Industrial Hygiene An Introduction For Chemical Engineers Mohd
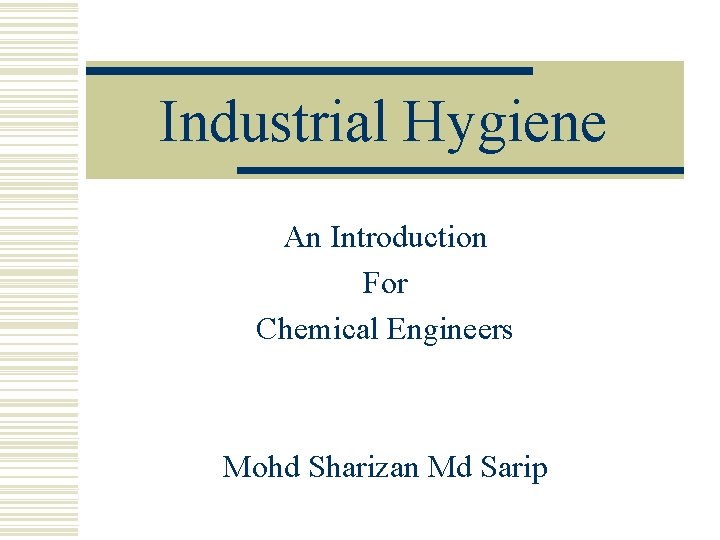
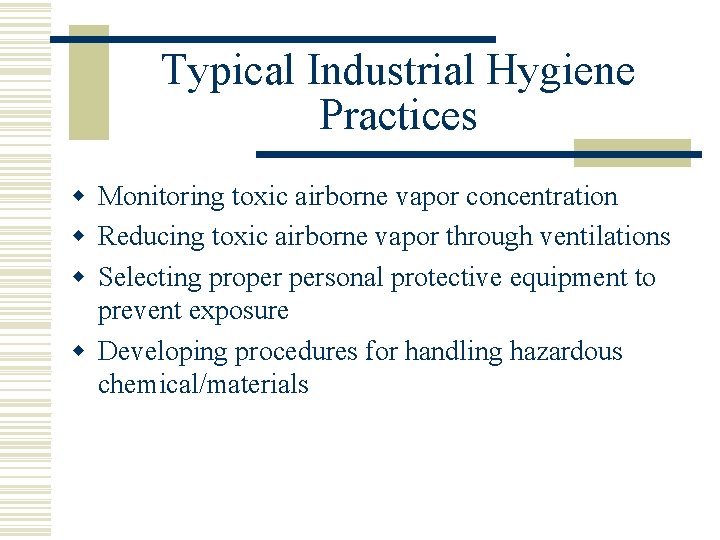
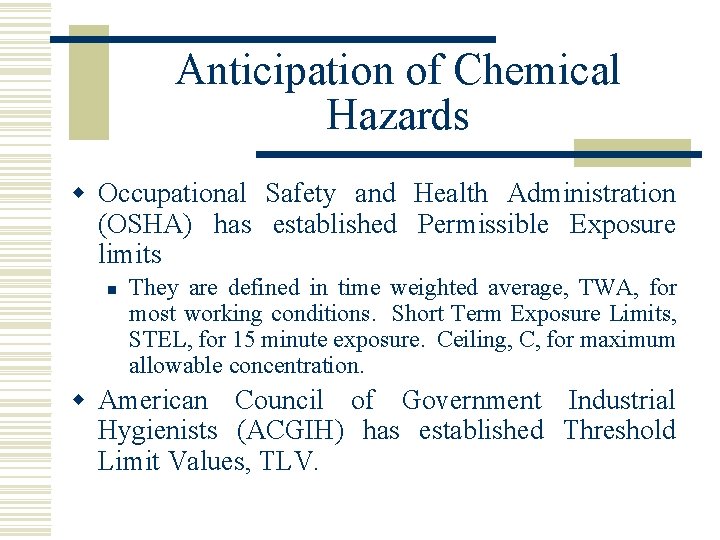
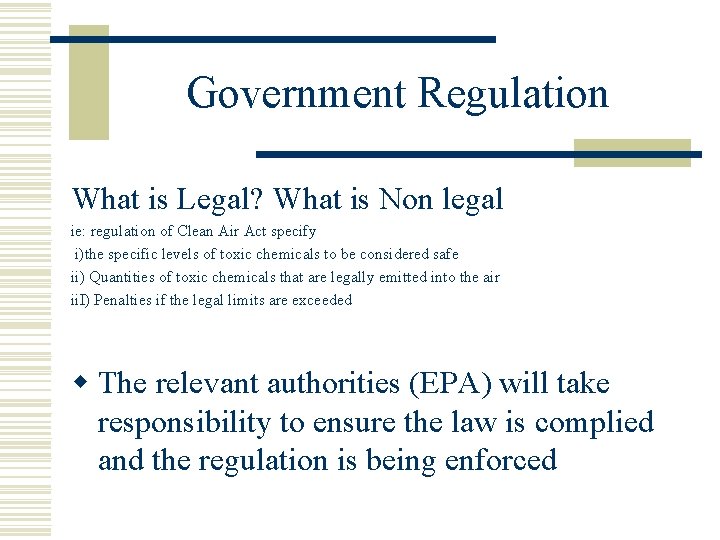
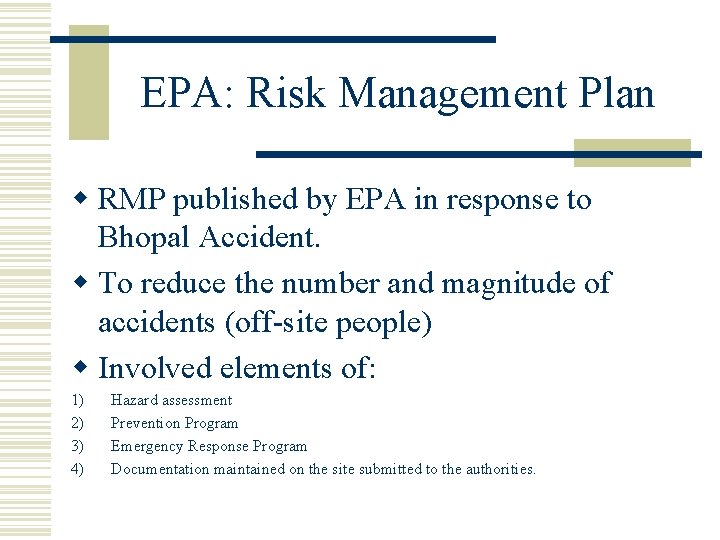
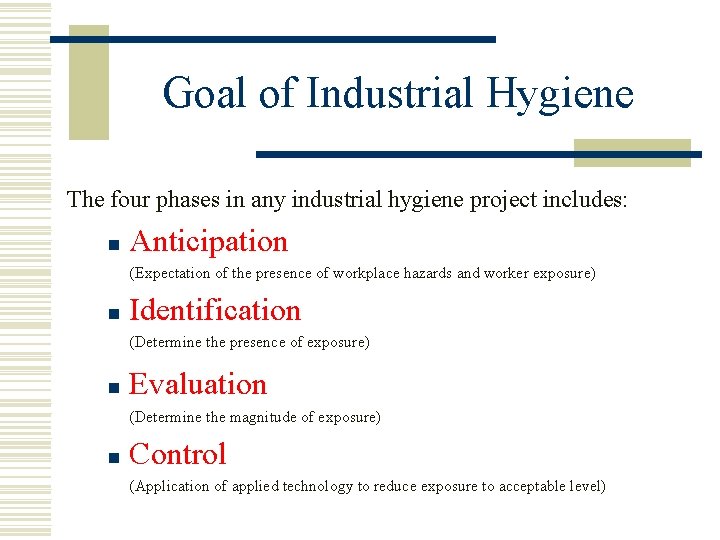
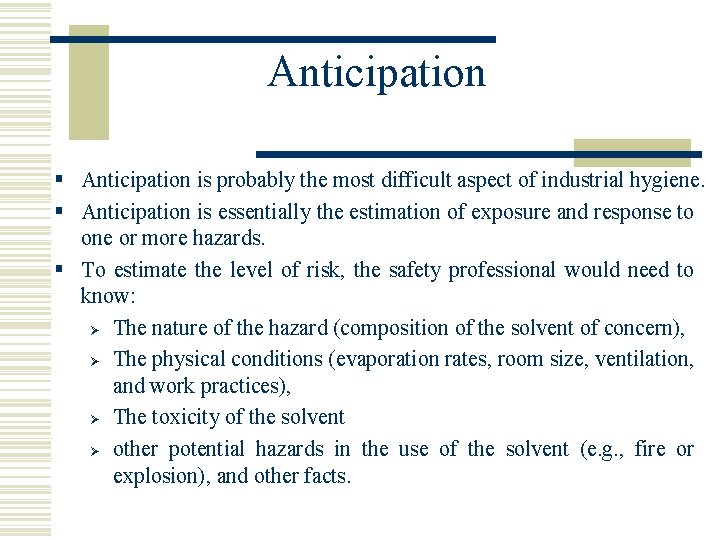
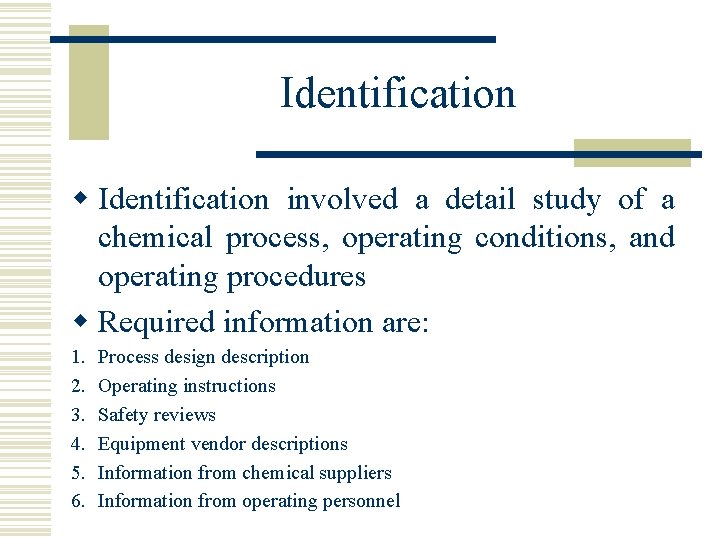
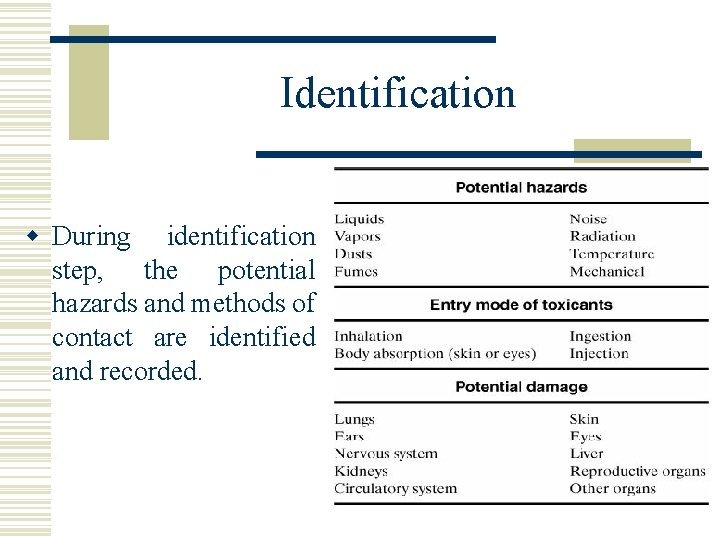
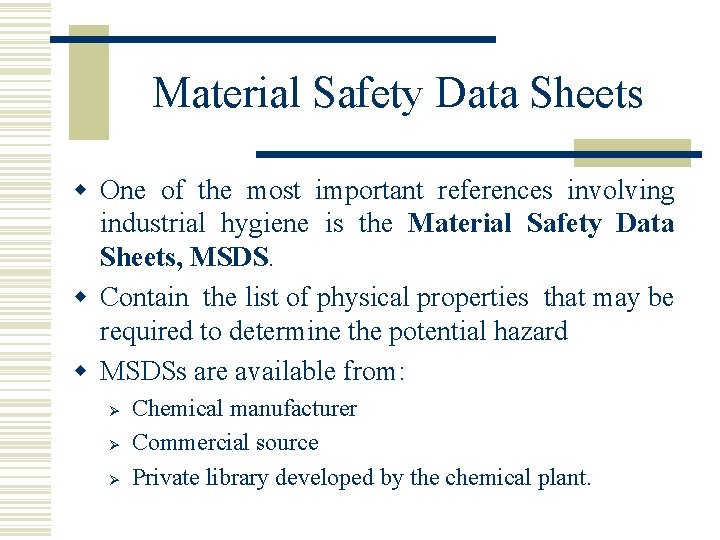
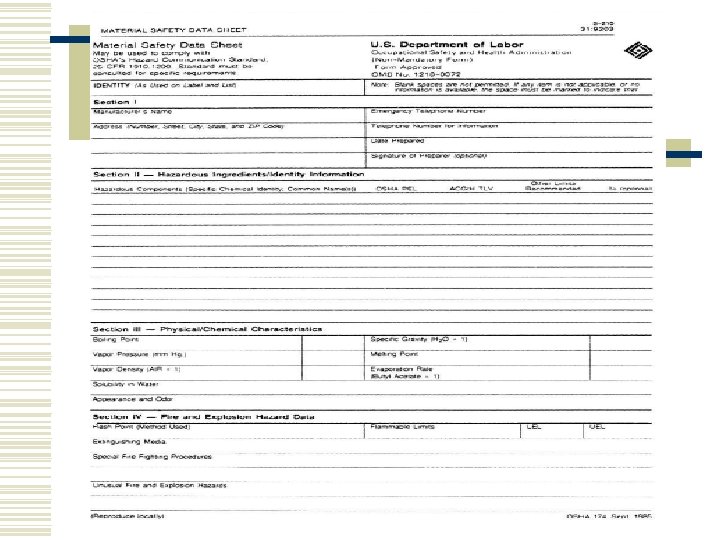
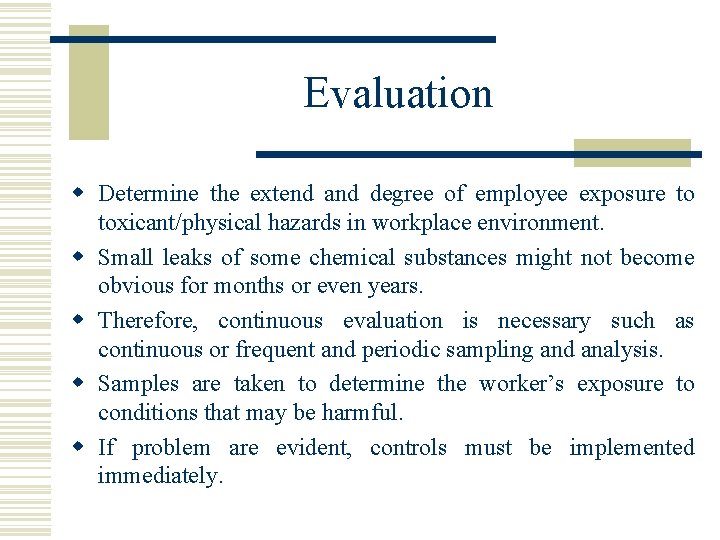
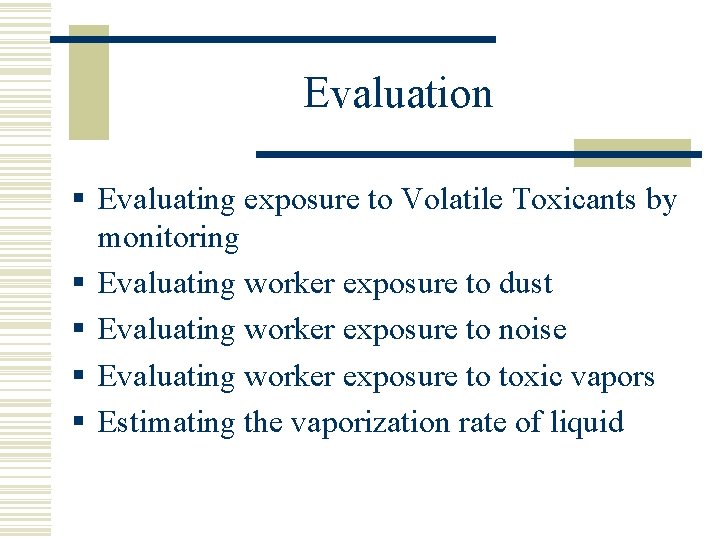
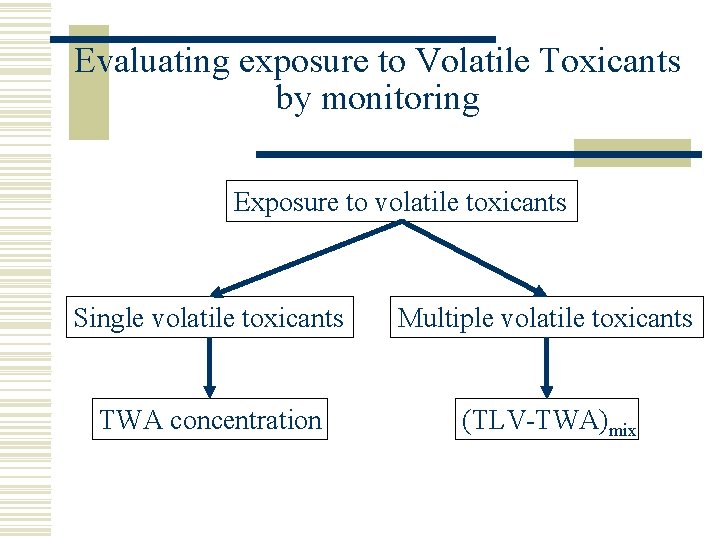
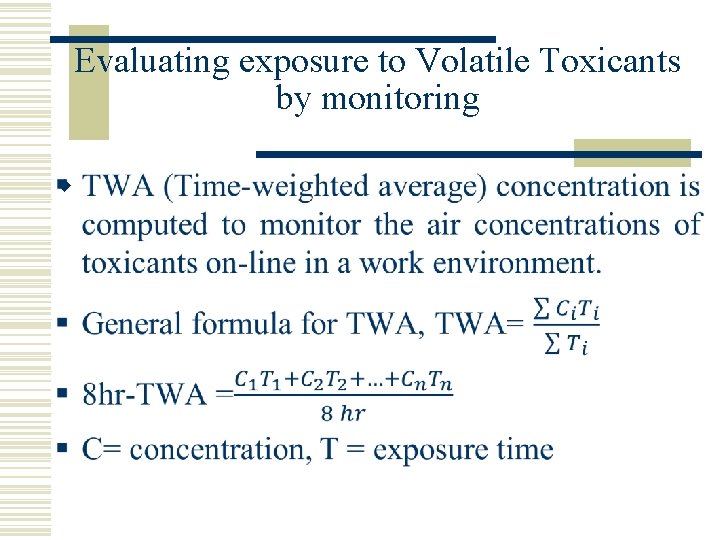
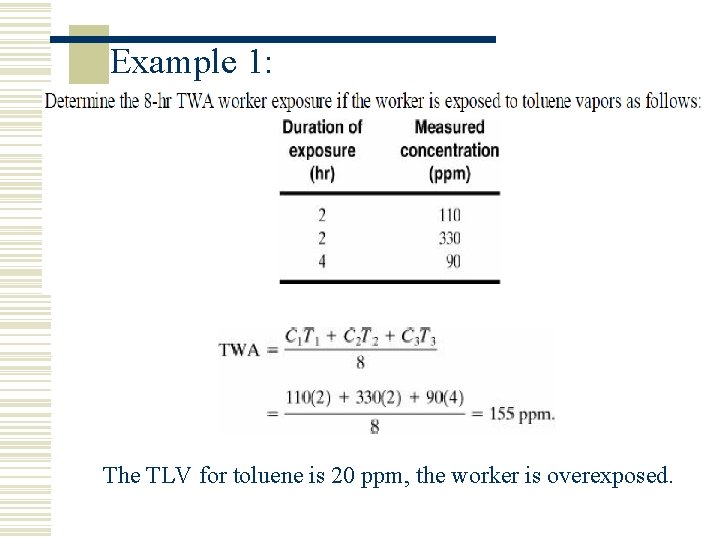
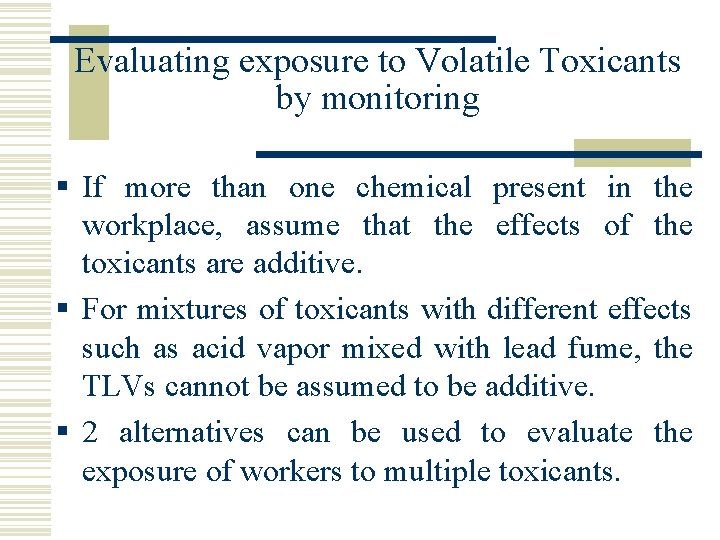
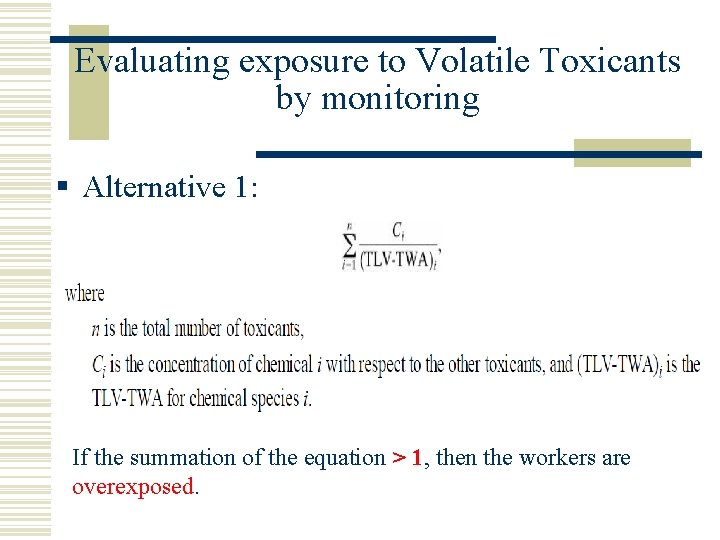
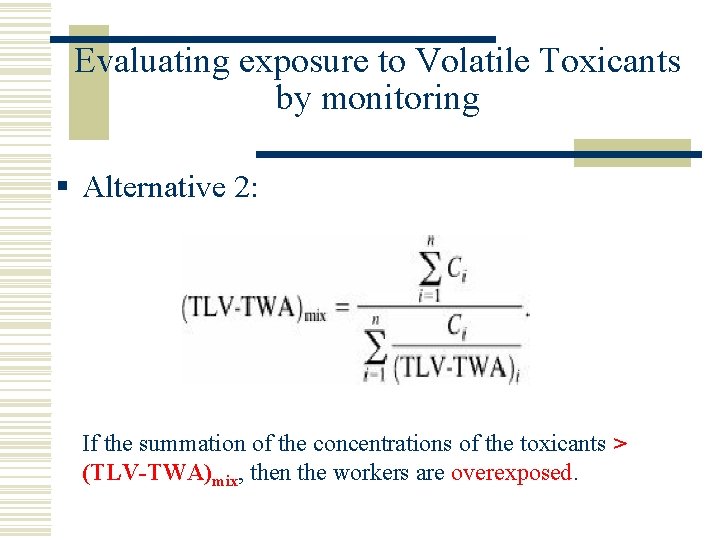
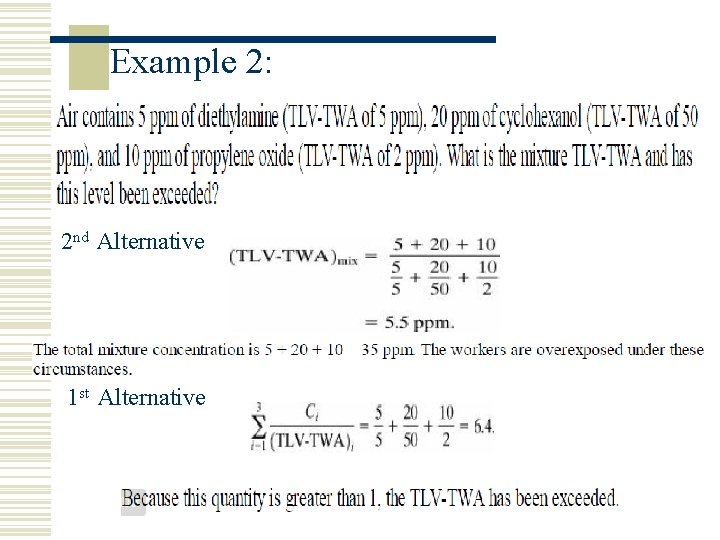
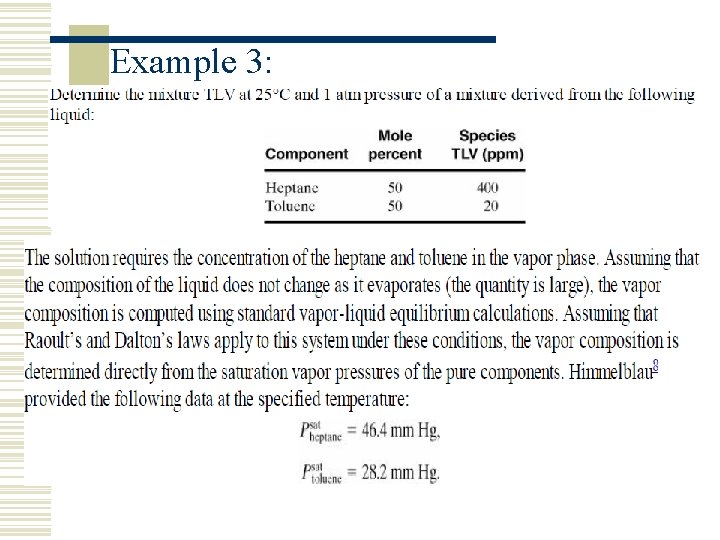
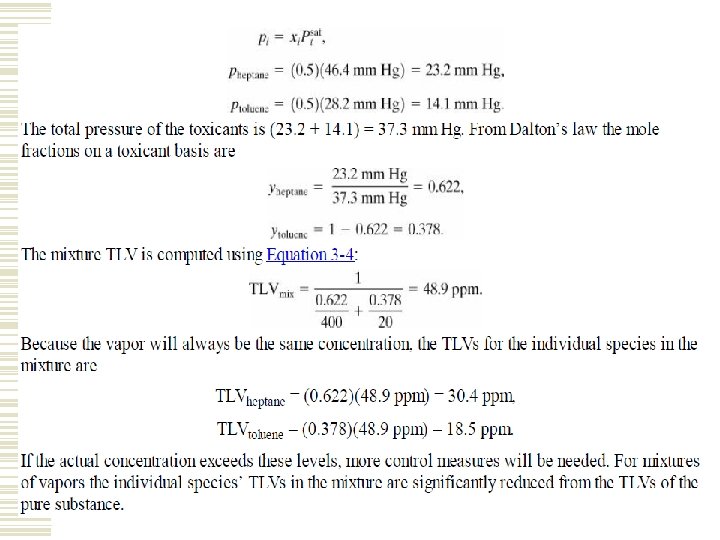
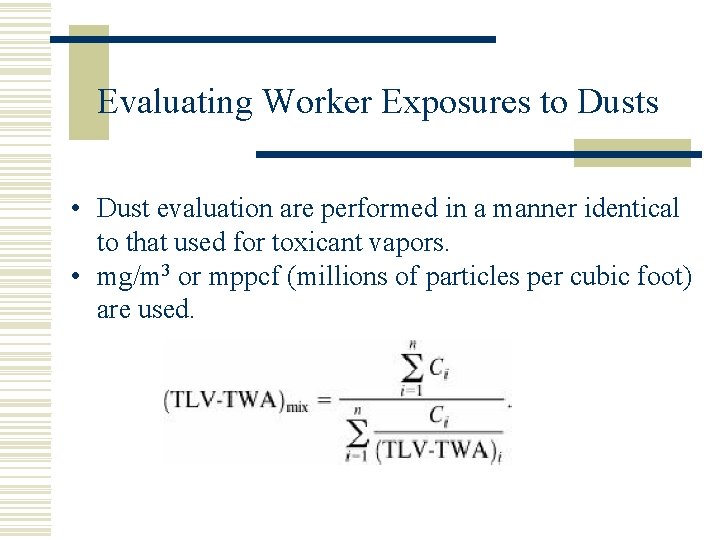
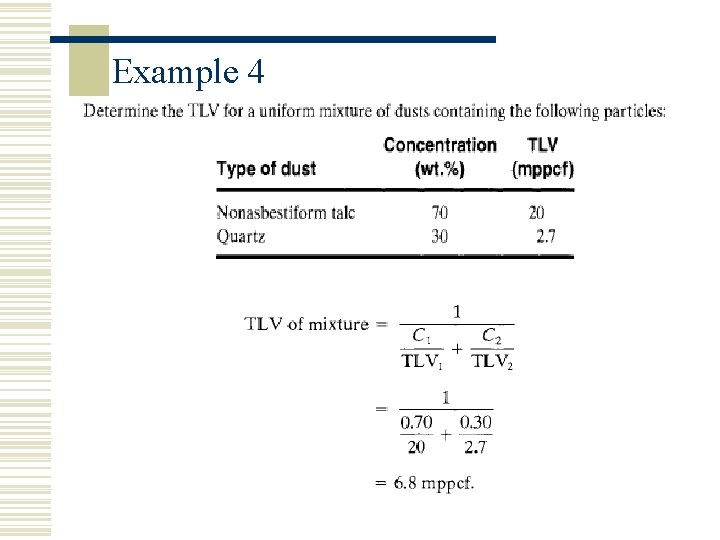
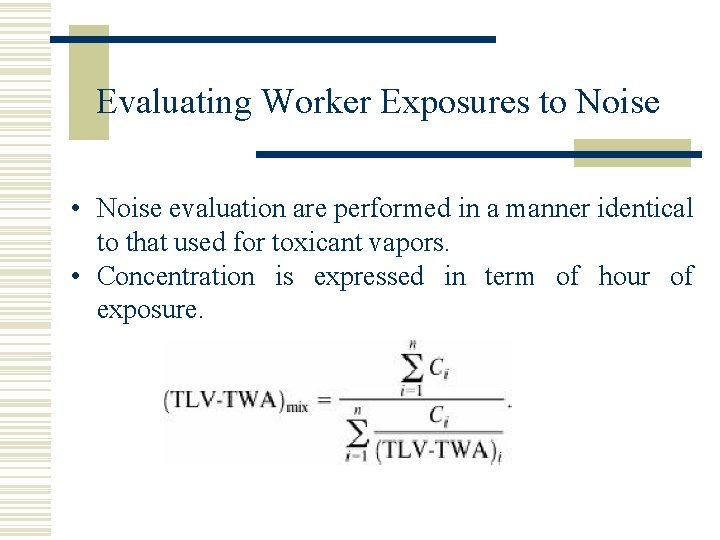
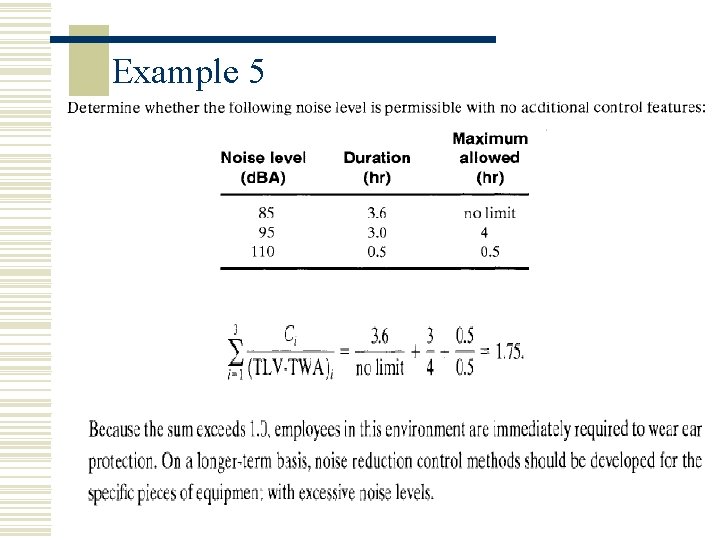
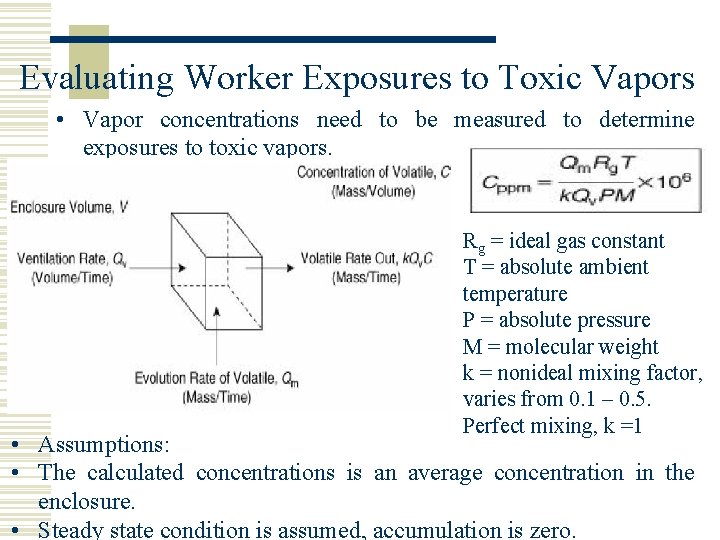
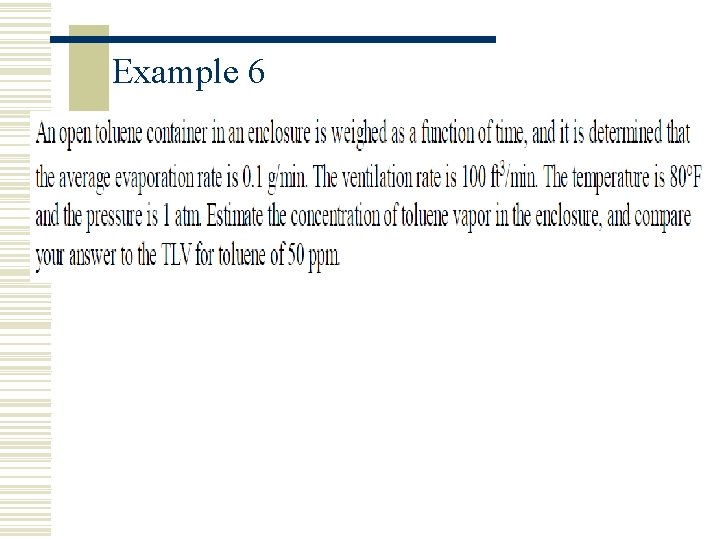
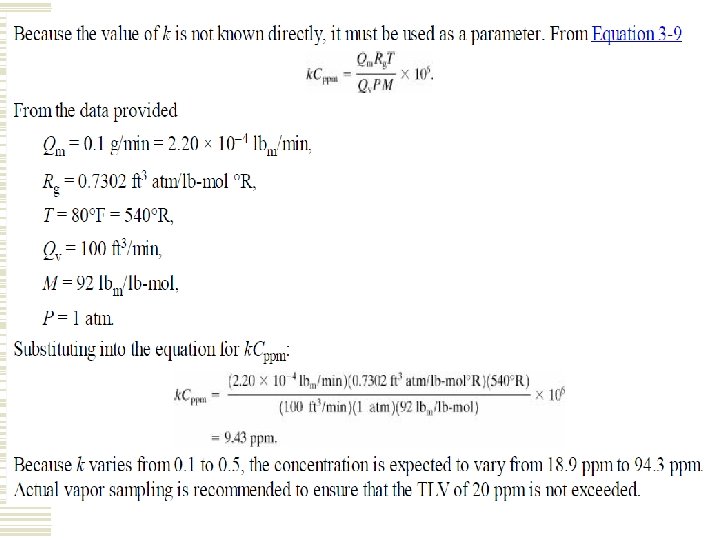
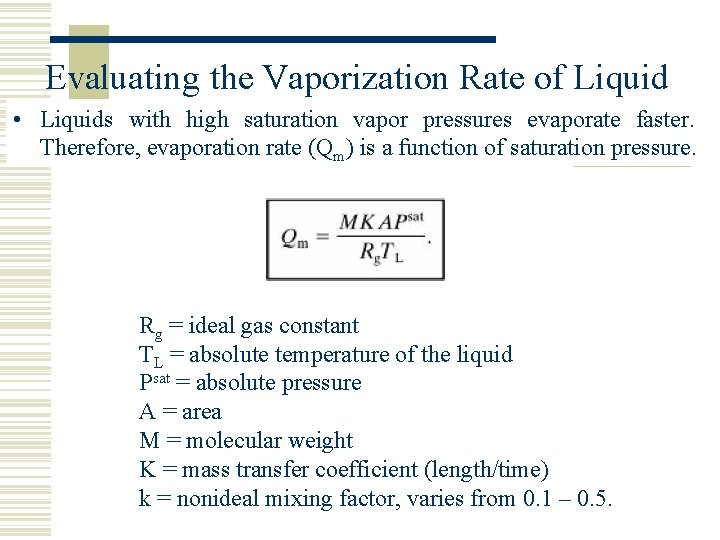
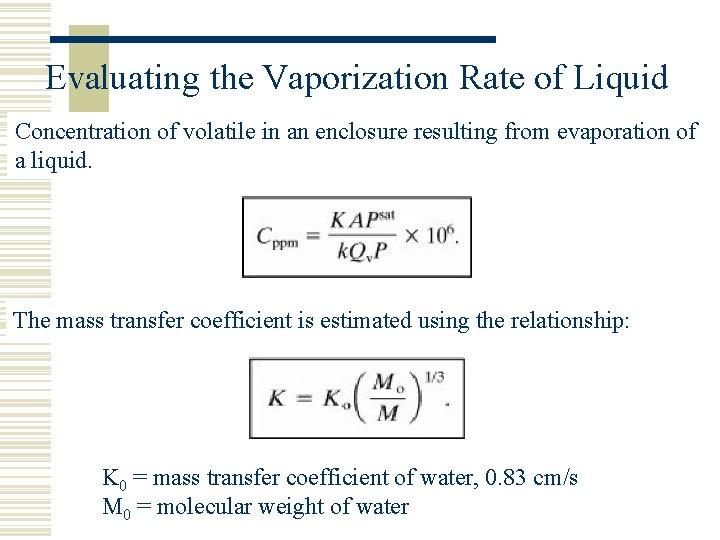
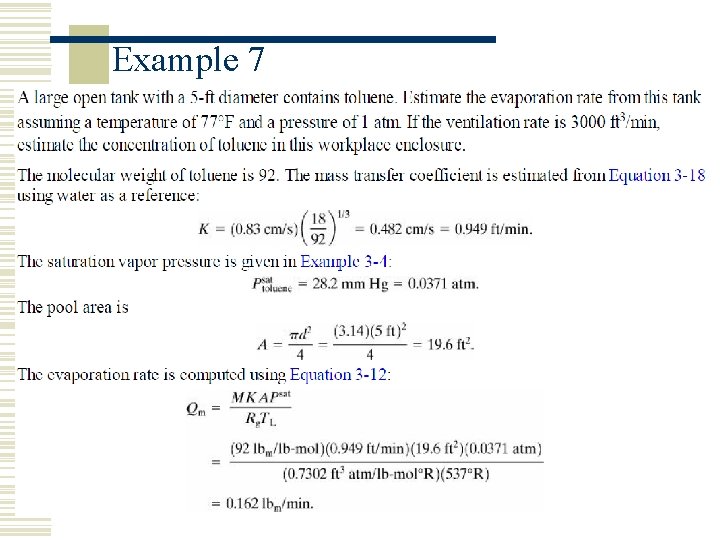
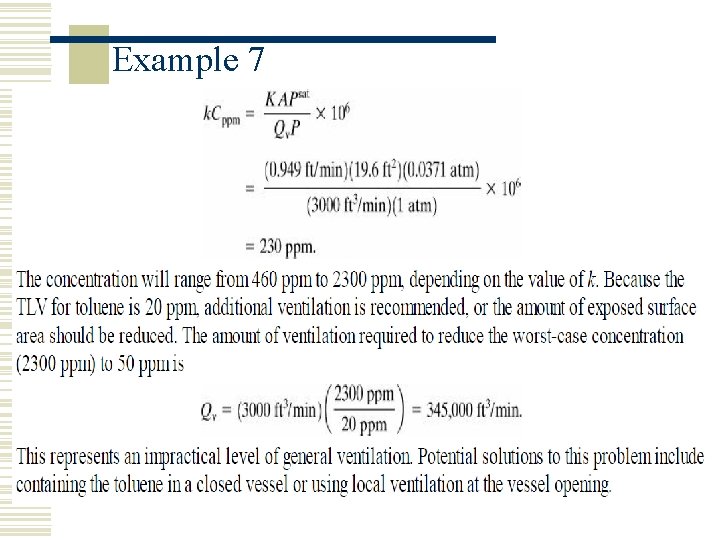
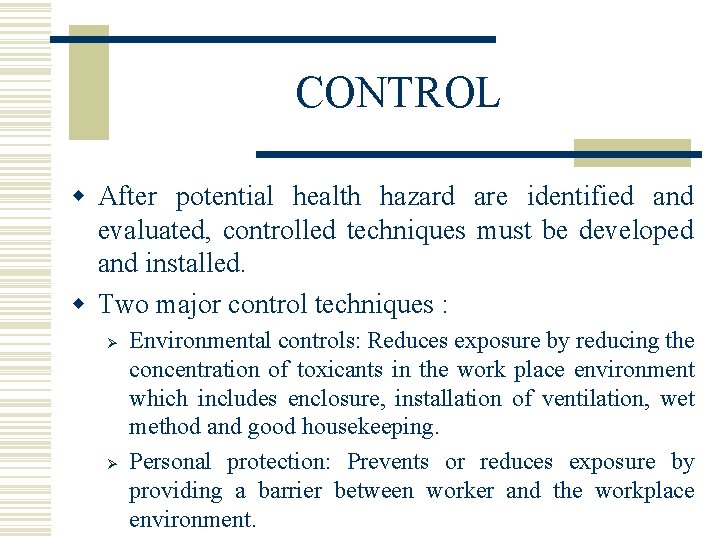
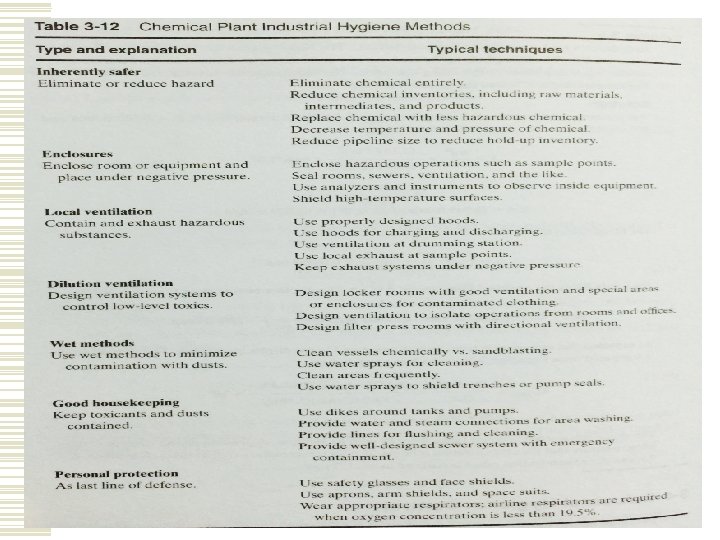
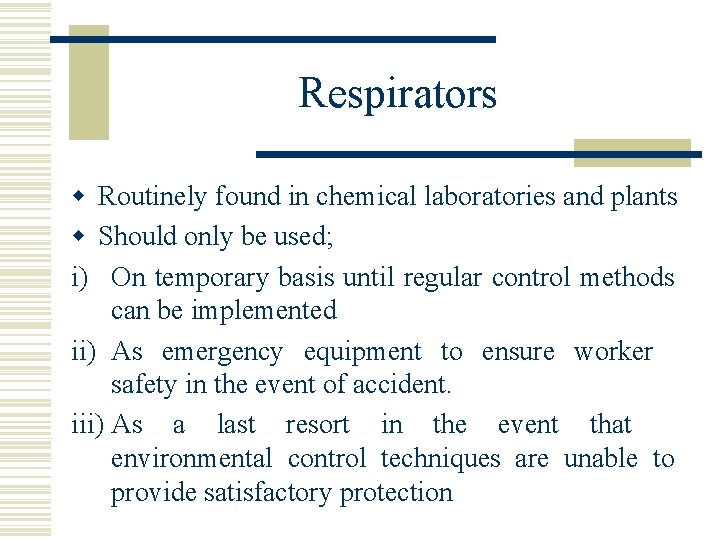
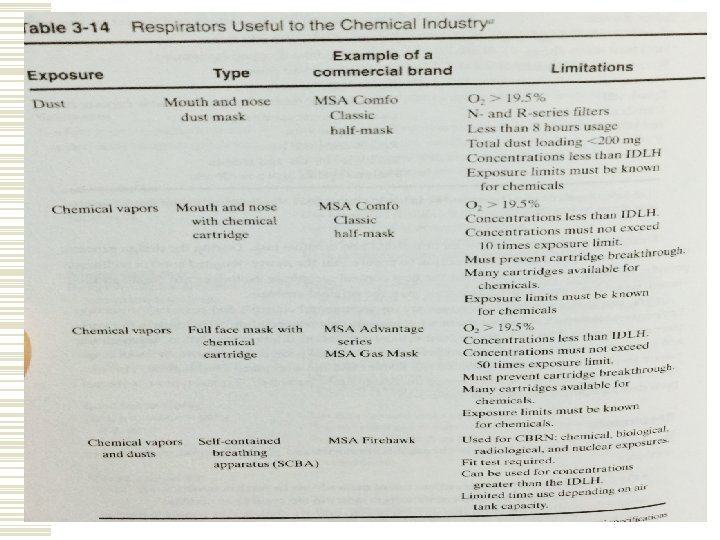
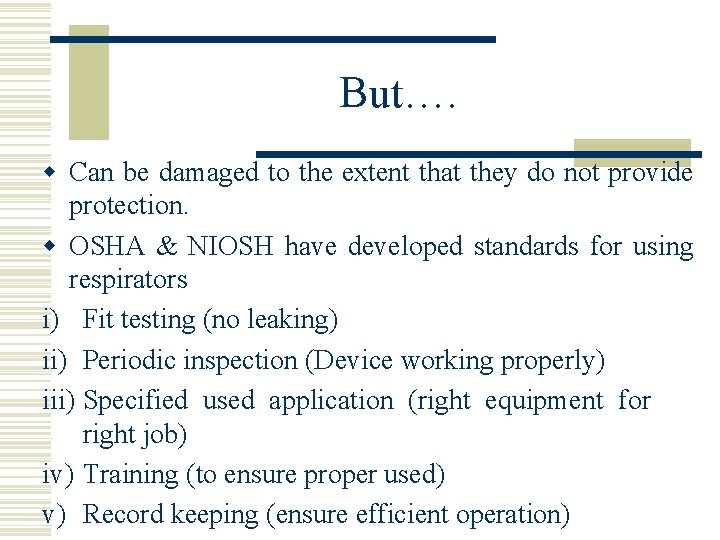
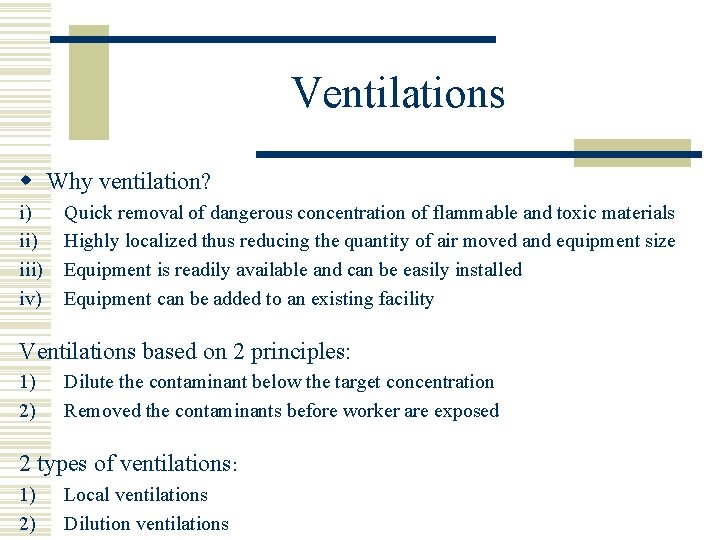
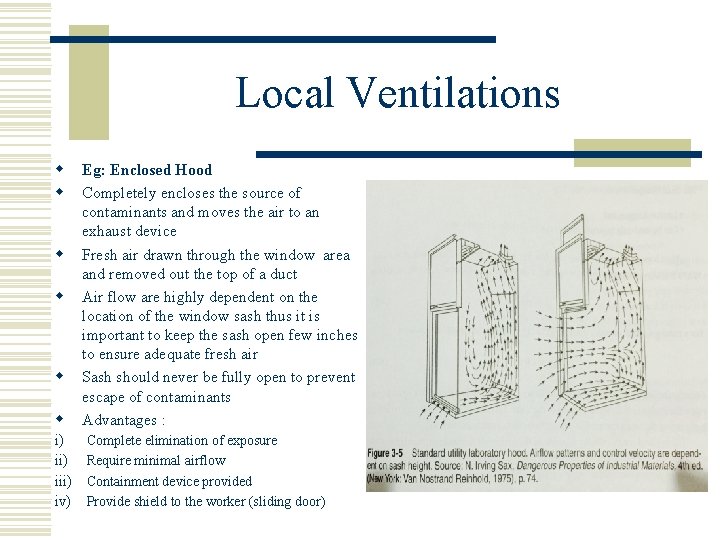
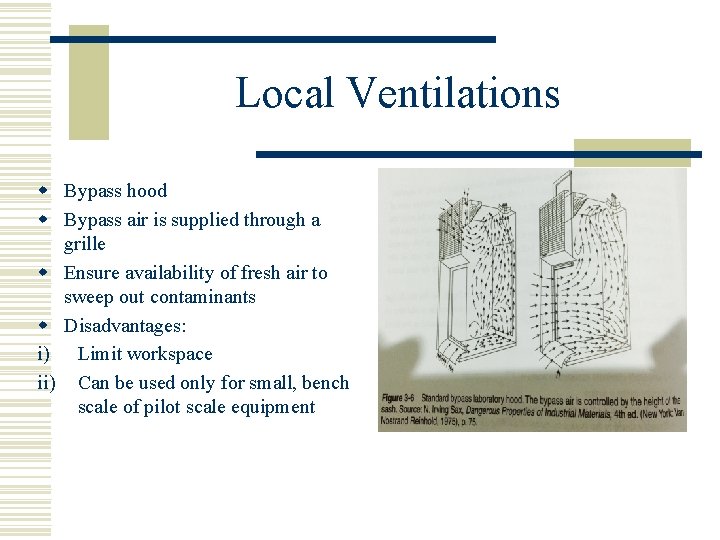
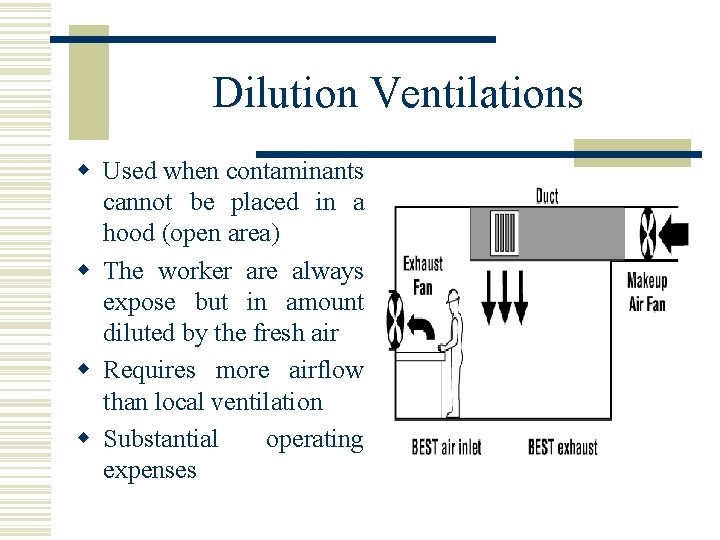
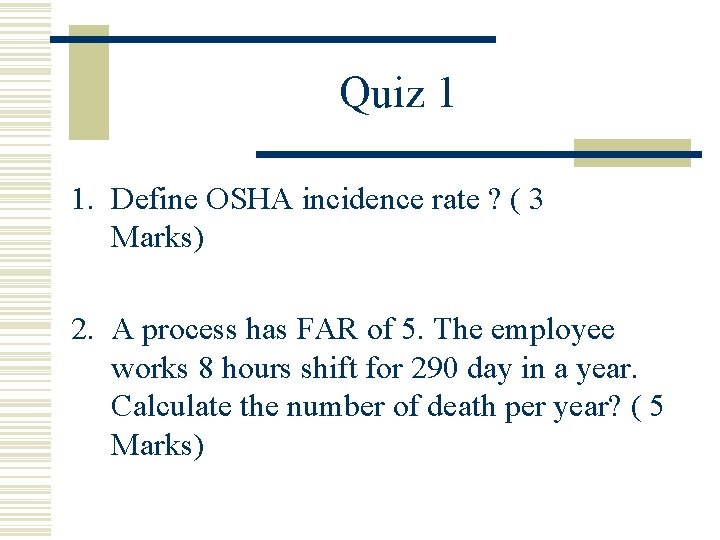
- Slides: 43
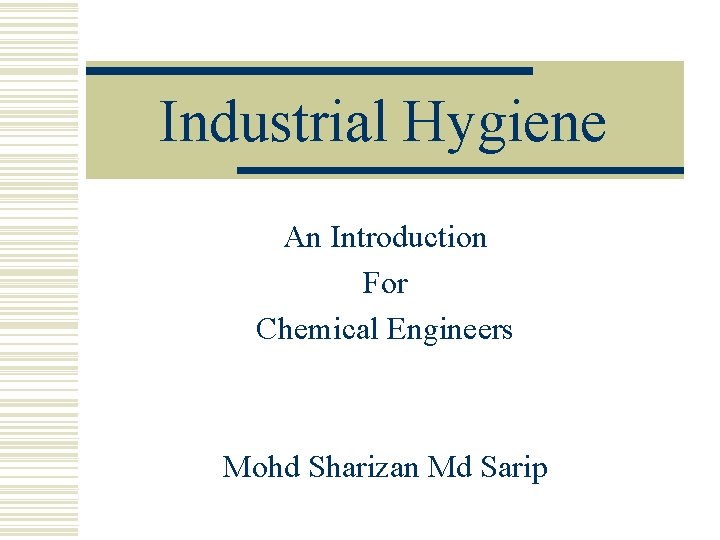
Industrial Hygiene An Introduction For Chemical Engineers Mohd Sharizan Md Sarip
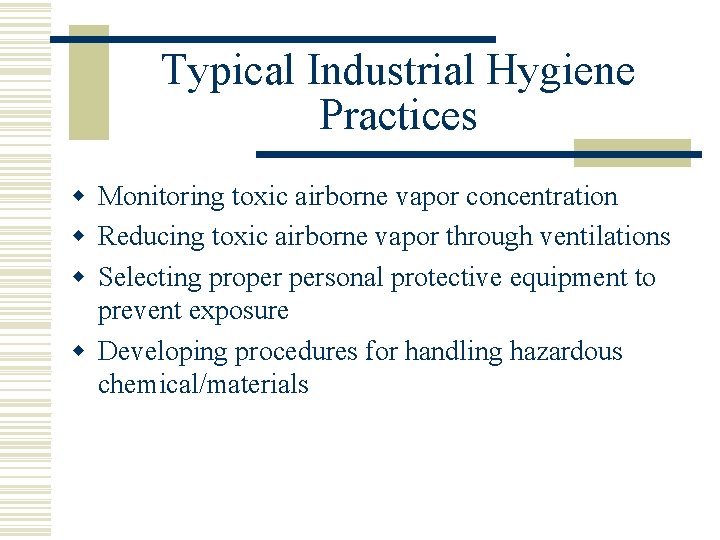
Typical Industrial Hygiene Practices w Monitoring toxic airborne vapor concentration w Reducing toxic airborne vapor through ventilations w Selecting proper personal protective equipment to prevent exposure w Developing procedures for handling hazardous chemical/materials
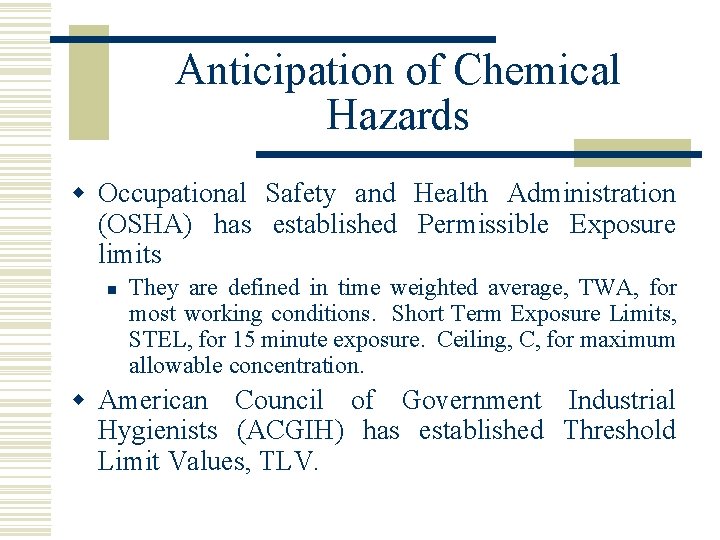
Anticipation of Chemical Hazards w Occupational Safety and Health Administration (OSHA) has established Permissible Exposure limits n They are defined in time weighted average, TWA, for most working conditions. Short Term Exposure Limits, STEL, for 15 minute exposure. Ceiling, C, for maximum allowable concentration. w American Council of Government Industrial Hygienists (ACGIH) has established Threshold Limit Values, TLV.
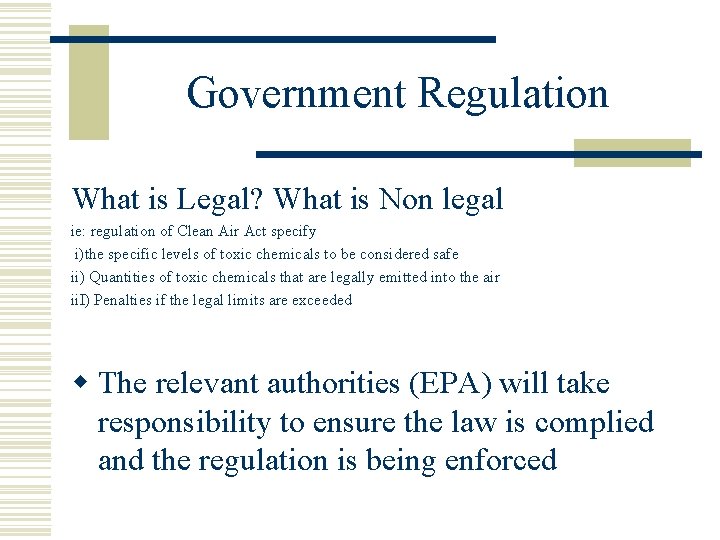
Government Regulation What is Legal? What is Non legal ie: regulation of Clean Air Act specify i)the specific levels of toxic chemicals to be considered safe ii) Quantities of toxic chemicals that are legally emitted into the air ii. I) Penalties if the legal limits are exceeded w The relevant authorities (EPA) will take responsibility to ensure the law is complied and the regulation is being enforced
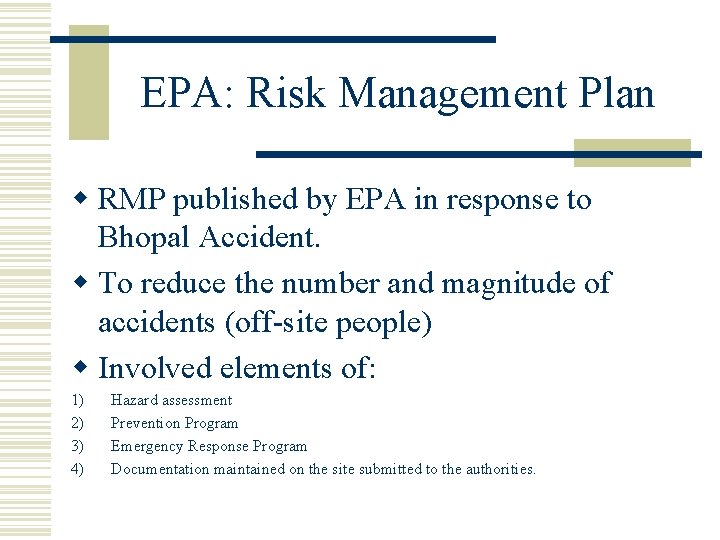
EPA: Risk Management Plan w RMP published by EPA in response to Bhopal Accident. w To reduce the number and magnitude of accidents (off-site people) w Involved elements of: 1) 2) 3) 4) Hazard assessment Prevention Program Emergency Response Program Documentation maintained on the site submitted to the authorities.
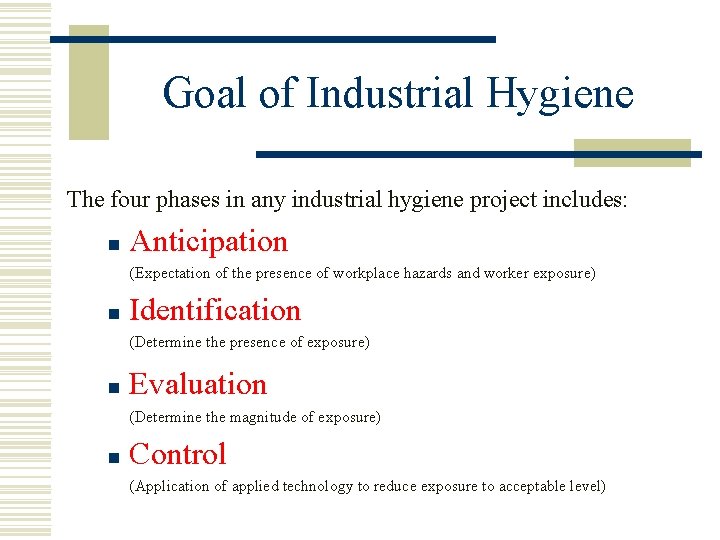
Goal of Industrial Hygiene The four phases in any industrial hygiene project includes: n Anticipation (Expectation of the presence of workplace hazards and worker exposure) n Identification (Determine the presence of exposure) n Evaluation (Determine the magnitude of exposure) n Control (Application of applied technology to reduce exposure to acceptable level)
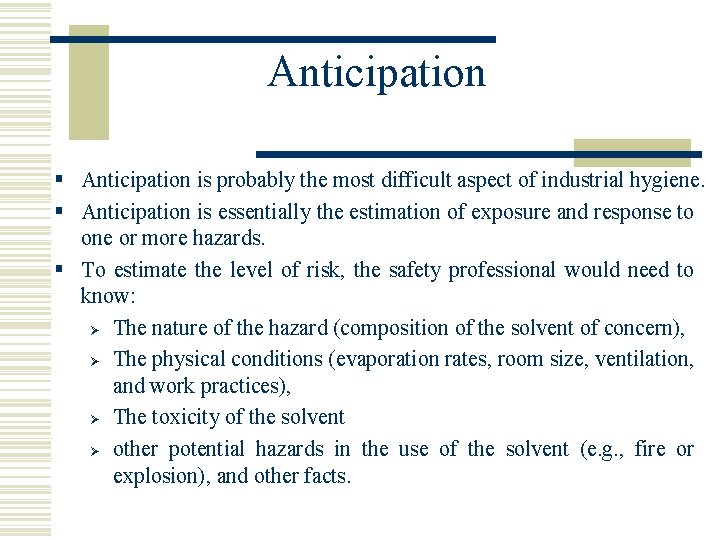
Anticipation § Anticipation is probably the most difficult aspect of industrial hygiene. § Anticipation is essentially the estimation of exposure and response to one or more hazards. § To estimate the level of risk, the safety professional would need to know: Ø The nature of the hazard (composition of the solvent of concern), Ø The physical conditions (evaporation rates, room size, ventilation, and work practices), Ø The toxicity of the solvent Ø other potential hazards in the use of the solvent (e. g. , fire or explosion), and other facts.
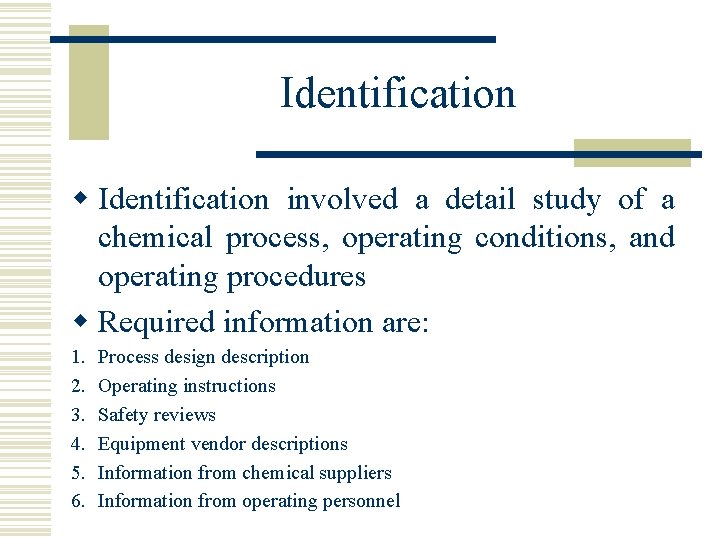
Identification w Identification involved a detail study of a chemical process, operating conditions, and operating procedures w Required information are: 1. 2. 3. 4. 5. 6. Process design description Operating instructions Safety reviews Equipment vendor descriptions Information from chemical suppliers Information from operating personnel
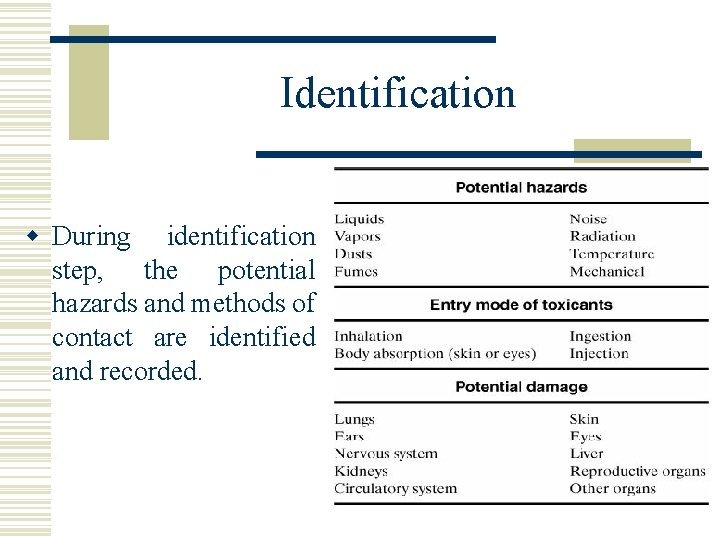
Identification w During identification step, the potential hazards and methods of contact are identified and recorded.
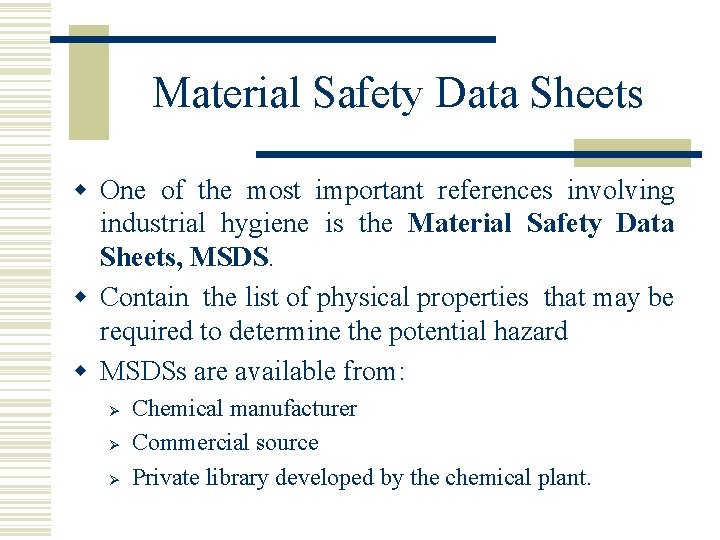
Material Safety Data Sheets w One of the most important references involving industrial hygiene is the Material Safety Data Sheets, MSDS. w Contain the list of physical properties that may be required to determine the potential hazard w MSDSs are available from: Ø Ø Ø Chemical manufacturer Commercial source Private library developed by the chemical plant.
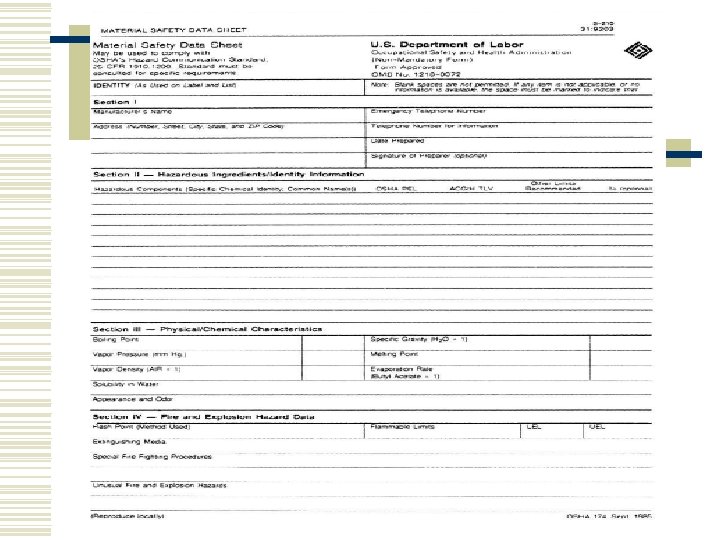
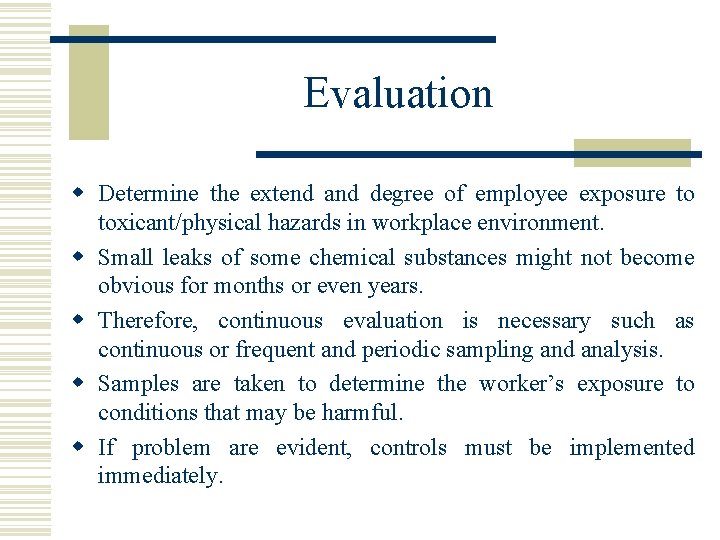
Evaluation w Determine the extend and degree of employee exposure to toxicant/physical hazards in workplace environment. w Small leaks of some chemical substances might not become obvious for months or even years. w Therefore, continuous evaluation is necessary such as continuous or frequent and periodic sampling and analysis. w Samples are taken to determine the worker’s exposure to conditions that may be harmful. w If problem are evident, controls must be implemented immediately.
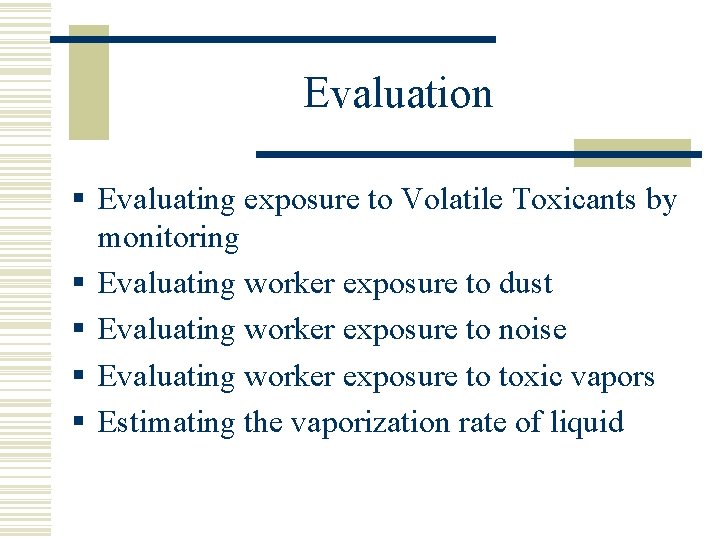
Evaluation § Evaluating exposure to Volatile Toxicants by monitoring § Evaluating worker exposure to dust § Evaluating worker exposure to noise § Evaluating worker exposure to toxic vapors § Estimating the vaporization rate of liquid
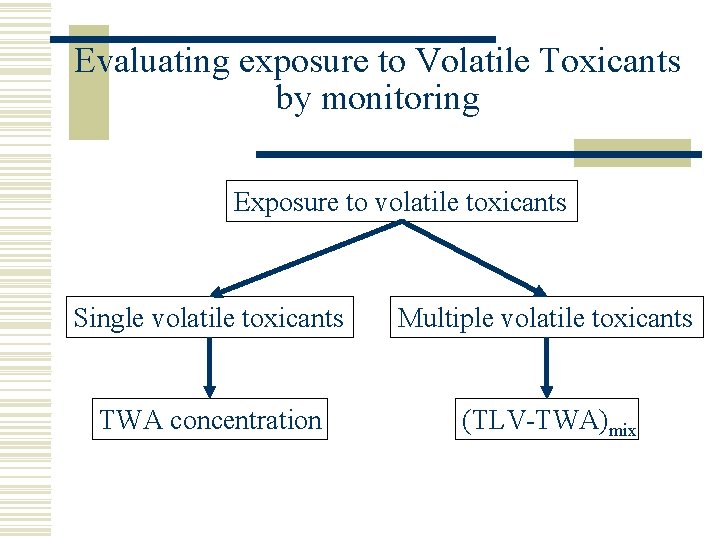
Evaluating exposure to Volatile Toxicants by monitoring Exposure to volatile toxicants Single volatile toxicants Multiple volatile toxicants TWA concentration (TLV-TWA)mix
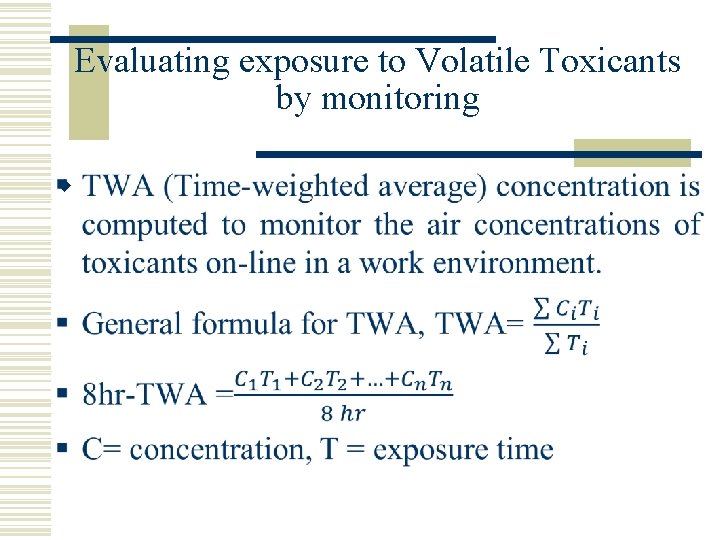
Evaluating exposure to Volatile Toxicants by monitoring w
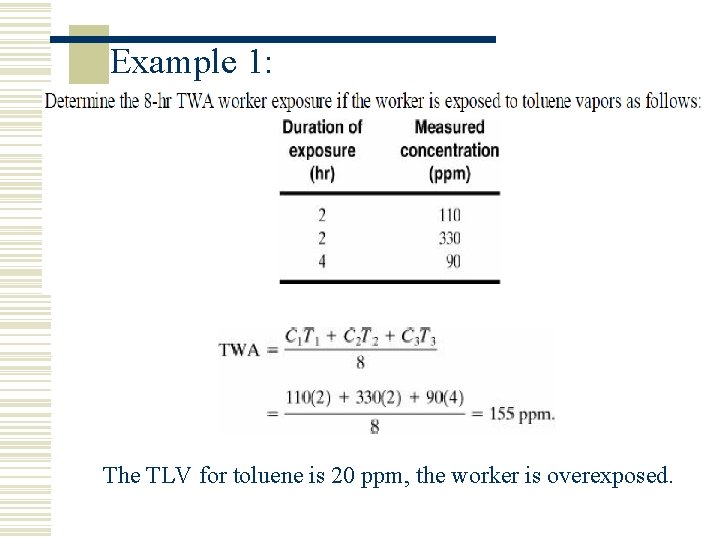
Example 1: The TLV for toluene is 20 ppm, the worker is overexposed.
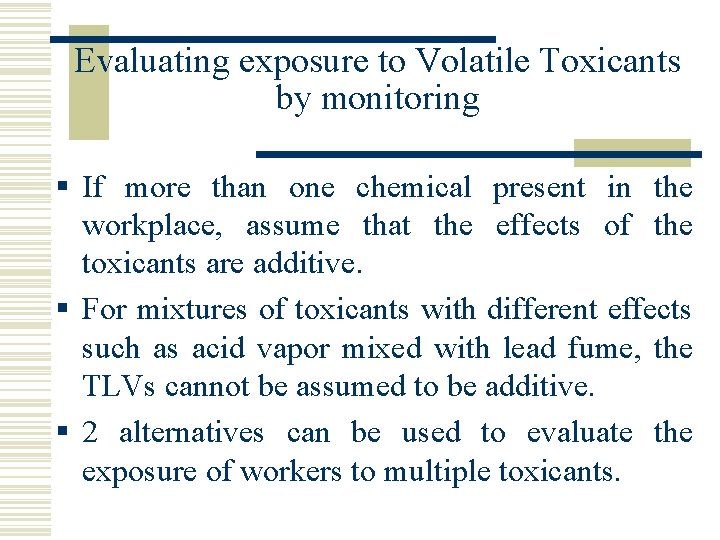
Evaluating exposure to Volatile Toxicants by monitoring § If more than one chemical present in the workplace, assume that the effects of the toxicants are additive. § For mixtures of toxicants with different effects such as acid vapor mixed with lead fume, the TLVs cannot be assumed to be additive. § 2 alternatives can be used to evaluate the exposure of workers to multiple toxicants.
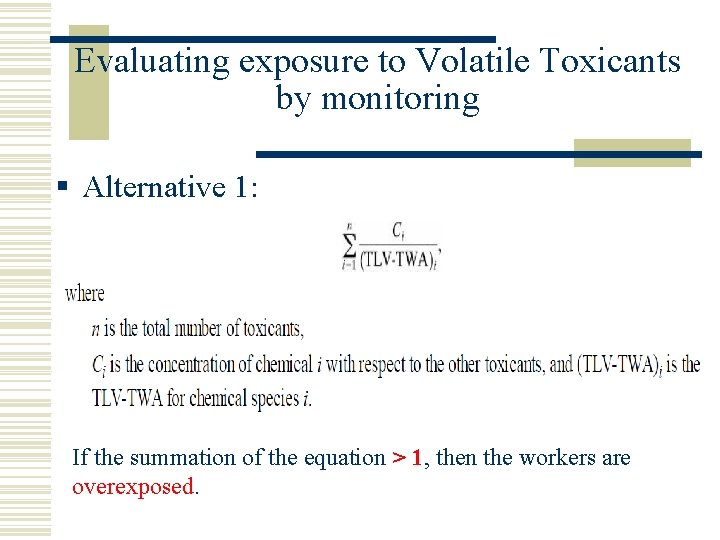
Evaluating exposure to Volatile Toxicants by monitoring § Alternative 1: If the summation of the equation > 1, then the workers are overexposed.
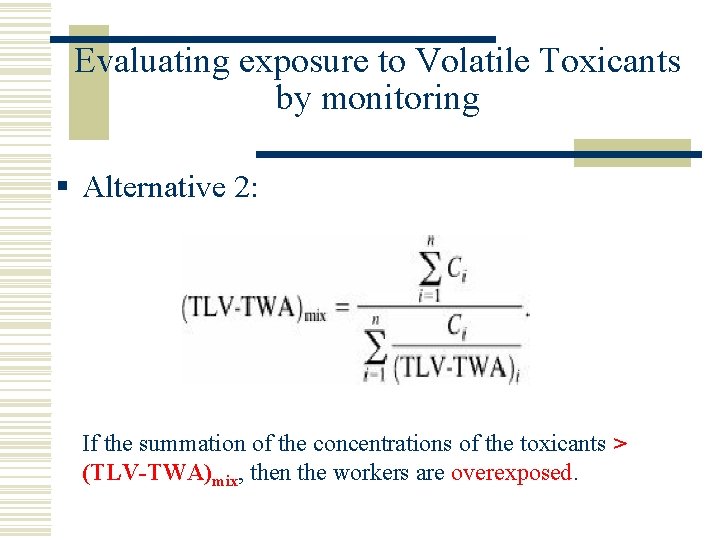
Evaluating exposure to Volatile Toxicants by monitoring § Alternative 2: If the summation of the concentrations of the toxicants > (TLV-TWA)mix, then the workers are overexposed.
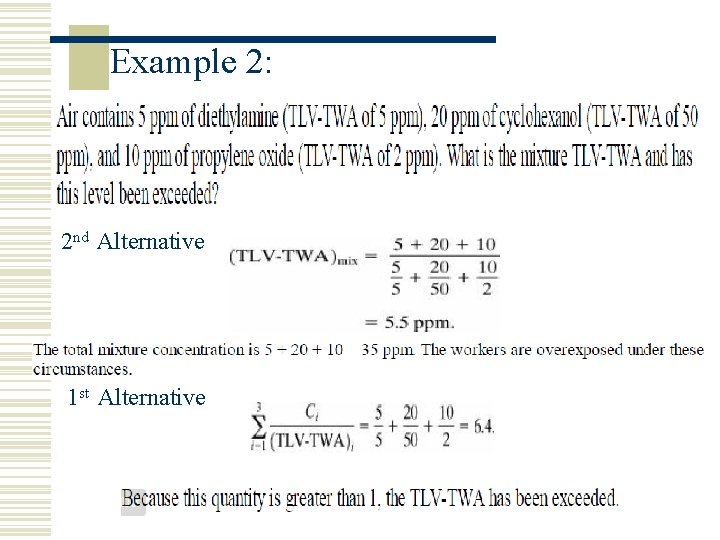
Example 2: 2 nd Alternative 1 st Alternative
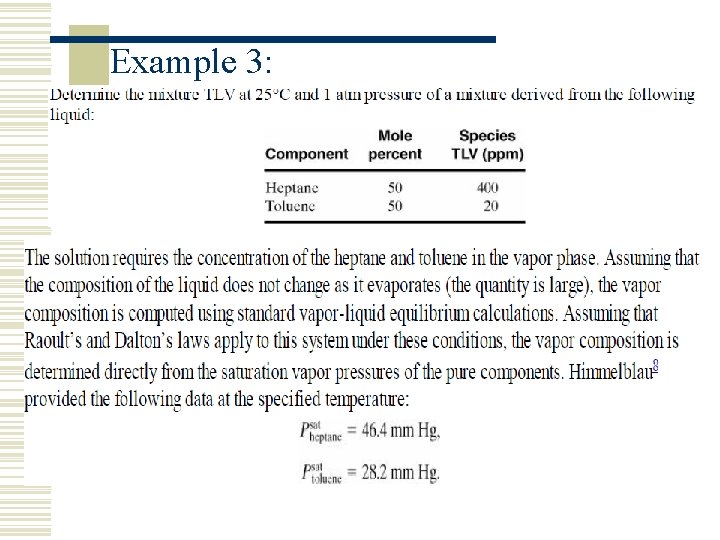
Example 3:
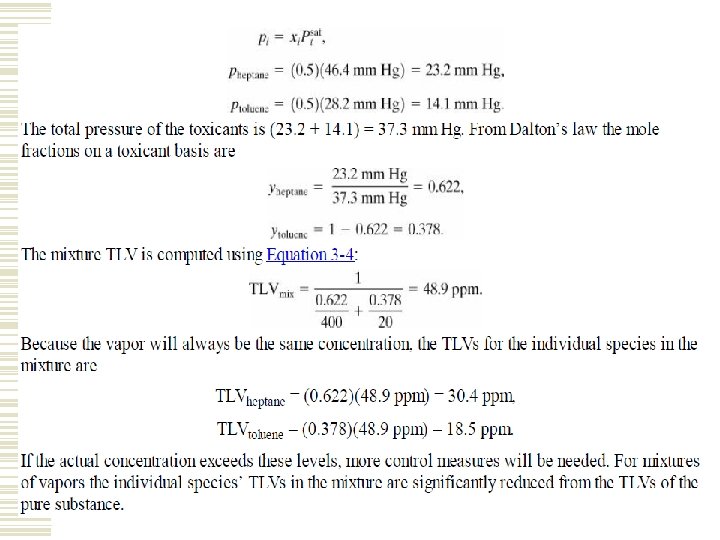
Example:
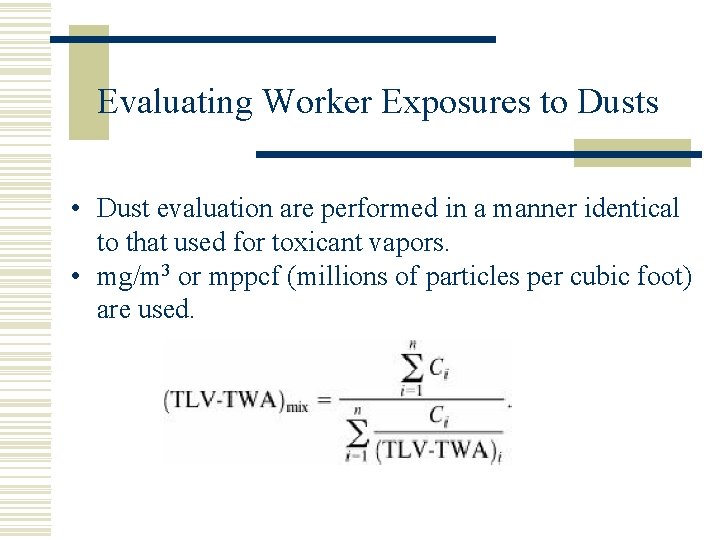
Evaluating Worker Exposures to Dusts • Dust evaluation are performed in a manner identical to that used for toxicant vapors. • mg/m 3 or mppcf (millions of particles per cubic foot) are used.
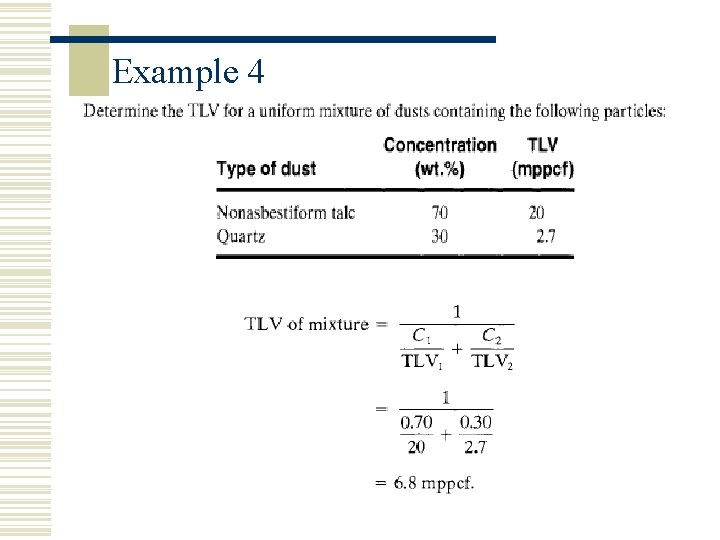
Example 4
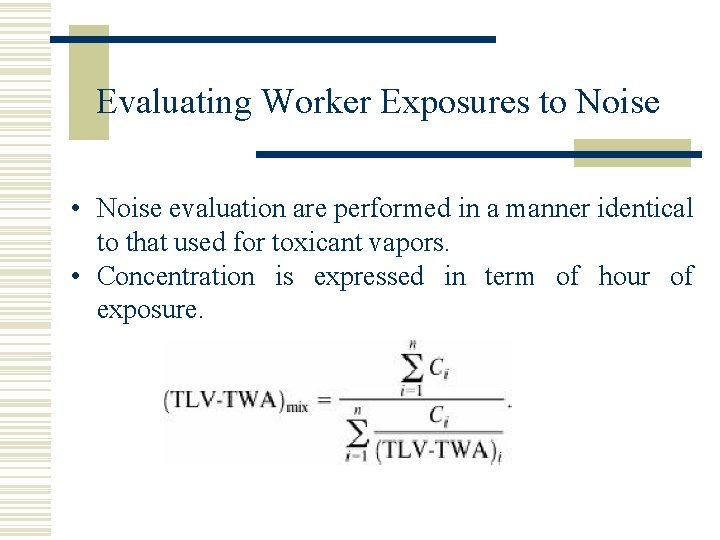
Evaluating Worker Exposures to Noise • Noise evaluation are performed in a manner identical to that used for toxicant vapors. • Concentration is expressed in term of hour of exposure.
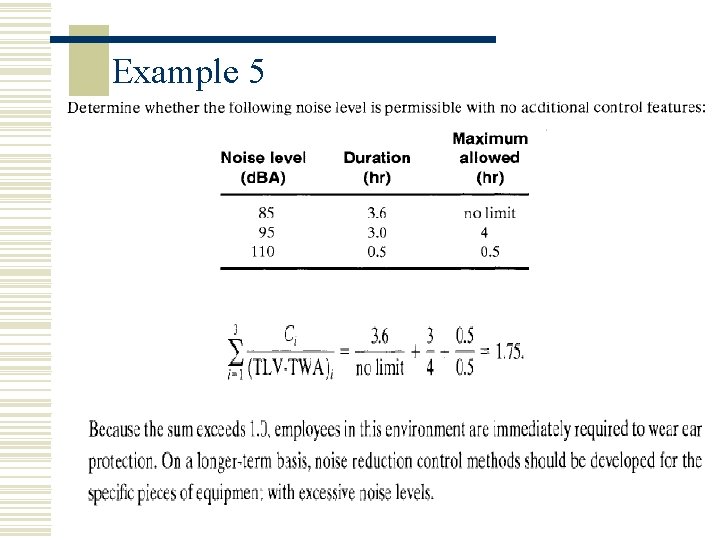
Example 5
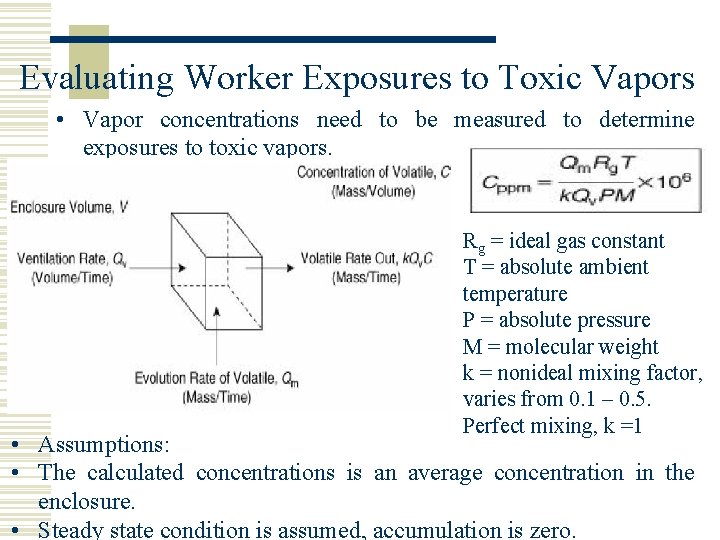
Evaluating Worker Exposures to Toxic Vapors • Vapor concentrations need to be measured to determine exposures to toxic vapors. Rg = ideal gas constant T = absolute ambient temperature P = absolute pressure M = molecular weight k = nonideal mixing factor, varies from 0. 1 – 0. 5. Perfect mixing, k =1 • Assumptions: • The calculated concentrations is an average concentration in the enclosure. • Steady state condition is assumed, accumulation is zero.
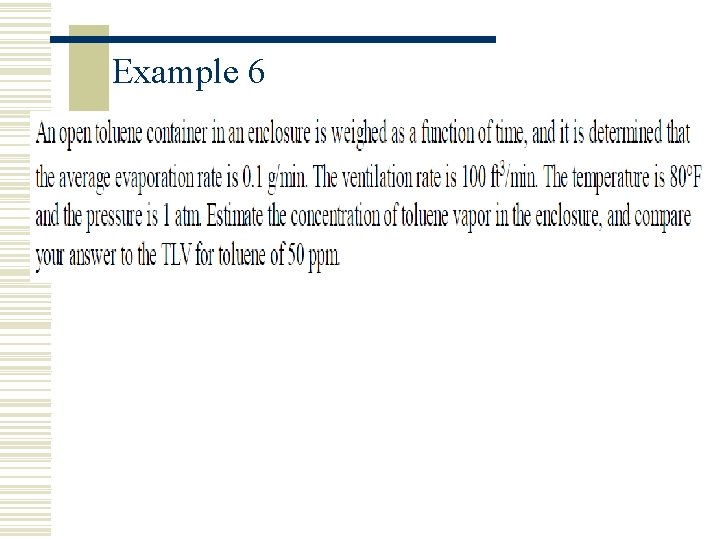
Example 6
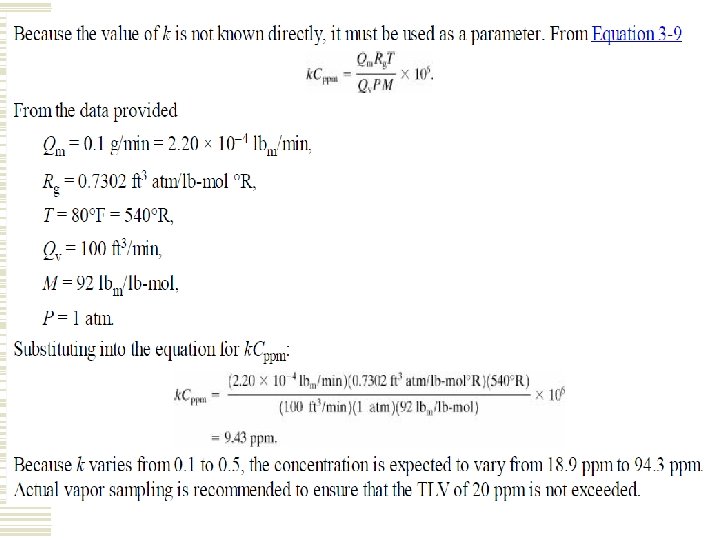
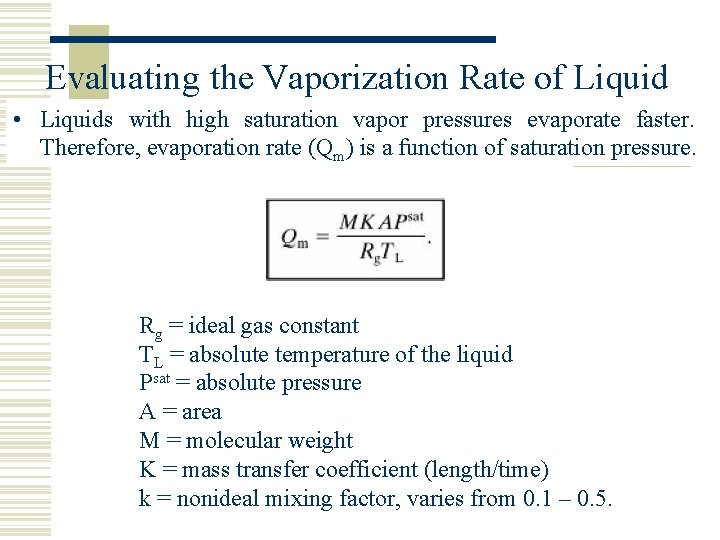
Evaluating the Vaporization Rate of Liquid • Liquids with high saturation vapor pressures evaporate faster. Therefore, evaporation rate (Qm) is a function of saturation pressure. Rg = ideal gas constant TL = absolute temperature of the liquid Psat = absolute pressure A = area M = molecular weight K = mass transfer coefficient (length/time) k = nonideal mixing factor, varies from 0. 1 – 0. 5.
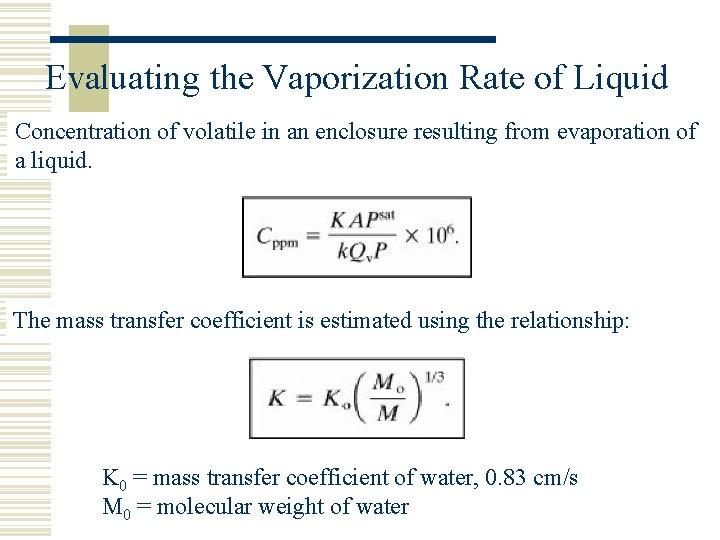
Evaluating the Vaporization Rate of Liquid Concentration of volatile in an enclosure resulting from evaporation of a liquid. The mass transfer coefficient is estimated using the relationship: K 0 = mass transfer coefficient of water, 0. 83 cm/s M 0 = molecular weight of water
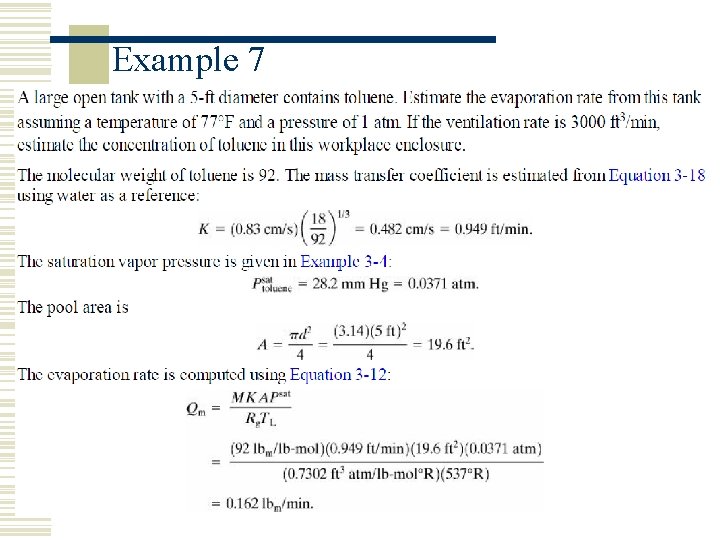
Example 7
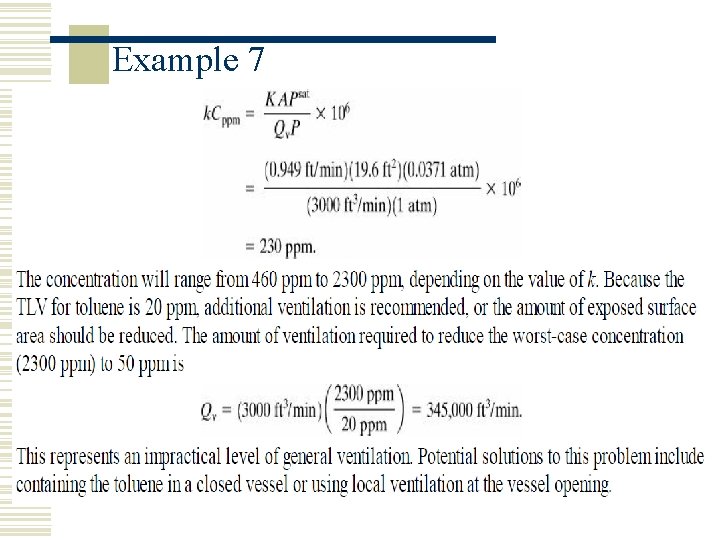
Example 7
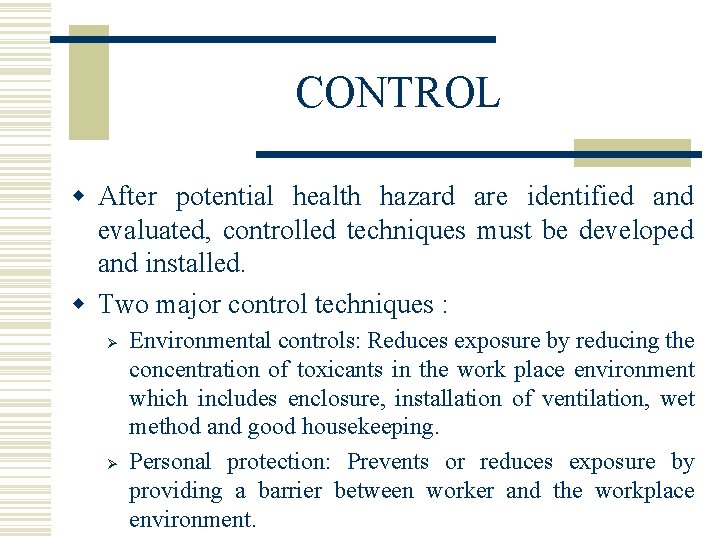
CONTROL w After potential health hazard are identified and evaluated, controlled techniques must be developed and installed. w Two major control techniques : Ø Ø Environmental controls: Reduces exposure by reducing the concentration of toxicants in the work place environment which includes enclosure, installation of ventilation, wet method and good housekeeping. Personal protection: Prevents or reduces exposure by providing a barrier between worker and the workplace environment.
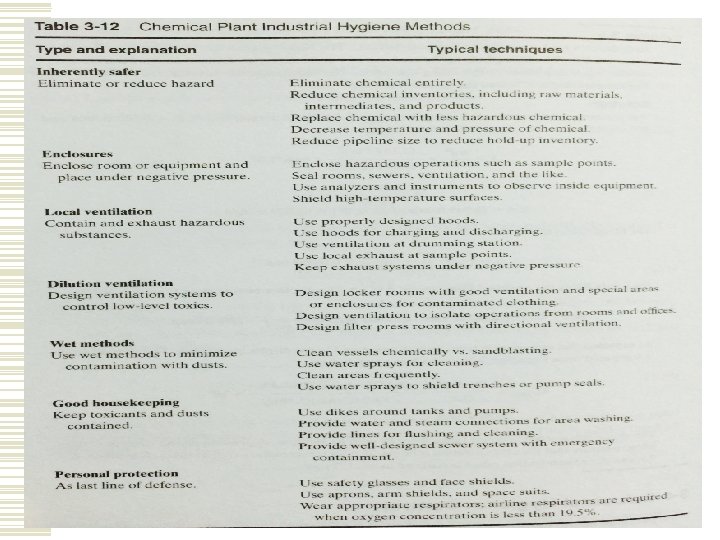
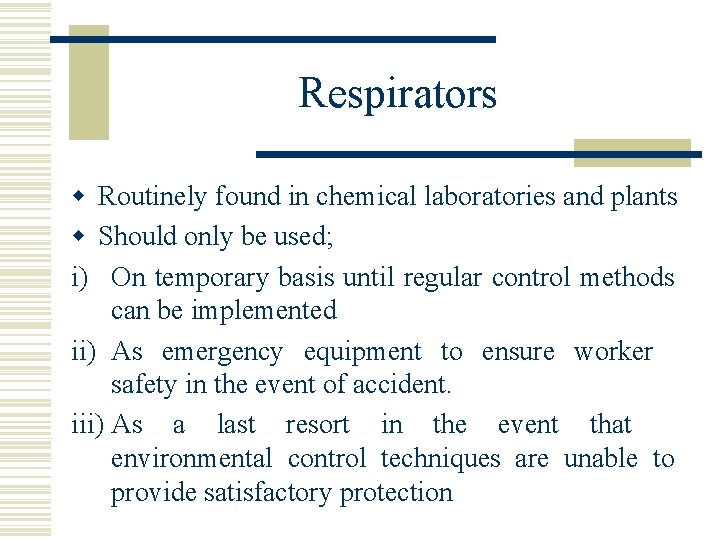
Respirators w Routinely found in chemical laboratories and plants w Should only be used; i) On temporary basis until regular control methods can be implemented ii) As emergency equipment to ensure worker safety in the event of accident. iii) As a last resort in the event that environmental control techniques are unable to provide satisfactory protection
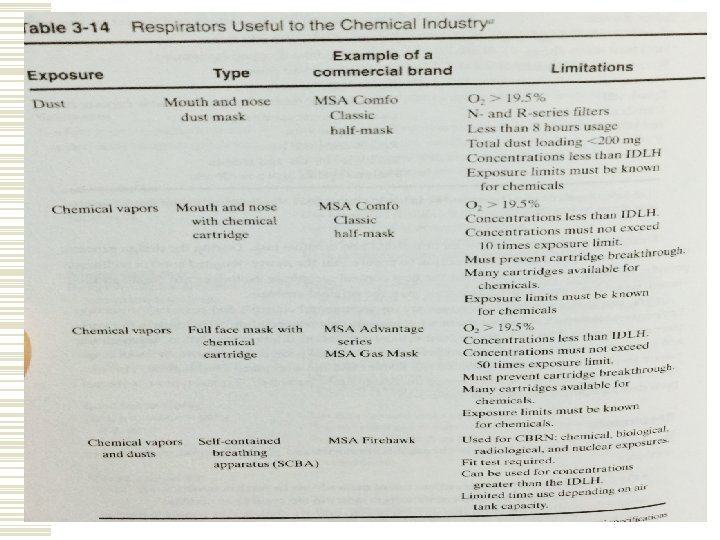
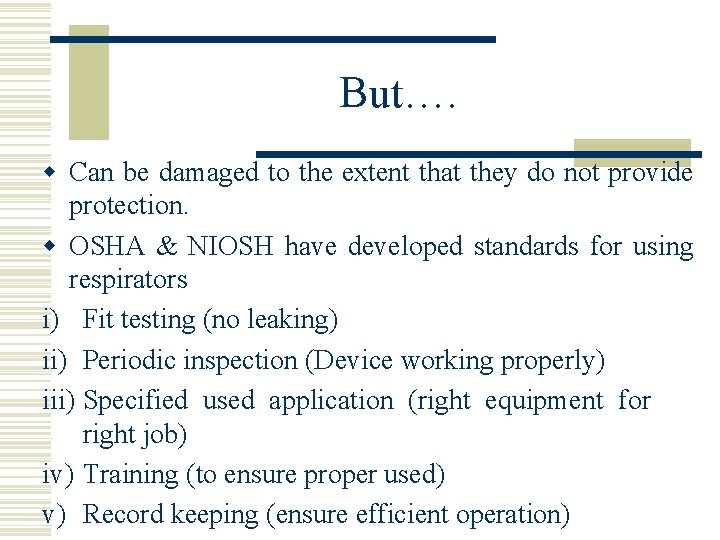
But…. w Can be damaged to the extent that they do not provide protection. w OSHA & NIOSH have developed standards for using respirators i) Fit testing (no leaking) ii) Periodic inspection (Device working properly) iii) Specified used application (right equipment for right job) iv) Training (to ensure proper used) v) Record keeping (ensure efficient operation)
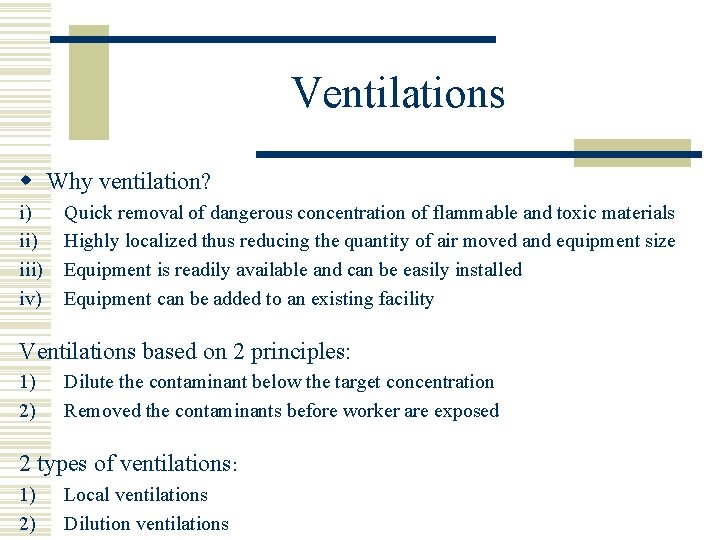
Ventilations w Why ventilation? i) iii) iv) Quick removal of dangerous concentration of flammable and toxic materials Highly localized thus reducing the quantity of air moved and equipment size Equipment is readily available and can be easily installed Equipment can be added to an existing facility Ventilations based on 2 principles: 1) 2) Dilute the contaminant below the target concentration Removed the contaminants before worker are exposed 2 types of ventilations: 1) 2) Local ventilations Dilution ventilations
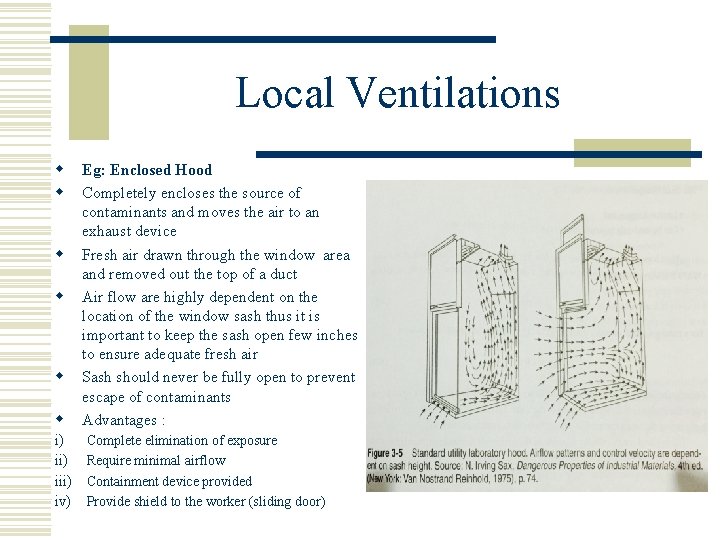
Local Ventilations w w w i) iii) iv) Eg: Enclosed Hood Completely encloses the source of contaminants and moves the air to an exhaust device Fresh air drawn through the window area and removed out the top of a duct Air flow are highly dependent on the location of the window sash thus it is important to keep the sash open few inches to ensure adequate fresh air Sash should never be fully open to prevent escape of contaminants Advantages : Complete elimination of exposure Require minimal airflow Containment device provided Provide shield to the worker (sliding door)
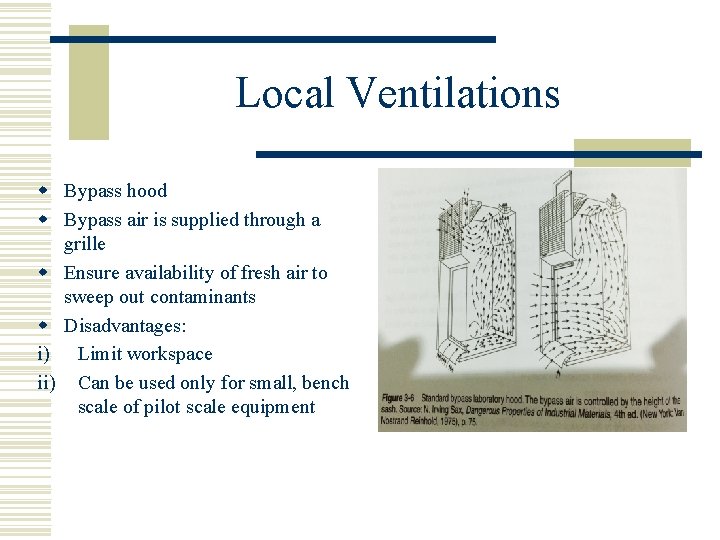
Local Ventilations w Bypass hood w Bypass air is supplied through a grille w Ensure availability of fresh air to sweep out contaminants w Disadvantages: i) Limit workspace ii) Can be used only for small, bench scale of pilot scale equipment
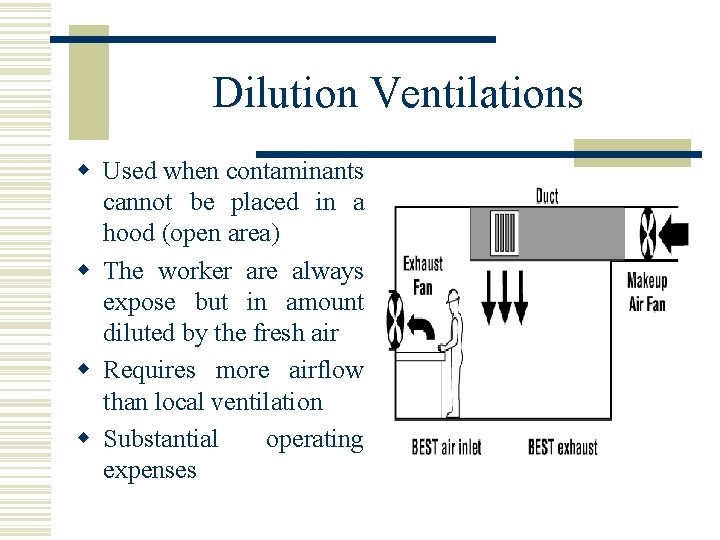
Dilution Ventilations w Used when contaminants cannot be placed in a hood (open area) w The worker are always expose but in amount diluted by the fresh air w Requires more airflow than local ventilation w Substantial operating expenses
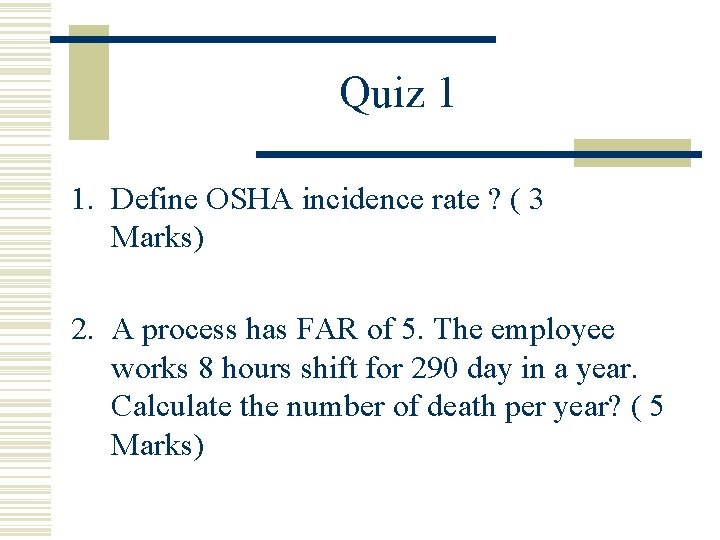
Quiz 1 1. Define OSHA incidence rate ? ( 3 Marks) 2. A process has FAR of 5. The employee works 8 hours shift for 290 day in a year. Calculate the number of death per year? ( 5 Marks)
Mohd ridzal bin mohd sheriff
Hygiene risk assessment
Wolf
Industrial hygiene procedure
Fundamentals of industrial hygiene
Aiche code of ethics
Syahid mohd zain
Armyn fahmy mohd fahmy
Mohd talib latif
Sarah binti puteh
Contract first
Nazari ismail
Prof mohd faiz
Putra mohd aidil rizal
Ain syafinaz mohd razip
Wan mohd faizal
Kathrina haji mohd daud
Introduction to materials science for engineers chapter 10
Introduction to materials science for engineers chapter 10
Matlab programming for engineers
Basic introduction to food hygiene
Fspos vägledning för kontinuitetshantering
Typiska drag för en novell
Nationell inriktning för artificiell intelligens
Returpilarna
Varför kallas perioden 1918-1939 för mellankrigstiden
En lathund för arbete med kontinuitetshantering
Personalliggare bygg undantag
Tidbok
A gastrica
Förklara densitet för barn
Datorkunskap för nybörjare
Boverket ka
Mall för debattartikel
För och nackdelar med firo
Nyckelkompetenser för livslångt lärande
Påbyggnader för flakfordon
Vätsketryck formel
Publik sektor
Bo bergman jag fryser om dina händer
Presentera för publik crossboss
Jiddisch
Bat mitza
Klassificeringsstruktur för kommunala verksamheter