What we do Enterprise Software for achieving excellence
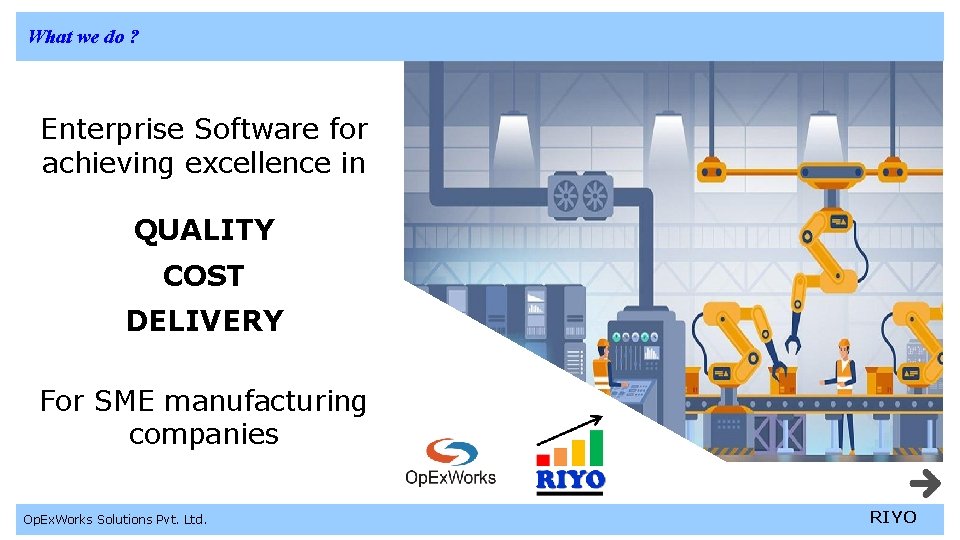
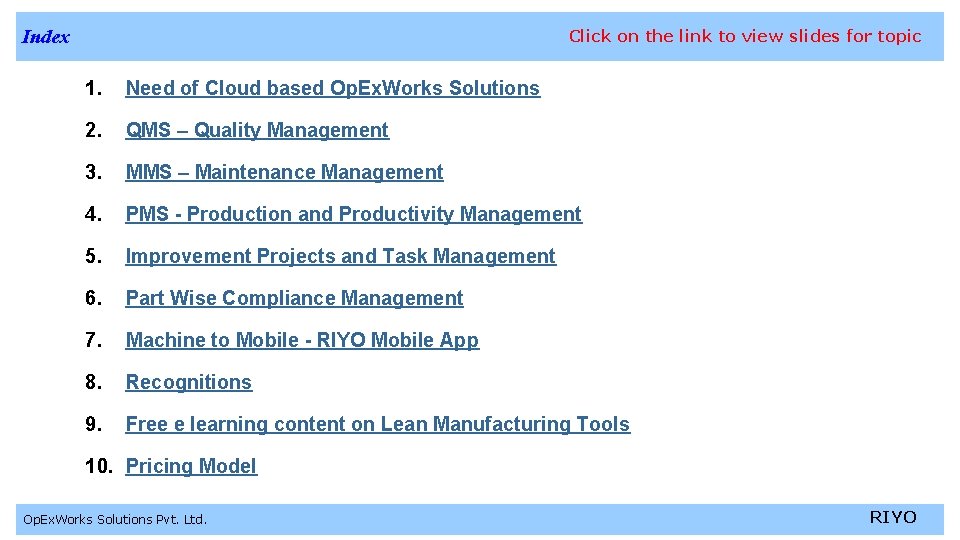
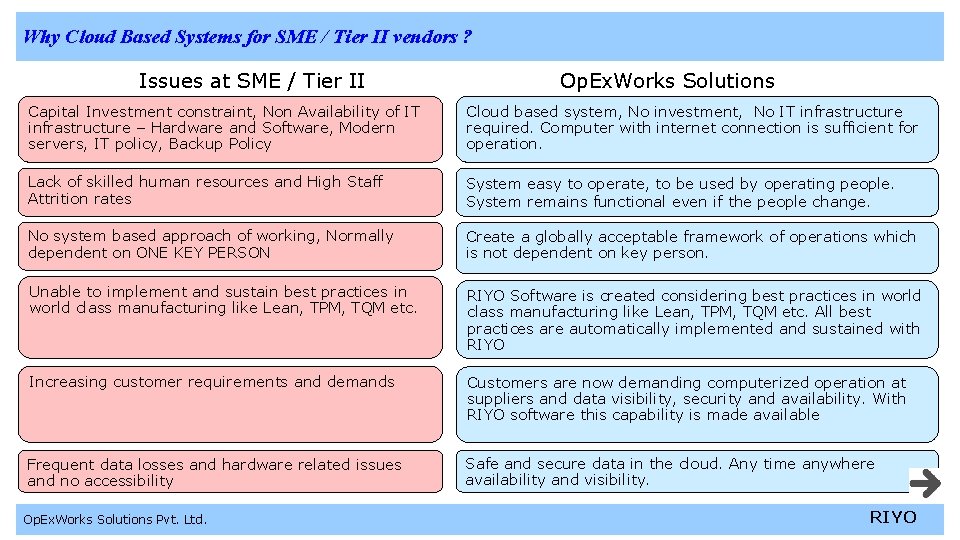
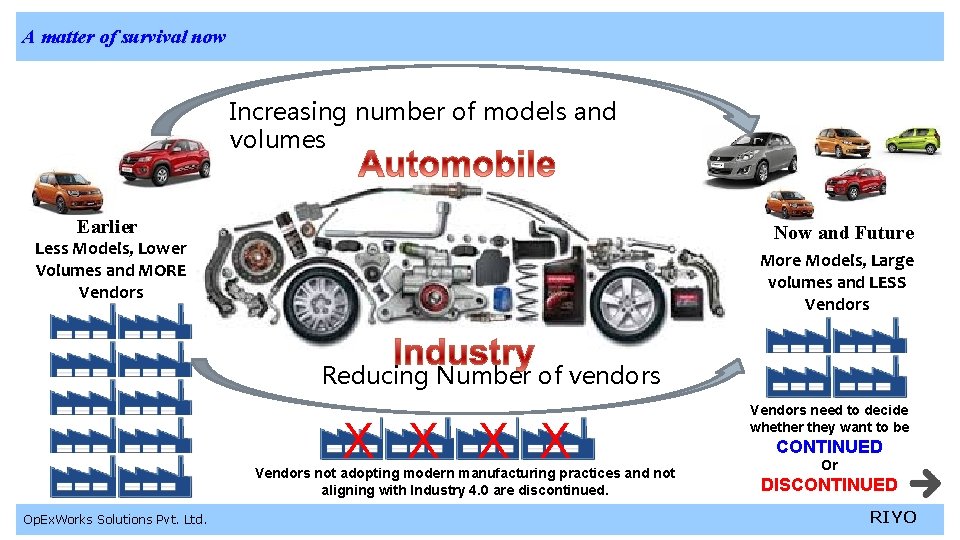
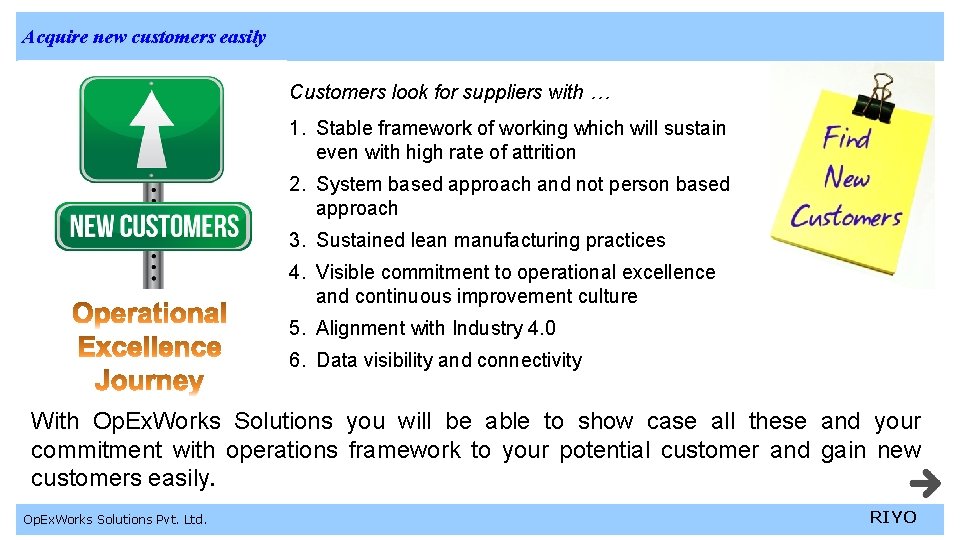
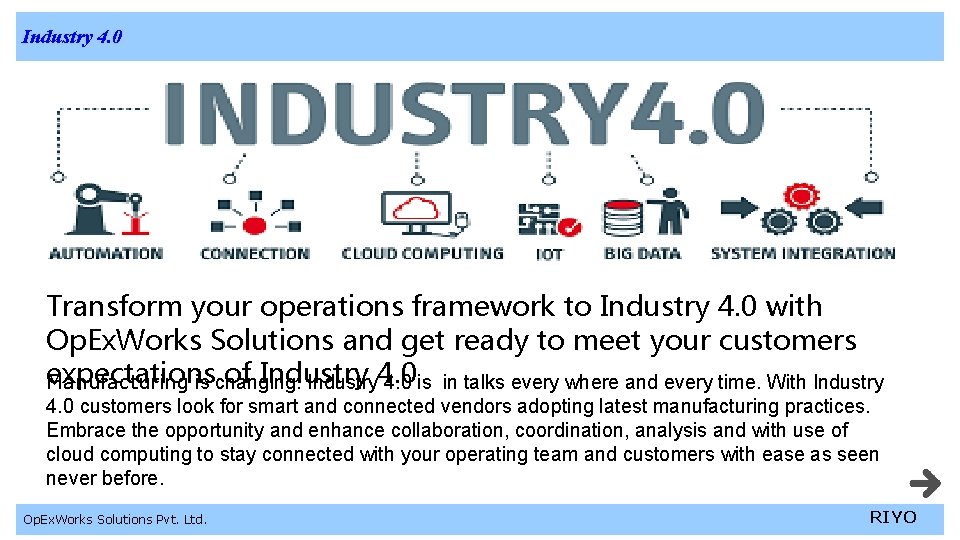
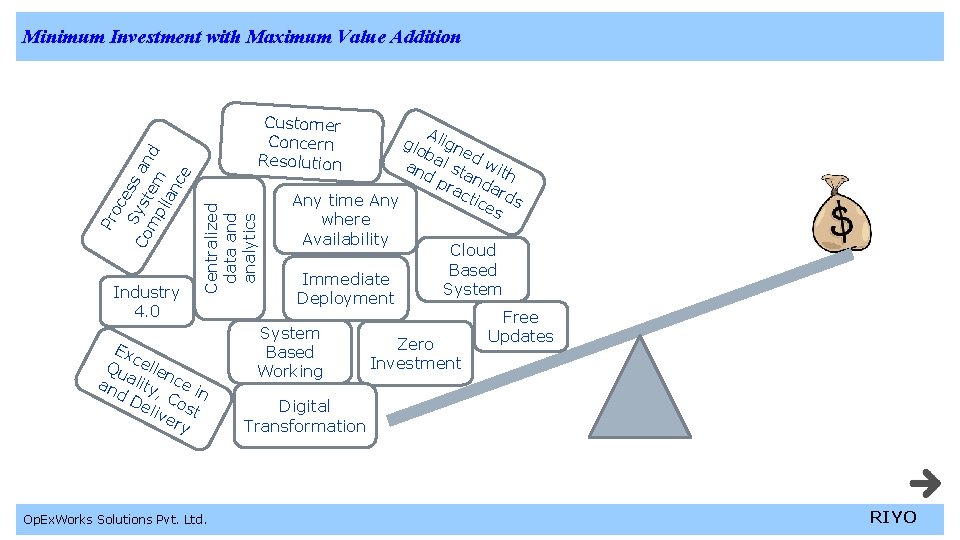
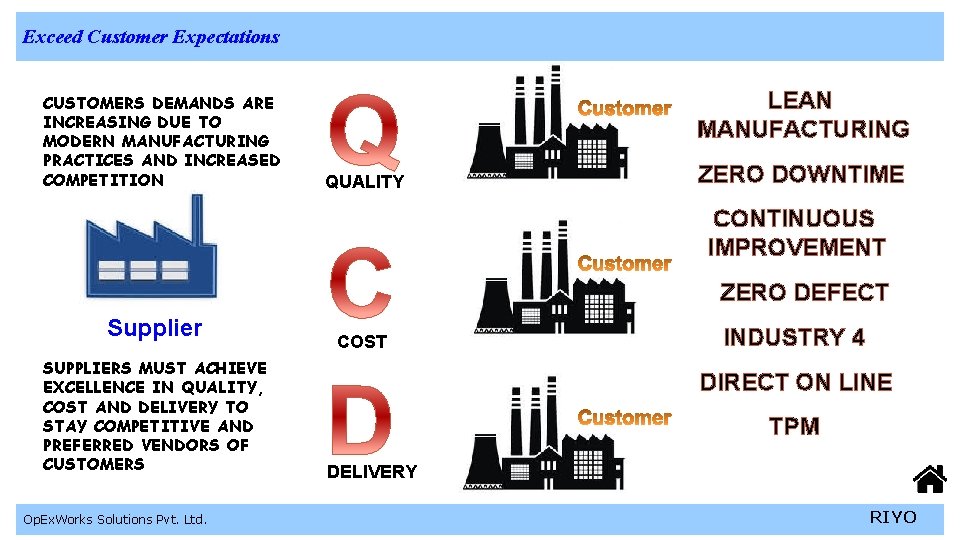
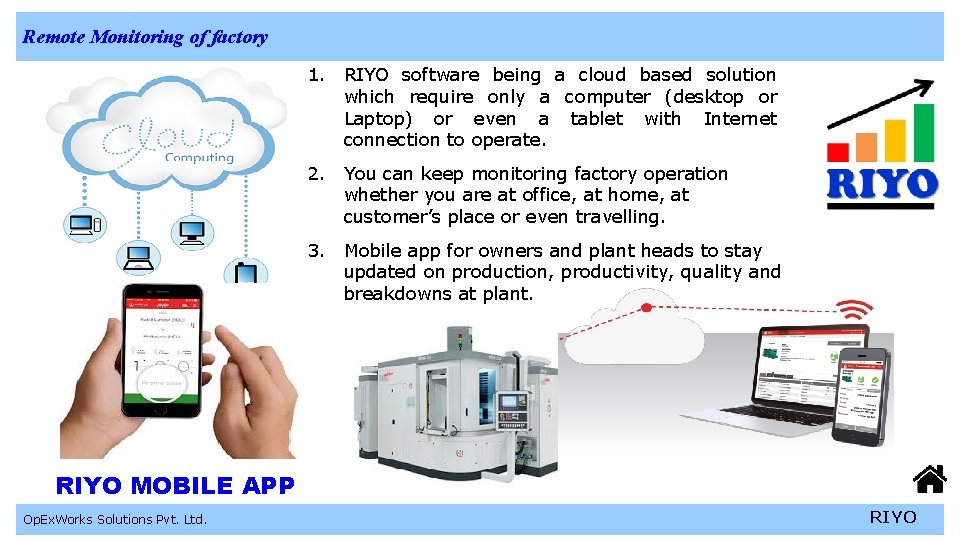
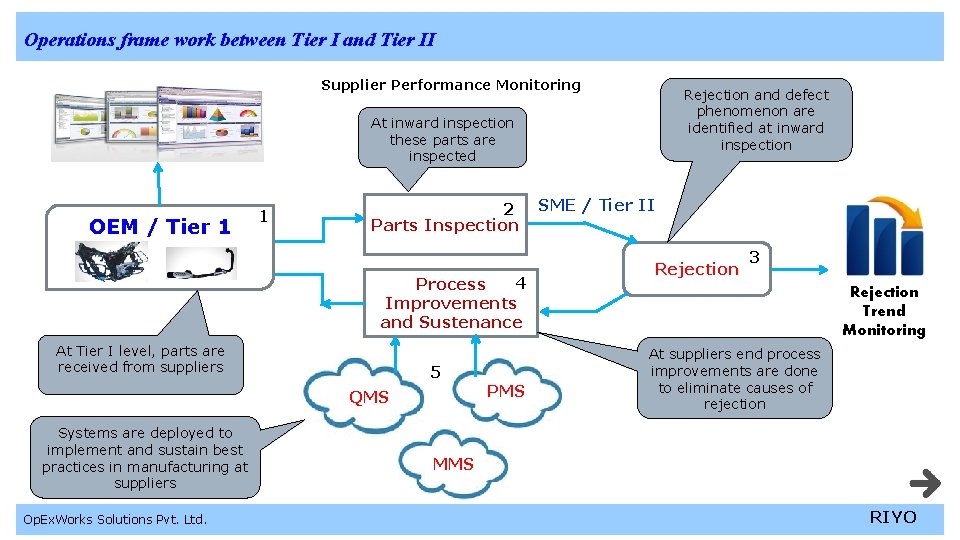
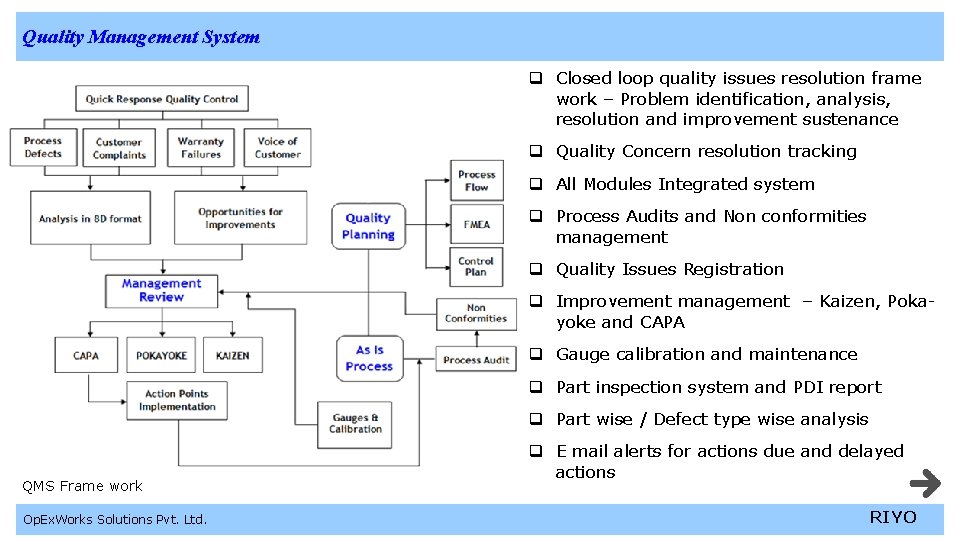
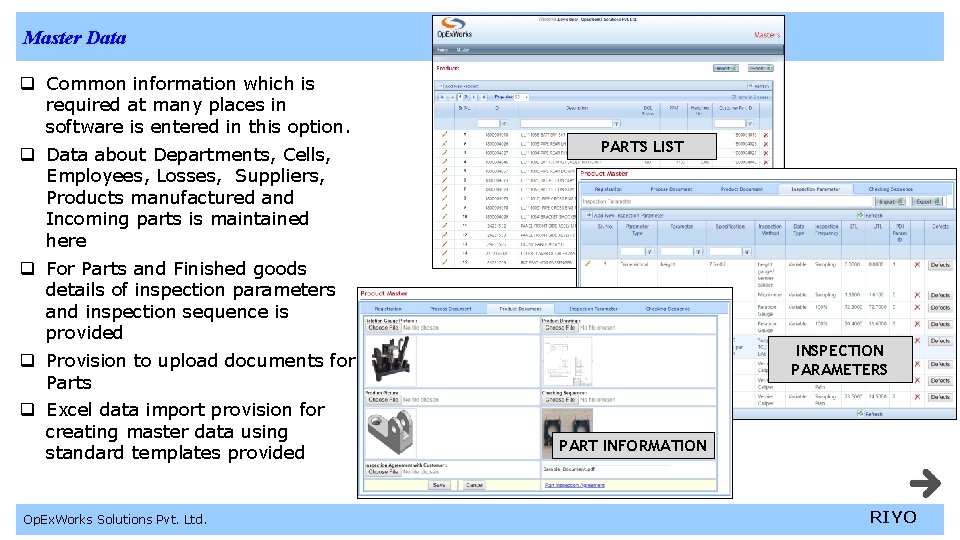
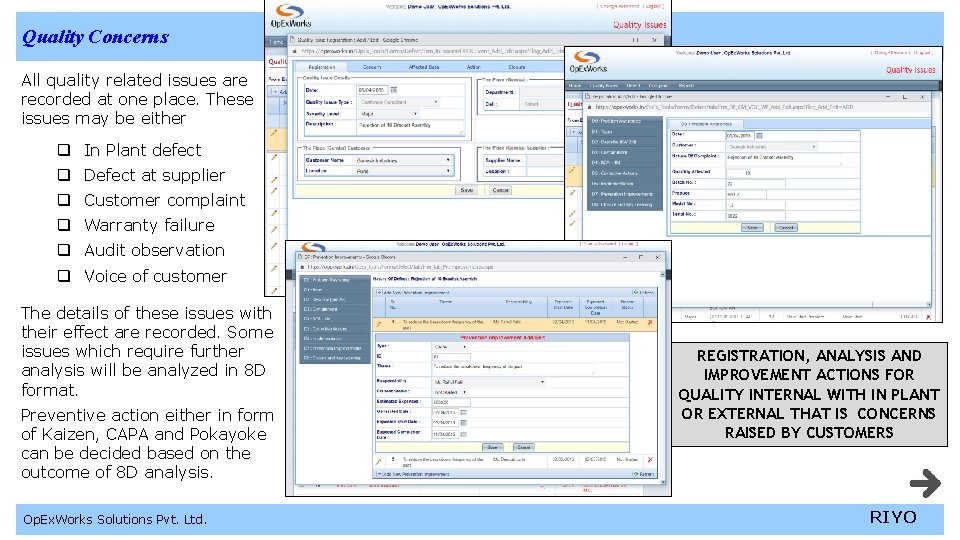
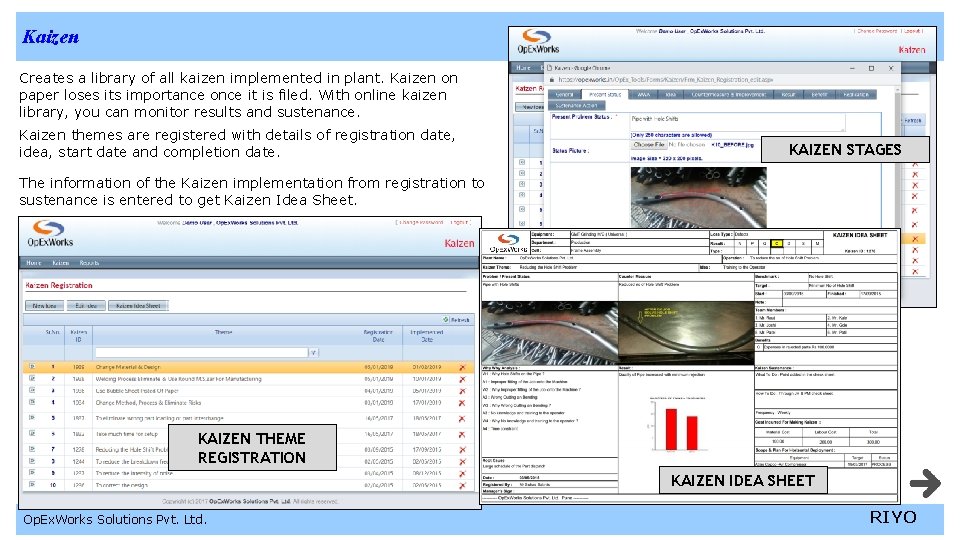
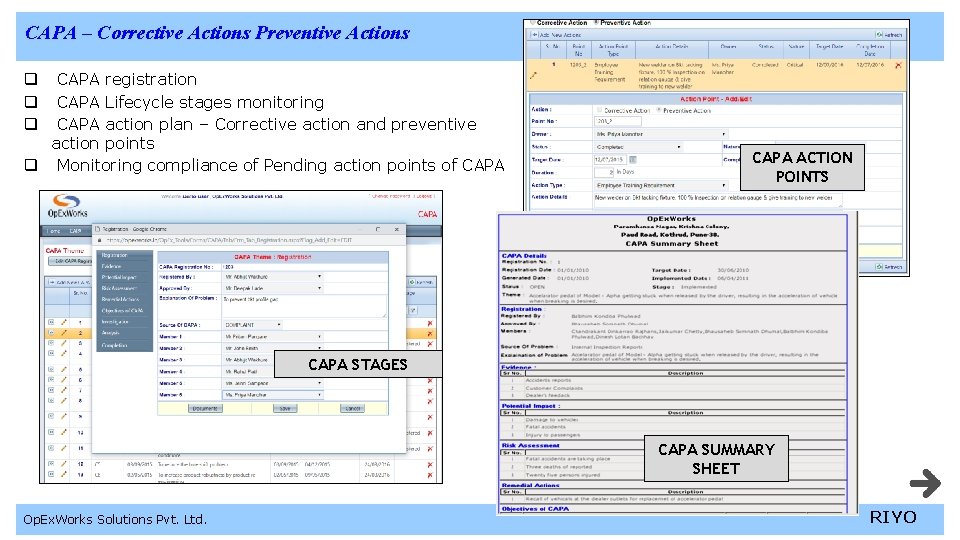
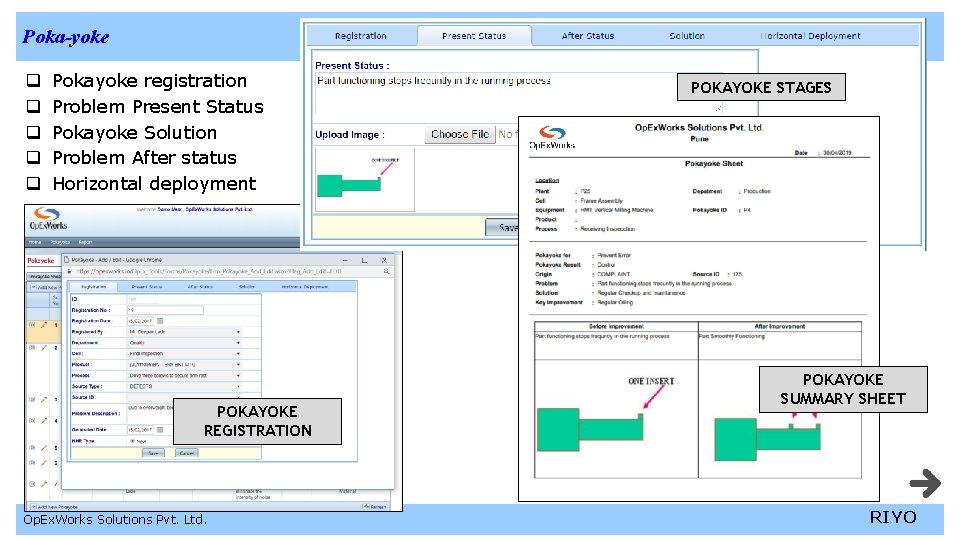
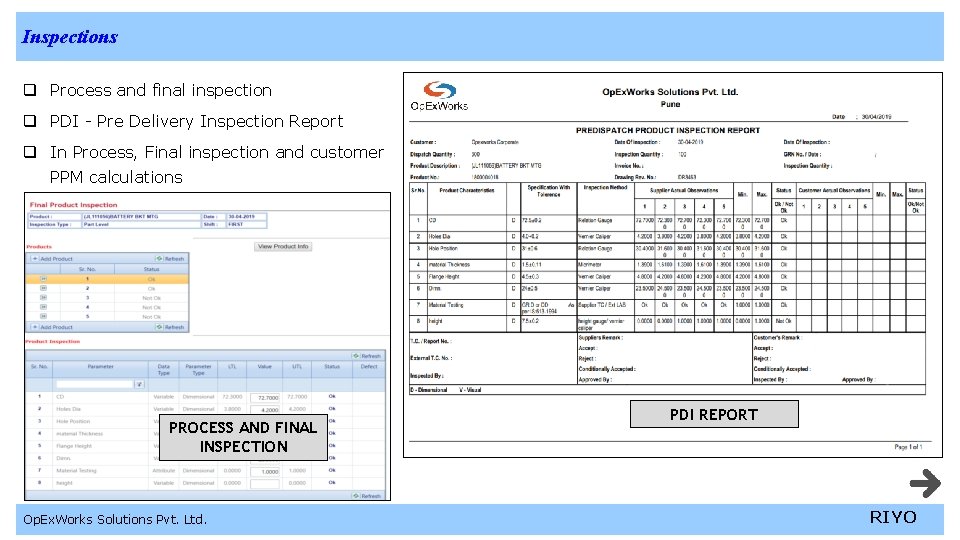
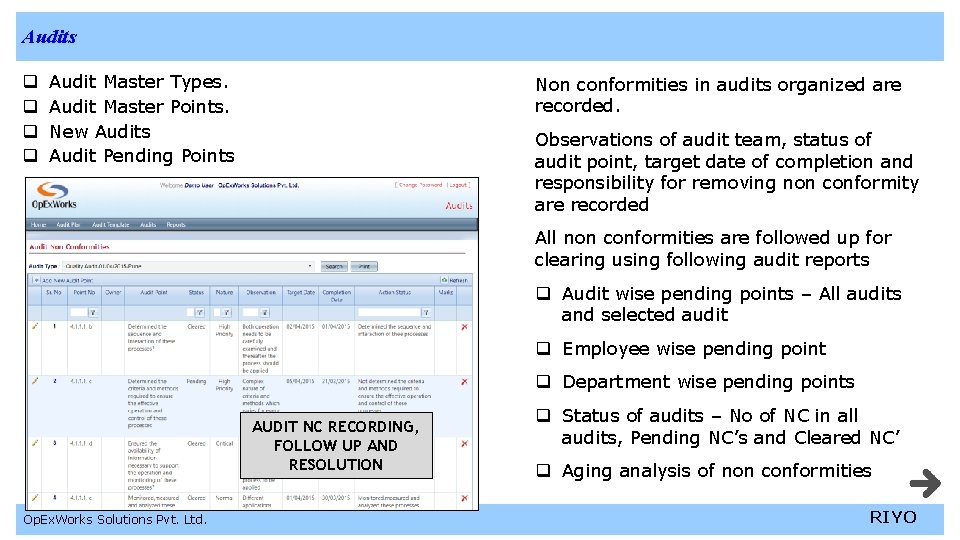
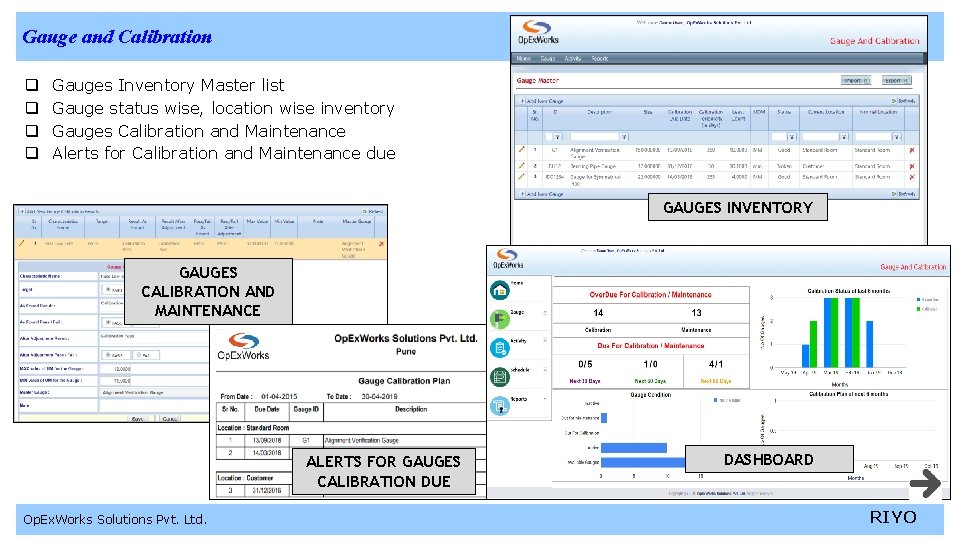
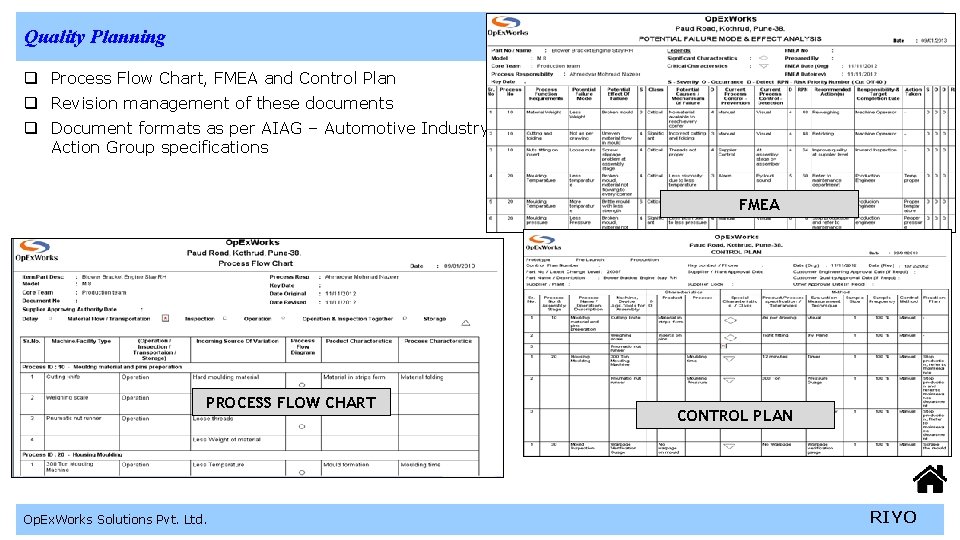
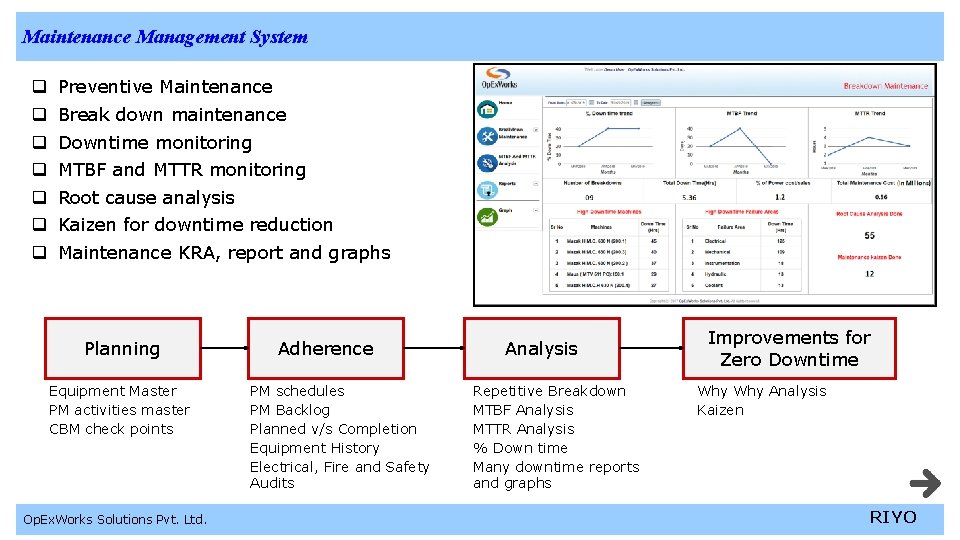
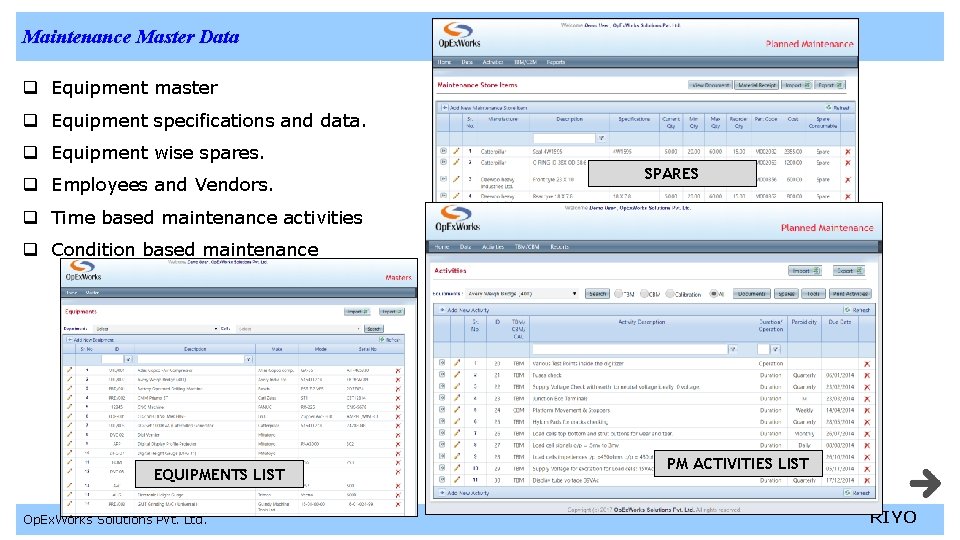
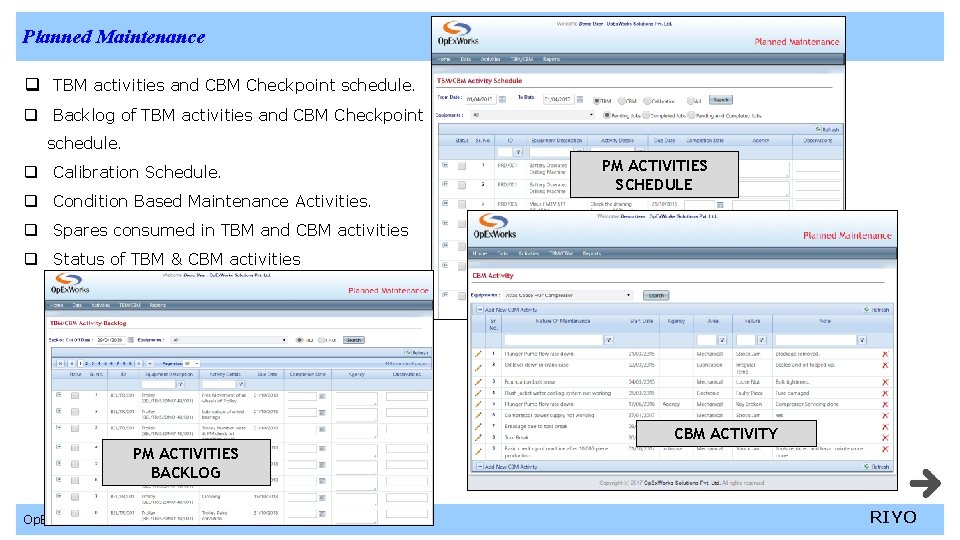
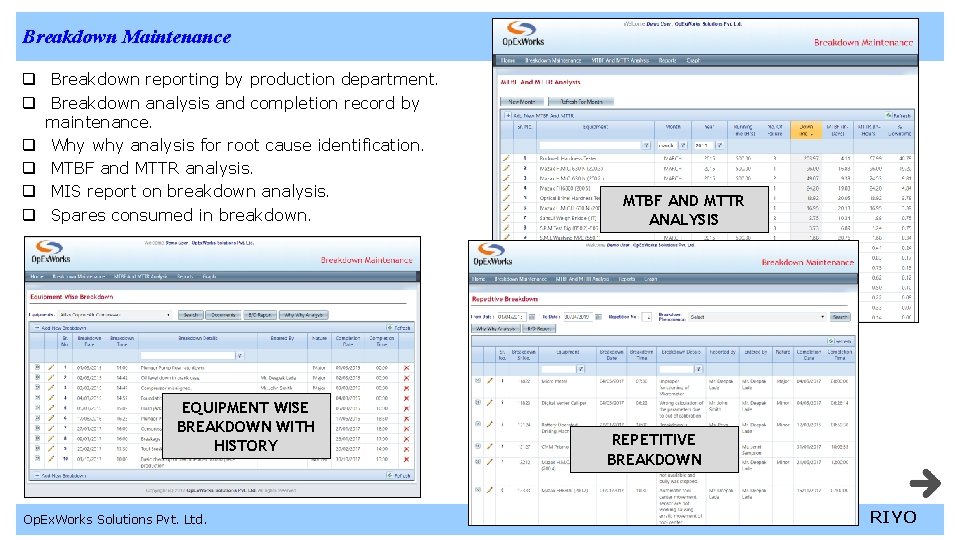
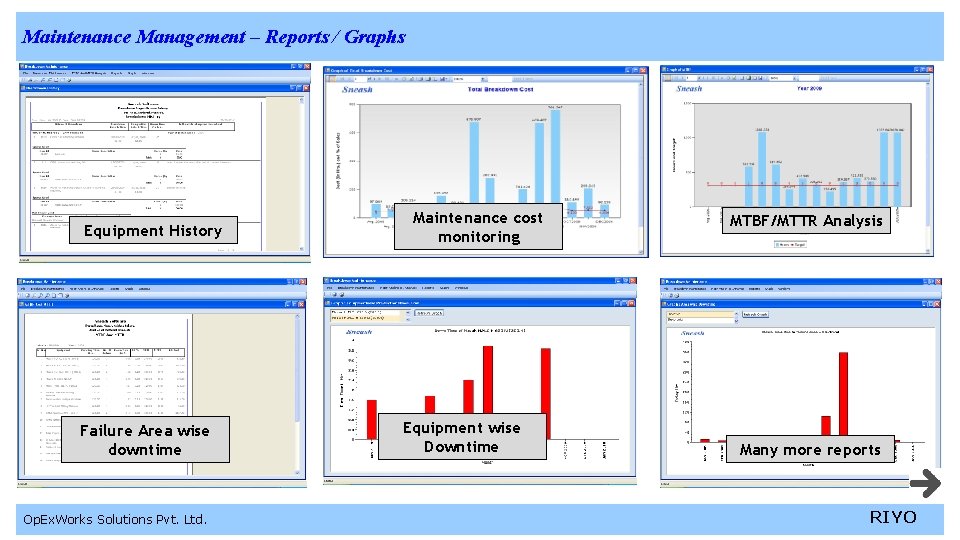
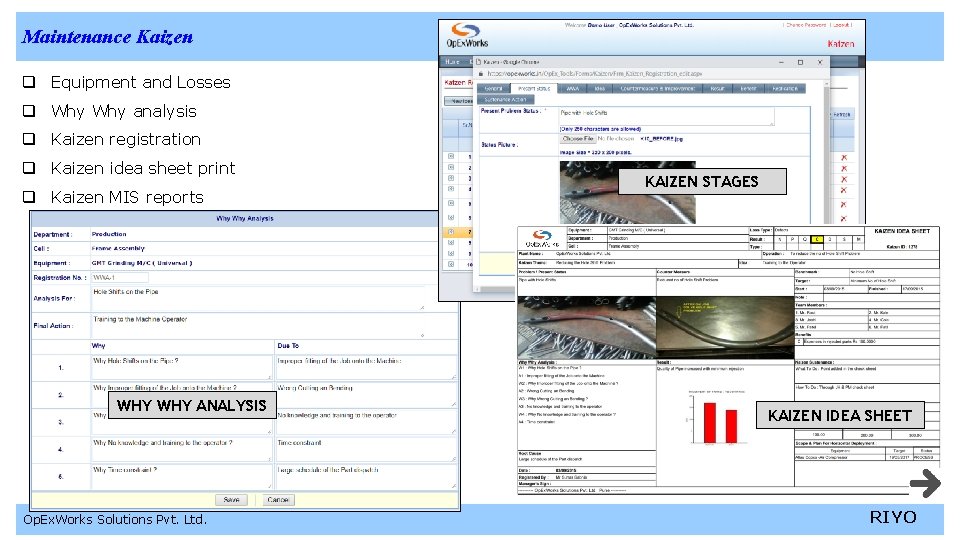
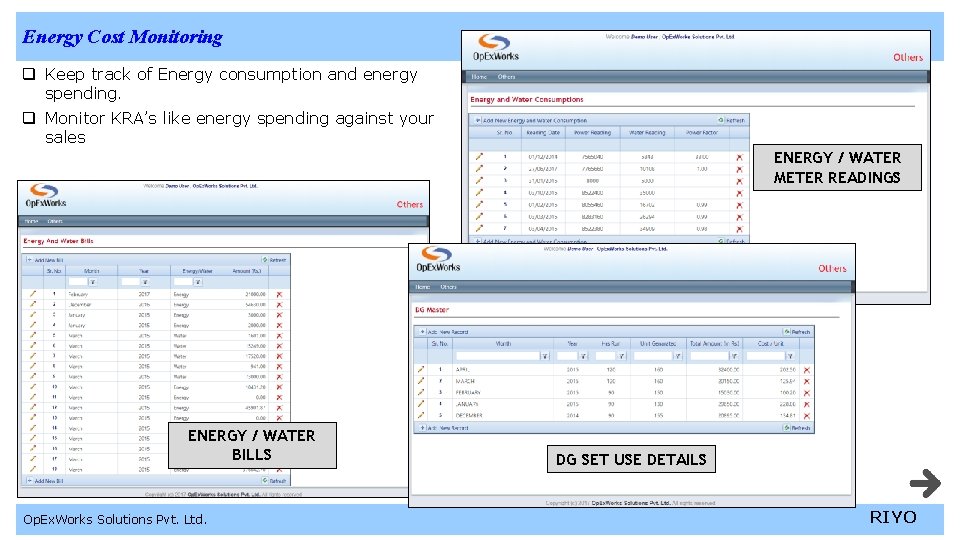
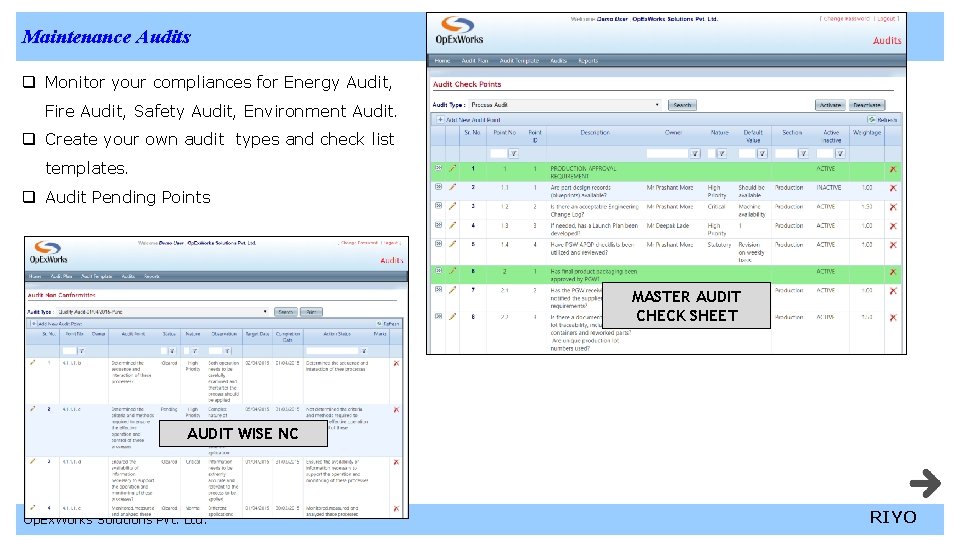
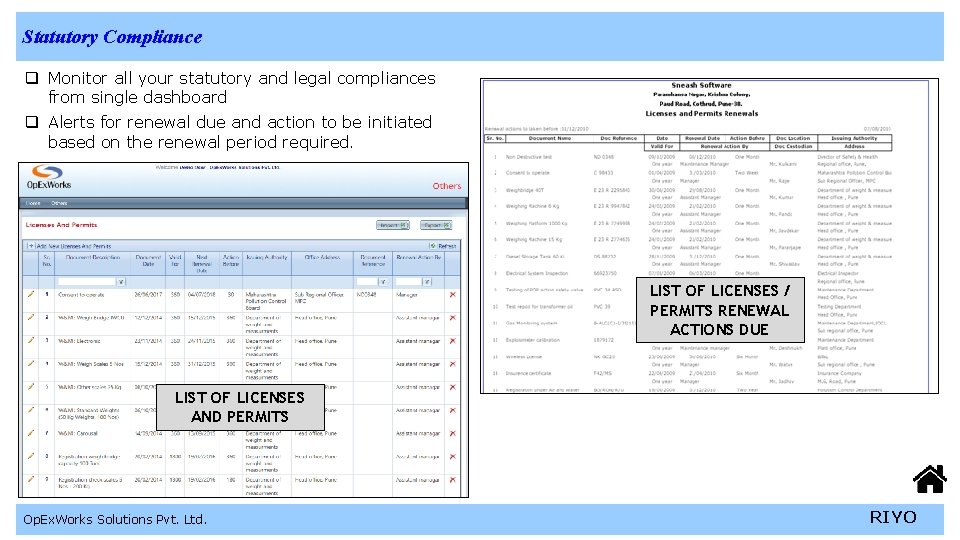
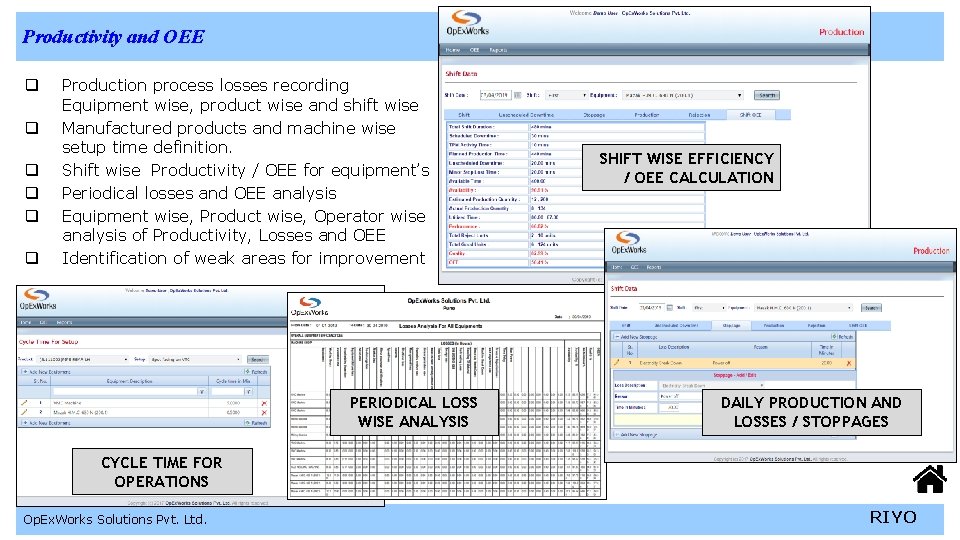
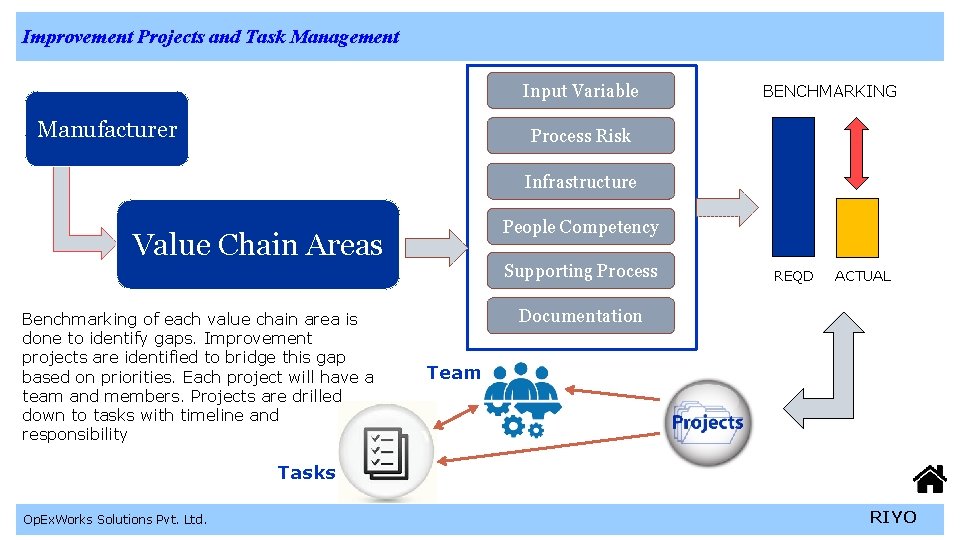
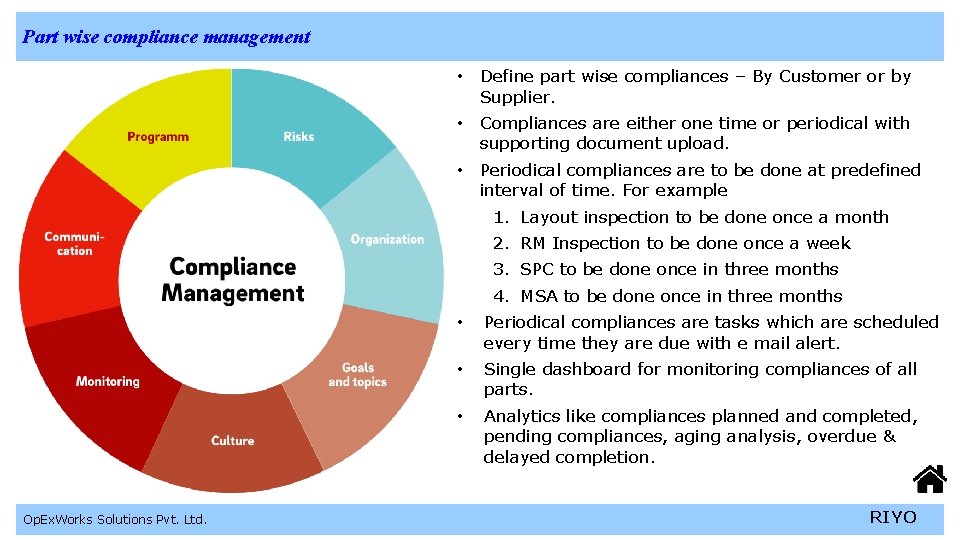
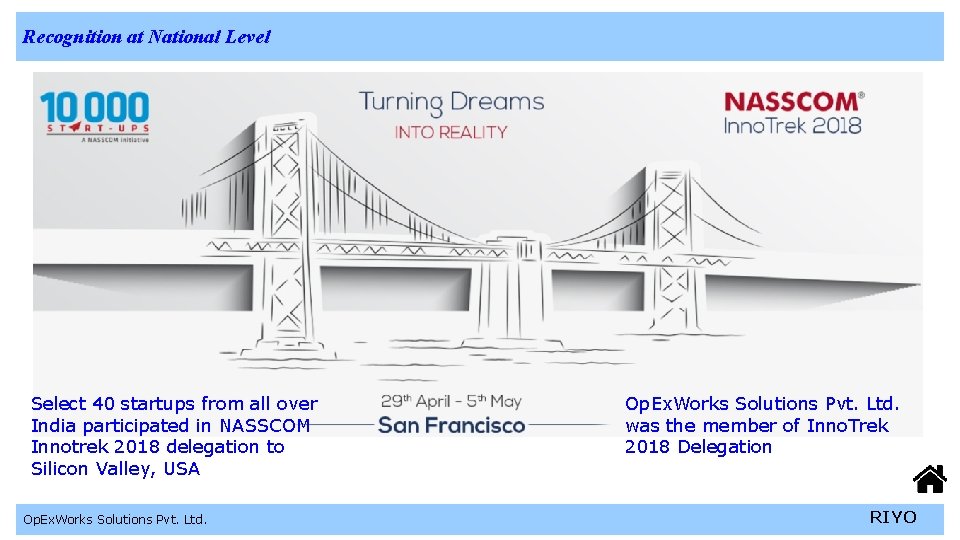
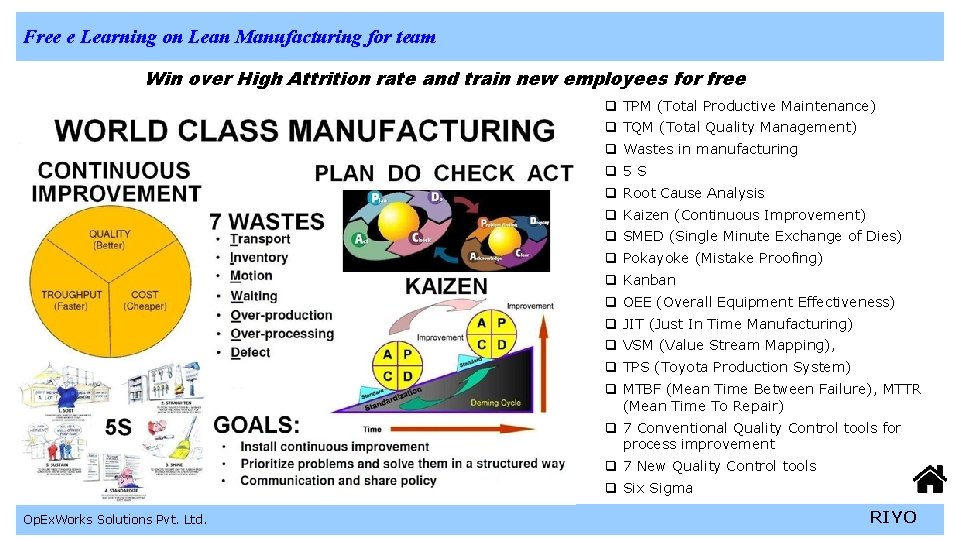
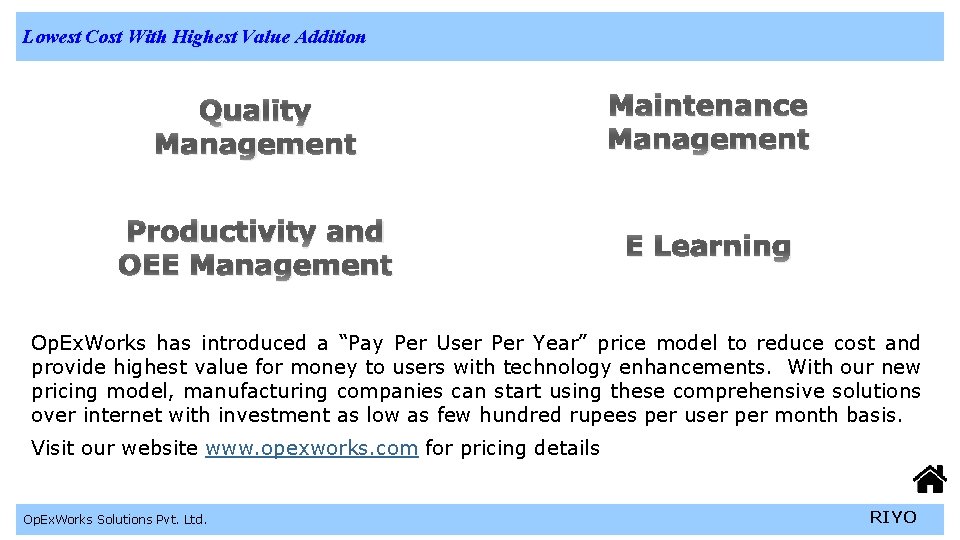

- Slides: 36
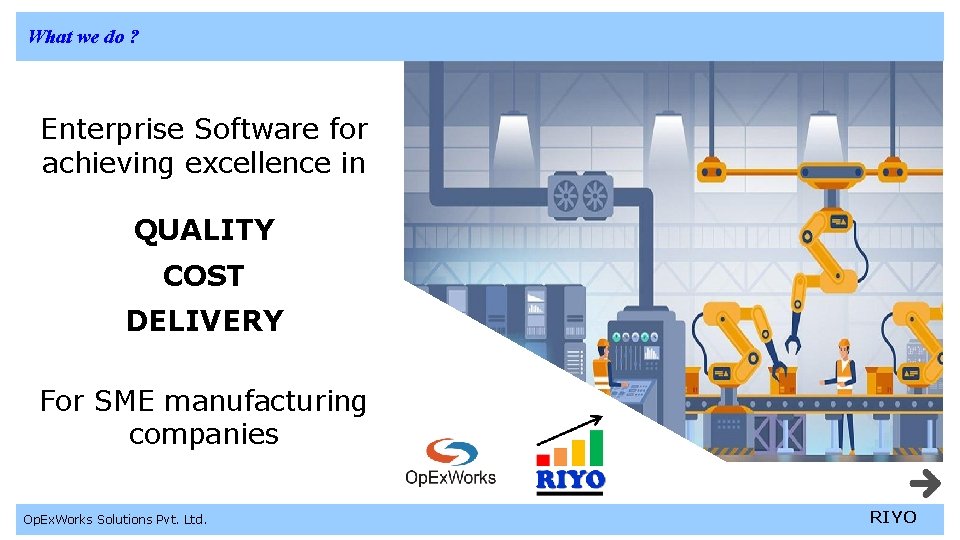
What we do ? Enterprise Software for achieving excellence in QUALITY COST DELIVERY For SME manufacturing companies Op. Ex. Works Solutions Pvt. Ltd. RIYO
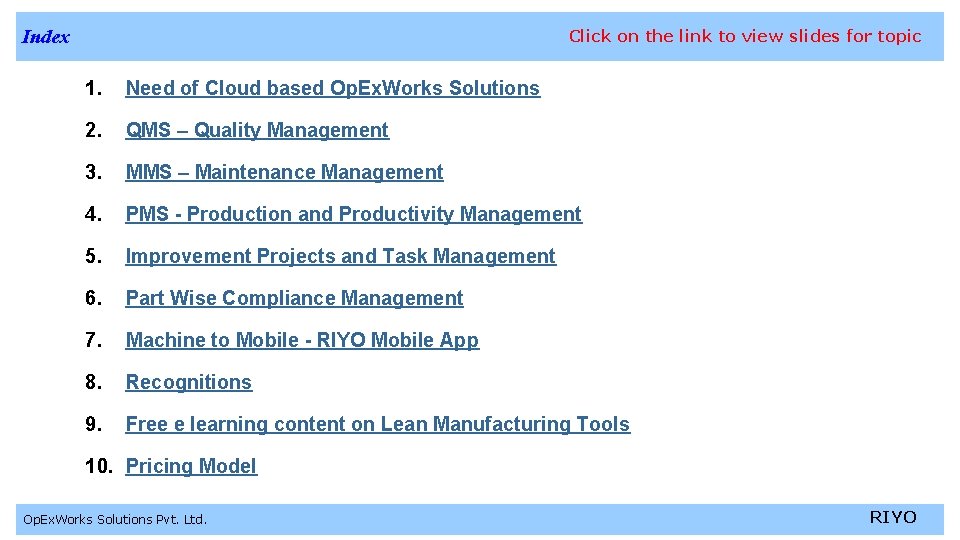
Index Click on the link to view slides for topic 1. Need of Cloud based Op. Ex. Works Solutions 2. QMS – Quality Management 3. MMS – Maintenance Management 4. PMS - Production and Productivity Management 5. Improvement Projects and Task Management 6. Part Wise Compliance Management 7. Machine to Mobile - RIYO Mobile App 8. Recognitions 9. Free e learning content on Lean Manufacturing Tools 10. Pricing Model Op. Ex. Works Solutions Pvt. Ltd. RIYO
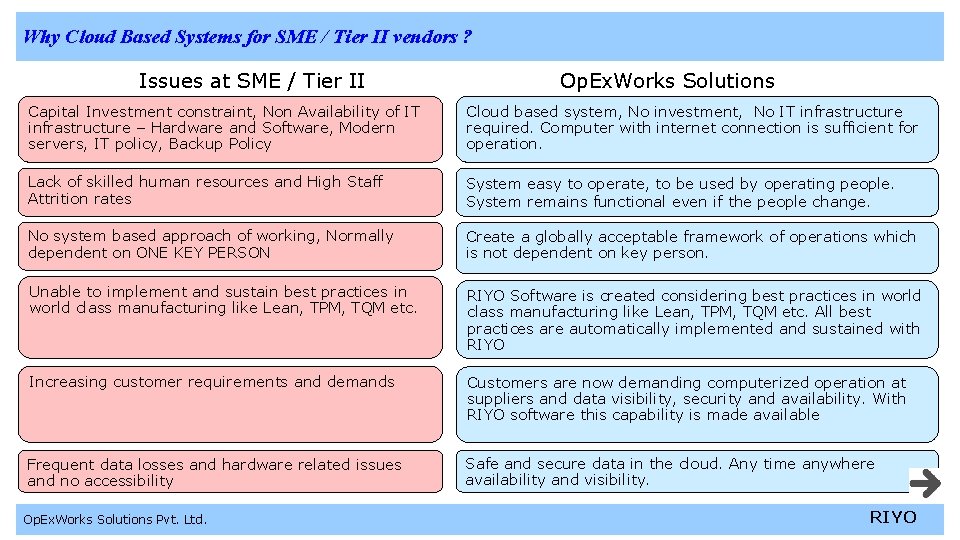
Why Cloud Based Systems for SME / Tier II vendors ? Issues at SME / Tier II Op. Ex. Works Solutions Capital Investment constraint, Non Availability of IT infrastructure – Hardware and Software, Modern servers, IT policy, Backup Policy Cloud based system, No investment, No IT infrastructure required. Computer with internet connection is sufficient for operation. Lack of skilled human resources and High Staff Attrition rates System easy to operate, to be used by operating people. System remains functional even if the people change. No system based approach of working, Normally dependent on ONE KEY PERSON Create a globally acceptable framework of operations which is not dependent on key person. Unable to implement and sustain best practices in world class manufacturing like Lean, TPM, TQM etc. RIYO Software is created considering best practices in world class manufacturing like Lean, TPM, TQM etc. All best practices are automatically implemented and sustained with RIYO Increasing customer requirements and demands Customers are now demanding computerized operation at suppliers and data visibility, security and availability. With RIYO software this capability is made available Frequent data losses and hardware related issues and no accessibility Safe and secure data in the cloud. Any time anywhere availability and visibility. Op. Ex. Works Solutions Pvt. Ltd. RIYO
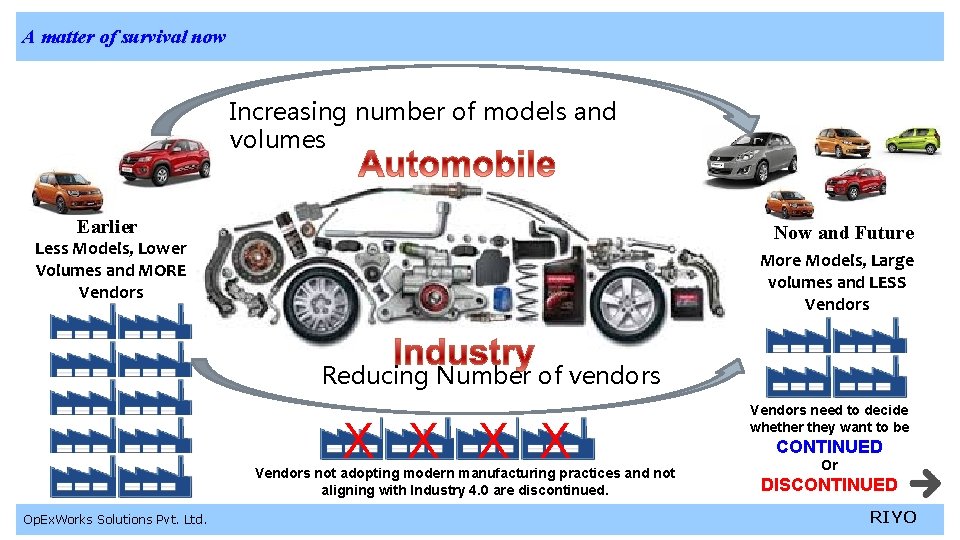
A matter of survival now Increasing number of models and volumes Earlier Now and Future Less Models, Lower Volumes and MORE Vendors More Models, Large volumes and LESS Vendors Reducing Number of vendors X X Vendors not adopting modern manufacturing practices and not aligning with Industry 4. 0 are discontinued. Op. Ex. Works Solutions Pvt. Ltd. Vendors need to decide whether they want to be CONTINUED Or DISCONTINUED RIYO
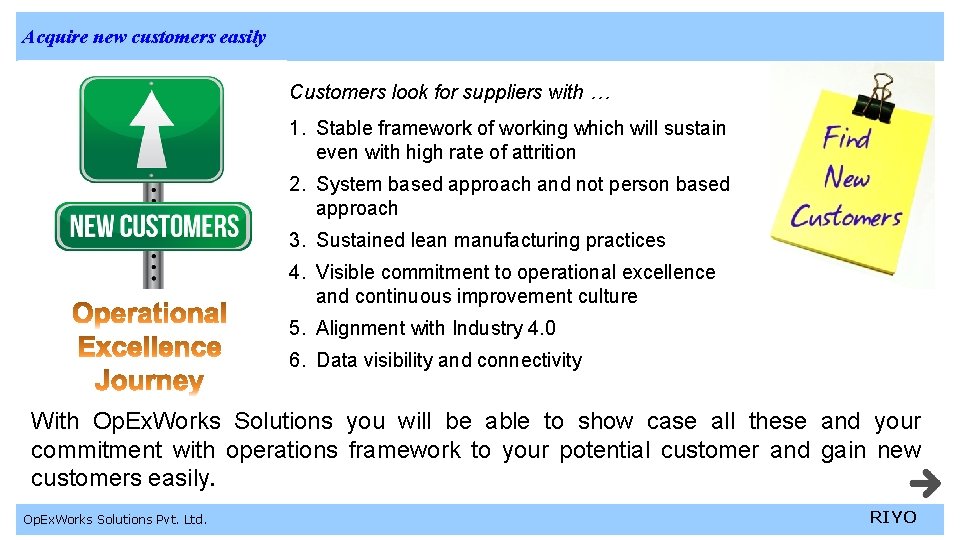
Acquire new customers easily Customers look for suppliers with … 1. Stable framework of working which will sustain even with high rate of attrition 2. System based approach and not person based approach 3. Sustained lean manufacturing practices 4. Visible commitment to operational excellence and continuous improvement culture 5. Alignment with Industry 4. 0 6. Data visibility and connectivity With Op. Ex. Works Solutions you will be able to show case all these and your commitment with operations framework to your potential customer and gain new customers easily. Op. Ex. Works Solutions Pvt. Ltd. RIYO
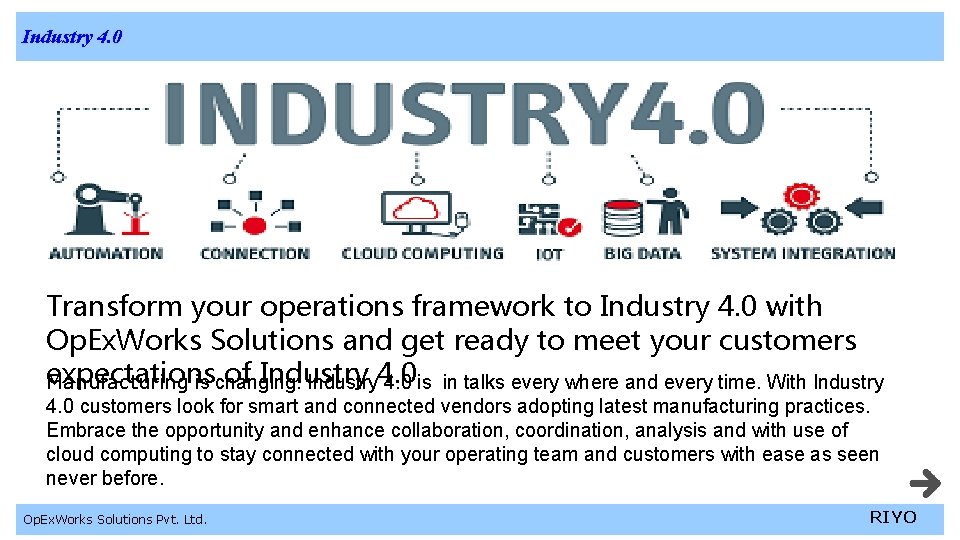
Industry 4. 0 Transform your operations framework to Industry 4. 0 with Op. Ex. Works Solutions and get ready to meet your customers expectations of Industry Manufacturing is changing. Industry 4. 0 is in talks every where and every time. With Industry 4. 0 customers look for smart and connected vendors adopting latest manufacturing practices. Embrace the opportunity and enhance collaboration, coordination, analysis and with use of cloud computing to stay connected with your operating team and customers with ease as seen never before. Op. Ex. Works Solutions Pvt. Ltd. RIYO
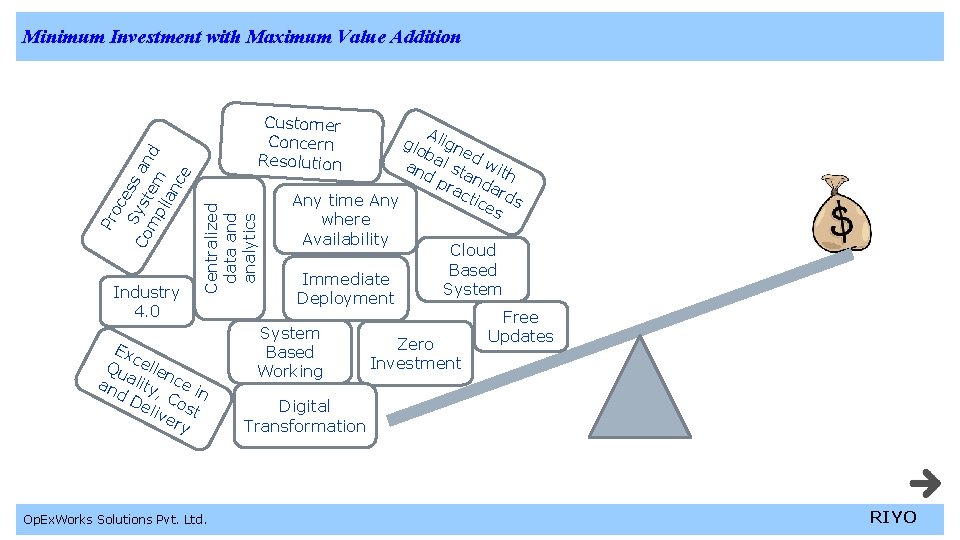
Industry 4. 0 Customer Concern Resolution A glo lign ed b an al st wit h d p an rac dar tic ds Any time Any es where Availability Cloud Based Immediate System Deployment Free System Updates Zero Based Investment Working Centralized data and analytics Pr oc es S Co yst s an m em d pli an ce Minimum Investment with Maximum Value Addition Ex c Qu elle n an ality ce i d. D , C n eli ost ve ry Op. Ex. Works Solutions Pvt. Ltd. Digital Transformation RIYO
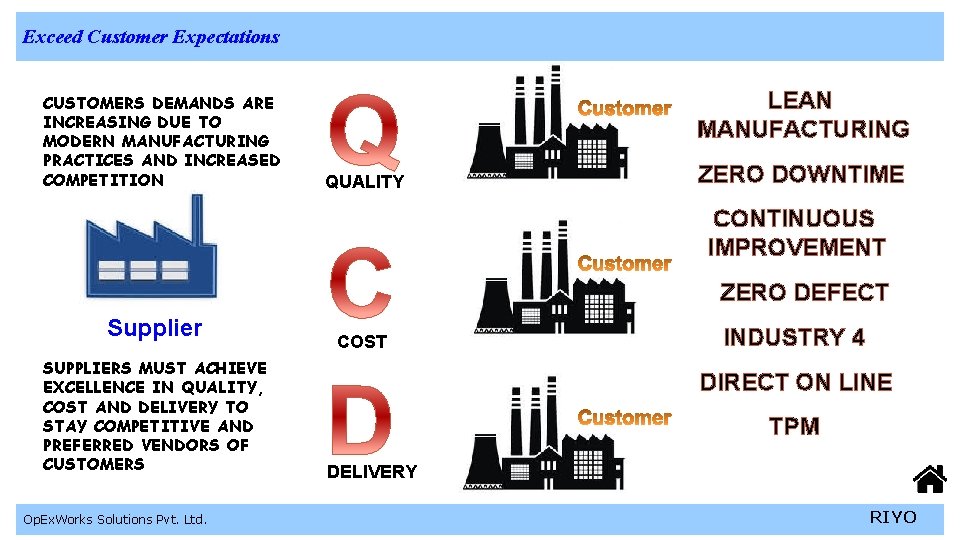
Exceed Customer Expectations CUSTOMERS DEMANDS ARE INCREASING DUE TO MODERN MANUFACTURING PRACTICES AND INCREASED COMPETITION LEAN MANUFACTURING QUALITY ZERO DOWNTIME CONTINUOUS IMPROVEMENT ZERO DEFECT Supplier SUPPLIERS MUST ACHIEVE EXCELLENCE IN QUALITY, COST AND DELIVERY TO STAY COMPETITIVE AND PREFERRED VENDORS OF CUSTOMERS Op. Ex. Works Solutions Pvt. Ltd. COST INDUSTRY 4 DIRECT ON LINE TPM DELIVERY RIYO
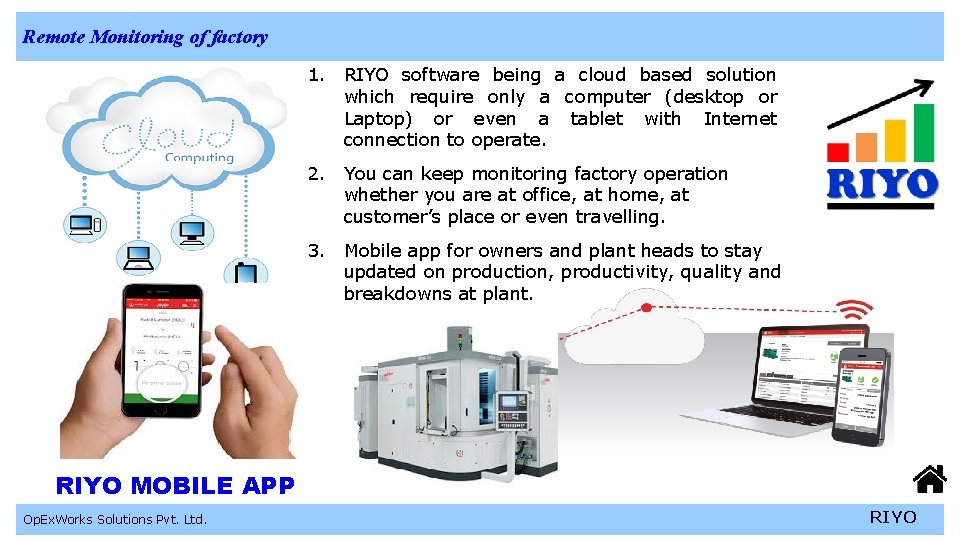
Remote Monitoring of factory 1. RIYO software being a cloud based solution which require only a computer (desktop or Laptop) or even a tablet with Internet connection to operate. 2. You can keep monitoring factory operation whether you are at office, at home, at customer’s place or even travelling. 3. Mobile app for owners and plant heads to stay updated on production, productivity, quality and breakdowns at plant. RIYO MOBILE APP Op. Ex. Works Solutions Pvt. Ltd. RIYO
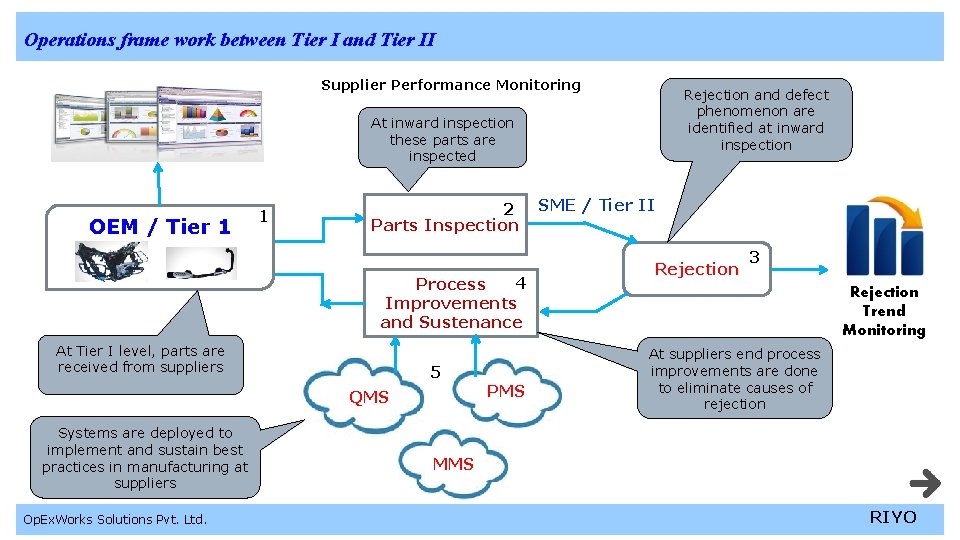
Operations frame work between Tier I and Tier II Supplier Performance Monitoring Rejection and defect phenomenon are identified at inward inspection At inward inspection these parts are inspected OEM / Tier 1 1 2 Parts Inspection 4 Process Improvements and Sustenance At Tier I level, parts are received from suppliers 5 PMS QMS Systems are deployed to implement and sustain best practices in manufacturing at suppliers Op. Ex. Works Solutions Pvt. Ltd. SME / Tier II Rejection 3 Rejection Trend Monitoring At suppliers end process improvements are done to eliminate causes of rejection MMS RIYO
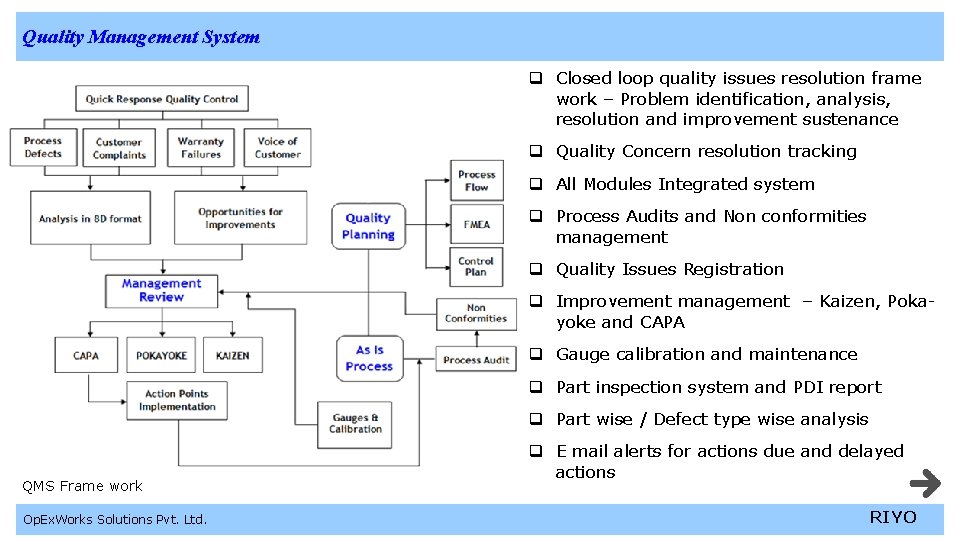
Quality Management System q Closed loop quality issues resolution frame work – Problem identification, analysis, resolution and improvement sustenance q Quality Concern resolution tracking q All Modules Integrated system q Process Audits and Non conformities management q Quality Issues Registration q Improvement management – Kaizen, Pokayoke and CAPA q Gauge calibration and maintenance q Part inspection system and PDI report q Part wise / Defect type wise analysis QMS Frame work Op. Ex. Works Solutions Pvt. Ltd. q E mail alerts for actions due and delayed actions RIYO
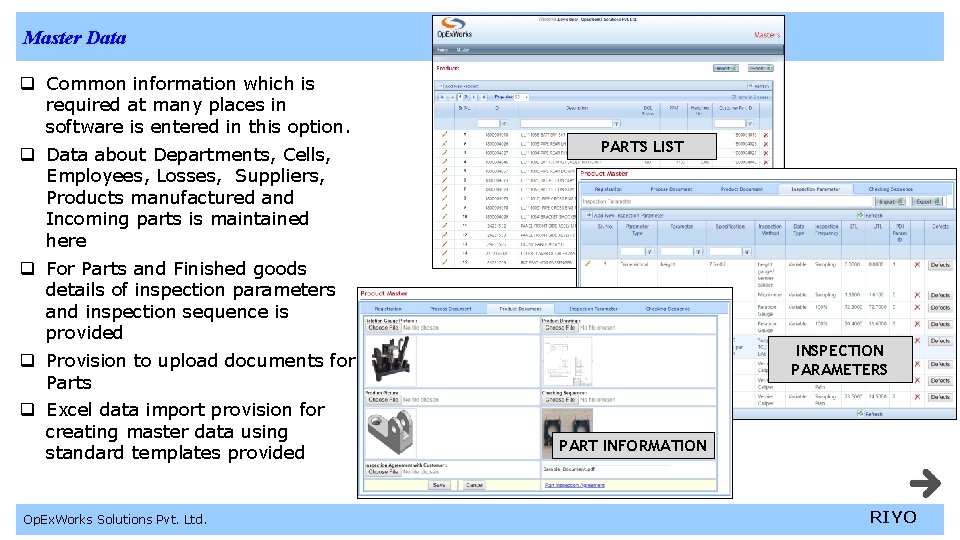
Master Data q Common information which is required at many places in software is entered in this option. q Data about Departments, Cells, Employees, Losses, Suppliers, Products manufactured and Incoming parts is maintained here q For Parts and Finished goods details of inspection parameters and inspection sequence is provided q Provision to upload documents for Parts q Excel data import provision for creating master data using standard templates provided Op. Ex. Works Solutions Pvt. Ltd. PARTS LIST INSPECTION PARAMETERS PART INFORMATION RIYO
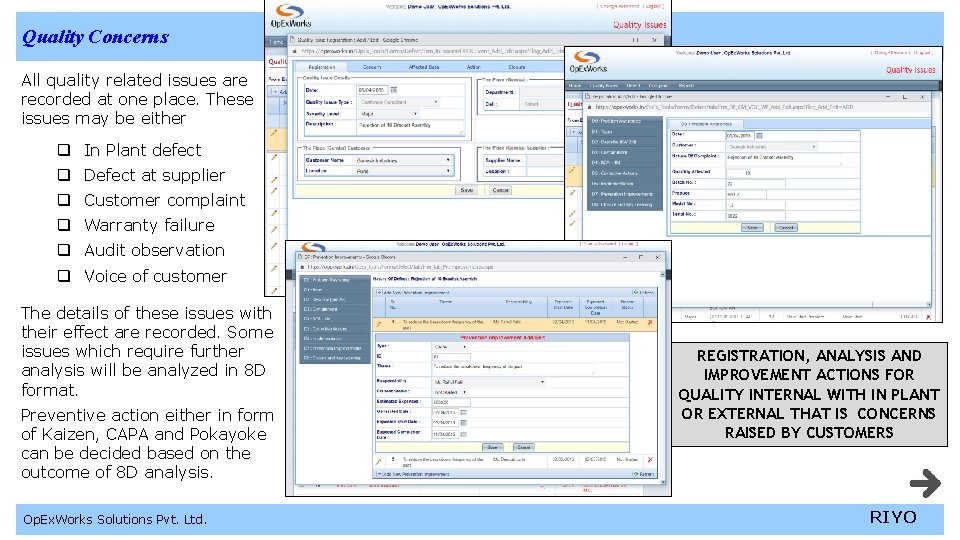
Quality Concerns All quality related issues are recorded at one place. These issues may be either q In Plant defect q Defect at supplier q Customer complaint q Warranty failure q Audit observation q Voice of customer The details of these issues with their effect are recorded. Some issues which require further analysis will be analyzed in 8 D format. Preventive action either in form of Kaizen, CAPA and Pokayoke can be decided based on the outcome of 8 D analysis. Op. Ex. Works Solutions Pvt. Ltd. REGISTRATION, ANALYSIS AND IMPROVEMENT ACTIONS FOR QUALITY INTERNAL WITH IN PLANT OR EXTERNAL THAT IS CONCERNS RAISED BY CUSTOMERS RIYO
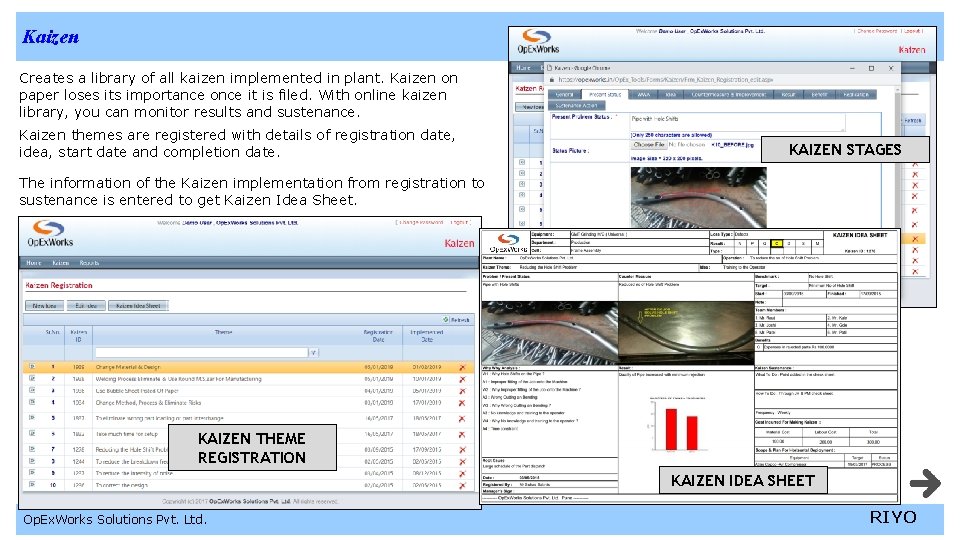
Kaizen Creates a library of all kaizen implemented in plant. Kaizen on paper loses its importance once it is filed. With online kaizen library, you can monitor results and sustenance. Kaizen themes are registered with details of registration date, idea, start date and completion date. KAIZEN STAGES The information of the Kaizen implementation from registration to sustenance is entered to get Kaizen Idea Sheet. KAIZEN THEME REGISTRATION KAIZEN IDEA SHEET Op. Ex. Works Solutions Pvt. Ltd. RIYO
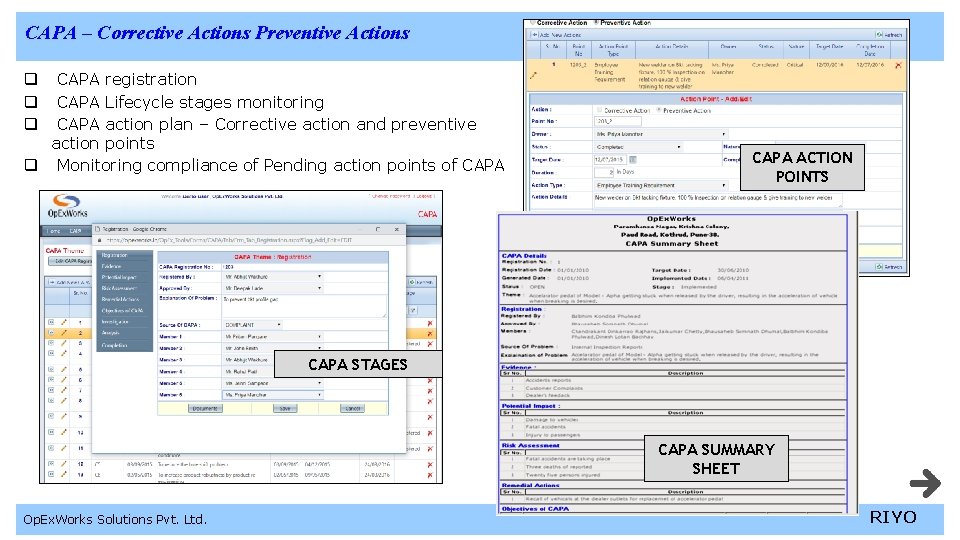
CAPA – Corrective Actions Preventive Actions CAPA registration CAPA Lifecycle stages monitoring CAPA action plan – Corrective action and preventive action points q Monitoring compliance of Pending action points of CAPA q q q CAPA ACTION POINTS CAPA STAGES CAPA SUMMARY SHEET Op. Ex. Works Solutions Pvt. Ltd. RIYO
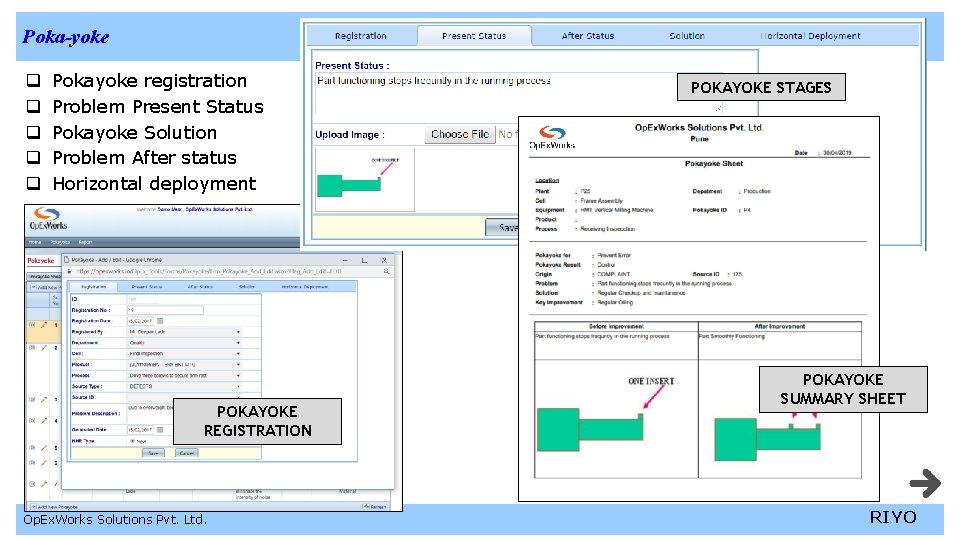
Poka-yoke q q q Pokayoke registration Problem Present Status Pokayoke Solution Problem After status Horizontal deployment POKAYOKE REGISTRATION Op. Ex. Works Solutions Pvt. Ltd. POKAYOKE STAGES POKAYOKE SUMMARY SHEET RIYO
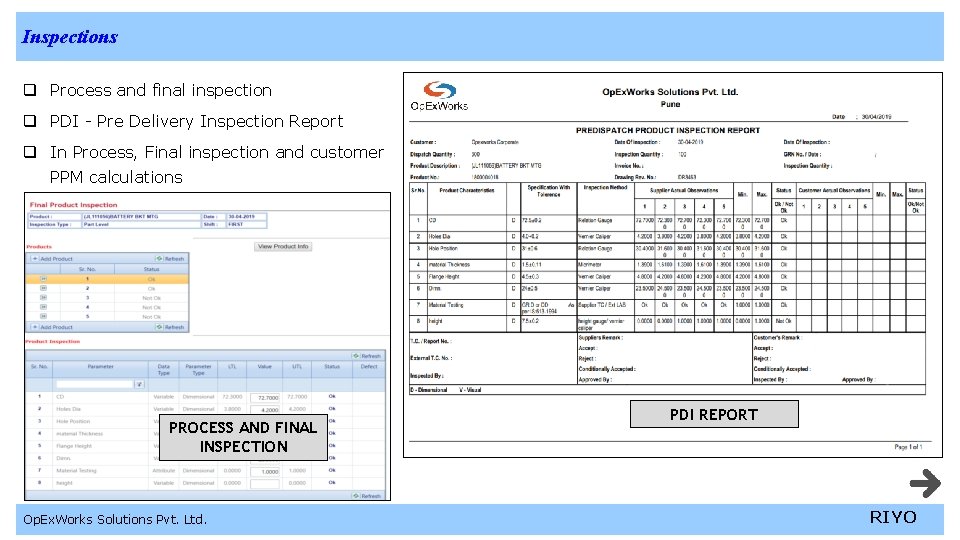
Inspections q Process and final inspection q PDI - Pre Delivery Inspection Report q In Process, Final inspection and customer PPM calculations PROCESS AND FINAL INSPECTION Op. Ex. Works Solutions Pvt. Ltd. PDI REPORT RIYO
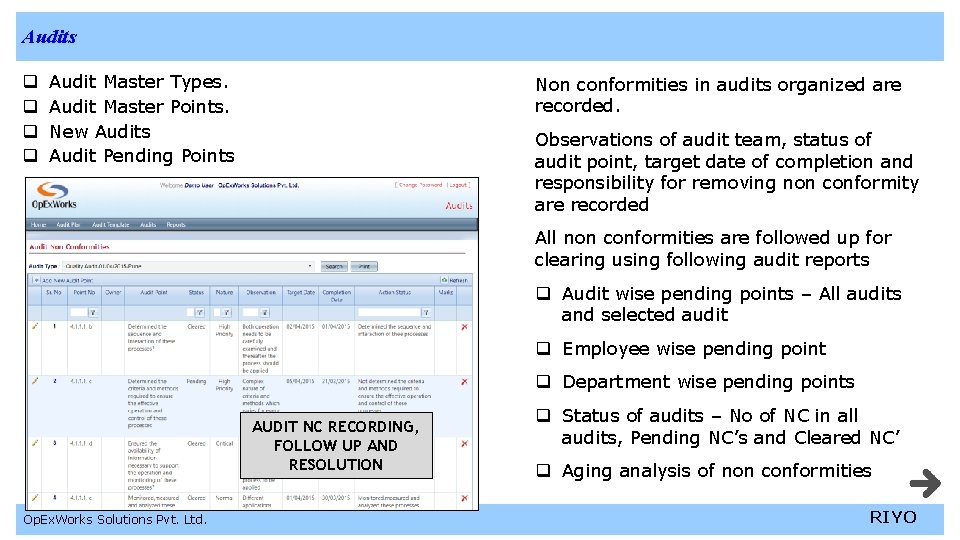
Audits q q Audit Master Types. Audit Master Points. New Audits Audit Pending Points Non conformities in audits organized are recorded. Observations of audit team, status of audit point, target date of completion and responsibility for removing non conformity are recorded All non conformities are followed up for clearing using following audit reports q Audit wise pending points – All audits and selected audit q Employee wise pending point q Department wise pending points AUDIT NC RECORDING, FOLLOW UP AND RESOLUTION Op. Ex. Works Solutions Pvt. Ltd. q Status of audits – No of NC in all audits, Pending NC’s and Cleared NC’ q Aging analysis of non conformities RIYO
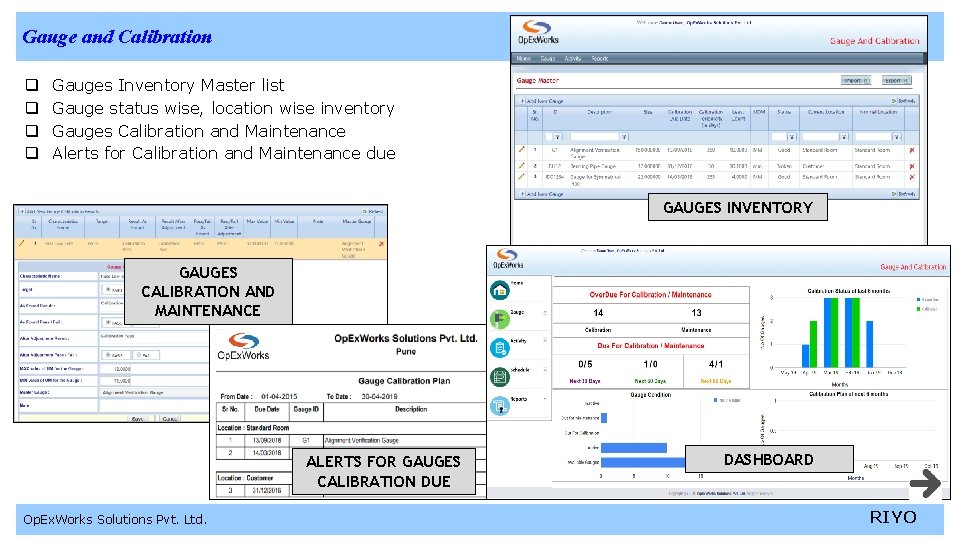
Gauge and Calibration q q Gauges Inventory Master list Gauge status wise, location wise inventory Gauges Calibration and Maintenance Alerts for Calibration and Maintenance due GAUGES INVENTORY GAUGES CALIBRATION AND MAINTENANCE ALERTS FOR GAUGES CALIBRATION DUE Op. Ex. Works Solutions Pvt. Ltd. DASHBOARD RIYO
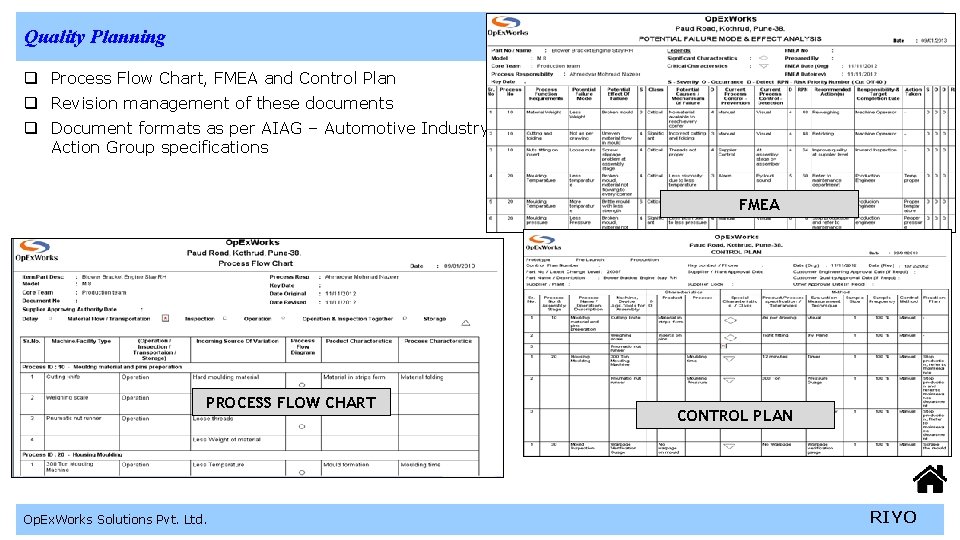
Quality Planning q Process Flow Chart, FMEA and Control Plan q Revision management of these documents q Document formats as per AIAG – Automotive Industry Action Group specifications FMEA PROCESS FLOW CHART Op. Ex. Works Solutions Pvt. Ltd. CONTROL PLAN RIYO
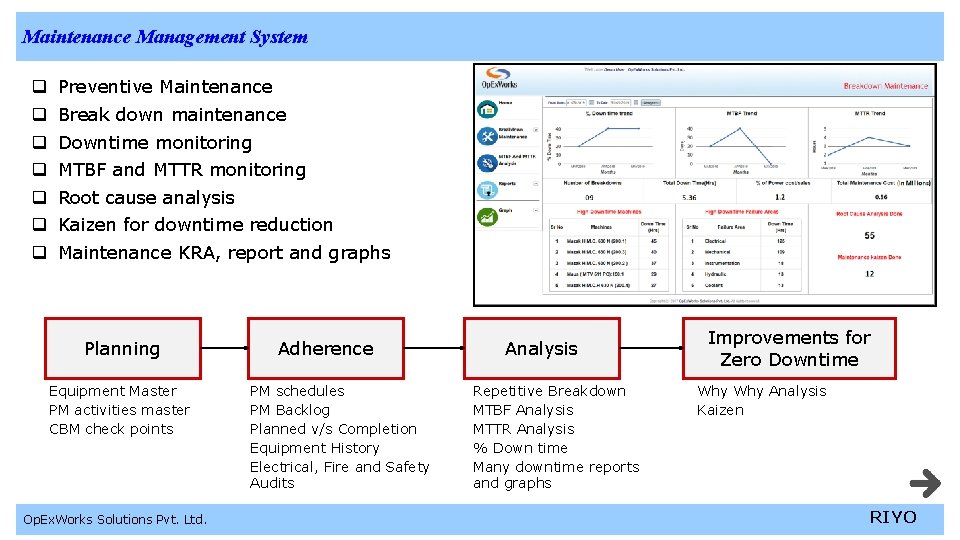
Maintenance Management System q q q q Preventive Maintenance Break down maintenance Downtime monitoring MTBF and MTTR monitoring Root cause analysis Kaizen for downtime reduction Maintenance KRA, report and graphs Planning Equipment Master PM activities master CBM check points Op. Ex. Works Solutions Pvt. Ltd. Adherence PM schedules PM Backlog Planned v/s Completion Equipment History Electrical, Fire and Safety Audits Analysis Repetitive Breakdown MTBF Analysis MTTR Analysis % Down time Many downtime reports and graphs Improvements for Zero Downtime Why Analysis Kaizen RIYO
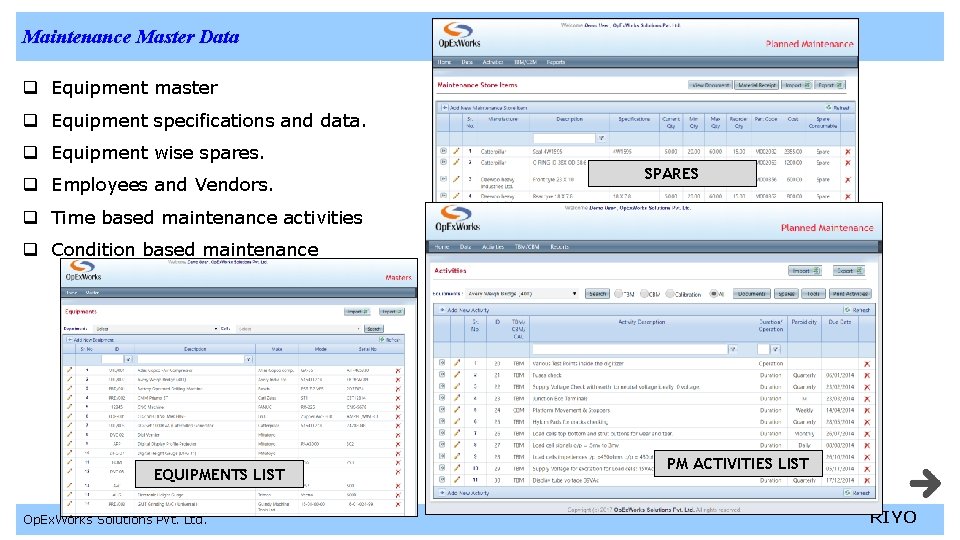
Maintenance Master Data q Equipment master q Equipment specifications and data. q Equipment wise spares. q Employees and Vendors. SPARES q Time based maintenance activities q Condition based maintenance EQUIPMENTS LIST Op. Ex. Works Solutions Pvt. Ltd. PM ACTIVITIES LIST RIYO
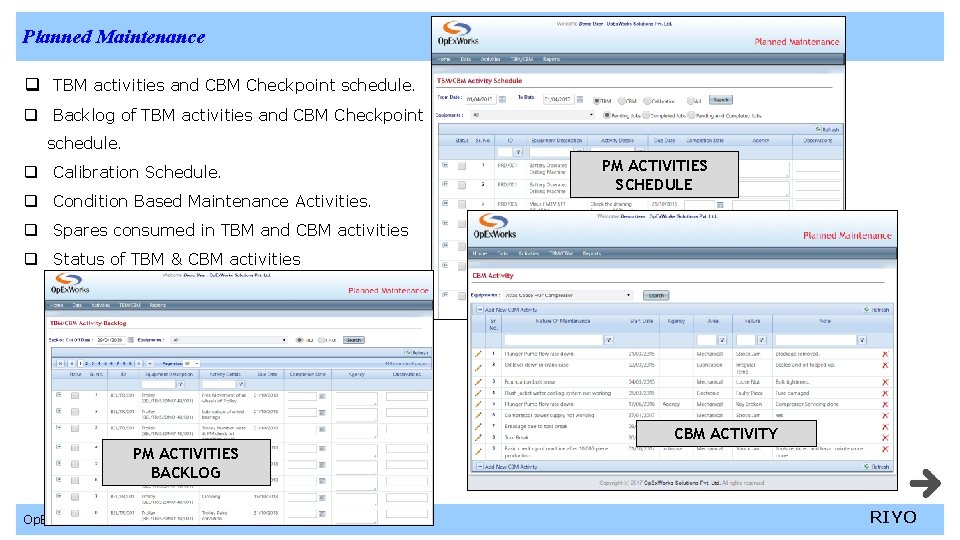
Planned Maintenance q TBM activities and CBM Checkpoint schedule. q Backlog of TBM activities and CBM Checkpoint schedule. q Calibration Schedule. q Condition Based Maintenance Activities. PM ACTIVITIES SCHEDULE q Spares consumed in TBM and CBM activities q Status of TBM & CBM activities CBM ACTIVITY PM ACTIVITIES BACKLOG Op. Ex. Works Solutions Pvt. Ltd. RIYO
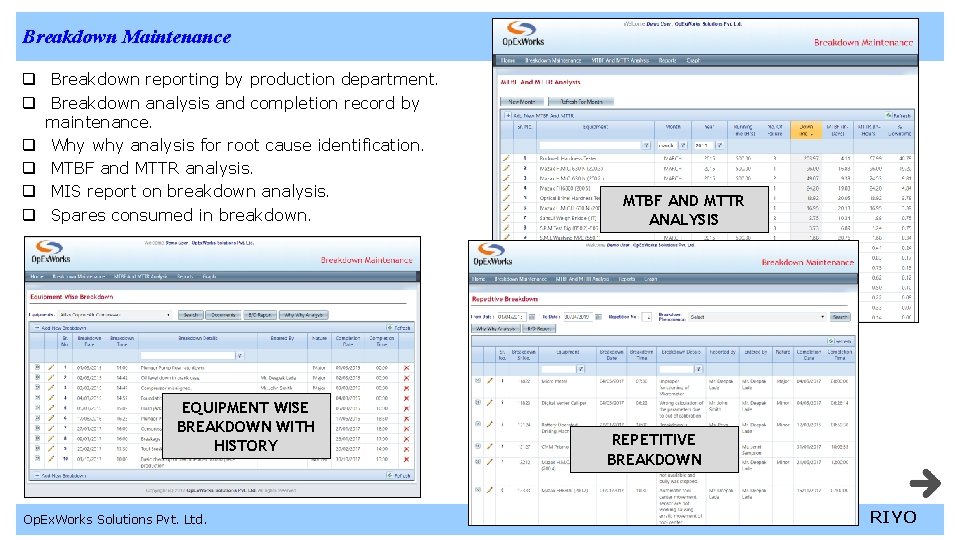
Breakdown Maintenance q Breakdown reporting by production department. q Breakdown analysis and completion record by maintenance. q Why why analysis for root cause identification. q MTBF and MTTR analysis. q MIS report on breakdown analysis. q Spares consumed in breakdown. EQUIPMENT WISE BREAKDOWN WITH HISTORY Op. Ex. Works Solutions Pvt. Ltd. MTBF AND MTTR ANALYSIS REPETITIVE BREAKDOWN RIYO
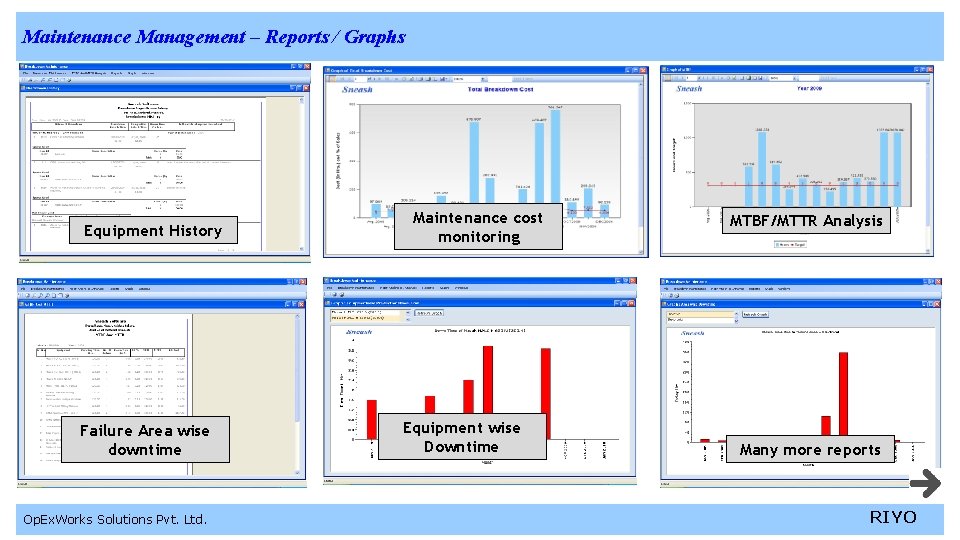
Maintenance Management – Reports / Graphs Equipment History Failure Area wise downtime Op. Ex. Works Solutions Pvt. Ltd. Maintenance cost monitoring Equipment wise Downtime MTBF/MTTR Analysis Many more reports RIYO
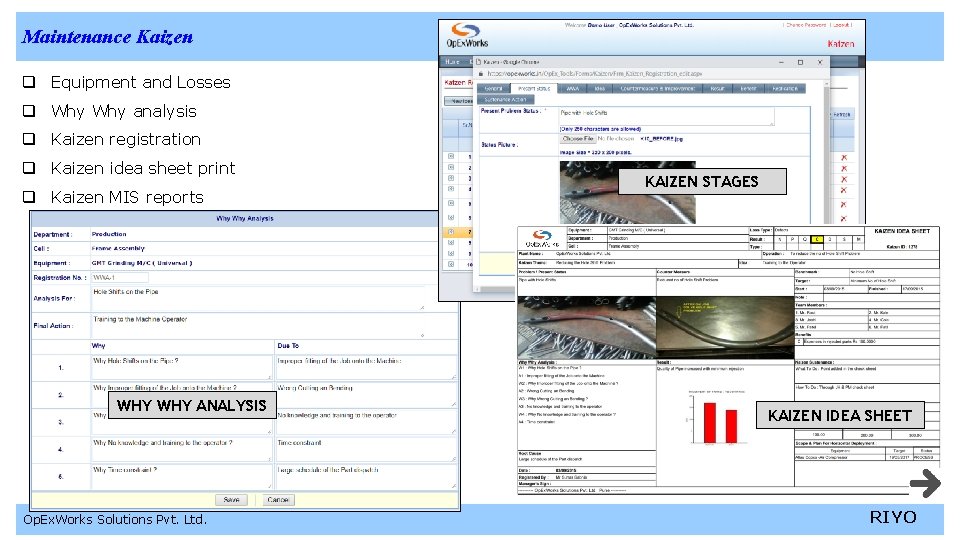
Maintenance Kaizen q Equipment and Losses q Why analysis q Kaizen registration q Kaizen idea sheet print q Kaizen MIS reports WHY ANALYSIS Op. Ex. Works Solutions Pvt. Ltd. KAIZEN STAGES KAIZEN IDEA SHEET RIYO
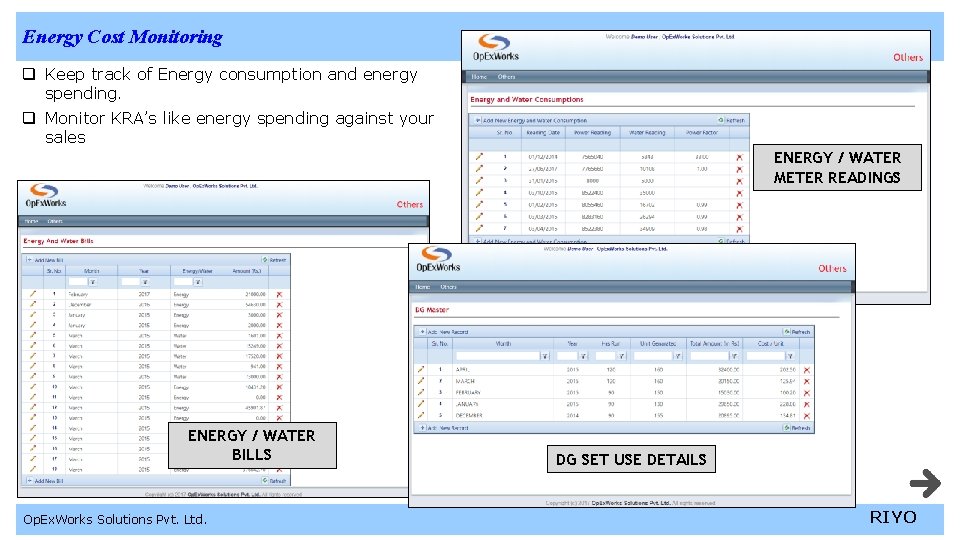
Energy Cost Monitoring q Keep track of Energy consumption and energy spending. q Monitor KRA’s like energy spending against your sales ENERGY / WATER METER READINGS ENERGY / WATER BILLS Op. Ex. Works Solutions Pvt. Ltd. DG SET USE DETAILS RIYO
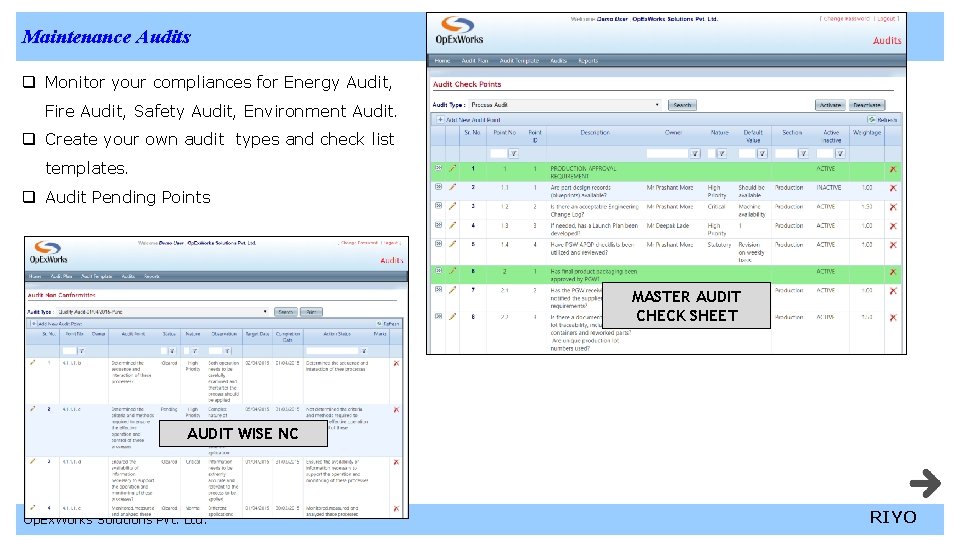
Maintenance Audits q Monitor your compliances for Energy Audit, Fire Audit, Safety Audit, Environment Audit. q Create your own audit types and check list templates. q Audit Pending Points MASTER AUDIT CHECK SHEET AUDIT WISE NC Op. Ex. Works Solutions Pvt. Ltd. RIYO
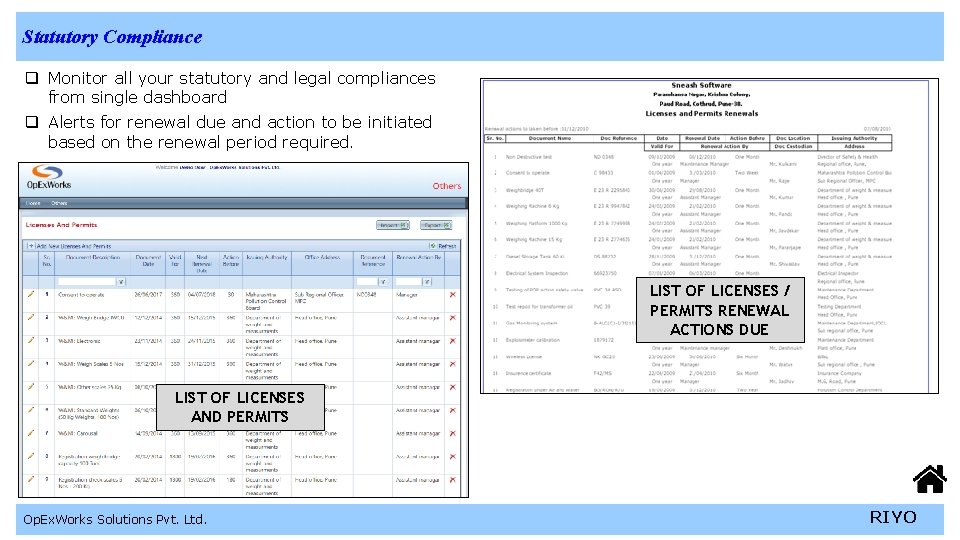
Statutory Compliance q Monitor all your statutory and legal compliances from single dashboard q Alerts for renewal due and action to be initiated based on the renewal period required. LIST OF LICENSES / PERMITS RENEWAL ACTIONS DUE LIST OF LICENSES AND PERMITS Op. Ex. Works Solutions Pvt. Ltd. RIYO
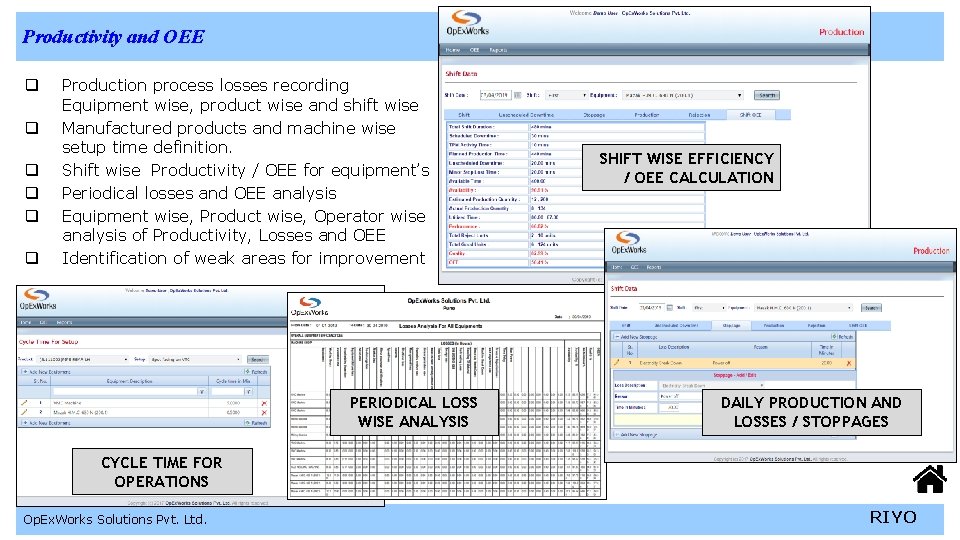
Productivity and OEE q q q Production process losses recording Equipment wise, product wise and shift wise Manufactured products and machine wise setup time definition. Shift wise Productivity / OEE for equipment’s Periodical losses and OEE analysis Equipment wise, Product wise, Operator wise analysis of Productivity, Losses and OEE Identification of weak areas for improvement PERIODICAL LOSS WISE ANALYSIS SHIFT WISE EFFICIENCY / OEE CALCULATION DAILY PRODUCTION AND LOSSES / STOPPAGES CYCLE TIME FOR OPERATIONS Op. Ex. Works Solutions Pvt. Ltd. RIYO
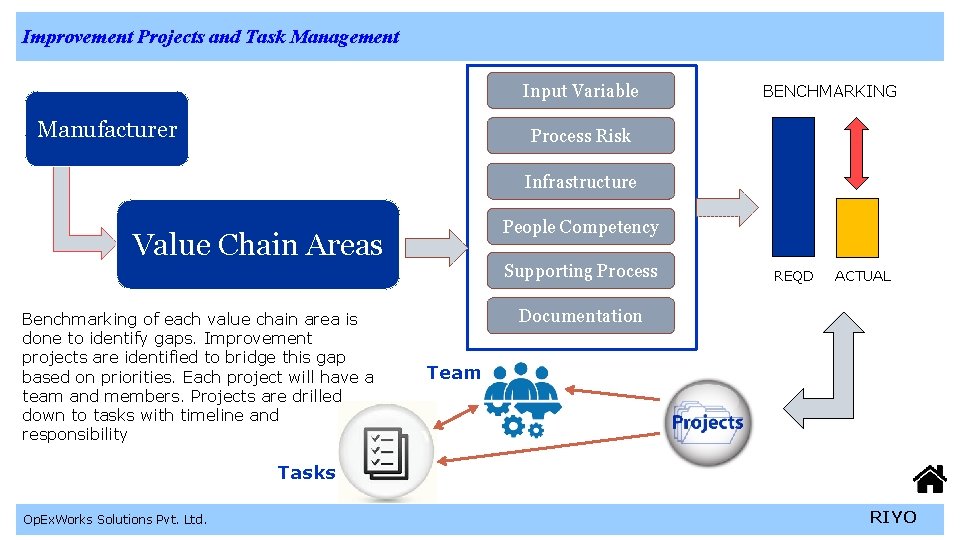
Improvement Projects and Task Management Input Variable Manufacturer BENCHMARKING Process Risk Infrastructure People Competency Value Chain Areas Benchmarking of each value chain area is done to identify gaps. Improvement projects are identified to bridge this gap based on priorities. Each project will have a team and members. Projects are drilled down to tasks with timeline and responsibility Supporting Process REQD ACTUAL Documentation Team Tasks Op. Ex. Works Solutions Pvt. Ltd. RIYO
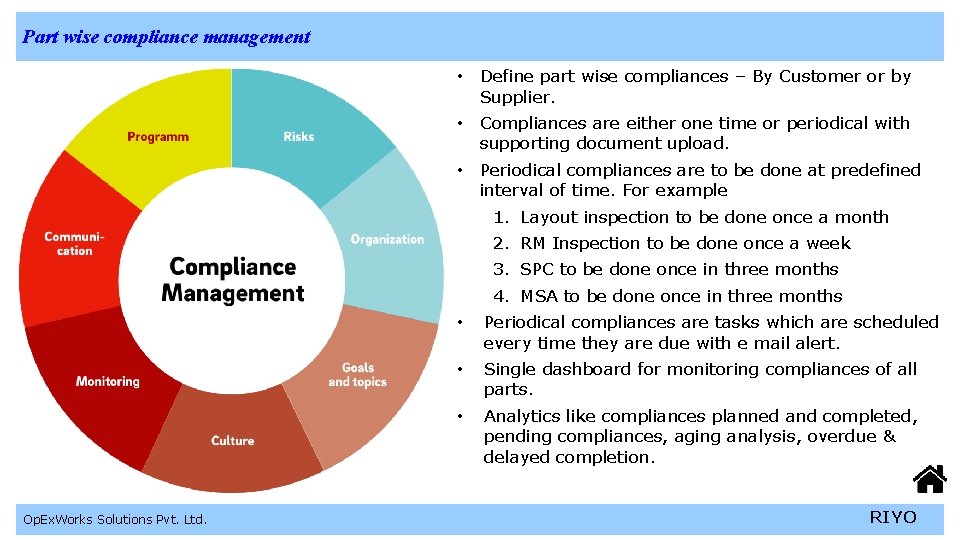
Part wise compliance management • Define part wise compliances – By Customer or by Supplier. • Compliances are either one time or periodical with supporting document upload. • Periodical compliances are to be done at predefined interval of time. For example 1. Layout inspection to be done once a month 2. RM Inspection to be done once a week 3. SPC to be done once in three months 4. MSA to be done once in three months Op. Ex. Works Solutions Pvt. Ltd. • Periodical compliances are tasks which are scheduled every time they are due with e mail alert. • Single dashboard for monitoring compliances of all parts. • Analytics like compliances planned and completed, pending compliances, aging analysis, overdue & delayed completion. RIYO
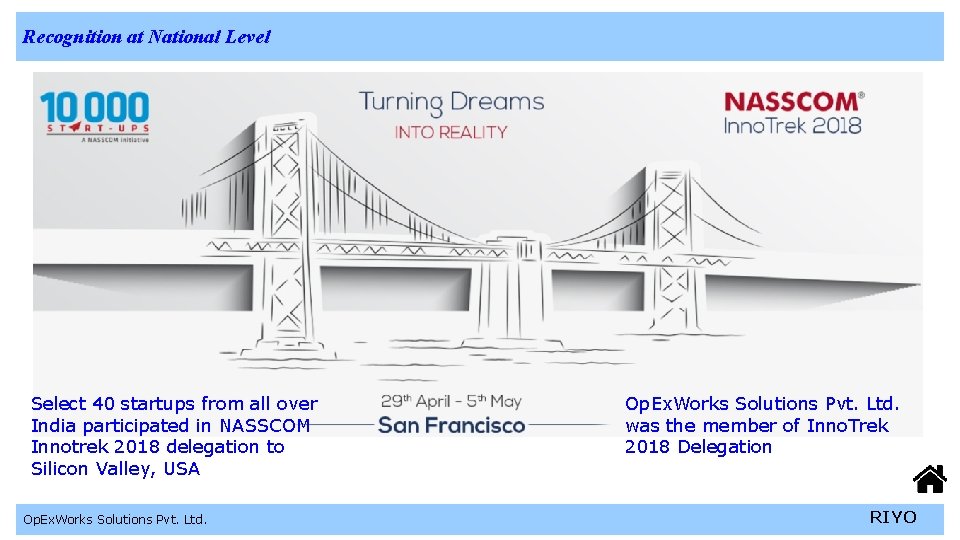
Recognition at National Level Select 40 startups from all over India participated in NASSCOM Innotrek 2018 delegation to Silicon Valley, USA Op. Ex. Works Solutions Pvt. Ltd. was the member of Inno. Trek 2018 Delegation RIYO
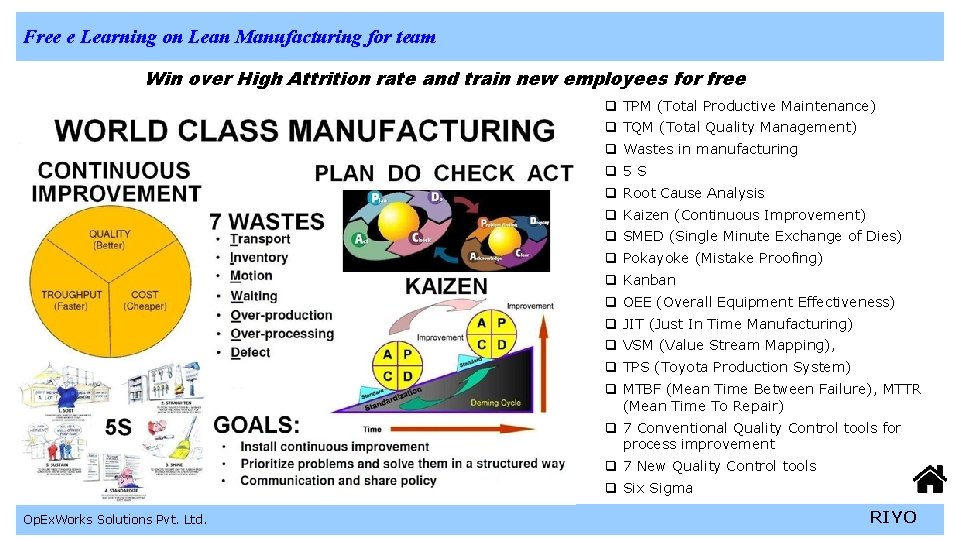
Free e Learning on Lean Manufacturing for team Win over High Attrition rate and train new employees for free q TPM (Total Productive Maintenance) q TQM (Total Quality Management) q Wastes in manufacturing q 5 S q Root Cause Analysis q Kaizen (Continuous Improvement) q SMED (Single Minute Exchange of Dies) q Pokayoke (Mistake Proofing) q Kanban q OEE (Overall Equipment Effectiveness) q JIT (Just In Time Manufacturing) q VSM (Value Stream Mapping), q TPS (Toyota Production System) q MTBF (Mean Time Between Failure), MTTR (Mean Time To Repair) q 7 Conventional Quality Control tools for process improvement q 7 New Quality Control tools q Six Sigma Op. Ex. Works Solutions Pvt. Ltd. RIYO
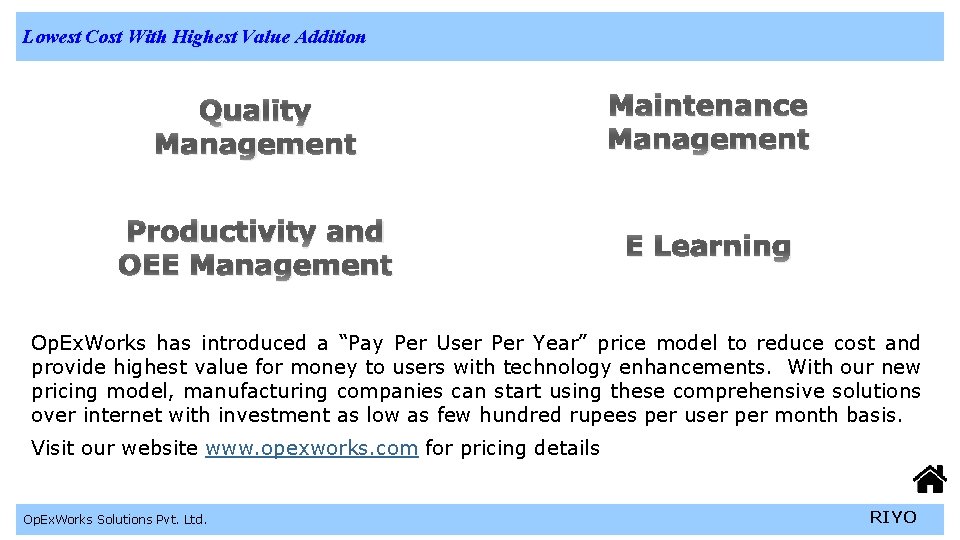
Lowest Cost With Highest Value Addition Quality Management Maintenance Management Productivity and OEE Management E Learning Op. Ex. Works has introduced a “Pay Per User Per Year” price model to reduce cost and provide highest value for money to users with technology enhancements. With our new pricing model, manufacturing companies can start using these comprehensive solutions over internet with investment as low as few hundred rupees per user per month basis. Visit our website www. opexworks. com for pricing details Op. Ex. Works Solutions Pvt. Ltd. RIYO

Contact Us Op. Ex. Works Solutions Pvt. Ltd. Pune, India. Web : www. opexworks. com Email : info@opexworks. com Contact no : 8380069538 Op. Ex. Works Solutions Pvt. Ltd. RIYO
Achieving operational excellence and customer intimacy
Operational excellence and customer intimacy
How to build a cloud center of excellence gartner
What is delivery excellence in software projects
Putting the enterprise into the enterprise system
Enterprise
Iso 22301 utbildning
Typiska drag för en novell
Tack för att ni lyssnade bild
Returpilarna
Shingelfrisyren
En lathund för arbete med kontinuitetshantering
Underlag för särskild löneskatt på pensionskostnader
Personlig tidbok
Sura för anatom
Vad är densitet
Datorkunskap för nybörjare
Tack för att ni lyssnade bild
Hur skriver man en tes
Autokratiskt ledarskap
Nyckelkompetenser för livslångt lärande
Påbyggnader för flakfordon
Arkimedes princip formel
Publik sektor
Kyssande vind
Presentera för publik crossboss
Jiddisch
Kanaans land
Treserva lathund
Luftstrupen för medicinare
Claes martinsson
Cks
Verifikationsplan
Bra mat för unga idrottare
Verktyg för automatisering av utbetalningar
Rutin för avvikelsehantering
Smärtskolan kunskap för livet