Forming and Shaping Process for Plastic and Composite
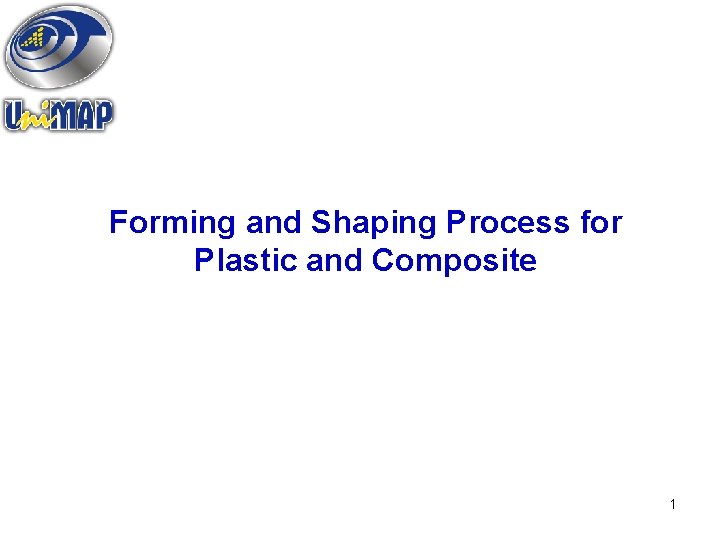
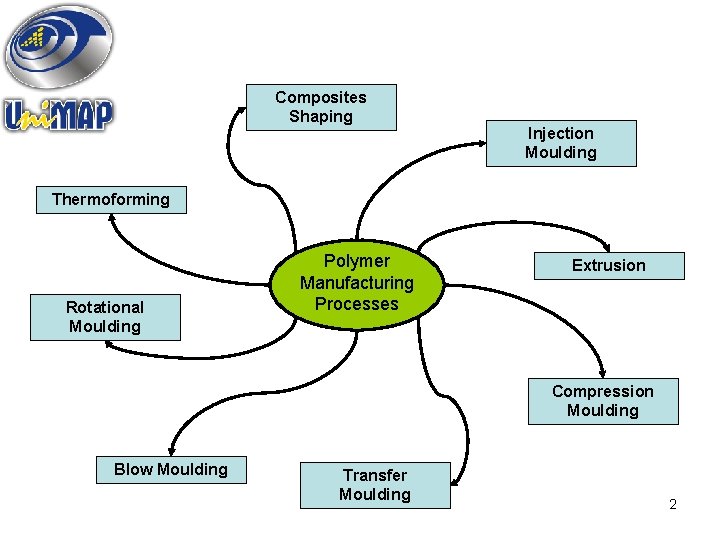
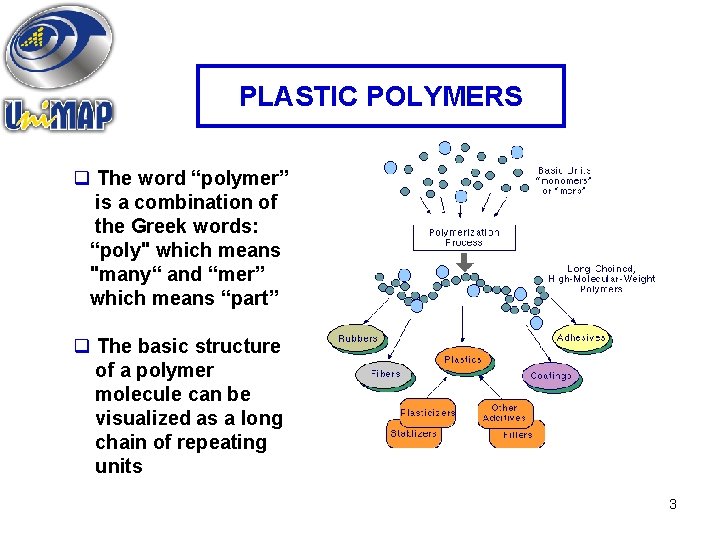
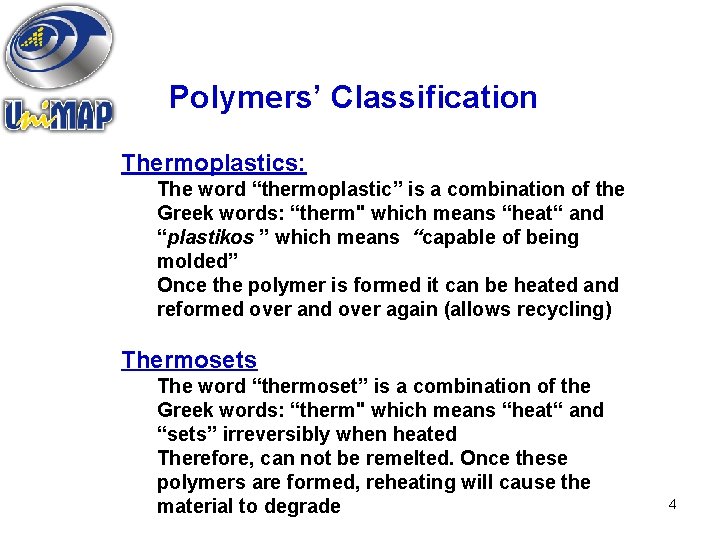
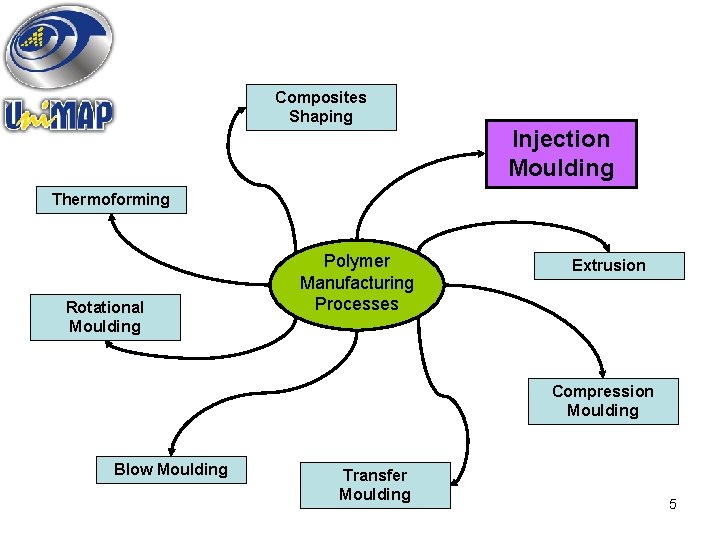
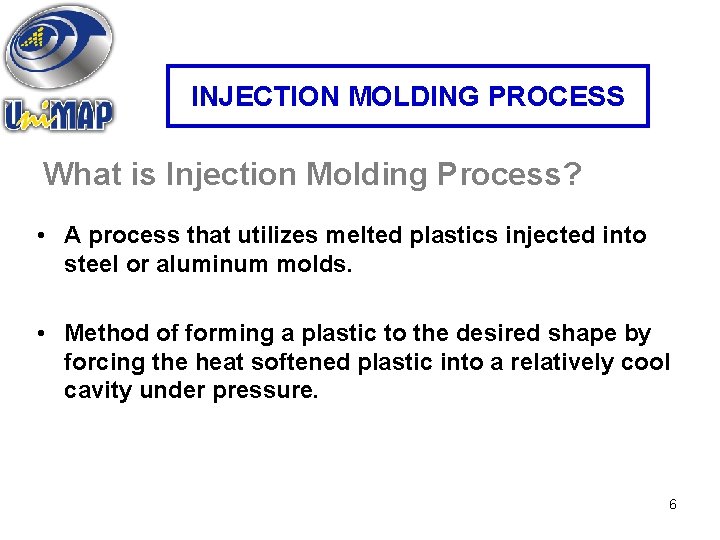
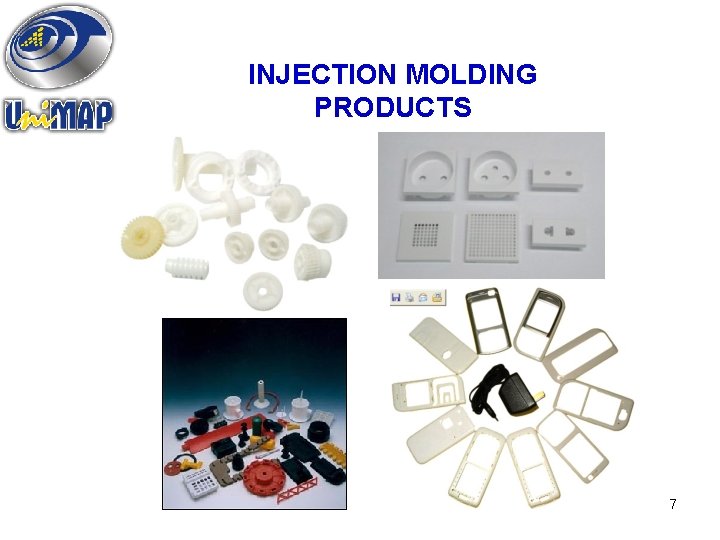
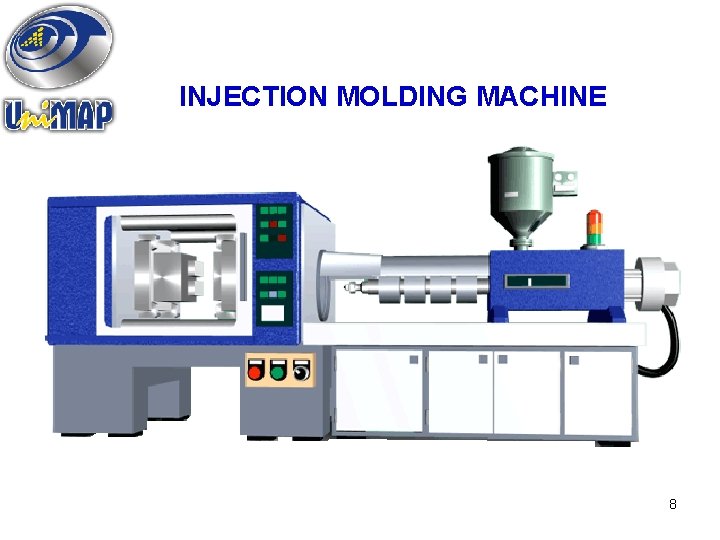
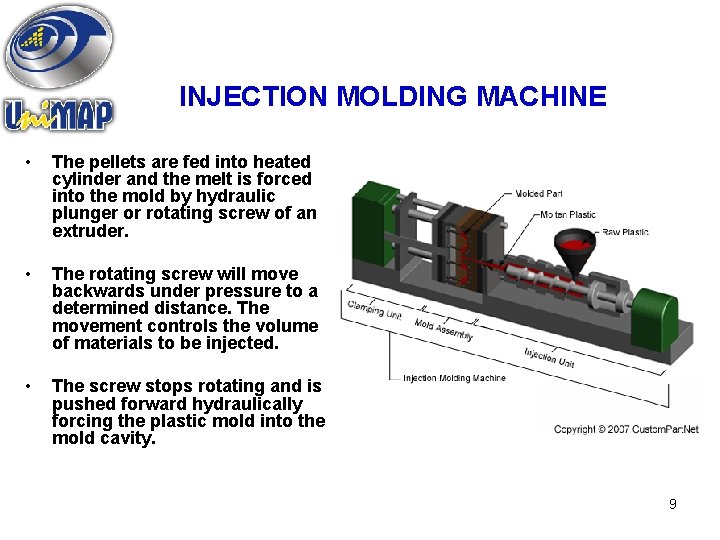
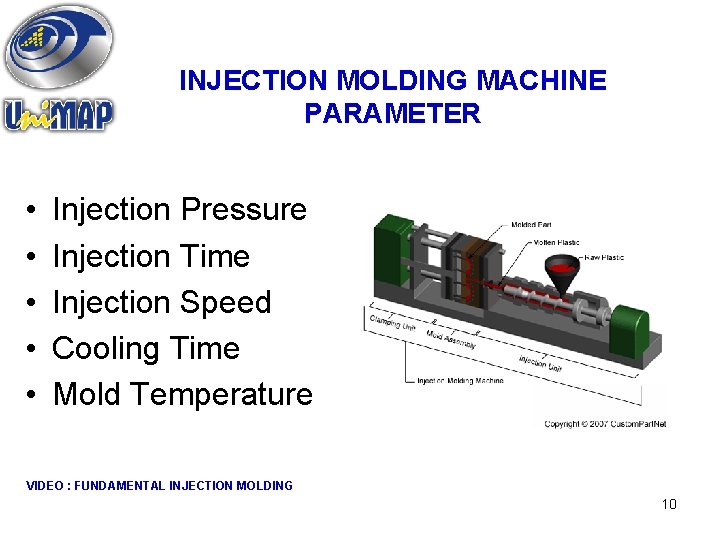
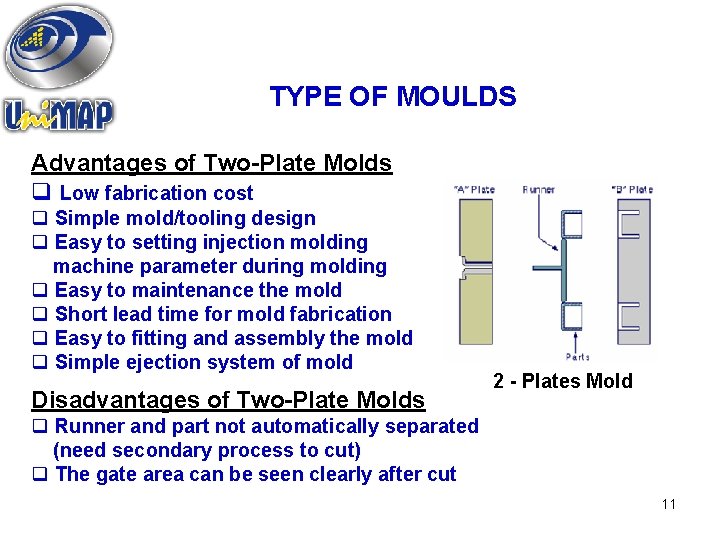
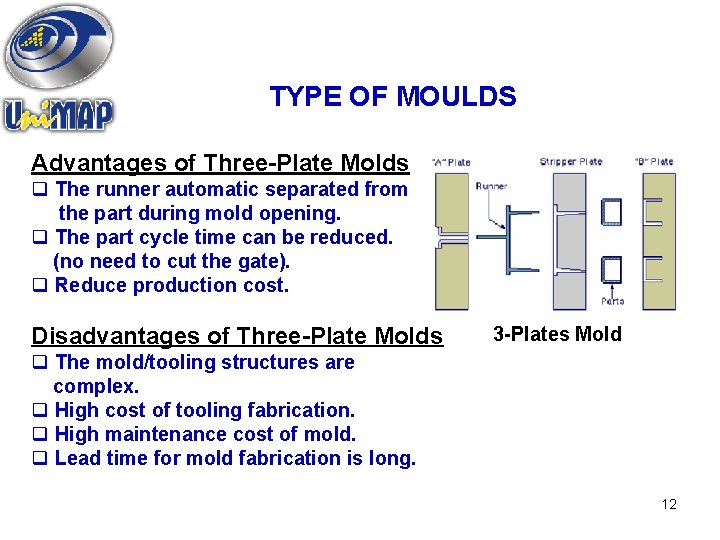
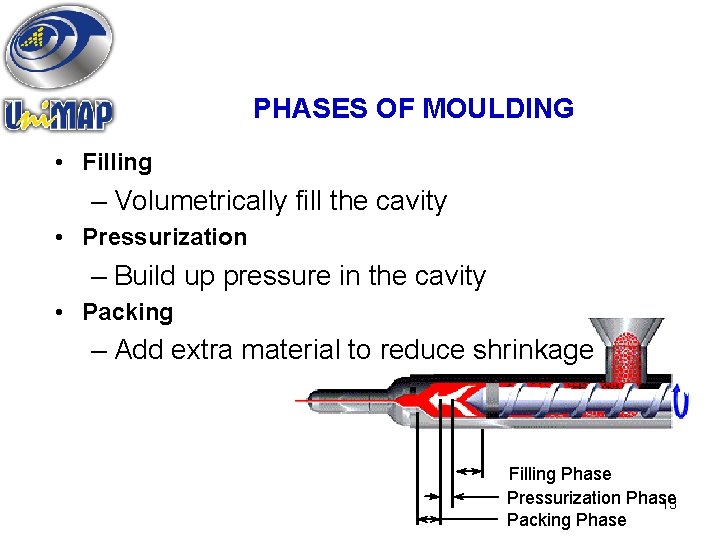
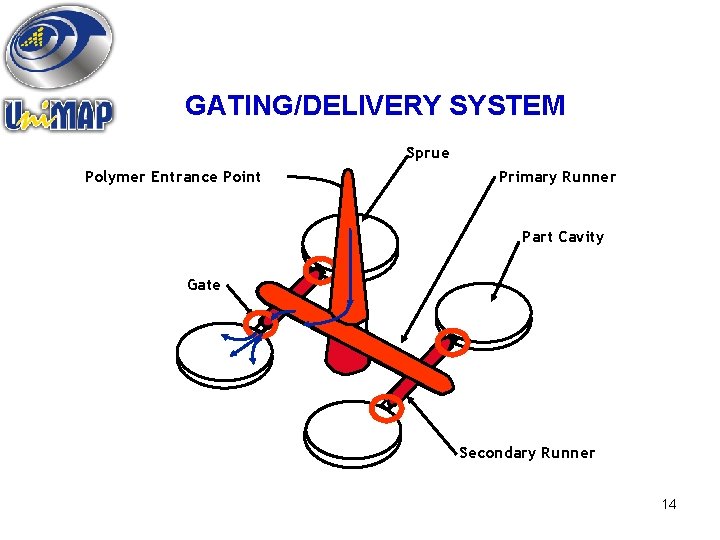
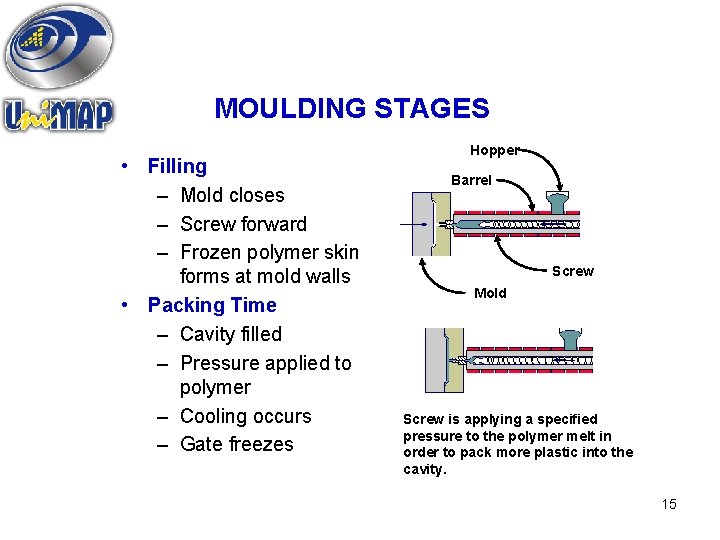
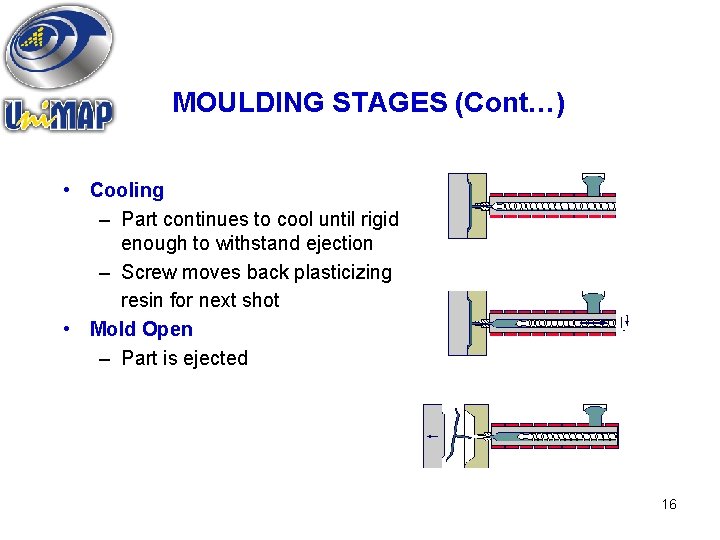
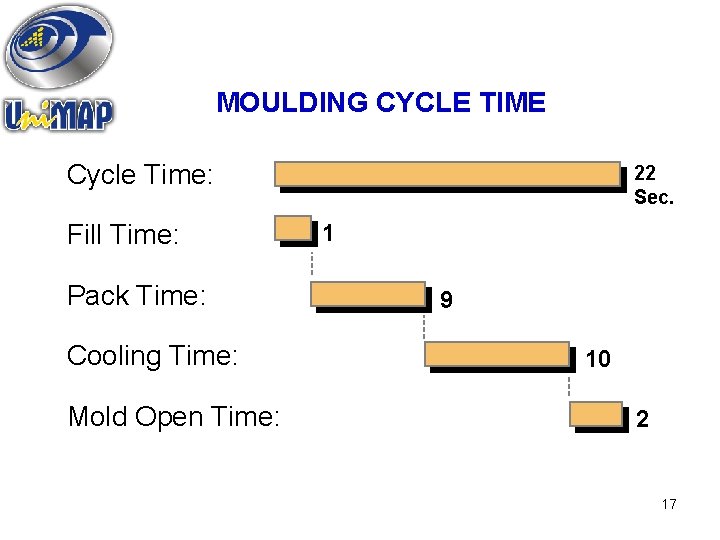
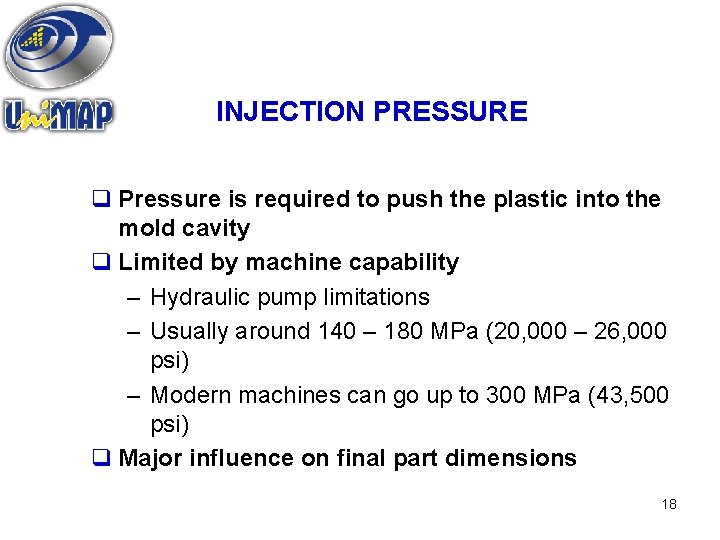
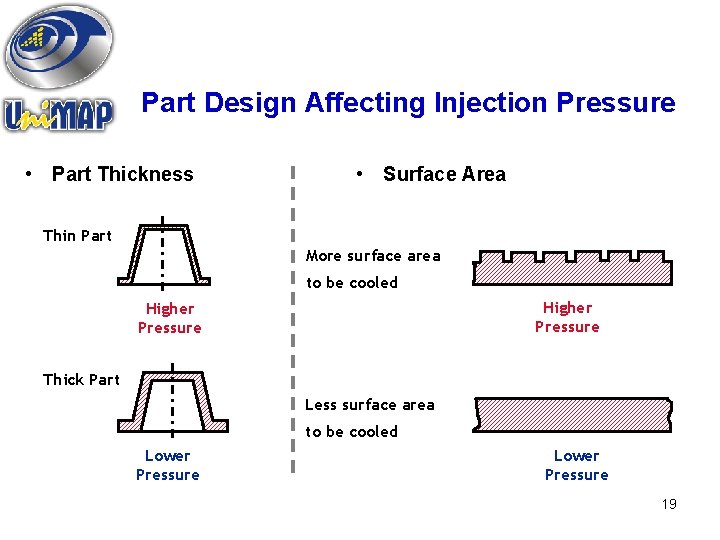
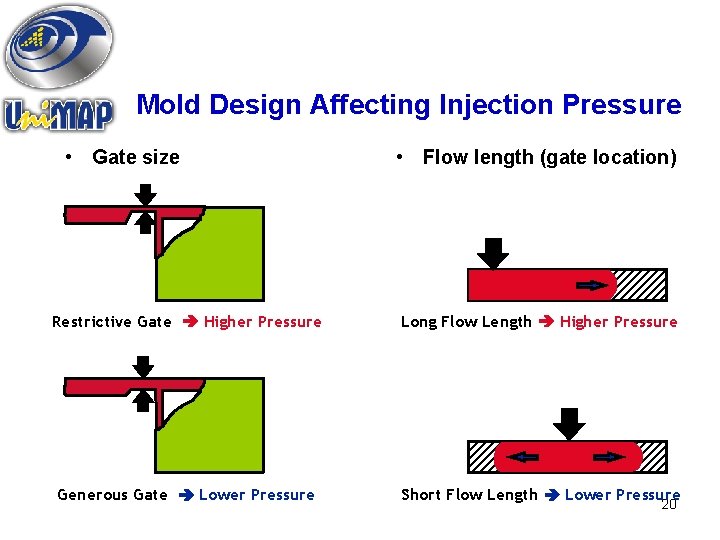
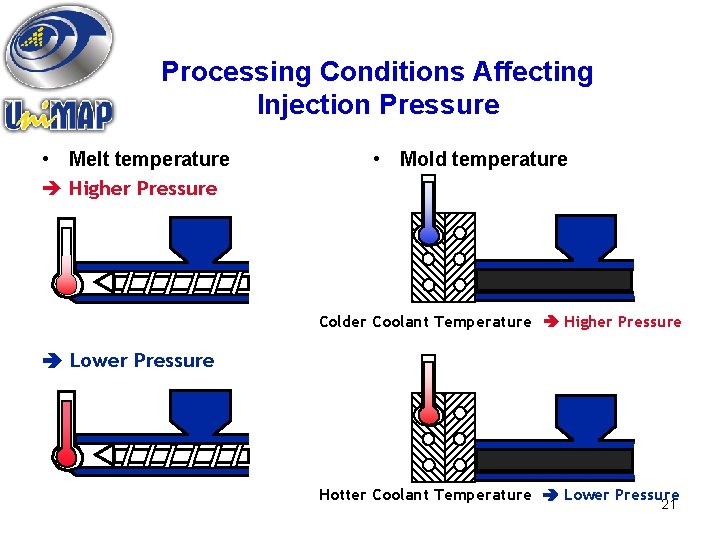
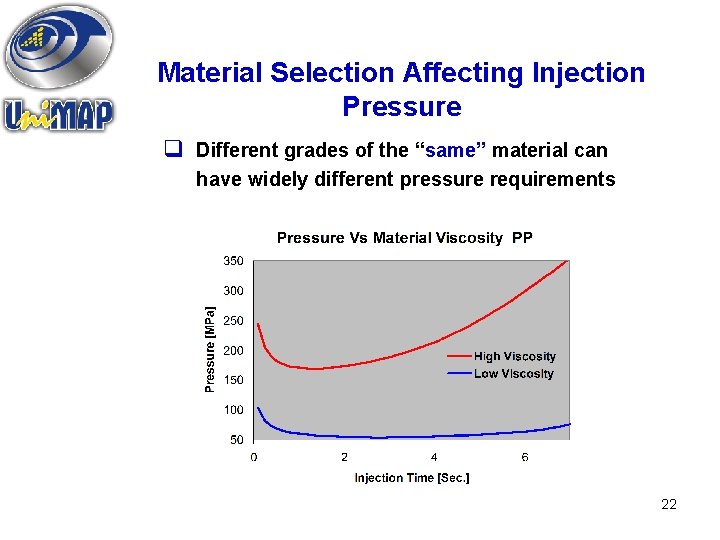
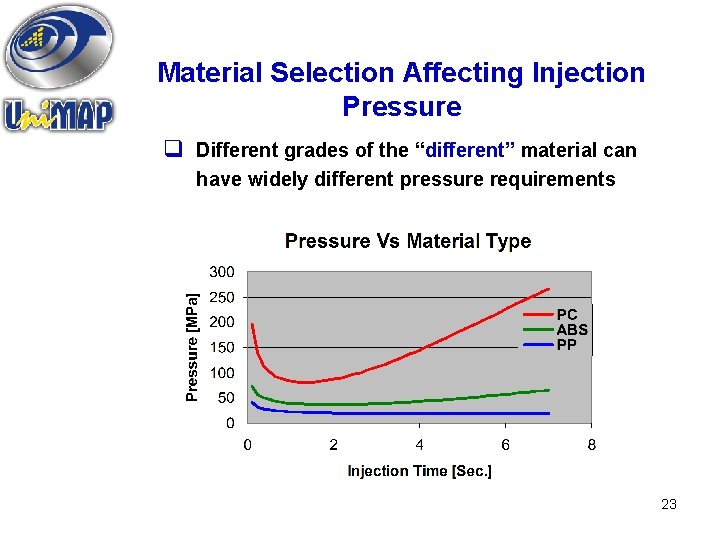
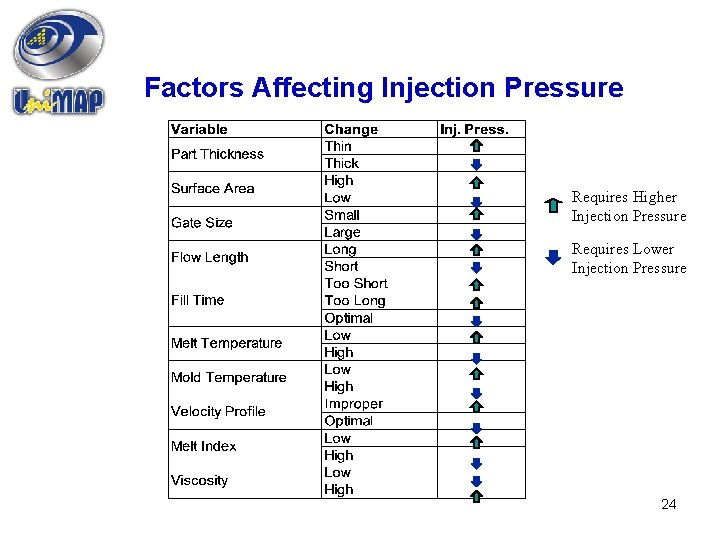
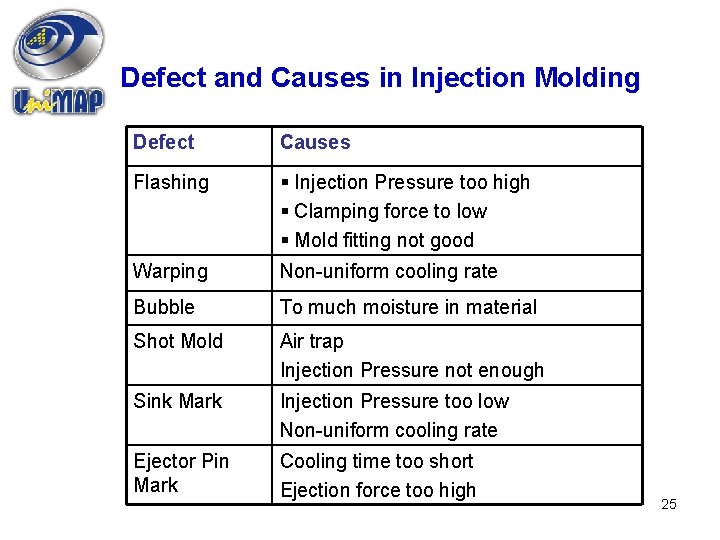
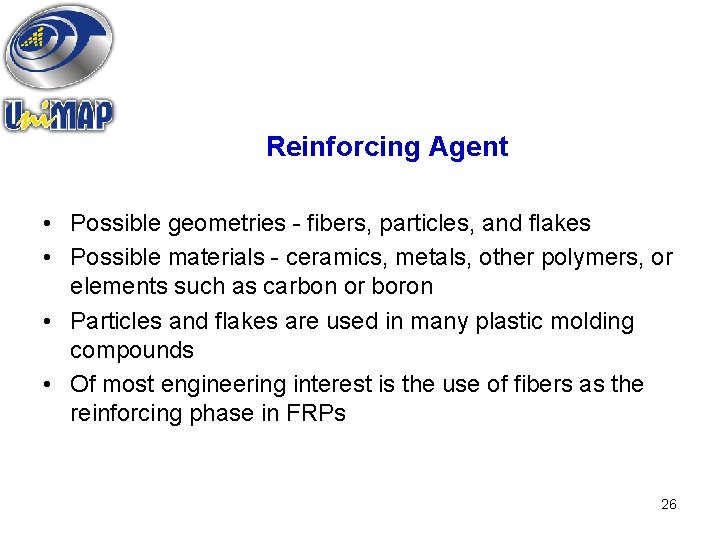
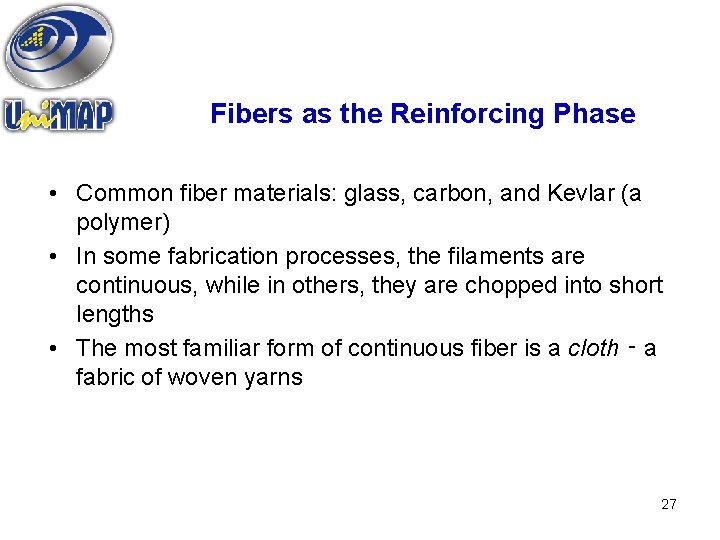
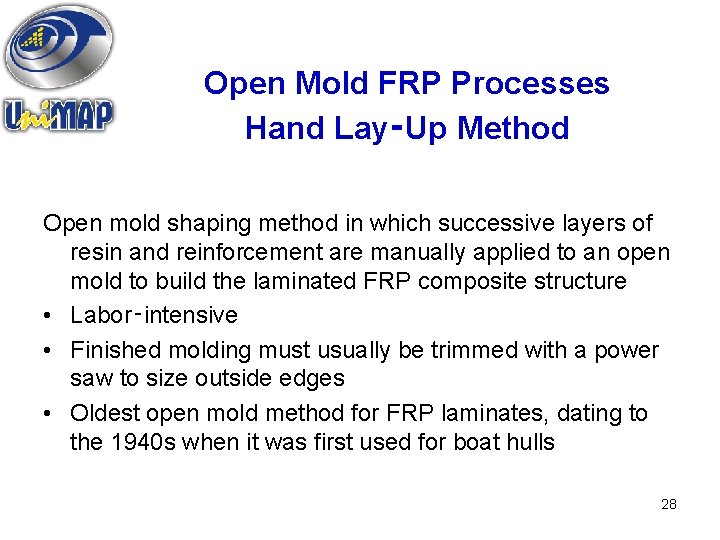
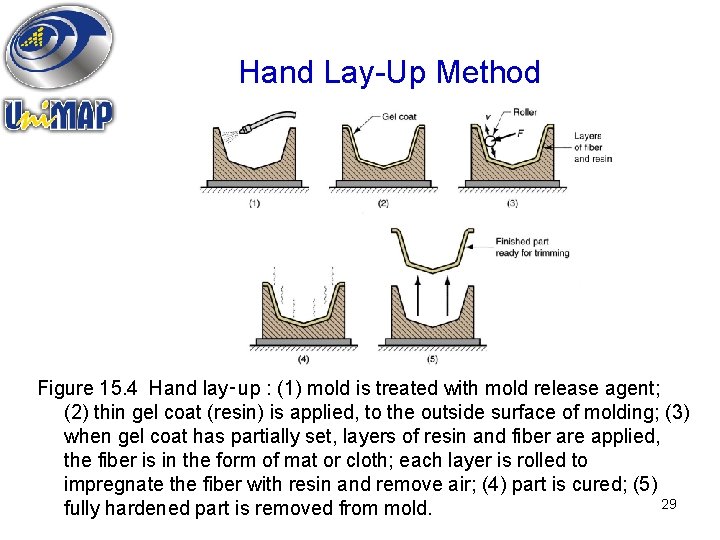
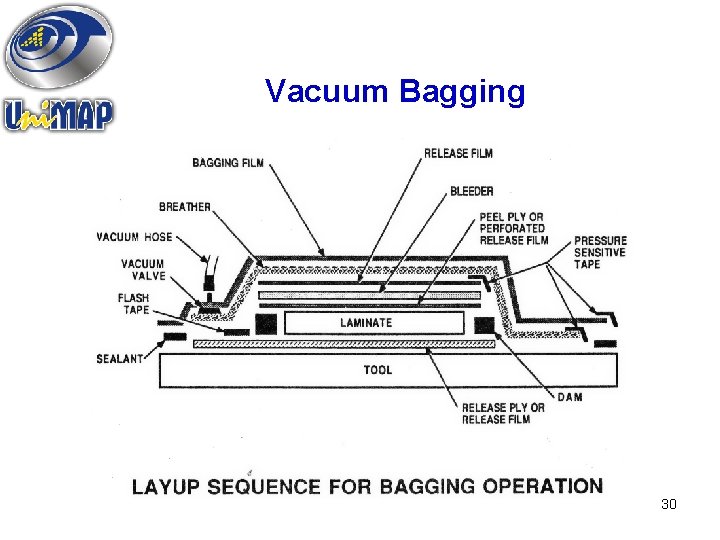
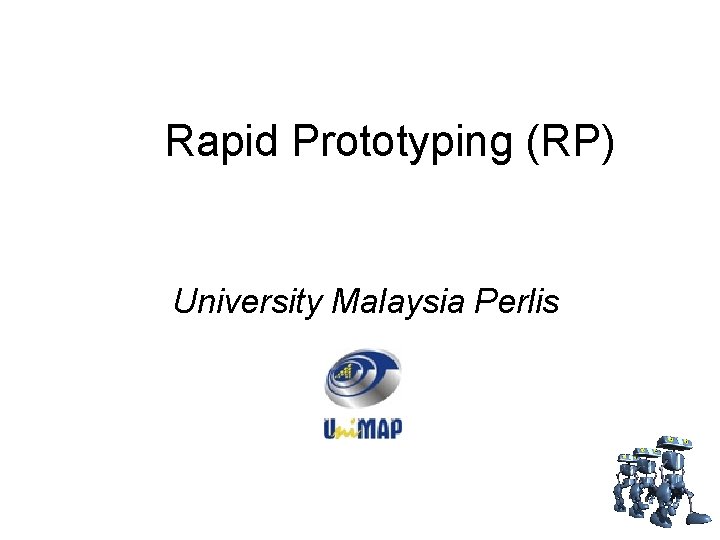

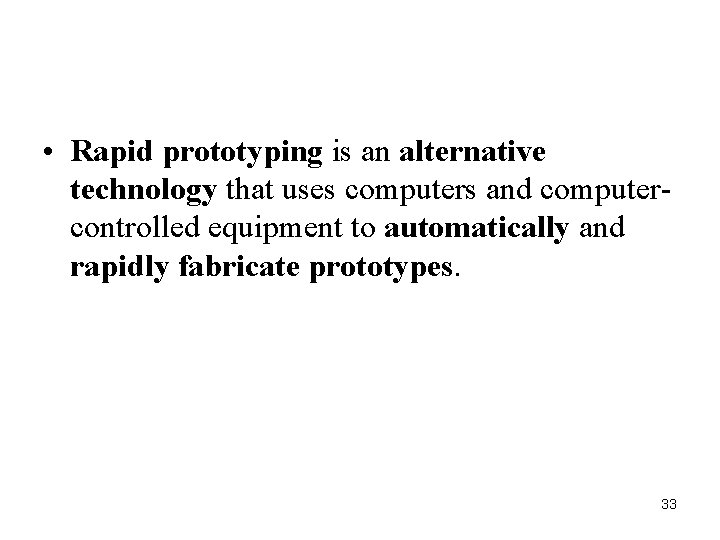
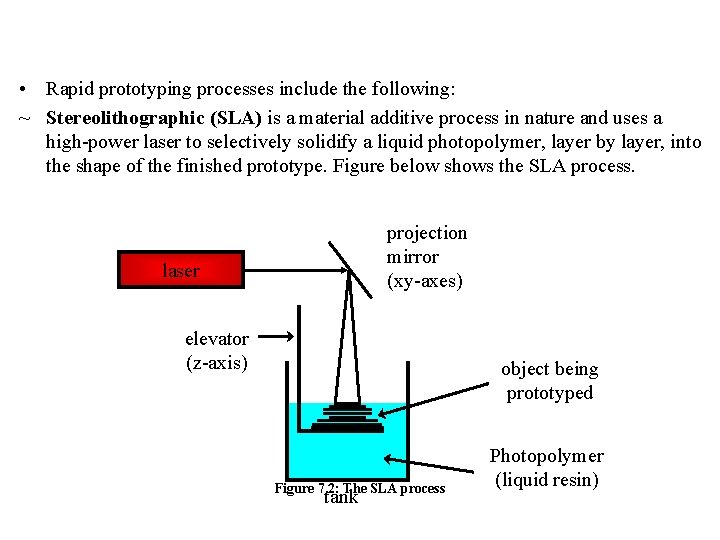
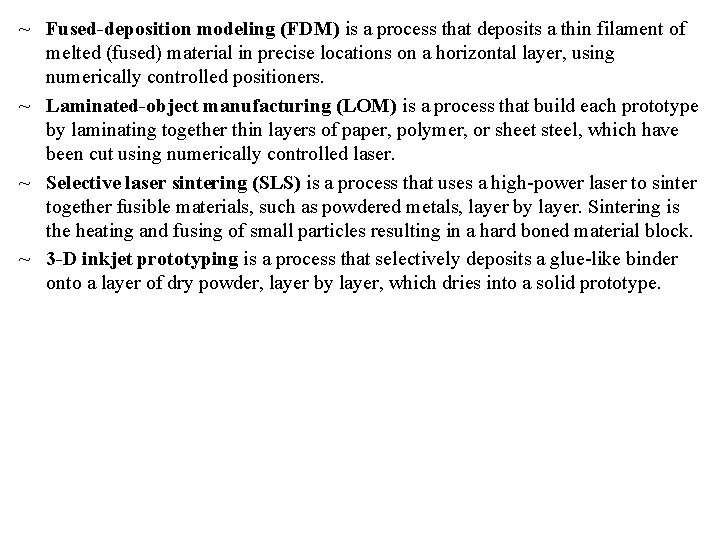
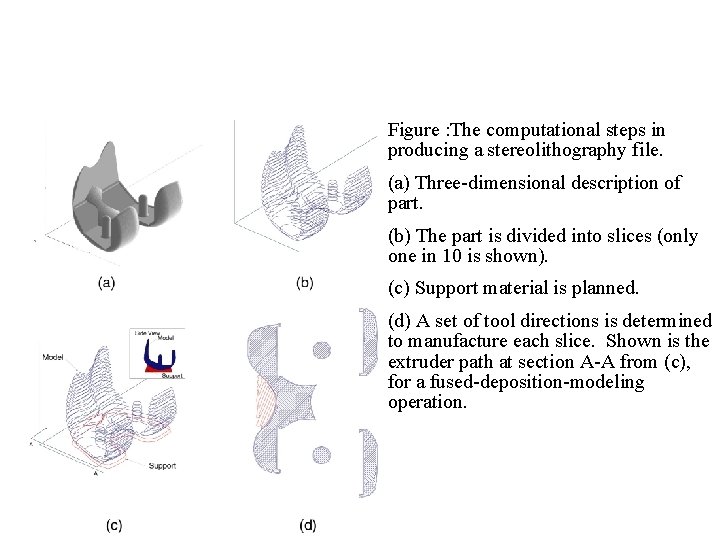
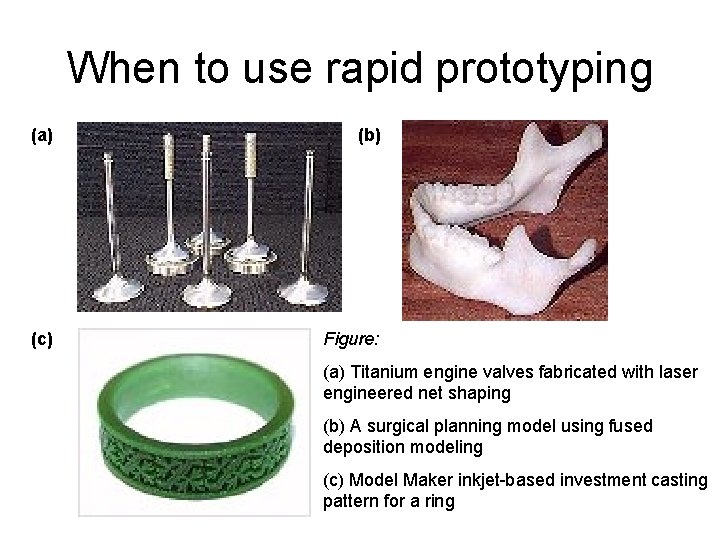
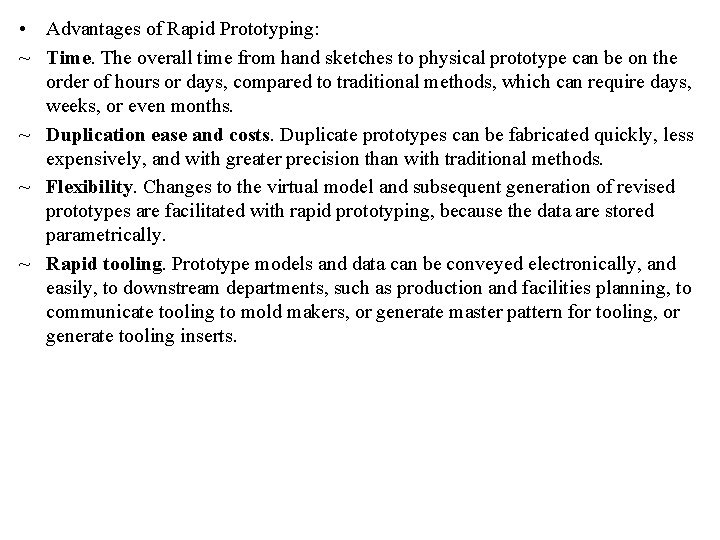
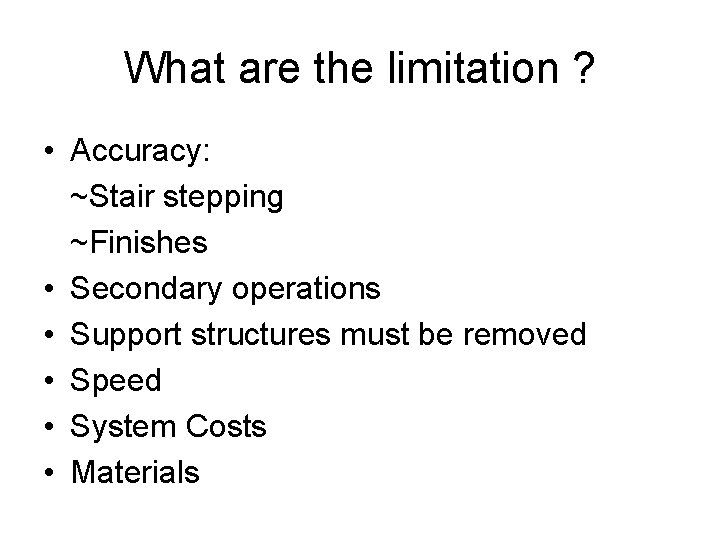
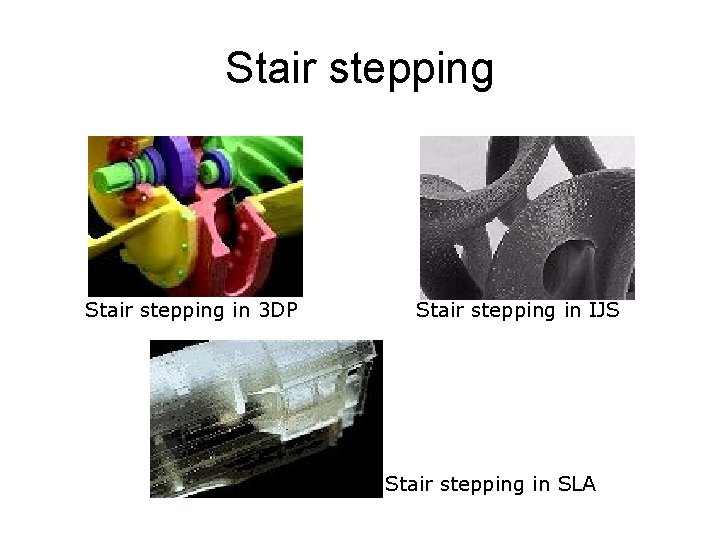
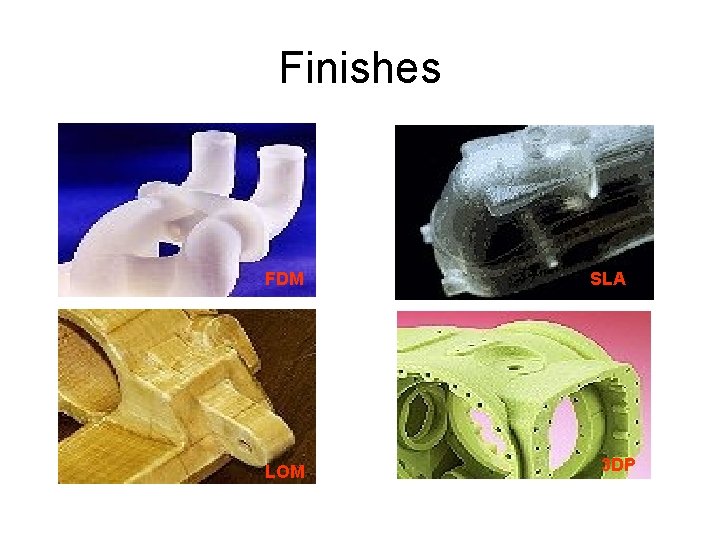
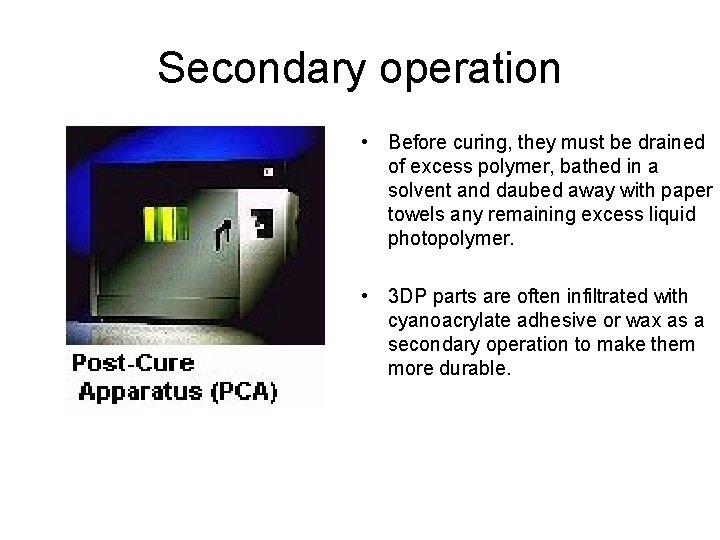
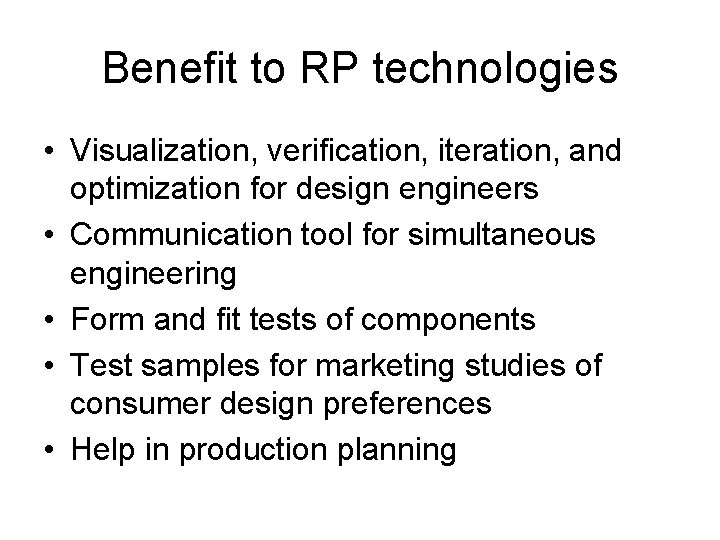
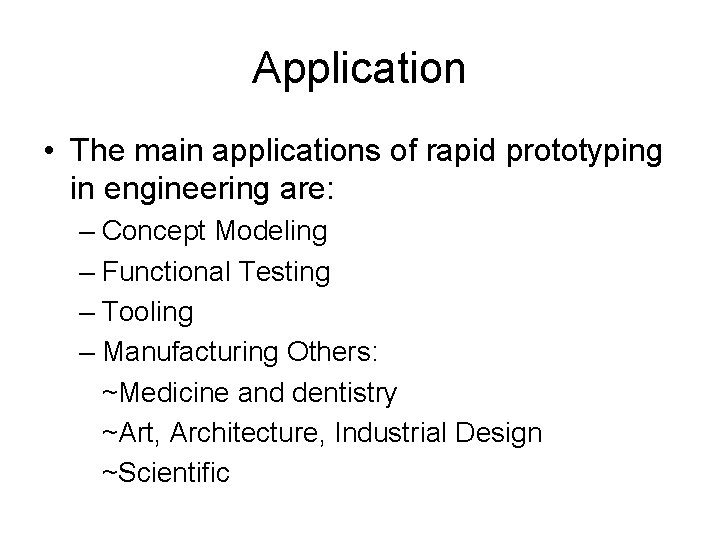
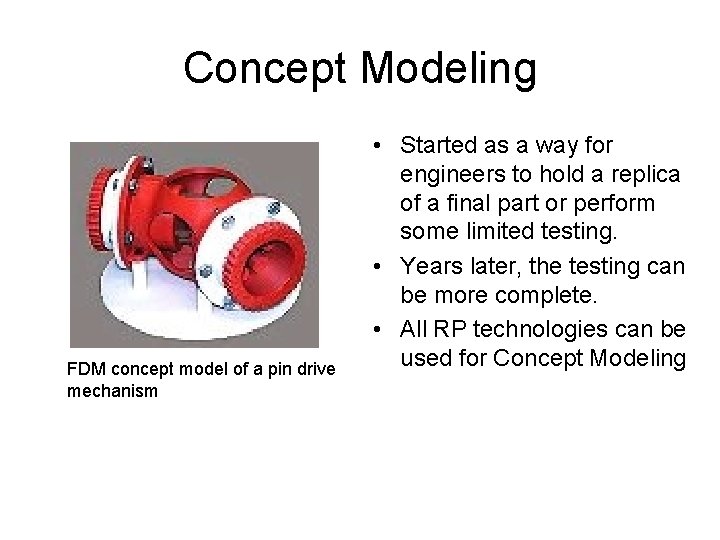
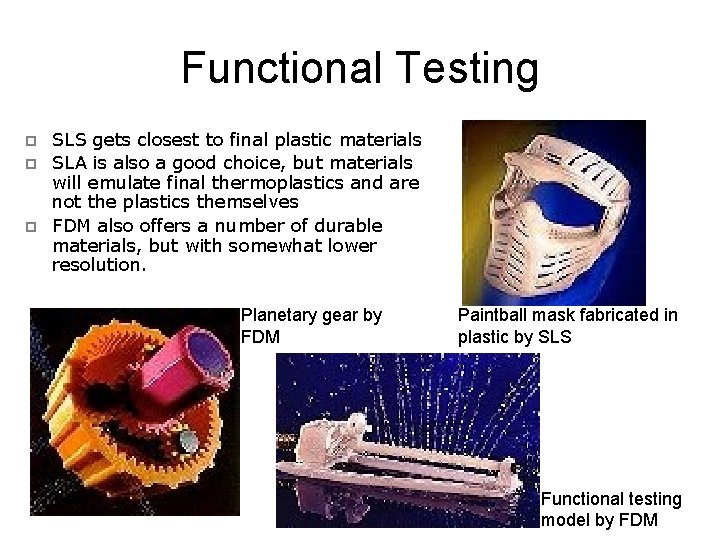
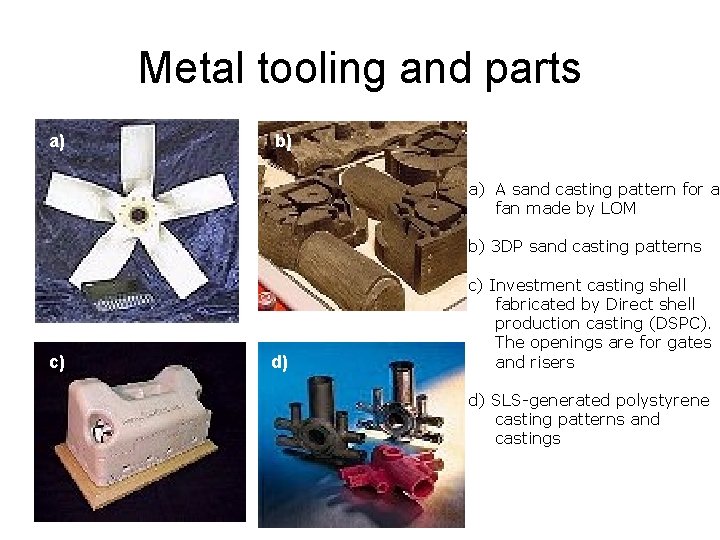
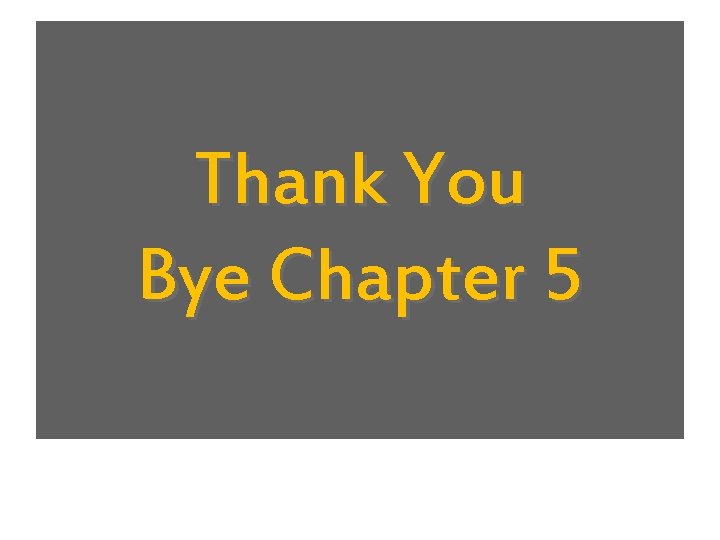
- Slides: 48
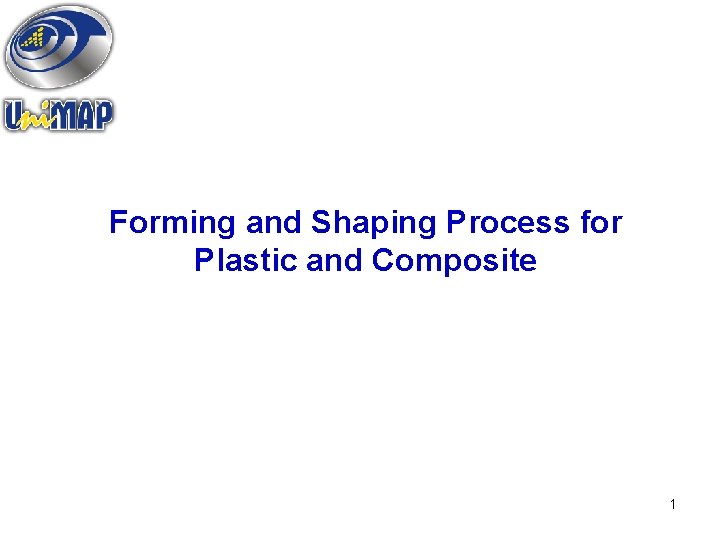
Forming and Shaping Process for Plastic and Composite 1
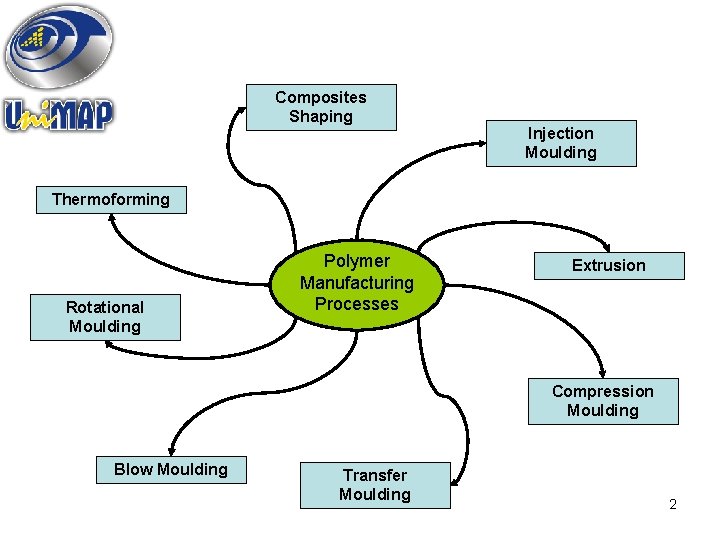
Composites Shaping Injection Moulding Thermoforming Rotational Moulding Polymer Manufacturing Processes Extrusion Compression Moulding Blow Moulding Transfer Moulding 2
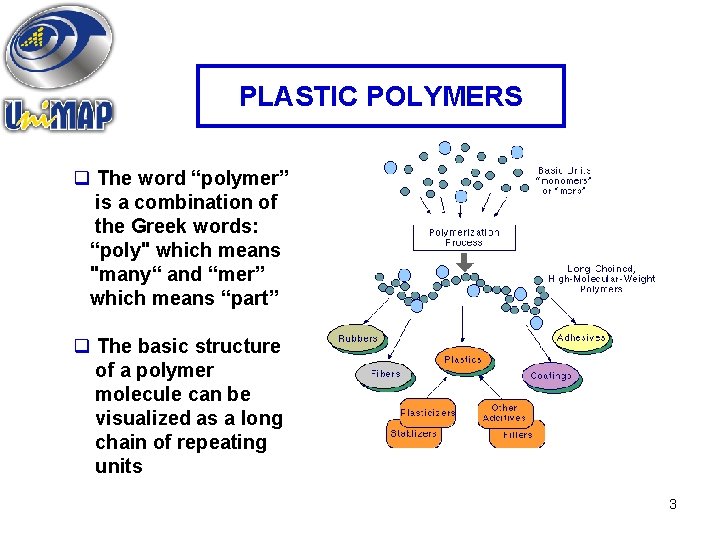
PLASTIC POLYMERS q The word “polymer” is a combination of the Greek words: “poly" which means "many“ and “mer” which means “part” q The basic structure of a polymer molecule can be visualized as a long chain of repeating units 3
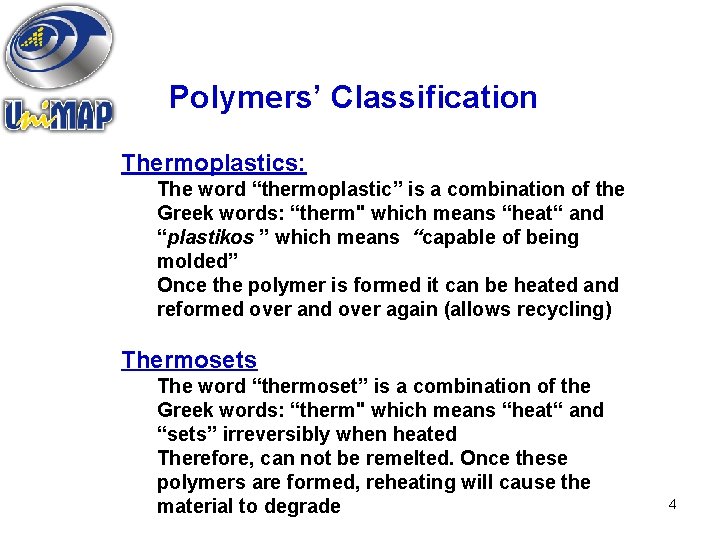
Polymers’ Classification Thermoplastics: The word “thermoplastic” is a combination of the Greek words: “therm" which means “heat“ and “plastikos ” which means “capable of being molded” Once the polymer is formed it can be heated and reformed over and over again (allows recycling) Thermosets The word “thermoset” is a combination of the Greek words: “therm" which means “heat“ and “sets” irreversibly when heated Therefore, can not be remelted. Once these polymers are formed, reheating will cause the material to degrade 4
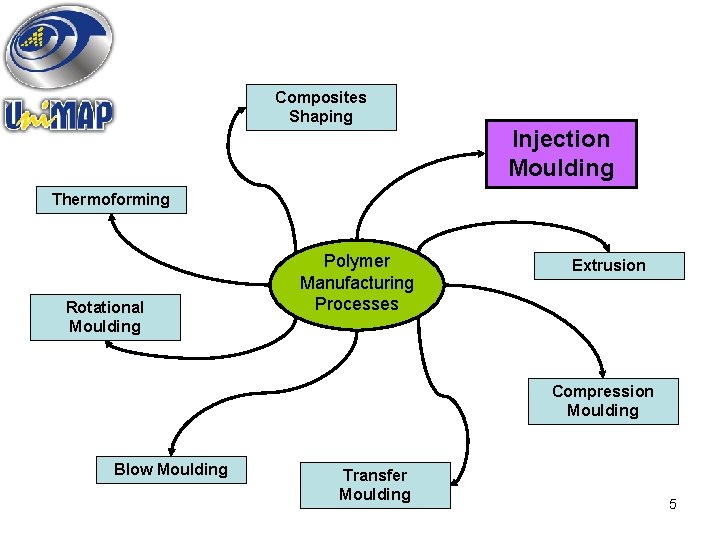
Composites Shaping Injection Moulding Thermoforming Rotational Moulding Polymer Manufacturing Processes Extrusion Compression Moulding Blow Moulding Transfer Moulding 5
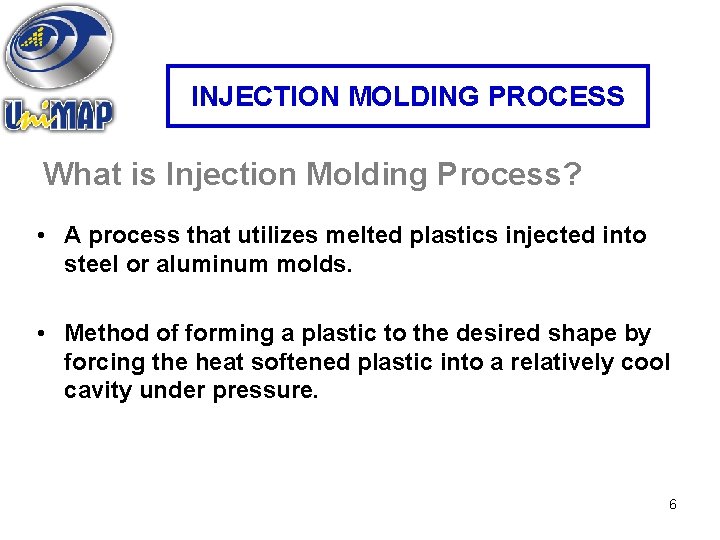
INJECTION MOLDING PROCESS What is Injection Molding Process? • A process that utilizes melted plastics injected into steel or aluminum molds. • Method of forming a plastic to the desired shape by forcing the heat softened plastic into a relatively cool cavity under pressure. 6
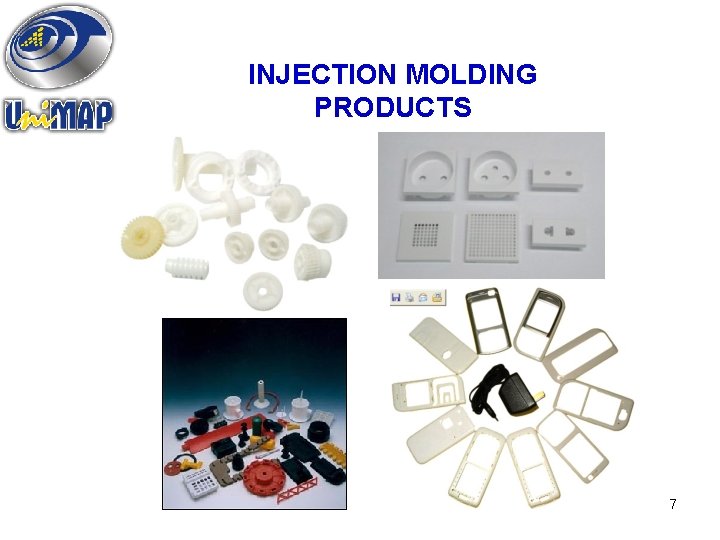
INJECTION MOLDING PRODUCTS 7
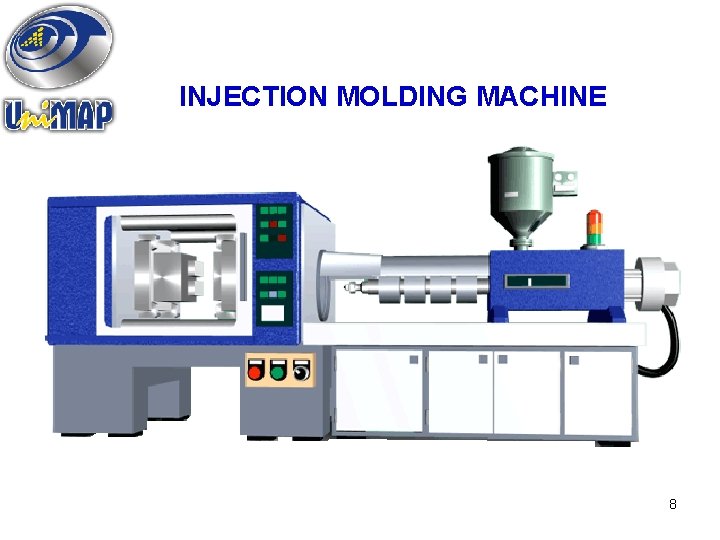
INJECTION MOLDING MACHINE 8
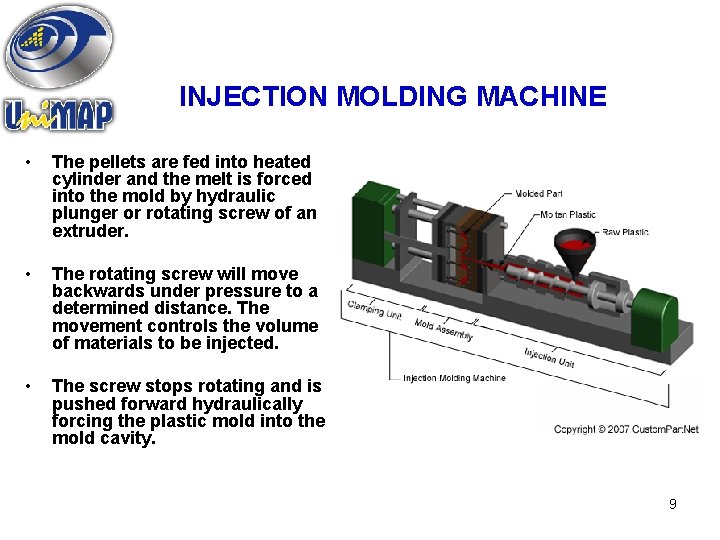
INJECTION MOLDING MACHINE • The pellets are fed into heated cylinder and the melt is forced into the mold by hydraulic plunger or rotating screw of an extruder. • The rotating screw will move backwards under pressure to a determined distance. The movement controls the volume of materials to be injected. • The screw stops rotating and is pushed forward hydraulically forcing the plastic mold into the mold cavity. 9
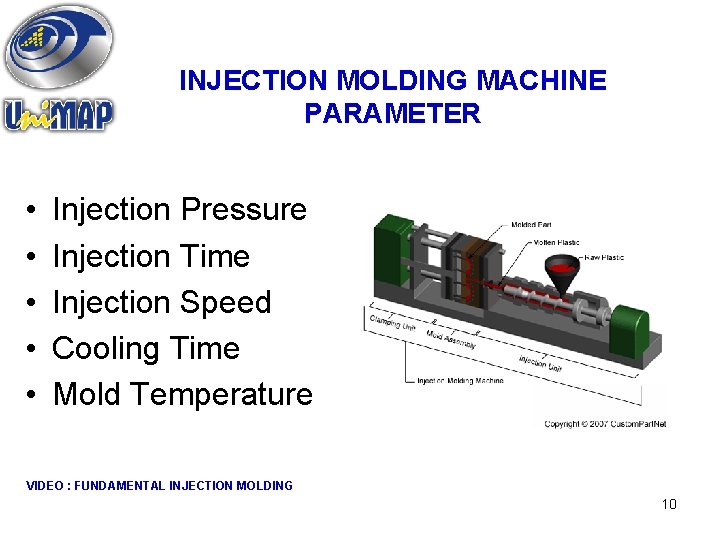
INJECTION MOLDING MACHINE PARAMETER • • • Injection Pressure Injection Time Injection Speed Cooling Time Mold Temperature VIDEO : FUNDAMENTAL INJECTION MOLDING 10
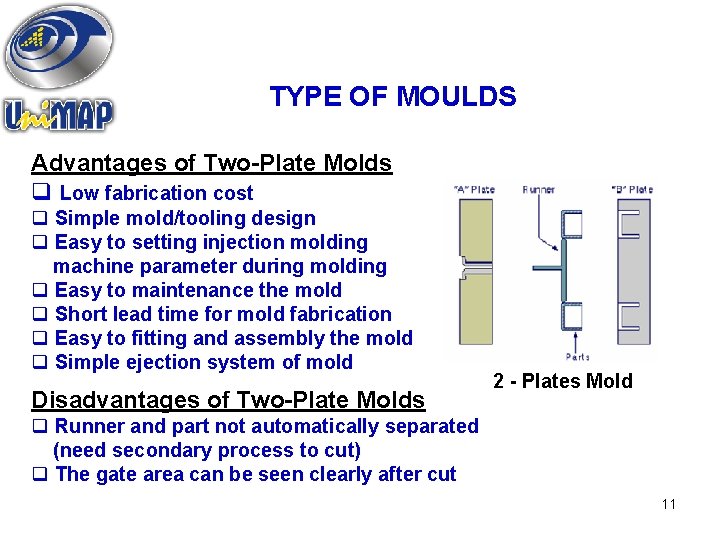
TYPE OF MOULDS Advantages of Two-Plate Molds q Low fabrication cost q Simple mold/tooling design q Easy to setting injection molding machine parameter during molding q Easy to maintenance the mold q Short lead time for mold fabrication q Easy to fitting and assembly the mold q Simple ejection system of mold Disadvantages of Two-Plate Molds 2 - Plates Mold q Runner and part not automatically separated (need secondary process to cut) q The gate area can be seen clearly after cut 11
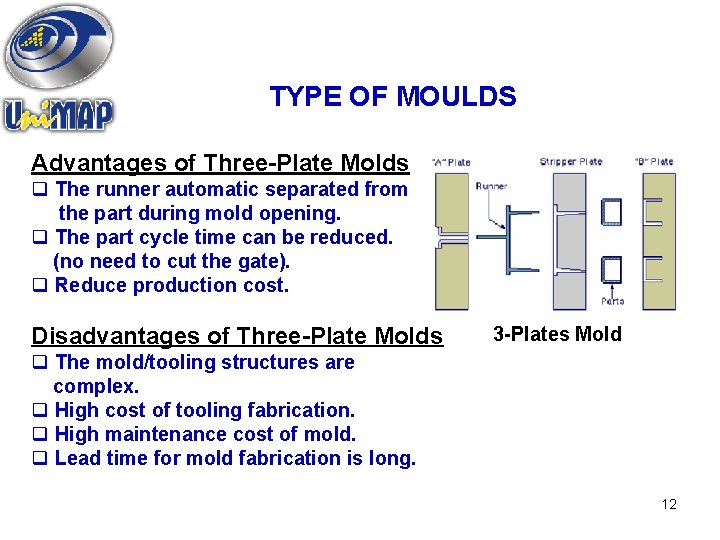
TYPE OF MOULDS Advantages of Three-Plate Molds q The runner automatic separated from the part during mold opening. q The part cycle time can be reduced. (no need to cut the gate). q Reduce production cost. Disadvantages of Three-Plate Molds 3 -Plates Mold q The mold/tooling structures are complex. q High cost of tooling fabrication. q High maintenance cost of mold. q Lead time for mold fabrication is long. 12
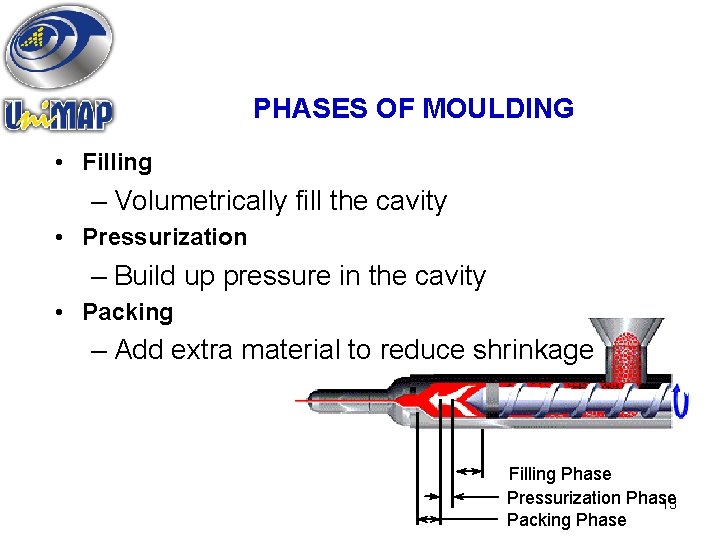
PHASES OF MOULDING • Filling – Volumetrically fill the cavity • Pressurization – Build up pressure in the cavity • Packing – Add extra material to reduce shrinkage Filling Phase Pressurization Phase 13 Packing Phase
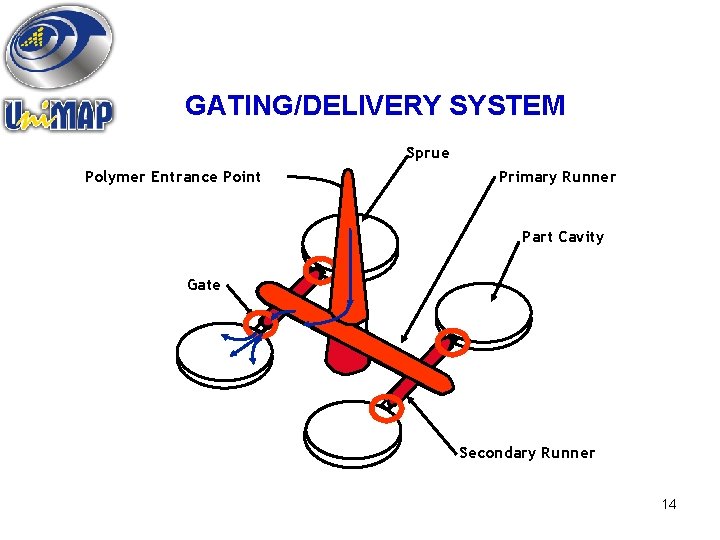
GATING/DELIVERY SYSTEM Sprue Polymer Entrance Point Primary Runner Part Cavity Gate Secondary Runner 14
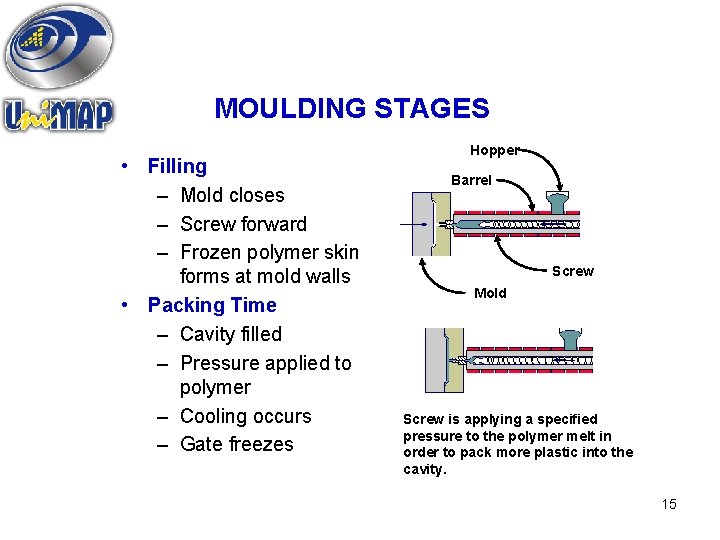
MOULDING STAGES • Filling – Mold closes – Screw forward – Frozen polymer skin forms at mold walls • Packing Time – Cavity filled – Pressure applied to polymer – Cooling occurs – Gate freezes Hopper Barrel Screw Mold Screw is applying a specified pressure to the polymer melt in order to pack more plastic into the cavity. 15
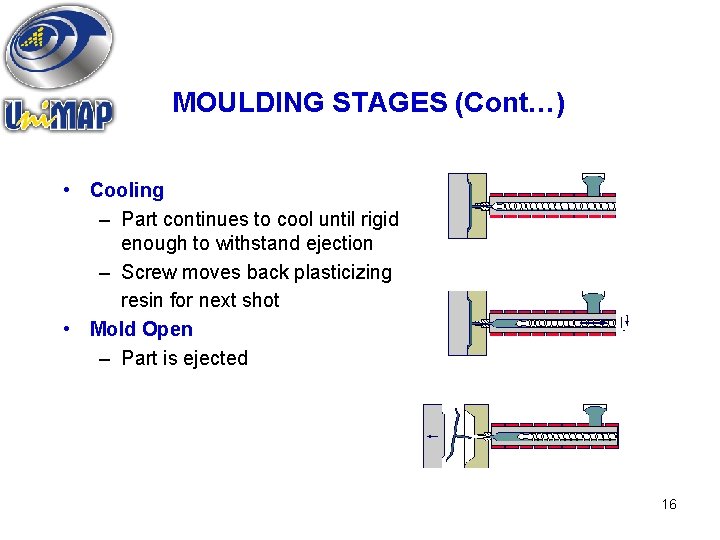
MOULDING STAGES (Cont…) • Cooling – Part continues to cool until rigid enough to withstand ejection – Screw moves back plasticizing resin for next shot • Mold Open – Part is ejected 16
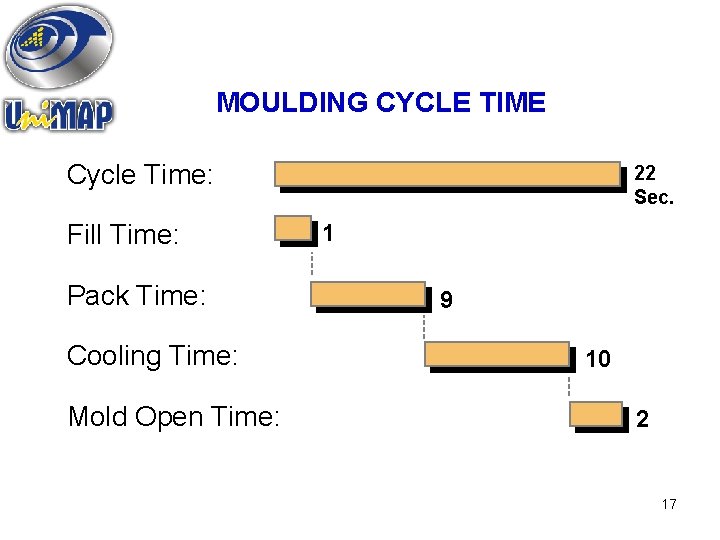
MOULDING CYCLE TIME Cycle Time: Fill Time: Pack Time: Cooling Time: Mold Open Time: 22 Sec. 1 9 10 2 17
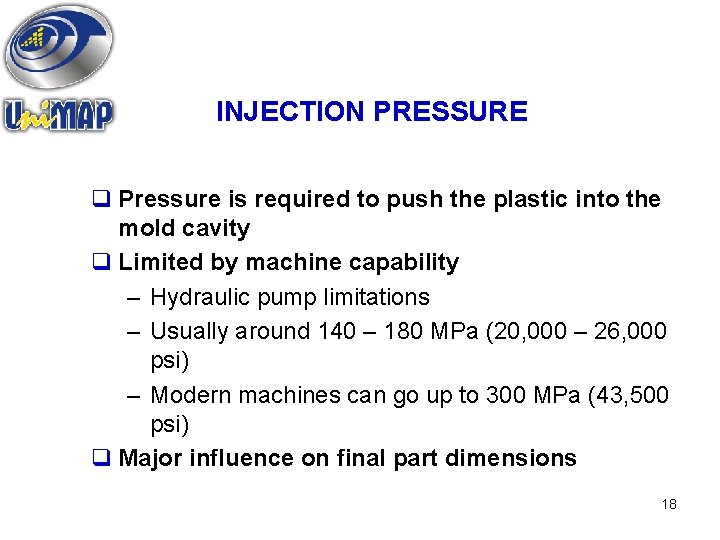
INJECTION PRESSURE q Pressure is required to push the plastic into the mold cavity q Limited by machine capability – Hydraulic pump limitations – Usually around 140 – 180 MPa (20, 000 – 26, 000 psi) – Modern machines can go up to 300 MPa (43, 500 psi) q Major influence on final part dimensions 18
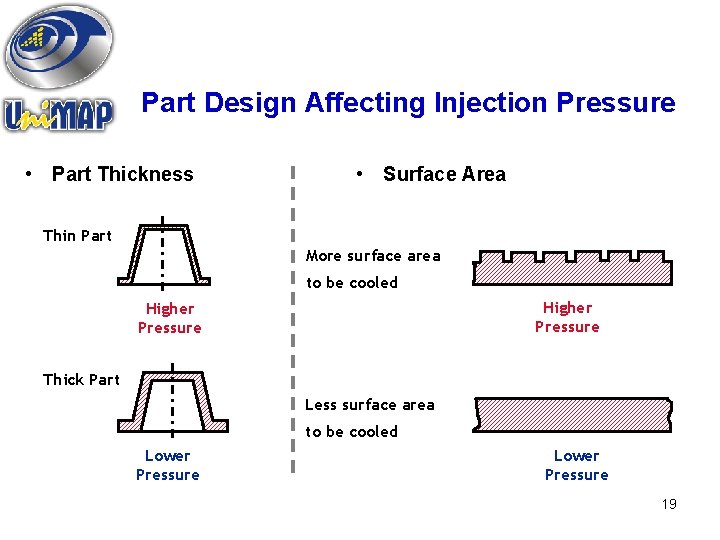
Part Design Affecting Injection Pressure • Part Thickness • Surface Area Thin Part More surface area to be cooled Higher Pressure Thick Part Less surface area to be cooled Lower Pressure 19
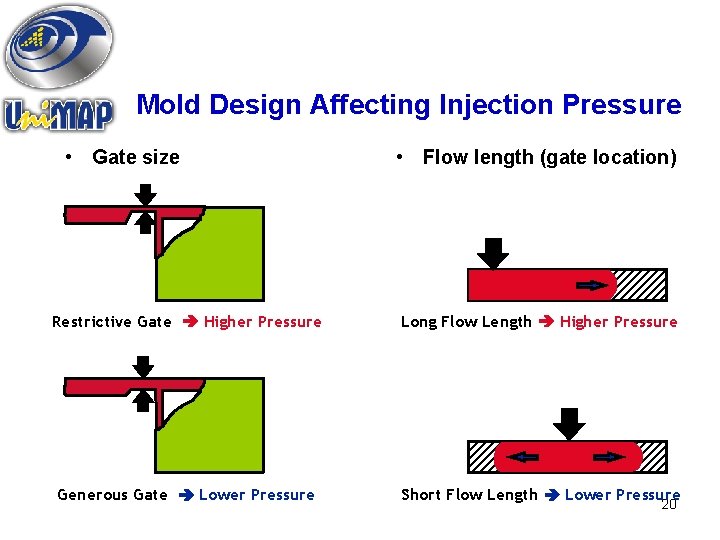
Mold Design Affecting Injection Pressure • Gate size • Flow length (gate location) Restrictive Gate Higher Pressure Long Flow Length Higher Pressure Generous Gate Lower Pressure Short Flow Length Lower Pressure 20
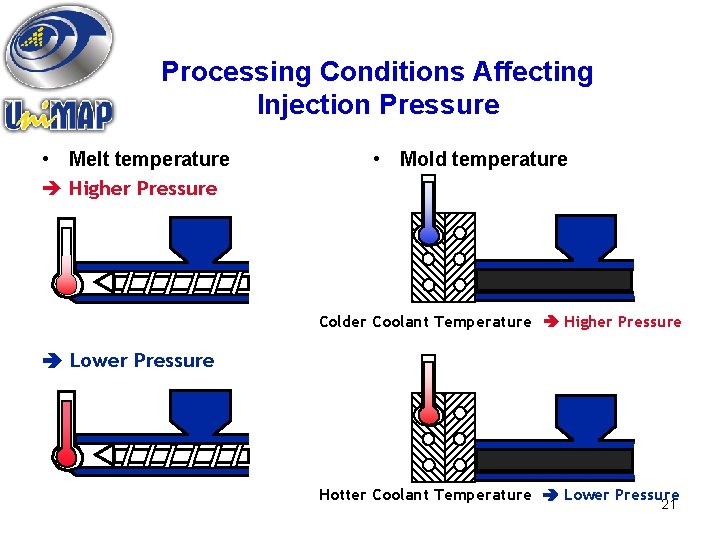
Processing Conditions Affecting Injection Pressure • Melt temperature è Higher Pressure • Mold temperature Colder Coolant Temperature Higher Pressure Lower Pressure Hotter Coolant Temperature Lower Pressure 21
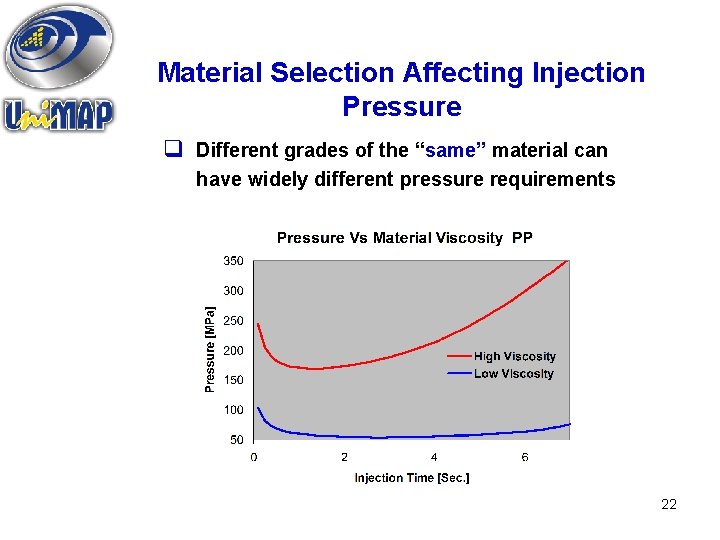
Material Selection Affecting Injection Pressure q Different grades of the “same” material can have widely different pressure requirements 22
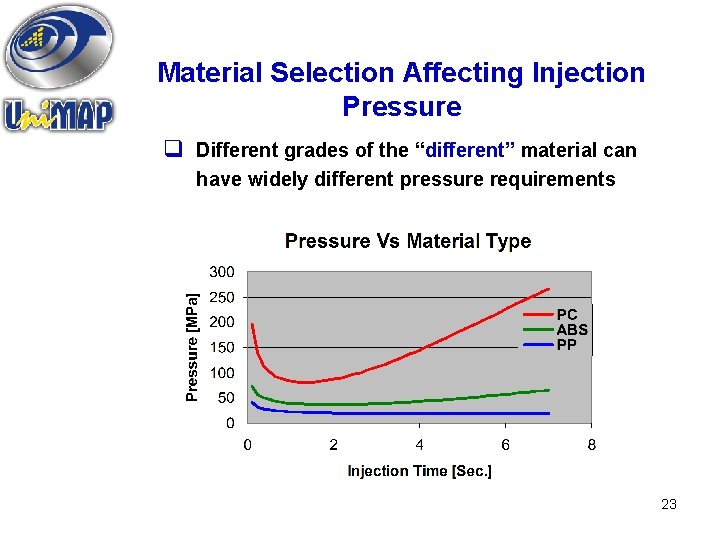
Material Selection Affecting Injection Pressure q Different grades of the “different” material can have widely different pressure requirements 23
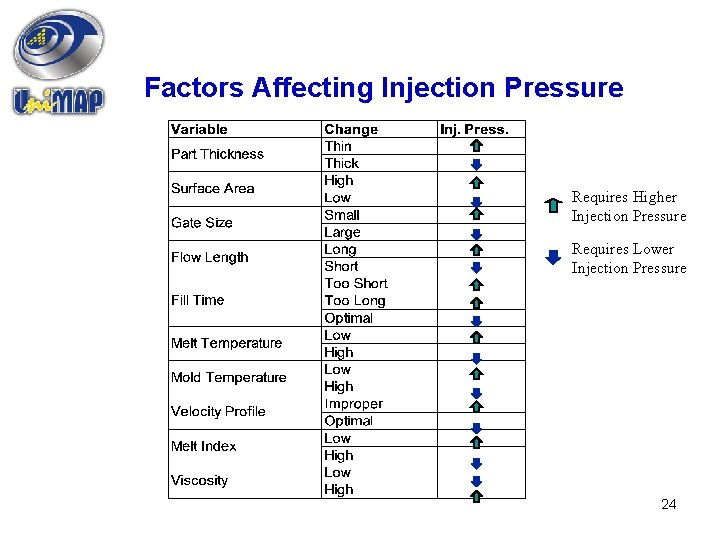
Factors Affecting Injection Pressure Requires Higher Injection Pressure Requires Lower Injection Pressure 24
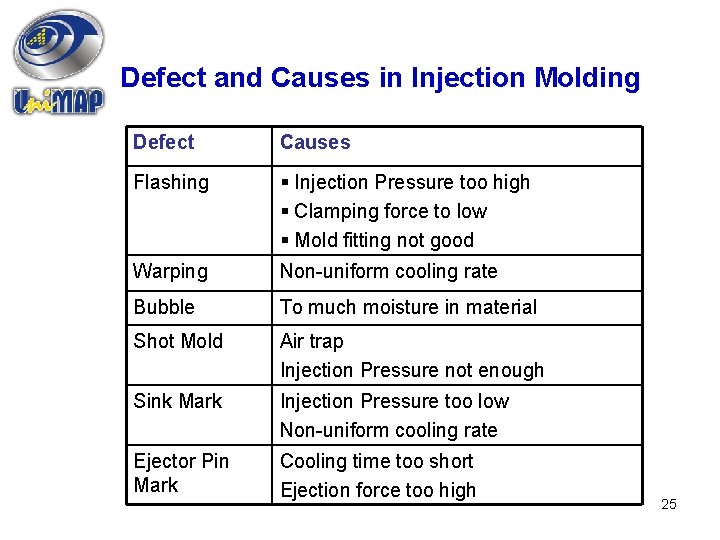
Defect and Causes in Injection Molding Defect Causes Flashing § Injection Pressure too high § Clamping force to low § Mold fitting not good Warping Non-uniform cooling rate Bubble To much moisture in material Shot Mold Air trap Injection Pressure not enough Sink Mark Injection Pressure too low Non-uniform cooling rate Ejector Pin Mark Cooling time too short Ejection force too high 25
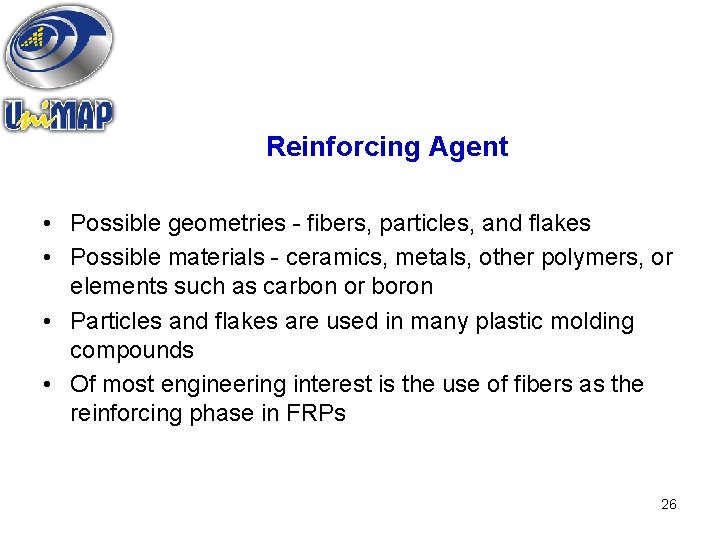
Reinforcing Agent • Possible geometries - fibers, particles, and flakes • Possible materials - ceramics, metals, other polymers, or elements such as carbon or boron • Particles and flakes are used in many plastic molding compounds • Of most engineering interest is the use of fibers as the reinforcing phase in FRPs 26
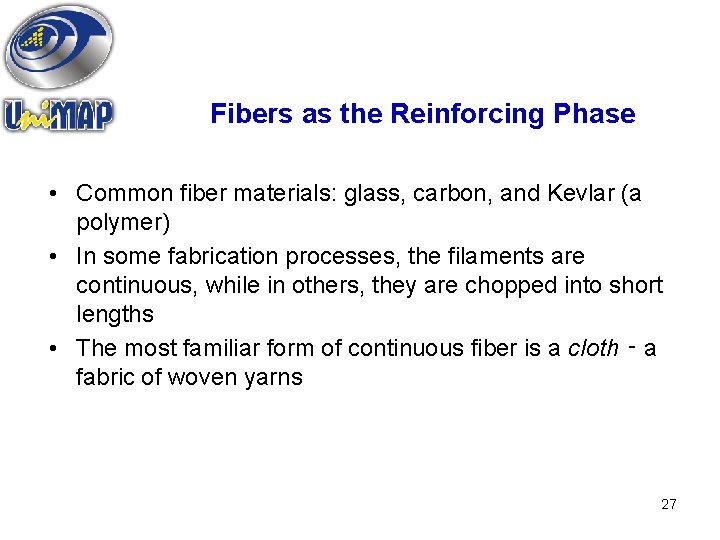
Fibers as the Reinforcing Phase • Common fiber materials: glass, carbon, and Kevlar (a polymer) • In some fabrication processes, the filaments are continuous, while in others, they are chopped into short lengths • The most familiar form of continuous fiber is a cloth ‑ a fabric of woven yarns 27
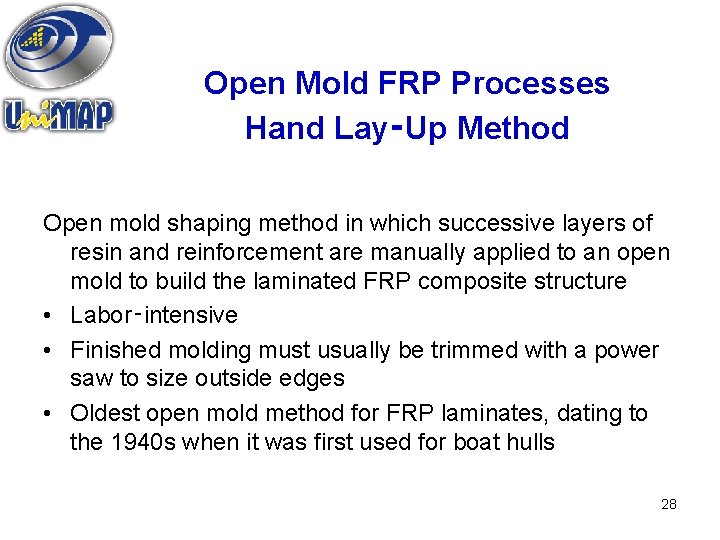
Open Mold FRP Processes Hand Lay‑Up Method Open mold shaping method in which successive layers of resin and reinforcement are manually applied to an open mold to build the laminated FRP composite structure • Labor‑intensive • Finished molding must usually be trimmed with a power saw to size outside edges • Oldest open mold method for FRP laminates, dating to the 1940 s when it was first used for boat hulls 28
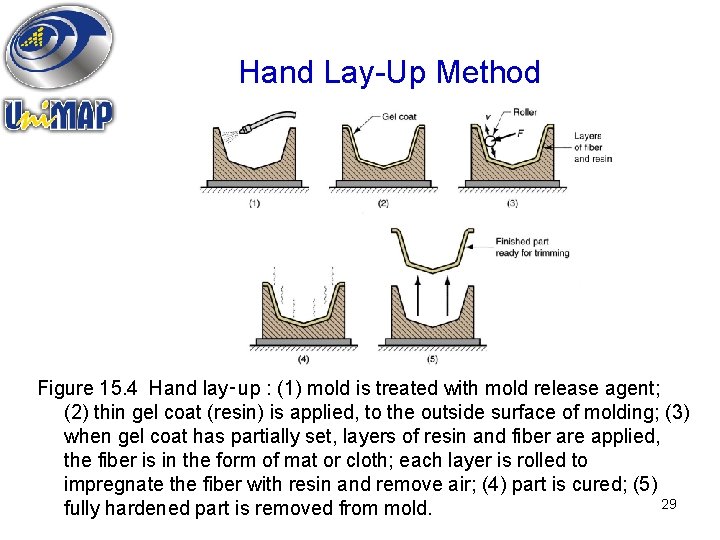
Hand Lay-Up Method Figure 15. 4 Hand lay‑up : (1) mold is treated with mold release agent; (2) thin gel coat (resin) is applied, to the outside surface of molding; (3) when gel coat has partially set, layers of resin and fiber are applied, the fiber is in the form of mat or cloth; each layer is rolled to impregnate the fiber with resin and remove air; (4) part is cured; (5) 29 fully hardened part is removed from mold.
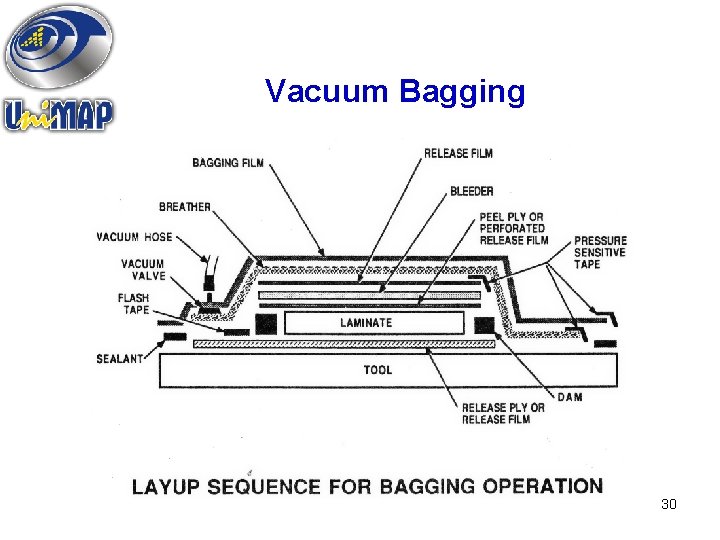
Vacuum Bagging 30
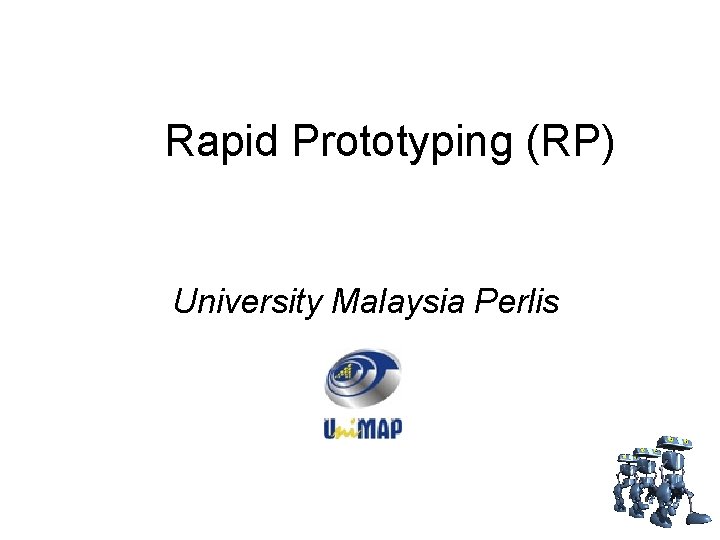
Rapid Prototyping (RP) University Malaysia Perlis

Introduction • RP or freeform fabrication - one of the fastest growing new technologies since its introduction in 1986. • RP started as a process to fabricate polymer prototypes in minimum lead time based on a CAD model of the item. • These prototypes were fabricated “freeform” directly from CAD files without the use of molds.
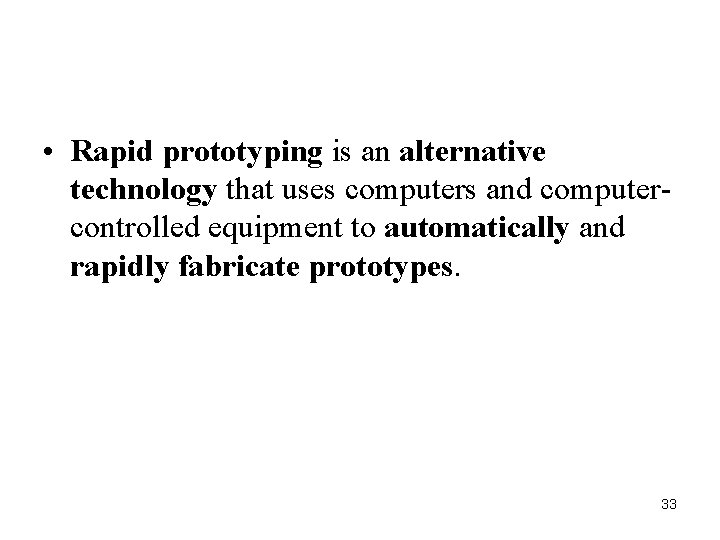
• Rapid prototyping is an alternative technology that uses computers and computercontrolled equipment to automatically and rapidly fabricate prototypes. 33
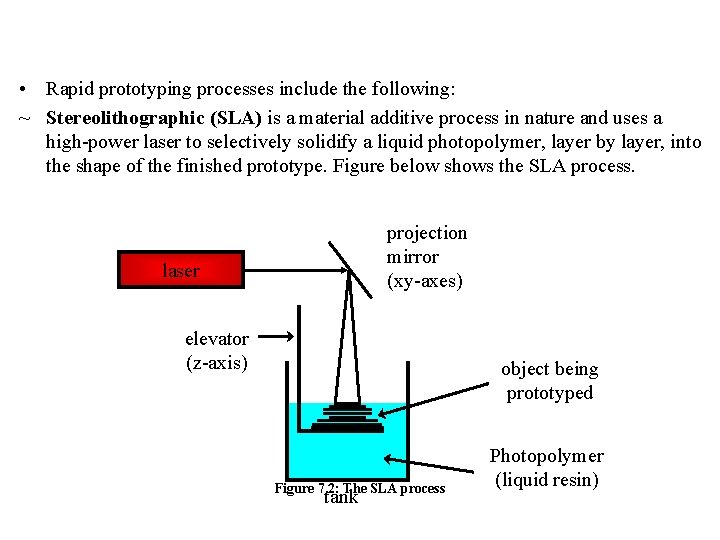
• Rapid prototyping processes include the following: ~ Stereolithographic (SLA) is a material additive process in nature and uses a high-power laser to selectively solidify a liquid photopolymer, layer by layer, into the shape of the finished prototype. Figure below shows the SLA process. projection mirror (xy-axes) laser elevator (z-axis) object being prototyped Figure 7. 2: The SLA process tank Photopolymer (liquid resin)
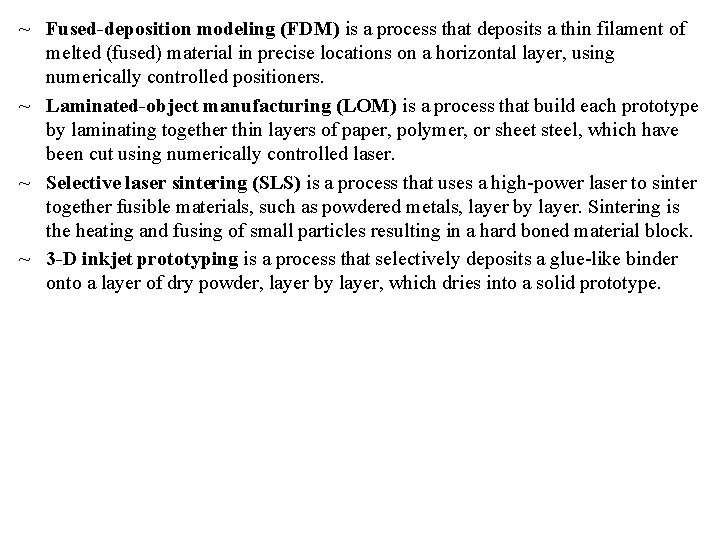
~ Fused-deposition modeling (FDM) is a process that deposits a thin filament of melted (fused) material in precise locations on a horizontal layer, using numerically controlled positioners. ~ Laminated-object manufacturing (LOM) is a process that build each prototype by laminating together thin layers of paper, polymer, or sheet steel, which have been cut using numerically controlled laser. ~ Selective laser sintering (SLS) is a process that uses a high-power laser to sinter together fusible materials, such as powdered metals, layer by layer. Sintering is the heating and fusing of small particles resulting in a hard boned material block. ~ 3 -D inkjet prototyping is a process that selectively deposits a glue-like binder onto a layer of dry powder, layer by layer, which dries into a solid prototype.
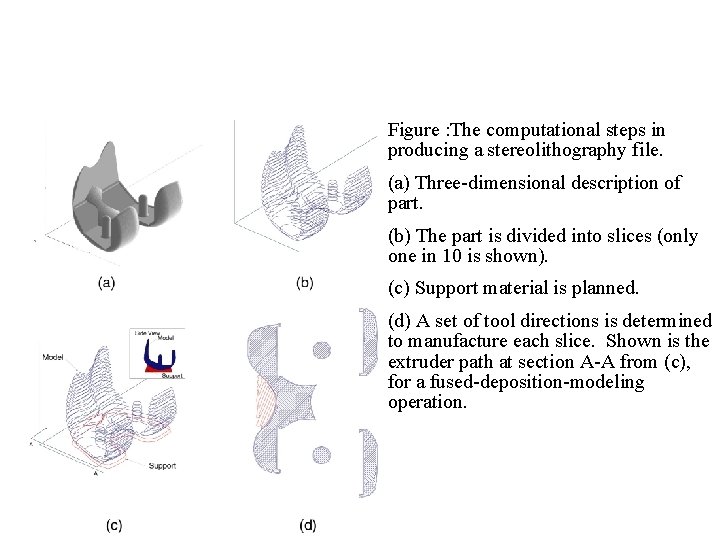
Figure : The computational steps in producing a stereolithography file. (a) Three-dimensional description of part. (b) The part is divided into slices (only one in 10 is shown). (c) Support material is planned. (d) A set of tool directions is determined to manufacture each slice. Shown is the extruder path at section A-A from (c), for a fused-deposition-modeling operation.
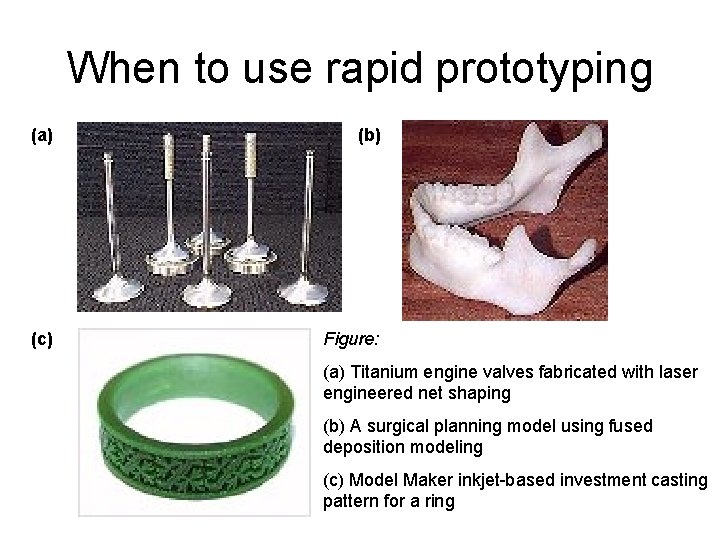
When to use rapid prototyping (a) (b) (c) Figure: (a) Titanium engine valves fabricated with laser engineered net shaping (b) A surgical planning model using fused deposition modeling (c) Model Maker inkjet-based investment casting pattern for a ring
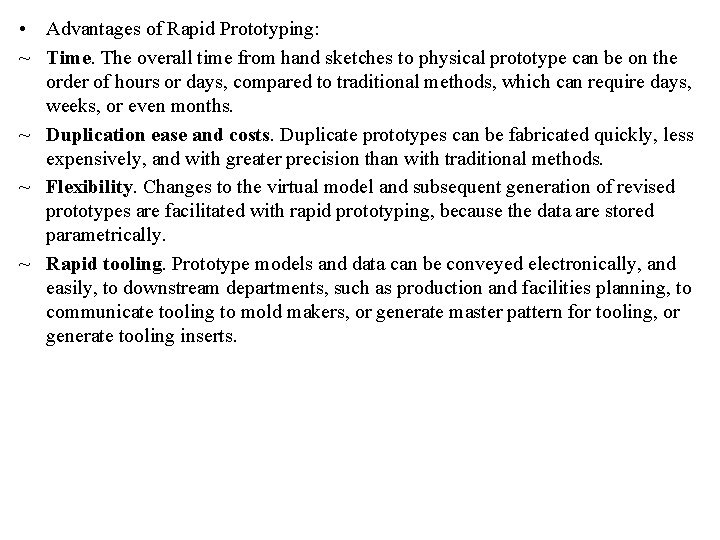
• Advantages of Rapid Prototyping: ~ Time. The overall time from hand sketches to physical prototype can be on the order of hours or days, compared to traditional methods, which can require days, weeks, or even months. ~ Duplication ease and costs. Duplicate prototypes can be fabricated quickly, less expensively, and with greater precision than with traditional methods. ~ Flexibility. Changes to the virtual model and subsequent generation of revised prototypes are facilitated with rapid prototyping, because the data are stored parametrically. ~ Rapid tooling. Prototype models and data can be conveyed electronically, and easily, to downstream departments, such as production and facilities planning, to communicate tooling to mold makers, or generate master pattern for tooling, or generate tooling inserts.
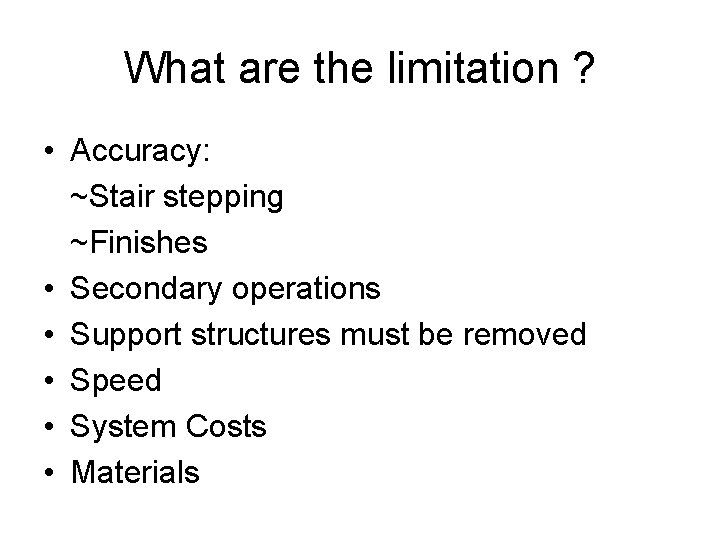
What are the limitation ? • Accuracy: ~Stair stepping ~Finishes • Secondary operations • Support structures must be removed • Speed • System Costs • Materials
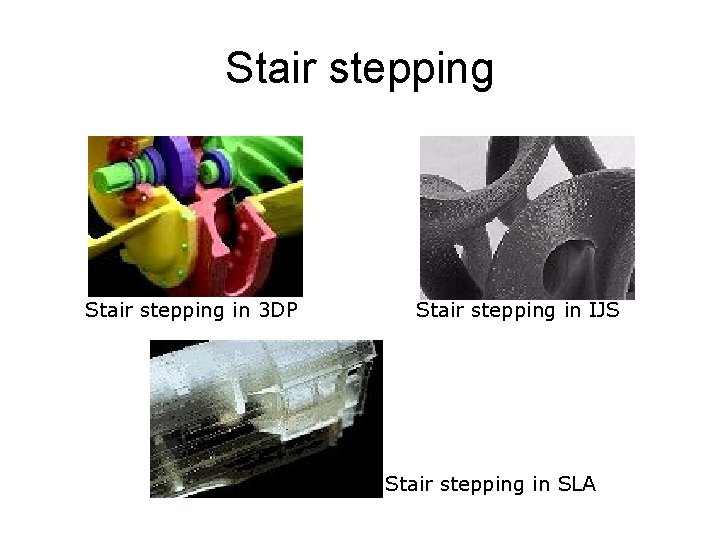
Stair stepping in 3 DP Stair stepping in IJS Stair stepping in SLA
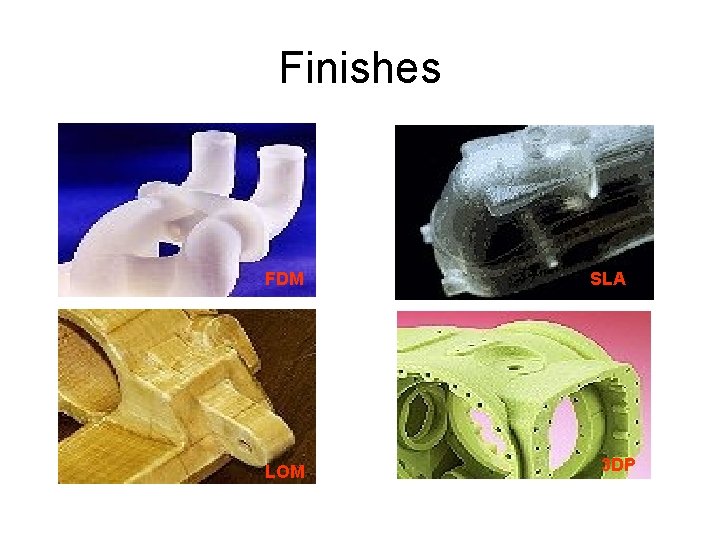
Finishes FDM LOM SLA 3 DP
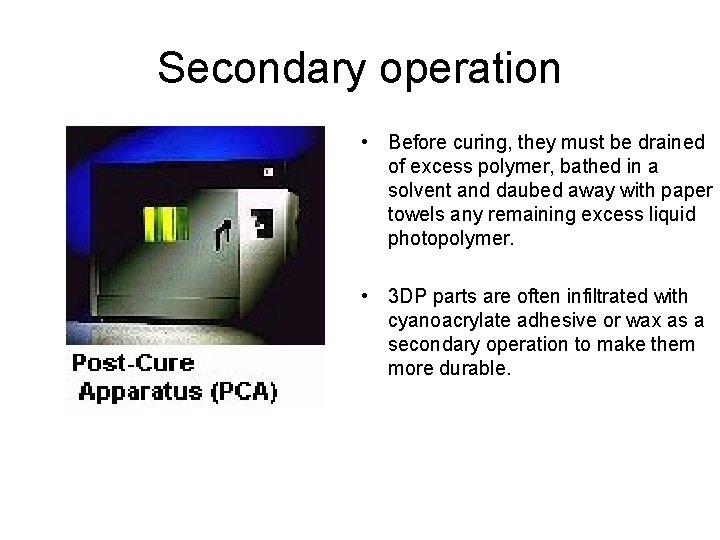
Secondary operation • Before curing, they must be drained of excess polymer, bathed in a solvent and daubed away with paper towels any remaining excess liquid photopolymer. • 3 DP parts are often infiltrated with cyanoacrylate adhesive or wax as a secondary operation to make them more durable.
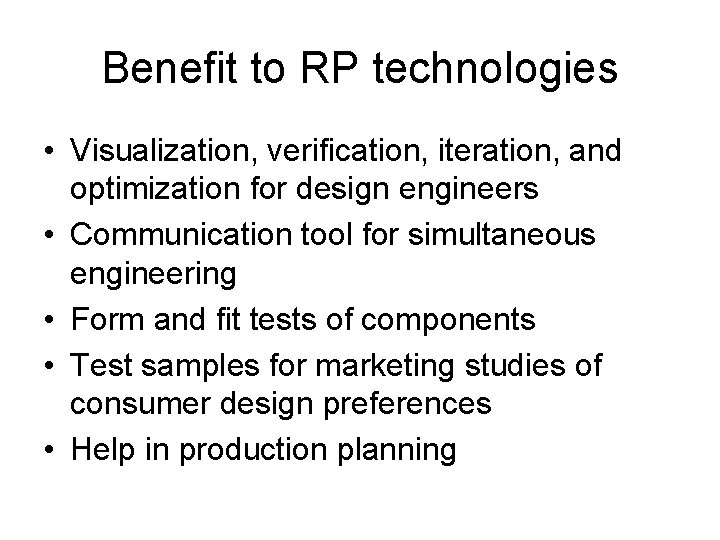
Benefit to RP technologies • Visualization, verification, iteration, and optimization for design engineers • Communication tool for simultaneous engineering • Form and fit tests of components • Test samples for marketing studies of consumer design preferences • Help in production planning
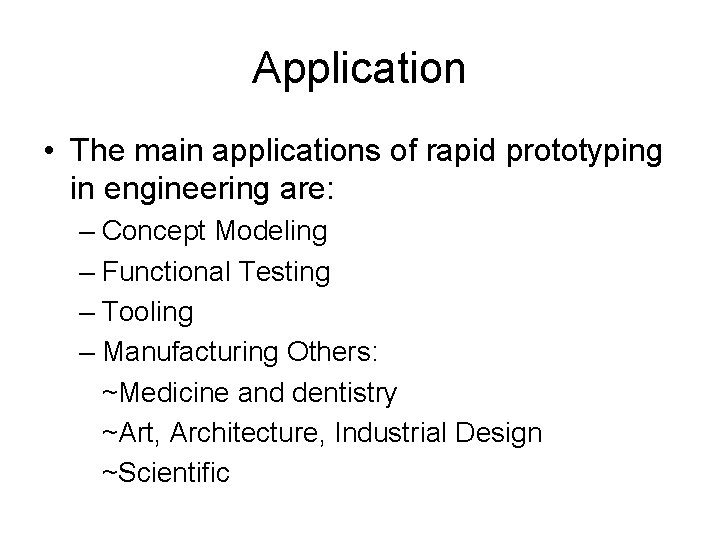
Application • The main applications of rapid prototyping in engineering are: – Concept Modeling – Functional Testing – Tooling – Manufacturing Others: ~Medicine and dentistry ~Art, Architecture, Industrial Design ~Scientific
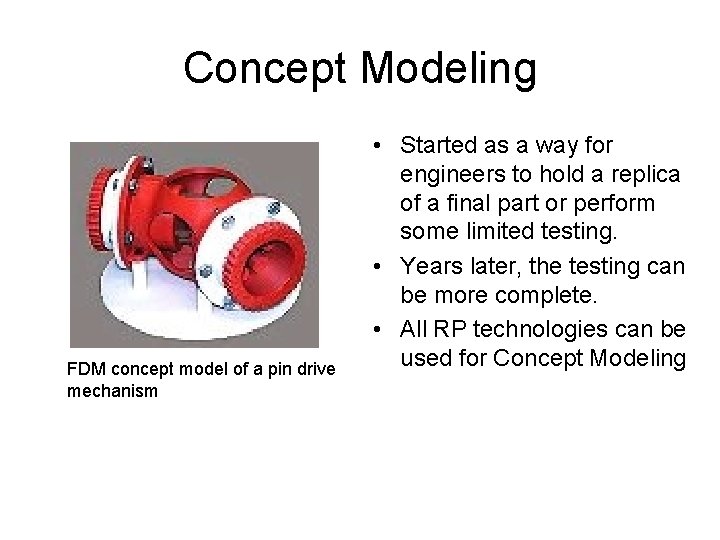
Concept Modeling FDM concept model of a pin drive mechanism • Started as a way for engineers to hold a replica of a final part or perform some limited testing. • Years later, the testing can be more complete. • All RP technologies can be used for Concept Modeling
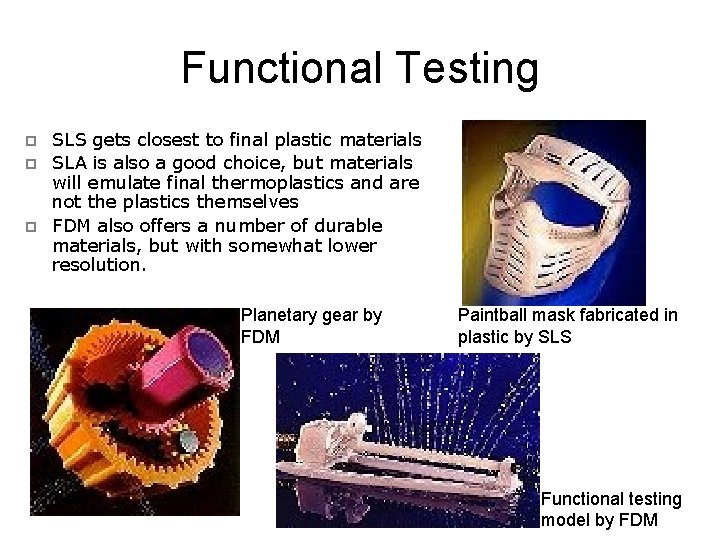
Functional Testing p p p SLS gets closest to final plastic materials SLA is also a good choice, but materials will emulate final thermoplastics and are not the plastics themselves FDM also offers a number of durable materials, but with somewhat lower resolution. Planetary gear by FDM Paintball mask fabricated in plastic by SLS Functional testing model by FDM
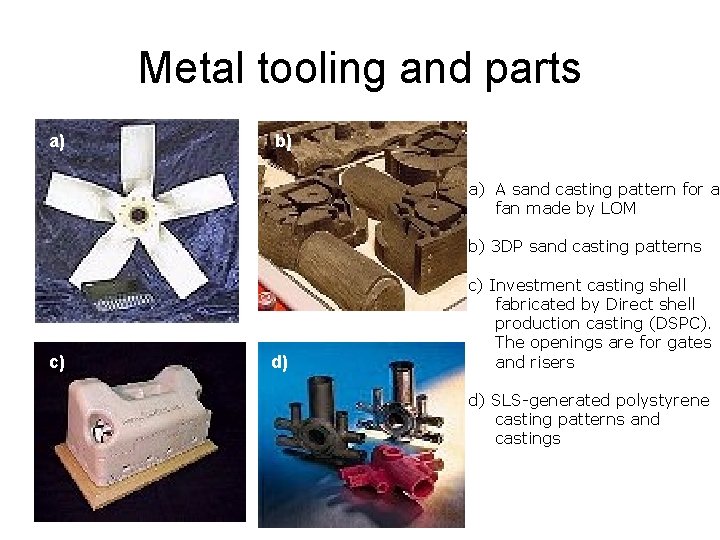
Metal tooling and parts a) b) a) A sand casting pattern for a fan made by LOM b) 3 DP sand casting patterns c) d) c) Investment casting shell fabricated by Direct shell production casting (DSPC). The openings are for gates and risers d) SLS-generated polystyrene casting patterns and castings
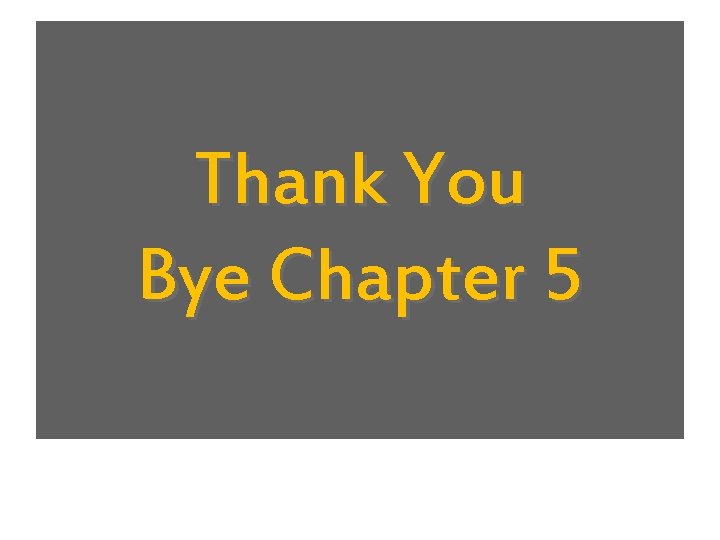
Thank You Bye Chapter 5
Processing ceramics
Forming composite functions
Composite vs non composite
Shaping and planning process
Shaping process adalah
Shaping process
Shaping manufacturing process
Sheet metal adalah
Forming process in sheet metal
Die blanks ceramics
Vacuum forming process steps
Plastic recycling process flow chart
Advantages and disadvantages of pultrusion process
Kontinuitetshantering
Typiska drag för en novell
Nationell inriktning för artificiell intelligens
Ekologiskt fotavtryck
Varför kallas perioden 1918-1939 för mellankrigstiden
En lathund för arbete med kontinuitetshantering
Särskild löneskatt för pensionskostnader
Vilotidsbok
Sura för anatom
Förklara densitet för barn
Datorkunskap för nybörjare
Stig kerman
Att skriva debattartikel
Delegerande ledarstil
Nyckelkompetenser för livslångt lärande
Påbyggnader för flakfordon
Tryck formel
Publik sektor
Kyssande vind
Presentera för publik crossboss
Jiddisch
Vem räknas som jude
Klassificeringsstruktur för kommunala verksamheter
Luftstrupen för medicinare
Bästa kameran för astrofoto
Centrum för kunskap och säkerhet
Programskede byggprocessen
Mat för unga idrottare
Verktyg för automatisering av utbetalningar
Rutin för avvikelsehantering
Smärtskolan kunskap för livet
Ministerstyre för och nackdelar
Tack för att ni har lyssnat
Mall för referat
Redogör för vad psykologi är
Borstål, egenskaper