CoMatrix Filters for Electrolyte Filtration Spin Tek Filtration
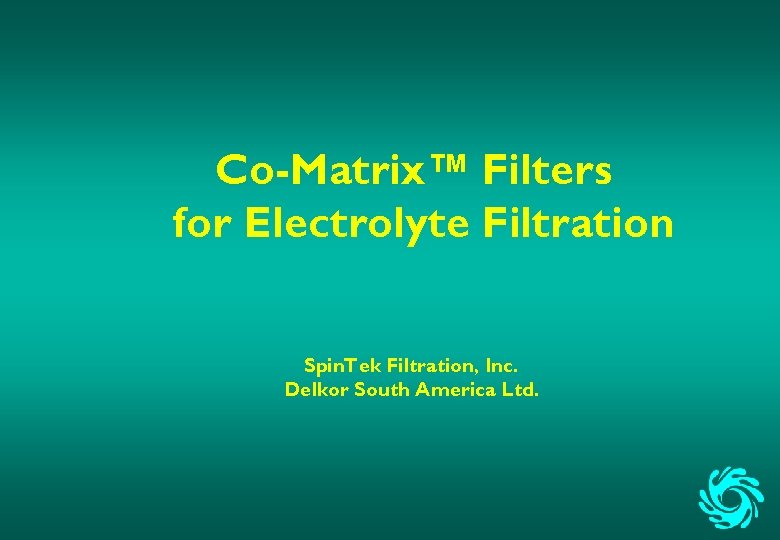
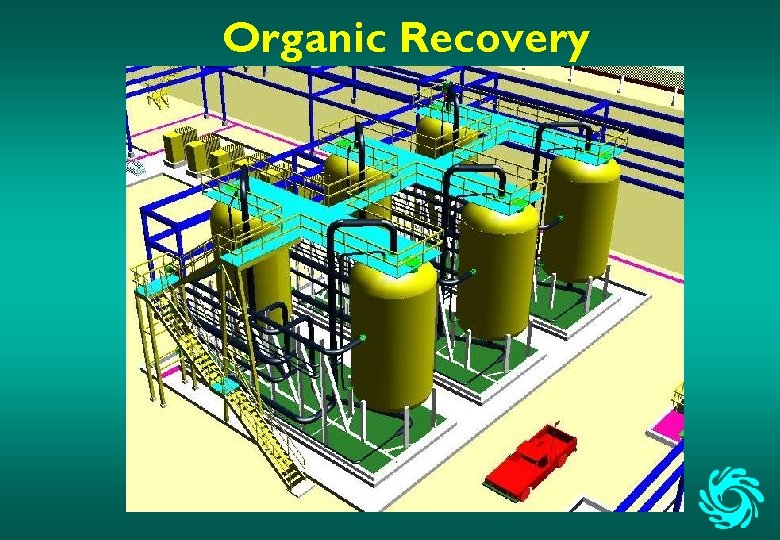
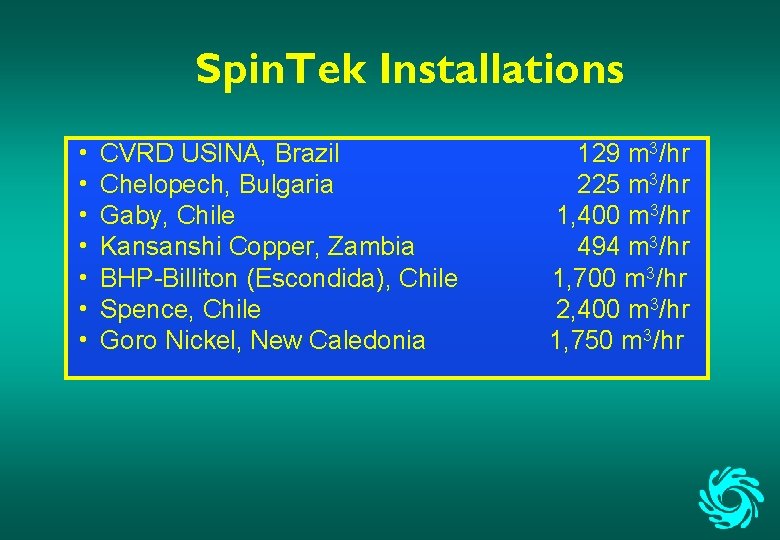
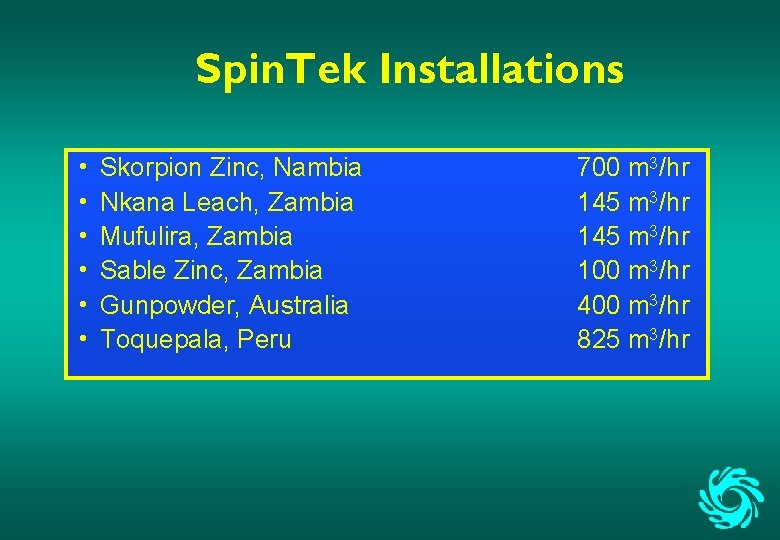
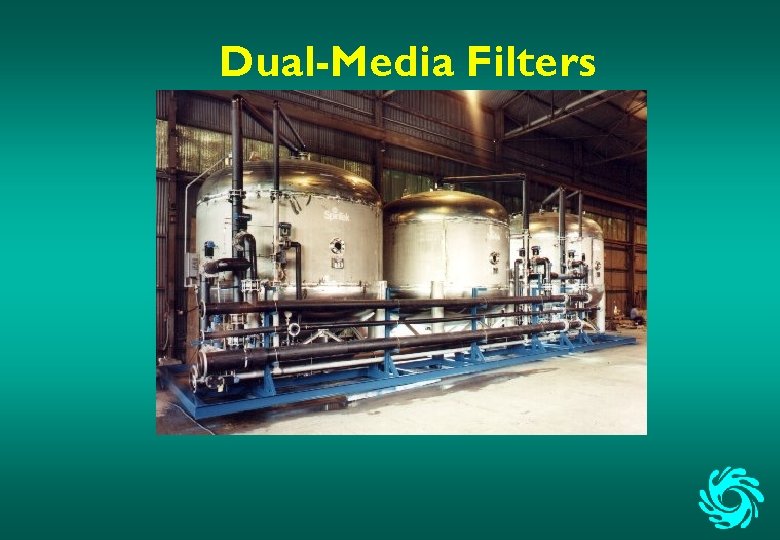
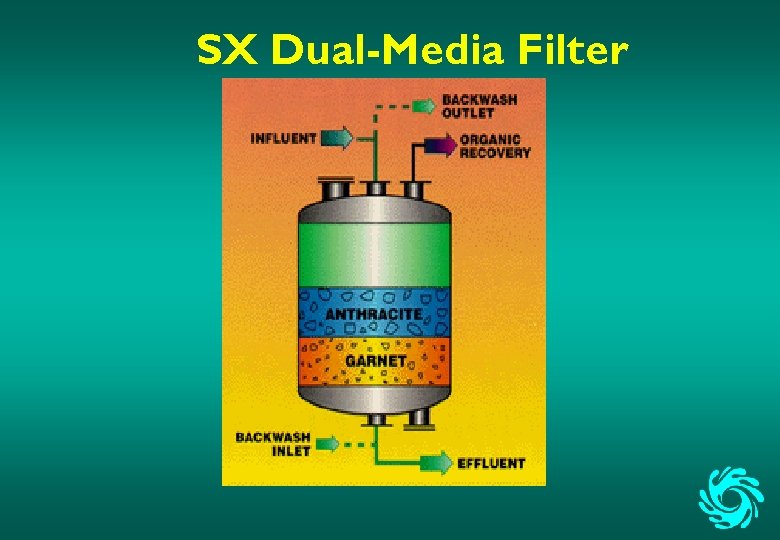
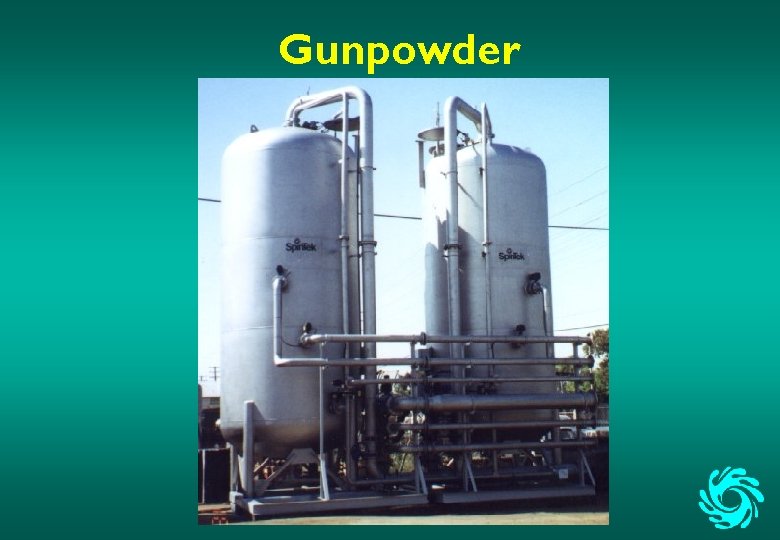
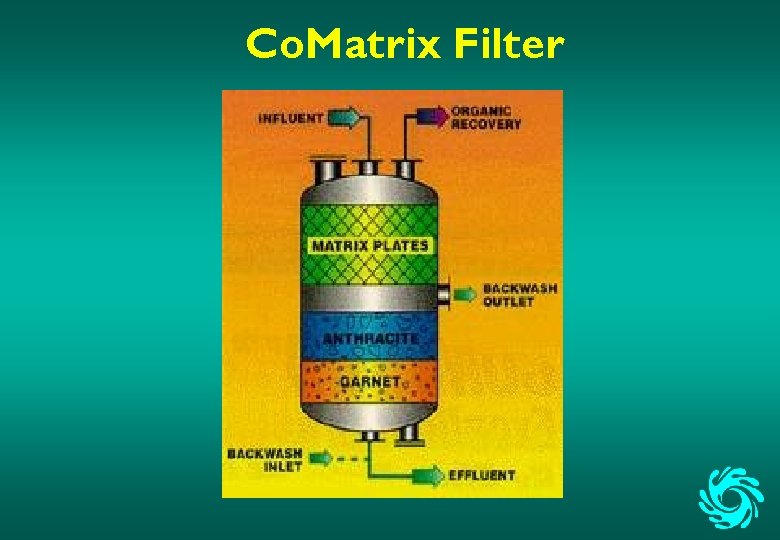
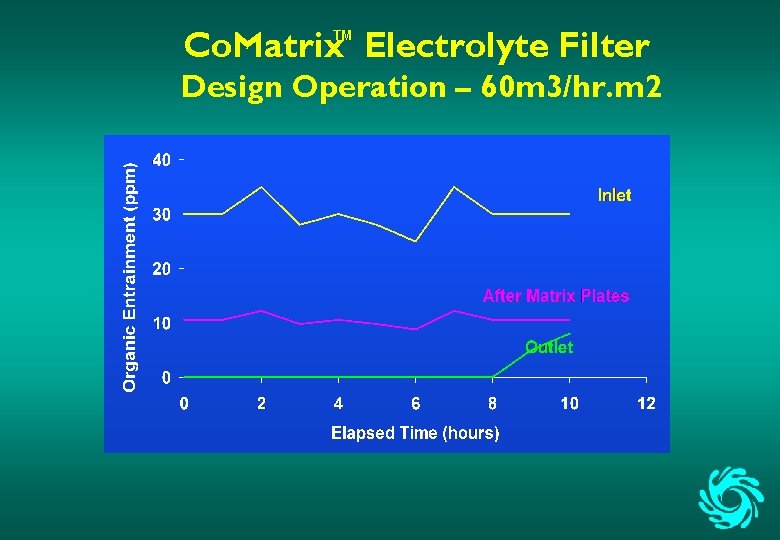
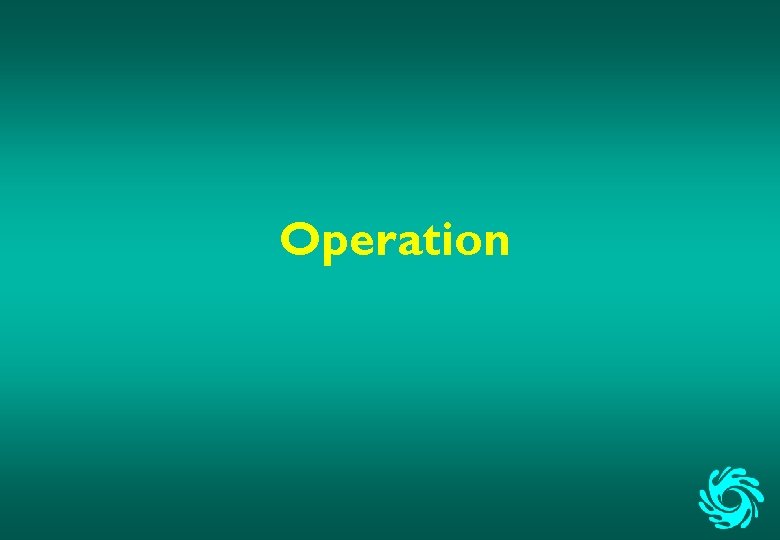
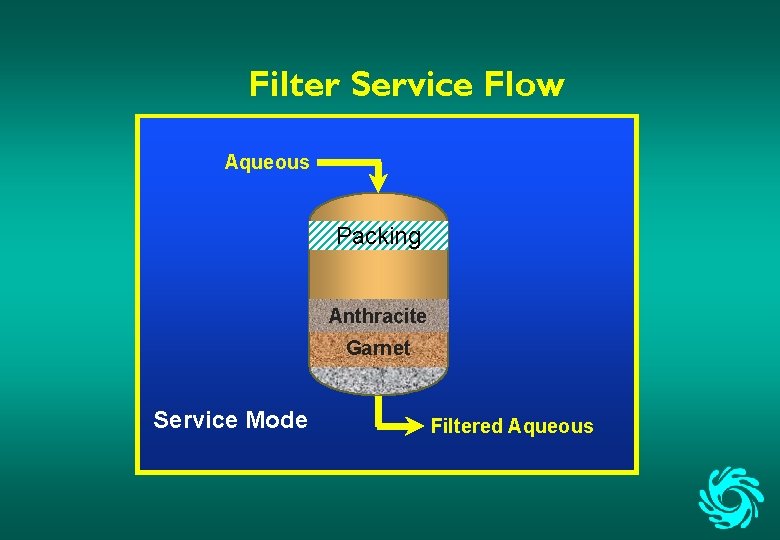
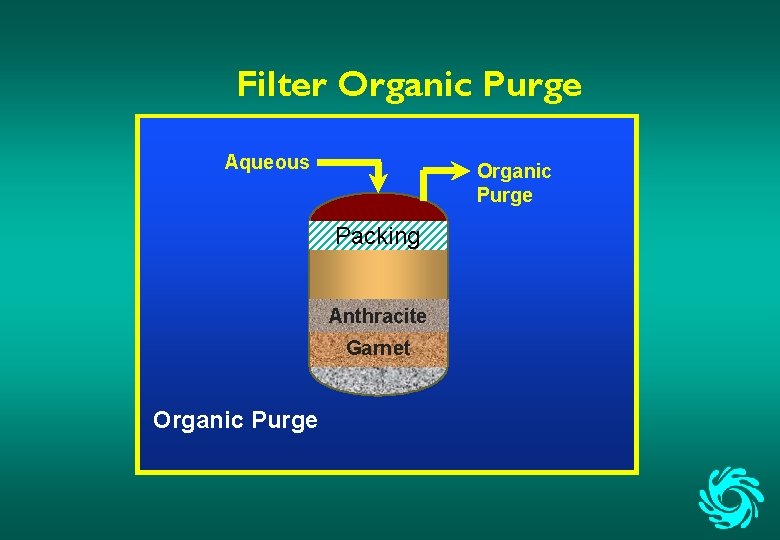
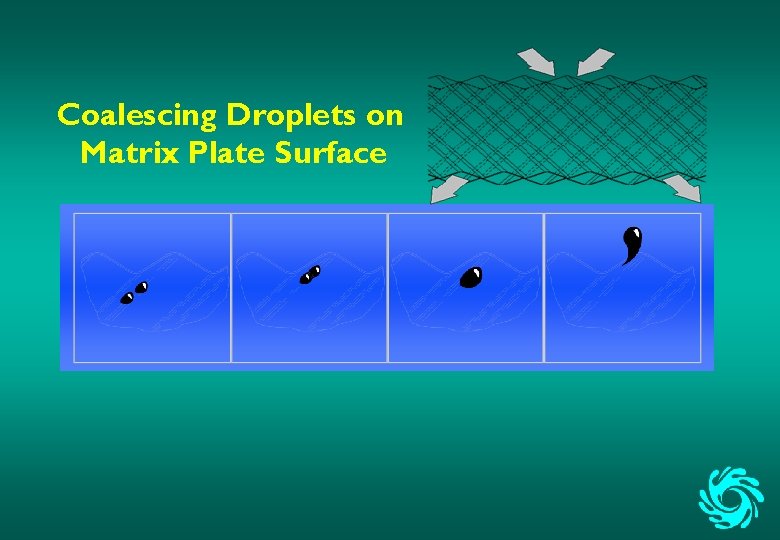
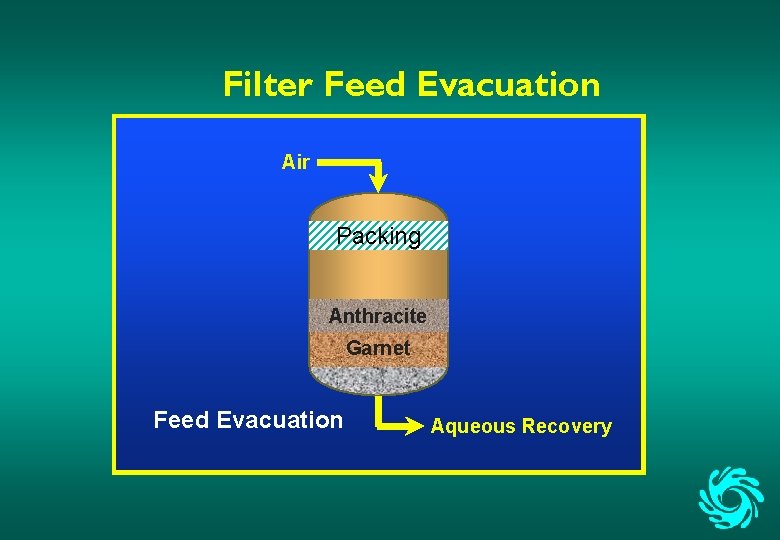
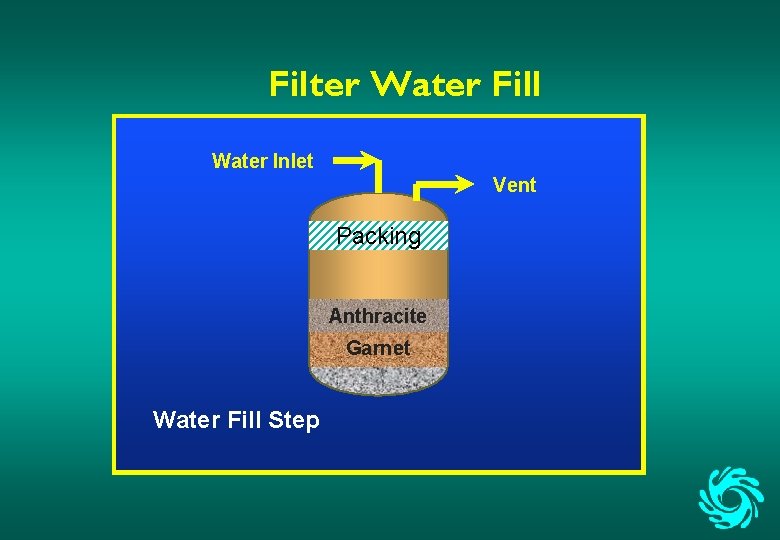
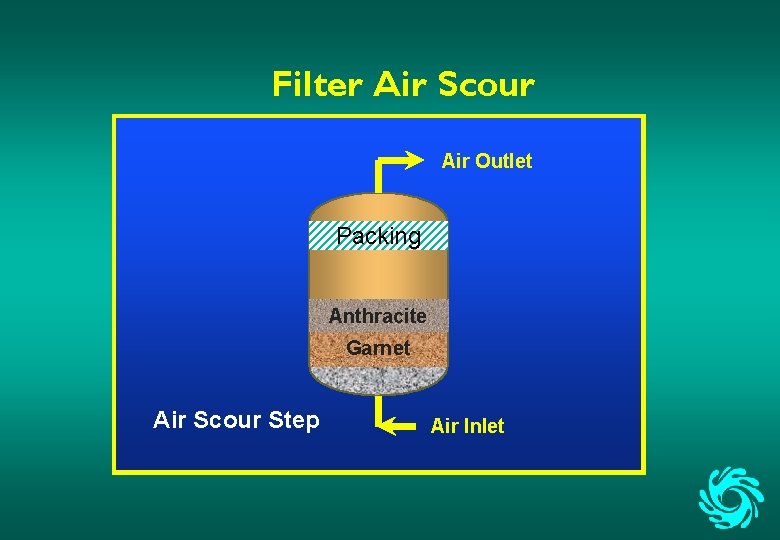
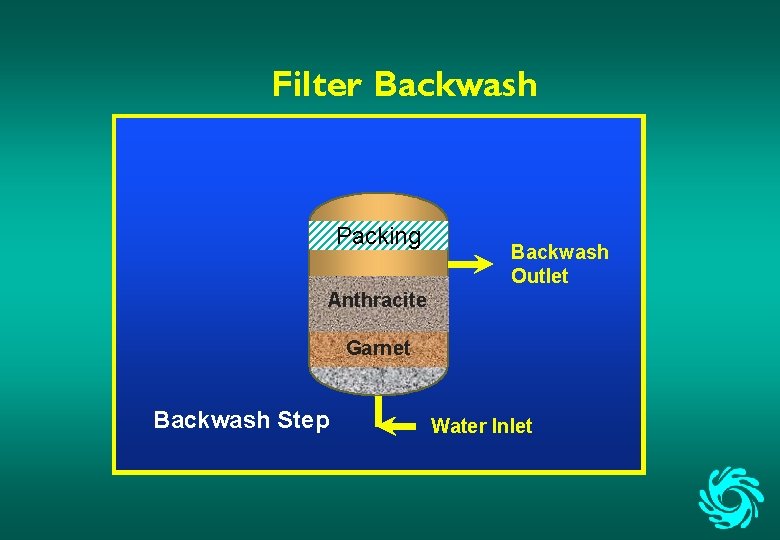
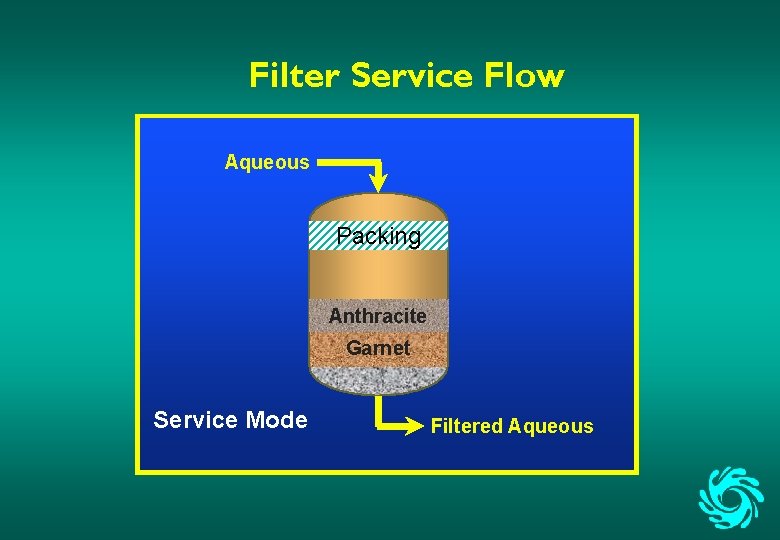
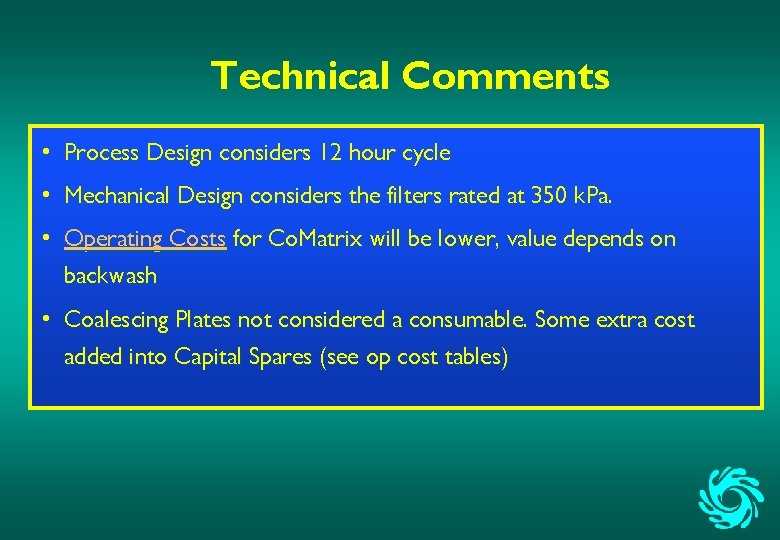
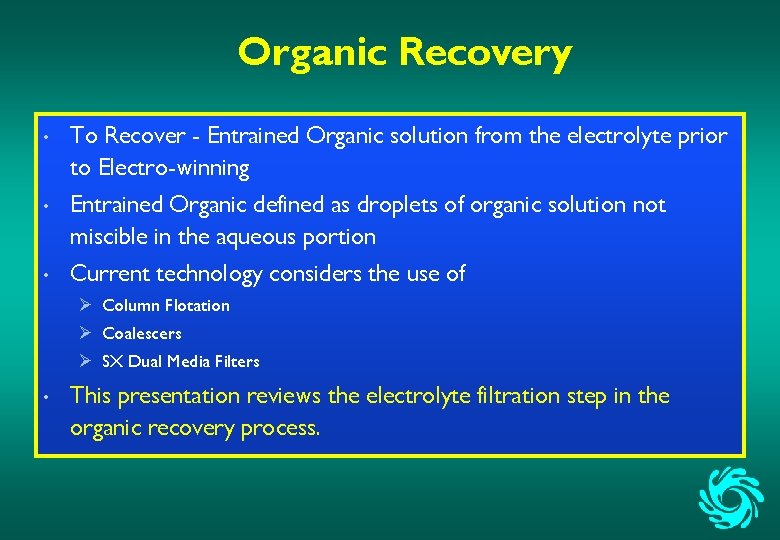
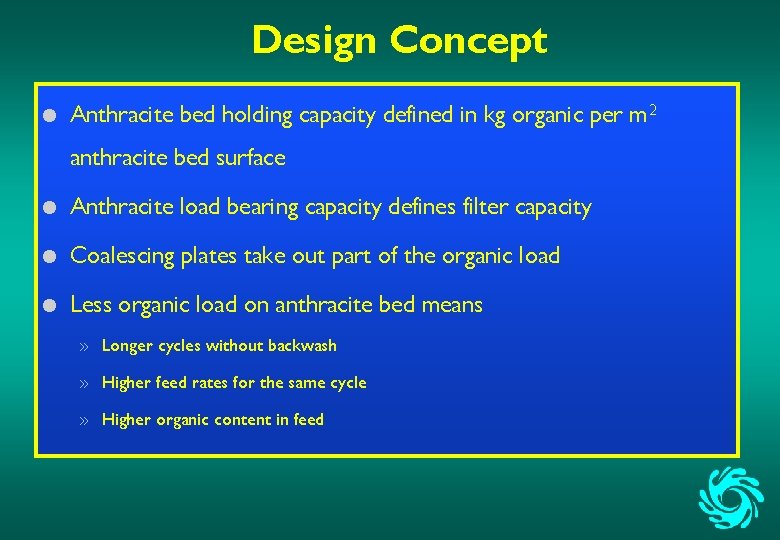
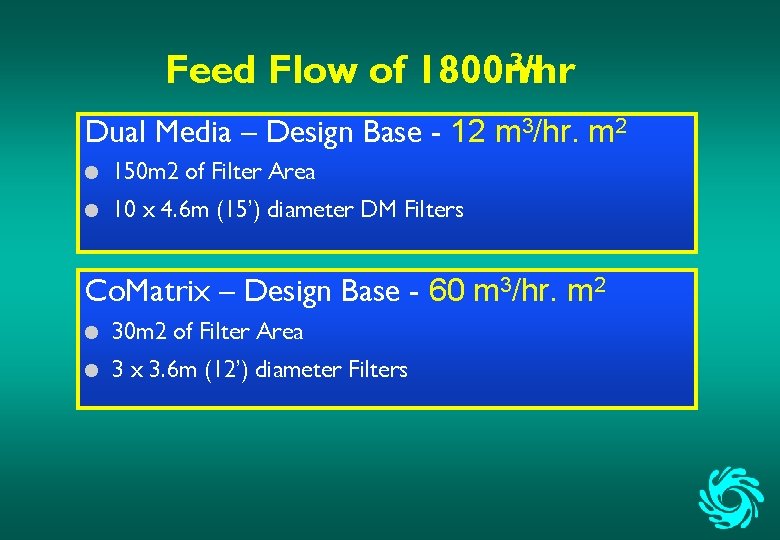
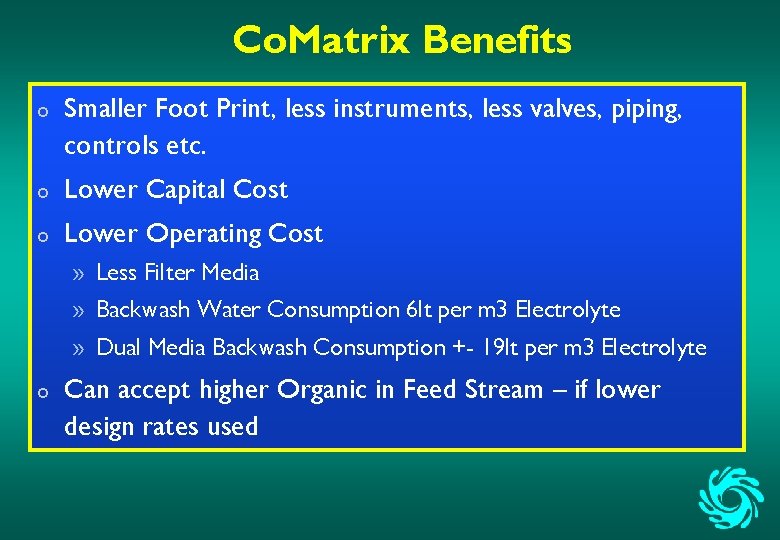
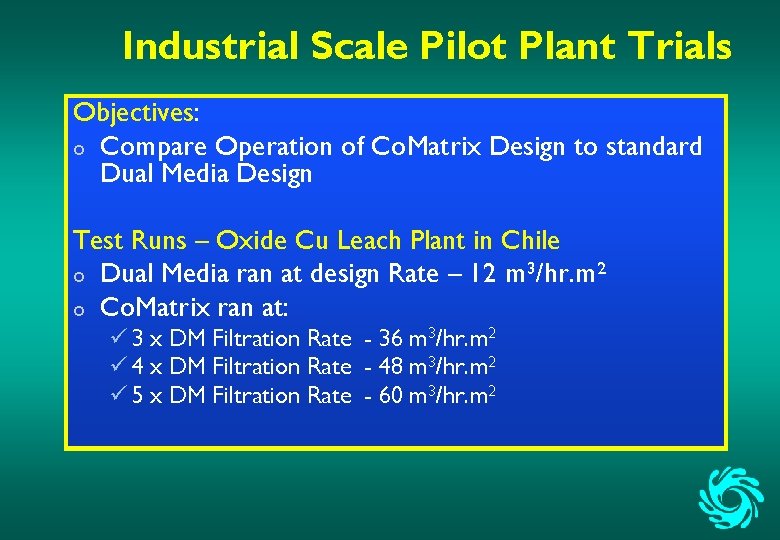
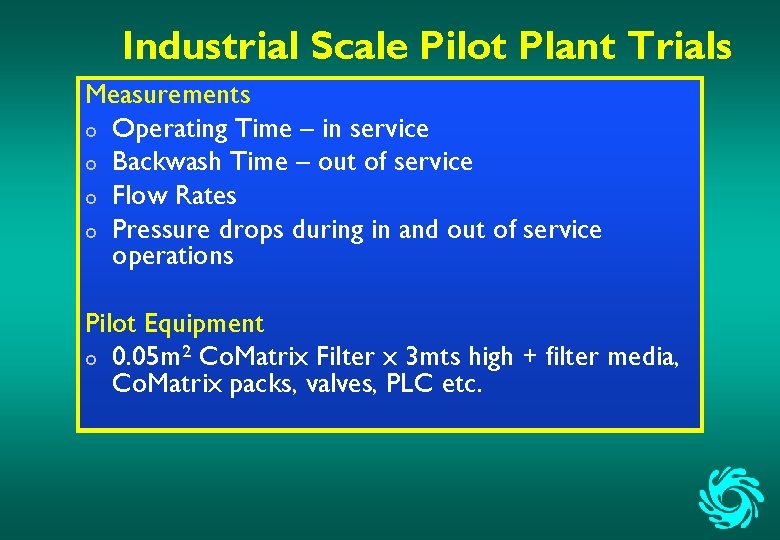
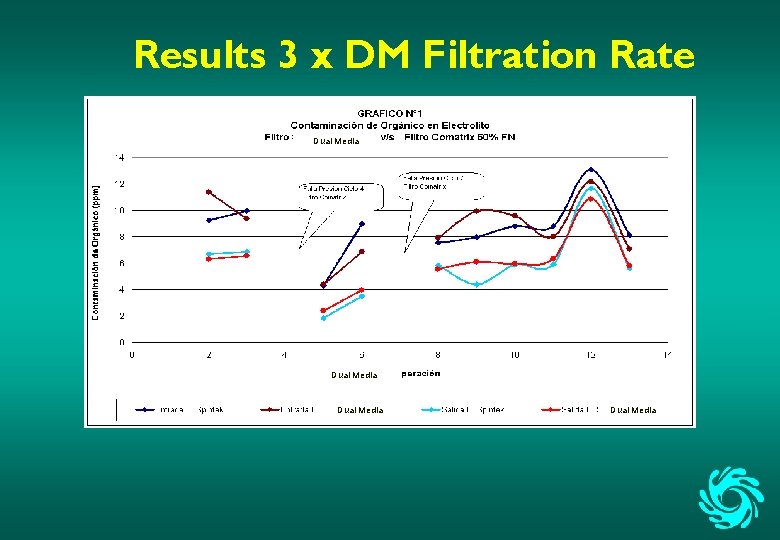
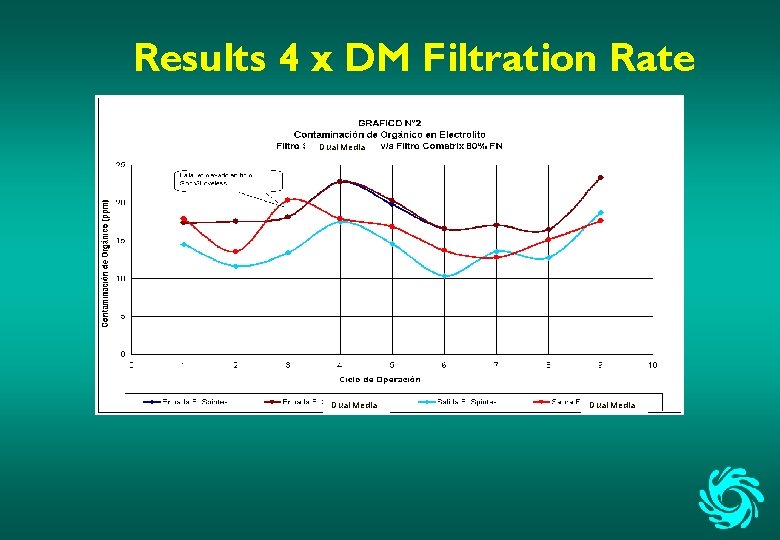

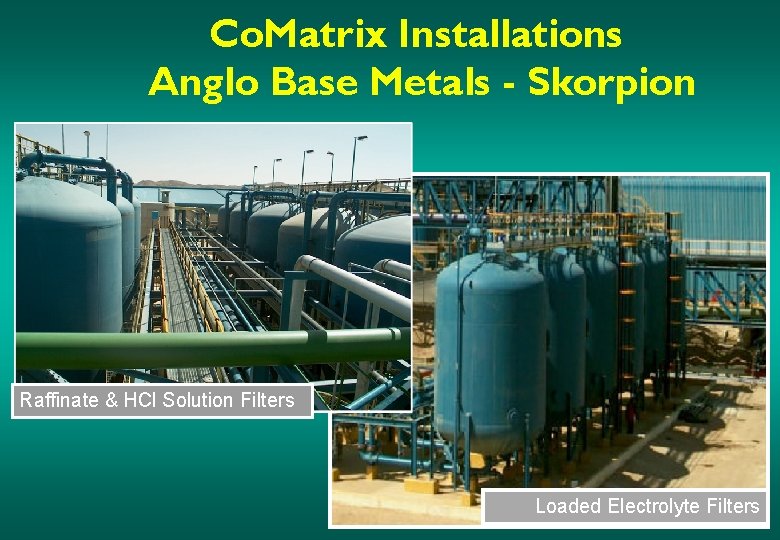
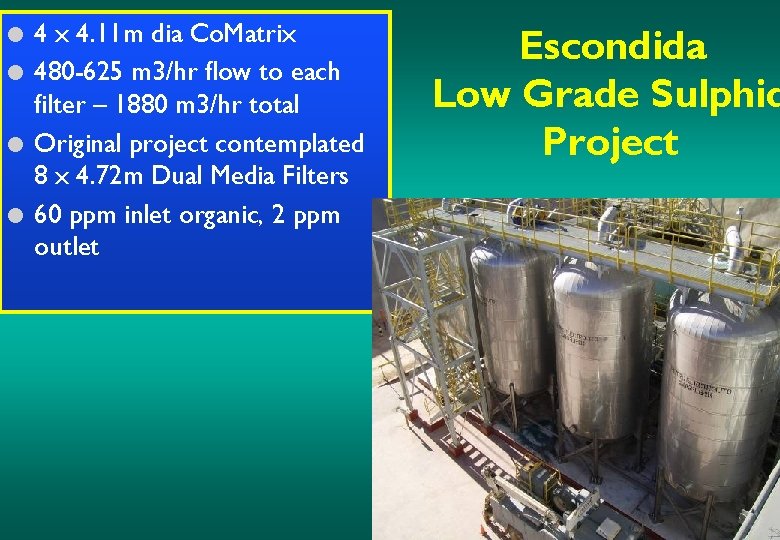
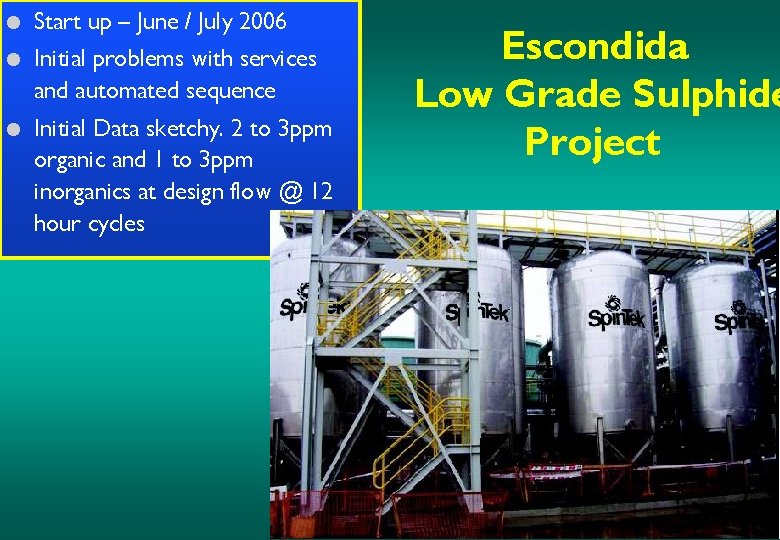
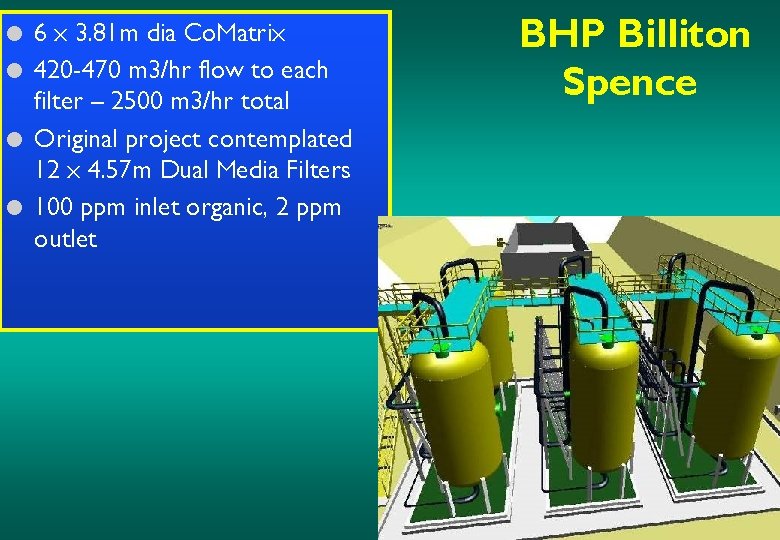
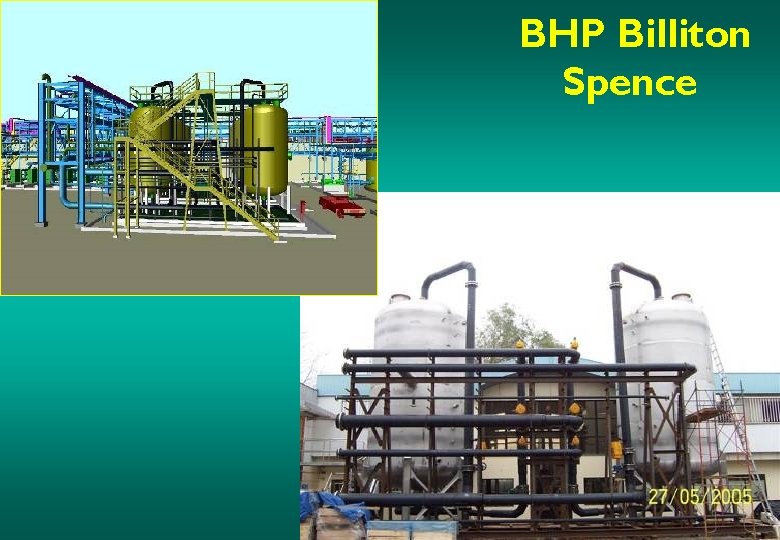
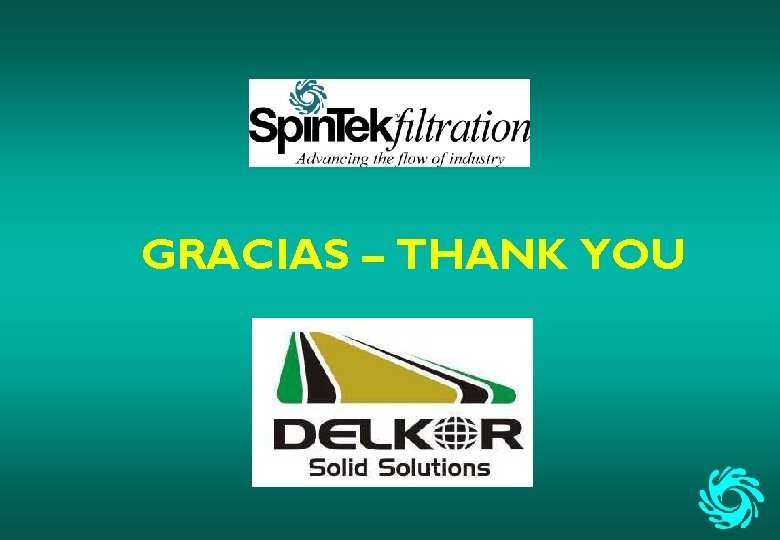
- Slides: 34
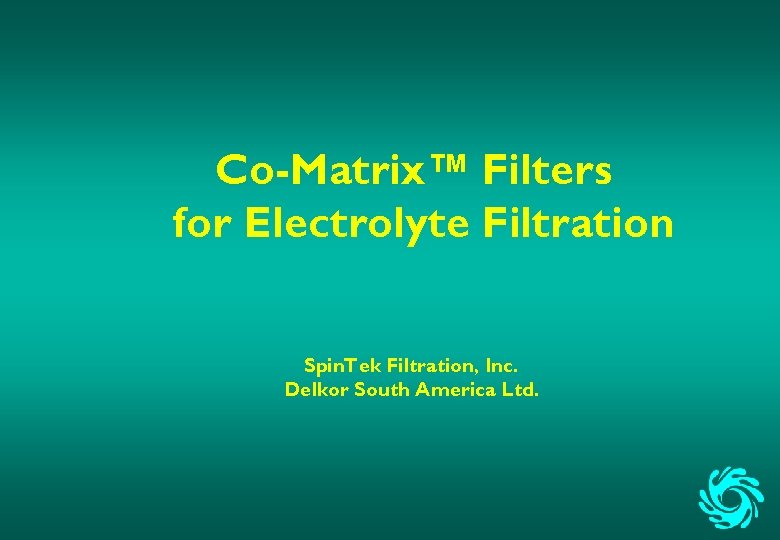
Co-Matrix™ Filters for Electrolyte Filtration Spin. Tek Filtration, Inc. Delkor South America Ltd.
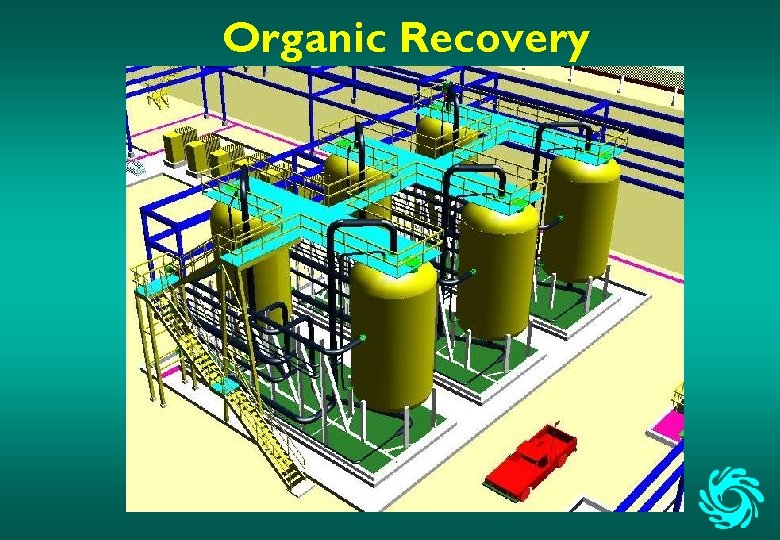
Organic Recovery
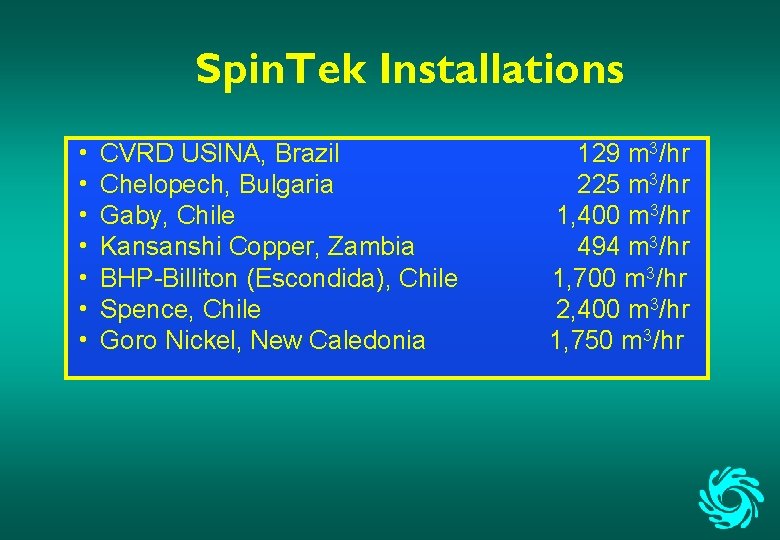
Spin. Tek Installations CVRD USINA, Brazil h Chelopech, Bulgaria h Gaby, Chile h Kansanshi Copper, Zambia h BHP-Billiton (Escondida), Chile h Spence, Chile h Goro Nickel, New Caledonia h 129 m 3/hr 225 m 3/hr 1, 400 m 3/hr 494 m 3/hr 1, 700 m 3/hr 2, 400 m 3/hr 1, 750 m 3/hr
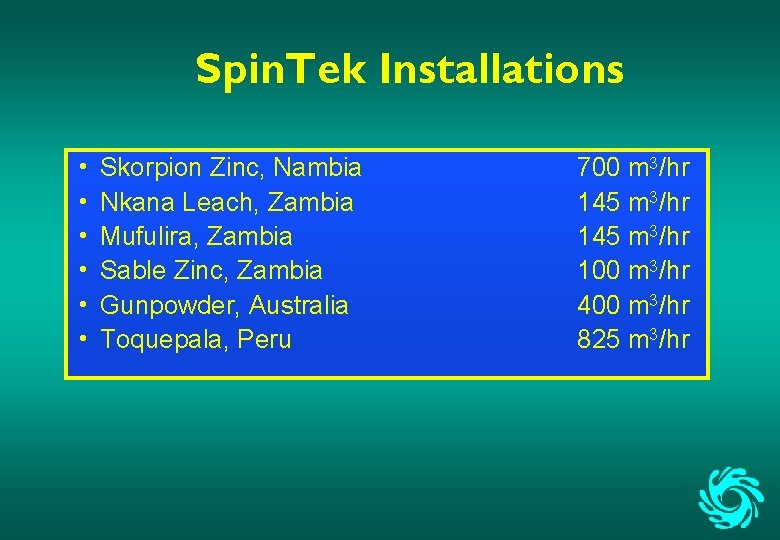
Spin. Tek Installations Skorpion Zinc, Nambia h Nkana Leach, Zambia h Mufulira, Zambia h Sable Zinc, Zambia h Gunpowder, Australia h Toquepala, Peru h 700 m 3/hr 145 m 3/hr 100 m 3/hr 400 m 3/hr 825 m 3/hr
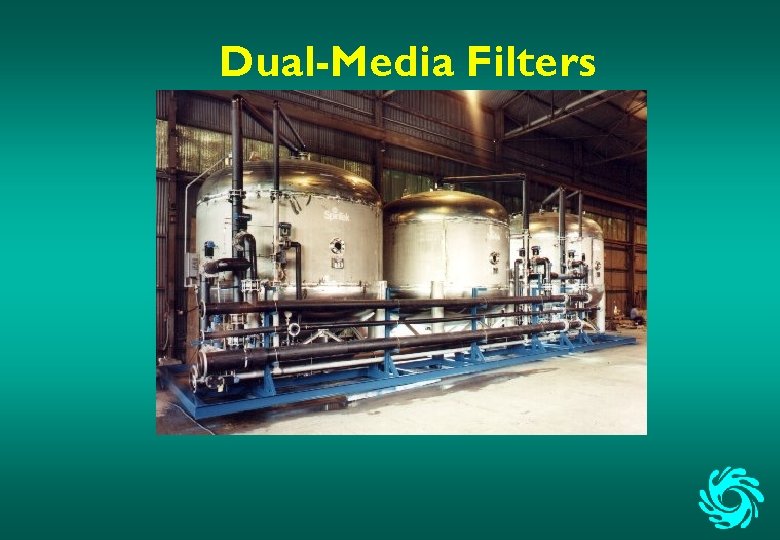
Dual-Media Filters
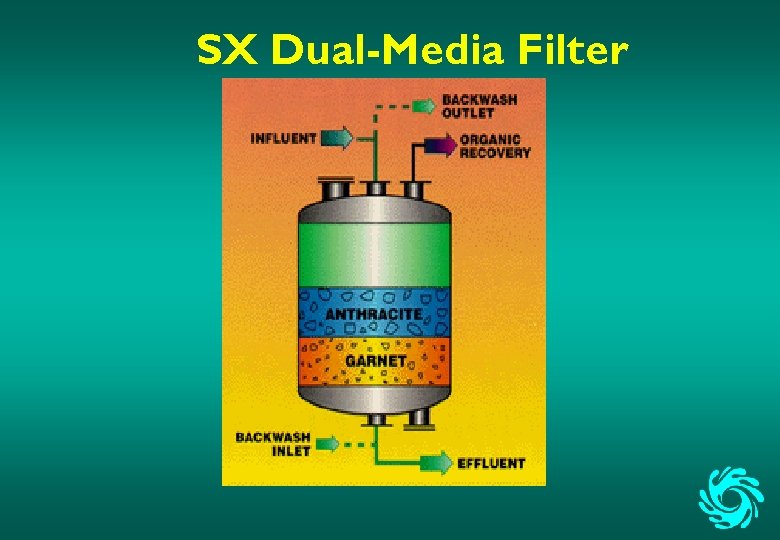
SX Dual-Media Filter
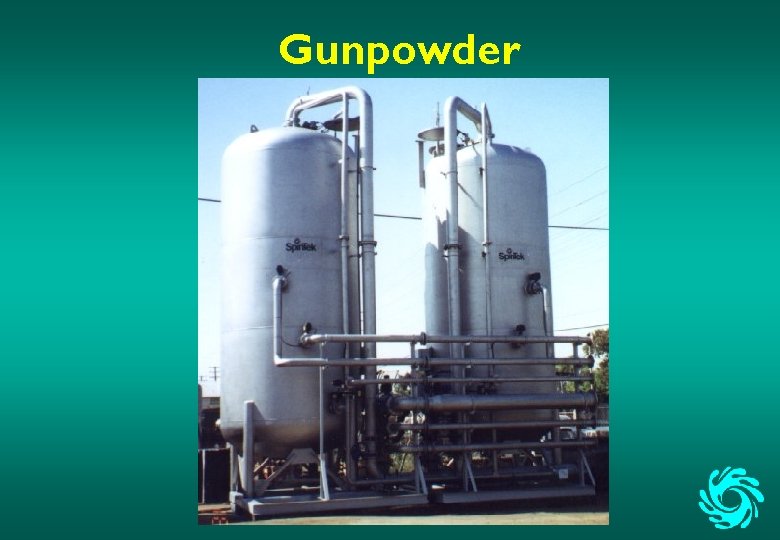
Gunpowder
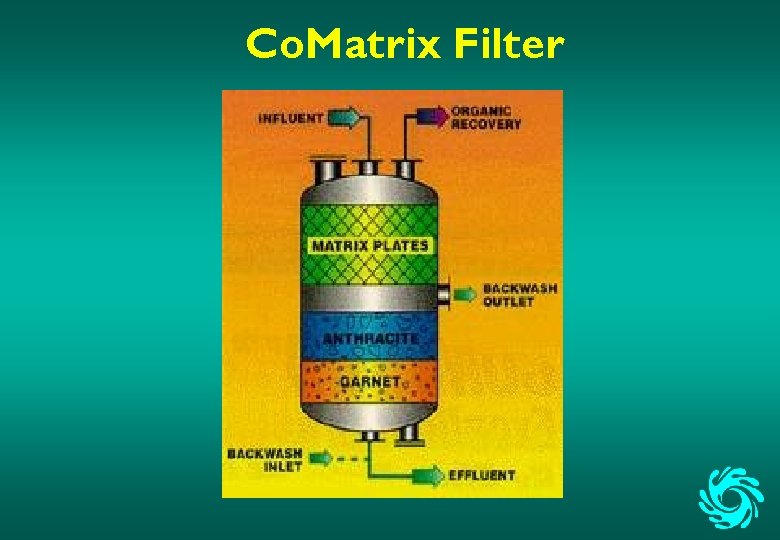
Co. Matrix Filter
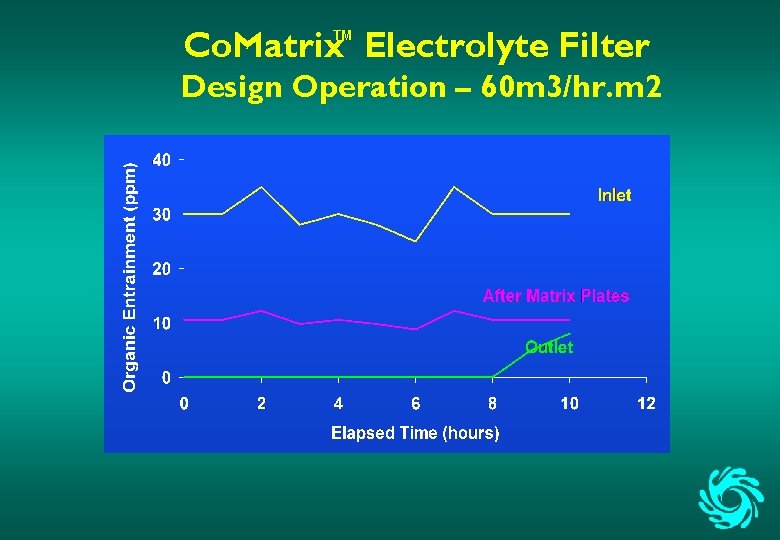
Co. Matrix™ Electrolyte Filter Design Operation – 60 m 3/hr. m 2
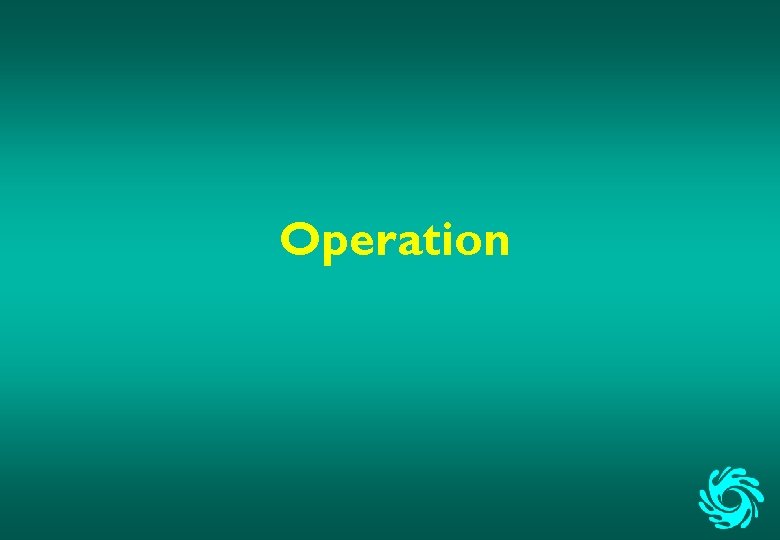
Operation
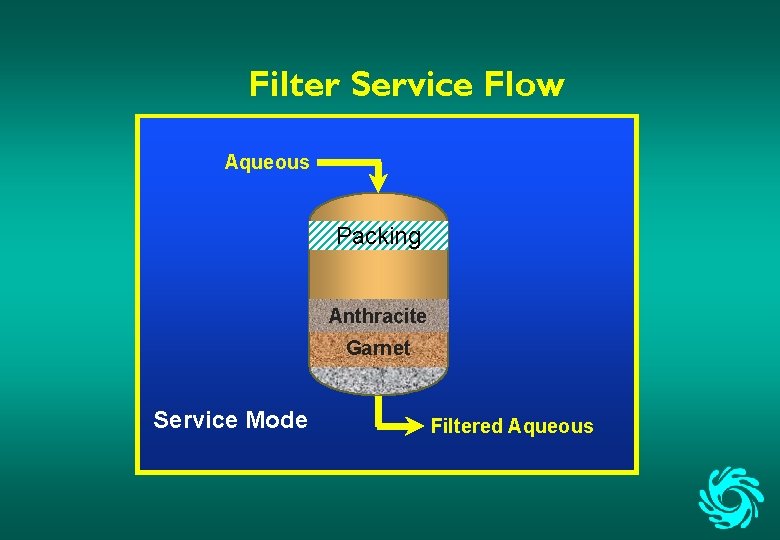
Filter Service Flow Aqueous Packing Anthracite Garnet Service Mode Filtered Aqueous
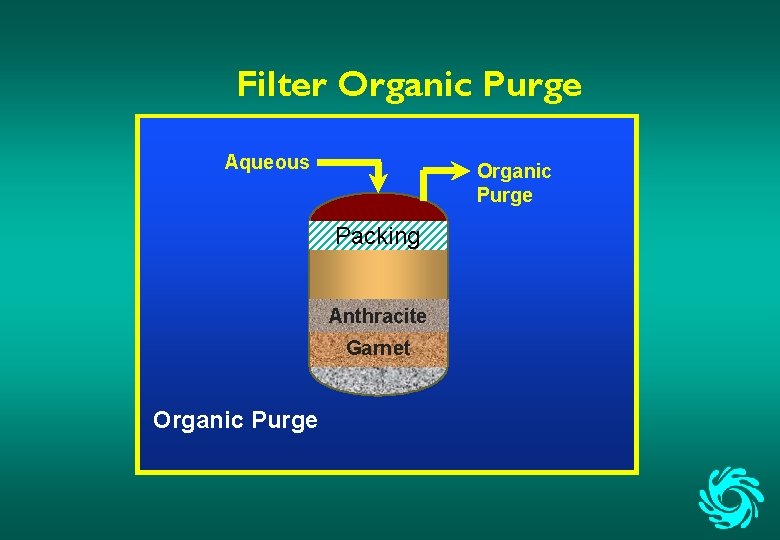
Filter Organic Purge Aqueous Organic Purge Packing Anthracite Garnet Organic Purge
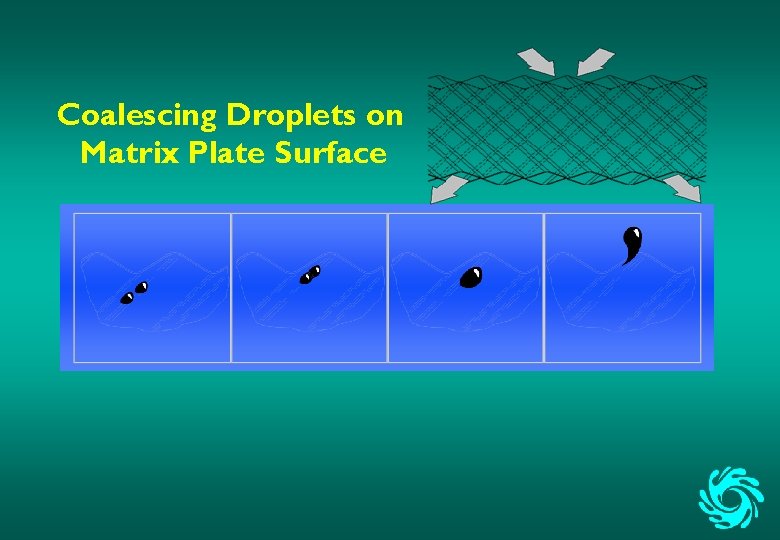
Coalescing Droplets on Matrix Plate Surface
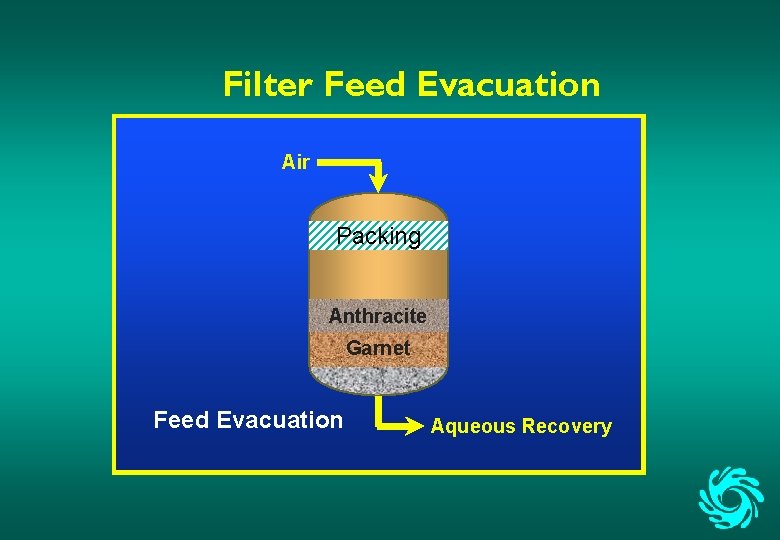
Filter Feed Evacuation Air Packing Anthracite Garnet Feed Evacuation Aqueous Recovery
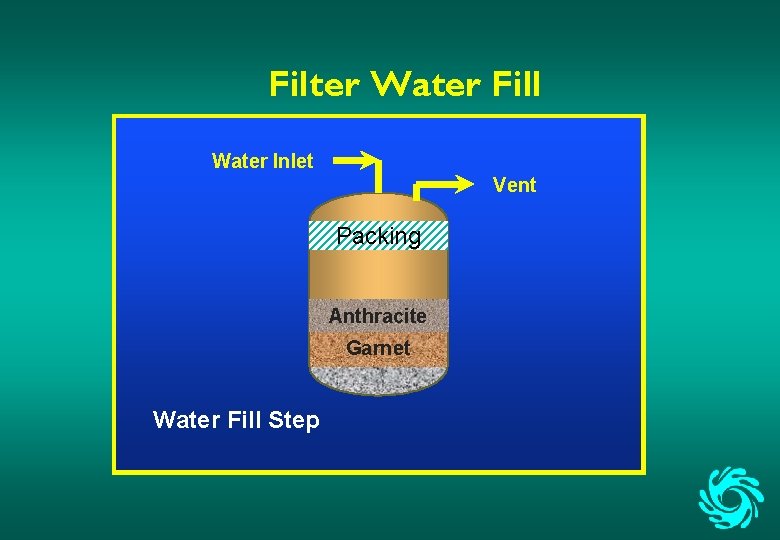
Filter Water Fill Water Inlet Vent Packing Anthracite Garnet Water Fill Step
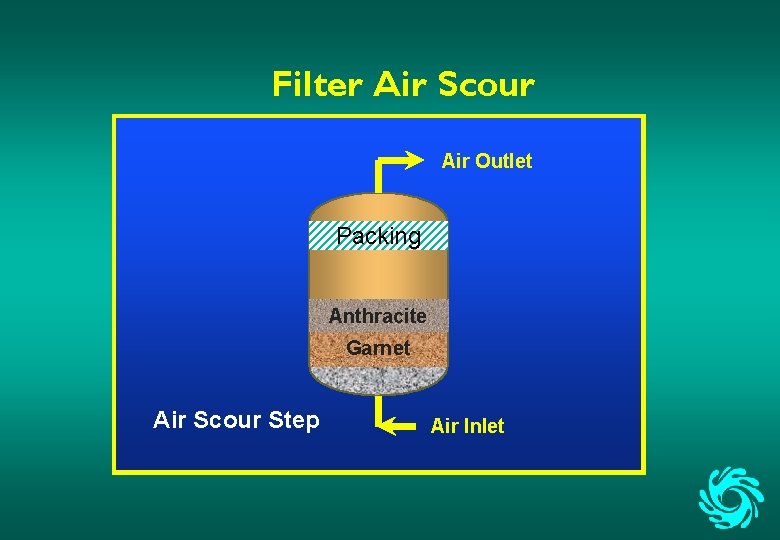
Filter Air Scour Air Outlet Packing Anthracite Garnet Air Scour Step Air Inlet
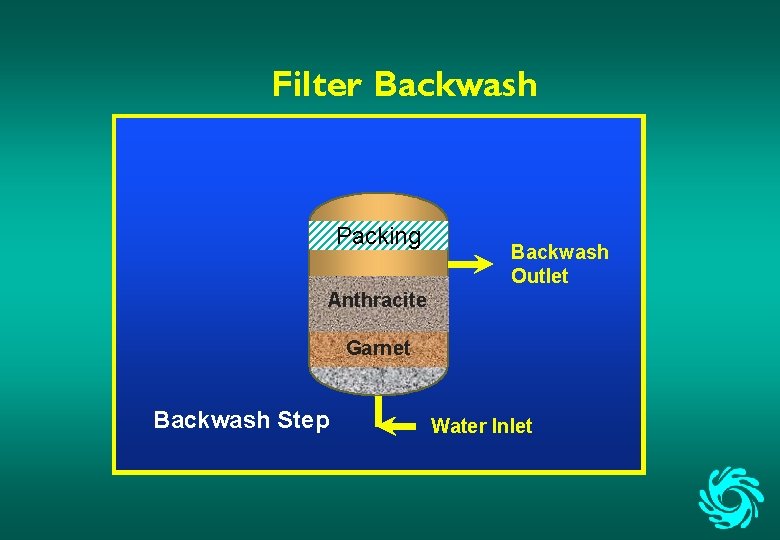
Filter Backwash Packing Backwash Outlet Anthracite Garnet Backwash Step Water Inlet
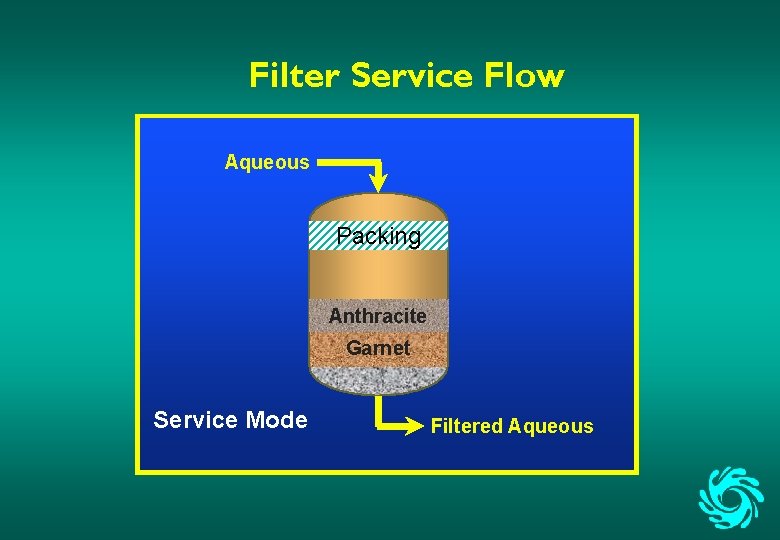
Filter Service Flow Aqueous Packing Anthracite Garnet Service Mode Filtered Aqueous
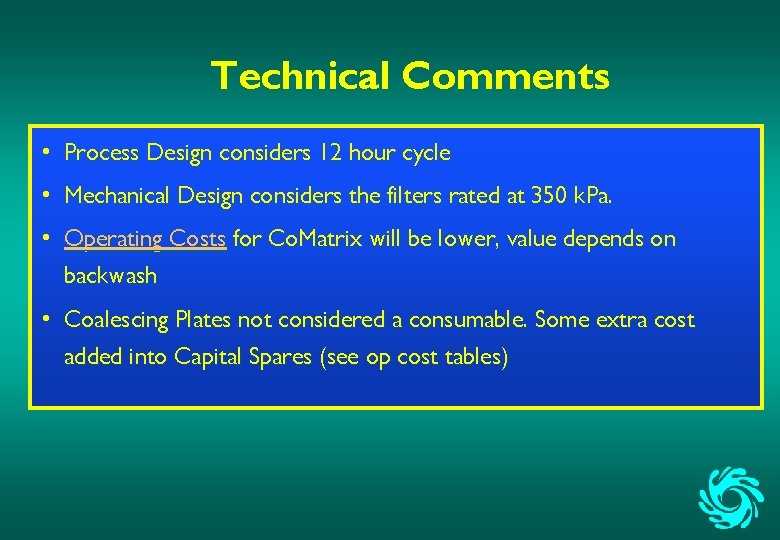
Technical Comments i Process Design considers 12 hour cycle i Mechanical Design considers the filters rated at 350 k. Pa. i Operating Costs for Co. Matrix will be lower, value depends on backwash i Coalescing Plates not considered a consumable. Some extra cost added into Capital Spares (see op cost tables)
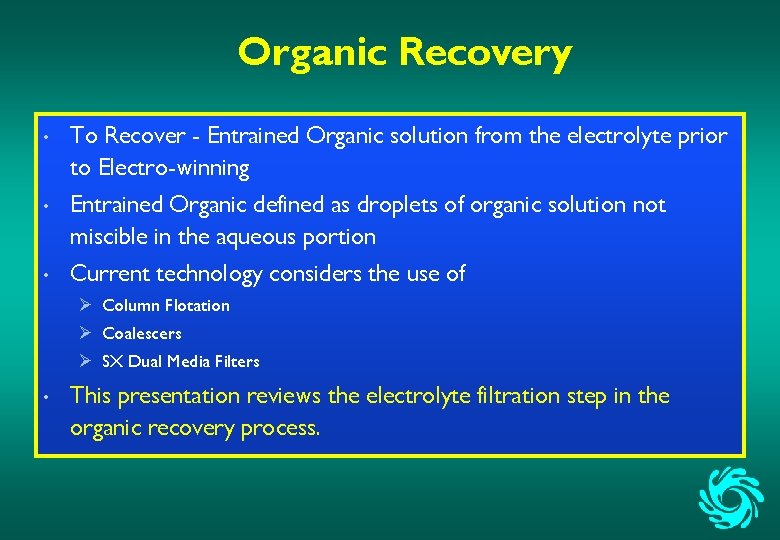
Organic Recovery • To Recover - Entrained Organic solution from the electrolyte prior to Electro-winning • Entrained Organic defined as droplets of organic solution not miscible in the aqueous portion • Current technology considers the use of Ø Column Flotation Ø Coalescers Ø SX Dual Media Filters • This presentation reviews the electrolyte filtration step in the organic recovery process.
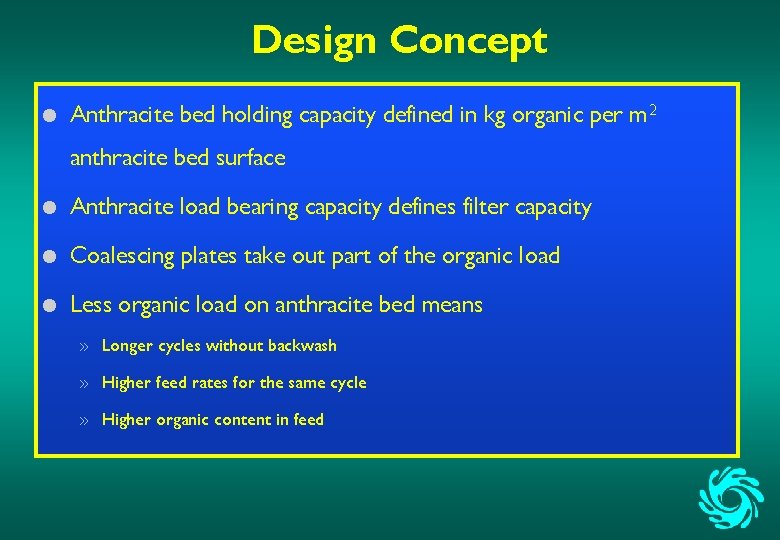
Design Concept l Anthracite bed holding capacity defined in kg organic per m 2 anthracite bed surface l Anthracite load bearing capacity defines filter capacity l Coalescing plates take out part of the organic load l Less organic load on anthracite bed means » Longer cycles without backwash » Higher feed rates for the same cycle » Higher organic content in feed
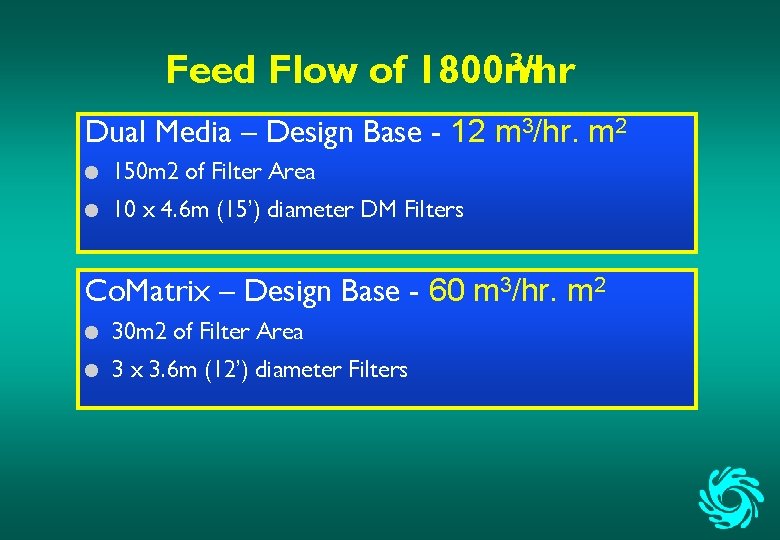
3/hr Feed Flow of 1800 m Dual Media – Design Base - 12 m 3/hr. m 2 l 150 m 2 of Filter Area l 10 x 4. 6 m (15’) diameter DM Filters Co. Matrix – Design Base - 60 m 3/hr. m 2 l 30 m 2 of Filter Area l 3 x 3. 6 m (12’) diameter Filters
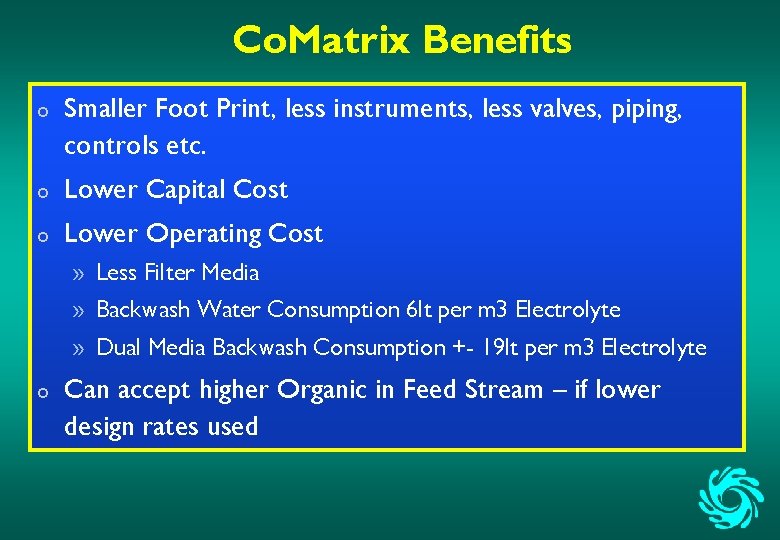
Co. Matrix Benefits o Smaller Foot Print, less instruments, less valves, piping, controls etc. o Lower Capital Cost o Lower Operating Cost » Less Filter Media » Backwash Water Consumption 6 lt per m 3 Electrolyte » Dual Media Backwash Consumption +- 19 lt per m 3 Electrolyte o Can accept higher Organic in Feed Stream – if lower design rates used
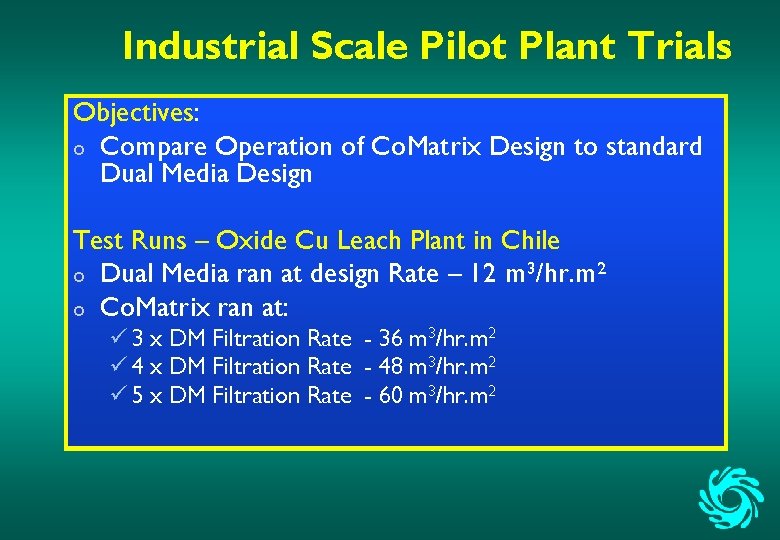
Industrial Scale Pilot Plant Trials Objectives: o Compare Operation of Co. Matrix Design to standard Dual Media Design Test Runs – Oxide Cu Leach Plant in Chile o Dual Media ran at design Rate – 12 m 3/hr. m 2 o Co. Matrix ran at: ü 3 x DM Filtration Rate - 36 m 3/hr. m 2 ü 4 x DM Filtration Rate - 48 m 3/hr. m 2 ü 5 x DM Filtration Rate - 60 m 3/hr. m 2
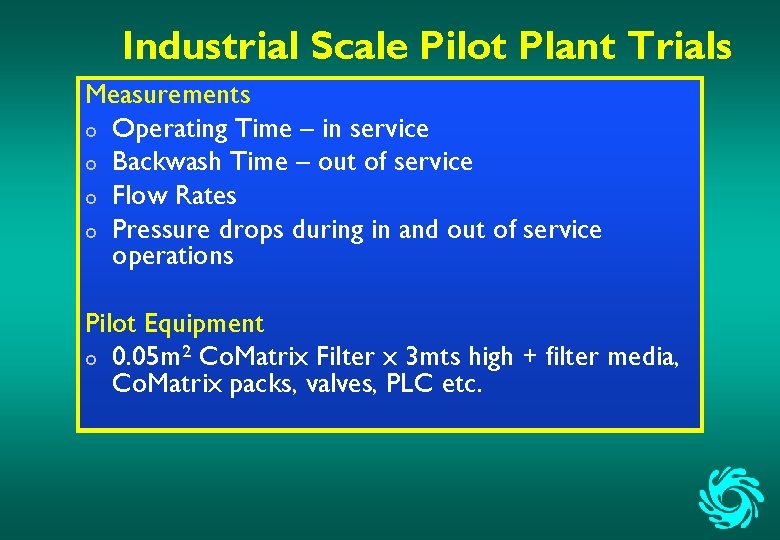
Industrial Scale Pilot Plant Trials Measurements o Operating Time – in service o Backwash Time – out of service o Flow Rates o Pressure drops during in and out of service operations Pilot Equipment o 0. 05 m 2 Co. Matrix Filter x 3 mts high + filter media, Co. Matrix packs, valves, PLC etc.
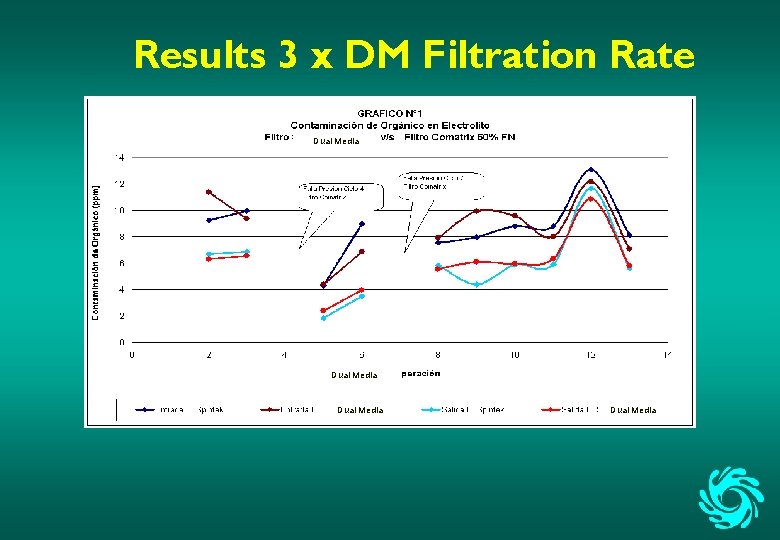
Results 3 x DM Filtration Rate Dual Media
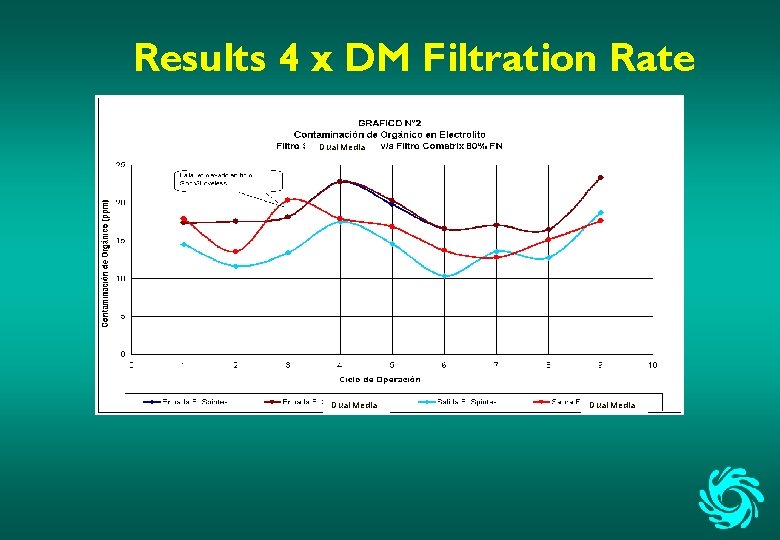
Results 4 x DM Filtration Rate Dual Media

Results 5 x DM Filtration Rate Dual Media Organic Break Through after 8 hours
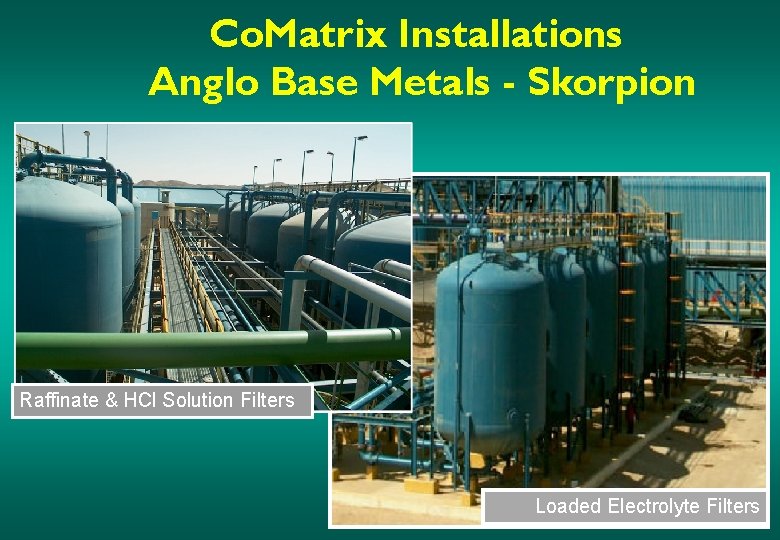
Co. Matrix Installations Anglo Base Metals - Skorpion Raffinate & HCl Solution Filters Loaded Electrolyte Filters
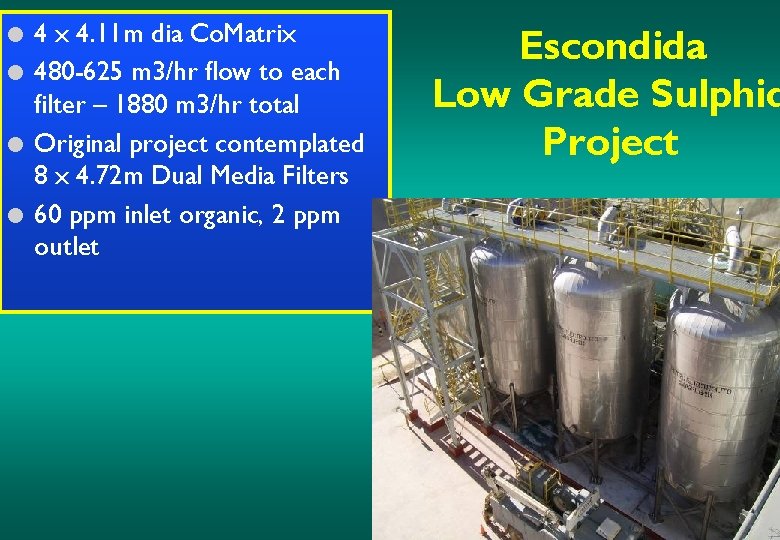
l l 4 x 4. 11 m dia Co. Matrix 480 -625 m 3/hr flow to each filter – 1880 m 3/hr total Original project contemplated 8 x 4. 72 m Dual Media Filters 60 ppm inlet organic, 2 ppm outlet Escondida Low Grade Sulphid Project
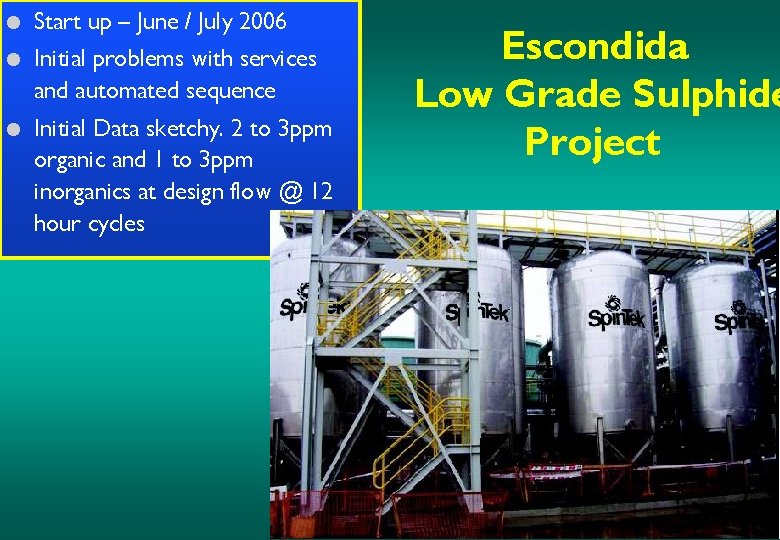
l Start up – June / July 2006 l Initial problems with services and automated sequence l Initial Data sketchy. 2 to 3 ppm organic and 1 to 3 ppm inorganics at design flow @ 12 hour cycles Escondida Low Grade Sulphide Project
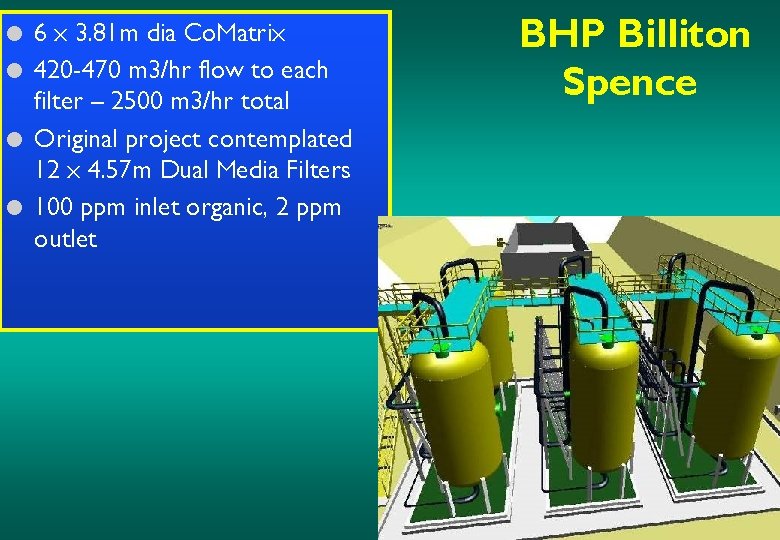
l l 6 x 3. 81 m dia Co. Matrix 420 -470 m 3/hr flow to each filter – 2500 m 3/hr total Original project contemplated 12 x 4. 57 m Dual Media Filters 100 ppm inlet organic, 2 ppm outlet BHP Billiton Spence
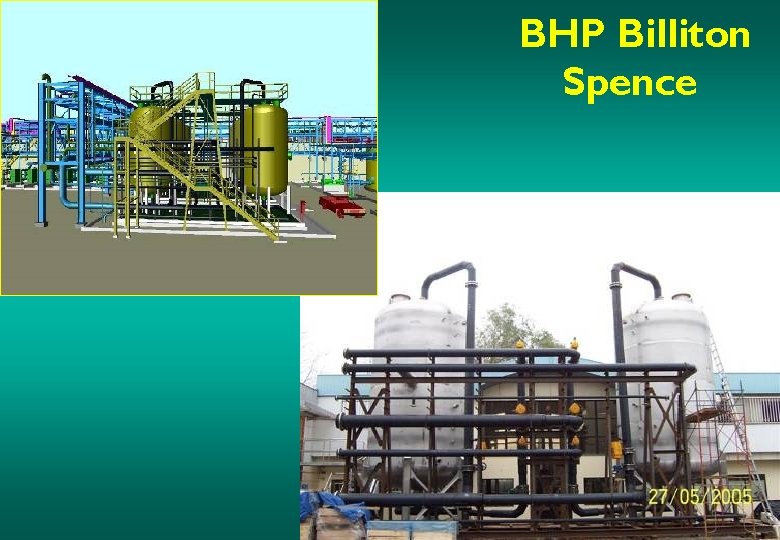
BHP Billiton Spence
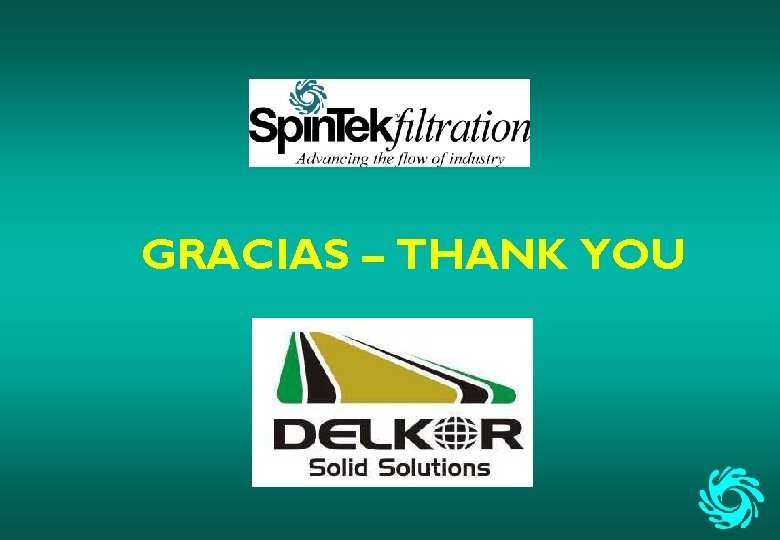
GRACIAS – THANK YOU
Larox dm dual media electrolyte filter
Disc filters galaxy 4 spin klin series
What is a low spin complex
優點
J'
Spin spin coupling
Spin spin coupling
Filter medium resistance formula
Weak electrolyte examples
Normal electrolytes values
Degree of dissociation of electrolyte depends on
Water distribution in the body
Hf electrolyte
Role of lungs and kidneys in acid base balance
Fluid and electrolyte balance ppt
Chapter 26 fluid electrolyte and acid-base balance
Refeeding syndrome electrolyte abnormalities
Hypochloremia
Water electrolyte imbalance
Anp
Normal electrolyte values
Electrolyte replacement therapy
Discriminative training of kalman filters
[ie8s]http://www.microsoft.com/*
Jlv new user training quizlet
Active vs passive filter
Erp boot camp
Lymph nodes: “filters of the blood”
Impulse invariant method formula
Our personal filters assumptions
Difference between linear and nonlinear spatial filters
Columbus industries filters
Event list filters packet tracer
Spectral transformation of iir filters
Wet etch clean and filter