Shielded Metal Arc Welding SMAW Arc welding Heat
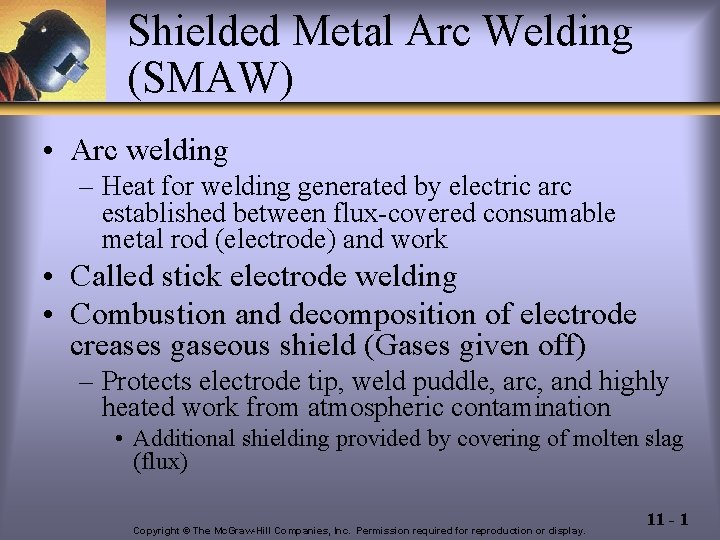
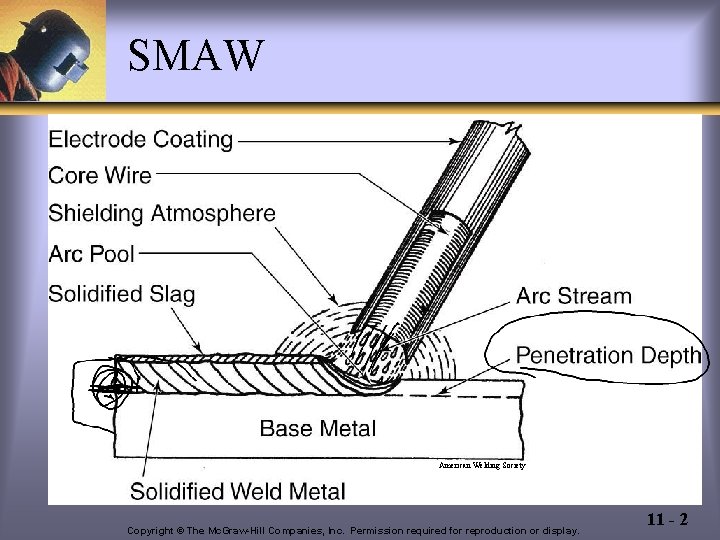
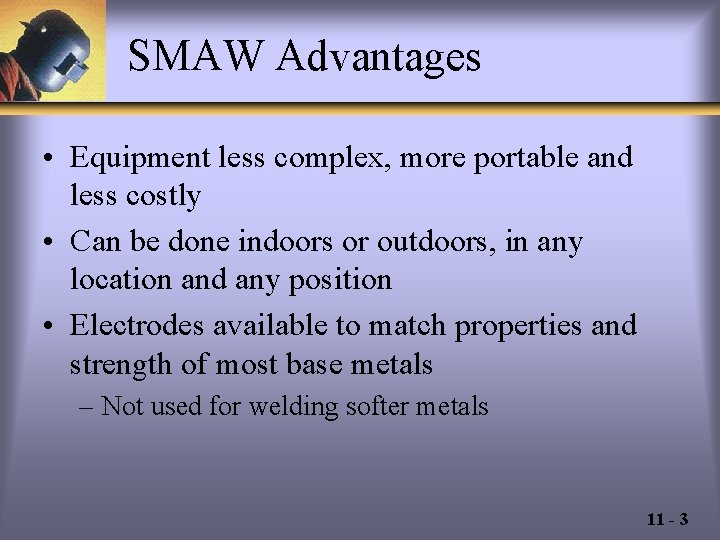
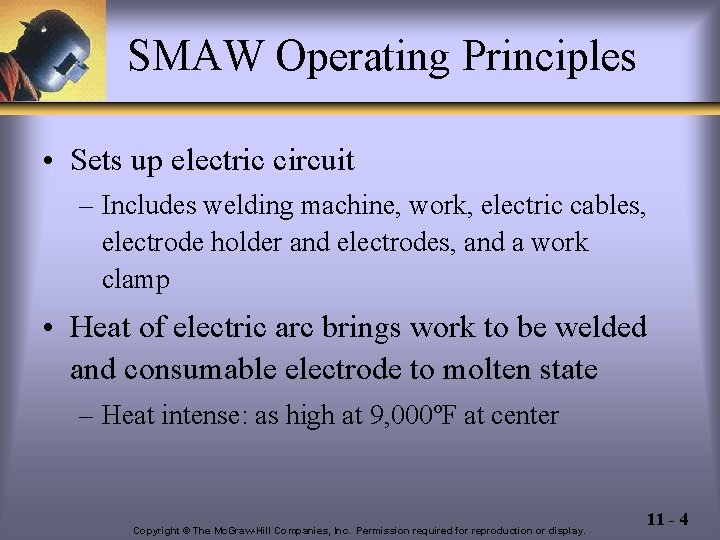
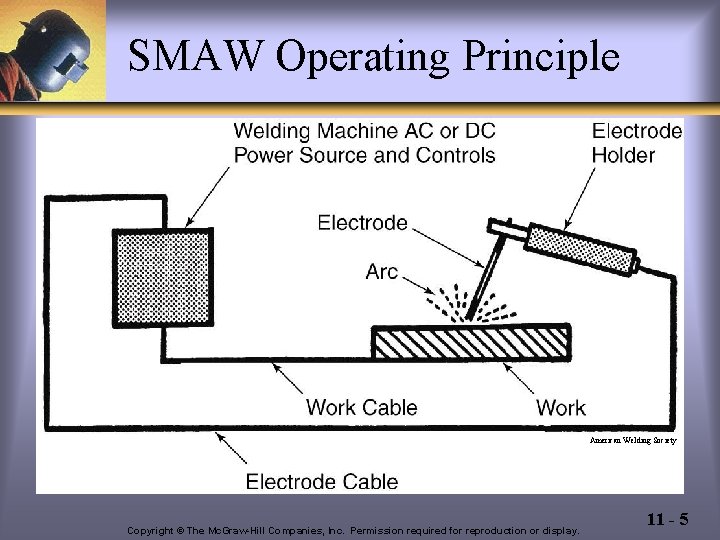
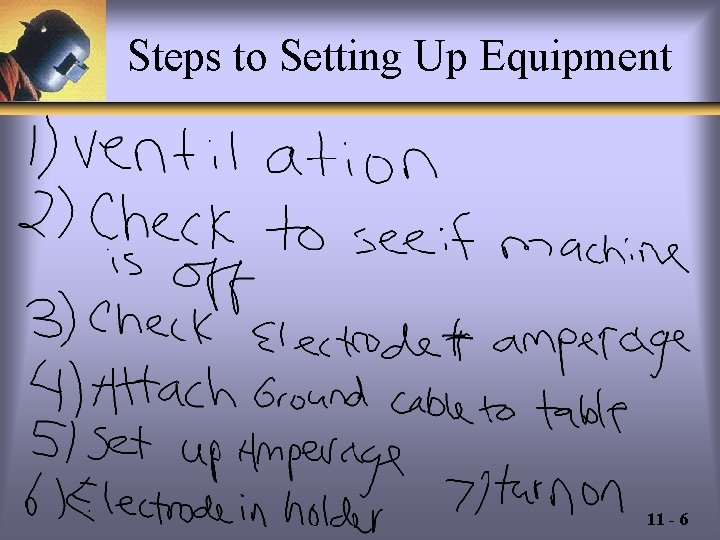
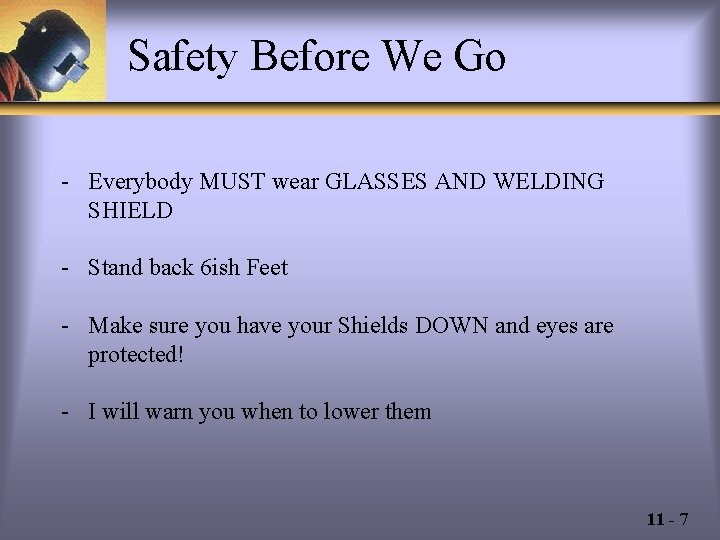
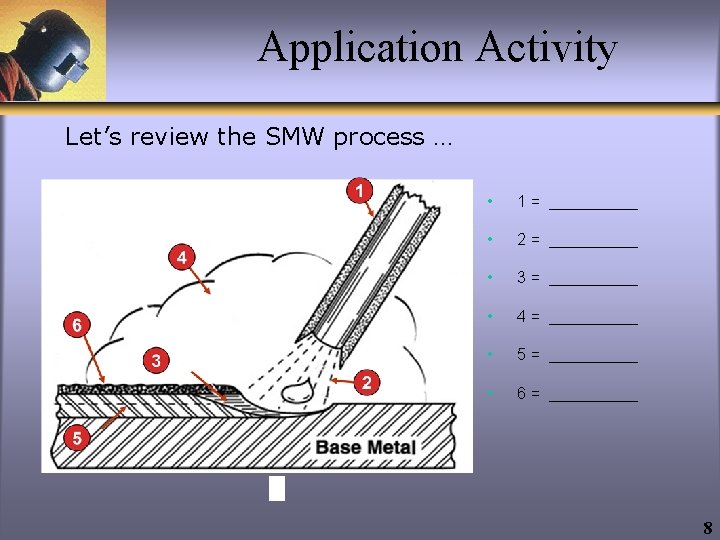
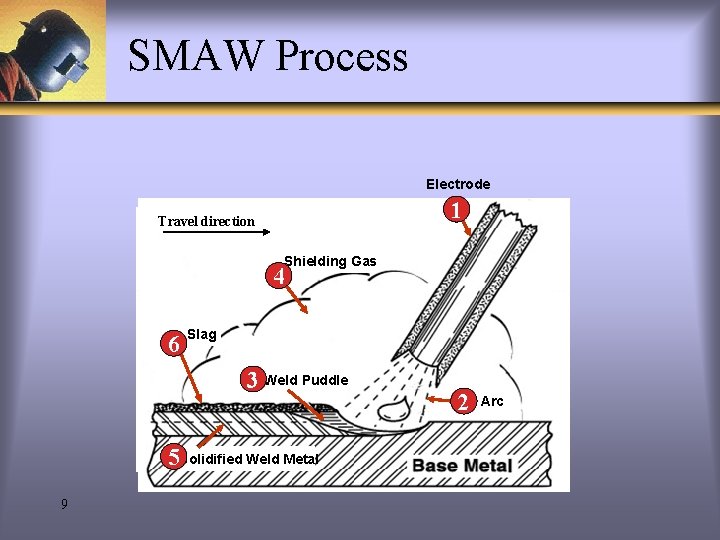
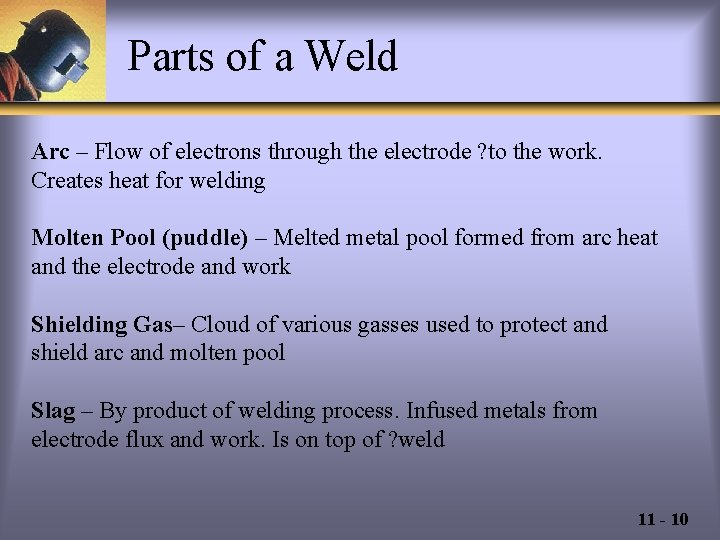
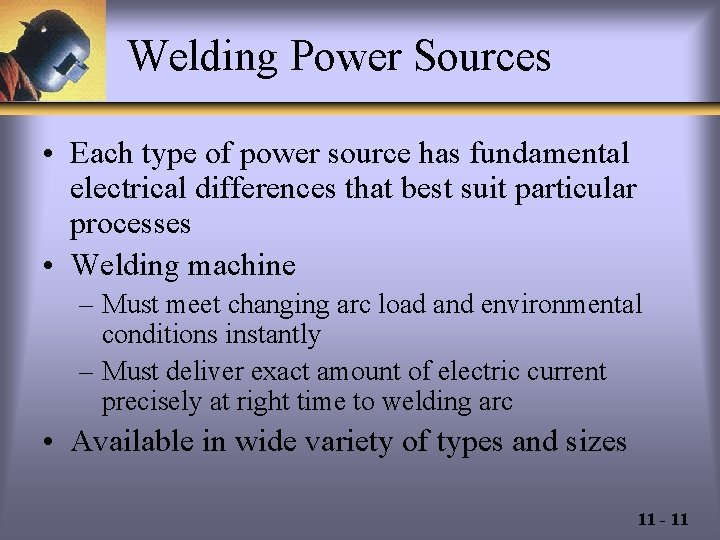
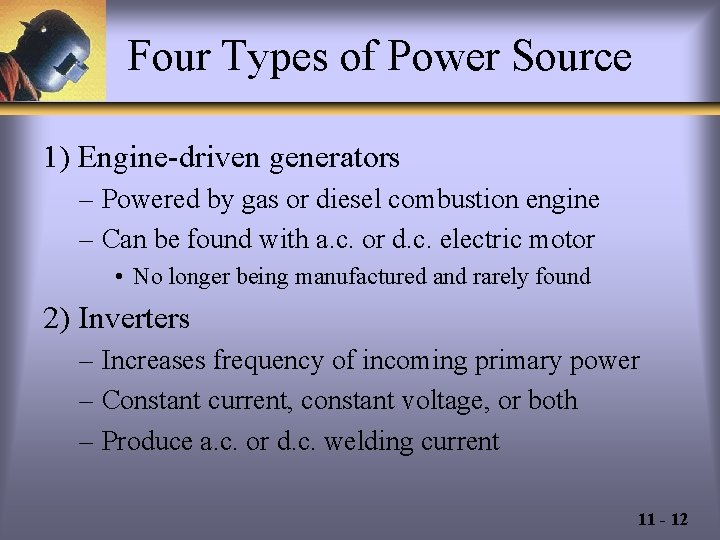
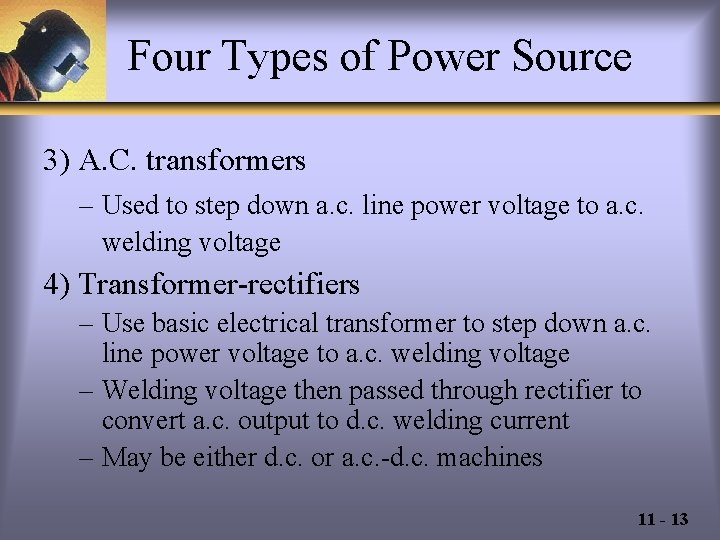
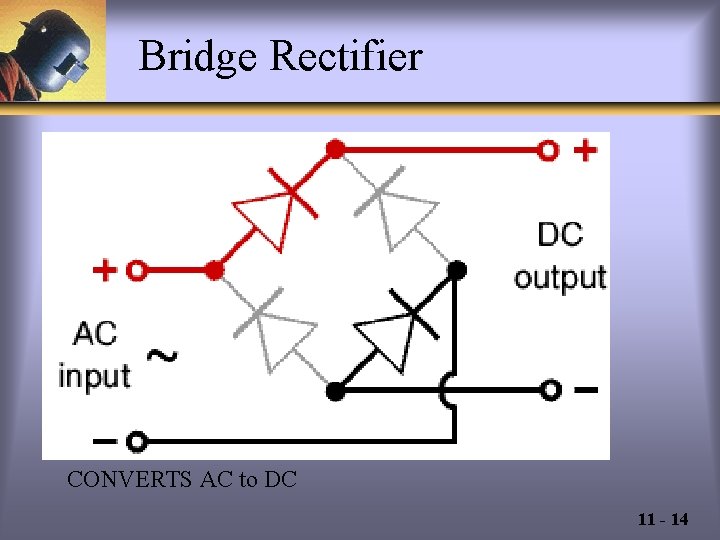
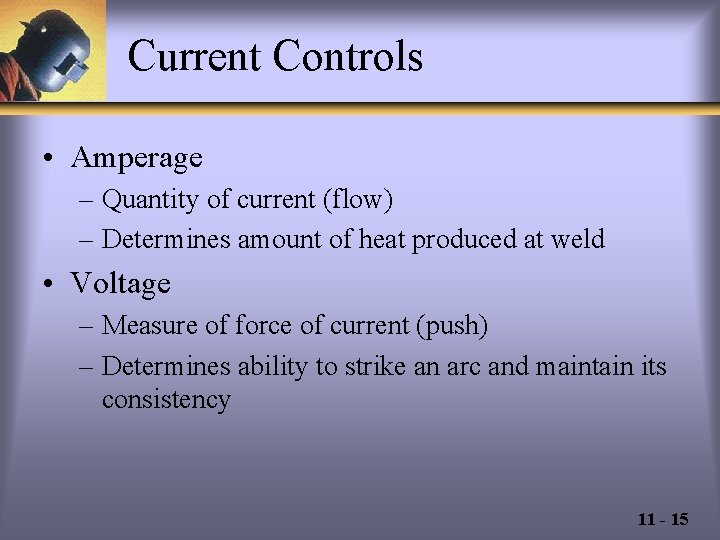
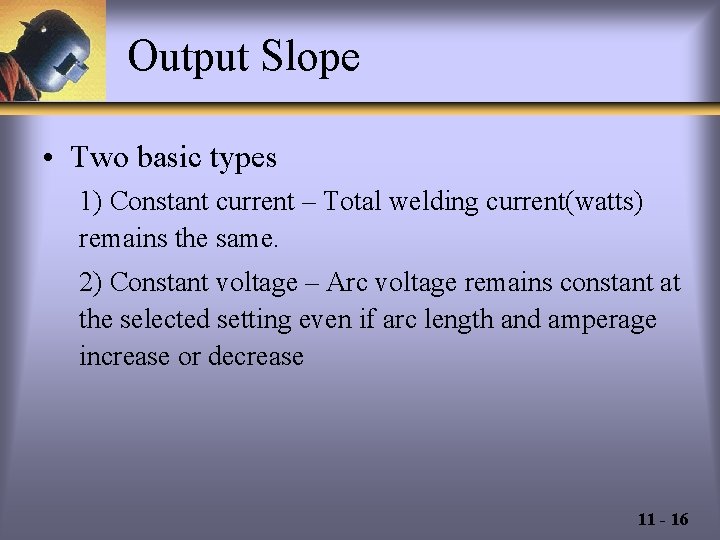
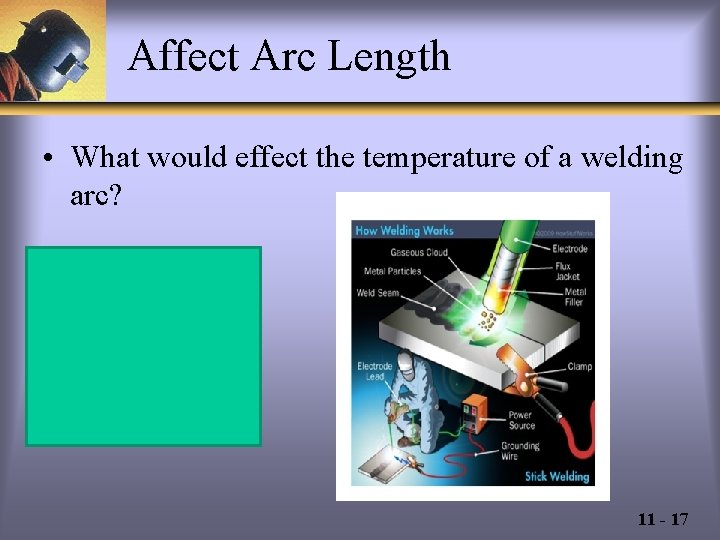
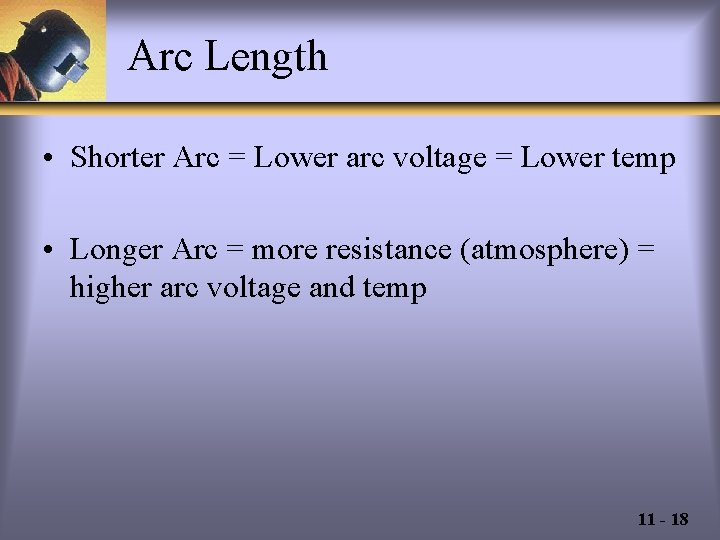
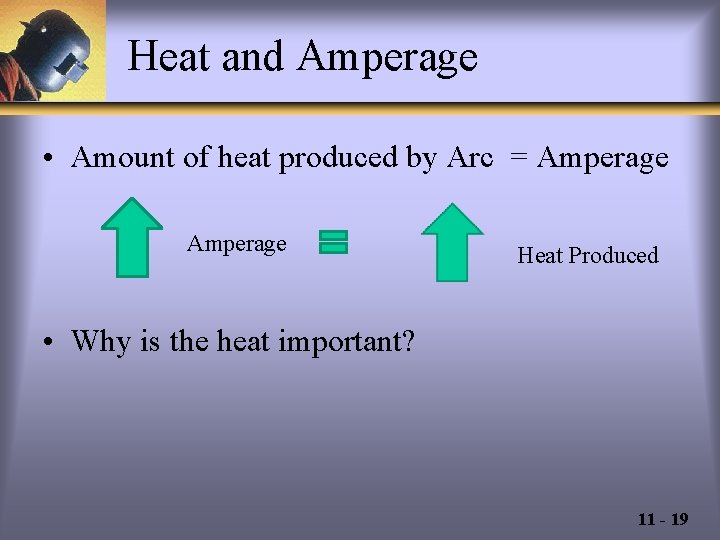
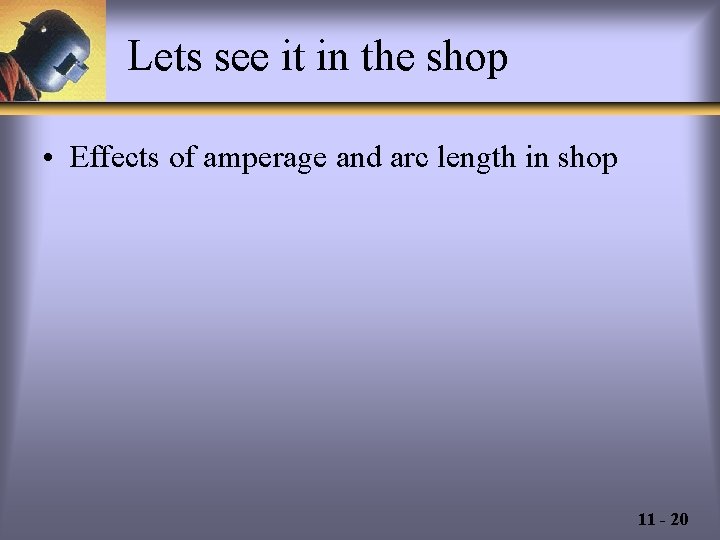
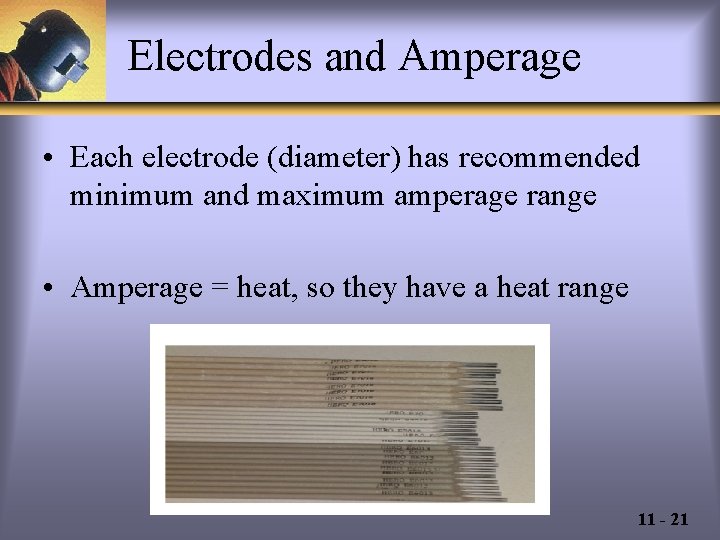
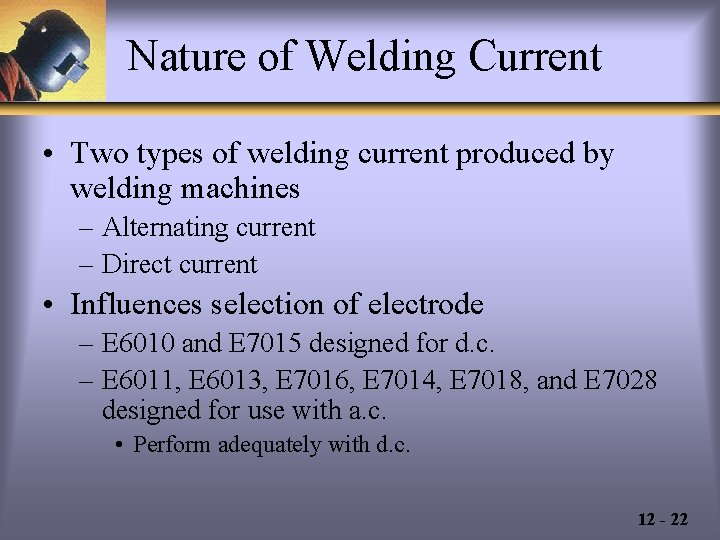
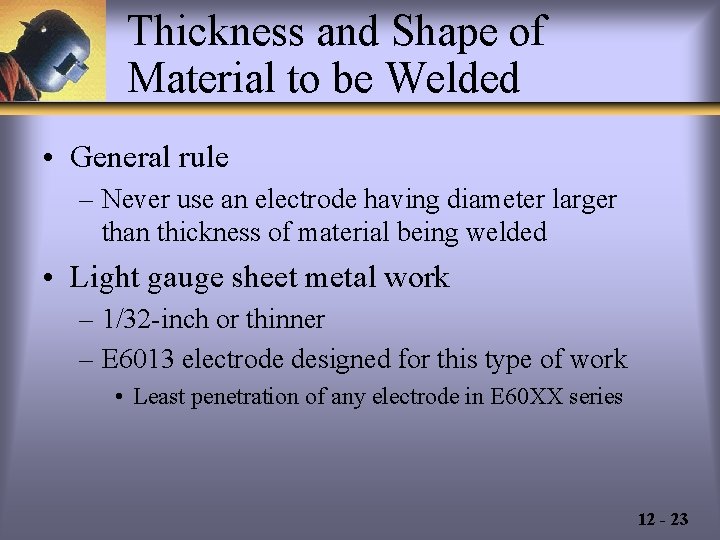
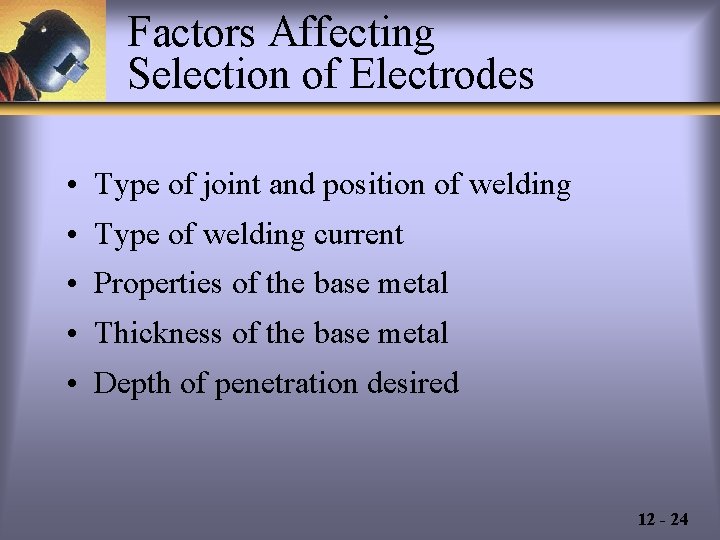
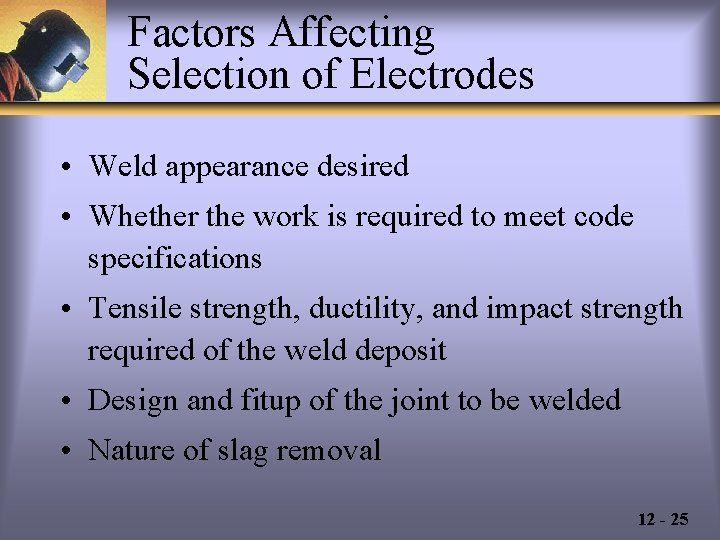
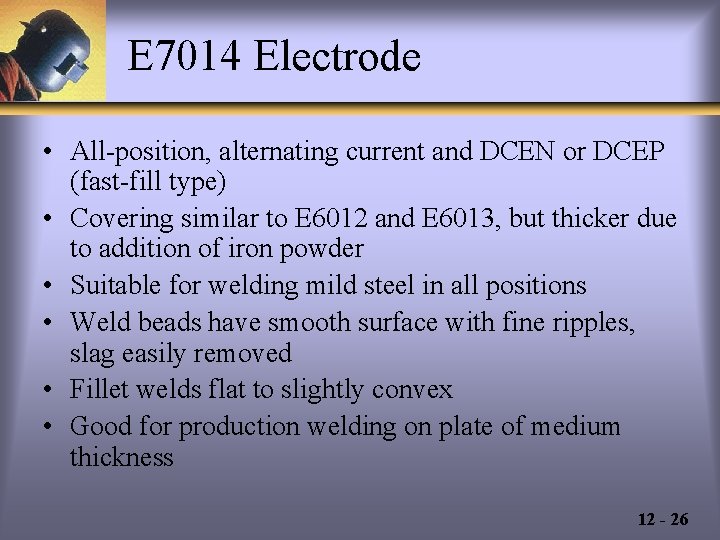
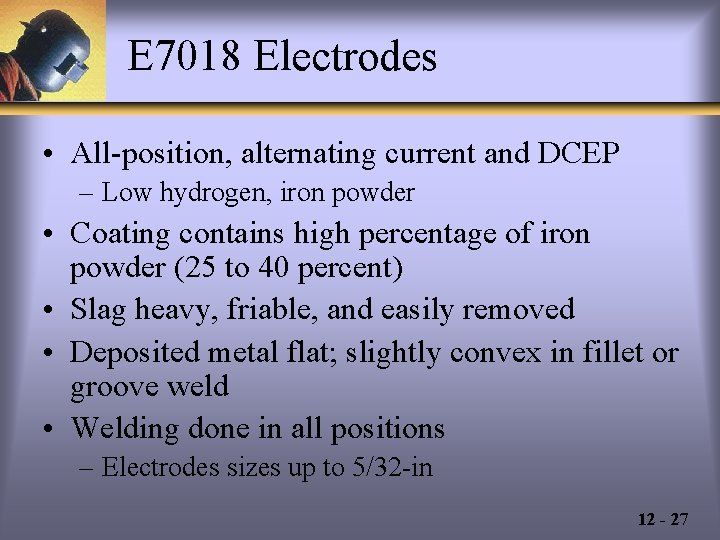
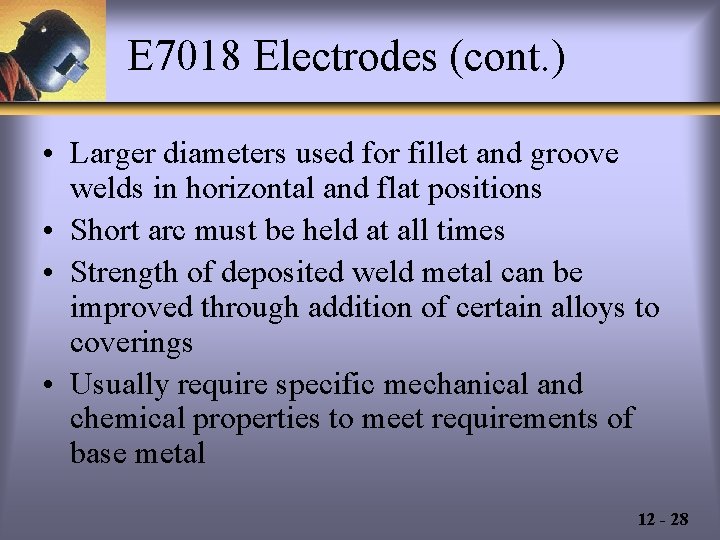
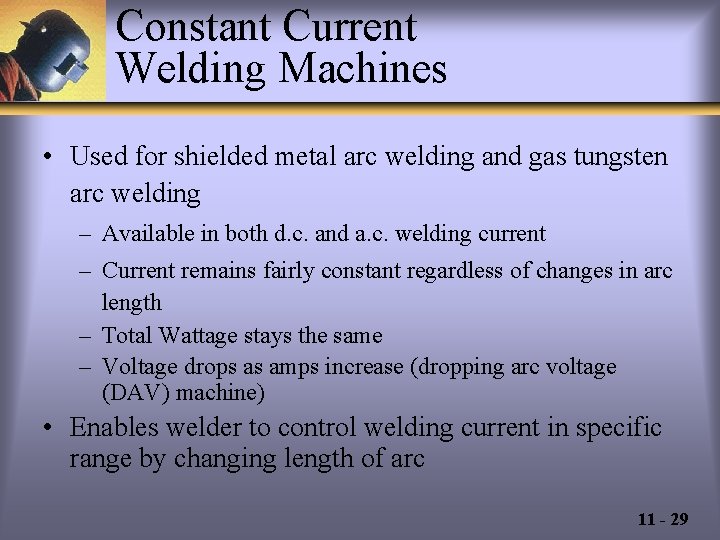
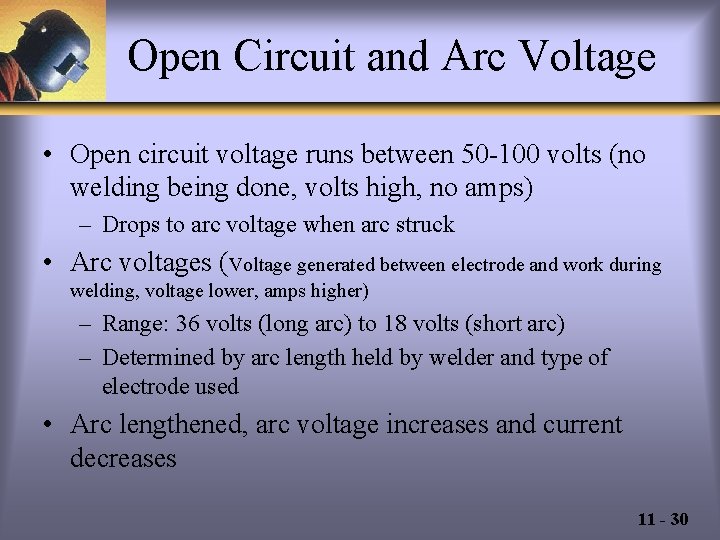
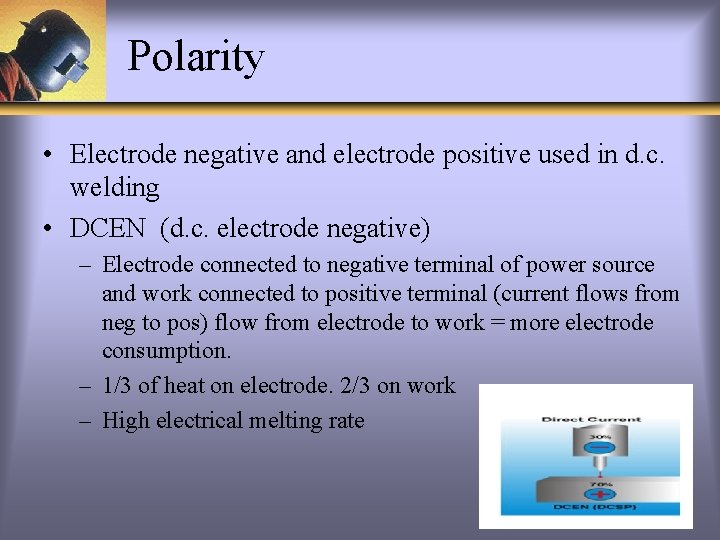
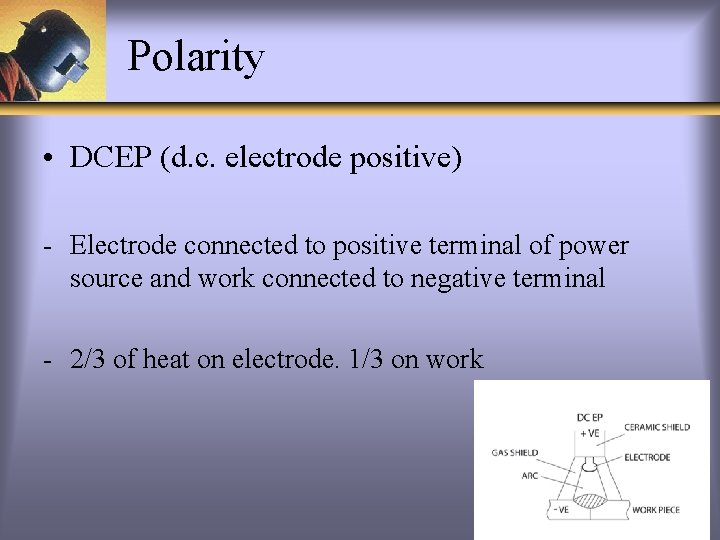
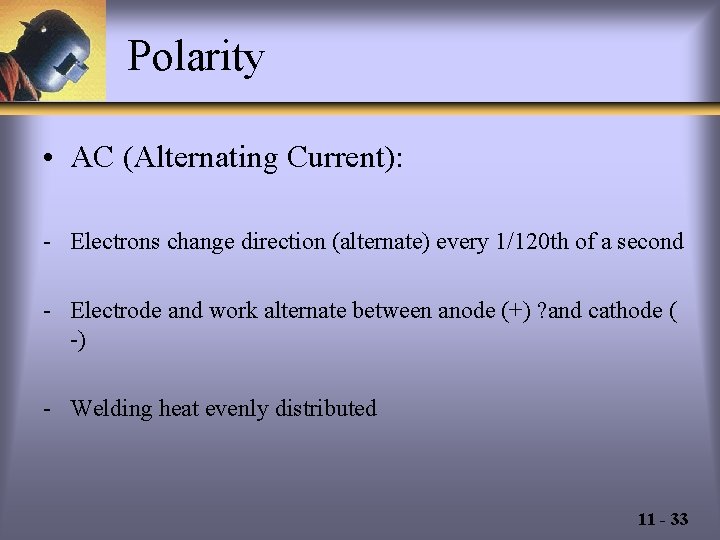
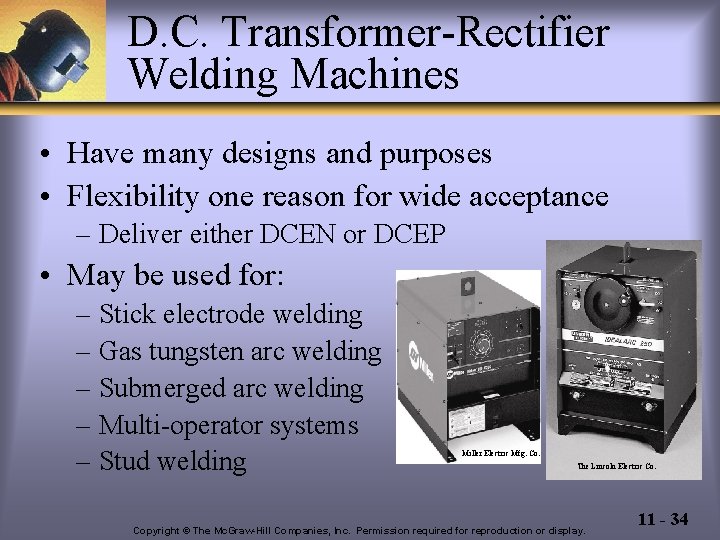
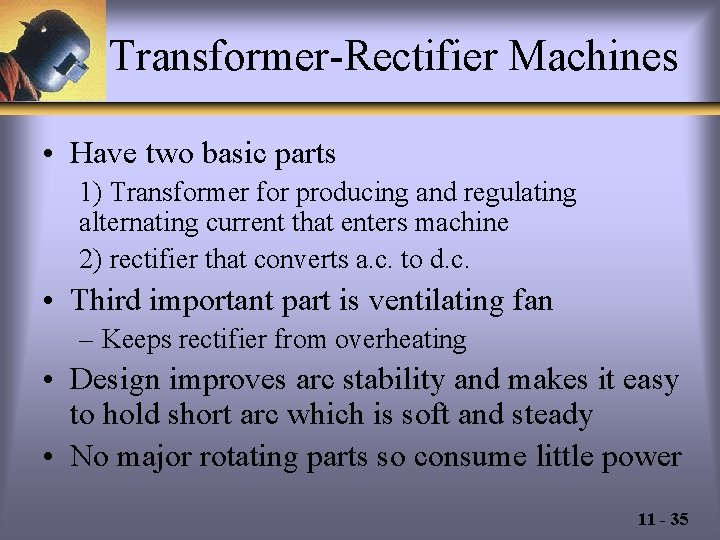
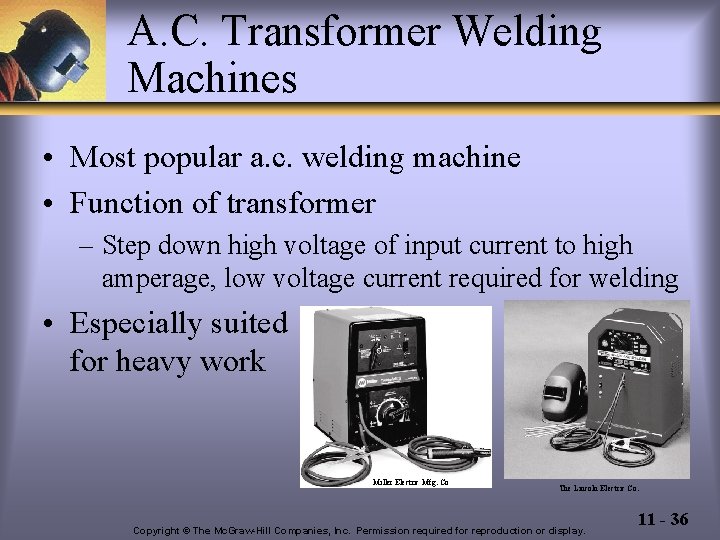
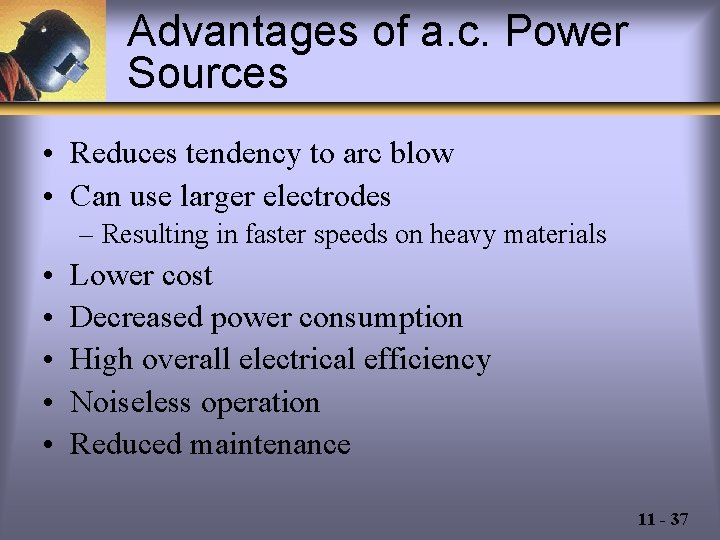
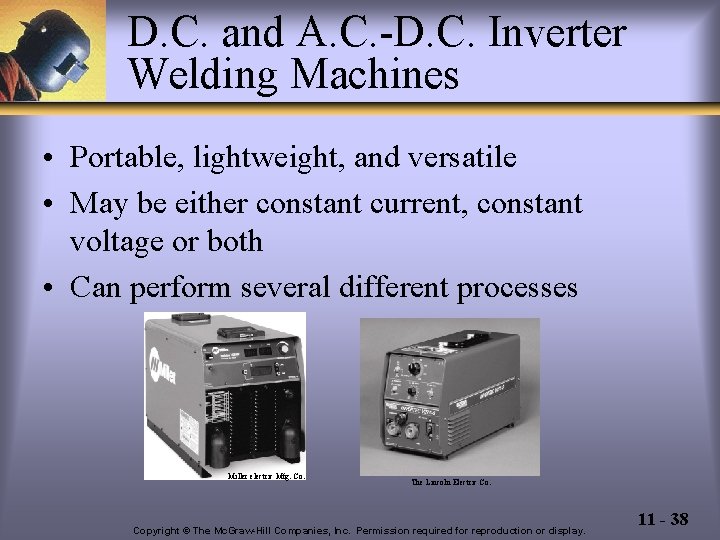
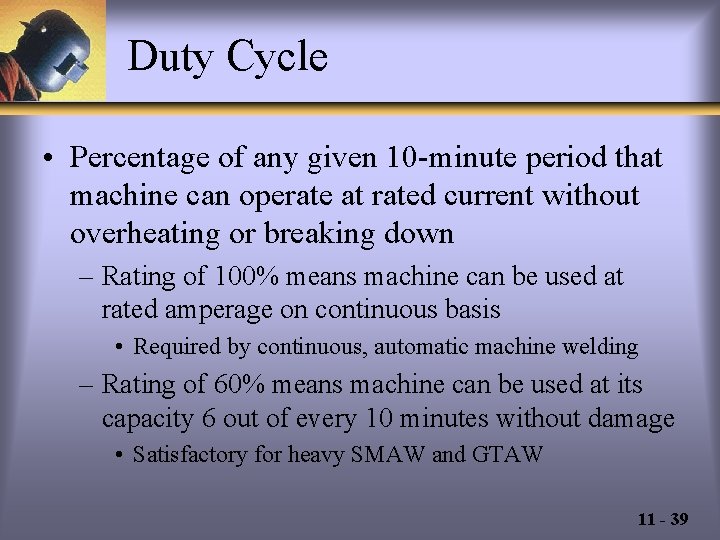
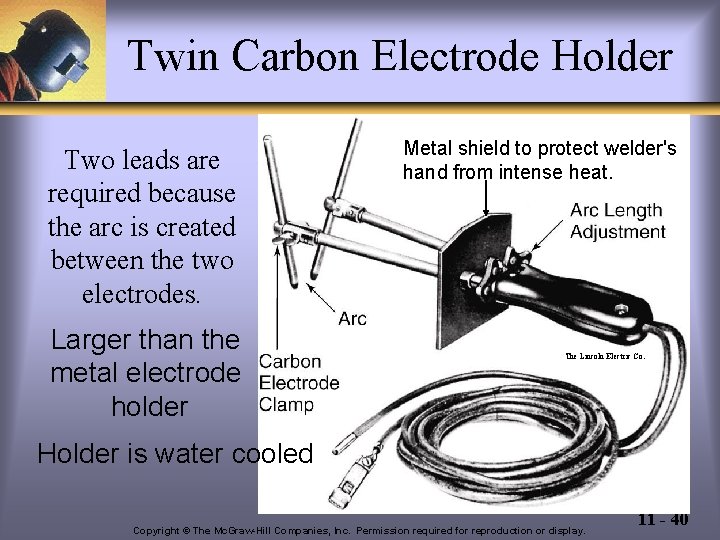
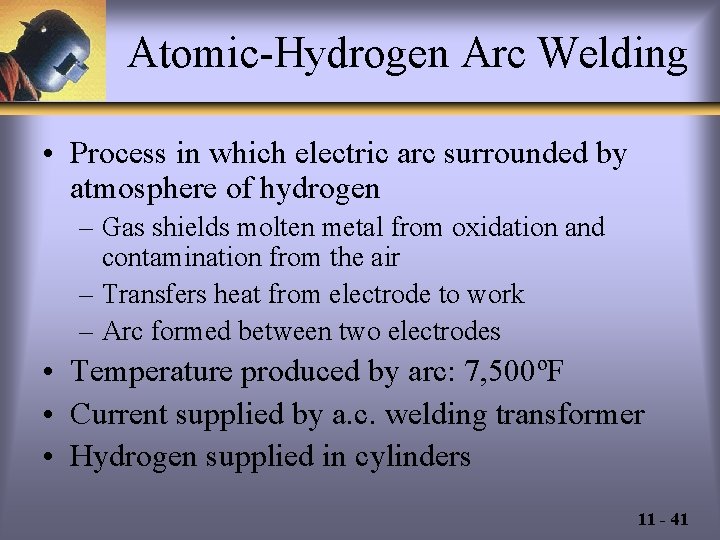
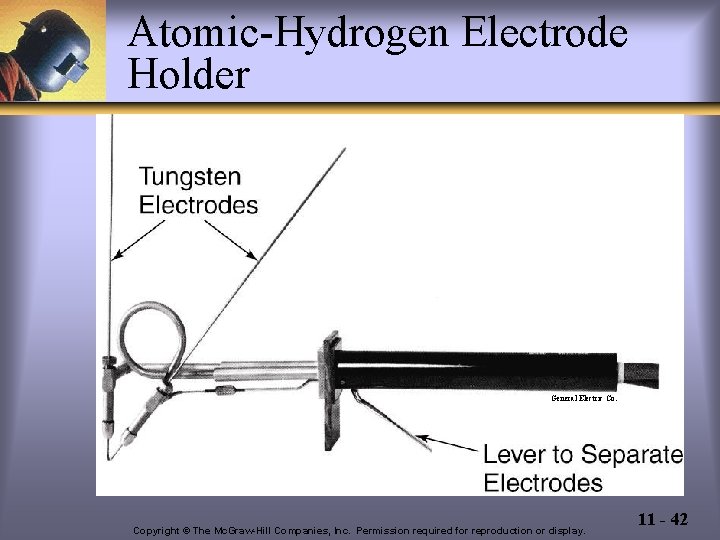
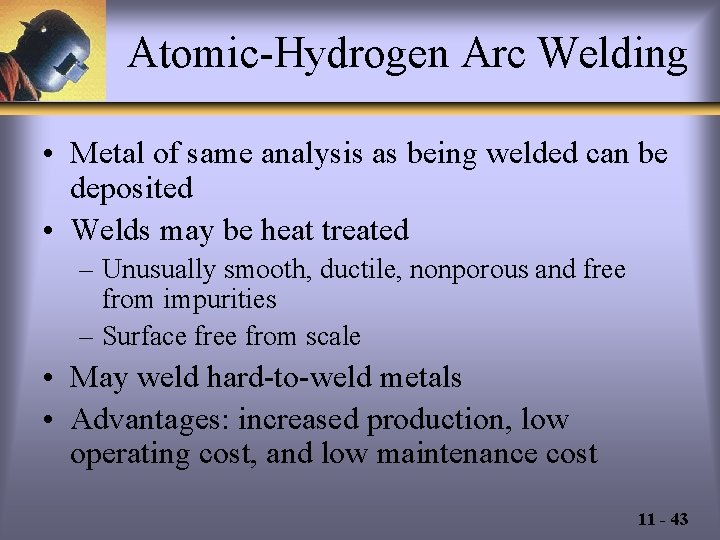
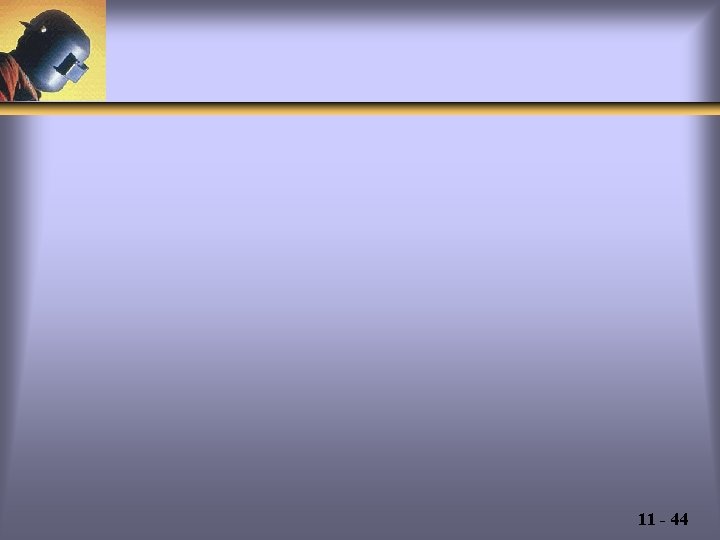
- Slides: 44
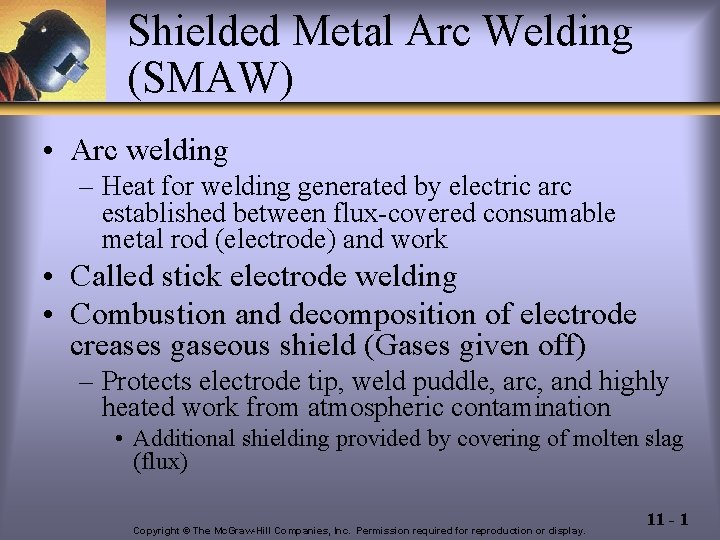
Shielded Metal Arc Welding (SMAW) • Arc welding – Heat for welding generated by electric arc established between flux-covered consumable metal rod (electrode) and work • Called stick electrode welding • Combustion and decomposition of electrode creases gaseous shield (Gases given off) – Protects electrode tip, weld puddle, arc, and highly heated work from atmospheric contamination • Additional shielding provided by covering of molten slag (flux) Copyright © The Mc. Graw-Hill Companies, Inc. Permission required for reproduction or display. 11 - 1
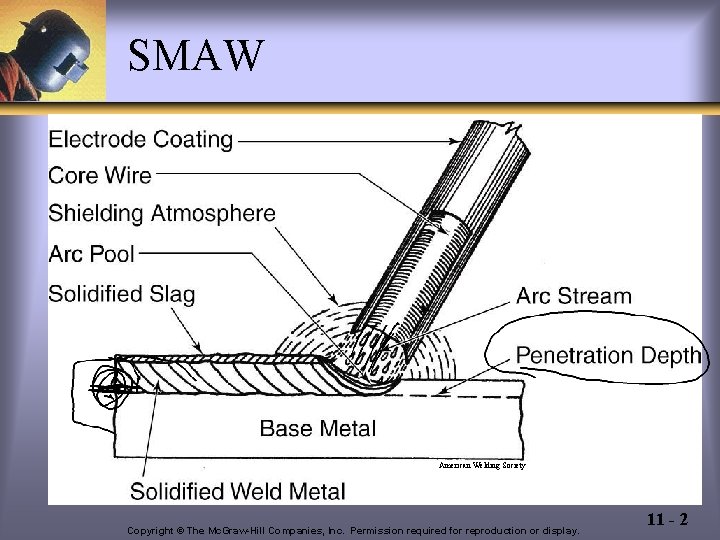
SMAW American Welding Society Copyright © The Mc. Graw-Hill Companies, Inc. Permission required for reproduction or display. 11 - 2
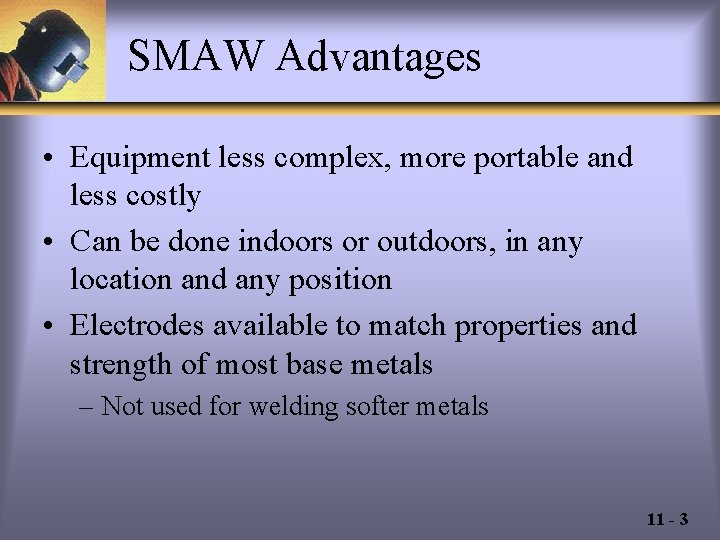
SMAW Advantages • Equipment less complex, more portable and less costly • Can be done indoors or outdoors, in any location and any position • Electrodes available to match properties and strength of most base metals – Not used for welding softer metals 11 - 3
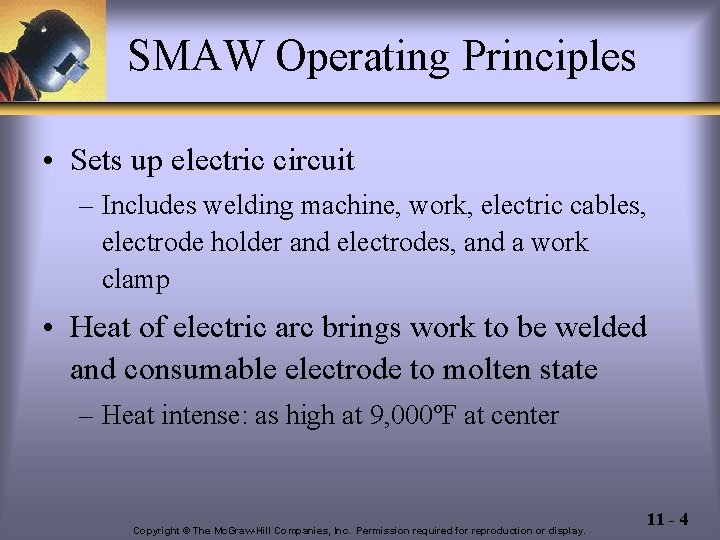
SMAW Operating Principles • Sets up electric circuit – Includes welding machine, work, electric cables, electrode holder and electrodes, and a work clamp • Heat of electric arc brings work to be welded and consumable electrode to molten state – Heat intense: as high at 9, 000ºF at center Copyright © The Mc. Graw-Hill Companies, Inc. Permission required for reproduction or display. 11 - 4
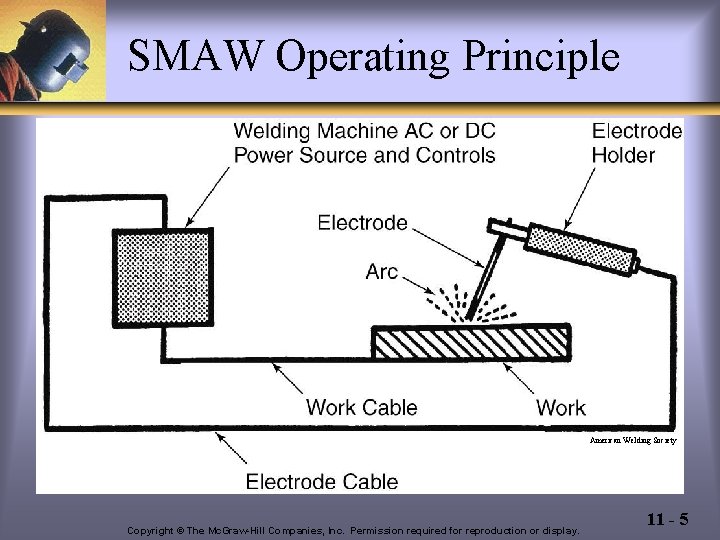
SMAW Operating Principle American Welding Society Copyright © The Mc. Graw-Hill Companies, Inc. Permission required for reproduction or display. 11 - 5
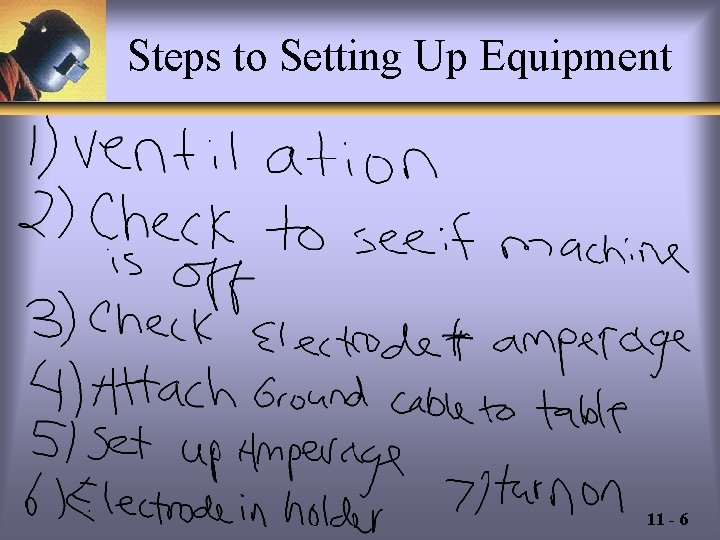
Steps to Setting Up Equipment 11 - 6
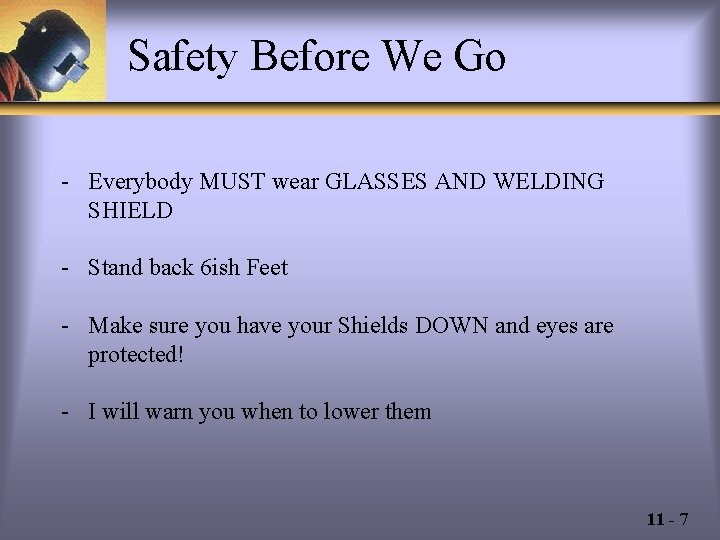
Safety Before We Go - Everybody MUST wear GLASSES AND WELDING SHIELD - Stand back 6 ish Feet - Make sure you have your Shields DOWN and eyes are protected! - I will warn you when to lower them 11 - 7
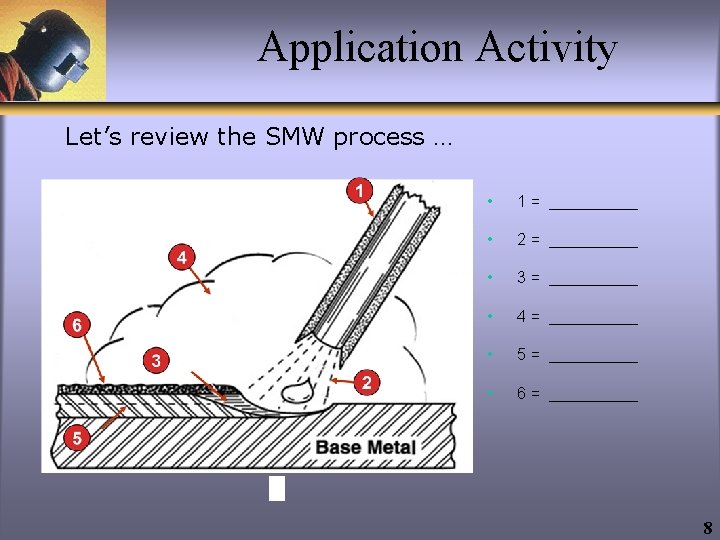
Application Activity Let’s review the SMW process … • 1 = _____ • 2 = _____ • 3 = _____ • 4 = _____ • 5 = _____ • 6 = _____ 8
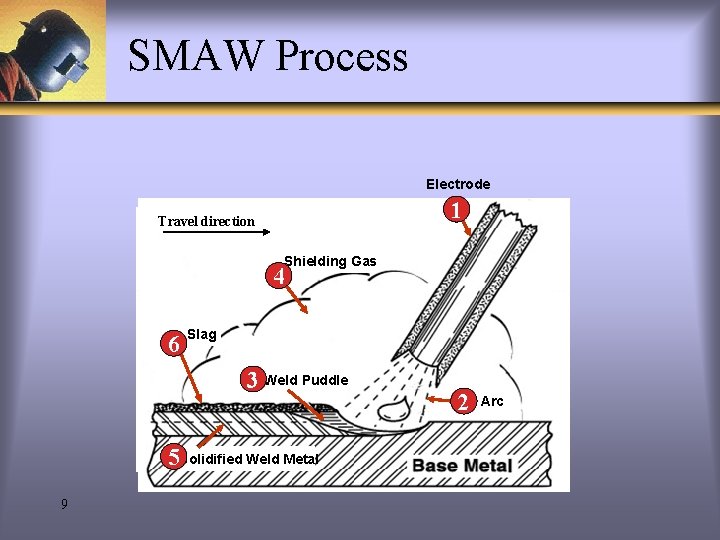
SMAW Process Electrode 1 Travel direction Shielding Gas 4 Slag 66 Slag 3 Weld Puddle 3 5 Solidified Weld Metal 9 2 2 Arc
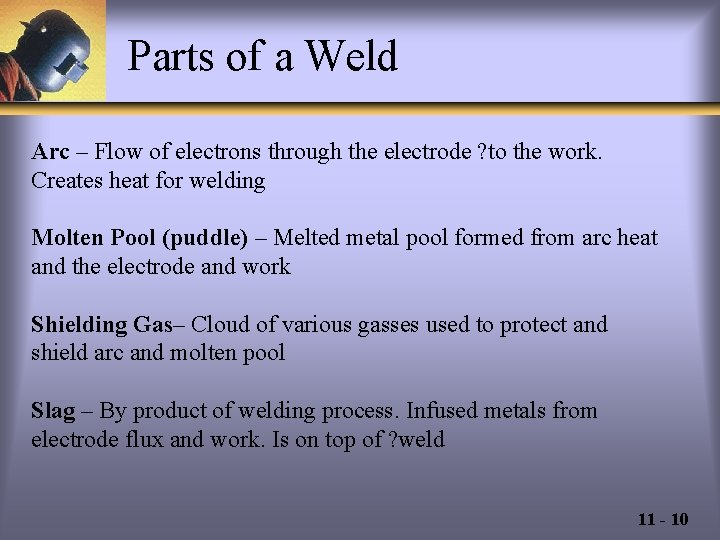
Parts of a Weld Arc – Flow of electrons through the electrode ? to the work. Creates heat for welding Molten Pool (puddle) – Melted metal pool formed from arc heat and the electrode and work Shielding Gas– Cloud of various gasses used to protect and shield arc and molten pool Slag – By product of welding process. Infused metals from electrode flux and work. Is on top of ? weld 11 - 10
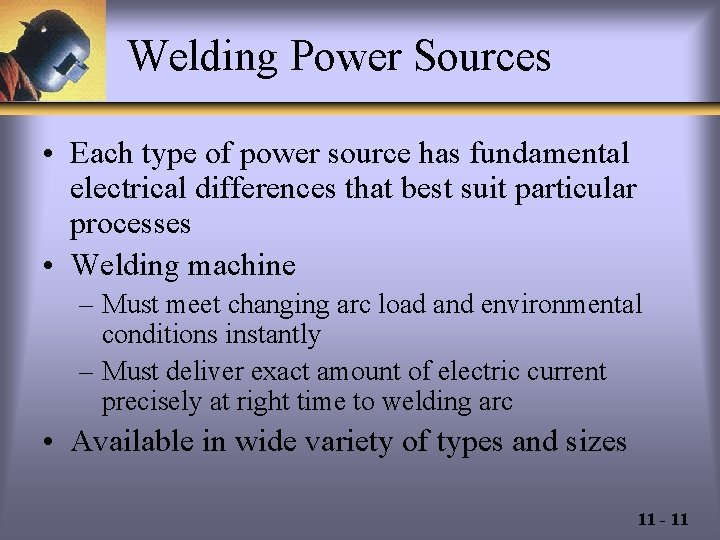
Welding Power Sources • Each type of power source has fundamental electrical differences that best suit particular processes • Welding machine – Must meet changing arc load and environmental conditions instantly – Must deliver exact amount of electric current precisely at right time to welding arc • Available in wide variety of types and sizes 11 - 11
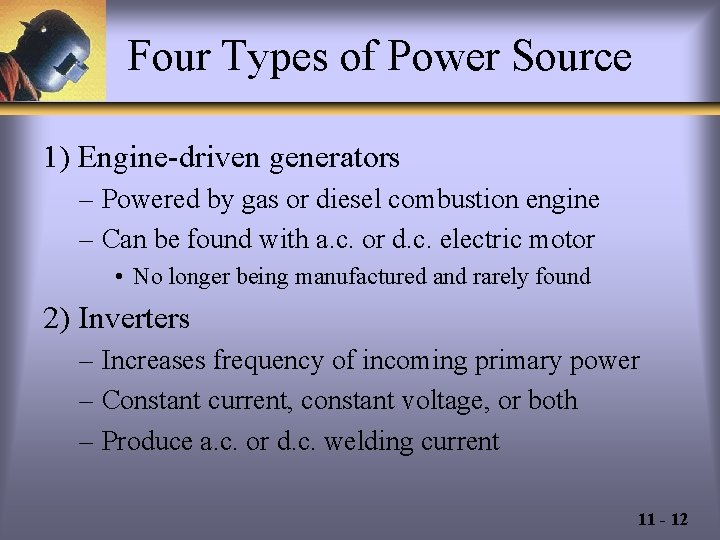
Four Types of Power Source 1) Engine-driven generators – Powered by gas or diesel combustion engine – Can be found with a. c. or d. c. electric motor • No longer being manufactured and rarely found 2) Inverters – Increases frequency of incoming primary power – Constant current, constant voltage, or both – Produce a. c. or d. c. welding current 11 - 12
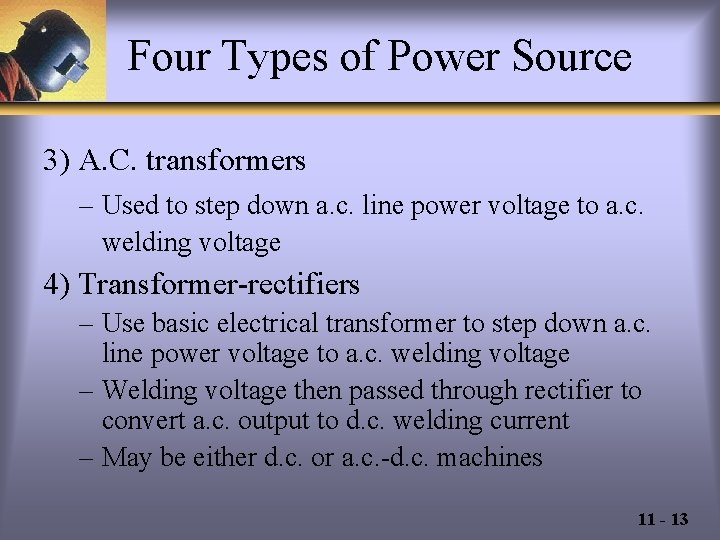
Four Types of Power Source 3) A. C. transformers – Used to step down a. c. line power voltage to a. c. welding voltage 4) Transformer-rectifiers – Use basic electrical transformer to step down a. c. line power voltage to a. c. welding voltage – Welding voltage then passed through rectifier to convert a. c. output to d. c. welding current – May be either d. c. or a. c. -d. c. machines 11 - 13
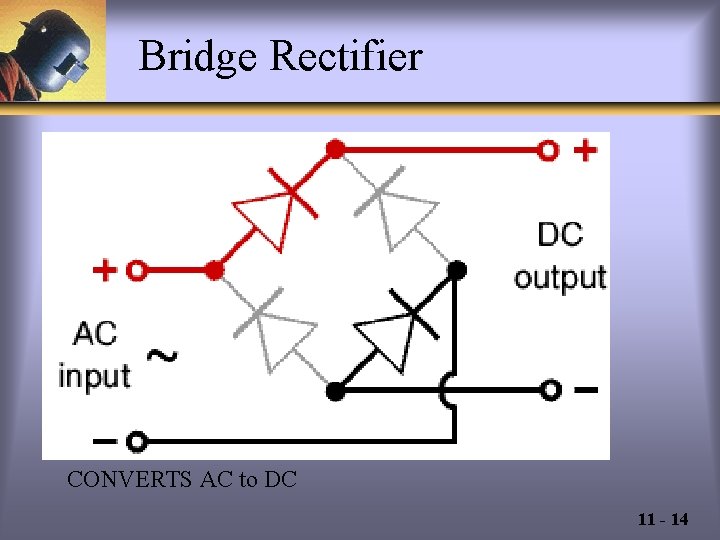
Bridge Rectifier CONVERTS AC to DC 11 - 14
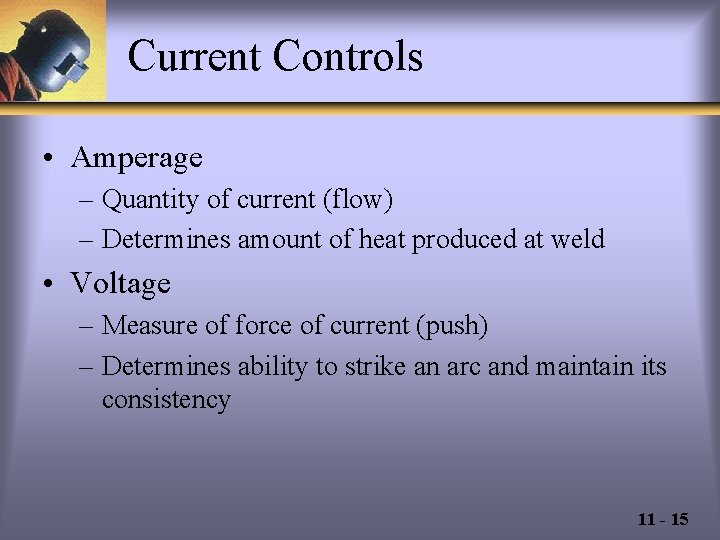
Current Controls • Amperage – Quantity of current (flow) – Determines amount of heat produced at weld • Voltage – Measure of force of current (push) – Determines ability to strike an arc and maintain its consistency 11 - 15
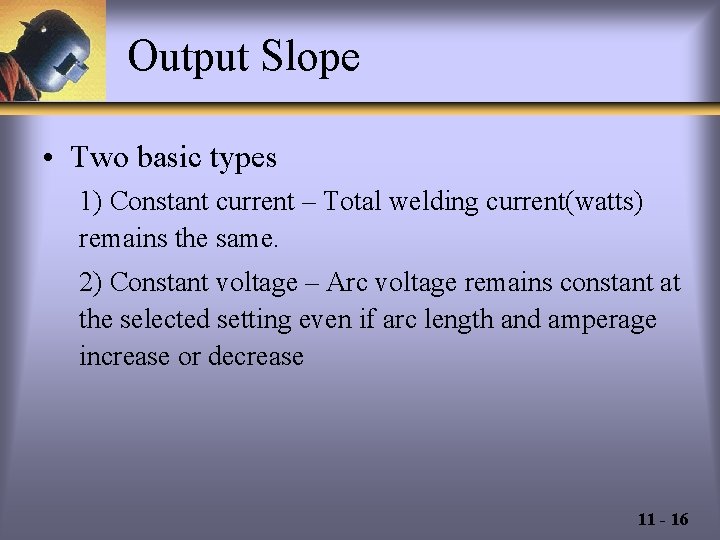
Output Slope • Two basic types 1) Constant current – Total welding current(watts) remains the same. 2) Constant voltage – Arc voltage remains constant at the selected setting even if arc length and amperage increase or decrease 11 - 16
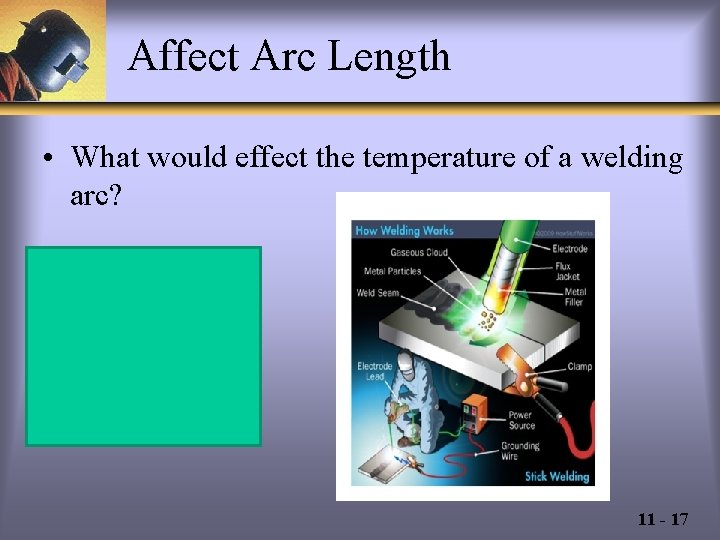
Affect Arc Length • What would effect the temperature of a welding arc? • Voltage • Arc Length • Atmosphere 11 - 17
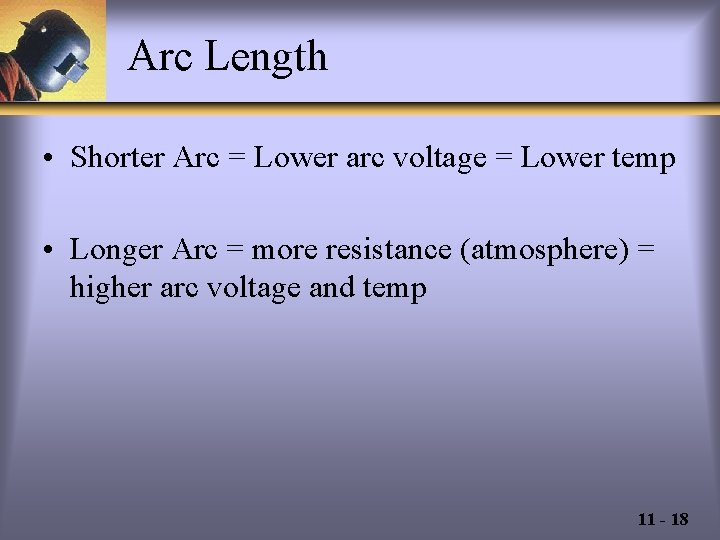
Arc Length • Shorter Arc = Lower arc voltage = Lower temp • Longer Arc = more resistance (atmosphere) = higher arc voltage and temp 11 - 18
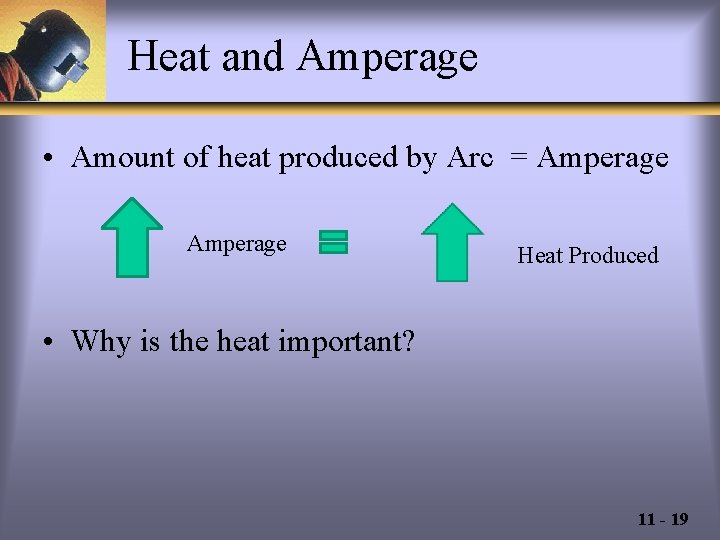
Heat and Amperage • Amount of heat produced by Arc = Amperage Heat Produced • Why is the heat important? 11 - 19
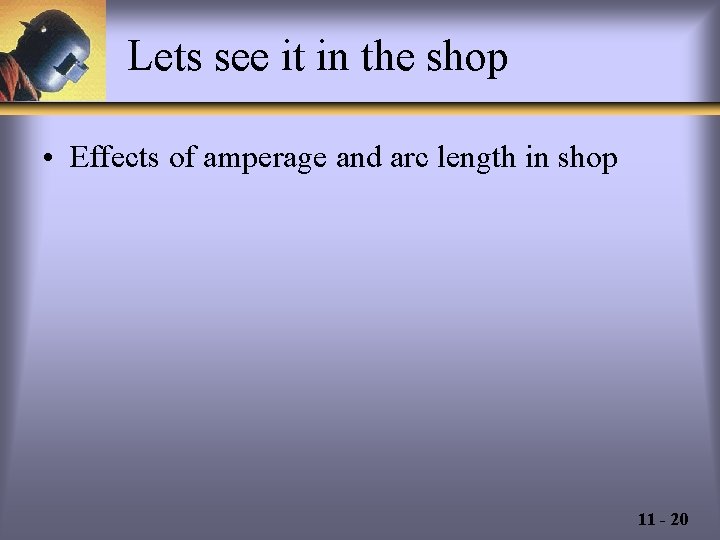
Lets see it in the shop • Effects of amperage and arc length in shop 11 - 20
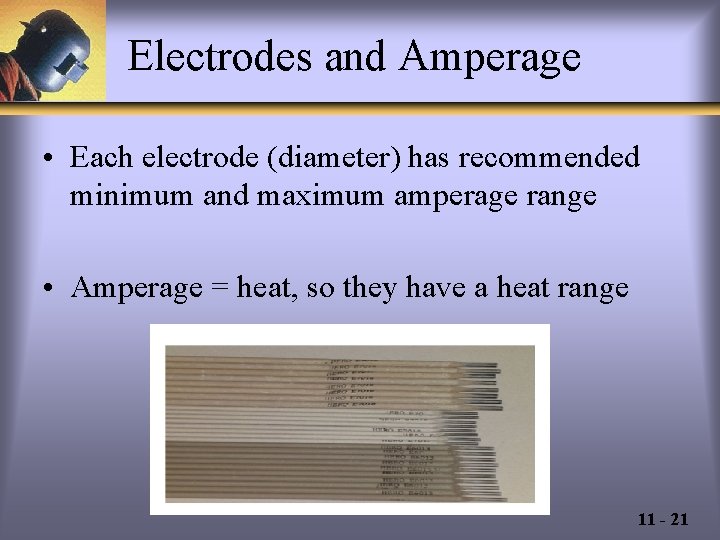
Electrodes and Amperage • Each electrode (diameter) has recommended minimum and maximum amperage range • Amperage = heat, so they have a heat range 11 - 21
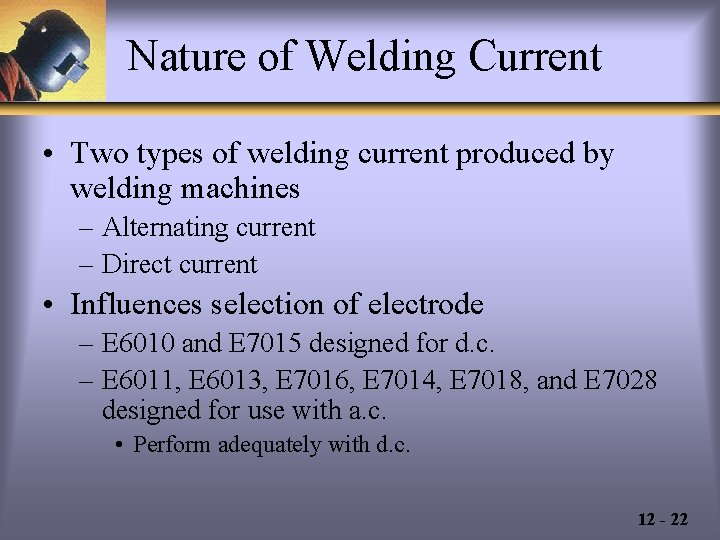
Nature of Welding Current • Two types of welding current produced by welding machines – Alternating current – Direct current • Influences selection of electrode – E 6010 and E 7015 designed for d. c. – E 6011, E 6013, E 7016, E 7014, E 7018, and E 7028 designed for use with a. c. • Perform adequately with d. c. 12 - 22
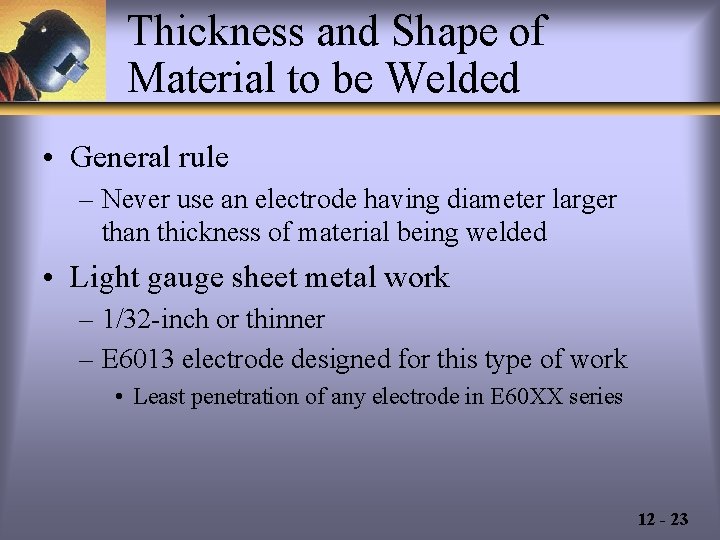
Thickness and Shape of Material to be Welded • General rule – Never use an electrode having diameter larger than thickness of material being welded • Light gauge sheet metal work – 1/32 -inch or thinner – E 6013 electrode designed for this type of work • Least penetration of any electrode in E 60 XX series 12 - 23
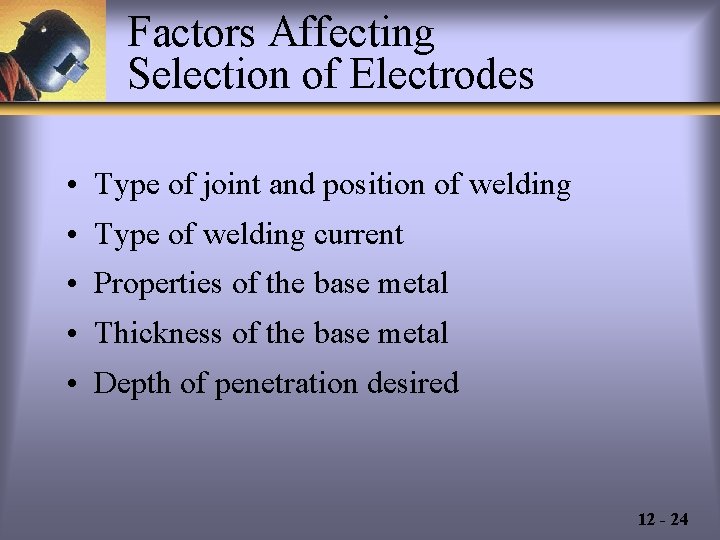
Factors Affecting Selection of Electrodes • Type of joint and position of welding • Type of welding current • Properties of the base metal • Thickness of the base metal • Depth of penetration desired 12 - 24
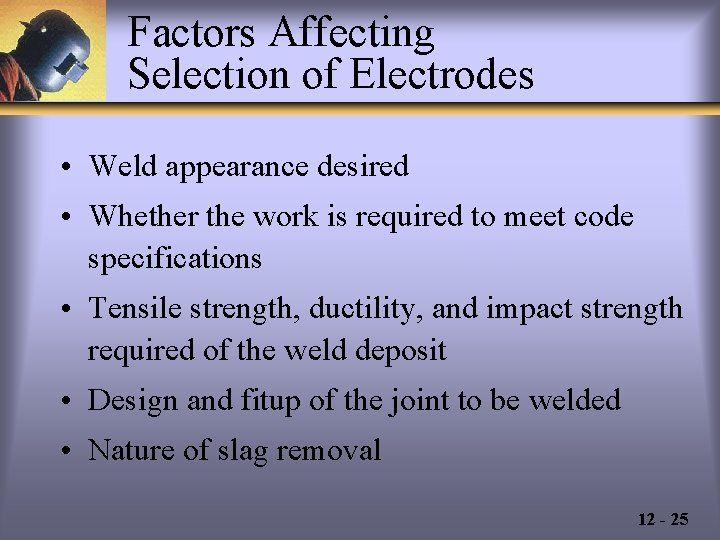
Factors Affecting Selection of Electrodes • Weld appearance desired • Whether the work is required to meet code specifications • Tensile strength, ductility, and impact strength required of the weld deposit • Design and fitup of the joint to be welded • Nature of slag removal 12 - 25
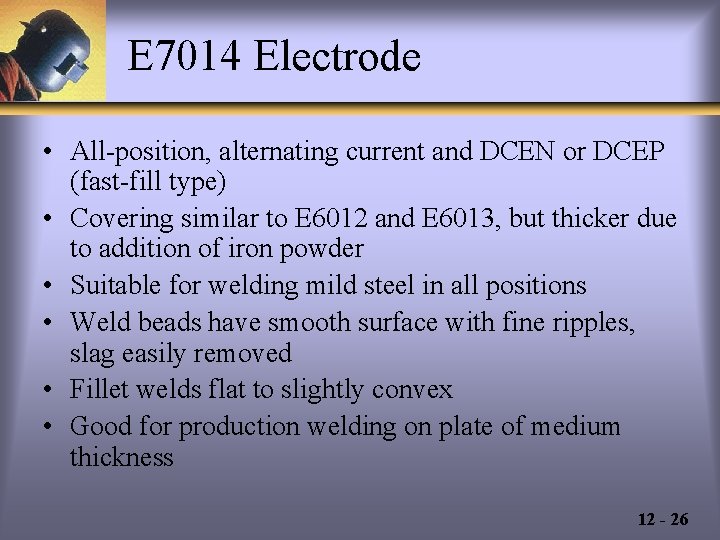
E 7014 Electrode • All-position, alternating current and DCEN or DCEP (fast-fill type) • Covering similar to E 6012 and E 6013, but thicker due to addition of iron powder • Suitable for welding mild steel in all positions • Weld beads have smooth surface with fine ripples, slag easily removed • Fillet welds flat to slightly convex • Good for production welding on plate of medium thickness 12 - 26
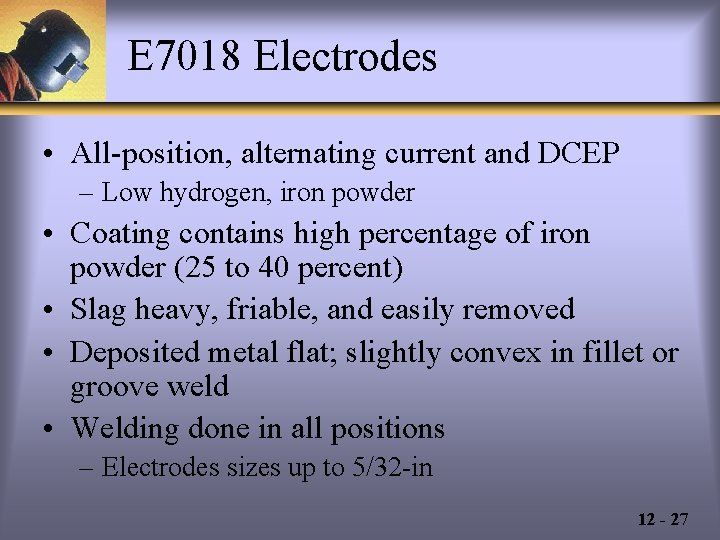
E 7018 Electrodes • All-position, alternating current and DCEP – Low hydrogen, iron powder • Coating contains high percentage of iron powder (25 to 40 percent) • Slag heavy, friable, and easily removed • Deposited metal flat; slightly convex in fillet or groove weld • Welding done in all positions – Electrodes sizes up to 5/32 -in 12 - 27
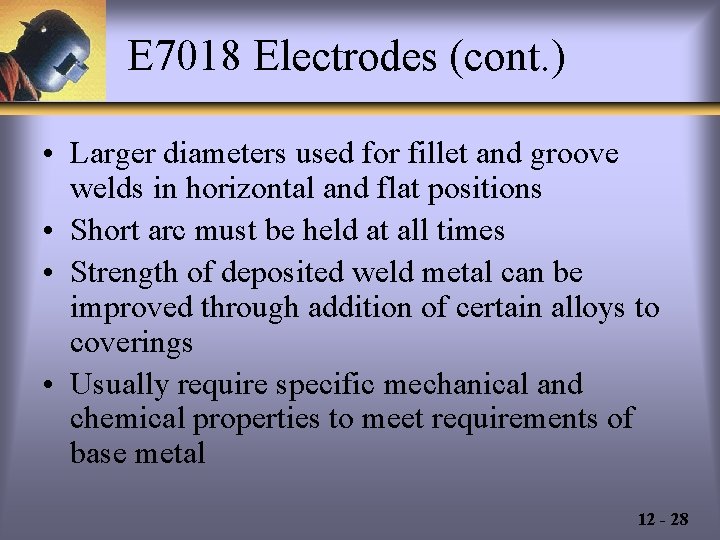
E 7018 Electrodes (cont. ) • Larger diameters used for fillet and groove welds in horizontal and flat positions • Short arc must be held at all times • Strength of deposited weld metal can be improved through addition of certain alloys to coverings • Usually require specific mechanical and chemical properties to meet requirements of base metal 12 - 28
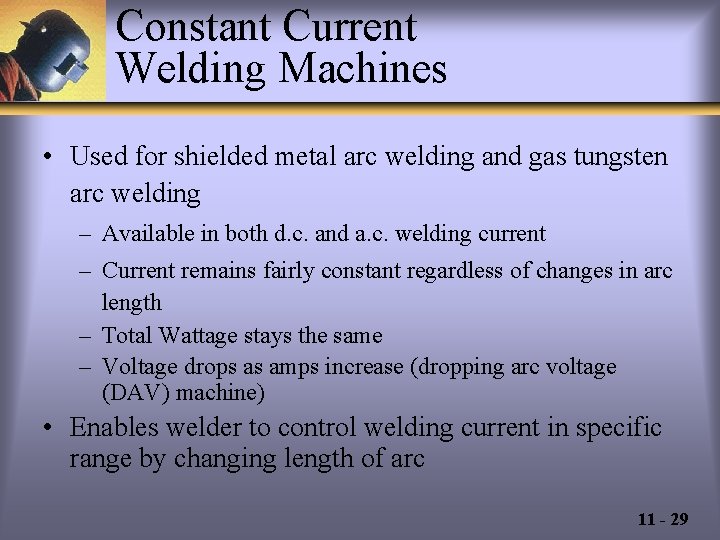
Constant Current Welding Machines • Used for shielded metal arc welding and gas tungsten arc welding – Available in both d. c. and a. c. welding current – Current remains fairly constant regardless of changes in arc length – Total Wattage stays the same – Voltage drops as amps increase (dropping arc voltage (DAV) machine) • Enables welder to control welding current in specific range by changing length of arc 11 - 29
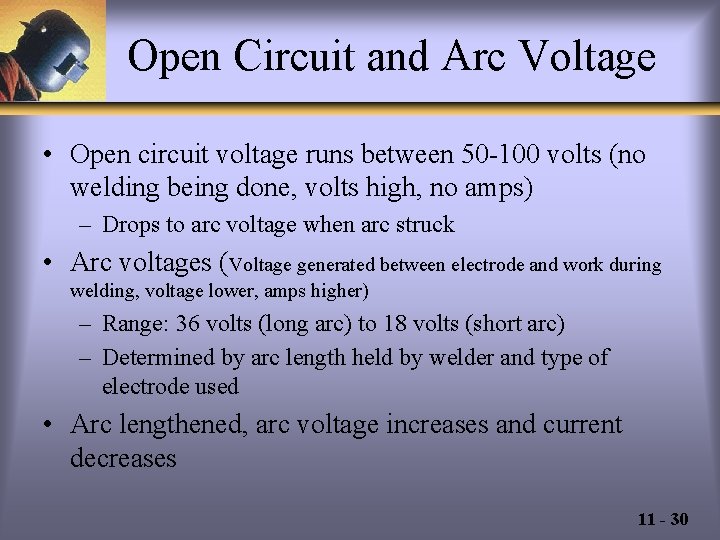
Open Circuit and Arc Voltage • Open circuit voltage runs between 50 -100 volts (no welding being done, volts high, no amps) – Drops to arc voltage when arc struck • Arc voltages (Voltage generated between electrode and work during welding, voltage lower, amps higher) – Range: 36 volts (long arc) to 18 volts (short arc) – Determined by arc length held by welder and type of electrode used • Arc lengthened, arc voltage increases and current decreases 11 - 30
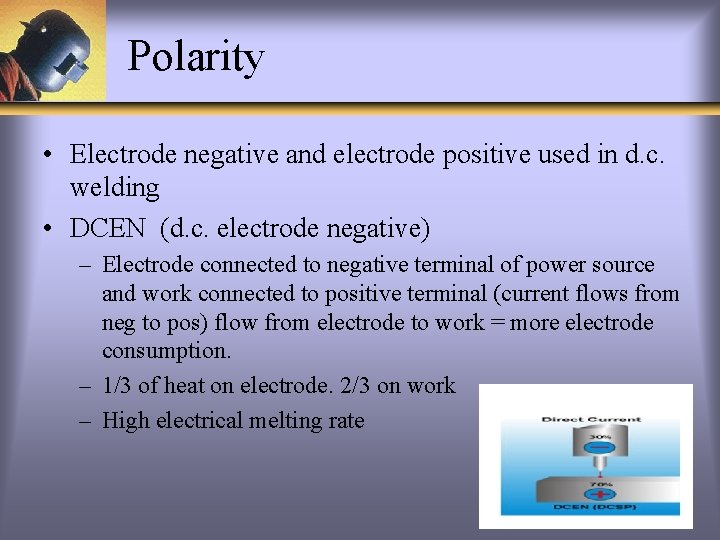
Polarity • Electrode negative and electrode positive used in d. c. welding • DCEN (d. c. electrode negative) – Electrode connected to negative terminal of power source and work connected to positive terminal (current flows from neg to pos) flow from electrode to work = more electrode consumption. – 1/3 of heat on electrode. 2/3 on work – High electrical melting rate 11 - 31
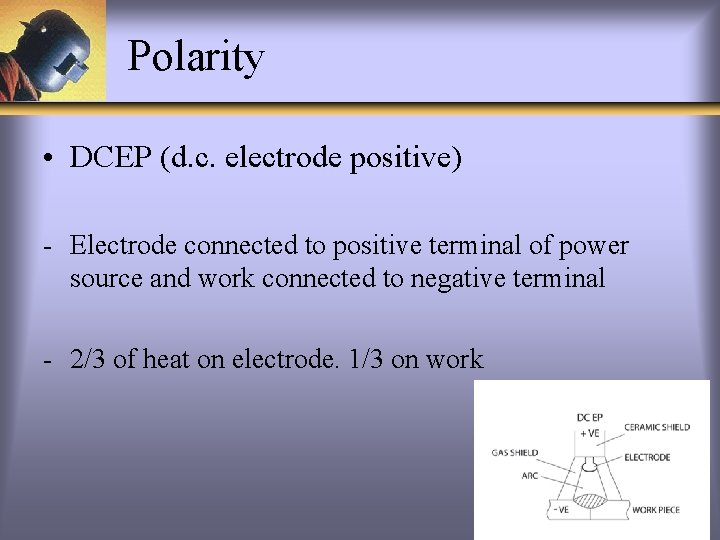
Polarity • DCEP (d. c. electrode positive) - Electrode connected to positive terminal of power source and work connected to negative terminal - 2/3 of heat on electrode. 1/3 on work 11 - 32
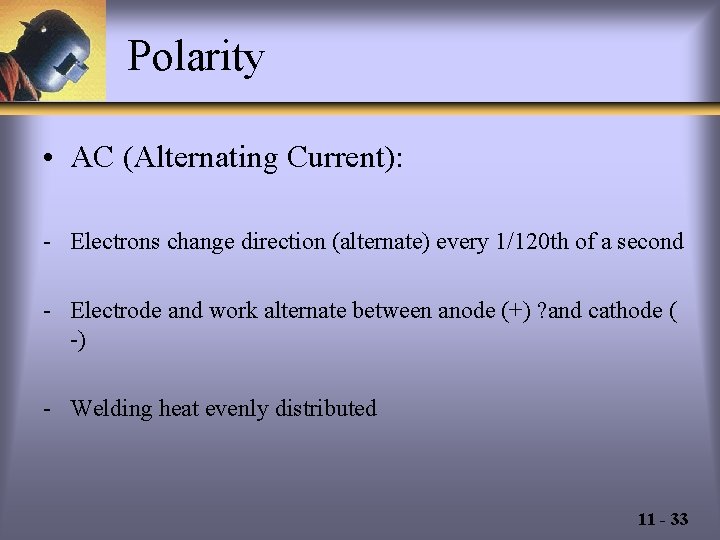
Polarity • AC (Alternating Current): - Electrons change direction (alternate) every 1/120 th of a second - Electrode and work alternate between anode (+) ? and cathode ( -) - Welding heat evenly distributed 11 - 33
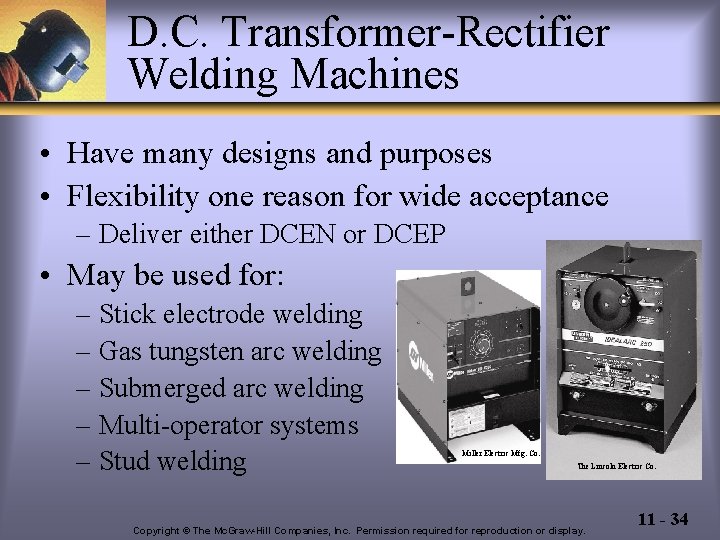
D. C. Transformer-Rectifier Welding Machines • Have many designs and purposes • Flexibility one reason for wide acceptance – Deliver either DCEN or DCEP • May be used for: – Stick electrode welding – Gas tungsten arc welding – Submerged arc welding – Multi-operator systems – Stud welding Miller Electric Mfg. Co. The Lincoln Electric Co. Copyright © The Mc. Graw-Hill Companies, Inc. Permission required for reproduction or display. 11 - 34
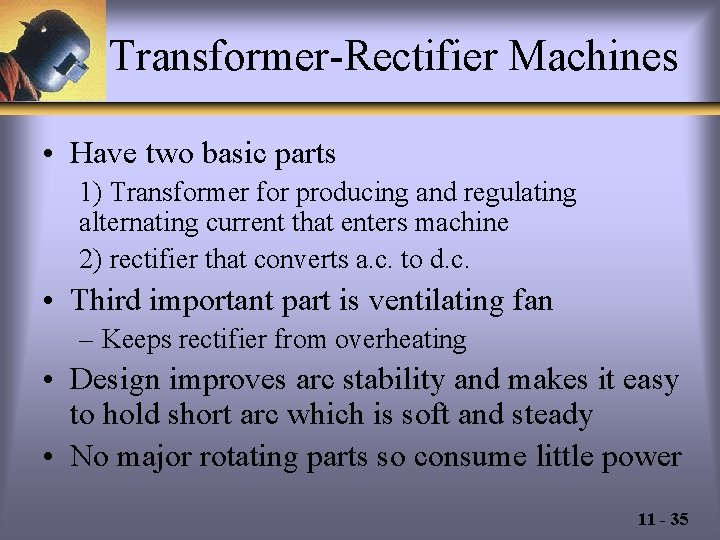
Transformer-Rectifier Machines • Have two basic parts 1) Transformer for producing and regulating alternating current that enters machine 2) rectifier that converts a. c. to d. c. • Third important part is ventilating fan – Keeps rectifier from overheating • Design improves arc stability and makes it easy to hold short arc which is soft and steady • No major rotating parts so consume little power 11 - 35
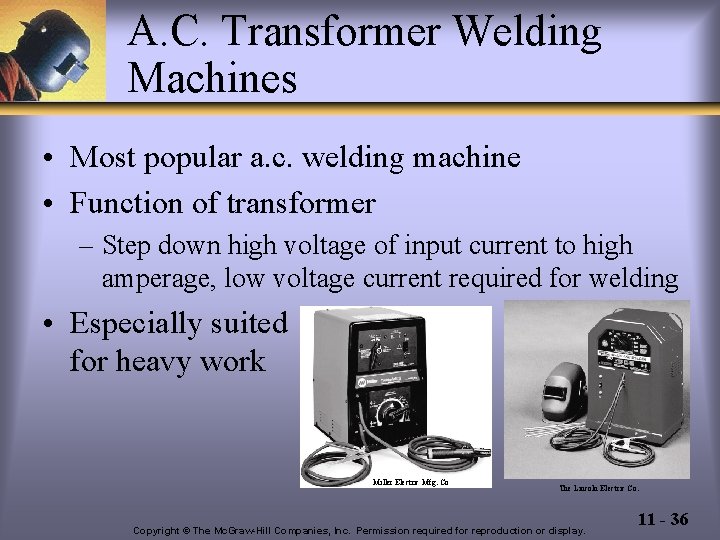
A. C. Transformer Welding Machines • Most popular a. c. welding machine • Function of transformer – Step down high voltage of input current to high amperage, low voltage current required for welding • Especially suited for heavy work Miller Electric Mfg. Co The Lincoln Electric Co. Copyright © The Mc. Graw-Hill Companies, Inc. Permission required for reproduction or display. 11 - 36
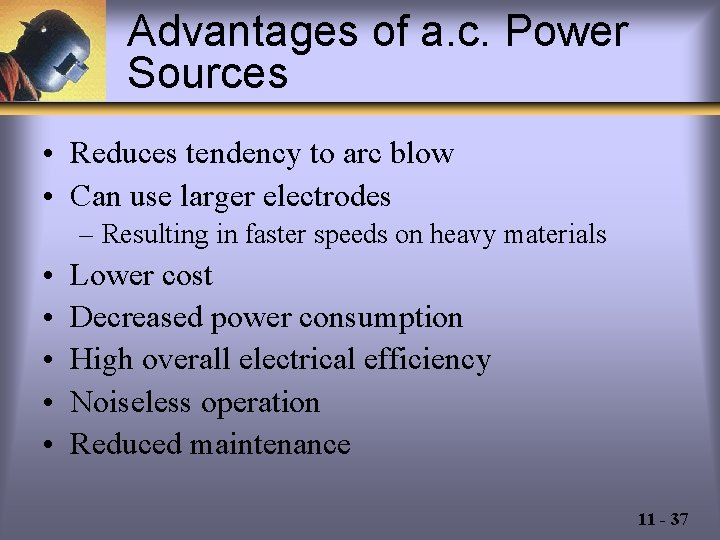
Advantages of a. c. Power Sources • Reduces tendency to arc blow • Can use larger electrodes – Resulting in faster speeds on heavy materials • • • Lower cost Decreased power consumption High overall electrical efficiency Noiseless operation Reduced maintenance 11 - 37
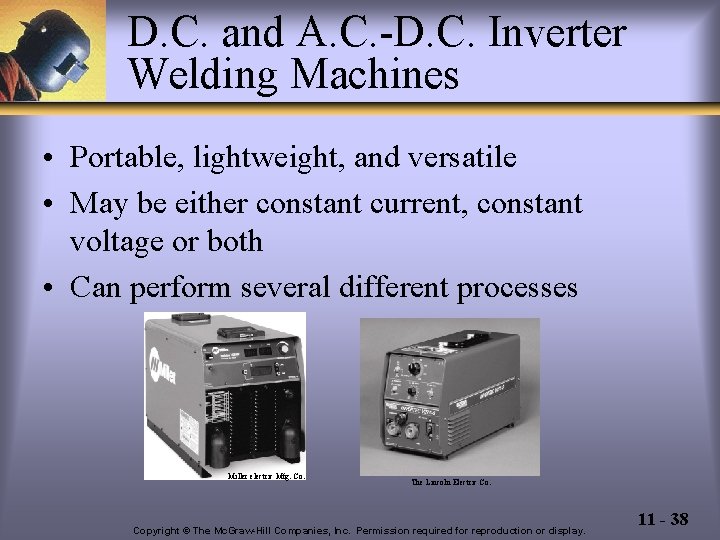
D. C. and A. C. -D. C. Inverter Welding Machines • Portable, lightweight, and versatile • May be either constant current, constant voltage or both • Can perform several different processes Miller electric Mfg. Co. The Lincoln Electric Co. Copyright © The Mc. Graw-Hill Companies, Inc. Permission required for reproduction or display. 11 - 38
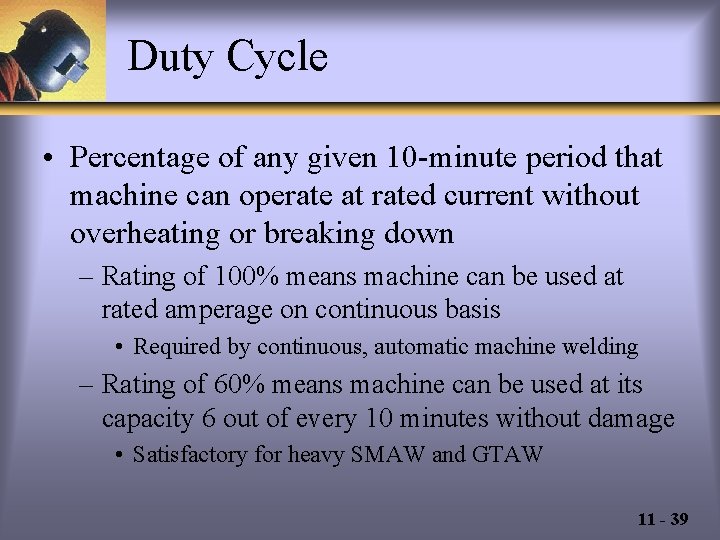
Duty Cycle • Percentage of any given 10 -minute period that machine can operate at rated current without overheating or breaking down – Rating of 100% means machine can be used at rated amperage on continuous basis • Required by continuous, automatic machine welding – Rating of 60% means machine can be used at its capacity 6 out of every 10 minutes without damage • Satisfactory for heavy SMAW and GTAW 11 - 39
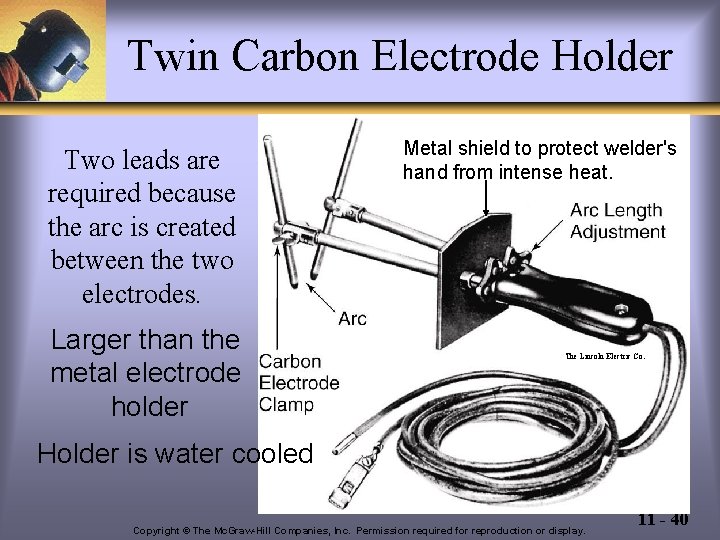
Twin Carbon Electrode Holder Two leads are required because the arc is created between the two electrodes. Larger than the metal electrode holder Metal shield to protect welder's hand from intense heat. The Lincoln Electric Co. Holder is water cooled Copyright © The Mc. Graw-Hill Companies, Inc. Permission required for reproduction or display. 11 - 40
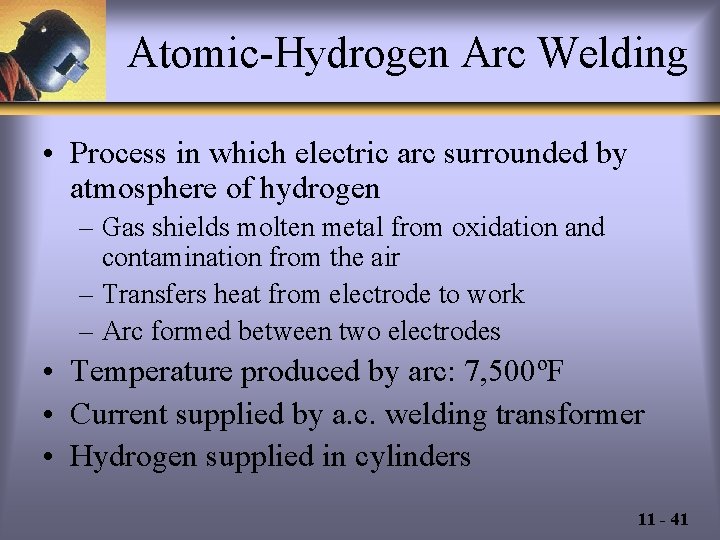
Atomic-Hydrogen Arc Welding • Process in which electric arc surrounded by atmosphere of hydrogen – Gas shields molten metal from oxidation and contamination from the air – Transfers heat from electrode to work – Arc formed between two electrodes • Temperature produced by arc: 7, 500ºF • Current supplied by a. c. welding transformer • Hydrogen supplied in cylinders 11 - 41
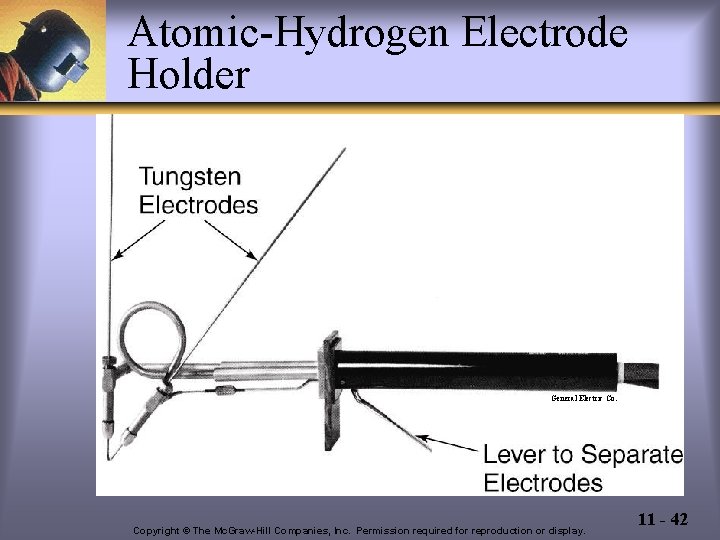
Atomic-Hydrogen Electrode Holder General Electric Co. Copyright © The Mc. Graw-Hill Companies, Inc. Permission required for reproduction or display. 11 - 42
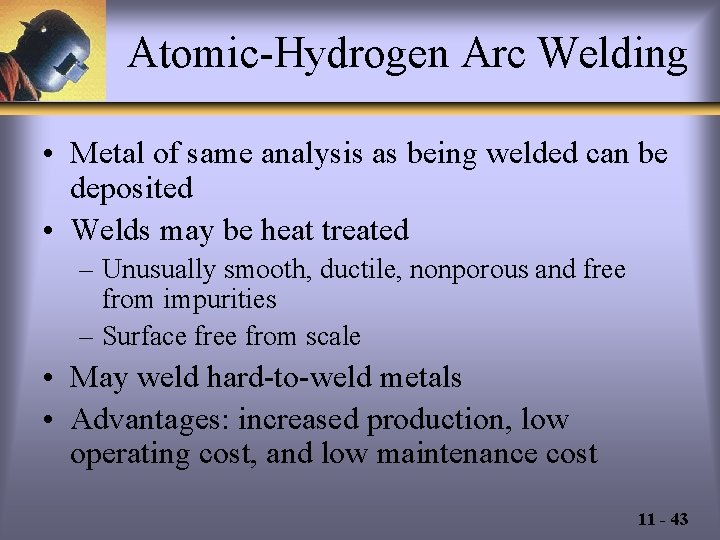
Atomic-Hydrogen Arc Welding • Metal of same analysis as being welded can be deposited • Welds may be heat treated – Unusually smooth, ductile, nonporous and free from impurities – Surface free from scale • May weld hard-to-weld metals • Advantages: increased production, low operating cost, and low maintenance cost 11 - 43
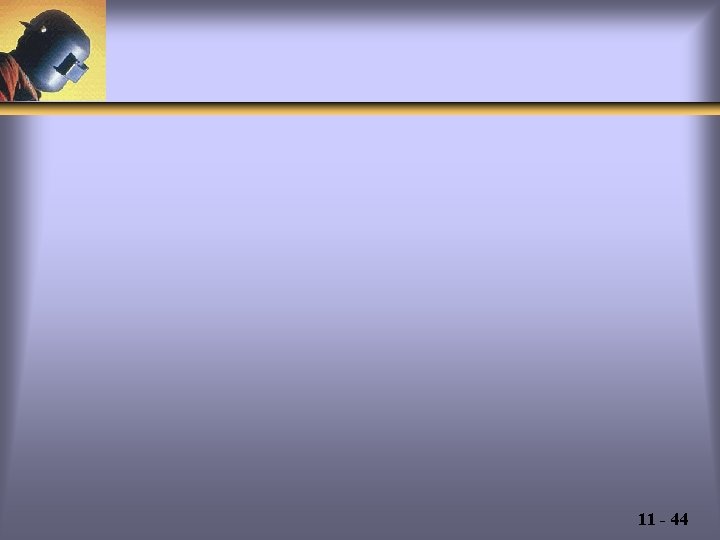
11 - 44