CHAPTER 3 REPAIR MATERIALS AND TECHNIQUES Introduction In
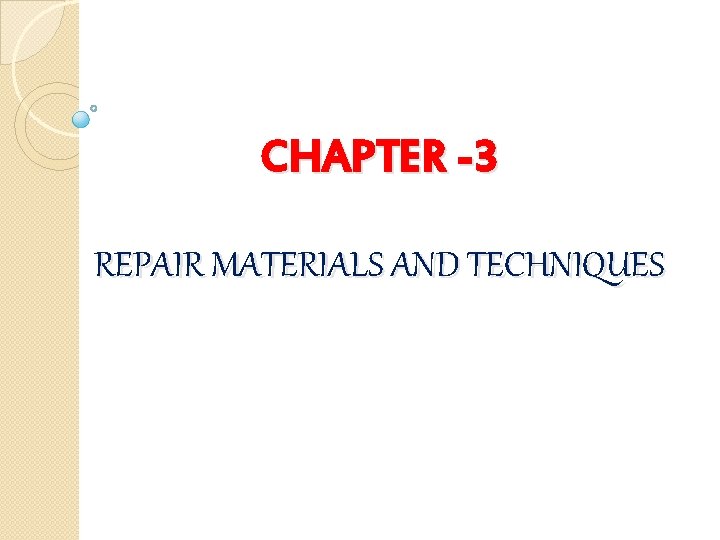
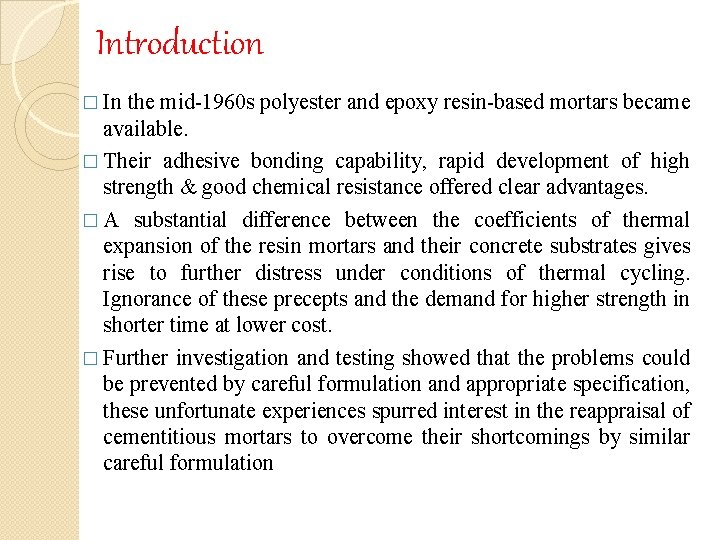
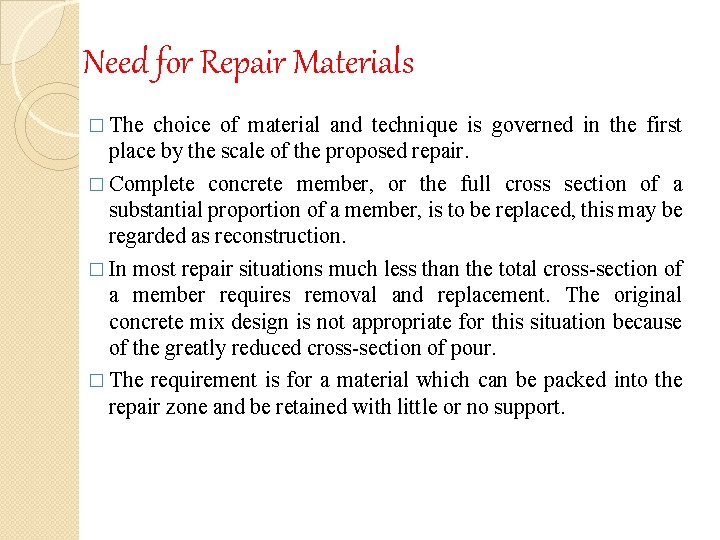
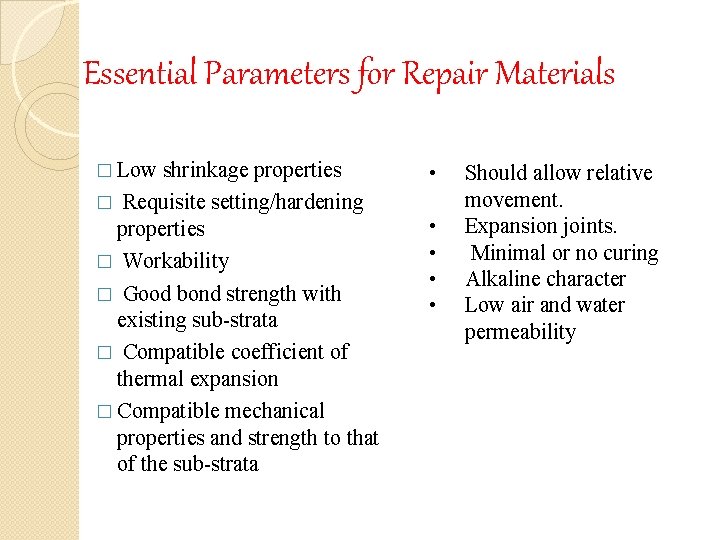
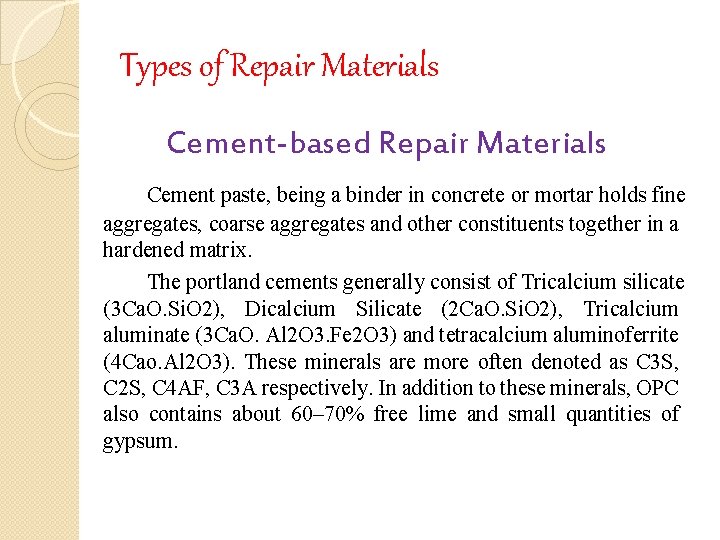
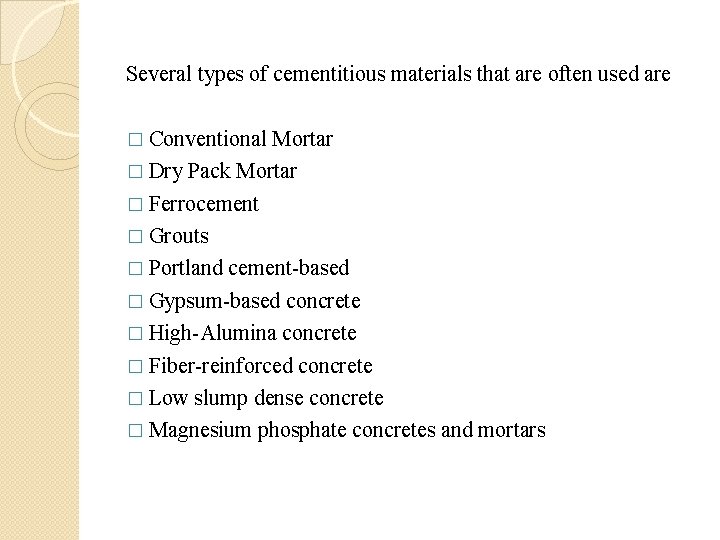
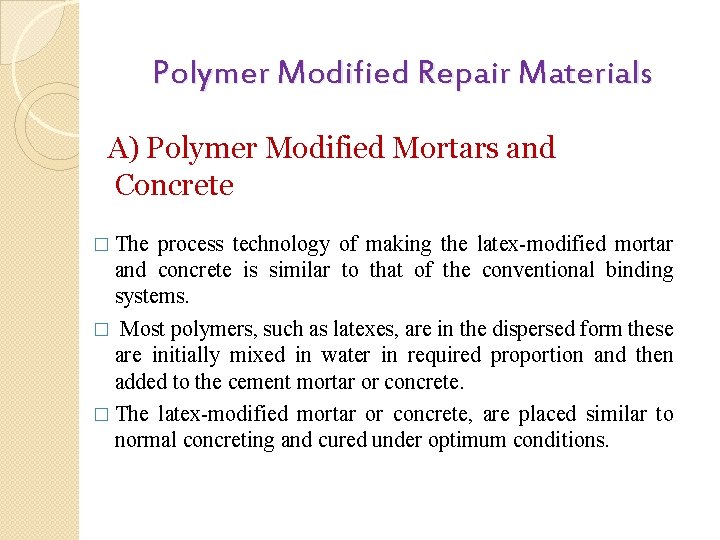
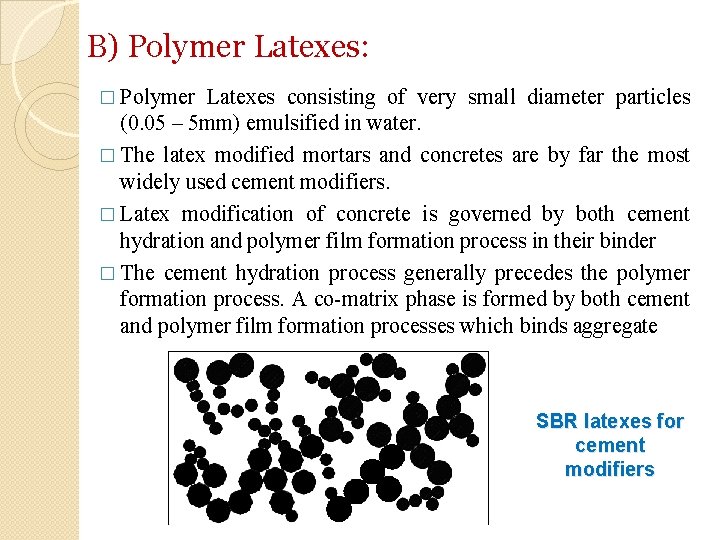
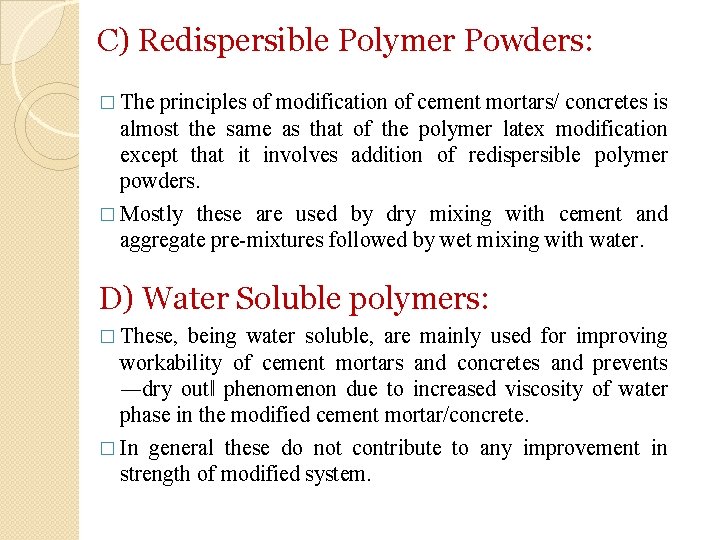
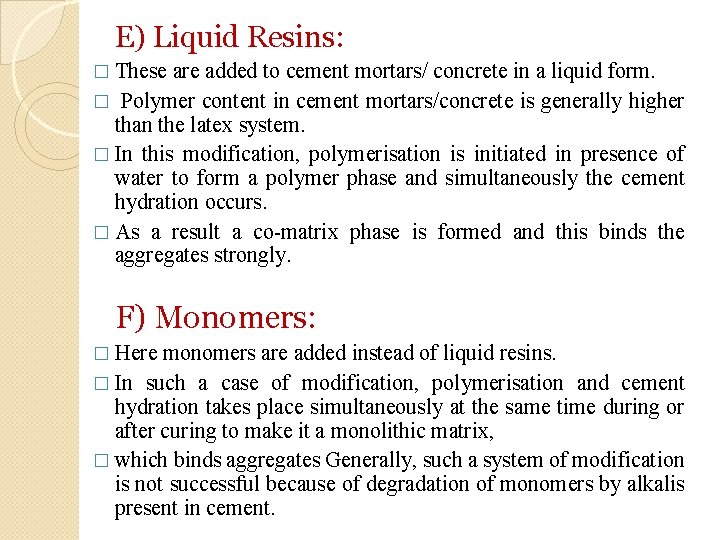
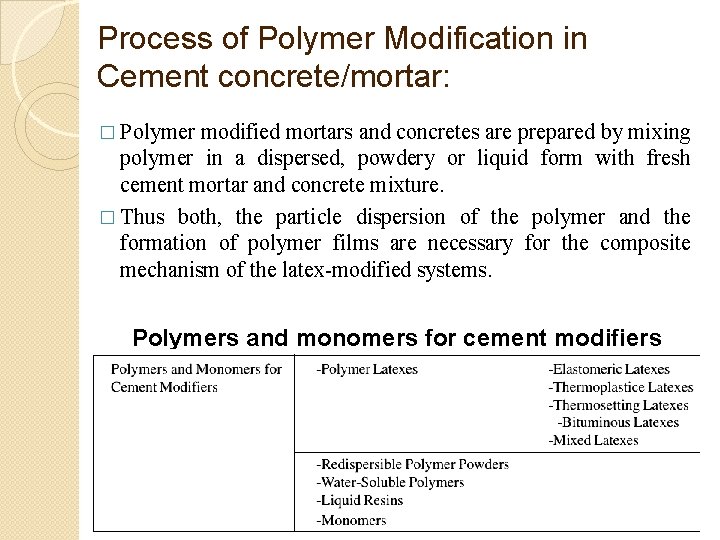
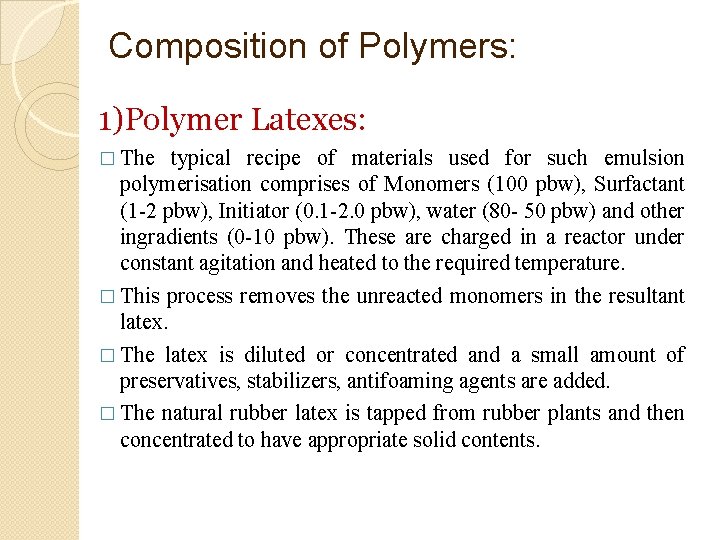
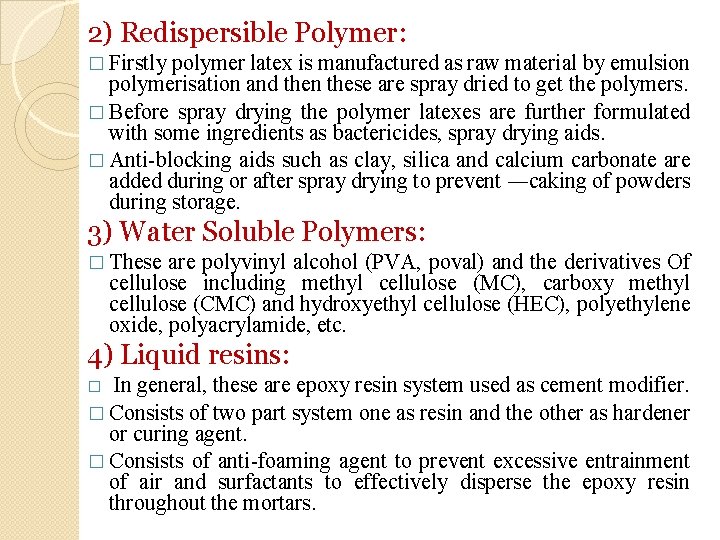
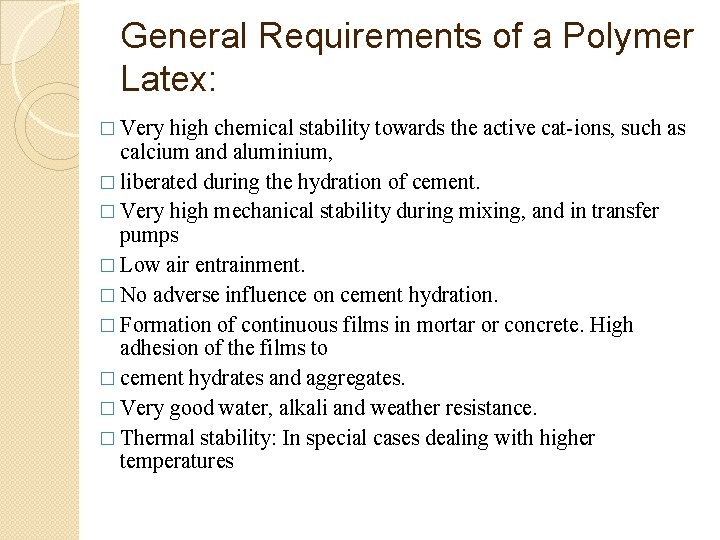
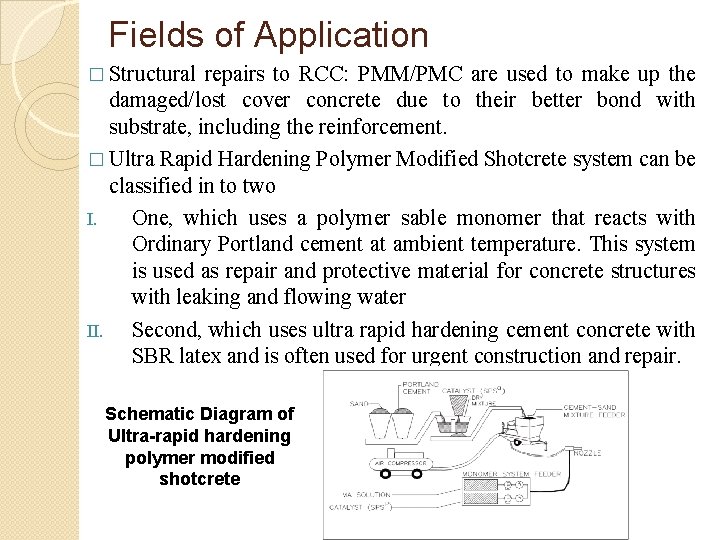
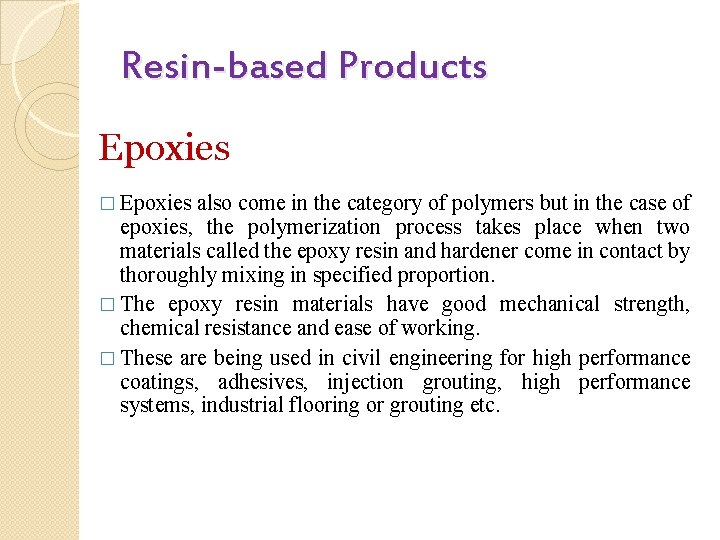
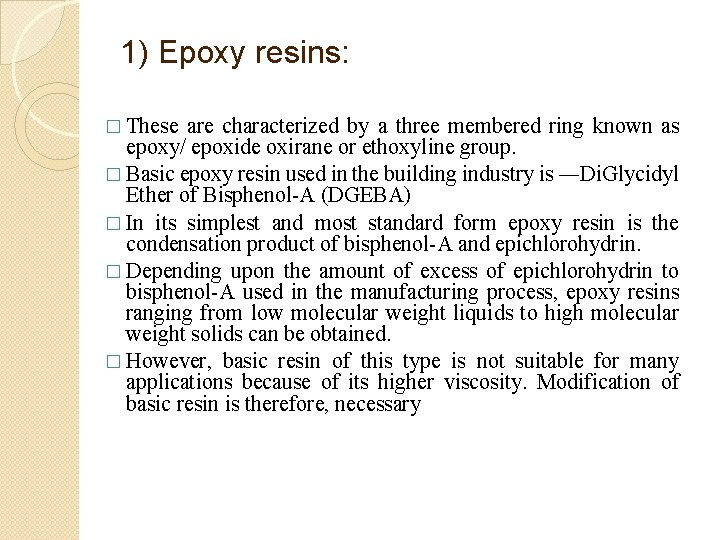
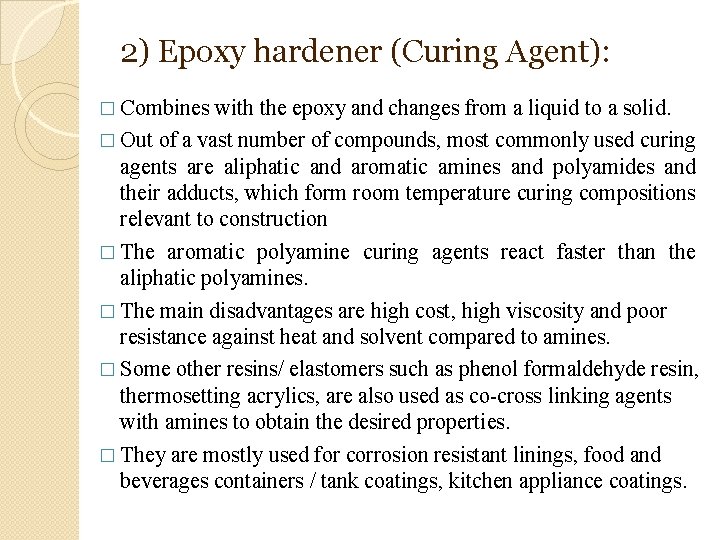
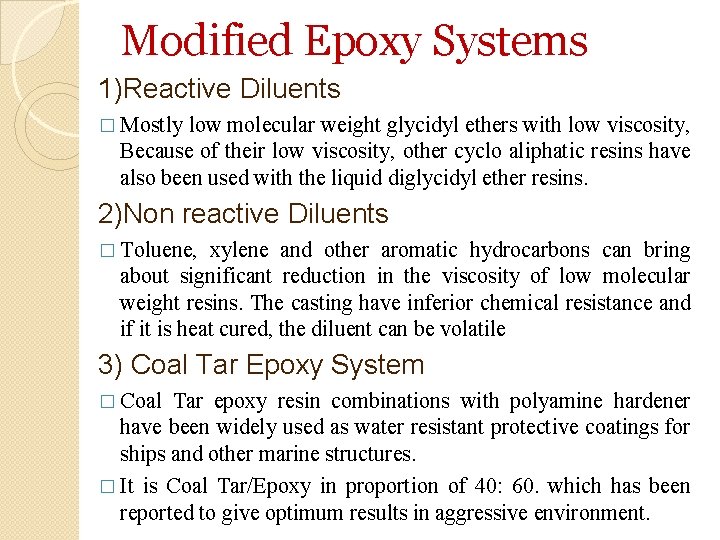
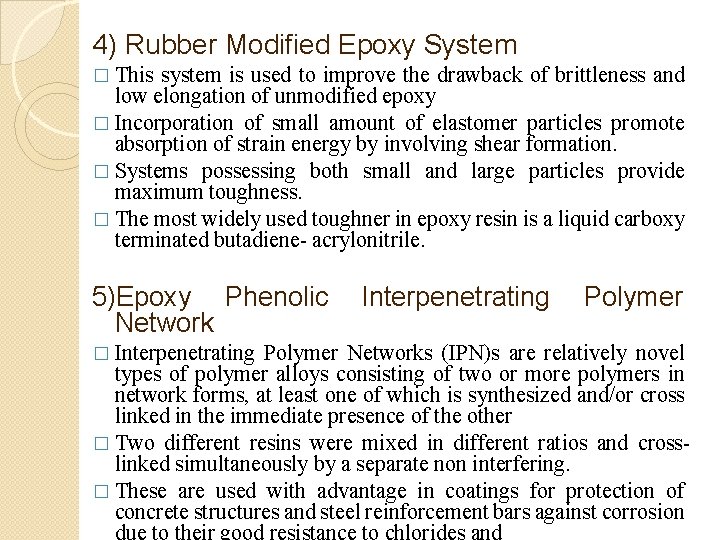
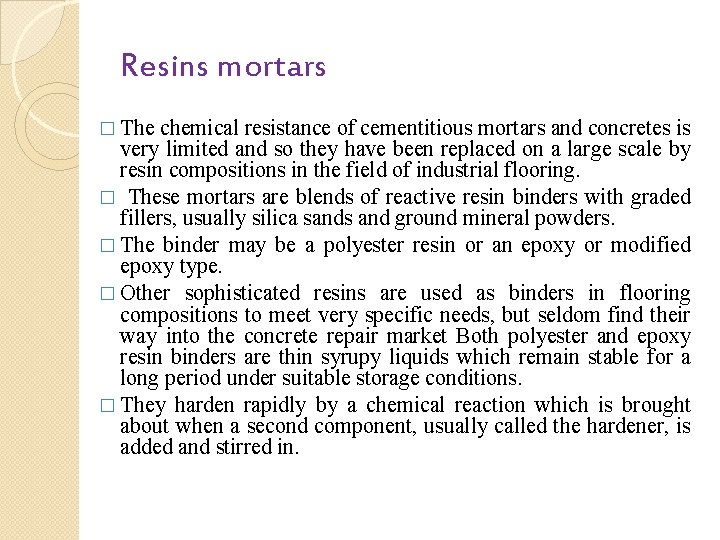
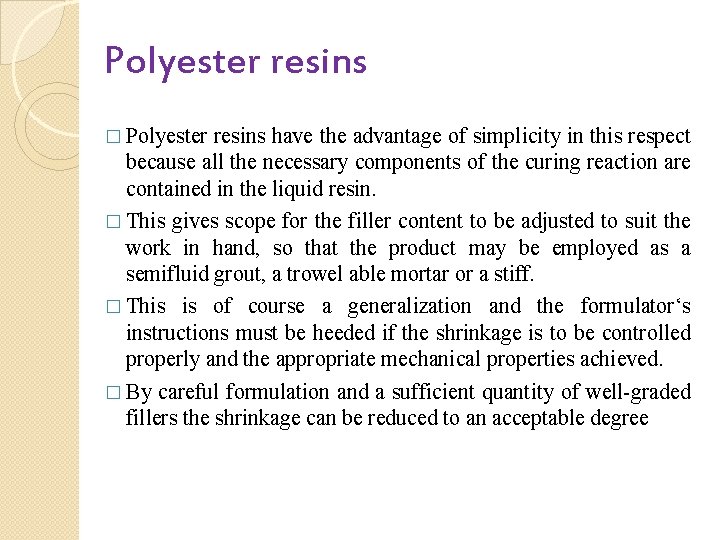
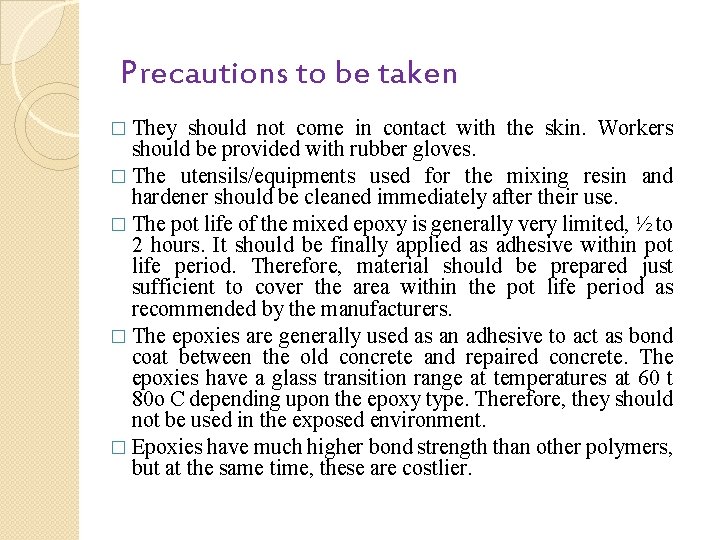
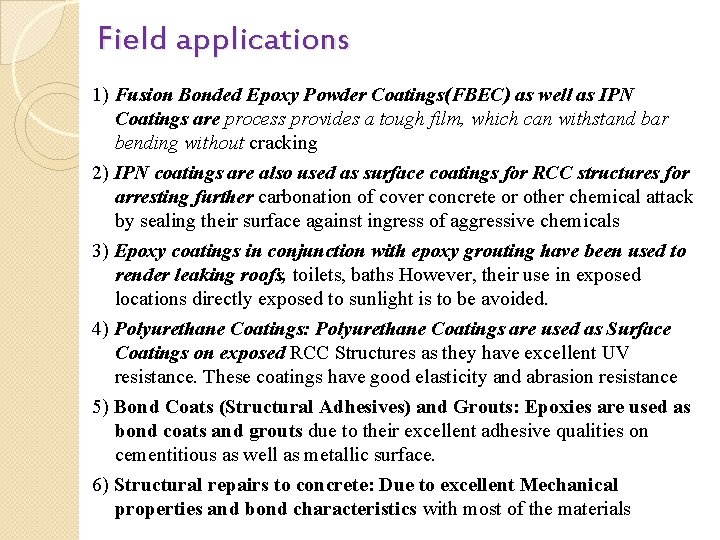
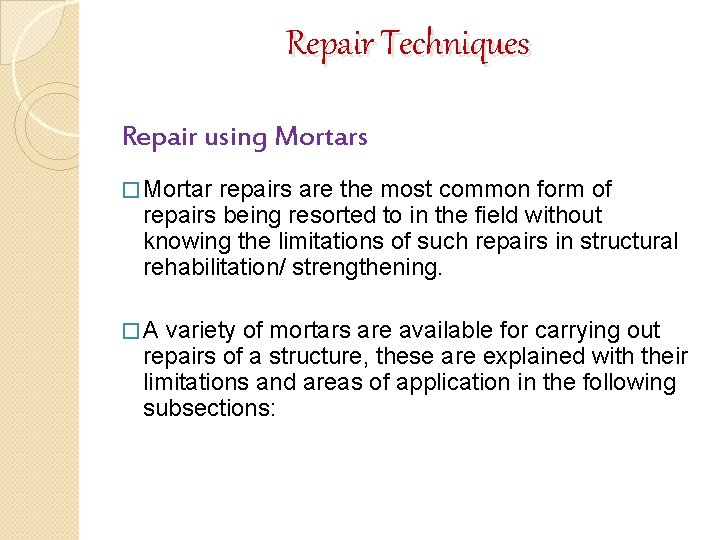
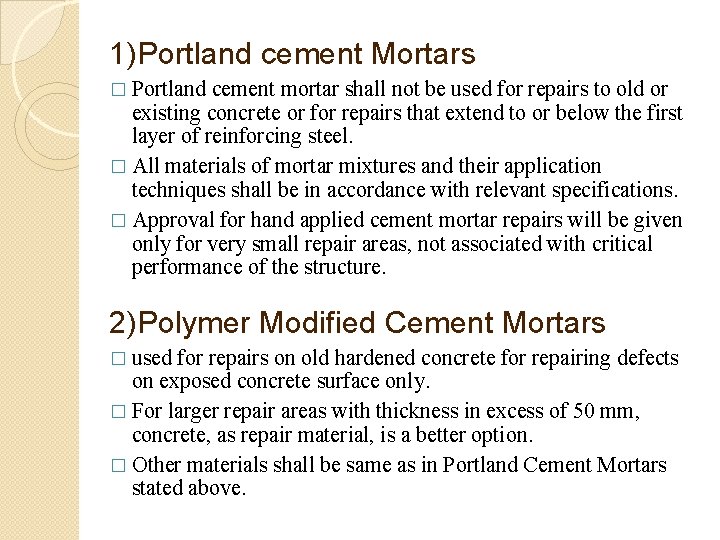
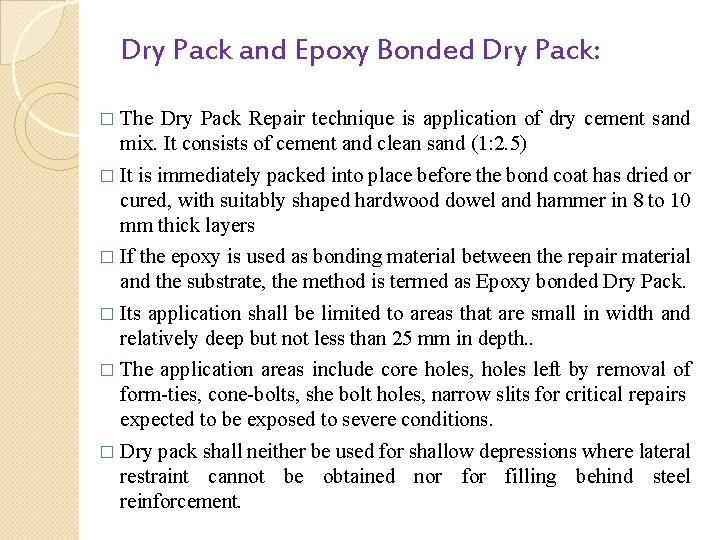
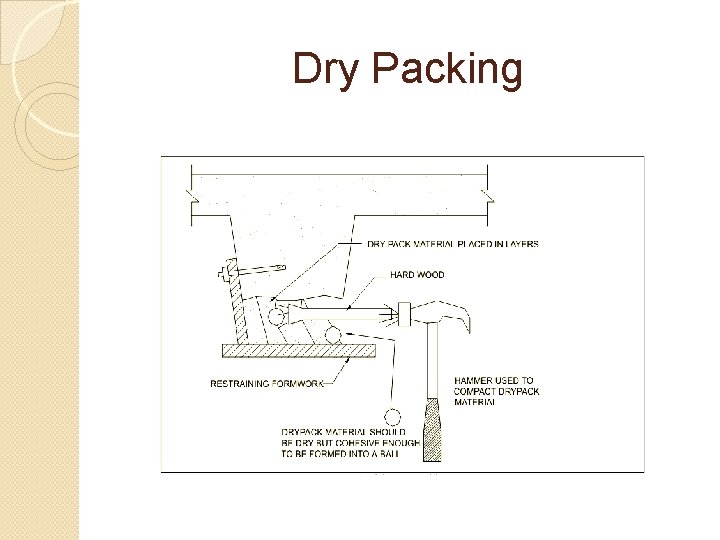
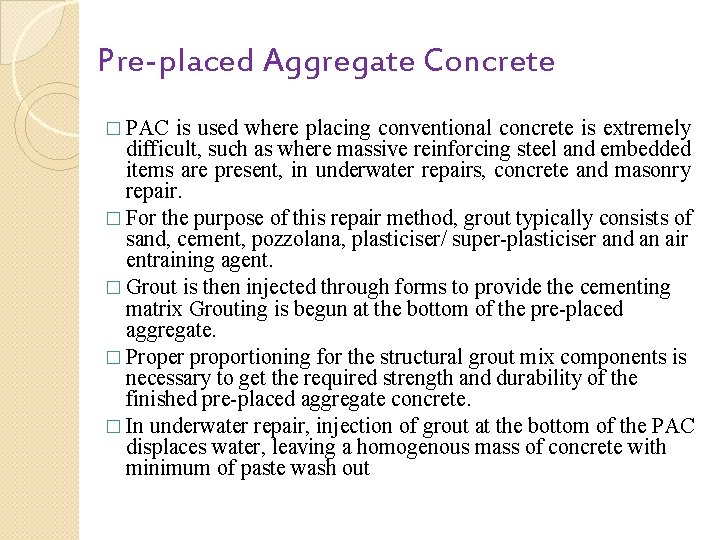
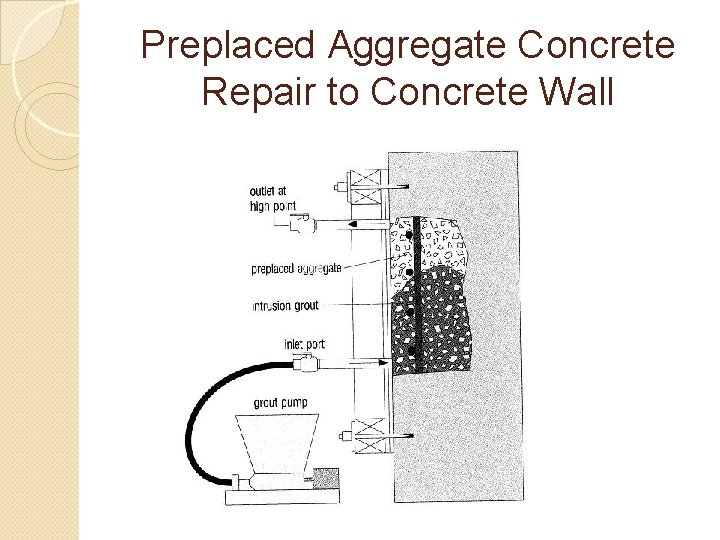
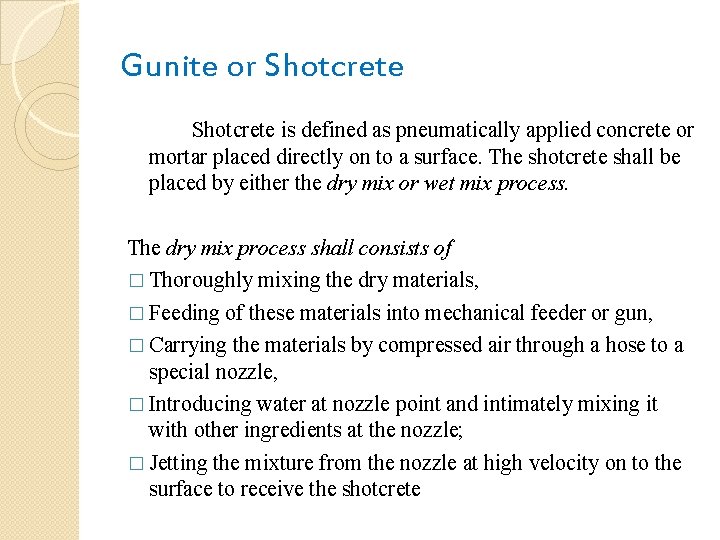
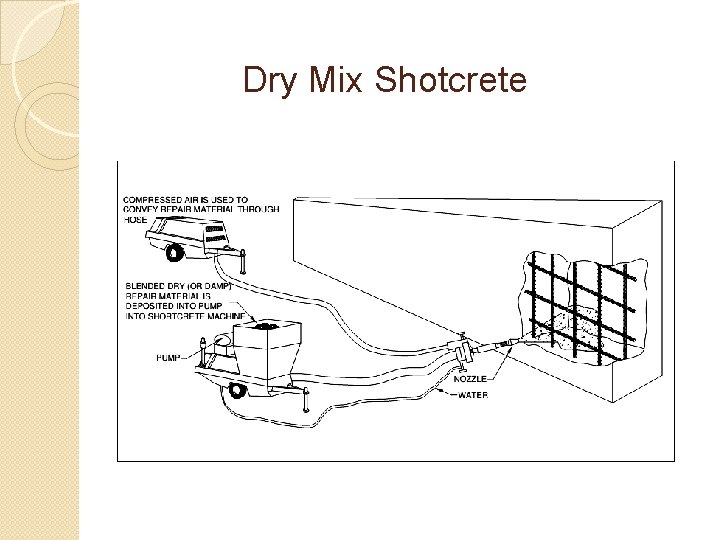
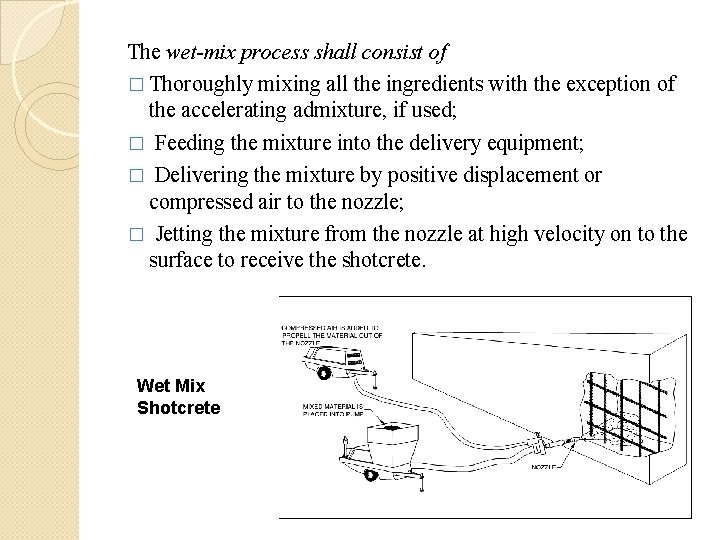
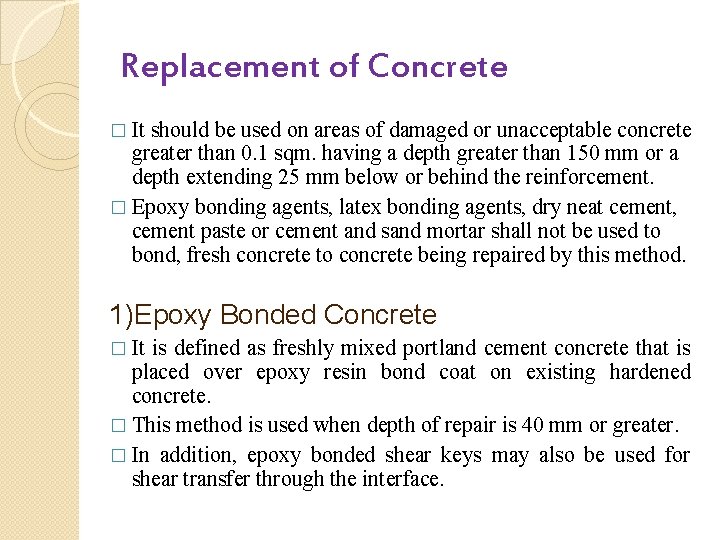
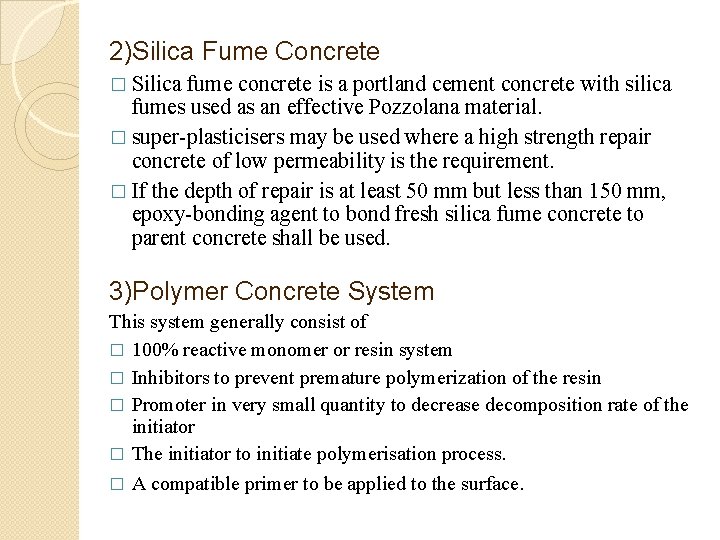
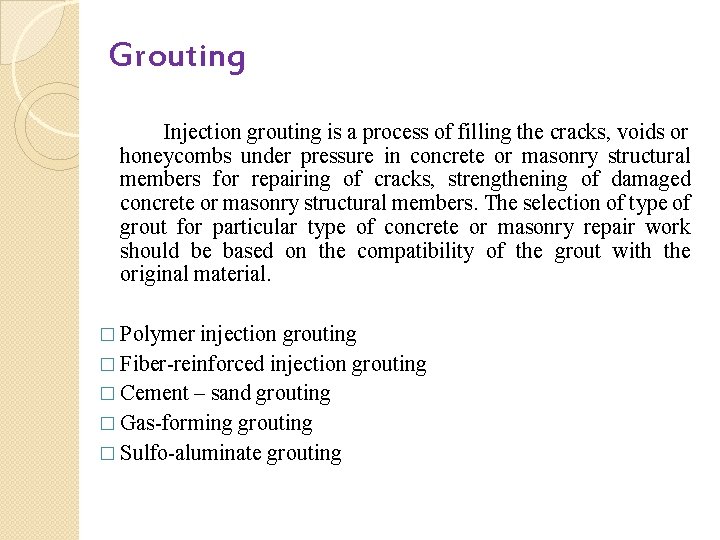
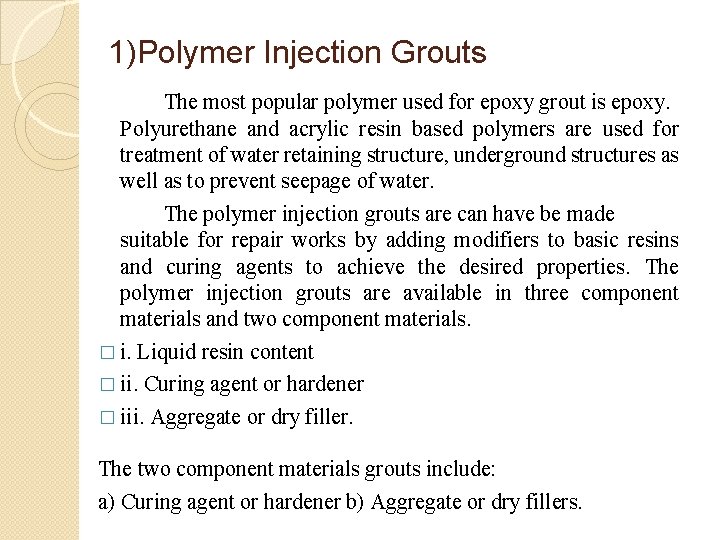
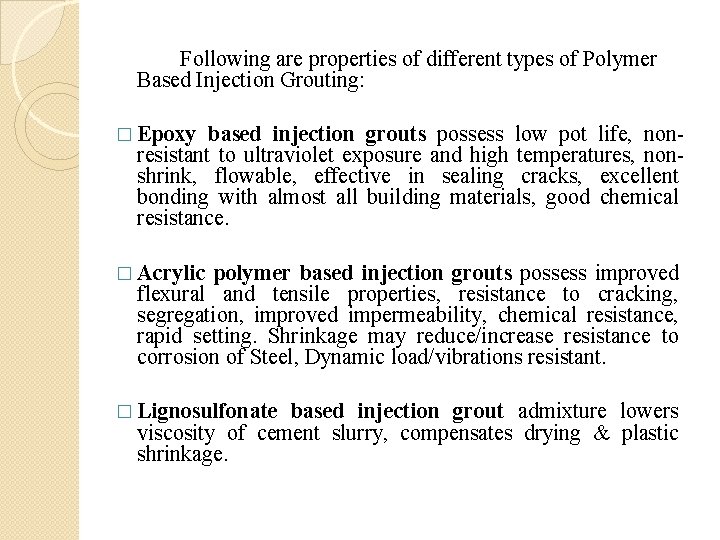
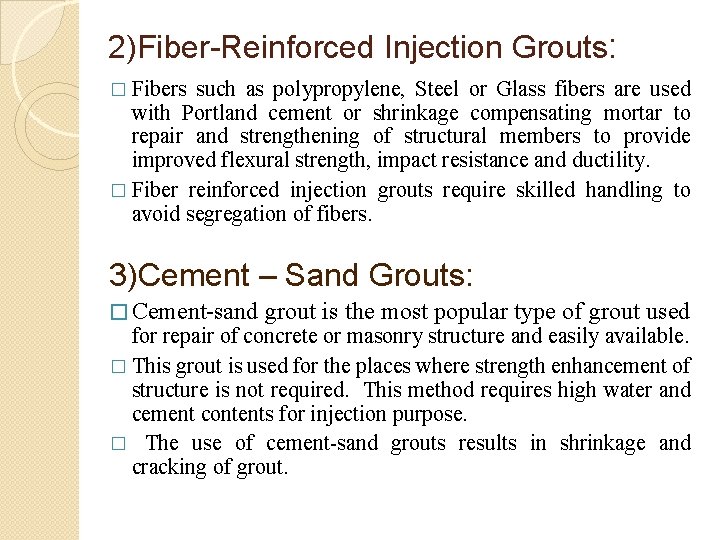
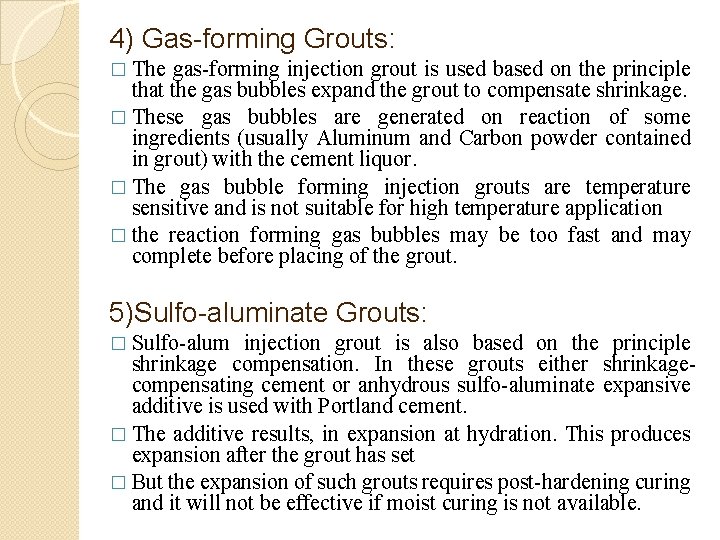
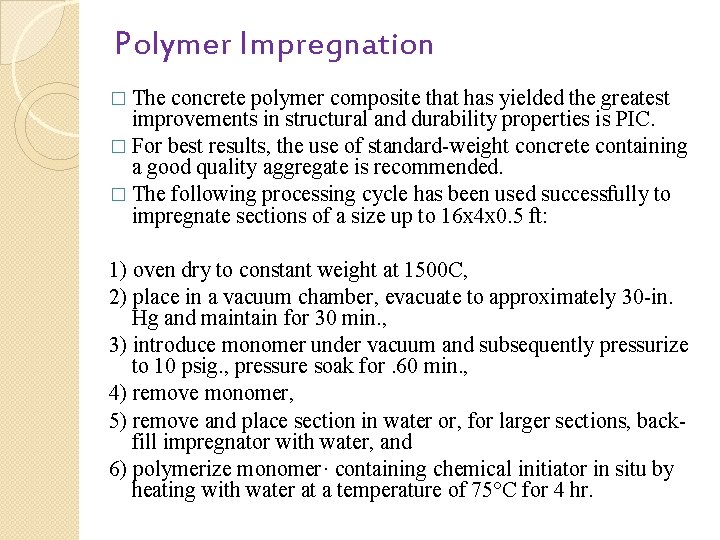
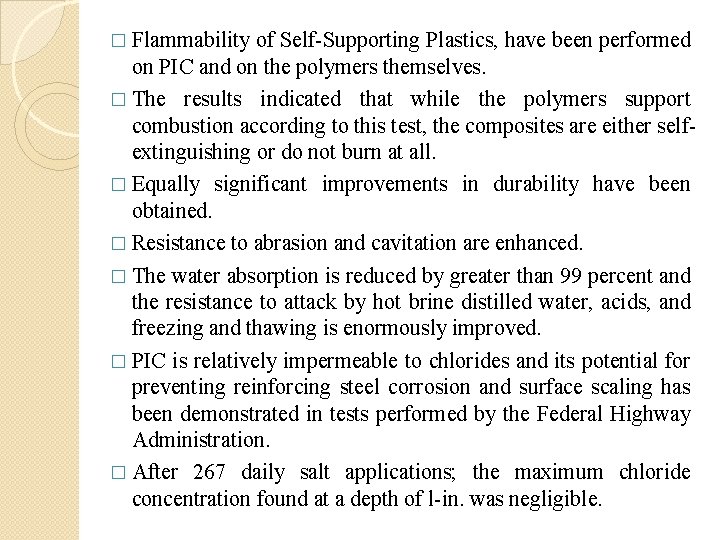
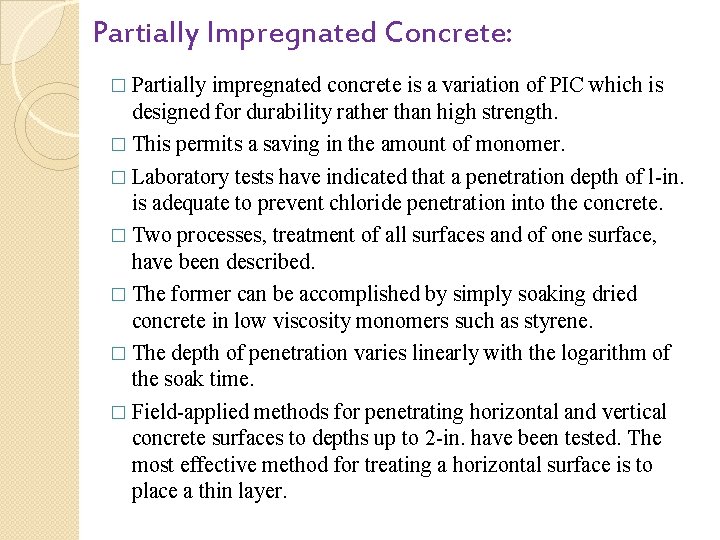
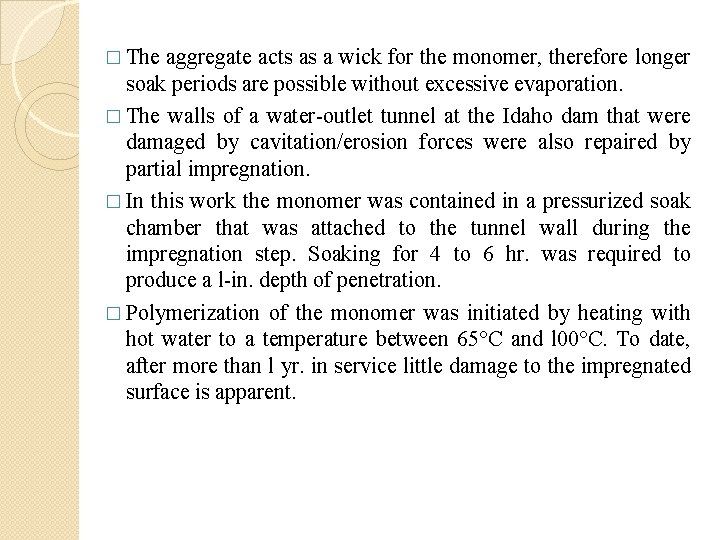
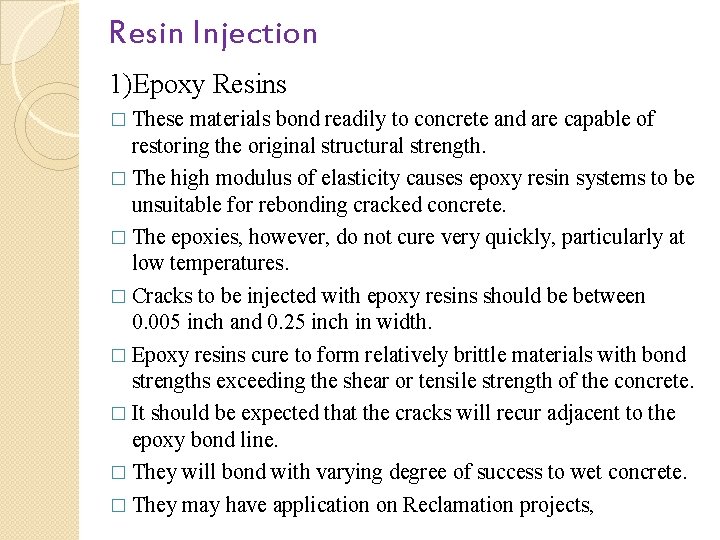
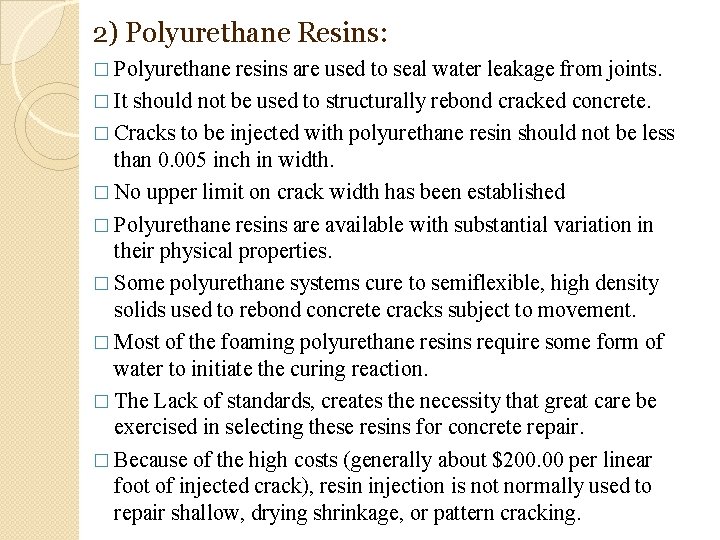
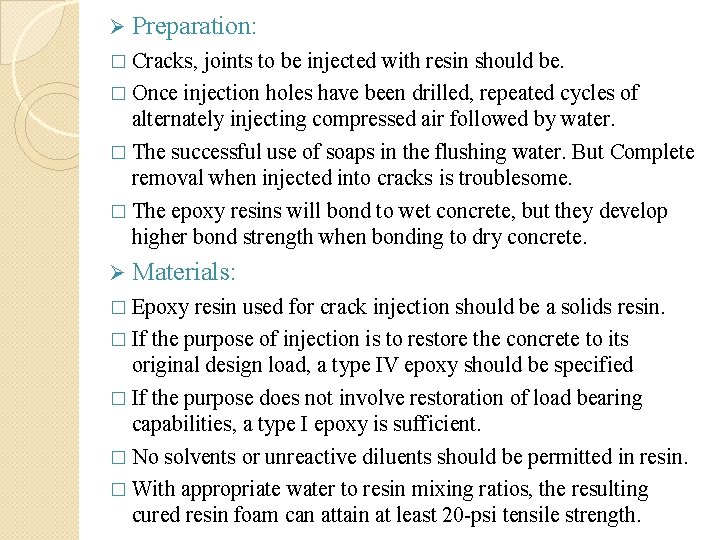
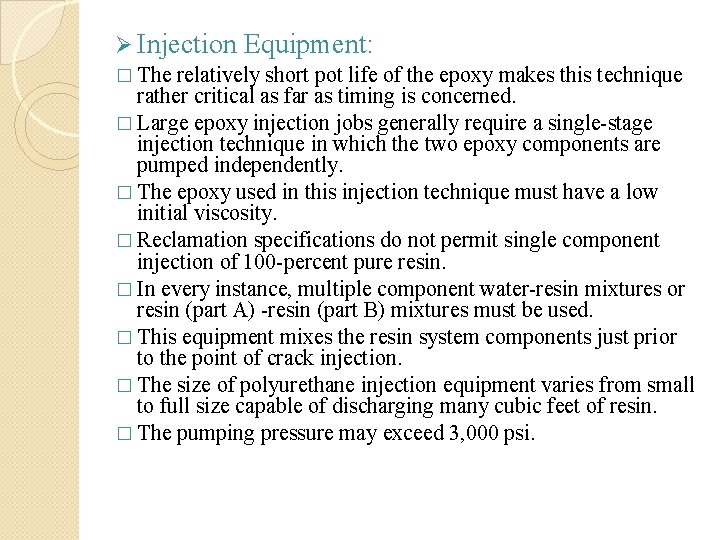
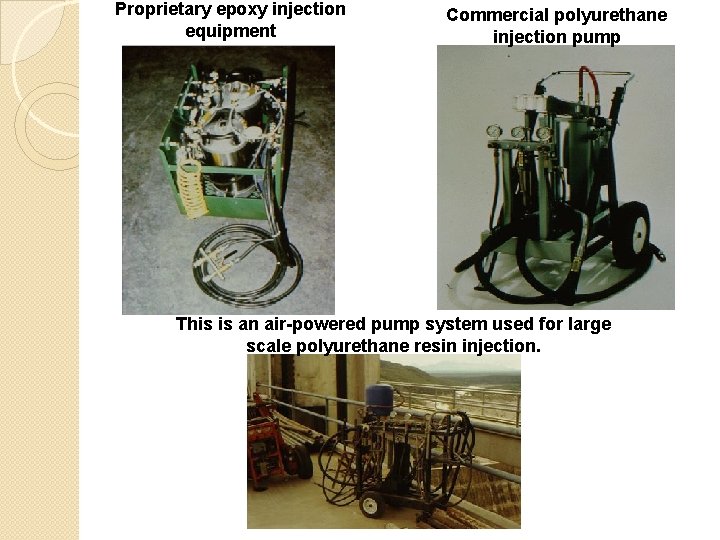
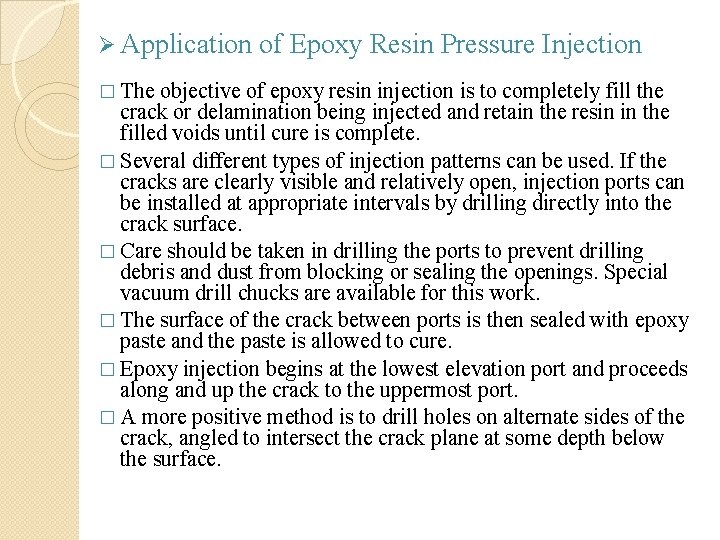
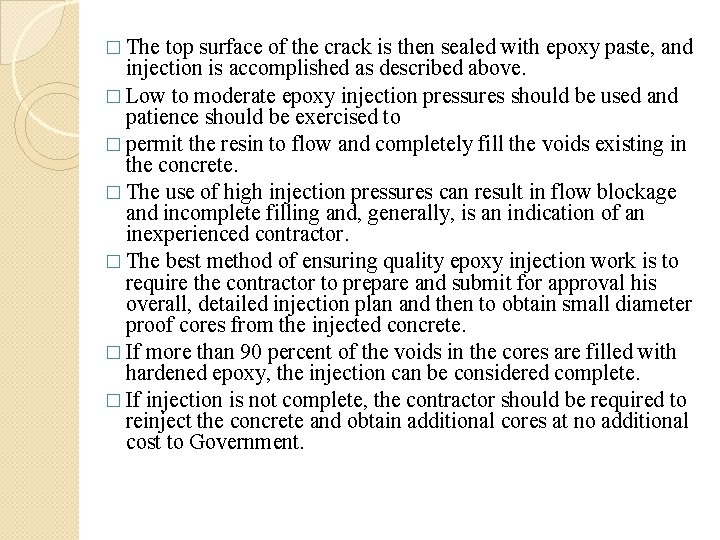
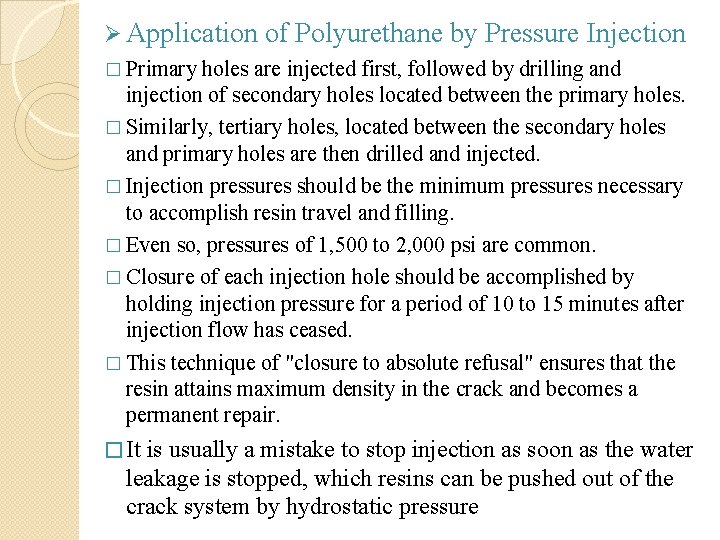
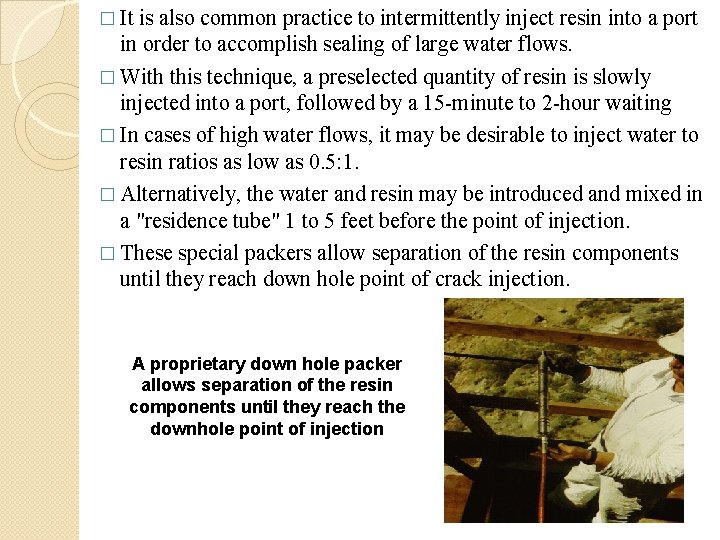
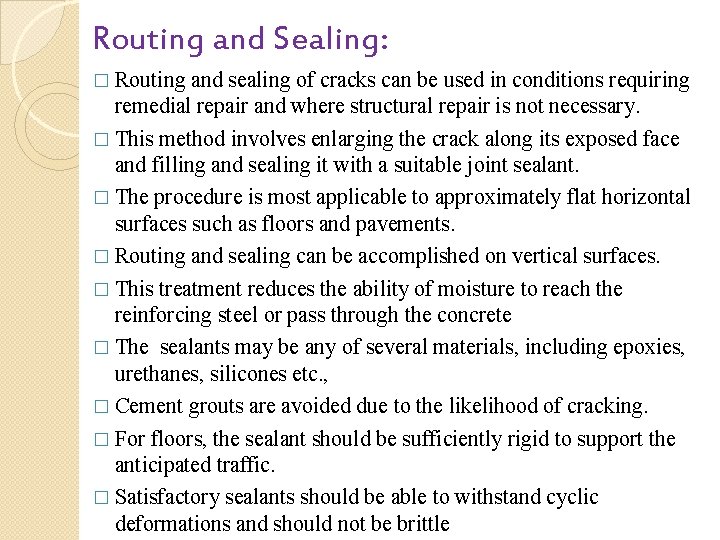
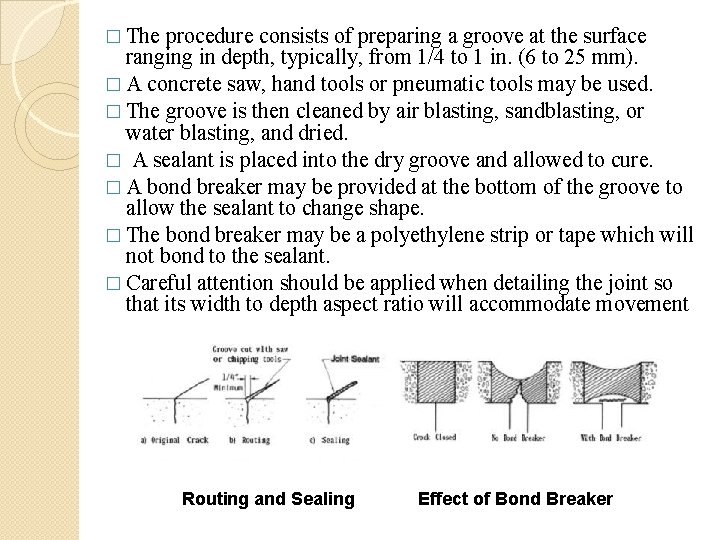
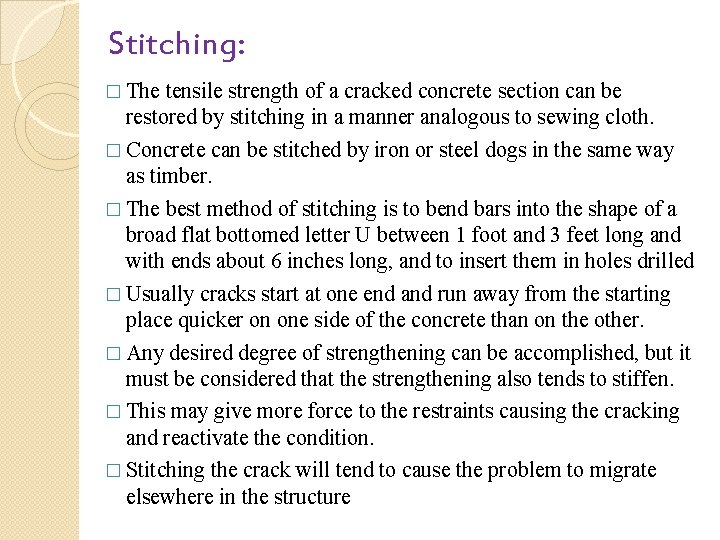
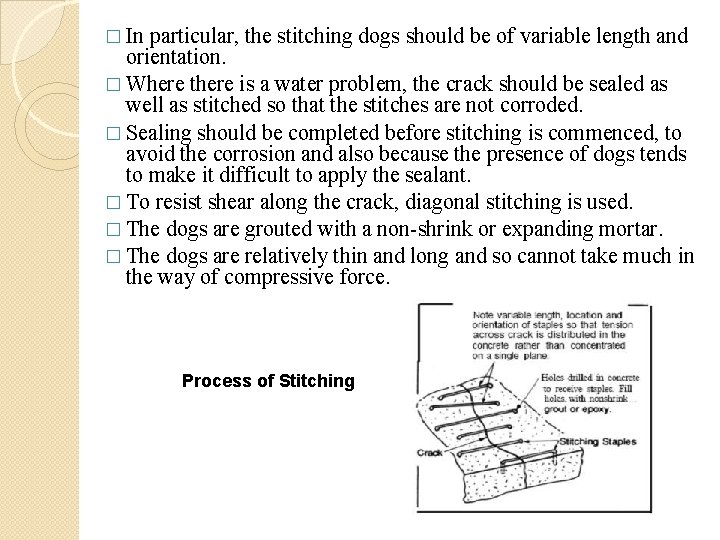
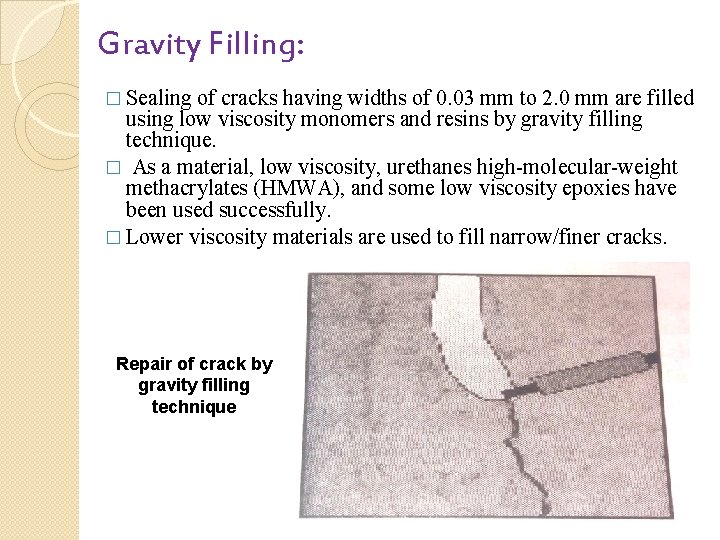
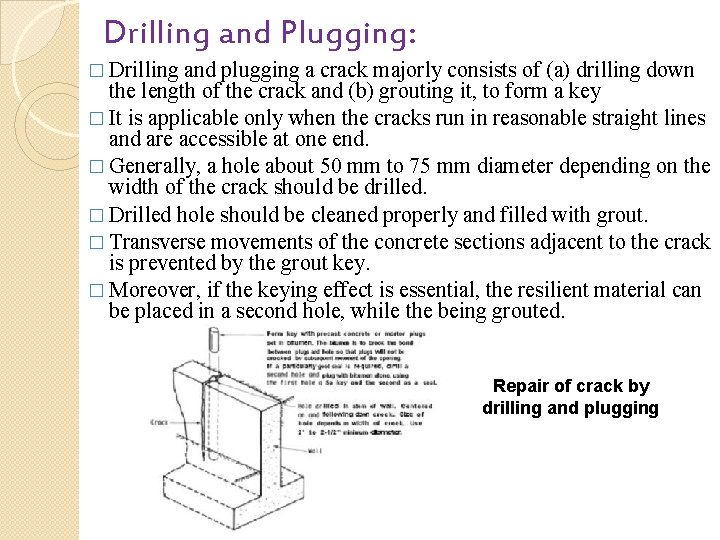
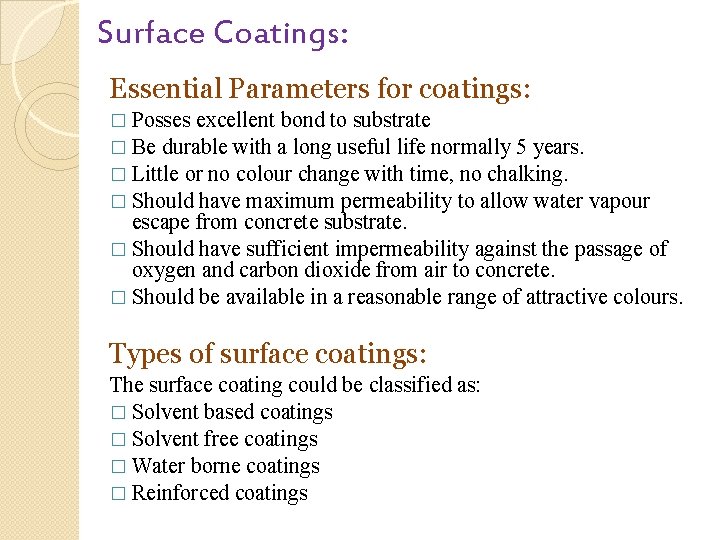
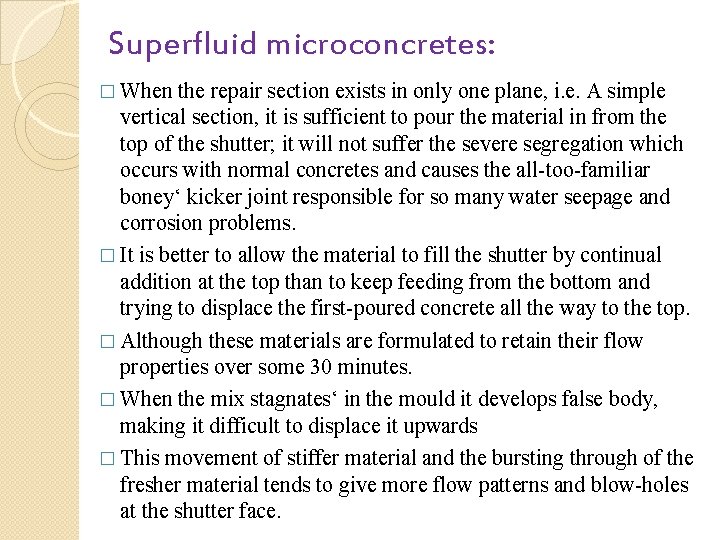
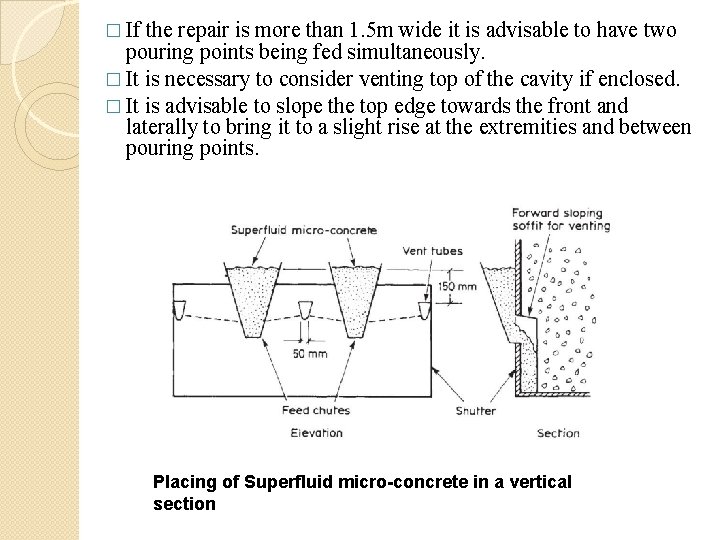
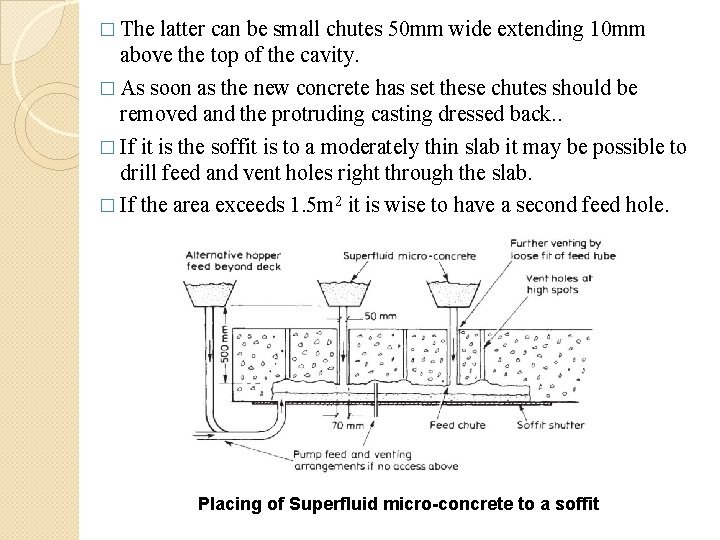
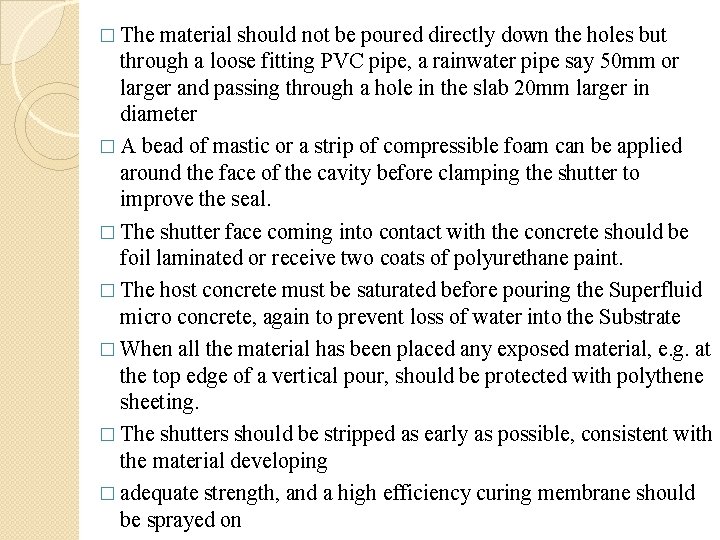
- Slides: 64
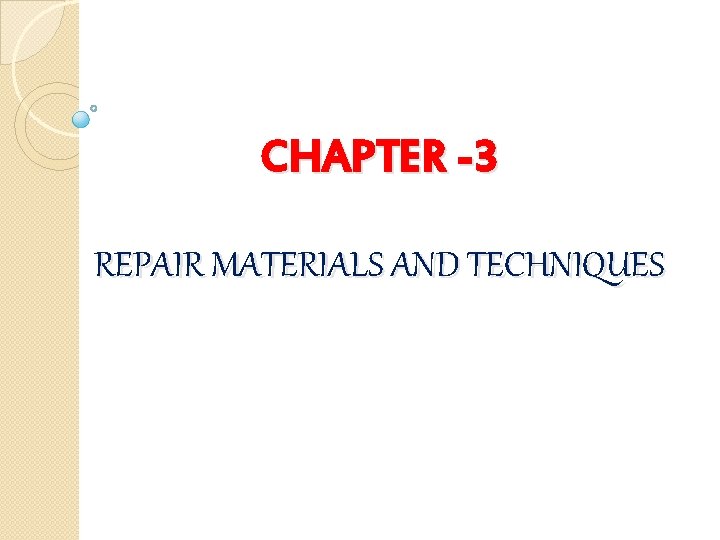
CHAPTER -3 REPAIR MATERIALS AND TECHNIQUES
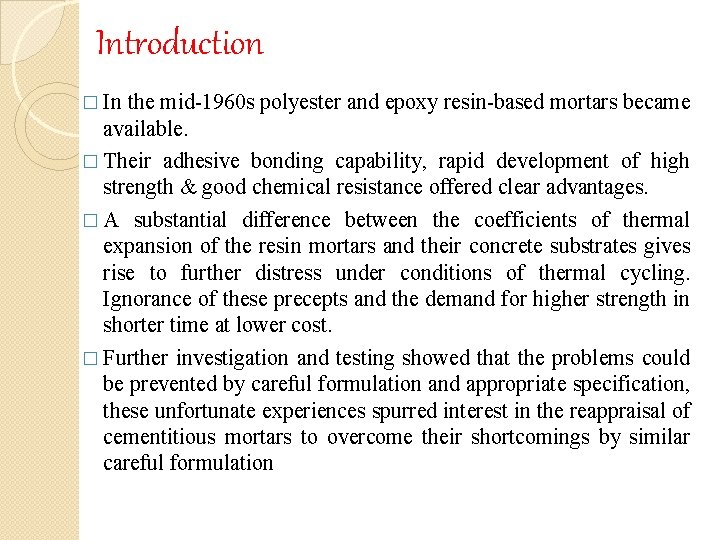
Introduction � In the mid-1960 s polyester and epoxy resin-based mortars became available. � Their adhesive bonding capability, rapid development of high strength & good chemical resistance offered clear advantages. � A substantial difference between the coefficients of thermal expansion of the resin mortars and their concrete substrates gives rise to further distress under conditions of thermal cycling. Ignorance of these precepts and the demand for higher strength in shorter time at lower cost. � Further investigation and testing showed that the problems could be prevented by careful formulation and appropriate specification, these unfortunate experiences spurred interest in the reappraisal of cementitious mortars to overcome their shortcomings by similar careful formulation
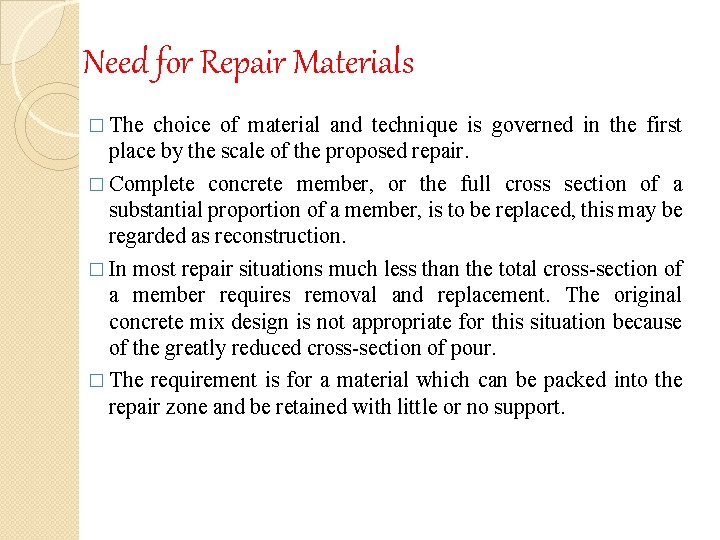
Need for Repair Materials � The choice of material and technique is governed in the first place by the scale of the proposed repair. � Complete concrete member, or the full cross section of a substantial proportion of a member, is to be replaced, this may be regarded as reconstruction. � In most repair situations much less than the total cross-section of a member requires removal and replacement. The original concrete mix design is not appropriate for this situation because of the greatly reduced cross-section of pour. � The requirement is for a material which can be packed into the repair zone and be retained with little or no support.
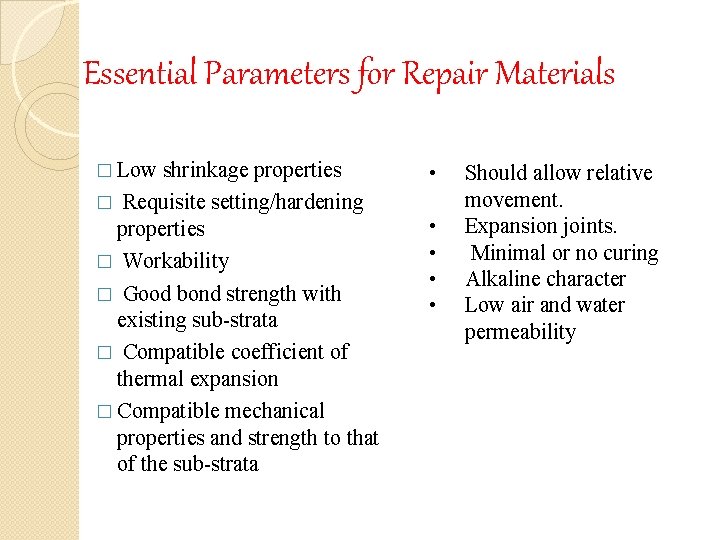
Essential Parameters for Repair Materials � Low shrinkage properties � Requisite setting/hardening properties � Workability � Good bond strength with existing sub-strata � Compatible coefficient of thermal expansion � Compatible mechanical properties and strength to that of the sub-strata • • • Should allow relative movement. Expansion joints. Minimal or no curing Alkaline character Low air and water permeability
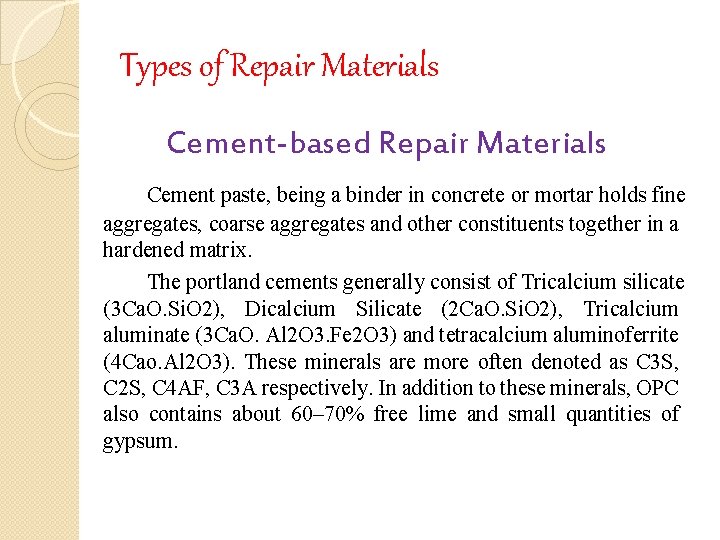
Types of Repair Materials Cement-based Repair Materials Cement paste, being a binder in concrete or mortar holds fine aggregates, coarse aggregates and other constituents together in a hardened matrix. The portland cements generally consist of Tricalcium silicate (3 Ca. O. Si. O 2), Dicalcium Silicate (2 Ca. O. Si. O 2), Tricalcium aluminate (3 Ca. O. Al 2 O 3. Fe 2 O 3) and tetracalcium aluminoferrite (4 Cao. Al 2 O 3). These minerals are more often denoted as C 3 S, C 2 S, C 4 AF, C 3 A respectively. In addition to these minerals, OPC also contains about 60– 70% free lime and small quantities of gypsum.
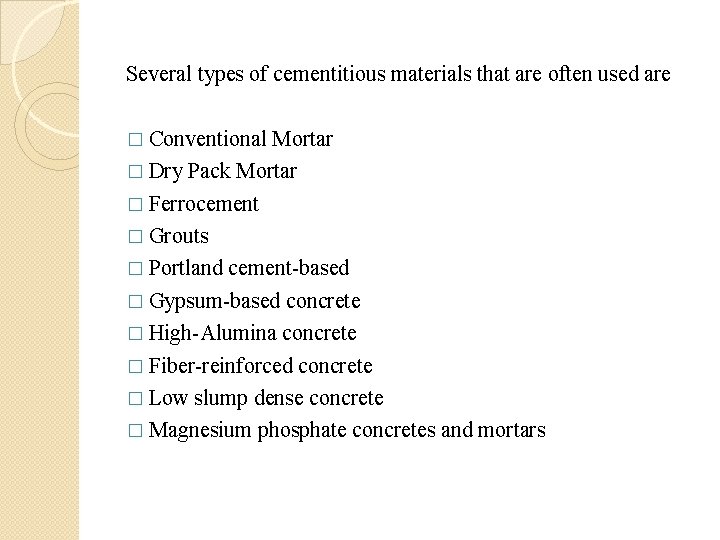
Several types of cementitious materials that are often used are � Conventional Mortar � Dry Pack Mortar � Ferrocement � Grouts � Portland cement-based � Gypsum-based concrete � High-Alumina concrete � Fiber-reinforced concrete � Low slump dense concrete � Magnesium phosphate concretes and mortars
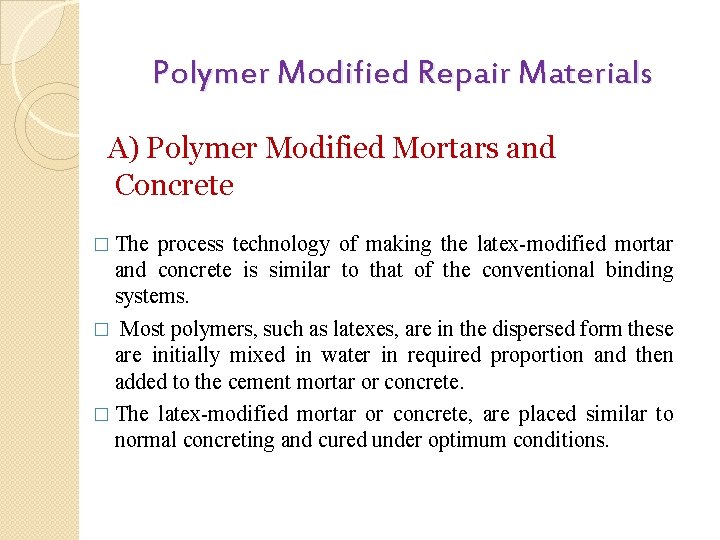
Polymer Modified Repair Materials A) Polymer Modified Mortars and Concrete � The process technology of making the latex-modified mortar and concrete is similar to that of the conventional binding systems. � Most polymers, such as latexes, are in the dispersed form these are initially mixed in water in required proportion and then added to the cement mortar or concrete. � The latex-modified mortar or concrete, are placed similar to normal concreting and cured under optimum conditions.
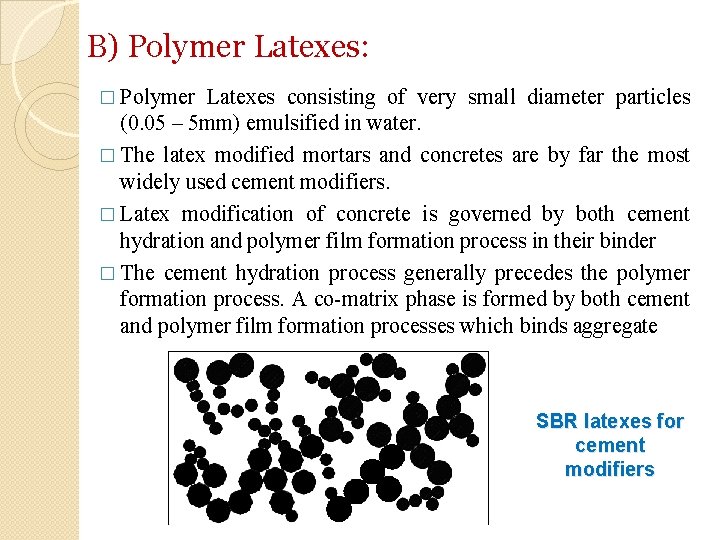
B) Polymer Latexes: � Polymer Latexes consisting of very small diameter particles (0. 05 – 5 mm) emulsified in water. � The latex modified mortars and concretes are by far the most widely used cement modifiers. � Latex modification of concrete is governed by both cement hydration and polymer film formation process in their binder � The cement hydration process generally precedes the polymer formation process. A co-matrix phase is formed by both cement and polymer film formation processes which binds aggregate SBR latexes for cement modifiers
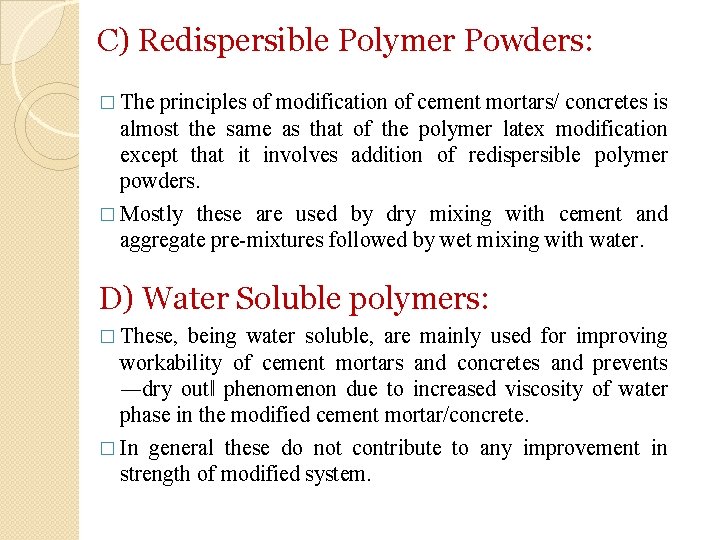
C) Redispersible Polymer Powders: � The principles of modification of cement mortars/ concretes is almost the same as that of the polymer latex modification except that it involves addition of redispersible polymer powders. � Mostly these are used by dry mixing with cement and aggregate pre-mixtures followed by wet mixing with water. D) Water Soluble polymers: � These, being water soluble, are mainly used for improving workability of cement mortars and concretes and prevents ―dry out‖ phenomenon due to increased viscosity of water phase in the modified cement mortar/concrete. � In general these do not contribute to any improvement in strength of modified system.
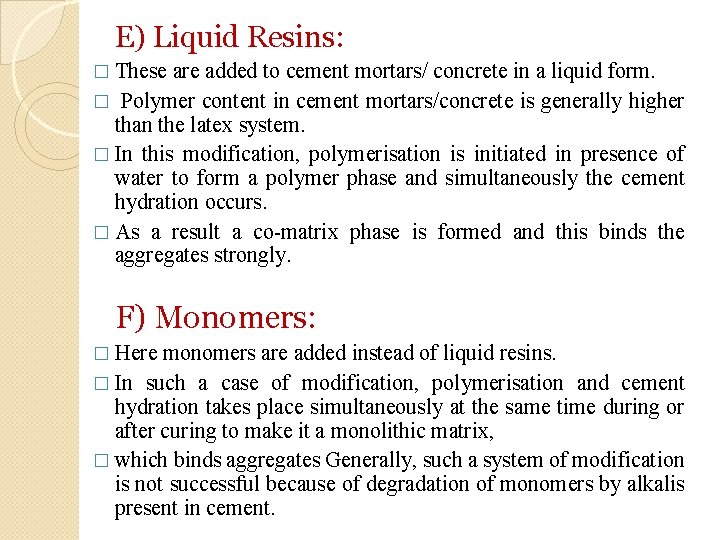
E) Liquid Resins: � These are added to cement mortars/ concrete in a liquid form. � Polymer content in cement mortars/concrete is generally higher than the latex system. � In this modification, polymerisation is initiated in presence of water to form a polymer phase and simultaneously the cement hydration occurs. � As a result a co-matrix phase is formed and this binds the aggregates strongly. F) Monomers: � Here monomers are added instead of liquid resins. � In such a case of modification, polymerisation and cement hydration takes place simultaneously at the same time during or after curing to make it a monolithic matrix, � which binds aggregates Generally, such a system of modification is not successful because of degradation of monomers by alkalis present in cement.
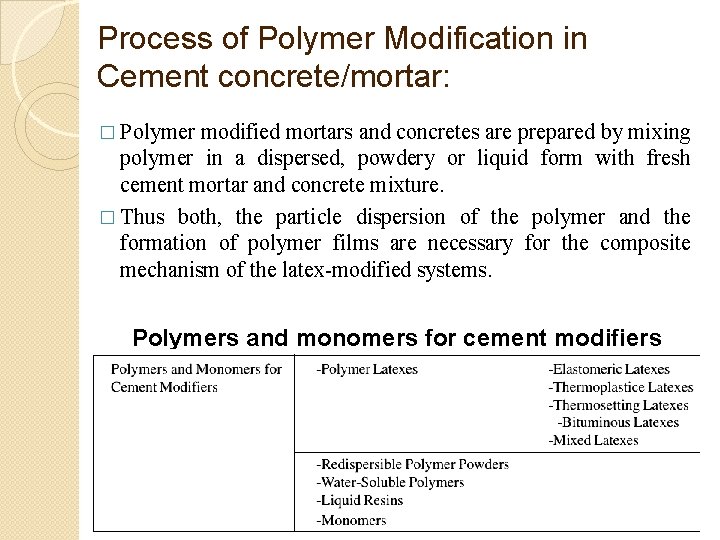
Process of Polymer Modification in Cement concrete/mortar: � Polymer modified mortars and concretes are prepared by mixing polymer in a dispersed, powdery or liquid form with fresh cement mortar and concrete mixture. � Thus both, the particle dispersion of the polymer and the formation of polymer films are necessary for the composite mechanism of the latex-modified systems. Polymers and monomers for cement modifiers
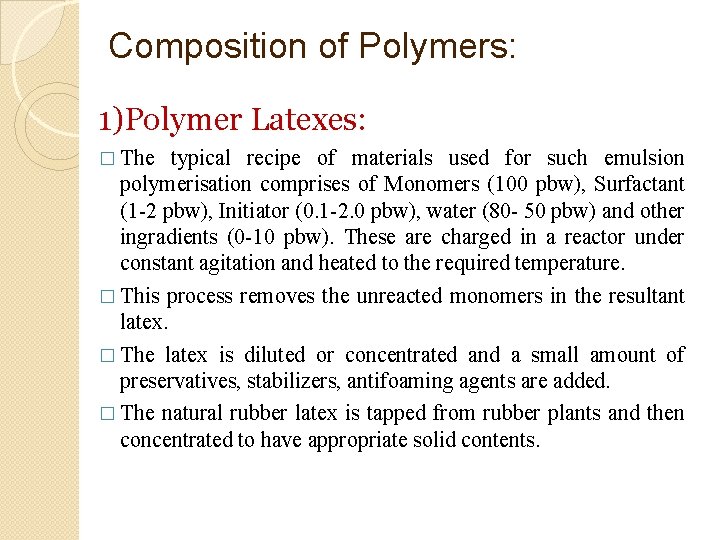
Composition of Polymers: 1)Polymer Latexes: � The typical recipe of materials used for such emulsion polymerisation comprises of Monomers (100 pbw), Surfactant (1 -2 pbw), Initiator (0. 1 -2. 0 pbw), water (80 - 50 pbw) and other ingradients (0 -10 pbw). These are charged in a reactor under constant agitation and heated to the required temperature. � This process removes the unreacted monomers in the resultant latex. � The latex is diluted or concentrated and a small amount of preservatives, stabilizers, antifoaming agents are added. � The natural rubber latex is tapped from rubber plants and then concentrated to have appropriate solid contents.
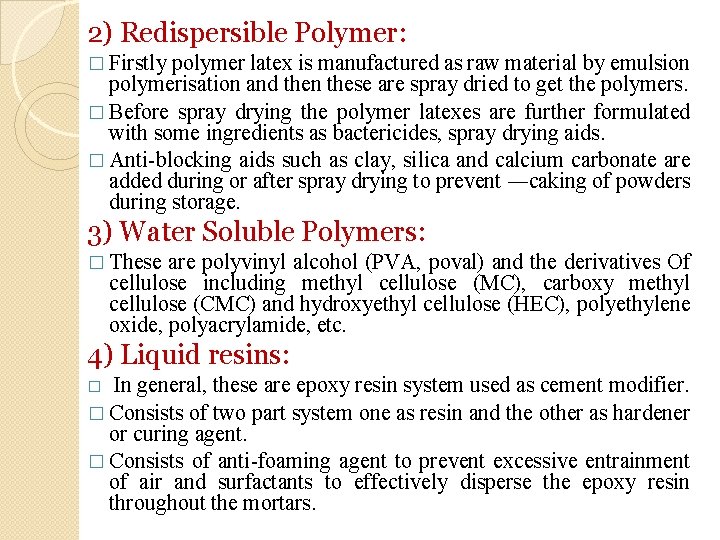
2) Redispersible Polymer: � Firstly polymer latex is manufactured as raw material by emulsion polymerisation and then these are spray dried to get the polymers. � Before spray drying the polymer latexes are further formulated with some ingredients as bactericides, spray drying aids. � Anti-blocking aids such as clay, silica and calcium carbonate are added during or after spray drying to prevent ―caking of powders during storage. 3) Water Soluble Polymers: � These are polyvinyl alcohol (PVA, poval) and the derivatives Of cellulose including methyl cellulose (MC), carboxy methyl cellulose (CMC) and hydroxyethyl cellulose (HEC), polyethylene oxide, polyacrylamide, etc. 4) Liquid resins: In general, these are epoxy resin system used as cement modifier. � Consists of two part system one as resin and the other as hardener or curing agent. � Consists of anti-foaming agent to prevent excessive entrainment of air and surfactants to effectively disperse the epoxy resin throughout the mortars. �
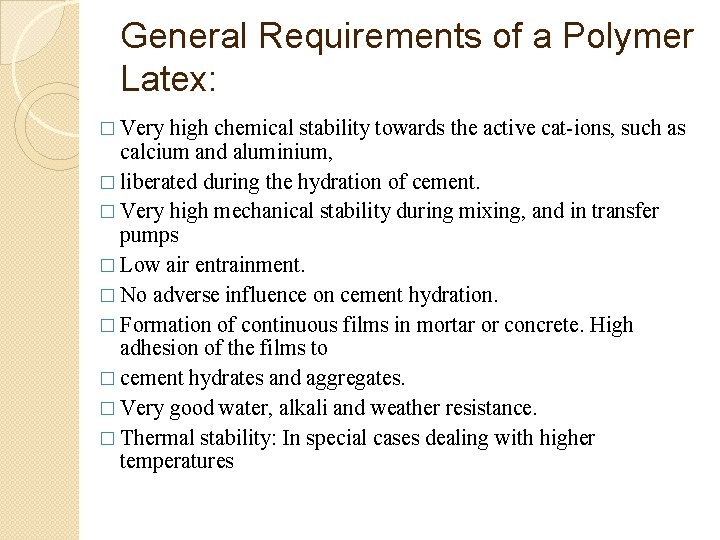
General Requirements of a Polymer Latex: � Very high chemical stability towards the active cat-ions, such as calcium and aluminium, � liberated during the hydration of cement. � Very high mechanical stability during mixing, and in transfer pumps � Low air entrainment. � No adverse influence on cement hydration. � Formation of continuous films in mortar or concrete. High adhesion of the films to � cement hydrates and aggregates. � Very good water, alkali and weather resistance. � Thermal stability: In special cases dealing with higher temperatures
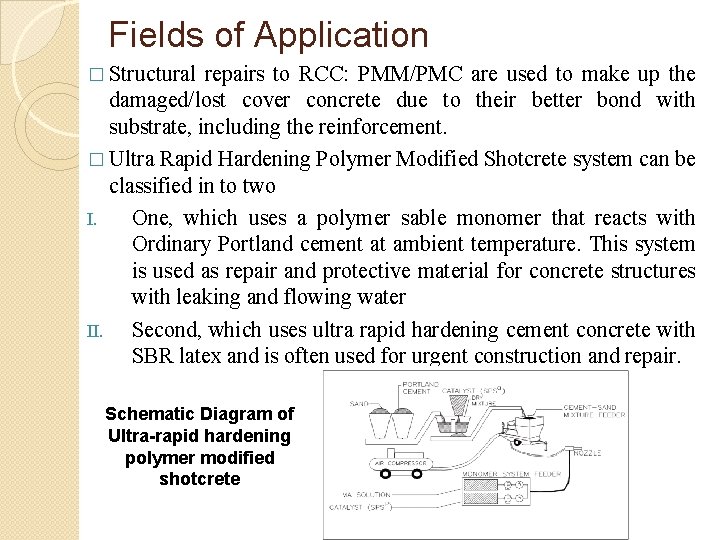
Fields of Application � Structural repairs to RCC: PMM/PMC are used to make up the damaged/lost cover concrete due to their better bond with substrate, including the reinforcement. � Ultra Rapid Hardening Polymer Modified Shotcrete system can be classified in to two I. One, which uses a polymer sable monomer that reacts with Ordinary Portland cement at ambient temperature. This system is used as repair and protective material for concrete structures with leaking and flowing water II. Second, which uses ultra rapid hardening cement concrete with SBR latex and is often used for urgent construction and repair. Schematic Diagram of Ultra-rapid hardening polymer modified shotcrete
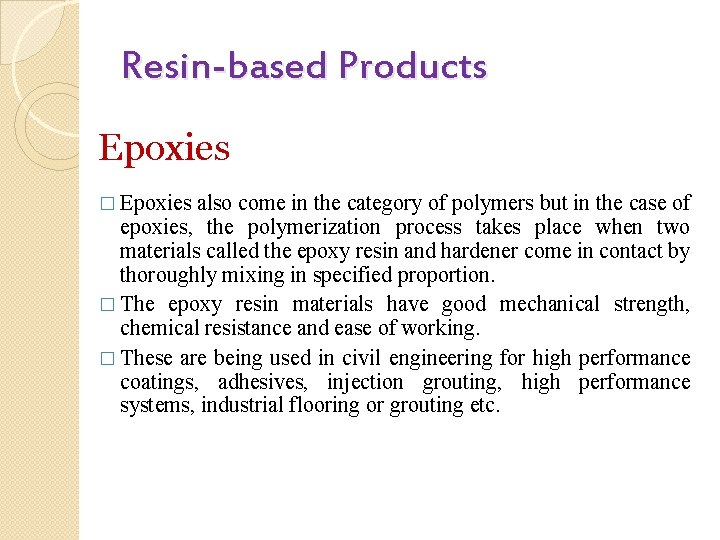
Resin-based Products Epoxies � Epoxies also come in the category of polymers but in the case of epoxies, the polymerization process takes place when two materials called the epoxy resin and hardener come in contact by thoroughly mixing in specified proportion. � The epoxy resin materials have good mechanical strength, chemical resistance and ease of working. � These are being used in civil engineering for high performance coatings, adhesives, injection grouting, high performance systems, industrial flooring or grouting etc.
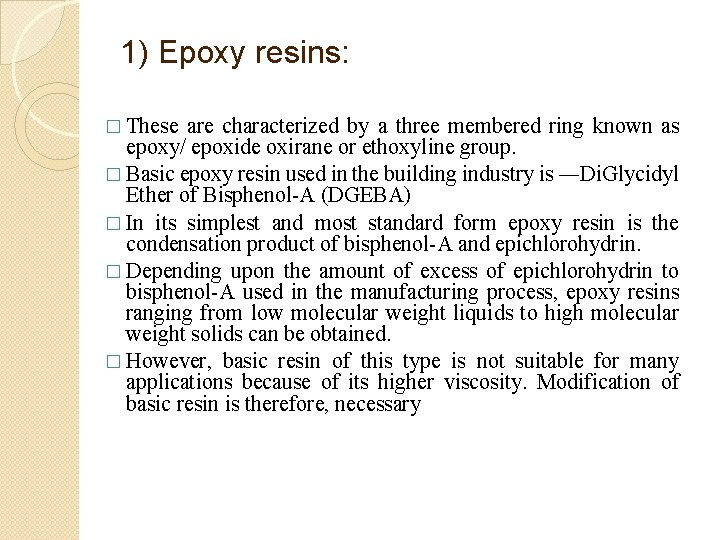
1) Epoxy resins: � These are characterized by a three membered ring known as epoxy/ epoxide oxirane or ethoxyline group. � Basic epoxy resin used in the building industry is ―Di. Glycidyl Ether of Bisphenol-A (DGEBA) � In its simplest and most standard form epoxy resin is the condensation product of bisphenol-A and epichlorohydrin. � Depending upon the amount of excess of epichlorohydrin to bisphenol-A used in the manufacturing process, epoxy resins ranging from low molecular weight liquids to high molecular weight solids can be obtained. � However, basic resin of this type is not suitable for many applications because of its higher viscosity. Modification of basic resin is therefore, necessary
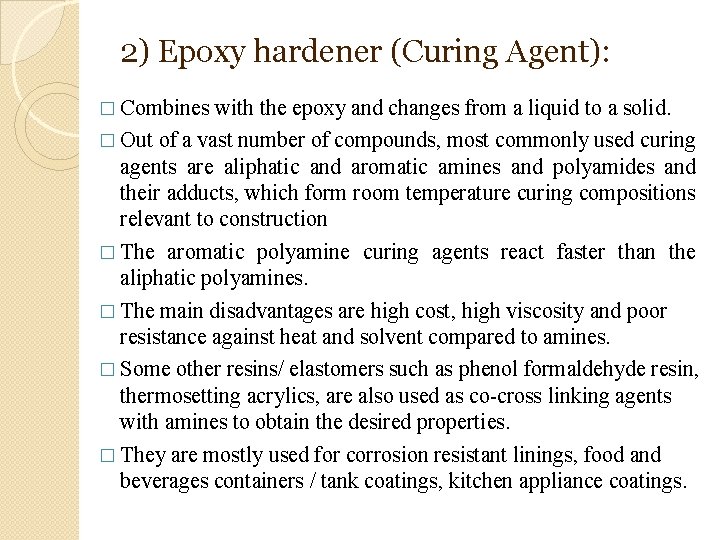
2) Epoxy hardener (Curing Agent): � Combines with the epoxy and changes from a liquid to a solid. � Out of a vast number of compounds, most commonly used curing agents are aliphatic and aromatic amines and polyamides and their adducts, which form room temperature curing compositions relevant to construction � The aromatic polyamine curing agents react faster than the aliphatic polyamines. � The main disadvantages are high cost, high viscosity and poor resistance against heat and solvent compared to amines. � Some other resins/ elastomers such as phenol formaldehyde resin, thermosetting acrylics, are also used as co-cross linking agents with amines to obtain the desired properties. � They are mostly used for corrosion resistant linings, food and beverages containers / tank coatings, kitchen appliance coatings.
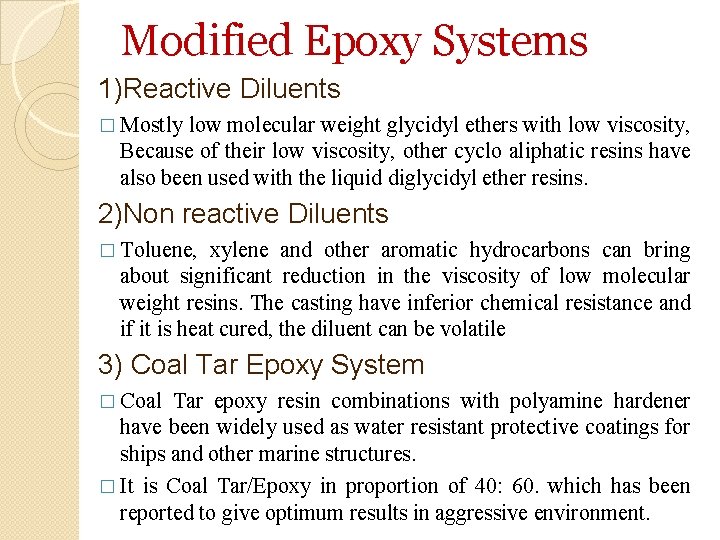
Modified Epoxy Systems 1)Reactive Diluents � Mostly low molecular weight glycidyl ethers with low viscosity, Because of their low viscosity, other cyclo aliphatic resins have also been used with the liquid diglycidyl ether resins. 2)Non reactive Diluents � Toluene, xylene and other aromatic hydrocarbons can bring about significant reduction in the viscosity of low molecular weight resins. The casting have inferior chemical resistance and if it is heat cured, the diluent can be volatile 3) Coal Tar Epoxy System � Coal Tar epoxy resin combinations with polyamine hardener have been widely used as water resistant protective coatings for ships and other marine structures. � It is Coal Tar/Epoxy in proportion of 40: 60. which has been reported to give optimum results in aggressive environment.
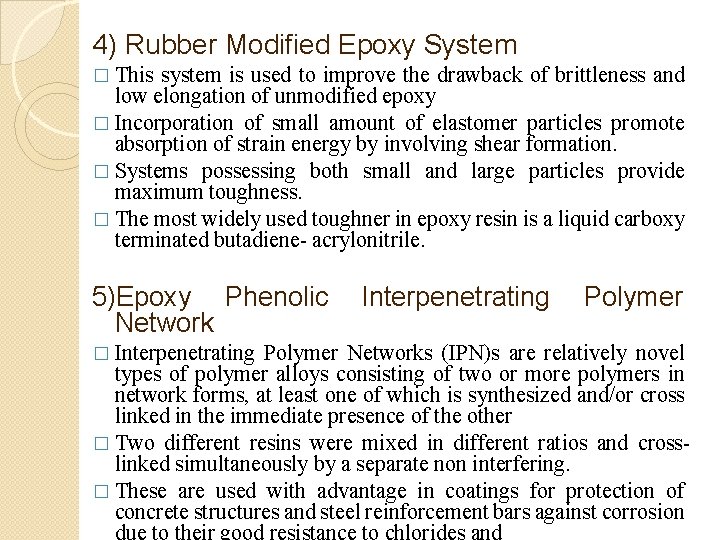
4) Rubber Modified Epoxy System � This system is used to improve the drawback of brittleness and low elongation of unmodified epoxy � Incorporation of small amount of elastomer particles promote absorption of strain energy by involving shear formation. � Systems possessing both small and large particles provide maximum toughness. � The most widely used toughner in epoxy resin is a liquid carboxy terminated butadiene- acrylonitrile. 5)Epoxy Phenolic Network � Interpenetrating Polymer Networks (IPN)s are relatively novel types of polymer alloys consisting of two or more polymers in network forms, at least one of which is synthesized and/or cross linked in the immediate presence of the other � Two different resins were mixed in different ratios and crosslinked simultaneously by a separate non interfering. � These are used with advantage in coatings for protection of concrete structures and steel reinforcement bars against corrosion
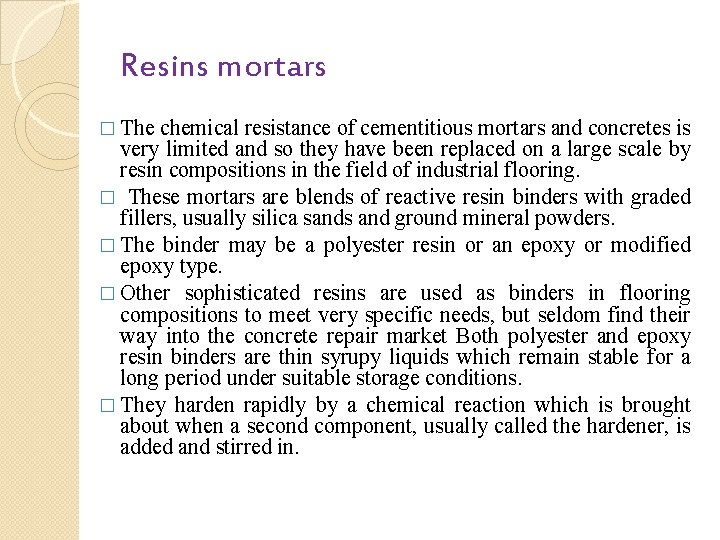
Resins mortars � The chemical resistance of cementitious mortars and concretes is very limited and so they have been replaced on a large scale by resin compositions in the field of industrial flooring. � These mortars are blends of reactive resin binders with graded fillers, usually silica sands and ground mineral powders. � The binder may be a polyester resin or an epoxy or modified epoxy type. � Other sophisticated resins are used as binders in flooring compositions to meet very specific needs, but seldom find their way into the concrete repair market Both polyester and epoxy resin binders are thin syrupy liquids which remain stable for a long period under suitable storage conditions. � They harden rapidly by a chemical reaction which is brought about when a second component, usually called the hardener, is added and stirred in.
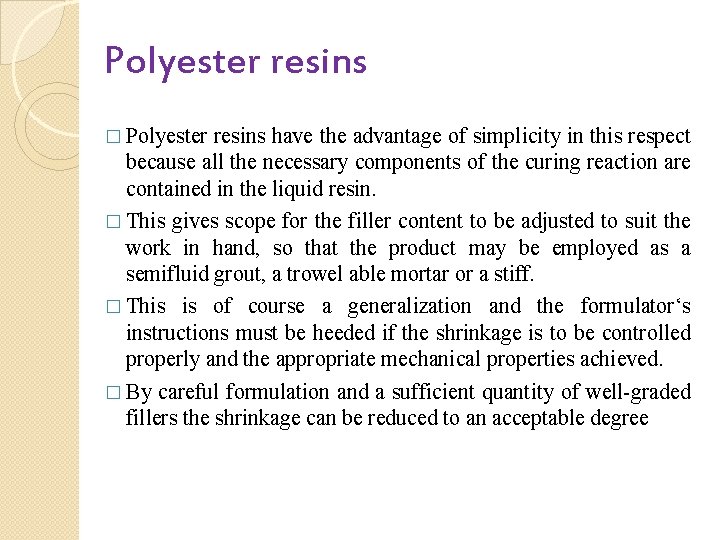
Polyester resins � Polyester resins have the advantage of simplicity in this respect because all the necessary components of the curing reaction are contained in the liquid resin. � This gives scope for the filler content to be adjusted to suit the work in hand, so that the product may be employed as a semifluid grout, a trowel able mortar or a stiff. � This is of course a generalization and the formulator‘s instructions must be heeded if the shrinkage is to be controlled properly and the appropriate mechanical properties achieved. � By careful formulation and a sufficient quantity of well-graded fillers the shrinkage can be reduced to an acceptable degree
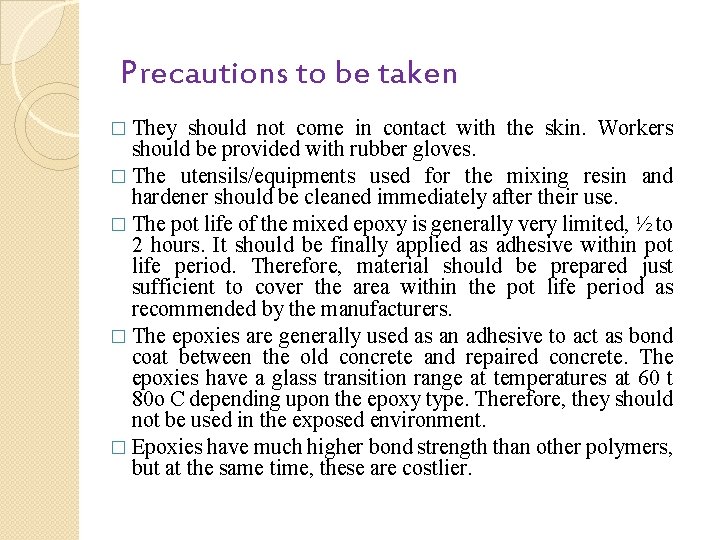
Precautions to be taken � They should not come in contact with the skin. Workers should be provided with rubber gloves. � The utensils/equipments used for the mixing resin and hardener should be cleaned immediately after their use. � The pot life of the mixed epoxy is generally very limited, ½ to 2 hours. It should be finally applied as adhesive within pot life period. Therefore, material should be prepared just sufficient to cover the area within the pot life period as recommended by the manufacturers. � The epoxies are generally used as an adhesive to act as bond coat between the old concrete and repaired concrete. The epoxies have a glass transition range at temperatures at 60 t 80 o C depending upon the epoxy type. Therefore, they should not be used in the exposed environment. � Epoxies have much higher bond strength than other polymers, but at the same time, these are costlier.
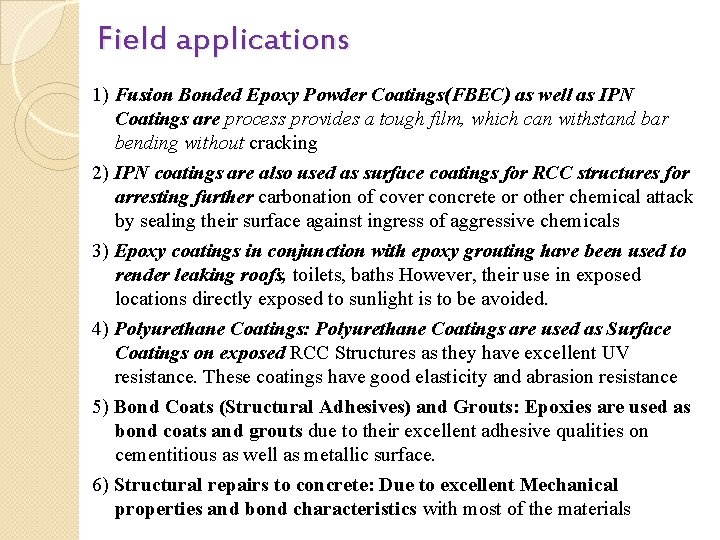
Field applications 1) Fusion Bonded Epoxy Powder Coatings(FBEC) as well as IPN Coatings are process provides a tough film, which can withstand bar bending without cracking 2) IPN coatings are also used as surface coatings for RCC structures for arresting further carbonation of cover concrete or other chemical attack by sealing their surface against ingress of aggressive chemicals 3) Epoxy coatings in conjunction with epoxy grouting have been used to render leaking roofs, toilets, baths However, their use in exposed locations directly exposed to sunlight is to be avoided. 4) Polyurethane Coatings: Polyurethane Coatings are used as Surface Coatings on exposed RCC Structures as they have excellent UV resistance. These coatings have good elasticity and abrasion resistance 5) Bond Coats (Structural Adhesives) and Grouts: Epoxies are used as bond coats and grouts due to their excellent adhesive qualities on cementitious as well as metallic surface. 6) Structural repairs to concrete: Due to excellent Mechanical properties and bond characteristics with most of the materials
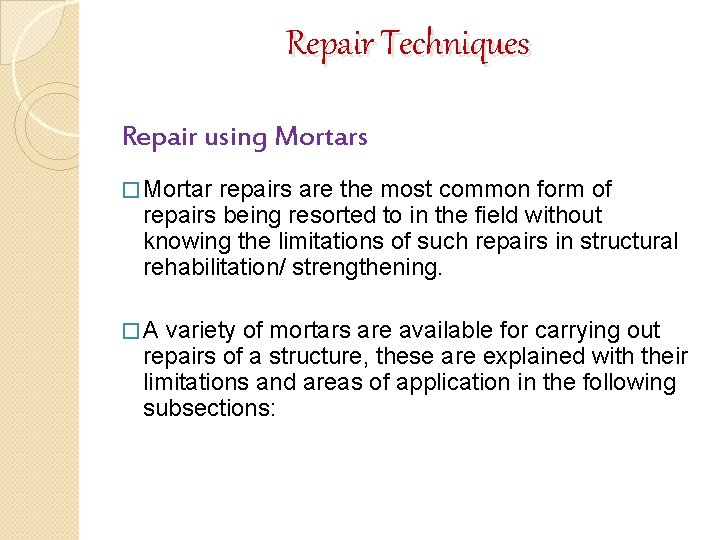
Repair Techniques Repair using Mortars � Mortar repairs are the most common form of repairs being resorted to in the field without knowing the limitations of such repairs in structural rehabilitation/ strengthening. �A variety of mortars are available for carrying out repairs of a structure, these are explained with their limitations and areas of application in the following subsections:
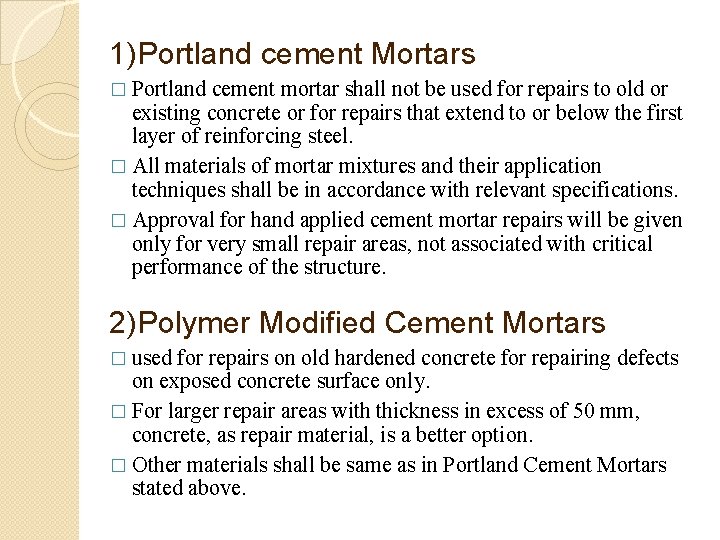
1)Portland cement Mortars � Portland cement mortar shall not be used for repairs to old or existing concrete or for repairs that extend to or below the first layer of reinforcing steel. � All materials of mortar mixtures and their application techniques shall be in accordance with relevant specifications. � Approval for hand applied cement mortar repairs will be given only for very small repair areas, not associated with critical performance of the structure. 2)Polymer Modified Cement Mortars � used for repairs on old hardened concrete for repairing defects on exposed concrete surface only. � For larger repair areas with thickness in excess of 50 mm, concrete, as repair material, is a better option. � Other materials shall be same as in Portland Cement Mortars stated above.
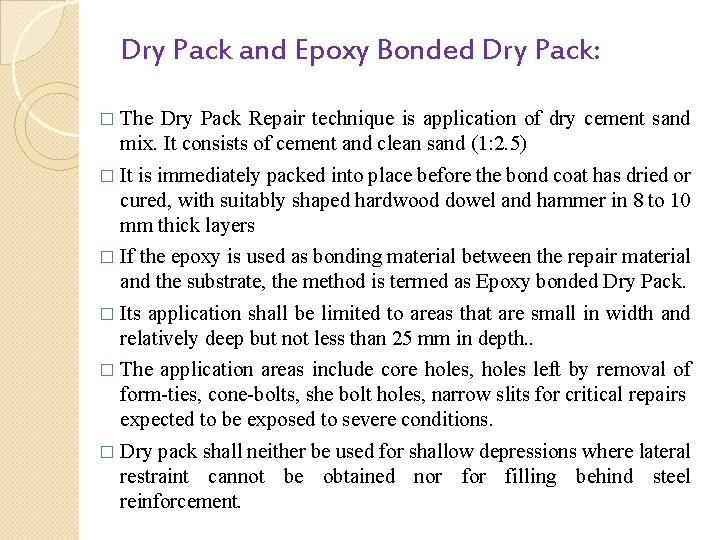
Dry Pack and Epoxy Bonded Dry Pack: � The Dry Pack Repair technique is application of dry cement sand mix. It consists of cement and clean sand (1: 2. 5) � It is immediately packed into place before the bond coat has dried or cured, with suitably shaped hardwood dowel and hammer in 8 to 10 mm thick layers � If the epoxy is used as bonding material between the repair material and the substrate, the method is termed as Epoxy bonded Dry Pack. � Its application shall be limited to areas that are small in width and relatively deep but not less than 25 mm in depth. . � The application areas include core holes, holes left by removal of form-ties, cone-bolts, she bolt holes, narrow slits for critical repairs expected to be exposed to severe conditions. � Dry pack shall neither be used for shallow depressions where lateral restraint cannot be obtained nor filling behind steel reinforcement.
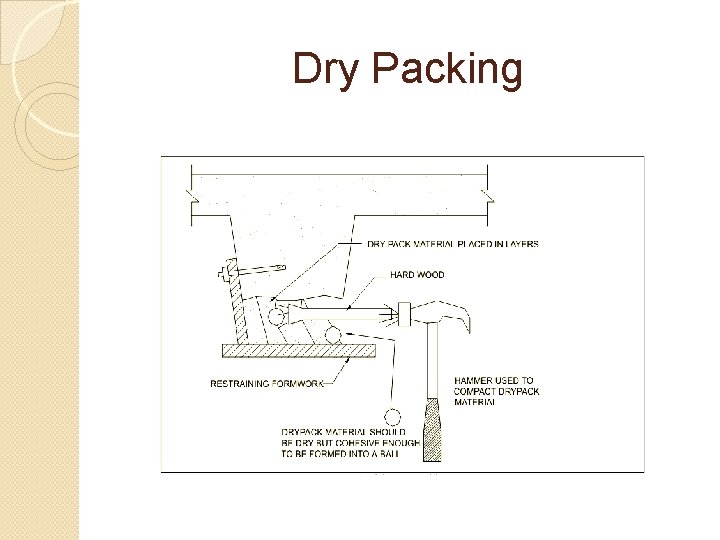
Dry Packing
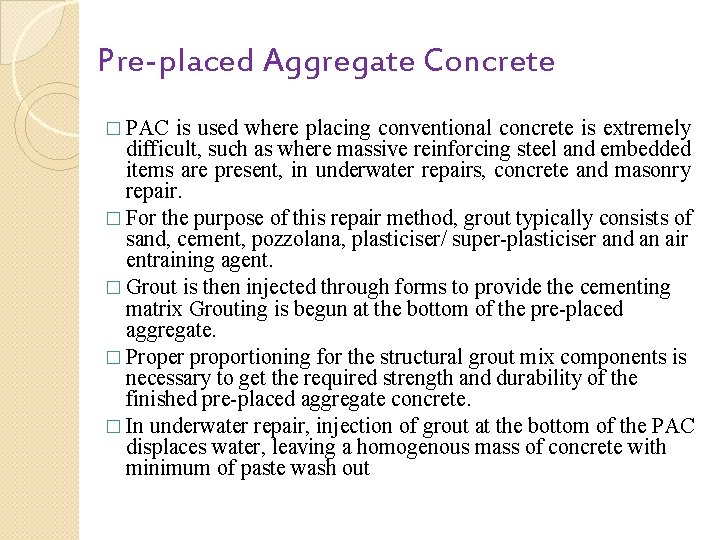
Pre-placed Aggregate Concrete � PAC is used where placing conventional concrete is extremely difficult, such as where massive reinforcing steel and embedded items are present, in underwater repairs, concrete and masonry repair. � For the purpose of this repair method, grout typically consists of sand, cement, pozzolana, plasticiser/ super-plasticiser and an air entraining agent. � Grout is then injected through forms to provide the cementing matrix Grouting is begun at the bottom of the pre-placed aggregate. � Proper proportioning for the structural grout mix components is necessary to get the required strength and durability of the finished pre-placed aggregate concrete. � In underwater repair, injection of grout at the bottom of the PAC displaces water, leaving a homogenous mass of concrete with minimum of paste wash out
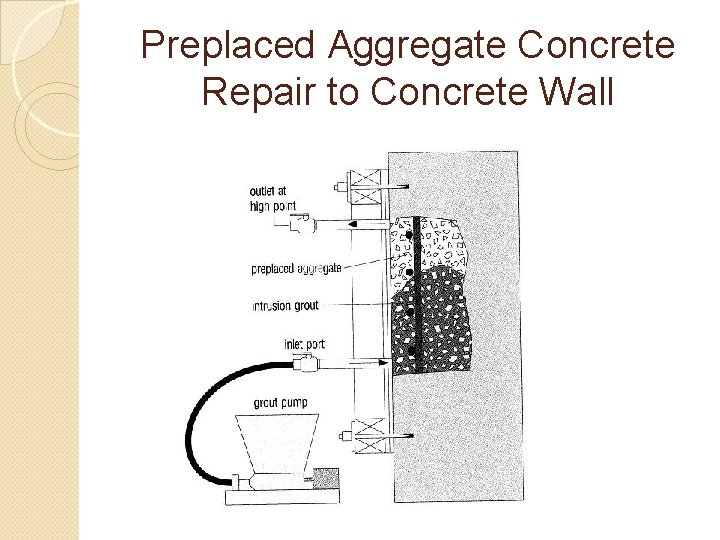
Preplaced Aggregate Concrete Repair to Concrete Wall
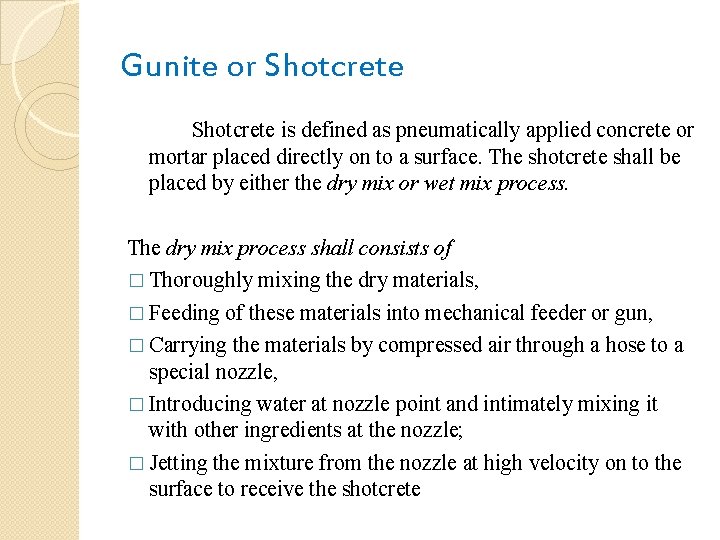
Gunite or Shotcrete is defined as pneumatically applied concrete or mortar placed directly on to a surface. The shotcrete shall be placed by either the dry mix or wet mix process. The dry mix process shall consists of � Thoroughly mixing the dry materials, � Feeding of these materials into mechanical feeder or gun, � Carrying the materials by compressed air through a hose to a special nozzle, � Introducing water at nozzle point and intimately mixing it with other ingredients at the nozzle; � Jetting the mixture from the nozzle at high velocity on to the surface to receive the shotcrete
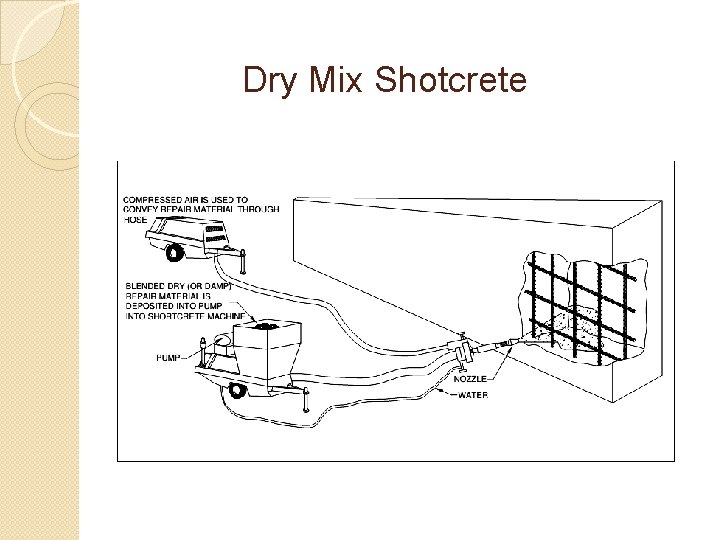
Dry Mix Shotcrete
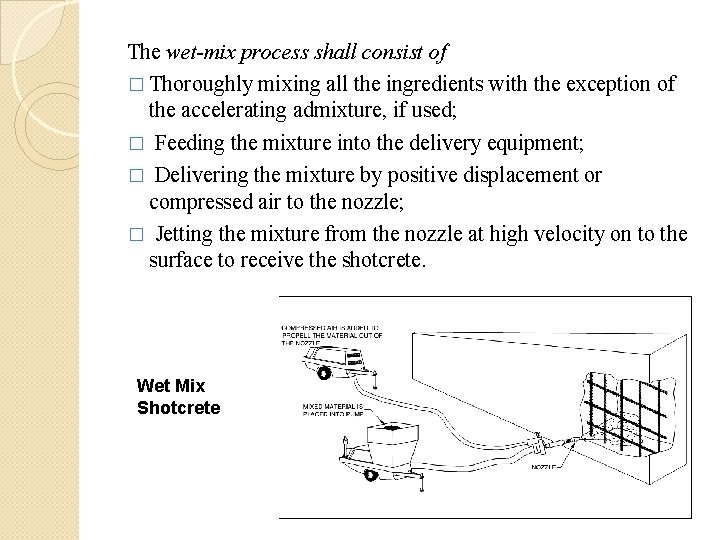
The wet-mix process shall consist of � Thoroughly mixing all the ingredients with the exception of the accelerating admixture, if used; � Feeding the mixture into the delivery equipment; � Delivering the mixture by positive displacement or compressed air to the nozzle; � Jetting the mixture from the nozzle at high velocity on to the surface to receive the shotcrete. Wet Mix Shotcrete
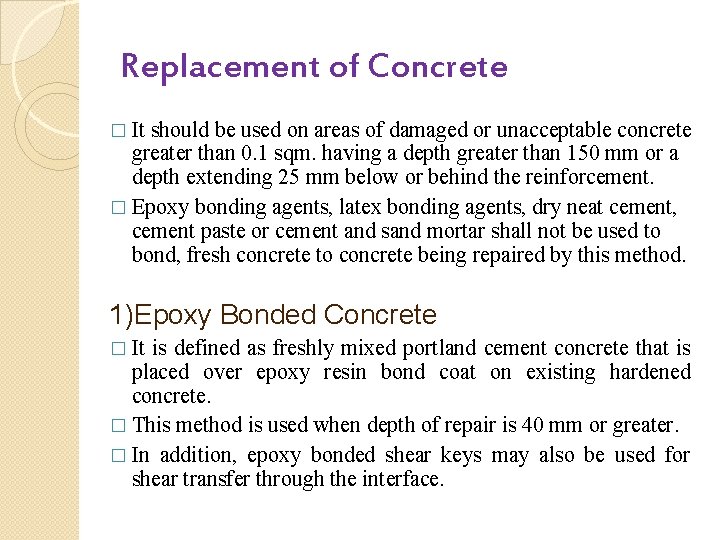
Replacement of Concrete � It should be used on areas of damaged or unacceptable concrete greater than 0. 1 sqm. having a depth greater than 150 mm or a depth extending 25 mm below or behind the reinforcement. � Epoxy bonding agents, latex bonding agents, dry neat cement, cement paste or cement and sand mortar shall not be used to bond, fresh concrete to concrete being repaired by this method. 1)Epoxy Bonded Concrete � It is defined as freshly mixed portland cement concrete that is placed over epoxy resin bond coat on existing hardened concrete. � This method is used when depth of repair is 40 mm or greater. � In addition, epoxy bonded shear keys may also be used for shear transfer through the interface.
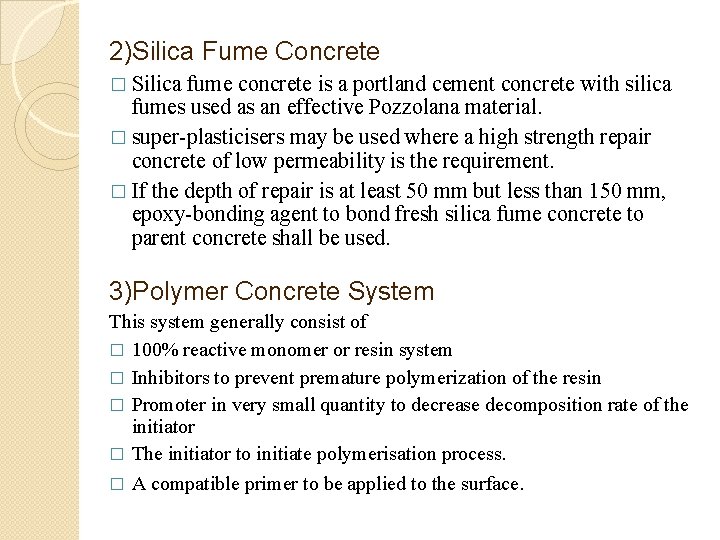
2)Silica Fume Concrete � Silica fume concrete is a portland cement concrete with silica fumes used as an effective Pozzolana material. � super-plasticisers may be used where a high strength repair concrete of low permeability is the requirement. � If the depth of repair is at least 50 mm but less than 150 mm, epoxy-bonding agent to bond fresh silica fume concrete to parent concrete shall be used. 3)Polymer Concrete System This system generally consist of � 100% reactive monomer or resin system � Inhibitors to prevent premature polymerization of the resin � Promoter in very small quantity to decrease decomposition rate of the initiator � The initiator to initiate polymerisation process. � A compatible primer to be applied to the surface.
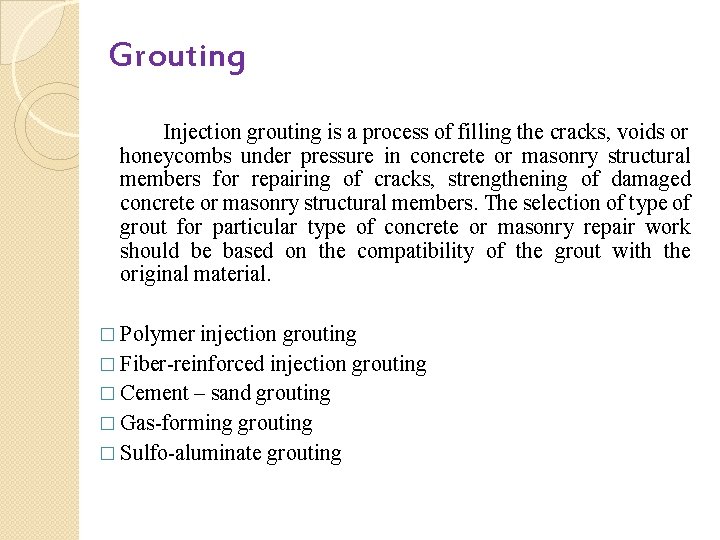
Grouting Injection grouting is a process of filling the cracks, voids or honeycombs under pressure in concrete or masonry structural members for repairing of cracks, strengthening of damaged concrete or masonry structural members. The selection of type of grout for particular type of concrete or masonry repair work should be based on the compatibility of the grout with the original material. � Polymer injection grouting � Fiber-reinforced injection grouting � Cement – sand grouting � Gas-forming grouting � Sulfo-aluminate grouting
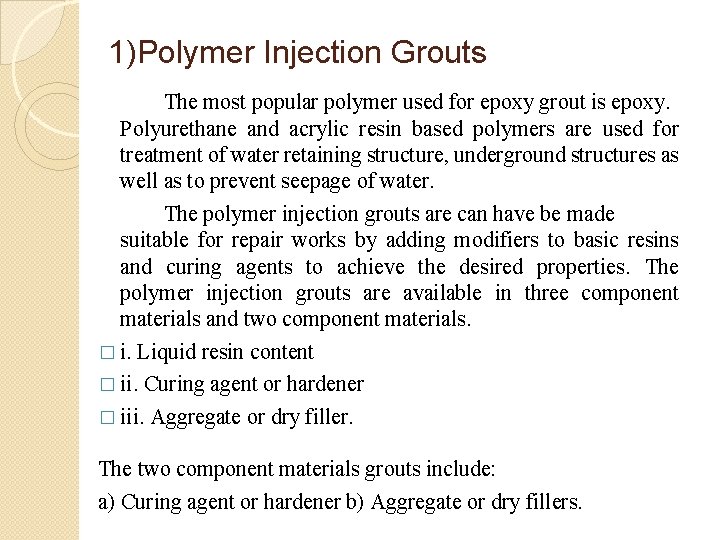
1)Polymer Injection Grouts The most popular polymer used for epoxy grout is epoxy. Polyurethane and acrylic resin based polymers are used for treatment of water retaining structure, underground structures as well as to prevent seepage of water. The polymer injection grouts are can have be made suitable for repair works by adding modifiers to basic resins and curing agents to achieve the desired properties. The polymer injection grouts are available in three component materials and two component materials. � i. Liquid resin content � ii. Curing agent or hardener � iii. Aggregate or dry filler. The two component materials grouts include: a) Curing agent or hardener b) Aggregate or dry fillers.
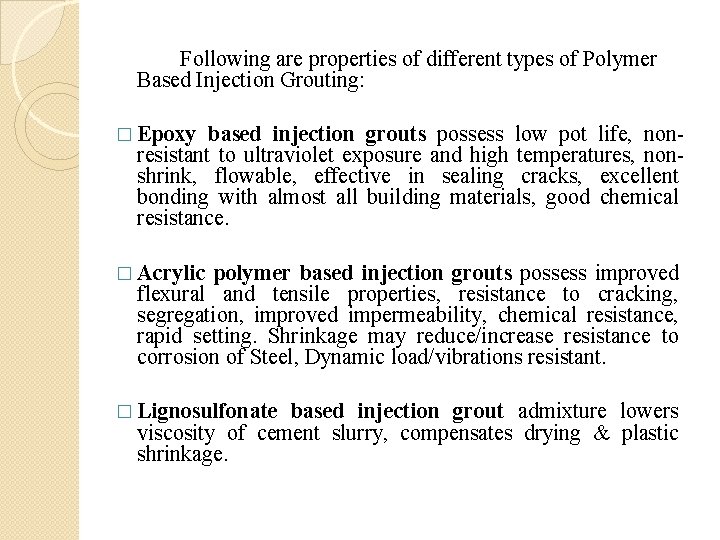
Following are properties of different types of Polymer Based Injection Grouting: � Epoxy based injection grouts possess low pot life, nonresistant to ultraviolet exposure and high temperatures, nonshrink, flowable, effective in sealing cracks, excellent bonding with almost all building materials, good chemical resistance. � Acrylic polymer based injection grouts possess improved flexural and tensile properties, resistance to cracking, segregation, improved impermeability, chemical resistance, rapid setting. Shrinkage may reduce/increase resistance to corrosion of Steel, Dynamic load/vibrations resistant. � Lignosulfonate based injection grout admixture lowers viscosity of cement slurry, compensates drying & plastic shrinkage.
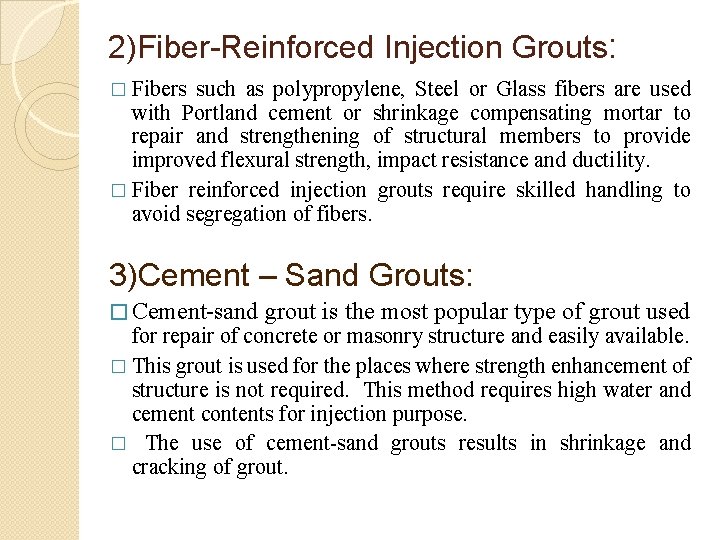
2)Fiber-Reinforced Injection Grouts: � Fibers such as polypropylene, Steel or Glass fibers are used with Portland cement or shrinkage compensating mortar to repair and strengthening of structural members to provide improved flexural strength, impact resistance and ductility. � Fiber reinforced injection grouts require skilled handling to avoid segregation of fibers. 3)Cement – Sand Grouts: � Cement-sand grout is the most popular type of grout used for repair of concrete or masonry structure and easily available. � This grout is used for the places where strength enhancement of structure is not required. This method requires high water and cement contents for injection purpose. � The use of cement-sand grouts results in shrinkage and cracking of grout.
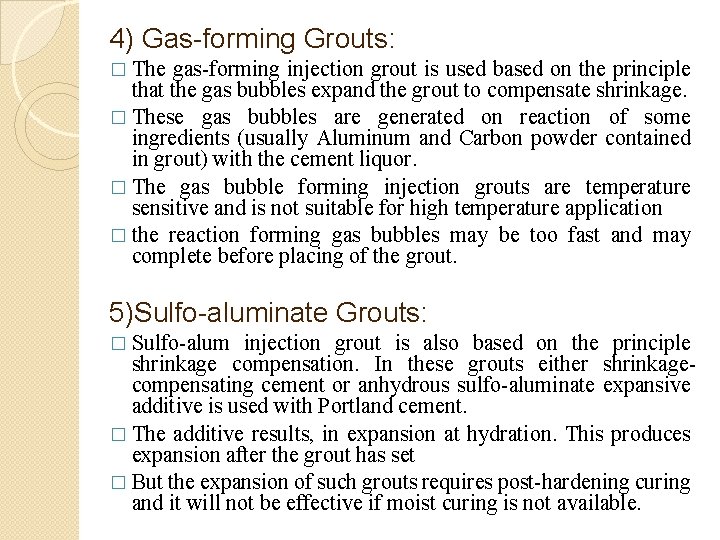
4) Gas-forming Grouts: � The gas-forming injection grout is used based on the principle that the gas bubbles expand the grout to compensate shrinkage. � These gas bubbles are generated on reaction of some ingredients (usually Aluminum and Carbon powder contained in grout) with the cement liquor. � The gas bubble forming injection grouts are temperature sensitive and is not suitable for high temperature application � the reaction forming gas bubbles may be too fast and may complete before placing of the grout. 5)Sulfo-aluminate Grouts: � Sulfo-alum injection grout is also based on the principle shrinkage compensation. In these grouts either shrinkagecompensating cement or anhydrous sulfo-aluminate expansive additive is used with Portland cement. � The additive results, in expansion at hydration. This produces expansion after the grout has set � But the expansion of such grouts requires post-hardening curing and it will not be effective if moist curing is not available.
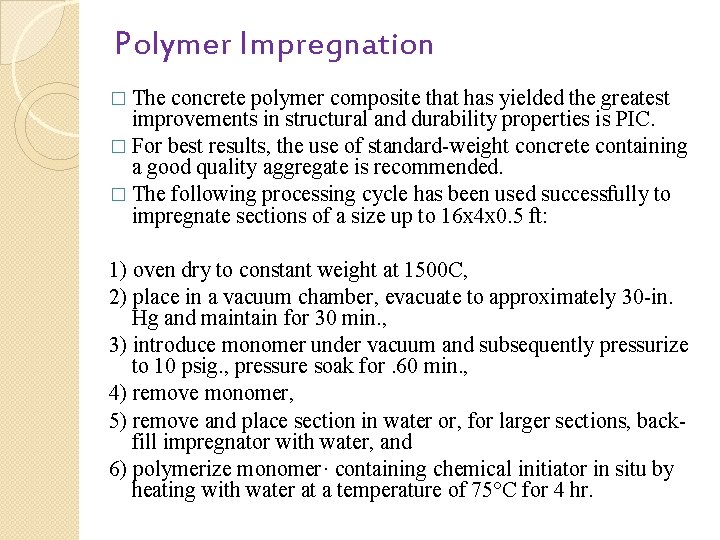
Polymer Impregnation � The concrete polymer composite that has yielded the greatest improvements in structural and durability properties is PIC. � For best results, the use of standard-weight concrete containing a good quality aggregate is recommended. � The following processing cycle has been used successfully to impregnate sections of a size up to 16 x 4 x 0. 5 ft: 1) oven dry to constant weight at 1500 C, 2) place in a vacuum chamber, evacuate to approximately 30 -in. Hg and maintain for 30 min. , 3) introduce monomer under vacuum and subsequently pressurize to 10 psig. , pressure soak for. 60 min. , 4) remove monomer, 5) remove and place section in water or, for larger sections, backfill impregnator with water, and 6) polymerize monomer· containing chemical initiator in situ by heating with water at a temperature of 75°C for 4 hr.
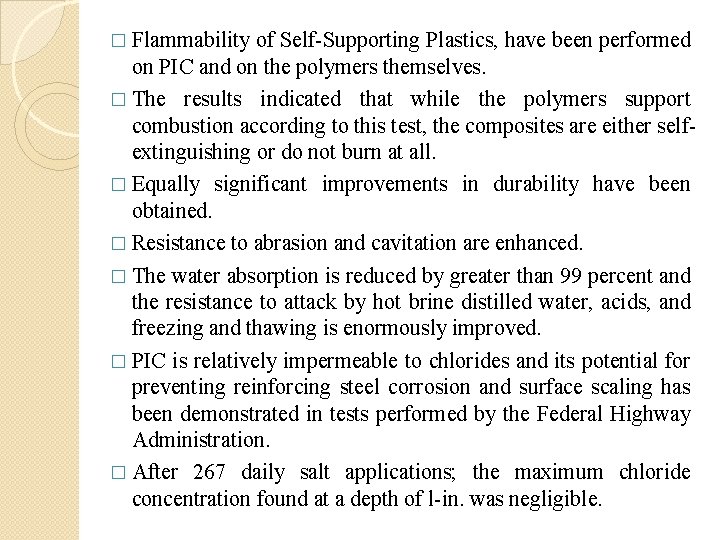
� Flammability of Self-Supporting Plastics, have been performed on PIC and on the polymers themselves. � The results indicated that while the polymers support combustion according to this test, the composites are either selfextinguishing or do not burn at all. � Equally significant improvements in durability have been obtained. � Resistance to abrasion and cavitation are enhanced. � The water absorption is reduced by greater than 99 percent and the resistance to attack by hot brine distilled water, acids, and freezing and thawing is enormously improved. � PIC is relatively impermeable to chlorides and its potential for preventing reinforcing steel corrosion and surface scaling has been demonstrated in tests performed by the Federal Highway Administration. � After 267 daily salt applications; the maximum chloride concentration found at a depth of l-in. was negligible.
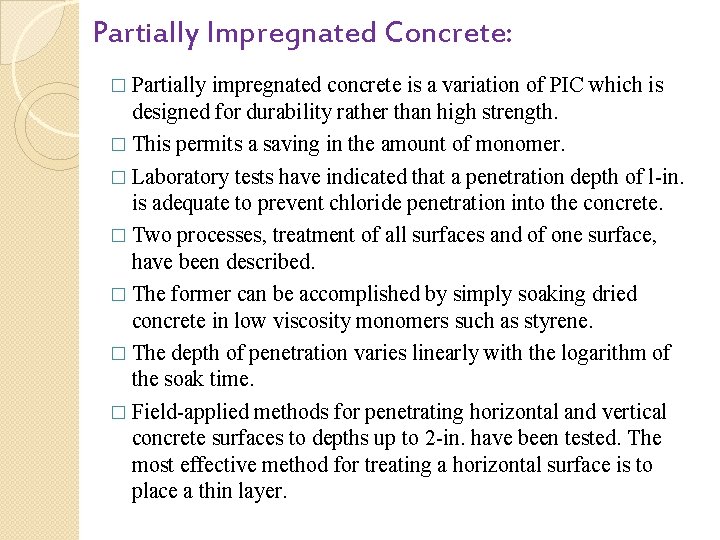
Partially Impregnated Concrete: � Partially impregnated concrete is a variation of PIC which is designed for durability rather than high strength. � This permits a saving in the amount of monomer. � Laboratory tests have indicated that a penetration depth of l-in. is adequate to prevent chloride penetration into the concrete. � Two processes, treatment of all surfaces and of one surface, have been described. � The former can be accomplished by simply soaking dried concrete in low viscosity monomers such as styrene. � The depth of penetration varies linearly with the logarithm of the soak time. � Field-applied methods for penetrating horizontal and vertical concrete surfaces to depths up to 2 -in. have been tested. The most effective method for treating a horizontal surface is to place a thin layer.
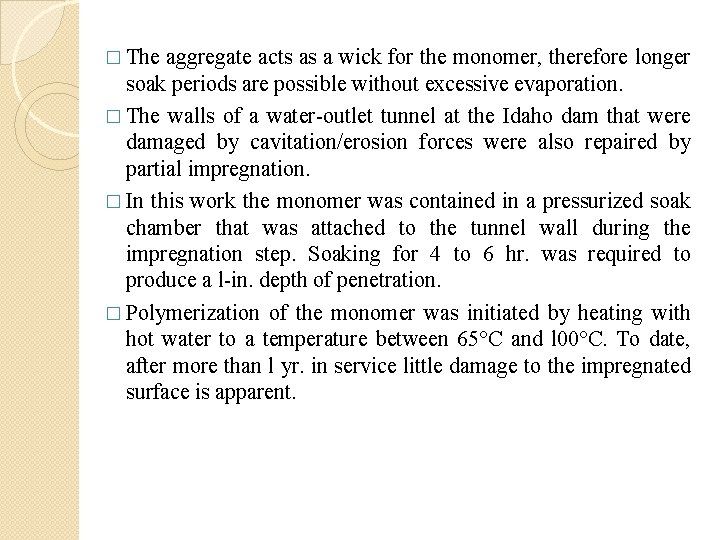
� The aggregate acts as a wick for the monomer, therefore longer soak periods are possible without excessive evaporation. � The walls of a water-outlet tunnel at the Idaho dam that were damaged by cavitation/erosion forces were also repaired by partial impregnation. � In this work the monomer was contained in a pressurized soak chamber that was attached to the tunnel wall during the impregnation step. Soaking for 4 to 6 hr. was required to produce a l-in. depth of penetration. � Polymerization of the monomer was initiated by heating with hot water to a temperature between 65°C and l 00°C. To date, after more than l yr. in service little damage to the impregnated surface is apparent.
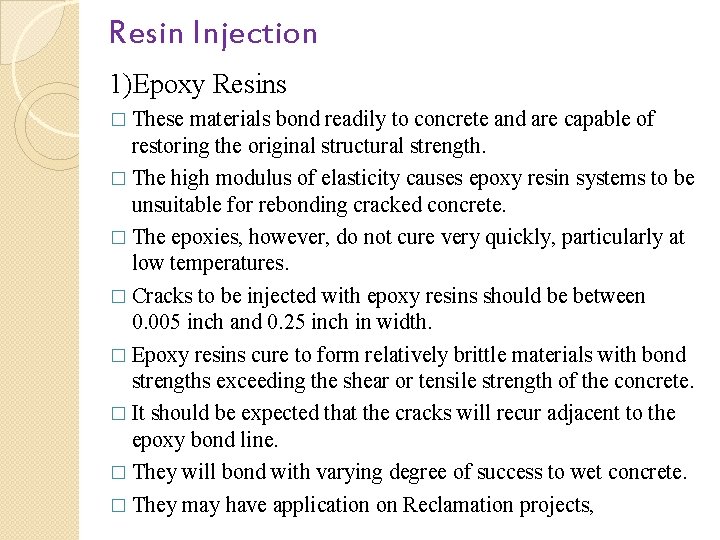
Resin Injection 1)Epoxy Resins � These materials bond readily to concrete and are capable of restoring the original structural strength. � The high modulus of elasticity causes epoxy resin systems to be unsuitable for rebonding cracked concrete. � The epoxies, however, do not cure very quickly, particularly at low temperatures. � Cracks to be injected with epoxy resins should be between 0. 005 inch and 0. 25 inch in width. � Epoxy resins cure to form relatively brittle materials with bond strengths exceeding the shear or tensile strength of the concrete. � It should be expected that the cracks will recur adjacent to the epoxy bond line. � They will bond with varying degree of success to wet concrete. � They may have application on Reclamation projects,
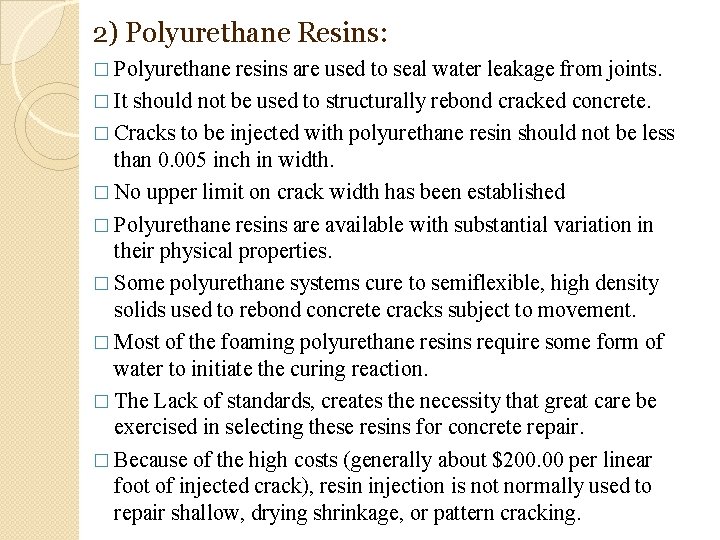
2) Polyurethane Resins: � Polyurethane resins are used to seal water leakage from joints. � It should not be used to structurally rebond cracked concrete. � Cracks to be injected with polyurethane resin should not be less than 0. 005 inch in width. � No upper limit on crack width has been established � Polyurethane resins are available with substantial variation in their physical properties. � Some polyurethane systems cure to semiflexible, high density solids used to rebond concrete cracks subject to movement. � Most of the foaming polyurethane resins require some form of water to initiate the curing reaction. � The Lack of standards, creates the necessity that great care be exercised in selecting these resins for concrete repair. � Because of the high costs (generally about $200. 00 per linear foot of injected crack), resin injection is not normally used to repair shallow, drying shrinkage, or pattern cracking.
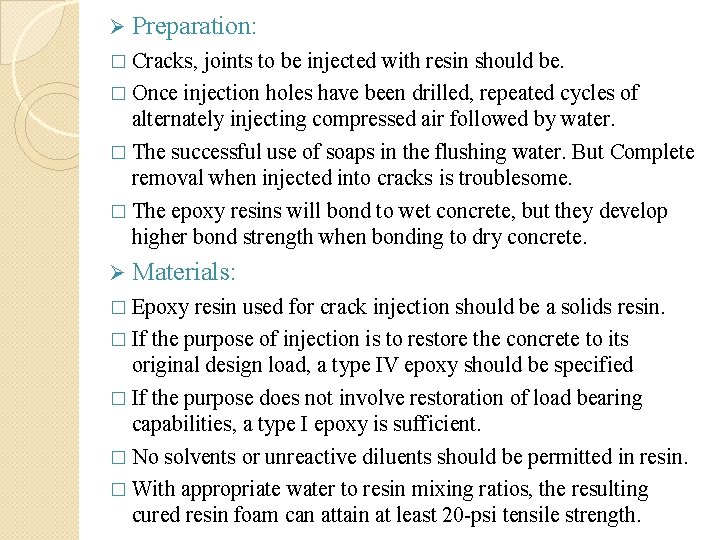
Ø Preparation: � Cracks, joints to be injected with resin should be. � Once injection holes have been drilled, repeated cycles of alternately injecting compressed air followed by water. � The successful use of soaps in the flushing water. But Complete removal when injected into cracks is troublesome. � The epoxy resins will bond to wet concrete, but they develop higher bond strength when bonding to dry concrete. Ø Materials: � Epoxy resin used for crack injection should be a solids resin. � If the purpose of injection is to restore the concrete to its original design load, a type IV epoxy should be specified � If the purpose does not involve restoration of load bearing capabilities, a type I epoxy is sufficient. � No solvents or unreactive diluents should be permitted in resin. � With appropriate water to resin mixing ratios, the resulting cured resin foam can attain at least 20 -psi tensile strength.
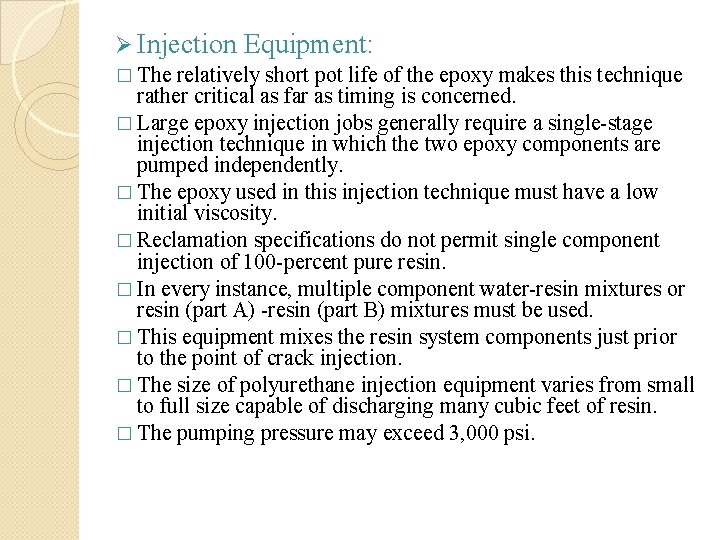
Ø Injection Equipment: � The relatively short pot life of the epoxy makes this technique rather critical as far as timing is concerned. � Large epoxy injection jobs generally require a single-stage injection technique in which the two epoxy components are pumped independently. � The epoxy used in this injection technique must have a low initial viscosity. � Reclamation specifications do not permit single component injection of 100 -percent pure resin. � In every instance, multiple component water-resin mixtures or resin (part A) -resin (part B) mixtures must be used. � This equipment mixes the resin system components just prior to the point of crack injection. � The size of polyurethane injection equipment varies from small to full size capable of discharging many cubic feet of resin. � The pumping pressure may exceed 3, 000 psi.
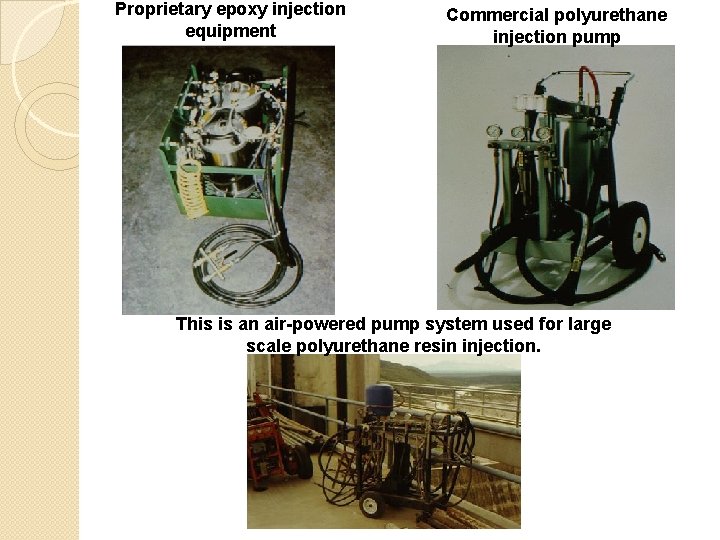
Proprietary epoxy injection equipment Commercial polyurethane injection pump This is an air-powered pump system used for large scale polyurethane resin injection.
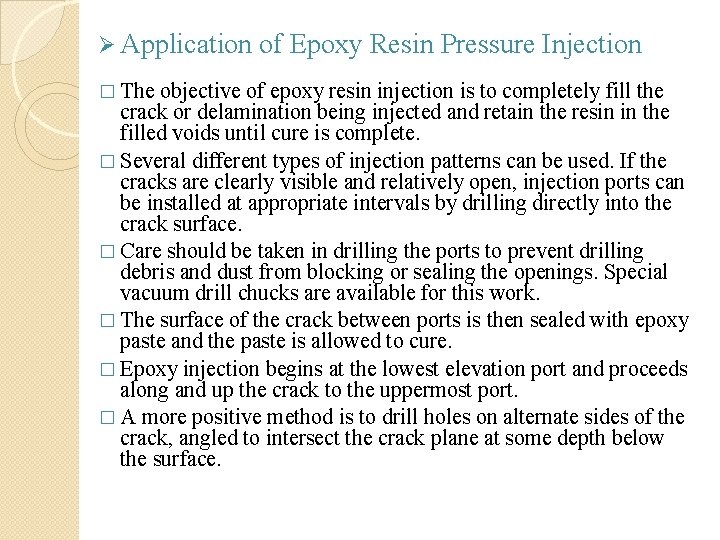
Ø Application � The of Epoxy Resin Pressure Injection objective of epoxy resin injection is to completely fill the crack or delamination being injected and retain the resin in the filled voids until cure is complete. � Several different types of injection patterns can be used. If the cracks are clearly visible and relatively open, injection ports can be installed at appropriate intervals by drilling directly into the crack surface. � Care should be taken in drilling the ports to prevent drilling debris and dust from blocking or sealing the openings. Special vacuum drill chucks are available for this work. � The surface of the crack between ports is then sealed with epoxy paste and the paste is allowed to cure. � Epoxy injection begins at the lowest elevation port and proceeds along and up the crack to the uppermost port. � A more positive method is to drill holes on alternate sides of the crack, angled to intersect the crack plane at some depth below the surface.
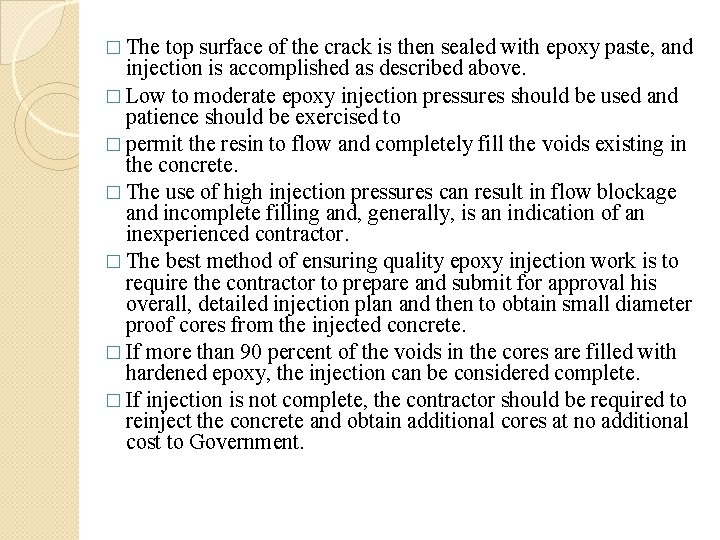
� The top surface of the crack is then sealed with epoxy paste, and injection is accomplished as described above. � Low to moderate epoxy injection pressures should be used and patience should be exercised to � permit the resin to flow and completely fill the voids existing in the concrete. � The use of high injection pressures can result in flow blockage and incomplete filling and, generally, is an indication of an inexperienced contractor. � The best method of ensuring quality epoxy injection work is to require the contractor to prepare and submit for approval his overall, detailed injection plan and then to obtain small diameter proof cores from the injected concrete. � If more than 90 percent of the voids in the cores are filled with hardened epoxy, the injection can be considered complete. � If injection is not complete, the contractor should be required to reinject the concrete and obtain additional cores at no additional cost to Government.
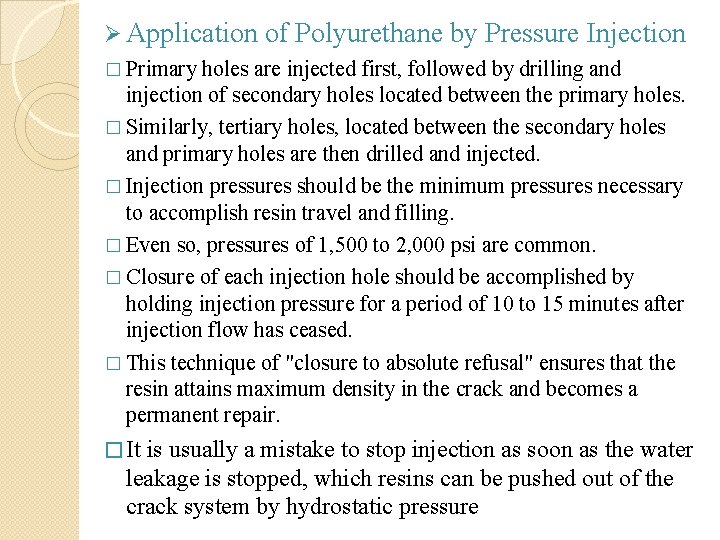
Ø Application of Polyurethane by Pressure Injection � Primary holes are injected first, followed by drilling and injection of secondary holes located between the primary holes. � Similarly, tertiary holes, located between the secondary holes and primary holes are then drilled and injected. � Injection pressures should be the minimum pressures necessary to accomplish resin travel and filling. � Even so, pressures of 1, 500 to 2, 000 psi are common. � Closure of each injection hole should be accomplished by holding injection pressure for a period of 10 to 15 minutes after injection flow has ceased. � This technique of "closure to absolute refusal" ensures that the resin attains maximum density in the crack and becomes a permanent repair. � It is usually a mistake to stop injection as soon as the water leakage is stopped, which resins can be pushed out of the crack system by hydrostatic pressure
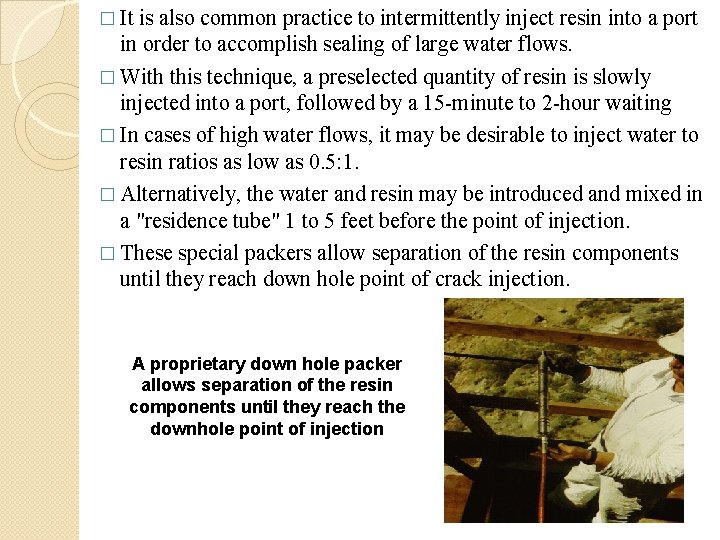
� It is also common practice to intermittently inject resin into a port in order to accomplish sealing of large water flows. � With this technique, a preselected quantity of resin is slowly injected into a port, followed by a 15 -minute to 2 -hour waiting � In cases of high water flows, it may be desirable to inject water to resin ratios as low as 0. 5: 1. � Alternatively, the water and resin may be introduced and mixed in a "residence tube" 1 to 5 feet before the point of injection. � These special packers allow separation of the resin components until they reach down hole point of crack injection. A proprietary down hole packer allows separation of the resin components until they reach the downhole point of injection
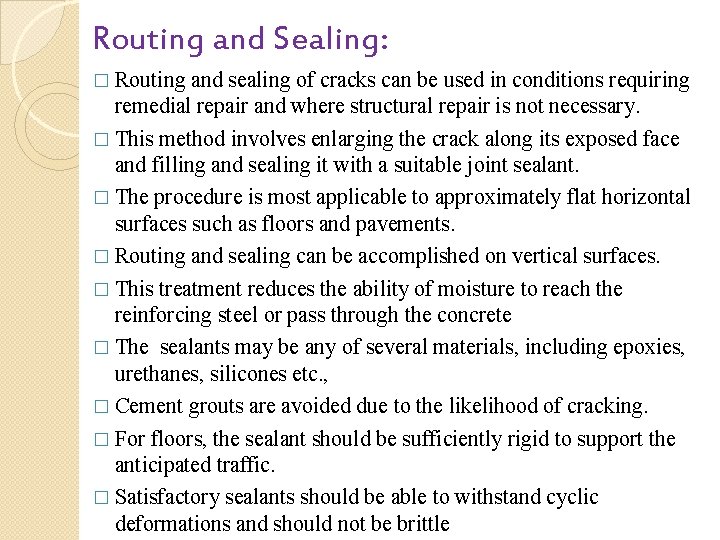
Routing and Sealing: � Routing and sealing of cracks can be used in conditions requiring remedial repair and where structural repair is not necessary. � This method involves enlarging the crack along its exposed face and filling and sealing it with a suitable joint sealant. � The procedure is most applicable to approximately flat horizontal surfaces such as floors and pavements. � Routing and sealing can be accomplished on vertical surfaces. � This treatment reduces the ability of moisture to reach the reinforcing steel or pass through the concrete � The sealants may be any of several materials, including epoxies, urethanes, silicones etc. , � Cement grouts are avoided due to the likelihood of cracking. � For floors, the sealant should be sufficiently rigid to support the anticipated traffic. � Satisfactory sealants should be able to withstand cyclic deformations and should not be brittle
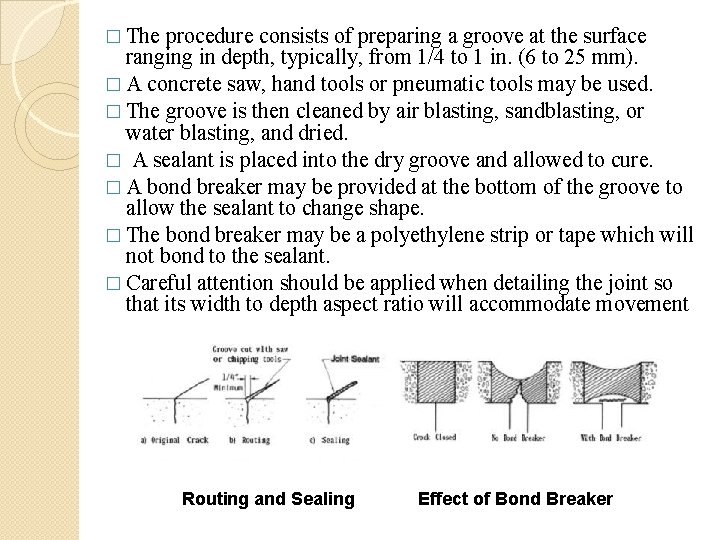
� The procedure consists of preparing a groove at the surface ranging in depth, typically, from 1/4 to 1 in. (6 to 25 mm). � A concrete saw, hand tools or pneumatic tools may be used. � The groove is then cleaned by air blasting, sandblasting, or water blasting, and dried. � A sealant is placed into the dry groove and allowed to cure. � A bond breaker may be provided at the bottom of the groove to allow the sealant to change shape. � The bond breaker may be a polyethylene strip or tape which will not bond to the sealant. � Careful attention should be applied when detailing the joint so that its width to depth aspect ratio will accommodate movement Routing and Sealing Effect of Bond Breaker
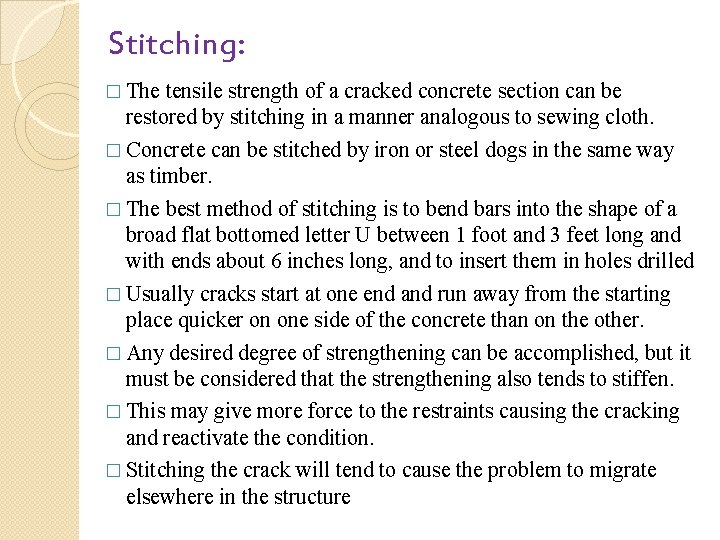
Stitching: � The tensile strength of a cracked concrete section can be restored by stitching in a manner analogous to sewing cloth. � Concrete can be stitched by iron or steel dogs in the same way as timber. � The best method of stitching is to bend bars into the shape of a broad flat bottomed letter U between 1 foot and 3 feet long and with ends about 6 inches long, and to insert them in holes drilled � Usually cracks start at one end and run away from the starting place quicker on one side of the concrete than on the other. � Any desired degree of strengthening can be accomplished, but it must be considered that the strengthening also tends to stiffen. � This may give more force to the restraints causing the cracking and reactivate the condition. � Stitching the crack will tend to cause the problem to migrate elsewhere in the structure
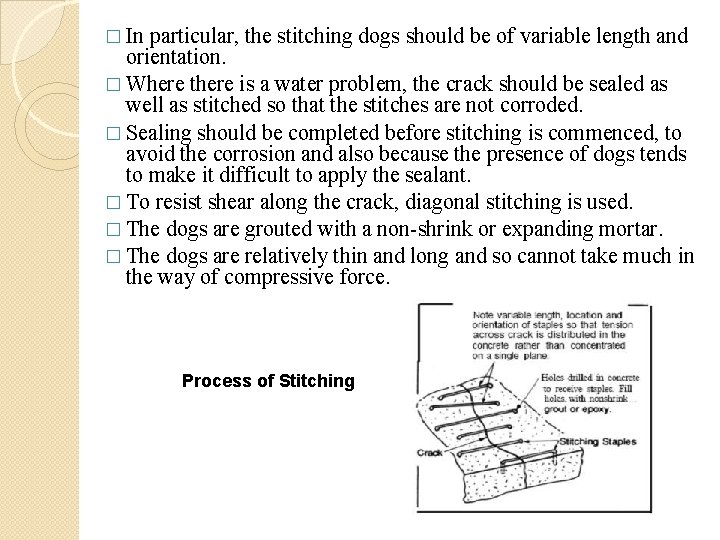
� In particular, the stitching dogs should be of variable length and orientation. � Where there is a water problem, the crack should be sealed as well as stitched so that the stitches are not corroded. � Sealing should be completed before stitching is commenced, to avoid the corrosion and also because the presence of dogs tends to make it difficult to apply the sealant. � To resist shear along the crack, diagonal stitching is used. � The dogs are grouted with a non-shrink or expanding mortar. � The dogs are relatively thin and long and so cannot take much in the way of compressive force. Process of Stitching
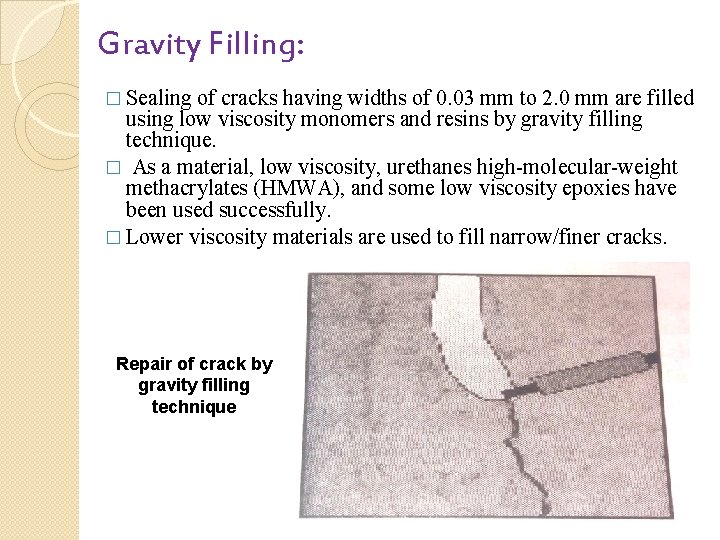
Gravity Filling: � Sealing of cracks having widths of 0. 03 mm to 2. 0 mm are filled using low viscosity monomers and resins by gravity filling technique. � As a material, low viscosity, urethanes high-molecular-weight methacrylates (HMWA), and some low viscosity epoxies have been used successfully. � Lower viscosity materials are used to fill narrow/finer cracks. Repair of crack by gravity filling technique
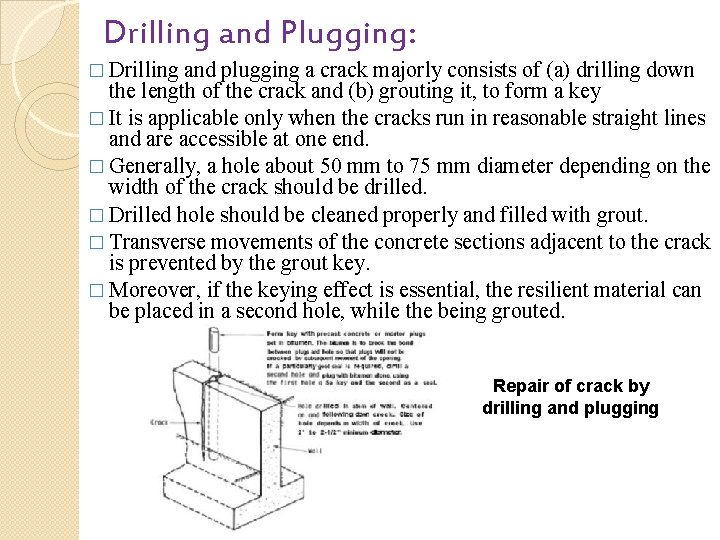
Drilling and Plugging: � Drilling and plugging a crack majorly consists of (a) drilling down the length of the crack and (b) grouting it, to form a key � It is applicable only when the cracks run in reasonable straight lines and are accessible at one end. � Generally, a hole about 50 mm to 75 mm diameter depending on the width of the crack should be drilled. � Drilled hole should be cleaned properly and filled with grout. � Transverse movements of the concrete sections adjacent to the crack is prevented by the grout key. � Moreover, if the keying effect is essential, the resilient material can be placed in a second hole, while the being grouted. Repair of crack by drilling and plugging
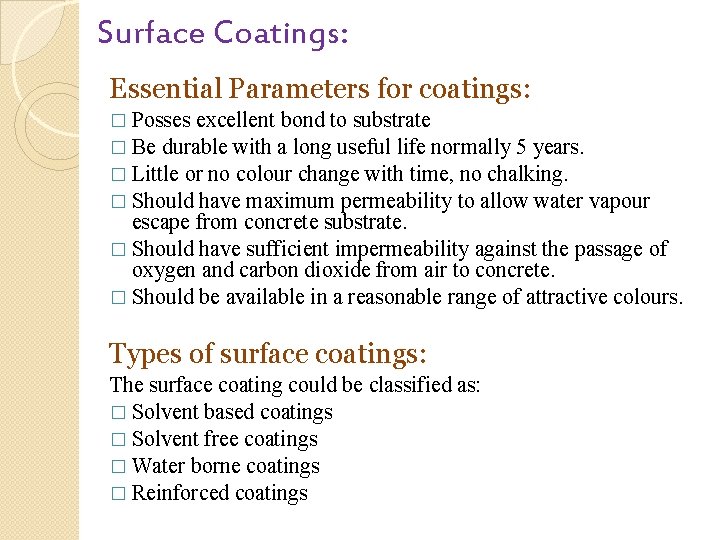
Surface Coatings: Essential Parameters for coatings: � Posses excellent bond to substrate � Be durable with a long useful life normally 5 years. � Little or no colour change with time, no chalking. � Should have maximum permeability to allow water vapour escape from concrete substrate. � Should have sufficient impermeability against the passage of oxygen and carbon dioxide from air to concrete. � Should be available in a reasonable range of attractive colours. Types of surface coatings: The surface coating could be classified as: � Solvent based coatings � Solvent free coatings � Water borne coatings � Reinforced coatings
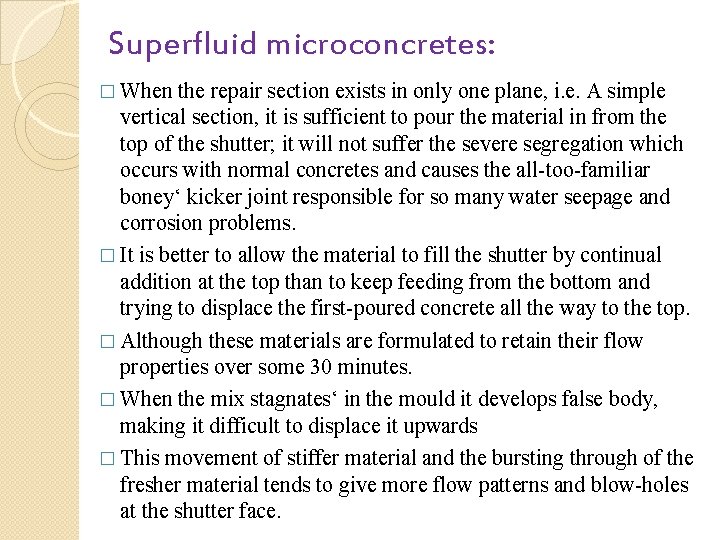
Superfluid microconcretes: � When the repair section exists in only one plane, i. e. A simple vertical section, it is sufficient to pour the material in from the top of the shutter; it will not suffer the severe segregation which occurs with normal concretes and causes the all-too-familiar boney‘ kicker joint responsible for so many water seepage and corrosion problems. � It is better to allow the material to fill the shutter by continual addition at the top than to keep feeding from the bottom and trying to displace the first-poured concrete all the way to the top. � Although these materials are formulated to retain their flow properties over some 30 minutes. � When the mix stagnates‘ in the mould it develops false body, making it difficult to displace it upwards � This movement of stiffer material and the bursting through of the fresher material tends to give more flow patterns and blow-holes at the shutter face.
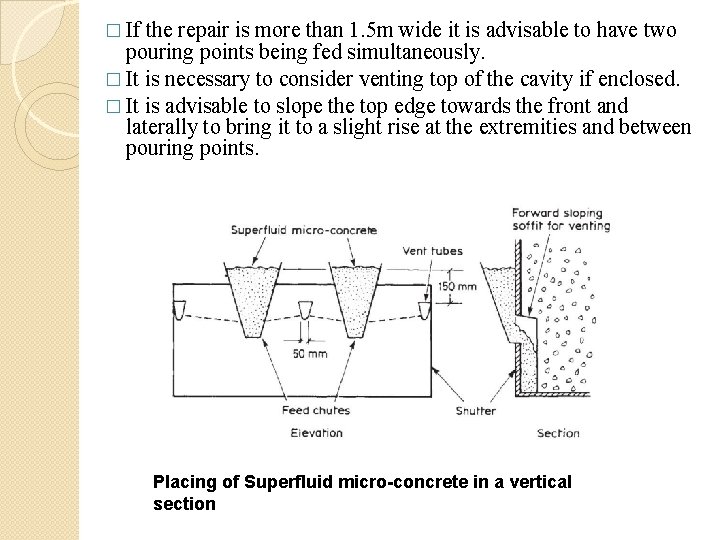
� If the repair is more than 1. 5 m wide it is advisable to have two pouring points being fed simultaneously. � It is necessary to consider venting top of the cavity if enclosed. � It is advisable to slope the top edge towards the front and laterally to bring it to a slight rise at the extremities and between pouring points. Placing of Superfluid micro-concrete in a vertical section
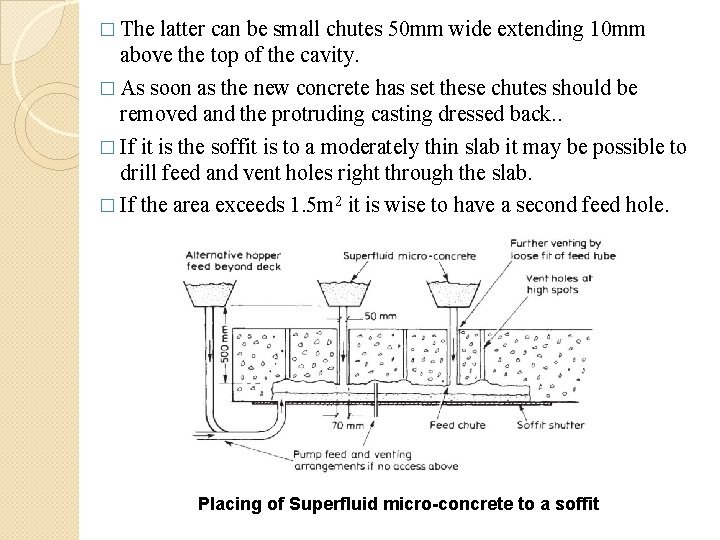
� The latter can be small chutes 50 mm wide extending 10 mm above the top of the cavity. � As soon as the new concrete has set these chutes should be removed and the protruding casting dressed back. . � If it is the soffit is to a moderately thin slab it may be possible to drill feed and vent holes right through the slab. � If the area exceeds 1. 5 m 2 it is wise to have a second feed hole. Placing of Superfluid micro-concrete to a soffit
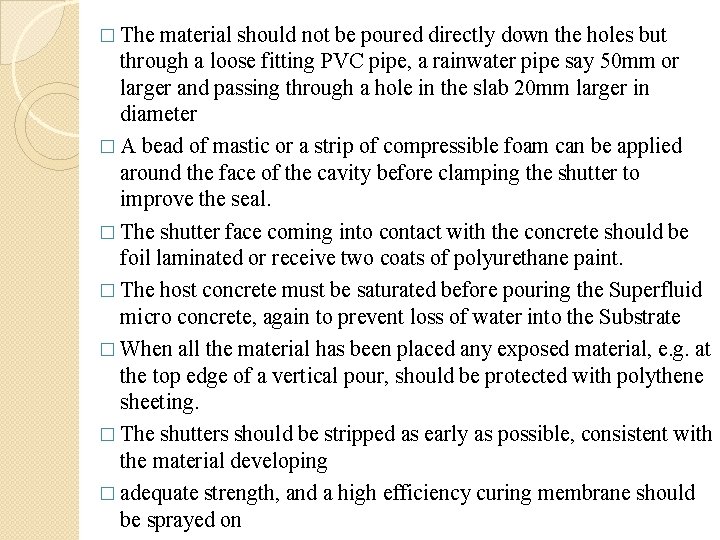
� The material should not be poured directly down the holes but through a loose fitting PVC pipe, a rainwater pipe say 50 mm or larger and passing through a hole in the slab 20 mm larger in diameter � A bead of mastic or a strip of compressible foam can be applied around the face of the cavity before clamping the shutter to improve the seal. � The shutter face coming into contact with the concrete should be foil laminated or receive two coats of polyurethane paint. � The host concrete must be saturated before pouring the Superfluid micro concrete, again to prevent loss of water into the Substrate � When all the material has been placed any exposed material, e. g. at the top edge of a vertical pour, should be protected with polythene sheeting. � The shutters should be stripped as early as possible, consistent with the material developing � adequate strength, and a high efficiency curing membrane should be sprayed on
Base excision repair
Base excision repair vs mismatch repair
Culvert repair techniques
Cement squeeze job procedure
Go noodle cant stop the feeling
Why are materials useful
Natural materials and man made materials
Adopting and adapting teaching materials
Brake system diagnosis and repair
Electronic suspension system
Peak and hold injector waveform
Chapter 44 automotive wiring and wire repair
Introduction to materials science for engineers chapter 10
Introduction to materials science for engineers chapter 10
Direct materials budget with multiple materials
Fonctions techniques et solutions techniques
Dna polymerase
Data flow diagram for parking management system
Faa field approval
Brake system diagnosis and repair
Auto upkeep answer key
Repair and restoration theory of sleep
Repair renovation and restoration of water bodies
Repair theory of sleep
What are reference materials
Crown lengthening procedure steps ppt
Define material handling
Introduction to dental materials
Introduction to materials testing
Material handling introduction
Chapter 47 laboratory materials and procedures
Chapter 4 materials metals and nonmetals
Basic laboratory techniques introduction
Introduction to sql programming techniques
Introduction to sql programming techniques
Sports medicine taping techniques
Tru count air clutch parts diagram
Duct repair serpentine
Decompressive laminectomy icd 10
Ems equipment repair
Self initiated other repair examples
Centurylink control center
Aci224
Switchboard maintenance
Maag gearbox repair
Verb 3 destroy
Repair analysis
External ring
Texture repair glencoe
Join in 3. hali
Fatty hernia of linea alba treatment
Process data flow
Heavy duty truck axle repair
Write it right bureau of automotive repair
Pcb repair training
Wells fargo identity theft repair kit
Repair guide
Neodura dural repair patch
Mend and recycle
Coding system part repair
Healing by first intention
Cladding repair specialists
Commercial door repair edmonton
Farmington roof repair
Surface repair technician