Spot Welding Spot Welding Lesson Objectives When you
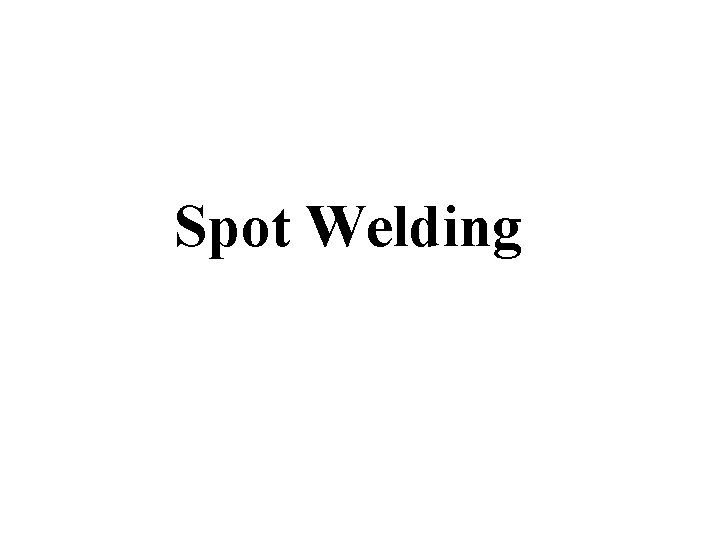
Spot Welding
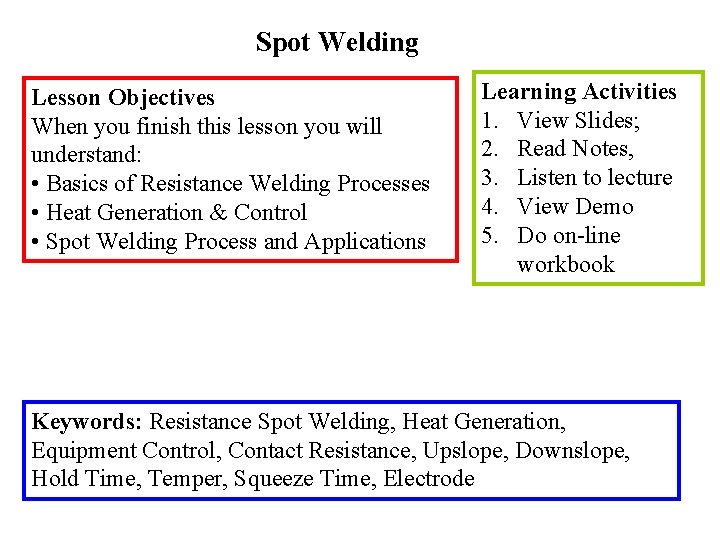
Spot Welding Lesson Objectives When you finish this lesson you will understand: • Basics of Resistance Welding Processes • Heat Generation & Control • Spot Welding Process and Applications Learning Activities 1. View Slides; 2. Read Notes, 3. Listen to lecture 4. View Demo 5. Do on-line workbook Keywords: Resistance Spot Welding, Heat Generation, Equipment Control, Contact Resistance, Upslope, Downslope, Hold Time, Temper, Squeeze Time, Electrode
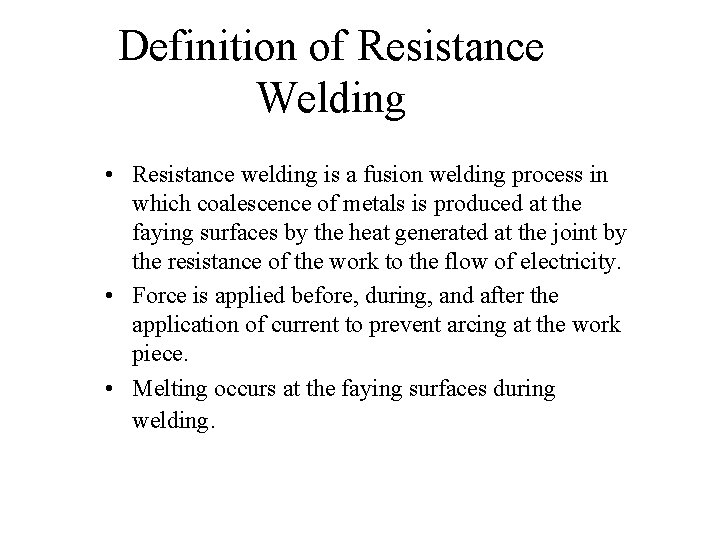
Definition of Resistance Welding • Resistance welding is a fusion welding process in which coalescence of metals is produced at the faying surfaces by the heat generated at the joint by the resistance of the work to the flow of electricity. • Force is applied before, during, and after the application of current to prevent arcing at the work piece. • Melting occurs at the faying surfaces during welding.
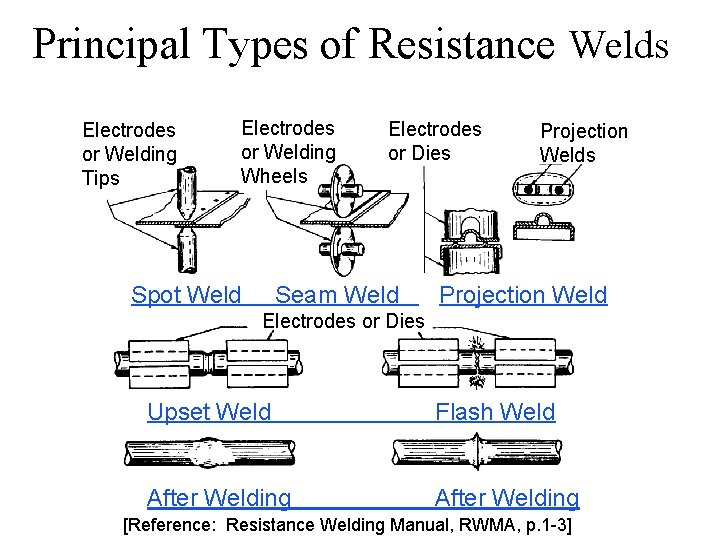
Principal Types of Resistance Welds Electrodes or Welding Tips Electrodes or Welding Wheels Spot Weld Electrodes or Dies Seam Weld Projection Welds Projection Weld Electrodes or Dies Upset Weld Flash Weld After Welding [Reference: Resistance Welding Manual, RWMA, p. 1 -3]
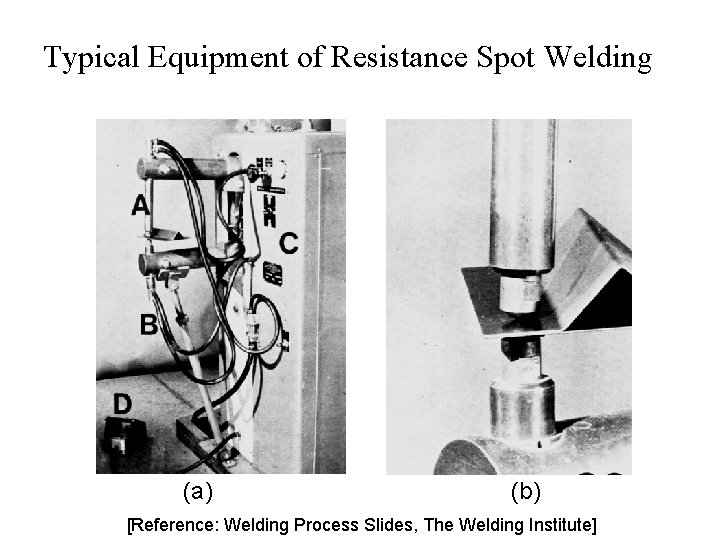
Typical Equipment of Resistance Spot Welding (a) (b) [Reference: Welding Process Slides, The Welding Institute]
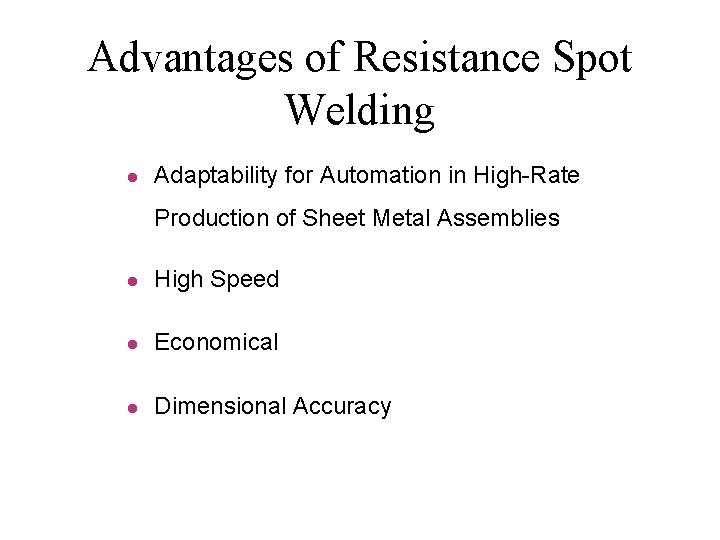
Advantages of Resistance Spot Welding l Adaptability for Automation in High-Rate Production of Sheet Metal Assemblies l High Speed l Economical l Dimensional Accuracy
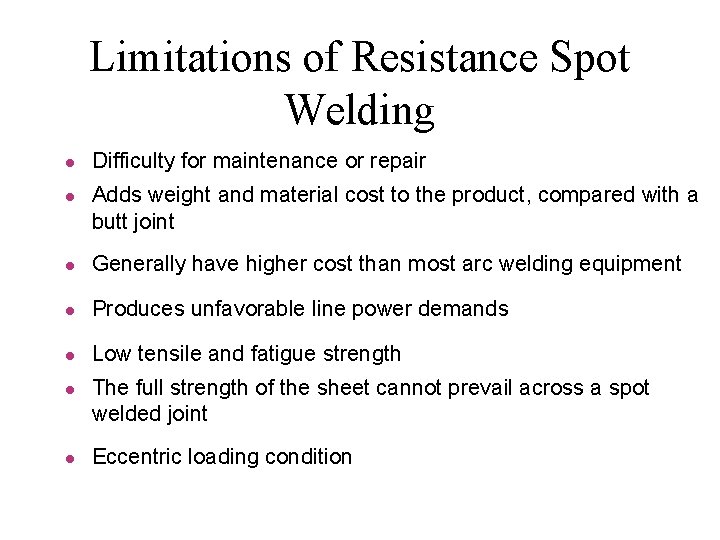
Limitations of Resistance Spot Welding l l Difficulty for maintenance or repair Adds weight and material cost to the product, compared with a butt joint l Generally have higher cost than most arc welding equipment l Produces unfavorable line power demands l Low tensile and fatigue strength l l The full strength of the sheet cannot prevail across a spot welded joint Eccentric loading condition
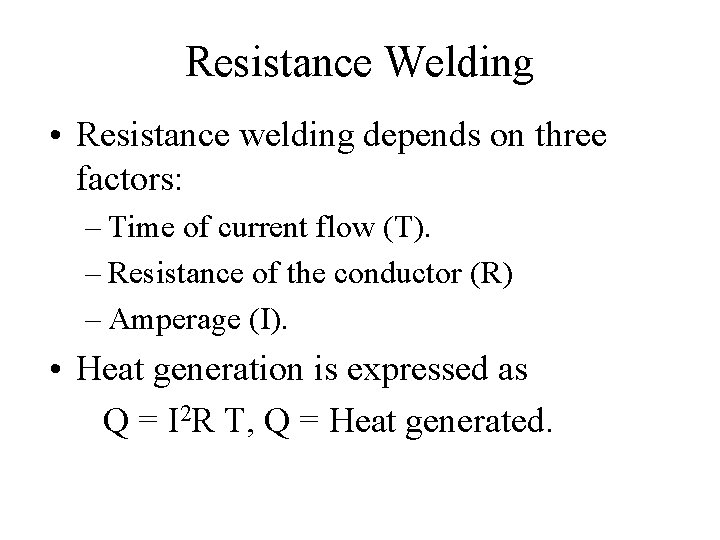
Resistance Welding • Resistance welding depends on three factors: – Time of current flow (T). – Resistance of the conductor (R) – Amperage (I). • Heat generation is expressed as Q = I 2 R T, Q = Heat generated.
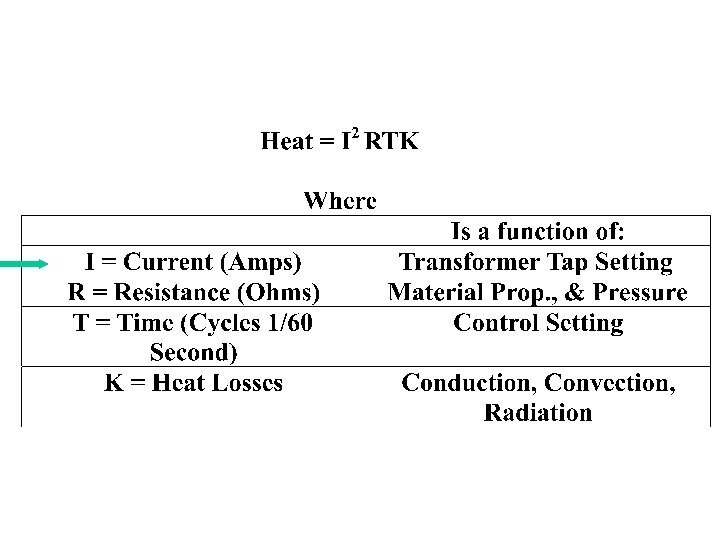
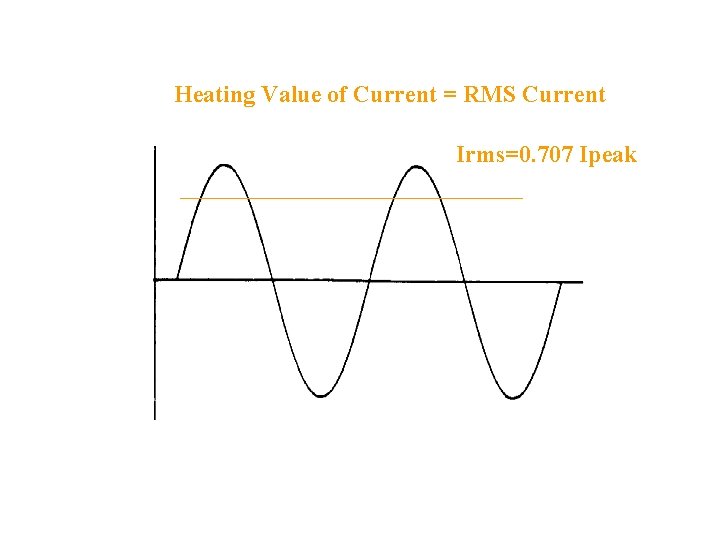
Heating Value of Current = RMS Current Irms=0. 707 Ipeak
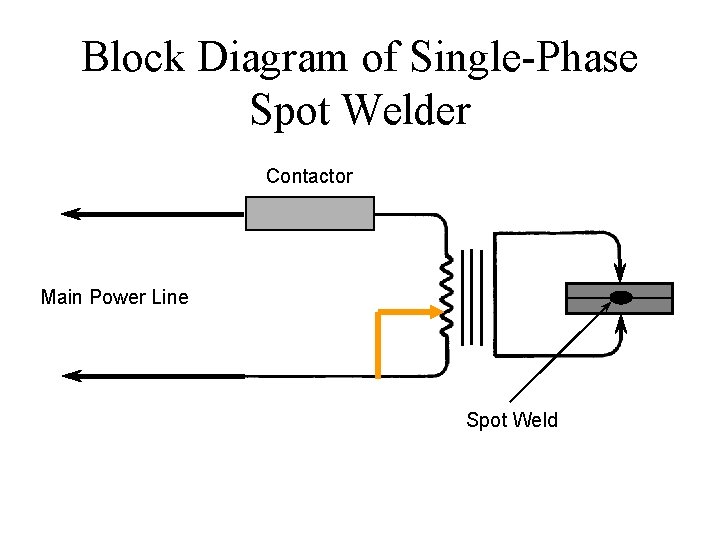
Block Diagram of Single-Phase Spot Welder Contactor Main Power Line Spot Weld
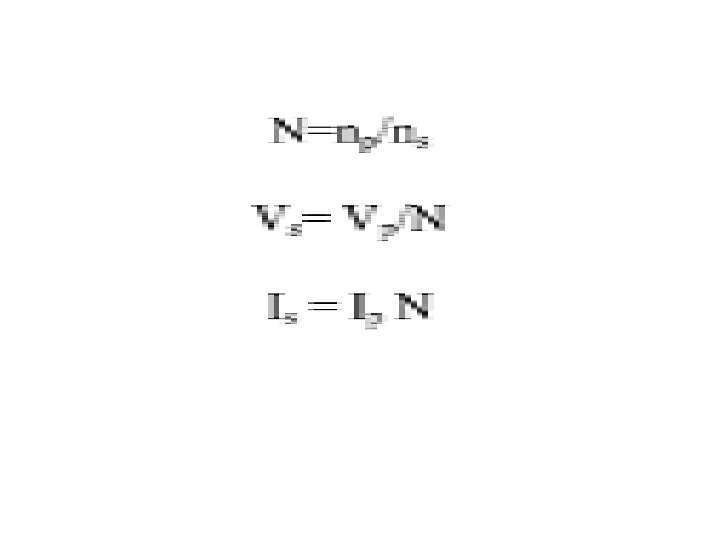
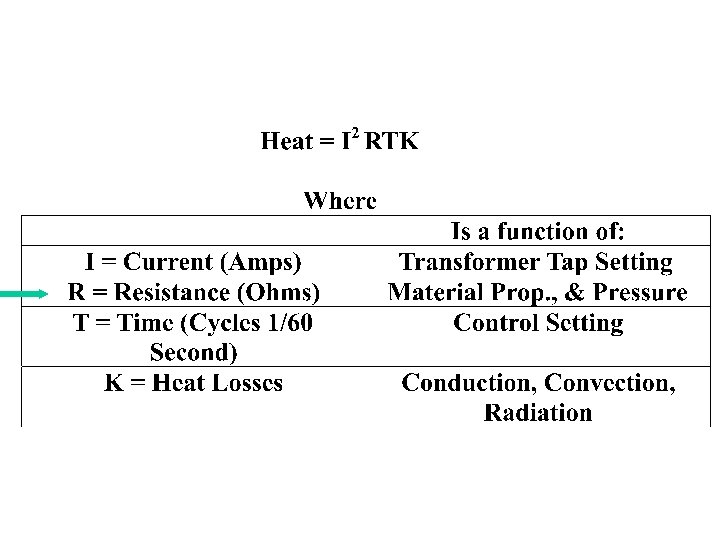
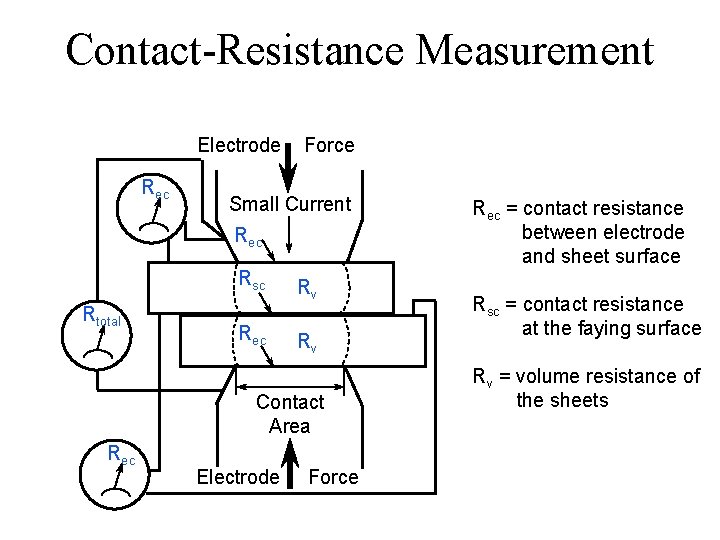
Contact-Resistance Measurement Electrode Rec Force Small Current Rec Rsc Rtotal Rec Rv Rv Contact Area Rec Electrode Force Rec = contact resistance between electrode and sheet surface Rsc = contact resistance at the faying surface Rv = volume resistance of the sheets
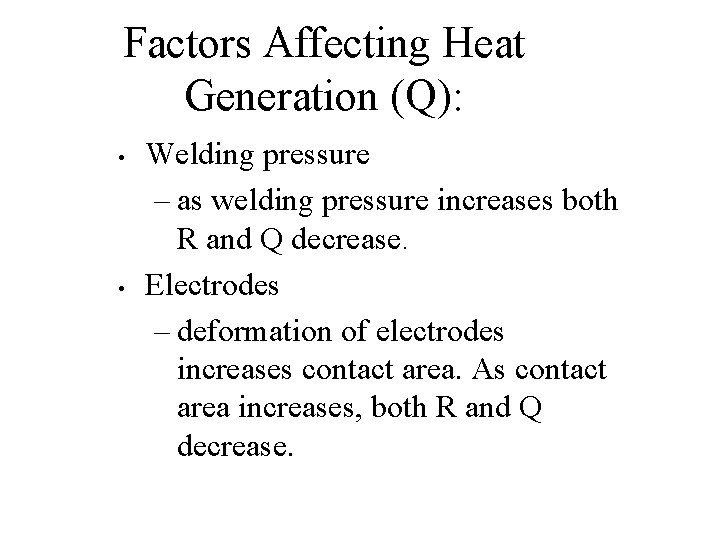
Factors Affecting Heat Generation (Q): • • Welding pressure – as welding pressure increases both R and Q decrease. Electrodes – deformation of electrodes increases contact area. As contact area increases, both R and Q decrease.
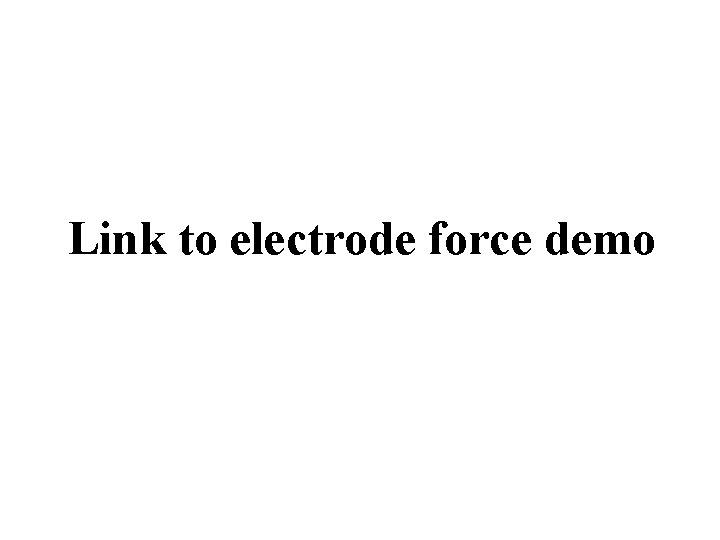
Link to electrode force demo
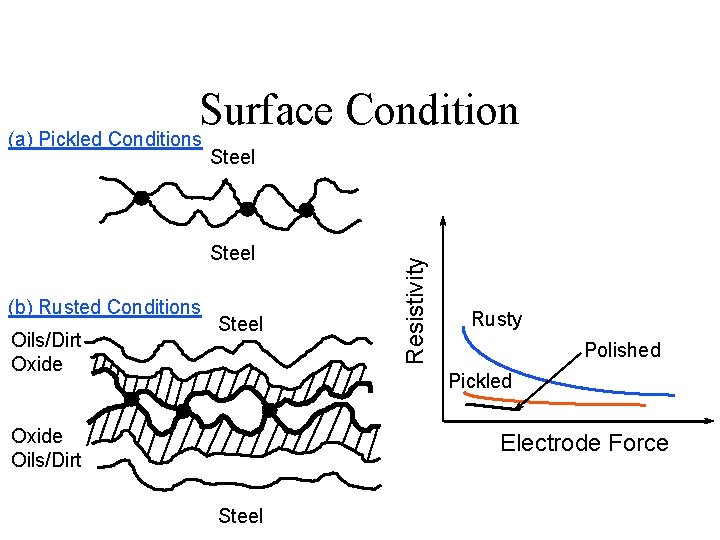
Surface Condition Steel (b) Rusted Conditions Oils/Dirt Oxide Steel Resistivity (a) Pickled Conditions Rusty Polished Pickled Oxide Oils/Dirt Electrode Force Steel
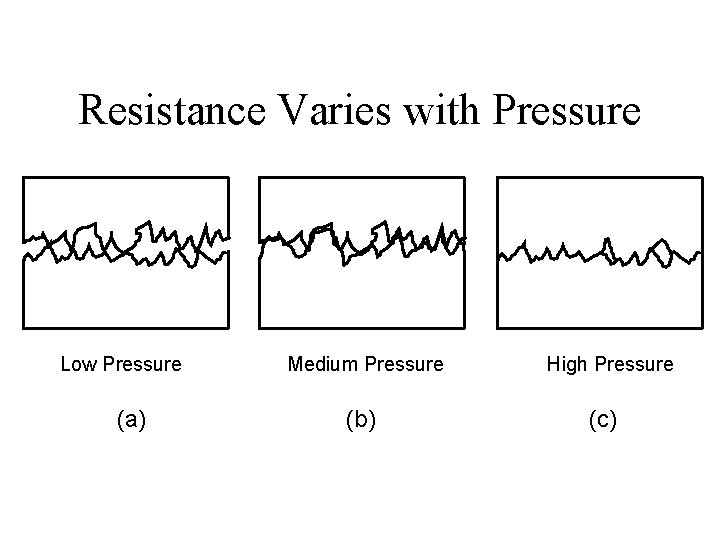
Resistance Varies with Pressure Low Pressure (a) Medium Pressure (b) High Pressure (c)
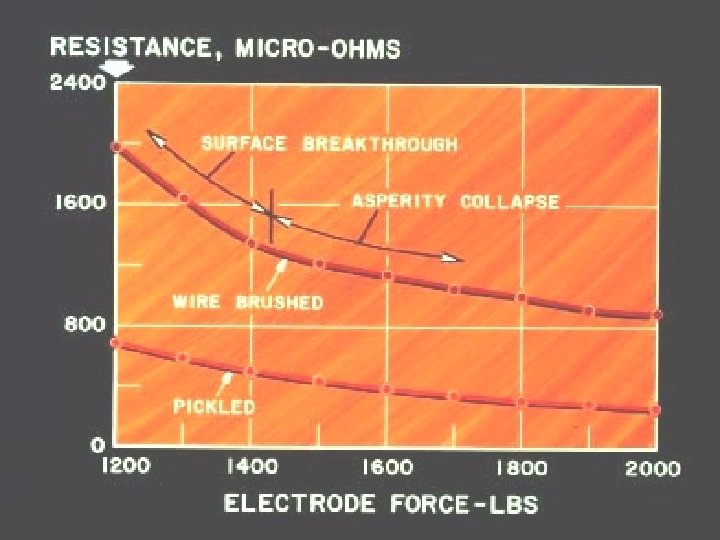
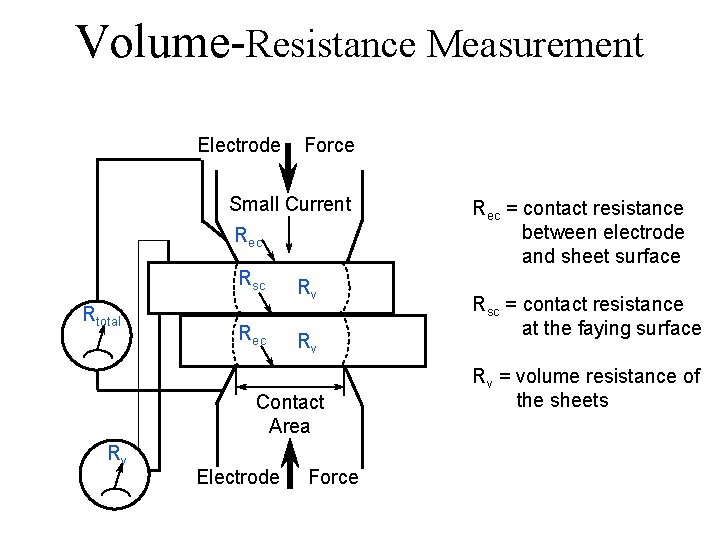
Volume-Resistance Measurement Electrode Force Small Current Rec Rsc Rtotal Rec Rv Rv Contact Area Rv Electrode Force Rec = contact resistance between electrode and sheet surface Rsc = contact resistance at the faying surface Rv = volume resistance of the sheets
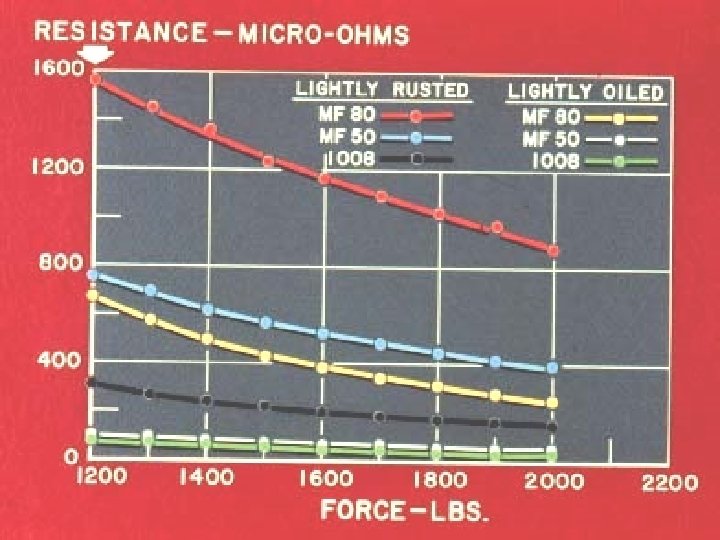
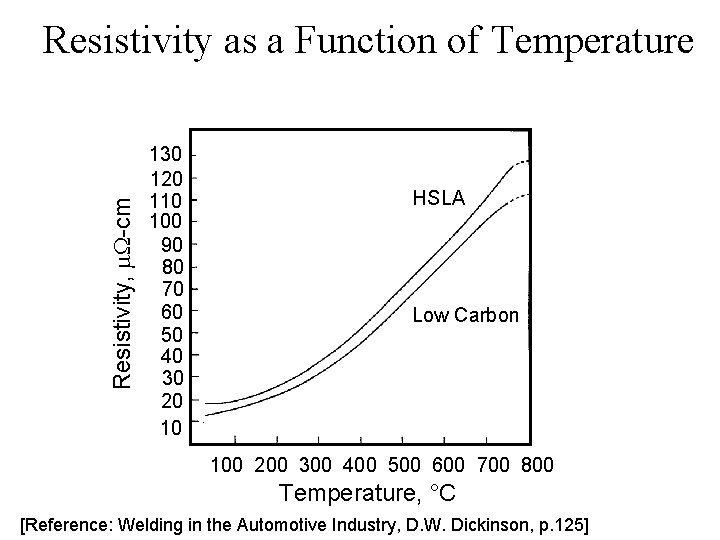
Resistivity, m. W-cm Resistivity as a Function of Temperature 130 120 110 100 90 80 70 60 50 40 30 20 10 HSLA Low Carbon 100 200 300 400 500 600 700 800 Temperature, °C [Reference: Welding in the Automotive Industry, D. W. Dickinson, p. 125]
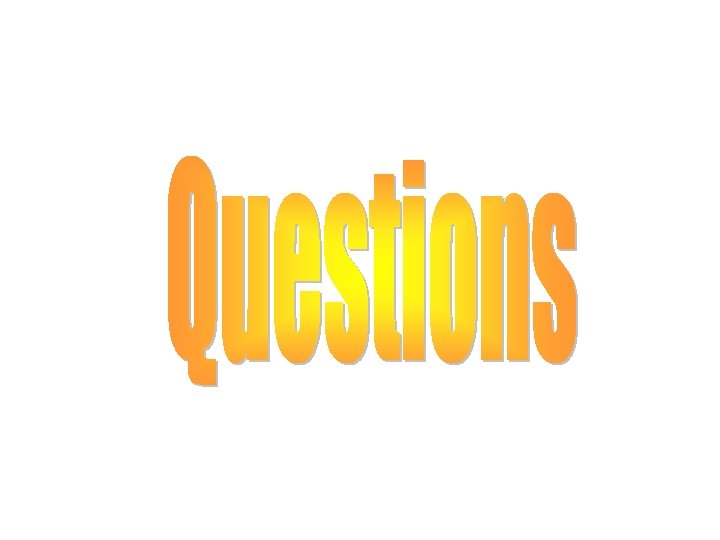
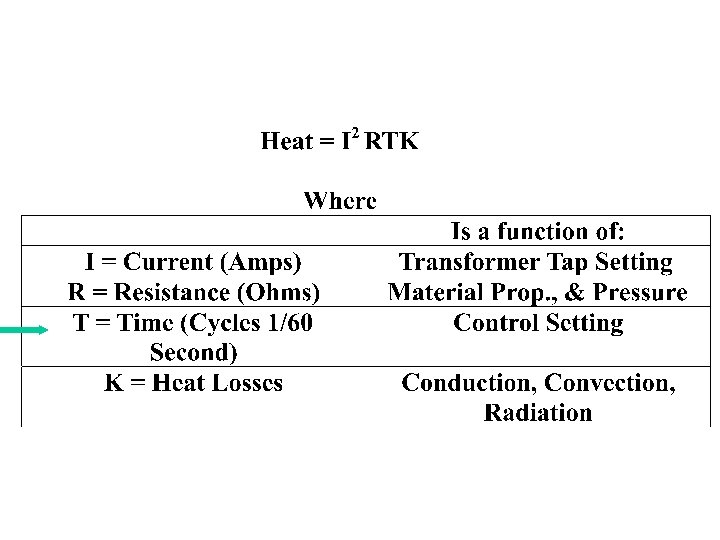
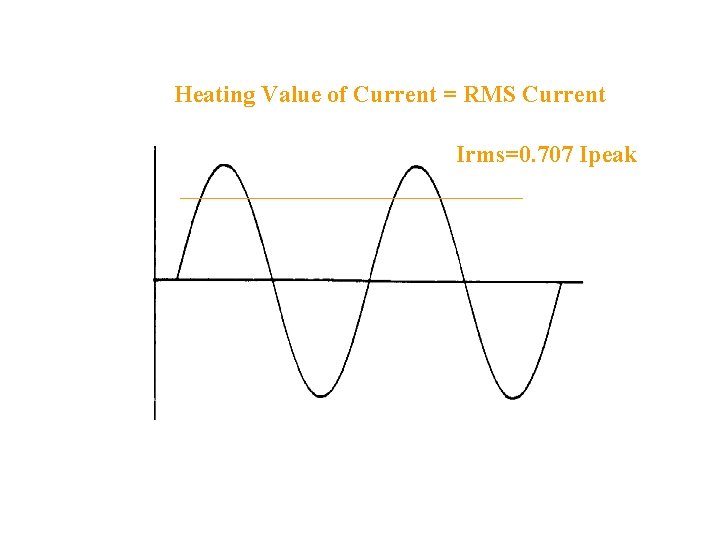
Heating Value of Current = RMS Current Irms=0. 707 Ipeak
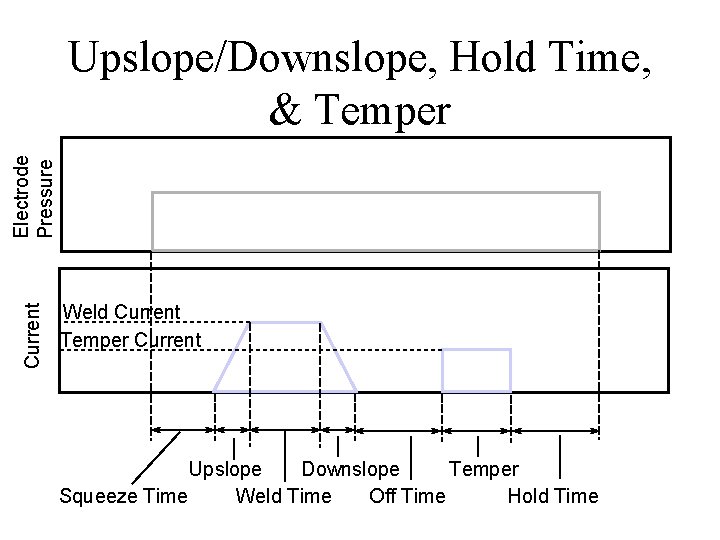
Current Electrode Pressure Upslope/Downslope, Hold Time, & Temper Weld Current Temper Current Upslope Downslope Temper Squeeze Time Weld Time Off Time Hold Time
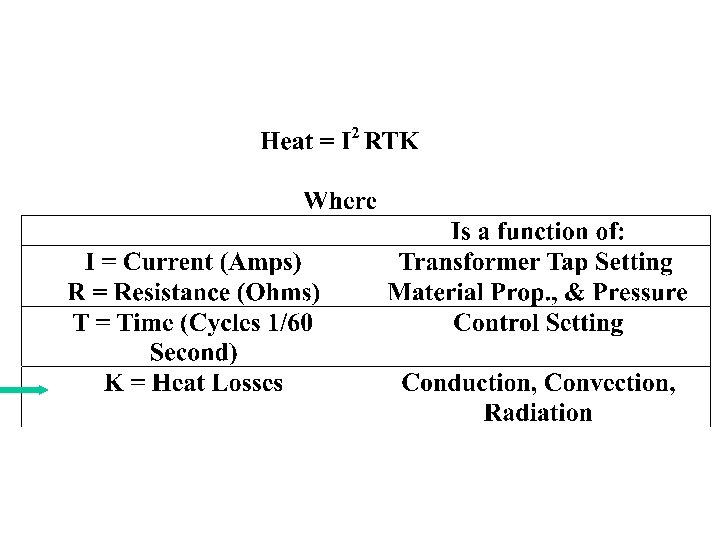
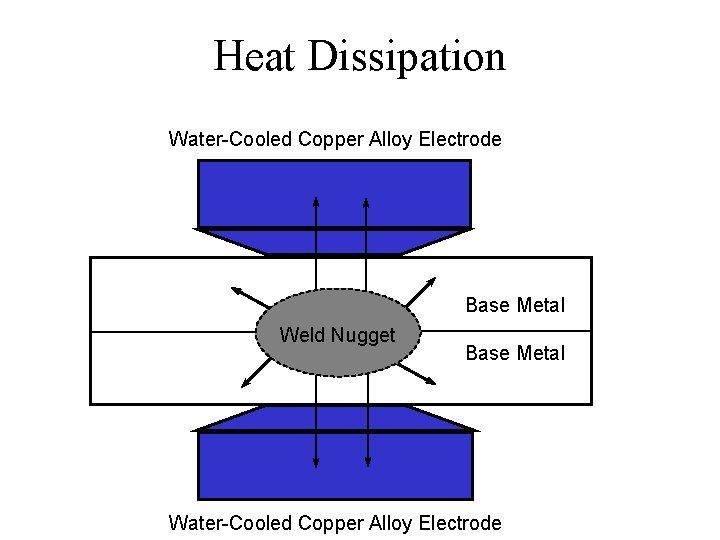
Heat Dissipation Water-Cooled Copper Alloy Electrode Base Metal Weld Nugget Base Metal Water-Cooled Copper Alloy Electrode
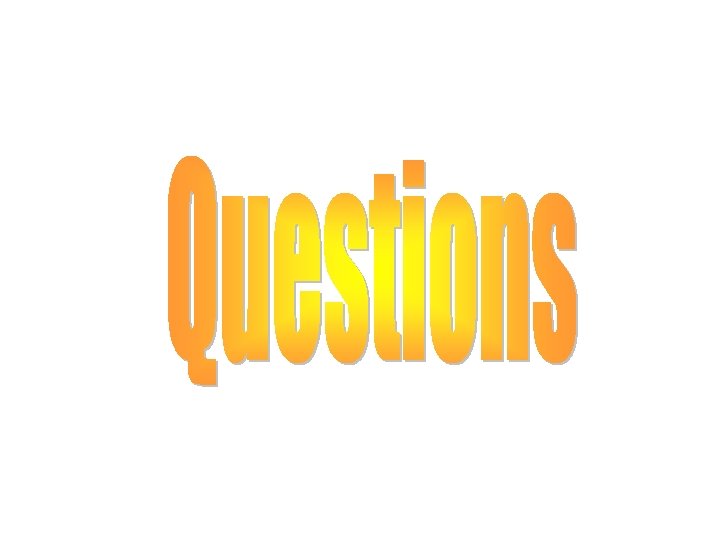
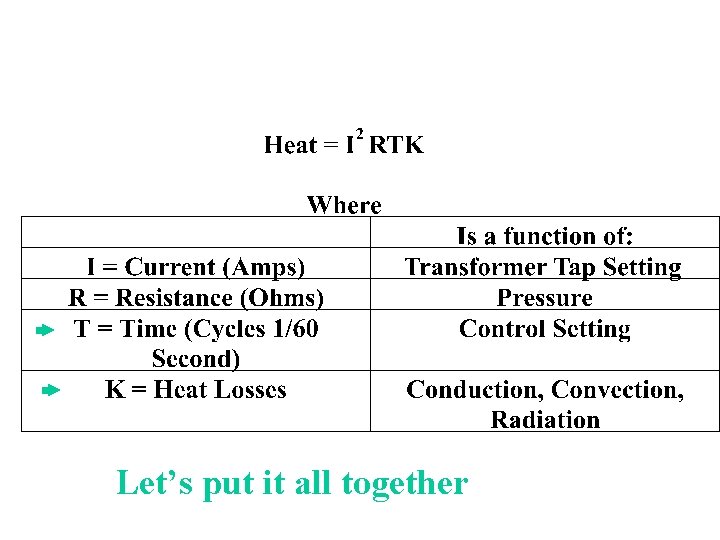
Let’s put it all together
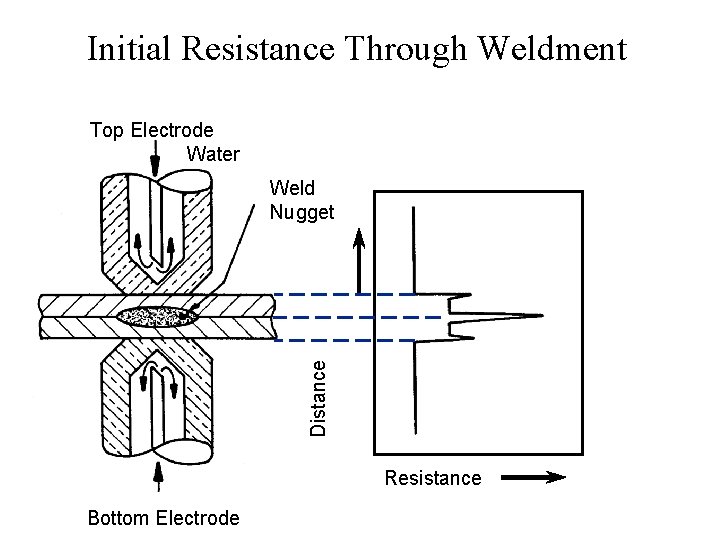
Initial Resistance Through Weldment Top Electrode Water Distance Weld Nugget Resistance Bottom Electrode
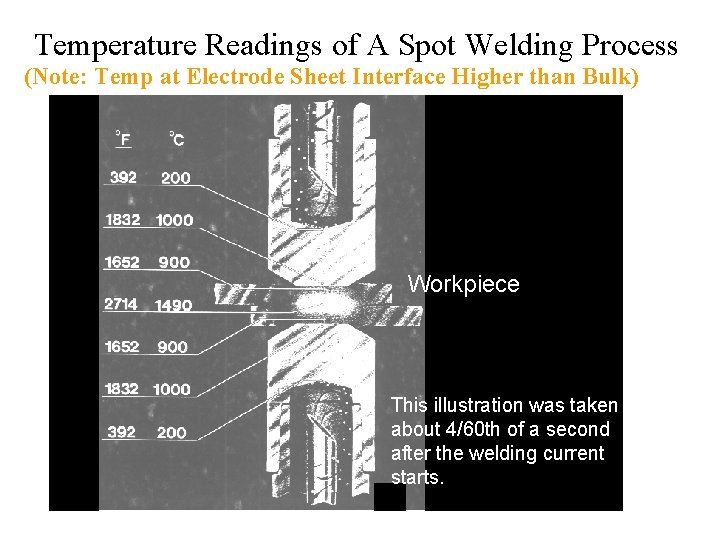
Temperature Readings of A Spot Welding Process (Note: Temp at Electrode Sheet Interface Higher than Bulk) Workpiece This illustration was taken about 4/60 th of a second after the welding current starts.
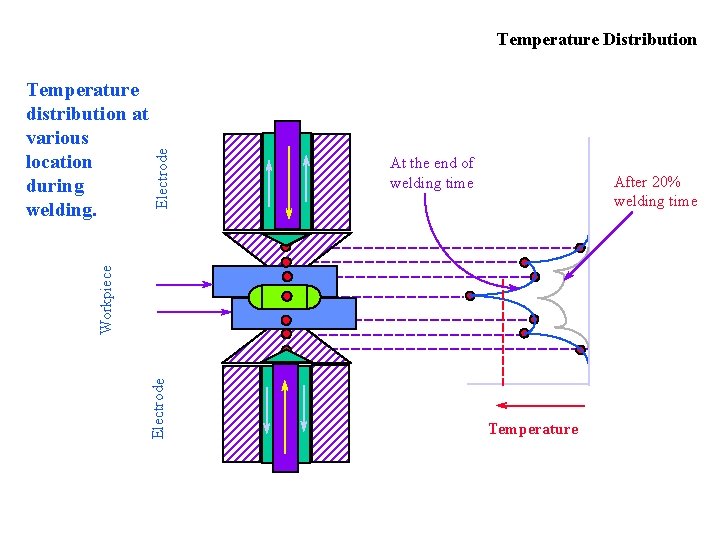
At the end of welding time After 20% welding time Electrode Workpiece Temperature distribution at various location during welding. Electrode Temperature Distribution Temperature
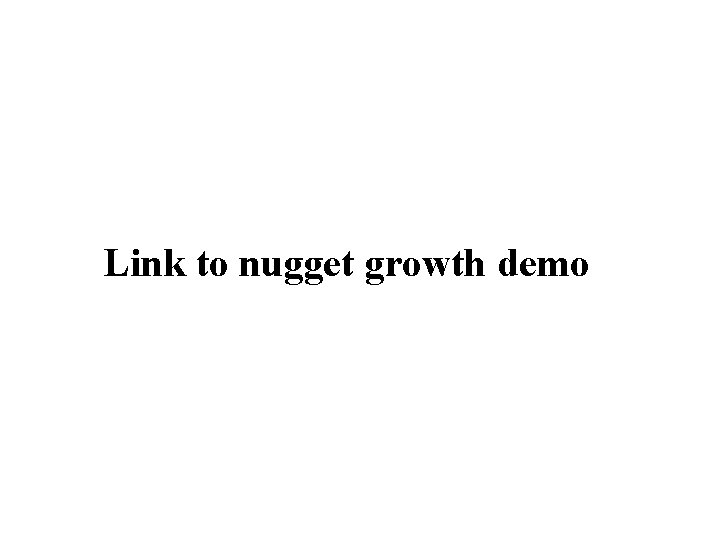
Link to nugget growth demo

Nugget Solidification
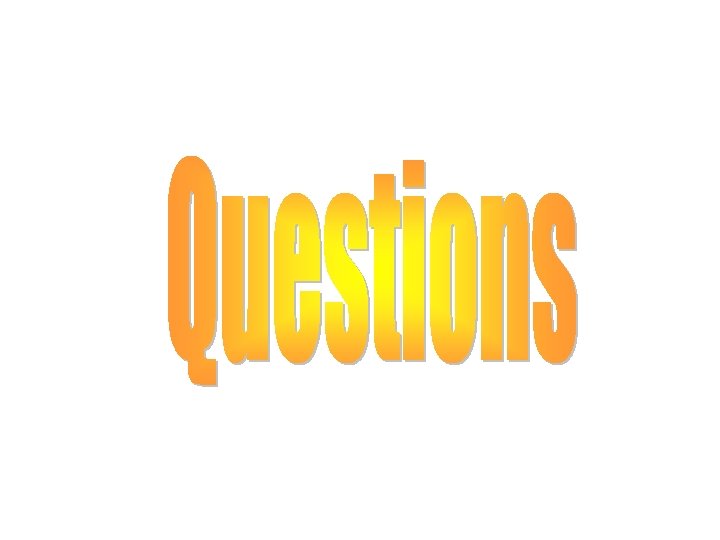
- Slides: 36