COATING 1 Coating di materiali tessili Tessuti tessuti
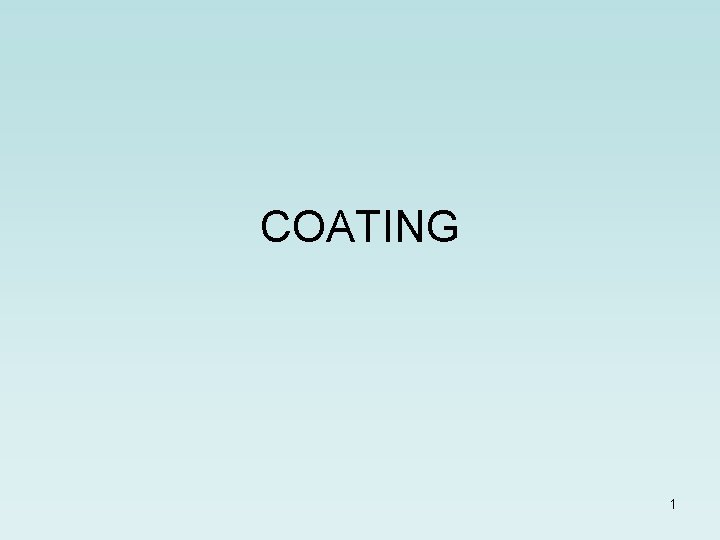
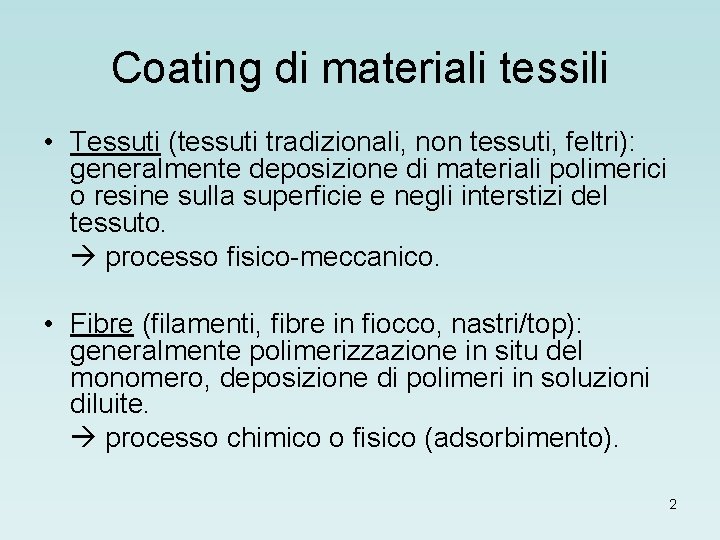
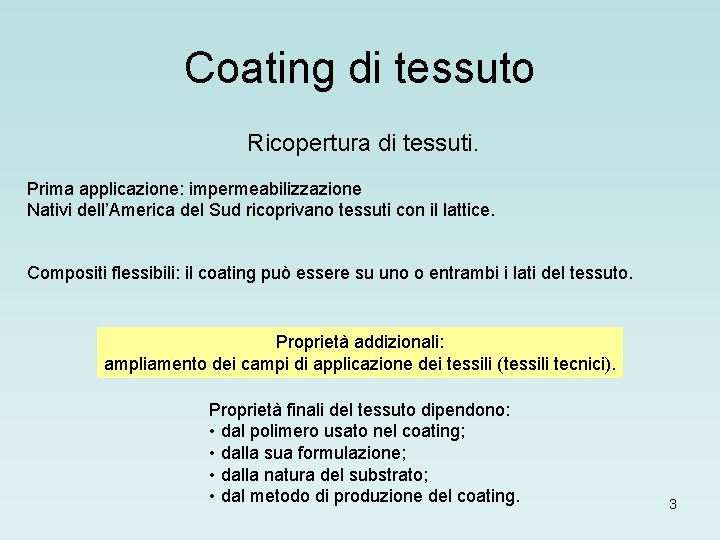
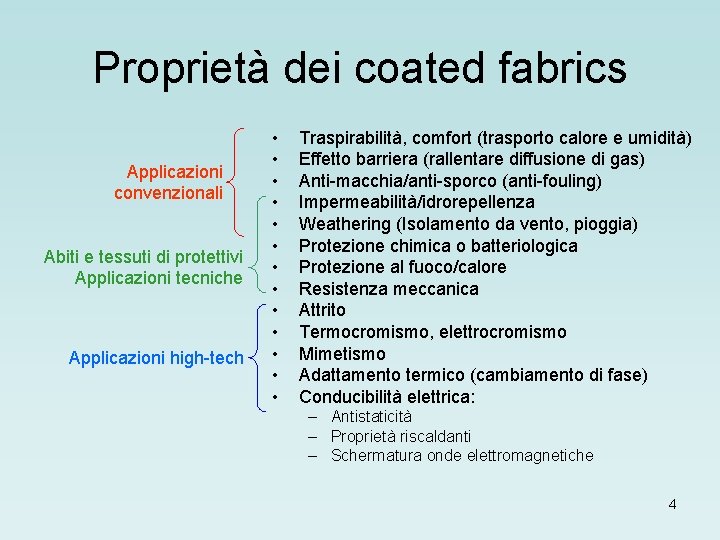
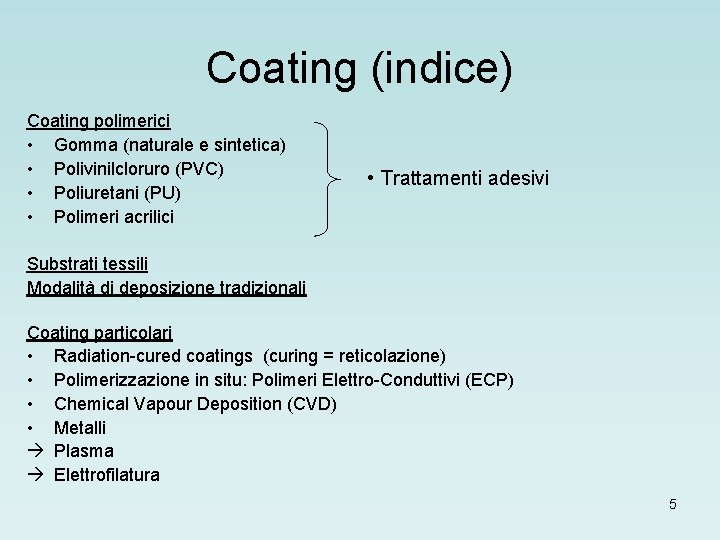
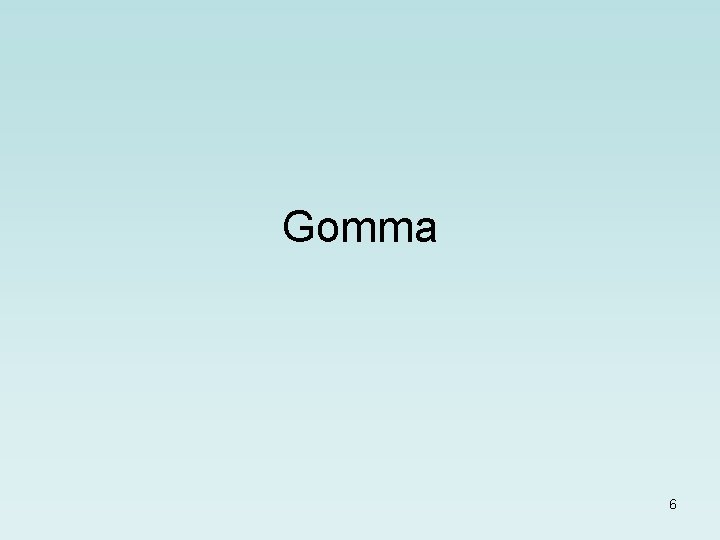

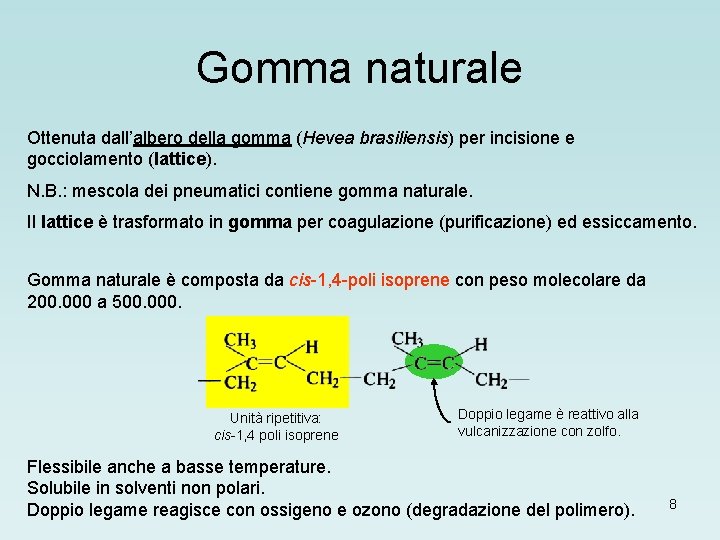
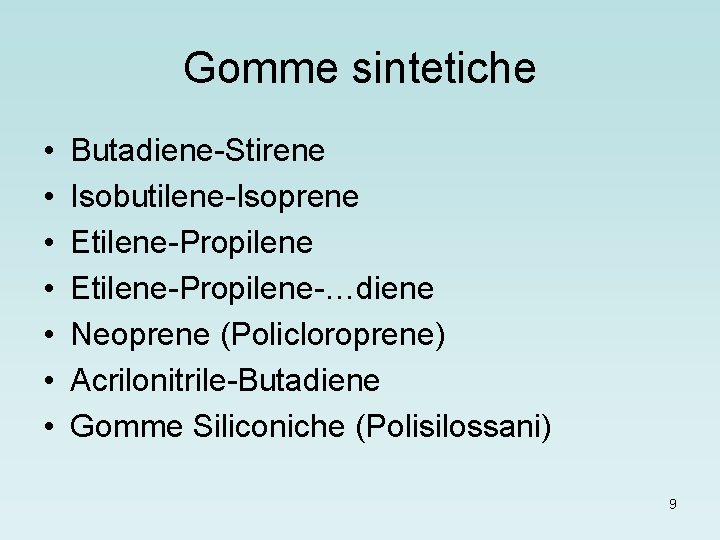
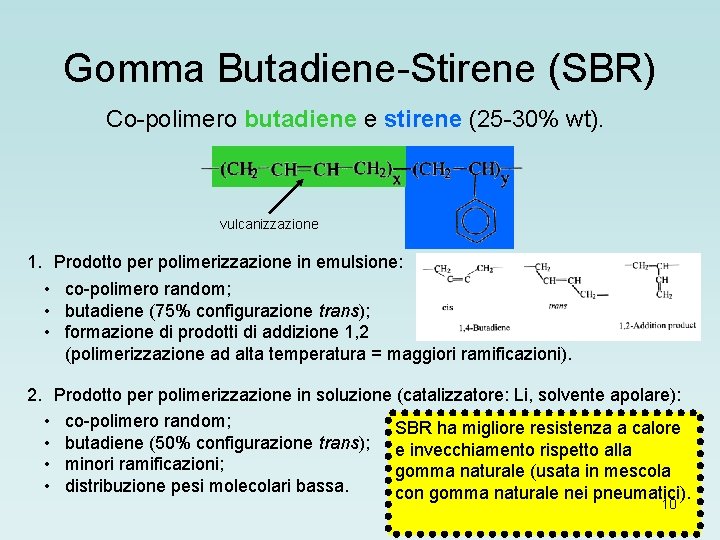
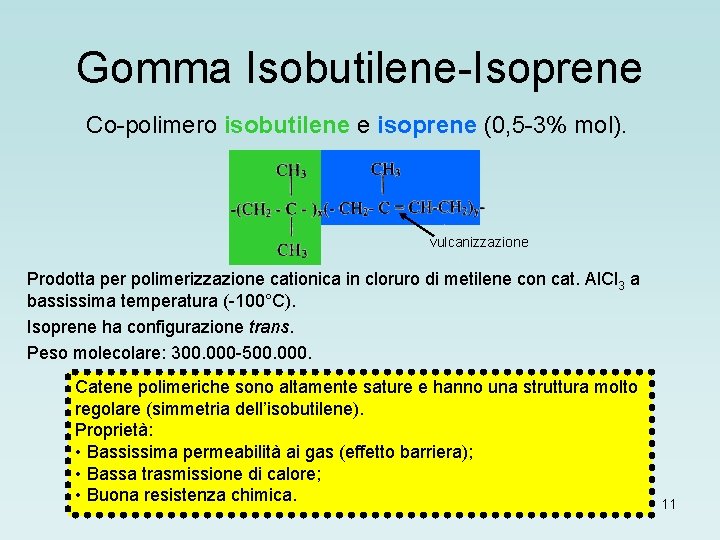
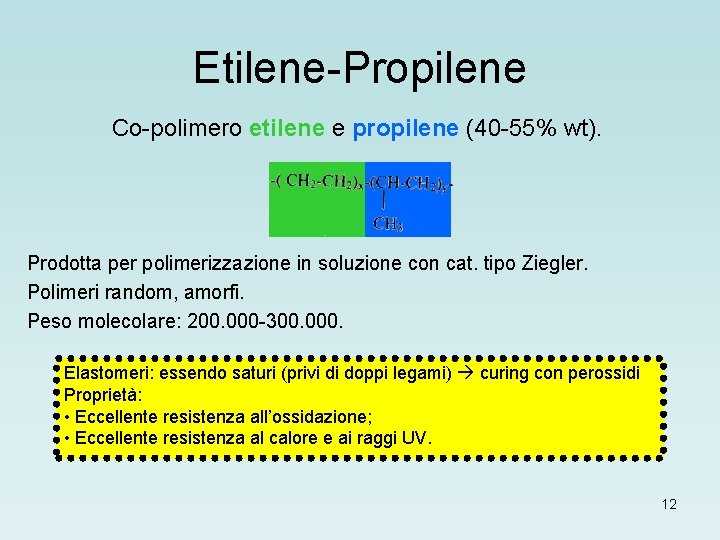
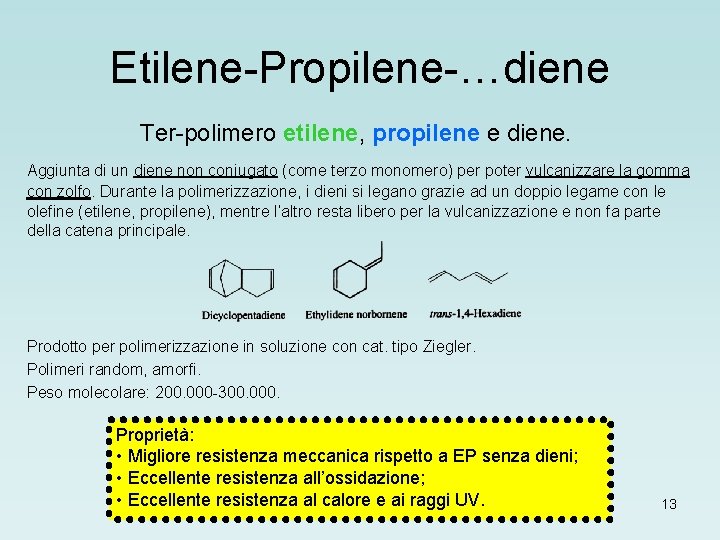
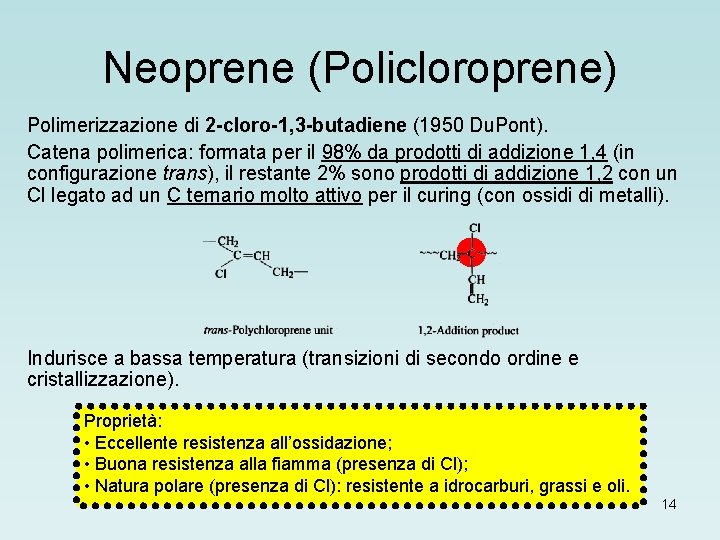
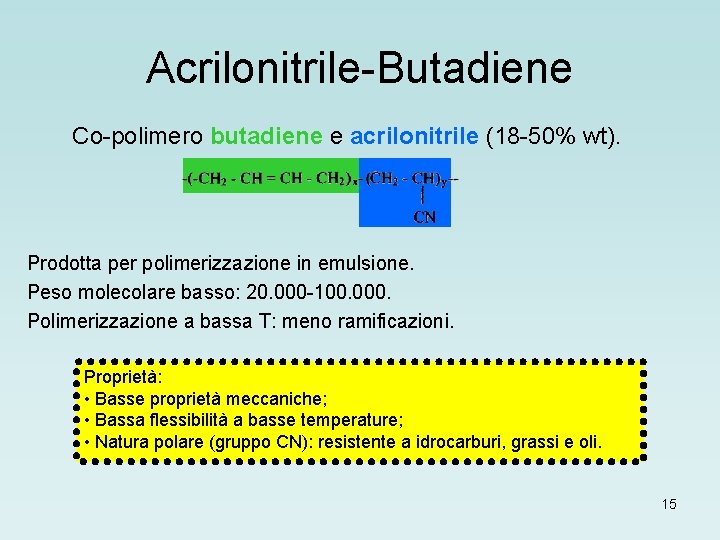
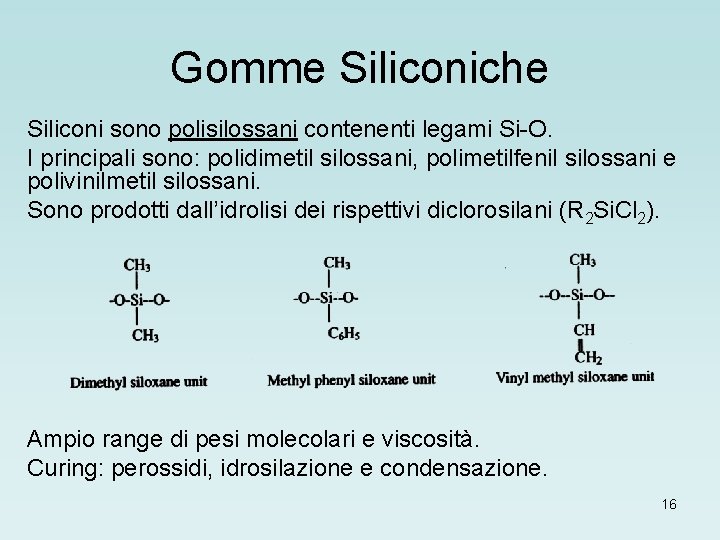
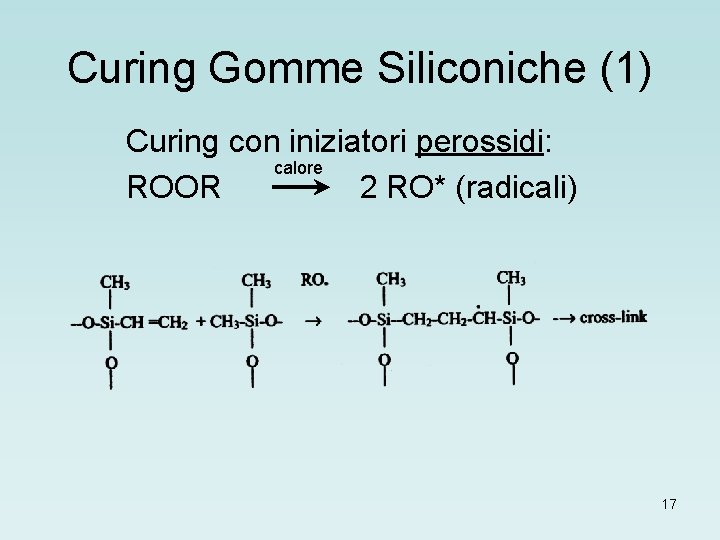
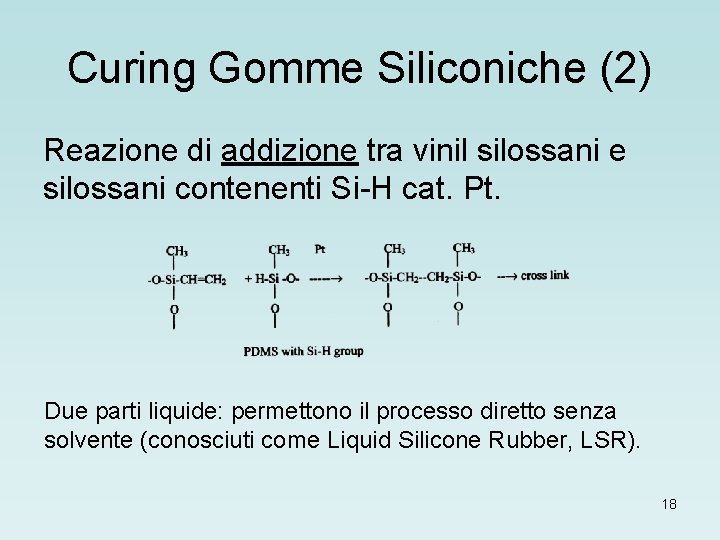
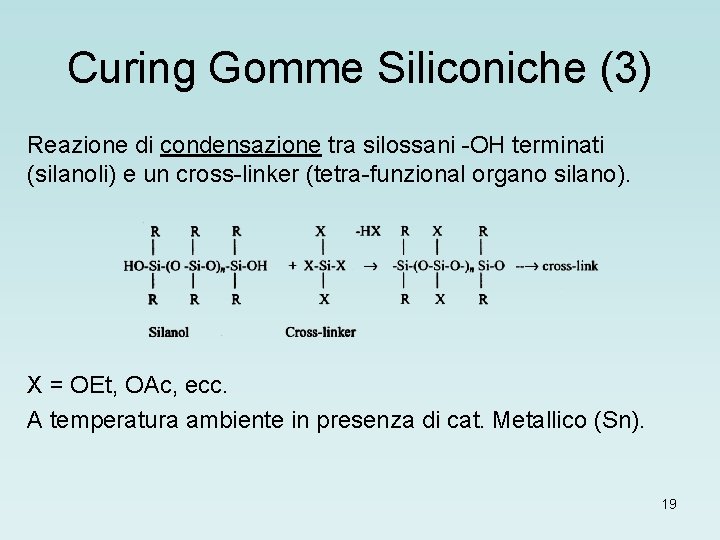
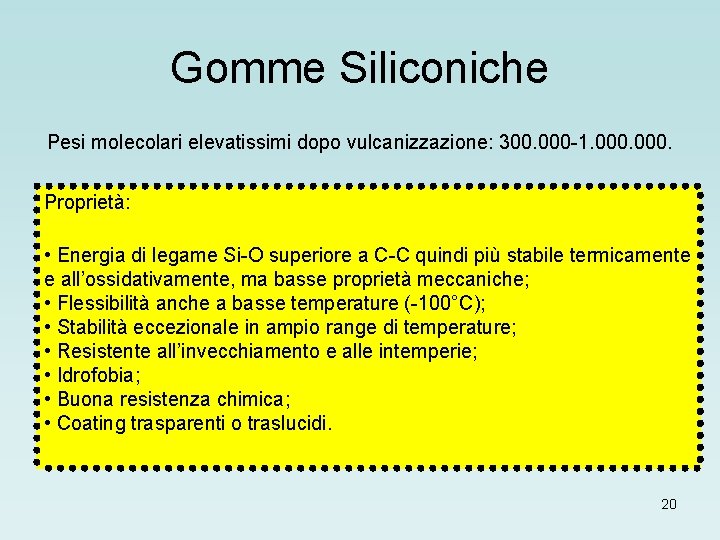
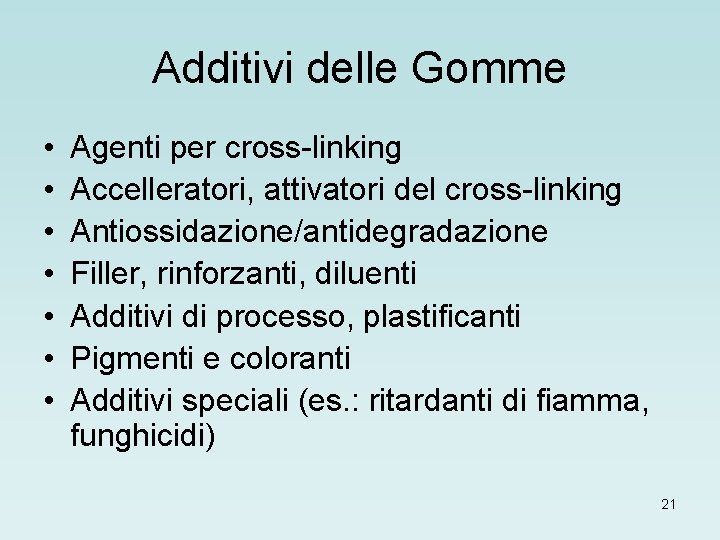
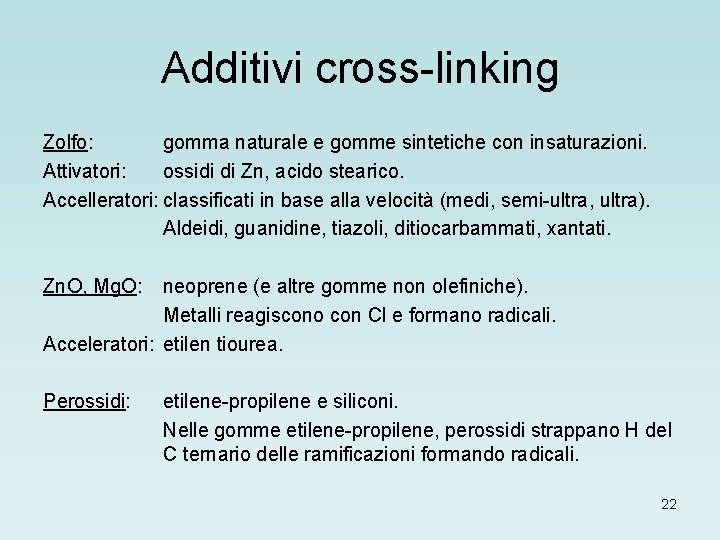
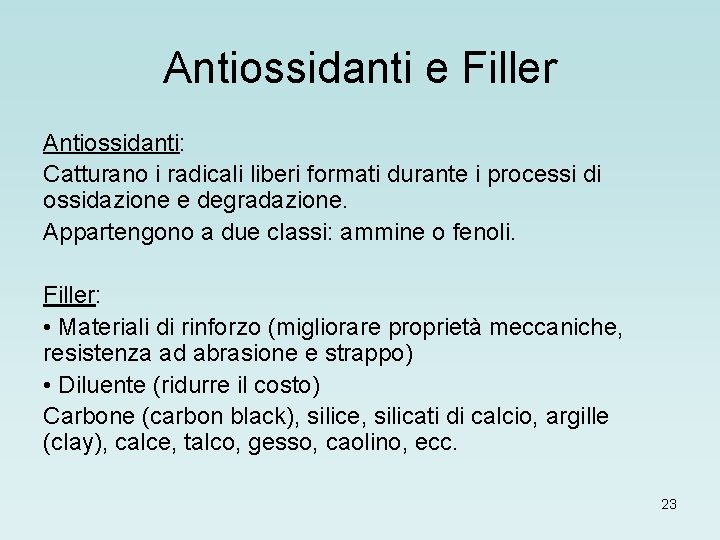
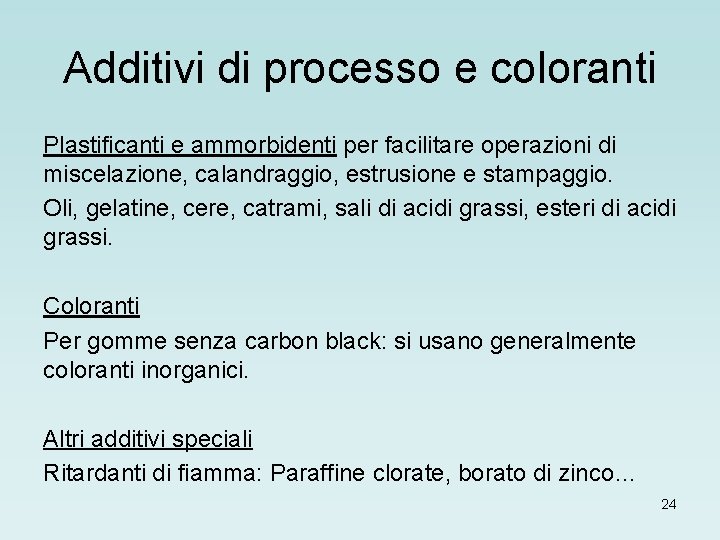
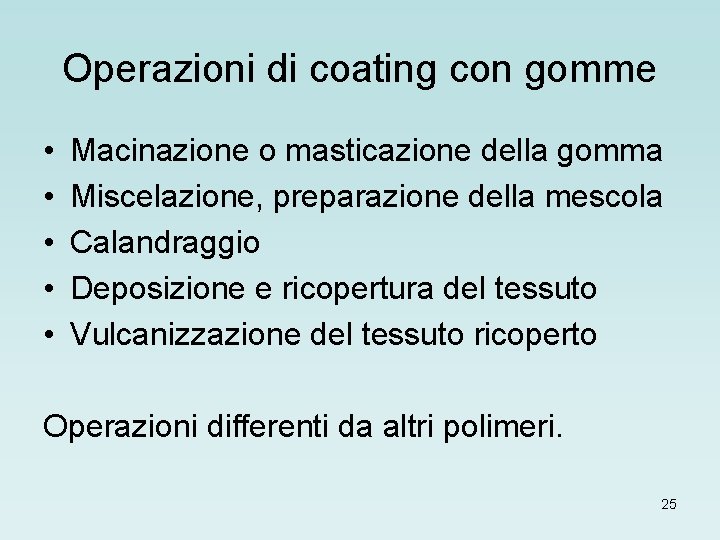
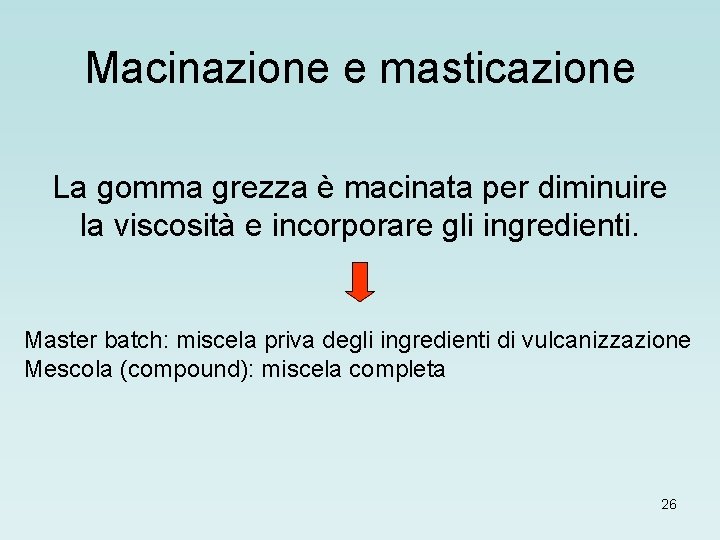
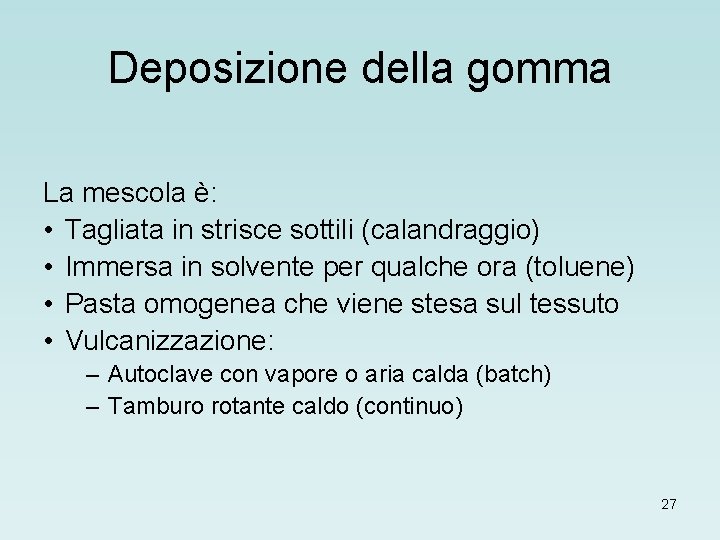
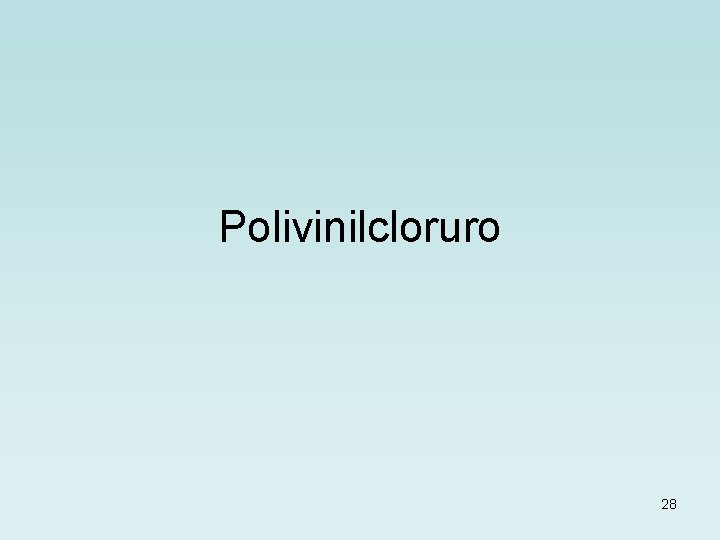
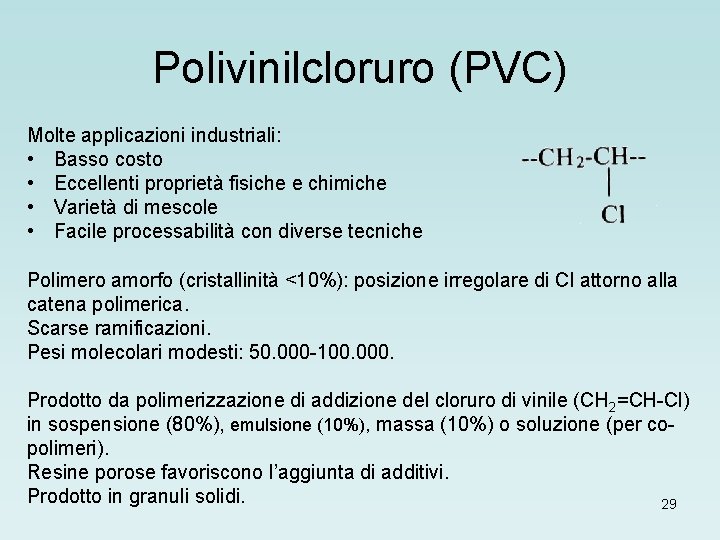
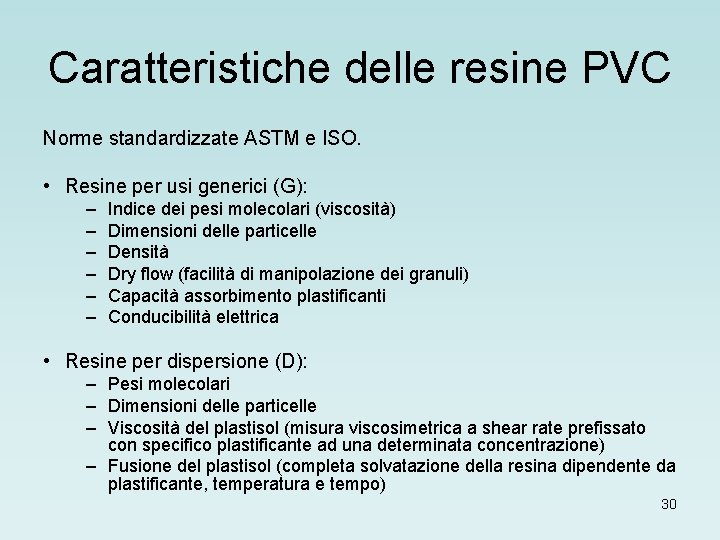
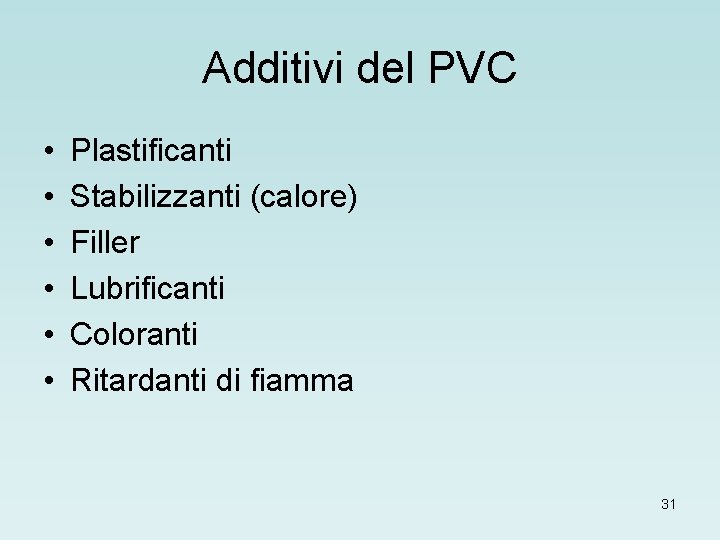
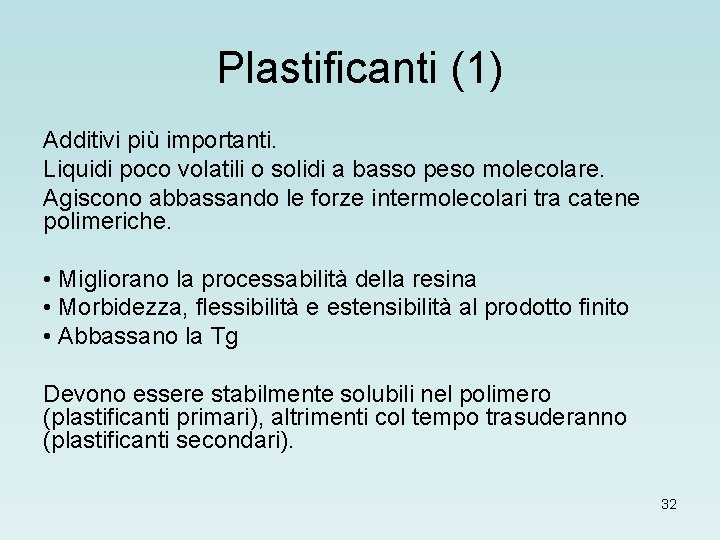
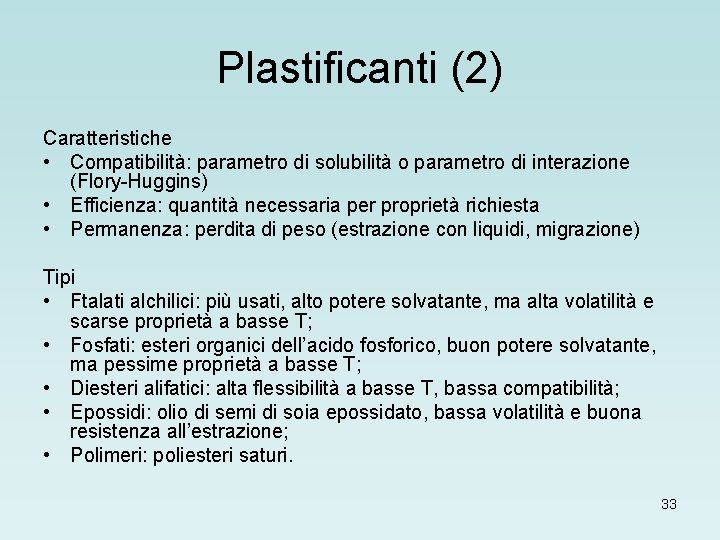
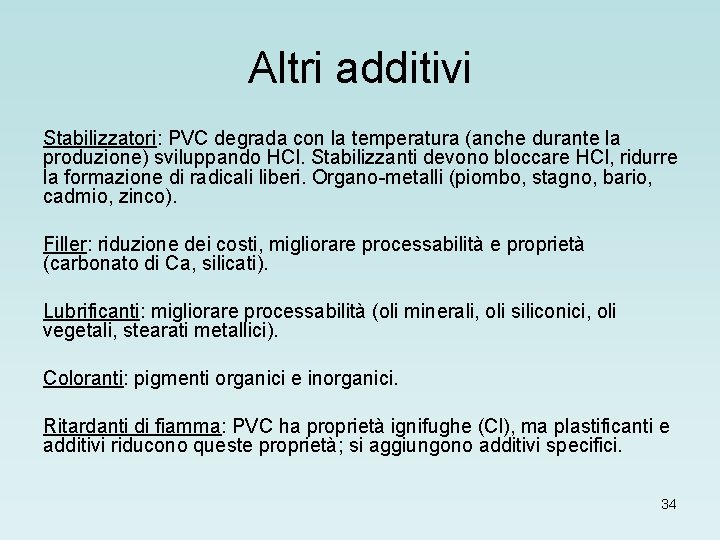
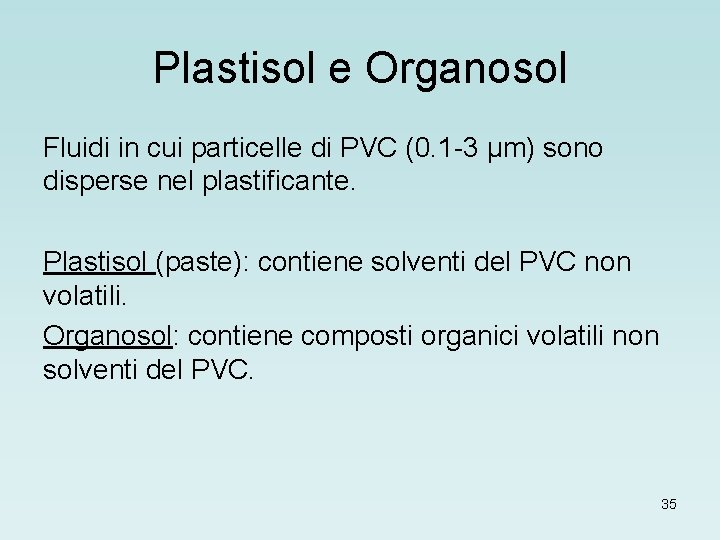
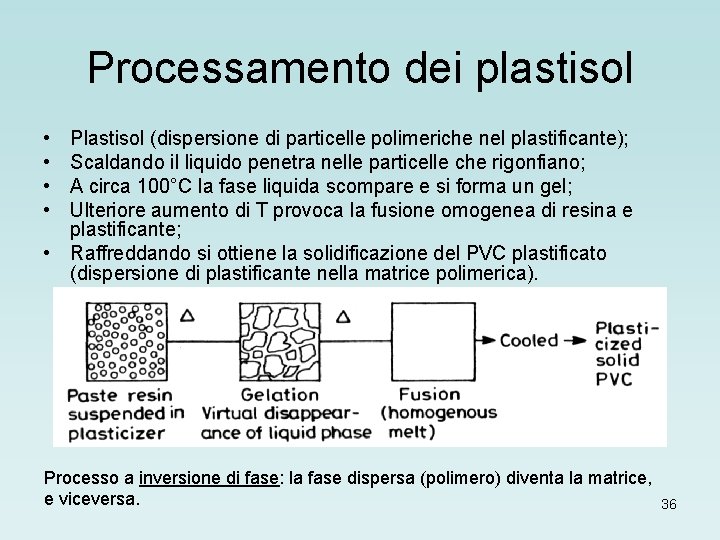
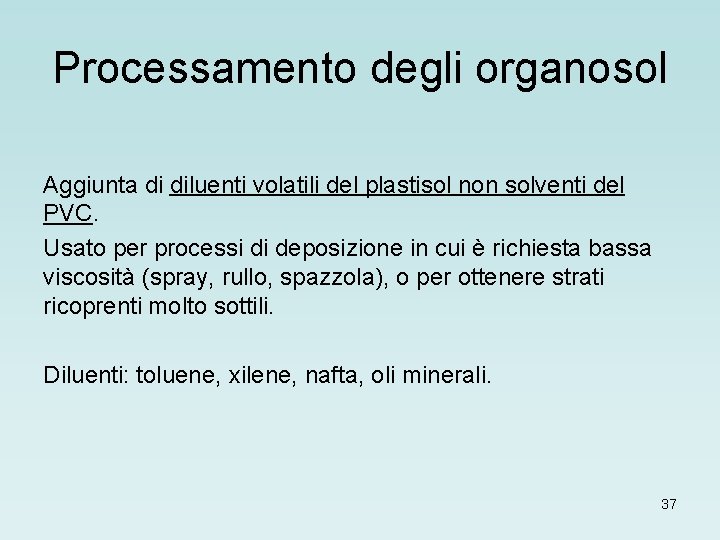
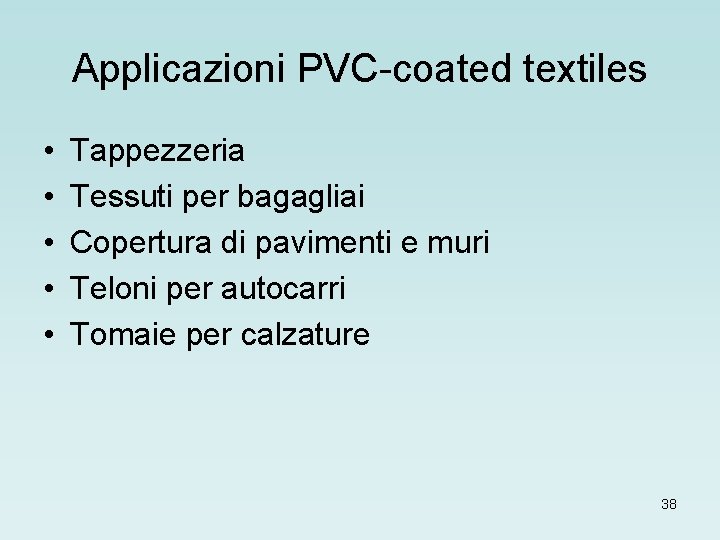
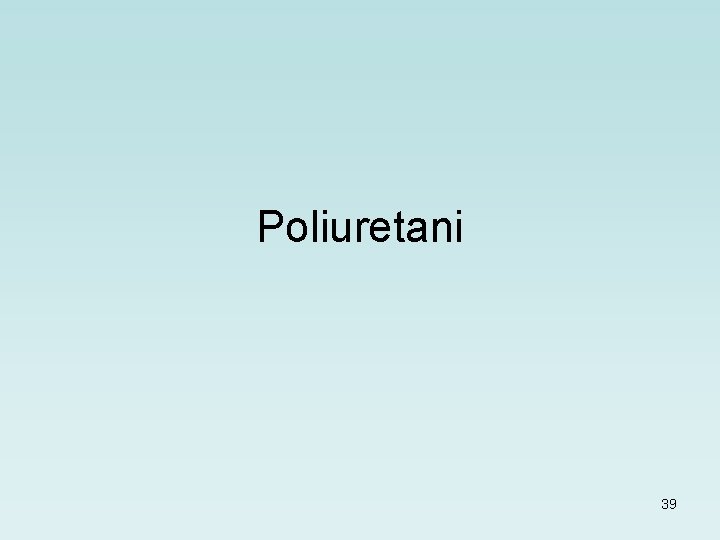
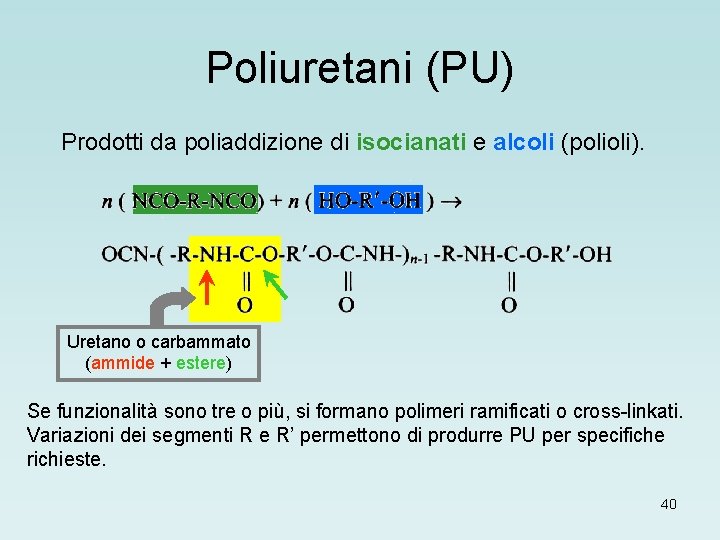
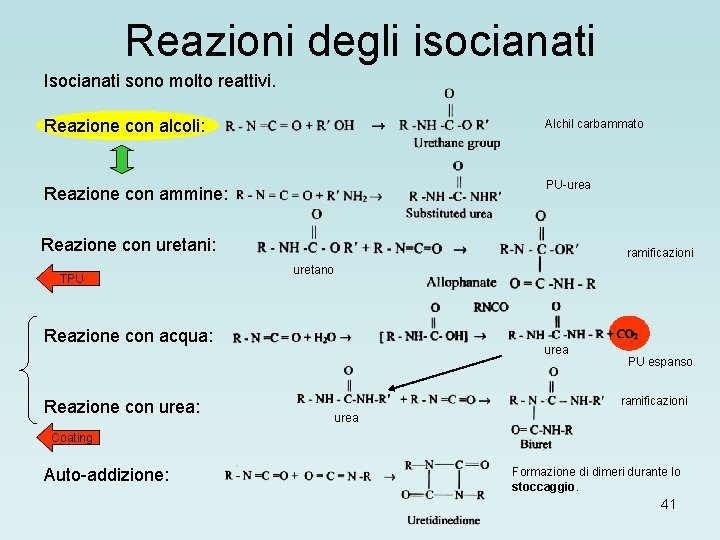
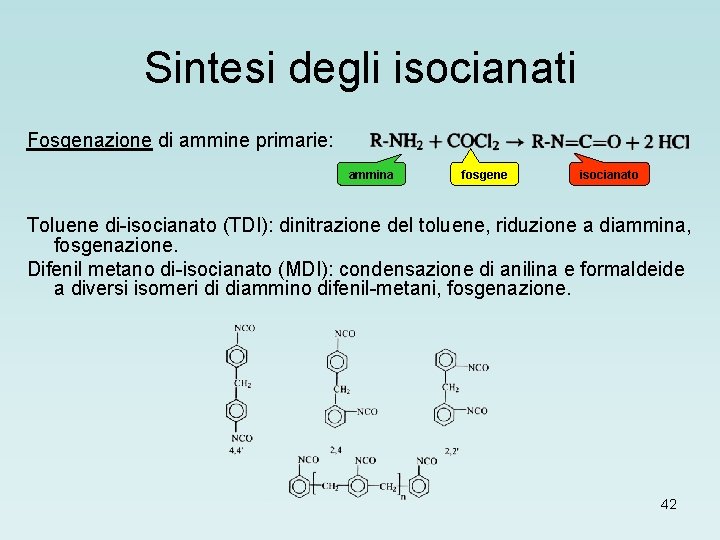
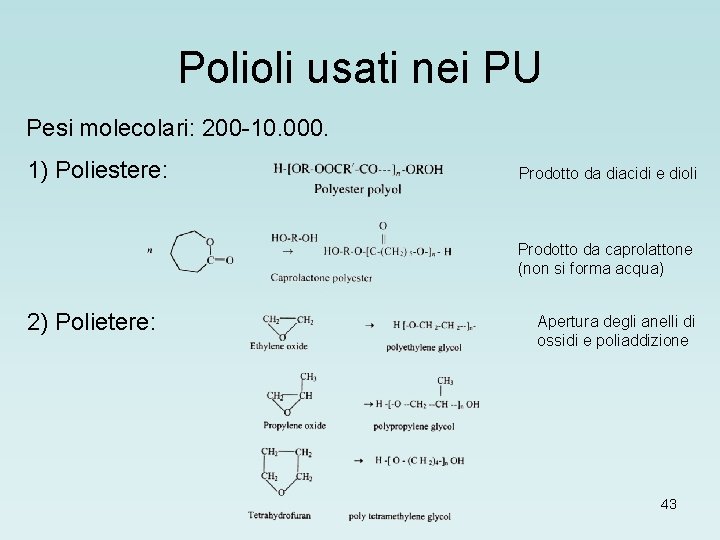
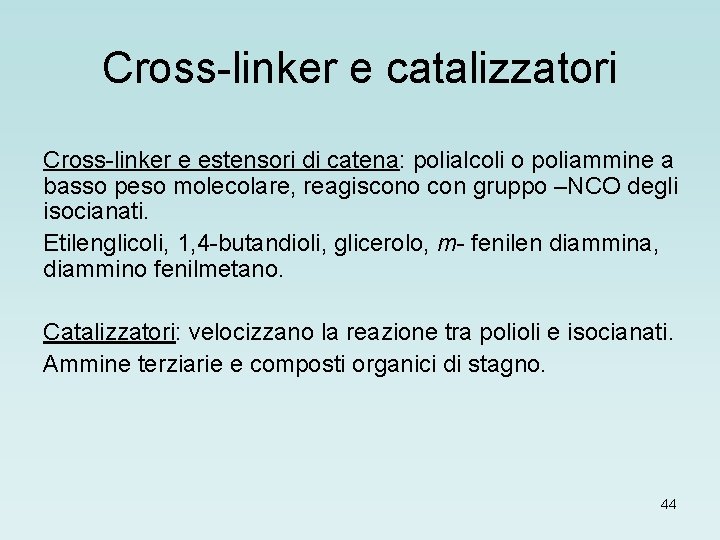
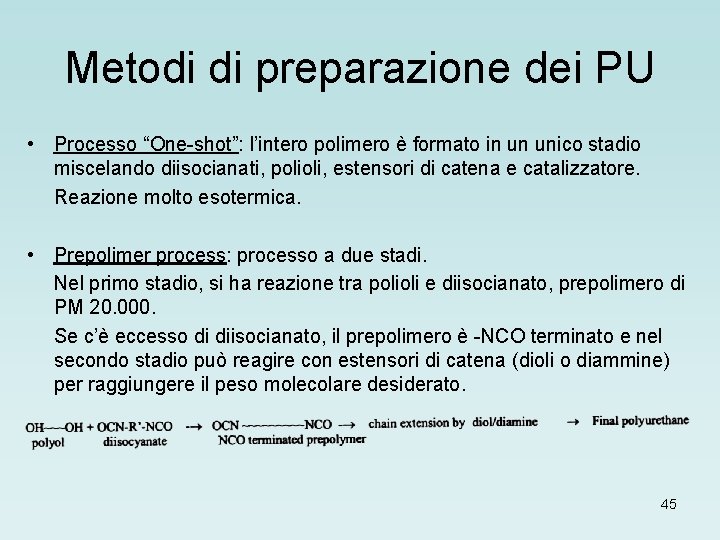
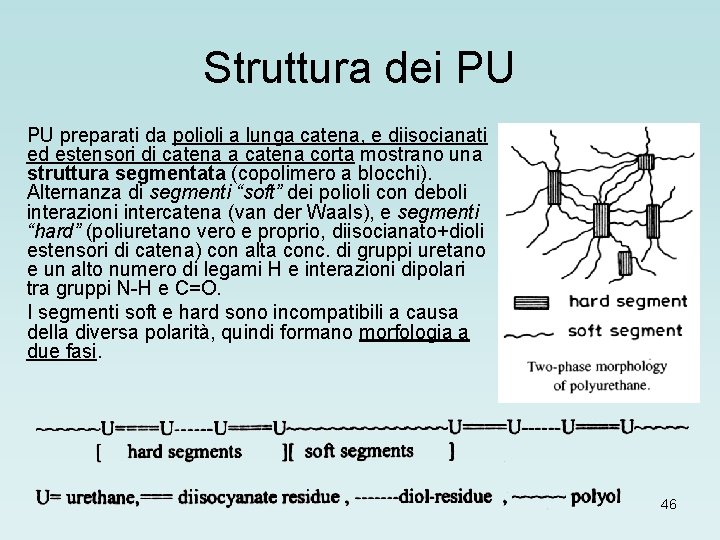
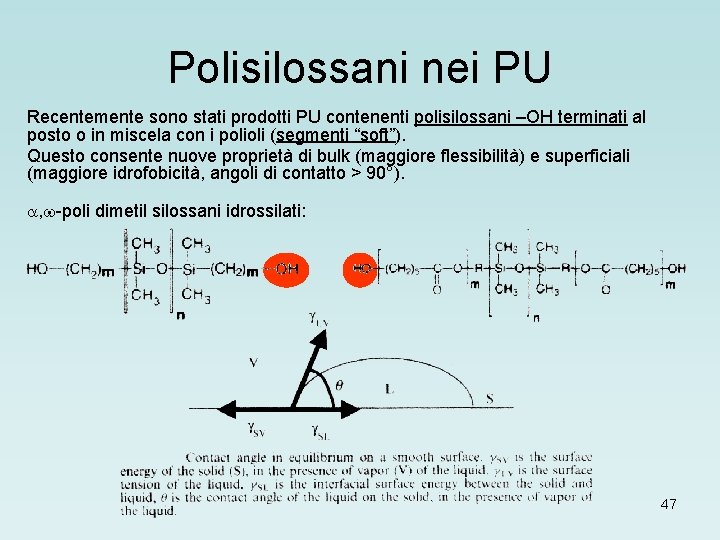
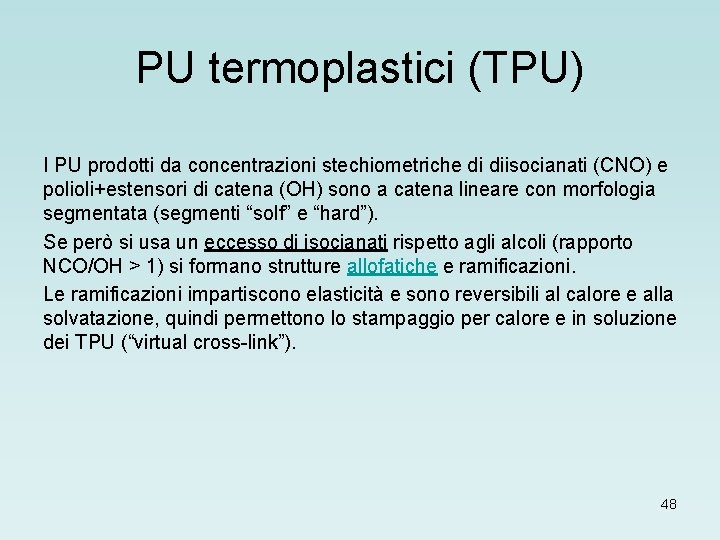
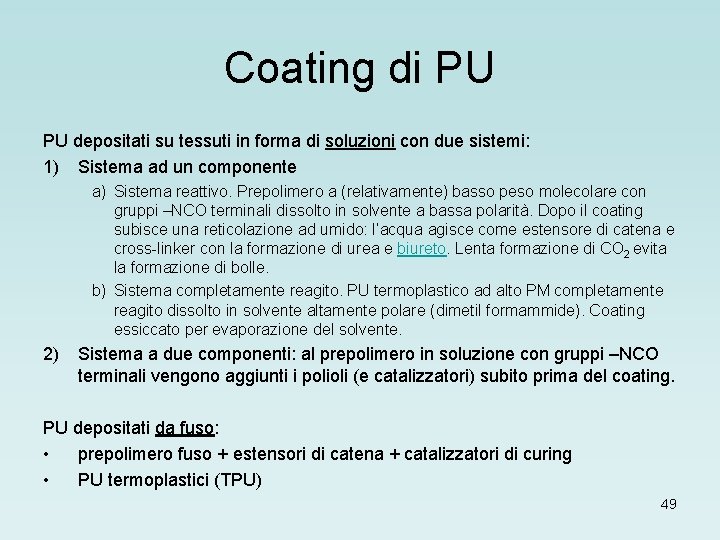
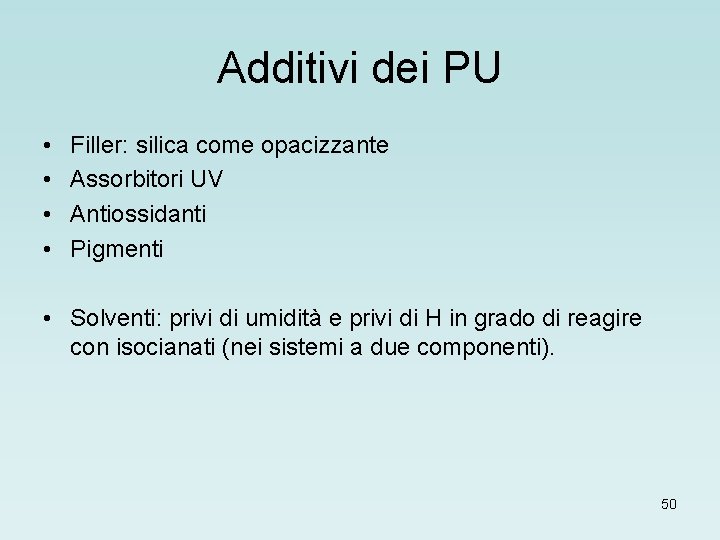
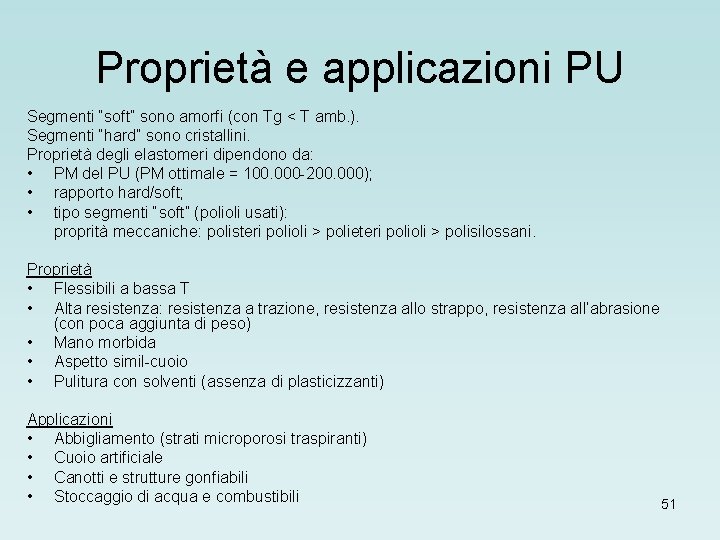
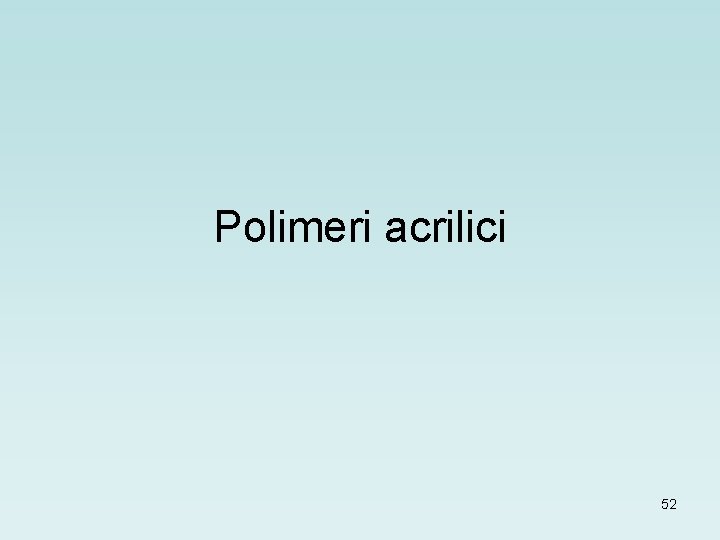

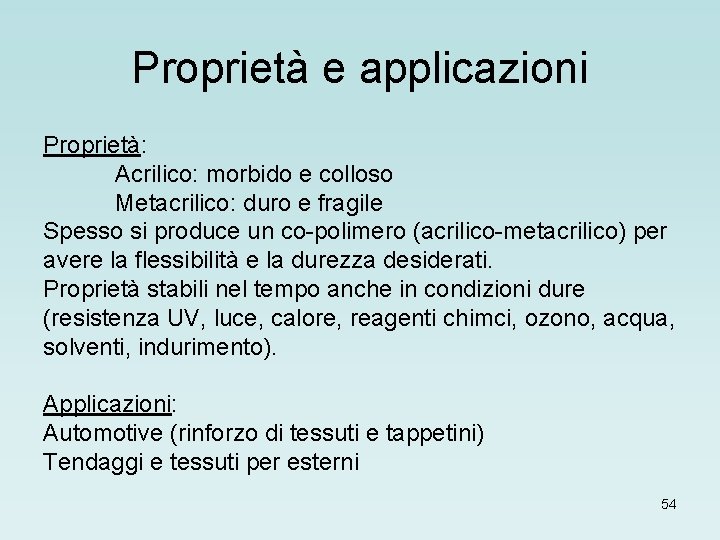
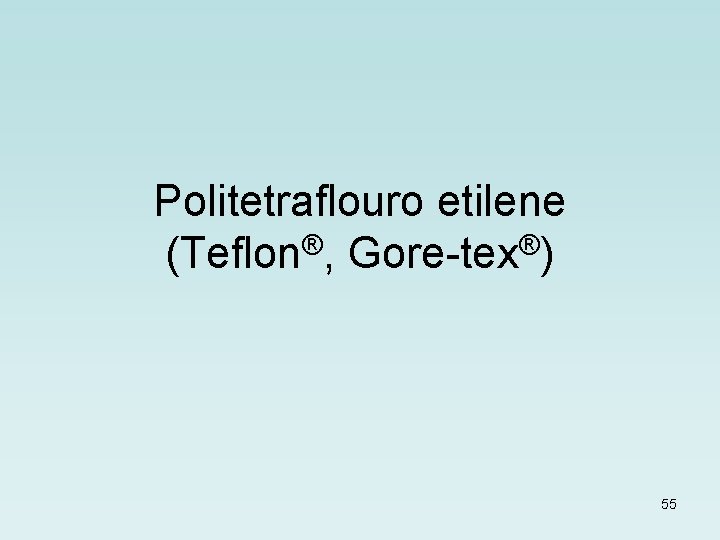
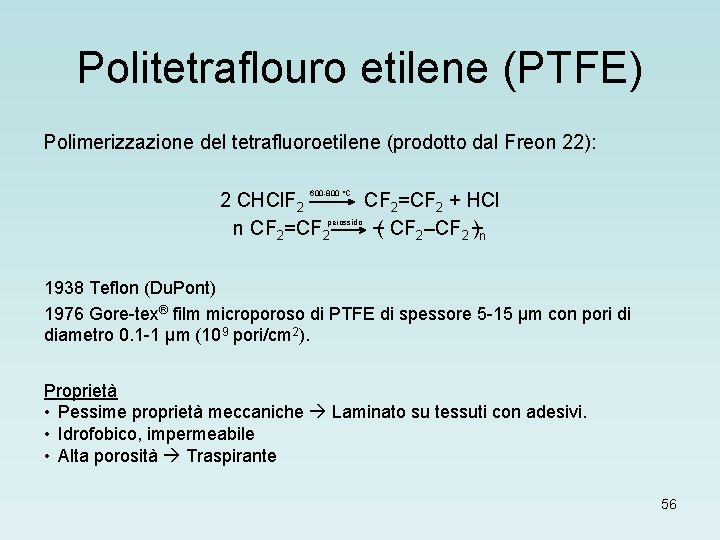
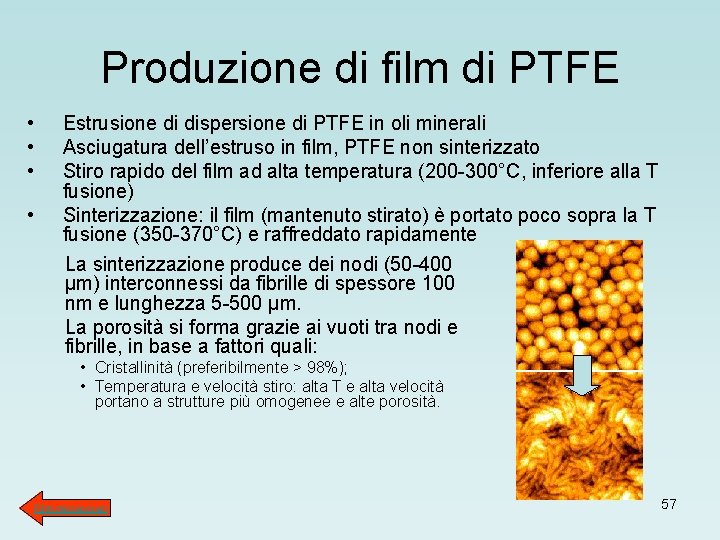
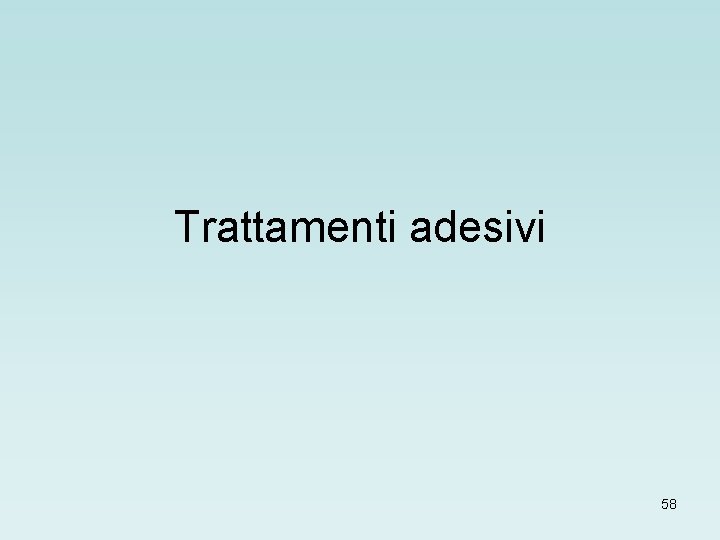
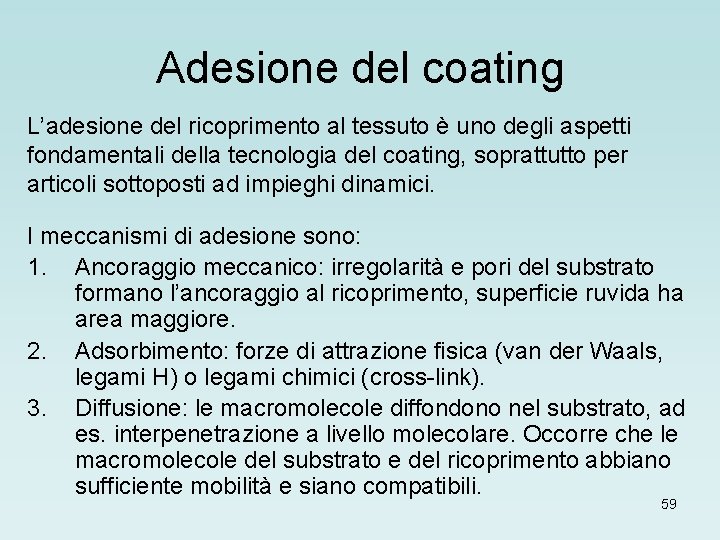
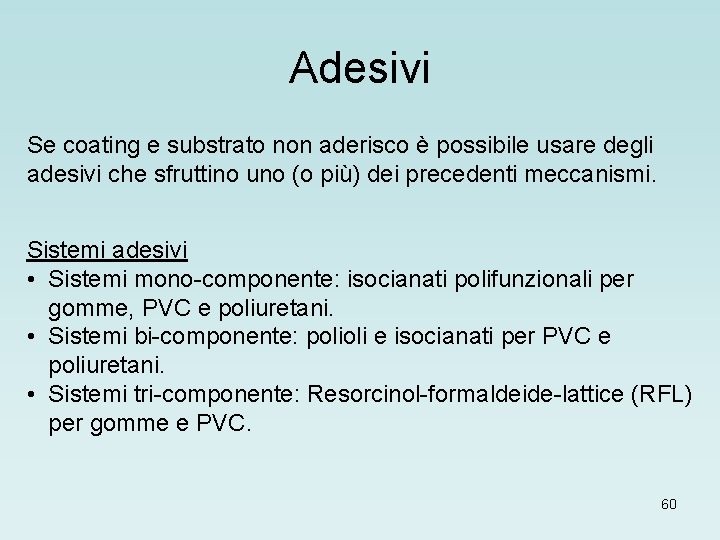
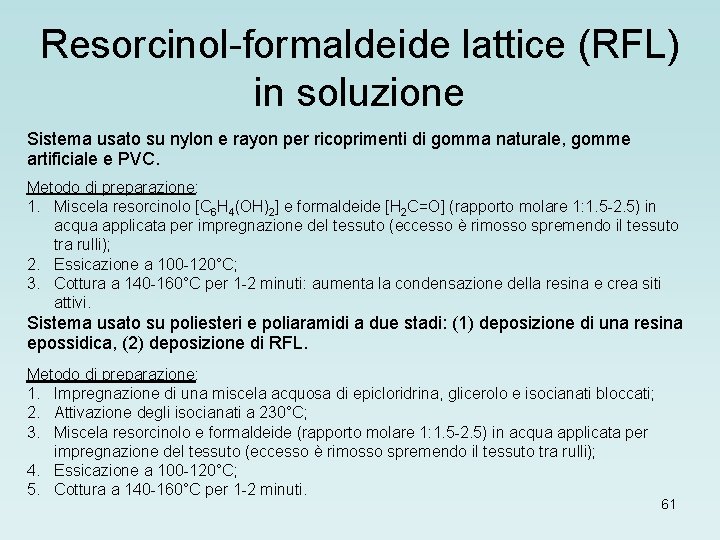
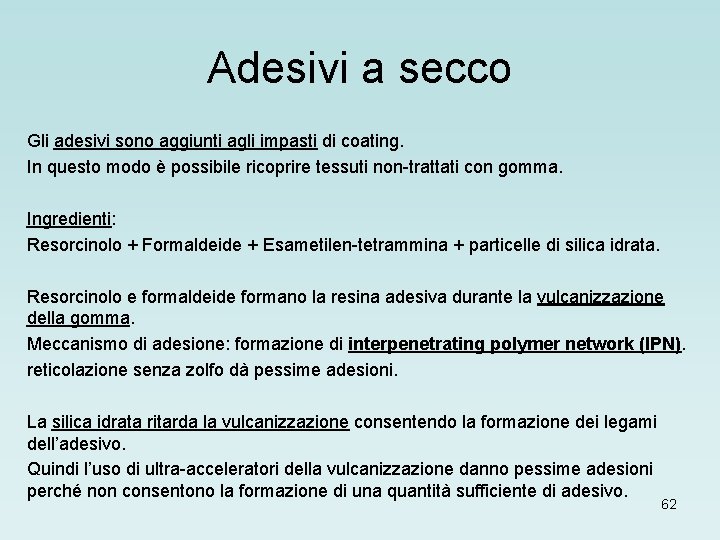
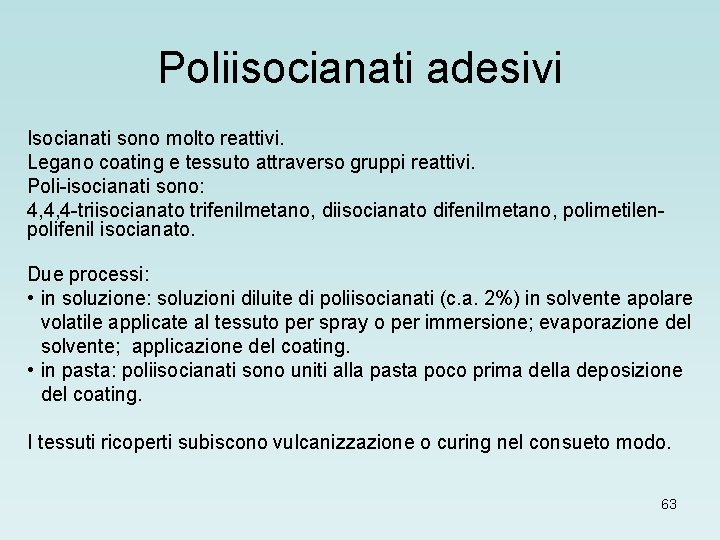
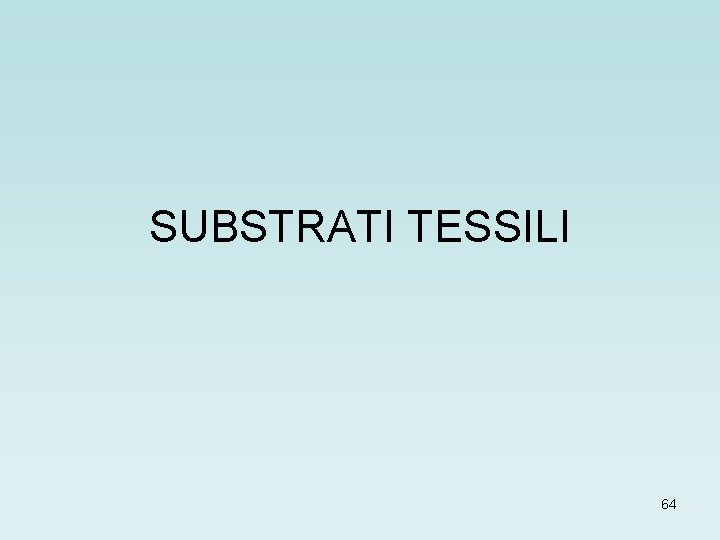
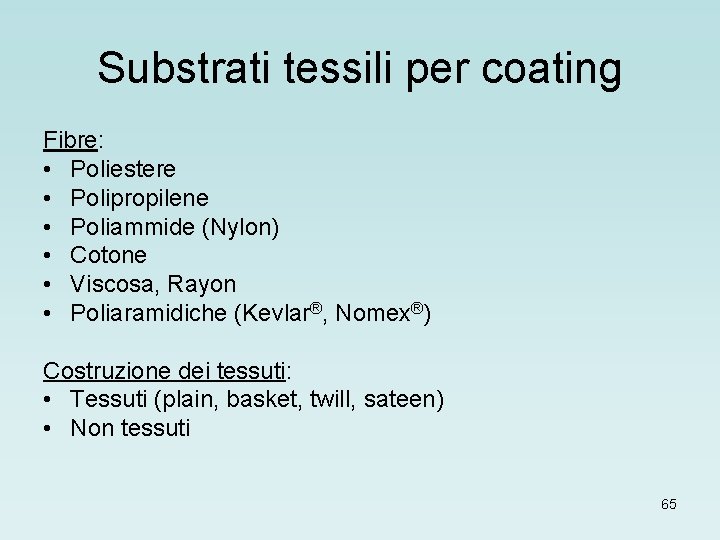
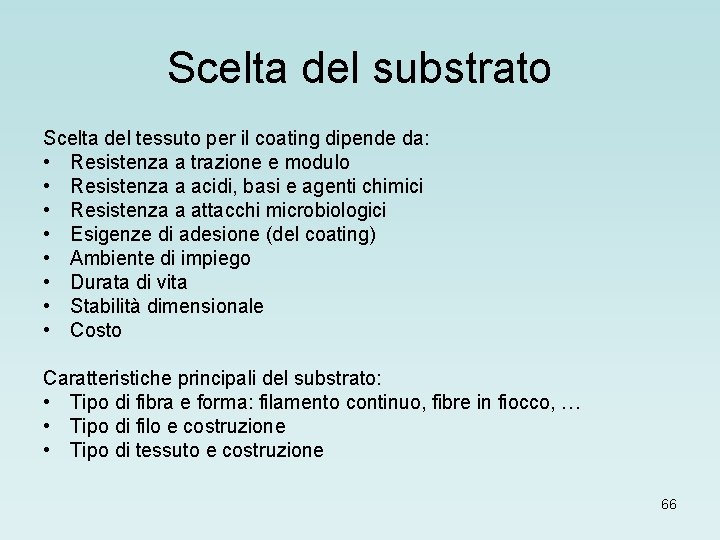
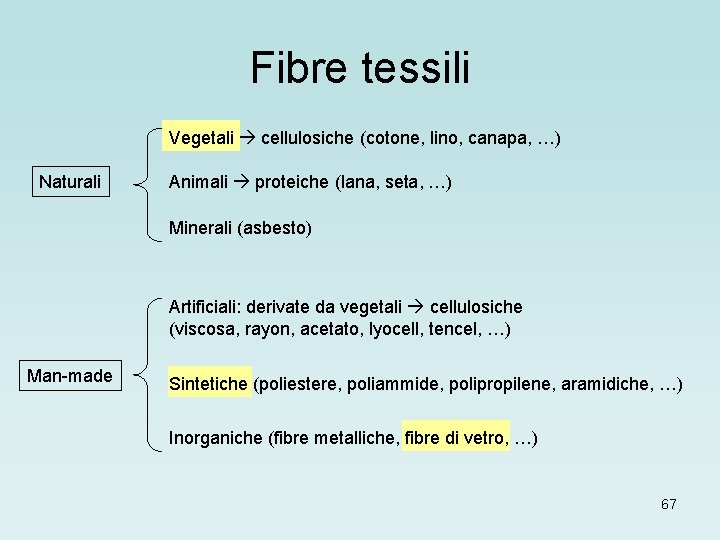
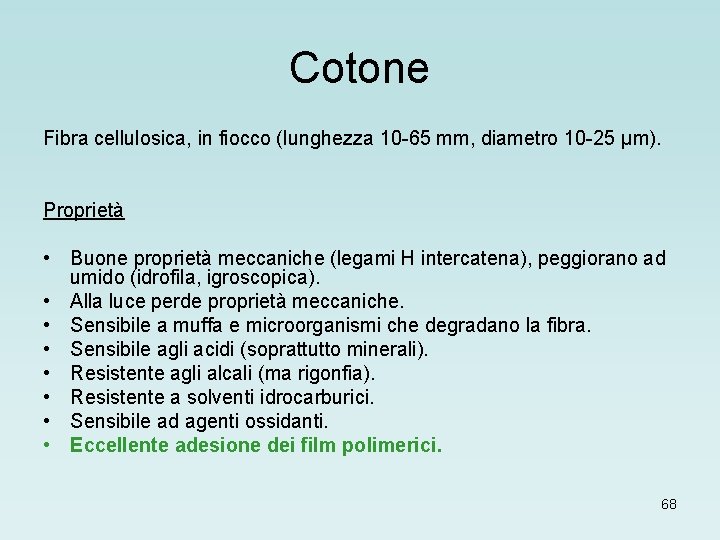
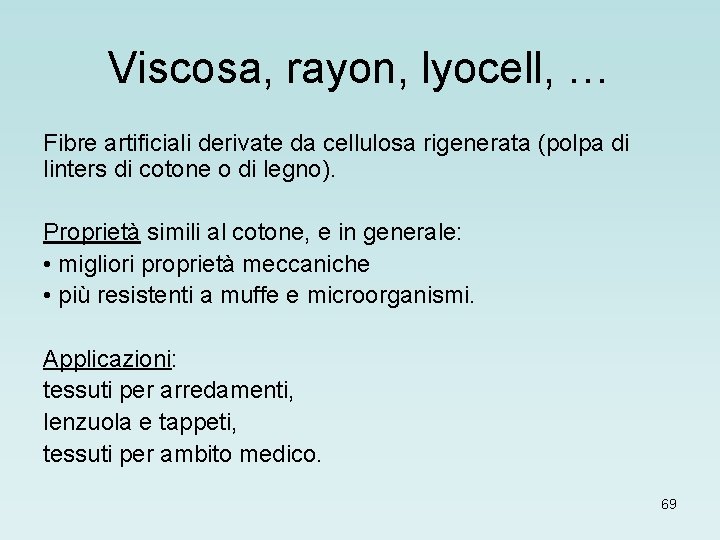
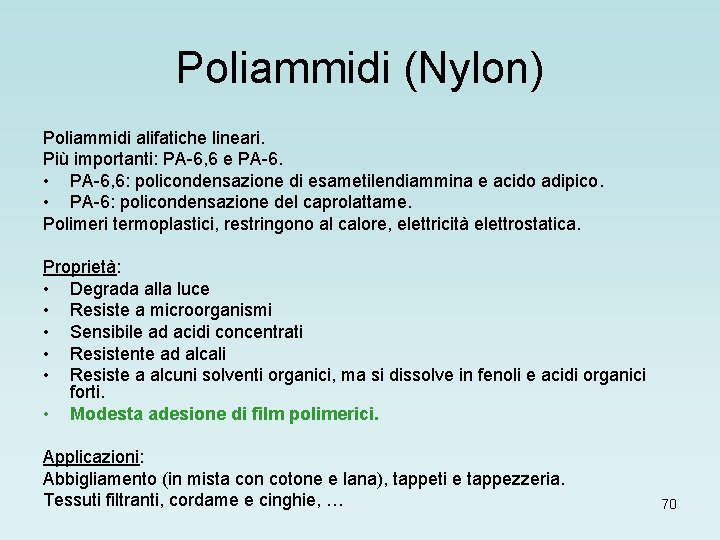
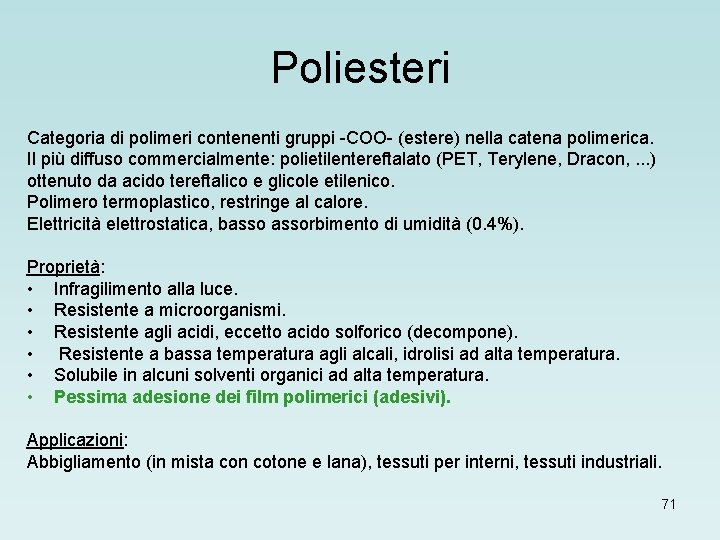
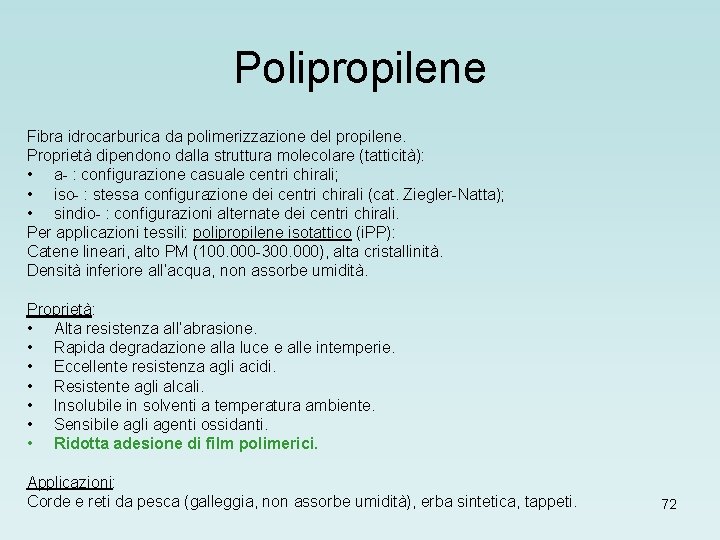
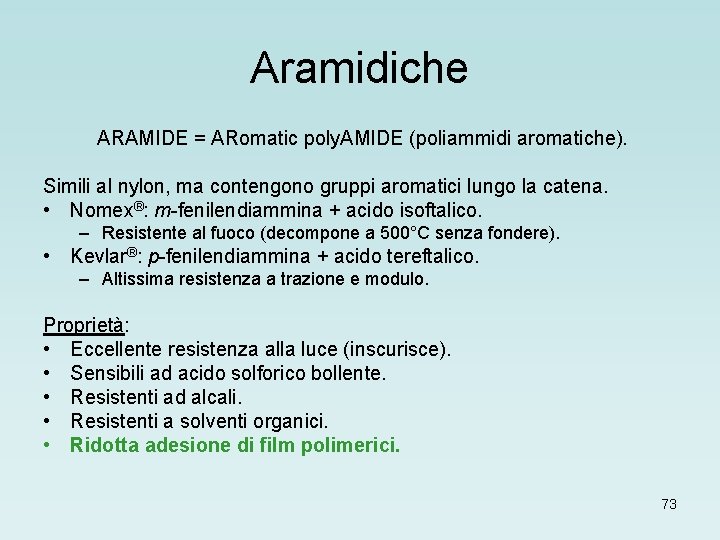
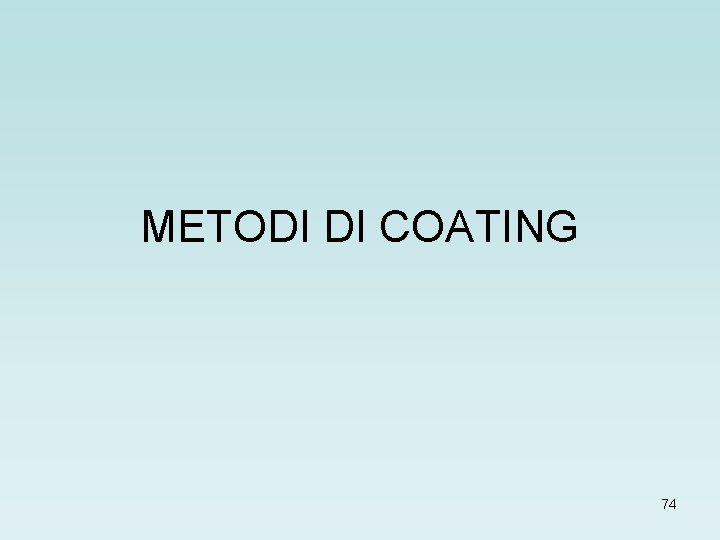
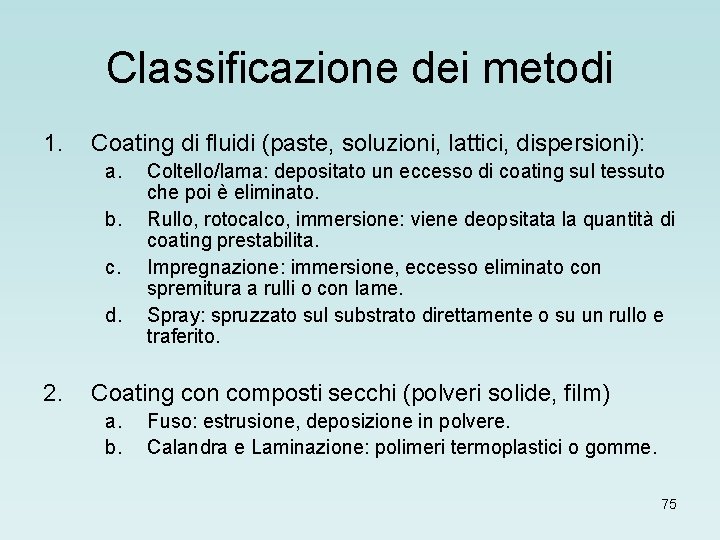
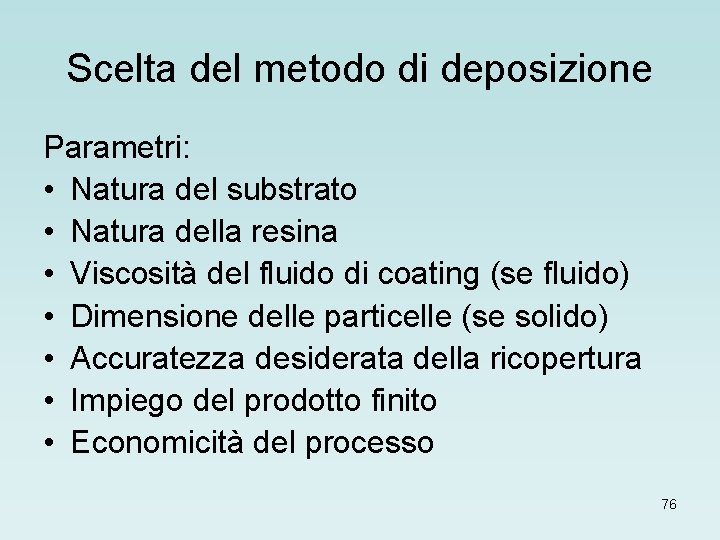
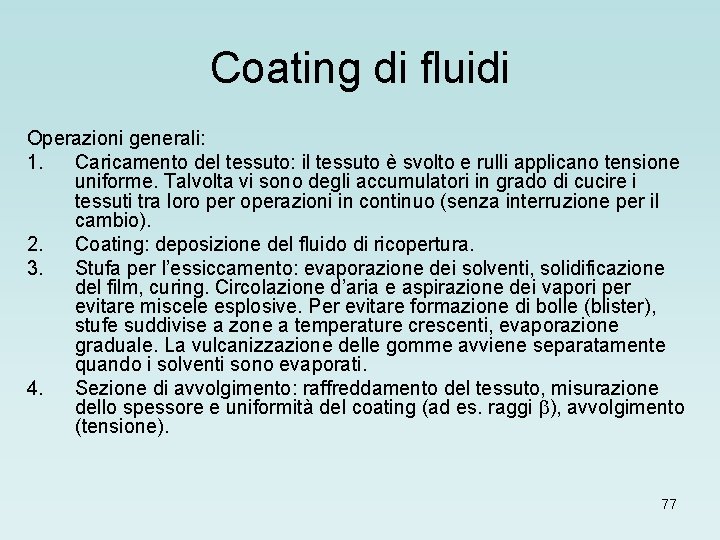
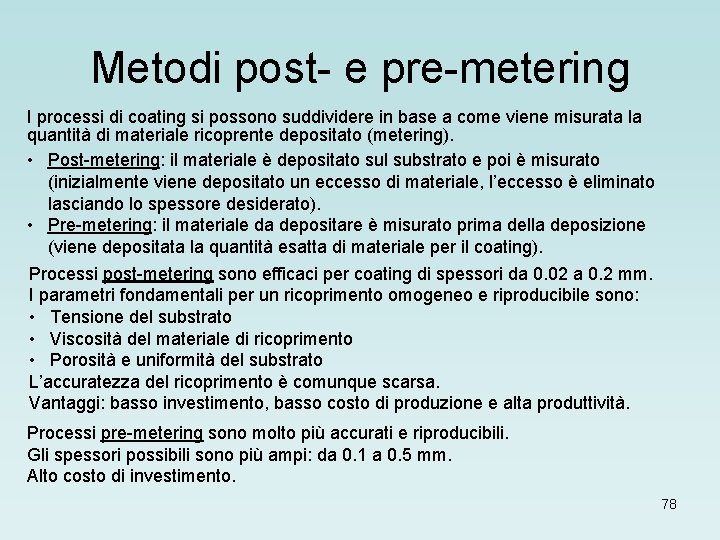
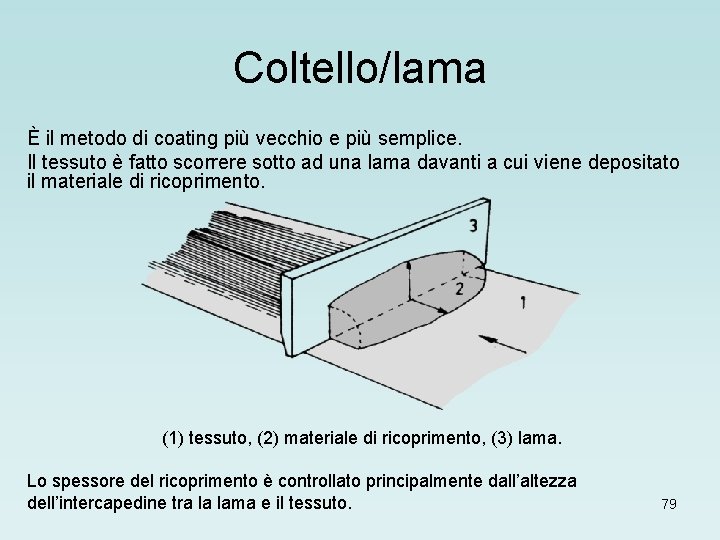
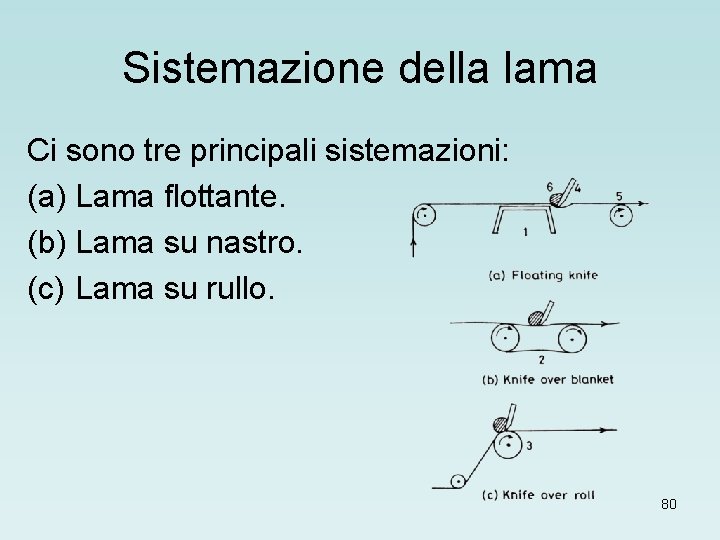
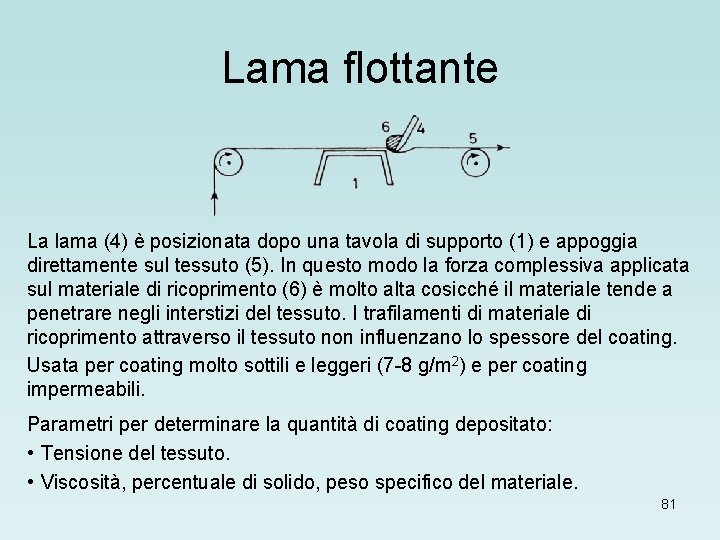
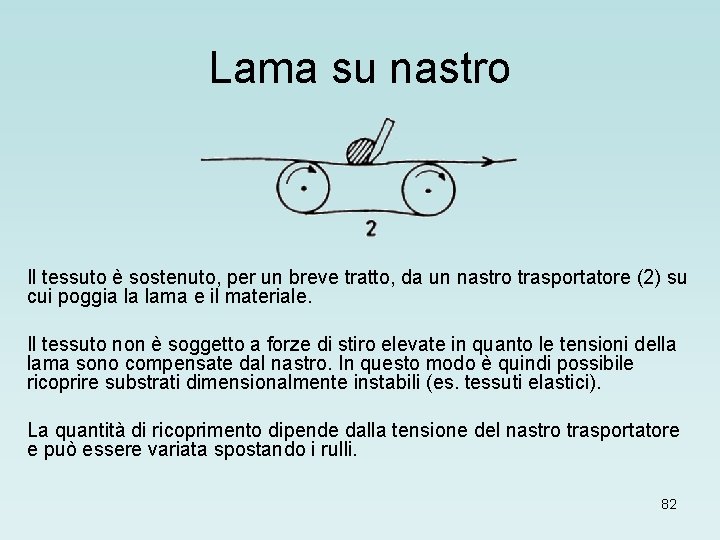
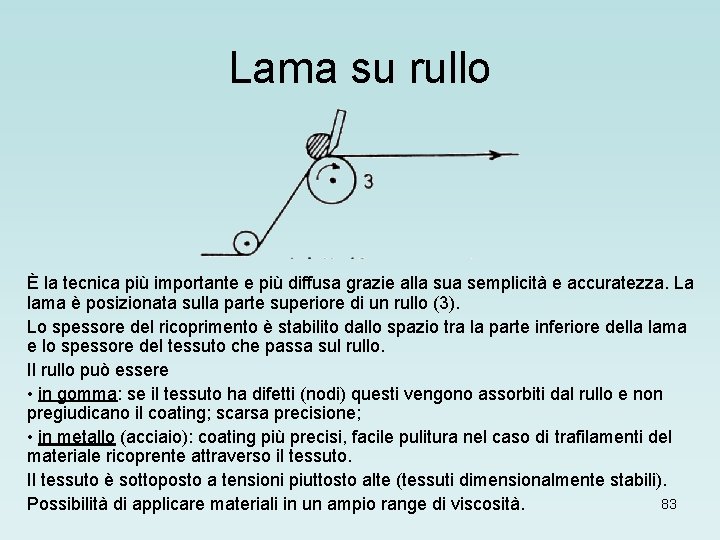
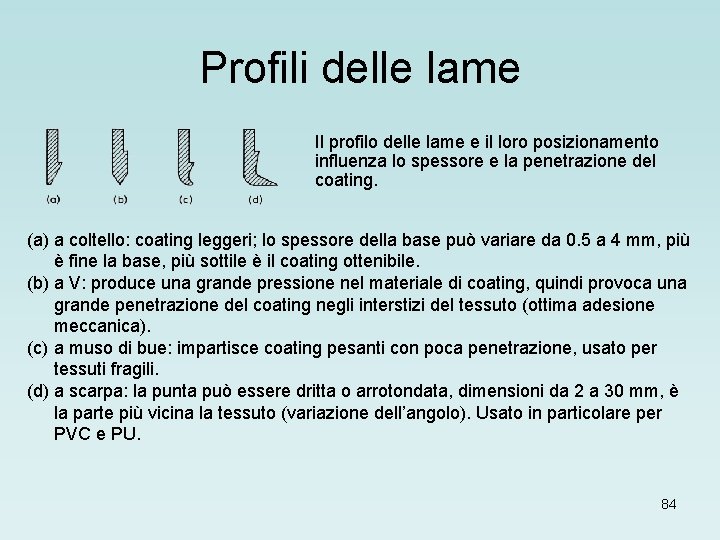
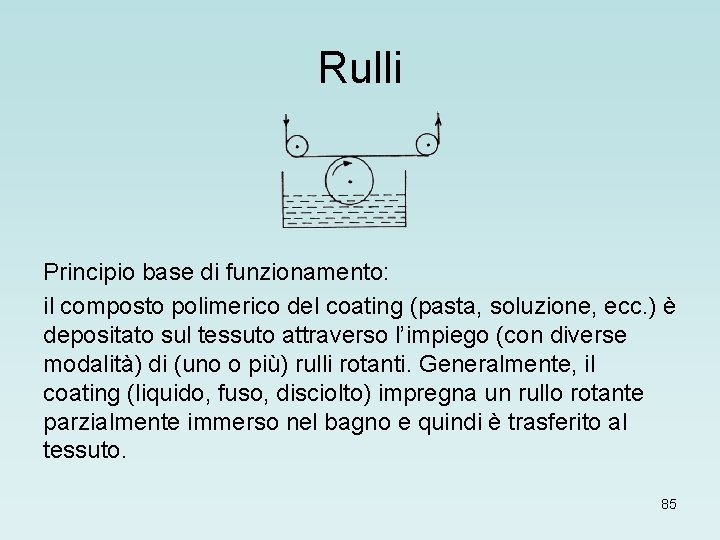
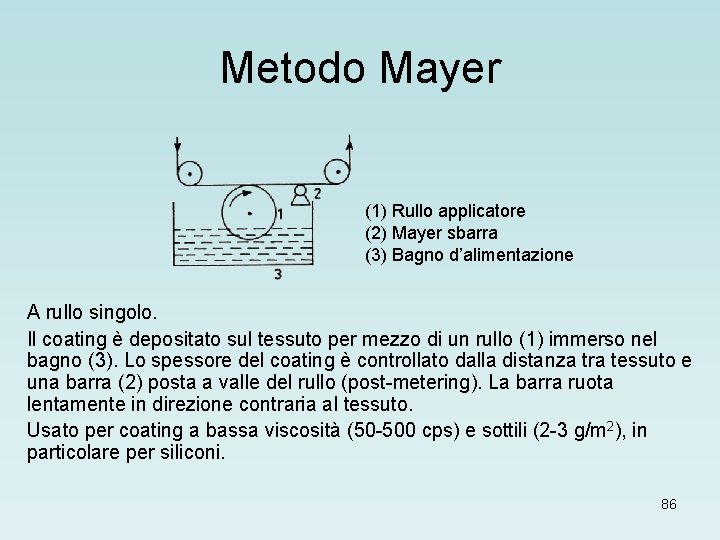
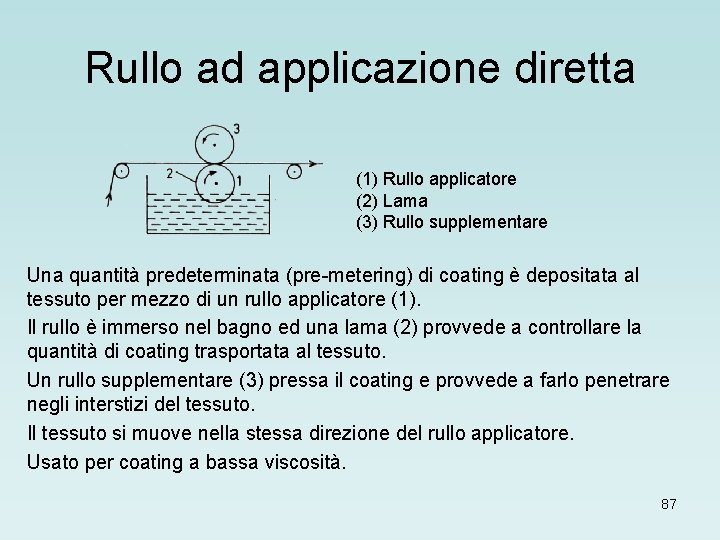
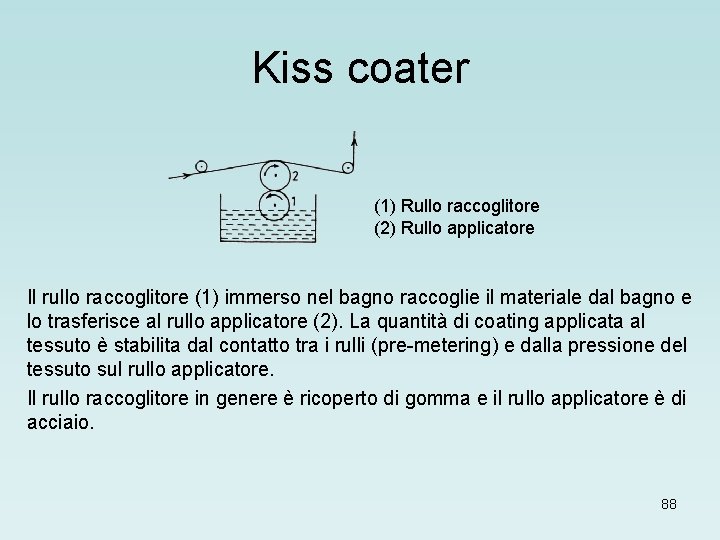
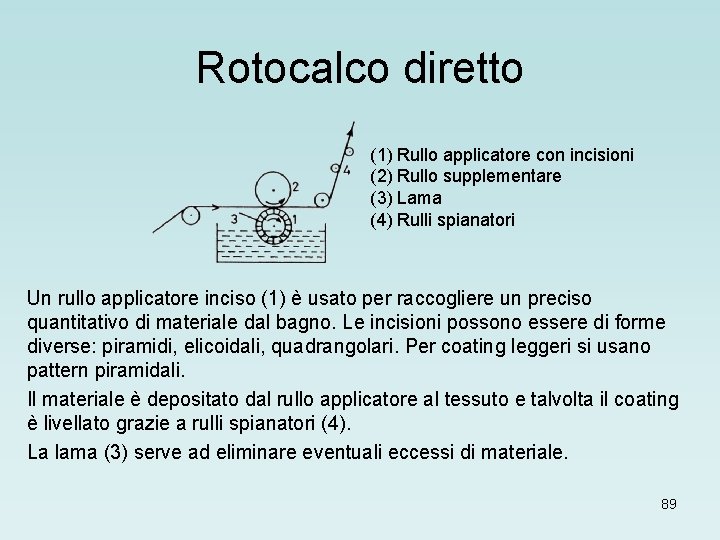
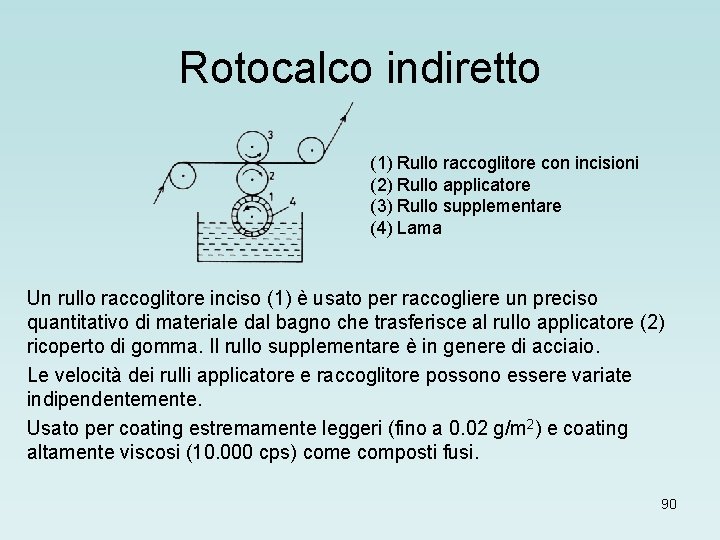
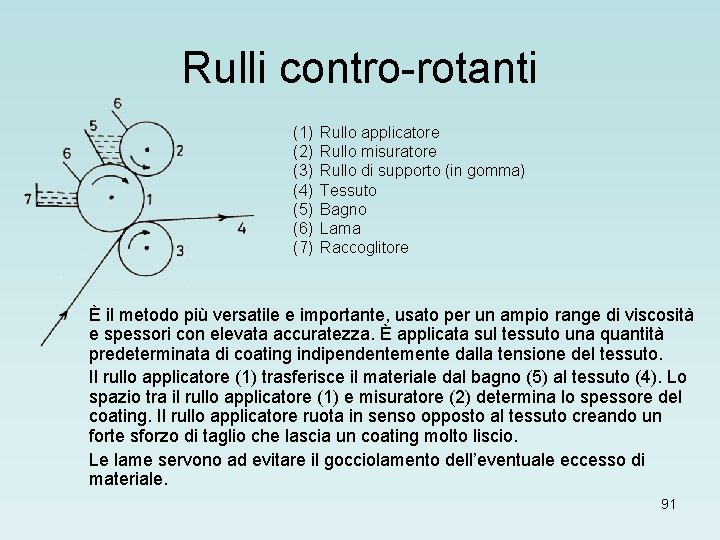
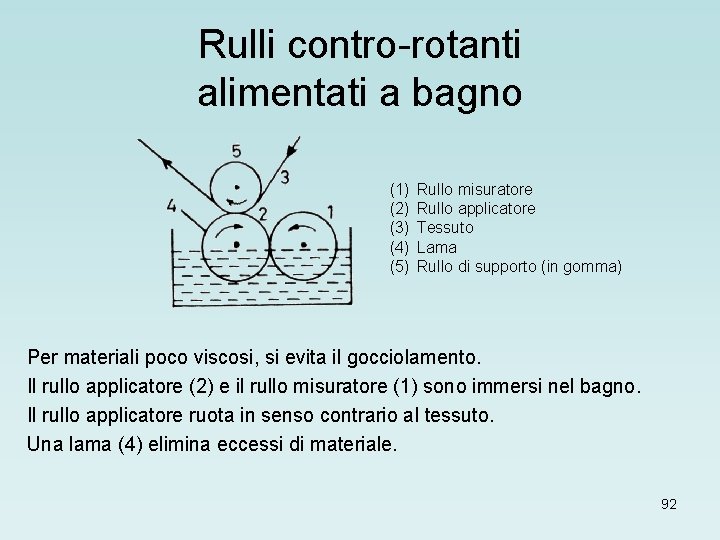
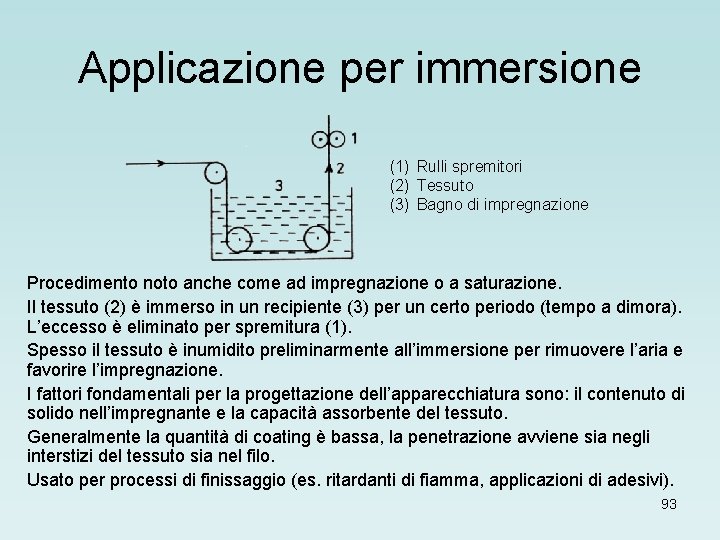
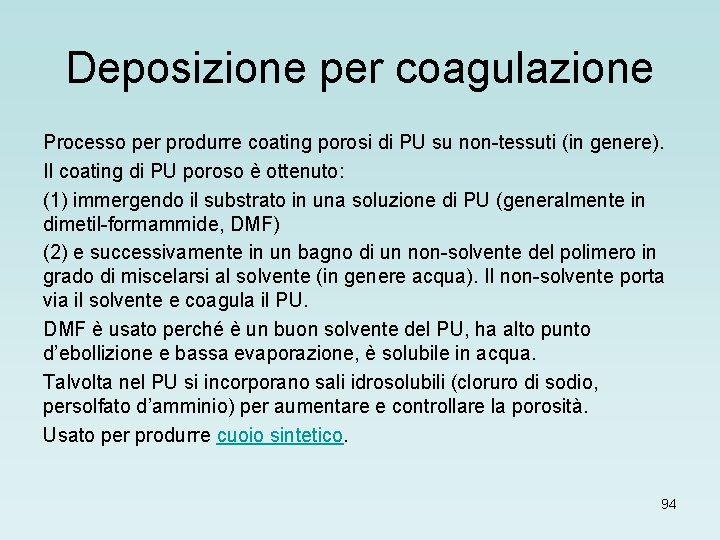
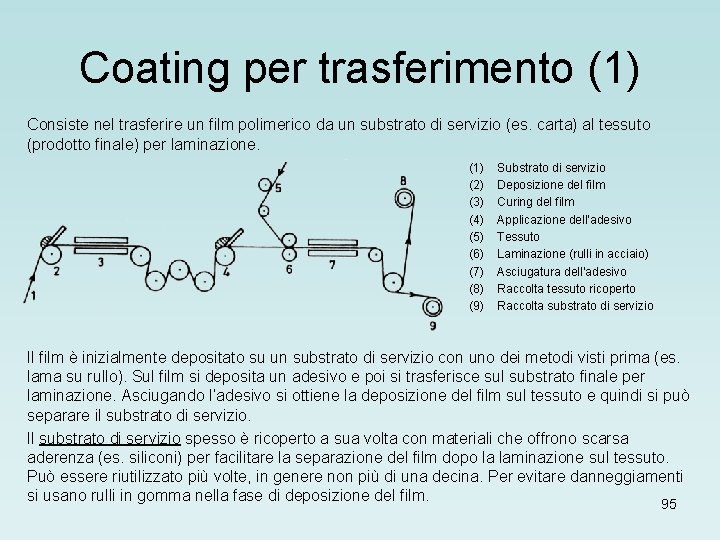
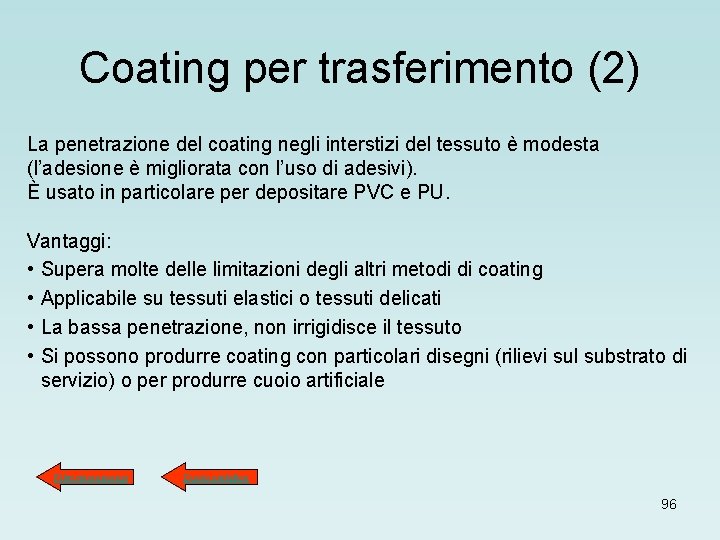
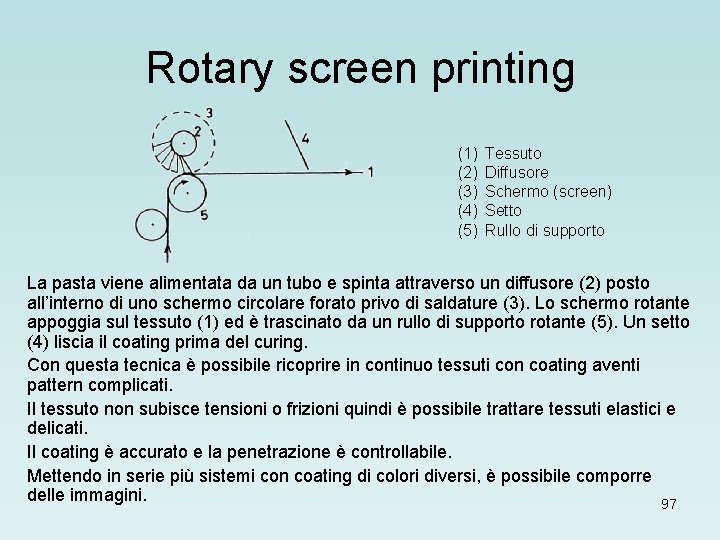
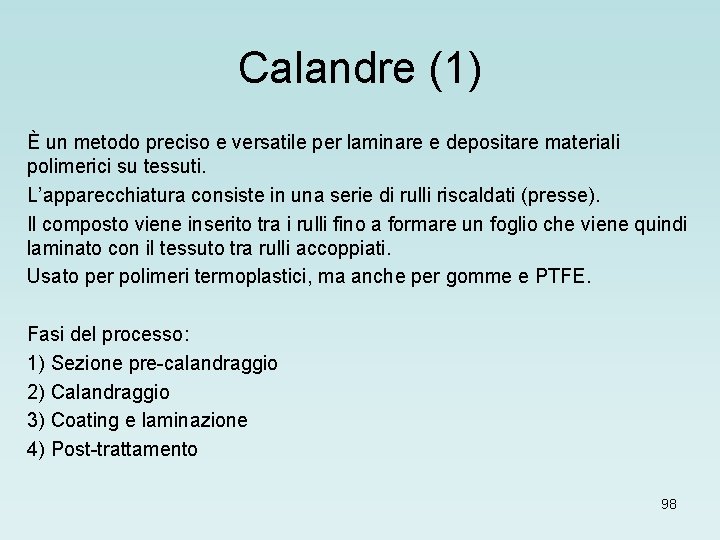
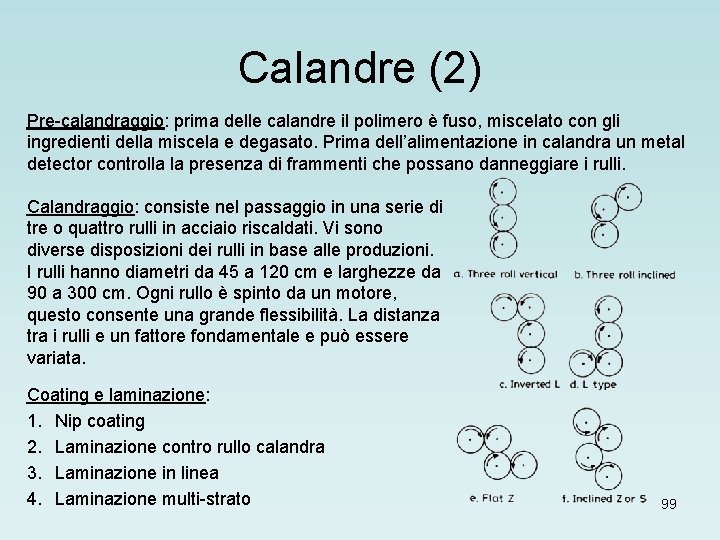
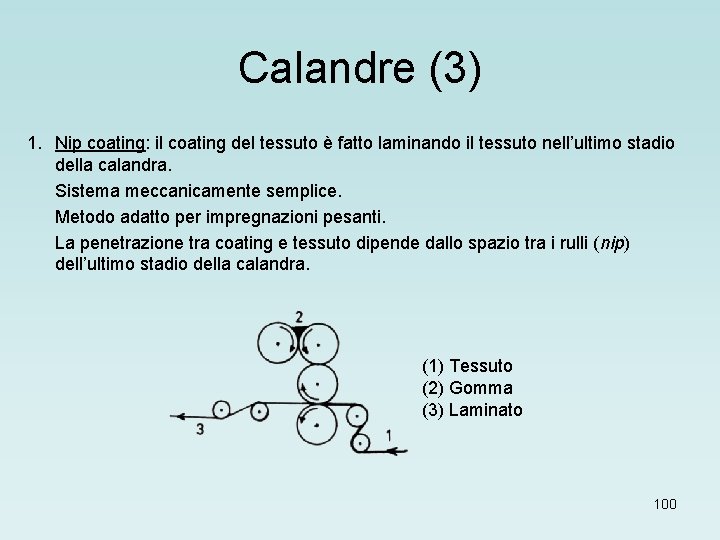
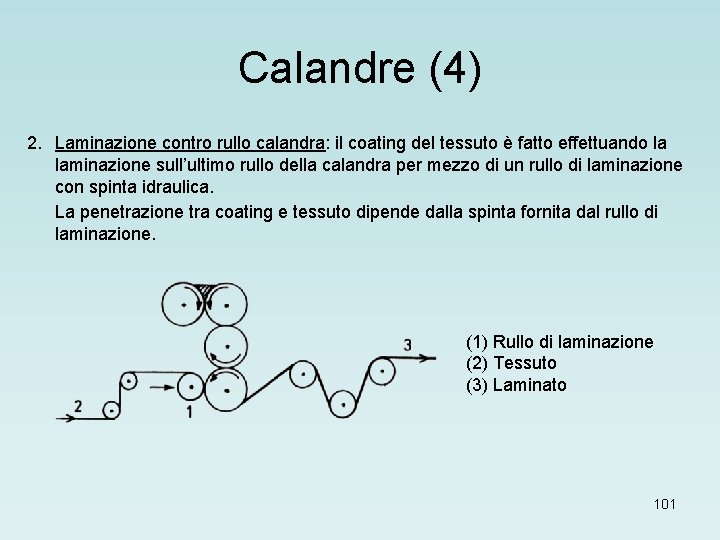
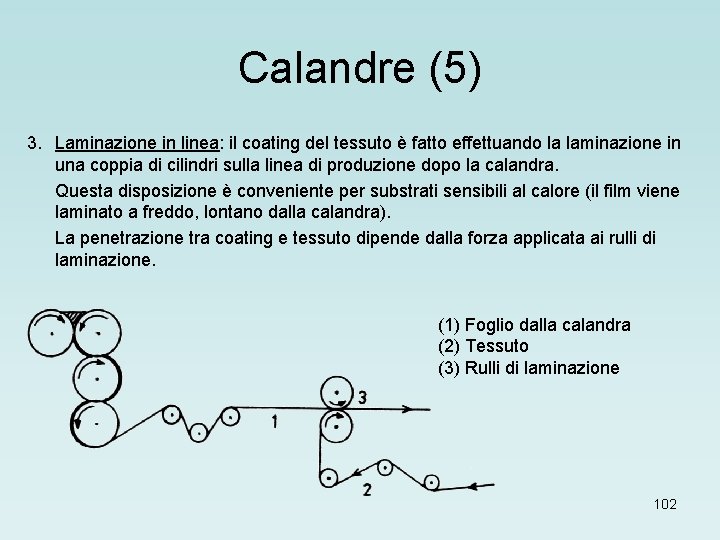
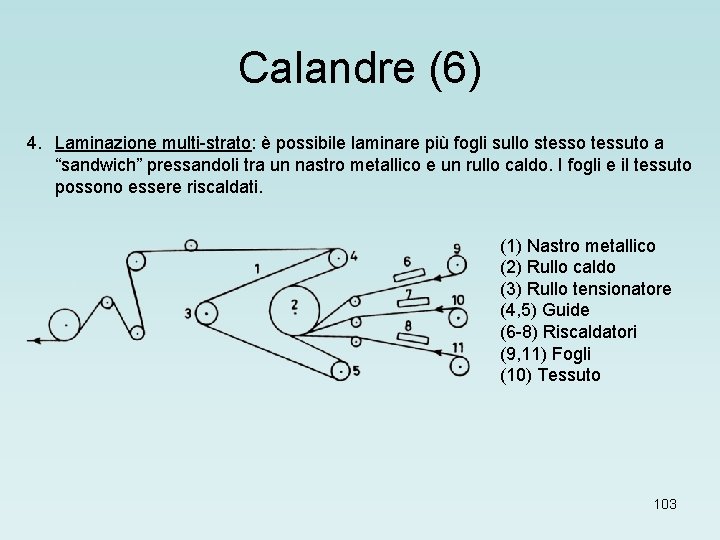
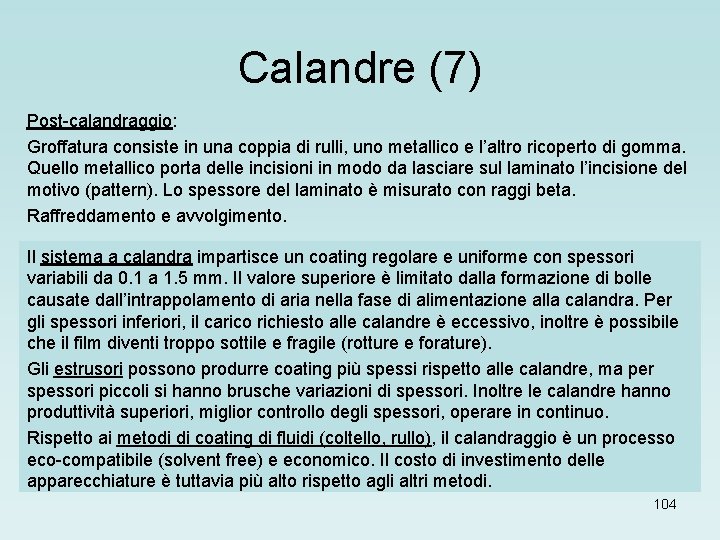
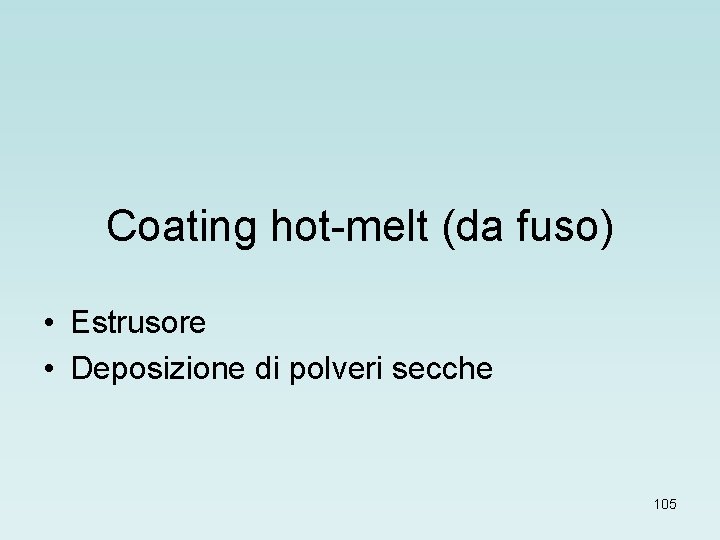
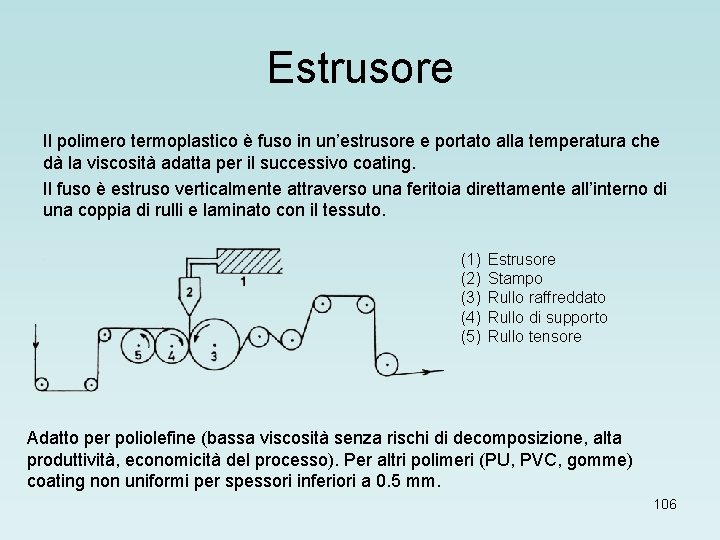
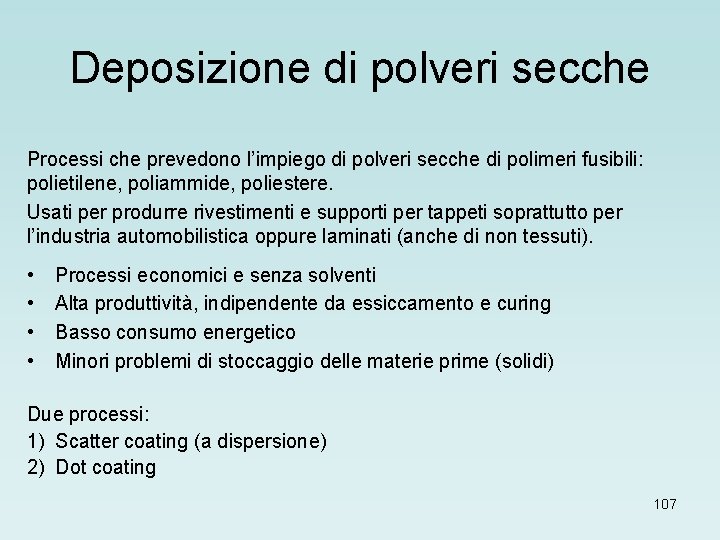
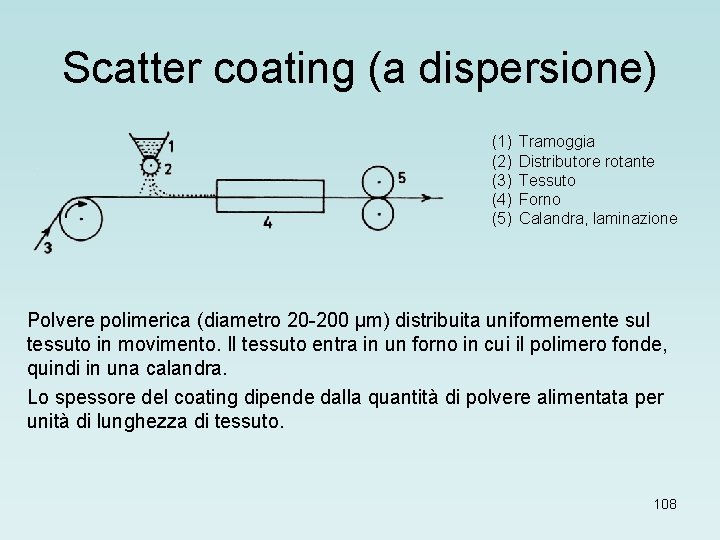
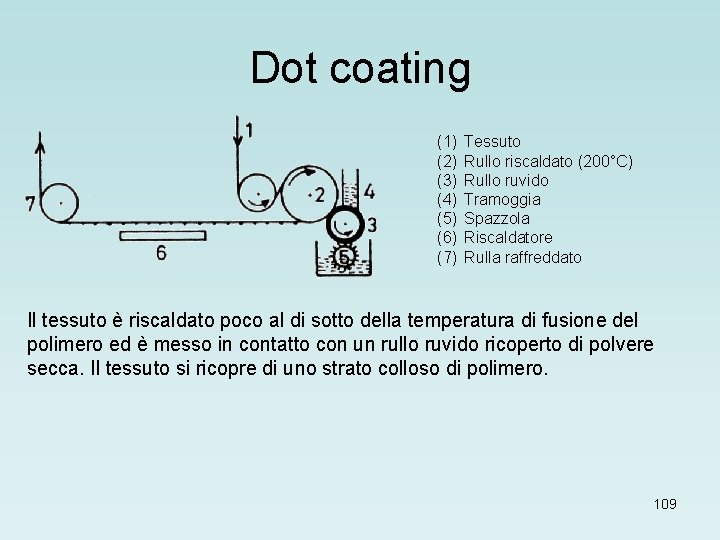
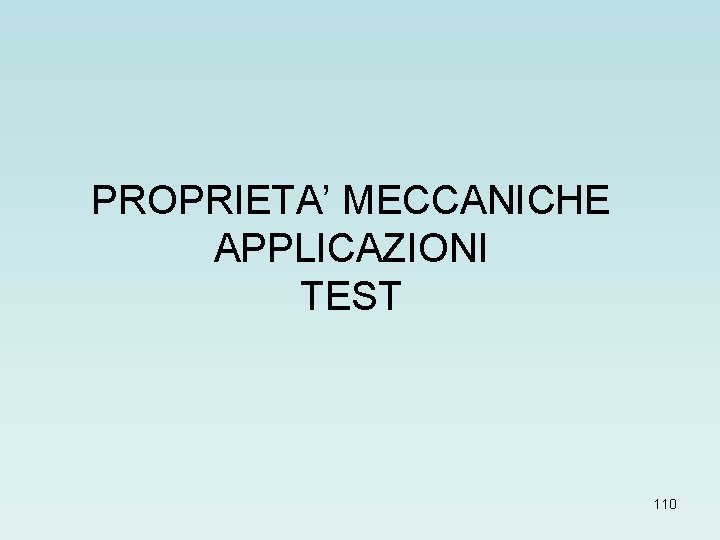
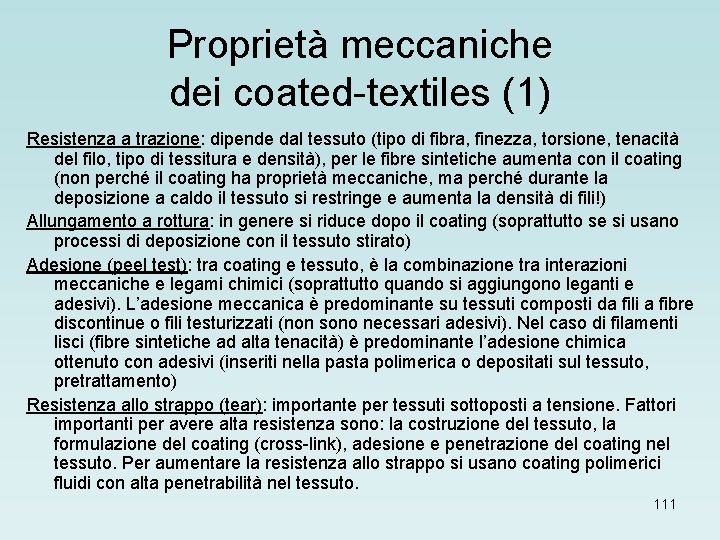
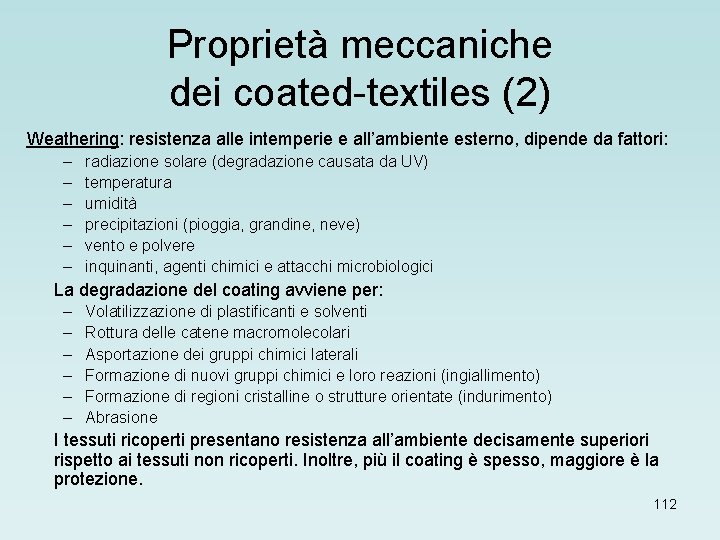
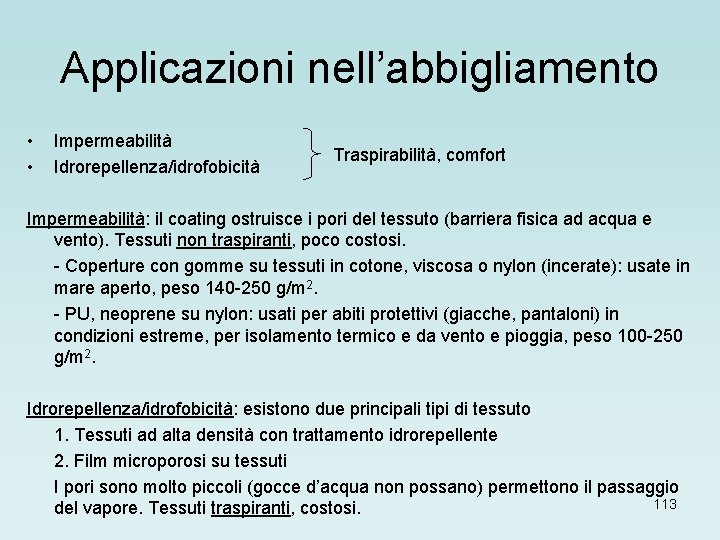
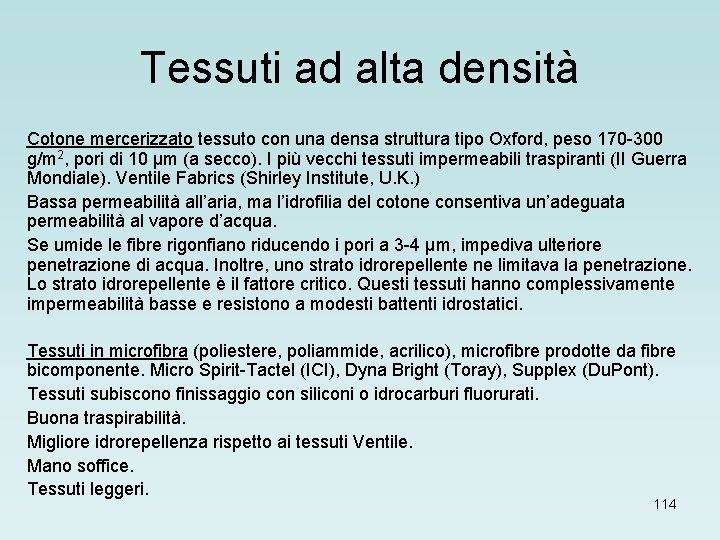
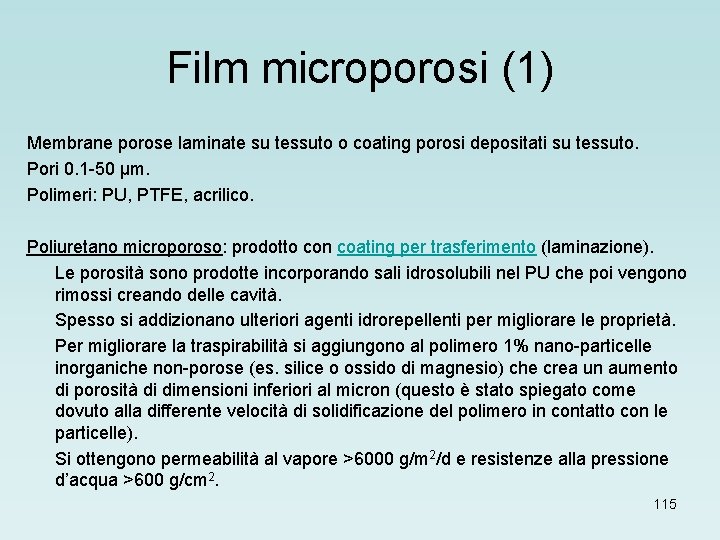
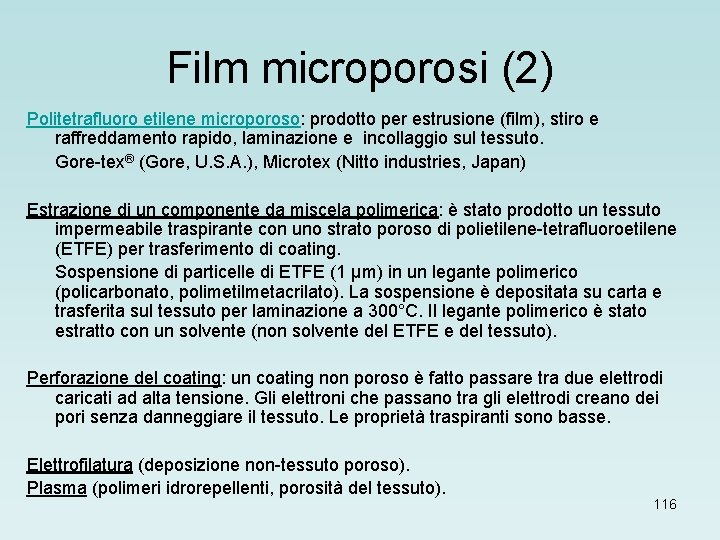

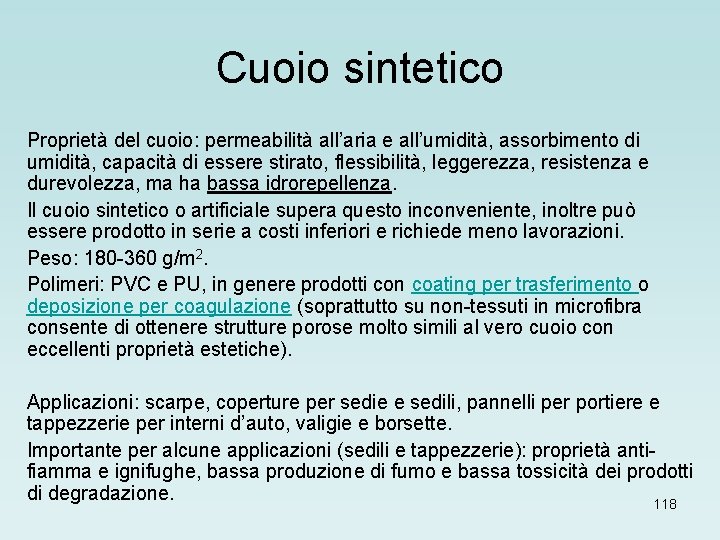
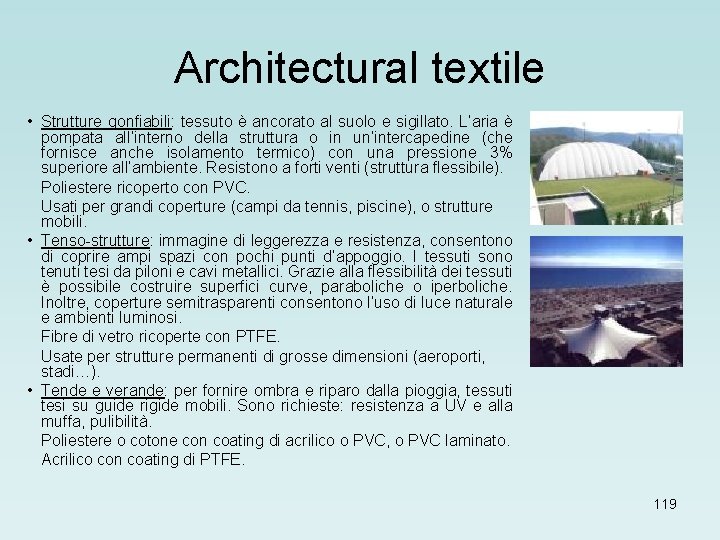
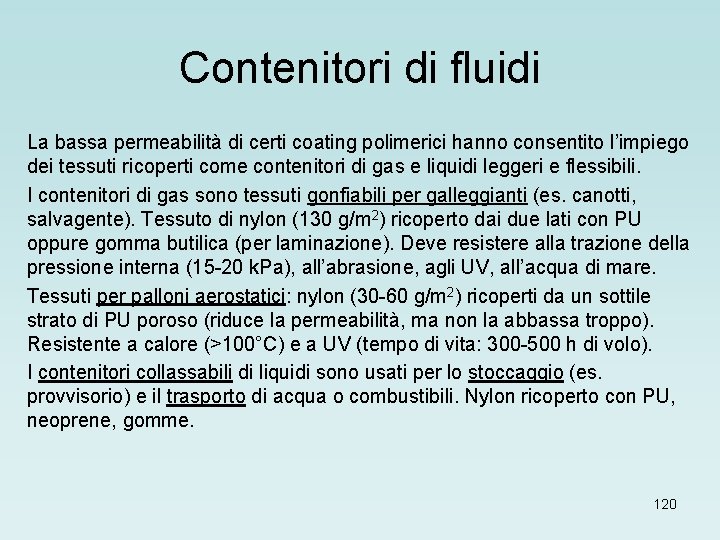
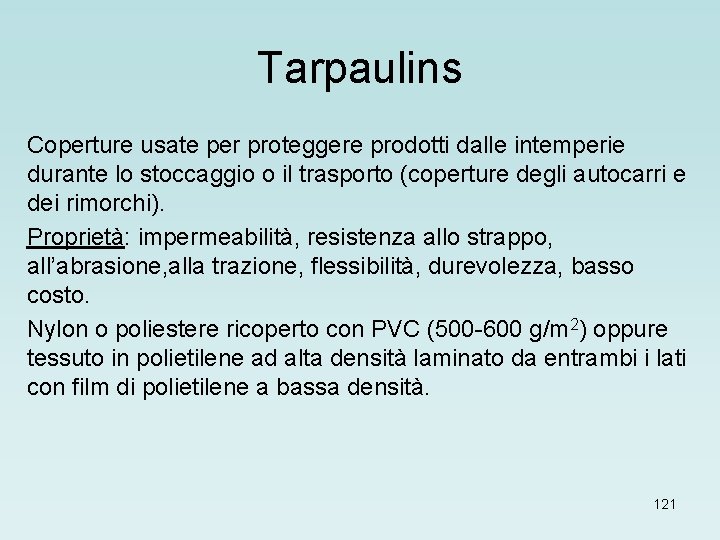

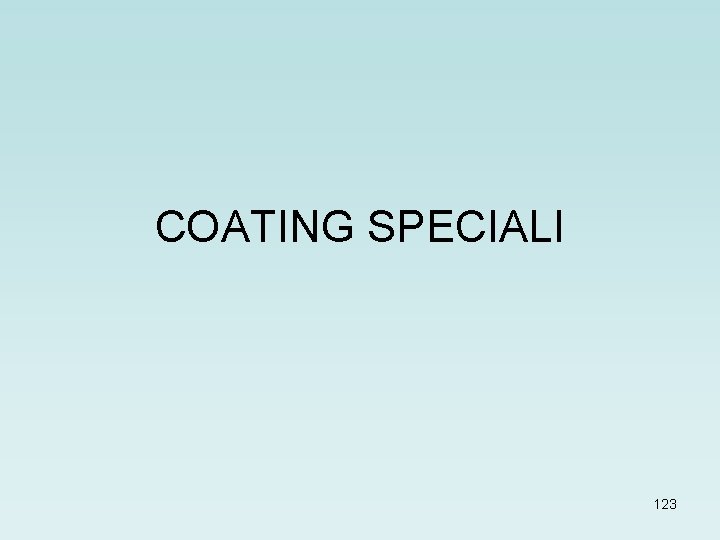
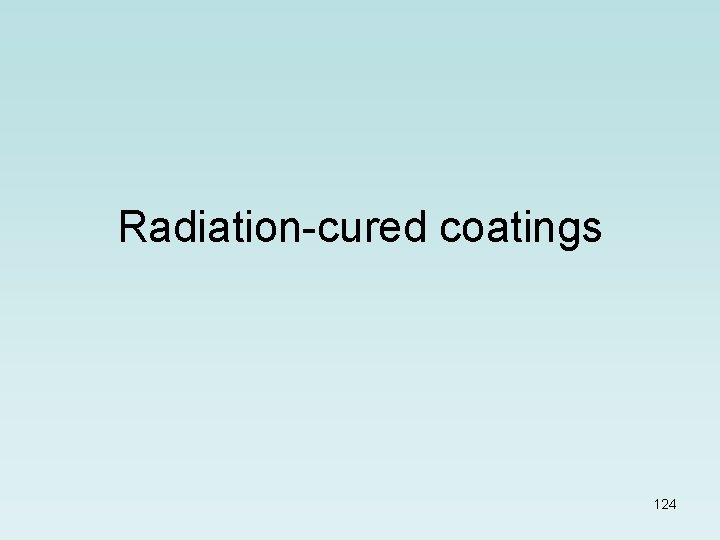
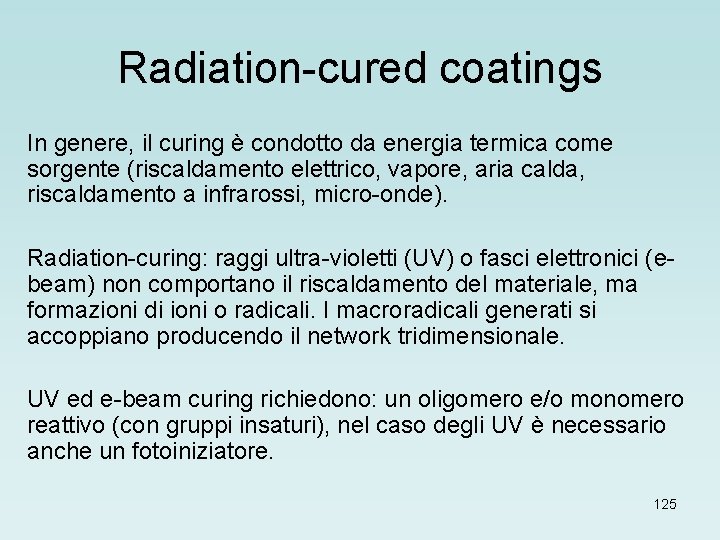
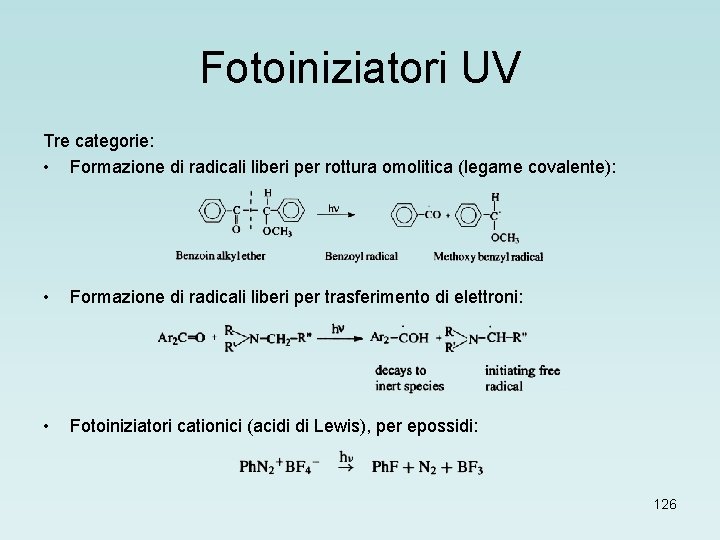
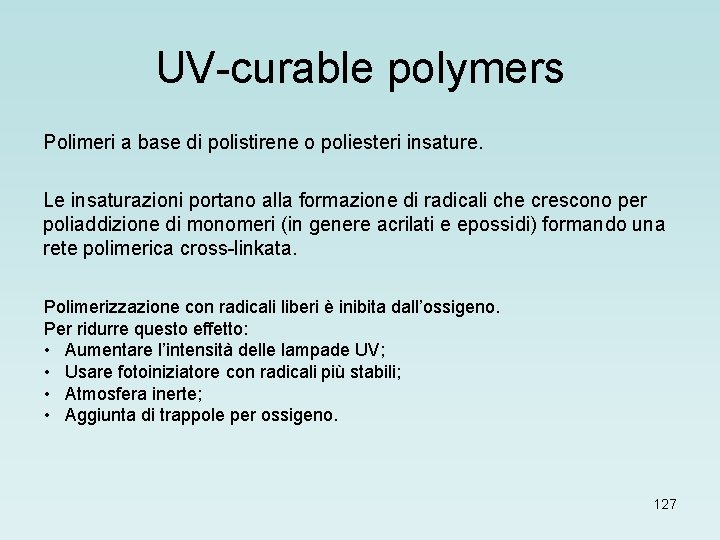
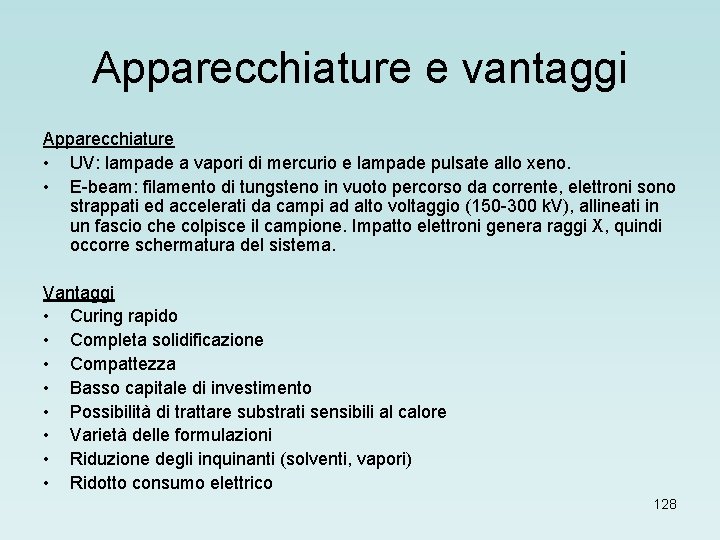
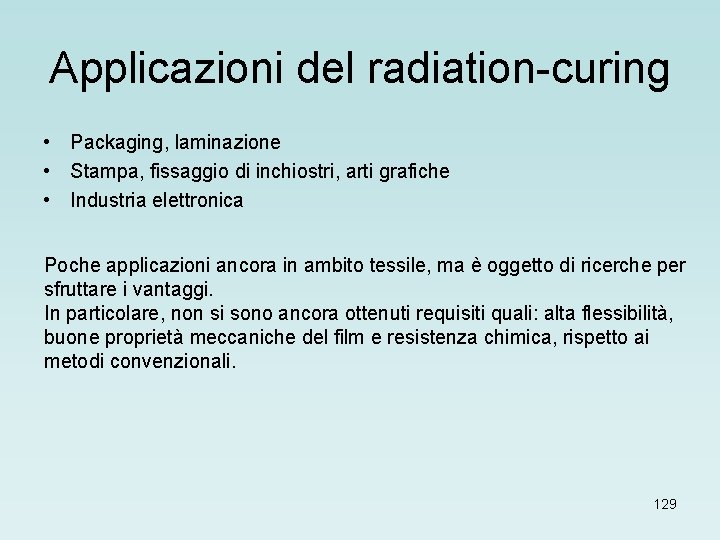
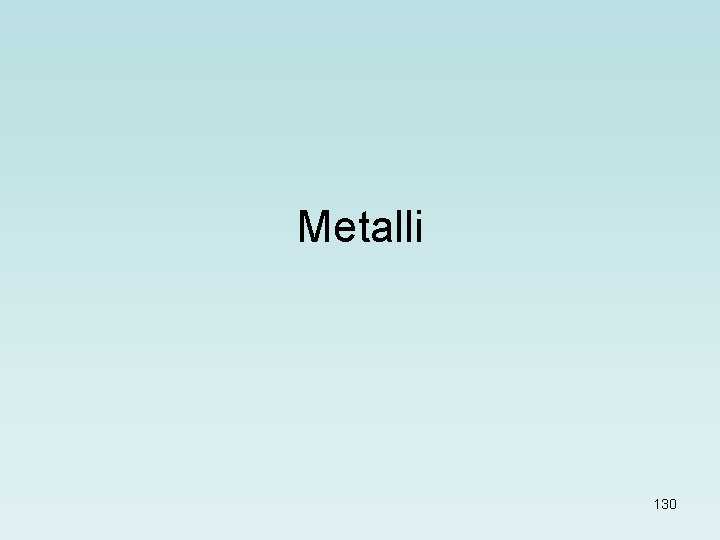
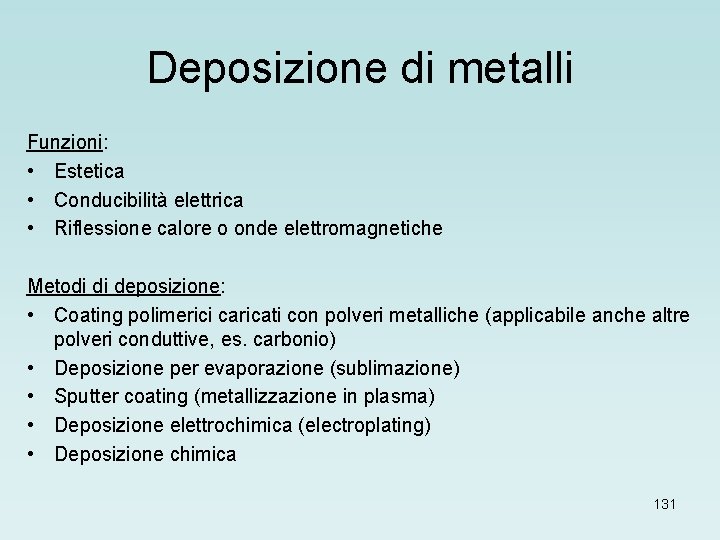
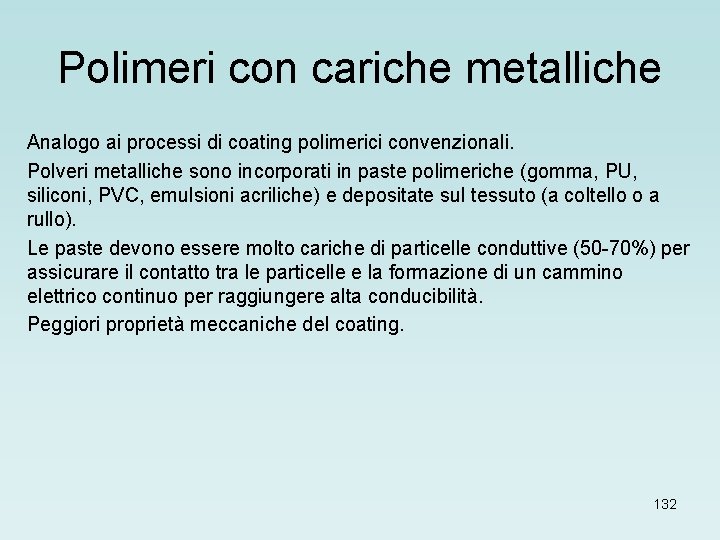
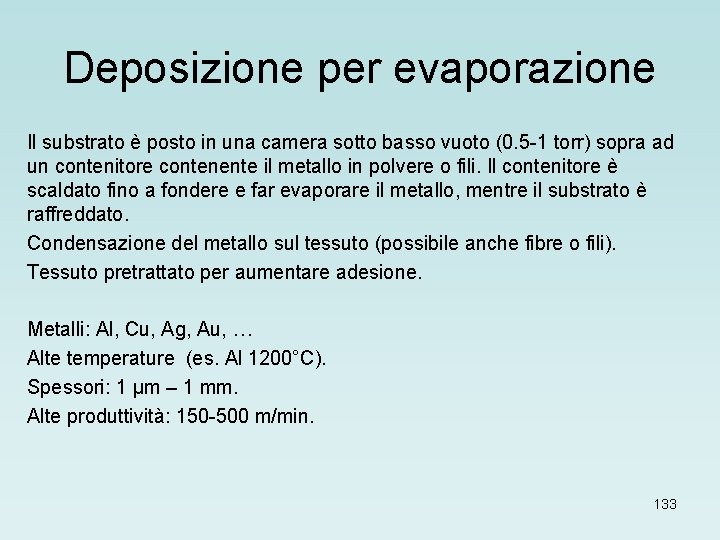
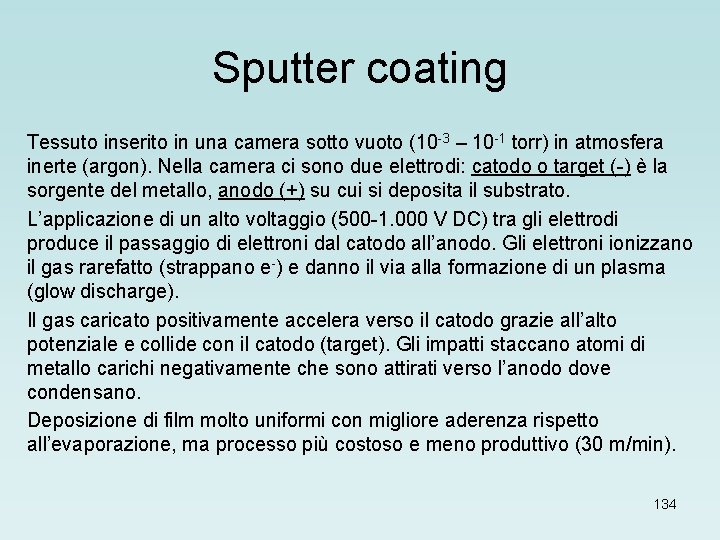
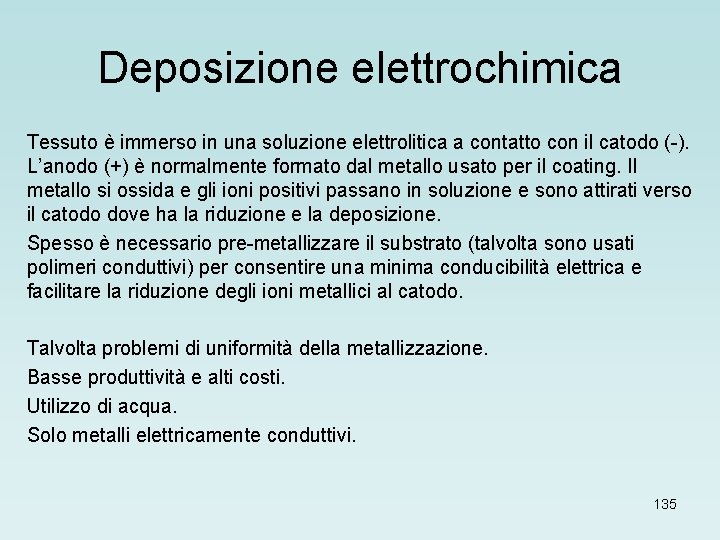
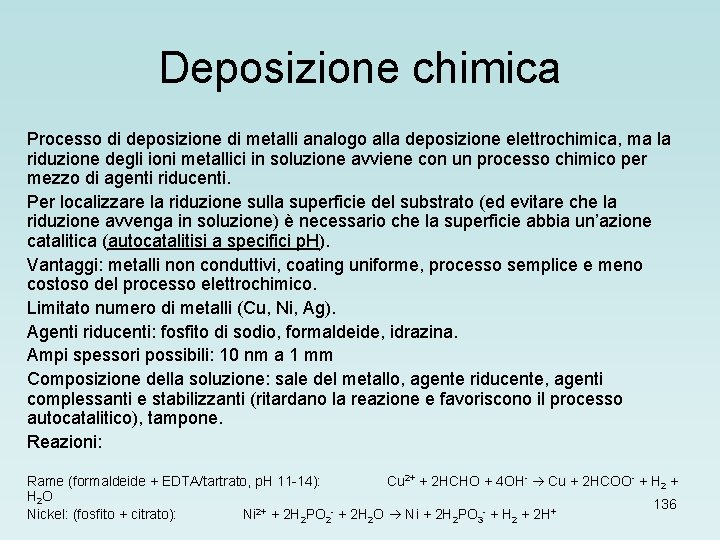
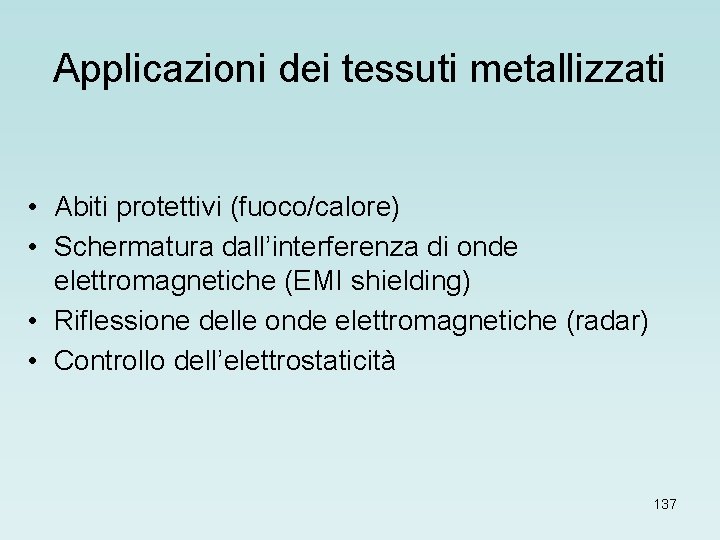
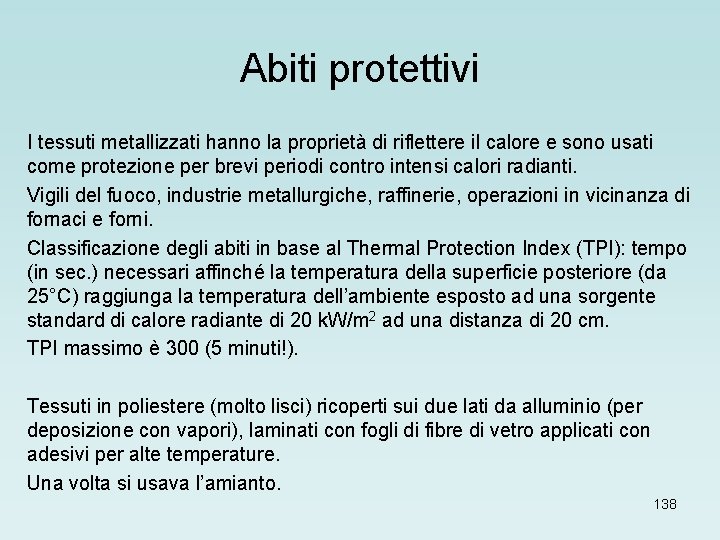
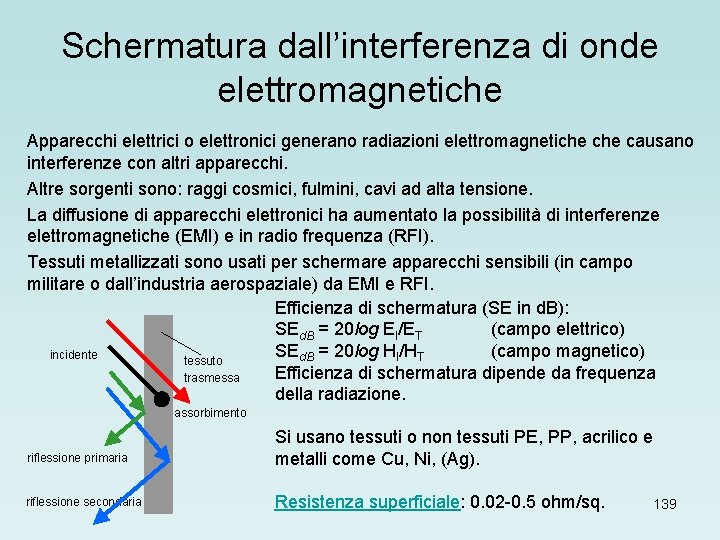
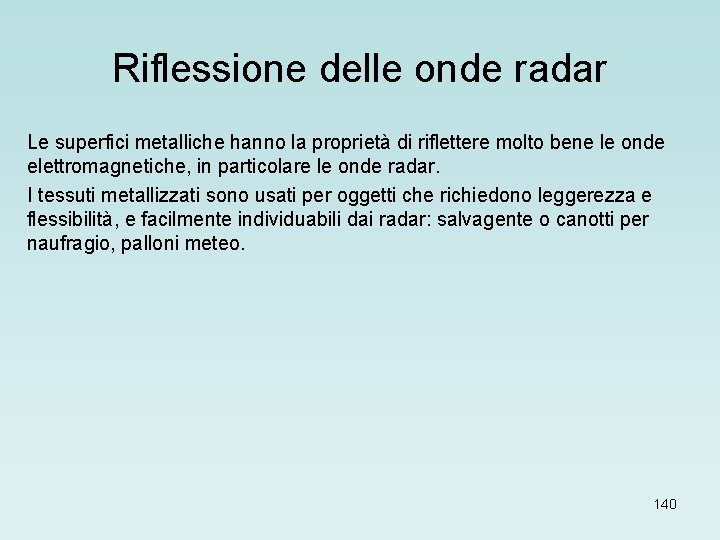

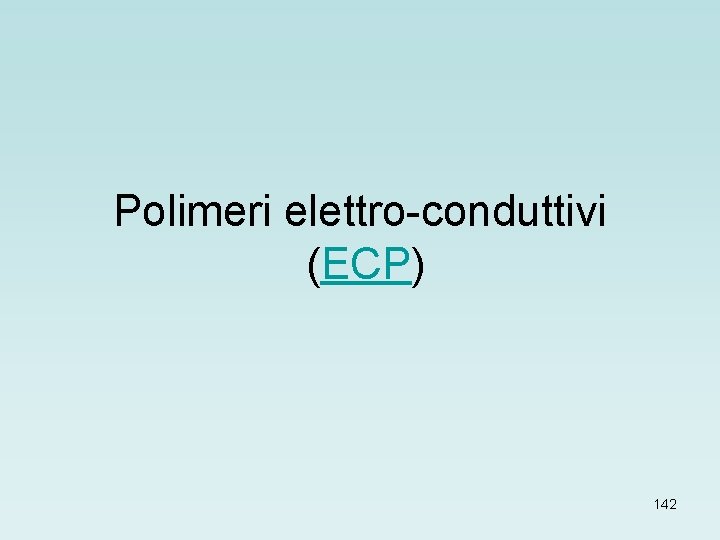
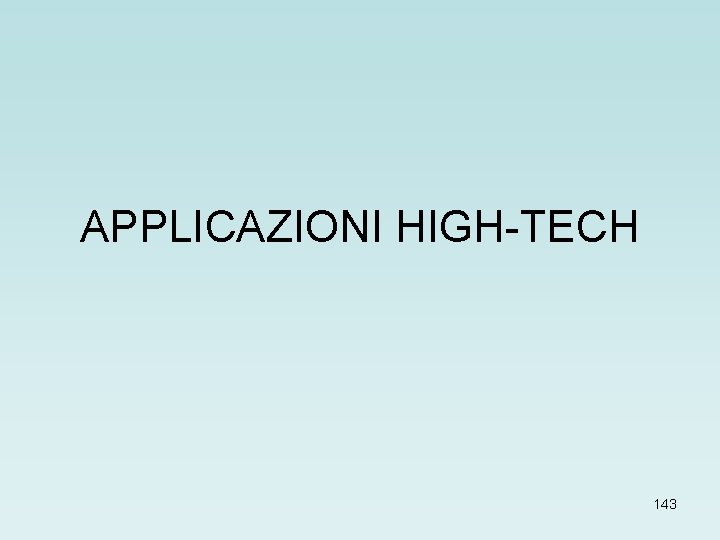
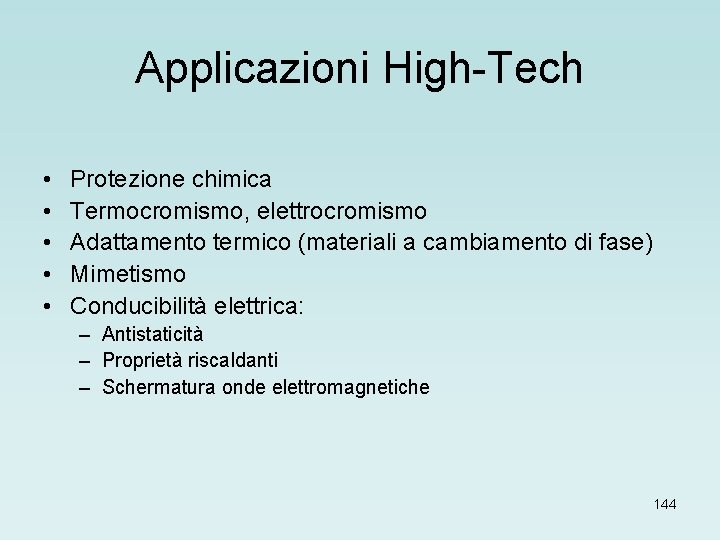
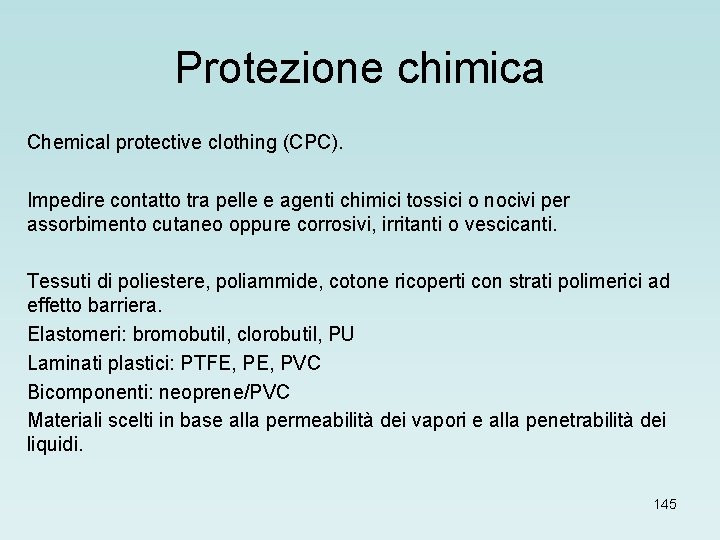
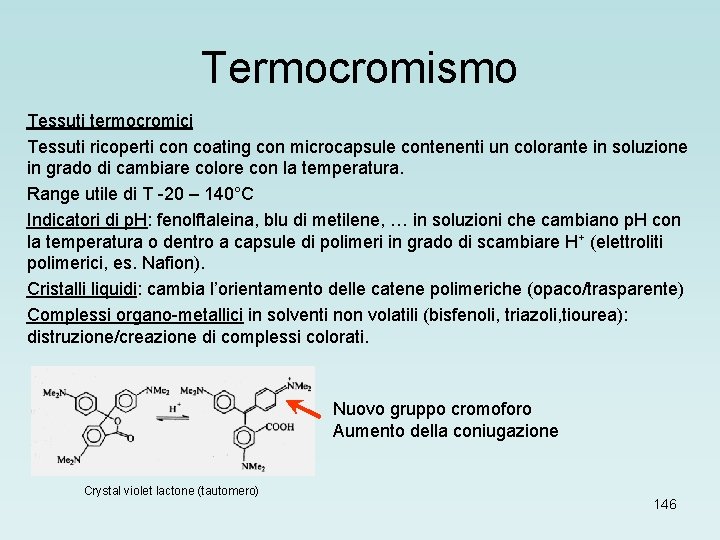
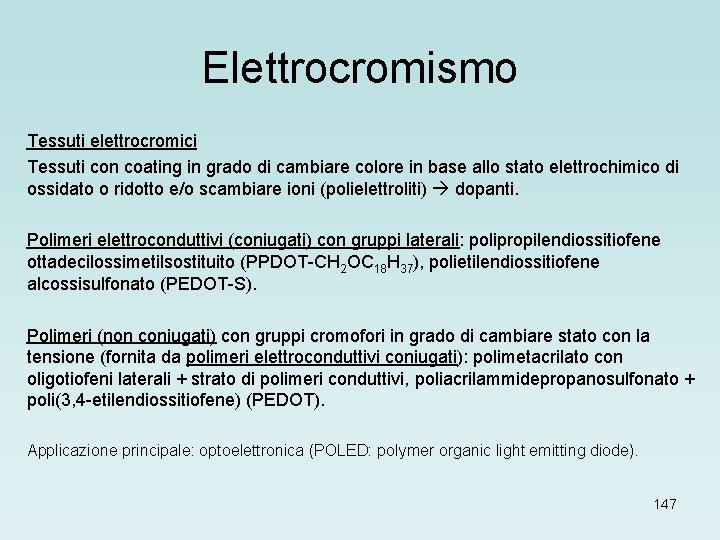
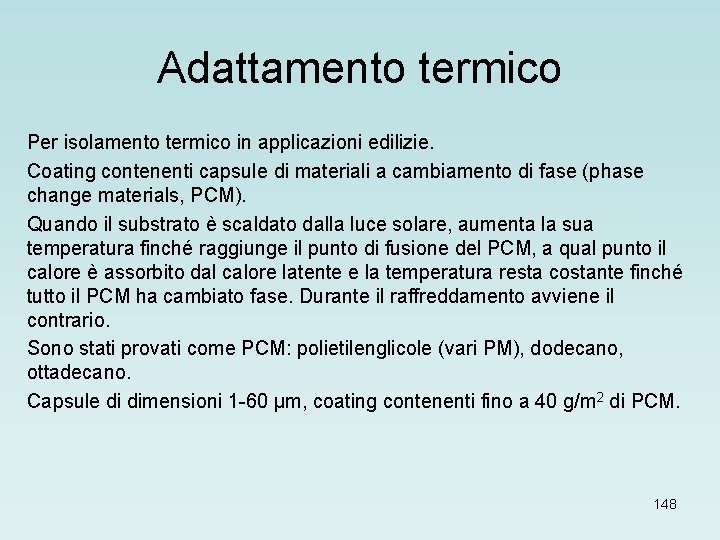
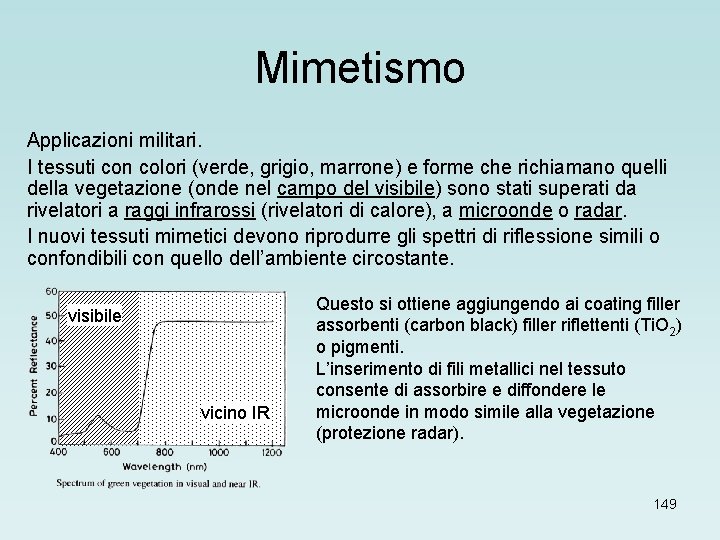
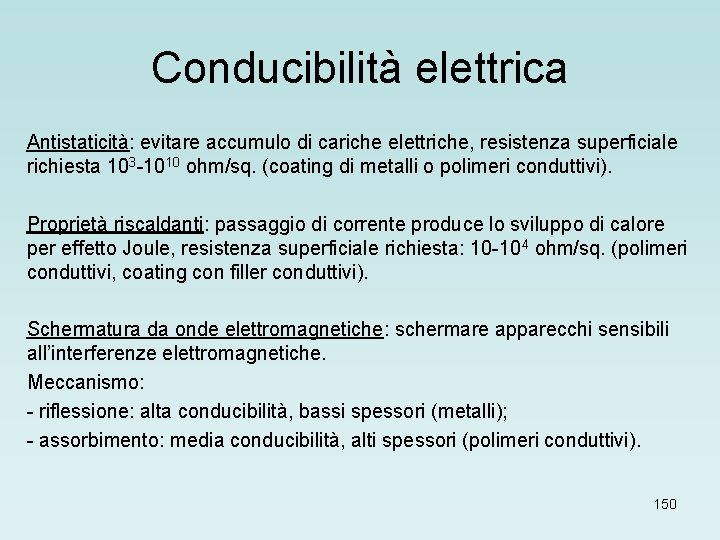
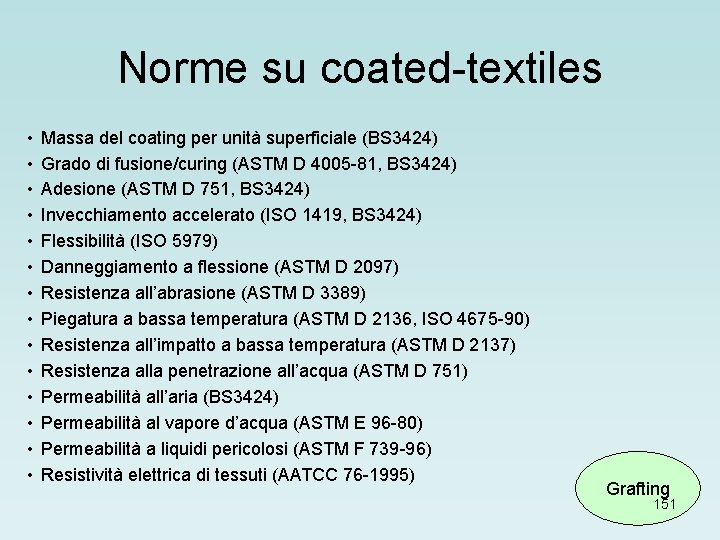
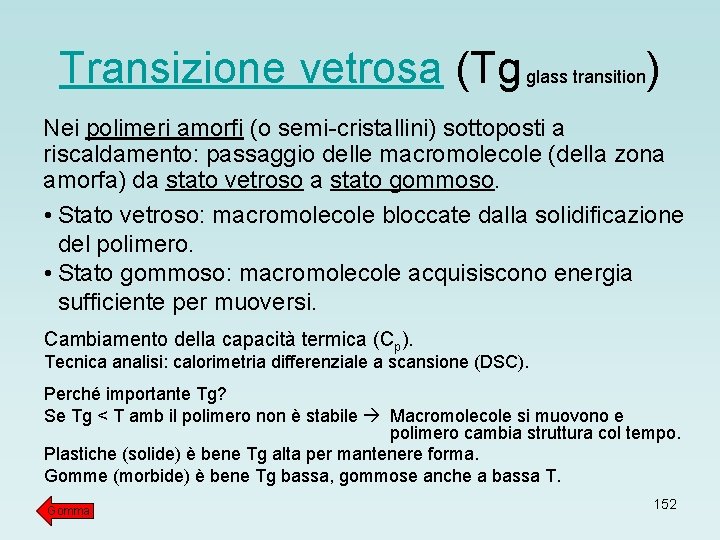
![Resistenza superficiale (RS) RS = [ohm/square] Elettrodi concentrici: RS = 2. 73 R log Resistenza superficiale (RS) RS = [ohm/square] Elettrodi concentrici: RS = 2. 73 R log](https://slidetodoc.com/presentation_image_h/fc1702f15e1df2157e92fcaac0f6b1b6/image-153.jpg)
- Slides: 153
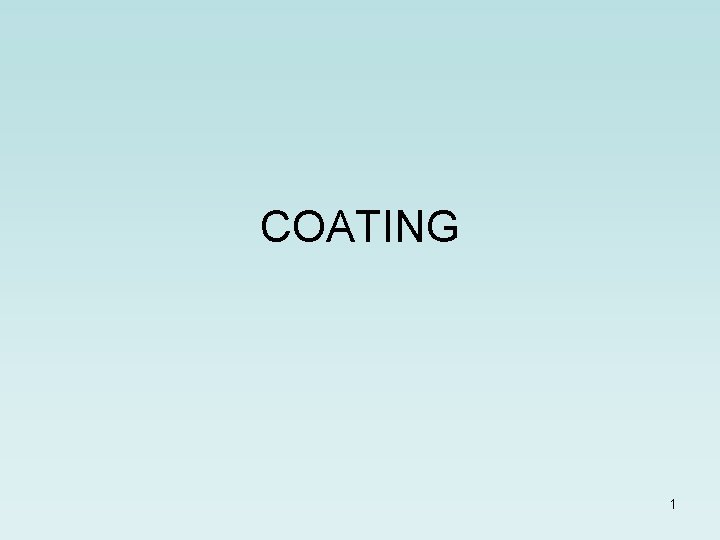
COATING 1
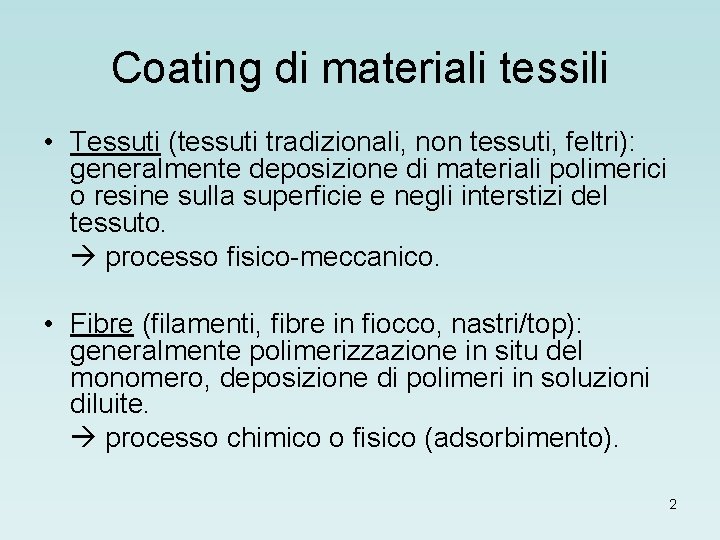
Coating di materiali tessili • Tessuti (tessuti tradizionali, non tessuti, feltri): generalmente deposizione di materiali polimerici o resine sulla superficie e negli interstizi del tessuto. processo fisico-meccanico. • Fibre (filamenti, fibre in fiocco, nastri/top): generalmente polimerizzazione in situ del monomero, deposizione di polimeri in soluzioni diluite. processo chimico o fisico (adsorbimento). 2
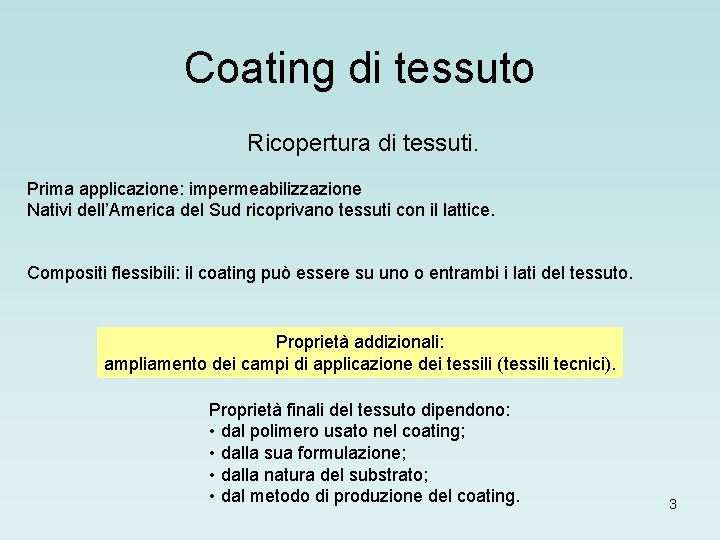
Coating di tessuto Ricopertura di tessuti. Prima applicazione: impermeabilizzazione Nativi dell’America del Sud ricoprivano tessuti con il lattice. Compositi flessibili: il coating può essere su uno o entrambi i lati del tessuto. Proprietà addizionali: ampliamento dei campi di applicazione dei tessili (tessili tecnici). Proprietà finali del tessuto dipendono: • dal polimero usato nel coating; • dalla sua formulazione; • dalla natura del substrato; • dal metodo di produzione del coating. 3
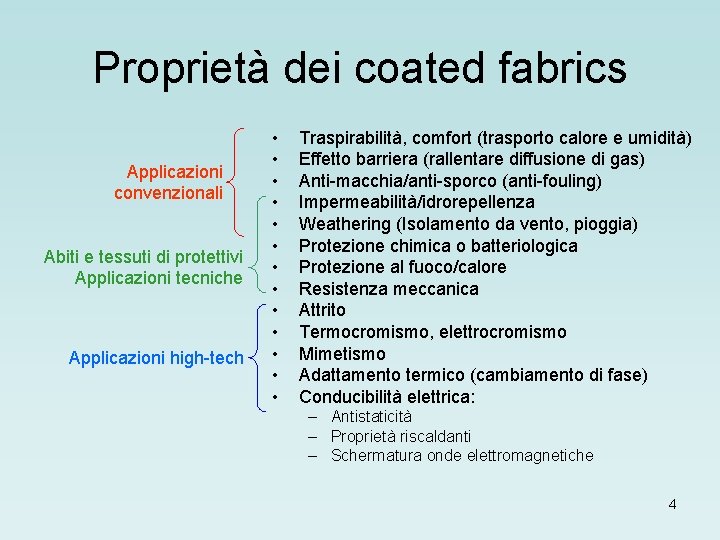
Proprietà dei coated fabrics Applicazioni convenzionali Abiti e tessuti di protettivi Applicazioni tecniche Applicazioni high-tech • • • • Traspirabilità, comfort (trasporto calore e umidità) Effetto barriera (rallentare diffusione di gas) Anti-macchia/anti-sporco (anti-fouling) Impermeabilità/idrorepellenza Weathering (Isolamento da vento, pioggia) Protezione chimica o batteriologica Protezione al fuoco/calore Resistenza meccanica Attrito Termocromismo, elettrocromismo Mimetismo Adattamento termico (cambiamento di fase) Conducibilità elettrica: – Antistaticità – Proprietà riscaldanti – Schermatura onde elettromagnetiche 4
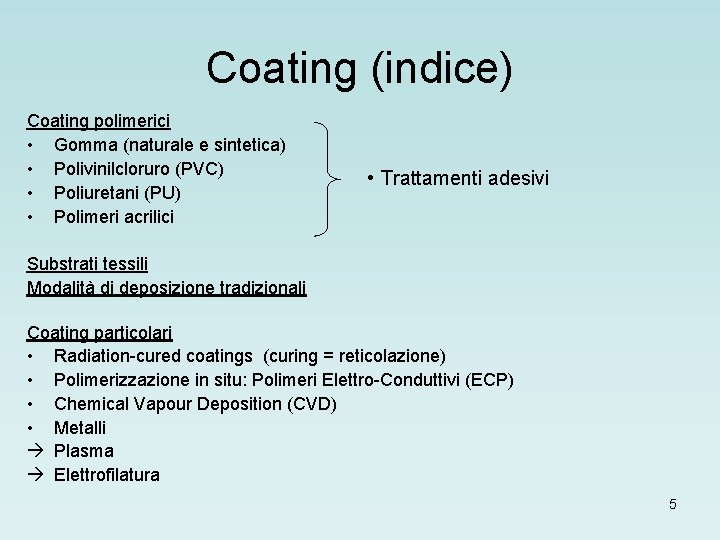
Coating (indice) Coating polimerici • Gomma (naturale e sintetica) • Polivinilcloruro (PVC) • Poliuretani (PU) • Polimeri acrilici • Trattamenti adesivi Substrati tessili Modalità di deposizione tradizionali Coating particolari • Radiation-cured coatings (curing = reticolazione) • Polimerizzazione in situ: Polimeri Elettro-Conduttivi (ECP) • Chemical Vapour Deposition (CVD) • Metalli Plasma Elettrofilatura 5
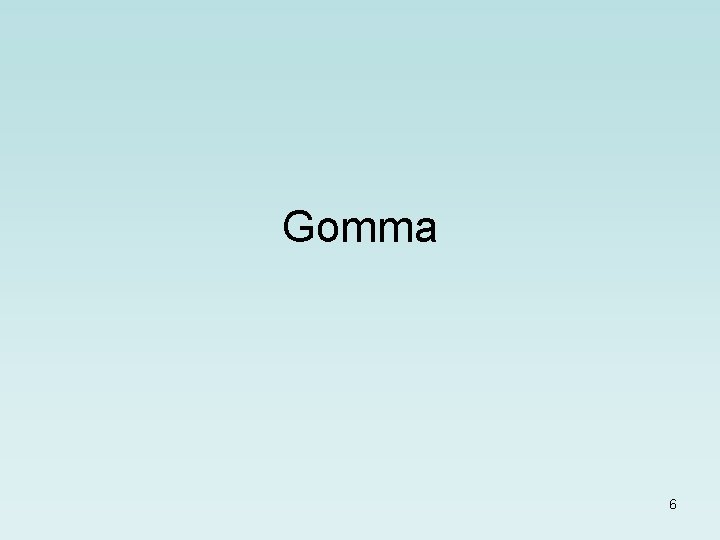
Gomma 6

Gomma (naturale o sintetica) è un materiale macromolecolare amorfo a temperatura ambiente che ha una temperatura di transizione vetrosa (Tg) molto inferiore alla temperatura ambiente. La gomma grezza si deforma in modo plastico (se deformato non recupera la forma) perché priva di struttura rigida (macromolecole separate tra loro). La gomma può essere “cross-linkata” o reticolata (formazione di legami intermacromolecolari) e formare un elastomero che ha proprietà elastiche (recupero della forma originale dopo deformazione). Per la gomma (naturale o sintetica) la reticolazione è ottenuta con lo zolfo (vulcanizzazione) che forma ponti -Sx- tra le macromolecole e crea un network tridimensionale di macromolecole (Charles Goodyear). 7
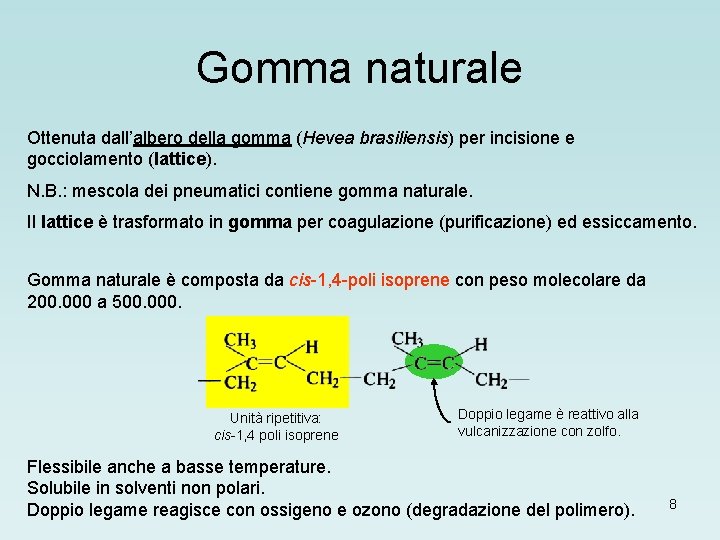
Gomma naturale Ottenuta dall’albero della gomma (Hevea brasiliensis) per incisione e gocciolamento (lattice). N. B. : mescola dei pneumatici contiene gomma naturale. Il lattice è trasformato in gomma per coagulazione (purificazione) ed essiccamento. Gomma naturale è composta da cis-1, 4 -poli isoprene con peso molecolare da 200. 000 a 500. 000. Unità ripetitiva: cis-1, 4 poli isoprene Doppio legame è reattivo alla vulcanizzazione con zolfo. Flessibile anche a basse temperature. Solubile in solventi non polari. Doppio legame reagisce con ossigeno e ozono (degradazione del polimero). 8
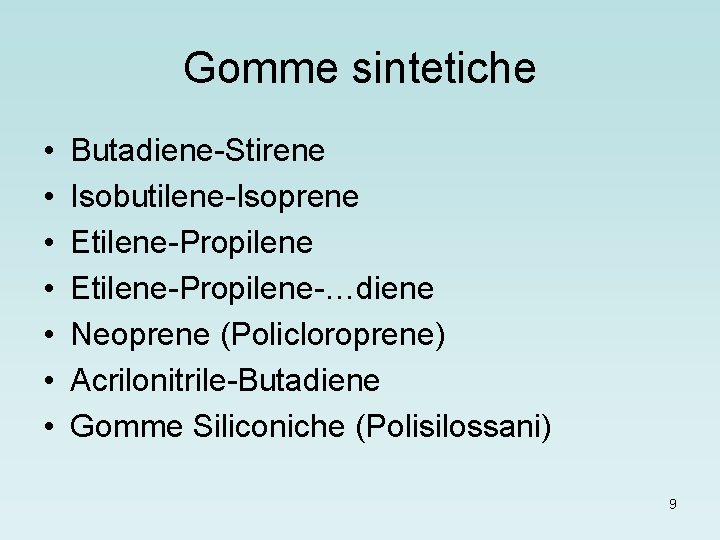
Gomme sintetiche • • Butadiene-Stirene Isobutilene-Isoprene Etilene-Propilene-…diene Neoprene (Policloroprene) Acrilonitrile-Butadiene Gomme Siliconiche (Polisilossani) 9
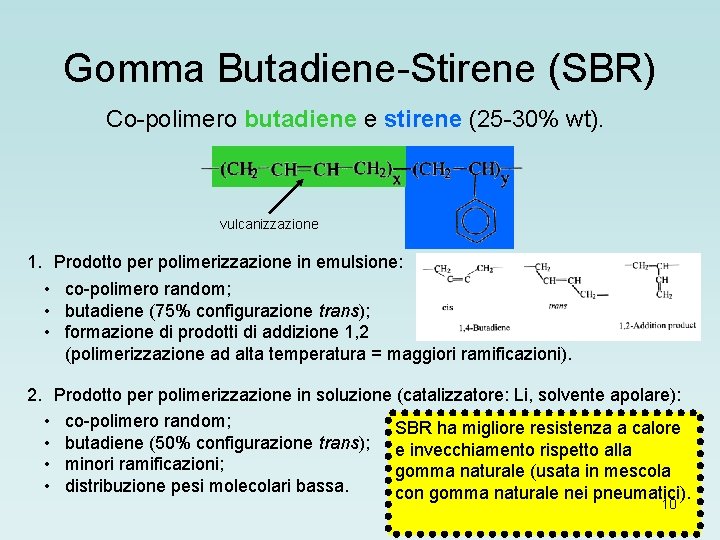
Gomma Butadiene-Stirene (SBR) Co-polimero butadiene e stirene (25 -30% wt). vulcanizzazione 1. Prodotto per polimerizzazione in emulsione: • co-polimero random; • butadiene (75% configurazione trans); • formazione di prodotti di addizione 1, 2 (polimerizzazione ad alta temperatura = maggiori ramificazioni). 2. Prodotto per polimerizzazione in soluzione (catalizzatore: Li, solvente apolare): • co-polimero random; SBR ha migliore resistenza a calore • butadiene (50% configurazione trans); e invecchiamento rispetto alla • minori ramificazioni; gomma naturale (usata in mescola • distribuzione pesi molecolari bassa. con gomma naturale nei pneumatici). 10
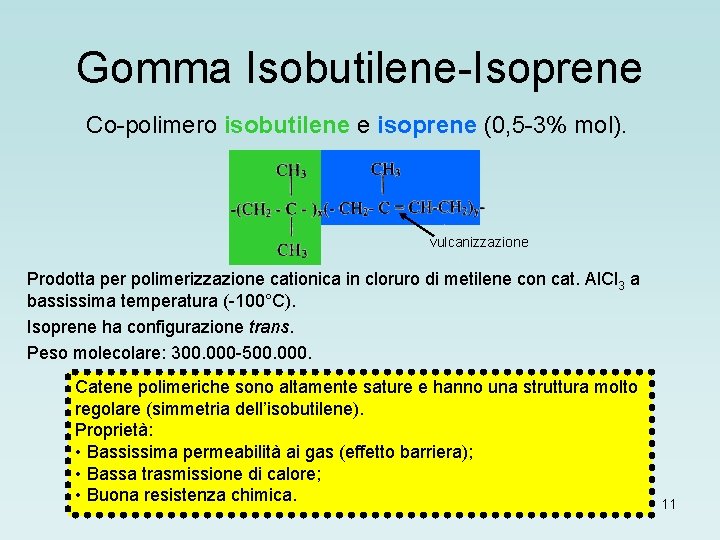
Gomma Isobutilene-Isoprene Co-polimero isobutilene e isoprene (0, 5 -3% mol). vulcanizzazione Prodotta per polimerizzazione cationica in cloruro di metilene con cat. Al. Cl 3 a bassissima temperatura (-100°C). Isoprene ha configurazione trans. Peso molecolare: 300. 000 -500. 000. Catene polimeriche sono altamente sature e hanno una struttura molto regolare (simmetria dell’isobutilene). Proprietà: • Bassissima permeabilità ai gas (effetto barriera); • Bassa trasmissione di calore; • Buona resistenza chimica. 11
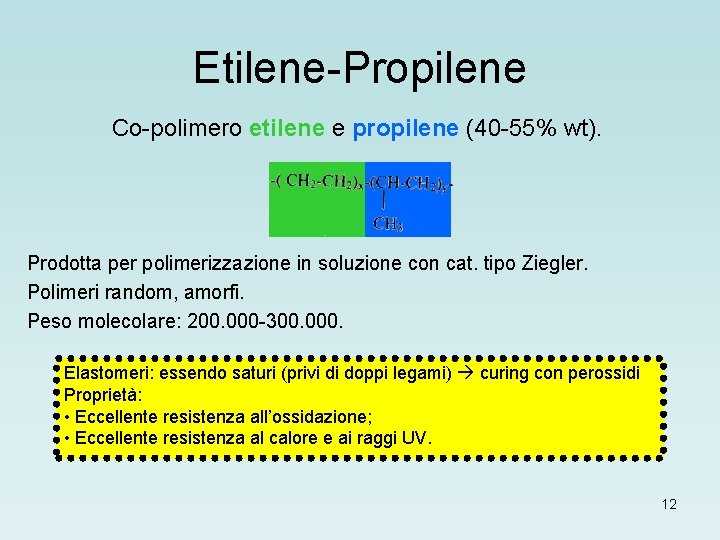
Etilene-Propilene Co-polimero etilene e propilene (40 -55% wt). Prodotta per polimerizzazione in soluzione con cat. tipo Ziegler. Polimeri random, amorfi. Peso molecolare: 200. 000 -300. 000. Elastomeri: essendo saturi (privi di doppi legami) curing con perossidi Proprietà: • Eccellente resistenza all’ossidazione; • Eccellente resistenza al calore e ai raggi UV. 12
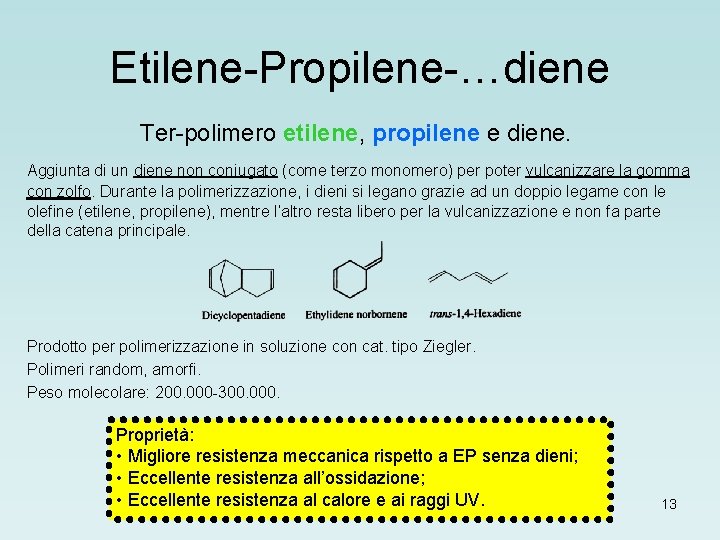
Etilene-Propilene-…diene Ter-polimero etilene, propilene e diene. Aggiunta di un diene non coniugato (come terzo monomero) per poter vulcanizzare la gomma con zolfo. Durante la polimerizzazione, i dieni si legano grazie ad un doppio legame con le olefine (etilene, propilene), mentre l’altro resta libero per la vulcanizzazione e non fa parte della catena principale. Prodotto per polimerizzazione in soluzione con cat. tipo Ziegler. Polimeri random, amorfi. Peso molecolare: 200. 000 -300. 000. Proprietà: • Migliore resistenza meccanica rispetto a EP senza dieni; • Eccellente resistenza all’ossidazione; • Eccellente resistenza al calore e ai raggi UV. 13
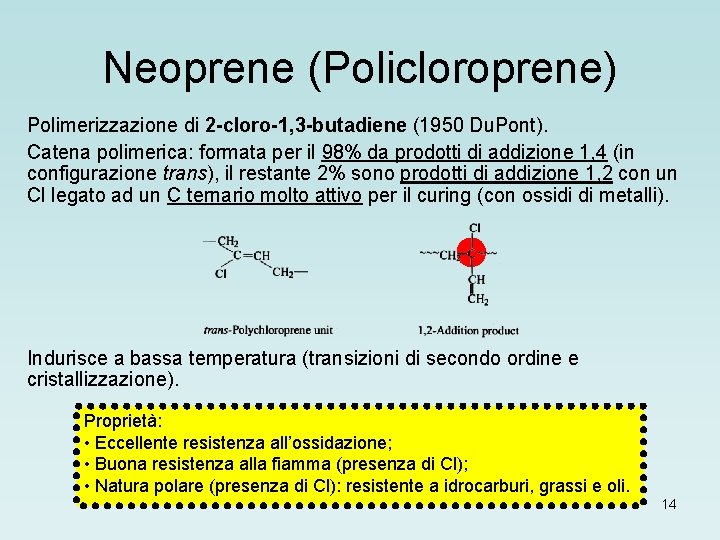
Neoprene (Policloroprene) Polimerizzazione di 2 -cloro-1, 3 -butadiene (1950 Du. Pont). Catena polimerica: formata per il 98% da prodotti di addizione 1, 4 (in configurazione trans), il restante 2% sono prodotti di addizione 1, 2 con un Cl legato ad un C ternario molto attivo per il curing (con ossidi di metalli). Indurisce a bassa temperatura (transizioni di secondo ordine e cristallizzazione). Proprietà: • Eccellente resistenza all’ossidazione; • Buona resistenza alla fiamma (presenza di Cl); • Natura polare (presenza di Cl): resistente a idrocarburi, grassi e oli. 14
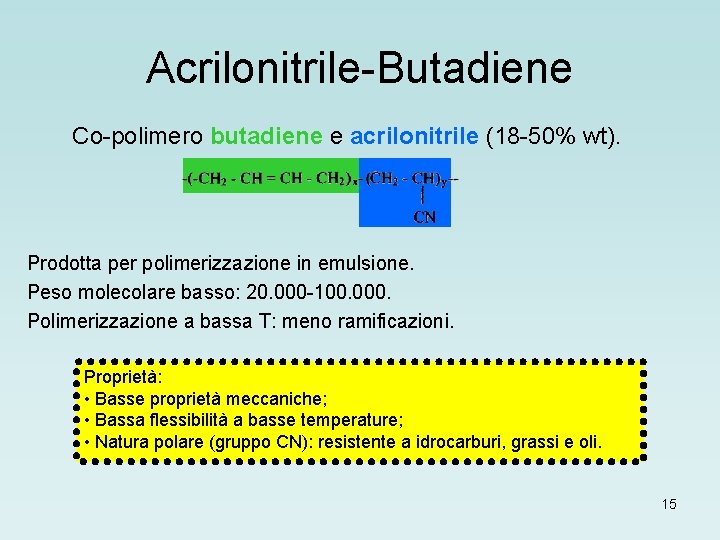
Acrilonitrile-Butadiene Co-polimero butadiene e acrilonitrile (18 -50% wt). Prodotta per polimerizzazione in emulsione. Peso molecolare basso: 20. 000 -100. 000. Polimerizzazione a bassa T: meno ramificazioni. Proprietà: • Basse proprietà meccaniche; • Bassa flessibilità a basse temperature; • Natura polare (gruppo CN): resistente a idrocarburi, grassi e oli. 15
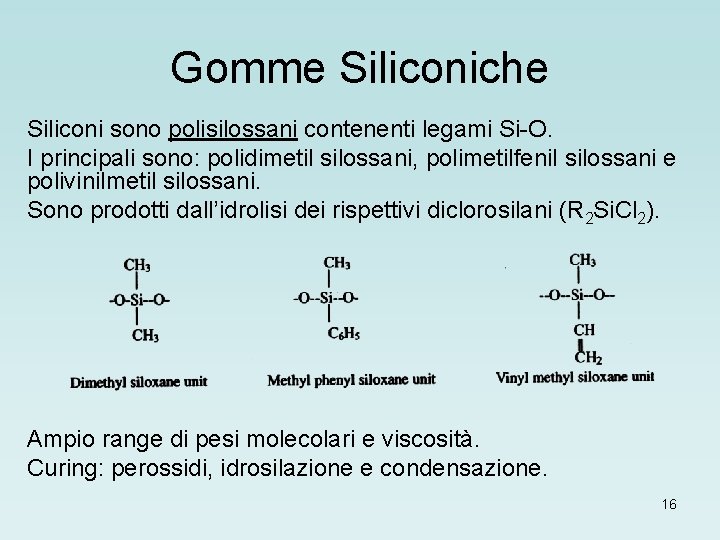
Gomme Siliconiche Siliconi sono polisilossani contenenti legami Si-O. I principali sono: polidimetil silossani, polimetilfenil silossani e polivinilmetil silossani. Sono prodotti dall’idrolisi dei rispettivi diclorosilani (R 2 Si. Cl 2). Ampio range di pesi molecolari e viscosità. Curing: perossidi, idrosilazione e condensazione. 16
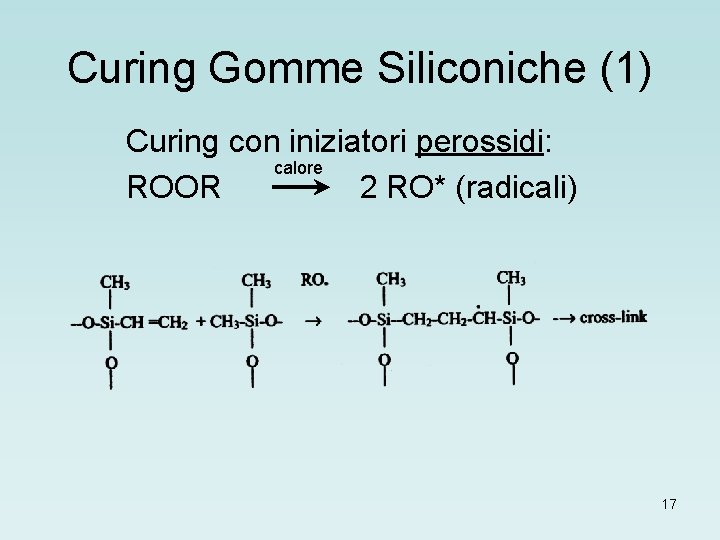
Curing Gomme Siliconiche (1) Curing con iniziatori perossidi: calore ROOR 2 RO* (radicali) 17
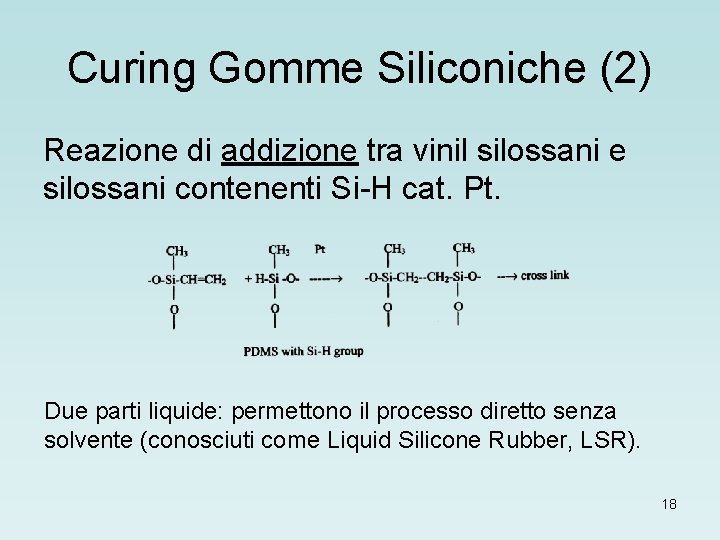
Curing Gomme Siliconiche (2) Reazione di addizione tra vinil silossani e silossani contenenti Si-H cat. Pt. Due parti liquide: permettono il processo diretto senza solvente (conosciuti come Liquid Silicone Rubber, LSR). 18
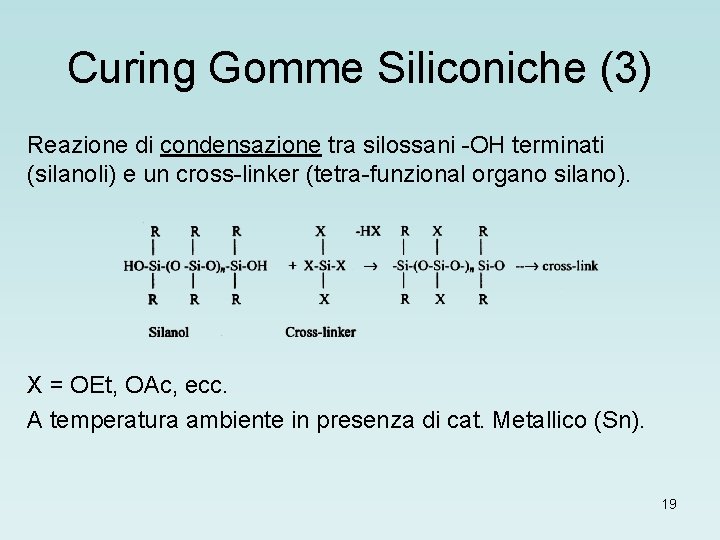
Curing Gomme Siliconiche (3) Reazione di condensazione tra silossani -OH terminati (silanoli) e un cross-linker (tetra-funzional organo silano). X = OEt, OAc, ecc. A temperatura ambiente in presenza di cat. Metallico (Sn). 19
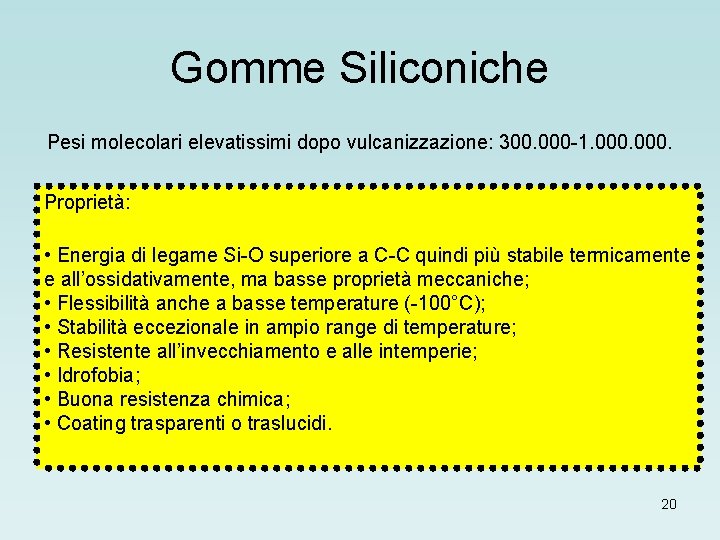
Gomme Siliconiche Pesi molecolari elevatissimi dopo vulcanizzazione: 300. 000 -1. 000. Proprietà: • Energia di legame Si-O superiore a C-C quindi più stabile termicamente e all’ossidativamente, ma basse proprietà meccaniche; • Flessibilità anche a basse temperature (-100°C); • Stabilità eccezionale in ampio range di temperature; • Resistente all’invecchiamento e alle intemperie; • Idrofobia; • Buona resistenza chimica; • Coating trasparenti o traslucidi. 20
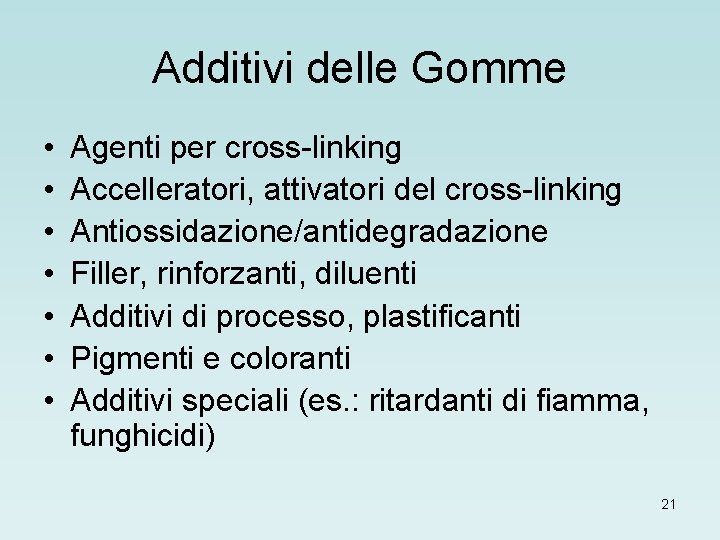
Additivi delle Gomme • • Agenti per cross-linking Accelleratori, attivatori del cross-linking Antiossidazione/antidegradazione Filler, rinforzanti, diluenti Additivi di processo, plastificanti Pigmenti e coloranti Additivi speciali (es. : ritardanti di fiamma, funghicidi) 21
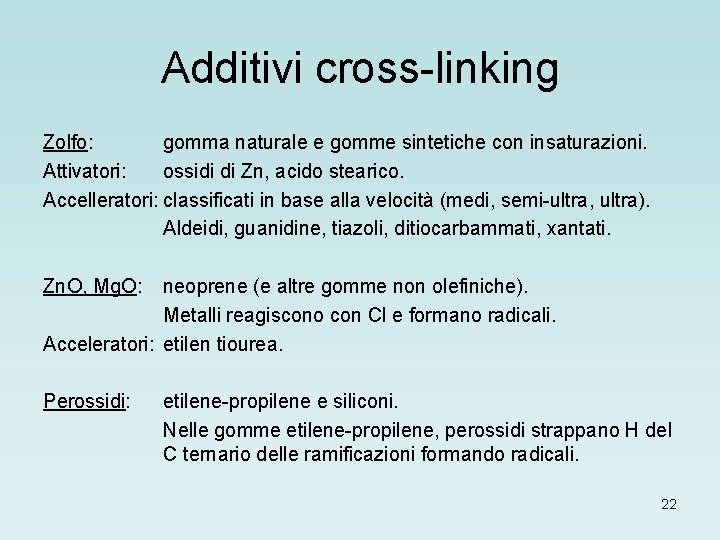
Additivi cross-linking Zolfo: gomma naturale e gomme sintetiche con insaturazioni. Attivatori: ossidi di Zn, acido stearico. Accelleratori: classificati in base alla velocità (medi, semi-ultra, ultra). Aldeidi, guanidine, tiazoli, ditiocarbammati, xantati. Zn. O, Mg. O: neoprene (e altre gomme non olefiniche). Metalli reagiscono con Cl e formano radicali. Acceleratori: etilen tiourea. Perossidi: etilene-propilene e siliconi. Nelle gomme etilene-propilene, perossidi strappano H del C ternario delle ramificazioni formando radicali. 22
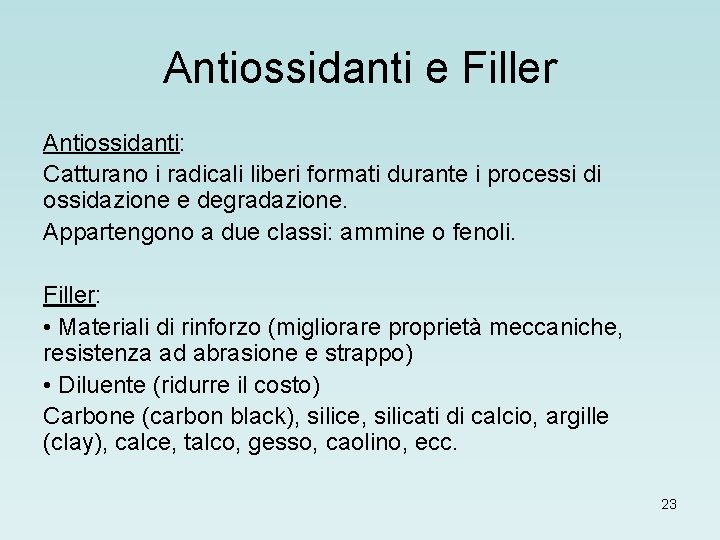
Antiossidanti e Filler Antiossidanti: Catturano i radicali liberi formati durante i processi di ossidazione e degradazione. Appartengono a due classi: ammine o fenoli. Filler: • Materiali di rinforzo (migliorare proprietà meccaniche, resistenza ad abrasione e strappo) • Diluente (ridurre il costo) Carbone (carbon black), silice, silicati di calcio, argille (clay), calce, talco, gesso, caolino, ecc. 23
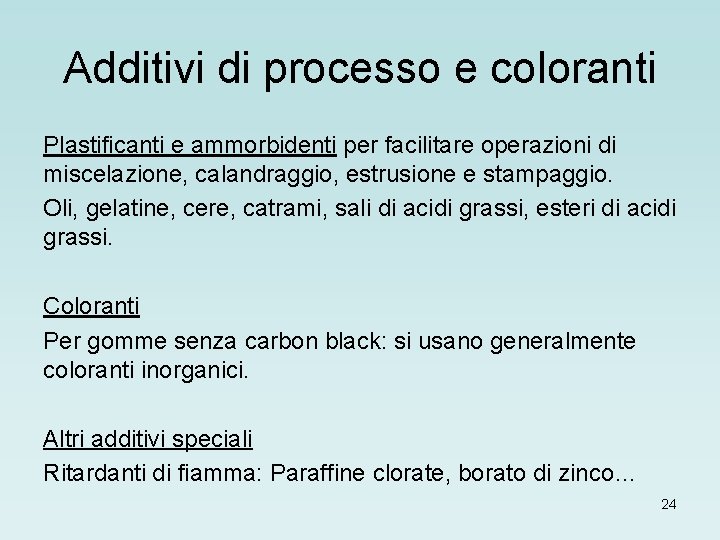
Additivi di processo e coloranti Plastificanti e ammorbidenti per facilitare operazioni di miscelazione, calandraggio, estrusione e stampaggio. Oli, gelatine, cere, catrami, sali di acidi grassi, esteri di acidi grassi. Coloranti Per gomme senza carbon black: si usano generalmente coloranti inorganici. Altri additivi speciali Ritardanti di fiamma: Paraffine clorate, borato di zinco… 24
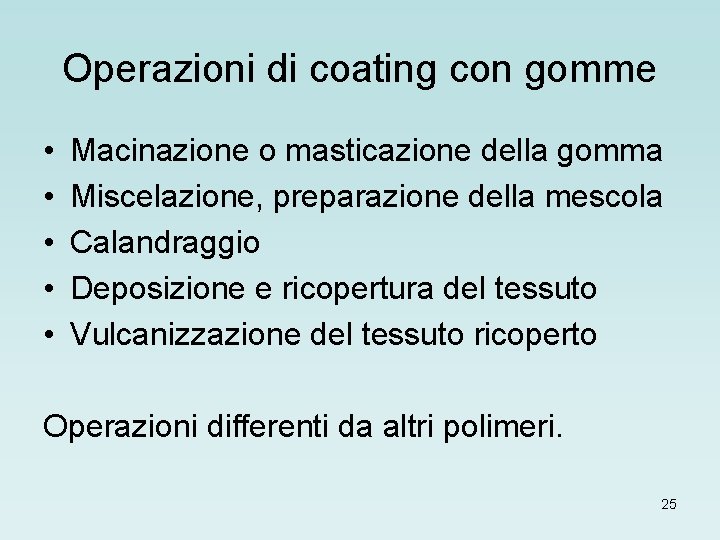
Operazioni di coating con gomme • • • Macinazione o masticazione della gomma Miscelazione, preparazione della mescola Calandraggio Deposizione e ricopertura del tessuto Vulcanizzazione del tessuto ricoperto Operazioni differenti da altri polimeri. 25
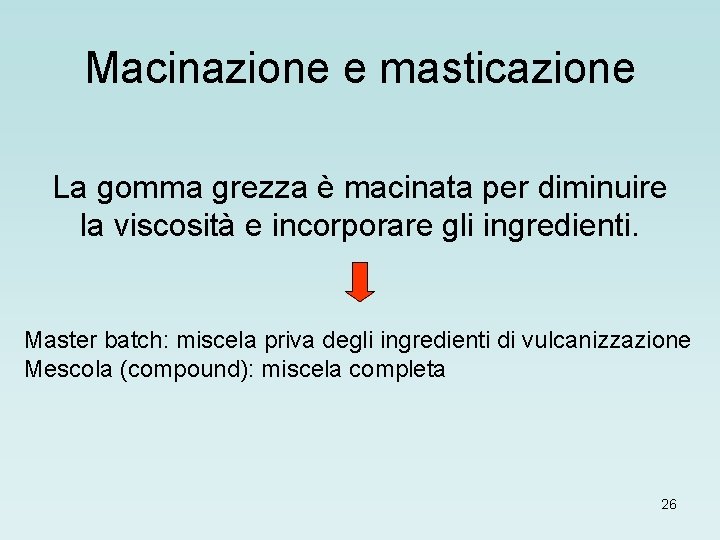
Macinazione e masticazione La gomma grezza è macinata per diminuire la viscosità e incorporare gli ingredienti. Master batch: miscela priva degli ingredienti di vulcanizzazione Mescola (compound): miscela completa 26
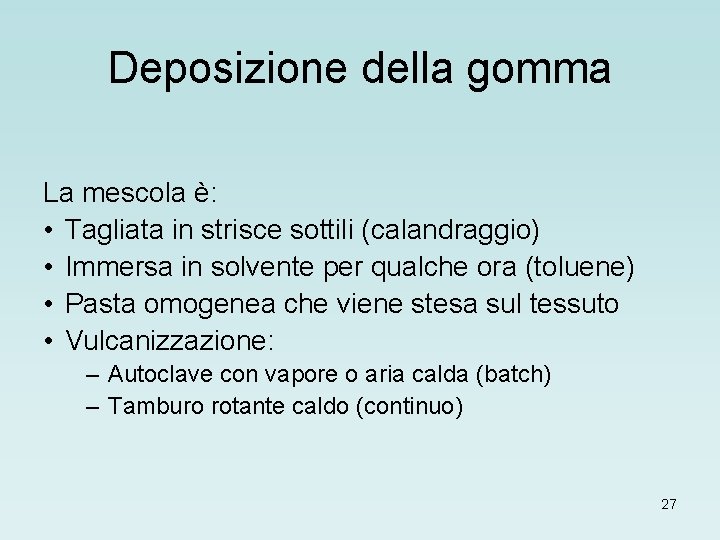
Deposizione della gomma La mescola è: • Tagliata in strisce sottili (calandraggio) • Immersa in solvente per qualche ora (toluene) • Pasta omogenea che viene stesa sul tessuto • Vulcanizzazione: – Autoclave con vapore o aria calda (batch) – Tamburo rotante caldo (continuo) 27
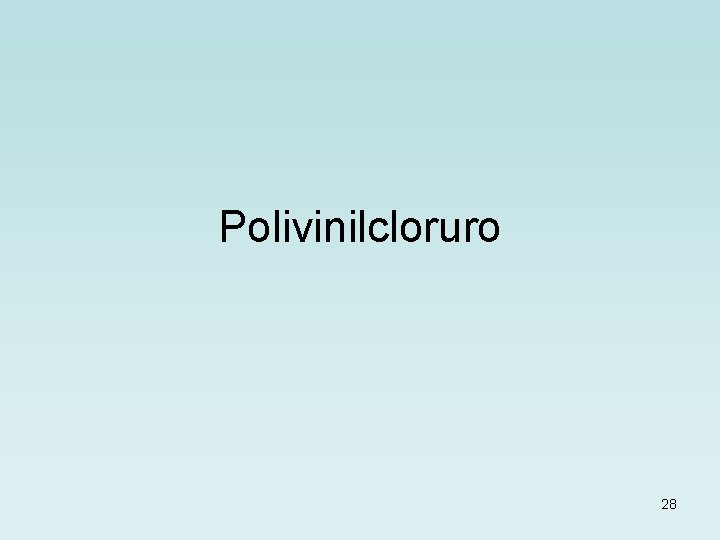
Polivinilcloruro 28
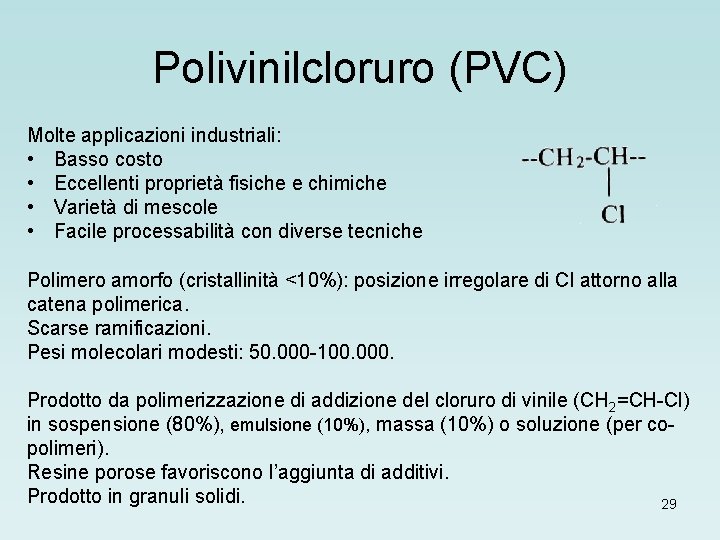
Polivinilcloruro (PVC) Molte applicazioni industriali: • Basso costo • Eccellenti proprietà fisiche e chimiche • Varietà di mescole • Facile processabilità con diverse tecniche Polimero amorfo (cristallinità <10%): posizione irregolare di Cl attorno alla catena polimerica. Scarse ramificazioni. Pesi molecolari modesti: 50. 000 -100. 000. Prodotto da polimerizzazione di addizione del cloruro di vinile (CH 2=CH-Cl) in sospensione (80%), emulsione (10%), massa (10%) o soluzione (per copolimeri). Resine porose favoriscono l’aggiunta di additivi. Prodotto in granuli solidi. 29
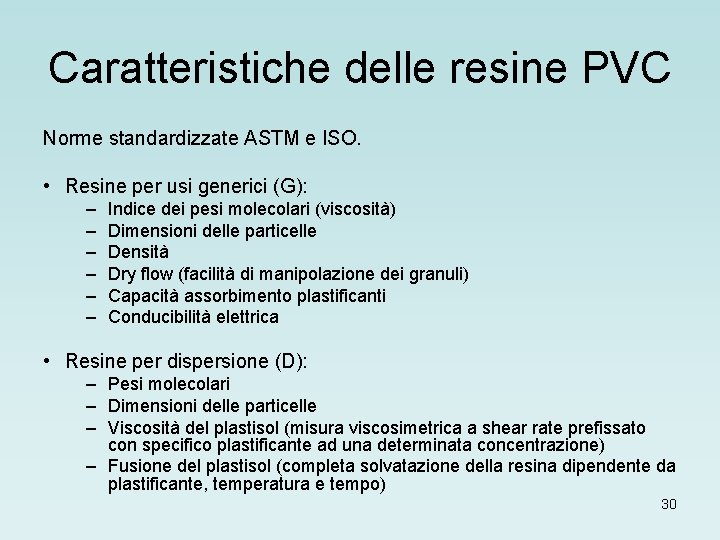
Caratteristiche delle resine PVC Norme standardizzate ASTM e ISO. • Resine per usi generici (G): – – – Indice dei pesi molecolari (viscosità) Dimensioni delle particelle Densità Dry flow (facilità di manipolazione dei granuli) Capacità assorbimento plastificanti Conducibilità elettrica • Resine per dispersione (D): – Pesi molecolari – Dimensioni delle particelle – Viscosità del plastisol (misura viscosimetrica a shear rate prefissato con specifico plastificante ad una determinata concentrazione) – Fusione del plastisol (completa solvatazione della resina dipendente da plastificante, temperatura e tempo) 30
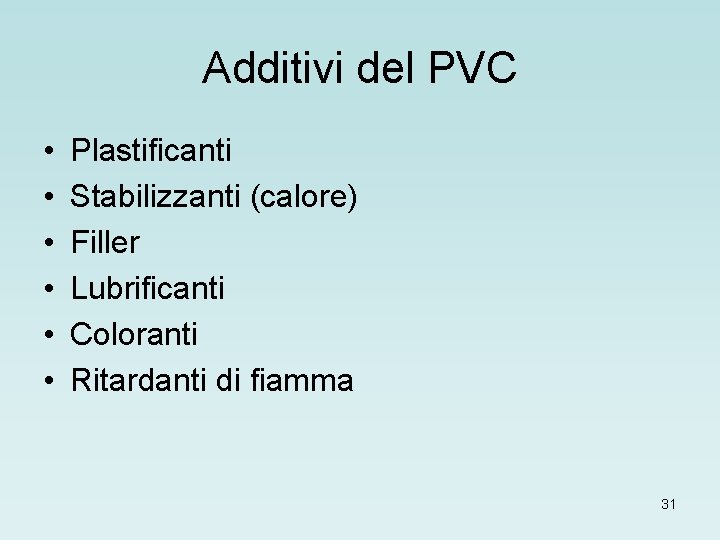
Additivi del PVC • • • Plastificanti Stabilizzanti (calore) Filler Lubrificanti Coloranti Ritardanti di fiamma 31
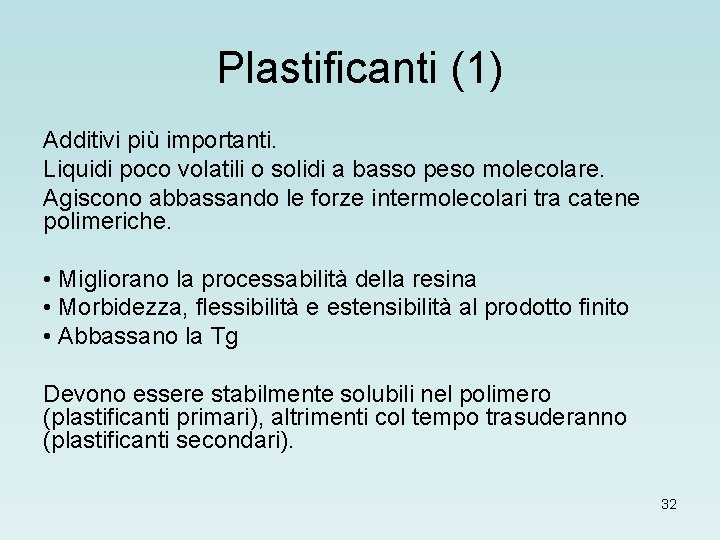
Plastificanti (1) Additivi più importanti. Liquidi poco volatili o solidi a basso peso molecolare. Agiscono abbassando le forze intermolecolari tra catene polimeriche. • Migliorano la processabilità della resina • Morbidezza, flessibilità e estensibilità al prodotto finito • Abbassano la Tg Devono essere stabilmente solubili nel polimero (plastificanti primari), altrimenti col tempo trasuderanno (plastificanti secondari). 32
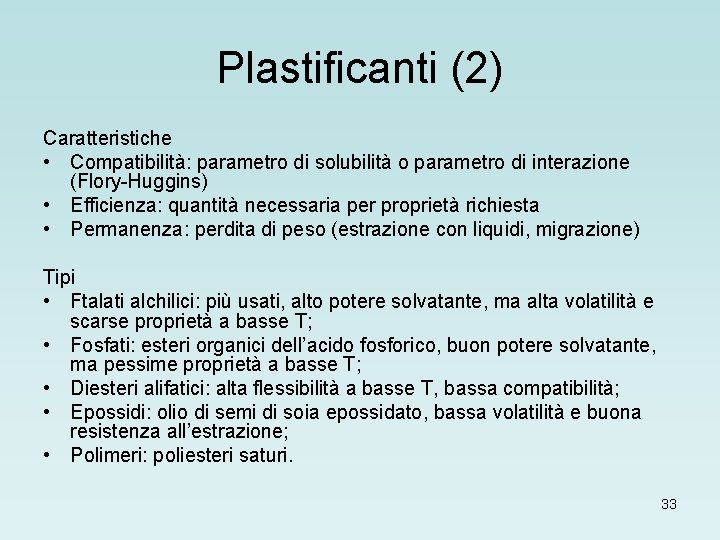
Plastificanti (2) Caratteristiche • Compatibilità: parametro di solubilità o parametro di interazione (Flory-Huggins) • Efficienza: quantità necessaria per proprietà richiesta • Permanenza: perdita di peso (estrazione con liquidi, migrazione) Tipi • Ftalati alchilici: più usati, alto potere solvatante, ma alta volatilità e scarse proprietà a basse T; • Fosfati: esteri organici dell’acido fosforico, buon potere solvatante, ma pessime proprietà a basse T; • Diesteri alifatici: alta flessibilità a basse T, bassa compatibilità; • Epossidi: olio di semi di soia epossidato, bassa volatilità e buona resistenza all’estrazione; • Polimeri: poliesteri saturi. 33
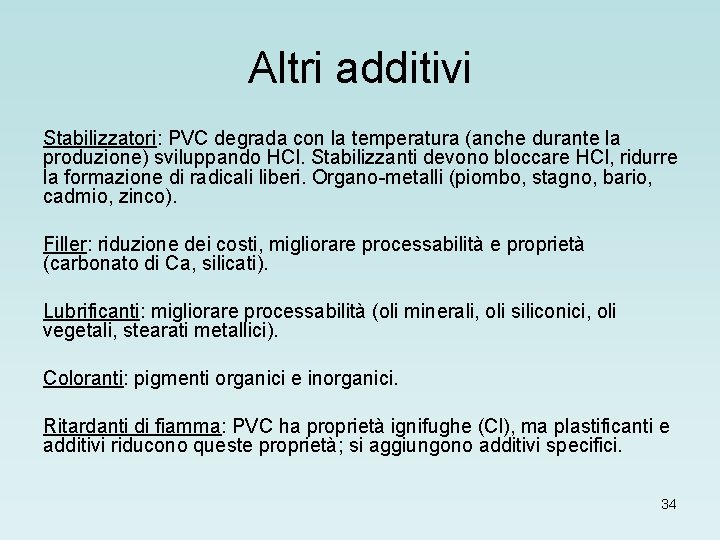
Altri additivi Stabilizzatori: PVC degrada con la temperatura (anche durante la produzione) sviluppando HCl. Stabilizzanti devono bloccare HCl, ridurre la formazione di radicali liberi. Organo-metalli (piombo, stagno, bario, cadmio, zinco). Filler: riduzione dei costi, migliorare processabilità e proprietà (carbonato di Ca, silicati). Lubrificanti: migliorare processabilità (oli minerali, oli siliconici, oli vegetali, stearati metallici). Coloranti: pigmenti organici e inorganici. Ritardanti di fiamma: PVC ha proprietà ignifughe (Cl), ma plastificanti e additivi riducono queste proprietà; si aggiungono additivi specifici. 34
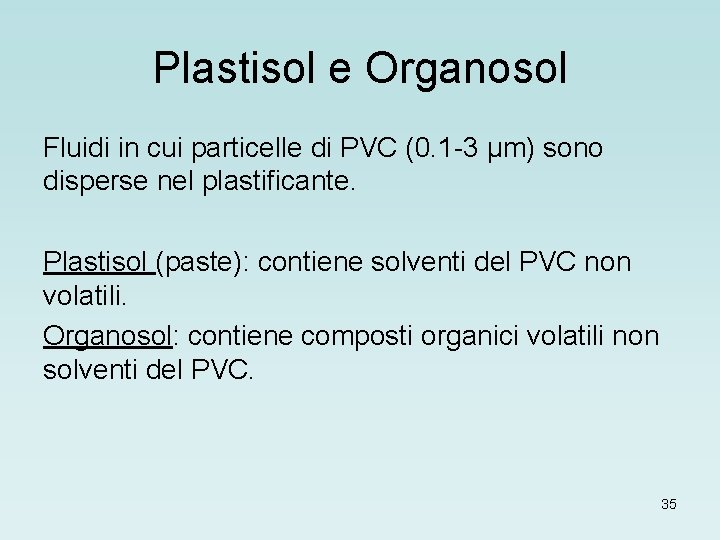
Plastisol e Organosol Fluidi in cui particelle di PVC (0. 1 -3 µm) sono disperse nel plastificante. Plastisol (paste): contiene solventi del PVC non volatili. Organosol: contiene composti organici volatili non solventi del PVC. 35
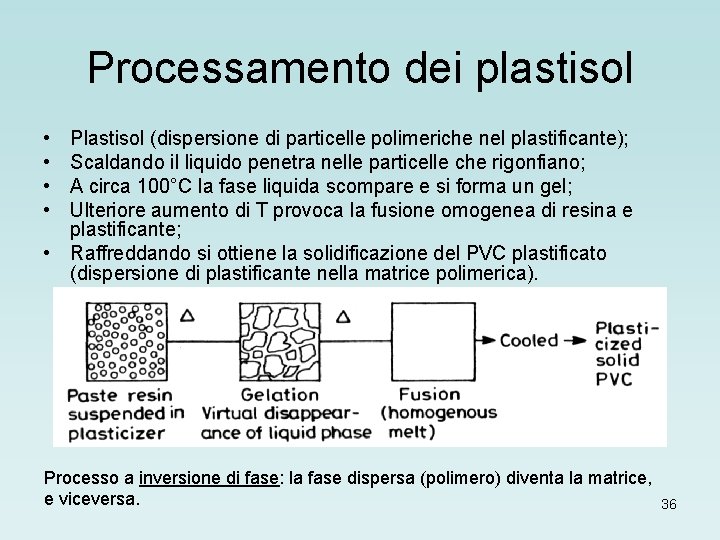
Processamento dei plastisol • • Plastisol (dispersione di particelle polimeriche nel plastificante); Scaldando il liquido penetra nelle particelle che rigonfiano; A circa 100°C la fase liquida scompare e si forma un gel; Ulteriore aumento di T provoca la fusione omogenea di resina e plastificante; • Raffreddando si ottiene la solidificazione del PVC plastificato (dispersione di plastificante nella matrice polimerica). Processo a inversione di fase: la fase dispersa (polimero) diventa la matrice, e viceversa. 36
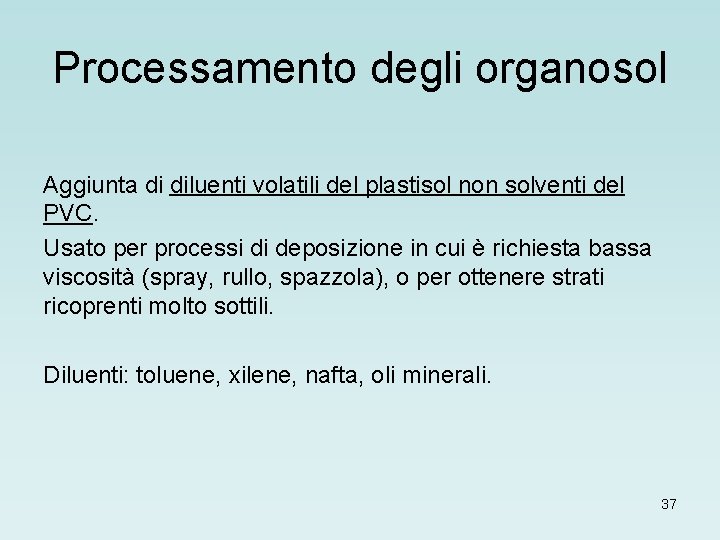
Processamento degli organosol Aggiunta di diluenti volatili del plastisol non solventi del PVC. Usato per processi di deposizione in cui è richiesta bassa viscosità (spray, rullo, spazzola), o per ottenere strati ricoprenti molto sottili. Diluenti: toluene, xilene, nafta, oli minerali. 37
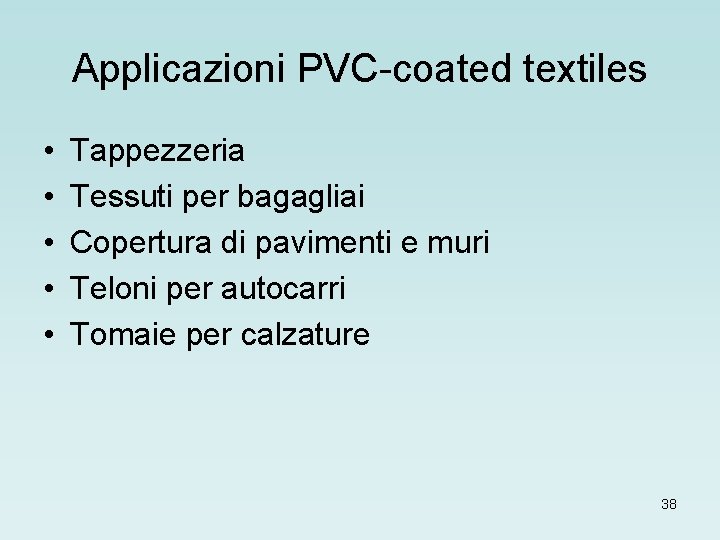
Applicazioni PVC-coated textiles • • • Tappezzeria Tessuti per bagagliai Copertura di pavimenti e muri Teloni per autocarri Tomaie per calzature 38
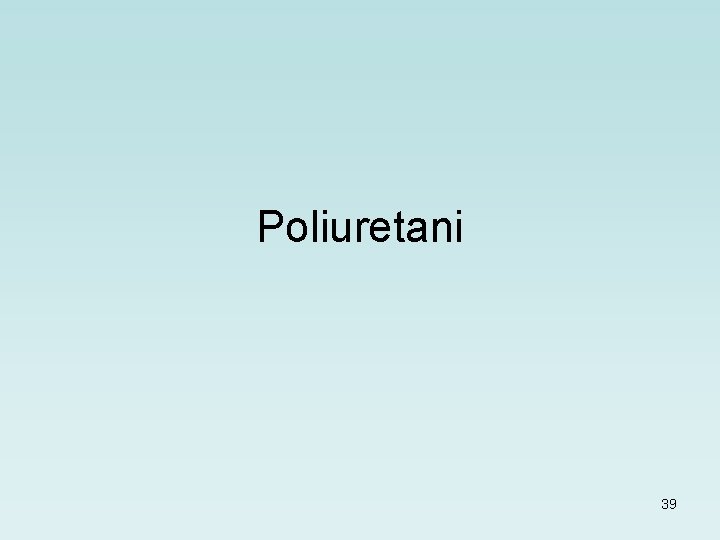
Poliuretani 39
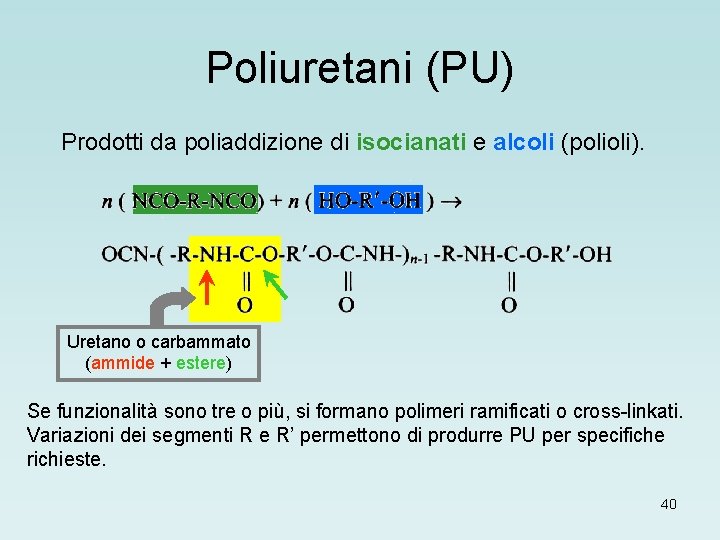
Poliuretani (PU) Prodotti da poliaddizione di isocianati e alcoli (polioli). Uretano o carbammato (ammide + estere) Se funzionalità sono tre o più, si formano polimeri ramificati o cross-linkati. Variazioni dei segmenti R e R’ permettono di produrre PU per specifiche richieste. 40
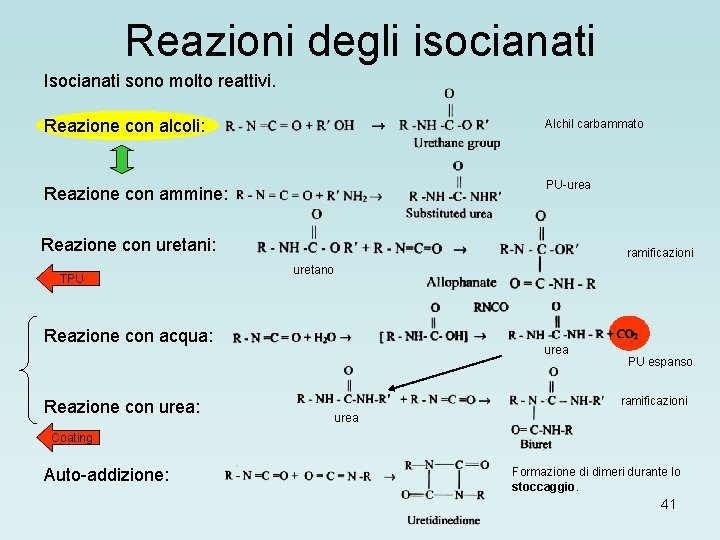
Reazioni degli isocianati Isocianati sono molto reattivi. Reazione con alcoli: Alchil carbammato Reazione con ammine: PU-urea Reazione con uretani: TPU ramificazioni uretano Reazione con acqua: Reazione con urea: urea PU espanso ramificazioni urea Coating Auto-addizione: Formazione di dimeri durante lo stoccaggio. 41
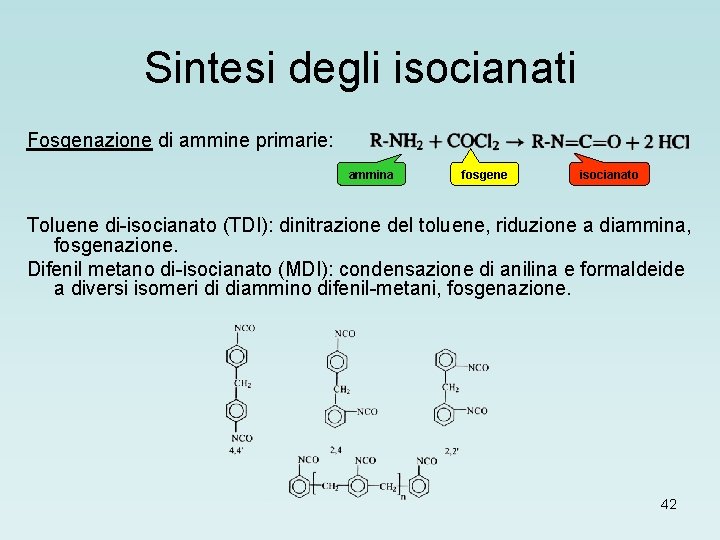
Sintesi degli isocianati Fosgenazione di ammine primarie: ammina fosgene isocianato Toluene di-isocianato (TDI): dinitrazione del toluene, riduzione a diammina, fosgenazione. Difenil metano di-isocianato (MDI): condensazione di anilina e formaldeide a diversi isomeri di diammino difenil-metani, fosgenazione. 42
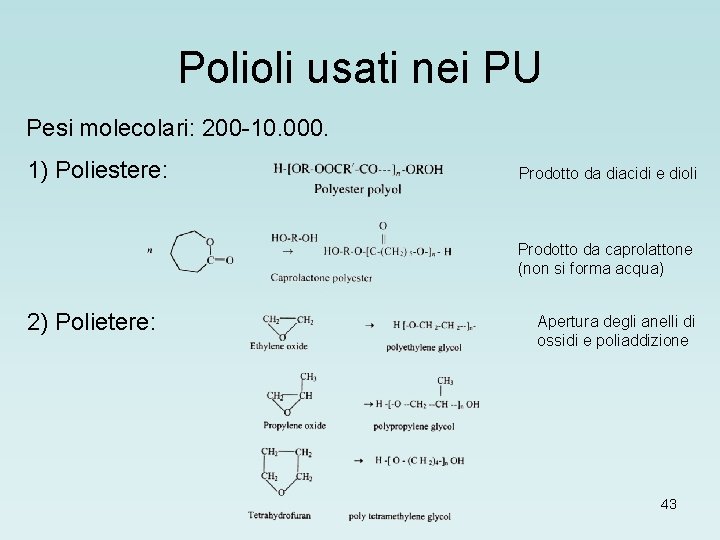
Polioli usati nei PU Pesi molecolari: 200 -10. 000. 1) Poliestere: Prodotto da diacidi e dioli Prodotto da caprolattone (non si forma acqua) 2) Polietere: Apertura degli anelli di ossidi e poliaddizione 43
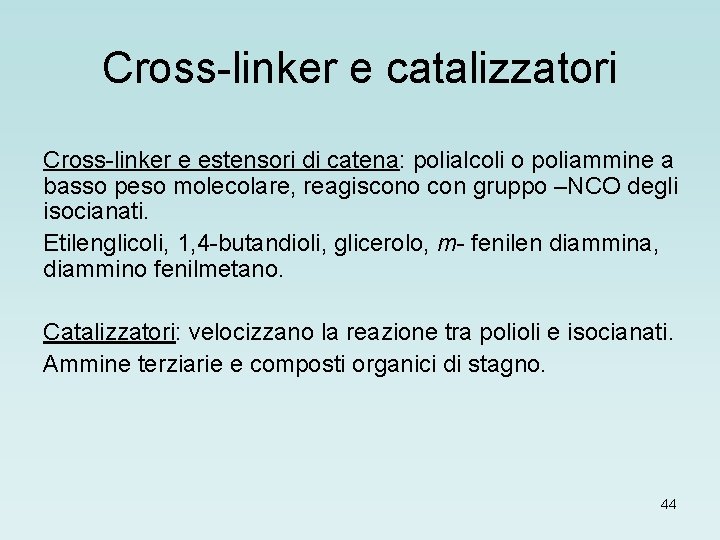
Cross-linker e catalizzatori Cross-linker e estensori di catena: polialcoli o poliammine a basso peso molecolare, reagiscono con gruppo –NCO degli isocianati. Etilenglicoli, 1, 4 -butandioli, glicerolo, m- fenilen diammina, diammino fenilmetano. Catalizzatori: velocizzano la reazione tra polioli e isocianati. Ammine terziarie e composti organici di stagno. 44
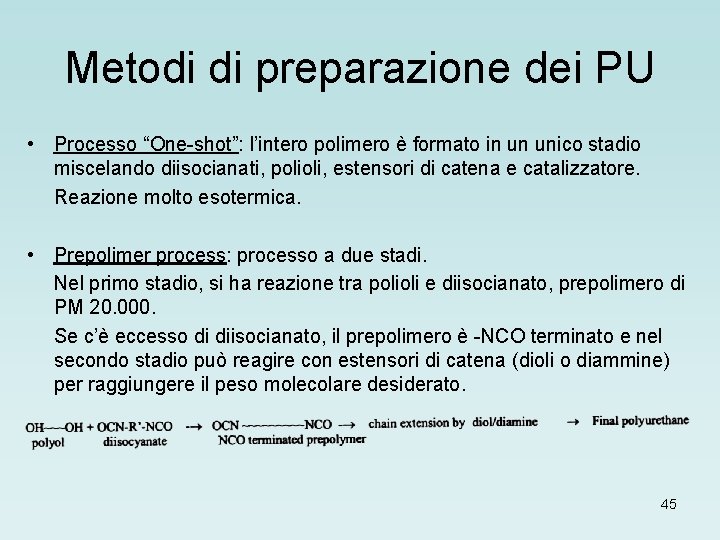
Metodi di preparazione dei PU • Processo “One-shot”: l’intero polimero è formato in un unico stadio miscelando diisocianati, polioli, estensori di catena e catalizzatore. Reazione molto esotermica. • Prepolimer process: processo a due stadi. Nel primo stadio, si ha reazione tra polioli e diisocianato, prepolimero di PM 20. 000. Se c’è eccesso di diisocianato, il prepolimero è -NCO terminato e nel secondo stadio può reagire con estensori di catena (dioli o diammine) per raggiungere il peso molecolare desiderato. 45
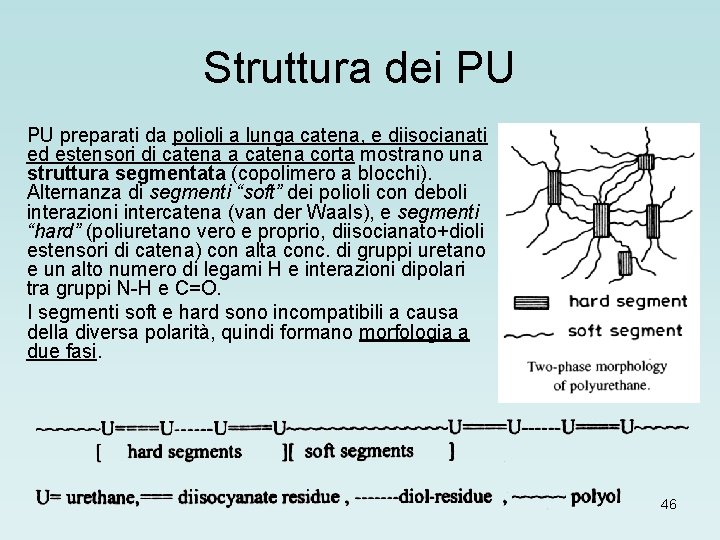
Struttura dei PU PU preparati da polioli a lunga catena, e diisocianati ed estensori di catena a catena corta mostrano una struttura segmentata (copolimero a blocchi). Alternanza di segmenti “soft” dei polioli con deboli interazioni intercatena (van der Waals), e segmenti “hard” (poliuretano vero e proprio, diisocianato+dioli estensori di catena) con alta conc. di gruppi uretano e un alto numero di legami H e interazioni dipolari tra gruppi N-H e C=O. I segmenti soft e hard sono incompatibili a causa della diversa polarità, quindi formano morfologia a due fasi. 46
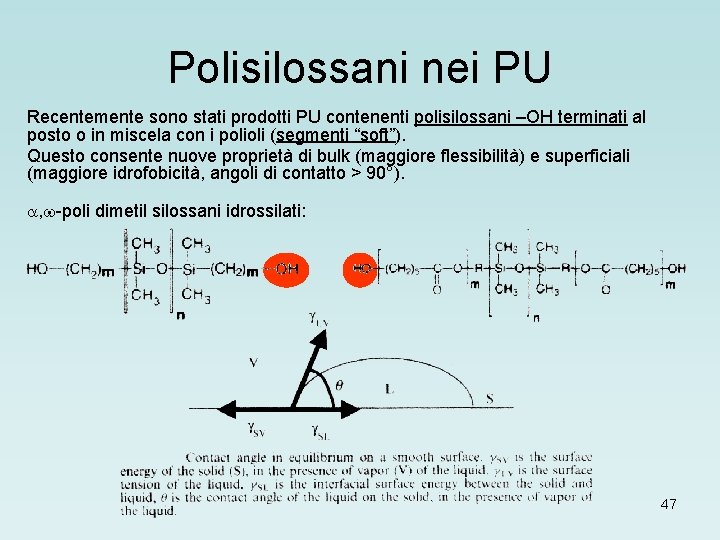
Polisilossani nei PU Recentemente sono stati prodotti PU contenenti polisilossani –OH terminati al posto o in miscela con i polioli (segmenti “soft”). Questo consente nuove proprietà di bulk (maggiore flessibilità) e superficiali (maggiore idrofobicità, angoli di contatto > 90°). , -poli dimetil silossani idrossilati: 47
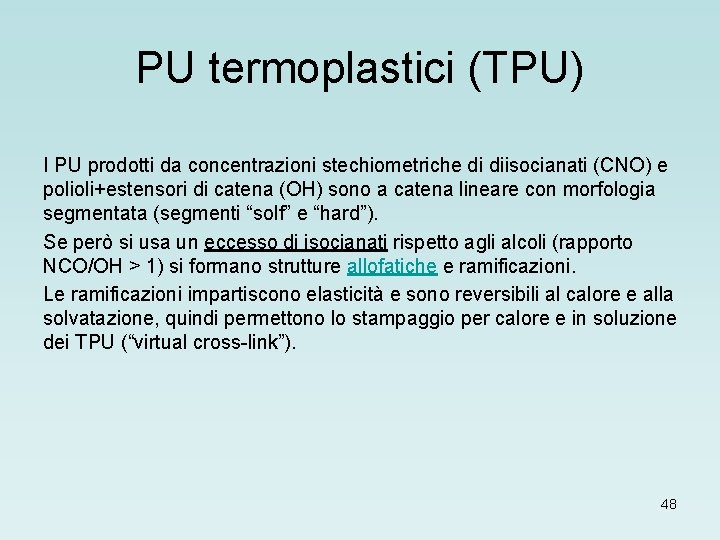
PU termoplastici (TPU) I PU prodotti da concentrazioni stechiometriche di diisocianati (CNO) e polioli+estensori di catena (OH) sono a catena lineare con morfologia segmentata (segmenti “solf” e “hard”). Se però si usa un eccesso di isocianati rispetto agli alcoli (rapporto NCO/OH > 1) si formano strutture allofatiche e ramificazioni. Le ramificazioni impartiscono elasticità e sono reversibili al calore e alla solvatazione, quindi permettono lo stampaggio per calore e in soluzione dei TPU (“virtual cross-link”). 48
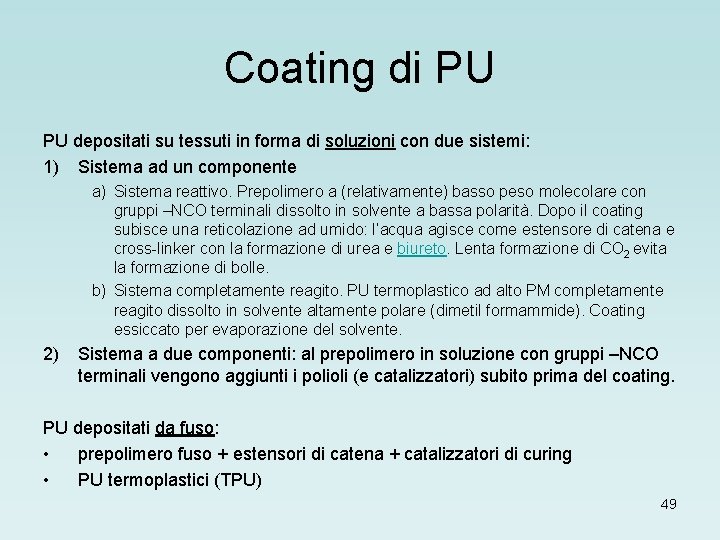
Coating di PU PU depositati su tessuti in forma di soluzioni con due sistemi: 1) Sistema ad un componente a) Sistema reattivo. Prepolimero a (relativamente) basso peso molecolare con gruppi –NCO terminali dissolto in solvente a bassa polarità. Dopo il coating subisce una reticolazione ad umido: l’acqua agisce come estensore di catena e cross-linker con la formazione di urea e biureto. Lenta formazione di CO 2 evita la formazione di bolle. b) Sistema completamente reagito. PU termoplastico ad alto PM completamente reagito dissolto in solvente altamente polare (dimetil formammide). Coating essiccato per evaporazione del solvente. 2) Sistema a due componenti: al prepolimero in soluzione con gruppi –NCO terminali vengono aggiunti i polioli (e catalizzatori) subito prima del coating. PU depositati da fuso: • prepolimero fuso + estensori di catena + catalizzatori di curing • PU termoplastici (TPU) 49
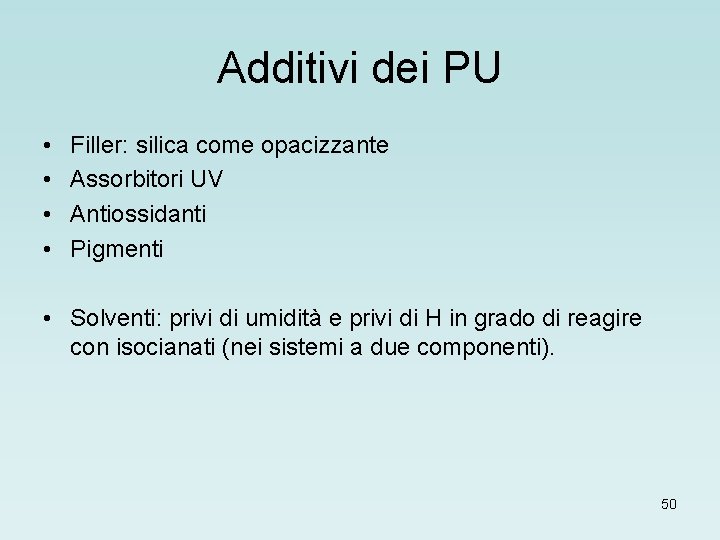
Additivi dei PU • • Filler: silica come opacizzante Assorbitori UV Antiossidanti Pigmenti • Solventi: privi di umidità e privi di H in grado di reagire con isocianati (nei sistemi a due componenti). 50
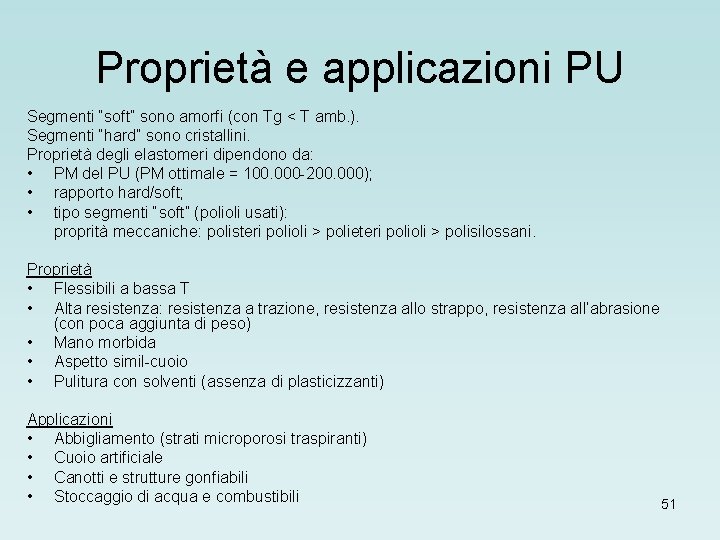
Proprietà e applicazioni PU Segmenti “soft” sono amorfi (con Tg < T amb. ). Segmenti “hard” sono cristallini. Proprietà degli elastomeri dipendono da: • PM del PU (PM ottimale = 100. 000 -200. 000); • rapporto hard/soft; • tipo segmenti “soft” (polioli usati): proprità meccaniche: polisteri polioli > polieteri polioli > polisilossani. Proprietà • Flessibili a bassa T • Alta resistenza: resistenza a trazione, resistenza allo strappo, resistenza all’abrasione (con poca aggiunta di peso) • Mano morbida • Aspetto simil-cuoio • Pulitura con solventi (assenza di plasticizzanti) Applicazioni • Abbigliamento (strati microporosi traspiranti) • Cuoio artificiale • Canotti e strutture gonfiabili • Stoccaggio di acqua e combustibili 51
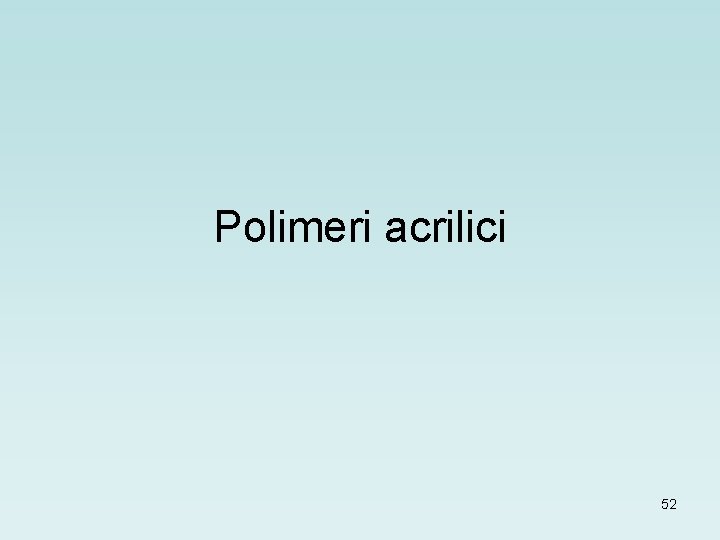
Polimeri acrilici 52

Polimeri acrilici Polimerizzazione radicalica di esteri di acido acrilico o metacrilico: Acrilico: R = H Metacrilico: R = CH 3 R’ in genere è: metil, n-butil, isobutil, … La natura dei gruppi R e R’ determina le proprietà del polimero. Iniziatori: azo-composti, perossidi. Polimerizzazione: massa, soluzione e emulsione (usati in coating e adesivi), sospensione (per produrre polveri per stampaggio). 53
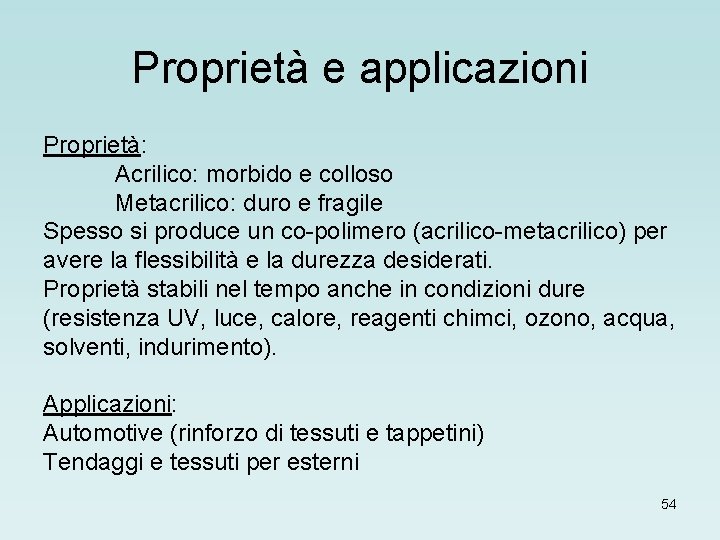
Proprietà e applicazioni Proprietà: Acrilico: morbido e colloso Metacrilico: duro e fragile Spesso si produce un co-polimero (acrilico-metacrilico) per avere la flessibilità e la durezza desiderati. Proprietà stabili nel tempo anche in condizioni dure (resistenza UV, luce, calore, reagenti chimci, ozono, acqua, solventi, indurimento). Applicazioni: Automotive (rinforzo di tessuti e tappetini) Tendaggi e tessuti per esterni 54
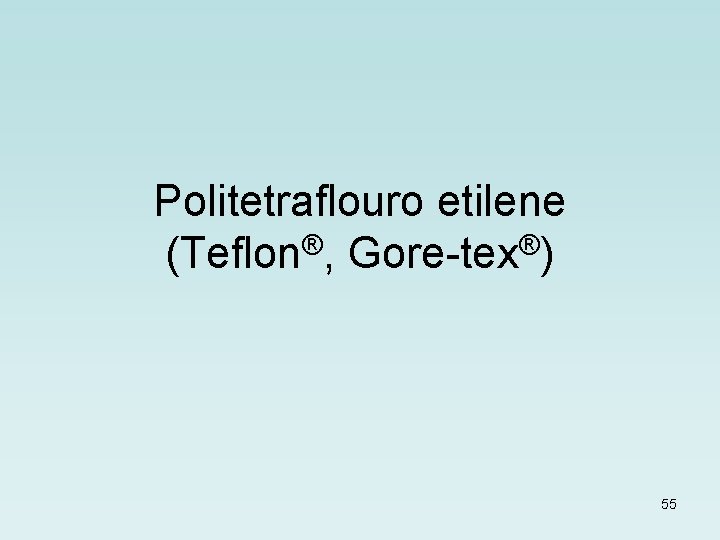
Politetraflouro etilene ® ® (Teflon , Gore-tex ) 55
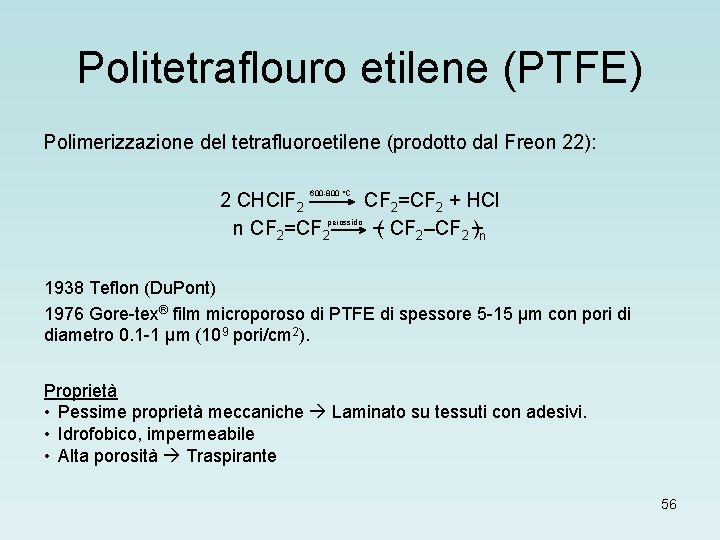
Politetraflouro etilene (PTFE) Polimerizzazione del tetrafluoroetilene (prodotto dal Freon 22): 2 CHCl. F 2 n CF 2=CF 2 600 -800 °C perossido CF 2=CF 2 + HCl –( CF 2–CF 2 – )n 1938 Teflon (Du. Pont) 1976 Gore-tex® film microporoso di PTFE di spessore 5 -15 µm con pori di diametro 0. 1 -1 µm (109 pori/cm 2). Proprietà • Pessime proprietà meccaniche Laminato su tessuti con adesivi. • Idrofobico, impermeabile • Alta porosità Traspirante 56
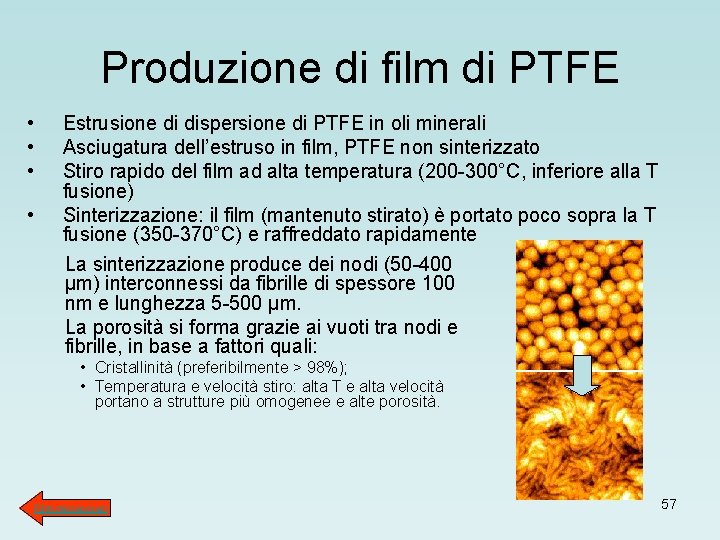
Produzione di film di PTFE • • Estrusione di dispersione di PTFE in oli minerali Asciugatura dell’estruso in film, PTFE non sinterizzato Stiro rapido del film ad alta temperatura (200 -300°C, inferiore alla T fusione) Sinterizzazione: il film (mantenuto stirato) è portato poco sopra la T fusione (350 -370°C) e raffreddato rapidamente La sinterizzazione produce dei nodi (50 -400 µm) interconnessi da fibrille di spessore 100 nm e lunghezza 5 -500 µm. La porosità si forma grazie ai vuoti tra nodi e fibrille, in base a fattori quali: • Cristallinità (preferibilmente > 98%); • Temperatura e velocità stiro: alta T e alta velocità portano a strutture più omogenee e alte porosità. Film microporosi 57
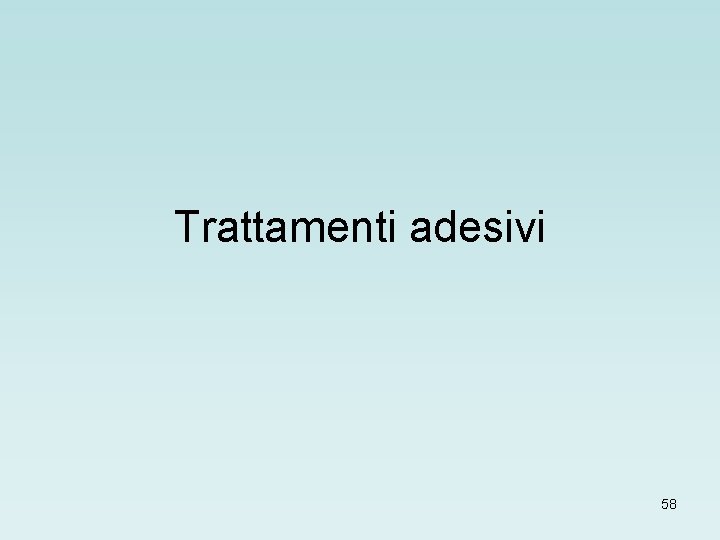
Trattamenti adesivi 58
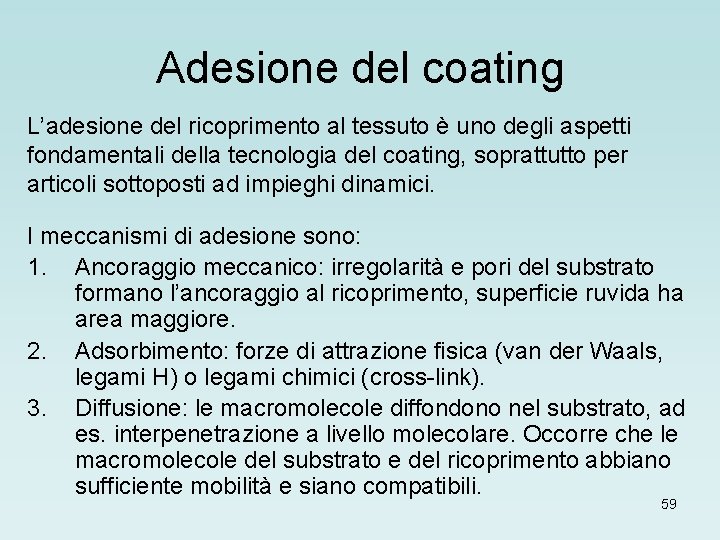
Adesione del coating L’adesione del ricoprimento al tessuto è uno degli aspetti fondamentali della tecnologia del coating, soprattutto per articoli sottoposti ad impieghi dinamici. I meccanismi di adesione sono: 1. Ancoraggio meccanico: irregolarità e pori del substrato formano l’ancoraggio al ricoprimento, superficie ruvida ha area maggiore. 2. Adsorbimento: forze di attrazione fisica (van der Waals, legami H) o legami chimici (cross-link). 3. Diffusione: le macromolecole diffondono nel substrato, ad es. interpenetrazione a livello molecolare. Occorre che le macromolecole del substrato e del ricoprimento abbiano sufficiente mobilità e siano compatibili. 59
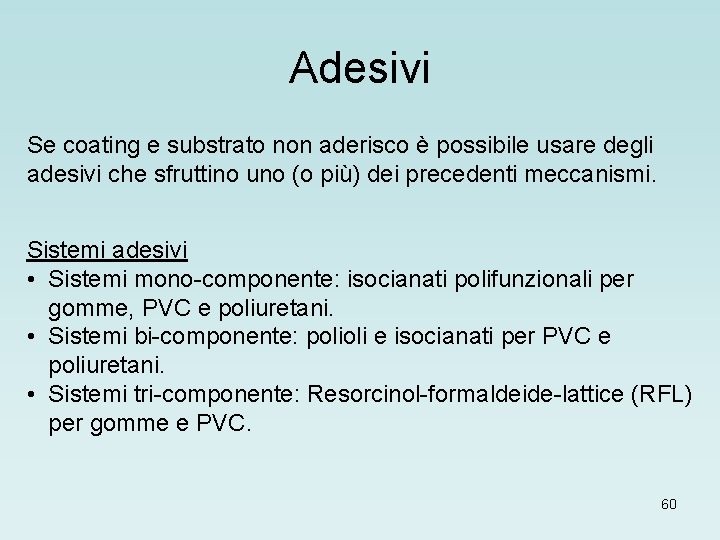
Adesivi Se coating e substrato non aderisco è possibile usare degli adesivi che sfruttino uno (o più) dei precedenti meccanismi. Sistemi adesivi • Sistemi mono-componente: isocianati polifunzionali per gomme, PVC e poliuretani. • Sistemi bi-componente: polioli e isocianati per PVC e poliuretani. • Sistemi tri-componente: Resorcinol-formaldeide-lattice (RFL) per gomme e PVC. 60
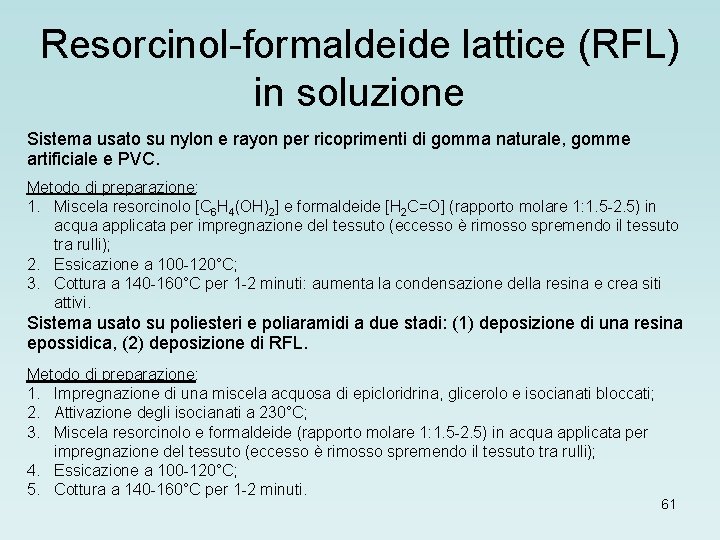
Resorcinol-formaldeide lattice (RFL) in soluzione Sistema usato su nylon e rayon per ricoprimenti di gomma naturale, gomme artificiale e PVC. Metodo di preparazione: 1. Miscela resorcinolo [C 6 H 4(OH)2] e formaldeide [H 2 C=O] (rapporto molare 1: 1. 5 -2. 5) in acqua applicata per impregnazione del tessuto (eccesso è rimosso spremendo il tessuto tra rulli); 2. Essicazione a 100 -120°C; 3. Cottura a 140 -160°C per 1 -2 minuti: aumenta la condensazione della resina e crea siti attivi. Sistema usato su poliesteri e poliaramidi a due stadi: (1) deposizione di una resina epossidica, (2) deposizione di RFL. Metodo di preparazione: 1. Impregnazione di una miscela acquosa di epicloridrina, glicerolo e isocianati bloccati; 2. Attivazione degli isocianati a 230°C; 3. Miscela resorcinolo e formaldeide (rapporto molare 1: 1. 5 -2. 5) in acqua applicata per impregnazione del tessuto (eccesso è rimosso spremendo il tessuto tra rulli); 4. Essicazione a 100 -120°C; 5. Cottura a 140 -160°C per 1 -2 minuti. 61
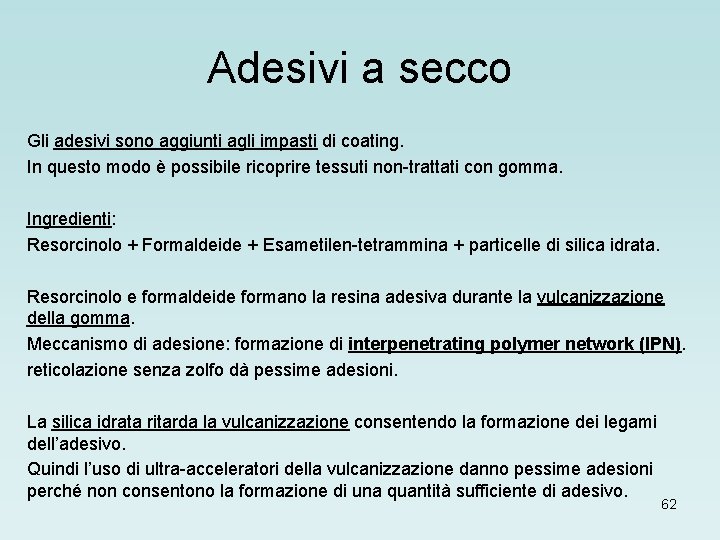
Adesivi a secco Gli adesivi sono aggiunti agli impasti di coating. In questo modo è possibile ricoprire tessuti non-trattati con gomma. Ingredienti: Resorcinolo + Formaldeide + Esametilen-tetrammina + particelle di silica idrata. Resorcinolo e formaldeide formano la resina adesiva durante la vulcanizzazione della gomma. Meccanismo di adesione: formazione di interpenetrating polymer network (IPN). reticolazione senza zolfo dà pessime adesioni. La silica idrata ritarda la vulcanizzazione consentendo la formazione dei legami dell’adesivo. Quindi l’uso di ultra-acceleratori della vulcanizzazione danno pessime adesioni perché non consentono la formazione di una quantità sufficiente di adesivo. 62
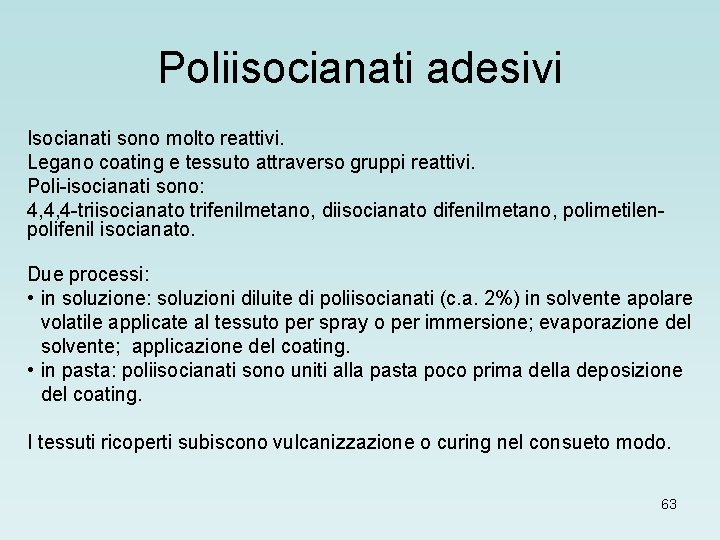
Poliisocianati adesivi Isocianati sono molto reattivi. Legano coating e tessuto attraverso gruppi reattivi. Poli-isocianati sono: 4, 4, 4 -triisocianato trifenilmetano, diisocianato difenilmetano, polimetilenpolifenil isocianato. Due processi: • in soluzione: soluzioni diluite di poliisocianati (c. a. 2%) in solvente apolare volatile applicate al tessuto per spray o per immersione; evaporazione del solvente; applicazione del coating. • in pasta: poliisocianati sono uniti alla pasta poco prima della deposizione del coating. I tessuti ricoperti subiscono vulcanizzazione o curing nel consueto modo. 63
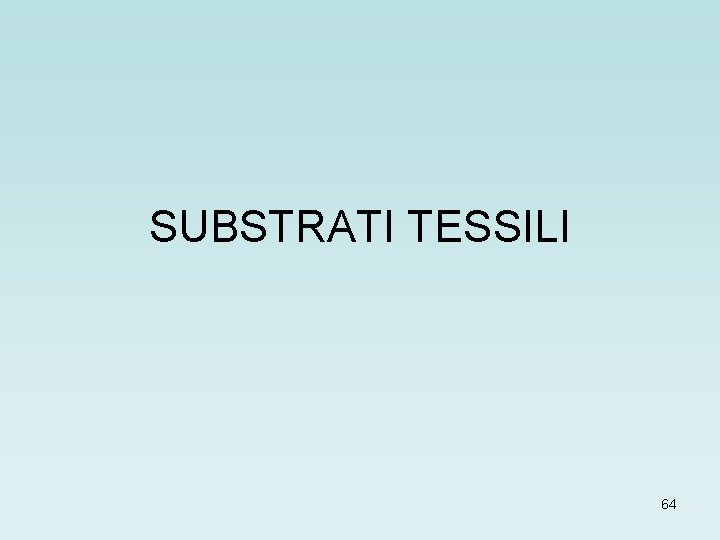
SUBSTRATI TESSILI 64
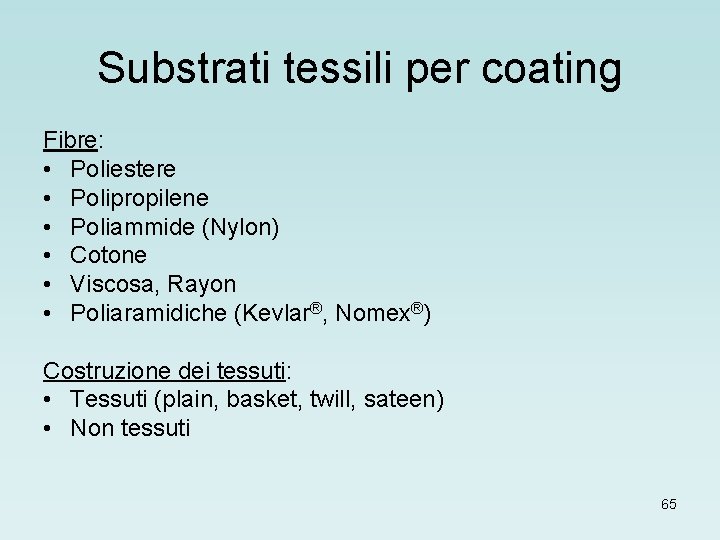
Substrati tessili per coating Fibre: • Poliestere • Polipropilene • Poliammide (Nylon) • Cotone • Viscosa, Rayon • Poliaramidiche (Kevlar®, Nomex®) Costruzione dei tessuti: • Tessuti (plain, basket, twill, sateen) • Non tessuti 65
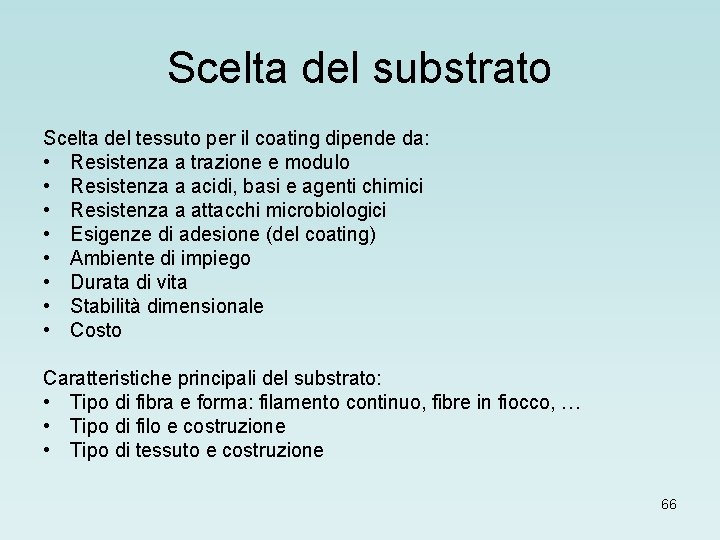
Scelta del substrato Scelta del tessuto per il coating dipende da: • Resistenza a trazione e modulo • Resistenza a acidi, basi e agenti chimici • Resistenza a attacchi microbiologici • Esigenze di adesione (del coating) • Ambiente di impiego • Durata di vita • Stabilità dimensionale • Costo Caratteristiche principali del substrato: • Tipo di fibra e forma: filamento continuo, fibre in fiocco, … • Tipo di filo e costruzione • Tipo di tessuto e costruzione 66
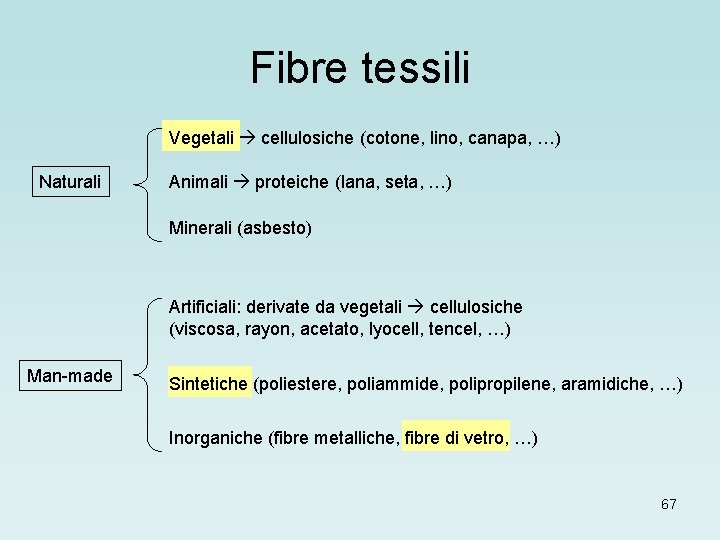
Fibre tessili Vegetali cellulosiche (cotone, lino, canapa, …) Naturali Animali proteiche (lana, seta, …) Minerali (asbesto) Artificiali: derivate da vegetali cellulosiche (viscosa, rayon, acetato, lyocell, tencel, …) Man-made Sintetiche (poliestere, poliammide, polipropilene, aramidiche, …) Inorganiche (fibre metalliche, fibre di vetro, …) 67
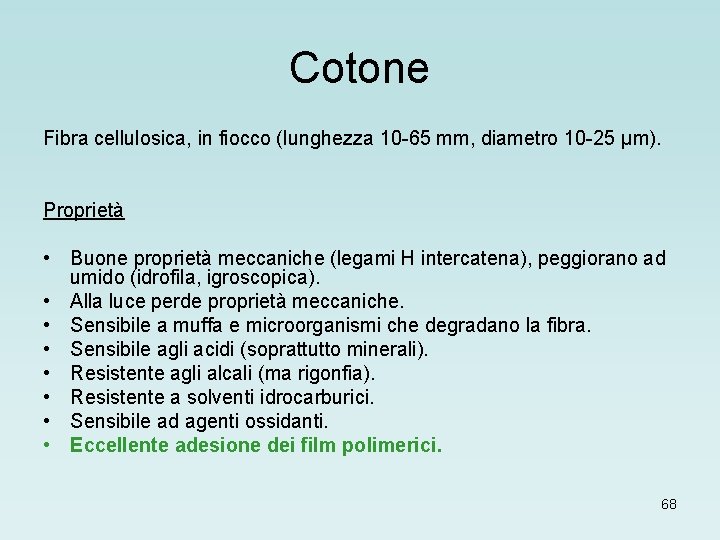
Cotone Fibra cellulosica, in fiocco (lunghezza 10 -65 mm, diametro 10 -25 µm). Proprietà • Buone proprietà meccaniche (legami H intercatena), peggiorano ad umido (idrofila, igroscopica). • Alla luce perde proprietà meccaniche. • Sensibile a muffa e microorganismi che degradano la fibra. • Sensibile agli acidi (soprattutto minerali). • Resistente agli alcali (ma rigonfia). • Resistente a solventi idrocarburici. • Sensibile ad agenti ossidanti. • Eccellente adesione dei film polimerici. 68
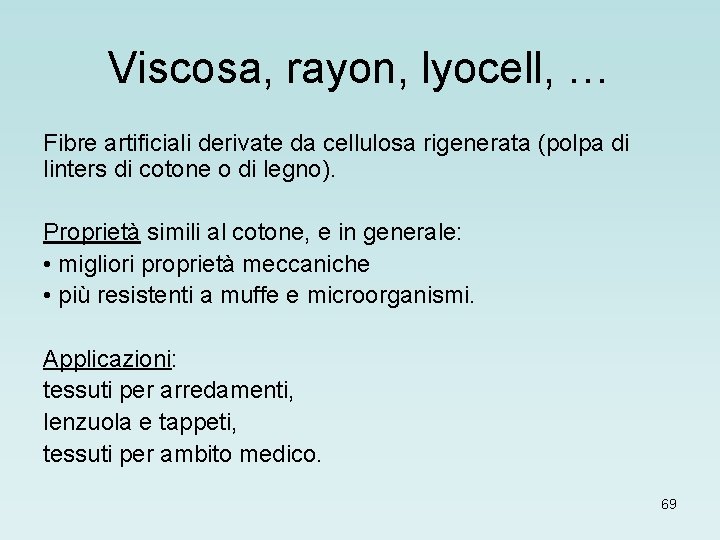
Viscosa, rayon, lyocell, … Fibre artificiali derivate da cellulosa rigenerata (polpa di linters di cotone o di legno). Proprietà simili al cotone, e in generale: • migliori proprietà meccaniche • più resistenti a muffe e microorganismi. Applicazioni: tessuti per arredamenti, lenzuola e tappeti, tessuti per ambito medico. 69
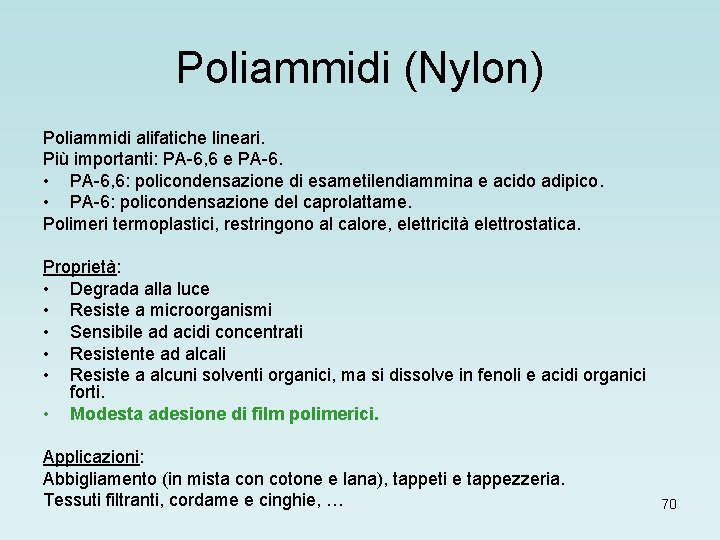
Poliammidi (Nylon) Poliammidi alifatiche lineari. Più importanti: PA-6, 6 e PA-6. • PA-6, 6: policondensazione di esametilendiammina e acido adipico. • PA-6: policondensazione del caprolattame. Polimeri termoplastici, restringono al calore, elettricità elettrostatica. Proprietà: • Degrada alla luce • Resiste a microorganismi • Sensibile ad acidi concentrati • Resistente ad alcali • Resiste a alcuni solventi organici, ma si dissolve in fenoli e acidi organici forti. • Modesta adesione di film polimerici. Applicazioni: Abbigliamento (in mista con cotone e lana), tappeti e tappezzeria. Tessuti filtranti, cordame e cinghie, … 70
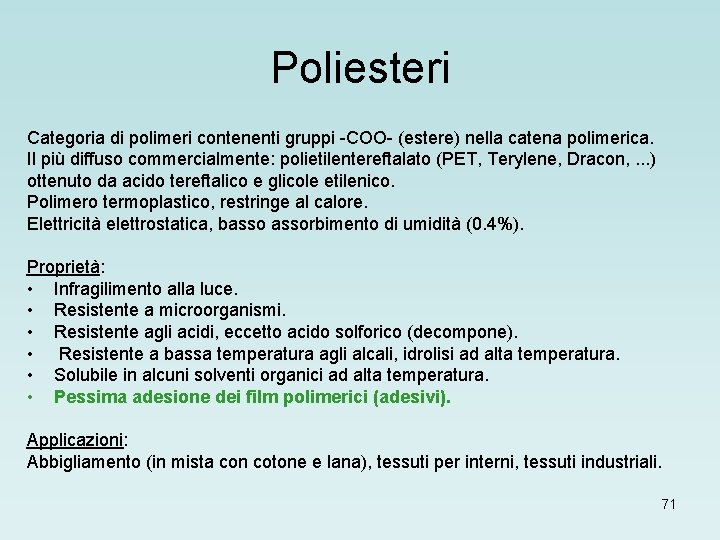
Poliesteri Categoria di polimeri contenenti gruppi -COO- (estere) nella catena polimerica. Il più diffuso commercialmente: polietilentereftalato (PET, Terylene, Dracon, . . . ) ottenuto da acido tereftalico e glicole etilenico. Polimero termoplastico, restringe al calore. Elettricità elettrostatica, bassorbimento di umidità (0. 4%). Proprietà: • Infragilimento alla luce. • Resistente a microorganismi. • Resistente agli acidi, eccetto acido solforico (decompone). • Resistente a bassa temperatura agli alcali, idrolisi ad alta temperatura. • Solubile in alcuni solventi organici ad alta temperatura. • Pessima adesione dei film polimerici (adesivi). Applicazioni: Abbigliamento (in mista con cotone e lana), tessuti per interni, tessuti industriali. 71
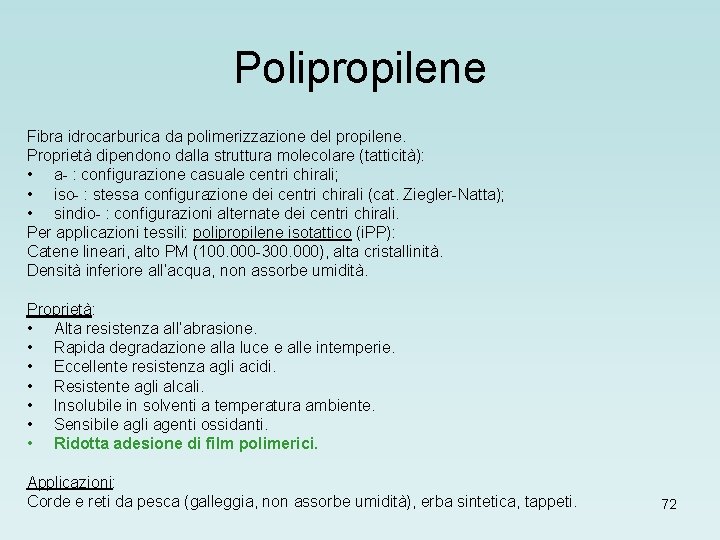
Polipropilene Fibra idrocarburica da polimerizzazione del propilene. Proprietà dipendono dalla struttura molecolare (tatticità): • a- : configurazione casuale centri chirali; • iso- : stessa configurazione dei centri chirali (cat. Ziegler-Natta); • sindio- : configurazioni alternate dei centri chirali. Per applicazioni tessili: polipropilene isotattico (i. PP): Catene lineari, alto PM (100. 000 -300. 000), alta cristallinità. Densità inferiore all’acqua, non assorbe umidità. Proprietà: • Alta resistenza all’abrasione. • Rapida degradazione alla luce e alle intemperie. • Eccellente resistenza agli acidi. • Resistente agli alcali. • Insolubile in solventi a temperatura ambiente. • Sensibile agli agenti ossidanti. • Ridotta adesione di film polimerici. Applicazioni: Corde e reti da pesca (galleggia, non assorbe umidità), erba sintetica, tappeti. 72
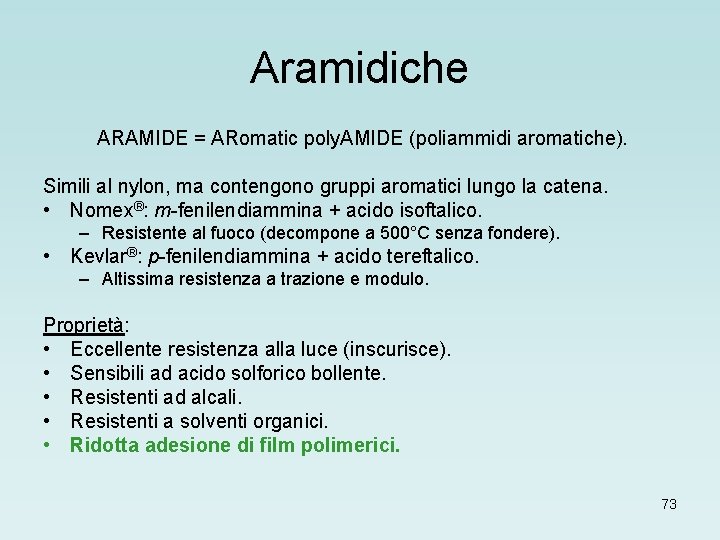
Aramidiche ARAMIDE = ARomatic poly. AMIDE (poliammidi aromatiche). Simili al nylon, ma contengono gruppi aromatici lungo la catena. • Nomex®: m-fenilendiammina + acido isoftalico. – Resistente al fuoco (decompone a 500°C senza fondere). • Kevlar®: p-fenilendiammina + acido tereftalico. – Altissima resistenza a trazione e modulo. Proprietà: • Eccellente resistenza alla luce (inscurisce). • Sensibili ad acido solforico bollente. • Resistenti ad alcali. • Resistenti a solventi organici. • Ridotta adesione di film polimerici. 73
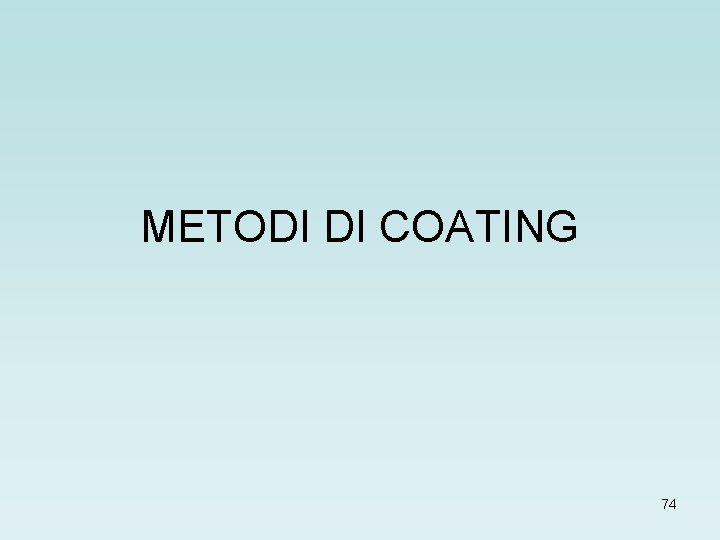
METODI DI COATING 74
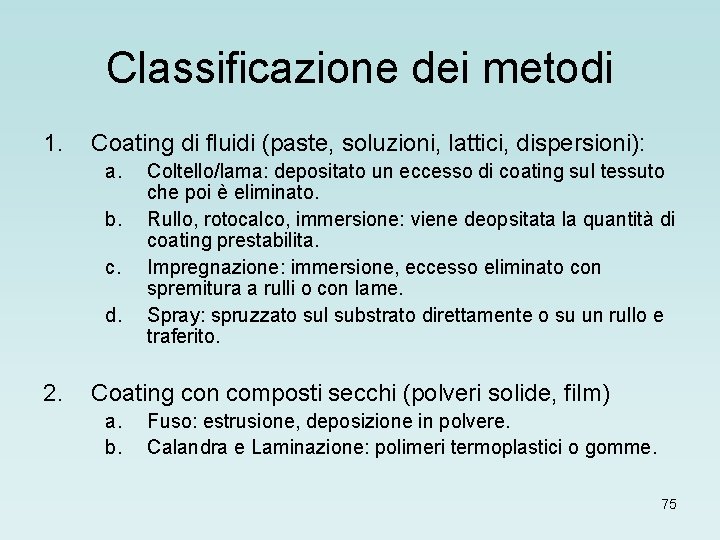
Classificazione dei metodi 1. Coating di fluidi (paste, soluzioni, lattici, dispersioni): a. b. c. d. 2. Coltello/lama: depositato un eccesso di coating sul tessuto che poi è eliminato. Rullo, rotocalco, immersione: viene deopsitata la quantità di coating prestabilita. Impregnazione: immersione, eccesso eliminato con spremitura a rulli o con lame. Spray: spruzzato sul substrato direttamente o su un rullo e traferito. Coating con composti secchi (polveri solide, film) a. b. Fuso: estrusione, deposizione in polvere. Calandra e Laminazione: polimeri termoplastici o gomme. 75
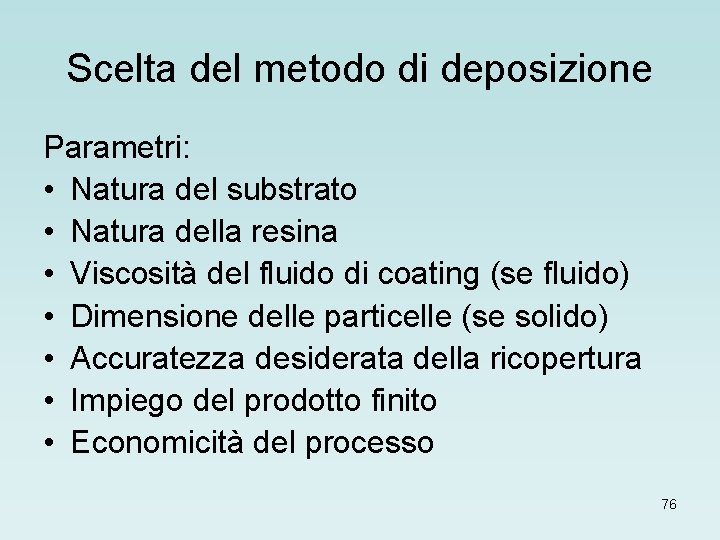
Scelta del metodo di deposizione Parametri: • Natura del substrato • Natura della resina • Viscosità del fluido di coating (se fluido) • Dimensione delle particelle (se solido) • Accuratezza desiderata della ricopertura • Impiego del prodotto finito • Economicità del processo 76
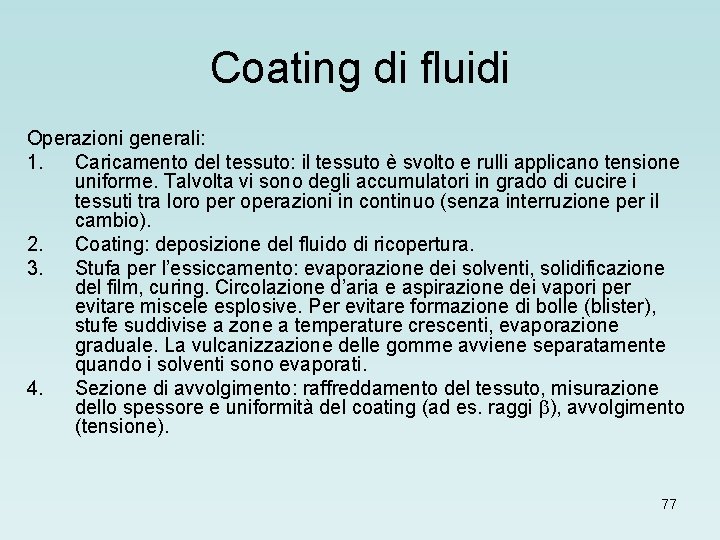
Coating di fluidi Operazioni generali: 1. Caricamento del tessuto: il tessuto è svolto e rulli applicano tensione uniforme. Talvolta vi sono degli accumulatori in grado di cucire i tessuti tra loro per operazioni in continuo (senza interruzione per il cambio). 2. Coating: deposizione del fluido di ricopertura. 3. Stufa per l’essiccamento: evaporazione dei solventi, solidificazione del film, curing. Circolazione d’aria e aspirazione dei vapori per evitare miscele esplosive. Per evitare formazione di bolle (blister), stufe suddivise a zone a temperature crescenti, evaporazione graduale. La vulcanizzazione delle gomme avviene separatamente quando i solventi sono evaporati. 4. Sezione di avvolgimento: raffreddamento del tessuto, misurazione dello spessore e uniformità del coating (ad es. raggi ), avvolgimento (tensione). 77
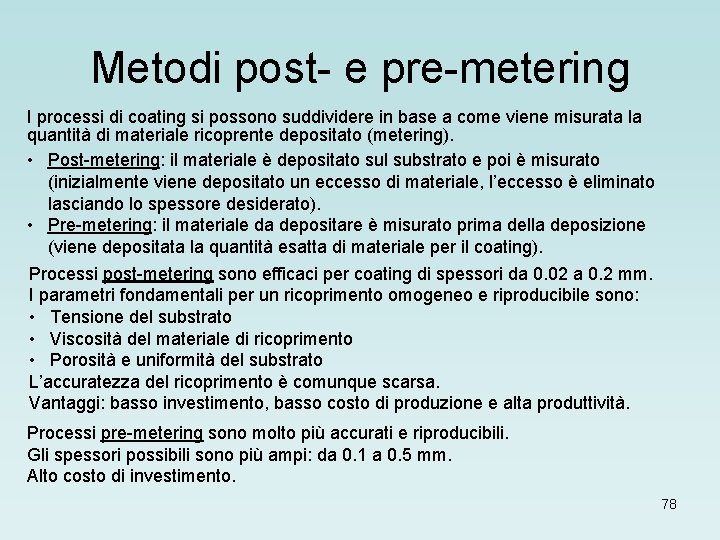
Metodi post- e pre-metering I processi di coating si possono suddividere in base a come viene misurata la quantità di materiale ricoprente depositato (metering). • Post-metering: il materiale è depositato sul substrato e poi è misurato (inizialmente viene depositato un eccesso di materiale, l’eccesso è eliminato lasciando lo spessore desiderato). • Pre-metering: il materiale da depositare è misurato prima della deposizione (viene depositata la quantità esatta di materiale per il coating). Processi post-metering sono efficaci per coating di spessori da 0. 02 a 0. 2 mm. I parametri fondamentali per un ricoprimento omogeneo e riproducibile sono: • Tensione del substrato • Viscosità del materiale di ricoprimento • Porosità e uniformità del substrato L’accuratezza del ricoprimento è comunque scarsa. Vantaggi: basso investimento, basso costo di produzione e alta produttività. Processi pre-metering sono molto più accurati e riproducibili. Gli spessori possibili sono più ampi: da 0. 1 a 0. 5 mm. Alto costo di investimento. 78
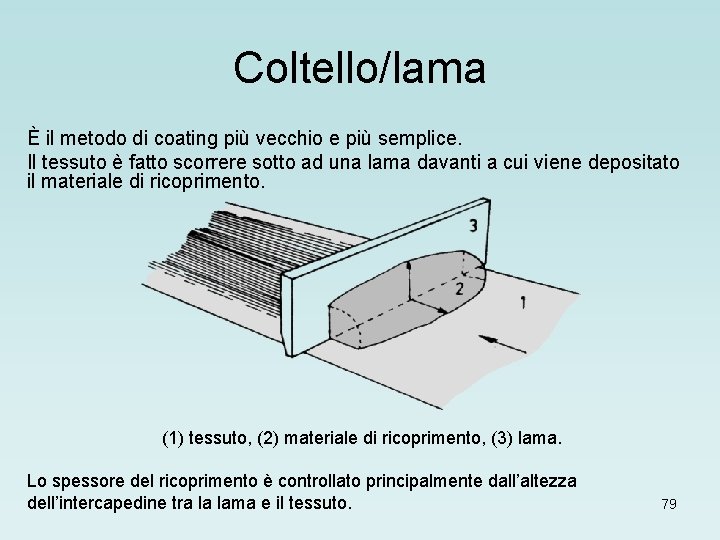
Coltello/lama È il metodo di coating più vecchio e più semplice. Il tessuto è fatto scorrere sotto ad una lama davanti a cui viene depositato il materiale di ricoprimento. (1) tessuto, (2) materiale di ricoprimento, (3) lama. Lo spessore del ricoprimento è controllato principalmente dall’altezza dell’intercapedine tra la lama e il tessuto. 79
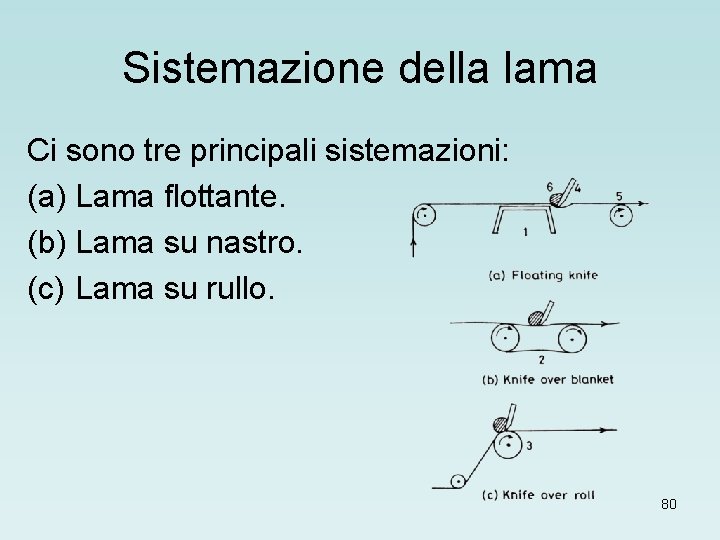
Sistemazione della lama Ci sono tre principali sistemazioni: (a) Lama flottante. (b) Lama su nastro. (c) Lama su rullo. 80
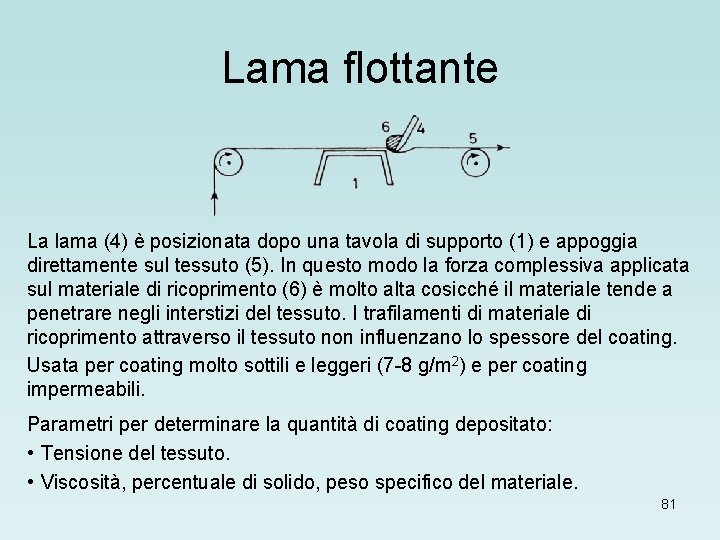
Lama flottante La lama (4) è posizionata dopo una tavola di supporto (1) e appoggia direttamente sul tessuto (5). In questo modo la forza complessiva applicata sul materiale di ricoprimento (6) è molto alta cosicché il materiale tende a penetrare negli interstizi del tessuto. I trafilamenti di materiale di ricoprimento attraverso il tessuto non influenzano lo spessore del coating. Usata per coating molto sottili e leggeri (7 -8 g/m 2) e per coating impermeabili. Parametri per determinare la quantità di coating depositato: • Tensione del tessuto. • Viscosità, percentuale di solido, peso specifico del materiale. 81
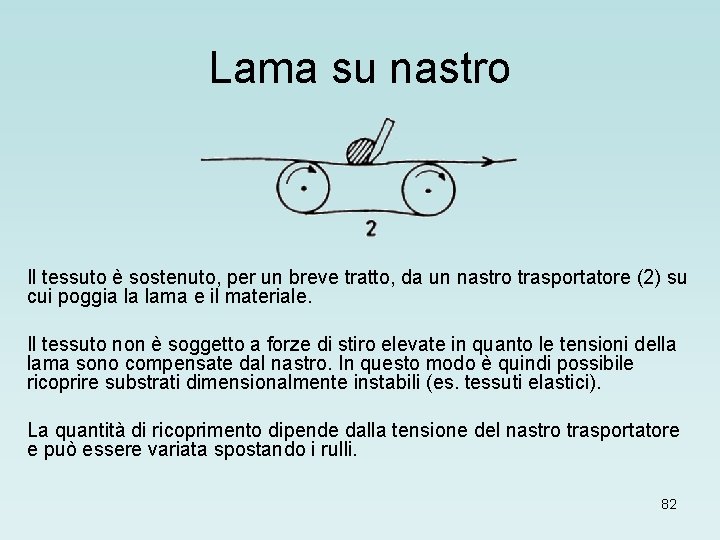
Lama su nastro Il tessuto è sostenuto, per un breve tratto, da un nastro trasportatore (2) su cui poggia la lama e il materiale. Il tessuto non è soggetto a forze di stiro elevate in quanto le tensioni della lama sono compensate dal nastro. In questo modo è quindi possibile ricoprire substrati dimensionalmente instabili (es. tessuti elastici). La quantità di ricoprimento dipende dalla tensione del nastro trasportatore e può essere variata spostando i rulli. 82
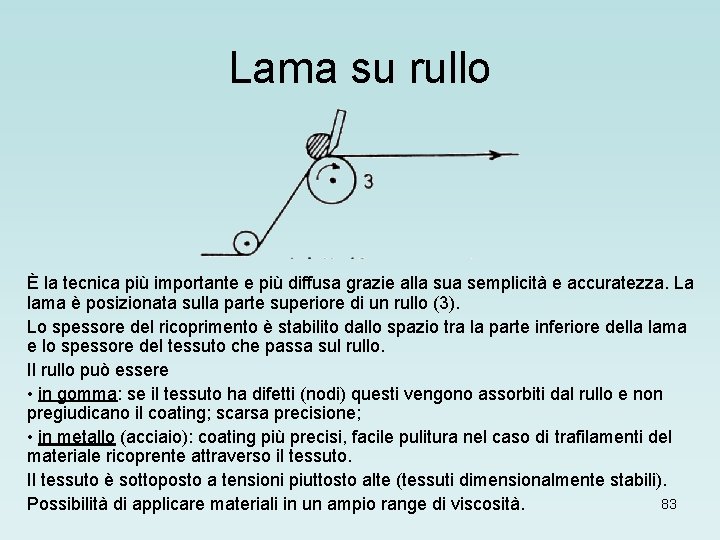
Lama su rullo È la tecnica più importante e più diffusa grazie alla sua semplicità e accuratezza. La lama è posizionata sulla parte superiore di un rullo (3). Lo spessore del ricoprimento è stabilito dallo spazio tra la parte inferiore della lama e lo spessore del tessuto che passa sul rullo. Il rullo può essere • in gomma: se il tessuto ha difetti (nodi) questi vengono assorbiti dal rullo e non pregiudicano il coating; scarsa precisione; • in metallo (acciaio): coating più precisi, facile pulitura nel caso di trafilamenti del materiale ricoprente attraverso il tessuto. Il tessuto è sottoposto a tensioni piuttosto alte (tessuti dimensionalmente stabili). 83 Possibilità di applicare materiali in un ampio range di viscosità.
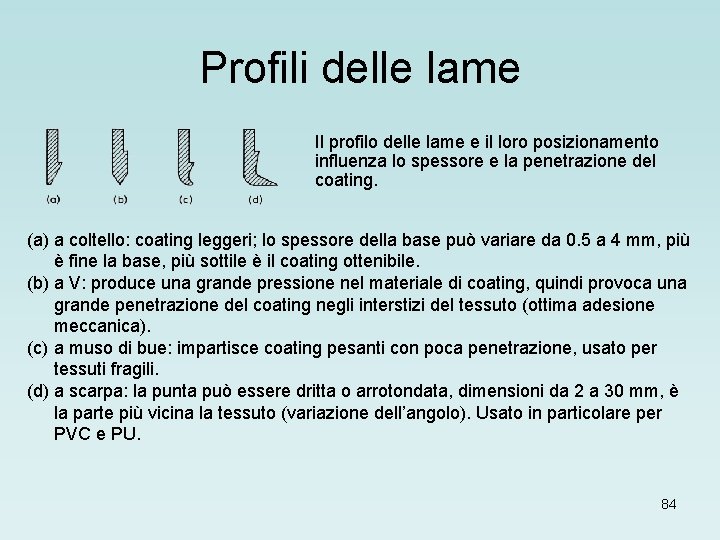
Profili delle lame Il profilo delle lame e il loro posizionamento influenza lo spessore e la penetrazione del coating. (a) a coltello: coating leggeri; lo spessore della base può variare da 0. 5 a 4 mm, più è fine la base, più sottile è il coating ottenibile. (b) a V: produce una grande pressione nel materiale di coating, quindi provoca una grande penetrazione del coating negli interstizi del tessuto (ottima adesione meccanica). (c) a muso di bue: impartisce coating pesanti con poca penetrazione, usato per tessuti fragili. (d) a scarpa: la punta può essere dritta o arrotondata, dimensioni da 2 a 30 mm, è la parte più vicina la tessuto (variazione dell’angolo). Usato in particolare per PVC e PU. 84
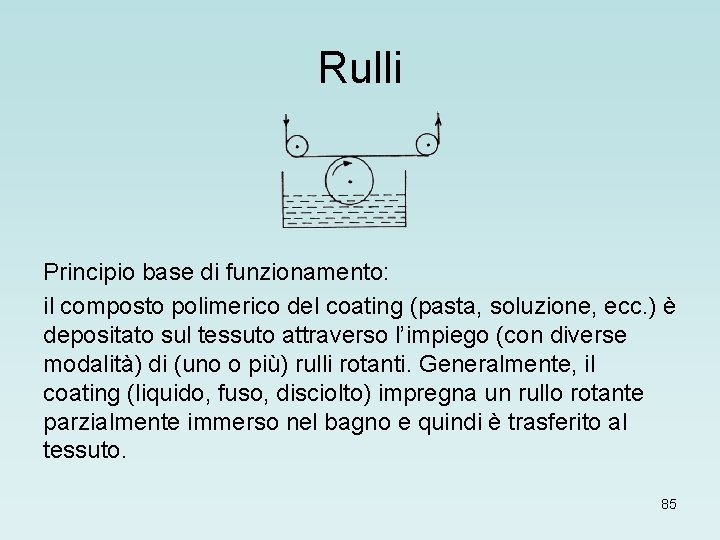
Rulli Principio base di funzionamento: il composto polimerico del coating (pasta, soluzione, ecc. ) è depositato sul tessuto attraverso l’impiego (con diverse modalità) di (uno o più) rulli rotanti. Generalmente, il coating (liquido, fuso, disciolto) impregna un rullo rotante parzialmente immerso nel bagno e quindi è trasferito al tessuto. 85
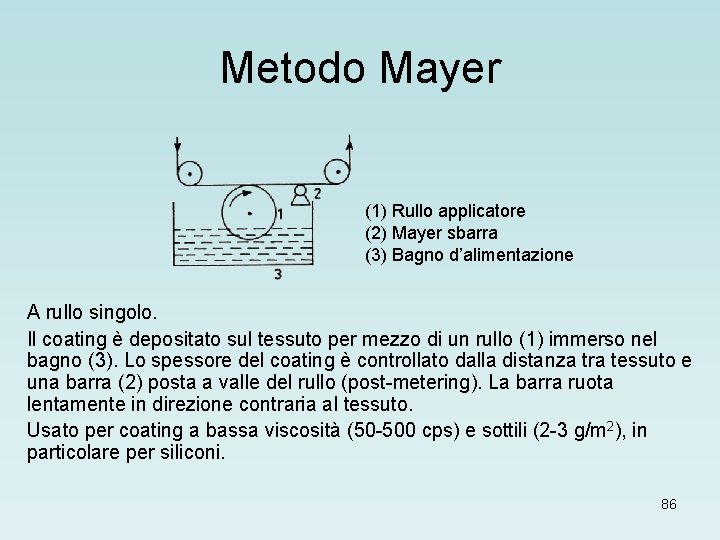
Metodo Mayer (1) Rullo applicatore (2) Mayer sbarra (3) Bagno d’alimentazione A rullo singolo. Il coating è depositato sul tessuto per mezzo di un rullo (1) immerso nel bagno (3). Lo spessore del coating è controllato dalla distanza tra tessuto e una barra (2) posta a valle del rullo (post-metering). La barra ruota lentamente in direzione contraria al tessuto. Usato per coating a bassa viscosità (50 -500 cps) e sottili (2 -3 g/m 2), in particolare per siliconi. 86
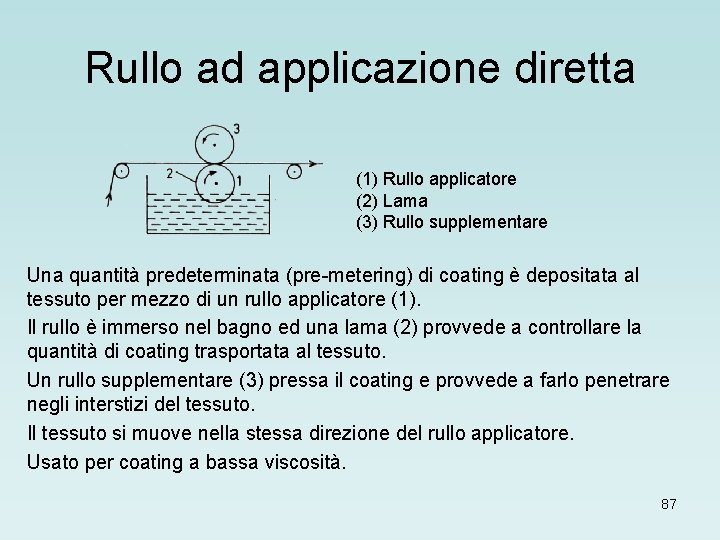
Rullo ad applicazione diretta (1) Rullo applicatore (2) Lama (3) Rullo supplementare Una quantità predeterminata (pre-metering) di coating è depositata al tessuto per mezzo di un rullo applicatore (1). Il rullo è immerso nel bagno ed una lama (2) provvede a controllare la quantità di coating trasportata al tessuto. Un rullo supplementare (3) pressa il coating e provvede a farlo penetrare negli interstizi del tessuto. Il tessuto si muove nella stessa direzione del rullo applicatore. Usato per coating a bassa viscosità. 87
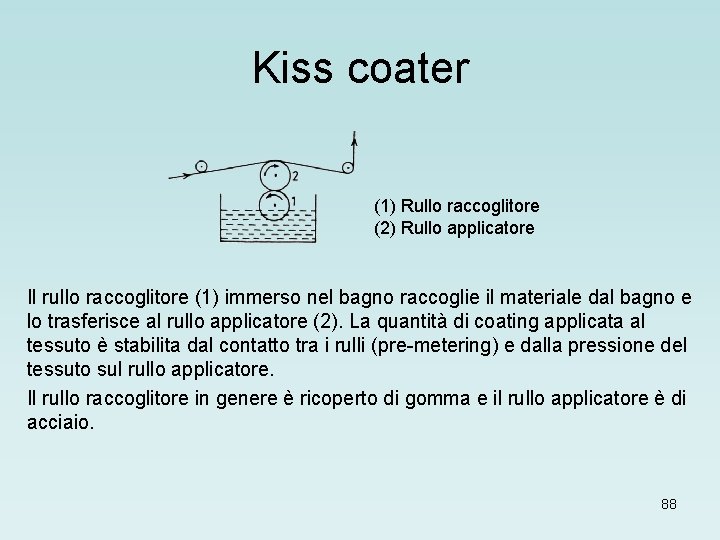
Kiss coater (1) Rullo raccoglitore (2) Rullo applicatore Il rullo raccoglitore (1) immerso nel bagno raccoglie il materiale dal bagno e lo trasferisce al rullo applicatore (2). La quantità di coating applicata al tessuto è stabilita dal contatto tra i rulli (pre-metering) e dalla pressione del tessuto sul rullo applicatore. Il rullo raccoglitore in genere è ricoperto di gomma e il rullo applicatore è di acciaio. 88
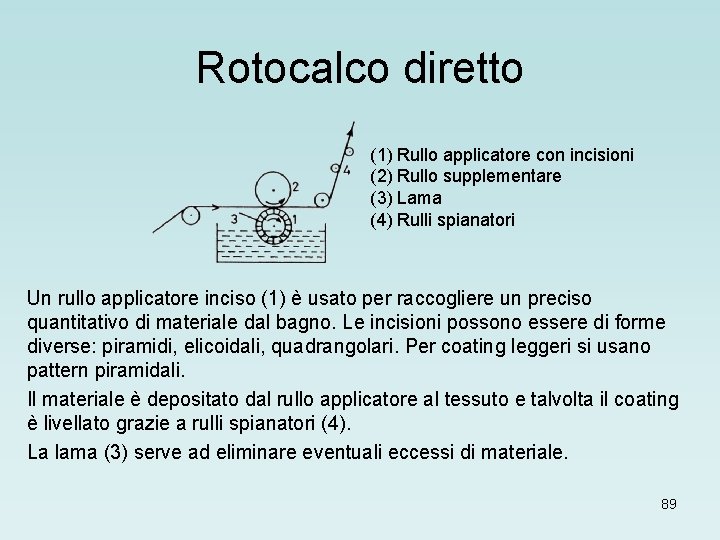
Rotocalco diretto (1) Rullo applicatore con incisioni (2) Rullo supplementare (3) Lama (4) Rulli spianatori Un rullo applicatore inciso (1) è usato per raccogliere un preciso quantitativo di materiale dal bagno. Le incisioni possono essere di forme diverse: piramidi, elicoidali, quadrangolari. Per coating leggeri si usano pattern piramidali. Il materiale è depositato dal rullo applicatore al tessuto e talvolta il coating è livellato grazie a rulli spianatori (4). La lama (3) serve ad eliminare eventuali eccessi di materiale. 89
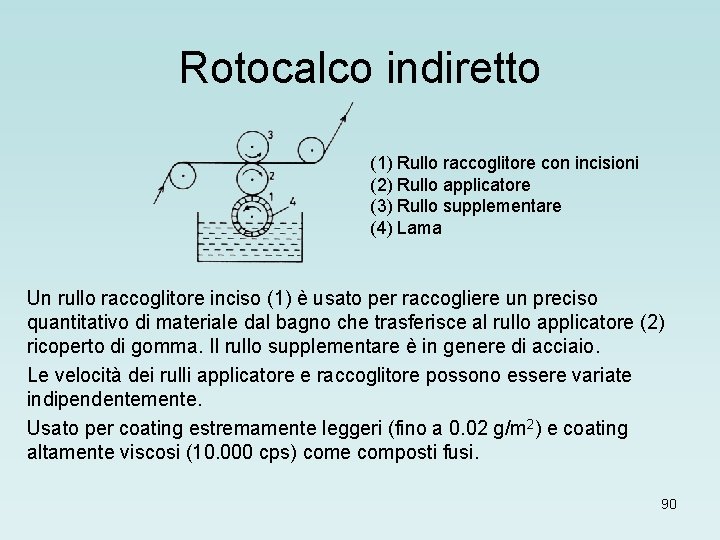
Rotocalco indiretto (1) Rullo raccoglitore con incisioni (2) Rullo applicatore (3) Rullo supplementare (4) Lama Un rullo raccoglitore inciso (1) è usato per raccogliere un preciso quantitativo di materiale dal bagno che trasferisce al rullo applicatore (2) ricoperto di gomma. Il rullo supplementare è in genere di acciaio. Le velocità dei rulli applicatore e raccoglitore possono essere variate indipendentemente. Usato per coating estremamente leggeri (fino a 0. 02 g/m 2) e coating altamente viscosi (10. 000 cps) come composti fusi. 90
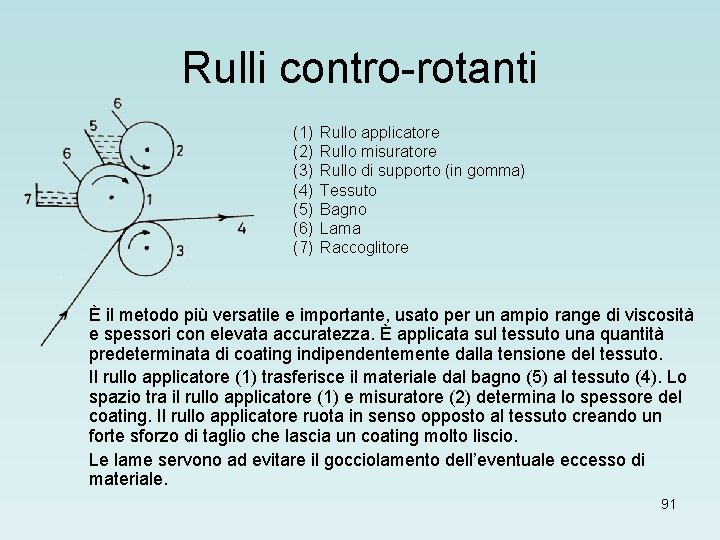
Rulli contro-rotanti (1) (2) (3) (4) (5) (6) (7) Rullo applicatore Rullo misuratore Rullo di supporto (in gomma) Tessuto Bagno Lama Raccoglitore È il metodo più versatile e importante, usato per un ampio range di viscosità e spessori con elevata accuratezza. È applicata sul tessuto una quantità predeterminata di coating indipendentemente dalla tensione del tessuto. Il rullo applicatore (1) trasferisce il materiale dal bagno (5) al tessuto (4). Lo spazio tra il rullo applicatore (1) e misuratore (2) determina lo spessore del coating. Il rullo applicatore ruota in senso opposto al tessuto creando un forte sforzo di taglio che lascia un coating molto liscio. Le lame servono ad evitare il gocciolamento dell’eventuale eccesso di materiale. 91
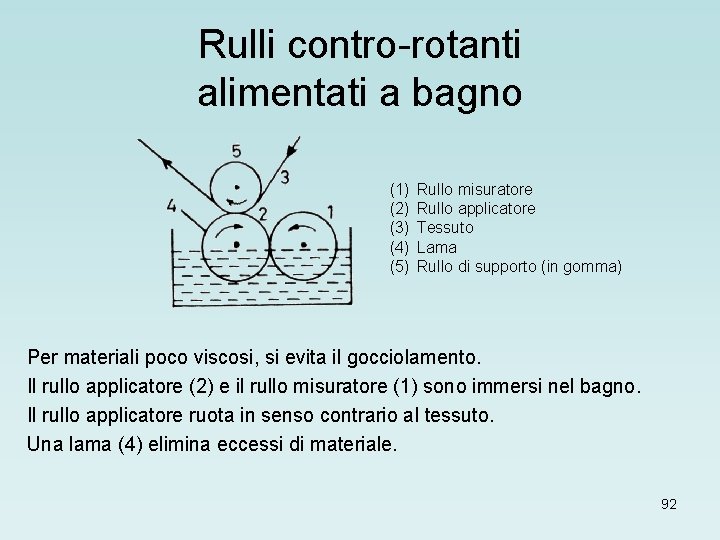
Rulli contro-rotanti alimentati a bagno (1) (2) (3) (4) (5) Rullo misuratore Rullo applicatore Tessuto Lama Rullo di supporto (in gomma) Per materiali poco viscosi, si evita il gocciolamento. Il rullo applicatore (2) e il rullo misuratore (1) sono immersi nel bagno. Il rullo applicatore ruota in senso contrario al tessuto. Una lama (4) elimina eccessi di materiale. 92
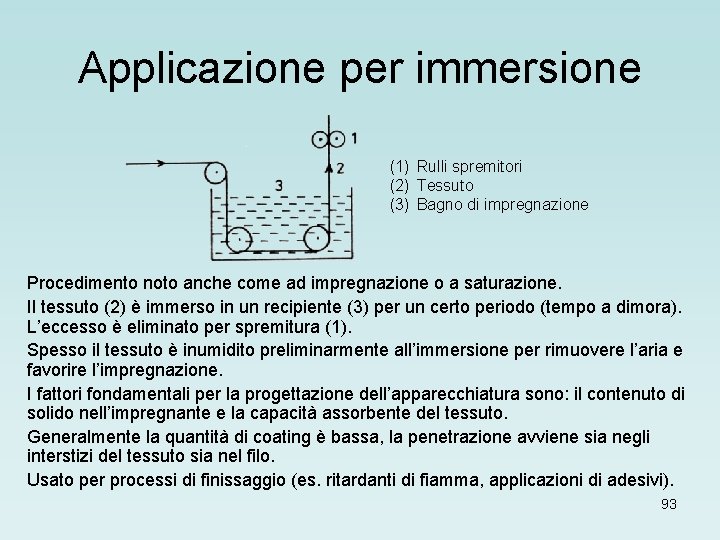
Applicazione per immersione (1) Rulli spremitori (2) Tessuto (3) Bagno di impregnazione Procedimento noto anche come ad impregnazione o a saturazione. Il tessuto (2) è immerso in un recipiente (3) per un certo periodo (tempo a dimora). L’eccesso è eliminato per spremitura (1). Spesso il tessuto è inumidito preliminarmente all’immersione per rimuovere l’aria e favorire l’impregnazione. I fattori fondamentali per la progettazione dell’apparecchiatura sono: il contenuto di solido nell’impregnante e la capacità assorbente del tessuto. Generalmente la quantità di coating è bassa, la penetrazione avviene sia negli interstizi del tessuto sia nel filo. Usato per processi di finissaggio (es. ritardanti di fiamma, applicazioni di adesivi). 93
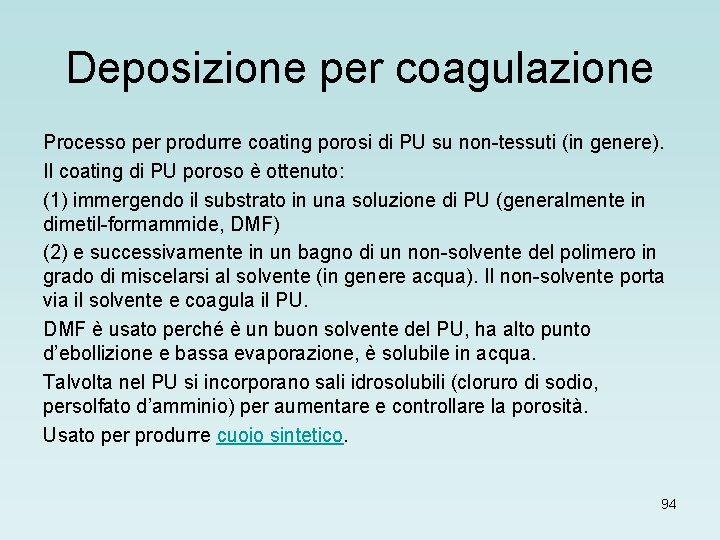
Deposizione per coagulazione Processo per produrre coating porosi di PU su non-tessuti (in genere). Il coating di PU poroso è ottenuto: (1) immergendo il substrato in una soluzione di PU (generalmente in dimetil-formammide, DMF) (2) e successivamente in un bagno di un non-solvente del polimero in grado di miscelarsi al solvente (in genere acqua). Il non-solvente porta via il solvente e coagula il PU. DMF è usato perché è un buon solvente del PU, ha alto punto d’ebollizione e bassa evaporazione, è solubile in acqua. Talvolta nel PU si incorporano sali idrosolubili (cloruro di sodio, persolfato d’amminio) per aumentare e controllare la porosità. Usato per produrre cuoio sintetico. 94
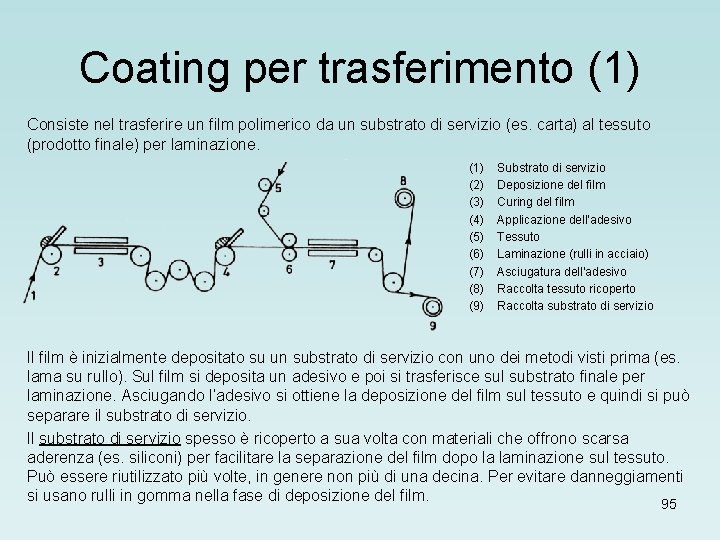
Coating per trasferimento (1) Consiste nel trasferire un film polimerico da un substrato di servizio (es. carta) al tessuto (prodotto finale) per laminazione. (1) (2) (3) (4) (5) (6) (7) (8) (9) Substrato di servizio Deposizione del film Curing del film Applicazione dell’adesivo Tessuto Laminazione (rulli in acciaio) Asciugatura dell’adesivo Raccolta tessuto ricoperto Raccolta substrato di servizio Il film è inizialmente depositato su un substrato di servizio con uno dei metodi visti prima (es. lama su rullo). Sul film si deposita un adesivo e poi si trasferisce sul substrato finale per laminazione. Asciugando l’adesivo si ottiene la deposizione del film sul tessuto e quindi si può separare il substrato di servizio. Il substrato di servizio spesso è ricoperto a sua volta con materiali che offrono scarsa aderenza (es. siliconi) per facilitare la separazione del film dopo la laminazione sul tessuto. Può essere riutilizzato più volte, in genere non più di una decina. Per evitare danneggiamenti si usano rulli in gomma nella fase di deposizione del film. 95
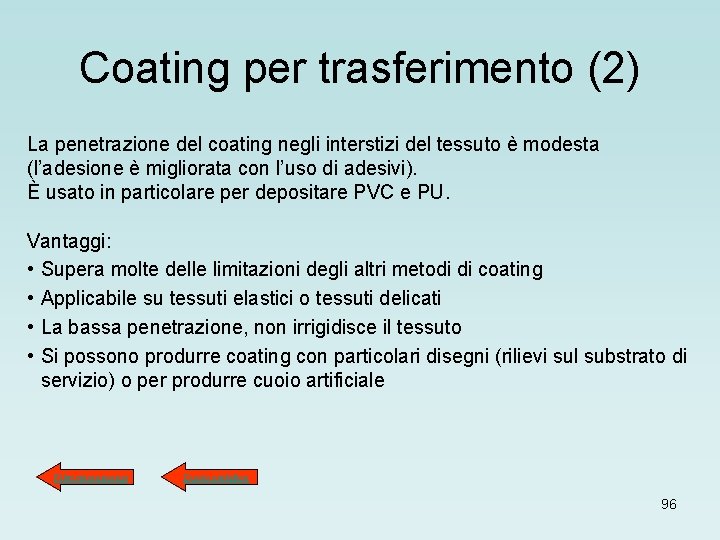
Coating per trasferimento (2) La penetrazione del coating negli interstizi del tessuto è modesta (l’adesione è migliorata con l’uso di adesivi). È usato in particolare per depositare PVC e PU. Vantaggi: • Supera molte delle limitazioni degli altri metodi di coating • Applicabile su tessuti elastici o tessuti delicati • La bassa penetrazione, non irrigidisce il tessuto • Si possono produrre coating con particolari disegni (rilievi sul substrato di servizio) o per produrre cuoio artificiale Film microporosi Cuoio sintetico 96
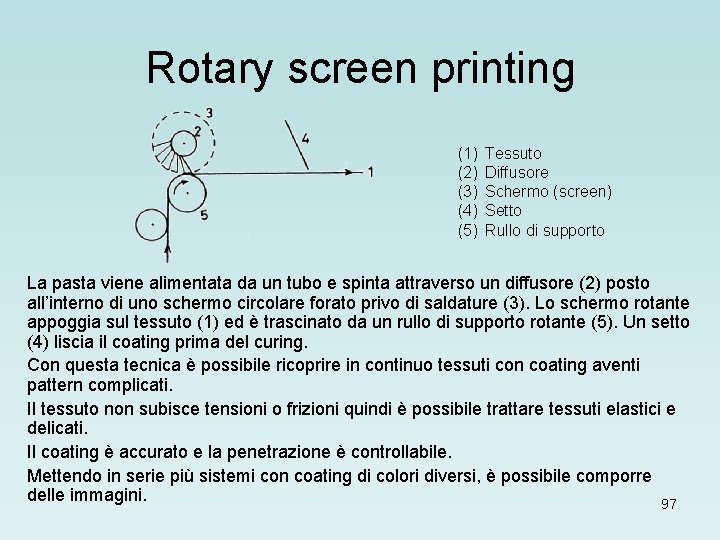
Rotary screen printing (1) (2) (3) (4) (5) Tessuto Diffusore Schermo (screen) Setto Rullo di supporto La pasta viene alimentata da un tubo e spinta attraverso un diffusore (2) posto all’interno di uno schermo circolare forato privo di saldature (3). Lo schermo rotante appoggia sul tessuto (1) ed è trascinato da un rullo di supporto rotante (5). Un setto (4) liscia il coating prima del curing. Con questa tecnica è possibile ricoprire in continuo tessuti con coating aventi pattern complicati. Il tessuto non subisce tensioni o frizioni quindi è possibile trattare tessuti elastici e delicati. Il coating è accurato e la penetrazione è controllabile. Mettendo in serie più sistemi con coating di colori diversi, è possibile comporre delle immagini. 97
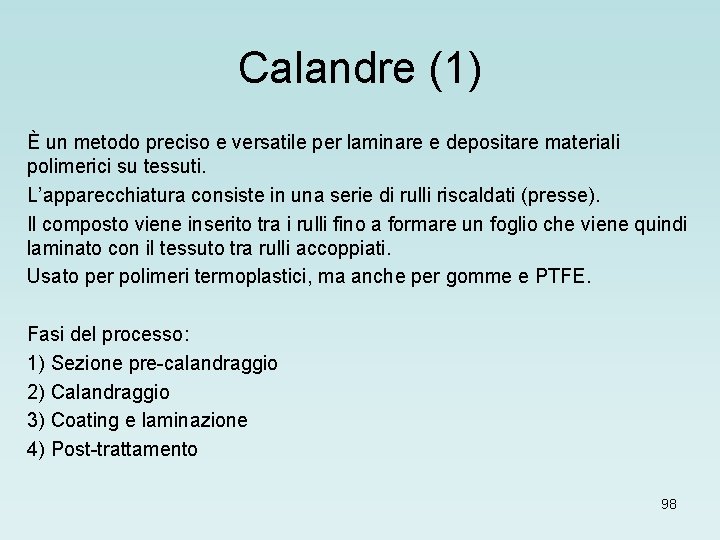
Calandre (1) È un metodo preciso e versatile per laminare e depositare materiali polimerici su tessuti. L’apparecchiatura consiste in una serie di rulli riscaldati (presse). Il composto viene inserito tra i rulli fino a formare un foglio che viene quindi laminato con il tessuto tra rulli accoppiati. Usato per polimeri termoplastici, ma anche per gomme e PTFE. Fasi del processo: 1) Sezione pre-calandraggio 2) Calandraggio 3) Coating e laminazione 4) Post-trattamento 98
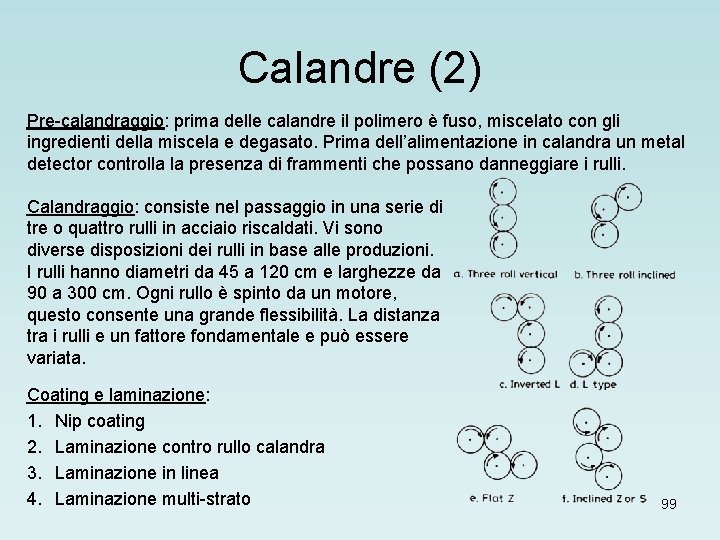
Calandre (2) Pre-calandraggio: prima delle calandre il polimero è fuso, miscelato con gli ingredienti della miscela e degasato. Prima dell’alimentazione in calandra un metal detector controlla la presenza di frammenti che possano danneggiare i rulli. Calandraggio: consiste nel passaggio in una serie di tre o quattro rulli in acciaio riscaldati. Vi sono diverse disposizioni dei rulli in base alle produzioni. I rulli hanno diametri da 45 a 120 cm e larghezze da 90 a 300 cm. Ogni rullo è spinto da un motore, questo consente una grande flessibilità. La distanza tra i rulli e un fattore fondamentale e può essere variata. Coating e laminazione: 1. Nip coating 2. Laminazione contro rullo calandra 3. Laminazione in linea 4. Laminazione multi-strato 99
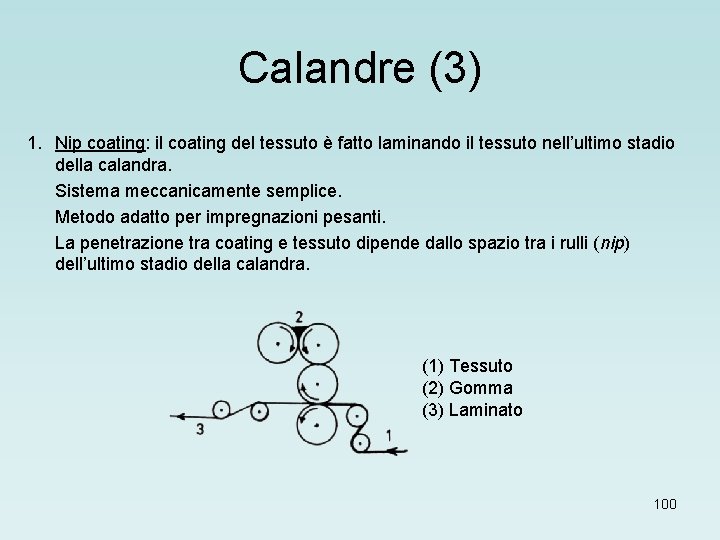
Calandre (3) 1. Nip coating: il coating del tessuto è fatto laminando il tessuto nell’ultimo stadio della calandra. Sistema meccanicamente semplice. Metodo adatto per impregnazioni pesanti. La penetrazione tra coating e tessuto dipende dallo spazio tra i rulli (nip) dell’ultimo stadio della calandra. (1) Tessuto (2) Gomma (3) Laminato 100
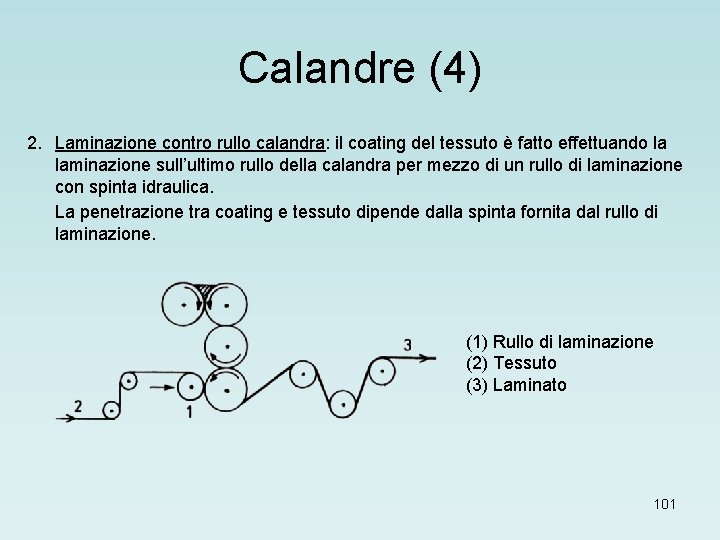
Calandre (4) 2. Laminazione contro rullo calandra: il coating del tessuto è fatto effettuando la laminazione sull’ultimo rullo della calandra per mezzo di un rullo di laminazione con spinta idraulica. La penetrazione tra coating e tessuto dipende dalla spinta fornita dal rullo di laminazione. (1) Rullo di laminazione (2) Tessuto (3) Laminato 101
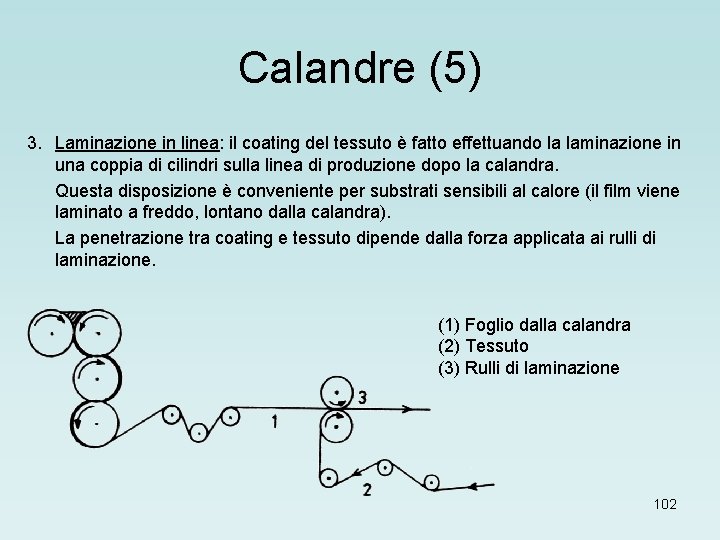
Calandre (5) 3. Laminazione in linea: il coating del tessuto è fatto effettuando la laminazione in una coppia di cilindri sulla linea di produzione dopo la calandra. Questa disposizione è conveniente per substrati sensibili al calore (il film viene laminato a freddo, lontano dalla calandra). La penetrazione tra coating e tessuto dipende dalla forza applicata ai rulli di laminazione. (1) Foglio dalla calandra (2) Tessuto (3) Rulli di laminazione 102
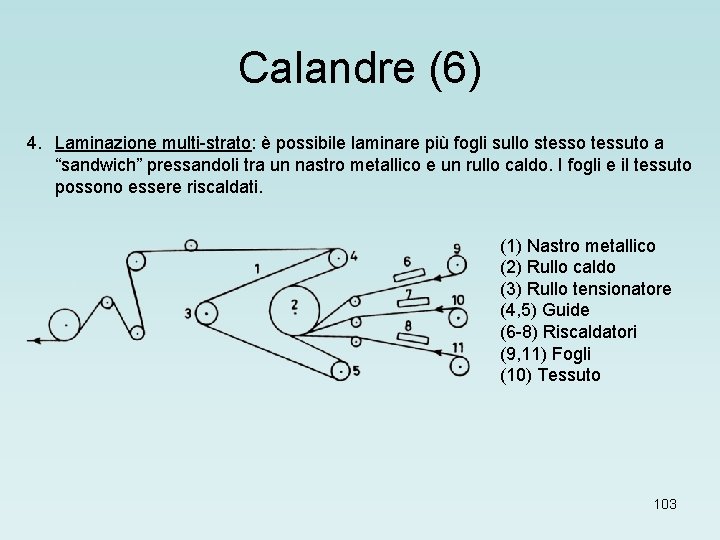
Calandre (6) 4. Laminazione multi-strato: è possibile laminare più fogli sullo stesso tessuto a “sandwich” pressandoli tra un nastro metallico e un rullo caldo. I fogli e il tessuto possono essere riscaldati. (1) Nastro metallico (2) Rullo caldo (3) Rullo tensionatore (4, 5) Guide (6 -8) Riscaldatori (9, 11) Fogli (10) Tessuto 103
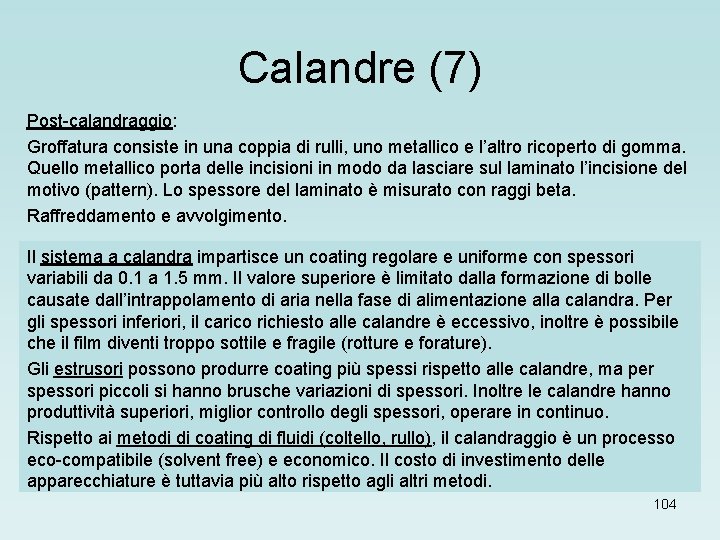
Calandre (7) Post-calandraggio: Groffatura consiste in una coppia di rulli, uno metallico e l’altro ricoperto di gomma. Quello metallico porta delle incisioni in modo da lasciare sul laminato l’incisione del motivo (pattern). Lo spessore del laminato è misurato con raggi beta. Raffreddamento e avvolgimento. Il sistema a calandra impartisce un coating regolare e uniforme con spessori variabili da 0. 1 a 1. 5 mm. Il valore superiore è limitato dalla formazione di bolle causate dall’intrappolamento di aria nella fase di alimentazione alla calandra. Per gli spessori inferiori, il carico richiesto alle calandre è eccessivo, inoltre è possibile che il film diventi troppo sottile e fragile (rotture e forature). Gli estrusori possono produrre coating più spessi rispetto alle calandre, ma per spessori piccoli si hanno brusche variazioni di spessori. Inoltre le calandre hanno produttività superiori, miglior controllo degli spessori, operare in continuo. Rispetto ai metodi di coating di fluidi (coltello, rullo), il calandraggio è un processo eco-compatibile (solvent free) e economico. Il costo di investimento delle apparecchiature è tuttavia più alto rispetto agli altri metodi. 104
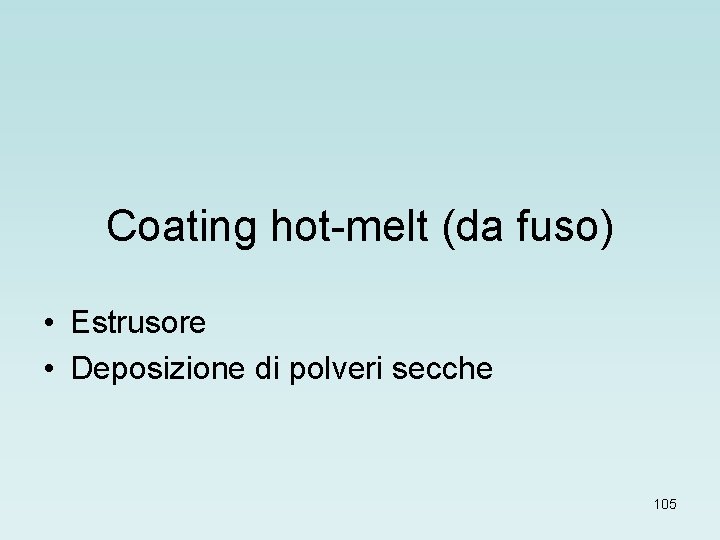
Coating hot-melt (da fuso) • Estrusore • Deposizione di polveri secche 105
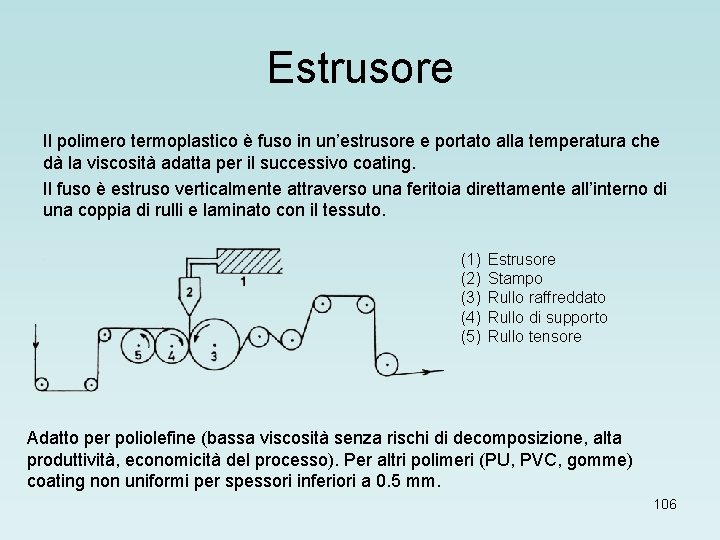
Estrusore Il polimero termoplastico è fuso in un’estrusore e portato alla temperatura che dà la viscosità adatta per il successivo coating. Il fuso è estruso verticalmente attraverso una feritoia direttamente all’interno di una coppia di rulli e laminato con il tessuto. (1) (2) (3) (4) (5) Estrusore Stampo Rullo raffreddato Rullo di supporto Rullo tensore Adatto per poliolefine (bassa viscosità senza rischi di decomposizione, alta produttività, economicità del processo). Per altri polimeri (PU, PVC, gomme) coating non uniformi per spessori inferiori a 0. 5 mm. 106
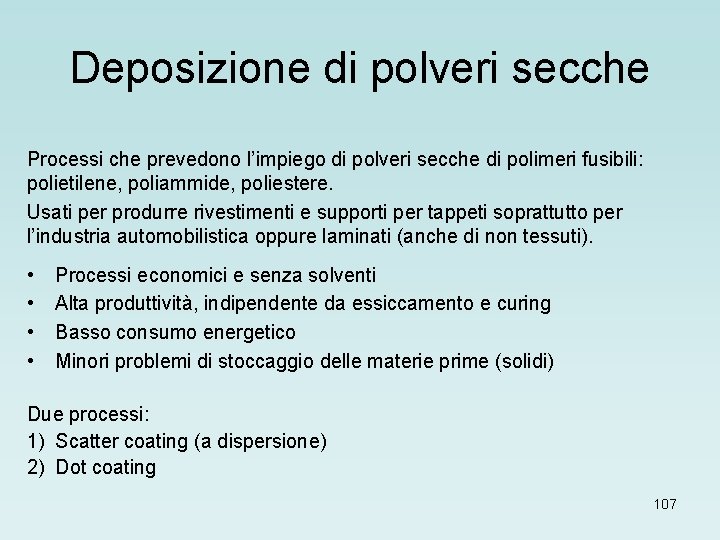
Deposizione di polveri secche Processi che prevedono l’impiego di polveri secche di polimeri fusibili: polietilene, poliammide, poliestere. Usati per produrre rivestimenti e supporti per tappeti soprattutto per l’industria automobilistica oppure laminati (anche di non tessuti). • • Processi economici e senza solventi Alta produttività, indipendente da essiccamento e curing Basso consumo energetico Minori problemi di stoccaggio delle materie prime (solidi) Due processi: 1) Scatter coating (a dispersione) 2) Dot coating 107
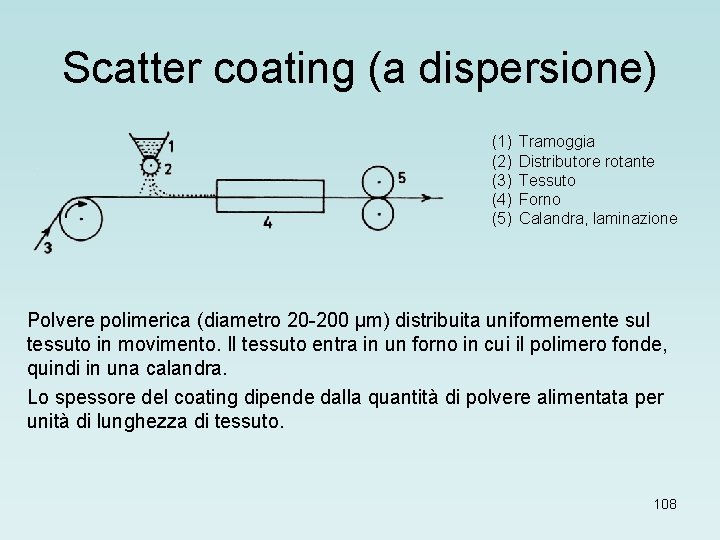
Scatter coating (a dispersione) (1) (2) (3) (4) (5) Tramoggia Distributore rotante Tessuto Forno Calandra, laminazione Polvere polimerica (diametro 20 -200 µm) distribuita uniformemente sul tessuto in movimento. Il tessuto entra in un forno in cui il polimero fonde, quindi in una calandra. Lo spessore del coating dipende dalla quantità di polvere alimentata per unità di lunghezza di tessuto. 108
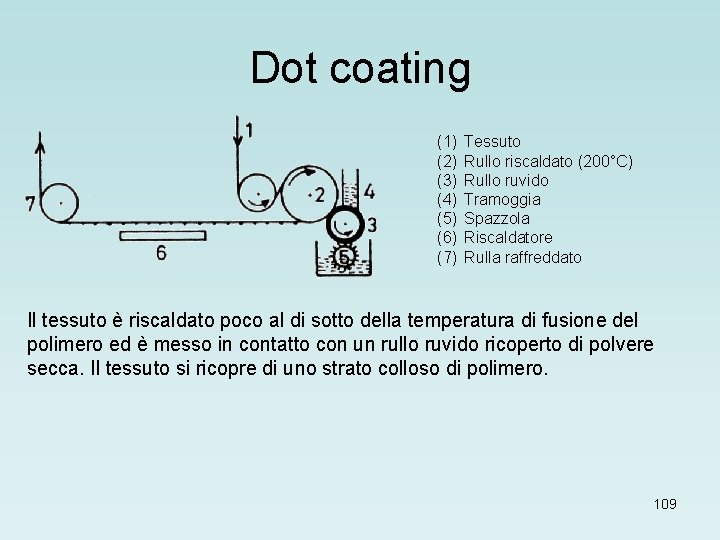
Dot coating (1) (2) (3) (4) (5) (6) (7) Tessuto Rullo riscaldato (200°C) Rullo ruvido Tramoggia Spazzola Riscaldatore Rulla raffreddato Il tessuto è riscaldato poco al di sotto della temperatura di fusione del polimero ed è messo in contatto con un rullo ruvido ricoperto di polvere secca. Il tessuto si ricopre di uno strato colloso di polimero. 109
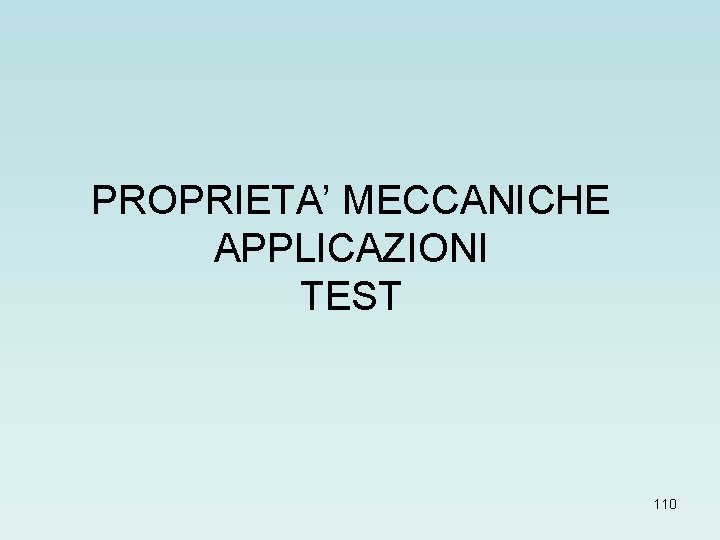
PROPRIETA’ MECCANICHE APPLICAZIONI TEST 110
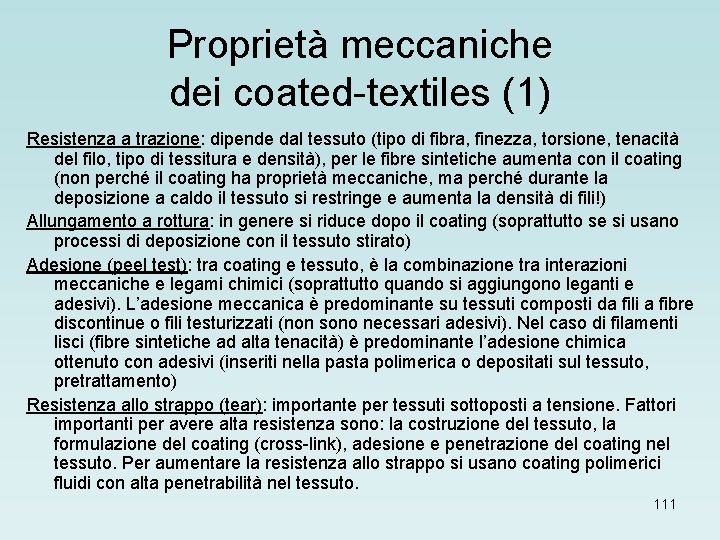
Proprietà meccaniche dei coated-textiles (1) Resistenza a trazione: dipende dal tessuto (tipo di fibra, finezza, torsione, tenacità del filo, tipo di tessitura e densità), per le fibre sintetiche aumenta con il coating (non perché il coating ha proprietà meccaniche, ma perché durante la deposizione a caldo il tessuto si restringe e aumenta la densità di fili!) Allungamento a rottura: in genere si riduce dopo il coating (soprattutto se si usano processi di deposizione con il tessuto stirato) Adesione (peel test): tra coating e tessuto, è la combinazione tra interazioni meccaniche e legami chimici (soprattutto quando si aggiungono leganti e adesivi). L’adesione meccanica è predominante su tessuti composti da fili a fibre discontinue o fili testurizzati (non sono necessari adesivi). Nel caso di filamenti lisci (fibre sintetiche ad alta tenacità) è predominante l’adesione chimica ottenuto con adesivi (inseriti nella pasta polimerica o depositati sul tessuto, pretrattamento) Resistenza allo strappo (tear): importante per tessuti sottoposti a tensione. Fattori importanti per avere alta resistenza sono: la costruzione del tessuto, la formulazione del coating (cross-link), adesione e penetrazione del coating nel tessuto. Per aumentare la resistenza allo strappo si usano coating polimerici fluidi con alta penetrabilità nel tessuto. 111
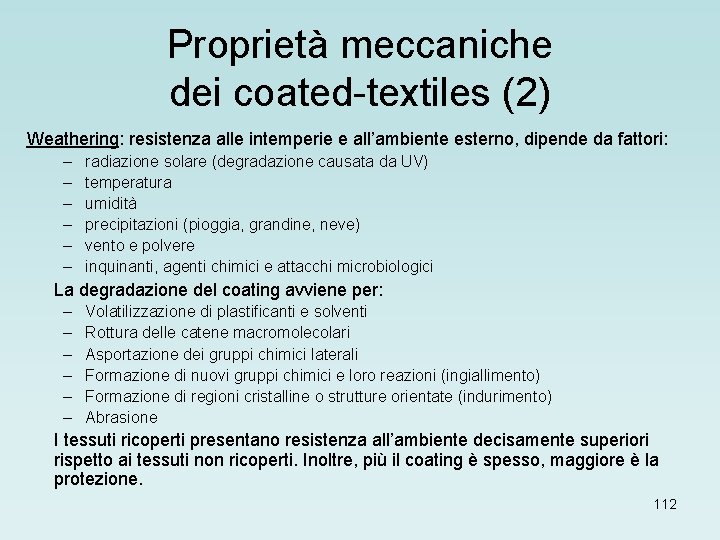
Proprietà meccaniche dei coated-textiles (2) Weathering: resistenza alle intemperie e all’ambiente esterno, dipende da fattori: – – – radiazione solare (degradazione causata da UV) temperatura umidità precipitazioni (pioggia, grandine, neve) vento e polvere inquinanti, agenti chimici e attacchi microbiologici La degradazione del coating avviene per: – – – Volatilizzazione di plastificanti e solventi Rottura delle catene macromolecolari Asportazione dei gruppi chimici laterali Formazione di nuovi gruppi chimici e loro reazioni (ingiallimento) Formazione di regioni cristalline o strutture orientate (indurimento) Abrasione I tessuti ricoperti presentano resistenza all’ambiente decisamente superiori rispetto ai tessuti non ricoperti. Inoltre, più il coating è spesso, maggiore è la protezione. 112
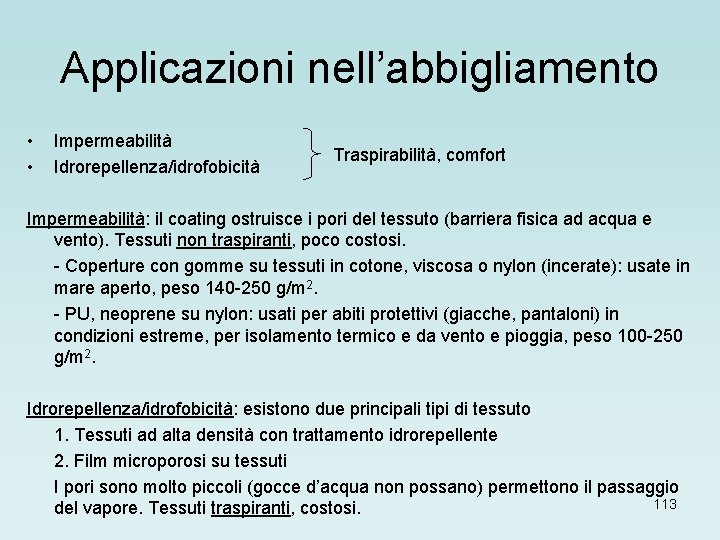
Applicazioni nell’abbigliamento • • Impermeabilità Idrorepellenza/idrofobicità Traspirabilità, comfort Impermeabilità: il coating ostruisce i pori del tessuto (barriera fisica ad acqua e vento). Tessuti non traspiranti, poco costosi. - Coperture con gomme su tessuti in cotone, viscosa o nylon (incerate): usate in mare aperto, peso 140 -250 g/m 2. - PU, neoprene su nylon: usati per abiti protettivi (giacche, pantaloni) in condizioni estreme, per isolamento termico e da vento e pioggia, peso 100 -250 g/m 2. Idrorepellenza/idrofobicità: esistono due principali tipi di tessuto 1. Tessuti ad alta densità con trattamento idrorepellente 2. Film microporosi su tessuti I pori sono molto piccoli (gocce d’acqua non possano) permettono il passaggio 113 del vapore. Tessuti traspiranti, costosi.
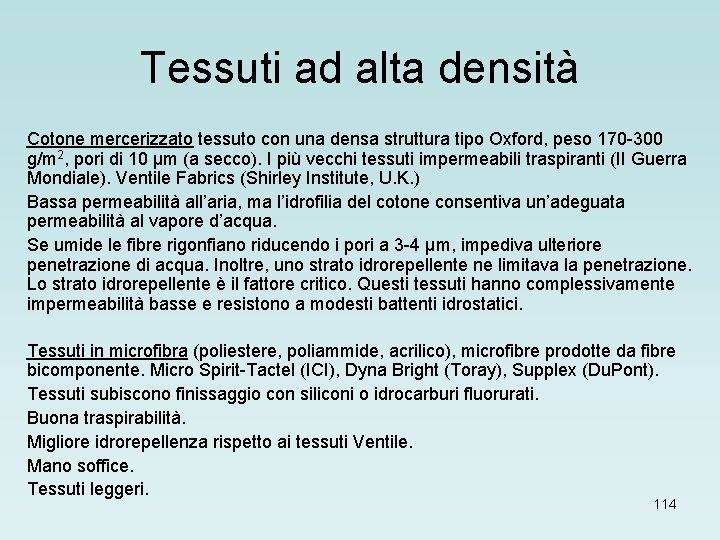
Tessuti ad alta densità Cotone mercerizzato tessuto con una densa struttura tipo Oxford, peso 170 -300 g/m 2, pori di 10 µm (a secco). I più vecchi tessuti impermeabili traspiranti (II Guerra Mondiale). Ventile Fabrics (Shirley Institute, U. K. ) Bassa permeabilità all’aria, ma l’idrofilia del cotone consentiva un’adeguata permeabilità al vapore d’acqua. Se umide le fibre rigonfiano riducendo i pori a 3 -4 µm, impediva ulteriore penetrazione di acqua. Inoltre, uno strato idrorepellente ne limitava la penetrazione. Lo strato idrorepellente è il fattore critico. Questi tessuti hanno complessivamente impermeabilità basse e resistono a modesti battenti idrostatici. Tessuti in microfibra (poliestere, poliammide, acrilico), microfibre prodotte da fibre bicomponente. Micro Spirit-Tactel (ICI), Dyna Bright (Toray), Supplex (Du. Pont). Tessuti subiscono finissaggio con siliconi o idrocarburi fluorurati. Buona traspirabilità. Migliore idrorepellenza rispetto ai tessuti Ventile. Mano soffice. Tessuti leggeri. 114
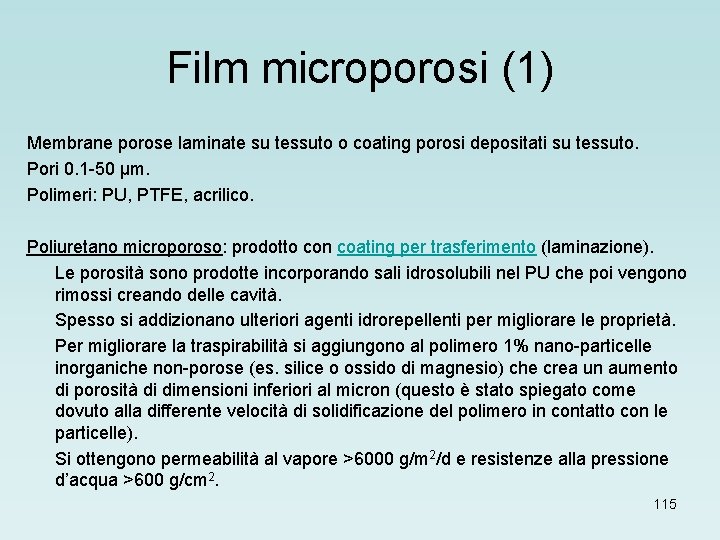
Film microporosi (1) Membrane porose laminate su tessuto o coating porosi depositati su tessuto. Pori 0. 1 -50 μm. Polimeri: PU, PTFE, acrilico. Poliuretano microporoso: prodotto con coating per trasferimento (laminazione). Le porosità sono prodotte incorporando sali idrosolubili nel PU che poi vengono rimossi creando delle cavità. Spesso si addizionano ulteriori agenti idrorepellenti per migliorare le proprietà. Per migliorare la traspirabilità si aggiungono al polimero 1% nano-particelle inorganiche non-porose (es. silice o ossido di magnesio) che crea un aumento di porosità di dimensioni inferiori al micron (questo è stato spiegato come dovuto alla differente velocità di solidificazione del polimero in contatto con le particelle). Si ottengono permeabilità al vapore >6000 g/m 2/d e resistenze alla pressione d’acqua >600 g/cm 2. 115
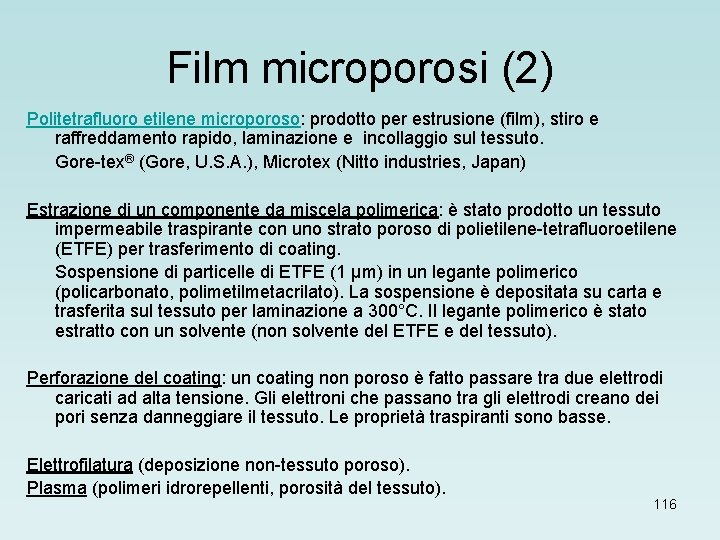
Film microporosi (2) Politetrafluoro etilene microporoso: prodotto per estrusione (film), stiro e raffreddamento rapido, laminazione e incollaggio sul tessuto. Gore-tex® (Gore, U. S. A. ), Microtex (Nitto industries, Japan) Estrazione di un componente da miscela polimerica: è stato prodotto un tessuto impermeabile traspirante con uno strato poroso di polietilene-tetrafluoroetilene (ETFE) per trasferimento di coating. Sospensione di particelle di ETFE (1 μm) in un legante polimerico (policarbonato, polimetilmetacrilato). La sospensione è depositata su carta e trasferita sul tessuto per laminazione a 300°C. Il legante polimerico è stato estratto con un solvente (non solvente del ETFE e del tessuto). Perforazione del coating: un coating non poroso è fatto passare tra due elettrodi caricati ad alta tensione. Gli elettroni che passano tra gli elettrodi creano dei pori senza danneggiare il tessuto. Le proprietà traspiranti sono basse. Elettrofilatura (deposizione non-tessuto poroso). Plasma (polimeri idrorepellenti, porosità del tessuto). 116

Applicazioni “non-apparel” • • • Cuoio sintetico Architectural textile Contenitori di fluidi Tarpaulins Tessuti per air-bag 117
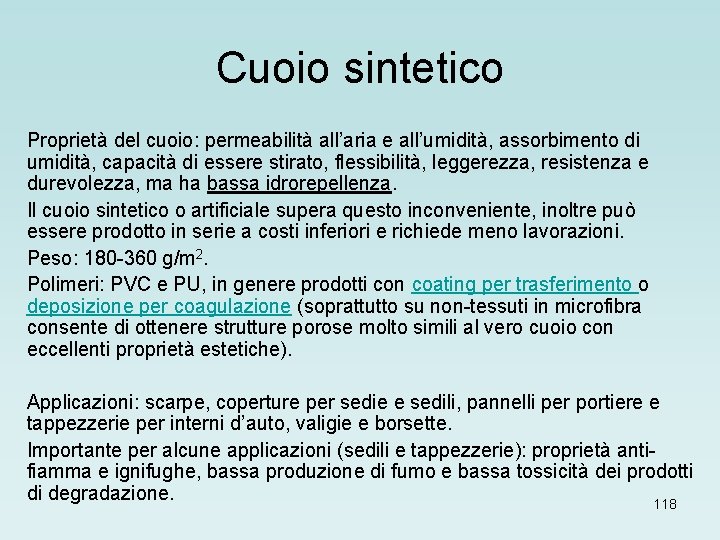
Cuoio sintetico Proprietà del cuoio: permeabilità all’aria e all’umidità, assorbimento di umidità, capacità di essere stirato, flessibilità, leggerezza, resistenza e durevolezza, ma ha bassa idrorepellenza. Il cuoio sintetico o artificiale supera questo inconveniente, inoltre può essere prodotto in serie a costi inferiori e richiede meno lavorazioni. Peso: 180 -360 g/m 2. Polimeri: PVC e PU, in genere prodotti con coating per trasferimento o deposizione per coagulazione (soprattutto su non-tessuti in microfibra consente di ottenere strutture porose molto simili al vero cuoio con eccellenti proprietà estetiche). Applicazioni: scarpe, coperture per sedie e sedili, pannelli per portiere e tappezzerie per interni d’auto, valigie e borsette. Importante per alcune applicazioni (sedili e tappezzerie): proprietà antifiamma e ignifughe, bassa produzione di fumo e bassa tossicità dei prodotti di degradazione. 118
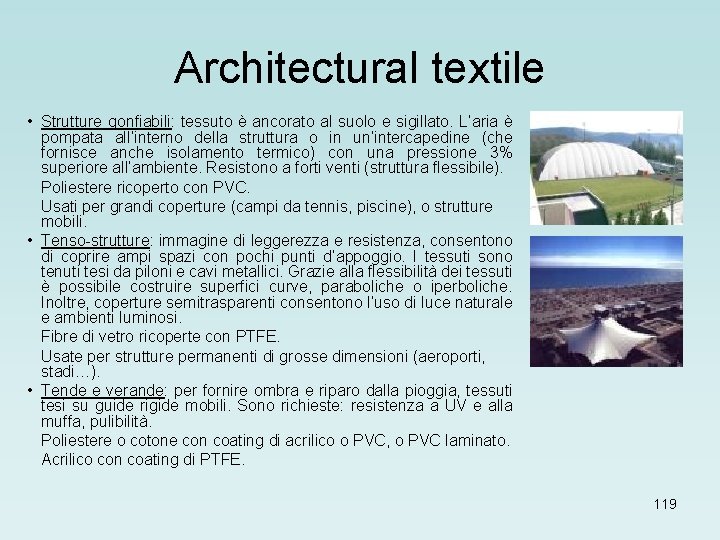
Architectural textile • Strutture gonfiabili: tessuto è ancorato al suolo e sigillato. L’aria è pompata all’interno della struttura o in un’intercapedine (che fornisce anche isolamento termico) con una pressione 3% superiore all’ambiente. Resistono a forti venti (struttura flessibile). Poliestere ricoperto con PVC. Usati per grandi coperture (campi da tennis, piscine), o strutture mobili. • Tenso-strutture: immagine di leggerezza e resistenza, consentono di coprire ampi spazi con pochi punti d’appoggio. I tessuti sono tenuti tesi da piloni e cavi metallici. Grazie alla flessibilità dei tessuti è possibile costruire superfici curve, paraboliche o iperboliche. Inoltre, coperture semitrasparenti consentono l’uso di luce naturale e ambienti luminosi. Fibre di vetro ricoperte con PTFE. Usate per strutture permanenti di grosse dimensioni (aeroporti, stadi…). • Tende e verande: per fornire ombra e riparo dalla pioggia, tessuti tesi su guide rigide mobili. Sono richieste: resistenza a UV e alla muffa, pulibilità. Poliestere o cotone con coating di acrilico o PVC, o PVC laminato. Acrilico con coating di PTFE. 119
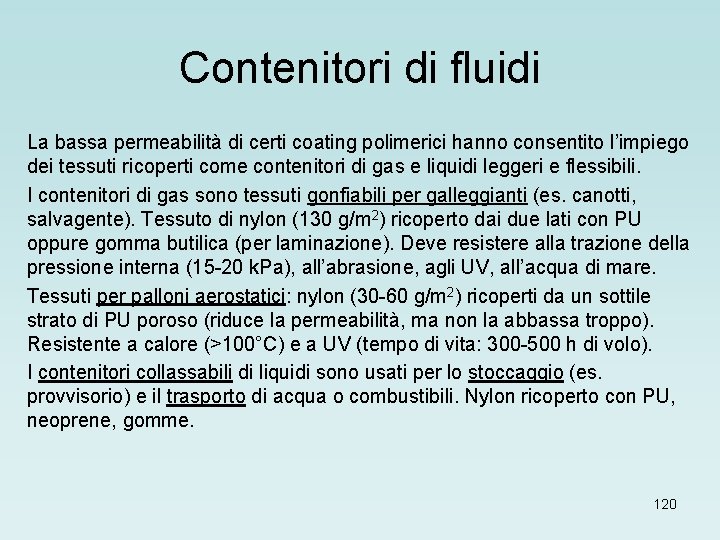
Contenitori di fluidi La bassa permeabilità di certi coating polimerici hanno consentito l’impiego dei tessuti ricoperti come contenitori di gas e liquidi leggeri e flessibili. I contenitori di gas sono tessuti gonfiabili per galleggianti (es. canotti, salvagente). Tessuto di nylon (130 g/m 2) ricoperto dai due lati con PU oppure gomma butilica (per laminazione). Deve resistere alla trazione della pressione interna (15 -20 k. Pa), all’abrasione, agli UV, all’acqua di mare. Tessuti per palloni aerostatici: nylon (30 -60 g/m 2) ricoperti da un sottile strato di PU poroso (riduce la permeabilità, ma non la abbassa troppo). Resistente a calore (>100°C) e a UV (tempo di vita: 300 -500 h di volo). I contenitori collassabili di liquidi sono usati per lo stoccaggio (es. provvisorio) e il trasporto di acqua o combustibili. Nylon ricoperto con PU, neoprene, gomme. 120
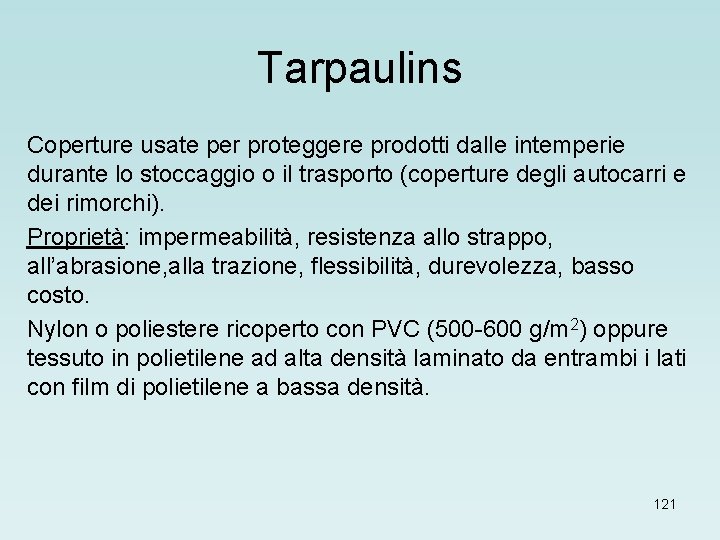
Tarpaulins Coperture usate per proteggere prodotti dalle intemperie durante lo stoccaggio o il trasporto (coperture degli autocarri e dei rimorchi). Proprietà: impermeabilità, resistenza allo strappo, all’abrasione, alla trazione, flessibilità, durevolezza, basso costo. Nylon o poliestere ricoperto con PVC (500 -600 g/m 2) oppure tessuto in polietilene ad alta densità laminato da entrambi i lati con film di polietilene a bassa densità. 121

Tessuti per air-bag Tessuti in nylon 6, 6 grazie all’alto rapporto peso-forza, sono preferiti al poliestere per il più alto allungamento. I tessuti sono ricoperti con un coating elastomerico (neoprene, gomme siliconiche) per proteggere il tessuto dal calore e dall’abrasione dei gas caldi. Inoltre, il coating sigilla i pori del tessuto e consente un controllo preciso del gonfiamento dell’air-bag. Proprietà: anti-autoincollaggio (talco), resistenza a trazione e a strappo, flessibilità dopo ciclici cambiamenti di temperatura (da -10 a 120°C), superficie liscia (non deve causare abrasioni), leggerezza (200 g/m 2) e impaccamento. Produzione: 50 -75 milioni di m 2. 122
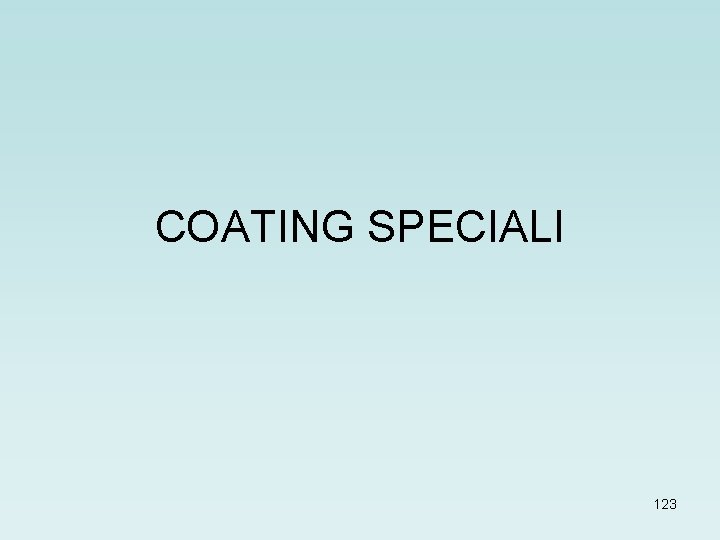
COATING SPECIALI 123
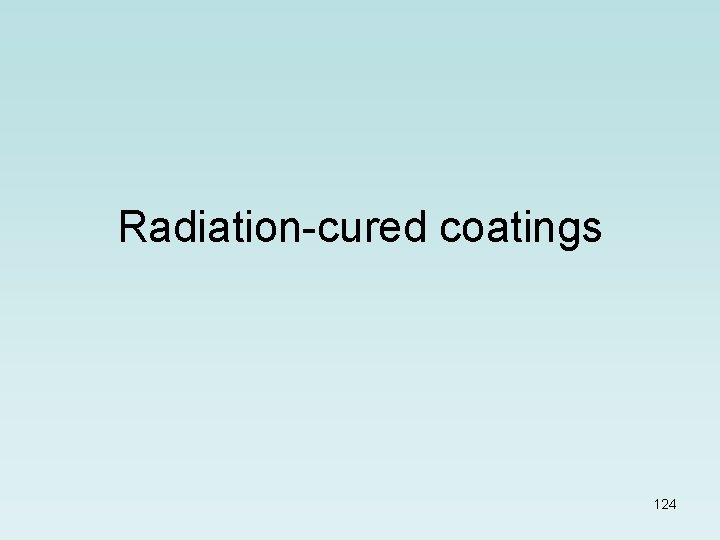
Radiation-cured coatings 124
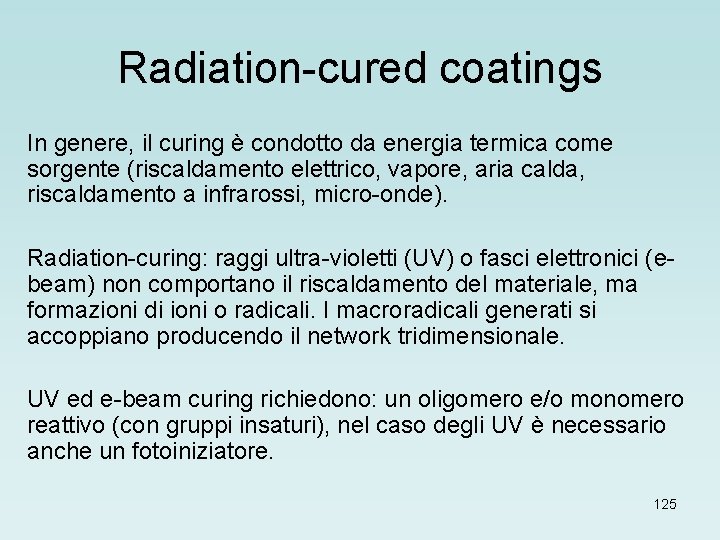
Radiation-cured coatings In genere, il curing è condotto da energia termica come sorgente (riscaldamento elettrico, vapore, aria calda, riscaldamento a infrarossi, micro-onde). Radiation-curing: raggi ultra-violetti (UV) o fasci elettronici (ebeam) non comportano il riscaldamento del materiale, ma formazioni di ioni o radicali. I macroradicali generati si accoppiano producendo il network tridimensionale. UV ed e-beam curing richiedono: un oligomero e/o monomero reattivo (con gruppi insaturi), nel caso degli UV è necessario anche un fotoiniziatore. 125
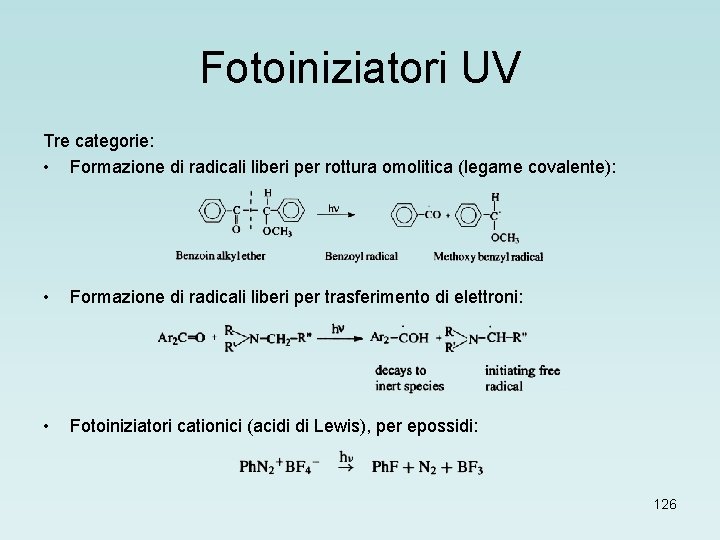
Fotoiniziatori UV Tre categorie: • Formazione di radicali liberi per rottura omolitica (legame covalente): • Formazione di radicali liberi per trasferimento di elettroni: • Fotoiniziatori cationici (acidi di Lewis), per epossidi: 126
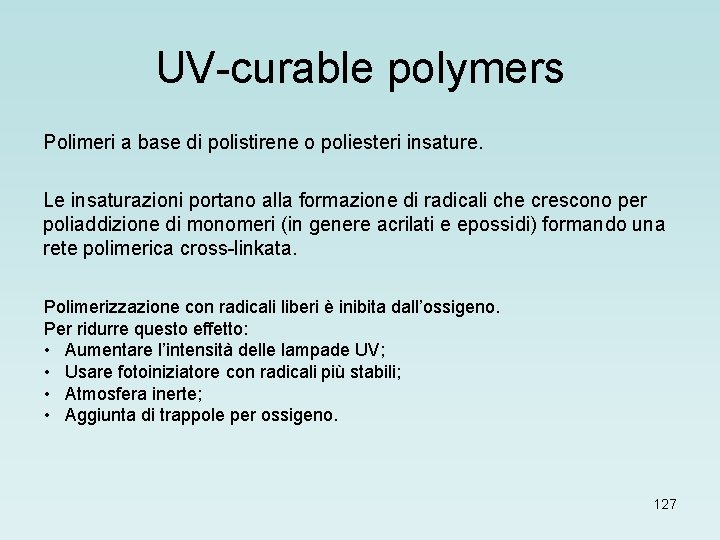
UV-curable polymers Polimeri a base di polistirene o poliesteri insature. Le insaturazioni portano alla formazione di radicali che crescono per poliaddizione di monomeri (in genere acrilati e epossidi) formando una rete polimerica cross-linkata. Polimerizzazione con radicali liberi è inibita dall’ossigeno. Per ridurre questo effetto: • Aumentare l’intensità delle lampade UV; • Usare fotoiniziatore con radicali più stabili; • Atmosfera inerte; • Aggiunta di trappole per ossigeno. 127
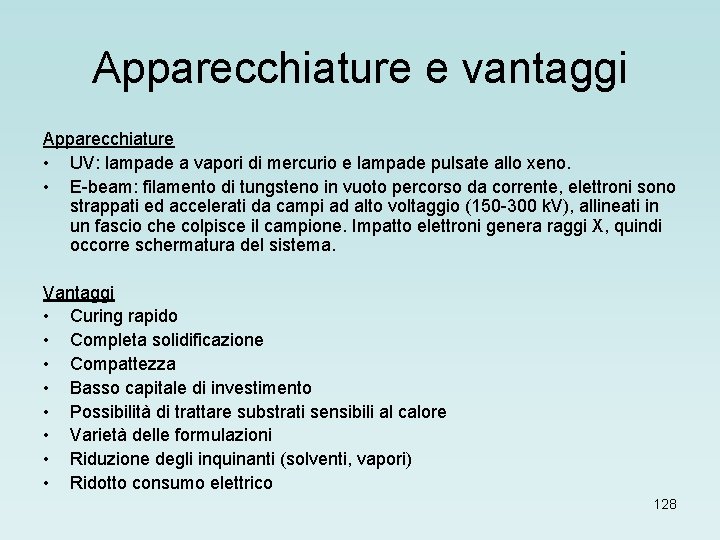
Apparecchiature e vantaggi Apparecchiature • UV: lampade a vapori di mercurio e lampade pulsate allo xeno. • E-beam: filamento di tungsteno in vuoto percorso da corrente, elettroni sono strappati ed accelerati da campi ad alto voltaggio (150 -300 k. V), allineati in un fascio che colpisce il campione. Impatto elettroni genera raggi X, quindi occorre schermatura del sistema. Vantaggi • Curing rapido • Completa solidificazione • Compattezza • Basso capitale di investimento • Possibilità di trattare substrati sensibili al calore • Varietà delle formulazioni • Riduzione degli inquinanti (solventi, vapori) • Ridotto consumo elettrico 128
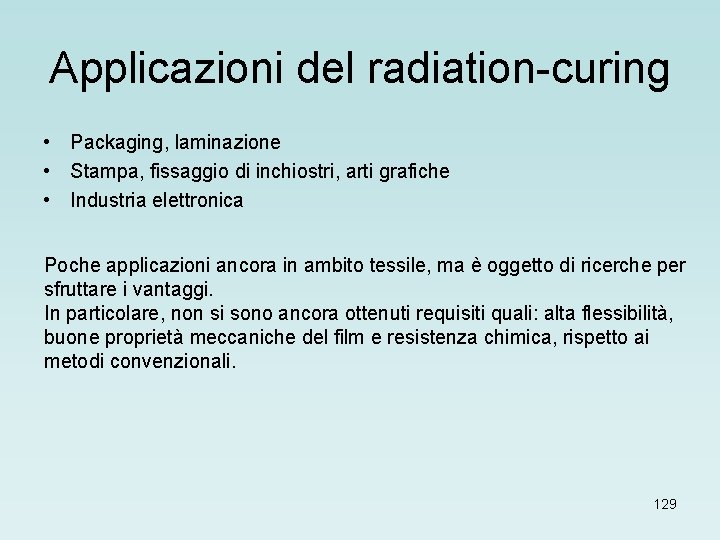
Applicazioni del radiation-curing • Packaging, laminazione • Stampa, fissaggio di inchiostri, arti grafiche • Industria elettronica Poche applicazioni ancora in ambito tessile, ma è oggetto di ricerche per sfruttare i vantaggi. In particolare, non si sono ancora ottenuti requisiti quali: alta flessibilità, buone proprietà meccaniche del film e resistenza chimica, rispetto ai metodi convenzionali. 129
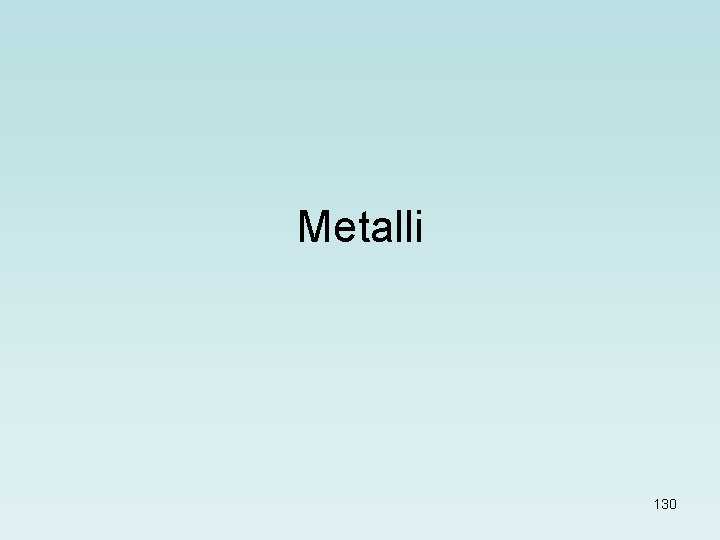
Metalli 130
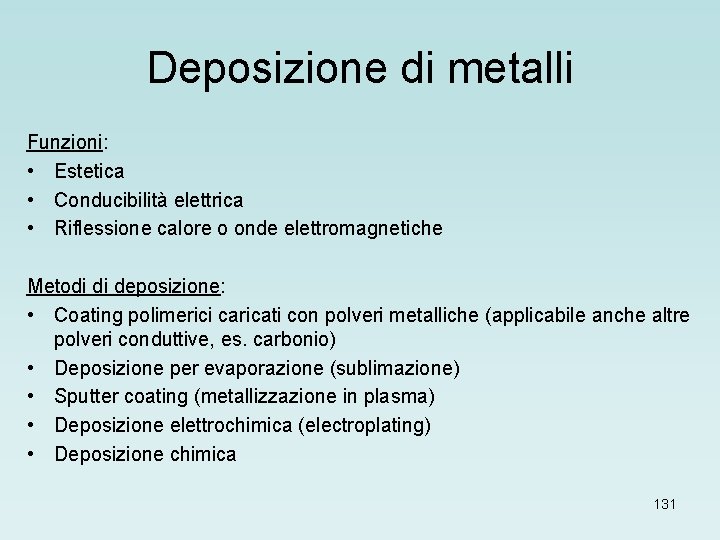
Deposizione di metalli Funzioni: • Estetica • Conducibilità elettrica • Riflessione calore o onde elettromagnetiche Metodi di deposizione: • Coating polimerici caricati con polveri metalliche (applicabile anche altre polveri conduttive, es. carbonio) • Deposizione per evaporazione (sublimazione) • Sputter coating (metallizzazione in plasma) • Deposizione elettrochimica (electroplating) • Deposizione chimica 131
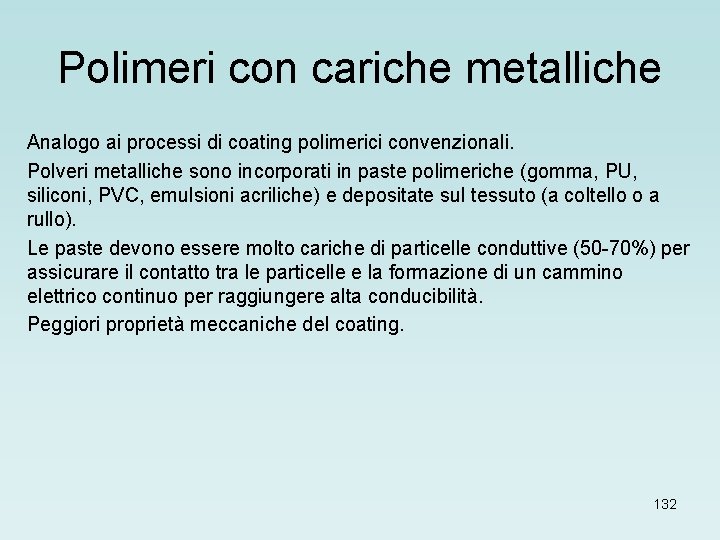
Polimeri con cariche metalliche Analogo ai processi di coating polimerici convenzionali. Polveri metalliche sono incorporati in paste polimeriche (gomma, PU, siliconi, PVC, emulsioni acriliche) e depositate sul tessuto (a coltello o a rullo). Le paste devono essere molto cariche di particelle conduttive (50 -70%) per assicurare il contatto tra le particelle e la formazione di un cammino elettrico continuo per raggiungere alta conducibilità. Peggiori proprietà meccaniche del coating. 132
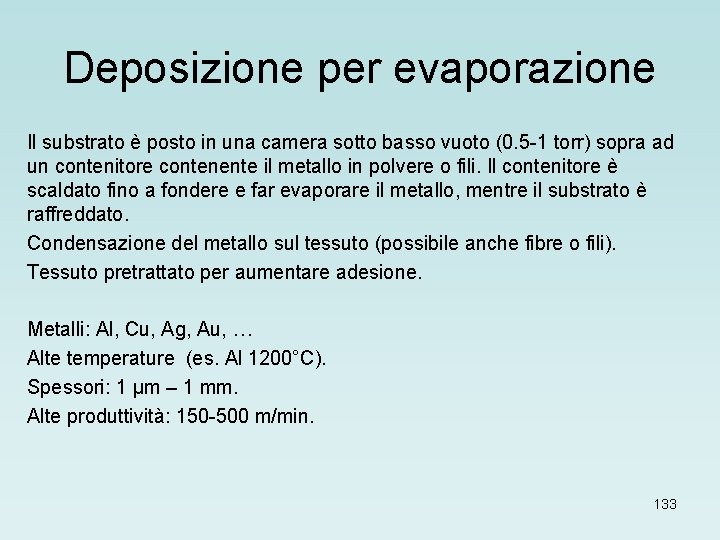
Deposizione per evaporazione Il substrato è posto in una camera sotto basso vuoto (0. 5 -1 torr) sopra ad un contenitore contenente il metallo in polvere o fili. Il contenitore è scaldato fino a fondere e far evaporare il metallo, mentre il substrato è raffreddato. Condensazione del metallo sul tessuto (possibile anche fibre o fili). Tessuto pretrattato per aumentare adesione. Metalli: Al, Cu, Ag, Au, … Alte temperature (es. Al 1200°C). Spessori: 1 μm – 1 mm. Alte produttività: 150 -500 m/min. 133
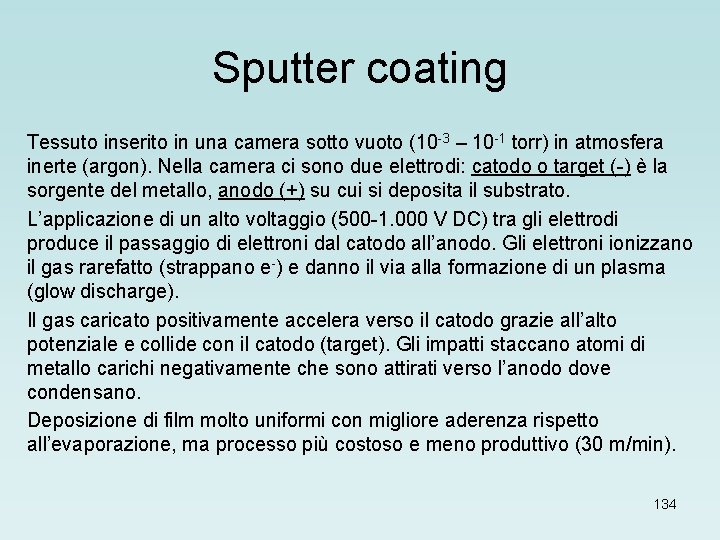
Sputter coating Tessuto inserito in una camera sotto vuoto (10 -3 – 10 -1 torr) in atmosfera inerte (argon). Nella camera ci sono due elettrodi: catodo o target (-) è la sorgente del metallo, anodo (+) su cui si deposita il substrato. L’applicazione di un alto voltaggio (500 -1. 000 V DC) tra gli elettrodi produce il passaggio di elettroni dal catodo all’anodo. Gli elettroni ionizzano il gas rarefatto (strappano e-) e danno il via alla formazione di un plasma (glow discharge). Il gas caricato positivamente accelera verso il catodo grazie all’alto potenziale e collide con il catodo (target). Gli impatti staccano atomi di metallo carichi negativamente che sono attirati verso l’anodo dove condensano. Deposizione di film molto uniformi con migliore aderenza rispetto all’evaporazione, ma processo più costoso e meno produttivo (30 m/min). 134
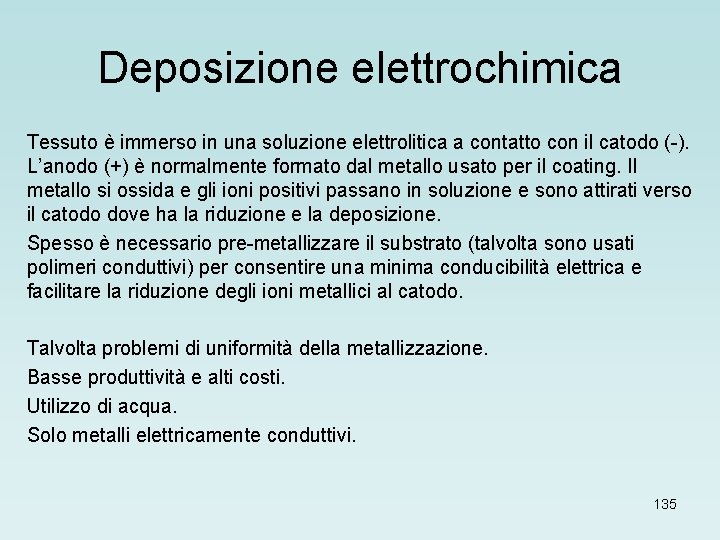
Deposizione elettrochimica Tessuto è immerso in una soluzione elettrolitica a contatto con il catodo (-). L’anodo (+) è normalmente formato dal metallo usato per il coating. Il metallo si ossida e gli ioni positivi passano in soluzione e sono attirati verso il catodo dove ha la riduzione e la deposizione. Spesso è necessario pre-metallizzare il substrato (talvolta sono usati polimeri conduttivi) per consentire una minima conducibilità elettrica e facilitare la riduzione degli ioni metallici al catodo. Talvolta problemi di uniformità della metallizzazione. Basse produttività e alti costi. Utilizzo di acqua. Solo metalli elettricamente conduttivi. 135
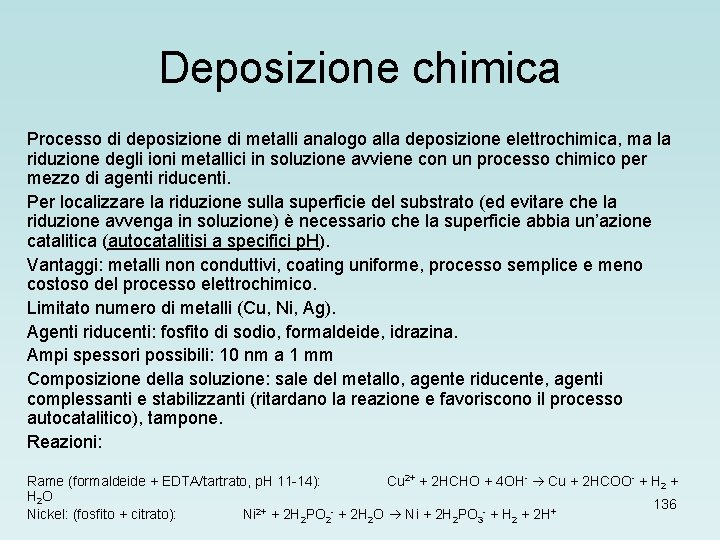
Deposizione chimica Processo di deposizione di metalli analogo alla deposizione elettrochimica, ma la riduzione degli ioni metallici in soluzione avviene con un processo chimico per mezzo di agenti riducenti. Per localizzare la riduzione sulla superficie del substrato (ed evitare che la riduzione avvenga in soluzione) è necessario che la superficie abbia un’azione catalitica (autocatalitisi a specifici p. H). Vantaggi: metalli non conduttivi, coating uniforme, processo semplice e meno costoso del processo elettrochimico. Limitato numero di metalli (Cu, Ni, Ag). Agenti riducenti: fosfito di sodio, formaldeide, idrazina. Ampi spessori possibili: 10 nm a 1 mm Composizione della soluzione: sale del metallo, agente riducente, agenti complessanti e stabilizzanti (ritardano la reazione e favoriscono il processo autocatalitico), tampone. Reazioni: Rame (formaldeide + EDTA/tartrato, p. H 11 -14): Cu 2+ + 2 HCHO + 4 OH- Cu + 2 HCOO- + H 2 O 136 Nickel: (fosfito + citrato): Ni 2+ + 2 H 2 PO 2 - + 2 H 2 O Ni + 2 H 2 PO 3 - + H 2 + 2 H+
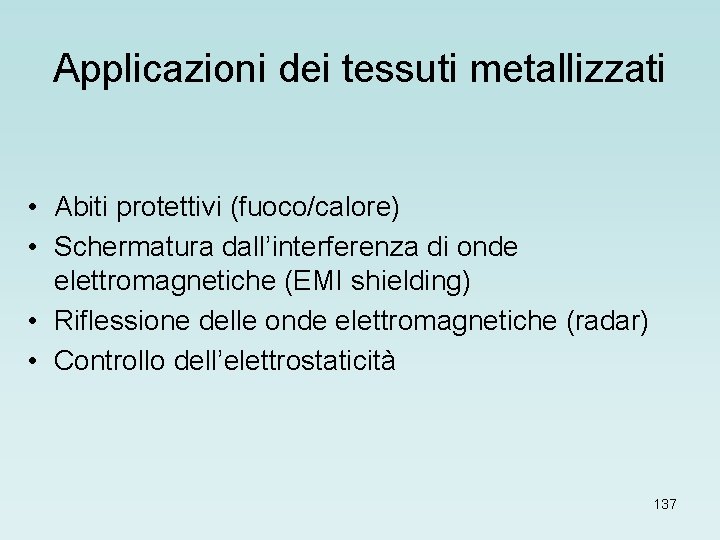
Applicazioni dei tessuti metallizzati • Abiti protettivi (fuoco/calore) • Schermatura dall’interferenza di onde elettromagnetiche (EMI shielding) • Riflessione delle onde elettromagnetiche (radar) • Controllo dell’elettrostaticità 137
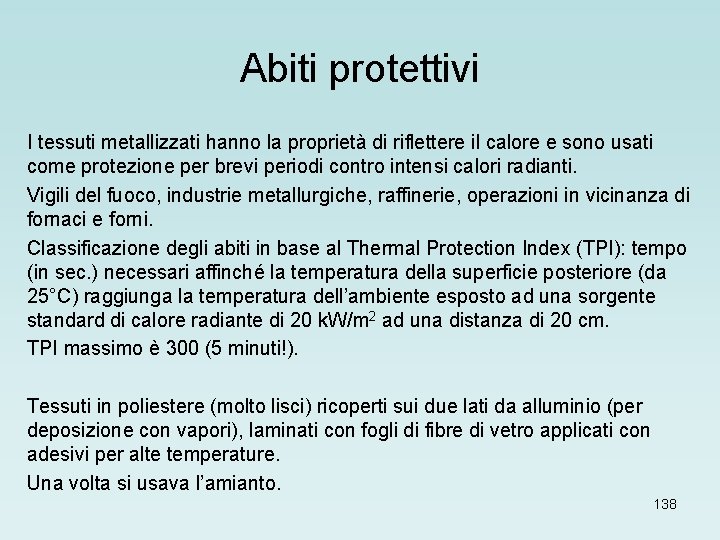
Abiti protettivi I tessuti metallizzati hanno la proprietà di riflettere il calore e sono usati come protezione per brevi periodi contro intensi calori radianti. Vigili del fuoco, industrie metallurgiche, raffinerie, operazioni in vicinanza di fornaci e forni. Classificazione degli abiti in base al Thermal Protection Index (TPI): tempo (in sec. ) necessari affinché la temperatura della superficie posteriore (da 25°C) raggiunga la temperatura dell’ambiente esposto ad una sorgente standard di calore radiante di 20 k. W/m 2 ad una distanza di 20 cm. TPI massimo è 300 (5 minuti!). Tessuti in poliestere (molto lisci) ricoperti sui due lati da alluminio (per deposizione con vapori), laminati con fogli di fibre di vetro applicati con adesivi per alte temperature. Una volta si usava l’amianto. 138
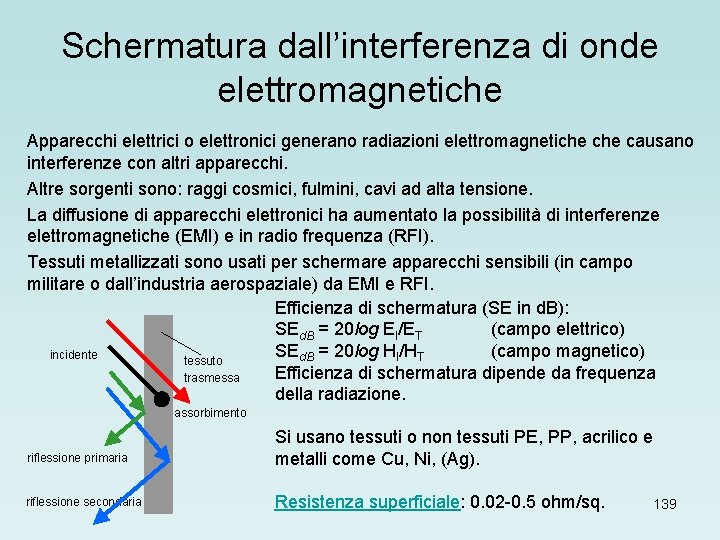
Schermatura dall’interferenza di onde elettromagnetiche Apparecchi elettrici o elettronici generano radiazioni elettromagnetiche causano interferenze con altri apparecchi. Altre sorgenti sono: raggi cosmici, fulmini, cavi ad alta tensione. La diffusione di apparecchi elettronici ha aumentato la possibilità di interferenze elettromagnetiche (EMI) e in radio frequenza (RFI). Tessuti metallizzati sono usati per schermare apparecchi sensibili (in campo militare o dall’industria aerospaziale) da EMI e RFI. Efficienza di schermatura (SE in d. B): SEd. B = 20 log EI/ET (campo elettrico) SEd. B = 20 log HI/HT (campo magnetico) incidente tessuto Efficienza di schermatura dipende da frequenza trasmessa della radiazione. assorbimento riflessione primaria Si usano tessuti o non tessuti PE, PP, acrilico e metalli come Cu, Ni, (Ag). riflessione secondaria Resistenza superficiale: 0. 02 -0. 5 ohm/sq. 139
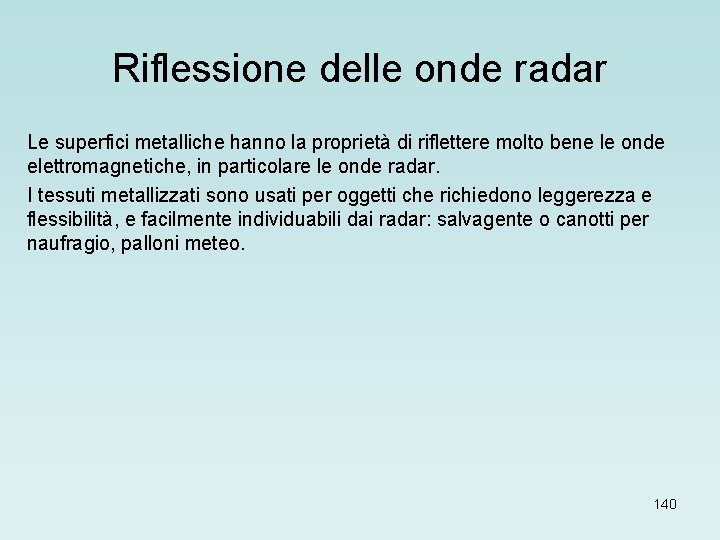
Riflessione delle onde radar Le superfici metalliche hanno la proprietà di riflettere molto bene le onde elettromagnetiche, in particolare le onde radar. I tessuti metallizzati sono usati per oggetti che richiedono leggerezza e flessibilità, e facilmente individuabili dai radar: salvagente o canotti per naufragio, palloni meteo. 140

Controllo dell’elettrostaticità Electrostatic discharge (ESD) protection Lo sfregamento tra superfici non conduttive (o il passaggio di gas secchi) provoca il trasferimento di elettroni da un corpo all’altro e la generazione di cariche elettriche statiche ad alto voltaggio (>3000 V). Campo industriale (passaggio di gas attraverso tubi di gomma, filtri tessili in presenza di vapori, sfregamento di polveri): pericolo di esplosioni per generazioni di scintille, danni a circuiti elettrici, accumulo di polveri. Campo civile (camminare su tappeti, sfregamento di abiti): scosse elettriche (fastidio), danni ad apparecchi elettronici, accumulo di polveri. Resistenza tessuti convenzionali: 1013 ohm/sq. Resistenza tessuti antistatici: 103 -1010 ohm/sq. Alte conducibilità ottenute con coating di metalli o polimeri elettroconduttivi oppure incorporando fibre conduttive (fibre di carbonio o metalliche) rigidezza e comfort. Basse conducibilità sono ottenibili con finissaggi che aumentano l’igroscopia (assorbimento di umidità dall’ambiente): esteri di acido fosforico, sali d’ammonio quaternario. 141
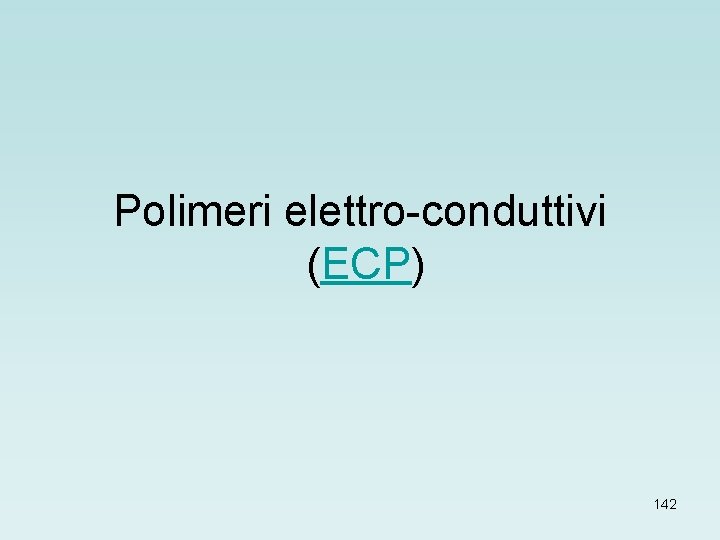
Polimeri elettro-conduttivi (ECP) 142
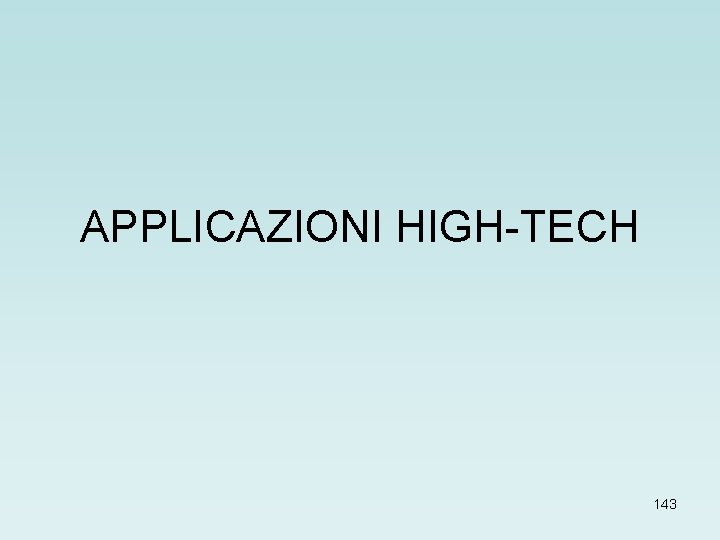
APPLICAZIONI HIGH-TECH 143
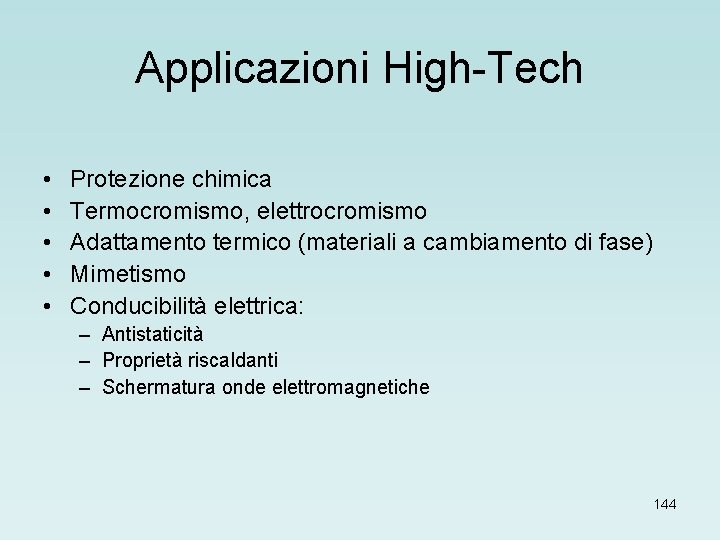
Applicazioni High-Tech • • • Protezione chimica Termocromismo, elettrocromismo Adattamento termico (materiali a cambiamento di fase) Mimetismo Conducibilità elettrica: – Antistaticità – Proprietà riscaldanti – Schermatura onde elettromagnetiche 144
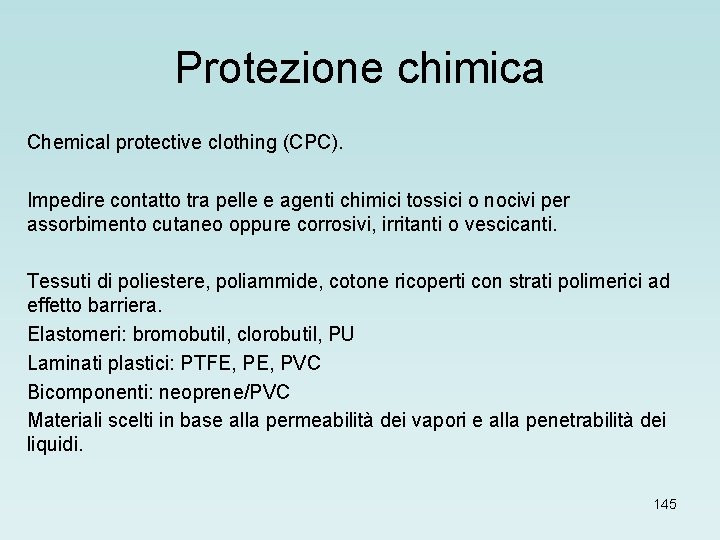
Protezione chimica Chemical protective clothing (CPC). Impedire contatto tra pelle e agenti chimici tossici o nocivi per assorbimento cutaneo oppure corrosivi, irritanti o vescicanti. Tessuti di poliestere, poliammide, cotone ricoperti con strati polimerici ad effetto barriera. Elastomeri: bromobutil, clorobutil, PU Laminati plastici: PTFE, PVC Bicomponenti: neoprene/PVC Materiali scelti in base alla permeabilità dei vapori e alla penetrabilità dei liquidi. 145
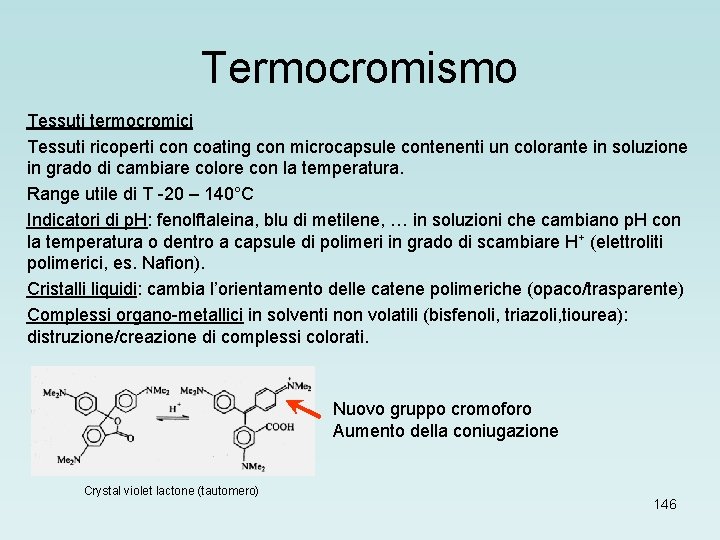
Termocromismo Tessuti termocromici Tessuti ricoperti con coating con microcapsule contenenti un colorante in soluzione in grado di cambiare colore con la temperatura. Range utile di T -20 – 140°C Indicatori di p. H: fenolftaleina, blu di metilene, … in soluzioni che cambiano p. H con la temperatura o dentro a capsule di polimeri in grado di scambiare H+ (elettroliti polimerici, es. Nafion). Cristalli liquidi: cambia l’orientamento delle catene polimeriche (opaco/trasparente) Complessi organo-metallici in solventi non volatili (bisfenoli, triazoli, tiourea): distruzione/creazione di complessi colorati. Nuovo gruppo cromoforo Aumento della coniugazione Crystal violet lactone (tautomero) 146
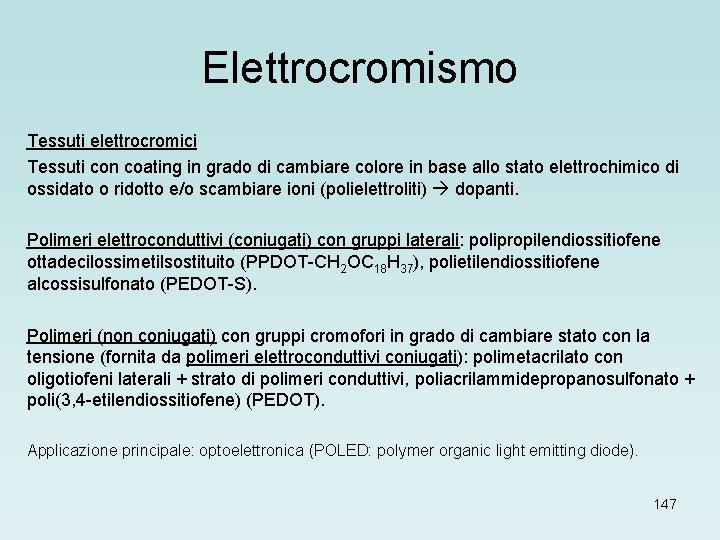
Elettrocromismo Tessuti elettrocromici Tessuti con coating in grado di cambiare colore in base allo stato elettrochimico di ossidato o ridotto e/o scambiare ioni (polielettroliti) dopanti. Polimeri elettroconduttivi (coniugati) con gruppi laterali: polipropilendiossitiofene ottadecilossimetilsostituito (PPDOT-CH 2 OC 18 H 37), polietilendiossitiofene alcossisulfonato (PEDOT-S). Polimeri (non coniugati) con gruppi cromofori in grado di cambiare stato con la tensione (fornita da polimeri elettroconduttivi coniugati): polimetacrilato con oligotiofeni laterali + strato di polimeri conduttivi, poliacrilammidepropanosulfonato + poli(3, 4 -etilendiossitiofene) (PEDOT). Applicazione principale: optoelettronica (POLED: polymer organic light emitting diode). 147
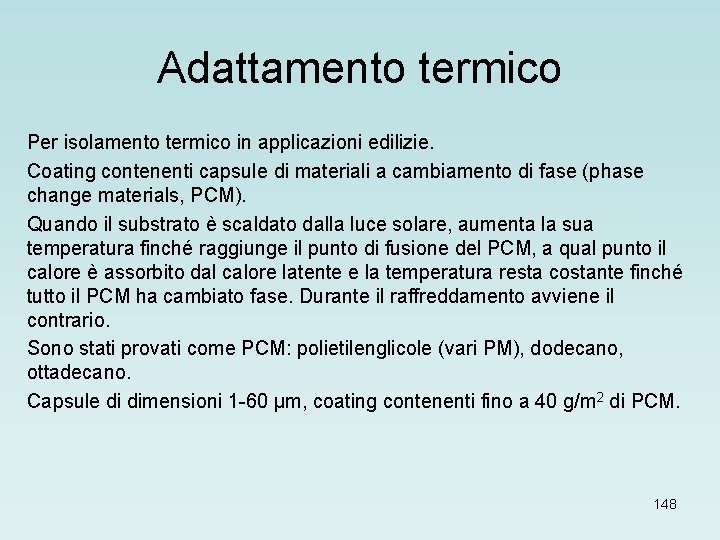
Adattamento termico Per isolamento termico in applicazioni edilizie. Coating contenenti capsule di materiali a cambiamento di fase (phase change materials, PCM). Quando il substrato è scaldato dalla luce solare, aumenta la sua temperatura finché raggiunge il punto di fusione del PCM, a qual punto il calore è assorbito dal calore latente e la temperatura resta costante finché tutto il PCM ha cambiato fase. Durante il raffreddamento avviene il contrario. Sono stati provati come PCM: polietilenglicole (vari PM), dodecano, ottadecano. Capsule di dimensioni 1 -60 μm, coating contenenti fino a 40 g/m 2 di PCM. 148
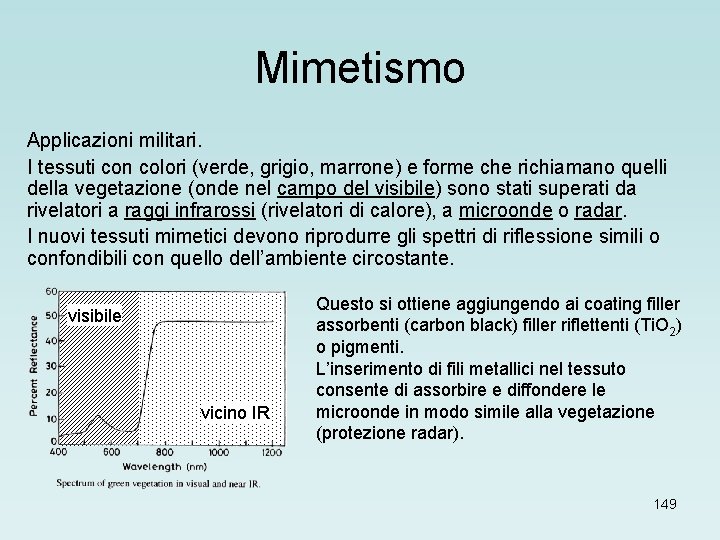
Mimetismo Applicazioni militari. I tessuti con colori (verde, grigio, marrone) e forme che richiamano quelli della vegetazione (onde nel campo del visibile) sono stati superati da rivelatori a raggi infrarossi (rivelatori di calore), a microonde o radar. I nuovi tessuti mimetici devono riprodurre gli spettri di riflessione simili o confondibili con quello dell’ambiente circostante. visibile vicino IR Questo si ottiene aggiungendo ai coating filler assorbenti (carbon black) filler riflettenti (Ti. O 2) o pigmenti. L’inserimento di fili metallici nel tessuto consente di assorbire e diffondere le microonde in modo simile alla vegetazione (protezione radar). 149
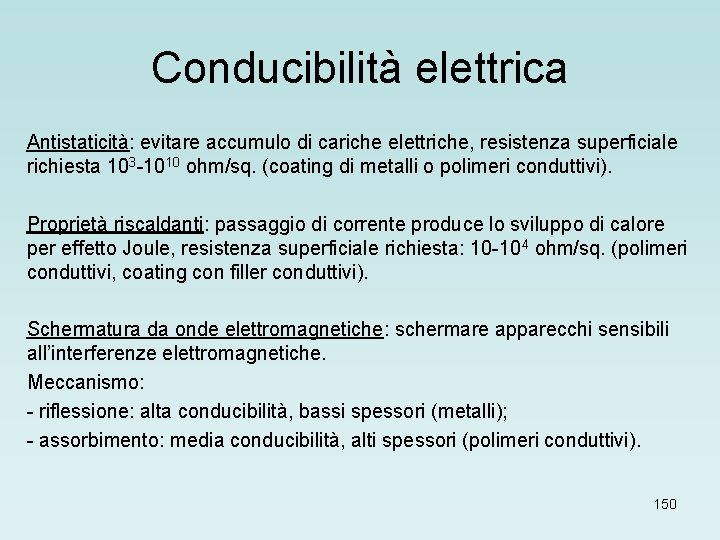
Conducibilità elettrica Antistaticità: evitare accumulo di cariche elettriche, resistenza superficiale richiesta 103 -1010 ohm/sq. (coating di metalli o polimeri conduttivi). Proprietà riscaldanti: passaggio di corrente produce lo sviluppo di calore per effetto Joule, resistenza superficiale richiesta: 10 -104 ohm/sq. (polimeri conduttivi, coating con filler conduttivi). Schermatura da onde elettromagnetiche: schermare apparecchi sensibili all’interferenze elettromagnetiche. Meccanismo: - riflessione: alta conducibilità, bassi spessori (metalli); - assorbimento: media conducibilità, alti spessori (polimeri conduttivi). 150
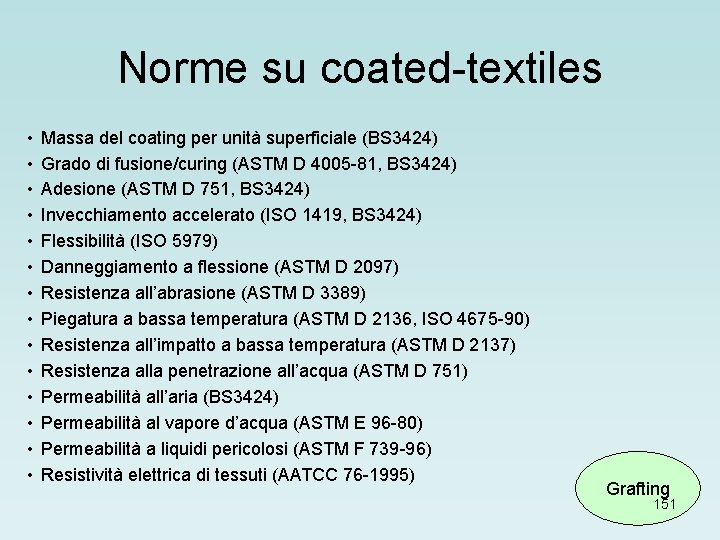
Norme su coated-textiles • • • • Massa del coating per unità superficiale (BS 3424) Grado di fusione/curing (ASTM D 4005 -81, BS 3424) Adesione (ASTM D 751, BS 3424) Invecchiamento accelerato (ISO 1419, BS 3424) Flessibilità (ISO 5979) Danneggiamento a flessione (ASTM D 2097) Resistenza all’abrasione (ASTM D 3389) Piegatura a bassa temperatura (ASTM D 2136, ISO 4675 -90) Resistenza all’impatto a bassa temperatura (ASTM D 2137) Resistenza alla penetrazione all’acqua (ASTM D 751) Permeabilità all’aria (BS 3424) Permeabilità al vapore d’acqua (ASTM E 96 -80) Permeabilità a liquidi pericolosi (ASTM F 739 -96) Resistività elettrica di tessuti (AATCC 76 -1995) Grafting 151
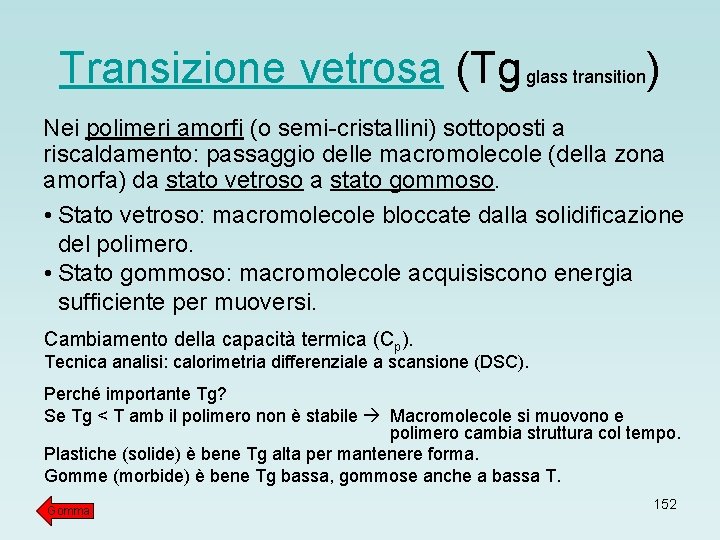
Transizione vetrosa (Tg glass transition) Nei polimeri amorfi (o semi-cristallini) sottoposti a riscaldamento: passaggio delle macromolecole (della zona amorfa) da stato vetroso a stato gommoso. • Stato vetroso: macromolecole bloccate dalla solidificazione del polimero. • Stato gommoso: macromolecole acquisiscono energia sufficiente per muoversi. Cambiamento della capacità termica (Cp). Tecnica analisi: calorimetria differenziale a scansione (DSC). Perché importante Tg? Se Tg < T amb il polimero non è stabile Macromolecole si muovono e polimero cambia struttura col tempo. Plastiche (solide) è bene Tg alta per mantenere forma. Gomme (morbide) è bene Tg bassa, gommose anche a bassa T. Gomma 152
![Resistenza superficiale RS RS ohmsquare Elettrodi concentrici RS 2 73 R log Resistenza superficiale (RS) RS = [ohm/square] Elettrodi concentrici: RS = 2. 73 R log](https://slidetodoc.com/presentation_image_h/fc1702f15e1df2157e92fcaac0f6b1b6/image-153.jpg)
Resistenza superficiale (RS) RS = [ohm/square] Elettrodi concentrici: RS = 2. 73 R log r 0/r 1 r 0 square o sq. o □ è adimensionale (m/m) Elettrodi paralleli: RS = R L/D R: resistenza misurata D: distanza elettrodi L: larghezza campione L D EMI 153
Le fibre tessili mappa concettuale
Materiali conduttori e isolanti
Fibre tessili artificiali
Tessuti del dente
Collenchima
Ciclo glucosio alanina
Tessuto
Modulo elastico materiali
Materiali da costruzione naturali
Artefatti materiali
Schema rendiconto finanziario metodo indiretto
Materiali ceramici tradizionali
Viedie materiāli
Dimensioni embrici
La classificazione dei materiali
Dalla materia prima al prodotto finito scuola primaria
Forza di lorentz zanichelli
Ingegneria dei materiali
Materiali ceramici tradizionali
Materiali biomimetici
Solida
Dinamica dei sistemi di punti materiali
Oggetti fatti con materiali naturali
Spinte metallostatiche
I materiali più leggeri della terra solida si trovano
Tabella dosaggio calcestruzzo
Fendibilità dei materiali
Hera modena
Callister scienza e ingegneria dei materiali
Prove meccaniche sui metalli
Automated spray coating systems
Apex metal oxide coating
Edible coating definition
Plural component pump
Naval coating
Pvd cvd coating
Architectural metal coating
Lithography
Color software
Coating application specialist
Sarah coating
Powder coating kildare
Dursan coating
Conformal coating standards
Abu dhabi coating enterprises
Opaquant meaning
Optical coating stress
Advantages of enteric coating
Balinit futura nano coating
Air suspension technique slideshare
Bfb boiler coating
Fluoroethylene vinyl ether resins
Coating plasma innovation
Cold feed extruder
Which part of the neuron serves as the protective coating?
Define enteric coated tablet
Ivd coating wiki
Stripe
Photoresist coating
Spraylat copper conductive coating
Davenport powder coating oven
Plastic coated u bolts
J&c powder coating
Zinc coating analysis
Brandvertragende verf hout
Kermetico
Sugar coating
Inline coating
Spin coating thickness equation