Company LOGO Conceptual Design Review Akshay Ashok Nithin
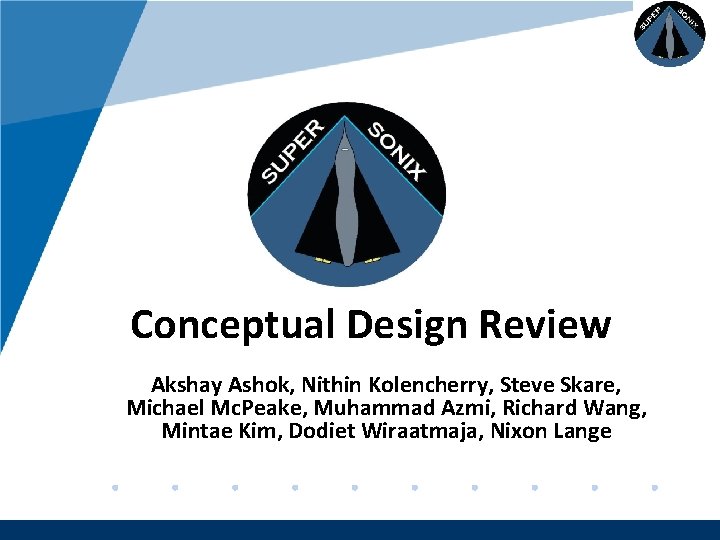
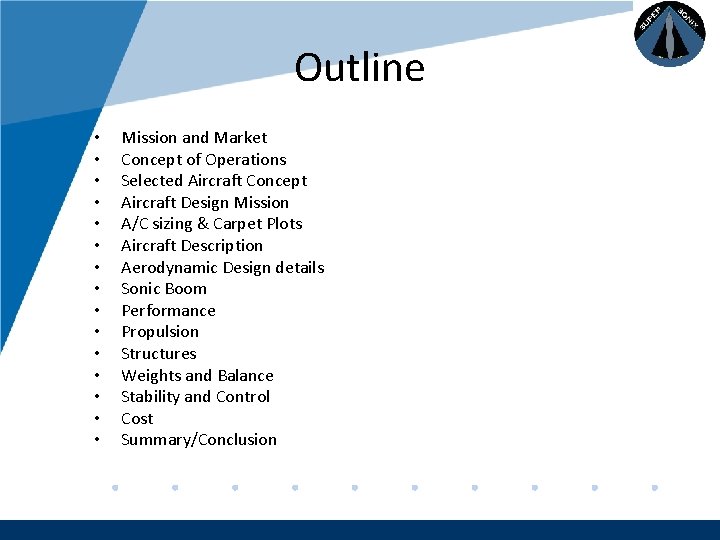
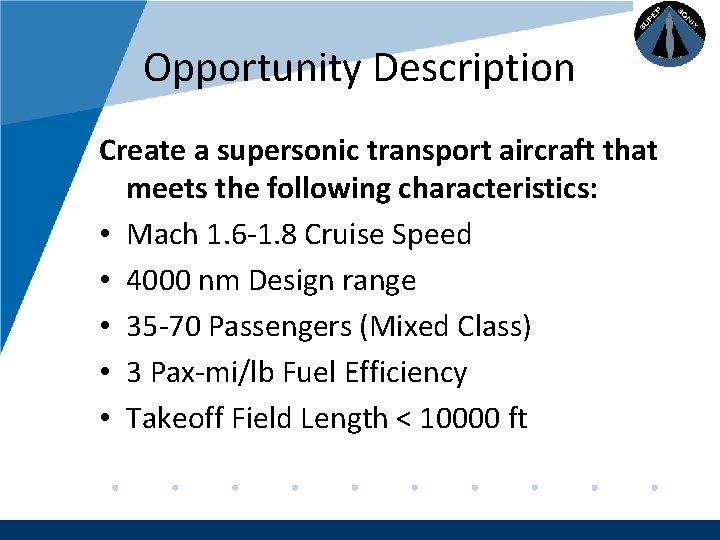
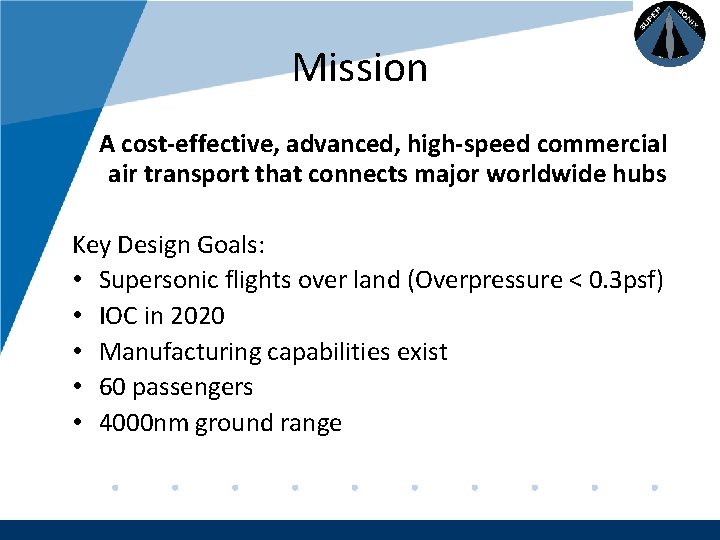
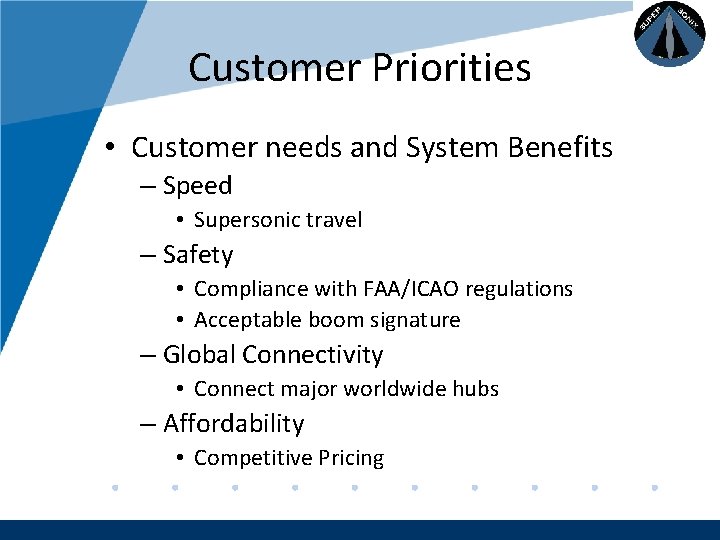
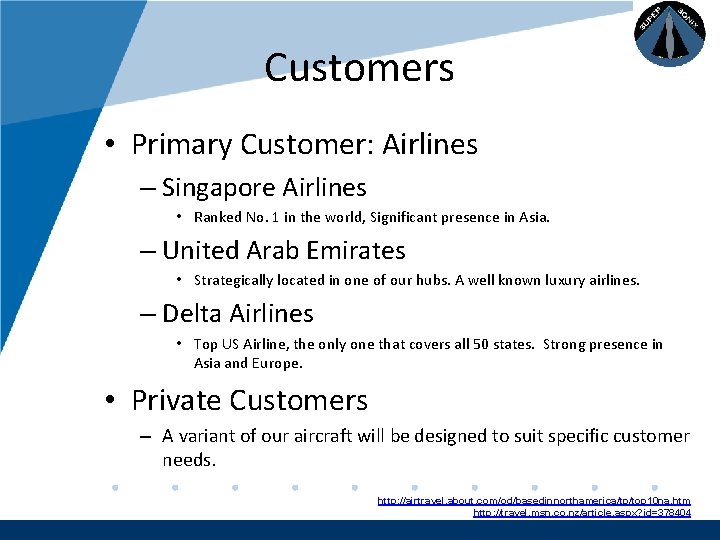
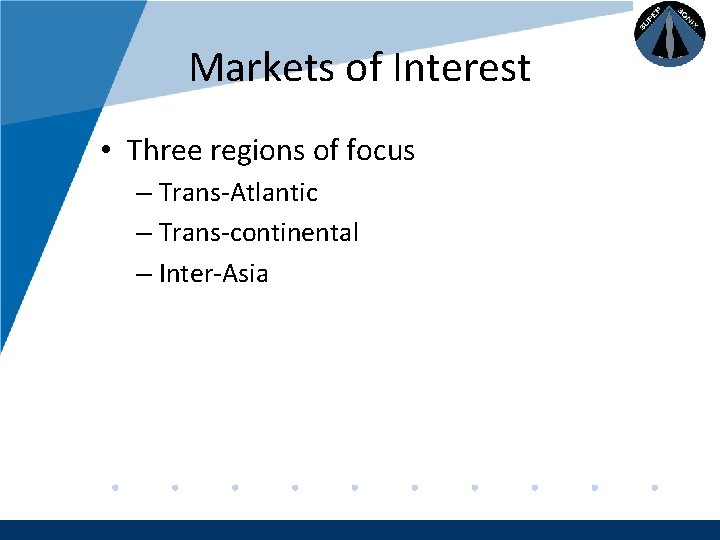
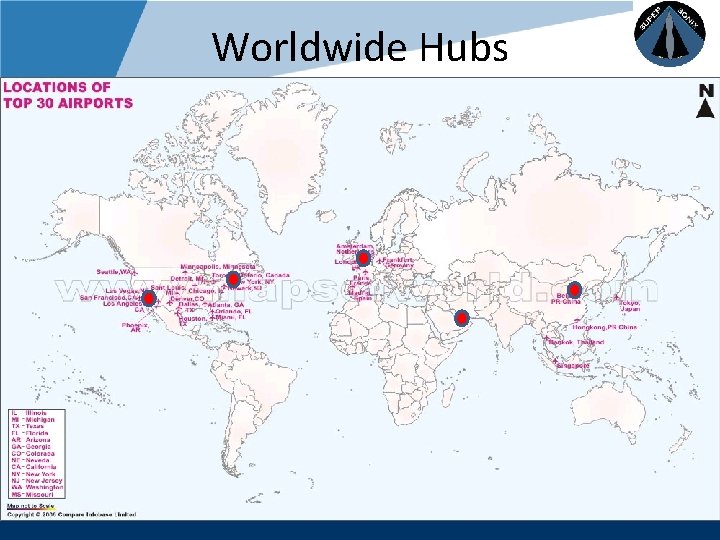
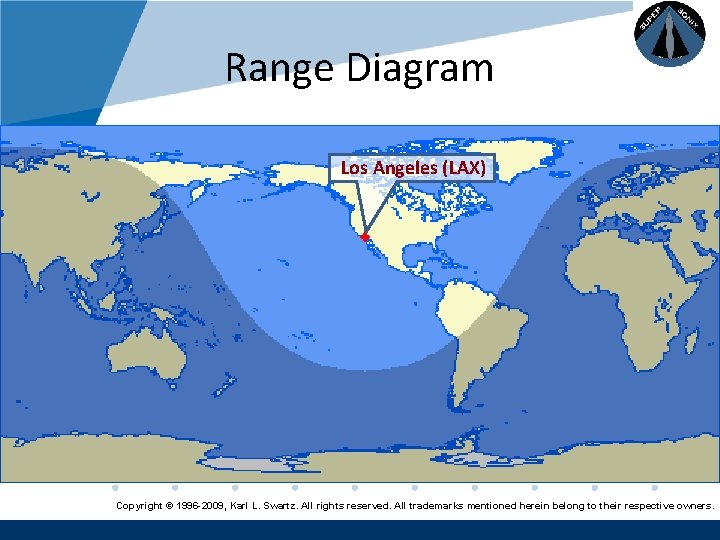
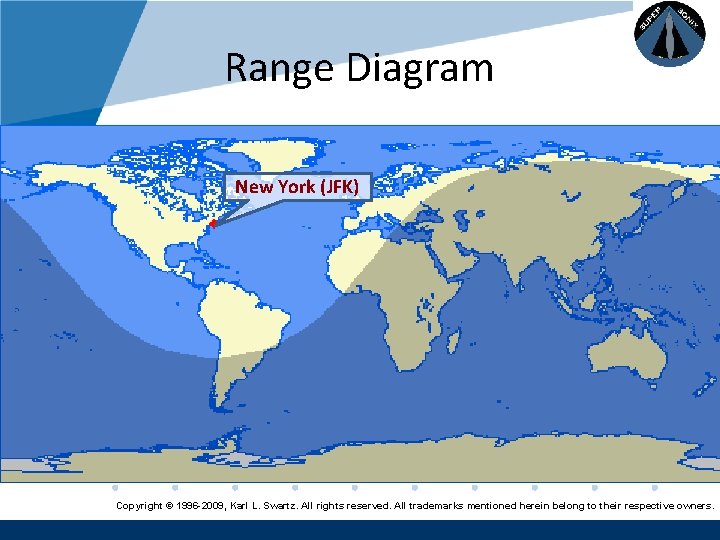
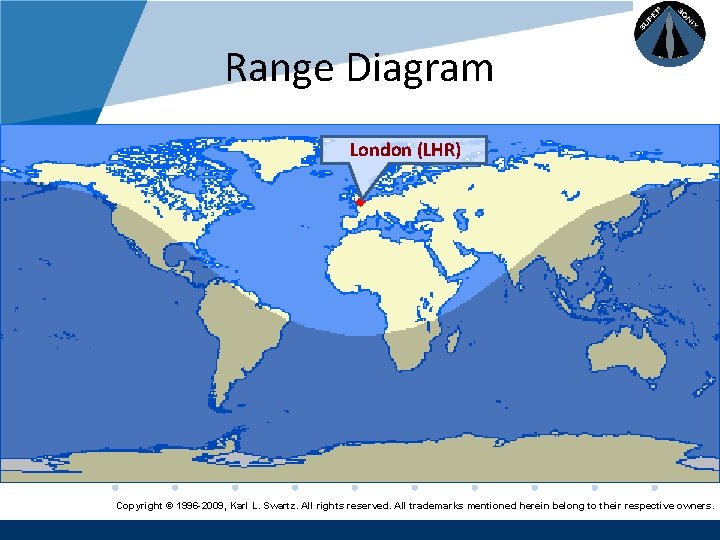
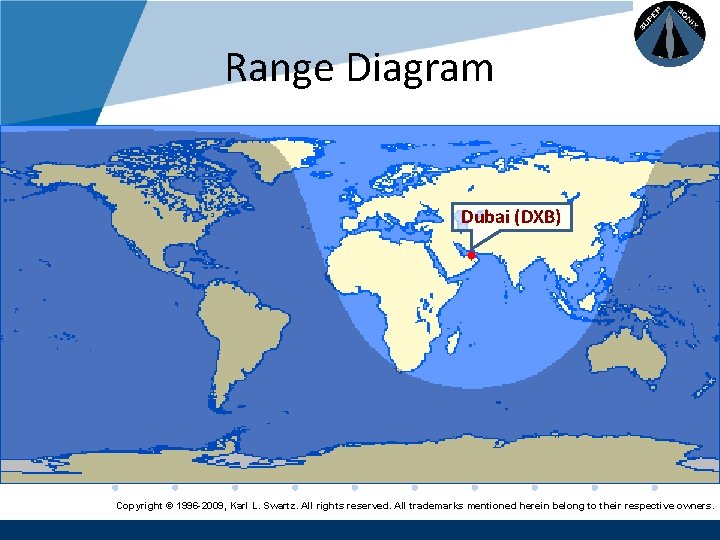
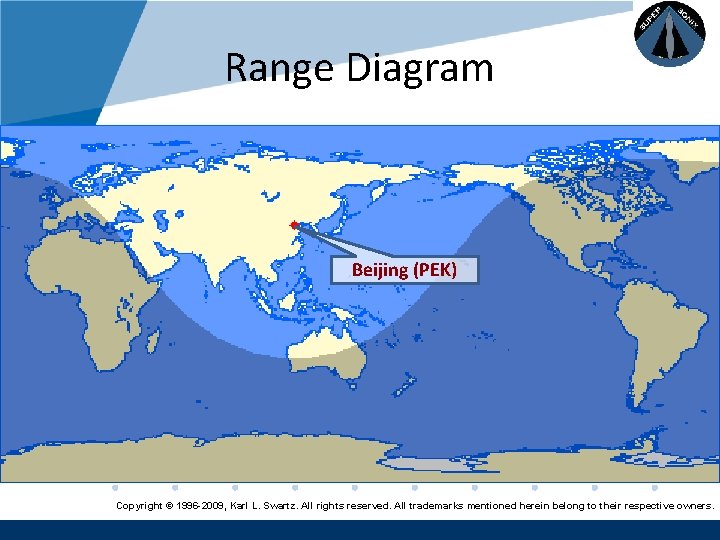
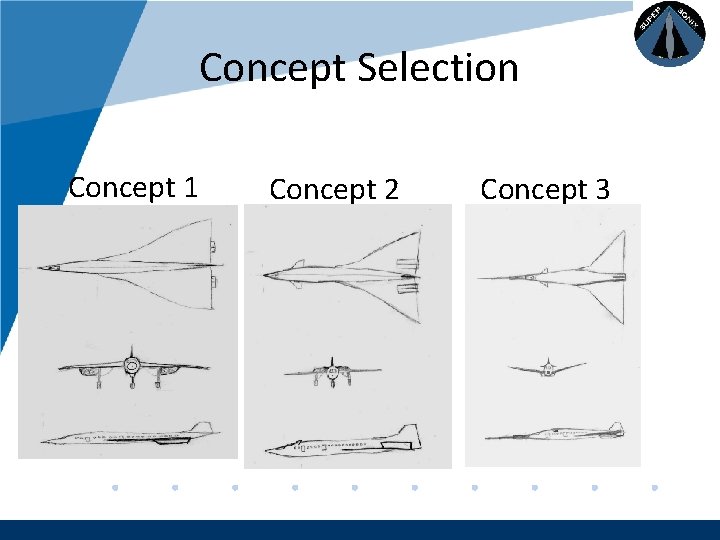
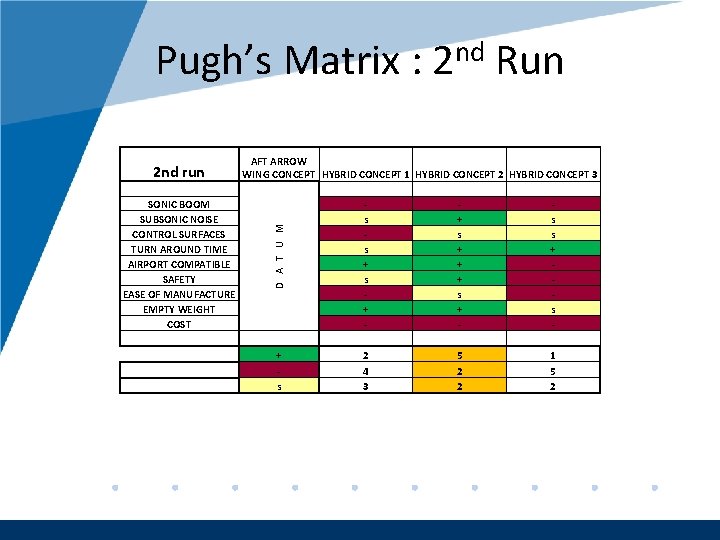
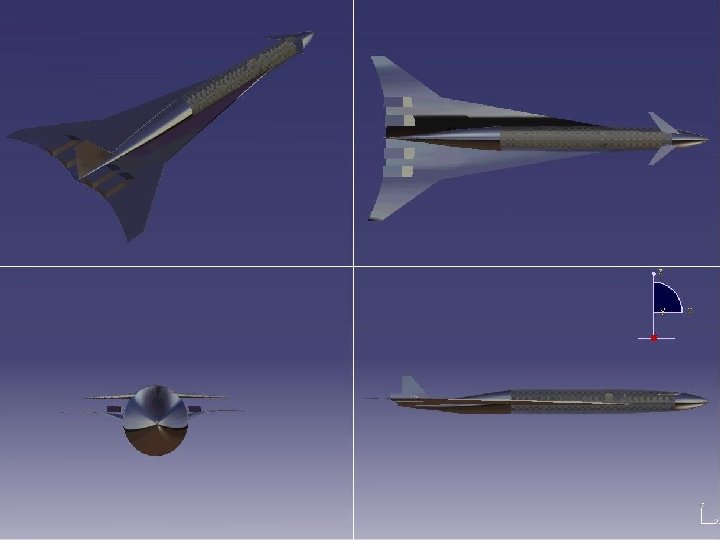
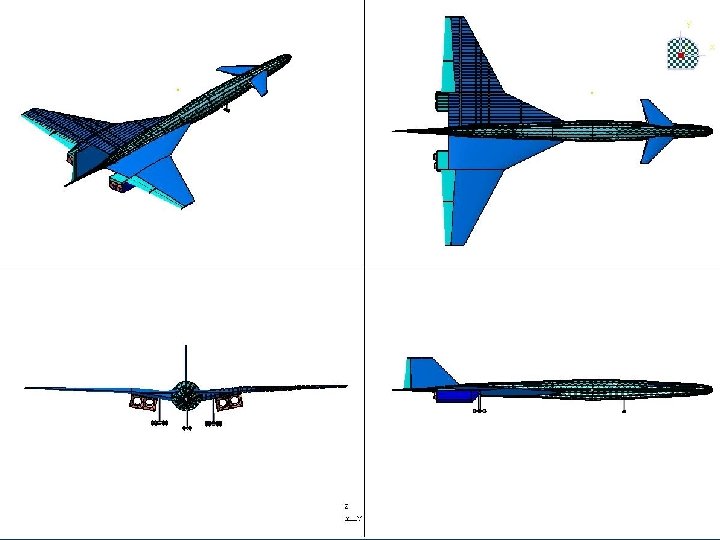
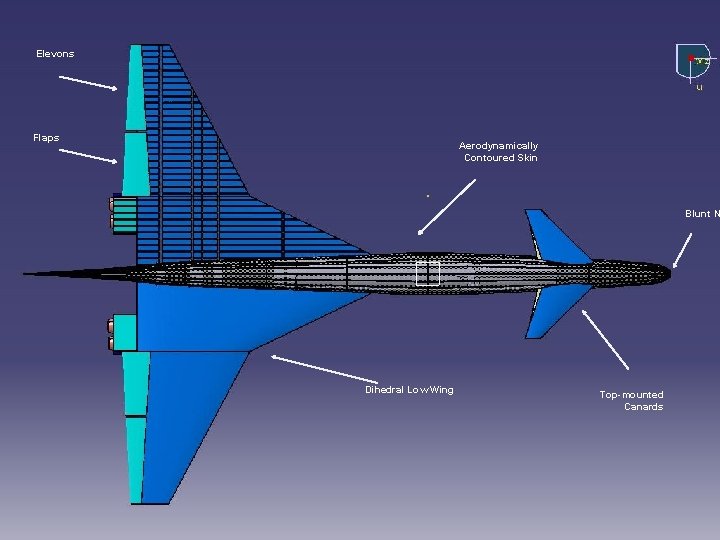
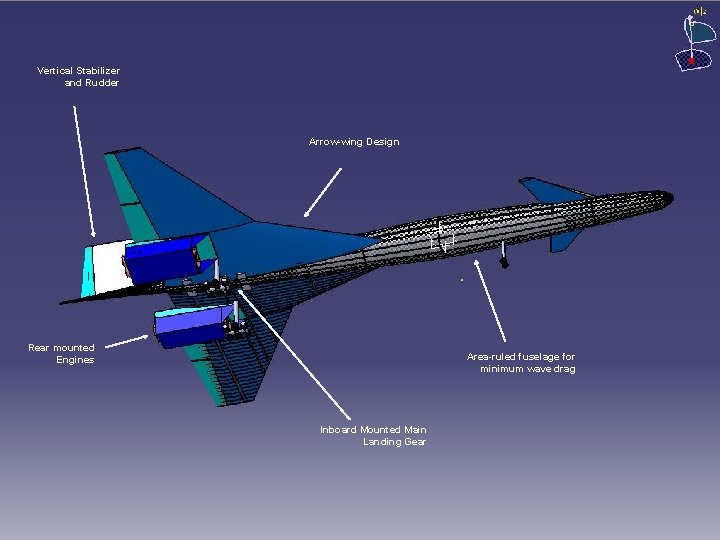
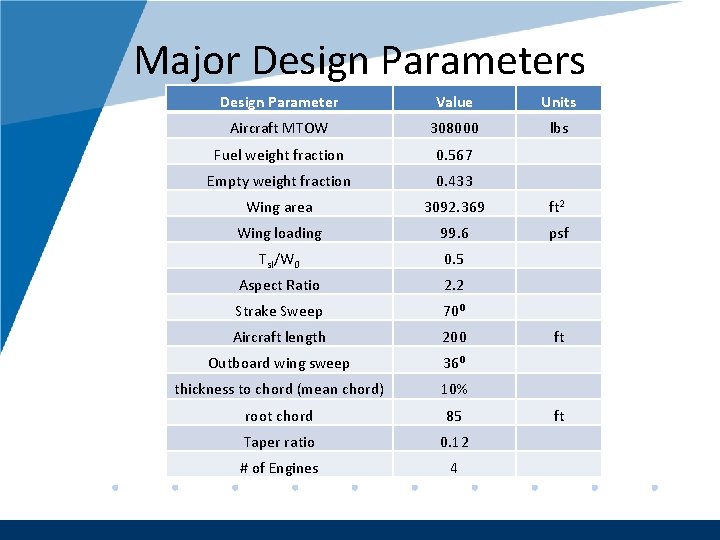
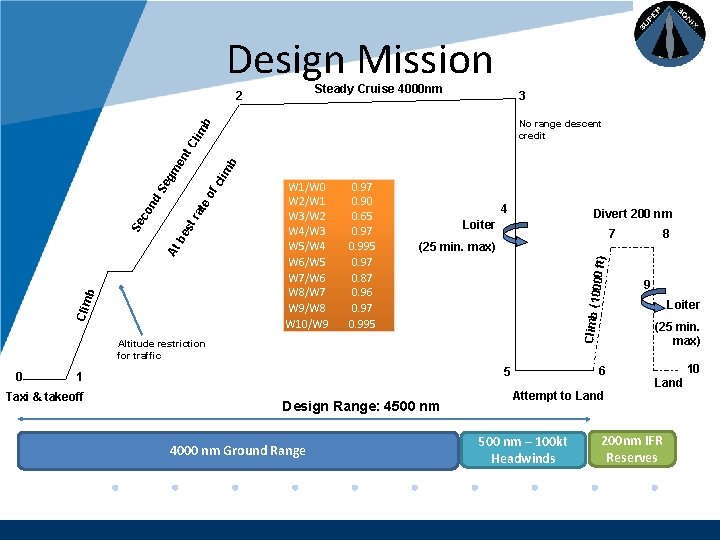
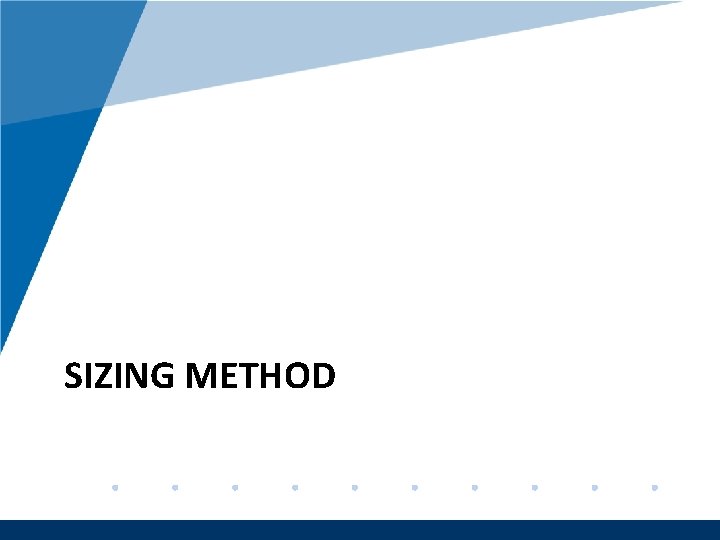
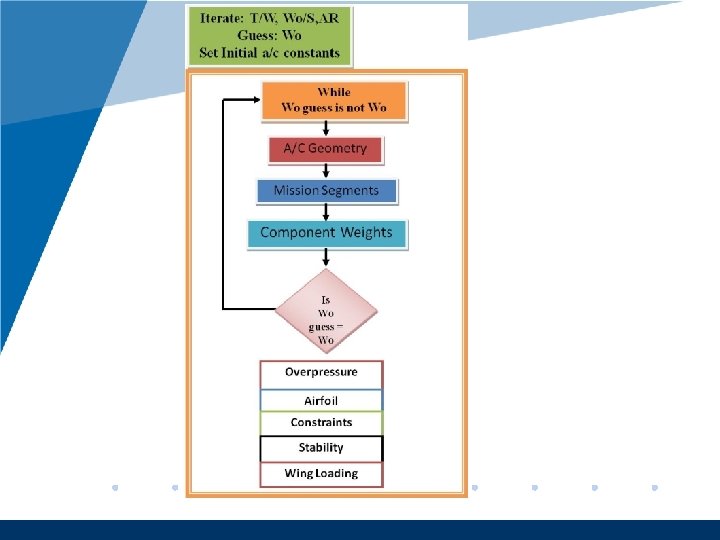
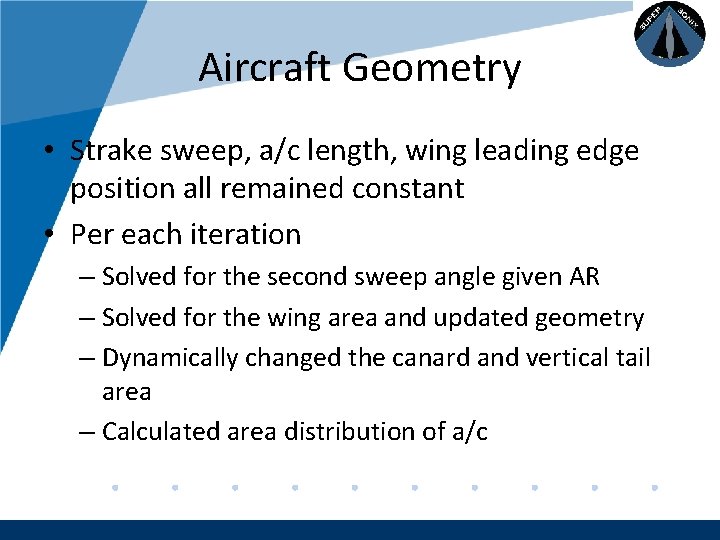
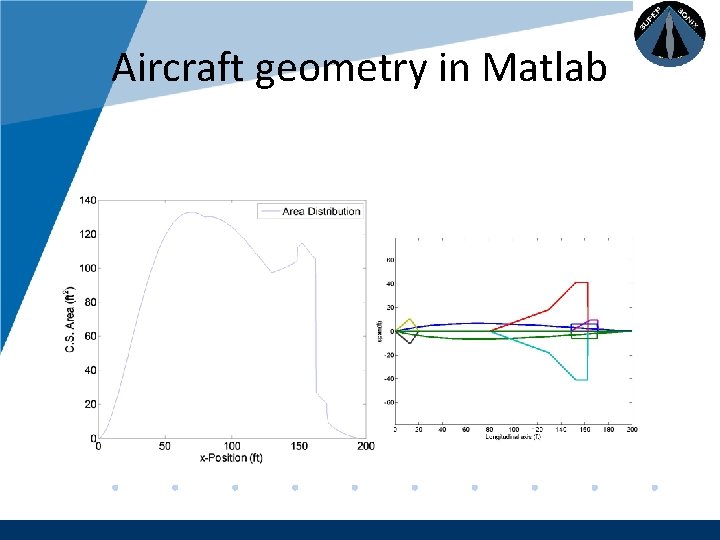
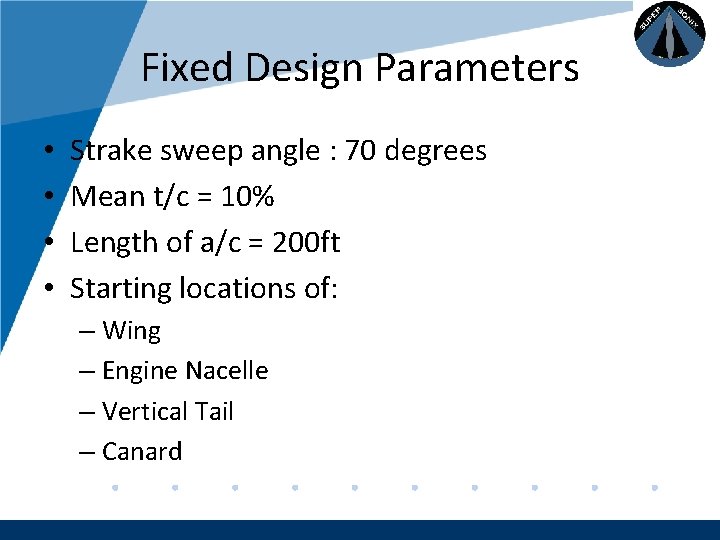
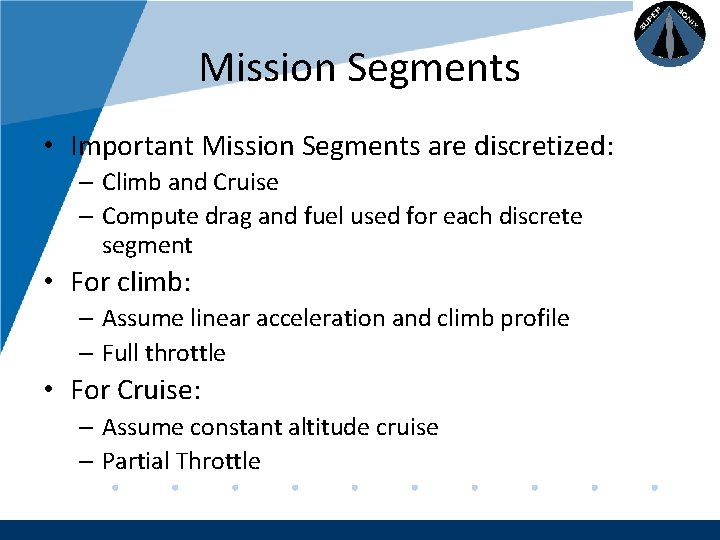
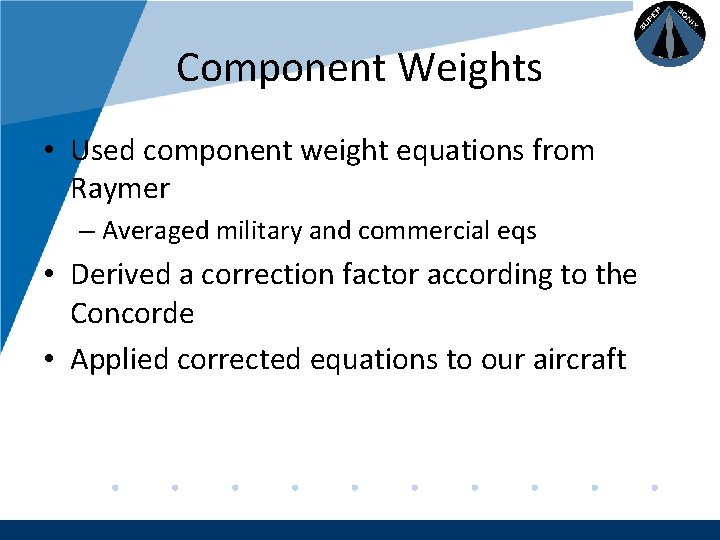
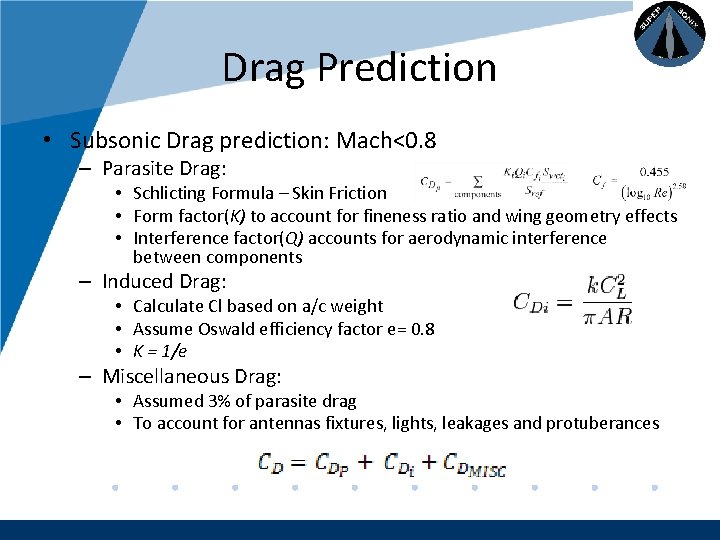
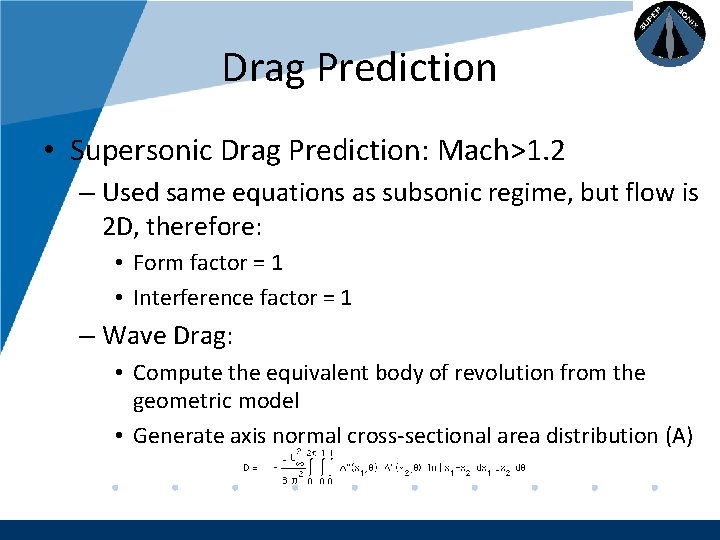
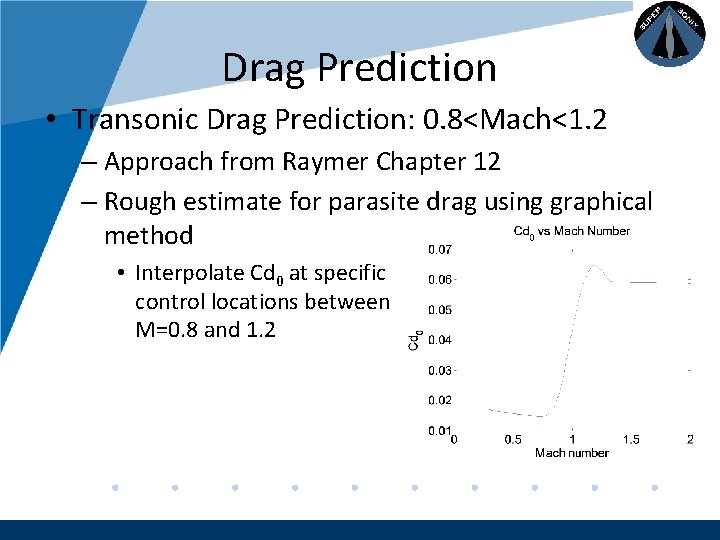
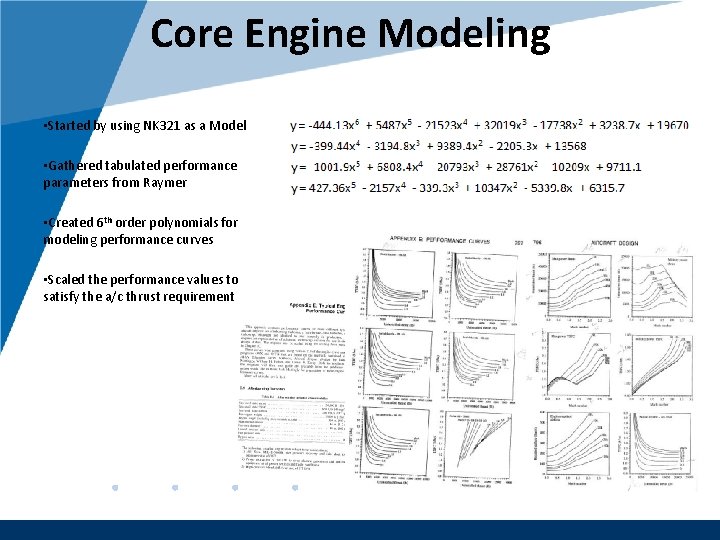
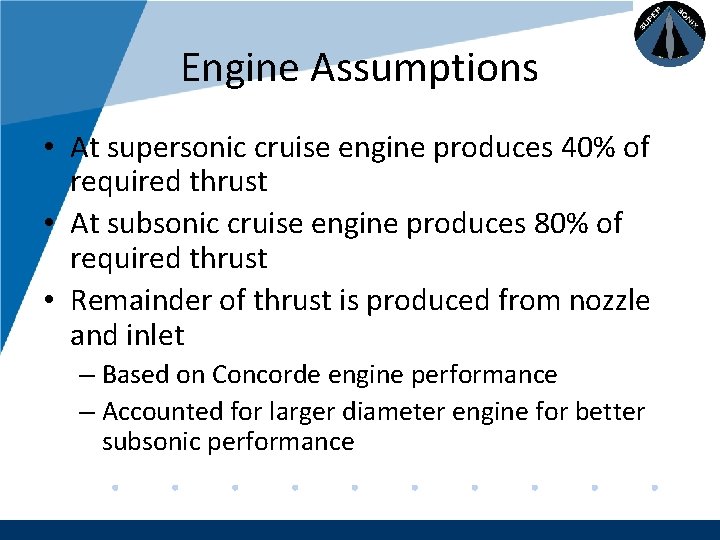
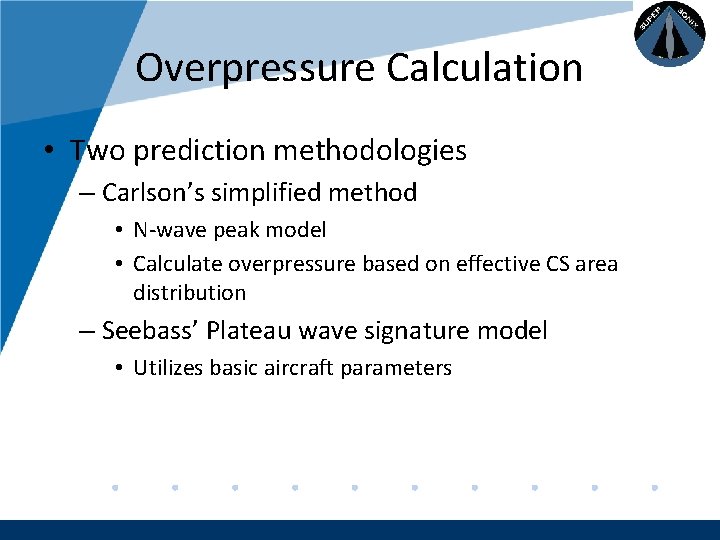
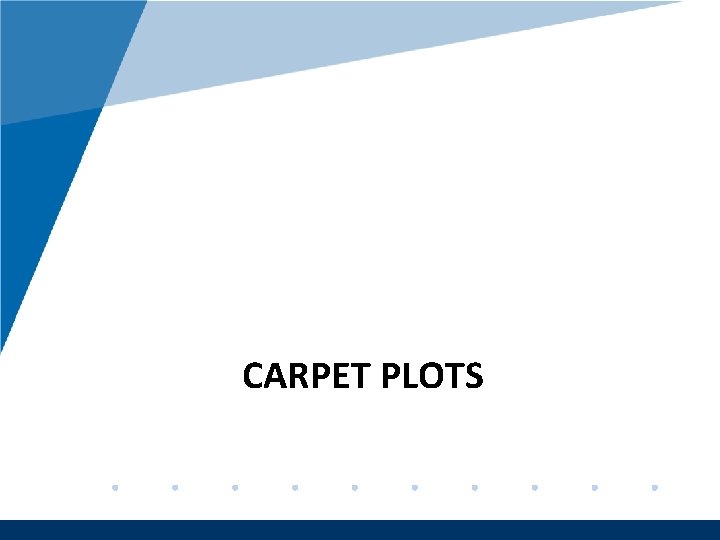
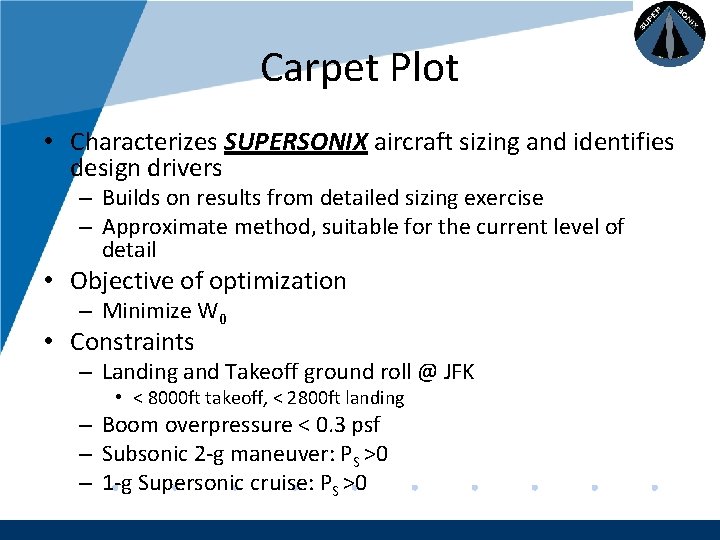
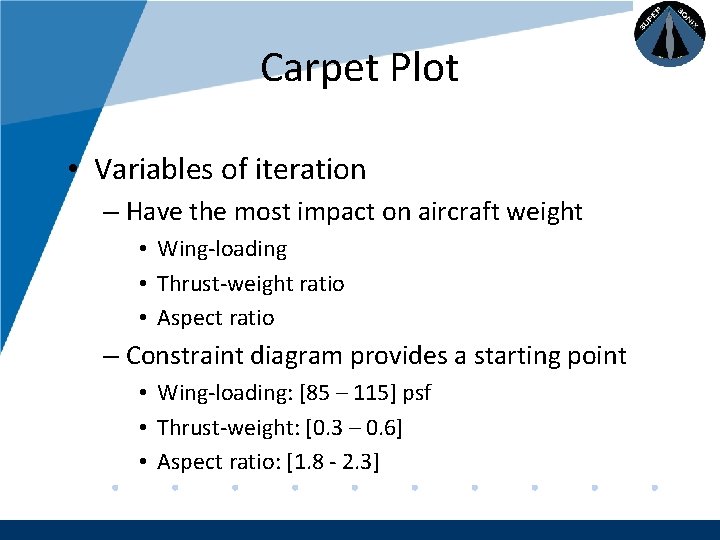
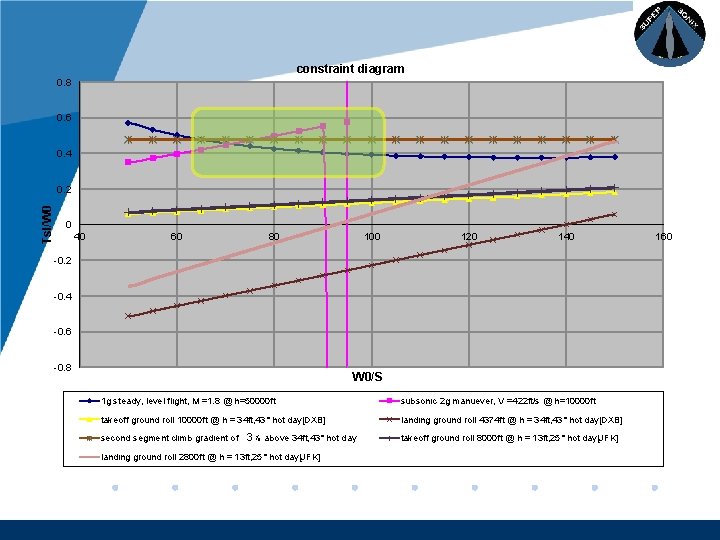

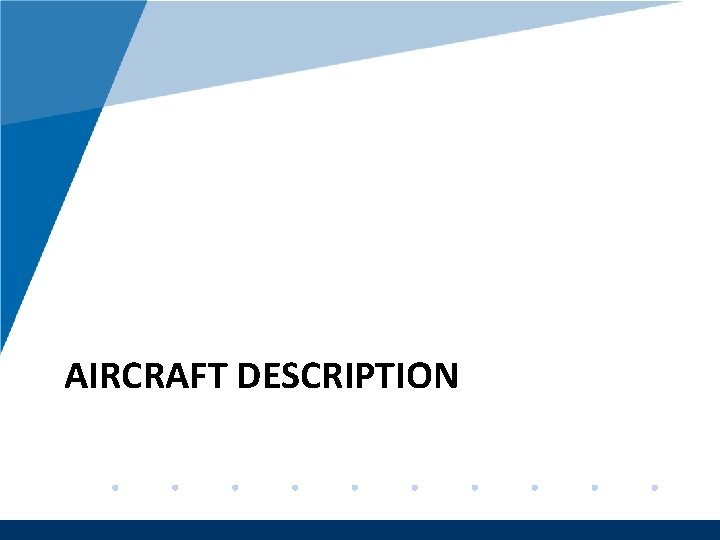
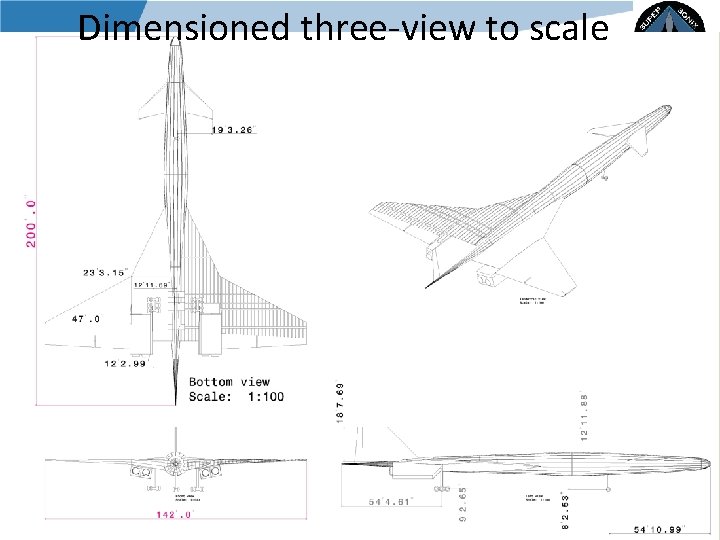
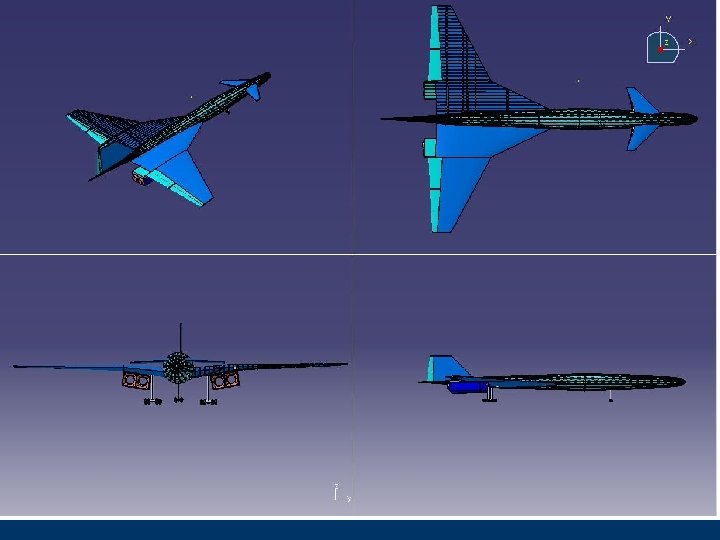
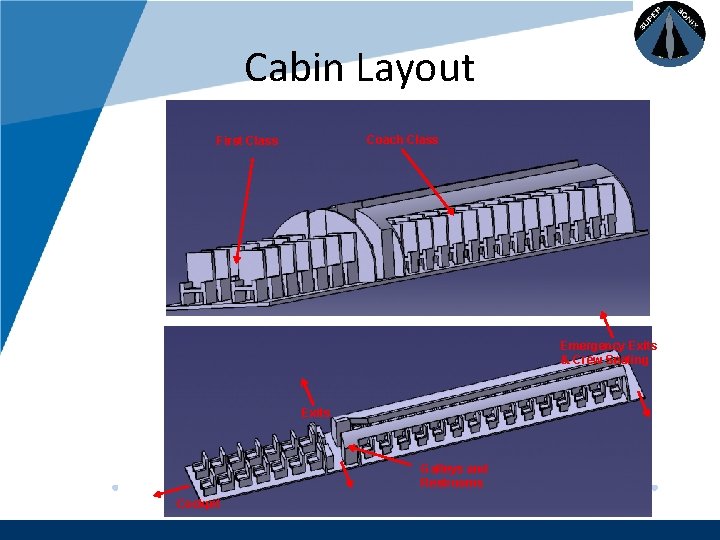
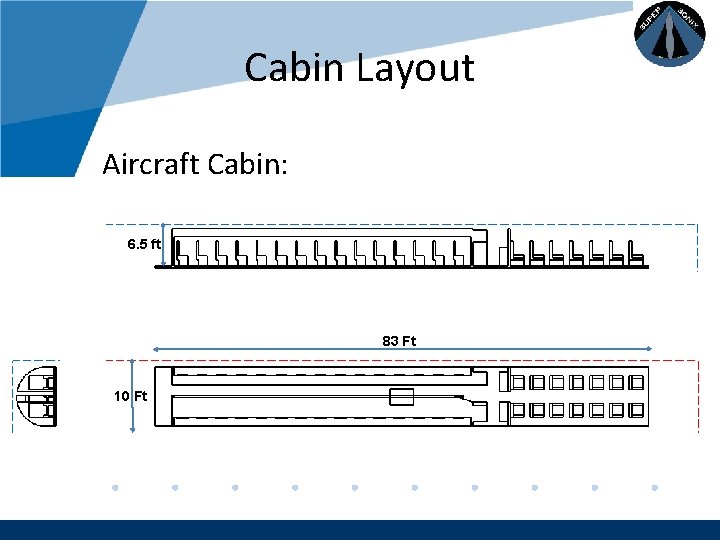
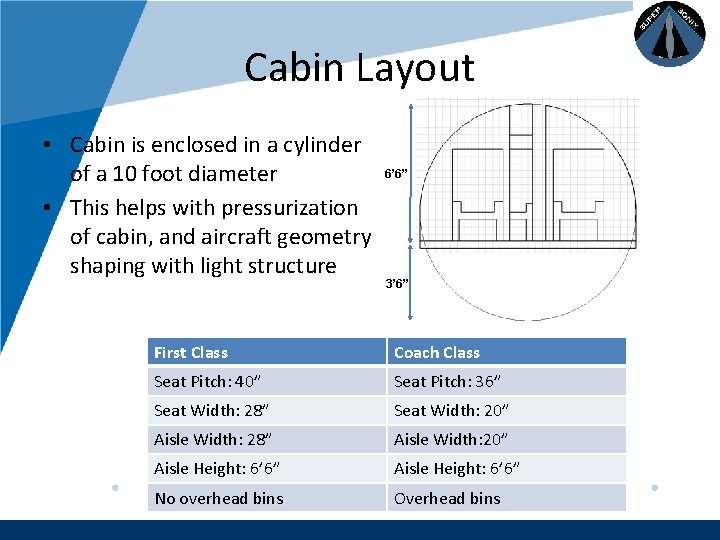

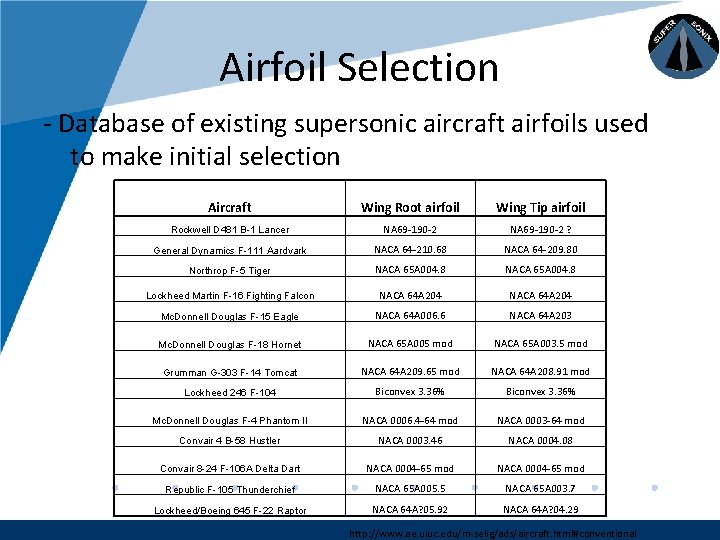
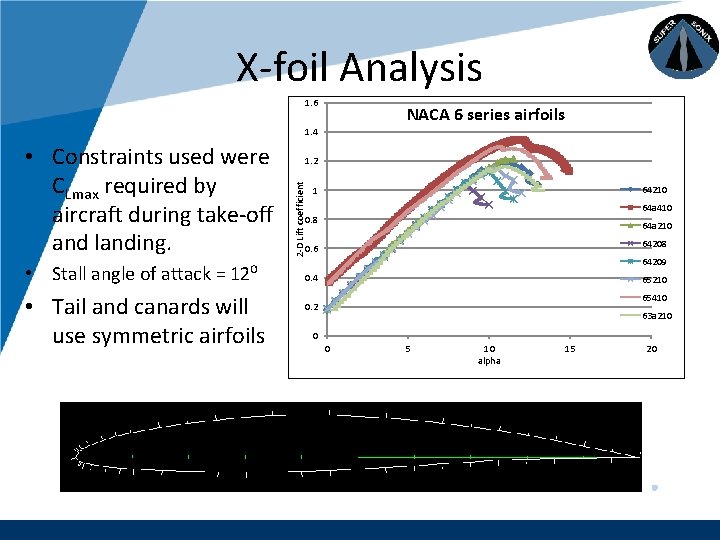
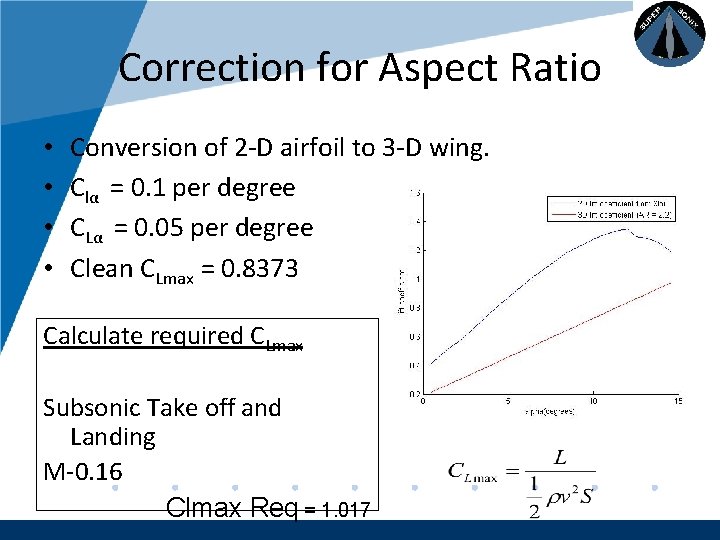
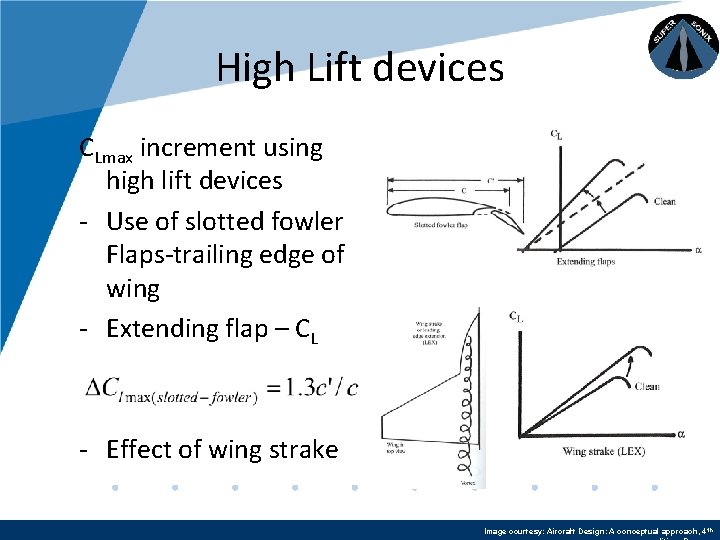
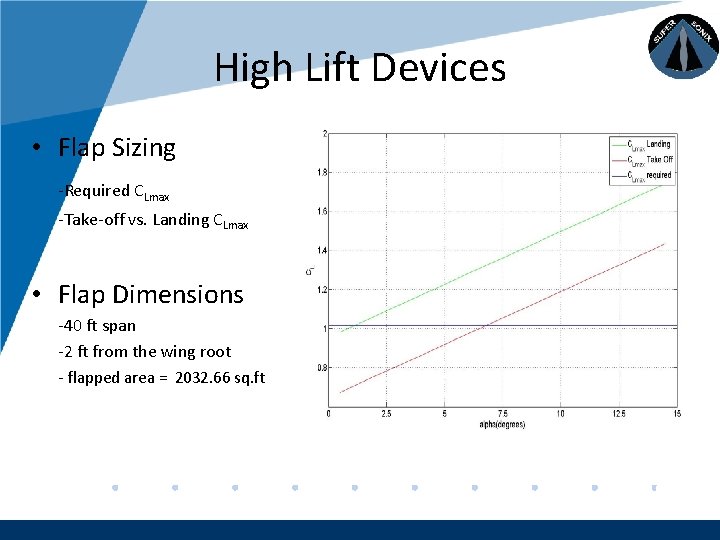
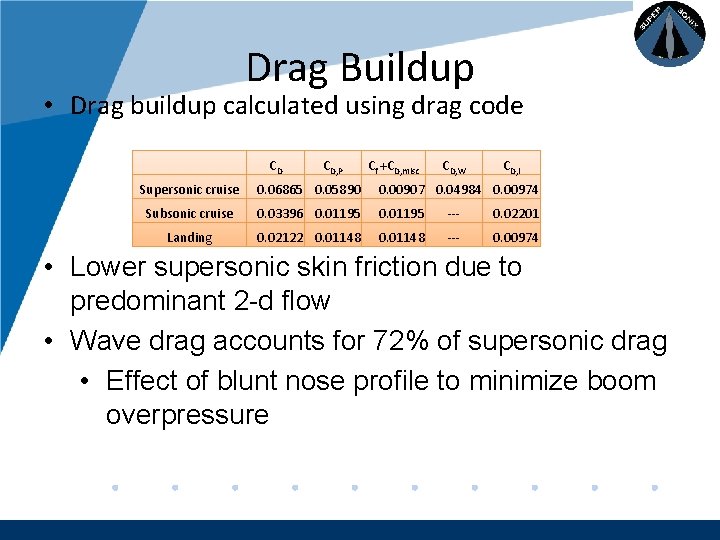
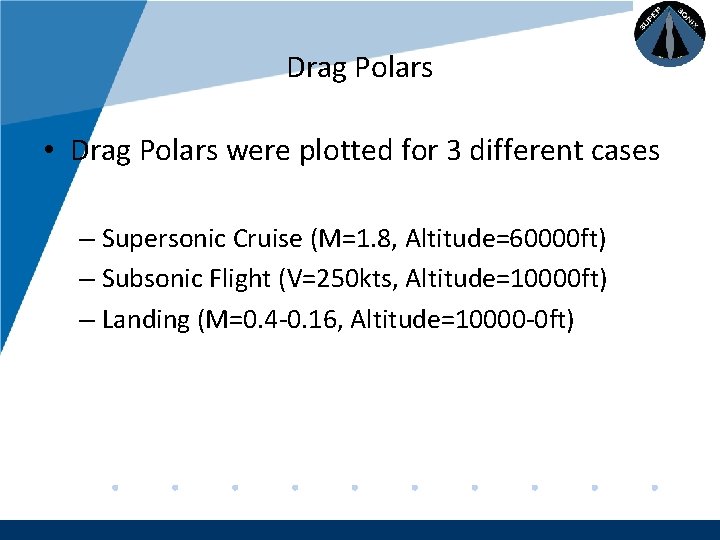
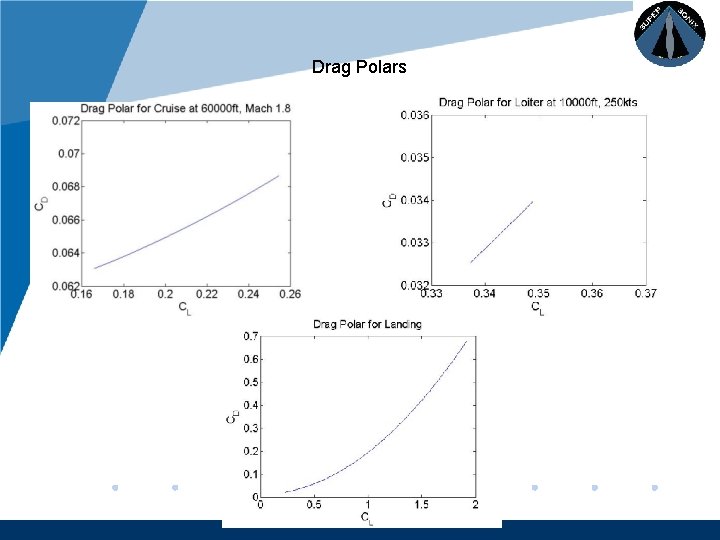
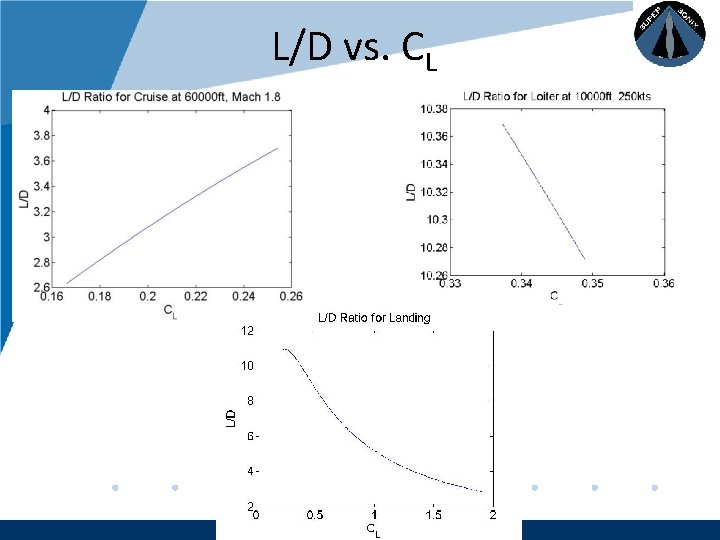
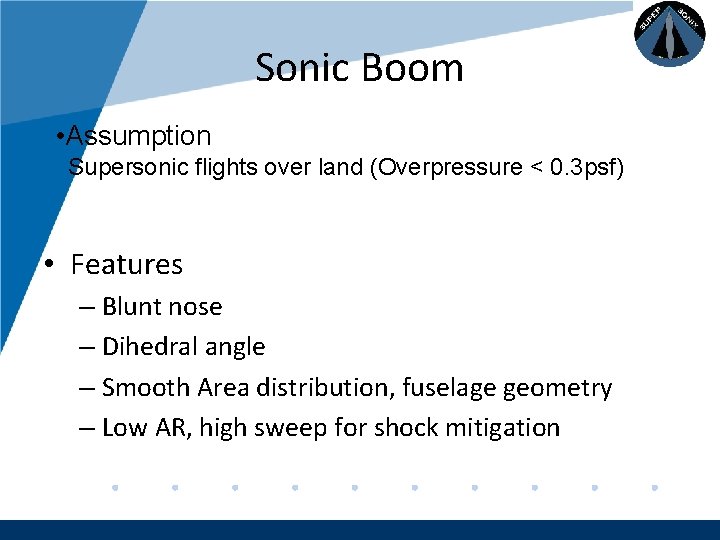
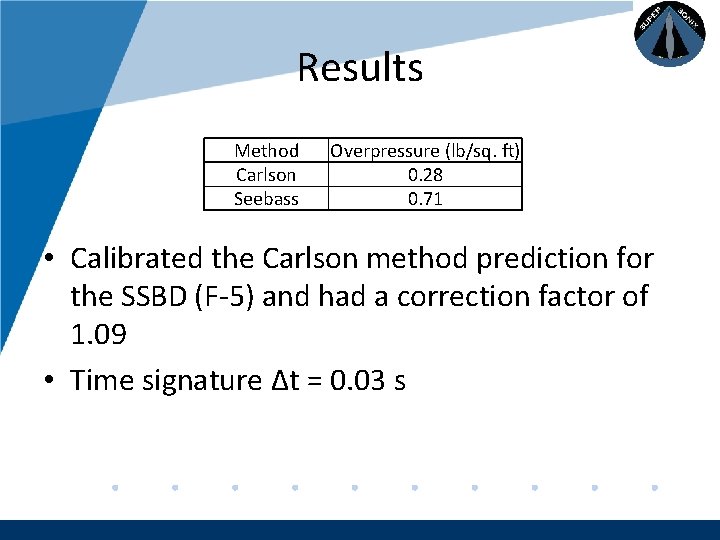
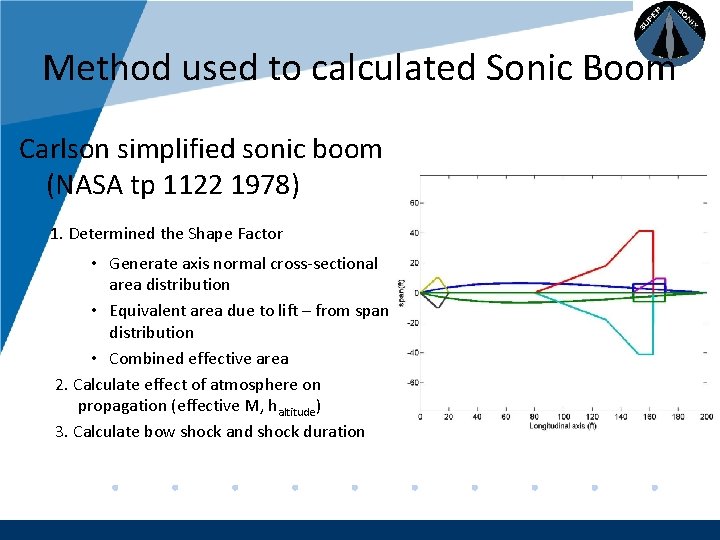
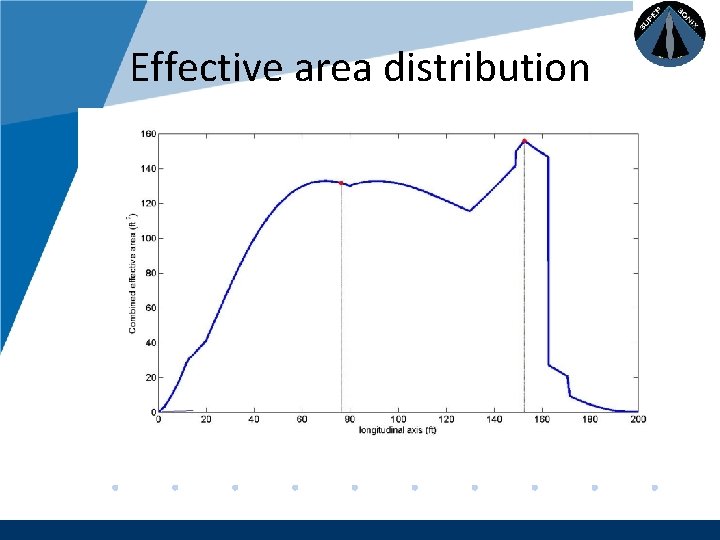
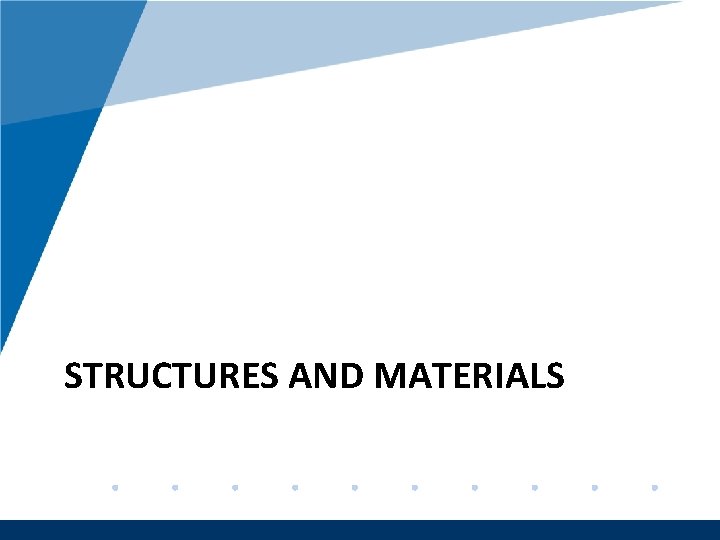
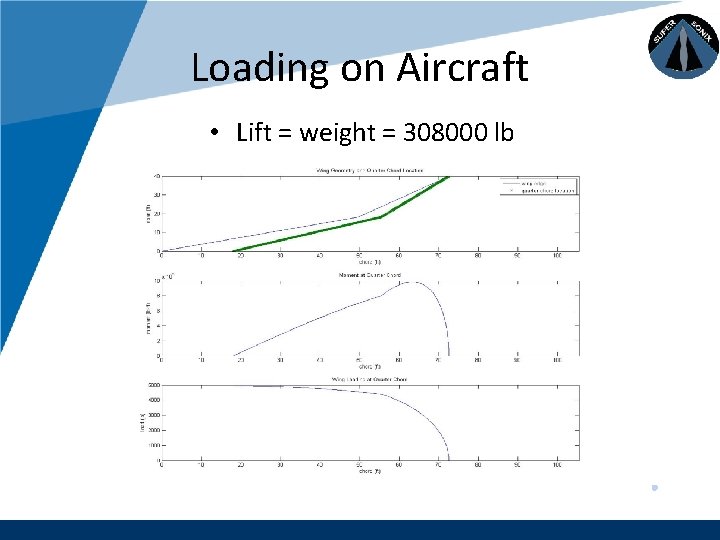
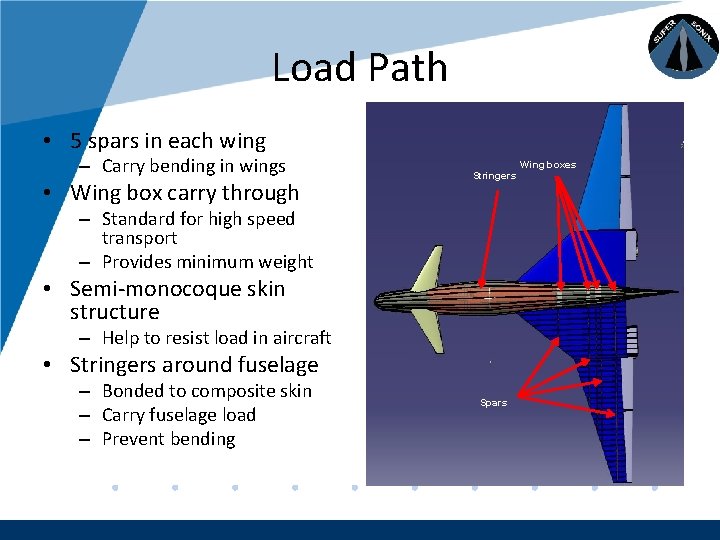
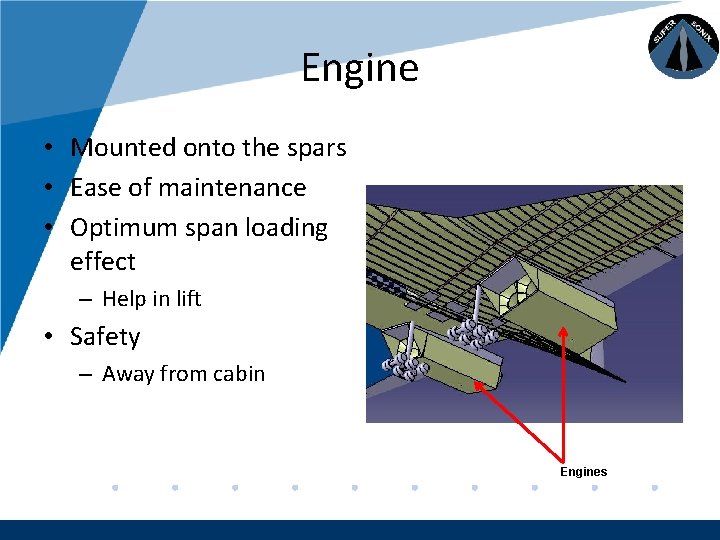
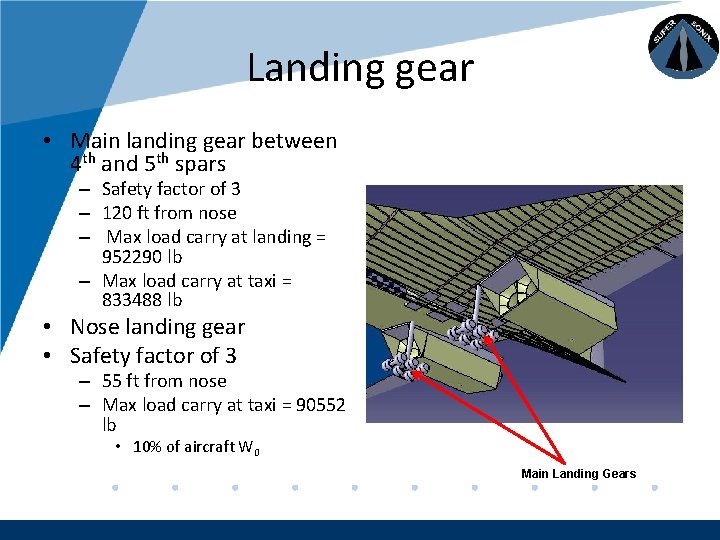
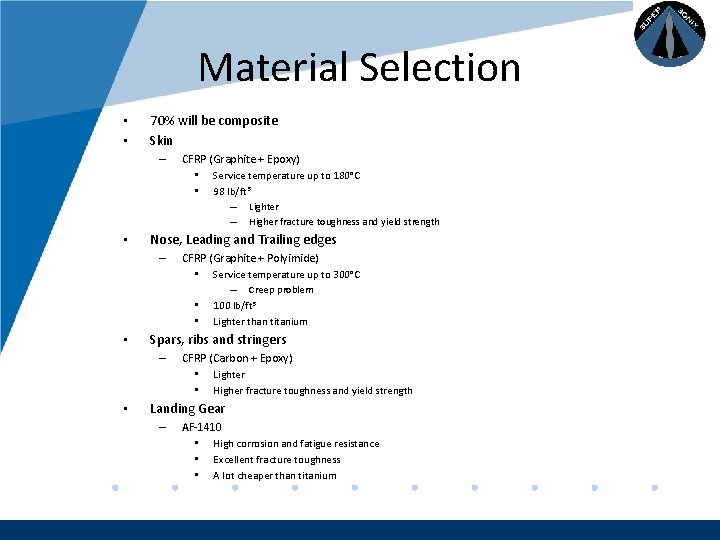
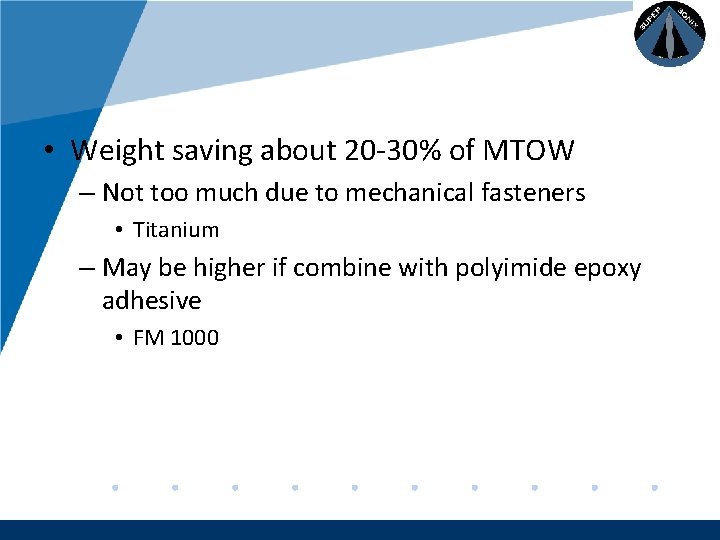
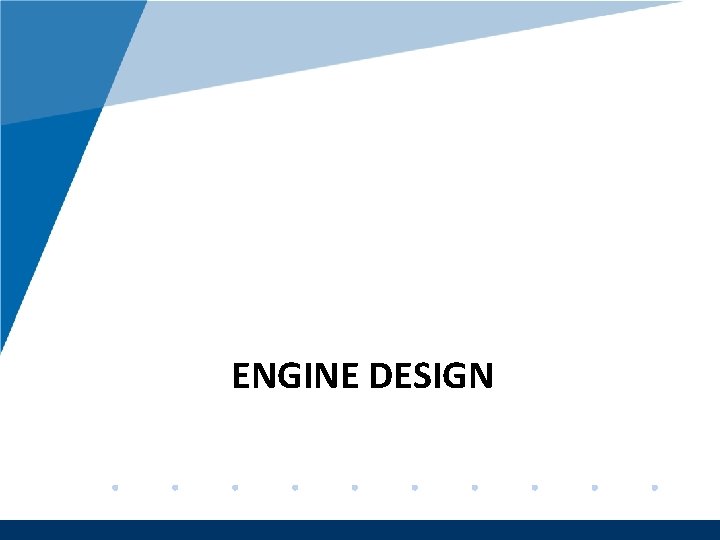
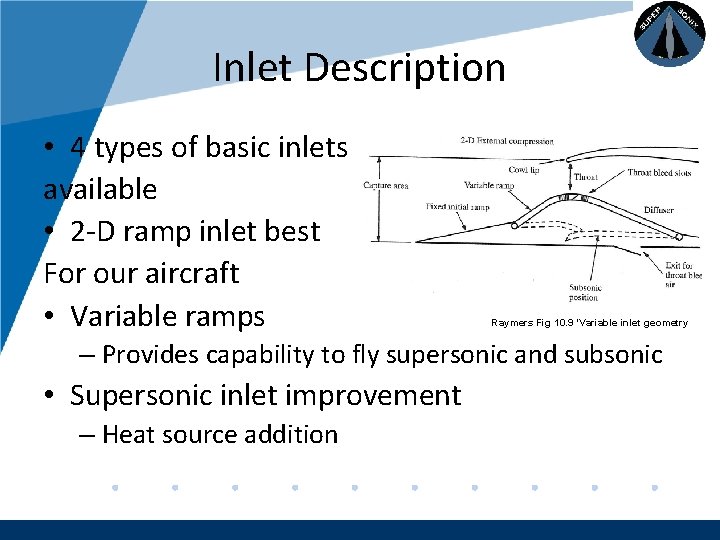
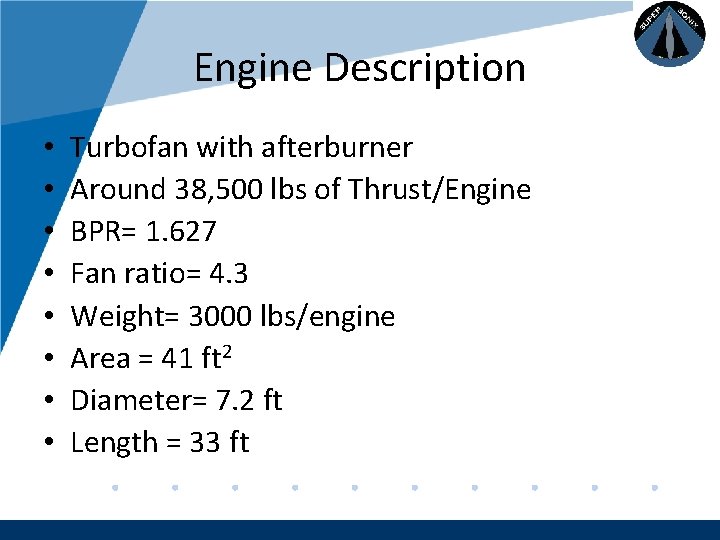
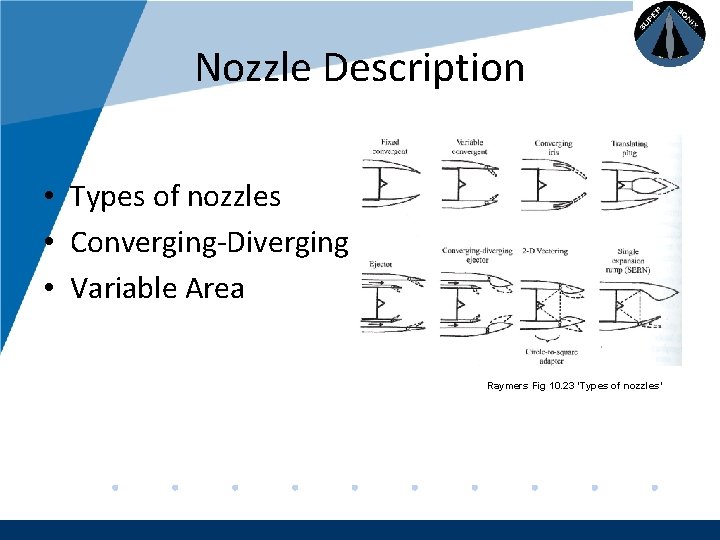
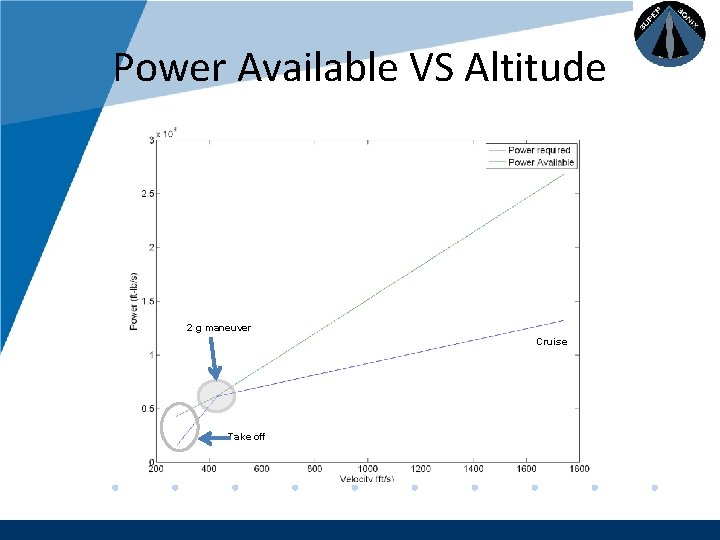

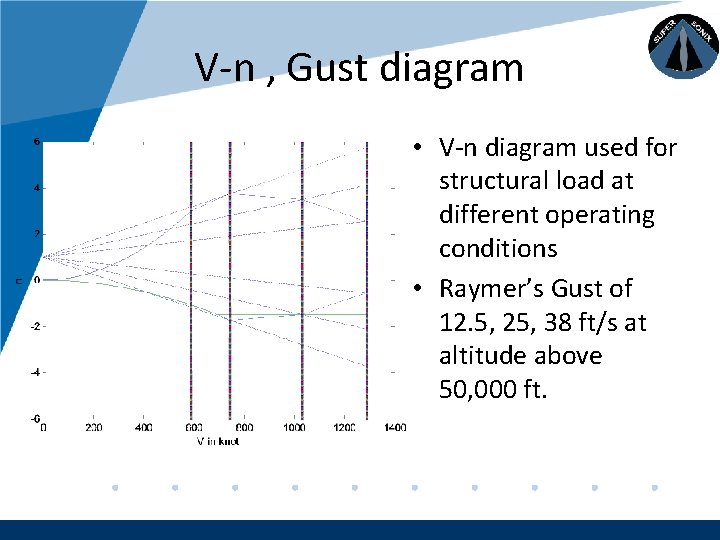
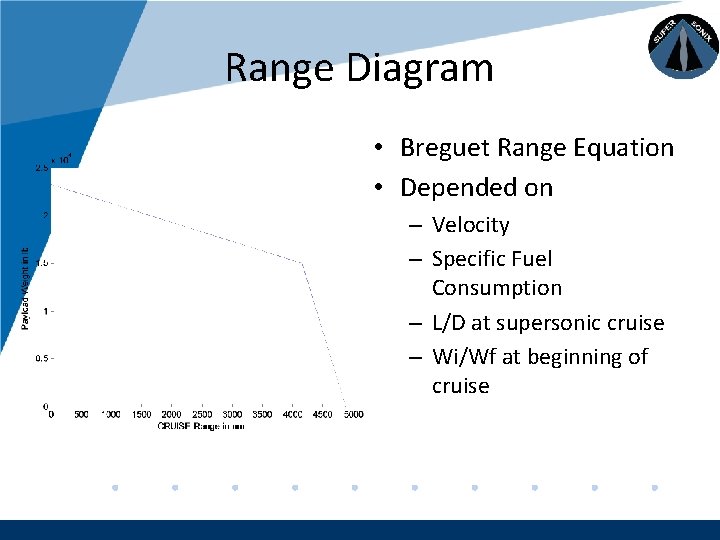
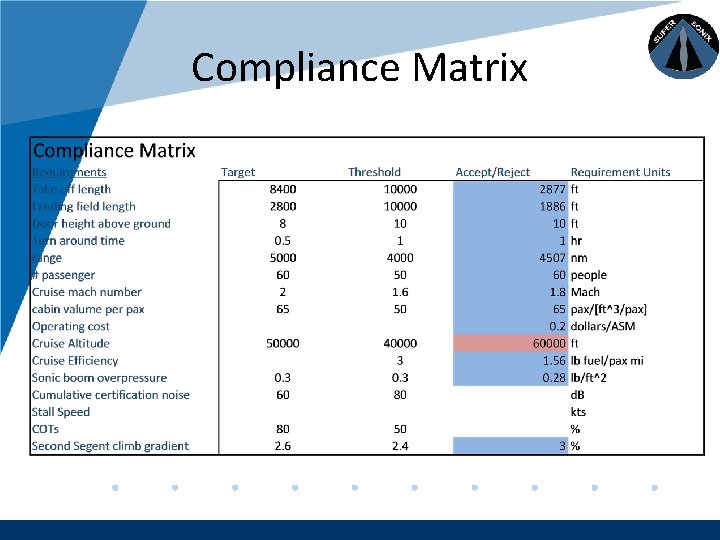
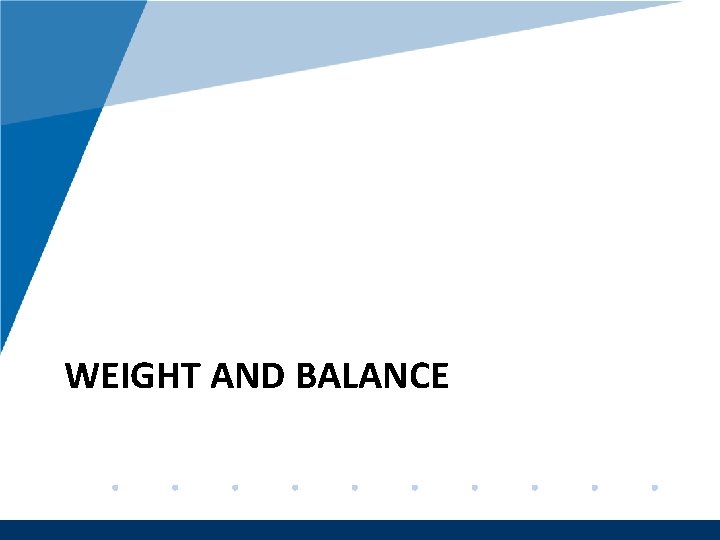
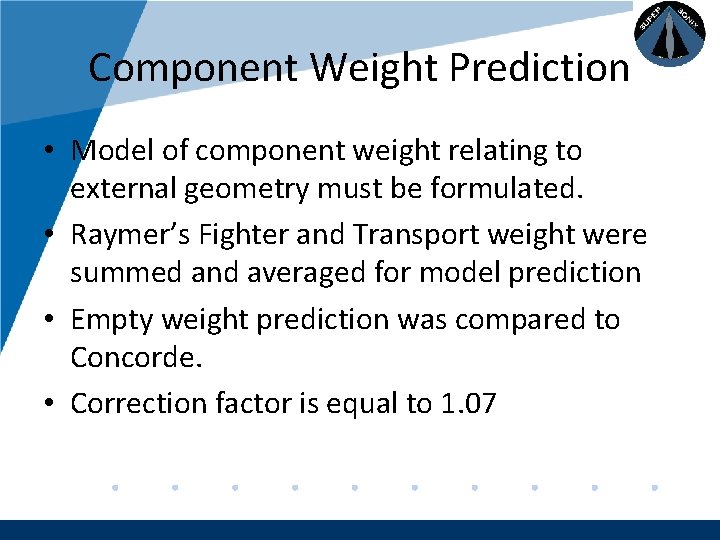
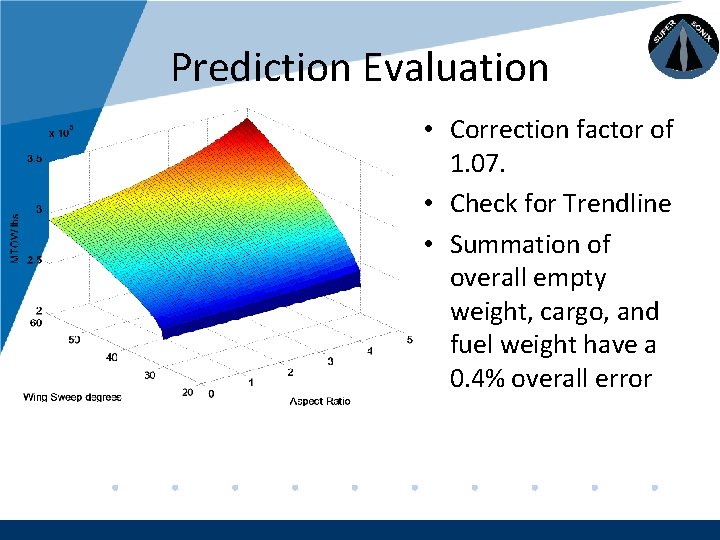
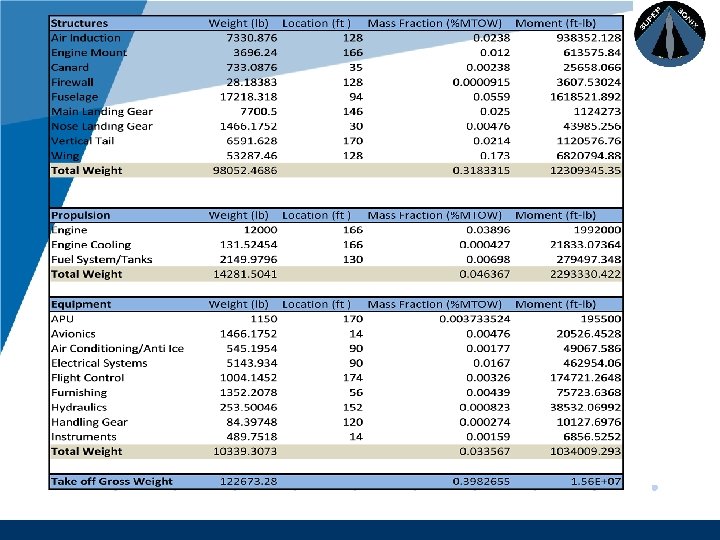
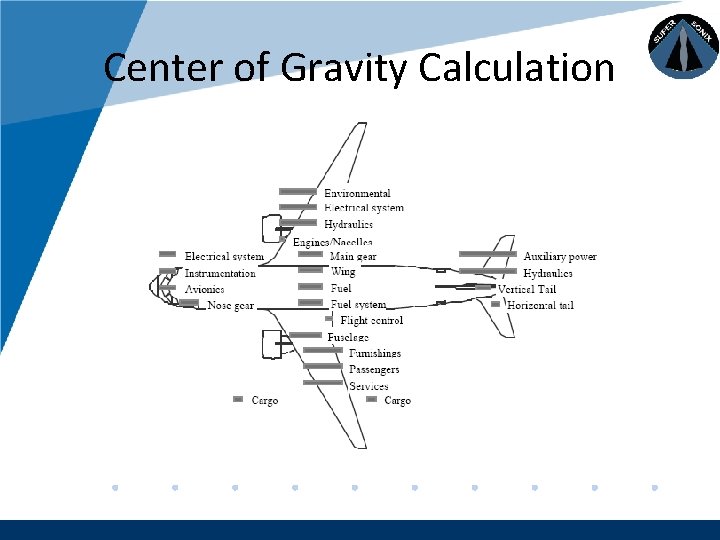
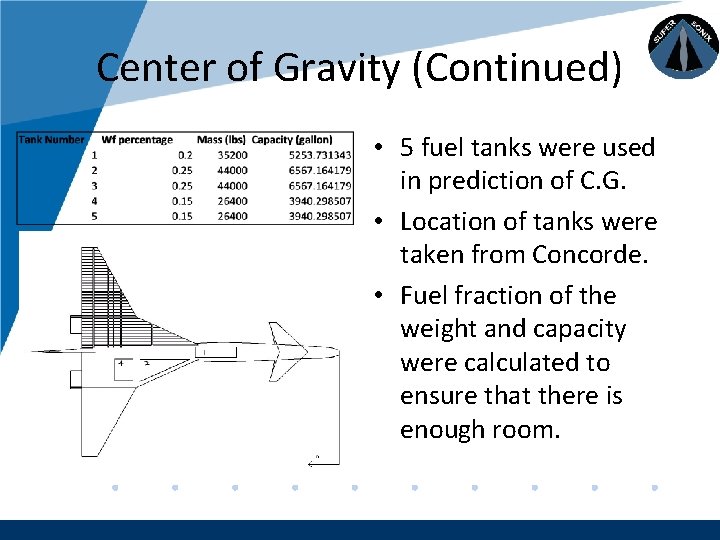
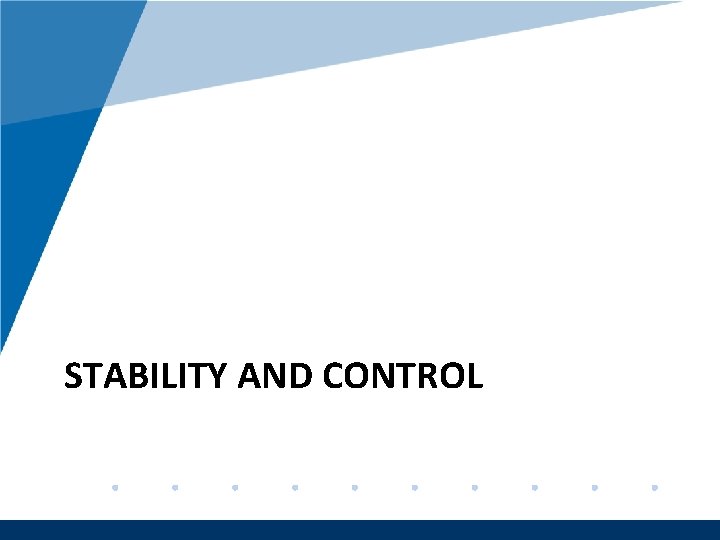
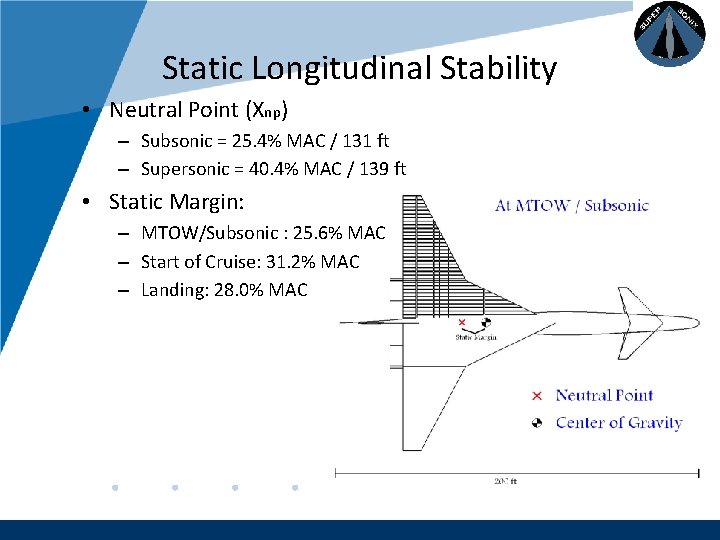
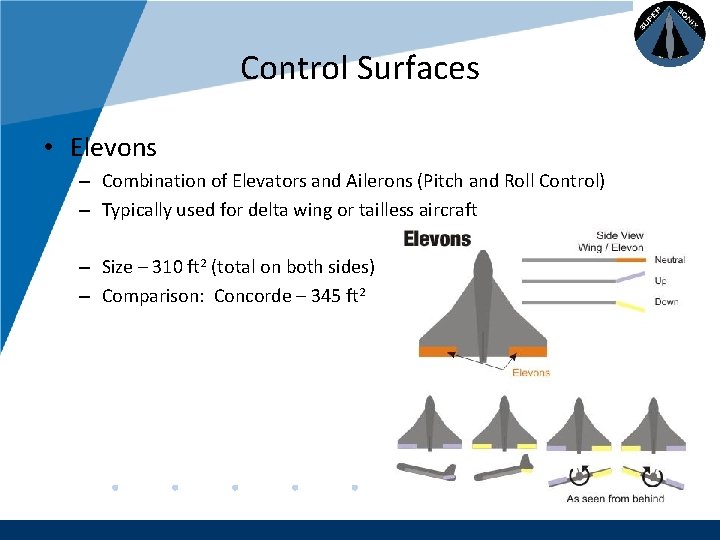
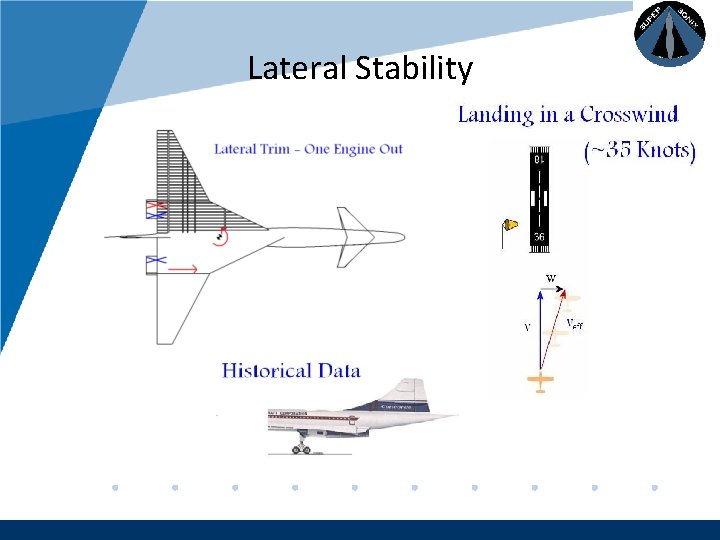
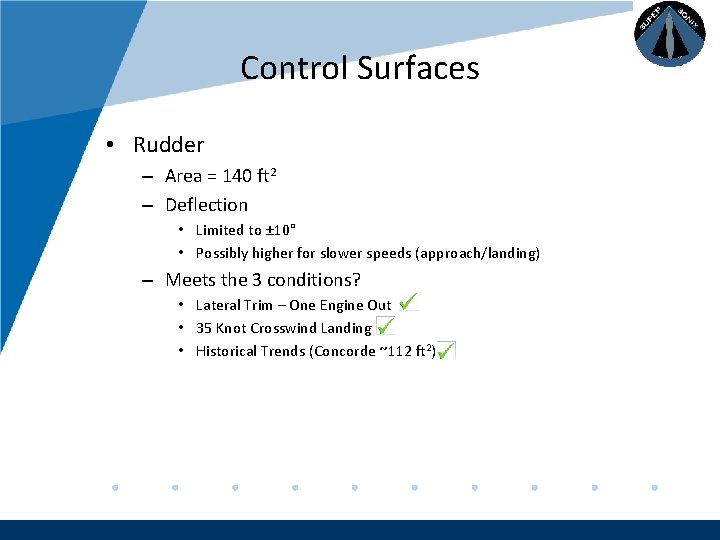
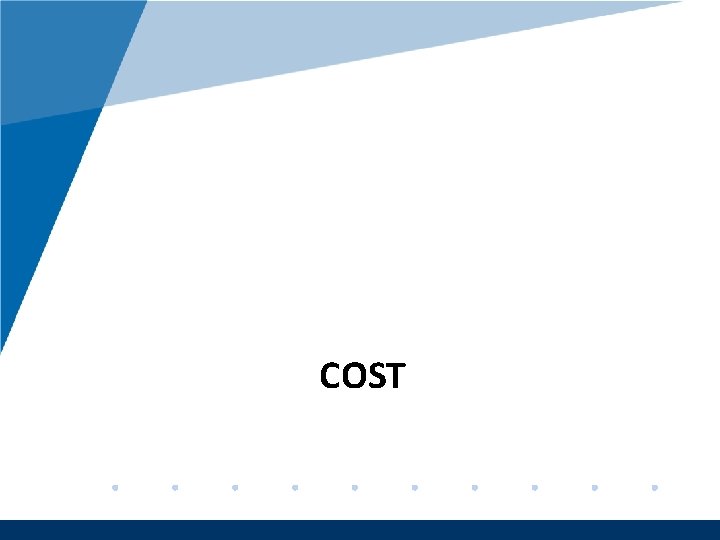
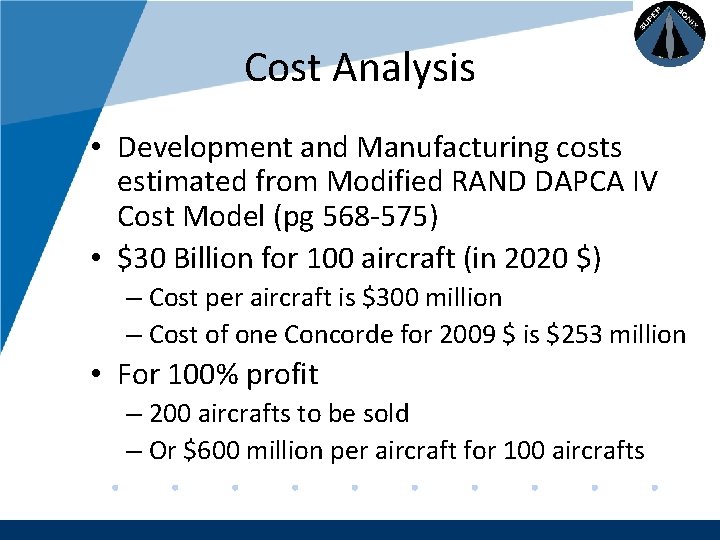
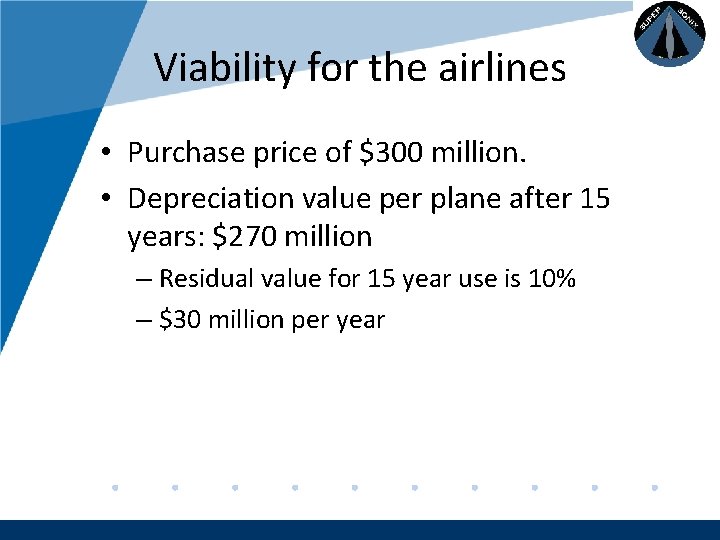
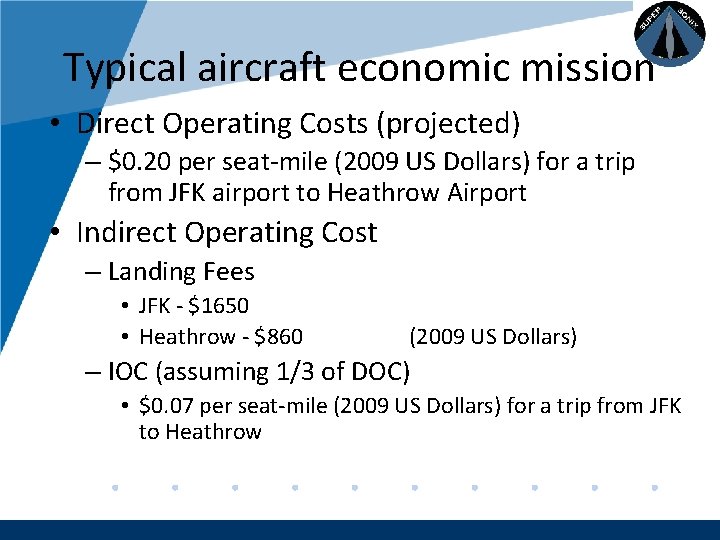
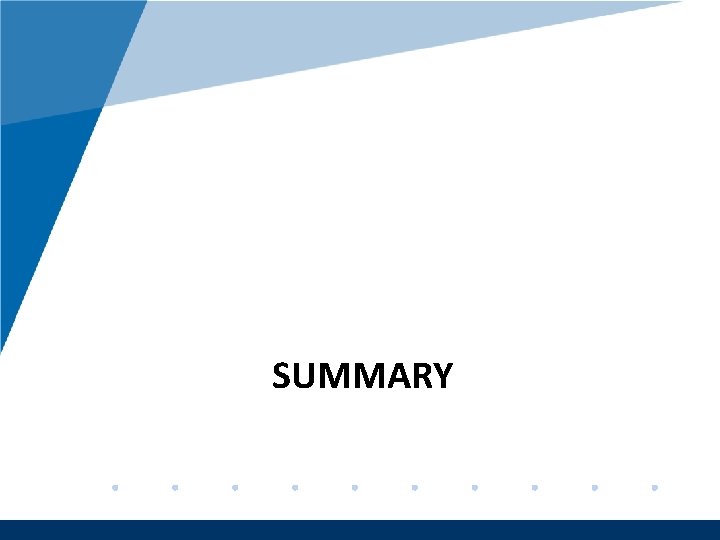
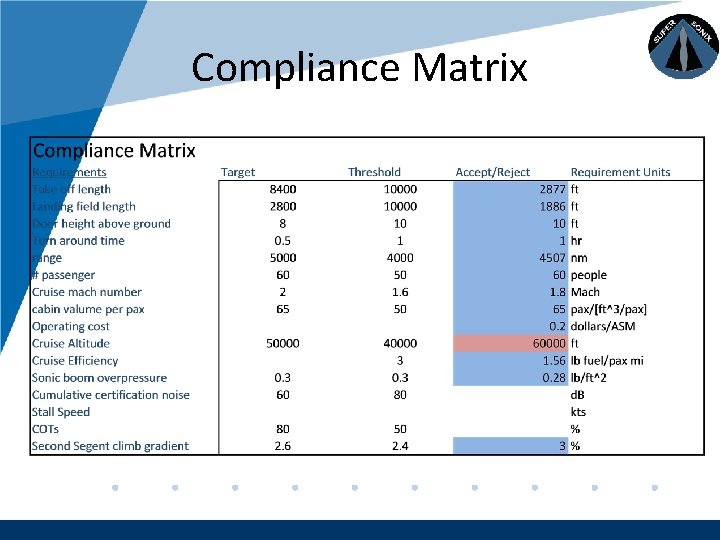
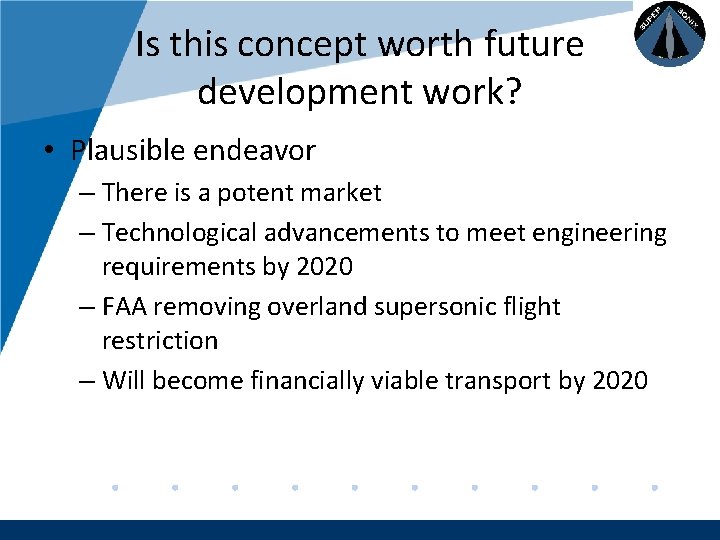

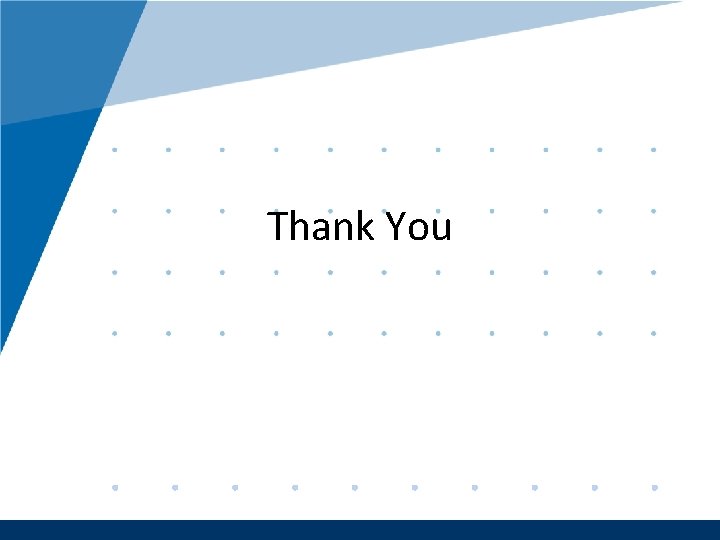
- Slides: 95
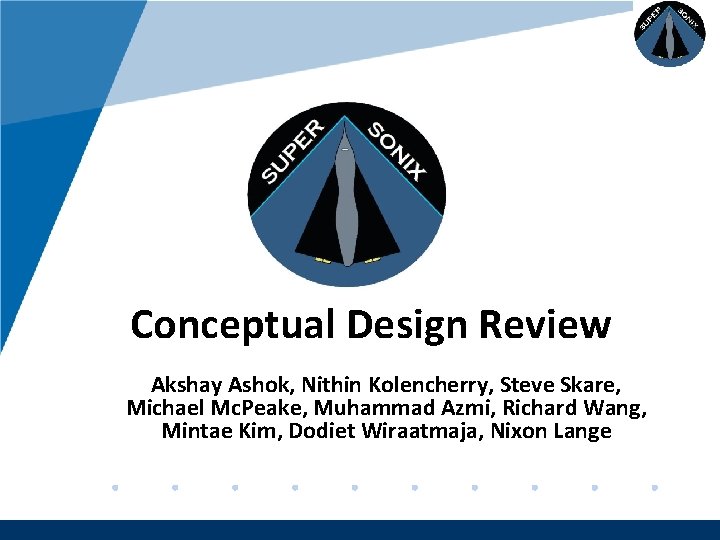
Company LOGO Conceptual Design Review Akshay Ashok, Nithin Kolencherry, Steve Skare, Michael Mc. Peake, Muhammad Azmi, Richard Wang, Mintae Kim, Dodiet Wiraatmaja, Nixon Lange www. company. com
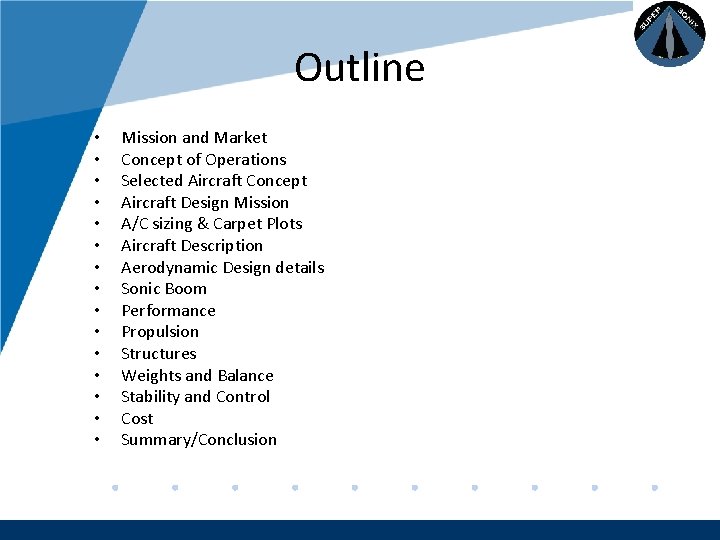
Company LOGO • • • • Outline Mission and Market Concept of Operations Selected Aircraft Concept Aircraft Design Mission A/C sizing & Carpet Plots Aircraft Description Aerodynamic Design details Sonic Boom Performance Propulsion Structures Weights and Balance Stability and Control Cost Summary/Conclusion www. company. com
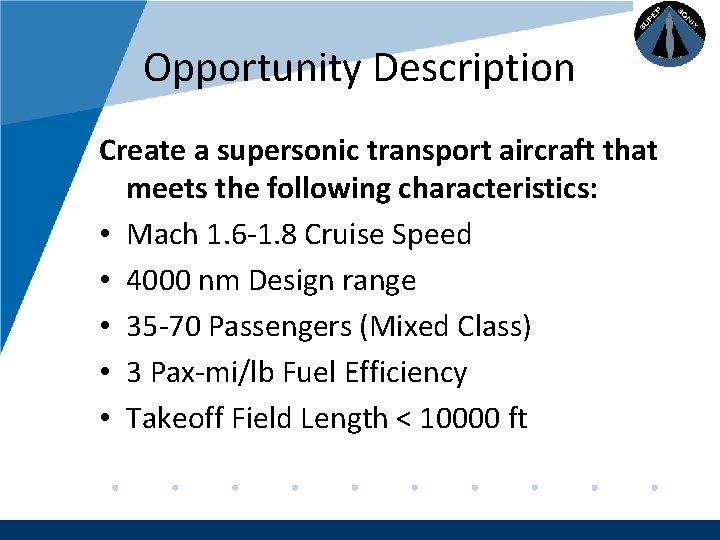
Company LOGO Opportunity Description Create a supersonic transport aircraft that meets the following characteristics: • Mach 1. 6 -1. 8 Cruise Speed • 4000 nm Design range • 35 -70 Passengers (Mixed Class) • 3 Pax-mi/lb Fuel Efficiency • Takeoff Field Length < 10000 ft www. company. com
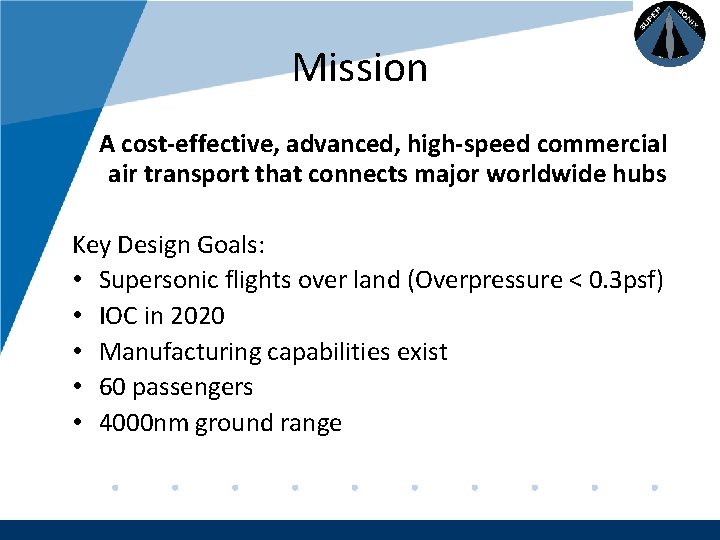
Company LOGO Mission A cost-effective, advanced, high-speed commercial air transport that connects major worldwide hubs Key Design Goals: • Supersonic flights over land (Overpressure < 0. 3 psf) • IOC in 2020 • Manufacturing capabilities exist • 60 passengers • 4000 nm ground range www. company. com
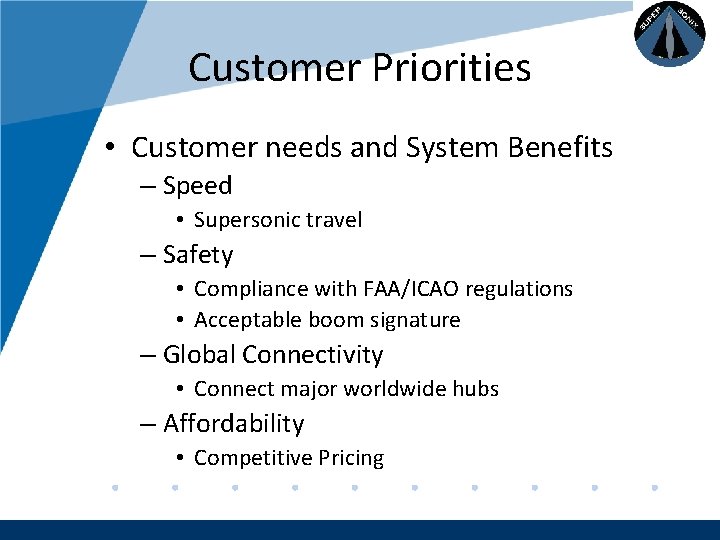
Company LOGO Customer Priorities • Customer needs and System Benefits – Speed • Supersonic travel – Safety • Compliance with FAA/ICAO regulations • Acceptable boom signature – Global Connectivity • Connect major worldwide hubs – Affordability • Competitive Pricing www. company. com
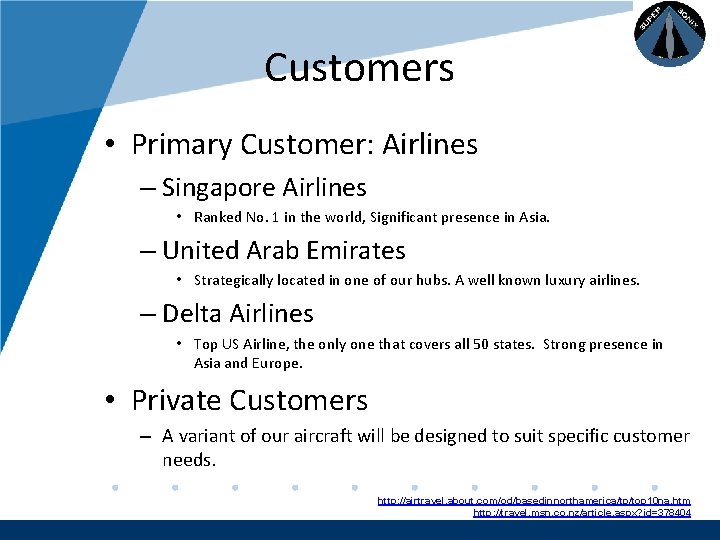
Company LOGO Customers • Primary Customer: Airlines – Singapore Airlines • Ranked No. 1 in the world, Significant presence in Asia. – United Arab Emirates • Strategically located in one of our hubs. A well known luxury airlines. – Delta Airlines • Top US Airline, the only one that covers all 50 states. Strong presence in Asia and Europe. • Private Customers – A variant of our aircraft will be designed to suit specific customer needs. http: //airtravel. about. com/od/basedinnorthamerica/tp/top 10 na. htm http: //travel. msn. co. nz/article. aspx? id=378404 www. company. com
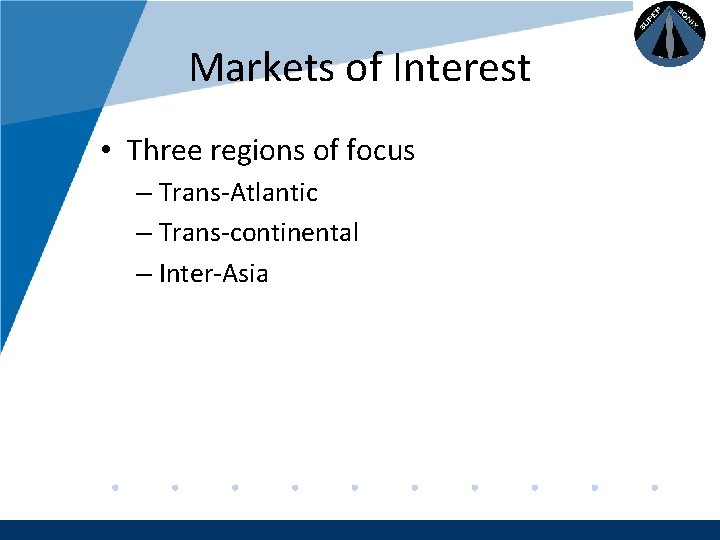
Company LOGO Markets of Interest • Three regions of focus – Trans-Atlantic – Trans-continental – Inter-Asia www. company. com
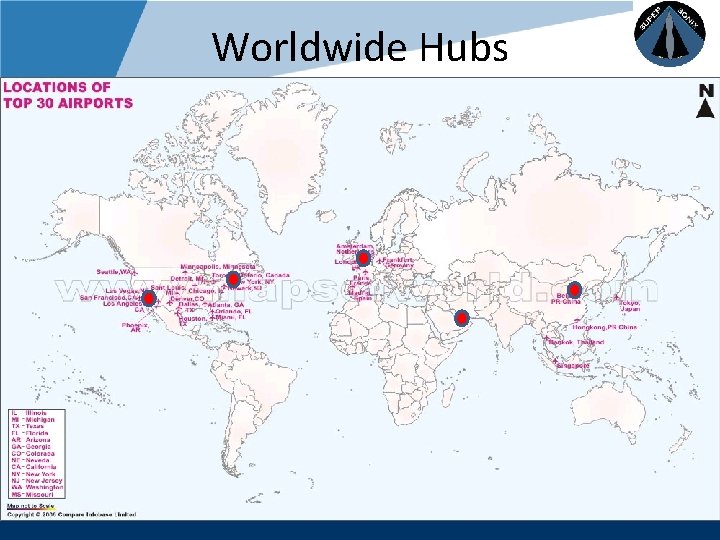
Company LOGO Worldwide Hubs www. company. com
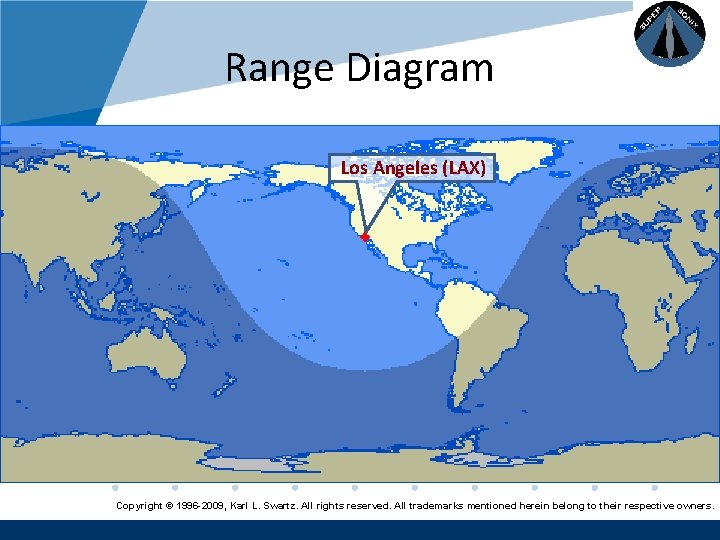
Company LOGO Range Diagram Los Angeles (LAX) Copyright © 1996 -2009, Karl L. Swartz. All rights reserved. All trademarks mentioned herein belong to their respective owners. www. company. com
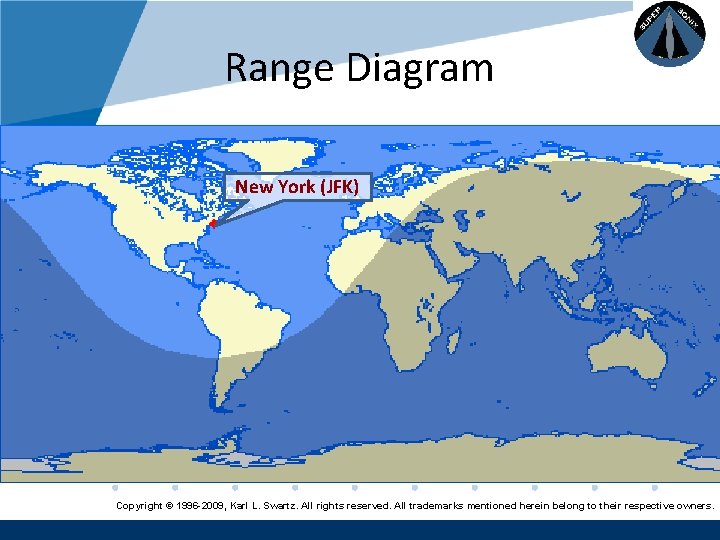
Company LOGO Range Diagram New York (JFK) Copyright © 1996 -2009, Karl L. Swartz. All rights reserved. All trademarks mentioned herein belong to their respective owners. www. company. com
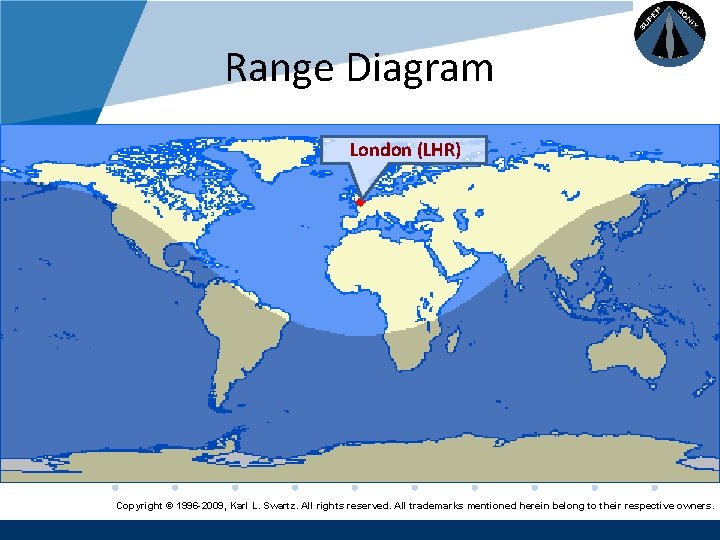
Company LOGO Range Diagram London (LHR) Copyright © 1996 -2009, Karl L. Swartz. All rights reserved. All trademarks mentioned herein belong to their respective owners. www. company. com
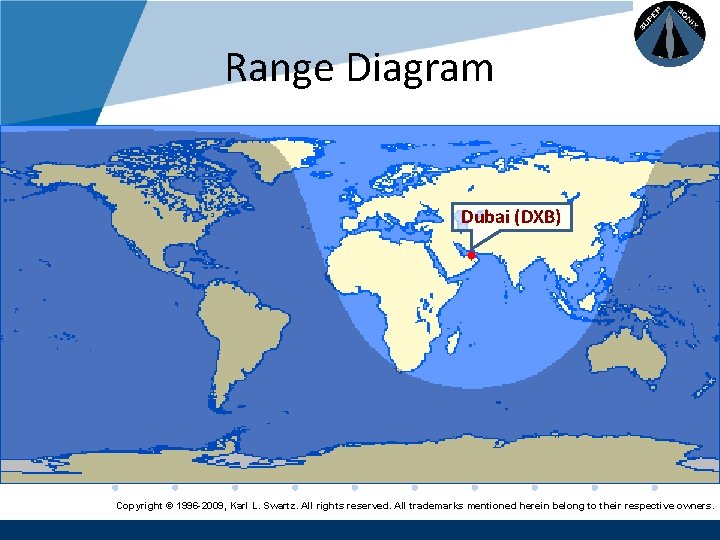
Company LOGO Range Diagram Dubai (DXB) Copyright © 1996 -2009, Karl L. Swartz. All rights reserved. All trademarks mentioned herein belong to their respective owners. www. company. com
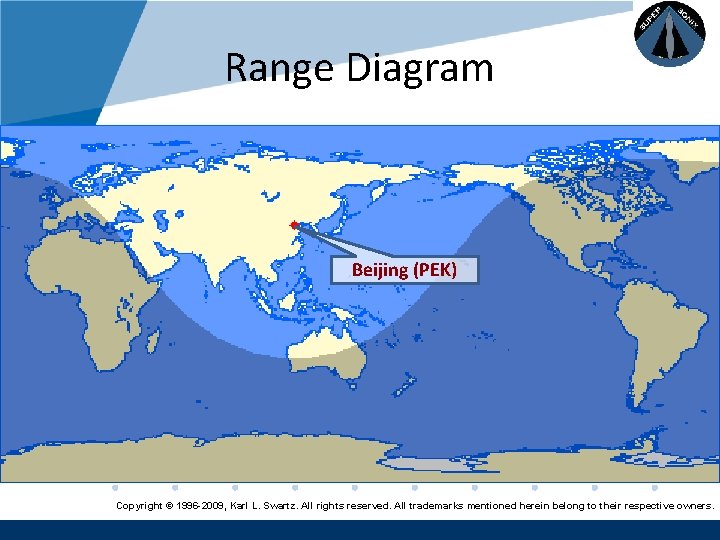
Company LOGO Range Diagram Beijing (PEK) Copyright © 1996 -2009, Karl L. Swartz. All rights reserved. All trademarks mentioned herein belong to their respective owners. www. company. com
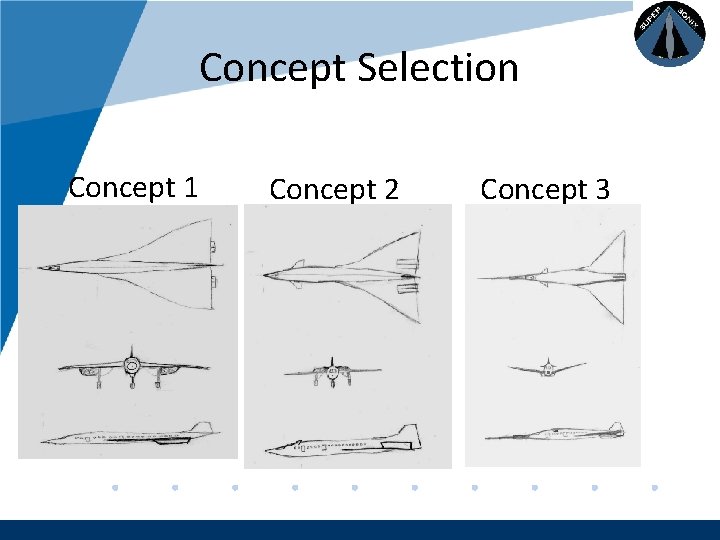
Company LOGO Concept 1 Concept Selection Concept 2 Concept 3 www. company. com
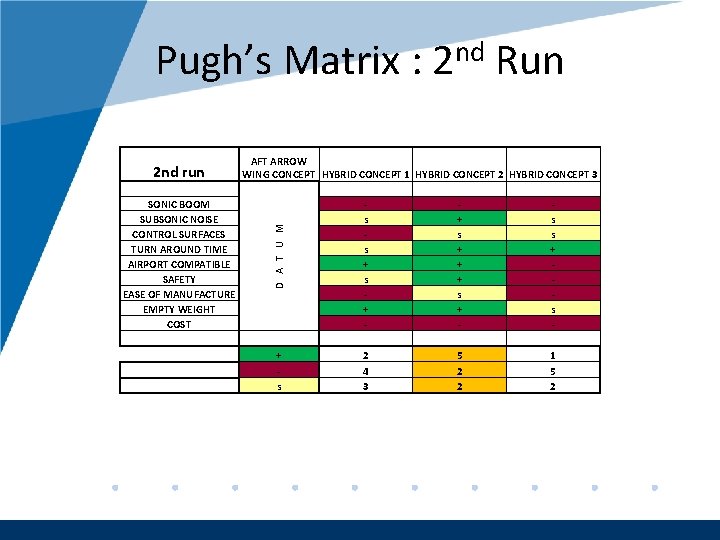
Pugh’s Matrix : 2 nd Run AFT ARROW WING CONCEPT HYBRID CONCEPT 1 HYBRID CONCEPT 2 HYBRID CONCEPT 3 SONIC BOOM SUBSONIC NOISE s + s CONTROL SURFACES s s TURN AROUND TIME s + + AIRPORT COMPATIBLE + + SAFETY s + EASE OF MANUFACTURE s EMPTY WEIGHT + + s COST + 2 5 1 4 2 5 s 3 2 2 D A T U M 2 nd run Company LOGO www. company. com
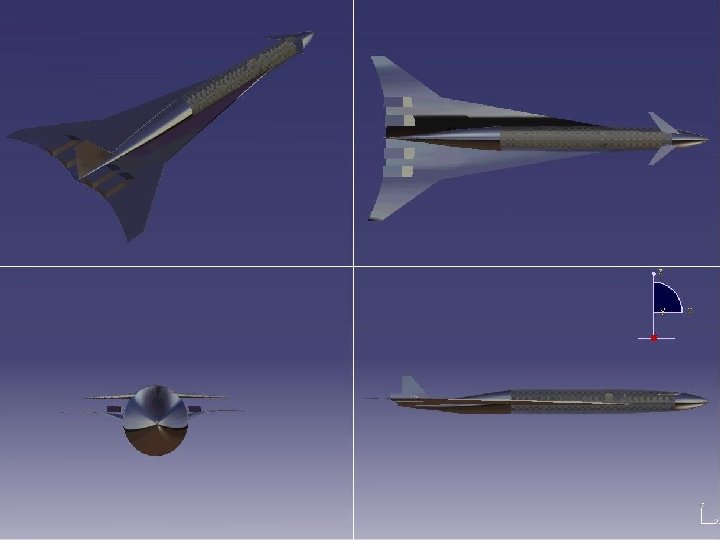
Company LOGO www. company. com
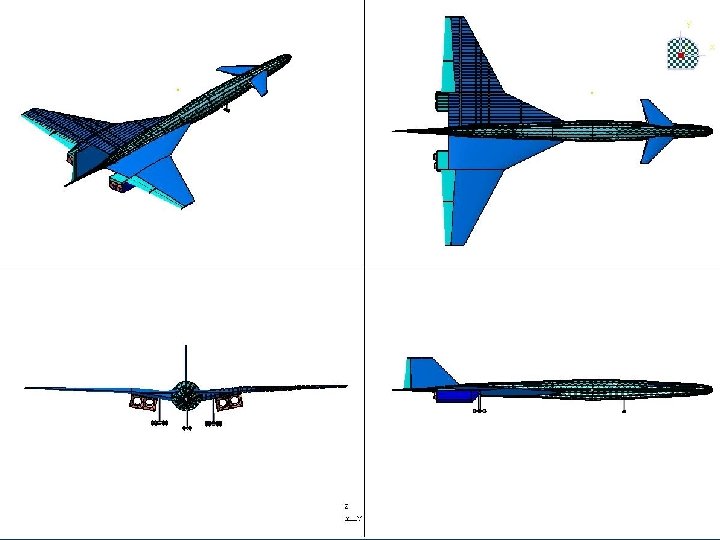
Company LOGO Aircraft Walk-Around www. company. com
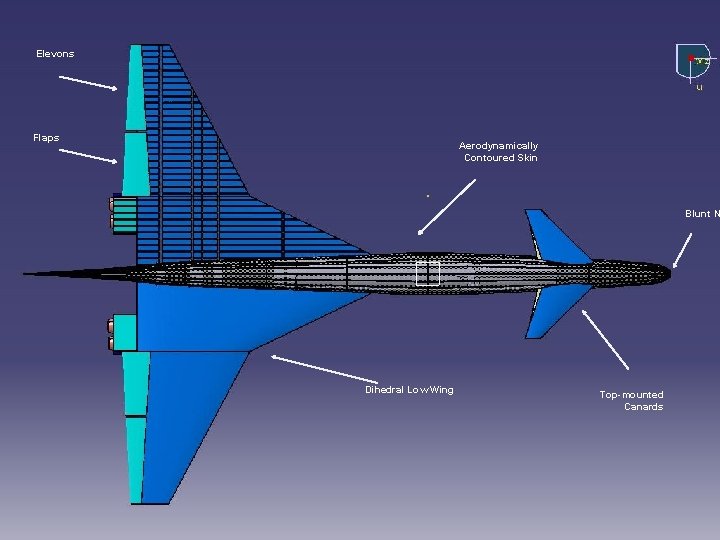
Company LOGO Elevons Flaps Aerodynamically Contoured Skin Blunt N Dihedral Low Wing Top-mounted Canards www. company. com
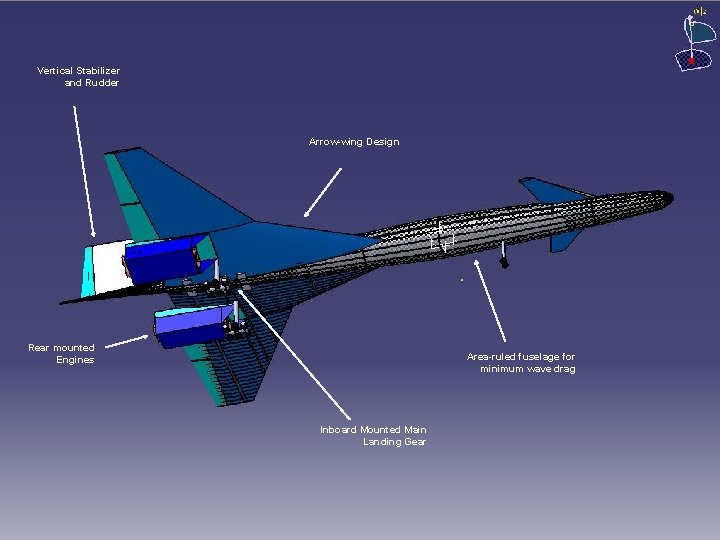
Company LOGO Vertical Stabilizer and Rudder Arrow-wing Design Rear mounted Engines Area-ruled fuselage for minimum wave drag Inboard Mounted Main Landing Gear www. company. com
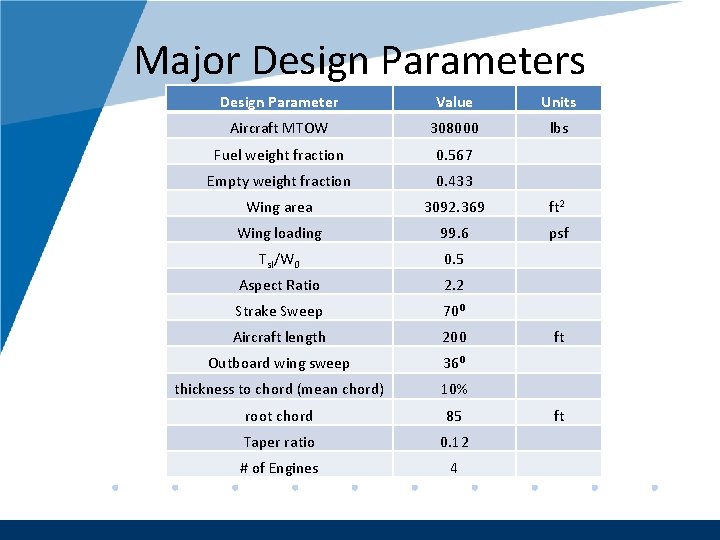
Company LOGO Major Design Parameters Design Parameter Value Units Aircraft MTOW 308000 lbs Fuel weight fraction 0. 567 Empty weight fraction 0. 433 Wing area 3092. 369 ft 2 Wing loading 99. 6 psf Tsl/W 0 0. 5 Aspect Ratio 2. 2 Strake Sweep 70⁰ Aircraft length 200 ft Outboard wing sweep 36⁰ thickness to chord (mean chord) 10% root chord 85 ft Taper ratio 0. 12 # of Engines 4 www. company. com
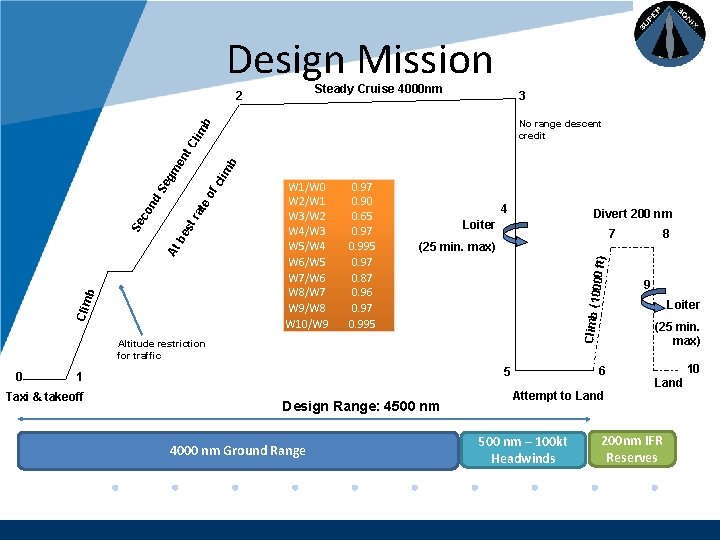
Company LOGO Design Mission Steady Cruise 4000 nm 2 3 0. 97 0. 90 0. 65 0. 97 0. 995 0. 97 0. 87 0. 96 0. 97 0. 995 4 Divert 200 nm Loiter 7 (25 min. max) 0000 ft) W 1/W 0 W 2/W 1 W 3/W 2 W 4/W 3 W 5/W 4 W 6/W 5 W 7/W 6 W 8/W 7 W 9/W 8 W 10/W 9 Climb (1 te ra st be Clim b At Se co nd of cli Se g me mb nt Cl im b No range descent credit Altitude restriction for traffic 0 Taxi & takeoff Design Range: 4500 nm 4000 nm Ground Range (25 min. max) Attempt to Land 500 nm – 100 kt Headwinds 9 Loiter 6 5 1 8 10 Land 200 nm IFR Reserves www. company. com
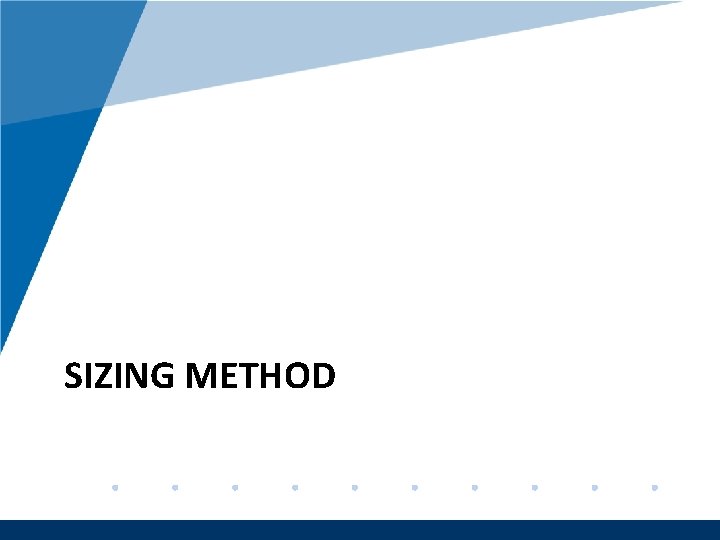
Company LOGO SIZING METHOD www. company. com
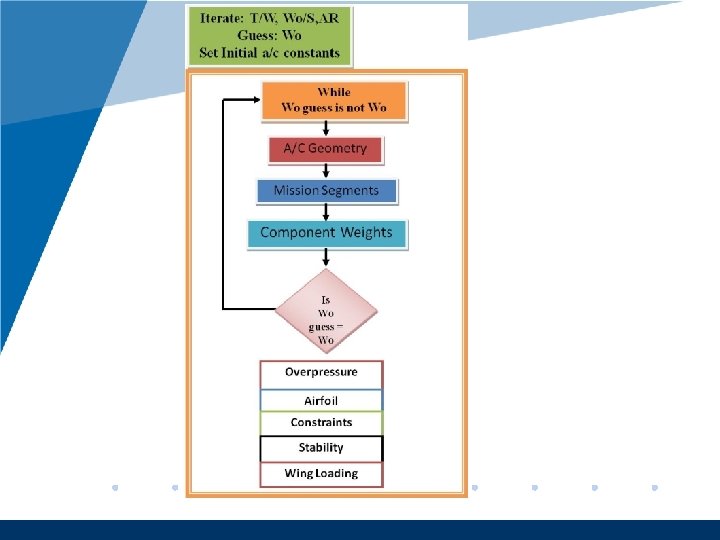
Company LOGO www. company. com
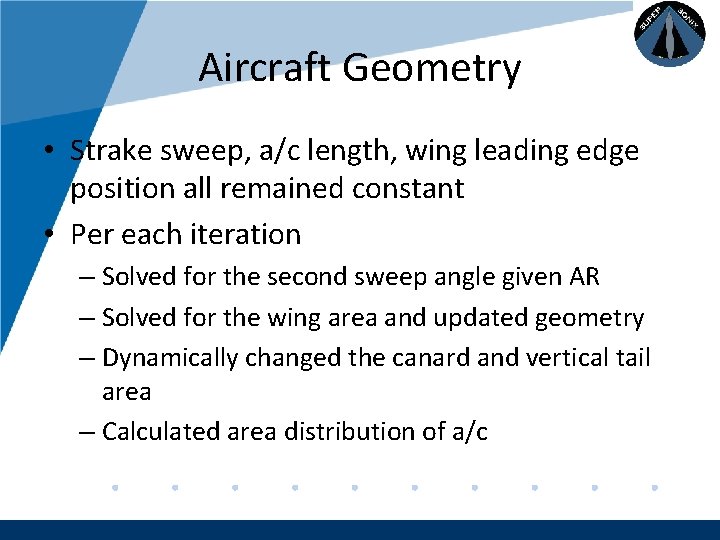
Company LOGO Aircraft Geometry • Strake sweep, a/c length, wing leading edge position all remained constant • Per each iteration – Solved for the second sweep angle given AR – Solved for the wing area and updated geometry – Dynamically changed the canard and vertical tail area – Calculated area distribution of a/c www. company. com
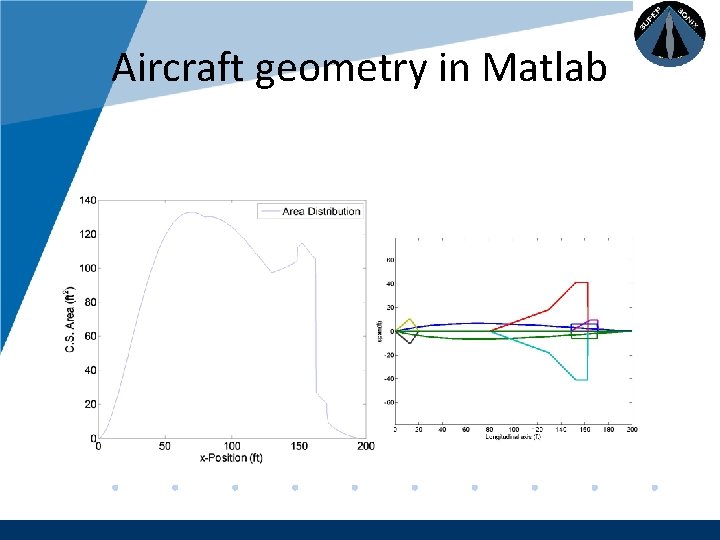
Company LOGO Aircraft geometry in Matlab www. company. com
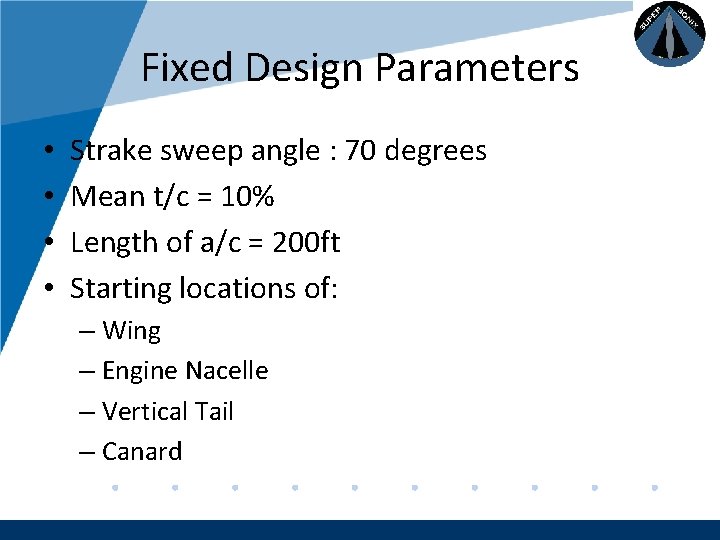
Company LOGO • • Fixed Design Parameters Strake sweep angle : 70 degrees Mean t/c = 10% Length of a/c = 200 ft Starting locations of: – Wing – Engine Nacelle – Vertical Tail – Canard www. company. com
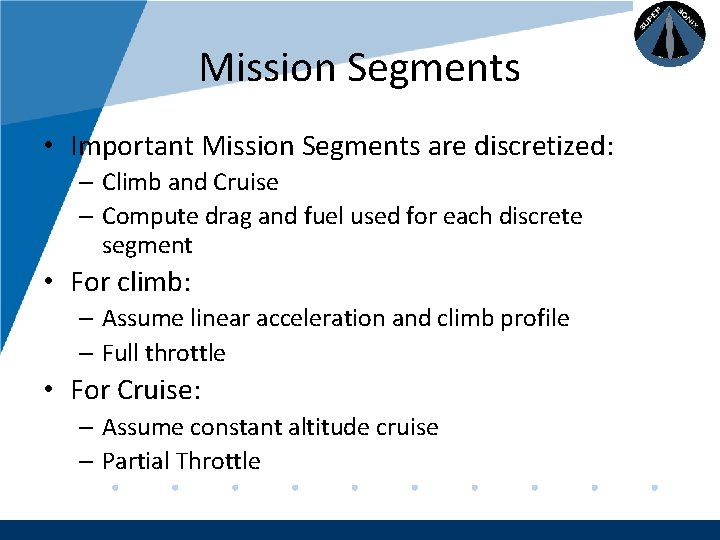
Company LOGO Mission Segments • Important Mission Segments are discretized: – Climb and Cruise – Compute drag and fuel used for each discrete segment • For climb: – Assume linear acceleration and climb profile – Full throttle • For Cruise: – Assume constant altitude cruise – Partial Throttle www. company. com
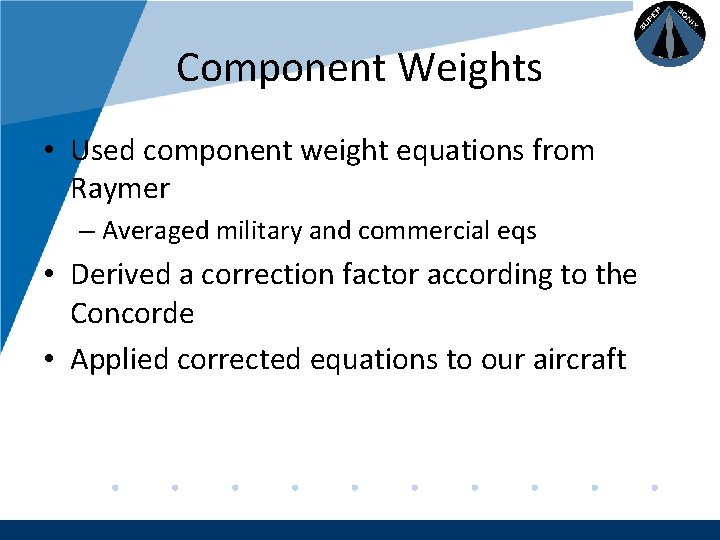
Company LOGO Component Weights • Used component weight equations from Raymer – Averaged military and commercial eqs • Derived a correction factor according to the Concorde • Applied corrected equations to our aircraft www. company. com
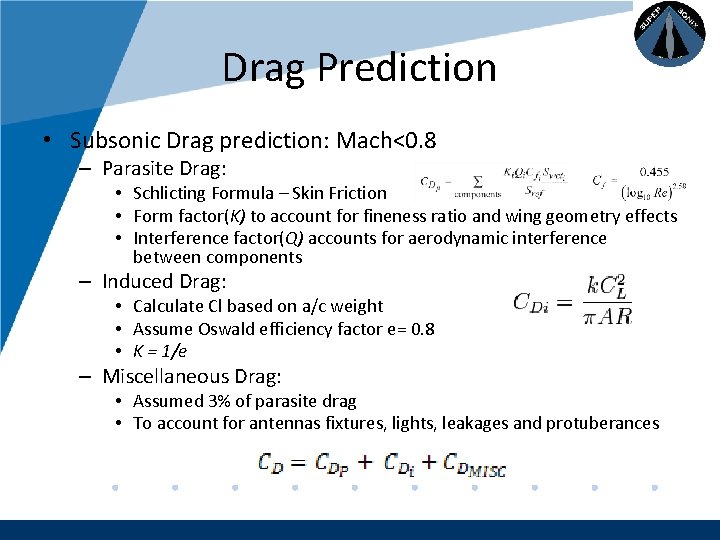
Company LOGO Drag Prediction • Subsonic Drag prediction: Mach<0. 8 – Parasite Drag: • Schlicting Formula – Skin Friction • Form factor(K) to account for fineness ratio and wing geometry effects • Interference factor(Q) accounts for aerodynamic interference between components – Induced Drag: • Calculate Cl based on a/c weight • Assume Oswald efficiency factor e= 0. 8 • K = 1/e – Miscellaneous Drag: • Assumed 3% of parasite drag • To account for antennas fixtures, lights, leakages and protuberances www. company. com
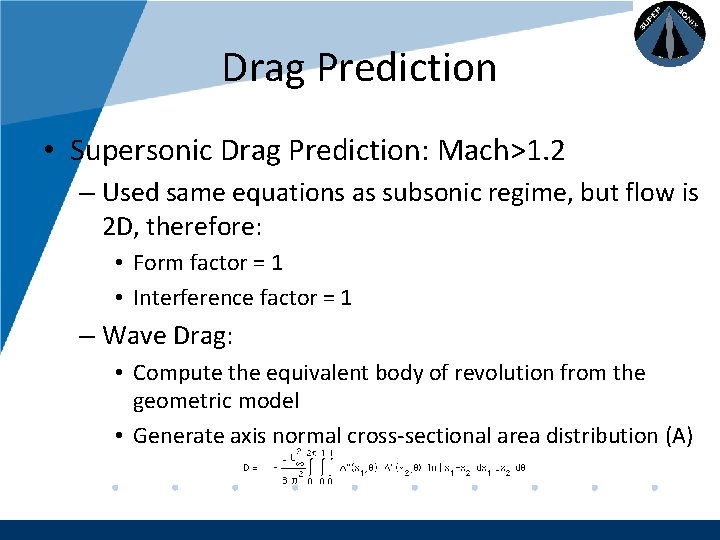
Company LOGO Drag Prediction • Supersonic Drag Prediction: Mach>1. 2 – Used same equations as subsonic regime, but flow is 2 D, therefore: • Form factor = 1 • Interference factor = 1 – Wave Drag: • Compute the equivalent body of revolution from the geometric model • Generate axis normal cross-sectional area distribution (A) www. company. com
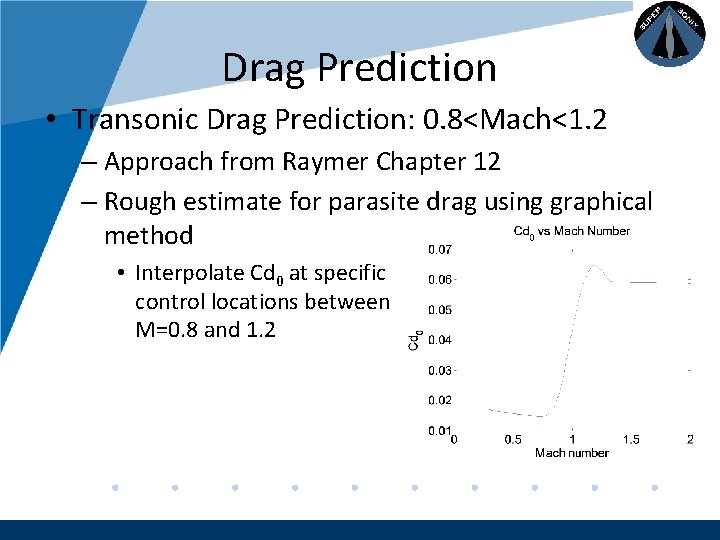
Company LOGO Drag Prediction • Transonic Drag Prediction: 0. 8<Mach<1. 2 – Approach from Raymer Chapter 12 – Rough estimate for parasite drag using graphical method • Interpolate Cd 0 at specific control locations between M=0. 8 and 1. 2 www. company. com
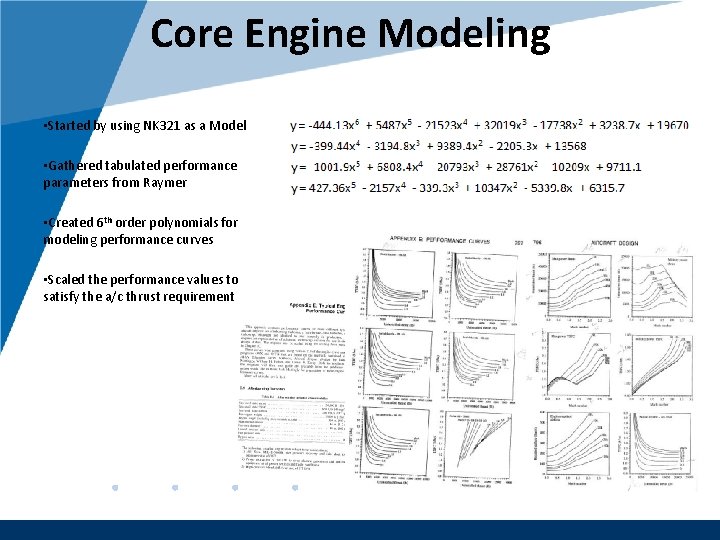
Company LOGO Core Engine Modeling • Started by using NK 321 as a Model • Gathered tabulated performance parameters from Raymer • Created 6 th order polynomials for modeling performance curves • Scaled the performance values to satisfy the a/c thrust requirement www. company. com
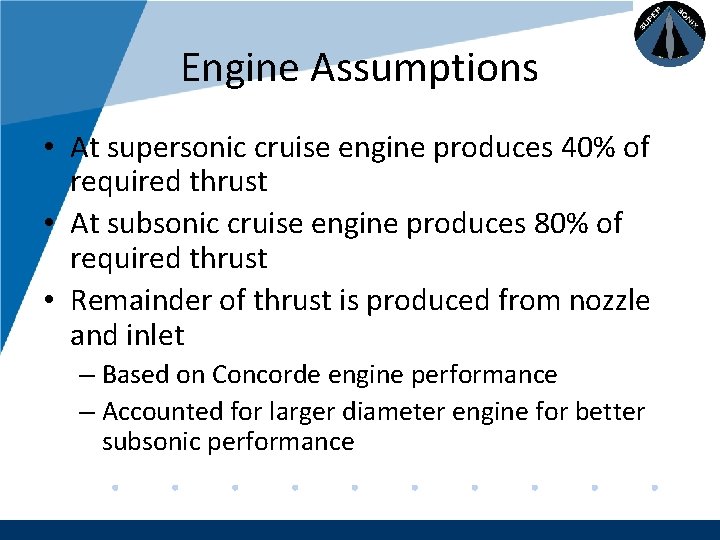
Company LOGO Engine Assumptions • At supersonic cruise engine produces 40% of required thrust • At subsonic cruise engine produces 80% of required thrust • Remainder of thrust is produced from nozzle and inlet – Based on Concorde engine performance – Accounted for larger diameter engine for better subsonic performance www. company. com
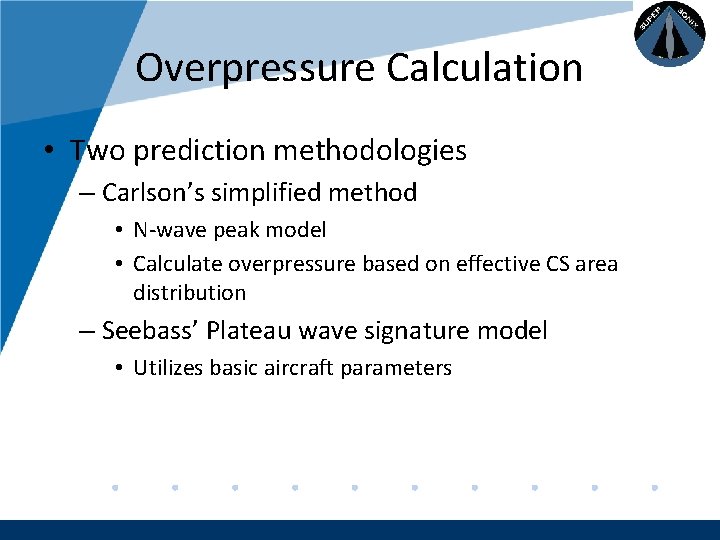
Company LOGO Overpressure Calculation • Two prediction methodologies – Carlson’s simplified method • N-wave peak model • Calculate overpressure based on effective CS area distribution – Seebass’ Plateau wave signature model • Utilizes basic aircraft parameters www. company. com
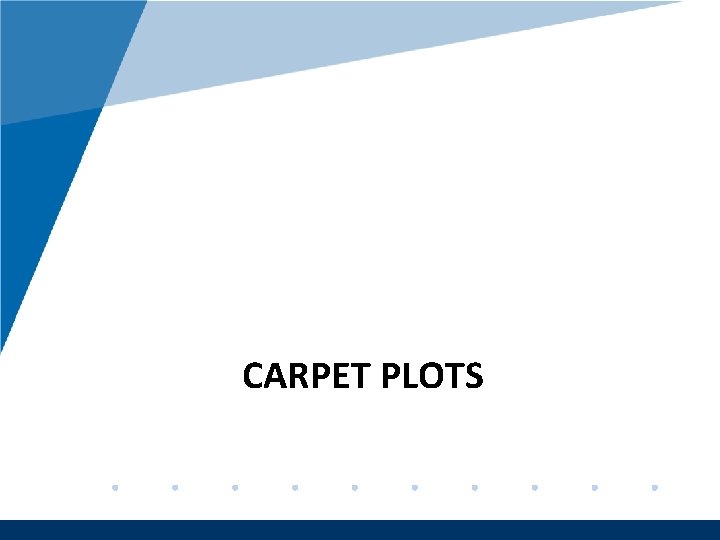
Company LOGO CARPET PLOTS www. company. com
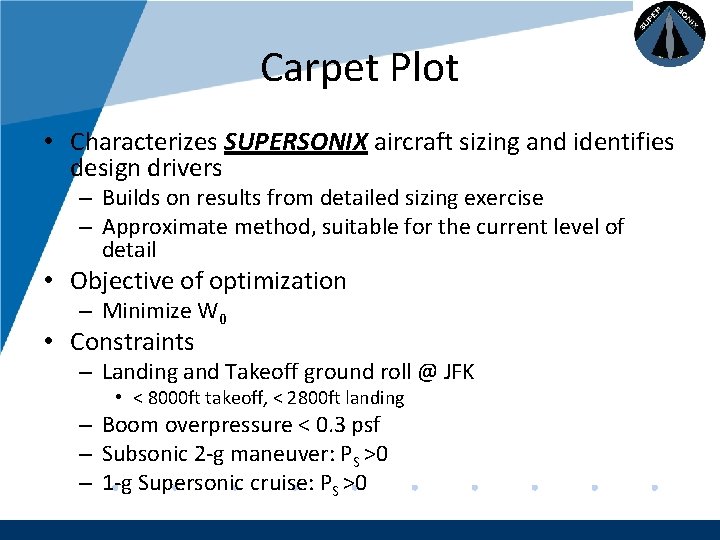
Company LOGO Carpet Plot • Characterizes SUPERSONIX aircraft sizing and identifies design drivers – Builds on results from detailed sizing exercise – Approximate method, suitable for the current level of detail • Objective of optimization – Minimize W 0 • Constraints – Landing and Takeoff ground roll @ JFK • < 8000 ft takeoff, < 2800 ft landing – Boom overpressure < 0. 3 psf – Subsonic 2 -g maneuver: PS >0 – 1 -g Supersonic cruise: PS >0 www. company. com
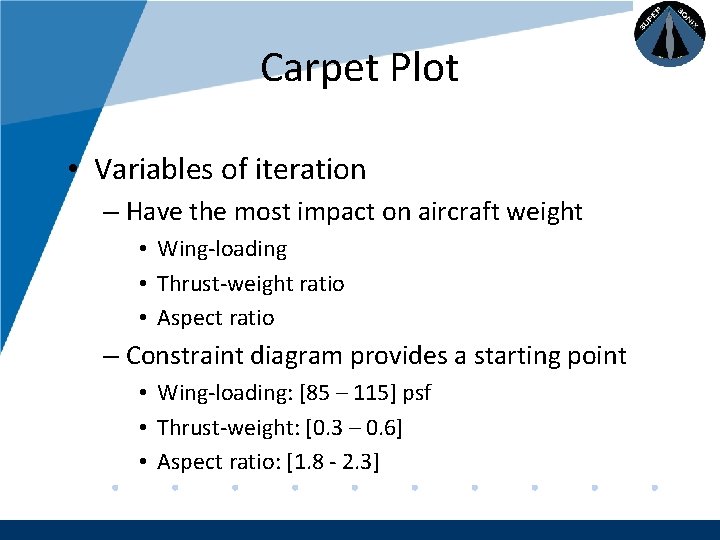
Company LOGO Carpet Plot • Variables of iteration – Have the most impact on aircraft weight • Wing-loading • Thrust-weight ratio • Aspect ratio – Constraint diagram provides a starting point • Wing-loading: [85 – 115] psf • Thrust-weight: [0. 3 – 0. 6] • Aspect ratio: [1. 8 - 2. 3] www. company. com
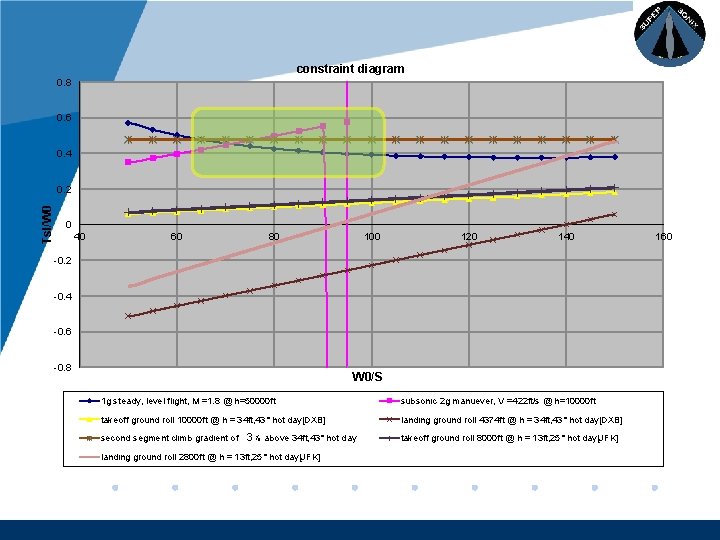
Company LOGO constraint diagram 0. 8 0. 6 0. 4 Tsl/W 0 0. 2 0 40 60 80 100 120 140 160 -0. 2 -0. 4 -0. 6 -0. 8 W 0/S 1 g steady, level flight, M =1. 8 @ h=50000 ft subsonic 2 g manuever, V =422 ft/s @ h=10000 ft takeoff ground roll 10000 ft @ h = 34 ft, 43° hot day[DXB] landing ground roll 4374 ft @ h = 34 ft, 43° hot day[DXB] 3 above 34 ft, 43° hot day second segment climb gradient of 2. 7% takeoff ground roll 8000 ft @ h = 13 ft, 25° hot day[JFK] landing ground roll 2800 ft @ h = 13 ft, 25° hot day[JFK] www. company. com

Company LOGO Carpet plot www. company. com
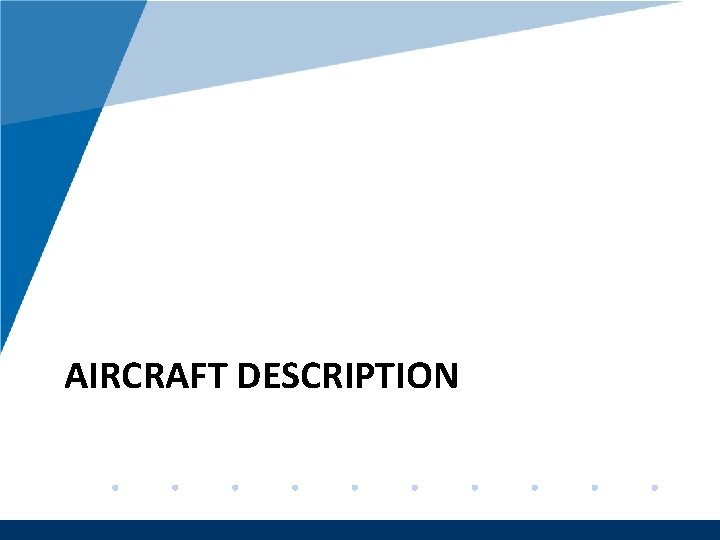
Company LOGO AIRCRAFT DESCRIPTION www. company. com
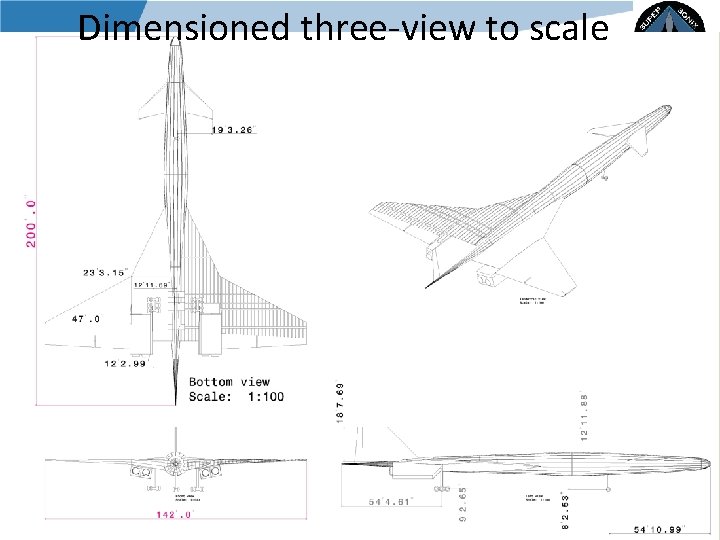
Dimensioned three-view to scale Company LOGO www. company. com
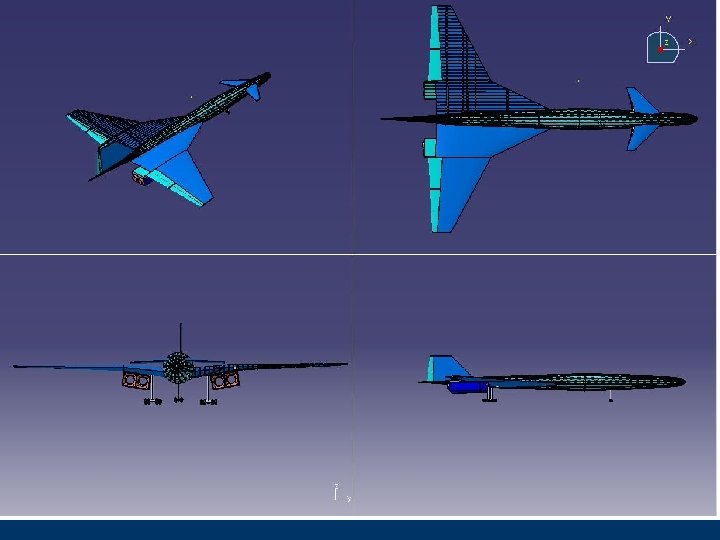
Company LOGO www. company. com
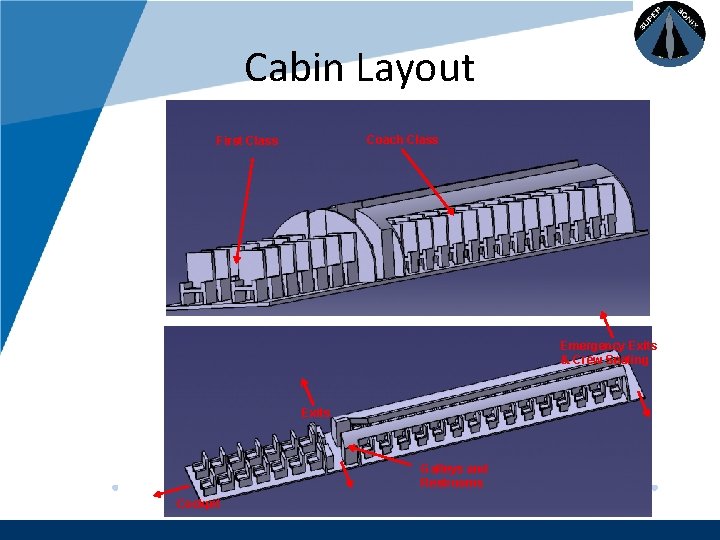
Company LOGO Cabin Layout Coach Class First Class Emergency Exits & Crew Seating Exits Galleys and Restrooms Cockpit www. company. com
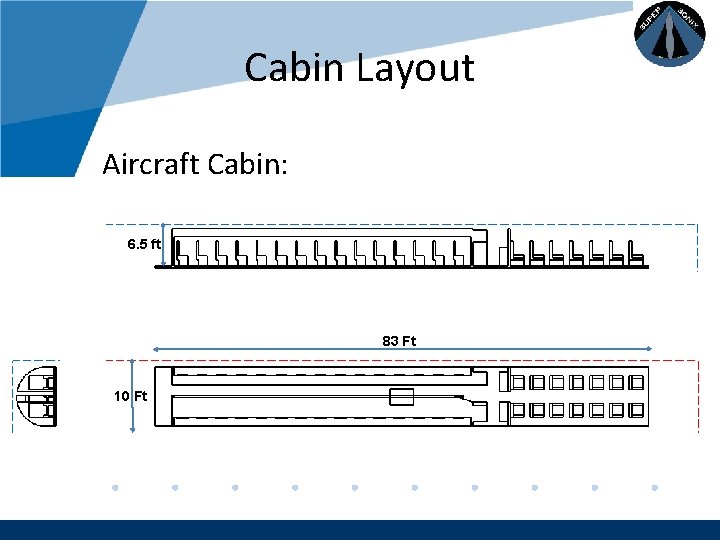
Company LOGO Cabin Layout Aircraft Cabin: 6. 5 ft 83 Ft 10 Ft www. company. com
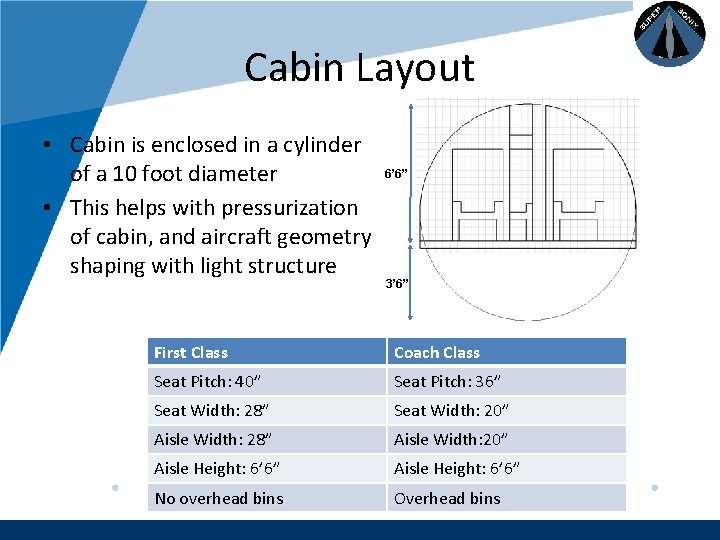
Company LOGO Cabin Layout • Cabin is enclosed in a cylinder of a 10 foot diameter • This helps with pressurization of cabin, and aircraft geometry shaping with light structure 6’ 6” 3’ 6” First Class Coach Class Seat Pitch: 40” Seat Pitch: 36” Seat Width: 28” Seat Width: 20” Aisle Width: 28” Aisle Width: 20” Aisle Height: 6’ 6” No overhead bins Overhead bins www. company. com

Company LOGO AERODYNAMIC DESIGN & SONIC BOOM ANALYSIS www. company. com
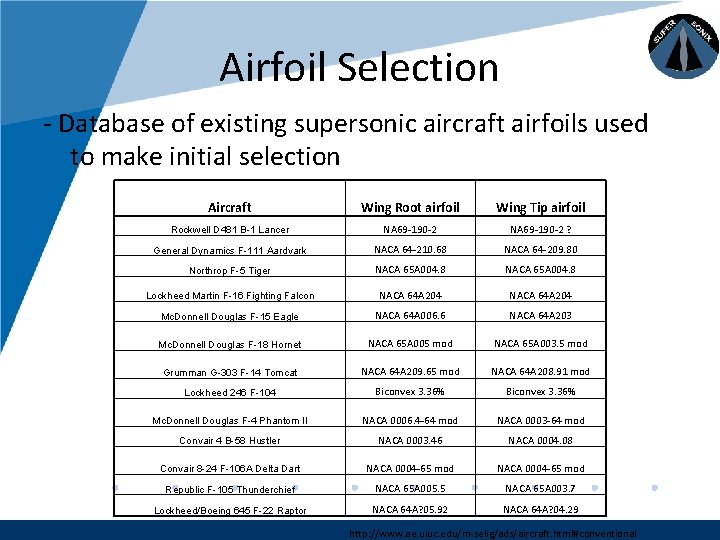
Company LOGO Airfoil Selection - Database of existing supersonic aircraft airfoils used to make initial selection Aircraft Wing Root airfoil Wing Tip airfoil Rockwell D 481 B-1 Lancer NA 69 -190 -2 ? General Dynamics F-111 Aardvark NACA 64 -210. 68 NACA 64 -209. 80 Northrop F-5 Tiger NACA 65 A 004. 8 Lockheed Martin F-16 Fighting Falcon NACA 64 A 204 Mc. Donnell Douglas F-15 Eagle NACA 64 A 006. 6 NACA 64 A 203 Mc. Donnell Douglas F-18 Hornet NACA 65 A 005 mod NACA 65 A 003. 5 mod Grumman G-303 F-14 Tomcat NACA 64 A 209. 65 mod NACA 64 A 208. 91 mod Lockheed 246 F-104 Biconvex 3. 36% Mc. Donnell Douglas F-4 Phantom II NACA 0006. 4 -64 mod NACA 0003 -64 mod Convair 4 B-58 Hustler NACA 0003. 46 NACA 0004. 08 Convair 8 -24 F-106 A Delta Dart NACA 0004 -65 mod Republic F-105 Thunderchief NACA 65 A 005. 5 NACA 65 A 003. 7 Lockheed/Boeing 645 F-22 Raptor NACA 64 A? 05. 92 NACA 64 A? 04. 29 www. company. com http: //www. ae. uiuc. edu/m-selig/ads/aircraft. html#conventional
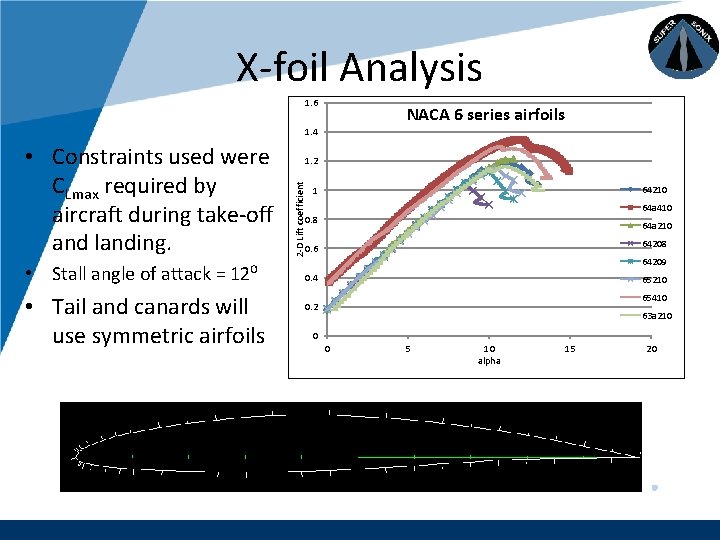
Company LOGO X-foil Analysis 1. 6 NACA 6 series airfoils 1. 4 • Stall angle of attack = 12⁰ • Tail and canards will use symmetric airfoils 1. 2 2 -D Lift coefficient • Constraints used were CLmax required by aircraft during take-off and landing. 64210 1 64 a 410 0. 8 64 a 210 64208 0. 6 64209 0. 4 65210 65410 0. 2 63 a 210 0 0 5 10 alpha 15 20 NACA 64 -A-410 www. company. com
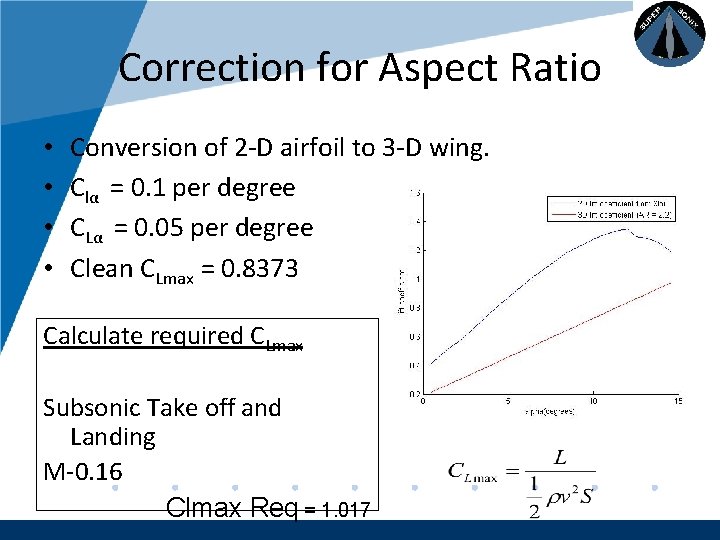
Company LOGO • • Correction for Aspect Ratio Conversion of 2 -D airfoil to 3 -D wing. Clα = 0. 1 per degree CLα = 0. 05 per degree Clean CLmax = 0. 8373 Calculate required CLmax Subsonic Take off and Landing M-0. 16 Clmax Req = 1. 017 www. company. com
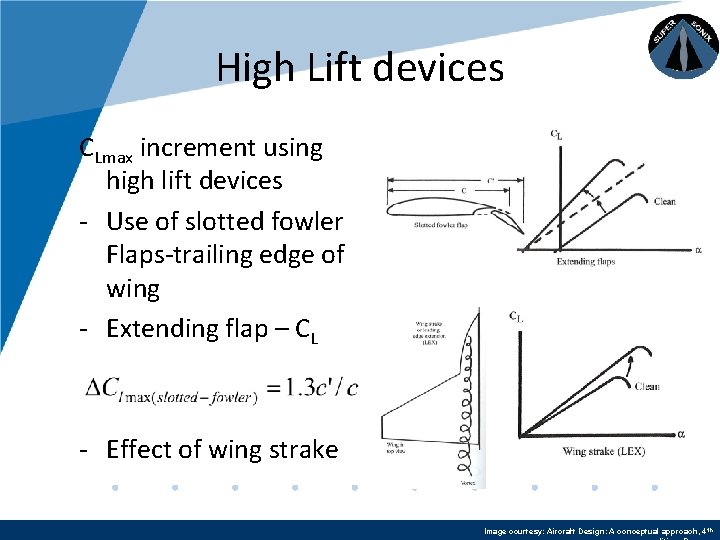
Company LOGO High Lift devices CLmax increment using high lift devices - Use of slotted fowler Flaps-trailing edge of wing - Extending flap – CL - Effect of wing strake www. company. com Image courtesy: Aircraft Design: A conceptual approach, 4 th
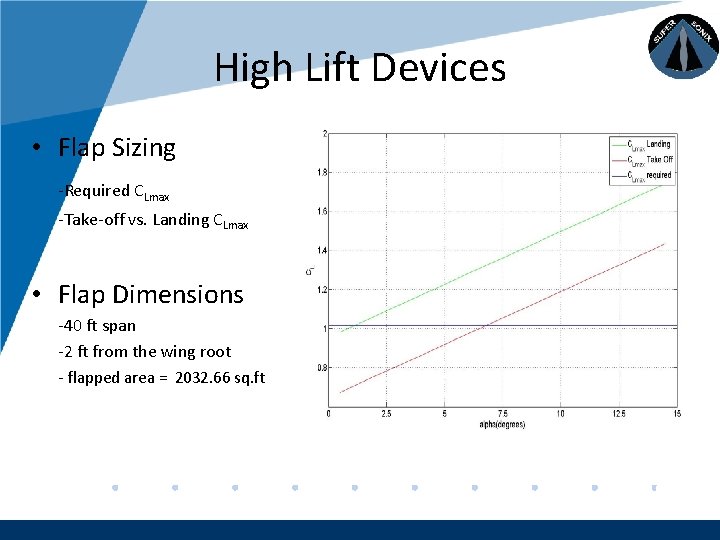
Company LOGO High Lift Devices • Flap Sizing -Required CLmax • PLOT WITH CLMAX FOR TAKE OFF AND LANDNG -Take-off vs. Landing CLmax • Flap Dimensions -40 ft span -2 ft from the wing root - flapped area = 2032. 66 sq. ft Take off ΔCLmax = 60%-80% Landing ΔCLmax www. company. com
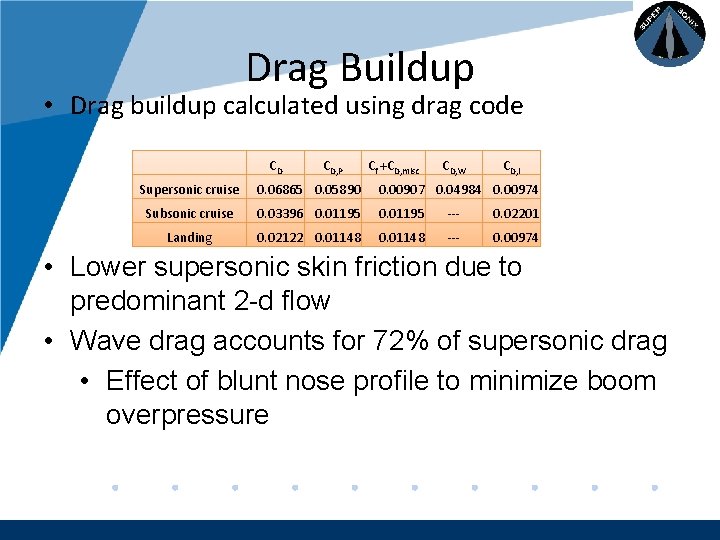
Company LOGO Drag Buildup • Drag buildup calculated using drag code CD CD, P Cf +CD, misc CD, W CD, i Supersonic cruise 0. 06865 0. 05890 0. 00907 0. 04984 0. 00974 Subsonic cruise 0. 03396 0. 01195 --- 0. 02201 Landing 0. 02122 0. 01148 --- 0. 00974 • Lower supersonic skin friction due to predominant 2 -d flow • Wave drag accounts for 72% of supersonic drag • Effect of blunt nose profile to minimize boom overpressure www. company. com
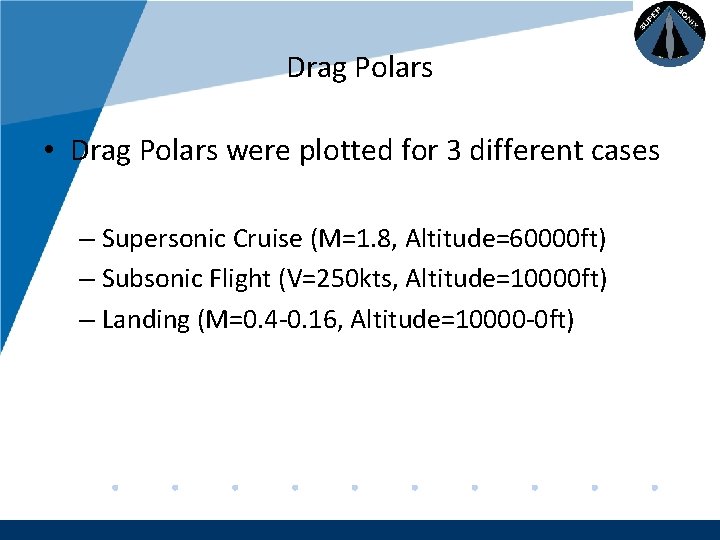
Company LOGO Drag Polars • Drag Polars were plotted for 3 different cases – Supersonic Cruise (M=1. 8, Altitude=60000 ft) – Subsonic Flight (V=250 kts, Altitude=10000 ft) – Landing (M=0. 4 -0. 16, Altitude=10000 -0 ft) www. company. com
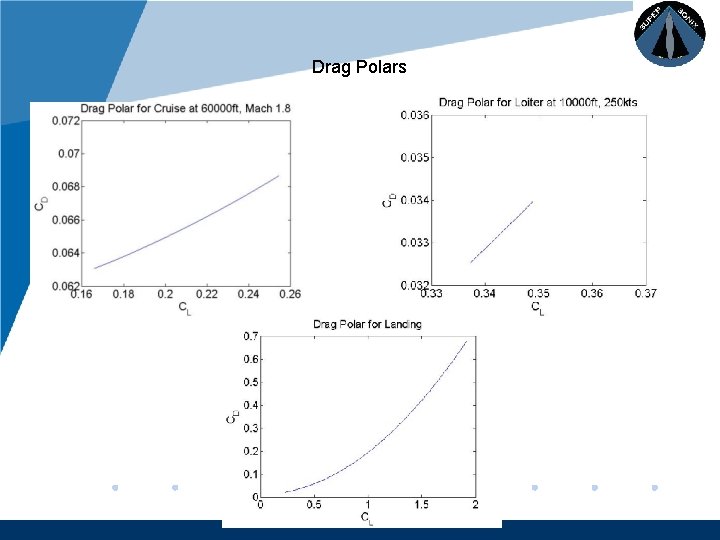
Company LOGO Drag Polars www. company. com
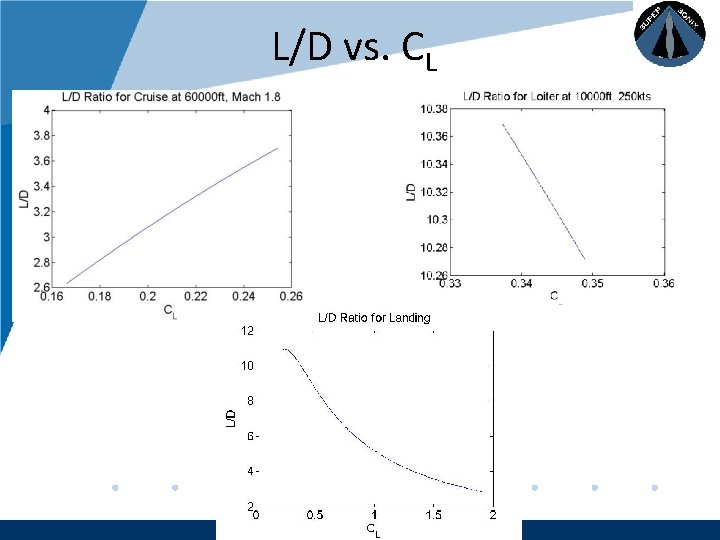
Company LOGO L/D vs. CL www. company. com
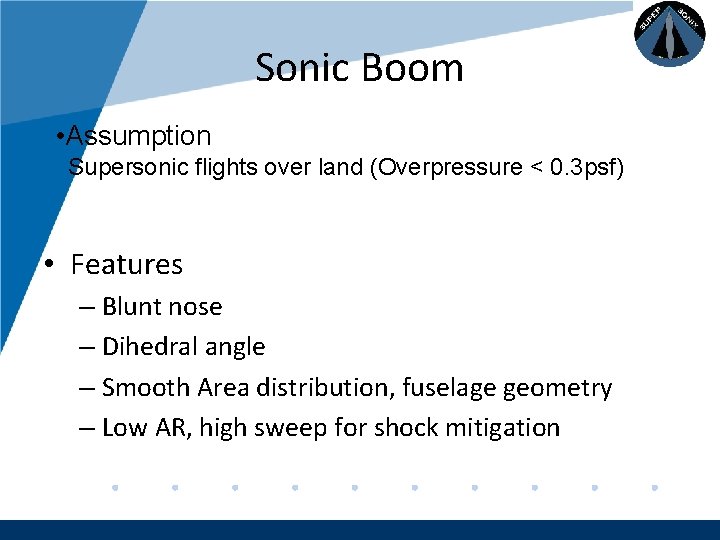
Company LOGO Sonic Boom • Assumption Supersonic flights over land (Overpressure < 0. 3 psf) • Features – Blunt nose – Dihedral angle – Smooth Area distribution, fuselage geometry – Low AR, high sweep for shock mitigation www. company. com
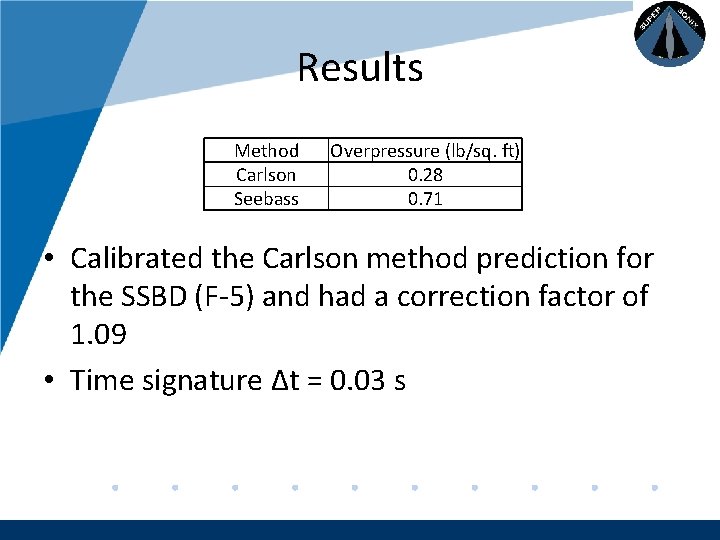
Company LOGO Results Method Carlson Seebass Overpressure (lb/sq. ft) 0. 28 0. 71 • Calibrated the Carlson method prediction for the SSBD (F-5) and had a correction factor of 1. 09 • Time signature Δt = 0. 03 s www. company. com
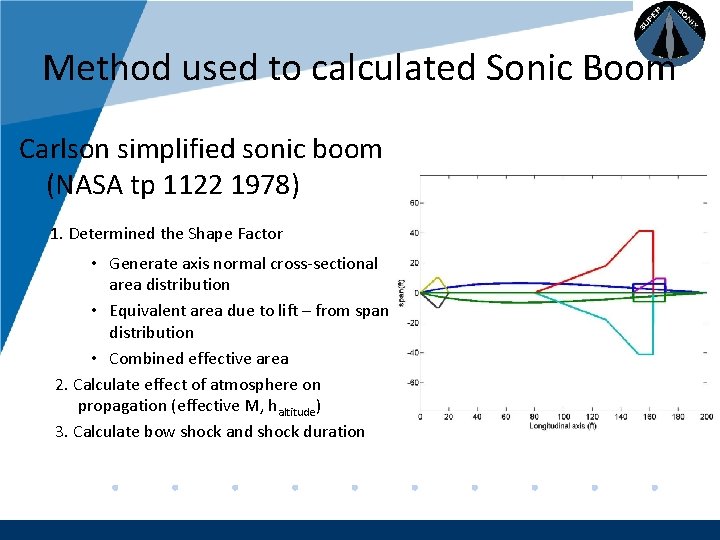
Company LOGO Method used to calculated Sonic Boom Carlson simplified sonic boom (NASA tp 1122 1978) 1. Determined the Shape Factor • Generate axis normal cross-sectional area distribution • Equivalent area due to lift – from span distribution • Combined effective area 2. Calculate effect of atmosphere on propagation (effective M, haltitude) 3. Calculate bow shock and shock duration www. company. com
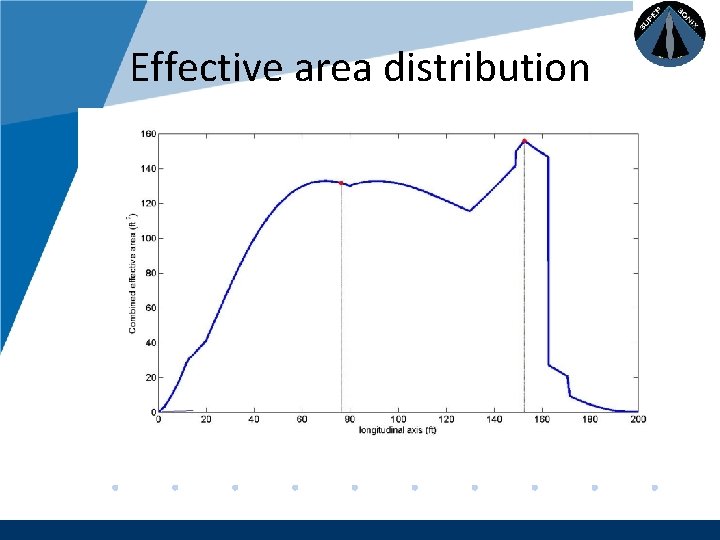
Company LOGO Effective area distribution www. company. com
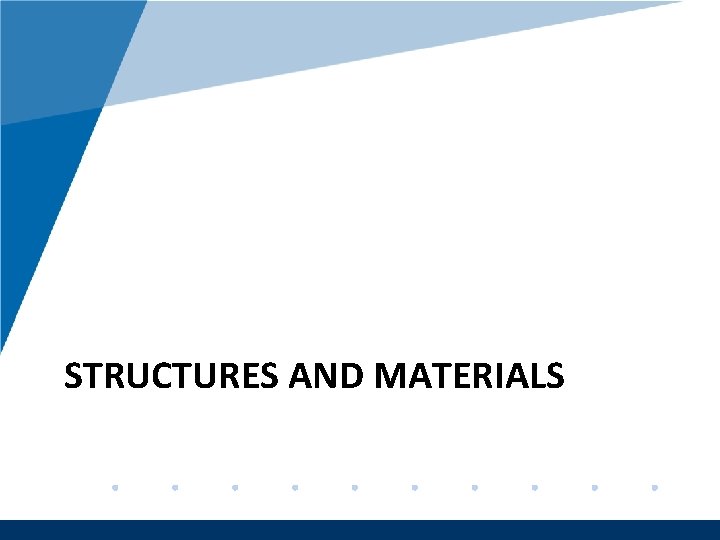
Company LOGO STRUCTURES AND MATERIALS www. company. com
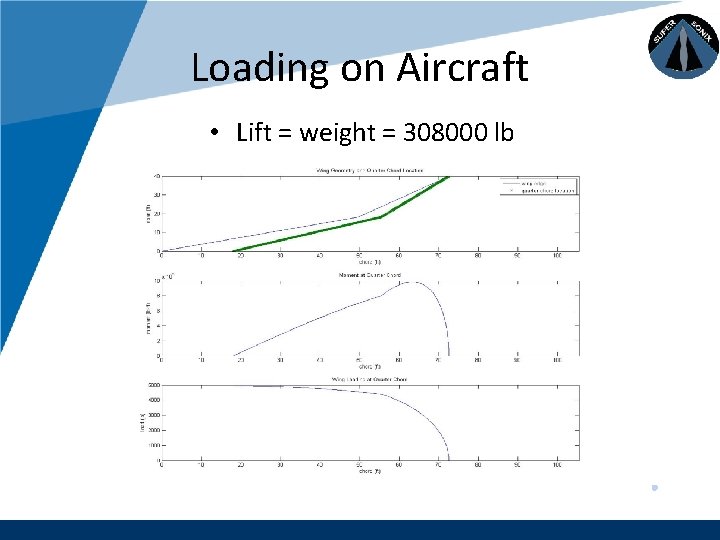
Company LOGO Loading on Aircraft • Lift = weight = 308000 lb www. company. com
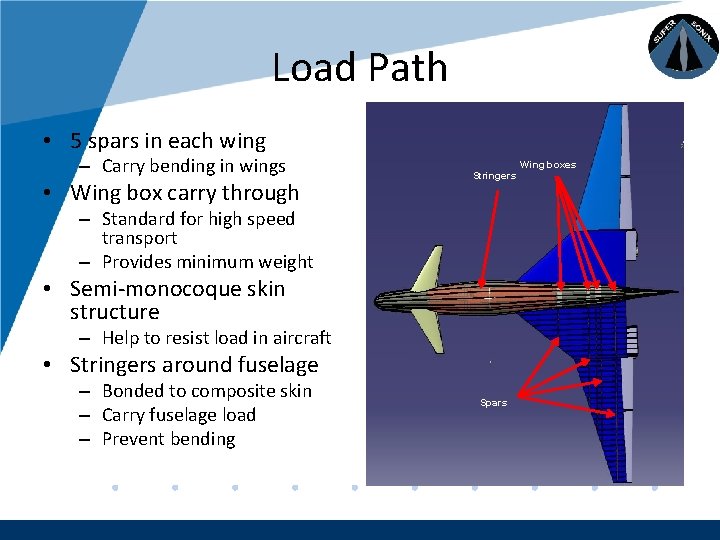
Company LOGO Load Path • 5 spars in each wing – Carry bending in wings • Wing box carry through Wing boxes Stringers – Standard for high speed transport – Provides minimum weight • Semi-monocoque skin structure – Help to resist load in aircraft • Stringers around fuselage – Bonded to composite skin – Carry fuselage load – Prevent bending Spars www. company. com
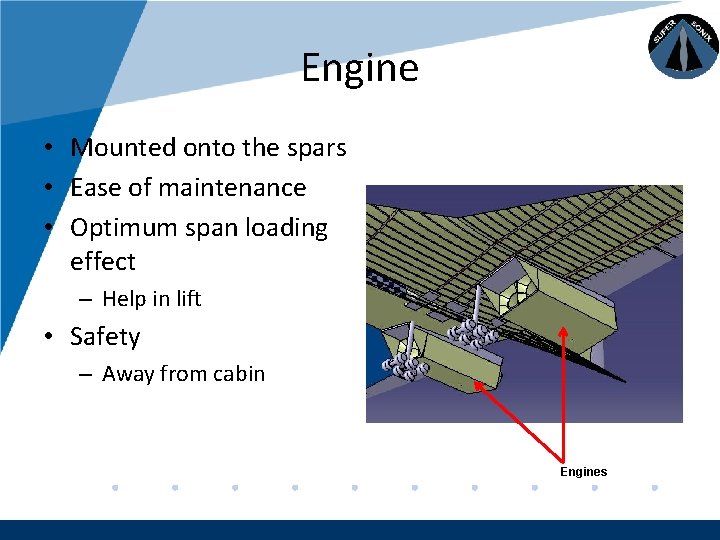
Company LOGO Engine • Mounted onto the spars • Ease of maintenance • Optimum span loading effect – Help in lift • Safety – Away from cabin Engines www. company. com
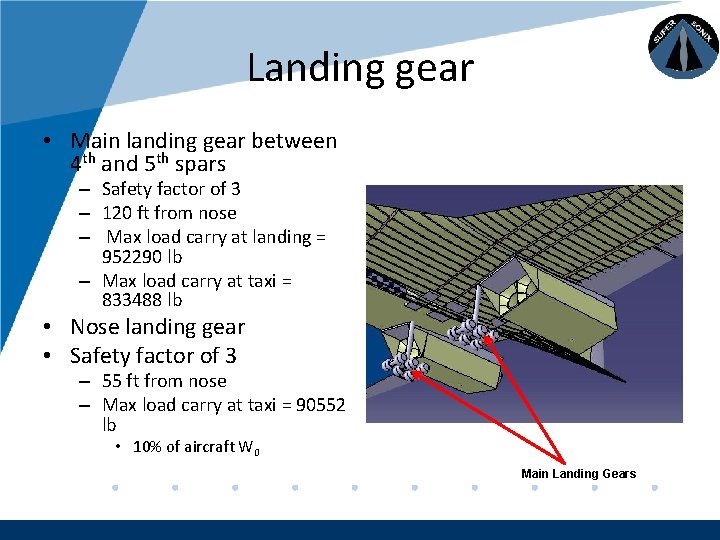
Company LOGO Landing gear • Main landing gear between 4 th and 5 th spars – Safety factor of 3 – 120 ft from nose – Max load carry at landing = 952290 lb – Max load carry at taxi = 833488 lb • Nose landing gear • Safety factor of 3 – 55 ft from nose – Max load carry at taxi = 90552 lb • 10% of aircraft W 0 Main Landing Gears www. company. com
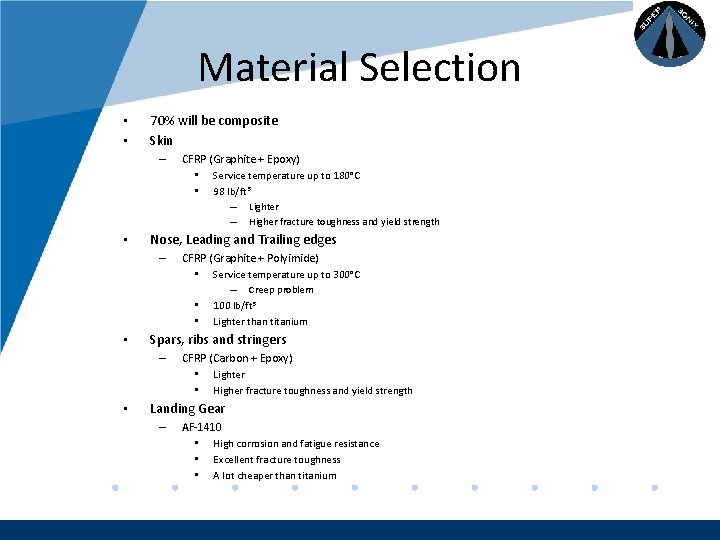
Company LOGO Material Selection • • 70% will be composite Skin – CFRP (Graphite + Epoxy) • Service temperature up to 180°C • 98 lb/ft 3 – – • Nose, Leading and Trailing edges – CFRP (Graphite + Polyimide) • Service temperature up to 300°C • • • – Creep problem 100 lb/ft 3 Lighter than titanium Spars, ribs and stringers – • Lighter Higher fracture toughness and yield strength CFRP (Carbon + Epoxy) • Lighter • Higher fracture toughness and yield strength Landing Gear – AF-1410 • High corrosion and fatigue resistance • Excellent fracture toughness • A lot cheaper than titanium www. company. com
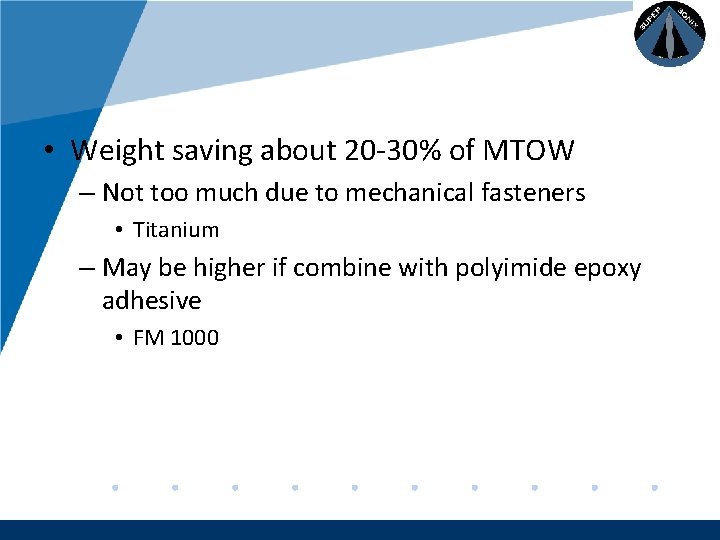
Company LOGO • Weight saving about 20 -30% of MTOW – Not too much due to mechanical fasteners • Titanium – May be higher if combine with polyimide epoxy adhesive • FM 1000 www. company. com
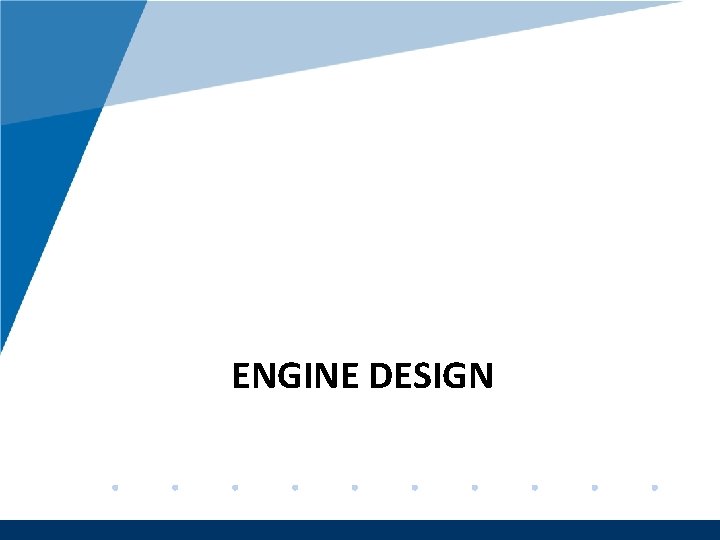
Company LOGO ENGINE DESIGN www. company. com
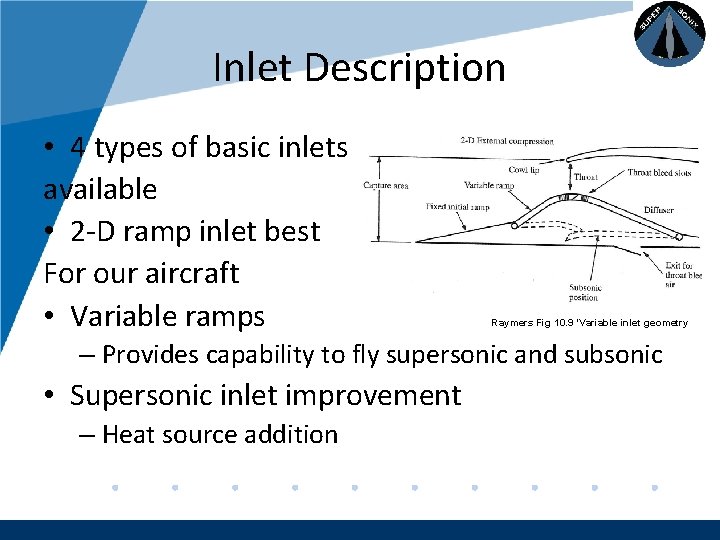
Company LOGO Inlet Description • 4 types of basic inlets available • 2 -D ramp inlet best For our aircraft • Variable ramps Raymers Fig 10. 9 ‘Variable inlet geometry – Provides capability to fly supersonic and subsonic • Supersonic inlet improvement – Heat source addition www. company. com
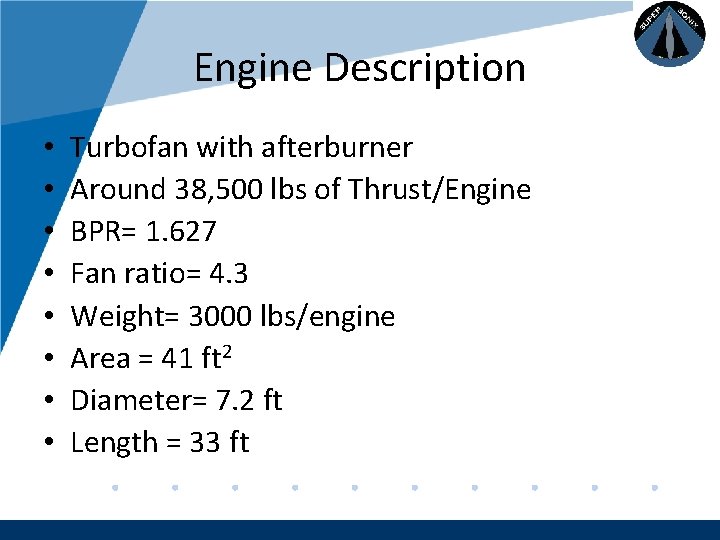
Company LOGO • • Engine Description Turbofan with afterburner Around 38, 500 lbs of Thrust/Engine BPR= 1. 627 Fan ratio= 4. 3 Weight= 3000 lbs/engine Area = 41 ft 2 Diameter= 7. 2 ft Length = 33 ft www. company. com
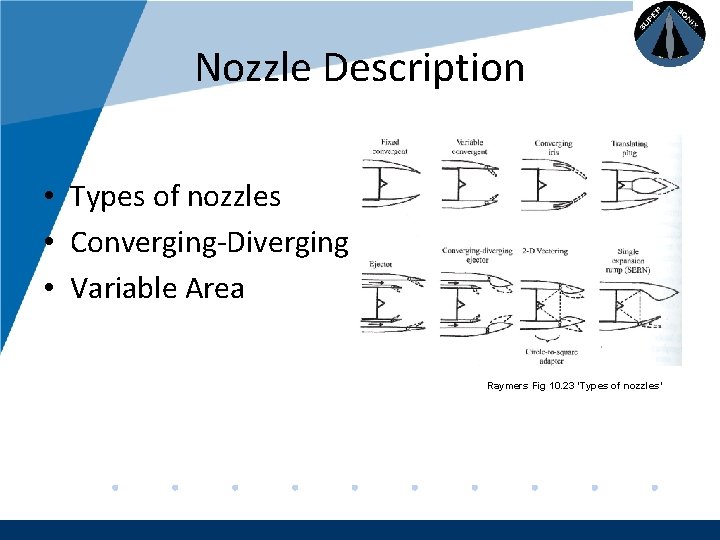
Company LOGO Nozzle Description • Types of nozzles • Converging-Diverging • Variable Area Raymers Fig 10. 23 ‘Types of nozzles’ www. company. com
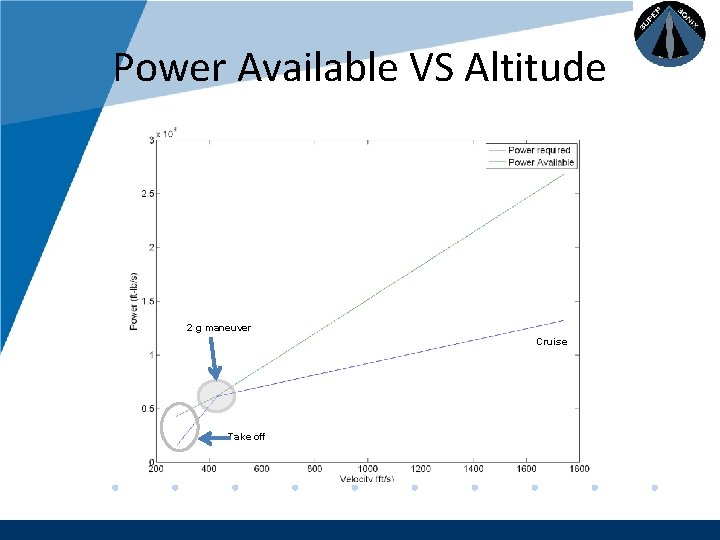
Company LOGO Power Available VS Altitude 22 g maneuver 32 g Cruise Take off Take www. company. com

Company LOGO PERFORMANCE www. company. com
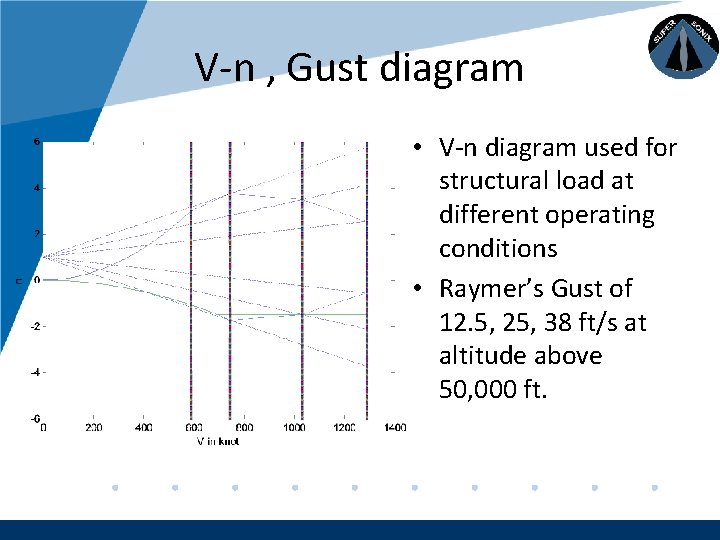
Company LOGO V-n , Gust diagram • V-n diagram used for structural load at different operating conditions • Raymer’s Gust of 12. 5, 25, 38 ft/s at altitude above 50, 000 ft. www. company. com
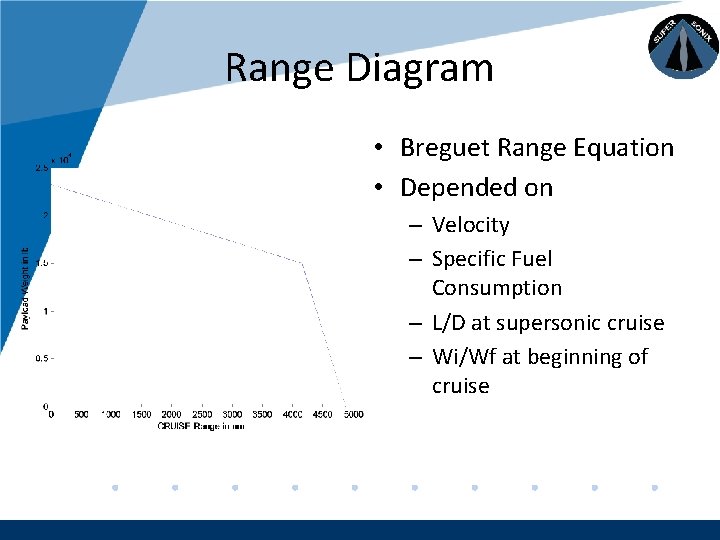
Company LOGO Range Diagram • Breguet Range Equation • Depended on – Velocity – Specific Fuel Consumption – L/D at supersonic cruise – Wi/Wf at beginning of cruise www. company. com
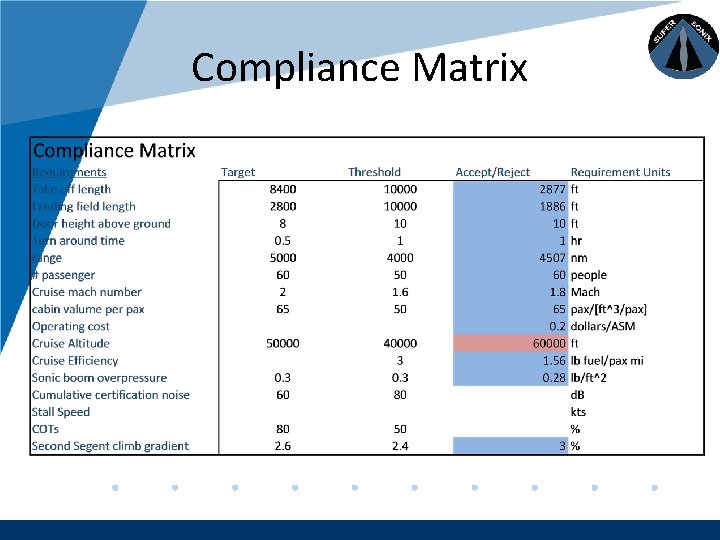
Company LOGO Compliance Matrix www. company. com
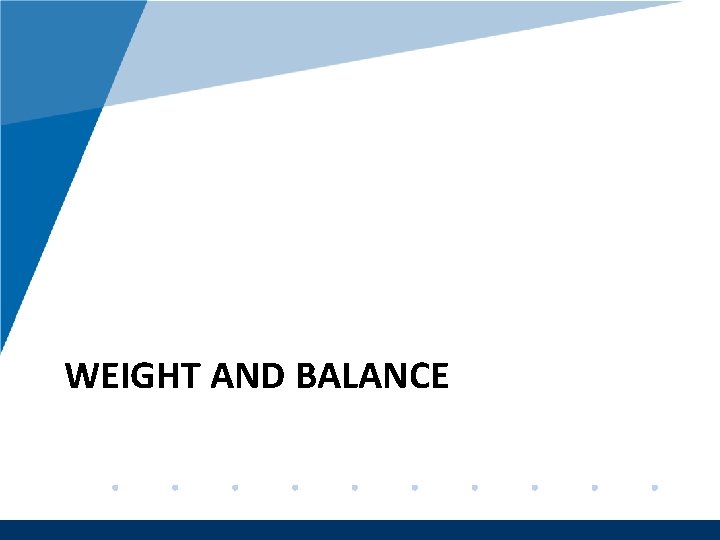
Company LOGO WEIGHT AND BALANCE www. company. com
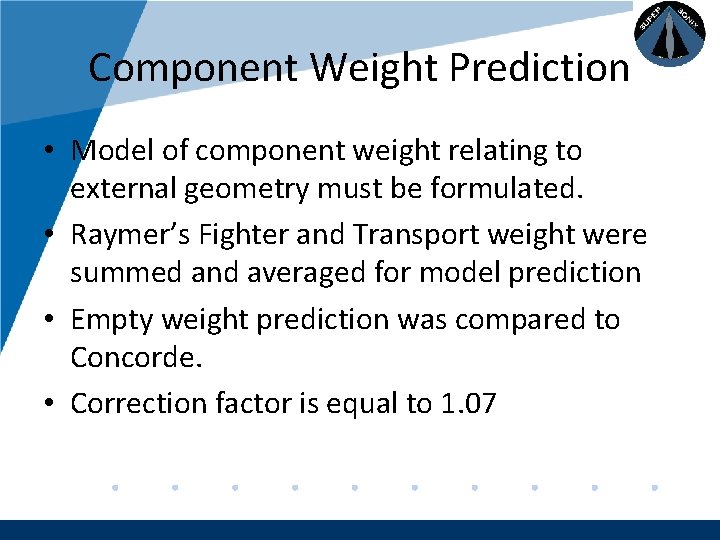
Company LOGO Component Weight Prediction • Model of component weight relating to external geometry must be formulated. • Raymer’s Fighter and Transport weight were summed and averaged for model prediction • Empty weight prediction was compared to Concorde. • Correction factor is equal to 1. 07 www. company. com
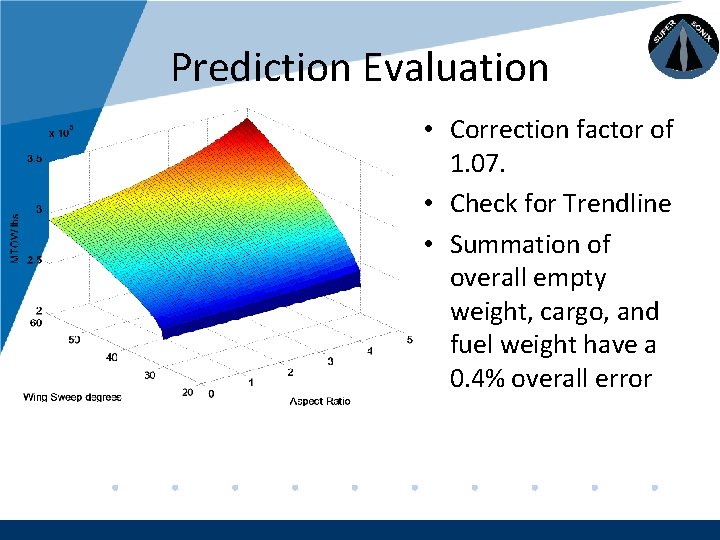
Company LOGO Prediction Evaluation • Correction factor of 1. 07. • Check for Trendline • Summation of overall empty weight, cargo, and fuel weight have a 0. 4% overall error www. company. com
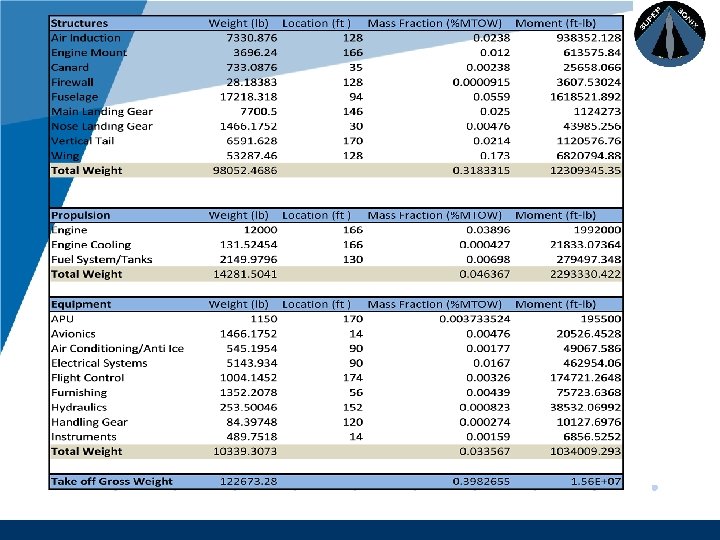
Company LOGO www. company. com
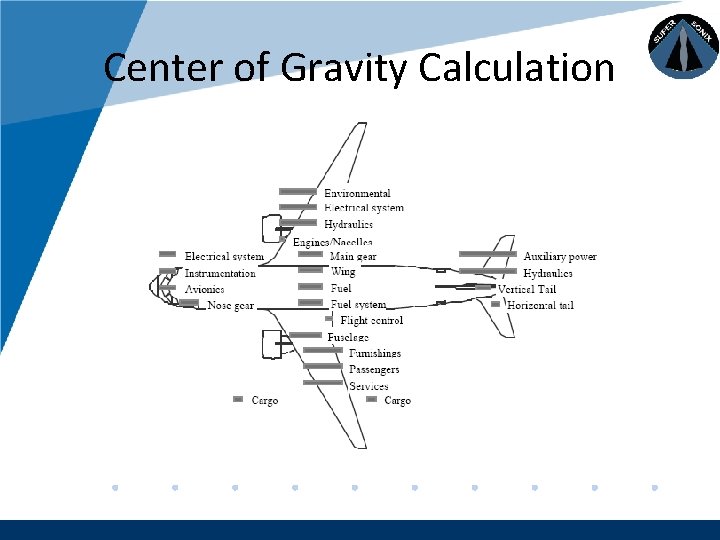
Company LOGO Center of Gravity Calculation www. company. com
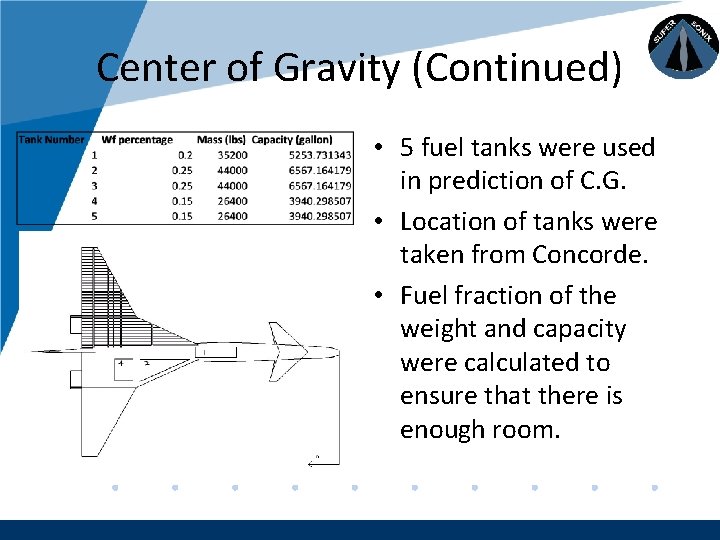
Company LOGO Center of Gravity (Continued) • 5 fuel tanks were used in prediction of C. G. • Location of tanks were taken from Concorde. • Fuel fraction of the weight and capacity were calculated to ensure that there is enough room. www. company. com
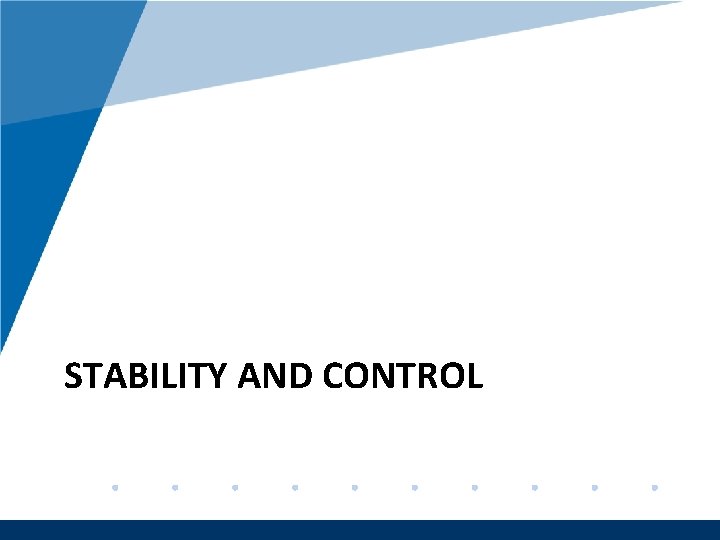
Company LOGO STABILITY AND CONTROL www. company. com
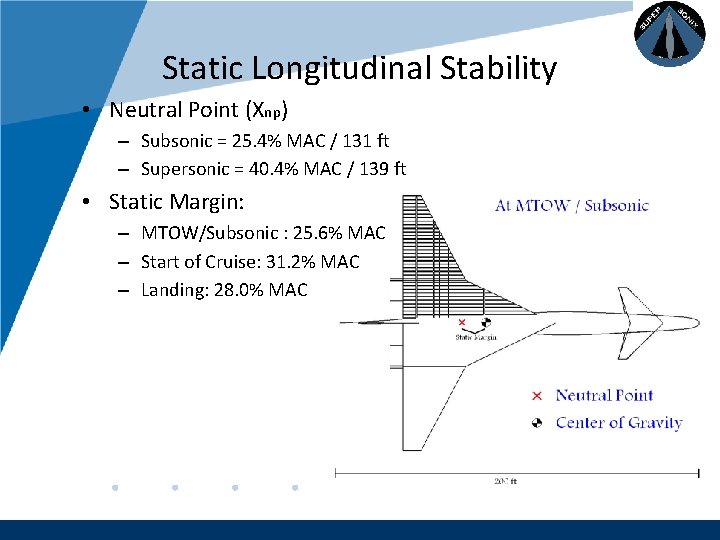
Company LOGO Static Longitudinal Stability • Neutral Point (Xnp) – Subsonic = 25. 4% MAC / 131 ft – Supersonic = 40. 4% MAC / 139 ft • Static Margin: – MTOW/Subsonic : 25. 6% MAC – Start of Cruise: 31. 2% MAC – Landing: 28. 0% MAC www. company. com
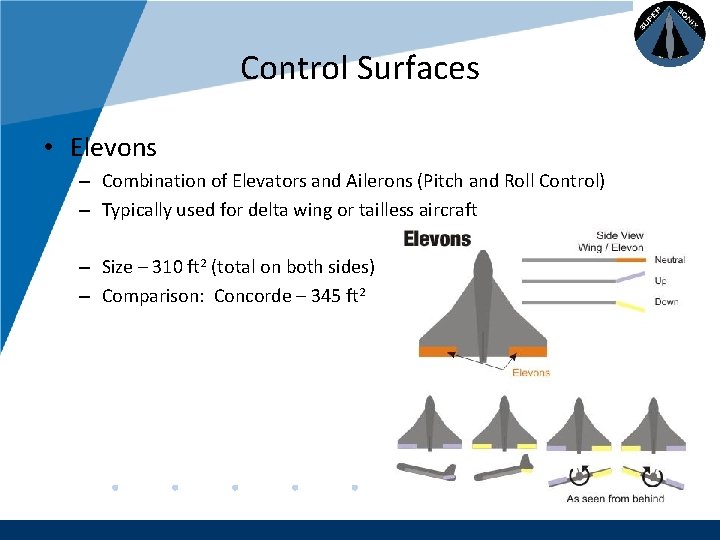
Company LOGO Control Surfaces • Elevons – Combination of Elevators and Ailerons (Pitch and Roll Control) – Typically used for delta wing or tailless aircraft – Size – 310 ft 2 (total on both sides) – Comparison: Concorde – 345 ft 2 www. company. com
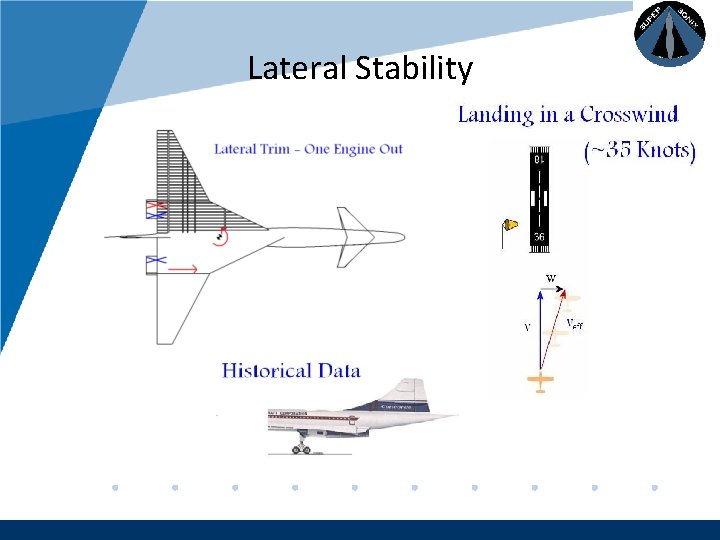
Company LOGO Lateral Stability www. company. com
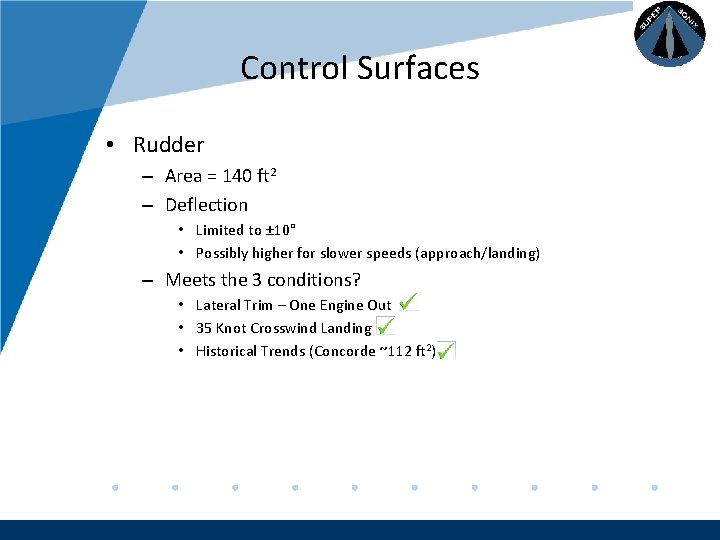
Company LOGO Control Surfaces • Rudder – Area = 140 ft 2 – Deflection • Limited to ± 10° • Possibly higher for slower speeds (approach/landing) – Meets the 3 conditions? • Lateral Trim – One Engine Out • 35 Knot Crosswind Landing • Historical Trends (Concorde ~112 ft 2) www. company. com
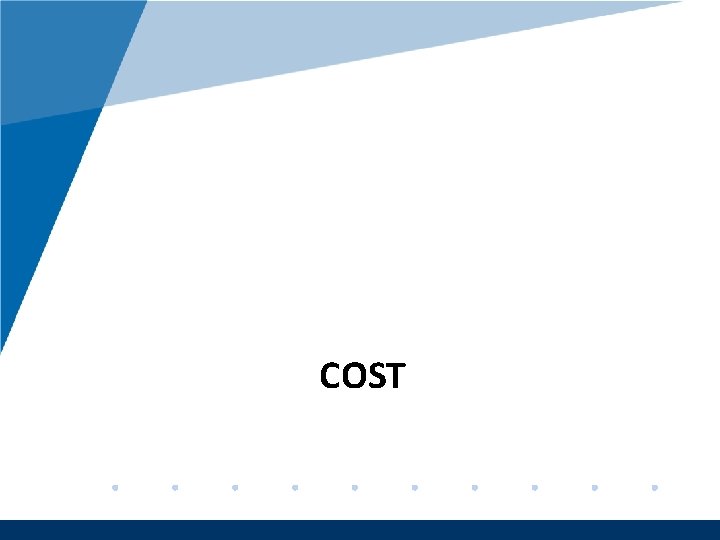
Company LOGO COST www. company. com
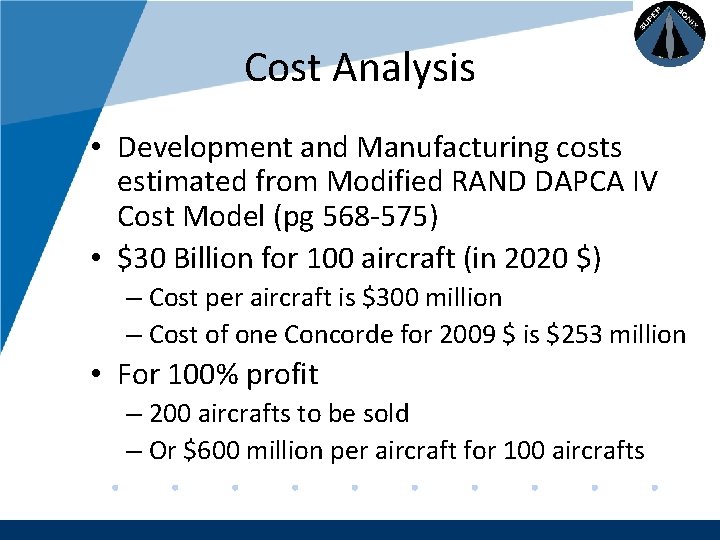
Company LOGO Cost Analysis • Development and Manufacturing costs estimated from Modified RAND DAPCA IV Cost Model (pg 568 -575) • $30 Billion for 100 aircraft (in 2020 $) – Cost per aircraft is $300 million – Cost of one Concorde for 2009 $ is $253 million • For 100% profit – 200 aircrafts to be sold – Or $600 million per aircraft for 100 aircrafts www. company. com
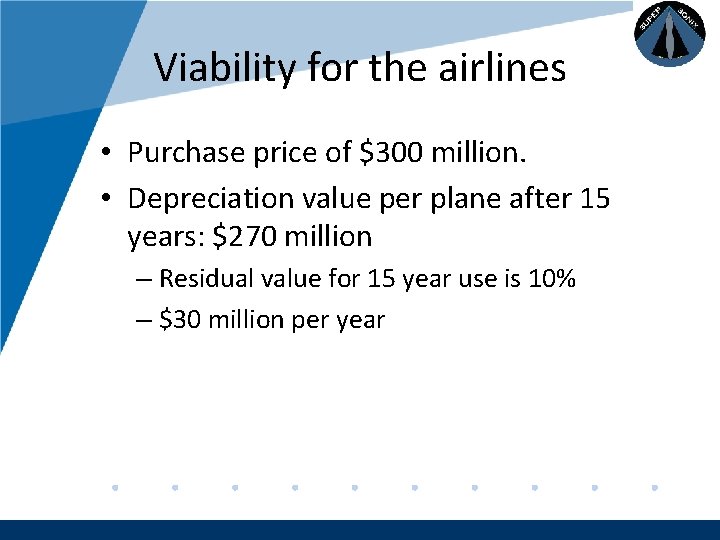
Company LOGO Viability for the airlines • Purchase price of $300 million. • Depreciation value per plane after 15 years: $270 million – Residual value for 15 year use is 10% – $30 million per year www. company. com
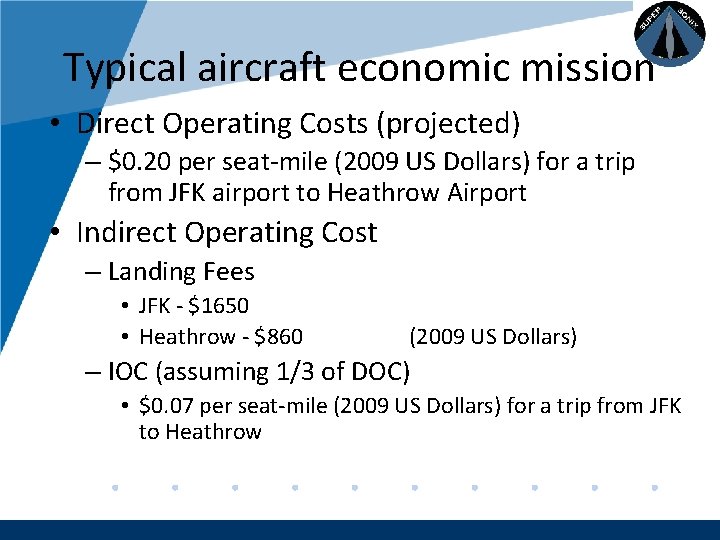
Company LOGO Typical aircraft economic mission • Direct Operating Costs (projected) – $0. 20 per seat-mile (2009 US Dollars) for a trip from JFK airport to Heathrow Airport • Indirect Operating Cost – Landing Fees • JFK - $1650 • Heathrow - $860 (2009 US Dollars) – IOC (assuming 1/3 of DOC) • $0. 07 per seat-mile (2009 US Dollars) for a trip from JFK to Heathrow www. company. com
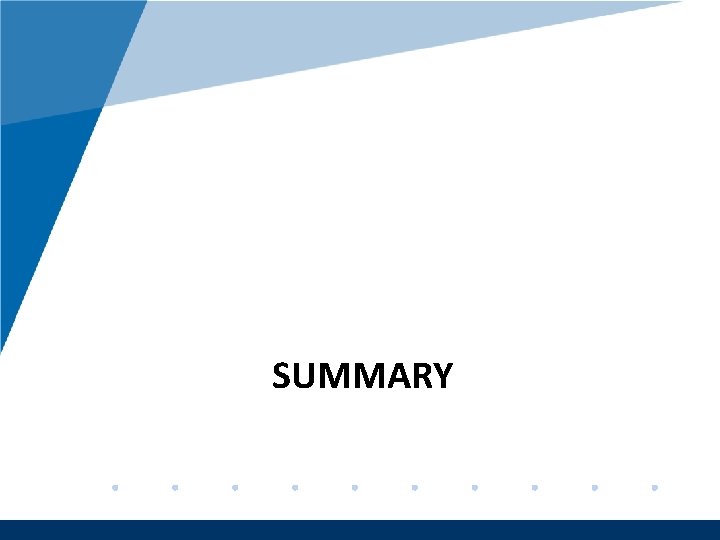
Company LOGO SUMMARY www. company. com
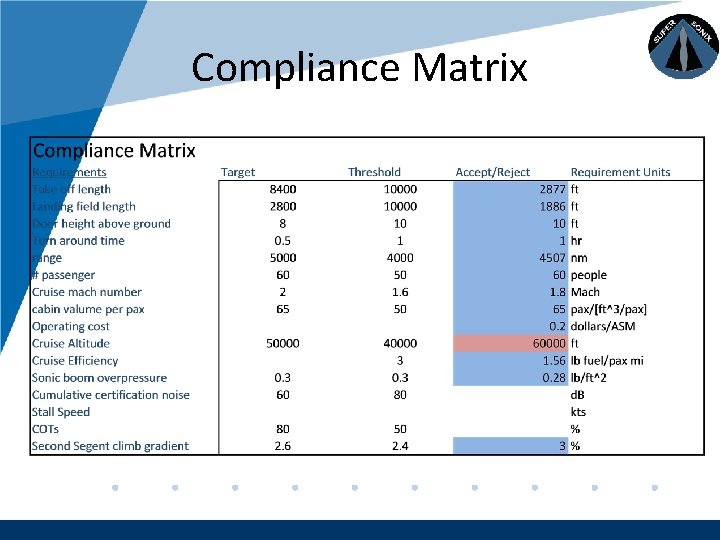
Company LOGO Compliance Matrix www. company. com
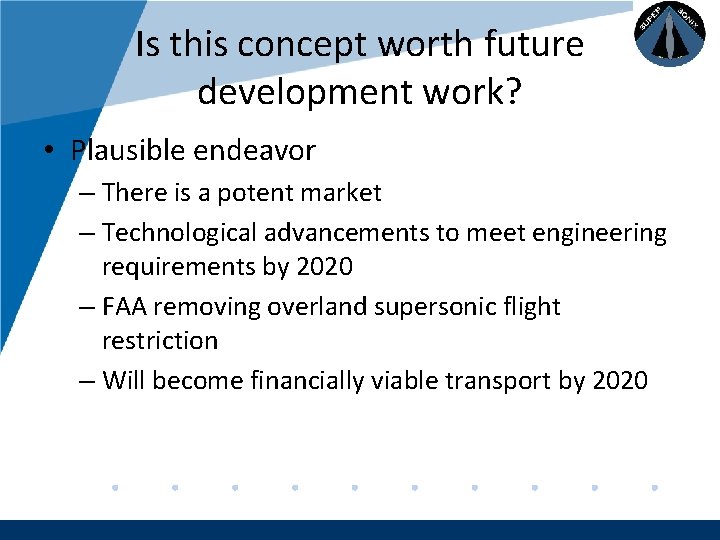
Company LOGO Is this concept worth future development work? • Plausible endeavor – There is a potent market – Technological advancements to meet engineering requirements by 2020 – FAA removing overland supersonic flight restriction – Will become financially viable transport by 2020 www. company. com

Company LOGO Next Steps • Fine tune aerodynamic analysis – Boom prediction – Airfoil analysis • Engine Performance analysis – Engine deck – Engine component design • Structural analysis – Panel buckling www. company. com
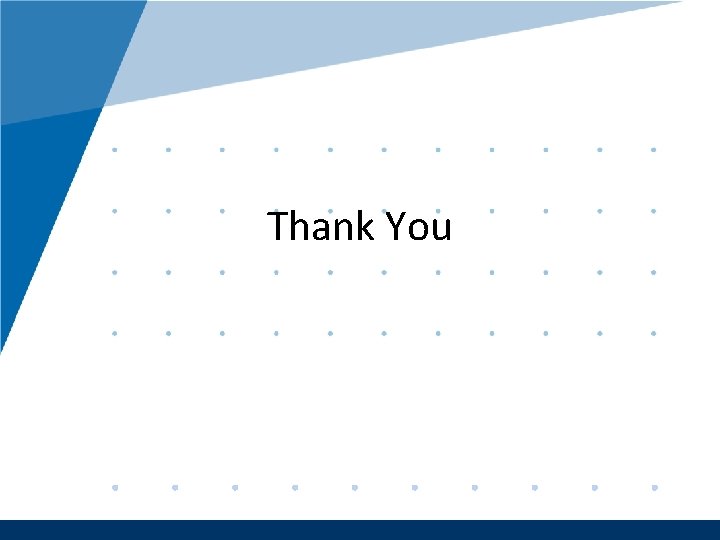
Company LOGO Thank You www. company. com
Akshay mody
Akshay kumar assistant
Akshay kumar
Kotak mkl
Akshay rangasai
Conceptual design review template
Conceptual design review
Ashok kumar pandey iith
Ashok sriram md
Panchayat raj committee
Ashok k. goel
Ashok kolaskar
Ashok mankad
Ct brain labelled
Ca ashok batra
Ashok emani
A. ashok os
Ashok leyland low floor bus
Telecom billing concepts
Donnie ashok
4 sacred mountains navajo
Libidau
Limited company vs partnership
Winding up of a company
Holdings company meaning
Multinational vs transnational corporations
What type of company was the virginia company?
Conceptual physics chapter 25
Company logo
Company logo
David cook company name logo
Company logo
Company name logo tagline
French east india company name
Company logo
Iso company logo
Company logo transfers
Virtual reality company in oman
Company logo
Lost and found notice
Company logo
Company logo
Company logo
Insert logo here
Abc company logo
Company profile review
Peer review company secretary
Chapter review motion part a vocabulary review answer key
Uncontrollable spending ap gov
Nader amin-salehi
What is inclusion and exclusion
Narrative review vs systematic review
Conceptual design examples
Contoh conceptual database design
High level conceptual data model for database design
Conceptual design database
Conceptual database design
A company needs to design a cylindrical can that holds 475
Src logo image
Logo design meaning
Logo design analysis
Logo design fundamentals
Principles of good logo design
Logo design principles
Metode logo
Bag logo design ideas
Bag logo ideas
Digital design
Preliminary design review example
Formal design reviews
Critical design review
Critical design review template
Critical design review
Cdr design review
Gmp design review
Billy blue college of design review
Oht design
Design review example
What are the five elements of hair design
Interim design review
Final design review
Chapter 3 joint design and welding terms
Internal design review
Cable installation design review
Ebay website design review
Design review presentation
Social impact statement for early design review
Pdr preliminary design review
Preliminary design review example
Design review report
Critical design review
Cdr critical design review
Social impact statement for early design review
Viscom design process
Input design
Structural design in fashion