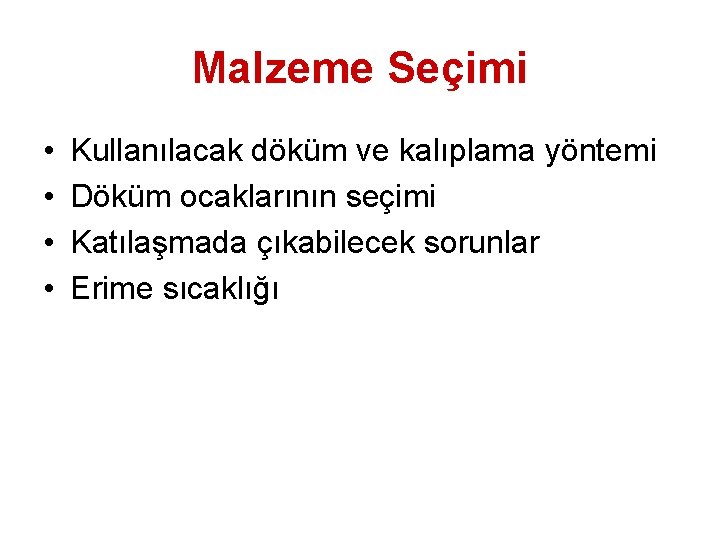
Malzeme Seçimi • • Kullanılacak döküm ve kalıplama yöntemi Döküm ocaklarının seçimi Katılaşmada çıkabilecek sorunlar Erime sıcaklığı
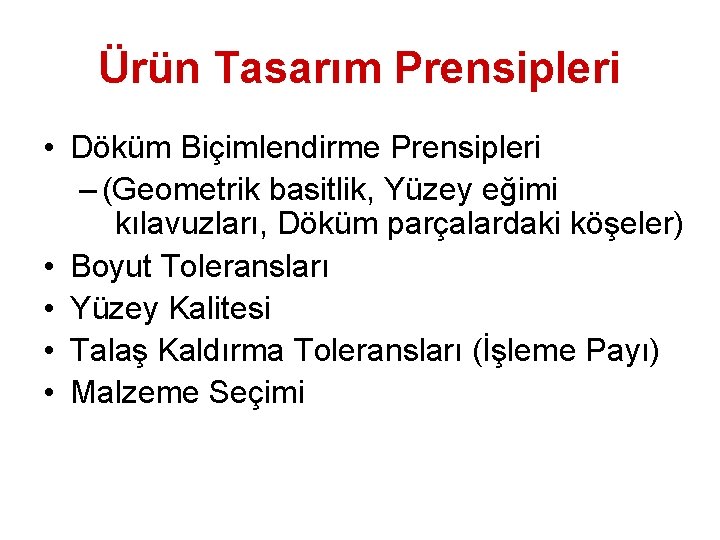
Ürün Tasarım Prensipleri • Döküm Biçimlendirme Prensipleri – (Geometrik basitlik, Yüzey eğimi kılavuzları, Döküm parçalardaki köşeler) • Boyut Toleransları • Yüzey Kalitesi • Talaş Kaldırma Toleransları (İşleme Payı) • Malzeme Seçimi
Blessed mal mal mal
Crosby sıfır hata aşamaları
Sentez tekstil
Kalite kontrol formu
P kontrol grafiği
Tommi jaakkola
Soğuk havanın betona etkileri
Dkm broker sa de cv
M cm dm mm
Mamul karması
Eşdeğer mamul miktarı hesaplama
Malatta
No devuelvas mal por mal ni insulto por insulto
Juran enstitüsünün kalite iyileştirme modeli
Matris veri analiz diyagramı
Donabediana göre verimlilik nedir
Başkent üniversitesi kalite mühendisliği yüksek lisans
Kalite güvence nedir
Lineer enerji transferi
Toplam kalite nedir
Uygulama şekillerine göre standartlar
Kalite çemberi nedir
Kalite ile ilgili kavramlar
Kalite risk analizi örneği
1. kalite nedir
ıso 9001:2015 kalite el kitabı örnekleri
Kalite yönetimi nedir
Sağlıkta kalite standartları adsh
Ex kalite uygunluk belgesi
Kalite eğitimi
Kpi raporu örneği
Hacettepe kalite komisyonu
Kalite ile ilgili yanlış düşünceler
Kalite risk analizi örneği
Kapan waktunya menggunakan instruksi kondisional
Westgard çoklu kontrol kuralları
Matriks 3 dimensi
Imleç kontrol tuşları
Teori kontrol adalah
Yarı deneysel desenler
Kontrol listesi derecelendirme ölçeği
Risk kontrol hiyerarşisi sıralaması
?fke kontrol?
Bentuk struktur kontrol pemilihan di atas adalah
Kontrol sistemleri
?fke kontrol?
Kontrol edilemeyen preanalitik faktörler
L tipi matris
Tutum ölçekleri
Glukogenez
Bağımlı değişken örnek
Struktur kontrol percabangan adalah
Nurdan bilgin otomatik kontrol
Kontrol sistemleri blok diyagramları soruları
Rlocus
Title bar berfungsi untuk …………
Duygu ve duygu durumları
Karasek krav kontrol model
Kapalı çevrim kontrol sistemi örnek
Kartu harga pokok pesanan
Icd nifas
?fke kontrol?
Hata ağacı analizi
Manajemen kontrol lingkungan tempat penyimpanan koleksi
Kontrol sistem tasarımı
Diagram blok sistem instrumentasi
Sosyal beceri kontrol listesi
Struktur kontrol pada pemrograman imperatif
Planla uygula kontrol et önlem al
Definisi struktur kontrol percabangan dalam pemrograman
Mizan kontrolü
Ukuran bak kontrol
Kontrol intrinsik dan ekstrinsik jantung
X-r kontrol çizelgesi