Development of a Solid Acid Catalyst Alkylation Process
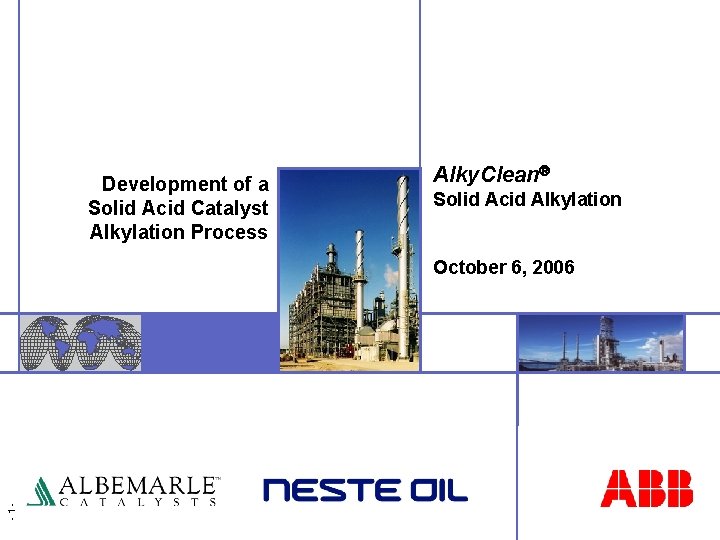
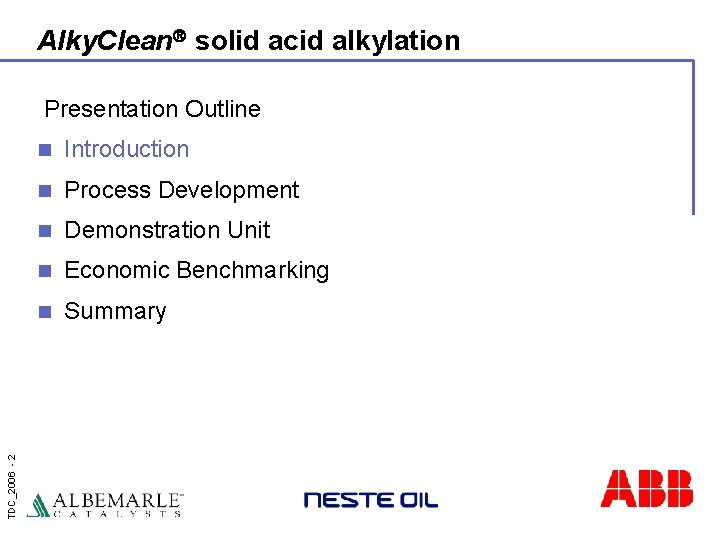
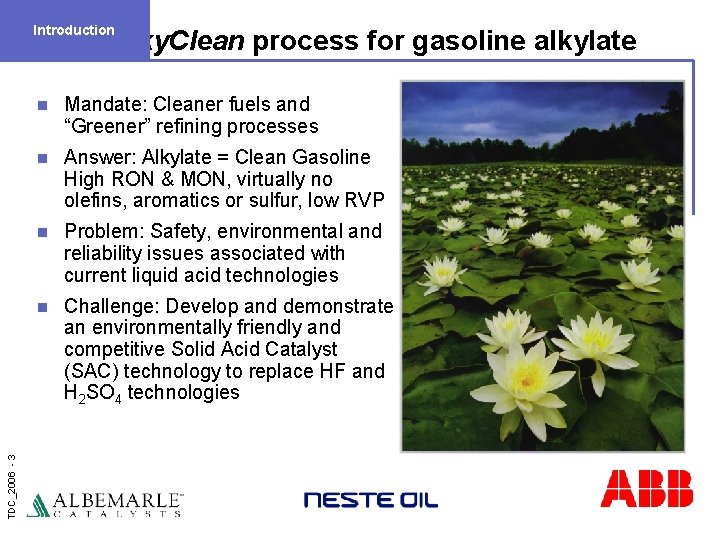
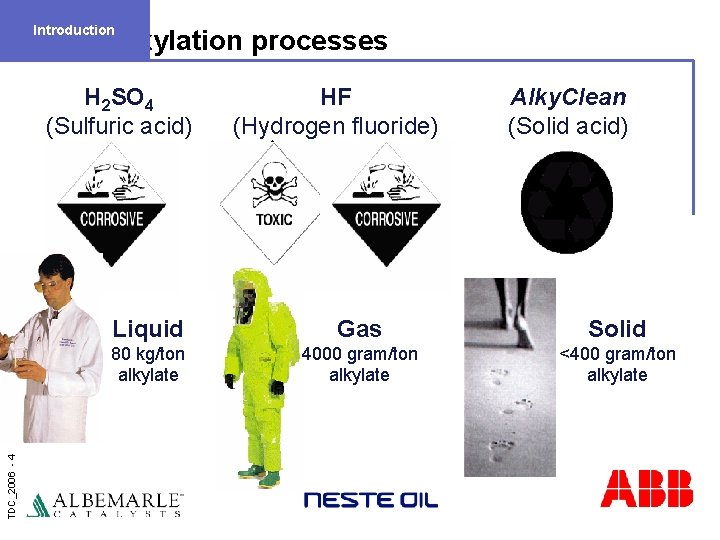
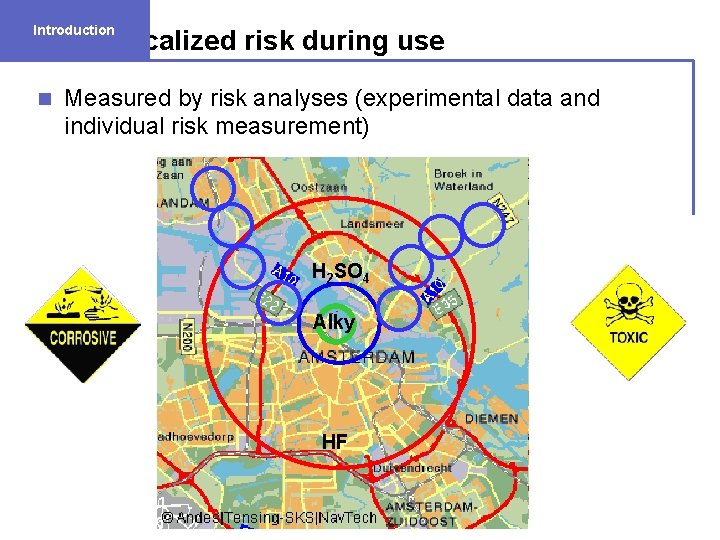
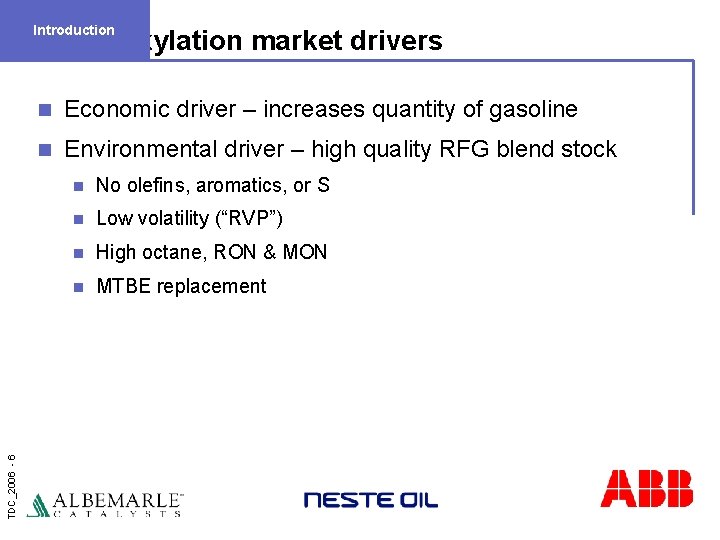
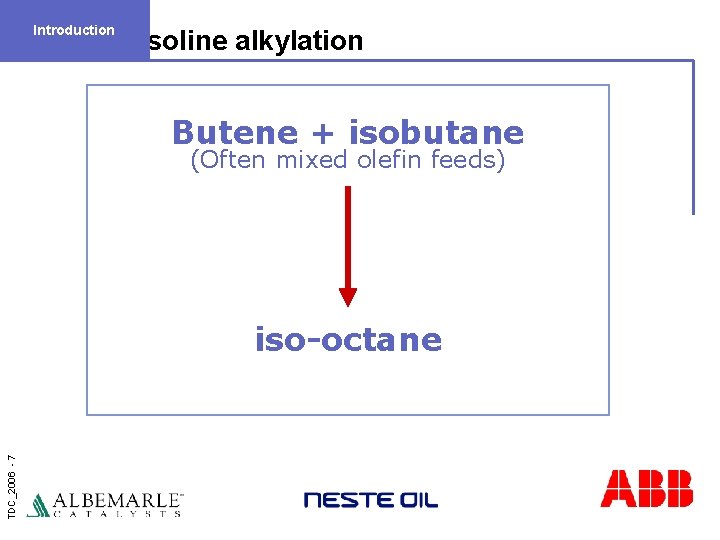
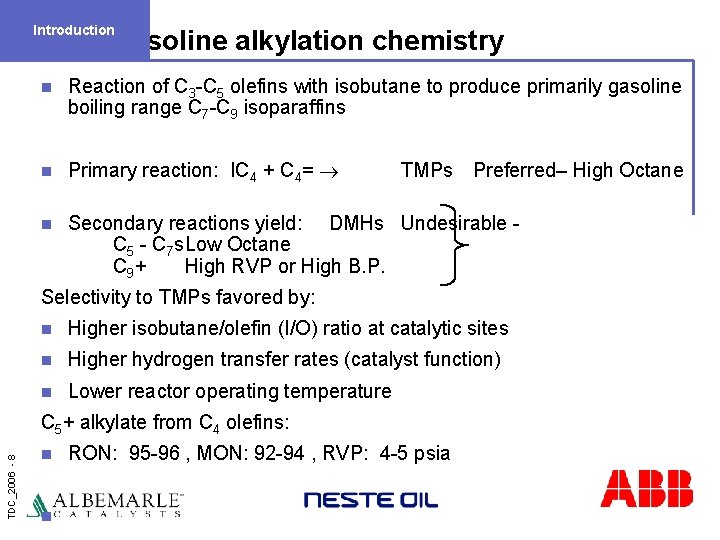
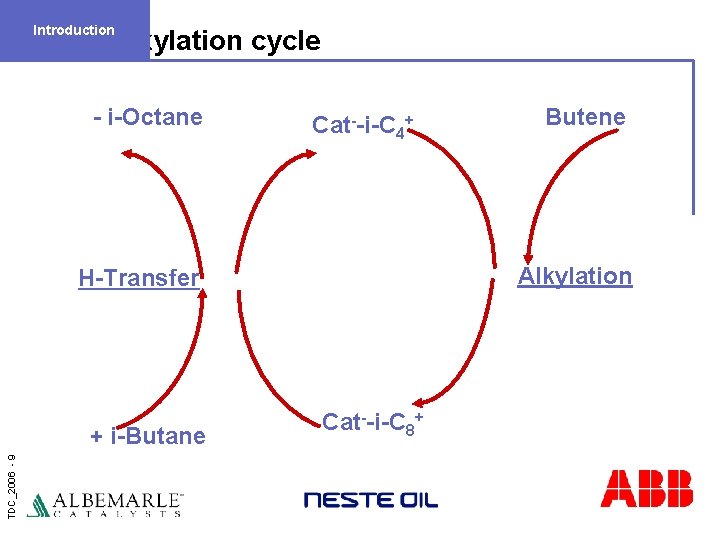
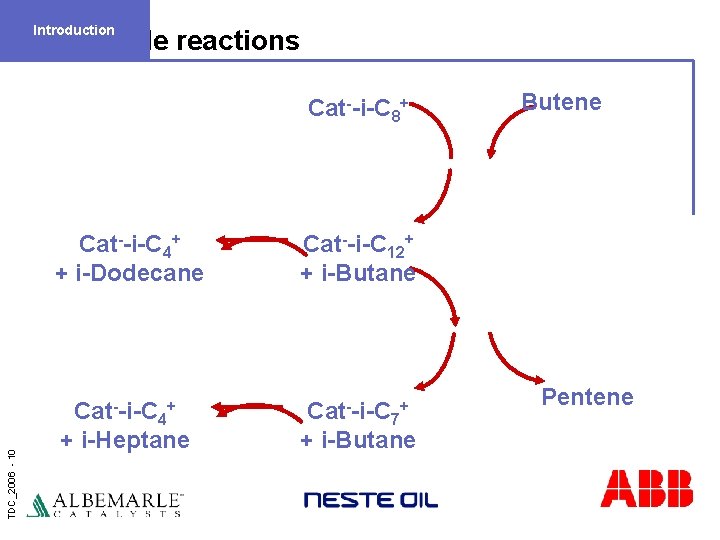
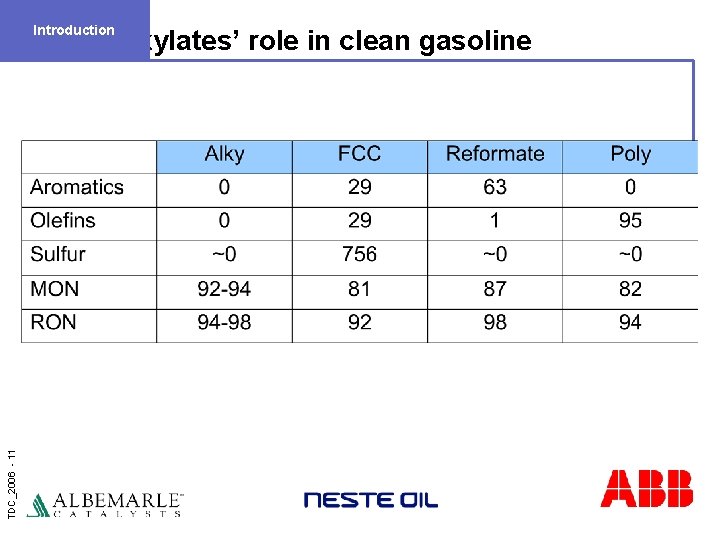
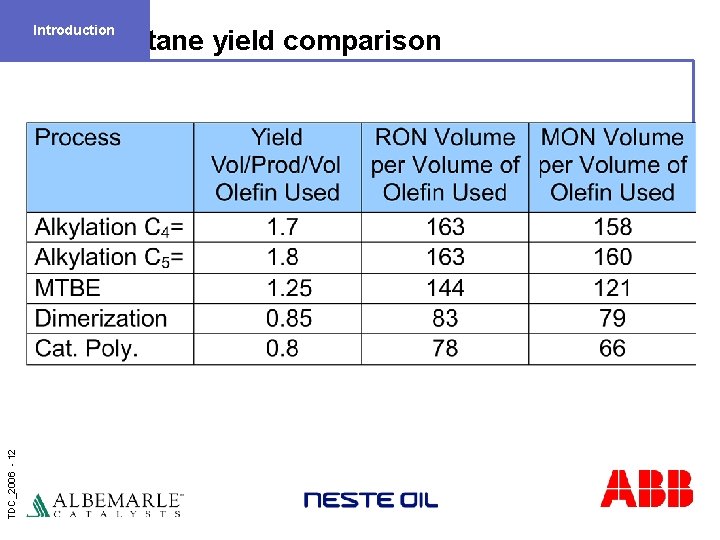
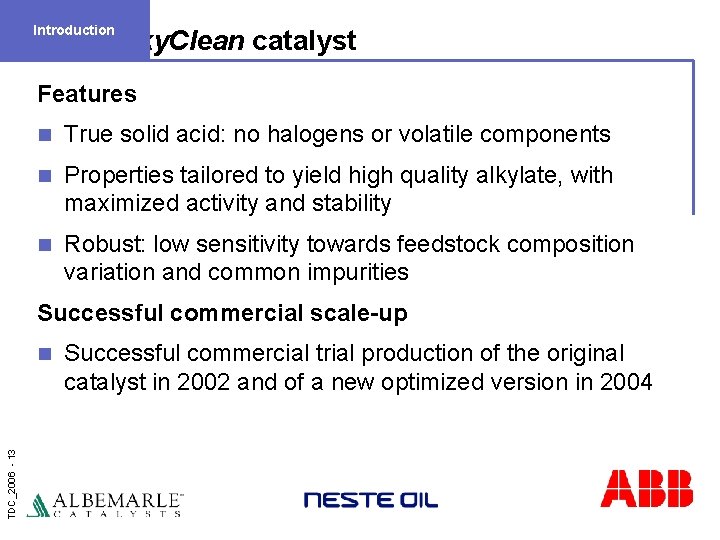
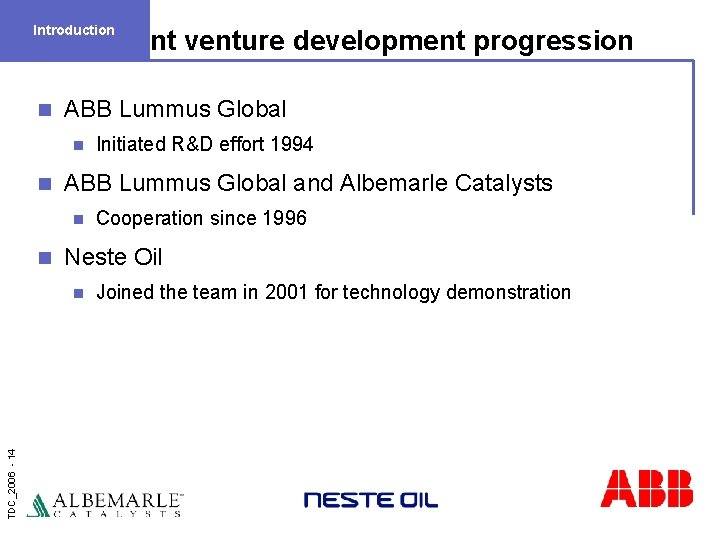
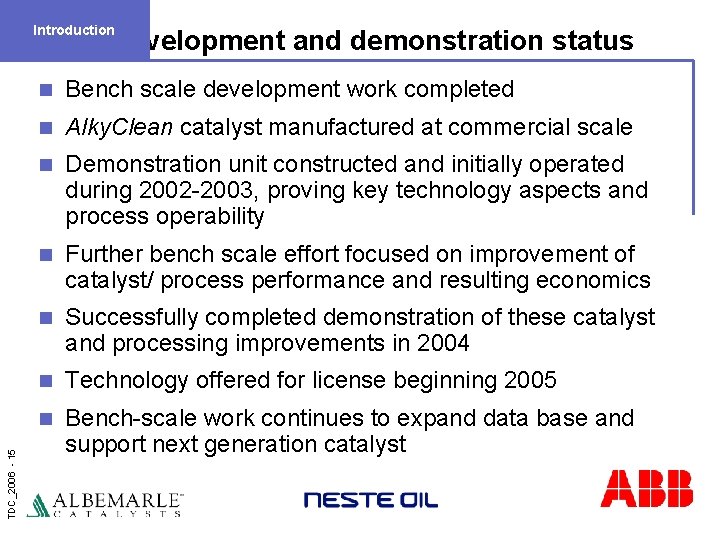
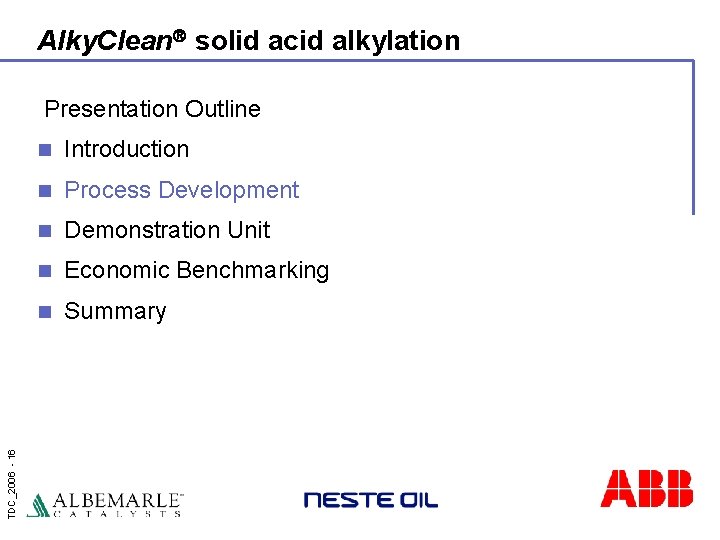
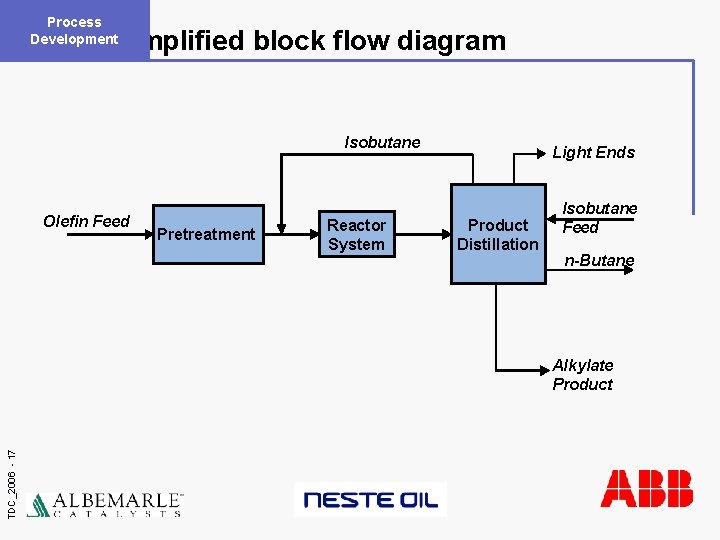
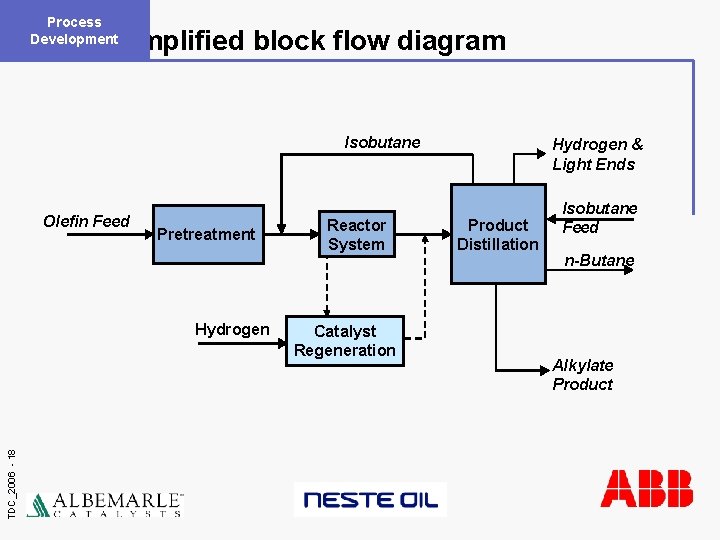
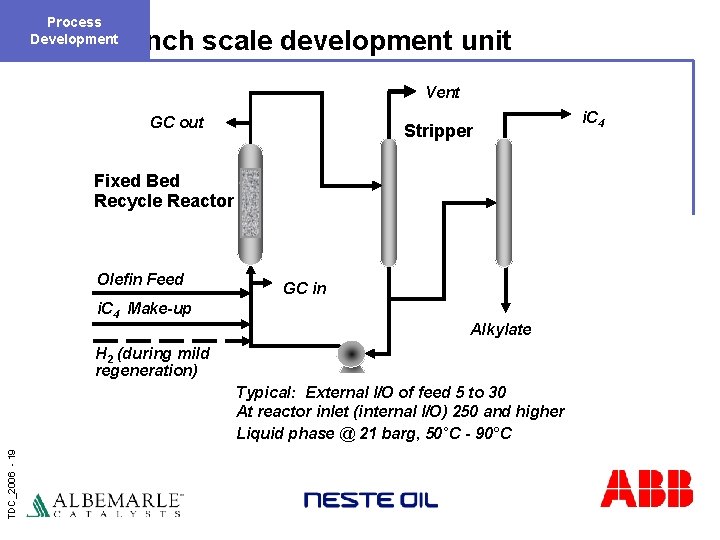

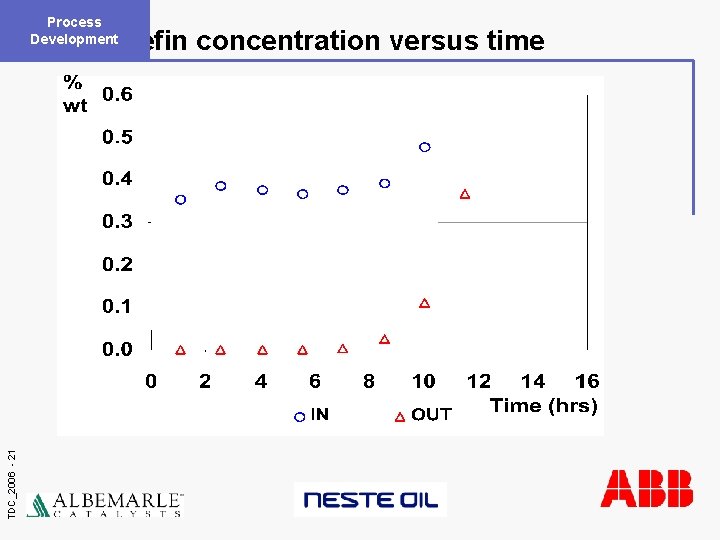
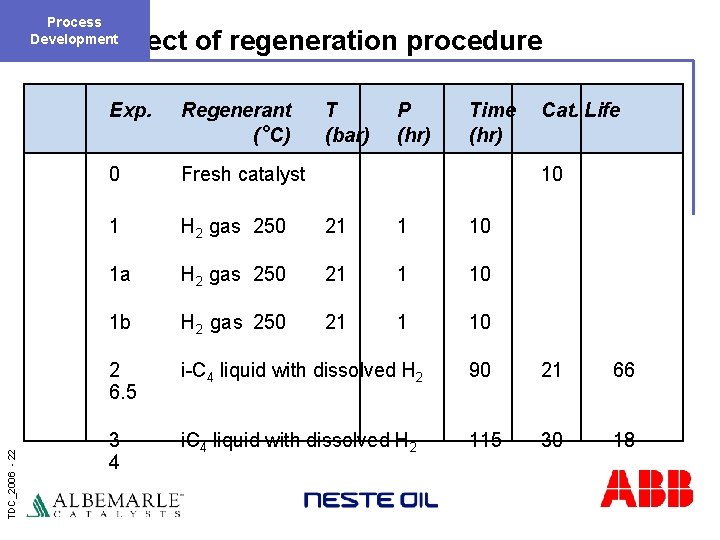
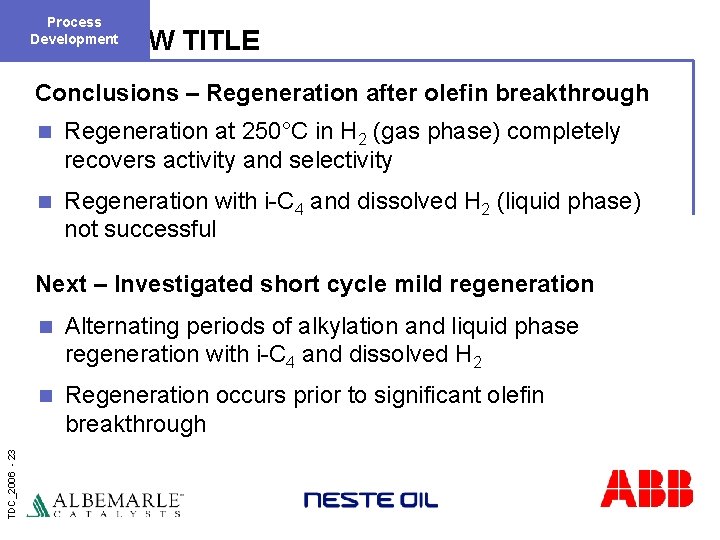
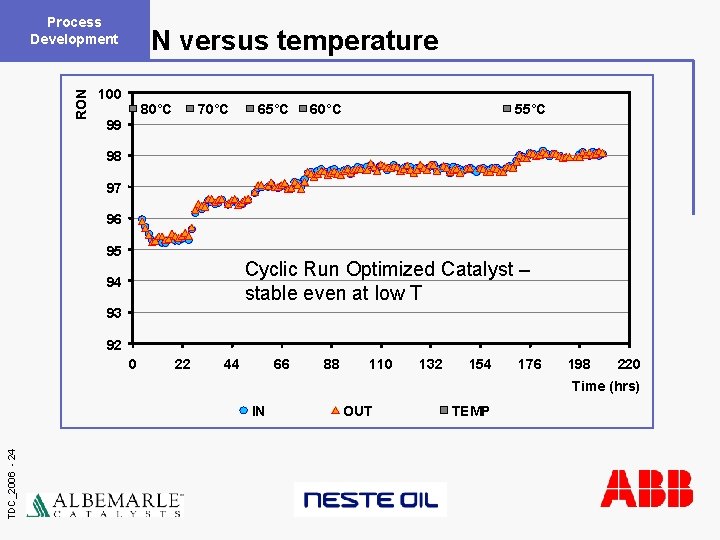
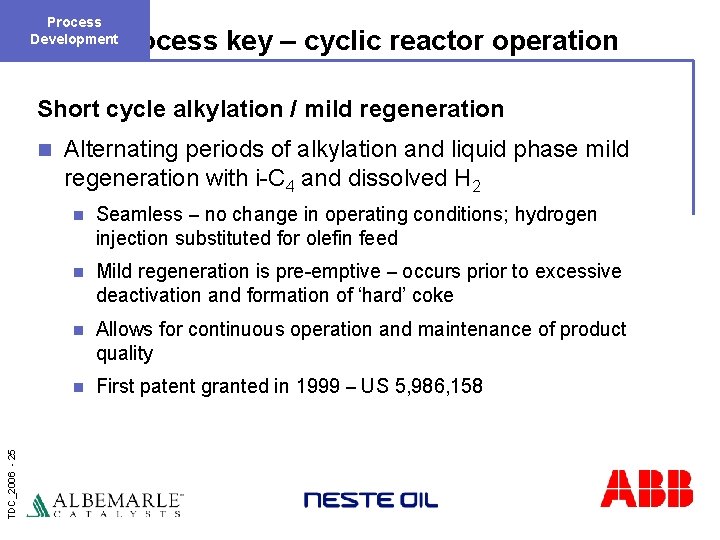
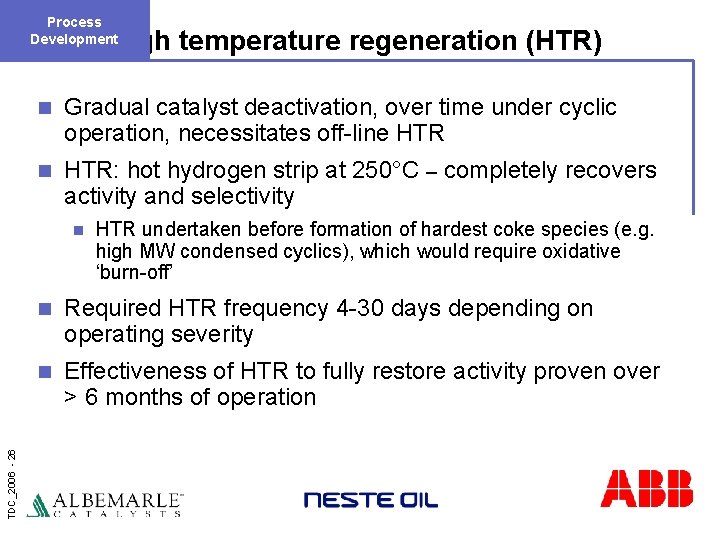
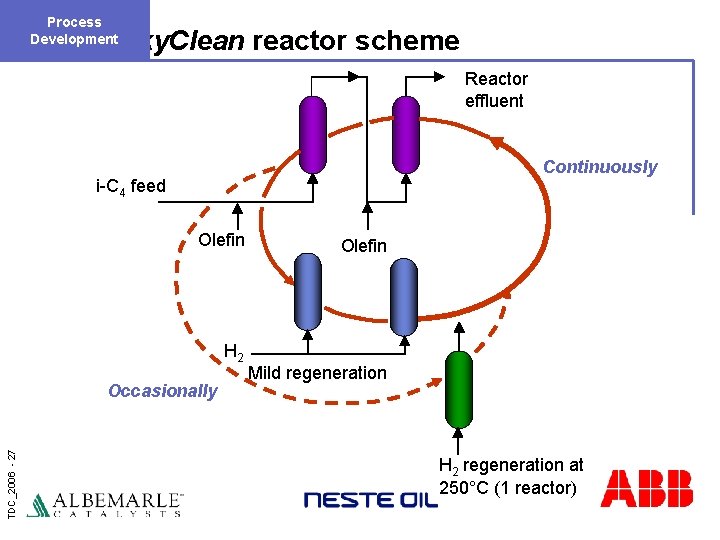
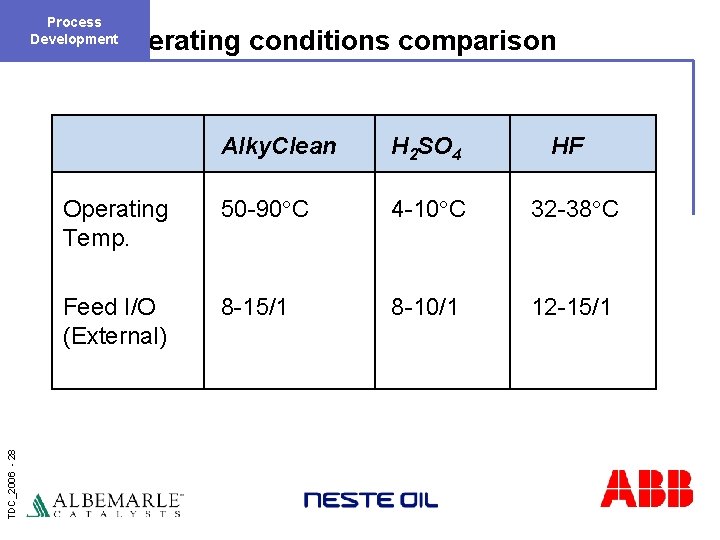
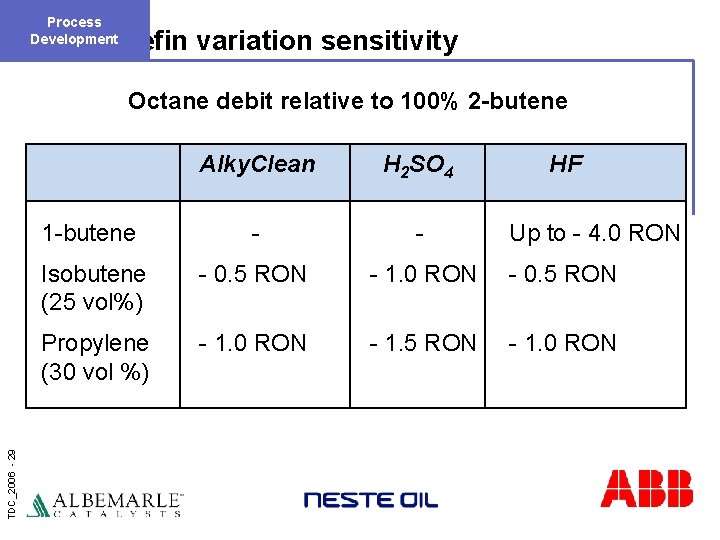
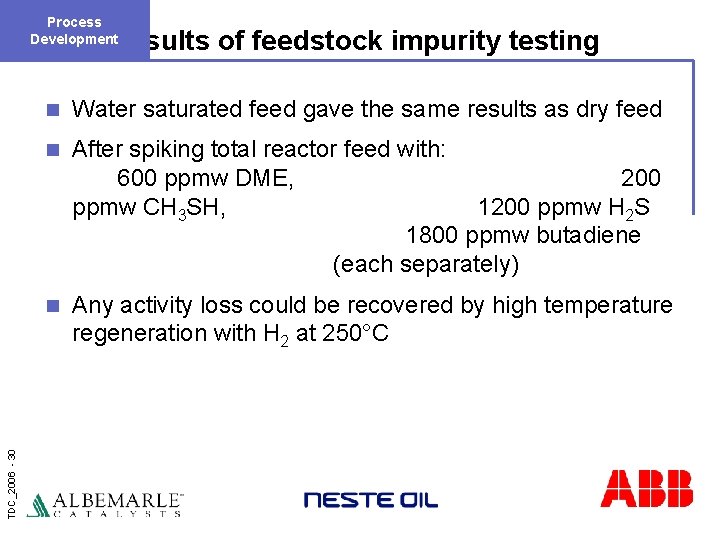
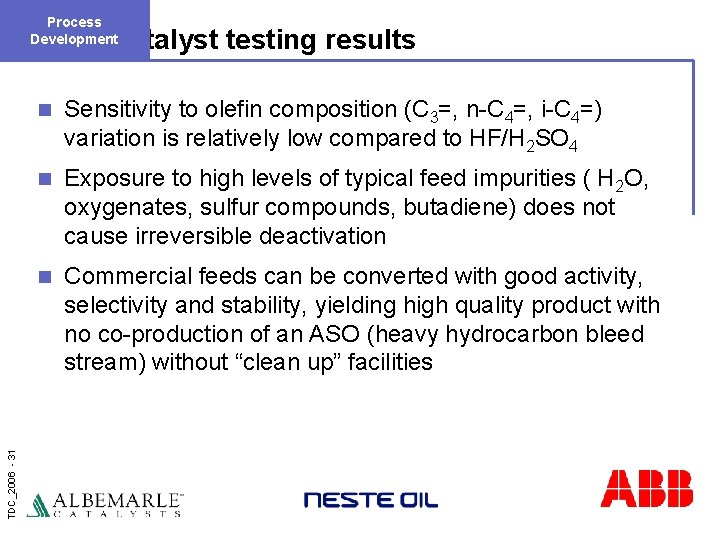
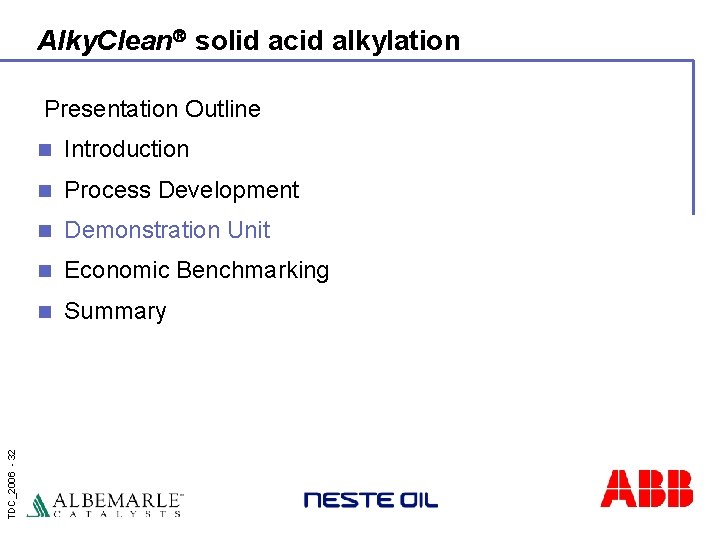
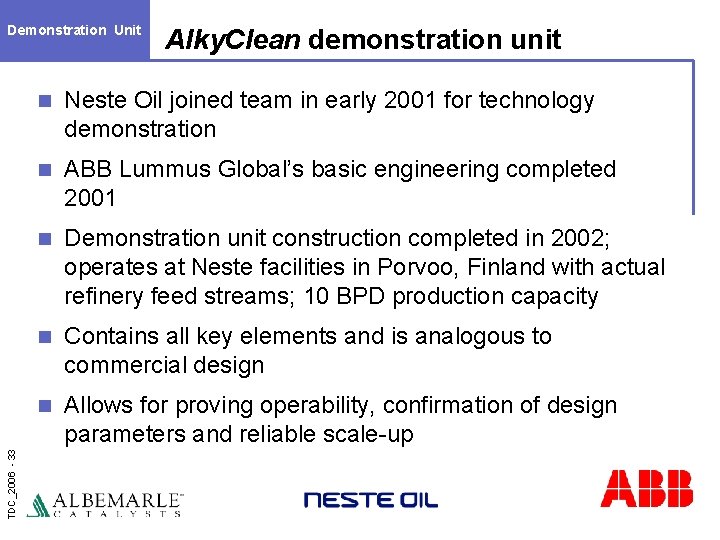
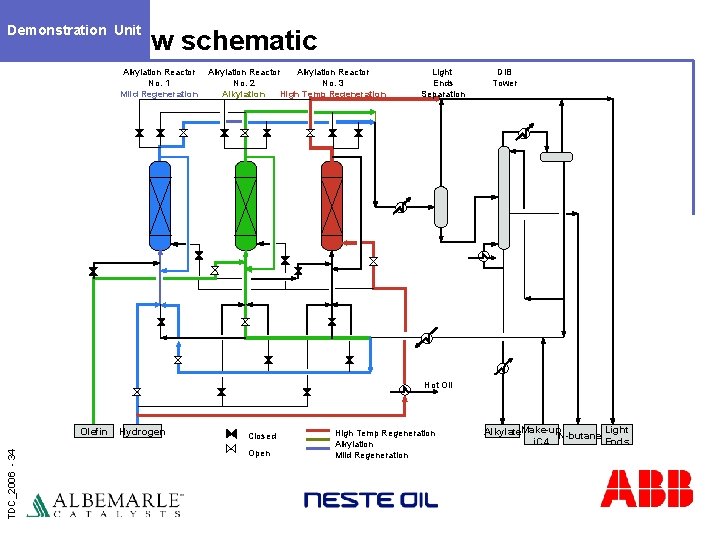
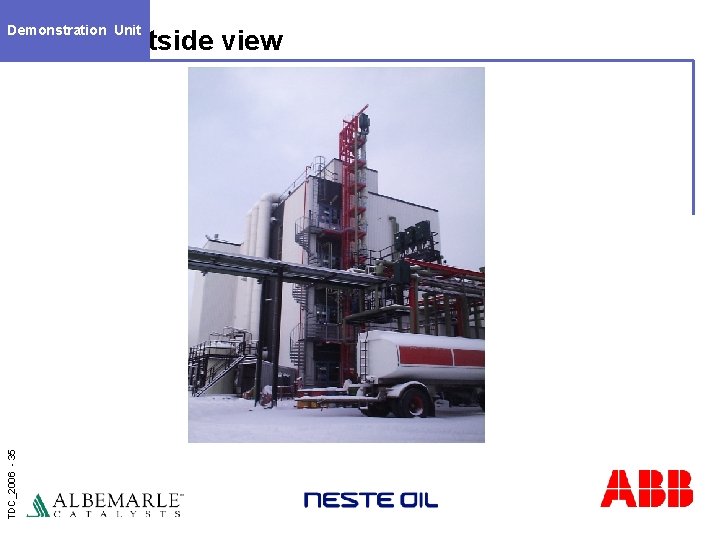
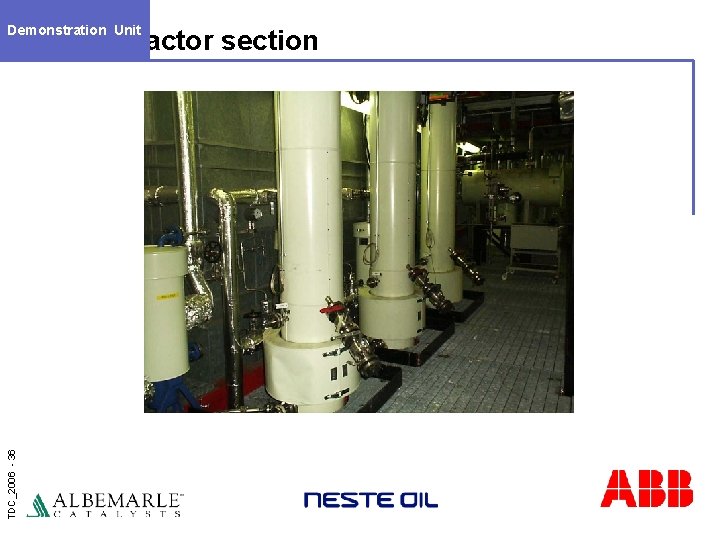
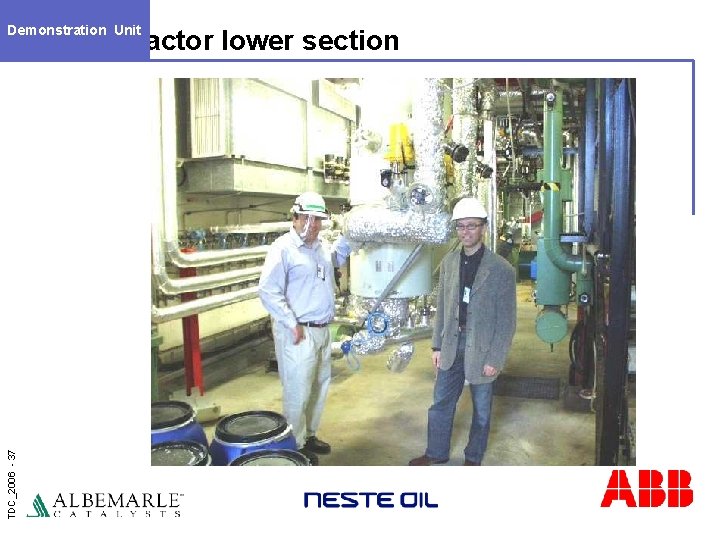
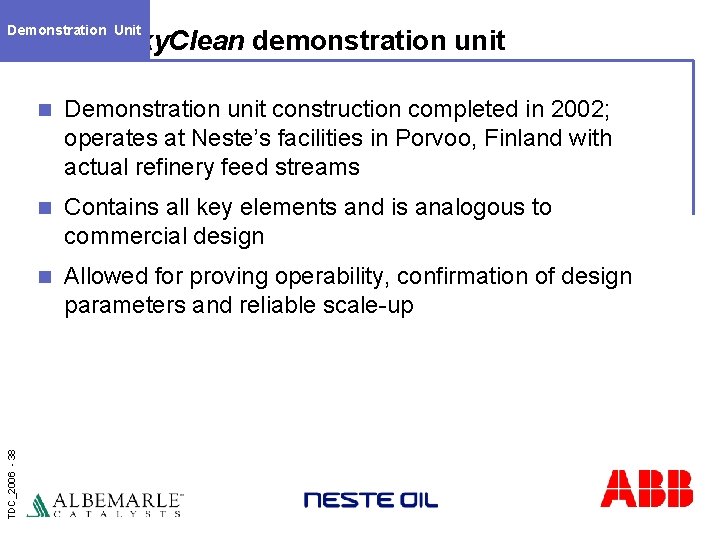
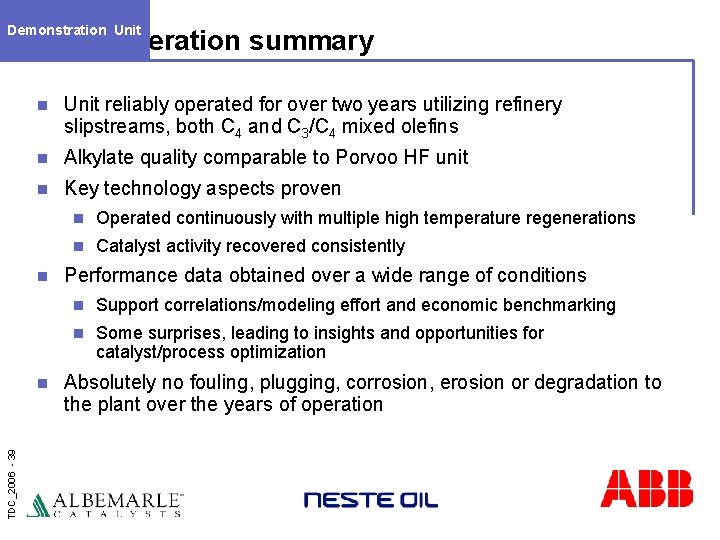
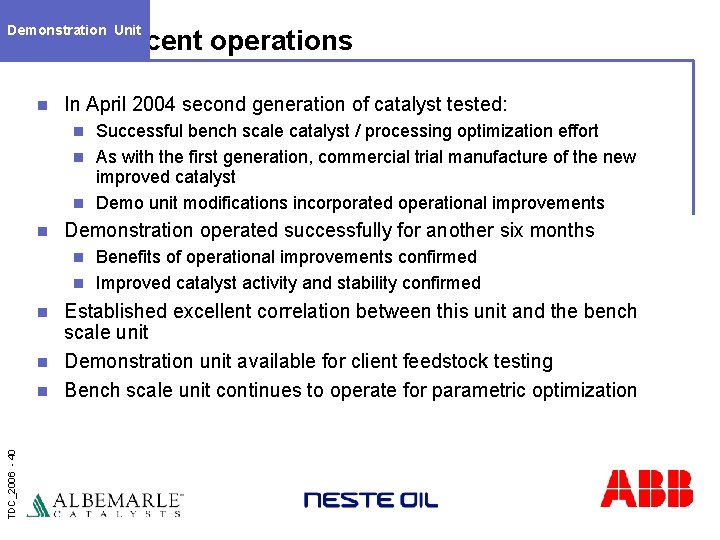
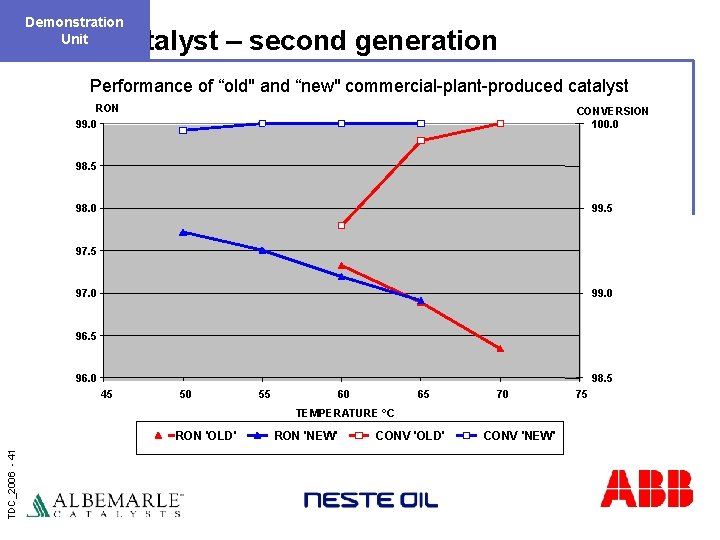
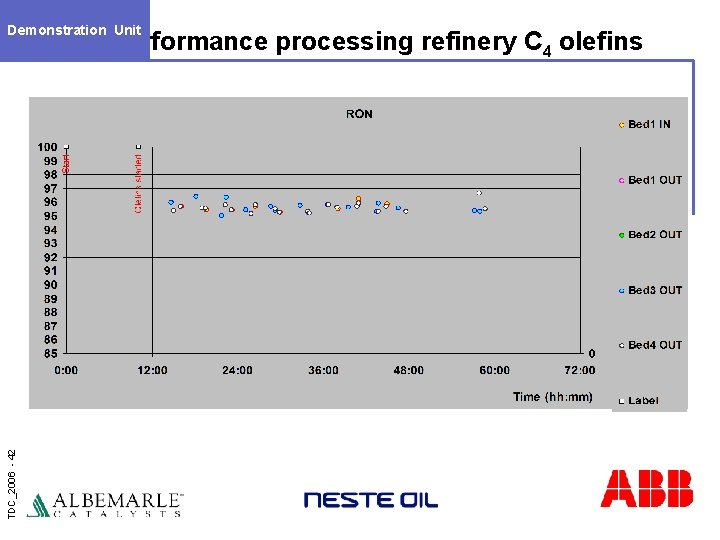
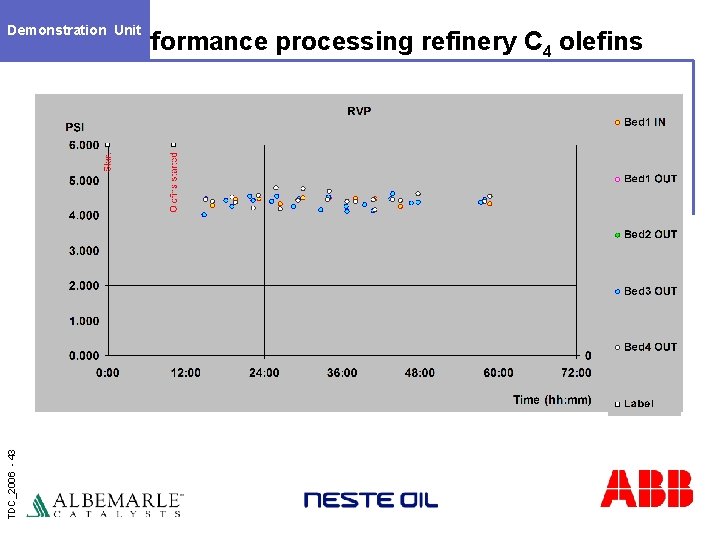
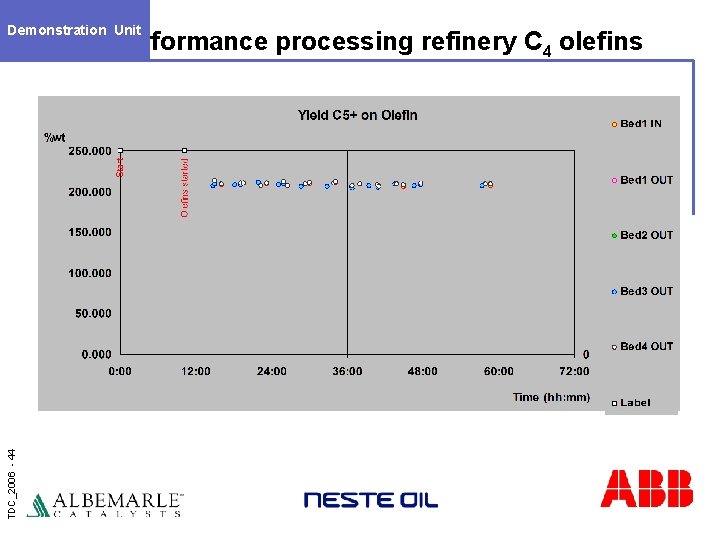
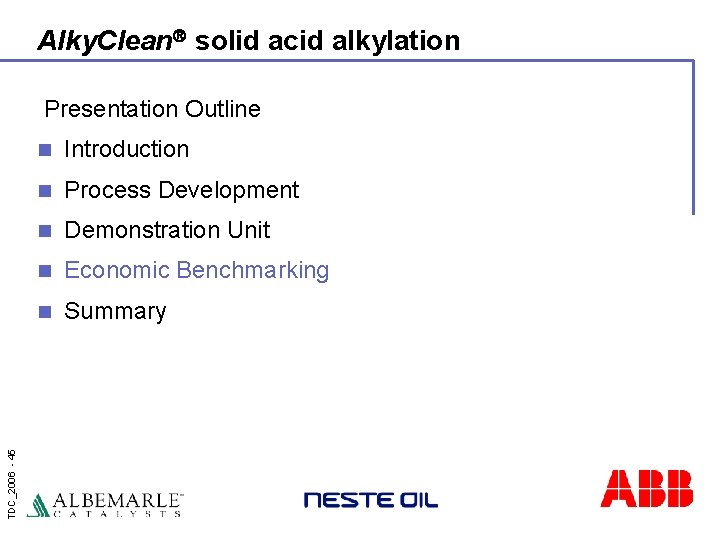
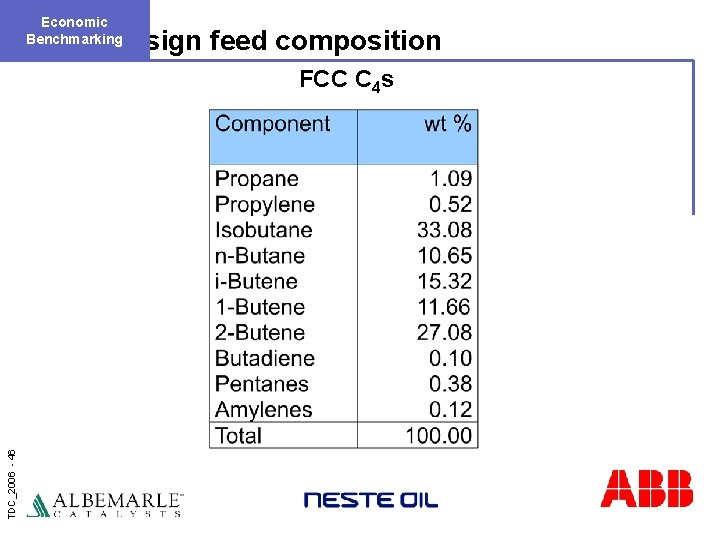
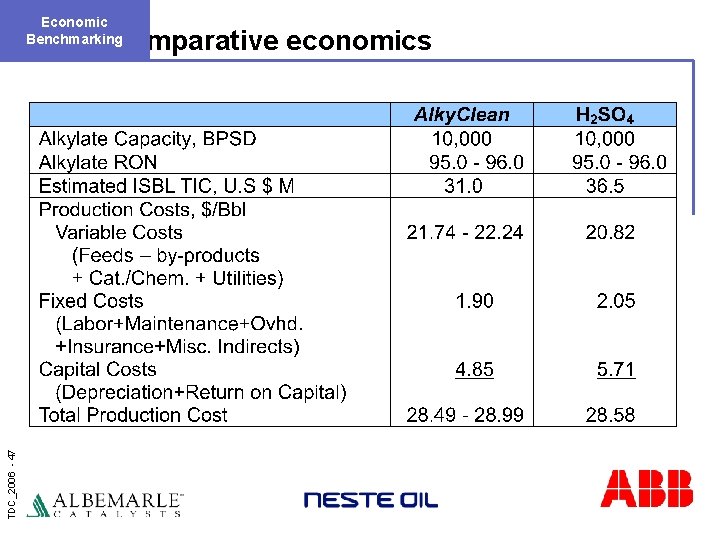
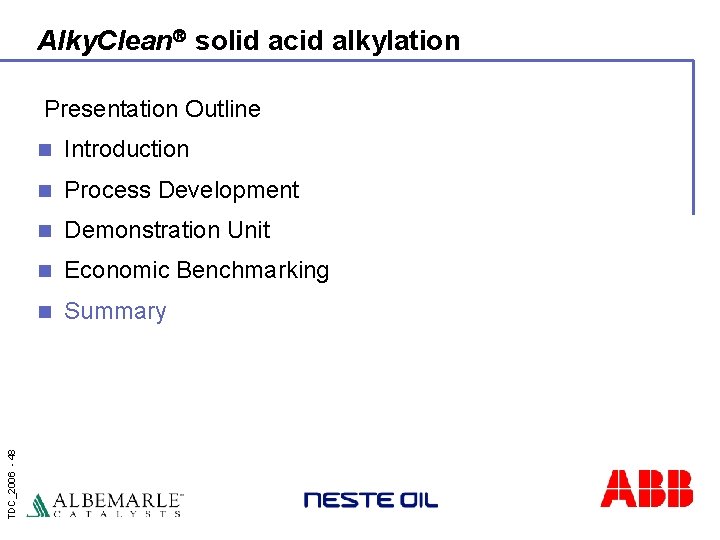
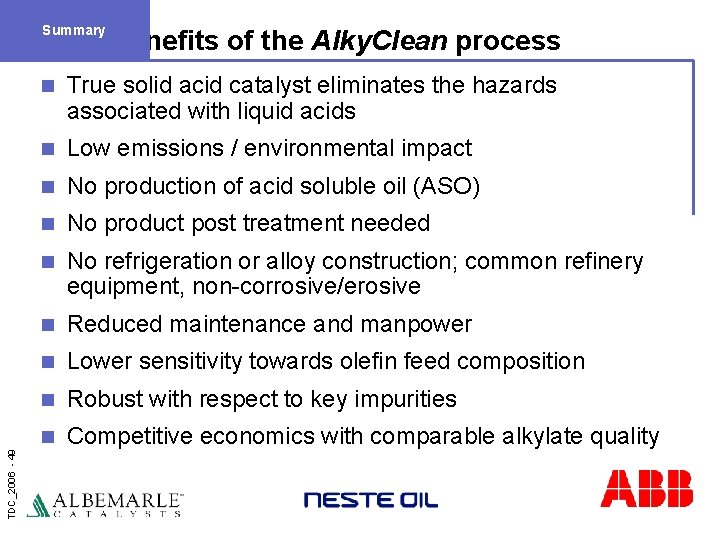
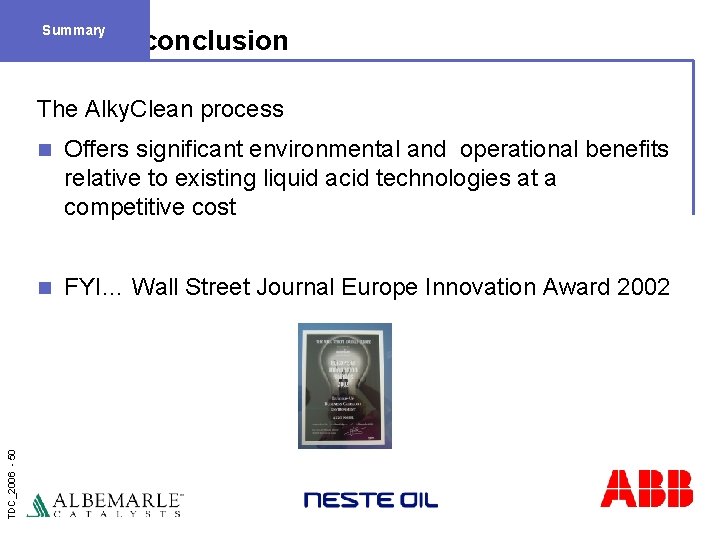
- Slides: 50
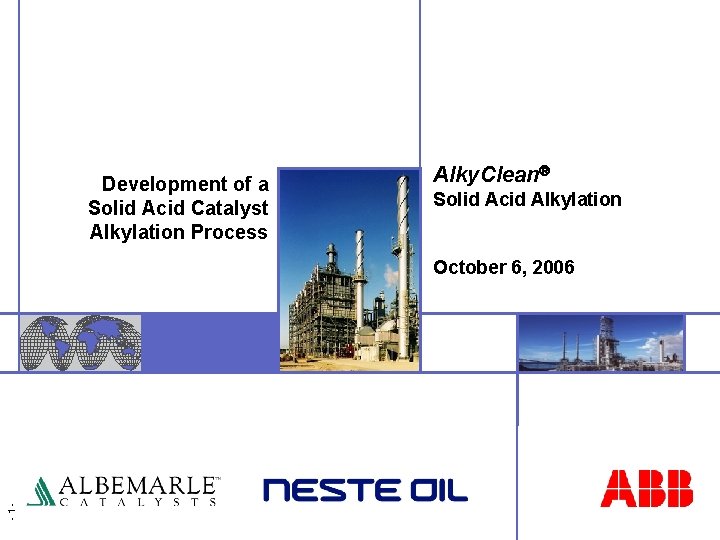
Development of a Solid Acid Catalyst Alkylation Process Alky. Clean Solid Acid Alkylation October 6, 2006 -1 -
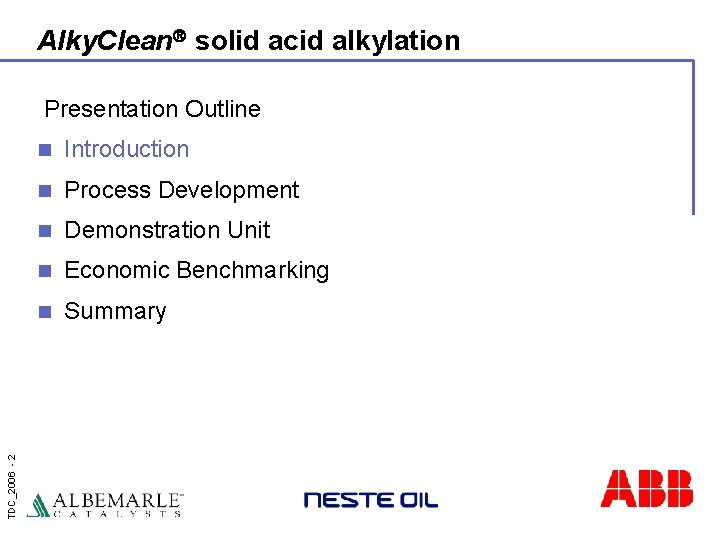
Alky. Clean solid acid alkylation TDC_2006 - 2 Presentation Outline n Introduction n Process Development n Demonstration Unit n Economic Benchmarking n Summary
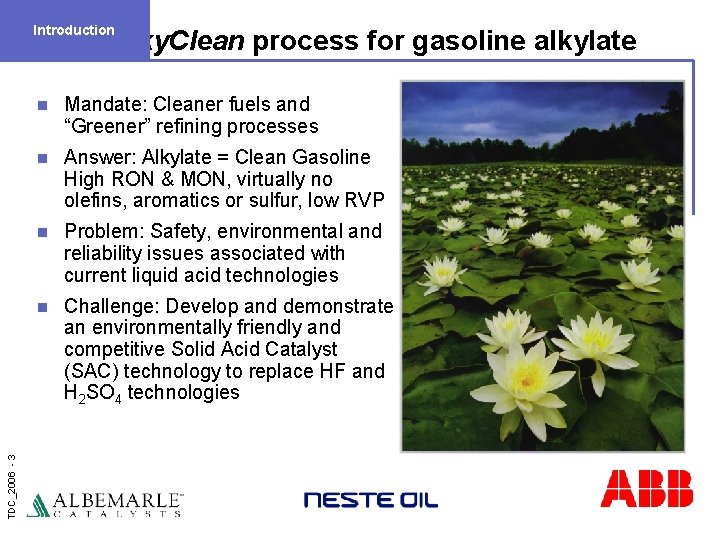
Introduction TDC_2006 - 3 Alky. Clean process for gasoline alkylate n Mandate: Cleaner fuels and “Greener” refining processes n Answer: Alkylate = Clean Gasoline High RON & MON, virtually no olefins, aromatics or sulfur, low RVP n Problem: Safety, environmental and reliability issues associated with current liquid acid technologies n Challenge: Develop and demonstrate an environmentally friendly and competitive Solid Acid Catalyst (SAC) technology to replace HF and H 2 SO 4 technologies
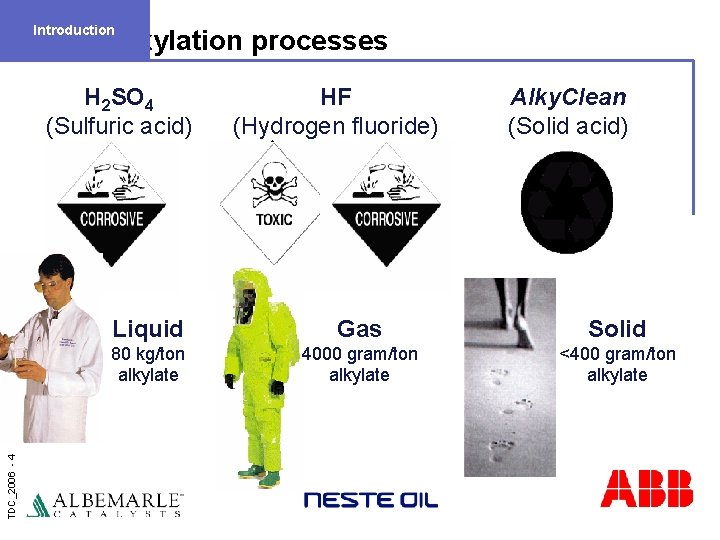
Introduction Alkylation processes TDC_2006 - 4 H 2 SO 4 (Sulfuric acid) HF (Hydrogen fluoride) Alky. Clean (Solid acid) Liquid Gas Solid 80 kg/ton alkylate 4000 gram/ton alkylate <400 gram/ton alkylate
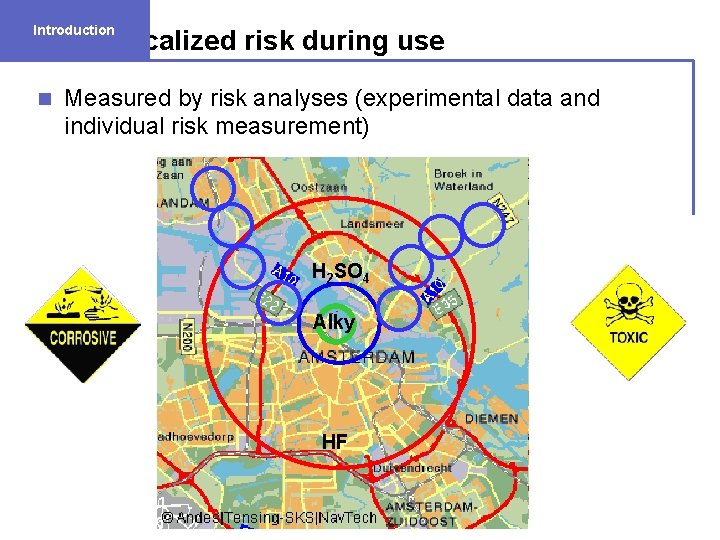
Introduction Localized risk during use n Measured by risk analyses (experimental data and individual risk measurement) H 2 SO 4 Alky HF
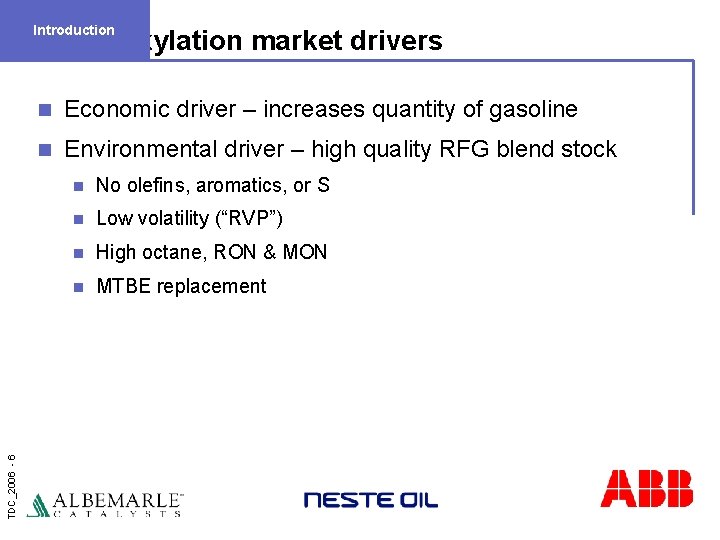
Introduction TDC_2006 - 6 Alkylation market drivers n Economic driver – increases quantity of gasoline n Environmental driver – high quality RFG blend stock n No olefins, aromatics, or S n Low volatility (“RVP”) n High octane, RON & MON n MTBE replacement
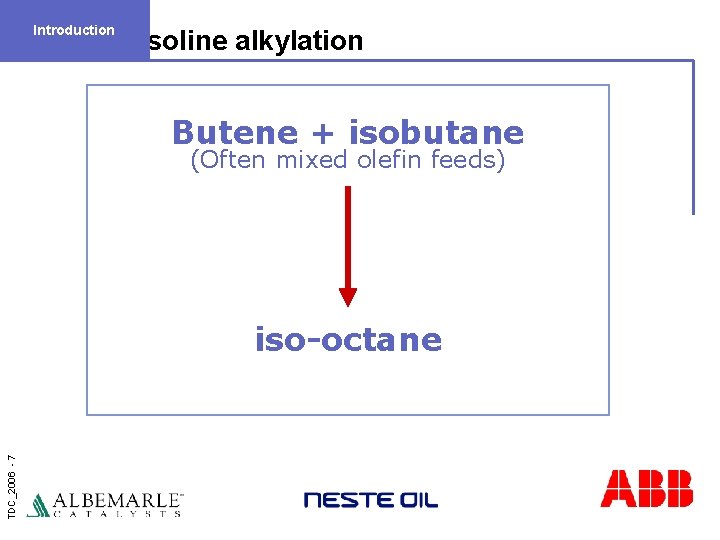
Introduction Gasoline alkylation Butene + isobutane (Often mixed olefin feeds) TDC_2006 - 7 iso-octane
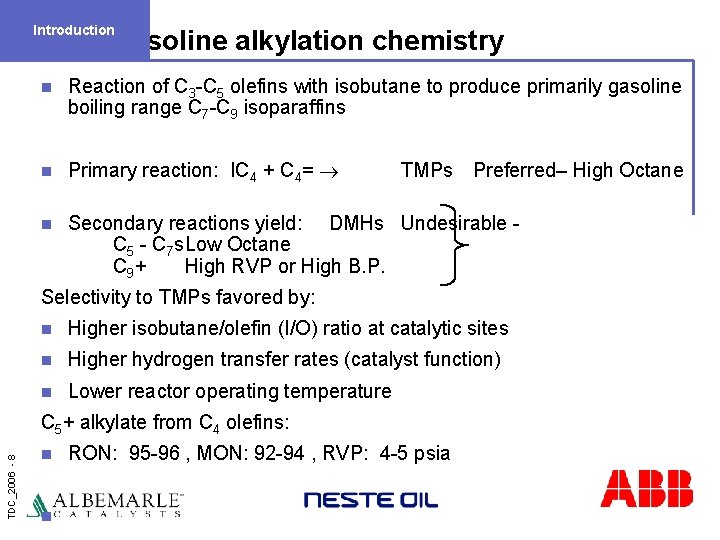
Introduction Gasoline alkylation chemistry n Reaction of C 3 -C 5 olefins with isobutane to produce primarily gasoline boiling range C 7 -C 9 isoparaffins n Primary reaction: IC 4 + C 4= ® n Secondary reactions yield: DMHs Undesirable C 5 - C 7 s. Low Octane C 9 + High RVP or High B. P. TMPs Preferred– High Octane Selectivity to TMPs favored by: n Higher isobutane/olefin (I/O) ratio at catalytic sites n Higher hydrogen transfer rates (catalyst function) n Lower reactor operating temperature TDC_2006 - 8 C 5+ alkylate from C 4 olefins: n n RON: 95 -96 , MON: 92 -94 , RVP: 4 -5 psia
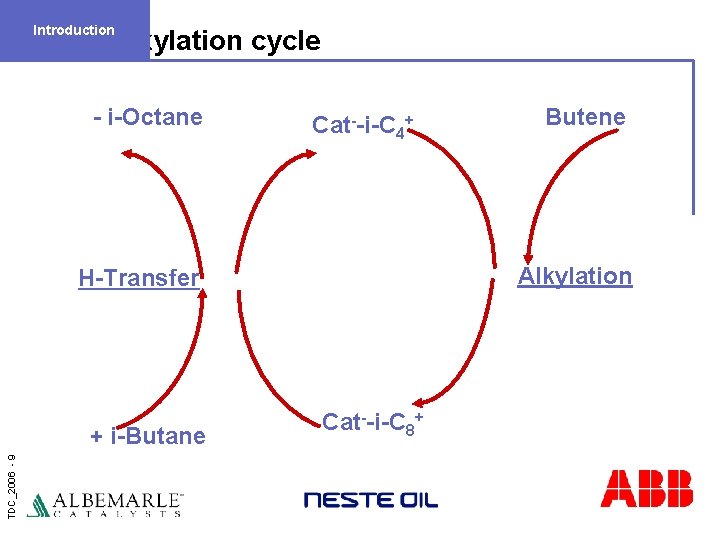
Introduction Alkylation cycle - i-Octane Cat--i-C 4+ Alkylation H-Transfer TDC_2006 - 9 + i-Butane Butene Cat--i-C 8+
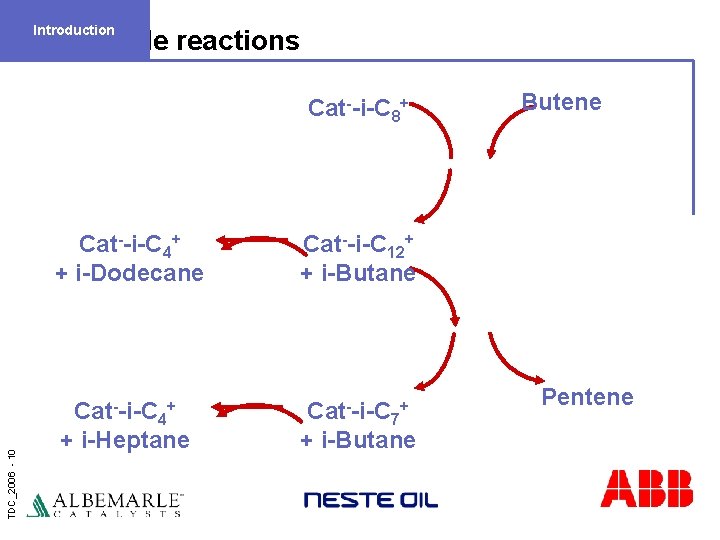
Introduction Side reactions TDC_2006 - 10 Cat--i-C 8+ Cat--i-C 4+ + i-Dodecane Cat--i-C 12+ + i-Butane Cat--i-C 4+ + i-Heptane Cat--i-C 7+ + i-Butane Butene Pentene
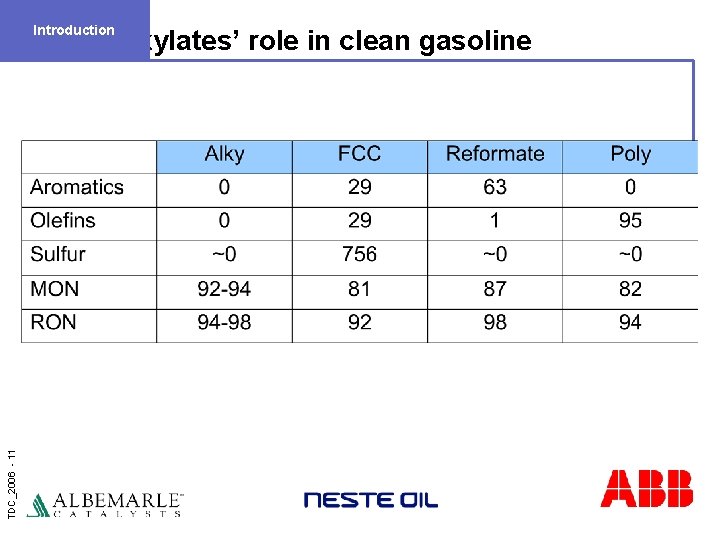
Introduction TDC_2006 - 11 Alkylates’ role in clean gasoline
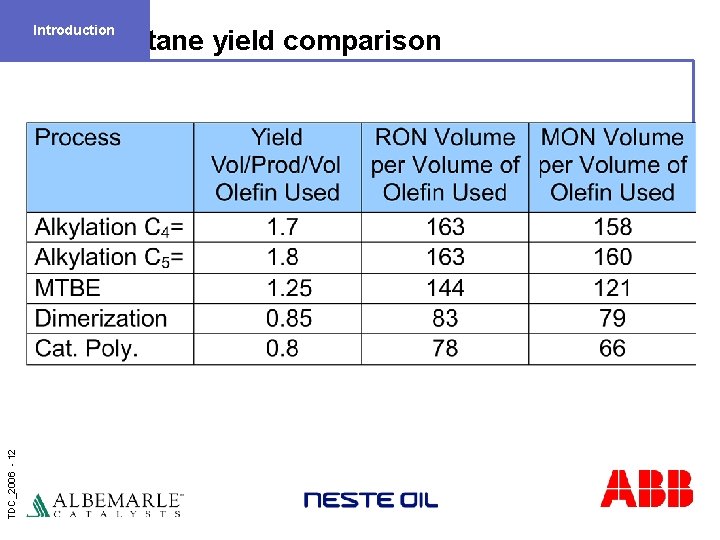
Introduction TDC_2006 - 12 Octane yield comparison
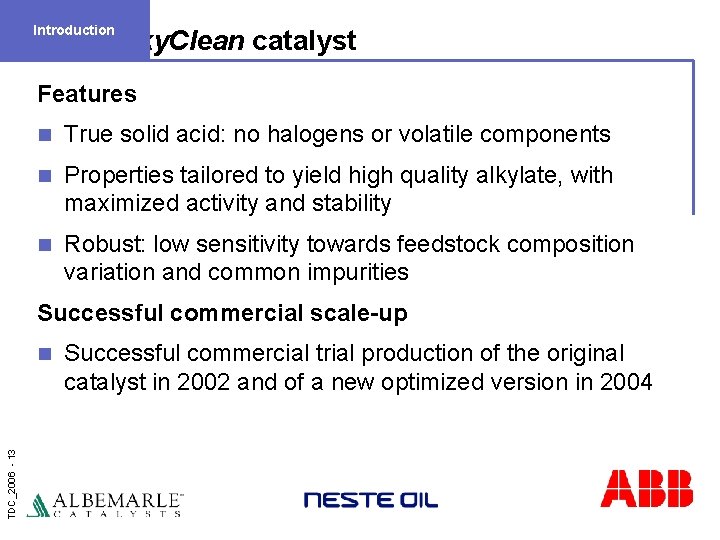
Introduction Alky. Clean catalyst Features n True solid acid: no halogens or volatile components n Properties tailored to yield high quality alkylate, with maximized activity and stability n Robust: low sensitivity towards feedstock composition variation and common impurities Successful commercial scale-up TDC_2006 - 13 n Successful commercial trial production of the original catalyst in 2002 and of a new optimized version in 2004
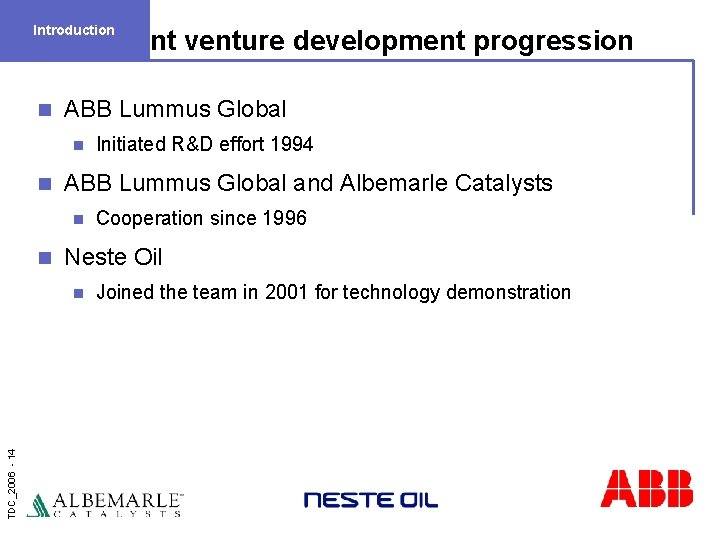
Introduction Joint venture development progression n ABB Lummus Global and Albemarle Catalysts n n Cooperation since 1996 Neste Oil n TDC_2006 - 14 Initiated R&D effort 1994 Joined the team in 2001 for technology demonstration
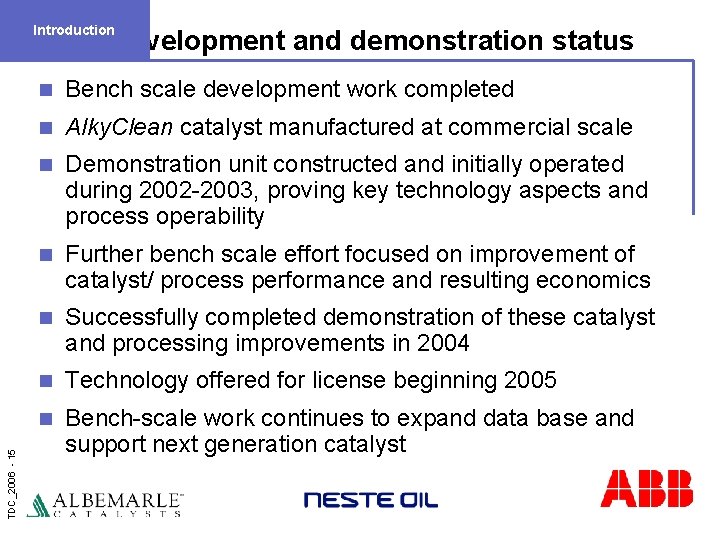
Introduction TDC_2006 - 15 Development and demonstration status n Bench scale development work completed n Alky. Clean catalyst manufactured at commercial scale n Demonstration unit constructed and initially operated during 2002 -2003, proving key technology aspects and process operability n Further bench scale effort focused on improvement of catalyst/ process performance and resulting economics n Successfully completed demonstration of these catalyst and processing improvements in 2004 n Technology offered for license beginning 2005 n Bench-scale work continues to expand data base and support next generation catalyst
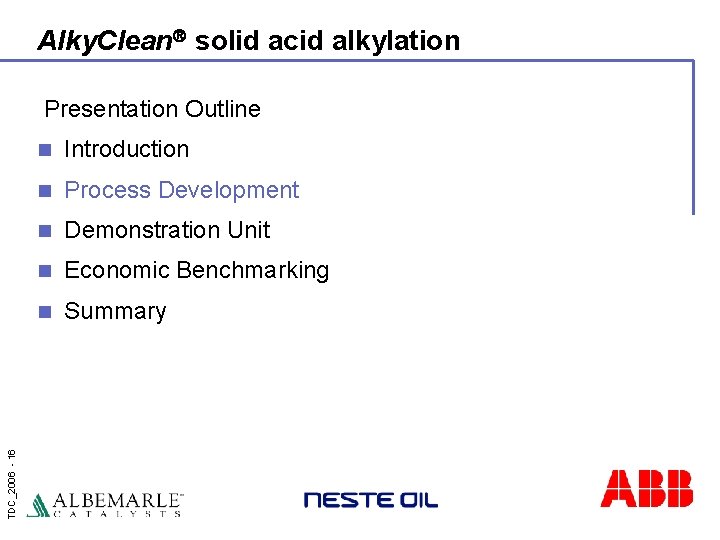
Alky. Clean solid acid alkylation TDC_2006 - 16 Presentation Outline n Introduction n Process Development n Demonstration Unit n Economic Benchmarking n Summary
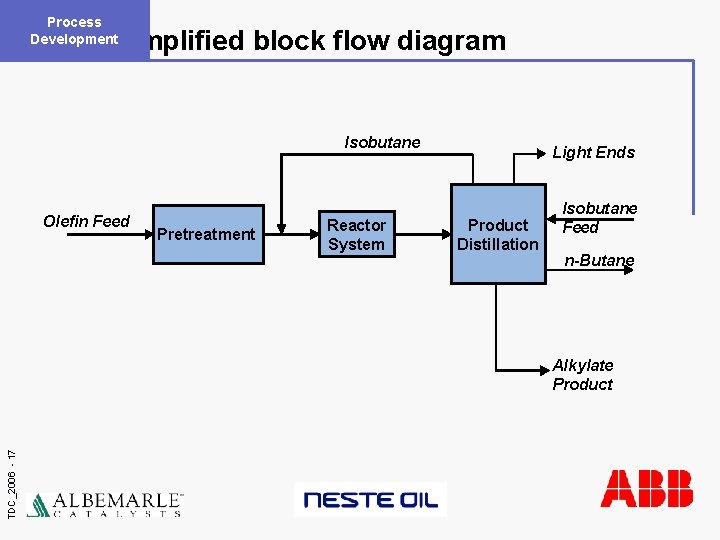
Process Development Simplified block flow diagram Isobutane Olefin Feed Pretreatment Reactor System Light Ends Product Distillation Isobutane Feed n-Butane TDC_2006 - 17 Alkylate Product
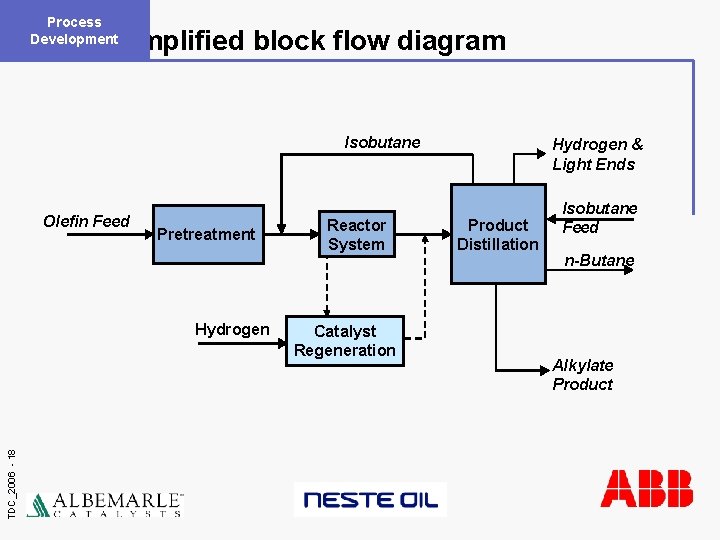
Process Development Simplified block flow diagram Isobutane Olefin Feed Pretreatment TDC_2006 - 18 Hydrogen Reactor System Catalyst Regeneration Hydrogen & Light Ends Product Distillation Isobutane Feed n-Butane Alkylate Product
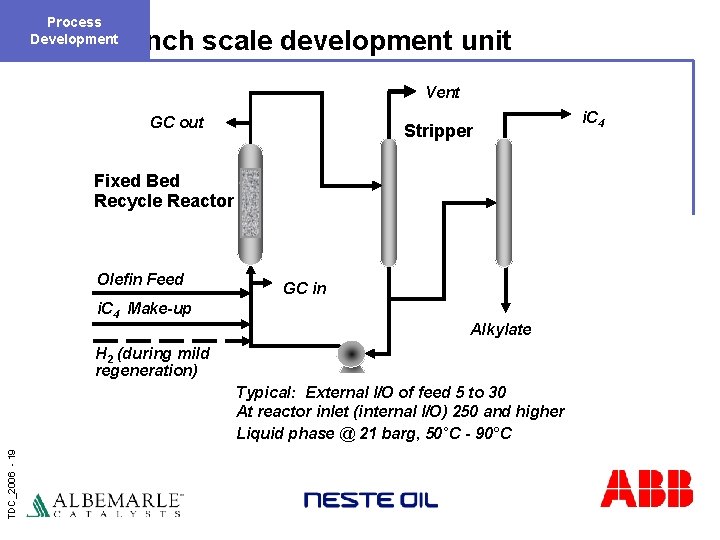
Process Development Bench scale development unit Vent GC out Stripper Fixed Bed Recycle Reactor Olefin Feed GC in i. C 4 Make-up Alkylate H 2 (during mild regeneration) TDC_2006 - 19 Typical: External I/O of feed 5 to 30 At reactor inlet (internal I/O) 250 and higher Liquid phase @ 21 barg, 50°C - 90°C i. C 4

Process Development TDC_2006 - 20 Cyclic pilot unit in Amsterdam
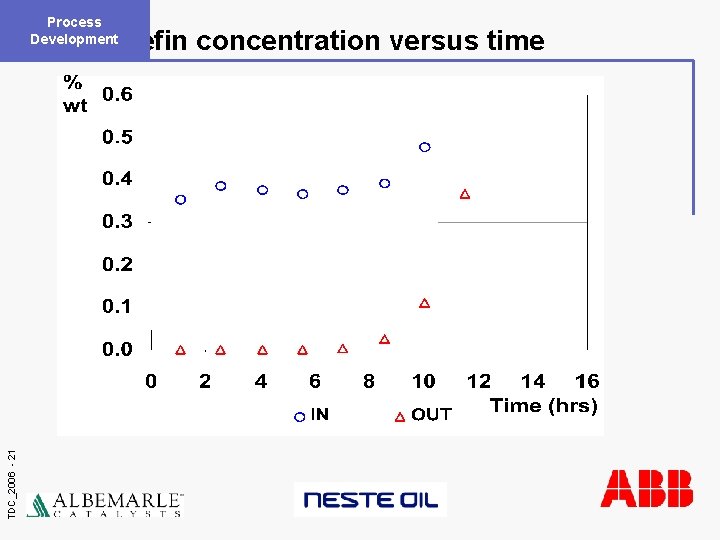
Process Development TDC_2006 - 21 Olefin concentration versus time
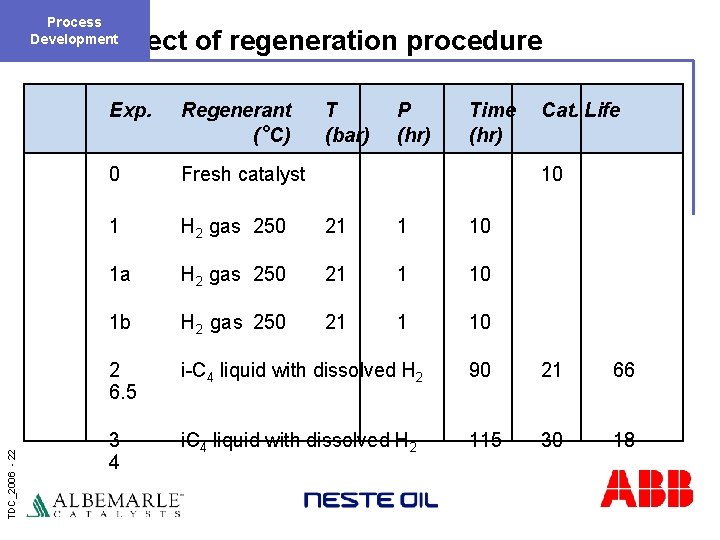
Process Development TDC_2006 - 22 Effect of regeneration procedure Exp. Regenerant (°C) T (bar) P (hr) Time (hr) Cat. Life 0 Fresh catalyst 1 H 2 gas 250 21 1 10 1 a H 2 gas 250 21 1 10 1 b H 2 gas 250 21 1 10 2 6. 5 i-C 4 liquid with dissolved H 2 90 21 66 3 4 i. C 4 liquid with dissolved H 2 115 30 18 10
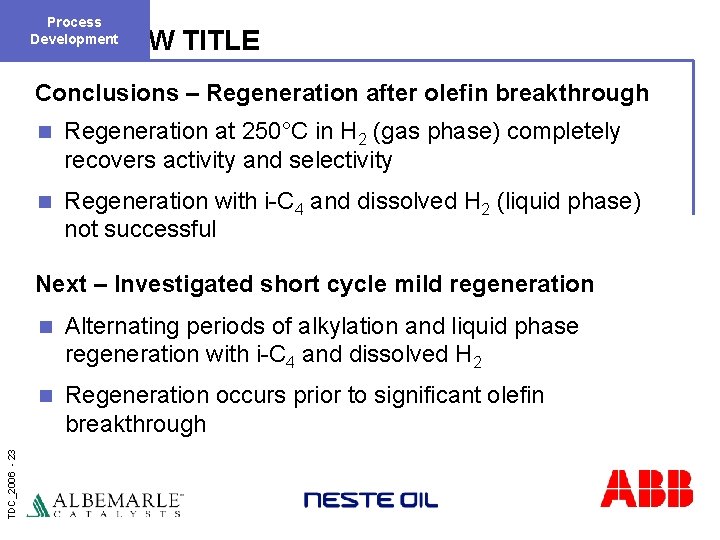
Process Development NEW TITLE Conclusions – Regeneration after olefin breakthrough n Regeneration at 250°C in H 2 (gas phase) completely recovers activity and selectivity n Regeneration with i-C 4 and dissolved H 2 (liquid phase) not successful TDC_2006 - 23 Next – Investigated short cycle mild regeneration n Alternating periods of alkylation and liquid phase regeneration with i-C 4 and dissolved H 2 n Regeneration occurs prior to significant olefin breakthrough
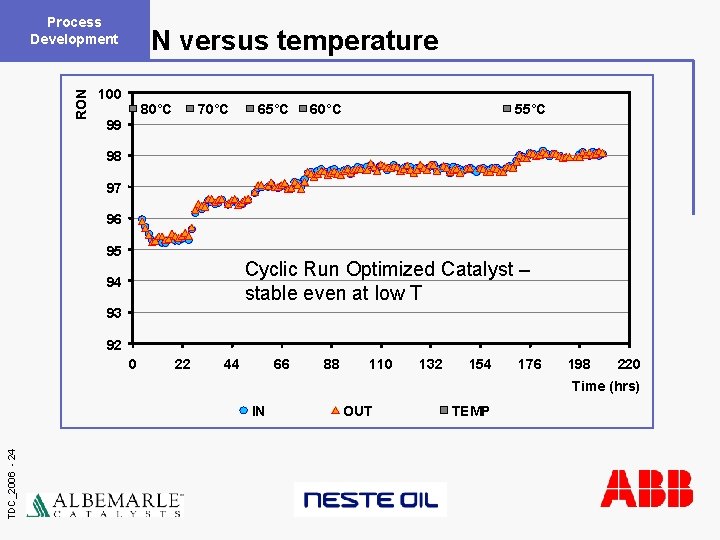
Process Development RON versus temperature 100 80°C 70°C 65°C 60°C 55°C 99 98 97 96 95 Cyclic Run Optimized Catalyst – stable even at low T 94 93 92 0 22 44 66 88 110 132 154 176 198 220 Time (hrs) TDC_2006 - 24 IN OUT TEMP
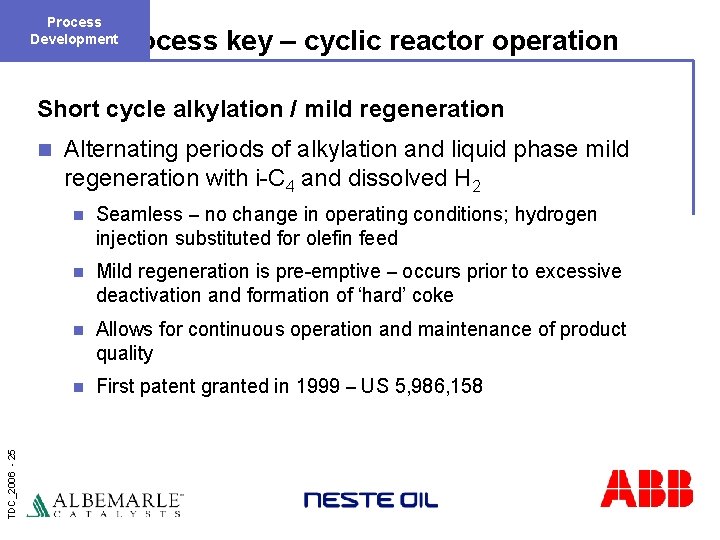
Process Development Process key – cyclic reactor operation Short cycle alkylation / mild regeneration TDC_2006 - 25 n Alternating periods of alkylation and liquid phase mild regeneration with i-C 4 and dissolved H 2 n Seamless – no change in operating conditions; hydrogen injection substituted for olefin feed n Mild regeneration is pre-emptive – occurs prior to excessive deactivation and formation of ‘hard’ coke n Allows for continuous operation and maintenance of product quality n First patent granted in 1999 – US 5, 986, 158
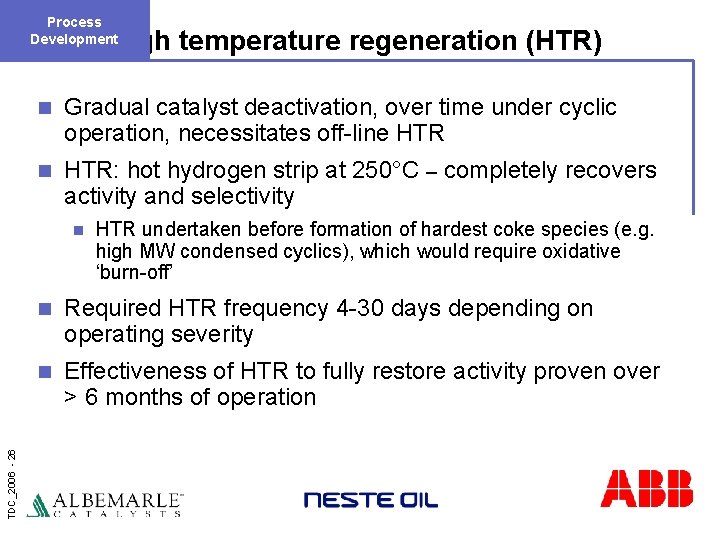
Process Development High temperature regeneration (HTR) n Gradual catalyst deactivation, over time under cyclic operation, necessitates off-line HTR n HTR: hot hydrogen strip at 250°C – completely recovers activity and selectivity TDC_2006 - 26 n HTR undertaken before formation of hardest coke species (e. g. high MW condensed cyclics), which would require oxidative ‘burn-off’ n Required HTR frequency 4 -30 days depending on operating severity n Effectiveness of HTR to fully restore activity proven over > 6 months of operation
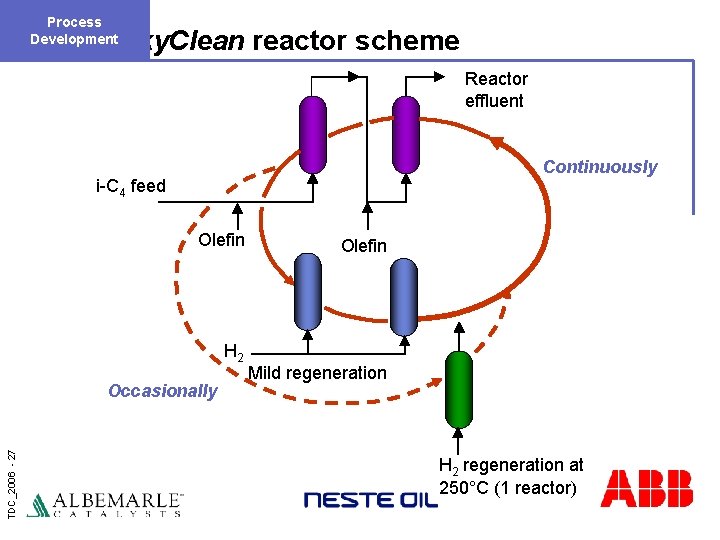
Process Development Alky. Clean reactor scheme Reactor effluent Continuously i-C 4 feed Olefin H 2 TDC_2006 - 27 Occasionally Olefin Mild regeneration H 2 regeneration at 250°C (1 reactor)
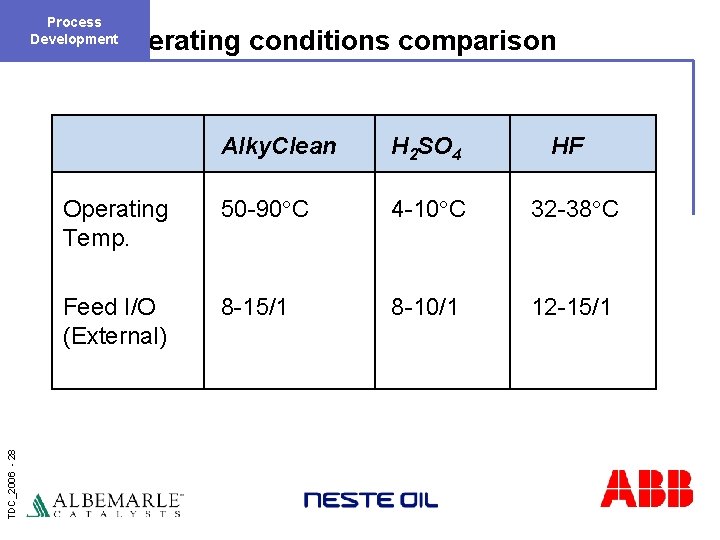
Process Development TDC_2006 - 28 Operating conditions comparison Alky. Clean H 2 SO 4 HF Operating Temp. 50 -90°C 4 -10°C 32 -38°C Feed I/O (External) 8 -15/1 8 -10/1 12 -15/1
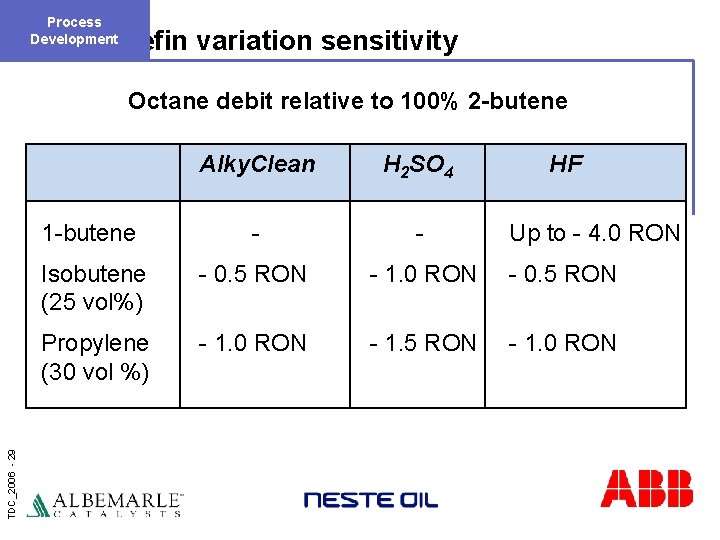
Process Development Olefin variation sensitivity TDC_2006 - 29 Octane debit relative to 100% 2 -butene Alky. Clean H 2 SO 4 HF 1 -butene - - Isobutene (25 vol%) - 0. 5 RON - 1. 0 RON - 0. 5 RON Propylene (30 vol %) - 1. 0 RON - 1. 5 RON - 1. 0 RON Up to - 4. 0 RON
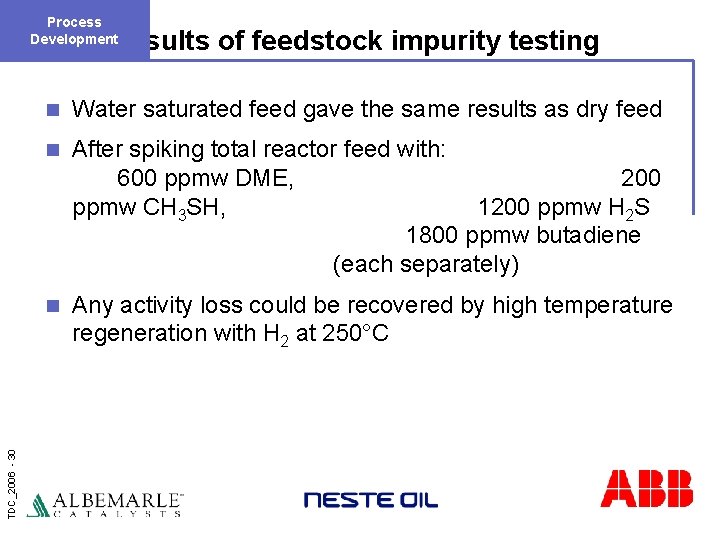
Process Development TDC_2006 - 30 Results of feedstock impurity testing n Water saturated feed gave the same results as dry feed n After spiking total reactor feed with: 600 ppmw DME, 200 ppmw CH 3 SH, 1200 ppmw H 2 S 1800 ppmw butadiene (each separately) n Any activity loss could be recovered by high temperature regeneration with H 2 at 250°C
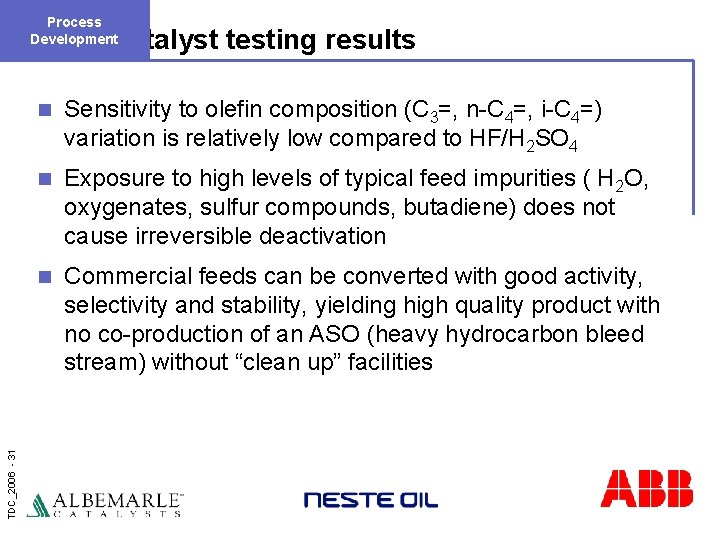
Process Development TDC_2006 - 31 Catalyst testing results n Sensitivity to olefin composition (C 3=, n-C 4=, i-C 4=) variation is relatively low compared to HF/H 2 SO 4 n Exposure to high levels of typical feed impurities ( H 2 O, oxygenates, sulfur compounds, butadiene) does not cause irreversible deactivation n Commercial feeds can be converted with good activity, selectivity and stability, yielding high quality product with no co-production of an ASO (heavy hydrocarbon bleed stream) without “clean up” facilities
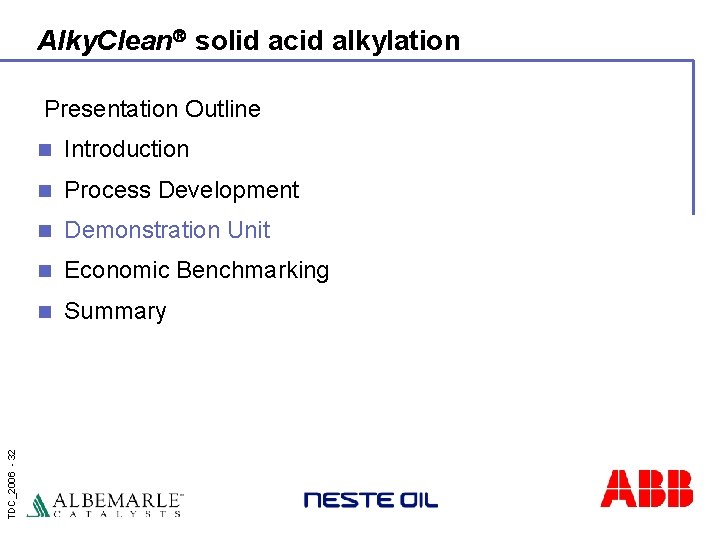
Alky. Clean solid acid alkylation TDC_2006 - 32 Presentation Outline n Introduction n Process Development n Demonstration Unit n Economic Benchmarking n Summary
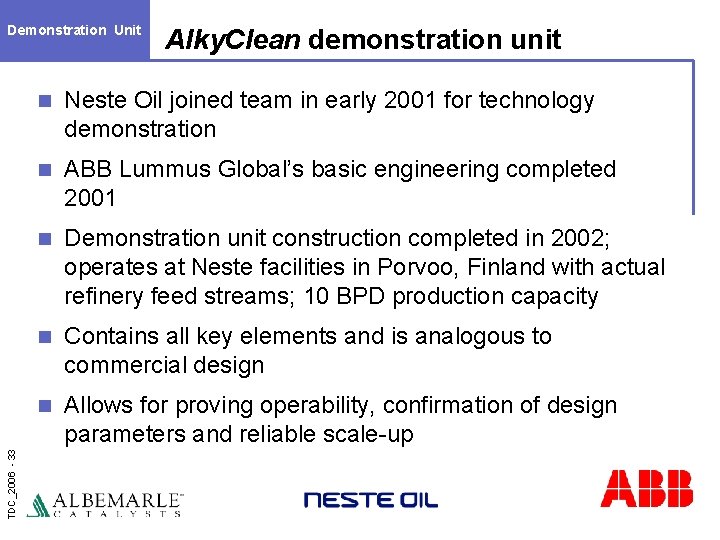
TDC_2006 - 33 Demonstration Unit Alky. Clean demonstration unit n Neste Oil joined team in early 2001 for technology demonstration n ABB Lummus Global’s basic engineering completed 2001 n Demonstration unit construction completed in 2002; operates at Neste facilities in Porvoo, Finland with actual refinery feed streams; 10 BPD production capacity n Contains all key elements and is analogous to commercial design n Allows for proving operability, confirmation of design parameters and reliable scale-up
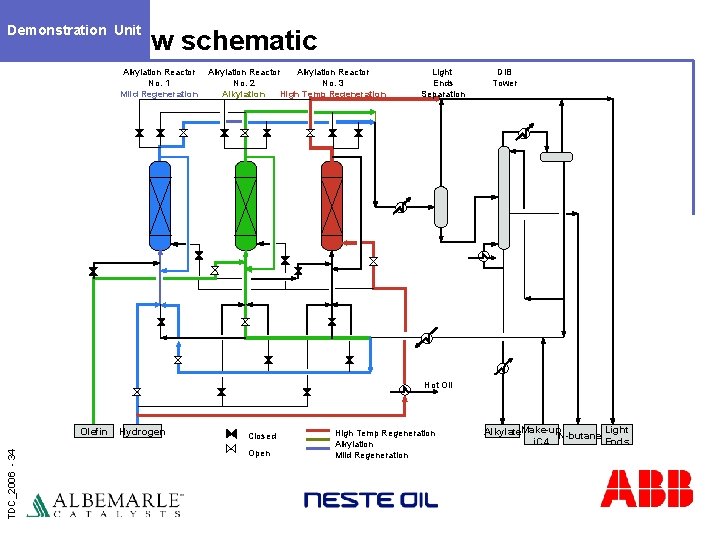
Demonstration Unit Flow schematic Alkylation Reactor No. 1 Mild Regeneration Alkylation Reactor No. 2 No. 3 Alkylation High Temp Regeneration Light Ends Separation DIB Tower Hot Oil TDC_2006 - 34 Olefin Hydrogen Closed Open High Temp Regeneration Alkylation Mild Regeneration Alkylate. Make-up. N-butane Light i. C 4 Ends
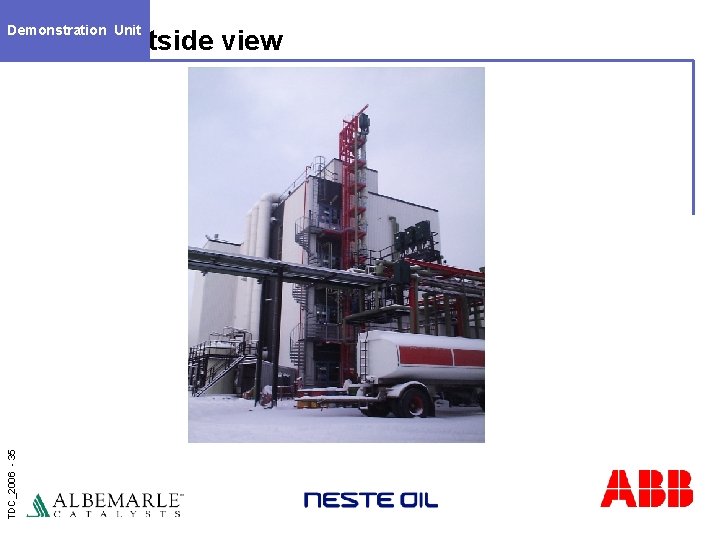
Demonstration Unit TDC_2006 - 35 Outside view
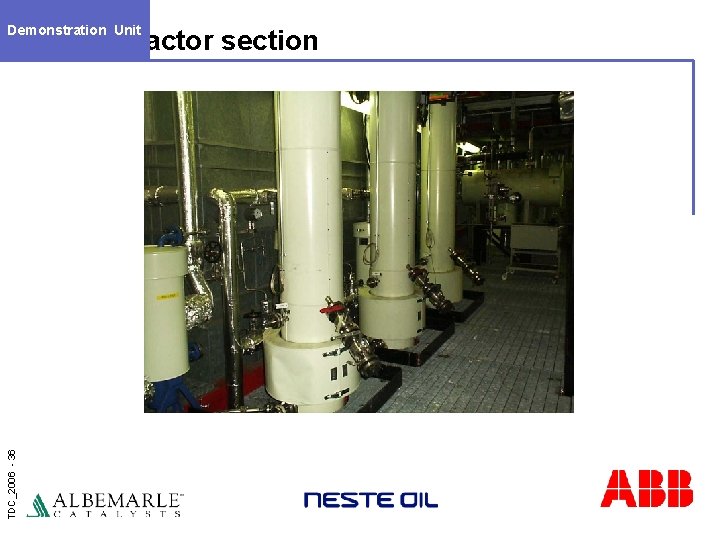
Demonstration Unit TDC_2006 - 36 Reactor section
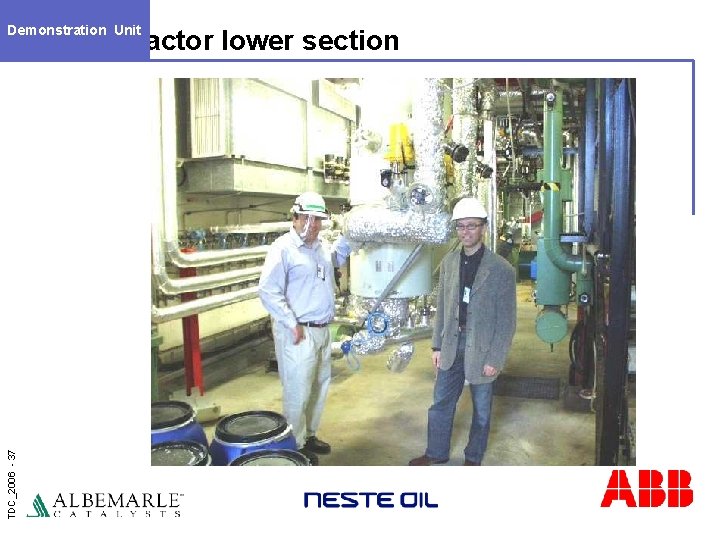
Demonstration Unit TDC_2006 - 37 Reactor lower section
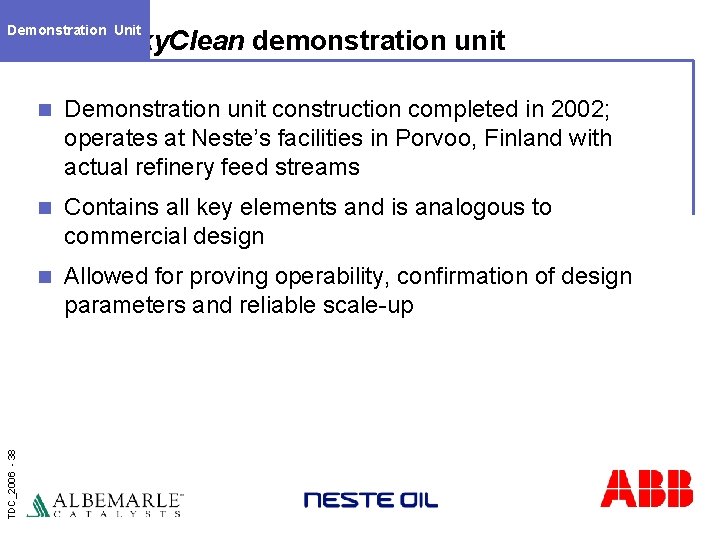
Demonstration Unit TDC_2006 - 38 Alky. Clean demonstration unit n Demonstration unit construction completed in 2002; operates at Neste’s facilities in Porvoo, Finland with actual refinery feed streams n Contains all key elements and is analogous to commercial design n Allowed for proving operability, confirmation of design parameters and reliable scale-up
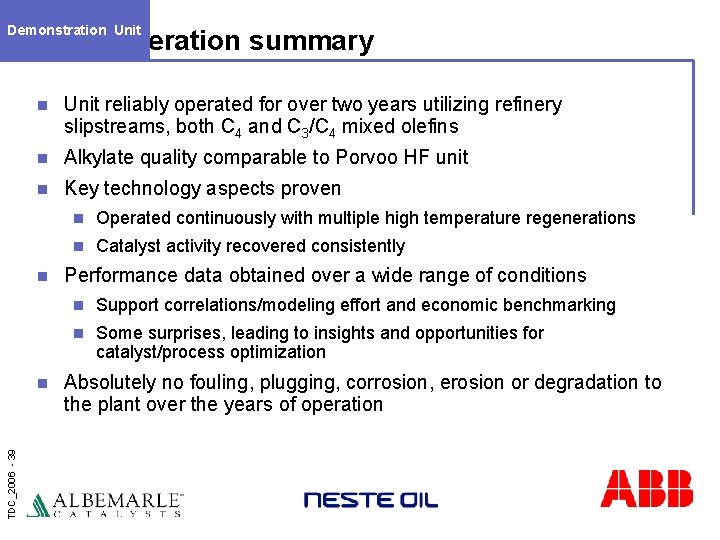
Demonstration Unit Operation summary n Unit reliably operated for over two years utilizing refinery slipstreams, both C 4 and C 3/C 4 mixed olefins n Alkylate quality comparable to Porvoo HF unit n Key technology aspects proven n TDC_2006 - 39 n n Operated continuously with multiple high temperature regenerations n Catalyst activity recovered consistently Performance data obtained over a wide range of conditions n Support correlations/modeling effort and economic benchmarking n Some surprises, leading to insights and opportunities for catalyst/process optimization Absolutely no fouling, plugging, corrosion, erosion or degradation to the plant over the years of operation
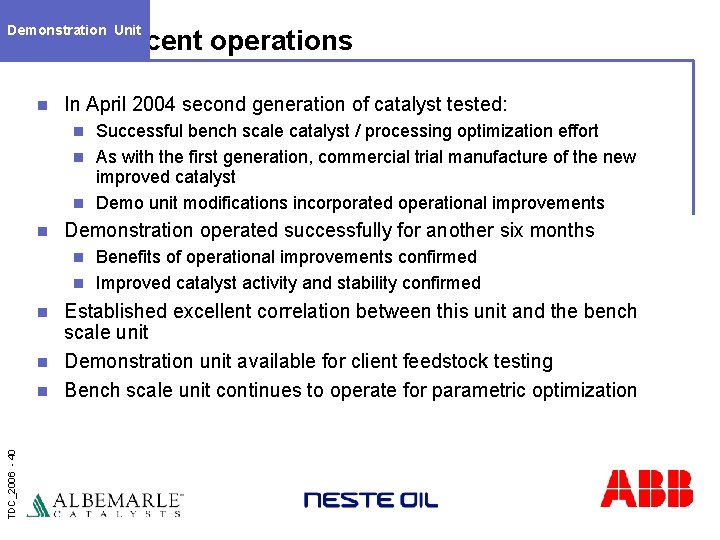
Demonstration Unit Recent operations n In April 2004 second generation of catalyst tested: Successful bench scale catalyst / processing optimization effort n As with the first generation, commercial trial manufacture of the new improved catalyst n Demo unit modifications incorporated operational improvements n n Demonstration operated successfully for another six months Benefits of operational improvements confirmed n Improved catalyst activity and stability confirmed n Established excellent correlation between this unit and the bench scale unit n Demonstration unit available for client feedstock testing n Bench scale unit continues to operate for parametric optimization TDC_2006 - 40 n
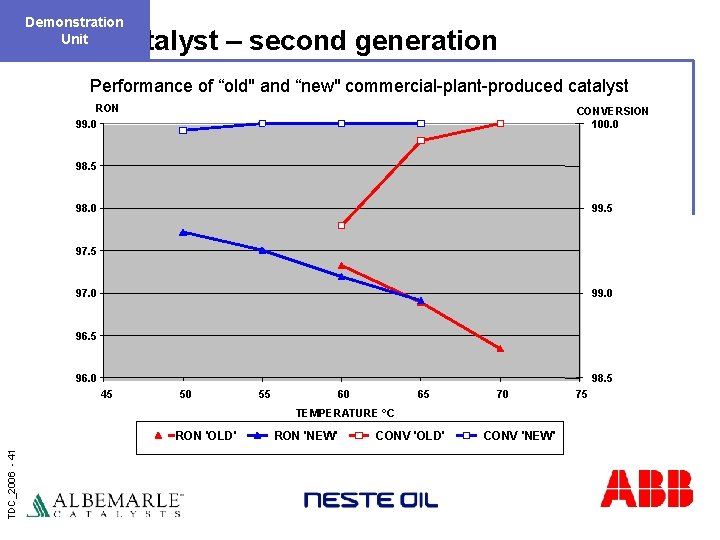
Demonstration Unit Catalyst – second generation Performance of “old" and “new" commercial-plant-produced catalyst RON 99. 0 CONVERSION 100. 0 98. 5 98. 0 99. 5 97. 0 99. 0 96. 5 96. 0 98. 5 45 50 55 60 65 70 TEMPERATURE °C TDC_2006 - 41 RON 'OLD' RON 'NEW' CONV 'OLD' CONV 'NEW' 75
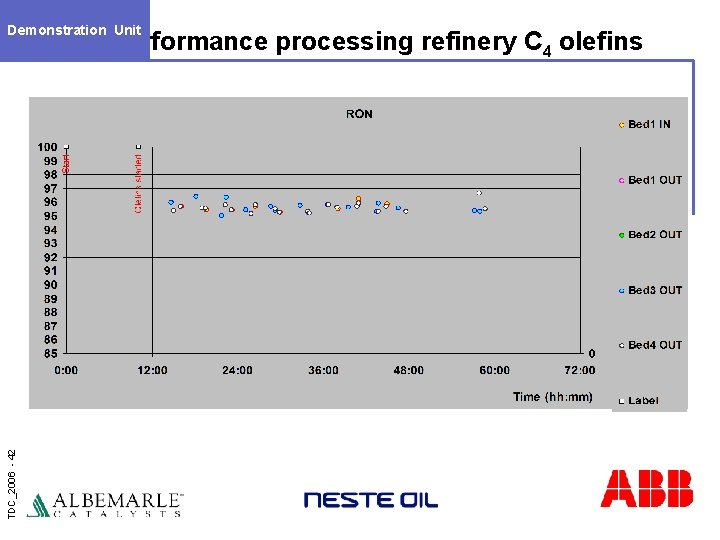
Demonstration Unit TDC_2006 - 42 Performance processing refinery C 4 olefins
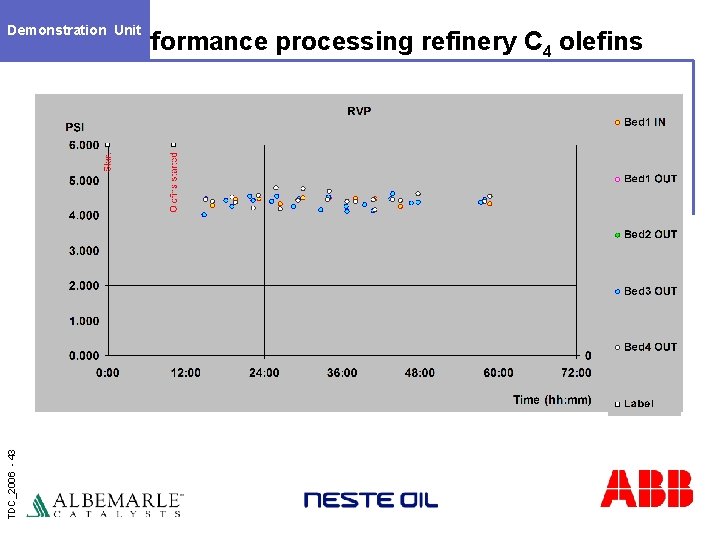
Demonstration Unit TDC_2006 - 43 Performance processing refinery C 4 olefins
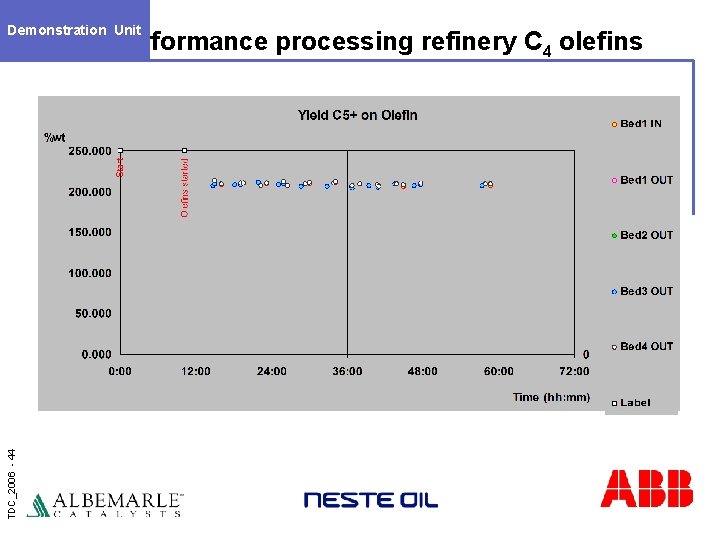
Demonstration Unit TDC_2006 - 44 Performance processing refinery C 4 olefins
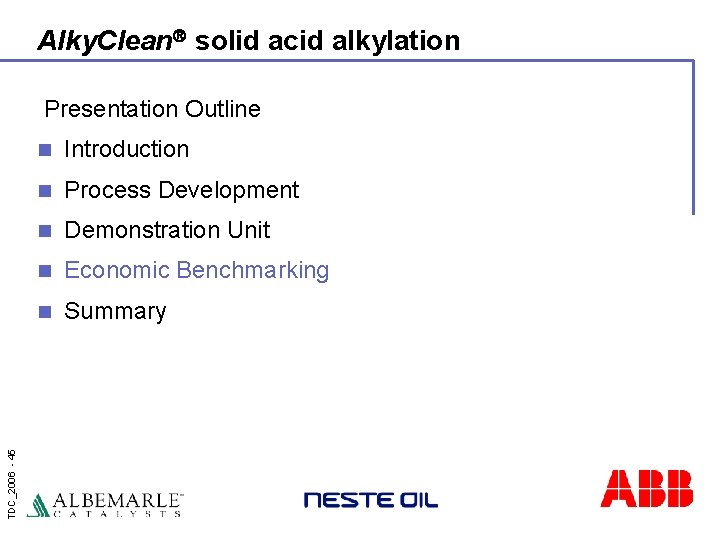
Alky. Clean solid acid alkylation TDC_2006 - 45 Presentation Outline n Introduction n Process Development n Demonstration Unit n Economic Benchmarking n Summary
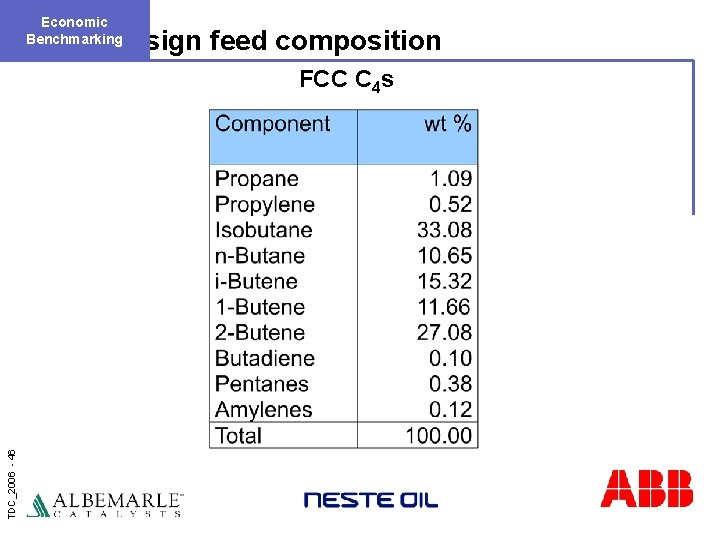
Economic Benchmarking Design feed composition TDC_2006 - 46 FCC C 4 s
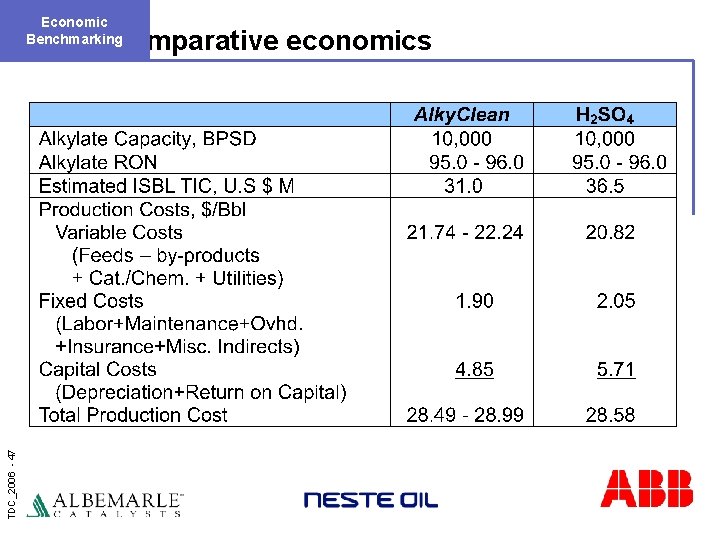
Economic Benchmarking TDC_2006 - 47 Comparative economics
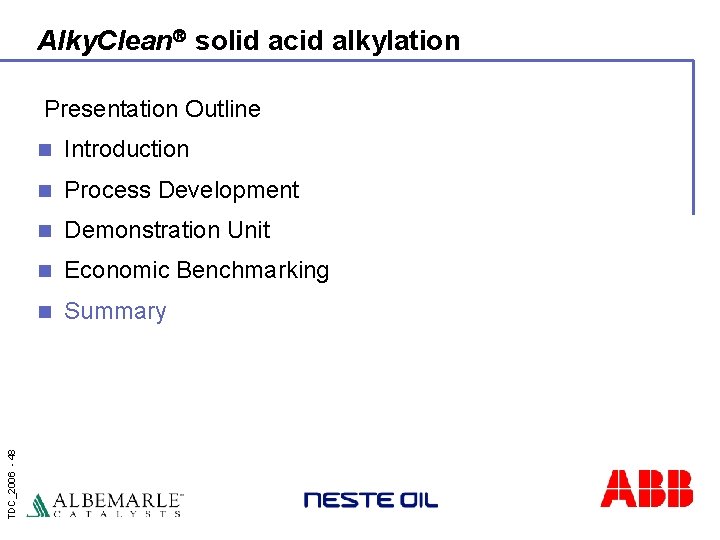
Alky. Clean solid acid alkylation TDC_2006 - 48 Presentation Outline n Introduction n Process Development n Demonstration Unit n Economic Benchmarking n Summary
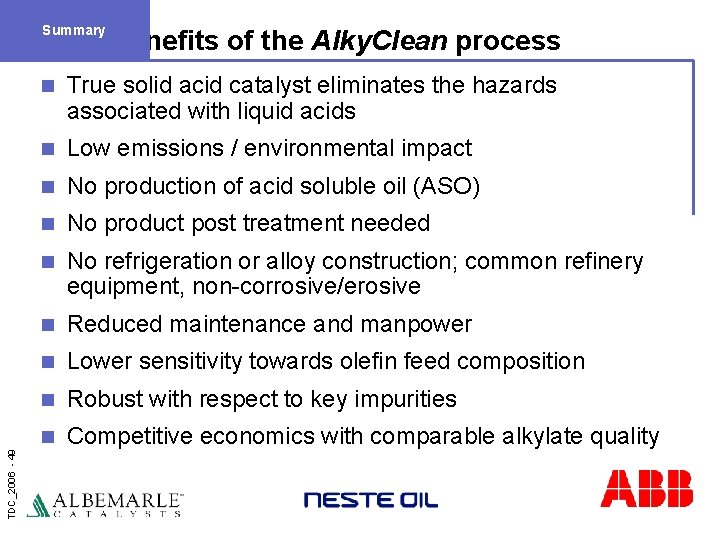
TDC_2006 - 49 Summary Benefits of the Alky. Clean process n True solid acid catalyst eliminates the hazards associated with liquid acids n Low emissions / environmental impact n No production of acid soluble oil (ASO) n No product post treatment needed n No refrigeration or alloy construction; common refinery equipment, non-corrosive/erosive n Reduced maintenance and manpower n Lower sensitivity towards olefin feed composition n Robust with respect to key impurities n Competitive economics with comparable alkylate quality
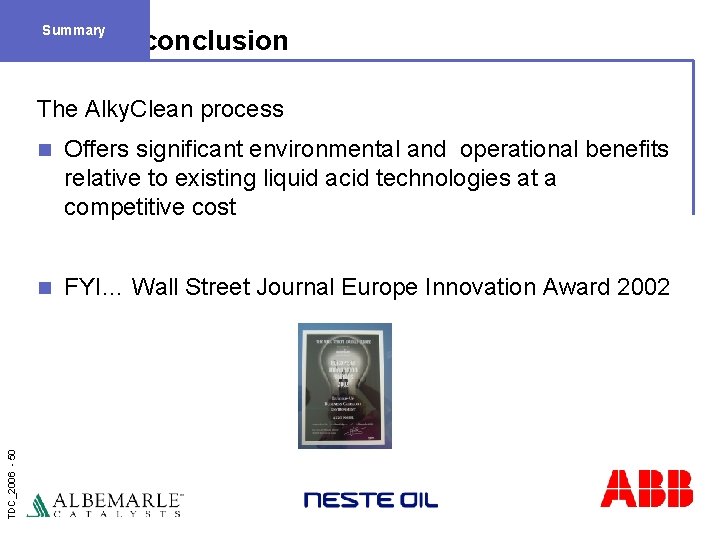
Summary In conclusion TDC_2006 - 50 The Alky. Clean process n Offers significant environmental and operational benefits relative to existing liquid acid technologies at a competitive cost n FYI… Wall Street Journal Europe Innovation Award 2002
Alkylation process flow diagram
Alkylation of alkanes
Friedel crafts acetylation of benzene
Multi tubular reactor
Crystalline vs amorphous
Example of solid solution?
Covalent network solid vs molecular solid
Crystallography types
Crystalline solids
Crystalline solid and amorphous solid
Anisotropic
When a solid completely penetrates another solid
Interpenetration of solids
Mixture evaporation
9-which acid is not considered a strong acid?
Differentiate between acid fast and non acid fast bacteria
Alcohol and anhydride reaction
Acid fast and non acid fast bacteria
Identifying lewis acids and bases practice
Lewis acid bronsted acid
Seven strong acids
Hcl lewis acid or base
Monoprotic acid
Stomach acid vs battery acid
Carboxylic acid to acid halide
Xxxx websites
Catalyst literature
Twisted laurie halse anderson summary
Ziegler natta catalyst
Rna catalyst
Poem using the word catalyst
Finely divided catalyst
What's a biological catalyst
Classification of coenzymes
Important properties of enzymes
3 characteristics of enzymes
What does wiesel mean when he says anger must be a catalyst
"catalyst for change"
Does a catalyst affect enthalpy
What is catalyst and how it affects reaction rate
Inorganic catalyst vs enzyme
Catalyst protein
The catalyst
Prometheus catalyst
Covalent bond of ethanol
Healthcare data warehousing
3750 stack
Maxwell boltzmann distribution catalyst
Cisco catalyst 2950 configuration
Policy catalyst first period 1780s to late 1800s
Catalyst pharma consulting