Shielded Metal Arc Welding SMAW Welding Most economical
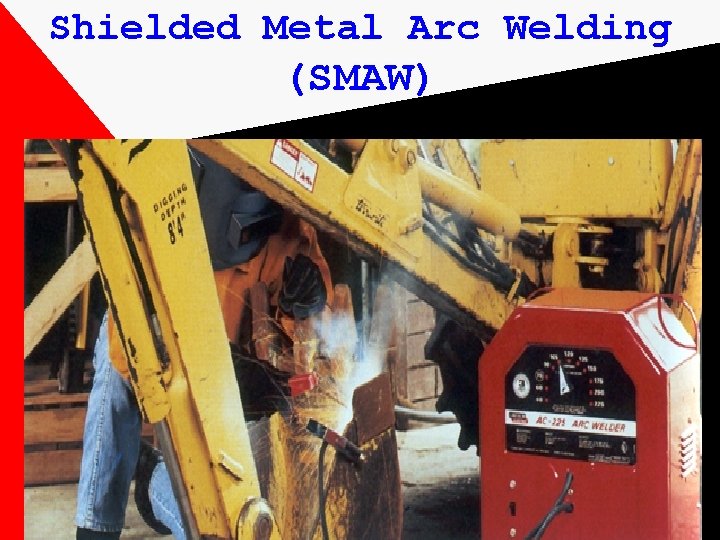
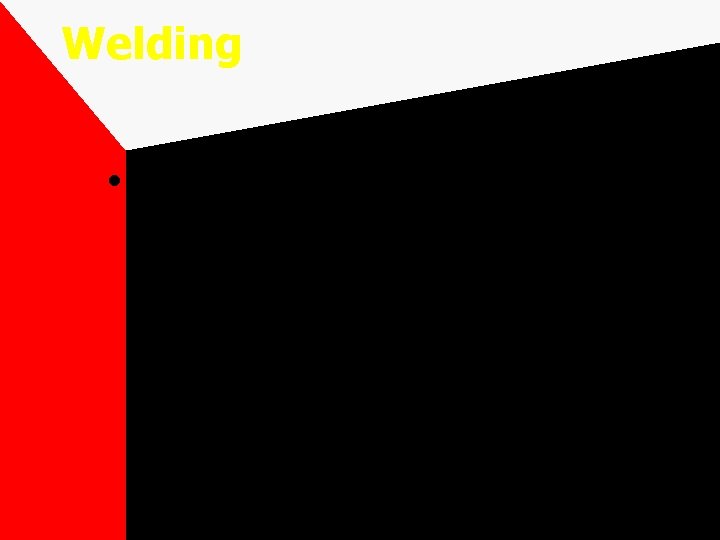
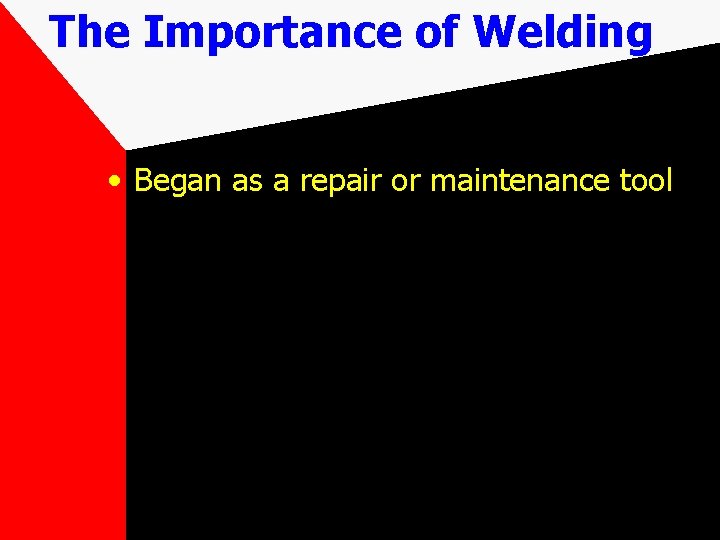
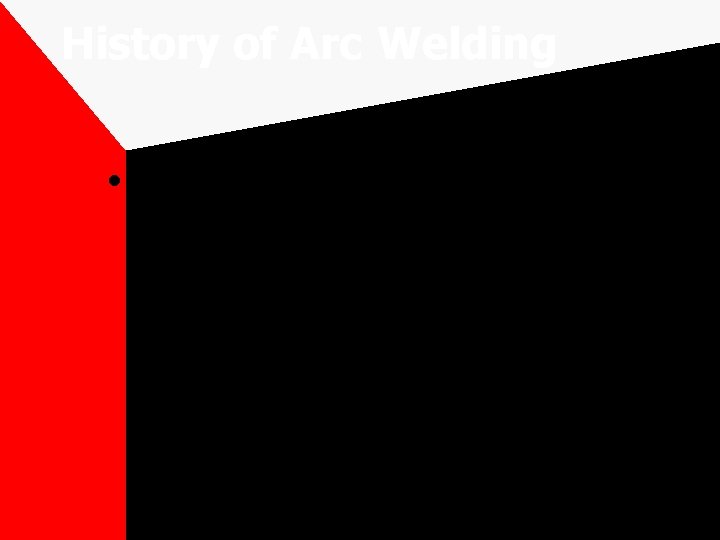
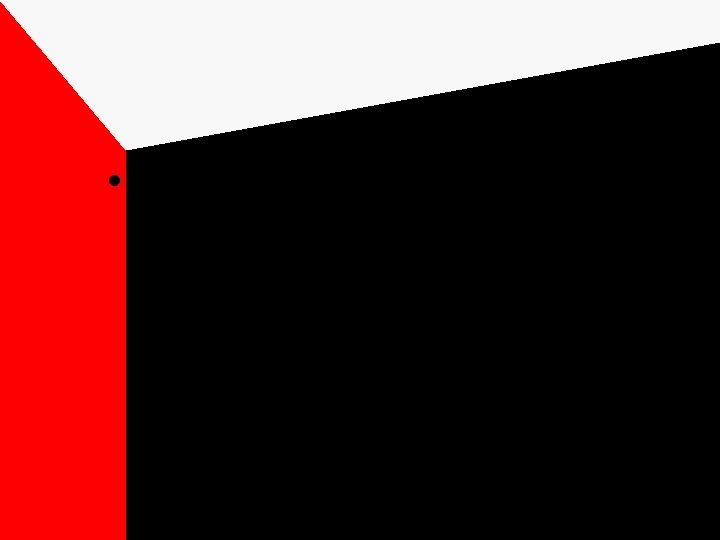
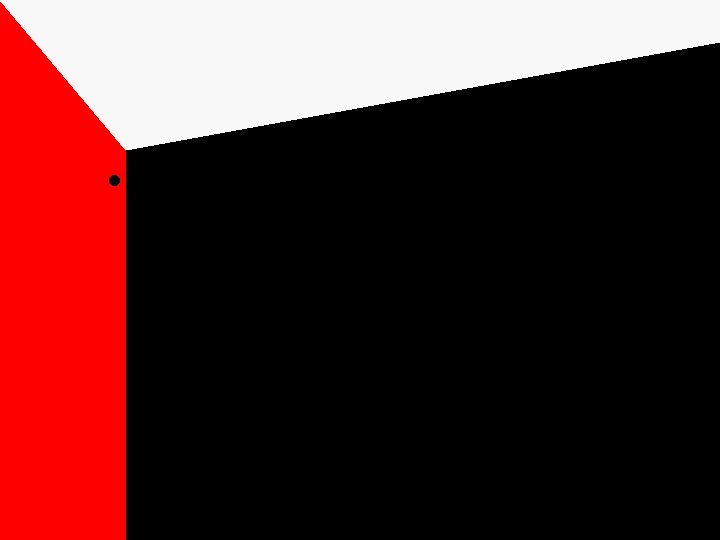
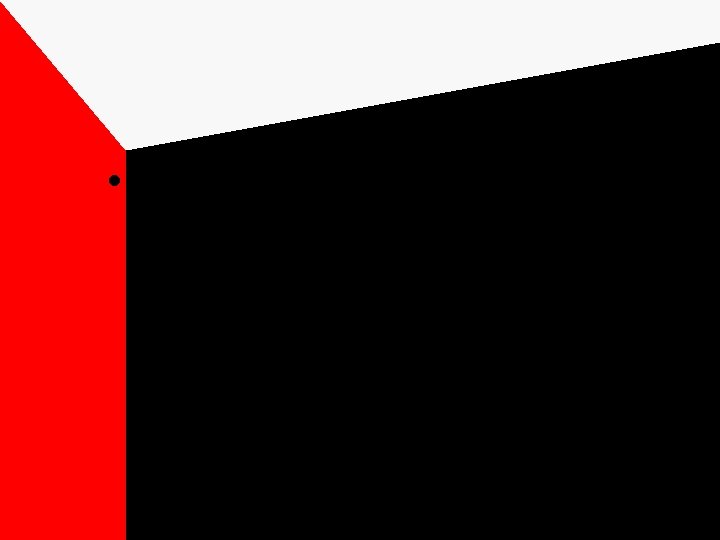
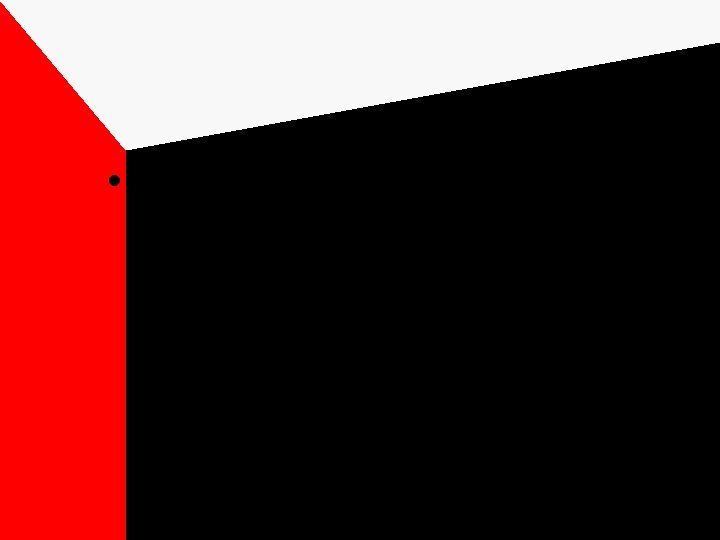
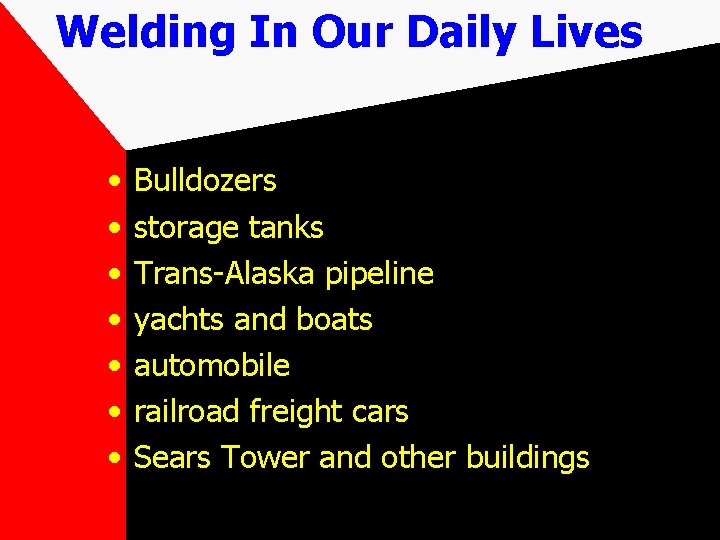
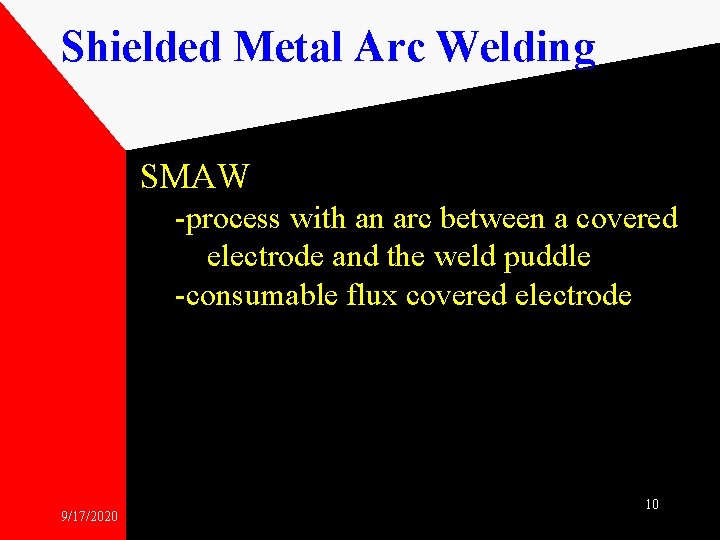
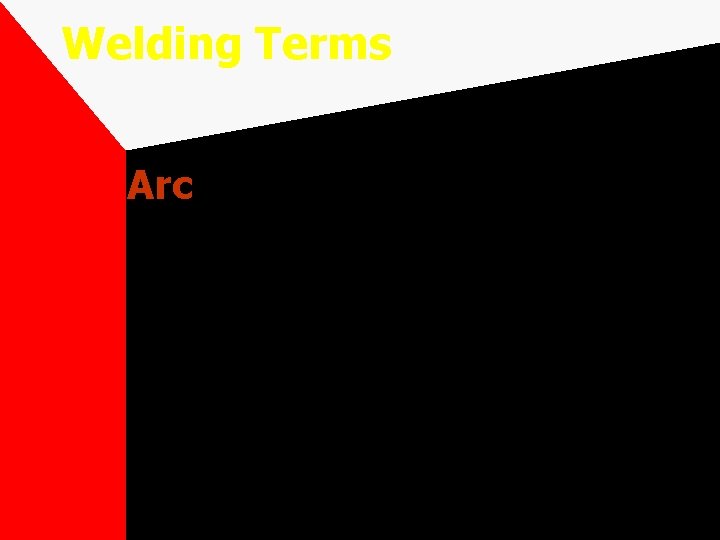
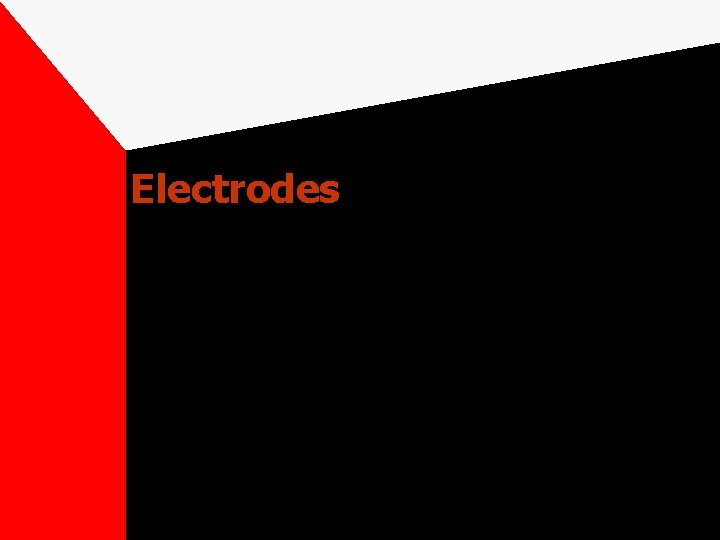
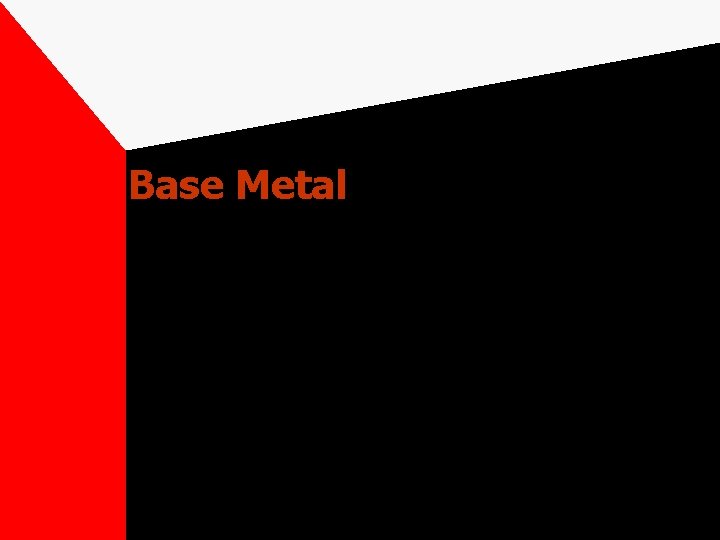
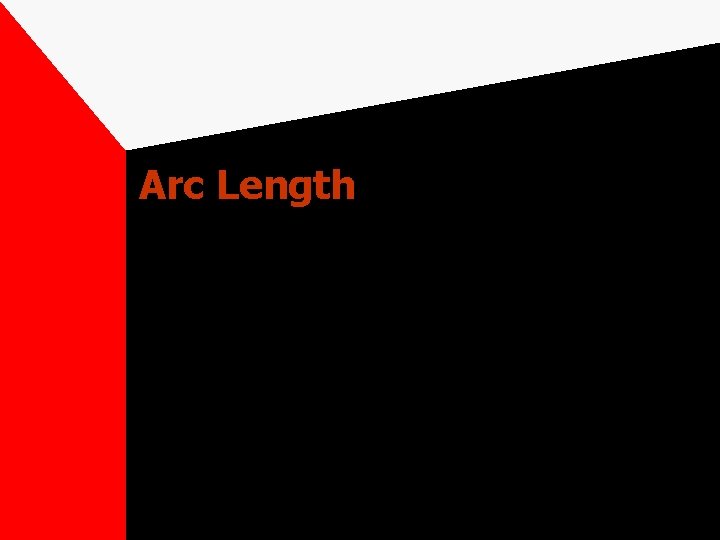
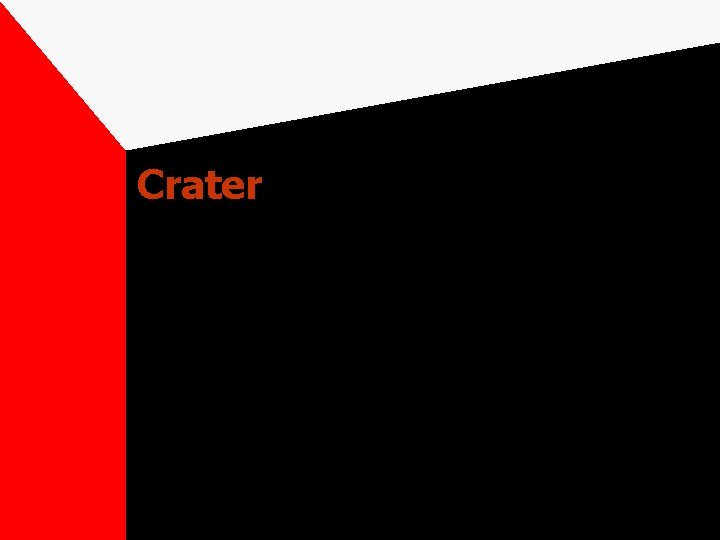
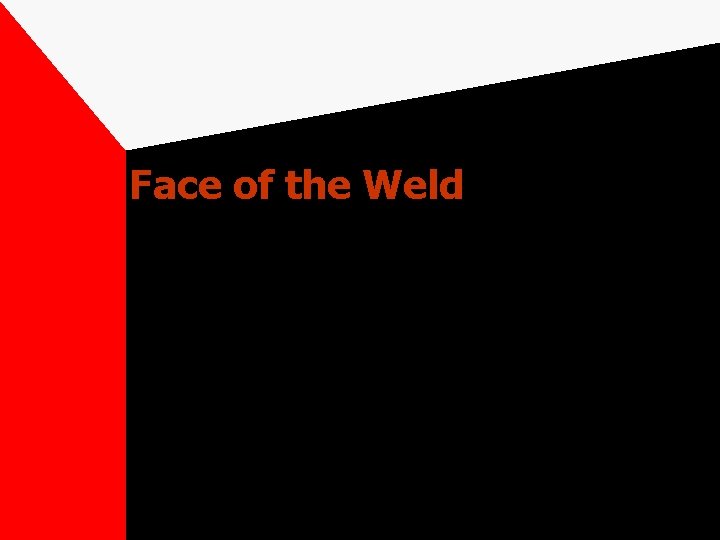
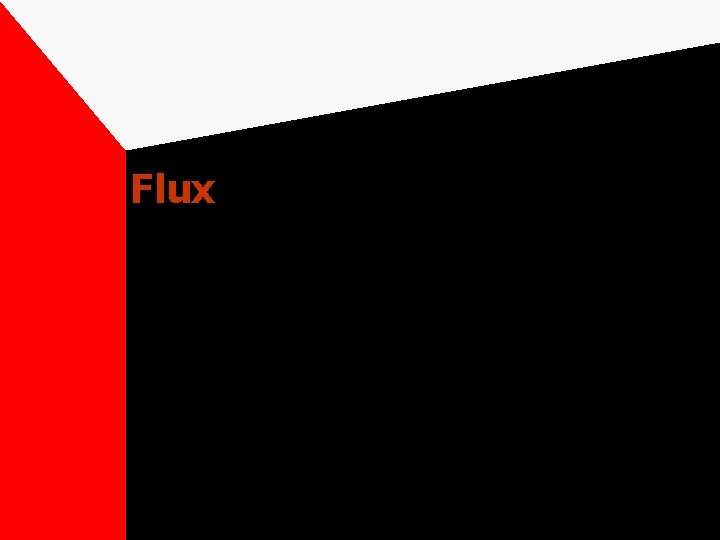
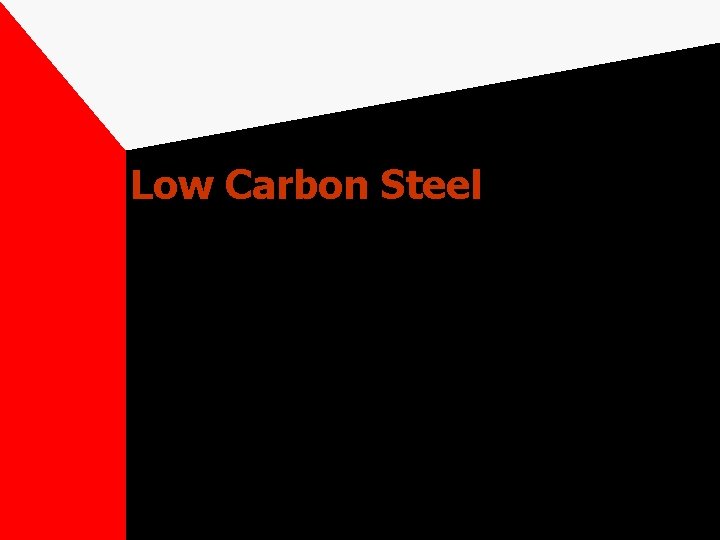
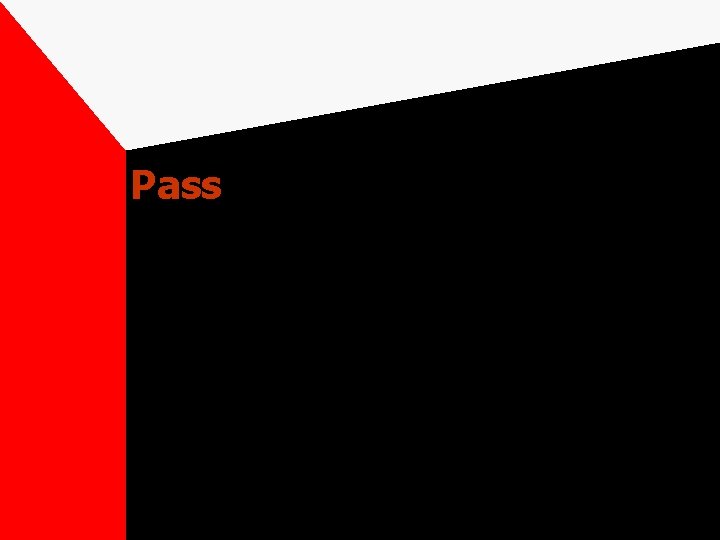
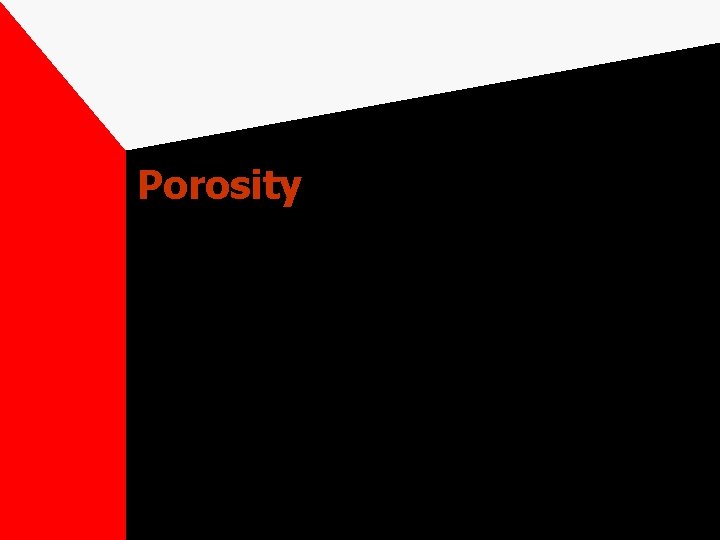
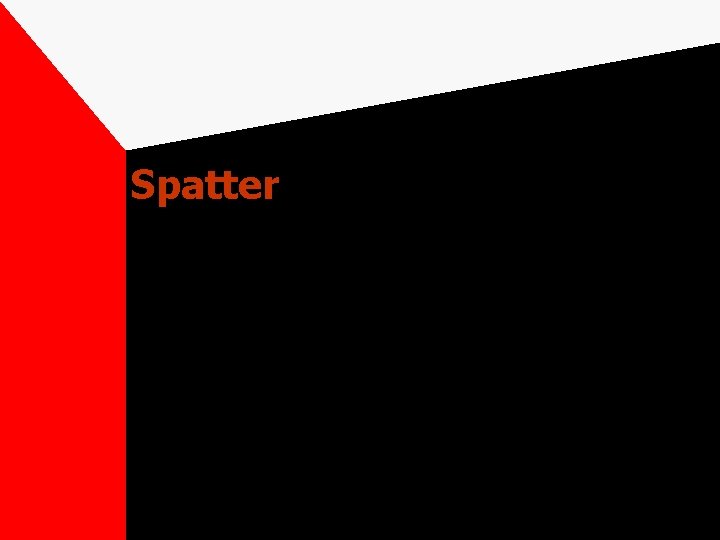
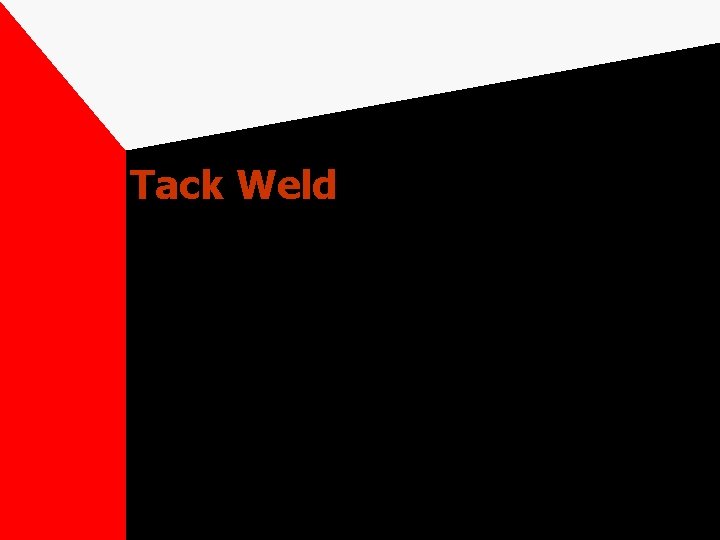
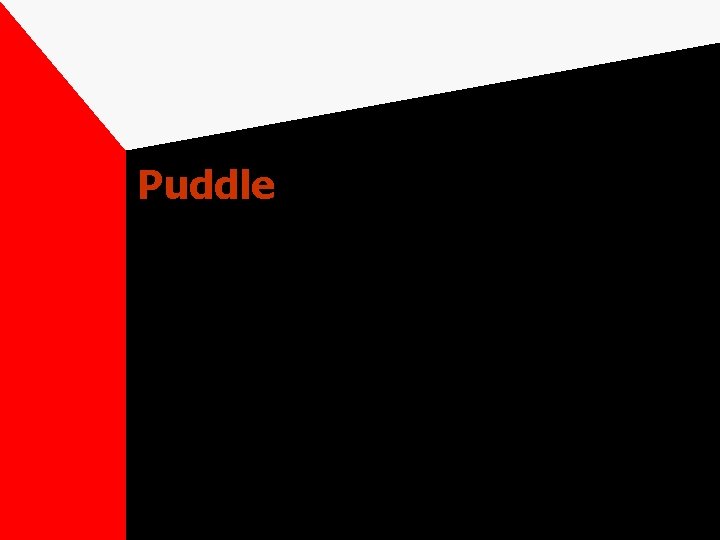
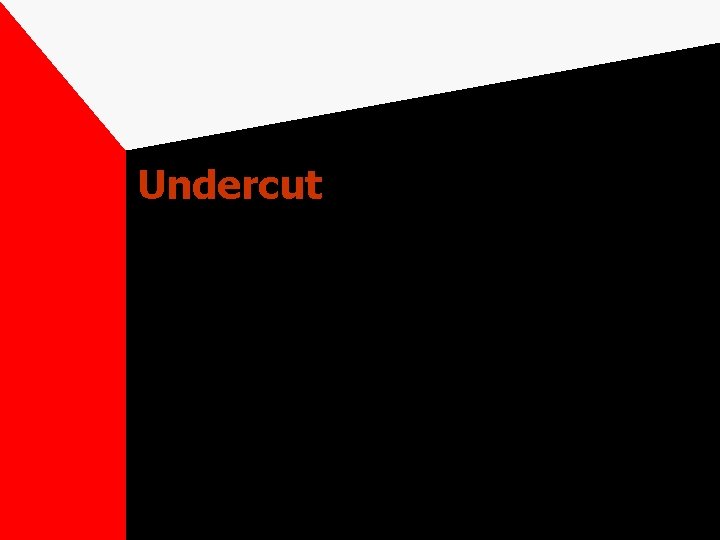
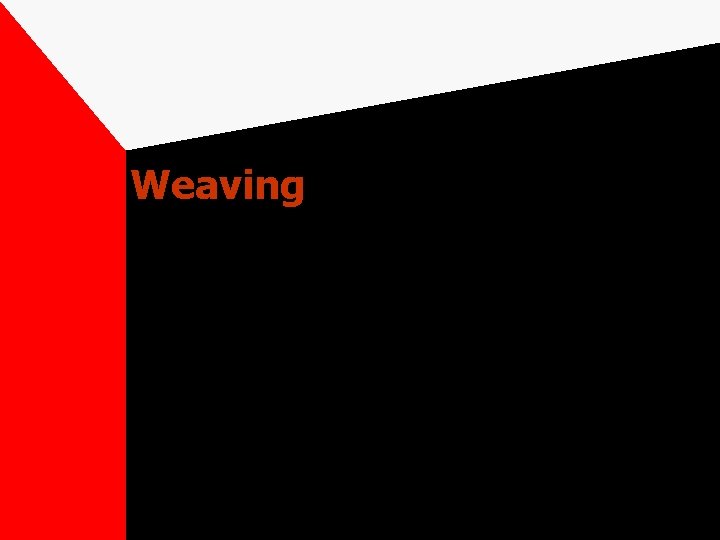
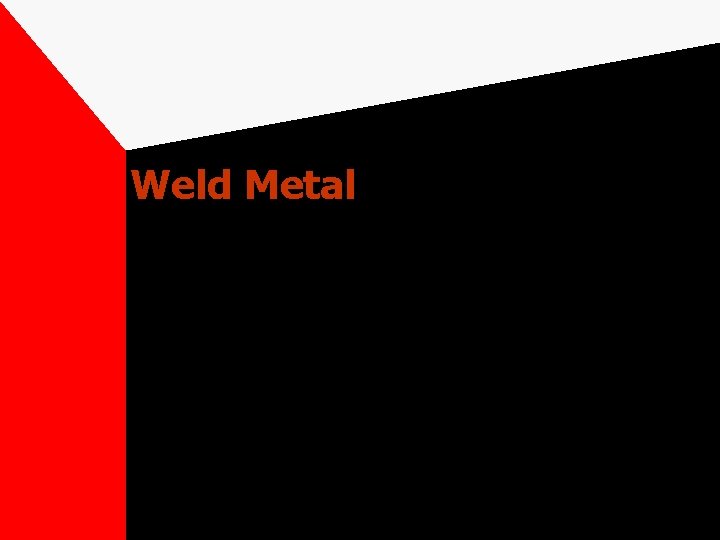
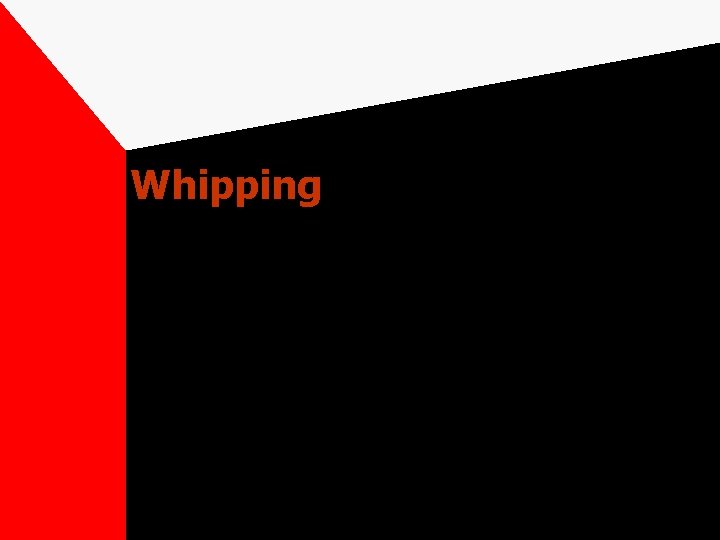
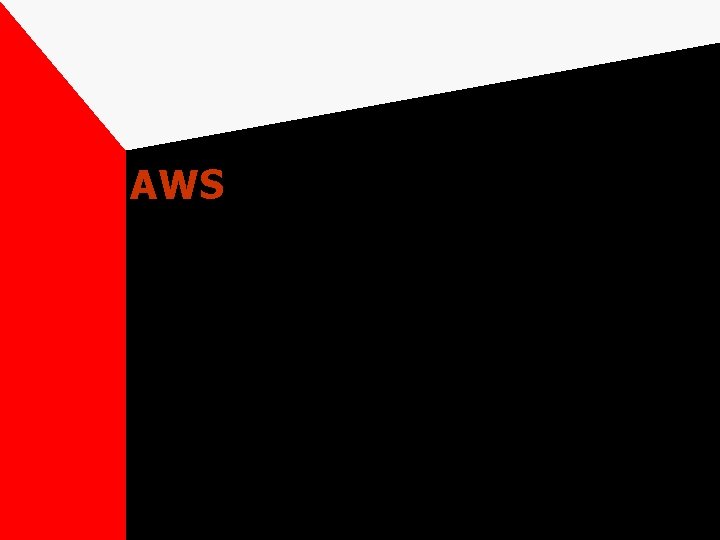
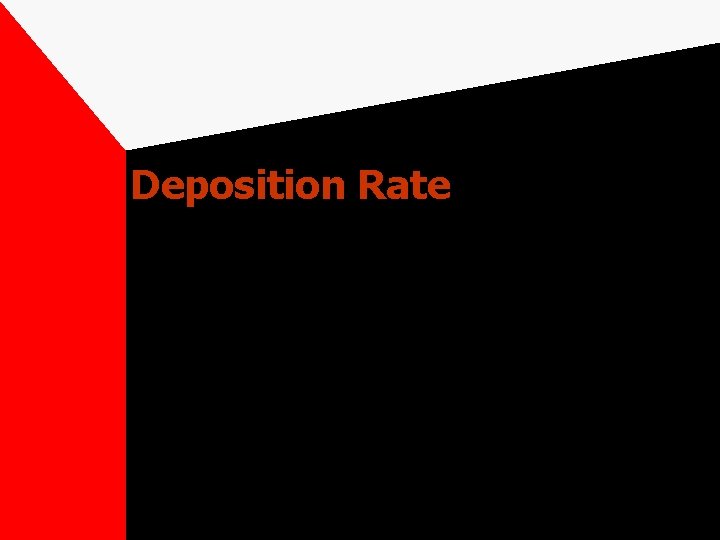
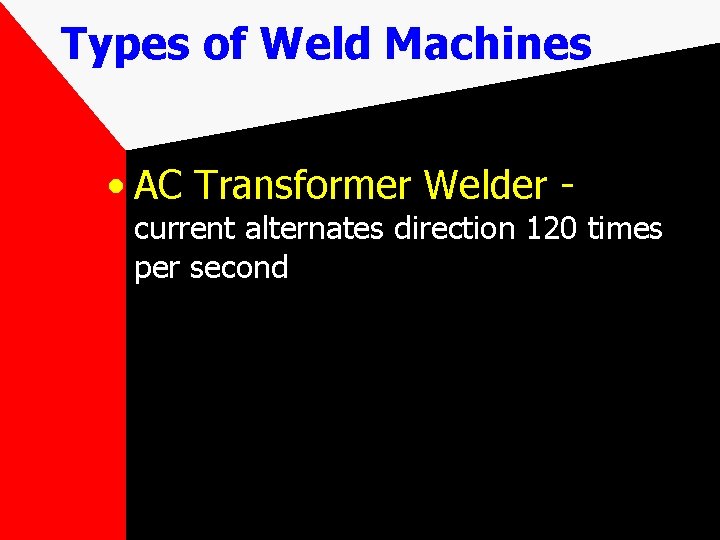
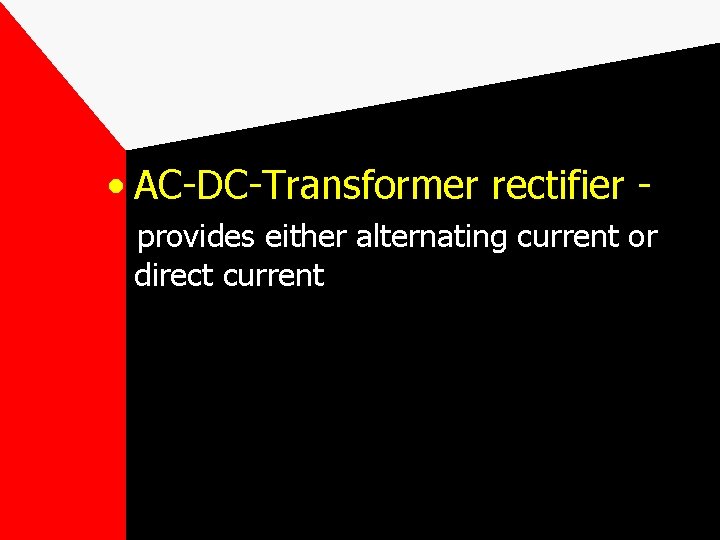
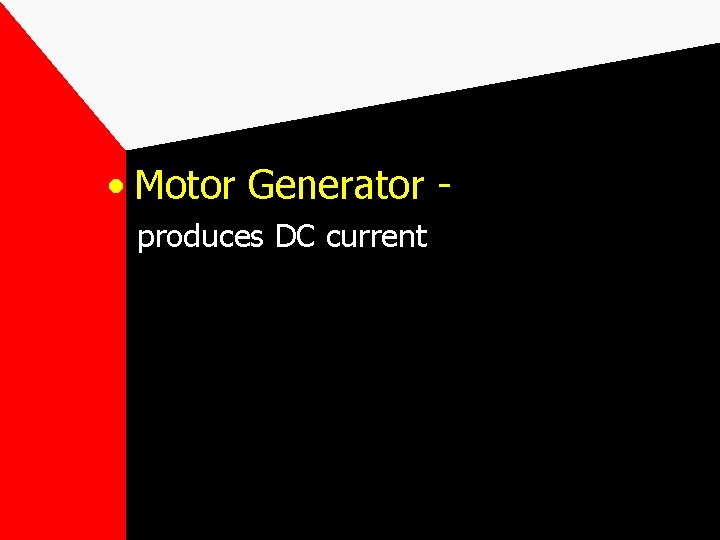
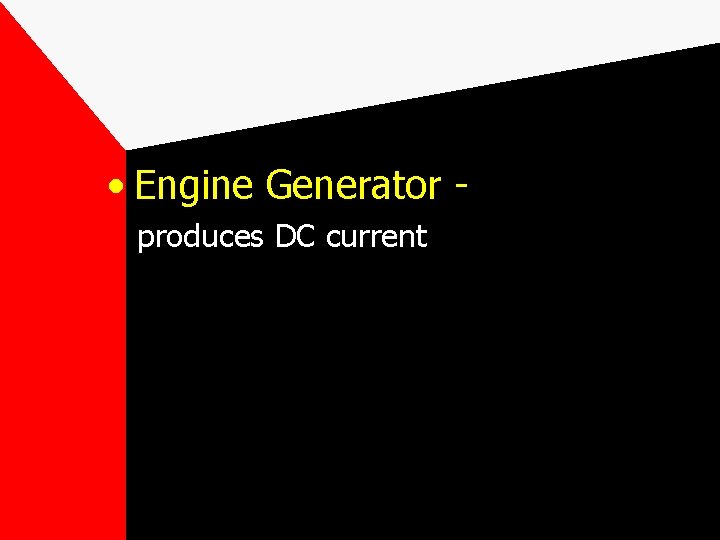
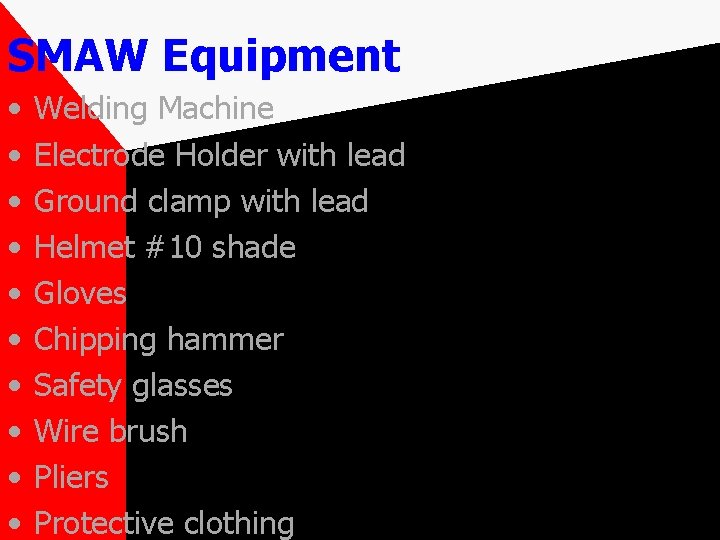

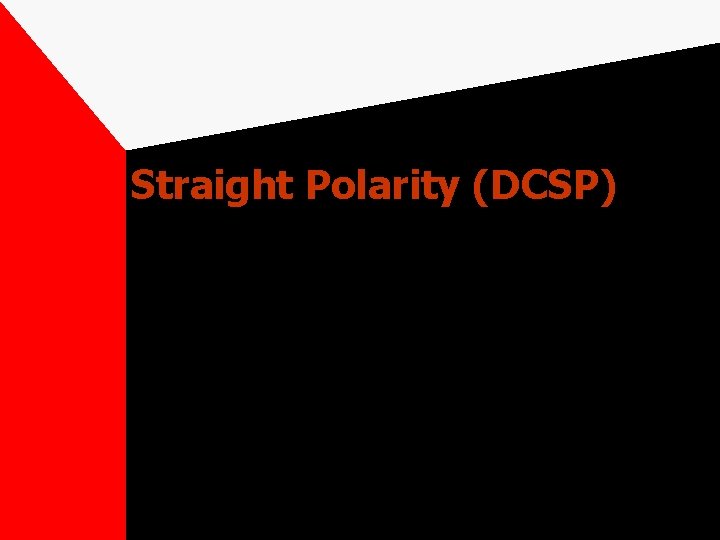
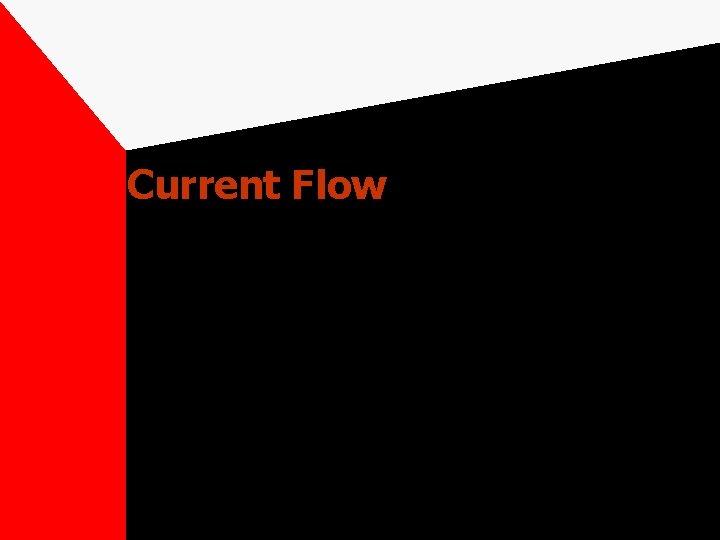
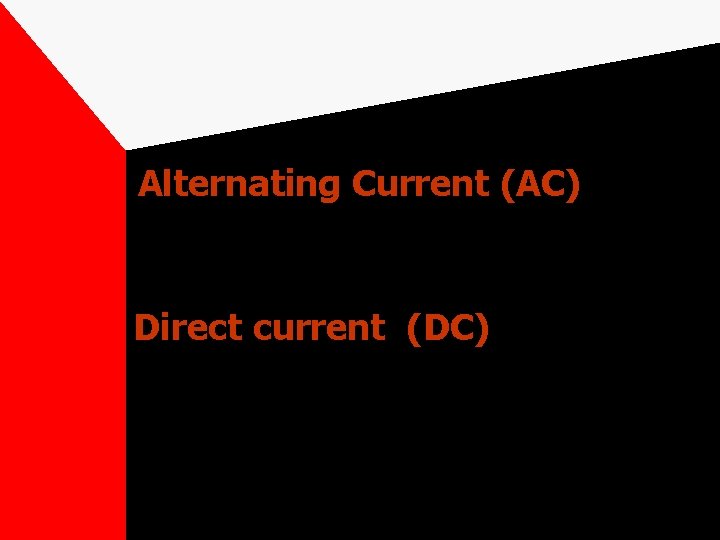
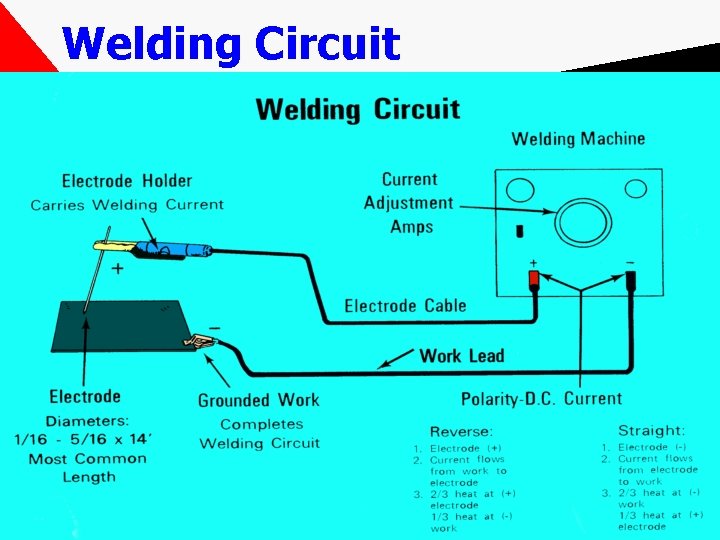
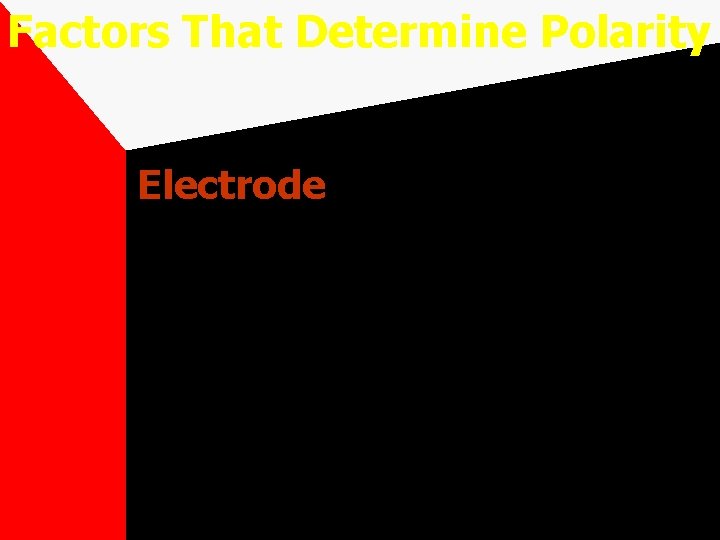
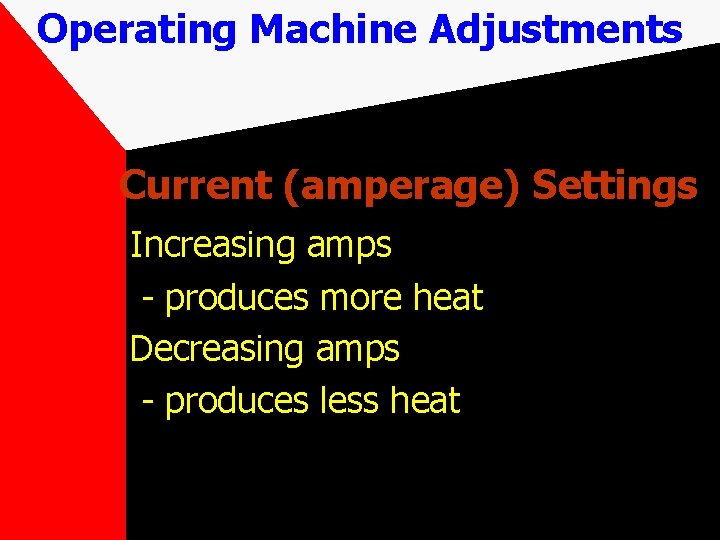
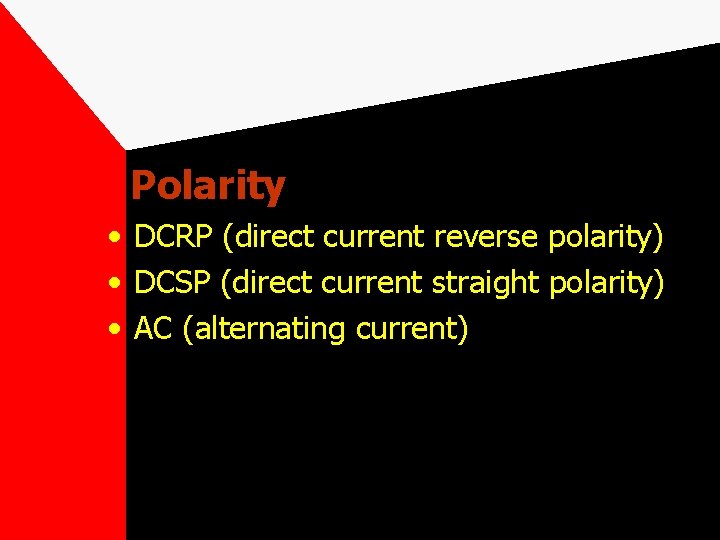
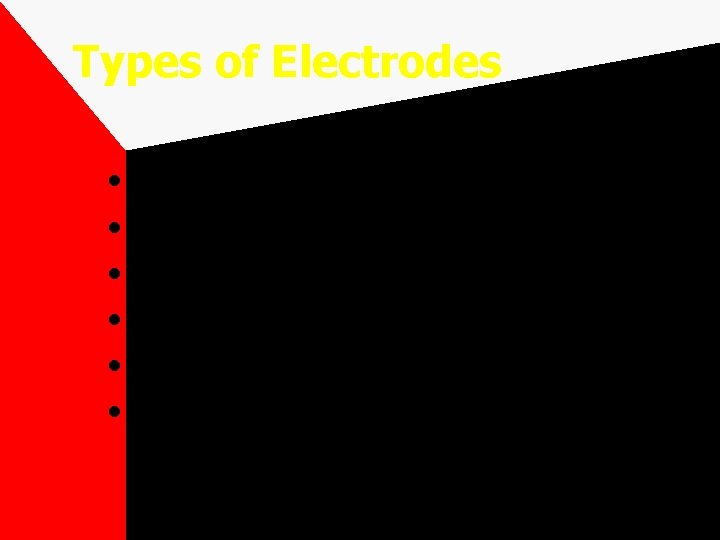
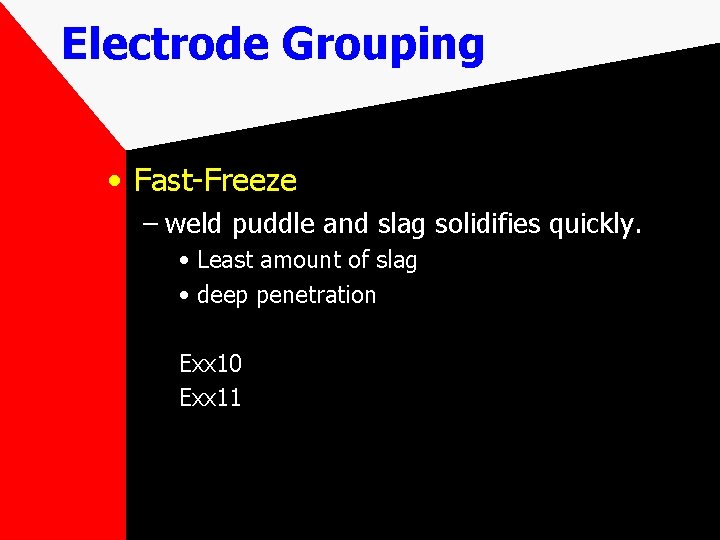
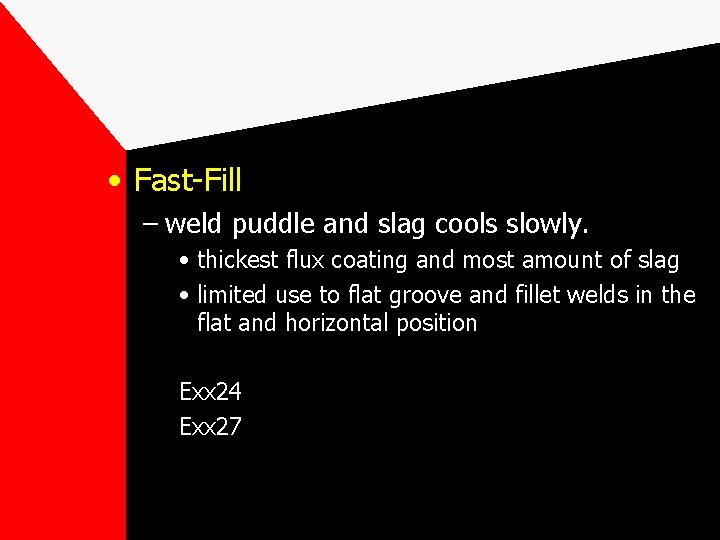
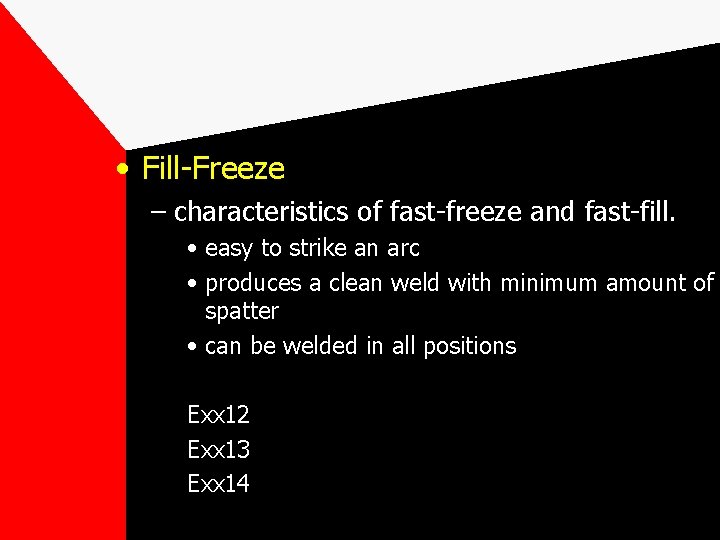
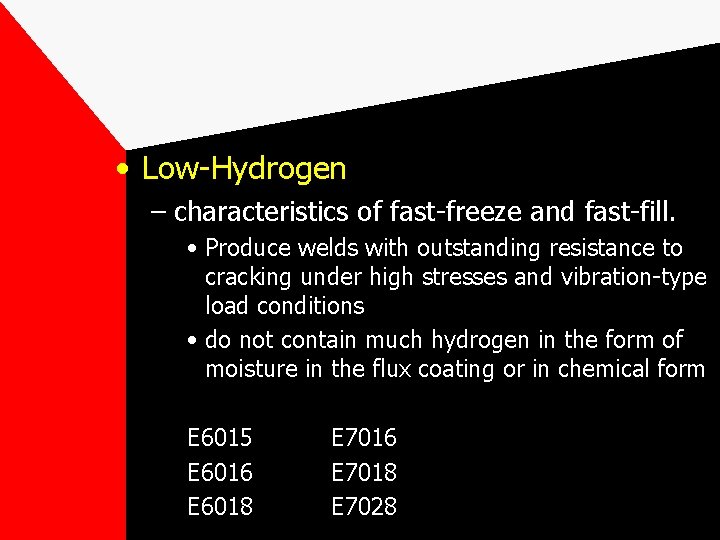
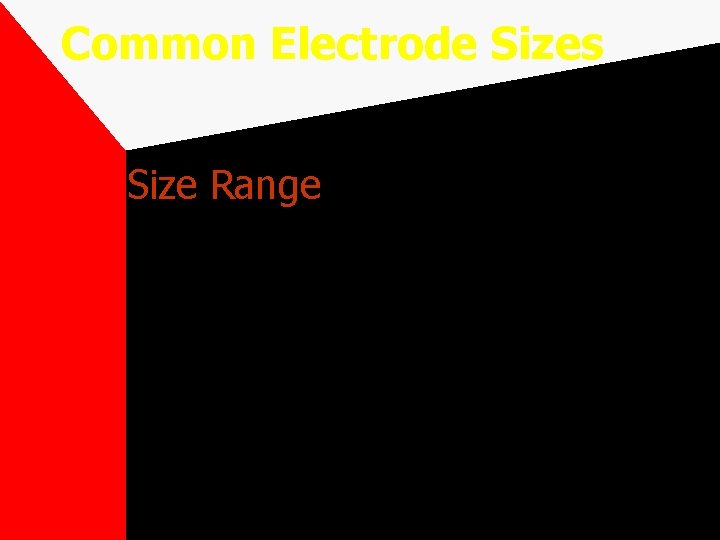
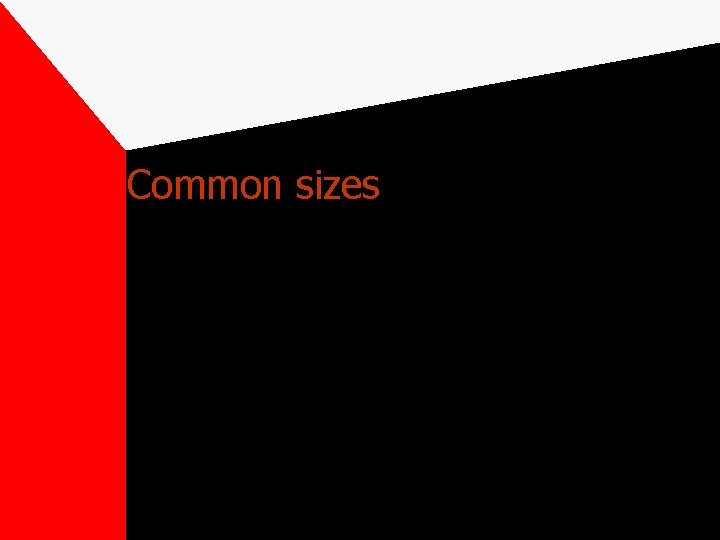
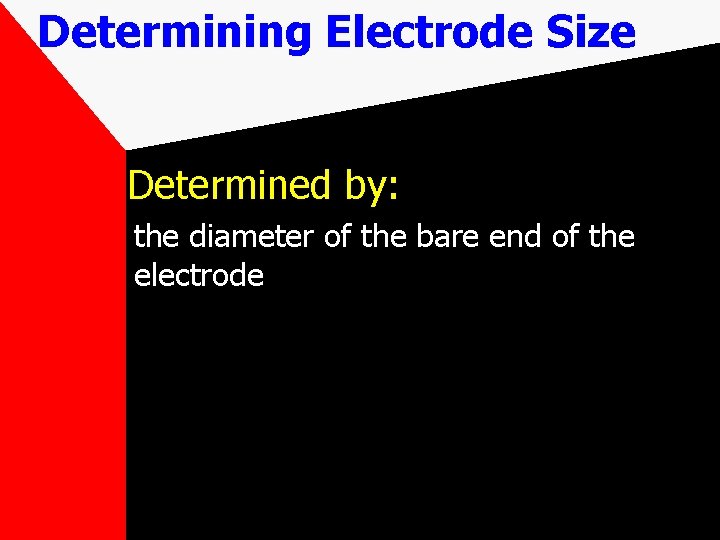
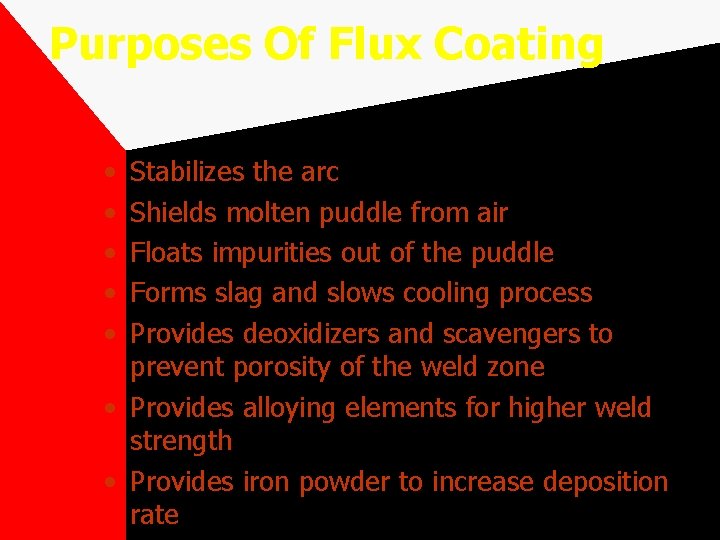
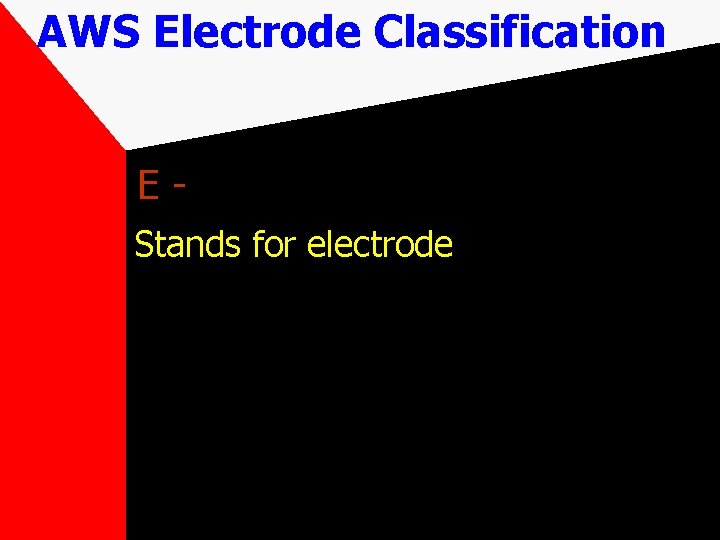

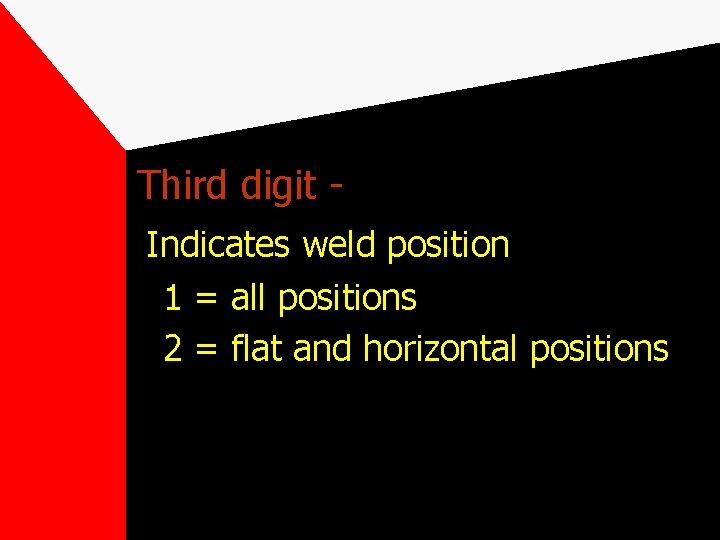
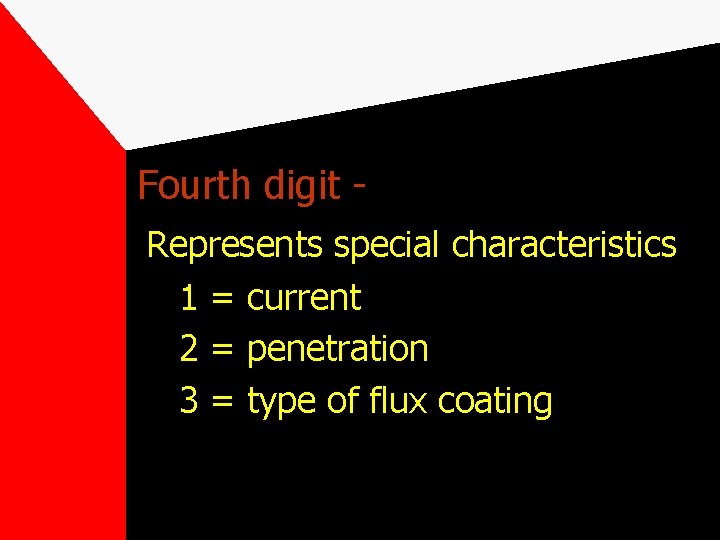
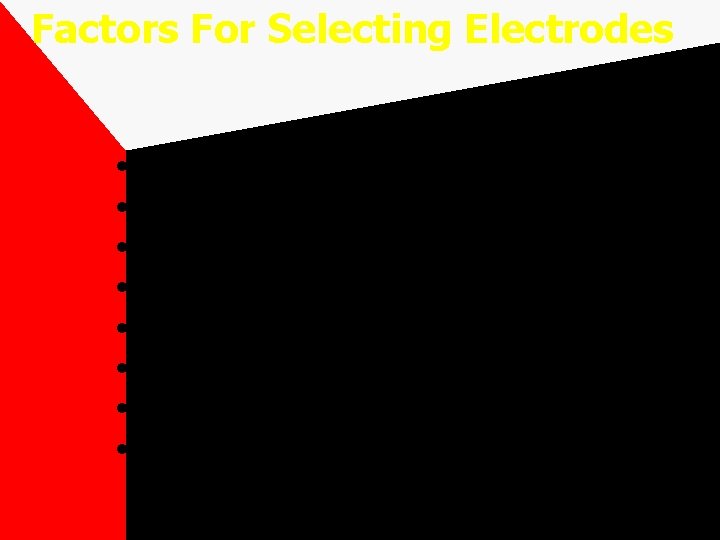
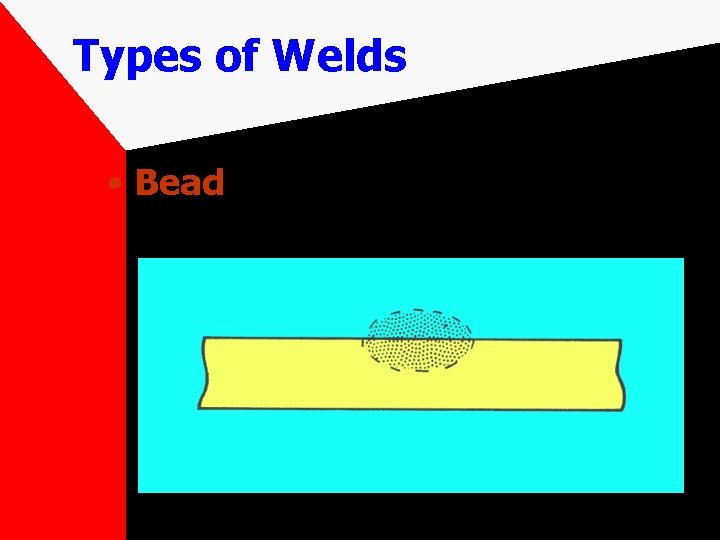
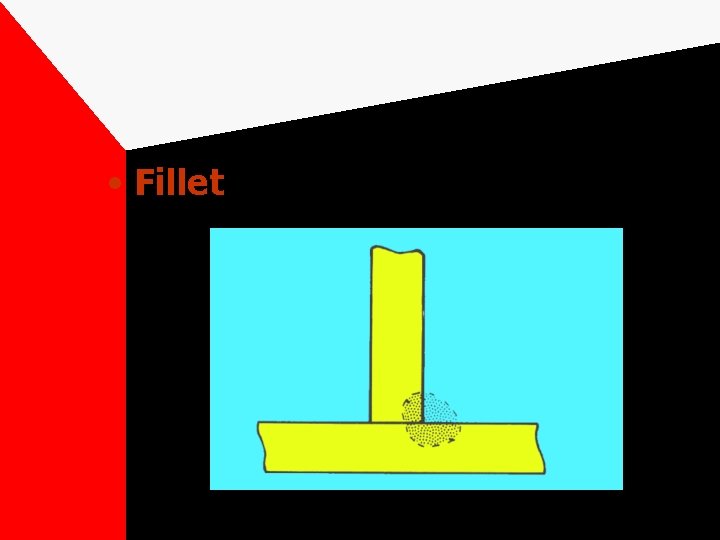
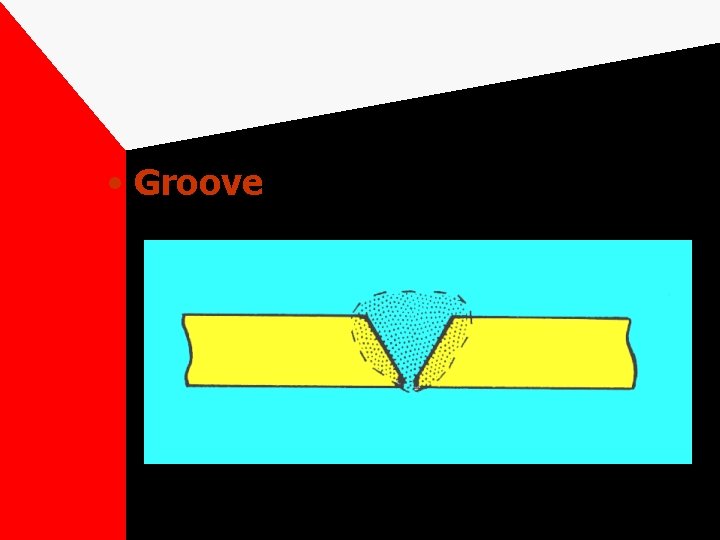
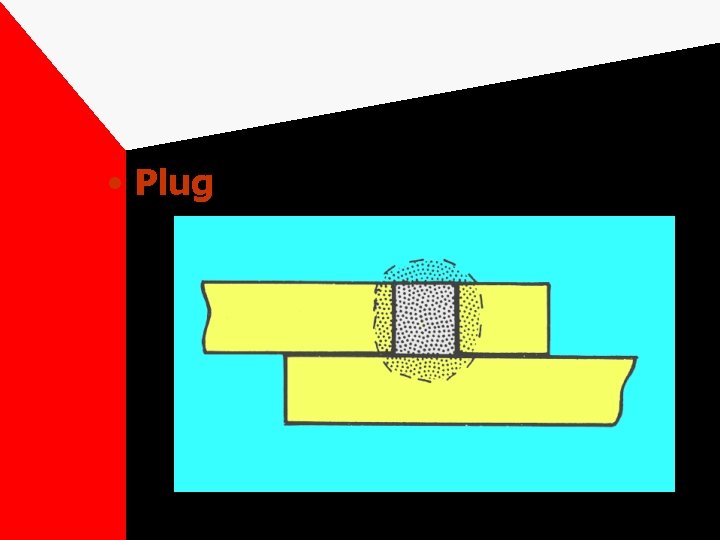
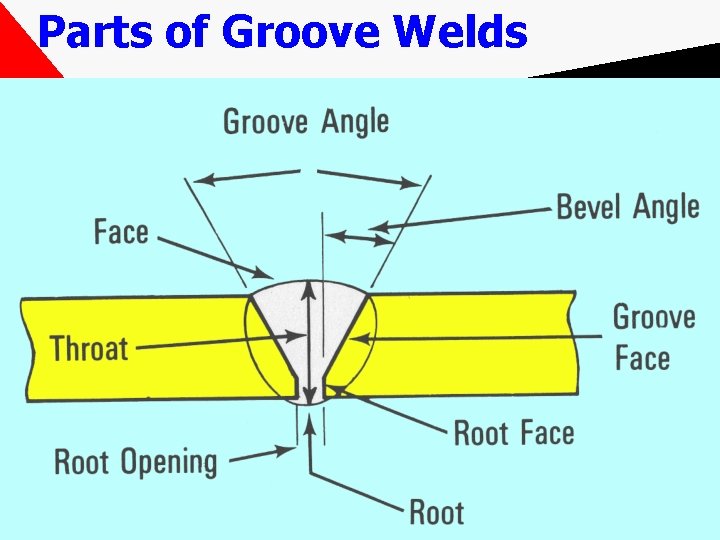
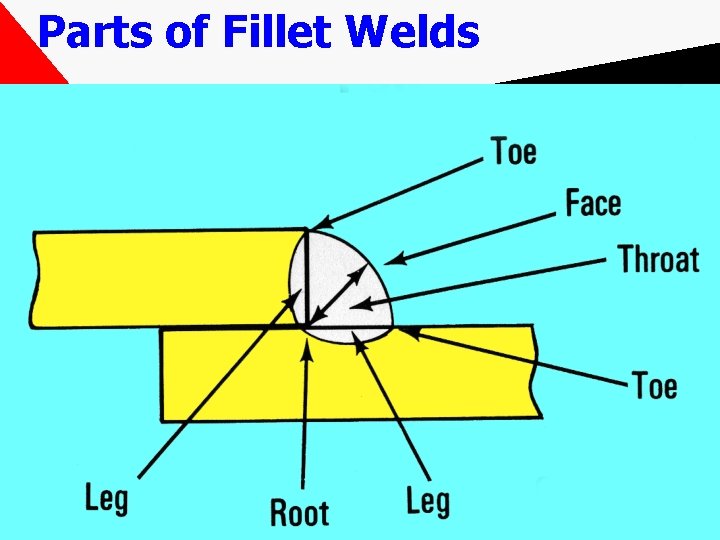
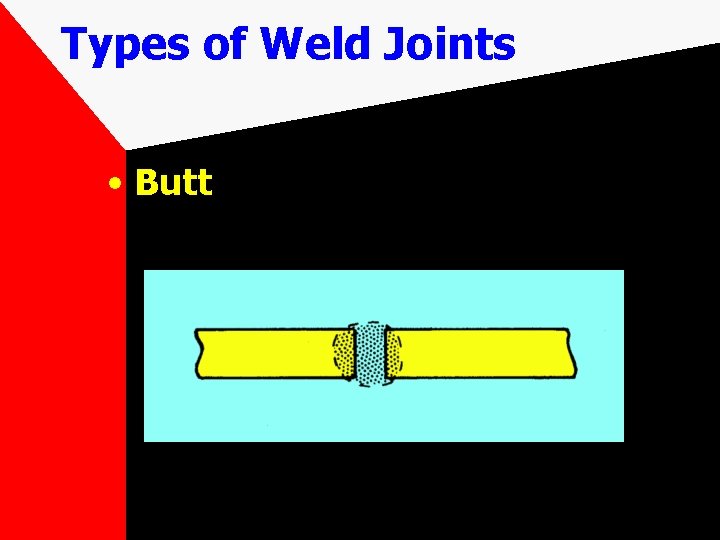
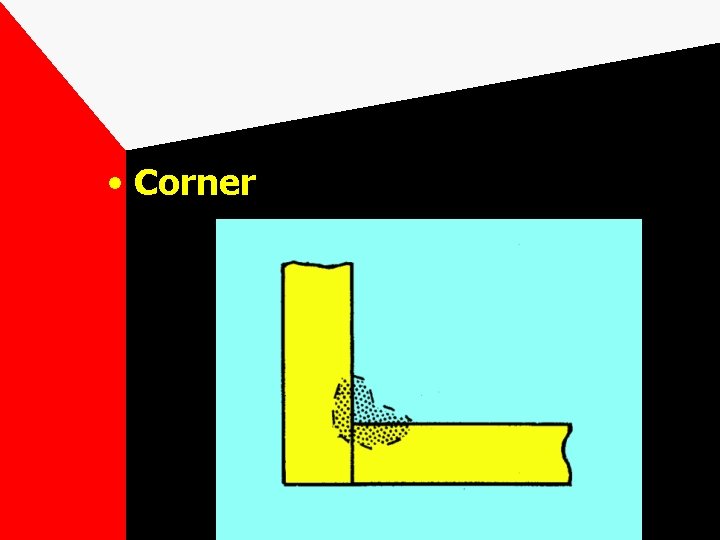
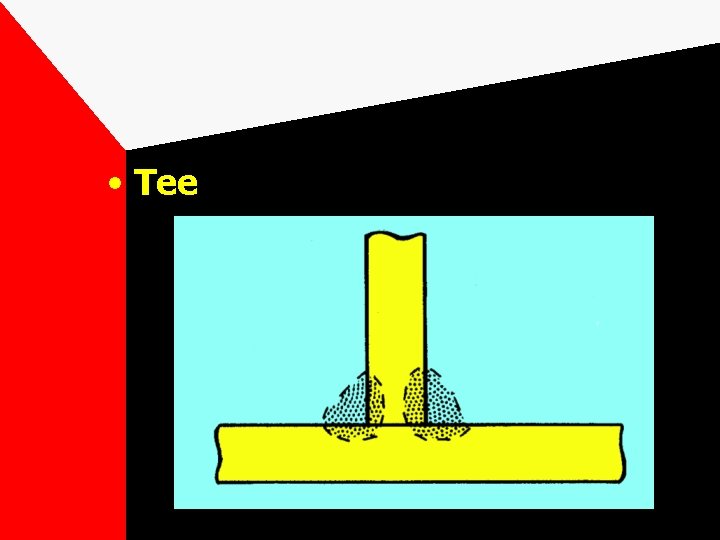
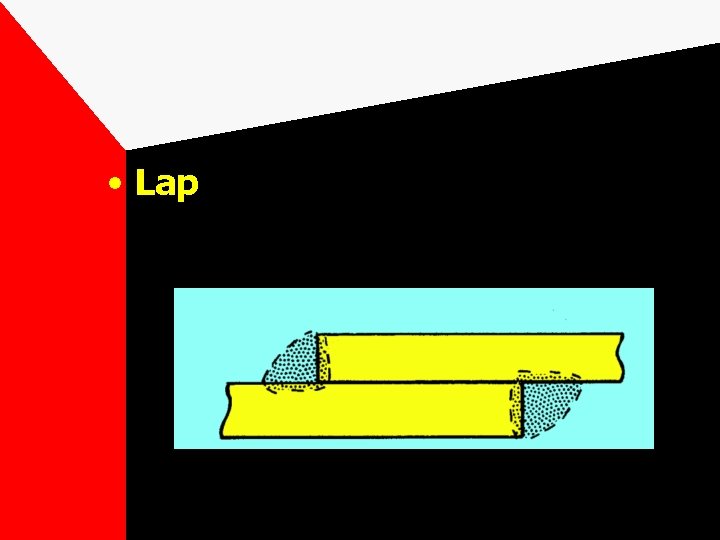
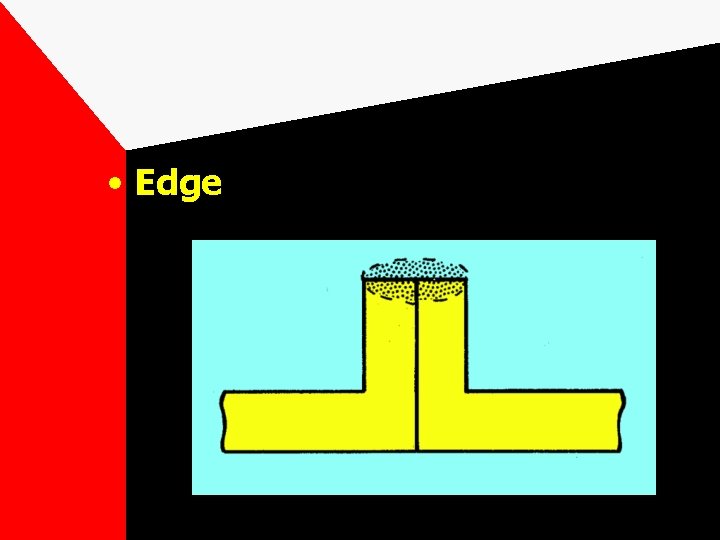
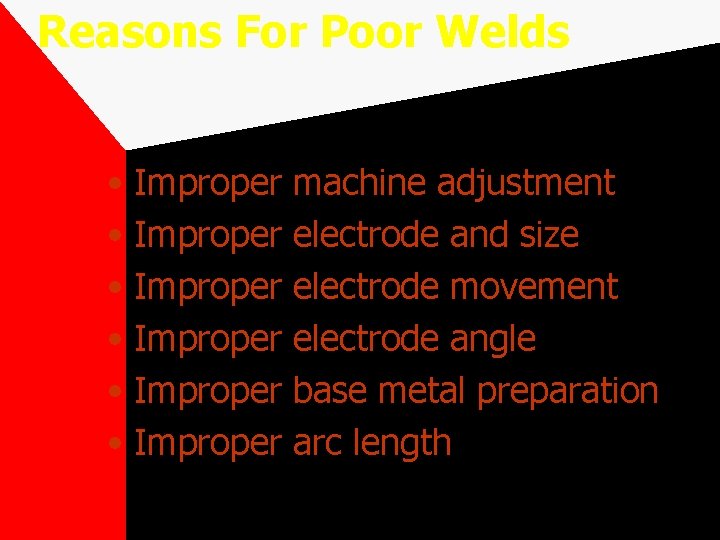
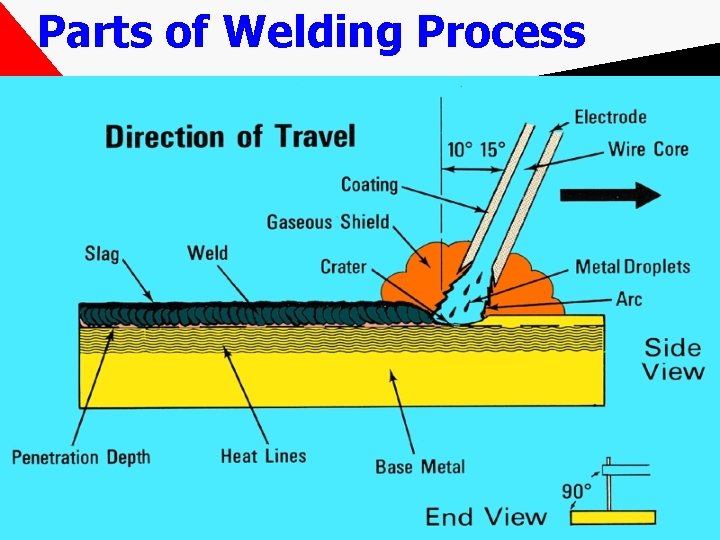
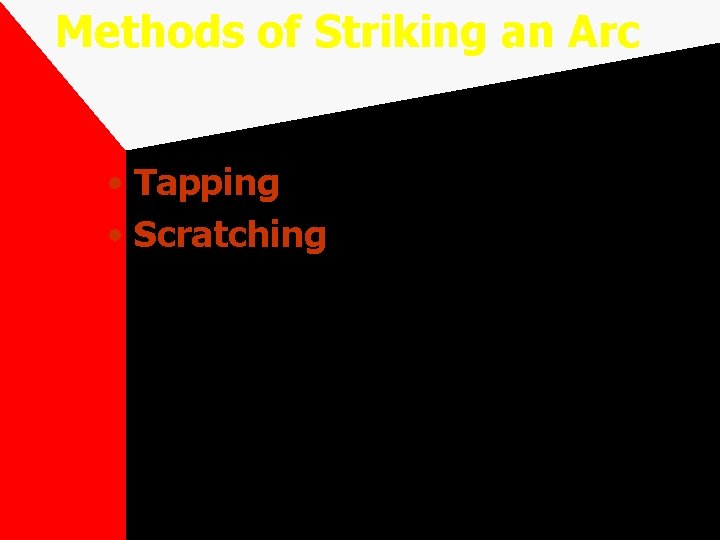
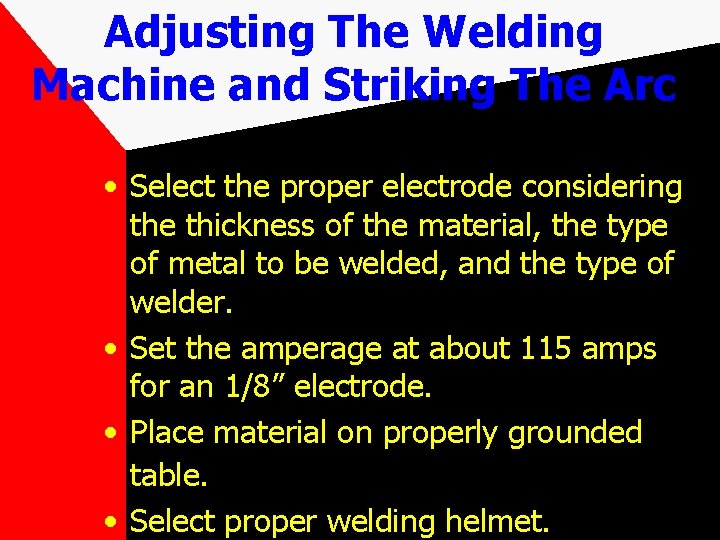
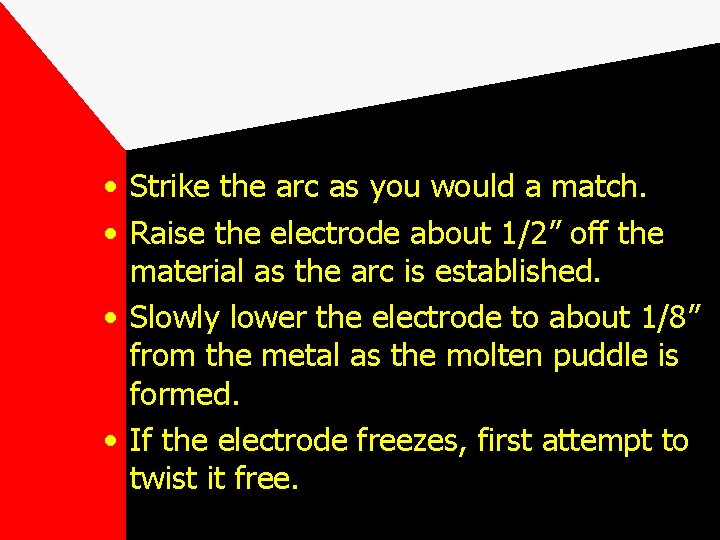
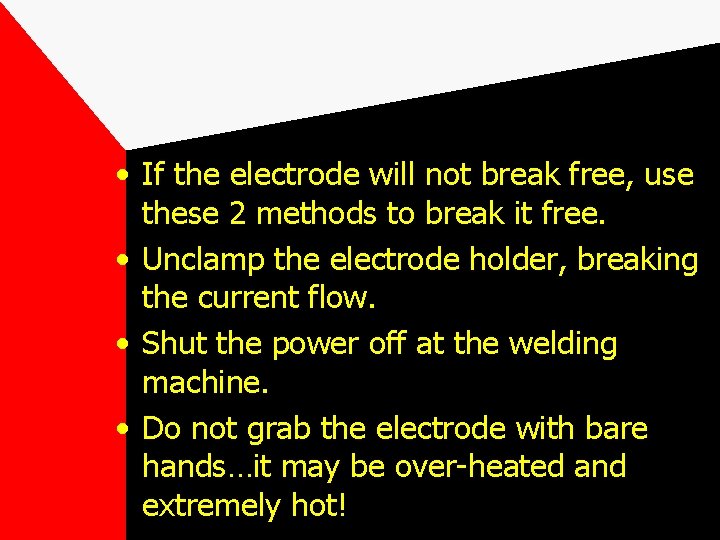
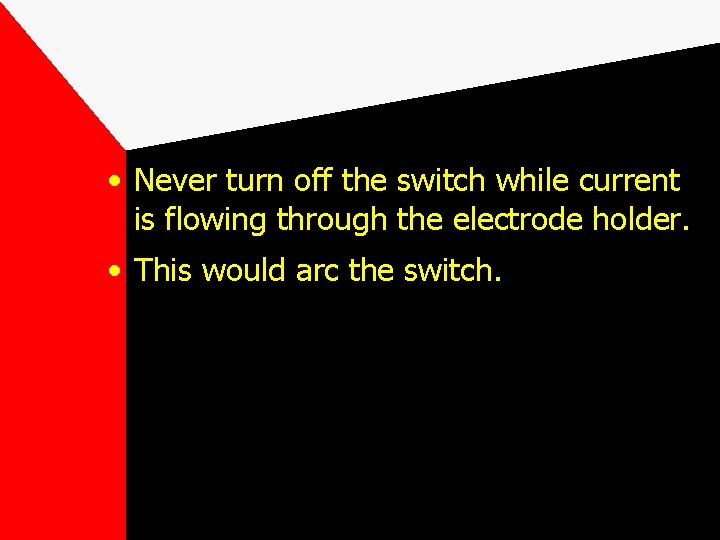
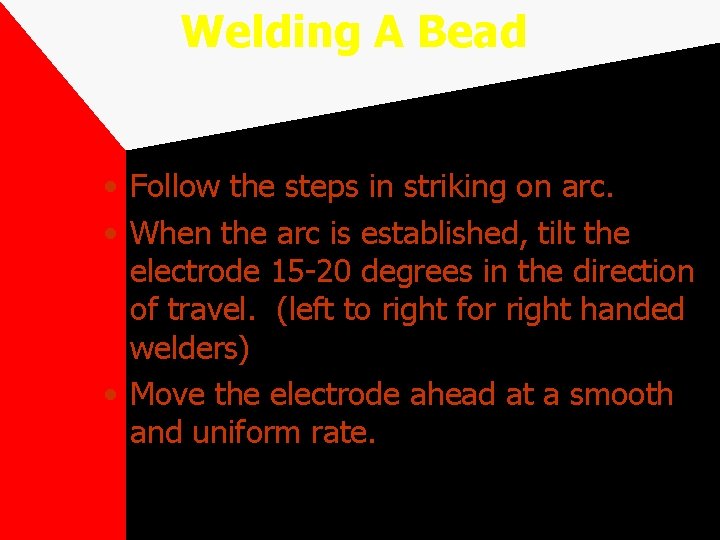
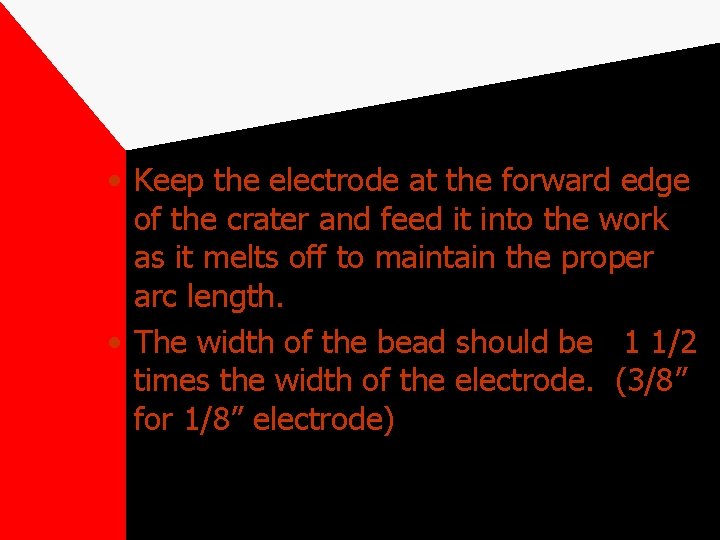
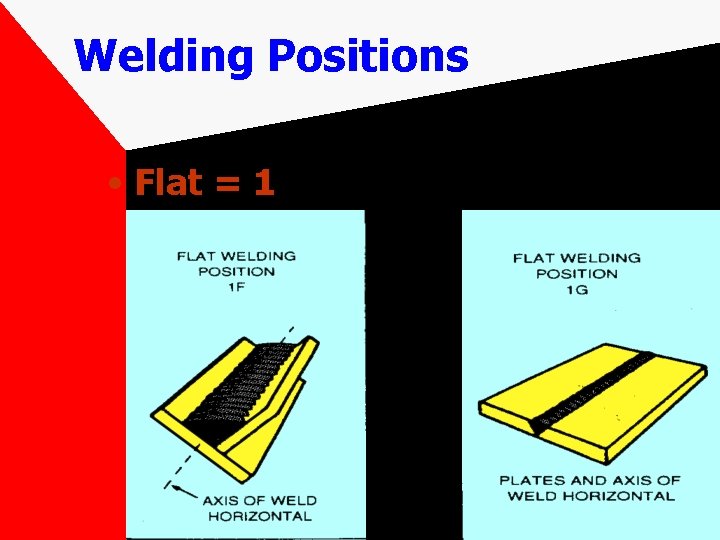
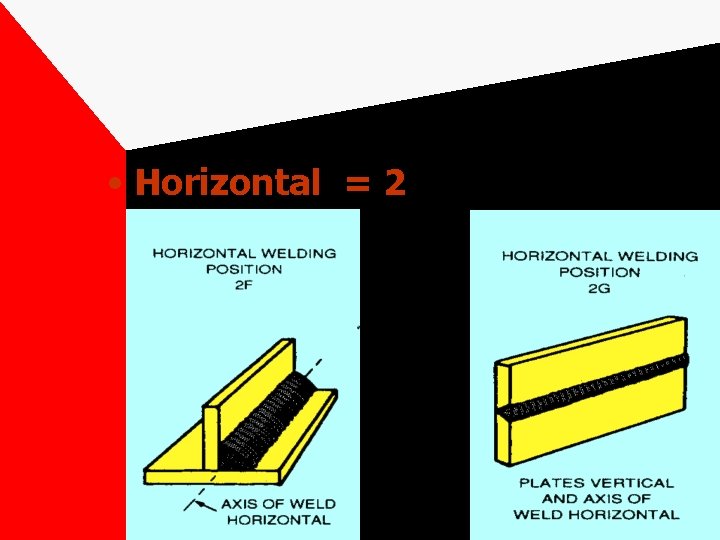
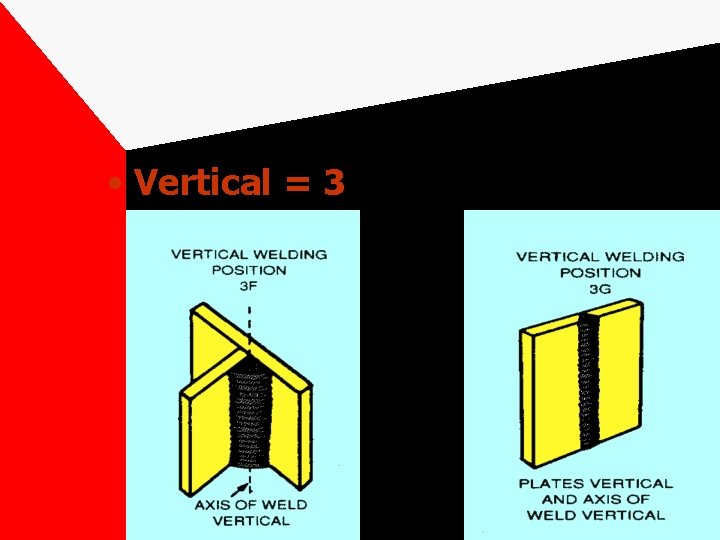
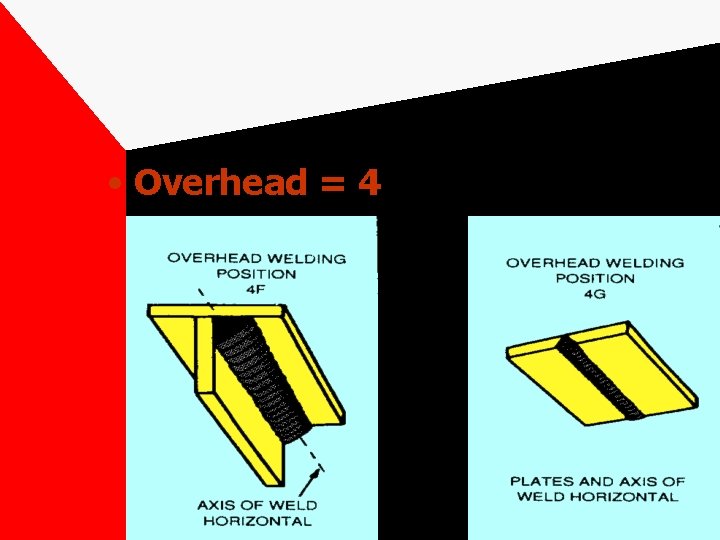
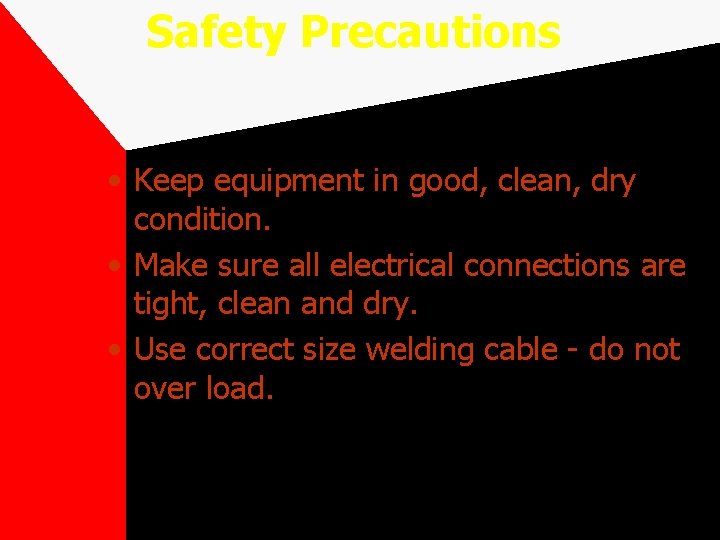
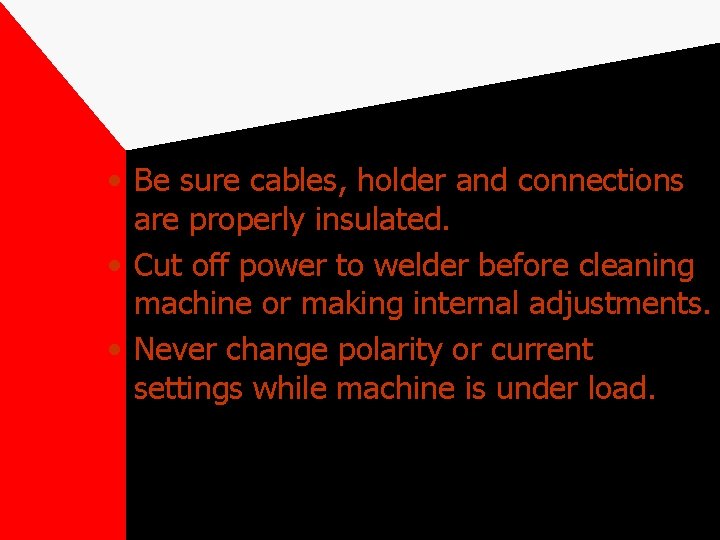
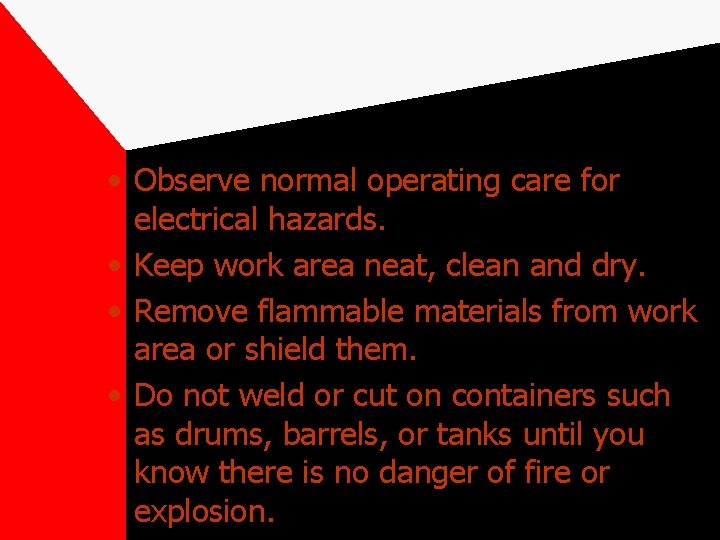
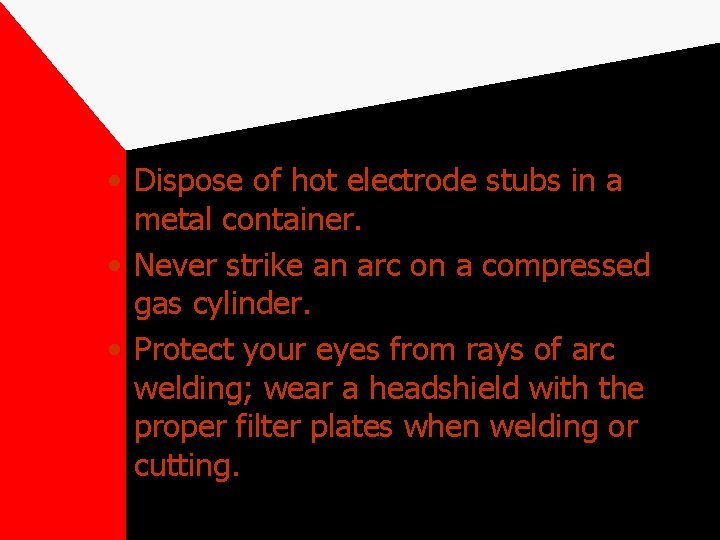
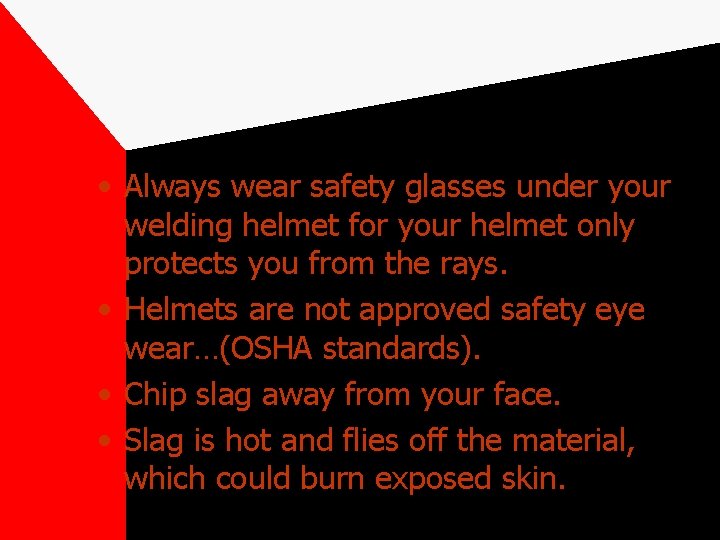
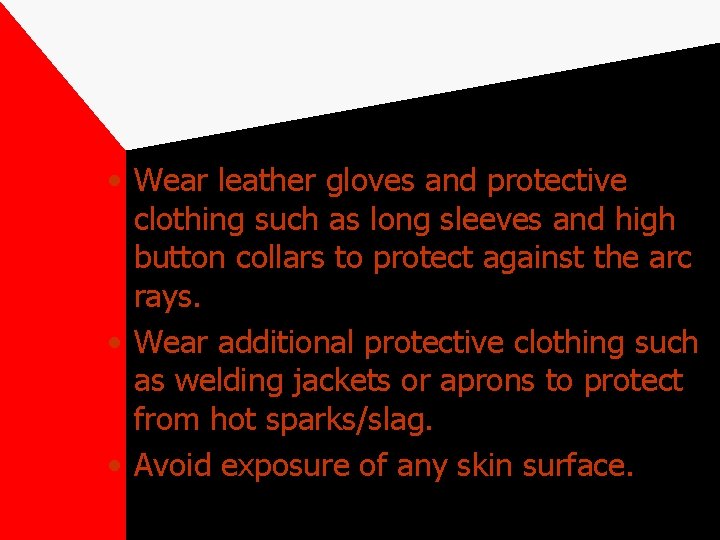
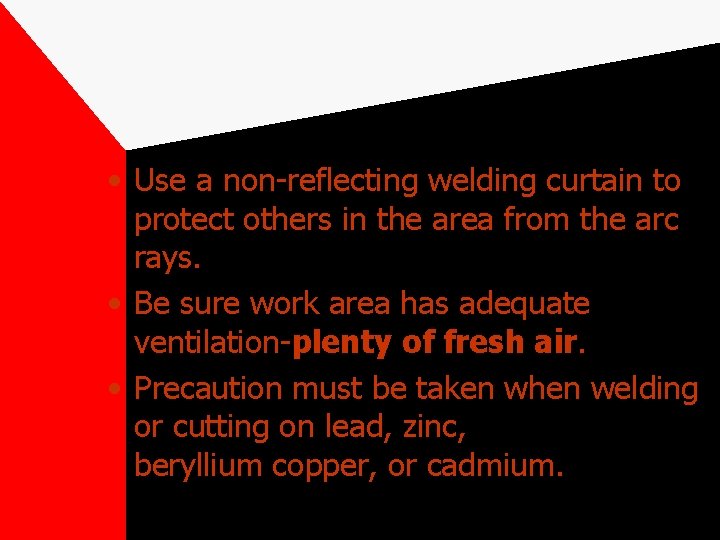
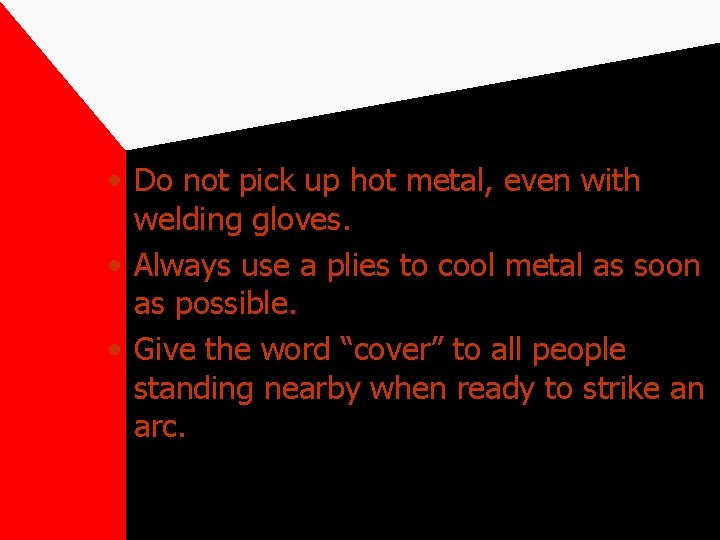
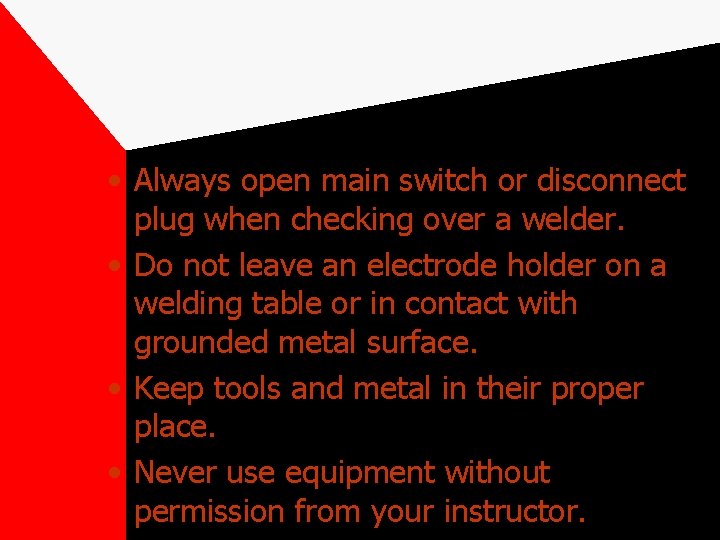
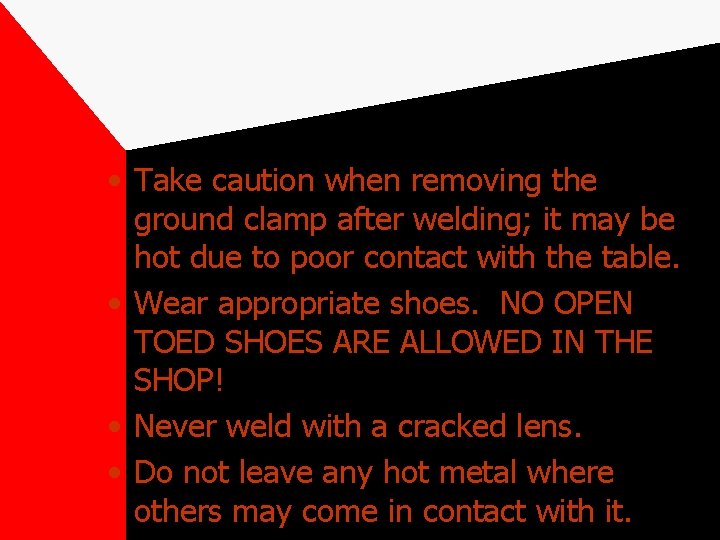
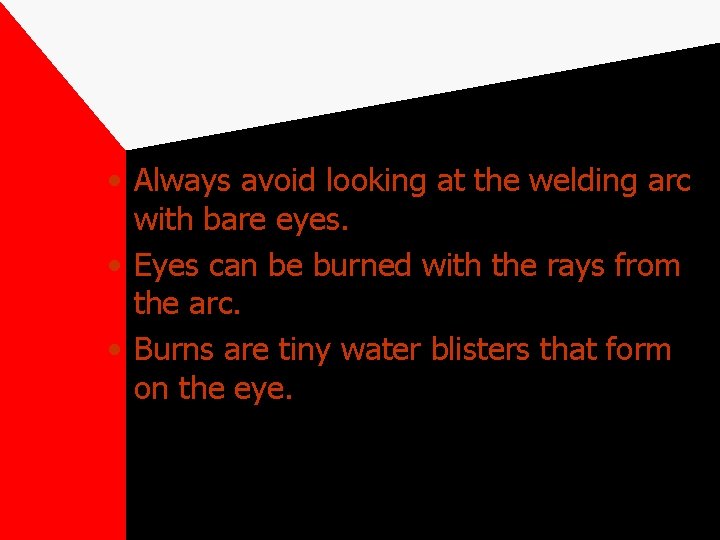
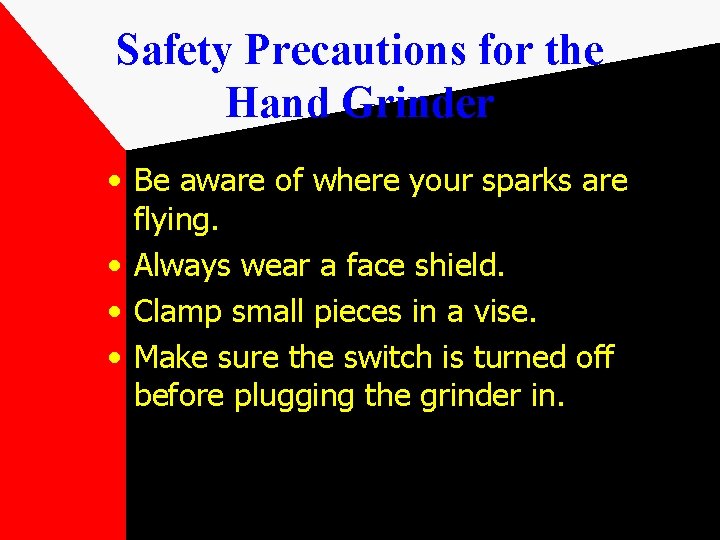
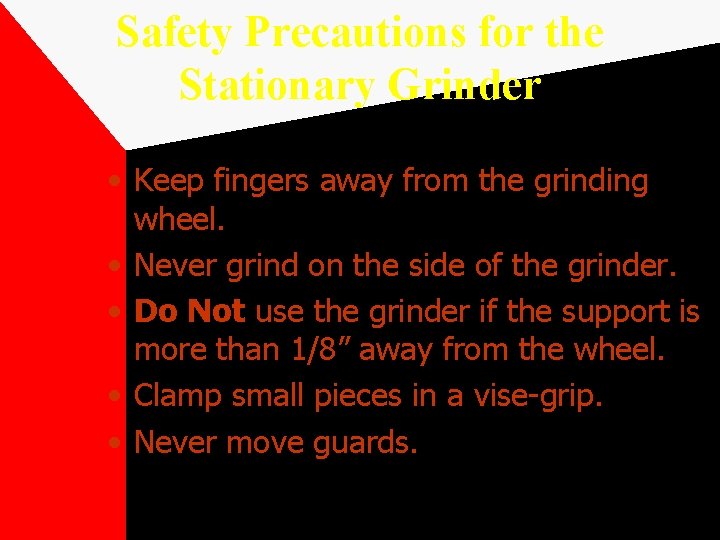
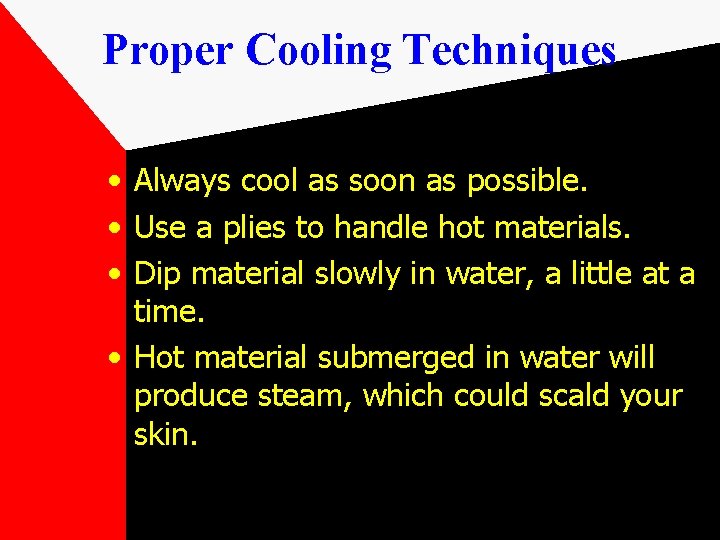
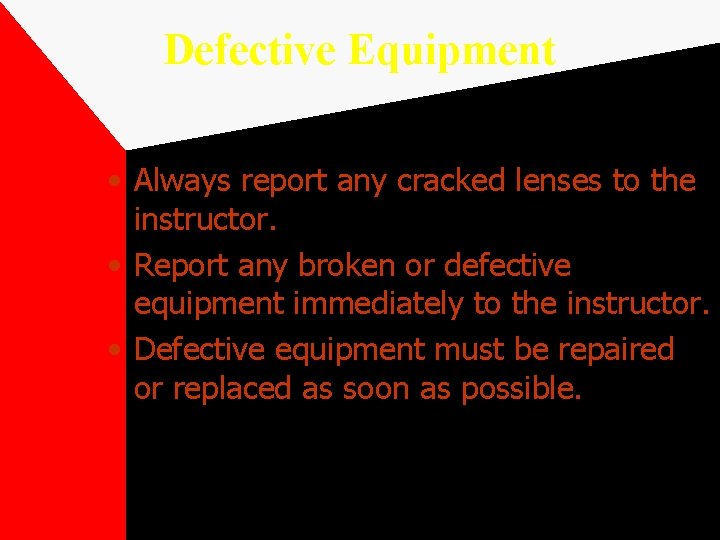
- Slides: 95
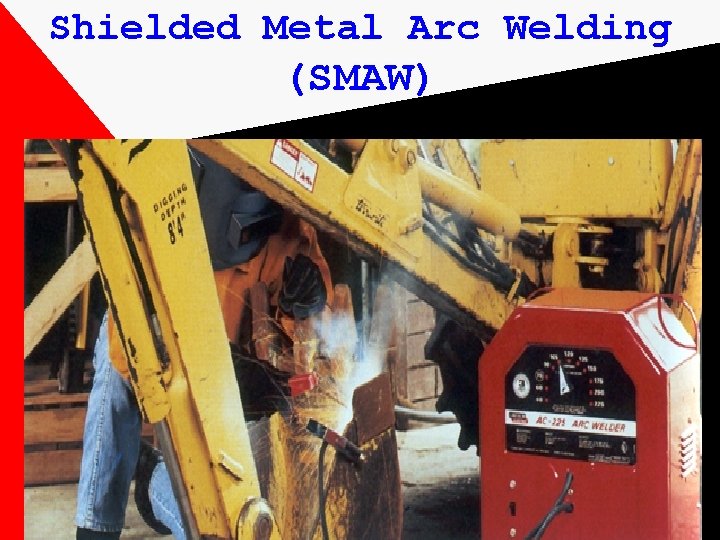
Shielded Metal Arc Welding (SMAW)
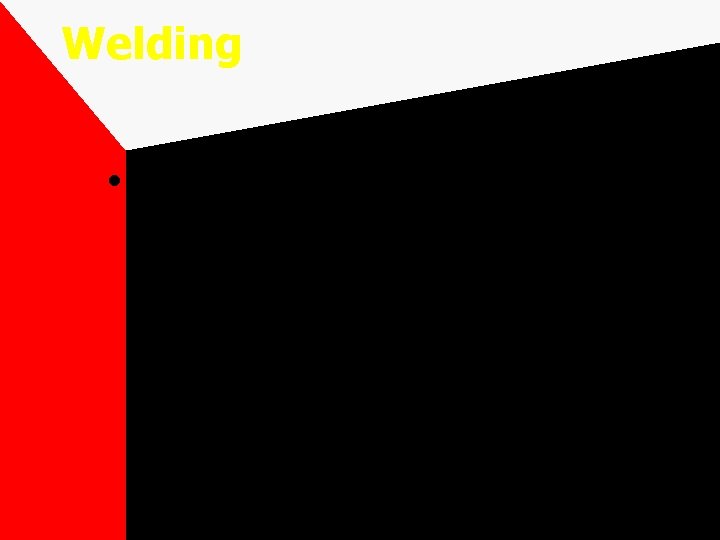
Welding • Most economical and efficient way to join metals together permanently
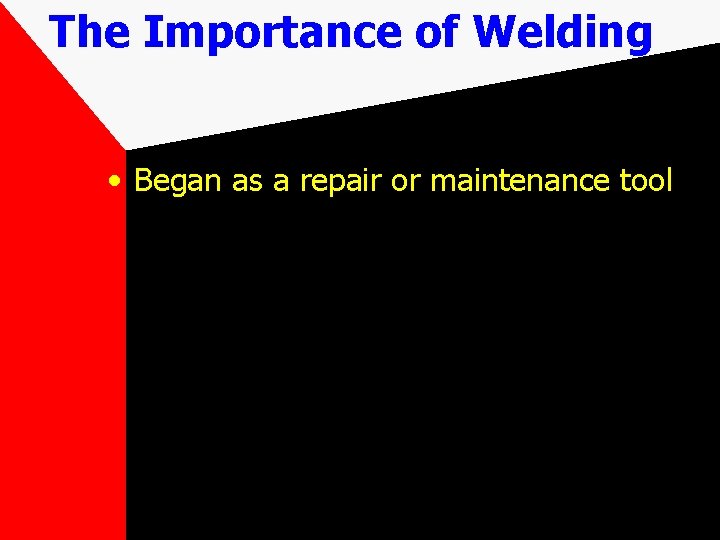
The Importance of Welding • Began as a repair or maintenance tool
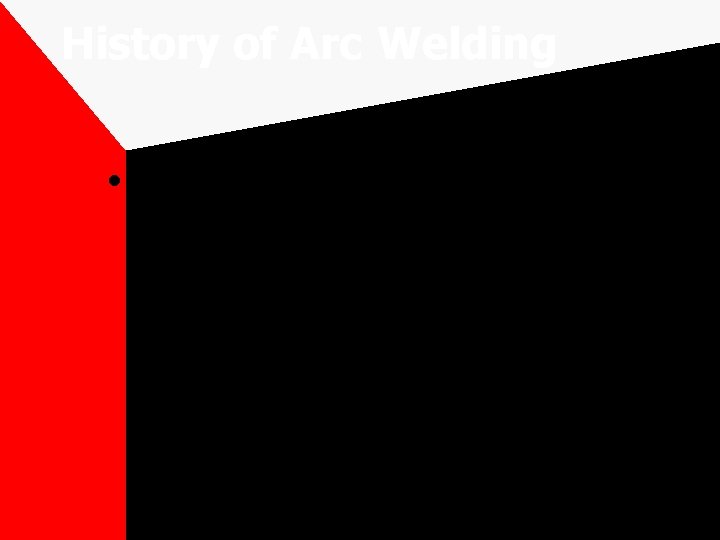
History of Arc Welding • Bronze age – gold circular boxes were made by pressurewelding lap joints together
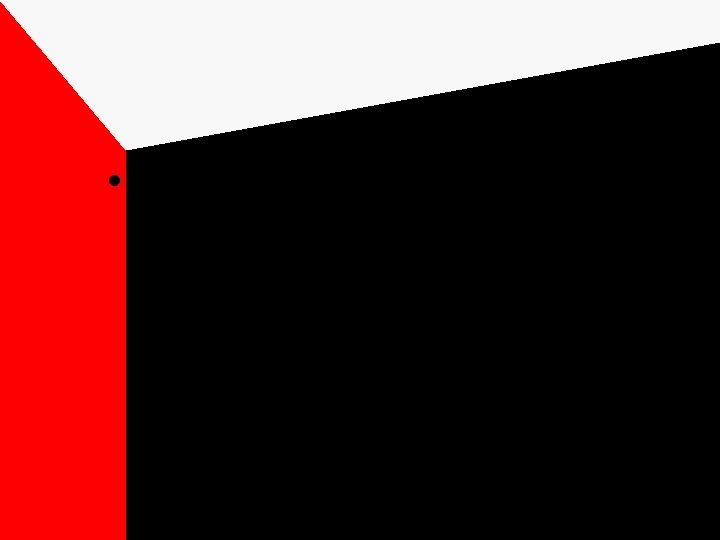
• Iron Age – Egyptians and eastern Mediterranean people welded pieces of iron together – forging and forge welding items found in the pyramids of Egypt
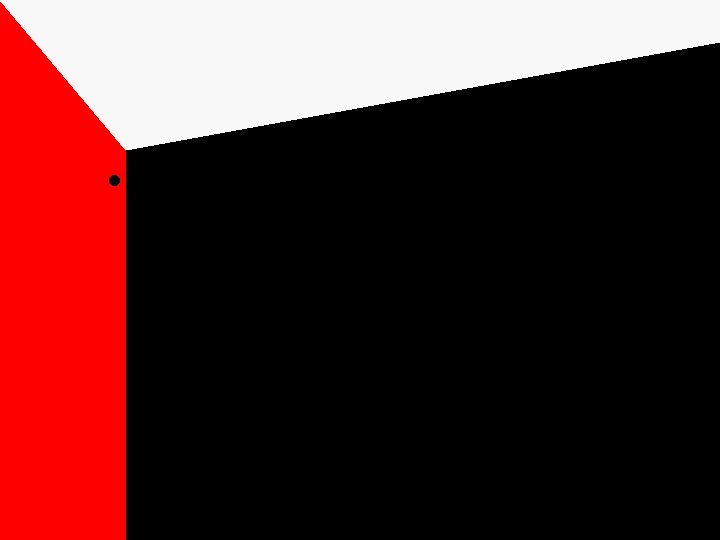
• Middle Ages – art of blacksmithing developed – India – Germany – Scandinavia – England
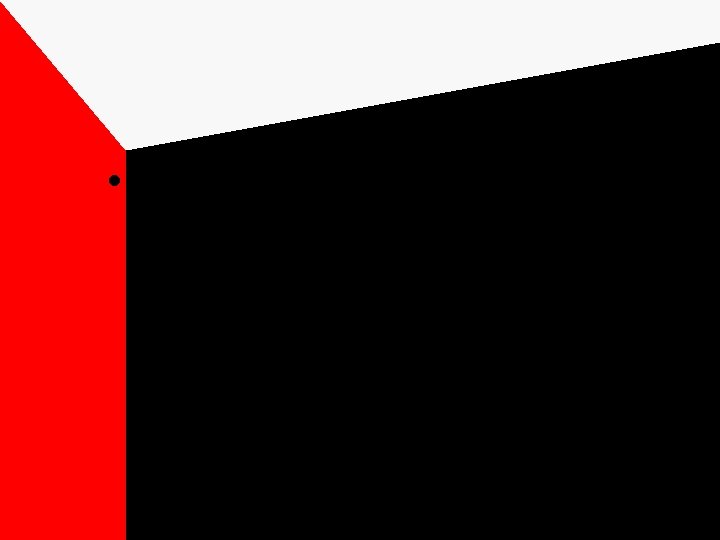
• Mid-nineteenth century – gas welding and cutting developed – arc and carbon arc welding developed – 1890 C. L. Coffin of Detroit received the first patent for an arc welding process using a metal electrode
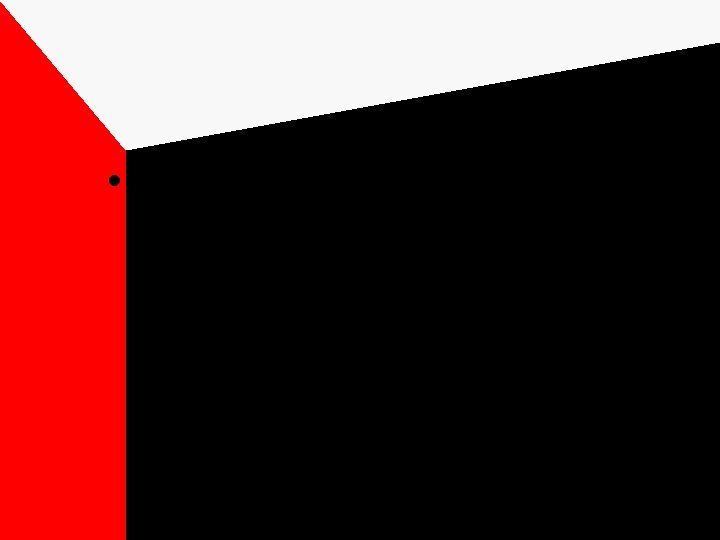
• World War I & II – brought a tremendous demand for welding • fuselages for airplanes • ships and ship repair • 1920 brought first automatic welding process
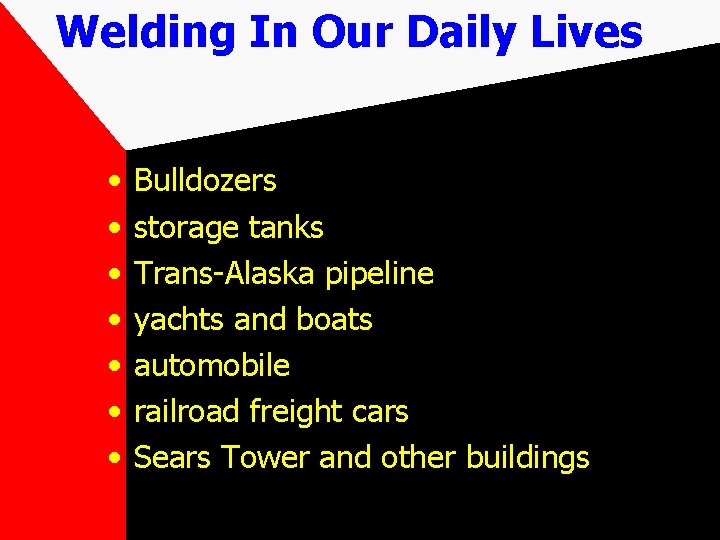
Welding In Our Daily Lives • • Bulldozers storage tanks Trans-Alaska pipeline yachts and boats automobile railroad freight cars Sears Tower and other buildings
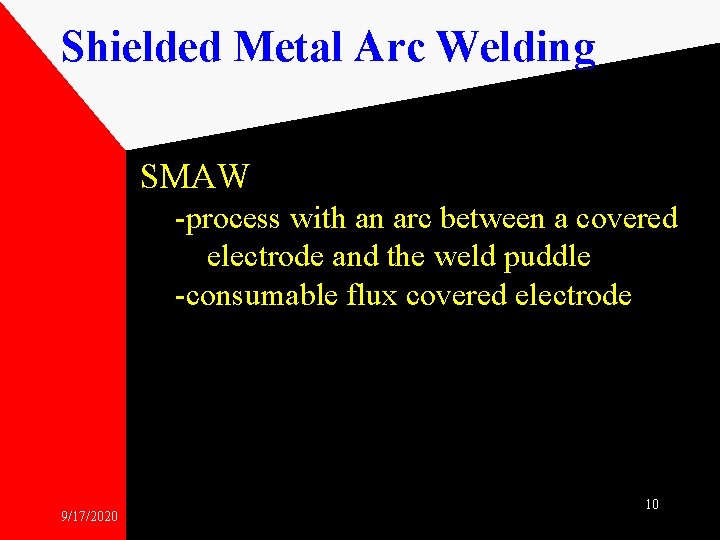
Shielded Metal Arc Welding SMAW -process with an arc between a covered electrode and the weld puddle -consumable flux covered electrode 9/17/2020 10
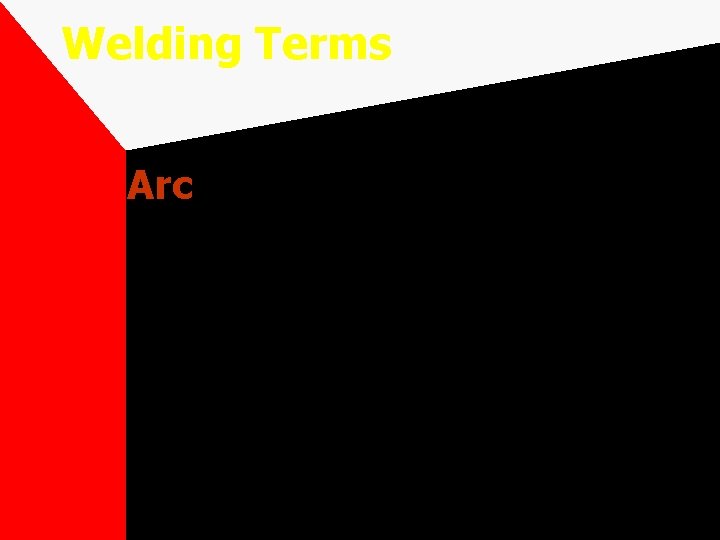
Welding Terms Arc The flow of electrical current from the tip of the electrode holder to the base metal.
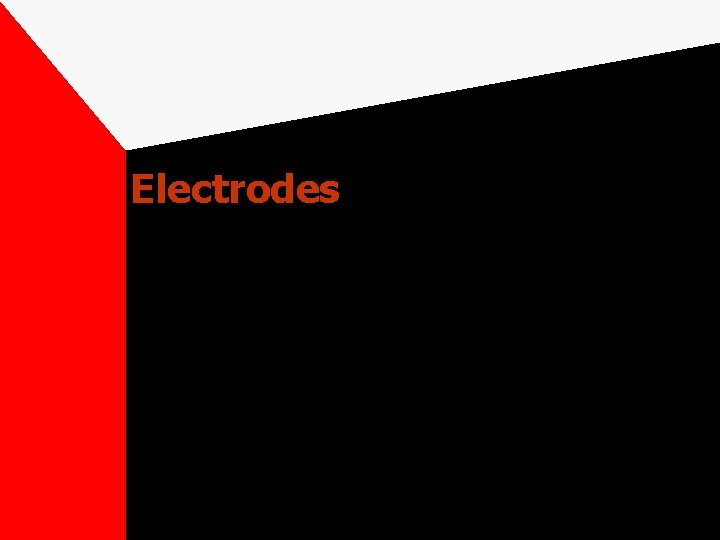
Electrodes Metal rods which conduct a current from an electrode holder to the base metal.
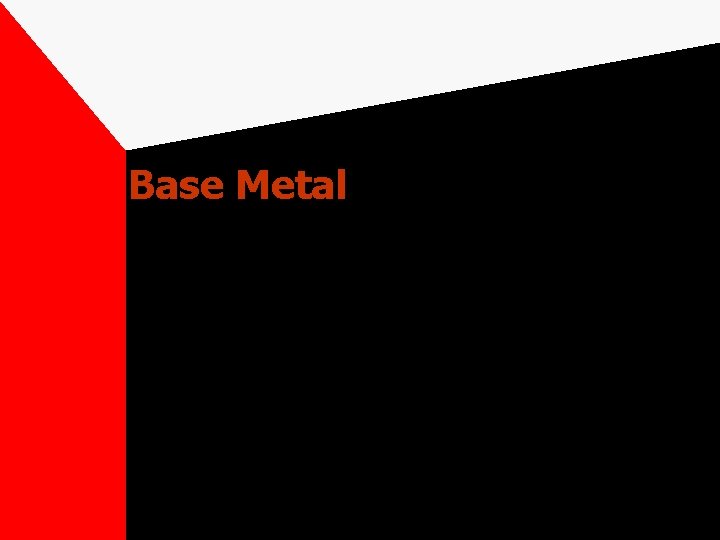
Base Metal The metal to be welded or cut.
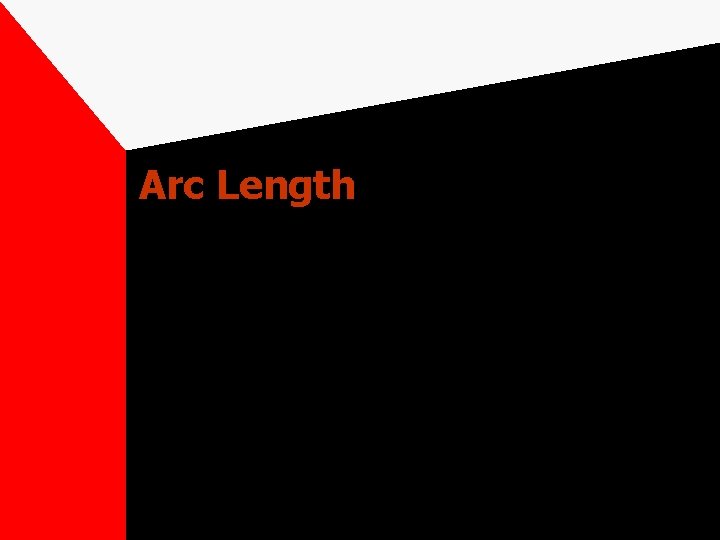
Arc Length The distance from the end of the electrode to the point where the arc makes contact with the work surface.
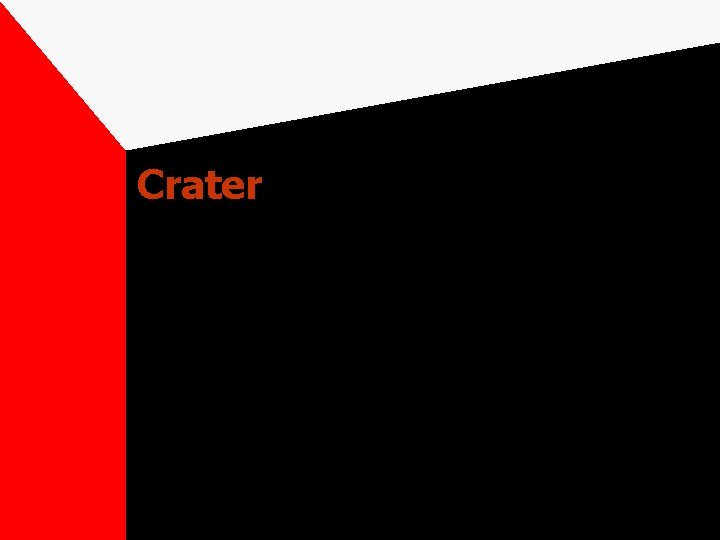
Crater A depression at the termination of a weld.
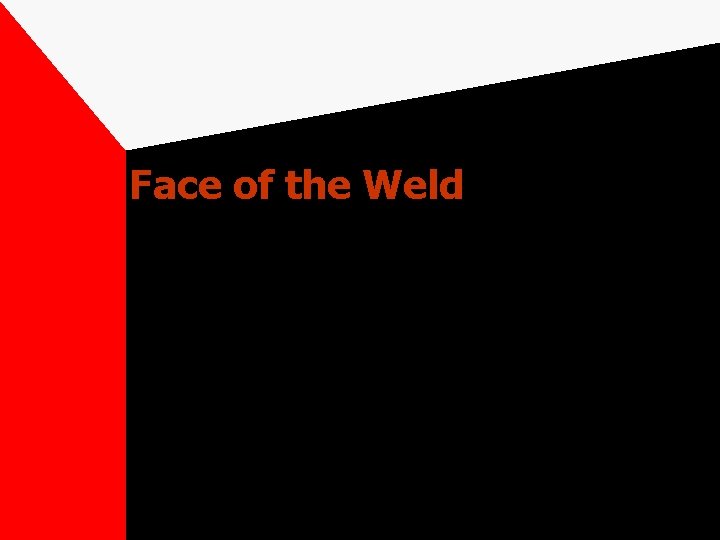
Face of the Weld The exposed surface of a weld, made by an arc or gas welding process, on the side from which the welding was done.
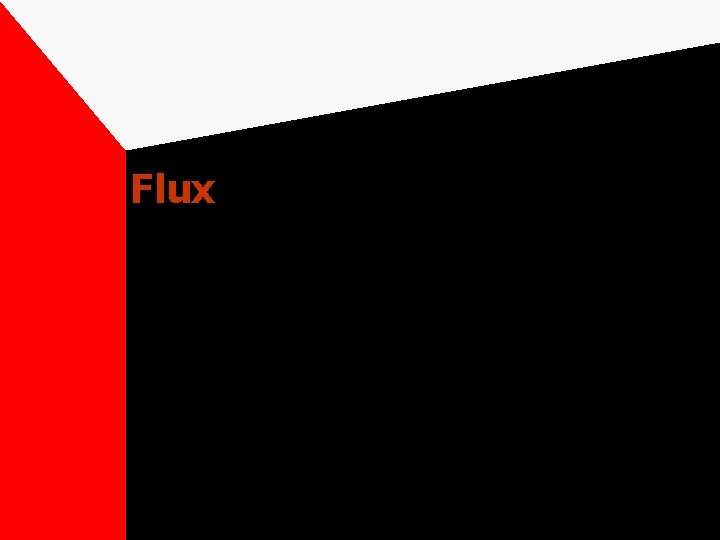
Flux A fusible material or gas used to dissolve and/or prevent the formation of oxides, nitrides, or other undesirable inclusions formed in welding.
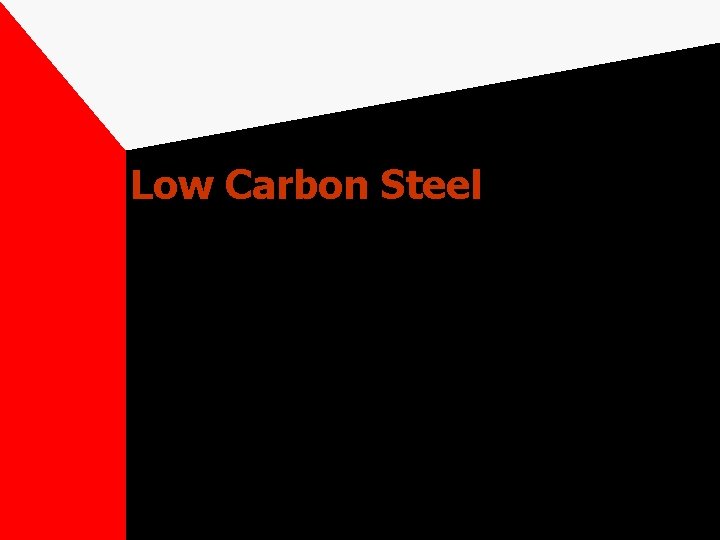
Low Carbon Steel containing. 20% or less carbon.
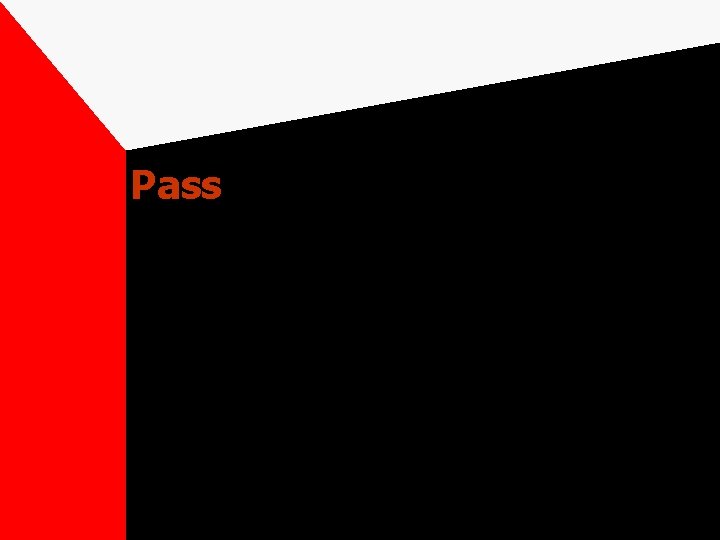
Pass A single longitudinal progression of a welding operation along a joint or weld deposit.
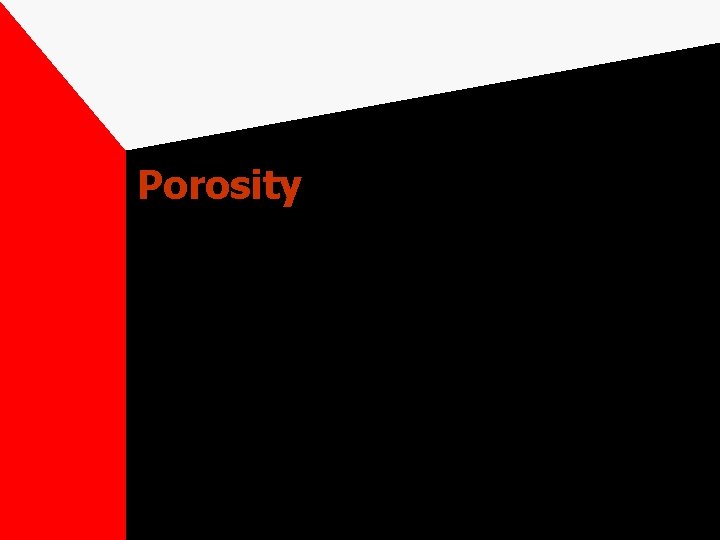
Porosity Gas pockets or voids in metal.
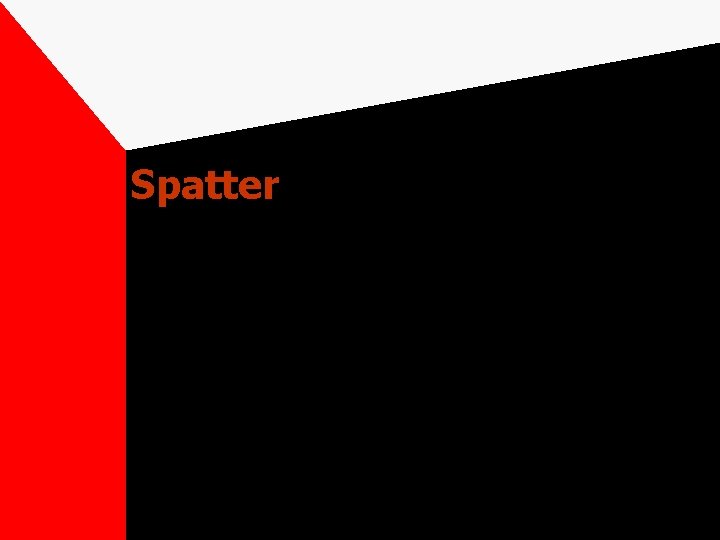
Spatter The metal particles given off during welding which do not form a part of the weld.
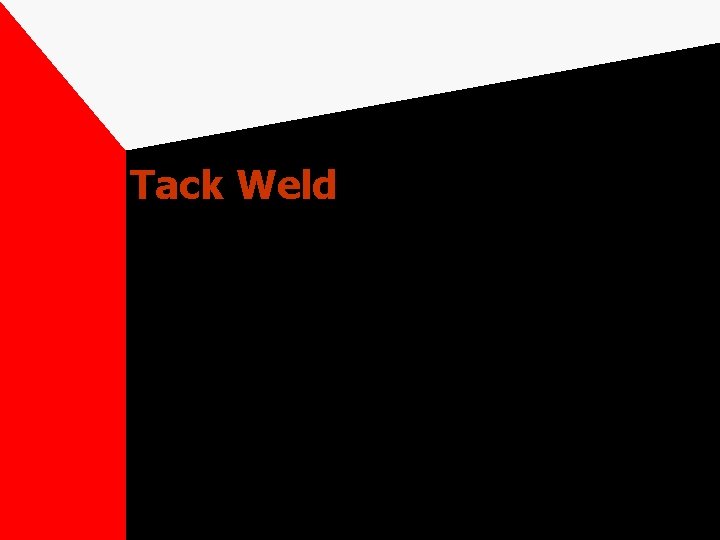
Tack Weld A weld made to hold parts in proper alignment until the final welds are made.
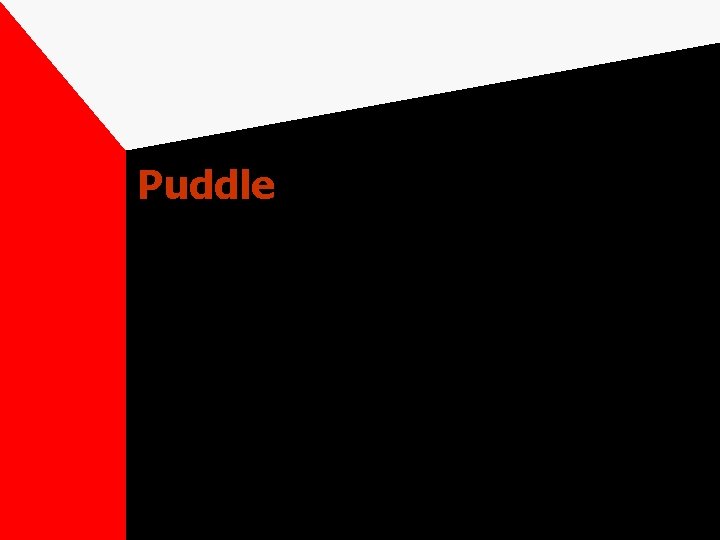
Puddle That portion of a weld that is molten at the place the heat is supplied.
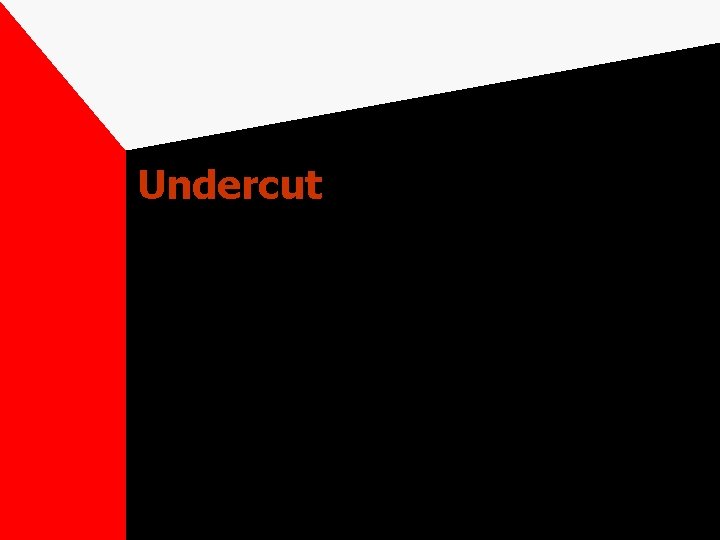
Undercut A groove melted into the base metal adjacent to the weld and left unfilled by the weld process.
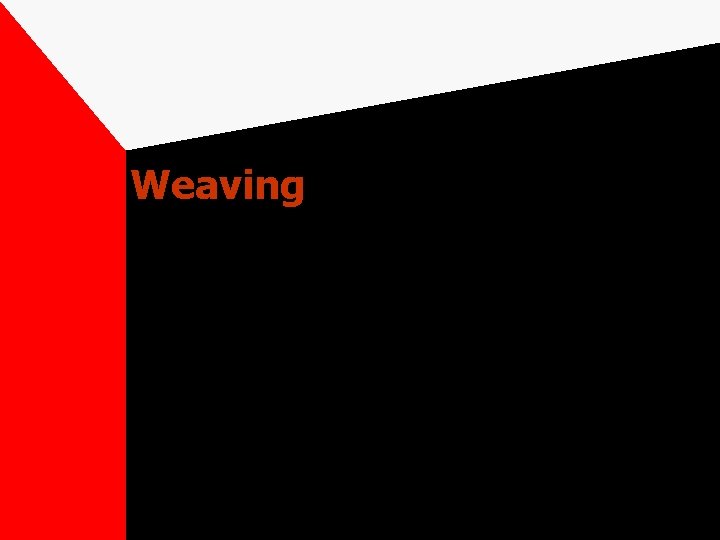
Weaving A technique of depositing weld metal in which the electrode is oscillated.
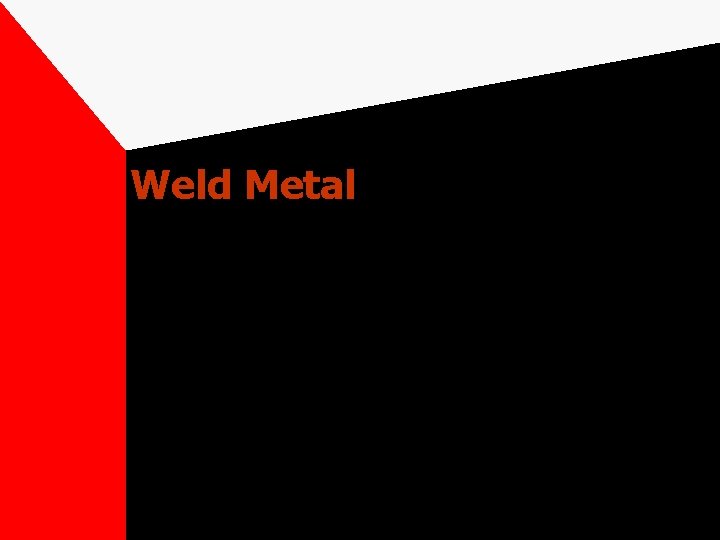
Weld Metal That portion of a weld which has been melted during welding.
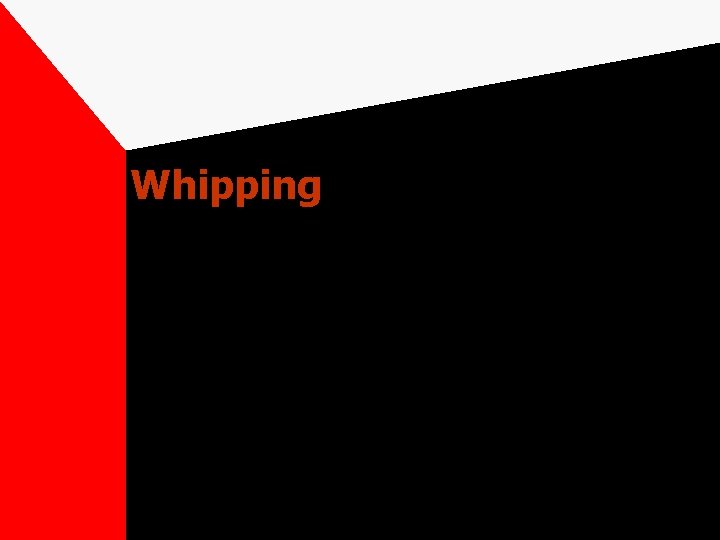
Whipping A term applied to an inward and upward movement of the electrode which is used in vertical welding to avoid undercut.
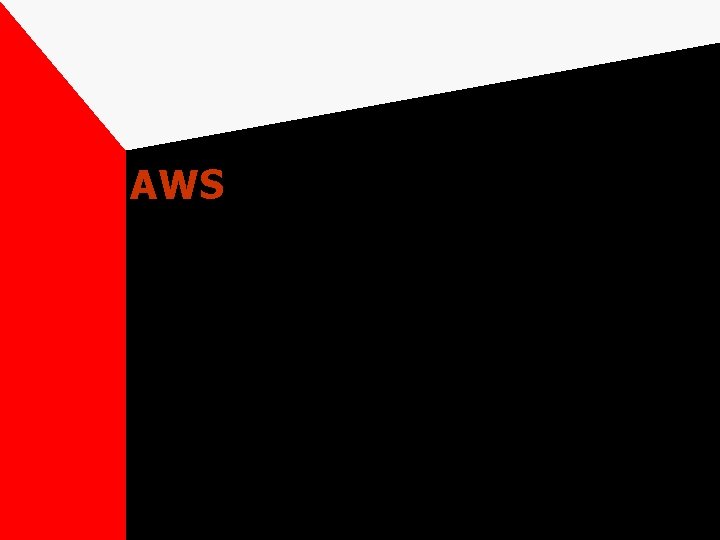
AWS American Welding Society.
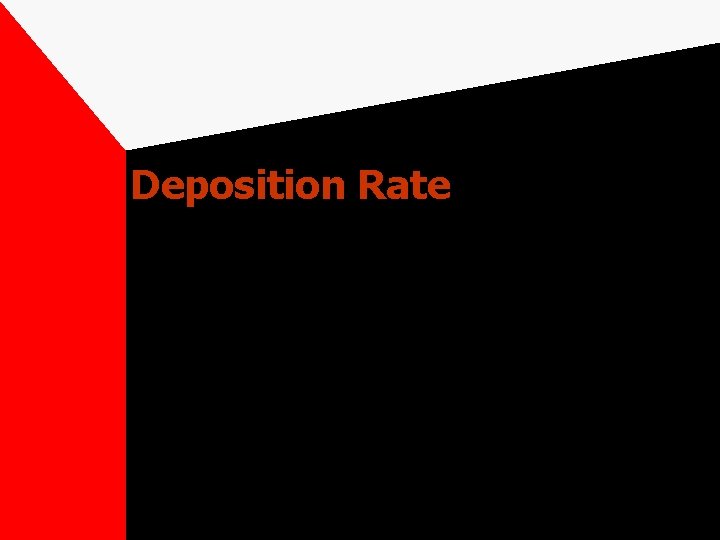
Deposition Rate The amount of filler metal deposited in any welding process; rated in pounds per hour.
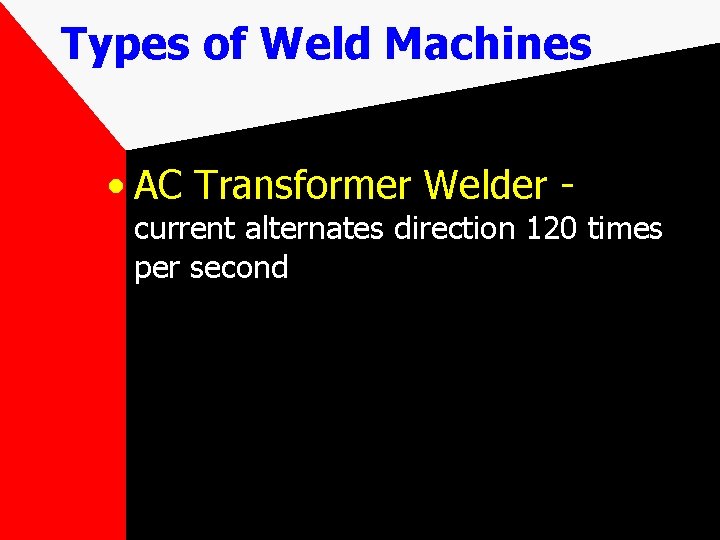
Types of Weld Machines • AC Transformer Welder - current alternates direction 120 times per second
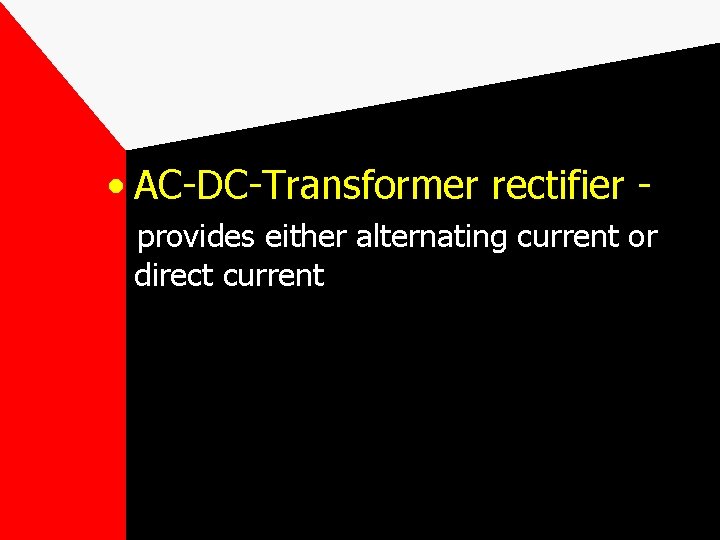
• AC-DC-Transformer rectifier provides either alternating current or direct current
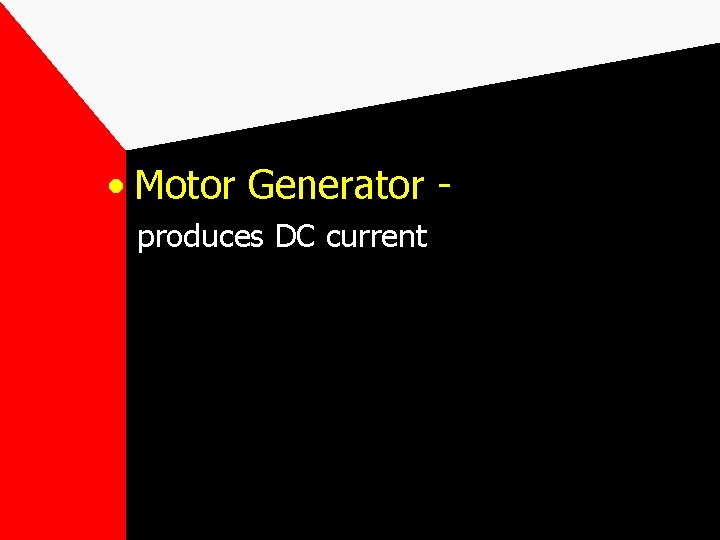
• Motor Generator produces DC current
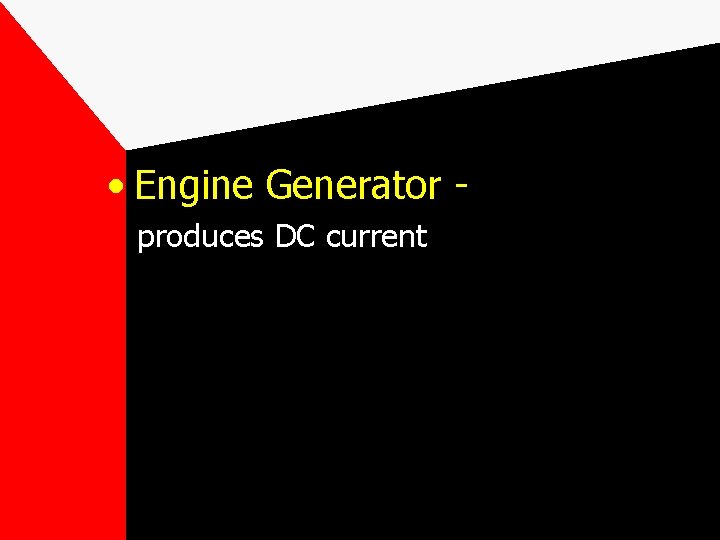
• Engine Generator produces DC current
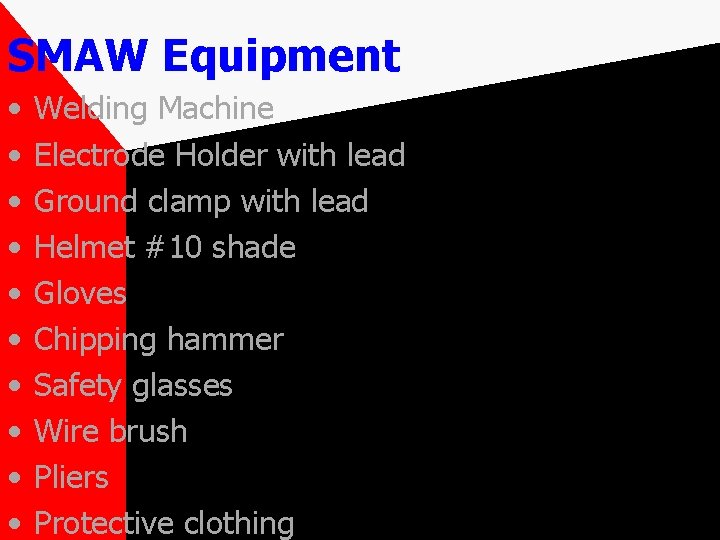
SMAW Equipment • • • Welding Machine Electrode Holder with lead Ground clamp with lead Helmet #10 shade Gloves Chipping hammer Safety glasses Wire brush Pliers Protective clothing

Polarity Reverse Polarity(DCRP) Current flows from base metal to electrode. Base metal is negative, electrode is positive.
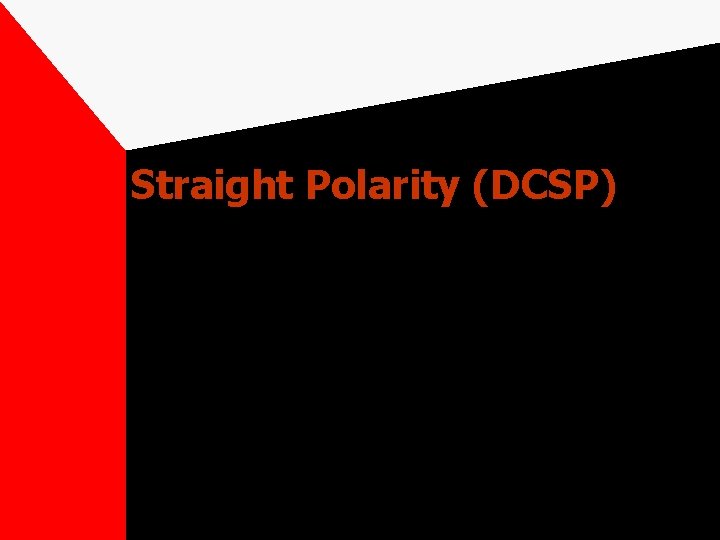
Straight Polarity (DCSP) Current flows from electrode to base metal. Base metal is positive, electrode is negative.
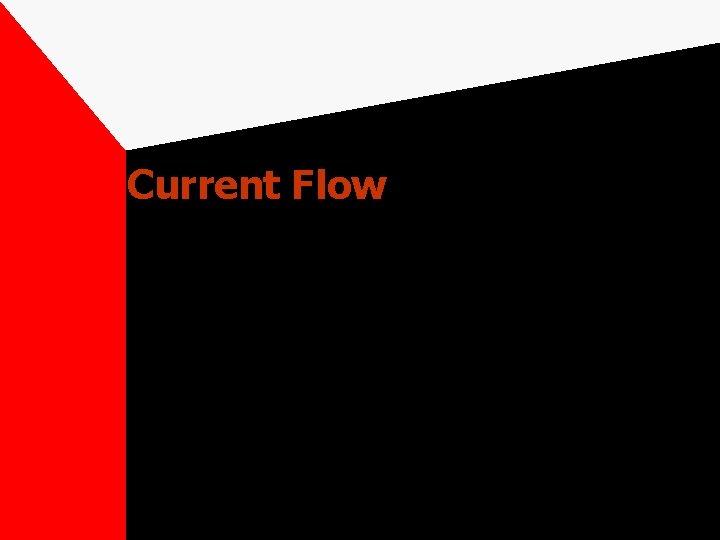
Current Flow Negative to positive.
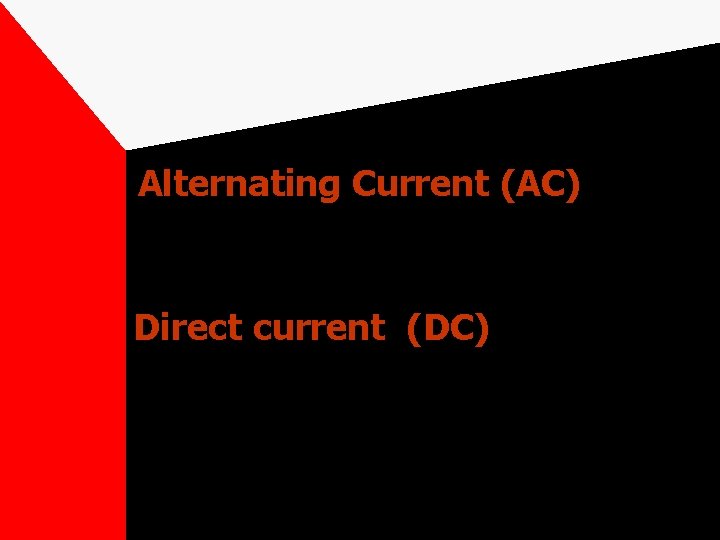
Alternating Current (AC) – current alternates its direction 120 times per second Direct current (DC) – electrical current that flows in only one direction
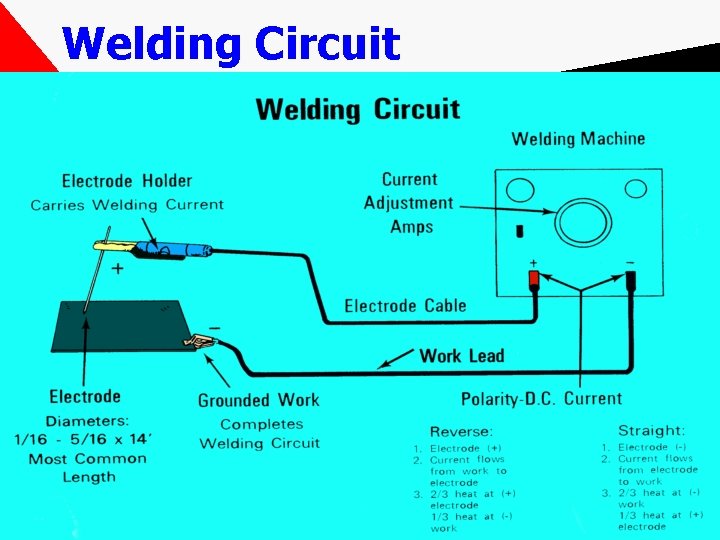
Welding Circuit
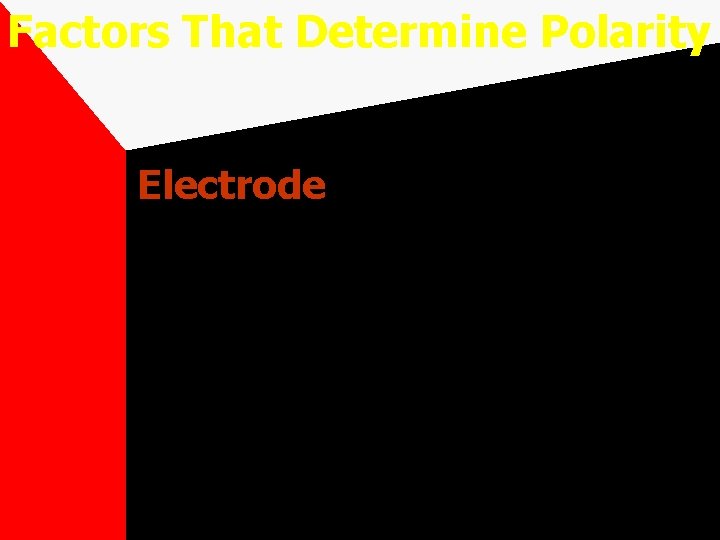
Factors That Determine Polarity Electrode Type of flux on electrode
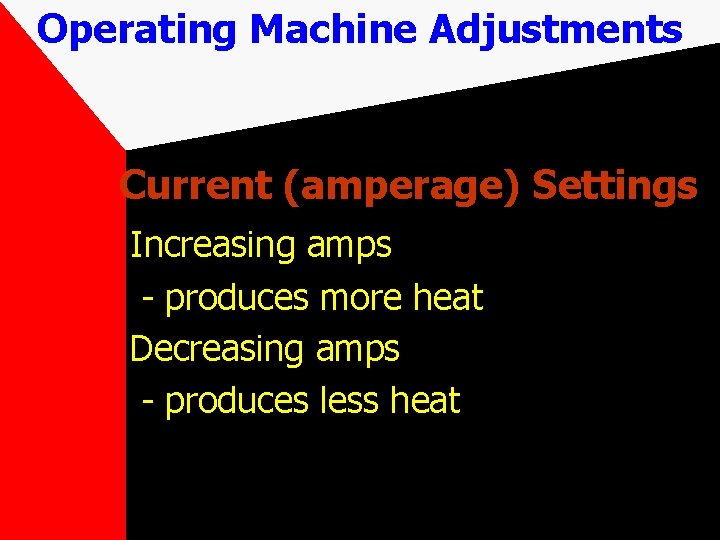
Operating Machine Adjustments Current (amperage) Settings Increasing amps - produces more heat Decreasing amps - produces less heat
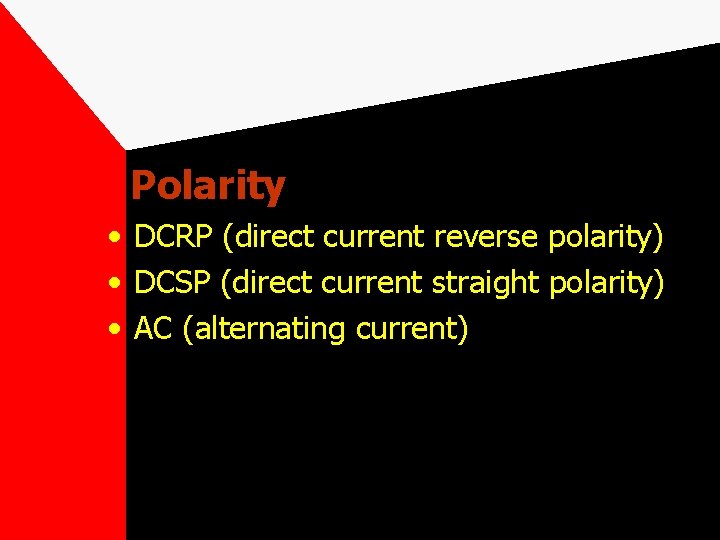
Polarity • DCRP (direct current reverse polarity) • DCSP (direct current straight polarity) • AC (alternating current)
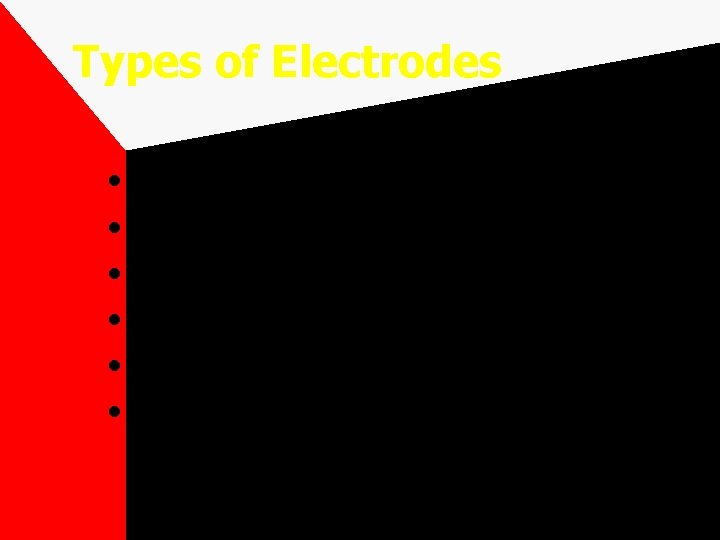
Types of Electrodes • • • Mild Steel Low Hydrogen Non-ferrous Hard surfacing Cast iron Stainless steel
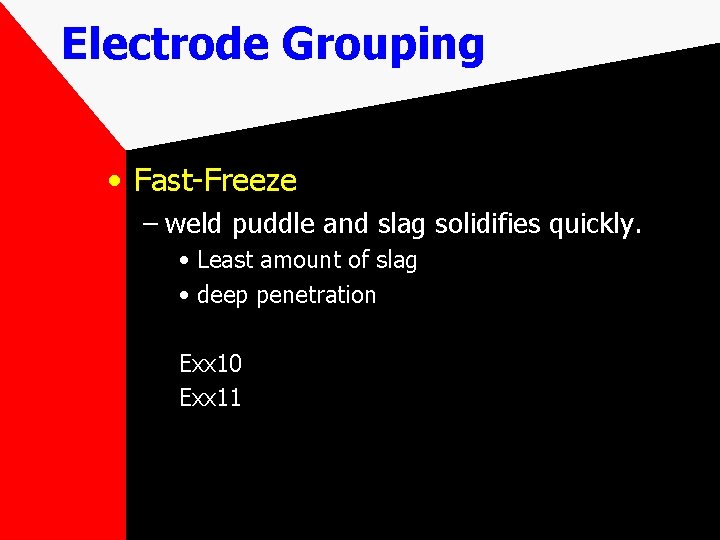
Electrode Grouping • Fast-Freeze – weld puddle and slag solidifies quickly. • Least amount of slag • deep penetration Exx 10 Exx 11
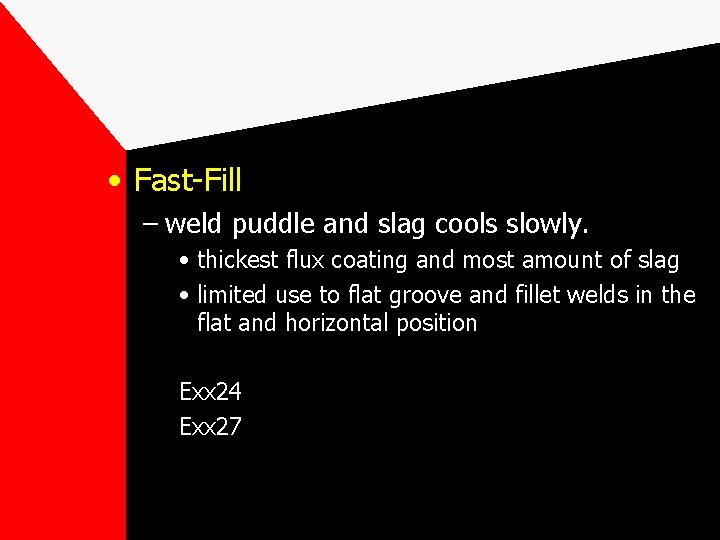
• Fast-Fill – weld puddle and slag cools slowly. • thickest flux coating and most amount of slag • limited use to flat groove and fillet welds in the flat and horizontal position Exx 24 Exx 27
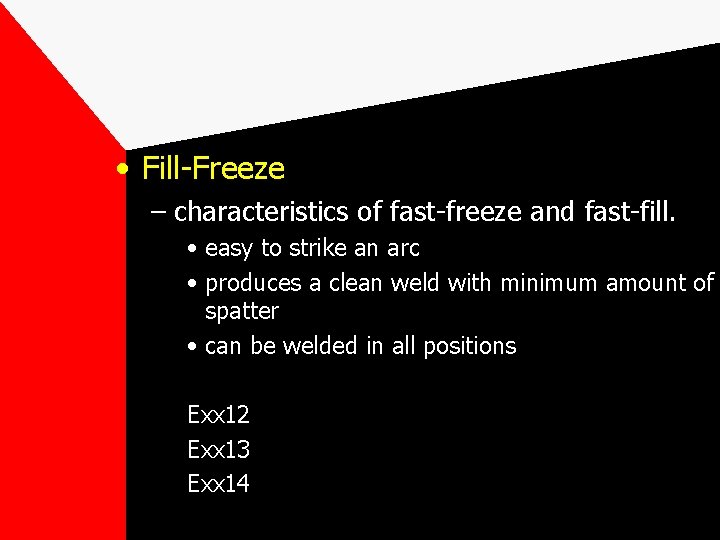
• Fill-Freeze – characteristics of fast-freeze and fast-fill. • easy to strike an arc • produces a clean weld with minimum amount of spatter • can be welded in all positions Exx 12 Exx 13 Exx 14
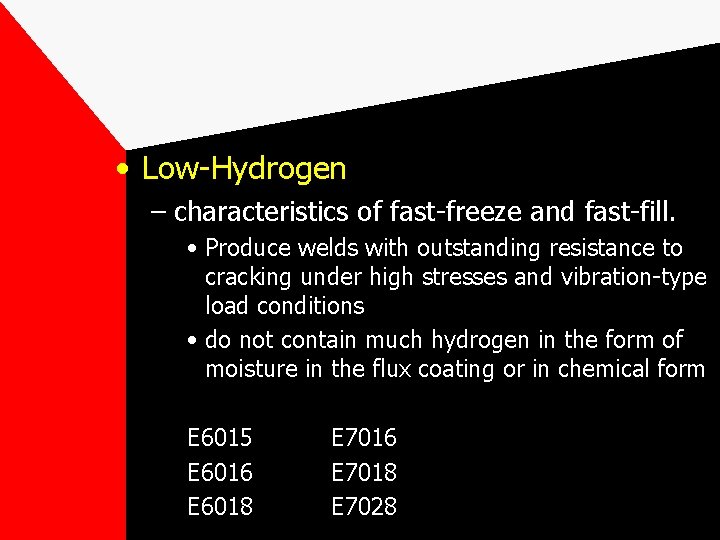
• Low-Hydrogen – characteristics of fast-freeze and fast-fill. • Produce welds with outstanding resistance to cracking under high stresses and vibration-type load conditions • do not contain much hydrogen in the form of moisture in the flux coating or in chemical form E 6015 E 6016 E 6018 E 7016 E 7018 E 7028
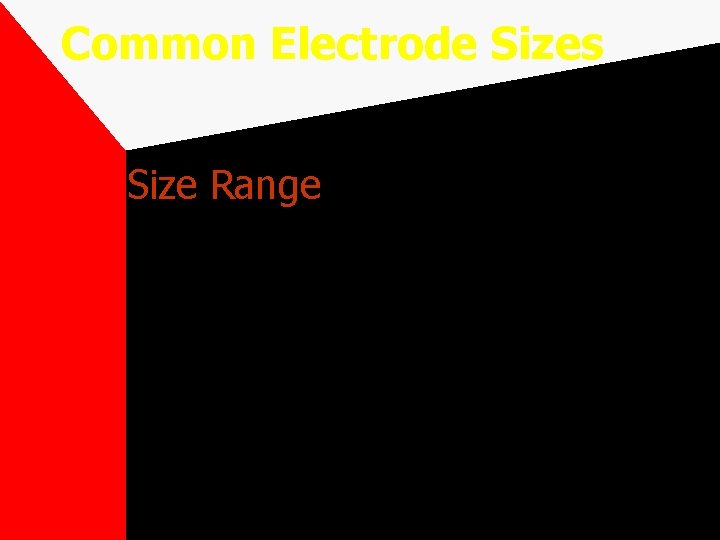
Common Electrode Sizes Size Range 1/16 to 5/16
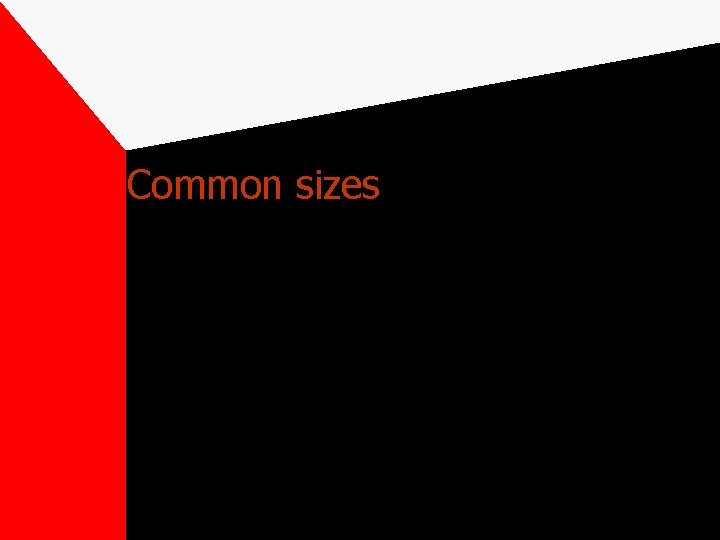
Common sizes 3/32 1/8 5/32 7/32 1/4 5/16
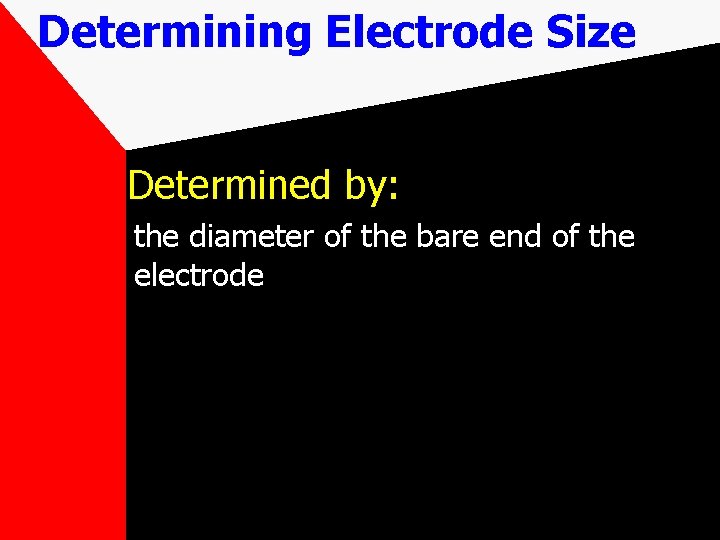
Determining Electrode Size Determined by: the diameter of the bare end of the electrode
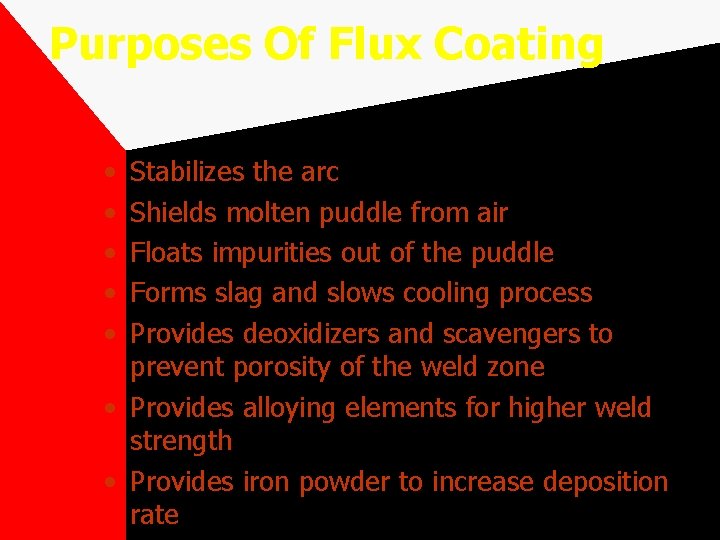
Purposes Of Flux Coating • • • Stabilizes the arc Shields molten puddle from air Floats impurities out of the puddle Forms slag and slows cooling process Provides deoxidizers and scavengers to prevent porosity of the weld zone • Provides alloying elements for higher weld strength • Provides iron powder to increase deposition rate
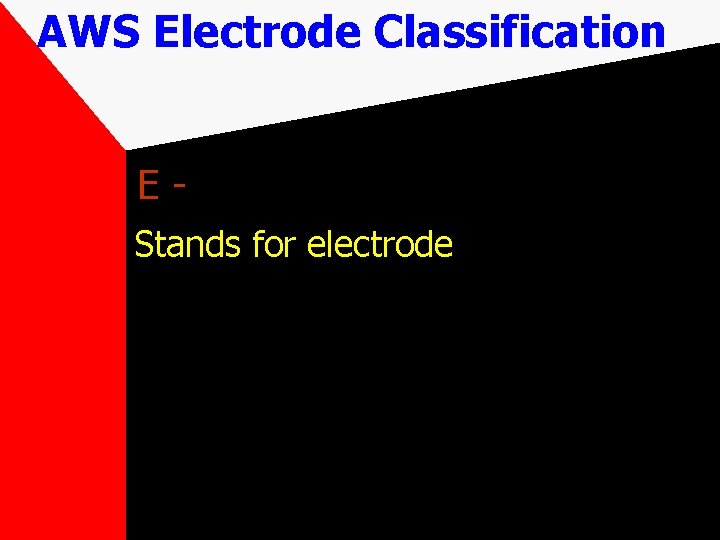
AWS Electrode Classification EStands for electrode

First two digits Tensile strength deposited in thousand pounds per square inch
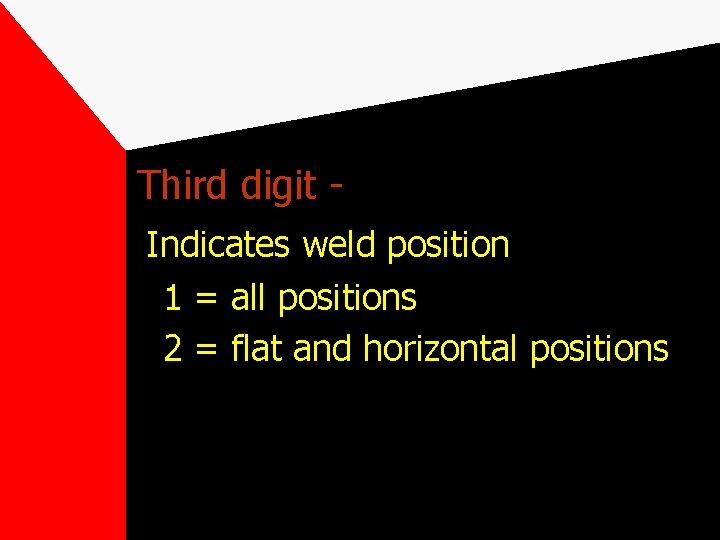
Third digit Indicates weld position 1 = all positions 2 = flat and horizontal positions
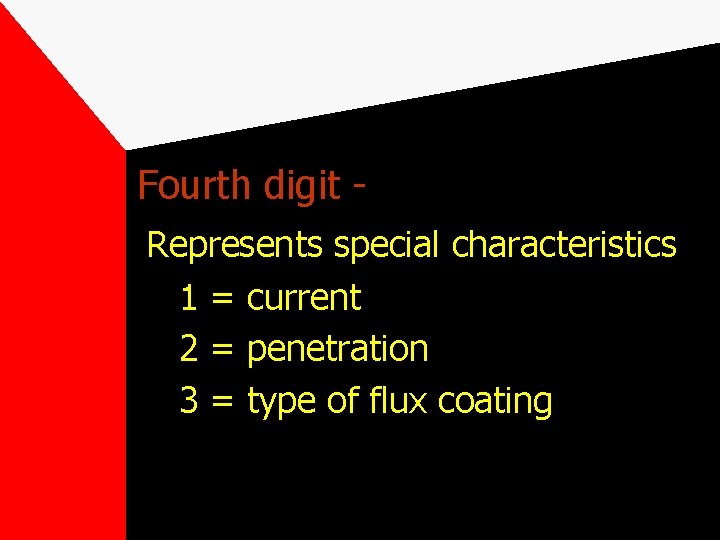
Fourth digit Represents special characteristics 1 = current 2 = penetration 3 = type of flux coating
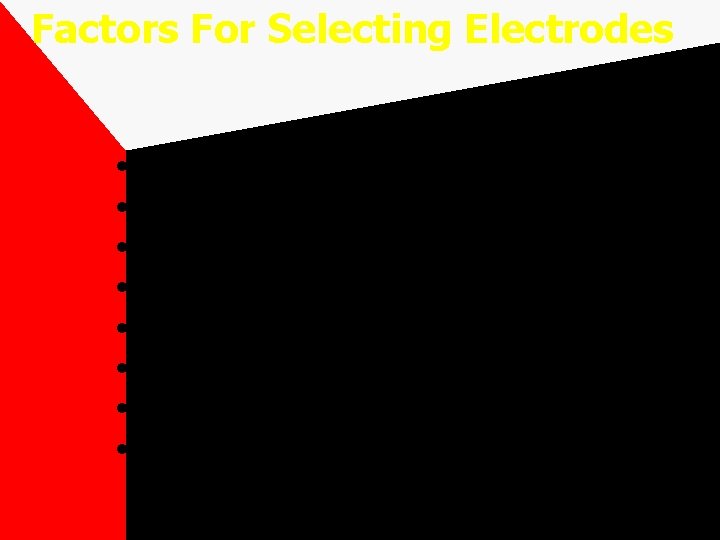
Factors For Selecting Electrodes • • Base metal strength properties Base metal composition Welding current Joint design and fit-up Thickness and shape of the base metal Service conditions and/or specifications Production efficiency and job conditions
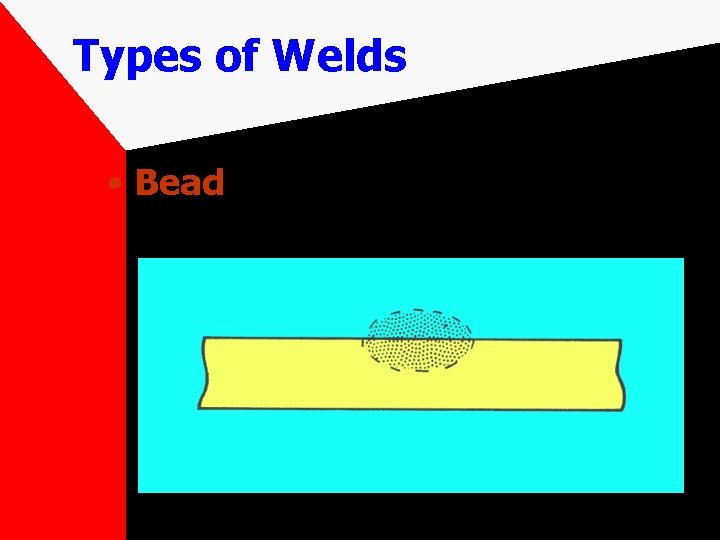
Types of Welds • Bead
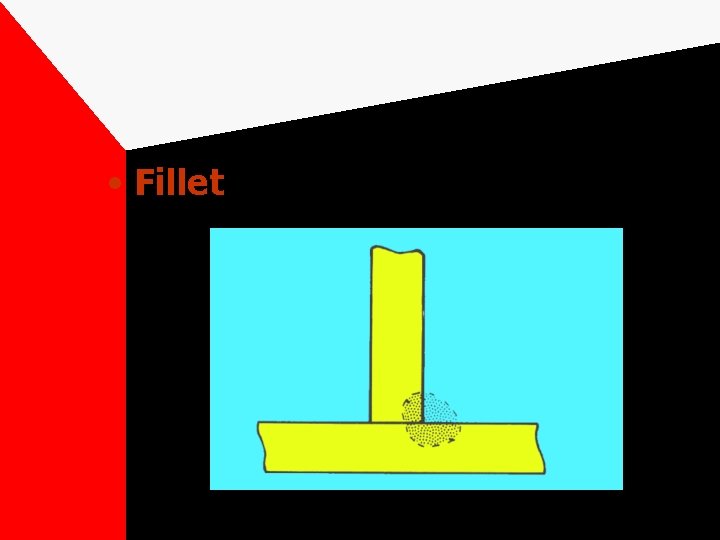
• Fillet
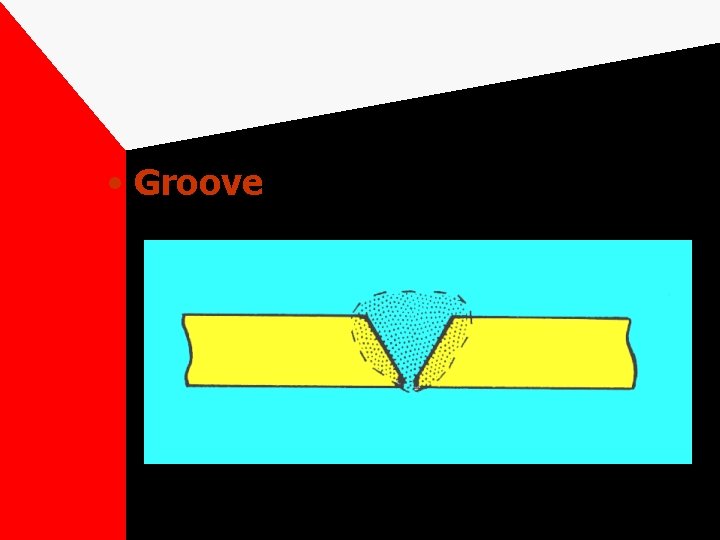
• Groove
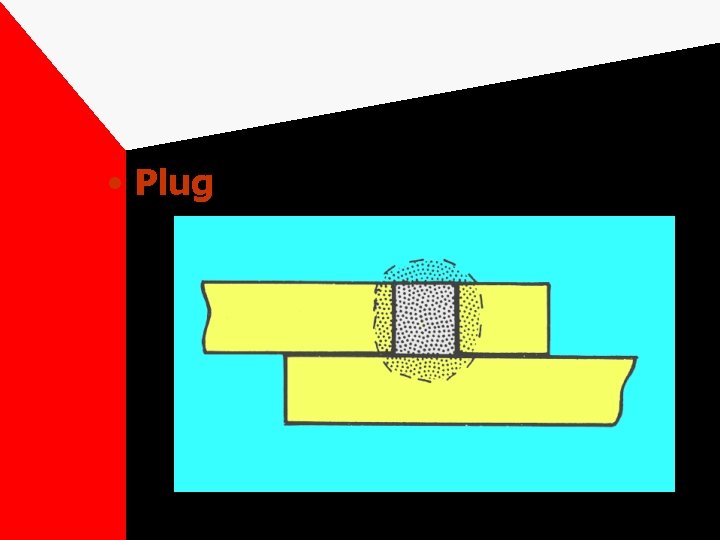
• Plug
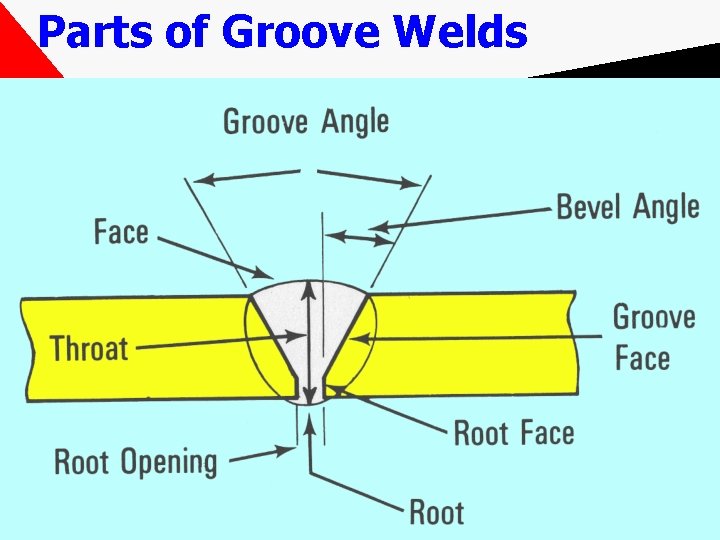
Parts of Groove Welds
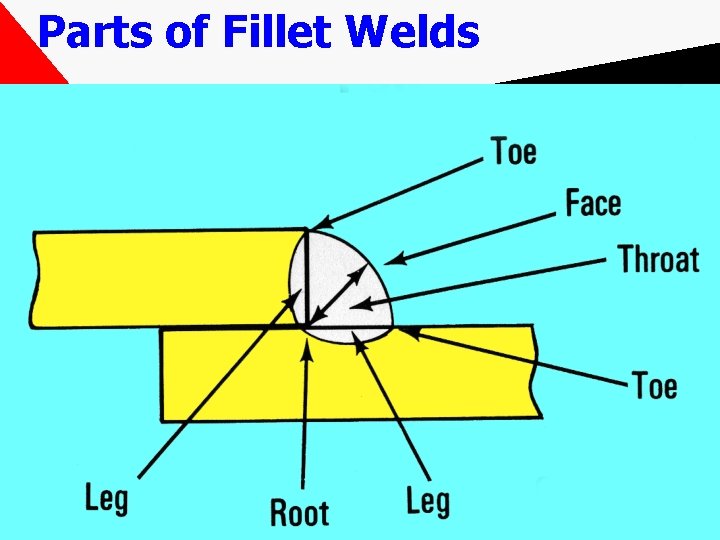
Parts of Fillet Welds
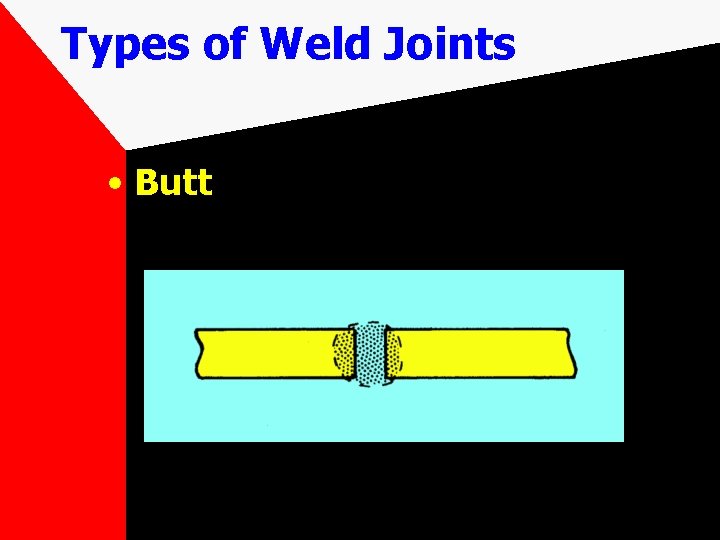
Types of Weld Joints • Butt
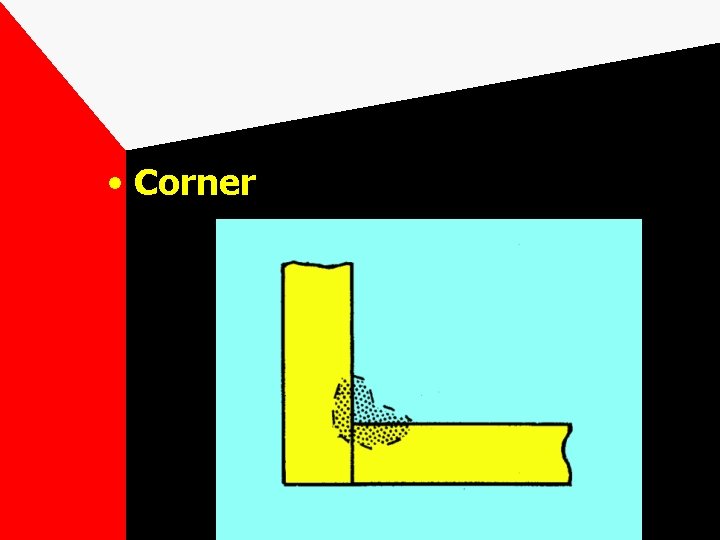
• Corner
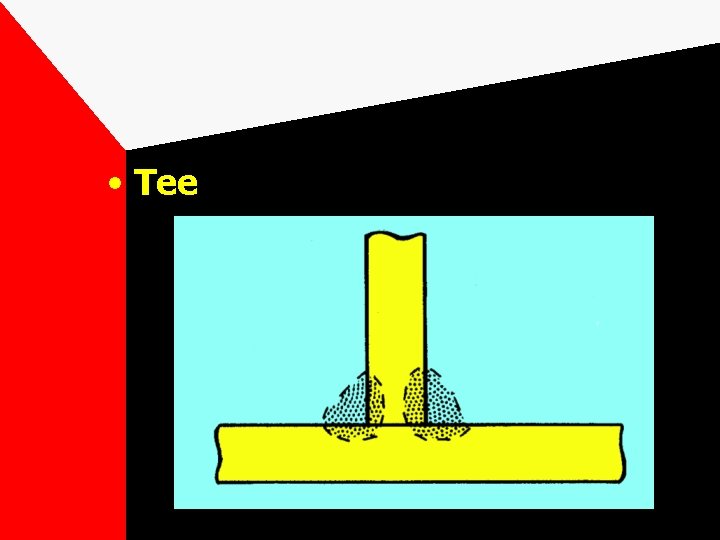
• Tee
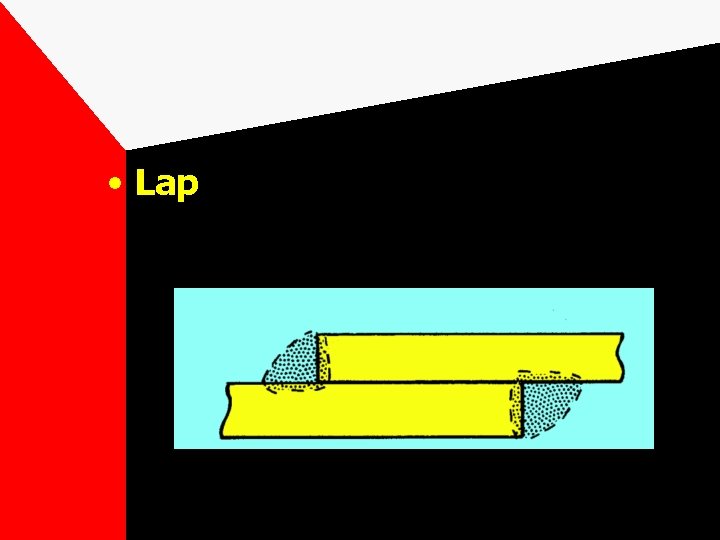
• Lap
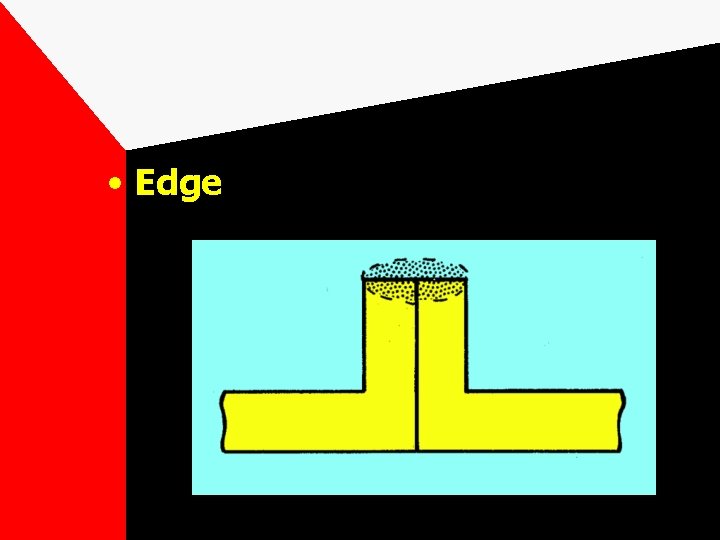
• Edge
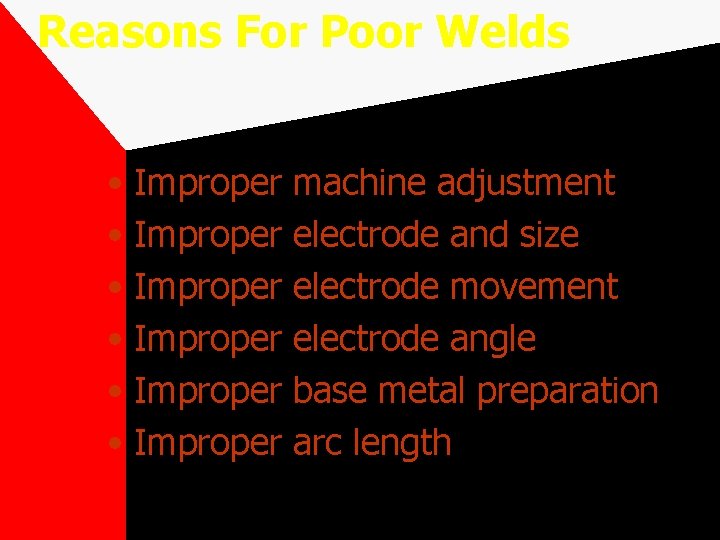
Reasons For Poor Welds • Improper • Improper machine adjustment electrode and size electrode movement electrode angle base metal preparation arc length
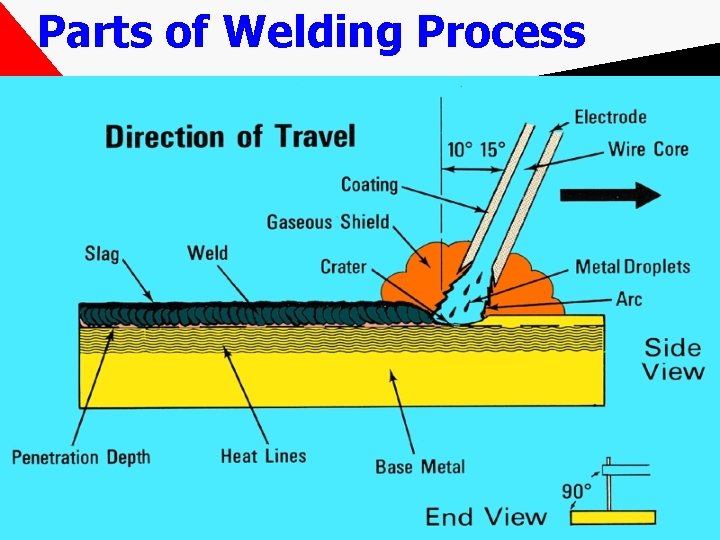
Parts of Welding Process
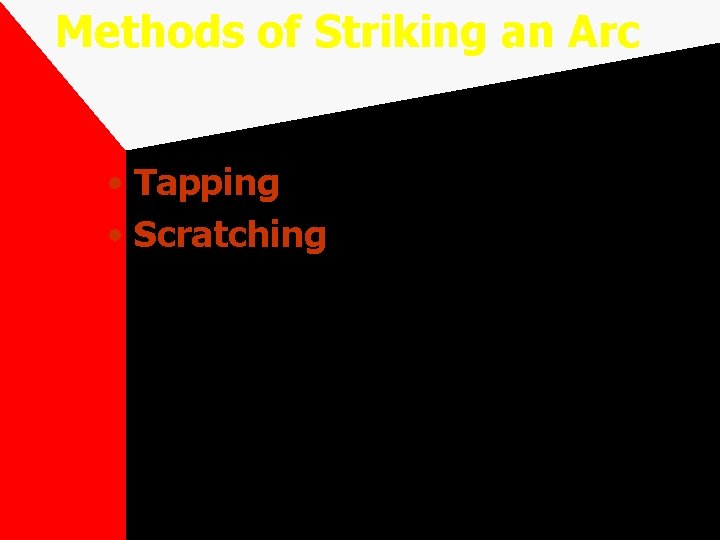
Methods of Striking an Arc • Tapping • Scratching
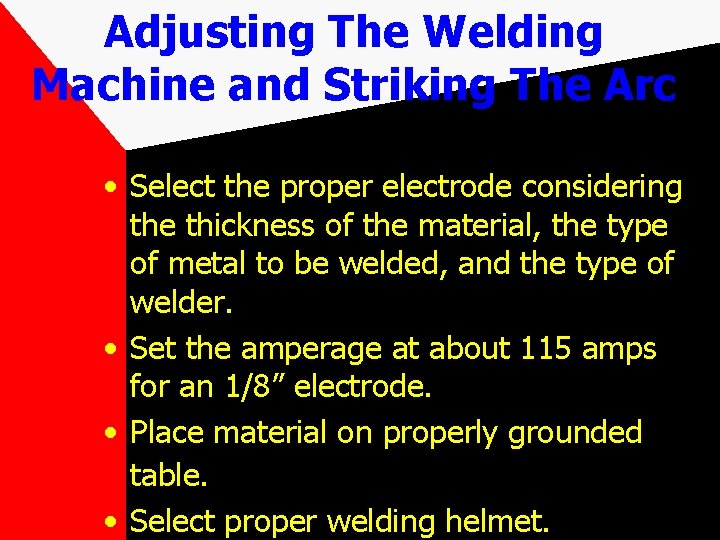
Adjusting The Welding Machine and Striking The Arc • Select the proper electrode considering the thickness of the material, the type of metal to be welded, and the type of welder. • Set the amperage at about 115 amps for an 1/8” electrode. • Place material on properly grounded table. • Select proper welding helmet.
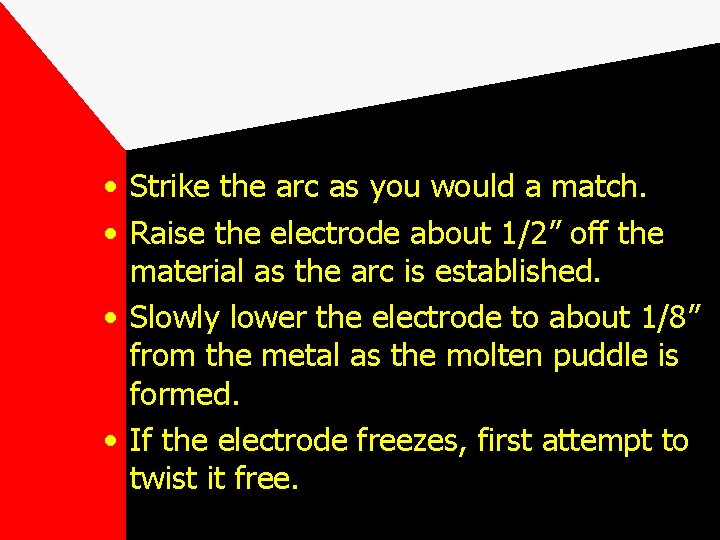
• Strike the arc as you would a match. • Raise the electrode about 1/2” off the material as the arc is established. • Slowly lower the electrode to about 1/8” from the metal as the molten puddle is formed. • If the electrode freezes, first attempt to twist it free.
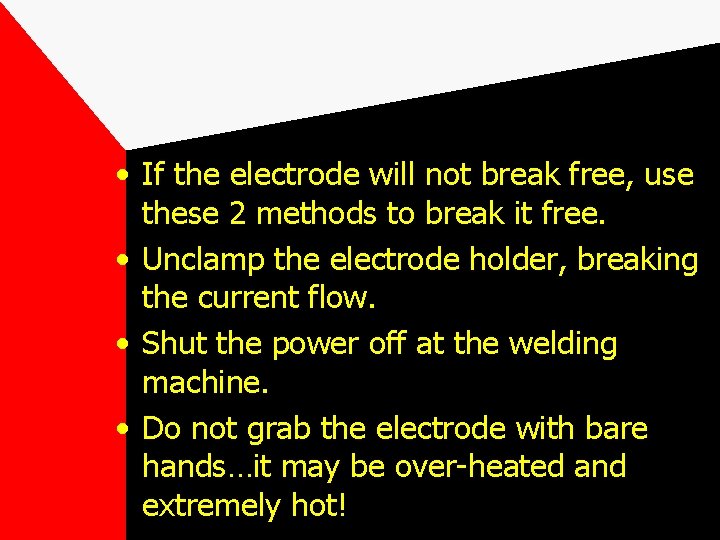
• If the electrode will not break free, use these 2 methods to break it free. • Unclamp the electrode holder, breaking the current flow. • Shut the power off at the welding machine. • Do not grab the electrode with bare hands…it may be over-heated and extremely hot!
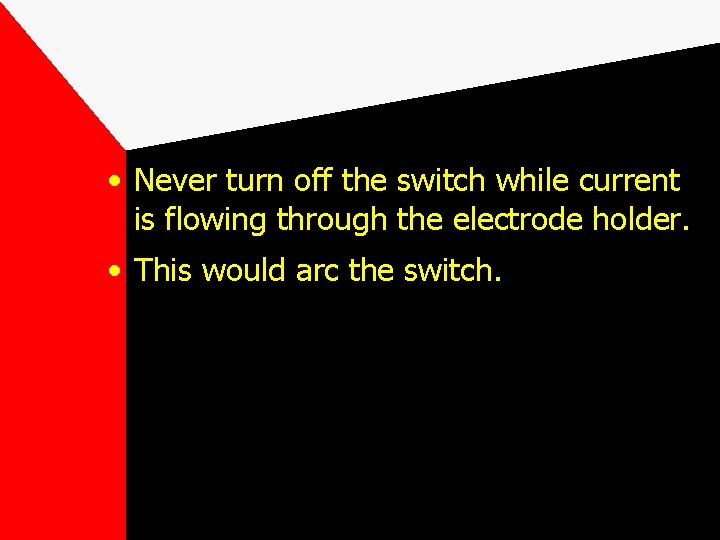
• Never turn off the switch while current is flowing through the electrode holder. • This would arc the switch.
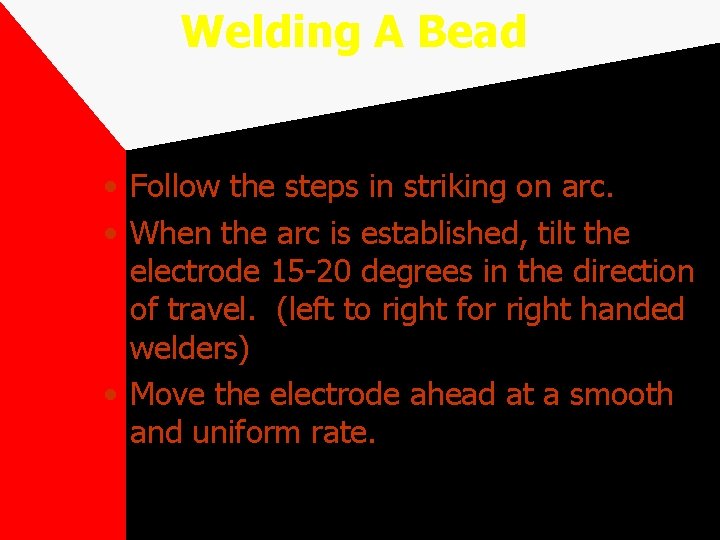
Welding A Bead • Follow the steps in striking on arc. • When the arc is established, tilt the electrode 15 -20 degrees in the direction of travel. (left to right for right handed welders) • Move the electrode ahead at a smooth and uniform rate.
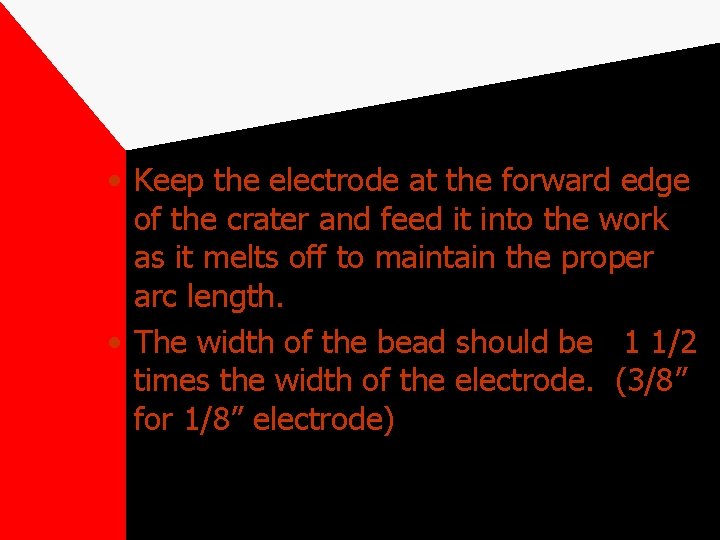
• Keep the electrode at the forward edge of the crater and feed it into the work as it melts off to maintain the proper arc length. • The width of the bead should be 1 1/2 times the width of the electrode. (3/8” for 1/8” electrode)
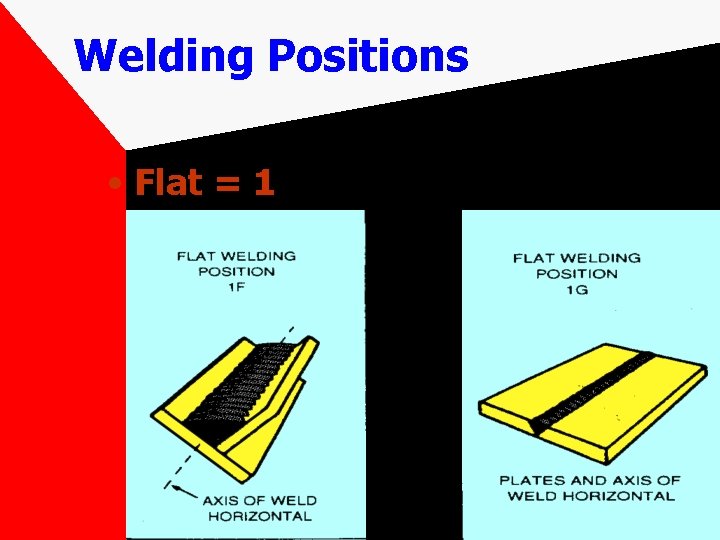
Welding Positions • Flat = 1
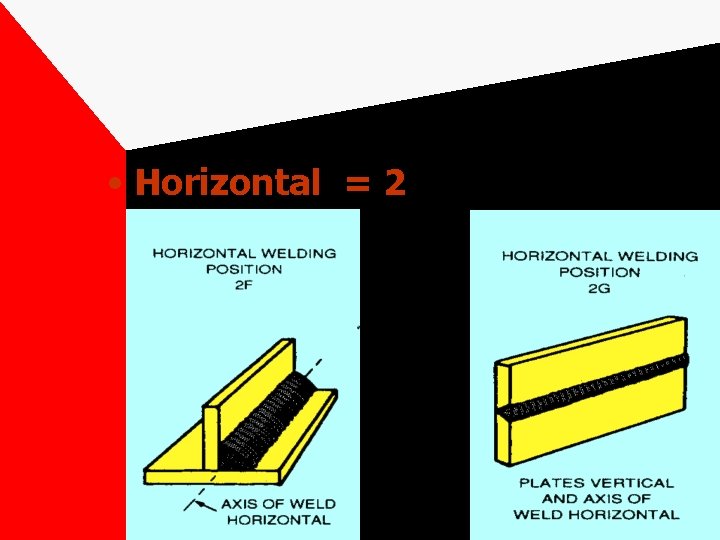
• Horizontal = 2
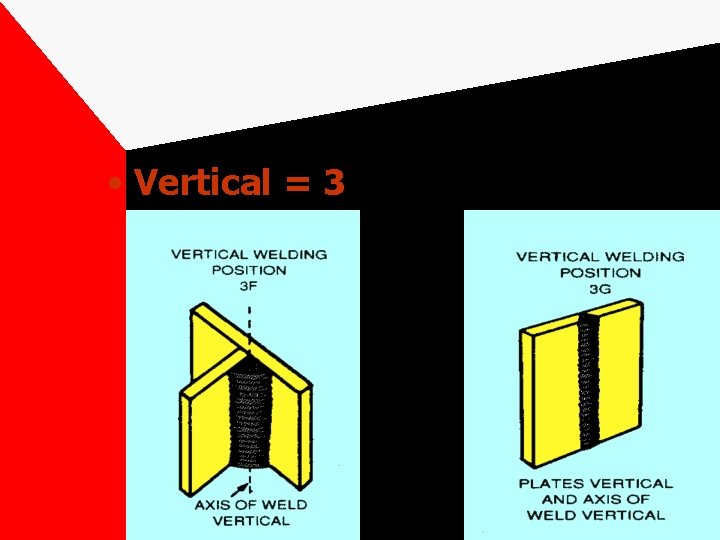
• Vertical = 3
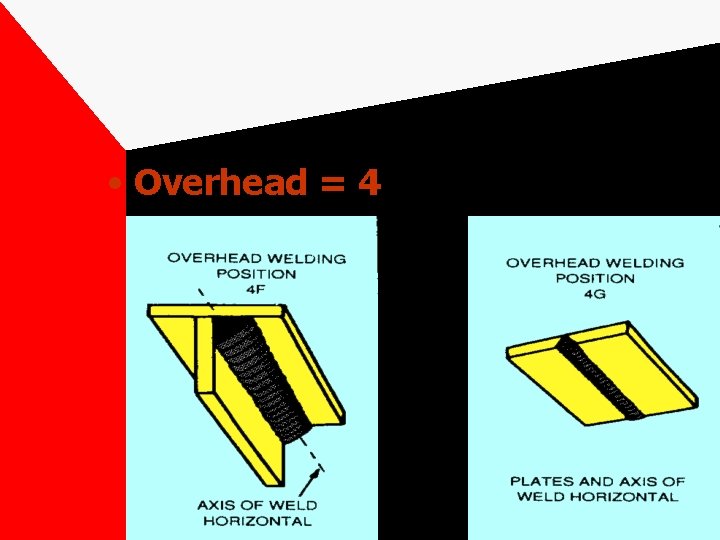
• Overhead = 4
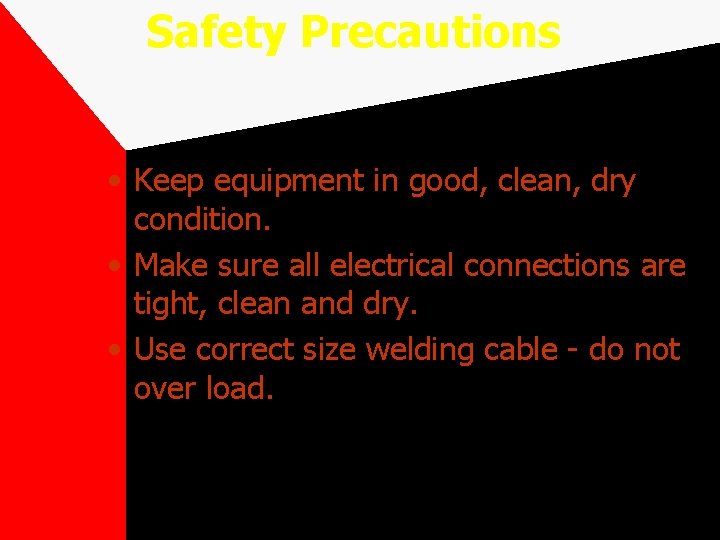
Safety Precautions • Keep equipment in good, clean, dry condition. • Make sure all electrical connections are tight, clean and dry. • Use correct size welding cable - do not over load.
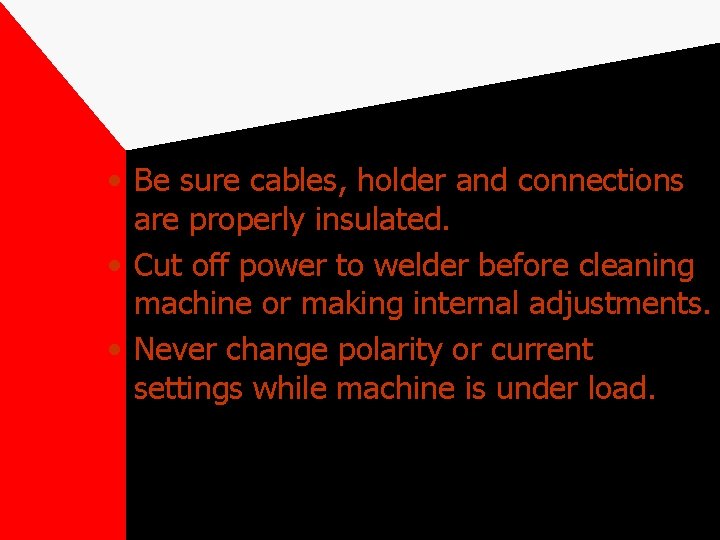
• Be sure cables, holder and connections are properly insulated. • Cut off power to welder before cleaning machine or making internal adjustments. • Never change polarity or current settings while machine is under load.
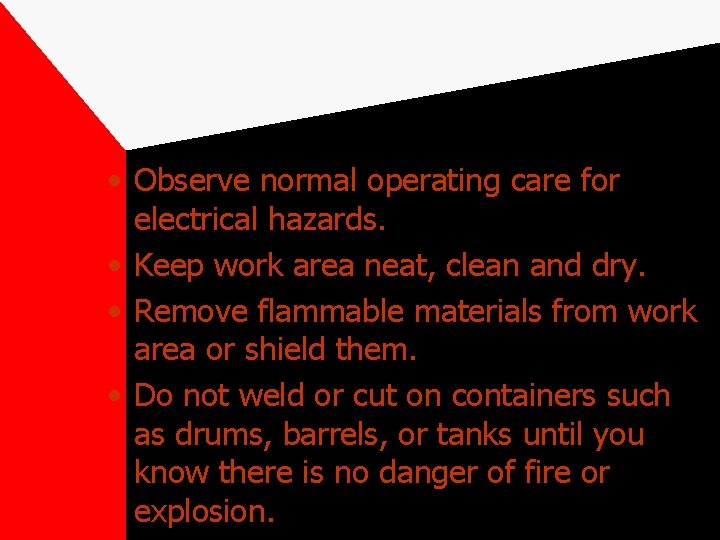
• Observe normal operating care for electrical hazards. • Keep work area neat, clean and dry. • Remove flammable materials from work area or shield them. • Do not weld or cut on containers such as drums, barrels, or tanks until you know there is no danger of fire or explosion.
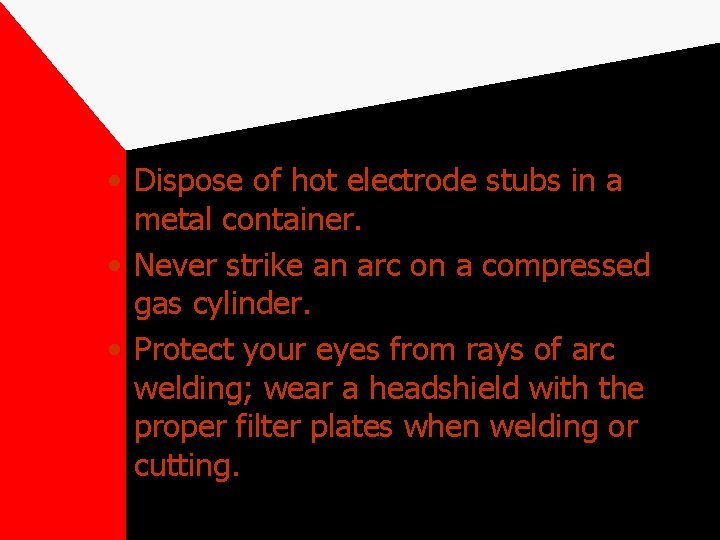
• Dispose of hot electrode stubs in a metal container. • Never strike an arc on a compressed gas cylinder. • Protect your eyes from rays of arc welding; wear a headshield with the proper filter plates when welding or cutting.
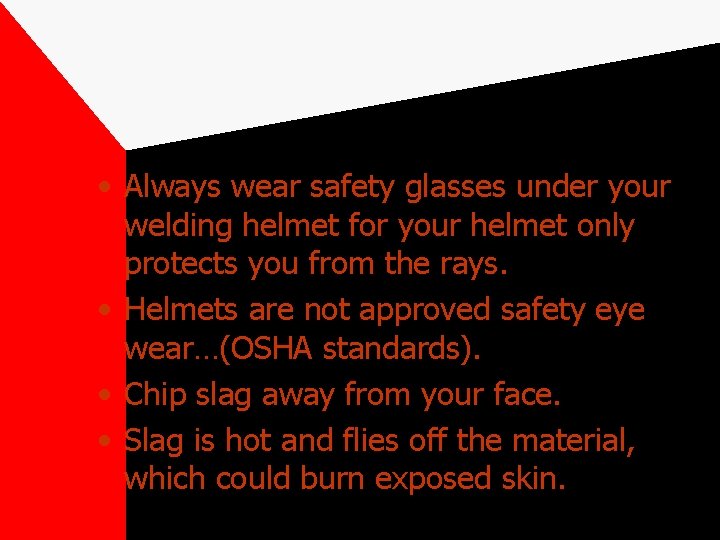
• Always wear safety glasses under your welding helmet for your helmet only protects you from the rays. • Helmets are not approved safety eye wear…(OSHA standards). • Chip slag away from your face. • Slag is hot and flies off the material, which could burn exposed skin.
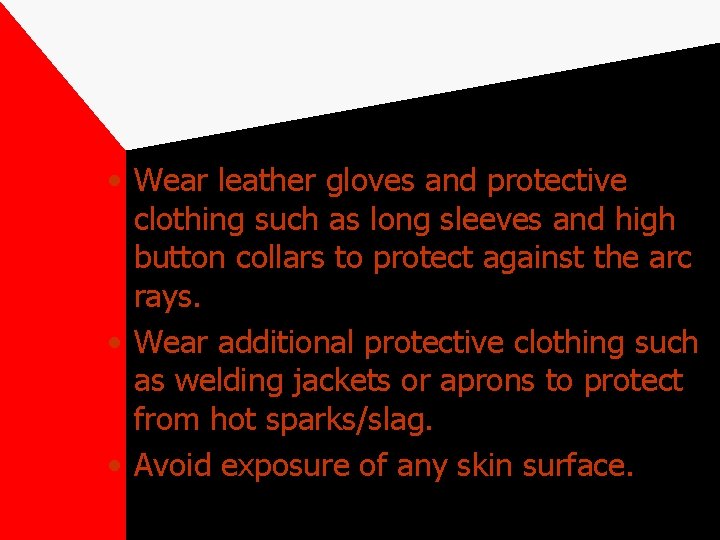
• Wear leather gloves and protective clothing such as long sleeves and high button collars to protect against the arc rays. • Wear additional protective clothing such as welding jackets or aprons to protect from hot sparks/slag. • Avoid exposure of any skin surface.
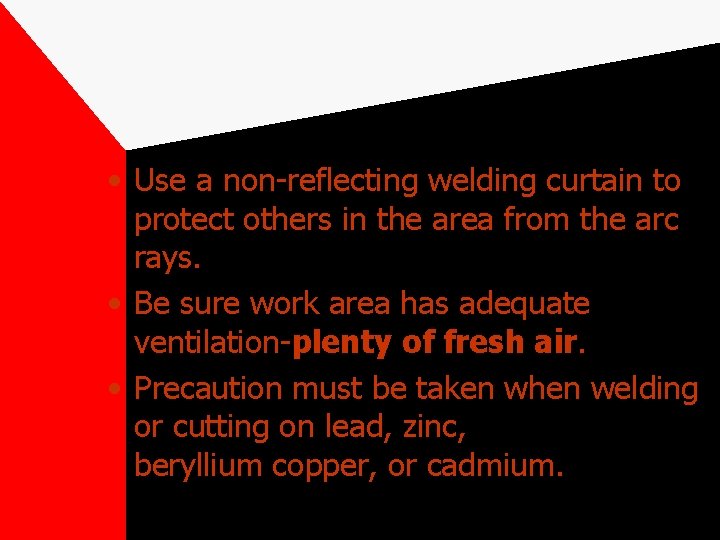
• Use a non-reflecting welding curtain to protect others in the area from the arc rays. • Be sure work area has adequate ventilation-plenty of fresh air. • Precaution must be taken when welding or cutting on lead, zinc, beryllium copper, or cadmium.
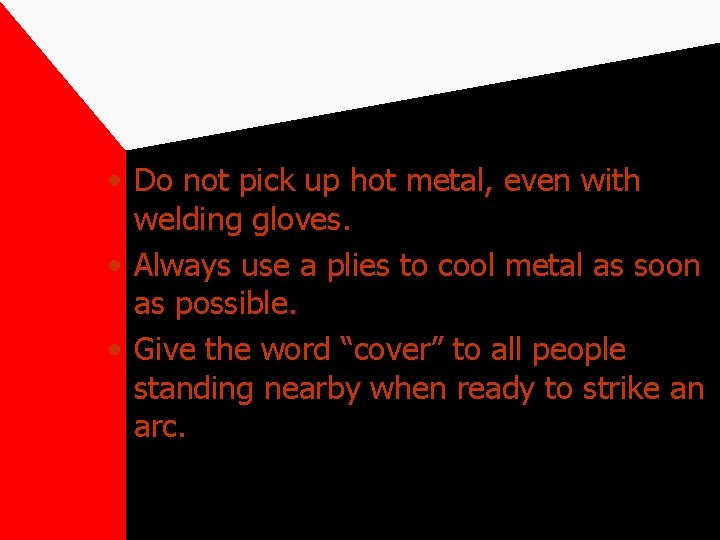
• Do not pick up hot metal, even with welding gloves. • Always use a plies to cool metal as soon as possible. • Give the word “cover” to all people standing nearby when ready to strike an arc.
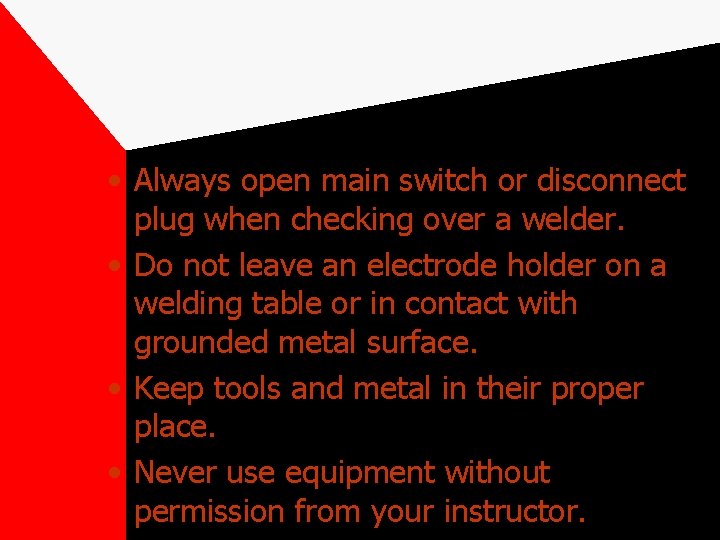
• Always open main switch or disconnect plug when checking over a welder. • Do not leave an electrode holder on a welding table or in contact with grounded metal surface. • Keep tools and metal in their proper place. • Never use equipment without permission from your instructor.
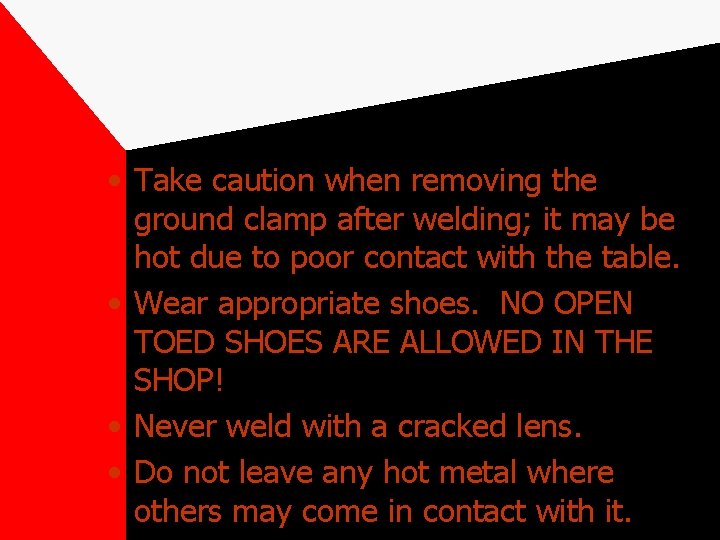
• Take caution when removing the ground clamp after welding; it may be hot due to poor contact with the table. • Wear appropriate shoes. NO OPEN TOED SHOES ARE ALLOWED IN THE SHOP! • Never weld with a cracked lens. • Do not leave any hot metal where others may come in contact with it.
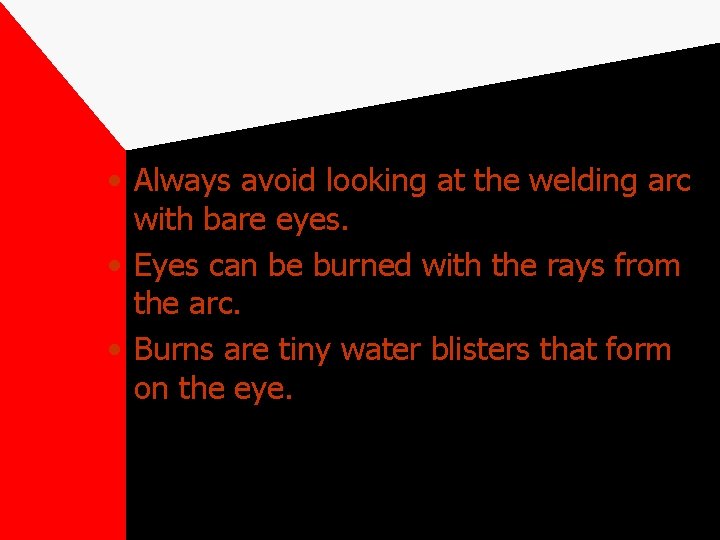
• Always avoid looking at the welding arc with bare eyes. • Eyes can be burned with the rays from the arc. • Burns are tiny water blisters that form on the eye.
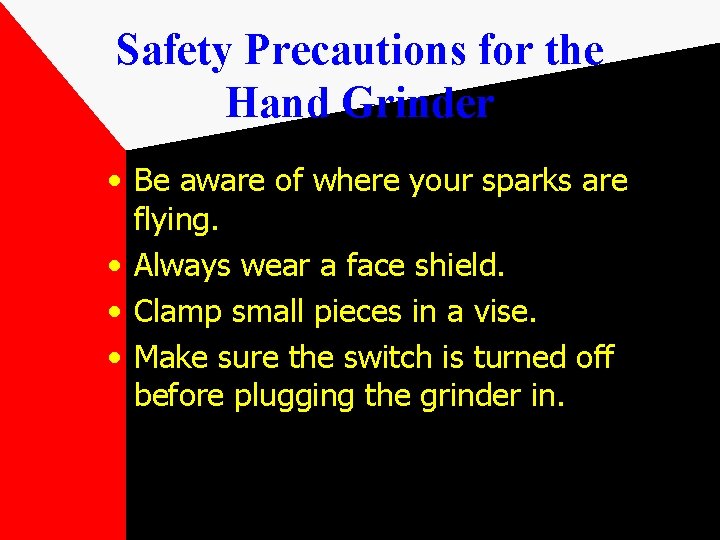
Safety Precautions for the Hand Grinder • Be aware of where your sparks are flying. • Always wear a face shield. • Clamp small pieces in a vise. • Make sure the switch is turned off before plugging the grinder in.
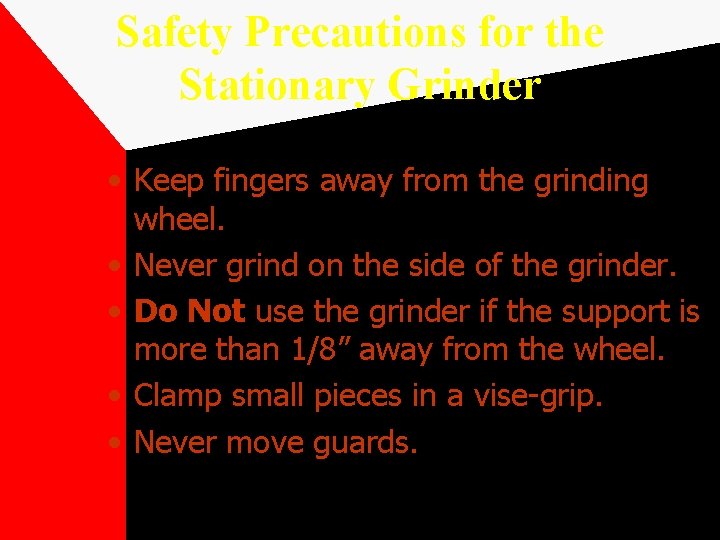
Safety Precautions for the Stationary Grinder • Keep fingers away from the grinding wheel. • Never grind on the side of the grinder. • Do Not use the grinder if the support is more than 1/8” away from the wheel. • Clamp small pieces in a vise-grip. • Never move guards.
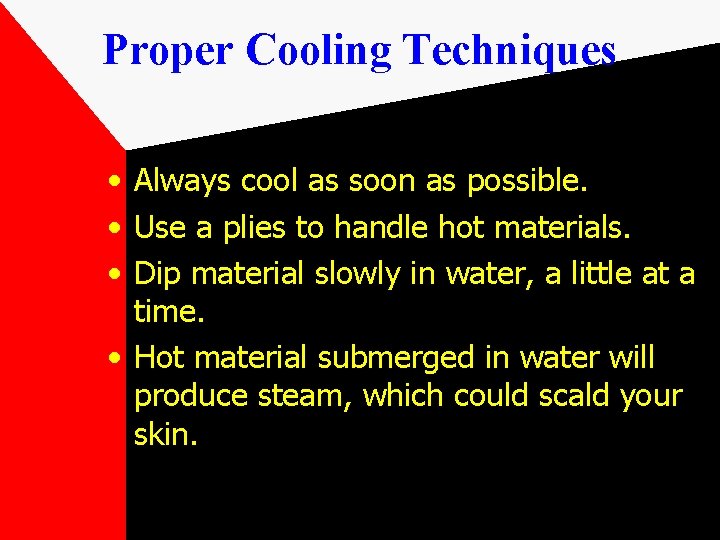
Proper Cooling Techniques • Always cool as soon as possible. • Use a plies to handle hot materials. • Dip material slowly in water, a little at a time. • Hot material submerged in water will produce steam, which could scald your skin.
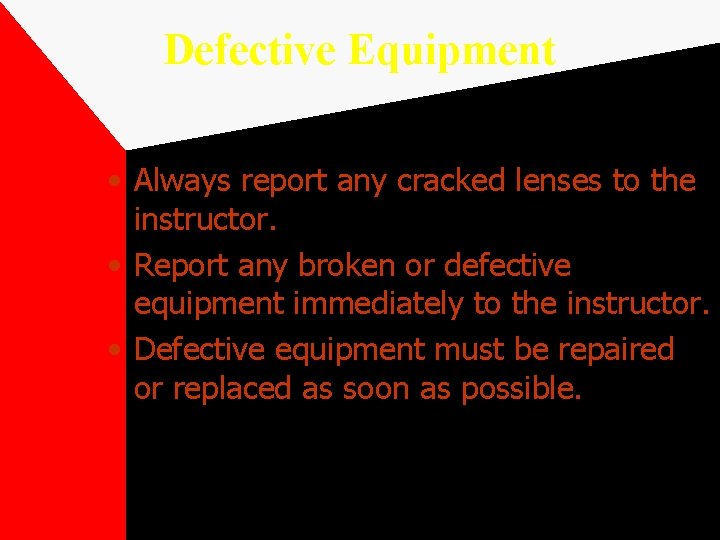
Defective Equipment • Always report any cracked lenses to the instructor. • Report any broken or defective equipment immediately to the instructor. • Defective equipment must be repaired or replaced as soon as possible.
Mma welding
Shielded metal arc welding (smaw) definition
All of the heat produced by sma weld stays in the weld.
Principle of shielded metal arc welding
Shielded metal arc welding safety
Stringer or weave bead
Cover pass welding definition
Smaw is often referred to as
Arc welding objectives
In alternators the welding current is produced on the
Welding bead patterns
Chapter 6 advanced shielded metal arc welding
Shielded metal arc welding definition
Gas shielded arc welding
Metal cored arc welding
What is mig welding
Smaw welding lesson plans
Smaw safety
Smaw pipe welding
Minor and major arcs
What is the arc
Arc emu88 com arc info 47 100047 html
Arc promoteur vs arc investigateur
Css meaning
Economic comparative and superlative
Secondary stresses in roof trusses
Have it your way slogan
Economical comparative and superlative
Thousands of possibilities get yours slogan
Beautiful paradise economical are examples
Traditional economic system example
Planning business messages chapter 2
El sodio es metal o no metal
Metal and nonmetal
Spraggins fitness
Dp periodic table
Pure substance periodic table
Características de los gases nobles
Melting point of nonmetals
Metals react with nonmetals to form ionic compounds by
Solid liquid gas venn diagram
Examples of non metals
Metal 1 metal 2
Grupo b tabla periódica
Metals vs nonmetals properties
Chapter 2 welding safety quiz answers
Ppe for arc welding
Principle of electric arc welding
Resistance welding basics
Objectives of welding
Groover
Plasma transferred arc welding equipment
Resistance arc welding
Fusion arc welding
Joan of arc heretic
Arc welding introduction
Paw welding process
Welding flux definition
Tungsten contamination
Tig (tungsten inert gas)
Resistance arc welding
Principle of arc welding
Welding chapter 13 answers
Shielded storage store
Reactivity series anagram
Brazing weld symbol
Smaw equipment set up
Smaw-d missile
Pengertian teknik las
Smaw unit
Smaw electrode designation
Surface weld symbol
Most welding environment fires occur during
Aqeedah
Guddi baji
In the name of allah the most gracious the most merciful
Almighty allah the most merciful
In the name of god most gracious prayer
Most general to most specific classification
In the name of allah the beneficent the merciful in arabic
Most general to most specific classification
The most
In the name of allah the most beneficent the most merciful
Arrangement of organisms
In the name of god most gracious most merciful
Most general to most specific classification
Beneficent pronunciation
In the name of god, most gracious, most merciful prayer
Angle subtended by an arc
Arc processing
Fracture voillemier
How to find length of arc
Blind arc
Spinal cord anatomy
M.i.a.
Circumference