Chip Seal Design Chapter 2 Chip Seal Design
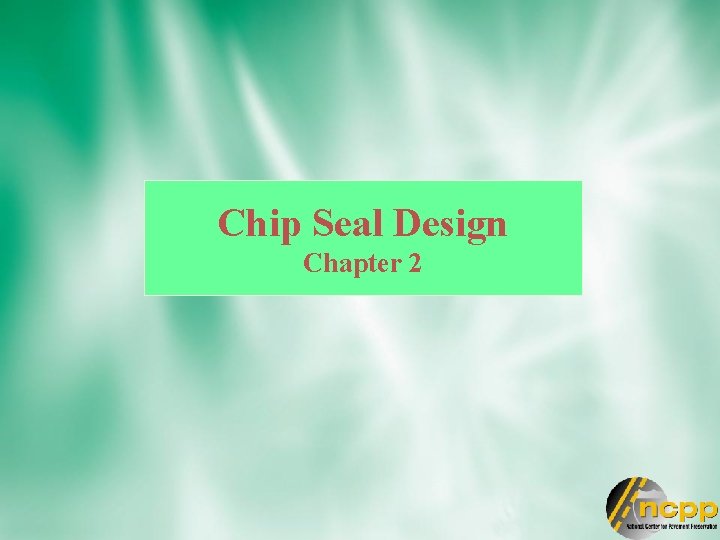
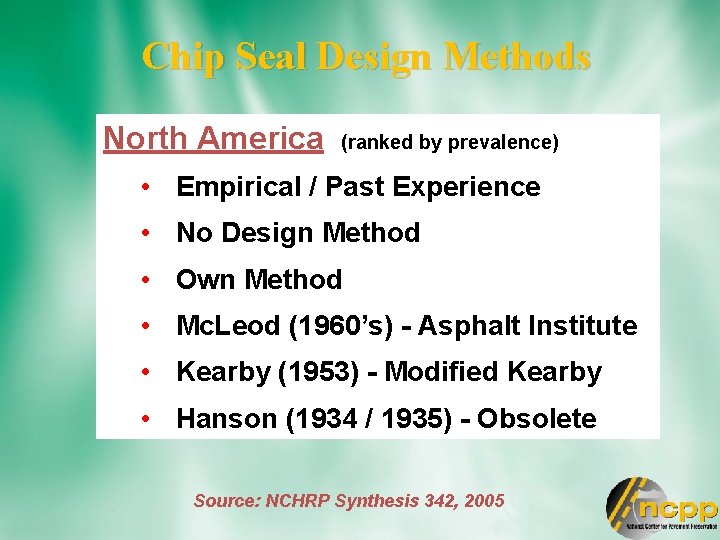
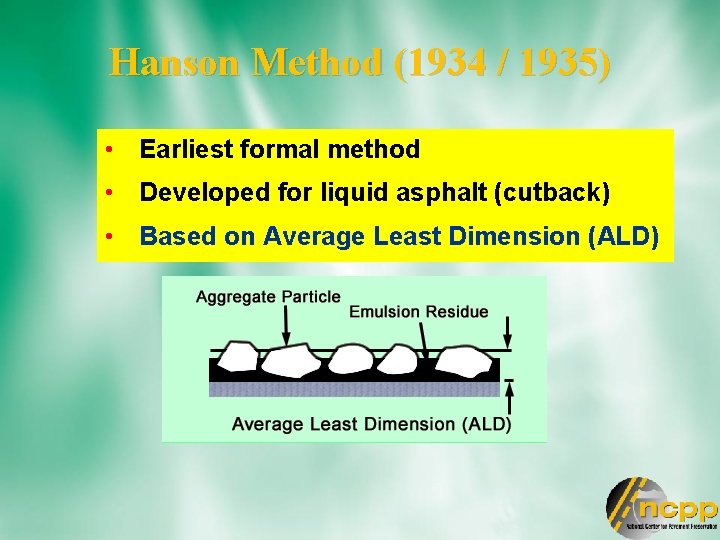
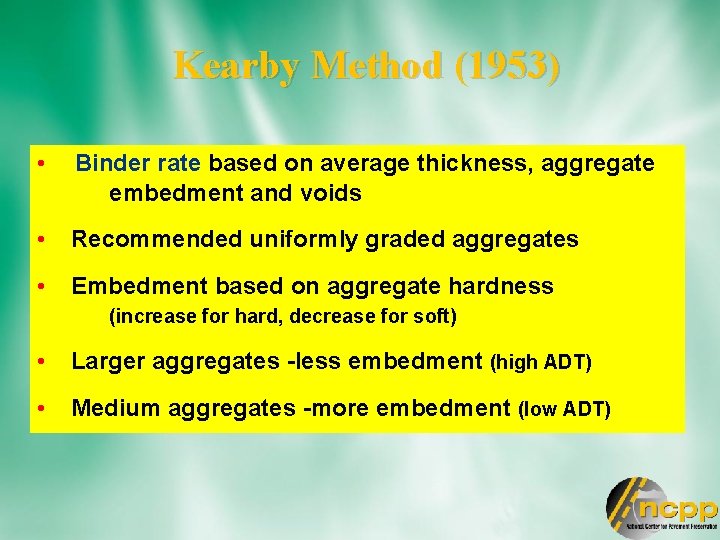
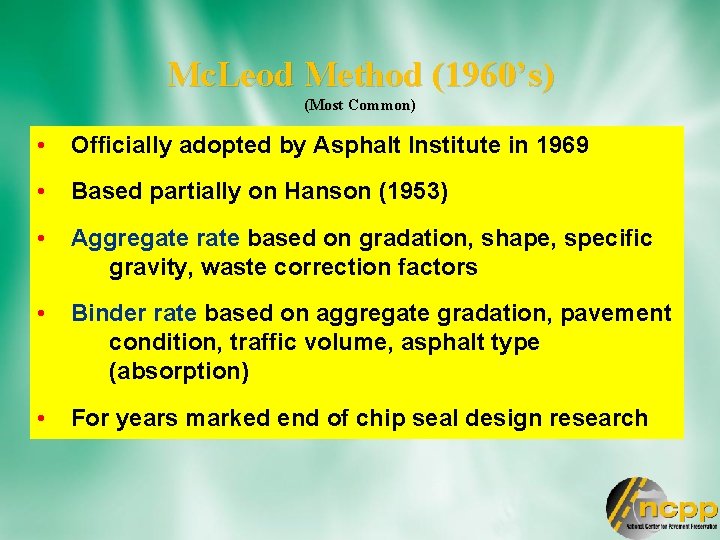
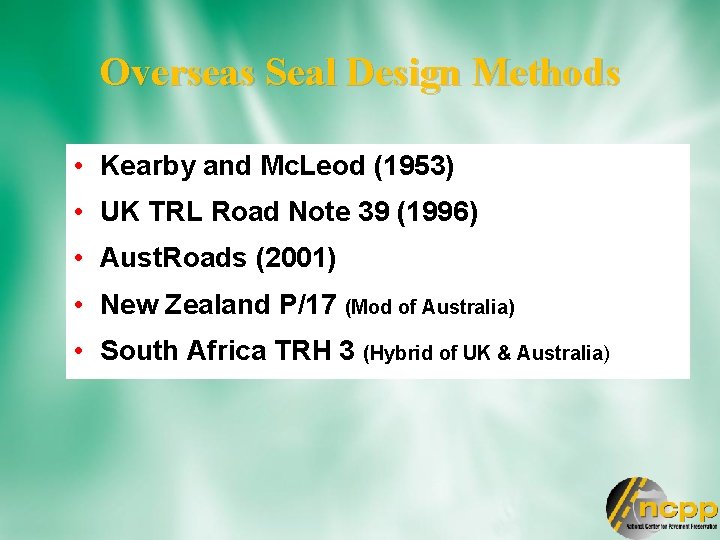
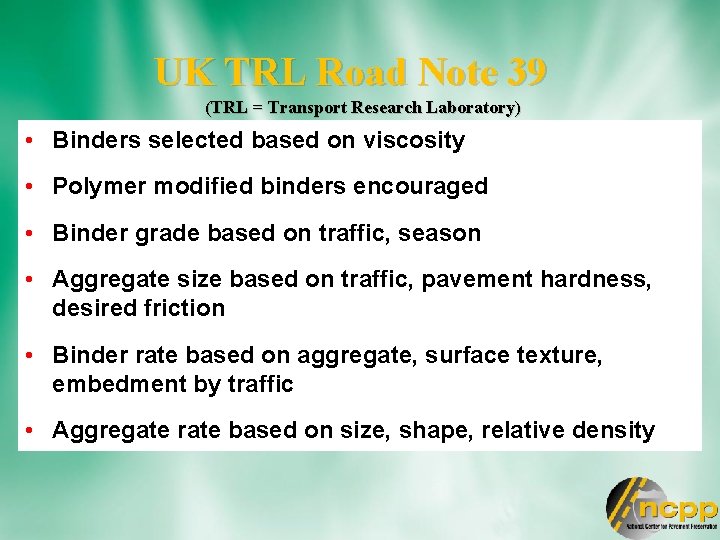
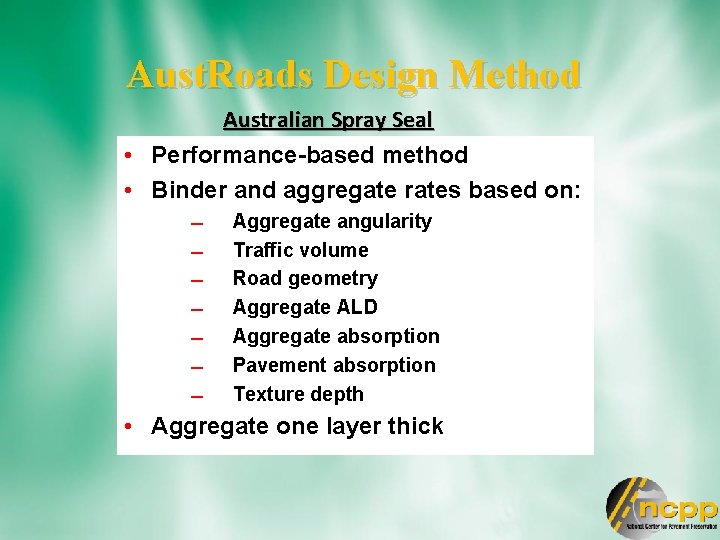
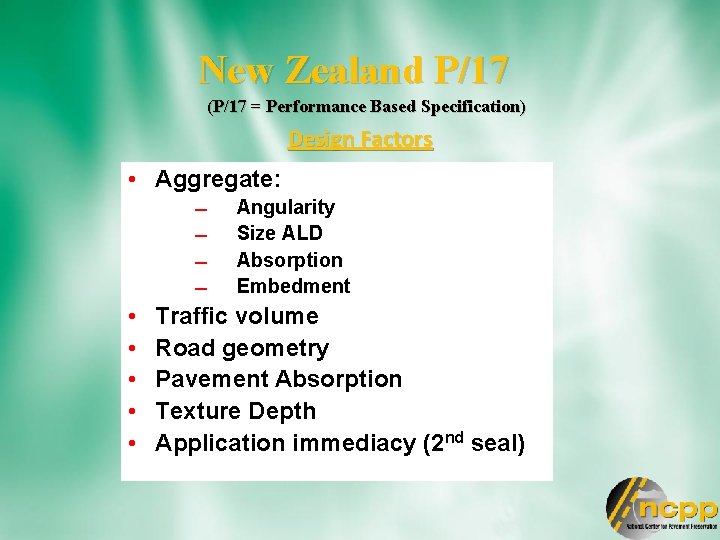
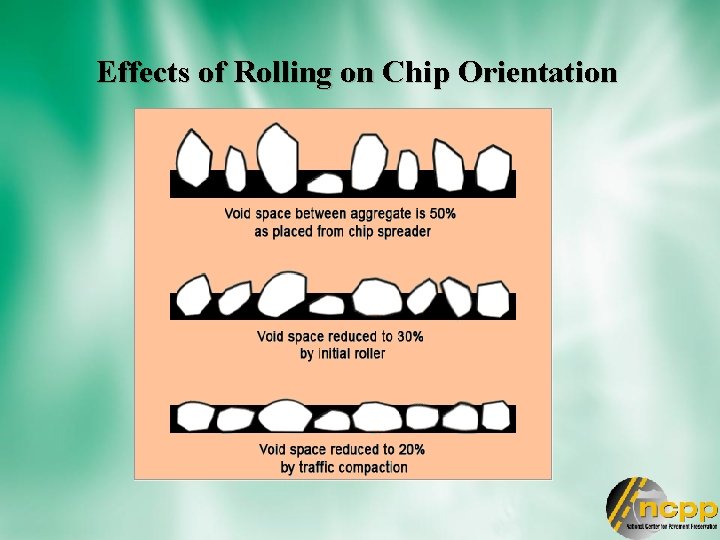
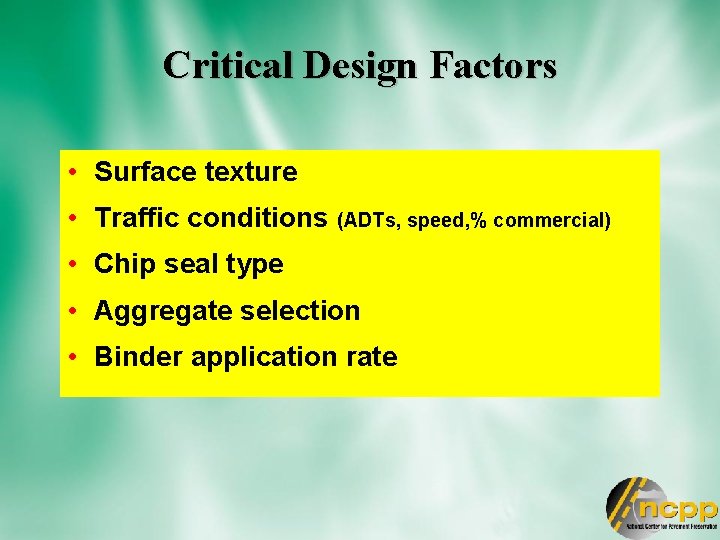
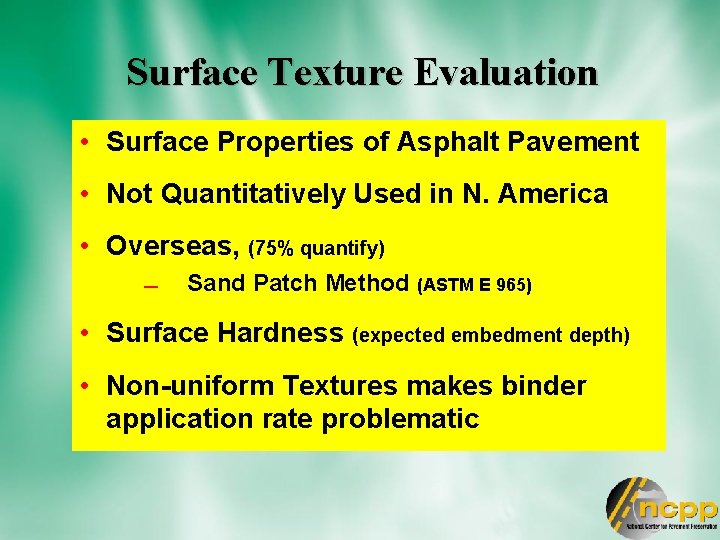
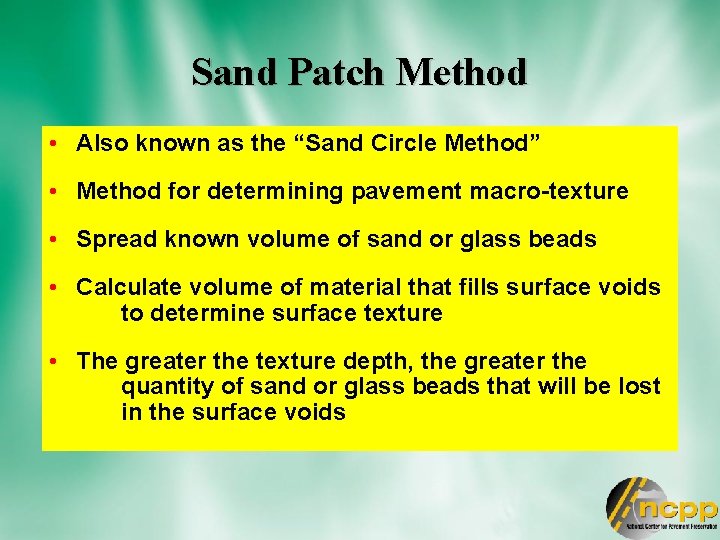
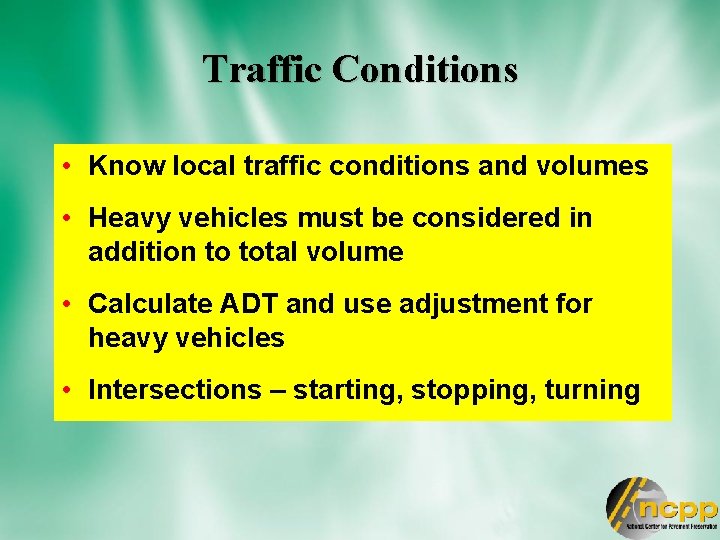
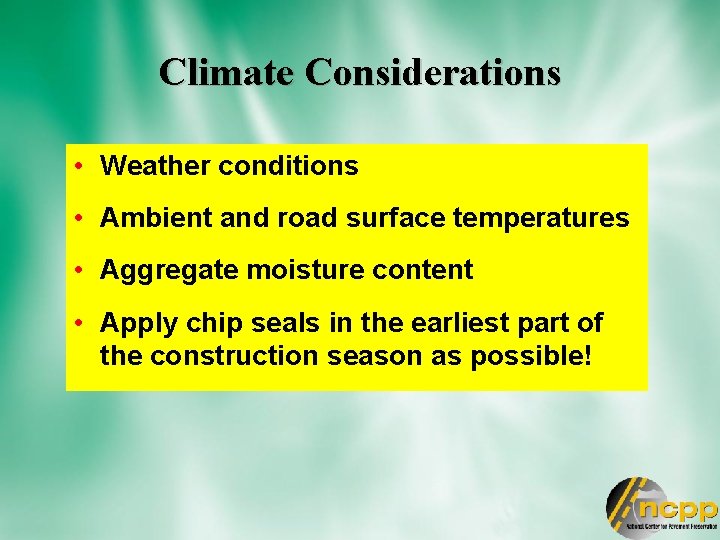
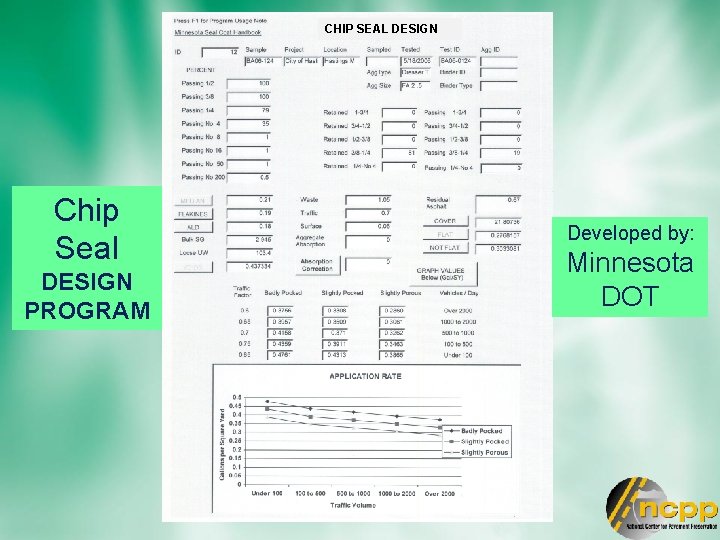
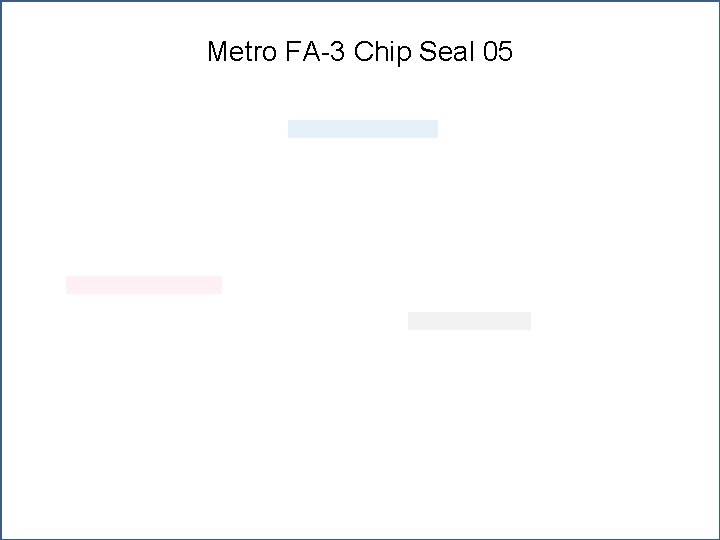
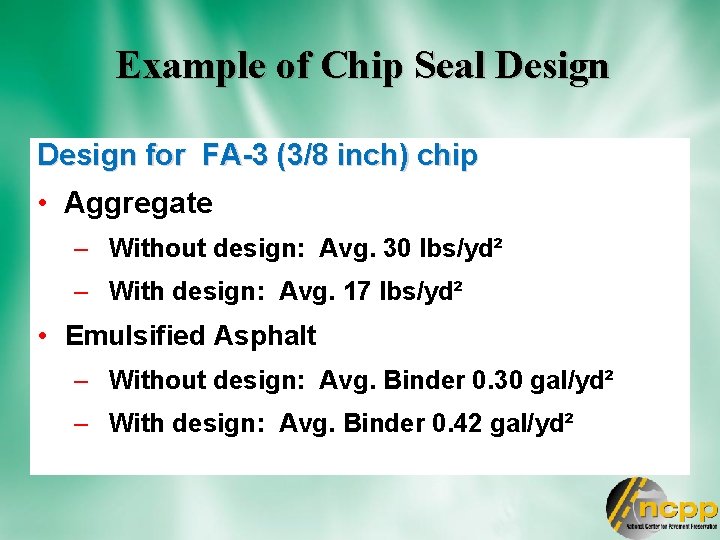

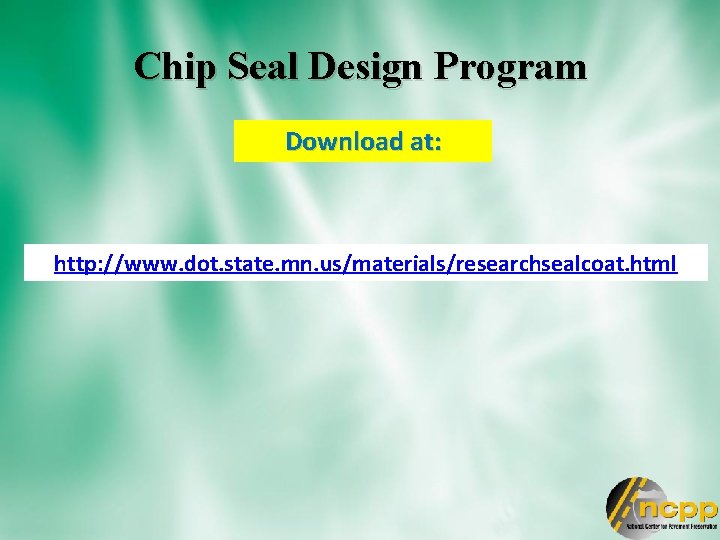
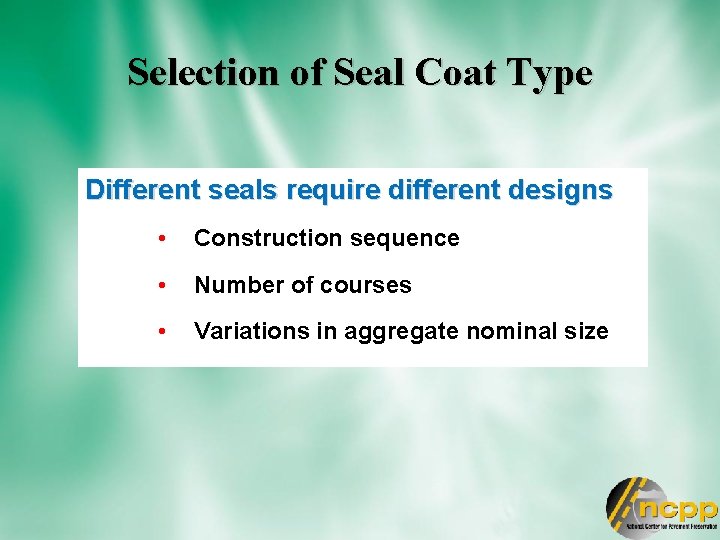
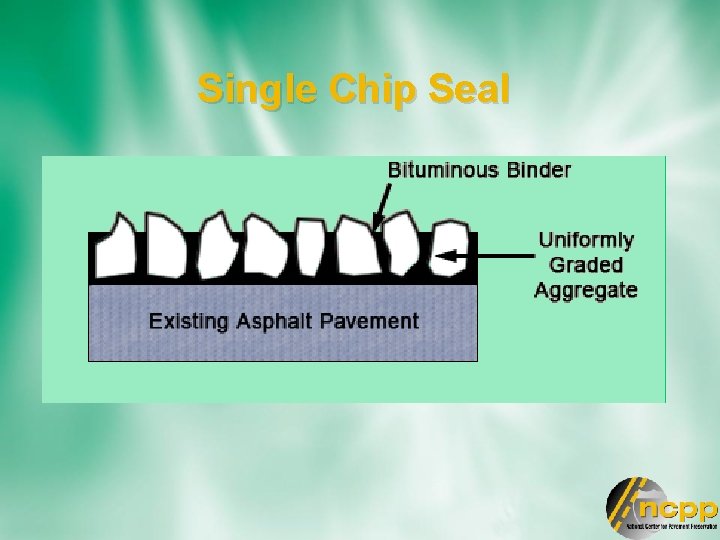
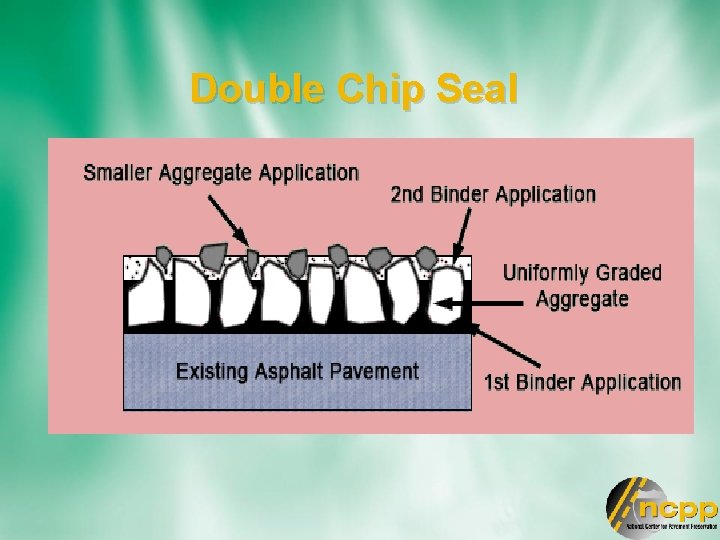
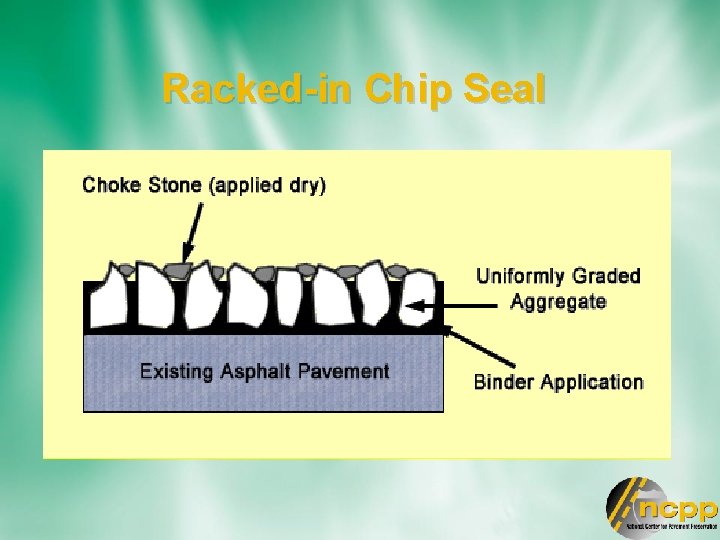
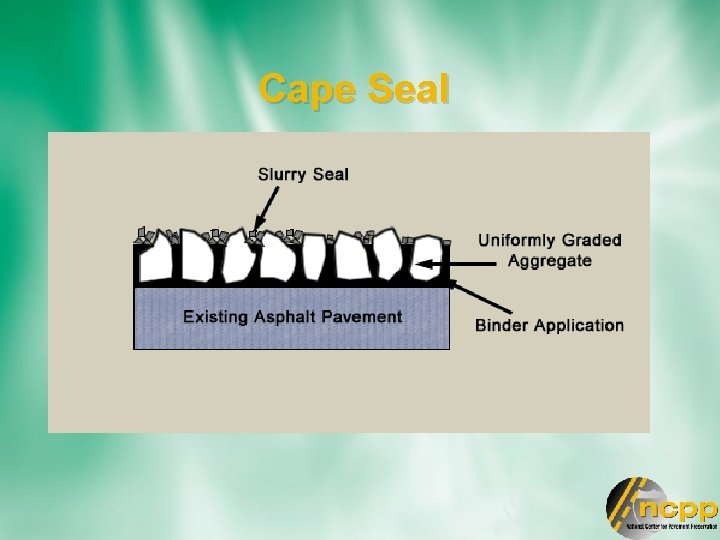
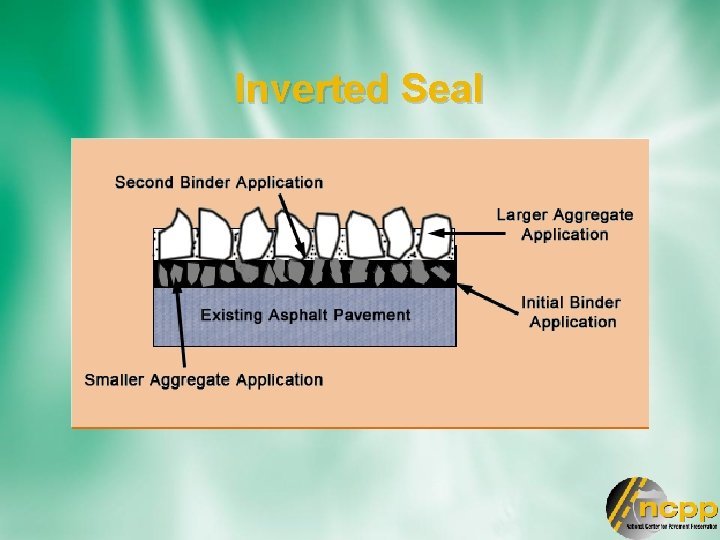
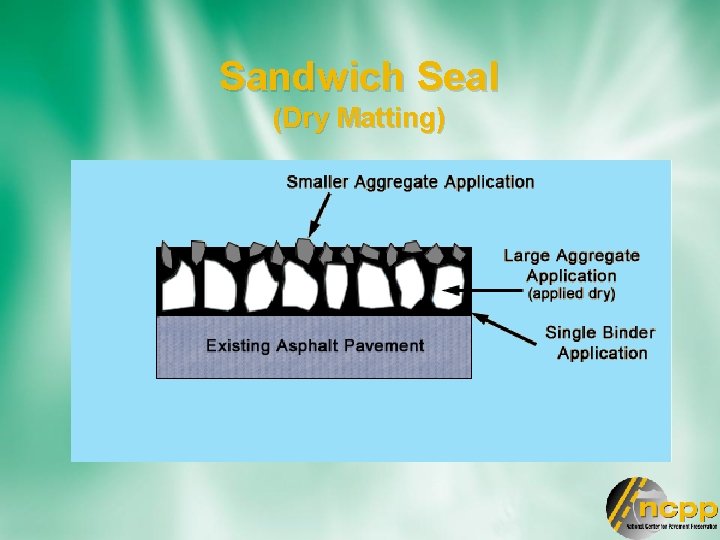
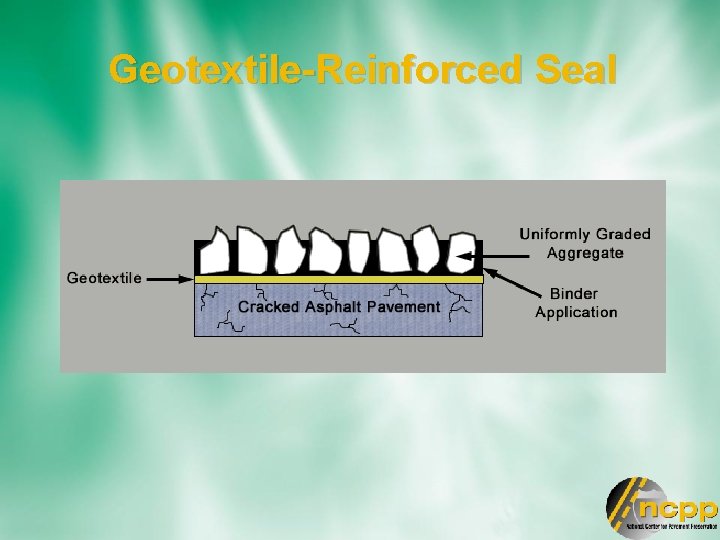

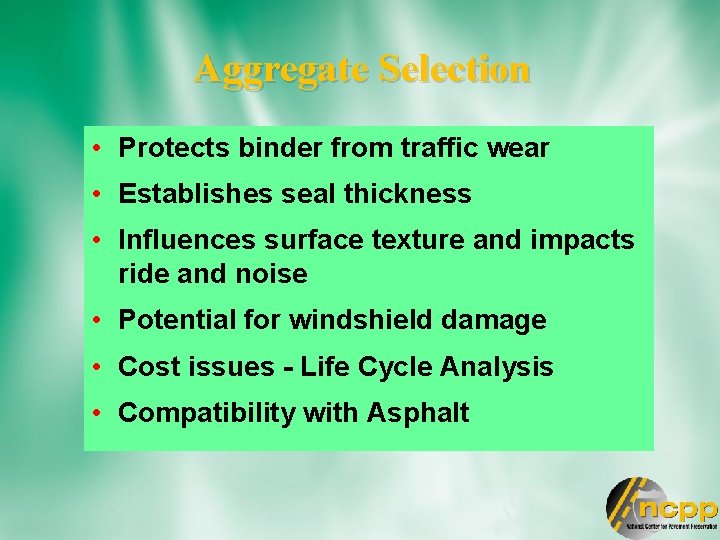
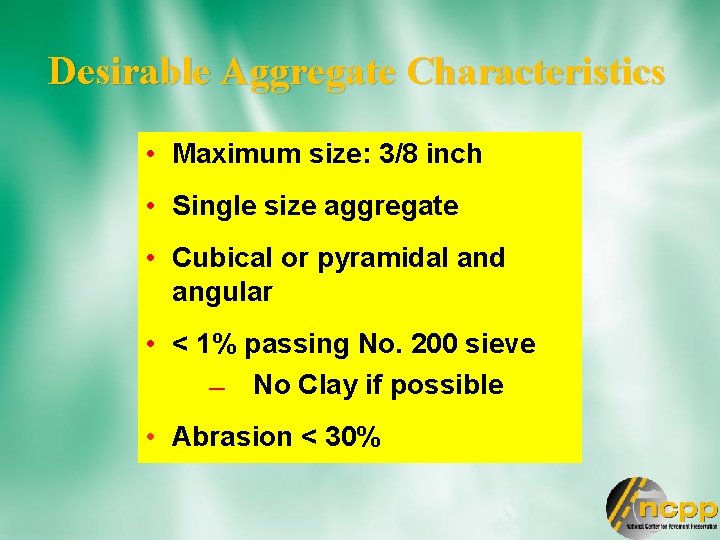
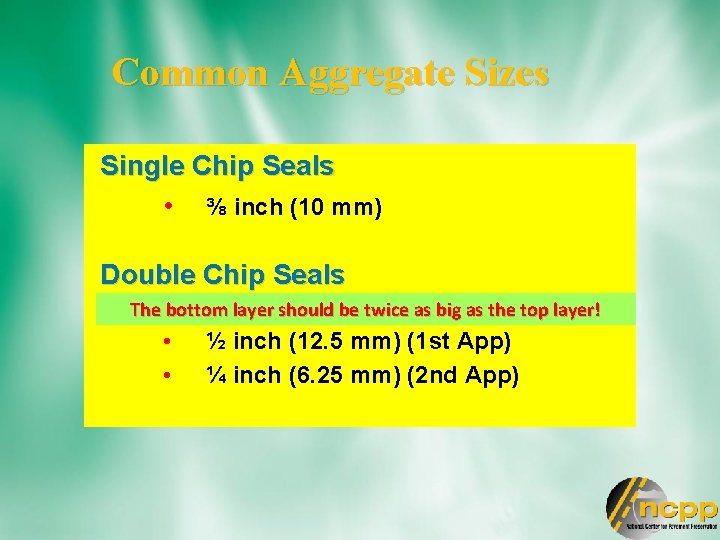
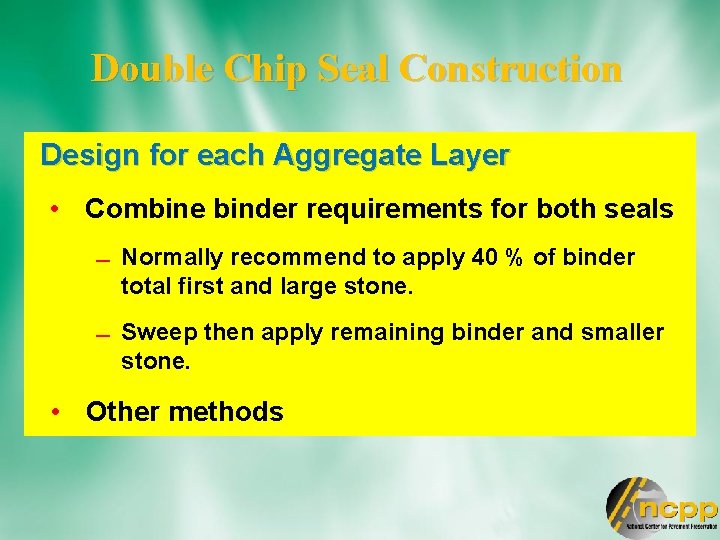
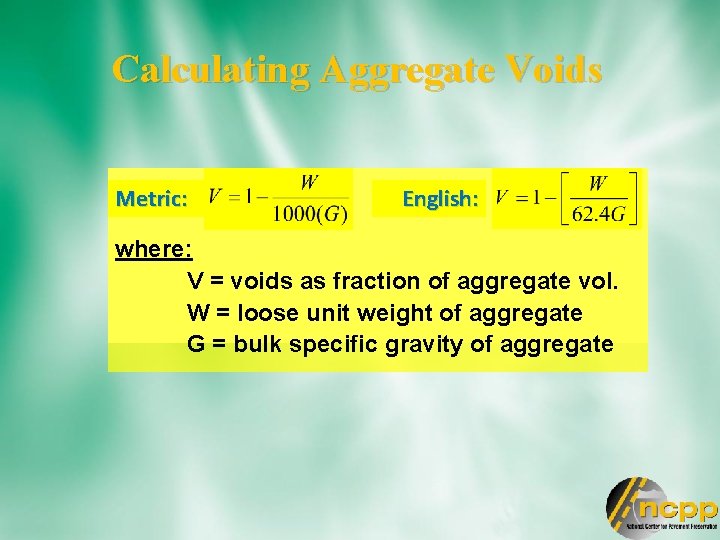
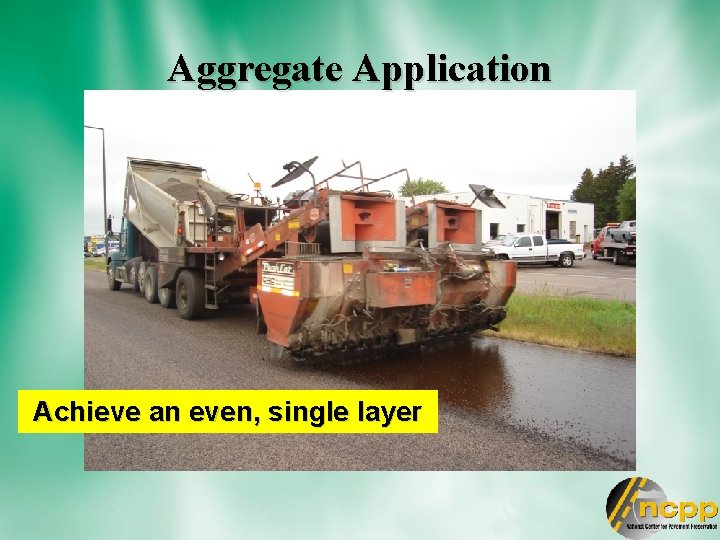
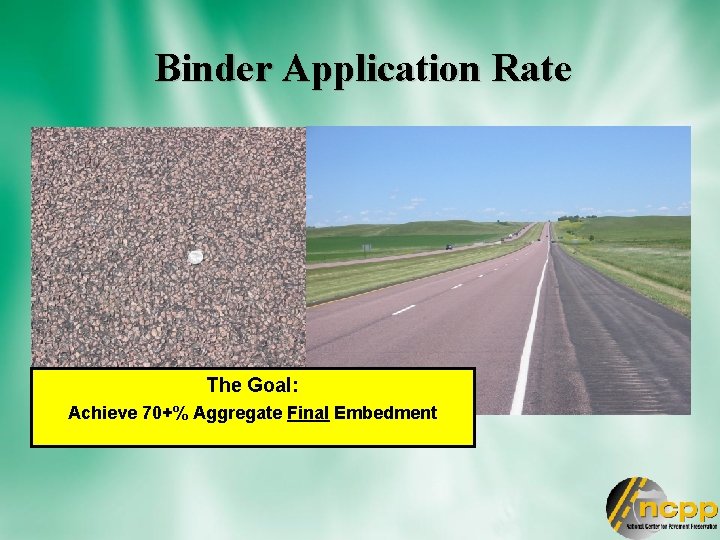
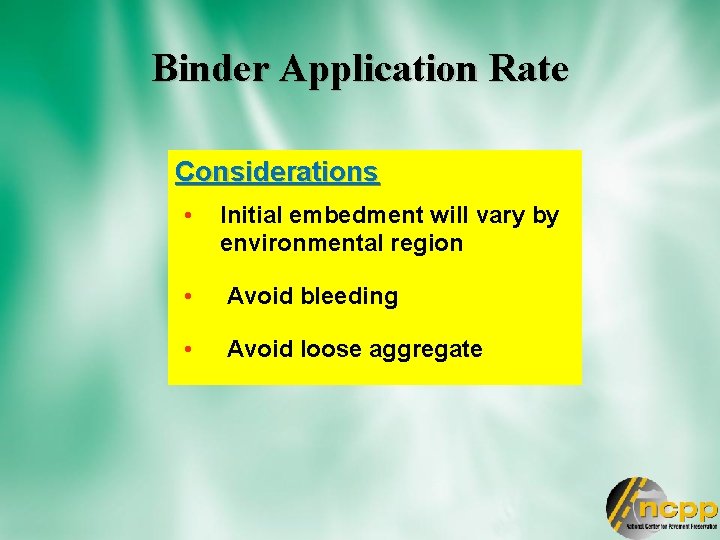
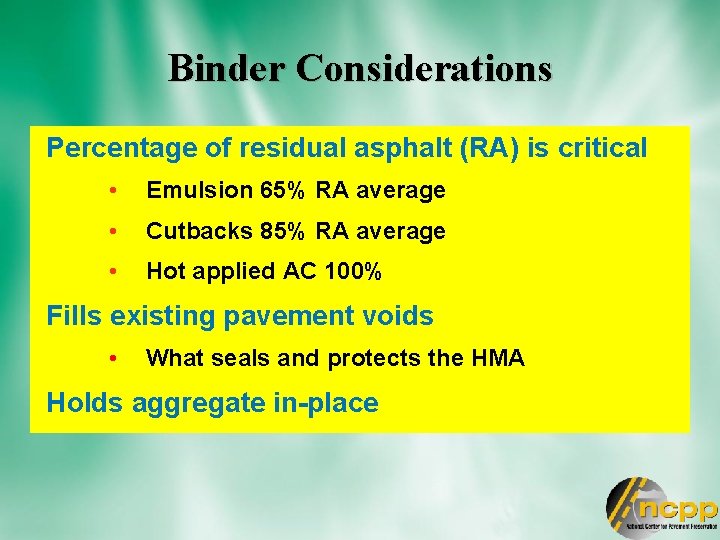
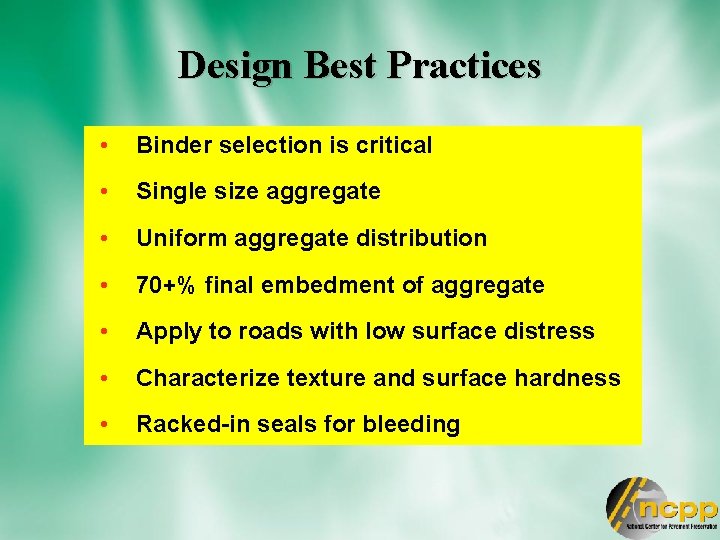
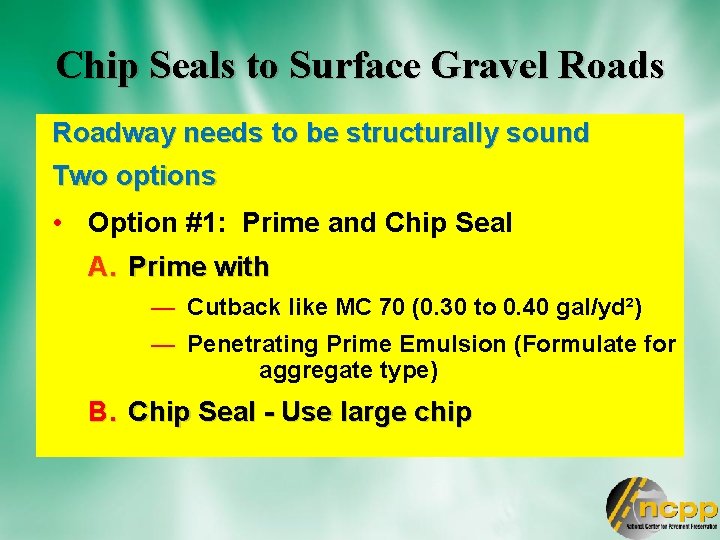
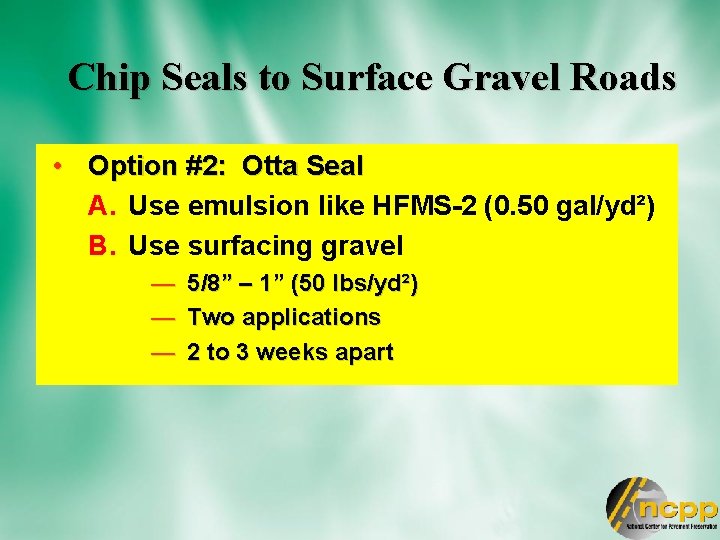
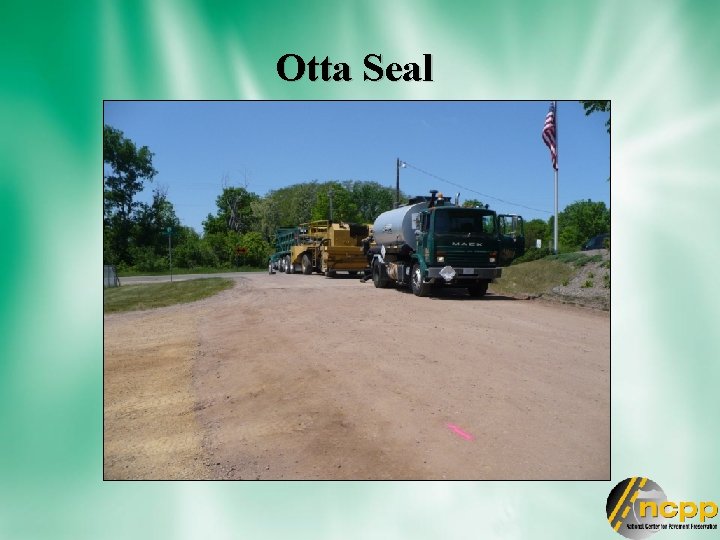
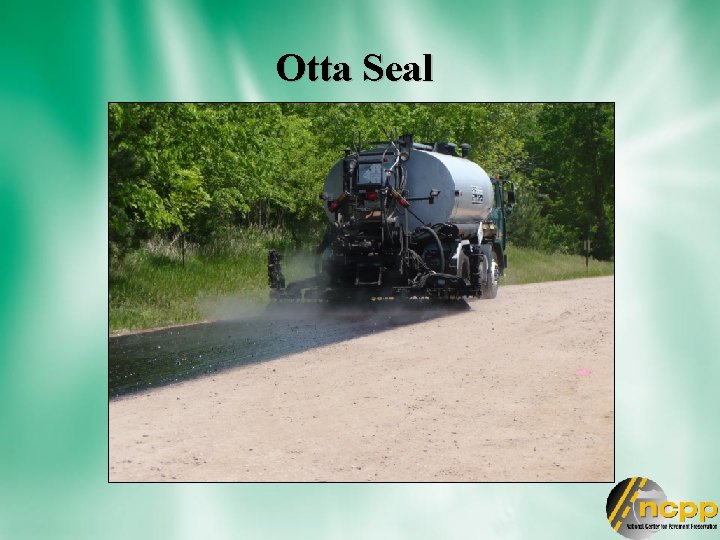
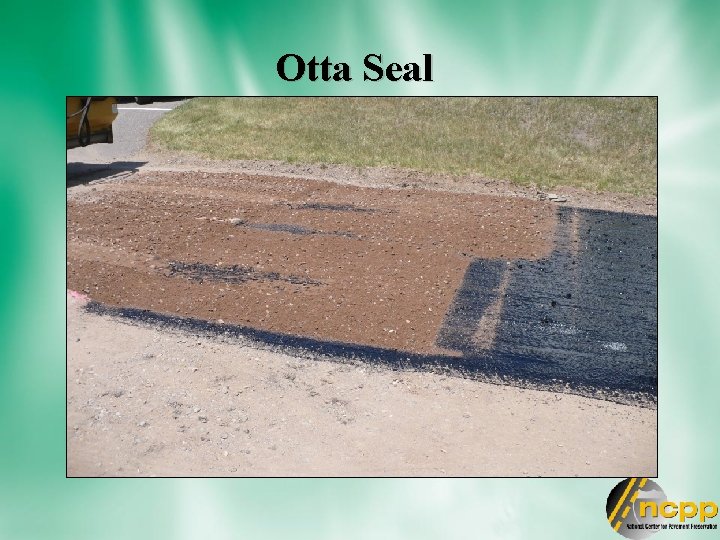
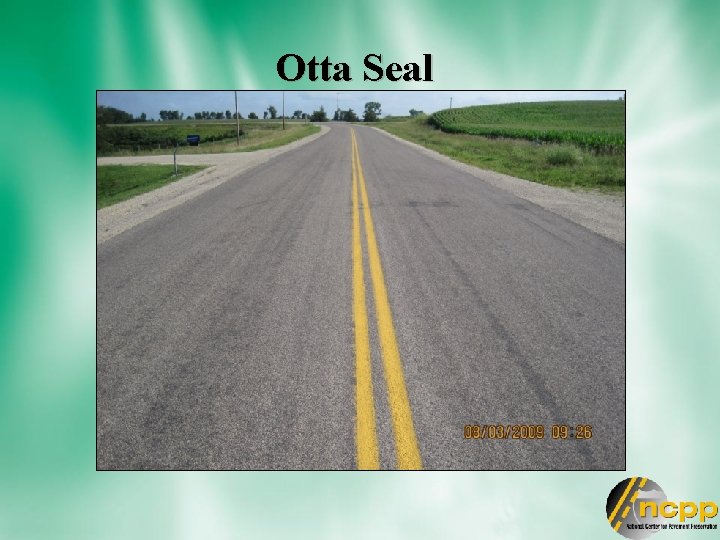
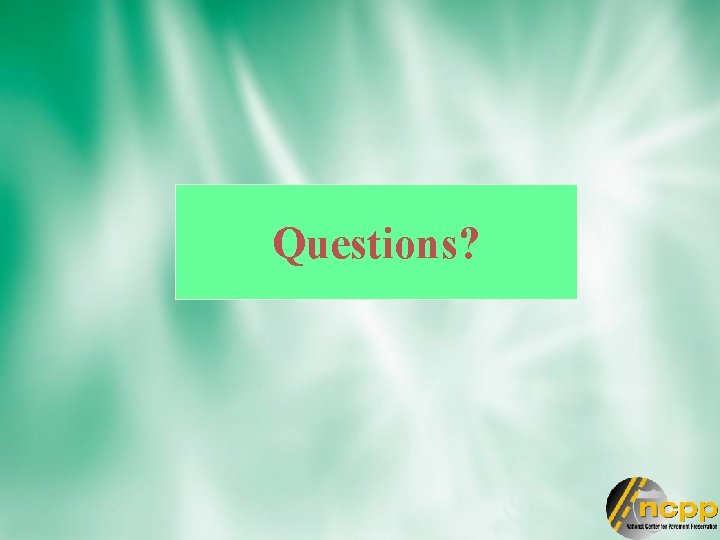
- Slides: 46
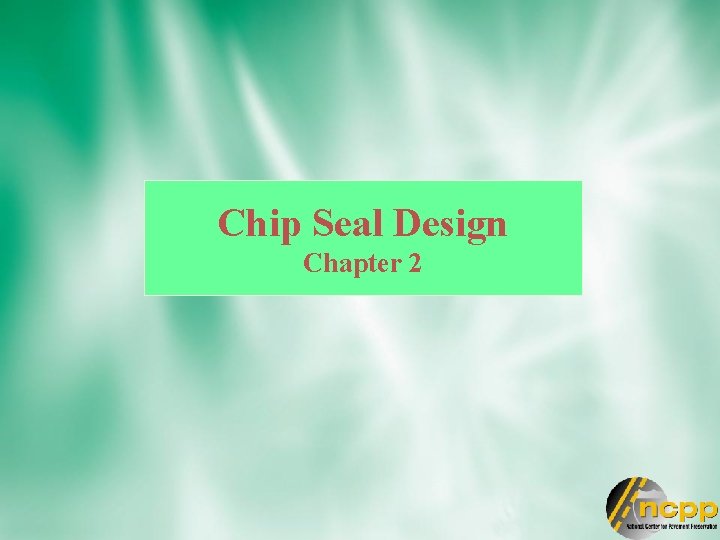
Chip Seal Design Chapter 2
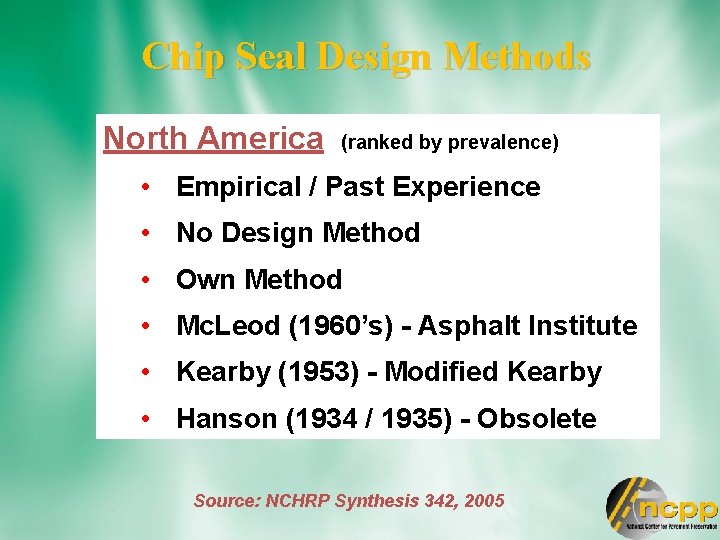
Chip Seal Design Methods North America (ranked by prevalence) • Empirical / Past Experience • No Design Method • Own Method • Mc. Leod (1960’s) - Asphalt Institute • Kearby (1953) - Modified Kearby • Hanson (1934 / 1935) - Obsolete Source: NCHRP Synthesis 342, 2005
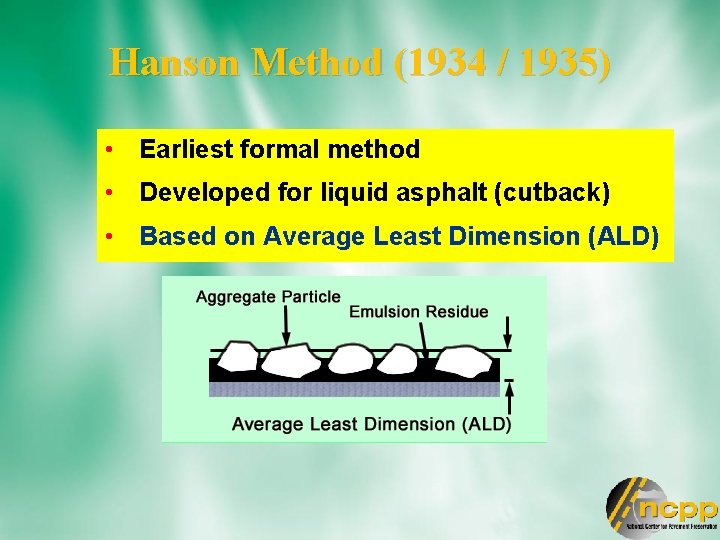
Hanson Method (1934 / 1935) • Earliest formal method • Developed for liquid asphalt (cutback) • Based on Average Least Dimension (ALD)
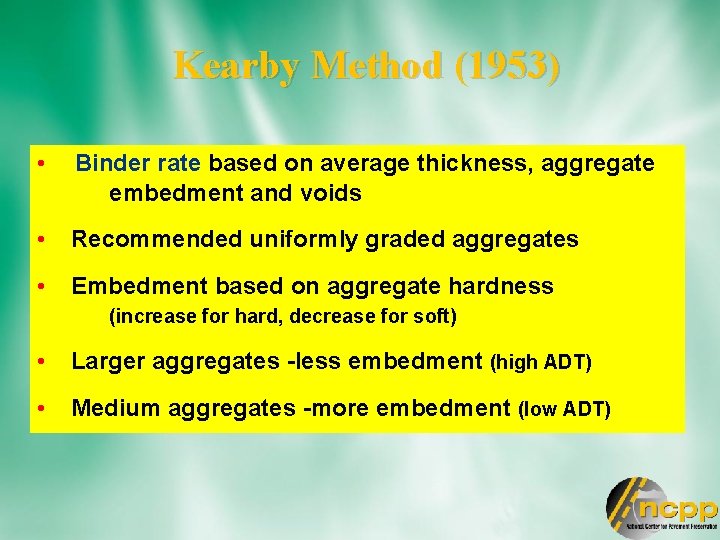
Kearby Method (1953) • Binder rate based on average thickness, aggregate embedment and voids • Recommended uniformly graded aggregates • Embedment based on aggregate hardness (increase for hard, decrease for soft) • Larger aggregates -less embedment (high ADT) • Medium aggregates -more embedment (low ADT)
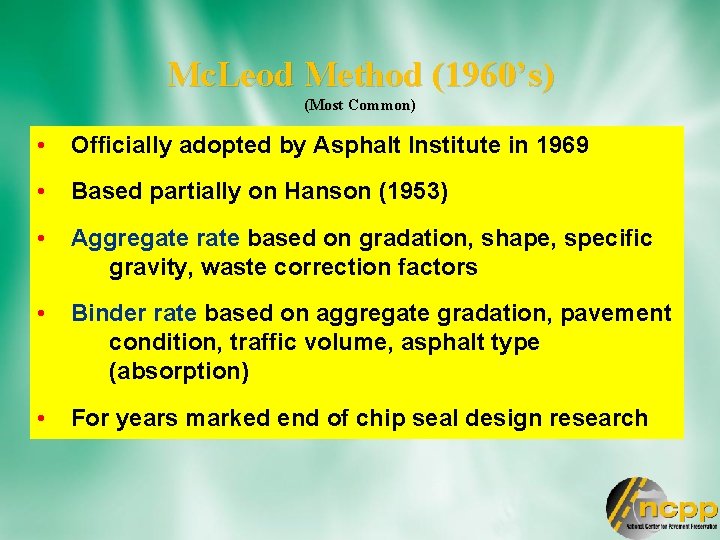
Mc. Leod Method (1960’s) (Most Common) • Officially adopted by Asphalt Institute in 1969 • Based partially on Hanson (1953) • Aggregate rate based on gradation, shape, specific gravity, waste correction factors • Binder rate based on aggregate gradation, pavement condition, traffic volume, asphalt type (absorption) • For years marked end of chip seal design research
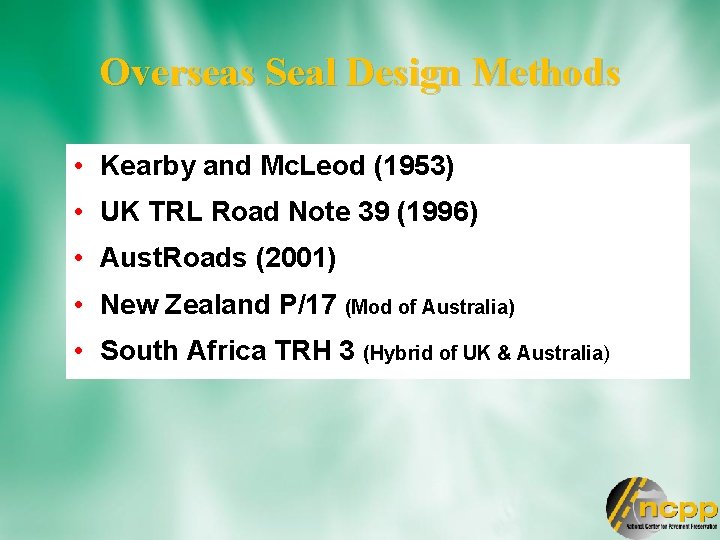
Overseas Seal Design Methods • Kearby and Mc. Leod (1953) • UK TRL Road Note 39 (1996) • Aust. Roads (2001) • New Zealand P/17 (Mod of Australia) • South Africa TRH 3 (Hybrid of UK & Australia)
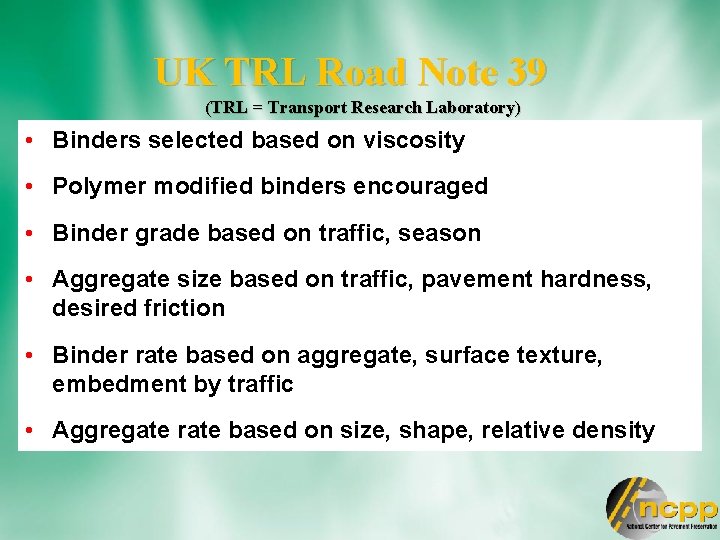
UK TRL Road Note 39 (TRL = Transport Research Laboratory) • Binders selected based on viscosity • Polymer modified binders encouraged • Binder grade based on traffic, season • Aggregate size based on traffic, pavement hardness, desired friction • Binder rate based on aggregate, surface texture, embedment by traffic • Aggregate rate based on size, shape, relative density
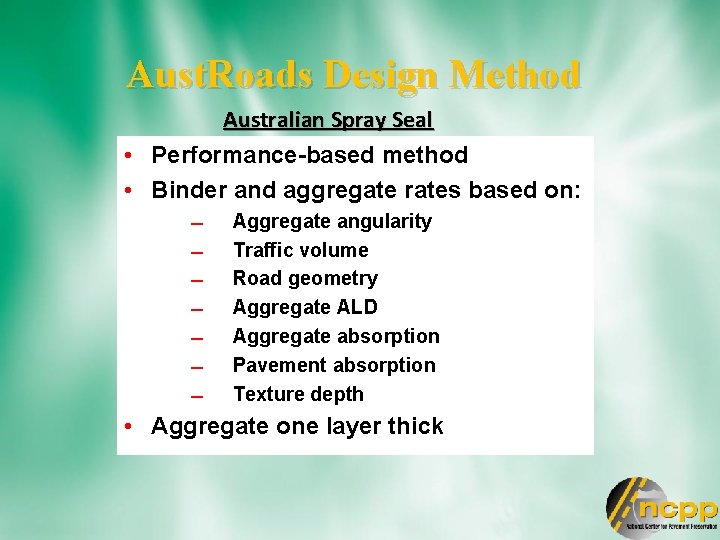
Aust. Roads Design Method Australian Spray Seal • Performance-based method • Binder and aggregate rates based on: Aggregate angularity Traffic volume Road geometry Aggregate ALD Aggregate absorption Pavement absorption Texture depth • Aggregate one layer thick
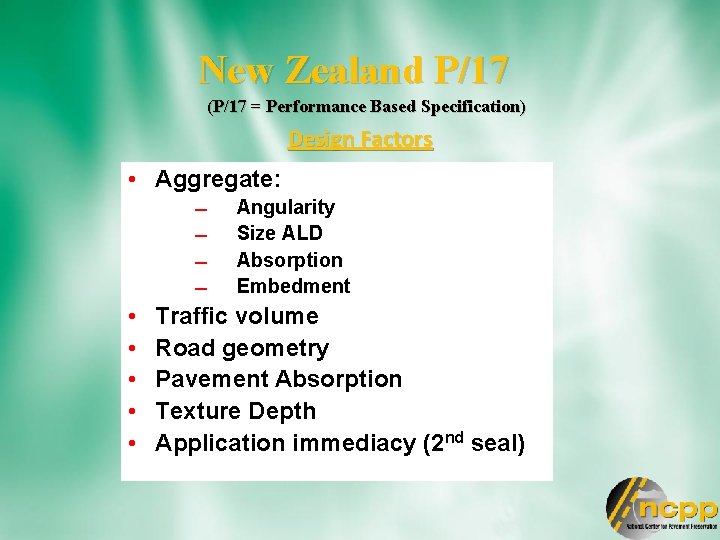
New Zealand P/17 (P/17 = Performance Based Specification) Design Factors • Aggregate: • • • Angularity Size ALD Absorption Embedment Traffic volume Road geometry Pavement Absorption Texture Depth Application immediacy (2 nd seal)
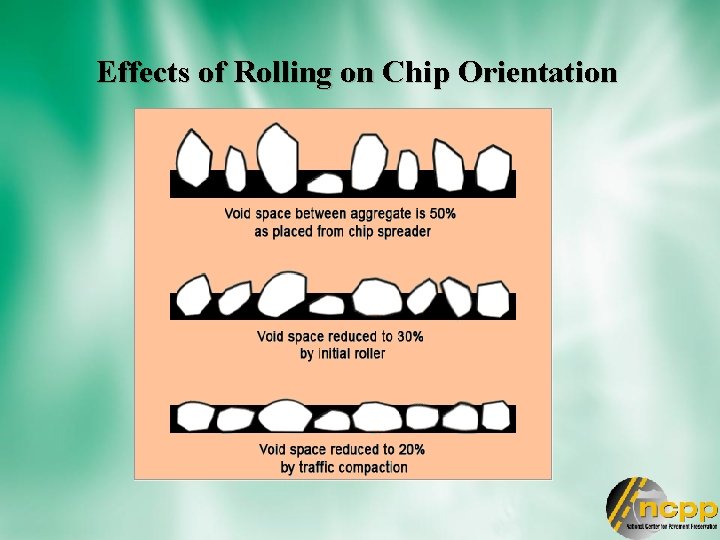
Effects of Rolling on Chip Orientation
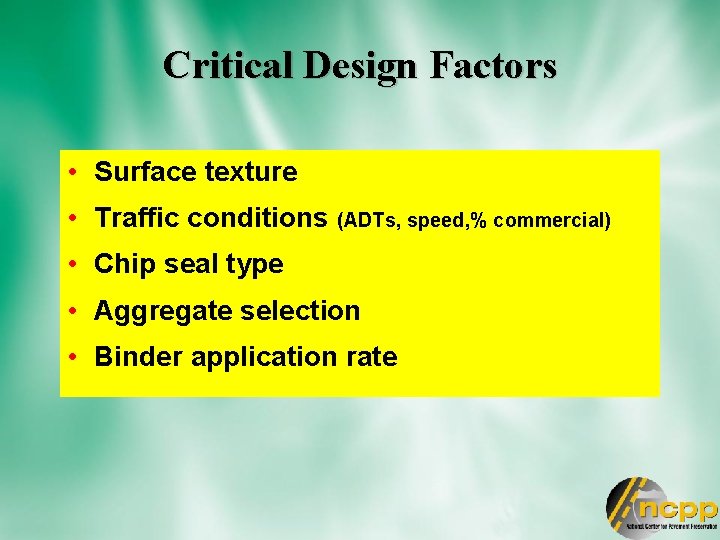
Critical Design Factors • Surface texture • Traffic conditions (ADTs, speed, % commercial) • Chip seal type • Aggregate selection • Binder application rate
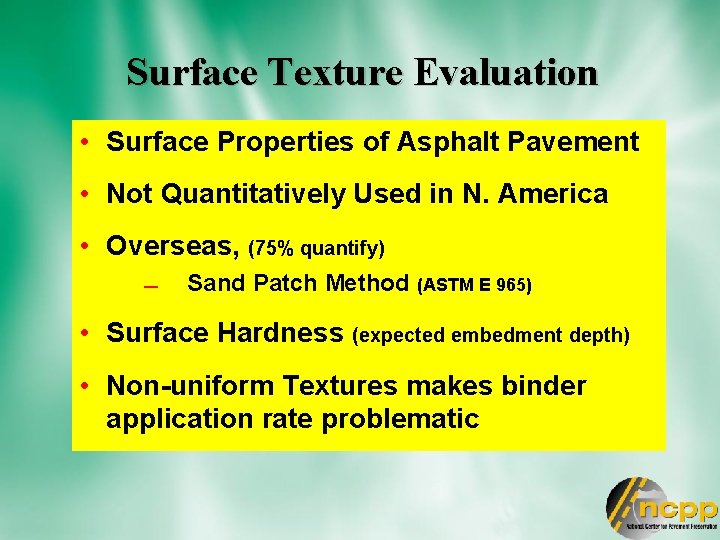
Surface Texture Evaluation • Surface Properties of Asphalt Pavement • Not Quantitatively Used in N. America • Overseas, (75% quantify) Sand Patch Method (ASTM E 965) • Surface Hardness (expected embedment depth) • Non-uniform Textures makes binder application rate problematic
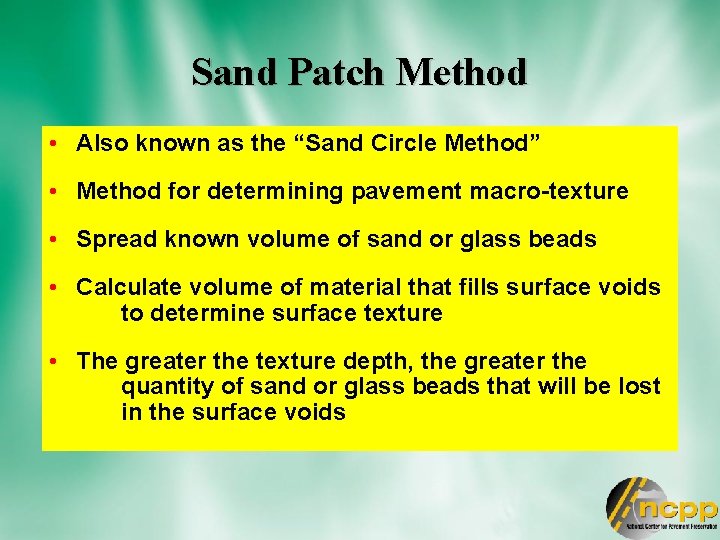
Sand Patch Method • Also known as the “Sand Circle Method” • Method for determining pavement macro-texture • Spread known volume of sand or glass beads • Calculate volume of material that fills surface voids to determine surface texture • The greater the texture depth, the greater the quantity of sand or glass beads that will be lost in the surface voids
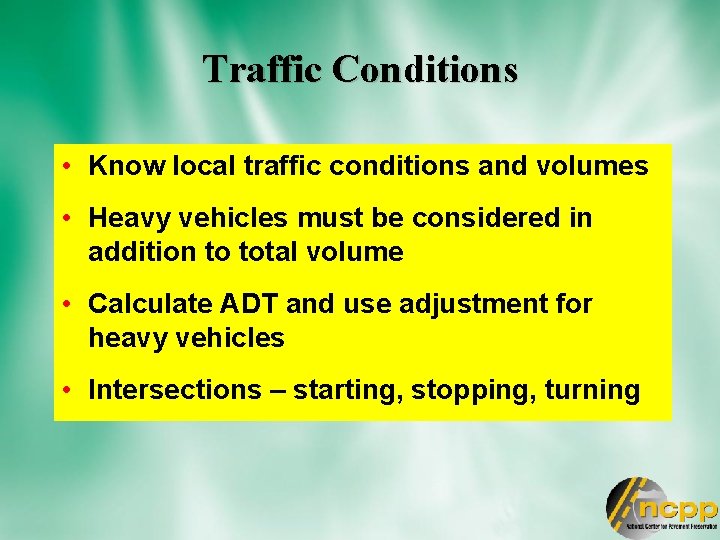
Traffic Conditions • Know local traffic conditions and volumes • Heavy vehicles must be considered in addition to total volume • Calculate ADT and use adjustment for heavy vehicles • Intersections – starting, stopping, turning
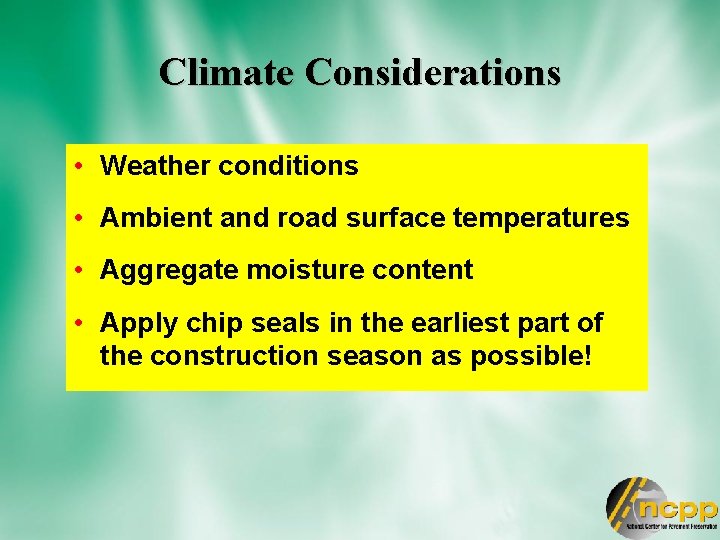
Climate Considerations • Weather conditions • Ambient and road surface temperatures • Aggregate moisture content • Apply chip seals in the earliest part of the construction season as possible!
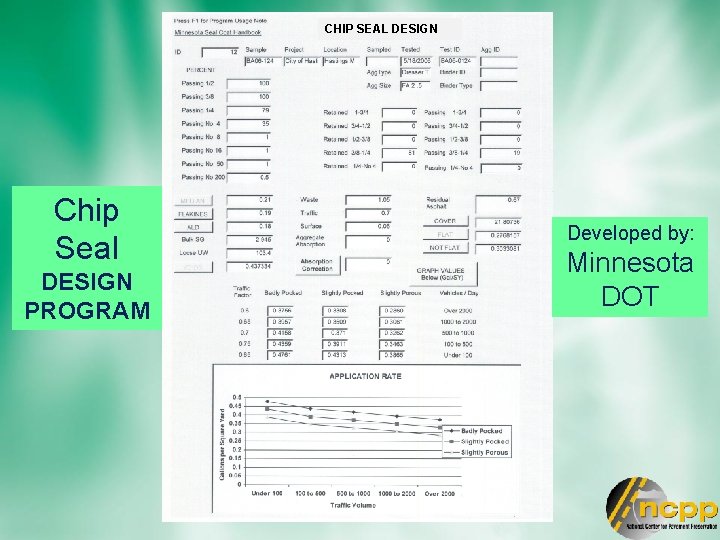
CHIP SEAL DESIGN Chip Seal DESIGN PROGRAM Developed by: Minnesota DOT
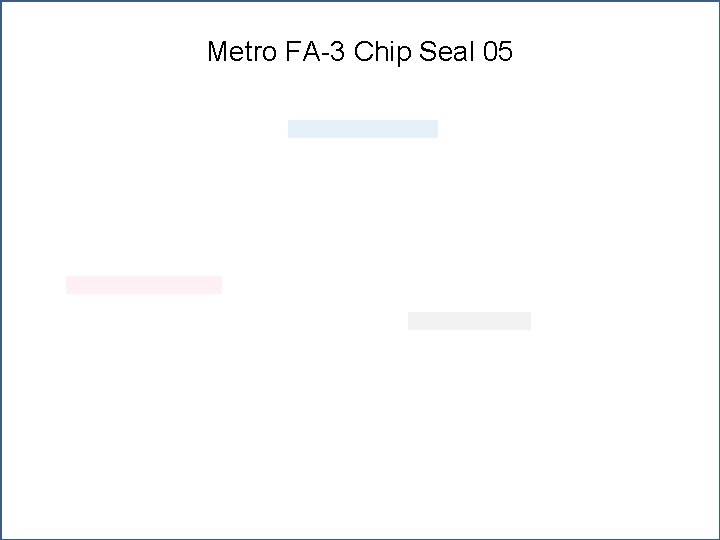
Metro FA-3 Chip Seal 05
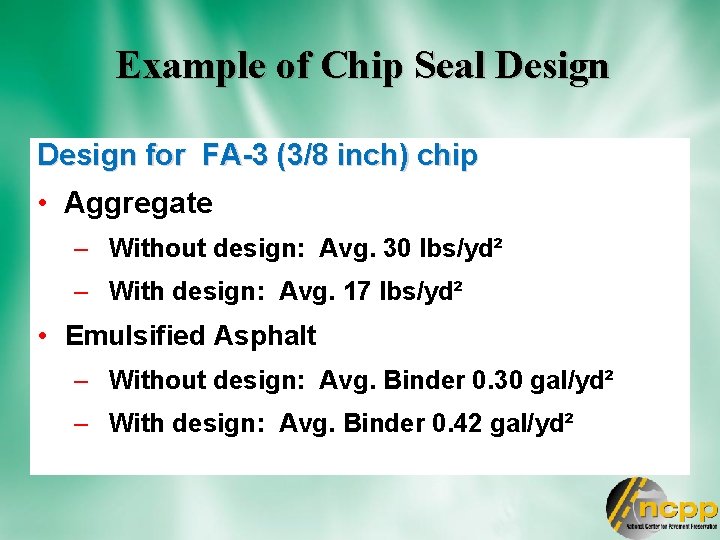
Example of Chip Seal Design for FA-3 (3/8 inch) chip • Aggregate – Without design: Avg. 30 lbs/yd² – With design: Avg. 17 lbs/yd² • Emulsified Asphalt – Without design: Avg. Binder 0. 30 gal/yd² – With design: Avg. Binder 0. 42 gal/yd²

Benefit of a Chip Seal Design • Chip Seal Designs and Proper Construction: Allows more miles Uses less money Achieves better results
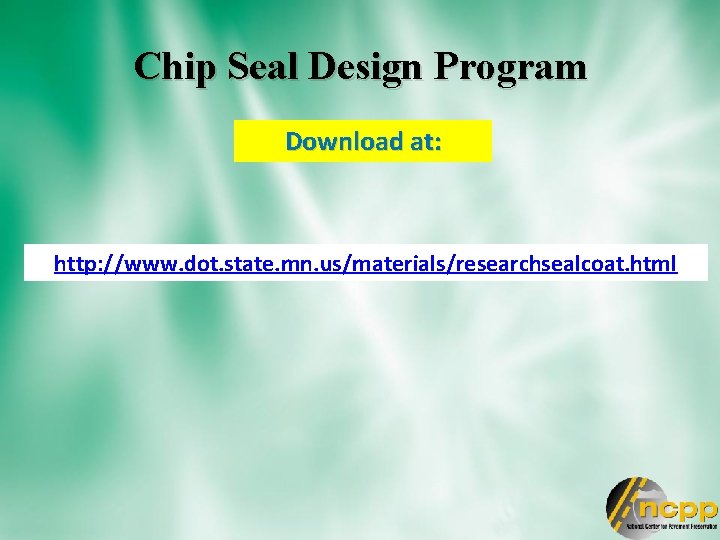
Chip Seal Design Program Download at: http: //www. dot. state. mn. us/materials/researchsealcoat. html
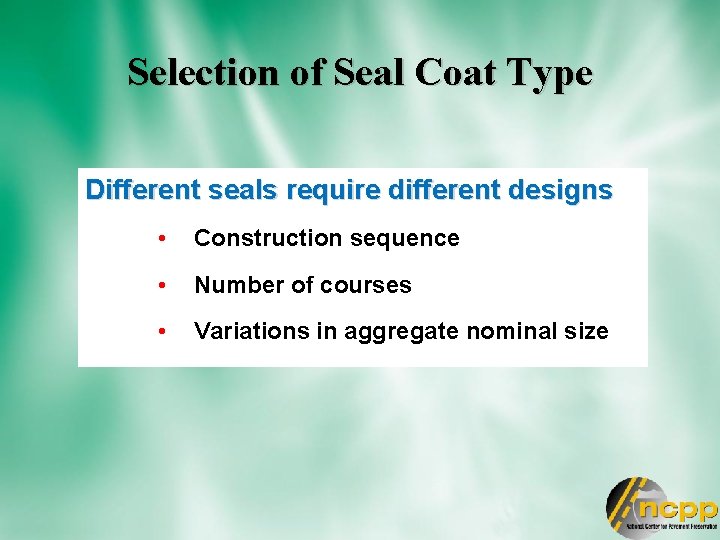
Selection of Seal Coat Type Different seals require different designs • Construction sequence • Number of courses • Variations in aggregate nominal size
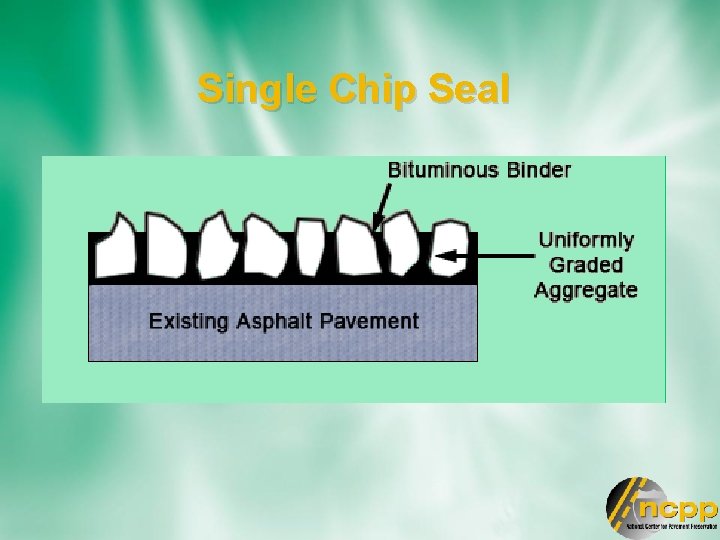
Single Chip Seal
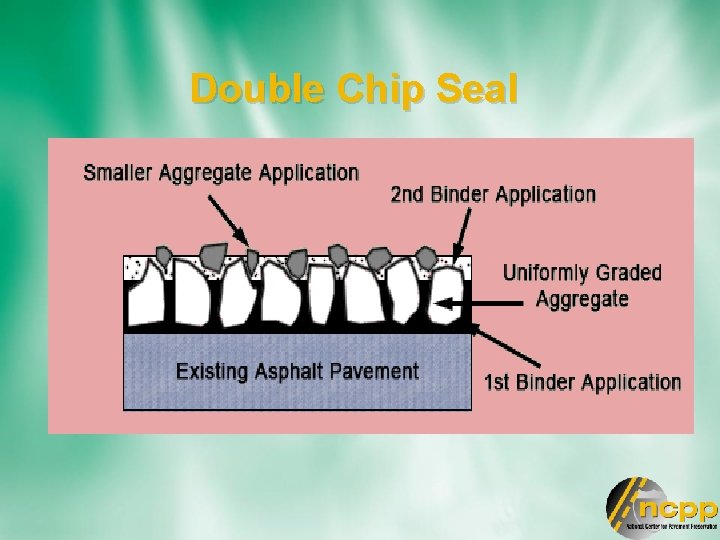
Double Chip Seal
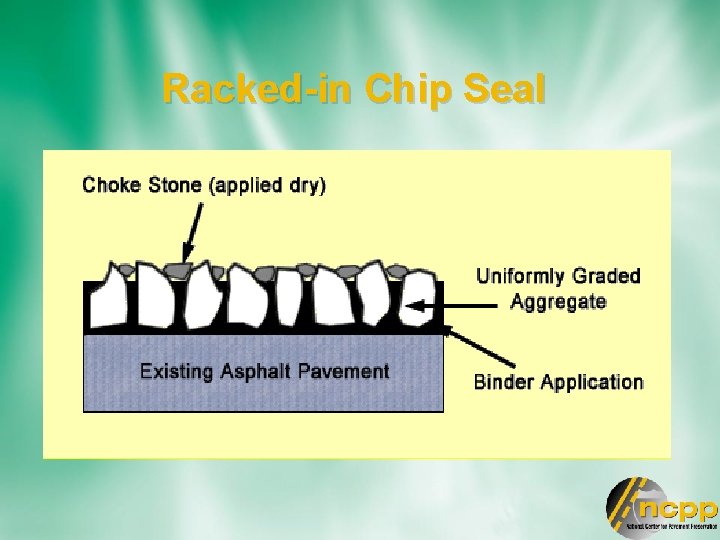
Racked-in Chip Seal
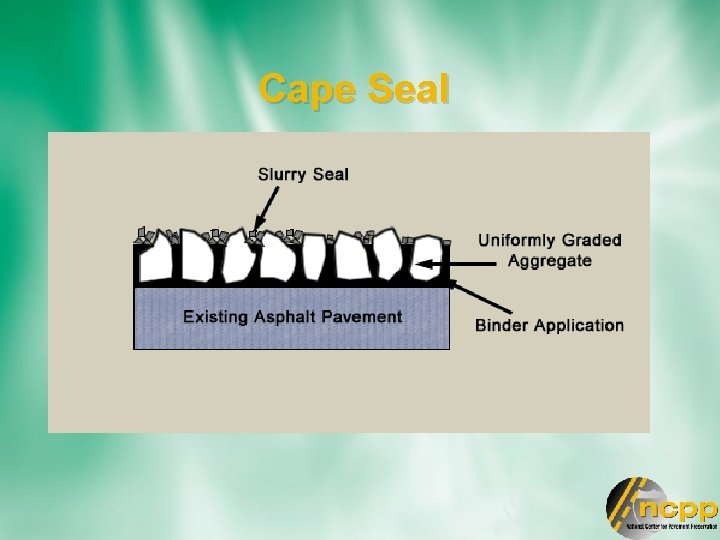
Cape Seal
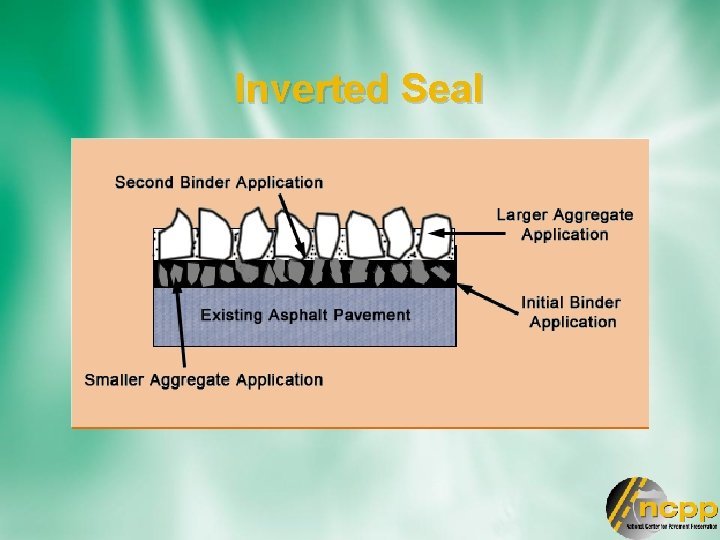
Inverted Seal
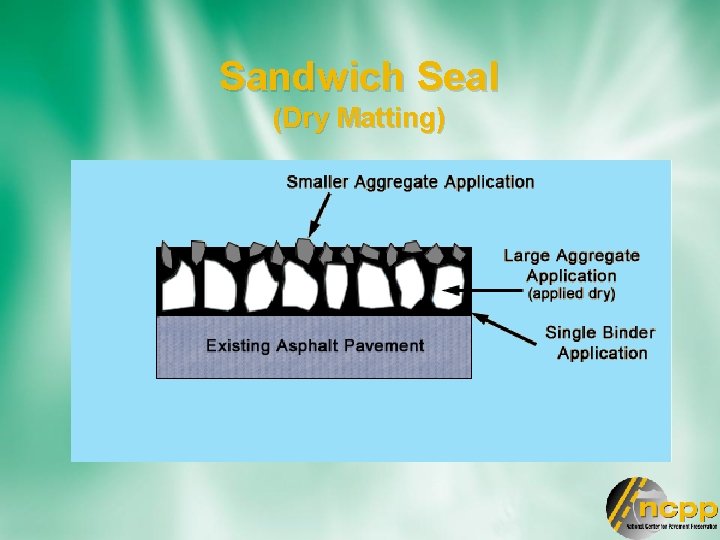
Sandwich Seal (Dry Matting)
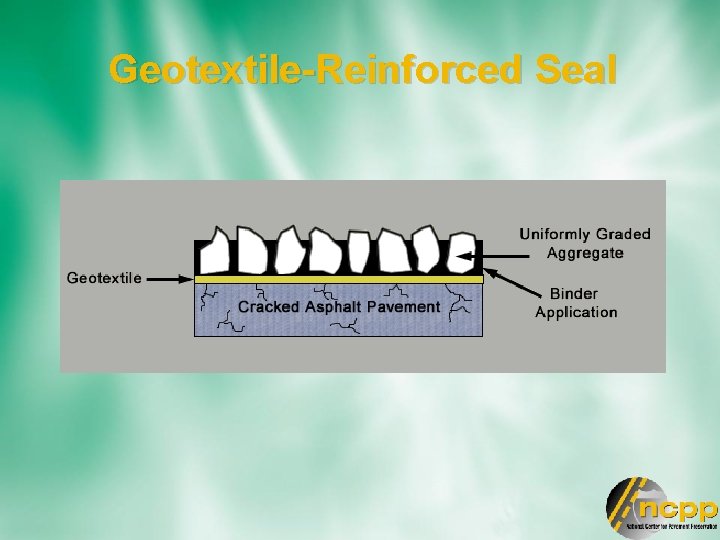
Geotextile-Reinforced Seal

Fiber-Reinforced Seal Chopped Fiberglass Strands
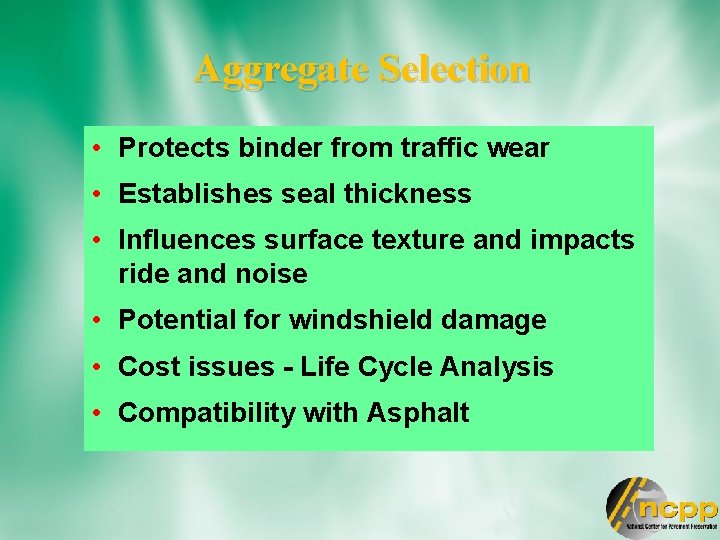
Aggregate Selection • Protects binder from traffic wear • Establishes seal thickness • Influences surface texture and impacts ride and noise • Potential for windshield damage • Cost issues - Life Cycle Analysis • Compatibility with Asphalt
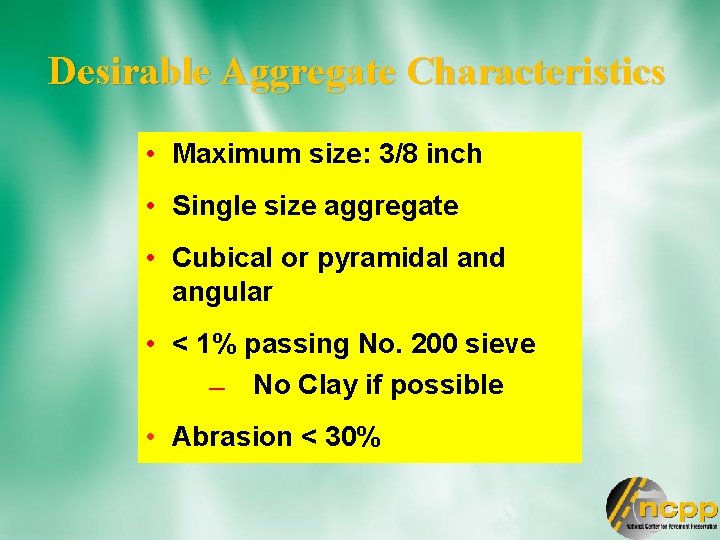
Desirable Aggregate Characteristics • Maximum size: 3/8 inch • Single size aggregate • Cubical or pyramidal and angular • < 1% passing No. 200 sieve No Clay if possible • Abrasion < 30%
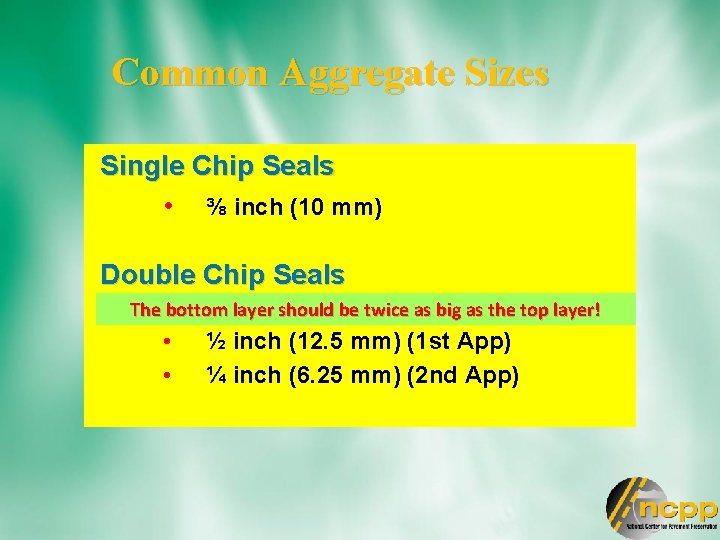
Common Aggregate Sizes Single Chip Seals • ⅜ inch (10 mm) Double Chip Seals The bottom layer should be twice as big as the top layer! • • ½ inch (12. 5 mm) (1 st App) ¼ inch (6. 25 mm) (2 nd App)
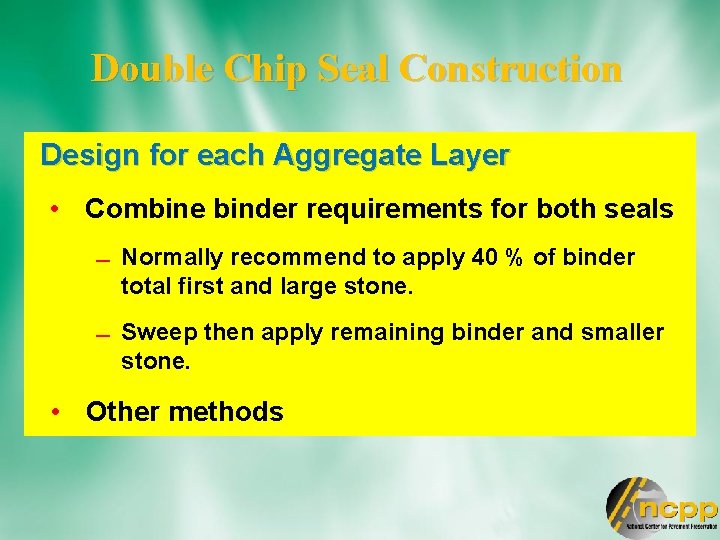
Double Chip Seal Construction Design for each Aggregate Layer • Combine binder requirements for both seals Normally recommend to apply 40 % of binder total first and large stone. Sweep then apply remaining binder and smaller stone. • Other methods
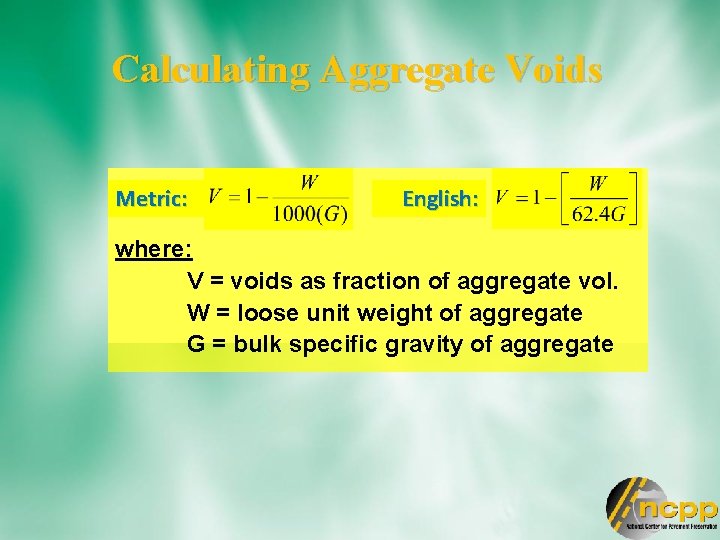
Calculating Aggregate Voids Metric: English: where: V = voids as fraction of aggregate vol. W = loose unit weight of aggregate G = bulk specific gravity of aggregate
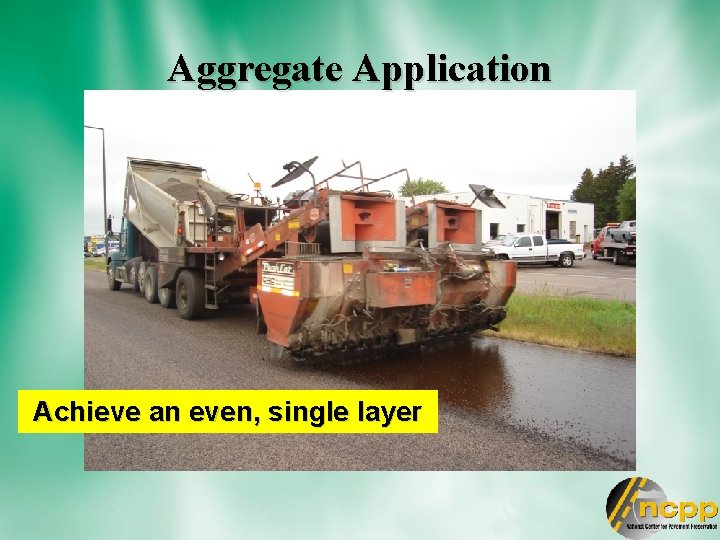
Aggregate Application Achieve an even, single layer
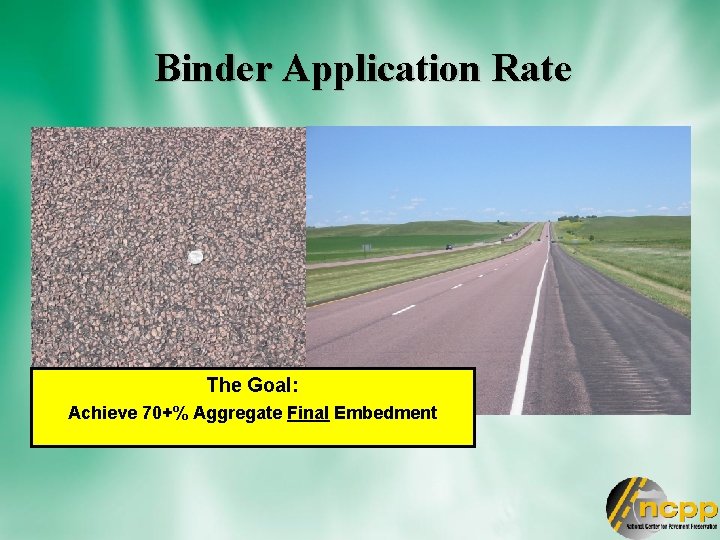
Binder Application Rate The Goal: Achieve 70+% Aggregate Final Embedment
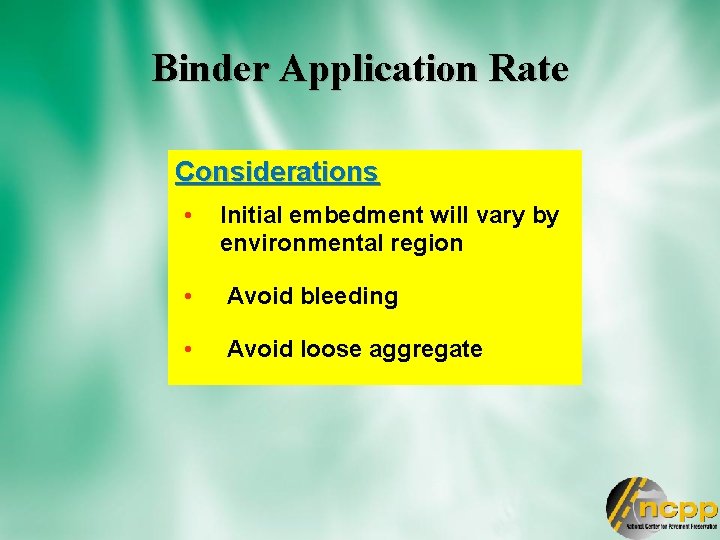
Binder Application Rate Considerations • Initial embedment will vary by environmental region • Avoid bleeding • Avoid loose aggregate
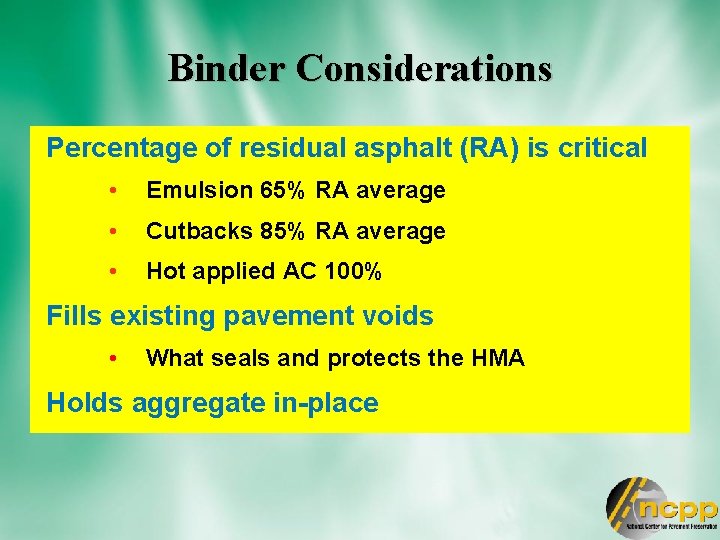
Binder Considerations Percentage of residual asphalt (RA) is critical • Emulsion 65% RA average • Cutbacks 85% RA average • Hot applied AC 100% Fills existing pavement voids • What seals and protects the HMA Holds aggregate in-place
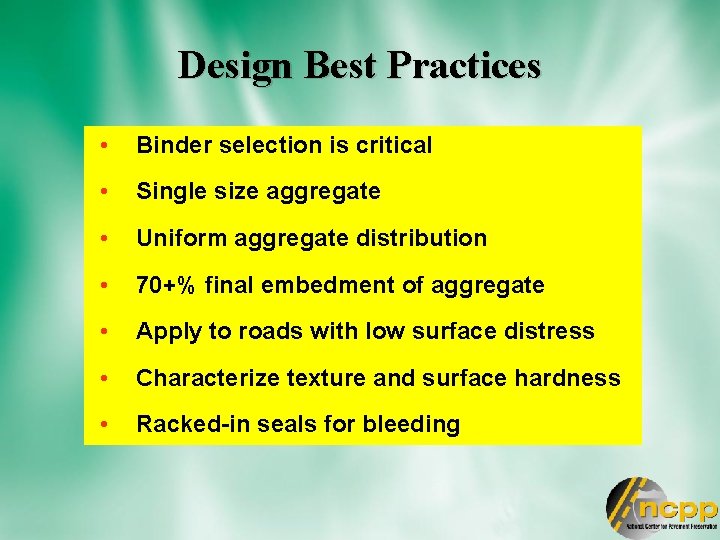
Design Best Practices • Binder selection is critical • Single size aggregate • Uniform aggregate distribution • 70+% final embedment of aggregate • Apply to roads with low surface distress • Characterize texture and surface hardness • Racked-in seals for bleeding
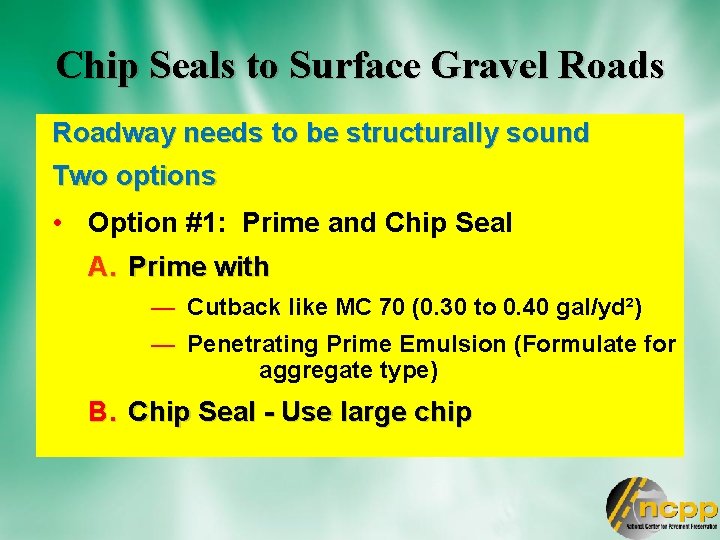
Chip Seals to Surface Gravel Roads Roadway needs to be structurally sound Two options • Option #1: Prime and Chip Seal A. Prime with — Cutback like MC 70 (0. 30 to 0. 40 gal/yd²) — Penetrating Prime Emulsion (Formulate for aggregate type) B. Chip Seal - Use large chip
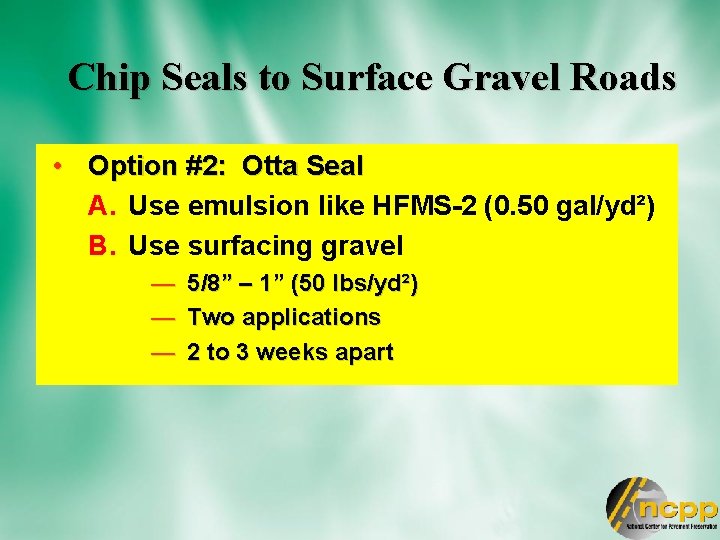
Chip Seals to Surface Gravel Roads • Option #2: Otta Seal A. Use emulsion like HFMS-2 (0. 50 gal/yd²) B. Use surfacing gravel — 5/8” – 1” (50 lbs/yd²) — Two applications — 2 to 3 weeks apart
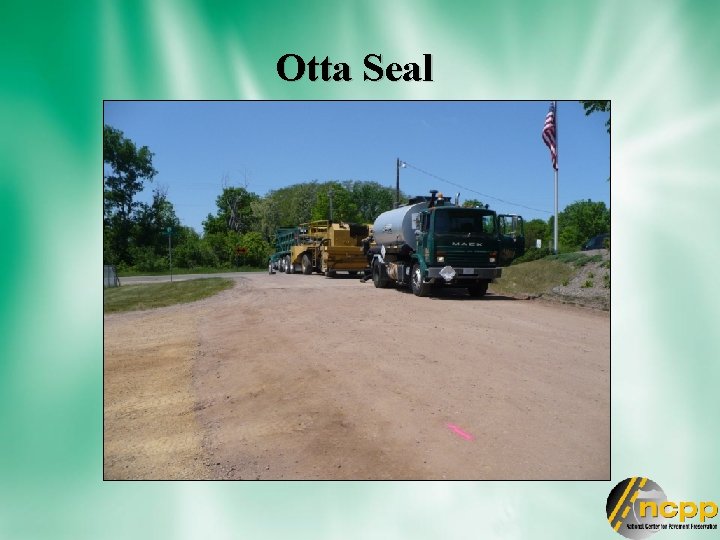
Otta Seal
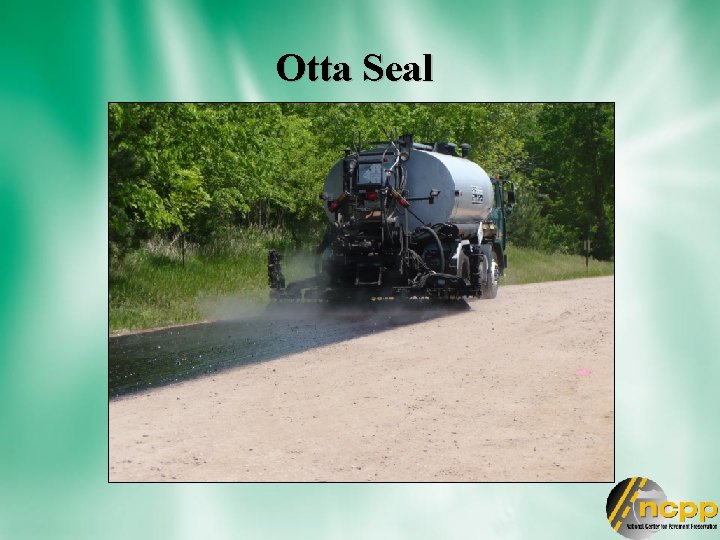
Otta Seal
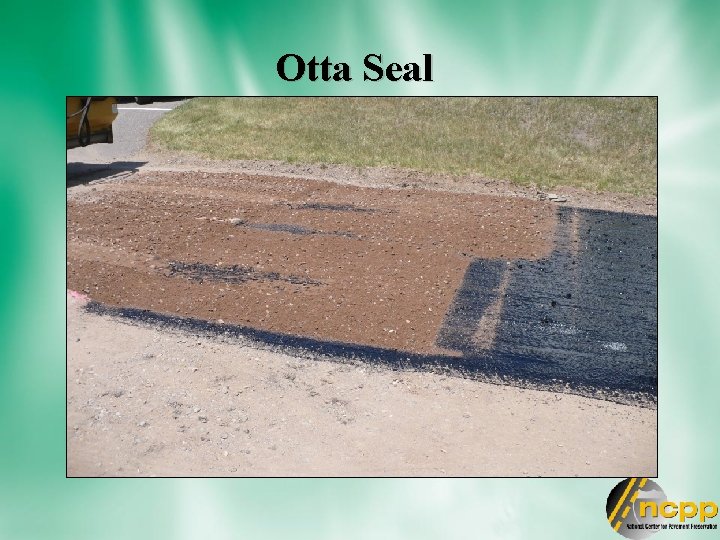
Otta Seal
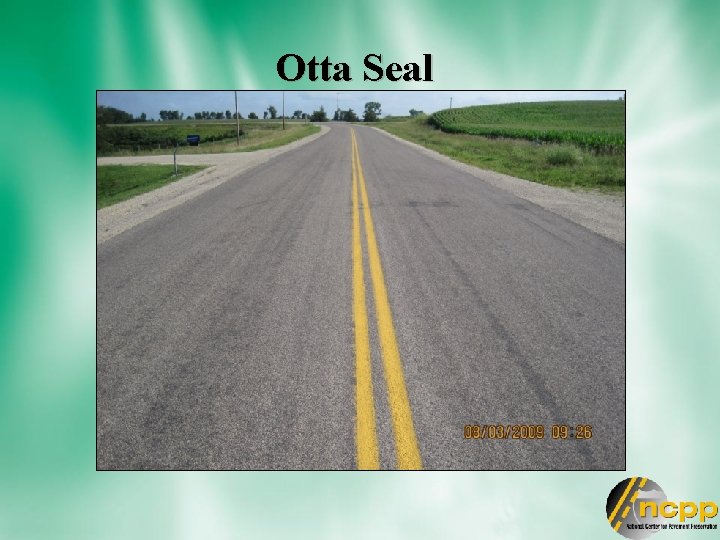
Otta Seal
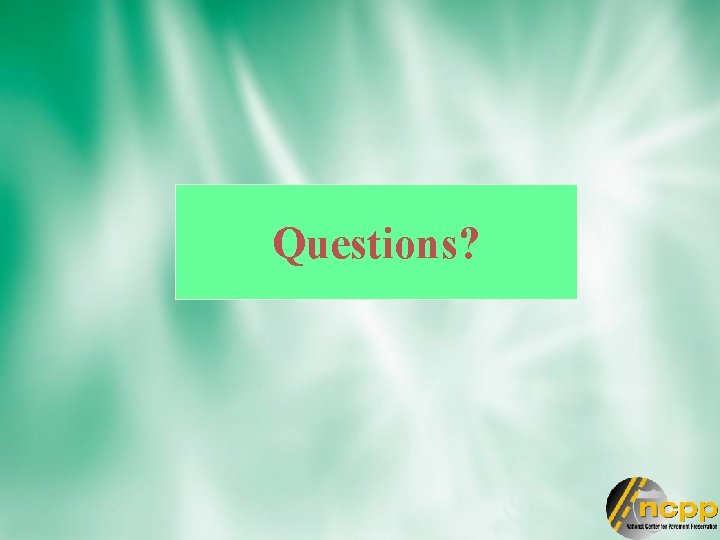
Questions?
Methylation & chip-on-chip microarray platform
Labyrinth seal design guidelines
Static crush seal
You gave me your peanut butter chocolate chip cookie
Pocketknife pledge
Continuous chip
Chip kirkpatrick
Chip krotee
Simultaneous multithreading: maximizing on-chip parallelism
Chip cosse law firm
Paint chip poetry template
Gene chip software
Give the structure of commercial 8mx 8 bit dram chip
Schärfster chip der welt
Continuous chip
Ic packaging miniaturization
Saasm chip
Gifi chip
Gi fi technology
Chip im schuh demenz
Digital light processing introduction
Stoxx blue chip
Chip inserter with pin straightener
Bump process
Chiptest
Output device
Baymax scanner
Wilf and wilma
Metal resistance to shear during chip formation is known as
8255 is ppi pit dma pic
A chip of glass ruby memorandum 2017
Eprom example
Doc pack 51
Virochip
Martin d f wong
Programmable chip card
Affymetrix chip
Ocdd definition
Chip cosse net worth
Studio wg3
Dsp processor architecture
Chip decapsulation
Vfbk hr
Circular movement around an axis
Generator chisel
Biff chip kipper floppy
Audio oscillator circuit